Consent Manager Tag v2.0 (for TCF 2.0) -->
Farnell PDF
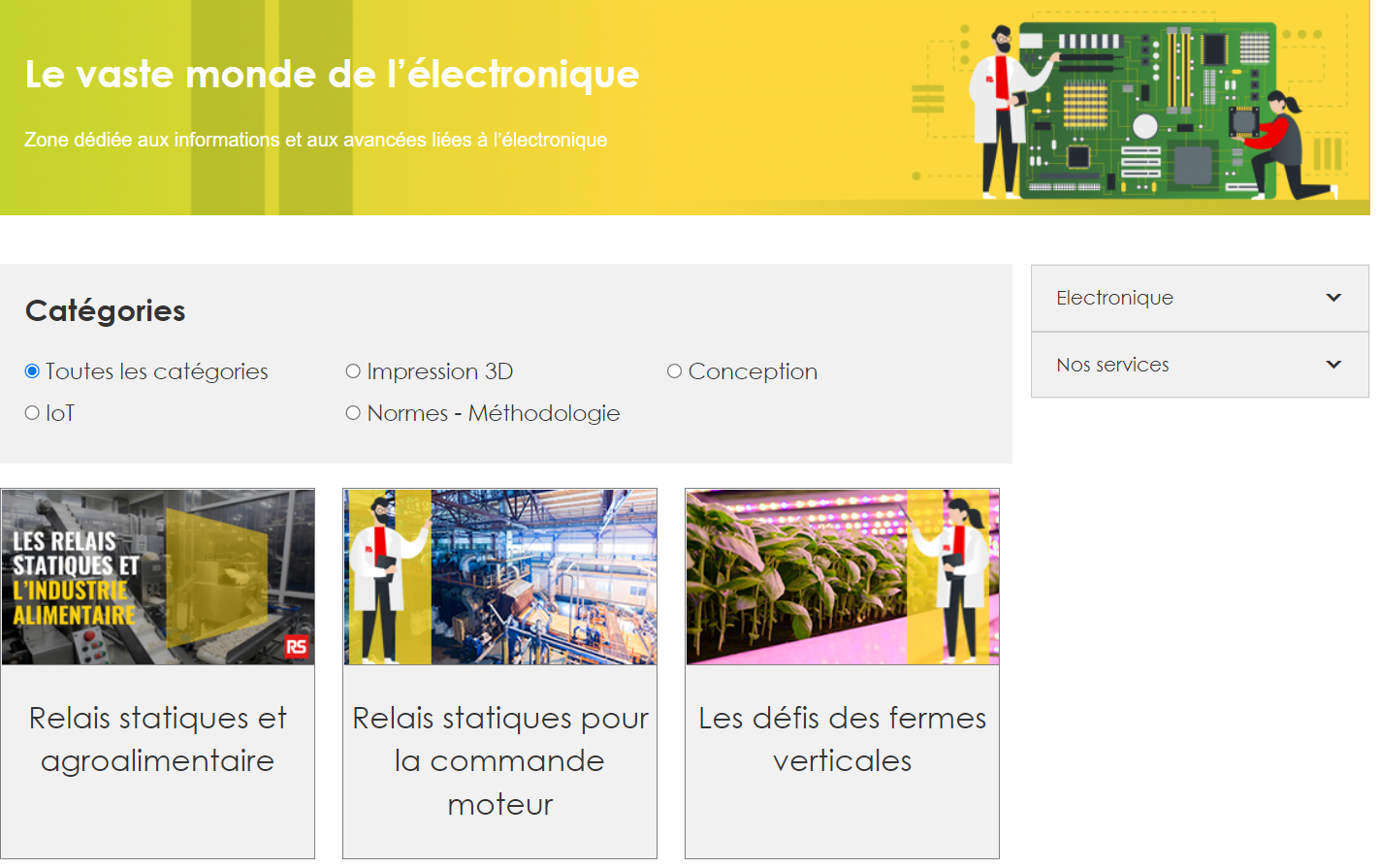
Evaluating the ADE7878 Energy Metering IC - Farnell Element 14
Evaluating the ADE7878 Energy Metering IC - Farnell Element 14
- Revenir à l'accueil

Farnell Element 14 :
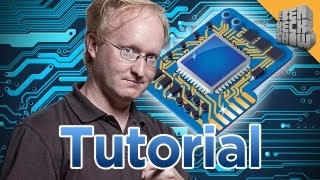
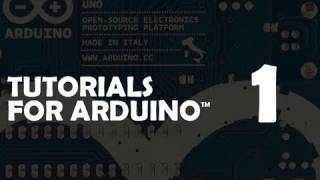
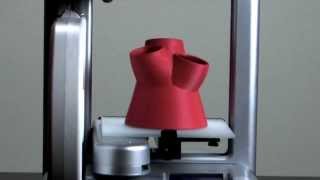
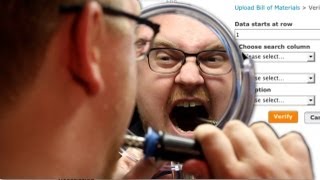
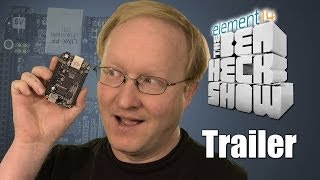
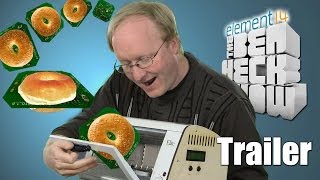
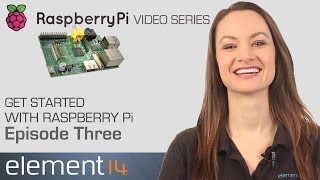
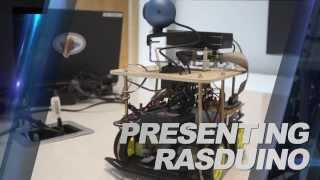
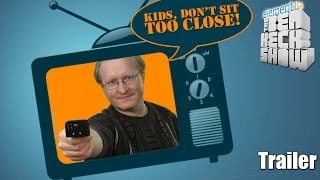
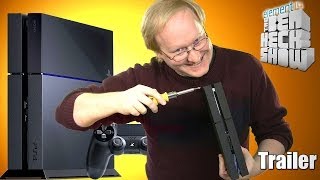
See the trailer for the next exciting episode of The Ben Heck show. Check back on Friday to be among the first to see the exclusive full show on element…
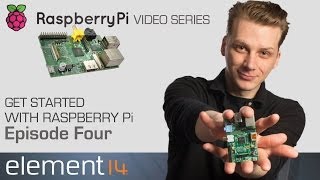
Connect your Raspberry Pi to a breadboard, download some code and create a push-button audio play project.

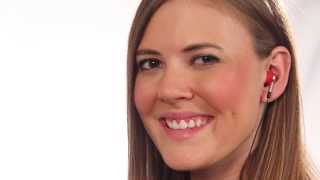
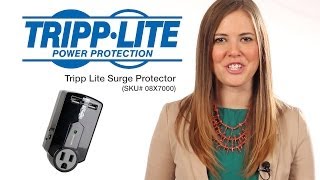
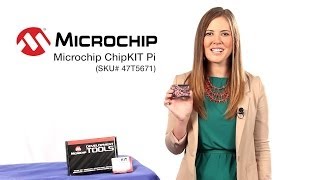
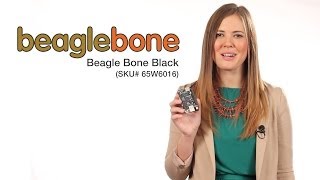
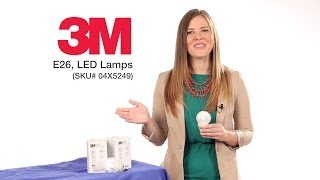
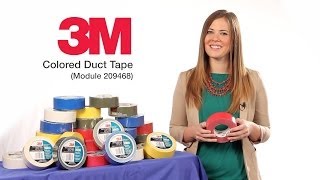
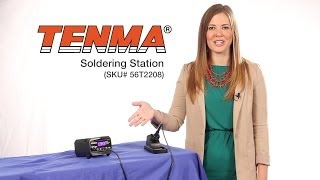
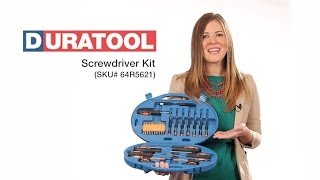
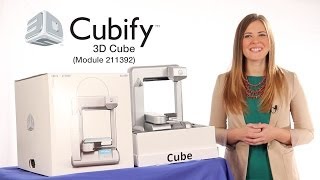
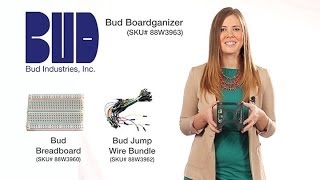
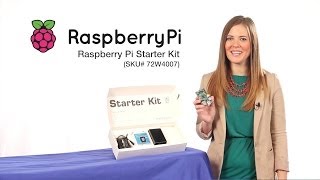
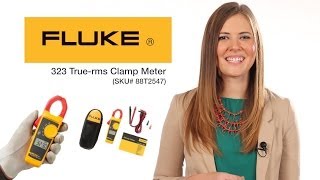
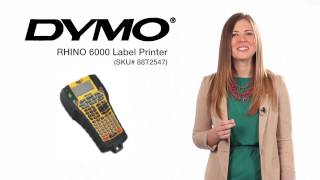
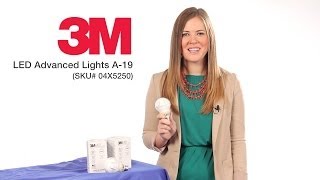
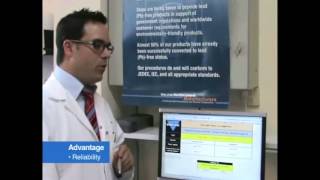
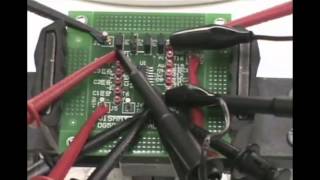
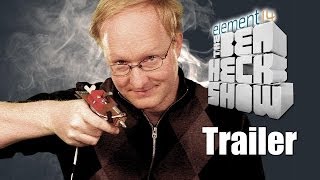
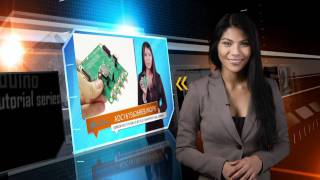
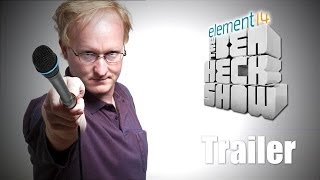
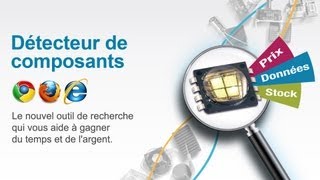
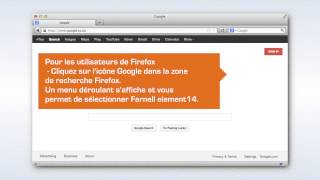
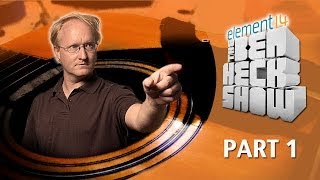
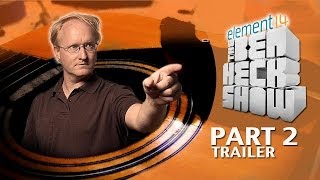

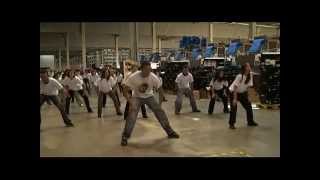
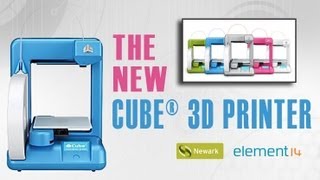










Puce électronique / Microchip :
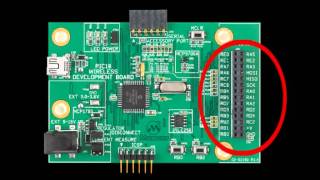
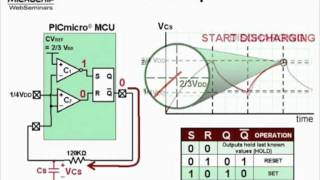
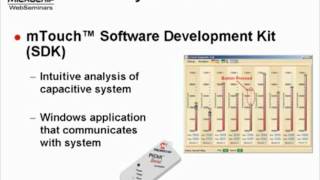
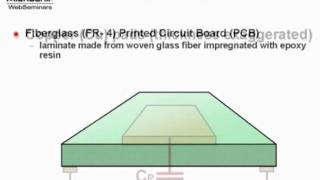
Sans fil - Wireless :
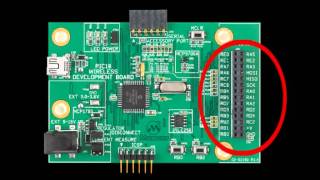
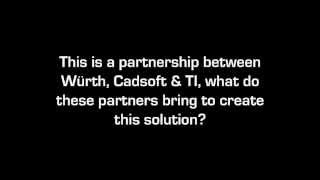
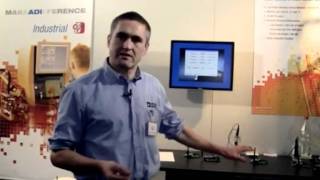
Texas instrument :
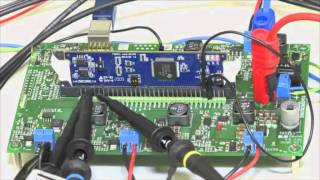
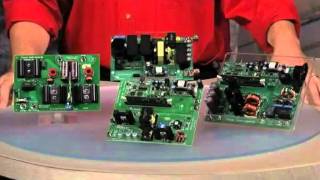
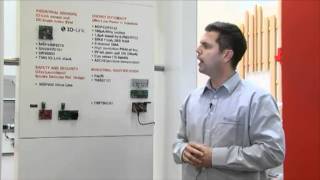
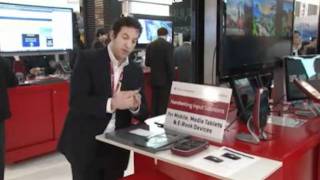
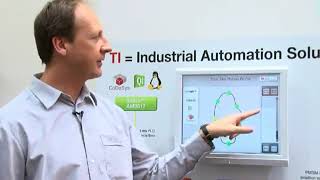
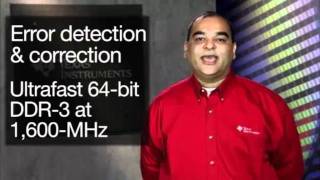
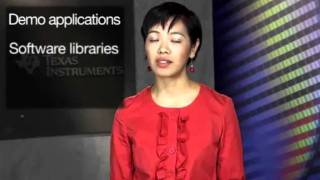

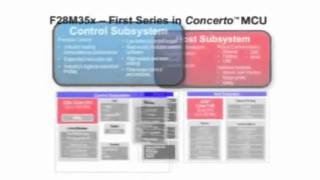
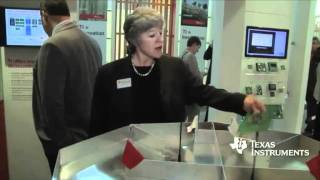
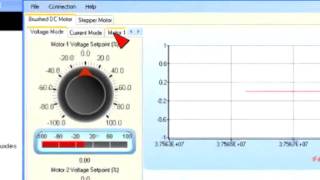
Ordinateurs :
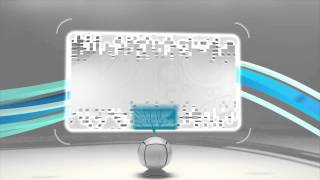
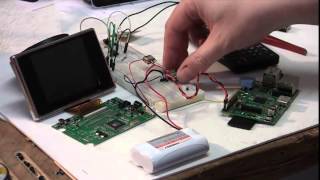
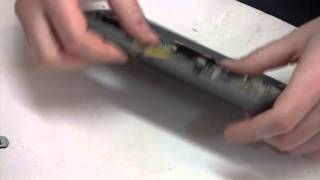
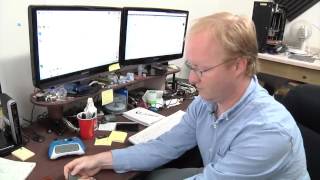
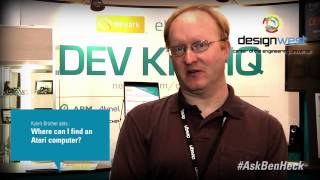
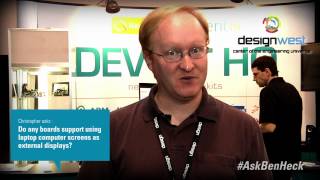
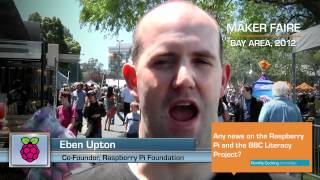
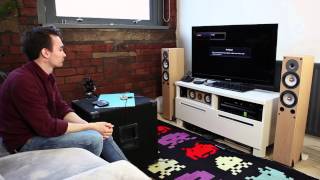
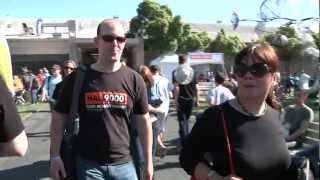
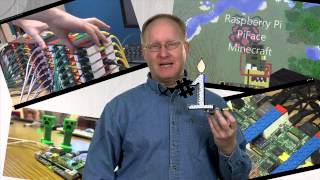
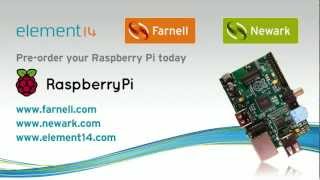
Logiciels :
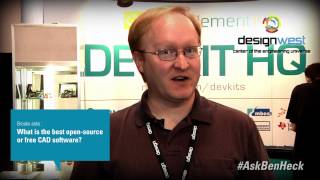
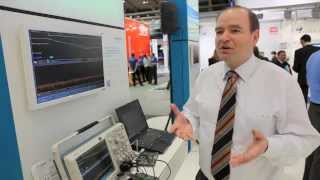
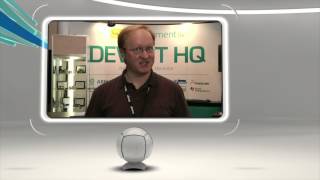
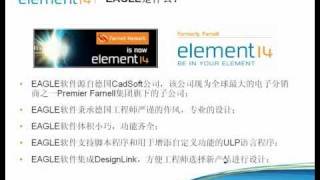
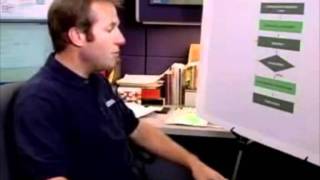
Tutoriels :
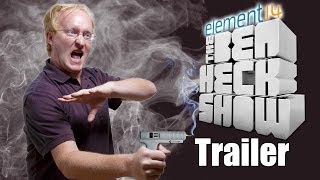
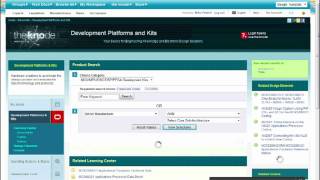
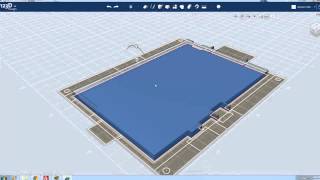
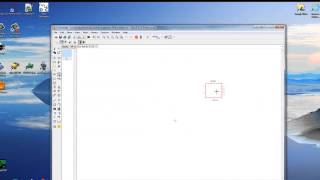
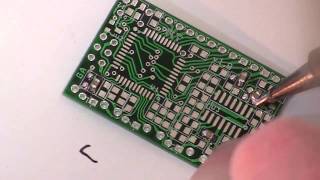
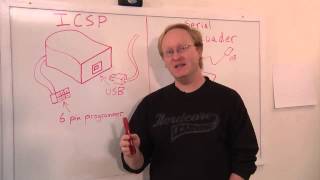
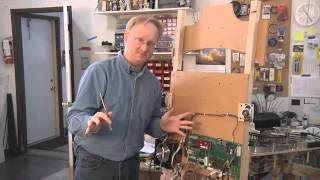
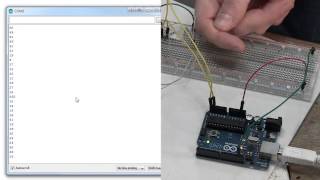

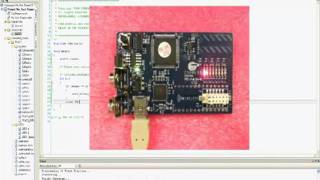
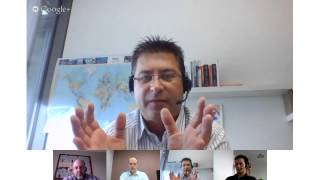
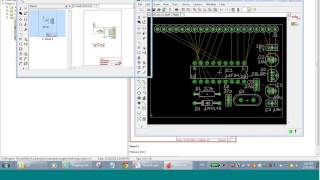
Autres documentations :
Farnell-Full-Datashe..> 15-Jul-2014 17:08 951K
![[TXT]](http://www.audentia-gestion.fr/icons/text.gif)
Farnell-pmbta13_pmbt..> 15-Jul-2014 17:06 959K
![[TXT]](http://www.audentia-gestion.fr/icons/text.gif)
Farnell-EE-SPX303N-4..> 15-Jul-2014 17:06 969K
![[TXT]](http://www.audentia-gestion.fr/icons/text.gif)
Farnell-Datasheet-NX..> 15-Jul-2014 17:06 1.0M
![[TXT]](http://www.audentia-gestion.fr/icons/text.gif)
Farnell-Datasheet-Fa..> 15-Jul-2014 17:05 1.0M
![[TXT]](http://www.audentia-gestion.fr/icons/text.gif)
Farnell-MIDAS-un-tra..> 15-Jul-2014 17:05 1.0M
![[TXT]](http://www.audentia-gestion.fr/icons/text.gif)
Farnell-SERIAL-TFT-M..> 15-Jul-2014 17:05 1.0M
![[TXT]](http://www.audentia-gestion.fr/icons/text.gif)
Farnell-MCOC1-Farnel..> 15-Jul-2014 17:05 1.0M
![[TXT]](http://www.audentia-gestion.fr/icons/text.gif)
Farnell-TMR-2-series..> 15-Jul-2014 16:48 787K
![[TXT]](http://www.audentia-gestion.fr/icons/text.gif)
Farnell-DC-DC-Conver..> 15-Jul-2014 16:48 781K
![[TXT]](http://www.audentia-gestion.fr/icons/text.gif)
Farnell-Full-Datashe..> 15-Jul-2014 16:47 803K
![[TXT]](http://www.audentia-gestion.fr/icons/text.gif)
Farnell-TMLM-Series-..> 15-Jul-2014 16:47 810K
![[TXT]](http://www.audentia-gestion.fr/icons/text.gif)
Farnell-TEL-5-Series..> 15-Jul-2014 16:47 814K
![[TXT]](http://www.audentia-gestion.fr/icons/text.gif)
Farnell-TXL-series-t..> 15-Jul-2014 16:47 829K
![[TXT]](http://www.audentia-gestion.fr/icons/text.gif)
Farnell-TEP-150WI-Se..> 15-Jul-2014 16:47 837K
![[TXT]](http://www.audentia-gestion.fr/icons/text.gif)
Farnell-AC-DC-Power-..> 15-Jul-2014 16:47 845K
![[TXT]](http://www.audentia-gestion.fr/icons/text.gif)
Farnell-TIS-Instruct..> 15-Jul-2014 16:47 845K
![[TXT]](http://www.audentia-gestion.fr/icons/text.gif)
Farnell-TOS-tracopow..> 15-Jul-2014 16:47 852K
![[TXT]](http://www.audentia-gestion.fr/icons/text.gif)
Farnell-TCL-DC-traco..> 15-Jul-2014 16:46 858K
![[TXT]](http://www.audentia-gestion.fr/icons/text.gif)
Farnell-TIS-series-t..> 15-Jul-2014 16:46 875K
![[TXT]](http://www.audentia-gestion.fr/icons/text.gif)
Farnell-TMR-2-Series..> 15-Jul-2014 16:46 897K
![[TXT]](http://www.audentia-gestion.fr/icons/text.gif)
Farnell-TMR-3-WI-Ser..> 15-Jul-2014 16:46 939K
![[TXT]](http://www.audentia-gestion.fr/icons/text.gif)
Farnell-TEN-8-WI-Ser..> 15-Jul-2014 16:46 939K
![[TXT]](http://www.audentia-gestion.fr/icons/text.gif)
Farnell-Full-Datashe..> 15-Jul-2014 16:46 947K
Farnell-HIP4081A-Int..> 07-Jul-2014 19:47 1.0M
![[TXT]](http://www.audentia-gestion.fr/icons/text.gif)
Farnell-ISL6251-ISL6..> 07-Jul-2014 19:47 1.1M
![[TXT]](http://www.audentia-gestion.fr/icons/text.gif)
Farnell-DG411-DG412-..> 07-Jul-2014 19:47 1.0M
![[TXT]](http://www.audentia-gestion.fr/icons/text.gif)
Farnell-3367-ARALDIT..> 07-Jul-2014 19:46 1.2M
![[TXT]](http://www.audentia-gestion.fr/icons/text.gif)
Farnell-ICM7228-Inte..> 07-Jul-2014 19:46 1.1M
![[TXT]](http://www.audentia-gestion.fr/icons/text.gif)
Farnell-Data-Sheet-K..> 07-Jul-2014 19:46 1.2M
![[TXT]](http://www.audentia-gestion.fr/icons/text.gif)
Farnell-Silica-Gel-M..> 07-Jul-2014 19:46 1.2M
![[TXT]](http://www.audentia-gestion.fr/icons/text.gif)
Farnell-TKC2-Dusters..> 07-Jul-2014 19:46 1.2M
![[TXT]](http://www.audentia-gestion.fr/icons/text.gif)
Farnell-CRC-HANDCLEA..> 07-Jul-2014 19:46 1.2M
![[TXT]](http://www.audentia-gestion.fr/icons/text.gif)
Farnell-760G-French-..> 07-Jul-2014 19:45 1.2M
![[TXT]](http://www.audentia-gestion.fr/icons/text.gif)
Farnell-Decapant-KF-..> 07-Jul-2014 19:45 1.2M
![[TXT]](http://www.audentia-gestion.fr/icons/text.gif)
Farnell-1734-ARALDIT..> 07-Jul-2014 19:45 1.2M
![[TXT]](http://www.audentia-gestion.fr/icons/text.gif)
Farnell-Araldite-Fus..> 07-Jul-2014 19:45 1.2M
![[TXT]](http://www.audentia-gestion.fr/icons/text.gif)
Farnell-fiche-de-don..> 07-Jul-2014 19:44 1.4M
![[TXT]](http://www.audentia-gestion.fr/icons/text.gif)
Farnell-safety-data-..> 07-Jul-2014 19:44 1.4M
![[TXT]](http://www.audentia-gestion.fr/icons/text.gif)
Farnell-A-4-Hardener..> 07-Jul-2014 19:44 1.4M
![[TXT]](http://www.audentia-gestion.fr/icons/text.gif)
Farnell-CC-Debugger-..> 07-Jul-2014 19:44 1.5M
![[TXT]](http://www.audentia-gestion.fr/icons/text.gif)
Farnell-MSP430-Hardw..> 07-Jul-2014 19:43 1.8M
![[TXT]](http://www.audentia-gestion.fr/icons/text.gif)
Farnell-SmartRF06-Ev..> 07-Jul-2014 19:43 1.6M
![[TXT]](http://www.audentia-gestion.fr/icons/text.gif)
Farnell-CC2531-USB-H..> 07-Jul-2014 19:43 1.8M
![[TXT]](http://www.audentia-gestion.fr/icons/text.gif)
Farnell-Alimentation..> 07-Jul-2014 19:43 1.8M
![[TXT]](http://www.audentia-gestion.fr/icons/text.gif)
Farnell-BK889B-PONT-..> 07-Jul-2014 19:42 1.8M
![[TXT]](http://www.audentia-gestion.fr/icons/text.gif)
Farnell-User-Guide-M..> 07-Jul-2014 19:41 2.0M
![[TXT]](http://www.audentia-gestion.fr/icons/text.gif)
Farnell-T672-3000-Se..> 07-Jul-2014 19:41 2.0M
Farnell-0050375063-D..> 18-Jul-2014 17:03 2.5M
![[TXT]](http://www.audentia-gestion.fr/icons/text.gif)
Farnell-Mini-Fit-Jr-..> 18-Jul-2014 17:03 2.5M
![[TXT]](http://www.audentia-gestion.fr/icons/text.gif)
Farnell-43031-0002-M..> 18-Jul-2014 17:03 2.5M
![[TXT]](http://www.audentia-gestion.fr/icons/text.gif)
Farnell-0433751001-D..> 18-Jul-2014 17:02 2.5M
![[TXT]](http://www.audentia-gestion.fr/icons/text.gif)
Farnell-Cube-3D-Prin..> 18-Jul-2014 17:02 2.5M
![[TXT]](http://www.audentia-gestion.fr/icons/text.gif)
Farnell-MTX-Compact-..> 18-Jul-2014 17:01 2.5M
![[TXT]](http://www.audentia-gestion.fr/icons/text.gif)
Farnell-MTX-3250-MTX..> 18-Jul-2014 17:01 2.5M
![[TXT]](http://www.audentia-gestion.fr/icons/text.gif)
Farnell-ATtiny26-L-A..> 18-Jul-2014 17:00 2.6M
![[TXT]](http://www.audentia-gestion.fr/icons/text.gif)
Farnell-MCP3421-Micr..> 18-Jul-2014 17:00 1.2M
![[TXT]](http://www.audentia-gestion.fr/icons/text.gif)
Farnell-LM19-Texas-I..> 18-Jul-2014 17:00 1.2M
![[TXT]](http://www.audentia-gestion.fr/icons/text.gif)
Farnell-Data-Sheet-S..> 18-Jul-2014 17:00 1.2M
![[TXT]](http://www.audentia-gestion.fr/icons/text.gif)
Farnell-LMH6518-Texa..> 18-Jul-2014 16:59 1.3M
![[TXT]](http://www.audentia-gestion.fr/icons/text.gif)
Farnell-AD7719-Low-V..> 18-Jul-2014 16:59 1.4M
![[TXT]](http://www.audentia-gestion.fr/icons/text.gif)
Farnell-DAC8143-Data..> 18-Jul-2014 16:59 1.5M
![[TXT]](http://www.audentia-gestion.fr/icons/text.gif)
Farnell-BGA7124-400-..> 18-Jul-2014 16:59 1.5M
![[TXT]](http://www.audentia-gestion.fr/icons/text.gif)
Farnell-SICK-OPTIC-E..> 18-Jul-2014 16:58 1.5M
![[TXT]](http://www.audentia-gestion.fr/icons/text.gif)
Farnell-LT3757-Linea..> 18-Jul-2014 16:58 1.6M
![[TXT]](http://www.audentia-gestion.fr/icons/text.gif)
Farnell-LT1961-Linea..> 18-Jul-2014 16:58 1.6M
![[TXT]](http://www.audentia-gestion.fr/icons/text.gif)
Farnell-PIC18F2420-2..> 18-Jul-2014 16:57 2.5M
![[TXT]](http://www.audentia-gestion.fr/icons/text.gif)
Farnell-DS3231-DS-PD..> 18-Jul-2014 16:57 2.5M
![[TXT]](http://www.audentia-gestion.fr/icons/text.gif)
Farnell-RDS-80-PDF.htm 18-Jul-2014 16:57 1.3M
![[TXT]](http://www.audentia-gestion.fr/icons/text.gif)
Farnell-AD8300-Data-..> 18-Jul-2014 16:56 1.3M
![[TXT]](http://www.audentia-gestion.fr/icons/text.gif)
Farnell-LT6233-Linea..> 18-Jul-2014 16:56 1.3M
![[TXT]](http://www.audentia-gestion.fr/icons/text.gif)
Farnell-MAX1365-MAX1..> 18-Jul-2014 16:56 1.4M
![[TXT]](http://www.audentia-gestion.fr/icons/text.gif)
Farnell-XPSAF5130-PD..> 18-Jul-2014 16:56 1.4M
![[TXT]](http://www.audentia-gestion.fr/icons/text.gif)
Farnell-DP83846A-DsP..> 18-Jul-2014 16:55 1.5M
![[TXT]](http://www.audentia-gestion.fr/icons/text.gif)
Farnell-Dremel-Exper..> 18-Jul-2014 16:55 1.6M
![[TXT]](http://www.audentia-gestion.fr/icons/text.gif)
Farnell-MCOC1-Farnel..> 16-Jul-2014 09:04 1.0M
![[TXT]](http://www.audentia-gestion.fr/icons/text.gif)
Farnell-SL3S1203_121..> 16-Jul-2014 09:04 1.1M
![[TXT]](http://www.audentia-gestion.fr/icons/text.gif)
Farnell-PN512-Full-N..> 16-Jul-2014 09:03 1.4M
![[TXT]](http://www.audentia-gestion.fr/icons/text.gif)
Farnell-SL3S4011_402..> 16-Jul-2014 09:03 1.1M
![[TXT]](http://www.audentia-gestion.fr/icons/text.gif)
Farnell-LPC408x-7x 3..> 16-Jul-2014 09:03 1.6M
![[TXT]](http://www.audentia-gestion.fr/icons/text.gif)
Farnell-PCF8574-PCF8..> 16-Jul-2014 09:03 1.7M
![[TXT]](http://www.audentia-gestion.fr/icons/text.gif)
Farnell-LPC81xM-32-b..> 16-Jul-2014 09:02 2.0M
![[TXT]](http://www.audentia-gestion.fr/icons/text.gif)
Farnell-LPC1769-68-6..> 16-Jul-2014 09:02 1.9M
![[TXT]](http://www.audentia-gestion.fr/icons/text.gif)
Farnell-Download-dat..> 16-Jul-2014 09:02 2.2M
![[TXT]](http://www.audentia-gestion.fr/icons/text.gif)
Farnell-LPC3220-30-4..> 16-Jul-2014 09:02 2.2M
![[TXT]](http://www.audentia-gestion.fr/icons/text.gif)
Farnell-LPC11U3x-32-..> 16-Jul-2014 09:01 2.4M
![[TXT]](http://www.audentia-gestion.fr/icons/text.gif)
Farnell-SL3ICS1002-1..> 16-Jul-2014 09:01 2.5M
![[TXT]](http://www.audentia-gestion.fr/icons/text.gif)
Farnell-T672-3000-Se..> 08-Jul-2014 18:59 2.0M
![[TXT]](http://www.audentia-gestion.fr/icons/text.gif)
Farnell-tesa®pack63..> 08-Jul-2014 18:56 2.0M
![[TXT]](http://www.audentia-gestion.fr/icons/text.gif)
Farnell-Encodeur-USB..> 08-Jul-2014 18:56 2.0M
![[TXT]](http://www.audentia-gestion.fr/icons/text.gif)
Farnell-CC2530ZDK-Us..> 08-Jul-2014 18:55 2.1M
![[TXT]](http://www.audentia-gestion.fr/icons/text.gif)
Farnell-2020-Manuel-..> 08-Jul-2014 18:55 2.1M
![[TXT]](http://www.audentia-gestion.fr/icons/text.gif)
Farnell-Synchronous-..> 08-Jul-2014 18:54 2.1M
![[TXT]](http://www.audentia-gestion.fr/icons/text.gif)
Farnell-Arithmetic-L..> 08-Jul-2014 18:54 2.1M
![[TXT]](http://www.audentia-gestion.fr/icons/text.gif)
Farnell-NA555-NE555-..> 08-Jul-2014 18:53 2.2M
![[TXT]](http://www.audentia-gestion.fr/icons/text.gif)
Farnell-4-Bit-Magnit..> 08-Jul-2014 18:53 2.2M
![[TXT]](http://www.audentia-gestion.fr/icons/text.gif)
Farnell-LM555-Timer-..> 08-Jul-2014 18:53 2.2M
![[TXT]](http://www.audentia-gestion.fr/icons/text.gif)
Farnell-L293d-Texas-..> 08-Jul-2014 18:53 2.2M
![[TXT]](http://www.audentia-gestion.fr/icons/text.gif)
Farnell-SN54HC244-SN..> 08-Jul-2014 18:52 2.3M
![[TXT]](http://www.audentia-gestion.fr/icons/text.gif)
Farnell-MAX232-MAX23..> 08-Jul-2014 18:52 2.3M
![[TXT]](http://www.audentia-gestion.fr/icons/text.gif)
Farnell-High-precisi..> 08-Jul-2014 18:51 2.3M
![[TXT]](http://www.audentia-gestion.fr/icons/text.gif)
Farnell-SMU-Instrume..> 08-Jul-2014 18:51 2.3M
![[TXT]](http://www.audentia-gestion.fr/icons/text.gif)
Farnell-900-Series-B..> 08-Jul-2014 18:50 2.3M
![[TXT]](http://www.audentia-gestion.fr/icons/text.gif)
Farnell-BA-Series-Oh..> 08-Jul-2014 18:50 2.3M
![[TXT]](http://www.audentia-gestion.fr/icons/text.gif)
Farnell-UTS-Series-S..> 08-Jul-2014 18:49 2.5M
![[TXT]](http://www.audentia-gestion.fr/icons/text.gif)
Farnell-270-Series-O..> 08-Jul-2014 18:49 2.3M
![[TXT]](http://www.audentia-gestion.fr/icons/text.gif)
Farnell-UTS-Series-S..> 08-Jul-2014 18:49 2.8M
![[TXT]](http://www.audentia-gestion.fr/icons/text.gif)
Farnell-Tiva-C-Serie..> 08-Jul-2014 18:49 2.6M
![[TXT]](http://www.audentia-gestion.fr/icons/text.gif)
Farnell-UTO-Souriau-..> 08-Jul-2014 18:48 2.8M
![[TXT]](http://www.audentia-gestion.fr/icons/text.gif)
Farnell-Clipper-Seri..> 08-Jul-2014 18:48 2.8M
![[TXT]](http://www.audentia-gestion.fr/icons/text.gif)
Farnell-SOURIAU-Cont..> 08-Jul-2014 18:47 3.0M
![[TXT]](http://www.audentia-gestion.fr/icons/text.gif)
Farnell-851-Series-P..> 08-Jul-2014 18:47 3.0M
Farnell-SL59830-Inte..> 06-Jul-2014 10:07 1.0M
![[TXT]](http://www.audentia-gestion.fr/icons/text.gif)
Farnell-ALF1210-PDF.htm 06-Jul-2014 10:06 4.0M
![[TXT]](http://www.audentia-gestion.fr/icons/text.gif)
Farnell-AD7171-16-Bi..> 06-Jul-2014 10:06 1.0M
![[TXT]](http://www.audentia-gestion.fr/icons/text.gif)
Farnell-Low-Noise-24..> 06-Jul-2014 10:05 1.0M
![[TXT]](http://www.audentia-gestion.fr/icons/text.gif)
Farnell-ESCON-Featur..> 06-Jul-2014 10:05 938K
![[TXT]](http://www.audentia-gestion.fr/icons/text.gif)
Farnell-74LCX573-Fai..> 06-Jul-2014 10:05 1.9M
![[TXT]](http://www.audentia-gestion.fr/icons/text.gif)
Farnell-1N4148WS-Fai..> 06-Jul-2014 10:04 1.9M
![[TXT]](http://www.audentia-gestion.fr/icons/text.gif)
Farnell-FAN6756-Fair..> 06-Jul-2014 10:04 850K
![[TXT]](http://www.audentia-gestion.fr/icons/text.gif)
Farnell-Datasheet-Fa..> 06-Jul-2014 10:04 861K
![[TXT]](http://www.audentia-gestion.fr/icons/text.gif)
Farnell-ES1F-ES1J-fi..> 06-Jul-2014 10:04 867K
![[TXT]](http://www.audentia-gestion.fr/icons/text.gif)
Farnell-QRE1113-Fair..> 06-Jul-2014 10:03 879K
![[TXT]](http://www.audentia-gestion.fr/icons/text.gif)
Farnell-2N7002DW-Fai..> 06-Jul-2014 10:03 886K
![[TXT]](http://www.audentia-gestion.fr/icons/text.gif)
Farnell-FDC2512-Fair..> 06-Jul-2014 10:03 886K
![[TXT]](http://www.audentia-gestion.fr/icons/text.gif)
Farnell-FDV301N-Digi..> 06-Jul-2014 10:03 886K
![[TXT]](http://www.audentia-gestion.fr/icons/text.gif)
Farnell-S1A-Fairchil..> 06-Jul-2014 10:03 896K
![[TXT]](http://www.audentia-gestion.fr/icons/text.gif)
Farnell-BAV99-Fairch..> 06-Jul-2014 10:03 896K
![[TXT]](http://www.audentia-gestion.fr/icons/text.gif)
Farnell-74AC00-74ACT..> 06-Jul-2014 10:03 911K
![[TXT]](http://www.audentia-gestion.fr/icons/text.gif)
Farnell-NaPiOn-Panas..> 06-Jul-2014 10:02 911K
![[TXT]](http://www.audentia-gestion.fr/icons/text.gif)
Farnell-LQ-RELAYS-AL..> 06-Jul-2014 10:02 924K
![[TXT]](http://www.audentia-gestion.fr/icons/text.gif)
Farnell-ev-relays-ae..> 06-Jul-2014 10:02 926K
![[TXT]](http://www.audentia-gestion.fr/icons/text.gif)
Farnell-ESCON-Featur..> 06-Jul-2014 10:02 931K
![[TXT]](http://www.audentia-gestion.fr/icons/text.gif)
Farnell-Amplifier-In..> 06-Jul-2014 10:02 940K
![[TXT]](http://www.audentia-gestion.fr/icons/text.gif)
Farnell-Serial-File-..> 06-Jul-2014 10:02 941K
![[TXT]](http://www.audentia-gestion.fr/icons/text.gif)
Farnell-Both-the-Del..> 06-Jul-2014 10:01 948K
![[TXT]](http://www.audentia-gestion.fr/icons/text.gif)
Farnell-Videk-PDF.htm 06-Jul-2014 10:01 948K
![[TXT]](http://www.audentia-gestion.fr/icons/text.gif)
Farnell-EPCOS-173438..> 04-Jul-2014 10:43 3.3M
![[TXT]](http://www.audentia-gestion.fr/icons/text.gif)
Farnell-Sensorless-C..> 04-Jul-2014 10:42 3.3M
![[TXT]](http://www.audentia-gestion.fr/icons/text.gif)
Farnell-197.31-KB-Te..> 04-Jul-2014 10:42 3.3M
![[TXT]](http://www.audentia-gestion.fr/icons/text.gif)
Farnell-PIC12F609-61..> 04-Jul-2014 10:41 3.7M
![[TXT]](http://www.audentia-gestion.fr/icons/text.gif)
Farnell-PADO-semi-au..> 04-Jul-2014 10:41 3.7M
![[TXT]](http://www.audentia-gestion.fr/icons/text.gif)
Farnell-03-iec-runds..> 04-Jul-2014 10:40 3.7M
![[TXT]](http://www.audentia-gestion.fr/icons/text.gif)
Farnell-ACC-Silicone..> 04-Jul-2014 10:40 3.7M
![[TXT]](http://www.audentia-gestion.fr/icons/text.gif)
Farnell-Series-TDS10..> 04-Jul-2014 10:39 4.0M
![[TXT]](http://www.audentia-gestion.fr/icons/text.gif)
Farnell-03-iec-runds..> 04-Jul-2014 10:40 3.7M
![[TXT]](http://www.audentia-gestion.fr/icons/text.gif)
Farnell-0430300011-D..> 14-Jun-2014 18:13 2.0M
![[TXT]](http://www.audentia-gestion.fr/icons/text.gif)
Farnell-06-6544-8-PD..> 26-Mar-2014 17:56 2.7M
![[TXT]](http://www.audentia-gestion.fr/icons/text.gif)
Farnell-3M-Polyimide..> 21-Mar-2014 08:09 3.9M
![[TXT]](http://www.audentia-gestion.fr/icons/text.gif)
Farnell-3M-VolitionT..> 25-Mar-2014 08:18 3.3M
![[TXT]](http://www.audentia-gestion.fr/icons/text.gif)
Farnell-10BQ060-PDF.htm 14-Jun-2014 09:50 2.4M
![[TXT]](http://www.audentia-gestion.fr/icons/text.gif)
Farnell-10TPB47M-End..> 14-Jun-2014 18:16 3.4M
![[TXT]](http://www.audentia-gestion.fr/icons/text.gif)
Farnell-12mm-Size-In..> 14-Jun-2014 09:50 2.4M
![[TXT]](http://www.audentia-gestion.fr/icons/text.gif)
Farnell-24AA024-24LC..> 23-Jun-2014 10:26 3.1M
![[TXT]](http://www.audentia-gestion.fr/icons/text.gif)
Farnell-50A-High-Pow..> 20-Mar-2014 17:31 2.9M
![[TXT]](http://www.audentia-gestion.fr/icons/text.gif)
Farnell-197.31-KB-Te..> 04-Jul-2014 10:42 3.3M
![[TXT]](http://www.audentia-gestion.fr/icons/text.gif)
Farnell-1907-2006-PD..> 26-Mar-2014 17:56 2.7M
![[TXT]](http://www.audentia-gestion.fr/icons/text.gif)
Farnell-5910-PDF.htm 25-Mar-2014 08:15 3.0M
![[TXT]](http://www.audentia-gestion.fr/icons/text.gif)
Farnell-6517b-Electr..> 29-Mar-2014 11:12 3.3M
![[TXT]](http://www.audentia-gestion.fr/icons/text.gif)
Farnell-A-True-Syste..> 29-Mar-2014 11:13 3.3M
![[TXT]](http://www.audentia-gestion.fr/icons/text.gif)
Farnell-ACC-Silicone..> 04-Jul-2014 10:40 3.7M
![[TXT]](http://www.audentia-gestion.fr/icons/text.gif)
Farnell-AD524-PDF.htm 20-Mar-2014 17:33 2.8M
![[TXT]](http://www.audentia-gestion.fr/icons/text.gif)
Farnell-ADL6507-PDF.htm 14-Jun-2014 18:19 3.4M
![[TXT]](http://www.audentia-gestion.fr/icons/text.gif)
Farnell-ADSP-21362-A..> 20-Mar-2014 17:34 2.8M
![[TXT]](http://www.audentia-gestion.fr/icons/text.gif)
Farnell-ALF1210-PDF.htm 04-Jul-2014 10:39 4.0M
![[TXT]](http://www.audentia-gestion.fr/icons/text.gif)
Farnell-ALF1225-12-V..> 01-Apr-2014 07:40 3.4M
![[TXT]](http://www.audentia-gestion.fr/icons/text.gif)
Farnell-ALF2412-24-V..> 01-Apr-2014 07:39 3.4M
![[TXT]](http://www.audentia-gestion.fr/icons/text.gif)
Farnell-AN10361-Phil..> 23-Jun-2014 10:29 2.1M
![[TXT]](http://www.audentia-gestion.fr/icons/text.gif)
Farnell-ARADUR-HY-13..> 26-Mar-2014 17:55 2.8M
![[TXT]](http://www.audentia-gestion.fr/icons/text.gif)
Farnell-ARALDITE-201..> 21-Mar-2014 08:12 3.7M
![[TXT]](http://www.audentia-gestion.fr/icons/text.gif)
Farnell-ARALDITE-CW-..> 26-Mar-2014 17:56 2.7M
![[TXT]](http://www.audentia-gestion.fr/icons/text.gif)
Farnell-ATMEL-8-bit-..> 19-Mar-2014 18:04 2.1M
![[TXT]](http://www.audentia-gestion.fr/icons/text.gif)
Farnell-ATMEL-8-bit-..> 11-Mar-2014 07:55 2.1M
![[TXT]](http://www.audentia-gestion.fr/icons/text.gif)
Farnell-ATmega640-VA..> 14-Jun-2014 09:49 2.5M
![[TXT]](http://www.audentia-gestion.fr/icons/text.gif)
Farnell-ATtiny20-PDF..> 25-Mar-2014 08:19 3.6M
![[TXT]](http://www.audentia-gestion.fr/icons/text.gif)
Farnell-ATtiny26-L-A..> 13-Jun-2014 18:40 1.8M
![[TXT]](http://www.audentia-gestion.fr/icons/text.gif)
Farnell-Alimentation..> 14-Jun-2014 18:24 2.5M
![[TXT]](http://www.audentia-gestion.fr/icons/text.gif)
Farnell-Alimentation..> 01-Apr-2014 07:42 3.4M
![[TXT]](http://www.audentia-gestion.fr/icons/text.gif)
Farnell-Amplificateu..> 29-Mar-2014 11:11 3.3M
![[TXT]](http://www.audentia-gestion.fr/icons/text.gif)
Farnell-An-Improved-..> 14-Jun-2014 09:49 2.5M
![[TXT]](http://www.audentia-gestion.fr/icons/text.gif)
Farnell-Atmel-ATmega..> 19-Mar-2014 18:03 2.2M
![[TXT]](http://www.audentia-gestion.fr/icons/text.gif)
Farnell-Avvertenze-e..> 14-Jun-2014 18:20 3.3M
![[TXT]](http://www.audentia-gestion.fr/icons/text.gif)
Farnell-BC846DS-NXP-..> 13-Jun-2014 18:42 1.6M
![[TXT]](http://www.audentia-gestion.fr/icons/text.gif)
Farnell-BC847DS-NXP-..> 23-Jun-2014 10:24 3.3M
![[TXT]](http://www.audentia-gestion.fr/icons/text.gif)
Farnell-BF545A-BF545..> 23-Jun-2014 10:28 2.1M
![[TXT]](http://www.audentia-gestion.fr/icons/text.gif)
Farnell-BK2650A-BK26..> 29-Mar-2014 11:10 3.3M
![[TXT]](http://www.audentia-gestion.fr/icons/text.gif)
Farnell-BT151-650R-N..> 13-Jun-2014 18:40 1.7M
![[TXT]](http://www.audentia-gestion.fr/icons/text.gif)
Farnell-BTA204-800C-..> 13-Jun-2014 18:42 1.6M
![[TXT]](http://www.audentia-gestion.fr/icons/text.gif)
Farnell-BUJD203AX-NX..> 13-Jun-2014 18:41 1.7M
![[TXT]](http://www.audentia-gestion.fr/icons/text.gif)
Farnell-BYV29F-600-N..> 13-Jun-2014 18:42 1.6M
![[TXT]](http://www.audentia-gestion.fr/icons/text.gif)
Farnell-BYV79E-serie..> 10-Mar-2014 16:19 1.6M
![[TXT]](http://www.audentia-gestion.fr/icons/text.gif)
Farnell-BZX384-serie..> 23-Jun-2014 10:29 2.1M
![[TXT]](http://www.audentia-gestion.fr/icons/text.gif)
Farnell-Battery-GBA-..> 14-Jun-2014 18:13 2.0M
![[TXT]](http://www.audentia-gestion.fr/icons/text.gif)
Farnell-C.A-6150-C.A..> 14-Jun-2014 18:24 2.5M
![[TXT]](http://www.audentia-gestion.fr/icons/text.gif)
Farnell-C.A 8332B-C...> 01-Apr-2014 07:40 3.4M
![[TXT]](http://www.audentia-gestion.fr/icons/text.gif)
Farnell-CC2560-Bluet..> 29-Mar-2014 11:14 2.8M
![[TXT]](http://www.audentia-gestion.fr/icons/text.gif)
Farnell-CD4536B-Type..> 14-Jun-2014 18:13 2.0M
![[TXT]](http://www.audentia-gestion.fr/icons/text.gif)
Farnell-CIRRUS-LOGIC..> 10-Mar-2014 17:20 2.1M
![[TXT]](http://www.audentia-gestion.fr/icons/text.gif)
Farnell-CS5532-34-BS..> 01-Apr-2014 07:39 3.5M
![[TXT]](http://www.audentia-gestion.fr/icons/text.gif)
Farnell-Cannon-ZD-PD..> 11-Mar-2014 08:13 2.8M
![[TXT]](http://www.audentia-gestion.fr/icons/text.gif)
Farnell-Ceramic-tran..> 14-Jun-2014 18:19 3.4M
![[TXT]](http://www.audentia-gestion.fr/icons/text.gif)
Farnell-Circuit-Note..> 26-Mar-2014 18:00 2.8M
![[TXT]](http://www.audentia-gestion.fr/icons/text.gif)
Farnell-Circuit-Note..> 26-Mar-2014 18:00 2.8M
![[TXT]](http://www.audentia-gestion.fr/icons/text.gif)
Farnell-Cles-electro..> 21-Mar-2014 08:13 3.9M
![[TXT]](http://www.audentia-gestion.fr/icons/text.gif)
Farnell-Conception-d..> 11-Mar-2014 07:49 2.4M
![[TXT]](http://www.audentia-gestion.fr/icons/text.gif)
Farnell-Connectors-N..> 14-Jun-2014 18:12 2.1M
![[TXT]](http://www.audentia-gestion.fr/icons/text.gif)
Farnell-Construction..> 14-Jun-2014 18:25 2.5M
![[TXT]](http://www.audentia-gestion.fr/icons/text.gif)
Farnell-Controle-de-..> 11-Mar-2014 08:16 2.8M
![[TXT]](http://www.audentia-gestion.fr/icons/text.gif)
Farnell-Cordless-dri..> 14-Jun-2014 18:13 2.0M
![[TXT]](http://www.audentia-gestion.fr/icons/text.gif)
Farnell-Current-Tran..> 26-Mar-2014 17:58 2.7M
![[TXT]](http://www.audentia-gestion.fr/icons/text.gif)
Farnell-Current-Tran..> 26-Mar-2014 17:58 2.7M
![[TXT]](http://www.audentia-gestion.fr/icons/text.gif)
Farnell-Current-Tran..> 26-Mar-2014 17:59 2.7M
![[TXT]](http://www.audentia-gestion.fr/icons/text.gif)
Farnell-Current-Tran..> 26-Mar-2014 17:59 2.7M
![[TXT]](http://www.audentia-gestion.fr/icons/text.gif)
Farnell-DC-Fan-type-..> 14-Jun-2014 09:48 2.5M
![[TXT]](http://www.audentia-gestion.fr/icons/text.gif)
Farnell-DC-Fan-type-..> 14-Jun-2014 09:51 1.8M
![[TXT]](http://www.audentia-gestion.fr/icons/text.gif)
Farnell-Davum-TMC-PD..> 14-Jun-2014 18:27 2.4M
![[TXT]](http://www.audentia-gestion.fr/icons/text.gif)
Farnell-De-la-puissa..> 29-Mar-2014 11:10 3.3M
![[TXT]](http://www.audentia-gestion.fr/icons/text.gif)
Farnell-Directive-re..> 25-Mar-2014 08:16 3.0M
![[TXT]](http://www.audentia-gestion.fr/icons/text.gif)
Farnell-Documentatio..> 14-Jun-2014 18:26 2.5M
![[TXT]](http://www.audentia-gestion.fr/icons/text.gif)
Farnell-Download-dat..> 13-Jun-2014 18:40 1.8M
![[TXT]](http://www.audentia-gestion.fr/icons/text.gif)
Farnell-ECO-Series-T..> 20-Mar-2014 08:14 2.5M
![[TXT]](http://www.audentia-gestion.fr/icons/text.gif)
Farnell-ELMA-PDF.htm 29-Mar-2014 11:13 3.3M
![[TXT]](http://www.audentia-gestion.fr/icons/text.gif)
Farnell-EMC1182-PDF.htm 25-Mar-2014 08:17 3.0M
![[TXT]](http://www.audentia-gestion.fr/icons/text.gif)
Farnell-EPCOS-173438..> 04-Jul-2014 10:43 3.3M
![[TXT]](http://www.audentia-gestion.fr/icons/text.gif)
Farnell-EPCOS-Sample..> 11-Mar-2014 07:53 2.2M
![[TXT]](http://www.audentia-gestion.fr/icons/text.gif)
Farnell-ES2333-PDF.htm 11-Mar-2014 08:14 2.8M
![[TXT]](http://www.audentia-gestion.fr/icons/text.gif)
Farnell-Ed.081002-DA..> 19-Mar-2014 18:02 2.5M
![[TXT]](http://www.audentia-gestion.fr/icons/text.gif)
Farnell-F28069-Picco..> 14-Jun-2014 18:14 2.0M
![[TXT]](http://www.audentia-gestion.fr/icons/text.gif)
Farnell-F42202-PDF.htm 19-Mar-2014 18:00 2.5M
![[TXT]](http://www.audentia-gestion.fr/icons/text.gif)
Farnell-FDS-ITW-Spra..> 14-Jun-2014 18:22 3.3M
![[TXT]](http://www.audentia-gestion.fr/icons/text.gif)
Farnell-FICHE-DE-DON..> 10-Mar-2014 16:17 1.6M
![[TXT]](http://www.audentia-gestion.fr/icons/text.gif)
Farnell-Fastrack-Sup..> 23-Jun-2014 10:25 3.3M
![[TXT]](http://www.audentia-gestion.fr/icons/text.gif)
Farnell-Ferric-Chlor..> 29-Mar-2014 11:14 2.8M
![[TXT]](http://www.audentia-gestion.fr/icons/text.gif)
Farnell-Fiche-de-don..> 14-Jun-2014 09:47 2.5M
![[TXT]](http://www.audentia-gestion.fr/icons/text.gif)
Farnell-Fiche-de-don..> 14-Jun-2014 18:26 2.5M
![[TXT]](http://www.audentia-gestion.fr/icons/text.gif)
Farnell-Fluke-1730-E..> 14-Jun-2014 18:23 2.5M
![[TXT]](http://www.audentia-gestion.fr/icons/text.gif)
Farnell-GALVA-A-FROI..> 26-Mar-2014 17:56 2.7M
![[TXT]](http://www.audentia-gestion.fr/icons/text.gif)
Farnell-GALVA-MAT-Re..> 26-Mar-2014 17:57 2.7M
![[TXT]](http://www.audentia-gestion.fr/icons/text.gif)
Farnell-GN-RELAYS-AG..> 20-Mar-2014 08:11 2.6M
![[TXT]](http://www.audentia-gestion.fr/icons/text.gif)
Farnell-HC49-4H-Crys..> 14-Jun-2014 18:20 3.3M
![[TXT]](http://www.audentia-gestion.fr/icons/text.gif)
Farnell-HFE1600-Data..> 14-Jun-2014 18:22 3.3M
![[TXT]](http://www.audentia-gestion.fr/icons/text.gif)
Farnell-HI-70300-Sol..> 14-Jun-2014 18:27 2.4M
![[TXT]](http://www.audentia-gestion.fr/icons/text.gif)
Farnell-HUNTSMAN-Adv..> 10-Mar-2014 16:17 1.7M
![[TXT]](http://www.audentia-gestion.fr/icons/text.gif)
Farnell-Haute-vitess..> 11-Mar-2014 08:17 2.4M
![[TXT]](http://www.audentia-gestion.fr/icons/text.gif)
Farnell-IP4252CZ16-8..> 13-Jun-2014 18:41 1.7M
![[TXT]](http://www.audentia-gestion.fr/icons/text.gif)
Farnell-Instructions..> 19-Mar-2014 18:01 2.5M
![[TXT]](http://www.audentia-gestion.fr/icons/text.gif)
Farnell-KSZ8851SNL-S..> 23-Jun-2014 10:28 2.1M
![[TXT]](http://www.audentia-gestion.fr/icons/text.gif)
Farnell-L-efficacite..> 11-Mar-2014 07:52 2.3M
![[TXT]](http://www.audentia-gestion.fr/icons/text.gif)
Farnell-LCW-CQ7P.CC-..> 25-Mar-2014 08:19 3.2M
![[TXT]](http://www.audentia-gestion.fr/icons/text.gif)
Farnell-LME49725-Pow..> 14-Jun-2014 09:49 2.5M
![[TXT]](http://www.audentia-gestion.fr/icons/text.gif)
Farnell-LOCTITE-542-..> 25-Mar-2014 08:15 3.0M
![[TXT]](http://www.audentia-gestion.fr/icons/text.gif)
Farnell-LOCTITE-3463..> 25-Mar-2014 08:19 3.0M
![[TXT]](http://www.audentia-gestion.fr/icons/text.gif)
Farnell-LUXEON-Guide..> 11-Mar-2014 07:52 2.3M
![[TXT]](http://www.audentia-gestion.fr/icons/text.gif)
Farnell-Leaded-Trans..> 23-Jun-2014 10:26 3.2M
![[TXT]](http://www.audentia-gestion.fr/icons/text.gif)
Farnell-Les-derniers..> 11-Mar-2014 07:50 2.3M
![[TXT]](http://www.audentia-gestion.fr/icons/text.gif)
Farnell-Loctite3455-..> 25-Mar-2014 08:16 3.0M
![[TXT]](http://www.audentia-gestion.fr/icons/text.gif)
Farnell-Low-cost-Enc..> 13-Jun-2014 18:42 1.7M
![[TXT]](http://www.audentia-gestion.fr/icons/text.gif)
Farnell-Lubrifiant-a..> 26-Mar-2014 18:00 2.7M
![[TXT]](http://www.audentia-gestion.fr/icons/text.gif)
Farnell-MC3510-PDF.htm 25-Mar-2014 08:17 3.0M
![[TXT]](http://www.audentia-gestion.fr/icons/text.gif)
Farnell-MC21605-PDF.htm 11-Mar-2014 08:14 2.8M
![[TXT]](http://www.audentia-gestion.fr/icons/text.gif)
Farnell-MCF532x-7x-E..> 29-Mar-2014 11:14 2.8M
![[TXT]](http://www.audentia-gestion.fr/icons/text.gif)
Farnell-MICREL-KSZ88..> 11-Mar-2014 07:54 2.2M
![[TXT]](http://www.audentia-gestion.fr/icons/text.gif)
Farnell-MICROCHIP-PI..> 19-Mar-2014 18:02 2.5M
![[TXT]](http://www.audentia-gestion.fr/icons/text.gif)
Farnell-MOLEX-39-00-..> 10-Mar-2014 17:19 1.9M
![[TXT]](http://www.audentia-gestion.fr/icons/text.gif)
Farnell-MOLEX-43020-..> 10-Mar-2014 17:21 1.9M
![[TXT]](http://www.audentia-gestion.fr/icons/text.gif)
Farnell-MOLEX-43160-..> 10-Mar-2014 17:21 1.9M
![[TXT]](http://www.audentia-gestion.fr/icons/text.gif)
Farnell-MOLEX-87439-..> 10-Mar-2014 17:21 1.9M
![[TXT]](http://www.audentia-gestion.fr/icons/text.gif)
Farnell-MPXV7002-Rev..> 20-Mar-2014 17:33 2.8M
![[TXT]](http://www.audentia-gestion.fr/icons/text.gif)
Farnell-MX670-MX675-..> 14-Jun-2014 09:46 2.5M
![[TXT]](http://www.audentia-gestion.fr/icons/text.gif)
Farnell-Microchip-MC..> 13-Jun-2014 18:27 1.8M
![[TXT]](http://www.audentia-gestion.fr/icons/text.gif)
Farnell-Microship-PI..> 11-Mar-2014 07:53 2.2M
![[TXT]](http://www.audentia-gestion.fr/icons/text.gif)
Farnell-Midas-Active..> 14-Jun-2014 18:17 3.4M
![[TXT]](http://www.audentia-gestion.fr/icons/text.gif)
Farnell-Midas-MCCOG4..> 14-Jun-2014 18:11 2.1M
![[TXT]](http://www.audentia-gestion.fr/icons/text.gif)
Farnell-Miniature-Ci..> 26-Mar-2014 17:55 2.8M
![[TXT]](http://www.audentia-gestion.fr/icons/text.gif)
Farnell-Mistral-PDF.htm 14-Jun-2014 18:12 2.1M
![[TXT]](http://www.audentia-gestion.fr/icons/text.gif)
Farnell-Molex-83421-..> 14-Jun-2014 18:17 3.4M
![[TXT]](http://www.audentia-gestion.fr/icons/text.gif)
Farnell-Molex-COMMER..> 14-Jun-2014 18:16 3.4M
![[TXT]](http://www.audentia-gestion.fr/icons/text.gif)
Farnell-Molex-Crimp-..> 10-Mar-2014 16:27 1.7M
![[TXT]](http://www.audentia-gestion.fr/icons/text.gif)
Farnell-Multi-Functi..> 20-Mar-2014 17:38 3.0M
![[TXT]](http://www.audentia-gestion.fr/icons/text.gif)
Farnell-NTE_SEMICOND..> 11-Mar-2014 07:52 2.3M
![[TXT]](http://www.audentia-gestion.fr/icons/text.gif)
Farnell-NXP-74VHC126..> 10-Mar-2014 16:17 1.6M
![[TXT]](http://www.audentia-gestion.fr/icons/text.gif)
Farnell-NXP-BT136-60..> 11-Mar-2014 07:52 2.3M
![[TXT]](http://www.audentia-gestion.fr/icons/text.gif)
Farnell-NXP-PBSS9110..> 10-Mar-2014 17:21 1.9M
![[TXT]](http://www.audentia-gestion.fr/icons/text.gif)
Farnell-NXP-PCA9555 ..> 11-Mar-2014 07:54 2.2M
![[TXT]](http://www.audentia-gestion.fr/icons/text.gif)
Farnell-NXP-PMBFJ620..> 10-Mar-2014 16:16 1.7M
![[TXT]](http://www.audentia-gestion.fr/icons/text.gif)
Farnell-NXP-PSMN1R7-..> 10-Mar-2014 16:17 1.6M
![[TXT]](http://www.audentia-gestion.fr/icons/text.gif)
Farnell-NXP-PSMN7R0-..> 10-Mar-2014 17:19 2.1M
![[TXT]](http://www.audentia-gestion.fr/icons/text.gif)
Farnell-NXP-TEA1703T..> 11-Mar-2014 08:15 2.8M
![[TXT]](http://www.audentia-gestion.fr/icons/text.gif)
Farnell-Nilï¬-sk-E-..> 14-Jun-2014 09:47 2.5M
![[TXT]](http://www.audentia-gestion.fr/icons/text.gif)
Farnell-Novembre-201..> 20-Mar-2014 17:38 3.3M
![[TXT]](http://www.audentia-gestion.fr/icons/text.gif)
Farnell-OMRON-Master..> 10-Mar-2014 16:26 1.8M
![[TXT]](http://www.audentia-gestion.fr/icons/text.gif)
Farnell-OSLON-SSL-Ce..> 19-Mar-2014 18:03 2.1M
![[TXT]](http://www.audentia-gestion.fr/icons/text.gif)
Farnell-OXPCIE958-FB..> 13-Jun-2014 18:40 1.8M
![[TXT]](http://www.audentia-gestion.fr/icons/text.gif)
Farnell-PADO-semi-au..> 04-Jul-2014 10:41 3.7M
![[TXT]](http://www.audentia-gestion.fr/icons/text.gif)
Farnell-PBSS5160T-60..> 19-Mar-2014 18:03 2.1M
![[TXT]](http://www.audentia-gestion.fr/icons/text.gif)
Farnell-PDTA143X-ser..> 20-Mar-2014 08:12 2.6M
![[TXT]](http://www.audentia-gestion.fr/icons/text.gif)
Farnell-PDTB123TT-NX..> 13-Jun-2014 18:43 1.5M
![[TXT]](http://www.audentia-gestion.fr/icons/text.gif)
Farnell-PESD5V0F1BL-..> 13-Jun-2014 18:43 1.5M
![[TXT]](http://www.audentia-gestion.fr/icons/text.gif)
Farnell-PESD9X5.0L-P..> 13-Jun-2014 18:43 1.6M
![[TXT]](http://www.audentia-gestion.fr/icons/text.gif)
Farnell-PIC12F609-61..> 04-Jul-2014 10:41 3.7M
![[TXT]](http://www.audentia-gestion.fr/icons/text.gif)
Farnell-PIC18F2455-2..> 23-Jun-2014 10:27 3.1M
![[TXT]](http://www.audentia-gestion.fr/icons/text.gif)
Farnell-PIC24FJ256GB..> 14-Jun-2014 09:51 2.4M
![[TXT]](http://www.audentia-gestion.fr/icons/text.gif)
Farnell-PMBT3906-PNP..> 13-Jun-2014 18:44 1.5M
![[TXT]](http://www.audentia-gestion.fr/icons/text.gif)
Farnell-PMBT4403-PNP..> 23-Jun-2014 10:27 3.1M
![[TXT]](http://www.audentia-gestion.fr/icons/text.gif)
Farnell-PMEG4002EL-N..> 14-Jun-2014 18:18 3.4M
![[TXT]](http://www.audentia-gestion.fr/icons/text.gif)
Farnell-PMEG4010CEH-..> 13-Jun-2014 18:43 1.6M
![[TXT]](http://www.audentia-gestion.fr/icons/text.gif)
Farnell-Panasonic-15..> 23-Jun-2014 10:29 2.1M
![[TXT]](http://www.audentia-gestion.fr/icons/text.gif)
Farnell-Panasonic-EC..> 20-Mar-2014 17:36 2.6M
![[TXT]](http://www.audentia-gestion.fr/icons/text.gif)
Farnell-Panasonic-EZ..> 20-Mar-2014 08:10 2.6M
![[TXT]](http://www.audentia-gestion.fr/icons/text.gif)
Farnell-Panasonic-Id..> 20-Mar-2014 17:35 2.6M
![[TXT]](http://www.audentia-gestion.fr/icons/text.gif)
Farnell-Panasonic-Ne..> 20-Mar-2014 17:36 2.6M
![[TXT]](http://www.audentia-gestion.fr/icons/text.gif)
Farnell-Panasonic-Ra..> 20-Mar-2014 17:37 2.6M
![[TXT]](http://www.audentia-gestion.fr/icons/text.gif)
Farnell-Panasonic-TS..> 20-Mar-2014 08:12 2.6M
![[TXT]](http://www.audentia-gestion.fr/icons/text.gif)
Farnell-Panasonic-Y3..> 20-Mar-2014 08:11 2.6M
![[TXT]](http://www.audentia-gestion.fr/icons/text.gif)
Farnell-Pico-Spox-Wi..> 10-Mar-2014 16:16 1.7M
![[TXT]](http://www.audentia-gestion.fr/icons/text.gif)
Farnell-Pompes-Charg..> 24-Apr-2014 20:23 3.3M
![[TXT]](http://www.audentia-gestion.fr/icons/text.gif)
Farnell-Ponts-RLC-po..> 14-Jun-2014 18:23 3.3M
![[TXT]](http://www.audentia-gestion.fr/icons/text.gif)
Farnell-Portable-Ana..> 29-Mar-2014 11:16 2.8M
![[TXT]](http://www.audentia-gestion.fr/icons/text.gif)
Farnell-Premier-Farn..> 21-Mar-2014 08:11 3.8M
![[TXT]](http://www.audentia-gestion.fr/icons/text.gif)
Farnell-Produit-3430..> 14-Jun-2014 09:48 2.5M
![[TXT]](http://www.audentia-gestion.fr/icons/text.gif)
Farnell-Proskit-SS-3..> 10-Mar-2014 16:26 1.8M
![[TXT]](http://www.audentia-gestion.fr/icons/text.gif)
Farnell-Puissance-ut..> 11-Mar-2014 07:49 2.4M
![[TXT]](http://www.audentia-gestion.fr/icons/text.gif)
Farnell-Q48-PDF.htm 23-Jun-2014 10:29 2.1M
![[TXT]](http://www.audentia-gestion.fr/icons/text.gif)
Farnell-Radial-Lead-..> 20-Mar-2014 08:12 2.6M
![[TXT]](http://www.audentia-gestion.fr/icons/text.gif)
Farnell-Realiser-un-..> 11-Mar-2014 07:51 2.3M
![[TXT]](http://www.audentia-gestion.fr/icons/text.gif)
Farnell-Reglement-RE..> 21-Mar-2014 08:08 3.9M
![[TXT]](http://www.audentia-gestion.fr/icons/text.gif)
Farnell-Repartiteurs..> 14-Jun-2014 18:26 2.5M
![[TXT]](http://www.audentia-gestion.fr/icons/text.gif)
Farnell-S-TRI-SWT860..> 21-Mar-2014 08:11 3.8M
![[TXT]](http://www.audentia-gestion.fr/icons/text.gif)
Farnell-SB175-Connec..> 11-Mar-2014 08:14 2.8M
![[TXT]](http://www.audentia-gestion.fr/icons/text.gif)
Farnell-SMBJ-Transil..> 29-Mar-2014 11:12 3.3M
![[TXT]](http://www.audentia-gestion.fr/icons/text.gif)
Farnell-SOT-23-Multi..> 11-Mar-2014 07:51 2.3M
![[TXT]](http://www.audentia-gestion.fr/icons/text.gif)
Farnell-SPLC780A1-16..> 14-Jun-2014 18:25 2.5M
![[TXT]](http://www.audentia-gestion.fr/icons/text.gif)
Farnell-SSC7102-Micr..> 23-Jun-2014 10:25 3.2M
![[TXT]](http://www.audentia-gestion.fr/icons/text.gif)
Farnell-SVPE-series-..> 14-Jun-2014 18:15 2.0M
![[TXT]](http://www.audentia-gestion.fr/icons/text.gif)
Farnell-Sensorless-C..> 04-Jul-2014 10:42 3.3M
![[TXT]](http://www.audentia-gestion.fr/icons/text.gif)
Farnell-Septembre-20..> 20-Mar-2014 17:46 3.7M
![[TXT]](http://www.audentia-gestion.fr/icons/text.gif)
Farnell-Serie-PicoSc..> 19-Mar-2014 18:01 2.5M
![[TXT]](http://www.audentia-gestion.fr/icons/text.gif)
Farnell-Serie-Standa..> 14-Jun-2014 18:23 3.3M
![[TXT]](http://www.audentia-gestion.fr/icons/text.gif)
Farnell-Series-2600B..> 20-Mar-2014 17:30 3.0M
![[TXT]](http://www.audentia-gestion.fr/icons/text.gif)
Farnell-Series-TDS10..> 04-Jul-2014 10:39 4.0M
![[TXT]](http://www.audentia-gestion.fr/icons/text.gif)
Farnell-Signal-PCB-R..> 14-Jun-2014 18:11 2.1M
![[TXT]](http://www.audentia-gestion.fr/icons/text.gif)
Farnell-Strangkuhlko..> 21-Mar-2014 08:09 3.9M
![[TXT]](http://www.audentia-gestion.fr/icons/text.gif)
Farnell-Supercapacit..> 26-Mar-2014 17:57 2.7M
![[TXT]](http://www.audentia-gestion.fr/icons/text.gif)
Farnell-TDK-Lambda-H..> 14-Jun-2014 18:21 3.3M
![[TXT]](http://www.audentia-gestion.fr/icons/text.gif)
Farnell-TEKTRONIX-DP..> 10-Mar-2014 17:20 2.0M
![[TXT]](http://www.audentia-gestion.fr/icons/text.gif)
Farnell-Tektronix-AC..> 13-Jun-2014 18:44 1.5M
![[TXT]](http://www.audentia-gestion.fr/icons/text.gif)
Farnell-Telemetres-l..> 20-Mar-2014 17:46 3.7M
![[TXT]](http://www.audentia-gestion.fr/icons/text.gif)
Farnell-Termometros-..> 14-Jun-2014 18:14 2.0M
![[TXT]](http://www.audentia-gestion.fr/icons/text.gif)
Farnell-The-essentia..> 10-Mar-2014 16:27 1.7M
![[TXT]](http://www.audentia-gestion.fr/icons/text.gif)
Farnell-U2270B-PDF.htm 14-Jun-2014 18:15 3.4M
![[TXT]](http://www.audentia-gestion.fr/icons/text.gif)
Farnell-USB-Buccanee..> 14-Jun-2014 09:48 2.5M
![[TXT]](http://www.audentia-gestion.fr/icons/text.gif)
Farnell-USB1T11A-PDF..> 19-Mar-2014 18:03 2.1M
![[TXT]](http://www.audentia-gestion.fr/icons/text.gif)
Farnell-V4N-PDF.htm 14-Jun-2014 18:11 2.1M
![[TXT]](http://www.audentia-gestion.fr/icons/text.gif)
Farnell-WetTantalum-..> 11-Mar-2014 08:14 2.8M
![[TXT]](http://www.audentia-gestion.fr/icons/text.gif)
Farnell-XPS-AC-Octop..> 14-Jun-2014 18:11 2.1M
![[TXT]](http://www.audentia-gestion.fr/icons/text.gif)
Farnell-XPS-MC16-XPS..> 11-Mar-2014 08:15 2.8M
![[TXT]](http://www.audentia-gestion.fr/icons/text.gif)
Farnell-YAGEO-DATA-S..> 11-Mar-2014 08:13 2.8M
![[TXT]](http://www.audentia-gestion.fr/icons/text.gif)
Farnell-ZigBee-ou-le..> 11-Mar-2014 07:50 2.4M
![[TXT]](http://www.audentia-gestion.fr/icons/text.gif)
Farnell-celpac-SUL84..> 21-Mar-2014 08:11 3.8M
![[TXT]](http://www.audentia-gestion.fr/icons/text.gif)
Farnell-china_rohs_o..> 21-Mar-2014 10:04 3.9M
![[TXT]](http://www.audentia-gestion.fr/icons/text.gif)
Farnell-cree-Xlamp-X..> 20-Mar-2014 17:34 2.8M
![[TXT]](http://www.audentia-gestion.fr/icons/text.gif)
Farnell-cree-Xlamp-X..> 20-Mar-2014 17:35 2.7M
![[TXT]](http://www.audentia-gestion.fr/icons/text.gif)
Farnell-cree-Xlamp-X..> 20-Mar-2014 17:31 2.9M
![[TXT]](http://www.audentia-gestion.fr/icons/text.gif)
Farnell-cree-Xlamp-m..> 20-Mar-2014 17:32 2.9M
![[TXT]](http://www.audentia-gestion.fr/icons/text.gif)
Farnell-cree-Xlamp-m..> 20-Mar-2014 17:32 2.9M
![[TXT]](http://www.audentia-gestion.fr/icons/text.gif)
Farnell-ir1150s_fr.p..> 29-Mar-2014 11:11 3.3M
![[TXT]](http://www.audentia-gestion.fr/icons/text.gif)
Farnell-manual-bus-p..> 10-Mar-2014 16:29 1.9M
![[TXT]](http://www.audentia-gestion.fr/icons/text.gif)
Farnell-propose-plus..> 11-Mar-2014 08:19 2.8M
![[TXT]](http://www.audentia-gestion.fr/icons/text.gif)
Farnell-techfirst_se..> 21-Mar-2014 08:08 3.9M
![[TXT]](http://www.audentia-gestion.fr/icons/text.gif)
Farnell-testo-205-20..> 20-Mar-2014 17:37 3.0M
![[TXT]](http://www.audentia-gestion.fr/icons/text.gif)
Farnell-testo-470-Fo..> 20-Mar-2014 17:38 3.0M
![[TXT]](http://www.audentia-gestion.fr/icons/text.gif)
Farnell-uC-OS-III-Br..> 10-Mar-2014 17:20 2.0M
![[TXT]](http://www.audentia-gestion.fr/icons/text.gif)
Sefram-7866HD.pdf-PD..> 29-Mar-2014 11:46 472K
![[TXT]](http://www.audentia-gestion.fr/icons/text.gif)
Sefram-CAT_ENREGISTR..> 29-Mar-2014 11:46 461K
![[TXT]](http://www.audentia-gestion.fr/icons/text.gif)
Sefram-CAT_MESUREURS..> 29-Mar-2014 11:46 435K
![[TXT]](http://www.audentia-gestion.fr/icons/text.gif)
Sefram-GUIDE_SIMPLIF..> 29-Mar-2014 11:46 481K
![[TXT]](http://www.audentia-gestion.fr/icons/text.gif)
Sefram-GUIDE_SIMPLIF..> 29-Mar-2014 11:46 442K
![[TXT]](http://www.audentia-gestion.fr/icons/text.gif)
Sefram-GUIDE_SIMPLIF..> 29-Mar-2014 11:46 422K
![[TXT]](http://www.audentia-gestion.fr/icons/text.gif)
Sefram-SP270.pdf-PDF..> 29-Mar-2014 11:46 464K
Evaluation Board User Guide
UG-146
One Technology Way • P.O. Box 9106 • Norwood, MA 02062-9106, U.S.A. • Tel: 781.329.4700 • Fax: 781.461.3113 • www.analog.com
Evaluating the ADE7878 Energy Metering IC
PLEASE SEE THE LAST PAGE FOR AN IMPORTANT
WARNING AND LEGAL TERMS AND CONDITIONS. Rev. 0 | Page 1 of 36
FEATURES
Evaluation board designed to be used with accompanying software to implement a fully functional 3-phase energy meter Easy connection of external transducers via screw terminals Easy modification of signal conditioning components using PCB sockets LED indicators on the CF1, CF2, CF3, IRQ0, and IRQ1 logic outputs Optically isolated metering components and USB-based communication with a PC External voltage reference option available for on-chip reference evaluation PC COM port-based firmware updates
GENERAL DESCRIPTION
The ADE7878 is a high accuracy, 3-phase electrical energy measurement IC with serial interfaces and three flexible pulse outputs. The ADE7878 incorporates seven ADCs, reference circuitry, and all signal processing required to perform total (fundamental and harmonic) active, reactive, and apparent energy measurement, fundamental active and reactive energy measurement, and rms calculations.
This user guide describes the ADE7878 evaluation kit hardware, firmware, and software functionality. The evaluation board contains an ADE7878 and a LPC2368 microcontroller (from NXP Semiconductors). The ADE7878 and its associated metering components are optically isolated from the microcontroller. The microcontroller communicates with the PC using a USB interface. Firmware updates can be loaded using one PC com port and a regular serial cable.
The ADE7878 evaluation board and this user guide, together with the ADE7878 data sheet, provide a complete evaluation platform for the ADE7878.
The evaluation board has been designed so that the ADE7878 can be evaluated in an energy meter. Using appropriate current transducers, the evaluation board can be connected to a test bench or high voltage (240 V rms) test circuit. On-board resistor divider networks provide the attenuation for the line voltages. This user guide describes how the current transducers should be connected for the best performance. The evaluation board requires two external 3.3 V power supplies and the appropriate current transducers.
EVALUATION BOARD CONNECTION DIAGRAM
ADE78xxP1P2P3P4P5P6P7P8P9IAPIANIBPIBNICPICNINPINNGNDVNGNDVCPGNDVBPGNDVAPGNDVDDFILTERNETWORKFILTER NETWORKAND ATTENUATIONADR280OPTIONAL EXTERNAL1.2V REFERENCEOPTIONALEXTERNALCLOCK INDIGITALISOLATORSLPC2368P10GND2VDD2P12MCU_GNDMCU_VDDUSB PORTJ2J3J4CF3CF2CF1P13JTAGINTERFACEP15CONNECTOR TOPC COM PORT09078-001 Figure 1.
UG-146 Evaluation Board User Guide
Rev. 0 | Page 2 of 36
TABLE OF CONTENTS
Features .............................................................................................. 1
General Description ......................................................................... 1
Evaluation Board Connection Diagram ........................................ 1
Revision History ............................................................................... 2
Evaluation Board Hardware ............................................................ 3
Power Supplies .............................................................................. 3
Analog Inputs (P1 to P4 and P5 to P8) ...................................... 3
Setting Up the Evaluation Board as an Energy Meter ............. 6
Evaluation Board Software .............................................................. 8
Installing and Uninstalling the ADE7878 Software ................. 8
Front Panel .................................................................................... 8
PSM0 Mode—Normal Power Mode .......................................... 9
PSM1 Mode ................................................................................. 17
PSM2 Mode ................................................................................. 17
PSM3 Mode ................................................................................. 18
Managing the Communication Protocol Between the Microcontroller and the ADE7878 .............................................. 19
Acquiring HSDC Data Continuously ...................................... 21
Starting the ADE7878 DSP ....................................................... 22
Stopping the ADE7878 DSP ..................................................... 22
Upgrading Microcontroller Firmware ......................................... 23
Control Registers Data File ....................................................... 23
Evaluation Board Schematics and Layout ................................... 25
Schematic..................................................................................... 25
Layout .......................................................................................... 32
Ordering Information .................................................................... 34
Bill of Materials ........................................................................... 34
REVISION HISTORY
8/10—Revision 0: Initial Version
Evaluation Board User Guide UG-146
Rev. 0 | Page 3 of 36
EVALUATION BOARD HARDWARE
POWER SUPPLIES
The evaluation board has three power domains: one that supplies the microcontroller and one side of the isocouplers, one that supplies the other side of the optocouplers, and one that supplies the ADE7878. The ground of the microcontroller’s power domain is connected to the ground of the PC through the USB cable. The ground of the ADE7878 power domain is determined by the ground of the phase voltages, VAP, VBP, VCP, and VN, and must be different from the ground of the micro-controller’s power domain.
The microcontroller 3.3 V supply is provided at the P12 connector. The ADE7878 3.3 V supply is provided at the P9 connector. Close jumper JP2 to ensure that the same 3.3 V supply from ADE7878 is also provided at the isocouplers.
ANALOG INPUTS (P1 TO P4 AND P5 TO P8)
Current and voltage signals are connected at the screw terminal, P1 to P4 and P5 to P8, respectively. All analog input signals are filtered using the on-board antialiasing filters before the signals are connected to the ADE7878. The components used on the board are the recommended values to be used with the ADE7878.
Current Sense Inputs (P1, P2, P3, and P4)
The ADE7878 measures three phase currents and the neutral current. Current transformers or Rogowski coils can be used to sense the current but should not be mixed together. The ADE7878 contains different internal PGA gains on phase currents and on the neutral current; therefore, sensors with different ratios can be used. The only requirement is to have the same scale signals at the PGA outputs; otherwise, the mismatch functionality of the ADE7878 is compromised (see the ADE7878 data sheet for more details about neutral current mismatch). Figure 2 shows the structure used for the Phase A current; the sensor outputs are connected to the P1 connector. The R1 and R2 resistors are the burden resistors and, by default, they are not populated. They can also be disabled using the JP1A and JP2A jumpers. The R9/C9 and R10/C10 RC networks are used in conjunction with Rogowski coils. They can be disabled using the JP3A and JP4A jumpers. The R17/C17 and R18/C18 RC networks are the antialiasing filters. The default corner frequency of these low pass filters is 7.2 kHz (1 kΩ/22 nF). These filters can easily be adjusted by replacing the components on the evaluation board. All the other current channels (that is, Phase B, Phase C, and the neutral current) have a similar input structure.
Using a Current Transformer as the Current Sensor
Figure 3 shows how a current transformer can be used as a current sensor in one phase of a 3-phase, 4-wire distribution system (Phase A). The other two phases and the neutral current require similar connections. P1IAPIANJP1AJP2AR1R2R17R10R18100Ω1kΩ100Ω1kΩC922,000pFC1022,000pFC1722,000pFC1822,000pFR9JP4AJP5AJP3AJP6AIAPIANADE78xxTP1TP209078-002
Figure 2. Phase A Current Input Structure on the Evaluation Board IMAX = 6A rmsCT1:2000P1JP1AJP2AR150ΩR250ΩR17R10R18100Ω1kΩ100Ω1kΩC922,000pFC1022,000pFC1722,000pFC1822,000pFR9JP4AJP5AJP3AJP6AIAPIANADE78xxTP1TP209078-003
Figure 3. Example of a Current Transformer Connection The R1 and R2 burden resistors must be defined as functions of the current transformer ratio and maximum current of the system, using the following formula: R1 = R2 = 1/2 × 0.5/sqrt(2) × N/IFS where: 0.5/sqrt(2) is the rms value of the full-scale voltage accepted at the ADC input. N is the input-to-output ratio of the current transformer. IFS is the maximum rms current to be measured.
The JP1A and JP2A jumpers should be opened if R1 and R2 are used. The antialiasing filters should be enabled by opening the J5A and J6A jumpers (see Figure 3). The secondary current of the transformer is converted to a voltage by using a burden resistor across the secondary winding outputs. Care should be taken when using a current transformer as the current sensor. If the secondary is left open (that is, no burden is connected), a large voltage may be present at the secondary outputs. This can cause an electric shock hazard and potentially damage electronic components.
Most current transformers introduce a phase shift that the manufacturer indicates in the data sheet. This phase shift can lead to significant energy measurement errors, especially at low power factors. The ADE7878 can correct the phase error using the APHCAL[9:0], BPHCAL[9:0], and CPHCAL[9:0] phase calibration registers as long as the error stays between −6.732° and +1.107° at 50 Hz (see the ADE7878 data sheet for more
UG-146 Evaluation Board User Guide
Rev. 0 | Page 4 of 36
details). The software supplied with the ADE7878 evaluation board allows user adjustment of phase calibration registers.
For this particular example, burden resistors of 50 Ω signify an input current of 7.05 A rms at the ADE7878 ADC full-scale input (0.5 V). In addition, the PGA gains for the current channel must be set at 1. For more information about setting PGA gains, see the ADE7878 data sheet. The evaluation software allows the user to configure the current channel gain.
Using a Rogowski Coil as the Current Sensor
Figure 4 shows how a Rogowski coil can be used as a current sensor in one phase of a 3-phase, 4-wire distribution system (Phase A). The other two phases and the neutral current require similar connections. The Rogowski coil does not require any burden resistors; therefore, R1 and R2 should not be populated. The antialiasing filters should be enabled by opening the J5A and J6A jumpers. To account for the high frequency noise introduced by the coil, an additional antialiasing filter must be introduced by opening the JP3A and JP4A jumpers. Then, to compensate for the 20 dB/dec gain introduced by the di/dt sensor, the integrator of the ADE7878 must be enabled by setting Bit 0 (INTEN) of the CONFIG register. The integrator has a −20 dB/dec attenuation and an approximately −90° phase shift and, when combined with the di/dt sensor, results in a magnitude and phase response with a flat gain over the frequency band of interest. ROGOWSKICOILP1JP1AJP2AR1R2R17R10R18100Ω1kΩ100Ω1kΩC922,000pFC1022,000pFC1722,000pFC1822,000pFR9JP4AJP5AJP3AJP6AIAPIANADE78xxTP1TP209078-004
Figure 4. Example of a Rogowski Coil Connection
Voltage Sense Inputs (P5, P6, P7, and P8 Connectors)
The voltage input connections on the ADE7878 evaluation board can be directly connected to the line voltage sources. The line voltages are attenuated using a simple resistor divider network before they are supplied to the ADE7878. The attenuation network on the voltage channels is designed so that the corner frequency (3 dB frequency) of the network matches that of the antialiasing filters in the current channel inputs. This prevents the occurrence of large energy errors at low power factors.
Figure 5 shows a typical connection of the Phase A voltage inputs; the resistor divider is enabled by opening the JP7A jumper. The antialiasing filter on the VN data path is enabled by opening the JP7N jumper. JP8A and JP8N are also opened. The VN analog input is connected to AGND via the R25/C25 antialiasing filter using the JP8N connector. The attenuation networks can be easily modified by the user to accommodate any input level. However, the value of R32 (1 kΩ), should be modified only together with the corresponding resistors in the current channel (R17 and R18 on the Phase A current data path). P8JP8AVAPVNR291MΩ100kΩR321kΩC3222,000pFC2522,000pFR26JP7AVAPADE78xxTP12JP9AVNPHASE ANEUTRALP5JP8N1kΩR25JP7NVNTP9ACOMB12309078-005
Figure 5. Phase A Voltage Input Structure on the Evaluation Board
The maximum signal level permissible at the VAP, VBP, and VCP pins of the ADE7878 is 0.5 V peak. Although the ADE7878 analog inputs can withstand ±2 V without risk of permanent damage, the signal range should not exceed ±0.5 V with respect to AGND for a specified operation.
Evaluation Board User Guide UG-146
Rev. 0 | Page 5 of 36 Table 1. Recommended Settings for Evaluation Board Connectors Jumper Option Description
JP1 Soldered Connects AGND to ground. By default, it is soldered. JP1A, JP1B,
JP1C, JP1N,
Open Connect IAP, IBP, IC, and INP to AGND. By default, they are open.
JP2 Closed Connects the ADE7878 VDD power supply (VDD_F at the P9 connector) to the power supply of the
isocouplers (VDD2 at the P10 connector). By default, it is closed. JP2A, JP2B,
JP2C, JP2N
Open Connect IAN, IBN, ICN, and INN to AGND. By default, they are open.
JP3 Unsoldered Connects the pad metal below the ADE7878 to AGND. By default, it is unsoldered.
JP3A, JP3B,
JP3C, JP3N
Closed Disable the phase compensation network in the IAP, IBP, ICP, and INP data path. By default, they are
closed. JP4 Soldered Connects C3 to DVDD. By default, it is soldered.
JP4A, JP4B,
JP4C, JP4N
Closed Disable the phase compensation network in the IAN, IBN, ICN, and INN data path. By default, they are
closed. JP5 Soldered Connects C5 to AVDD. By default, it is soldered.
JP5A, JP5B,
JP5C, JP5N
Open Disable the phase antialiasing filter in the IAP, IBP, ICP, and INP data path. By default, they are open.
JP6 Soldered Connects C41 to the REF pin of the ADE7878. By default, it is soldered. JP6A, JP6B,
JP6C, JP6N
Open Disable the phase antialiasing filter in the IAN, IBN, ICN, and INN data path. By default, they are open.
JP7 Closed Enables the supply to the microcontroller. When open, takes out the supply to the microcontroller. By default, it is closed.
JP7A, JP7B,
JP7C
Open Disable the resistor divider in the VAP, VBP, and VCP data path. By default, they are open.
JP7N Open Disables the antialiasing filter in the VN data path. By default, it is open.
JP8 Open Sets the microcontroller in flash memory programming mode. By default, it is open.
JP8A, JP8B,
JP8C
Open Connect VAP, VBP, and VCP to AGND. By default, they are open.
JP8N Closed Connects VN to AGND. By default, it is closed.
JP9 Open When closed, signals the microcontroller to declare all I/O pins as outputs. It is used when another
microcontroller is used to manage the ADE7878 through the P38 socket. By default, it is open. JP9A, JP9B,
JP9C
Soldered to Pin
1 (AGND) Connect the ground of antialiasing filters in the VAP, VB, and VCP data path to AGND or VN. By default,
they are soldered to AGND. JP10 Open Connects the external voltage reference to ADE7878. By default, it is open. JP11 Soldered to Pin
1
Connects the CLKIN pin of the ADE7878 to a 16,384 MHz crystal (Pin 1 of JP11) or to an external clock
input provided at J1. By default, it is soldered to Pin 1.
JP12 Soldered to Pin
3 (AGND) Connects DGND (Pin 2 of JP12) of the ADE7878 to ground (Pin 1 of JP12) or to AGND (Pin 3 of JP12).
JP35, JP33 Open If I2C communication between the NXP LPC2368 and the ADE7878 is used, these connectors should be
closed with 0 Ω resistors, and the JP36 and JP34 connectors should be opened. By default, the SPI is the
communication used between the NXP LPC2368 and the ADE7878; therefore, these connectors are open. JP31, JP37 Open If HSDC communication is used, these connectors should be closed with 0 Ω resistors, and the JP35 and JP33 connectors should also be closed. By default, the SPI is the communication used between the NXP
LPC2368 and the ADE7878; therefore, these connectors are open.
JP36, JP34,
JP32, JP38
Closed with
0 Ω resistors If SPI communication is used between the NXP LPC2368 and the ADE7878, these connectors should be
closed and JP35, JP33, JP31, and JP37 should be opened. By default, the SPI is the communication used
between the NXP LPC2368 and the ADE7878; therefore, these connectors are closed.
UG-146 Evaluation Board User Guide
Rev. 0 | Page 6 of 36
SETTING UP THE EVALUATION BOARD AS AN ENERGY METER
Figure 6 shows a typical setup for the ADE7878 evaluation board. In this example, an energy meter for a 4-wire, 3-phase distribution system is shown. Current transformers are used to sense the phase and neutral currents and are connected as shown in Figure 6. The line voltages are connected directly to the evaluation board as shown. Note that the state of all jumpers must match the states shown in Figure 6, keeping in mind that the board is supplied from two different 3.3 V power supplies, one for the ADE7878 domain, VDD, and one for the NXP LPC2368 domain, MCU_VDD. Because the two domains are isolated to ensure that there is no electrical connection between the high voltage test circuit and the control circuit, the power supplies should have floating voltage outputs. The evaluation board is connected to the PC using a regular USB cable supplied with the board. When the evaluation board is powered up and connected to the PC, the enumeration process begins and the PC recognizes new hardware and asks to install the appropriate driver. The drive can be found in the VirCOM_ Driver_XP folder of the CD. After the driver is installed, the supplied evaluation software can be launched. The next section describes the ADE7878 evaluation software in detail and how it can be installed and uninstalled.
Activating Serial Communication Between the ADE7878 and the NXP LPC2368
The ADE7878 evaluation board is supplied with communica-tion between the ADE7878 and the NXP LPC2368 that is set through the SPI ports. The JP32, JP34, JP36, and JP38 jumpers are closed using 0 Ω resistors, and the JP31, JP33, JP35, and JP37 jumpers are open. The SPI port should be chosen as the active port in the ADE7878 control panel.
Communication between the ADE7878 and the NXP LPC2368 is also possible using the I2C ports. To accomplish this, the JP31, JP33, JP35, and JP37 jumpers should be closed using 0 Ω resistors, and the JP32, JP34, JP36, and JP38 jumpers should be open. In this case, the I2C port should be chosen as the active port in the ADE7878 control panel (see Table 2).
Table 2. Jumper State to Activate SPI or I2C Communication
Active Communication
Jumpers Closed with 0 Ω Resistors
Jumpers Open
SPI (Default)
JP32, JP34, JP36, JP38
JP31, JP33, JP35, JP37
I2C
JP31, JP33, JP35, JP37
JP32, JP34, JP36, JP38
Using the Evaluation Board with Another Microcontroller
It is possible to manage the ADE7878 mounted on the evalua-tion board with a different microcontroller mounted on another board. The ADE7878 can be connected to this second board through one of two connectors: P11 or P38. P11 is placed on the same power domain as the ADE7878. P38 is placed on the power domain of the NXP LPC2368 and communicates with the ADE7878 through the isocouplers. If P11 is used, the power domain of the NXP LPC2368 should not be supplied at P12. If P38 is used, a conflict may arise with the NXP LPC2368 I/O ports. The following two options are provided to deal with this situation:
• One option is to keep the NXP LPC2368 running and close JP9. This tells the NXP LPC2368 to set all of its I/Os high to allow the other microcontroller to communicate with the ADE7878. After JP9 is closed, the S2 reset button should be pressed low to force the NXP LPC2368 to reset. This is necessary because the state of JP9 is checked inside the NXP LPC2368 program only once after reset.
• The other option is to cut the power supply of the NXP LPC2368 by disconnecting JP7.
Evaluation Board User Guide UG-146
Rev. 0 | Page 7 of 36
P1IAPIANIAPIANVAPVOLTAGE SOURCEGNDP9VDDJP1A, JP2A = OPENJP3A, JP4A = CLOSEDJP5A, JP6A = OPENNEUTRALPHASE BPHASE CLOADNEUTRALVOLTAGE SOURCEMCU_GNDP12MCU_VDDJP1, JP2 = CLOSEDR1R2P2IBPIBNIBPIBNJP1B, JP2B = OPENJP3B, JP4B = CLOSEDJP5B, JP6B = OPENR3R4P3ICPICNICPICNJP1C, JP2C = OPENJP3C, JP4C = CLOSEDJP5C, JP6C = OPENR5R6P4INPINNINPINNJP1N, JP2N = OPENJP3N, JP4N = CLOSEDJP5N, JP6N = OPENJP7A, JP8A = OPENR7R8P8VAPR26R29R32C32VBPJP7B, JP8B = OPENP7VBPR27R30R33C33VCPJP7C, JP8C = OPENJP7N = OPENJP8N = CLOSEDP6VCPR28R31R34C34C34VNP5VNR2509078-006
Figure 6. Typical Setup for the ADE7878 Evaluation Board
UG-146 Evaluation Board User Guide
Rev. 0 | Page 8 of 36 EVALUATION BOARD SOFTWARE
The ADE7878 evaluation board is supported by Windows®
based software that allows the user to access all the functionality
of the ADE7878. The software communicates with the NXP
LPC2368 microcontroller using the USB as a virtual COM port.
The NXP LPC2368 communicates with the ADE7878 to process the requests that are sent from the PC. INSTALLING AND UNINSTALLING THE ADE7878
SOFTWARE
The ADE7878 software is supplied on one CD-ROM. It contains two projects: one that represents the NXP LPC2368
project and one LabVIEW™ based program that runs on the PC.
The NXP LPC2368 project is already loaded into the processor, but the LabVIEW based program must be installed. 1. To install the ADE7878 software, place the CD-ROM in the CD-ROM reader and double-click
LabView_project\installation_files\setup.exe. This
launches the setup program that automatically installs all the software components, including the uninstall
program, and creates the required directories. 2. To launch the software, go to the Start/Programs/ ADE7878 Eval Software menu and click ADE7878
Eval Software.
Both the ADE7878 evaluation software program and the NI
run-time engine are easily uninstalled by using the Add/ Remove Programs option in the control panel. 1. Before installing a new version of the ADE7878 evaluation software, first uninstall the previous version. 2. Select the Add/Remove Programs option in the Windows control panel. 3. Select the program to uninstall and click the Add/Remove
button. FRONT PANEL When the software is launched, the Front Panel is opened. This panel contains three areas: the main menu at the left, the sub-
menu at the right, and a box that displays the name of the communication port used by the PC to connect to the
evaluation port, also at the right (see Figure 7). The COM port used to connect the PC with the evaluation board must be selected first. The program displays a list of the
active COM ports, allowing you to select the right one. To learn
what COM port is used by the evaluation board, launch the
Windows Device Manager (the devmgmt.msc file) in the Run
window on the Windows Start menu. By default, the program offers the option of searching for the COM port. Serial communication between the microcontroller and the
ADE7878 is introduced using a switch. By default, the SPI port is used. Note that the active serial port must first be set in the
hardware. See the Activating Serial Communication Between the ADE7878 and the NXP LPC2368 section for details on how
to set it up. The main menu has only one choice, other than Exit, enabled,
Find COM Port. Clicking it starts a process in which the PC
tries to connect to the evaluation board using the port indicated
in the Start menu. It uses the echo function of the communica-
tion protocol (see the Managing the Communication Protocol Between the Microcontroller and the ADE7878 section). It displays the port that matches the protocol and then sets it to 115,200 baud, eight data bits, no parity, no flow control, one
stop bit. 09078-007
Figure 7. Front Panel of ADE7878 Software If the evaluation board is not connected, the port is displayed as
XXXXX. In this case, the evaluation software is still accessible, but no communication can be executed. In both cases, whether
the search for the COM port is successful or not, the cursor is
positioned back at Please select from the following options in
the main menu, Find COM Port is grayed out, and the next main menu options are enabled (see Figure 8). These options allow
you to command the ADE7878 in either the PSM0 or PSM3
power mode. The other power modes, PSM1 and PSM2, are not
available because initializations have to be made in PSM0 before the ADE7878 can be used in one of these other modes.
Evaluation Board User Guide UG-146
Rev. 0 | Page 9 of 36
09078-008
Figure 8. Front Panel After the COM Port Is Identified
PSM0 MODE—NORMAL POWER MODE
Enter PSM0 Mode
When the evaluation board is powered up, the ADE7878 is in PSM3 sleep mode. When Enter PSM0 mode is selected, the microcontroller manipulates the PM0 and PM1 pins of the ADE7878 to switch it into PSM0 mode. It waits 50 ms for the circuit to power up and, if SPI communication is activated on the board, it executes three SPI write operations to Address 0xEBFF of the ADE7878 to activate the SPI port. If the operation has been correctly executed or I2C communi-cation is used, the message Configuring LPC2368 – ADE7878 communication was successful is displayed, and you must click OK to continue. The only error that may occur during this operation is communication related; if this happens, the following message is displayed: Configuring LPC2368 – ADE7878 communication was not successful. Please check the communication between the PC and ADE7878 evaluation board and between LPC2368 and ADE78xx.
Bit 1 (I2C_LOCK) of the CONFIG2[7:0] register is now set to 1 to lock in the serial port choice. Then the DICOEFF register is initialized with 0xFF8000, and the DSP of the ADE7878 is started when the software program writes RUN = 0x1. At the end of this process, the entire main menu is grayed out, and the submenu is enabled. You can now manage all functionality of the ADE7878 in PSM0 mode. To switch the ADE7878 to another power mode, click the Exit button on the submenu. The state of the Front Panel is shown in Figure 9.
09078-009
Figure 9. Front Panel After the ADE7878 Enters PSM0 Mode
Reset ADE7878
When Reset ADE78xx is selected on the Front Panel, the RESET pin of the ADE7878 is kept low for 20 ms and then is set high. If the operation is correctly executed, the message ADE7878 was reset successfully is displayed, and you must click OK to continue. The only error that may occur during this operation is communication related; if this happens, the following message is displayed: The communication between PC and ADE7878 evaluation board or between LPC2368 and ADE78xx did not function correctly. There is no guarantee the reset of ADE7878 has been performed.
Configure Communication
When Configure Communication is selected on the Front Panel, the panel shown in Figure 10 is opened. This panel is useful if an ADE7878 reset has been performed and the SPI is no longer the active serial port. Select the SPI port by clicking the I2C/SPI Selector button and then click OK to update the selection and lock the port. If the port selection is successful, the message, Configuring LPC2368 – ADE7878 communica-tion was successful, is displayed, and you must click OK to continue. If a communication error occurs, the message, Configuring LPC2368 – ADE7878 communication was not successful. Please check the communication between the PC and ADE7878 evaluation board, is displayed.
UG-146 Evaluation Board User Guide
Rev. 0 | Page 10 of 36
09078-010
Figure 10. Configure Communication Panel The CONFIG2[7:0] register is written with Bit 1 (I2C_LOCK) set to 1 so that you do not need to remember to set it once the communication is set. The contents of CONFIG2[7:0] are then read back and displayed with Bit 1 (I2C_LOCK). To close the panel, click the Exit button; the cursor is positioned at Please select from the following options in the submenu of the Front Panel.
Total Active Power
When Total Active Power is selected on the Front Panel, the panel shown in Figure 11 is opened. The screen has an upper half and a lower half: the lower half shows the total active power data path of one phase, and the upper half shows bits, registers, and commands necessary to power management. 09078-011
Figure 11. Total Active Power Panel
The Active Data Path button manages which data path is shown in the bottom half. Some registers or bits, like the WTHR0[23:0] register or Bit 0 (INTEN) of the CONFIG[15:0] register, are common to all data paths, independent of the phase shown. When these registers are updated, all the values in all data paths are updated. The HPFDIS[23:0] register is included twice in the data path, but only the register value from the current data path is written into the ADE7878. All the other instances take this value directly.
1. Click the Read Configuration button to cause all registers that manage the total active power to be read and displayed. Registers from the inactive data paths are also read and updated.
2. Click the Write Configuration button to cause all registers that manage the total active power to be written into the ADE7878. Registers from the inactive data paths are also written. The ADE78xx status box shows the power mode that the ADE7878 is in (it should always be PSM0 in this window), the active serial port (it should always be SPI), and the CHECKSUM[31:0] register. After every read and write operation, the CHECKSUM[31:0] register is read and its contents displayed.
3. Click the CFx Configuration button to open a new panel (see Figure 12). This panel gives access to all bits and registers that configure the CF1, CF2, and CF3 outputs of the ADE7878. The Read Setup and Write Setup buttons update and display the CF1, CF2, and CF3 output values.
09078-012
Figure 12. CFx Configuration Panel Like the Total Active Power panel, the CHECKSUM[31:0] register is read back whenever a read or write operation is executed in the CFx Configuration panel. To select more than one option for a TERMSELx bit in the COMPMODE [15:0] register, press the CTRL key while clicking the options you want.
Clicking the Exit button closes the panel and redisplays the Total Active Power panel. When the Read Energy Registers button in the Total Active Power panel is clicked, a new panel is opened (see Figure 13). This panel gives access to bits and registers that configure the energy accumulation. The Read Setup and Write Setup buttons update and display the bit and register values.
Evaluation Board User Guide UG-146
Rev. 0 | Page 11 of 36
The CHECKSUM[31:0] register is read back whenever a read or write operation is executed in the Read Energy Registers panel. Clicking the Read all energy registers button causes all energy registers to be read immediately, without regard to the modes in which they function. 09078-013
Figure 13. Read Energy Registers Panel The panel also gives the choice of reading the energy registers synchronous to CFx interrupts (pulses) or using line cycle accumulation mode. When the Read energy registers synchronous with CF1 pulses button is clicked, the following happens:
1. The STATUS0[31:0] register is read and then written back to so that all nonzero interrupt flag bits are cancelled.
2. Bit 14 (CF1) in the MASK0[31:0] register is set to 1, and the interrupt protocol is started (see the Managing the Communication Protocol Between the Microcontroller and the ADE7878 section for protocol details).
3. The microcontroller then waits until the IRQ0 pin goes low. If the wait is longer than the timeout you indicate in 3 sec increments, the following error message is displayed: No CF1 pulse was generated. Verify all the settings before attempting to read energy registers in this mode!
4. When the IRQ0 pin goes low, the STATUS0[31:0] register is read and written back to cancel Bit 14 (CF1); then the energy registers involved in the CF1 signal are read and their contents are displayed. A timer in 10 ms increments can be used to measure the reaction time after the IRQ0 pin goes low.
5. The operation is repeated until the button is clicked again.
The process is similar when the other CF2, CF3, and line accum-ulation (Read Energy Registers panel) buttons are clicked. It is recommended to always use a timeout when dealing with interrupts. By default, the timeout is set to 10 (indicating a 30 sec timeout), and the timer is set to 0 (indicating that the STATUSx[31:0] and energy registers are read immediately after the IRQ0 pin goes low).
When clicked on the Front Panel, the Total Reactive Power, Fundamental Active Power, and Fundamental Reactive Power buttons open panels that are very similar to the Total Active Power panel. These panels are shown in Figure 14, Figure 15, and Figure 16.
09078-014
Figure 14. Total Reactive Power Panel 09078-015
Figure 15. Fundamental Active Power Panel 09078-016
Figure 16. Fundamental Reactive Power Panel
UG-146 Evaluation Board User Guide
Rev. 0 | Page 12 of 36
Apparent Power
When Apparent Power is selected on the Front Panel, a new panel is opened (see Figure 17). Similar to the other panels that deal with power measurement, this panel is divided into two parts: the lower half shows the apparent power data path of one phase and the ADE7878 status; the upper half shows the bits, registers, and commands necessary to power management. 09078-017
Figure 17. Apparent Power Panel
Current RMS
When RMS Current is selected on the Front Panel, a new panel is opened (see Figure 18). All data paths of all phases are available. 09078-018
Figure 18. Current RMS panel Clicking the Read Setup button causes a read of all registers shown in the panel. Clicking the Write Setup button causes writes to the xIRMSOS[23:0] registers.
You can use the Start Digital Signal Processor and Stop Digital Signal Processor buttons to manage the Run[15:0] register and the Read xIRMS registers button, which uses the ZXIA, ZXIB, and ZXIC interrupts at the IRQ1 pin, to read the xIRMS[23:0]registers 500 consecutive times and then compute and display their average. If no interrupt occurs for the time indicated by the timeout (in 3 sec increments), the following message is displayed: No ZXIA, ZXIB or ZXIC interrupt was generated. Verify at least one sinusoidal signal is provided between IAP-IAN, IBP-IBN or ICP-ICN pins. A delay can be introduced (in 10 ms increments) between the time the IRQ1 pin goes low and the moment the xIRMS registers are read. The operation is repeated until the button is clicked again.
Mean Absolute Value Current
When Mean Absolute Value Current is selected on the Front Panel, a new panel is opened (see Figure 19). When the Read xIMAV registers button is clicked, the xIMAV[19:0] registers are read 10 consecutive times, and their average is computed and displayed. After this operation, the button is returned to high automatically. The ADE7878 status is also displayed. 09078-019
Figure 19. Mean Absolute Value Current Panel
Voltage RMS
When RMS Voltage is selected on the Front Panel, the Voltage RMS panel is opened (see Figure 20). This panel is very similar to the Current RMS panel. Clicking the Read Setup button executes a read of the xVRMSOS[23:0] and xVRMS[23:0] registers.
Clicking Write Setup writes the xVRMSOS[23:0] registers into the ADE7878. The Start Digital Signal Processor and Stop Digital Signal Processor buttons manage the Run[15:0] register. When the Read xVRMS registers button is clicked, the xVRMS[23:0] registers are read 500 consecutive times and the average is displayed. The operation is repeated until the button is clicked again. Note that the ZXVA, ZXVB, and ZXVC zero-crossing interrupts are not used in this case because they are disabled when the voltages go below 10% of full scale. This allows rms voltage registers to be read even when the phase voltages are very low.
Evaluation Board User Guide UG-146
Rev. 0 | Page 13 of 36
09078-020
Figure 20. Voltage RMS Panel
Power Quality
The Power Quality panel is accessible from the Front Panel and is divided into two parts (see Figure 21). The lower part displays registers that manage the power quality measurement functions for the Active Measurement button in the upper part of the panel. The upper part also displays the ADE7878 status and the buttons that manage the measurements.
When the READ CONFIGURATION button is clicked, all power quality registers (MASK1[31:0], STATUS1[31:0], PERIOD[15:0], MMODE[7:0], ISUM[27:0], OVLVL[23:0], OILVL[23:0], PHSTATUS[15:0], IPEAK[31:0], VPEAK[31:0], SAGLVL[23:0], SAGCYC[7:0], ANGLE0[15:0], ANGLE1[15:0], ANGLE2[15:0], COMPMODE[15:0], CHECKSUM[31:0], and PEAKCYC[7:0]) are read, and the ones belonging to the active panel are displayed. Based on the PERIOD[15:0] register, the line frequency is computed and displayed in the lower part of the panel, in Zero Crossing Measurements. Based on the ANGLEx[15:0] registers, cos(ANGLEx) is computed and displayed in the Time Intervals Between Phases panel that is accessible from the Active Measurement Zero Crossing dropdown box (see Figure 21).
When the WRITE CONFIGURATION button is clicked, MMODE[7:0], OVLVL[23:0], OILVL[23:0], SAGLVL[23:0], SAGCYC[7:0], COMPMODE[15:0], and PEAKCYC[7:0] are written into the ADE7878, and CHECKSUM[31:0] is read back and displayed in the CHECKSUM[31:0] box at the top of the upper part of the panel. 09078-021
Figure 21. Power Quality Zero-Crossing Measurements Panel When the WAIT FOR INTERRUPTS button is clicked, the interrupts that you have enabled in the MASK1[31:0] register are monitored. When the IRQ1 pin goes low, the STATUS1[31:0] register is read and its bits are displayed. The ISUM[27:0], PHSTATUS[15:0], IPEAK[31:0], VPEAK[31:0], ANGLE0[15:0], ANGLE1[15:0], and ANGLE2[15:0] registers are also read and displayed. A timeout should be introduced in 3 sec increments to ensure that the program does not wait indefinitely for interrupts. A timer (in 10 ms increments) is provided to allow reading of the registers with a delay from the moment the interrupt is triggered.
The Active Measurement Zero Crossing button gives access to the Zero Crossing, Neutral Current Mismatch, Overvoltage and Overcurrent Measurement, Peak Detection, and Time Intervals Between Phases panels (see Figure 21 through Figure 25). The line frequency is computed using the PERIOD[15:0] register, based on the following formula: ][000,256HzPeriodf= The cosine of the ANGLE0[15:0], ANGLE1[15:0], and ANGLE2[15:0] measurements is computed using the following formula: =000,256×360×)(fANGLExcosANGLExcos
UG-146 Evaluation Board User Guide
Rev. 0 | Page 14 of 36
09078-022
Figure 22. Neutral Current Mismatch Panel 09078-023
Figure 23. Overvoltage and Overcurrent Measurements Panel 09078-024
Figure 24. Peak Detection Panel 09078-025
Figure 25. Time Intervals Between Phases Panel
Waveform Sampling
The Waveform Sampling panel (see Figure 26) is accessible from the Front Panel and uses the HSDC port to acquire data from the ADE7878 and display it. It can be accessed only if the communication between the ADE7878 and the NXP LPC2368 is through the I2C. See the Activating Serial Communication Between the ADE7878 and the NXP LPC2368 section for details on how to set I2C communication on the ADE7878 evaluation board. 09078-026
Figure 26. Waveform Sampling Panel
Evaluation Board User Guide UG-146
Rev. 0 | Page 15 of 36
The HSDC transmits data to the NXP LPC2368 at 4 MHz because this is the maximum speed at which the slave SPI of the NXP LPC2368 can receive data. The panel contains some switches that must be set before acquiring data.
• One switch chooses the quantities that are displayed: phase currents and voltages or phase powers. For every set of quantities, only one can be acquired at a time. This choice is made using the Select Waveform button.
• A second switch allows acquired data to be stored in files for further use. This switch is set with the ACQUIRE DATA button.
• The acquisition time should also be set before an acquis-ition is ordered. By default, this time is 150 ms. It is unlimited for phase currents and voltages and for phase powers. The NXP LPC2368 executes in real time three tasks using the ping pong buffer method: continuously receiving data from HSDC, storing the data into its USB memory, and sending the data to the PC. Transmitting seven phase currents and voltages at 4 MHz takes 103.25 μs (which is less than 125 μs); therefore, the HSDC update rate is 8 kHz (HSDC_CFG = 0x0F). Transmitting nine phase powers takes 72 μs (again, less than 125 μs); therefore, the HSDC update rate is also 8 kHz (HSDC_CGF = 0x11).
To start the acquisition, click the ACQUIRE DATA button. The data is displayed on one plot. If you click the Write waveforms to file?/No writing to files switch to enable the writing of waveforms to a file, the program asks for the name and location of the files before storing the waveform.
Checksum Register
The Checksum Register panel is accessible from the Front Panel and gives access to all ADE7878 registers that are used to compute the CHECKSUM[31:0] register (see Figure 27). You can read/write the values of these registers by clicking the Read and Write buttons. The LabView program estimates the value of the CHECKSUM[31:0] register and displays it whenever one of the registers is changed. When the Read button is pressed, the registers are read and the CHECKSUM[31:0] register is read and its values displayed. This allows you to compare the value of the CHECKSUM[31:0] register estimated by LabView with the value read from the ADE7878. The values should always be identical. 09078-027
Figure 27. Checksum Register Panel
All Registers Access
The All Registers Access panel is accessible from the Front Panel and gives read/write access to all ADE7878 registers. Because there are many, the panel can scroll up and down and has multiple read, write, and exit buttons (see Figure 28 and Figure 29). The registers are listed in columns in alphabetical order, starting at the upper left. The panel also allows you to save all control registers into a data file by clicking the Save All Regs into a file button. By clicking the Load All Regs from a file button, you can load all control registers from a data file. Then, by clicking the Write All Regs button, you can load these values into the ADE7878. The order in which the registers are stored into a file is shown in the Control Registers Data File section. 09078-028
Figure 28. Panel Giving Access to All ADE7878 Registers (1)
UG-146 Evaluation Board User Guide
Rev. 0 | Page 16 of 36
09078-029
Figure 29. Panel Giving Access to All ADE7878 Registers (2)
Quick Startup
The Quick Startup panel is accessible from the Front Panel and can be used to rapidly initialize a 3-phase meter (see Figure 30). 09078-030
Figure 30. Panel Used to Quickly Set Up the 3-Phase Meter The meter constant (MC, in impulses/kWh), the nominal voltage (Un, in V rms units), the nominal current (In, in A rms units), and the nominal line frequency (fn, in either 50 Hz or 60 Hz) must be introduced in the panel controls. Then phase voltages and phase currents must be provided through the relative sensors.
Clicking the Begin Computations button starts the program that reads rms voltages and currents and calculates the full-scale voltage and currents used to further initialize the meter. This process takes 7 sec as the program reads the rms voltages 100 times and the rms currents 100 times and then averages them (this is because the PC reads the rms values directly and cannot synchronize the readings with the zero crossings).
The program then computes the full-scale voltages and currents and the constants that are important for setting up the ADE7878: nominal values (n), CFDEN, WTHR1, VARTHR1, VATHR1 and WTHR0, VARTHR0, and VATHR0. At this point, you can overwrite these values. You can also click the Update Registers button to cause the program to do the following:
• Initialize the CFxDEN and xTHR registers
• Enable the CF1 pin to provide a signal proportional to the total active power, the CF2 pin to provide a signal proportional to the total reactive power, and the CF3 pin to provide a signal proportional to the apparent power.
Throughout the program, it is assumed that PGA gains are 1 (for simplicity) and that the Rogowski coil integrators are disabled. You can enter and modify the PGAs and enable the integrators before executing this quick startup if necessary.
At this point, the evaluation board is set up as a 3-phase meter, and calibration can be executed. To store the register initializa-tions, click the Save All Regs into a file button in the All Registers Access panel. After the board is powered down and then powered up again, the registers can be loaded into the ADE7878 by simply loading back the content of the data file. To do this, click the Load All Regs from a file button in the All Registers Access panel.
PSM2 Settings
The PSM2 Settings panel, which is accessible from the Front Panel, gives access to the LPOILVL[7:0] register that is used to access PSM2 low power mode (see Figure 31). You can manipulate its LPOIL[2:0] and LPLINE[4:0] bits. The value shown in the LPOILVL[7:0] register is composed from these bits and then displayed. Note that you cannot write a value into the register by writing a value in the LPOILVL[7:0] register box.
Evaluation Board User Guide UG-146
Rev. 0 | Page 17 of 36
09078-031
Figure 31. PSM2 Settings Panel
PSM1 MODE
Enter PSM1 Mode
When Enter PSM1 mode is selected on the Front Panel, the microcontroller manipulates the PM0 and PM1 pins of the ADE7878 to switch the ADE7878 into PSM1 reduced power mode. Then, the submenu allows access only to the Mean Absolute Value Current function because this is the only ADE7878 functionality available in this reduced power mode (see Figure 32). 09078-032
Figure 32. Front Panel After the ADE7878 Enters PSM1 Mode
Mean Absolute Value Current in PSM1 Mode
The Mean Absolute Value Current panel, which is accessible from the Front Panel when Enter PSM1 mode is selected, is very similar to the panel accessible in PSM0 mode (see the Mean Absolute Value Current section for details). The only difference is that ADE7878 status does not show the CHECKSUM[31:0] register because it is not available in PSM1 mode (see Figure 33) 09078-033
Figure 33. Mean Absolute Value Currents Panel in PSM1 Mode
PSM2 MODE
Enter PSM2 Mode
When Enter PSM2 mode is selected on the Front Panel, the microcontroller manipulates the PM0 and PM1 pins of the ADE7878 to switch the ADE7878 into PSM2 low power mode. Then the submenu allows access only to the Phase Current Monitoring function because this is the only ADE7878 functionality available in this low power mode. 09078-034 Figure 34. Front Panel After the ADE7878 Enters PSM2 Mode
UG-146 Evaluation Board User Guide
Rev. 0 | Page 18 of 36
Phase Current Monitoring
The Phase Current Monitoring panel is accessible from the Front Panel when Enter PSM2 mode is selected; it allows you to display the state of the IRQ0and IRQ1 pins because, in PSM2 low power mode, the ADE7878 compares the phase currents against a threshold determined by the LPOILVL[7:0] register (see Figure 35). Clicking the READ STATUS OF IRQ0 AND IRQ1 PINS button reads the status of these pins and displays and interprets the status.
This operation is managed by the LPOILVL[7:0] register and can be modified only in PSM0 mode. The panel offers this option by switching the ADE7878 into PSM0 mode and then back to PSM2 mode when one of the READ LPOILVL/WRITE LPOILVL buttons is clicked. To avoid toggling both the PM0 and PM1 pins at the same time during this switch, the ADE7878 is set to PSM3 when changing modes.
09078-035
Figure 35. Panel Managing Current Monitoring in PSM2 Mode
PSM3 MODE
Enter PSM3 Mode
In PSM3 sleep mode, most of the internal circuits of the ADE7878 are turned off. Therefore, no submenu is activated while in this mode. You can click the Enter PSM0 mode, Enter PSM1 mode, or Enter PSM2 mode button to set the ADE7878 to one of these power modes.
Evaluation Board User Guide UG-146
Rev. 0 | Page 19 of 36
MANAGING THE COMMUNICATION PROTOCOL BETWEEN THE MICROCONTROLLER AND
THE ADE7878
In this section, the protocol commands are listed that have been
implemented to manage the ADE7878 from the PC using the
microcontroller. The microcontroller is a pure slave during the communication
process. It receives a command from the PC, executes the
command, and sends an answer to the PC. The PC should wait for the answer before sending a new command to the micro-
controller.
Table 3. Echo Command—Message from the PC to the Micro-
controller
Byte Description
0 A = 0x41
1 N = number of bytes transmitted after this byte
2 Data Byte N − 1 (MSB)
3 Data Byte N − 2 4 Data Byte N − 3 … …
N Data Byte 1 N + 1 Data Byte 0 (LSB)
Table 4. Echo Command—Answer from the Microcontroller to
the PC
Byte Description
0 R = 0x52
1 A = 0x41
2 N = number of bytes transmitted after this byte
3 Data byte N − 1 (MSB)
4 Data byte N − 2
… …
N + 1 Data Byte 1 N + 2 Data Byte 0 (LB)
Table 5. Power Mode Select—Message from the PC to the
Microcontroller
Byte Description
0 B = 0x42, change PSM mode 1 N = 1
2 Data Byte 0: 0x00 = PSM0
0x01 = PSM1
0x02 = PSM2
0x03 = PSM3
Table 6. Power Mode Select—Answer from the Microcon-
troller to the PC
Byte Description
0 R = 0x52
1 ~ = 0x7E, to acknowledge that the operation was
successful
Table 7. Reset—Message from the PC to the Microcontroller
Byte Description
0 C = 0x43, toggle the RESET pin and keep it low for at least 10 ms
1 N = 1
2 Data Byte 0: this byte can have any value
Table 8. Reset—Answer from the Microcontroller to the PC
Byte Description
0 R = 0x52
1 ~ = 0x7E, to acknowledge that the operation was
successful
Table 9. I2C/SPI Select (Configure Communication)—
Message from the PC to the Microcontroller
Byte Description
0 D = 0x44, select I2C and SPI and initialize them; then set
CONFIG2[7:0] = 0x2 to lock in the port choice. When I2C
is selected, also enable SSP0 of the LPC2368 (used for
HSDC). 1 N = 1.
2 Data Byte 0: 0x00 = I2C, 0x01 = SPI.
Table 10. I2C/SPI Select (Configure Communication)—
Answer from the Microcontroller to the PC
Byte Description
0 R = 0x52
1 ~ = 0x7E, to acknowledge that the operation was
successful
Table 11. Data Write—Message from the PC to the Micro-
controller
Byte Description
0 E = 0x45.
1 N = number of bytes transmitted after this byte. N can
be 1 + 2, 2 + 2, 4 + 2, or 6 + 2.
2 MSB of the address. 3 LSB of the address. 4 Data Byte N − 3 (MSN). 5 Data Byte N − 4. 6 Data Byte N − 5. … …
N + 2 Data Byte 1.
N + 3 Data Byte 0 (LSB).
Table 12. Data Write—Answer from the Microcontroller to
the PC
Byte Description
0 R = 0x52
1 ~ = 0x7E, to acknowledge that the operation was
successful
UG-146 Evaluation Board User Guide
Rev. 0 | Page 20 of 36
Table 13. Data Read—Message from the PC to the Micro-
controller
Byte Description
0 F = 0x46.
1 N = number of bytes transmitted after this byte; N = 3.
2 MSB of the address. 3 LSB of the address. 4 M = number of bytes to be read from the address above.
M can be 1, 2, 4, or 6.
Table 14. Data Read—Answer from the Microcontroller to
the PC
Byte Description
0 R = 0x52.
1 MSB of the address. 2 LSB of the address. 3 Byte 5, Byte 3, Byte 1, or Byte 0 (MSB) read at the location
indicated by the address. The location may contain 6, 4,
2, or 1 byte. The content is transmitted MSB first.
4 Byte 4, Byte 2, or Byte 0. 5 Byte 3, Byte 1. 6 Byte 2, Byte 0. 7 Byte 1. 8 Byte 0. Table 15. Interrupt Setup—Message from the PC to the
Microcontroller
Byte Description
0 J = 0x4A. 1 N = 8, number of bytes transmitted after this byte.
2 MSB of the MASK1[31:0] or MASK0[31:0] register.
3 LSB of the MASK1[31:0] or MASK0[31:0] register.
4 Byte 3 of the desired value of the MASK0[31:0] or MASK1[31:0] register.
5 Byte 2. 6 Byte 1. 7 Byte 0. 8 Time out byte: time the MCU must wait for the interrupt
to be triggered. It is measured in 3 sec increments. Time out byte (TOB) = 0 means that timeout is disabled. 9 IRQ timer: time the MCU leaves the IRQx pin low before writing back to clear the interrupt flag. It is measured in
10 ms increments.
Timer = 0 means that timeout is disabled. Table 16. Interrupt Setup—Message from the Microcon-
troller to the PC
Byte Description
0 R = 0x52.
1 Byte 3 of the STATUS0[31:0] or STATUS1[31:0] register.
If the program waited for TOB × 3 sec and the interrupt
was not triggered, then Byte 3 = Byte 2 = Byte 1 = Byte 0
= 0xFF. 2 Byte 2 of the STATUS0[31:0] or STATUS1[31:0] register.
3 Byte 1 of the STATUS0[31:0] or STATUS1[31:0] register.
4 Byte 0 of the STATUS0[31:0] or STATUS1[31:0] register.
The microcontroller executes the following operations once the
interrupt setup command is received: 1. Reads the STATUS0[31:0] or STATUS1[31:0] register
(depending on the address received from the PC) and, if it shows an interrupt already triggered (one of its bits is equal
to 1), it erases the interrupt by writing it back. 2. Writes to the MASK0[31:0] or MASK1[31:0] register with the value received from the PC. 3. Waits for the interrupt to be triggered. If the wait is more
than the timeout specified in the command, 0xFFFFFFFF
is sent back. 4. If the interrupt is triggered, the STATUS0[31:0] or STATUS1[31:0] register is read and then written back to clear it. The value read at this point is the value sent back
to the PC so that you can see the source of the interrupts. 5. Sends back the answer. Table 17. Interrupt Pins Status—Message from the PC to the
Microcontroller
Byte Description
0 H = 0x48.
1 N = 1, number of bytes transmitted after this byte.
2 Any byte. This value is not used by the program but it is
used in the communication because N must not be equal
to 0.
Table 18. Interrupt Pins Status—Answer from the Micro-
controller to the PC
Byte Description
0 R = 0x52.
1 A number representing the status of the IRQ0 and IRQ1
pins.
0: IRQ0 = low, IRQ1 = low 1: IRQ0 = low, IRQ1 = high.
2: IRQ0 = high, IRQ1 = low. 3: IRQ0 = high, IRQ1 = high.
The reason for the IRQ0 and IRQ1 order is that on the
microcontroller IO port, IRQ0= P0.1 and IRQ1 = P0.0.
Evaluation Board User Guide UG-146
Rev. 0 | Page 21 of 36
ACQUIRING HSDC DATA CONTINUOUSLY
This function acquires data from the HSDC continuously for a defined time period and for up to two variables. The microcon-troller sends data in packages of 4 kB.
Table 19 describes the protocol when two instantaneous phase currents or voltages are acquired.
Table 19. Acquire HSDC Data Continuously—Message from the PC to the Microcontroller If Phase Currents and Voltages Are Acquired
Byte
Description
0
G = 0x47.
1
N = number of bytes transmitted after this byte. N = 32.
2
0: corresponds to Byte 3 of IA. Because this byte is only a sign extension of Byte 2, it is not sent back by the microcontroller.
3
Increment_IA_Byte2. If IA is to be acquired, Byte 3, Byte 4, and Byte 5 are 1. Otherwise, they are 0.
4
Increment_IA_Byte1.
5
Increment_IA_Byte2.
6
0.
7
Increment_VA_Byte2. If VA is to be acquired, Byte 7, Byte 8, and Byte 9 are 1. Otherwise, they are 0.
8
Increment_VA_Byte1.
9
Increment_VA_Byte0.
10
0.
11
Increment_IB_Byte2. If IB is to be acquired, Byte 11, Byte 12, and Byte 13 are 1. Otherwise, they are 0.
12
Increment_IB_Byte1.
13
Increment_IB_Byte0.
14
0.
15
Increment_VB_Byte2. If VB is to be acquired, Byte 15, Byte 16, and Byte 17 are 1. Otherwise, they are 0.
16
Increment_VB_Byte1.
17
Increment_VB_Byte0.
18
0.
19
Increment_IC_Byte2. If IC is to be acquired, Byte 19, Byte 20, and Byte 21 are 1. Otherwise, they are 0.
20
Increment_IC_Byte1.
21
Increment_IC_Byte0.
22
0.
23
Increment_VC_Byte2. If VC is to be acquired, Byte 23, Byte 24, and Byte 25 are 1. Otherwise, they are 0.
24
Increment_VC_Byte1.
25
Increment_VC_Byte0.
26
0.
27
Increment_IN_Byte2. If IN is to be acquired, Byte 27, Byte 28, and Byte 29 are 1. Otherwise, they are 0.
28
Increment_IN_Byte1.
29
Increment_IN_Byte0.
30
Byte 1 of M. M is a 16-bit number. The number of 32-bit samples acquired by the microcontroller is (2 × M + 1) × 67 per channel.
31
Byte 0 of M.
If two of the phase powers are to be acquired, the protocol changes (see Table 20).
Table 20. Acquire HSDC Data Continuously—Message from the PC to the Microcontroller If Phase Powers Are Acquired
Byte
Description
0
G = 0x47
1
N = number of bytes transmitted after this byte. N = 38.
2
0: corresponds to Byte 3 of AVA. Because this byte is only a sign extension of Byte 2, it is not sent back by the microcontroller.
3
Increment_AVA_Byte2. If AVA is to be acquired, Byte 3, Byte 4, and Byte 5 are 1. Otherwise, they are 0.
4
Increment_AVA_Byte1.
5
Increment_AVA_Byte2.
6
0.
7
Increment_BVA_Byte2. If BVA is to be acquired, Byte 7, Byte 8, and Byte 9 are 1. Otherwise, they are 0.
8
Increment_BVA_Byte1.
9
Increment_BVA_Byte0.
10
0.
11
Increment_CVA_Byte2. If CVA is to be acquired, Byte 11, Byte 12, and Byte 13 are 1. Otherwise, they are 0.
12
Increment_CVA_Byte1.
13
Increment_CVA_Byte0.
14
0.
15
Increment_AWATT_Byte2. If AWATT is to be acquired, Byte 15, Byte 16, and Byte 17 are 1. Otherwise, they are 0.
16
Increment_AWATT_Byte1.
17
Increment_AWATT_Byte0.
18
0.
19
Increment_BWATT_Byte2. If BWATT is to be acquired, then Byte 19, Byte 20, and Byte 21 are 1. Otherwise, they are 0.
20
Increment_BWATT_Byte1.
21
Increment_BWATT_Byte0.
22
0.
23
Increment_CWATT_Byte2. If CWATT is to be acquired, Byte 23, Byte 24, and Byte 25 are 1. Otherwise, they are 0.
24
Increment_CWATT_Byte1.
25
Increment_CWATT_Byte0.
26
0.
27
Increment_AVAR_Byte2. If AVAR is to be acquired, Byte 27, Byte 28, and Byte 29 are 1. Otherwise, they are 0.
28
Increment_AVAR_Byte1.
29
Increment_AVAR_Byte0.
30
0.
31
Increment_BVAR_Byte2. If BVAR is to be acquired, then Byte 31, Byte 32, and Byte 33 are 1. Otherwise, they are 0.
32
Increment_BVAR_Byte1.
33
Increment_BVAR_Byte0.
34
0.
35
Increment_CVAR_Byte2. If CVAR is to be acquired, Byte 35, Byte 36, and Byte 37 are 1. Otherwise, they are 0.
UG-146 Evaluation Board User Guide
Rev. 0 | Page 22 of 36
Byte
Description
36
Increment_CVAR_Byte1.
37
Increment_CVAR_Byte0.
38
Byte 1 of M. M is a 16-bit number. The number of 32-bit samples acquired by the microcontroller is (2 × M + 1) × 67 per channel.
39
Byte 0 of M.
After receiving the command, the microcontroller enables the HSDC port and acquires 67 × 7 × 4 = 1876 bytes into BUFFER0. As soon as BUFFER0 is filled, data is acquired in BUFFER1 (equal in size to BUFFER0), while 2 × 3 × 67 = 402 bytes (134 24-bit words) from BUFFER0 are transmitted to the PC. As soon as BUFFER1 is filled, data is acquired into BUFFER0 while 402 bytes from BUFFER1 are transmitted to the PC. Only the less significant 24 bits of every 32-bit instantaneous value are sent to the PC to decrease the size of the buffer sent to the PC. The most significant eight bits are only an extension of a 24-bit signed word; therefore, no information is lost. The protocol used by the microcontroller to send data to the PC is shown in Table 21.
Table 21. Acquire HSDC Data Continuously—Answer from the Microcontroller to the PC
Byte
Description
0
R = 0x52
1
Byte 2 (MSB) of Word 1
2
Byte 1 of Word 1
3
Byte 0 (LSB) of Word 1
4
Byte 2 (MSB) of Word 2
5
Byte 1 (MSB) of Word 2
…
…
402
Byte 0 (LSB) of Word 134
STARTING THE ADE7878 DSP
This function orders the microcontroller to start the DSP. The microcontroller writes to the run register with 0x1. Table 22. Start ADE7878 DSP—Message from the PC to the Microcontroller
Byte
Description
0
N = 0x4E
1
N = number of bytes transmitted after this byte; N = 1
2
Any byte
Table 23. Start ADE7878 DSP—Answer from the Micro-controller to the PC
Byte
Description
0
R = 0x52
1
~ = 0x7E, to acknowledge that the operation was successful
STOPPING THE ADE7878 DSP
This function orders the microcontroller to stop the DSP. The microcontroller writes to the run register with 0x0. Table 24. Stop ADE7878 DSP—Message from the PC to the Microcontroller
Byte
Description
0
O = 0x4F
1
N = number of bytes transmitted after this byte; N = 1
2
Any byte
Table 25. Stop ADE7878 DSP—Answer from the Micro-controller to the PC
Byte
Description
0
R = 0x52
1
~ = 0x7E to acknowledge that the operation was successful
Evaluation Board User Guide UG-146
Rev. 0 | Page 23 of 36
UPGRADING MICROCONTROLLER FIRMWARE
Although the evaluation board is supplied with the microcontroller firmware already installed, the ADE7878 evaluation software CD provides the NXP LPC2368 microcontroller project developed under the IAR embedded workbench environment for ARM. Users in possession of this tool can modify the project at will and can download it using an IAR J-link debugger. As an alternative, the executable can be downloaded using a program called Flash Magic, available on the evaluation software CD or at the following website: http://www.flashmagictool.com/. Flash Magic uses the PC COM port to download the micro-controller firmware. The procedure for using Flash Magic is as follows:
1. Plug a serial cable into connector P15 of the ADE7878 evaluation board and into a PC COM port. As an alternative, use the ADE8052Z-DWDL1 ADE downloader from Analog Devices, Inc., together with a USB cable.
2. Launch the Device Manager under Windows XP by writing devmgmt.msc into the Start/Run box. This helps to identify which COM port is used by the serial cable.
3. Plug the USB2UART board into the P15 connector of the ADE7878 evaluation board with the VDD pin of the USB2UART aligned at Pin 1 of P15.
4. Connect Jumper JP8. The P2.10/EINT0 pin of the microcontroller is now connected to ground.
5. Supply the board with two 3.3 V supplies at the P10 and P12 connectors.
6. Press and release the reset button, S2, on the ADE7878 evaluation board.
7. Launch Flash Magic and do the following:
a. Select a COM port (COMx as seen in the Device Manager).
b. Set the baud rate to 115,200.
c. Select the NXP LPC2368 device.
d. Set the interface to none (ISP).
e. Set the DOscillator frequency (MHz) to 12.0.
f. Select Erase all Flash + Code Rd Block.
g. Choose ADE7878_Eval_Board.hex from the \Debug\Exe project folder.
h. Select Verify after programming.
The Flash Magic settings are shown in Figure 36. 09078-036
Figure 36. Flash Magic Settings
8. Click Start to begin the download process.
9. After the process finishes, extract the JP8 jumper.
10. Reset the ADE7878 evaluation board by pressing and releasing the S2 reset button.
At this point, the program should be functional, and a USB cable can be connected to the board. When the PC recognizes the evaluation board and asks for a driver, point it to the project \VirCOM_Driver_XP folder. The ADE7878_eval_board_ vircomport.inf file is the driver.
CONTROL REGISTERS DATA FILE
Table 26 shows the order in which the control registers of the ADE7878 are stored into a data file when you click the Save All Regs into a file button in the All Registers Access panel.
UG-146 Evaluation Board User Guide
Rev. 0 | Page 24 of 36
Table 26. Control Register Data File Content
Line Number
Register
1
AIGAIN
2
AVGAIN
3
BIGAIN
4
BVGAIN
5
CIGAIN
6
CVGAIN
7
NIGAIN
8
AIRMSOS
9
AVRMSOS
10
BIRMSOS
11
BVRMSOS
12
CIRMSOS
13
CVRMSOS
14
NIRMSOS
15
AVAGAIN
16
BVAGAIN
17
CVAGAIN
18
AWGAIN
19
AWATTOS
20
BWGAIN
21
BWATTOS
22
CWGAIN
23
CWATTOS
24
AVARGAIN
25
AVAROS
26
BVARGAIN
27
BVAROS
28
CVARGAIN
29
CVAROS
30
AFWGAIN
31
AFWATTOS
32
BFWGAIN
33
BFWATTOS
34
CFWGAIN
35
CFWATTOS
36
AFVARGAIN
37
AFVAROS
38
BFVARGAIN
39
BFVAROS
40
CFVARGAIN
41
CFVAROS
Line Number
Register
42
VATHR1
43
VATHR0
44
WTHR1
45
WTHR0
46
VARTHR1
47
VARTHR0
48
VANOLOAD
49
APNOLOAD
50
VARNOLOAD
51
VLEVEL
52
DICOEFF
53
HPFDIS
54
ISUMLVL
55
RUN
56
OILVL
57
OVLVL
58
SAGLVL
59
MASK0
60
MASK1
61
VNOM
62
LINECYC
63
ZXTOUT
64
COMPMODE
65
Gain
66
CFMODE
67
CF1DEN
68
CF2DEN
69
CF3DEN
70
APHCAL
71
BPHCAL
72
CPHCAL
73
CONFIG
74
MMODE
75
ACCMODE
76
LCYCMODE
77
PEAKCYC
78
SAGCYC
79
CFCYC
80
HSDC_CFG
81
LPOILVL
82
CONFIG2
Evaluation Board User Guide UG-146
Rev. 0 | Page 25 of 36
EVALUATION BOARD SCHEMATICS AND LAYOUT
SCHEMATIC
09078-037NOTE:MOUNT JP? DIRECTLY BELOWPAD METAL. CONNECT TO PADWITH MULTIPLE VIAS.REPEAT VIA GRID TO AGND PLANEEXTRA GROUND TP FOR PROBINGOUTPUT LED CIRCUITIRQ1BCF1CF2IRQ0BCF3DEVICE INTERFACE HEADERREFERENCE DECOUPLING AND EXTERNAL REFRESONANT CIRCUIT. THIS OPTION SHOULD BE PLACED ASXTAL CKTBY DEFAULT SELECT OPTION A
TO COMPLETE PARALLELCLOSE TO DEVICE AS POSSIBLE.C27C26C25C6C4NPC41NPC5NPC321C38C43C42C40C7C2NPC8NPC1NPC44ACCR5ACCR4ACCR3ACCR2ACCR1RSBR43R42R41R40R3921E8NR69R84R85R70R68231JP12R35R361TP293421S121JP321JP421JP521JP621JP101TP49231A11TP511TP501TP341TP361TP381TP371TP391TP351TP331TP321TP311TP301TP281TP271TP261TP251TP241TP231TP2221JP221P10R371TP151TP141TP139876543231303292827262524232221202191817161514131211101P111826192223393641732PAD3837322915161314912785628273534332425U1213Q5213Q2213Q4213Q3213Q121JP121P9R381TP921P521JP7NR2521JP8N54321CLKIN21Y1231JP11DGND_DCLKOUTIRQ0B20PF20PF3PIN_SOLDER_JUMPERBLKCLKINAMP227699-2BLK1.0UFIBP10KCF2CMD28-21VGCTR8T1BLKVDD_FBLKVDD_F10UFVDD0.1UF0.1UF0.1UFBLKBLKBLKVDD2VDD0BLKJPR04021500 OHMSVNBERG69157-1021KBERG69157-102BLKBLKREFEXT_CLKINBLKBLKBLKBLKCF1SSB/HSAMOSI/SDACF3/HSCLKIRQ0B16.384MHZIRQ1BPM0PM1RESETBCLKOUTEXT_CLKINSAMTSW-1-30-08-GDSCLK/SCLCF2MISO/HSDFDV302P10KCF3/HSCLKFDV302PFDV302P10KVDD2CF1JPR0402JPR0402BLKWEILAND25.161.0253VDD2DVDDAVDD3PIN_SOLDER_JUMPERBLKBLKB3S1000BLKBLKBLKBLKPAD_CNVDD_FICNPM0PM1VCPVBPVAPCLKININPINNVNCF2IRQ0BBERG69157-102BLKJPR0402ADR280ARTZ10K499499499ICPIANIAPRESETBFDV302P4994992VDD2FDV302PIRQ1B10KCMD28-21VGCTR8T1CMD28-21VGCTR8T1CMD28-21VGCTR8T1CMD28-21VGCTR8T1XREF10UFVDD_F10UFVDD_F10KJPR04024.7UFMOSI/SDAIBNADE7858CPZSCLK/SCLPAD_CNBLKSSB/HSAMISO/HSD0.1UF4.7UFCF3/HSCLKCF1IRQ1BDVDDCLKOUTREFAVDDBERG69157-102BLK0.22UF0.22UF10KVDD20.1UFVDDBLK4.7UFDGND_DWEILAND25.161.025310KWEILAND25.161.0253VN_IN22NFAGNDDGNDBCOMADGNDDGNDAGNDAGNDAGNDDGNDAGNDAGNDAGNDV-V+VODGNDSCLK_SCLSS_N_HSAMISO_HSDMOSI_SDAIRQ1_N_SBSDAIRQ0_N_SBSCLRESET_NCF3_HSCLKCF2VNINNINPCF1CLKOUTCLKINVDDVAPVBPVCPREFIN_OUTDVDDPM1PM0PADAVDDAGNDDGNDICNICPIBNIBPIANIAPDGNDGDSDGNDGDSDGNDGDSDGNDGDSDGNDGDSDGNDAGNDAGNDAGNDAGNDAGNDAGNDBCOMA Figure 37.
UG-146 Evaluation Board User Guide
Rev. 0 | Page 26 of 36
INPUT ANTI-ALIAS AND DEVICE CONNECTIONC12C11C20C19C24C23C16C15C22C14C13C18C17C10C9C2121E2N21E1N21E2C21E1C21E1A21E2A21E1B21E2B21JP2N21JP1N21JP2C21JP1C21JP2B21JP1B21JP1A21JP2A21JP6N21JP4N21JP5N21JP3N21JP6C21JP5C21JP4C21JP3C21JP6B21JP4B21JP5B21JP3B21JP6A21JP4A21JP5A21JP3A21P421P321P121P21TP7R71TP8R23R24R15R16R81TP5R51TP6R21R22R13R14R6R4R3R12R11R20R191TP41TP31TP21TP1R17R18R2R1R10R9TBD12061500 OHMSBERG69157-102100TBD1206INN_INWEILAND25.161.0253TBD1206BERG69157-102BERG69157-102BERG69157-102WEILAND25.161.0253IBP_INIBN_INBERG69157-102BERG69157-102100TBD12061001K1KBERG69157-102BLKBERG69157-102BERG69157-102BERG69157-1021001KBLKBERG69157-102IBNIAPBERG69157-102BLK1KBLK100TBD12061KBLKBERG69157-102BERG69157-102TBD1206100INPINN1500 OHMS1500 OHMSTBD12061500 OHMSIAP_INICP100BERG69157-102IBPBERG69157-102TBD1206BERG69157-102ICN100BERG69157-102BLK1KBERG69157-1021500 OHMSIAN_IN1500 OHMSICP_INBLK1KBERG69157-1021500 OHMSICN_INWEILAND25.161.0253BERG69157-102BERG69157-102WEILAND25.161.02531500 OHMS1KBLKIAN22NF22NF22NF22NF22NF22NF22NF22NFBERG69157-102BERG69157-102INP_IN22NF22NF22NF22NF22NF22NF22NF22NFAGNDAGNDAGNDAGNDAGNDAGNDAGNDAGNDAGNDAGNDAGNDAGND09078-043 Figure 38.
Evaluation Board User Guide UG-146
Rev. 0 | Page 27 of 36
PHASE A VOLTAGEPHASE C VOLTAGEPHASE B VOLTAGEC34C33C32R26R28R2721E8C21E8B21E8A1TP10231JP9C21P621JP8CR3121JP7CR3421P721JP8BR3021JP7BR331TP11231JP9B21JP8A1TP1221JP7A21P8231JP9AR32R2922NF3PIN_SOLDER_JUMPERBERG69157-1021K1500 OHMSWEILAND25.161.0253WEILAND25.161.0253BERG69157-1021KBLK3PIN_SOLDER_JUMPERVBP1500 OHMSVCP_INVBP_INVN100KBERG69157-1021500 OHMS1KBERG69157-102VNBLK100KBERG69157-1021M1MWEILAND25.161.02531M3PIN_SOLDER_JUMPER100KBERG69157-102VCPVNBLKVAPVAP_IN22NF22NFBCOMAAGNDAGNDAGNDAGNDAGNDAGNDBCOMAAGNDAGNDAGNDBCOMA09078-044 Figure 39.
UG-146 Evaluation Board User Guide
Rev. 0 | Page 28 of 36
BYPASSING CONTROLLER(OPTIONAL; CUSTOMER SUPPLIED)TP FOR EVAL PROBE - DISTRIBUTE AROUND ISOLATED CIRCUITSNCD-D+GNDVBUS(5V)USB IFMRESETMCU CIRCUITUARTSHIELD D+, D-, VREF_MCU WITH GNDFROM CONN TO MCUISOLATED PSU CONNECTIONSP2_11P2_12PM0_CTRLP1_29P1_28P1_27P1_19CF3_HSCLK_ISOP2_9P2_8P2_7P2_6PM1_CTRLMCU_XT2P1_15SSB_ISOCF2_ISOP4_29IRQ1B_ISOP1_26P1_25P1_0P1_4P1_8MCU_XT1TMSP1_22P0_24P0_26MOSI_ISOGNDGNDGNDAMP227699-2CF1_ISOCF2_ISOAMP227699-2AMP227699-2CF3_HSCLK_ISOP0_20SML-LXT0805GW-TRBLK680CF3_HSCLK_ISOIRQ0B_ISOP2_1310KRTCK0.1UFWEILAND25.161.0253MCU_VDD_ISO10KBERG69157-102P2_2SAMTSW-1-30-08-GDRXDTXD10KBLKP1_31MCU_RSTSAMTECTSW10608GS4PINMCU_VDD10K27BLKMCU_VDD10UF0.1UF1UF0.1UF0.1UF0.1UF0.1UF0.1UF0.1UF0.1UF0.1UF0.1UF1.5KP1_23MCU_VDDMCU_VDD10KLPC2368FBD100P0_22MCU_VDDD+D-D-_MCUD+_MCUVBUS274-1734376-8RSTOUT_NRTCX2P1_1USB_UPP4_28P3_26P3_25D+_MCUSDA_ISOIRQ_OUT_EN_ISOIRQ_IN_ENMISO_ISOSCLK_ISORESB_CTRLPM0_CTRLIRQ1B_ISOPM1_CTRLSBENB_ISOSSB_ISOTCLKTRST_NTDI10K10KP0_21P0_19P0_5D-_MCURXDTXDWPP0_4P0_9BLKBLKBLKBLKBLKBLKBLKBLKBLKBLKVBUSP2_1P2_0P2_3P2_5HSDATA_ISOMCU_XT120PFMCU_XT220PF12.000MHZMCU_RSTMCU_VDDB3S100010KP1_9P1_17P1_14P1_10P1_16MCU_VDDSAMTECTSW11008GDTMS10K10KTDITCLKRTCKTDOMCU_RST10KTDOSCL_ISOTRST_NHSA_ISOBLKBLKBLKP2_4IRQ0B_ISOMCU_RSTRESB_CTRLHSA_ISOMOSI_ISOSDA_ISOMISO_HSD_ISOSCLK_ISOSCL_ISOCF1_ISOR79R80R81TP461TP421TP431TP411P151234R82P1212C78PNC79TP161TP171TP181CF312345CF212345CF112345C72U8464849626361605947585756987625242998309981807978777695908988878632339434353637383940434445212093929175535251507473706968676665642726828517141001618521341928547196134284101215314155728397112223C75C73C76C77C83C84C80C81C82R78P131101112131415161718192203456789R44R45R75R73R72R71R83TP521TP441TP541TP451TP551TP531TP481TP471TP401S21243R74C74Y212C70C71CR6CAR77P14123456R76JP712P381101112131415161718192202122232425262728293303132456789P2_10TRST_NTCKP1_18_USB_UP_LED_PWM1_1VBATVREFVDDAVDD_DCDC_3V3_3VDD_DCDC_3V3_2VDD_DCDC_3V3_1VDD_3V3_4VDD_3V3_3VDD_3V3_2VDD_3V3_1VSSAVSSP1_0_ENET_TXD0P2_12_EINT2_MCIDAT2_I2STX_WSP2_11_EINT1_MCIDAT1_I2STX_CLKP2_10_EINT0P2_9_USB_CONNECT_RXD2_EXTIN0P2_8_TD2_TXD2_TRACEPKT3P2_7_RD2_RTS1_TRACEPKT2P2_6_PCAP1_0_RI1_TRACEPKT1P2_5_PWM1_6_DTR1_TRACEPKT0P2_4_PWM1_5_DSR1_TRACESYNCP2_3_PWM1_4_DCD1_PIPESTAT2P2_2_PWM1_3_CTS1_PIPESTAT1P2_1_PWM1_2_RXD1_PIPESTAT0P2_0_PWM1_1_TXD1_TRACECLKP1_31_SCK1_AD0_5P1_30_VBUS_AD0_4P1_29_PCAP1_1_MAT0_1P1_28_PCAP1_0_MAT0_0P1_27_CAP0_1P1_26_PWM1_6_CAP0_0P1_25_MAT1_1P1_24_PWM1_5_MOSI0P1_23_PWM1_4_MISO0P1_22_MAT1_0P1_21_PWM1_3_SSEL0P1_20_PWM1_2_SCK0P1_19_CAP1_1P1_17_ENET_MDIOP1_16_ENET_MDCP1_15_ENET_REF_CLKP1_14_ENET_RX_ERP1_10_ENET_RXD1P1_9_ENET_RXD0P1_8_ENET_CRSP1_4_ENET_TX_ENP1_1_ENET_TXD1RTCX2XTAL2RSTOUT_NTDORTCKP2_13_EINT3_MCIDAT3_I2STX_SDAP4_29_MAT2_1_RXD3P4_28_MAT2_0_TXD3P3_26_MAT0_1_PWM1_3P3_25_MAT0_0_PWM1_2P0_30_USB_DNP0_29_USB_DPP0_28_SCL0P0_27_SDA0P0_26_AD0_3_AOUT_RXD3P0_25_AD0_2_I2SRX_SDA_TXD3P0_24_AD0_1_I2SRX_WS_CAP3_1P0_23_AD0_0_I2SRX_CLK_CAP3_0P0_22_RTS1_MCIDAT0_TD1P0_21_RI1_MCIPWR_RD1P0_20_DTR1_MCICMD_SCL1P0_19_DSR1_MCICLK_SDA1P0_18_DCD1_MOSI0_MOSIP0_17_CTS1_MISO0_MISOP0_16_RXD1_SSEL0_SSELP0_15_TXD1_SCK0_SCKP0_11_RXD2_SCL2_MAT3_1P0_10_TXD2_SDA2_MAT3_0P0_9_I2STX_SDA_MOSI1_MAT2_3P0_8_I2STX_WS_MISO1_MAT2_2P0_7_I2STX_CLK_SCK1_MAT2_1P0_6_I2SRX_SDA_SSEL1_MAT2_0P0_5_I2SRX_WS_TD2_CAP2_1P0_4_I2SRX_CLK_RD2_CAP2_0P0_3_RXD0P0_2_TXD0P0_1_TD1_RXD3_SCL1P0_0_RD1_TXD3_SDA1RTCX1XTAL1RESET_NTMSTDI09078-038 Figure 40.
Evaluation Board User Guide UG-146
Rev. 0 | Page 29 of 36
<- DUTISOLATION CIRCUITI2C/HSDC CONFIGSPI CONFIGSPI CONFIGI2C/HSDC CONFIGMCU ->0SDA_ISOSDA_ISO0.1UF0.1UF0.1UF0.1UF0.1UF0.1UF0.1UF0.1UF0.1UF0.1UFSB_ENBSCL_ISOSCLSDASCLKSSBMOSISCLK_ISOMOSI_ISOSSB_ISOIRQ_OUT_ENMISO_HSD_ISOCF3_HSCLK_ISOHSA_ISOVE2_U6MISO/HSDCF3/HSCLKHSACTIVEIRQ_OUT_EN_ISOIRQ1BWP_UXIRQ0BIRQ1BCF2IRQ_IN_ENSBENB_ISOCF1_ISORESETBPM0PM1RESB_CTRLPM1_CTRLCF1ADUM1401BRWZ10KVE2_U310KADUM1401BRWZHSDATA_ISOSCLK/SCLSDAVDD2MCU_VDDSCLIRQ1B_ISOIRQ1B_ISOIRQ0B_ISO10KVE2_U610KADUM1401BRWZ10KHSACTIVESSB/HSASCLSSBSCLK00MISO_ISOMISO_HSD_ISO00SCL_ISO10K10KADUM1401BRWZ10K10K10KADUM1401BRWZIRQ_IN_ENCF2_ISOIRQ0B_ISO10K10KPM0_CTRLVE2_U3WPIRQ0B0.1UF10KIRQ_OUT_EN0.1UFADUM1250ARZMOSI/SDA0SDADNIDNIDNIDNIMOSI010K0A245362718U428915116710345111413126U328915116710345111413126U628915116710345111413126R48R49R51R55R54JP35JP33JP37JP3612JP3412JP3812JP3212JP31C58C59R58BR58AR59BR59AC56C57U728915116710345111413126R57R53U528915116710345111413126R50R46R47C55C54C53C52C51C50C49C48GND2VDD2VOAVOBVICVIDVE2GND1VE1VODVOCVIBVIAVDD1GND2VDD2VOAVOBVICVIDVE2GND1VE1VODVOCVIBVIAVDD1GND2VDD2VOAVOBVICVIDVE2GND1VE1VODVOCVIBVIAVDD1DGNDGNDSCL2SCL1SDA2SDA1VDD1VDD2GND1GND2GND2VDD2VOAVOBVICVIDVE2GND1VE1VODVOCVIBVIAVDD1GND2VDD2VOAVOBVICVIDVE2GND1VE1VODVOCVIBVIAVDD109078-045 Figure 41.
UG-146 Evaluation Board User Guide
Rev. 0 | Page 30 of 36
09078-039LEFT MOST PINS SHOULD BE FURTHEST FROM DUT26ALIGN PORTS AS DRAWN NEXT TO MCUSIDE WITH PINS76 -
100100755025DO NOT INSTALLSIDE WITH PINS1 -
25DO NOT INSTALLSIDE WITH PINS51 -
75DO NOT INSTALLDO NOT INSTALLALIGN PORTS AS DRAWN NEXT TO MCUALIGN PORTS AS DRAWN NEXT TO MCU1SIDE WITH PINS26 -
50ALIGN PORTS AS DRAWN NEXT TO MCU5176R5221JP9R5621JP8R8654321P1954321P2154321P2554321P2954321P3354321P3754321P2054321P2454321P2854321P3254321P3654321P2354321P2754321P3554321P3154321P2654321P3054321P3454321P2254321P18P1_29SAMTECTSW10608GS5PINBERG69157-102SAMTECTSW10608GS5PINP3_25D+_MCUP2_10SAMTECTSW10608GS5PINP0_20SAMTECTSW10608GS5PINDNIDNIDNIDNIDNIDNIDNIDNIDNIDNIDNIDNIDNIDNIDNIDNIDNIDNIDNITDOSAMTECTSW10608GS5PINSAMTECTSW10608GS5PINMISO_ISOSAMTECTSW10608GS5PINP1_28P1_22SAMTECTSW10608GS5PINSAMTECTSW10608GS5PINSAMTECTSW10608GS5PINHSA_ISOP1_19USB_UPP0_19P0_21TDISAMTECTSW10608GS5PINSAMTECTSW10608GS5PINP0_5PM1_CTRLP3_26P2_12P0_9SAMTECTSW10608GS5PINMCU_XT2SCL_ISOVBUSMCU_XT1SAMTECTSW10608GS5PINP1_31WPIRQ0B_ISOIRQ1B_ISOP2_13P2_0P2_1P2_2SAMTECTSW10608GS5PINP1_27P2_6P2_4P2_5RXDTXDRTCKSAMTECTSW10608GS5PINP1_8P1_0RSTOUT_NP1_26P1_25P1_23P2_8P2_9SSB_ISOSCLK_ISOSAMTECTSW10608GS5PINP1_16P1_17P1_10P1_15P1_14P1_4P1_1P1_9CF3_HSCLK_ISOSDA_ISOMCU_RSTRTCX2PM0_CTRLSBENB_ISOD-_MCUP4_29MOSI_ISOP2_3TMSP0_26IRQ_OUT_EN_ISOSAMTECTSW10608GS5PINSAMTECTSW10608GS5PINDNITRST_NTCLKIRQ_IN_ENP2_11P0_22P0_4P4_28RESB_CTRL10KBERG69157-10210K10KP0_24MCU_VDDP2_7HSDATA_ISOP0_24SAMTECTSW10608GS5PINGNDGND Figure 42.
Evaluation Board User Guide UG-146
Rev. 0 | Page 31 of 36
DO NOT POPULATE U2SELF BOOT EEPROMFACTORY USE ONLYCURRENT MEASUREMENT - DO NOT INSTALLC61C62C63R66R651TP611TP6221P17482631A3R6221JP6021JP61R61R63R6074295310186A4321P16R6474856321U20.1UFVDD2VDD210KMICRO24LC128-I-SN0.1UFWP_UXSBSCLDNIDNIBLKBLKISNS_OUTWEILAND25.161.0253AD8553ARMZDNIDNI560PFVDD_F200KIRQ0BDNIDNI4.02KDNIDNIDO NOT INSTALLDNI100K100KVREF_ISNSVDDDNI10KVDD2SBSCLVDD200SBSDAIRQ1B10KSBCONSBCONSB_ENBMOLEX22-03-2031SBSDAADG820BRMZDNIDGNDDGNDDGNDDGNDVDDS2S1INGNDDVFBGNDVREFENVCCVORGBRGASCLA1A2A0WPSDAVSSVCC09078-046 Figure 43.
UG-146 Evaluation Board User Guide
Rev. 0 | Page 32 of 36
LAYOUT
09078-040 Figure 44. 09078-041
Figure 45.
Evaluation Board User Guide UG-146
Rev. 0 | Page 33 of 36
09078-042 Figure 46. 09078-043 Figure 47.
UG-146 Evaluation Board User Guide
Rev. 0 | Page 34 of 36
ORDERING INFORMATION
BILL OF MATERIALS
Table 27.
Qty Designator Description Manufacturer/Part Number
1 A1 IC-ADI, 1.2 V, ultralow power, high PSRR voltage
reference Analog Devices, Inc./ADR280ARTZ 1 A2 IC swappable dual isolator Analog Devices, Inc./ADUM1250ARZ 4 C1, C8, C44, C78 Capacitor, tantalum, 10 μF AVX
20 C9 to C25, C32 to C34 Capacitor, ceramic, 22 nF AVX
30 C2, C7, C40, C42, C43, C48 to C59,
C61, C62, C72, C73, C75 to C77, C79
to C84
Capacitor, chip, X7R 0805, 0.1 μF Murata
4 C26, C27, C70, C71 Capacitor, mono, ceramic, C0G, 0402, 20 pF Murata
3 C3, C5, C41 Capacitor, tantalum, 4.7 μF AVX
2 C38, C74 Capacitor, ceramic chip, 1206, X7R, 1.0 μF Taiyo Yuden
2 C4, C6 Capacitor, ceramic, X7R, 0.22 μF Phycomp (Yageo)
4 CF1 to CF3, CLKIN Connector, PCB coax, BNC, ST AMP (Tyco)/227699-2
5 CR1 to CR5 Diode, LED, green, SMD Chicago Mini Lamp (CML Innovative Technologies)/CMD28-21VGCTR8T1 1 CR6 LED, green, surface mount LUMEX/SML-LXT0805GW-TR
12 E1A, E1B, E1C, E1N, E2A, E2B, E2C,
E2N, E8A, E8B, E8C, E8N Inductor, chip, ferrite bead, 0805, 1500 Ω Murata
37 JP2, JP7 to JP10, JP1A to JP8A, JP1B
to JP8B, JP1C to JP8C, JP1N to JP8N Connector, PCB Berg jumper, ST, male 2-pin Berg/69157-102
5 JP11, JP12, JP9A, JP9B, JP9C 3-pin solder jumper N/A
6 JP32, JP34, JP36, JP38, JP60, JP61 Resistor jumper, SMD 0805 (open), 0 Ω Panasonic
11 P1 to P10, P12 Connector, PCB TERM, black, 2-pin, ST WeilandD/25.161.0253
2 P11, P38 Connector, PCB, header, SHRD, ST, male 32-pin Samtec/TSW-1-30-08-G-D
1 P13 Connector, PCB, Berg, header, ST, male 20-pin Samtec/TSW-110-08-G-D
1 P14 Connector, PCB, USB, Type B, R/A, through hole AMP (Tyco)/4-1734376-8
1 P15 Connector, PCB, Berg, header, ST, male 4-pin Samtec/TSW106-08-G-S
1 P16 Connector, PCB straight header 3-pin Molex/22-03-2031
5 Q1 to Q5 Trans digital FET P channel Fairchild/FDV302P
8 R1 to R8 Do not install (TBD_R1206) N/A
8 R9 to R16 Resistor, PREC, thick film chip, R1206, 100 Ω Panasonic
12 R17 to R25, R32 to R34 Resistor, PREC, thick film chip, R0805, 1 kΩ Panasonic
3 R26 to R28 Resistor, MF, RN55, 1 M Vishay-Dale 3 R29 to R31 Resistor, MF, RN5, 100 kΩ Vishay-Dale 39 R35, R36, R38, R44 to R57, R64 to R66, R68 to R76, R78, R82 to R86, R58A, R58B, R59A, R59B
Resistor PREC thick film chip, R0805, 10 kΩ Panasonic
1 R37 Resistor, film, SMD 0805, 2 Ω Panasonic
5 R39 to R43 Resistor, PREC, thick film chip, R1206, 499 Panasonic
1 R77 Resistor, film, SMD, 0805, 680 Ω Multicomp
2 R79, R80 Resistor, film, SMD, 1206, 27 Ω Yageo-Phycomp
1 R81 Resistor, PREC, thick film chip, R1206, 1.5 kΩ Panasonic
1 RSB Resistor, jumper, SMD, 1206 (open), 0 Panasonic
2 S1, S2 SW SM mechanical key switch Omron/B3S1000
52 TP1 to TP18, TP22 to TP55 Connector, PCB, test point, black Components Corporation
1 U1 IC-ADI, polyphase, multifunction, energy metering IC Analog Devices, Inc./ADE7878CPZ 5 U3 to U7 IC-ADI quad channel digital isolator Analog Devices, Inc./ADum1401BRWZ
1 U8 IC ARM7, MCU, flash, 512 kΩ, 100 LQFP NXP/LPC2368FBD100
Evaluation Board User Guide UG-146
Rev. 0 | Page 35 of 36
Qty Designator Description Manufacturer/Part Number
1 Y1 IC crystal, 16.384 MHz Valpey Fisher Corporation
1 Y2 IC crystal quartz, 12.000 MHz ECS
1 A3 IC-ADI 1.8 V to 5.5 V 2:1 MUX/SPDT switches Analog Devices, Inc./ADG820BRMZ
1 A4 IC-ADI 1.8 V to 5 V auto-zero in amp with shutdown Analog Devices, Inc./AD8553ARMZ
1 C63 Capacitor, ceramic, NP0, 560 pF Phycomp (Yageo)
4 JP31, JP33, JP35, JP37 Resistor, jumper, SMD, 0805 (SHRT), 0 Panasonic
1 P17 Connector, PCB, TERM, black, 2-pin, ST Weiland/25.161.0253
20 P18 to P37 Connector, PCB, Berg, header, ST, male 5-pin Samtec/TSW106-08-G-S
1 R60 Resistor, PREC, thick film chip, R0805, 4.02 kΩ Panasonic
2 R61, R62 Resistor, PREC, thick film chip, R0805, 100 kΩ Panasonic
1 R63 Resistor, PREC, thick film chip, R1206, 200 kΩ Panasonic
2 TP61, TP62 Connector, PCB test point, black Components Corporation 1 U2 IC, serial EEPROM, 128 kΩ, 2.5 V Microchip/24LC128-I-SN
UG-146 Evaluation Board User Guide
Rev. 0 | Page 36 of 36
NOTES I2C refers to a communications protocol originally developed by Philips Semiconductors (now NXP Semiconductors).
ESD Caution ESD (electrostatic discharge) sensitive device. Charged devices and circuit boards can discharge without detection. Although this product features patented or proprietary protection circuitry, damage may occur on devices subjected to high energy ESD. Therefore, proper ESD precautions should be taken to avoid performance degradation or loss of functionality.
Legal Terms and Conditions By using the evaluation board discussed herein (together with any tools, components documentation or support materials, the “Evaluation Board”), you are agreeing to be bound by the terms and conditions set forth below (“Agreement”) unless you have purchased the Evaluation Board, in which case the Analog Devices Standard Terms and Conditions of Sale shall govern. Do not use the Evaluation Board until you have read and agreed to the Agreement. Your use of the Evaluation Board shall signify your acceptance of the Agreement. This Agreement is made by and between you (“Customer”) and Analog Devices, Inc. (“ADI”), with its principal place of business at One Technology Way, Norwood, MA 02062, USA. Subject to the terms and conditions of the Agreement, ADI hereby grants to Customer a free, limited, personal, temporary, non-exclusive, non-sublicensable, non-transferable license to use the Evaluation Board FOR EVALUATION PURPOSES ONLY. Customer understands and agrees that the Evaluation Board is provided for the sole and exclusive purpose referenced above, and agrees not to use the Evaluation Board for any other purpose. Furthermore, the license granted is expressly made subject to the following additional limitations: Customer shall not (i) rent, lease, display, sell, transfer, assign, sublicense, or distribute the Evaluation Board; and (ii) permit any Third Party to access the Evaluation Board. As used herein, the term “Third Party” includes any entity other than ADI, Customer, their employees, affiliates and in-house consultants. The Evaluation Board is NOT sold to Customer; all rights not expressly granted herein, including ownership of the Evaluation Board, are reserved by ADI. CONFIDENTIALITY. This Agreement and the Evaluation Board shall all be considered the confidential and proprietary information of ADI. Customer may not disclose or transfer any portion of the Evaluation Board to any other party for any reason. Upon discontinuation of use of the Evaluation Board or termination of this Agreement, Customer agrees to promptly return the Evaluation Board to ADI. ADDITIONAL RESTRICTIONS. Customer may not disassemble, decompile or reverse engineer chips on the Evaluation Board. Customer shall inform ADI of any occurred damages or any modifications or alterations it makes to the Evaluation Board, including but not limited to soldering or any other activity that affects the material content of the Evaluation Board. Modifications to the Evaluation Board must comply with applicable law, including but not limited to the RoHS Directive. TERMINATION. ADI may terminate this Agreement at any time upon giving written notice to Customer. Customer agrees to return to ADI the Evaluation Board at that time. LIMITATION OF LIABILITY. THE EVALUATION BOARD PROVIDED HEREUNDER IS PROVIDED “AS IS” AND ADI MAKES NO WARRANTIES OR REPRESENTATIONS OF ANY KIND WITH RESPECT TO IT. ADI SPECIFICALLY DISCLAIMS ANY REPRESENTATIONS, ENDORSEMENTS, GUARANTEES, OR WARRANTIES, EXPRESS OR IMPLIED, RELATED TO THE EVALUATION BOARD INCLUDING, BUT NOT LIMITED TO, THE IMPLIED WARRANTY OF MERCHANTABILITY, TITLE, FITNESS FOR A PARTICULAR PURPOSE OR NONINFRINGEMENT OF INTELLECTUAL PROPERTY RIGHTS. IN NO EVENT WILL ADI AND ITS LICENSORS BE LIABLE FOR ANY INCIDENTAL, SPECIAL, INDIRECT, OR CONSEQUENTIAL DAMAGES RESULTING FROM CUSTOMER’S POSSESSION OR USE OF THE EVALUATION BOARD, INCLUDING BUT NOT LIMITED TO LOST PROFITS, DELAY COSTS, LABOR COSTS OR LOSS OF GOODWILL. ADI’S TOTAL LIABILITY FROM ANY AND ALL CAUSES SHALL BE LIMITED TO THE AMOUNT OF ONE HUNDRED US DOLLARS ($100.00). EXPORT. Customer agrees that it will not directly or indirectly export the Evaluation Board to another country, and that it will comply with all applicable United States federal laws and regulations relating to exports. GOVERNING LAW. This Agreement shall be governed by and construed in accordance with the substantive laws of the Commonwealth of Massachusetts (excluding conflict of law rules). Any legal action regarding this Agreement will be heard in the state or federal courts having jurisdiction in Suffolk County, Massachusetts, and Customer hereby submits to the personal jurisdiction and venue of such courts. The United Nations Convention on Contracts for the International Sale of Goods shall not apply to this Agreement and is expressly disclaimed.
©2010 Analog Devices, Inc. All rights reserved. Trademarks and registered trademarks are the property of their respective owners. UG09078-0-8/10(0)
UCD3138
Highly Integrated Digital Controller for Isolated Power
Data Manual
PRODUCTION DATA information is current as of publication date.
Products conform to specifications per the terms of the Texas
Instruments standard warranty. Production processing does not
necessarily include testing of all parameters.
Literature Number: SLUSAP2B
March 2012–Revised July 2012
UCD3138
www.ti.com SLUSAP2B –MARCH 2012–REVISED JULY 2012
Contents
1 Introduction ........................................................................................................................ 6
1.1 Features ...................................................................................................................... 6
1.2 Applications .................................................................................................................. 7
2 Overview ............................................................................................................................ 7
2.1 Description ................................................................................................................... 7
2.2 Ordering Information ........................................................................................................ 8
2.3 Product Selection Matrix ................................................................................................... 8
2.4 Functional Block Diagram .................................................................................................. 9
2.5 UCD3138 64 QFN – Pin Assignments ................................................................................. 10
2.6 Pin Functions .............................................................................................................. 11
2.7 UCD3138 40 QFN – Pin Assignments ................................................................................. 13
2.8 Pin Functions .............................................................................................................. 14
3 Electrical Specifications ..................................................................................................... 15
3.1 ABSOLUTE MAXIMUM RATINGS ...................................................................................... 15
3.2 THERMAL INFORMATION .............................................................................................. 15
3.3 RECOMMENDED OPERATING CONDITIONS ....................................................................... 15
3.4 ELECTRICAL CHARACTERISTICS .................................................................................... 16
3.5 PMBus/SMBus/I2C Timing ............................................................................................... 19
3.6 Power On Reset (POR) / Brown Out Reset (BOR) ................................................................... 20
3.7 Typical Clock Gating Power Savings ................................................................................... 21
3.8 Typical Temperature Characteristics ................................................................................... 22
4 Functional Overview .......................................................................................................... 23
4.1 ARM Processor ............................................................................................................ 23
4.2 Memory ..................................................................................................................... 23
4.2.1 CPU Memory Map and Interrupts ............................................................................ 23
4.2.1.1 Memory Map (After Reset Operation) ........................................................... 23
4.2.1.2 Memory Map (Normal Operation) ................................................................ 24
4.2.1.3 Memory Map (System and Peripherals Blocks) ................................................ 24
4.2.2 Boot ROM ....................................................................................................... 24
4.2.3 Customer Boot Program ....................................................................................... 25
4.2.4 Flash Management ............................................................................................. 25
4.3 System Module ............................................................................................................ 25
4.3.1 Address Decoder (DEC) ....................................................................................... 25
4.3.2 Memory Management Controller (MMC) .................................................................... 25
4.3.3 System Management (SYS) ................................................................................... 25
4.3.4 Central Interrupt Module (CIM) ............................................................................... 26
4.4 Peripherals ................................................................................................................. 27
4.4.1 Digital Power Peripherals ...................................................................................... 27
4.4.1.1 Front End ............................................................................................ 27
4.4.1.2 DPWM Module ..................................................................................... 28
4.4.1.3 DPWM Events ...................................................................................... 29
4.4.1.4 High Resolution DPWM ........................................................................... 31
4.4.1.5 Over Sampling ...................................................................................... 31
4.4.1.6 DPWM Interrupt Generation ...................................................................... 31
4.4.1.7 DPWM Interrupt Scaling/Range .................................................................. 31
4.5 DPWM Modes of Operation .............................................................................................. 32
4.5.1 Normal Mode .................................................................................................... 32
4.6 Phase Shifting ............................................................................................................. 34
4.7 DPWM Multiple Output Mode ............................................................................................ 35
4.8 DPWM Resonant Mode .................................................................................................. 36
4.9 Triangular Mode ........................................................................................................... 38
2 Contents Copyright © 2012, Texas Instruments Incorporated
UCD3138
www.ti.com SLUSAP2B –MARCH 2012–REVISED JULY 2012
4.10 Leading Edge Mode ....................................................................................................... 39
4.11 Sync FET Ramp and IDE Calculation .................................................................................. 41
4.12 Automatic Mode Switching ............................................................................................... 41
4.12.1 Phase Shifted Full Bridge Example .......................................................................... 41
4.12.2 LLC Example .................................................................................................... 42
4.12.3 Mechanism for Automatic Mode Switching .................................................................. 44
4.13 DPWMC, Edge Generation, IntraMux .................................................................................. 45
4.14 Filter ......................................................................................................................... 46
4.14.1 Loop Multiplexer ................................................................................................ 48
4.14.2 Fault Multiplexer ................................................................................................ 49
4.15 Communication Ports ..................................................................................................... 51
4.15.1 SCI (UART) Serial Communication Interface ............................................................... 51
4.15.2 PMBUS .......................................................................................................... 51
4.15.3 General Purpose ADC12 ...................................................................................... 52
4.15.4 Timers ............................................................................................................ 53
4.15.4.1 24-bit PWM Timer .................................................................................. 53
4.15.4.2 16-Bit PWM Timers ................................................................................ 54
4.15.4.3 Watchdog Timer .................................................................................... 54
4.16 Miscellaneous Analog ..................................................................................................... 54
4.17 Package ID Information ................................................................................................... 54
4.18 Brownout ................................................................................................................... 54
4.19 Global I/O ................................................................................................................... 55
4.20 Temperature Sensor Control ............................................................................................. 56
4.21 I/O Mux Control ............................................................................................................ 56
4.21.1 JTAG Use for I/O and JTAG Security ........................................................................ 57
4.22 Current Sharing Control .................................................................................................. 57
4.23 Temperature Reference .................................................................................................. 58
5 IC Grounding and Layout Recommendations ........................................................................ 59
6 Tools and Documentation ................................................................................................... 60
7 References ....................................................................................................................... 62
Revision History ......................................................................................................................... 63
Copyright © 2012, Texas Instruments Incorporated Contents 3
UCD3138
SLUSAP2B –MARCH 2012–REVISED JULY 2012 www.ti.com
List of Figures
3-1 I2C/SMBus/PMBus Timing Diagram ........................................................................................... 20
3-2 Bus Timing in Extended Mode.................................................................................................. 20
3-3 Power On Reset (POR) / Brown Out Reset (BOR) .......................................................................... 20
3-4 EADC LSB Size with 4X Gain (mV) vs. Temperature ....................................................................... 22
3-5 ADC12 Measurement Temperature Sensor Voltage vs. Temperature.................................................... 22
3-6 ADC12 2.5-V Reference vs. Temperature .................................................................................... 22
3-7 ADC12 Temperature Sensor Measurement Error vs. Temperature....................................................... 22
3-8 UCD3138 Oscillator Frequency (2MHz Reference, Divided Down from 250MHz) vs. Temperature.................. 22
4-1 Input Stage of EADC Module ................................................................................................... 28
4-2 Front End Module ................................................................................................................ 28
4-3 Secondary-Referenced Phase-Shifted Full Bridge Control
With Synchronous Rectification ................................................................................................ 42
4-4 Secondary-Referenced Half-Bridge Resonant LLC Control
With Synchronous Rectification ................................................................................................ 43
4-5 Fault Mux Block Diagram ....................................................................................................... 51
4-6 PMBus Address Detection Method ............................................................................................ 52
4-7 ADC12 Control Block Diagram ................................................................................................. 53
4-8 Internal Temp Sensor............................................................................................................ 56
4-9 Simplified Current Sharing Circuitry ........................................................................................... 57
4 List of Figures Copyright © 2012, Texas Instruments Incorporated
UCD3138
www.ti.com SLUSAP2B –MARCH 2012–REVISED JULY 2012
List of Tables
2-1 Pin Functions ..................................................................................................................... 11
2-2 Pin Functions ..................................................................................................................... 14
3-1 I2C/SMBus/PMBus Timing Characteristics.................................................................................... 19
4-1 Interrupt Priority Table ........................................................................................................... 26
4-2 DPWM Interrupt Divide Ratio ................................................................................................... 31
Copyright © 2012, Texas Instruments Incorporated List of Tables 5
UCD3138
SLUSAP2B –MARCH 2012–REVISED JULY 2012 www.ti.com
Highly Integrated Digital Controller for Isolated Power
Check for Samples: UCD3138
1 Introduction
1.1 Features
1
• Digital Control of up to 3 Independent – Synchronous Rectifier Soft On/Off
Feedback Loops – Low IC Standby Power
– Dedicated PID based hardware • Soft Start / Stop with and without Pre-bias
– 2-pole/2-zero configurable • Fast Input Voltage Feed Forward Hardware
– Non-Linear Control • Primary Side Voltage Sensing
• Up to 16MHz Error Analog to Digital Converter • Copper Trace Current Sensing
(EADC) • Flux and Phase Current Balancing for Non-
– Configurable Resolution as Small as Peak Current Mode Control Applications
1mV/LSB • Current Share Bus Support
– Automatic Resolution Selection – Analog Average
– Up to 8x Oversampling – Master/Slave
– Hardware Based Averaging (up to 8x) • Feature Rich Fault Protection Options
– 14 bit Effective DAC – 7 High Speed Analog Comparators
– Adaptive Sample Trigger Positioning – Cycle-by-Cycle Current Limiting
• Up to 8 High Resolution Digital Pulse Width – Programmable Fault Counting
Modulated (DPWM) Outputs – External Fault Inputs
– 250ps Pulse Width Resolution – 10 Digital Comparators
– 4ns Frequency Resolution – Programmable blanking time
– 4ns Phase Resolution • Synchronization of DPWM waveforms between
– Adjustable Phase Shift Between Outputs multiple UCD3138 devices
– Adjustable Dead-band Between Pairs • 14 channel, 12 bit, 267 ksps General Purpose
– Cycle-by-Cycle Duty Cycle Matching ADC with integrated
– Up to 2MHz Switching Frequency – Programmable averaging filters
• Configurable PWM Edge Movement – Dual sample and hold
– Trailing Modulation • Internal Temperature Sensor
– Leading Modulation • Fully Programmable High-Performance
– Triangular Modulation 31.25MHz, 32-bit ARM7TDMI-S Processor
• Configurable Feedback Control – 32 kByte (kB) Program Flash
– Voltage Mode – 2 kB Data Flash with ECC
– Average Current Mode – 4 kB Data RAM
– Peak Current Mode Control – 4 kB Boot ROM Enables Firmware Boot-Load
– Constant Current in the Field via I2C or UART
– Constant Power • Communication Peripherals
• Configurable Modulation Methods – I2C/PMBus
– Frequency Modulation – 2 UARTs on UCD3138RGC (64-pin QFN)
– Phase Shift Modulation – 1 UART on UCD3138RHA (40-pin QFN)
– Pulse Width Modulation • JTAG Debug Port
• Fast, Automatic and Smooth Mode Switching • Timer capture with selectable input pins
– Frequency Modulation and PWM • Up to 5 Additional General Purpose Timers
– Phase Shift Modulation and PWM • Built In Watchdog: BOD and POR
• High Efficiency and Light Load Management • 64-pin QFN and 40-pin QFN packages
– Burst Mode • Operating Temperature: –40°C to 125°C
– Ideal Diode Emulation • Fusion_Digital_Power_Designer GUI Support 1
Please be aware that an important notice concerning availability, standard warranty, and use in critical applications of
Texas Instruments semiconductor products and disclaimers thereto appears at the end of this data sheet.
Copyright © 2012, Texas Instruments Incorporated PRODUCTION DATA information is current as of publication date. Products conform to
specifications per the terms of the Texas Instruments standard warranty. Production
processing does not necessarily include testing of all parameters.
UCD3138
www.ti.com SLUSAP2B –MARCH 2012–REVISED JULY 2012
1.2 Applications
• Power Supplies and Telecom Rectifiers
• Power Factor Correction
• Isolated dc-dc Modules
2 Overview
2.1 Description
The UCD3138 is a digital power supply controller from Texas Instruments offering superior levels of
integration and performance in a single chip solution. The flexible nature of the UCD3138 makes it
suitable for a wide variety of power conversion applications. In addition, multiple peripherals inside the
device have been specifically optimized to enhance the performance of ac/dc and isolated dc/dc
applications and reduce the solution component count in the IT and network infrastructure space.
The UCD3138 is a fully programmable solution offering customers complete control of their application,
along with ample ability to differentiate their solution. At the same time, TI is committed to simplifying our
customer’s development effort through offering best in class development tools, including application
firmware, Code Composer Studio™ software development environment, and TI’s power development GUI
which enables customers to configure and monitor key system parameters.
At the core of the UCD3138 controller are the digital control loop peripherals, also known as Digital Power
Peripherals (DPP). Each DPP implements a high speed digital control loop consisting of a dedicated Error
Analog to Digital Converter (EADC), a PID based 2 pole–2 zero digital compensator and DPWM outputs
with 250 ps pulse width resolution. The device also contains a 12-bit, 267ksps general purpose ADC with
up to 14 channels, timers, interrupt control, JTAG debug and PMBus and UART communications ports.
The device is based on a 32-bit ARM7TDMI-S RISC microcontroller that performs real-time monitoring,
configures peripherals and manages communications. The ARM microcontroller executes its program out
of programmable flash memory as well as on-chip RAM and ROM.
In addition to the FDPP, specific power management peripherals have been added to enable high
efficiency across the entire operating range, high integration for increased power density, reliability, and
lowest overall system cost and high flexibility with support for the widest number of control schemes and
topologies. Such peripherals include: light load burst mode, synchronous rectification, LLC and phase
shifted full bridge mode switching, input voltage feed forward, copper trace current sense, ideal diode
emulation, constant current constant power control, synchronous rectification soft on and off, peak current
mode control, flux balancing, secondary side input voltage sensing, high resolution current sharing,
hardware configurable soft start with pre bias, as well as several other features. Topology support has
been optimized for voltage mode and peak current mode controlled phase shifted full bridge, single and
dual phase PFC, bridgeless PFC, hard switched full bridge and half bridge, and LLC half bridge and full
bridge.
Copyright © 2012, Texas Instruments Incorporated Overview 7
Submit Documentation Feedback
Product Folder Link(s): UCD3138
UCD3138
SLUSAP2B –MARCH 2012–REVISED JULY 2012 www.ti.com
2.2 Ordering Information
PART NUMBER PIN COUNT PACKAGE SUPPLY TOP SIDE MARKING OPERATING TEMPERATURE RANGE, TA
UCD3138RGCT 64 QFN 250 (Small Reel) UCD3138 –40°C to 125°C
UCD3138RGCR 64 QFN 2000 (Large Reel) UCD3138 –40°C to 125°C
UCD3138RHAT 40 QFN 250 (Small Reel) UCD3138 –40°C to 125°C
UCD3138RHAR 40 QFN 2500 (large Reel) UCD3138 –40°C to 125°C
2.3 Product Selection Matrix
FEATURE UCD3138 64 PIN UCD3138 40 PIN
ARM7TDMI-S Core Processor 31.25 MHz 31.25 MHz
High Resolution DPWM Outputs (250ps Resolution) 8 8
Number of High Speed Independent Feedback Loops (# Regulated Output 3 3 Voltages)
12-bit, 267ksps, General Purpose ADC Channels 14 7
Digital Comparators at ADC Outputs 4 4
Flash Memory (Program) 32 KB 32 KB
Flash Memory (Data) 2 KB 2 KB
Flash Security √ √
RAM 4 KB 4 KB
DPWM Switching Frequency up to 2 MHz up to 2 MHz
Programmable Fault Inputs 4 1 + 2(1)
High Speed Analog Comparators with Cycle-by-Cycle Current Limiting 7(2) 6(2)
UART (SCI) 2 1(1)
PMBus √ √
Timers 4 (16 bit) and 1 (24 bit) 4 (16 bit) and 1 (24 bit)
Timer PWM Outputs 2 1
Timer Capture Inputs 1 1(1)
Watchdog √ √
On Chip Oscillator √ √
Power-On Reset and Brown-Out Reset √ √
JTAG √ √
Package Offering 64 Pin QFN (9mm x 9mm) 40 Pin QFN (6mm x 6mm)
Sync IN and Sync OUT Functions √ √
Total GPIO (includes all pins with multiplexed functions such as, DPWM, Fault 30 18 Inputs, SCI, etc.)
External Interrupts 1 0
(1) This number represents an alternate pin out that is programmable via firmware. See the UCD3138 Digital Power Peripherals
Programmer’s Manual for details.
(2) To facilitate simple OVP and UVP connections both comparators B and C are connected to the AD03 pin.
8 Overview Copyright © 2012, Texas Instruments Incorporated
Submit Documentation Feedback
Product Folder Link(s): UCD3138
Front End 2
Analog
Comparators
Power and
1.8 V Voltage
Regulator
AD07
AD06
AD04
V33DIO /RESET
SCI_RX0
SCI_TX0
PMBUS_CLK
PMBUS_DATA
AGND
V33D
BP18
FAULT3
FAULT2
TCAP
TMS
TDI
TDO
TCK
EXT_INT
FAULT1
FAULT0
PWM1
PWM0
SCI_RX1
SCI_TX1
PMBUS_CTRL
PMBUS_ALERT
SYNC
DGND
DPWM3B
DPWM3A
DPWM2B
DPWM2A
DPWM1B
DPWM1A
DPWM0B
DPWM0A
EAP0
EAN0
EAP1
EAN1
V33 A
AD00
AD01
AD0 2
AD1 3
PID Based
Filter 0
DPWM0
DPWM1
DPWM2
DPWM3
PID Based
Filter 1
PID Based
Filter 2
ADC_EXT_ TRIG
ADC12
ADC12 Control
Sequencing, Averaging,
Digital Compare, Dual
Sample and hold AD[13:0 ]
A
B
C
D
E
F
G
Current Share
Analog, Average, Master/Slave
AD03
AD0 2
AD1 3
AGND
PMBus
Timers
4 – 16 bit (PWM)
1 – 24 bit
UART0
UART1
GPIO
Control
JTAG
Loop MUX
ARM7TDMI-S
32 bit, 31.25 MHz
Memory
PFLASH 32 kB
DFLASH 2 kB
RAM 4 kB
ROM 4 kB
Power On Reset
Brown Out Detection
Oscillator
Internal Temperature
Sensor
Advanced Power Control
Mode Switching, Burst Mode, IDE,
Synchronous Rectification soft on & off
Front End 1
Constant Power Constant
Current
Input Voltage Feed Forward
Front End Averaging
Digital Comparators
Fault MUX &
Control
Cycle by Cycle
Current Limit
Digital
Comparators
DAC0
EADC
X
AFE
Value
Dither
!
CPCC
Filter x
Ramp
SAR/Prebias
Abs()
2 Avg() AFE
23-AFE
Peak Current Mode
Control Comparator
A0
EAP2
EAN2
Front End 0
UCD3138
www.ti.com SLUSAP2B –MARCH 2012–REVISED JULY 2012
2.4 Functional Block Diagram
Copyright © 2012, Texas Instruments Incorporated Overview 9
Submit Documentation Feedback
Product Folder Link(s): UCD3138
UCD3138
(64 QFN)
AGND 1
AD13 2
AD12 3
AD10 4
AD07 5
AD06 6
AD04 7
AD03 8
V33DIO 9
10
/RESET 11
ADC_EXT_TRIG/TCAP/SYNC/PWM0 12
SCI_RX0 13
SCI_TX0 14
DGND
PMBUS_CLK/SCI_TX0 15
PMBUS_DATA/SCI_RX0 16
48 AGND
47 V33D
46 BP18
45 V33DIO
44 DGND
43 FAULT3
42 FAULT2
41 TCAP
40 TMS
39 TDI/SCI_RX0/PMBUS_CTRL/FAULT1
38 TDO/SCI_TX0/PMBUS_ALERT/FAULT0
37 TCK/TCAP/SYNC/PWM0
36 FAULT1
35 FAULT0
34 INT_EXT
33 DGND
32
PWM1
31
PWM0
30
SCI_RX1/PMBUS_CTRL
29
SCI_TX1/PMBUS_ALERT
28
PMBUS_CTRL
27
PMBUS_ALERT
26
SYNC/TCAP/ADC_EXT_TRIG/PWM0
25
DGND
24
DPWM3B
23
DPWM3A
22
DPWM2B
21
DPWM2A
20
DPWM1B
19
DPWM1A
18
DPWM0B
17
DPWM0A
64
AGND
63
EAP0
62
EAN0
61
EAP1
60
EAN1
59
EAP2
58
EAN2
57
AGND
56
V33A
55
AD00
54
AD01
53
AD02
52
AD05
51
AD08
50
AD09
49
AD11
UCD3138
SLUSAP2B –MARCH 2012–REVISED JULY 2012 www.ti.com
2.5 UCD3138 64 QFN – Pin Assignments
10 Overview Copyright © 2012, Texas Instruments Incorporated
Submit Documentation Feedback
Product Folder Link(s): UCD3138
UCD3138
www.ti.com SLUSAP2B –MARCH 2012–REVISED JULY 2012
2.6 Pin Functions
Additional pin functionality is specified in the following table.
Table 2-1. Pin Functions
ALTERNATE ASSIGNMENT PIN NAME PRIMARY ASSIGNMENT CONFIGURABLE NO. 1 NO. 2 NO. 3 AS A GPIO?
1 AGND Analog ground
2 AD13 12-bit ADC, Ch 13, comparator E, I-share DAC output
3 AD12 12-bit ADC, Ch 12
4 AD10 12-bit ADC, Ch 10
5 AD07 12-bit ADC, Ch 7, Connected to comparator F and reference DAC output to comparator G
6 AD06 12-bit ADC, Ch 6, Connected to comparator F DAC output
7 AD04 12-bit ADC, Ch 4, Connected to comparator D DAC output
8 AD03 12-bit ADC, Ch 3, Connected to comparator B and C
9 V33DIO Digital I/O 3.3V core supply
10 DGND Digital ground
11 RESET Device Reset Input, active low
12 ADC_EXT_TRIG ADC conversion external trigger input TCAP SYNC PWM0 Yes
13 SCI_RX0 SCI RX 0 Yes
14 SCI_TX0 SCI TX 0 Yes
15 PMBUS_CLK PMBUS Clock (Open Drain) SCI TX 0 Yes
16 PMBUS_DATA PMBus data (Open Drain) SCI RX 0 Yes
17 DPWM0A DPWM 0A output Yes
18 DPWM0B DPWM 0B output Yes
19 DPWM1A DPWM 1A output Yes
20 DPWM1B DPWM 1B output Yes
21 DPWM2A DPWM 2A output Yes
22 DPWM2B DPWM 2B output Yes
23 DPWM3A DPWM 3A output Yes
24 DPWM3B DPWM 3B output Yes
25 DGND Digital ground
26 SYNC DPWM Synchronize pin TCAP ADC_EXT_ PWM0 Yes TRIG
27 PMBUS_ALERT PMBus Alert (Open Drain) Yes
28 PMBUS_CTRL PMBus Control (Open Drain) Yes
29 SCI_TX1 SCI TX 1 PMBUS_AL Yes ERT
30 SCI_RX1 SCI RX 1 PMBUS_CT Yes RL
31 PWM0 General purpose PWM 0 Yes
32 PWM1 General purpose PWM 1 Yes
33 DGND Digital ground
34 INT_EXT External Interrupt Yes
35 FAULT0 External fault input 0 Yes
36 FAULT1 External fault input 1 Yes
37 TCK JTAG TCK TCAP SYNC PWM0 Yes
38 TDO JTAG TDO SCI_TX0 PMBUS_AL FAULT0 Yes ERT
39 TDI JTAG TDI SCI_RX0 PMBUS_CT FAULT1 Yes RL
40 TMS JTAG TMS Yes
41 TCAP Timer capture input Yes
42 FAULT2 External fault input 2 Yes
43 FAULT3 External fault input 3 Yes
Copyright © 2012, Texas Instruments Incorporated Overview 11
Submit Documentation Feedback
Product Folder Link(s): UCD3138
UCD3138
SLUSAP2B –MARCH 2012–REVISED JULY 2012 www.ti.com
Table 2-1. Pin Functions (continued)
ALTERNATE ASSIGNMENT PIN NAME PRIMARY ASSIGNMENT CONFIGURABLE NO. 1 NO. 2 NO. 3 AS A GPIO?
44 DGND Digital ground
45 V33DIO Digital I/O 3.3V core supply
46 BP18 1.8V Bypass
47 V33D Digital 3.3V core supply
48 AGND Substrate analog ground
49 AGND Analog ground
50 EAP0 Channel #0, differential analog voltage, positive input
51 EAN0 Channel #0, differential analog voltage, negative input
52 EAP1 Channel #1, differential analog voltage, positive input
53 EAN1 Channel #1, differential analog voltage, negative input
54 EAP2 Channel #2, differential analog voltage, positive input
55 EAN2 Channel #2, differential analog voltage, negative input
56 AGND Analog ground
57 V33A Analog 3.3V supply
58 AD00 12-bit ADC, Ch 0, Connected to current source
59 AD01 12-bit ADC, Ch 1, Connected to current source
60 AD02 12-bit ADC, Ch 2, Connected to comparator A, I-share
61 AD05 12-bit ADC, Ch 5
62 AD08 12-bit ADC, Ch 8
63 AD09 12-bit ADC, Ch 9
64 AD11 12-bit ADC, Ch 11
12 Overview Copyright © 2012, Texas Instruments Incorporated
Submit Documentation Feedback
Product Folder Link(s): UCD3138
UCD3138
(40 QFN)
AGND 1
2
3
4
5
AD13
6
AD06
7
AD04
8
AD03
9
DGND
10
/RESET
11
ADC_EXT_TRIG/TCAP/SYNC/PWM0
12 13 14 15
PMBUS_CLK/SCI_TX0
16
PMBUS_DATA/SCI_RX0
AGND
BP18
DGND
V33D
40 39
TMS
38
TDI/SCI_RX0/PMBUS_CTRL/FAULT1
37
TDO/SCI_TX0/PMBUS_ALERT/FAULT0
36
TCK/TCAP/SYNC/PWM0
35 34 33
FAULT2
32 31
AGND
30
29
28
27
26
DPWM3B
25
DPWM3A
24
PMBUS_CTRL
23
PMBUS_ALERT
22
DPWM2B
21
DPWM2A
20
DPWM1B
19
DPWM1A
18
DPWM0B
17
DPWM0A
EAP0
EAN0
EAP1
EAN1
EAP2
AGND
V33A
AD00
AD01
AD02
UCD3138
www.ti.com SLUSAP2B –MARCH 2012–REVISED JULY 2012
2.7 UCD3138 40 QFN – Pin Assignments
Copyright © 2012, Texas Instruments Incorporated Overview 13
Submit Documentation Feedback
Product Folder Link(s): UCD3138
UCD3138
SLUSAP2B –MARCH 2012–REVISED JULY 2012 www.ti.com
2.8 Pin Functions
Additional pin functionality is specified in the following table.
Table 2-2. Pin Functions
ALTERNATE ASSIGNMENT PIN NAME PRIMARY ASSIGNMENT CONFIGURABLE NO. 1 NO. 2 NO. 3 AS A GPIO?
1 AGND Analog ground
2 AD13 12-bit ADC, Ch 13, Connected to comparator E, I-share
3 AD06 12-bit ADC, Ch 6, Connected to comparator F
4 AD04 12-bit ADC, Ch 4, Connected to comparator D
5 AD03 12-bit ADC, Ch 3, Connected to comparator B & C
6 DGND Digital ground
7 RESET Device Reset Input, active low
8 ADC_EXT_TRIG ADC conversion external trigger input TCAP SYNC PWM0 Yes
9 PMBUS_CLK PMBUS Clock (Open Drain) SCI_TX0 Yes
10 PMBUS_DATA PMBus data (Open Drain) SCI_RX0 Yes
11 DPWM0A DPWM 0A output Yes
12 DPWM0B DPWM 0B output Yes
13 DPWM1A DPWM 1A output Yes
14 DPWM1B DPWM 1B output Yes
15 DPWM2A DPWM 2A output Yes
16 DPWM2B DPWM 2B output Yes
17 DWPM3A DPWM 3A output Yes
18 DPWM3B DPWM 3B output Yes
19 PMBUS_ALERT PMBus Alert (Open Drain) Yes
20 PMBUS_CTRL PMBus Control (Open Drain) Yes
21 TCK JTAG TCK TCAP SYNC PWM0 Yes
22 TDO JTAG TDO SCI_TX0 PMBUS_A FAULT0 Yes
LERT
23 TDI JTAG TDI SCI_RX0 PMBUS_C FAULT1 Yes
TRL
24 TMS JTAG TMS Yes
25 FAULT2 External fault input 2 Yes
26 DGND Digital ground
27 V33D Digital 3.3V core supply
28 BP18 1.8V Bypass
29 AGND Substrate analog ground
30 AGND Analog ground
31 EAP0 Channel #0, differential analog voltage, positive input
32 EAN0 Channel #0, differential analog voltage, negative input
33 EAP1 Channel #1, differential analog voltage, positive input
34 EAN1 Channel #1, differential analog voltage, negative input
35 EAP2 Channel #2, differential analog voltage, positive input
36 AGND Analog ground
37 V33A Analog 3.3V supply
38 AD00 12-bit ADC, Ch 0, Connected to current source
39 AD01 12-bit ADC, Ch 1, Connected to current source
40 AD02 12-bit ADC, Ch 2, Connected to comparator A, I-share
14 Overview Copyright © 2012, Texas Instruments Incorporated
Submit Documentation Feedback
Product Folder Link(s): UCD3138
UCD3138
www.ti.com SLUSAP2B –MARCH 2012–REVISED JULY 2012
3 Electrical Specifications
3.1 ABSOLUTE MAXIMUM RATINGS (1)
over operating free-air temperature range (unless otherwise noted)
VALUE UNIT
MIN MAX
V33D V33D to DGND –0.3 3.8 V
V33DIO V33DIO to DGND –0.3 3.8 V
V33A V33A to AGND –0.3 3.8 V
|DGND – AGND| Ground difference 0.3 V
All Pins, excluding AGND(2) Voltage applied to any pin –0.3 3.8 V
TOPT Junction Temperature –40 125 °C
TSTG Storage temperature –55 150 °C
(1) Stresses beyond those listed under absolute maximum ratings may cause permanent damage to the device. These are stress ratings
only, and functional operation of the device at these or any other conditions beyond those indicated under recommended operating
conditions is not implied. Exposure to absolute-maximum-rated conditions for extended periods may affect device reliability.
(2) Referenced to DGND
3.2 THERMAL INFORMATION
UCD3138 UCD3138
THERMAL METRIC(1) 64 PIN QFN 40 PIN UNITS
QFN
θJA Junction-to-ambient thermal resistance (2) 25.1 31.8
θJCtop Junction-to-case (top) thermal resistance (3) 10.5 18.5
θJB Junction-to-board thermal resistance (4) 4.6 6.8
°C/W
ψJT Junction-to-top characterization parameter(5) 0.2 0.2
ψJB Junction-to-board characterization parameter (6) 4.6 6.7
θJCbot Junction-to-case (bottom) thermal resistance (7) 1.2 1.8
(1) For more information about traditional and new thermal metrics, see the IC Package Thermal Metrics application report, SPRA953
(2) The junction-to-ambient thermal resistance under natural convection is obtained in a simulation on a JEDEC-standard, high-K board, as
specified in JESD51-7, in an environment described in JESD51-2a.
(3) The junction-to-case (top) thermal resistance is obtained by simulating a cold plate test on the package top. No specific JEDECstandard
test exists, but a close description can be found in the ANSI SEMI standard G30-88.
(4) The junction-to-board thermal resistance is obtained by simulating in an environment with a ring cold plate fixture to control the PCB
temperature, as described in JESD51-8.
(5) The junction-to-top characterization parameter, ψJT, estimates the junction temperature of a device in a real system and is extracted
from the simulation data for obtaining θJA, using a procedure described in JESD51-2a (sections 6 and 7).
(6) The junction-to-board characterization parameter, ψJB, estimates the junction temperature of a device in a real system and is extracted
from the simulation data for obtaining θJA , using a procedure described in JESD51-2a (sections 6 and 7).
(7) The junction-to-case (bottom) thermal resistance is obtained by simulating a cold plate test on the exposed (power) pad. No specific
JEDEC standard test exists, but a close description can be found in the ANSI SEMI standard G30-88.
Spacer
3.3 RECOMMENDED OPERATING CONDITIONS
over operating free-air temperature range (unless otherwise noted)
MIN TYP MAX UNIT
V33D Digital power 3.0 3.3 3.6 V
V33DIO Digital I/O power 3.0 3.3 3.6
V33A Analog power 3.0 3.3 3.6 V
TJ Junction temperature -40 - 125 °C
Copyright © 2012, Texas Instruments Incorporated Electrical Specifications 15
Submit Documentation Feedback
Product Folder Link(s): UCD3138
UCD3138
SLUSAP2B –MARCH 2012–REVISED JULY 2012 www.ti.com
3.4 ELECTRICAL CHARACTERISTICS
V33A = V33D = V33DIO = 3.3V; 1μF from BP18 to DGND, TJ = –40°C to 125°C (unless otherwise noted)
PARAMETER TEST CONDITION MIN TYP MAX UNIT
SUPPLY CURRENT
Measured on V33A. The device is
I33A powered up but all ADC12 and EADC 6.3 mA
sampling is disabled
I33DIO All GPIO and communication pins are 0.35 mA open
I33D ROM program execution 60 mA
I33D Flash programming in ROM mode 70 mA
The device is in ROM mode with all
I33 DPWMs enabled and switching at 2 100 mA
MHz. The DPWMs are all unloaded.
ERROR ADC INPUTS EAP, EAN
EAP – AGND –0.15 1.998 V
EAP – EAN –0.256 1.848 V
Typical error range AFE = 0 –256 248 mV
AFE = 3 0.8 1 1.20 mV
AFE = 2 1.7 2 2.30 mV
EAP – EAN Error voltage digital resolution
AFE = 1 3.55 4 4.45 mV
AFE = 0 6.90 8 9.10 mV
REA Input impedance (See Figure 4-1) AGND reference 0.5 MΩ
IOFFSET Input offset current (See Figure 4-1) –5 5 μA
Input voltage = 0 V at AFE = 0 –2 2 LSB
Input voltage = 0 V at AFE = 1 –2.5 2.5 LSB
EADC Offset
Input voltage = 0 V at AFE = 2 –3 -3 LSB
Input voltage = 0 V at AFE = 3 –4 4 LSB
Sample Rate 16 MHz
Analog Front End Amplifier Bandwidth 100 MHz
Gain See Figure 4-2 1 V/V
A0 Minimum output voltage 100 mV
EADC DAC
DAC range 0 1.6 V
VREF DAC reference resolution 10 bit, No dithering enabled 1.56 mV
VREF DAC reference resolution With 4 bit dithering enabled 97.6 μV
INL –3.0 3.0 LSB
DNL Does not include MSB transition –2.1 1.6 LSB
DNL at MSB transition -1.4 LSB
DAC reference voltage 1.58 1.61 V
τ Settling Time From 10% to 90% 250 ns
ADC12
IBIAS Bias current for PMBus address pins 9.5 10.5 μA
Measurement range for voltage monitoring 0 2.5 V
Internal ADC reference voltage –40°C to 125°C 2.475 2.500 2.525 V
–40°C to 25°C –0.4
Change in Internal ADC reference from 25°C to 85°C –1.8 mV 25°C reference voltage(1)
25°C to 125°C –4.2
(1) As designed and characterized. Not 100% tested in production.
16 Electrical Specifications Copyright © 2012, Texas Instruments Incorporated
Submit Documentation Feedback
Product Folder Link(s): UCD3138
UCD3138
www.ti.com SLUSAP2B –MARCH 2012–REVISED JULY 2012
ELECTRICAL CHARACTERISTICS (continued)
V33A = V33D = V33DIO = 3.3V; 1μF from BP18 to DGND, TJ = –40°C to 125°C (unless otherwise noted)
PARAMETER TEST CONDITION MIN TYP MAX UNIT
ADC12 INL integral nonlinearity(1) +/-2.5 LSB
ADC12 DNL differential nonlinearity(1) ADC_SAMPLINGSEL = 6 for all ADC12 –0.7/+2.5 LSB
ADC Zero Scale Error data, 25 °C to 125 °C –7 7 mV
ADC Full Scale Error –35 35 mV
Input bias 2.5 V applied to pin 400 nA
Input leakage resistance(1) ADC_SAMPLINGSEL= 6 or 0 1 MΩ
Input Capacitance(1) 10 pF
ADC single sample conversion time(1) ADC_SAMPLINGSEL= 6 or 0 3.9 μs
DIGITAL INPUTS/OUTPUTS(2) (3)
V DGND OL Low-level output voltage(4) IOH = 4 mA, V33DIO = 3 V + 0.25 V
V V33DIO OH High-level output voltage (4) IOH = –4 mA, V33DIO = 3 V – 0.6 V
VIH High-level input voltage V33DIO = 3 V 2.1 V
VIL Low-level input voltage V33DIO = 3 V 1.1 V
IOH Output sinking current 4 mA
IOL Output sourcing current –4 mA
SYSTEM PERFORMANCE
TWD Watchdog time out range Total time is: TWD x 14.6 17 20.5 ms (WDCTRL.PERIOD+1)
Time to disable DPWM output based on High level on FAULT pin 70 ns active FAULT pin signal
Processor master clock (MCLK) 31.25 MHz
tDelay Digital compensator delay(5) (1 clock = 32ns) 6 clocks
VDD Slew minimum VDD slew rate(6) VDD slew rate between 2.3 V and 2.9 V 0.25 V/ms
t(reset) Pulse width needed at reset(6) 10 μs
Retention period of flash content (data TJ = 25°C 100 years retention and program)
Program time to erase one page or block in 20 ms data flash or program flash
Program time to write one word in data 20 μs flash or program flash
f(PCLK) Internal oscillator frequency 240 250 260 MHz
Sync-in/sync-out pulse width Sync pin 256 ns
Flash Read 1 MCLKs
Flash Write 20 μs
I Current share current source (See SHARE Figure 4-9) 238 259 μA
RSHARE Current share resistor (See Figure 4-9) 9.75 10.3 kΩ
POWER ON RESET AND BROWN OUT (V33D pin, See Figure 3-3)
VGH Voltage good High 2.7 V
VGL Voltage good Low 2.5 V
Vres Voltage at which IReset signal is valid 0.8 V
(2) DPWM outputs are low after reset. Other GPIO pins are configured as inputs after reset.
(3) On the 40 pin package V33DIO is connected to V33D internally.
(4) The maximum total current, IOHmax and IOLmax for all outputs combined, should not exceed 12 mA to hold the maximum voltage drop
specified. Maximum sink current per pin = –6 mA at VOL; maximum source current per pin = 6 mA at VOH.
(5) Time from close of error ADC sample window to time when digitally calculated control effort (duty cycle) is available. This delay, which
has no variation associated with it, must be accounted for when calculating the system dynamic response.
(6) As designed and characterized. Not 100% tested in production.
Copyright © 2012, Texas Instruments Incorporated Electrical Specifications 17
Submit Documentation Feedback
Product Folder Link(s): UCD3138
UCD3138
SLUSAP2B –MARCH 2012–REVISED JULY 2012 www.ti.com
ELECTRICAL CHARACTERISTICS (continued)
V33A = V33D = V33DIO = 3.3V; 1μF from BP18 to DGND, TJ = –40°C to 125°C (unless otherwise noted)
PARAMETER TEST CONDITION MIN TYP MAX UNIT
T Time delay after Power is good or POR RESET* relinquished 1 ms
Brownout Internal signal warning of brownout 2.9 V conditions
TEMPERATURE SENSOR(7)
VTEMP Voltage range of sensor 1.46 2.44 V
Voltage resolution Volts/°C 5.9 mV/ºC
Temperature resolution Degree C per bit 0.1034 ºC/LSB
Accuracy(7) (8) -40°C to 125°C –10 ±5 10 ºC
Temperature range -40°C to 125°C –40 125 ºC
ITEMP Current draw of sensor when active 30 μA
TON Turn on time / settling time of sensor 100 μs
VAMB Ambient temperature Trimmed 25°C reading 1.85 V
ANALOG COMPARATOR
DAC Reference DAC Range 0 2.5 V
Reference Voltage 2.478 2.5 2.513 V
Bits 7 bits
INL(7) –0.42 0.21 LSB
DNL(7) 0.06 0.12 LSB
Offset –5.5 19.5 mV
Time to disable DPWM output based on 0
V to 2.5 V step input on the analog 150 ns
comparator.(9)
Reference DAC buffered output load(10) 0.5 1 mA
Buffer offset (-0.5 mA) 4.6 8.3 mV
Buffer offset (1.0 mA) –0.05 17 mV
(7) Characterized by design and not production tested.
(8) Ambient temperature offset value should be used from the TEMPSENCTRL register to meet accuracy.
(9) As designed and characterized. Not 100% tested in production.
(10) Available from reference DACs for comparators D, E, F and G.
18 Electrical Specifications Copyright © 2012, Texas Instruments Incorporated
Submit Documentation Feedback
Product Folder Link(s): UCD3138
UCD3138
www.ti.com SLUSAP2B –MARCH 2012–REVISED JULY 2012
3.5 PMBus/SMBus/I2C Timing
The timing characteristics and timing diagram for the communications interface that supports I2C, SMBus,
and PMBus in Slave or Master mode are shown in Table 3-1, Figure 3-1, and Figure 3-2. The numbers in
Table 3-1 are for 400 kHz operating frequency. However, the device supports all three speeds, standard
(100 kHz), fast (400 kHz), and fast mode plus (1 MHz).
Table 3-1. I2C/SMBus/PMBus Timing Characteristics
PARAMETER TEST CONDITIONS MIN TYP MAX UNIT
Typical values at TA = 25°C and VCC = 3.3 V (unless otherwise noted)
fSMB SMBus/PMBus operating frequency Slave mode, SMBC 50% duty cycle 100 1000 kHz
fI2C I2C operating frequency Slave mode, SCL 50% duty cycle 100 1000 kHz
t(BUF) Bus free time between start and stop 1.3 ms
t(HD:STA) Hold time after (repeated) start 0.6 ms
t(SU:STA) Repeated start setup time 0.6 ms
t(SU:STO) Stop setup time 0.6 ms
t(HD:DAT) Data hold time Receive mode 0 ns
t(SU:DAT) Data setup time 100 ns
t(TIMEOUT) Error signal/detect(1) 35 ms
t(LOW) Clock low period 1.3 ms
t(HIGH) Clock high period(2) 0.6 ms
t Cumulative clock low slave extend (LOW:SEXT) time(3) 25 ms
t 20 + 0.1 f Clock/data fall time Rise time tr = (VILmax – 0.15) to (VIHmin + 0.15) Cb(4) 300 ns
t 20 + 0.1 r Clock/data rise time Fall time tf = 0.9 VDD to (VILmax – 0.15) Cb(4) 300 ns
Cb Total capacitance of one bus line 400 pF
(1) The device times out when any clock low exceeds t(TIMEOUT).
(2) t(HIGH), Max, is the minimum bus idle time. SMBC = SMBD = 1 for t > 50 ms causes reset of any transaction that is in progress. This
specification is valid when the NC_SMB control bit remains in the default cleared state (CLK[0] = 0).
(3) t(LOW:SEXT) is the cumulative time a slave device is allowed to extend the clock cycles in one message from initial start to the stop.
(4) Cb (pF)
Figure 3-1. I2C/SMBus/PMBus Timing Diagram
Copyright © 2012, Texas Instruments Incorporated Electrical Specifications 19
Submit Documentation Feedback
Product Folder Link(s): UCD3138
TPOR
undefined
V33D
IReset
3.3 V
TPOR
VGH
VGL
Vres
t
t
Brown Out
UCD3138
SLUSAP2B –MARCH 2012–REVISED JULY 2012 www.ti.com
Figure 3-2. Bus Timing in Extended Mode
3.6 Power On Reset (POR) / Brown Out Reset (BOR)
Figure 3-3. Power On Reset (POR) / Brown Out Reset (BOR)
VGH – This is the V33D threshold where the internal power is declared good. The UCD3138 comes
out of reset when above this threshold.
VGL – This is the V33D threshold where the internal power is declared bad. The device goes into
reset when below this threshold.
Vres – This is the V33D threshold where the internal reset signal is no longer valid. Below this
threshold the device is in an indeterminate state.
IReset – This is the internal reset signal. When low, the device is held in reset. This is equivalent to
holding the reset pin on the IC high.
TPOR – The time delay from when VGH is exceeded to when the device comes out of reset.
Brown – This is the V33D voltage threshold at which the device sets the brown out status bit. In
Out addition an interrupt can be triggered if enabled.
20 Electrical Specifications Copyright © 2012, Texas Instruments Incorporated
Submit Documentation Feedback
Product Folder Link(s): UCD3138
DPWM FE_CTRL PCM ADC12 PMBUS TIMER CPCC FILTER SCI SCI GIO
0
1
2
3
4
5
6
UCD3138 Function
Power Savings (mA)
G001
4.9
2.57
1.2
0.8
0.4 0.4
0.2 0.2
0.1 0.1
0
UCD3138
www.ti.com SLUSAP2B –MARCH 2012–REVISED JULY 2012
3.7 Typical Clock Gating Power Savings
Power disable control register provides control bits that can enable or disable arrival of clock to several
peripherals such as, PCM, CPCC, digital filters, front ends, DPWMs, UARTs, ADC-12 and more.
All these controls are enabled as default. If a specific peripheral is not used in a specific application the
clock gate can be disabled in order to block the propagation of clock signal to that peripheral and therefore
reduce the overall current consumption of the device.
Copyright © 2012, Texas Instruments Incorporated Electrical Specifications 21
Submit Documentation Feedback
Product Folder Link(s): UCD3138
2.475
2.480
2.485
2.490
2.495
2.500
2.505
2.510
2.515
−40 −20 0 20 40 60 80 100 120
Temperature (°C)
ADC12 Reference
G003b
ADC12 2.5-V Reference
1.92
1.96
2
2.04
2.08
−40 −20 0 20 40 60 80 100 120
Temperature (°C)
2-MHZ Reference
G004b
UCD3138 Oscillator Frequency
−4
−2
0
2
4
6
8
−40 −20 0 20 40 60 80 100 120
Temperature (°C)
ADC12 Error (LSB)
G002b
ADC12 Temperature Sensor Measurement Error
1.4
1.6
1.8
2.0
2.2
2.4
2.6
−60 −40 −20 0 20 40 60 80 100 120 140 160
Temperature (°C)
Sensor Voltage (V)
G006b
ADC12 Measurement Temperature Sensor Voltage
1.6
1.7
1.8
1.9
2
2.1
−40 −20 0 20 40 60 80 100 120
Temperature (°C)
EADC LSB Size (mV)
G005a
UCD3138
SLUSAP2B –MARCH 2012–REVISED JULY 2012 www.ti.com
3.8 Typical Temperature Characteristics
Figure 3-4. EADC LSB Size with 4X Gain (mV) vs. Temperature
Figure 3-5. ADC12 Measurement Temperature Figure 3-7. ADC12 Temperature Sensor
Sensor Voltage vs. Temperature Measurement Error vs. Temperature
Figure 3-6. ADC12 2.5-V Reference vs. Figure 3-8. UCD3138 Oscillator Frequency (2MHz
Temperature Reference, Divided Down from 250MHz) vs.
Temperature
22 Electrical Specifications Copyright © 2012, Texas Instruments Incorporated
Submit Documentation Feedback
Product Folder Link(s): UCD3138
UCD3138
www.ti.com SLUSAP2B –MARCH 2012–REVISED JULY 2012
4 Functional Overview
4.1 ARM Processor
The ARM7TDMI-S processor is a synthesizable member of the ARM family of general purpose 32-bit
microprocessors. The ARM architecture is based on RISC (Reduced Instruction Set Computer) principles
where two instruction sets are available. The 32-bit ARM instruction set and the 16-bit Thumb instruction
set. The Thumb instruction allows for higher code density equivalent to a 16-bit microprocessor, with the
performance of the 32-bit microprocessor.
The three-staged pipelined ARM processor has fetch, decode and execute stage architecture. Major
blocks in the ARM processor include a 32-bit ALU, 32 x 8 multiplier, and a barrel shifter. A JTAG port is
also available for firmware debugging.
4.2 Memory
The UCD3138 (ARM7TDMI-S) is a Von-Neumann architecture, where a single bus provides access to all
of the memory modules. All of the memory module addresses are sequentially aligned along the same
address range. This applies to program flash, data flash, ROM and all other peripherals.
Within the UCD3138 architecture, there is a 1024x32-bit Boot ROM that contains the initial firmware
startup routines for PMBUS communication and non-volatile (FLASH) memory download. This boot ROM
is executed after power-up-reset checks if there is a valid FLASH program written. If a valid program is
present, the ROM code branches to the main FLASH-program execution.
UCD3138 also supports customization of the boot program by allowing an alternative boot routine to be
executed from program FLASH. This feature enables assignment of a unique address to each device;
therefore, enabling firmware reprogramming even when several devices are connected on the same
communication bus.
Two separate FLASH memory areas are present inside the device. The 32 kB Program FLASH is
organized as an 8 k x 32 bit memory block and is intended to be for the firmware program. The block is
configured with page erase capability for erasing blocks as small as 1kB per page, or with a mass erase
for erasing the entire program FLASH array. The FLASH endurance is specified at 1000 erase/write
cycles and the data retention is good for 100 years. The 2 kB data FLASH array is organized as a 512 x
32 bit memory (32 byte page size). The Data FLASH is intended for firmware data value storage and data
logging. Thus, the Data FLASH is specified as a high endurance memory of 20 k cycles with embedded
error correction code (ECC).
For run time data storage and scratchpad memory, a 4 kB RAM is available. The RAM is organized as a 1
k x 32 bit array.
4.2.1 CPU Memory Map and Interrupts
When the device comes out of power-on-reset, the data memories are mapped to the processor as
follows:
4.2.1.1 Memory Map (After Reset Operation)
Address Size Module
0x0000_0000 – 0x0000_FFFF In 16 repeated blocks of 4K each 16 X 4K Boot ROM
0x0001_0000 – 0x0001_7FFF 32K Program Flash
0x0001_8800 – 0x0001_8FFF 2K Data Flash
0x0001_9000 – 0x0001_9FFF 4K Data RAM
Copyright © 2012, Texas Instruments Incorporated Functional Overview 23
Submit Documentation Feedback
Product Folder Link(s): UCD3138
UCD3138
SLUSAP2B –MARCH 2012–REVISED JULY 2012 www.ti.com
4.2.1.2 Memory Map (Normal Operation)
Just before the boot ROM program gives control to FLASH program, the ROM configures the memory as
follows:
Address Size Module
0x0000_0000 – 0x0000_7FFF 32K Program Flash
0x0001_0000 – 0x0001_AFFF 4K Boot ROM
0x0001_8800 – 0x0001_8FFF 2K Data Flash
0x0001_9000 – 0x0001_9FFF 4K Data RAM
4.2.1.3 Memory Map (System and Peripherals Blocks)
Address Size Module
0x0002_0000 - 0x0002_00FF 256 Loop Mux
0x0003_0000 - 0x0003_00FF 256 Fault Mux
0x0004_0000 - 0x0004_00FF 256 ADC
0x0005_0000 - 0x0005_00FF 256 DPWM 3
0x0006_0000 - 0x0006_00FF 256 Filter 2
0x0007_0000 - 0x0007_00FF 256 DPWM 2
0x0008_0000 - 0x0008_00FF 256 Front End/Ramp I/F 2
0x0009_0000 - 0x0009_00FF 256 Filter 1
0x000A_0000 - 0x000A_00FF 256 DPWM 1
0x000B_0000 – 0x000B_00FF 256 Front End/Ramp I/F 1
0x000C_0000 - 0x000C_00FF 256 Filter 0
0x000D_0000 - 0x000D_00FF 256 DPWM 0
0x000E_0000 - 0x000E_00FF 256 Front End/Ramp I/F 0
0xFFF7_EC00 - 0xFFF7_ECFF 256 UART 0
0xFFF7_ED00 - 0xFFF7_EDFF 256 UART 1
0xFFF7_F000 - 0xFFF7_F0FF 256 Miscellaneous Analog Control
0xFFF7_F600 - 0xFFF7_F6FF 256 PMBus Interface
0xFFF7_FA00 - 0xFFF7_FAFF 256 GIO
0xFFF7_FD00 - 0xFFF7_FDFF 256 Timer
0xFFFF_FD00 - 0xFFFF_FDFF 256 MMC
0xFFFF_FE00 - 0xFFFF_FEFF 256 DEC
0xFFFF_FF20 - 0xFFFF_FF37 23 CIM
0xFFFF_FF40 - 0xFFFF_FF50 16 PSA
0xFFFF_FFD0 - 0xFFFF_FFEC 28 SYS
The registers and bit definitions inside the System and Peripheral blocks are detailed in the programmer’s
guide for each peripheral.
4.2.2 Boot ROM
The UCD3138 incorporates a 4k boot ROM. This boot ROM includes support for:
• Program download through the PMBus
• Device initialization
• Examining and modifying registers and memory
• Verifying and executing program FLASH automatically
• Jumping to a customer defined boot program
24 Functional Overview Copyright © 2012, Texas Instruments Incorporated
Submit Documentation Feedback
Product Folder Link(s): UCD3138
UCD3138
www.ti.com SLUSAP2B –MARCH 2012–REVISED JULY 2012
The Boot ROM is entered automatically on device reset. It initializes the device and then performs
checksums on the Program FLASH. If the first 2 kB of program FLASH has a valid checksum, the
program jumps to location 0 in the Program FLASH. This permits the use of a customer boot program. If
the first checksum fails, it performs a checksum on the complete 32 kB of program flash. If this is valid, it
also jumps to location 0 in the program flash. This permits full automated program memory checking,
when there is no need for a custom boot program.
If neither checksum is valid, the Boot ROM stays in control, and accepts commands via the PMBus
interface
These functions can be used to read and write to all memory locations in the UCD3138. Typically they are
used to download a program to Program Flash, and to command its execution
4.2.3 Customer Boot Program
As described above, it is possible to generate a user boot program using 2 kB or more of the Program
Flash. This can support things which the Boot ROM does not support, including:
• Program download via UART – useful especially for applications where the UCD3138 is isolated from
the host (e.g., PFC)
• Encrypted download – useful for code security in field updates.
4.2.4 Flash Management
The UCD3138 offers a variety of features providing for easy prototyping and easy flash programming. At
the same time, high levels of security are possible for production code, even with field updates. Standard
firmware will be provided for storing multiple copies of system parameters in data flash. This is minimizes
the risk of losing information if programming is interrupted.
4.3 System Module
The System Module contains the interface logic and configuration registers to control and configure all the
memory, peripherals and interrupt mechanisms. The blocks inside the system module are the address
decoder, memory management controller, system management unit, central interrupt unit, and clock
control unit.
4.3.1 Address Decoder (DEC)
The Address Decoder generates the memory selects for the FLASH, ROM and RAM arrays. The memory
map addresses are selectable through configurable register settings. These memory selects can be
configured from 1 kB to 16 MB. Power on reset uses the default addresses in the memory map for ROM
execution, which is then configured by the ROM code to the application setup. During access to the DEC
registers, a wait state is asserted to the CPU. DEC registers are only writable in the ARM privilege mode
for user mode protection.
4.3.2 Memory Management Controller (MMC)
The MMC manages the interface to the peripherals by controlling the interface bus for extending the read
and write accesses to each peripheral. The unit generates eight peripheral select lines with 1 kB of
address space decoding.
4.3.3 System Management (SYS)
The SYS unit contains the software access protection by configuring user privilege levels to memory or
peripherals modules. It contains the ability to generate fault or reset conditions on decoding of illegal
address or access conditions. A clock control setup for the processor clock (MCLK) speed, is also
available.
Copyright © 2012, Texas Instruments Incorporated Functional Overview 25
Submit Documentation Feedback
Product Folder Link(s): UCD3138
UCD3138
SLUSAP2B –MARCH 2012–REVISED JULY 2012 www.ti.com
4.3.4 Central Interrupt Module (CIM)
The CIM accepts 32 interrupt requests for meeting firmware timing requirements. The ARM processor
supports two interrupt levels: FIQ and IRQ. FIQ is the highest priority interrupt. The CIM provides
hardware expansion of interrupts by use of FIQ/IRQ vector registers for providing the offset index in a
vector table. This numerical index value indicates the highest precedence channel with a pending interrupt
and is used to locate the interrupt vector address from the interrupt vector table. Interrupt channel 0 has
the lowest precedence and interrupt channel 31 has the highest precedence. To remove the interrupt
request, the firmware should clear the request as the first action in the interrupt service routine. The
request channels are maskable, allowing individual channels to be selectively disabled or enabled.
Table 4-1. Interrupt Priority Table
NAME MODULE COMPONENT OR DESCRIPTION PRIORITY REGISTER
BRN_OUT_INT Brownout Brownout interrupt 0 (Lowest)
EXT_INT External Interrupts Interrupt on external input pin 1
WDRST_INT Watchdog Control Interrupt from watchdog exceeded (reset) 2
WDWAKE_INT Watchdog Control Wakeup interrupt when watchdog equals half of set 3 watch time
SCI_ERR_INT UART or SCI Control UART or SCI error Interrupt. Frame, parity or overrun 4
SCI_RX_0_INT UART or SCI Control UART0 RX buffer has a byte 5
SCI_TX_0_INT UART or SCI Control UART0 TX buffer empty 6
SCI_RX_1_INT UART or SCI Control UART1 RX buffer has a byte 7
SCI_TX_1_INT UART or SCI Control UART1 TX buffer empty 8
PMBUS_INT PMBus related interrupt 9
DIG_COMP_INT 12-bit ADC Control Digital comparator interrupt 10
“Prebias complete”, “Ramp Delay Complete”, “Ramp
FE0_INT Front End 0 Complete”, “Load Step Detected”, 11
“Over-Voltage Detected”, “EADC saturated”
“Prebias complete”, “Ramp Delay Complete”, “Ramp
FE1_INT Front End 1 Complete”, “Load Step Detected”, 12
“Over-Voltage Detected”, “EADC saturated”
“Prebias complete”, “Ramp Delay Complete”, “Ramp
FE2_INT Front End 2 Complete”, “Load Step Detected”, 13
“Over-Voltage Detected”, “EADC saturated”
PWM3_INT 16-bit Timer PWM 3 16-bit Timer PWM3 counter overflow or compare interrupt 14
PWM2_INT 16-bit Timer PWM 2 16-bit Timer PWM2 counter Overflow or compare 15 interrupt
PWM1_INT 16-bit Timer PWM 1 16-bit Timer PWM1 counter overflow or compare interrupt 16
PWM0_INT 16-bit timer PWM 0 16-bit Timer PWM1 counter overflow or compare interrupt 17
OVF24_INT 24-bit Timer Control 24-bit Timer counter overflow interrupt 18
CAPTURE_1_INT 24-bit Timer Control 24-bit Timer capture 1 interrupt 19
COMP_1_INT 24-bit Timer Control 24-bit Timer compare 1 interrupt 20
CAPTURE_0_INT 24-bit Timer Control 24-bit Timer capture 0 interrupt 21
COMP_0_INT 24-bit Timer Control 24-bit Timer compare 0 interrupt 22
CPCC_INT Constant Power Constant Current Mode switched in CPCC module Flag needs to be read 23 for details
ADC_CONV_INT 12-bit ADC Control ADC end of conversion interrupt 24
Analog comparator interrupts, Over-Voltage detection,
FAULT_INT Fault Mux Interrupt Under-Voltage detection, 25
LLM load step detection
26 Functional Overview Copyright © 2012, Texas Instruments Incorporated
Submit Documentation Feedback
Product Folder Link(s): UCD3138
Error ADC
(Front End)
Filter
Digital
PWM
EAP
EAN
DPWMA
DPWMB
UCD3138
www.ti.com SLUSAP2B –MARCH 2012–REVISED JULY 2012
Table 4-1. Interrupt Priority Table (continued)
NAME MODULE COMPONENT OR DESCRIPTION PRIORITY REGISTER
DPWM3 DPWM3 Same as DPWM1 26
DPWM2 DPWM2 Same as DPWM1 27
1) Every (1-256) switching cycles
DPWM1 DPWM1 2) Fault Detection 28
3) Mode switching
DPWM0 DPWM0 Same as DPWM1 29
EXT_FAULT_INT External Faults Fault pin interrupt 30
SYS_SSI_INT System Software System software interrupt 31 (highest)
4.4 Peripherals
4.4.1 Digital Power Peripherals
At the core of the UCD3138 controller are 3 Digital Power Peripherals (DPP). Each DPP can be
configured to drive from one to eight DPWM outputs. Each DPP consists of:
• Differential input error ADC (EADC) with sophisticated controls
• Hardware accelerated digital 2-pole/2-zero PID based compensator
• Digital PWM module with support for a variety of topologies
These can be connected in many different combinations, with multiple filters and DPWMs. They are
capable of supporting functions like input voltage feed forward, current mode control, and constant
current/constant power, etc.. The simplest configuration is shown in the following figure:
4.4.1.1 Front End
Figure 4-1 shows the block diagram of the front end module. It consists of a differential amplifier, an
adjustable gain error amplifier, a high speed flash analog to digital converter (EADC), digital averaging
filters and a precision high resolution set point DAC reference. The programmable gain amplifier in concert
with the EADC and the adjustable digital gain on the EADC output work together to provide 9 bits of range
with 6 bits of resolution on the EADC output. The output of the Front End module is a 9 bit sign extended
result with a gain of 1 LSB / mV. Depending on the value of AFE selected, the resolution of this output
could be either 1, 2, 4 or 8 LSBs. In addition Front End 0 has the ability to automatically select the AFE
value such that the minimum resolution is maintained that still allows the voltage to fit within the range of
the measurement. The EADC control logic receives the sample request from the DPWM module for
initiating an EADC conversion. EADC control circuitry captures the EADC-9-bit-code and strobes the
digital compensator for processing of the representative error. The set point DAC has 10 bits with an
additional 4 bits of dithering resulting in an effective resolution of 14 bits. This DAC can be driven from a
variety of sources to facilitate things like soft start, nested loops, etc. Some additional features include the
ability to change the polarity of the error measurement and an absolute value mode which automatically
adds the DAC value to the error.
It is possible to operate the controller in a peak current mode control configuration. In this mode topologies
like the phase shifted full bridge converter can be controlled to maintain transformer flux balance. The
internal DAC can be ramped at a synchronously controlled slew rate to achieve a programmable slope
compensation. This eliminates the sub-harmonic oscillation as well as improves input voltage feed-forward
performance. A0 is a unity gain buffer used to isolate the peak current mode comparator. The offset of this
buffer is specified in the Electrical Characteristics table.
Copyright © 2012, Texas Instruments Incorporated Functional Overview 27
Submit Documentation Feedback
Product Folder Link(s): UCD3138
EAP0
EAN0
DAC0
EADC
4 bit dithering gives 14 bits of effective resolution
97.65625 μV/LSB effective resolution
X
6 bit ADC
8 mV/LSB
Signed 9 bit result
(error) 1 mV /LSB
AFE_GAIN
10 bit DAC
1.5625 mV/LSB Value
Dither
S
CPCC
Filter x
Ramp
SAR/Prebias
Absolute Value
Calculation
Averaging
10 bit result
1.5625 mV/LSB
2
3-AFE_GAIN
Peak Current Mode
Comparator
Peak Current
Detected
A0
2
AFE_GAIN
IOFFSET
REA
EAP
EAN
AGND
AGND
IOFFSET
REA
Front End Differential
Amplifier
UCD3138
SLUSAP2B –MARCH 2012–REVISED JULY 2012 www.ti.com
Figure 4-1. Input Stage of EADC Module
Figure 4-2. Front End Module
4.4.1.2 DPWM Module
The DPWM module represents one complete DPWM channel with 2 independent outputs, A and B.
Multiple DPWM modules within the UCD3138 system can be configured to support all key power
topologies. DPWM modules can be used as independent DPWM outputs, each controlling one power
supply output voltage rail. It can also be used as a synchronized DPWM—with user selectable phase shift
between the DPWM channels to control power supply outputs with multiphase or interleaved DPWM
configurations.
28 Functional Overview Copyright © 2012, Texas Instruments Incorporated
Submit Documentation Feedback
Product Folder Link(s): UCD3138
UCD3138
www.ti.com SLUSAP2B –MARCH 2012–REVISED JULY 2012
The output of the filter feeds the high resolution DPWM module. The DPWM module produces the pulse
width modulated outputs for the power stage switches. The compensator calculates the necessary duty
ratio as a 24-bit number in Q23 fixed point format (23 bit integer with 1 sign bit). This represents a value
within the range 0.0 to 1.0. This duty ratio value is used to generate the corresponding DPWM output ON
time. The resolution of the DPWM ON time is 250 psec.
Each DPWM module can be synchronized to another module or to an external sync signal. An input
SYNC signal causes a DPWM ramp timer to reset. The SYNC signal outputs—from each of the four
DPWM modules—occur when the ramp timer crosses a programmed threshold. In this way the phase of
the DPWM outputs for multiple power stages can be tightly controlled.
The DPWM logic is probably the most complex of the Digital Peripherals. It takes the output of the
compensator and converts it into the correct DPWM output for several power supply topologies. It
provides for programmable dead times and cycle adjustments for current balancing between phases. It
controls the triggering of the EADC. It can synchronize to other DPWMs or to external sources. It can
provide synchronization information to other DPWMs or to external recipients. In addition, it interfaces to
several fault handling circuits. Some of the control for these fault handling circuits is in the DPWM
registers. Fault handling is covered in the Fault Mux section.
Each DPWM module supports the following features:
• Dedicated 14 bit time-base with period and frequency control
• Shadow period register for end of period updates.
• Quad-event control registers (A and B, rising and falling) (Events 1-4)
– Used for on/off DPWM duty ratio updates.
• Phase control relative to other DPWM modules
• Sample trigger placement for output voltage sensing at any point during the DPWM cycle.
• Support for 2 independent edge placement DPWM outputs (same frequency or period setting)
• Dead-time between DPWM A and B outputs
• High Resolution capabilities – 250 ps
• Pulse cycle adjustment of up to ±8.192 μs ( 32768 × 250 ps)
• Active high/ active low output polarity selection
• Provides events to trigger both CPU interrupts and start of ADC12 conversions.
4.4.1.3 DPWM Events
Each DPWM can control the following timing events:
1. Sample Trigger Count–This register defines where the error voltage is sampled by the EADC in
relationship to the DPWM period. The programmed value set in the register should be one fourth of the
value calculated based on the DPWM clock. As the DCLK (DCLK = 62.5 MHz max) controlling the
circuitry runs at one fourth of the DPWM clock (PCLK = 250MHz max). When this sample trigger count
is equal to the DPWM Counter, it initiates a front end calculation by triggering the EADC, resulting in a
CLA calculation, and a DPWM update. Over-sampling can be set for 2, 4 or 8 times the sampling rate.
2. Phase Trigger Count–count offset for slaving another DPWM (Multi-Phase/Interleaved operation).
3. Period–low resolution switching period count. (count of PCLK cycles)
4. Event 1–count offset for rising DPWM A event. (PCLK cycles)
5. Event 2–DPWM count for falling DPWM A event that sets the duty ratio. Last 4 bits of the register are
for high resolution control. Upper 14 bits are the number of PCLK cycle counts.
6. Event 3–DPWM count for rising DPWM B event. Last 4 bits of the register are for high resolution
control. Upper 14 bits are the number of PCLK cycle counts.
7. Event 4–DPWM count for falling DPWM B event. Last 4 bits of the register are for high resolution
control. Upper 14 bits are the number of PCLK cycle counts.
8. Cycle Adjust–Constant offset for Event 2 and Event 4 adjustments.
Copyright © 2012, Texas Instruments Incorporated Functional Overview 29
Submit Documentation Feedback
Product Folder Link(s): UCD3138
Start of Period
Period Counter
Start of Period
Period
Sample Trigger 1
DPWM Output A
Cycle Adjust A (High Resolution)
Event 2 (High Resolution)
Event 1
Event 3 (High Resolution)
Cycle Adjust B (High Resolution)
Event 4 (High Resolution)
DPWM Output B
Blanking A Begin
Blanking A End
Blanking B Begin
Blanking B End
Phase Trigger
Sample Trigger 2
To Other
Modules
To Other
Modules
Multi Mode Open Loop
Events which change with DPWM mode:
DPWM A Rising Edge = Event 1
DPWM A Falling Edge = Event 2 + Cycle Adjust A
DPWM B Rising Edge = Event 3
DPWM B Falling Edge = Event 4 + Cycle Adjust B
Phase Trigger = Phase Trigger Register value
Events always set by their registers, regardless of mode:
Sample Trigger 1, Sample Trigger 2, Blanking A Begin, Blanking A End, Blanking B Begin,
Blanking B End
UCD3138
SLUSAP2B –MARCH 2012–REVISED JULY 2012 www.ti.com
Basic comparisons between the programmed registers and the DPWM counter can create the desired
edge placements in the DPWM. High resolution edge capability is available on Events 2, 3 and 4.
The drawing above is for multi-mode, open loop. Open loop means that the DPWM is controlled entirely
by its own registers, not by the filter output. In other words, the power supply control loop is not closed.
30 Functional Overview Copyright © 2012, Texas Instruments Incorporated
Submit Documentation Feedback
Product Folder Link(s): UCD3138
UCD3138
www.ti.com SLUSAP2B –MARCH 2012–REVISED JULY 2012
The Sample Trigger signals are used to trigger the Front End to sample input signals. The Blanking
signals are used to blank fault measurements during noisy events, such as FET turn on and turn off.
Additional DPWM modes are described below.
4.4.1.4 High Resolution DPWM
Unlike conventional PWM controllers where the frequency of the clock dictates the maximum resolution of
PWM edges, the UCD3138 DPWM can generate waveforms with resolutions as small as 250 ps. This is
16 times the resolution of the clock driving the DPWM module.
This is achieved by providing the DPWM mechanism with 16 phase shifted clock signals of 250 MHz
each. The high resolution section of DPWM can be enabled or disabled, also the resolution can be defined
in several steps between 4ns to 250ps. This is done by setting the values of PWM_HR_MULTI_OUT_EN ,
HIRES_SCALE and ALL_PHASE_CLK_ENA inside the DPWM Control Register 1. See the Power
Peripherals programmer’s manual for details.
4.4.1.5 Over Sampling
The DPWM module has the capability to trigger an over sampling event by initiating the EADC to sample
the error voltage. The default “00” configuration has the DPWM trigger the EADC once based on the
sample trigger register value. The over sampling register has the ability to trigger the sampling 2, 4 or 8
times per PWM period. Thus the time the over sample happens is at the divide by 2, 4, or 8 time set in the
sampling register. The “01” setting triggers 2X over sampling, the “10” setting triggers 4X over sampling,
and the “11” triggers over sampling at 8X.
4.4.1.6 DPWM Interrupt Generation
The DPWM has the capability to generate a CPU interrupt based on the PWM frequency programmed in
the period register. The interrupt can be scaled by a divider ratio of up to 255 for developing a slower
interrupt service execution loop. This interrupt can be fed to the ADC circuitry for providing an ADC12
trigger for sequence synchronization. Table 4-2 outlines the divide ratios that can be programmed.
4.4.1.7 DPWM Interrupt Scaling/Range
Table 4-2. DPWM Interrupt Divide Ratio
Interrupt Divide Interrupt Divide Interrupt Divide Switching Period Number of 32 MHz Setting Count Count (hex) Frames (assume 1MHz Processor Cycles loop)
1 0 00 1 32
2 1 01 2 64
3 3 03 4 128
4 7 07 8 256
5 15 0F 16 512
6 31 1F 32 1024
7 47 2F 48 1536
8 63 3F 64 2048
9 79 4F 80 2560
10 95 5F 96 3072
11 127 7F 128 4096
12 159 9F 160 5120
13 191 BF 192 6144
14 223 DF 224 7168
15 255 FF 256 8192
Copyright © 2012, Texas Instruments Incorporated Functional Overview 31
Submit Documentation Feedback
Product Folder Link(s): UCD3138
UCD3138
SLUSAP2B –MARCH 2012–REVISED JULY 2012 www.ti.com
4.5 DPWM Modes of Operation
The DPWM is a complex logic system which is highly configurable to support several different power
supply topologies. The discussion below will focus primarily on waveforms, timing and register settings,
rather than on logic design.
The DPWM is centered on a period counter, which counts up from 0 to PRD, and then is reset and starts
over again.
The DPWM logic causes transitions in many digital signals when the period counter hits the target value
for that signal.
4.5.1 Normal Mode
In Normal mode, the Filter output determines the pulse width on DPWM A. DPWM B fits into the rest of
the switching period, with a dead time separating it from the DPWM A on-time. It is useful for buck
topologies, among others. Here is a drawing of the Normal Mode waveforms:
32 Functional Overview Copyright © 2012, Texas Instruments Incorporated
Submit Documentation Feedback
Product Folder Link(s): UCD3138
Start of Period
Period Counter
Start of Period
Period
DPWM Output A
Cycle Adjust A (High Resolution)
Filter Duty (High Resolution)
Event 1
Event 3 – Event 2 (High Res)
Event 4 (High Res)
DPWM Output B
Blanking B Begin
Blanking B End
Phase Trigger
Sample Trigger 2
To Other
Modules
Normal Mode Closed Loop
Events which change with DPWM mode:
DPWM A Rising Edge = Event 1
DPWM A Falling Edge = Event 1 + Filter Duty + Cycle Adjust A
Adaptive Sample Trigger A = Event 1 + Filter Duty + Adaptive Sample Register or
Adaptive Sample Trigger B = Event 1 + Filter Duty/2 + Adaptive Sample Register
DPWM B Rising Edge = Event 1 + Filter Duty + Cycle Adjust A + (Event 3 – Event 2)
DPWM B Falling Edge = Event 4
Phase Trigger = Phase Trigger Register value or Filter Duty
Events always set by their registers, regardless of mode:
Sample Trigger 1, Sample Trigger 2, Blanking A Begin, Blanking A End, Blanking B
Begin, Blanking B End
Filter controlled edge
Sample Trigger 1
Blanking A Begin
Blanking A End
To Other
Modules
Adaptive Sample Trigger A
Adaptive Sample Trigger B
UCD3138
www.ti.com SLUSAP2B –MARCH 2012–REVISED JULY 2012
Cycle adjust A can be used to adjust pulse widths on individual phases of a multi-phase system. This can
be used for functions like current balancing. The Adaptive Sample Triggers can be used to sample in the
middle of the on-time (for an average output), or at the end of the on-time (to minimize phase delay) The
Adaptive Sample Register provides an offset from the center of the on-time. This can compensate for
external delays, such as MOSFET and gate driver turn on times.
Copyright © 2012, Texas Instruments Incorporated Functional Overview 33
Submit Documentation Feedback
Product Folder Link(s): UCD3138
Phase Shift
Phase Trigger = Phase Trigger Register value or Filter Duty
DPWM0 Start of Period
Period Counter
DPWM0 Start of Period
DPWM1 Start of Period
Period Counter
DPWM1 Start of Period
UCD3138
SLUSAP2B –MARCH 2012–REVISED JULY 2012 www.ti.com
Blanking A-Begin and Blanking A-End can be used to blank out noise from the MOSFET turn on at the
beginning of the period (DPWMA rising edge). Blanking B could be used at the turn off time of DPWMB.
The other edges are dynamic, so blanking is more difficult.
Cycle Adjust B has no effect in Normal Mode.
4.6 Phase Shifting
In most modes, it is possible to synchronize multiple DPWM modules using the phase shift signal. The
phase shift signal has two possible sources. It can come from the Phase Shift Register. This provides a
fixed value, which is useful for an interleaved PFC, for example.
The phase shift value can also come from the filter output. In this case, the changes in the filter output
causes changes in the phase relationship of two DPWM modules. This is useful for phase shifted full
bridge topologies.
The following figure shows the mechanism of phase shift:
34 Functional Overview Copyright © 2012, Texas Instruments Incorporated
Submit Documentation Feedback
Product Folder Link(s): UCD3138
Adaptive Sample Trigger B
Start of Period
Period Counter
Start of Period
Period
Adaptive Sample Trigger A
DPWM Output A
Cycle Adjust A (High Resolution)
Filter Duty (High Resolution)
Event 1
To Other
Modules
Multi Mode Closed Loop
Events which change with DPWM mode:
DPWM A Rising Edge = Event 1
DPWM A Falling Edge = Event 1 + Filter Duty + Cycle Adjust A
Adaptive Sample Trigger A = Event 1 + Filter Duty + Adaptive Sample Register or
Adaptive Sample Trigger B = Event 1 + Filter Duty/2 + Adaptive Sample Register
DPWM B Rising Edge = Event 3
DPWM B Falling Edge = Event 3 + Filter Duty + Cycle Adjust B
Phase Trigger = Phase Trigger Register value or Filter Duty
Events always set by their registers, regardless of mode:
Sample Trigger 1, Sample Trigger 2, Blanking A Begin, Blanking A End, Blanking B
Begin, Blanking B End
Filter controlled edge
Event 3 (High Resolution)
Cycle Adjust B (High Resolution)
Filter Duty (High Resolution)
DPWM Output B
Blanking B Begin
Blanking B End
Phase Trigger
Sample Trigger 2
To Other
Modules
Sample Trigger 1
Blanking A Begin
Blanking A End
UCD3138
www.ti.com SLUSAP2B –MARCH 2012–REVISED JULY 2012
4.7 DPWM Multiple Output Mode
Multi mode is used for systems where each phase has only one driver signal. It enables each DPWM
peripheral to drive two phases with the same pulse width, but with a time offset between the phases, and
with different cycle adjusts for each phase.
Here is a diagram for Multi-Mode:
Copyright © 2012, Texas Instruments Incorporated Functional Overview 35
Submit Documentation Feedback
Product Folder Link(s): UCD3138
UCD3138
SLUSAP2B –MARCH 2012–REVISED JULY 2012 www.ti.com
Event 2 and Event 4 are not relevant in Multi mode.
DPWMB can cross over the period boundary safely, and still have the proper pulse width, so full 100%
pulse width operation is possible. DPWMA cannot cross over the period boundary.
Since the rising edge on DPWM B is also fixed, Blanking B-Begin and Blanking B-End can be used for
blanking this rising edge.
And, of course, Cycle Adjust B is usable on DPWM B.
4.8 DPWM Resonant Mode
This mode provides a symmetrical waveform where DPWMA and DPWMB have the same pulse width. As
the switching frequency changes, the dead times between the pulses remain the same.
The equations for this mode are designed for a smooth transition from PWM mode to resonant mode, as
described in the LLC Example section. Here is a diagram of this mode:
36 Functional Overview Copyright © 2012, Texas Instruments Incorporated
Submit Documentation Feedback
Product Folder Link(s): UCD3138
Start of Period
Period Counter
Start of Period
Filter Period
Adaptive Sample Trigger A
Sample Trigger 1
DPWM Output A
Filter Duty – Average Dead Time
Event 1
Event 3 - Event 2
Period Register – Event 4
DPWM Output B
Blanking A Begin
Blanking A End
Blanking B Begin
Blanking B End
Phase Trigger
Sample Trigger 2
To Other
Modules
To Other
Modules
Resonant Symmetrical Closed Loop
Events which change with DPWM mode:
Dead Time 1 = Event 3 – Event 2
Dead Time 2 = Event 1 + Period Register – Event 4)
Average Dead Time = (Dead Time 1 + Dead Time 2)/2
DPWM A Rising Edge = Event 1
DPWM A Falling Edge = Event 1 + Filter Duty – Average Dead Time
Adaptive Sample Trigger A = Event 1 + Filter Duty + Adaptive Sample Register
Adaptive Sample Trigger B = Event 1 + Filter Duty/2 + Adaptive Sample Register
DPWM B Rising Edge = Event 1 + Filter Duty – Average Dead Time + (Event 3 – Event 2)
DPWM B Falling Edge = Filter Period – (Period Register – Event 4)
Phase Trigger = Phase Trigger Register value or Filter Duty
Events always set by their registers, regardless of mode:
Sample Trigger 1, Sample Trigger 2, Blanking A Begin, Blanking A End, Blanking B Begin,
Blanking B End
Filter controlled edge
Adaptive Sample Trigger B
UCD3138
www.ti.com SLUSAP2B –MARCH 2012–REVISED JULY 2012
The Filter has two outputs, Filter Duty and Filter Period. In this case, the Filter is configured so that the
Filter Period is twice the Filter Duty. So if there were no dead times, each DPWM pin would be on for half
of the period. For dead time handling, the average of the two dead times is subtracted from the Filter Duty
for both DPWM pins. Therefore, both pins will have the same on-time, and the dead times will be fixed
regardless of the period. The only edge which is fixed relative to the start of the period is the rising edge of
DPWM A. This is the only edge for which the blanking signals can be used easily.
Copyright © 2012, Texas Instruments Incorporated Functional Overview 37
Submit Documentation Feedback
Product Folder Link(s): UCD3138
Start of Period
Period Counter
Start of Period
Period
Sample Trigger 1
DPWM Output A
Filter Duty/2 (High Resolution)
Period/2
DPWM Output B
Blanking A Begin
Blanking A End
Blanking B Begin
Blanking B End
Phase Trigger
Sample Trigger 2
To Other
Modules
To Other
Modules
Triangular Mode Closed Loop
Events which change with DPWM mode:
DPWM A Rising Edge = None
DPWM A Falling Edge = None
Adaptive Sample Trigger = None
DPWM B Rising Edge = Period/2 - Filter Duty/2 + Cycle Adjust A
DPWM B Falling Edge = Period/2 + Filter Duty/2 + Cycle Adjust B
Phase Trigger = Phase Trigger Register value or Filter Duty
Events always set by their registers, regardless of mode:
Sample Trigger 1, Sample Trigger 2, Blanking A Begin, Blanking A End, Blanking B
Begin, Blanking B End
Filter controlled edge
Cycle Adjust A (High Resolution)
Cycle Adjust B (High Resolution)
UCD3138
SLUSAP2B –MARCH 2012–REVISED JULY 2012 www.ti.com
4.9 Triangular Mode
Triangular mode provides a stable phase shift in interleaved PFC and similar topologies. In this case, the
PWM pulse is centered in the middle of the period, rather than starting at one end or the other. In
Triangular Mode, only DPWM-B is available. Here is a diagram for Triangular Mode:
All edges are dynamic in triangular mode, so fixed blanking is not that useful. The adaptive sample trigger
is not needed. It is very easy to put a fixed sample trigger exactly in the center of the FET on-time,
because the center of the on-time does not move in this mode.
38 Functional Overview Copyright © 2012, Texas Instruments Incorporated
Submit Documentation Feedback
Product Folder Link(s): UCD3138
UCD3138
www.ti.com SLUSAP2B –MARCH 2012–REVISED JULY 2012
4.10 Leading Edge Mode
Leading edge mode is very similar to Normal mode, reversed in time. The DPWM A falling edge is fixed,
and the rising edge moves to the left, or backwards in time, as the filter output increases. The DPWM B
falling edge stays ahead of the DPWMA rising edge by a fixed dead time. Here is a diagram of the
Leading Edge Mode:
Copyright © 2012, Texas Instruments Incorporated Functional Overview 39
Submit Documentation Feedback
Product Folder Link(s): UCD3138
Start of Period
Period Counter
Start of Period
Period
Adaptive Sample Trigger B
Sample Trigger 1
DPWM Output A
Cycle Adjust A (High Resolution)
Filter Duty (High Resolution)
Event 1
Event 2 - Event 3 (High Resolution)
Event 4 (High Resolution)
DPWM Output B
Blanking A Begin
Blanking A End
Blanking B Begin
Blanking B End
Phase Trigger
Sample Trigger 2
To Other
Modules
To Other
Modules
Leading Edge Closed Loop
Events which change with DPWM mode:
DPWM A Falling Edge = Event 1
DPWM A Rising Edge = Event 1 - Filter Duty + Cycle Adjust A
Adaptive Sample Trigger A = Event 1 - Filter Duty + Adaptive Sample Register or
Adaptive Sample Trigger B = Event 1 - Filter Duty/2 + Adaptive Sample Register
DPWM B Rising Edge = Event 4
DPWM B Falling Edge = Event 1 - Filter Duty + Cycle Adjust A -(Event 2 – Event 3)
Phase Trigger = Phase Trigger Register value or Filter Duty
Events always set by their registers, regardless of mode:
Sample Trigger 1, Sample Trigger 2, Blanking A Begin, Blanking A End, Blanking B
Begin, Blanking B End
Adaptive Sample Trigger A
UCD3138
SLUSAP2B –MARCH 2012–REVISED JULY 2012 www.ti.com
As in the Normal mode, the two edges in the middle of the period are dynamic, so the fixed blanking
intervals are mainly useful for the edges at the beginning and end of the period.
40 Functional Overview Copyright © 2012, Texas Instruments Incorporated
Submit Documentation Feedback
Product Folder Link(s): UCD3138
DPWM3B
(QT1)
DPWM2A
(QT2)
DPWM2B
(QB2)
VTrans
DPWM0B
(QSYN2,4)
DPWM1B
(QSYN1,3)
IPRI
DPWM3A
(QB1)
UCD3138
www.ti.com SLUSAP2B –MARCH 2012–REVISED JULY 2012
4.11 Sync FET Ramp and IDE Calculation
The UCD3138 has built in logic for controlling MOSFETs for synchronous rectification (Sync FETs). This
comes in two forms:
• Sync FET ramp
• Ideal Diode Emulation (IDE) calculation
When starting up a power supply, sometimes there is already a voltage on the output – this is called
prebias. It is very difficult to calculate the ideal Sync FET on-time for this case. If it is not calculated
correctly, it may pull down the pre-bias voltage, causing the power supply to sink current.
To avoid this, Sync FETs are not turned on until after the power supply has ramped up to the nominal
voltage. The Sync FETs are turned on gradually in order to avoid an output voltage glitch. The Sync FET
Ramp logic can be used to turn them on at a rate below the bandwidth of the filter.
In discontinuous mode, the ideal on-time for the Sync FETs is a function of Vin, Vout, and the primary side
duty cycle (D). The IDE logic in the UCD3138 takes Vin and Vout data from the firmware and combines it
with D data from the filter hardware. It uses this information to calculate the ideal on-time for the Sync
FETs.
4.12 Automatic Mode Switching
Automatic Mode switching enables the DPWM module to switch between modes automatically, with no
firmware intervention. This is useful to increase efficiency and power range. The following paragraphs
describe phase-shifted full bridge and LLC examples:
4.12.1 Phase Shifted Full Bridge Example
In phase shifted full bridge topologies, efficiency can be increased by using pulse width modulation, rather
than phase shift, at light load. This is shown below:
Copyright © 2012, Texas Instruments Incorporated Functional Overview 41
Submit Documentation Feedback
Product Folder Link(s): UCD3138
Q1B
Q1T
QSR1
QSR2
fs< fr
fr
fs= fr_max fs> fr
PWM
Mode LLC Mode
Tr= 1/fr
Tr= 1/fr
ISEC(t )
SynFET Primary
QT1
QB1
Lr
ISOLATED
GATE Transformer SYNCHRONOUS
GATE DRIVE
PRIM
CURRENT
VOUT
+12V
T1
T1
ORING
CTL
VA
VBUS
QT2
QB2
D1
D2
T2
L1
Q5
C1 RL
C2
R2
Q6
Q7
I_SHARE
Vout
Iout
I_pri
temp
Vin
VA
UCD 3138
ARM7
FAULT 0
AD01
AD02/CMP0
AD03/CMP1/CMP2
AD04/CMP3
AD05/CMP4
AD00
AD06/CMP5
FAULT 1
FAULT 2
GPIO2
GPIO3
GPIO1
AD07/CMP6
AD08
AD09
DPWM0B
DPWM1B
DPWM2A
DPWM2B
ORING_CRTL
P_GOOD
DPWM3A
DPWM3B
Vout
ON/OFF
FAILURE
ACFAIL_OUT
ACFAIL_IN
I_pri
Iout
EADC0
EADC1
CLA0
CLA1
EADC2
DPWM0
DPWM1
DPWM2
DPWM3
Duty for mode
switching
Vref
Load Current
PCM
CBC
<
DPWM3A
DPWM3B
DPWM2A
DPWM2B
DPWM0B
DPWM1B
CPCC
PMBus
UART1
UART0
Primary
OSC
WD
RST
Memory
FAULT
Current
Sensing
I_pri
UCD3138
SLUSAP2B –MARCH 2012–REVISED JULY 2012 www.ti.com
Figure 4-3. Secondary-Referenced Phase-Shifted Full Bridge Control
With Synchronous Rectification
4.12.2 LLC Example
In LLC, three modes are used. At the highest frequency, a pulse width modulated mode (Multi Mode) is
used. As the frequency decreases, resonant mode is used. As the frequency gets still lower, the
synchronous MOSFET drive changes so that the on-time is fixed and does not increase. In addition, the
LLC control supports cycle-by-cycle current limiting. This protection function operates by a comparator
monitoring the maximum current during the DPWMA conduction time. Any time this current exceeds the
programmable comparator reference the pulse is immediately terminated. Due to classic instability issues
associated with half-bridge topologies it is also possible to force DPWMB to match the truncated pulse
width of DPWMA. Here are the waveforms for the LLC:
42 Functional Overview Copyright © 2012, Texas Instruments Incorporated
Submit Documentation Feedback
Product Folder Link(s): UCD3138
Q1T
CRES
CRES
LM
LK
Q1B
VBUS
VBUS
Transformer
COUT1
QSR1
QSR2
LRES
DPWM0A
DPWM0B
DPWM1A
DPWM1B
Driver
Driver
Driver
Driver
RS
RS1
RS2
CS
RF2 CF
RF1
RLRES
ESR1
COUT2
ESR2
EAP0
EAN0
NP
NS
NS
AD04
ADC13
EAP1
AD03
Oring Circuitry
VOUT
ILR(t)
ILM(t)
ISEC(t)
VCR(t)
VOUT(t)
Rectifier and filter
UCD3138
www.ti.com SLUSAP2B –MARCH 2012–REVISED JULY 2012
Figure 4-4. Secondary-Referenced Half-Bridge Resonant LLC Control
With Synchronous Rectification
Copyright © 2012, Texas Instruments Incorporated Functional Overview 43
Submit Documentation Feedback
Product Folder Link(s): UCD3138
Filter Duty
Low – Lower Threshold
High – Lower Threshold
Control
Register 1
Auto Config High
Auto Config Mid
High – Upper Threshold
Low – Upper Threshold
0
Full Range
Automatic Mode Switching
With Hysteresis
UCD3138
SLUSAP2B –MARCH 2012–REVISED JULY 2012 www.ti.com
4.12.3 Mechanism for Automatic Mode Switching
The UCD3138 allows the customer to enable up to two distinct levels of automatic mode switching. These
different modes are used to enhance light load operation, short circuit operation and soft start. Many of the
configuration parameters for the DPWM are in DPWM Control Register 1. For automatic mode switching,
some of these parameters are duplicated in the Auto Config Mid and Auto Config High registers.
If automatic mode switching is enabled, the filter duty signal is used to select which of these three
registers is used. There are 4 registers which are used to select the points at which the mode switching
takes place. They are used as shown below.
As shown, the registers are used in pairs for hysteresis. The transition from Control Register 1 to Auto
Config Mid only takes place when the Filter Duty goes above the Low Upper threshold. It does not go
back to Auto Config Mid until the Low Lower Threshold is passed. This prevents oscillation between
modes if the filter duty is close to a mode switching point.
44 Functional Overview Copyright © 2012, Texas Instruments Incorporated
Submit Documentation Feedback
Product Folder Link(s): UCD3138
A ON SELECT
A OFF SELECT
B ON SELECT
B OFF SELECT
EGEN A
EGEN B
EDGE GEN
PWM A
PWM B
B SELECT
A SELECT
INTRAMUX
A/B/C (N)
A/B/C (N+1)
C (N+2)
C (N+3)
A(N)
B(N)
A(N+1)
B(N+1)
UCD3138
www.ti.com SLUSAP2B –MARCH 2012–REVISED JULY 2012
4.13 DPWMC, Edge Generation, IntraMux
The UCD3138 has hardware for generating complex waveforms beyond the simple DPWMA and DPWMB
waveforms already discussed – DPWMC, the Edge Generation Module, and the IntraMux.
DPWMC is a signal inside the DPWM logic. It goes high at the Blanking A begin time, and low at the
Blanking A end time.
The Edge Gen module takes DPWMA and DPWMB from its own DPWM module, and the next one, and
uses them to generate edges for two outputs. For DPWM3, the DPWM0 is considered to be the next
DPWM. Each edge (rising and falling for DPWMA and DPWMB) has 8 options which can cause it.
The options are:
0 = DPWM(n) A Rising edge
1 = DPWM(n) A Falling edge
2 = DPWM(n) B Rising edge
3 = DPWM(n) B Falling edge
4 = DPWM(n+1) A Rising edge
5 = DPWM(n+1) A Falling edge
6 = DPWM(n+1) B Rising edge
7 = DPWM(n+1) B Falling edge
Where “n" is the numerical index of the DPWM module of interest. For example n=1 refers to DPWM1.
The Edge Gen is controlled by the DPWMEDGEGEN register. It also has an enable/disable bit.
The IntraMux is controlled by the Auto Config registers. Intra Mux is short for intra multiplexer. The
IntraMux takes signals from multiple DPWMs and from the Edge Gen and combines them logically to
generate DPWMA and DPWMB signals This is useful for topologies like phase-shifted full bridge,
especially when they are controlled with automatic mode switching. Of course, it can all be disabled, and
DPWMA and DPWMB will be driven as described in the sections above. If the Intra Mux is enabled, high
resolution must be disabled, and DPWM edge resolution goes down to 4 ns.
Here is a drawing of the Edge Gen/Intra Mux:
Here is a list of the IntraMux modes for DPWMA:
0 = DPWMA(n) pass through (default)
1 = Edge-gen output, DPWMA(n)
2 = DPWNC(n)
3 = DPWMB(n) (Crossover)
4 = DPWMA(n+1)
Copyright © 2012, Texas Instruments Incorporated Functional Overview 45
Submit Documentation Feedback
Product Folder Link(s): UCD3138
UCD3138
SLUSAP2B –MARCH 2012–REVISED JULY 2012 www.ti.com
5 = DPWMB(n+1)
6 = DPWMC(n+1)
7 = DPWMC(n+2)
8 = DPWMC(n+3)
and for DPWMB:
0 = DPWMB(n) pass through (default)
1 = Edge-gen output, DPWMB(n)
2 = DPWNC(n)
3 = DPWMA(n) (Crossover)
4 = DPWMA(n+1)
5 = DPWMB(n+1)
6 = DPWMC(n+1)
7 = DPWMC(n+2)
8 = DPWMC(n+3)
The DPWM number wraps around just like the Edge Gen unit. For DPWM3 the following definitions apply:
DPWM(n) DPWM3
DPWM(n+1) DPWM0
DPWM(n+2) DPWM1
DPWM(n+3) DPWM2
4.14 Filter
The UCD3138 filter is a PID filter with many enhancements for power supply control. Some of its features
include:
• Traditional PID Architecture
• Programmable non-linear limits for automated modification of filter coefficients based on received
EADC error
• Multiple coefficient sets fully configurable by firmware
• Full 24-bit precision throughout filter calculations
• Programmable clamps on integrator branch and filter output
• Ability to load values into internal filter registers while system is running
• Ability to stall calculations on any of the individual filter branches
• Ability to turn off calculations on any of the individual filter branches
• Duty cycle, resonant period, or phase shift generation based on filter output.
• Flux balancing
• Voltage feed forward
46 Functional Overview Copyright © 2012, Texas Instruments Incorporated
Submit Documentation Feedback
Product Folder Link(s): UCD3138
P
I 26
D
24
All are S0.23
24 +
24
Saturate Yn
S2.23 S0.23
24
Shifter
S0.23
24
Yn Scale
Clamp
S0.23
24
Filter Yn
Clamp High
Filter Yn
Clamp Low
Filter Yn
X
24
24
24
Ki_yn reg
Kp Coef
Xn-1 Reg
Xn 16
24
<>
9
9
16
24 24
24
24
24
24
Clamp
Kd yn_reg
Kd alpha
9
16
9 24
24
24
24
P
I
D
Limit Comparator
PID Filter Branch Stages
Ki High
EADC_DATA
9
9 9
9
24
32
Ki Coef
Kd coef
Limit 5
9
9
Limit 6
…..
Limit 0
Coefficient
select
Ki Low
Optional
Selected
by
KI_ADDER_
MODE
Clamp
X
X
X
+
-
+
+
Round
X X +1 n n –
UCD3138
www.ti.com SLUSAP2B –MARCH 2012–REVISED JULY 2012
Here is the first section of the Filter :
The filter input, Xn, generally comes from a front end. Then there are three branches, P, I. and D. Note
that the D branch also has a pole, Kd Alpha. Clamps are provided both on the I branch and on the D
alpha pole.
The filter also supports a nonlinear mode, where up to 7 different sets of coefficients can be selected
depending on the magnitude of the error input Xn. This can be used to increase the filter gain for higher
errors to improve transient response.
Here is the output section of the filter (S0.23 means that there is 1 sign bit, 0 integer bits and 23 fractional
bits).:
This section combines the P, I, and D sections, and provides for saturation, scaling, and clamping.
Copyright © 2012, Texas Instruments Incorporated Functional Overview 47
Submit Documentation Feedback
Product Folder Link(s): UCD3138
18
24
14
38 18
KCompx
DPWMx Period
Loop_VFF
Filter YN (Duty %) Filter Duty
S0.23
14.0
14.0
14.0
14.0
S14.23
Resonant Duty 14.0
Round to
18 bits,
Clamp to
Positive
Clamp
Filter Output
Clamp High
Filter Output
Clamp Low
X 14.4 14.4
OUTPUT_MULT_SEL
14
Bits [17:4]
Filter Period
24
14
38 18
KCompx
DPWMx Period
Filter YN
S0.23
14.0 14.0
14.0
S14.23
Round to
18 bits,
Clamp to
Positive
Truncate
X low 4 bits
14.0
PERIOD_MULT_SEL
14.4
UCD3138
SLUSAP2B –MARCH 2012–REVISED JULY 2012 www.ti.com
There is a final section for the filter, which permits its output to be matched to the DPWM:
This permits the filter output to be multiplied by a variety of correction factors to match the DPWM Period,
to provide for Voltage Feed Forward, or for other purposes. After this, there is another clamp. For resonant
mode, the filter can be used to generate both period and duty cycle.
4.14.1 Loop Multiplexer
The Loop Mux controls interconnections between the filters, front ends, and DPWMs. Any filter, front end,
and DPWM can be combined with each other in many configurations.
It also controls the following connections:
• DPWM to Front End
• Front End DAC control from Filters or Constant Current/Constant Power Module
• Filter Special Coefficients and Feed Forward
• DPWM synchronization
• Filter to DPWM
The following control modules are configured in the Loop Mux:
• Constant Power/Constant Current
• Cycle Adjustment (Current and flux balancing)
• Global Period
• Light Load (Burst Mode)
• Analog Peak Current Mode
48 Functional Overview Copyright © 2012, Texas Instruments Incorporated
Submit Documentation Feedback
Product Folder Link(s): UCD3138
FAULT - CBC
FAULT - AB
FAULT -A
DCOMP– 4X
EXT GPIO– 4X
ACOMP– 7X
FAULT -B
FAULT MODULE
FAULT MODULE
FAULT MODULE
CYCLE BY CYCLE
AB FLAG
AB FLAG
A FLAG
B FLAG
FAULT MUX
ALL_FAULT_EN DPWM_EN
DPWM
CBC_FAULT_EN
CBC_PWM_AB_EN
FAULT MODULE
ANALOG PCM
Bit20 in DPWMCTRL0
Bit30 in DPWMFLTCTRL
Bit 31 in DPWMFLTCTRL Bit0 in DPWMCTRL0
DISABLE PWM A AND B
DISABLE PWM A AND B
DISABLE PWM A ONLY
DISABLE PWM B ONLY
UCD3138
www.ti.com SLUSAP2B –MARCH 2012–REVISED JULY 2012
4.14.2 Fault Multiplexer
In order to allow a flexible way of mapping several fault triggering sources to all the DPWMs channels, the
UCD3138 provides an extensive array of multiplexers that are united under the name Fault Mux module.
The Fault Mux Module supports the following types of mapping between all the sources of fault and all
different fault response mechanism inside each DPWM module.
• Many fault sources mapped to a single fault response mechanism. For instance an analog comparator
in charge of over voltage protection, a digital comparator in charge of over current protection and an
external digital fault pin can be all mapped to a fault-A signal connected to a single FAULT MODULE
and shut down DPWM1-A.
• A single fault source can be mapped to many fault response mechanisms inside many DPWM
modules. For instance an analog comparator in charge of over current protection can be mapped to
DPWM-0 through DPWM-3 by way of several fault modules.
• Many fault sources can be mapped to many fault modules inside many DPWM modules.
Copyright © 2012, Texas Instruments Incorporated Functional Overview 49
Submit Documentation Feedback
Product Folder Link(s): UCD3138
CYCLE BY CYCLE
FAULT - CBC CLIM
FAULT MODULE
FAULT IN FAULT FLAG
MAX COUNT
FAULT EN
DPWM EN
UCD3138
SLUSAP2B –MARCH 2012–REVISED JULY 2012 www.ti.com
The Fault Mux Module provides a multitude of fault protection functions within the UCD3138 high-speed
loop (Front End Control, Filter, DPWM and Loop Mux modules). The Fault Mux Module allows highly
configurable fault generation based on digital comparators, high-speed analog comparators and external
fault pins. Each of the fault inputs to the DPWM modules can be configured to one or any combination of
the fault events provided in the Fault Mux Module.
Each one of the DPWM engines has four fault modules. The modules are called CBC fault module, AB
fault module, A fault module and B fault module.
The internal circuitry in all the four fault modules is identical, and the difference between the modules is
limited to the way the modules are attached to the DPWMs.
All fault modules provide immediate fault detection but only once per DPWM switching cycle. Each one of
the fault modules own a separate max_count and the fault flag will be set only if sequential cycle-by-cycle
faults count exceeds max_count.
Once the fault flag is set DPWMs need to be disabled by DPWM_EN going low in order to clear the fault
flags. Please note, all four Fault Modules share the same DPWM_EN control, all fault flags (output of Fault
Modules) will be cleared simultaneously.
All four Fault Modules share the same global FAULT_EN as well. Therefore a specific Fault Module
cannot be enabled/ disabled separately.
Unlike Fault Modules, only one Cycle by Cycle block is available in each DPWM module.
The Cycle by Cycle block works in conjunction with CBC Fault Module and enables DPWM reaction to
signals arriving from Analog Peak current mode (PCM) module.
The Fault Mux Module supports the following basic functions:
• 4 digital comparators with programmable thresholds and fault generation
• Configuration for 7 high speed analog comparators with programmable thresholds and fault generation
• External GPIO detection control with programmable fault generation
• Configurable DPWM fault generation for DPWM Current Limit Fault, DPWM Over-Voltage Detection
Fault, DPWM A External Fault, DPWM B External Fault and DPWM IDE Flag
• Clock Failure Detection for High and Low Frequency Oscillator blocks
• Discontinuous Conduction Mode Detection
50 Functional Overview Copyright © 2012, Texas Instruments Incorporated
Submit Documentation Feedback
Product Folder Link(s): UCD3138
Digital Comparator 0
Control
Digital Comparator 1
Control
Digital Comparator 2
Control
Digital Comparator 3
Control
Front End
Control 0
Front End
Control 1
Front End
Control 2
Analog
Comparator 0
Analog Comparator 0
Control
Analog
Comparator 1
Analog Comparator 1
Control
Analog
Comparator 2
Analog Comparator 2
Control
Analog
Comparator 3
Analog Comparator 3
Control
Analog
Comparator 4
Analog Comparator 4
Control
Analog
Comparator 5
Analog Comparator 5
Control
Analog
Comparator 6
Analog Comparator 6
Control
External GPIO
Detection
fault[2:0]
DPWM 0 DPWM 1 DPWM 2 DPWM 3
DPWM 0
Fault Control
DPWM 1
Fault Control
DPWM 2
Fault Control
DPWM 3
Fault Control
Analog Comparator
Automated Ramp
DCM Detection
HFO/LFO
Fail Detect
UCD3138
www.ti.com SLUSAP2B –MARCH 2012–REVISED JULY 2012
Figure 4-5. Fault Mux Block Diagram
4.15 Communication Ports
4.15.1 SCI (UART) Serial Communication Interface
A maximum of two independent Serial Communication Interface (SCI) or Universal Asynchronous
Receiver/Transmitter pre-scaler (UART) interfaces are included within the device for asynchronous startstop
serial data communication (see the pin out sections for details) Each interface has a 24 bit for
supporting programmable baud rates and has programmable data word and stop bit options. Half or full
duplex operation is configurable through register bits. A loop back feature can also be setup for firmware
verification. Both SCI-TX and SCI-RX pin sets can be used as GPIO pins when the peripheral is not being
used.
4.15.2 PMBUS
The PMBus Interface supports independent master and slave modes controlled directly by firmware
through a processor bus interface. Individual control and status registers enable firmware to send or
receive I2C, SMBus or PMBus messages in any of the accepted protocols, in accordance with the I2C
Specification, SMBus Specification (Version 2.0) and the PMBUS Power System Management Protocol
Specification.
The PMBus interface is controlled through a processor bus interface, utilizing a 32-bit data bus and 6-bit
address bus. The PMBus interface is connected to the expansion bus, which features 4 byte write
enables, a peripheral select dedicated for the PMBus interface, separated 32-bit data buses for reading
and writing of data and active-low write and output enable control signals. In addition, the PMBus Interface
connects directly to the I2C/SMBus/PMBus Clock, Data, Alert, and Control signals.
Example: PMBus Address Decode via ADC12 Reading
The user can allocate 2 pins of the 12-bit ADC input channels, AD_00 and AD_01, for PMBus address
decoding. At power-up the device applies IBIAS to each address detect pin and the voltage on that pin is
captured by the internal 12-bit ADC.
Where bin(VAD0x) is the address bin for one of 12 address as shown in Figure 4-6.
Copyright © 2012, Texas Instruments Incorporated Functional Overview 51
Submit Documentation Feedback
Product Folder Link(s): UCD3138
Vdd
IBIAS
To ADC Mux
On/Off Control
AD00,
AD01
pin
Resistor to
set PMBus
Address
UCD3138
SLUSAP2B –MARCH 2012–REVISED JULY 2012 www.ti.com
Figure 4-6. PMBus Address Detection Method
4.15.3 General Purpose ADC12
The ADC12 is a 12 bit, high speed analog to digital converter, equipped with the following options:
• Typical conversion speed of 267 ksps
• Conversions can consist from 1 to 16 ADC channel conversions in any desired sequence
• Post conversion averaging capability, ranging from 4X, 8X, 16X or 32X samples
• Configurable triggering for ADC conversions from the following sources: firmware, DPWM rising edge,
ADC_EXT_TRIG pin or Analog Comparator results
• Interrupt capability to embedded processor at completion of ADC conversion
• Six digital comparators on the first 6 channels of the conversion sequence using either raw ADC data
or averaged ADC data
• Two 10 μA current sources for excitation of PMBus addressing resistors
• Dual sample and hold for accurate power measurement
• Internal temperature sensor for temperature protection and monitoring
The control module ( ADC12 Contol Block Diagram) contains the control and conversion logic for autosequencing
a series of conversions. The sequencing is fully configurable for any combination of 16
possible ADC channels through an analog multiplexer embedded in the ADC12 block. Once converted,
the selected channel value is stored in the result register associated with the sequence number. Input
channels can be sampled in any desired order or programmed to repeat conversions on the same channel
multiple times during a conversion sequence. Selected channel conversions are also stored in the result
registers in order of conversion, where the result 0 register is the first conversion of a 16-channel
sequence and result 15 register is the last conversion of a 16-channel sequence. The number of channels
converted in a sequence can vary from 1 to 16.
Unlike EADC0 through EADC2, which are primarily designed for closing high speed compensation loops,
the ADC12 is not usually used for loop compensation purposes. The EADC converters have a
substantially faster conversion rate, thus making them more attractive for closed loop control. The ADC12
features make it best suited for monitoring and detection of currents, voltages, temperatures and faults.
Please see the Typical Characteristics plots for the temperature variation associated with this function.
52 Functional Overview Copyright © 2012, Texas Instruments Incorporated
Submit Documentation Feedback
Product Folder Link(s): UCD3138
ADC
Channels
S/H
12-bit SAR
ADC
ADC12 Block
ADC12
Control
ADC Channel
ADC
Averaging
Digital
Comparators
DPWM
Modules
ADC12 Registers
Analog
Comparators
ADC External Trigger (from pin)
UCD3138
www.ti.com SLUSAP2B –MARCH 2012–REVISED JULY 2012
Figure 4-7. ADC12 Control Block Diagram
4.15.4 Timers
External to the Digital Power Peripherals there are 3 different types of timers in UCD3138. They are the
24-bit timer, 16-bit timer and the Watchdog timer
4.15.4.1 24-bit PWM Timer
There is one 24 bit counter PWM timer which runs off the Interface Clock and can further be divided down
by an 8-bit pre-scalar to generate a slower PWM time period. The timer has two compare registers (Data
Registers) for generating the PWM set/unset events. Additionally, the timer has a shadow register (Data
Buffer register) which can be used to store CPU updates of the compare events while still using the timer.
The selected shadow register update mode happens after the compare event matches.
The two capture pins TCMP0 and TCMP1 are inputs for recording a capture event. A capture event can
be set either to rising, falling, or both edges of the capture pin. Upon this event, the counter value is stored
in the corresponding capture data register.
The counter reset can be configured to happen on a counter roll over, a compare equal event, or by
software controlled register. Five Interrupts from the PWM timer can be set, which are the counter rollover
event (overflow), either capture event 0 or 1, or the two comparison match events. Each interrupt can be
disabled or enabled.
Upon an event comparison on only the second event, the TCMP pin can be configured to set, clear, toggle
or have no action at the output. The value of PWM pin output can be read for status or simply configured
as general purpose I/O for reading the value of the input at the pin. The first compare event can only be
used as an interrupt.
Copyright © 2012, Texas Instruments Incorporated Functional Overview 53
Submit Documentation Feedback
Product Folder Link(s): UCD3138
UCD3138
SLUSAP2B –MARCH 2012–REVISED JULY 2012 www.ti.com
4.15.4.2 16-Bit PWM Timers
There are four 16 bit counter PWM timers which run off the Interface Clock and can further be divided
down by a 8-bit pre-scaler to generate slower PWM time periods. Each timer has two compare registers
(Data Registers) for generating the PWM set/unset events. Additionally, each timer has a shadow register
(Data Buffer register) which can be used to store CPU updates of compare events while still using the
timer. The selected shadow register update mode happens after the compare event matches.
The counter reset can be configured to happen on a counter roll over, a compare equal event, or by a
software controlled register. Interrupts from the PWM timer can be set due to the counter rollover event
(overflow) or by the two comparison match events. Each comparison match and the overflow interrupts
can be disabled or enabled.
Upon an event comparison, the PWM pin can be configured to set, clear, toggle or have no action at the
output. The value of PWM pin output can be read for status or simply configured as General Purpose I/O
for reading the value of the input at the pin.
4.15.4.3 Watchdog Timer
A watchdog timer is provided on the device for ensuring proper firmware loop execution. The timer is
clocked off of a separate low speed oscillator source. If the timer is allowed to expire, a reset condition is
issued to the ARM processor. The watchdog is reset by a simple CPU write bit to the watchdog key
register by the firmware routine. On device power-up the watchdog is disabled. Yet after it is enabled, the
watchdog cannot be disabled by firmware. Only a device reset can put this bit back to the default disabled
state. A half timer flag is also provided for status monitoring of the watchdog.
4.16 Miscellaneous Analog
The Miscellaneous Analog Control (MAC) Registers are a catch-all of registers that control and monitor a
wide variety of functions. These functions include device supervisory features such as Brown-Out and
power saving configuration, general purpose input/output configuration and interfacing, internal
temperature sensor control and current sharing control.
The MAC module also provides trim signals to the oscillator and AFE blocks. These controls are usually
used at the time of trimming at manufacturing; therefore this document will not cover these trim controls.
The MAC registers and peripherals are all available in the UCD3138 (64 pin version). Other UCD3138
devices may have reduced resources. See the device pin out description for details.
4.17 Package ID Information
Package ID register includes information regarding the package type of the device and can be read by
firmware for reporting through PMBus or for other package sensitive decisions.
BIT NUMBER 1:0
Bit Name PKG_ID
Access R/W
Default 0 – UCD3138RGC, 1 – UCD3138RHA
4.18 Brownout
Brownout function is used to determine if the device supply voltage is lower than a threshold voltage, a
condition that may be considered unsafe for proper operation of the device.
The brownout threshold is higher than the reset threshold voltage; therefore, when the supply voltage is
lower than brownout threshold, it still does not necessarily trigger a device reset.
The brownout interrupt flag can be polled or alternatively can trigger an interrupt to service such case by
an interrupt service routine. Please see the Power On Reset (POR) / Brown Out Reset (BOR) section.
54 Functional Overview Copyright © 2012, Texas Instruments Incorporated
Submit Documentation Feedback
Product Folder Link(s): UCD3138
UCD3138
www.ti.com SLUSAP2B –MARCH 2012–REVISED JULY 2012
4.19 Global I/O
Up to 30 pins in UCD3138 can be configured to serve as a general purpose input or output pin (GPIO).
This includes all digital input or output pins except for the RESET pin.
The pins that cannot be configured as GPIO pins are the supply pins, ground pins, ADC-12 analog input
pins, EADC analog input pins and the RESET pin.
There are two ways to configure and use the digital pins as GPIO pins:
1. Through the centralized Global I/O control registers.
2. Through the distributed control registers in the specific peripheral that shares it pins with the standard
GPIO functionality.
The Global I/O registers offer full control of:
1. Configuring each pin as a GPIO.
2. Setting each pin as input or output.
3. Reading the pin’s logic state, if it is configured as an input pin.
4. Setting the logic state of the pin, if it is configured as an output pin.
5. Connecting pin/pins to high rail through internal pull up resistors.
The Global I/O registers include Global I/O EN register, Global I/O OE Register, Global I/O Open Drain
Control Register, Global I/O Value Register and Global I/O Read Register.
The following is showing the format of Global I/O EN Register (GLBIOEN) as an example:
BIT NUMBER 29:0
Bit Name GLOBAL_IO_EN
Access R/W
Default 00_0000_0000_0000_0000_0000_0000_0000
Bits 29-0: GLOBAL_IO_EN – This register enables the global control of digital I/O pins
0 = Control of IO is done by the functional block assigned to the IO (Default)
1 = Control of IO is done by Global IO registers.
PIN NUMBER
BIT PIN_NAME
UCD3138-64 PIN UCD3138-40 PIN
29 FAULT[3] 43 NA
28 ADC_EXT_TRIG 12, 26 8
27 TCK 37 21
26 TDO 38 20
25 TMS 40 24
24 TDI 39 23
23 SCI_TX[1] 29 NA
22 SCI_TX[0] 14 22
21 SCI_RX[1] 30 NA
20 SCI_RX[0] 13 23
19 TMR_CAP 12, 26, 41 8, 21
18 TMR_PWM[1] 32 NA
17 TMR_PWM[0] 12, 26, 31, 37 21
16 PMBUS-CLK 15 9
15 PMBUS-DATA 16 10
14 CONTROL 30 20
13 ALERT 29 19
12 EXT_INT 26, 34 NA
Copyright © 2012, Texas Instruments Incorporated Functional Overview 55
Submit Documentation Feedback
Product Folder Link(s): UCD3138
Temperature
Sensor
Ch14
ADC 12
Temp Cal
UCD3138
SLUSAP2B –MARCH 2012–REVISED JULY 2012 www.ti.com
PIN NUMBER
BIT PIN_NAME
UCD3138-64 PIN UCD3138-40 PIN
11 FAULT[2] 42 25
10 FAULT[1] 36 23
9 FAULT[0] 35, 39 22
8 SYNC 12, 26,37 8, 21
7 DPWM3B 24 18
6 DPWM3A 23 17
5 DPWM2B 22 16
4 DPWM2A 21 15
3 DPWM1B 20 14
2 DPWM1A 19 13
1 DPWM0B 18 12
0 DPWM0A 17 11
4.20 Temperature Sensor Control
Temperature sensor control register provides internal temperature sensor enabling and trimming
capabilities. The internal temperature sensor is disabled as default.
Figure 4-8. Internal Temp Sensor
Temperature sensor is calibrated at room temperature (25 °C) via a calibration register value.
The temperature sensor is measured using ADC12 (via Ch14). The temperature is then calculated using a
mathematical formula involving the calibration register (this effectively adds a delta to the ADC
measurement).
The temperature sensor can be enabled or disabled.
4.21 I/O Mux Control
In different packages of UCD3138 several I/O functions are multiplexed and routed toward a single
physical pin. I/O Mux Control register may be used in order to choose a single specific functionality that is
desired to be assigned to a physical device pin for your application.
56 Functional Overview Copyright © 2012, Texas Instruments Incorporated
Submit Documentation Feedback
Product Folder Link(s): UCD3138
EXT CAP
AD02
400 Ω
Digital
RSHARE
250 Ω
3.3 V
ISHARE
ADC12 and
CMP
ESD
ESD
3.2 kΩ 250 Ω
ESD
AD13
3.3V
SW2
SW1
SW3
3.3 V
ADC12 and
CMP
UCD3138
www.ti.com SLUSAP2B –MARCH 2012–REVISED JULY 2012
4.21.1 JTAG Use for I/O and JTAG Security
The UCD3138 provides a JTAG interface for debugging and for uploading data and programs. The pins
are multiplexed with other pins, and will not be available in certain topologies. For power supplies, other
debugging techniques (PMBus, UART, code instrumentation) are often superior to JTAG. Code
downloading is much faster via PMBus, or with a user boot program via UART. PMBus support is
available from TI. JTAG for debugging has limited support from TI’s Code Composer Studio. JTAG
parameter download may be supported by third parties.
4.22 Current Sharing Control
UCD3138 provides three separate modes of current sharing operation.
• Analog bus current sharing
• PWM bus current sharing
• Master/Slave current sharing
• AD02 has a special ESD protection mechanism that prevents the pin from pulling down the currentshare
bus if power is missing from the UCD3138
The simplified current sharing circuitry is shown in the drawing below:
Figure 4-9. Simplified Current Sharing Circuitry
CURRENT SHARING MODE FOR TEST ONLY, CS_MODE EN_SW1 EN_SW2 DPWM ALWAYS KEEP 00
Off or Slave Mode (3-state) 00 00 (default) 0 0 0
PWM Bus 00 01 1 0 ACTIVE
Off or Slave Mode (3-state) 00 10 0 0 0
Analog Bus or Master 00 11 0 1 0
Copyright © 2012, Texas Instruments Incorporated Functional Overview 57
Submit Documentation Feedback
Product Folder Link(s): UCD3138
UCD3138
SLUSAP2B –MARCH 2012–REVISED JULY 2012 www.ti.com
The period and the duty of 8-bit PWM current source and the state of the SW1 and SW2 switches can be
controlled through the current sharing control register (CSCTRL).
4.23 Temperature Reference
The temperature reference register (TEMPREF) provides the ADC12 count when ADC12 measures the
internal temperature sensor (channel 14) during the factory trim and calibration.
This information can be used by different periodic temperature compensation routines implemented in the
firmware. But it should not be overwritten by firmware, otherwise this factory written value will be lost.
58 Functional Overview Copyright © 2012, Texas Instruments Incorporated
Submit Documentation Feedback
Product Folder Link(s): UCD3138
2 .2 μF
1 .0 μF
BPCAP
DGND
V33D
UCD3138
www.ti.com SLUSAP2B –MARCH 2012–REVISED JULY 2012
5 IC Grounding and Layout Recommendations
• Two grounds are recommended: AGND (analog) and DGND (digital).
– AGND plane should be on a different layer than DGND, and right under the UCD3138 device.
– UCD3138 power pad should be tied to AGND plane by at least 4 vias
– AGND plane should be just large enough to connect to all required components.
– Power ground (PGND) can be independent or combined with DGND
– The power pad of the driver IC should be tied to DGND
• Both 3.3VD and 3.3VA should have a local 4.7μF capacitor placed as close as possible to the device
pins
• BPCAP decoupling (2.2 μF typically) MUST be connected to DGND
• All analog signal filter capacitors should be tied to AGND
– If the gate driver device, such as UCD27524 or UCD27511/7 driver is used, the filter capacitor for
the current sensing pin can be tied to DGND for easy layout
• All digital signals, such as GPIO, PMBus and PWM are referenced to DGND.
• The RESET pin capacitor (0.1μF) should be connected to either DGND or AGND locally. A 10kΩ pullup
resistor to 3.3V is recommended.
• All filter and decoupling capacitors should be placed close to UCD3138 as possible
– Resistor placement is less critical and can be moved a little further away
• The DGND and AGND net-short resistor MUST be placed right between one UCD3138’s DGND pin
and one AGND pin. Ground connections to the net short element should be made by a large via (or
multiple paralleled vias) for each terminal of the net-short element.
• If a gate driver device such as UCC27524 or UCC27511/7 is on the control card and there is a PGND
connection, a net-short resistor should be tied to the DGND plane and PGND plane by multiple vias. In
addition the net-short element should be close to the driver IC.
Copyright © 2012, Texas Instruments Incorporated IC Grounding and Layout Recommendations 59
Submit Documentation Feedback
Product Folder Link(s): UCD3138
UCD3138
SLUSAP2B –MARCH 2012–REVISED JULY 2012 www.ti.com
6 Tools and Documentation
The application firmware for UCD3138 is developed on Texas Instruments Code Composer Studio (CCS)
integrated development environment (v3.3 recommended).
Monitoring and Configuration of key device parameters and real time debug capabilities are offered
through Texas Instruments’ FUSION_DIGITAL_POWER_DESIGNER Graphical User Interface (GUI),
http://www.ti.com/tool/fusion_digital_power_designer.
The FUSION_DIGITAL_POWER_DESIGNER software application uses PMBus protocol to communicate
with the device over serial bus by way of a interface adaptor known as USB-TO-GPIO, available as an
EVM from Texas Instruments (http://www.ti.com/tool/usb-to-gpio).
The software application can also be used to program the devices, with a version of the tool known as
FUSION_MFR_GUI optimized for manufacturing environments (http://www.ti.com/tool/fusion_mfr_gui).
The FUSION_MFR_GUI tool supports multiple devices on a board, and includes built-in logging and
reporting capabilities.
In terms of reference documentation, the following 3 programmer’s manuals are available offering detailed
information regarding the application and usage of UCD3138 digital controller:
1. UCD3138 Digital Power Peripheral Programmer's Manual Key topics covered in this manual include:
– Digital Pulse Width Modulator (DPWM)
– Modes of Operation (Normal/Multi/Phase-shift/Resonant etc)
– Automatic Mode Switching
– DPWMC, Edge Generation & Intra-Mux
– Front End
– Analog Front End
– Error ADC or EADC
– Front End DAC
– Ramp Module
– Successive Approximation Register Module
– Filter
– Filter Math
– Loop Mux
– Analog Peak Current Mode
– Constant Current/Constant Power (CCCP)
– Automatic Cycle Adjustment
– Fault Mux
– Analog Comparators
– Digital Comparators
– Fault Pin functions
– DPWM Fault Action
– Ideal Diode Emulation (IDE), DCM Detection
– Oscillator Failure Detection
– Register Map for all of the above peripherals in UCD3138
2. UCD3138 Monitoring and Communications Programmer’s Manual
Key topics covered in this manual include:
– ADC12
– Control, Conversion, Sequencing & Averaging
– Digital Comparators
– Temperature Sensor
– PMBUS Addressing
– Dual Sample & Hold
– Miscellaneous Analog Controls (Current Sharing, Brown-Out, Clock-Gating)
– PMBUS Interface
– General Purpose Input Output (GPIO)
60 Tools and Documentation Copyright © 2012, Texas Instruments Incorporated
Submit Documentation Feedback
Product Folder Link(s): UCD3138
UCD3138
www.ti.com SLUSAP2B –MARCH 2012–REVISED JULY 2012
– Timer Modules
– PMBus
– Register Map for all of the above peripherals in UCD3138
3. UCD3138 ARM and Digital System Programmer’s Manual
Key topics covered in this manual include:
– Boot ROM & Boot Flash
– BootROM Function
– Memory Read/Write Functions
– Checksum Functions
– Flash Functions
– Avoiding Program Flash Lock-Up
– ARM7 Architecture
– Modes of Operation
– Hardware/Software Interrupts
– Instruction Set
– Dual State Inter-working (Thumb 16-bit Mode/ARM 32-bit Mode)
– Memory & System Module
– Address Decoder, DEC (Memory Mapping)
– Memory Controller (MMC)
– Central Interrupt Module
– Register Map for all of the above peripherals in UCD3138
In addition to the tools and documentation described above, for the most up to date information regarding
evaluation modules, reference application firmware and application notes/design tips, please visit
http://www.ti.com/product/ucd3138.
Copyright © 2012, Texas Instruments Incorporated Tools and Documentation 61
Submit Documentation Feedback
Product Folder Link(s): UCD3138
UCD3138
SLUSAP2B –MARCH 2012–REVISED JULY 2012 www.ti.com
7 References
1. UCD3138 Digital Power Peripherals Programmer’s Manual (Literature Number:SLUU995)
2. UCD3138 Monitoring & Communications Programmer’s Manual (Literature Number:SLUU996)
3. UCD3138 ARM and Digital System Programmer’s Manual (Literature Number:SLUU994)
4. Code Composer Studio Development Tools v3.3 – Getting Started Guide, (Literature Number:
SPRU509H)
5. ARM7TDMI-S Technical Reference Manual
6. System Management Bus (SMBus) Specification
7. PMBusTM Power System Management Prototcol Specification (1)
(1) PMBus is a trademark of SMIF, Inc.
62 References Copyright © 2012, Texas Instruments Incorporated
Submit Documentation Feedback
Product Folder Link(s): UCD3138
UCD3138
www.ti.com SLUSAP2B –MARCH 2012–REVISED JULY 2012
Revision History
NOTE: Page numbers for previous revisions may differ from page numbers in the current version.
Changes from Original (March 2012) to Revision A Page
• Added Production Data statement to footnote and removed "Product Preview" banner ........................... 6
Changes from Revision A (March 2012) to Revision B Page
• Added Feature bullets ............................................................................................................. 6
• Changed "Dual Edge Modulation" to "Triangular Modulation" in Features section ................................. 6
• Changed "265 ksps" to "267 ksps" in Features section ................................................................... 6
• Clarified number of UARTs in Feature section ............................................................................... 6
• Changed "FDPP" to "DDP" throughout. ....................................................................................... 7
• Changed Total GPIO pin count for the UCD3138 40-pin device from "17" to "18" in the Product Selection
Matrix table. .......................................................................................................................... 8
• Changed "VREG" to "BP18" in conditions statement for Electrical Characteristics table. ....................... 16
• Changed EAP – EAN Error voltage digital resolution MIN values for AFE=3, AFE=2, AFE=1, AFE=0 from
0.95, 1.90, 3.72, and 7.3 respectively; to, 0.8, 1.7, 3.55, and 6.90 respectively. ....................................... 16
• Changed "VREG" to "BP18" in conditions statement for Electrical Characteristics table. ....................... 17
• Changed conditions for VOL and VOH specs in the Electrical Characteristics table ................................. 17
• Added TWD spec to Electrical Characteristics table ...................................................................... 17
• Changed "VREG" to "BP18" in conditions statement for Electrical Characteristics table. ....................... 18
• Changed "PWM" to "DPWM" in DPWM Module. ............................................................................ 29
• Changed "PWMA" and "PWMB" to "DPWMA" and "DPWMB" in . ...................................................... 34
• Changed waveforms graphic for "Phase Shifted Full Bridge Example" for clarification .......................... 41
• Added text to section LLC Example .......................................................................................... 42
• Changed typical conversion speed from "268 ksps" to "267 ksps" in the General Purpose ADC12
section. .............................................................................................................................. 52
• Added package ID information for the UCD3138RGC and UCD3138RHA devices. ................................. 54
• Added bullet "AD02 has a special ESD protection mechanism that prevents the pin from pulling down
the current-share bus if power is missing from the UCD3138" to Current Sharing Control. ..................... 57
• Added sub-bullet "The power pad of the driver IC should be tied to DGND" and changed capacitor value
from "0.1 μF" to "4.7 μF" in IC Grounding and Layout Recommendations ........................................... 59
• Added "Tools and Documentation" section ................................................................................. 60
• Changed " Mechanical Data" section to "References" section ......................................................... 62
Copyright © 2012, Texas Instruments Incorporated References 63
Submit Documentation Feedback
Product Folder Link(s): UCD3138
PACKAGE OPTION ADDENDUM
www.ti.com 26-Jul-2012
Addendum-Page 1
PACKAGING INFORMATION
Orderable Device Status (1) Package Type Package
Drawing
Pins Package Qty Eco Plan (2) Lead/
Ball Finish
MSL Peak Temp (3) Samples
(Requires Login)
UCD3138RGCR ACTIVE VQFN RGC 64 2000 Green (RoHS
& no Sb/Br)
CU NIPDAU Level-3-260C-168 HR
UCD3138RGCT ACTIVE VQFN RGC 64 250 Green (RoHS
& no Sb/Br)
CU NIPDAU Level-3-260C-168 HR
UCD3138RHAR ACTIVE VQFN RHA 40 2500 Green (RoHS
& no Sb/Br)
CU NIPDAU Level-3-260C-168 HR
UCD3138RHAT ACTIVE VQFN RHA 40 250 Green (RoHS
& no Sb/Br)
CU NIPDAU Level-3-260C-168 HR
(1) The marketing status values are defined as follows:
ACTIVE: Product device recommended for new designs.
LIFEBUY: TI has announced that the device will be discontinued, and a lifetime-buy period is in effect.
NRND: Not recommended for new designs. Device is in production to support existing customers, but TI does not recommend using this part in a new design.
PREVIEW: Device has been announced but is not in production. Samples may or may not be available.
OBSOLETE: TI has discontinued the production of the device.
(2) Eco Plan - The planned eco-friendly classification: Pb-Free (RoHS), Pb-Free (RoHS Exempt), or Green (RoHS & no Sb/Br) - please check http://www.ti.com/productcontent for the latest availability
information and additional product content details.
TBD: The Pb-Free/Green conversion plan has not been defined.
Pb-Free (RoHS): TI's terms "Lead-Free" or "Pb-Free" mean semiconductor products that are compatible with the current RoHS requirements for all 6 substances, including the requirement that
lead not exceed 0.1% by weight in homogeneous materials. Where designed to be soldered at high temperatures, TI Pb-Free products are suitable for use in specified lead-free processes.
Pb-Free (RoHS Exempt): This component has a RoHS exemption for either 1) lead-based flip-chip solder bumps used between the die and package, or 2) lead-based die adhesive used between
the die and leadframe. The component is otherwise considered Pb-Free (RoHS compatible) as defined above.
Green (RoHS & no Sb/Br): TI defines "Green" to mean Pb-Free (RoHS compatible), and free of Bromine (Br) and Antimony (Sb) based flame retardants (Br or Sb do not exceed 0.1% by weight
in homogeneous material)
(3) MSL, Peak Temp. -- The Moisture Sensitivity Level rating according to the JEDEC industry standard classifications, and peak solder temperature.
Important Information and Disclaimer:The information provided on this page represents TI's knowledge and belief as of the date that it is provided. TI bases its knowledge and belief on information
provided by third parties, and makes no representation or warranty as to the accuracy of such information. Efforts are underway to better integrate information from third parties. TI has taken and
continues to take reasonable steps to provide representative and accurate information but may not have conducted destructive testing or chemical analysis on incoming materials and chemicals.
TI and TI suppliers consider certain information to be proprietary, and thus CAS numbers and other limited information may not be available for release.
In no event shall TI's liability arising out of such information exceed the total purchase price of the TI part(s) at issue in this document sold by TI to Customer on an annual basis.
TAPE AND REEL INFORMATION
*All dimensions are nominal
Device Package
Type
Package
Drawing
Pins SPQ Reel
Diameter
(mm)
Reel
Width
W1 (mm)
A0
(mm)
B0
(mm)
K0
(mm)
P1
(mm)
W
(mm)
Pin1
Quadrant
UCD3138RGCR VQFN RGC 64 2000 330.0 16.4 9.3 9.3 1.5 12.0 16.0 Q2
UCD3138RGCT VQFN RGC 64 250 180.0 16.4 9.3 9.3 1.5 12.0 16.0 Q2
UCD3138RHAR VQFN RHA 40 2500 330.0 16.4 6.3 6.3 1.5 12.0 16.0 Q2
UCD3138RHAT VQFN RHA 40 250 180.0 16.4 6.3 6.3 1.5 12.0 16.0 Q2
PACKAGE MATERIALS INFORMATION
www.ti.com 26-Jul-2012
Pack Materials-Page 1
*All dimensions are nominal
Device Package Type Package Drawing Pins SPQ Length (mm) Width (mm) Height (mm)
UCD3138RGCR VQFN RGC 64 2000 367.0 367.0 38.0
UCD3138RGCT VQFN RGC 64 250 210.0 185.0 35.0
UCD3138RHAR VQFN RHA 40 2500 367.0 367.0 38.0
UCD3138RHAT VQFN RHA 40 250 210.0 185.0 35.0
PACKAGE MATERIALS INFORMATION
www.ti.com 26-Jul-2012
Pack Materials-Page 2
IMPORTANT NOTICE
Texas Instruments Incorporated and its subsidiaries (TI) reserve the right to make corrections, enhancements, improvements and other
changes to its semiconductor products and services per JESD46C and to discontinue any product or service per JESD48B. Buyers should
obtain the latest relevant information before placing orders and should verify that such information is current and complete. All
semiconductor products (also referred to herein as “components”) are sold subject to TI’s terms and conditions of sale supplied at the time
of order acknowledgment.
TI warrants performance of its components to the specifications applicable at the time of sale, in accordance with the warranty in TI’s terms
and conditions of sale of semiconductor products. Testing and other quality control techniques are used to the extent TI deems necessary
to support this warranty. Except where mandated by applicable law, testing of all parameters of each component is not necessarily
performed.
TI assumes no liability for applications assistance or the design of Buyers’ products. Buyers are responsible for their products and
applications using TI components. To minimize the risks associated with Buyers’ products and applications, Buyers should provide
adequate design and operating safeguards.
TI does not warrant or represent that any license, either express or implied, is granted under any patent right, copyright, mask work right, or
other intellectual property right relating to any combination, machine, or process in which TI components or services are used. Information
published by TI regarding third-party products or services does not constitute a license to use such products or services or a warranty or
endorsement thereof. Use of such information may require a license from a third party under the patents or other intellectual property of the
third party, or a license from TI under the patents or other intellectual property of TI.
Reproduction of significant portions of TI information in TI data books or data sheets is permissible only if reproduction is without alteration
and is accompanied by all associated warranties, conditions, limitations, and notices. TI is not responsible or liable for such altered
documentation. Information of third parties may be subject to additional restrictions.
Resale of TI components or services with statements different from or beyond the parameters stated by TI for that component or service
voids all express and any implied warranties for the associated TI component or service and is an unfair and deceptive business practice.
TI is not responsible or liable for any such statements.
Buyer acknowledges and agrees that it is solely responsible for compliance with all legal, regulatory and safety-related requirements
concerning its products, and any use of TI components in its applications, notwithstanding any applications-related information or support
that may be provided by TI. Buyer represents and agrees that it has all the necessary expertise to create and implement safeguards which
anticipate dangerous consequences of failures, monitor failures and their consequences, lessen the likelihood of failures that might cause
harm and take appropriate remedial actions. Buyer will fully indemnify TI and its representatives against any damages arising out of the use
of any TI components in safety-critical applications.
In some cases, TI components may be promoted specifically to facilitate safety-related applications. With such components, TI’s goal is to
help enable customers to design and create their own end-product solutions that meet applicable functional safety standards and
requirements. Nonetheless, such components are subject to these terms.
No TI components are authorized for use in FDA Class III (or similar life-critical medical equipment) unless authorized officers of the parties
have executed a special agreement specifically governing such use.
Only those TI components which TI has specifically designated as military grade or “enhanced plastic” are designed and intended for use in
military/aerospace applications or environments. Buyer acknowledges and agrees that any military or aerospace use of TI components
which have not been so designated is solely at the Buyer's risk, and that Buyer is solely responsible for compliance with all legal and
regulatory requirements in connection with such use.
TI has specifically designated certain components which meet ISO/TS16949 requirements, mainly for automotive use. Components which
have not been so designated are neither designed nor intended for automotive use; and TI will not be responsible for any failure of such
components to meet such requirements.
Products Applications
Audio www.ti.com/audio Automotive and Transportation www.ti.com/automotive
Amplifiers amplifier.ti.com Communications and Telecom www.ti.com/communications
Data Converters dataconverter.ti.com Computers and Peripherals www.ti.com/computers
DLP® Products www.dlp.com Consumer Electronics www.ti.com/consumer-apps
DSP dsp.ti.com Energy and Lighting www.ti.com/energy
Clocks and Timers www.ti.com/clocks Industrial www.ti.com/industrial
Interface interface.ti.com Medical www.ti.com/medical
Logic logic.ti.com Security www.ti.com/security
Power Mgmt power.ti.com Space, Avionics and Defense www.ti.com/space-avionics-defense
Microcontrollers microcontroller.ti.com Video and Imaging www.ti.com/video
RFID www.ti-rfid.com
OMAP Mobile Processors www.ti.com/omap TI E2E Community e2e.ti.com
Wireless Connectivity www.ti.com/wirelessconnectivity
Mailing Address: Texas Instruments, Post Office Box 655303, Dallas, Texas 75265
Copyright © 2012, Texas Instruments Incorporated
CLASSIFICATION PRODUCT SPECIFICATION No.
DS-13xx-2400-102
REV.
3.40
SUBJECT CLASS 1 or 2 BLUETOOTH MODULE PAGE 1 of 57
CUSTOMER’S CODE
PAN13XX Core Specification
PANASONIC’S CODE
See Chapter 28. Ordering Information DATE 18.07.2012
Power Electronics R&D Center
Wireless Connectivity
Panasonic Industrial Devices Europe GmbH
APPROVED
CHECKED
DESIGNED
Specification for Production
Panasonic Industrial Devices Europe GmbH
Zeppelinstrasse 19
21337 Lüneburg
Applicant / Manufacturer
Hardware
Germany
Not applikable
Applicant / Manufacturer
Software
Software Version
Not applikable
Contents
Approval for Mass Production
Customer
Bluetooth QDL ID
Qualified Design Listing (QDL) ID: B019784
As Controller Sub-System Listing for PAN13xx Series.
By purchase of any products described in this document the customer accepts the document's validity and declares their agreement and understanding of its contents and recommendations. Panasonic reserves the right to make changes as required without notification.
CLASSIFICATION PRODUCT SPECIFICATION No.
DS-13xx-2400-102
REV.
3.40
SUBJECT CLASS 1 or 2 BLUETOOTH MODULE PAGE 2 of 57
CUSTOMER’S CODE
PAN13XX Core Specification
PANASONIC’S CODE
See Chapter 28. Ordering Information DATE 18.07.2012
PANASONIC INDUSTRIAL DEVICES EUROPE GMBH www.pedeu.pansonic.de
TABLE OF CONTENTS
1 Scope of this Document..................................................................................................5
1.1 New PAN1315A, PAN1325A.................................................................................5
2 Key Features...................................................................................................................6
2.1 Software Block Diagram........................................................................................6
3 Applications for the Module.............................................................................................7
4 Description for the Module..............................................................................................7
5 Detailed Description........................................................................................................8
5.1 Terminal Layout.....................................................................................................8
5.1.1 5.1.1. Terminal Layout PAN131x without antenna...................................8
5.1.2 5.1.2. Terminal Layout PAN132x with antenna........................................9
5.2 Pin Description.....................................................................................................10
5.3 Device Power Supply...........................................................................................11
5.4 Clock Inputs.........................................................................................................12
6 Bluetooth Features........................................................................................................12
7 Block Diagram...............................................................................................................13
8 Test Conditions.............................................................................................................14
9 General Device Requirements and Operation..............................................................14
9.1 Absolute Maximum Ratings.................................................................................14
9.2 Recommended Operating Conditions..................................................................15
9.3 Current Consumption...........................................................................................15
9.4 General Electrical Characteristics........................................................................16
9.5 nSHUTD Requirements.......................................................................................16
9.6 External Digital Slow Clock Requirements (–20°C to +70°C)..............................16
10 Host Controller Interface...............................................................................................17
11 Audio/Voice Codec Interface.........................................................................................18
11.1 PCM Hardware Interface.....................................................................................18
11.2 Data Format.........................................................................................................18
11.3 Frame Idle Period................................................................................................19
11.4 Clock-Edge Operation.........................................................................................20
11.5 Two-Channel PCM Bus Example........................................................................20
11.6 Audio Encoding....................................................................................................20
11.7 Improved Algorithm For Lost Packets..................................................................21
11.8 Bluetooth/PCM Clock Mismatch Handling...........................................................21
11.9 Bluetooth Inter-IC Sound (I2S)............................................................................21
11.10Current Consumption for Different Bluetooth Scenarios......................................22
12 Bluetooth RF Performance............................................................................................22
13 Soldering Temperature-Time Profile (for reflow soldering)...........................................25
13.1 For lead solder.....................................................................................................25
13.2 For leadfree solder...............................................................................................26
CLASSIFICATION PRODUCT SPECIFICATION No.
DS-13xx-2400-102
REV.
3.40
SUBJECT CLASS 1 or 2 BLUETOOTH MODULE PAGE 3 of 57
CUSTOMER’S CODE
PAN13XX Core Specification
PANASONIC’S CODE
See Chapter 28. Ordering Information DATE 18.07.2012
PANASONIC INDUSTRIAL DEVICES EUROPE GMBH www.pedeu.pansonic.de
14 Module Dimension........................................................................................................27
14.1 Module Dimensions PAN131X without Antenna..................................................27
14.2 Module Dimensions PAN132X with Antenna.......................................................28
15 Footprint of the Module.................................................................................................29
15.1 Footprint PAN131x without antenna....................................................................29
15.2 Footprint PAN132x with antenna.........................................................................30
16 Labeling Drawing..........................................................................................................31
17 Mechanical Requirements.............................................................................................31
18 Recommended Foot Pattern.........................................................................................32
18.1 recommended foot pattern PAN131x without antenna........................................32
18.2 recommended foot pattern PAN132x with antenna.............................................33
19 Layout Recommendations with Antenna (PAN132x)....................................................34
20 Bluetooth LE (LOW ENERGY) PAN1316/26................................................................34
20.1 Network Topology................................................................................................34
20.2 module features...................................................................................................35
20.3 Current consumption for different LE scenarios..................................................36
21 ANT PAN1317/27..........................................................................................................36
21.1 Network topology.................................................................................................36
21.2 module features..................................................................................................37
21.3 ANT Current consumption...................................................................................37
22 Triple mode (BR/EDR + Bluetooth low energy + ANT) PAN1323................................38
22.1 Triple Mode Current consumption.......................................................................38
23 Development of Applications.........................................................................................39
23.1 Tools to be needed..............................................................................................39
24 List of Profiles...............................................................................................................40
25 Reliability Tests.............................................................................................................40
26 Cautions........................................................................................................................41
26.1 Design Notes.......................................................................................................41
26.2 Installation Notes.................................................................................................41
26.3 Usage Conditions Notes......................................................................................42
26.4 Storage Notes......................................................................................................42
26.5 Safety Cautions...................................................................................................43
26.6 Other cautions.....................................................................................................43
27 Packaging.....................................................................................................................44
27.1 Packaging of PAN131x without antenna.............................................................44
27.2 Packaging for PAN132x with antenna.................................................................47
28 Ordering Information.....................................................................................................48
29 RoHS Declaration.........................................................................................................49
30 Data Sheet Status.........................................................................................................49
31 History for this Document..............................................................................................50
32 Related Documents.......................................................................................................50
CLASSIFICATION PRODUCT SPECIFICATION No.
DS-13xx-2400-102
REV.
3.40
SUBJECT CLASS 1 or 2 BLUETOOTH MODULE PAGE 4 of 57
CUSTOMER’S CODE
PAN13XX Core Specification
PANASONIC’S CODE
See Chapter 28. Ordering Information DATE 18.07.2012
PANASONIC INDUSTRIAL DEVICES EUROPE GMBH www.pedeu.pansonic.de
33 General Information......................................................................................................52
34 Regulatory Information..................................................................................................52
34.1 FCC for US..........................................................................................................52
34.1.1 FCC Notice.............................................................................................52
34.1.2 Caution...................................................................................................53
34.1.3 Labeling Requirements..........................................................................53
34.1.4 Antenna Warning....................................................................................53
34.1.5 Approved Antenna List...........................................................................53
34.1.6 RF Exposure PAN13xx..........................................................................54
34.2 Industry Canada Certification..............................................................................54
34.3 European R&TTE Declaration of Conformity.......................................................54
34.4 NCC for Taiwan...................................................................................................56
34.4.1 Labeling Requirements..........................................................................56
34.4.2 NCC Statement......................................................................................56
34.5 Bluetooth SIG Statement.....................................................................................56
35 Life Support Policy........................................................................................................56
CLASSIFICATION PRODUCT SPECIFICATION No.
DS-13xx-2400-102
REV.
3.40
SUBJECT CLASS 1 or 2 BLUETOOTH MODULE PAGE 5 of 57
CUSTOMER’S CODE
PAN13XX Core Specification
PANASONIC’S CODE
See Chapter 28. Ordering Information DATE 18.07.2012
PANASONIC INDUSTRIAL DEVICES EUROPE GMBH www.pedeu.pansonic.de
1
SCOPE OF THIS DOCUMENT
This product specification describes Panasonic’s HCI, Class 1.5 , TI based, Bluetooth®1 modules, series number 13xx.
For detailed family overview that includes part numbers see Chapter 28, Ordering Information.
Non-antenna versions will be refered to as PAN131x, versions with antenna will be refered to as PAN132x in this document.
Fore information and features on Bluetooth Low Energy 4.0 refer to Chapter 19, for information on ANT refer to Chapter 21.
1.1
NEW PAN1315A, PAN1325A
The PAN1315A/1325A Series is based on Texas Instruments’ NEW CC2560A controller. A ROM update from Texas Instruments to the CC2560 IC has allowed Panasonic to improve PAN1315/1325 Series. The NEW PAN1315A/1325A Series Modules has increased power and system efficiency resulting from reduced initialization script size, start-up time and decreased system memory requirements.
Compatibility:
PAN1315, PAN1315A, PAN1316 and PAN1317 are 100% footprint compatible
PAN1325, PAN1325A, PAN1326 and PAN1327 are 100% footprint compatible
As an updated initialization script resident on the application microcontroller is required for modules based on the CC2560A, compatibility between the PAN1315/PAN1325 and PAN1315A/PAN1325A is dependant on the Bluetooth stack. Stacks are available that will operate with all PAN1315/1325 variations.
BT-Stack solutions provided by software development partners are available for most processors, including linux based host systems..
For detailed family overview that includes part numbers see Chapter 28 Ordering Information.
Contact your stack provider or local Panasonic sales company for currently available Bluetooth Profiles.
1 Bluetooth is a registered trademark of the Bluetooth Special Interest Group.
CLASSIFICATION PRODUCT SPECIFICATION No.
DS-13xx-2400-102
REV.
3.40
SUBJECT CLASS 1 or 2 BLUETOOTH MODULE PAGE 6 of 57
CUSTOMER’S CODE
PAN13XX Core Specification
PANASONIC’S CODE
See Chapter 28. Ordering Information DATE 18.07.2012
PANASONIC INDUSTRIAL DEVICES EUROPE GMBH www.pedeu.pansonic.de
2
KEY FEATURES
•
Bluetooth specification v2.1 + EDR (Enhanced Data Rate)
•
Surface mount type 6.5(9.5 w. Ant.) x 9.0 x 1.8 mm³
•
Up to 10.5dBm Tx power (typical) with transmit power control
•
High sensitivity (-93 dBm typ.)
•
Texas Instrument’s CC256X BlueLink 7.0 inside
•
Fast Connection Setup
•
Extended SCO Link
•
Supports convenient direct connection to battery (2.2-4.8 V), or connect to DC/DC (1.7-1.98 V) for improved power efficiency
•
Internal crystal oscillator (26MHz)
•
Fully shielded for immunity
•
Full Bluetooth data rate up to 2,178kbps asymmetric
•
Support for Bluetooth power saving modes (Sniff, Hold)
•
Support for very low-power modes (deep sleep and power down)
•
Optional support for ultra-low-power mode. Standby with Battery-Backup
•
PCM Interface Master / Slave supporting 13 or 16 bit linear, 8 bit μ-law or A-law Codecs and CVSD transcoders on up to 3 SCO channels
•
Full 8- to 128-bit encryption
•
UART, I²C and PCM Interface
•
IO operating voltage = 1.8 V nominal
•
3 Channel ADC and 1 Channel DAC
•
Bluetooth profiles such as SPP, A2DP and others are available. Refer to Panasonic’s RF module website for a listing of the most current releases.
•
Manufactured in conformance with RoHS
2.1
SOFTWARE BLOCK DIAGRAM
PAN13xxHost ProcessorApplicationBD/EDRBLEANTHCIL2CAPHCIRF BlockPAN13xxHost Block
CLASSIFICATION PRODUCT SPECIFICATION No.
DS-13xx-2400-102
REV.
3.40
SUBJECT CLASS 1 or 2 BLUETOOTH MODULE PAGE 7 of 57
CUSTOMER’S CODE
PAN13XX Core Specification
PANASONIC’S CODE
See Chapter 28. Ordering Information DATE 18.07.2012
PANASONIC INDUSTRIAL DEVICES EUROPE GMBH www.pedeu.pansonic.de
3
APPLICATIONS FOR THE MODULE
All Embedded Wireless Applications
•
Smart Phones
•
Cable Replacement
•
Industrial Control
•
Automotive
•
Medical
•
Access Points
•
Scanners
•
Consumer Electronics
•
Wireless Sensors
•
Monitoring and Control
•
Low Power
•
Access Points
4
DESCRIPTION FOR THE MODULE
The PAN1315 and PAN1315A are short-range, Class 1 or 2, HCI modules for implementing Bluetooth functionality into various electronic devices. A block diagram can be found in Chapter 7.
Communication between the module and the host controller is carried out via UART.
New designs can be completed quickly by mating the PAN13xx series modules with Texas Instruments’ MSP430BT5190 that contains Mindtree’s EtherMind Bluetooth Protocol Stack and serial port profile, additional computing power can be achieved by choosing TI’s Stellaris ARM7 controller that includes StoneStreet One's A2DP profile. Other BT profiles are available on custom development basis.
Additional controllers are also supported by the PAN13xx series by using a TI/Panasonic software development partner to port the Bluetooth stack and profiles. Mindtree's Software Development Kit (SDK) is available on TI's website -- www.ti.com/connectivity.com
Contact your local sales office for further details on additional options and services, by visiting www.panasonic.com/rfmodules or write an e-mail to wireless@eu.panasonic.com.
CLASSIFICATION PRODUCT SPECIFICATION No.
DS-13xx-2400-102
REV.
3.40
SUBJECT CLASS 1 or 2 BLUETOOTH MODULE PAGE 8 of 57
CUSTOMER’S CODE
PAN13XX Core Specification
PANASONIC’S CODE
See Chapter 28. Ordering Information DATE 18.07.2012
PANASONIC INDUSTRIAL DEVICES EUROPE GMBH www.pedeu.pansonic.de
5
DETAILED DESCRIPTION
5.1
TERMINAL LAYOUT
5.1.1
5.1.1. Terminal Layout PAN131x without antenna
No
Pin Name
Pull at Reset
Def. Dir. 2
I/O Type 3
Description of Options (Common)
1
GND
Connect to Ground
2
TX_DBG
PU
O
2 mA
Logger output
3
HCI_CTS
PU
I
8 mA
HCI UART clear-to-send.
4
HCI_RTS
PU
O
8 mA
HCI UART request-to-send.
5
HCI_RX
PU
I
8 mA
HCI UART data receive
6
HCI_TX
PU
O
8 mA
HCI UART data transmit
7
AUD_FSYNC
PD
IO
4 mA
PCM frame synch. (NC if not used) Fail safe4
8
SLOW_CLK_IN
I
32.768-kHz clock in Fail safe
9
NC
IO
Not connected
10
MLDO_OUT
O
Main LDO output (1.8 V nom.)
11
CL1.5_LDO_IN
I
PA LDO input
12
GND
Connect to Ground
13
RF
IO
Bluetooth RF IO
14
GND
Connect to Ground
15
MLDO_IN
I
Main LDO input
16
nSHUTD
PD
I
Shutdown input (active low).
17
AUD_OUT
PD
O
4 mA
PCM data output. (NC if not used) Fail safe
18
AUD_IN
PD
I
4 mA
PCM data input. (NC if not used) Fail safe
19
AUD_CLK
PD
IO
HY, 4 mA
PCM clock. (NC if not used) Fail safe
20
GND
Connect to Ground
21
NC
EEPROM I²C SDA (Internal)
22
VDD_IO
PI
I/O power supply 1.8 V Nom
23
NC
EEPROM I²C SCL (Internal)
24
NC
IO
Not connected
2 I = input; O = output; IO = bidirectional; P = power; PU = pulled up; PD = pulled down
3 I/O Type: Digital I/O cells. HY = input hysteresis, current = typ. output current
4 No signals are allowed on the IO pins if no VDD_IO (Pin 22) power supplied, except pin 7, 8, 17-19.
CLASSIFICATION PRODUCT SPECIFICATION No.
DS-13xx-2400-102
REV.
3.40
SUBJECT CLASS 1 or 2 BLUETOOTH MODULE PAGE 9 of 57
CUSTOMER’S CODE
PAN13XX Core Specification
PANASONIC’S CODE
See Chapter 28. Ordering Information DATE 18.07.2012
PANASONIC INDUSTRIAL DEVICES EUROPE GMBH www.pedeu.pansonic.de
5.1.2
5.1.2. Terminal Layout PAN132x with antenna
No
Pin Name
Pull at Reset
Def. Dir. 5
I/O Type 6
Description of Options (Common)
A
GND
Connect to Ground
B
GND
Connect to Ground
C
GND
Connect to Ground
D
GND
Connect to Ground
No 1-24 see above in Chapter 5.1.1. Except PIN 13 is not connected. For RF conducted measurements, either use the PAN1323ETU or de-solder the antenna and solder an antenna connector to the hot pin.
5 I = input; O = output; IO = bidirectional; P = power; PU = pulled up; PD = pulled down
6 I/O Type: Digital I/O cells. HY = input hysteresis, current = typ. output current
CLASSIFICATION PRODUCT SPECIFICATION No.
DS-13xx-2400-102
REV.
3.40
SUBJECT CLASS 1 or 2 BLUETOOTH MODULE PAGE 10 of 57
CUSTOMER’S CODE
PAN13XX Core Specification
PANASONIC’S CODE
See Chapter 28. Ordering Information DATE 18.07.2012
PANASONIC INDUSTRIAL DEVICES EUROPE GMBH www.pedeu.pansonic.de
5.2
PIN DESCRIPTION
Pin Name
No
ESD 7 (V)
Pull at Reset
Def. Dir. 8
I/O Type 9
Description of Options
Bluetooth IO SIGNALS
HCI_RX
5
750
PU
I
8 mA
HCI UART data receive
HCI_TX
6
750
PU
O
8 mA
HCI UART data transmit
HCI_RTS
4
750
PU
O
8 mA
HCI UART request-to-send.
HCI_CTS
3
750
PU
I
8 mA
HCI UART clear-to-send.
AUD_FYSNC
7
500
PD
IO
4 mA
PCM frame synch (NC if not used) Fail safe
AUD_CLK
19
500
PD
IO
HY, 4 mS
PCM clock (NC if not used) Fail safe
AUD_IN
18
500
PD
I
4 mA
PCM data input (NC if not used) Fail safe
AUD_OUT
17
500
PD
O
4 mA
PCM data output (NC if not used) Fail safe
Logger output
TX_DBG
2
1000
PU
O
2 mA
OPTION: nTX_DBG – logger out (low = 1)
CLOCK SIGNALS
SLOW_CLK_IN
8
1000
I
32.768-kHz clock in Fail safe
Bluetooth ANALOG SIGNALS
RF
13
1000
IO
Bluetooth RF IO (not connected with antenna)
nSHUTD
16
1000
PD
I
Shutdown input (active low).
Bluetooth POWER AND GND SIGNALS
VDD_IO
22
1000
PI
I/O power supply 1.8 V Nom
MLDO_IN
15
1000
I
Main LDO inputConnect directly to battery or to a pre-regulated 1.8-V supply
MLDO_OUT
10
1000
O
Main LDO output (1.8 V nom.) Can not be used as 1.8V supply due to internal connection to the RF part.
CL1.5_LDO_IN
11
1000
I
PA LDO input
Connect directly to battery or to a pre-regulated 1.8-V supply
GND
1
P
Connect to Ground
GND
12
P
Connect to Ground
GND
14
P
Connect to Ground
GND
20
P
Connect to Ground
EEPROM IO SIGNALS (EEPROM is optional in PAN13x product line)
NC
23
1000
PU/PD
I
HY, 4mA
EEPROM I²C SCL (Internal)
NC
21
1000
PU/PD
IO
HY, 4mA
EEPROM I²C IRQ (Internal)
Remark:
HCI_CTS is an input signal to the CC256X device:
- When HCI_CTS is low, then CC256X is allowed to send data to Host device.
- When HCI_CTS is high, then CC256X is not allowed to send data to Host device.
7 ESD: Human Body Model (HBM). JEDEC 22-A114
8 I = input; O = output; IO = bidirectional; P = power; PU = pulled up; PD = pulled down
9 I/O Type: Digital I/O cells. HY = input hysteresis, current = typ output current
CLASSIFICATION PRODUCT SPECIFICATION No.
DS-13xx-2400-102
REV.
3.40
SUBJECT CLASS 1 or 2 BLUETOOTH MODULE PAGE 11 of 57
CUSTOMER’S CODE
PAN13XX Core Specification
PANASONIC’S CODE
See Chapter 28. Ordering Information DATE 18.07.2012
PANASONIC INDUSTRIAL DEVICES EUROPE GMBH www.pedeu.pansonic.de
5.3
DEVICE POWER SUPPLY
The PAN13XX Bluetooth radio solution is intended to work in devices with a limited power budget such as cellular phones, headsets, hand-held PC’s and other battery-operated devices. One of the main differentiators of the PAN13XX is its power management – its ability to draw as little current as possible.
The PAN13XX device requires two kinds of power sources:
• Main power supply for the Bluetooth - VDD_IN = VBAT
• Power source for the 1.8 V I/O ring - VDD_IO
The PAN13XX includes several on-chip voltage regulators for increased noise immunity. The PAN13XX can be connected either directly to the battery or to an external 1.8-V DC to DC converter.
There are three ways to supply power:
•
Full-VBAT system:
Maximum RF output power, but not optimum system power:
•
Full-DC2DC system:
Lower RF output power, but optimum system power:
CLASSIFICATION PRODUCT SPECIFICATION No.
DS-13xx-2400-102
REV.
3.40
SUBJECT CLASS 1 or 2 BLUETOOTH MODULE PAGE 12 of 57
CUSTOMER’S CODE
PAN13XX Core Specification
PANASONIC’S CODE
See Chapter 28. Ordering Information DATE 18.07.2012
PANASONIC INDUSTRIAL DEVICES EUROPE GMBH www.pedeu.pansonic.de
•
Mixed DC2DC-VBAT system:
Maximum RF output power and optimum system power, but requires routing of VBAT:
5.4
CLOCK INPUTS
The slow clock is always supplied from an external source. It is connected to the SLOW_CLK_IN pin number 8 and can be a digital signal with peak to peak of 0-1.8 V.
The slow clock's frequency accuracy must be 32.768 kHz ±250 ppm for Bluetooth usage (according to the Bluetooth specification).
The Slow Clock 32.768 kHz is mandatory to start the internal controller, otherwise the module does not start up.
6
BLUETOOTH FEATURES
•
Support of Bluetooth2.1+EDR (Lisbon Release) up to HCI level.
•
Very fast AFH algorithm for both ACL and eSCO.
•
Supports typically 4 dBm Class 2 TX power w/o external PA, improving Bluetooth link robustness. Adjusting the host settings, the TX power can be increased to 10 dBm. However it is important, that the national regulations and Bluetooth specification are met.
•
Digital Radio Processor (DRP) single-ended 50 ohm.
•
Internal temperature detection and compensation ensures minimal variation in the RF performance over temperature.
•
Flexible PCM and I2S digital audio/voice interfaces: Full flexibility of data-format (Linear, a-Law, μ-Law), data-width, data order, sampling and slot positioning, master/slave modes, high clock rates up to 15 MHz for slave mode (or 4.096 MHz for Master Mode). Lost packet concealment for improved audio.
•
Proprietary low-power scan method for page and inquiry scans, achieves page and inquiry scans at 1/3rd normal power.
CLASSIFICATION PRODUCT SPECIFICATION No.
DS-13xx-2400-102
REV.
3.40
SUBJECT CLASS 1 or 2 BLUETOOTH MODULE PAGE 13 of 57
CUSTOMER’S CODE
PAN13XX Core Specification
PANASONIC’S CODE
See Chapter 28. Ordering Information DATE 18.07.2012
PANASONIC INDUSTRIAL DEVICES EUROPE GMBH www.pedeu.pansonic.de
7
BLOCK DIAGRAM
Note: The Slow Clock 32.768 kHz is mandatory, otherwise the module does not start up, refer to Chapter 5.4 for additional information.
Note: The IO are 1.8V driven and might need external level shifter and LDO. The MLDO_OUT PIN can not be used as reference due to RF internal connection.
CLASSIFICATION PRODUCT SPECIFICATION No.
DS-13xx-2400-102
REV.
3.40
SUBJECT CLASS 1 or 2 BLUETOOTH MODULE PAGE 14 of 57
CUSTOMER’S CODE
PAN13XX Core Specification
PANASONIC’S CODE
See Chapter 28. Ordering Information DATE 18.07.2012
PANASONIC INDUSTRIAL DEVICES EUROPE GMBH www.pedeu.pansonic.de
8
TEST CONDITIONS
Measurements shall be made under room temperature and humidity unless otherwise specified.
9
GENERAL DEVICE REQUIREMENTS AND OPERATION
Temperature 25 ± 10°C Humidity 40 to 85%RH SW-Patch V2.30 Supply Voltage 3.3V
All specifications are over temperature and process, unless indicated otherwise.
9.1
ABSOLUTE MAXIMUM RATINGS
Over operating free-air temperature range (unless otherwise noted).
Note
All parameters are measured as follows unless stated otherwise:
VDD_IN 10 = 3.3 V, VDD_IO = 1.8 V.
No
See 11
Value
Unit
Ratings Over Operating Free-Air Temperature Range
1
VDD_IN
Supply voltage range
–0.5 to 5.5
V 12
2
VDDIO_1.8V
–0.5 to 2.145
V
3
Input voltage to RF (Pin 13)
–0.5 to 2.1
V
4
Operating ambient temperature range
–20 to 70
°C
5
Storage temperature range
–40 to 125
°C
6
Bluetooth RF inputs (Pin 13)
10
dBm
7
ESD: Human Body Model (HBM). JEDEC 22-A114
500
V
10 VDD_IN is supplied to MLDO_IN (Pin 15) and CL1.5_LDO_IN (Pin 11), other options are described in Chapter 5.3.
11 Stresses beyond those listed under “absolute maximum ratings” may cause permanent damage to the device. These are stress ratings only and functional operation of the device at these or any other conditions beyond those indicated under “recommended operating conditions” is not implied. Exposure to absolute-maximum-rated conditions for extended periods may affect device reliability.
12 Maximum allowed depends on accumulated time at that voltage: VDD_IN is defined in Reference schematics. When DC2DC supply is used, maximum voltage into MLDO_OUT and LDO_IN = 2.145 V.
CLASSIFICATION PRODUCT SPECIFICATION No.
DS-13xx-2400-102
REV.
3.40
SUBJECT CLASS 1 or 2 BLUETOOTH MODULE PAGE 15 of 57
CUSTOMER’S CODE
PAN13XX Core Specification
PANASONIC’S CODE
See Chapter 28. Ordering Information DATE 18.07.2012
PANASONIC INDUSTRIAL DEVICES EUROPE GMBH www.pedeu.pansonic.de
9.2
RECOMMENDED OPERATING CONDITIONS
No
Rating
Condition
Symbol
Min
Max
Unit
1
Power supply voltage 13
VDD_IN
1.7
4.8
V
2
IO power supply voltage
VDD_IO
1.62
1.92
V
3
High-level input voltage
Default
VIH
0.65 x VDD_IO
VDD_IO
V
4
Low-level input voltage
Default
VIL
0
0.35 x VDD_IO
V
5
IO Input rise/fall times, 10% to 90% 14
Tr/Tf
1
10
ns
0 to 0.1 MHz
60
0.1 to 0.5 MHz
50
0.5 to 2.5 MHz
30
2.5 to 3.0 MHz
15
6
Maximum ripple on VDD_IN (Sine wave) for 1.8 V (DC2DC) mode
> 3.0 MHz
5
mVp-p
7
Voltage dips on VDD_IN (VBAT) (duration = 577 μs to2.31 ms, period = 4.6 ms)
400
mV
8
Maximum ambient operating temperature 15
70
°C
9
Minimum ambient operating temperature 16
-20
C
9.3
CURRENT CONSUMPTION
No
Characteristics
Min
25°C
Typ
25°C
Max
25°C
Min
-20°C
Typ
-20°C
Max
-20°C
Min
+70°C
Typ
+70°C
Max
+70°C
Unit
1
Current consumption in shutdown mode 17
1
3
7
μA
2
Current consumption in deep sleep mode 18
40
105
700
μA
3
Total IO current consumption for active mode
1
1
1
mA
4
Current consumption during transmit DH5 full throughput
40
mA
13 Excluding 1.98 < VDD_IN < 2.2 V range – not allowed.
14 Asynchronous mode.
15 The device can be reliably operated for 7 years at Tambient of 70°C, assuming 25% active mode and 75% sleep mode (15,400 cumulative active power-on hours).
16 The device can be reliably operated for 7 years at Tambient of 70°C, assuming 25% active mode and 75% sleep mode (15,400 cumulative active power-on hours).
17 Vbat + Vio
18 Vbat + Vio + Vsd (shutdown)
CLASSIFICATION PRODUCT SPECIFICATION No.
DS-13xx-2400-102
REV.
3.40
SUBJECT CLASS 1 or 2 BLUETOOTH MODULE PAGE 16 of 57
CUSTOMER’S CODE
PAN13XX Core Specification
PANASONIC’S CODE
See Chapter 28. Ordering Information DATE 18.07.2012
PANASONIC INDUSTRIAL DEVICES EUROPE GMBH www.pedeu.pansonic.de
9.4
GENERAL ELECTRICAL CHARACTERISTICS
No
Rating
Condition
Min
Max
Value
at 2/4/8 mA
0.8 x VDD_IO
VDD_IO
V
1
High-level output voltage, VOH
at 0.1 mA
VDD_IO – 0.2
VDD_IO
V
at 2/4/8 mA
0
0.2 x VDD_IO
V
2
Low-level output voltage, VOL
at 0.1 mA
0
0.2
V
Resistance
1
MΩ
3
IO input impedance
Capacitance
5
pF
4
Output rise/fall times,10% to 90% (Digital pins)
CL = 20 pF
10
Ns
PU
typ = 6.5
3.5
9.7
TX_DBG, us
PCM b
PD
typ = 27
9.5
55
μA
PU
typ = 100
100
300
5 IO pull currents
All others
PD
typ = 100
100
360
μA
9.5
NSHUTD REQUIREMENTS
No
Parameter
Symbol
Min
Max
Unit
1
Operation mode level 19 V
IH
1.42
1.98
V
2
Shutdown mode level
VIL
0
0.4
V
3
Minimum time for nSHUT_DOWN low to reset the device
5
ms
4
Rise/fall times
Tr/Tf
20
μs
9.6
EXTERNAL DIGITAL SLOW CLOCK REQUIREMENTS (–20°C TO +70°C)
No
Characteristics
Condition
Symbol
Min
Typ
Max
Unit
1
Input slow clock frequency
32768
Hz
2
Input slow clock accuracy (Initial + temp + aging)
Bluetooth
±250
Ppm
3
Input transition time Tr/Tf – 10% to 90%
Tr/Tf
100
Ns
4
Frequency input duty cycle
15%
50%
85%
5
Phase noise
at 1 kHz
-125
dBc/Hz
6
Jitter
Integrated over 300 to 15000 Hz
1
Hz
VIH
0.65 x
VDD_IO
VDD_IO
7
Slow clock input voltage limits
Square wave, DC coupled
VIL
0
0.35 x
VDD_IO
V peak
8
Input impedance
1
MΩ
9
Input capacitance
5
pF
19 Internal pull down retains shut down mode when no external signal is applied to this pin.
CLASSIFICATION PRODUCT SPECIFICATION No.
DS-13xx-2400-102
REV.
3.40
SUBJECT CLASS 1 or 2 BLUETOOTH MODULE PAGE 17 of 57
CUSTOMER’S CODE
PAN13XX Core Specification
PANASONIC’S CODE
See Chapter 28. Ordering Information DATE 18.07.2012
PANASONIC INDUSTRIAL DEVICES EUROPE GMBH www.pedeu.pansonic.de
10
HOST CONTROLLER INTERFACE
The CC256X incorporates one UART module dedicated to the host controller interface (HCI) transport layer. The HCI interface transports commands, events, ACL, and synchronous data between the Bluetooth device and its host using HCI data packets.
The UART module supports H4 (4-wires) protocol with maximum baud rate of 4 Mbps for all fast clock frequencies.
After power up the baud rate is set for 115.2 kbps, irrespective of fast clock frequency. The baud rate can thereafter be changed with a vendor specific command. The CC256X responds with a Command Complete Event (still at 115.2 kbps), after which the baud rate change takes place. HCI hardware includes the following features:
• Receiver detection of break, idle, framing, FIFO overflow, and parity error conditions
• Transmitter underflow detection
• CTS/RTS hardware flow control
The interface includes four signals: TXD, RXD, CTS, and RTS. Flow control between the host and the CC256X is byte-wise by hardware.
Flow control is obtained by the following:
When the UART RX buffer of the CC256X passes the “flow control” threshold, it will set the UART_RTS signal high to stop transmission from the host.
When the UART_CTS signal is set high, the CC256X will stop its transmission on the interface. In case HCI_CTS is set high in the middle of transmitting a byte, the CC256X will finish transmitting the byte and stop the transmission.
CLASSIFICATION PRODUCT SPECIFICATION No.
DS-13xx-2400-102
REV.
3.40
SUBJECT CLASS 1 or 2 BLUETOOTH MODULE PAGE 18 of 57
CUSTOMER’S CODE
PAN13XX Core Specification
PANASONIC’S CODE
See Chapter 28. Ordering Information DATE 18.07.2012
PANASONIC INDUSTRIAL DEVICES EUROPE GMBH www.pedeu.pansonic.de
11
AUDIO/VOICE CODEC INTERFACE
The codec interface is a fully-dedicated programmable serial port that provides the logic to interface to several kinds of PCM or I2S codec’s. PAN13XX supports all voice coding schemes required by Bluetooth specification – Log PCM (A-Law or μ-Law) and Linear (CVSD). In addition, module also supports transparent scheme:
• Two voice channels
• Master / slave modes
• μ-Law, A-Law, Linear, Transparent coding schemes
• Long and short frames
• Different data sizes, order, and positions.
• High rate PCM interface for EDR
• Enlarged interface options to support a wider variety of codecs
• PCM bus sharing
11.1
PCM HARDWARE INTERFACE
The PCM interface is one implementation of the codec interface. It contains the following four lines:
• Clock—configurable direction (input or output)
• Frame Sync—configurable direction (input or output)
• Data In—Input
• Data Out—Output/3-state
The Bluetooth device can be either the master of the interface where it generates the clock and the frame-sync signals, or slave where it receives these two signals. The PCM interface is fully configured by a vendor specific command.
For slave mode, clock input frequencies of up to 16 MHz are supported. At clock rates above 12 MHz, the maximum data burst size is 32 bits. For master mode, the CC256X can generate any clock frequency between 64 kHz and 6 MHz.
Please contact your sales representative if using the I2S bus over PCM. We strongly recommend adding a low pass filter (series resistor and capacitor to GND) to the bus for better noise suppression. It is not recommended to directly contact the host μController/DSP with the PCM interface.
11.2
DATA FORMAT
The data format is fully configurable:
• The data length can be from 8 to 320 bits, in 1-bit increments, when working with two channels, or up to 640 bits when using 1 channel. The Data length can be set independently for each channel.
• The data position within a frame is also configurable in with 1 clock (bit) resolution and can be set independently (relative to the edge of the Frame Sync signal) for each channel.
• The Data_In and Data_Out bit order can be configured independently. For example; Data_In can start with the MSB while Data_Out starts with LSB. Each channel is separately configurable. The inverse bit order (that is, LSB first) is supported only for sample sizes up to 24 bits.
• It is not necessary for the data in and data out size to be the same length.
CLASSIFICATION PRODUCT SPECIFICATION No.
DS-13xx-2400-102
REV.
3.40
SUBJECT CLASS 1 or 2 BLUETOOTH MODULE PAGE 19 of 57
CUSTOMER’S CODE
PAN13XX Core Specification
PANASONIC’S CODE
See Chapter 28. Ordering Information DATE 18.07.2012
PANASONIC INDUSTRIAL DEVICES EUROPE GMBH www.pedeu.pansonic.de
• The Data_Out line is configured to ‘high-Z’ output between data words. Data_Out can also be set for permanent high-Z, irrespective of data out. This allows the CC256X to be a bus slave in a multi-slave PCM environment. At powerup, Data Out is configured as high-Z.
11.3
FRAME IDLE PERIOD
The codec interface has the capability for frame idle periods, where the PCM clock can “take a break” and become ‘0’ at the end of the PCM frame, after all data has been transferred.
The CC256X supports frame idle periods both as master and slave of the PCM bus.
When CC256X is the master of the interface, the frame idle period is configurable. There are two configurable parameters:
• Clk_Idle_Start – Indicates the number of PCM clock cycles from the beginning of the frame until the beginning of the idle period. After Clk_Idle_Start clock cycles, the clock will become ‘0’.
• Clk_Idle_End – Indicates the time from the beginning of the frame till the end of the idle period. This time is given in multiples of PCM clock periods.
The delta between Clk_Idle_Start and Clk_Idle_End is the clock idle period.
For example, for PCM clock rate = 1 MHz, frame sync period = 10 kHz, Clk_Idle_Start = 60, Clk_Idle_End = 90.
Between each two frame syncs there are 70 clock cycles (instead of 100). The clock idle period starts 60 clock cycles after the beginning of the frame, and lasts 90 – 60 = 30 clock cycles. This means that the idle period ends 100 – 90 = 10 clock cycles before the end of the frame. The data transmission must end prior to the beginning of the idle period.
CLASSIFICATION PRODUCT SPECIFICATION No.
DS-13xx-2400-102
REV.
3.40
SUBJECT CLASS 1 or 2 BLUETOOTH MODULE PAGE 20 of 57
CUSTOMER’S CODE
PAN13XX Core Specification
PANASONIC’S CODE
See Chapter 28. Ordering Information DATE 18.07.2012
PANASONIC INDUSTRIAL DEVICES EUROPE GMBH www.pedeu.pansonic.de
11.4
CLOCK-EDGE OPERATION
The codec interface of the CC256X can work on the rising or the falling edge of the clock. It also has the ability to sample the frame sync and the data at inversed polarity.
This is the operation of a falling-edge-clock type of codec. The codec is the master of the PCM bus. The frame sync signal is updated (by the codec) on the falling clock edge and therefore shall be sampled (by the CC256X) on the next rising clock. The data from the codec is sampled (by the CC256X) on the clock falling edge.
11.5
TWO-CHANNEL PCM BUS EXAMPLE
In below figure, a 2-channel PCM bus is shown where the two channels have different word sizes and arbitrary positions in the bus frame. (FT stands for Frame Timer)
11.6
AUDIO ENCODING
The CC256X codec interface can use one of four audio-coding patterns:
• A-Law (8-bit)
• μ-Law (8-bit)
• Linear (8- or 16-bit)
CLASSIFICATION PRODUCT SPECIFICATION No.
DS-13xx-2400-102
REV.
3.40
SUBJECT CLASS 1 or 2 BLUETOOTH MODULE PAGE 21 of 57
CUSTOMER’S CODE
PAN13XX Core Specification
PANASONIC’S CODE
See Chapter 28. Ordering Information DATE 18.07.2012
PANASONIC INDUSTRIAL DEVICES EUROPE GMBH www.pedeu.pansonic.de
11.7
IMPROVED ALGORITHM FOR LOST PACKETS
The CC256X features an improved algorithm for improving voice quality when received voice data packets are lost. There are two options:
• Repeat the last sample – possible only for sample sizes up to 24 bits. For sample sizes >24 bits, the last byte is repeated.
• Repeat a configurable sample of 8 to 24 bits (depends on the real sample size), in order to simulate silence (or anything else) in the PCM bus. The configured sample will be written in a specific register for each channel.
The choice between those two options is configurable separately for each channel.
11.8
BLUETOOTH/PCM CLOCK MISMATCH HANDLING
In Bluetooth RX, the CC256X receives RF voice packets and writes these to the codec I/F. If the CC256X receives data faster than the codec I/F output allows, an overflow will occur. In this case, the Bluetooth has two possible behaviour modes: ‘allow overflow’ and ‘don’t allow overflow’.
• If overflow is allowed, the Bluetooth will continue receiving data and will overwrite any data not yet sent to the codec.
• If overflow is not allowed, RF voice packets received when buffer is full will be discarded.
11.9
BLUETOOTH INTER-IC SOUND (I2S)
The CC256X can be configured as an Inter-IC Sound (I2S) serial interface to an I2S codec device. In this mode, the CC256X audio codec interface is configured as a bi-directional, full-duplex interface, with two time slots per frame: Time slot 0 is used for the left channel audio data and time slot 1 for the right channel audio data. Each time slot is configurable up to 40 serial clock cycles in length and the frame is configurable up to 80 serial clock cycles in length.
Do not connect the the microcontroller/DSP directly to the module's PCM interface, a simple RC low pass filter is recommended to improve noise suppression.
CLASSIFICATION PRODUCT SPECIFICATION No.
DS-13xx-2400-102
REV.
3.40
SUBJECT CLASS 1 or 2 BLUETOOTH MODULE PAGE 22 of 57
CUSTOMER’S CODE
PAN13XX Core Specification
PANASONIC’S CODE
See Chapter 28. Ordering Information DATE 18.07.2012
PANASONIC INDUSTRIAL DEVICES EUROPE GMBH www.pedeu.pansonic.de
11.10
CURRENT CONSUMPTION FOR DIFFERENT BLUETOOTH SCENARIOS
The following table gives average current consumption for different Bluetooth scenarios.
Conditions: VDD_IN = 3.6 V, 25°C, 26-MHz fast clock, nominal unit, 4 dBm output power.
12
BLUETOOTH RF PERFORMANCE
No
Characteristics
Typ
BT Spec Max
BT Spec Min
Class1
Class1
1
Average Power Hopping DH5 [dBm] 21, 22
7.2
20
4
2
Average Power: Ch0 [dBm] 21, 22
7.5
20
4
3
Peak Power: Ch0 [dBm] 21, 22
7.7
23
4
Average Power: Ch39 [dBm] 21, 22
7.0
20
4
5
Peak Power: Ch39 [dBm] 21, 22
7.2
23
6
Average Power: Ch78 [dBm] 21, 22
6.7
20
4
7
Peak Power: Ch78 [dBm] 21, 22
7.0
23
8
Max. Frequency Tolerance: Ch0 [kHz]
-2.6
75
-75
9
Max. Frequency Tolerance: Ch39 [kHz]
-2.2
75
-75
10
Max. Frequency Tolerance: Ch78 [kHz]
-2.1
75
-75
11
Max. Drift: Ch0_DH1 [kHz]
3.6
25
-25
12
Max. Drift: Ch0_DH3 [kHz]
3.7
40
-40
13
Max. Drift: Ch0_DH5 [kHz]
4.0
40
-40
14
Max. Drift Rate: Ch0_DH1 [kHz]
-2.6
20
-20
15
Max. Drift Rate: Ch0_DH3 [kHz]
-3.2
20
-20
16
Max. Drift Rate: Ch0_DH5 [kHz]
-3.3
20
-20
17
Max. Drift: Ch39_DH1 [kHz]
4.0
25
-25
18
Max. Drift: Ch39_DH3 [kHz]
4.3
40
-40
19
Max. Drift: Ch39_DH5 [kHz]
4.3
40
-40
20
Max. Drift Rate: Ch39_DH1 [kHz]
-3.1
20
-20
21
Max. Drift Rate: Ch39_DH3 [kHz]
-3.6
20
-20
22
Max. Drift Rate: Ch39_DH5 [kHz]
-3.7
20
-20
CLASSIFICATION PRODUCT SPECIFICATION No.
DS-13xx-2400-102
REV.
3.40
SUBJECT CLASS 1 or 2 BLUETOOTH MODULE PAGE 23 of 57
CUSTOMER’S CODE
PAN13XX Core Specification
PANASONIC’S CODE
See Chapter 28. Ordering Information DATE 18.07.2012
PANASONIC INDUSTRIAL DEVICES EUROPE GMBH www.pedeu.pansonic.de
No Characteristics Typ
BT Spec
Max
BT Spec
Min
Class1 Class1
23
Max. Drift: Ch78_DH1 [kHz]
4.1
25
-25
24
Max. Drift: Ch78_DH3 [kHz]
4.5
40
-40
25
Max. Drift: Ch78_DH5 [kHz]
4.4
40
-40
26
Max. Drift Rate: Ch78_DH1 [kHz]
-3.4
20
-20
27
Max. Drift Rate: Ch78_DH3 [kHz]
-3.9
20
-20
28
Max. Drift Rate: Ch78_DH5 [kHz]
-4.1
20
-20
29
Delta F1 Avg: Ch0 [kHz]
159.5
175
140
30
Delta F2 Max.: Ch0 [%]
100.0
99.9
31
Delta F2 Avg/Delta F1 Avg: Ch0
0.9
0.8
32
Delta F1 Avg: Ch39 [kHz]
159.8
175
140
33
Delta F2 Max.: Ch39 [%]
100.0
99.9
34
Delta F2 Avg/Delta F1 Avg: Ch39
0.9
0.8
35
Delta F1 Avg: Ch78 [kHz]
159.1
175
140
36
Delta F2 Max.: Ch78 [%]
100.0
99.9
37
Delta F2 Avg/Delta F1 Avg: Ch78
0.9
0.8
45
Sensitivity
-93.0
-81
46
f(H)-f(L): Ch0 [kHz]
918.4
1000
47
f(H)-f(L): Ch39 [kHz]
918.3
1000
48
f(H)-f(L): Ch78 [kHz]
918.2
1000
49
ACPower -3: Ch3 [dBm]
-51.5
-40
50
ACPower -2: Ch3 [dBm]
-50.4
-40
51
ACPower -1: Ch3 [dBm]
-18.5
52
ACPower Center: Ch3 [dBm]
8.1
20
4
53
ACPower +1: Ch3 [dBm]
-19.2
54
ACPower +2: Ch3 [dBm]
-50.7
-40
55
ACPower +3: Ch3 [dBm]
-53.3
-40
56
ACPower -3: Ch39 [dBm]
-51.6
-40
57
ACPower -2: Ch39 [dBm]
-50.7
-40
58
ACPower -1: Ch39 [dBm]
-19.0
59
ACPower Center: Ch39 [dBm]
7.7
20
4
60
ACPower +1: Ch39 [dBm]
-19.7
61
ACPower +2: Ch39 [dBm]
-50.9
-40
62
ACPower +3: Ch39 [dBm]
-53.2
-40
63
ACPower -3: Ch75 [dBm]
-51.7
-40
64
ACPower -2: Ch75 [dBm]
-50.7
-40
65
ACPower -1: Ch75 [dBm]
-19.2
66
ACPower Center: Ch75 [dBm]
7.5
20
4
67
ACPower +1: Ch75 [dBm]
-20.0
68
ACPower +2: Ch75 [dBm]
-51.0
-40
69
ACPower +3: Ch75 [dBm]
-53.4
-40
70
omega i 2-DH5: Ch0 [kHz]
-4.7
75
-75
71
omega o + omega i 2-DH5: Ch0 [kHz]
-6.0
75
-75
72
omega o 2-DH5: Ch0 [kHz]
-1.5
10
-10
73
DEVM RMS 2-DH5: Ch0 [%]
0.0
0.2
74
DEVM Peak 2-DH5: Ch0 [%]
0.1
0.35
CLASSIFICATION PRODUCT SPECIFICATION No.
DS-13xx-2400-102
REV.
3.40
SUBJECT CLASS 1 or 2 BLUETOOTH MODULE PAGE 24 of 57
CUSTOMER’S CODE
PAN13XX Core Specification
PANASONIC’S CODE
See Chapter 28. Ordering Information DATE 18.07.2012
PANASONIC INDUSTRIAL DEVICES EUROPE GMBH www.pedeu.pansonic.de
No Characteristics Typ
BT Spec
Max
BT Spec
Min
Class1 Class1
75
DEVM 99% 2-DH5: Ch0 [%]
100.0
99
76
omega i 3-DH5: Ch0 [kHz]
-3.7
75
-75
77
omega o + omega i 3-DH5: Ch0 [kHz]
-5.8
75
-75
78
omega o 3-DH5: Ch0 [kHz]
-2.6
10
-10
79
DEVM RMS 3-DH5: Ch0 [%]
0.0
0.13
80
DEVM Peak 3-DH5: Ch0 [%]
0.1
0.25
81
DEVM 99% 3-DH5: Ch0 [%]
100.0
99
82
omega i 2-DH5: Ch39 [kHz]
-4.8
75
-75
83
omega o + omega i 2-DH5: Ch39 [kHz]
-6.1
75
-75
84
omega o 2-DH5: Ch39 [kHz]
-1.4
10
-10
85
DEVM RMS 2-DH5: Ch39 [%]
0.0
0.2
86
DEVM Peak 2-DH5: Ch39 [%]
0.1
0.35
87
DEVM 99% 2-DH5: Ch39 [%]
100.0
99
88
omega i 3-DH5: Ch39 [kHz]
-3.8
75
-75
89
omega o + omega i 3-DH5: Ch39 [kHz]
-5.9
75
-75
90
omega o 3-DH5: Ch39 [kHz]
-2.6
10
-10
91
DEVM RMS 3-DH5: Ch39 [%]
0.0
0.13
92
DEVM Peak 3-DH5: Ch39 [%]
0.1
0.25
93
DEVM 99% 3-DH5: Ch39 [%]
100.0
99
94
omega i 2-DH5: Ch78 [kHz]
-4.9
75
-75
95
omega o + omega i 2-DH5: Ch78 [kHz]
-6.2
75
-75
96
omega o 2-DH5: Ch78 [kHz]
-1.4
10
-10
97
DEVM RMS 2-DH5: Ch78 [%]
0.0
0.2
98
DEVM Peak 2-DH5: Ch78 [%]
0.1
0.35
99
DEVM 99% 2-DH5: Ch78 [%]
100.0
99
100
omega i 3-DH5: Ch78 [kHz]
-3.8
75
-75
101
omega o + omega i 3-DH5: Ch78 [kHz]
-6.0
75
-75
102
omega o 3-DH5: Ch78 [kHz]
-2.7
10
-10
103
DEVM RMS 3-DH5: Ch78 [%]
0.0
0.13
104
DEVM Peak 3-DH5: Ch78 [%]
0.1
0.25
105
DEVM 99% 3-DH5: Ch78 [%]
100.0
99
No
Characteristics
Condition
Min
Typ
Max
BT Spec
Unit
1
Operation frequency range
2402
2480
MHz
2
Channel spacing
1
MHz
3
Input impedance
50
Ω
GFSK, BER = 0.1%
-93.0
-70
Pi/4-DQPSK, BER = 0.01%
-92.5
-70
4
Sensitivity, Dirty Tx on
8DPSK, BER = 0.01%
-85.5
-70
dBm
CLASSIFICATION PRODUCT SPECIFICATION No.
DS-13xx-2400-102
REV.
3.40
SUBJECT CLASS 1 or 2 BLUETOOTH MODULE PAGE 25 of 57
CUSTOMER’S CODE
PAN13XX Core Specification
PANASONIC’S CODE
See Chapter 28. Ordering Information DATE 18.07.2012
PANASONIC INDUSTRIAL DEVICES EUROPE GMBH www.pedeu.pansonic.de
No
Characteristics
Condition
Typ
Max
Unit
30 kHz to 1 GHz 20, 21, 22
-30
1
Tx and Rx out-of-band emissions
Output signal = 7dBm
1 to 12.75 GHz 20, 21, 22
-30
dBm
2
2nd harmonic
at 7dBm output power 20, 21, 22
-30
dBm
3
3rd harmonic
at 7dBm output power 20, 21, 22
-30
dBm
The values are measured conducted. Better suppression of the spurious emissions with an antenna can be expected as, antenna frequently have band pass filter characteristics.
13
SOLDERING TEMPERATURE-TIME PROFILE (FOR REFLOW SOLDERING)
13.1
FOR LEAD SOLDER
Recommended temp. profile for reflow soldering Temp.[°C] Time [s] 235°C max. 220 ±5°C 200°C150 ±10°C 90 ±30s 10 ±1s 30 +20/-10s
20 Includes effects of frequency hopping
21 Average according FCC, IC and ETSI requirements. Above +7dBm output power (refer also to 22) the customer has to verify the final product against national regulations.
22 +7dBm related to power register value 18, according to TI service pack 2.30
CLASSIFICATION PRODUCT SPECIFICATION No.
DS-13xx-2400-102
REV.
3.40
SUBJECT CLASS 1 or 2 BLUETOOTH MODULE PAGE 26 of 57
CUSTOMER’S CODE
PAN13XX Core Specification
PANASONIC’S CODE
See Chapter 28. Ordering Information DATE 18.07.2012
PANASONIC INDUSTRIAL DEVICES EUROPE GMBH www.pedeu.pansonic.de
13.2
FOR LEADFREE SOLDER
Our used temp. profile for reflow soldering Temp.[°C] Time [s] 230°C -250°C max. 220°C150°C – 190°C 90 ±30s 30 +20/-10s
Reflow permissible cycle: 2 Opposite side reflow is prohibited due to module weight.
CLASSIFICATION PRODUCT SPECIFICATION No.
DS-13xx-2400-102
REV.
3.40
SUBJECT CLASS 1 or 2 BLUETOOTH MODULE PAGE 27 of 57
CUSTOMER’S CODE
PAN13XX Core Specification
PANASONIC’S CODE
See Chapter 28. Ordering Information DATE 18.07.2012
PANASONIC INDUSTRIAL DEVICES EUROPE GMBH www.pedeu.pansonic.de
14
MODULE DIMENSION
14.1
MODULE DIMENSIONS PAN131X WITHOUT ANTENNA
No.
Item
Dimension
Tolerance
Remark
1
Width
6.50
± 0.20
2
Lenght
9.00
± 0.20
3
Height
1.80
± 0.20
With case
PAN131X Module Drawing
CLASSIFICATION PRODUCT SPECIFICATION No.
DS-13xx-2400-102
REV.
3.40
SUBJECT CLASS 1 or 2 BLUETOOTH MODULE PAGE 28 of 57
CUSTOMER’S CODE
PAN13XX Core Specification
PANASONIC’S CODE
See Chapter 28. Ordering Information DATE 18.07.2012
PANASONIC INDUSTRIAL DEVICES EUROPE GMBH www.pedeu.pansonic.de
14.2
MODULE DIMENSIONS PAN132X WITH ANTENNA
No.
Item
Dimension
Tolerance
Remark
1
Width
9.50
± 0.20
2
Lenght
9.00
± 0.20
3
Height
1.80
± 0.20
With case
PAN132X Module Drawing
CLASSIFICATION PRODUCT SPECIFICATION No.
DS-13xx-2400-102
REV.
3.40
SUBJECT CLASS 1 or 2 BLUETOOTH MODULE PAGE 29 of 57
CUSTOMER’S CODE
PAN13XX Core Specification
PANASONIC’S CODE
See Chapter 28. Ordering Information DATE 18.07.2012
PANASONIC INDUSTRIAL DEVICES EUROPE GMBH www.pedeu.pansonic.de
15
FOOTPRINT OF THE MODULE
15.1
FOOTPRINT PAN131X WITHOUT ANTENNA
All dimensions are in millimeters. The outer dimensions have a tolerance of ± 0.2mm.
The layout is symetric to center. The inner pins (2,4,6,9,11,14,16,18,21,23) are shifted to the center by 1mm.
0.901.706,500.901.809,00171513141211987653212324211819202210416Pad =
24 x
0.60mm x
0.60mmTop View1.802.702.953.95
CLASSIFICATION PRODUCT SPECIFICATION No.
DS-13xx-2400-102
REV.
3.40
SUBJECT CLASS 1 or 2 BLUETOOTH MODULE PAGE 30 of 57
CUSTOMER’S CODE
PAN13XX Core Specification
PANASONIC’S CODE
See Chapter 28. Ordering Information DATE 18.07.2012
PANASONIC INDUSTRIAL DEVICES EUROPE GMBH www.pedeu.pansonic.de
15.2
FOOTPRINT PAN132X WITH ANTENNA
All dimensions are in millimeters. The outer dimensions have a tolerance of ± 0.2mm.
The layout is symetric to center. The inner pins (2,4,6,9,11,14,16,18,21,23) are shifted to the center by 1mm. 2.700.901.709.50171513141211987653212324211819202210416Pad =
28 x
0.60mm x 0.60mm1.80ACBD1.800.551.001.80
CLASSIFICATION PRODUCT SPECIFICATION No.
DS-13xx-2400-102
REV.
3.40
SUBJECT CLASS 1 or 2 BLUETOOTH MODULE PAGE 31 of 57
CUSTOMER’S CODE
PAN13XX Core Specification
PANASONIC’S CODE
See Chapter 28. Ordering Information DATE 18.07.2012
PANASONIC INDUSTRIAL DEVICES EUROPE GMBH www.pedeu.pansonic.de
16
LABELING DRAWING
The above pictures show the laser marking on the top case, this is only an example from PAN1315.
17
MECHANICAL REQUIREMENTS
No.
Item
Limit
Condition
1
Solderability
More than 75% of the soldering area shall be coated by solder
Reflow soldering with recommendable temperature profile
2
Resistance to soldering heat
It shall be satisfied electrical requirements and not be mechanical damage
See Chapter 13.2
CLASSIFICATION PRODUCT SPECIFICATION No.
DS-13xx-2400-102
REV.
3.40
SUBJECT CLASS 1 or 2 BLUETOOTH MODULE PAGE 32 of 57
CUSTOMER’S CODE
PAN13XX Core Specification
PANASONIC’S CODE
See Chapter 28. Ordering Information DATE 18.07.2012
PANASONIC INDUSTRIAL DEVICES EUROPE GMBH www.pedeu.pansonic.de
18
RECOMMENDED FOOT PATTERN
18.1
RECOMMENDED FOOT PATTERN PAN131X WITHOUT ANTENNA
Dimensions in mm.
171513141211987653212324211819202210416Pad = 24 x 0.60mm x 0.60mmTop View9,00 6,008,50
The land pattern dimensions above are meant to serve only as a guide. This information is provided without any legal liability.
For the solder paste screen, use as a first guideline the same foot print as shown in the figure above. Solder paste screen cutouts (with slightly different dimensions) might be optimum depending on your soldering process. For example, the solder paste screen thickness chosen might have an effect. The solder screen thickness depends on your production standard 120μm to 150μm is recommended.
IMPORTANT: Although the bottom side of PAN131X is fully coated, no copper such as through hole vias, planes or tracks on the board component layer should be located below the PAN131X to avoid creating a short. In cases where a track or through hole via has to be located under the module, it must be kept away from PAN131X bottom pads. The PAN131X multilayer pcb contains an inner RF shielding plane, therefore no pcb shielding plane below the module is needed.
When using an onboard ceramic antenna, place the antenna on the edge of your carrier board (if allowable).
If you have any questions on these points, contact your local Panasonic representative.
Schematics and layouts may be sent to wireless@eu.panasonic.com for final review.
CLASSIFICATION PRODUCT SPECIFICATION No.
DS-13xx-2400-102
REV.
3.40
SUBJECT CLASS 1 or 2 BLUETOOTH MODULE PAGE 33 of 57
CUSTOMER’S CODE
PAN13XX Core Specification
PANASONIC’S CODE
See Chapter 28. Ordering Information DATE 18.07.2012
PANASONIC INDUSTRIAL DEVICES EUROPE GMBH www.pedeu.pansonic.de
18.2
RECOMMENDED FOOT PATTERN PAN132X WITH ANTENNA
Dimensions in mm.
The land pattern dimensions above are meant to serve only as a guide.
For the solder paste screen, use as a first guideline the same foot print as shown in the Figure above. Solder paste screen cutouts (with slightly different dimensions) might be optimum depending on your soldering process. For example, the solder paste screen thickness chosen might have an effect. The solder screen thickness depends on your production standard 120μm to 150μm is recommended.
IMPORTANT: In cases where a track or through hole via has to be located under the module, it must be kept away from PAN132X bottom pads. The PAN132X multilayer pcb contains an inner RF shielding plane, therefore no pcb shielding plane below the module is needed.
If you have any questions on these points, contact your local Panasonic representative.
Schematics and layouts may be sent to wireless@eu.panasonic.com for final review.
CLASSIFICATION PRODUCT SPECIFICATION No.
DS-13xx-2400-102
REV.
3.40
SUBJECT CLASS 1 or 2 BLUETOOTH MODULE PAGE 34 of 57
CUSTOMER’S CODE
PAN13XX Core Specification
PANASONIC’S CODE
See Chapter 28. Ordering Information DATE 18.07.2012
PANASONIC INDUSTRIAL DEVICES EUROPE GMBH www.pedeu.pansonic.de
19
LAYOUT RECOMMENDATIONS WITH ANTENNA (PAN132X)
20
BLUETOOTH LE (LOW ENERGY) PAN1316/26
20.1
NETWORK TOPOLOGY
Bluetooth Low Energy is designed to reduce power consumption. It can be put into a sleep mode and is only activated for event activities such as sending files to a gateway, PC or mobile phone. Furthermore the maximum power consumption is set to less than 15 mA and the average power consumption is about 1 uA. The benefit of low energy consumption are short messages and establishing very fast connections (few ms). Using these techniques, energy consumption is reduced to a tenth of a Classic Bluetooth unit. Thus, a small coin cell – such as a CR2032 – is capable of powering a device for up to 10 years of operation.
T
o be backwards compatible with Classic Bluetooth and to be able to offer an affordable solution for very inexpensive devices, Panasonic Low Energy Bluetooth modules are offered in two versions:
CLASSIFICATION PRODUCT SPECIFICATION No.
DS-13xx-2400-102
REV.
3.40
SUBJECT CLASS 1 or 2 BLUETOOTH MODULE PAGE 35 of 57
CUSTOMER’S CODE
PAN13XX Core Specification
PANASONIC’S CODE
See Chapter 28. Ordering Information DATE 18.07.2012
PANASONIC INDUSTRIAL DEVICES EUROPE GMBH www.pedeu.pansonic.de
Dual-mode: Bluetooth Low Energy technology combined with Classic Bluetooth functionality on a single module. Dual mode devices act as gateways between these two technologies.
Single Mode: Bluetooth Low Energy technology to optimize power consumption, which is particularly useful for products powered by small batteries. These modules have embedded controllers allowing the module to operate autonomously in low cost applications that lack intelligence.
This data sheet describes dual-mode Bluetooth Low Energy technology combined with Classic Bluetooth functionality on a single module. Additional information on Panasonic’s single mode products can be found by visiting www.panasonic.com/rfmodules or write an e-mail to wireless@eu.panasonic.com.
20.2
MODULE FEATURES
Fully compliant with Bluetooth 4.0:
•
Optimized for proximity and sports use
•
Supports up to 10 simultaneous connections
•
Multiple sniff instances are tightly coupled to minimize power consumption
•
Independent buffering allows a large number of multiple connections without affecting BR/EDR performance
•
Includes built-in coexistence and prioritization handling for BR/EDR and LE
CLASSIFICATION PRODUCT SPECIFICATION No.
DS-13xx-2400-102
REV.
3.40
SUBJECT CLASS 1 or 2 BLUETOOTH MODULE PAGE 36 of 57
CUSTOMER’S CODE
PAN13XX Core Specification
PANASONIC’S CODE
See Chapter 28. Ordering Information DATE 18.07.2012
PANASONIC INDUSTRIAL DEVICES EUROPE GMBH www.pedeu.pansonic.de
20.3
CURRENT CONSUMPTION FOR DIFFERENT LE SCENARIOS
Conditions: VDD_IN = 3.6 V, 25°C, 26-MHz fast clock, nominal unit, 10 dBm output power
Mode
Description
Average Current
Unit
Advertising, non-connectable
Advertising in all 3 channels
1.28msec advertising interval
15Bytes advertise Data
104
μA
Advertising, discoverable
Advertising in all 3 channels
1.28msec advertising interval
15Bytes advertise Data
121
μA
Scanning
Listening to a single frequency per window
1.28msec scan interval
11.25msec scan window
302
μA
Connected
(master role)
500msec connection interval
0msec Slave connection latency
Empty Tx/Rx LL packets
169
μA
21
ANT PAN1317/27
ANT+ (sometimes ANT + or ANT Plus) is an interoperability function that can be added to the base ANT protocol (a proprietary wireless sensor network technology).[
21.1
NETWORK TOPOLOGY
ANT™ is a wireless sensor network protocol operating in the 2.4 GHz spectrum. Designed for ultra-low power, ease of use, efficiency and scalability, ANT supports peer-to-peer, star, tree and fixed mesh topologies. It provides reliable data communications, flexible and adaptive network operation and cross-talk immunity. The ANT protocol stack is compact, requiring minimal microcontroller resources to reduce system costs, lighten the computational burden and improve efficiency. Low-level security is implemented to allow user-defined network security.
PAN1317/1327 provides the first wireless, single-chip solution with dual-mode ANT and Bluetooth connectivity with inclusion of TI’s CC2567 device. This solution wirelessly connects 13 million ANT-based devices to the more than 3 billion Bluetooth endpoint devices used by people every day, creating new market opportunities for companies building ANT products and Bluetooth products alike. CC2567 requires 80% less board area than a design with two single-mode solutions (one ANT+, one Bluetooth) and increases the wireless transmission range up to two times the distance of a single-mode ANT+ solution.
CLASSIFICATION PRODUCT SPECIFICATION No.
DS-13xx-2400-102
REV.
3.40
SUBJECT CLASS 1 or 2 BLUETOOTH MODULE PAGE 37 of 57
CUSTOMER’S CODE
PAN13XX Core Specification
PANASONIC’S CODE
See Chapter 28. Ordering Information DATE 18.07.2012
PANASONIC INDUSTRIAL DEVICES EUROPE GMBH www.pedeu.pansonic.de
21.2
MODULE FEATURES
Fully compliant with ANT protocol:
• ANT solution optimized for fitness, health and consumers use cases
• Supports up to eight simultaneous connections, various network topologies and high-resolution proximity pairing
• Includes built-in coexistence and prioritization handling for BR/EDR and ANT
Features
Benefits
Dual-mode ANT+ and Bluetooth (Bluetooth v2.1 + EDR) on a single chip
- Requires 80% less board area than any dual module or device design
- Reduces costs associated with incorporating two wireless technologies
Fully validated optimized single antenna solution
- Enables simultaneous operation of ANT+ and Bluetooth without the need for two devices or modules
- Includes built-in coexistence
Best-in-class Bluetooth and ANT RF performance:
- +10 dBm Tx power with transmit power control
- -93 dBm sensitivity
- Delivers twice the distance between the aggregator and ANT sensor device than competitive single-mode ANT solutions
- Enables a robust and high-throughput connection with extended range
Support for:
- ANT+ ultra low power (master and slave devices)
- Bluetooth power saving modes (park, sniff, hold)
- Bluetooth ultra low power modes (deep sleep, power down)
- Improves battery life and power efficiency of the finished product
Turnkey solution:
- Fully integrated module
- Complete development kit with software and documentation
- TI MSP430 hardware and software platform integration (optional)
- Ease of integration into system allows quick time to market
- Reduces costs and time associated with certification
21.3
ANT CURRENT CONSUMPTION
Mode
Description
Average Current
Unit
Rx message mode
250msec interval
380
μA
Rx message mode
500msec interval
205
μA
Rx message mode
1000msec interval
118
μA
CLASSIFICATION PRODUCT SPECIFICATION No.
DS-13xx-2400-102
REV.
3.40
SUBJECT CLASS 1 or 2 BLUETOOTH MODULE PAGE 38 of 57
CUSTOMER’S CODE
PAN13XX Core Specification
PANASONIC’S CODE
See Chapter 28. Ordering Information DATE 18.07.2012
PANASONIC INDUSTRIAL DEVICES EUROPE GMBH www.pedeu.pansonic.de
22
TRIPLE MODE (BR/EDR + BLUETOOTH LOW ENERGY + ANT) PAN1323
The PAN1323 has been engineered to give designers the flexibility to implement Bluetooth Classic (BR/EDR), Bluetooth Low Energy and ANT into an application using a single module, reducing cost and footprint area. Refer to the paragraphs above for complete descriptions on each of the three protocols. The module is fully hardware compatible with the PAN1315, 15A, 16, 17, 25, 25A, 26 and 27. A highly efficent single RF block serves all three protocols. Protocols access the RF block using time division multiplexing. The application layer determines the priority and timing of the RF block.Customers interested in this unique module are encouraged to contact StoneStreetOne for a Bluetooth SIG certified stack.
22.1
TRIPLE MODE CURRENT CONSUMPTION
The current consumption of the PAN1326 is a function of the protocol that the module is running at any point in time. Refer to the paragraphs above for details on current consumption for each of the three protocols or software vendor.
CLASSIFICATION PRODUCT SPECIFICATION No.
DS-13xx-2400-102
REV.
3.40
SUBJECT CLASS 1 or 2 BLUETOOTH MODULE PAGE 39 of 57
CUSTOMER’S CODE
PAN13XX Core Specification
PANASONIC’S CODE
See Chapter 28. Ordering Information DATE 18.07.2012
PANASONIC INDUSTRIAL DEVICES EUROPE GMBH www.pedeu.pansonic.de
23
DEVELOPMENT OF APPLICATIONS
Mindtree Ltd. has developed a Bluetooth SPP freeware for TIs MSP430 and Panasonics PAN1315(A) and PAN1325(A). For other software refer to Chapter 24 or visit the following link www.panasonic.com/rfmodules.
23.1
TOOLS TO BE NEEDED
PAN1323ETU
Tool
Source
TI - MSP-EXP430F5438 - Experimenter Board
MSP-EXP430F5438
TI - MSP-FET430UIF430 - Debugging Interface
MSP-FET430UIF430
TI PAN1323EMK
PAN1323EMK - Bluetooth Evaluation Module Kit for MSP430
Panasonic PAN1323ETU
CC2567-PAN1327ANT-BTKIT
For information on Bluetooth + ANT kit for PAN1327
CC2567 + PAN1327 wiki
In addition you need the software development environment, e.g. IAR Embedded Workbench, refer to:
http://wiki.msp430.com/index.php/MSP430_Bluetooth_Platform
Evaluation kits and modules are available through Panasonic’s network of authorized distributors. For any additional information, please visit www.panasonic.com/rfmodules.
CLASSIFICATION PRODUCT SPECIFICATION No.
DS-13xx-2400-102
REV.
3.40
SUBJECT CLASS 1 or 2 BLUETOOTH MODULE PAGE 40 of 57
CUSTOMER’S CODE
PAN13XX Core Specification
PANASONIC’S CODE
See Chapter 28. Ordering Information DATE 18.07.2012
PANASONIC INDUSTRIAL DEVICES EUROPE GMBH www.pedeu.pansonic.de
24
LIST OF PROFILES
Profile
Software Developer
Controller
Availability
Bluetooth
SPP and others
MindTree
TI, MSP430
Now
SPP
Seeran
STM32, MSP430
Now
HDP, SPP
Stollmann
TI, MSP430
Now
A2DP, AVRCP, SPP
StoneStreetOne
TI, Stellaris
Now
SPP and others
ARS
Multiple
Now
Bluetooth LE
All
ARS, MindTree, StoneStreetOne, Stollmann
TI, MSP430 and others
Upon request
ANT Protocoll
ANT
Dynastream
MSP430 and others
Now
Triple Mode Stack
SPP
StoneStreetOne
MSP430 and others
Now
For all other profiles contact your local sales representative.
25
RELIABILITY TESTS
The measurement should be done after being exposed to room temperature and humidity for 1 hour.
No.
Item
Limit
Condition
1
Vibration test
Electrical parameter should be in specification
a) Freq.:10~50Hz,Amplitude:1.5mm
a) 20min. / cycle,1hrs. each of XYZ axis
b) Freq.:30~100Hz, 6G
b) 20min. / cycle,1hrs. each of XYZ axis
2
Shock test
the same as above
Dropped onto hard wood from height of 50cm for 3 times
3
Heat cycle test
the same as above
-40°C for 30min. and +85°C for 30min.;
each temperature 300 cycles
4
Moisture test
the same as above
+60°C, 90% RH, 300h
5
Low temp. test
the same as above
-40°C, 300h
6
High temp. test
the same as above
+85°C, 300h
CLASSIFICATION PRODUCT SPECIFICATION No.
DS-13xx-2400-102
REV.
3.40
SUBJECT CLASS 1 or 2 BLUETOOTH MODULE PAGE 41 of 57
CUSTOMER’S CODE
PAN13XX Core Specification
PANASONIC’S CODE
See Chapter 28. Ordering Information DATE 18.07.2012
PANASONIC INDUSTRIAL DEVICES EUROPE GMBH www.pedeu.pansonic.de
26
CAUTIONS
Failure to follow the guidelines set forth in this document may result in degrading of the product’s functions and damage to the product.
26.1
DESIGN NOTES
(1)
Follow the conditions written in this specification, especially the control signals of this module.
(2)
The supply voltage has to be free of AC ripple voltage (for example from a battery or a low noise regulator output). For noisy supply voltages, provide a decoupling circuit (for example a ferrite in series connection and a bypass capacitor to ground of at least 47uF directly at the module).
(3)
This product should not be mechanically stressed when installed.
(4)
Keep this product away from heat. Heat is the major cause of decreasing the life of these products.
(5)
Avoid assembly and use of the target equipment in conditions where the products' temperature may exceed the maximum tolerance.
(6)
The supply voltage should not be exceedingly high or reversed. It should not carry noise and/or spikes.
(7)
Keep this product away from other high frequency circuits.
26.2
INSTALLATION NOTES
(1) Reflow soldering is possible twice based on the conditions in Chapter 15. Set up the temperature at the soldering portion of this product according to this reflow profile.
(2)
Carefully position the products so that their heat will not burn into printed circuit boards or affect the other components that are susceptible to heat.
(3)
Carefully locate these products so that their temperatures will not increase due to the effects of heat generated by neighboring components.
(4)
If a vinyl-covered wire comes into contact with the products, then the cover will melt and generate toxic gas, damaging the insulation. Never allow contact between the cover and these products to occur.
(5)
This product should not be mechanically stressed or vibrated when reflowed.
(6)
To repair a board by hand soldering, keep the conditions of this chapter.
(7)
Do not wash this product.
(8)
Refer to the recommended pattern when designing a board.
(9)
Pressing on parts of the metal cover or fastening objects to the metal will cause damage to the unit.
CLASSIFICATION PRODUCT SPECIFICATION No.
DS-13xx-2400-102
REV.
3.40
SUBJECT CLASS 1 or 2 BLUETOOTH MODULE PAGE 42 of 57
CUSTOMER’S CODE
PAN13XX Core Specification
PANASONIC’S CODE
See Chapter 28. Ordering Information DATE 18.07.2012
PANASONIC INDUSTRIAL DEVICES EUROPE GMBH www.pedeu.pansonic.de
26.
3 USAGE CONDITIONS NOTES
(1) T
ake measures to protect the unit against static electricity. If pulses or other transient loads (a large load applied in a short time) are applied to the products, check and evaluate their operation befor assembly on the final products.
(2)
Do not use dropped products.
(3)
Do not touch, damage or soil the pins.
(4)
Follow the recommended condition ratings about the power supply applied to this product.
(5)
Electrode peeling strength: Do not add pressure of more than 4.9N when soldered on PCB.
(6)
Pressing on parts of the metal cover or fastening objects to the metal cover will cause damage.
(7)
These products are intended for general purpose and standard use in general electronic equipment, such as home appliances, office equipment, information and communication equipment.
26.
4 STORAGE NOTES
(1) T
he module should not be stressed mechanically during storage.
(2)
Do not store these products in the following conditions or the performance characteristics of the product, such as RF performance will be adversely affected:
• St
orage in salty air or in an environment with a high concentration of corrosive gas, such as Cl2, H2S, NH3, SO2, or NOX
•
Storage in direct sunlight
•
Storage in an environment where the temperature may be outside the range of 5°C to 35°C range, or where the humidity may be outside the 45 to 85% range.
•
Storage of the products for more than one year after the date of delivery Storage period: check the adhesive strength of the embossed tape and soldering after 6 months of storage.
(
3) Keep this product away from water, poisonous gas and corrosive gas.
(4)
This product should not be stressed or shocked when transported.
(5)
Follow the specification when stacking packed crates (max. 10).
CLASSIFICATION PRODUCT SPECIFICATION No.
DS-13xx-2400-102
REV.
3.40
SUBJECT CLASS 1 or 2 BLUETOOTH MODULE PAGE 43 of 57
CUSTOMER’S CODE
PAN13XX Core Specification
PANASONIC’S CODE
See Chapter 28. Ordering Information DATE 18.07.2012
PANASONIC INDUSTRIAL DEVICES EUROPE GMBH www.pedeu.pansonic.de
26.
5 SAFETY CAUTIONS
These specifications are intended to preserve the quality assurance of products and individual components.
Before use, check and evaluate the operation when mounted on your products. Abide by these specifications, without deviation when using the products. These products may short-circuit. If electrical shocks, smoke, fire, and/or accidents involving human life are anticipated when a short circuit occurs, then provide the following failsafe functions, as a minimum.
(1)
Ensure the safety of the whole system by installing a protection circuit and a protection device.
(2)
Ensure the safety of the whole system by installing a redundant circuit or another system to prevent a single fault causing an unsafe status.
26.
6 OTHER CAUTIONS
(1) T
his specification sheet is copyrighted.
(2)
Do not use the products for other purposes than those listed.
(3)
Be sure to provide an appropriate fail-safe function on your product to prevent an additional damage that may be caused by the abnormal function or the failure of the product.
(4)
This product has been manufactured without any ozone chemical controlled under the Montreal Protocol.
(5)
These products are not intended for other uses, other than under the special conditions shown below. Before using these products under such special conditions, check their performance and reliability under the said special conditions carefully to determine whether or not they can be used in such a manner.
• In
liquid, such as water, salt water, oil, alkali, or organic solvent, or in places where liquid may splash.
•
In direct sunlight, outdoors, or in a dusty environment
•
In an environment where condensation occurs.
•
In an environment with a high concentration of harmful gas (e.g. salty air, HCl, Cl2, SO2, H2S, NH3, and NOX)
(
6) If an abnormal voltage is applied due to a problem occurring in other components or circuits, replace these products with new products because they may not be able to provide normal performance even if their electronic characteristics and appearances appear satisfactory.
(7)
When you have any question or uncertainty, contact Panasonic.
CLASSIFICATION PRODUCT SPECIFICATION No.
DS-13xx-2400-102
REV.
3.40
SUBJECT CLASS 1 or 2 BLUETOOTH MODULE PAGE 44 of 57
CUSTOMER’S CODE
PAN13XX Core Specification
PANASONIC’S CODE
See Chapter 28. Ordering Information DATE 18.07.2012
PANASONIC INDUSTRIAL DEVICES EUROPE GMBH www.pedeu.pansonic.de
27
PACKAGING
27
.1 PACKAGING OF PAN131X WITHOUT ANTENNA
Tape Dimension
Packing in Tape
trailer (empty)1 x circumference /hub(min 160mm)component packed areastandard 1500pcsleader (empty)minimum 10 pitchTop cover tape more than 1 x circumference plus 100mm to avoid fixing of tape end on sealed modules.Direction of unreeling (for customer)PAN1315 01/01ENW89809M5AYYWWDLLFCC ID: T7V1315Machine readable 2D-BarcodePAN1315 01/01ENW89809M5AYYWWDLLFCC ID: T7V1315Machine readable 2D-Barcode
Empty spaces in component packed area shall be less than two per reel and those spaces shall not be consecutive.
Top cover tape shall not be found on reel holes and shall not stick out from reel.
CLASSIFICATION PRODUCT SPECIFICATION No.
DS-13xx-2400-102
REV.
3.40
SUBJECT CLASS 1 or 2 BLUETOOTH MODULE PAGE 45 of 57
CUSTOMER’S CODE
PAN13XX Core Specification
PANASONIC’S CODE
See Chapter 28. Ordering Information DATE 18.07.2012
PANASONIC INDUSTRIAL DEVICES EUROPE GMBH www.pedeu.pansonic.de
Component direction
PAN1315 01/01ENW89809M5AYYWWDLLFCC ID: T7V1315Machine readable 2D-Barcode
Reel dimension
A BD NW2MAXMINMIN±1.0MAX13 +0.525.0 +2.024.4 +3.0 -0.2 -0.0 -0.5*Latch (2PC)All dimensions in millimeters unless otherwise stated Assembly Method24mm330.01.520.2100.030.4*LatchTAPE SIZECW1W3
CLASSIFICATION PRODUCT SPECIFICATION No.
DS-13xx-2400-102
REV.
3.40
SUBJECT CLASS 1 or 2 BLUETOOTH MODULE PAGE 46 of 57
CUSTOMER’S CODE
PAN13XX Core Specification
PANASONIC’S CODE
See Chapter 28. Ordering Information DATE 18.07.2012
PANASONIC INDUSTRIAL DEVICES EUROPE GMBH www.pedeu.pansonic.de
Label for Package PAN1315Customer CodeENW89818C2JF105 mm
(1T) Lotcode [YYWWDLL] Example from above: YY year printed 08 WW normal calendar week printed 01 D day printed 5 (Friday) L line identifier, if more as one printed 1 L lot identifier per day printed 1 (1P) Customer Order Code, if any, otherwise company name will be printed
(2P) Panasonic Order Code fix as ENW89818C2JF
(9D) Datecode as [YYWW]
(Q) Quantity [XXXX], variable max. 1500
(HW/SW) Hardware /Software Release
Total Package
CLASSIFICATION PRODUCT SPECIFICATION No.
DS-13xx-2400-102
REV.
3.40
SUBJECT CLASS 1 or 2 BLUETOOTH MODULE PAGE 47 of 57
CUSTOMER’S CODE
PAN13XX Core Specification
PANASONIC’S CODE
See Chapter 28. Ordering Information DATE 18.07.2012
PANASONIC INDUSTRIAL DEVICES EUROPE GMBH www.pedeu.pansonic.de
27.2
PACKAGING FOR PAN132X WITH ANTENNA
Tape Dimension
Measured from centreline of sprocket holeMeasured holeCumulative tolerance of 10 sprocketMeasured from centreline of sprocketto centreline of pocket.holes is ± 0.20 .hole to centreline of pocket.(I)(II)(III)(IV)Other material available.ALL DIMENSIONS IN MILLIMETRES UNLESS OTHERWISE STATED.WFP1+/-0.10+/-0.10+/-0.307.5012.0016.00K12.00+/-0.102.80+/-0.10+/-0.109.40BoKo9.90Ao+/-0.10 Tooling code: Flatbed -9 Estimated Max Length: 72m per 22B3 YYXXSECTION Y-Y SCALE 3.5 : 1SECTION X-X SCALE 3.5 : 1
Packing in Tape
All other packaging information is similar to Chapter 27.1
Pin1 Marking
CLASSIFICATION PRODUCT SPECIFICATION No.
DS-13xx-2400-102
REV.
3.40
SUBJECT CLASS 1 or 2 BLUETOOTH MODULE PAGE 48 of 57
CUSTOMER’S CODE
PAN13XX Core Specification
PANASONIC’S CODE
See Chapter 28. Ordering Information DATE 18.07.2012
PANASONIC INDUSTRIAL DEVICES EUROPE GMBH www.pedeu.pansonic.de
28 O
RDERING INFORMATION
Version
Function
Controller
Part number
Antenna on board
Notes
MOQ (1)
PAN1315(2)
CC2560
ENW89818C2JF
NO
PAN1315A
Bluetooth v2.1 + EDR
CC2560A
ENW89829C2JF
NO
CC2560A offers reductions in init script size over CC2560 and is recommended for all new designs
1500
PAN1325(2)
CC2560
ENW89818A2JF
YES
PAN1325A
Bluetooth v2.1 + EDR
CC2560A
ENW89829A2JF
YES
CC2560A offers reductions in init script size over CC2560 and is recommended for all new designs.
1500
PAN1316
Bluetooth v2.1 + EDR
BLE 4.0
CC2564
ENW89823C2JF
NO
1500
PAN1326
Bluetooth v2.1 + EDR BLE 4.0
CC2564
ENW89823C2JF
YES
1500
PAN1317
Bluetooth v2.1 + EDR ANT
CC2567
ENW89827C2JF
NO
1500
PAN1327
Bluetooth v2.1 + EDR ANT
CC2567
ENW89827A2JF
YES
1500
PAN1323
Bluetooth v2.1 + EDR BLE 4.0 ANT
CC2569
ENW89842A2JF
YES
Check with your software developer for details on triple mode functionality.
1500
PAN1323ETU
Bluetooth v2.1 + EDR BLE 4.0 ANT
CC25xx
ENW89825A2JF
YES
Evaluation kit for the whole series. PAN1315-PAN1327.
1
Notes:
(1
) Abbreviation for Minimum Order Quantity (MOQ). The standard MOQ for mass production are 1500 pieces, fewer only on customer demand. Samples for evaluation can be delivered at any quantity.
(2) Not recommended for new designs, please refer to Chapter 1.1
CLASSIFICATION PRODUCT SPECIFICATION No.
DS-13xx-2400-102
REV.
3.40
SUBJECT CLASS 1 or 2 BLUETOOTH MODULE PAGE 49 of 57
CUSTOMER’S CODE
PAN13XX Core Specification
PANASONIC’S CODE
See Chapter 28. Ordering Information DATE 18.07.2012
PANASONIC INDUSTRIAL DEVICES EUROPE GMBH www.pedeu.pansonic.de
29
ROHS DECLARATION
Declaration of environmental compatibility for supplied products:
Hereby we declare to our best present knowledge based on declaration of our suppliers that this product do not contain by now the following substances which are banned by Directive 2002/95/EC (RoHS) or if contain a maximum concentration of 0,1% by weight in homogeneous materials for
• Le
ad and lead compounds
• M
ercury and mercury compounds
•
Chromium (VI)
•
PBB (polybrominated biphenyl) category
•
PBDE (polybrominated biphenyl ether) category
And a maximum concentration of 0,01% by weight in homogeneous materials for
•
Cadmium and cadmium compounds
3
0 DATA SHEET STATUS
This data sheet contains the final specification (RELEASE).
Panasonic reserves the right to make changes at any time without notice in order to improve design and supply the best possible product.
Supplementary data will be published at a later date.
Consult the most recently issued data sheet before initiating or completing a design.
Use this URL to search for the most recent version of this data sheet: PAN13xx Latest Data Sheet!
CLASSIFICATION PRODUCT SPECIFICATION No.
DS-13xx-2400-102
REV.
3.40
SUBJECT CLASS 1 or 2 BLUETOOTH MODULE PAGE 50 of 57
CUSTOMER’S CODE
PAN13XX Core Specification
PANASONIC’S CODE
See Chapter 28. Ordering Information DATE 18.07.2012
PANASONIC INDUSTRIAL DEVICES EUROPE GMBH www.pedeu.pansonic.de
3
1 HISTORY FOR THIS DOCUMENT
Revision
Date
Modification / Remarks
0.90
18.12.2009
1st preliminary version
0.95
01.03.2010
Updated Chapter 14.2 and 28.
0.96
Not released
Change ESD Information on foot note 7 in chapter
Pin Description
0.97
25.03.2010
Various updates. Deleted links to TI Datasheet.
0.98
21.04.2010
Updated Links Some minor changes in Chapter 8 and 9.1 and change the base for the values in Chapter 9.
0.99
22.10.2010
Adopted changes according to CC2560 Datasheet. Included Interface Description, performance values. Not released.
1.00
04.11.2010
1st internal Release.
1.01
03.12.2010
Included reference to PAN1325 Application Note. AN-1325-2420-111.pdf
1.02
10.01.2011
Changed wording in Chapter 34.2 ”
Industry Canada Certification
”.
1.03
23.05.2011
Included DOC for PAN1315 series. Included PAN13xx ANT and BLE Addendum Rev1.x.pdf reference. Included Note for IO voltage and MLD_OUT pin.
1.04
02.07.2011
Corrected wording in Chapter 34.3
Europ
ean R&TTE Declaration of Conformity
.
1.05
28.10.2011
Including CC2560A silicon PAN1315A HW40 at Chapter 1.1, Chapter and Chapter 0. Deleted ES label in Chapter
1.06
15.11.2011
Added overview for the core specification and their addendums. Updated front page. Updated Related Documents.
3.00
11.01.2012
Merging PAN13xx documents into this specification and correct some format
3.10
16.01.2012
Minor mistakes fixed
3.20
29.05.2012
DoC replaced with revised version
3.30
11.06.2012
Added triple mode stack Module PAN1323, add PAN1323 to ordering and software information overview, Software Block Diagram added, Bluetooth Inter IC-Sound chapter information added
Layout Recommandations with Antenna added, Application Note LGA added
3.31
27.06.2012
Added design information to use low pass filter (chapter 11.1 / 11.9) for better noise surpression when using PCM interface
3.40
18.07.2012
Re-organize chapter
Re
gulatory Information
and added 2 chapters
1.
NCC St
atement
(only valid for PAN1325)
2.
Blu
etooth SIG Statement
3. Chapter 11.9, Second Paragraph was updated
4. Link in Chapter 34.1.1. was fixed
32
RELATED DOCUMENTS
For an update, search in the suitable homepage.
[1
] PAN1323ETU Design-Guide: http://www.panasonic.com/industrial/includes/pdf/PAN1323ETUDesignGuide.pdf
[2
] CC2560 Product Bulletin: http://focus.ti.com/pdfs/wtbu/cc2560_slyt377.pdf
[3] Bluetooth SW for MSP430 is supported by IAR IDE service pack 5.10.6 and later. Use full IAR version edition (not the kick-start version). You can find info on IAR at http://www.iar.com/website1/1.0.1.0/3/1/ and www.MSP430.com . Note, that there is an option for a 30-day free version of IAR evaluation edition.
CLASSIFICATION PRODUCT SPECIFICATION No.
DS-13xx-2400-102
REV.
3.40
SUBJECT CLASS 1 or 2 BLUETOOTH MODULE PAGE 51 of 57
CUSTOMER’S CODE
PAN13XX Core Specification
PANASONIC’S CODE
See Chapter 28. Ordering Information DATE 18.07.2012
PANASONIC INDUSTRIAL DEVICES EUROPE GMBH www.pedeu.pansonic.de
[4] PAN13xx CAD data: http://www.pedeu.panasonic.de/pdf/174ext.zip
[5] Application Note Land Grid Array: http://www.pedeu.panasonic.de/pdf/184ext.pdf
CLASSIFICATION PRODUCT SPECIFICATION No.
DS-13xx-2400-102
REV.
3.40
SUBJECT CLASS 1 or 2 BLUETOOTH MODULE PAGE 52 of 57
CUSTOMER’S CODE
PAN13XX Core Specification
PANASONIC’S CODE
See Chapter 28. Ordering Information DATE 18.07.2012
PANASONIC INDUSTRIAL DEVICES EUROPE GMBH www.pedeu.pansonic.de
33
GENERAL INFORMATION
© Panasonic Industrial Devices Europe GmbH.
All rights reserved.
This document may contain errors. Panasonic reserves the right to make corrections, modifications, enhancements, improvements, and other changes to its literature at any time. Customers should obtain the latest relevant information before placing orders and should verify that such information is current and complete. All products are sold subject to Panasonic’s terms and conditions of sale supplied at the time of order acknowledgment.
If we deliver ES samples to the customer, these samples have the status Engineering Samples. This means, the design of this product is not yet concluded. Engineering Samples may be partially or fully functional, and there may be differences to be published Data Sheet.
Engineering Samples are not qualified and are not to be used for reliability testing or series production.
Disclaimer:
Customer acknowledges that samples may deviate from the Data Sheet and may bear defects due to their status of development and the lack of qualification mentioned above.
Panasonic rejects any liability or product warranty for Engineering Samples. In particular, Panasonic disclaims liability for damages caused by
• th
e use of the Engineering Sample other than for Evaluation Purposes, particularly the installation or integration in an other product to be sold by Customer,
• de
viation or lapse in function of Engineering Sample,
• im
proper use of Engineering Samples.
Panasonic disclaimes any liability for consequential and incidental damages. Panasonic assumes no liability for applications assistance or customer product design. Customers are responsible for their products and applications using Panasonic components. To minimize the risks associated with customer products and applications, customers should provide adequate design and operating safeguards. In case of any questions, contact your local sales representative.
34 REGULATORY INFORMATION
34
.1 FCC FOR US
3
4.1.1 FCC Notice
The devices PAN13xx, for details refer to Chapter 28 in this document, including the antennas, which are listed in Chapter 34.5 of this data sheet, complies with Part 15 of the FCC Rules. The device meets the requirements for modular transmitter approval as detailed in FCC public Notice DA00-1407.transmitter. Operation is subject to the following two conditions: (1) This device may not cause harmful interference, and (2) This device must accept any interference received, including interference that may
cause undesired operation.
CLASSIFICATION PRODUCT SPECIFICATION No.
DS-13xx-2400-102
REV.
3.40
SUBJECT CLASS 1 or 2 BLUETOOTH MODULE PAGE 53 of 57
CUSTOMER’S CODE
PAN13XX Core Specification
PANASONIC’S CODE
See Chapter 28. Ordering Information DATE 18.07.2012
PANASONIC INDUSTRIAL DEVICES EUROPE GMBH www.pedeu.pansonic.de
3
4.1.2 Caution
The FCC requires the user to be notified that any changes or modifications made to this device that are not expressly approved by Panasonic Industrial Devices Europe GmbH may void the user's authority to operate the equipment.
This equipment has been tested and found to comply with the limits for a Class B digital device, pursuant to Part 15 of the FCC Rules. These limits are designed to provide reasonable protection against harmful interference in a residential installation. This equipment generates, uses and can radiate radio frequency energy and, if not installed and used in accordance with the instructions, may cause harmful interference to radio communications. However, there is no guarantee that interference will not occur in a particular installation. If this equipment does cause harmful interference to radio or television reception, which can be determined by turning the equipment off and on, the user is encouraged to try to correct the interference by one or more of the following measures:
•
Reorient or relocate the receiving antenna.
• I
ncrease the separation between the equipment and receiver.
• Con
nect the equipment into an outlet on a circuit different from that to which the receiver is connected.
• Consu
lt the dealer or an experienced radio/TV technician for help
34.1.3
Labeling Requirements
The Original Equipment Manufacturer (OEM) must ensure that FCC labeling requirements are met. This includes a clearly visible label on the outside of the OEM enclosure specifying the appropriate Panasonic FCC identifier for this product as well as the FCC Notice above. The FCC identifier are FCC ID: T7V1315. This FCC identifier is valid for all PAN13xx modules, for details, see the Chapter 28. Ordering Information.
In any case the end product must be labelled exterior with "Contains FCC ID: T7V1315"
3
4.1.4 Antenna Warning
For the related part number of PAN13xx refer to Chapter 28. Ordering Information.
This devices are tested with a standard SMA connector and with the antennas listed below. When integrated in the OEMs product, these fixed antennas require installation preventing end-users from replacing them with non-approved antennas. Any antenna not in the following table must be tested to comply with FCC Section 15.203 for unique antenna connectors and Section 15.247 for emissions. The FCC identifier for this device with the antenna listed in item 1 are the same (FCC ID: T7V1315).
3
4.1.5 Approved Antenna List
Note: We are able to qualify your antenna and will add to this list as that process is completed.
Item
Part Number
Manufacturer
Frequency Band
Type
Gain (dBi)
1
2450AT43B100
Johanson Technologies
2.4GHz
Chip-Antenna
+1.3
2
LDA212G3110K
Murata
2.4GHz
Chip-Antenna
+0.9
3
4788930245
Würth Elektronik
2.4GHz
Chip-Antenna
+0.5
CLASSIFICATION PRODUCT SPECIFICATION No.
DS-13xx-2400-102
REV.
3.40
SUBJECT CLASS 1 or 2 BLUETOOTH MODULE PAGE 54 of 57
CUSTOMER’S CODE
PAN13XX Core Specification
PANASONIC’S CODE
See Chapter 28. Ordering Information DATE 18.07.2012
PANASONIC INDUSTRIAL DEVICES EUROPE GMBH www.pedeu.pansonic.de
3
4.1.6 RF Exposure PAN13xx
To comply with FCC RF Exposure requirements, the Original Equipment Manufacturer (OEM) must ensure that the approved antenna in the previous table must be installed.
The preceding statement must be included as a CAUTION statement in manuals for products operating with the approved antennas in the previous table to alert users on FCC RF Exposure compliance.
Any notification to the end user of installation or removal instructions about the integrated radio module is not allowed.
The radiated output power of PAN13xx with mounted ceramic antenna (FCC ID: T7V1315) is far below the FCC radio frequency exposure limits. Nevertheless, the PAN13xx shall be used in such a manner that the potential for human contact during normal operation is minimized.
End users may not be provided with the module installation instructions. OEM integrators and end users must be provided with transmitter operating conditions for satisfying RF exposure compliance.
34.2 INDUSTRY CANADA CERTIFICATION
PAN1315 is licensed to meet the regulatory requirements of Industry Canada (IC), license: IC: 216Q-1315
Manufacturers of mobile, fixed or portable devices incorporating this module are advised to clarify any regulatory questions and ensure compliance for SAR and/or RF exposure limits. Users can obtain Canadian information on RF exposure and compliance from www.ic.gc.ca.
This device has been designed to operate with the antennas listed in Table 20 above, having a maximum gain of 1.3 dBi. Antennas not included in this list or having a gain greater than 1.3 dBi are strictly prohibited for use with this device. The required antenna impedance is 50 ohms. The antenna used for this transmitter must not be co-located or operating in conjunction with any other antenna or transmitter. due to the model size the IC identifier is displayed in the installation instruction.
34.3 EUROPEAN R&TTE DECLARATION OF CONFORMITY
Hereby, Panasonic Industrial Devices Europe GmbH, declares that the Bluetooth module PAN1315 and their versions is in compliance with the essential requirements and other relevant provisions of Directive 1999/5/EC. As a result of the conformity assessment procedure described in Annex III of the Directive 1999/5/EC, the end-customer equipment should be labelled as follows:
PAN13xx and their versions in the specified reference design can be used in the following countries: Austria, Belgium, Cyprus, Czech Republic, Denmark, Estonia, Finland, France, Germany, Greece, Hungary, Ireland, Italy, Latvia, Lithuania, Luxembourg, Malta, Poland, Portugal, Slovakia, Slovenia, Spain, Sweden, The Netherlands, the United Kingdom, Switzerland, and Norway.
CLASSIFICATION PRODUCT SPECIFICATION No.
DS-13xx-2400-102
REV.
3.40
SUBJECT CLASS 1 or 2 BLUETOOTH MODULE PAGE 55 of 57
CUSTOMER’S CODE
PAN13XX Core Specification
PANASONIC’S CODE
See Chapter 28. Ordering Information DATE 18.07.2012
PANASONIC INDUSTRIAL DEVICES EUROPE GMBH www.pedeu.pansonic.de
CLASSIFICATION PRODUCT SPECIFICATION No.
DS-13xx-2400-102
REV.
3.40
SUBJECT CLASS 1 or 2 BLUETOOTH MODULE PAGE 56 of 57
CUSTOMER’S CODE
PAN13XX Core Specification
PANASONIC’S CODE
See Chapter 28. Ordering Information DATE 18.07.2012
PANASONIC INDUSTRIAL DEVICES EUROPE GMBH www.pedeu.pansonic.de
34.4 N
CC FOR TAIWAN
34.4.1
Labeling Requirements
Due to the limited size on the module, the NCC ID is not visible on the module.
When the module is installed inside another device, then the outside of the device into which the module is installed must also display a label referring to the enclosed module. This exterior label can use wording such as the following:
“Contains Transmitter Module NCC ID:” or “Contains NCC ID:” CCAJ11LPxxxxTx
Any similar wording that expresses the same meaning may be used.
Panasonic is able to provide the above content from the label as a vector graphic, please ask at wireless@eu.panasonic.com.
34.4.2 NCC Statement
Due to the national rule from Taiwan we have to print the below statement in Chinese language.
34.5 BLUETOOTH SIG STATEMENT
35 L
IFE SUPPORT POLICY
This Panasonic product is not designed for use in life support appliances, devices, or systems where malfunction can reasonably be expected to result in a significant personal injury to the user, or as a critical component in any life support device or system whose failure to perform can be reasonably expected to cause the failure of the
CLASSIFICATION PRODUCT SPECIFICATION No.
DS-13xx-2400-102
REV.
3.40
SUBJECT CLASS 1 or 2 BLUETOOTH MODULE PAGE 57 of 57
CUSTOMER’S CODE
PAN13XX Core Specification
PANASONIC’S CODE
See Chapter 28. Ordering Information DATE 18.07.2012
PANASONIC INDUSTRIAL DEVICES EUROPE GMBH www.pedeu.pansonic.de
life support device or system, or to affect its safety or effectiveness. Panasonic customers using or selling these products for use in such applications do so at their own risk and agree to fully indemnify Panasonic for any damages resulting.
LM3S8933 Microcontroller
DATA SHEET
DS-LM3S8933-2550 Copyright © 2007-2008 Luminary Micro, Inc.
PRELIMINARY
Legal Disclaimers and Trademark Information
INFORMATION IN THIS DOCUMENT IS PROVIDED IN CONNECTION WITH LUMINARY MICRO PRODUCTS. NO LICENSE, EXPRESS OR
IMPLIED, BY ESTOPPEL OR OTHERWISE, TO ANY INTELLECTUAL PROPERTY RIGHTS IS GRANTED BY THIS DOCUMENT. EXCEPT
AS PROVIDED IN LUMINARY MICRO'S TERMS AND CONDITIONS OF SALE FOR SUCH PRODUCTS, LUMINARY MICRO ASSUMES NO
LIABILITY WHATSOEVER, AND LUMINARY MICRO DISCLAIMS ANY EXPRESS OR IMPLIED WARRANTY, RELATING TO SALE AND/OR
USE OF LUMINARY MICRO'S PRODUCTS INCLUDING LIABILITY OR WARRANTIES RELATING TO FITNESS FOR A PARTICULAR
PURPOSE, MERCHANTABILITY, OR INFRINGEMENT OF ANY PATENT, COPYRIGHT OR OTHER INTELLECTUAL PROPERTY RIGHT.
LUMINARY MICRO'S PRODUCTS ARE NOT INTENDED FOR USE IN MEDICAL, LIFE SAVING, OR LIFE-SUSTAINING APPLICATIONS.
Luminary Micro may make changes to specifications and product descriptions at any time, without notice. Contact your local Luminary Micro sales office
or your distributor to obtain the latest specifications before placing your product order.
Designers must not rely on the absence or characteristics of any features or instructions marked "reserved" or "undefined." Luminary Micro reserves these
for future definition and shall have no responsibility whatsoever for conflicts or incompatibilities arising from future changes to them.
Copyright © 2007-2008 Luminary Micro, Inc. All rights reserved. Stellaris, Luminary Micro, and the Luminary Micro logo are registered trademarks of
Luminary Micro, Inc. or its subsidiaries in the United States and other countries. ARM and Thumb are registered trademarks and Cortex is a trademark
of ARM Limited. Other names and brands may be claimed as the property of others.
Luminary Micro, Inc.
108 Wild Basin, Suite 350
®
Austin, TX 78746
Main: +1-512-279-8800
Fax: +1-512-279-8879
http://www.luminarymicro.com
2 March 17, 2008
Preliminary
Table of Contents
About This Document .................................................................................................................... 20
Audience .............................................................................................................................................. 20
About This Manual ................................................................................................................................ 20
Related Documents ............................................................................................................................... 20
Documentation Conventions .................................................................................................................. 20
1 Architectural Overview ...................................................................................................... 22
1.1 Product Features ...................................................................................................................... 22
1.2 Target Applications .................................................................................................................... 27
1.3 High-Level Block Diagram ......................................................................................................... 28
1.4 Functional Overview .................................................................................................................. 28
1.4.1 ARM Cortex™-M3 ..................................................................................................................... 29
1.4.2 Motor Control Peripherals .......................................................................................................... 29
1.4.3 Analog Peripherals .................................................................................................................... 30
1.4.4 Serial Communications Peripherals ............................................................................................ 30
1.4.5 System Peripherals ................................................................................................................... 32
1.4.6 Memory Peripherals .................................................................................................................. 33
1.4.7 Additional Features ................................................................................................................... 33
1.4.8 Hardware Details ...................................................................................................................... 34
2 ARM Cortex-M3 Processor Core ...................................................................................... 35
2.1 Block Diagram .......................................................................................................................... 36
2.2 Functional Description ............................................................................................................... 36
2.2.1 Serial Wire and JTAG Debug ..................................................................................................... 36
2.2.2 Embedded Trace Macrocell (ETM) ............................................................................................. 37
2.2.3 Trace Port Interface Unit (TPIU) ................................................................................................. 37
2.2.4 ROM Table ............................................................................................................................... 37
2.2.5 Memory Protection Unit (MPU) ................................................................................................... 37
2.2.6 Nested Vectored Interrupt Controller (NVIC) ................................................................................ 37
3 Memory Map ....................................................................................................................... 41
4 Interrupts ............................................................................................................................ 43
5 JTAG Interface .................................................................................................................... 46
5.1 Block Diagram .......................................................................................................................... 47
5.2 Functional Description ............................................................................................................... 47
5.2.1 JTAG Interface Pins .................................................................................................................. 48
5.2.2 JTAG TAP Controller ................................................................................................................. 49
5.2.3 Shift Registers .......................................................................................................................... 50
5.2.4 Operational Considerations ........................................................................................................ 50
5.3 Initialization and Configuration ................................................................................................... 53
5.4 Register Descriptions ................................................................................................................ 53
5.4.1 Instruction Register (IR) ............................................................................................................. 53
5.4.2 Data Registers .......................................................................................................................... 55
6 System Control ................................................................................................................... 57
6.1 Functional Description ............................................................................................................... 57
6.1.1 Device Identification .................................................................................................................. 57
6.1.2 Reset Control ............................................................................................................................ 57
March 17, 2008 3
Preliminary
LM3S8933 Microcontroller
6.1.3 Power Control ........................................................................................................................... 60
6.1.4 Clock Control ............................................................................................................................ 60
6.1.5 System Control ......................................................................................................................... 62
6.2 Initialization and Configuration ................................................................................................... 63
6.3 Register Map ............................................................................................................................ 64
6.4 Register Descriptions ................................................................................................................ 65
7 Hibernation Module .......................................................................................................... 119
7.1 Block Diagram ........................................................................................................................ 120
7.2 Functional Description ............................................................................................................. 120
7.2.1 Register Access Timing ........................................................................................................... 120
7.2.2 Clock Source .......................................................................................................................... 121
7.2.3 Battery Management ............................................................................................................... 121
7.2.4 Real-Time Clock ...................................................................................................................... 121
7.2.5 Non-Volatile Memory ............................................................................................................... 122
7.2.6 Power Control ......................................................................................................................... 122
7.2.7 Interrupts and Status ............................................................................................................... 122
7.3 Initialization and Configuration ................................................................................................. 123
7.3.1 Initialization ............................................................................................................................. 123
7.3.2 RTC Match Functionality (No Hibernation) ................................................................................ 123
7.3.3 RTC Match/Wake-Up from Hibernation ..................................................................................... 123
7.3.4 External Wake-Up from Hibernation .......................................................................................... 124
7.3.5 RTC/External Wake-Up from Hibernation .................................................................................. 124
7.4 Register Map .......................................................................................................................... 124
7.5 Register Descriptions .............................................................................................................. 125
8 Internal Memory ............................................................................................................... 138
8.1 Block Diagram ........................................................................................................................ 138
8.2 Functional Description ............................................................................................................. 138
8.2.1 SRAM Memory ........................................................................................................................ 138
8.2.2 Flash Memory ......................................................................................................................... 139
8.3 Flash Memory Initialization and Configuration ........................................................................... 140
8.3.1 Flash Programming ................................................................................................................. 140
8.3.2 Nonvolatile Register Programming ........................................................................................... 141
8.4 Register Map .......................................................................................................................... 141
8.5 Flash Register Descriptions (Flash Control Offset) ..................................................................... 142
8.6 Flash Register Descriptions (System Control Offset) .................................................................. 149
9 General-Purpose Input/Outputs (GPIOs) ....................................................................... 162
9.1 Functional Description ............................................................................................................. 162
9.1.1 Data Control ........................................................................................................................... 163
9.1.2 Interrupt Control ...................................................................................................................... 164
9.1.3 Mode Control .......................................................................................................................... 165
9.1.4 Commit Control ....................................................................................................................... 165
9.1.5 Pad Control ............................................................................................................................. 165
9.1.6 Identification ........................................................................................................................... 165
9.2 Initialization and Configuration ................................................................................................. 165
9.3 Register Map .......................................................................................................................... 167
9.4 Register Descriptions .............................................................................................................. 169
4 March 17, 2008
Preliminary
Table of Contents
10 General-Purpose Timers ................................................................................................. 204
10.1 Block Diagram ........................................................................................................................ 204
10.2 Functional Description ............................................................................................................. 205
10.2.1 GPTM Reset Conditions .......................................................................................................... 206
10.2.2 32-Bit Timer Operating Modes .................................................................................................. 206
10.2.3 16-Bit Timer Operating Modes .................................................................................................. 207
10.3 Initialization and Configuration ................................................................................................. 211
10.3.1 32-Bit One-Shot/Periodic Timer Mode ....................................................................................... 211
10.3.2 32-Bit Real-Time Clock (RTC) Mode ......................................................................................... 212
10.3.3 16-Bit One-Shot/Periodic Timer Mode ....................................................................................... 212
10.3.4 16-Bit Input Edge Count Mode ................................................................................................. 213
10.3.5 16-Bit Input Edge Timing Mode ................................................................................................ 213
10.3.6 16-Bit PWM Mode ................................................................................................................... 214
10.4 Register Map .......................................................................................................................... 214
10.5 Register Descriptions .............................................................................................................. 215
11 Watchdog Timer ............................................................................................................... 240
11.1 Block Diagram ........................................................................................................................ 240
11.2 Functional Description ............................................................................................................. 240
11.3 Initialization and Configuration ................................................................................................. 241
11.4 Register Map .......................................................................................................................... 241
11.5 Register Descriptions .............................................................................................................. 242
12 Analog-to-Digital Converter (ADC) ................................................................................. 263
12.1 Block Diagram ........................................................................................................................ 264
12.2 Functional Description ............................................................................................................. 264
12.2.1 Sample Sequencers ................................................................................................................ 264
12.2.2 Module Control ........................................................................................................................ 265
12.2.3 Hardware Sample Averaging Circuit ......................................................................................... 266
12.2.4 Analog-to-Digital Converter ...................................................................................................... 266
12.2.5 Differential Sampling ............................................................................................................... 266
12.2.6 Test Modes ............................................................................................................................. 268
12.2.7 Internal Temperature Sensor .................................................................................................... 268
12.3 Initialization and Configuration ................................................................................................. 269
12.3.1 Module Initialization ................................................................................................................. 269
12.3.2 Sample Sequencer Configuration ............................................................................................. 269
12.4 Register Map .......................................................................................................................... 269
12.5 Register Descriptions .............................................................................................................. 270
13 Universal Asynchronous Receivers/Transmitters (UARTs) ......................................... 296
13.1 Block Diagram ........................................................................................................................ 297
13.2 Functional Description ............................................................................................................. 297
13.2.1 Transmit/Receive Logic ........................................................................................................... 297
13.2.2 Baud-Rate Generation ............................................................................................................. 298
13.2.3 Data Transmission .................................................................................................................. 299
13.2.4 Serial IR (SIR) ......................................................................................................................... 299
13.2.5 FIFO Operation ....................................................................................................................... 300
13.2.6 Interrupts ................................................................................................................................ 300
13.2.7 Loopback Operation ................................................................................................................ 301
13.2.8 IrDA SIR block ........................................................................................................................ 301
13.3 Initialization and Configuration ................................................................................................. 301
March 17, 2008 5
Preliminary
LM3S8933 Microcontroller
13.4 Register Map .......................................................................................................................... 302
13.5 Register Descriptions .............................................................................................................. 303
14 Synchronous Serial Interface (SSI) ................................................................................ 337
14.1 Block Diagram ........................................................................................................................ 337
14.2 Functional Description ............................................................................................................. 337
14.2.1 Bit Rate Generation ................................................................................................................. 338
14.2.2 FIFO Operation ....................................................................................................................... 338
14.2.3 Interrupts ................................................................................................................................ 338
14.2.4 Frame Formats ....................................................................................................................... 339
14.3 Initialization and Configuration ................................................................................................. 346
14.4 Register Map .......................................................................................................................... 347
14.5 Register Descriptions .............................................................................................................. 348
15 Inter-Integrated Circuit (I2C) Interface ............................................................................ 374
15.1 Block Diagram ........................................................................................................................ 374
15.2 Functional Description ............................................................................................................. 374
15.2.1 I2C Bus Functional Overview .................................................................................................... 375
15.2.2 Available Speed Modes ........................................................................................................... 377
15.2.3 Interrupts ................................................................................................................................ 378
15.2.4 Loopback Operation ................................................................................................................ 378
15.2.5 Command Sequence Flow Charts ............................................................................................ 379
15.3 Initialization and Configuration ................................................................................................. 385
15.4 I2C Register Map ..................................................................................................................... 386
15.5 Register Descriptions (I2C Master) ........................................................................................... 387
15.6 Register Descriptions (I2C Slave) ............................................................................................. 400
16 Controller Area Network (CAN) Module ......................................................................... 409
16.1 Controller Area Network Overview ............................................................................................ 409
16.2 Controller Area Network Features ............................................................................................ 409
16.3 Controller Area Network Block Diagram .................................................................................... 410
16.4 Controller Area Network Functional Description ......................................................................... 410
16.4.1 Initialization ............................................................................................................................. 411
16.4.2 Operation ............................................................................................................................... 411
16.4.3 Transmitting Message Objects ................................................................................................. 412
16.4.4 Configuring a Transmit Message Object .................................................................................... 412
16.4.5 Updating a Transmit Message Object ....................................................................................... 413
16.4.6 Accepting Received Message Objects ...................................................................................... 413
16.4.7 Receiving a Data Frame .......................................................................................................... 413
16.4.8 Receiving a Remote Frame ...................................................................................................... 413
16.4.9 Receive/Transmit Priority ......................................................................................................... 414
16.4.10 Configuring a Receive Message Object .................................................................................... 414
16.4.11 Handling of Received Message Objects .................................................................................... 415
16.4.12 Handling of Interrupts .............................................................................................................. 415
16.4.13 Bit Timing Configuration Error Considerations ........................................................................... 416
16.4.14 Bit Time and Bit Rate ............................................................................................................... 416
16.4.15 Calculating the Bit Timing Parameters ...................................................................................... 418
16.5 Controller Area Network Register Map ...................................................................................... 420
16.6 Register Descriptions .............................................................................................................. 421
6 March 17, 2008
Preliminary
Table of Contents
17 Ethernet Controller .......................................................................................................... 449
17.1 Block Diagram ........................................................................................................................ 450
17.2 Functional Description ............................................................................................................. 450
17.2.1 Internal MII Operation .............................................................................................................. 450
17.2.2 PHY Configuration/Operation ................................................................................................... 451
17.2.3 MAC Configuration/Operation .................................................................................................. 452
17.2.4 Interrupts ................................................................................................................................ 455
17.3 Initialization and Configuration ................................................................................................. 455
17.4 Ethernet Register Map ............................................................................................................. 456
17.5 Ethernet MAC Register Descriptions ......................................................................................... 457
17.6 MII Management Register Descriptions ..................................................................................... 475
18 Analog Comparators ....................................................................................................... 494
18.1 Block Diagram ........................................................................................................................ 495
18.2 Functional Description ............................................................................................................. 495
18.2.1 Internal Reference Programming .............................................................................................. 497
18.3 Initialization and Configuration ................................................................................................. 498
18.4 Register Map .......................................................................................................................... 498
18.5 Register Descriptions .............................................................................................................. 499
19 Pin Diagram ...................................................................................................................... 507
20 Signal Tables .................................................................................................................... 509
20.1 100-Pin LQFP Package Pin Tables ........................................................................................... 509
20.2 108-Pin BGA Package Pin Tables ............................................................................................ 520
21 Operating Characteristics ............................................................................................... 534
22 Electrical Characteristics ................................................................................................ 535
22.1 DC Characteristics .................................................................................................................. 535
22.1.1 Maximum Ratings ................................................................................................................... 535
22.1.2 Recommended DC Operating Conditions .................................................................................. 535
22.1.3 On-Chip Low Drop-Out (LDO) Regulator Characteristics ............................................................ 536
22.1.4 Power Specifications ............................................................................................................... 536
22.1.5 Flash Memory Characteristics .................................................................................................. 538
22.2 AC Characteristics ................................................................................................................... 538
22.2.1 Load Conditions ...................................................................................................................... 538
22.2.2 Clocks .................................................................................................................................... 538
22.2.3 Analog-to-Digital Converter ...................................................................................................... 539
22.2.4 Analog Comparator ................................................................................................................. 540
22.2.5 I2C ......................................................................................................................................... 540
22.2.6 Ethernet Controller .................................................................................................................. 541
22.2.7 Hibernation Module ................................................................................................................. 544
22.2.8 Synchronous Serial Interface (SSI) ........................................................................................... 544
22.2.9 JTAG and Boundary Scan ........................................................................................................ 546
22.2.10 General-Purpose I/O ............................................................................................................... 547
22.2.11 Reset ..................................................................................................................................... 548
23 Package Information ........................................................................................................ 550
A Serial Flash Loader .......................................................................................................... 554
A.1 Serial Flash Loader ................................................................................................................. 554
A.2 Interfaces ............................................................................................................................... 554
March 17, 2008 7
Preliminary
LM3S8933 Microcontroller
A.2.1 UART ..................................................................................................................................... 554
A.2.2 SSI ......................................................................................................................................... 554
A.3 Packet Handling ...................................................................................................................... 555
A.3.1 Packet Format ........................................................................................................................ 555
A.3.2 Sending Packets ..................................................................................................................... 555
A.3.3 Receiving Packets ................................................................................................................... 555
A.4 Commands ............................................................................................................................. 556
A.4.1 COMMAND_PING (0X20) ........................................................................................................ 556
A.4.2 COMMAND_GET_STATUS (0x23) ........................................................................................... 556
A.4.3 COMMAND_DOWNLOAD (0x21) ............................................................................................. 556
A.4.4 COMMAND_SEND_DATA (0x24) ............................................................................................. 557
A.4.5 COMMAND_RUN (0x22) ......................................................................................................... 557
A.4.6 COMMAND_RESET (0x25) ..................................................................................................... 557
B Register Quick Reference ............................................................................................... 559
C Ordering and Contact Information ................................................................................. 578
C.1 Ordering Information ................................................................................................................ 578
C.2 Kits ......................................................................................................................................... 578
C.3 Company Information .............................................................................................................. 579
C.4 Support Information ................................................................................................................. 579
8 March 17, 2008
Preliminary
Table of Contents
List of Figures
Figure 1-1. Stellaris® 8000 Series High-Level Block Diagram ............................................................... 28
Figure 2-1. CPU Block Diagram ......................................................................................................... 36
Figure 2-2. TPIU Block Diagram ........................................................................................................ 37
Figure 5-1. JTAG Module Block Diagram ............................................................................................ 47
Figure 5-2. Test Access Port State Machine ....................................................................................... 50
Figure 5-3. IDCODE Register Format ................................................................................................. 55
Figure 5-4. BYPASS Register Format ................................................................................................ 56
Figure 5-5. Boundary Scan Register Format ....................................................................................... 56
Figure 6-1. External Circuitry to Extend Reset .................................................................................... 58
Figure 6-2. Main Clock Tree .............................................................................................................. 61
Figure 7-1. Hibernation Module Block Diagram ................................................................................. 120
Figure 8-1. Flash Block Diagram ...................................................................................................... 138
Figure 9-1. GPIO Port Block Diagram ............................................................................................... 163
Figure 9-2. GPIODATA Write Example ............................................................................................. 164
Figure 9-3. GPIODATA Read Example ............................................................................................. 164
Figure 10-1. GPTM Module Block Diagram ........................................................................................ 205
Figure 10-2. 16-Bit Input Edge Count Mode Example .......................................................................... 209
Figure 10-3. 16-Bit Input Edge Time Mode Example ........................................................................... 210
Figure 10-4. 16-Bit PWM Mode Example ............................................................................................ 211
Figure 11-1. WDT Module Block Diagram .......................................................................................... 240
Figure 12-1. ADC Module Block Diagram ........................................................................................... 264
Figure 12-2. Differential Sampling Range, Vin(-) = 1.5 V ...................................................................... 267
Figure 12-3. Differential Sampling Range, Vin(-) = 0.75 V .................................................................... 267
Figure 12-4. Differential Sampling Range, Vin(-) = 2.25 V .................................................................... 268
Figure 12-5. Internal Temperature Sensor Characteristic ..................................................................... 268
Figure 13-1. UART Module Block Diagram ......................................................................................... 297
Figure 13-2. UART Character Frame ................................................................................................. 298
Figure 13-3. IrDA Data Modulation ..................................................................................................... 300
Figure 14-1. SSI Module Block Diagram ............................................................................................. 337
Figure 14-2. TI Synchronous Serial Frame Format (Single Transfer) .................................................... 340
Figure 14-3. TI Synchronous Serial Frame Format (Continuous Transfer) ............................................ 340
Figure 14-4. Freescale SPI Format (Single Transfer) with SPO=0 and SPH=0 ...................................... 341
Figure 14-5. Freescale SPI Format (Continuous Transfer) with SPO=0 and SPH=0 .............................. 341
Figure 14-6. Freescale SPI Frame Format with SPO=0 and SPH=1 ..................................................... 342
Figure 14-7. Freescale SPI Frame Format (Single Transfer) with SPO=1 and SPH=0 ........................... 343
Figure 14-8. Freescale SPI Frame Format (Continuous Transfer) with SPO=1 and SPH=0 .................... 343
Figure 14-9. Freescale SPI Frame Format with SPO=1 and SPH=1 ..................................................... 344
Figure 14-10. MICROWIRE Frame Format (Single Frame) .................................................................... 345
Figure 14-11. MICROWIRE Frame Format (Continuous Transfer) ......................................................... 346
Figure 14-12. MICROWIRE Frame Format, SSIFss Input Setup and Hold Requirements ........................ 346
Figure 15-1. I2C Block Diagram ......................................................................................................... 374
Figure 15-2. I2C Bus Configuration .................................................................................................... 375
Figure 15-3. START and STOP Conditions ......................................................................................... 375
Figure 15-4. Complete Data Transfer with a 7-Bit Address ................................................................... 376
Figure 15-5. R/S Bit in First Byte ........................................................................................................ 376
March 17, 2008 9
Preliminary
LM3S8933 Microcontroller
Figure 15-6. Data Validity During Bit Transfer on the I2C Bus ............................................................... 376
Figure 15-7. Master Single SEND ...................................................................................................... 379
Figure 15-8. Master Single RECEIVE ................................................................................................. 380
Figure 15-9. Master Burst SEND ....................................................................................................... 381
Figure 15-10. Master Burst RECEIVE .................................................................................................. 382
Figure 15-11. Master Burst RECEIVE after Burst SEND ........................................................................ 383
Figure 15-12. Master Burst SEND after Burst RECEIVE ........................................................................ 384
Figure 15-13. Slave Command Sequence ............................................................................................ 385
Figure 16-1. CAN Module Block Diagram ........................................................................................... 410
Figure 16-2. CAN Bit Time ................................................................................................................ 417
Figure 17-1. Ethernet Controller Block Diagram .................................................................................. 450
Figure 17-2. Ethernet Controller ......................................................................................................... 450
Figure 17-3. Ethernet Frame ............................................................................................................. 452
Figure 18-1. Analog Comparator Module Block Diagram ..................................................................... 495
Figure 18-2. Structure of Comparator Unit .......................................................................................... 496
Figure 18-3. Comparator Internal Reference Structure ........................................................................ 497
Figure 19-1. 100-Pin LQFP Package Pin Diagram .............................................................................. 507
Figure 19-2. 108-Ball BGA Package Pin Diagram (Top View) ............................................................... 508
Figure 22-1. Load Conditions ............................................................................................................ 538
Figure 22-2. I2C Timing ..................................................................................................................... 541
Figure 22-3. External XTLP Oscillator Characteristics ......................................................................... 543
Figure 22-4. Hibernation Module Timing ............................................................................................. 544
Figure 22-5. SSI Timing for TI Frame Format (FRF=01), Single Transfer Timing Measurement .............. 545
Figure 22-6. SSI Timing for MICROWIRE Frame Format (FRF=10), Single Transfer ............................. 545
Figure 22-7. SSI Timing for SPI Frame Format (FRF=00), with SPH=1 ................................................. 546
Figure 22-8. JTAG Test Clock Input Timing ......................................................................................... 547
Figure 22-9. JTAG Test Access Port (TAP) Timing .............................................................................. 547
Figure 22-10. JTAG TRST Timing ........................................................................................................ 547
Figure 22-11. External Reset Timing (RST) .......................................................................................... 548
Figure 22-12. Power-On Reset Timing ................................................................................................. 549
Figure 22-13. Brown-Out Reset Timing ................................................................................................ 549
Figure 22-14. Software Reset Timing ................................................................................................... 549
Figure 22-15. Watchdog Reset Timing ................................................................................................. 549
Figure 23-1. 100-Pin LQFP Package .................................................................................................. 550
Figure 23-2. 100-Ball BGA Package .................................................................................................. 552
10 March 17, 2008
Preliminary
Table of Contents
List of Tables
Table 1. Documentation Conventions ............................................................................................ 20
Table 3-1. Memory Map ................................................................................................................... 41
Table 4-1. Exception Types .............................................................................................................. 43
Table 4-2. Interrupts ........................................................................................................................ 44
Table 5-1. JTAG Port Pins Reset State ............................................................................................. 48
Table 5-2. JTAG Instruction Register Commands ............................................................................... 53
Table 6-1. System Control Register Map ........................................................................................... 64
Table 7-1. Hibernation Module Register Map ................................................................................... 124
Table 8-1. Flash Protection Policy Combinations ............................................................................. 140
Table 8-2. Flash Resident Registers ............................................................................................... 141
Table 8-3. Flash Register Map ........................................................................................................ 141
Table 9-1. GPIO Pad Configuration Examples ................................................................................. 166
Table 9-2. GPIO Interrupt Configuration Example ............................................................................ 166
Table 9-3. GPIO Register Map ....................................................................................................... 168
Table 10-1. Available CCP Pins ........................................................................................................ 205
Table 10-2. 16-Bit Timer With Prescaler Configurations ..................................................................... 208
Table 10-3. Timers Register Map ...................................................................................................... 214
Table 11-1. Watchdog Timer Register Map ........................................................................................ 241
Table 12-1. Samples and FIFO Depth of Sequencers ........................................................................ 264
Table 12-2. Differential Sampling Pairs ............................................................................................. 266
Table 12-3. ADC Register Map ......................................................................................................... 269
Table 13-1. UART Register Map ....................................................................................................... 302
Table 14-1. SSI Register Map .......................................................................................................... 347
Table 15-1. Examples of I2C Master Timer Period versus Speed Mode ............................................... 377
Table 15-2. Inter-Integrated Circuit (I2C) Interface Register Map ......................................................... 386
Table 15-3. Write Field Decoding for I2CMCS[3:0] Field (Sheet 1 of 3) ................................................ 391
Table 16-1. Transmit Message Object Bit Settings ............................................................................. 412
Table 16-2. Receive Message Object Bit Settings .............................................................................. 414
Table 16-3. CAN Protocol Ranges .................................................................................................... 417
Table 16-4. CAN Register Map ......................................................................................................... 420
Table 17-1. TX & RX FIFO Organization ........................................................................................... 453
Table 17-2. Ethernet Register Map ................................................................................................... 456
Table 18-1. Comparator 0 Operating Modes ..................................................................................... 496
Table 18-2. Comparator 1 Operating Modes ..................................................................................... 496
Table 18-3. Comparator 2 Operating Modes ...................................................................................... 497
Table 18-4. Internal Reference Voltage and ACREFCTL Field Values ................................................. 497
Table 18-5. Analog Comparators Register Map ................................................................................. 499
Table 20-1. Signals by Pin Number ................................................................................................... 509
Table 20-2. Signals by Signal Name ................................................................................................. 513
Table 20-3. Signals by Function, Except for GPIO ............................................................................. 517
Table 20-4. GPIO Pins and Alternate Functions ................................................................................. 519
Table 20-5. Signals by Pin Number ................................................................................................... 520
Table 20-6. Signals by Signal Name ................................................................................................. 525
Table 20-7. Signals by Function, Except for GPIO ............................................................................. 529
Table 20-8. GPIO Pins and Alternate Functions ................................................................................. 532
Table 21-1. Temperature Characteristics ........................................................................................... 534
March 17, 2008 11
Preliminary
LM3S8933 Microcontroller
Table 21-2. Thermal Characteristics ................................................................................................. 534
Table 22-1. Maximum Ratings .......................................................................................................... 535
Table 22-2. Recommended DC Operating Conditions ........................................................................ 535
Table 22-3. LDO Regulator Characteristics ....................................................................................... 536
Table 22-4. Detailed Power Specifications ........................................................................................ 537
Table 22-5. Flash Memory Characteristics ........................................................................................ 538
Table 22-6. Phase Locked Loop (PLL) Characteristics ....................................................................... 538
Table 22-7. Clock Characteristics ..................................................................................................... 538
Table 22-8. Crystal Characteristics ................................................................................................... 539
Table 22-9. ADC Characteristics ....................................................................................................... 539
Table 22-10. Analog Comparator Characteristics ................................................................................. 540
Table 22-11. Analog Comparator Voltage Reference Characteristics .................................................... 540
Table 22-12. I2C Characteristics ......................................................................................................... 540
Table 22-13. 100BASE-TX Transmitter Characteristics ........................................................................ 541
Table 22-14. 100BASE-TX Transmitter Characteristics (informative) ..................................................... 541
Table 22-15. 100BASE-TX Receiver Characteristics ............................................................................ 541
Table 22-16. 10BASE-T Transmitter Characteristics ............................................................................ 541
Table 22-17. 10BASE-T Transmitter Characteristics (informative) ......................................................... 542
Table 22-18. 10BASE-T Receiver Characteristics ................................................................................ 542
Table 22-19. Isolation Transformers ................................................................................................... 542
Table 22-20. Ethernet Reference Crystal ............................................................................................ 543
Table 22-21. External XTLP Oscillator Characteristics ......................................................................... 543
Table 22-22. Hibernation Module Characteristics ................................................................................. 544
Table 22-23. SSI Characteristics ........................................................................................................ 544
Table 22-24. JTAG Characteristics ..................................................................................................... 546
Table 22-25. GPIO Characteristics ..................................................................................................... 548
Table 22-26. Reset Characteristics ..................................................................................................... 548
Table C-1. Part Ordering Information ............................................................................................... 578
12 March 17, 2008
Preliminary
Table of Contents
List of Registers
System Control .............................................................................................................................. 57
Register 1: Device Identification 0 (DID0), offset 0x000 ....................................................................... 66
Register 2: Brown-Out Reset Control (PBORCTL), offset 0x030 .......................................................... 68
Register 3: LDO Power Control (LDOPCTL), offset 0x034 ................................................................... 69
Register 4: Raw Interrupt Status (RIS), offset 0x050 ........................................................................... 70
Register 5: Interrupt Mask Control (IMC), offset 0x054 ........................................................................ 71
Register 6: Masked Interrupt Status and Clear (MISC), offset 0x058 .................................................... 72
Register 7: Reset Cause (RESC), offset 0x05C .................................................................................. 73
Register 8: Run-Mode Clock Configuration (RCC), offset 0x060 .......................................................... 74
Register 9: XTAL to PLL Translation (PLLCFG), offset 0x064 .............................................................. 78
Register 10: Run-Mode Clock Configuration 2 (RCC2), offset 0x070 ...................................................... 79
Register 11: Deep Sleep Clock Configuration (DSLPCLKCFG), offset 0x144 .......................................... 81
Register 12: Device Identification 1 (DID1), offset 0x004 ....................................................................... 82
Register 13: Device Capabilities 0 (DC0), offset 0x008 ......................................................................... 84
Register 14: Device Capabilities 1 (DC1), offset 0x010 ......................................................................... 85
Register 15: Device Capabilities 2 (DC2), offset 0x014 ......................................................................... 87
Register 16: Device Capabilities 3 (DC3), offset 0x018 ......................................................................... 89
Register 17: Device Capabilities 4 (DC4), offset 0x01C ......................................................................... 91
Register 18: Run Mode Clock Gating Control Register 0 (RCGC0), offset 0x100 .................................... 93
Register 19: Sleep Mode Clock Gating Control Register 0 (SCGC0), offset 0x110 .................................. 95
Register 20: Deep Sleep Mode Clock Gating Control Register 0 (DCGC0), offset 0x120 ......................... 97
Register 21: Run Mode Clock Gating Control Register 1 (RCGC1), offset 0x104 .................................... 99
Register 22: Sleep Mode Clock Gating Control Register 1 (SCGC1), offset 0x114 ................................. 102
Register 23: Deep Sleep Mode Clock Gating Control Register 1 (DCGC1), offset 0x124 ....................... 105
Register 24: Run Mode Clock Gating Control Register 2 (RCGC2), offset 0x108 ................................... 108
Register 25: Sleep Mode Clock Gating Control Register 2 (SCGC2), offset 0x118 ................................. 110
Register 26: Deep Sleep Mode Clock Gating Control Register 2 (DCGC2), offset 0x128 ....................... 112
Register 27: Software Reset Control 0 (SRCR0), offset 0x040 ............................................................. 114
Register 28: Software Reset Control 1 (SRCR1), offset 0x044 ............................................................. 115
Register 29: Software Reset Control 2 (SRCR2), offset 0x048 ............................................................. 117
Hibernation Module ..................................................................................................................... 119
Register 1: Hibernation RTC Counter (HIBRTCC), offset 0x000 ......................................................... 126
Register 2: Hibernation RTC Match 0 (HIBRTCM0), offset 0x004 ....................................................... 127
Register 3: Hibernation RTC Match 1 (HIBRTCM1), offset 0x008 ....................................................... 128
Register 4: Hibernation RTC Load (HIBRTCLD), offset 0x00C ........................................................... 129
Register 5: Hibernation Control (HIBCTL), offset 0x010 ..................................................................... 130
Register 6: Hibernation Interrupt Mask (HIBIM), offset 0x014 ............................................................. 132
Register 7: Hibernation Raw Interrupt Status (HIBRIS), offset 0x018 .................................................. 133
Register 8: Hibernation Masked Interrupt Status (HIBMIS), offset 0x01C ............................................ 134
Register 9: Hibernation Interrupt Clear (HIBIC), offset 0x020 ............................................................. 135
Register 10: Hibernation RTC Trim (HIBRTCT), offset 0x024 ............................................................... 136
Register 11: Hibernation Data (HIBDATA), offset 0x030-0x12C ............................................................ 137
Internal Memory ........................................................................................................................... 138
Register 1: Flash Memory Address (FMA), offset 0x000 .................................................................... 143
Register 2: Flash Memory Data (FMD), offset 0x004 ......................................................................... 144
March 17, 2008 13
Preliminary
LM3S8933 Microcontroller
Register 3: Flash Memory Control (FMC), offset 0x008 ..................................................................... 145
Register 4: Flash Controller Raw Interrupt Status (FCRIS), offset 0x00C ............................................ 147
Register 5: Flash Controller Interrupt Mask (FCIM), offset 0x010 ........................................................ 148
Register 6: Flash Controller Masked Interrupt Status and Clear (FCMISC), offset 0x014 ..................... 149
Register 7: USec Reload (USECRL), offset 0x140 ............................................................................ 150
Register 8: Flash Memory Protection Read Enable 0 (FMPRE0), offset 0x130 and 0x200 ................... 151
Register 9: Flash Memory Protection Program Enable 0 (FMPPE0), offset 0x134 and 0x400 ............... 152
Register 10: User Debug (USER_DBG), offset 0x1D0 ......................................................................... 153
Register 11: User Register 0 (USER_REG0), offset 0x1E0 .................................................................. 154
Register 12: User Register 1 (USER_REG1), offset 0x1E4 .................................................................. 155
Register 13: Flash Memory Protection Read Enable 1 (FMPRE1), offset 0x204 .................................... 156
Register 14: Flash Memory Protection Read Enable 2 (FMPRE2), offset 0x208 .................................... 157
Register 15: Flash Memory Protection Read Enable 3 (FMPRE3), offset 0x20C ................................... 158
Register 16: Flash Memory Protection Program Enable 1 (FMPPE1), offset 0x404 ............................... 159
Register 17: Flash Memory Protection Program Enable 2 (FMPPE2), offset 0x408 ............................... 160
Register 18: Flash Memory Protection Program Enable 3 (FMPPE3), offset 0x40C ............................... 161
General-Purpose Input/Outputs (GPIOs) ................................................................................... 162
Register 1: GPIO Data (GPIODATA), offset 0x000 ............................................................................ 170
Register 2: GPIO Direction (GPIODIR), offset 0x400 ......................................................................... 171
Register 3: GPIO Interrupt Sense (GPIOIS), offset 0x404 .................................................................. 172
Register 4: GPIO Interrupt Both Edges (GPIOIBE), offset 0x408 ........................................................ 173
Register 5: GPIO Interrupt Event (GPIOIEV), offset 0x40C ................................................................ 174
Register 6: GPIO Interrupt Mask (GPIOIM), offset 0x410 ................................................................... 175
Register 7: GPIO Raw Interrupt Status (GPIORIS), offset 0x414 ........................................................ 176
Register 8: GPIO Masked Interrupt Status (GPIOMIS), offset 0x418 ................................................... 177
Register 9: GPIO Interrupt Clear (GPIOICR), offset 0x41C ................................................................ 178
Register 10: GPIO Alternate Function Select (GPIOAFSEL), offset 0x420 ............................................ 179
Register 11: GPIO 2-mA Drive Select (GPIODR2R), offset 0x500 ........................................................ 181
Register 12: GPIO 4-mA Drive Select (GPIODR4R), offset 0x504 ........................................................ 182
Register 13: GPIO 8-mA Drive Select (GPIODR8R), offset 0x508 ........................................................ 183
Register 14: GPIO Open Drain Select (GPIOODR), offset 0x50C ......................................................... 184
Register 15: GPIO Pull-Up Select (GPIOPUR), offset 0x510 ................................................................ 185
Register 16: GPIO Pull-Down Select (GPIOPDR), offset 0x514 ........................................................... 186
Register 17: GPIO Slew Rate Control Select (GPIOSLR), offset 0x518 ................................................ 187
Register 18: GPIO Digital Enable (GPIODEN), offset 0x51C ................................................................ 188
Register 19: GPIO Lock (GPIOLOCK), offset 0x520 ............................................................................ 189
Register 20: GPIO Commit (GPIOCR), offset 0x524 ............................................................................ 190
Register 21: GPIO Peripheral Identification 4 (GPIOPeriphID4), offset 0xFD0 ....................................... 192
Register 22: GPIO Peripheral Identification 5 (GPIOPeriphID5), offset 0xFD4 ....................................... 193
Register 23: GPIO Peripheral Identification 6 (GPIOPeriphID6), offset 0xFD8 ....................................... 194
Register 24: GPIO Peripheral Identification 7 (GPIOPeriphID7), offset 0xFDC ...................................... 195
Register 25: GPIO Peripheral Identification 0 (GPIOPeriphID0), offset 0xFE0 ....................................... 196
Register 26: GPIO Peripheral Identification 1 (GPIOPeriphID1), offset 0xFE4 ....................................... 197
Register 27: GPIO Peripheral Identification 2 (GPIOPeriphID2), offset 0xFE8 ....................................... 198
Register 28: GPIO Peripheral Identification 3 (GPIOPeriphID3), offset 0xFEC ...................................... 199
Register 29: GPIO PrimeCell Identification 0 (GPIOPCellID0), offset 0xFF0 .......................................... 200
Register 30: GPIO PrimeCell Identification 1 (GPIOPCellID1), offset 0xFF4 .......................................... 201
Register 31: GPIO PrimeCell Identification 2 (GPIOPCellID2), offset 0xFF8 .......................................... 202
14 March 17, 2008
Preliminary
Table of Contents
Register 32: GPIO PrimeCell Identification 3 (GPIOPCellID3), offset 0xFFC ......................................... 203
General-Purpose Timers ............................................................................................................. 204
Register 1: GPTM Configuration (GPTMCFG), offset 0x000 .............................................................. 216
Register 2: GPTM TimerA Mode (GPTMTAMR), offset 0x004 ............................................................ 217
Register 3: GPTM TimerB Mode (GPTMTBMR), offset 0x008 ............................................................ 219
Register 4: GPTM Control (GPTMCTL), offset 0x00C ........................................................................ 221
Register 5: GPTM Interrupt Mask (GPTMIMR), offset 0x018 .............................................................. 224
Register 6: GPTM Raw Interrupt Status (GPTMRIS), offset 0x01C ..................................................... 226
Register 7: GPTM Masked Interrupt Status (GPTMMIS), offset 0x020 ................................................ 227
Register 8: GPTM Interrupt Clear (GPTMICR), offset 0x024 .............................................................. 228
Register 9: GPTM TimerA Interval Load (GPTMTAILR), offset 0x028 ................................................. 230
Register 10: GPTM TimerB Interval Load (GPTMTBILR), offset 0x02C ................................................ 231
Register 11: GPTM TimerA Match (GPTMTAMATCHR), offset 0x030 ................................................... 232
Register 12: GPTM TimerB Match (GPTMTBMATCHR), offset 0x034 .................................................. 233
Register 13: GPTM TimerA Prescale (GPTMTAPR), offset 0x038 ........................................................ 234
Register 14: GPTM TimerB Prescale (GPTMTBPR), offset 0x03C ....................................................... 235
Register 15: GPTM TimerA Prescale Match (GPTMTAPMR), offset 0x040 ........................................... 236
Register 16: GPTM TimerB Prescale Match (GPTMTBPMR), offset 0x044 ........................................... 237
Register 17: GPTM TimerA (GPTMTAR), offset 0x048 ........................................................................ 238
Register 18: GPTM TimerB (GPTMTBR), offset 0x04C ....................................................................... 239
Watchdog Timer ........................................................................................................................... 240
Register 1: Watchdog Load (WDTLOAD), offset 0x000 ...................................................................... 243
Register 2: Watchdog Value (WDTVALUE), offset 0x004 ................................................................... 244
Register 3: Watchdog Control (WDTCTL), offset 0x008 ..................................................................... 245
Register 4: Watchdog Interrupt Clear (WDTICR), offset 0x00C .......................................................... 246
Register 5: Watchdog Raw Interrupt Status (WDTRIS), offset 0x010 .................................................. 247
Register 6: Watchdog Masked Interrupt Status (WDTMIS), offset 0x014 ............................................. 248
Register 7: Watchdog Test (WDTTEST), offset 0x418 ....................................................................... 249
Register 8: Watchdog Lock (WDTLOCK), offset 0xC00 ..................................................................... 250
Register 9: Watchdog Peripheral Identification 4 (WDTPeriphID4), offset 0xFD0 ................................. 251
Register 10: Watchdog Peripheral Identification 5 (WDTPeriphID5), offset 0xFD4 ................................. 252
Register 11: Watchdog Peripheral Identification 6 (WDTPeriphID6), offset 0xFD8 ................................. 253
Register 12: Watchdog Peripheral Identification 7 (WDTPeriphID7), offset 0xFDC ................................ 254
Register 13: Watchdog Peripheral Identification 0 (WDTPeriphID0), offset 0xFE0 ................................. 255
Register 14: Watchdog Peripheral Identification 1 (WDTPeriphID1), offset 0xFE4 ................................. 256
Register 15: Watchdog Peripheral Identification 2 (WDTPeriphID2), offset 0xFE8 ................................. 257
Register 16: Watchdog Peripheral Identification 3 (WDTPeriphID3), offset 0xFEC ................................. 258
Register 17: Watchdog PrimeCell Identification 0 (WDTPCellID0), offset 0xFF0 .................................... 259
Register 18: Watchdog PrimeCell Identification 1 (WDTPCellID1), offset 0xFF4 .................................... 260
Register 19: Watchdog PrimeCell Identification 2 (WDTPCellID2), offset 0xFF8 .................................... 261
Register 20: Watchdog PrimeCell Identification 3 (WDTPCellID3 ), offset 0xFFC .................................. 262
Analog-to-Digital Converter (ADC) ............................................................................................. 263
Register 1: ADC Active Sample Sequencer (ADCACTSS), offset 0x000 ............................................. 271
Register 2: ADC Raw Interrupt Status (ADCRIS), offset 0x004 ........................................................... 272
Register 3: ADC Interrupt Mask (ADCIM), offset 0x008 ..................................................................... 273
Register 4: ADC Interrupt Status and Clear (ADCISC), offset 0x00C .................................................. 274
Register 5: ADC Overflow Status (ADCOSTAT), offset 0x010 ............................................................ 275
Register 6: ADC Event Multiplexer Select (ADCEMUX), offset 0x014 ................................................. 276
March 17, 2008 15
Preliminary
LM3S8933 Microcontroller
Register 7: ADC Underflow Status (ADCUSTAT), offset 0x018 ........................................................... 279
Register 8: ADC Sample Sequencer Priority (ADCSSPRI), offset 0x020 ............................................. 280
Register 9: ADC Processor Sample Sequence Initiate (ADCPSSI), offset 0x028 ................................. 281
Register 10: ADC Sample Averaging Control (ADCSAC), offset 0x030 ................................................. 282
Register 11: ADC Sample Sequence Input Multiplexer Select 0 (ADCSSMUX0), offset 0x040 ............... 283
Register 12: ADC Sample Sequence Control 0 (ADCSSCTL0), offset 0x044 ........................................ 285
Register 13: ADC Sample Sequence Result FIFO 0 (ADCSSFIFO0), offset 0x048 ................................ 288
Register 14: ADC Sample Sequence Result FIFO 1 (ADCSSFIFO1), offset 0x068 ................................ 288
Register 15: ADC Sample Sequence Result FIFO 2 (ADCSSFIFO2), offset 0x088 ................................ 288
Register 16: ADC Sample Sequence Result FIFO 3 (ADCSSFIFO3), offset 0x0A8 ............................... 288
Register 17: ADC Sample Sequence FIFO 0 Status (ADCSSFSTAT0), offset 0x04C ............................. 289
Register 18: ADC Sample Sequence FIFO 1 Status (ADCSSFSTAT1), offset 0x06C ............................. 289
Register 19: ADC Sample Sequence FIFO 2 Status (ADCSSFSTAT2), offset 0x08C ............................ 289
Register 20: ADC Sample Sequence FIFO 3 Status (ADCSSFSTAT3), offset 0x0AC ............................ 289
Register 21: ADC Sample Sequence Input Multiplexer Select 1 (ADCSSMUX1), offset 0x060 ............... 290
Register 22: ADC Sample Sequence Input Multiplexer Select 2 (ADCSSMUX2), offset 0x080 ............... 290
Register 23: ADC Sample Sequence Control 1 (ADCSSCTL1), offset 0x064 ........................................ 291
Register 24: ADC Sample Sequence Control 2 (ADCSSCTL2), offset 0x084 ........................................ 291
Register 25: ADC Sample Sequence Input Multiplexer Select 3 (ADCSSMUX3), offset 0x0A0 ............... 293
Register 26: ADC Sample Sequence Control 3 (ADCSSCTL3), offset 0x0A4 ........................................ 294
Register 27: ADC Test Mode Loopback (ADCTMLB), offset 0x100 ....................................................... 295
Universal Asynchronous Receivers/Transmitters (UARTs) ..................................................... 296
Register 1: UART Data (UARTDR), offset 0x000 ............................................................................... 304
Register 2: UART Receive Status/Error Clear (UARTRSR/UARTECR), offset 0x004 ........................... 306
Register 3: UART Flag (UARTFR), offset 0x018 ................................................................................ 308
Register 4: UART IrDA Low-Power Register (UARTILPR), offset 0x020 ............................................. 310
Register 5: UART Integer Baud-Rate Divisor (UARTIBRD), offset 0x024 ............................................ 311
Register 6: UART Fractional Baud-Rate Divisor (UARTFBRD), offset 0x028 ....................................... 312
Register 7: UART Line Control (UARTLCRH), offset 0x02C ............................................................... 313
Register 8: UART Control (UARTCTL), offset 0x030 ......................................................................... 315
Register 9: UART Interrupt FIFO Level Select (UARTIFLS), offset 0x034 ........................................... 317
Register 10: UART Interrupt Mask (UARTIM), offset 0x038 ................................................................. 319
Register 11: UART Raw Interrupt Status (UARTRIS), offset 0x03C ...................................................... 321
Register 12: UART Masked Interrupt Status (UARTMIS), offset 0x040 ................................................. 322
Register 13: UART Interrupt Clear (UARTICR), offset 0x044 ............................................................... 323
Register 14: UART Peripheral Identification 4 (UARTPeriphID4), offset 0xFD0 ..................................... 325
Register 15: UART Peripheral Identification 5 (UARTPeriphID5), offset 0xFD4 ..................................... 326
Register 16: UART Peripheral Identification 6 (UARTPeriphID6), offset 0xFD8 ..................................... 327
Register 17: UART Peripheral Identification 7 (UARTPeriphID7), offset 0xFDC ..................................... 328
Register 18: UART Peripheral Identification 0 (UARTPeriphID0), offset 0xFE0 ...................................... 329
Register 19: UART Peripheral Identification 1 (UARTPeriphID1), offset 0xFE4 ...................................... 330
Register 20: UART Peripheral Identification 2 (UARTPeriphID2), offset 0xFE8 ...................................... 331
Register 21: UART Peripheral Identification 3 (UARTPeriphID3), offset 0xFEC ..................................... 332
Register 22: UART PrimeCell Identification 0 (UARTPCellID0), offset 0xFF0 ........................................ 333
Register 23: UART PrimeCell Identification 1 (UARTPCellID1), offset 0xFF4 ........................................ 334
Register 24: UART PrimeCell Identification 2 (UARTPCellID2), offset 0xFF8 ........................................ 335
Register 25: UART PrimeCell Identification 3 (UARTPCellID3), offset 0xFFC ........................................ 336
16 March 17, 2008
Preliminary
Table of Contents
Synchronous Serial Interface (SSI) ............................................................................................ 337
Register 1: SSI Control 0 (SSICR0), offset 0x000 .............................................................................. 349
Register 2: SSI Control 1 (SSICR1), offset 0x004 .............................................................................. 351
Register 3: SSI Data (SSIDR), offset 0x008 ...................................................................................... 353
Register 4: SSI Status (SSISR), offset 0x00C ................................................................................... 354
Register 5: SSI Clock Prescale (SSICPSR), offset 0x010 .................................................................. 356
Register 6: SSI Interrupt Mask (SSIIM), offset 0x014 ......................................................................... 357
Register 7: SSI Raw Interrupt Status (SSIRIS), offset 0x018 .............................................................. 359
Register 8: SSI Masked Interrupt Status (SSIMIS), offset 0x01C ........................................................ 360
Register 9: SSI Interrupt Clear (SSIICR), offset 0x020 ....................................................................... 361
Register 10: SSI Peripheral Identification 4 (SSIPeriphID4), offset 0xFD0 ............................................. 362
Register 11: SSI Peripheral Identification 5 (SSIPeriphID5), offset 0xFD4 ............................................. 363
Register 12: SSI Peripheral Identification 6 (SSIPeriphID6), offset 0xFD8 ............................................. 364
Register 13: SSI Peripheral Identification 7 (SSIPeriphID7), offset 0xFDC ............................................ 365
Register 14: SSI Peripheral Identification 0 (SSIPeriphID0), offset 0xFE0 ............................................. 366
Register 15: SSI Peripheral Identification 1 (SSIPeriphID1), offset 0xFE4 ............................................. 367
Register 16: SSI Peripheral Identification 2 (SSIPeriphID2), offset 0xFE8 ............................................. 368
Register 17: SSI Peripheral Identification 3 (SSIPeriphID3), offset 0xFEC ............................................ 369
Register 18: SSI PrimeCell Identification 0 (SSIPCellID0), offset 0xFF0 ............................................... 370
Register 19: SSI PrimeCell Identification 1 (SSIPCellID1), offset 0xFF4 ............................................... 371
Register 20: SSI PrimeCell Identification 2 (SSIPCellID2), offset 0xFF8 ............................................... 372
Register 21: SSI PrimeCell Identification 3 (SSIPCellID3), offset 0xFFC ............................................... 373
Inter-Integrated Circuit (I2C) Interface ........................................................................................ 374
Register 1: I2C Master Slave Address (I2CMSA), offset 0x000 ........................................................... 388
Register 2: I2C Master Control/Status (I2CMCS), offset 0x004 ........................................................... 389
Register 3: I2C Master Data (I2CMDR), offset 0x008 ......................................................................... 393
Register 4: I2C Master Timer Period (I2CMTPR), offset 0x00C ........................................................... 394
Register 5: I2C Master Interrupt Mask (I2CMIMR), offset 0x010 ......................................................... 395
Register 6: I2C Master Raw Interrupt Status (I2CMRIS), offset 0x014 ................................................. 396
Register 7: I2C Master Masked Interrupt Status (I2CMMIS), offset 0x018 ........................................... 397
Register 8: I2C Master Interrupt Clear (I2CMICR), offset 0x01C ......................................................... 398
Register 9: I2C Master Configuration (I2CMCR), offset 0x020 ............................................................ 399
Register 10: I2C Slave Own Address (I2CSOAR), offset 0x000 ............................................................ 401
Register 11: I2C Slave Control/Status (I2CSCSR), offset 0x004 ........................................................... 402
Register 12: I2C Slave Data (I2CSDR), offset 0x008 ........................................................................... 404
Register 13: I2C Slave Interrupt Mask (I2CSIMR), offset 0x00C ........................................................... 405
Register 14: I2C Slave Raw Interrupt Status (I2CSRIS), offset 0x010 ................................................... 406
Register 15: I2C Slave Masked Interrupt Status (I2CSMIS), offset 0x014 .............................................. 407
Register 16: I2C Slave Interrupt Clear (I2CSICR), offset 0x018 ............................................................ 408
Controller Area Network (CAN) Module ..................................................................................... 409
Register 1: CAN Control (CANCTL), offset 0x000 ............................................................................. 422
Register 2: CAN Status (CANSTS), offset 0x004 ............................................................................... 424
Register 3: CAN Error Counter (CANERR), offset 0x008 ................................................................... 427
Register 4: CAN Bit Timing (CANBIT), offset 0x00C .......................................................................... 428
Register 5: CAN Interrupt (CANINT), offset 0x010 ............................................................................. 430
Register 6: CAN Test (CANTST), offset 0x014 .................................................................................. 431
Register 7: CAN Baud Rate Prescalar Extension (CANBRPE), offset 0x018 ....................................... 433
March 17, 2008 17
Preliminary
LM3S8933 Microcontroller
Register 8: CAN IF1 Command Request (CANIF1CRQ), offset 0x020 ................................................ 434
Register 9: CAN IF2 Command Request (CANIF2CRQ), offset 0x080 ................................................ 434
Register 10: CAN IF1 Command Mask (CANIF1CMSK), offset 0x024 .................................................. 435
Register 11: CAN IF2 Command Mask (CANIF2CMSK), offset 0x084 .................................................. 435
Register 12: CAN IF1 Mask 1 (CANIF1MSK1), offset 0x028 ................................................................ 438
Register 13: CAN IF2 Mask 1 (CANIF2MSK1), offset 0x088 ................................................................ 438
Register 14: CAN IF1 Mask 2 (CANIF1MSK2), offset 0x02C ................................................................ 439
Register 15: CAN IF2 Mask 2 (CANIF2MSK2), offset 0x08C ................................................................ 439
Register 16: CAN IF1 Arbitration 1 (CANIF1ARB1), offset 0x030 ......................................................... 440
Register 17: CAN IF2 Arbitration 1 (CANIF2ARB1), offset 0x090 ......................................................... 440
Register 18: CAN IF1 Arbitration 2 (CANIF1ARB2), offset 0x034 ......................................................... 441
Register 19: CAN IF2 Arbitration 2 (CANIF2ARB2), offset 0x094 ......................................................... 441
Register 20: CAN IF1 Message Control (CANIF1MCTL), offset 0x038 .................................................. 442
Register 21: CAN IF2 Message Control (CANIF2MCTL), offset 0x098 .................................................. 442
Register 22: CAN IF1 Data A1 (CANIF1DA1), offset 0x03C ................................................................. 444
Register 23: CAN IF1 Data A2 (CANIF1DA2), offset 0x040 ................................................................. 444
Register 24: CAN IF1 Data B1 (CANIF1DB1), offset 0x044 ................................................................. 444
Register 25: CAN IF1 Data B2 (CANIF1DB2), offset 0x048 ................................................................. 444
Register 26: CAN IF2 Data A1 (CANIF2DA1), offset 0x09C ................................................................. 444
Register 27: CAN IF2 Data A2 (CANIF2DA2), offset 0x0A0 ................................................................. 444
Register 28: CAN IF2 Data B1 (CANIF2DB1), offset 0x0A4 ................................................................. 444
Register 29: CAN IF2 Data B2 (CANIF2DB2), offset 0x0A8 ................................................................. 444
Register 30: CAN Transmission Request 1 (CANTXRQ1), offset 0x100 ................................................ 445
Register 31: CAN Transmission Request 2 (CANTXRQ2), offset 0x104 ................................................ 445
Register 32: CAN New Data 1 (CANNWDA1), offset 0x120 ................................................................. 446
Register 33: CAN New Data 2 (CANNWDA2), offset 0x124 ................................................................. 446
Register 34: CAN Message 1 Interrupt Pending (CANMSG1INT), offset 0x140 ..................................... 447
Register 35: CAN Message 2 Interrupt Pending (CANMSG2INT), offset 0x144 ..................................... 447
Register 36: CAN Message 1 Valid (CANMSG1VAL), offset 0x160 ....................................................... 448
Register 37: CAN Message 2 Valid (CANMSG2VAL), offset 0x164 ....................................................... 448
Ethernet Controller ...................................................................................................................... 449
Register 1: Ethernet MAC Raw Interrupt Status (MACRIS), offset 0x000 ............................................ 458
Register 2: Ethernet MAC Interrupt Acknowledge (MACIACK), offset 0x000 ....................................... 460
Register 3: Ethernet MAC Interrupt Mask (MACIM), offset 0x004 ....................................................... 461
Register 4: Ethernet MAC Receive Control (MACRCTL), offset 0x008 ................................................ 462
Register 5: Ethernet MAC Transmit Control (MACTCTL), offset 0x00C ............................................... 463
Register 6: Ethernet MAC Data (MACDATA), offset 0x010 ................................................................. 464
Register 7: Ethernet MAC Individual Address 0 (MACIA0), offset 0x014 ............................................. 466
Register 8: Ethernet MAC Individual Address 1 (MACIA1), offset 0x018 ............................................. 467
Register 9: Ethernet MAC Threshold (MACTHR), offset 0x01C .......................................................... 468
Register 10: Ethernet MAC Management Control (MACMCTL), offset 0x020 ........................................ 469
Register 11: Ethernet MAC Management Divider (MACMDV), offset 0x024 .......................................... 470
Register 12: Ethernet MAC Management Transmit Data (MACMTXD), offset 0x02C ............................. 471
Register 13: Ethernet MAC Management Receive Data (MACMRXD), offset 0x030 .............................. 472
Register 14: Ethernet MAC Number of Packets (MACNP), offset 0x034 ............................................... 473
Register 15: Ethernet MAC Transmission Request (MACTR), offset 0x038 ........................................... 474
Register 16: Ethernet MAC Timer Support (MACTS), offset 0x03C ...................................................... 475
Register 17: Ethernet PHY Management Register 0 – Control (MR0), address 0x00 ............................. 476
18 March 17, 2008
Preliminary
Table of Contents
Register 18: Ethernet PHY Management Register 1 – Status (MR1), address 0x01 .............................. 478
Register 19: Ethernet PHY Management Register 2 – PHY Identifier 1 (MR2), address 0x02 ................. 480
Register 20: Ethernet PHY Management Register 3 – PHY Identifier 2 (MR3), address 0x03 ................. 481
Register 21: Ethernet PHY Management Register 4 – Auto-Negotiation Advertisement (MR4), address
0x04 ............................................................................................................................. 482
Register 22: Ethernet PHY Management Register 5 – Auto-Negotiation Link Partner Base Page Ability
(MR5), address 0x05 ..................................................................................................... 484
Register 23: Ethernet PHY Management Register 6 – Auto-Negotiation Expansion (MR6), address
0x06 ............................................................................................................................. 485
Register 24: Ethernet PHY Management Register 16 – Vendor-Specific (MR16), address 0x10 ............. 486
Register 25: Ethernet PHY Management Register 17 – Interrupt Control/Status (MR17), address
0x11 .............................................................................................................................. 488
Register 26: Ethernet PHY Management Register 18 – Diagnostic (MR18), address 0x12 ..................... 490
Register 27: Ethernet PHY Management Register 19 – Transceiver Control (MR19), address 0x13 ....... 491
Register 28: Ethernet PHY Management Register 23 – LED Configuration (MR23), address 0x17 ......... 492
Register 29: Ethernet PHY Management Register 24 –MDI/MDIX Control (MR24), address 0x18 .......... 493
Analog Comparators ................................................................................................................... 494
Register 1: Analog Comparator Masked Interrupt Status (ACMIS), offset 0x00 .................................... 500
Register 2: Analog Comparator Raw Interrupt Status (ACRIS), offset 0x04 ......................................... 501
Register 3: Analog Comparator Interrupt Enable (ACINTEN), offset 0x08 ........................................... 502
Register 4: Analog Comparator Reference Voltage Control (ACREFCTL), offset 0x10 ......................... 503
Register 5: Analog Comparator Status 0 (ACSTAT0), offset 0x20 ....................................................... 504
Register 6: Analog Comparator Status 1 (ACSTAT1), offset 0x40 ....................................................... 504
Register 7: Analog Comparator Status 2 (ACSTAT2), offset 0x60 ....................................................... 504
Register 8: Analog Comparator Control 0 (ACCTL0), offset 0x24 ....................................................... 505
Register 9: Analog Comparator Control 1 (ACCTL1), offset 0x44 ....................................................... 505
Register 10: Analog Comparator Control 2 (ACCTL2), offset 0x64 ...................................................... 505
March 17, 2008 19
Preliminary
LM3S8933 Microcontroller
About This Document
This data sheet provides reference information for the LM3S8933 microcontroller, describing the
functional blocks of the system-on-chip (SoC) device designed around the ARM® Cortex™-M3
core.
Audience
This manual is intended for system software developers, hardware designers, and application
developers.
About This Manual
This document is organized into sections that correspond to each major feature.
Related Documents
The following documents are referenced by the data sheet, and available on the documentation CD
or from the Luminary Micro web site at www.luminarymicro.com:
■ ARM® Cortex™-M3 Technical Reference Manual
■ ARM® CoreSight Technical Reference Manual
■ ARM® v7-M Architecture Application Level Reference Manual
The following related documents are also referenced:
■ IEEE Standard 1149.1-Test Access Port and Boundary-Scan Architecture
This documentation list was current as of publication date. Please check the Luminary Micro web
site for additional documentation, including application notes and white papers.
Documentation Conventions
This document uses the conventions shown in Table 1 on page 20.
Table 1. Documentation Conventions
Notation Meaning
General Register Notation
APB registers are indicated in uppercase bold. For example, PBORCTL is the Power-On and
Brown-Out Reset Control register. If a register name contains a lowercase n, it represents more
than one register. For example, SRCRn represents any (or all) of the three Software Reset Control
registers: SRCR0, SRCR1 , and SRCR2.
REGISTER
bit A single bit in a register.
bit field Two or more consecutive and related bits.
A hexadecimal increment to a register's address, relative to that module's base address as specified
in “Memory Map” on page 41.
offset 0xnnn
Registers are numbered consecutively throughout the document to aid in referencing them. The
register number has no meaning to software.
Register N
20 March 17, 2008
Preliminary
About This Document
Notation Meaning
Register bits marked reserved are reserved for future use. In most cases, reserved bits are set to
0; however, user software should not rely on the value of a reserved bit. To provide software
compatibility with future products, the value of a reserved bit should be preserved across a
read-modify-write operation.
reserved
The range of register bits inclusive from xx to yy. For example, 31:15 means bits 15 through 31 in
that register.
yy:xx
This value in the register bit diagram indicates whether software running on the controller can
change the value of the bit field.
Register Bit/Field
Types
RC Software can read this field. The bit or field is cleared by hardware after reading the bit/field.
RO Software can read this field. Always write the chip reset value.
R/W Software can read or write this field.
Software can read or write this field. A write of a 0 to a W1C bit does not affect the bit value in the
register. A write of a 1 clears the value of the bit in the register; the remaining bits remain unchanged.
This register type is primarily used for clearing interrupt status bits where the read operation
provides the interrupt status and the write of the read value clears only the interrupts being reported
at the time the register was read.
R/W1C
Software can read or write a 1 to this field. A write of a 0 to a R/W1S bit does not affect the bit
value in the register.
R/W1S
Software can write this field. A write of a 0 to a W1C bit does not affect the bit value in the register.
A write of a 1 clears the value of the bit in the register; the remaining bits remain unchanged. A
read of the register returns no meaningful data.
This register is typically used to clear the corresponding bit in an interrupt register.
W1C
WO Only a write by software is valid; a read of the register returns no meaningful data.
Register Bit/Field This value in the register bit diagram shows the bit/field value after any reset, unless noted.
Reset Value
0 Bit cleared to 0 on chip reset.
1 Bit set to 1 on chip reset.
- Nondeterministic.
Pin/Signal Notation
[ ] Pin alternate function; a pin defaults to the signal without the brackets.
pin Refers to the physical connection on the package.
signal Refers to the electrical signal encoding of a pin.
Change the value of the signal from the logically False state to the logically True state. For active
High signals, the asserted signal value is 1 (High); for active Low signals, the asserted signal value
is 0 (Low). The active polarity (High or Low) is defined by the signal name (see SIGNAL and SIGNAL
below).
assert a signal
deassert a signal Change the value of the signal from the logically True state to the logically False state.
Signal names are in uppercase and in the Courier font. An overbar on a signal name indicates that
it is active Low. To assert SIGNAL is to drive it Low; to deassert SIGNAL is to drive it High.
SIGNAL
Signal names are in uppercase and in the Courier font. An active High signal has no overbar. To
assert SIGNAL is to drive it High; to deassert SIGNAL is to drive it Low.
SIGNAL
Numbers
An uppercase X indicates any of several values is allowed, where X can be any legal pattern. For
example, a binary value of 0X00 can be either 0100 or 0000, a hex value of 0xX is 0x0 or 0x1, and
so on.
X
Hexadecimal numbers have a prefix of 0x. For example, 0x00FF is the hexadecimal number FF.
All other numbers within register tables are assumed to be binary. Within conceptual information,
binary numbers are indicated with a b suffix, for example, 1011b, and decimal numbers are written
without a prefix or suffix.
0x
March 17, 2008 21
Preliminary
LM3S8933 Microcontroller
1 Architectural Overview
The Luminary Micro Stellaris® family of microcontrollers—the first ARM® Cortex™-M3 based
controllers—brings high-performance 32-bit computing to cost-sensitive embedded microcontroller
applications. These pioneering parts deliver customers 32-bit performance at a cost equivalent to
legacy 8- and 16-bit devices, all in a package with a small footprint.
The Stellaris® family offers efficient performance and extensive integration, favorably positioning
the device into cost-conscious applications requiring significant control-processing and connectivity
capabilities. The Stellaris® LM3S8000 series combines Bosch Controller Area Network technology
with both a 10/100 Ethernet Media Access Control (MAC) and Physical (PHY) layer.
The LM3S8933 microcontroller is targeted for industrial applications, including remote monitoring,
electronic point-of-sale machines, test and measurement equipment, network appliances and
switches, factory automation, HVAC and building control, gaming equipment, motion control, medical
instrumentation, and fire and security.
For applications requiring extreme conservation of power, the LM3S8933 microcontroller features
a Battery-backed Hibernation module to efficiently power down the LM3S8933 to a low-power state
during extended periods of inactivity. With a power-up/power-down sequencer, a continuous time
counter (RTC), a pair of match registers, an APB interface to the system bus, and dedicated
non-volatile memory, the Hibernation module positions the LM3S8933 microcontroller perfectly for
battery applications.
In addition, the LM3S8933 microcontroller offers the advantages of ARM's widely available
development tools, System-on-Chip (SoC) infrastructure IP applications, and a large user community.
Additionally, the microcontroller uses ARM's Thumb®-compatible Thumb-2 instruction set to reduce
memory requirements and, thereby, cost. Finally, the LM3S8933 microcontroller is code-compatible
to all members of the extensive Stellaris® family; providing flexibility to fit our customers' precise
needs.
Luminary Micro offers a complete solution to get to market quickly, with evaluation and development
boards, white papers and application notes, an easy-to-use peripheral driver library, and a strong
support, sales, and distributor network. See “Ordering and Contact Information” on page 578 for
ordering information for Stellaris® family devices.
1.1 Product Features
The LM3S8933 microcontroller includes the following product features:
■ 32-Bit RISC Performance
– 32-bit ARM® Cortex™-M3 v7M architecture optimized for small-footprint embedded
applications
– System timer (SysTick), providing a simple, 24-bit clear-on-write, decrementing, wrap-on-zero
counter with a flexible control mechanism
– Thumb®-compatible Thumb-2-only instruction set processor core for high code density
– 50-MHz operation
– Hardware-division and single-cycle-multiplication
22 March 17, 2008
Preliminary
Architectural Overview
– Integrated Nested Vectored Interrupt Controller (NVIC) providing deterministic interrupt
handling
– 32 interrupts with eight priority levels
– Memory protection unit (MPU), providing a privileged mode for protected operating system
functionality
– Unaligned data access, enabling data to be efficiently packed into memory
– Atomic bit manipulation (bit-banding), delivering maximum memory utilization and streamlined
peripheral control
■ Internal Memory
– 256 KB single-cycle flash
• User-managed flash block protection on a 2-KB block basis
• User-managed flash data programming
• User-defined and managed flash-protection block
– 64 KB single-cycle SRAM
■ General-Purpose Timers
– Four General-Purpose Timer Modules (GPTM), each of which provides two 16-bit timers.
Each GPTM can be configured to operate independently:
• As a single 32-bit timer
• As one 32-bit Real-Time Clock (RTC) to event capture
• For Pulse Width Modulation (PWM)
• To trigger analog-to-digital conversions
– 32-bit Timer modes
• Programmable one-shot timer
• Programmable periodic timer
• Real-Time Clock when using an external 32.768-KHz clock as the input
• User-enabled stalling in periodic and one-shot mode when the controller asserts the CPU
Halt flag during debug
• ADC event trigger
– 16-bit Timer modes
• General-purpose timer function with an 8-bit prescaler
• Programmable one-shot timer
March 17, 2008 23
Preliminary
LM3S8933 Microcontroller
• Programmable periodic timer
• User-enabled stalling when the controller asserts CPU Halt flag during debug
• ADC event trigger
– 16-bit Input Capture modes
• Input edge count capture
• Input edge time capture
– 16-bit PWM mode
• Simple PWM mode with software-programmable output inversion of the PWM signal
■ ARM FiRM-compliant Watchdog Timer
– 32-bit down counter with a programmable load register
– Separate watchdog clock with an enable
– Programmable interrupt generation logic with interrupt masking
– Lock register protection from runaway software
– Reset generation logic with an enable/disable
– User-enabled stalling when the controller asserts the CPU Halt flag during debug
■ Controller Area Network (CAN)
– Supports CAN protocol version 2.0 part A/B
– Bit rates up to 1Mb/s
– 32 message objects, each with its own identifier mask
– Maskable interrupt
– Disable automatic retransmission mode for TTCAN
– Programmable loop-back mode for self-test operation
■ 10/100 Ethernet Controller
– Conforms to the IEEE 802.3-2002 Specification
– Hardware assistance for IEEE 1588-2002 Precision Time Protocol (PTP)
– Full- and half-duplex for both 100 Mbps and 10 Mbps operation
– Integrated 10/100 Mbps Transceiver (PHY)
– Automatic MDI/MDI-X cross-over correction
– Programmable MAC address
24 March 17, 2008
Preliminary
Architectural Overview
– Power-saving and power-down modes
■ Synchronous Serial Interface (SSI)
– Master or slave operation
– Programmable clock bit rate and prescale
– Separate transmit and receive FIFOs, 16 bits wide, 8 locations deep
– Programmable interface operation for Freescale SPI, MICROWIRE, or Texas Instruments
synchronous serial interfaces
– Programmable data frame size from 4 to 16 bits
– Internal loopback test mode for diagnostic/debug testing
■ UART
– Two fully programmable 16C550-type UARTs with IrDA support
– Separate 16x8 transmit (TX) and 16x12 receive (RX) FIFOs to reduce CPU interrupt service
loading
– Programmable baud-rate generator allowing speeds up to 3.125 Mbps
– Programmable FIFO length, including 1-byte deep operation providing conventional
double-buffered interface
– FIFO trigger levels of 1/8, 1/4, 1/2, 3/4, and 7/8
– Standard asynchronous communication bits for start, stop, and parity
– False-start-bit detection
– Line-break generation and detection
■ ADC
– Single- and differential-input configurations
– Four 10-bit channels (inputs) when used as single-ended inputs
– Sample rate of one million samples/second
– Flexible, configurable analog-to-digital conversion
– Four programmable sample conversion sequences from one to eight entries long, with
corresponding conversion result FIFOs
– Each sequence triggered by software or internal event (timers, analog comparators, or GPIO)
– On-chip temperature sensor
■ Analog Comparators
– Three independent integrated analog comparators
March 17, 2008 25
Preliminary
LM3S8933 Microcontroller
– Configurable for output to: drive an output pin, generate an interrupt, or initiate an ADC sample
sequence
– Compare external pin input to external pin input or to internal programmable voltage reference
■ I2C
– Master and slave receive and transmit operation with transmission speed up to 100 Kbps in
Standard mode and 400 Kbps in Fast mode
– Interrupt generation
– Master with arbitration and clock synchronization, multimaster support, and 7-bit addressing
mode
■ GPIOs
– 6-36 GPIOs, depending on configuration
– 5-V-tolerant input/outputs
– Programmable interrupt generation as either edge-triggered or level-sensitive
– Bit masking in both read and write operations through address lines
– Can initiate an ADC sample sequence
– Programmable control for GPIO pad configuration:
• Weak pull-up or pull-down resistors
• 2-mA, 4-mA, and 8-mA pad drive
• Slew rate control for the 8-mA drive
• Open drain enables
• Digital input enables
■ Power
– On-chip Low Drop-Out (LDO) voltage regulator, with programmable output user-adjustable
from 2.25 V to 2.75 V
– Hibernation module handles the power-up/down 3.3 V sequencing and control for the core
digital logic and analog circuits
– Low-power options on controller: Sleep and Deep-sleep modes
– Low-power options for peripherals: software controls shutdown of individual peripherals
– User-enabled LDO unregulated voltage detection and automatic reset
– 3.3-V supply brown-out detection and reporting via interrupt or reset
■ Flexible Reset Sources
26 March 17, 2008
Preliminary
Architectural Overview
– Power-on reset (POR)
– Reset pin assertion
– Brown-out (BOR) detector alerts to system power drops
– Software reset
– Watchdog timer reset
– Internal low drop-out (LDO) regulator output goes unregulated
■ Additional Features
– Six reset sources
– Programmable clock source control
– Clock gating to individual peripherals for power savings
– IEEE 1149.1-1990 compliant Test Access Port (TAP) controller
– Debug access via JTAG and Serial Wire interfaces
– Full JTAG boundary scan
■ Industrial and extended temperature 100-pin RoHS-compliant LQFP package
■ Industrial-range 108-ball RoHS-compliant BGA package
1.2 Target Applications
■ Remote monitoring
■ Electronic point-of-sale (POS) machines
■ Test and measurement equipment
■ Network appliances and switches
■ Factory automation
■ HVAC and building control
■ Gaming equipment
■ Motion control
■ Medical instrumentation
■ Fire and security
■ Power and energy
■ Transportation
March 17, 2008 27
Preliminary
LM3S8933 Microcontroller
1.3 High-Level Block Diagram
Figure 1-1 on page 28 represents the full set of features in the Stellaris® 8000 series of devices;
not all features may be available on the LM3S8933 microcontroller.
Figure 1-1. Stellaris® 8000 Series High-Level Block Diagram
1.4 Functional Overview
The following sections provide an overview of the features of the LM3S8933 microcontroller. The
page number in parenthesis indicates where that feature is discussed in detail. Ordering and support
information can be found in “Ordering and Contact Information” on page 578.
28 March 17, 2008
Preliminary
Architectural Overview
1.4.1 ARM Cortex™-M3
1.4.1.1 Processor Core (see page 35)
All members of the Stellaris® product family, including the LM3S8933 microcontroller, are designed
around an ARM Cortex™-M3 processor core. The ARM Cortex-M3 processor provides the core for
a high-performance, low-cost platform that meets the needs of minimal memory implementation,
reduced pin count, and low-power consumption, while delivering outstanding computational
performance and exceptional system response to interrupts.
“ARM Cortex-M3 Processor Core” on page 35 provides an overview of the ARM core; the core is
detailed in the ARM® Cortex™-M3 Technical Reference Manual.
1.4.1.2 System Timer (SysTick)
Cortex-M3 includes an integrated system timer, SysTick. SysTick provides a simple, 24-bit
clear-on-write, decrementing, wrap-on-zero counter with a flexible control mechanism. The counter
can be used in several different ways, for example:
■ An RTOS tick timer which fires at a programmable rate (for example, 100 Hz) and invokes a
SysTick routine.
■ A high-speed alarm timer using the system clock.
■ A variable rate alarm or signal timer—the duration is range-dependent on the reference clock
used and the dynamic range of the counter.
■ A simple counter. Software can use this to measure time to completion and time used.
■ An internal clock source control based on missing/meeting durations. The COUNTFLAG bit-field
in the control and status register can be used to determine if an action completed within a set
duration, as part of a dynamic clock management control loop.
1.4.1.3 Nested Vectored Interrupt Controller (NVIC)
The LM3S8933 controller includes the ARM Nested Vectored Interrupt Controller (NVIC) on the
ARM Cortex-M3 core. The NVIC and Cortex-M3 prioritize and handle all exceptions. All exceptions
are handled in Handler Mode. The processor state is automatically stored to the stack on an
exception, and automatically restored from the stack at the end of the Interrupt Service Routine
(ISR). The vector is fetched in parallel to the state saving, which enables efficient interrupt entry.
The processor supports tail-chaining, which enables back-to-back interrupts to be performed without
the overhead of state saving and restoration. Software can set eight priority levels on 7 exceptions
(system handlers) and 32 interrupts.
“Interrupts” on page 43 provides an overview of the NVIC controller and the interrupt map. Exceptions
and interrupts are detailed in the ARM® Cortex™-M3 Technical Reference Manual.
1.4.2 Motor Control Peripherals
To enhance motor control, the LM3S8933 controller features Pulse Width Modulation (PWM) outputs.
1.4.2.1 PWM
Pulse width modulation (PWM) is a powerful technique for digitally encoding analog signal levels.
High-resolution counters are used to generate a square wave, and the duty cycle of the square
wave is modulated to encode an analog signal. Typical applications include switching power supplies
and motor control.
March 17, 2008 29
Preliminary
LM3S8933 Microcontroller
On the LM3S8933, PWM motion control functionality can be achieved through:
■ The motion control features of the general-purpose timers using the CCP pins
CCP Pins (see page 210)
The General-Purpose Timer Module's CCP (Capture Compare PWM) pins are software programmable
to support a simple PWM mode with a software-programmable output inversion of the PWM signal.
1.4.3 Analog Peripherals
To handle analog signals, the LM3S8933 microcontroller offers an Analog-to-Digital Converter
(ADC).
For support of analog signals, the LM3S8933 microcontroller offers three analog comparators.
1.4.3.1 ADC (see page 263)
An analog-to-digital converter (ADC) is a peripheral that converts a continuous analog voltage to a
discrete digital number.
The LM3S8933 ADC module features 10-bit conversion resolution and supports four input channels,
plus an internal temperature sensor. Four buffered sample sequences allow rapid sampling of up
to eight analog input sources without controller intervention. Each sample sequence provides flexible
programming with fully configurable input source, trigger events, interrupt generation, and sequence
priority.
1.4.3.2 Analog Comparators (see page 494)
An analog comparator is a peripheral that compares two analog voltages, and provides a logical
output that signals the comparison result.
The LM3S8933 microcontroller provides three independent integrated analog comparators that can
be configured to drive an output or generate an interrupt or ADC event.
A comparator can compare a test voltage against any one of these voltages:
■ An individual external reference voltage
■ A shared single external reference voltage
■ A shared internal reference voltage
The comparator can provide its output to a device pin, acting as a replacement for an analog
comparator on the board, or it can be used to signal the application via interrupts or triggers to the
ADC to cause it to start capturing a sample sequence. The interrupt generation and ADC triggering
logic is separate. This means, for example, that an interrupt can be generated on a rising edge and
the ADC triggered on a falling edge.
1.4.4 Serial Communications Peripherals
The LM3S8933 controller supports both asynchronous and synchronous serial communications
with:
■ Two fully programmable 16C550-type UARTs
■ One SSI module
■ One I2C module
30 March 17, 2008
Preliminary
Architectural Overview
■ One CAN unit
■ Ethernet controller
1.4.4.1 UART (see page 296)
A Universal Asynchronous Receiver/Transmitter (UART) is an integrated circuit used for RS-232C
serial communications, containing a transmitter (parallel-to-serial converter) and a receiver
(serial-to-parallel converter), each clocked separately.
The LM3S8933 controller includes two fully programmable 16C550-type UARTs that support data
transfer speeds up to 3.125 Mbps. (Although similar in functionality to a 16C550 UART, it is not
register-compatible.) In addition, each UART is capable of supporting IrDA.
Separate 16x8 transmit (TX) and 16x12 receive (RX) FIFOs reduce CPU interrupt service loading.
The UART can generate individually masked interrupts from the RX, TX, modem status, and error
conditions. The module provides a single combined interrupt when any of the interrupts are asserted
and are unmasked.
1.4.4.2 SSI (see page 337)
Synchronous Serial Interface (SSI) is a four-wire bi-directional communications interface.
The LM3S8933 controller includes one SSI module that provides the functionality for synchronous
serial communications with peripheral devices, and can be configured to use the Freescale SPI,
MICROWIRE, or TI synchronous serial interface frame formats. The size of the data frame is also
configurable, and can be set between 4 and 16 bits, inclusive.
The SSI module performs serial-to-parallel conversion on data received from a peripheral device,
and parallel-to-serial conversion on data transmitted to a peripheral device. The TX and RX paths
are buffered with internal FIFOs, allowing up to eight 16-bit values to be stored independently.
The SSI module can be configured as either a master or slave device. As a slave device, the SSI
module can also be configured to disable its output, which allows a master device to be coupled
with multiple slave devices.
The SSI module also includes a programmable bit rate clock divider and prescaler to generate the
output serial clock derived from the SSI module's input clock. Bit rates are generated based on the
input clock and the maximum bit rate is determined by the connected peripheral.
1.4.4.3 I2C (see page 374)
The Inter-Integrated Circuit (I2C) bus provides bi-directional data transfer through a two-wire design
(a serial data line SDA and a serial clock line SCL).
The I2C bus interfaces to external I2C devices such as serial memory (RAMs and ROMs), networking
devices, LCDs, tone generators, and so on. The I2C bus may also be used for system testing and
diagnostic purposes in product development and manufacture.
The LM3S8933 controller includes one I2C module that provides the ability to communicate to other
IC devices over an I2C bus. The I2C bus supports devices that can both transmit and receive (write
and read) data.
Devices on the I2C bus can be designated as either a master or a slave. The I2C module supports
both sending and receiving data as either a master or a slave, and also supports the simultaneous
operation as both a master and a slave. The four I2C modes are: Master Transmit, Master Receive,
Slave Transmit, and Slave Receive.
A Stellaris® I2C module can operate at two speeds: Standard (100 Kbps) and Fast (400 Kbps).
March 17, 2008 31
Preliminary
LM3S8933 Microcontroller
Both the I2C master and slave can generate interrupts. The I2C master generates interrupts when
a transmit or receive operation completes (or aborts due to an error). The I2C slave generates
interrupts when data has been sent or requested by a master.
1.4.4.4 Controller Area Network (see page 409)
Controller Area Network (CAN) is a multicast shared serial-bus standard for connecting electronic
control units (ECUs). CAN was specifically designed to be robust in electromagnetically noisy
environments and can utilize a differential balanced line like RS-485 or a more robust twisted-pair
wire. Originally created for automotive purposes, now it is used in many embedded control
applications (for example, industrial or medical). Bit rates up to 1Mb/s are possible at network lengths
below 40 meters. Decreased bit rates allow longer network distances (for example, 125 Kb/s at
500m).
A transmitter sends a message to all CAN nodes (broadcasting). Each node decides on the basis
of the identifier received whether it should process the message. The identifier also determines the
priority that the message enjoys in competition for bus access. Each CAN message can transmit
from 0 to 8 bytes of user information. The LM3S8933 includes one CAN units.
1.4.4.5 Ethernet Controller (see page 449)
Ethernet is a frame-based computer networking technology for local area networks (LANs). Ethernet
has been standardized as IEEE 802.3. It defines a number of wiring and signaling standards for the
physical layer, two means of network access at the Media Access Control (MAC)/Data Link Layer,
and a common addressing format.
The Stellaris® Ethernet Controller consists of a fully integrated media access controller (MAC) and
network physical (PHY) interface device. The Ethernet Controller conforms to IEEE 802.3
specifications and fully supports 10BASE-T and 100BASE-TX standards. In addition, the Ethernet
Controller supports automatic MDI/MDI-X cross-over correction.
1.4.5 System Peripherals
1.4.5.1 Programmable GPIOs (see page 162)
General-purpose input/output (GPIO) pins offer flexibility for a variety of connections.
The Stellaris® GPIO module is comprised of seven physical GPIO blocks, each corresponding to
an individual GPIO port. The GPIO module is FiRM-compliant (compliant to the ARM Foundation
IP for Real-Time Microcontrollers specification) and supports 6-36 programmable input/output pins.
The number of GPIOs available depends on the peripherals being used (see “Signal Tables” on page
509 for the signals available to each GPIO pin).
The GPIO module features programmable interrupt generation as either edge-triggered or
level-sensitive on all pins, programmable control for GPIO pad configuration, and bit masking in
both read and write operations through address lines.
1.4.5.2 Four Programmable Timers (see page 204)
Programmable timers can be used to count or time external events that drive the Timer input pins.
The Stellaris® General-Purpose Timer Module (GPTM) contains four GPTM blocks. Each GPTM
block provides two 16-bit timers/counters that can be configured to operate independently as timers
or event counters, or configured to operate as one 32-bit timer or one 32-bit Real-Time Clock (RTC).
Timers can also be used to trigger analog-to-digital (ADC) conversions.
When configured in 32-bit mode, a timer can run as a Real-Time Clock (RTC), one-shot timer or
periodic timer. When in 16-bit mode, a timer can run as a one-shot timer or periodic timer, and can
32 March 17, 2008
Preliminary
Architectural Overview
extend its precision by using an 8-bit prescaler. A 16-bit timer can also be configured for event
capture or Pulse Width Modulation (PWM) generation.
1.4.5.3 Watchdog Timer (see page 240)
A watchdog timer can generate nonmaskable interrupts (NMIs) or a reset when a time-out value is
reached. The watchdog timer is used to regain control when a system has failed due to a software
error or to the failure of an external device to respond in the expected way.
The Stellaris® Watchdog Timer module consists of a 32-bit down counter, a programmable load
register, interrupt generation logic, and a locking register.
The Watchdog Timer can be configured to generate an interrupt to the controller on its first time-out,
and to generate a reset signal on its second time-out. Once the Watchdog Timer has been configured,
the lock register can be written to prevent the timer configuration from being inadvertently altered.
1.4.6 Memory Peripherals
The LM3S8933 controller offers both single-cycle SRAM and single-cycle Flash memory.
1.4.6.1 SRAM (see page 138)
The LM3S8933 static random access memory (SRAM) controller supports 64 KB SRAM. The internal
SRAM of the Stellaris® devices is located at offset 0x0000.0000 of the device memory map. To
reduce the number of time-consuming read-modify-write (RMW) operations, ARM has introduced
bit-banding technology in the new Cortex-M3 processor. With a bit-band-enabled processor, certain
regions in the memory map (SRAM and peripheral space) can use address aliases to access
individual bits in a single, atomic operation.
1.4.6.2 Flash (see page 139)
The LM3S8933 Flash controller supports 256 KB of flash memory. The flash is organized as a set
of 1-KB blocks that can be individually erased. Erasing a block causes the entire contents of the
block to be reset to all 1s. These blocks are paired into a set of 2-KB blocks that can be individually
protected. The blocks can be marked as read-only or execute-only, providing different levels of code
protection. Read-only blocks cannot be erased or programmed, protecting the contents of those
blocks from being modified. Execute-only blocks cannot be erased or programmed, and can only
be read by the controller instruction fetch mechanism, protecting the contents of those blocks from
being read by either the controller or by a debugger.
1.4.7 Additional Features
1.4.7.1 Memory Map (see page 41)
A memory map lists the location of instructions and data in memory. The memory map for the
LM3S8933 controller can be found in “Memory Map” on page 41. Register addresses are given as
a hexadecimal increment, relative to the module's base address as shown in the memory map.
The ARM® Cortex™-M3 Technical Reference Manual provides further information on the memory
map.
1.4.7.2 JTAG TAP Controller (see page 46)
The Joint Test Action Group (JTAG) port is an IEEE standard that defines a Test Access Port and
Boundary Scan Architecture for digital integrated circuits and provides a standardized serial interface
for controlling the associated test logic. The TAP, Instruction Register (IR), and Data Registers (DR)
can be used to test the interconnections of assembled printed circuit boards and obtain manufacturing
March 17, 2008 33
Preliminary
LM3S8933 Microcontroller
information on the components. The JTAG Port also provides a means of accessing and controlling
design-for-test features such as I/O pin observation and control, scan testing, and debugging.
The JTAG port is composed of the standard five pins: TRST, TCK, TMS, TDI, and TDO. Data is
transmitted serially into the controller on TDI and out of the controller on TDO. The interpretation of
this data is dependent on the current state of the TAP controller. For detailed information on the
operation of the JTAG port and TAP controller, please refer to the IEEE Standard 1149.1-Test
Access Port and Boundary-Scan Architecture.
The Luminary Micro JTAG controller works with the ARM JTAG controller built into the Cortex-M3
core. This is implemented by multiplexing the TDO outputs from both JTAG controllers. ARM JTAG
instructions select the ARM TDO output while Luminary Micro JTAG instructions select the Luminary
Micro TDO outputs. The multiplexer is controlled by the Luminary Micro JTAG controller, which has
comprehensive programming for the ARM, Luminary Micro, and unimplemented JTAG instructions.
1.4.7.3 System Control and Clocks (see page 57)
System control determines the overall operation of the device. It provides information about the
device, controls the clocking of the device and individual peripherals, and handles reset detection
and reporting.
1.4.7.4 Hibernation Module (see page 119)
The Hibernation module provides logic to switch power off to the main processor and peripherals,
and to wake on external or time-based events. The Hibernation module includes power-sequencing
logic, a real-time clock with a pair of match registers, low-battery detection circuitry, and interrupt
signalling to the processor. It also includes 64 32-bit words of non-volatile memory that can be used
for saving state during hibernation.
1.4.8 Hardware Details
Details on the pins and package can be found in the following sections:
■ “Pin Diagram” on page 507
■ “Signal Tables” on page 509
■ “Operating Characteristics” on page 534
■ “Electrical Characteristics” on page 535
■ “Package Information” on page 550
34 March 17, 2008
Preliminary
Architectural Overview
2 ARM Cortex-M3 Processor Core
The ARM Cortex-M3 processor provides the core for a high-performance, low-cost platform that
meets the needs of minimal memory implementation, reduced pin count, and low power consumption,
while delivering outstanding computational performance and exceptional system response to
interrupts. Features include:
■ Compact core.
■ Thumb-2 instruction set, delivering the high-performance expected of an ARM core in the memory
size usually associated with 8- and 16-bit devices; typically in the range of a few kilobytes of
memory for microcontroller class applications.
■ Rapid application execution through Harvard architecture characterized by separate buses for
instruction and data.
■ Exceptional interrupt handling, by implementing the register manipulations required for handling
an interrupt in hardware.
■ Deterministic, fast interrupt processing: always 12 cycles, or just 6 cycles with tail-chaining
■ Memory protection unit (MPU) to provide a privileged mode of operation for complex applications.
■ Migration from the ARM7™ processor family for better performance and power efficiency.
■ Full-featured debug solution with a:
– Serial Wire JTAG Debug Port (SWJ-DP)
– Flash Patch and Breakpoint (FPB) unit for implementing breakpoints
– Data Watchpoint and Trigger (DWT) unit for implementing watchpoints, trigger resources,
and system profiling
– Instrumentation Trace Macrocell (ITM) for support of printf style debugging
– Trace Port Interface Unit (TPIU) for bridging to a Trace Port Analyzer
■ Optimized for single-cycle flash usage
■ Three sleep modes with clock gating for low power
■ Single-cycle multiply instruction and hardware divide
■ Atomic operations
■ ARM Thumb2 mixed 16-/32-bit instruction set
■ 1.25 DMIPS/MHz
The Stellaris® family of microcontrollers builds on this core to bring high-performance 32-bit computing
to cost-sensitive embedded microcontroller applications, such as factory automation and control,
industrial control power devices, building and home automation, and stepper motors.
March 17, 2008 35
Preliminary
LM3S8933 Microcontroller
For more information on the ARM Cortex-M3 processor core, see the ARM® Cortex™-M3 Technical
Reference Manual. For information on SWJ-DP, see the ARM® CoreSight Technical Reference
Manual.
2.1 Block Diagram
Figure 2-1. CPU Block Diagram
Private Peripheral
Bus
(internal)
Data
Watchpoint
and Trace
Interrupts
Debug
Sleep
Instrumentation
Trace Macrocell
Trace
Port
Interface
Unit
CM3 Core
Instructions Data
Flash
Patch and
Breakpoint
Memory
Protection
Unit
Adv. High-
Perf. Bus
Access Port
Nested
Vectored
Interrupt
Controller
Serial Wire JTAG
Debug Port
Bus
Matrix
Adv. Peripheral
Bus
I-code bus
D-code bus
System bus
ROM
Table
Private
Peripheral
Bus
(external)
Serial
Wire
Output
Trace
Port
(SWO)
ARM
Cortex-M3
2.2 Functional Description
Important: The ARM® Cortex™-M3 Technical Reference Manual describes all the features of an
ARM Cortex-M3 in detail. However, these features differ based on the implementation.
This section describes the Stellaris® implementation.
Luminary Micro has implemented the ARM Cortex-M3 core as shown in Figure 2-1 on page 36. As
noted in the ARM® Cortex™-M3 Technical Reference Manual, several Cortex-M3 components are
flexible in their implementation: SW/JTAG-DP, ETM, TPIU, the ROM table, the MPU, and the Nested
Vectored Interrupt Controller (NVIC). Each of these is addressed in the sections that follow.
2.2.1 Serial Wire and JTAG Debug
Luminary Micro has replaced the ARM SW-DP and JTAG-DP with the ARM CoreSight™-compliant
Serial Wire JTAG Debug Port (SWJ-DP) interface. This means Chapter 12, “Debug Port,” of the
ARM® Cortex™-M3 Technical Reference Manual does not apply to Stellaris® devices.
36 March 17, 2008
Preliminary
ARM Cortex-M3 Processor Core
The SWJ-DP interface combines the SWD and JTAG debug ports into one module. See the
CoreSight™ Design Kit Technical Reference Manual for details on SWJ-DP.
2.2.2 Embedded Trace Macrocell (ETM)
ETM was not implemented in the Stellaris® devices. This means Chapters 15 and 16 of the ARM®
Cortex™-M3 Technical Reference Manual can be ignored.
2.2.3 Trace Port Interface Unit (TPIU)
The TPIU acts as a bridge between the Cortex-M3 trace data from the ITM, and an off-chip Trace
Port Analyzer. The Stellaris® devices have implemented TPIU as shown in Figure 2-2 on page 37.
This is similar to the non-ETM version described in the ARM® Cortex™-M3 Technical Reference
Manual, however, SWJ-DP only provides SWV output for the TPIU.
Figure 2-2. TPIU Block Diagram
ATB
Interface
Asynchronous FIFO
APB
Interface
Trace Out
(serializer)
Debug
ATB
Slave
Port
APB
Slave
Port
Serial Wire
Trace Port
(SWO)
2.2.4 ROM Table
The default ROM table was implemented as described in the ARM® Cortex™-M3 Technical
Reference Manual.
2.2.5 Memory Protection Unit (MPU)
The Memory Protection Unit (MPU) is included on the LM3S8933 controller and supports the standard
ARMv7 Protected Memory System Architecture (PMSA) model. The MPU provides full support for
protection regions, overlapping protection regions, access permissions, and exporting memory
attributes to the system.
2.2.6 Nested Vectored Interrupt Controller (NVIC)
The Nested Vectored Interrupt Controller (NVIC):
■ Facilitates low-latency exception and interrupt handling
March 17, 2008 37
Preliminary
LM3S8933 Microcontroller
■ Controls power management
■ Implements system control registers
The NVIC supports up to 240 dynamically reprioritizable interrupts each with up to 256 levels of
priority. The NVIC and the processor core interface are closely coupled, which enables low latency
interrupt processing and efficient processing of late arriving interrupts. The NVIC maintains knowledge
of the stacked (nested) interrupts to enable tail-chaining of interrupts.
You can only fully access the NVIC from privileged mode, but you can pend interrupts in user-mode
if you enable the Configuration Control Register (see the ARM® Cortex™-M3 Technical Reference
Manual). Any other user-mode access causes a bus fault.
All NVIC registers are accessible using byte, halfword, and word unless otherwise stated.
2.2.6.1 Interrupts
The ARM® Cortex™-M3 Technical Reference Manual describes the maximum number of interrupts
and interrupt priorities. The LM3S8933 microcontroller supports 32 interrupts with eight priority
levels.
2.2.6.2 System Timer (SysTick)
Cortex-M3 includes an integrated system timer, SysTick. SysTick provides a simple, 24-bit
clear-on-write, decrementing, wrap-on-zero counter with a flexible control mechanism. The counter
can be used in several different ways, for example:
■ An RTOS tick timer which fires at a programmable rate (for example, 100 Hz) and invokes a
SysTick routine.
■ A high-speed alarm timer using the system clock.
■ A variable rate alarm or signal timer—the duration is range-dependent on the reference clock
used and the dynamic range of the counter.
■ A simple counter. Software can use this to measure time to completion and time used.
■ An internal clock source control based on missing/meeting durations. The COUNTFLAG bit-field
in the control and status register can be used to determine if an action completed within a set
duration, as part of a dynamic clock management control loop.
Functional Description
The timer consists of three registers:
■ A control and status counter to configure its clock, enable the counter, enable the SysTick
interrupt, and determine counter status.
■ The reload value for the counter, used to provide the counter's wrap value.
■ The current value of the counter.
A fourth register, the SysTick Calibration Value Register, is not implemented in the Stellaris® devices.
When enabled, the timer counts down from the reload value to zero, reloads (wraps) to the value
in the SysTick Reload Value register on the next clock edge, then decrements on subsequent clocks.
Writing a value of zero to the Reload Value register disables the counter on the next wrap. When
the counter reaches zero, the COUNTFLAG status bit is set. The COUNTFLAG bit clears on reads.
38 March 17, 2008
Preliminary
ARM Cortex-M3 Processor Core
Writing to the Current Value register clears the register and the COUNTFLAG status bit. The write
does not trigger the SysTick exception logic. On a read, the current value is the value of the register
at the time the register is accessed.
If the core is in debug state (halted), the counter will not decrement. The timer is clocked with respect
to a reference clock. The reference clock can be the core clock or an external clock source.
SysTick Control and Status Register
Use the SysTick Control and Status Register to enable the SysTick features. The reset is
0x0000.0000.
Bit/Field Name Type Reset Description
Software should not rely on the value of a reserved bit. To provide compatibility with
future products, the value of a reserved bit should be preserved across a
read-modify-write operation.
31:17 reserved RO 0
Count Flag
Returns 1 if timer counted to 0 since last time this was read. Clears on read by
application. If read by the debugger using the DAP, this bit is cleared on read-only
if the MasterType bit in the AHB-AP Control Register is set to 0. Otherwise, the
COUNTFLAG bit is not changed by the debugger read.
16 COUNTFLAG R/W 0
Software should not rely on the value of a reserved bit. To provide compatibility with
future products, the value of a reserved bit should be preserved across a
read-modify-write operation.
15:3 reserved RO 0
Clock Source
Value Description
0 External reference clock. (Not implemented for Stellaris microcontrollers.)
1 Core clock
If no reference clock is provided, it is held at 1 and so gives the same time as the
core clock. The core clock must be at least 2.5 times faster than the reference clock.
If it is not, the count values are unpredictable.
2 CLKSOURCE R/W 0
Tick Int
Value Description
Counting down to 0 does not pend the SysTick handler. Software can use
the COUNTFLAG to determine if ever counted to 0.
0
1 Counting down to 0 pends the SysTick handler.
1 TICKINT R/W 0
Enable
Value Description
0 Counter disabled.
Counter operates in a multi-shot way. That is, counter loads with the Reload
value and then begins counting down. On reaching 0, it sets the
COUNTFLAG to 1 and optionally pends the SysTick handler, based on
TICKINT. It then loads the Reload value again, and begins counting.
1
0 ENABLE R/W 0
SysTick Reload Value Register
Use the SysTick Reload Value Register to specify the start value to load into the current value
register when the counter reaches 0. It can be any value between 1 and 0x00FF.FFFF. A start value
March 17, 2008 39
Preliminary
LM3S8933 Microcontroller
of 0 is possible, but has no effect because the SysTick interrupt and COUNTFLAG are activated
when counting from 1 to 0.
Therefore, as a multi-shot timer, repeated over and over, it fires every N+1 clock pulse, where N is
any value from 1 to 0x00FF.FFFF. So, if the tick interrupt is required every 100 clock pulses, 99
must be written into the RELOAD. If a new value is written on each tick interrupt, so treated as single
shot, then the actual count down must be written. For example, if a tick is next required after 400
clock pulses, 400 must be written into the RELOAD.
Bit/Field Name Type Reset Description
Software should not rely on the value of a reserved bit. To provide compatibility with
future products, the value of a reserved bit should be preserved across a read-modify-write
operation.
31:24 reserved RO 0
Reload
Value to load into the SysTick Current Value Register when the counter reaches 0.
23:0 RELOAD W1C -
SysTick Current Value Register
Use the SysTick Current Value Register to find the current value in the register.
Bit/Field Name Type Reset Description
Software should not rely on the value of a reserved bit. To provide compatibility with
future products, the value of a reserved bit should be preserved across a
read-modify-write operation.
31:24 reserved RO 0
Current Value
Current value at the time the register is accessed. No read-modify-write protection is
provided, so change with care.
This register is write-clear. Writing to it with any value clears the register to 0. Clearing
this register also clears the COUNTFLAG bit of the SysTick Control and Status Register.
23:0 CURRENT W1C -
SysTick Calibration Value Register
The SysTick Calibration Value register is not implemented.
40 March 17, 2008
Preliminary
ARM Cortex-M3 Processor Core
3 Memory Map
The memory map for the LM3S8933 controller is provided in Table 3-1 on page 41.
In this manual, register addresses are given as a hexadecimal increment, relative to the module’s
base address as shown in the memory map. See also Chapter 4, “Memory Map” in the ARM®
Cortex™-M3 Technical Reference Manual.
Important: In Table 3-1 on page 41, addresses not listed are reserved.
Table 3-1. Memory Mapa
For details on
registers, see
page ...
Start End Description
Memory
0x0000.0000 0x0003.FFFF On-chip flash b 142
0x0004.0000 0x00FF.FFFF Reserved -
0x0100.0000 0x1FFF.FFFF Reserved -
0x2000.0000 0x2000.FFFF Bit-banded on-chip SRAMc 142
0x2001.0000 0x200F.FFFF Reserved -
0x2010.0000 0x21FF.FFFF Reserved -
0x2200.0000 0x221F.FFFF Bit-band alias of 0x2000.0000 through 0x200F.FFFF 138
0x2220.0000 0x3FFF.FFFF Reserved -
FiRM Peripherals
0x4000.0000 0x4000.0FFF Watchdog timer 242
0x4000.1000 0x4000.3FFF Reserved -
0x4000.4000 0x4000.4FFF GPIO Port A 169
0x4000.5000 0x4000.5FFF GPIO Port B 169
0x4000.6000 0x4000.6FFF GPIO Port C 169
0x4000.7000 0x4000.7FFF GPIO Port D 169
0x4000.8000 0x4000.8FFF SSI0 348
0x4000.A000 0x4000.BFFF Reserved -
0x4000.C000 0x4000.CFFF UART0 303
0x4000.D000 0x4000.DFFF UART1 303
0x4000.F000 0x4000.FFFF Reserved -
0x4001.0000 0x4001.FFFF Reserved -
Peripherals
0x4002.0000 0x4002.07FF I2C Master 0 387
0x4002.0800 0x4002.0FFF I2C Slave 0 400
0x4002.2000 0x4002.3FFF Reserved -
0x4002.4000 0x4002.4FFF GPIO Port E 169
0x4002.5000 0x4002.5FFF GPIO Port F 169
0x4002.6000 0x4002.6FFF GPIO Port G 169
0x4002.9000 0x4002.BFFF Reserved -
0x4002.E000 0x4002.FFFF Reserved -
March 17, 2008 41
Preliminary
LM3S8933 Microcontroller
For details on
registers, see
page ...
Start End Description
0x4003.0000 0x4003.0FFF Timer0 215
0x4003.1000 0x4003.1FFF Timer1 215
0x4003.2000 0x4003.2FFF Timer2 215
0x4003.3000 0x4003.3FFF Timer3 215
0x4003.4000 0x4003.7FFF Reserved -
0x4003.8000 0x4003.8FFF ADC 270
0x4003.9000 0x4003.BFFF Reserved -
0x4003.C000 0x4003.CFFF Analog Comparators 494
0x4003.D000 0x4003.FFFF Reserved -
0x4004.0000 0x4004.0FFF CAN0 Controller 421
0x4004.3000 0x4004.7FFF Reserved -
0x4004.8000 0x4004.8FFF Ethernet Controller 457
0x4004.9000 0x4004.BFFF Reserved -
0x4004.C000 0x4004.FFFF Reserved -
0x4005.1000 0x4005.3FFF Reserved -
0x4005.4000 0x4005.7FFF Reserved -
0x4006.0000 0x400F.BFFF Reserved -
0x400F.C000 0x400F.CFFF Hibernation Module 125
0x400F.D000 0x400F.DFFF Flash control 142
0x400F.E000 0x400F.EFFF System control 65
0x4010.0000 0x41FF.FFFF Reserved -
0x4200.0000 0x43FF.FFFF Bit-banded alias of 0x4000.0000 through 0x400F.FFFF -
0x4400.0000 0x5FFF.FFFF Reserved -
0x6000.0000 0xDFFF.FFFF Reserved -
Private Peripheral Bus
ARM®
Cortex™-M3
Technical
Reference
Manual
0xE000.0000 0xE000.0FFF Instrumentation Trace Macrocell (ITM)
0xE000.1000 0xE000.1FFF Data Watchpoint and Trace (DWT)
0xE000.2000 0xE000.2FFF Flash Patch and Breakpoint (FPB)
0xE000.3000 0xE000.DFFF Reserved
0xE000.E000 0xE000.EFFF Nested Vectored Interrupt Controller (NVIC)
0xE000.F000 0xE003.FFFF Reserved
0xE004.0000 0xE004.0FFF Trace Port Interface Unit (TPIU)
0xE004.1000 0xFFFF.FFFF Reserved -
a. All reserved space returns a bus fault when read or written.
b. The unavailable flash will bus fault throughout this range.
c. The unavailable SRAM will bus fault throughout this range.
42 March 17, 2008
Preliminary
Memory Map
4 Interrupts
The ARM Cortex-M3 processor and the Nested Vectored Interrupt Controller (NVIC) prioritize and
handle all exceptions. All exceptions are handled in Handler Mode. The processor state is
automatically stored to the stack on an exception, and automatically restored from the stack at the
end of the Interrupt Service Routine (ISR). The vector is fetched in parallel to the state saving, which
enables efficient interrupt entry. The processor supports tail-chaining, which enables back-to-back
interrupts to be performed without the overhead of state saving and restoration.
Table 4-1 on page 43 lists all exception types. Software can set eight priority levels on seven of
these exceptions (system handlers) as well as on 32 interrupts (listed in Table 4-2 on page 44).
Priorities on the system handlers are set with the NVIC System Handler Priority registers. Interrupts
are enabled through the NVIC Interrupt Set Enable register and prioritized with the NVIC Interrupt
Priority registers. You also can group priorities by splitting priority levels into pre-emption priorities
and subpriorities. All of the interrupt registers are described in Chapter 8, “Nested Vectored Interrupt
Controller” in the ARM® Cortex™-M3 Technical Reference Manual.
Internally, the highest user-settable priority (0) is treated as fourth priority, after a Reset, NMI, and
a Hard Fault. Note that 0 is the default priority for all the settable priorities.
If you assign the same priority level to two or more interrupts, their hardware priority (the lower
position number) determines the order in which the processor activates them. For example, if both
GPIO Port A and GPIO Port B are priority level 1, then GPIO Port A has higher priority.
See Chapter 5, “Exceptions” and Chapter 8, “Nested Vectored Interrupt Controller” in the ARM®
Cortex™-M3 Technical Reference Manual for more information on exceptions and interrupts.
Note: In Table 4-2 on page 44 interrupts not listed are reserved.
Table 4-1. Exception Types
Exception Type Position Prioritya Description
- 0 - Stack top is loaded from first entry of vector table on reset.
Invoked on power up and warm reset. On first instruction, drops to lowest
priority (and then is called the base level of activation). This is
asynchronous.
Reset 1 -3 (highest)
Cannot be stopped or preempted by any exception but reset. This is
asynchronous.
An NMI is only producible by software, using the NVIC Interrupt Control
State register.
Non-Maskable 2 -2
Interrupt (NMI)
All classes of Fault, when the fault cannot activate due to priority or the
configurable fault handler has been disabled. This is synchronous.
Hard Fault 3 -1
MPU mismatch, including access violation and no match. This is
synchronous.
The priority of this exception can be changed.
Memory Management 4 settable
Pre-fetch fault, memory access fault, and other address/memory related
faults. This is synchronous when precise and asynchronous when
imprecise.
You can enable or disable this fault.
Bus Fault 5 settable
Usage fault, such as undefined instruction executed or illegal state
transition attempt. This is synchronous.
Usage Fault 6 settable
- 7-10 - Reserved.
SVCall 11 settable System service call with SVC instruction. This is synchronous.
March 17, 2008 43
Preliminary
LM3S8933 Microcontroller
Exception Type Position Prioritya Description
Debug monitor (when not halting). This is synchronous, but only active
when enabled. It does not activate if lower priority than the current
activation.
Debug Monitor 12 settable
- 13 - Reserved.
Pendable request for system service. This is asynchronous and only
pended by software.
PendSV 14 settable
SysTick 15 settable System tick timer has fired. This is asynchronous.
Asserted from outside the ARM Cortex-M3 core and fed through the NVIC
(prioritized). These are all asynchronous. Table 4-2 on page 44 lists the
interrupts on the LM3S8933 controller.
16 and settable
above
Interrupts
a. 0 is the default priority for all the settable priorities.
Table 4-2. Interrupts
Interrupt (Bit in Interrupt Registers) Description
0 GPIO Port A
1 GPIO Port B
2 GPIO Port C
3 GPIO Port D
4 GPIO Port E
5 UART0
6 UART1
7 SSI0
8 I2C0
14 ADC Sequence 0
15 ADC Sequence 1
16 ADC Sequence 2
17 ADC Sequence 3
18 Watchdog timer
19 Timer0 A
20 Timer0 B
21 Timer1 A
22 Timer1 B
23 Timer2 A
24 Timer2 B
25 Analog Comparator 0
26 Analog Comparator 1
27 Analog Comparator 2
28 System Control
29 Flash Control
30 GPIO Port F
31 GPIO Port G
35 Timer3 A
36 Timer3 B
39 CAN0
44 March 17, 2008
Preliminary
Interrupts
Interrupt (Bit in Interrupt Registers) Description
42 Ethernet Controller
43 Hibernation Module
March 17, 2008 45
Preliminary
LM3S8933 Microcontroller
5 JTAG Interface
The Joint Test Action Group (JTAG) port is an IEEE standard that defines a Test Access Port and
Boundary Scan Architecture for digital integrated circuits and provides a standardized serial interface
for controlling the associated test logic. The TAP, Instruction Register (IR), and Data Registers (DR)
can be used to test the interconnections of assembled printed circuit boards and obtain manufacturing
information on the components. The JTAG Port also provides a means of accessing and controlling
design-for-test features such as I/O pin observation and control, scan testing, and debugging.
The JTAG port is comprised of five pins: TRST, TCK, TMS, TDI, and TDO. Data is transmitted serially
into the controller on TDI and out of the controller on TDO. The interpretation of this data is dependent
on the current state of the TAP controller. For detailed information on the operation of the JTAG
port and TAP controller, please refer to the IEEE Standard 1149.1-Test Access Port and
Boundary-Scan Architecture.
The Luminary Micro JTAG controller works with the ARM JTAG controller built into the Cortex-M3
core. This is implemented by multiplexing the TDO outputs from both JTAG controllers. ARM JTAG
instructions select the ARM TDO output while Luminary Micro JTAG instructions select the Luminary
Micro TDO outputs. The multiplexer is controlled by the Luminary Micro JTAG controller, which has
comprehensive programming for the ARM, Luminary Micro, and unimplemented JTAG instructions.
The JTAG module has the following features:
■ IEEE 1149.1-1990 compatible Test Access Port (TAP) controller
■ Four-bit Instruction Register (IR) chain for storing JTAG instructions
■ IEEE standard instructions:
– BYPASS instruction
– IDCODE instruction
– SAMPLE/PRELOAD instruction
– EXTEST instruction
– INTEST instruction
■ ARM additional instructions:
– APACC instruction
– DPACC instruction
– ABORT instruction
■ Integrated ARM Serial Wire Debug (SWD)
See the ARM® Cortex™-M3 Technical Reference Manual for more information on the ARM JTAG
controller.
46 March 17, 2008
Preliminary
JTAG Interface
5.1 Block Diagram
Figure 5-1. JTAG Module Block Diagram
Instruction Register (IR)
TAP Controller
BYPASS Data Register
Boundary Scan Data Register
IDCODE Data Register
ABORT Data Register
DPACC Data Register
APACC Data Register
TCK
TMS
TDI
TDO
Cortex-M3
Debug
Port
TRST
5.2 Functional Description
A high-level conceptual drawing of the JTAG module is shown in Figure 5-1 on page 47. The JTAG
module is composed of the Test Access Port (TAP) controller and serial shift chains with parallel
update registers. The TAP controller is a simple state machine controlled by the TRST, TCK and
TMS inputs. The current state of the TAP controller depends on the current value of TRST and the
sequence of values captured on TMS at the rising edge of TCK. The TAP controller determines when
the serial shift chains capture new data, shift data from TDI towards TDO, and update the parallel
load registers. The current state of the TAP controller also determines whether the Instruction
Register (IR) chain or one of the Data Register (DR) chains is being accessed.
The serial shift chains with parallel load registers are comprised of a single Instruction Register (IR)
chain and multiple Data Register (DR) chains. The current instruction loaded in the parallel load
register determines which DR chain is captured, shifted, or updated during the sequencing of the
TAP controller.
Some instructions, like EXTEST and INTEST, operate on data currently in a DR chain and do not
capture, shift, or update any of the chains. Instructions that are not implemented decode to the
BYPASS instruction to ensure that the serial path between TDI and TDO is always connected (see
Table 5-2 on page 53 for a list of implemented instructions).
See “JTAG and Boundary Scan” on page 546 for JTAG timing diagrams.
March 17, 2008 47
Preliminary
LM3S8933 Microcontroller
5.2.1 JTAG Interface Pins
The JTAG interface consists of five standard pins: TRST,TCK, TMS, TDI, and TDO. These pins and
their associated reset state are given in Table 5-1 on page 48. Detailed information on each pin
follows.
Table 5-1. JTAG Port Pins Reset State
Pin Name Data Direction Internal Pull-Up Internal Pull-Down Drive Strength Drive Value
TRST Input Enabled Disabled N/A N/A
TCK Input Enabled Disabled N/A N/A
TMS Input Enabled Disabled N/A N/A
TDI Input Enabled Disabled N/A N/A
TDO Output Enabled Disabled 2-mA driver High-Z
5.2.1.1 Test Reset Input (TRST)
The TRST pin is an asynchronous active Low input signal for initializing and resetting the JTAG TAP
controller and associated JTAG circuitry. When TRST is asserted, the TAP controller resets to the
Test-Logic-Reset state and remains there while TRST is asserted. When the TAP controller enters
the Test-Logic-Reset state, the JTAG Instruction Register (IR) resets to the default instruction,
IDCODE.
By default, the internal pull-up resistor on the TRST pin is enabled after reset. Changes to the pull-up
resistor settings on GPIO Port B should ensure that the internal pull-up resistor remains enabled
on PB7/TRST; otherwise JTAG communication could be lost.
5.2.1.2 Test Clock Input (TCK)
The TCK pin is the clock for the JTAG module. This clock is provided so the test logic can operate
independently of any other system clocks. In addition, it ensures that multiple JTAG TAP controllers
that are daisy-chained together can synchronously communicate serial test data between
components. During normal operation, TCK is driven by a free-running clock with a nominal 50%
duty cycle. When necessary, TCK can be stopped at 0 or 1 for extended periods of time. While TCK
is stopped at 0 or 1, the state of the TAP controller does not change and data in the JTAG Instruction
and Data Registers is not lost.
By default, the internal pull-up resistor on the TCK pin is enabled after reset. This assures that no
clocking occurs if the pin is not driven from an external source. The internal pull-up and pull-down
resistors can be turned off to save internal power as long as the TCK pin is constantly being driven
by an external source.
5.2.1.3 Test Mode Select (TMS)
The TMS pin selects the next state of the JTAG TAP controller. TMS is sampled on the rising edge
of TCK. Depending on the current TAP state and the sampled value of TMS, the next state is entered.
Because the TMS pin is sampled on the rising edge of TCK, the IEEE Standard 1149.1 expects the
value on TMS to change on the falling edge of TCK.
Holding TMS high for five consecutive TCK cycles drives the TAP controller state machine to the
Test-Logic-Reset state. When the TAP controller enters the Test-Logic-Reset state, the JTAG
Instruction Register (IR) resets to the default instruction, IDCODE. Therefore, this sequence can
be used as a reset mechanism, similar to asserting TRST. The JTAG Test Access Port state machine
can be seen in its entirety in Figure 5-2 on page 50.
48 March 17, 2008
Preliminary
JTAG Interface
By default, the internal pull-up resistor on the TMS pin is enabled after reset. Changes to the pull-up
resistor settings on GPIO Port C should ensure that the internal pull-up resistor remains enabled
on PC1/TMS; otherwise JTAG communication could be lost.
5.2.1.4 Test Data Input (TDI)
The TDI pin provides a stream of serial information to the IR chain and the DR chains. TDI is
sampled on the rising edge of TCK and, depending on the current TAP state and the current
instruction, presents this data to the proper shift register chain. Because the TDI pin is sampled on
the rising edge of TCK, the IEEE Standard 1149.1 expects the value on TDI to change on the falling
edge of TCK.
By default, the internal pull-up resistor on the TDI pin is enabled after reset. Changes to the pull-up
resistor settings on GPIO Port C should ensure that the internal pull-up resistor remains enabled
on PC2/TDI; otherwise JTAG communication could be lost.
5.2.1.5 Test Data Output (TDO)
The TDO pin provides an output stream of serial information from the IR chain or the DR chains.
The value of TDO depends on the current TAP state, the current instruction, and the data in the
chain being accessed. In order to save power when the JTAG port is not being used, the TDO pin
is placed in an inactive drive state when not actively shifting out data. Because TDO can be connected
to the TDI of another controller in a daisy-chain configuration, the IEEE Standard 1149.1 expects
the value on TDO to change on the falling edge of TCK.
By default, the internal pull-up resistor on the TDO pin is enabled after reset. This assures that the
pin remains at a constant logic level when the JTAG port is not being used. The internal pull-up and
pull-down resistors can be turned off to save internal power if a High-Z output value is acceptable
during certain TAP controller states.
5.2.2 JTAG TAP Controller
The JTAG TAP controller state machine is shown in Figure 5-2 on page 50. The TAP controller
state machine is reset to the Test-Logic-Reset state on the assertion of a Power-On-Reset (POR)
or the assertion of TRST. Asserting the correct sequence on the TMS pin allows the JTAG module
to shift in new instructions, shift in data, or idle during extended testing sequences. For detailed
information on the function of the TAP controller and the operations that occur in each state, please
refer to IEEE Standard 1149.1.
March 17, 2008 49
Preliminary
LM3S8933 Microcontroller
Figure 5-2. Test Access Port State Machine
Test Logic Reset
Run Test Idle Select DR Scan Select IR Scan
Capture DR Capture IR
Shift DR Shift IR
Exit 1 DR Exit 1 IR
Exit 2 DR Exit 2 IR
Pause DR Pause IR
Update DR Update IR
1 1 1
1 1
1
1 1
1 1
1 1
1 1
1 0 1 0
0 0
0 0
0 0
0 0
0 0
0 0
0
0
5.2.3 Shift Registers
The Shift Registers consist of a serial shift register chain and a parallel load register. The serial shift
register chain samples specific information during the TAP controller’s CAPTURE states and allows
this information to be shifted out of TDO during the TAP controller’s SHIFT states. While the sampled
data is being shifted out of the chain on TDO, new data is being shifted into the serial shift register
on TDI. This new data is stored in the parallel load register during the TAP controller’s UPDATE
states. Each of the shift registers is discussed in detail in “Register Descriptions” on page 53.
5.2.4 Operational Considerations
There are certain operational considerations when using the JTAG module. Because the JTAG pins
can be programmed to be GPIOs, board configuration and reset conditions on these pins must be
considered. In addition, because the JTAG module has integrated ARM Serial Wire Debug, the
method for switching between these two operational modes is described below.
50 March 17, 2008
Preliminary
JTAG Interface
5.2.4.1 GPIO Functionality
When the controller is reset with either a POR or RST, the JTAG/SWD port pins default to their
JTAG/SWD configurations. The default configuration includes enabling digital functionality (setting
GPIODEN to 1), enabling the pull-up resistors (setting GPIOPUR to 1), and enabling the alternate
hardware function (setting GPIOAFSEL to 1) for the PB7 and PC[3:0] JTAG/SWD pins.
It is possible for software to configure these pins as GPIOs after reset by writing 0s to PB7 and
PC[3:0] in the GPIOAFSEL register. If the user does not require the JTAG/SWD port for debugging
or board-level testing, this provides five more GPIOs for use in the design.
Caution – If the JTAG pins are used as GPIOs in a design, PB7 and PC2 cannot have external pull-down
resistors connected to both of them at the same time. If both pins are pulled Low during reset, the
controller has unpredictable behavior. If this happens, remove one or both of the pull-down resistors,
and apply RST or power-cycle the part.
In addition, it is possible to create a software sequence that prevents the debugger from connecting to
the Stellaris® microcontroller. If the program code loaded into flash immediately changes the JTAG
pins to their GPIO functionality, the debugger may not have enough time to connect and halt the
controller before the JTAG pin functionality switches. This may lock the debugger out of the part. This
can be avoided with a software routine that restores JTAG functionality based on an external or software
trigger.
The commit control registers provide a layer of protection against accidental programming of critical
hardware peripherals. Writes to protected bits of the GPIO Alternate Function Select (GPIOAFSEL)
register (see page 179) are not committed to storage unless the GPIO Lock (GPIOLOCK) register
(see page 189) has been unlocked and the appropriate bits of the GPIO Commit (GPIOCR) register
(see page 190) have been set to 1.
Recovering a "Locked" Device
If software configures any of the JTAG/SWD pins as GPIO and loses the ability to communicate
with the debugger, there is a debug sequence that can be used to recover the device. Performing
a total of ten JTAG-to-SWD and SWD-to-JTAG switch sequences while holding the device in reset
mass erases the flash memory. The sequence to recover the device is:
1. Assert and hold the RST signal.
2. Perform the JTAG-to-SWD switch sequence.
3. Perform the SWD-to-JTAG switch sequence.
4. Perform the JTAG-to-SWD switch sequence.
5. Perform the SWD-to-JTAG switch sequence.
6. Perform the JTAG-to-SWD switch sequence.
7. Perform the SWD-to-JTAG switch sequence.
8. Perform the JTAG-to-SWD switch sequence.
9. Perform the SWD-to-JTAG switch sequence.
10. Perform the JTAG-to-SWD switch sequence.
11. Perform the SWD-to-JTAG switch sequence.
March 17, 2008 51
Preliminary
LM3S8933 Microcontroller
12. Release the RST signal.
The JTAG-to-SWD and SWD-to-JTAG switch sequences are described in “ARM Serial Wire Debug
(SWD)” on page 52. When performing switch sequences for the purpose of recovering the debug
capabilities of the device, only steps 1 and 2 of the switch sequence need to be performed.
5.2.4.2 ARM Serial Wire Debug (SWD)
In order to seamlessly integrate the ARM Serial Wire Debug (SWD) functionality, a serial-wire
debugger must be able to connect to the Cortex-M3 core without having to perform, or have any
knowledge of, JTAG cycles. This is accomplished with a SWD preamble that is issued before the
SWD session begins.
The preamble used to enable the SWD interface of the SWJ-DP module starts with the TAP controller
in the Test-Logic-Reset state. From here, the preamble sequences the TAP controller through the
following states: Run Test Idle, Select DR, Select IR, Test Logic Reset, Test Logic Reset, Run Test
Idle, Run Test Idle, Select DR, Select IR, Test Logic Reset, Test Logic Reset, Run Test Idle, Run
Test Idle, Select DR, Select IR, and Test Logic Reset states.
Stepping through this sequences of the TAP state machine enables the SWD interface and disables
the JTAG interface. For more information on this operation and the SWD interface, see the ARM®
Cortex™-M3 Technical Reference Manual and the ARM® CoreSight Technical Reference Manual.
Because this sequence is a valid series of JTAG operations that could be issued, the ARM JTAG
TAP controller is not fully compliant to the IEEE Standard 1149.1. This is the only instance where
the ARM JTAG TAP controller does not meet full compliance with the specification. Due to the low
probability of this sequence occurring during normal operation of the TAP controller, it should not
affect normal performance of the JTAG interface.
JTAG-to-SWD Switching
To switch the operating mode of the Debug Access Port (DAP) from JTAG to SWD mode, the
external debug hardware must send a switch sequence to the device. The 16-bit switch sequence
for switching to SWD mode is defined as b1110011110011110, transmitted LSB first. This can also
be represented as 16'hE79E when transmitted LSB first. The complete switch sequence should
consist of the following transactions on the TCK/SWCLK and TMS/SWDIO signals:
1. Send at least 50 TCK/SWCLK cycles with TMS/SWDIO set to 1. This ensures that both JTAG and
SWD are in their reset/idle states.
2. Send the 16-bit JTAG-to-SWD switch sequence, 16'hE79E.
3. Send at least 50 TCK/SWCLK cycles with TMS/SWDIO set to 1. This ensures that if SWJ-DP was
already in SWD mode, before sending the switch sequence, the SWD goes into the line reset
state.
SWD-to-JTAG Switching
To switch the operating mode of the Debug Access Port (DAP) from SWD to JTAG mode, the
external debug hardware must send a switch sequence to the device. The 16-bit switch sequence
for switching to JTAG mode is defined as b1110011110011110, transmitted LSB first. This can also
be represented as 16'hE73C when transmitted LSB first. The complete switch sequence should
consist of the following transactions on the TCK/SWCLK and TMS/SWDIO signals:
1. Send at least 50 TCK/SWCLK cycles with TMS/SWDIO set to 1. This ensures that both JTAG and
SWD are in their reset/idle states.
52 March 17, 2008
Preliminary
JTAG Interface
2. Send the 16-bit SWD-to-JTAG switch sequence, 16'hE73C.
3. Send at least 5 TCK/SWCLK cycles with TMS/SWDIO set to 1. This ensures that if SWJ-DP was
already in JTAG mode, before sending the switch sequence, the JTAG goes into the Test Logic
Reset state.
5.3 Initialization and Configuration
After a Power-On-Reset or an external reset (RST), the JTAG pins are automatically configured for
JTAG communication. No user-defined initialization or configuration is needed. However, if the user
application changes these pins to their GPIO function, they must be configured back to their JTAG
functionality before JTAG communication can be restored. This is done by enabling the five JTAG
pins (PB7 and PC[3:0]) for their alternate function using the GPIOAFSEL register.
5.4 Register Descriptions
There are no APB-accessible registers in the JTAG TAP Controller or Shift Register chains. The
registers within the JTAG controller are all accessed serially through the TAP Controller. The registers
can be broken down into two main categories: Instruction Registers and Data Registers.
5.4.1 Instruction Register (IR)
The JTAG TAP Instruction Register (IR) is a four-bit serial scan chain with a parallel load register
connected between the JTAG TDI and TDO pins. When the TAP Controller is placed in the correct
states, bits can be shifted into the Instruction Register. Once these bits have been shifted into the
chain and updated, they are interpreted as the current instruction. The decode of the Instruction
Register bits is shown in Table 5-2 on page 53. A detailed explanation of each instruction, along
with its associated Data Register, follows.
Table 5-2. JTAG Instruction Register Commands
IR[3:0] Instruction Description
Drives the values preloaded into the Boundary Scan Chain by the SAMPLE/PRELOAD
instruction onto the pads.
0000 EXTEST
Drives the values preloaded into the Boundary Scan Chain by the SAMPLE/PRELOAD
instruction into the controller.
0001 INTEST
Captures the current I/O values and shifts the sampled values out of the Boundary Scan
Chain while new preload data is shifted in.
0010 SAMPLE / PRELOAD
1000 ABORT Shifts data into the ARM Debug Port Abort Register.
1010 DPACC Shifts data into and out of the ARM DP Access Register.
1011 APACC Shifts data into and out of the ARM AC Access Register.
Loads manufacturing information defined by the IEEE Standard 1149.1 into the IDCODE
chain and shifts it out.
1110 IDCODE
1111 BYPASS Connects TDI to TDO through a single Shift Register chain.
All Others Reserved Defaults to the BYPASS instruction to ensure that TDI is always connected to TDO.
5.4.1.1 EXTEST Instruction
The EXTEST instruction does not have an associated Data Register chain. The EXTEST instruction
uses the data that has been preloaded into the Boundary Scan Data Register using the
SAMPLE/PRELOAD instruction. When the EXTEST instruction is present in the Instruction Register,
the preloaded data in the Boundary Scan Data Register associated with the outputs and output
enables are used to drive the GPIO pads rather than the signals coming from the core. This allows
March 17, 2008 53
Preliminary
LM3S8933 Microcontroller
tests to be developed that drive known values out of the controller, which can be used to verify
connectivity.
5.4.1.2 INTEST Instruction
The INTEST instruction does not have an associated Data Register chain. The INTEST instruction
uses the data that has been preloaded into the Boundary Scan Data Register using the
SAMPLE/PRELOAD instruction. When the INTEST instruction is present in the Instruction Register,
the preloaded data in the Boundary Scan Data Register associated with the inputs are used to drive
the signals going into the core rather than the signals coming from the GPIO pads. This allows tests
to be developed that drive known values into the controller, which can be used for testing. It is
important to note that although the RST input pin is on the Boundary Scan Data Register chain, it
is only observable.
5.4.1.3 SAMPLE/PRELOAD Instruction
The SAMPLE/PRELOAD instruction connects the Boundary Scan Data Register chain between
TDI and TDO. This instruction samples the current state of the pad pins for observation and preloads
new test data. Each GPIO pad has an associated input, output, and output enable signal. When the
TAP controller enters the Capture DR state during this instruction, the input, output, and output-enable
signals to each of the GPIO pads are captured. These samples are serially shifted out of TDO while
the TAP controller is in the Shift DR state and can be used for observation or comparison in various
tests.
While these samples of the inputs, outputs, and output enables are being shifted out of the Boundary
Scan Data Register, new data is being shifted into the Boundary Scan Data Register from TDI.
Once the new data has been shifted into the Boundary Scan Data Register, the data is saved in the
parallel load registers when the TAP controller enters the Update DR state. This update of the
parallel load register preloads data into the Boundary Scan Data Register that is associated with
each input, output, and output enable. This preloaded data can be used with the EXTEST and
INTEST instructions to drive data into or out of the controller. Please see “Boundary Scan Data
Register” on page 56 for more information.
5.4.1.4 ABORT Instruction
The ABORT instruction connects the associated ABORT Data Register chain between TDI and
TDO. This instruction provides read and write access to the ABORT Register of the ARM Debug
Access Port (DAP). Shifting the proper data into this Data Register clears various error bits or initiates
a DAP abort of a previous request. Please see the “ABORT Data Register” on page 56 for more
information.
5.4.1.5 DPACC Instruction
The DPACC instruction connects the associated DPACC Data Register chain between TDI and
TDO. This instruction provides read and write access to the DPACC Register of the ARM Debug
Access Port (DAP). Shifting the proper data into this register and reading the data output from this
register allows read and write access to the ARM debug and status registers. Please see “DPACC
Data Register” on page 56 for more information.
5.4.1.6 APACC Instruction
The APACC instruction connects the associated APACC Data Register chain between TDI and
TDO. This instruction provides read and write access to the APACC Register of the ARM Debug
Access Port (DAP). Shifting the proper data into this register and reading the data output from this
register allows read and write access to internal components and buses through the Debug Port.
Please see “APACC Data Register” on page 56 for more information.
54 March 17, 2008
Preliminary
JTAG Interface
5.4.1.7 IDCODE Instruction
The IDCODE instruction connects the associated IDCODE Data Register chain between TDI and
TDO. This instruction provides information on the manufacturer, part number, and version of the
ARM core. This information can be used by testing equipment and debuggers to automatically
configure their input and output data streams. IDCODE is the default instruction that is loaded into
the JTAG Instruction Register when a power-on-reset (POR) is asserted, TRST is asserted, or the
Test-Logic-Reset state is entered. Please see “IDCODE Data Register” on page 55 for more
information.
5.4.1.8 BYPASS Instruction
The BYPASS instruction connects the associated BYPASS Data Register chain between TDI and
TDO. This instruction is used to create a minimum length serial path between the TDI and TDO ports.
The BYPASS Data Register is a single-bit shift register. This instruction improves test efficiency by
allowing components that are not needed for a specific test to be bypassed in the JTAG scan chain
by loading them with the BYPASS instruction. Please see “BYPASS Data Register” on page 55 for
more information.
5.4.2 Data Registers
The JTAG module contains six Data Registers. These include: IDCODE, BYPASS, Boundary Scan,
APACC, DPACC, and ABORT serial Data Register chains. Each of these Data Registers is discussed
in the following sections.
5.4.2.1 IDCODE Data Register
The format for the 32-bit IDCODE Data Register defined by the IEEE Standard 1149.1 is shown in
Figure 5-3 on page 55. The standard requires that every JTAG-compliant device implement either
the IDCODE instruction or the BYPASS instruction as the default instruction. The LSB of the IDCODE
Data Register is defined to be a 1 to distinguish it from the BYPASS instruction, which has an LSB
of 0. This allows auto configuration test tools to determine which instruction is the default instruction.
The major uses of the JTAG port are for manufacturer testing of component assembly, and program
development and debug. To facilitate the use of auto-configuration debug tools, the IDCODE
instruction outputs a value of 0x3BA00477. This value indicates an ARM Cortex-M3, Version 1
processor. This allows the debuggers to automatically configure themselves to work correctly with
the Cortex-M3 during debug.
Figure 5-3. IDCODE Register Format
Version Part Number Manufacturer ID 1
31 28 27 12 11 1 0
TDI TDO
5.4.2.2 BYPASS Data Register
The format for the 1-bit BYPASS Data Register defined by the IEEE Standard 1149.1 is shown in
Figure 5-4 on page 56. The standard requires that every JTAG-compliant device implement either
the BYPASS instruction or the IDCODE instruction as the default instruction. The LSB of the BYPASS
Data Register is defined to be a 0 to distinguish it from the IDCODE instruction, which has an LSB
of 1. This allows auto configuration test tools to determine which instruction is the default instruction.
March 17, 2008 55
Preliminary
LM3S8933 Microcontroller
Figure 5-4. BYPASS Register Format
TDI 0 TDO
0
5.4.2.3 Boundary Scan Data Register
The format of the Boundary Scan Data Register is shown in Figure 5-5 on page 56. Each GPIO
pin, in a counter-clockwise direction from the JTAG port pins, is included in the Boundary Scan Data
Register. Each GPIO pin has three associated digital signals that are included in the chain. These
signals are input, output, and output enable, and are arranged in that order as can be seen in the
figure. In addition to the GPIO pins, the controller reset pin, RST, is included in the chain. Because
the reset pin is always an input, only the input signal is included in the Data Register chain.
When the Boundary Scan Data Register is accessed with the SAMPLE/PRELOAD instruction, the
input, output, and output enable from each digital pad are sampled and then shifted out of the chain
to be verified. The sampling of these values occurs on the rising edge of TCK in the Capture DR
state of the TAP controller. While the sampled data is being shifted out of the Boundary Scan chain
in the Shift DR state of the TAP controller, new data can be preloaded into the chain for use with
the EXTEST and INTEST instructions. These instructions either force data out of the controller, with
the EXTEST instruction, or into the controller, with the INTEST instruction.
Figure 5-5. Boundary Scan Register Format
O TDO TDI O IN
E UT
O O IN
U E
T
O O IN
E UT
O O IN
U E
T
I
N ... ...
GPIO PB6 GPIO m RST GPIO m+1 GPIO n
For detailed information on the order of the input, output, and output enable bits for each of the
GPIO ports, please refer to the Stellaris® Family Boundary Scan Description Language (BSDL) files,
downloadable from www.luminarymicro.com.
5.4.2.4 APACC Data Register
The format for the 35-bit APACC Data Register defined by ARM is described in the ARM®
Cortex™-M3 Technical Reference Manual.
5.4.2.5 DPACC Data Register
The format for the 35-bit DPACC Data Register defined by ARM is described in the ARM®
Cortex™-M3 Technical Reference Manual.
5.4.2.6 ABORT Data Register
The format for the 35-bit ABORT Data Register defined by ARM is described in the ARM®
Cortex™-M3 Technical Reference Manual.
56 March 17, 2008
Preliminary
JTAG Interface
6 System Control
System control determines the overall operation of the device. It provides information about the
device, controls the clocking to the core and individual peripherals, and handles reset detection and
reporting.
6.1 Functional Description
The System Control module provides the following capabilities:
■ Device identification, see “Device Identification” on page 57
■ Local control, such as reset (see “Reset Control” on page 57), power (see “Power
Control” on page 60) and clock control (see “Clock Control” on page 60)
■ System control (Run, Sleep, and Deep-Sleep modes), see “System Control” on page 62
6.1.1 Device Identification
Seven read-only registers provide software with information on the microcontroller, such as version,
part number, SRAM size, flash size, and other features. See the DID0, DID1, and DC0-DC4 registers.
6.1.2 Reset Control
This section discusses aspects of hardware functions during reset as well as system software
requirements following the reset sequence.
6.1.2.1 CMOD0 and CMOD1 Test-Mode Control Pins
Two pins, CMOD0 and CMOD1, are defined for use by Luminary Micro for testing the devices during
manufacture. They have no end-user function and should not be used. The CMOD pins should be
connected to ground.
6.1.2.2 Reset Sources
The controller has five sources of reset:
1. External reset input pin (RST) assertion, see “RST Pin Assertion” on page 57.
2. Power-on reset (POR), see “Power-On Reset (POR)” on page 58.
3. Internal brown-out (BOR) detector, see “Brown-Out Reset (BOR)” on page 58.
4. Software-initiated reset (with the software reset registers), see “Software Reset” on page 59.
5. A watchdog timer reset condition violation, see “Watchdog Timer Reset” on page 59.
After a reset, the Reset Cause (RESC) register is set with the reset cause. The bits in this register
are sticky and maintain their state across multiple reset sequences, except when an internal POR
is the cause, and then all the other bits in the RESC register are cleared except for the POR indicator.
6.1.2.3 RST Pin Assertion
The external reset pin (RST) resets the controller. This resets the core and all the peripherals except
the JTAG TAP controller (see “JTAG Interface” on page 46). The external reset sequence is as
follows:
March 17, 2008 57
Preliminary
LM3S8933 Microcontroller
1. The external reset pin (RST) is asserted and then de-asserted.
2. The internal reset is released and the core loads from memory the initial stack pointer, the initial
program counter, the first instruction designated by the program counter, and begins execution.
A few clocks cycles from RST de-assertion to the start of the reset sequence is necessary for
synchronization.
The external reset timing is shown in Figure 22-11 on page 548.
6.1.2.4 Power-On Reset (POR)
The Power-On Reset (POR) circuit monitors the power supply voltage (VDD). The POR circuit
generates a reset signal to the internal logic when the power supply ramp reaches a threshold value
(VTH). If the application only uses the POR circuit, the RST input needs to be connected to the power
supply (VDD) through a pull-up resistor (1K to 10K Ω).
The device must be operating within the specified operating parameters at the point when the on-chip
power-on reset pulse is complete. The 3.3-V power supply to the device must reach 3.0 V within
10 msec of it crossing 2.0 V to guarantee proper operation. For applications that require the use of
an external reset to hold the device in reset longer than the internal POR, the RST input may be
used with the circuit as shown in Figure 6-1 on page 58.
Figure 6-1. External Circuitry to Extend Reset
R1
C1
R2
RST
Stellaris
D1
The R1 and C1 components define the power-on delay. The R2 resistor mitigates any leakage from
the RST input. The diode (D1) discharges C1 rapidly when the power supply is turned off.
The Power-On Reset sequence is as follows:
1. The controller waits for the later of external reset (RST) or internal POR to go inactive.
2. The internal reset is released and the core loads from memory the initial stack pointer, the initial
program counter, the first instruction designated by the program counter, and begins execution.
The internal POR is only active on the initial power-up of the controller. The Power-On Reset timing
is shown in Figure 22-12 on page 549.
Note: The power-on reset also resets the JTAG controller. An external reset does not.
6.1.2.5 Brown-Out Reset (BOR)
A drop in the input voltage resulting in the assertion of the internal brown-out detector can be used
to reset the controller. This is initially disabled and may be enabled by software.
The system provides a brown-out detection circuit that triggers if the power supply (VDD) drops
below a brown-out threshold voltage (VBTH). If a brown-out condition is detected, the system may
generate a controller interrupt or a system reset.
58 March 17, 2008
Preliminary
System Control
Brown-out resets are controlled with the Power-On and Brown-Out Reset Control (PBORCTL)
register. The BORIOR bit in the PBORCTL register must be set for a brown-out condition to trigger
a reset.
The brown-out reset is equivelent to an assertion of the external RST input and the reset is held
active until the proper VDD level is restored. The RESC register can be examined in the reset interrupt
handler to determine if a Brown-Out condition was the cause of the reset, thus allowing software to
determine what actions are required to recover.
The internal Brown-Out Reset timing is shown in Figure 22-13 on page 549.
6.1.2.6 Software Reset
Software can reset a specific peripheral or generate a reset to the entire system .
Peripherals can be individually reset by software via three registers that control reset signals to each
peripheral (see the SRCRn registers). If the bit position corresponding to a peripheral is set and
subsequently cleared, the peripheral is reset. The encoding of the reset registers is consistent with
the encoding of the clock gating control for peripherals and on-chip functions (see “System
Control” on page 62). Note that all reset signals for all clocks of the specified unit are asserted as
a result of a software-initiated reset.
The entire system can be reset by software by setting the SYSRESETREQ bit in the Cortex-M3
Application Interrupt and Reset Control register resets the entire system including the core. The
software-initiated system reset sequence is as follows:
1. A software system reset is initiated by writing the SYSRESETREQ bit in the ARM Cortex-M3
Application Interrupt and Reset Control register.
2. An internal reset is asserted.
3. The internal reset is deasserted and the controller loads from memory the initial stack pointer,
the initial program counter, and the first instruction designated by the program counter, and
then begins execution.
The software-initiated system reset timing is shown in Figure 22-14 on page 549.
6.1.2.7 Watchdog Timer Reset
The watchdog timer module's function is to prevent system hangs. The watchdog timer can be
configured to generate an interrupt to the controller on its first time-out, and to generate a reset
signal on its second time-out.
After the first time-out event, the 32-bit counter is reloaded with the value of the Watchdog Timer
Load (WDTLOAD) register, and the timer resumes counting down from that value. If the timer counts
down to its zero state again before the first time-out interrupt is cleared, and the reset signal has
been enabled, the watchdog timer asserts its reset signal to the system. The watchdog timer reset
sequence is as follows:
1. The watchdog timer times out for the second time without being serviced.
2. An internal reset is asserted.
3. The internal reset is released and the controller loads from memory the initial stack pointer, the
initial program counter, the first instruction designated by the program counter, and begins
execution.
March 17, 2008 59
Preliminary
LM3S8933 Microcontroller
The watchdog reset timing is shown in Figure 22-15 on page 549.
6.1.3 Power Control
The Stellaris® microcontroller provides an integrated LDO regulator that may be used to provide
power to the majority of the controller's internal logic. The LDO regulator provides software a
mechanism to adjust the regulated value, in small increments (VSTEP), over the range of 2.25 V
to 2.75 V (inclusive)—or 2.5 V ± 10%. The adjustment is made by changing the value of the VADJ
field in the LDO Power Control (LDOPCTL) register.
Note: The use of the LDO is optional. The internal logic may be supplied by the on-chip LDO or
by an external regulator. If the LDO is used, the LDO output pin is connected to the VDD25
pins on the printed circuit board. The LDO requires decoupling capacitors on the printed
circuit board. If an external regulator is used, it is strongly recommended that the external
regulator supply the controller only and not be shared with other devices on the printed
circuit board.
6.1.4 Clock Control
System control determines the control of clocks in this part.
6.1.4.1 Fundamental Clock Sources
There are four clock sources for use in the device:
■ Internal Oscillator (IOSC): The internal oscillator is an on-chip clock source. It does not require
the use of any external components. The frequency of the internal oscillator is 12 MHz ± 30%.
Applications that do not depend on accurate clock sources may use this clock source to reduce
system cost. The internal oscillator is the clock source the device uses during and following POR.
If the main oscillator is required, software must enable the main oscillator following reset and
allow the main oscillator to stabilize before changing the clock reference.
■ Main Oscillator (MOSC): The main oscillator provides a frequency-accurate clock source by
one of two means: an external single-ended clock source is connected to the OSC0 input pin, or
an external crystal is connected across the OSC0 input and OSC1 output pins. The crystal value
allowed depends on whether the main oscillator is used as the clock reference source to the
PLL. If so, the crystal must be one of the supported frequencies between 3.579545 MHz through
8.192 MHz (inclusive). If the PLL is not being used, the crystal may be any one of the supported
frequencies between 1 MHz and 8.192 MHz. The single-ended clock source range is from DC
through the specified speed of the device. The supported crystals are listed in the XTAL bit field
in the RCC register (see page 74).
■ Internal 30-kHz Oscillator: The internal 30-kHz oscillator is similar to the internal oscillator,
except that it provides an operational frequency of 30 kHz ± 30%. It is intended for use during
Deep-Sleep power-saving modes. This power-savings mode benefits from reduced internal
switching and also allows the main oscillator to be powered down.
■ External Real-Time Oscillator: The external real-time oscillator provides a low-frequency,
accurate clock reference. It is intended to provide the system with a real-time clock source. The
real-time oscillator is part of the Hibernation Module (“Hibernation Module” on page 119) and may
also provide an accurate source of Deep-Sleep or Hibernate mode power savings.
The internal system clock (SysClk), is derived from any of the four sources plus two others: the
output of the main internal PLL, and the internal oscillator divided by four (3 MHz ± 30%). The
frequency of the PLL clock reference must be in the range of 3.579545 MHz to 8.192 MHz (inclusive).
60 March 17, 2008
Preliminary
System Control
The Run-Mode Clock Configuration (RCC) and Run-Mode Clock Configuration 2 (RCC2)
registers provide control for the system clock. The RCC2 register is provided to extend fields that
offer additional encodings over the RCC register. When used, the RCC2 register field values are
used by the logic over the corresponding field in the RCC register. In particular, RCC2 provides for
a larger assortment of clock configuration options.
Figure 6-2 on page 61 shows the logic for the main clock tree. The peripheral blocks are driven by
the system clock signal and can be programmatically enabled/disabled. The ADC clock signal is
automatically divided down to 16 MHz for proper ADC operation.
Figure 6-2. Main Clock Tree
PLL
(240 MHz) ÷ 4
PLL
Main OSC (400 MHz)
Internal
OSC
(12 MHz)
Internal
OSC
(30 kHz)
÷ 4
Hibernation
Module
(32.768 kHz)
÷ 25
PWRDN
ADC Clock
System Clock
USB Clock
XTALa
USBPWRDNc
XTALa
PWRDN b
MOSCDIS a
IOSCDISa
OSCSRCb,d
BYPASS b,d
SYSDIVb,d
USESYSDIV a,d
PWMDW a
USEPWMDIVa
PWM Clock
a. Control provided by RCC register bit/field.
b. Control provided by RCC register bit/field or RCC2 register bit/field, if overridden with RCC2 register bit USERCC2.
c. Control provided by RCC2 register bit/field.
d. Also may be controlled by DSLPCLKCFG when in deep sleep mode.
6.1.4.2 Crystal Configuration for the Main Oscillator (MOSC)
The main oscillator supports the use of a select number of crystals. If the main oscillator is used by
the PLL as a reference clock, the supported range of crystals is 3.579545 to 8.192 MHz, otherwise,
the range of supported crystals is 1 to 8.192 MHz.
The XTAL bit in the RCC register (see page 74) describes the available crystal choices and default
programming values.
Software configures the RCC register XTAL field with the crystal number. If the PLL is used in the
design, the XTAL field value is internally translated to the PLL settings.
March 17, 2008 61
Preliminary
LM3S8933 Microcontroller
6.1.4.3 Main PLL Frequency Configuration
The main PLL is disabled by default during power-on reset and is enabled later by software if
required. Software configures the main PLL input reference clock source, specifies the output divisor
to set the system clock frequency, and enables the main PLL to drive the output.
If the main oscillator provides the clock reference to the main PLL, the translation provided by
hardware and used to program the PLL is available for software in the XTAL to PLL Translation
(PLLCFG) register (see page 78). The internal translation provides a translation within ± 1% of the
targeted PLL VCO frequency.
The Crystal Value field (XTAL) on page 74 describes the available crystal choices and default
programming of the PLLCFG register. The crystal number is written into the XTAL field of the
Run-Mode Clock Configuration (RCC) register. Any time the XTAL field changes, the new settings
are translated and the internal PLL settings are updated.
6.1.4.4 PLL Modes
The PLL has two modes of operation: Normal and Power-Down
■ Normal: The PLL multiplies the input clock reference and drives the output.
■ Power-Down: Most of the PLL internal circuitry is disabled and the PLL does not drive the output.
The modes are programmed using the RCC/RCC2 register fields (see page 74 and page 79).
6.1.4.5 PLL Operation
If a PLL configuration is changed, the PLL output frequency is unstable until it reconverges (relocks)
to the new setting. The time between the configuration change and relock is TREADY (see Table
22-6 on page 538). During the relock time, the affected PLL is not usable as a clock reference.
The PLL is changed by one of the following:
■ Change to the XTAL value in the RCC register—writes of the same value do not cause a relock.
■ Change in the PLL from Power-Down to Normal mode.
A counter is defined to measure the TREADY requirement. The counter is clocked by the main
oscillator. The range of the main oscillator has been taken into account and the down counter is set
to 0x1200 (that is, ~600 μs at an 8.192 MHz external oscillator clock). . Hardware is provided to
keep the PLL from being used as a system clock until the TREADY condition is met after one of the
two changes above. It is the user's responsibility to have a stable clock source (like the main oscillator)
before the RCC/RCC2 register is switched to use the PLL.
If the main PLL is enabled and the system clock is switched to use the PLL in one step, the system
control hardware continues to clock the controller from the source to the PLL until the main PLL is
stable (TREADY time met), after which it changes to the PLL. Software can use many methods to
ensure that the system is clocked from the main PLL, including periodically polling the PLLLRIS bit
in the Raw Interrupt Status (RIS) register, and enabling the PLL Lock interrupt.
6.1.5 System Control
For power-savings purposes, the RCGCn , SCGCn , and DCGCn registers control the clock gating
logic for each peripheral or block in the system while the controller is in Run, Sleep, and Deep-Sleep
mode, respectively.
62 March 17, 2008
Preliminary
System Control
In Run mode, the processor executes code. In Sleep mode, the clock frequency of the active
peripherals is unchanged, but the processor is not clocked and therefore no longer executes code.
In Deep-Sleep mode, the clock frequency of the active peripherals may change (depending on the
Run mode clock configuration) in addition to the processor clock being stopped. An interrupt returns
the device to Run mode from one of the sleep modes; the sleep modes are entered on request from
the code. Each mode is described in more detail below.
There are four levels of operation for the device defined as:
■ Run Mode. Run mode provides normal operation of the processor and all of the peripherals that
are currently enabled by the RCGCn registers. The system clock can be any of the available
clock sources including the PLL.
■ Sleep Mode. Sleep mode is entered by the Cortex-M3 core executing a WFI (Wait for
Interrupt) instruction. Any properly configured interrupt event in the system will bring the
processor back into Run mode. See the system control NVIC section of the ARM® Cortex™-M3
Technical Reference Manual for more details.
In Sleep mode, the Cortex-M3 processor core and the memory subsystem are not clocked.
Peripherals are clocked that are enabled in the SCGCn register when auto-clock gating is enabled
(see the RCC register) or the RCGCn register when the auto-clock gating is disabled. The system
clock has the same source and frequency as that during Run mode.
■ Deep-Sleep Mode. Deep-Sleep mode is entered by first writing the Deep Sleep Enable bit in
the ARM Cortex-M3 NVIC system control register and then executing a WFI instruction. Any
properly configured interrupt event in the system will bring the processor back into Run mode.
See the system control NVIC section of the ARM® Cortex™-M3 Technical Reference Manual
for more details.
The Cortex-M3 processor core and the memory subsystem are not clocked. Peripherals are
clocked that are enabled in the DCGCn register when auto-clock gating is enabled (see the RCC
register) or the RCGCn register when auto-clock gating is disabled. The system clock source is
the main oscillator by default or the internal oscillator specified in the DSLPCLKCFG register if
one is enabled. When the DSLPCLKCFG register is used, the internal oscillator is powered up,
if necessary, and the main oscillator is powered down. If the PLL is running at the time of the
WFI instruction, hardware will power the PLL down and override the SYSDIV field of the active
RCC/RCC2 register to be /16 or /64, respectively. When the Deep-Sleep exit event occurs,
hardware brings the system clock back to the source and frequency it had at the onset of
Deep-Sleep mode before enabling the clocks that had been stopped during the Deep-Sleep
duration.
■ Hibernate Mode. In this mode, the power supplies are turned off to the main part of the device
and only the Hibernation module's circuitry is active. An external wake event or RTC event is
required to bring the device back to Run mode. The Cortex-M3 processor and peripherals outside
of the Hibernation module see a normal "power on" sequence and the processor starts running
code. It can determine that it has been restarted from Hibernate mode by inspecting the
Hibernation module registers.
6.2 Initialization and Configuration
The PLL is configured using direct register writes to the RCC/RCC2 register. If the RCC2 register
is being used, the USERCC2 bit must be set and the appropriate RCC2 bit/field is used. The steps
required to successfully change the PLL-based system clock are:
March 17, 2008 63
Preliminary
LM3S8933 Microcontroller
1. Bypass the PLL and system clock divider by setting the BYPASS bit and clearing the USESYS
bit in the RCC register. This configures the system to run off a “raw” clock source (using the
main oscillator or internal oscillator) and allows for the new PLL configuration to be validated
before switching the system clock to the PLL.
2. Select the crystal value (XTAL) and oscillator source (OSCSRC), and clear the PWRDN bit in
RCC/RCC2. Setting the XTAL field automatically pulls valid PLL configuration data for the
appropriate crystal, and clearing the PWRDN bit powers and enables the PLL and its output.
3. Select the desired system divider (SYSDIV) in RCC/RCC2 and set the USESYS bit in RCC. The
SYSDIV field determines the system frequency for the microcontroller.
4. Wait for the PLL to lock by polling the PLLLRIS bit in the Raw Interrupt Status (RIS) register.
5. Enable use of the PLL by clearing the BYPASS bit in RCC/RCC2.
6.3 Register Map
Table 6-1 on page 64 lists the System Control registers, grouped by function. The offset listed is a
hexadecimal increment to the register’s address, relative to the System Control base address of
0x400F.E000.
Note: Spaces in the System Control register space that are not used are reserved for future or
internal use by Luminary Micro, Inc. Software should not modify any reserved memory
address.
Table 6-1. System Control Register Map
See
Offset Name Type Reset Description page
0x000 DID0 RO - Device Identification 0 66
0x004 DID1 RO - Device Identification 1 82
0x008 DC0 RO 0x00FF.007F Device Capabilities 0 84
0x010 DC1 RO 0x0101.33FF Device Capabilities 1 85
0x014 DC2 RO 0x070F.1013 Device Capabilities 2 87
0x018 DC3 RO 0x0F0F.3FC0 Device Capabilities 3 89
0x01C DC4 RO 0x5100.007F Device Capabilities 4 91
0x030 PBORCTL R/W 0x0000.7FFD Brown-Out Reset Control 68
0x034 LDOPCTL R/W 0x0000.0000 LDO Power Control 69
0x040 SRCR0 R/W 0x00000000 Software Reset Control 0 114
0x044 SRCR1 R/W 0x00000000 Software Reset Control 1 115
0x048 SRCR2 R/W 0x00000000 Software Reset Control 2 117
0x050 RIS RO 0x0000.0000 Raw Interrupt Status 70
0x054 IMC R/W 0x0000.0000 Interrupt Mask Control 71
0x058 MISC R/W1C 0x0000.0000 Masked Interrupt Status and Clear 72
0x05C RESC R/W - Reset Cause 73
64 March 17, 2008
Preliminary
System Control
See
Offset Name Type Reset Description page
0x060 RCC R/W 0x0780.3AD1 Run-Mode Clock Configuration 74
0x064 PLLCFG RO - XTAL to PLL Translation 78
0x070 RCC2 R/W 0x0780.2800 Run-Mode Clock Configuration 2 79
0x100 RCGC0 R/W 0x00000040 Run Mode Clock Gating Control Register 0 93
0x104 RCGC1 R/W 0x00000000 Run Mode Clock Gating Control Register 1 99
0x108 RCGC2 R/W 0x00000000 Run Mode Clock Gating Control Register 2 108
0x110 SCGC0 R/W 0x00000040 Sleep Mode Clock Gating Control Register 0 95
0x114 SCGC1 R/W 0x00000000 Sleep Mode Clock Gating Control Register 1 102
0x118 SCGC2 R/W 0x00000000 Sleep Mode Clock Gating Control Register 2 110
0x120 DCGC0 R/W 0x00000040 Deep Sleep Mode Clock Gating Control Register 0 97
0x124 DCGC1 R/W 0x00000000 Deep Sleep Mode Clock Gating Control Register 1 105
0x128 DCGC2 R/W 0x00000000 Deep Sleep Mode Clock Gating Control Register 2 112
0x144 DSLPCLKCFG R/W 0x0780.0000 Deep Sleep Clock Configuration 81
6.4 Register Descriptions
All addresses given are relative to the System Control base address of 0x400F.E000.
March 17, 2008 65
Preliminary
LM3S8933 Microcontroller
Register 1: Device Identification 0 (DID0), offset 0x000
This register identifies the version of the device.
Device Identification 0 (DID0)
Base 0x400F.E000
Offset 0x000
Type RO, reset -
31 30 29 28 27 26 25 24 23 22 21 20 19 18 17 16
reserved VER reserved CLASS
Type RO RO RO RO RO RO RO RO RO RO RO RO RO RO RO RO
Reset 0 0 0 1 0 0 0 0 0 0 0 0 0 0 0 1
15 14 13 12 11 10 9 8 7 6 5 4 3 2 1 0
MAJOR MINOR
Type RO RO RO RO RO RO RO RO RO RO RO RO RO RO RO RO
Reset - - - - - - - - - - - - - - - -
Bit/Field Name Type Reset Description
Software should not rely on the value of a reserved bit. To provide
compatibility with future products, the value of a reserved bit should be
preserved across a read-modify-write operation.
31 reserved RO 0
DID0 Version
This field defines the DID0 register format version. The version number
is numeric. The value of the VER field is encoded as follows:
Value Description
0x1 Second version of the DID0 register format.
30:28 VER RO 0x1
Software should not rely on the value of a reserved bit. To provide
compatibility with future products, the value of a reserved bit should be
preserved across a read-modify-write operation.
27:24 reserved RO 0x0
Device Class
The CLASS field value identifies the internal design from which all mask
sets are generated for all devices in a particular product line. The CLASS
field value is changed for new product lines, for changes in fab process
(for example, a remap or shrink), or any case where the MAJOR or MINOR
fields require differentiation from prior devices. The value of the CLASS
field is encoded as follows (all other encodings are reserved):
Value Description
0x1 Stellaris® Fury-class devices.
23:16 CLASS RO 0x1
66 March 17, 2008
Preliminary
System Control
Bit/Field Name Type Reset Description
Major Revision
This field specifies the major revision number of the device. The major
revision reflects changes to base layers of the design. The major revision
number is indicated in the part number as a letter (A for first revision, B
for second, and so on). This field is encoded as follows:
Value Description
0x0 Revision A (initial device)
0x1 Revision B (first base layer revision)
0x2 Revision C (second base layer revision)
and so on.
15:8 MAJOR RO -
Minor Revision
This field specifies the minor revision number of the device. The minor
revision reflects changes to the metal layers of the design. The MINOR
field value is reset when the MAJOR field is changed. This field is numeric
and is encoded as follows:
Value Description
0x0 Initial device, or a major revision update.
0x1 First metal layer change.
0x2 Second metal layer change.
and so on.
7:0 MINOR RO -
March 17, 2008 67
Preliminary
LM3S8933 Microcontroller
Register 2: Brown-Out Reset Control (PBORCTL), offset 0x030
This register is responsible for controlling reset conditions after initial power-on reset.
Brown-Out Reset Control (PBORCTL)
Base 0x400F.E000
Offset 0x030
Type R/W, reset 0x0000.7FFD
31 30 29 28 27 26 25 24 23 22 21 20 19 18 17 16
reserved
Type RO RO RO RO RO RO RO RO RO RO RO RO RO RO RO RO
Reset 0 0 0 0 0 0 0 0 0 0 0 0 0 0 0 0
15 14 13 12 11 10 9 8 7 6 5 4 3 2 1 0
reserved BORIOR reserved
Type RO RO RO RO RO RO RO RO RO RO RO RO RO RO R/W RO
Reset 0 0 0 0 0 0 0 0 0 0 0 0 0 0 0 0
Bit/Field Name Type Reset Description
Software should not rely on the value of a reserved bit. To provide
compatibility with future products, the value of a reserved bit should be
preserved across a read-modify-write operation.
31:2 reserved RO 0x0
BOR Interrupt or Reset
This bit controls how a BOR event is signaled to the controller. If set, a
reset is signaled. Otherwise, an interrupt is signaled.
1 BORIOR R/W 0
Software should not rely on the value of a reserved bit. To provide
compatibility with future products, the value of a reserved bit should be
preserved across a read-modify-write operation.
0 reserved RO 0
68 March 17, 2008
Preliminary
System Control
Register 3: LDO Power Control (LDOPCTL), offset 0x034
The VADJ field in this register adjusts the on-chip output voltage (VOUT).
LDO Power Control (LDOPCTL)
Base 0x400F.E000
Offset 0x034
Type R/W, reset 0x0000.0000
31 30 29 28 27 26 25 24 23 22 21 20 19 18 17 16
reserved
Type RO RO RO RO RO RO RO RO RO RO RO RO RO RO RO RO
Reset 0 0 0 0 0 0 0 0 0 0 0 0 0 0 0 0
15 14 13 12 11 10 9 8 7 6 5 4 3 2 1 0
reserved VADJ
Type RO RO RO RO RO RO RO RO RO RO R/W R/W R/W R/W R/W R/W
Reset 0 0 0 0 0 0 0 0 0 0 0 0 0 0 0 0
Bit/Field Name Type Reset Description
Software should not rely on the value of a reserved bit. To provide
compatibility with future products, the value of a reserved bit should be
preserved across a read-modify-write operation.
31:6 reserved RO 0
LDO Output Voltage
This field sets the on-chip output voltage. The programming values for
the VADJ field are provided below.
Value VOUT (V)
0x00 2.50
0x01 2.45
0x02 2.40
0x03 2.35
0x04 2.30
0x05 2.25
0x06-0x3F Reserved
0x1B 2.75
0x1C 2.70
0x1D 2.65
0x1E 2.60
0x1F 2.55
5:0 VADJ R/W 0x0
March 17, 2008 69
Preliminary
LM3S8933 Microcontroller
Register 4: Raw Interrupt Status (RIS), offset 0x050
Central location for system control raw interrupts. These are set and cleared by hardware.
Raw Interrupt Status (RIS)
Base 0x400F.E000
Offset 0x050
Type RO, reset 0x0000.0000
31 30 29 28 27 26 25 24 23 22 21 20 19 18 17 16
reserved
Type RO RO RO RO RO RO RO RO RO RO RO RO RO RO RO RO
Reset 0 0 0 0 0 0 0 0 0 0 0 0 0 0 0 0
15 14 13 12 11 10 9 8 7 6 5 4 3 2 1 0
reserved PLLLRIS reserved BORRIS reserved
Type RO RO RO RO RO RO RO RO RO RO RO RO RO RO RO RO
Reset 0 0 0 0 0 0 0 0 0 0 0 0 0 0 0 0
Bit/Field Name Type Reset Description
Software should not rely on the value of a reserved bit. To provide
compatibility with future products, the value of a reserved bit should be
preserved across a read-modify-write operation.
31:7 reserved RO 0
PLL Lock Raw Interrupt Status
This bit is set when the PLL TREADY Timer asserts.
6 PLLLRIS RO 0
Software should not rely on the value of a reserved bit. To provide
compatibility with future products, the value of a reserved bit should be
preserved across a read-modify-write operation.
5:2 reserved RO 0
Brown-Out Reset Raw Interrupt Status
This bit is the raw interrupt status for any brown-out conditions. If set,
a brown-out condition is currently active. This is an unregistered signal
from the brown-out detection circuit. An interrupt is reported if the BORIM
bit in the IMC register is set and the BORIOR bit in the PBORCTL register
is cleared.
1 BORRIS RO 0
Software should not rely on the value of a reserved bit. To provide
compatibility with future products, the value of a reserved bit should be
preserved across a read-modify-write operation.
0 reserved RO 0
70 March 17, 2008
Preliminary
System Control
Register 5: Interrupt Mask Control (IMC), offset 0x054
Central location for system control interrupt masks.
Interrupt Mask Control (IMC)
Base 0x400F.E000
Offset 0x054
Type R/W, reset 0x0000.0000
31 30 29 28 27 26 25 24 23 22 21 20 19 18 17 16
reserved
Type RO RO RO RO RO RO RO RO RO RO RO RO RO RO RO RO
Reset 0 0 0 0 0 0 0 0 0 0 0 0 0 0 0 0
15 14 13 12 11 10 9 8 7 6 5 4 3 2 1 0
reserved PLLLIM reserved BORIM reserved
Type RO RO RO RO RO RO RO RO RO R/W RO RO RO RO R/W RO
Reset 0 0 0 0 0 0 0 0 0 0 0 0 0 0 0 0
Bit/Field Name Type Reset Description
Software should not rely on the value of a reserved bit. To provide
compatibility with future products, the value of a reserved bit should be
preserved across a read-modify-write operation.
31:7 reserved RO 0
PLL Lock Interrupt Mask
This bit specifies whether a current limit detection is promoted to a
controller interrupt. If set, an interrupt is generated if PLLLRIS in RIS
is set; otherwise, an interrupt is not generated.
6 PLLLIM R/W 0
Software should not rely on the value of a reserved bit. To provide
compatibility with future products, the value of a reserved bit should be
preserved across a read-modify-write operation.
5:2 reserved RO 0
Brown-Out Reset Interrupt Mask
This bit specifies whether a brown-out condition is promoted to a
controller interrupt. If set, an interrupt is generated if BORRIS is set;
otherwise, an interrupt is not generated.
1 BORIM R/W 0
Software should not rely on the value of a reserved bit. To provide
compatibility with future products, the value of a reserved bit should be
preserved across a read-modify-write operation.
0 reserved RO 0
March 17, 2008 71
Preliminary
LM3S8933 Microcontroller
Register 6: Masked Interrupt Status and Clear (MISC), offset 0x058
Central location for system control result of RIS AND IMC to generate an interrupt to the controller.
All of the bits are R/W1C and this action also clears the corresponding raw interrupt bit in the RIS
register (see page 70).
Masked Interrupt Status and Clear (MISC)
Base 0x400F.E000
Offset 0x058
Type R/W1C, reset 0x0000.0000
31 30 29 28 27 26 25 24 23 22 21 20 19 18 17 16
reserved
Type RO RO RO RO RO RO RO RO RO RO RO RO RO RO RO RO
Reset 0 0 0 0 0 0 0 0 0 0 0 0 0 0 0 0
15 14 13 12 11 10 9 8 7 6 5 4 3 2 1 0
reserved PLLLMIS reserved BORMIS reserved
Type RO RO RO RO RO RO RO RO RO R/W1C RO RO RO RO R/W1C RO
Reset 0 0 0 0 0 0 0 0 0 0 0 0 0 0 0 0
Bit/Field Name Type Reset Description
Software should not rely on the value of a reserved bit. To provide
compatibility with future products, the value of a reserved bit should be
preserved across a read-modify-write operation.
31:7 reserved RO 0
PLL Lock Masked Interrupt Status
This bit is set when the PLL TREADY timer asserts. The interrupt is cleared
by writing a 1 to this bit.
6 PLLLMIS R/W1C 0
Software should not rely on the value of a reserved bit. To provide
compatibility with future products, the value of a reserved bit should be
preserved across a read-modify-write operation.
5:2 reserved RO 0
BOR Masked Interrupt Status
The BORMIS is simply the BORRIS ANDed with the mask value, BORIM.
1 BORMIS R/W1C 0
Software should not rely on the value of a reserved bit. To provide
compatibility with future products, the value of a reserved bit should be
preserved across a read-modify-write operation.
0 reserved RO 0
72 March 17, 2008
Preliminary
System Control
Register 7: Reset Cause (RESC), offset 0x05C
This register is set with the reset cause after reset. The bits in this register are sticky and maintain
their state across multiple reset sequences, except when an external reset is the cause, and then
all the other bits in the RESC register are cleared.
Reset Cause (RESC)
Base 0x400F.E000
Offset 0x05C
Type R/W, reset -
31 30 29 28 27 26 25 24 23 22 21 20 19 18 17 16
reserved
Type RO RO RO RO RO RO RO RO RO RO RO RO RO RO RO RO
Reset 0 0 0 0 0 0 0 0 0 0 0 0 0 0 0 0
15 14 13 12 11 10 9 8 7 6 5 4 3 2 1 0
reserved LDO SW WDT BOR POR EXT
Type RO RO RO RO RO RO RO RO RO RO R/W R/W R/W R/W R/W R/W
Reset 0 0 0 0 0 0 0 0 0 0 - - - - - -
Bit/Field Name Type Reset Description
Software should not rely on the value of a reserved bit. To provide
compatibility with future products, the value of a reserved bit should be
preserved across a read-modify-write operation.
31:6 reserved RO 0
LDO Reset
When set, indicates the LDO circuit has lost regulation and has
generated a reset event.
5 LDO R/W -
Software Reset
When set, indicates a software reset is the cause of the reset event.
4 SW R/W -
Watchdog Timer Reset
When set, indicates a watchdog reset is the cause of the reset event.
3 WDT R/W -
Brown-Out Reset
When set, indicates a brown-out reset is the cause of the reset event.
2 BOR R/W -
Power-On Reset
When set, indicates a power-on reset is the cause of the reset event.
1 POR R/W -
External Reset
When set, indicates an external reset (RST assertion) is the cause of
the reset event.
0 EXT R/W -
March 17, 2008 73
Preliminary
LM3S8933 Microcontroller
Register 8: Run-Mode Clock Configuration (RCC), offset 0x060
This register is defined to provide source control and frequency speed.
Run-Mode Clock Configuration (RCC)
Base 0x400F.E000
Offset 0x060
Type R/W, reset 0x0780.3AD1
31 30 29 28 27 26 25 24 23 22 21 20 19 18 17 16
reserved ACG SYSDIV USESYSDIV reserved
Type RO RO RO RO R/W R/W R/W R/W R/W R/W RO RO RO RO RO RO
Reset 0 0 0 0 0 1 1 1 1 0 0 0 0 0 0 0
15 14 13 12 11 10 9 8 7 6 5 4 3 2 1 0
reserved PWRDN reserved BYPASS reserved XTAL OSCSRC reserved IOSCDIS MOSCDIS
Type RO RO R/W RO R/W RO R/W R/W R/W R/W R/W R/W RO RO R/W R/W
Reset 0 0 1 1 1 0 1 0 1 1 0 1 0 0 0 1
Bit/Field Name Type Reset Description
Software should not rely on the value of a reserved bit. To provide
compatibility with future products, the value of a reserved bit should be
preserved across a read-modify-write operation.
31:28 reserved RO 0x0
Auto Clock Gating
This bit specifies whether the system uses the Sleep-Mode Clock
Gating Control (SCGCn) registers and Deep-Sleep-Mode Clock
Gating Control (DCGCn) registers if the controller enters a Sleep or
Deep-Sleep mode (respectively). If set, the SCGCn or DCGCn registers
are used to control the clocks distributed to the peripherals when the
controller is in a sleep mode. Otherwise, the Run-Mode Clock Gating
Control (RCGCn) registers are used when the controller enters a sleep
mode.
The RCGCn registers are always used to control the clocks in Run
mode.
This allows peripherals to consume less power when the controller is
in a sleep mode and the peripheral is unused.
27 ACG R/W 0
74 March 17, 2008
Preliminary
System Control
Bit/Field Name Type Reset Description
System Clock Divisor
Specifies which divisor is used to generate the system clock from the
PLL output.
The PLL VCO frequency is 400 MHz.
Value Divisor (BYPASS=1) Frequency (BYPASS=0)
0x0 reserved reserved
0x1 /2 reserved
0x2 /3 reserved
0x3 /4 50 MHz
0x4 /5 40 MHz
0x5 /6 33.33 MHz
0x6 /7 28.57 MHz
0x7 /8 25 MHz
0x8 /9 22.22 MHz
0x9 /10 20 MHz
0xA /11 18.18 MHz
0xB /12 16.67 MHz
0xC /13 15.38 MHz
0xD /14 14.29 MHz
0xE /15 13.33 MHz
0xF /16 12.5 MHz (default)
When reading the Run-Mode Clock Configuration (RCC) register (see
page 74), the SYSDIV value is MINSYSDIV if a lower divider was
requested and the PLL is being used. This lower value is allowed to
divide a non-PLL source.
26:23 SYSDIV R/W 0xF
Enable System Clock Divider
Use the system clock divider as the source for the system clock. The
system clock divider is forced to be used when the PLL is selected as
the source.
22 USESYSDIV R/W 0
Software should not rely on the value of a reserved bit. To provide
compatibility with future products, the value of a reserved bit should be
preserved across a read-modify-write operation.
21:14 reserved RO 0
PLL Power Down
This bit connects to the PLL PWRDN input. The reset value of 1 powers
down the PLL.
13 PWRDN R/W 1
Software should not rely on the value of a reserved bit. To provide
compatibility with future products, the value of a reserved bit should be
preserved across a read-modify-write operation.
12 reserved RO 1
March 17, 2008 75
Preliminary
LM3S8933 Microcontroller
Bit/Field Name Type Reset Description
PLL Bypass
Chooses whether the system clock is derived from the PLL output or
the OSC source. If set, the clock that drives the system is the OSC
source. Otherwise, the clock that drives the system is the PLL output
clock divided by the system divider.
Note: The ADC must be clocked from the PLL or directly from a
14-MHz to 18-MHz clock source to operate properly. While
the ADC works in a 14-18 MHz range, to maintain a 1 M
sample/second rate, the ADC must be provided a 16-MHz
clock source.
11 BYPASS R/W 1
Software should not rely on the value of a reserved bit. To provide
compatibility with future products, the value of a reserved bit should be
preserved across a read-modify-write operation.
10 reserved RO 0
Crystal Value
This field specifies the crystal value attached to the main oscillator. The
encoding for this field is provided below.
Crystal Frequency (MHz)
Using the PLL
Crystal Frequency (MHz)
Not Using the PLL
Value
0x0 1.000 reserved
0x1 1.8432 reserved
0x2 2.000 reserved
0x3 2.4576 reserved
0x4 3.579545 MHz
0x5 3.6864 MHz
0x6 4 MHz
0x7 4.096 MHz
0x8 4.9152 MHz
0x9 5 MHz
0xA 5.12 MHz
0xB 6 MHz (reset value)
0xC 6.144 MHz
0xD 7.3728 MHz
0xE 8 MHz
0xF 8.192 MHz
9:6 XTAL R/W 0xB
Oscillator Source
Picks among the four input sources for the OSC. The values are:
Value Input Source
0x0 Main oscillator
0x1 Internal oscillator (default)
0x2 Internal oscillator / 4 (this is necessary if used as input to PLL)
0x3 reserved
5:4 OSCSRC R/W 0x1
76 March 17, 2008
Preliminary
System Control
Bit/Field Name Type Reset Description
Software should not rely on the value of a reserved bit. To provide
compatibility with future products, the value of a reserved bit should be
preserved across a read-modify-write operation.
3:2 reserved RO 0x0
Internal Oscillator Disable
0: Internal oscillator (IOSC) is enabled.
1: Internal oscillator is disabled.
1 IOSCDIS R/W 0
Main Oscillator Disable
0: Main oscillator is enabled .
1: Main oscillator is disabled (default).
0 MOSCDIS R/W 1
March 17, 2008 77
Preliminary
LM3S8933 Microcontroller
Register 9: XTAL to PLL Translation (PLLCFG), offset 0x064
This register provides a means of translating external crystal frequencies into the appropriate PLL
settings. This register is initialized during the reset sequence and updated anytime that the XTAL
field changes in the Run-Mode Clock Configuration (RCC) register (see page 74).
The PLL frequency is calculated using the PLLCFG field values, as follows:
PLLFreq = OSCFreq * F / (R + 1)
XTAL to PLL Translation (PLLCFG)
Base 0x400F.E000
Offset 0x064
Type RO, reset -
31 30 29 28 27 26 25 24 23 22 21 20 19 18 17 16
reserved
Type RO RO RO RO RO RO RO RO RO RO RO RO RO RO RO RO
Reset 0 0 0 0 0 0 0 0 0 0 0 0 0 0 0 0
15 14 13 12 11 10 9 8 7 6 5 4 3 2 1 0
reserved F R
Type RO RO RO RO RO RO RO RO RO RO RO RO RO RO RO RO
Reset 0 0 - - - - - - - - - - - - - -
Bit/Field Name Type Reset Description
Software should not rely on the value of a reserved bit. To provide
compatibility with future products, the value of a reserved bit should be
preserved across a read-modify-write operation.
31:14 reserved RO 0x0
PLL F Value
This field specifies the value supplied to the PLL’s F input.
13:5 F RO -
PLL R Value
This field specifies the value supplied to the PLL’s R input.
4:0 R RO -
78 March 17, 2008
Preliminary
System Control
Register 10: Run-Mode Clock Configuration 2 (RCC2), offset 0x070
This register overrides the RCC equivalent register fields when the USERCC2 bit is set. This allows
RCC2 to be used to extend the capabilities, while also providing a means to be backward-compatible
to previous parts. The fields within the RCC2 register occupy the same bit positions as they do
within the RCC register as LSB-justified.
The SYSDIV2 field is wider so that additional larger divisors are possible. This allows a lower system
clock frequency for improved Deep Sleep power consumption.
Run-Mode Clock Configuration 2 (RCC2)
Base 0x400F.E000
Offset 0x070
Type R/W, reset 0x0780.2800
31 30 29 28 27 26 25 24 23 22 21 20 19 18 17 16
USERCC2 reserved SYSDIV2 reserved
Type R/W RO RO R/W R/W R/W R/W R/W R/W RO RO RO RO RO RO RO
Reset 0 0 0 0 0 1 1 1 1 0 0 0 0 0 0 0
15 14 13 12 11 10 9 8 7 6 5 4 3 2 1 0
reserved PWRDN2 reserved BYPASS2 reserved OSCSRC2 reserved
Type RO RO R/W RO R/W RO RO RO RO R/W R/W R/W RO RO RO RO
Reset 0 0 1 0 1 0 0 0 0 0 0 0 0 0 0 0
Bit/Field Name Type Reset Description
Use RCC2
When set, overrides the RCC register fields.
31 USERCC2 R/W 0
Software should not rely on the value of a reserved bit. To provide
compatibility with future products, the value of a reserved bit should be
preserved across a read-modify-write operation.
30:29 reserved RO 0x0
System Clock Divisor
Specifies which divisor is used to generate the system clock from the
PLL output.
The PLL VCO frequency is 400 MHz.
This field is wider than the RCC register SYSDIV field in order to provide
additional divisor values. This permits the system clock to be run at
much lower frequencies during Deep Sleep mode. For example, where
the RCC register SYSDIV encoding of 1111 provides /16, the RCC2
register SYSDIV2 encoding of 111111 provides /64.
28:23 SYSDIV2 R/W 0x0F
Software should not rely on the value of a reserved bit. To provide
compatibility with future products, the value of a reserved bit should be
preserved across a read-modify-write operation.
22:14 reserved RO 0x0
Power-Down PLL
When set, powers down the PLL.
13 PWRDN2 R/W 1
Software should not rely on the value of a reserved bit. To provide
compatibility with future products, the value of a reserved bit should be
preserved across a read-modify-write operation.
12 reserved RO 0
Bypass PLL
When set, bypasses the PLL for the clock source.
11 BYPASS2 R/W 1
March 17, 2008 79
Preliminary
LM3S8933 Microcontroller
Bit/Field Name Type Reset Description
Software should not rely on the value of a reserved bit. To provide
compatibility with future products, the value of a reserved bit should be
preserved across a read-modify-write operation.
10:7 reserved RO 0x0
System Clock Source
Value Description
0x0 Main oscillator (MOSC)
0x1 Internal oscillator (IOSC)
0x2 Internal oscillator / 4
0x3 30 kHz internal oscillator
0x7 32 kHz external oscillator
6:4 OSCSRC2 R/W 0x0
Software should not rely on the value of a reserved bit. To provide
compatibility with future products, the value of a reserved bit should be
preserved across a read-modify-write operation.
3:0 reserved RO 0
80 March 17, 2008
Preliminary
System Control
Register 11: Deep Sleep Clock Configuration (DSLPCLKCFG), offset 0x144
This register provides configuration information for the hardware control of Deep Sleep Mode.
Deep Sleep Clock Configuration (DSLPCLKCFG)
Base 0x400F.E000
Offset 0x144
Type R/W, reset 0x0780.0000
31 30 29 28 27 26 25 24 23 22 21 20 19 18 17 16
reserved DSDIVORIDE reserved
Type RO RO RO R/W R/W R/W R/W R/W R/W RO RO RO RO RO RO RO
Reset 0 0 0 0 0 1 1 1 1 0 0 0 0 0 0 0
15 14 13 12 11 10 9 8 7 6 5 4 3 2 1 0
reserved DSOSCSRC reserved
Type RO RO RO RO RO RO RO RO RO R/W R/W R/W RO RO RO RO
Reset 0 0 0 0 0 0 0 0 0 0 0 0 0 0 0 0
Bit/Field Name Type Reset Description
Software should not rely on the value of a reserved bit. To provide
compatibility with future products, the value of a reserved bit should be
preserved across a read-modify-write operation.
31:29 reserved RO 0x0
Divider Field Override
6-bit system divider field to override when Deep-Sleep occurs with PLL
running.
28:23 DSDIVORIDE R/W 0x0F
Software should not rely on the value of a reserved bit. To provide
compatibility with future products, the value of a reserved bit should be
preserved across a read-modify-write operation.
22:7 reserved RO 0x0
Clock Source
When set, forces IOSC to be clock source during Deep Sleep mode.
Value Name Description
0x0 NOORIDE No override to the oscillator clock source is done
0x1 IOSC Use internal 12 MHz oscillator as source
0x3 30kHz Use 30 kHz internal oscillator
0x7 32kHz Use 32 kHz external oscillator
6:4 DSOSCSRC R/W 0x0
Software should not rely on the value of a reserved bit. To provide
compatibility with future products, the value of a reserved bit should be
preserved across a read-modify-write operation.
3:0 reserved RO 0x0
March 17, 2008 81
Preliminary
LM3S8933 Microcontroller
Register 12: Device Identification 1 (DID1), offset 0x004
This register identifies the device family, part number, temperature range, pin count, and package
type.
Device Identification 1 (DID1)
Base 0x400F.E000
Offset 0x004
Type RO, reset -
31 30 29 28 27 26 25 24 23 22 21 20 19 18 17 16
VER FAM PARTNO
Type RO RO RO RO RO RO RO RO RO RO RO RO RO RO RO RO
Reset 0 0 0 1 0 0 0 0 1 0 0 0 1 1 0 0
15 14 13 12 11 10 9 8 7 6 5 4 3 2 1 0
PINCOUNT reserved TEMP PKG ROHS QUAL
Type RO RO RO RO RO RO RO RO RO RO RO RO RO RO RO RO
Reset 0 1 0 0 0 0 0 0 - - - - - 1 - -
Bit/Field Name Type Reset Description
DID1 Version
This field defines the DID1 register format version. The version number
is numeric. The value of the VER field is encoded as follows (all other
encodings are reserved):
Value Description
0x1 Second version of the DID1 register format.
31:28 VER RO 0x1
Family
This field provides the family identification of the device within the
Luminary Micro product portfolio. The value is encoded as follows (all
other encodings are reserved):
Value Description
Stellaris family of microcontollers, that is, all devices with
external part numbers starting with LM3S.
0x0
27:24 FAM RO 0x0
Part Number
This field provides the part number of the device within the family. The
value is encoded as follows (all other encodings are reserved):
Value Description
0x8C LM3S8933
23:16 PARTNO RO 0x8C
Package Pin Count
This field specifies the number of pins on the device package. The value
is encoded as follows (all other encodings are reserved):
Value Description
0x2 100-pin or 108-ball package
15:13 PINCOUNT RO 0x2
82 March 17, 2008
Preliminary
System Control
Bit/Field Name Type Reset Description
Software should not rely on the value of a reserved bit. To provide
compatibility with future products, the value of a reserved bit should be
preserved across a read-modify-write operation.
12:8 reserved RO 0
Temperature Range
This field specifies the temperature rating of the device. The value is
encoded as follows (all other encodings are reserved):
Value Description
0x0 Commercial temperature range (0°C to 70°C)
0x1 Industrial temperature range (-40°C to 85°C)
0x2 Extended temperature range (-40°C to 105°C)
7:5 TEMP RO -
Package Type
This field specifies the package type. The value is encoded as follows
(all other encodings are reserved):
Value Description
0x0 SOIC package
0x1 LQFP package
0x2 BGA package
4:3 PKG RO -
RoHS-Compliance
This bit specifies whether the device is RoHS-compliant. A 1 indicates
the part is RoHS-compliant.
2 ROHS RO 1
Qualification Status
This field specifies the qualification status of the device. The value is
encoded as follows (all other encodings are reserved):
Value Description
0x0 Engineering Sample (unqualified)
0x1 Pilot Production (unqualified)
0x2 Fully Qualified
1:0 QUAL RO -
March 17, 2008 83
Preliminary
LM3S8933 Microcontroller
Register 13: Device Capabilities 0 (DC0), offset 0x008
This register is predefined by the part and can be used to verify features.
Device Capabilities 0 (DC0)
Base 0x400F.E000
Offset 0x008
Type RO, reset 0x00FF.007F
31 30 29 28 27 26 25 24 23 22 21 20 19 18 17 16
SRAMSZ
Type RO RO RO RO RO RO RO RO RO RO RO RO RO RO RO RO
Reset 0 0 0 0 0 0 0 0 1 1 1 1 1 1 1 1
15 14 13 12 11 10 9 8 7 6 5 4 3 2 1 0
FLASHSZ
Type RO RO RO RO RO RO RO RO RO RO RO RO RO RO RO RO
Reset 0 0 0 0 0 0 0 0 0 1 1 1 1 1 1 1
Bit/Field Name Type Reset Description
SRAM Size
Indicates the size of the on-chip SRAM memory.
Value Description
0x00FF 64 KB of SRAM
31:16 SRAMSZ RO 0x00FF
Flash Size
Indicates the size of the on-chip flash memory.
Value Description
0x007F 256 KB of Flash
15:0 FLASHSZ RO 0x007F
84 March 17, 2008
Preliminary
System Control
Register 14: Device Capabilities 1 (DC1), offset 0x010
This register provides a list of features available in the system. The Stellaris family uses this register
format to indicate the availability of the following family features in the specific device: CANs, PWM,
ADC, Watchdog timer, Hibernation module, and debug capabilities. This register also indicates the
maximum clock frequency and maximum ADC sample rate. The format of this register is consistent
with the RCGC0, SCGC0, and DCGC0 clock control registers and the SRCR0 software reset control
register.
Device Capabilities 1 (DC1)
Base 0x400F.E000
Offset 0x010
Type RO, reset 0x0101.33FF
31 30 29 28 27 26 25 24 23 22 21 20 19 18 17 16
reserved CAN0 reserved ADC
Type RO RO RO RO RO RO RO RO RO RO RO RO RO RO RO RO
Reset 0 0 0 0 0 0 0 1 0 0 0 0 0 0 0 1
15 14 13 12 11 10 9 8 7 6 5 4 3 2 1 0
MINSYSDIV MAXADCSPD MPU HIB TEMPSNS PLL WDT SWO SWD JTAG
Type RO RO RO RO RO RO RO RO RO RO RO RO RO RO RO RO
Reset 0 0 1 1 0 0 1 1 1 1 1 1 1 1 1 1
Bit/Field Name Type Reset Description
Software should not rely on the value of a reserved bit. To provide
compatibility with future products, the value of a reserved bit should be
preserved across a read-modify-write operation.
31:25 reserved RO 0
CAN Module 0 Present
When set, indicates that CAN unit 0 is present.
24 CAN0 RO 1
Software should not rely on the value of a reserved bit. To provide
compatibility with future products, the value of a reserved bit should be
preserved across a read-modify-write operation.
23:17 reserved RO 0
ADC Module Present
When set, indicates that the ADC module is present.
16 ADC RO 1
System Clock Divider
Minimum 4-bit divider value for system clock. The reset value is
hardware-dependent. See the RCC register for how to change the
system clock divisor using the SYSDIV bit.
Value Description
0x3 Specifies a 50-MHz CPU clock with a PLL divider of 4.
15:12 MINSYSDIV RO 0x3
Max ADC Speed
Indicates the maximum rate at which the ADC samples data.
Value Description
0x3 1M samples/second
11:8 MAXADCSPD RO 0x3
March 17, 2008 85
Preliminary
LM3S8933 Microcontroller
Bit/Field Name Type Reset Description
MPU Present
When set, indicates that the Cortex-M3 Memory Protection Unit (MPU)
module is present. See the ARM Cortex-M3 Technical Reference Manual
for details on the MPU.
7 MPU RO 1
Hibernation Module Present
When set, indicates that the Hibernation module is present.
6 HIB RO 1
Temp Sensor Present
When set, indicates that the on-chip temperature sensor is present.
5 TEMPSNS RO 1
PLL Present
When set, indicates that the on-chip Phase Locked Loop (PLL) is
present.
4 PLL RO 1
Watchdog Timer Present
When set, indicates that a watchdog timer is present.
3 WDT RO 1
SWO Trace Port Present
When set, indicates that the Serial Wire Output (SWO) trace port is
present.
2 SWO RO 1
SWD Present
When set, indicates that the Serial Wire Debugger (SWD) is present.
1 SWD RO 1
JTAG Present
When set, indicates that the JTAG debugger interface is present.
0 JTAG RO 1
86 March 17, 2008
Preliminary
System Control
Register 15: Device Capabilities 2 (DC2), offset 0x014
This register provides a list of features available in the system. The Stellaris family uses this register
format to indicate the availability of the following family features in the specific device: Analog
Comparators, General-Purpose Timers, I2Cs, QEIs, SSIs, and UARTs. The format of this register
is consistent with the RCGC1, SCGC1, and DCGC1 clock control registers and the SRCR1 software
reset control register.
Device Capabilities 2 (DC2)
Base 0x400F.E000
Offset 0x014
Type RO, reset 0x070F.1013
31 30 29 28 27 26 25 24 23 22 21 20 19 18 17 16
reserved COMP2 COMP1 COMP0 reserved TIMER3 TIMER2 TIMER1 TIMER0
Type RO RO RO RO RO RO RO RO RO RO RO RO RO RO RO RO
Reset 0 0 0 0 0 1 1 1 0 0 0 0 1 1 1 1
15 14 13 12 11 10 9 8 7 6 5 4 3 2 1 0
reserved I2C0 reserved SSI0 reserved UART1 UART0
Type RO RO RO RO RO RO RO RO RO RO RO RO RO RO RO RO
Reset 0 0 0 1 0 0 0 0 0 0 0 1 0 0 1 1
Bit/Field Name Type Reset Description
Software should not rely on the value of a reserved bit. To provide
compatibility with future products, the value of a reserved bit should be
preserved across a read-modify-write operation.
31:27 reserved RO 0
Analog Comparator 2 Present
When set, indicates that analog comparator 2 is present.
26 COMP2 RO 1
Analog Comparator 1 Present
When set, indicates that analog comparator 1 is present.
25 COMP1 RO 1
Analog Comparator 0 Present
When set, indicates that analog comparator 0 is present.
24 COMP0 RO 1
Software should not rely on the value of a reserved bit. To provide
compatibility with future products, the value of a reserved bit should be
preserved across a read-modify-write operation.
23:20 reserved RO 0
Timer 3 Present
When set, indicates that General-Purpose Timer module 3 is present.
19 TIMER3 RO 1
Timer 2 Present
When set, indicates that General-Purpose Timer module 2 is present.
18 TIMER2 RO 1
Timer 1 Present
When set, indicates that General-Purpose Timer module 1 is present.
17 TIMER1 RO 1
Timer 0 Present
When set, indicates that General-Purpose Timer module 0 is present.
16 TIMER0 RO 1
Software should not rely on the value of a reserved bit. To provide
compatibility with future products, the value of a reserved bit should be
preserved across a read-modify-write operation.
15:13 reserved RO 0
March 17, 2008 87
Preliminary
LM3S8933 Microcontroller
Bit/Field Name Type Reset Description
I2C Module 0 Present
When set, indicates that I2C module 0 is present.
12 I2C0 RO 1
Software should not rely on the value of a reserved bit. To provide
compatibility with future products, the value of a reserved bit should be
preserved across a read-modify-write operation.
11:5 reserved RO 0
SSI0 Present
When set, indicates that SSI module 0 is present.
4 SSI0 RO 1
Software should not rely on the value of a reserved bit. To provide
compatibility with future products, the value of a reserved bit should be
preserved across a read-modify-write operation.
3:2 reserved RO 0
UART1 Present
When set, indicates that UART module 1 is present.
1 UART1 RO 1
UART0 Present
When set, indicates that UART module 0 is present.
0 UART0 RO 1
88 March 17, 2008
Preliminary
System Control
Register 16: Device Capabilities 3 (DC3), offset 0x018
This register provides a list of features available in the system. The Stellaris family uses this register
format to indicate the availability of the following family features in the specific device: Analog
Comparator I/Os, CCP I/Os, ADC I/Os, and PWM I/Os.
Device Capabilities 3 (DC3)
Base 0x400F.E000
Offset 0x018
Type RO, reset 0x0F0F.3FC0
31 30 29 28 27 26 25 24 23 22 21 20 19 18 17 16
reserved CCP3 CCP2 CCP1 CCP0 reserved ADC3 ADC2 ADC1 ADC0
Type RO RO RO RO RO RO RO RO RO RO RO RO RO RO RO RO
Reset 0 0 0 0 1 1 1 1 0 0 0 0 1 1 1 1
15 14 13 12 11 10 9 8 7 6 5 4 3 2 1 0
reserved C2PLUS C2MINUS C1O C1PLUS C1MINUS C0O C0PLUS C0MINUS reserved
Type RO RO RO RO RO RO RO RO RO RO RO RO RO RO RO RO
Reset 0 0 1 1 1 1 1 1 1 1 0 0 0 0 0 0
Bit/Field Name Type Reset Description
Software should not rely on the value of a reserved bit. To provide
compatibility with future products, the value of a reserved bit should be
preserved across a read-modify-write operation.
31:28 reserved RO 0
CCP3 Pin Present
When set, indicates that Capture/Compare/PWM pin 3 is present.
27 CCP3 RO 1
CCP2 Pin Present
When set, indicates that Capture/Compare/PWM pin 2 is present.
26 CCP2 RO 1
CCP1 Pin Present
When set, indicates that Capture/Compare/PWM pin 1 is present.
25 CCP1 RO 1
CCP0 Pin Present
When set, indicates that Capture/Compare/PWM pin 0 is present.
24 CCP0 RO 1
Software should not rely on the value of a reserved bit. To provide
compatibility with future products, the value of a reserved bit should be
preserved across a read-modify-write operation.
23:20 reserved RO 0
ADC3 Pin Present
When set, indicates that ADC pin 3 is present.
19 ADC3 RO 1
ADC2 Pin Present
When set, indicates that ADC pin 2 is present.
18 ADC2 RO 1
ADC1 Pin Present
When set, indicates that ADC pin 1 is present.
17 ADC1 RO 1
ADC0 Pin Present
When set, indicates that ADC pin 0 is present.
16 ADC0 RO 1
March 17, 2008 89
Preliminary
LM3S8933 Microcontroller
Bit/Field Name Type Reset Description
Software should not rely on the value of a reserved bit. To provide
compatibility with future products, the value of a reserved bit should be
preserved across a read-modify-write operation.
15:14 reserved RO 0
C2+ Pin Present
When set, indicates that the analog comparator 2 (+) input pin is present.
13 C2PLUS RO 1
C2- Pin Present
When set, indicates that the analog comparator 2 (-) input pin is present.
12 C2MINUS RO 1
C1o Pin Present
When set, indicates that the analog comparator 1 output pin is present.
11 C1O RO 1
C1+ Pin Present
When set, indicates that the analog comparator 1 (+) input pin is present.
10 C1PLUS RO 1
C1- Pin Present
When set, indicates that the analog comparator 1 (-) input pin is present.
9 C1MINUS RO 1
C0o Pin Present
When set, indicates that the analog comparator 0 output pin is present.
8 C0O RO 1
C0+ Pin Present
When set, indicates that the analog comparator 0 (+) input pin is present.
7 C0PLUS RO 1
C0- Pin Present
When set, indicates that the analog comparator 0 (-) input pin is present.
6 C0MINUS RO 1
Software should not rely on the value of a reserved bit. To provide
compatibility with future products, the value of a reserved bit should be
preserved across a read-modify-write operation.
5:0 reserved RO 0
90 March 17, 2008
Preliminary
System Control
Register 17: Device Capabilities 4 (DC4), offset 0x01C
This register provides a list of features available in the system. The Stellaris family uses this register
format to indicate the availability of the following family features in the specific device: Ethernet MAC
and PHY, GPIOs, and CCP I/Os. The format of this register is consistent with the RCGC2, SCGC2,
and DCGC2 clock control registers and the SRCR2 software reset control register.
Device Capabilities 4 (DC4)
Base 0x400F.E000
Offset 0x01C
Type RO, reset 0x5100.007F
31 30 29 28 27 26 25 24 23 22 21 20 19 18 17 16
reserved EPHY0 reserved EMAC0 reserved E1588 reserved
Type RO RO RO RO RO RO RO RO RO RO RO RO RO RO RO RO
Reset 0 1 0 1 0 0 0 1 0 0 0 0 0 0 0 0
15 14 13 12 11 10 9 8 7 6 5 4 3 2 1 0
reserved GPIOG GPIOF GPIOE GPIOD GPIOC GPIOB GPIOA
Type RO RO RO RO RO RO RO RO RO RO RO RO RO RO RO RO
Reset 0 0 0 0 0 0 0 0 0 1 1 1 1 1 1 1
Bit/Field Name Type Reset Description
Software should not rely on the value of a reserved bit. To provide
compatibility with future products, the value of a reserved bit should be
preserved across a read-modify-write operation.
31 reserved RO 0
Ethernet PHY0 Present
When set, indicates that Ethernet PHY module 0 is present.
30 EPHY0 RO 1
Software should not rely on the value of a reserved bit. To provide
compatibility with future products, the value of a reserved bit should be
preserved across a read-modify-write operation.
29 reserved RO 0
Ethernet MAC0 Present
When set, indicates that Ethernet MAC module 0 is present.
28 EMAC0 RO 1
Software should not rely on the value of a reserved bit. To provide
compatibility with future products, the value of a reserved bit should be
preserved across a read-modify-write operation.
27:25 reserved RO 0
1588 Capable
When set, indicates that that EMAC0 is 1588-capable.
24 E1588 RO 1
Software should not rely on the value of a reserved bit. To provide
compatibility with future products, the value of a reserved bit should be
preserved across a read-modify-write operation.
23:7 reserved RO 0
GPIO Port G Present
When set, indicates that GPIO Port G is present.
6 GPIOG RO 1
GPIO Port F Present
When set, indicates that GPIO Port F is present.
5 GPIOF RO 1
GPIO Port E Present
When set, indicates that GPIO Port E is present.
4 GPIOE RO 1
March 17, 2008 91
Preliminary
LM3S8933 Microcontroller
Bit/Field Name Type Reset Description
GPIO Port D Present
When set, indicates that GPIO Port D is present.
3 GPIOD RO 1
GPIO Port C Present
When set, indicates that GPIO Port C is present.
2 GPIOC RO 1
GPIO Port B Present
When set, indicates that GPIO Port B is present.
1 GPIOB RO 1
GPIO Port A Present
When set, indicates that GPIO Port A is present.
0 GPIOA RO 1
92 March 17, 2008
Preliminary
System Control
Register 18: Run Mode Clock Gating Control Register 0 (RCGC0), offset 0x100
This register controls the clock gating logic. Each bit controls a clock enable for a given interface,
function, or unit. If set, the unit receives a clock and functions. Otherwise, the unit is unclocked and
disabled (saving power). If the unit is unclocked, reads or writes to the unit will generate a bus fault.
The reset state of these bits is 0 (unclocked) unless otherwise noted, so that all functional units are
disabled. It is the responsibility of software to enable the ports necessary for the application. Note
that these registers may contain more bits than there are interfaces, functions, or units to control.
This is to assure reasonable code compatibility with other family and future parts. RCGC0 is the
clock configuration register for running operation, SCGC0 for Sleep operation, and DCGC0 for
Deep-Sleep operation. Setting the ACG bit in the Run-Mode Clock Configuration (RCC) register
specifies that the system uses sleep modes.
Run Mode Clock Gating Control Register 0 (RCGC0)
Base 0x400F.E000
Offset 0x100
Type R/W, reset 0x00000040
31 30 29 28 27 26 25 24 23 22 21 20 19 18 17 16
reserved CAN0 reserved ADC
Type RO RO RO RO RO RO RO R/W RO RO RO RO RO RO RO R/W
Reset 0 0 0 0 0 0 0 0 0 0 0 0 0 0 0 0
15 14 13 12 11 10 9 8 7 6 5 4 3 2 1 0
reserved MAXADCSPD reserved HIB reserved WDT reserved
Type RO RO RO RO R/W R/W R/W R/W RO R/W RO RO R/W RO RO RO
Reset 0 0 0 0 0 0 0 0 0 0 0 0 0 0 0 0
Bit/Field Name Type Reset Description
Software should not rely on the value of a reserved bit. To provide
compatibility with future products, the value of a reserved bit should be
preserved across a read-modify-write operation.
31:25 reserved RO 0
CAN0 Clock Gating Control
This bit controls the clock gating for CAN unit 0. If set, the unit receives
a clock and functions. Otherwise, the unit is unclocked and disabled.
24 CAN0 R/W 0
Software should not rely on the value of a reserved bit. To provide
compatibility with future products, the value of a reserved bit should be
preserved across a read-modify-write operation.
23:17 reserved RO 0
ADC0 Clock Gating Control
This bit controls the clock gating for SAR ADC module 0. If set, the unit
receives a clock and functions. Otherwise, the unit is unclocked and
disabled. If the unit is unclocked, a read or write to the unit generates
a bus fault.
16 ADC R/W 0
Software should not rely on the value of a reserved bit. To provide
compatibility with future products, the value of a reserved bit should be
preserved across a read-modify-write operation.
15:12 reserved RO 0
March 17, 2008 93
Preliminary
LM3S8933 Microcontroller
Bit/Field Name Type Reset Description
ADC Sample Speed
This field sets the rate at which the ADC samples data. You cannot set
the rate higher than the maximum rate. You can set the sample rate by
setting the MAXADCSPD bit as follows:
Value Description
0x3 1M samples/second
0x2 500K samples/second
0x1 250K samples/second
0x0 125K samples/second
11:8 MAXADCSPD R/W 0
Software should not rely on the value of a reserved bit. To provide
compatibility with future products, the value of a reserved bit should be
preserved across a read-modify-write operation.
7 reserved RO 0
HIB Clock Gating Control
This bit controls the clock gating for the Hibernation module. If set, the
unit receives a clock and functions. Otherwise, the unit is unclocked and
disabled.
6 HIB R/W 0
Software should not rely on the value of a reserved bit. To provide
compatibility with future products, the value of a reserved bit should be
preserved across a read-modify-write operation.
5:4 reserved RO 0
WDT Clock Gating Control
This bit controls the clock gating for the WDT module. If set, the unit
receives a clock and functions. Otherwise, the unit is unclocked and
disabled. If the unit is unclocked, a read or write to the unit generates
a bus fault.
3 WDT R/W 0
Software should not rely on the value of a reserved bit. To provide
compatibility with future products, the value of a reserved bit should be
preserved across a read-modify-write operation.
2:0 reserved RO 0
94 March 17, 2008
Preliminary
System Control
Register 19: Sleep Mode Clock Gating Control Register 0 (SCGC0), offset
0x110
This register controls the clock gating logic. Each bit controls a clock enable for a given interface,
function, or unit. If set, the unit receives a clock and functions. Otherwise, the unit is unclocked and
disabled (saving power). If the unit is unclocked, reads or writes to the unit will generate a bus fault.
The reset state of these bits is 0 (unclocked) unless otherwise noted, so that all functional units are
disabled. It is the responsibility of software to enable the ports necessary for the application. Note
that these registers may contain more bits than there are interfaces, functions, or units to control.
This is to assure reasonable code compatibility with other family and future parts. RCGC0 is the
clock configuration register for running operation, SCGC0 for Sleep operation, and DCGC0 for
Deep-Sleep operation. Setting the ACG bit in the Run-Mode Clock Configuration (RCC) register
specifies that the system uses sleep modes.
Sleep Mode Clock Gating Control Register 0 (SCGC0)
Base 0x400F.E000
Offset 0x110
Type R/W, reset 0x00000040
31 30 29 28 27 26 25 24 23 22 21 20 19 18 17 16
reserved CAN0 reserved ADC
Type RO RO RO RO RO RO RO R/W RO RO RO RO RO RO RO R/W
Reset 0 0 0 0 0 0 0 0 0 0 0 0 0 0 0 0
15 14 13 12 11 10 9 8 7 6 5 4 3 2 1 0
reserved MAXADCSPD reserved HIB reserved WDT reserved
Type RO RO RO RO R/W R/W R/W R/W RO R/W RO RO R/W RO RO RO
Reset 0 0 0 0 0 0 0 0 0 0 0 0 0 0 0 0
Bit/Field Name Type Reset Description
Software should not rely on the value of a reserved bit. To provide
compatibility with future products, the value of a reserved bit should be
preserved across a read-modify-write operation.
31:25 reserved RO 0
CAN0 Clock Gating Control
This bit controls the clock gating for CAN unit 0. If set, the unit receives
a clock and functions. Otherwise, the unit is unclocked and disabled.
24 CAN0 R/W 0
Software should not rely on the value of a reserved bit. To provide
compatibility with future products, the value of a reserved bit should be
preserved across a read-modify-write operation.
23:17 reserved RO 0
ADC0 Clock Gating Control
This bit controls the clock gating for SAR ADC module 0. If set, the unit
receives a clock and functions. Otherwise, the unit is unclocked and
disabled. If the unit is unclocked, a read or write to the unit generates
a bus fault.
16 ADC R/W 0
Software should not rely on the value of a reserved bit. To provide
compatibility with future products, the value of a reserved bit should be
preserved across a read-modify-write operation.
15:12 reserved RO 0
March 17, 2008 95
Preliminary
LM3S8933 Microcontroller
Bit/Field Name Type Reset Description
ADC Sample Speed
This field sets the rate at which the ADC samples data. You cannot set
the rate higher than the maximum rate. You can set the sample rate by
setting the MAXADCSPD bit as follows:
Value Description
0x3 1M samples/second
0x2 500K samples/second
0x1 250K samples/second
0x0 125K samples/second
11:8 MAXADCSPD R/W 0
Software should not rely on the value of a reserved bit. To provide
compatibility with future products, the value of a reserved bit should be
preserved across a read-modify-write operation.
7 reserved RO 0
HIB Clock Gating Control
This bit controls the clock gating for the Hibernation module. If set, the
unit receives a clock and functions. Otherwise, the unit is unclocked and
disabled.
6 HIB R/W 0
Software should not rely on the value of a reserved bit. To provide
compatibility with future products, the value of a reserved bit should be
preserved across a read-modify-write operation.
5:4 reserved RO 0
WDT Clock Gating Control
This bit controls the clock gating for the WDT module. If set, the unit
receives a clock and functions. Otherwise, the unit is unclocked and
disabled. If the unit is unclocked, a read or write to the unit generates
a bus fault.
3 WDT R/W 0
Software should not rely on the value of a reserved bit. To provide
compatibility with future products, the value of a reserved bit should be
preserved across a read-modify-write operation.
2:0 reserved RO 0
96 March 17, 2008
Preliminary
System Control
Register 20: Deep Sleep Mode Clock Gating Control Register 0 (DCGC0),
offset 0x120
This register controls the clock gating logic. Each bit controls a clock enable for a given interface,
function, or unit. If set, the unit receives a clock and functions. Otherwise, the unit is unclocked and
disabled (saving power). If the unit is unclocked, reads or writes to the unit will generate a bus fault.
The reset state of these bits is 0 (unclocked) unless otherwise noted, so that all functional units are
disabled. It is the responsibility of software to enable the ports necessary for the application. Note
that these registers may contain more bits than there are interfaces, functions, or units to control.
This is to assure reasonable code compatibility with other family and future parts. RCGC0 is the
clock configuration register for running operation, SCGC0 for Sleep operation, and DCGC0 for
Deep-Sleep operation. Setting the ACG bit in the Run-Mode Clock Configuration (RCC) register
specifies that the system uses sleep modes.
Deep Sleep Mode Clock Gating Control Register 0 (DCGC0)
Base 0x400F.E000
Offset 0x120
Type R/W, reset 0x00000040
31 30 29 28 27 26 25 24 23 22 21 20 19 18 17 16
reserved CAN0 reserved ADC
Type RO RO RO RO RO RO RO R/W RO RO RO RO RO RO RO R/W
Reset 0 0 0 0 0 0 0 0 0 0 0 0 0 0 0 0
15 14 13 12 11 10 9 8 7 6 5 4 3 2 1 0
reserved MAXADCSPD reserved HIB reserved WDT reserved
Type RO RO RO RO R/W R/W R/W R/W RO R/W RO RO R/W RO RO RO
Reset 0 0 0 0 0 0 0 0 0 0 0 0 0 0 0 0
Bit/Field Name Type Reset Description
Software should not rely on the value of a reserved bit. To provide
compatibility with future products, the value of a reserved bit should be
preserved across a read-modify-write operation.
31:25 reserved RO 0
CAN0 Clock Gating Control
This bit controls the clock gating for CAN unit 0. If set, the unit receives
a clock and functions. Otherwise, the unit is unclocked and disabled.
24 CAN0 R/W 0
Software should not rely on the value of a reserved bit. To provide
compatibility with future products, the value of a reserved bit should be
preserved across a read-modify-write operation.
23:17 reserved RO 0
ADC0 Clock Gating Control
This bit controls the clock gating for SAR ADC module 0. If set, the unit
receives a clock and functions. Otherwise, the unit is unclocked and
disabled. If the unit is unclocked, a read or write to the unit generates
a bus fault.
16 ADC R/W 0
Software should not rely on the value of a reserved bit. To provide
compatibility with future products, the value of a reserved bit should be
preserved across a read-modify-write operation.
15:12 reserved RO 0
March 17, 2008 97
Preliminary
LM3S8933 Microcontroller
Bit/Field Name Type Reset Description
ADC Sample Speed
This field sets the rate at which the ADC samples data. You cannot set
the rate higher than the maximum rate. You can set the sample rate by
setting the MAXADCSPD bit as follows:
Value Description
0x3 1M samples/second
0x2 500K samples/second
0x1 250K samples/second
0x0 125K samples/second
11:8 MAXADCSPD R/W 0
Software should not rely on the value of a reserved bit. To provide
compatibility with future products, the value of a reserved bit should be
preserved across a read-modify-write operation.
7 reserved RO 0
HIB Clock Gating Control
This bit controls the clock gating for the Hibernation module. If set, the
unit receives a clock and functions. Otherwise, the unit is unclocked and
disabled.
6 HIB R/W 0
Software should not rely on the value of a reserved bit. To provide
compatibility with future products, the value of a reserved bit should be
preserved across a read-modify-write operation.
5:4 reserved RO 0
WDT Clock Gating Control
This bit controls the clock gating for the WDT module. If set, the unit
receives a clock and functions. Otherwise, the unit is unclocked and
disabled. If the unit is unclocked, a read or write to the unit generates
a bus fault.
3 WDT R/W 0
Software should not rely on the value of a reserved bit. To provide
compatibility with future products, the value of a reserved bit should be
preserved across a read-modify-write operation.
2:0 reserved RO 0
98 March 17, 2008
Preliminary
System Control
Register 21: Run Mode Clock Gating Control Register 1 (RCGC1), offset 0x104
This register controls the clock gating logic. Each bit controls a clock enable for a given interface,
function, or unit. If set, the unit receives a clock and functions. Otherwise, the unit is unclocked and
disabled (saving power). If the unit is unclocked, reads or writes to the unit will generate a bus fault.
The reset state of these bits is 0 (unclocked) unless otherwise noted, so that all functional units are
disabled. It is the responsibility of software to enable the ports necessary for the application. Note
that these registers may contain more bits than there are interfaces, functions, or units to control.
This is to assure reasonable code compatibility with other family and future parts. RCGC1 is the
clock configuration register for running operation, SCGC1 for Sleep operation, and DCGC1 for
Deep-Sleep operation. Setting the ACG bit in the Run-Mode Clock Configuration (RCC) register
specifies that the system uses sleep modes.
Run Mode Clock Gating Control Register 1 (RCGC1)
Base 0x400F.E000
Offset 0x104
Type R/W, reset 0x00000000
31 30 29 28 27 26 25 24 23 22 21 20 19 18 17 16
reserved COMP2 COMP1 COMP0 reserved TIMER3 TIMER2 TIMER1 TIMER0
Type RO RO RO RO RO R/W R/W R/W RO RO RO RO R/W R/W R/W R/W
Reset 0 0 0 0 0 0 0 0 0 0 0 0 0 0 0 0
15 14 13 12 11 10 9 8 7 6 5 4 3 2 1 0
reserved I2C0 reserved SSI0 reserved UART1 UART0
Type RO RO RO R/W RO RO RO RO RO RO RO R/W RO RO R/W R/W
Reset 0 0 0 0 0 0 0 0 0 0 0 0 0 0 0 0
Bit/Field Name Type Reset Description
Software should not rely on the value of a reserved bit. To provide
compatibility with future products, the value of a reserved bit should be
preserved across a read-modify-write operation.
31:27 reserved RO 0
Analog Comparator 2 Clock Gating
This bit controls the clock gating for analog comparator 2. If set, the unit
receives a clock and functions. Otherwise, the unit is unclocked and
disabled. If the unit is unclocked, reads or writes to the unit will generate
a bus fault.
26 COMP2 R/W 0
Analog Comparator 1 Clock Gating
This bit controls the clock gating for analog comparator 1. If set, the unit
receives a clock and functions. Otherwise, the unit is unclocked and
disabled. If the unit is unclocked, reads or writes to the unit will generate
a bus fault.
25 COMP1 R/W 0
Analog Comparator 0 Clock Gating
This bit controls the clock gating for analog comparator 0. If set, the unit
receives a clock and functions. Otherwise, the unit is unclocked and
disabled. If the unit is unclocked, reads or writes to the unit will generate
a bus fault.
24 COMP0 R/W 0
Software should not rely on the value of a reserved bit. To provide
compatibility with future products, the value of a reserved bit should be
preserved across a read-modify-write operation.
23:20 reserved RO 0
March 17, 2008 99
Preliminary
LM3S8933 Microcontroller
Bit/Field Name Type Reset Description
Timer 3 Clock Gating Control
This bit controls the clock gating for General-Purpose Timer module 3.
If set, the unit receives a clock and functions. Otherwise, the unit is
unclocked and disabled. If the unit is unclocked, reads or writes to the
unit will generate a bus fault.
19 TIMER3 R/W 0
Timer 2 Clock Gating Control
This bit controls the clock gating for General-Purpose Timer module 2.
If set, the unit receives a clock and functions. Otherwise, the unit is
unclocked and disabled. If the unit is unclocked, reads or writes to the
unit will generate a bus fault.
18 TIMER2 R/W 0
Timer 1 Clock Gating Control
This bit controls the clock gating for General-Purpose Timer module 1.
If set, the unit receives a clock and functions. Otherwise, the unit is
unclocked and disabled. If the unit is unclocked, reads or writes to the
unit will generate a bus fault.
17 TIMER1 R/W 0
Timer 0 Clock Gating Control
This bit controls the clock gating for General-Purpose Timer module 0.
If set, the unit receives a clock and functions. Otherwise, the unit is
unclocked and disabled. If the unit is unclocked, reads or writes to the
unit will generate a bus fault.
16 TIMER0 R/W 0
Software should not rely on the value of a reserved bit. To provide
compatibility with future products, the value of a reserved bit should be
preserved across a read-modify-write operation.
15:13 reserved RO 0
I2C0 Clock Gating Control
This bit controls the clock gating for I2C module 0. If set, the unit receives
a clock and functions. Otherwise, the unit is unclocked and disabled. If
the unit is unclocked, reads or writes to the unit will generate a bus fault.
12 I2C0 R/W 0
Software should not rely on the value of a reserved bit. To provide
compatibility with future products, the value of a reserved bit should be
preserved across a read-modify-write operation.
11:5 reserved RO 0
SSI0 Clock Gating Control
This bit controls the clock gating for SSI module 0. If set, the unit receives
a clock and functions. Otherwise, the unit is unclocked and disabled. If
the unit is unclocked, reads or writes to the unit will generate a bus fault.
4 SSI0 R/W 0
Software should not rely on the value of a reserved bit. To provide
compatibility with future products, the value of a reserved bit should be
preserved across a read-modify-write operation.
3:2 reserved RO 0
UART1 Clock Gating Control
This bit controls the clock gating for UART module 1. If set, the unit
receives a clock and functions. Otherwise, the unit is unclocked and
disabled. If the unit is unclocked, reads or writes to the unit will generate
a bus fault.
1 UART1 R/W 0
100 March 17, 2008
Preliminary
System Control
Bit/Field Name Type Reset Description
UART0 Clock Gating Control
This bit controls the clock gating for UART module 0. If set, the unit
receives a clock and functions. Otherwise, the unit is unclocked and
disabled. If the unit is unclocked, reads or writes to the unit will generate
a bus fault.
0 UART0 R/W 0
March 17, 2008 101
Preliminary
LM3S8933 Microcontroller
Register 22: Sleep Mode Clock Gating Control Register 1 (SCGC1), offset
0x114
This register controls the clock gating logic. Each bit controls a clock enable for a given interface,
function, or unit. If set, the unit receives a clock and functions. Otherwise, the unit is unclocked and
disabled (saving power). If the unit is unclocked, reads or writes to the unit will generate a bus fault.
The reset state of these bits is 0 (unclocked) unless otherwise noted, so that all functional units are
disabled. It is the responsibility of software to enable the ports necessary for the application. Note
that these registers may contain more bits than there are interfaces, functions, or units to control.
This is to assure reasonable code compatibility with other family and future parts. RCGC1 is the
clock configuration register for running operation, SCGC1 for Sleep operation, and DCGC1 for
Deep-Sleep operation. Setting the ACG bit in the Run-Mode Clock Configuration (RCC) register
specifies that the system uses sleep modes.
Sleep Mode Clock Gating Control Register 1 (SCGC1)
Base 0x400F.E000
Offset 0x114
Type R/W, reset 0x00000000
31 30 29 28 27 26 25 24 23 22 21 20 19 18 17 16
reserved COMP2 COMP1 COMP0 reserved TIMER3 TIMER2 TIMER1 TIMER0
Type RO RO RO RO RO R/W R/W R/W RO RO RO RO R/W R/W R/W R/W
Reset 0 0 0 0 0 0 0 0 0 0 0 0 0 0 0 0
15 14 13 12 11 10 9 8 7 6 5 4 3 2 1 0
reserved I2C0 reserved SSI0 reserved UART1 UART0
Type RO RO RO R/W RO RO RO RO RO RO RO R/W RO RO R/W R/W
Reset 0 0 0 0 0 0 0 0 0 0 0 0 0 0 0 0
Bit/Field Name Type Reset Description
Software should not rely on the value of a reserved bit. To provide
compatibility with future products, the value of a reserved bit should be
preserved across a read-modify-write operation.
31:27 reserved RO 0
Analog Comparator 2 Clock Gating
This bit controls the clock gating for analog comparator 2. If set, the unit
receives a clock and functions. Otherwise, the unit is unclocked and
disabled. If the unit is unclocked, reads or writes to the unit will generate
a bus fault.
26 COMP2 R/W 0
Analog Comparator 1 Clock Gating
This bit controls the clock gating for analog comparator 1. If set, the unit
receives a clock and functions. Otherwise, the unit is unclocked and
disabled. If the unit is unclocked, reads or writes to the unit will generate
a bus fault.
25 COMP1 R/W 0
Analog Comparator 0 Clock Gating
This bit controls the clock gating for analog comparator 0. If set, the unit
receives a clock and functions. Otherwise, the unit is unclocked and
disabled. If the unit is unclocked, reads or writes to the unit will generate
a bus fault.
24 COMP0 R/W 0
Software should not rely on the value of a reserved bit. To provide
compatibility with future products, the value of a reserved bit should be
preserved across a read-modify-write operation.
23:20 reserved RO 0
102 March 17, 2008
Preliminary
System Control
Bit/Field Name Type Reset Description
Timer 3 Clock Gating Control
This bit controls the clock gating for General-Purpose Timer module 3.
If set, the unit receives a clock and functions. Otherwise, the unit is
unclocked and disabled. If the unit is unclocked, reads or writes to the
unit will generate a bus fault.
19 TIMER3 R/W 0
Timer 2 Clock Gating Control
This bit controls the clock gating for General-Purpose Timer module 2.
If set, the unit receives a clock and functions. Otherwise, the unit is
unclocked and disabled. If the unit is unclocked, reads or writes to the
unit will generate a bus fault.
18 TIMER2 R/W 0
Timer 1 Clock Gating Control
This bit controls the clock gating for General-Purpose Timer module 1.
If set, the unit receives a clock and functions. Otherwise, the unit is
unclocked and disabled. If the unit is unclocked, reads or writes to the
unit will generate a bus fault.
17 TIMER1 R/W 0
Timer 0 Clock Gating Control
This bit controls the clock gating for General-Purpose Timer module 0.
If set, the unit receives a clock and functions. Otherwise, the unit is
unclocked and disabled. If the unit is unclocked, reads or writes to the
unit will generate a bus fault.
16 TIMER0 R/W 0
Software should not rely on the value of a reserved bit. To provide
compatibility with future products, the value of a reserved bit should be
preserved across a read-modify-write operation.
15:13 reserved RO 0
I2C0 Clock Gating Control
This bit controls the clock gating for I2C module 0. If set, the unit receives
a clock and functions. Otherwise, the unit is unclocked and disabled. If
the unit is unclocked, reads or writes to the unit will generate a bus fault.
12 I2C0 R/W 0
Software should not rely on the value of a reserved bit. To provide
compatibility with future products, the value of a reserved bit should be
preserved across a read-modify-write operation.
11:5 reserved RO 0
SSI0 Clock Gating Control
This bit controls the clock gating for SSI module 0. If set, the unit receives
a clock and functions. Otherwise, the unit is unclocked and disabled. If
the unit is unclocked, reads or writes to the unit will generate a bus fault.
4 SSI0 R/W 0
Software should not rely on the value of a reserved bit. To provide
compatibility with future products, the value of a reserved bit should be
preserved across a read-modify-write operation.
3:2 reserved RO 0
UART1 Clock Gating Control
This bit controls the clock gating for UART module 1. If set, the unit
receives a clock and functions. Otherwise, the unit is unclocked and
disabled. If the unit is unclocked, reads or writes to the unit will generate
a bus fault.
1 UART1 R/W 0
March 17, 2008 103
Preliminary
LM3S8933 Microcontroller
Bit/Field Name Type Reset Description
UART0 Clock Gating Control
This bit controls the clock gating for UART module 0. If set, the unit
receives a clock and functions. Otherwise, the unit is unclocked and
disabled. If the unit is unclocked, reads or writes to the unit will generate
a bus fault.
0 UART0 R/W 0
104 March 17, 2008
Preliminary
System Control
Register 23: Deep Sleep Mode Clock Gating Control Register 1 (DCGC1),
offset 0x124
This register controls the clock gating logic. Each bit controls a clock enable for a given interface,
function, or unit. If set, the unit receives a clock and functions. Otherwise, the unit is unclocked and
disabled (saving power). If the unit is unclocked, reads or writes to the unit will generate a bus fault.
The reset state of these bits is 0 (unclocked) unless otherwise noted, so that all functional units are
disabled. It is the responsibility of software to enable the ports necessary for the application. Note
that these registers may contain more bits than there are interfaces, functions, or units to control.
This is to assure reasonable code compatibility with other family and future parts. RCGC1 is the
clock configuration register for running operation, SCGC1 for Sleep operation, and DCGC1 for
Deep-Sleep operation. Setting the ACG bit in the Run-Mode Clock Configuration (RCC) register
specifies that the system uses sleep modes.
Deep Sleep Mode Clock Gating Control Register 1 (DCGC1)
Base 0x400F.E000
Offset 0x124
Type R/W, reset 0x00000000
31 30 29 28 27 26 25 24 23 22 21 20 19 18 17 16
reserved COMP2 COMP1 COMP0 reserved TIMER3 TIMER2 TIMER1 TIMER0
Type RO RO RO RO RO R/W R/W R/W RO RO RO RO R/W R/W R/W R/W
Reset 0 0 0 0 0 0 0 0 0 0 0 0 0 0 0 0
15 14 13 12 11 10 9 8 7 6 5 4 3 2 1 0
reserved I2C0 reserved SSI0 reserved UART1 UART0
Type RO RO RO R/W RO RO RO RO RO RO RO R/W RO RO R/W R/W
Reset 0 0 0 0 0 0 0 0 0 0 0 0 0 0 0 0
Bit/Field Name Type Reset Description
Software should not rely on the value of a reserved bit. To provide
compatibility with future products, the value of a reserved bit should be
preserved across a read-modify-write operation.
31:27 reserved RO 0
Analog Comparator 2 Clock Gating
This bit controls the clock gating for analog comparator 2. If set, the unit
receives a clock and functions. Otherwise, the unit is unclocked and
disabled. If the unit is unclocked, reads or writes to the unit will generate
a bus fault.
26 COMP2 R/W 0
Analog Comparator 1 Clock Gating
This bit controls the clock gating for analog comparator 1. If set, the unit
receives a clock and functions. Otherwise, the unit is unclocked and
disabled. If the unit is unclocked, reads or writes to the unit will generate
a bus fault.
25 COMP1 R/W 0
Analog Comparator 0 Clock Gating
This bit controls the clock gating for analog comparator 0. If set, the unit
receives a clock and functions. Otherwise, the unit is unclocked and
disabled. If the unit is unclocked, reads or writes to the unit will generate
a bus fault.
24 COMP0 R/W 0
Software should not rely on the value of a reserved bit. To provide
compatibility with future products, the value of a reserved bit should be
preserved across a read-modify-write operation.
23:20 reserved RO 0
March 17, 2008 105
Preliminary
LM3S8933 Microcontroller
Bit/Field Name Type Reset Description
Timer 3 Clock Gating Control
This bit controls the clock gating for General-Purpose Timer module 3.
If set, the unit receives a clock and functions. Otherwise, the unit is
unclocked and disabled. If the unit is unclocked, reads or writes to the
unit will generate a bus fault.
19 TIMER3 R/W 0
Timer 2 Clock Gating Control
This bit controls the clock gating for General-Purpose Timer module 2.
If set, the unit receives a clock and functions. Otherwise, the unit is
unclocked and disabled. If the unit is unclocked, reads or writes to the
unit will generate a bus fault.
18 TIMER2 R/W 0
Timer 1 Clock Gating Control
This bit controls the clock gating for General-Purpose Timer module 1.
If set, the unit receives a clock and functions. Otherwise, the unit is
unclocked and disabled. If the unit is unclocked, reads or writes to the
unit will generate a bus fault.
17 TIMER1 R/W 0
Timer 0 Clock Gating Control
This bit controls the clock gating for General-Purpose Timer module 0.
If set, the unit receives a clock and functions. Otherwise, the unit is
unclocked and disabled. If the unit is unclocked, reads or writes to the
unit will generate a bus fault.
16 TIMER0 R/W 0
Software should not rely on the value of a reserved bit. To provide
compatibility with future products, the value of a reserved bit should be
preserved across a read-modify-write operation.
15:13 reserved RO 0
I2C0 Clock Gating Control
This bit controls the clock gating for I2C module 0. If set, the unit receives
a clock and functions. Otherwise, the unit is unclocked and disabled. If
the unit is unclocked, reads or writes to the unit will generate a bus fault.
12 I2C0 R/W 0
Software should not rely on the value of a reserved bit. To provide
compatibility with future products, the value of a reserved bit should be
preserved across a read-modify-write operation.
11:5 reserved RO 0
SSI0 Clock Gating Control
This bit controls the clock gating for SSI module 0. If set, the unit receives
a clock and functions. Otherwise, the unit is unclocked and disabled. If
the unit is unclocked, reads or writes to the unit will generate a bus fault.
4 SSI0 R/W 0
Software should not rely on the value of a reserved bit. To provide
compatibility with future products, the value of a reserved bit should be
preserved across a read-modify-write operation.
3:2 reserved RO 0
UART1 Clock Gating Control
This bit controls the clock gating for UART module 1. If set, the unit
receives a clock and functions. Otherwise, the unit is unclocked and
disabled. If the unit is unclocked, reads or writes to the unit will generate
a bus fault.
1 UART1 R/W 0
106 March 17, 2008
Preliminary
System Control
Bit/Field Name Type Reset Description
UART0 Clock Gating Control
This bit controls the clock gating for UART module 0. If set, the unit
receives a clock and functions. Otherwise, the unit is unclocked and
disabled. If the unit is unclocked, reads or writes to the unit will generate
a bus fault.
0 UART0 R/W 0
March 17, 2008 107
Preliminary
LM3S8933 Microcontroller
Register 24: Run Mode Clock Gating Control Register 2 (RCGC2), offset 0x108
This register controls the clock gating logic. Each bit controls a clock enable for a given interface,
function, or unit. If set, the unit receives a clock and functions. Otherwise, the unit is unclocked and
disabled (saving power). If the unit is unclocked, reads or writes to the unit will generate a bus fault.
The reset state of these bits is 0 (unclocked) unless otherwise noted, so that all functional units are
disabled. It is the responsibility of software to enable the ports necessary for the application. Note
that these registers may contain more bits than there are interfaces, functions, or units to control.
This is to assure reasonable code compatibility with other family and future parts. RCGC2 is the
clock configuration register for running operation, SCGC2 for Sleep operation, and DCGC2 for
Deep-Sleep operation. Setting the ACG bit in the Run-Mode Clock Configuration (RCC) register
specifies that the system uses sleep modes.
Run Mode Clock Gating Control Register 2 (RCGC2)
Base 0x400F.E000
Offset 0x108
Type R/W, reset 0x00000000
31 30 29 28 27 26 25 24 23 22 21 20 19 18 17 16
reserved EPHY0 reserved EMAC0 reserved
Type RO R/W RO R/W RO RO RO RO RO RO RO RO RO RO RO RO
Reset 0 0 0 0 0 0 0 0 0 0 0 0 0 0 0 0
15 14 13 12 11 10 9 8 7 6 5 4 3 2 1 0
reserved GPIOG GPIOF GPIOE GPIOD GPIOC GPIOB GPIOA
Type RO RO RO RO RO RO RO RO RO R/W R/W R/W R/W R/W R/W R/W
Reset 0 0 0 0 0 0 0 0 0 0 0 0 0 0 0 0
Bit/Field Name Type Reset Description
Software should not rely on the value of a reserved bit. To provide
compatibility with future products, the value of a reserved bit should be
preserved across a read-modify-write operation.
31 reserved RO 0
PHY0 Clock Gating Control
This bit controls the clock gating for Ethernet PHY unit 0. If set, the unit
receives a clock and functions. Otherwise, the unit is unclocked and
disabled. If the unit is unclocked, reads or writes to the unit will generate
a bus fault.
30 EPHY0 R/W 0
Software should not rely on the value of a reserved bit. To provide
compatibility with future products, the value of a reserved bit should be
preserved across a read-modify-write operation.
29 reserved RO 0
MAC0 Clock Gating Control
This bit controls the clock gating for Ethernet MAC unit 0. If set, the unit
receives a clock and functions. Otherwise, the unit is unclocked and
disabled. If the unit is unclocked, reads or writes to the unit will generate
a bus fault.
28 EMAC0 R/W 0
Software should not rely on the value of a reserved bit. To provide
compatibility with future products, the value of a reserved bit should be
preserved across a read-modify-write operation.
27:7 reserved RO 0
Port G Clock Gating Control
This bit controls the clock gating for Port G. If set, the unit receives a
clock and functions. Otherwise, the unit is unclocked and disabled. If
the unit is unclocked, reads or writes to the unit will generate a bus fault.
6 GPIOG R/W 0
108 March 17, 2008
Preliminary
System Control
Bit/Field Name Type Reset Description
Port F Clock Gating Control
This bit controls the clock gating for Port F. If set, the unit receives a
clock and functions. Otherwise, the unit is unclocked and disabled. If
the unit is unclocked, reads or writes to the unit will generate a bus fault.
5 GPIOF R/W 0
Port E Clock Gating Control
This bit controls the clock gating for Port E. If set, the unit receives a
clock and functions. Otherwise, the unit is unclocked and disabled. If
the unit is unclocked, reads or writes to the unit will generate a bus fault.
4 GPIOE R/W 0
Port D Clock Gating Control
This bit controls the clock gating for Port D. If set, the unit receives a
clock and functions. Otherwise, the unit is unclocked and disabled. If
the unit is unclocked, reads or writes to the unit will generate a bus fault.
3 GPIOD R/W 0
Port C Clock Gating Control
This bit controls the clock gating for Port C. If set, the unit receives a
clock and functions. Otherwise, the unit is unclocked and disabled. If
the unit is unclocked, reads or writes to the unit will generate a bus fault.
2 GPIOC R/W 0
Port B Clock Gating Control
This bit controls the clock gating for Port B. If set, the unit receives a
clock and functions. Otherwise, the unit is unclocked and disabled. If
the unit is unclocked, reads or writes to the unit will generate a bus fault.
1 GPIOB R/W 0
Port A Clock Gating Control
This bit controls the clock gating for Port A. If set, the unit receives a
clock and functions. Otherwise, the unit is unclocked and disabled. If
the unit is unclocked, reads or writes to the unit will generate a bus fault.
0 GPIOA R/W 0
March 17, 2008 109
Preliminary
LM3S8933 Microcontroller
Register 25: Sleep Mode Clock Gating Control Register 2 (SCGC2), offset
0x118
This register controls the clock gating logic. Each bit controls a clock enable for a given interface,
function, or unit. If set, the unit receives a clock and functions. Otherwise, the unit is unclocked and
disabled (saving power). If the unit is unclocked, reads or writes to the unit will generate a bus fault.
The reset state of these bits is 0 (unclocked) unless otherwise noted, so that all functional units are
disabled. It is the responsibility of software to enable the ports necessary for the application. Note
that these registers may contain more bits than there are interfaces, functions, or units to control.
This is to assure reasonable code compatibility with other family and future parts. RCGC2 is the
clock configuration register for running operation, SCGC2 for Sleep operation, and DCGC2 for
Deep-Sleep operation. Setting the ACG bit in the Run-Mode Clock Configuration (RCC) register
specifies that the system uses sleep modes.
Sleep Mode Clock Gating Control Register 2 (SCGC2)
Base 0x400F.E000
Offset 0x118
Type R/W, reset 0x00000000
31 30 29 28 27 26 25 24 23 22 21 20 19 18 17 16
reserved EPHY0 reserved EMAC0 reserved
Type RO R/W RO R/W RO RO RO RO RO RO RO RO RO RO RO RO
Reset 0 0 0 0 0 0 0 0 0 0 0 0 0 0 0 0
15 14 13 12 11 10 9 8 7 6 5 4 3 2 1 0
reserved GPIOG GPIOF GPIOE GPIOD GPIOC GPIOB GPIOA
Type RO RO RO RO RO RO RO RO RO R/W R/W R/W R/W R/W R/W R/W
Reset 0 0 0 0 0 0 0 0 0 0 0 0 0 0 0 0
Bit/Field Name Type Reset Description
Software should not rely on the value of a reserved bit. To provide
compatibility with future products, the value of a reserved bit should be
preserved across a read-modify-write operation.
31 reserved RO 0
PHY0 Clock Gating Control
This bit controls the clock gating for Ethernet PHY unit 0. If set, the unit
receives a clock and functions. Otherwise, the unit is unclocked and
disabled. If the unit is unclocked, reads or writes to the unit will generate
a bus fault.
30 EPHY0 R/W 0
Software should not rely on the value of a reserved bit. To provide
compatibility with future products, the value of a reserved bit should be
preserved across a read-modify-write operation.
29 reserved RO 0
MAC0 Clock Gating Control
This bit controls the clock gating for Ethernet MAC unit 0. If set, the unit
receives a clock and functions. Otherwise, the unit is unclocked and
disabled. If the unit is unclocked, reads or writes to the unit will generate
a bus fault.
28 EMAC0 R/W 0
Software should not rely on the value of a reserved bit. To provide
compatibility with future products, the value of a reserved bit should be
preserved across a read-modify-write operation.
27:7 reserved RO 0
110 March 17, 2008
Preliminary
System Control
Bit/Field Name Type Reset Description
Port G Clock Gating Control
This bit controls the clock gating for Port G. If set, the unit receives a
clock and functions. Otherwise, the unit is unclocked and disabled. If
the unit is unclocked, reads or writes to the unit will generate a bus fault.
6 GPIOG R/W 0
Port F Clock Gating Control
This bit controls the clock gating for Port F. If set, the unit receives a
clock and functions. Otherwise, the unit is unclocked and disabled. If
the unit is unclocked, reads or writes to the unit will generate a bus fault.
5 GPIOF R/W 0
Port E Clock Gating Control
This bit controls the clock gating for Port E. If set, the unit receives a
clock and functions. Otherwise, the unit is unclocked and disabled. If
the unit is unclocked, reads or writes to the unit will generate a bus fault.
4 GPIOE R/W 0
Port D Clock Gating Control
This bit controls the clock gating for Port D. If set, the unit receives a
clock and functions. Otherwise, the unit is unclocked and disabled. If
the unit is unclocked, reads or writes to the unit will generate a bus fault.
3 GPIOD R/W 0
Port C Clock Gating Control
This bit controls the clock gating for Port C. If set, the unit receives a
clock and functions. Otherwise, the unit is unclocked and disabled. If
the unit is unclocked, reads or writes to the unit will generate a bus fault.
2 GPIOC R/W 0
Port B Clock Gating Control
This bit controls the clock gating for Port B. If set, the unit receives a
clock and functions. Otherwise, the unit is unclocked and disabled. If
the unit is unclocked, reads or writes to the unit will generate a bus fault.
1 GPIOB R/W 0
Port A Clock Gating Control
This bit controls the clock gating for Port A. If set, the unit receives a
clock and functions. Otherwise, the unit is unclocked and disabled. If
the unit is unclocked, reads or writes to the unit will generate a bus fault.
0 GPIOA R/W 0
March 17, 2008 111
Preliminary
LM3S8933 Microcontroller
Register 26: Deep Sleep Mode Clock Gating Control Register 2 (DCGC2),
offset 0x128
This register controls the clock gating logic. Each bit controls a clock enable for a given interface,
function, or unit. If set, the unit receives a clock and functions. Otherwise, the unit is unclocked and
disabled (saving power). If the unit is unclocked, reads or writes to the unit will generate a bus fault.
The reset state of these bits is 0 (unclocked) unless otherwise noted, so that all functional units are
disabled. It is the responsibility of software to enable the ports necessary for the application. Note
that these registers may contain more bits than there are interfaces, functions, or units to control.
This is to assure reasonable code compatibility with other family and future parts. RCGC2 is the
clock configuration register for running operation, SCGC2 for Sleep operation, and DCGC2 for
Deep-Sleep operation. Setting the ACG bit in the Run-Mode Clock Configuration (RCC) register
specifies that the system uses sleep modes.
Deep Sleep Mode Clock Gating Control Register 2 (DCGC2)
Base 0x400F.E000
Offset 0x128
Type R/W, reset 0x00000000
31 30 29 28 27 26 25 24 23 22 21 20 19 18 17 16
reserved EPHY0 reserved EMAC0 reserved
Type RO R/W RO R/W RO RO RO RO RO RO RO RO RO RO RO RO
Reset 0 0 0 0 0 0 0 0 0 0 0 0 0 0 0 0
15 14 13 12 11 10 9 8 7 6 5 4 3 2 1 0
reserved GPIOG GPIOF GPIOE GPIOD GPIOC GPIOB GPIOA
Type RO RO RO RO RO RO RO RO RO R/W R/W R/W R/W R/W R/W R/W
Reset 0 0 0 0 0 0 0 0 0 0 0 0 0 0 0 0
Bit/Field Name Type Reset Description
Software should not rely on the value of a reserved bit. To provide
compatibility with future products, the value of a reserved bit should be
preserved across a read-modify-write operation.
31 reserved RO 0
PHY0 Clock Gating Control
This bit controls the clock gating for Ethernet PHY unit 0. If set, the unit
receives a clock and functions. Otherwise, the unit is unclocked and
disabled. If the unit is unclocked, reads or writes to the unit will generate
a bus fault.
30 EPHY0 R/W 0
Software should not rely on the value of a reserved bit. To provide
compatibility with future products, the value of a reserved bit should be
preserved across a read-modify-write operation.
29 reserved RO 0
MAC0 Clock Gating Control
This bit controls the clock gating for Ethernet MAC unit 0. If set, the unit
receives a clock and functions. Otherwise, the unit is unclocked and
disabled. If the unit is unclocked, reads or writes to the unit will generate
a bus fault.
28 EMAC0 R/W 0
Software should not rely on the value of a reserved bit. To provide
compatibility with future products, the value of a reserved bit should be
preserved across a read-modify-write operation.
27:7 reserved RO 0
112 March 17, 2008
Preliminary
System Control
Bit/Field Name Type Reset Description
Port G Clock Gating Control
This bit controls the clock gating for Port G. If set, the unit receives a
clock and functions. Otherwise, the unit is unclocked and disabled. If
the unit is unclocked, reads or writes to the unit will generate a bus fault.
6 GPIOG R/W 0
Port F Clock Gating Control
This bit controls the clock gating for Port F. If set, the unit receives a
clock and functions. Otherwise, the unit is unclocked and disabled. If
the unit is unclocked, reads or writes to the unit will generate a bus fault.
5 GPIOF R/W 0
Port E Clock Gating Control
This bit controls the clock gating for Port E. If set, the unit receives a
clock and functions. Otherwise, the unit is unclocked and disabled. If
the unit is unclocked, reads or writes to the unit will generate a bus fault.
4 GPIOE R/W 0
Port D Clock Gating Control
This bit controls the clock gating for Port D. If set, the unit receives a
clock and functions. Otherwise, the unit is unclocked and disabled. If
the unit is unclocked, reads or writes to the unit will generate a bus fault.
3 GPIOD R/W 0
Port C Clock Gating Control
This bit controls the clock gating for Port C. If set, the unit receives a
clock and functions. Otherwise, the unit is unclocked and disabled. If
the unit is unclocked, reads or writes to the unit will generate a bus fault.
2 GPIOC R/W 0
Port B Clock Gating Control
This bit controls the clock gating for Port B. If set, the unit receives a
clock and functions. Otherwise, the unit is unclocked and disabled. If
the unit is unclocked, reads or writes to the unit will generate a bus fault.
1 GPIOB R/W 0
Port A Clock Gating Control
This bit controls the clock gating for Port A. If set, the unit receives a
clock and functions. Otherwise, the unit is unclocked and disabled. If
the unit is unclocked, reads or writes to the unit will generate a bus fault.
0 GPIOA R/W 0
March 17, 2008 113
Preliminary
LM3S8933 Microcontroller
Register 27: Software Reset Control 0 (SRCR0), offset 0x040
Writes to this register are masked by the bits in the Device Capabilities 1 (DC1) register.
Software Reset Control 0 (SRCR0)
Base 0x400F.E000
Offset 0x040
Type R/W, reset 0x00000000
31 30 29 28 27 26 25 24 23 22 21 20 19 18 17 16
reserved CAN0 reserved ADC
Type RO RO RO RO RO RO RO R/W RO RO RO RO RO RO RO R/W
Reset 0 0 0 0 0 0 0 0 0 0 0 0 0 0 0 0
15 14 13 12 11 10 9 8 7 6 5 4 3 2 1 0
reserved HIB reserved WDT reserved
Type RO RO RO RO RO RO RO RO RO R/W RO RO R/W RO RO RO
Reset 0 0 0 0 0 0 0 0 0 0 0 0 0 0 0 0
Bit/Field Name Type Reset Description
Software should not rely on the value of a reserved bit. To provide
compatibility with future products, the value of a reserved bit should be
preserved across a read-modify-write operation.
31:25 reserved RO 0
CAN0 Reset Control
Reset control for CAN unit 0.
24 CAN0 R/W 0
Software should not rely on the value of a reserved bit. To provide
compatibility with future products, the value of a reserved bit should be
preserved across a read-modify-write operation.
23:17 reserved RO 0
ADC0 Reset Control
Reset control for SAR ADC module 0.
16 ADC R/W 0
Software should not rely on the value of a reserved bit. To provide
compatibility with future products, the value of a reserved bit should be
preserved across a read-modify-write operation.
15:7 reserved RO 0
HIB Reset Control
Reset control for the Hibernation module.
6 HIB R/W 0
Software should not rely on the value of a reserved bit. To provide
compatibility with future products, the value of a reserved bit should be
preserved across a read-modify-write operation.
5:4 reserved RO 0
WDT Reset Control
Reset control for Watchdog unit.
3 WDT R/W 0
Software should not rely on the value of a reserved bit. To provide
compatibility with future products, the value of a reserved bit should be
preserved across a read-modify-write operation.
2:0 reserved RO 0
114 March 17, 2008
Preliminary
System Control
Register 28: Software Reset Control 1 (SRCR1), offset 0x044
Writes to this register are masked by the bits in the Device Capabilities 2 (DC2) register.
Software Reset Control 1 (SRCR1)
Base 0x400F.E000
Offset 0x044
Type R/W, reset 0x00000000
31 30 29 28 27 26 25 24 23 22 21 20 19 18 17 16
reserved COMP2 COMP1 COMP0 reserved TIMER3 TIMER2 TIMER1 TIMER0
Type RO RO RO RO RO R/W R/W R/W RO RO RO RO R/W R/W R/W R/W
Reset 0 0 0 0 0 0 0 0 0 0 0 0 0 0 0 0
15 14 13 12 11 10 9 8 7 6 5 4 3 2 1 0
reserved I2C0 reserved SSI0 reserved UART1 UART0
Type RO RO RO R/W RO RO RO RO RO RO RO R/W RO RO R/W R/W
Reset 0 0 0 0 0 0 0 0 0 0 0 0 0 0 0 0
Bit/Field Name Type Reset Description
Software should not rely on the value of a reserved bit. To provide
compatibility with future products, the value of a reserved bit should be
preserved across a read-modify-write operation.
31:27 reserved RO 0
Analog Comp 2 Reset Control
Reset control for analog comparator 2.
26 COMP2 R/W 0
Analog Comp 1 Reset Control
Reset control for analog comparator 1.
25 COMP1 R/W 0
Analog Comp 0 Reset Control
Reset control for analog comparator 0.
24 COMP0 R/W 0
Software should not rely on the value of a reserved bit. To provide
compatibility with future products, the value of a reserved bit should be
preserved across a read-modify-write operation.
23:20 reserved RO 0
Timer 3 Reset Control
Reset control for General-Purpose Timer module 3.
19 TIMER3 R/W 0
Timer 2 Reset Control
Reset control for General-Purpose Timer module 2.
18 TIMER2 R/W 0
Timer 1 Reset Control
Reset control for General-Purpose Timer module 1.
17 TIMER1 R/W 0
Timer 0 Reset Control
Reset control for General-Purpose Timer module 0.
16 TIMER0 R/W 0
Software should not rely on the value of a reserved bit. To provide
compatibility with future products, the value of a reserved bit should be
preserved across a read-modify-write operation.
15:13 reserved RO 0
I2C0 Reset Control
Reset control for I2C unit 0.
12 I2C0 R/W 0
March 17, 2008 115
Preliminary
LM3S8933 Microcontroller
Bit/Field Name Type Reset Description
Software should not rely on the value of a reserved bit. To provide
compatibility with future products, the value of a reserved bit should be
preserved across a read-modify-write operation.
11:5 reserved RO 0
SSI0 Reset Control
Reset control for SSI unit 0.
4 SSI0 R/W 0
Software should not rely on the value of a reserved bit. To provide
compatibility with future products, the value of a reserved bit should be
preserved across a read-modify-write operation.
3:2 reserved RO 0
UART1 Reset Control
Reset control for UART unit 1.
1 UART1 R/W 0
UART0 Reset Control
Reset control for UART unit 0.
0 UART0 R/W 0
116 March 17, 2008
Preliminary
System Control
Register 29: Software Reset Control 2 (SRCR2), offset 0x048
Writes to this register are masked by the bits in the Device Capabilities 4 (DC4) register.
Software Reset Control 2 (SRCR2)
Base 0x400F.E000
Offset 0x048
Type R/W, reset 0x00000000
31 30 29 28 27 26 25 24 23 22 21 20 19 18 17 16
reserved EPHY0 reserved EMAC0 reserved
Type RO R/W RO R/W RO RO RO RO RO RO RO RO RO RO RO RO
Reset 0 0 0 0 0 0 0 0 0 0 0 0 0 0 0 0
15 14 13 12 11 10 9 8 7 6 5 4 3 2 1 0
reserved GPIOG GPIOF GPIOE GPIOD GPIOC GPIOB GPIOA
Type RO RO RO RO RO RO RO RO RO R/W R/W R/W R/W R/W R/W R/W
Reset 0 0 0 0 0 0 0 0 0 0 0 0 0 0 0 0
Bit/Field Name Type Reset Description
Software should not rely on the value of a reserved bit. To provide
compatibility with future products, the value of a reserved bit should be
preserved across a read-modify-write operation.
31 reserved RO 0
PHY0 Reset Control
Reset control for Ethernet PHY unit 0.
30 EPHY0 R/W 0
Software should not rely on the value of a reserved bit. To provide
compatibility with future products, the value of a reserved bit should be
preserved across a read-modify-write operation.
29 reserved RO 0
MAC0 Reset Control
Reset control for Ethernet MAC unit 0.
28 EMAC0 R/W 0
Software should not rely on the value of a reserved bit. To provide
compatibility with future products, the value of a reserved bit should be
preserved across a read-modify-write operation.
27:7 reserved RO 0
Port G Reset Control
Reset control for GPIO Port G.
6 GPIOG R/W 0
Port F Reset Control
Reset control for GPIO Port F.
5 GPIOF R/W 0
Port E Reset Control
Reset control for GPIO Port E.
4 GPIOE R/W 0
Port D Reset Control
Reset control for GPIO Port D.
3 GPIOD R/W 0
Port C Reset Control
Reset control for GPIO Port C.
2 GPIOC R/W 0
Port B Reset Control
Reset control for GPIO Port B.
1 GPIOB R/W 0
March 17, 2008 117
Preliminary
LM3S8933 Microcontroller
Bit/Field Name Type Reset Description
Port A Reset Control
Reset control for GPIO Port A.
0 GPIOA R/W 0
118 March 17, 2008
Preliminary
System Control
7 Hibernation Module
The Hibernation Module manages removal and restoration of power to the rest of the microcontroller
to provide a means for reducing power consumption. When the processor and peripherals are idle,
power can be completely removed with only the Hibernation Module remaining powered. Power
can be restored based on an external signal, or at a certain time using the built-in real-time clock
(RTC). The Hibernation module can be independently supplied from a battery or an auxiliary power
supply.
The Hibernation module has the following features:
■ Power-switching logic to discrete external regulator
■ Dedicated pin for waking from an external signal
■ Low-battery detection, signaling, and interrupt generation
■ 32-bit real-time counter (RTC)
■ Two 32-bit RTC match registers for timed wake-up and interrupt generation
■ Clock source from a 32.768-kHz external oscillator or a 4.194304-MHz crystal
■ RTC predivider trim for making fine adjustments to the clock rate
■ 64 32-bit words of non-volatile memory
■ Programmable interrupts for RTC match, external wake, and low battery events
March 17, 2008 119
Preliminary
LM3S8933 Microcontroller
7.1 Block Diagram
Figure 7-1. Hibernation Module Block Diagram
HIBIM
HIBRIS
HIBMIS
HIBIC
HIBRTCT
Pre-Divider
/128
XOSC0
XOSC1
HIBCTL.CLK32EN
HIBCTL.CLKSEL
HIBRTCC
HIBRTCLD
HIBRTCM0
HIBRTCM1
RTC
Interrupts
Power
Sequence
Logic
MATCH0/1
WAKE
Interrupts
to CPU
Low Battery
Detect
LOWBAT
VDD
VBAT
HIB
HIBCTL.LOWBATEN HIBCTL.PWRCUT
HIBCTL.EXTWEN
HIBCTL.RTCWEN
HIBCTL.VABORT
Non-Volatile
Memory
HIBDATA
7.2 Functional Description
The Hibernation module controls the power to the processor with an enable signal (HIB) that signals
an external voltage regulator to turn off. The Hibernation module power is determined dynamically.
The supply voltage of the Hibernation module is the larger of the main voltage source (VDD) or the
battery/auxilliary voltage source (VBAT). A voting circuit indicates the larger and an internal power
switch selects the appropriate voltage source. The Hibernation module also has a separate clock
source to maintain a real-time clock (RTC). Once in hibernation, the module signals an external
voltage regulator to turn back on the power when an external pin (WAKE) is asserted, or when the
internal RTC reaches a certain value. The Hibernation module can also detect when the battery
voltage is low, and optionally prevent hibernation when this occurs.
Power-up from a power cut to code execution is defined as the regulator turn-on time (specified at
tHIB_TO_VDD maximum) plus the normal chip POR (see “Hibernation Module” on page 544).
7.2.1 Register Access Timing
Because the Hibernation module has an independent clocking domain, certain registers must be
written only with a timing gap between accesses. The delay time is tHIB_REG_WRITE, therefore software
must guarantee that a delay of tHIB_REG_WRITE is inserted between back-to-back writes to certain
120 March 17, 2008
Preliminary
Hibernation Module
Hibernation registers, or between a write followed by a read to those same registers. There is no
restriction on timing for back-to-back reads from the Hibernation module.
7.2.2 Clock Source
The Hibernation module must be clocked by an external source, even if the RTC feature will not be
used. An external oscillator or crystal can be used for this purpose. To use a crystal, a 4.194304-MHz
crystal is connected to the XOSC0 and XOSC1 pins. This clock signal is divided by 128 internally to
produce the 32.768-kHz clock reference. To use a more precise clock source, a 32.768-kHz oscillator
can be connected to the XOSC0 pin.
The clock source is enabled by setting the CLK32EN bit of the HIBCTL register. The type of clock
source is selected by setting the CLKSEL bit to 0 for a 4.194304-MHz clock source, and to 1 for a
32.768-kHz clock source. If the bit is set to 0, the input clock is divided by 128, resulting in a
32.768-kHz clock source. If a crystal is used for the clock source, the software must leave a delay
of tXOSC_SETTLE after setting the CLK32EN bit and before any other accesses to the Hibernation
module registers. The delay allows the crystal to power up and stabilize. If an oscillator is used for
the clock source, no delay is needed.
7.2.3 Battery Management
The Hibernation module can be independently powered by a battery or an auxiliary power source.
The module can monitor the voltage level of the battery and detect when the voltage drops below
2.35 V. When this happens, an interrupt can be generated. The module also can be configured so
that it will not go into Hibernate mode if the battery voltage drops below this threshold.
Note that the Hibernation module draws power from whichever source (VBAT or VDD) has the higher
voltage. Therefore, it is important to design the circuit to ensure that VDD is higher that VBAT under
nominal conditions or else the Hibernation module draws power from the battery even when VDD
is available.
The Hibernation module can be configured to detect a low battery condition by setting the LOWBATEN
bit of the HIBCTL register. In this configuration, the LOWBAT bit of the HIBRIS register will be set
when the battery level is low. If the VABORT bit is also set, then the module is prevented from entering
Hibernation mode when a low battery is detected. The module can also be configured to generate
an interrupt for the low-battery condition (see “Interrupts and Status” on page 122).
7.2.4 Real-Time Clock
The Hibernation module includes a 32-bit counter that increments once per second with a proper
clock source and configuration (see “Clock Source” on page 121). The 32.768-kHz clock signal is
fed into a predivider register which counts down the 32.768-kHz clock ticks to achieve a once per
second clock rate for the RTC. The rate can be adjusted to compensate for inaccuracies in the clock
source by using the predivider trim register, HIBRTCT. This register has a nominal value of 0x7FFF,
and is used for one second out of every 64 seconds to divide the input clock. This allows the software
to make fine corrections to the clock rate by adjusting the predivider trim register up or down from
0x7FFF. The predivider trim should be adjusted up from 0x7FFF in order to slow down the RTC
rate, and down from 0x7FFF in order to speed up the RTC rate.
The Hibernation module includes two 32-bit match registers that are compared to the value of the
RTC counter. The match registers can be used to wake the processor from hibernation mode, or
to generate an interrupt to the processor if it is not in hibernation.
The RTC must be enabled with the RTCEN bit of the HIBCTL register. The value of the RTC can be
set at any time by writing to the HIBRTCLD register. The predivider trim can be adjusted by reading
and writing the HIBRTCT register. The predivider uses this register once every 64 seconds to adjust
March 17, 2008 121
Preliminary
LM3S8933 Microcontroller
the clock rate. The two match registers can be set by writing to the HIBRTCM0 and HIBRTCM1
registers. The RTC can be configured to generate interrupts by using the interrupt registers (see
“Interrupts and Status” on page 122).
7.2.5 Non-Volatile Memory
The Hibernation module contains 64 32-bit words of memory which are retained during hibernation.
This memory is powered from the battery or auxiliary power supply during hibernation. The processor
software can save state information in this memory prior to hibernation, and can then recover the
state upon waking. The non-volatile memory can be accessed through the HIBDATA registers.
7.2.6 Power Control
The Hibernation module controls power to the processor through the use of the HIB pin, which is
intended to be connected to the enable signal of the external regulator(s) providing 3.3 V and/or
2.5 V to the microcontroller. When the HIB signal is asserted by the Hibernation module, the external
regulator is turned off and no longer powers the microcontroller. The Hibernation module remains
powered from the VBAT supply, which could be a battery or an auxiliary power source. Hibernation
mode is initiated by the microcontroller setting the HIBREQ bit of the HIBCTL register. Prior to doing
this, a wake-up condition must be configured, either from the external WAKE pin, or by using an RTC
match.
The Hibernation module is configured to wake from the external WAKE pin by setting the PINWEN
bit of the HIBCTL register. It is configured to wake from RTC match by setting the RTCWEN bit. Either
one or both of these bits can be set prior to going into hibernation. The WAKE pin includes a weak
internal pull-up. Note that both the HIB and WAKE pins use the Hibernation module's internal power
supply as the logic 1 reference.
When the Hibernation module wakes, the microcontroller will see a normal power-on reset. It can
detect that the power-on was due to a wake from hibernation by examining the raw interrupt status
register (see “Interrupts and Status” on page 122) and by looking for state data in the non-volatile
memory (see “Non-Volatile Memory” on page 122).
When the HIB signal deasserts, enabling the external regulator, the external regulator must reach
the operating voltage within tHIB_TO_VDD.
7.2.7 Interrupts and Status
The Hibernation module can generate interrupts when the following conditions occur:
■ Assertion of WAKE pin
■ RTC match
■ Low battery detected
All of the interrupts are ORed together before being sent to the interrupt controller, so the Hibernate
module can only generate a single interrupt request to the controller at any given time. The software
interrupt handler can service multiple interrupt events by reading the HIBMIS register. Software can
also read the status of the Hibernation module at any time by reading the HIBRIS register which
shows all of the pending events. This register can be used at power-on to see if a wake condition
is pending, which indicates to the software that a hibernation wake occurred.
The events that can trigger an interrupt are configured by setting the appropriate bits in the HIBIM
register. Pending interrupts can be cleared by writing the corresponding bit in the HIBIC register.
122 March 17, 2008
Preliminary
Hibernation Module
7.3 Initialization and Configuration
The Hibernation module can be set in several different configurations. The following sections show
the recommended programming sequence for various scenarios. The examples below assume that
a 32.768-kHz oscillator is used, and thus always show bit 2 (CLKSEL) of the HIBCTL register set
to 1. If a 4.194304-MHz crystal is used instead, then the CLKSEL bit remains cleared. Because the
Hibernation module runs at 32 kHz and is asynchronous to the rest of the system, software must
allow a delay of tHIB_REG_WRITE after writes to certain registers (see “Register Access
Timing” on page 120). The registers that require a delay are listed in a note in “Register Map” on page
124 as well as in each register description.
7.3.1 Initialization
The clock source must be enabled first, even if the RTC will not be used. If a 4.194304-MHz crystal
is used, perform the following steps:
1. Write 0x40 to the HIBCTL register at offset 0x10 to enable the crystal and select the divide-by-128
input path.
2. Wait for a time of tXOSC_SETTLE for the crystal to power up and stabilize before performing any
other operations with the Hibernation module.
If a 32.678-kHz oscillator is used, then perform the following steps:
1. Write 0x44 to the HIBCTL register at offset 0x10 to enable the oscillator input.
2. No delay is necessary.
The above is only necessary when the entire system is initialized for the first time. If the processor
is powered due to a wake from hibernation, then the Hibernation module has already been powered
up and the above steps are not necessary. The software can detect that the Hibernation module
and clock are already powered by examining the CLK32EN bit of the HIBCTL register.
7.3.2 RTC Match Functionality (No Hibernation)
Use the following steps to implement the RTC match functionality of the Hibernation module:
1. Write the required RTC match value to one of the HIBRTCMn registers at offset 0x004 or 0x008.
2. Write the required RTC load value to the HIBRTCLD register at offset 0x00C.
3. Set the required RTC match interrupt mask in the RTCALT0 and RTCALT1 bits (bits 1:0) in the
HIBIM register at offset 0x014.
4. Write 0x0000.0041 to the HIBCTL register at offset 0x010 to enable the RTC to begin counting.
7.3.3 RTC Match/Wake-Up from Hibernation
Use the following steps to implement the RTC match and wake-up functionality of the Hibernation
module:
1. Write the required RTC match value to the HIBRTCMn registers at offset 0x004 or 0x008.
2. Write the required RTC load value to the HIBRTCLD register at offset 0x00C.
3. Write any data to be retained during power cut to the HIBDATA register at offsets 0x030-0x12C.
March 17, 2008 123
Preliminary
LM3S8933 Microcontroller
4. Set the RTC Match Wake-Up and start the hibernation sequence by writing 0x0000.004F to the
HIBCTL register at offset 0x010.
7.3.4 External Wake-Up from Hibernation
Use the following steps to implement the Hibernation module with the external WAKE pin as the
wake-up source for the microcontroller:
1. Write any data to be retained during power cut to the HIBDATA register at offsets 0x030-0x12C.
2. Enable the external wake and start the hibernation sequence by writing 0x0000.0056 to the
HIBCTL register at offset 0x010.
7.3.5 RTC/External Wake-Up from Hibernation
1. Write the required RTC match value to the HIBRTCMn registers at offset 0x004 or 0x008.
2. Write the required RTC load value to the HIBRTCLD register at offset 0x00C.
3. Write any data to be retained during power cut to the HIBDATA register at offsets 0x030-0x12C.
4. Set the RTC Match/External Wake-Up and start the hibernation sequence by writing 0x0000.005F
to the HIBCTL register at offset 0x010.
7.4 Register Map
Table 7-1 on page 124 lists the Hibernation registers. All addresses given are relative to the Hibernation
Module base address at 0x400F.C000.
Note: HIBRTCC, HIBRTCM0, HIBRTCM1, HIBRTCLD, HIBRTCT, and HIBDATA are on the
Hibernation module clock domain and require a delay of tHIB_REG_WRITE between write
accesses. See “Register Access Timing” on page 120.
Table 7-1. Hibernation Module Register Map
See
Offset Name Type Reset Description page
0x000 HIBRTCC RO 0x0000.0000 Hibernation RTC Counter 126
0x004 HIBRTCM0 R/W 0xFFFF.FFFF Hibernation RTC Match 0 127
0x008 HIBRTCM1 R/W 0xFFFF.FFFF Hibernation RTC Match 1 128
0x00C HIBRTCLD R/W 0xFFFF.FFFF Hibernation RTC Load 129
0x010 HIBCTL R/W 0x0000.0000 Hibernation Control 130
0x014 HIBIM R/W 0x0000.0000 Hibernation Interrupt Mask 132
0x018 HIBRIS RO 0x0000.0000 Hibernation Raw Interrupt Status 133
0x01C HIBMIS RO 0x0000.0000 Hibernation Masked Interrupt Status 134
0x020 HIBIC R/W1C 0x0000.0000 Hibernation Interrupt Clear 135
0x024 HIBRTCT R/W 0x0000.7FFF Hibernation RTC Trim 136
0x030- HIBDATA R/W 0x0000.0000 Hibernation Data 137
0x12C
124 March 17, 2008
Preliminary
Hibernation Module
7.5 Register Descriptions
The remainder of this section lists and describes the Hibernation module registers, in numerical
order by address offset.
March 17, 2008 125
Preliminary
LM3S8933 Microcontroller
Register 1: Hibernation RTC Counter (HIBRTCC), offset 0x000
This register is the current 32-bit value of the RTC counter.
Note: HIBRTCC, HIBRTCM0, HIBRTCM1, HIBRTCLD, HIBRTCT, and HIBDATA are on the
Hibernation module clock domain and require a delay of tHIB_REG_WRITE between write
accesses. See “Register Access Timing” on page 120.
Hibernation RTC Counter (HIBRTCC)
Base 0x400F.C000
Offset 0x000
Type RO, reset 0x0000.0000
31 30 29 28 27 26 25 24 23 22 21 20 19 18 17 16
RTCC
Type RO RO RO RO RO RO RO RO RO RO RO RO RO RO RO RO
Reset 0 0 0 0 0 0 0 0 0 0 0 0 0 0 0 0
15 14 13 12 11 10 9 8 7 6 5 4 3 2 1 0
RTCC
Type RO RO RO RO RO RO RO RO RO RO RO RO RO RO RO RO
Reset 0 0 0 0 0 0 0 0 0 0 0 0 0 0 0 0
Bit/Field Name Type Reset Description
RTC Counter
A read returns the 32-bit counter value. This register is read-only. To
change the value, use the HIBRTCLD register.
31:0 RTCC RO 0x0000.0000
126 March 17, 2008
Preliminary
Hibernation Module
Register 2: Hibernation RTC Match 0 (HIBRTCM0), offset 0x004
This register is the 32-bit match 0 register for the RTC counter.
Note: HIBRTCC, HIBRTCM0, HIBRTCM1, HIBRTCLD, HIBRTCT, and HIBDATA are on the
Hibernation module clock domain and require a delay of tHIB_REG_WRITE between write
accesses. See “Register Access Timing” on page 120.
Hibernation RTC Match 0 (HIBRTCM0)
Base 0x400F.C000
Offset 0x004
Type R/W, reset 0xFFFF.FFFF
31 30 29 28 27 26 25 24 23 22 21 20 19 18 17 16
RTCM0
Type R/W R/W R/W R/W R/W R/W R/W R/W R/W R/W R/W R/W R/W R/W R/W R/W
Reset 1 1 1 1 1 1 1 1 1 1 1 1 1 1 1 1
15 14 13 12 11 10 9 8 7 6 5 4 3 2 1 0
RTCM0
Type R/W R/W R/W R/W R/W R/W R/W R/W R/W R/W R/W R/W R/W R/W R/W R/W
Reset 1 1 1 1 1 1 1 1 1 1 1 1 1 1 1 1
Bit/Field Name Type Reset Description
RTC Match 0
A write loads the value into the RTC match register.
A read returns the current match value.
31:0 RTCM0 R/W 0xFFFF.FFFF
March 17, 2008 127
Preliminary
LM3S8933 Microcontroller
Register 3: Hibernation RTC Match 1 (HIBRTCM1), offset 0x008
This register is the 32-bit match 1 register for the RTC counter.
Note: HIBRTCC, HIBRTCM0, HIBRTCM1, HIBRTCLD, HIBRTCT, and HIBDATA are on the
Hibernation module clock domain and require a delay of tHIB_REG_WRITE between write
accesses. See “Register Access Timing” on page 120.
Hibernation RTC Match 1 (HIBRTCM1)
Base 0x400F.C000
Offset 0x008
Type R/W, reset 0xFFFF.FFFF
31 30 29 28 27 26 25 24 23 22 21 20 19 18 17 16
RTCM1
Type R/W R/W R/W R/W R/W R/W R/W R/W R/W R/W R/W R/W R/W R/W R/W R/W
Reset 1 1 1 1 1 1 1 1 1 1 1 1 1 1 1 1
15 14 13 12 11 10 9 8 7 6 5 4 3 2 1 0
RTCM1
Type R/W R/W R/W R/W R/W R/W R/W R/W R/W R/W R/W R/W R/W R/W R/W R/W
Reset 1 1 1 1 1 1 1 1 1 1 1 1 1 1 1 1
Bit/Field Name Type Reset Description
RTC Match 1
A write loads the value into the RTC match register.
A read returns the current match value.
31:0 RTCM1 R/W 0xFFFF.FFFF
128 March 17, 2008
Preliminary
Hibernation Module
Register 4: Hibernation RTC Load (HIBRTCLD), offset 0x00C
This register is the 32-bit value loaded into the RTC counter.
Note: HIBRTCC, HIBRTCM0, HIBRTCM1, HIBRTCLD, HIBRTCT, and HIBDATA are on the
Hibernation module clock domain and require a delay of tHIB_REG_WRITE between write
accesses. See “Register Access Timing” on page 120.
Hibernation RTC Load (HIBRTCLD)
Base 0x400F.C000
Offset 0x00C
Type R/W, reset 0xFFFF.FFFF
31 30 29 28 27 26 25 24 23 22 21 20 19 18 17 16
RTCLD
Type R/W R/W R/W R/W R/W R/W R/W R/W R/W R/W R/W R/W R/W R/W R/W R/W
Reset 1 1 1 1 1 1 1 1 1 1 1 1 1 1 1 1
15 14 13 12 11 10 9 8 7 6 5 4 3 2 1 0
RTCLD
Type R/W R/W R/W R/W R/W R/W R/W R/W R/W R/W R/W R/W R/W R/W R/W R/W
Reset 1 1 1 1 1 1 1 1 1 1 1 1 1 1 1 1
Bit/Field Name Type Reset Description
RTC Load
A write loads the current value into the RTC counter (RTCC).
A read returns the 32-bit load value.
31:0 RTCLD R/W 0xFFFF.FFFF
March 17, 2008 129
Preliminary
LM3S8933 Microcontroller
Register 5: Hibernation Control (HIBCTL), offset 0x010
This register is the control register for the Hibernation module.
Hibernation Control (HIBCTL)
Base 0x400F.C000
Offset 0x010
Type R/W, reset 0x0000.0000
31 30 29 28 27 26 25 24 23 22 21 20 19 18 17 16
reserved
Type RO RO RO RO RO RO RO RO RO RO RO RO RO RO RO RO
Reset 0 0 0 0 0 0 0 0 0 0 0 0 0 0 0 0
15 14 13 12 11 10 9 8 7 6 5 4 3 2 1 0
reserved VABORT CLK32EN LOWBATEN PINWEN RTCWEN CLKSEL HIBREQ RTCEN
Type RO RO RO RO RO RO RO RO R/W R/W R/W R/W R/W R/W R/W R/W
Reset 0 0 0 0 0 0 0 0 0 0 0 0 0 0 0 0
Bit/Field Name Type Reset Description
Software should not rely on the value of a reserved bit. To provide
compatibility with future products, the value of a reserved bit should be
preserved across a read-modify-write operation.
31:8 reserved RO 0x00
Power Cut Abort Enable
Value Description
0 Power cut occurs during a low-battery alert.
1 Power cut is aborted.
7 VABORT R/W 0
32-kHz Oscillator Enable
Value Description
0 Disabled
1 Enabled
This bit must be enabled to use the Hibernation module. If a crystal is
used, then software should wait 20 ms after setting this bit to allow the
crystal to power up and stabilize.
6 CLK32EN R/W 0
Low Battery Monitoring Enable
Value Description
0 Disabled
1 Enabled
When set, low battery voltage detection is enabled (VBAT < 2.35 V).
5 LOWBATEN R/W 0
External WAKE Pin Enable
Value Description
0 Disabled
1 Enabled
When set, an external event on the WAKE pin will re-power the device.
4 PINWEN R/W 0
130 March 17, 2008
Preliminary
Hibernation Module
Bit/Field Name Type Reset Description
RTC Wake-up Enable
Value Description
0 Disabled
1 Enabled
When set, an RTC match event (RTCM0 or RTCM1) will re-power the
device based on the RTC counter value matching the corresponding
match register 0 or 1.
3 RTCWEN R/W 0
Hibernation Module Clock Select
Value Description
0 Use Divide by 128 output. Use this value for a 4-MHz crystal.
1 Use raw output. Use this value for a 32-kHz oscillator.
2 CLKSEL R/W 0
Hibernation Request
Value Description
0 Disabled
1 Hibernation initiated
After a wake-up event, this bit is cleared by hardware.
1 HIBREQ R/W 0
RTC Timer Enable
Value Description
0 Disabled
1 Enabled
0 RTCEN R/W 0
March 17, 2008 131
Preliminary
LM3S8933 Microcontroller
Register 6: Hibernation Interrupt Mask (HIBIM), offset 0x014
This register is the interrupt mask register for the Hibernation module interrupt sources.
Hibernation Interrupt Mask (HIBIM)
Base 0x400F.C000
Offset 0x014
Type R/W, reset 0x0000.0000
31 30 29 28 27 26 25 24 23 22 21 20 19 18 17 16
reserved
Type RO RO RO RO RO RO RO RO RO RO RO RO RO RO RO RO
Reset 0 0 0 0 0 0 0 0 0 0 0 0 0 0 0 0
15 14 13 12 11 10 9 8 7 6 5 4 3 2 1 0
reserved EXTW LOWBAT RTCALT1 RTCALT0
Type RO RO RO RO RO RO RO RO RO RO RO RO R/W R/W R/W R/W
Reset 0 0 0 0 0 0 0 0 0 0 0 0 0 0 0 0
Bit/Field Name Type Reset Description
Software should not rely on the value of a reserved bit. To provide
compatibility with future products, the value of a reserved bit should be
preserved across a read-modify-write operation.
31:4 reserved RO 0x000.0000
External Wake-Up Interrupt Mask
Value Description
0 Masked
1 Unmasked
3 EXTW R/W 0
Low Battery Voltage Interrupt Mask
Value Description
0 Masked
1 Unmasked
2 LOWBAT R/W 0
RTC Alert1 Interrupt Mask
Value Description
0 Masked
1 Unmasked
1 RTCALT1 R/W 0
RTC Alert0 Interrupt Mask
Value Description
0 Masked
1 Unmasked
0 RTCALT0 R/W 0
132 March 17, 2008
Preliminary
Hibernation Module
Register 7: Hibernation Raw Interrupt Status (HIBRIS), offset 0x018
This register is the raw interrupt status for the Hibernation module interrupt sources.
Hibernation Raw Interrupt Status (HIBRIS)
Base 0x400F.C000
Offset 0x018
Type RO, reset 0x0000.0000
31 30 29 28 27 26 25 24 23 22 21 20 19 18 17 16
reserved
Type RO RO RO RO RO RO RO RO RO RO RO RO RO RO RO RO
Reset 0 0 0 0 0 0 0 0 0 0 0 0 0 0 0 0
15 14 13 12 11 10 9 8 7 6 5 4 3 2 1 0
reserved EXTW LOWBAT RTCALT1 RTCALT0
Type RO RO RO RO RO RO RO RO RO RO RO RO RO RO RO RO
Reset 0 0 0 0 0 0 0 0 0 0 0 0 0 0 0 0
Bit/Field Name Type Reset Description
Software should not rely on the value of a reserved bit. To provide
compatibility with future products, the value of a reserved bit should be
preserved across a read-modify-write operation.
31:4 reserved RO 0x000.0000
3 EXTW RO 0 External Wake-Up Raw Interrupt Status
2 LOWBAT RO 0 Low Battery Voltage Raw Interrupt Status
1 RTCALT1 RO 0 RTC Alert1 Raw Interrupt Status
0 RTCALT0 RO 0 RTC Alert0 Raw Interrupt Status
March 17, 2008 133
Preliminary
LM3S8933 Microcontroller
Register 8: Hibernation Masked Interrupt Status (HIBMIS), offset 0x01C
This register is the masked interrupt status for the Hibernation module interrupt sources.
Hibernation Masked Interrupt Status (HIBMIS)
Base 0x400F.C000
Offset 0x01C
Type RO, reset 0x0000.0000
31 30 29 28 27 26 25 24 23 22 21 20 19 18 17 16
reserved
Type RO RO RO RO RO RO RO RO RO RO RO RO RO RO RO RO
Reset 0 0 0 0 0 0 0 0 0 0 0 0 0 0 0 0
15 14 13 12 11 10 9 8 7 6 5 4 3 2 1 0
reserved EXTW LOWBAT RTCALT1 RTCALT0
Type RO RO RO RO RO RO RO RO RO RO RO RO RO RO RO RO
Reset 0 0 0 0 0 0 0 0 0 0 0 0 0 0 0 0
Bit/Field Name Type Reset Description
Software should not rely on the value of a reserved bit. To provide
compatibility with future products, the value of a reserved bit should be
preserved across a read-modify-write operation.
31:4 reserved RO 0x000.0000
3 EXTW RO 0 External Wake-Up Masked Interrupt Status
2 LOWBAT RO 0 Low Battery Voltage Masked Interrupt Status
1 RTCALT1 RO 0 RTC Alert1 Masked Interrupt Status
0 RTCALT0 RO 0 RTC Alert0 Masked Interrupt Status
134 March 17, 2008
Preliminary
Hibernation Module
Register 9: Hibernation Interrupt Clear (HIBIC), offset 0x020
This register is the interrupt write-one-to-clear register for the Hibernation module interrupt sources.
Hibernation Interrupt Clear (HIBIC)
Base 0x400F.C000
Offset 0x020
Type R/W1C, reset 0x0000.0000
31 30 29 28 27 26 25 24 23 22 21 20 19 18 17 16
reserved
Type RO RO RO RO RO RO RO RO RO RO RO RO RO RO RO RO
Reset 0 0 0 0 0 0 0 0 0 0 0 0 0 0 0 0
15 14 13 12 11 10 9 8 7 6 5 4 3 2 1 0
reserved EXTW LOWBAT RTCALT1 RTCALT0
Type RO RO RO RO RO RO RO RO RO RO RO RO R/W1C R/W1C R/W1C R/W1C
Reset 0 0 0 0 0 0 0 0 0 0 0 0 0 0 0 0
Bit/Field Name Type Reset Description
Software should not rely on the value of a reserved bit. To provide
compatibility with future products, the value of a reserved bit should be
preserved across a read-modify-write operation.
31:4 reserved RO 0x000.0000
External Wake-Up Masked Interrupt Clear
Reads return an indeterminate value.
3 EXTW R/W1C 0
Low Battery Voltage Masked Interrupt Clear
Reads return an indeterminate value.
2 LOWBAT R/W1C 0
RTC Alert1 Masked Interrupt Clear
Reads return an indeterminate value.
1 RTCALT1 R/W1C 0
RTC Alert0 Masked Interrupt Clear
Reads return an indeterminate value.
0 RTCALT0 R/W1C 0
March 17, 2008 135
Preliminary
LM3S8933 Microcontroller
Register 10: Hibernation RTC Trim (HIBRTCT), offset 0x024
This register contains the value that is used to trim the RTC clock predivider. It represents the
computed underflow value that is used during the trim cycle. It is represented as 0x7FFF ± N clock
cycles.
Note: HIBRTCC, HIBRTCM0, HIBRTCM1, HIBRTCLD, HIBRTCT, and HIBDATA are on the
Hibernation module clock domain and require a delay of tHIB_REG_WRITE between write
accesses. See “Register Access Timing” on page 120.
Hibernation RTC Trim (HIBRTCT)
Base 0x400F.C000
Offset 0x024
Type R/W, reset 0x0000.7FFF
31 30 29 28 27 26 25 24 23 22 21 20 19 18 17 16
reserved
Type RO RO RO RO RO RO RO RO RO RO RO RO RO RO RO RO
Reset 0 0 0 0 0 0 0 0 0 0 0 0 0 0 0 0
15 14 13 12 11 10 9 8 7 6 5 4 3 2 1 0
TRIM
Type R/W R/W R/W R/W R/W R/W R/W R/W R/W R/W R/W R/W R/W R/W R/W R/W
Reset 0 1 1 1 1 1 1 1 1 1 1 1 1 1 1 1
Bit/Field Name Type Reset Description
Software should not rely on the value of a reserved bit. To provide
compatibility with future products, the value of a reserved bit should be
preserved across a read-modify-write operation.
31:16 reserved RO 0x0000
RTC Trim Value
This value is loaded into the RTC predivider every 64 seconds. It is used
to adjust the RTC rate to account for drift and inaccuracy in the clock
source. The compensation is made by software by adjusting the default
value of 0x7FFF up or down.
15:0 TRIM R/W 0x7FFF
136 March 17, 2008
Preliminary
Hibernation Module
Register 11: Hibernation Data (HIBDATA), offset 0x030-0x12C
This address space is implemented as a 64x32-bit memory (256 bytes). It can be loaded by the
system processor in order to store any non-volatile state data and will not lose power during a power
cut operation.
Note: HIBRTCC, HIBRTCM0, HIBRTCM1, HIBRTCLD, HIBRTCT, and HIBDATA are on the
Hibernation module clock domain and require a delay of tHIB_REG_WRITE between write
accesses. See “Register Access Timing” on page 120.
Hibernation Data (HIBDATA)
Base 0x400F.C000
Offset 0x030-0x12C
Type R/W, reset 0x0000.0000
31 30 29 28 27 26 25 24 23 22 21 20 19 18 17 16
RTD
Type R/W R/W R/W R/W R/W R/W R/W R/W R/W R/W R/W R/W R/W R/W R/W R/W
Reset 0 0 0 0 0 0 0 0 0 0 0 0 0 0 0 0
15 14 13 12 11 10 9 8 7 6 5 4 3 2 1 0
RTD
Type R/W R/W R/W R/W R/W R/W R/W R/W R/W R/W R/W R/W R/W R/W R/W R/W
Reset 0 0 0 0 0 0 0 0 0 0 0 0 0 0 0 0
Bit/Field Name Type Reset Description
31:0 RTD R/W 0x0000.0000 Hibernation Module NV Registers[63:0]
March 17, 2008 137
Preliminary
LM3S8933 Microcontroller
8 Internal Memory
The LM3S8933 microcontroller comes with 64 KB of bit-banded SRAM and 256 KB of flash memory.
The flash controller provides a user-friendly interface, making flash programming a simple task.
Flash protection can be applied to the flash memory on a 2-KB block basis.
8.1 Block Diagram
Figure 8-1. Flash Block Diagram
Flash Control
FMA
FCMISC
FCIM
FCRIS
FMC
FMD
Flash Timing
USECRL
Flash Protection
FMPREn
FMPPEn
Flash Array
SRAM Array
Bridge
Cortex-M3
ICode
DCode
System Bus
APB
User Registers
USER_REG0
USER_REG1
USER_DBG
8.2 Functional Description
This section describes the functionality of both the flash and SRAM memories.
8.2.1 SRAM Memory
The internal SRAM of the Stellaris® devices is located at address 0x2000.0000 of the device memory
map. To reduce the number of time consuming read-modify-write (RMW) operations, ARM has
introduced bit-banding technology in the Cortex-M3 processor. With a bit-band-enabled processor,
certain regions in the memory map (SRAM and peripheral space) can use address aliases to access
individual bits in a single, atomic operation.
The bit-band alias is calculated by using the formula:
138 March 17, 2008
Preliminary
Internal Memory
bit-band alias = bit-band base + (byte offset * 32) + (bit number * 4)
For example, if bit 3 at address 0x2000.1000 is to be modified, the bit-band alias is calculated as:
0x2200.0000 + (0x1000 * 32) + (3 * 4) = 0x2202.000C
With the alias address calculated, an instruction performing a read/write to address 0x2202.000C
allows direct access to only bit 3 of the byte at address 0x2000.1000.
For details about bit-banding, please refer to Chapter 4, “Memory Map” in the ARM® Cortex™-M3
Technical Reference Manual.
8.2.2 Flash Memory
The flash is organized as a set of 1-KB blocks that can be individually erased. Erasing a block
causes the entire contents of the block to be reset to all 1s. An individual 32-bit word can be
programmed to change bits that are currently 1 to a 0. These blocks are paired into a set of 2-KB
blocks that can be individually protected. The protection allows blocks to be marked as read-only
or execute-only, providing different levels of code protection. Read-only blocks cannot be erased
or programmed, protecting the contents of those blocks from being modified. Execute-only blocks
cannot be erased or programmed, and can only be read by the controller instruction fetch mechanism,
protecting the contents of those blocks from being read by either the controller or by a debugger.
See also “Serial Flash Loader” on page 554 for a preprogrammed flash-resident utility used to
download code to the flash memory of a device without the use of a debug interface.
8.2.2.1 Flash Memory Timing
The timing for the flash is automatically handled by the flash controller. However, in order to do so,
it must know the clock rate of the system in order to time its internal signals properly. The number
of clock cycles per microsecond must be provided to the flash controller for it to accomplish this
timing. It is software's responsibility to keep the flash controller updated with this information via the
USec Reload (USECRL) register.
On reset, the USECRL register is loaded with a value that configures the flash timing so that it works
with the maximum clock rate of the part. If software changes the system operating frequency, the
new operating frequency minus 1 (in MHz) must be loaded into USECRL before any flash
modifications are attempted. For example, if the device is operating at a speed of 20 MHz, a value
of 0x13 (20-1) must be written to the USECRL register.
8.2.2.2 Flash Memory Protection
The user is provided two forms of flash protection per 2-KB flash blocks in four pairs of 32-bit wide
registers. The protection policy for each form is controlled by individual bits (per policy per block)
in the FMPPEn and FMPREn registers.
■ Flash Memory Protection Program Enable (FMPPEn): If set, the block may be programmed
(written) or erased. If cleared, the block may not be changed.
■ Flash Memory Protection Read Enable (FMPREn): If set, the block may be executed or read
by software or debuggers. If cleared, the block may only be executed and contents of the memory
block are prohibited from being accessed as data.
The policies may be combined as shown in Table 8-1 on page 140.
March 17, 2008 139
Preliminary
LM3S8933 Microcontroller
Table 8-1. Flash Protection Policy Combinations
FMPPEn FMPREn Protection
Execute-only protection. The block may only be executed and may not be written or erased. This mode
is used to protect code.
0 0
1 0 The block may be written, erased or executed, but not read. This combination is unlikely to be used.
Read-only protection. The block may be read or executed but may not be written or erased. This mode
is used to lock the block from further modification while allowing any read or execute access.
0 1
1 1 No protection. The block may be written, erased, executed or read.
An access that attempts to program or erase a PE-protected block is prohibited. A controller interrupt
may be optionally generated (by setting the AMASK bit in the FIM register) to alert software developers
of poorly behaving software during the development and debug phases.
An access that attempts to read an RE-protected block is prohibited. Such accesses return data
filled with all 0s. A controller interrupt may be optionally generated to alert software developers of
poorly behaving software during the development and debug phases.
The factory settings for the FMPREn and FMPPEn registers are a value of 1 for all implemented
banks. This implements a policy of open access and programmability. The register bits may be
changed by writing the specific register bit. The changes are not permanent until the register is
committed (saved), at which point the bit change is permanent. If a bit is changed from a 1 to a 0
and not committed, it may be restored by executing a power-on reset sequence. Details on
programming these bits are discussed in “Nonvolatile Register Programming” on page 141.
8.3 Flash Memory Initialization and Configuration
8.3.1 Flash Programming
The Stellaris® devices provide a user-friendly interface for flash programming. All erase/program
operations are handled via three registers: FMA, FMD, and FMC.
8.3.1.1 To program a 32-bit word
1. Write source data to the FMD register.
2. Write the target address to the FMA register.
3. Write the flash write key and the WRITE bit (a value of 0xA442.0001) to the FMC register.
4. Poll the FMC register until the WRITE bit is cleared.
8.3.1.2 To perform an erase of a 1-KB page
1. Write the page address to the FMA register.
2. Write the flash write key and the ERASE bit (a value of 0xA442.0002) to the FMC register.
3. Poll the FMC register until the ERASE bit is cleared.
8.3.1.3 To perform a mass erase of the flash
1. Write the flash write key and the MERASE bit (a value of 0xA442.0004) to the FMC register.
2. Poll the FMC register until the MERASE bit is cleared.
140 March 17, 2008
Preliminary
Internal Memory
8.3.2 Nonvolatile Register Programming
This section discusses how to update registers that are resident within the flash memory itself.
These registers exist in a separate space from the main flash array and are not affected by an
ERASE or MASS ERASE operation. These nonvolatile registers are updated by using the COMT bit
in the FMC register to activate a write operation. For the USER_DBG register, the data to be written
must be loaded into the FMD register before it is "committed". All other registers are R/W and can
have their operation tried before committing them to nonvolatile memory.
Important: These registers can only have bits changed from 1 to 0 by the user and there is no
mechanism for the user to erase them back to a 1 value.
In addition, the USER_REG0, USER_REG1, and USER_DBG use bit 31 (NW) of their respective
registers to indicate that they are available for user write. These three registers can only be written
once whereas the flash protection registers may be written multiple times. Table 8-2 on page 141
provides the FMA address required for commitment of each of the registers and the source of the
data to be written when the COMT bit of the FMC register is written with a value of 0xA442.0008.
After writing the COMT bit, the user may poll the FMC register to wait for the commit operation to
complete.
Table 8-2. Flash Resident Registersa
Register to be Committed FMA Value Data Source
FMPRE0 0x0000.0000 FMPRE0
FMPRE1 0x0000.0002 FMPRE1
FMPRE2 0x0000.0004 FMPRE2
FMPRE3 0x0000.0008 FMPRE3
FMPPE0 0x0000.0001 FMPPE0
FMPPE1 0x0000.0003 FMPPE1
FMPPE2 0x0000.0005 FMPPE2
FMPPE3 0x0000.0007 FMPPE3
USER_REG0 0x8000.0000 USER_REG0
USER_REG1 0x8000.0001 USER_REG1
USER_DBG 0x7510.0000 FMD
a. Which FMPREn and FMPPEn registers are available depend on the flash size of your particular Stellaris® device.
8.4 Register Map
Table 8-3 on page 141 lists the Flash memory and control registers. The offset listed is a hexadecimal
increment to the register's address. The FMA, FMD, FMC, FCRIS, FCIM, and FCMISC registers
are relative to the Flash control base address of 0x400F.D000. The FMPREn, FMPPEn, USECRL,
USER_DBG, and USER_REGn registers are relative to the System Control base address of
0x400F.E000.
Table 8-3. Flash Register Map
See
Offset Name Type Reset Description page
Flash Control Offset
0x000 FMA R/W 0x0000.0000 Flash Memory Address 143
March 17, 2008 141
Preliminary
LM3S8933 Microcontroller
See
Offset Name Type Reset Description page
0x004 FMD R/W 0x0000.0000 Flash Memory Data 144
0x008 FMC R/W 0x0000.0000 Flash Memory Control 145
0x00C FCRIS RO 0x0000.0000 Flash Controller Raw Interrupt Status 147
0x010 FCIM R/W 0x0000.0000 Flash Controller Interrupt Mask 148
0x014 FCMISC R/W1C 0x0000.0000 Flash Controller Masked Interrupt Status and Clear 149
System Control Offset
0x130 FMPRE0 R/W 0xFFFF.FFFF Flash Memory Protection Read Enable 0 151
0x200 FMPRE0 R/W 0xFFFF.FFFF Flash Memory Protection Read Enable 0 151
0x134 FMPPE0 R/W 0xFFFF.FFFF Flash Memory Protection Program Enable 0 152
0x400 FMPPE0 R/W 0xFFFF.FFFF Flash Memory Protection Program Enable 0 152
0x140 USECRL R/W 0x31 USec Reload 150
0x1D0 USER_DBG R/W 0xFFFF.FFFE User Debug 153
0x1E0 USER_REG0 R/W 0xFFFF.FFFF User Register 0 154
0x1E4 USER_REG1 R/W 0xFFFF.FFFF User Register 1 155
0x204 FMPRE1 R/W 0xFFFF.FFFF Flash Memory Protection Read Enable 1 156
0x208 FMPRE2 R/W 0xFFFF.FFFF Flash Memory Protection Read Enable 2 157
0x20C FMPRE3 R/W 0xFFFF.FFFF Flash Memory Protection Read Enable 3 158
0x404 FMPPE1 R/W 0xFFFF.FFFF Flash Memory Protection Program Enable 1 159
0x408 FMPPE2 R/W 0xFFFF.FFFF Flash Memory Protection Program Enable 2 160
0x40C FMPPE3 R/W 0xFFFF.FFFF Flash Memory Protection Program Enable 3 161
8.5 Flash Register Descriptions (Flash Control Offset)
This section lists and describes the Flash Memory registers, in numerical order by address offset.
Registers in this section are relative to the Flash control base address of 0x400F.D000.
142 March 17, 2008
Preliminary
Internal Memory
Register 1: Flash Memory Address (FMA), offset 0x000
During a write operation, this register contains a 4-byte-aligned address and specifies where the
data is written. During erase operations, this register contains a 1 KB-aligned address and specifies
which page is erased. Note that the alignment requirements must be met by software or the results
of the operation are unpredictable.
Flash Memory Address (FMA)
Base 0x400F.D000
Offset 0x000
Type R/W, reset 0x0000.0000
31 30 29 28 27 26 25 24 23 22 21 20 19 18 17 16
reserved OFFSET
Type RO RO RO RO RO RO RO RO RO RO RO RO RO RO R/W R/W
Reset 0 0 0 0 0 0 0 0 0 0 0 0 0 0 0 0
15 14 13 12 11 10 9 8 7 6 5 4 3 2 1 0
OFFSET
Type R/W R/W R/W R/W R/W R/W R/W R/W R/W R/W R/W R/W R/W R/W R/W R/W
Reset 0 0 0 0 0 0 0 0 0 0 0 0 0 0 0 0
Bit/Field Name Type Reset Description
Software should not rely on the value of a reserved bit. To provide
compatibility with future products, the value of a reserved bit should be
preserved across a read-modify-write operation.
31:18 reserved RO 0x0
Address Offset
Address offset in flash where operation is performed, except for
nonvolatile registers (see “Nonvolatile Register Programming” on page
141 for details on values for this field).
17:0 OFFSET R/W 0x0
March 17, 2008 143
Preliminary
LM3S8933 Microcontroller
Register 2: Flash Memory Data (FMD), offset 0x004
This register contains the data to be written during the programming cycle or read during the read
cycle. Note that the contents of this register are undefined for a read access of an execute-only
block. This register is not used during the erase cycles.
Flash Memory Data (FMD)
Base 0x400F.D000
Offset 0x004
Type R/W, reset 0x0000.0000
31 30 29 28 27 26 25 24 23 22 21 20 19 18 17 16
DATA
Type R/W R/W R/W R/W R/W R/W R/W R/W R/W R/W R/W R/W R/W R/W R/W R/W
Reset 0 0 0 0 0 0 0 0 0 0 0 0 0 0 0 0
15 14 13 12 11 10 9 8 7 6 5 4 3 2 1 0
DATA
Type R/W R/W R/W R/W R/W R/W R/W R/W R/W R/W R/W R/W R/W R/W R/W R/W
Reset 0 0 0 0 0 0 0 0 0 0 0 0 0 0 0 0
Bit/Field Name Type Reset Description
Data Value
Data value for write operation.
31:0 DATA R/W 0x0
144 March 17, 2008
Preliminary
Internal Memory
Register 3: Flash Memory Control (FMC), offset 0x008
When this register is written, the flash controller initiates the appropriate access cycle for the location
specified by the Flash Memory Address (FMA) register (see page 143). If the access is a write
access, the data contained in the Flash Memory Data (FMD) register (see page 144) is written.
This is the final register written and initiates the memory operation. There are four control bits in the
lower byte of this register that, when set, initiate the memory operation. The most used of these
register bits are the ERASE and WRITE bits.
It is a programming error to write multiple control bits and the results of such an operation are
unpredictable.
Flash Memory Control (FMC)
Base 0x400F.D000
Offset 0x008
Type R/W, reset 0x0000.0000
31 30 29 28 27 26 25 24 23 22 21 20 19 18 17 16
WRKEY
Type WO WO WO WO WO WO WO WO WO WO WO WO WO WO WO WO
Reset 0 0 0 0 0 0 0 0 0 0 0 0 0 0 0 0
15 14 13 12 11 10 9 8 7 6 5 4 3 2 1 0
reserved COMT MERASE ERASE WRITE
Type RO RO RO RO RO RO RO RO RO RO RO RO R/W R/W R/W R/W
Reset 0 0 0 0 0 0 0 0 0 0 0 0 0 0 0 0
Bit/Field Name Type Reset Description
Flash Write Key
This field contains a write key, which is used to minimize the incidence
of accidental flash writes. The value 0xA442 must be written into this
field for a write to occur. Writes to the FMC register without this WRKEY
value are ignored. A read of this field returns the value 0.
31:16 WRKEY WO 0x0
Software should not rely on the value of a reserved bit. To provide
compatibility with future products, the value of a reserved bit should be
preserved across a read-modify-write operation.
15:4 reserved RO 0x0
Commit Register Value
Commit (write) of register value to nonvolatile storage. A write of 0 has
no effect on the state of this bit.
If read, the state of the previous commit access is provided. If the
previous commit access is complete, a 0 is returned; otherwise, if the
commit access is not complete, a 1 is returned.
This can take up to 50 μs.
3 COMT R/W 0
Mass Erase Flash Memory
If this bit is set, the flash main memory of the device is all erased. A
write of 0 has no effect on the state of this bit.
If read, the state of the previous mass erase access is provided. If the
previous mass erase access is complete, a 0 is returned; otherwise, if
the previous mass erase access is not complete, a 1 is returned.
This can take up to 250 ms.
2 MERASE R/W 0
March 17, 2008 145
Preliminary
LM3S8933 Microcontroller
Bit/Field Name Type Reset Description
Erase a Page of Flash Memory
If this bit is set, the page of flash main memory as specified by the
contents of FMA is erased. A write of 0 has no effect on the state of this
bit.
If read, the state of the previous erase access is provided. If the previous
erase access is complete, a 0 is returned; otherwise, if the previous
erase access is not complete, a 1 is returned.
This can take up to 25 ms.
1 ERASE R/W 0
Write a Word into Flash Memory
If this bit is set, the data stored in FMD is written into the location as
specified by the contents of FMA. A write of 0 has no effect on the state
of this bit.
If read, the state of the previous write update is provided. If the previous
write access is complete, a 0 is returned; otherwise, if the write access
is not complete, a 1 is returned.
This can take up to 50 μs.
0 WRITE R/W 0
146 March 17, 2008
Preliminary
Internal Memory
Register 4: Flash Controller Raw Interrupt Status (FCRIS), offset 0x00C
This register indicates that the flash controller has an interrupt condition. An interrupt is only signaled
if the corresponding FCIM register bit is set.
Flash Controller Raw Interrupt Status (FCRIS)
Base 0x400F.D000
Offset 0x00C
Type RO, reset 0x0000.0000
31 30 29 28 27 26 25 24 23 22 21 20 19 18 17 16
reserved
Type RO RO RO RO RO RO RO RO RO RO RO RO RO RO RO RO
Reset 0 0 0 0 0 0 0 0 0 0 0 0 0 0 0 0
15 14 13 12 11 10 9 8 7 6 5 4 3 2 1 0
reserved PRIS ARIS
Type RO RO RO RO RO RO RO RO RO RO RO RO RO RO RO RO
Reset 0 0 0 0 0 0 0 0 0 0 0 0 0 0 0 0
Bit/Field Name Type Reset Description
Software should not rely on the value of a reserved bit. To provide
compatibility with future products, the value of a reserved bit should be
preserved across a read-modify-write operation.
31:2 reserved RO 0x0
Programming Raw Interrupt Status
This bit indicates the current state of the programming cycle. If set, the
programming cycle completed; if cleared, the programming cycle has
not completed. Programming cycles are either write or erase actions
generated through the Flash Memory Control (FMC) register bits (see
page 145).
1 PRIS RO 0
Access Raw Interrupt Status
This bit indicates if the flash was improperly accessed. If set, the program
tried to access the flash counter to the policy as set in the Flash Memory
Protection Read Enable (FMPREn) and Flash Memory Protection
Program Enable (FMPPEn) registers. Otherwise, no access has tried
to improperly access the flash.
0 ARIS RO 0
March 17, 2008 147
Preliminary
LM3S8933 Microcontroller
Register 5: Flash Controller Interrupt Mask (FCIM), offset 0x010
This register controls whether the flash controller generates interrupts to the controller.
Flash Controller Interrupt Mask (FCIM)
Base 0x400F.D000
Offset 0x010
Type R/W, reset 0x0000.0000
31 30 29 28 27 26 25 24 23 22 21 20 19 18 17 16
reserved
Type RO RO RO RO RO RO RO RO RO RO RO RO RO RO RO RO
Reset 0 0 0 0 0 0 0 0 0 0 0 0 0 0 0 0
15 14 13 12 11 10 9 8 7 6 5 4 3 2 1 0
reserved PMASK AMASK
Type RO RO RO RO RO RO RO RO RO RO RO RO RO RO R/W R/W
Reset 0 0 0 0 0 0 0 0 0 0 0 0 0 0 0 0
Bit/Field Name Type Reset Description
Software should not rely on the value of a reserved bit. To provide
compatibility with future products, the value of a reserved bit should be
preserved across a read-modify-write operation.
31:2 reserved RO 0x0
Programming Interrupt Mask
This bit controls the reporting of the programming raw interrupt status
to the controller. If set, a programming-generated interrupt is promoted
to the controller. Otherwise, interrupts are recorded but suppressed from
the controller.
1 PMASK R/W 0
Access Interrupt Mask
This bit controls the reporting of the access raw interrupt status to the
controller. If set, an access-generated interrupt is promoted to the
controller. Otherwise, interrupts are recorded but suppressed from the
controller.
0 AMASK R/W 0
148 March 17, 2008
Preliminary
Internal Memory
Register 6: Flash Controller Masked Interrupt Status and Clear (FCMISC),
offset 0x014
This register provides two functions. First, it reports the cause of an interrupt by indicating which
interrupt source or sources are signalling the interrupt. Second, it serves as the method to clear the
interrupt reporting.
Flash Controller Masked Interrupt Status and Clear (FCMISC)
Base 0x400F.D000
Offset 0x014
Type R/W1C, reset 0x0000.0000
31 30 29 28 27 26 25 24 23 22 21 20 19 18 17 16
reserved
Type RO RO RO RO RO RO RO RO RO RO RO RO RO RO RO RO
Reset 0 0 0 0 0 0 0 0 0 0 0 0 0 0 0 0
15 14 13 12 11 10 9 8 7 6 5 4 3 2 1 0
reserved PMISC AMISC
Type RO RO RO RO RO RO RO RO RO RO RO RO RO RO R/W1C R/W1C
Reset 0 0 0 0 0 0 0 0 0 0 0 0 0 0 0 0
Bit/Field Name Type Reset Description
Software should not rely on the value of a reserved bit. To provide
compatibility with future products, the value of a reserved bit should be
preserved across a read-modify-write operation.
31:2 reserved RO 0x0
Programming Masked Interrupt Status and Clear
This bit indicates whether an interrupt was signaled because a
programming cycle completed and was not masked. This bit is cleared
by writing a 1. The PRIS bit in the FCRIS register (see page 147) is also
cleared when the PMISC bit is cleared.
1 PMISC R/W1C 0
Access Masked Interrupt Status and Clear
This bit indicates whether an interrupt was signaled because an improper
access was attempted and was not masked. This bit is cleared by writing
a 1. The ARIS bit in the FCRIS register is also cleared when the AMISC
bit is cleared.
0 AMISC R/W1C 0
8.6 Flash Register Descriptions (System Control Offset)
The remainder of this section lists and describes the Flash Memory registers, in numerical order by
address offset. Registers in this section are relative to the System Control base address of
0x400F.E000.
March 17, 2008 149
Preliminary
LM3S8933 Microcontroller
Register 7: USec Reload (USECRL), offset 0x140
Note: Offset is relative to System Control base address of 0x400F.E000
This register is provided as a means of creating a 1-μs tick divider reload value for the flash controller.
The internal flash has specific minimum and maximum requirements on the length of time the high
voltage write pulse can be applied. It is required that this register contain the operating frequency
(in MHz -1) whenever the flash is being erased or programmed. The user is required to change this
value if the clocking conditions are changed for a flash erase/program operation.
USec Reload (USECRL)
Base 0x400F.E000
Offset 0x140
Type R/W, reset 0x31
31 30 29 28 27 26 25 24 23 22 21 20 19 18 17 16
reserved
Type RO RO RO RO RO RO RO RO RO RO RO RO RO RO RO RO
Reset 0 0 0 0 0 0 0 0 0 0 0 0 0 0 0 0
15 14 13 12 11 10 9 8 7 6 5 4 3 2 1 0
reserved USEC
Type RO RO RO RO RO RO RO RO R/W R/W R/W R/W R/W R/W R/W R/W
Reset 0 0 0 0 0 0 0 0 0 0 1 1 0 0 0 1
Bit/Field Name Type Reset Description
Software should not rely on the value of a reserved bit. To provide
compatibility with future products, the value of a reserved bit should be
preserved across a read-modify-write operation.
31:8 reserved RO 0x0
Microsecond Reload Value
MHz -1 of the controller clock when the flash is being erased or
programmed.
USEC should be set to 0x31 (50 MHz) whenever the flash is being erased
or programmed.
7:0 USEC R/W 0x31
150 March 17, 2008
Preliminary
Internal Memory
Register 8: Flash Memory Protection Read Enable 0 (FMPRE0), offset 0x130
and 0x200
Note: This register is aliased for backwards compatability.
Note: Offset is relative to System Control base address of 0x400FE000.
This register stores the read-only protection bits for each 2-KB flash block (FMPPEn stores the
execute-only bits). This register is loaded during the power-on reset sequence. The factory settings
for the FMPREn and FMPPEn registers are a value of 1 for all implemented banks. This achieves
a policy of open access and programmability. The register bits may be changed by writing the
specific register bit. However, this register is R/W0; the user can only change the protection bit from
a 1 to a 0 (and may NOT change a 0 to a 1). The changes are not permanent until the register is
committed (saved), at which point the bit change is permanent. If a bit is changed from a 1 to a 0
and not committed, it may be restored by executing a power-on reset sequence. For additional
information, see the "Flash Memory Protection" section.
Flash Memory Protection Read Enable 0 (FMPRE0)
Base 0x400F.D000
Offset 0x130 and 0x200
Type R/W, reset 0xFFFF.FFFF
31 30 29 28 27 26 25 24 23 22 21 20 19 18 17 16
READ_ENABLE
Type R/W R/W R/W R/W R/W R/W R/W R/W R/W R/W R/W R/W R/W R/W R/W R/W
Reset 1 1 1 1 1 1 1 1 1 1 1 1 1 1 1 1
15 14 13 12 11 10 9 8 7 6 5 4 3 2 1 0
READ_ENABLE
Type R/W R/W R/W R/W R/W R/W R/W R/W R/W R/W R/W R/W R/W R/W R/W R/W
Reset 1 1 1 1 1 1 1 1 1 1 1 1 1 1 1 1
Bit/Field Name Type Reset Description
Flash Read Enable
Enables 2-KB flash blocks to be executed or read. The policies may be
combined as shown in the table “Flash Protection Policy Combinations”.
Value Description
0xFFFFFFFF Enables 256 KB of flash.
31:0 READ_ENABLE R/W 0xFFFFFFFF
March 17, 2008 151
Preliminary
LM3S8933 Microcontroller
Register 9: Flash Memory Protection Program Enable 0 (FMPPE0), offset
0x134 and 0x400
Note: This register is aliased for backwards compatability.
Note: Offset is relative to System Control base address of 0x400FE000.
This register stores the execute-only protection bits for each 2-KB flash block (FMPREn stores the
execute-only bits). This register is loaded during the power-on reset sequence. The factory settings
for the FMPREn and FMPPEn registers are a value of 1 for all implemented banks. This achieves
a policy of open access and programmability. The register bits may be changed by writing the
specific register bit. However, this register is R/W0; the user can only change the protection bit from
a 1 to a 0 (and may NOT change a 0 to a 1). The changes are not permanent until the register is
committed (saved), at which point the bit change is permanent. If a bit is changed from a 1 to a 0
and not committed, it may be restored by executing a power-on reset sequence. For additional
information, see the "Flash Memory Protection" section.
Flash Memory Protection Program Enable 0 (FMPPE0)
Base 0x400F.D000
Offset 0x134 and 0x400
Type R/W, reset 0xFFFF.FFFF
31 30 29 28 27 26 25 24 23 22 21 20 19 18 17 16
PROG_ENABLE
Type R/W R/W R/W R/W R/W R/W R/W R/W R/W R/W R/W R/W R/W R/W R/W R/W
Reset 1 1 1 1 1 1 1 1 1 1 1 1 1 1 1 1
15 14 13 12 11 10 9 8 7 6 5 4 3 2 1 0
PROG_ENABLE
Type R/W R/W R/W R/W R/W R/W R/W R/W R/W R/W R/W R/W R/W R/W R/W R/W
Reset 1 1 1 1 1 1 1 1 1 1 1 1 1 1 1 1
Bit/Field Name Type Reset Description
Flash Programming Enable
Configures 2-KB flash blocks to be execute only. The policies may be
combined as shown in the table “Flash Protection Policy Combinations”.
Value Description
0xFFFFFFFF Enables 256 KB of flash.
31:0 PROG_ENABLE R/W 0xFFFFFFFF
152 March 17, 2008
Preliminary
Internal Memory
Register 10: User Debug (USER_DBG), offset 0x1D0
Note: Offset is relative to System Control base address of 0x400FE000.
This register provides a write-once mechanism to disable external debugger access to the device
in addition to 27 additional bits of user-defined data. The DBG0 bit (bit 0) is set to 0 from the factory
and the DBG1 bit (bit 1) is set to 1, which enables external debuggers. Changing the DBG1 bit to 0
disables any external debugger access to the device permanently, starting with the next power-up
cycle of the device. The NOTWRITTEN bit (bit 31) indicates that the register is available to be written
and is controlled through hardware to ensure that the register is only written once.
User Debug (USER_DBG)
Base 0x400F.E000
Offset 0x1D0
Type R/W, reset 0xFFFF.FFFE
31 30 29 28 27 26 25 24 23 22 21 20 19 18 17 16
NW DATA
Type R/W R/W R/W R/W R/W R/W R/W R/W R/W R/W R/W R/W R/W R/W R/W R/W
Reset 1 1 1 1 1 1 1 1 1 1 1 1 1 1 1 1
15 14 13 12 11 10 9 8 7 6 5 4 3 2 1 0
DATA DBG1 DBG0
Type R/W R/W R/W R/W R/W R/W R/W R/W R/W R/W R/W R/W R/W R/W R/W R/W
Reset 1 1 1 1 1 1 1 1 1 1 1 1 1 1 1 0
Bit/Field Name Type Reset Description
User Debug Not Written
Specifies that this 32-bit dword has not been written.
31 NW R/W 1
User Data
Contains the user data value. This field is initialized to all 1s and can
only be written once.
30:2 DATA R/W 0x1FFFFFFF
Debug Control 1
The DBG1 bit must be 1 and DBG0 must be 0 for debug to be available.
1 DBG1 R/W 1
Debug Control 0
The DBG1 bit must be 1 and DBG0 must be 0 for debug to be available.
0 DBG0 R/W 0
March 17, 2008 153
Preliminary
LM3S8933 Microcontroller
Register 11: User Register 0 (USER_REG0), offset 0x1E0
Note: Offset is relative to System Control base address of 0x400FE000.
This register provides 31 bits of user-defined data that is non-volatile and can only be written once.
Bit 31 indicates that the register is available to be written and is controlled through hardware to
ensure that the register is only written once. The write-once characteristics of this register are useful
for keeping static information like communication addresses that need to be unique per part and
would otherwise require an external EEPROM or other non-volatile device.
User Register 0 (USER_REG0)
Base 0x400F.E000
Offset 0x1E0
Type R/W, reset 0xFFFF.FFFF
31 30 29 28 27 26 25 24 23 22 21 20 19 18 17 16
NW DATA
Type R/W R/W R/W R/W R/W R/W R/W R/W R/W R/W R/W R/W R/W R/W R/W R/W
Reset 1 1 1 1 1 1 1 1 1 1 1 1 1 1 1 1
15 14 13 12 11 10 9 8 7 6 5 4 3 2 1 0
DATA
Type R/W R/W R/W R/W R/W R/W R/W R/W R/W R/W R/W R/W R/W R/W R/W R/W
Reset 1 1 1 1 1 1 1 1 1 1 1 1 1 1 1 1
Bit/Field Name Type Reset Description
Not Written
Specifies that this 32-bit dword has not been written.
31 NW R/W 1
User Data
Contains the user data value. This field is initialized to all 1s and can
only be written once.
30:0 DATA R/W 0x7FFFFFFF
154 March 17, 2008
Preliminary
Internal Memory
Register 12: User Register 1 (USER_REG1), offset 0x1E4
Note: Offset is relative to System Control base address of 0x400FE000.
This register provides 31 bits of user-defined data that is non-volatile and can only be written once.
Bit 31 indicates that the register is available to be written and is controlled through hardware to
ensure that the register is only written once. The write-once characteristics of this register are useful
for keeping static information like communication addresses that need to be unique per part and
would otherwise require an external EEPROM or other non-volatile device.
User Register 1 (USER_REG1)
Base 0x400F.E000
Offset 0x1E4
Type R/W, reset 0xFFFF.FFFF
31 30 29 28 27 26 25 24 23 22 21 20 19 18 17 16
NW DATA
Type R/W R/W R/W R/W R/W R/W R/W R/W R/W R/W R/W R/W R/W R/W R/W R/W
Reset 1 1 1 1 1 1 1 1 1 1 1 1 1 1 1 1
15 14 13 12 11 10 9 8 7 6 5 4 3 2 1 0
DATA
Type R/W R/W R/W R/W R/W R/W R/W R/W R/W R/W R/W R/W R/W R/W R/W R/W
Reset 1 1 1 1 1 1 1 1 1 1 1 1 1 1 1 1
Bit/Field Name Type Reset Description
Not Written
Specifies that this 32-bit dword has not been written.
31 NW R/W 1
User Data
Contains the user data value. This field is initialized to all 1s and can
only be written once.
30:0 DATA R/W 0x7FFFFFFF
March 17, 2008 155
Preliminary
LM3S8933 Microcontroller
Register 13: Flash Memory Protection Read Enable 1 (FMPRE1), offset 0x204
Note: Offset is relative to System Control base address of 0x400FE000.
This register stores the read-only protection bits for each 2-KB flash block (FMPPEn stores the
execute-only bits). This register is loaded during the power-on reset sequence. The factory settings
for the FMPREn and FMPPEn registers are a value of 1 for all implemented banks. This achieves
a policy of open access and programmability. The register bits may be changed by writing the
specific register bit. However, this register is R/W0; the user can only change the protection bit from
a 1 to a 0 (and may NOT change a 0 to a 1). The changes are not permanent until the register is
committed (saved), at which point the bit change is permanent. If a bit is changed from a 1 to a 0
and not committed, it may be restored by executing a power-on reset sequence. For additional
information, see the "Flash Memory Protection" section.
Flash Memory Protection Read Enable 1 (FMPRE1)
Base 0x400F.E000
Offset 0x204
Type R/W, reset 0xFFFF.FFFF
31 30 29 28 27 26 25 24 23 22 21 20 19 18 17 16
READ_ENABLE
Type R/W R/W R/W R/W R/W R/W R/W R/W R/W R/W R/W R/W R/W R/W R/W R/W
Reset 1 1 1 1 1 1 1 1 1 1 1 1 1 1 1 1
15 14 13 12 11 10 9 8 7 6 5 4 3 2 1 0
READ_ENABLE
Type R/W R/W R/W R/W R/W R/W R/W R/W R/W R/W R/W R/W R/W R/W R/W R/W
Reset 1 1 1 1 1 1 1 1 1 1 1 1 1 1 1 1
Bit/Field Name Type Reset Description
Flash Read Enable
Enables 2-KB flash blocks to be executed or read. The policies may be
combined as shown in the table “Flash Protection Policy Combinations”.
Value Description
0xFFFFFFFF Enables 256 KB of flash.
31:0 READ_ENABLE R/W 0xFFFFFFFF
156 March 17, 2008
Preliminary
Internal Memory
Register 14: Flash Memory Protection Read Enable 2 (FMPRE2), offset 0x208
Note: Offset is relative to System Control base address of 0x400FE000.
This register stores the read-only protection bits for each 2-KB flash block (FMPPEn stores the
execute-only bits). This register is loaded during the power-on reset sequence. The factory settings
for the FMPREn and FMPPEn registers are a value of 1 for all implemented banks. This achieves
a policy of open access and programmability. The register bits may be changed by writing the
specific register bit. However, this register is R/W0; the user can only change the protection bit from
a 1 to a 0 (and may NOT change a 0 to a 1). The changes are not permanent until the register is
committed (saved), at which point the bit change is permanent. If a bit is changed from a 1 to a 0
and not committed, it may be restored by executing a power-on reset sequence. For additional
information, see the "Flash Memory Protection" section.
Flash Memory Protection Read Enable 2 (FMPRE2)
Base 0x400F.E000
Offset 0x208
Type R/W, reset 0xFFFF.FFFF
31 30 29 28 27 26 25 24 23 22 21 20 19 18 17 16
READ_ENABLE
Type R/W R/W R/W R/W R/W R/W R/W R/W R/W R/W R/W R/W R/W R/W R/W R/W
Reset 1 1 1 1 1 1 1 1 1 1 1 1 1 1 1 1
15 14 13 12 11 10 9 8 7 6 5 4 3 2 1 0
READ_ENABLE
Type R/W R/W R/W R/W R/W R/W R/W R/W R/W R/W R/W R/W R/W R/W R/W R/W
Reset 1 1 1 1 1 1 1 1 1 1 1 1 1 1 1 1
Bit/Field Name Type Reset Description
Flash Read Enable
Enables 2-KB flash blocks to be executed or read. The policies may be
combined as shown in the table “Flash Protection Policy Combinations”.
Value Description
0xFFFFFFFF Enables 256 KB of flash.
31:0 READ_ENABLE R/W 0xFFFFFFFF
March 17, 2008 157
Preliminary
LM3S8933 Microcontroller
Register 15: Flash Memory Protection Read Enable 3 (FMPRE3), offset 0x20C
Note: Offset is relative to System Control base address of 0x400FE000.
This register stores the read-only protection bits for each 2-KB flash block (FMPPEn stores the
execute-only bits). This register is loaded during the power-on reset sequence. The factory settings
for the FMPREn and FMPPEn registers are a value of 1 for all implemented banks. This achieves
a policy of open access and programmability. The register bits may be changed by writing the
specific register bit. However, this register is R/W0; the user can only change the protection bit from
a 1 to a 0 (and may NOT change a 0 to a 1). The changes are not permanent until the register is
committed (saved), at which point the bit change is permanent. If a bit is changed from a 1 to a 0
and not committed, it may be restored by executing a power-on reset sequence. For additional
information, see the "Flash Memory Protection" section.
Flash Memory Protection Read Enable 3 (FMPRE3)
Base 0x400F.E000
Offset 0x20C
Type R/W, reset 0xFFFF.FFFF
31 30 29 28 27 26 25 24 23 22 21 20 19 18 17 16
READ_ENABLE
Type R/W R/W R/W R/W R/W R/W R/W R/W R/W R/W R/W R/W R/W R/W R/W R/W
Reset 1 1 1 1 1 1 1 1 1 1 1 1 1 1 1 1
15 14 13 12 11 10 9 8 7 6 5 4 3 2 1 0
READ_ENABLE
Type R/W R/W R/W R/W R/W R/W R/W R/W R/W R/W R/W R/W R/W R/W R/W R/W
Reset 1 1 1 1 1 1 1 1 1 1 1 1 1 1 1 1
Bit/Field Name Type Reset Description
Flash Read Enable
Enables 2-KB flash blocks to be executed or read. The policies may be
combined as shown in the table “Flash Protection Policy Combinations”.
Value Description
0xFFFFFFFF Enables 256 KB of flash.
31:0 READ_ENABLE R/W 0xFFFFFFFF
158 March 17, 2008
Preliminary
Internal Memory
Register 16: Flash Memory Protection Program Enable 1 (FMPPE1), offset
0x404
Note: Offset is relative to System Control base address of 0x400FE000.
This register stores the execute-only protection bits for each 2-KB flash block (FMPREn stores the
execute-only bits). This register is loaded during the power-on reset sequence. The factory settings
for the FMPREn and FMPPEn registers are a value of 1 for all implemented banks. This achieves
a policy of open access and programmability. The register bits may be changed by writing the
specific register bit. However, this register is R/W0; the user can only change the protection bit from
a 1 to a 0 (and may NOT change a 0 to a 1). The changes are not permanent until the register is
committed (saved), at which point the bit change is permanent. If a bit is changed from a 1 to a 0
and not committed, it may be restored by executing a power-on reset sequence. For additional
information, see the "Flash Memory Protection" section.
Flash Memory Protection Program Enable 1 (FMPPE1)
Base 0x400F.E000
Offset 0x404
Type R/W, reset 0xFFFF.FFFF
31 30 29 28 27 26 25 24 23 22 21 20 19 18 17 16
PROG_ENABLE
Type R/W R/W R/W R/W R/W R/W R/W R/W R/W R/W R/W R/W R/W R/W R/W R/W
Reset 1 1 1 1 1 1 1 1 1 1 1 1 1 1 1 1
15 14 13 12 11 10 9 8 7 6 5 4 3 2 1 0
PROG_ENABLE
Type R/W R/W R/W R/W R/W R/W R/W R/W R/W R/W R/W R/W R/W R/W R/W R/W
Reset 1 1 1 1 1 1 1 1 1 1 1 1 1 1 1 1
Bit/Field Name Type Reset Description
Flash Programming Enable
Configures 2-KB flash blocks to be execute only. The policies may be
combined as shown in the table “Flash Protection Policy Combinations”.
Value Description
0xFFFFFFFF Enables 256 KB of flash.
31:0 PROG_ENABLE R/W 0xFFFFFFFF
March 17, 2008 159
Preliminary
LM3S8933 Microcontroller
Register 17: Flash Memory Protection Program Enable 2 (FMPPE2), offset
0x408
Note: Offset is relative to System Control base address of 0x400FE000.
This register stores the execute-only protection bits for each 2-KB flash block (FMPREn stores the
execute-only bits). This register is loaded during the power-on reset sequence. The factory settings
for the FMPREn and FMPPEn registers are a value of 1 for all implemented banks. This achieves
a policy of open access and programmability. The register bits may be changed by writing the
specific register bit. However, this register is R/W0; the user can only change the protection bit from
a 1 to a 0 (and may NOT change a 0 to a 1). The changes are not permanent until the register is
committed (saved), at which point the bit change is permanent. If a bit is changed from a 1 to a 0
and not committed, it may be restored by executing a power-on reset sequence. For additional
information, see the "Flash Memory Protection" section.
Flash Memory Protection Program Enable 2 (FMPPE2)
Base 0x400F.E000
Offset 0x408
Type R/W, reset 0xFFFF.FFFF
31 30 29 28 27 26 25 24 23 22 21 20 19 18 17 16
PROG_ENABLE
Type R/W R/W R/W R/W R/W R/W R/W R/W R/W R/W R/W R/W R/W R/W R/W R/W
Reset 1 1 1 1 1 1 1 1 1 1 1 1 1 1 1 1
15 14 13 12 11 10 9 8 7 6 5 4 3 2 1 0
PROG_ENABLE
Type R/W R/W R/W R/W R/W R/W R/W R/W R/W R/W R/W R/W R/W R/W R/W R/W
Reset 1 1 1 1 1 1 1 1 1 1 1 1 1 1 1 1
Bit/Field Name Type Reset Description
Flash Programming Enable
Configures 2-KB flash blocks to be execute only. The policies may be
combined as shown in the table “Flash Protection Policy Combinations”.
Value Description
0xFFFFFFFF Enables 256 KB of flash.
31:0 PROG_ENABLE R/W 0xFFFFFFFF
160 March 17, 2008
Preliminary
Internal Memory
Register 18: Flash Memory Protection Program Enable 3 (FMPPE3), offset
0x40C
Note: Offset is relative to System Control base address of 0x400FE000.
This register stores the execute-only protection bits for each 2-KB flash block (FMPREn stores the
execute-only bits). This register is loaded during the power-on reset sequence. The factory settings
for the FMPREn and FMPPEn registers are a value of 1 for all implemented banks. This achieves
a policy of open access and programmability. The register bits may be changed by writing the
specific register bit. However, this register is R/W0; the user can only change the protection bit from
a 1 to a 0 (and may NOT change a 0 to a 1). The changes are not permanent until the register is
committed (saved), at which point the bit change is permanent. If a bit is changed from a 1 to a 0
and not committed, it may be restored by executing a power-on reset sequence. For additional
information, see the "Flash Memory Protection" section.
Flash Memory Protection Program Enable 3 (FMPPE3)
Base 0x400F.E000
Offset 0x40C
Type R/W, reset 0xFFFF.FFFF
31 30 29 28 27 26 25 24 23 22 21 20 19 18 17 16
PROG_ENABLE
Type R/W R/W R/W R/W R/W R/W R/W R/W R/W R/W R/W R/W R/W R/W R/W R/W
Reset 1 1 1 1 1 1 1 1 1 1 1 1 1 1 1 1
15 14 13 12 11 10 9 8 7 6 5 4 3 2 1 0
PROG_ENABLE
Type R/W R/W R/W R/W R/W R/W R/W R/W R/W R/W R/W R/W R/W R/W R/W R/W
Reset 1 1 1 1 1 1 1 1 1 1 1 1 1 1 1 1
Bit/Field Name Type Reset Description
Flash Programming Enable
Configures 2-KB flash blocks to be execute only. The policies may be
combined as shown in the table “Flash Protection Policy Combinations”.
Value Description
0xFFFFFFFF Enables 256 KB of flash.
31:0 PROG_ENABLE R/W 0xFFFFFFFF
March 17, 2008 161
Preliminary
LM3S8933 Microcontroller
9 General-Purpose Input/Outputs (GPIOs)
The GPIO module is composed of seven physical GPIO blocks, each corresponding to an individual
GPIO port (Port A, Port B, Port C, Port D, Port E, Port F, and Port G, ). The GPIO module supports
6-36 programmable input/output pins, depending on the peripherals being used.
The GPIO module has the following features:
■ Programmable control for GPIO interrupts
– Interrupt generation masking
– Edge-triggered on rising, falling, or both
– Level-sensitive on High or Low values
■ 5-V-tolerant input/outputs
■ 4 high-drive GPIO capacity per device: 18mA maximum at Vol = 1.2V (a maximum of two
high-drive pins per device side or BGA pin group).
■ Bit masking in both read and write operations through address lines
■ Programmable control for GPIO pad configuration:
– Weak pull-up or pull-down resistors
– 2-mA, 4-mA, and 8-mA pad drive for digital communication; 18mA pad drive for high current
applications
– Slew rate control for the 8-mA drive
– Open drain enables
– Digital input enables
9.1 Functional Description
Important: All GPIO pins are tri-stated by default (GPIOAFSEL=0, GPIODEN=0, GPIOPDR=0,
and GPIOPUR=0), with the exception of the five JTAG/SWD pins (PB7 and PC[3:0]).
The JTAG/SWD pins default to their JTAG/SWD functionality (GPIOAFSEL=1,
GPIODEN=1 and GPIOPUR=1). A Power-On-Reset (POR) or asserting RST puts both
groups of pins back to their default state.
Each GPIO port is a separate hardware instantiation of the same physical block (see Figure
9-1 on page 163). The LM3S8933 microcontroller contains seven ports and thus seven of these
physical GPIO blocks.
162 March 17, 2008
Preliminary
General-Purpose Input/Outputs (GPIOs)
Figure 9-1. GPIO Port Block Diagram
Alternate Input
Alternate Output
Alternate Output Enable
Interrupt
GPIO Input
GPIO Output
GPIO Output Enable
Pad Output
Pad Output Enable
Package I/O Pin
GPIODATA
GPIODIR
Data
Control
GPIOIS
GPIOIBE
GPIOIEV
GPIOIM
GPIORIS
GPIOMIS
GPIOICR
Interrupt
Control
GPIODR2R
GPIODR4R
GPIODR8R
GPIOSLR
GPIOPUR
GPIOPDR
GPIOODR
GPIODEN
Pad
Control
GPIOPeriphID0
GPIOPeriphID1
GPIOPeriphID2
GPIOPeriphID3
GPIOPeriphID4
GPIOPeriphID5
GPIOPeriphID6
GPIOPeriphID7
GPIOPCellID0
GPIOPCellID1
GPIOPCellID2
GPIOPCellID3
Identification Registers
GPIOAFSEL
Mode
Control
DEMUX MUX MUX
Digital
I/O Pad
Pad Input
GPIOLOCK
Commit
Control
GPIOCR
9.1.1 Data Control
The data control registers allow software to configure the operational modes of the GPIOs. The data
direction register configures the GPIO as an input or an output while the data register either captures
incoming data or drives it out to the pads.
9.1.1.1 Data Direction Operation
The GPIO Direction (GPIODIR) register (see page 171) is used to configure each individual pin as
an input or output. When the data direction bit is set to 0, the GPIO is configured as an input and
the corresponding data register bit will capture and store the value on the GPIO port. When the data
direction bit is set to 1, the GPIO is configured as an output and the corresponding data register bit
will be driven out on the GPIO port.
9.1.1.2 Data Register Operation
To aid in the efficiency of software, the GPIO ports allow for the modification of individual bits in the
GPIO Data (GPIODATA) register (see page 170) by using bits [9:2] of the address bus as a mask.
This allows software drivers to modify individual GPIO pins in a single instruction, without affecting
the state of the other pins. This is in contrast to the "typical" method of doing a read-modify-write
operation to set or clear an individual GPIO pin. To accommodate this feature, the GPIODATA
register covers 256 locations in the memory map.
During a write, if the address bit associated with that data bit is set to 1, the value of the GPIODATA
register is altered. If it is cleared to 0, it is left unchanged.
March 17, 2008 163
Preliminary
LM3S8933 Microcontroller
For example, writing a value of 0xEB to the address GPIODATA + 0x098 would yield as shown in
Figure 9-2 on page 164, where u is data unchanged by the write.
Figure 9-2. GPIODATA Write Example
0 0 1 0 0 1 1 0 1 0
u u 1 u u 0 1 u
9 8 7 6 5 4 3 2 1 0
1 1 1 0 1 0 1 1
7 6 5 4 3 2 1 0
GPIODATA
0xEB
0x098
ADDR[9:2]
During a read, if the address bit associated with the data bit is set to 1, the value is read. If the
address bit associated with the data bit is set to 0, it is read as a zero, regardless of its actual value.
For example, reading address GPIODATA + 0x0C4 yields as shown in Figure 9-3 on page 164.
Figure 9-3. GPIODATA Read Example
0 0 1 1 0 0 0 1 0 0
0 0 1 1 0 0 0 0
9 8 7 6 5 4 3 2 1 0
1 0 1 1 1 1 1 0
7 6 5 4 3 2 1 0
Returned Value
GPIODATA
0x0C4
ADDR[9:2]
9.1.2 Interrupt Control
The interrupt capabilities of each GPIO port are controlled by a set of seven registers. With these
registers, it is possible to select the source of the interrupt, its polarity, and the edge properties.
When one or more GPIO inputs cause an interrupt, a single interrupt output is sent to the interrupt
controller for the entire GPIO port. For edge-triggered interrupts, software must clear the interrupt
to enable any further interrupts. For a level-sensitive interrupt, it is assumed that the external source
holds the level constant for the interrupt to be recognized by the controller.
Three registers are required to define the edge or sense that causes interrupts:
■ GPIO Interrupt Sense (GPIOIS) register (see page 172)
■ GPIO Interrupt Both Edges (GPIOIBE) register (see page 173)
■ GPIO Interrupt Event (GPIOIEV) register (see page 174)
Interrupts are enabled/disabled via the GPIO Interrupt Mask (GPIOIM) register (see page 175).
When an interrupt condition occurs, the state of the interrupt signal can be viewed in two locations:
the GPIO Raw Interrupt Status (GPIORIS) and GPIO Masked Interrupt Status (GPIOMIS) registers
(see page 176 and page 177). As the name implies, the GPIOMIS register only shows interrupt
conditions that are allowed to be passed to the controller. The GPIORIS register indicates that a
GPIO pin meets the conditions for an interrupt, but has not necessarily been sent to the controller.
164 March 17, 2008
Preliminary
General-Purpose Input/Outputs (GPIOs)
In addition to providing GPIO functionality, PB4 can also be used as an external trigger for the ADC.
If PB4 is configured as a non-masked interrupt pin (the appropriate bit of GPIOIM is set to 1), not
only is an interrupt for PortB generated, but an external trigger signal is sent to the ADC. If the ADC
Event Multiplexer Select (ADCEMUX) register is configured to use the external trigger, an ADC
conversion is initiated.
If no other PortB pins are being used to generate interrupts, the ARM Integrated Nested Vectored
Interrupt Controller (NVIC) Interrupt Set Enable (SETNA) register can disable the PortB interrupts
and the ADC interrupt can be used to read back the converted data. Otherwise, the PortB interrupt
handler needs to ignore and clear interrupts on B4, and wait for the ADC interrupt or the ADC
interrupt needs to be disabled in the SETNA register and the PortB interrupt handler polls the ADC
registers until the conversion is completed.
Interrupts are cleared by writing a 1 to the appropriate bit of the GPIO Interrupt Clear (GPIOICR)
register (see page 178).
When programming the following interrupt control registers, the interrupts should be masked (GPIOIM
set to 0). Writing any value to an interrupt control register (GPIOIS, GPIOIBE, or GPIOIEV) can
generate a spurious interrupt if the corresponding bits are enabled.
9.1.3 Mode Control
The GPIO pins can be controlled by either hardware or software. When hardware control is enabled
via the GPIO Alternate Function Select (GPIOAFSEL) register (see page 179), the pin state is
controlled by its alternate function (that is, the peripheral). Software control corresponds to GPIO
mode, where the GPIODATA register is used to read/write the corresponding pins.
9.1.4 Commit Control
The commit control registers provide a layer of protection against accidental programming of critical
hardware peripherals. Writes to protected bits of the GPIO Alternate Function Select (GPIOAFSEL)
register (see page 179) are not committed to storage unless the GPIO Lock (GPIOLOCK) register
(see page 189) has been unlocked and the appropriate bits of the GPIO Commit (GPIOCR) register
(see page 190) have been set to 1.
9.1.5 Pad Control
The pad control registers allow for GPIO pad configuration by software based on the application
requirements. The pad control registers include the GPIODR2R, GPIODR4R, GPIODR8R, GPIOODR,
GPIOPUR, GPIOPDR, GPIOSLR, and GPIODEN registers.
9.1.6 Identification
The identification registers configured at reset allow software to detect and identify the module as
a GPIO block. The identification registers include the GPIOPeriphID0-GPIOPeriphID7 registers as
well as the GPIOPCellID0-GPIOPCellID3 registers.
9.2 Initialization and Configuration
To use the GPIO, the peripheral clock must be enabled by setting the appropriate GPIO Port bit
field (GPIOn) in the RCGC2 register.
On reset, all GPIO pins (except for the five JTAG pins) are configured out of reset to be undriven
(tristate): GPIOAFSEL=0, GPIODEN=0, GPIOPDR=0, and GPIOPUR=0. Table 9-1 on page 166
shows all possible configurations of the GPIO pads and the control register settings required to
March 17, 2008 165
Preliminary
LM3S8933 Microcontroller
achieve them. Table 9-2 on page 166 shows how a rising edge interrupt would be configured for pin
2 of a GPIO port.
Table 9-1. GPIO Pad Configuration Examples
Configuration GPIO Register Bit Valuea
AFSEL DIR ODR DEN PUR PDR DR2R DR4R DR8R SLR
Digital Input (GPIO) 0 0 0 1 ? ? X X X X
Digital Output (GPIO) 0 1 0 1 ? ? ? ? ? ?
Open Drain Input 0 0 1 1 X X X X X X
(GPIO)
Open Drain Output 0 1 1 1 X X ? ? ? ?
(GPIO)
Open Drain 1 X 1 1 X X ? ? ? ?
Input/Output (I2C)
Digital Input (Timer 1 X 0 1 ? ? X X X X
CCP)
Digital Output (Timer 1 X 0 1 ? ? ? ? ? ?
PWM)
Digital Input/Output 1 X 0 1 ? ? ? ? ? ?
(SSI)
Digital Input/Output 1 X 0 1 ? ? ? ? ? ?
(UART)
Analog Input 0 0 0 0 0 0 X X X X
(Comparator)
Digital Output 1 X 0 1 ? ? ? ? ? ?
(Comparator)
a. X=Ignored (don’t care bit)
?=Can be either 0 or 1, depending on the configuration
Table 9-2. GPIO Interrupt Configuration Example
Desired Pin 2 Bit Valuea
Interrupt
Event
Trigger
Register
7 6 5 4 3 2 1 0
0=edge X X X X X 0 X X
1=level
GPIOIS
0=single X X X X X 0 X X
edge
1=both
edges
GPIOIBE
0=Low level, X X X X X 1 X X
or negative
edge
1=High level,
or positive
edge
GPIOIEV
166 March 17, 2008
Preliminary
General-Purpose Input/Outputs (GPIOs)
Desired Pin 2 Bit Valuea
Interrupt
Event
Trigger
Register
7 6 5 4 3 2 1 0
0=masked 0 0 0 0 0 1 0 0
1=not
masked
GPIOIM
a. X=Ignored (don’t care bit)
9.3 Register Map
Table 9-3 on page 168 lists the GPIO registers. The offset listed is a hexadecimal increment to the
register’s address, relative to that GPIO port’s base address:
■ GPIO Port A: 0x4000.4000
■ GPIO Port B: 0x4000.5000
■ GPIO Port C: 0x4000.6000
■ GPIO Port D: 0x4000.7000
■ GPIO Port E: 0x4002.4000
■ GPIO Port F: 0x4002.5000
■ GPIO Port G: 0x4002.6000
Important: The GPIO registers in this chapter are duplicated in each GPIO block, however,
depending on the block, all eight bits may not be connected to a GPIO pad. In those
cases, writing to those unconnected bits has no effect and reading those unconnected
bits returns no meaningful data.
Note: The default reset value for the GPIOAFSEL, GPIOPUR, and GPIODEN registers are
0x0000.0000 for all GPIO pins, with the exception of the five JTAG/SWD pins (PB7 and
PC[3:0]). These five pins default to JTAG/SWD functionality. Because of this, the default
reset value of these registers for GPIO Port B is 0x0000.0080 while the default reset value
for Port C is 0x0000.000F.
The default register type for the GPIOCR register is RO for all GPIO pins, with the exception
of the five JTAG/SWD pins (PB7 and PC[3:0]). These five pins are currently the only
GPIOs that are protected by the GPIOCR register. Because of this, the register type for
GPIO Port B7 and GPIO Port C[3:0] is R/W.
The default reset value for the GPIOCR register is 0x0000.00FF for all GPIO pins, with the
exception of the five JTAG/SWD pins (PB7 and PC[3:0]). To ensure that the JTAG port
is not accidentally programmed as a GPIO, these five pins default to non-committable.
Because of this, the default reset value of GPIOCR for GPIO Port B is 0x0000.007F while
the default reset value of GPIOCR for Port C is 0x0000.00F0.
March 17, 2008 167
Preliminary
LM3S8933 Microcontroller
Table 9-3. GPIO Register Map
See
Offset Name Type Reset Description page
0x000 GPIODATA R/W 0x0000.0000 GPIO Data 170
0x400 GPIODIR R/W 0x0000.0000 GPIO Direction 171
0x404 GPIOIS R/W 0x0000.0000 GPIO Interrupt Sense 172
0x408 GPIOIBE R/W 0x0000.0000 GPIO Interrupt Both Edges 173
0x40C GPIOIEV R/W 0x0000.0000 GPIO Interrupt Event 174
0x410 GPIOIM R/W 0x0000.0000 GPIO Interrupt Mask 175
0x414 GPIORIS RO 0x0000.0000 GPIO Raw Interrupt Status 176
0x418 GPIOMIS RO 0x0000.0000 GPIO Masked Interrupt Status 177
0x41C GPIOICR W1C 0x0000.0000 GPIO Interrupt Clear 178
0x420 GPIOAFSEL R/W - GPIO Alternate Function Select 179
0x500 GPIODR2R R/W 0x0000.00FF GPIO 2-mA Drive Select 181
0x504 GPIODR4R R/W 0x0000.0000 GPIO 4-mA Drive Select 182
0x508 GPIODR8R R/W 0x0000.0000 GPIO 8-mA Drive Select 183
0x50C GPIOODR R/W 0x0000.0000 GPIO Open Drain Select 184
0x510 GPIOPUR R/W - GPIO Pull-Up Select 185
0x514 GPIOPDR R/W 0x0000.0000 GPIO Pull-Down Select 186
0x518 GPIOSLR R/W 0x0000.0000 GPIO Slew Rate Control Select 187
0x51C GPIODEN R/W - GPIO Digital Enable 188
0x520 GPIOLOCK R/W 0x0000.0001 GPIO Lock 189
0x524 GPIOCR - - GPIO Commit 190
0xFD0 GPIOPeriphID4 RO 0x0000.0000 GPIO Peripheral Identification 4 192
0xFD4 GPIOPeriphID5 RO 0x0000.0000 GPIO Peripheral Identification 5 193
0xFD8 GPIOPeriphID6 RO 0x0000.0000 GPIO Peripheral Identification 6 194
0xFDC GPIOPeriphID7 RO 0x0000.0000 GPIO Peripheral Identification 7 195
0xFE0 GPIOPeriphID0 RO 0x0000.0061 GPIO Peripheral Identification 0 196
0xFE4 GPIOPeriphID1 RO 0x0000.0000 GPIO Peripheral Identification 1 197
0xFE8 GPIOPeriphID2 RO 0x0000.0018 GPIO Peripheral Identification 2 198
0xFEC GPIOPeriphID3 RO 0x0000.0001 GPIO Peripheral Identification 3 199
0xFF0 GPIOPCellID0 RO 0x0000.000D GPIO PrimeCell Identification 0 200
0xFF4 GPIOPCellID1 RO 0x0000.00F0 GPIO PrimeCell Identification 1 201
0xFF8 GPIOPCellID2 RO 0x0000.0005 GPIO PrimeCell Identification 2 202
0xFFC GPIOPCellID3 RO 0x0000.00B1 GPIO PrimeCell Identification 3 203
168 March 17, 2008
Preliminary
General-Purpose Input/Outputs (GPIOs)
9.4 Register Descriptions
The remainder of this section lists and describes the GPIO registers, in numerical order by address
offset.
March 17, 2008 169
Preliminary
LM3S8933 Microcontroller
Register 1: GPIO Data (GPIODATA), offset 0x000
The GPIODATA register is the data register. In software control mode, values written in the
GPIODATA register are transferred onto the GPIO port pins if the respective pins have been
configured as outputs through the GPIO Direction (GPIODIR) register (see page 171).
In order to write to GPIODATA, the corresponding bits in the mask, resulting from the address bus
bits [9:2], must be High. Otherwise, the bit values remain unchanged by the write.
Similarly, the values read from this register are determined for each bit by the mask bit derived from
the address used to access the data register, bits [9:2]. Bits that are 1 in the address mask cause
the corresponding bits in GPIODATA to be read, and bits that are 0 in the address mask cause the
corresponding bits in GPIODATA to be read as 0, regardless of their value.
A read from GPIODATA returns the last bit value written if the respective pins are configured as
outputs, or it returns the value on the corresponding input pin when these are configured as inputs.
All bits are cleared by a reset.
GPIO Data (GPIODATA)
GPIO Port A base: 0x4000.4000
GPIO Port B base: 0x4000.5000
GPIO Port C base: 0x4000.6000
GPIO Port D base: 0x4000.7000
GPIO Port E base: 0x4002.4000
GPIO Port F base: 0x4002.5000
GPIO Port G base: 0x4002.6000
Offset 0x000
Type R/W, reset 0x0000.0000
31 30 29 28 27 26 25 24 23 22 21 20 19 18 17 16
reserved
Type RO RO RO RO RO RO RO RO RO RO RO RO RO RO RO RO
Reset 0 0 0 0 0 0 0 0 0 0 0 0 0 0 0 0
15 14 13 12 11 10 9 8 7 6 5 4 3 2 1 0
reserved DATA
Type RO RO RO RO RO RO RO RO R/W R/W R/W R/W R/W R/W R/W R/W
Reset 0 0 0 0 0 0 0 0 0 0 0 0 0 0 0 0
Bit/Field Name Type Reset Description
Software should not rely on the value of a reserved bit. To provide
compatibility with future products, the value of a reserved bit should be
preserved across a read-modify-write operation.
31:8 reserved RO 0x00
GPIO Data
This register is virtually mapped to 256 locations in the address space.
To facilitate the reading and writing of data to these registers by
independent drivers, the data read from and the data written to the
registers are masked by the eight address lines ipaddr[9:2]. Reads
from this register return its current state. Writes to this register only affect
bits that are not masked by ipaddr[9:2] and are configured as
outputs. See “Data Register Operation” on page 163 for examples of
reads and writes.
7:0 DATA R/W 0x00
170 March 17, 2008
Preliminary
General-Purpose Input/Outputs (GPIOs)
Register 2: GPIO Direction (GPIODIR), offset 0x400
The GPIODIR register is the data direction register. Bits set to 1 in the GPIODIR register configure
the corresponding pin to be an output, while bits set to 0 configure the pins to be inputs. All bits are
cleared by a reset, meaning all GPIO pins are inputs by default.
GPIO Direction (GPIODIR)
GPIO Port A base: 0x4000.4000
GPIO Port B base: 0x4000.5000
GPIO Port C base: 0x4000.6000
GPIO Port D base: 0x4000.7000
GPIO Port E base: 0x4002.4000
GPIO Port F base: 0x4002.5000
GPIO Port G base: 0x4002.6000
Offset 0x400
Type R/W, reset 0x0000.0000
31 30 29 28 27 26 25 24 23 22 21 20 19 18 17 16
reserved
Type RO RO RO RO RO RO RO RO RO RO RO RO RO RO RO RO
Reset 0 0 0 0 0 0 0 0 0 0 0 0 0 0 0 0
15 14 13 12 11 10 9 8 7 6 5 4 3 2 1 0
reserved DIR
Type RO RO RO RO RO RO RO RO R/W R/W R/W R/W R/W R/W R/W R/W
Reset 0 0 0 0 0 0 0 0 0 0 0 0 0 0 0 0
Bit/Field Name Type Reset Description
Software should not rely on the value of a reserved bit. To provide
compatibility with future products, the value of a reserved bit should be
preserved across a read-modify-write operation.
31:8 reserved RO 0x00
GPIO Data Direction
The DIR values are defined as follows:
Value Description
0 Pins are inputs.
1 Pins are outputs.
7:0 DIR R/W 0x00
March 17, 2008 171
Preliminary
LM3S8933 Microcontroller
Register 3: GPIO Interrupt Sense (GPIOIS), offset 0x404
The GPIOIS register is the interrupt sense register. Bits set to 1 in GPIOIS configure the
corresponding pins to detect levels, while bits set to 0 configure the pins to detect edges. All bits
are cleared by a reset.
GPIO Interrupt Sense (GPIOIS)
GPIO Port A base: 0x4000.4000
GPIO Port B base: 0x4000.5000
GPIO Port C base: 0x4000.6000
GPIO Port D base: 0x4000.7000
GPIO Port E base: 0x4002.4000
GPIO Port F base: 0x4002.5000
GPIO Port G base: 0x4002.6000
Offset 0x404
Type R/W, reset 0x0000.0000
31 30 29 28 27 26 25 24 23 22 21 20 19 18 17 16
reserved
Type RO RO RO RO RO RO RO RO RO RO RO RO RO RO RO RO
Reset 0 0 0 0 0 0 0 0 0 0 0 0 0 0 0 0
15 14 13 12 11 10 9 8 7 6 5 4 3 2 1 0
reserved IS
Type RO RO RO RO RO RO RO RO R/W R/W R/W R/W R/W R/W R/W R/W
Reset 0 0 0 0 0 0 0 0 0 0 0 0 0 0 0 0
Bit/Field Name Type Reset Description
Software should not rely on the value of a reserved bit. To provide
compatibility with future products, the value of a reserved bit should be
preserved across a read-modify-write operation.
31:8 reserved RO 0x00
GPIO Interrupt Sense
The IS values are defined as follows:
Value Description
0 Edge on corresponding pin is detected (edge-sensitive).
1 Level on corresponding pin is detected (level-sensitive).
7:0 IS R/W 0x00
172 March 17, 2008
Preliminary
General-Purpose Input/Outputs (GPIOs)
Register 4: GPIO Interrupt Both Edges (GPIOIBE), offset 0x408
The GPIOIBE register is the interrupt both-edges register. When the corresponding bit in the GPIO
Interrupt Sense (GPIOIS) register (see page 172) is set to detect edges, bits set to High in GPIOIBE
configure the corresponding pin to detect both rising and falling edges, regardless of the
corresponding bit in the GPIO Interrupt Event (GPIOIEV) register (see page 174). Clearing a bit
configures the pin to be controlled by GPIOIEV. All bits are cleared by a reset.
GPIO Interrupt Both Edges (GPIOIBE)
GPIO Port A base: 0x4000.4000
GPIO Port B base: 0x4000.5000
GPIO Port C base: 0x4000.6000
GPIO Port D base: 0x4000.7000
GPIO Port E base: 0x4002.4000
GPIO Port F base: 0x4002.5000
GPIO Port G base: 0x4002.6000
Offset 0x408
Type R/W, reset 0x0000.0000
31 30 29 28 27 26 25 24 23 22 21 20 19 18 17 16
reserved
Type RO RO RO RO RO RO RO RO RO RO RO RO RO RO RO RO
Reset 0 0 0 0 0 0 0 0 0 0 0 0 0 0 0 0
15 14 13 12 11 10 9 8 7 6 5 4 3 2 1 0
reserved IBE
Type RO RO RO RO RO RO RO RO R/W R/W R/W R/W R/W R/W R/W R/W
Reset 0 0 0 0 0 0 0 0 0 0 0 0 0 0 0 0
Bit/Field Name Type Reset Description
Software should not rely on the value of a reserved bit. To provide
compatibility with future products, the value of a reserved bit should be
preserved across a read-modify-write operation.
31:8 reserved RO 0x00
GPIO Interrupt Both Edges
The IBE values are defined as follows:
Value Description
Interrupt generation is controlled by the GPIO Interrupt Event
(GPIOIEV) register (see page 174).
0
1 Both edges on the corresponding pin trigger an interrupt.
Note: Single edge is determined by the corresponding bit
in GPIOIEV.
7:0 IBE R/W 0x00
March 17, 2008 173
Preliminary
LM3S8933 Microcontroller
Register 5: GPIO Interrupt Event (GPIOIEV), offset 0x40C
The GPIOIEV register is the interrupt event register. Bits set to High in GPIOIEV configure the
corresponding pin to detect rising edges or high levels, depending on the corresponding bit value
in the GPIO Interrupt Sense (GPIOIS) register (see page 172). Clearing a bit configures the pin to
detect falling edges or low levels, depending on the corresponding bit value in GPIOIS. All bits are
cleared by a reset.
GPIO Interrupt Event (GPIOIEV)
GPIO Port A base: 0x4000.4000
GPIO Port B base: 0x4000.5000
GPIO Port C base: 0x4000.6000
GPIO Port D base: 0x4000.7000
GPIO Port E base: 0x4002.4000
GPIO Port F base: 0x4002.5000
GPIO Port G base: 0x4002.6000
Offset 0x40C
Type R/W, reset 0x0000.0000
31 30 29 28 27 26 25 24 23 22 21 20 19 18 17 16
reserved
Type RO RO RO RO RO RO RO RO RO RO RO RO RO RO RO RO
Reset 0 0 0 0 0 0 0 0 0 0 0 0 0 0 0 0
15 14 13 12 11 10 9 8 7 6 5 4 3 2 1 0
reserved IEV
Type RO RO RO RO RO RO RO RO R/W R/W R/W R/W R/W R/W R/W R/W
Reset 0 0 0 0 0 0 0 0 0 0 0 0 0 0 0 0
Bit/Field Name Type Reset Description
Software should not rely on the value of a reserved bit. To provide
compatibility with future products, the value of a reserved bit should be
preserved across a read-modify-write operation.
31:8 reserved RO 0x00
GPIO Interrupt Event
The IEV values are defined as follows:
Value Description
Falling edge or Low levels on corresponding pins trigger
interrupts.
0
Rising edge or High levels on corresponding pins trigger
interrupts.
1
7:0 IEV R/W 0x00
174 March 17, 2008
Preliminary
General-Purpose Input/Outputs (GPIOs)
Register 6: GPIO Interrupt Mask (GPIOIM), offset 0x410
The GPIOIM register is the interrupt mask register. Bits set to High in GPIOIM allow the corresponding
pins to trigger their individual interrupts and the combined GPIOINTR line. Clearing a bit disables
interrupt triggering on that pin. All bits are cleared by a reset.
GPIO Interrupt Mask (GPIOIM)
GPIO Port A base: 0x4000.4000
GPIO Port B base: 0x4000.5000
GPIO Port C base: 0x4000.6000
GPIO Port D base: 0x4000.7000
GPIO Port E base: 0x4002.4000
GPIO Port F base: 0x4002.5000
GPIO Port G base: 0x4002.6000
Offset 0x410
Type R/W, reset 0x0000.0000
31 30 29 28 27 26 25 24 23 22 21 20 19 18 17 16
reserved
Type RO RO RO RO RO RO RO RO RO RO RO RO RO RO RO RO
Reset 0 0 0 0 0 0 0 0 0 0 0 0 0 0 0 0
15 14 13 12 11 10 9 8 7 6 5 4 3 2 1 0
reserved IME
Type RO RO RO RO RO RO RO RO R/W R/W R/W R/W R/W R/W R/W R/W
Reset 0 0 0 0 0 0 0 0 0 0 0 0 0 0 0 0
Bit/Field Name Type Reset Description
Software should not rely on the value of a reserved bit. To provide
compatibility with future products, the value of a reserved bit should be
preserved across a read-modify-write operation.
31:8 reserved RO 0x00
GPIO Interrupt Mask Enable
The IME values are defined as follows:
Value Description
0 Corresponding pin interrupt is masked.
1 Corresponding pin interrupt is not masked.
7:0 IME R/W 0x00
March 17, 2008 175
Preliminary
LM3S8933 Microcontroller
Register 7: GPIO Raw Interrupt Status (GPIORIS), offset 0x414
The GPIORIS register is the raw interrupt status register. Bits read High in GPIORIS reflect the
status of interrupt trigger conditions detected (raw, prior to masking), indicating that all the
requirements have been met, before they are finally allowed to trigger by the GPIO Interrupt Mask
(GPIOIM) register (see page 175). Bits read as zero indicate that corresponding input pins have not
initiated an interrupt. All bits are cleared by a reset.
GPIO Raw Interrupt Status (GPIORIS)
GPIO Port A base: 0x4000.4000
GPIO Port B base: 0x4000.5000
GPIO Port C base: 0x4000.6000
GPIO Port D base: 0x4000.7000
GPIO Port E base: 0x4002.4000
GPIO Port F base: 0x4002.5000
GPIO Port G base: 0x4002.6000
Offset 0x414
Type RO, reset 0x0000.0000
31 30 29 28 27 26 25 24 23 22 21 20 19 18 17 16
reserved
Type RO RO RO RO RO RO RO RO RO RO RO RO RO RO RO RO
Reset 0 0 0 0 0 0 0 0 0 0 0 0 0 0 0 0
15 14 13 12 11 10 9 8 7 6 5 4 3 2 1 0
reserved RIS
Type RO RO RO RO RO RO RO RO RO RO RO RO RO RO RO RO
Reset 0 0 0 0 0 0 0 0 0 0 0 0 0 0 0 0
Bit/Field Name Type Reset Description
Software should not rely on the value of a reserved bit. To provide
compatibility with future products, the value of a reserved bit should be
preserved across a read-modify-write operation.
31:8 reserved RO 0x00
GPIO Interrupt Raw Status
Reflects the status of interrupt trigger condition detection on pins (raw,
prior to masking).
The RIS values are defined as follows:
Value Description
0 Corresponding pin interrupt requirements not met.
1 Corresponding pin interrupt has met requirements.
7:0 RIS RO 0x00
176 March 17, 2008
Preliminary
General-Purpose Input/Outputs (GPIOs)
Register 8: GPIO Masked Interrupt Status (GPIOMIS), offset 0x418
The GPIOMIS register is the masked interrupt status register. Bits read High in GPIOMIS reflect
the status of input lines triggering an interrupt. Bits read as Low indicate that either no interrupt has
been generated, or the interrupt is masked.
In addition to providing GPIO functionality, PB4 can also be used as an external trigger for the ADC.
If PB4 is configured as a non-masked interrupt pin (the appropriate bit of GPIOIM is set to 1), not
only is an interrupt for PortB generated, but an external trigger signal is sent to the ADC. If the ADC
Event Multiplexer Select (ADCEMUX) register is configured to use the external trigger, an ADC
conversion is initiated.
If no other PortB pins are being used to generate interrupts, the ARM Integrated Nested Vectored
Interrupt Controller (NVIC) Interrupt Set Enable (SETNA) register can disable the PortB interrupts
and the ADC interrupt can be used to read back the converted data. Otherwise, the PortB interrupt
handler needs to ignore and clear interrupts on B4, and wait for the ADC interrupt or the ADC
interrupt needs to be disabled in the SETNA register and the PortB interrupt handler polls the ADC
registers until the conversion is completed.
GPIOMIS is the state of the interrupt after masking.
GPIO Masked Interrupt Status (GPIOMIS)
GPIO Port A base: 0x4000.4000
GPIO Port B base: 0x4000.5000
GPIO Port C base: 0x4000.6000
GPIO Port D base: 0x4000.7000
GPIO Port E base: 0x4002.4000
GPIO Port F base: 0x4002.5000
GPIO Port G base: 0x4002.6000
Offset 0x418
Type RO, reset 0x0000.0000
31 30 29 28 27 26 25 24 23 22 21 20 19 18 17 16
reserved
Type RO RO RO RO RO RO RO RO RO RO RO RO RO RO RO RO
Reset 0 0 0 0 0 0 0 0 0 0 0 0 0 0 0 0
15 14 13 12 11 10 9 8 7 6 5 4 3 2 1 0
reserved MIS
Type RO RO RO RO RO RO RO RO RO RO RO RO RO RO RO RO
Reset 0 0 0 0 0 0 0 0 0 0 0 0 0 0 0 0
Bit/Field Name Type Reset Description
Software should not rely on the value of a reserved bit. To provide
compatibility with future products, the value of a reserved bit should be
preserved across a read-modify-write operation.
31:8 reserved RO 0x00
GPIO Masked Interrupt Status
Masked value of interrupt due to corresponding pin.
The MIS values are defined as follows:
Value Description
0 Corresponding GPIO line interrupt not active.
1 Corresponding GPIO line asserting interrupt.
7:0 MIS RO 0x00
March 17, 2008 177
Preliminary
LM3S8933 Microcontroller
Register 9: GPIO Interrupt Clear (GPIOICR), offset 0x41C
The GPIOICR register is the interrupt clear register. Writing a 1 to a bit in this register clears the
corresponding interrupt edge detection logic register. Writing a 0 has no effect.
GPIO Interrupt Clear (GPIOICR)
GPIO Port A base: 0x4000.4000
GPIO Port B base: 0x4000.5000
GPIO Port C base: 0x4000.6000
GPIO Port D base: 0x4000.7000
GPIO Port E base: 0x4002.4000
GPIO Port F base: 0x4002.5000
GPIO Port G base: 0x4002.6000
Offset 0x41C
Type W1C, reset 0x0000.0000
31 30 29 28 27 26 25 24 23 22 21 20 19 18 17 16
reserved
Type RO RO RO RO RO RO RO RO RO RO RO RO RO RO RO RO
Reset 0 0 0 0 0 0 0 0 0 0 0 0 0 0 0 0
15 14 13 12 11 10 9 8 7 6 5 4 3 2 1 0
reserved IC
Type RO RO RO RO RO RO RO RO W1C W1C W1C W1C W1C W1C W1C W1C
Reset 0 0 0 0 0 0 0 0 0 0 0 0 0 0 0 0
Bit/Field Name Type Reset Description
Software should not rely on the value of a reserved bit. To provide
compatibility with future products, the value of a reserved bit should be
preserved across a read-modify-write operation.
31:8 reserved RO 0x00
GPIO Interrupt Clear
The IC values are defined as follows:
Value Description
0 Corresponding interrupt is unaffected.
1 Corresponding interrupt is cleared.
7:0 IC W1C 0x00
178 March 17, 2008
Preliminary
General-Purpose Input/Outputs (GPIOs)
Register 10: GPIO Alternate Function Select (GPIOAFSEL), offset 0x420
The GPIOAFSEL register is the mode control select register. Writing a 1 to any bit in this register
selects the hardware control for the corresponding GPIO line. All bits are cleared by a reset, therefore
no GPIO line is set to hardware control by default.
The commit control registers provide a layer of protection against accidental programming of critical
hardware peripherals. Writes to protected bits of the GPIO Alternate Function Select (GPIOAFSEL)
register (see page 179) are not committed to storage unless the GPIO Lock (GPIOLOCK) register
(see page 189) has been unlocked and the appropriate bits of the GPIO Commit (GPIOCR) register
(see page 190) have been set to 1.
Important: All GPIO pins are tri-stated by default (GPIOAFSEL=0, GPIODEN=0, GPIOPDR=0,
and GPIOPUR=0), with the exception of the five JTAG/SWD pins (PB7 and PC[3:0]).
The JTAG/SWD pins default to their JTAG/SWD functionality (GPIOAFSEL=1,
GPIODEN=1 and GPIOPUR=1). A Power-On-Reset (POR) or asserting RST puts both
groups of pins back to their default state.
Caution – If the JTAG pins are used as GPIOs in a design, PB7 and PC2 cannot have external pull-down
resistors connected to both of them at the same time. If both pins are pulled Low during reset, the
controller has unpredictable behavior. If this happens, remove one or both of the pull-down resistors,
and apply RST or power-cycle the part.
In addition, it is possible to create a software sequence that prevents the debugger from connecting to
the Stellaris® microcontroller. If the program code loaded into flash immediately changes the JTAG
pins to their GPIO functionality, the debugger may not have enough time to connect and halt the
controller before the JTAG pin functionality switches. This may lock the debugger out of the part. This
can be avoided with a software routine that restores JTAG functionality based on an external or software
trigger.
GPIO Alternate Function Select (GPIOAFSEL)
GPIO Port A base: 0x4000.4000
GPIO Port B base: 0x4000.5000
GPIO Port C base: 0x4000.6000
GPIO Port D base: 0x4000.7000
GPIO Port E base: 0x4002.4000
GPIO Port F base: 0x4002.5000
GPIO Port G base: 0x4002.6000
Offset 0x420
Type R/W, reset -
31 30 29 28 27 26 25 24 23 22 21 20 19 18 17 16
reserved
Type RO RO RO RO RO RO RO RO RO RO RO RO RO RO RO RO
Reset 0 0 0 0 0 0 0 0 0 0 0 0 0 0 0 0
15 14 13 12 11 10 9 8 7 6 5 4 3 2 1 0
reserved AFSEL
Type RO RO RO RO RO RO RO RO R/W R/W R/W R/W R/W R/W R/W R/W
Reset 0 0 0 0 0 0 0 0 - - - - - - - -
Bit/Field Name Type Reset Description
Software should not rely on the value of a reserved bit. To provide
compatibility with future products, the value of a reserved bit should be
preserved across a read-modify-write operation.
31:8 reserved RO 0x00
March 17, 2008 179
Preliminary
LM3S8933 Microcontroller
Bit/Field Name Type Reset Description
GPIO Alternate Function Select
The AFSEL values are defined as follows:
Value Description
0 Software control of corresponding GPIO line (GPIO mode).
Hardware control of corresponding GPIO line (alternate
hardware function).
1
Note: The default reset value for the GPIOAFSEL,
GPIOPUR, and GPIODEN registers are 0x0000.0000
for all GPIO pins, with the exception of the five
JTAG/SWD pins (PB7 and PC[3:0]). These five pins
default to JTAG/SWD functionality. Because of this,
the default reset value of these registers for GPIO
Port B is 0x0000.0080 while the default reset value
for Port C is 0x0000.000F.
7:0 AFSEL R/W -
180 March 17, 2008
Preliminary
General-Purpose Input/Outputs (GPIOs)
Register 11: GPIO 2-mA Drive Select (GPIODR2R), offset 0x500
The GPIODR2R register is the 2-mA drive control register. It allows for each GPIO signal in the port
to be individually configured without affecting the other pads. When writing a DRV2 bit for a GPIO
signal, the corresponding DRV4 bit in the GPIODR4R register and the DRV8 bit in the GPIODR8R
register are automatically cleared by hardware.
GPIO 2-mA Drive Select (GPIODR2R)
GPIO Port A base: 0x4000.4000
GPIO Port B base: 0x4000.5000
GPIO Port C base: 0x4000.6000
GPIO Port D base: 0x4000.7000
GPIO Port E base: 0x4002.4000
GPIO Port F base: 0x4002.5000
GPIO Port G base: 0x4002.6000
Offset 0x500
Type R/W, reset 0x0000.00FF
31 30 29 28 27 26 25 24 23 22 21 20 19 18 17 16
reserved
Type RO RO RO RO RO RO RO RO RO RO RO RO RO RO RO RO
Reset 0 0 0 0 0 0 0 0 0 0 0 0 0 0 0 0
15 14 13 12 11 10 9 8 7 6 5 4 3 2 1 0
reserved DRV2
Type RO RO RO RO RO RO RO RO R/W R/W R/W R/W R/W R/W R/W R/W
Reset 0 0 0 0 0 0 0 0 1 1 1 1 1 1 1 1
Bit/Field Name Type Reset Description
Software should not rely on the value of a reserved bit. To provide
compatibility with future products, the value of a reserved bit should be
preserved across a read-modify-write operation.
31:8 reserved RO 0x00
Output Pad 2-mA Drive Enable
A write of 1 to either GPIODR4[n] or GPIODR8[n] clears the
corresponding 2-mA enable bit. The change is effective on the second
clock cycle after the write.
7:0 DRV2 R/W 0xFF
March 17, 2008 181
Preliminary
LM3S8933 Microcontroller
Register 12: GPIO 4-mA Drive Select (GPIODR4R), offset 0x504
The GPIODR4R register is the 4-mA drive control register. It allows for each GPIO signal in the port
to be individually configured without affecting the other pads. When writing the DRV4 bit for a GPIO
signal, the corresponding DRV2 bit in the GPIODR2R register and the DRV8 bit in the GPIODR8R
register are automatically cleared by hardware.
GPIO 4-mA Drive Select (GPIODR4R)
GPIO Port A base: 0x4000.4000
GPIO Port B base: 0x4000.5000
GPIO Port C base: 0x4000.6000
GPIO Port D base: 0x4000.7000
GPIO Port E base: 0x4002.4000
GPIO Port F base: 0x4002.5000
GPIO Port G base: 0x4002.6000
Offset 0x504
Type R/W, reset 0x0000.0000
31 30 29 28 27 26 25 24 23 22 21 20 19 18 17 16
reserved
Type RO RO RO RO RO RO RO RO RO RO RO RO RO RO RO RO
Reset 0 0 0 0 0 0 0 0 0 0 0 0 0 0 0 0
15 14 13 12 11 10 9 8 7 6 5 4 3 2 1 0
reserved DRV4
Type RO RO RO RO RO RO RO RO R/W R/W R/W R/W R/W R/W R/W R/W
Reset 0 0 0 0 0 0 0 0 0 0 0 0 0 0 0 0
Bit/Field Name Type Reset Description
Software should not rely on the value of a reserved bit. To provide
compatibility with future products, the value of a reserved bit should be
preserved across a read-modify-write operation.
31:8 reserved RO 0x00
Output Pad 4-mA Drive Enable
A write of 1 to either GPIODR2[n] or GPIODR8[n] clears the
corresponding 4-mA enable bit. The change is effective on the second
clock cycle after the write.
7:0 DRV4 R/W 0x00
182 March 17, 2008
Preliminary
General-Purpose Input/Outputs (GPIOs)
Register 13: GPIO 8-mA Drive Select (GPIODR8R), offset 0x508
The GPIODR8R register is the 8-mA drive control register. It allows for each GPIO signal in the port
to be individually configured without affecting the other pads. When writing the DRV8 bit for a GPIO
signal, the corresponding DRV2 bit in the GPIODR2R register and the DRV4 bit in the GPIODR4R
register are automatically cleared by hardware.
GPIO 8-mA Drive Select (GPIODR8R)
GPIO Port A base: 0x4000.4000
GPIO Port B base: 0x4000.5000
GPIO Port C base: 0x4000.6000
GPIO Port D base: 0x4000.7000
GPIO Port E base: 0x4002.4000
GPIO Port F base: 0x4002.5000
GPIO Port G base: 0x4002.6000
Offset 0x508
Type R/W, reset 0x0000.0000
31 30 29 28 27 26 25 24 23 22 21 20 19 18 17 16
reserved
Type RO RO RO RO RO RO RO RO RO RO RO RO RO RO RO RO
Reset 0 0 0 0 0 0 0 0 0 0 0 0 0 0 0 0
15 14 13 12 11 10 9 8 7 6 5 4 3 2 1 0
reserved DRV8
Type RO RO RO RO RO RO RO RO R/W R/W R/W R/W R/W R/W R/W R/W
Reset 0 0 0 0 0 0 0 0 0 0 0 0 0 0 0 0
Bit/Field Name Type Reset Description
Software should not rely on the value of a reserved bit. To provide
compatibility with future products, the value of a reserved bit should be
preserved across a read-modify-write operation.
31:8 reserved RO 0x00
Output Pad 8-mA Drive Enable
A write of 1 to either GPIODR2[n] or GPIODR4[n] clears the
corresponding 8-mA enable bit. The change is effective on the second
clock cycle after the write.
7:0 DRV8 R/W 0x00
March 17, 2008 183
Preliminary
LM3S8933 Microcontroller
Register 14: GPIO Open Drain Select (GPIOODR), offset 0x50C
The GPIOODR register is the open drain control register. Setting a bit in this register enables the
open drain configuration of the corresponding GPIO pad. When open drain mode is enabled, the
corresponding bit should also be set in the GPIO Digital Input Enable (GPIODEN) register (see
page 188). Corresponding bits in the drive strength registers (GPIODR2R, GPIODR4R, GPIODR8R,
and GPIOSLR ) can be set to achieve the desired rise and fall times. The GPIO acts as an open
drain input if the corresponding bit in the GPIODIR register is set to 0; and as an open drain output
when set to 1.
GPIO Open Drain Select (GPIOODR)
GPIO Port A base: 0x4000.4000
GPIO Port B base: 0x4000.5000
GPIO Port C base: 0x4000.6000
GPIO Port D base: 0x4000.7000
GPIO Port E base: 0x4002.4000
GPIO Port F base: 0x4002.5000
GPIO Port G base: 0x4002.6000
Offset 0x50C
Type R/W, reset 0x0000.0000
31 30 29 28 27 26 25 24 23 22 21 20 19 18 17 16
reserved
Type RO RO RO RO RO RO RO RO RO RO RO RO RO RO RO RO
Reset 0 0 0 0 0 0 0 0 0 0 0 0 0 0 0 0
15 14 13 12 11 10 9 8 7 6 5 4 3 2 1 0
reserved ODE
Type RO RO RO RO RO RO RO RO R/W R/W R/W R/W R/W R/W R/W R/W
Reset 0 0 0 0 0 0 0 0 0 0 0 0 0 0 0 0
Bit/Field Name Type Reset Description
Software should not rely on the value of a reserved bit. To provide
compatibility with future products, the value of a reserved bit should be
preserved across a read-modify-write operation.
31:8 reserved RO 0x00
Output Pad Open Drain Enable
The ODE values are defined as follows:
Value Description
0 Open drain configuration is disabled.
1 Open drain configuration is enabled.
7:0 ODE R/W 0x00
184 March 17, 2008
Preliminary
General-Purpose Input/Outputs (GPIOs)
Register 15: GPIO Pull-Up Select (GPIOPUR), offset 0x510
The GPIOPUR register is the pull-up control register. When a bit is set to 1, it enables a weak pull-up
resistor on the corresponding GPIO signal. Setting a bit in GPIOPUR automatically clears the
corresponding bit in the GPIO Pull-Down Select (GPIOPDR) register (see page 186).
The commit control registers provide a layer of protection against accidental programming of critical
hardware peripherals. Writes to protected bits of the GPIO Alternate Function Select (GPIOAFSEL)
register (see page 179) are not committed to storage unless the GPIO Lock (GPIOLOCK) register
(see page 189) has been unlocked and the appropriate bits of the GPIO Commit (GPIOCR) register
(see page 190) have been set to 1.
GPIO Pull-Up Select (GPIOPUR)
GPIO Port A base: 0x4000.4000
GPIO Port B base: 0x4000.5000
GPIO Port C base: 0x4000.6000
GPIO Port D base: 0x4000.7000
GPIO Port E base: 0x4002.4000
GPIO Port F base: 0x4002.5000
GPIO Port G base: 0x4002.6000
Offset 0x510
Type R/W, reset -
31 30 29 28 27 26 25 24 23 22 21 20 19 18 17 16
reserved
Type RO RO RO RO RO RO RO RO RO RO RO RO RO RO RO RO
Reset 0 0 0 0 0 0 0 0 0 0 0 0 0 0 0 0
15 14 13 12 11 10 9 8 7 6 5 4 3 2 1 0
reserved PUE
Type RO RO RO RO RO RO RO RO R/W R/W R/W R/W R/W R/W R/W R/W
Reset 0 0 0 0 0 0 0 0 - - - - - - - -
Bit/Field Name Type Reset Description
Software should not rely on the value of a reserved bit. To provide
compatibility with future products, the value of a reserved bit should be
preserved across a read-modify-write operation.
31:8 reserved RO 0x00
Pad Weak Pull-Up Enable
A write of 1 to GPIOPDR[n] clears the corresponding GPIOPUR[n]
enables. The change is effective on the second clock cycle after the
write.
Note: The default reset value for the GPIOAFSEL, GPIOPUR, and
GPIODEN registers are 0x0000.0000 for all GPIO pins, with
the exception of the five JTAG/SWD pins (PB7 and PC[3:0]).
These five pins default to JTAG/SWD functionality. Because
of this, the default reset value of these registers for GPIO Port
B is 0x0000.0080 while the default reset value for Port C is
0x0000.000F.
7:0 PUE R/W -
March 17, 2008 185
Preliminary
LM3S8933 Microcontroller
Register 16: GPIO Pull-Down Select (GPIOPDR), offset 0x514
The GPIOPDR register is the pull-down control register. When a bit is set to 1, it enables a weak
pull-down resistor on the corresponding GPIO signal. Setting a bit in GPIOPDR automatically clears
the corresponding bit in the GPIO Pull-Up Select (GPIOPUR) register (see page 185).
GPIO Pull-Down Select (GPIOPDR)
GPIO Port A base: 0x4000.4000
GPIO Port B base: 0x4000.5000
GPIO Port C base: 0x4000.6000
GPIO Port D base: 0x4000.7000
GPIO Port E base: 0x4002.4000
GPIO Port F base: 0x4002.5000
GPIO Port G base: 0x4002.6000
Offset 0x514
Type R/W, reset 0x0000.0000
31 30 29 28 27 26 25 24 23 22 21 20 19 18 17 16
reserved
Type RO RO RO RO RO RO RO RO RO RO RO RO RO RO RO RO
Reset 0 0 0 0 0 0 0 0 0 0 0 0 0 0 0 0
15 14 13 12 11 10 9 8 7 6 5 4 3 2 1 0
reserved PDE
Type RO RO RO RO RO RO RO RO R/W R/W R/W R/W R/W R/W R/W R/W
Reset 0 0 0 0 0 0 0 0 0 0 0 0 0 0 0 0
Bit/Field Name Type Reset Description
Software should not rely on the value of a reserved bit. To provide
compatibility with future products, the value of a reserved bit should be
preserved across a read-modify-write operation.
31:8 reserved RO 0x00
Pad Weak Pull-Down Enable
A write of 1 to GPIOPUR[n] clears the corresponding GPIOPDR[n]
enables. The change is effective on the second clock cycle after the
write.
7:0 PDE R/W 0x00
186 March 17, 2008
Preliminary
General-Purpose Input/Outputs (GPIOs)
Register 17: GPIO Slew Rate Control Select (GPIOSLR), offset 0x518
The GPIOSLR register is the slew rate control register. Slew rate control is only available when
using the 8-mA drive strength option via the GPIO 8-mA Drive Select (GPIODR8R) register (see
page 183).
GPIO Slew Rate Control Select (GPIOSLR)
GPIO Port A base: 0x4000.4000
GPIO Port B base: 0x4000.5000
GPIO Port C base: 0x4000.6000
GPIO Port D base: 0x4000.7000
GPIO Port E base: 0x4002.4000
GPIO Port F base: 0x4002.5000
GPIO Port G base: 0x4002.6000
Offset 0x518
Type R/W, reset 0x0000.0000
31 30 29 28 27 26 25 24 23 22 21 20 19 18 17 16
reserved
Type RO RO RO RO RO RO RO RO RO RO RO RO RO RO RO RO
Reset 0 0 0 0 0 0 0 0 0 0 0 0 0 0 0 0
15 14 13 12 11 10 9 8 7 6 5 4 3 2 1 0
reserved SRL
Type RO RO RO RO RO RO RO RO R/W R/W R/W R/W R/W R/W R/W R/W
Reset 0 0 0 0 0 0 0 0 0 0 0 0 0 0 0 0
Bit/Field Name Type Reset Description
Software should not rely on the value of a reserved bit. To provide
compatibility with future products, the value of a reserved bit should be
preserved across a read-modify-write operation.
31:8 reserved RO 0x00
Slew Rate Limit Enable (8-mA drive only)
The SRL values are defined as follows:
Value Description
0 Slew rate control disabled.
1 Slew rate control enabled.
7:0 SRL R/W 0x00
March 17, 2008 187
Preliminary
LM3S8933 Microcontroller
Register 18: GPIO Digital Enable (GPIODEN), offset 0x51C
The GPIODEN register is the digital enable register. By default, with the exception of the GPIO
signals used for JTAG/SWD function, all other GPIO signals are configured out of reset to be undriven
(tristate). Their digital function is disabled; they do not drive a logic value on the pin and they do not
allow the pin voltage into the GPIO receiver. To use the pin in a digital function (either GPIO or
alternate function), the corresponding GPIODEN bit must be set.
The commit control registers provide a layer of protection against accidental programming of critical
hardware peripherals. Writes to protected bits of the GPIO Alternate Function Select (GPIOAFSEL)
register (see page 179) are not committed to storage unless the GPIO Lock (GPIOLOCK) register
(see page 189) has been unlocked and the appropriate bits of the GPIO Commit (GPIOCR) register
(see page 190) have been set to 1.
GPIO Digital Enable (GPIODEN)
GPIO Port A base: 0x4000.4000
GPIO Port B base: 0x4000.5000
GPIO Port C base: 0x4000.6000
GPIO Port D base: 0x4000.7000
GPIO Port E base: 0x4002.4000
GPIO Port F base: 0x4002.5000
GPIO Port G base: 0x4002.6000
Offset 0x51C
Type R/W, reset -
31 30 29 28 27 26 25 24 23 22 21 20 19 18 17 16
reserved
Type RO RO RO RO RO RO RO RO RO RO RO RO RO RO RO RO
Reset 0 0 0 0 0 0 0 0 0 0 0 0 0 0 0 0
15 14 13 12 11 10 9 8 7 6 5 4 3 2 1 0
reserved DEN
Type RO RO RO RO RO RO RO RO R/W R/W R/W R/W R/W R/W R/W R/W
Reset 0 0 0 0 0 0 0 0 - - - - - - - -
Bit/Field Name Type Reset Description
Software should not rely on the value of a reserved bit. To provide
compatibility with future products, the value of a reserved bit should be
preserved across a read-modify-write operation.
31:8 reserved RO 0x00
Digital Enable
The DEN values are defined as follows:
Value Description
0 Digital functions disabled.
1 Digital functions enabled.
Note: The default reset value for the GPIOAFSEL,
GPIOPUR, and GPIODEN registers are 0x0000.0000
for all GPIO pins, with the exception of the five
JTAG/SWD pins (PB7 and PC[3:0]). These five pins
default to JTAG/SWD functionality. Because of this,
the default reset value of these registers for GPIO
Port B is 0x0000.0080 while the default reset value
for Port C is 0x0000.000F.
7:0 DEN R/W -
188 March 17, 2008
Preliminary
General-Purpose Input/Outputs (GPIOs)
Register 19: GPIO Lock (GPIOLOCK), offset 0x520
The GPIOLOCK register enables write access to the GPIOCR register (see page 190). Writing
0x1ACC.E551 to the GPIOLOCK register will unlock the GPIOCR register. Writing any other value
to the GPIOLOCK register re-enables the locked state. Reading the GPIOLOCK register returns
the lock status rather than the 32-bit value that was previously written. Therefore, when write accesses
are disabled, or locked, reading the GPIOLOCK register returns 0x00000001. When write accesses
are enabled, or unlocked, reading the GPIOLOCK register returns 0x00000000.
GPIO Lock (GPIOLOCK)
GPIO Port A base: 0x4000.4000
GPIO Port B base: 0x4000.5000
GPIO Port C base: 0x4000.6000
GPIO Port D base: 0x4000.7000
GPIO Port E base: 0x4002.4000
GPIO Port F base: 0x4002.5000
GPIO Port G base: 0x4002.6000
Offset 0x520
Type R/W, reset 0x0000.0001
31 30 29 28 27 26 25 24 23 22 21 20 19 18 17 16
LOCK
Type R/W R/W R/W R/W R/W R/W R/W R/W R/W R/W R/W R/W R/W R/W R/W R/W
Reset 0 0 0 0 0 0 0 0 0 0 0 0 0 0 0 0
15 14 13 12 11 10 9 8 7 6 5 4 3 2 1 0
LOCK
Type R/W R/W R/W R/W R/W R/W R/W R/W R/W R/W R/W R/W R/W R/W R/W R/W
Reset 0 0 0 0 0 0 0 0 0 0 0 0 0 0 0 1
Bit/Field Name Type Reset Description
GPIO Lock
A write of the value 0x1ACC.E551 unlocks the GPIO Commit (GPIOCR)
register for write access.
A write of any other value or a write to the GPIOCR register reapplies
the lock, preventing any register updates. A read of this register returns
the following values:
Value Description
0x0000.0001 locked
0x0000.0000 unlocked
31:0 LOCK R/W 0x0000.0001
March 17, 2008 189
Preliminary
LM3S8933 Microcontroller
Register 20: GPIO Commit (GPIOCR), offset 0x524
The GPIOCR register is the commit register. The value of the GPIOCR register determines which
bits of the GPIOAFSEL register are committed when a write to the GPIOAFSEL register is performed.
If a bit in the GPIOCR register is a zero, the data being written to the corresponding bit in the
GPIOAFSEL register will not be committed and will retain its previous value. If a bit in the GPIOCR
register is a one, the data being written to the corresponding bit of the GPIOAFSEL register will be
committed to the register and will reflect the new value.
The contents of the GPIOCR register can only be modified if the GPIOLOCK register is unlocked.
Writes to the GPIOCR register are ignored if the GPIOLOCK register is locked.
Important: This register is designed to prevent accidental programming of the registers that control
connectivity to the JTAG/SWD debug hardware. By initializing the bits of the GPIOCR
register to 0 for PB7 and PC[3:0], the JTAG/SWD debug port can only be converted
to GPIOs through a deliberate set of writes to the GPIOLOCK, GPIOCR, and the
corresponding registers.
Because this protection is currently only implemented on the JTAG/SWD pins on PB7
and PC[3:0], all of the other bits in the GPIOCR registers cannot be written with 0x0.
These bits are hardwired to 0x1, ensuring that it is always possible to commit new
values to the GPIOAFSEL register bits of these other pins.
GPIO Commit (GPIOCR)
GPIO Port A base: 0x4000.4000
GPIO Port B base: 0x4000.5000
GPIO Port C base: 0x4000.6000
GPIO Port D base: 0x4000.7000
GPIO Port E base: 0x4002.4000
GPIO Port F base: 0x4002.5000
GPIO Port G base: 0x4002.6000
Offset 0x524
Type -, reset -
31 30 29 28 27 26 25 24 23 22 21 20 19 18 17 16
reserved
Type RO RO RO RO RO RO RO RO RO RO RO RO RO RO RO RO
Reset 0 0 0 0 0 0 0 0 0 0 0 0 0 0 0 0
15 14 13 12 11 10 9 8 7 6 5 4 3 2 1 0
reserved CR
Type RO RO RO RO RO RO RO RO - - - - - - - -
Reset 0 0 0 0 0 0 0 0 - - - - - - - -
Bit/Field Name Type Reset Description
Software should not rely on the value of a reserved bit. To provide
compatibility with future products, the value of a reserved bit should be
preserved across a read-modify-write operation.
31:8 reserved RO 0x00
190 March 17, 2008
Preliminary
General-Purpose Input/Outputs (GPIOs)
Bit/Field Name Type Reset Description
GPIO Commit
On a bit-wise basis, any bit set allows the corresponding GPIOAFSEL
bit to be set to its alternate function.
Note: The default register type for the GPIOCR register is RO for
all GPIO pins, with the exception of the five JTAG/SWD pins
(PB7 and PC[3:0]). These five pins are currently the only
GPIOs that are protected by the GPIOCR register. Because
of this, the register type for GPIO Port B7 and GPIO Port
C[3:0] is R/W.
The default reset value for the GPIOCR register is
0x0000.00FF for all GPIO pins, with the exception of the five
JTAG/SWD pins (PB7 and PC[3:0]). To ensure that the
JTAG port is not accidentally programmed as a GPIO, these
five pins default to non-committable. Because of this, the
default reset value of GPIOCR for GPIO Port B is
0x0000.007F while the default reset value of GPIOCR for Port
C is 0x0000.00F0.
7:0 CR - -
March 17, 2008 191
Preliminary
LM3S8933 Microcontroller
Register 21: GPIO Peripheral Identification 4 (GPIOPeriphID4), offset 0xFD0
The GPIOPeriphID4, GPIOPeriphID5, GPIOPeriphID6, and GPIOPeriphID7 registers can
conceptually be treated as one 32-bit register; each register contains eight bits of the 32-bit register,
used by software to identify the peripheral.
GPIO Peripheral Identification 4 (GPIOPeriphID4)
GPIO Port A base: 0x4000.4000
GPIO Port B base: 0x4000.5000
GPIO Port C base: 0x4000.6000
GPIO Port D base: 0x4000.7000
GPIO Port E base: 0x4002.4000
GPIO Port F base: 0x4002.5000
GPIO Port G base: 0x4002.6000
Offset 0xFD0
Type RO, reset 0x0000.0000
31 30 29 28 27 26 25 24 23 22 21 20 19 18 17 16
reserved
Type RO RO RO RO RO RO RO RO RO RO RO RO RO RO RO RO
Reset 0 0 0 0 0 0 0 0 0 0 0 0 0 0 0 0
15 14 13 12 11 10 9 8 7 6 5 4 3 2 1 0
reserved PID4
Type RO RO RO RO RO RO RO RO RO RO RO RO RO RO RO RO
Reset 0 0 0 0 0 0 0 0 0 0 0 0 0 0 0 0
Bit/Field Name Type Reset Description
Software should not rely on the value of a reserved bit. To provide
compatibility with future products, the value of a reserved bit should be
preserved across a read-modify-write operation.
31:8 reserved RO 0x00
7:0 PID4 RO 0x00 GPIO Peripheral ID Register[7:0]
192 March 17, 2008
Preliminary
General-Purpose Input/Outputs (GPIOs)
Register 22: GPIO Peripheral Identification 5 (GPIOPeriphID5), offset 0xFD4
The GPIOPeriphID4, GPIOPeriphID5, GPIOPeriphID6, and GPIOPeriphID7 registers can
conceptually be treated as one 32-bit register; each register contains eight bits of the 32-bit register,
used by software to identify the peripheral.
GPIO Peripheral Identification 5 (GPIOPeriphID5)
GPIO Port A base: 0x4000.4000
GPIO Port B base: 0x4000.5000
GPIO Port C base: 0x4000.6000
GPIO Port D base: 0x4000.7000
GPIO Port E base: 0x4002.4000
GPIO Port F base: 0x4002.5000
GPIO Port G base: 0x4002.6000
Offset 0xFD4
Type RO, reset 0x0000.0000
31 30 29 28 27 26 25 24 23 22 21 20 19 18 17 16
reserved
Type RO RO RO RO RO RO RO RO RO RO RO RO RO RO RO RO
Reset 0 0 0 0 0 0 0 0 0 0 0 0 0 0 0 0
15 14 13 12 11 10 9 8 7 6 5 4 3 2 1 0
reserved PID5
Type RO RO RO RO RO RO RO RO RO RO RO RO RO RO RO RO
Reset 0 0 0 0 0 0 0 0 0 0 0 0 0 0 0 0
Bit/Field Name Type Reset Description
Software should not rely on the value of a reserved bit. To provide
compatibility with future products, the value of a reserved bit should be
preserved across a read-modify-write operation.
31:8 reserved RO 0x00
7:0 PID5 RO 0x00 GPIO Peripheral ID Register[15:8]
March 17, 2008 193
Preliminary
LM3S8933 Microcontroller
Register 23: GPIO Peripheral Identification 6 (GPIOPeriphID6), offset 0xFD8
The GPIOPeriphID4, GPIOPeriphID5, GPIOPeriphID6, and GPIOPeriphID7 registers can
conceptually be treated as one 32-bit register; each register contains eight bits of the 32-bit register,
used by software to identify the peripheral.
GPIO Peripheral Identification 6 (GPIOPeriphID6)
GPIO Port A base: 0x4000.4000
GPIO Port B base: 0x4000.5000
GPIO Port C base: 0x4000.6000
GPIO Port D base: 0x4000.7000
GPIO Port E base: 0x4002.4000
GPIO Port F base: 0x4002.5000
GPIO Port G base: 0x4002.6000
Offset 0xFD8
Type RO, reset 0x0000.0000
31 30 29 28 27 26 25 24 23 22 21 20 19 18 17 16
reserved
Type RO RO RO RO RO RO RO RO RO RO RO RO RO RO RO RO
Reset 0 0 0 0 0 0 0 0 0 0 0 0 0 0 0 0
15 14 13 12 11 10 9 8 7 6 5 4 3 2 1 0
reserved PID6
Type RO RO RO RO RO RO RO RO RO RO RO RO RO RO RO RO
Reset 0 0 0 0 0 0 0 0 0 0 0 0 0 0 0 0
Bit/Field Name Type Reset Description
Software should not rely on the value of a reserved bit. To provide
compatibility with future products, the value of a reserved bit should be
preserved across a read-modify-write operation.
31:8 reserved RO 0x00
7:0 PID6 RO 0x00 GPIO Peripheral ID Register[23:16]
194 March 17, 2008
Preliminary
General-Purpose Input/Outputs (GPIOs)
Register 24: GPIO Peripheral Identification 7 (GPIOPeriphID7), offset 0xFDC
The GPIOPeriphID4, GPIOPeriphID5, GPIOPeriphID6, and GPIOPeriphID7 registers can
conceptually be treated as one 32-bit register; each register contains eight bits of the 32-bit register,
used by software to identify the peripheral.
GPIO Peripheral Identification 7 (GPIOPeriphID7)
GPIO Port A base: 0x4000.4000
GPIO Port B base: 0x4000.5000
GPIO Port C base: 0x4000.6000
GPIO Port D base: 0x4000.7000
GPIO Port E base: 0x4002.4000
GPIO Port F base: 0x4002.5000
GPIO Port G base: 0x4002.6000
Offset 0xFDC
Type RO, reset 0x0000.0000
31 30 29 28 27 26 25 24 23 22 21 20 19 18 17 16
reserved
Type RO RO RO RO RO RO RO RO RO RO RO RO RO RO RO RO
Reset 0 0 0 0 0 0 0 0 0 0 0 0 0 0 0 0
15 14 13 12 11 10 9 8 7 6 5 4 3 2 1 0
reserved PID7
Type RO RO RO RO RO RO RO RO RO RO RO RO RO RO RO RO
Reset 0 0 0 0 0 0 0 0 0 0 0 0 0 0 0 0
Bit/Field Name Type Reset Description
Software should not rely on the value of a reserved bit. To provide
compatibility with future products, the value of a reserved bit should be
preserved across a read-modify-write operation.
31:8 reserved RO 0x00
7:0 PID7 RO 0x00 GPIO Peripheral ID Register[31:24]
March 17, 2008 195
Preliminary
LM3S8933 Microcontroller
Register 25: GPIO Peripheral Identification 0 (GPIOPeriphID0), offset 0xFE0
The GPIOPeriphID0, GPIOPeriphID1, GPIOPeriphID2, and GPIOPeriphID3 registers can
conceptually be treated as one 32-bit register; each register contains eight bits of the 32-bit register,
used by software to identify the peripheral.
GPIO Peripheral Identification 0 (GPIOPeriphID0)
GPIO Port A base: 0x4000.4000
GPIO Port B base: 0x4000.5000
GPIO Port C base: 0x4000.6000
GPIO Port D base: 0x4000.7000
GPIO Port E base: 0x4002.4000
GPIO Port F base: 0x4002.5000
GPIO Port G base: 0x4002.6000
Offset 0xFE0
Type RO, reset 0x0000.0061
31 30 29 28 27 26 25 24 23 22 21 20 19 18 17 16
reserved
Type RO RO RO RO RO RO RO RO RO RO RO RO RO RO RO RO
Reset 0 0 0 0 0 0 0 0 0 0 0 0 0 0 0 0
15 14 13 12 11 10 9 8 7 6 5 4 3 2 1 0
reserved PID0
Type RO RO RO RO RO RO RO RO RO RO RO RO RO RO RO RO
Reset 0 0 0 0 0 0 0 0 0 1 1 0 0 0 0 1
Bit/Field Name Type Reset Description
Software should not rely on the value of a reserved bit. To provide
compatibility with future products, the value of a reserved bit should be
preserved across a read-modify-write operation.
31:8 reserved RO 0x00
GPIO Peripheral ID Register[7:0]
Can be used by software to identify the presence of this peripheral.
7:0 PID0 RO 0x61
196 March 17, 2008
Preliminary
General-Purpose Input/Outputs (GPIOs)
Register 26: GPIO Peripheral Identification 1 (GPIOPeriphID1), offset 0xFE4
The GPIOPeriphID0, GPIOPeriphID1, GPIOPeriphID2, and GPIOPeriphID3 registers can
conceptually be treated as one 32-bit register; each register contains eight bits of the 32-bit register,
used by software to identify the peripheral.
GPIO Peripheral Identification 1 (GPIOPeriphID1)
GPIO Port A base: 0x4000.4000
GPIO Port B base: 0x4000.5000
GPIO Port C base: 0x4000.6000
GPIO Port D base: 0x4000.7000
GPIO Port E base: 0x4002.4000
GPIO Port F base: 0x4002.5000
GPIO Port G base: 0x4002.6000
Offset 0xFE4
Type RO, reset 0x0000.0000
31 30 29 28 27 26 25 24 23 22 21 20 19 18 17 16
reserved
Type RO RO RO RO RO RO RO RO RO RO RO RO RO RO RO RO
Reset 0 0 0 0 0 0 0 0 0 0 0 0 0 0 0 0
15 14 13 12 11 10 9 8 7 6 5 4 3 2 1 0
reserved PID1
Type RO RO RO RO RO RO RO RO RO RO RO RO RO RO RO RO
Reset 0 0 0 0 0 0 0 0 0 0 0 0 0 0 0 0
Bit/Field Name Type Reset Description
Software should not rely on the value of a reserved bit. To provide
compatibility with future products, the value of a reserved bit should be
preserved across a read-modify-write operation.
31:8 reserved RO 0x00
GPIO Peripheral ID Register[15:8]
Can be used by software to identify the presence of this peripheral.
7:0 PID1 RO 0x00
March 17, 2008 197
Preliminary
LM3S8933 Microcontroller
Register 27: GPIO Peripheral Identification 2 (GPIOPeriphID2), offset 0xFE8
The GPIOPeriphID0, GPIOPeriphID1, GPIOPeriphID2, and GPIOPeriphID3 registers can
conceptually be treated as one 32-bit register; each register contains eight bits of the 32-bit register,
used by software to identify the peripheral.
GPIO Peripheral Identification 2 (GPIOPeriphID2)
GPIO Port A base: 0x4000.4000
GPIO Port B base: 0x4000.5000
GPIO Port C base: 0x4000.6000
GPIO Port D base: 0x4000.7000
GPIO Port E base: 0x4002.4000
GPIO Port F base: 0x4002.5000
GPIO Port G base: 0x4002.6000
Offset 0xFE8
Type RO, reset 0x0000.0018
31 30 29 28 27 26 25 24 23 22 21 20 19 18 17 16
reserved
Type RO RO RO RO RO RO RO RO RO RO RO RO RO RO RO RO
Reset 0 0 0 0 0 0 0 0 0 0 0 0 0 0 0 0
15 14 13 12 11 10 9 8 7 6 5 4 3 2 1 0
reserved PID2
Type RO RO RO RO RO RO RO RO RO RO RO RO RO RO RO RO
Reset 0 0 0 0 0 0 0 0 0 0 0 1 1 0 0 0
Bit/Field Name Type Reset Description
Software should not rely on the value of a reserved bit. To provide
compatibility with future products, the value of a reserved bit should be
preserved across a read-modify-write operation.
31:8 reserved RO 0x00
GPIO Peripheral ID Register[23:16]
Can be used by software to identify the presence of this peripheral.
7:0 PID2 RO 0x18
198 March 17, 2008
Preliminary
General-Purpose Input/Outputs (GPIOs)
Register 28: GPIO Peripheral Identification 3 (GPIOPeriphID3), offset 0xFEC
The GPIOPeriphID0, GPIOPeriphID1, GPIOPeriphID2, and GPIOPeriphID3 registers can
conceptually be treated as one 32-bit register; each register contains eight bits of the 32-bit register,
used by software to identify the peripheral.
GPIO Peripheral Identification 3 (GPIOPeriphID3)
GPIO Port A base: 0x4000.4000
GPIO Port B base: 0x4000.5000
GPIO Port C base: 0x4000.6000
GPIO Port D base: 0x4000.7000
GPIO Port E base: 0x4002.4000
GPIO Port F base: 0x4002.5000
GPIO Port G base: 0x4002.6000
Offset 0xFEC
Type RO, reset 0x0000.0001
31 30 29 28 27 26 25 24 23 22 21 20 19 18 17 16
reserved
Type RO RO RO RO RO RO RO RO RO RO RO RO RO RO RO RO
Reset 0 0 0 0 0 0 0 0 0 0 0 0 0 0 0 0
15 14 13 12 11 10 9 8 7 6 5 4 3 2 1 0
reserved PID3
Type RO RO RO RO RO RO RO RO RO RO RO RO RO RO RO RO
Reset 0 0 0 0 0 0 0 0 0 0 0 0 0 0 0 1
Bit/Field Name Type Reset Description
Software should not rely on the value of a reserved bit. To provide
compatibility with future products, the value of a reserved bit should be
preserved across a read-modify-write operation.
31:8 reserved RO 0x00
GPIO Peripheral ID Register[31:24]
Can be used by software to identify the presence of this peripheral.
7:0 PID3 RO 0x01
March 17, 2008 199
Preliminary
LM3S8933 Microcontroller
Register 29: GPIO PrimeCell Identification 0 (GPIOPCellID0), offset 0xFF0
The GPIOPCellID0, GPIOPCellID1, GPIOPCellID2, and GPIOPCellID3 registers are four 8-bit wide
registers, that can conceptually be treated as one 32-bit register. The register is used as a standard
cross-peripheral identification system.
GPIO PrimeCell Identification 0 (GPIOPCellID0)
GPIO Port A base: 0x4000.4000
GPIO Port B base: 0x4000.5000
GPIO Port C base: 0x4000.6000
GPIO Port D base: 0x4000.7000
GPIO Port E base: 0x4002.4000
GPIO Port F base: 0x4002.5000
GPIO Port G base: 0x4002.6000
Offset 0xFF0
Type RO, reset 0x0000.000D
31 30 29 28 27 26 25 24 23 22 21 20 19 18 17 16
reserved
Type RO RO RO RO RO RO RO RO RO RO RO RO RO RO RO RO
Reset 0 0 0 0 0 0 0 0 0 0 0 0 0 0 0 0
15 14 13 12 11 10 9 8 7 6 5 4 3 2 1 0
reserved CID0
Type RO RO RO RO RO RO RO RO RO RO RO RO RO RO RO RO
Reset 0 0 0 0 0 0 0 0 0 0 0 0 1 1 0 1
Bit/Field Name Type Reset Description
Software should not rely on the value of a reserved bit. To provide
compatibility with future products, the value of a reserved bit should be
preserved across a read-modify-write operation.
31:8 reserved RO 0x00
GPIO PrimeCell ID Register[7:0]
Provides software a standard cross-peripheral identification system.
7:0 CID0 RO 0x0D
200 March 17, 2008
Preliminary
General-Purpose Input/Outputs (GPIOs)
Register 30: GPIO PrimeCell Identification 1 (GPIOPCellID1), offset 0xFF4
The GPIOPCellID0, GPIOPCellID1, GPIOPCellID2, and GPIOPCellID3 registers are four 8-bit wide
registers, that can conceptually be treated as one 32-bit register. The register is used as a standard
cross-peripheral identification system.
GPIO PrimeCell Identification 1 (GPIOPCellID1)
GPIO Port A base: 0x4000.4000
GPIO Port B base: 0x4000.5000
GPIO Port C base: 0x4000.6000
GPIO Port D base: 0x4000.7000
GPIO Port E base: 0x4002.4000
GPIO Port F base: 0x4002.5000
GPIO Port G base: 0x4002.6000
Offset 0xFF4
Type RO, reset 0x0000.00F0
31 30 29 28 27 26 25 24 23 22 21 20 19 18 17 16
reserved
Type RO RO RO RO RO RO RO RO RO RO RO RO RO RO RO RO
Reset 0 0 0 0 0 0 0 0 0 0 0 0 0 0 0 0
15 14 13 12 11 10 9 8 7 6 5 4 3 2 1 0
reserved CID1
Type RO RO RO RO RO RO RO RO RO RO RO RO RO RO RO RO
Reset 0 0 0 0 0 0 0 0 1 1 1 1 0 0 0 0
Bit/Field Name Type Reset Description
Software should not rely on the value of a reserved bit. To provide
compatibility with future products, the value of a reserved bit should be
preserved across a read-modify-write operation.
31:8 reserved RO 0x00
GPIO PrimeCell ID Register[15:8]
Provides software a standard cross-peripheral identification system.
7:0 CID1 RO 0xF0
March 17, 2008 201
Preliminary
LM3S8933 Microcontroller
Register 31: GPIO PrimeCell Identification 2 (GPIOPCellID2), offset 0xFF8
The GPIOPCellID0, GPIOPCellID1, GPIOPCellID2, and GPIOPCellID3 registers are four 8-bit wide
registers, that can conceptually be treated as one 32-bit register. The register is used as a standard
cross-peripheral identification system.
GPIO PrimeCell Identification 2 (GPIOPCellID2)
GPIO Port A base: 0x4000.4000
GPIO Port B base: 0x4000.5000
GPIO Port C base: 0x4000.6000
GPIO Port D base: 0x4000.7000
GPIO Port E base: 0x4002.4000
GPIO Port F base: 0x4002.5000
GPIO Port G base: 0x4002.6000
Offset 0xFF8
Type RO, reset 0x0000.0005
31 30 29 28 27 26 25 24 23 22 21 20 19 18 17 16
reserved
Type RO RO RO RO RO RO RO RO RO RO RO RO RO RO RO RO
Reset 0 0 0 0 0 0 0 0 0 0 0 0 0 0 0 0
15 14 13 12 11 10 9 8 7 6 5 4 3 2 1 0
reserved CID2
Type RO RO RO RO RO RO RO RO RO RO RO RO RO RO RO RO
Reset 0 0 0 0 0 0 0 0 0 0 0 0 0 1 0 1
Bit/Field Name Type Reset Description
Software should not rely on the value of a reserved bit. To provide
compatibility with future products, the value of a reserved bit should be
preserved across a read-modify-write operation.
31:8 reserved RO 0x00
GPIO PrimeCell ID Register[23:16]
Provides software a standard cross-peripheral identification system.
7:0 CID2 RO 0x05
202 March 17, 2008
Preliminary
General-Purpose Input/Outputs (GPIOs)
Register 32: GPIO PrimeCell Identification 3 (GPIOPCellID3), offset 0xFFC
The GPIOPCellID0, GPIOPCellID1, GPIOPCellID2, and GPIOPCellID3 registers are four 8-bit wide
registers, that can conceptually be treated as one 32-bit register. The register is used as a standard
cross-peripheral identification system.
GPIO PrimeCell Identification 3 (GPIOPCellID3)
GPIO Port A base: 0x4000.4000
GPIO Port B base: 0x4000.5000
GPIO Port C base: 0x4000.6000
GPIO Port D base: 0x4000.7000
GPIO Port E base: 0x4002.4000
GPIO Port F base: 0x4002.5000
GPIO Port G base: 0x4002.6000
Offset 0xFFC
Type RO, reset 0x0000.00B1
31 30 29 28 27 26 25 24 23 22 21 20 19 18 17 16
reserved
Type RO RO RO RO RO RO RO RO RO RO RO RO RO RO RO RO
Reset 0 0 0 0 0 0 0 0 0 0 0 0 0 0 0 0
15 14 13 12 11 10 9 8 7 6 5 4 3 2 1 0
reserved CID3
Type RO RO RO RO RO RO RO RO RO RO RO RO RO RO RO RO
Reset 0 0 0 0 0 0 0 0 1 0 1 1 0 0 0 1
Bit/Field Name Type Reset Description
Software should not rely on the value of a reserved bit. To provide
compatibility with future products, the value of a reserved bit should be
preserved across a read-modify-write operation.
31:8 reserved RO 0x00
GPIO PrimeCell ID Register[31:24]
Provides software a standard cross-peripheral identification system.
7:0 CID3 RO 0xB1
March 17, 2008 203
Preliminary
LM3S8933 Microcontroller
10 General-Purpose Timers
Programmable timers can be used to count or time external events that drive the Timer input pins.
The Stellaris® General-Purpose Timer Module (GPTM) contains four GPTM blocks (Timer0, Timer1,
Timer 2, and Timer 3). Each GPTM block provides two 16-bit timers/counters (referred to as TimerA
and TimerB) that can be configured to operate independently as timers or event counters, or
configured to operate as one 32-bit timer or one 32-bit Real-Time Clock (RTC). Timers can also be
used to trigger analog-to-digital (ADC) conversions. The trigger signals from all of the general-purpose
timers are ORed together before reaching the ADC module, so only one timer should be used to
trigger ADC events.
The General-Purpose Timer Module is one timing resource available on the Stellaris® microcontrollers.
Other timer resources include the System Timer (SysTick) (see “System Timer
(SysTick)” on page 38).
The following modes are supported:
■ 32-bit Timer modes
– Programmable one-shot timer
– Programmable periodic timer
– Real-Time Clock using 32.768-KHz input clock
– Software-controlled event stalling (excluding RTC mode)
■ 16-bit Timer modes
– General-purpose timer function with an 8-bit prescaler (for one-shot and periodic modes only)
– Programmable one-shot timer
– Programmable periodic timer
– Software-controlled event stalling
■ 16-bit Input Capture modes
– Input edge count capture
– Input edge time capture
■ 16-bit PWM mode
– Simple PWM mode with software-programmable output inversion of the PWM signal
10.1 Block Diagram
Note: In Figure 10-1 on page 205, the specific CCP pins available depend on the Stellaris® device.
See Table 10-1 on page 205 for the available CCPs.
204 March 17, 2008
Preliminary
General-Purpose Timers
Figure 10-1. GPTM Module Block Diagram
TA Comparator
TB Comparator
GPTMTBR
GPTMAR
Clock / Edge
Detect
RTC Divider
Clock / Edge
Detect
TimerA
Interrupt
TimerB
Interrupt
System
Clock
0x0000 (Down Counter Modes)
0x0000 (Down Counter Modes)
32 KHz or
Even CCP Pin
Odd CCP Pin
En
En
TimerA Control
GPTMTAPMR
GPTMTAILR
GPTMTAMATCHR
GPTMTAPR
GPTMTAMR
TimerB Control
GPTMTBPMR
GPTMTBILR
GPTMTBMATCHR
GPTMTBPR
GPTMTBMR
Interrupt / Config
GPTMCFG
GPTMRIS
GPTMICR
GPTMMIS
GPTMIMR
GPTMCTL
Table 10-1. Available CCP Pins
Timer 16-Bit Up/Down Counter Even CCP Pin Odd CCP Pin
Timer 0 TimerA CCP0 -
TimerB - CCP1
Timer 1 TimerA CCP2 -
TimerB - CCP3
Timer 2 TimerA - -
TimerB - -
Timer 3 TimerA - -
TimerB - -
10.2 Functional Description
The main components of each GPTM block are two free-running 16-bit up/down counters (referred
to as TimerA and TimerB), two 16-bit match registers, two prescaler match registers, and two 16-bit
load/initialization registers and their associated control functions. The exact functionality of each
GPTM is controlled by software and configured through the register interface.
Software configures the GPTM using the GPTM Configuration (GPTMCFG) register (see page 216),
the GPTM TimerA Mode (GPTMTAMR) register (see page 217), and the GPTM TimerB Mode
(GPTMTBMR) register (see page 219). When in one of the 32-bit modes, the timer can only act as
a 32-bit timer. However, when configured in 16-bit mode, the GPTM can have its two 16-bit timers
configured in any combination of the 16-bit modes.
March 17, 2008 205
Preliminary
LM3S8933 Microcontroller
10.2.1 GPTM Reset Conditions
After reset has been applied to the GPTM module, the module is in an inactive state, and all control
registers are cleared and in their default states. Counters TimerA and TimerB are initialized to
0xFFFF, along with their corresponding load registers: the GPTM TimerA Interval Load
(GPTMTAILR) register (see page 230) and the GPTM TimerB Interval Load (GPTMTBILR) register
(see page 231). The prescale counters are initialized to 0x00: the GPTM TimerA Prescale
(GPTMTAPR) register (see page 234) and the GPTM TimerB Prescale (GPTMTBPR) register (see
page 235).
10.2.2 32-Bit Timer Operating Modes
This section describes the three GPTM 32-bit timer modes (One-Shot, Periodic, and RTC) and their
configuration.
The GPTM is placed into 32-bit mode by writing a 0 (One-Shot/Periodic 32-bit timer mode) or a 1
(RTC mode) to the GPTM Configuration (GPTMCFG) register. In both configurations, certain GPTM
registers are concatenated to form pseudo 32-bit registers. These registers include:
■ GPTM TimerA Interval Load (GPTMTAILR) register [15:0], see page 230
■ GPTM TimerB Interval Load (GPTMTBILR) register [15:0], see page 231
■ GPTM TimerA (GPTMTAR) register [15:0], see page 238
■ GPTM TimerB (GPTMTBR) register [15:0], see page 239
In the 32-bit modes, the GPTM translates a 32-bit write access to GPTMTAILR into a write access
to both GPTMTAILR and GPTMTBILR. The resulting word ordering for such a write operation is:
GPTMTBILR[15:0]:GPTMTAILR[15:0]
Likewise, a read access to GPTMTAR returns the value:
GPTMTBR[15:0]:GPTMTAR[15:0]
10.2.2.1 32-Bit One-Shot/Periodic Timer Mode
In 32-bit one-shot and periodic timer modes, the concatenated versions of the TimerA and TimerB
registers are configured as a 32-bit down-counter. The selection of one-shot or periodic mode is
determined by the value written to the TAMR field of the GPTM TimerA Mode (GPTMTAMR) register
(see page 217), and there is no need to write to the GPTM TimerB Mode (GPTMTBMR) register.
When software writes the TAEN bit in the GPTM Control (GPTMCTL) register (see page 221), the
timer begins counting down from its preloaded value. Once the 0x0000.0000 state is reached, the
timer reloads its start value from the concatenated GPTMTAILR on the next cycle. If configured to
be a one-shot timer, the timer stops counting and clears the TAEN bit in the GPTMCTL register. If
configured as a periodic timer, it continues counting.
In addition to reloading the count value, the GPTM generates interrupts and triggers when it reaches
the 0x000.0000 state. The GPTM sets the TATORIS bit in the GPTM Raw Interrupt Status
(GPTMRIS) register (see page 226), and holds it until it is cleared by writing the GPTM Interrupt
Clear (GPTMICR) register (see page 228). If the time-out interrupt is enabled in the GPTM Interrupt
Mask (GPTIMR) register (see page 224), the GPTM also sets the TATOMIS bit in the GPTM Masked
Interrupt Status (GPTMMIS) register (see page 227). The trigger is enabled by setting the TAOTE
bit in GPTMCTL, and can trigger SoC-level events such as ADC conversions.
206 March 17, 2008
Preliminary
General-Purpose Timers
If software reloads the GPTMTAILR register while the counter is running, the counter loads the new
value on the next clock cycle and continues counting from the new value.
If the TASTALL bit in the GPTMCTL register is asserted, the timer freezes counting until the signal
is deasserted.
10.2.2.2 32-Bit Real-Time Clock Timer Mode
In Real-Time Clock (RTC) mode, the concatenated versions of the TimerA and TimerB registers
are configured as a 32-bit up-counter. When RTC mode is selected for the first time, the counter is
loaded with a value of 0x0000.0001. All subsequent load values must be written to the GPTM TimerA
Match (GPTMTAMATCHR) register (see page 232) by the controller.
The input clock on the CCP0, CCP2, or CCP4 pins is required to be 32.768 KHz in RTC mode. The
clock signal is then divided down to a 1 Hz rate and is passed along to the input of the 32-bit counter.
When software writes the TAEN bit inthe GPTMCTL register, the counter starts counting up from its
preloaded value of 0x0000.0001. When the current count value matches the preloaded value in the
GPTMTAMATCHR register, it rolls over to a value of 0x0000.0000 and continues counting until
either a hardware reset, or it is disabled by software (clearing the TAEN bit). When a match occurs,
the GPTM asserts the RTCRIS bit in GPTMRIS. If the RTC interrupt is enabled in GPTIMR, the
GPTM also sets the RTCMIS bit in GPTMISR and generates a controller interrupt. The status flags
are cleared by writing the RTCCINT bit in GPTMICR.
If the TASTALL and/or TBSTALL bits in the GPTMCTL register are set, the timer does not freeze if
the RTCEN bit is set in GPTMCTL.
10.2.3 16-Bit Timer Operating Modes
The GPTM is placed into global 16-bit mode by writing a value of 0x4 to the GPTM Configuration
(GPTMCFG) register (see page 216). This section describes each of the GPTM 16-bit modes of
operation. TimerA and TimerB have identical modes, so a single description is given using an n to
reference both.
10.2.3.1 16-Bit One-Shot/Periodic Timer Mode
In 16-bit one-shot and periodic timer modes, the timer is configured as a 16-bit down-counter with
an optional 8-bit prescaler that effectively extends the counting range of the timer to 24 bits. The
selection of one-shot or periodic mode is determined by the value written to the TnMR field of the
GPTMTnMR register. The optional prescaler is loaded into the GPTM Timern Prescale (GPTMTnPR)
register.
When software writes the TnEN bit in the GPTMCTL register, the timer begins counting down from
its preloaded value. Once the 0x0000 state is reached, the timer reloads its start value from
GPTMTnILR and GPTMTnPR on the next cycle. If configured to be a one-shot timer, the timer stops
counting and clears the TnEN bit in the GPTMCTL register. If configured as a periodic timer, it
continues counting.
In addition to reloading the count value, the timer generates interrupts and triggers when it reaches
the 0x0000 state. The GPTM sets the TnTORIS bit in the GPTMRIS register, and holds it until it is
cleared by writing the GPTMICR register. If the time-out interrupt is enabled in GPTIMR, the GPTM
also sets the TnTOMIS bit in GPTMISR and generates a controller interrupt. The trigger is enabled
by setting the TnOTE bit in the GPTMCTL register, and can trigger SoC-level events such as ADC
conversions.
If software reloads the GPTMTAILR register while the counter is running, the counter loads the new
value on the next clock cycle and continues counting from the new value.
March 17, 2008 207
Preliminary
LM3S8933 Microcontroller
If the TnSTALL bit in the GPTMCTL register is enabled, the timer freezes counting until the signal
is deasserted.
The following example shows a variety of configurations for a 16-bit free running timer while using
the prescaler. All values assume a 50-MHz clock with Tc=20 ns (clock period).
Table 10-2. 16-Bit Timer With Prescaler Configurations
Prescale #Clock (T c)a Max Time Units
00000000 1 1.3107 mS
00000001 2 2.6214 mS
00000010 3 3.9321 mS
------------ -- -- --
11111100 254 332.9229 mS
11111110 255 334.2336 mS
11111111 256 335.5443 mS
a. Tc is the clock period.
10.2.3.2 16-Bit Input Edge Count Mode
Note: For rising-edge detection, the input signal must be High for at least two system clock periods
following the rising edge. Similarly, for falling-edge detection, the input signal must be Low
for at least two system clock periods following the falling edge. Based on this criteria, the
maximum input frequency for edge detection is 1/4 of the system frequency.
Note: The prescaler is not available in 16-Bit Input Edge Count mode.
In Edge Count mode, the timer is configured as a down-counter capable of capturing three types
of events: rising edge, falling edge, or both. To place the timer in Edge Count mode, the TnCMR bit
of the GPTMTnMR register must be set to 0. The type of edge that the timer counts is determined
by the TnEVENT fields of the GPTMCTL register. During initialization, the GPTM Timern Match
(GPTMTnMATCHR) register is configured so that the difference between the value in the
GPTMTnILR register and the GPTMTnMATCHR register equals the number of edge events that
must be counted.
When software writes the TnEN bit in the GPTM Control (GPTMCTL) register, the timer is enabled
for event capture. Each input event on the CCP pin decrements the counter by 1 until the event count
matches GPTMTnMATCHR. When the counts match, the GPTM asserts the CnMRIS bit in the
GPTMRIS register (and the CnMMIS bit, if the interrupt is not masked). The counter is then reloaded
using the value in GPTMTnILR, and stopped since the GPTM automatically clears the TnEN bit in
the GPTMCTL register. Once the event count has been reached, all further events are ignored until
TnEN is re-enabled by software.
Figure 10-2 on page 209 shows how input edge count mode works. In this case, the timer start value
is set to GPTMnILR =0x000A and the match value is set to GPTMnMATCHR =0x0006 so that four
edge events are counted. The counter is configured to detect both edges of the input signal.
Note that the last two edges are not counted since the timer automatically clears the TnEN bit after
the current count matches the value in the GPTMnMR register.
208 March 17, 2008
Preliminary
General-Purpose Timers
Figure 10-2. 16-Bit Input Edge Count Mode Example
0x000A
0x0006
0x0007
0x0008
0x0009
Input Signal
Timer stops,
flags
asserted
Timer reload
Count on next cycle Ignored Ignored
10.2.3.3 16-Bit Input Edge Time Mode
Note: For rising-edge detection, the input signal must be High for at least two system clock periods
following the rising edge. Similarly, for falling edge detection, the input signal must be Low
for at least two system clock periods following the falling edge. Based on this criteria, the
maximum input frequency for edge detection is 1/4 of the system frequency.
Note: The prescaler is not available in 16-Bit Input Edge Time mode.
In Edge Time mode, the timer is configured as a free-running down-counter initialized to the value
loaded in the GPTMTnILR register (or 0xFFFF at reset). This mode allows for event capture of
either rising or falling edges, but not both. The timer is placed into Edge Time mode by setting the
TnCMR bit in the GPTMTnMR register, and the type of event that the timer captures is determined
by the TnEVENT fields of the GPTMCnTL register.
When software writes the TnEN bit in the GPTMCTL register, the timer is enabled for event capture.
When the selected input event is detected, the current Tn counter value is captured in the GPTMTnR
register and is available to be read by the controller. The GPTM then asserts the CnERIS bit (and
the CnEMIS bit, if the interrupt is not masked).
After an event has been captured, the timer does not stop counting. It continues to count until the
TnEN bit is cleared. When the timer reaches the 0x0000 state, it is reloaded with the value from the
GPTMnILR register.
Figure 10-3 on page 210 shows how input edge timing mode works. In the diagram, it is assumed
that the start value of the timer is the default value of 0xFFFF, and the timer is configured to capture
rising edge events.
Each time a rising edge event is detected, the current count value is loaded into the GPTMTnR
register, and is held there until another rising edge is detected (at which point the new count value
is loaded into GPTMTnR).
March 17, 2008 209
Preliminary
LM3S8933 Microcontroller
Figure 10-3. 16-Bit Input Edge Time Mode Example
GPTMTnR=Y
Input Signal
Time
Count
GPTMTnR=X GPTMTnR=Z
Z
X
Y
0xFFFF
10.2.3.4 16-Bit PWM Mode
Note: The prescaler is not available in 16-Bit PWM mode.
The GPTM supports a simple PWM generation mode. In PWM mode, the timer is configured as a
down-counter with a start value (and thus period) defined by GPTMTnILR. PWM mode is enabled
with the GPTMTnMR register by setting the TnAMS bit to 0x1, the TnCMR bit to 0x0, and the TnMR
field to 0x2.
When software writes the TnEN bit in the GPTMCTL register, the counter begins counting down
until it reaches the 0x0000 state. On the next counter cycle, the counter reloads its start value from
GPTMTnILR and continues counting until disabled by software clearing the TnEN bit in the GPTMCTL
register. No interrupts or status bits are asserted in PWM mode.
The output PWM signal asserts when the counter is at the value of the GPTMTnILR register (its
start state), and is deasserted when the counter value equals the value in the GPTM Timern Match
Register (GPTMnMATCHR). Software has the capability of inverting the output PWM signal by
setting the TnPWML bit in the GPTMCTL register.
Figure 10-4 on page 211 shows how to generate an output PWM with a 1-ms period and a 66% duty
cycle assuming a 50-MHz input clock and TnPWML =0 (duty cycle would be 33% for the TnPWML
=1 configuration). For this example, the start value is GPTMnIRL=0xC350 and the match value is
GPTMnMR=0x411A.
210 March 17, 2008
Preliminary
General-Purpose Timers
Figure 10-4. 16-Bit PWM Mode Example
Output
Signal
Time
Count GPTMTnR=GPTMnMR GPTMTnR=GPTMnMR
0xC350
0x411A
TnPWML = 0
TnPWML = 1
TnEN set
10.3 Initialization and Configuration
To use the general-purpose timers, the peripheral clock must be enabled by setting the TIMER0,
TIMER1, TIMER2, and TIMER3 bits in the RCGC1 register.
This section shows module initialization and configuration examples for each of the supported timer
modes.
10.3.1 32-Bit One-Shot/Periodic Timer Mode
The GPTM is configured for 32-bit One-Shot and Periodic modes by the following sequence:
1. Ensure the timer is disabled (the TAEN bit in the GPTMCTL register is cleared) before making
any changes.
2. Write the GPTM Configuration Register (GPTMCFG) with a value of 0x0.
3. Set the TAMR field in the GPTM TimerA Mode Register (GPTMTAMR):
a. Write a value of 0x1 for One-Shot mode.
b. Write a value of 0x2 for Periodic mode.
4. Load the start value into the GPTM TimerA Interval Load Register (GPTMTAILR).
5. If interrupts are required, set the TATOIM bit in the GPTM Interrupt Mask Register (GPTMIMR).
6. Set the TAEN bit in the GPTMCTL register to enable the timer and start counting.
March 17, 2008 211
Preliminary
LM3S8933 Microcontroller
7. Poll the TATORIS bit in the GPTMRIS register or wait for the interrupt to be generated (if enabled).
In both cases, the status flags are cleared by writing a 1 to the TATOCINT bit of the GPTM
Interrupt Clear Register (GPTMICR).
In One-Shot mode, the timer stops counting after step 7 on page 212. To re-enable the timer, repeat
the sequence. A timer configured in Periodic mode does not stop counting after it times out.
10.3.2 32-Bit Real-Time Clock (RTC) Mode
To use the RTC mode, the timer must have a 32.768-KHz input signal on its CCP0, CCP2, or CCP4
pins. To enable the RTC feature, follow these steps:
1. Ensure the timer is disabled (the TAEN bit is cleared) before making any changes.
2. Write the GPTM Configuration Register (GPTMCFG) with a value of 0x1.
3. Write the desired match value to the GPTM TimerA Match Register (GPTMTAMATCHR).
4. Set/clear the RTCEN bit in the GPTM Control Register (GPTMCTL) as desired.
5. If interrupts are required, set the RTCIM bit in the GPTM Interrupt Mask Register (GPTMIMR).
6. Set the TAEN bit in the GPTMCTL register to enable the timer and start counting.
When the timer count equals the value in the GPTMTAMATCHR register, the counter is re-loaded
with 0x0000.0000 and begins counting. If an interrupt is enabled, it does not have to be cleared.
10.3.3 16-Bit One-Shot/Periodic Timer Mode
A timer is configured for 16-bit One-Shot and Periodic modes by the following sequence:
1. Ensure the timer is disabled (the TnEN bit is cleared) before making any changes.
2. Write the GPTM Configuration Register (GPTMCFG) with a value of 0x4.
3. Set the TnMR field in the GPTM Timer Mode (GPTMTnMR) register:
a. Write a value of 0x1 for One-Shot mode.
b. Write a value of 0x2 for Periodic mode.
4. If a prescaler is to be used, write the prescale value to the GPTM Timern Prescale Register
(GPTMTnPR).
5. Load the start value into the GPTM Timer Interval Load Register (GPTMTnILR).
6. If interrupts are required, set the TnTOIM bit in the GPTM Interrupt Mask Register (GPTMIMR).
7. Set the TnEN bit in the GPTM Control Register (GPTMCTL) to enable the timer and start
counting.
8. Poll the TnTORIS bit in the GPTMRIS register or wait for the interrupt to be generated (if enabled).
In both cases, the status flags are cleared by writing a 1 to the TnTOCINT bit of the GPTM
Interrupt Clear Register (GPTMICR).
212 March 17, 2008
Preliminary
General-Purpose Timers
In One-Shot mode, the timer stops counting after step 8 on page 212. To re-enable the timer, repeat
the sequence. A timer configured in Periodic mode does not stop counting after it times out.
10.3.4 16-Bit Input Edge Count Mode
A timer is configured to Input Edge Count mode by the following sequence:
1. Ensure the timer is disabled (the TnEN bit is cleared) before making any changes.
2. Write the GPTM Configuration (GPTMCFG) register with a value of 0x4.
3. In the GPTM Timer Mode (GPTMTnMR) register, write the TnCMR field to 0x0 and the TnMR
field to 0x3.
4. Configure the type of event(s) that the timer captures by writing the TnEVENT field of the GPTM
Control (GPTMCTL) register.
5. Load the timer start value into the GPTM Timern Interval Load (GPTMTnILR) register.
6. Load the desired event count into the GPTM Timern Match (GPTMTnMATCHR) register.
7. If interrupts are required, set the CnMIM bit in the GPTM Interrupt Mask (GPTMIMR) register.
8. Set the TnEN bit in the GPTMCTL register to enable the timer and begin waiting for edge events.
9. Poll the CnMRIS bit in the GPTMRIS register or wait for the interrupt to be generated (if enabled).
In both cases, the status flags are cleared by writing a 1 to the CnMCINT bit of the GPTM
Interrupt Clear (GPTMICR) register.
In Input Edge Count Mode, the timer stops after the desired number of edge events has been
detected. To re-enable the timer, ensure that the TnEN bit is cleared and repeat step 4 on page 213
through step 9 on page 213.
10.3.5 16-Bit Input Edge Timing Mode
A timer is configured to Input Edge Timing mode by the following sequence:
1. Ensure the timer is disabled (the TnEN bit is cleared) before making any changes.
2. Write the GPTM Configuration (GPTMCFG) register with a value of 0x4.
3. In the GPTM Timer Mode (GPTMTnMR) register, write the TnCMR field to 0x1 and the TnMR
field to 0x3.
4. Configure the type of event that the timer captures by writing the TnEVENT field of the GPTM
Control (GPTMCTL) register.
5. Load the timer start value into the GPTM Timern Interval Load (GPTMTnILR) register.
6. If interrupts are required, set the CnEIM bit in the GPTM Interrupt Mask (GPTMIMR) register.
7. Set the TnEN bit in the GPTM Control (GPTMCTL) register to enable the timer and start counting.
8. Poll the CnERIS bit in the GPTMRIS register or wait for the interrupt to be generated (if enabled).
In both cases, the status flags are cleared by writing a 1 to the CnECINT bit of the GPTM
March 17, 2008 213
Preliminary
LM3S8933 Microcontroller
Interrupt Clear (GPTMICR) register. The time at which the event happened can be obtained
by reading the GPTM Timern (GPTMTnR) register.
In Input Edge Timing mode, the timer continues running after an edge event has been detected,
but the timer interval can be changed at any time by writing the GPTMTnILR register. The change
takes effect at the next cycle after the write.
10.3.6 16-Bit PWM Mode
A timer is configured to PWM mode using the following sequence:
1. Ensure the timer is disabled (the TnEN bit is cleared) before making any changes.
2. Write the GPTM Configuration (GPTMCFG) register with a value of 0x4.
3. In the GPTM Timer Mode (GPTMTnMR) register, set the TnAMS bit to 0x1, the TnCMR bit to
0x0, and the TnMR field to 0x2.
4. Configure the output state of the PWM signal (whether or not it is inverted) in the TnEVENT field
of the GPTM Control (GPTMCTL) register.
5. Load the timer start value into the GPTM Timern Interval Load (GPTMTnILR) register.
6. Load the GPTM Timern Match (GPTMTnMATCHR) register with the desired value.
7. Set the TnEN bit in the GPTM Control (GPTMCTL) register to enable the timer and begin
generation of the output PWM signal.
In PWM Timing mode, the timer continues running after the PWM signal has been generated. The
PWM period can be adjusted at any time by writing the GPTMTnILR register, and the change takes
effect at the next cycle after the write.
10.4 Register Map
Table 10-3 on page 214 lists the GPTM registers. The offset listed is a hexadecimal increment to the
register’s address, relative to that timer’s base address:
■ Timer0: 0x4003.0000
■ Timer1: 0x4003.1000
■ Timer2: 0x4003.2000
■ Timer3: 0x4003.3000
Table 10-3. Timers Register Map
See
Offset Name Type Reset Description page
0x000 GPTMCFG R/W 0x0000.0000 GPTM Configuration 216
0x004 GPTMTAMR R/W 0x0000.0000 GPTM TimerA Mode 217
0x008 GPTMTBMR R/W 0x0000.0000 GPTM TimerB Mode 219
0x00C GPTMCTL R/W 0x0000.0000 GPTM Control 221
214 March 17, 2008
Preliminary
General-Purpose Timers
See
Offset Name Type Reset Description page
0x018 GPTMIMR R/W 0x0000.0000 GPTM Interrupt Mask 224
0x01C GPTMRIS RO 0x0000.0000 GPTM Raw Interrupt Status 226
0x020 GPTMMIS RO 0x0000.0000 GPTM Masked Interrupt Status 227
0x024 GPTMICR W1C 0x0000.0000 GPTM Interrupt Clear 228
GPTM TimerA Interval Load 230
0x0000.FFFF
(16-bit mode)
0xFFFF.FFFF
(32-bit mode)
0x028 GPTMTAILR R/W
0x02C GPTMTBILR R/W 0x0000.FFFF GPTM TimerB Interval Load 231
GPTM TimerA Match 232
0x0000.FFFF
(16-bit mode)
0xFFFF.FFFF
(32-bit mode)
0x030 GPTMTAMATCHR R/W
0x034 GPTMTBMATCHR R/W 0x0000.FFFF GPTM TimerB Match 233
0x038 GPTMTAPR R/W 0x0000.0000 GPTM TimerA Prescale 234
0x03C GPTMTBPR R/W 0x0000.0000 GPTM TimerB Prescale 235
0x040 GPTMTAPMR R/W 0x0000.0000 GPTM TimerA Prescale Match 236
0x044 GPTMTBPMR R/W 0x0000.0000 GPTM TimerB Prescale Match 237
GPTM TimerA 238
0x0000.FFFF
(16-bit mode)
0xFFFF.FFFF
(32-bit mode)
0x048 GPTMTAR RO
0x04C GPTMTBR RO 0x0000.FFFF GPTM TimerB 239
10.5 Register Descriptions
The remainder of this section lists and describes the GPTM registers, in numerical order by address
offset.
March 17, 2008 215
Preliminary
LM3S8933 Microcontroller
Register 1: GPTM Configuration (GPTMCFG), offset 0x000
This register configures the global operation of the GPTM module. The value written to this register
determines whether the GPTM is in 32- or 16-bit mode.
GPTM Configuration (GPTMCFG)
Timer0 base: 0x4003.0000
Timer1 base: 0x4003.1000
Timer2 base: 0x4003.2000
Timer3 base: 0x4003.3000
Offset 0x000
Type R/W, reset 0x0000.0000
31 30 29 28 27 26 25 24 23 22 21 20 19 18 17 16
reserved
Type RO RO RO RO RO RO RO RO RO RO RO RO RO RO RO RO
Reset 0 0 0 0 0 0 0 0 0 0 0 0 0 0 0 0
15 14 13 12 11 10 9 8 7 6 5 4 3 2 1 0
reserved GPTMCFG
Type RO RO RO RO RO RO RO RO RO RO RO RO RO R/W R/W R/W
Reset 0 0 0 0 0 0 0 0 0 0 0 0 0 0 0 0
Bit/Field Name Type Reset Description
Software should not rely on the value of a reserved bit. To provide
compatibility with future products, the value of a reserved bit should be
preserved across a read-modify-write operation.
31:3 reserved RO 0x00
GPTM Configuration
The GPTMCFG values are defined as follows:
Value Description
0x0 32-bit timer configuration.
0x1 32-bit real-time clock (RTC) counter configuration.
0x2 Reserved
0x3 Reserved
16-bit timer configuration, function is controlled by bits 1:0 of
GPTMTAMR and GPTMTBMR.
0x4-0x7
2:0 GPTMCFG R/W 0x0
216 March 17, 2008
Preliminary
General-Purpose Timers
Register 2: GPTM TimerA Mode (GPTMTAMR), offset 0x004
This register configures the GPTM based on the configuration selected in the GPTMCFG register.
When in 16-bit PWM mode, set the TAAMS bit to 0x1, the TACMR bit to 0x0, and the TAMR field to
0x2.
GPTM TimerA Mode (GPTMTAMR)
Timer0 base: 0x4003.0000
Timer1 base: 0x4003.1000
Timer2 base: 0x4003.2000
Timer3 base: 0x4003.3000
Offset 0x004
Type R/W, reset 0x0000.0000
31 30 29 28 27 26 25 24 23 22 21 20 19 18 17 16
reserved
Type RO RO RO RO RO RO RO RO RO RO RO RO RO RO RO RO
Reset 0 0 0 0 0 0 0 0 0 0 0 0 0 0 0 0
15 14 13 12 11 10 9 8 7 6 5 4 3 2 1 0
reserved TAAMS TACMR TAMR
Type RO RO RO RO RO RO RO RO RO RO RO RO R/W R/W R/W R/W
Reset 0 0 0 0 0 0 0 0 0 0 0 0 0 0 0 0
Bit/Field Name Type Reset Description
Software should not rely on the value of a reserved bit. To provide
compatibility with future products, the value of a reserved bit should be
preserved across a read-modify-write operation.
31:4 reserved RO 0x00
GPTM TimerA Alternate Mode Select
The TAAMS values are defined as follows:
Value Description
0 Capture mode is enabled.
1 PWM mode is enabled.
Note: To enable PWM mode, you must also clear the TACMR
bit and set the TAMR field to 0x2.
3 TAAMS R/W 0
GPTM TimerA Capture Mode
The TACMR values are defined as follows:
Value Description
0 Edge-Count mode
1 Edge-Time mode
2 TACMR R/W 0
March 17, 2008 217
Preliminary
LM3S8933 Microcontroller
Bit/Field Name Type Reset Description
GPTM TimerA Mode
The TAMR values are defined as follows:
Value Description
0x0 Reserved
0x1 One-Shot Timer mode
0x2 Periodic Timer mode
0x3 Capture mode
The Timer mode is based on the timer configuration defined by bits 2:0
in the GPTMCFG register (16-or 32-bit).
In 16-bit timer configuration, TAMR controls the 16-bit timer modes for
TimerA.
In 32-bit timer configuration, this register controls the mode and the
contents of GPTMTBMR are ignored.
1:0 TAMR R/W 0x0
218 March 17, 2008
Preliminary
General-Purpose Timers
Register 3: GPTM TimerB Mode (GPTMTBMR), offset 0x008
This register configures the GPTM based on the configuration selected in the GPTMCFG register.
When in 16-bit PWM mode, set the TBAMS bit to 0x1, the TBCMR bit to 0x0, and the TBMR field to
0x2.
GPTM TimerB Mode (GPTMTBMR)
Timer0 base: 0x4003.0000
Timer1 base: 0x4003.1000
Timer2 base: 0x4003.2000
Timer3 base: 0x4003.3000
Offset 0x008
Type R/W, reset 0x0000.0000
31 30 29 28 27 26 25 24 23 22 21 20 19 18 17 16
reserved
Type RO RO RO RO RO RO RO RO RO RO RO RO RO RO RO RO
Reset 0 0 0 0 0 0 0 0 0 0 0 0 0 0 0 0
15 14 13 12 11 10 9 8 7 6 5 4 3 2 1 0
reserved TBAMS TBCMR TBMR
Type RO RO RO RO RO RO RO RO RO RO RO RO R/W R/W R/W R/W
Reset 0 0 0 0 0 0 0 0 0 0 0 0 0 0 0 0
Bit/Field Name Type Reset Description
Software should not rely on the value of a reserved bit. To provide
compatibility with future products, the value of a reserved bit should be
preserved across a read-modify-write operation.
31:4 reserved RO 0x00
GPTM TimerB Alternate Mode Select
The TBAMS values are defined as follows:
Value Description
0 Capture mode is enabled.
1 PWM mode is enabled.
Note: To enable PWM mode, you must also clear the TBCMR
bit and set the TBMR field to 0x2.
3 TBAMS R/W 0
GPTM TimerB Capture Mode
The TBCMR values are defined as follows:
Value Description
0 Edge-Count mode
1 Edge-Time mode
2 TBCMR R/W 0
March 17, 2008 219
Preliminary
LM3S8933 Microcontroller
Bit/Field Name Type Reset Description
GPTM TimerB Mode
The TBMR values are defined as follows:
Value Description
0x0 Reserved
0x1 One-Shot Timer mode
0x2 Periodic Timer mode
0x3 Capture mode
The timer mode is based on the timer configuration defined by bits 2:0
in the GPTMCFG register.
In 16-bit timer configuration, these bits control the 16-bit timer modes
for TimerB.
In 32-bit timer configuration, this register’s contents are ignored and
GPTMTAMR is used.
1:0 TBMR R/W 0x0
220 March 17, 2008
Preliminary
General-Purpose Timers
Register 4: GPTM Control (GPTMCTL), offset 0x00C
This register is used alongside the GPTMCFG and GMTMTnMR registers to fine-tune the timer
configuration, and to enable other features such as timer stall and the output trigger. The output
trigger can be used to initiate transfers on the ADC module.
GPTM Control (GPTMCTL)
Timer0 base: 0x4003.0000
Timer1 base: 0x4003.1000
Timer2 base: 0x4003.2000
Timer3 base: 0x4003.3000
Offset 0x00C
Type R/W, reset 0x0000.0000
31 30 29 28 27 26 25 24 23 22 21 20 19 18 17 16
reserved
Type RO RO RO RO RO RO RO RO RO RO RO RO RO RO RO RO
Reset 0 0 0 0 0 0 0 0 0 0 0 0 0 0 0 0
15 14 13 12 11 10 9 8 7 6 5 4 3 2 1 0
reserved TBPWML TBOTE reserved TBEVENT TBSTALL TBEN reserved TAPWML TAOTE RTCEN TAEVENT TASTALL TAEN
Type RO R/W R/W RO R/W R/W R/W R/W RO R/W R/W R/W R/W R/W R/W R/W
Reset 0 0 0 0 0 0 0 0 0 0 0 0 0 0 0 0
Bit/Field Name Type Reset Description
Software should not rely on the value of a reserved bit. To provide
compatibility with future products, the value of a reserved bit should be
preserved across a read-modify-write operation.
31:15 reserved RO 0x00
GPTM TimerB PWM Output Level
The TBPWML values are defined as follows:
Value Description
0 Output is unaffected.
1 Output is inverted.
14 TBPWML R/W 0
GPTM TimerB Output Trigger Enable
The TBOTE values are defined as follows:
Value Description
0 The output TimerB trigger is disabled.
1 The output TimerB trigger is enabled.
13 TBOTE R/W 0
Software should not rely on the value of a reserved bit. To provide
compatibility with future products, the value of a reserved bit should be
preserved across a read-modify-write operation.
12 reserved RO 0
March 17, 2008 221
Preliminary
LM3S8933 Microcontroller
Bit/Field Name Type Reset Description
GPTM TimerB Event Mode
The TBEVENT values are defined as follows:
Value Description
0x0 Positive edge
0x1 Negative edge
0x2 Reserved
0x3 Both edges
11:10 TBEVENT R/W 0x0
GPTM TimerB Stall Enable
The TBSTALL values are defined as follows:
Value Description
0 TimerB stalling is disabled.
1 TimerB stalling is enabled.
9 TBSTALL R/W 0
GPTM TimerB Enable
The TBEN values are defined as follows:
Value Description
0 TimerB is disabled.
TimerB is enabled and begins counting or the capture logic is
enabled based on the GPTMCFG register.
1
8 TBEN R/W 0
Software should not rely on the value of a reserved bit. To provide
compatibility with future products, the value of a reserved bit should be
preserved across a read-modify-write operation.
7 reserved RO 0
GPTM TimerA PWM Output Level
The TAPWML values are defined as follows:
Value Description
0 Output is unaffected.
1 Output is inverted.
6 TAPWML R/W 0
GPTM TimerA Output Trigger Enable
The TAOTE values are defined as follows:
Value Description
0 The output TimerA trigger is disabled.
1 The output TimerA trigger is enabled.
5 TAOTE R/W 0
222 March 17, 2008
Preliminary
General-Purpose Timers
Bit/Field Name Type Reset Description
GPTM RTC Enable
The RTCEN values are defined as follows:
Value Description
0 RTC counting is disabled.
1 RTC counting is enabled.
4 RTCEN R/W 0
GPTM TimerA Event Mode
The TAEVENT values are defined as follows:
Value Description
0x0 Positive edge
0x1 Negative edge
0x2 Reserved
0x3 Both edges
3:2 TAEVENT R/W 0x0
GPTM TimerA Stall Enable
The TASTALL values are defined as follows:
Value Description
0 TimerA stalling is disabled.
1 TimerA stalling is enabled.
1 TASTALL R/W 0
GPTM TimerA Enable
The TAEN values are defined as follows:
Value Description
0 TimerA is disabled.
TimerA is enabled and begins counting or the capture logic is
enabled based on the GPTMCFG register.
1
0 TAEN R/W 0
March 17, 2008 223
Preliminary
LM3S8933 Microcontroller
Register 5: GPTM Interrupt Mask (GPTMIMR), offset 0x018
This register allows software to enable/disable GPTM controller-level interrupts. Writing a 1 enables
the interrupt, while writing a 0 disables it.
GPTM Interrupt Mask (GPTMIMR)
Timer0 base: 0x4003.0000
Timer1 base: 0x4003.1000
Timer2 base: 0x4003.2000
Timer3 base: 0x4003.3000
Offset 0x018
Type R/W, reset 0x0000.0000
31 30 29 28 27 26 25 24 23 22 21 20 19 18 17 16
reserved
Type RO RO RO RO RO RO RO RO RO RO RO RO RO RO RO RO
Reset 0 0 0 0 0 0 0 0 0 0 0 0 0 0 0 0
15 14 13 12 11 10 9 8 7 6 5 4 3 2 1 0
reserved CBEIM CBMIM TBTOIM reserved RTCIM CAEIM CAMIM TATOIM
Type RO RO RO RO RO R/W R/W R/W RO RO RO RO R/W R/W R/W R/W
Reset 0 0 0 0 0 0 0 0 0 0 0 0 0 0 0 0
Bit/Field Name Type Reset Description
Software should not rely on the value of a reserved bit. To provide
compatibility with future products, the value of a reserved bit should be
preserved across a read-modify-write operation.
31:11 reserved RO 0x00
GPTM CaptureB Event Interrupt Mask
The CBEIM values are defined as follows:
Value Description
0 Interrupt is disabled.
1 Interrupt is enabled.
10 CBEIM R/W 0
GPTM CaptureB Match Interrupt Mask
The CBMIM values are defined as follows:
Value Description
0 Interrupt is disabled.
1 Interrupt is enabled.
9 CBMIM R/W 0
GPTM TimerB Time-Out Interrupt Mask
The TBTOIM values are defined as follows:
Value Description
0 Interrupt is disabled.
1 Interrupt is enabled.
8 TBTOIM R/W 0
Software should not rely on the value of a reserved bit. To provide
compatibility with future products, the value of a reserved bit should be
preserved across a read-modify-write operation.
7:4 reserved RO 0
224 March 17, 2008
Preliminary
General-Purpose Timers
Bit/Field Name Type Reset Description
GPTM RTC Interrupt Mask
The RTCIM values are defined as follows:
Value Description
0 Interrupt is disabled.
1 Interrupt is enabled.
3 RTCIM R/W 0
GPTM CaptureA Event Interrupt Mask
The CAEIM values are defined as follows:
Value Description
0 Interrupt is disabled.
1 Interrupt is enabled.
2 CAEIM R/W 0
GPTM CaptureA Match Interrupt Mask
The CAMIM values are defined as follows:
Value Description
0 Interrupt is disabled.
1 Interrupt is enabled.
1 CAMIM R/W 0
GPTM TimerA Time-Out Interrupt Mask
The TATOIM values are defined as follows:
Value Description
0 Interrupt is disabled.
1 Interrupt is enabled.
0 TATOIM R/W 0
March 17, 2008 225
Preliminary
LM3S8933 Microcontroller
Register 6: GPTM Raw Interrupt Status (GPTMRIS), offset 0x01C
This register shows the state of the GPTM's internal interrupt signal. These bits are set whether or
not the interrupt is masked in the GPTMIMR register. Each bit can be cleared by writing a 1 to its
corresponding bit in GPTMICR.
GPTM Raw Interrupt Status (GPTMRIS)
Timer0 base: 0x4003.0000
Timer1 base: 0x4003.1000
Timer2 base: 0x4003.2000
Timer3 base: 0x4003.3000
Offset 0x01C
Type RO, reset 0x0000.0000
31 30 29 28 27 26 25 24 23 22 21 20 19 18 17 16
reserved
Type RO RO RO RO RO RO RO RO RO RO RO RO RO RO RO RO
Reset 0 0 0 0 0 0 0 0 0 0 0 0 0 0 0 0
15 14 13 12 11 10 9 8 7 6 5 4 3 2 1 0
reserved CBERIS CBMRIS TBTORIS reserved RTCRIS CAERIS CAMRIS TATORIS
Type RO RO RO RO RO RO RO RO RO RO RO RO RO RO RO RO
Reset 0 0 0 0 0 0 0 0 0 0 0 0 0 0 0 0
Bit/Field Name Type Reset Description
Software should not rely on the value of a reserved bit. To provide
compatibility with future products, the value of a reserved bit should be
preserved across a read-modify-write operation.
31:11 reserved RO 0x00
GPTM CaptureB Event Raw Interrupt
This is the CaptureB Event interrupt status prior to masking.
10 CBERIS RO 0
GPTM CaptureB Match Raw Interrupt
This is the CaptureB Match interrupt status prior to masking.
9 CBMRIS RO 0
GPTM TimerB Time-Out Raw Interrupt
This is the TimerB time-out interrupt status prior to masking.
8 TBTORIS RO 0
Software should not rely on the value of a reserved bit. To provide
compatibility with future products, the value of a reserved bit should be
preserved across a read-modify-write operation.
7:4 reserved RO 0x0
GPTM RTC Raw Interrupt
This is the RTC Event interrupt status prior to masking.
3 RTCRIS RO 0
GPTM CaptureA Event Raw Interrupt
This is the CaptureA Event interrupt status prior to masking.
2 CAERIS RO 0
GPTM CaptureA Match Raw Interrupt
This is the CaptureA Match interrupt status prior to masking.
1 CAMRIS RO 0
GPTM TimerA Time-Out Raw Interrupt
This the TimerA time-out interrupt status prior to masking.
0 TATORIS RO 0
226 March 17, 2008
Preliminary
General-Purpose Timers
Register 7: GPTM Masked Interrupt Status (GPTMMIS), offset 0x020
This register show the state of the GPTM's controller-level interrupt. If an interrupt is unmasked in
GPTMIMR, and there is an event that causes the interrupt to be asserted, the corresponding bit is
set in this register. All bits are cleared by writing a 1 to the corresponding bit in GPTMICR.
GPTM Masked Interrupt Status (GPTMMIS)
Timer0 base: 0x4003.0000
Timer1 base: 0x4003.1000
Timer2 base: 0x4003.2000
Timer3 base: 0x4003.3000
Offset 0x020
Type RO, reset 0x0000.0000
31 30 29 28 27 26 25 24 23 22 21 20 19 18 17 16
reserved
Type RO RO RO RO RO RO RO RO RO RO RO RO RO RO RO RO
Reset 0 0 0 0 0 0 0 0 0 0 0 0 0 0 0 0
15 14 13 12 11 10 9 8 7 6 5 4 3 2 1 0
reserved CBEMIS CBMMIS TBTOMIS reserved RTCMIS CAEMIS CAMMIS TATOMIS
Type RO RO RO RO RO RO RO RO RO RO RO RO RO RO RO RO
Reset 0 0 0 0 0 0 0 0 0 0 0 0 0 0 0 0
Bit/Field Name Type Reset Description
Software should not rely on the value of a reserved bit. To provide
compatibility with future products, the value of a reserved bit should be
preserved across a read-modify-write operation.
31:11 reserved RO 0x00
GPTM CaptureB Event Masked Interrupt
This is the CaptureB event interrupt status after masking.
10 CBEMIS RO 0
GPTM CaptureB Match Masked Interrupt
This is the CaptureB match interrupt status after masking.
9 CBMMIS RO 0
GPTM TimerB Time-Out Masked Interrupt
This is the TimerB time-out interrupt status after masking.
8 TBTOMIS RO 0
Software should not rely on the value of a reserved bit. To provide
compatibility with future products, the value of a reserved bit should be
preserved across a read-modify-write operation.
7:4 reserved RO 0x0
GPTM RTC Masked Interrupt
This is the RTC event interrupt status after masking.
3 RTCMIS RO 0
GPTM CaptureA Event Masked Interrupt
This is the CaptureA event interrupt status after masking.
2 CAEMIS RO 0
GPTM CaptureA Match Masked Interrupt
This is the CaptureA match interrupt status after masking.
1 CAMMIS RO 0
GPTM TimerA Time-Out Masked Interrupt
This is the TimerA time-out interrupt status after masking.
0 TATOMIS RO 0
March 17, 2008 227
Preliminary
LM3S8933 Microcontroller
Register 8: GPTM Interrupt Clear (GPTMICR), offset 0x024
This register is used to clear the status bits in the GPTMRIS and GPTMMIS registers. Writing a 1
to a bit clears the corresponding bit in the GPTMRIS and GPTMMIS registers.
GPTM Interrupt Clear (GPTMICR)
Timer0 base: 0x4003.0000
Timer1 base: 0x4003.1000
Timer2 base: 0x4003.2000
Timer3 base: 0x4003.3000
Offset 0x024
Type W1C, reset 0x0000.0000
31 30 29 28 27 26 25 24 23 22 21 20 19 18 17 16
reserved
Type RO RO RO RO RO RO RO RO RO RO RO RO RO RO RO RO
Reset 0 0 0 0 0 0 0 0 0 0 0 0 0 0 0 0
15 14 13 12 11 10 9 8 7 6 5 4 3 2 1 0
reserved CBECINT CBMCINT TBTOCINT reserved RTCCINT CAECINT CAMCINT TATOCINT
Type RO RO RO RO RO W1C W1C W1C RO RO RO RO W1C W1C W1C W1C
Reset 0 0 0 0 0 0 0 0 0 0 0 0 0 0 0 0
Bit/Field Name Type Reset Description
Software should not rely on the value of a reserved bit. To provide
compatibility with future products, the value of a reserved bit should be
preserved across a read-modify-write operation.
31:11 reserved RO 0x00
GPTM CaptureB Event Interrupt Clear
The CBECINT values are defined as follows:
Value Description
0 The interrupt is unaffected.
1 The interrupt is cleared.
10 CBECINT W1C 0
GPTM CaptureB Match Interrupt Clear
The CBMCINT values are defined as follows:
Value Description
0 The interrupt is unaffected.
1 The interrupt is cleared.
9 CBMCINT W1C 0
GPTM TimerB Time-Out Interrupt Clear
The TBTOCINT values are defined as follows:
Value Description
0 The interrupt is unaffected.
1 The interrupt is cleared.
8 TBTOCINT W1C 0
Software should not rely on the value of a reserved bit. To provide
compatibility with future products, the value of a reserved bit should be
preserved across a read-modify-write operation.
7:4 reserved RO 0x0
228 March 17, 2008
Preliminary
General-Purpose Timers
Bit/Field Name Type Reset Description
GPTM RTC Interrupt Clear
The RTCCINT values are defined as follows:
Value Description
0 The interrupt is unaffected.
1 The interrupt is cleared.
3 RTCCINT W1C 0
GPTM CaptureA Event Interrupt Clear
The CAECINT values are defined as follows:
Value Description
0 The interrupt is unaffected.
1 The interrupt is cleared.
2 CAECINT W1C 0
GPTM CaptureA Match Raw Interrupt
This is the CaptureA match interrupt status after masking.
1 CAMCINT W1C 0
GPTM TimerA Time-Out Raw Interrupt
The TATOCINT values are defined as follows:
Value Description
0 The interrupt is unaffected.
1 The interrupt is cleared.
0 TATOCINT W1C 0
March 17, 2008 229
Preliminary
LM3S8933 Microcontroller
Register 9: GPTM TimerA Interval Load (GPTMTAILR), offset 0x028
This register is used to load the starting count value into the timer. When GPTM is configured to
one of the 32-bit modes, GPTMTAILR appears as a 32-bit register (the upper 16-bits correspond
to the contents of the GPTM TimerB Interval Load (GPTMTBILR) register). In 16-bit mode, the
upper 16 bits of this register read as 0s and have no effect on the state of GPTMTBILR.
GPTM TimerA Interval Load (GPTMTAILR)
Timer0 base: 0x4003.0000
Timer1 base: 0x4003.1000
Timer2 base: 0x4003.2000
Timer3 base: 0x4003.3000
Offset 0x028
Type R/W, reset 0x0000.FFFF (16-bit mode) and 0xFFFF.FFFF (32-bit mode)
31 30 29 28 27 26 25 24 23 22 21 20 19 18 17 16
TAILRH
Type R/W R/W R/W R/W R/W R/W R/W R/W R/W R/W R/W R/W R/W R/W R/W R/W
Reset 0 1 1 0 1 0 1 1 1 1 0 1 1 1 1 0
15 14 13 12 11 10 9 8 7 6 5 4 3 2 1 0
TAILRL
Type R/W R/W R/W R/W R/W R/W R/W R/W R/W R/W R/W R/W R/W R/W R/W R/W
Reset 1 1 1 1 1 1 1 1 1 1 1 1 1 1 1 1
Bit/Field Name Type Reset Description
GPTM TimerA Interval Load Register High
When configured for 32-bit mode via the GPTMCFG register, the GPTM
TimerB Interval Load (GPTMTBILR) register loads this value on a
write. A read returns the current value of GPTMTBILR.
In 16-bit mode, this field reads as 0 and does not have an effect on the
state of GPTMTBILR.
0xFFFF
(32-bit mode)
0x0000 (16-bit
mode)
31:16 TAILRH R/W
GPTM TimerA Interval Load Register Low
For both 16- and 32-bit modes, writing this field loads the counter for
TimerA. A read returns the current value of GPTMTAILR.
15:0 TAILRL R/W 0xFFFF
230 March 17, 2008
Preliminary
General-Purpose Timers
Register 10: GPTM TimerB Interval Load (GPTMTBILR), offset 0x02C
This register is used to load the starting count value into TimerB. When the GPTM is configured to
a 32-bit mode, GPTMTBILR returns the current value of TimerB and ignores writes.
GPTM TimerB Interval Load (GPTMTBILR)
Timer0 base: 0x4003.0000
Timer1 base: 0x4003.1000
Timer2 base: 0x4003.2000
Timer3 base: 0x4003.3000
Offset 0x02C
Type R/W, reset 0x0000.FFFF
31 30 29 28 27 26 25 24 23 22 21 20 19 18 17 16
reserved
Type RO RO RO RO RO RO RO RO RO RO RO RO RO RO RO RO
Reset 0 0 0 0 0 0 0 0 0 0 0 0 0 0 0 0
15 14 13 12 11 10 9 8 7 6 5 4 3 2 1 0
TBILRL
Type R/W R/W R/W R/W R/W R/W R/W R/W R/W R/W R/W R/W R/W R/W R/W R/W
Reset 1 1 1 1 1 1 1 1 1 1 1 1 1 1 1 1
Bit/Field Name Type Reset Description
Software should not rely on the value of a reserved bit. To provide
compatibility with future products, the value of a reserved bit should be
preserved across a read-modify-write operation.
31:16 reserved RO 0x0000
GPTM TimerB Interval Load Register
When the GPTM is not configured as a 32-bit timer, a write to this field
updates GPTMTBILR. In 32-bit mode, writes are ignored, and reads
return the current value of GPTMTBILR.
15:0 TBILRL R/W 0xFFFF
March 17, 2008 231
Preliminary
LM3S8933 Microcontroller
Register 11: GPTM TimerA Match (GPTMTAMATCHR), offset 0x030
This register is used in 32-bit Real-Time Clock mode and 16-bit PWM and Input Edge Count modes.
GPTM TimerA Match (GPTMTAMATCHR)
Timer0 base: 0x4003.0000
Timer1 base: 0x4003.1000
Timer2 base: 0x4003.2000
Timer3 base: 0x4003.3000
Offset 0x030
Type R/W, reset 0x0000.FFFF (16-bit mode) and 0xFFFF.FFFF (32-bit mode)
31 30 29 28 27 26 25 24 23 22 21 20 19 18 17 16
TAMRH
Type R/W R/W R/W R/W R/W R/W R/W R/W R/W R/W R/W R/W R/W R/W R/W R/W
Reset 0 1 1 0 1 0 1 1 1 1 0 1 1 1 1 0
15 14 13 12 11 10 9 8 7 6 5 4 3 2 1 0
TAMRL
Type R/W R/W R/W R/W R/W R/W R/W R/W R/W R/W R/W R/W R/W R/W R/W R/W
Reset 1 1 1 1 1 1 1 1 1 1 1 1 1 1 1 1
Bit/Field Name Type Reset Description
GPTM TimerA Match Register High
When configured for 32-bit Real-Time Clock (RTC) mode via the
GPTMCFG register, this value is compared to the upper half of
GPTMTAR, to determine match events.
In 16-bit mode, this field reads as 0 and does not have an effect on the
state of GPTMTBMATCHR.
0xFFFF
(32-bit mode)
0x0000 (16-bit
mode)
31:16 TAMRH R/W
GPTM TimerA Match Register Low
When configured for 32-bit Real-Time Clock (RTC) mode via the
GPTMCFG register, this value is compared to the lower half of
GPTMTAR, to determine match events.
When configured for PWM mode, this value along with GPTMTAILR,
determines the duty cycle of the output PWM signal.
When configured for Edge Count mode, this value along with
GPTMTAILR, determines how many edge events are counted. The total
number of edge events counted is equal to the value in GPTMTAILR
minus this value.
15:0 TAMRL R/W 0xFFFF
232 March 17, 2008
Preliminary
General-Purpose Timers
Register 12: GPTM TimerB Match (GPTMTBMATCHR), offset 0x034
This register is used in 16-bit PWM and Input Edge Count modes.
GPTM TimerB Match (GPTMTBMATCHR)
Timer0 base: 0x4003.0000
Timer1 base: 0x4003.1000
Timer2 base: 0x4003.2000
Timer3 base: 0x4003.3000
Offset 0x034
Type R/W, reset 0x0000.FFFF
31 30 29 28 27 26 25 24 23 22 21 20 19 18 17 16
reserved
Type RO RO RO RO RO RO RO RO RO RO RO RO RO RO RO RO
Reset 0 0 0 0 0 0 0 0 0 0 0 0 0 0 0 0
15 14 13 12 11 10 9 8 7 6 5 4 3 2 1 0
TBMRL
Type R/W R/W R/W R/W R/W R/W R/W R/W R/W R/W R/W R/W R/W R/W R/W R/W
Reset 1 1 1 1 1 1 1 1 1 1 1 1 1 1 1 1
Bit/Field Name Type Reset Description
Software should not rely on the value of a reserved bit. To provide
compatibility with future products, the value of a reserved bit should be
preserved across a read-modify-write operation.
31:16 reserved RO 0x0000
GPTM TimerB Match Register Low
When configured for PWM mode, this value along with GPTMTBILR,
determines the duty cycle of the output PWM signal.
When configured for Edge Count mode, this value along with
GPTMTBILR, determines how many edge events are counted. The total
number of edge events counted is equal to the value in GPTMTBILR
minus this value.
15:0 TBMRL R/W 0xFFFF
March 17, 2008 233
Preliminary
LM3S8933 Microcontroller
Register 13: GPTM TimerA Prescale (GPTMTAPR), offset 0x038
This register allows software to extend the range of the 16-bit timers when operating in one-shot or
periodic mode.
GPTM TimerA Prescale (GPTMTAPR)
Timer0 base: 0x4003.0000
Timer1 base: 0x4003.1000
Timer2 base: 0x4003.2000
Timer3 base: 0x4003.3000
Offset 0x038
Type R/W, reset 0x0000.0000
31 30 29 28 27 26 25 24 23 22 21 20 19 18 17 16
reserved
Type RO RO RO RO RO RO RO RO RO RO RO RO RO RO RO RO
Reset 0 0 0 0 0 0 0 0 0 0 0 0 0 0 0 0
15 14 13 12 11 10 9 8 7 6 5 4 3 2 1 0
reserved TAPSR
Type RO RO RO RO RO RO RO RO R/W R/W R/W R/W R/W R/W R/W R/W
Reset 0 0 0 0 0 0 0 0 0 0 0 0 0 0 0 0
Bit/Field Name Type Reset Description
Software should not rely on the value of a reserved bit. To provide
compatibility with future products, the value of a reserved bit should be
preserved across a read-modify-write operation.
31:8 reserved RO 0x00
GPTM TimerA Prescale
The register loads this value on a write. A read returns the current value
of the register.
Refer to Table 10-2 on page 208 for more details and an example.
7:0 TAPSR R/W 0x00
234 March 17, 2008
Preliminary
General-Purpose Timers
Register 14: GPTM TimerB Prescale (GPTMTBPR), offset 0x03C
This register allows software to extend the range of the 16-bit timers when operating in one-shot or
periodic mode.
GPTM TimerB Prescale (GPTMTBPR)
Timer0 base: 0x4003.0000
Timer1 base: 0x4003.1000
Timer2 base: 0x4003.2000
Timer3 base: 0x4003.3000
Offset 0x03C
Type R/W, reset 0x0000.0000
31 30 29 28 27 26 25 24 23 22 21 20 19 18 17 16
reserved
Type RO RO RO RO RO RO RO RO RO RO RO RO RO RO RO RO
Reset 0 0 0 0 0 0 0 0 0 0 0 0 0 0 0 0
15 14 13 12 11 10 9 8 7 6 5 4 3 2 1 0
reserved TBPSR
Type RO RO RO RO RO RO RO RO R/W R/W R/W R/W R/W R/W R/W R/W
Reset 0 0 0 0 0 0 0 0 0 0 0 0 0 0 0 0
Bit/Field Name Type Reset Description
Software should not rely on the value of a reserved bit. To provide
compatibility with future products, the value of a reserved bit should be
preserved across a read-modify-write operation.
31:8 reserved RO 0x00
GPTM TimerB Prescale
The register loads this value on a write. A read returns the current value
of this register.
Refer to Table 10-2 on page 208 for more details and an example.
7:0 TBPSR R/W 0x00
March 17, 2008 235
Preliminary
LM3S8933 Microcontroller
Register 15: GPTM TimerA Prescale Match (GPTMTAPMR), offset 0x040
This register effectively extends the range of GPTMTAMATCHR to 24 bits when operating in 16-bit
one-shot or periodic mode.
GPTM TimerA Prescale Match (GPTMTAPMR)
Timer0 base: 0x4003.0000
Timer1 base: 0x4003.1000
Timer2 base: 0x4003.2000
Timer3 base: 0x4003.3000
Offset 0x040
Type R/W, reset 0x0000.0000
31 30 29 28 27 26 25 24 23 22 21 20 19 18 17 16
reserved
Type RO RO RO RO RO RO RO RO RO RO RO RO RO RO RO RO
Reset 0 0 0 0 0 0 0 0 0 0 0 0 0 0 0 0
15 14 13 12 11 10 9 8 7 6 5 4 3 2 1 0
reserved TAPSMR
Type RO RO RO RO RO RO RO RO R/W R/W R/W R/W R/W R/W R/W R/W
Reset 0 0 0 0 0 0 0 0 0 0 0 0 0 0 0 0
Bit/Field Name Type Reset Description
Software should not rely on the value of a reserved bit. To provide
compatibility with future products, the value of a reserved bit should be
preserved across a read-modify-write operation.
31:8 reserved RO 0x00
GPTM TimerA Prescale Match
This value is used alongside GPTMTAMATCHR to detect timer match
events while using a prescaler.
7:0 TAPSMR R/W 0x00
236 March 17, 2008
Preliminary
General-Purpose Timers
Register 16: GPTM TimerB Prescale Match (GPTMTBPMR), offset 0x044
This register effectively extends the range of GPTMTBMATCHR to 24 bits when operating in 16-bit
one-shot or periodic mode.
GPTM TimerB Prescale Match (GPTMTBPMR)
Timer0 base: 0x4003.0000
Timer1 base: 0x4003.1000
Timer2 base: 0x4003.2000
Timer3 base: 0x4003.3000
Offset 0x044
Type R/W, reset 0x0000.0000
31 30 29 28 27 26 25 24 23 22 21 20 19 18 17 16
reserved
Type RO RO RO RO RO RO RO RO RO RO RO RO RO RO RO RO
Reset 0 0 0 0 0 0 0 0 0 0 0 0 0 0 0 0
15 14 13 12 11 10 9 8 7 6 5 4 3 2 1 0
reserved TBPSMR
Type RO RO RO RO RO RO RO RO R/W R/W R/W R/W R/W R/W R/W R/W
Reset 0 0 0 0 0 0 0 0 0 0 0 0 0 0 0 0
Bit/Field Name Type Reset Description
Software should not rely on the value of a reserved bit. To provide
compatibility with future products, the value of a reserved bit should be
preserved across a read-modify-write operation.
31:8 reserved RO 0x00
GPTM TimerB Prescale Match
This value is used alongside GPTMTBMATCHR to detect timer match
events while using a prescaler.
7:0 TBPSMR R/W 0x00
March 17, 2008 237
Preliminary
LM3S8933 Microcontroller
Register 17: GPTM TimerA (GPTMTAR), offset 0x048
This register shows the current value of the TimerA counter in all cases except for Input Edge Count
mode. When in this mode, this register contains the time at which the last edge event took place.
GPTM TimerA (GPTMTAR)
Timer0 base: 0x4003.0000
Timer1 base: 0x4003.1000
Timer2 base: 0x4003.2000
Timer3 base: 0x4003.3000
Offset 0x048
Type RO, reset 0x0000.FFFF (16-bit mode) and 0xFFFF.FFFF (32-bit mode)
31 30 29 28 27 26 25 24 23 22 21 20 19 18 17 16
TARH
Type RO RO RO RO RO RO RO RO RO RO RO RO RO RO RO RO
Reset 0 1 1 0 1 0 1 1 1 1 0 1 1 1 1 0
15 14 13 12 11 10 9 8 7 6 5 4 3 2 1 0
TARL
Type RO RO RO RO RO RO RO RO RO RO RO RO RO RO RO RO
Reset 1 1 1 1 1 1 1 1 1 1 1 1 1 1 1 1
Bit/Field Name Type Reset Description
GPTM TimerA Register High
If the GPTMCFG is in a 32-bit mode, TimerB value is read. If the
GPTMCFG is in a 16-bit mode, this is read as zero.
0xFFFF
(32-bit mode)
0x0000 (16-bit
mode)
31:16 TARH RO
GPTM TimerA Register Low
A read returns the current value of the GPTM TimerA Count Register,
except in Input Edge Count mode, when it returns the timestamp from
the last edge event.
15:0 TARL RO 0xFFFF
238 March 17, 2008
Preliminary
General-Purpose Timers
Register 18: GPTM TimerB (GPTMTBR), offset 0x04C
This register shows the current value of the TimerB counter in all cases except for Input Edge Count
mode. When in this mode, this register contains the time at which the last edge event took place.
GPTM TimerB (GPTMTBR)
Timer0 base: 0x4003.0000
Timer1 base: 0x4003.1000
Timer2 base: 0x4003.2000
Timer3 base: 0x4003.3000
Offset 0x04C
Type RO, reset 0x0000.FFFF
31 30 29 28 27 26 25 24 23 22 21 20 19 18 17 16
reserved
Type RO RO RO RO RO RO RO RO RO RO RO RO RO RO RO RO
Reset 0 0 0 0 0 0 0 0 0 0 0 0 0 0 0 0
15 14 13 12 11 10 9 8 7 6 5 4 3 2 1 0
TBRL
Type RO RO RO RO RO RO RO RO RO RO RO RO RO RO RO RO
Reset 1 1 1 1 1 1 1 1 1 1 1 1 1 1 1 1
Bit/Field Name Type Reset Description
Software should not rely on the value of a reserved bit. To provide
compatibility with future products, the value of a reserved bit should be
preserved across a read-modify-write operation.
31:16 reserved RO 0x0000
GPTM TimerB
A read returns the current value of the GPTM TimerB Count Register,
except in Input Edge Count mode, when it returns the timestamp from
the last edge event.
15:0 TBRL RO 0xFFFF
March 17, 2008 239
Preliminary
LM3S8933 Microcontroller
11 Watchdog Timer
A watchdog timer can generate nonmaskable interrupts (NMIs) or a reset when a time-out value is
reached. The watchdog timer is used to regain control when a system has failed due to a software
error or due to the failure of an external device to respond in the expected way.
The Stellaris® Watchdog Timer module consists of a 32-bit down counter, a programmable load
register, interrupt generation logic, a locking register, and user-enabled stalling.
The Watchdog Timer can be configured to generate an interrupt to the controller on its first time-out,
and to generate a reset signal on its second time-out. Once the Watchdog Timer has been configured,
the lock register can be written to prevent the timer configuration from being inadvertently altered.
11.1 Block Diagram
Figure 11-1. WDT Module Block Diagram
Control / Clock /
Interrupt
Generation
WDTCTL
WDTICR
WDTRIS
WDTMIS
WDTLOCK
WDTTEST
WDTLOAD
WDTVALUE
Comparator
32-Bit Down
Counter
0x00000000
Interrupt
System Clock
Identification Registers
WDTPCellID0 WDTPeriphID0 WDTPeriphID4
WDTPCellID1 WDTPeriphID1 WDTPeriphID5
WDTPCellID2 WDTPeriphID2 WDTPeriphID6
WDTPCellID3 WDTPeriphID3 WDTPeriphID7
11.2 Functional Description
The Watchdog Timer module generates the first time-out signal when the 32-bit counter reaches
the zero state after being enabled; enabling the counter also enables the watchdog timer interrupt.
After the first time-out event, the 32-bit counter is re-loaded with the value of the Watchdog Timer
Load (WDTLOAD) register, and the timer resumes counting down from that value. Once the
240 March 17, 2008
Preliminary
Watchdog Timer
Watchdog Timer has been configured, the Watchdog Timer Lock (WDTLOCK) register is written,
which prevents the timer configuration from being inadvertently altered by software.
If the timer counts down to its zero state again before the first time-out interrupt is cleared, and the
reset signal has been enabled (via the WatchdogResetEnable function), the Watchdog timer
asserts its reset signal to the system. If the interrupt is cleared before the 32-bit counter reaches its
second time-out, the 32-bit counter is loaded with the value in the WDTLOAD register, and counting
resumes from that value.
If WDTLOAD is written with a new value while the Watchdog Timer counter is counting, then the
counter is loaded with the new value and continues counting.
Writing to WDTLOAD does not clear an active interrupt. An interrupt must be specifically cleared
by writing to the Watchdog Interrupt Clear (WDTICR) register.
The Watchdog module interrupt and reset generation can be enabled or disabled as required. When
the interrupt is re-enabled, the 32-bit counter is preloaded with the load register value and not its
last state.
11.3 Initialization and Configuration
To use the WDT, its peripheral clock must be enabled by setting the WDT bit in the RCGC0 register.
The Watchdog Timer is configured using the following sequence:
1. Load the WDTLOAD register with the desired timer load value.
2. If the Watchdog is configured to trigger system resets, set the RESEN bit in the WDTCTL register.
3. Set the INTEN bit in the WDTCTL register to enable the Watchdog and lock the control register.
If software requires that all of the watchdog registers are locked, the Watchdog Timer module can
be fully locked by writing any value to the WDTLOCK register. To unlock the Watchdog Timer, write
a value of 0x1ACC.E551.
11.4 Register Map
Table 11-1 on page 241 lists the Watchdog registers. The offset listed is a hexadecimal increment
to the register’s address, relative to the Watchdog Timer base address of 0x4000.0000.
Table 11-1. Watchdog Timer Register Map
See
Offset Name Type Reset Description page
0x000 WDTLOAD R/W 0xFFFF.FFFF Watchdog Load 243
0x004 WDTVALUE RO 0xFFFF.FFFF Watchdog Value 244
0x008 WDTCTL R/W 0x0000.0000 Watchdog Control 245
0x00C WDTICR WO - Watchdog Interrupt Clear 246
0x010 WDTRIS RO 0x0000.0000 Watchdog Raw Interrupt Status 247
0x014 WDTMIS RO 0x0000.0000 Watchdog Masked Interrupt Status 248
0x418 WDTTEST R/W 0x0000.0000 Watchdog Test 249
0xC00 WDTLOCK R/W 0x0000.0000 Watchdog Lock 250
March 17, 2008 241
Preliminary
LM3S8933 Microcontroller
See
Offset Name Type Reset Description page
0xFD0 WDTPeriphID4 RO 0x0000.0000 Watchdog Peripheral Identification 4 251
0xFD4 WDTPeriphID5 RO 0x0000.0000 Watchdog Peripheral Identification 5 252
0xFD8 WDTPeriphID6 RO 0x0000.0000 Watchdog Peripheral Identification 6 253
0xFDC WDTPeriphID7 RO 0x0000.0000 Watchdog Peripheral Identification 7 254
0xFE0 WDTPeriphID0 RO 0x0000.0005 Watchdog Peripheral Identification 0 255
0xFE4 WDTPeriphID1 RO 0x0000.0018 Watchdog Peripheral Identification 1 256
0xFE8 WDTPeriphID2 RO 0x0000.0018 Watchdog Peripheral Identification 2 257
0xFEC WDTPeriphID3 RO 0x0000.0001 Watchdog Peripheral Identification 3 258
0xFF0 WDTPCellID0 RO 0x0000.000D Watchdog PrimeCell Identification 0 259
0xFF4 WDTPCellID1 RO 0x0000.00F0 Watchdog PrimeCell Identification 1 260
0xFF8 WDTPCellID2 RO 0x0000.0005 Watchdog PrimeCell Identification 2 261
0xFFC WDTPCellID3 RO 0x0000.00B1 Watchdog PrimeCell Identification 3 262
11.5 Register Descriptions
The remainder of this section lists and describes the WDT registers, in numerical order by address
offset.
242 March 17, 2008
Preliminary
Watchdog Timer
Register 1: Watchdog Load (WDTLOAD), offset 0x000
This register is the 32-bit interval value used by the 32-bit counter. When this register is written, the
value is immediately loaded and the counter restarts counting down from the new value. If the
WDTLOAD register is loaded with 0x0000.0000, an interrupt is immediately generated.
Watchdog Load (WDTLOAD)
Base 0x4000.0000
Offset 0x000
Type R/W, reset 0xFFFF.FFFF
31 30 29 28 27 26 25 24 23 22 21 20 19 18 17 16
WDTLoad
Type R/W R/W R/W R/W R/W R/W R/W R/W R/W R/W R/W R/W R/W R/W R/W R/W
Reset 1 1 1 1 1 1 1 1 1 1 1 1 1 1 1 1
15 14 13 12 11 10 9 8 7 6 5 4 3 2 1 0
WDTLoad
Type R/W R/W R/W R/W R/W R/W R/W R/W R/W R/W R/W R/W R/W R/W R/W R/W
Reset 1 1 1 1 1 1 1 1 1 1 1 1 1 1 1 1
Bit/Field Name Type Reset Description
31:0 WDTLoad R/W 0xFFFF.FFFF Watchdog Load Value
March 17, 2008 243
Preliminary
LM3S8933 Microcontroller
Register 2: Watchdog Value (WDTVALUE), offset 0x004
This register contains the current count value of the timer.
Watchdog Value (WDTVALUE)
Base 0x4000.0000
Offset 0x004
Type RO, reset 0xFFFF.FFFF
31 30 29 28 27 26 25 24 23 22 21 20 19 18 17 16
WDTValue
Type RO RO RO RO RO RO RO RO RO RO RO RO RO RO RO RO
Reset 1 1 1 1 1 1 1 1 1 1 1 1 1 1 1 1
15 14 13 12 11 10 9 8 7 6 5 4 3 2 1 0
WDTValue
Type RO RO RO RO RO RO RO RO RO RO RO RO RO RO RO RO
Reset 1 1 1 1 1 1 1 1 1 1 1 1 1 1 1 1
Bit/Field Name Type Reset Description
Watchdog Value
Current value of the 32-bit down counter.
31:0 WDTValue RO 0xFFFF.FFFF
244 March 17, 2008
Preliminary
Watchdog Timer
Register 3: Watchdog Control (WDTCTL), offset 0x008
This register is the watchdog control register. The watchdog timer can be configured to generate a
reset signal (on second time-out) or an interrupt on time-out.
When the watchdog interrupt has been enabled, all subsequent writes to the control register are
ignored. The only mechanism that can re-enable writes is a hardware reset.
Watchdog Control (WDTCTL)
Base 0x4000.0000
Offset 0x008
Type R/W, reset 0x0000.0000
31 30 29 28 27 26 25 24 23 22 21 20 19 18 17 16
reserved
Type RO RO RO RO RO RO RO RO RO RO RO RO RO RO RO RO
Reset 0 0 0 0 0 0 0 0 0 0 0 0 0 0 0 0
15 14 13 12 11 10 9 8 7 6 5 4 3 2 1 0
reserved RESEN INTEN
Type RO RO RO RO RO RO RO RO RO RO RO RO RO RO R/W R/W
Reset 0 0 0 0 0 0 0 0 0 0 0 0 0 0 0 0
Bit/Field Name Type Reset Description
Software should not rely on the value of a reserved bit. To provide
compatibility with future products, the value of a reserved bit should be
preserved across a read-modify-write operation.
31:2 reserved RO 0x00
Watchdog Reset Enable
The RESEN values are defined as follows:
Value Description
0 Disabled.
1 Enable the Watchdog module reset output.
1 RESEN R/W 0
Watchdog Interrupt Enable
The INTEN values are defined as follows:
Value Description
Interrupt event disabled (once this bit is set, it can only be
cleared by a hardware reset).
0
1 Interrupt event enabled. Once enabled, all writes are ignored.
0 INTEN R/W 0
March 17, 2008 245
Preliminary
LM3S8933 Microcontroller
Register 4: Watchdog Interrupt Clear (WDTICR), offset 0x00C
This register is the interrupt clear register. A write of any value to this register clears the Watchdog
interrupt and reloads the 32-bit counter from the WDTLOAD register. Value for a read or reset is
indeterminate.
Watchdog Interrupt Clear (WDTICR)
Base 0x4000.0000
Offset 0x00C
Type WO, reset -
31 30 29 28 27 26 25 24 23 22 21 20 19 18 17 16
WDTIntClr
Type WO WO WO WO WO WO WO WO WO WO WO WO WO WO WO WO
Reset - - - - - - - - - - - - - - - -
15 14 13 12 11 10 9 8 7 6 5 4 3 2 1 0
WDTIntClr
Type WO WO WO WO WO WO WO WO WO WO WO WO WO WO WO WO
Reset - - - - - - - - - - - - - - - -
Bit/Field Name Type Reset Description
31:0 WDTIntClr WO - Watchdog Interrupt Clear
246 March 17, 2008
Preliminary
Watchdog Timer
Register 5: Watchdog Raw Interrupt Status (WDTRIS), offset 0x010
This register is the raw interrupt status register. Watchdog interrupt events can be monitored via
this register if the controller interrupt is masked.
Watchdog Raw Interrupt Status (WDTRIS)
Base 0x4000.0000
Offset 0x010
Type RO, reset 0x0000.0000
31 30 29 28 27 26 25 24 23 22 21 20 19 18 17 16
reserved
Type RO RO RO RO RO RO RO RO RO RO RO RO RO RO RO RO
Reset 0 0 0 0 0 0 0 0 0 0 0 0 0 0 0 0
15 14 13 12 11 10 9 8 7 6 5 4 3 2 1 0
reserved WDTRIS
Type RO RO RO RO RO RO RO RO RO RO RO RO RO RO RO RO
Reset 0 0 0 0 0 0 0 0 0 0 0 0 0 0 0 0
Bit/Field Name Type Reset Description
Software should not rely on the value of a reserved bit. To provide
compatibility with future products, the value of a reserved bit should be
preserved across a read-modify-write operation.
31:1 reserved RO 0x00
Watchdog Raw Interrupt Status
Gives the raw interrupt state (prior to masking) of WDTINTR.
0 WDTRIS RO 0
March 17, 2008 247
Preliminary
LM3S8933 Microcontroller
Register 6: Watchdog Masked Interrupt Status (WDTMIS), offset 0x014
This register is the masked interrupt status register. The value of this register is the logical AND of
the raw interrupt bit and the Watchdog interrupt enable bit.
Watchdog Masked Interrupt Status (WDTMIS)
Base 0x4000.0000
Offset 0x014
Type RO, reset 0x0000.0000
31 30 29 28 27 26 25 24 23 22 21 20 19 18 17 16
reserved
Type RO RO RO RO RO RO RO RO RO RO RO RO RO RO RO RO
Reset 0 0 0 0 0 0 0 0 0 0 0 0 0 0 0 0
15 14 13 12 11 10 9 8 7 6 5 4 3 2 1 0
reserved WDTMIS
Type RO RO RO RO RO RO RO RO RO RO RO RO RO RO RO RO
Reset 0 0 0 0 0 0 0 0 0 0 0 0 0 0 0 0
Bit/Field Name Type Reset Description
Software should not rely on the value of a reserved bit. To provide
compatibility with future products, the value of a reserved bit should be
preserved across a read-modify-write operation.
31:1 reserved RO 0x00
Watchdog Masked Interrupt Status
Gives the masked interrupt state (after masking) of the WDTINTR
interrupt.
0 WDTMIS RO 0
248 March 17, 2008
Preliminary
Watchdog Timer
Register 7: Watchdog Test (WDTTEST), offset 0x418
This register provides user-enabled stalling when the microcontroller asserts the CPU halt flag
during debug.
Watchdog Test (WDTTEST)
Base 0x4000.0000
Offset 0x418
Type R/W, reset 0x0000.0000
31 30 29 28 27 26 25 24 23 22 21 20 19 18 17 16
reserved
Type RO RO RO RO RO RO RO RO RO RO RO RO RO RO RO RO
Reset 0 0 0 0 0 0 0 0 0 0 0 0 0 0 0 0
15 14 13 12 11 10 9 8 7 6 5 4 3 2 1 0
reserved STALL reserved
Type RO RO RO RO RO RO RO R/W RO RO RO RO RO RO RO RO
Reset 0 0 0 0 0 0 0 0 0 0 0 0 0 0 0 0
Bit/Field Name Type Reset Description
Software should not rely on the value of a reserved bit. To provide
compatibility with future products, the value of a reserved bit should be
preserved across a read-modify-write operation.
31:9 reserved RO 0x00
Watchdog Stall Enable
When set to 1, if the Stellaris® microcontroller is stopped with a
debugger, the watchdog timer stops counting. Once the microcontroller
is restarted, the watchdog timer resumes counting.
8 STALL R/W 0
Software should not rely on the value of a reserved bit. To provide
compatibility with future products, the value of a reserved bit should be
preserved across a read-modify-write operation.
7:0 reserved RO 0x00
March 17, 2008 249
Preliminary
LM3S8933 Microcontroller
Register 8: Watchdog Lock (WDTLOCK), offset 0xC00
Writing 0x1ACC.E551 to the WDTLOCK register enables write access to all other registers. Writing
any other value to the WDTLOCK register re-enables the locked state for register writes to all the
other registers. Reading the WDTLOCK register returns the lock status rather than the 32-bit value
written. Therefore, when write accesses are disabled, reading the WDTLOCK register returns
0x0000.0001 (when locked; otherwise, the returned value is 0x0000.0000 (unlocked)).
Watchdog Lock (WDTLOCK)
Base 0x4000.0000
Offset 0xC00
Type R/W, reset 0x0000.0000
31 30 29 28 27 26 25 24 23 22 21 20 19 18 17 16
WDTLock
Type R/W R/W R/W R/W R/W R/W R/W R/W R/W R/W R/W R/W R/W R/W R/W R/W
Reset 0 0 0 0 0 0 0 0 0 0 0 0 0 0 0 0
15 14 13 12 11 10 9 8 7 6 5 4 3 2 1 0
WDTLock
Type R/W R/W R/W R/W R/W R/W R/W R/W R/W R/W R/W R/W R/W R/W R/W R/W
Reset 0 0 0 0 0 0 0 0 0 0 0 0 0 0 0 0
Bit/Field Name Type Reset Description
Watchdog Lock
A write of the value 0x1ACC.E551 unlocks the watchdog registers for
write access. A write of any other value reapplies the lock, preventing
any register updates.
A read of this register returns the following values:
Value Description
0x0000.0001 Locked
0x0000.0000 Unlocked
31:0 WDTLock R/W 0x0000
250 March 17, 2008
Preliminary
Watchdog Timer
Register 9: Watchdog Peripheral Identification 4 (WDTPeriphID4), offset 0xFD0
The WDTPeriphIDn registers are hard-coded and the fields within the register determine the reset
value.
Watchdog Peripheral Identification 4 (WDTPeriphID4)
Base 0x4000.0000
Offset 0xFD0
Type RO, reset 0x0000.0000
31 30 29 28 27 26 25 24 23 22 21 20 19 18 17 16
reserved
Type RO RO RO RO RO RO RO RO RO RO RO RO RO RO RO RO
Reset 0 0 0 0 0 0 0 0 0 0 0 0 0 0 0 0
15 14 13 12 11 10 9 8 7 6 5 4 3 2 1 0
reserved PID4
Type RO RO RO RO RO RO RO RO RO RO RO RO RO RO RO RO
Reset 0 0 0 0 0 0 0 0 0 0 0 0 0 0 0 0
Bit/Field Name Type Reset Description
Software should not rely on the value of a reserved bit. To provide
compatibility with future products, the value of a reserved bit should be
preserved across a read-modify-write operation.
31:8 reserved RO 0x00
7:0 PID4 RO 0x00 WDT Peripheral ID Register[7:0]
March 17, 2008 251
Preliminary
LM3S8933 Microcontroller
Register 10: Watchdog Peripheral Identification 5 (WDTPeriphID5), offset
0xFD4
The WDTPeriphIDn registers are hard-coded and the fields within the register determine the reset
value.
Watchdog Peripheral Identification 5 (WDTPeriphID5)
Base 0x4000.0000
Offset 0xFD4
Type RO, reset 0x0000.0000
31 30 29 28 27 26 25 24 23 22 21 20 19 18 17 16
reserved
Type RO RO RO RO RO RO RO RO RO RO RO RO RO RO RO RO
Reset 0 0 0 0 0 0 0 0 0 0 0 0 0 0 0 0
15 14 13 12 11 10 9 8 7 6 5 4 3 2 1 0
reserved PID5
Type RO RO RO RO RO RO RO RO RO RO RO RO RO RO RO RO
Reset 0 0 0 0 0 0 0 0 0 0 0 0 0 0 0 0
Bit/Field Name Type Reset Description
Software should not rely on the value of a reserved bit. To provide
compatibility with future products, the value of a reserved bit should be
preserved across a read-modify-write operation.
31:8 reserved RO 0x00
7:0 PID5 RO 0x00 WDT Peripheral ID Register[15:8]
252 March 17, 2008
Preliminary
Watchdog Timer
Register 11: Watchdog Peripheral Identification 6 (WDTPeriphID6), offset
0xFD8
The WDTPeriphIDn registers are hard-coded and the fields within the register determine the reset
value.
Watchdog Peripheral Identification 6 (WDTPeriphID6)
Base 0x4000.0000
Offset 0xFD8
Type RO, reset 0x0000.0000
31 30 29 28 27 26 25 24 23 22 21 20 19 18 17 16
reserved
Type RO RO RO RO RO RO RO RO RO RO RO RO RO RO RO RO
Reset 0 0 0 0 0 0 0 0 0 0 0 0 0 0 0 0
15 14 13 12 11 10 9 8 7 6 5 4 3 2 1 0
reserved PID6
Type RO RO RO RO RO RO RO RO RO RO RO RO RO RO RO RO
Reset 0 0 0 0 0 0 0 0 0 0 0 0 0 0 0 0
Bit/Field Name Type Reset Description
Software should not rely on the value of a reserved bit. To provide
compatibility with future products, the value of a reserved bit should be
preserved across a read-modify-write operation.
31:8 reserved RO 0x00
7:0 PID6 RO 0x00 WDT Peripheral ID Register[23:16]
March 17, 2008 253
Preliminary
LM3S8933 Microcontroller
Register 12: Watchdog Peripheral Identification 7 (WDTPeriphID7), offset
0xFDC
The WDTPeriphIDn registers are hard-coded and the fields within the register determine the reset
value.
Watchdog Peripheral Identification 7 (WDTPeriphID7)
Base 0x4000.0000
Offset 0xFDC
Type RO, reset 0x0000.0000
31 30 29 28 27 26 25 24 23 22 21 20 19 18 17 16
reserved
Type RO RO RO RO RO RO RO RO RO RO RO RO RO RO RO RO
Reset 0 0 0 0 0 0 0 0 0 0 0 0 0 0 0 0
15 14 13 12 11 10 9 8 7 6 5 4 3 2 1 0
reserved PID7
Type RO RO RO RO RO RO RO RO RO RO RO RO RO RO RO RO
Reset 0 0 0 0 0 0 0 0 0 0 0 0 0 0 0 0
Bit/Field Name Type Reset Description
Software should not rely on the value of a reserved bit. To provide
compatibility with future products, the value of a reserved bit should be
preserved across a read-modify-write operation.
31:8 reserved RO 0x00
7:0 PID7 RO 0x00 WDT Peripheral ID Register[31:24]
254 March 17, 2008
Preliminary
Watchdog Timer
Register 13: Watchdog Peripheral Identification 0 (WDTPeriphID0), offset
0xFE0
The WDTPeriphIDn registers are hard-coded and the fields within the register determine the reset
value.
Watchdog Peripheral Identification 0 (WDTPeriphID0)
Base 0x4000.0000
Offset 0xFE0
Type RO, reset 0x0000.0005
31 30 29 28 27 26 25 24 23 22 21 20 19 18 17 16
reserved
Type RO RO RO RO RO RO RO RO RO RO RO RO RO RO RO RO
Reset 0 0 0 0 0 0 0 0 0 0 0 0 0 0 0 0
15 14 13 12 11 10 9 8 7 6 5 4 3 2 1 0
reserved PID0
Type RO RO RO RO RO RO RO RO RO RO RO RO RO RO RO RO
Reset 0 0 0 0 0 0 0 0 0 0 0 0 0 1 0 1
Bit/Field Name Type Reset Description
Software should not rely on the value of a reserved bit. To provide
compatibility with future products, the value of a reserved bit should be
preserved across a read-modify-write operation.
31:8 reserved RO 0x00
7:0 PID0 RO 0x05 Watchdog Peripheral ID Register[7:0]
March 17, 2008 255
Preliminary
LM3S8933 Microcontroller
Register 14: Watchdog Peripheral Identification 1 (WDTPeriphID1), offset
0xFE4
The WDTPeriphIDn registers are hard-coded and the fields within the register determine the reset
value.
Watchdog Peripheral Identification 1 (WDTPeriphID1)
Base 0x4000.0000
Offset 0xFE4
Type RO, reset 0x0000.0018
31 30 29 28 27 26 25 24 23 22 21 20 19 18 17 16
reserved
Type RO RO RO RO RO RO RO RO RO RO RO RO RO RO RO RO
Reset 0 0 0 0 0 0 0 0 0 0 0 0 0 0 0 0
15 14 13 12 11 10 9 8 7 6 5 4 3 2 1 0
reserved PID1
Type RO RO RO RO RO RO RO RO RO RO RO RO RO RO RO RO
Reset 0 0 0 0 0 0 0 0 0 0 0 1 1 0 0 0
Bit/Field Name Type Reset Description
Software should not rely on the value of a reserved bit. To provide
compatibility with future products, the value of a reserved bit should be
preserved across a read-modify-write operation.
31:8 reserved RO 0x00
7:0 PID1 RO 0x18 Watchdog Peripheral ID Register[15:8]
256 March 17, 2008
Preliminary
Watchdog Timer
Register 15: Watchdog Peripheral Identification 2 (WDTPeriphID2), offset
0xFE8
The WDTPeriphIDn registers are hard-coded and the fields within the register determine the reset
value.
Watchdog Peripheral Identification 2 (WDTPeriphID2)
Base 0x4000.0000
Offset 0xFE8
Type RO, reset 0x0000.0018
31 30 29 28 27 26 25 24 23 22 21 20 19 18 17 16
reserved
Type RO RO RO RO RO RO RO RO RO RO RO RO RO RO RO RO
Reset 0 0 0 0 0 0 0 0 0 0 0 0 0 0 0 0
15 14 13 12 11 10 9 8 7 6 5 4 3 2 1 0
reserved PID2
Type RO RO RO RO RO RO RO RO RO RO RO RO RO RO RO RO
Reset 0 0 0 0 0 0 0 0 0 0 0 1 1 0 0 0
Bit/Field Name Type Reset Description
Software should not rely on the value of a reserved bit. To provide
compatibility with future products, the value of a reserved bit should be
preserved across a read-modify-write operation.
31:8 reserved RO 0x00
7:0 PID2 RO 0x18 Watchdog Peripheral ID Register[23:16]
March 17, 2008 257
Preliminary
LM3S8933 Microcontroller
Register 16: Watchdog Peripheral Identification 3 (WDTPeriphID3), offset
0xFEC
The WDTPeriphIDn registers are hard-coded and the fields within the register determine the reset
value.
Watchdog Peripheral Identification 3 (WDTPeriphID3)
Base 0x4000.0000
Offset 0xFEC
Type RO, reset 0x0000.0001
31 30 29 28 27 26 25 24 23 22 21 20 19 18 17 16
reserved
Type RO RO RO RO RO RO RO RO RO RO RO RO RO RO RO RO
Reset 0 0 0 0 0 0 0 0 0 0 0 0 0 0 0 0
15 14 13 12 11 10 9 8 7 6 5 4 3 2 1 0
reserved PID3
Type RO RO RO RO RO RO RO RO RO RO RO RO RO RO RO RO
Reset 0 0 0 0 0 0 0 0 0 0 0 0 0 0 0 1
Bit/Field Name Type Reset Description
Software should not rely on the value of a reserved bit. To provide
compatibility with future products, the value of a reserved bit should be
preserved across a read-modify-write operation.
31:8 reserved RO 0x00
7:0 PID3 RO 0x01 Watchdog Peripheral ID Register[31:24]
258 March 17, 2008
Preliminary
Watchdog Timer
Register 17: Watchdog PrimeCell Identification 0 (WDTPCellID0), offset 0xFF0
The WDTPCellIDn registers are hard-coded and the fields within the register determine the reset
value.
Watchdog PrimeCell Identification 0 (WDTPCellID0)
Base 0x4000.0000
Offset 0xFF0
Type RO, reset 0x0000.000D
31 30 29 28 27 26 25 24 23 22 21 20 19 18 17 16
reserved
Type RO RO RO RO RO RO RO RO RO RO RO RO RO RO RO RO
Reset 0 0 0 0 0 0 0 0 0 0 0 0 0 0 0 0
15 14 13 12 11 10 9 8 7 6 5 4 3 2 1 0
reserved CID0
Type RO RO RO RO RO RO RO RO RO RO RO RO RO RO RO RO
Reset 0 0 0 0 0 0 0 0 0 0 0 0 1 1 0 1
Bit/Field Name Type Reset Description
Software should not rely on the value of a reserved bit. To provide
compatibility with future products, the value of a reserved bit should be
preserved across a read-modify-write operation.
31:8 reserved RO 0x00
7:0 CID0 RO 0x0D Watchdog PrimeCell ID Register[7:0]
March 17, 2008 259
Preliminary
LM3S8933 Microcontroller
Register 18: Watchdog PrimeCell Identification 1 (WDTPCellID1), offset 0xFF4
The WDTPCellIDn registers are hard-coded and the fields within the register determine the reset
value.
Watchdog PrimeCell Identification 1 (WDTPCellID1)
Base 0x4000.0000
Offset 0xFF4
Type RO, reset 0x0000.00F0
31 30 29 28 27 26 25 24 23 22 21 20 19 18 17 16
reserved
Type RO RO RO RO RO RO RO RO RO RO RO RO RO RO RO RO
Reset 0 0 0 0 0 0 0 0 0 0 0 0 0 0 0 0
15 14 13 12 11 10 9 8 7 6 5 4 3 2 1 0
reserved CID1
Type RO RO RO RO RO RO RO RO RO RO RO RO RO RO RO RO
Reset 0 0 0 0 0 0 0 0 1 1 1 1 0 0 0 0
Bit/Field Name Type Reset Description
Software should not rely on the value of a reserved bit. To provide
compatibility with future products, the value of a reserved bit should be
preserved across a read-modify-write operation.
31:8 reserved RO 0x00
7:0 CID1 RO 0xF0 Watchdog PrimeCell ID Register[15:8]
260 March 17, 2008
Preliminary
Watchdog Timer
Register 19: Watchdog PrimeCell Identification 2 (WDTPCellID2), offset 0xFF8
The WDTPCellIDn registers are hard-coded and the fields within the register determine the reset
value.
Watchdog PrimeCell Identification 2 (WDTPCellID2)
Base 0x4000.0000
Offset 0xFF8
Type RO, reset 0x0000.0005
31 30 29 28 27 26 25 24 23 22 21 20 19 18 17 16
reserved
Type RO RO RO RO RO RO RO RO RO RO RO RO RO RO RO RO
Reset 0 0 0 0 0 0 0 0 0 0 0 0 0 0 0 0
15 14 13 12 11 10 9 8 7 6 5 4 3 2 1 0
reserved CID2
Type RO RO RO RO RO RO RO RO RO RO RO RO RO RO RO RO
Reset 0 0 0 0 0 0 0 0 0 0 0 0 0 1 0 1
Bit/Field Name Type Reset Description
Software should not rely on the value of a reserved bit. To provide
compatibility with future products, the value of a reserved bit should be
preserved across a read-modify-write operation.
31:8 reserved RO 0x00
7:0 CID2 RO 0x05 Watchdog PrimeCell ID Register[23:16]
March 17, 2008 261
Preliminary
LM3S8933 Microcontroller
Register 20: Watchdog PrimeCell Identification 3 (WDTPCellID3 ), offset 0xFFC
The WDTPCellIDn registers are hard-coded and the fields within the register determine the reset
value.
Watchdog PrimeCell Identification 3 (WDTPCellID3)
Base 0x4000.0000
Offset 0xFFC
Type RO, reset 0x0000.00B1
31 30 29 28 27 26 25 24 23 22 21 20 19 18 17 16
reserved
Type RO RO RO RO RO RO RO RO RO RO RO RO RO RO RO RO
Reset 0 0 0 0 0 0 0 0 0 0 0 0 0 0 0 0
15 14 13 12 11 10 9 8 7 6 5 4 3 2 1 0
reserved CID3
Type RO RO RO RO RO RO RO RO RO RO RO RO RO RO RO RO
Reset 0 0 0 0 0 0 0 0 1 0 1 1 0 0 0 1
Bit/Field Name Type Reset Description
Software should not rely on the value of a reserved bit. To provide
compatibility with future products, the value of a reserved bit should be
preserved across a read-modify-write operation.
31:8 reserved RO 0x00
7:0 CID3 RO 0xB1 Watchdog PrimeCell ID Register[31:24]
262 March 17, 2008
Preliminary
Watchdog Timer
12 Analog-to-Digital Converter (ADC)
An analog-to-digital converter (ADC) is a peripheral that converts a continuous analog voltage to a
discrete digital number.
The Stellaris® ADC module features 10-bit conversion resolution and supports four input channels,
plus an internal temperature sensor. The ADC module contains a programmable sequencer which
allows for the sampling of multiple analog input sources without controller intervention. Each sample
sequence provides flexible programming with fully configurable input source, trigger events, interrupt
generation, and sequence priority.
The Stellaris® ADC provides the following features:
■ Four analog input channels
■ Single-ended and differential-input configurations
■ Internal temperature sensor
■ Sample rate of one million samples/second
■ Four programmable sample conversion sequences from one to eight entries long, with
corresponding conversion result FIFOs
■ Flexible trigger control
– Controller (software)
– Timers
– Analog Comparators
– GPIO
■ Hardware averaging of up to 64 samples for improved accuracy
March 17, 2008 263
Preliminary
LM3S8933 Microcontroller
12.1 Block Diagram
Figure 12-1. ADC Module Block Diagram
Analog-to-Digital
Converter
ADCSSFSTAT0
ADCSSCTL0
ADCSSMUX0
Sample
Sequencer 0
ADCSSFSTAT1
ADCSSCTL1
ADCSSMUX1
Sample
Sequencer 1
ADCSSFSTAT2
ADCSSCTL2
ADCSSMUX2
Sample
Sequencer 2
ADCSSFSTAT3
ADCSSCTL3
ADCSSMUX3
Sample
Sequencer 3
ADCUSTAT
ADCOSTAT
ADCACTSS
Control/Status
ADCSSPRI
ADCISC
ADCRIS
ADCIM
Interrupt Control
Analog Inputs
SS0 Interrupt
SS1 Interrupt
SS2 Interrupt
SS3 Interrupt
ADCEMUX
ADCPSSI
Trigger Events
SS0
SS1
SS2
SS3
Comparator
GPIO (PB4)
Timer
PWM
Comparator
GPIO (PB4)
Timer
PWM
Comparator
GPIO (PB4)
Timer
PWM
Comparator
GPIO (PB4)
Timer
PWM
ADCSSFIFO0
ADCSSFIFO1
ADCSSFIFO2
ADCSSFIFO3
FIFO Block
Hardware Averager
ADCSAC
12.2 Functional Description
The Stellaris® ADC collects sample data by using a programmable sequence-based approach
instead of the traditional single or double-sampling approach found on many ADC modules. Each
sample sequence is a fully programmed series of consecutive (back-to-back) samples, allowing the
ADC to collect data from multiple input sources without having to be re-configured or serviced by
the controller. The programming of each sample in the sample sequence includes parameters such
as the input source and mode (differential versus single-ended input), interrupt generation on sample
completion, and the indicator for the last sample in the sequence.
12.2.1 Sample Sequencers
The sampling control and data capture is handled by the Sample Sequencers. All of the sequencers
are identical in implementation except for the number of samples that can be captured and the depth
of the FIFO. Table 12-1 on page 264 shows the maximum number of samples that each Sequencer
can capture and its corresponding FIFO depth. In this implementation, each FIFO entry is a 32-bit
word, with the lower 10 bits containing the conversion result.
Table 12-1. Samples and FIFO Depth of Sequencers
Sequencer Number of Samples Depth of FIFO
SS3 1 1
SS2 4 4
SS1 4 4
SS0 8 8
264 March 17, 2008
Preliminary
Analog-to-Digital Converter (ADC)
For a given sample sequence, each sample is defined by two 4-bit nibbles in the ADC Sample
Sequence Input Multiplexer Select (ADCSSMUXn) and ADC Sample Sequence Control
(ADCSSCTLn) registers, where "n" corresponds to the sequence number. The ADCSSMUXn
nibbles select the input pin, while the ADCSSCTLn nibbles contain the sample control bits
corresponding to parameters such as temperature sensor selection, interrupt enable, end of
sequence, and differential input mode. Sample Sequencers are enabled by setting the respective
ASENn bit in the ADC Active Sample Sequencer (ADCACTSS) register, but can be configured
before being enabled.
When configuring a sample sequence, multiple uses of the same input pin within the same sequence
is allowed. In the ADCSSCTLn register, the Interrupt Enable (IE) bits can be set for any
combination of samples, allowing interrupts to be generated after every sample in the sequence if
necessary. Also, the END bit can be set at any point within a sample sequence. For example, if
Sequencer 0 is used, the END bit can be set in the nibble associated with the fifth sample, allowing
Sequencer 0 to complete execution of the sample sequence after the fifth sample.
After a sample sequence completes execution, the result data can be retrieved from the ADC
Sample Sequence Result FIFO (ADCSSFIFOn) registers. The FIFOs are simple circular buffers
that read a single address to "pop" result data. For software debug purposes, the positions of the
FIFO head and tail pointers are visible in the ADC Sample Sequence FIFO Status (ADCSSFSTATn)
registers along with FULL and EMPTY status flags. Overflow and underflow conditions are monitored
using the ADCOSTAT and ADCUSTAT registers.
12.2.2 Module Control
Outside of the Sample Sequencers, the remainder of the control logic is responsible for tasks such
as interrupt generation, sequence prioritization, and trigger configuration.
Most of the ADC control logic runs at the ADC clock rate of 14-18 MHz. The internal ADC divider
is configured automatically by hardware when the system XTAL is selected. The automatic clock
divider configuration targets 16.667 MHz operation for all Stellaris® devices.
12.2.2.1 Interrupts
The Sample Sequencers dictate the events that cause interrupts, but they don't have control over
whether the interrupt is actually sent to the interrupt controller. The ADC module's interrupt signal
is controlled by the state of the MASK bits in the ADC Interrupt Mask (ADCIM) register. Interrupt
status can be viewed at two locations: the ADC Raw Interrupt Status (ADCRIS) register, which
shows the raw status of a Sample Sequencer's interrupt signal, and the ADC Interrupt Status and
Clear (ADCISC) register, which shows the logical AND of the ADCRIS register’s INR bit and the
ADCIM register’s MASK bits. Interrupts are cleared by writing a 1 to the corresponding IN bit in
ADCISC.
12.2.2.2 Prioritization
When sampling events (triggers) happen concurrently, they are prioritized for processing by the
values in the ADC Sample Sequencer Priority (ADCSSPRI) register. Valid priority values are in
the range of 0-3, with 0 being the highest priority and 3 being the lowest. Multiple active Sample
Sequencer units with the same priority do not provide consistent results, so software must ensure
that all active Sample Sequencer units have a unique priority value.
12.2.2.3 Sampling Events
Sample triggering for each Sample Sequencer is defined in the ADC Event Multiplexer Select
(ADCEMUX) register. The external peripheral triggering sources vary by Stellaris® family member,
March 17, 2008 265
Preliminary
LM3S8933 Microcontroller
but all devices share the "Controller" and "Always" triggers. Software can initiate sampling by setting
the CH bits in the ADC Processor Sample Sequence Initiate (ADCPSSI) register.
When using the "Always" trigger, care must be taken. If a sequence's priority is too high, it is possible
to starve other lower priority sequences.
12.2.3 Hardware Sample Averaging Circuit
Higher precision results can be generated using the hardware averaging circuit, however, the
improved results are at the cost of throughput. Up to 64 samples can be accumulated and averaged
to form a single data entry in the sequencer FIFO. Throughput is decreased proportionally to the
number of samples in the averaging calculation. For example, if the averaging circuit is configured
to average 16 samples, the throughput is decreased by a factor of 16.
By default the averaging circuit is off and all data from the converter passes through to the sequencer
FIFO. The averaging hardware is controlled by the ADC Sample Averaging Control (ADCSAC)
register (see page 282). There is a single averaging circuit and all input channels receive the same
amount of averaging whether they are single-ended or differential.
12.2.4 Analog-to-Digital Converter
The converter itself generates a 10-bit output value for selected analog input. Special analog pads
are used to minimize the distortion on the input. An internal 3 V reference is used by the converter
resulting in sample values ranging from 0x000 at 0 V input to 0x3FF at 3 V input when in single-ended
input mode.
12.2.5 Differential Sampling
In addition to traditional single-ended sampling, the ADC module supports differential sampling of
two analog input channels. To enable differential sampling, software must set the D bit in a step's
configuration nibble.
When a sequence step is configured for differential sampling, its corresponding value in the
ADCSSMUX register must be set to one of the four differential pairs, numbered 0-3. Differential pair
0 samples analog inputs 0 and 1; differential pair 1 samples analog inputs 2 and 3; and so on (see
Table 12-2 on page 266). The ADC does not support other differential pairings such as analog input
0 with analog input 3. The number of differential pairs supported is dependent on the number of
analog inputs (see Table 12-2 on page 266).
Table 12-2. Differential Sampling Pairs
Differential Pair Analog Inputs
0 0 and 1
1 2 and 3
The voltage sampled in differential mode is the difference between the odd and even channels:
ΔV (differential voltage) = V0 (even channels) – V1 (odd channels), therefore:
■ If ΔV = 0, then the conversion result = 0x1FF
■ If ΔV > 0, then the conversion result > 0x1FF (range is 0x1FF–0x3FF)
■ If ΔV < 0, then the conversion result < 0x1FF (range is 0–0x1FF)
The differential pairs assign polarities to the analog inputs: the even-numbered input is always
positive, and the odd-numbered input is always negative. In order for a valid conversion result to
266 March 17, 2008
Preliminary
Analog-to-Digital Converter (ADC)
appear, the negative input must be in the range of ± 1.5 V of the positive input. If an analog input
is greater than 3 V or less than 0 V (the valid range for analog inputs), the input voltage is clipped,
meaning it appears as either 3 V or 0 V, respectively, to the ADC.
Figure 12-2 on page 267 shows an example of the negative input centered at 1.5 V. In this
configuration, the differential range spans from -1.5 V to 1.5 V. Figure 12-3 on page 267 shows an
example where the negative input is centered at -0.75 V, meaning inputs on the positive input
saturate past a differential voltage of -0.75 V since the input voltage is less than 0 V. Figure
12-4 on page 268 shows an example of the negative input centered at 2.25 V, where inputs on the
positive channel saturate past a differential voltage of 0.75 V since the input voltage would be greater
than 3 V.
Figure 12-2. Differential Sampling Range, Vin(-) = 1.5 V
ADC Conversion Result
Differential Voltage,
Vin (+) = 1.5V
-1.5V +1.5V
0x1FF
0x3FF
- Input Saturation
Figure 12-3. Differential Sampling Range, Vin(-) = 0.75 V
ADC Conversion Result
-1.5V +1.5V
0x1FF
0x3FF
Differential Voltage,
Vin (+) = 0.75V
0x0FF
-0.75V
- Input Saturation
March 17, 2008 267
Preliminary
LM3S8933 Microcontroller
Figure 12-4. Differential Sampling Range, Vin(-) = 2.25 V
ADC Conversion Result
-1.5V +1.5V
0x1FF
0x3FF
Differential Voltage,
Vin (+) = 2.25V
0x2FF
+0.75V
- Input Saturation
12.2.6 Test Modes
There is a user-available test mode that allows for loopback operation within the digital portion of
the ADC module. This can be useful for debugging software without having to provide actual analog
stimulus. This mode is available through the ADC Test Mode Loopback (ADCTMLB) register (see
page 295).
12.2.7 Internal Temperature Sensor
The internal temperature sensor provides an analog temperature reading as well as a reference
voltage. The voltage at the output terminal SENSO is given by the following equation:
SENSO = 2.7 - ((T + 55) / 75)
This relation is shown in Figure 12-5 on page 268.
Figure 12-5. Internal Temperature Sensor Characteristic
268 March 17, 2008
Preliminary
Analog-to-Digital Converter (ADC)
12.3 Initialization and Configuration
In order for the ADC module to be used, the PLL must be enabled and using a supported crystal
frequency (see the RCC register). Using unsupported frequencies can cause faulty operation in the
ADC module.
12.3.1 Module Initialization
Initialization of the ADC module is a simple process with very few steps. The main steps include
enabling the clock to the ADC and reconfiguring the Sample Sequencer priorities (if needed).
The initialization sequence for the ADC is as follows:
1. Enable the ADC clock by writing a value of 0x0001.0000 to the RCGC1 register (see page 99).
2. If required by the application, reconfigure the Sample Sequencer priorities in the ADCSSPRI
register. The default configuration has Sample Sequencer 0 with the highest priority, and Sample
Sequencer 3 as the lowest priority.
12.3.2 Sample Sequencer Configuration
Configuration of the Sample Sequencers is slightly more complex than the module initialization
since each sample sequence is completely programmable.
The configuration for each Sample Sequencer should be as follows:
1. Ensure that the Sample Sequencer is disabled by writing a 0 to the corresponding ASEN bit in
the ADCACTSS register. Programming of the Sample Sequencers is allowed without having
them enabled. Disabling the Sequencer during programming prevents erroneous execution if
a trigger event were to occur during the configuration process.
2. Configure the trigger event for the Sample Sequencer in the ADCEMUX register.
3. For each sample in the sample sequence, configure the corresponding input source in the
ADCSSMUXn register.
4. For each sample in the sample sequence, configure the sample control bits in the corresponding
nibble in the ADCSSCTLn register. When programming the last nibble, ensure that the END bit
is set. Failure to set the END bit causes unpredictable behavior.
5. If interrupts are to be used, write a 1 to the corresponding MASK bit in the ADCIM register.
6. Enable the Sample Sequencer logic by writing a 1 to the corresponding ASEN bit in the
ADCACTSS register.
12.4 Register Map
Table 12-3 on page 269 lists the ADC registers. The offset listed is a hexadecimal increment to the
register’s address, relative to the ADC base address of 0x4003.8000.
Table 12-3. ADC Register Map
See
Offset Name Type Reset Description page
0x000 ADCACTSS R/W 0x0000.0000 ADC Active Sample Sequencer 271
March 17, 2008 269
Preliminary
LM3S8933 Microcontroller
See
Offset Name Type Reset Description page
0x004 ADCRIS RO 0x0000.0000 ADC Raw Interrupt Status 272
0x008 ADCIM R/W 0x0000.0000 ADC Interrupt Mask 273
0x00C ADCISC R/W1C 0x0000.0000 ADC Interrupt Status and Clear 274
0x010 ADCOSTAT R/W1C 0x0000.0000 ADC Overflow Status 275
0x014 ADCEMUX R/W 0x0000.0000 ADC Event Multiplexer Select 276
0x018 ADCUSTAT R/W1C 0x0000.0000 ADC Underflow Status 279
0x020 ADCSSPRI R/W 0x0000.3210 ADC Sample Sequencer Priority 280
0x028 ADCPSSI WO - ADC Processor Sample Sequence Initiate 281
0x030 ADCSAC R/W 0x0000.0000 ADC Sample Averaging Control 282
0x040 ADCSSMUX0 R/W 0x0000.0000 ADC Sample Sequence Input Multiplexer Select 0 283
0x044 ADCSSCTL0 R/W 0x0000.0000 ADC Sample Sequence Control 0 285
0x048 ADCSSFIFO0 RO 0x0000.0000 ADC Sample Sequence Result FIFO 0 288
0x04C ADCSSFSTAT0 RO 0x0000.0100 ADC Sample Sequence FIFO 0 Status 289
0x060 ADCSSMUX1 R/W 0x0000.0000 ADC Sample Sequence Input Multiplexer Select 1 290
0x064 ADCSSCTL1 R/W 0x0000.0000 ADC Sample Sequence Control 1 291
0x068 ADCSSFIFO1 RO 0x0000.0000 ADC Sample Sequence Result FIFO 1 288
0x06C ADCSSFSTAT1 RO 0x0000.0100 ADC Sample Sequence FIFO 1 Status 289
0x080 ADCSSMUX2 R/W 0x0000.0000 ADC Sample Sequence Input Multiplexer Select 2 290
0x084 ADCSSCTL2 R/W 0x0000.0000 ADC Sample Sequence Control 2 291
0x088 ADCSSFIFO2 RO 0x0000.0000 ADC Sample Sequence Result FIFO 2 288
0x08C ADCSSFSTAT2 RO 0x0000.0100 ADC Sample Sequence FIFO 2 Status 289
0x0A0 ADCSSMUX3 R/W 0x0000.0000 ADC Sample Sequence Input Multiplexer Select 3 293
0x0A4 ADCSSCTL3 R/W 0x0000.0002 ADC Sample Sequence Control 3 294
0x0A8 ADCSSFIFO3 RO 0x0000.0000 ADC Sample Sequence Result FIFO 3 288
0x0AC ADCSSFSTAT3 RO 0x0000.0100 ADC Sample Sequence FIFO 3 Status 289
0x100 ADCTMLB R/W 0x0000.0000 ADC Test Mode Loopback 295
12.5 Register Descriptions
The remainder of this section lists and describes the ADC registers, in numerical order by address
offset.
270 March 17, 2008
Preliminary
Analog-to-Digital Converter (ADC)
Register 1: ADC Active Sample Sequencer (ADCACTSS), offset 0x000
This register controls the activation of the Sample Sequencers. Each Sample Sequencer can be
enabled/disabled independently.
ADC Active Sample Sequencer (ADCACTSS)
Base 0x4003.8000
Offset 0x000
Type R/W, reset 0x0000.0000
31 30 29 28 27 26 25 24 23 22 21 20 19 18 17 16
reserved
Type RO RO RO RO RO RO RO RO RO RO RO RO RO RO RO RO
Reset 0 0 0 0 0 0 0 0 0 0 0 0 0 0 0 0
15 14 13 12 11 10 9 8 7 6 5 4 3 2 1 0
reserved ASEN3 ASEN2 ASEN1 ASEN0
Type RO RO RO RO RO RO RO RO RO RO RO RO R/W R/W R/W R/W
Reset 0 0 0 0 0 0 0 0 0 0 0 0 0 0 0 0
Bit/Field Name Type Reset Description
Software should not rely on the value of a reserved bit. To provide
compatibility with future products, the value of a reserved bit should be
preserved across a read-modify-write operation.
31:4 reserved RO 0x00
ADC SS3 Enable
Specifies whether Sample Sequencer 3 is enabled. If set, the sample
sequence logic for Sequencer 3 is active. Otherwise, the Sequencer is
inactive.
3 ASEN3 R/W 0
ADC SS2 Enable
Specifies whether Sample Sequencer 2 is enabled. If set, the sample
sequence logic for Sequencer 2 is active. Otherwise, the Sequencer is
inactive.
2 ASEN2 R/W 0
ADC SS1 Enable
Specifies whether Sample Sequencer 1 is enabled. If set, the sample
sequence logic for Sequencer 1 is active. Otherwise, the Sequencer is
inactive.
1 ASEN1 R/W 0
ADC SS0 Enable
Specifies whether Sample Sequencer 0 is enabled. If set, the sample
sequence logic for Sequencer 0 is active. Otherwise, the Sequencer is
inactive.
0 ASEN0 R/W 0
March 17, 2008 271
Preliminary
LM3S8933 Microcontroller
Register 2: ADC Raw Interrupt Status (ADCRIS), offset 0x004
This register shows the status of the raw interrupt signal of each Sample Sequencer. These bits
may be polled by software to look for interrupt conditions without having to generate controller
interrupts.
ADC Raw Interrupt Status (ADCRIS)
Base 0x4003.8000
Offset 0x004
Type RO, reset 0x0000.0000
31 30 29 28 27 26 25 24 23 22 21 20 19 18 17 16
reserved
Type RO RO RO RO RO RO RO RO RO RO RO RO RO RO RO RO
Reset 0 0 0 0 0 0 0 0 0 0 0 0 0 0 0 0
15 14 13 12 11 10 9 8 7 6 5 4 3 2 1 0
reserved INR3 INR2 INR1 INR0
Type RO RO RO RO RO RO RO RO RO RO RO RO RO RO RO RO
Reset 0 0 0 0 0 0 0 0 0 0 0 0 0 0 0 0
Bit/Field Name Type Reset Description
Software should not rely on the value of a reserved bit. To provide
compatibility with future products, the value of a reserved bit should be
preserved across a read-modify-write operation.
31:4 reserved RO 0x00
SS3 Raw Interrupt Status
Set by hardware when a sample with its respective ADCSSCTL3 IE bit
has completed conversion. This bit is cleared by writing a 1 to the
ADCISC IN3 bit.
3 INR3 RO 0
SS2 Raw Interrupt Status
Set by hardware when a sample with its respective ADCSSCTL2 IE bit
has completed conversion. This bit is cleared by writing a 1 to the
ADCISC IN2 bit.
2 INR2 RO 0
SS1 Raw Interrupt Status
Set by hardware when a sample with its respective ADCSSCTL1 IE bit
has completed conversion. This bit is cleared by writing a 1 to the
ADCISC IN1 bit.
1 INR1 RO 0
SS0 Raw Interrupt Status
Set by hardware when a sample with its respective ADCSSCTL0 IE bit
has completed conversion. This bit is cleared by writing a 1 to the
ADCISC IN0 bit.
0 INR0 RO 0
272 March 17, 2008
Preliminary
Analog-to-Digital Converter (ADC)
Register 3: ADC Interrupt Mask (ADCIM), offset 0x008
This register controls whether the Sample Sequencer raw interrupt signals are promoted to controller
interrupts. The raw interrupt signal for each Sample Sequencer can be masked independently.
ADC Interrupt Mask (ADCIM)
Base 0x4003.8000
Offset 0x008
Type R/W, reset 0x0000.0000
31 30 29 28 27 26 25 24 23 22 21 20 19 18 17 16
reserved
Type RO RO RO RO RO RO RO RO RO RO RO RO RO RO RO RO
Reset 0 0 0 0 0 0 0 0 0 0 0 0 0 0 0 0
15 14 13 12 11 10 9 8 7 6 5 4 3 2 1 0
reserved MASK3 MASK2 MASK1 MASK0
Type RO RO RO RO RO RO RO RO RO RO RO RO R/W R/W R/W R/W
Reset 0 0 0 0 0 0 0 0 0 0 0 0 0 0 0 0
Bit/Field Name Type Reset Description
Software should not rely on the value of a reserved bit. To provide
compatibility with future products, the value of a reserved bit should be
preserved across a read-modify-write operation.
31:4 reserved RO 0x00
SS3 Interrupt Mask
Specifies whether the raw interrupt signal from Sample Sequencer 3
(ADCRIS register INR3 bit) is promoted to a controller interrupt. If set,
the raw interrupt signal is promoted to a controller interrupt. Otherwise,
it is not.
3 MASK3 R/W 0
SS2 Interrupt Mask
Specifies whether the raw interrupt signal from Sample Sequencer 2
(ADCRIS register INR2 bit) is promoted to a controller interrupt. If set,
the raw interrupt signal is promoted to a controller interrupt. Otherwise,
it is not.
2 MASK2 R/W 0
SS1 Interrupt Mask
Specifies whether the raw interrupt signal from Sample Sequencer 1
(ADCRIS register INR1 bit) is promoted to a controller interrupt. If set,
the raw interrupt signal is promoted to a controller interrupt. Otherwise,
it is not.
1 MASK1 R/W 0
SS0 Interrupt Mask
Specifies whether the raw interrupt signal from Sample Sequencer 0
(ADCRIS register INR0 bit) is promoted to a controller interrupt. If set,
the raw interrupt signal is promoted to a controller interrupt. Otherwise,
it is not.
0 MASK0 R/W 0
March 17, 2008 273
Preliminary
LM3S8933 Microcontroller
Register 4: ADC Interrupt Status and Clear (ADCISC), offset 0x00C
This register provides the mechanism for clearing interrupt conditions, and shows the status of
controller interrupts generated by the Sample Sequencers. When read, each bit field is the logical
AND of the respective INR and MASK bits. Interrupts are cleared by writing a 1 to the corresponding
bit position. If software is polling the ADCRIS instead of generating interrupts, the INR bits are still
cleared via the ADCISC register, even if the IN bit is not set.
ADC Interrupt Status and Clear (ADCISC)
Base 0x4003.8000
Offset 0x00C
Type R/W1C, reset 0x0000.0000
31 30 29 28 27 26 25 24 23 22 21 20 19 18 17 16
reserved
Type RO RO RO RO RO RO RO RO RO RO RO RO RO RO RO RO
Reset 0 0 0 0 0 0 0 0 0 0 0 0 0 0 0 0
15 14 13 12 11 10 9 8 7 6 5 4 3 2 1 0
reserved IN3 IN2 IN1 IN0
Type RO RO RO RO RO RO RO RO RO RO RO RO R/W1C R/W1C R/W1C R/W1C
Reset 0 0 0 0 0 0 0 0 0 0 0 0 0 0 0 0
Bit/Field Name Type Reset Description
Software should not rely on the value of a reserved bit. To provide
compatibility with future products, the value of a reserved bit should be
preserved across a read-modify-write operation.
31:4 reserved RO 0x00
SS3 Interrupt Status and Clear
This bit is set by hardware when the MASK3 and INR3 bits are both 1,
providing a level-based interrupt to the controller. It is cleared by writing
a 1, and also clears the INR3 bit.
3 IN3 R/W1C 0
SS2 Interrupt Status and Clear
This bit is set by hardware when the MASK2 and INR2 bits are both 1,
providing a level based interrupt to the controller. It is cleared by writing
a 1, and also clears the INR2 bit.
2 IN2 R/W1C 0
SS1 Interrupt Status and Clear
This bit is set by hardware when the MASK1 and INR1 bits are both 1,
providing a level based interrupt to the controller. It is cleared by writing
a 1, and also clears the INR1 bit.
1 IN1 R/W1C 0
SS0 Interrupt Status and Clear
This bit is set by hardware when the MASK0 and INR0 bits are both 1,
providing a level based interrupt to the controller. It is cleared by writing
a 1, and also clears the INR0 bit.
0 IN0 R/W1C 0
274 March 17, 2008
Preliminary
Analog-to-Digital Converter (ADC)
Register 5: ADC Overflow Status (ADCOSTAT), offset 0x010
This register indicates overflow conditions in the Sample Sequencer FIFOs. Once the overflow
condition has been handled by software, the condition can be cleared by writing a 1 to the
corresponding bit position.
ADC Overflow Status (ADCOSTAT)
Base 0x4003.8000
Offset 0x010
Type R/W1C, reset 0x0000.0000
31 30 29 28 27 26 25 24 23 22 21 20 19 18 17 16
reserved
Type RO RO RO RO RO RO RO RO RO RO RO RO RO RO RO RO
Reset 0 0 0 0 0 0 0 0 0 0 0 0 0 0 0 0
15 14 13 12 11 10 9 8 7 6 5 4 3 2 1 0
reserved OV3 OV2 OV1 OV0
Type RO RO RO RO RO RO RO RO RO RO RO RO R/W1C R/W1C R/W1C R/W1C
Reset 0 0 0 0 0 0 0 0 0 0 0 0 0 0 0 0
Bit/Field Name Type Reset Description
Software should not rely on the value of a reserved bit. To provide
compatibility with future products, the value of a reserved bit should be
preserved across a read-modify-write operation.
31:4 reserved RO 0x00
SS3 FIFO Overflow
This bit specifies that the FIFO for Sample Sequencer 3 has hit an
overflow condition where the FIFO is full and a write was requested.
When an overflow is detected, the most recent write is dropped and this
bit is set by hardware to indicate the occurrence of dropped data. This
bit is cleared by writing a 1.
3 OV3 R/W1C 0
SS2 FIFO Overflow
This bit specifies that the FIFO for Sample Sequencer 2 has hit an
overflow condition where the FIFO is full and a write was requested.
When an overflow is detected, the most recent write is dropped and this
bit is set by hardware to indicate the occurrence of dropped data. This
bit is cleared by writing a 1.
2 OV2 R/W1C 0
SS1 FIFO Overflow
This bit specifies that the FIFO for Sample Sequencer 1 has hit an
overflow condition where the FIFO is full and a write was requested.
When an overflow is detected, the most recent write is dropped and this
bit is set by hardware to indicate the occurrence of dropped data. This
bit is cleared by writing a 1.
1 OV1 R/W1C 0
SS0 FIFO Overflow
This bit specifies that the FIFO for Sample Sequencer 0 has hit an
overflow condition where the FIFO is full and a write was requested.
When an overflow is detected, the most recent write is dropped and this
bit is set by hardware to indicate the occurrence of dropped data. This
bit is cleared by writing a 1.
0 OV0 R/W1C 0
March 17, 2008 275
Preliminary
LM3S8933 Microcontroller
Register 6: ADC Event Multiplexer Select (ADCEMUX), offset 0x014
The ADCEMUX selects the event (trigger) that initiates sampling for each Sample Sequencer. Each
Sample Sequencer can be configured with a unique trigger source.
ADC Event Multiplexer Select (ADCEMUX)
Base 0x4003.8000
Offset 0x014
Type R/W, reset 0x0000.0000
31 30 29 28 27 26 25 24 23 22 21 20 19 18 17 16
reserved
Type RO RO RO RO RO RO RO RO RO RO RO RO RO RO RO RO
Reset 0 0 0 0 0 0 0 0 0 0 0 0 0 0 0 0
15 14 13 12 11 10 9 8 7 6 5 4 3 2 1 0
EM3 EM2 EM1 EM0
Type R/W R/W R/W R/W R/W R/W R/W R/W R/W R/W R/W R/W R/W R/W R/W R/W
Reset 0 0 0 0 0 0 0 0 0 0 0 0 0 0 0 0
Bit/Field Name Type Reset Description
Software should not rely on the value of a reserved bit. To provide
compatibility with future products, the value of a reserved bit should be
preserved across a read-modify-write operation.
31:16 reserved RO 0x00
SS3 Trigger Select
This field selects the trigger source for Sample Sequencer 3.
The valid configurations for this field are:
Value Event
0x0 Controller (default)
0x1 Analog Comparator 0
0x2 Analog Comparator 1
0x3 Analog Comparator 2
0x4 External (GPIO PB4)
0x5 Timer
0x6 Reserved
0x7 Reserved
0x8 Reserved
0x9-0xE reserved
0xF Always (continuously sample)
15:12 EM3 R/W 0x00
276 March 17, 2008
Preliminary
Analog-to-Digital Converter (ADC)
Bit/Field Name Type Reset Description
SS2 Trigger Select
This field selects the trigger source for Sample Sequencer 2.
The valid configurations for this field are:
Value Event
0x0 Controller (default)
0x1 Analog Comparator 0
0x2 Analog Comparator 1
0x3 Analog Comparator 2
0x4 External (GPIO PB4)
0x5 Timer
0x6 Reserved
0x7 Reserved
0x8 Reserved
0x9-0xE reserved
0xF Always (continuously sample)
11:8 EM2 R/W 0x00
SS1 Trigger Select
This field selects the trigger source for Sample Sequencer 1.
The valid configurations for this field are:
Value Event
0x0 Controller (default)
0x1 Analog Comparator 0
0x2 Analog Comparator 1
0x3 Analog Comparator 2
0x4 External (GPIO PB4)
0x5 Timer
0x6 Reserved
0x7 Reserved
0x8 Reserved
0x9-0xE reserved
0xF Always (continuously sample)
7:4 EM1 R/W 0x00
March 17, 2008 277
Preliminary
LM3S8933 Microcontroller
Bit/Field Name Type Reset Description
SS0 Trigger Select
This field selects the trigger source for Sample Sequencer 0.
The valid configurations for this field are:
Value Event
0x0 Controller (default)
0x1 Analog Comparator 0
0x2 Analog Comparator 1
0x3 Analog Comparator 2
0x4 External (GPIO PB4)
0x5 Timer
0x6 Reserved
0x7 Reserved
0x8 Reserved
0x9-0xE reserved
0xF Always (continuously sample)
3:0 EM0 R/W 0x00
278 March 17, 2008
Preliminary
Analog-to-Digital Converter (ADC)
Register 7: ADC Underflow Status (ADCUSTAT), offset 0x018
This register indicates underflow conditions in the Sample Sequencer FIFOs. The corresponding
underflow condition can be cleared by writing a 1 to the relevant bit position.
ADC Underflow Status (ADCUSTAT)
Base 0x4003.8000
Offset 0x018
Type R/W1C, reset 0x0000.0000
31 30 29 28 27 26 25 24 23 22 21 20 19 18 17 16
reserved
Type RO RO RO RO RO RO RO RO RO RO RO RO RO RO RO RO
Reset 0 0 0 0 0 0 0 0 0 0 0 0 0 0 0 0
15 14 13 12 11 10 9 8 7 6 5 4 3 2 1 0
reserved UV3 UV2 UV1 UV0
Type RO RO RO RO RO RO RO RO RO RO RO RO R/W1C R/W1C R/W1C R/W1C
Reset 0 0 0 0 0 0 0 0 0 0 0 0 0 0 0 0
Bit/Field Name Type Reset Description
Software should not rely on the value of a reserved bit. To provide
compatibility with future products, the value of a reserved bit should be
preserved across a read-modify-write operation.
31:4 reserved RO 0x00
SS3 FIFO Underflow
This bit specifies that the FIFO for Sample Sequencer 3 has hit an
underflow condition where the FIFO is empty and a read was requested.
The problematic read does not move the FIFO pointers, and 0s are
returned. This bit is cleared by writing a 1.
3 UV3 R/W1C 0
SS2 FIFO Underflow
This bit specifies that the FIFO for Sample Sequencer 2 has hit an
underflow condition where the FIFO is empty and a read was requested.
The problematic read does not move the FIFO pointers, and 0s are
returned. This bit is cleared by writing a 1.
2 UV2 R/W1C 0
SS1 FIFO Underflow
This bit specifies that the FIFO for Sample Sequencer 1 has hit an
underflow condition where the FIFO is empty and a read was requested.
The problematic read does not move the FIFO pointers, and 0s are
returned. This bit is cleared by writing a 1.
1 UV1 R/W1C 0
SS0 FIFO Underflow
This bit specifies that the FIFO for Sample Sequencer 0 has hit an
underflow condition where the FIFO is empty and a read was requested.
The problematic read does not move the FIFO pointers, and 0s are
returned. This bit is cleared by writing a 1.
0 UV0 R/W1C 0
March 17, 2008 279
Preliminary
LM3S8933 Microcontroller
Register 8: ADC Sample Sequencer Priority (ADCSSPRI), offset 0x020
This register sets the priority for each of the Sample Sequencers. Out of reset, Sequencer 0 has
the highest priority, and sample sequence 3 has the lowest priority. When reconfiguring sequence
priorities, each sequence must have a unique priority or the ADC behavior is inconsistent.
ADC Sample Sequencer Priority (ADCSSPRI)
Base 0x4003.8000
Offset 0x020
Type R/W, reset 0x0000.3210
31 30 29 28 27 26 25 24 23 22 21 20 19 18 17 16
reserved
Type RO RO RO RO RO RO RO RO RO RO RO RO RO RO RO RO
Reset 0 0 0 0 0 0 0 0 0 0 0 0 0 0 0 0
15 14 13 12 11 10 9 8 7 6 5 4 3 2 1 0
reserved SS3 reserved SS2 reserved SS1 reserved SS0
Type RO RO R/W R/W RO RO R/W R/W RO RO R/W R/W RO RO R/W R/W
Reset 0 0 1 1 0 0 1 0 0 0 0 1 0 0 0 0
Bit/Field Name Type Reset Description
Software should not rely on the value of a reserved bit. To provide
compatibility with future products, the value of a reserved bit should be
preserved across a read-modify-write operation.
31:14 reserved RO 0x00
SS3 Priority
The SS3 field contains a binary-encoded value that specifies the priority
encoding of Sample Sequencer 3. A priority encoding of 0 is highest
and 3 is lowest. The priorities assigned to the Sequencers must be
uniquely mapped. ADC behavior is not consistent if two or more fields
are equal.
13:12 SS3 R/W 0x3
Software should not rely on the value of a reserved bit. To provide
compatibility with future products, the value of a reserved bit should be
preserved across a read-modify-write operation.
11:10 reserved RO 0x0
SS2 Priority
The SS2 field contains a binary-encoded value that specifies the priority
encoding of Sample Sequencer 2.
9:8 SS2 R/W 0x2
Software should not rely on the value of a reserved bit. To provide
compatibility with future products, the value of a reserved bit should be
preserved across a read-modify-write operation.
7:6 reserved RO 0x0
SS1 Priority
The SS1 field contains a binary-encoded value that specifies the priority
encoding of Sample Sequencer 1.
5:4 SS1 R/W 0x1
Software should not rely on the value of a reserved bit. To provide
compatibility with future products, the value of a reserved bit should be
preserved across a read-modify-write operation.
3:2 reserved RO 0x0
SS0 Priority
The SS0 field contains a binary-encoded value that specifies the priority
encoding of Sample Sequencer 0.
1:0 SS0 R/W 0x0
280 March 17, 2008
Preliminary
Analog-to-Digital Converter (ADC)
Register 9: ADC Processor Sample Sequence Initiate (ADCPSSI), offset 0x028
This register provides a mechanism for application software to initiate sampling in the Sample
Sequencers. Sample sequences can be initiated individually or in any combination. When multiple
sequences are triggered simultaneously, the priority encodings in ADCSSPRI dictate execution
order.
ADC Processor Sample Sequence Initiate (ADCPSSI)
Base 0x4003.8000
Offset 0x028
Type WO, reset -
31 30 29 28 27 26 25 24 23 22 21 20 19 18 17 16
reserved
Type WO WO WO WO WO WO WO WO WO WO WO WO WO WO WO WO
Reset - - - - - - - - - - - - - - - -
15 14 13 12 11 10 9 8 7 6 5 4 3 2 1 0
reserved SS3 SS2 SS1 SS0
Type WO WO WO WO WO WO WO WO WO WO WO WO WO WO WO WO
Reset - - - - - - - - - - - - - - - -
Bit/Field Name Type Reset Description
Software should not rely on the value of a reserved bit. To provide
compatibility with future products, the value of a reserved bit should be
preserved across a read-modify-write operation.
31:4 reserved WO -
SS3 Initiate
Only a write by software is valid; a read of the register returns no
meaningful data. When set by software, sampling is triggered on Sample
Sequencer 3, assuming the Sequencer is enabled in the ADCACTSS
register.
3 SS3 WO -
SS2 Initiate
Only a write by software is valid; a read of the register returns no
meaningful data. When set by software, sampling is triggered on Sample
Sequencer 2, assuming the Sequencer is enabled in the ADCACTSS
register.
2 SS2 WO -
SS1 Initiate
Only a write by software is valid; a read of the register returns no
meaningful data. When set by software, sampling is triggered on Sample
Sequencer 1, assuming the Sequencer is enabled in the ADCACTSS
register.
1 SS1 WO -
SS0 Initiate
Only a write by software is valid; a read of the register returns no
meaningful data. When set by software, sampling is triggered on Sample
Sequencer 0, assuming the Sequencer is enabled in the ADCACTSS
register.
0 SS0 WO -
March 17, 2008 281
Preliminary
LM3S8933 Microcontroller
Register 10: ADC Sample Averaging Control (ADCSAC), offset 0x030
This register controls the amount of hardware averaging applied to conversion results. The final
conversion result stored in the FIFO is averaged from 2 AVG consecutive ADC samples at the specified
ADC speed. If AVG is 0, the sample is passed directly through without any averaging. If AVG=6,
then 64 consecutive ADC samples are averaged to generate one result in the sequencer FIFO. An
AVG = 7 provides unpredictable results.
ADC Sample Averaging Control (ADCSAC)
Base 0x4003.8000
Offset 0x030
Type R/W, reset 0x0000.0000
31 30 29 28 27 26 25 24 23 22 21 20 19 18 17 16
reserved
Type RO RO RO RO RO RO RO RO RO RO RO RO RO RO RO RO
Reset 0 0 0 0 0 0 0 0 0 0 0 0 0 0 0 0
15 14 13 12 11 10 9 8 7 6 5 4 3 2 1 0
reserved AVG
Type RO RO RO RO RO RO RO RO RO RO RO RO RO R/W R/W R/W
Reset 0 0 0 0 0 0 0 0 0 0 0 0 0 0 0 0
Bit/Field Name Type Reset Description
Software should not rely on the value of a reserved bit. To provide
compatibility with future products, the value of a reserved bit should be
preserved across a read-modify-write operation.
31:3 reserved RO 0x00
Hardware Averaging Control
Specifies the amount of hardware averaging that will be applied to ADC
samples. The AVG field can be any value between 0 and 6. Entering a
value of 7 creates unpredictable results.
Value Description
0x0 No hardware oversampling
0x1 2x hardware oversampling
0x2 4x hardware oversampling
0x3 8x hardware oversampling
0x4 16x hardware oversampling
0x5 32x hardware oversampling
0x6 64x hardware oversampling
0x7 Reserved
2:0 AVG R/W 0x0
282 March 17, 2008
Preliminary
Analog-to-Digital Converter (ADC)
Register 11: ADC Sample Sequence Input Multiplexer Select 0 (ADCSSMUX0),
offset 0x040
This register defines the analog input configuration for each sample in a sequence executed with
Sample Sequencer 0.
This register is 32-bits wide and contains information for eight possible samples.
ADC Sample Sequence Input Multiplexer Select 0 (ADCSSMUX0)
Base 0x4003.8000
Offset 0x040
Type R/W, reset 0x0000.0000
31 30 29 28 27 26 25 24 23 22 21 20 19 18 17 16
reserved MUX7 reserved MUX6 reserved MUX5 reserved MUX4
Type RO RO R/W R/W RO RO R/W R/W RO RO R/W R/W RO RO R/W R/W
Reset 0 0 0 0 0 0 0 0 0 0 0 0 0 0 0 0
15 14 13 12 11 10 9 8 7 6 5 4 3 2 1 0
reserved MUX3 reserved MUX2 reserved MUX1 reserved MUX0
Type RO RO R/W R/W RO RO R/W R/W RO RO R/W R/W RO RO R/W R/W
Reset 0 0 0 0 0 0 0 0 0 0 0 0 0 0 0 0
Bit/Field Name Type Reset Description
Software should not rely on the value of a reserved bit. To provide
compatibility with future products, the value of a reserved bit should be
preserved across a read-modify-write operation.
31:30 reserved RO 0
8th Sample Input Select
The MUX7 field is used during the eighth sample of a sequence executed
with the Sample Sequencer. It specifies which of the analog inputs is
sampled for the analog-to-digital conversion. The value set here indicates
the corresponding pin, for example, a value of 1 indicates the input is
ADC1.
29:28 MUX7 R/W 0
Software should not rely on the value of a reserved bit. To provide
compatibility with future products, the value of a reserved bit should be
preserved across a read-modify-write operation.
27:26 reserved RO 0
7th Sample Input Select
The MUX6 field is used during the seventh sample of a sequence
executed with the Sample Sequencer and specifies which of the analog
inputs is sampled for the analog-to-digital conversion.
25:24 MUX6 R/W 0
Software should not rely on the value of a reserved bit. To provide
compatibility with future products, the value of a reserved bit should be
preserved across a read-modify-write operation.
23:22 reserved RO 0
6th Sample Input Select
The MUX5 field is used during the sixth sample of a sequence executed
with the Sample Sequencer and specifies which of the analog inputs is
sampled for the analog-to-digital conversion.
21:20 MUX5 R/W 0
Software should not rely on the value of a reserved bit. To provide
compatibility with future products, the value of a reserved bit should be
preserved across a read-modify-write operation.
19:18 reserved RO 0
March 17, 2008 283
Preliminary
LM3S8933 Microcontroller
Bit/Field Name Type Reset Description
5th Sample Input Select
The MUX4 field is used during the fifth sample of a sequence executed
with the Sample Sequencer and specifies which of the analog inputs is
sampled for the analog-to-digital conversion.
17:16 MUX4 R/W 0
Software should not rely on the value of a reserved bit. To provide
compatibility with future products, the value of a reserved bit should be
preserved across a read-modify-write operation.
15:14 reserved RO 0
4th Sample Input Select
The MUX3 field is used during the fourth sample of a sequence executed
with the Sample Sequencer and specifies which of the analog inputs is
sampled for the analog-to-digital conversion.
13:12 MUX3 R/W 0
Software should not rely on the value of a reserved bit. To provide
compatibility with future products, the value of a reserved bit should be
preserved across a read-modify-write operation.
11:10 reserved RO 0
3rd Sample Input Select
The MUX2 field is used during the third sample of a sequence executed
with the Sample Sequencer and specifies which of the analog inputs is
sampled for the analog-to-digital conversion.
9:8 MUX2 R/W 0
Software should not rely on the value of a reserved bit. To provide
compatibility with future products, the value of a reserved bit should be
preserved across a read-modify-write operation.
7:6 reserved RO 0
2nd Sample Input Select
The MUX1 field is used during the second sample of a sequence
executed with the Sample Sequencer and specifies which of the analog
inputs is sampled for the analog-to-digital conversion.
5:4 MUX1 R/W 0
Software should not rely on the value of a reserved bit. To provide
compatibility with future products, the value of a reserved bit should be
preserved across a read-modify-write operation.
3:2 reserved RO 0
1st Sample Input Select
The MUX0 field is used during the first sample of a sequence executed
with the Sample Sequencer and specifies which of the analog inputs is
sampled for the analog-to-digital conversion.
1:0 MUX0 R/W 0
284 March 17, 2008
Preliminary
Analog-to-Digital Converter (ADC)
Register 12: ADC Sample Sequence Control 0 (ADCSSCTL0), offset 0x044
This register contains the configuration information for each sample for a sequence executed with
Sample Sequencer 0. When configuring a sample sequence, the END bit must be set at some point,
whether it be after the first sample, last sample, or any sample in between.
This register is 32-bits wide and contains information for eight possible samples.
ADC Sample Sequence Control 0 (ADCSSCTL0)
Base 0x4003.8000
Offset 0x044
Type R/W, reset 0x0000.0000
31 30 29 28 27 26 25 24 23 22 21 20 19 18 17 16
TS7 IE7 END7 D7 TS6 IE6 END6 D6 TS5 IE5 END5 D5 TS4 IE4 END4 D4
Type R/W R/W R/W R/W R/W R/W R/W R/W R/W R/W R/W R/W R/W R/W R/W R/W
Reset 0 0 0 0 0 0 0 0 0 0 0 0 0 0 0 0
15 14 13 12 11 10 9 8 7 6 5 4 3 2 1 0
TS3 IE3 END3 D3 TS2 IE2 END2 D2 TS1 IE1 END1 D1 TS0 IE0 END0 D0
Type R/W R/W R/W R/W R/W R/W R/W R/W R/W R/W R/W R/W R/W R/W R/W R/W
Reset 0 0 0 0 0 0 0 0 0 0 0 0 0 0 0 0
Bit/Field Name Type Reset Description
8th Sample Temp Sensor Select
The TS7 bit is used during the eighth sample of the sample sequence
and specifies the input source of the sample. If set, the temperature
sensor is read. Otherwise, the input pin specified by the ADCSSMUX
register is read.
31 TS7 R/W 0
8th Sample Interrupt Enable
The IE7 bit is used during the eighth sample of the sample sequence
and specifies whether the raw interrupt signal (INR0 bit) is asserted at
the end of the sample's conversion. If the MASK0 bit in the ADCIM
register is set, the interrupt is promoted to a controller-level interrupt.
When this bit is set, the raw interrupt is asserted, otherwise it is not. It
is legal to have multiple samples within a sequence generate interrupts.
30 IE7 R/W 0
8th Sample is End of Sequence
The END7 bit indicates that this is the last sample of the sequence. It is
possible to end the sequence on any sample position. Samples defined
after the sample containing a set END are not requested for conversion
even though the fields may be non-zero. It is required that software write
the END bit somewhere within the sequence. (Sample Sequencer 3,
which only has a single sample in the sequence, is hardwired to have
the END0 bit set.)
Setting this bit indicates that this sample is the last in the sequence.
29 END7 R/W 0
8th Sample Diff Input Select
The D7 bit indicates that the analog input is to be differentially sampled.
The corresponding ADCSSMUXx nibble must be set to the pair number
"i", where the paired inputs are "2i and 2i+1". The temperature sensor
does not have a differential option. When set, the analog inputs are
differentially sampled.
28 D7 R/W 0
7th Sample Temp Sensor Select
Same definition as TS7 but used during the seventh sample.
27 TS6 R/W 0
March 17, 2008 285
Preliminary
LM3S8933 Microcontroller
Bit/Field Name Type Reset Description
7th Sample Interrupt Enable
Same definition as IE7 but used during the seventh sample.
26 IE6 R/W 0
7th Sample is End of Sequence
Same definition as END7 but used during the seventh sample.
25 END6 R/W 0
7th Sample Diff Input Select
Same definition as D7 but used during the seventh sample.
24 D6 R/W 0
6th Sample Temp Sensor Select
Same definition as TS7 but used during the sixth sample.
23 TS5 R/W 0
6th Sample Interrupt Enable
Same definition as IE7 but used during the sixth sample.
22 IE5 R/W 0
6th Sample is End of Sequence
Same definition as END7 but used during the sixth sample.
21 END5 R/W 0
6th Sample Diff Input Select
Same definition as D7 but used during the sixth sample.
20 D5 R/W 0
5th Sample Temp Sensor Select
Same definition as TS7 but used during the fifth sample.
19 TS4 R/W 0
5th Sample Interrupt Enable
Same definition as IE7 but used during the fifth sample.
18 IE4 R/W 0
5th Sample is End of Sequence
Same definition as END7 but used during the fifth sample.
17 END4 R/W 0
5th Sample Diff Input Select
Same definition as D7 but used during the fifth sample.
16 D4 R/W 0
4th Sample Temp Sensor Select
Same definition as TS7 but used during the fourth sample.
15 TS3 R/W 0
4th Sample Interrupt Enable
Same definition as IE7 but used during the fourth sample.
14 IE3 R/W 0
4th Sample is End of Sequence
Same definition as END7 but used during the fourth sample.
13 END3 R/W 0
4th Sample Diff Input Select
Same definition as D7 but used during the fourth sample.
12 D3 R/W 0
3rd Sample Temp Sensor Select
Same definition as TS7 but used during the third sample.
11 TS2 R/W 0
286 March 17, 2008
Preliminary
Analog-to-Digital Converter (ADC)
Bit/Field Name Type Reset Description
3rd Sample Interrupt Enable
Same definition as IE7 but used during the third sample.
10 IE2 R/W 0
3rd Sample is End of Sequence
Same definition as END7 but used during the third sample.
9 END2 R/W 0
3rd Sample Diff Input Select
Same definition as D7 but used during the third sample.
8 D2 R/W 0
2nd Sample Temp Sensor Select
Same definition as TS7 but used during the second sample.
7 TS1 R/W 0
2nd Sample Interrupt Enable
Same definition as IE7 but used during the second sample.
6 IE1 R/W 0
2nd Sample is End of Sequence
Same definition as END7 but used during the second sample.
5 END1 R/W 0
2nd Sample Diff Input Select
Same definition as D7 but used during the second sample.
4 D1 R/W 0
1st Sample Temp Sensor Select
Same definition as TS7 but used during the first sample.
3 TS0 R/W 0
1st Sample Interrupt Enable
Same definition as IE7 but used during the first sample.
2 IE0 R/W 0
1st Sample is End of Sequence
Same definition as END7 but used during the first sample.
Since this sequencer has only one entry, this bit must be set.
1 END0 R/W 0
1st Sample Diff Input Select
Same definition as D7 but used during the first sample.
0 D0 R/W 0
March 17, 2008 287
Preliminary
LM3S8933 Microcontroller
Register 13: ADC Sample Sequence Result FIFO 0 (ADCSSFIFO0), offset 0x048
Register 14: ADC Sample Sequence Result FIFO 1 (ADCSSFIFO1), offset 0x068
Register 15: ADC Sample Sequence Result FIFO 2 (ADCSSFIFO2), offset 0x088
Register 16: ADC Sample Sequence Result FIFO 3 (ADCSSFIFO3), offset
0x0A8
This register contains the conversion results for samples collected with the Sample Sequencer (the
ADCSSFIFO0 register is used for Sample Sequencer 0, ADCSSFIFO1 for Sequencer 1,
ADCSSFIFO2 for Sequencer 2, and ADCSSFIFO3 for Sequencer 3). Reads of this register return
conversion result data in the order sample 0, sample 1, and so on, until the FIFO is empty. If the
FIFO is not properly handled by software, overflow and underflow conditions are registered in the
ADCOSTAT and ADCUSTAT registers.
ADC Sample Sequence Result FIFO 0 (ADCSSFIFO0)
Base 0x4003.8000
Offset 0x048
Type RO, reset 0x0000.0000
31 30 29 28 27 26 25 24 23 22 21 20 19 18 17 16
reserved
Type RO RO RO RO RO RO RO RO RO RO RO RO RO RO RO RO
Reset 0 0 0 0 0 0 0 0 0 0 0 0 0 0 0 0
15 14 13 12 11 10 9 8 7 6 5 4 3 2 1 0
reserved DATA
Type RO RO RO RO RO RO RO RO RO RO RO RO RO RO RO RO
Reset 0 0 0 0 0 0 0 0 0 0 0 0 0 0 0 0
Bit/Field Name Type Reset Description
Software should not rely on the value of a reserved bit. To provide
compatibility with future products, the value of a reserved bit should be
preserved across a read-modify-write operation.
31:10 reserved RO 0x00
9:0 DATA RO 0x00 Conversion Result Data
288 March 17, 2008
Preliminary
Analog-to-Digital Converter (ADC)
Register 17: ADC Sample Sequence FIFO 0 Status (ADCSSFSTAT0), offset
0x04C
Register 18: ADC Sample Sequence FIFO 1 Status (ADCSSFSTAT1), offset
0x06C
Register 19: ADC Sample Sequence FIFO 2 Status (ADCSSFSTAT2), offset
0x08C
Register 20: ADC Sample Sequence FIFO 3 Status (ADCSSFSTAT3), offset
0x0AC
This register provides a window into the Sample Sequencer, providing full/empty status information
as well as the positions of the head and tail pointers. The reset value of 0x100 indicates an empty
FIFO. The ADCSSFSTAT0 register provides status on FIF0, ADCSSFSTAT1 on FIFO1,
ADCSSFSTAT2 on FIFO2, and ADCSSFSTAT3 on FIFO3.
ADC Sample Sequence FIFO 0 Status (ADCSSFSTAT0)
Base 0x4003.8000
Offset 0x04C
Type RO, reset 0x0000.0100
31 30 29 28 27 26 25 24 23 22 21 20 19 18 17 16
reserved
Type RO RO RO RO RO RO RO RO RO RO RO RO RO RO RO RO
Reset 0 0 0 0 0 0 0 0 0 0 0 0 0 0 0 0
15 14 13 12 11 10 9 8 7 6 5 4 3 2 1 0
reserved FULL reserved EMPTY HPTR TPTR
Type RO RO RO RO RO RO RO RO RO RO RO RO RO RO RO RO
Reset 0 0 0 0 0 0 0 1 0 0 0 0 0 0 0 0
Bit/Field Name Type Reset Description
Software should not rely on the value of a reserved bit. To provide
compatibility with future products, the value of a reserved bit should be
preserved across a read-modify-write operation.
31:13 reserved RO 0x00
FIFO Full
When set, indicates that the FIFO is currently full.
12 FULL RO 0
Software should not rely on the value of a reserved bit. To provide
compatibility with future products, the value of a reserved bit should be
preserved across a read-modify-write operation.
11:9 reserved RO 0x00
FIFO Empty
When set, indicates that the FIFO is currently empty.
8 EMPTY RO 1
FIFO Head Pointer
This field contains the current "head" pointer index for the FIFO, that is,
the next entry to be written.
7:4 HPTR RO 0x00
FIFO Tail Pointer
This field contains the current "tail" pointer index for the FIFO, that is,
the next entry to be read.
3:0 TPTR RO 0x00
March 17, 2008 289
Preliminary
LM3S8933 Microcontroller
Register 21: ADC Sample Sequence Input Multiplexer Select 1 (ADCSSMUX1),
offset 0x060
Register 22: ADC Sample Sequence Input Multiplexer Select 2 (ADCSSMUX2),
offset 0x080
This register defines the analog input configuration for each sample in a sequence executed with
Sample Sequencer 1 or 2. These registers are 16-bits wide and contain information for four possible
samples. See the ADCSSMUX0 register on page 283 for detailed bit descriptions.
ADC Sample Sequence Input Multiplexer Select 1 (ADCSSMUX1)
Base 0x4003.8000
Offset 0x060
Type R/W, reset 0x0000.0000
31 30 29 28 27 26 25 24 23 22 21 20 19 18 17 16
reserved
Type RO RO RO RO RO RO RO RO RO RO RO RO RO RO RO RO
Reset 0 0 0 0 0 0 0 0 0 0 0 0 0 0 0 0
15 14 13 12 11 10 9 8 7 6 5 4 3 2 1 0
reserved MUX3 reserved MUX2 reserved MUX1 reserved MUX0
Type RO RO R/W R/W RO RO R/W R/W RO RO R/W R/W RO RO R/W R/W
Reset 0 0 0 0 0 0 0 0 0 0 0 0 0 0 0 0
Bit/Field Name Type Reset Description
Software should not rely on the value of a reserved bit. To provide
compatibility with future products, the value of a reserved bit should be
preserved across a read-modify-write operation.
31:14 reserved RO 0x00
13:12 MUX3 R/W 0 4th Sample Input Select
Software should not rely on the value of a reserved bit. To provide
compatibility with future products, the value of a reserved bit should be
preserved across a read-modify-write operation.
11:10 reserved RO 0
9:8 MUX2 R/W 0 3rd Sample Input Select
Software should not rely on the value of a reserved bit. To provide
compatibility with future products, the value of a reserved bit should be
preserved across a read-modify-write operation.
7:6 reserved RO 0
5:4 MUX1 R/W 0 2nd Sample Input Select
Software should not rely on the value of a reserved bit. To provide
compatibility with future products, the value of a reserved bit should be
preserved across a read-modify-write operation.
3:2 reserved RO 0
1:0 MUX0 R/W 0 1st Sample Input Select
290 March 17, 2008
Preliminary
Analog-to-Digital Converter (ADC)
Register 23: ADC Sample Sequence Control 1 (ADCSSCTL1), offset 0x064
Register 24: ADC Sample Sequence Control 2 (ADCSSCTL2), offset 0x084
These registers contain the configuration information for each sample for a sequence executed with
Sample Sequencer 1 or 2. When configuring a sample sequence, the END bit must be set at some
point, whether it be after the first sample, last sample, or any sample in between. This register is
16-bits wide and contains information for four possible samples. See the ADCSSCTL0 register on
page 285 for detailed bit descriptions.
ADC Sample Sequence Control 1 (ADCSSCTL1)
Base 0x4003.8000
Offset 0x064
Type R/W, reset 0x0000.0000
31 30 29 28 27 26 25 24 23 22 21 20 19 18 17 16
reserved
Type RO RO RO RO RO RO RO RO RO RO RO RO RO RO RO RO
Reset 0 0 0 0 0 0 0 0 0 0 0 0 0 0 0 0
15 14 13 12 11 10 9 8 7 6 5 4 3 2 1 0
TS3 IE3 END3 D3 TS2 IE2 END2 D2 TS1 IE1 END1 D1 TS0 IE0 END0 D0
Type R/W R/W R/W R/W R/W R/W R/W R/W R/W R/W R/W R/W R/W R/W R/W R/W
Reset 0 0 0 0 0 0 0 0 0 0 0 0 0 0 0 0
Bit/Field Name Type Reset Description
Software should not rely on the value of a reserved bit. To provide
compatibility with future products, the value of a reserved bit should be
preserved across a read-modify-write operation.
31:16 reserved RO 0x00
4th Sample Temp Sensor Select
Same definition as TS7 but used during the fourth sample.
15 TS3 R/W 0
4th Sample Interrupt Enable
Same definition as IE7 but used during the fourth sample.
14 IE3 R/W 0
4th Sample is End of Sequence
Same definition as END7 but used during the fourth sample.
13 END3 R/W 0
4th Sample Diff Input Select
Same definition as D7 but used during the fourth sample.
12 D3 R/W 0
3rd Sample Temp Sensor Select
Same definition as TS7 but used during the third sample.
11 TS2 R/W 0
3rd Sample Interrupt Enable
Same definition as IE7 but used during the third sample.
10 IE2 R/W 0
3rd Sample is End of Sequence
Same definition as END7 but used during the third sample.
9 END2 R/W 0
3rd Sample Diff Input Select
Same definition as D7 but used during the third sample.
8 D2 R/W 0
March 17, 2008 291
Preliminary
LM3S8933 Microcontroller
Bit/Field Name Type Reset Description
2nd Sample Temp Sensor Select
Same definition as TS7 but used during the second sample.
7 TS1 R/W 0
2nd Sample Interrupt Enable
Same definition as IE7 but used during the second sample.
6 IE1 R/W 0
2nd Sample is End of Sequence
Same definition as END7 but used during the second sample.
5 END1 R/W 0
2nd Sample Diff Input Select
Same definition as D7 but used during the second sample.
4 D1 R/W 0
1st Sample Temp Sensor Select
Same definition as TS7 but used during the first sample.
3 TS0 R/W 0
1st Sample Interrupt Enable
Same definition as IE7 but used during the first sample.
2 IE0 R/W 0
1st Sample is End of Sequence
Same definition as END7 but used during the first sample.
Since this sequencer has only one entry, this bit must be set.
1 END0 R/W 0
1st Sample Diff Input Select
Same definition as D7 but used during the first sample.
0 D0 R/W 0
292 March 17, 2008
Preliminary
Analog-to-Digital Converter (ADC)
Register 25: ADC Sample Sequence Input Multiplexer Select 3 (ADCSSMUX3),
offset 0x0A0
This register defines the analog input configuration for each sample in a sequence executed with
Sample Sequencer 3. This register is 4-bits wide and contains information for one possible sample.
See the ADCSSMUX0 register on page 283 for detailed bit descriptions.
ADC Sample Sequence Input Multiplexer Select 3 (ADCSSMUX3)
Base 0x4003.8000
Offset 0x0A0
Type R/W, reset 0x0000.0000
31 30 29 28 27 26 25 24 23 22 21 20 19 18 17 16
reserved
Type RO RO RO RO RO RO RO RO RO RO RO RO RO RO RO RO
Reset 0 0 0 0 0 0 0 0 0 0 0 0 0 0 0 0
15 14 13 12 11 10 9 8 7 6 5 4 3 2 1 0
reserved MUX0
Type RO RO RO RO RO RO RO RO RO RO RO RO RO RO R/W R/W
Reset 0 0 0 0 0 0 0 0 0 0 0 0 0 0 0 0
Bit/Field Name Type Reset Description
Software should not rely on the value of a reserved bit. To provide
compatibility with future products, the value of a reserved bit should be
preserved across a read-modify-write operation.
31:2 reserved RO 0x00
1:0 MUX0 R/W 0 1st Sample Input Select
March 17, 2008 293
Preliminary
LM3S8933 Microcontroller
Register 26: ADC Sample Sequence Control 3 (ADCSSCTL3), offset 0x0A4
This register contains the configuration information for each sample for a sequence executed with
Sample Sequencer 3. The END bit is always set since there is only one sample in this sequencer.
This register is 4-bits wide and contains information for one possible sample. See the ADCSSCTL0
register on page 285 for detailed bit descriptions.
ADC Sample Sequence Control 3 (ADCSSCTL3)
Base 0x4003.8000
Offset 0x0A4
Type R/W, reset 0x0000.0002
31 30 29 28 27 26 25 24 23 22 21 20 19 18 17 16
reserved
Type RO RO RO RO RO RO RO RO RO RO RO RO RO RO RO RO
Reset 0 0 0 0 0 0 0 0 0 0 0 0 0 0 0 0
15 14 13 12 11 10 9 8 7 6 5 4 3 2 1 0
reserved TS0 IE0 END0 D0
Type RO RO RO RO RO RO RO RO RO RO RO RO R/W R/W R/W R/W
Reset 0 0 0 0 0 0 0 0 0 0 0 0 0 0 1 0
Bit/Field Name Type Reset Description
Software should not rely on the value of a reserved bit. To provide
compatibility with future products, the value of a reserved bit should be
preserved across a read-modify-write operation.
31:4 reserved RO 0x00
1st Sample Temp Sensor Select
Same definition as TS7 but used during the first sample.
3 TS0 R/W 0
1st Sample Interrupt Enable
Same definition as IE7 but used during the first sample.
2 IE0 R/W 0
1st Sample is End of Sequence
Same definition as END7 but used during the first sample.
Since this sequencer has only one entry, this bit must be set.
1 END0 R/W 1
1st Sample Diff Input Select
Same definition as D7 but used during the first sample.
0 D0 R/W 0
294 March 17, 2008
Preliminary
Analog-to-Digital Converter (ADC)
Register 27: ADC Test Mode Loopback (ADCTMLB), offset 0x100
This register provides loopback operation within the digital logic of the ADC, which can be useful in
debugging software without having to provide actual analog stimulus. This test mode is entered by
writing a value of 0x0000.0001 to this register. When data is read from the FIFO in loopback mode,
the read-only portion of this register is returned.
ADC Test Mode Loopback (ADCTMLB)
Base 0x4003.8000
Offset 0x100
Type R/W, reset 0x0000.0000
31 30 29 28 27 26 25 24 23 22 21 20 19 18 17 16
reserved
Type RO RO RO RO RO RO RO RO RO RO RO RO RO RO RO RO
Reset 0 0 0 0 0 0 0 0 0 0 0 0 0 0 0 0
15 14 13 12 11 10 9 8 7 6 5 4 3 2 1 0
reserved LB
Type RO RO RO RO RO RO RO RO RO RO RO RO RO RO RO R/W
Reset 0 0 0 0 0 0 0 0 0 0 0 0 0 0 0 0
Bit/Field Name Type Reset Description
Software should not rely on the value of a reserved bit. To provide
compatibility with future products, the value of a reserved bit should be
preserved across a read-modify-write operation.
31:1 reserved RO 0x00
Loopback Mode Enable
When set, forces a loopback within the digital block to provide information
on input and unique numbering. The ADCSSFIFOn registers do not
provide sample data, but instead provide the 10-bit loopback data as
shown below.
Bit/Field Name Description
Continuous Sample Counter
Continuous sample counter that is initialized to 0 and
counts each sample as it processed. This helps
provide a unique value for the data received.
9:6 CNT
Continuation Sample Indicator
When set, indicates that this is a continuation sample.
For example, if two sequencers were to run
back-to-back, this indicates that the controller kept
continuously sampling at full rate.
5 CONT
Differential Sample Indicator
When set, indicates that this is a differential sample.
4 DIFF
Temp Sensor Sample Indicator
When set, indicates that this is a temperature sensor
sample.
3 TS
Analog Input Indicator
Indicates which analog input is to be sampled.
2:0 MUX
0 LB R/W 0
March 17, 2008 295
Preliminary
LM3S8933 Microcontroller
13 Universal Asynchronous Receivers/Transmitters
(UARTs)
The Stellaris® Universal Asynchronous Receiver/Transmitter (UART) provides fully programmable,
16C550-type serial interface characteristics. The LM3S8933 controller is equipped with two UART
modules.
Each UART has the following features:
■ Separate transmit and receive FIFOs
■ Programmable FIFO length, including 1-byte deep operation providing conventional
double-buffered interface
■ FIFO trigger levels of 1/8, 1/4, 1/2, 3/4, and 7/8
■ Programmable baud-rate generator allowing rates up to 3.125 Mbps
■ Standard asynchronous communication bits for start, stop, and parity
■ False start bit detection
■ Line-break generation and detection
■ Fully programmable serial interface characteristics:
– 5, 6, 7, or 8 data bits
– Even, odd, stick, or no-parity bit generation/detection
– 1 or 2 stop bit generation
■ IrDA serial-IR (SIR) encoder/decoder providing:
– Programmable use of IrDA Serial Infrared (SIR) or UART input/output
– Support of IrDA SIR encoder/decoder functions for data rates up to 115.2 Kbps half-duplex
– Support of normal 3/16 and low-power (1.41-2.23 μs) bit durations
– Programmable internal clock generator enabling division of reference clock by 1 to 256 for
low-power mode bit duration
296 March 17, 2008
Preliminary
Universal Asynchronous Receivers/Transmitters (UARTs)
13.1 Block Diagram
Figure 13-1. UART Module Block Diagram
Receiver
Transmitter
System Clock
Control / Status
UARTRSR/ECR
UARTFR
UARTLCRH
UARTCTL
UARTILPR
Interrupt Control
UARTIFLS
UARTIM
UARTMIS
UARTRIS
UARTICR
Baud Rate
Generator
UARTIBRD
UARTFBRD
Identification
Registers
UARTPCellID0
UARTPCellID1
UARTPCellID2
UARTPCellID3
UARTPeriphID0
UARTPeriphID1
UARTPeriphID2
UARTPeriphID3
UART PeriphID4
UARTPeriphID5
UARTPeriphID6
UARTPeriphID7
UARTDR
TXFIFO
16x8
...
RXFIFO
16x8
...
Interrupt
UnTx
UnRx
13.2 Functional Description
Each Stellaris® UART performs the functions of parallel-to-serial and serial-to-parallel conversions.
It is similar in functionality to a 16C550 UART, but is not register compatible.
The UART is configured for transmit and/or receive via the TXE and RXE bits of the UART Control
(UARTCTL) register (see page 315). Transmit and receive are both enabled out of reset. Before any
control registers are programmed, the UART must be disabled by clearing the UARTEN bit in
UARTCTL. If the UART is disabled during a TX or RX operation, the current transaction is completed
prior to the UART stopping.
The UART peripheral also includes a serial IR (SIR) encoder/decoder block that can be connected
to an infrared transceiver to implement an IrDA SIR physical layer. The SIR function is programmed
using the UARTCTL register.
13.2.1 Transmit/Receive Logic
The transmit logic performs parallel-to-serial conversion on the data read from the transmit FIFO.
The control logic outputs the serial bit stream beginning with a start bit, and followed by the data
March 17, 2008 297
Preliminary
LM3S8933 Microcontroller
bits (LSB first), parity bit, and the stop bits according to the programmed configuration in the control
registers. See Figure 13-2 on page 298 for details.
The receive logic performs serial-to-parallel conversion on the received bit stream after a valid start
pulse has been detected. Overrun, parity, frame error checking, and line-break detection are also
performed, and their status accompanies the data that is written to the receive FIFO.
Figure 13-2. UART Character Frame
1
0 5-8 data bits
LSB MSB
Parity bit
if enabled
1-2
stop bits
UnTX
n
Start
13.2.2 Baud-Rate Generation
The baud-rate divisor is a 22-bit number consisting of a 16-bit integer and a 6-bit fractional part.
The number formed by these two values is used by the baud-rate generator to determine the bit
period. Having a fractional baud-rate divider allows the UART to generate all the standard baud
rates.
The 16-bit integer is loaded through the UART Integer Baud-Rate Divisor (UARTIBRD) register
(see page 311) and the 6-bit fractional part is loaded with the UART Fractional Baud-Rate Divisor
(UARTFBRD) register (see page 312). The baud-rate divisor (BRD) has the following relationship
to the system clock (where BRDI is the integer part of the BRD and BRDF is the fractional part,
separated by a decimal place.)
BRD = BRDI + BRDF = UARTSysClk / (16 * Baud Rate)
where UARTSysClk is the system clock connected to the UART.
The 6-bit fractional number (that is to be loaded into the DIVFRAC bit field in the UARTFBRD register)
can be calculated by taking the fractional part of the baud-rate divisor, multiplying it by 64, and
adding 0.5 to account for rounding errors:
UARTFBRD[DIVFRAC] = integer(BRDF * 64 + 0.5)
The UART generates an internal baud-rate reference clock at 16x the baud-rate (referred to as
Baud16). This reference clock is divided by 16 to generate the transmit clock, and is used for error
detection during receive operations.
Along with the UART Line Control, High Byte (UARTLCRH) register (see page 313), the UARTIBRD
and UARTFBRD registers form an internal 30-bit register. This internal register is only updated
when a write operation to UARTLCRH is performed, so any changes to the baud-rate divisor must
be followed by a write to the UARTLCRH register for the changes to take effect.
To update the baud-rate registers, there are four possible sequences:
■ UARTIBRD write, UARTFBRD write, and UARTLCRH write
■ UARTFBRD write, UARTIBRD write, and UARTLCRH write
■ UARTIBRD write and UARTLCRH write
■ UARTFBRD write and UARTLCRH write
298 March 17, 2008
Preliminary
Universal Asynchronous Receivers/Transmitters (UARTs)
13.2.3 Data Transmission
Data received or transmitted is stored in two 16-byte FIFOs, though the receive FIFO has an extra
four bits per character for status information. For transmission, data is written into the transmit FIFO.
If the UART is enabled, it causes a data frame to start transmitting with the parameters indicated
in the UARTLCRH register. Data continues to be transmitted until there is no data left in the transmit
FIFO. The BUSY bit in the UART Flag (UARTFR) register (see page 308) is asserted as soon as
data is written to the transmit FIFO (that is, if the FIFO is non-empty) and remains asserted while
data is being transmitted. The BUSY bit is negated only when the transmit FIFO is empty, and the
last character has been transmitted from the shift register, including the stop bits. The UART can
indicate that it is busy even though the UART may no longer be enabled.
When the receiver is idle (the UnRx is continuously 1) and the data input goes Low (a start bit has
been received), the receive counter begins running and data is sampled on the eighth cycle of
Baud16 (described in “Transmit/Receive Logic” on page 297).
The start bit is valid if UnRx is still low on the eighth cycle of Baud16, otherwise a false start bit is
detected and it is ignored. Start bit errors can be viewed in the UART Receive Status (UARTRSR)
register (see page 306). If the start bit was valid, successive data bits are sampled on every 16th
cycle of Baud16 (that is, one bit period later) according to the programmed length of the data
characters. The parity bit is then checked if parity mode was enabled. Data length and parity are
defined in the UARTLCRH register.
Lastly, a valid stop bit is confirmed if UnRx is High, otherwise a framing error has occurred. When
a full word is received, the data is stored in the receive FIFO, with any error bits associated with
that word.
13.2.4 Serial IR (SIR)
The UART peripheral includes an IrDA serial-IR (SIR) encoder/decoder block. The IrDA SIR block
provides functionality that converts between an asynchronous UART data stream, and half-duplex
serial SIR interface. No analog processing is performed on-chip. The role of the SIR block is to
provide a digital encoded output, and decoded input to the UART. The UART signal pins can be
connected to an infrared transceiver to implement an IrDA SIR physical layer link. The SIR block
has two modes of operation:
■ In normal IrDA mode, a zero logic level is transmitted as high pulse of 3/16th duration of the
selected baud rate bit period on the output pin, while logic one levels are transmitted as a static
LOW signal. These levels control the driver of an infrared transmitter, sending a pulse of light
for each zero. On the reception side, the incoming light pulses energize the photo transistor base
of the receiver, pulling its output LOW. This drives the UART input pin LOW.
■ In low-power IrDA mode, the width of the transmitted infrared pulse is set to three times the
period of the internally generated IrLPBaud16 signal (1.63 μs, assuming a nominal 1.8432 MHz
frequency) by changing the appropriate bit in the UARTCR register. See page 310 for more
information on IrDA low-power pulse-duration configuration.
Figure 13-3 on page 300 shows the UART transmit and receive signals, with and without IrDA
modulation.
March 17, 2008 299
Preliminary
LM3S8933 Microcontroller
Figure 13-3. IrDA Data Modulation
0 1 0 1 0 0 1 1 0 1
Data bits
0 1 0 1 0 0 1 1 0 1
Start Data bits
bit
Start Stop
Bit period Bit period
3
16
UnTx
UnTx with IrDA
UnRx with IrDA
UnRx
Stop
bit
In both normal and low-power IrDA modes:
■ During transmission, the UART data bit is used as the base for encoding
■ During reception, the decoded bits are transferred to the UART receive logic
The IrDA SIR physical layer specifies a half-duplex communication link, with a minimum 10 ms delay
between transmission and reception. This delay must be generated by software because it is not
automatically supported by the UART. The delay is required because the infrared receiver electronics
might become biased, or even saturated from the optical power coupled from the adjacent transmitter
LED. This delay is known as latency, or receiver setup time.
13.2.5 FIFO Operation
The UART has two 16-entry FIFOs; one for transmit and one for receive. Both FIFOs are accessed
via the UART Data (UARTDR) register (see page 304). Read operations of the UARTDR register
return a 12-bit value consisting of 8 data bits and 4 error flags while write operations place 8-bit data
in the transmit FIFO.
Out of reset, both FIFOs are disabled and act as 1-byte-deep holding registers. The FIFOs are
enabled by setting the FEN bit in UARTLCRH (page 313).
FIFO status can be monitored via the UART Flag (UARTFR) register (see page 308) and the UART
Receive Status (UARTRSR) register. Hardware monitors empty, full and overrun conditions. The
UARTFR register contains empty and full flags (TXFE, TXFF, RXFE, and RXFF bits) and the
UARTRSR register shows overrun status via the OE bit.
The trigger points at which the FIFOs generate interrupts is controlled via the UART Interrupt FIFO
Level Select (UARTIFLS) register (see page 317). Both FIFOs can be individually configured to
trigger interrupts at different levels. Available configurations include 1/8, ¼, ½, ¾, and 7/8. For
example, if the ¼ option is selected for the receive FIFO, the UART generates a receive interrupt
after 4 data bytes are received. Out of reset, both FIFOs are configured to trigger an interrupt at the
½ mark.
13.2.6 Interrupts
The UART can generate interrupts when the following conditions are observed:
■ Overrun Error
■ Break Error
300 March 17, 2008
Preliminary
Universal Asynchronous Receivers/Transmitters (UARTs)
■ Parity Error
■ Framing Error
■ Receive Timeout
■ Transmit (when condition defined in the TXIFLSEL bit in the UARTIFLS register is met)
■ Receive (when condition defined in the RXIFLSEL bit in the UARTIFLS register is met)
All of the interrupt events are ORed together before being sent to the interrupt controller, so the
UART can only generate a single interrupt request to the controller at any given time. Software can
service multiple interrupt events in a single interrupt service routine by reading the UART Masked
Interrupt Status (UARTMIS) register (see page 322).
The interrupt events that can trigger a controller-level interrupt are defined in the UART Interrupt
Mask (UARTIM ) register (see page 319) by setting the corresponding IM bit to 1. If interrupts are
not used, the raw interrupt status is always visible via the UART Raw Interrupt Status (UARTRIS)
register (see page 321).
Interrupts are always cleared (for both the UARTMIS and UARTRIS registers) by setting the
corresponding bit in the UART Interrupt Clear (UARTICR) register (see page 323).
The receive timeout interrupt is asserted when the receive FIFO is not empty, and no further data
is received over a 32-bit period. The receive timeout interrupt is cleared either when the FIFO
becomes empty through reading all the data (or by reading the holding register), or when a 1 is
written to the corresponding bit in the UARTICR register.
13.2.7 Loopback Operation
The UART can be placed into an internal loopback mode for diagnostic or debug work. This is
accomplished by setting the LBE bit in the UARTCTL register (see page 315). In loopback mode,
data transmitted on UnTx is received on the UnRx input.
13.2.8 IrDA SIR block
The IrDA SIR block contains an IrDA serial IR (SIR) protocol encoder/decoder. When enabled, the
SIR block uses the UnTx and UnRx pins for the SIR protocol, which should be connected to an IR
transceiver.
The SIR block can receive and transmit, but it is only half-duplex so it cannot do both at the same
time. Transmission must be stopped before data can be received. The IrDA SIR physical layer
specifies a minimum 10-ms delay between transmission and reception.
13.3 Initialization and Configuration
To use the UARTs, the peripheral clock must be enabled by setting the UART0 or UART1 bits in the
RCGC1 register.
This section discusses the steps that are required to use a UART module. For this example, the
UART clock is assumed to be 20 MHz and the desired UART configuration is:
■ 115200 baud rate
■ Data length of 8 bits
■ One stop bit
March 17, 2008 301
Preliminary
LM3S8933 Microcontroller
■ No parity
■ FIFOs disabled
■ No interrupts
The first thing to consider when programming the UART is the baud-rate divisor (BRD), since the
UARTIBRD and UARTFBRD registers must be written before the UARTLCRH register. Using the
equation described in “Baud-Rate Generation” on page 298, the BRD can be calculated:
BRD = 20,000,000 / (16 * 115,200) = 10.8507
which means that the DIVINT field of the UARTIBRD register (see page 311) should be set to 10.
The value to be loaded into the UARTFBRD register (see page 312) is calculated by the equation:
UARTFBRD[DIVFRAC] = integer(0.8507 * 64 + 0.5) = 54
With the BRD values in hand, the UART configuration is written to the module in the following order:
1. Disable the UART by clearing the UARTEN bit in the UARTCTL register.
2. Write the integer portion of the BRD to the UARTIBRD register.
3. Write the fractional portion of the BRD to the UARTFBRD register.
4. Write the desired serial parameters to the UARTLCRH register (in this case, a value of
0x0000.0060).
5. Enable the UART by setting the UARTEN bit in the UARTCTL register.
13.4 Register Map
Table 13-1 on page 302 lists the UART registers. The offset listed is a hexadecimal increment to the
register’s address, relative to that UART’s base address:
■ UART0: 0x4000.C000
■ UART1: 0x4000.D000
Note: The UART must be disabled (see the UARTEN bit in the UARTCTL register on page 315)
before any of the control registers are reprogrammed. When the UART is disabled during
a TX or RX operation, the current transaction is completed prior to the UART stopping.
Table 13-1. UART Register Map
See
Offset Name Type Reset Description page
0x000 UARTDR R/W 0x0000.0000 UART Data 304
0x004 UARTRSR/UARTECR R/W 0x0000.0000 UART Receive Status/Error Clear 306
0x018 UARTFR RO 0x0000.0090 UART Flag 308
0x020 UARTILPR R/W 0x0000.0000 UART IrDA Low-Power Register 310
0x024 UARTIBRD R/W 0x0000.0000 UART Integer Baud-Rate Divisor 311
302 March 17, 2008
Preliminary
Universal Asynchronous Receivers/Transmitters (UARTs)
See
Offset Name Type Reset Description page
0x028 UARTFBRD R/W 0x0000.0000 UART Fractional Baud-Rate Divisor 312
0x02C UARTLCRH R/W 0x0000.0000 UART Line Control 313
0x030 UARTCTL R/W 0x0000.0300 UART Control 315
0x034 UARTIFLS R/W 0x0000.0012 UART Interrupt FIFO Level Select 317
0x038 UARTIM R/W 0x0000.0000 UART Interrupt Mask 319
0x03C UARTRIS RO 0x0000.000F UART Raw Interrupt Status 321
0x040 UARTMIS RO 0x0000.0000 UART Masked Interrupt Status 322
0x044 UARTICR W1C 0x0000.0000 UART Interrupt Clear 323
0xFD0 UARTPeriphID4 RO 0x0000.0000 UART Peripheral Identification 4 325
0xFD4 UARTPeriphID5 RO 0x0000.0000 UART Peripheral Identification 5 326
0xFD8 UARTPeriphID6 RO 0x0000.0000 UART Peripheral Identification 6 327
0xFDC UARTPeriphID7 RO 0x0000.0000 UART Peripheral Identification 7 328
0xFE0 UARTPeriphID0 RO 0x0000.0011 UART Peripheral Identification 0 329
0xFE4 UARTPeriphID1 RO 0x0000.0000 UART Peripheral Identification 1 330
0xFE8 UARTPeriphID2 RO 0x0000.0018 UART Peripheral Identification 2 331
0xFEC UARTPeriphID3 RO 0x0000.0001 UART Peripheral Identification 3 332
0xFF0 UARTPCellID0 RO 0x0000.000D UART PrimeCell Identification 0 333
0xFF4 UARTPCellID1 RO 0x0000.00F0 UART PrimeCell Identification 1 334
0xFF8 UARTPCellID2 RO 0x0000.0005 UART PrimeCell Identification 2 335
0xFFC UARTPCellID3 RO 0x0000.00B1 UART PrimeCell Identification 3 336
13.5 Register Descriptions
The remainder of this section lists and describes the UART registers, in numerical order by address
offset.
March 17, 2008 303
Preliminary
LM3S8933 Microcontroller
Register 1: UART Data (UARTDR), offset 0x000
This register is the data register (the interface to the FIFOs).
When FIFOs are enabled, data written to this location is pushed onto the transmit FIFO. If FIFOs
are disabled, data is stored in the transmitter holding register (the bottom word of the transmit FIFO).
A write to this register initiates a transmission from the UART.
For received data, if the FIFO is enabled, the data byte and the 4-bit status (break, frame, parity,
and overrun) is pushed onto the 12-bit wide receive FIFO. If FIFOs are disabled, the data byte and
status are stored in the receiving holding register (the bottom word of the receive FIFO). The received
data can be retrieved by reading this register.
UART Data (UARTDR)
UART0 base: 0x4000.C000
UART1 base: 0x4000.D000
Offset 0x000
Type R/W, reset 0x0000.0000
31 30 29 28 27 26 25 24 23 22 21 20 19 18 17 16
reserved
Type RO RO RO RO RO RO RO RO RO RO RO RO RO RO RO RO
Reset 0 0 0 0 0 0 0 0 0 0 0 0 0 0 0 0
15 14 13 12 11 10 9 8 7 6 5 4 3 2 1 0
reserved OE BE PE FE DATA
Type RO RO RO RO RO RO RO RO R/W R/W R/W R/W R/W R/W R/W R/W
Reset 0 0 0 0 0 0 0 0 0 0 0 0 0 0 0 0
Bit/Field Name Type Reset Description
Software should not rely on the value of a reserved bit. To provide
compatibility with future products, the value of a reserved bit should be
preserved across a read-modify-write operation.
31:12 reserved RO 0
UART Overrun Error
The OE values are defined as follows:
Value Description
0 There has been no data loss due to a FIFO overrun.
New data was received when the FIFO was full, resulting in
data loss.
1
11 OE RO 0
UART Break Error
This bit is set to 1 when a break condition is detected, indicating that
the receive data input was held Low for longer than a full-word
transmission time (defined as start, data, parity, and stop bits).
In FIFO mode, this error is associated with the character at the top of
the FIFO. When a break occurs, only one 0 character is loaded into the
FIFO. The next character is only enabled after the received data input
goes to a 1 (marking state) and the next valid start bit is received.
10 BE RO 0
304 March 17, 2008
Preliminary
Universal Asynchronous Receivers/Transmitters (UARTs)
Bit/Field Name Type Reset Description
UART Parity Error
This bit is set to 1 when the parity of the received data character does
not match the parity defined by bits 2 and 7 of the UARTLCRH register.
In FIFO mode, this error is associated with the character at the top of
the FIFO.
9 PE RO 0
UART Framing Error
This bit is set to 1 when the received character does not have a valid
stop bit (a valid stop bit is 1).
8 FE RO 0
Data Transmitted or Received
When written, the data that is to be transmitted via the UART. When
read, the data that was received by the UART.
7:0 DATA R/W 0
March 17, 2008 305
Preliminary
LM3S8933 Microcontroller
Register 2: UART Receive Status/Error Clear (UARTRSR/UARTECR), offset
0x004
The UARTRSR/UARTECR register is the receive status register/error clear register.
In addition to the UARTDR register, receive status can also be read from the UARTRSR register.
If the status is read from this register, then the status information corresponds to the entry read from
UARTDR prior to reading UARTRSR. The status information for overrun is set immediately when
an overrun condition occurs.
The UARTRSR register cannot be written.
A write of any value to the UARTECR register clears the framing, parity, break, and overrun errors.
All the bits are cleared to 0 on reset.
Read-Only Receive Status (UARTRSR) Register
UART Receive Status/Error Clear (UARTRSR/UARTECR)
UART0 base: 0x4000.C000
UART1 base: 0x4000.D000
Offset 0x004
Type RO, reset 0x0000.0000
31 30 29 28 27 26 25 24 23 22 21 20 19 18 17 16
reserved
Type RO RO RO RO RO RO RO RO RO RO RO RO RO RO RO RO
Reset 0 0 0 0 0 0 0 0 0 0 0 0 0 0 0 0
15 14 13 12 11 10 9 8 7 6 5 4 3 2 1 0
reserved OE BE PE FE
Type RO RO RO RO RO RO RO RO RO RO RO RO RO RO RO RO
Reset 0 0 0 0 0 0 0 0 0 0 0 0 0 0 0 0
Bit/Field Name Type Reset Description
Software should not rely on the value of a reserved bit. To provide
compatibility with future products, the value of a reserved bit should be
preserved across a read-modify-write operation.
31:4 reserved RO 0
UART Overrun Error
When this bit is set to 1, data is received and the FIFO is already full.
This bit is cleared to 0 by a write to UARTECR.
The FIFO contents remain valid since no further data is written when
the FIFO is full, only the contents of the shift register are overwritten.
The CPU must now read the data in order to empty the FIFO.
3 OE RO 0
UART Break Error
This bit is set to 1 when a break condition is detected, indicating that
the received data input was held Low for longer than a full-word
transmission time (defined as start, data, parity, and stop bits).
This bit is cleared to 0 by a write to UARTECR.
In FIFO mode, this error is associated with the character at the top of
the FIFO. When a break occurs, only one 0 character is loaded into the
FIFO. The next character is only enabled after the receive data input
goes to a 1 (marking state) and the next valid start bit is received.
2 BE RO 0
306 March 17, 2008
Preliminary
Universal Asynchronous Receivers/Transmitters (UARTs)
Bit/Field Name Type Reset Description
UART Parity Error
This bit is set to 1 when the parity of the received data character does
not match the parity defined by bits 2 and 7 of the UARTLCRH register.
This bit is cleared to 0 by a write to UARTECR.
1 PE RO 0
UART Framing Error
This bit is set to 1 when the received character does not have a valid
stop bit (a valid stop bit is 1).
This bit is cleared to 0 by a write to UARTECR.
In FIFO mode, this error is associated with the character at the top of
the FIFO.
0 FE RO 0
Write-Only Error Clear (UARTECR) Register
UART Receive Status/Error Clear (UARTRSR/UARTECR)
UART0 base: 0x4000.C000
UART1 base: 0x4000.D000
Offset 0x004
Type WO, reset 0x0000.0000
31 30 29 28 27 26 25 24 23 22 21 20 19 18 17 16
reserved
Type WO WO WO WO WO WO WO WO WO WO WO WO WO WO WO WO
Reset 0 0 0 0 0 0 0 0 0 0 0 0 0 0 0 0
15 14 13 12 11 10 9 8 7 6 5 4 3 2 1 0
reserved DATA
Type WO WO WO WO WO WO WO WO WO WO WO WO WO WO WO WO
Reset 0 0 0 0 0 0 0 0 0 0 0 0 0 0 0 0
Bit/Field Name Type Reset Description
Software should not rely on the value of a reserved bit. To provide
compatibility with future products, the value of a reserved bit should be
preserved across a read-modify-write operation.
31:8 reserved WO 0
Error Clear
A write to this register of any data clears the framing, parity, break, and
overrun flags.
7:0 DATA WO 0
March 17, 2008 307
Preliminary
LM3S8933 Microcontroller
Register 3: UART Flag (UARTFR), offset 0x018
The UARTFR register is the flag register. After reset, the TXFF, RXFF, and BUSY bits are 0, and
TXFE and RXFE bits are 1.
UART Flag (UARTFR)
UART0 base: 0x4000.C000
UART1 base: 0x4000.D000
Offset 0x018
Type RO, reset 0x0000.0090
31 30 29 28 27 26 25 24 23 22 21 20 19 18 17 16
reserved
Type RO RO RO RO RO RO RO RO RO RO RO RO RO RO RO RO
Reset 0 0 0 0 0 0 0 0 0 0 0 0 0 0 0 0
15 14 13 12 11 10 9 8 7 6 5 4 3 2 1 0
reserved TXFE RXFF TXFF RXFE BUSY reserved
Type RO RO RO RO RO RO RO RO RO RO RO RO RO RO RO RO
Reset 0 0 0 0 0 0 0 0 1 0 0 1 0 0 0 0
Bit/Field Name Type Reset Description
Software should not rely on the value of a reserved bit. To provide
compatibility with future products, the value of a reserved bit should be
preserved across a read-modify-write operation.
31:8 reserved RO 0
UART Transmit FIFO Empty
The meaning of this bit depends on the state of the FEN bit in the
UARTLCRH register.
If the FIFO is disabled (FEN is 0), this bit is set when the transmit holding
register is empty.
If the FIFO is enabled (FEN is 1), this bit is set when the transmit FIFO
is empty.
7 TXFE RO 1
UART Receive FIFO Full
The meaning of this bit depends on the state of the FEN bit in the
UARTLCRH register.
If the FIFO is disabled, this bit is set when the receive holding register
is full.
If the FIFO is enabled, this bit is set when the receive FIFO is full.
6 RXFF RO 0
UART Transmit FIFO Full
The meaning of this bit depends on the state of the FEN bit in the
UARTLCRH register.
If the FIFO is disabled, this bit is set when the transmit holding register
is full.
If the FIFO is enabled, this bit is set when the transmit FIFO is full.
5 TXFF RO 0
308 March 17, 2008
Preliminary
Universal Asynchronous Receivers/Transmitters (UARTs)
Bit/Field Name Type Reset Description
UART Receive FIFO Empty
The meaning of this bit depends on the state of the FEN bit in the
UARTLCRH register.
If the FIFO is disabled, this bit is set when the receive holding register
is empty.
If the FIFO is enabled, this bit is set when the receive FIFO is empty.
4 RXFE RO 1
UART Busy
When this bit is 1, the UART is busy transmitting data. This bit remains
set until the complete byte, including all stop bits, has been sent from
the shift register.
This bit is set as soon as the transmit FIFO becomes non-empty
(regardless of whether UART is enabled).
3 BUSY RO 0
Software should not rely on the value of a reserved bit. To provide
compatibility with future products, the value of a reserved bit should be
preserved across a read-modify-write operation.
2:0 reserved RO 0
March 17, 2008 309
Preliminary
LM3S8933 Microcontroller
Register 4: UART IrDA Low-Power Register (UARTILPR), offset 0x020
The UARTILPR register is an 8-bit read/write register that stores the low-power counter divisor
value used to derive the low-power SIR pulse width clock by dividing down the system clock (SysClk).
All the bits are cleared to 0 when reset.
The internal IrLPBaud16 clock is generated by dividing down SysClk according to the low-power
divisor value written to UARTILPR. The duration of SIR pulses generated when low-power mode
is enabled is three times the period of the IrLPBaud16 clock. The low-power divisor value is
calculated as follows:
ILPDVSR = SysClk / FIrLPBaud16
where FIrLPBaud16 is nominally 1.8432 MHz.
You must choose the divisor so that 1.42 MHz < FIrLPBaud16 < 2.12 MHz, which results in a low-power
pulse duration of 1.41–2.11 μs (three times the period of IrLPBaud16). The minimum frequency
of IrLPBaud16 ensures that pulses less than one period of IrLPBaud16 are rejected, but that
pulses greater than 1.4 μs are accepted as valid pulses.
Note: Zero is an illegal value. Programming a zero value results in no IrLPBaud16 pulses being
generated.
UART IrDA Low-Power Register (UARTILPR)
UART0 base: 0x4000.C000
UART1 base: 0x4000.D000
Offset 0x020
Type R/W, reset 0x0000.0000
31 30 29 28 27 26 25 24 23 22 21 20 19 18 17 16
reserved
Type RO RO RO RO RO RO RO RO RO RO RO RO RO RO RO RO
Reset 0 0 0 0 0 0 0 0 0 0 0 0 0 0 0 0
15 14 13 12 11 10 9 8 7 6 5 4 3 2 1 0
reserved ILPDVSR
Type RO RO RO RO RO RO RO RO R/W R/W R/W R/W R/W R/W R/W R/W
Reset 0 0 0 0 0 0 0 0 0 0 0 0 0 0 0 0
Bit/Field Name Type Reset Description
Software should not rely on the value of a reserved bit. To provide
compatibility with future products, the value of a reserved bit should be
preserved across a read-modify-write operation.
31:8 reserved RO 0
IrDA Low-Power Divisor
This is an 8-bit low-power divisor value.
7:0 ILPDVSR R/W 0x00
310 March 17, 2008
Preliminary
Universal Asynchronous Receivers/Transmitters (UARTs)
Register 5: UART Integer Baud-Rate Divisor (UARTIBRD), offset 0x024
The UARTIBRD register is the integer part of the baud-rate divisor value. All the bits are cleared
on reset. The minimum possible divide ratio is 1 (when UARTIBRD=0), in which case the UARTFBRD
register is ignored. When changing the UARTIBRD register, the new value does not take effect until
transmission/reception of the current character is complete. Any changes to the baud-rate divisor
must be followed by a write to the UARTLCRH register. See “Baud-Rate Generation” on page 298
for configuration details.
UART Integer Baud-Rate Divisor (UARTIBRD)
UART0 base: 0x4000.C000
UART1 base: 0x4000.D000
Offset 0x024
Type R/W, reset 0x0000.0000
31 30 29 28 27 26 25 24 23 22 21 20 19 18 17 16
reserved
Type RO RO RO RO RO RO RO RO RO RO RO RO RO RO RO RO
Reset 0 0 0 0 0 0 0 0 0 0 0 0 0 0 0 0
15 14 13 12 11 10 9 8 7 6 5 4 3 2 1 0
DIVINT
Type R/W R/W R/W R/W R/W R/W R/W R/W R/W R/W R/W R/W R/W R/W R/W R/W
Reset 0 0 0 0 0 0 0 0 0 0 0 0 0 0 0 0
Bit/Field Name Type Reset Description
Software should not rely on the value of a reserved bit. To provide
compatibility with future products, the value of a reserved bit should be
preserved across a read-modify-write operation.
31:16 reserved RO 0
15:0 DIVINT R/W 0x0000 Integer Baud-Rate Divisor
March 17, 2008 311
Preliminary
LM3S8933 Microcontroller
Register 6: UART Fractional Baud-Rate Divisor (UARTFBRD), offset 0x028
The UARTFBRD register is the fractional part of the baud-rate divisor value. All the bits are cleared
on reset. When changing the UARTFBRD register, the new value does not take effect until
transmission/reception of the current character is complete. Any changes to the baud-rate divisor
must be followed by a write to the UARTLCRH register. See “Baud-Rate Generation” on page 298
for configuration details.
UART Fractional Baud-Rate Divisor (UARTFBRD)
UART0 base: 0x4000.C000
UART1 base: 0x4000.D000
Offset 0x028
Type R/W, reset 0x0000.0000
31 30 29 28 27 26 25 24 23 22 21 20 19 18 17 16
reserved
Type RO RO RO RO RO RO RO RO RO RO RO RO RO RO RO RO
Reset 0 0 0 0 0 0 0 0 0 0 0 0 0 0 0 0
15 14 13 12 11 10 9 8 7 6 5 4 3 2 1 0
reserved DIVFRAC
Type RO RO RO RO RO RO RO RO RO RO R/W R/W R/W R/W R/W R/W
Reset 0 0 0 0 0 0 0 0 0 0 0 0 0 0 0 0
Bit/Field Name Type Reset Description
Software should not rely on the value of a reserved bit. To provide
compatibility with future products, the value of a reserved bit should be
preserved across a read-modify-write operation.
31:6 reserved RO 0x00
5:0 DIVFRAC R/W 0x000 Fractional Baud-Rate Divisor
312 March 17, 2008
Preliminary
Universal Asynchronous Receivers/Transmitters (UARTs)
Register 7: UART Line Control (UARTLCRH), offset 0x02C
The UARTLCRH register is the line control register. Serial parameters such as data length, parity,
and stop bit selection are implemented in this register.
When updating the baud-rate divisor (UARTIBRD and/or UARTIFRD), the UARTLCRH register
must also be written. The write strobe for the baud-rate divisor registers is tied to the UARTLCRH
register.
UART Line Control (UARTLCRH)
UART0 base: 0x4000.C000
UART1 base: 0x4000.D000
Offset 0x02C
Type R/W, reset 0x0000.0000
31 30 29 28 27 26 25 24 23 22 21 20 19 18 17 16
reserved
Type RO RO RO RO RO RO RO RO RO RO RO RO RO RO RO RO
Reset 0 0 0 0 0 0 0 0 0 0 0 0 0 0 0 0
15 14 13 12 11 10 9 8 7 6 5 4 3 2 1 0
reserved SPS WLEN FEN STP2 EPS PEN BRK
Type RO RO RO RO RO RO RO RO R/W R/W R/W R/W R/W R/W R/W R/W
Reset 0 0 0 0 0 0 0 0 0 0 0 0 0 0 0 0
Bit/Field Name Type Reset Description
Software should not rely on the value of a reserved bit. To provide
compatibility with future products, the value of a reserved bit should be
preserved across a read-modify-write operation.
31:8 reserved RO 0
UART Stick Parity Select
When bits 1, 2, and 7 of UARTLCRH are set, the parity bit is transmitted
and checked as a 0. When bits 1 and 7 are set and 2 is cleared, the
parity bit is transmitted and checked as a 1.
When this bit is cleared, stick parity is disabled.
7 SPS R/W 0
UART Word Length
The bits indicate the number of data bits transmitted or received in a
frame as follows:
Value Description
0x3 8 bits
0x2 7 bits
0x1 6 bits
0x0 5 bits (default)
6:5 WLEN R/W 0
UART Enable FIFOs
If this bit is set to 1, transmit and receive FIFO buffers are enabled (FIFO
mode).
When cleared to 0, FIFOs are disabled (Character mode). The FIFOs
become 1-byte-deep holding registers.
4 FEN R/W 0
March 17, 2008 313
Preliminary
LM3S8933 Microcontroller
Bit/Field Name Type Reset Description
UART Two Stop Bits Select
If this bit is set to 1, two stop bits are transmitted at the end of a frame.
The receive logic does not check for two stop bits being received.
3 STP2 R/W 0
UART Even Parity Select
If this bit is set to 1, even parity generation and checking is performed
during transmission and reception, which checks for an even number
of 1s in data and parity bits.
When cleared to 0, then odd parity is performed, which checks for an
odd number of 1s.
This bit has no effect when parity is disabled by the PEN bit.
2 EPS R/W 0
UART Parity Enable
If this bit is set to 1, parity checking and generation is enabled; otherwise,
parity is disabled and no parity bit is added to the data frame.
1 PEN R/W 0
UART Send Break
If this bit is set to 1, a Low level is continually output on the UnTX output,
after completing transmission of the current character. For the proper
execution of the break command, the software must set this bit for at
least two frames (character periods). For normal use, this bit must be
cleared to 0.
0 BRK R/W 0
314 March 17, 2008
Preliminary
Universal Asynchronous Receivers/Transmitters (UARTs)
Register 8: UART Control (UARTCTL), offset 0x030
The UARTCTL register is the control register. All the bits are cleared on reset except for the
Transmit Enable (TXE) and Receive Enable (RXE) bits, which are set to 1.
To enable the UART module, the UARTEN bit must be set to 1. If software requires a configuration
change in the module, the UARTEN bit must be cleared before the configuration changes are written.
If the UART is disabled during a transmit or receive operation, the current transaction is completed
prior to the UART stopping.
Note: The UARTCTL register should not be changed while the UART is enabled or else the results
are unpredictable. The following sequence is recommended for making changes to the
UARTCTL register.
1. Disable the UART.
2. Wait for the end of transmission or reception of the current character.
3. Flush the transmit FIFO by disabling bit 4 (FEN) in the line control register (UARTLCRH).
4. Reprogram the control register.
5. Enable the UART.
UART Control (UARTCTL)
UART0 base: 0x4000.C000
UART1 base: 0x4000.D000
Offset 0x030
Type R/W, reset 0x0000.0300
31 30 29 28 27 26 25 24 23 22 21 20 19 18 17 16
reserved
Type RO RO RO RO RO RO RO RO RO RO RO RO RO RO RO RO
Reset 0 0 0 0 0 0 0 0 0 0 0 0 0 0 0 0
15 14 13 12 11 10 9 8 7 6 5 4 3 2 1 0
reserved RXE TXE LBE reserved SIRLP SIREN UARTEN
Type RO RO RO RO RO RO R/W R/W R/W RO RO RO RO R/W R/W R/W
Reset 0 0 0 0 0 0 1 1 0 0 0 0 0 0 0 0
Bit/Field Name Type Reset Description
Software should not rely on the value of a reserved bit. To provide
compatibility with future products, the value of a reserved bit should be
preserved across a read-modify-write operation.
31:10 reserved RO 0
UART Receive Enable
If this bit is set to 1, the receive section of the UART is enabled. When
the UART is disabled in the middle of a receive, it completes the current
character before stopping.
Note: To enable reception, the UARTEN bit must also be set.
9 RXE R/W 1
UART Transmit Enable
If this bit is set to 1, the transmit section of the UART is enabled. When
the UART is disabled in the middle of a transmission, it completes the
current character before stopping.
Note: To enable transmission, the UARTEN bit must also be set.
8 TXE R/W 1
March 17, 2008 315
Preliminary
LM3S8933 Microcontroller
Bit/Field Name Type Reset Description
UART Loop Back Enable
If this bit is set to 1, the UnTX path is fed through the UnRX path.
7 LBE R/W 0
Software should not rely on the value of a reserved bit. To provide
compatibility with future products, the value of a reserved bit should be
preserved across a read-modify-write operation.
6:3 reserved RO 0
UART SIR Low Power Mode
This bit selects the IrDA encoding mode. If this bit is cleared to 0,
low-level bits are transmitted as an active High pulse with a width of
3/16th of the bit period. If this bit is set to 1, low-level bits are transmitted
with a pulse width which is 3 times the period of the IrLPBaud16 input
signal, regardless of the selected bit rate. Setting this bit uses less power,
but might reduce transmission distances. See page 310 for more
information.
2 SIRLP R/W 0
UART SIR Enable
If this bit is set to 1, the IrDA SIR block is enabled, and the UART will
transmit and receive data using SIR protocol.
1 SIREN R/W 0
UART Enable
If this bit is set to 1, the UART is enabled. When the UART is disabled
in the middle of transmission or reception, it completes the current
character before stopping.
0 UARTEN R/W 0
316 March 17, 2008
Preliminary
Universal Asynchronous Receivers/Transmitters (UARTs)
Register 9: UART Interrupt FIFO Level Select (UARTIFLS), offset 0x034
The UARTIFLS register is the interrupt FIFO level select register. You can use this register to define
the FIFO level at which the TXRIS and RXRIS bits in the UARTRIS register are triggered.
The interrupts are generated based on a transition through a level rather than being based on the
level. That is, the interrupts are generated when the fill level progresses through the trigger level.
For example, if the receive trigger level is set to the half-way mark, the interrupt is triggered as the
module is receiving the 9th character.
Out of reset, the TXIFLSEL and RXIFLSEL bits are configured so that the FIFOs trigger an interrupt
at the half-way mark.
UART Interrupt FIFO Level Select (UARTIFLS)
UART0 base: 0x4000.C000
UART1 base: 0x4000.D000
Offset 0x034
Type R/W, reset 0x0000.0012
31 30 29 28 27 26 25 24 23 22 21 20 19 18 17 16
reserved
Type RO RO RO RO RO RO RO RO RO RO RO RO RO RO RO RO
Reset 0 0 0 0 0 0 0 0 0 0 0 0 0 0 0 0
15 14 13 12 11 10 9 8 7 6 5 4 3 2 1 0
reserved RXIFLSEL TXIFLSEL
Type RO RO RO RO RO RO RO RO RO RO R/W R/W R/W R/W R/W R/W
Reset 0 0 0 0 0 0 0 0 0 0 0 1 0 0 1 0
Bit/Field Name Type Reset Description
Software should not rely on the value of a reserved bit. To provide
compatibility with future products, the value of a reserved bit should be
preserved across a read-modify-write operation.
31:6 reserved RO 0x00
UART Receive Interrupt FIFO Level Select
The trigger points for the receive interrupt are as follows:
Value Description
0x0 RX FIFO ≥ 1/8 full
0x1 RX FIFO ≥ ¼ full
0x2 RX FIFO ≥ ½ full (default)
0x3 RX FIFO ≥ ¾ full
0x4 RX FIFO ≥ 7/8 full
0x5-0x7 Reserved
5:3 RXIFLSEL R/W 0x2
March 17, 2008 317
Preliminary
LM3S8933 Microcontroller
Bit/Field Name Type Reset Description
UART Transmit Interrupt FIFO Level Select
The trigger points for the transmit interrupt are as follows:
Value Description
0x0 TX FIFO ≤ 1/8 full
0x1 TX FIFO ≤ ¼ full
0x2 TX FIFO ≤ ½ full (default)
0x3 TX FIFO ≤ ¾ full
0x4 TX FIFO ≤ 7/8 full
0x5-0x7 Reserved
2:0 TXIFLSEL R/W 0x2
318 March 17, 2008
Preliminary
Universal Asynchronous Receivers/Transmitters (UARTs)
Register 10: UART Interrupt Mask (UARTIM), offset 0x038
The UARTIM register is the interrupt mask set/clear register.
On a read, this register gives the current value of the mask on the relevant interrupt. Writing a 1 to
a bit allows the corresponding raw interrupt signal to be routed to the interrupt controller. Writing a
0 prevents the raw interrupt signal from being sent to the interrupt controller.
UART Interrupt Mask (UARTIM)
UART0 base: 0x4000.C000
UART1 base: 0x4000.D000
Offset 0x038
Type R/W, reset 0x0000.0000
31 30 29 28 27 26 25 24 23 22 21 20 19 18 17 16
reserved
Type RO RO RO RO RO RO RO RO RO RO RO RO RO RO RO RO
Reset 0 0 0 0 0 0 0 0 0 0 0 0 0 0 0 0
15 14 13 12 11 10 9 8 7 6 5 4 3 2 1 0
reserved OEIM BEIM PEIM FEIM RTIM TXIM RXIM reserved
Type RO RO RO RO RO R/W R/W R/W R/W R/W R/W R/W RO RO RO RO
Reset 0 0 0 0 0 0 0 0 0 0 0 0 0 0 0 0
Bit/Field Name Type Reset Description
Software should not rely on the value of a reserved bit. To provide
compatibility with future products, the value of a reserved bit should be
preserved across a read-modify-write operation.
31:11 reserved RO 0x00
UART Overrun Error Interrupt Mask
On a read, the current mask for the OEIM interrupt is returned.
Setting this bit to 1 promotes the OEIM interrupt to the interrupt controller.
10 OEIM R/W 0
UART Break Error Interrupt Mask
On a read, the current mask for the BEIM interrupt is returned.
Setting this bit to 1 promotes the BEIM interrupt to the interrupt controller.
9 BEIM R/W 0
UART Parity Error Interrupt Mask
On a read, the current mask for the PEIM interrupt is returned.
Setting this bit to 1 promotes the PEIM interrupt to the interrupt controller.
8 PEIM R/W 0
UART Framing Error Interrupt Mask
On a read, the current mask for the FEIM interrupt is returned.
Setting this bit to 1 promotes the FEIM interrupt to the interrupt controller.
7 FEIM R/W 0
UART Receive Time-Out Interrupt Mask
On a read, the current mask for the RTIM interrupt is returned.
Setting this bit to 1 promotes the RTIM interrupt to the interrupt controller.
6 RTIM R/W 0
UART Transmit Interrupt Mask
On a read, the current mask for the TXIM interrupt is returned.
Setting this bit to 1 promotes the TXIM interrupt to the interrupt controller.
5 TXIM R/W 0
March 17, 2008 319
Preliminary
LM3S8933 Microcontroller
Bit/Field Name Type Reset Description
UART Receive Interrupt Mask
On a read, the current mask for the RXIM interrupt is returned.
Setting this bit to 1 promotes the RXIM interrupt to the interrupt controller.
4 RXIM R/W 0
Software should not rely on the value of a reserved bit. To provide
compatibility with future products, the value of a reserved bit should be
preserved across a read-modify-write operation.
3:0 reserved RO 0x00
320 March 17, 2008
Preliminary
Universal Asynchronous Receivers/Transmitters (UARTs)
Register 11: UART Raw Interrupt Status (UARTRIS), offset 0x03C
The UARTRIS register is the raw interrupt status register. On a read, this register gives the current
raw status value of the corresponding interrupt. A write has no effect.
UART Raw Interrupt Status (UARTRIS)
UART0 base: 0x4000.C000
UART1 base: 0x4000.D000
Offset 0x03C
Type RO, reset 0x0000.000F
31 30 29 28 27 26 25 24 23 22 21 20 19 18 17 16
reserved
Type RO RO RO RO RO RO RO RO RO RO RO RO RO RO RO RO
Reset 0 0 0 0 0 0 0 0 0 0 0 0 0 0 0 0
15 14 13 12 11 10 9 8 7 6 5 4 3 2 1 0
reserved OERIS BERIS PERIS FERIS RTRIS TXRIS RXRIS reserved
Type RO RO RO RO RO RO RO RO RO RO RO RO RO RO RO RO
Reset 0 0 0 0 0 0 0 0 0 0 0 0 1 1 1 1
Bit/Field Name Type Reset Description
Software should not rely on the value of a reserved bit. To provide
compatibility with future products, the value of a reserved bit should be
preserved across a read-modify-write operation.
31:11 reserved RO 0x00
UART Overrun Error Raw Interrupt Status
Gives the raw interrupt state (prior to masking) of this interrupt.
10 OERIS RO 0
UART Break Error Raw Interrupt Status
Gives the raw interrupt state (prior to masking) of this interrupt.
9 BERIS RO 0
UART Parity Error Raw Interrupt Status
Gives the raw interrupt state (prior to masking) of this interrupt.
8 PERIS RO 0
UART Framing Error Raw Interrupt Status
Gives the raw interrupt state (prior to masking) of this interrupt.
7 FERIS RO 0
UART Receive Time-Out Raw Interrupt Status
Gives the raw interrupt state (prior to masking) of this interrupt.
6 RTRIS RO 0
UART Transmit Raw Interrupt Status
Gives the raw interrupt state (prior to masking) of this interrupt.
5 TXRIS RO 0
UART Receive Raw Interrupt Status
Gives the raw interrupt state (prior to masking) of this interrupt.
4 RXRIS RO 0
Software should not rely on the value of a reserved bit. To provide
compatibility with future products, the value of a reserved bit should be
preserved across a read-modify-write operation.
3:0 reserved RO 0xF
March 17, 2008 321
Preliminary
LM3S8933 Microcontroller
Register 12: UART Masked Interrupt Status (UARTMIS), offset 0x040
The UARTMIS register is the masked interrupt status register. On a read, this register gives the
current masked status value of the corresponding interrupt. A write has no effect.
UART Masked Interrupt Status (UARTMIS)
UART0 base: 0x4000.C000
UART1 base: 0x4000.D000
Offset 0x040
Type RO, reset 0x0000.0000
31 30 29 28 27 26 25 24 23 22 21 20 19 18 17 16
reserved
Type RO RO RO RO RO RO RO RO RO RO RO RO RO RO RO RO
Reset 0 0 0 0 0 0 0 0 0 0 0 0 0 0 0 0
15 14 13 12 11 10 9 8 7 6 5 4 3 2 1 0
reserved OEMIS BEMIS PEMIS FEMIS RTMIS TXMIS RXMIS reserved
Type RO RO RO RO RO RO RO RO RO RO RO RO RO RO RO RO
Reset 0 0 0 0 0 0 0 0 0 0 0 0 0 0 0 0
Bit/Field Name Type Reset Description
Software should not rely on the value of a reserved bit. To provide
compatibility with future products, the value of a reserved bit should be
preserved across a read-modify-write operation.
31:11 reserved RO 0x00
UART Overrun Error Masked Interrupt Status
Gives the masked interrupt state of this interrupt.
10 OEMIS RO 0
UART Break Error Masked Interrupt Status
Gives the masked interrupt state of this interrupt.
9 BEMIS RO 0
UART Parity Error Masked Interrupt Status
Gives the masked interrupt state of this interrupt.
8 PEMIS RO 0
UART Framing Error Masked Interrupt Status
Gives the masked interrupt state of this interrupt.
7 FEMIS RO 0
UART Receive Time-Out Masked Interrupt Status
Gives the masked interrupt state of this interrupt.
6 RTMIS RO 0
UART Transmit Masked Interrupt Status
Gives the masked interrupt state of this interrupt.
5 TXMIS RO 0
UART Receive Masked Interrupt Status
Gives the masked interrupt state of this interrupt.
4 RXMIS RO 0
Software should not rely on the value of a reserved bit. To provide
compatibility with future products, the value of a reserved bit should be
preserved across a read-modify-write operation.
3:0 reserved RO 0
322 March 17, 2008
Preliminary
Universal Asynchronous Receivers/Transmitters (UARTs)
Register 13: UART Interrupt Clear (UARTICR), offset 0x044
The UARTICR register is the interrupt clear register. On a write of 1, the corresponding interrupt
(both raw interrupt and masked interrupt, if enabled) is cleared. A write of 0 has no effect.
UART Interrupt Clear (UARTICR)
UART0 base: 0x4000.C000
UART1 base: 0x4000.D000
Offset 0x044
Type W1C, reset 0x0000.0000
31 30 29 28 27 26 25 24 23 22 21 20 19 18 17 16
reserved
Type RO RO RO RO RO RO RO RO RO RO RO RO RO RO RO RO
Reset 0 0 0 0 0 0 0 0 0 0 0 0 0 0 0 0
15 14 13 12 11 10 9 8 7 6 5 4 3 2 1 0
reserved OEIC BEIC PEIC FEIC RTIC TXIC RXIC reserved
Type RO RO RO RO RO W1C W1C W1C W1C W1C W1C W1C RO RO RO RO
Reset 0 0 0 0 0 0 0 0 0 0 0 0 0 0 0 0
Bit/Field Name Type Reset Description
Software should not rely on the value of a reserved bit. To provide
compatibility with future products, the value of a reserved bit should be
preserved across a read-modify-write operation.
31:11 reserved RO 0x00
Overrun Error Interrupt Clear
The OEIC values are defined as follows:
Value Description
0 No effect on the interrupt.
1 Clears interrupt.
10 OEIC W1C 0
Break Error Interrupt Clear
The BEIC values are defined as follows:
Value Description
0 No effect on the interrupt.
1 Clears interrupt.
9 BEIC W1C 0
Parity Error Interrupt Clear
The PEIC values are defined as follows:
Value Description
0 No effect on the interrupt.
1 Clears interrupt.
8 PEIC W1C 0
March 17, 2008 323
Preliminary
LM3S8933 Microcontroller
Bit/Field Name Type Reset Description
Framing Error Interrupt Clear
The FEIC values are defined as follows:
Value Description
0 No effect on the interrupt.
1 Clears interrupt.
7 FEIC W1C 0
Receive Time-Out Interrupt Clear
The RTIC values are defined as follows:
Value Description
0 No effect on the interrupt.
1 Clears interrupt.
6 RTIC W1C 0
Transmit Interrupt Clear
The TXIC values are defined as follows:
Value Description
0 No effect on the interrupt.
1 Clears interrupt.
5 TXIC W1C 0
Receive Interrupt Clear
The RXIC values are defined as follows:
Value Description
0 No effect on the interrupt.
1 Clears interrupt.
4 RXIC W1C 0
Software should not rely on the value of a reserved bit. To provide
compatibility with future products, the value of a reserved bit should be
preserved across a read-modify-write operation.
3:0 reserved RO 0x00
324 March 17, 2008
Preliminary
Universal Asynchronous Receivers/Transmitters (UARTs)
Register 14: UART Peripheral Identification 4 (UARTPeriphID4), offset 0xFD0
The UARTPeriphIDn registers are hard-coded and the fields within the registers determine the
reset values.
UART Peripheral Identification 4 (UARTPeriphID4)
UART0 base: 0x4000.C000
UART1 base: 0x4000.D000
Offset 0xFD0
Type RO, reset 0x0000.0000
31 30 29 28 27 26 25 24 23 22 21 20 19 18 17 16
reserved
Type RO RO RO RO RO RO RO RO RO RO RO RO RO RO RO RO
Reset 0 0 0 0 0 0 0 0 0 0 0 0 0 0 0 0
15 14 13 12 11 10 9 8 7 6 5 4 3 2 1 0
reserved PID4
Type RO RO RO RO RO RO RO RO RO RO RO RO RO RO RO RO
Reset 0 0 0 0 0 0 0 0 0 0 0 0 0 0 0 0
Bit/Field Name Type Reset Description
Software should not rely on the value of a reserved bit. To provide
compatibility with future products, the value of a reserved bit should be
preserved across a read-modify-write operation.
31:8 reserved RO 0x00
UART Peripheral ID Register[7:0]
Can be used by software to identify the presence of this peripheral.
7:0 PID4 RO 0x0000
March 17, 2008 325
Preliminary
LM3S8933 Microcontroller
Register 15: UART Peripheral Identification 5 (UARTPeriphID5), offset 0xFD4
The UARTPeriphIDn registers are hard-coded and the fields within the registers determine the
reset values.
UART Peripheral Identification 5 (UARTPeriphID5)
UART0 base: 0x4000.C000
UART1 base: 0x4000.D000
Offset 0xFD4
Type RO, reset 0x0000.0000
31 30 29 28 27 26 25 24 23 22 21 20 19 18 17 16
reserved
Type RO RO RO RO RO RO RO RO RO RO RO RO RO RO RO RO
Reset 0 0 0 0 0 0 0 0 0 0 0 0 0 0 0 0
15 14 13 12 11 10 9 8 7 6 5 4 3 2 1 0
reserved PID5
Type RO RO RO RO RO RO RO RO RO RO RO RO RO RO RO RO
Reset 0 0 0 0 0 0 0 0 0 0 0 0 0 0 0 0
Bit/Field Name Type Reset Description
Software should not rely on the value of a reserved bit. To provide
compatibility with future products, the value of a reserved bit should be
preserved across a read-modify-write operation.
31:8 reserved RO 0x00
UART Peripheral ID Register[15:8]
Can be used by software to identify the presence of this peripheral.
7:0 PID5 RO 0x0000
326 March 17, 2008
Preliminary
Universal Asynchronous Receivers/Transmitters (UARTs)
Register 16: UART Peripheral Identification 6 (UARTPeriphID6), offset 0xFD8
The UARTPeriphIDn registers are hard-coded and the fields within the registers determine the
reset values.
UART Peripheral Identification 6 (UARTPeriphID6)
UART0 base: 0x4000.C000
UART1 base: 0x4000.D000
Offset 0xFD8
Type RO, reset 0x0000.0000
31 30 29 28 27 26 25 24 23 22 21 20 19 18 17 16
reserved
Type RO RO RO RO RO RO RO RO RO RO RO RO RO RO RO RO
Reset 0 0 0 0 0 0 0 0 0 0 0 0 0 0 0 0
15 14 13 12 11 10 9 8 7 6 5 4 3 2 1 0
reserved PID6
Type RO RO RO RO RO RO RO RO RO RO RO RO RO RO RO RO
Reset 0 0 0 0 0 0 0 0 0 0 0 0 0 0 0 0
Bit/Field Name Type Reset Description
Software should not rely on the value of a reserved bit. To provide
compatibility with future products, the value of a reserved bit should be
preserved across a read-modify-write operation.
31:8 reserved RO 0x00
UART Peripheral ID Register[23:16]
Can be used by software to identify the presence of this peripheral.
7:0 PID6 RO 0x0000
March 17, 2008 327
Preliminary
LM3S8933 Microcontroller
Register 17: UART Peripheral Identification 7 (UARTPeriphID7), offset 0xFDC
The UARTPeriphIDn registers are hard-coded and the fields within the registers determine the
reset values.
UART Peripheral Identification 7 (UARTPeriphID7)
UART0 base: 0x4000.C000
UART1 base: 0x4000.D000
Offset 0xFDC
Type RO, reset 0x0000.0000
31 30 29 28 27 26 25 24 23 22 21 20 19 18 17 16
reserved
Type RO RO RO RO RO RO RO RO RO RO RO RO RO RO RO RO
Reset 0 0 0 0 0 0 0 0 0 0 0 0 0 0 0 0
15 14 13 12 11 10 9 8 7 6 5 4 3 2 1 0
reserved PID7
Type RO RO RO RO RO RO RO RO RO RO RO RO RO RO RO RO
Reset 0 0 0 0 0 0 0 0 0 0 0 0 0 0 0 0
Bit/Field Name Type Reset Description
Software should not rely on the value of a reserved bit. To provide
compatibility with future products, the value of a reserved bit should be
preserved across a read-modify-write operation.
31:8 reserved RO 0
UART Peripheral ID Register[31:24]
Can be used by software to identify the presence of this peripheral.
7:0 PID7 RO 0x0000
328 March 17, 2008
Preliminary
Universal Asynchronous Receivers/Transmitters (UARTs)
Register 18: UART Peripheral Identification 0 (UARTPeriphID0), offset 0xFE0
The UARTPeriphIDn registers are hard-coded and the fields within the registers determine the
reset values.
UART Peripheral Identification 0 (UARTPeriphID0)
UART0 base: 0x4000.C000
UART1 base: 0x4000.D000
Offset 0xFE0
Type RO, reset 0x0000.0011
31 30 29 28 27 26 25 24 23 22 21 20 19 18 17 16
reserved
Type RO RO RO RO RO RO RO RO RO RO RO RO RO RO RO RO
Reset 0 0 0 0 0 0 0 0 0 0 0 0 0 0 0 0
15 14 13 12 11 10 9 8 7 6 5 4 3 2 1 0
reserved PID0
Type RO RO RO RO RO RO RO RO RO RO RO RO RO RO RO RO
Reset 0 0 0 0 0 0 0 0 0 0 0 1 0 0 0 1
Bit/Field Name Type Reset Description
Software should not rely on the value of a reserved bit. To provide
compatibility with future products, the value of a reserved bit should be
preserved across a read-modify-write operation.
31:8 reserved RO 0x00
UART Peripheral ID Register[7:0]
Can be used by software to identify the presence of this peripheral.
7:0 PID0 RO 0x11
March 17, 2008 329
Preliminary
LM3S8933 Microcontroller
Register 19: UART Peripheral Identification 1 (UARTPeriphID1), offset 0xFE4
The UARTPeriphIDn registers are hard-coded and the fields within the registers determine the
reset values.
UART Peripheral Identification 1 (UARTPeriphID1)
UART0 base: 0x4000.C000
UART1 base: 0x4000.D000
Offset 0xFE4
Type RO, reset 0x0000.0000
31 30 29 28 27 26 25 24 23 22 21 20 19 18 17 16
reserved
Type RO RO RO RO RO RO RO RO RO RO RO RO RO RO RO RO
Reset 0 0 0 0 0 0 0 0 0 0 0 0 0 0 0 0
15 14 13 12 11 10 9 8 7 6 5 4 3 2 1 0
reserved PID1
Type RO RO RO RO RO RO RO RO RO RO RO RO RO RO RO RO
Reset 0 0 0 0 0 0 0 0 0 0 0 0 0 0 0 0
Bit/Field Name Type Reset Description
Software should not rely on the value of a reserved bit. To provide
compatibility with future products, the value of a reserved bit should be
preserved across a read-modify-write operation.
31:8 reserved RO 0x00
UART Peripheral ID Register[15:8]
Can be used by software to identify the presence of this peripheral.
7:0 PID1 RO 0x00
330 March 17, 2008
Preliminary
Universal Asynchronous Receivers/Transmitters (UARTs)
Register 20: UART Peripheral Identification 2 (UARTPeriphID2), offset 0xFE8
The UARTPeriphIDn registers are hard-coded and the fields within the registers determine the
reset values.
UART Peripheral Identification 2 (UARTPeriphID2)
UART0 base: 0x4000.C000
UART1 base: 0x4000.D000
Offset 0xFE8
Type RO, reset 0x0000.0018
31 30 29 28 27 26 25 24 23 22 21 20 19 18 17 16
reserved
Type RO RO RO RO RO RO RO RO RO RO RO RO RO RO RO RO
Reset 0 0 0 0 0 0 0 0 0 0 0 0 0 0 0 0
15 14 13 12 11 10 9 8 7 6 5 4 3 2 1 0
reserved PID2
Type RO RO RO RO RO RO RO RO RO RO RO RO RO RO RO RO
Reset 0 0 0 0 0 0 0 0 0 0 0 1 1 0 0 0
Bit/Field Name Type Reset Description
Software should not rely on the value of a reserved bit. To provide
compatibility with future products, the value of a reserved bit should be
preserved across a read-modify-write operation.
31:8 reserved RO 0x00
UART Peripheral ID Register[23:16]
Can be used by software to identify the presence of this peripheral.
7:0 PID2 RO 0x18
March 17, 2008 331
Preliminary
LM3S8933 Microcontroller
Register 21: UART Peripheral Identification 3 (UARTPeriphID3), offset 0xFEC
The UARTPeriphIDn registers are hard-coded and the fields within the registers determine the
reset values.
UART Peripheral Identification 3 (UARTPeriphID3)
UART0 base: 0x4000.C000
UART1 base: 0x4000.D000
Offset 0xFEC
Type RO, reset 0x0000.0001
31 30 29 28 27 26 25 24 23 22 21 20 19 18 17 16
reserved
Type RO RO RO RO RO RO RO RO RO RO RO RO RO RO RO RO
Reset 0 0 0 0 0 0 0 0 0 0 0 0 0 0 0 0
15 14 13 12 11 10 9 8 7 6 5 4 3 2 1 0
reserved PID3
Type RO RO RO RO RO RO RO RO RO RO RO RO RO RO RO RO
Reset 0 0 0 0 0 0 0 0 0 0 0 0 0 0 0 1
Bit/Field Name Type Reset Description
Software should not rely on the value of a reserved bit. To provide
compatibility with future products, the value of a reserved bit should be
preserved across a read-modify-write operation.
31:8 reserved RO 0x00
UART Peripheral ID Register[31:24]
Can be used by software to identify the presence of this peripheral.
7:0 PID3 RO 0x01
332 March 17, 2008
Preliminary
Universal Asynchronous Receivers/Transmitters (UARTs)
Register 22: UART PrimeCell Identification 0 (UARTPCellID0), offset 0xFF0
The UARTPCellIDn registers are hard-coded and the fields within the registers determine the reset
values.
UART PrimeCell Identification 0 (UARTPCellID0)
UART0 base: 0x4000.C000
UART1 base: 0x4000.D000
Offset 0xFF0
Type RO, reset 0x0000.000D
31 30 29 28 27 26 25 24 23 22 21 20 19 18 17 16
reserved
Type RO RO RO RO RO RO RO RO RO RO RO RO RO RO RO RO
Reset 0 0 0 0 0 0 0 0 0 0 0 0 0 0 0 0
15 14 13 12 11 10 9 8 7 6 5 4 3 2 1 0
reserved CID0
Type RO RO RO RO RO RO RO RO RO RO RO RO RO RO RO RO
Reset 0 0 0 0 0 0 0 0 0 0 0 0 1 1 0 1
Bit/Field Name Type Reset Description
Software should not rely on the value of a reserved bit. To provide
compatibility with future products, the value of a reserved bit should be
preserved across a read-modify-write operation.
31:8 reserved RO 0x00
UART PrimeCell ID Register[7:0]
Provides software a standard cross-peripheral identification system.
7:0 CID0 RO 0x0D
March 17, 2008 333
Preliminary
LM3S8933 Microcontroller
Register 23: UART PrimeCell Identification 1 (UARTPCellID1), offset 0xFF4
The UARTPCellIDn registers are hard-coded and the fields within the registers determine the reset
values.
UART PrimeCell Identification 1 (UARTPCellID1)
UART0 base: 0x4000.C000
UART1 base: 0x4000.D000
Offset 0xFF4
Type RO, reset 0x0000.00F0
31 30 29 28 27 26 25 24 23 22 21 20 19 18 17 16
reserved
Type RO RO RO RO RO RO RO RO RO RO RO RO RO RO RO RO
Reset 0 0 0 0 0 0 0 0 0 0 0 0 0 0 0 0
15 14 13 12 11 10 9 8 7 6 5 4 3 2 1 0
reserved CID1
Type RO RO RO RO RO RO RO RO RO RO RO RO RO RO RO RO
Reset 0 0 0 0 0 0 0 0 1 1 1 1 0 0 0 0
Bit/Field Name Type Reset Description
Software should not rely on the value of a reserved bit. To provide
compatibility with future products, the value of a reserved bit should be
preserved across a read-modify-write operation.
31:8 reserved RO 0x00
UART PrimeCell ID Register[15:8]
Provides software a standard cross-peripheral identification system.
7:0 CID1 RO 0xF0
334 March 17, 2008
Preliminary
Universal Asynchronous Receivers/Transmitters (UARTs)
Register 24: UART PrimeCell Identification 2 (UARTPCellID2), offset 0xFF8
The UARTPCellIDn registers are hard-coded and the fields within the registers determine the reset
values.
UART PrimeCell Identification 2 (UARTPCellID2)
UART0 base: 0x4000.C000
UART1 base: 0x4000.D000
Offset 0xFF8
Type RO, reset 0x0000.0005
31 30 29 28 27 26 25 24 23 22 21 20 19 18 17 16
reserved
Type RO RO RO RO RO RO RO RO RO RO RO RO RO RO RO RO
Reset 0 0 0 0 0 0 0 0 0 0 0 0 0 0 0 0
15 14 13 12 11 10 9 8 7 6 5 4 3 2 1 0
reserved CID2
Type RO RO RO RO RO RO RO RO RO RO RO RO RO RO RO RO
Reset 0 0 0 0 0 0 0 0 0 0 0 0 0 1 0 1
Bit/Field Name Type Reset Description
Software should not rely on the value of a reserved bit. To provide
compatibility with future products, the value of a reserved bit should be
preserved across a read-modify-write operation.
31:8 reserved RO 0x00
UART PrimeCell ID Register[23:16]
Provides software a standard cross-peripheral identification system.
7:0 CID2 RO 0x05
March 17, 2008 335
Preliminary
LM3S8933 Microcontroller
Register 25: UART PrimeCell Identification 3 (UARTPCellID3), offset 0xFFC
The UARTPCellIDn registers are hard-coded and the fields within the registers determine the reset
values.
UART PrimeCell Identification 3 (UARTPCellID3)
UART0 base: 0x4000.C000
UART1 base: 0x4000.D000
Offset 0xFFC
Type RO, reset 0x0000.00B1
31 30 29 28 27 26 25 24 23 22 21 20 19 18 17 16
reserved
Type RO RO RO RO RO RO RO RO RO RO RO RO RO RO RO RO
Reset 0 0 0 0 0 0 0 0 0 0 0 0 0 0 0 0
15 14 13 12 11 10 9 8 7 6 5 4 3 2 1 0
reserved CID3
Type RO RO RO RO RO RO RO RO RO RO RO RO RO RO RO RO
Reset 0 0 0 0 0 0 0 0 1 0 1 1 0 0 0 1
Bit/Field Name Type Reset Description
Software should not rely on the value of a reserved bit. To provide
compatibility with future products, the value of a reserved bit should be
preserved across a read-modify-write operation.
31:8 reserved RO 0x00
UART PrimeCell ID Register[31:24]
Provides software a standard cross-peripheral identification system.
7:0 CID3 RO 0xB1
336 March 17, 2008
Preliminary
Universal Asynchronous Receivers/Transmitters (UARTs)
14 Synchronous Serial Interface (SSI)
The Stellaris® Synchronous Serial Interface (SSI) is a master or slave interface for synchronous
serial communication with peripheral devices that have either Freescale SPI, MICROWIRE, or Texas
Instruments synchronous serial interfaces.
The Stellaris® SSI module has the following features:
■ Master or slave operation
■ Programmable clock bit rate and prescale
■ Separate transmit and receive FIFOs, 16 bits wide, 8 locations deep
■ Programmable interface operation for Freescale SPI, MICROWIRE, or Texas Instruments
synchronous serial interfaces
■ Programmable data frame size from 4 to 16 bits
■ Internal loopback test mode for diagnostic/debug testing
14.1 Block Diagram
Figure 14-1. SSI Module Block Diagram
Transmit/
Receive
Logic
Clock
Prescaler
SSICPSR
Control / Status
SSICR0
SSICR1
SSISR
Interrupt Control
SSIIM
SSIMIS
SSIRIS
SSIICR
SSIDR
TxFIFO
8 x 16
...
RxFIFO
8 x 16
...
System Clock
SSITx
SSIRx
SSIClk
SSIFss
Interrupt
Identification Registers
SSIPCellID0 SSIPeriphID0 SSIPeriphID4
SSIPCellID1 SSIPeriphID1 SSIPeriphID5
SSIPCellID2 SSIPeriphID2 SSIPeriphID6
SSIPCellID3 SSIPeriphID3 SSIPeriphID7
14.2 Functional Description
The SSI performs serial-to-parallel conversion on data received from a peripheral device. The CPU
accesses data, control, and status information. The transmit and receive paths are buffered with
March 17, 2008 337
Preliminary
LM3S8933 Microcontroller
internal FIFO memories allowing up to eight 16-bit values to be stored independently in both transmit
and receive modes.
14.2.1 Bit Rate Generation
The SSI includes a programmable bit rate clock divider and prescaler to generate the serial output
clock. Bit rates are supported to MHz and higher, although maximum bit rate is determined by
peripheral devices.
The serial bit rate is derived by dividing down the input clock (FSysClk). The clock is first divided
by an even prescale value CPSDVSR from 2 to 254, which is programmed in the SSI Clock Prescale
(SSICPSR) register (see page 356). The clock is further divided by a value from 1 to 256, which is
1 + SCR, where SCR is the value programmed in the SSI Control0 (SSICR0) register (see page 349).
The frequency of the output clock SSIClk is defined by:
FSSIClk = FSysClk / (CPSDVSR * (1 + SCR))
Note: Although the SSIClk transmit clock can theoretically be 25 MHz, the module may not be
able to operate at that speed. For master mode, the system clock must be at least two times
faster than the SSIClk. For slave mode, the system clock must be at least 12 times faster
than the SSIClk.
See “Synchronous Serial Interface (SSI)” on page 544 to view SSI timing parameters.
14.2.2 FIFO Operation
14.2.2.1 Transmit FIFO
The common transmit FIFO is a 16-bit wide, 8-locations deep, first-in, first-out memory buffer. The
CPU writes data to the FIFO by writing the SSI Data (SSIDR) register (see page 353), and data is
stored in the FIFO until it is read out by the transmission logic.
When configured as a master or a slave, parallel data is written into the transmit FIFO prior to serial
conversion and transmission to the attached slave or master, respectively, through the SSITx pin.
14.2.2.2 Receive FIFO
The common receive FIFO is a 16-bit wide, 8-locations deep, first-in, first-out memory buffer.
Received data from the serial interface is stored in the buffer until read out by the CPU, which
accesses the read FIFO by reading the SSIDR register.
When configured as a master or slave, serial data received through the SSIRx pin is registered
prior to parallel loading into the attached slave or master receive FIFO, respectively.
14.2.3 Interrupts
The SSI can generate interrupts when the following conditions are observed:
■ Transmit FIFO service
■ Receive FIFO service
■ Receive FIFO time-out
■ Receive FIFO overrun
338 March 17, 2008
Preliminary
Synchronous Serial Interface (SSI)
All of the interrupt events are ORed together before being sent to the interrupt controller, so the SSI
can only generate a single interrupt request to the controller at any given time. You can mask each
of the four individual maskable interrupts by setting the appropriate bits in the SSI Interrupt Mask
(SSIIM) register (see page 357). Setting the appropriate mask bit to 1 enables the interrupt.
Provision of the individual outputs, as well as a combined interrupt output, allows use of either a
global interrupt service routine, or modular device drivers to handle interrupts. The transmit and
receive dynamic dataflow interrupts have been separated from the status interrupts so that data
can be read or written in response to the FIFO trigger levels. The status of the individual interrupt
sources can be read from the SSI Raw Interrupt Status (SSIRIS) and SSI Masked Interrupt Status
(SSIMIS) registers (see page 359 and page 360, respectively).
14.2.4 Frame Formats
Each data frame is between 4 and 16 bits long, depending on the size of data programmed, and is
transmitted starting with the MSB. There are three basic frame types that can be selected:
■ Texas Instruments synchronous serial
■ Freescale SPI
■ MICROWIRE
For all three formats, the serial clock (SSIClk) is held inactive while the SSI is idle, and SSIClk
transitions at the programmed frequency only during active transmission or reception of data. The
idle state of SSIClk is utilized to provide a receive timeout indication that occurs when the receive
FIFO still contains data after a timeout period.
For Freescale SPI and MICROWIRE frame formats, the serial frame (SSIFss ) pin is active Low,
and is asserted (pulled down) during the entire transmission of the frame.
For Texas Instruments synchronous serial frame format, the SSIFss pin is pulsed for one serial
clock period starting at its rising edge, prior to the transmission of each frame. For this frame format,
both the SSI and the off-chip slave device drive their output data on the rising edge of SSIClk, and
latch data from the other device on the falling edge.
Unlike the full-duplex transmission of the other two frame formats, the MICROWIRE format uses a
special master-slave messaging technique, which operates at half-duplex. In this mode, when a
frame begins, an 8-bit control message is transmitted to the off-chip slave. During this transmit, no
incoming data is received by the SSI. After the message has been sent, the off-chip slave decodes
it and, after waiting one serial clock after the last bit of the 8-bit control message has been sent,
responds with the requested data. The returned data can be 4 to 16 bits in length, making the total
frame length anywhere from 13 to 25 bits.
14.2.4.1 Texas Instruments Synchronous Serial Frame Format
Figure 14-2 on page 340 shows the Texas Instruments synchronous serial frame format for a single
transmitted frame.
March 17, 2008 339
Preliminary
LM3S8933 Microcontroller
Figure 14-2. TI Synchronous Serial Frame Format (Single Transfer)
SSIClk
4 to 16 bits
SSIFss
SSITx/SSIRx MSB LSB
In this mode, SSIClk and SSIFss are forced Low, and the transmit data line SSITx is tristated
whenever the SSI is idle. Once the bottom entry of the transmit FIFO contains data, SSIFss is
pulsed High for one SSIClk period. The value to be transmitted is also transferred from the transmit
FIFO to the serial shift register of the transmit logic. On the next rising edge of SSIClk, the MSB
of the 4 to 16-bit data frame is shifted out on the SSITx pin. Likewise, the MSB of the received data
is shifted onto the SSIRx pin by the off-chip serial slave device.
Both the SSI and the off-chip serial slave device then clock each data bit into their serial shifter on
the falling edge of each SSIClk. The received data is transferred from the serial shifter to the receive
FIFO on the first rising edge of SSIClk after the LSB has been latched.
Figure 14-3 on page 340 shows the Texas Instruments synchronous serial frame format when
back-to-back frames are transmitted.
Figure 14-3. TI Synchronous Serial Frame Format (Continuous Transfer)
MSB LSB
4 to 16 bits
SSIClk
SSIFss
SSITx/SSIRx
14.2.4.2 Freescale SPI Frame Format
The Freescale SPI interface is a four-wire interface where the SSIFss signal behaves as a slave
select. The main feature of the Freescale SPI format is that the inactive state and phase of the
SSIClk signal are programmable through the SPO and SPH bits within the SSISCR0 control register.
SPO Clock Polarity Bit
When the SPO clock polarity control bit is Low, it produces a steady state Low value on the SSIClk
pin. If the SPO bit is High, a steady state High value is placed on the SSIClk pin when data is not
being transferred.
SPH Phase Control Bit
The SPH phase control bit selects the clock edge that captures data and allows it to change state.
It has the most impact on the first bit transmitted by either allowing or not allowing a clock transition
before the first data capture edge. When the SPH phase control bit is Low, data is captured on the
first clock edge transition. If the SPH bit is High, data is captured on the second clock edge transition.
340 March 17, 2008
Preliminary
Synchronous Serial Interface (SSI)
14.2.4.3 Freescale SPI Frame Format with SPO=0 and SPH=0
Single and continuous transmission signal sequences for Freescale SPI format with SPO=0 and
SPH=0 are shown in Figure 14-4 on page 341 and Figure 14-5 on page 341.
Figure 14-4. Freescale SPI Format (Single Transfer) with SPO=0 and SPH=0
4 to 16 bits
SSIClk
SSIFss
SSIRx Q
SSITx
MSB
MSB
LSB
LSB
Note: Q is undefined.
Figure 14-5. Freescale SPI Format (Continuous Transfer) with SPO=0 and SPH=0
SSIClk
SSIFss
SSIRx LSB
SSITx MSB LSB
4 to 16 bits
LSB MSB
MSB
MSB
LSB
In this configuration, during idle periods:
■ SSIClk is forced Low
■ SSIFss is forced High
■ The transmit data line SSITx is arbitrarily forced Low
■ When the SSI is configured as a master, it enables the SSIClk pad
■ When the SSI is configured as a slave, it disables the SSIClk pad
If the SSI is enabled and there is valid data within the transmit FIFO, the start of transmission is
signified by the SSIFss master signal being driven Low. This causes slave data to be enabled onto
the SSIRx input line of the master. The master SSITx output pad is enabled.
One half SSIClk period later, valid master data is transferred to the SSITx pin. Now that both the
master and slave data have been set, the SSIClk master clock pin goes High after one further half
SSIClk period.
The data is now captured on the rising and propagated on the falling edges of the SSIClk signal.
In the case of a single word transmission, after all bits of the data word have been transferred, the
SSIFss line is returned to its idle High state one SSIClk period after the last bit has been captured.
However, in the case of continuous back-to-back transmissions, the SSIFss signal must be pulsed
High between each data word transfer. This is because the slave select pin freezes the data in its
March 17, 2008 341
Preliminary
LM3S8933 Microcontroller
serial peripheral register and does not allow it to be altered if the SPH bit is logic zero. Therefore,
the master device must raise the SSIFss pin of the slave device between each data transfer to
enable the serial peripheral data write. On completion of the continuous transfer, the SSIFss pin
is returned to its idle state one SSIClk period after the last bit has been captured.
14.2.4.4 Freescale SPI Frame Format with SPO=0 and SPH=1
The transfer signal sequence for Freescale SPI format with SPO=0 and SPH=1 is shown in Figure
14-6 on page 342, which covers both single and continuous transfers.
Figure 14-6. Freescale SPI Frame Format with SPO=0 and SPH=1
4 to 16 bits
SSIClk
SSIFss
SSIRx
SSITx
Q
MSB
Q MSB
LSB
LSB
Note: Q is undefined.
In this configuration, during idle periods:
■ SSIClk is forced Low
■ SSIFss is forced High
■ The transmit data line SSITx is arbitrarily forced Low
■ When the SSI is configured as a master, it enables the SSIClk pad
■ When the SSI is configured as a slave, it disables the SSIClk pad
If the SSI is enabled and there is valid data within the transmit FIFO, the start of transmission is
signified by the SSIFss master signal being driven Low. The master SSITx output is enabled. After
a further one half SSIClk period, both master and slave valid data is enabled onto their respective
transmission lines. At the same time, the SSIClk is enabled with a rising edge transition.
Data is then captured on the falling edges and propagated on the rising edges of the SSIClk signal.
In the case of a single word transfer, after all bits have been transferred, the SSIFss line is returned
to its idle High state one SSIClk period after the last bit has been captured.
For continuous back-to-back transfers, the SSIFss pin is held Low between successive data words
and termination is the same as that of the single word transfer.
14.2.4.5 Freescale SPI Frame Format with SPO=1 and SPH=0
Single and continuous transmission signal sequences for Freescale SPI format with SPO=1 and
SPH=0 are shown in Figure 14-7 on page 343 and Figure 14-8 on page 343.
342 March 17, 2008
Preliminary
Synchronous Serial Interface (SSI)
Figure 14-7. Freescale SPI Frame Format (Single Transfer) with SPO=1 and SPH=0
4 to 16 bits
SSIClk
SSIFss
SSIRx
SSITx
MSB Q
MSB LSB
LSB
Note: Q is undefined.
Figure 14-8. Freescale SPI Frame Format (Continuous Transfer) with SPO=1 and SPH=0
SSIClk
SSIFss
SSITx/SSIRx MSB LSB
4 to 16 bits
LSB MSB
In this configuration, during idle periods:
■ SSIClk is forced High
■ SSIFss is forced High
■ The transmit data line SSITx is arbitrarily forced Low
■ When the SSI is configured as a master, it enables the SSIClk pad
■ When the SSI is configured as a slave, it disables the SSIClk pad
If the SSI is enabled and there is valid data within the transmit FIFO, the start of transmission is
signified by the SSIFss master signal being driven Low, which causes slave data to be immediately
transferred onto the SSIRx line of the master. The master SSITx output pad is enabled.
One half period later, valid master data is transferred to the SSITx line. Now that both the master
and slave data have been set, the SSIClk master clock pin becomes Low after one further half
SSIClk period. This means that data is captured on the falling edges and propagated on the rising
edges of the SSIClk signal.
In the case of a single word transmission, after all bits of the data word are transferred, the SSIFss
line is returned to its idle High state one SSIClk period after the last bit has been captured.
However, in the case of continuous back-to-back transmissions, the SSIFss signal must be pulsed
High between each data word transfer. This is because the slave select pin freezes the data in its
serial peripheral register and does not allow it to be altered if the SPH bit is logic zero. Therefore,
the master device must raise the SSIFss pin of the slave device between each data transfer to
enable the serial peripheral data write. On completion of the continuous transfer, the SSIFss pin
is returned to its idle state one SSIClk period after the last bit has been captured.
March 17, 2008 343
Preliminary
LM3S8933 Microcontroller
14.2.4.6 Freescale SPI Frame Format with SPO=1 and SPH=1
The transfer signal sequence for Freescale SPI format with SPO=1 and SPH=1 is shown in Figure
14-9 on page 344, which covers both single and continuous transfers.
Figure 14-9. Freescale SPI Frame Format with SPO=1 and SPH=1
4 to 16 bits
SSIClk
SSIFss
SSIRx
SSITx
Q Q
MSB
MSB
LSB
LSB
Note: Q is undefined.
In this configuration, during idle periods:
■ SSIClk is forced High
■ SSIFss is forced High
■ The transmit data line SSITx is arbitrarily forced Low
■ When the SSI is configured as a master, it enables the SSIClk pad
■ When the SSI is configured as a slave, it disables the SSIClk pad
If the SSI is enabled and there is valid data within the transmit FIFO, the start of transmission is
signified by the SSIFss master signal being driven Low. The master SSITx output pad is enabled.
After a further one-half SSIClk period, both master and slave data are enabled onto their respective
transmission lines. At the same time, SSIClk is enabled with a falling edge transition. Data is then
captured on the rising edges and propagated on the falling edges of the SSIClk signal.
After all bits have been transferred, in the case of a single word transmission, the SSIFss line is
returned to its idle high state one SSIClk period after the last bit has been captured.
For continuous back-to-back transmissions, the SSIFss pin remains in its active Low state, until
the final bit of the last word has been captured, and then returns to its idle state as described above.
For continuous back-to-back transfers, the SSIFss pin is held Low between successive data words
and termination is the same as that of the single word transfer.
14.2.4.7 MICROWIRE Frame Format
Figure 14-10 on page 345 shows the MICROWIRE frame format, again for a single frame. Figure
14-11 on page 346 shows the same format when back-to-back frames are transmitted.
344 March 17, 2008
Preliminary
Synchronous Serial Interface (SSI)
Figure 14-10. MICROWIRE Frame Format (Single Frame)
SSIClk
SSIFss
SSIRx MSB LSB
4 to 16 bits
output data
0
SSITx MSB LSB
8-bit control
MICROWIRE format is very similar to SPI format, except that transmission is half-duplex instead of
full-duplex, using a master-slave message passing technique. Each serial transmission begins with
an 8-bit control word that is transmitted from the SSI to the off-chip slave device. During this
transmission, no incoming data is received by the SSI. After the message has been sent, the off-chip
slave decodes it and, after waiting one serial clock after the last bit of the 8-bit control message has
been sent, responds with the required data. The returned data is 4 to 16 bits in length, making the
total frame length anywhere from 13 to 25 bits.
In this configuration, during idle periods:
■ SSIClk is forced Low
■ SSIFss is forced High
■ The transmit data line SSITx is arbitrarily forced Low
A transmission is triggered by writing a control byte to the transmit FIFO. The falling edge of SSIFss
causes the value contained in the bottom entry of the transmit FIFO to be transferred to the serial
shift register of the transmit logic, and the MSB of the 8-bit control frame to be shifted out onto the
SSITx pin. SSIFss remains Low for the duration of the frame transmission. The SSIRx pin remains
tristated during this transmission.
The off-chip serial slave device latches each control bit into its serial shifter on the rising edge of
each SSIClk. After the last bit is latched by the slave device, the control byte is decoded during a
one clock wait-state, and the slave responds by transmitting data back to the SSI. Each bit is driven
onto the SSIRx line on the falling edge of SSIClk. The SSI in turn latches each bit on the rising
edge of SSIClk. At the end of the frame, for single transfers, the SSIFss signal is pulled High one
clock period after the last bit has been latched in the receive serial shifter, which causes the data
to be transferred to the receive FIFO.
Note: The off-chip slave device can tristate the receive line either on the falling edge of SSIClk
after the LSB has been latched by the receive shifter, or when the SSIFss pin goes High.
For continuous transfers, data transmission begins and ends in the same manner as a single transfer.
However, the SSIFss line is continuously asserted (held Low) and transmission of data occurs
back-to-back. The control byte of the next frame follows directly after the LSB of the received data
from the current frame. Each of the received values is transferred from the receive shifter on the
falling edge of SSIClk, after the LSB of the frame has been latched into the SSI.
March 17, 2008 345
Preliminary
LM3S8933 Microcontroller
Figure 14-11. MICROWIRE Frame Format (Continuous Transfer)
8-bit control
SSIClk
SSIFss
SSIRx MSB LSB
4 to 16 bits
output data
0
SSITx LSB MSB LSB
MSB
In the MICROWIRE mode, the SSI slave samples the first bit of receive data on the rising edge of
SSIClk after SSIFss has gone Low. Masters that drive a free-running SSIClk must ensure that
the SSIFss signal has sufficient setup and hold margins with respect to the rising edge of SSIClk.
Figure 14-12 on page 346 illustrates these setup and hold time requirements. With respect to the
SSIClk rising edge on which the first bit of receive data is to be sampled by the SSI slave, SSIFss
must have a setup of at least two times the period of SSIClk on which the SSI operates. With
respect to the SSIClk rising edge previous to this edge, SSIFss must have a hold of at least one
SSIClk period.
Figure 14-12. MICROWIRE Frame Format, SSIFss Input Setup and Hold Requirements
SSIClk
SSIFss
SSIRx
First RX data to be
sampled by SSI slave
tSetup=(2*tSSIClk)
tHold=tSSIClk
14.3 Initialization and Configuration
To use the SSI, its peripheral clock must be enabled by setting the SSI bit in the RCGC1 register.
For each of the frame formats, the SSI is configured using the following steps:
1. Ensure that the SSE bit in the SSICR1 register is disabled before making any configuration
changes.
2. Select whether the SSI is a master or slave:
a. For master operations, set the SSICR1 register to 0x0000.0000.
b. For slave mode (output enabled), set the SSICR1 register to 0x0000.0004.
c. For slave mode (output disabled), set the SSICR1 register to 0x0000.000C.
3. Configure the clock prescale divisor by writing the SSICPSR register.
346 March 17, 2008
Preliminary
Synchronous Serial Interface (SSI)
4. Write the SSICR0 register with the following configuration:
■ Serial clock rate (SCR)
■ Desired clock phase/polarity, if using Freescale SPI mode (SPH and SPO)
■ The protocol mode: Freescale SPI, TI SSF, MICROWIRE (FRF)
■ The data size (DSS)
5. Enable the SSI by setting the SSE bit in the SSICR1 register.
As an example, assume the SSI must be configured to operate with the following parameters:
■ Master operation
■ Freescale SPI mode (SPO=1, SPH=1)
■ 1 Mbps bit rate
■ 8 data bits
Assuming the system clock is 20 MHz, the bit rate calculation would be:
FSSIClk = FSysClk / (CPSDVSR * (1 + SCR))
1x106 = 20x106 / (CPSDVSR * (1 + SCR))
In this case, if CPSDVSR=2, SCR must be 9.
The configuration sequence would be as follows:
1. Ensure that the SSE bit in the SSICR1 register is disabled.
2. Write the SSICR1 register with a value of 0x0000.0000.
3. Write the SSICPSR register with a value of 0x0000.0002.
4. Write the SSICR0 register with a value of 0x0000.09C7.
5. The SSI is then enabled by setting the SSE bit in the SSICR1 register to 1.
14.4 Register Map
Table 14-1 on page 347 lists the SSI registers. The offset listed is a hexadecimal increment to the
register’s address, relative to that SSI module’s base address:
■ SSI0: 0x4000.8000
Note: The SSI must be disabled (see the SSE bit in the SSICR1 register) before any of the control
registers are reprogrammed.
Table 14-1. SSI Register Map
See
Offset Name Type Reset Description page
0x000 SSICR0 R/W 0x0000.0000 SSI Control 0 349
March 17, 2008 347
Preliminary
LM3S8933 Microcontroller
See
Offset Name Type Reset Description page
0x004 SSICR1 R/W 0x0000.0000 SSI Control 1 351
0x008 SSIDR R/W 0x0000.0000 SSI Data 353
0x00C SSISR RO 0x0000.0003 SSI Status 354
0x010 SSICPSR R/W 0x0000.0000 SSI Clock Prescale 356
0x014 SSIIM R/W 0x0000.0000 SSI Interrupt Mask 357
0x018 SSIRIS RO 0x0000.0008 SSI Raw Interrupt Status 359
0x01C SSIMIS RO 0x0000.0000 SSI Masked Interrupt Status 360
0x020 SSIICR W1C 0x0000.0000 SSI Interrupt Clear 361
0xFD0 SSIPeriphID4 RO 0x0000.0000 SSI Peripheral Identification 4 362
0xFD4 SSIPeriphID5 RO 0x0000.0000 SSI Peripheral Identification 5 363
0xFD8 SSIPeriphID6 RO 0x0000.0000 SSI Peripheral Identification 6 364
0xFDC SSIPeriphID7 RO 0x0000.0000 SSI Peripheral Identification 7 365
0xFE0 SSIPeriphID0 RO 0x0000.0022 SSI Peripheral Identification 0 366
0xFE4 SSIPeriphID1 RO 0x0000.0000 SSI Peripheral Identification 1 367
0xFE8 SSIPeriphID2 RO 0x0000.0018 SSI Peripheral Identification 2 368
0xFEC SSIPeriphID3 RO 0x0000.0001 SSI Peripheral Identification 3 369
0xFF0 SSIPCellID0 RO 0x0000.000D SSI PrimeCell Identification 0 370
0xFF4 SSIPCellID1 RO 0x0000.00F0 SSI PrimeCell Identification 1 371
0xFF8 SSIPCellID2 RO 0x0000.0005 SSI PrimeCell Identification 2 372
0xFFC SSIPCellID3 RO 0x0000.00B1 SSI PrimeCell Identification 3 373
14.5 Register Descriptions
The remainder of this section lists and describes the SSI registers, in numerical order by address
offset.
348 March 17, 2008
Preliminary
Synchronous Serial Interface (SSI)
Register 1: SSI Control 0 (SSICR0), offset 0x000
SSICR0 is control register 0 and contains bit fields that control various functions within the SSI
module. Functionality such as protocol mode, clock rate, and data size are configured in this register.
SSI Control 0 (SSICR0)
SSI0 base: 0x4000.8000
Offset 0x000
Type R/W, reset 0x0000.0000
31 30 29 28 27 26 25 24 23 22 21 20 19 18 17 16
reserved
Type RO RO RO RO RO RO RO RO RO RO RO RO RO RO RO RO
Reset 0 0 0 0 0 0 0 0 0 0 0 0 0 0 0 0
15 14 13 12 11 10 9 8 7 6 5 4 3 2 1 0
SCR SPH SPO FRF DSS
Type R/W R/W R/W R/W R/W R/W R/W R/W R/W R/W R/W R/W R/W R/W R/W R/W
Reset 0 0 0 0 0 0 0 0 0 0 0 0 0 0 0 0
Bit/Field Name Type Reset Description
Software should not rely on the value of a reserved bit. To provide
compatibility with future products, the value of a reserved bit should be
preserved across a read-modify-write operation.
31:16 reserved RO 0x00
SSI Serial Clock Rate
The value SCR is used to generate the transmit and receive bit rate of
the SSI. The bit rate is:
BR=FSSIClk/(CPSDVSR * (1 + SCR))
where CPSDVSR is an even value from 2-254 programmed in the
SSICPSR register, and SCR is a value from 0-255.
15:8 SCR R/W 0x0000
SSI Serial Clock Phase
This bit is only applicable to the Freescale SPI Format.
The SPH control bit selects the clock edge that captures data and allows
it to change state. It has the most impact on the first bit transmitted by
either allowing or not allowing a clock transition before the first data
capture edge.
When the SPH bit is 0, data is captured on the first clock edge transition.
If SPH is 1, data is captured on the second clock edge transition.
7 SPH R/W 0
SSI Serial Clock Polarity
This bit is only applicable to the Freescale SPI Format.
When the SPO bit is 0, it produces a steady state Low value on the
SSIClk pin. If SPO is 1, a steady state High value is placed on the
SSIClk pin when data is not being transferred.
6 SPO R/W 0
March 17, 2008 349
Preliminary
LM3S8933 Microcontroller
Bit/Field Name Type Reset Description
SSI Frame Format Select
The FRF values are defined as follows:
Value Frame Format
0x0 Freescale SPI Frame Format
0x1 Texas Intruments Synchronous Serial Frame Format
0x2 MICROWIRE Frame Format
0x3 Reserved
5:4 FRF R/W 0x0
SSI Data Size Select
The DSS values are defined as follows:
Value Data Size
0x0-0x2 Reserved
0x3 4-bit data
0x4 5-bit data
0x5 6-bit data
0x6 7-bit data
0x7 8-bit data
0x8 9-bit data
0x9 10-bit data
0xA 11-bit data
0xB 12-bit data
0xC 13-bit data
0xD 14-bit data
0xE 15-bit data
0xF 16-bit data
3:0 DSS R/W 0x00
350 March 17, 2008
Preliminary
Synchronous Serial Interface (SSI)
Register 2: SSI Control 1 (SSICR1), offset 0x004
SSICR1 is control register 1 and contains bit fields that control various functions within the SSI
module. Master and slave mode functionality is controlled by this register.
SSI Control 1 (SSICR1)
SSI0 base: 0x4000.8000
Offset 0x004
Type R/W, reset 0x0000.0000
31 30 29 28 27 26 25 24 23 22 21 20 19 18 17 16
reserved
Type RO RO RO RO RO RO RO RO RO RO RO RO RO RO RO RO
Reset 0 0 0 0 0 0 0 0 0 0 0 0 0 0 0 0
15 14 13 12 11 10 9 8 7 6 5 4 3 2 1 0
reserved SOD MS SSE LBM
Type RO RO RO RO RO RO RO RO RO RO RO RO R/W R/W R/W R/W
Reset 0 0 0 0 0 0 0 0 0 0 0 0 0 0 0 0
Bit/Field Name Type Reset Description
Software should not rely on the value of a reserved bit. To provide
compatibility with future products, the value of a reserved bit should be
preserved across a read-modify-write operation.
31:4 reserved RO 0x00
SSI Slave Mode Output Disable
This bit is relevant only in the Slave mode (MS=1). In multiple-slave
systems, it is possible for the SSI master to broadcast a message to all
slaves in the system while ensuring that only one slave drives data onto
the serial output line. In such systems, the TXD lines from multiple slaves
could be tied together. To operate in such a system, the SOD bit can be
configured so that the SSI slave does not drive the SSITx pin.
The SOD values are defined as follows:
Value Description
0 SSI can drive SSITx output in Slave Output mode.
1 SSI must not drive the SSITx output in Slave mode.
3 SOD R/W 0
SSI Master/Slave Select
This bit selects Master or Slave mode and can be modified only when
SSI is disabled (SSE=0).
The MS values are defined as follows:
Value Description
0 Device configured as a master.
1 Device configured as a slave.
2 MS R/W 0
March 17, 2008 351
Preliminary
LM3S8933 Microcontroller
Bit/Field Name Type Reset Description
SSI Synchronous Serial Port Enable
Setting this bit enables SSI operation.
The SSE values are defined as follows:
Value Description
0 SSI operation disabled.
1 SSI operation enabled.
Note: This bit must be set to 0 before any control registers
are reprogrammed.
1 SSE R/W 0
SSI Loopback Mode
Setting this bit enables Loopback Test mode.
The LBM values are defined as follows:
Value Description
0 Normal serial port operation enabled.
Output of the transmit serial shift register is connected internally
to the input of the receive serial shift register.
1
0 LBM R/W 0
352 March 17, 2008
Preliminary
Synchronous Serial Interface (SSI)
Register 3: SSI Data (SSIDR), offset 0x008
SSIDR is the data register and is 16-bits wide. When SSIDR is read, the entry in the receive FIFO
(pointed to by the current FIFO read pointer) is accessed. As data values are removed by the SSI
receive logic from the incoming data frame, they are placed into the entry in the receive FIFO (pointed
to by the current FIFO write pointer).
When SSIDR is written to, the entry in the transmit FIFO (pointed to by the write pointer) is written
to. Data values are removed from the transmit FIFO one value at a time by the transmit logic. It is
loaded into the transmit serial shifter, then serially shifted out onto the SSITx pin at the programmed
bit rate.
When a data size of less than 16 bits is selected, the user must right-justify data written to the
transmit FIFO. The transmit logic ignores the unused bits. Received data less than 16 bits is
automatically right-justified in the receive buffer.
When the SSI is programmed for MICROWIRE frame format, the default size for transmit data is
eight bits (the most significant byte is ignored). The receive data size is controlled by the programmer.
The transmit FIFO and the receive FIFO are not cleared even when the SSE bit in the SSICR1
register is set to zero. This allows the software to fill the transmit FIFO before enabling the SSI.
SSI Data (SSIDR)
SSI0 base: 0x4000.8000
Offset 0x008
Type R/W, reset 0x0000.0000
31 30 29 28 27 26 25 24 23 22 21 20 19 18 17 16
reserved
Type RO RO RO RO RO RO RO RO RO RO RO RO RO RO RO RO
Reset 0 0 0 0 0 0 0 0 0 0 0 0 0 0 0 0
15 14 13 12 11 10 9 8 7 6 5 4 3 2 1 0
DATA
Type R/W R/W R/W R/W R/W R/W R/W R/W R/W R/W R/W R/W R/W R/W R/W R/W
Reset 0 0 0 0 0 0 0 0 0 0 0 0 0 0 0 0
Bit/Field Name Type Reset Description
Software should not rely on the value of a reserved bit. To provide
compatibility with future products, the value of a reserved bit should be
preserved across a read-modify-write operation.
31:16 reserved RO 0x0000
SSI Receive/Transmit Data
A read operation reads the receive FIFO. A write operation writes the
transmit FIFO.
Software must right-justify data when the SSI is programmed for a data
size that is less than 16 bits. Unused bits at the top are ignored by the
transmit logic. The receive logic automatically right-justifies the data.
15:0 DATA R/W 0x0000
March 17, 2008 353
Preliminary
LM3S8933 Microcontroller
Register 4: SSI Status (SSISR), offset 0x00C
SSISR is a status register that contains bits that indicate the FIFO fill status and the SSI busy status.
SSI Status (SSISR)
SSI0 base: 0x4000.8000
Offset 0x00C
Type RO, reset 0x0000.0003
31 30 29 28 27 26 25 24 23 22 21 20 19 18 17 16
reserved
Type RO RO RO RO RO RO RO RO RO RO RO RO RO RO RO RO
Reset 0 0 0 0 0 0 0 0 0 0 0 0 0 0 0 0
15 14 13 12 11 10 9 8 7 6 5 4 3 2 1 0
reserved BSY RFF RNE TNF TFE
Type RO RO RO RO RO RO RO RO RO RO RO RO RO RO RO R0
Reset 0 0 0 0 0 0 0 0 0 0 0 0 0 0 1 1
Bit/Field Name Type Reset Description
Software should not rely on the value of a reserved bit. To provide
compatibility with future products, the value of a reserved bit should be
preserved across a read-modify-write operation.
31:5 reserved RO 0x00
SSI Busy Bit
The BSY values are defined as follows:
Value Description
0 SSI is idle.
SSI is currently transmitting and/or receiving a frame, or the
transmit FIFO is not empty.
1
4 BSY RO 0
SSI Receive FIFO Full
The RFF values are defined as follows:
Value Description
0 Receive FIFO is not full.
1 Receive FIFO is full.
3 RFF RO 0
SSI Receive FIFO Not Empty
The RNE values are defined as follows:
Value Description
0 Receive FIFO is empty.
1 Receive FIFO is not empty.
2 RNE RO 0
SSI Transmit FIFO Not Full
The TNF values are defined as follows:
Value Description
0 Transmit FIFO is full.
1 Transmit FIFO is not full.
1 TNF RO 1
354 March 17, 2008
Preliminary
Synchronous Serial Interface (SSI)
Bit/Field Name Type Reset Description
SSI Transmit FIFO Empty
The TFE values are defined as follows:
Value Description
0 Transmit FIFO is not empty.
1 Transmit FIFO is empty.
0 TFE R0 1
March 17, 2008 355
Preliminary
LM3S8933 Microcontroller
Register 5: SSI Clock Prescale (SSICPSR), offset 0x010
SSICPSR is the clock prescale register and specifies the division factor by which the system clock
must be internally divided before further use.
The value programmed into this register must be an even number between 2 and 254. The
least-significant bit of the programmed number is hard-coded to zero. If an odd number is written
to this register, data read back from this register has the least-significant bit as zero.
SSI Clock Prescale (SSICPSR)
SSI0 base: 0x4000.8000
Offset 0x010
Type R/W, reset 0x0000.0000
31 30 29 28 27 26 25 24 23 22 21 20 19 18 17 16
reserved
Type RO RO RO RO RO RO RO RO RO RO RO RO RO RO RO RO
Reset 0 0 0 0 0 0 0 0 0 0 0 0 0 0 0 0
15 14 13 12 11 10 9 8 7 6 5 4 3 2 1 0
reserved CPSDVSR
Type RO RO RO RO RO RO RO RO R/W R/W R/W R/W R/W R/W R/W R/W
Reset 0 0 0 0 0 0 0 0 0 0 0 0 0 0 0 0
Bit/Field Name Type Reset Description
Software should not rely on the value of a reserved bit. To provide
compatibility with future products, the value of a reserved bit should be
preserved across a read-modify-write operation.
31:8 reserved RO 0x00
SSI Clock Prescale Divisor
This value must be an even number from 2 to 254, depending on the
frequency of SSIClk. The LSB always returns 0 on reads.
7:0 CPSDVSR R/W 0x00
356 March 17, 2008
Preliminary
Synchronous Serial Interface (SSI)
Register 6: SSI Interrupt Mask (SSIIM), offset 0x014
The SSIIM register is the interrupt mask set or clear register. It is a read/write register and all bits
are cleared to 0 on reset.
On a read, this register gives the current value of the mask on the relevant interrupt. A write of 1 to
the particular bit sets the mask, enabling the interrupt to be read. A write of 0 clears the corresponding
mask.
SSI Interrupt Mask (SSIIM)
SSI0 base: 0x4000.8000
Offset 0x014
Type R/W, reset 0x0000.0000
31 30 29 28 27 26 25 24 23 22 21 20 19 18 17 16
reserved
Type RO RO RO RO RO RO RO RO RO RO RO RO RO RO RO RO
Reset 0 0 0 0 0 0 0 0 0 0 0 0 0 0 0 0
15 14 13 12 11 10 9 8 7 6 5 4 3 2 1 0
reserved TXIM RXIM RTIM RORIM
Type RO RO RO RO RO RO RO RO RO RO RO RO R/W R/W R/W R/W
Reset 0 0 0 0 0 0 0 0 0 0 0 0 0 0 0 0
Bit/Field Name Type Reset Description
Software should not rely on the value of a reserved bit. To provide
compatibility with future products, the value of a reserved bit should be
preserved across a read-modify-write operation.
31:4 reserved RO 0x00
SSI Transmit FIFO Interrupt Mask
The TXIM values are defined as follows:
Value Description
0 TX FIFO half-full or less condition interrupt is masked.
1 TX FIFO half-full or less condition interrupt is not masked.
3 TXIM R/W 0
SSI Receive FIFO Interrupt Mask
The RXIM values are defined as follows:
Value Description
0 RX FIFO half-full or more condition interrupt is masked.
1 RX FIFO half-full or more condition interrupt is not masked.
2 RXIM R/W 0
SSI Receive Time-Out Interrupt Mask
The RTIM values are defined as follows:
Value Description
0 RX FIFO time-out interrupt is masked.
1 RX FIFO time-out interrupt is not masked.
1 RTIM R/W 0
March 17, 2008 357
Preliminary
LM3S8933 Microcontroller
Bit/Field Name Type Reset Description
SSI Receive Overrun Interrupt Mask
The RORIM values are defined as follows:
Value Description
0 RX FIFO overrun interrupt is masked.
1 RX FIFO overrun interrupt is not masked.
0 RORIM R/W 0
358 March 17, 2008
Preliminary
Synchronous Serial Interface (SSI)
Register 7: SSI Raw Interrupt Status (SSIRIS), offset 0x018
The SSIRIS register is the raw interrupt status register. On a read, this register gives the current
raw status value of the corresponding interrupt prior to masking. A write has no effect.
SSI Raw Interrupt Status (SSIRIS)
SSI0 base: 0x4000.8000
Offset 0x018
Type RO, reset 0x0000.0008
31 30 29 28 27 26 25 24 23 22 21 20 19 18 17 16
reserved
Type RO RO RO RO RO RO RO RO RO RO RO RO RO RO RO RO
Reset 0 0 0 0 0 0 0 0 0 0 0 0 0 0 0 0
15 14 13 12 11 10 9 8 7 6 5 4 3 2 1 0
reserved TXRIS RXRIS RTRIS RORRIS
Type RO RO RO RO RO RO RO RO RO RO RO RO RO RO RO RO
Reset 0 0 0 0 0 0 0 0 0 0 0 0 1 0 0 0
Bit/Field Name Type Reset Description
Software should not rely on the value of a reserved bit. To provide
compatibility with future products, the value of a reserved bit should be
preserved across a read-modify-write operation.
31:4 reserved RO 0x00
SSI Transmit FIFO Raw Interrupt Status
Indicates that the transmit FIFO is half full or less, when set.
3 TXRIS RO 1
SSI Receive FIFO Raw Interrupt Status
Indicates that the receive FIFO is half full or more, when set.
2 RXRIS RO 0
SSI Receive Time-Out Raw Interrupt Status
Indicates that the receive time-out has occurred, when set.
1 RTRIS RO 0
SSI Receive Overrun Raw Interrupt Status
Indicates that the receive FIFO has overflowed, when set.
0 RORRIS RO 0
March 17, 2008 359
Preliminary
LM3S8933 Microcontroller
Register 8: SSI Masked Interrupt Status (SSIMIS), offset 0x01C
The SSIMIS register is the masked interrupt status register. On a read, this register gives the current
masked status value of the corresponding interrupt. A write has no effect.
SSI Masked Interrupt Status (SSIMIS)
SSI0 base: 0x4000.8000
Offset 0x01C
Type RO, reset 0x0000.0000
31 30 29 28 27 26 25 24 23 22 21 20 19 18 17 16
reserved
Type RO RO RO RO RO RO RO RO RO RO RO RO RO RO RO RO
Reset 0 0 0 0 0 0 0 0 0 0 0 0 0 0 0 0
15 14 13 12 11 10 9 8 7 6 5 4 3 2 1 0
reserved TXMIS RXMIS RTMIS RORMIS
Type RO RO RO RO RO RO RO RO RO RO RO RO RO RO RO RO
Reset 0 0 0 0 0 0 0 0 0 0 0 0 0 0 0 0
Bit/Field Name Type Reset Description
Software should not rely on the value of a reserved bit. To provide
compatibility with future products, the value of a reserved bit should be
preserved across a read-modify-write operation.
31:4 reserved RO 0
SSI Transmit FIFO Masked Interrupt Status
Indicates that the transmit FIFO is half full or less, when set.
3 TXMIS RO 0
SSI Receive FIFO Masked Interrupt Status
Indicates that the receive FIFO is half full or more, when set.
2 RXMIS RO 0
SSI Receive Time-Out Masked Interrupt Status
Indicates that the receive time-out has occurred, when set.
1 RTMIS RO 0
SSI Receive Overrun Masked Interrupt Status
Indicates that the receive FIFO has overflowed, when set.
0 RORMIS RO 0
360 March 17, 2008
Preliminary
Synchronous Serial Interface (SSI)
Register 9: SSI Interrupt Clear (SSIICR), offset 0x020
The SSIICR register is the interrupt clear register. On a write of 1, the corresponding interrupt is
cleared. A write of 0 has no effect.
SSI Interrupt Clear (SSIICR)
SSI0 base: 0x4000.8000
Offset 0x020
Type W1C, reset 0x0000.0000
31 30 29 28 27 26 25 24 23 22 21 20 19 18 17 16
reserved
Type RO RO RO RO RO RO RO RO RO RO RO RO RO RO RO RO
Reset 0 0 0 0 0 0 0 0 0 0 0 0 0 0 0 0
15 14 13 12 11 10 9 8 7 6 5 4 3 2 1 0
reserved RTIC RORIC
Type RO RO RO RO RO RO RO RO RO RO RO RO RO RO W1C W1C
Reset 0 0 0 0 0 0 0 0 0 0 0 0 0 0 0 0
Bit/Field Name Type Reset Description
Software should not rely on the value of a reserved bit. To provide
compatibility with future products, the value of a reserved bit should be
preserved across a read-modify-write operation.
31:2 reserved RO 0x00
SSI Receive Time-Out Interrupt Clear
The RTIC values are defined as follows:
Value Description
0 No effect on interrupt.
1 Clears interrupt.
1 RTIC W1C 0
SSI Receive Overrun Interrupt Clear
The RORIC values are defined as follows:
Value Description
0 No effect on interrupt.
1 Clears interrupt.
0 RORIC W1C 0
March 17, 2008 361
Preliminary
LM3S8933 Microcontroller
Register 10: SSI Peripheral Identification 4 (SSIPeriphID4), offset 0xFD0
The SSIPeriphIDn registers are hard-coded and the fields within the register determine the reset
value.
SSI Peripheral Identification 4 (SSIPeriphID4)
SSI0 base: 0x4000.8000
Offset 0xFD0
Type RO, reset 0x0000.0000
31 30 29 28 27 26 25 24 23 22 21 20 19 18 17 16
reserved
Type RO RO RO RO RO RO RO RO RO RO RO RO RO RO RO RO
Reset 0 0 0 0 0 0 0 0 0 0 0 0 0 0 0 0
15 14 13 12 11 10 9 8 7 6 5 4 3 2 1 0
reserved PID4
Type RO RO RO RO RO RO RO RO RO RO RO RO RO RO RO RO
Reset 0 0 0 0 0 0 0 0 0 0 0 0 0 0 0 0
Bit/Field Name Type Reset Description
Software should not rely on the value of a reserved bit. To provide
compatibility with future products, the value of a reserved bit should be
preserved across a read-modify-write operation.
31:8 reserved RO 0x00
SSI Peripheral ID Register[7:0]
Can be used by software to identify the presence of this peripheral.
7:0 PID4 RO 0x00
362 March 17, 2008
Preliminary
Synchronous Serial Interface (SSI)
Register 11: SSI Peripheral Identification 5 (SSIPeriphID5), offset 0xFD4
The SSIPeriphIDn registers are hard-coded and the fields within the register determine the reset
value.
SSI Peripheral Identification 5 (SSIPeriphID5)
SSI0 base: 0x4000.8000
Offset 0xFD4
Type RO, reset 0x0000.0000
31 30 29 28 27 26 25 24 23 22 21 20 19 18 17 16
reserved
Type RO RO RO RO RO RO RO RO RO RO RO RO RO RO RO RO
Reset 0 0 0 0 0 0 0 0 0 0 0 0 0 0 0 0
15 14 13 12 11 10 9 8 7 6 5 4 3 2 1 0
reserved PID5
Type RO RO RO RO RO RO RO RO RO RO RO RO RO RO RO RO
Reset 0 0 0 0 0 0 0 0 0 0 0 0 0 0 0 0
Bit/Field Name Type Reset Description
Software should not rely on the value of a reserved bit. To provide
compatibility with future products, the value of a reserved bit should be
preserved across a read-modify-write operation.
31:8 reserved RO 0x00
SSI Peripheral ID Register[15:8]
Can be used by software to identify the presence of this peripheral.
7:0 PID5 RO 0x00
March 17, 2008 363
Preliminary
LM3S8933 Microcontroller
Register 12: SSI Peripheral Identification 6 (SSIPeriphID6), offset 0xFD8
The SSIPeriphIDn registers are hard-coded and the fields within the register determine the reset
value.
SSI Peripheral Identification 6 (SSIPeriphID6)
SSI0 base: 0x4000.8000
Offset 0xFD8
Type RO, reset 0x0000.0000
31 30 29 28 27 26 25 24 23 22 21 20 19 18 17 16
reserved
Type RO RO RO RO RO RO RO RO RO RO RO RO RO RO RO RO
Reset 0 0 0 0 0 0 0 0 0 0 0 0 0 0 0 0
15 14 13 12 11 10 9 8 7 6 5 4 3 2 1 0
reserved PID6
Type RO RO RO RO RO RO RO RO RO RO RO RO RO RO RO RO
Reset 0 0 0 0 0 0 0 0 0 0 0 0 0 0 0 0
Bit/Field Name Type Reset Description
Software should not rely on the value of a reserved bit. To provide
compatibility with future products, the value of a reserved bit should be
preserved across a read-modify-write operation.
31:8 reserved RO 0x00
SSI Peripheral ID Register[23:16]
Can be used by software to identify the presence of this peripheral.
7:0 PID6 RO 0x00
364 March 17, 2008
Preliminary
Synchronous Serial Interface (SSI)
Register 13: SSI Peripheral Identification 7 (SSIPeriphID7), offset 0xFDC
The SSIPeriphIDn registers are hard-coded and the fields within the register determine the reset
value.
SSI Peripheral Identification 7 (SSIPeriphID7)
SSI0 base: 0x4000.8000
Offset 0xFDC
Type RO, reset 0x0000.0000
31 30 29 28 27 26 25 24 23 22 21 20 19 18 17 16
reserved
Type RO RO RO RO RO RO RO RO RO RO RO RO RO RO RO RO
Reset 0 0 0 0 0 0 0 0 0 0 0 0 0 0 0 0
15 14 13 12 11 10 9 8 7 6 5 4 3 2 1 0
reserved PID7
Type RO RO RO RO RO RO RO RO RO RO RO RO RO RO RO RO
Reset 0 0 0 0 0 0 0 0 0 0 0 0 0 0 0 0
Bit/Field Name Type Reset Description
Software should not rely on the value of a reserved bit. To provide
compatibility with future products, the value of a reserved bit should be
preserved across a read-modify-write operation.
31:8 reserved RO 0x00
SSI Peripheral ID Register[31:24]
Can be used by software to identify the presence of this peripheral.
7:0 PID7 RO 0x00
March 17, 2008 365
Preliminary
LM3S8933 Microcontroller
Register 14: SSI Peripheral Identification 0 (SSIPeriphID0), offset 0xFE0
The SSIPeriphIDn registers are hard-coded and the fields within the register determine the reset
value.
SSI Peripheral Identification 0 (SSIPeriphID0)
SSI0 base: 0x4000.8000
Offset 0xFE0
Type RO, reset 0x0000.0022
31 30 29 28 27 26 25 24 23 22 21 20 19 18 17 16
reserved
Type RO RO RO RO RO RO RO RO RO RO RO RO RO RO RO RO
Reset 0 0 0 0 0 0 0 0 0 0 0 0 0 0 0 0
15 14 13 12 11 10 9 8 7 6 5 4 3 2 1 0
reserved PID0
Type RO RO RO RO RO RO RO RO RO RO RO RO RO RO RO RO
Reset 0 0 0 0 0 0 0 0 0 0 1 0 0 0 1 0
Bit/Field Name Type Reset Description
Software should not rely on the value of a reserved bit. To provide
compatibility with future products, the value of a reserved bit should be
preserved across a read-modify-write operation.
31:8 reserved RO 0
SSI Peripheral ID Register[7:0]
Can be used by software to identify the presence of this peripheral.
7:0 PID0 RO 0x22
366 March 17, 2008
Preliminary
Synchronous Serial Interface (SSI)
Register 15: SSI Peripheral Identification 1 (SSIPeriphID1), offset 0xFE4
The SSIPeriphIDn registers are hard-coded and the fields within the register determine the reset
value.
SSI Peripheral Identification 1 (SSIPeriphID1)
SSI0 base: 0x4000.8000
Offset 0xFE4
Type RO, reset 0x0000.0000
31 30 29 28 27 26 25 24 23 22 21 20 19 18 17 16
reserved
Type RO RO RO RO RO RO RO RO RO RO RO RO RO RO RO RO
Reset 0 0 0 0 0 0 0 0 0 0 0 0 0 0 0 0
15 14 13 12 11 10 9 8 7 6 5 4 3 2 1 0
reserved PID1
Type RO RO RO RO RO RO RO RO RO RO RO RO RO RO RO RO
Reset 0 0 0 0 0 0 0 0 0 0 0 0 0 0 0 0
Bit/Field Name Type Reset Description
Software should not rely on the value of a reserved bit. To provide
compatibility with future products, the value of a reserved bit should be
preserved across a read-modify-write operation.
31:8 reserved RO 0x00
SSI Peripheral ID Register [15:8]
Can be used by software to identify the presence of this peripheral.
7:0 PID1 RO 0x00
March 17, 2008 367
Preliminary
LM3S8933 Microcontroller
Register 16: SSI Peripheral Identification 2 (SSIPeriphID2), offset 0xFE8
The SSIPeriphIDn registers are hard-coded and the fields within the register determine the reset
value.
SSI Peripheral Identification 2 (SSIPeriphID2)
SSI0 base: 0x4000.8000
Offset 0xFE8
Type RO, reset 0x0000.0018
31 30 29 28 27 26 25 24 23 22 21 20 19 18 17 16
reserved
Type RO RO RO RO RO RO RO RO RO RO RO RO RO RO RO RO
Reset 0 0 0 0 0 0 0 0 0 0 0 0 0 0 0 0
15 14 13 12 11 10 9 8 7 6 5 4 3 2 1 0
reserved PID2
Type RO RO RO RO RO RO RO RO RO RO RO RO RO RO RO RO
Reset 0 0 0 0 0 0 0 0 0 0 0 1 1 0 0 0
Bit/Field Name Type Reset Description
Software should not rely on the value of a reserved bit. To provide
compatibility with future products, the value of a reserved bit should be
preserved across a read-modify-write operation.
31:8 reserved RO 0x00
SSI Peripheral ID Register [23:16]
Can be used by software to identify the presence of this peripheral.
7:0 PID2 RO 0x18
368 March 17, 2008
Preliminary
Synchronous Serial Interface (SSI)
Register 17: SSI Peripheral Identification 3 (SSIPeriphID3), offset 0xFEC
The SSIPeriphIDn registers are hard-coded and the fields within the register determine the reset
value.
SSI Peripheral Identification 3 (SSIPeriphID3)
SSI0 base: 0x4000.8000
Offset 0xFEC
Type RO, reset 0x0000.0001
31 30 29 28 27 26 25 24 23 22 21 20 19 18 17 16
reserved
Type RO RO RO RO RO RO RO RO RO RO RO RO RO RO RO RO
Reset 0 0 0 0 0 0 0 0 0 0 0 0 0 0 0 0
15 14 13 12 11 10 9 8 7 6 5 4 3 2 1 0
reserved PID3
Type RO RO RO RO RO RO RO RO RO RO RO RO RO RO RO RO
Reset 0 0 0 0 0 0 0 0 0 0 0 0 0 0 0 1
Bit/Field Name Type Reset Description
Software should not rely on the value of a reserved bit. To provide
compatibility with future products, the value of a reserved bit should be
preserved across a read-modify-write operation.
31:8 reserved RO 0x00
SSI Peripheral ID Register [31:24]
Can be used by software to identify the presence of this peripheral.
7:0 PID3 RO 0x01
March 17, 2008 369
Preliminary
LM3S8933 Microcontroller
Register 18: SSI PrimeCell Identification 0 (SSIPCellID0), offset 0xFF0
The SSIPCellIDn registers are hard-coded and the fields within the register determine the reset
value.
SSI PrimeCell Identification 0 (SSIPCellID0)
SSI0 base: 0x4000.8000
Offset 0xFF0
Type RO, reset 0x0000.000D
31 30 29 28 27 26 25 24 23 22 21 20 19 18 17 16
reserved
Type RO RO RO RO RO RO RO RO RO RO RO RO RO RO RO RO
Reset 0 0 0 0 0 0 0 0 0 0 0 0 0 0 0 0
15 14 13 12 11 10 9 8 7 6 5 4 3 2 1 0
reserved CID0
Type RO RO RO RO RO RO RO RO RO RO RO RO RO RO RO RO
Reset 0 0 0 0 0 0 0 0 0 0 0 0 1 1 0 1
Bit/Field Name Type Reset Description
Software should not rely on the value of a reserved bit. To provide
compatibility with future products, the value of a reserved bit should be
preserved across a read-modify-write operation.
31:8 reserved RO 0x00
SSI PrimeCell ID Register [7:0]
Provides software a standard cross-peripheral identification system.
7:0 CID0 RO 0x0D
370 March 17, 2008
Preliminary
Synchronous Serial Interface (SSI)
Register 19: SSI PrimeCell Identification 1 (SSIPCellID1), offset 0xFF4
The SSIPCellIDn registers are hard-coded and the fields within the register determine the reset
value.
SSI PrimeCell Identification 1 (SSIPCellID1)
SSI0 base: 0x4000.8000
Offset 0xFF4
Type RO, reset 0x0000.00F0
31 30 29 28 27 26 25 24 23 22 21 20 19 18 17 16
reserved
Type RO RO RO RO RO RO RO RO RO RO RO RO RO RO RO RO
Reset 0 0 0 0 0 0 0 0 0 0 0 0 0 0 0 0
15 14 13 12 11 10 9 8 7 6 5 4 3 2 1 0
reserved CID1
Type RO RO RO RO RO RO RO RO RO RO RO RO RO RO RO RO
Reset 0 0 0 0 0 0 0 0 1 1 1 1 0 0 0 0
Bit/Field Name Type Reset Description
Software should not rely on the value of a reserved bit. To provide
compatibility with future products, the value of a reserved bit should be
preserved across a read-modify-write operation.
31:8 reserved RO 0x00
SSI PrimeCell ID Register [15:8]
Provides software a standard cross-peripheral identification system.
7:0 CID1 RO 0xF0
March 17, 2008 371
Preliminary
LM3S8933 Microcontroller
Register 20: SSI PrimeCell Identification 2 (SSIPCellID2), offset 0xFF8
The SSIPCellIDn registers are hard-coded and the fields within the register determine the reset
value.
SSI PrimeCell Identification 2 (SSIPCellID2)
SSI0 base: 0x4000.8000
Offset 0xFF8
Type RO, reset 0x0000.0005
31 30 29 28 27 26 25 24 23 22 21 20 19 18 17 16
reserved
Type RO RO RO RO RO RO RO RO RO RO RO RO RO RO RO RO
Reset 0 0 0 0 0 0 0 0 0 0 0 0 0 0 0 0
15 14 13 12 11 10 9 8 7 6 5 4 3 2 1 0
reserved CID2
Type RO RO RO RO RO RO RO RO RO RO RO RO RO RO RO RO
Reset 0 0 0 0 0 0 0 0 0 0 0 0 0 1 0 1
Bit/Field Name Type Reset Description
Software should not rely on the value of a reserved bit. To provide
compatibility with future products, the value of a reserved bit should be
preserved across a read-modify-write operation.
31:8 reserved RO 0x00
SSI PrimeCell ID Register [23:16]
Provides software a standard cross-peripheral identification system.
7:0 CID2 RO 0x05
372 March 17, 2008
Preliminary
Synchronous Serial Interface (SSI)
Register 21: SSI PrimeCell Identification 3 (SSIPCellID3), offset 0xFFC
The SSIPCellIDn registers are hard-coded and the fields within the register determine the reset
value.
SSI PrimeCell Identification 3 (SSIPCellID3)
SSI0 base: 0x4000.8000
Offset 0xFFC
Type RO, reset 0x0000.00B1
31 30 29 28 27 26 25 24 23 22 21 20 19 18 17 16
reserved
Type RO RO RO RO RO RO RO RO RO RO RO RO RO RO RO RO
Reset 0 0 0 0 0 0 0 0 0 0 0 0 0 0 0 0
15 14 13 12 11 10 9 8 7 6 5 4 3 2 1 0
reserved CID3
Type RO RO RO RO RO RO RO RO RO RO RO RO RO RO RO RO
Reset 0 0 0 0 0 0 0 0 1 0 1 1 0 0 0 1
Bit/Field Name Type Reset Description
Software should not rely on the value of a reserved bit. To provide
compatibility with future products, the value of a reserved bit should be
preserved across a read-modify-write operation.
31:8 reserved RO 0x00
SSI PrimeCell ID Register [31:24]
Provides software a standard cross-peripheral identification system.
7:0 CID3 RO 0xB1
March 17, 2008 373
Preliminary
LM3S8933 Microcontroller
15 Inter-Integrated Circuit (I2C) Interface
The Inter-Integrated Circuit (I2C) bus provides bi-directional data transfer through a two-wire design
(a serial data line SDA and a serial clock line SCL), and interfaces to external I2C devices such as
serial memory (RAMs and ROMs), networking devices, LCDs, tone generators, and so on. The I2C
bus may also be used for system testing and diagnostic purposes in product development and
manufacture. The LM3S8933 microcontroller includes one I2C module, providing the ability to interact
(both send and receive) with other I2C devices on the bus.
Devices on the I2C bus can be designated as either a master or a slave. The Stellaris® I2C module
supports both sending and receiving data as either a master or a slave, and also supports the
simultaneous operation as both a master and a slave. There are a total of four I2C modes: Master
Transmit, Master Receive, Slave Transmit, and Slave Receive. The Stellaris® I2C module can
operate at two speeds: Standard (100 Kbps) and Fast (400 Kbps).
Both the I2C master and slave can generate interrupts; the I2C master generates interrupts when
a transmit or receive operation completes (or aborts due to an error) and the I2C slave generates
interrupts when data has been sent or requested by a master.
15.1 Block Diagram
Figure 15-1. I2C Block Diagram
I2C I/O Select
I2C Master Core
Interrupt
I2C Slave Core
I2CSCL
I2CSDA
I2CSDA
I2CSCL
I2CSDA
I2CSCL
I2CMSA
I2CMCS
I2CMDR
I2CMTPR
I2CMIMR
I2CMRIS
I2CMICR
I2CMCR
I2CSOAR
I2CSCSR
I2CSDR
I2CSIM
I2CSRIS
I2CSMIS
I2CMMIS I2CSICR
I2C Control
15.2 Functional Description
The I2C module is comprised of both master and slave functions which are implemented as separate
peripherals. For proper operation, the SDA and SCL pins must be connected to bi-directional
open-drain pads. A typical I2C bus configuration is shown in Figure 15-2 on page 375.
See “I2C” on page 540 for I2C timing diagrams.
374 March 17, 2008
Preliminary
Inter-Integrated Circuit (I2C) Interface
Figure 15-2. I2C Bus Configuration
RPUP
StellarisTM
I2CSCL I2CSDA
RPUP
3rd Party Device
with I2C Interface
SCL SDA
I2C Bus
SCL
SDA
3rd Party Device
with I2C Interface
SCL SDA
15.2.1 I2C Bus Functional Overview
The I2C bus uses only two signals: SDA and SCL, named I2CSDA and I2CSCL on Stellaris®
microcontrollers. SDA is the bi-directional serial data line and SCL is the bi-directional serial clock
line. The bus is considered idle when both lines are high.
Every transaction on the I2C bus is nine bits long, consisting of eight data bits and a single
acknowledge bit. The number of bytes per transfer (defined as the time between a valid START
and STOP condition, described in “START and STOP Conditions” on page 375) is unrestricted, but
each byte has to be followed by an acknowledge bit, and data must be transferred MSB first. When
a receiver cannot receive another complete byte, it can hold the clock line SCL Low and force the
transmitter into a wait state. The data transfer continues when the receiver releases the clock SCL.
15.2.1.1 START and STOP Conditions
The protocol of the I2C bus defines two states to begin and end a transaction: START and STOP.
A high-to-low transition on the SDA line while the SCL is high is defined as a START condition, and
a low-to-high transition on the SDA line while SCL is high is defined as a STOP condition. The bus
is considered busy after a START condition and free after a STOP condition. See Figure
15-3 on page 375.
Figure 15-3. START and STOP Conditions
START
condition
SDA
SCL
STOP
condition
SDA
SCL
15.2.1.2 Data Format with 7-Bit Address
Data transfers follow the format shown in Figure 15-4 on page 376. After the START condition, a
slave address is sent. This address is 7-bits long followed by an eighth bit, which is a data direction
bit (R/S bit in the I2CMSA register). A zero indicates a transmit operation (send), and a one indicates
a request for data (receive). A data transfer is always terminated by a STOP condition generated
by the master, however, a master can initiate communications with another device on the bus by
generating a repeated START condition and addressing another slave without first generating a
STOP condition. Various combinations of receive/send formats are then possible within a single
transfer.
March 17, 2008 375
Preliminary
LM3S8933 Microcontroller
Figure 15-4. Complete Data Transfer with a 7-Bit Address
Slave address Data
SDA MSB LSB R/S ACK MSB LSB ACK
SCL 1 2 7 8 9 1 2 7 8 9
The first seven bits of the first byte make up the slave address (see Figure 15-5 on page 376). The
eighth bit determines the direction of the message. A zero in the R/S position of the first byte means
that the master will write (send) data to the selected slave, and a one in this position means that
the master will receive data from the slave.
Figure 15-5. R/S Bit in First Byte
R/S
LSB
Slave address
MSB
15.2.1.3 Data Validity
The data on the SDA line must be stable during the high period of the clock, and the data line can
only change when SCL is low (see Figure 15-6 on page 376).
Figure 15-6. Data Validity During Bit Transfer on the I2C Bus
Change
of data
allowed
Dataline
stable
SDA
SCL
15.2.1.4 Acknowledge
All bus transactions have a required acknowledge clock cycle that is generated by the master. During
the acknowledge cycle, the transmitter (which can be the master or slave) releases the SDA line.
To acknowledge the transaction, the receiver must pull down SDA during the acknowledge clock
cycle. The data sent out by the receiver during the acknowledge cycle must comply with the data
validity requirements described in “Data Validity” on page 376.
When a slave receiver does not acknowledge the slave address, SDA must be left high by the slave
so that the master can generate a STOP condition and abort the current transfer. If the master
device is acting as a receiver during a transfer, it is responsible for acknowledging each transfer
made by the slave. Since the master controls the number of bytes in the transfer, it signals the end
of data to the slave transmitter by not generating an acknowledge on the last data byte. The slave
transmitter must then release SDA to allow the master to generate the STOP or a repeated START
condition.
376 March 17, 2008
Preliminary
Inter-Integrated Circuit (I2C) Interface
15.2.1.5 Arbitration
A master may start a transfer only if the bus is idle. It's possible for two or more masters to generate
a START condition within minimum hold time of the START condition. In these situations, an
arbitration scheme takes place on the SDA line, while SCL is high. During arbitration, the first of the
competing master devices to place a '1' (high) on SDA while another master transmits a '0' (low)
will switch off its data output stage and retire until the bus is idle again.
Arbitration can take place over several bits. Its first stage is a comparison of address bits, and if
both masters are trying to address the same device, arbitration continues on to the comparison of
data bits.
15.2.2 Available Speed Modes
The I2C clock rate is determined by the parameters: CLK_PRD, TIMER_PRD, SCL_LP, and SCL_HP.
where:
CLK_PRD is the system clock period
SCL_LP is the low phase of SCL (fixed at 6)
SCL_HP is the high phase of SCL (fixed at 4)
TIMER_PRD is the programmed value in the I2C Master Timer Period (I2CMTPR) register (see
page 394).
The I2C clock period is calculated as follows:
SCL_PERIOD = 2*(1 + TIMER_PRD)*(SCL_LP + SCL_HP)*CLK_PRD
For example:
CLK_PRD = 50 ns
TIMER_PRD = 2
SCL_LP=6
SCL_HP=4
yields a SCL frequency of:
1/T = 333 Khz
Table 15-1 on page 377 gives examples of timer period, system clock, and speed mode (Standard
or Fast).
Table 15-1. Examples of I2C Master Timer Period versus Speed Mode
System Clock Timer Period Standard Mode Timer Period Fast Mode
4 Mhz 0x01 100 Kbps - -
6 Mhz 0x02 100 Kbps - -
12.5 Mhz 0x06 89 Kbps 0x01 312 Kbps
16.7 Mhz 0x08 93 Kbps 0x02 278 Kbps
20 Mhz 0x09 100 Kbps 0x02 333 Kbps
25 Mhz 0x0C 96.2 Kbps 0x03 312 Kbps
33Mhz 0x10 97.1 Kbps 0x04 330 Kbps
40Mhz 0x13 100 Kbps 0x04 400 Kbps
March 17, 2008 377
Preliminary
LM3S8933 Microcontroller
System Clock Timer Period Standard Mode Timer Period Fast Mode
50Mhz 0x18 100 Kbps 0x06 357 Kbps
15.2.3 Interrupts
The I2C can generate interrupts when the following conditions are observed:
■ Master transaction completed
■ Master transaction error
■ Slave transaction received
■ Slave transaction requested
There is a separate interrupt signal for the I2C master and I2C modules. While both modules can
generate interrupts for multiple conditions, only a single interrupt signal is sent to the interrupt
controller.
15.2.3.1 I2C Master Interrupts
The I2C master module generates an interrupt when a transaction completes (either transmit or
receive), or when an error occurs during a transaction. To enable the I2C master interrupt, software
must write a '1' to the I2C Master Interrupt Mask (I2CMIMR) register. When an interrupt condition
is met, software must check the ERROR bit in the I2C Master Control/Status (I2CMCS) register to
verify that an error didn't occur during the last transaction. An error condition is asserted if the last
transaction wasn't acknowledge by the slave or if the master was forced to give up ownership of
the bus due to a lost arbitration round with another master. If an error is not detected, the application
can proceed with the transfer. The interrupt is cleared by writing a '1' to the I2C Master Interrupt
Clear (I2CMICR) register.
If the application doesn't require the use of interrupts, the raw interrupt status is always visible via
the I2C Master Raw Interrupt Status (I2CMRIS) register.
15.2.3.2 I2C Slave Interrupts
The slave module generates interrupts as it receives requests from an I2C master. To enable the
I2C slave interrupt, write a '1' to the I2C Slave Interrupt Mask (I2CSIMR) register. Software
determines whether the module should write (transmit) or read (receive) data from the I2C Slave
Data (I2CSDR) register, by checking the RREQ and TREQ bits of the I2C Slave Control/Status
(I2CSCSR) register. If the slave module is in receive mode and the first byte of a transfer is received,
the FBR bit is set along with the RREQ bit. The interrupt is cleared by writing a '1' to the I2C Slave
Interrupt Clear (I2CSICR) register.
If the application doesn't require the use of interrupts, the raw interrupt status is always visible via
the I2C Slave Raw Interrupt Status (I2CSRIS) register.
15.2.4 Loopback Operation
The I2C modules can be placed into an internal loopback mode for diagnostic or debug work. This
is accomplished by setting the LPBK bit in the I2C Master Configuration (I2CMCR) register. In
loopback mode, the SDA and SCL signals from the master and slave modules are tied together.
378 March 17, 2008
Preliminary
Inter-Integrated Circuit (I2C) Interface
15.2.5 Command Sequence Flow Charts
This section details the steps required to perform the various I2C transfer types in both master and
slave mode.
15.2.5.1 I2C Master Command Sequences
The figures that follow show the command sequences available for the I2C master.
Figure 15-7. Master Single SEND
Idle
Write Slave
Address to
I2CMSA
Write data to
I2CMDR
Read I2CMCS
Sequence
may be
omitted in a
Single Master
system
BUSBSY bit=0? NO
Write ---0-111 to
I2CMCS
YES
Read I2CMCS
BUSY bit=0?
ERROR bit=0?
YES
Error Service
Idle
YES
NO
NO
March 17, 2008 379
Preliminary
LM3S8933 Microcontroller
Figure 15-8. Master Single RECEIVE
Idle
Write Slave
Address to
I2CMSA
Read I2CMCS
Sequence may be
omitted in a Single
Master system
BUSBSY bit=0? NO
Write ---00111 to
I2CMCS
YES
Read I2CMCS
BUSY bit=0?
ERROR bit=0?
YES
Error Service
Idle
NO
NO
Read data from
I2CMDR
YES
380 March 17, 2008
Preliminary
Inter-Integrated Circuit (I2C) Interface
Figure 15-9. Master Burst SEND
Idle
Write Slave
Address to
I2CMSA
Write data to
I2CMDR
Read I2CMCS
BUSBSY bit=0?
YES
Write ---0-011 to
I2CMCS
NO
Read I2CMCS
BUSY bit=0?
YES
ERROR bit=0?
YES
Write data to ARBLST bit=1?
I2CMDR
Write ---0-100 to
Index=n? I2CMCS
NO
Error Service
Idle
YES
Write ---0-001 to
I2CMCS
Write ---0-101 to
I2CMCS
YES
Read I2CMCS
BUSY bit=0?
ERROR bit=0?
YES
NO
Idle
YES
Error Service NO
NO
NO
NO
Sequence
may be
omitted in a
Single Master
system
March 17, 2008 381
Preliminary
LM3S8933 Microcontroller
Figure 15-10. Master Burst RECEIVE
Idle
Write Slave
Address to
I2CMSA
Read I2CMCS
BUSBSY bit=0? NO
Write ---01011 to
I2CMCS
YES
Read I2CMCS
BUSY bit=0? NO
ERROR bit=0?
YES
ARBLST bit=1?
Write ---0-100 to
I2CMCS
NO
Error Service
YES
Idle
Read data from
I2CMDR
Index=m-1?
Write ---00101 to
I2CMCS
YES
Idle
Read data from
Error Service I2CMDR
ERROR bit=0?
YES
Write ---01001 to
I2CMCS
Read I2CMCS
BUSY bit=0? NO
YES
Sequence
may be
omitted in a
Single Master
system
NO
NO
NO
382 March 17, 2008
Preliminary
Inter-Integrated Circuit (I2C) Interface
Figure 15-11. Master Burst RECEIVE after Burst SEND
Idle
Master operates in
Master Transmit mode
STOP condition is not
generated
Write Slave
Address to
I2CMSA
Write ---01011 to
I2CMCS
Master operates in
Master Receive mode
Idle
Repeated START
condition is generated
with changing data
direction
March 17, 2008 383
Preliminary
LM3S8933 Microcontroller
Figure 15-12. Master Burst SEND after Burst RECEIVE
Idle
Master operates in
Master Receive mode
STOP condition is not
generated
Write Slave
Address to
I2CMSA
Write ---0-011 to
I2CMCS
Master operates in
Master Transmit mode
Idle
Repeated START
condition is generated
with changing data
direction
15.2.5.2 I2C Slave Command Sequences
Figure 15-13 on page 385 presents the command sequence available for the I2C slave.
384 March 17, 2008
Preliminary
Inter-Integrated Circuit (I2C) Interface
Figure 15-13. Slave Command Sequence
Idle
Write OWN Slave
Address to
I2CSOAR
Write -------1 to
I2CSCSR
Read I2CSCSR
RREQ bit=1?
Read data from
I2CSDR
YES
TREQ bit=1? NO
Write data to
I2CSDR
YES
NO
FBR is
also valid
15.3 Initialization and Configuration
The following example shows how to configure the I2C module to send a single byte as a master.
This assumes the system clock is 20 MHz.
1. Enable the I2C clock by writing a value of 0x0000.1000 to the RCGC1 register in the System
Control module.
2. Enable the clock to the appropriate GPIO module via the RCGC2 register in the System Control
module.
3. In the GPIO module, enable the appropriate pins for their alternate function using the
GPIOAFSEL register. Also, be sure to enable the same pins for Open Drain operation.
4. Initialize the I2C Master by writing the I2CMCR register with a value of 0x0000.0020.
5. Set the desired SCL clock speed of 100 Kbps by writing the I2CMTPR register with the correct
value. The value written to the I2CMTPR register represents the number of system clock periods
in one SCL clock period. The TPR value is determined by the following equation:
March 17, 2008 385
Preliminary
LM3S8933 Microcontroller
TPR = (System Clock / (2 * (SCL_LP + SCL_HP) * SCL_CLK)) - 1;
TPR = (20MHz / (2 * (6 + 4) * 100000)) - 1;
TPR = 9
Write the I2CMTPR register with the value of 0x0000.0009.
6. Specify the slave address of the master and that the next operation will be a Send by writing
the I2CMSA register with a value of 0x0000.0076. This sets the slave address to 0x3B.
7. Place data (byte) to be sent in the data register by writing the I2CMDR register with the desired
data.
8. Initiate a single byte send of the data from Master to Slave by writing the I2CMCS register with
a value of 0x0000.0007 (STOP, START, RUN).
9. Wait until the transmission completes by polling the I2CMCS register’s BUSBSY bit until it has
been cleared.
15.4 I2C Register Map
Table 15-2 on page 386 lists the I2C registers. All addresses given are relative to the I2C base
addresses for the master and slave:
■ I2C Master 0: 0x4002.0000
■ I2C Slave 0: 0x4002.0800
Table 15-2. Inter-Integrated Circuit (I2C) Interface Register Map
See
Offset Name Type Reset Description page
I2C Master
0x000 I2CMSA R/W 0x0000.0000 I2C Master Slave Address 388
0x004 I2CMCS R/W 0x0000.0000 I2C Master Control/Status 389
0x008 I2CMDR R/W 0x0000.0000 I2C Master Data 393
0x00C I2CMTPR R/W 0x0000.0001 I2C Master Timer Period 394
0x010 I2CMIMR R/W 0x0000.0000 I2C Master Interrupt Mask 395
0x014 I2CMRIS RO 0x0000.0000 I2C Master Raw Interrupt Status 396
0x018 I2CMMIS RO 0x0000.0000 I2C Master Masked Interrupt Status 397
0x01C I2CMICR WO 0x0000.0000 I2C Master Interrupt Clear 398
0x020 I2CMCR R/W 0x0000.0000 I2C Master Configuration 399
I2C Slave
0x000 I2CSOAR R/W 0x0000.0000 I2C Slave Own Address 401
0x004 I2CSCSR RO 0x0000.0000 I2C Slave Control/Status 402
0x008 I2CSDR R/W 0x0000.0000 I2C Slave Data 404
0x00C I2CSIMR R/W 0x0000.0000 I2C Slave Interrupt Mask 405
386 March 17, 2008
Preliminary
Inter-Integrated Circuit (I2C) Interface
See
Offset Name Type Reset Description page
0x010 I2CSRIS RO 0x0000.0000 I2C Slave Raw Interrupt Status 406
0x014 I2CSMIS RO 0x0000.0000 I2C Slave Masked Interrupt Status 407
0x018 I2CSICR WO 0x0000.0000 I2C Slave Interrupt Clear 408
15.5 Register Descriptions (I2C Master)
The remainder of this section lists and describes the I2C master registers, in numerical order by
address offset. See also “Register Descriptions (I2C Slave)” on page 400.
March 17, 2008 387
Preliminary
LM3S8933 Microcontroller
Register 1: I2C Master Slave Address (I2CMSA), offset 0x000
This register consists of eight bits: seven address bits (A6-A0), and a Receive/Send bit, which
determines if the next operation is a Receive (High), or Send (Low).
I2C Master Slave Address (I2CMSA)
I2C Master 0 base: 0x4002.0000
Offset 0x000
Type R/W, reset 0x0000.0000
31 30 29 28 27 26 25 24 23 22 21 20 19 18 17 16
reserved
Type RO RO RO RO RO RO RO RO RO RO RO RO RO RO RO RO
Reset 0 0 0 0 0 0 0 0 0 0 0 0 0 0 0 0
15 14 13 12 11 10 9 8 7 6 5 4 3 2 1 0
reserved SA R/S
Type RO RO RO RO RO RO RO RO R/W R/W R/W R/W R/W R/W R/W R/W
Reset 0 0 0 0 0 0 0 0 0 0 0 0 0 0 0 0
Bit/Field Name Type Reset Description
Software should not rely on the value of a reserved bit. To provide
compatibility with future products, the value of a reserved bit should be
preserved across a read-modify-write operation.
31:8 reserved RO 0x00
I2C Slave Address
This field specifies bits A6 through A0 of the slave address.
7:1 SA R/W 0
Receive/Send
The R/S bit specifies if the next operation is a Receive (High) or Send
(Low).
Value Description
0 Send.
1 Receive.
0 R/S R/W 0
388 March 17, 2008
Preliminary
Inter-Integrated Circuit (I2C) Interface
Register 2: I2C Master Control/Status (I2CMCS), offset 0x004
This register accesses four control bits when written, and accesses seven status bits when read.
The status register consists of seven bits, which when read determine the state of the I2C bus
controller.
The control register consists of four bits: the RUN, START, STOP, and ACK bits. The START bit causes
the generation of the START, or REPEATED START condition.
The STOP bit determines if the cycle stops at the end of the data cycle, or continues on to a burst.
To generate a single send cycle, the I2C Master Slave Address (I2CMSA) register is written with
the desired address, the R/S bit is set to 0, and the Control register is written with ACK=X (0 or 1),
STOP=1, START=1, and RUN=1 to perform the operation and stop. When the operation is completed
(or aborted due an error), the interrupt pin becomes active and the data may be read from the
I2CMDR register. When the I2C module operates in Master receiver mode, the ACK bit must be set
normally to logic 1. This causes the I2C bus controller to send an acknowledge automatically after
each byte. This bit must be reset when the I2C bus controller requires no further data to be sent
from the slave transmitter.
Read-Only Status Register
I2C Master Control/Status (I2CMCS)
I2C Master 0 base: 0x4002.0000
Offset 0x004
Type RO, reset 0x0000.0000
31 30 29 28 27 26 25 24 23 22 21 20 19 18 17 16
reserved
Type RO RO RO RO RO RO RO RO RO RO RO RO RO RO RO RO
Reset 0 0 0 0 0 0 0 0 0 0 0 0 0 0 0 0
15 14 13 12 11 10 9 8 7 6 5 4 3 2 1 0
reserved BUSBSY IDLE ARBLST DATACK ADRACK ERROR BUSY
Type RO RO RO RO RO RO RO RO RO RO RO RO RO RO RO RO
Reset 0 0 0 0 0 0 0 0 0 0 0 0 0 0 0 0
Bit/Field Name Type Reset Description
Software should not rely on the value of a reserved bit. To provide
compatibility with future products, the value of a reserved bit should be
preserved across a read-modify-write operation.
31:7 reserved RO 0x00
Bus Busy
This bit specifies the state of the I2C bus. If set, the bus is busy;
otherwise, the bus is idle. The bit changes based on the START and
STOP conditions.
6 BUSBSY RO 0
I2C Idle
This bit specifies the I2C controller state. If set, the controller is idle;
otherwise the controller is not idle.
5 IDLE RO 0
Arbitration Lost
This bit specifies the result of bus arbitration. If set, the controller lost
arbitration; otherwise, the controller won arbitration.
4 ARBLST RO 0
March 17, 2008 389
Preliminary
LM3S8933 Microcontroller
Bit/Field Name Type Reset Description
Acknowledge Data
This bit specifies the result of the last data operation. If set, the
transmitted data was not acknowledged; otherwise, the data was
acknowledged.
3 DATACK RO 0
Acknowledge Address
This bit specifies the result of the last address operation. If set, the
transmitted address was not acknowledged; otherwise, the address was
acknowledged.
2 ADRACK RO 0
Error
This bit specifies the result of the last bus operation. If set, an error
occurred on the last operation; otherwise, no error was detected. The
error can be from the slave address not being acknowledged, the
transmit data not being acknowledged, or because the controller lost
arbitration.
1 ERROR RO 0
I2C Busy
This bit specifies the state of the controller. If set, the controller is busy;
otherwise, the controller is idle. When the BUSY bit is set, the other status
bits are not valid.
0 BUSY RO 0
Write-Only Control Register
I2C Master Control/Status (I2CMCS)
I2C Master 0 base: 0x4002.0000
Offset 0x004
Type WO, reset 0x0000.0000
31 30 29 28 27 26 25 24 23 22 21 20 19 18 17 16
reserved
Type WO WO WO WO WO WO WO WO WO WO WO WO WO WO WO WO
Reset 0 0 0 0 0 0 0 0 0 0 0 0 0 0 0 0
15 14 13 12 11 10 9 8 7 6 5 4 3 2 1 0
reserved ACK STOP START RUN
Type WO WO WO WO WO WO WO WO WO WO WO WO WO WO WO WO
Reset 0 0 0 0 0 0 0 0 0 0 0 0 0 0 0 0
Bit/Field Name Type Reset Description
Software should not rely on the value of a reserved bit. To provide
compatibility with future products, the value of a reserved bit should be
preserved across a read-modify-write operation.
31:4 reserved WO 0x00
Data Acknowledge Enable
When set, causes received data byte to be acknowledged automatically
by the master. See field decoding in Table 15-3 on page 391.
3 ACK WO 0
Generate STOP
When set, causes the generation of the STOP condition. See field
decoding in Table 15-3 on page 391.
2 STOP WO 0
390 March 17, 2008
Preliminary
Inter-Integrated Circuit (I2C) Interface
Bit/Field Name Type Reset Description
Generate START
When set, causes the generation of a START or repeated START
condition. See field decoding in Table 15-3 on page 391.
1 START WO 0
I2C Master Enable
When set, allows the master to send or receive data. See field decoding
in Table 15-3 on page 391.
0 RUN WO 0
Table 15-3. Write Field Decoding for I2CMCS[3:0] Field (Sheet 1 of 3)
Current I2CMSA[0] I2CMCS[3:0] Description
State R/S ACK STOP START RUN
START condition followed by SEND (master goes to the
Master Transmit state).
Idle 0 Xa 0 1 1
START condition followed by a SEND and STOP
condition (master remains in Idle state).
0 X 1 1 1
START condition followed by RECEIVE operation with
negative ACK (master goes to the Master Receive state).
1 0 0 1 1
START condition followed by RECEIVE and STOP
condition (master remains in Idle state).
1 0 1 1 1
START condition followed by RECEIVE (master goes to
the Master Receive state).
1 1 0 1 1
1 1 1 1 1 Illegal.
All other combinations not listed are non-operations. NOP.
SEND operation (master remains in Master Transmit
state).
Master X X 0 0 1
Transmit
X X 1 0 0 STOP condition (master goes to Idle state).
SEND followed by STOP condition (master goes to Idle
state).
X X 1 0 1
Repeated START condition followed by a SEND (master
remains in Master Transmit state).
0 X 0 1 1
Repeated START condition followed by SEND and STOP
condition (master goes to Idle state).
0 X 1 1 1
Repeated START condition followed by a RECEIVE
operation with a negative ACK (master goes to Master
Receive state).
1 0 0 1 1
Repeated START condition followed by a SEND and
STOP condition (master goes to Idle state).
1 0 1 1 1
Repeated START condition followed by RECEIVE (master
goes to Master Receive state).
1 1 0 1 1
1 1 1 1 1 Illegal.
All other combinations not listed are non-operations. NOP.
March 17, 2008 391
Preliminary
LM3S8933 Microcontroller
Current I2CMSA[0] I2CMCS[3:0] Description
State R/S ACK STOP START RUN
RECEIVE operation with negative ACK (master remains
in Master Receive state).
Master X 0 0 0 1
Receive
X X 1 0 0 STOP condition (master goes to Idle state).b
RECEIVE followed by STOP condition (master goes to
Idle state).
X 0 1 0 1
RECEIVE operation (master remains in Master Receive
state).
X 1 0 0 1
X 1 1 0 1 Illegal.
Repeated START condition followed by RECEIVE
operation with a negative ACK (master remains in Master
Receive state).
1 0 0 1 1
Repeated START condition followed by RECEIVE and
STOP condition (master goes to Idle state).
1 0 1 1 1
Repeated START condition followed by RECEIVE (master
remains in Master Receive state).
1 1 0 1 1
Repeated START condition followed by SEND (master
goes to Master Transmit state).
0 X 0 1 1
Repeated START condition followed by SEND and STOP
condition (master goes to Idle state).
0 X 1 1 1
All other combinations not listed are non-operations. NOP.
a. An X in a table cell indicates the bit can be 0 or 1.
b. In Master Receive mode, a STOP condition should be generated only after a Data Negative Acknowledge executed by
the master or an Address Negative Acknowledge executed by the slave.
392 March 17, 2008
Preliminary
Inter-Integrated Circuit (I2C) Interface
Register 3: I2C Master Data (I2CMDR), offset 0x008
This register contains the data to be transmitted when in the Master Transmit state, and the data
received when in the Master Receive state.
I2C Master Data (I2CMDR)
I2C Master 0 base: 0x4002.0000
Offset 0x008
Type R/W, reset 0x0000.0000
31 30 29 28 27 26 25 24 23 22 21 20 19 18 17 16
reserved
Type RO RO RO RO RO RO RO RO RO RO RO RO RO RO RO RO
Reset 0 0 0 0 0 0 0 0 0 0 0 0 0 0 0 0
15 14 13 12 11 10 9 8 7 6 5 4 3 2 1 0
reserved DATA
Type RO RO RO RO RO RO RO RO R/W R/W R/W R/W R/W R/W R/W R/W
Reset 0 0 0 0 0 0 0 0 0 0 0 0 0 0 0 0
Bit/Field Name Type Reset Description
Software should not rely on the value of a reserved bit. To provide
compatibility with future products, the value of a reserved bit should be
preserved across a read-modify-write operation.
31:8 reserved RO 0x00
Data Transferred
Data transferred during transaction.
7:0 DATA R/W 0x00
March 17, 2008 393
Preliminary
LM3S8933 Microcontroller
Register 4: I2C Master Timer Period (I2CMTPR), offset 0x00C
This register specifies the period of the SCL clock.
I2C Master Timer Period (I2CMTPR)
I2C Master 0 base: 0x4002.0000
Offset 0x00C
Type R/W, reset 0x0000.0001
31 30 29 28 27 26 25 24 23 22 21 20 19 18 17 16
reserved
Type RO RO RO RO RO RO RO RO RO RO RO RO RO RO RO RO
Reset 0 0 0 0 0 0 0 0 0 0 0 0 0 0 0 0
15 14 13 12 11 10 9 8 7 6 5 4 3 2 1 0
reserved TPR
Type RO RO RO RO RO RO RO RO R/W R/W R/W R/W R/W R/W R/W R/W
Reset 0 0 0 0 0 0 0 0 0 0 0 0 0 0 0 1
Bit/Field Name Type Reset Description
Software should not rely on the value of a reserved bit. To provide
compatibility with future products, the value of a reserved bit should be
preserved across a read-modify-write operation.
31:8 reserved RO 0x00
SCL Clock Period
This field specifies the period of the SCL clock.
SCL_PRD = 2*(1 + TPR)*(SCL_LP + SCL_HP)*CLK_PRD
where:
SCL_PRD is the SCL line period (I2C clock).
TPR is the Timer Period register value (range of 1 to 255).
SCL_LP is the SCL Low period (fixed at 6).
SCL_HP is the SCL High period (fixed at 4).
7:0 TPR R/W 0x1
394 March 17, 2008
Preliminary
Inter-Integrated Circuit (I2C) Interface
Register 5: I2C Master Interrupt Mask (I2CMIMR), offset 0x010
This register controls whether a raw interrupt is promoted to a controller interrupt.
I2C Master Interrupt Mask (I2CMIMR)
I2C Master 0 base: 0x4002.0000
Offset 0x010
Type R/W, reset 0x0000.0000
31 30 29 28 27 26 25 24 23 22 21 20 19 18 17 16
reserved
Type RO RO RO RO RO RO RO RO RO RO RO RO RO RO RO RO
Reset 0 0 0 0 0 0 0 0 0 0 0 0 0 0 0 0
15 14 13 12 11 10 9 8 7 6 5 4 3 2 1 0
reserved IM
Type RO RO RO RO RO RO RO RO RO RO RO RO RO RO RO R/W
Reset 0 0 0 0 0 0 0 0 0 0 0 0 0 0 0 0
Bit/Field Name Type Reset Description
Software should not rely on the value of a reserved bit. To provide
compatibility with future products, the value of a reserved bit should be
preserved across a read-modify-write operation.
31:1 reserved RO 0x00
Interrupt Mask
This bit controls whether a raw interrupt is promoted to a controller
interrupt. If set, the interrupt is not masked and the interrupt is promoted;
otherwise, the interrupt is masked.
0 IM R/W 0
March 17, 2008 395
Preliminary
LM3S8933 Microcontroller
Register 6: I2C Master Raw Interrupt Status (I2CMRIS), offset 0x014
This register specifies whether an interrupt is pending.
I2C Master Raw Interrupt Status (I2CMRIS)
I2C Master 0 base: 0x4002.0000
Offset 0x014
Type RO, reset 0x0000.0000
31 30 29 28 27 26 25 24 23 22 21 20 19 18 17 16
reserved
Type RO RO RO RO RO RO RO RO RO RO RO RO RO RO RO RO
Reset 0 0 0 0 0 0 0 0 0 0 0 0 0 0 0 0
15 14 13 12 11 10 9 8 7 6 5 4 3 2 1 0
reserved RIS
Type RO RO RO RO RO RO RO RO RO RO RO RO RO RO RO RO
Reset 0 0 0 0 0 0 0 0 0 0 0 0 0 0 0 0
Bit/Field Name Type Reset Description
Software should not rely on the value of a reserved bit. To provide
compatibility with future products, the value of a reserved bit should be
preserved across a read-modify-write operation.
31:1 reserved RO 0x00
Raw Interrupt Status
This bit specifies the raw interrupt state (prior to masking) of the I2C
master block. If set, an interrupt is pending; otherwise, an interrupt is
not pending.
0 RIS RO 0
396 March 17, 2008
Preliminary
Inter-Integrated Circuit (I2C) Interface
Register 7: I2C Master Masked Interrupt Status (I2CMMIS), offset 0x018
This register specifies whether an interrupt was signaled.
I2C Master Masked Interrupt Status (I2CMMIS)
I2C Master 0 base: 0x4002.0000
Offset 0x018
Type RO, reset 0x0000.0000
31 30 29 28 27 26 25 24 23 22 21 20 19 18 17 16
reserved
Type RO RO RO RO RO RO RO RO RO RO RO RO RO RO RO RO
Reset 0 0 0 0 0 0 0 0 0 0 0 0 0 0 0 0
15 14 13 12 11 10 9 8 7 6 5 4 3 2 1 0
reserved MIS
Type RO RO RO RO RO RO RO RO RO RO RO RO RO RO RO RO
Reset 0 0 0 0 0 0 0 0 0 0 0 0 0 0 0 0
Bit/Field Name Type Reset Description
Software should not rely on the value of a reserved bit. To provide
compatibility with future products, the value of a reserved bit should be
preserved across a read-modify-write operation.
31:1 reserved RO 0x00
Masked Interrupt Status
This bit specifies the raw interrupt state (after masking) of the I2C master
block. If set, an interrupt was signaled; otherwise, an interrupt has not
been generated since the bit was last cleared.
0 MIS RO 0
March 17, 2008 397
Preliminary
LM3S8933 Microcontroller
Register 8: I2C Master Interrupt Clear (I2CMICR), offset 0x01C
This register clears the raw interrupt.
I2C Master Interrupt Clear (I2CMICR)
I2C Master 0 base: 0x4002.0000
Offset 0x01C
Type WO, reset 0x0000.0000
31 30 29 28 27 26 25 24 23 22 21 20 19 18 17 16
reserved
Type RO RO RO RO RO RO RO RO RO RO RO RO RO RO RO RO
Reset 0 0 0 0 0 0 0 0 0 0 0 0 0 0 0 0
15 14 13 12 11 10 9 8 7 6 5 4 3 2 1 0
reserved IC
Type RO RO RO RO RO RO RO RO RO RO RO RO RO RO RO WO
Reset 0 0 0 0 0 0 0 0 0 0 0 0 0 0 0 0
Bit/Field Name Type Reset Description
Software should not rely on the value of a reserved bit. To provide
compatibility with future products, the value of a reserved bit should be
preserved across a read-modify-write operation.
31:1 reserved RO 0x00
Interrupt Clear
This bit controls the clearing of the raw interrupt. A write of 1 clears the
interrupt; otherwise, a write of 0 has no affect on the interrupt state. A
read of this register returns no meaningful data.
0 IC WO 0
398 March 17, 2008
Preliminary
Inter-Integrated Circuit (I2C) Interface
Register 9: I2C Master Configuration (I2CMCR), offset 0x020
This register configures the mode (Master or Slave) and sets the interface for test mode loopback.
I2C Master Configuration (I2CMCR)
I2C Master 0 base: 0x4002.0000
Offset 0x020
Type R/W, reset 0x0000.0000
31 30 29 28 27 26 25 24 23 22 21 20 19 18 17 16
reserved
Type RO RO RO RO RO RO RO RO RO RO RO RO RO RO RO RO
Reset 0 0 0 0 0 0 0 0 0 0 0 0 0 0 0 0
15 14 13 12 11 10 9 8 7 6 5 4 3 2 1 0
reserved SFE MFE reserved LPBK
Type RO RO RO RO RO RO RO RO RO RO R/W R/W RO RO RO R/W
Reset 0 0 0 0 0 0 0 0 0 0 0 0 0 0 0 0
Bit/Field Name Type Reset Description
Software should not rely on the value of a reserved bit. To provide
compatibility with future products, the value of a reserved bit should be
preserved across a read-modify-write operation.
31:6 reserved RO 0x00
I2C Slave Function Enable
This bit specifies whether the interface may operate in Slave mode. If
set, Slave mode is enabled; otherwise, Slave mode is disabled.
5 SFE R/W 0
I2C Master Function Enable
This bit specifies whether the interface may operate in Master mode. If
set, Master mode is enabled; otherwise, Master mode is disabled and
the interface clock is disabled.
4 MFE R/W 0
Software should not rely on the value of a reserved bit. To provide
compatibility with future products, the value of a reserved bit should be
preserved across a read-modify-write operation.
3:1 reserved RO 0x00
I2C Loopback
This bit specifies whether the interface is operating normally or in
Loopback mode. If set, the device is put in a test mode loopback
configuration; otherwise, the device operates normally.
0 LPBK R/W 0
March 17, 2008 399
Preliminary
LM3S8933 Microcontroller
15.6 Register Descriptions (I2C Slave)
The remainder of this section lists and describes the I2C slave registers, in numerical order by
address offset. See also “Register Descriptions (I2C Master)” on page 387.
400 March 17, 2008
Preliminary
Inter-Integrated Circuit (I2C) Interface
Register 10: I2C Slave Own Address (I2CSOAR), offset 0x000
This register consists of seven address bits that identify the Stellaris® I2C device on the I2C bus.
I2C Slave Own Address (I2CSOAR)
I2C Slave 0 base: 0x4002.0800
Offset 0x000
Type R/W, reset 0x0000.0000
31 30 29 28 27 26 25 24 23 22 21 20 19 18 17 16
reserved
Type RO RO RO RO RO RO RO RO RO RO RO RO RO RO RO RO
Reset 0 0 0 0 0 0 0 0 0 0 0 0 0 0 0 0
15 14 13 12 11 10 9 8 7 6 5 4 3 2 1 0
reserved OAR
Type RO RO RO RO RO RO RO RO RO R/W R/W R/W R/W R/W R/W R/W
Reset 0 0 0 0 0 0 0 0 0 0 0 0 0 0 0 0
Bit/Field Name Type Reset Description
Software should not rely on the value of a reserved bit. To provide
compatibility with future products, the value of a reserved bit should be
preserved across a read-modify-write operation.
31:7 reserved RO 0x00
I2C Slave Own Address
This field specifies bits A6 through A0 of the slave address.
6:0 OAR R/W 0x00
March 17, 2008 401
Preliminary
LM3S8933 Microcontroller
Register 11: I2C Slave Control/Status (I2CSCSR), offset 0x004
This register accesses one control bit when written, and three status bits when read.
The read-only Status register consists of three bits: the FBR, RREQ, and TREQ bits. The First
Byte Received (FBR) bit is set only after the Stellaris® device detects its own slave address
and receives the first data byte from the I2C master. The Receive Request (RREQ) bit indicates
that the Stellaris® I2C device has received a data byte from an I2C master. Read one data byte from
the I2C Slave Data (I2CSDR) register to clear the RREQ bit. The Transmit Request (TREQ) bit
indicates that the Stellaris® I2C device is addressed as a Slave Transmitter. Write one data byte
into the I2C Slave Data (I2CSDR) register to clear the TREQ bit.
The write-only Control register consists of one bit: the DA bit. The DA bit enables and disables the
Stellaris® I2C slave operation.
Read-Only Status Register
I2C Slave Control/Status (I2CSCSR)
I2C Slave 0 base: 0x4002.0800
Offset 0x004
Type RO, reset 0x0000.0000
31 30 29 28 27 26 25 24 23 22 21 20 19 18 17 16
reserved
Type RO RO RO RO RO RO RO RO RO RO RO RO RO RO RO RO
Reset 0 0 0 0 0 0 0 0 0 0 0 0 0 0 0 0
15 14 13 12 11 10 9 8 7 6 5 4 3 2 1 0
reserved FBR TREQ RREQ
Type RO RO RO RO RO RO RO RO RO RO RO RO RO RO RO RO
Reset 0 0 0 0 0 0 0 0 0 0 0 0 0 0 0 0
Bit/Field Name Type Reset Description
Software should not rely on the value of a reserved bit. To provide
compatibility with future products, the value of a reserved bit should be
preserved across a read-modify-write operation.
31:3 reserved RO 0x00
First Byte Received
Indicates that the first byte following the slave’s own address is received.
This bit is only valid when the RREQ bit is set, and is automatically cleared
when data has been read from the I2CSDR register.
Note: This bit is not used for slave transmit operations.
2 FBR RO 0
Transmit Request
This bit specifies the state of the I2C slave with regards to outstanding
transmit requests. If set, the I2C unit has been addressed as a slave
transmitter and uses clock stretching to delay the master until data has
been written to the I2CSDR register. Otherwise, there is no outstanding
transmit request.
1 TREQ RO 0
402 March 17, 2008
Preliminary
Inter-Integrated Circuit (I2C) Interface
Bit/Field Name Type Reset Description
Receive Request
This bit specifies the status of the I2C slave with regards to outstanding
receive requests. If set, the I2C unit has outstanding receive data from
the I2C master and uses clock stretching to delay the master until the
data has been read from the I2CSDR register. Otherwise, no receive
data is outstanding.
0 RREQ RO 0
Write-Only Control Register
I2C Slave Control/Status (I2CSCSR)
I2C Slave 0 base: 0x4002.0800
Offset 0x004
Type WO, reset 0x0000.0000
31 30 29 28 27 26 25 24 23 22 21 20 19 18 17 16
reserved
Type RO RO RO RO RO RO RO RO RO RO RO RO RO RO RO RO
Reset 0 0 0 0 0 0 0 0 0 0 0 0 0 0 0 0
15 14 13 12 11 10 9 8 7 6 5 4 3 2 1 0
reserved DA
Type RO RO RO RO RO RO RO RO RO RO RO RO RO RO RO WO
Reset 0 0 0 0 0 0 0 0 0 0 0 0 0 0 0 0
Bit/Field Name Type Reset Description
Software should not rely on the value of a reserved bit. To provide
compatibility with future products, the value of a reserved bit should be
preserved across a read-modify-write operation.
31:1 reserved RO 0x00
Device Active
Value Description
0 Disables the I2C slave operation.
1 Enables the I2C slave operation.
0 DA WO 0
March 17, 2008 403
Preliminary
LM3S8933 Microcontroller
Register 12: I2C Slave Data (I2CSDR), offset 0x008
This register contains the data to be transmitted when in the Slave Transmit state, and the data
received when in the Slave Receive state.
I2C Slave Data (I2CSDR)
I2C Slave 0 base: 0x4002.0800
Offset 0x008
Type R/W, reset 0x0000.0000
31 30 29 28 27 26 25 24 23 22 21 20 19 18 17 16
reserved
Type RO RO RO RO RO RO RO RO RO RO RO RO RO RO RO RO
Reset 0 0 0 0 0 0 0 0 0 0 0 0 0 0 0 0
15 14 13 12 11 10 9 8 7 6 5 4 3 2 1 0
reserved DATA
Type RO RO RO RO RO RO RO RO R/W R/W R/W R/W R/W R/W R/W R/W
Reset 0 0 0 0 0 0 0 0 0 0 0 0 0 0 0 0
Bit/Field Name Type Reset Description
Software should not rely on the value of a reserved bit. To provide
compatibility with future products, the value of a reserved bit should be
preserved across a read-modify-write operation.
31:8 reserved RO 0x00
Data for Transfer
This field contains the data for transfer during a slave receive or transmit
operation.
7:0 DATA R/W 0x0
404 March 17, 2008
Preliminary
Inter-Integrated Circuit (I2C) Interface
Register 13: I2C Slave Interrupt Mask (I2CSIMR), offset 0x00C
This register controls whether a raw interrupt is promoted to a controller interrupt.
I2C Slave Interrupt Mask (I2CSIMR)
I2C Slave 0 base: 0x4002.0800
Offset 0x00C
Type R/W, reset 0x0000.0000
31 30 29 28 27 26 25 24 23 22 21 20 19 18 17 16
reserved
Type RO RO RO RO RO RO RO RO RO RO RO RO RO RO RO RO
Reset 0 0 0 0 0 0 0 0 0 0 0 0 0 0 0 0
15 14 13 12 11 10 9 8 7 6 5 4 3 2 1 0
reserved IM
Type RO RO RO RO RO RO RO RO RO RO RO RO RO RO RO R/W
Reset 0 0 0 0 0 0 0 0 0 0 0 0 0 0 0 0
Bit/Field Name Type Reset Description
Software should not rely on the value of a reserved bit. To provide
compatibility with future products, the value of a reserved bit should be
preserved across a read-modify-write operation.
31:1 reserved RO 0x00
Interrupt Mask
This bit controls whether a raw interrupt is promoted to a controller
interrupt. If set, the interrupt is not masked and the interrupt is promoted;
otherwise, the interrupt is masked.
0 IM R/W 0
March 17, 2008 405
Preliminary
LM3S8933 Microcontroller
Register 14: I2C Slave Raw Interrupt Status (I2CSRIS), offset 0x010
This register specifies whether an interrupt is pending.
I2C Slave Raw Interrupt Status (I2CSRIS)
I2C Slave 0 base: 0x4002.0800
Offset 0x010
Type RO, reset 0x0000.0000
31 30 29 28 27 26 25 24 23 22 21 20 19 18 17 16
reserved
Type RO RO RO RO RO RO RO RO RO RO RO RO RO RO RO RO
Reset 0 0 0 0 0 0 0 0 0 0 0 0 0 0 0 0
15 14 13 12 11 10 9 8 7 6 5 4 3 2 1 0
reserved RIS
Type RO RO RO RO RO RO RO RO RO RO RO RO RO RO RO RO
Reset 0 0 0 0 0 0 0 0 0 0 0 0 0 0 0 0
Bit/Field Name Type Reset Description
Software should not rely on the value of a reserved bit. To provide
compatibility with future products, the value of a reserved bit should be
preserved across a read-modify-write operation.
31:1 reserved RO 0x00
Raw Interrupt Status
This bit specifies the raw interrupt state (prior to masking) of the I2C
slave block. If set, an interrupt is pending; otherwise, an interrupt is not
pending.
0 RIS RO 0
406 March 17, 2008
Preliminary
Inter-Integrated Circuit (I2C) Interface
Register 15: I2C Slave Masked Interrupt Status (I2CSMIS), offset 0x014
This register specifies whether an interrupt was signaled.
I2C Slave Masked Interrupt Status (I2CSMIS)
I2C Slave 0 base: 0x4002.0800
Offset 0x014
Type RO, reset 0x0000.0000
31 30 29 28 27 26 25 24 23 22 21 20 19 18 17 16
reserved
Type RO RO RO RO RO RO RO RO RO RO RO RO RO RO RO RO
Reset 0 0 0 0 0 0 0 0 0 0 0 0 0 0 0 0
15 14 13 12 11 10 9 8 7 6 5 4 3 2 1 0
reserved MIS
Type RO RO RO RO RO RO RO RO RO RO RO RO RO RO RO RO
Reset 0 0 0 0 0 0 0 0 0 0 0 0 0 0 0 0
Bit/Field Name Type Reset Description
Software should not rely on the value of a reserved bit. To provide
compatibility with future products, the value of a reserved bit should be
preserved across a read-modify-write operation.
31:1 reserved RO 0x00
Masked Interrupt Status
This bit specifies the raw interrupt state (after masking) of the I2C slave
block. If set, an interrupt was signaled; otherwise, an interrupt has not
been generated since the bit was last cleared.
0 MIS RO 0
March 17, 2008 407
Preliminary
LM3S8933 Microcontroller
Register 16: I2C Slave Interrupt Clear (I2CSICR), offset 0x018
This register clears the raw interrupt.
I2C Slave Interrupt Clear (I2CSICR)
I2C Slave 0 base: 0x4002.0800
Offset 0x018
Type WO, reset 0x0000.0000
31 30 29 28 27 26 25 24 23 22 21 20 19 18 17 16
reserved
Type RO RO RO RO RO RO RO RO RO RO RO RO RO RO RO RO
Reset 0 0 0 0 0 0 0 0 0 0 0 0 0 0 0 0
15 14 13 12 11 10 9 8 7 6 5 4 3 2 1 0
reserved IC
Type RO RO RO RO RO RO RO RO RO RO RO RO RO RO RO WO
Reset 0 0 0 0 0 0 0 0 0 0 0 0 0 0 0 0
Bit/Field Name Type Reset Description
Software should not rely on the value of a reserved bit. To provide
compatibility with future products, the value of a reserved bit should be
preserved across a read-modify-write operation.
31:1 reserved RO 0x00
Clear Interrupt
This bit controls the clearing of the raw interrupt. A write of 1 clears the
interrupt; otherwise a write of 0 has no affect on the interrupt state. A
read of this register returns no meaningful data.
0 IC WO 0
408 March 17, 2008
Preliminary
Inter-Integrated Circuit (I2C) Interface
16 Controller Area Network (CAN) Module
16.1 Controller Area Network Overview
Controller Area Network (CAN) is a multicast shared serial bus standard for connecting electronic
control units (ECUs). CAN was specifically designed to be robust in electromagnetically noisy
environments and can utilize a differential balanced line like RS-485 or a more robust twisted-pair
wire. Originally created for automotive purposes, it is also used in many embedded control
applications (such as industrial and medical). Bit rates up to 1 Mbps are possible at network lengths
below 40 meters. Decreased bit rates allow longer network distances (for example, 125 Kbps at
500 m).
16.2 Controller Area Network Features
The Stellaris® CAN module supports the following features:
■ CAN protocol version 2.0 part A/B
■ Bit rates up to 1 Mbps
■ 32 message objects
■ Each message object has its own identifier mask
■ Maskable interrupt
■ Disable Automatic Retransmission mode for Time Triggered CAN (TTCAN) applications
■ Programmable Loopback mode for self-test operation
■ Programmable FIFO mode
■ Gluelessly attachable to an external CAN PHY through the CAN0Tx and CAN0Rx pins
March 17, 2008 409
Preliminary
LM3S8933 Microcontroller
16.3 Controller Area Network Block Diagram
Figure 16-1. CAN Module Block Diagram
APB
Interface CAN Core
CANCTL
CANSTS
CANBIT
CANINT
CANTST
CANBRPE
CANIF1CRQ
CANIF1CMSK
CANIF1MSK1
CANIF1MSK2
CANIF1ARB1
CANIF1ARB2
CANIF1MCTL
CANIF1DA1
CANIF1DA2
CANIF1DB1
CANIF1DB2
CANIF2CRQ
CANIF2CMSK
CANIF2MSK1
CANIF2MSK2
CANIF2ARB1
CANIF2ARB2
CANIF2MCTL
CANIF2DA1
CANIF2DA2
CANIF2DB1
CANIF2DB2
ABP Pins CAN Tx/Rx
Message RAM
32 Message Objects
16.4 Controller Area Network Functional Description
The CAN module conforms to the CAN protocol version 2.0 (parts A and B). Message transfers that
include data, remote, error, and overload frames with an 11-bit identifier (standard) or a 29-bit
identifier (extended) are supported. Transfer rates can be programmed up to 1 Mbps.
The CAN module consists of three major parts:
■ CAN protocol controller and message handler
■ Message memory
■ CAN register interface
The protocol controller transfers and receives the serial data from the CAN bus and passes the data
on to the message handler. The message handler then loads this information into the appropriate
message object based on the current filtering and identifiers in the message object memory. The
message handler is also responsible for generating interrupts based on events on the CAN bus.
410 March 17, 2008
Preliminary
Controller Area Network (CAN) Module
The message object memory is a set of 32 identical memory blocks that hold the current configuration,
status, and actual data for each message object. These are accessed via the CAN message object
register interface. The message memory is not directly accessable in the Stellaris® memory map,
so the Stellaris® CAN controller provides an interface to communicate with the message memory.
The CAN message object register interface provides two register sets for communicating with the
message objects. Since there is no direct access to the message object memory, these two interfaces
must be used to read or write to each message object. The two message object interfaces allow
parallel access to the CAN controller message objects when multiple objects may have new
information that needs to be processed.
16.4.1 Initialization
The software initialization is started by setting the INIT bit in the CAN Control (CANCTL) register
(with software or by a hardware reset) or by going bus-off, which occurs when the transmitter's error
counter exceeds a count of 255. While INIT is set, all message transfers to and from the CAN bus
are stopped and the status of the CAN transmit output is recessive (High). Entering the initialization
state does not change the configuration of the CAN controller, the message objects, or the error
counters. However, some configuration registers are only accessible when in the initialization state.
To initialize the CAN controller, set the CAN Bit Timing (CANBIT) register and configure each
message object. If a message object is not needed, it is sufficient to set it as not valid by clearing
the MsgVal bit in the CANIFnARB2 register. Otherwise, the whole message object has to be
initialized, as the fields of the message object may not have valid information, causing unexpected
results. Access to the CAN Bit Timing (CANBIT) register and to the CAN Baud Rate Prescalar
Extension (CANBRPE) register to configure the bit timing is enabled when both the INIT and CCE
bits in the CANCTL register are set. To leave the initialization state, the INIT bit must be cleared.
Afterwards, the internal Bit Stream Processor (BSP) synchronizes itself to the data transfer on the
CAN bus by waiting for the occurrence of a sequence of 11 consecutive recessive bits (Bus Idle)
before it takes part in bus activities and starts message transfers. The initialization of the message
objects is independent of being in the initialization state and can be done on the fly, but message
objects should all be configured to particular identifiers or set to not valid before the BSP starts the
message transfer. To change the configuration of a message object during normal operation, set
the MsgVal bit in the CANIFnARB2 register to 0 (not valid). When the configuration is completed,
MsgVal is set to 1 again (valid).
16.4.2 Operation
Once the CAN module is initialized and the INIT bit in the CANCTL register is reset to 0, the CAN
module synchronizes itself to the CAN bus and starts the message transfer. As messages are
received, they are stored in their appropriate message objects if they pass the message handler's
filtering. The whole message (including all arbitration bits, data-length code, and eight data bytes)
is stored in the message object. If the Identifier Mask (the Msk bits in the CANIFnMSKn registers)
is used, the arbitration bits that are masked to "don't care" may be overwritten in the message object.
The CPU may read or write each message at any time via the CAN Interface Registers (CANIFnCRQ,
CANIFnCMSK, CANIFnMSKn, CANIFnARBn, CANIFnMCTL, CANIFnDAn, and CANIFnDBn).
The message handler guarantees data consistency in case of concurrent accesses.
The transmission of message objects is under the control of the software that is managing the CAN
hardware. These can be message objects used for one-time data transfers, or permanent message
objects used to respond in a more periodic manner. Permanent message objects have all arbitration
and control set up, and only the data bytes are updated. To start the transmission, the TxRqst bit
in the CANTXRQn register and the NewDat bit in the CANNWDAn register are set. If several transmit
messages are assigned to the same message object (when the number of message objects is not
March 17, 2008 411
Preliminary
LM3S8933 Microcontroller
sufficient), the whole message object has to be configured before the transmission of this message
is requested.
The transmission of any number of message objects may be requested at the same time; they are
transmitted according to their internal priority, which is based on the message identifier for the
message object. Messages may be updated or set to not valid any time, even when their requested
transmission is still pending. The old data is discarded when a message is updated before its pending
transmission has started. Depending on the configuration of the message object, the transmission
of a message may be requested autonomously by the reception of a remote frame with a matching
identifier.
There are two sets of CAN Interface Registers (CANIF1x and CANIF2x), which are used to access
the Message Objects in the Message RAM. The CAN controller coordinates transfers to and from
the Message RAM to and from the registers. The function of the two sets are independent and
identical and can be used to queue transactions.
16.4.3 Transmitting Message Objects
If the internal transmit shift register of the CAN module is ready for loading, and if there is no data
transfer between the CAN Interface Registers and message RAM, the valid message object with
the highest priority that has a pending transmission request is loaded into the transmit shift register
by the message handler and the transmission is started. The message object's NewDat bit is reset
and can be viewed in the CANNWDAn register. After a successful transmission, and if no new data
was written to the message object since the start of the transmission, the TxRqst bit in the
CANIFnCMSK register is reset. If the TxIE bit in the CANIFnMCTL register is set, the IntPnd bit
in the CANIFnMCTL register is set after a successful transmission. If the CAN module has lost the
arbitration or if an error occurred during the transmission, the message is re-transmitted as soon
as the CAN bus is free again. If, meanwhile, the transmission of a message with higher priority has
been requested, the messages are transmitted in the order of their priority.
16.4.4 Configuring a Transmit Message Object
Table 16-1 on page 412 specifies the bit settings for a transmit message object.
Table 16-1. Transmit Message Object Bit Settings
Register CANIFnARB2 CANIFnCMSK CANIFnMCTL CANIFnARB2 CANIFnMCTL
Bit MsgVal Arb Data Mask EoB Dir NewDat MsgLst RxIE TxIE IntPnd RmtEn TxRqst
Value 1 appl appl appl 1 1 0 0 0 appl 0 appl 0
The Xtd and ID bit fields in the CANIFnARBn registers are set by an application. They define the
identifier and type of the outgoing message. If an 11-bit Identifier (Standard Frame) is used, it is
programmed to bits [12:2] of CANIFnARB2, and the remaining identifier bits are not used by the
CAN controller.
If the TxIE bit is set, the IntPnd bit is set after a successful transmission of the message object.
When the RmtEn bit is set, a matching received remote frame causes the TxRqst bit to be set and
the message object automatically transfers the message object's data or generates an interrupt
indicating a remote frame was requested. This can be strictly a single message identifier or it can
be a range of values specified in the message object. The CAN mask registers, CANIFnMSKn,
configure which groups of frames are identified as remote frame requests. The UMask bit in the
CANIFnMCTL register enables the Msk bits in the CANIFnMSKn register to filter which frames are
identified as a remote frame request. The MXtd bit should be set if only 29-bit extended identifiers
should trigger a remote frame request.
412 March 17, 2008
Preliminary
Controller Area Network (CAN) Module
The DLC bit in the CANIFnMCTL register is set to the number of bytes to transfer to the message
object. TxRqst and RmtEn should not be set before the data is valid, as the current data in the
message object can be transmitted as soon as these bits are set.
16.4.5 Updating a Transmit Message Object
The CPU may update the data bytes of a Transmit Message Object any time via the CAN Interface
Registers and neither the MsgVal nor the TxRqst bits have to be reset before the update.
Even if only a part of the data bytes are to be updated, all four bytes of the corresponding
CANIFnDAn or CANIFnDBn register have to be valid before the content of that register is transferred
to the message object. Either the CPU has to write all four bytes into the CANIFnDAn or CANIFnDBn
register or the message object is transferred to the CANIFnDAn or CANIFnDBn register before the
CPU writes the new data bytes.
In order to only update the data in a message object, the WR, NewDat, DataA, and DataB bits are
written to the CAN IFn Command Mask (CANIFnMSKn) register, followed by writing the CAN IFn
Data registers, and then the number of the message object is written to the CAN IFn Command
Request (CANIFnCRQ) register, to update the data bytes and the TxRqst bit at the same time.
To prevent the reset of TxRqst at the end of a transmission that may already be in progress while
the data is updated, NewDat has to be set together with TxRqst. When NewDat is set together
with TxRqst, NewDat is reset as soon as the new transmission has started.
16.4.6 Accepting Received Message Objects
When the arbitration and control field (ID + Xtd + RmtEn + DLC) of an incoming message is
completely shifted into the CAN module, the message handling capability of the module starts
scanning the message RAM for a matching valid message object. To scan the message RAM for
a matching message object, the Acceptance Filtering unit is loaded with the arbitration bits from the
core. Then the arbitration and mask fields (including MsgVal, UMask, NewDat, and EoB) of message
object 1 are loaded into the Acceptance Filtering unit and compared with the arbitration field from
the shift register. This is repeated with each following message object until a matching message
object is found or until the end of the message RAM is reached. If a match occurs, the scanning is
stopped and the message handler proceeds depending on the type of frame received.
16.4.7 Receiving a Data Frame
The message handler stores the message from the CAN module receive shift register into the
respective message object in the message RAM. It stores the data bytes, all arbitration bits, and
the Data Length Code into the corresponding message object. This is implemented to keep the data
bytes connected with the identifier even if arbitration mask registers are used. The NewDat bit of
the CANIFnMCTL register is set to indicate that new data has been received. The CPU should reset
this bit when it reads the message object to indicate to the controller that the message has been
received and the buffer is free to receive more messages. If the CAN controller receives a message
and the NewDat bit was already set, the MsgLst bit is set to indicate that the previous data was
lost. If the RxIE bit of the CANIFnMCTL register is set, the IntPnd bit of the same register is set,
causing the CANINT interrupt register to point to the message object that just received a message.
The TxRqst bit of this message object should be cleared to prevent the transmission of a remote
frame.
16.4.8 Receiving a Remote Frame
When a remote frame is received, three different configurations of the matching message object
have to be considered:
March 17, 2008 413
Preliminary
LM3S8933 Microcontroller
Configuration Description
At the reception of a matching remote frame, the TxRqst bit of this message object is set.
The rest of the message object remains unchanged, and the controller will transfer the data
in the message object.
Dir = 1 (direction = transmit)
RmtEn = 1
UMask = 1 or 0
At the reception of a matching remote frame, the TxRqst bit of this message object remains
unchanged; the remote frame is ignored. This remote frame is disabled and will not
automatically respond or indicate that the remote frame ever happened.
Dir = 1 (direction = transmit)
RmtEn = 0
UMask = 0
At the reception of a matching remote frame, the TxRqst bit of this message object is reset.
The arbitration and control field (ID + Xtd + RmtEn + DLC) from the shift register is stored
into the message object in the message RAM and the NewDat bit of this message object is
set. The data field of the message object remains unchanged; the remote frame is treated
similar to a received data frame. This is useful for a remote data request from another CAN
device for which the Stellaris® controller does not have readily available data. The software
must fill the data and answer the frame manually.
Dir = 1 (direction = transmit)
RmtEn = 0
UMask = 1
16.4.9 Receive/Transmit Priority
The receive/transmit priority for the message objects is controlled by the message number. Message
object 1 has the highest priority, while message object 32 has the lowest priority. If more than one
transmission request is pending, the message objects are transmitted in order based on the message
object with the lowest message number. This should not be confused with the message identifier
as that priority is enforced by the CAN bus. This means that if message object 1 and message object
2 both have valid messages that need to be transmitted, message object 1 will always be transmitted
first regardless of the message identifier in the message object itself.
16.4.10 Configuring a Receive Message Object
Table 16-2 on page 414 specifies the bit settings for a transmit message object.
Table 16-2. Receive Message Object Bit Settings
Register CANIFnARB2 CANIFnCMSK CANIFnMCTL CANIFnARB2 CANIFnMCTL
Bit MsgVal Arb Data Mask EoB Dir NewDat MsgLst RxIE TxIE IntPnd RmtEn TxRqst
Value 1 appl appl appl 1 0 0 0 appl 0 0 0 0
The Xtd and ID bit fields in the CANIFnARBn registers are set by an application. They define the
identifier and type of accepted received messages. If an 11-bit Identifier (Standard Frame) is used,
it is programmed to bits [12:2] of CANIFnARB2, and the remaining identifier bits are ignored by the
CAN controller. When a data frame with an 11-bit Identifier is received, only bits 12:2 of CANIFnARB2
are valid and the rest are set to 0.
If the RxIE bit is set, the IntPnd bit is set when a received data frame is accepted and stored in
the message object.
When the message handler stores a data frame in the message object, it stores the received Data
Length Code and eight data bytes. If the Data Length Code is less than 8, the remaining bytes of
the message object are overwritten by nonspecified values.
The CAN mask registers can be used to allow groups of data frames to be received by a message
object. The CAN mask registers, CANIFnMSKn, configure which groups of frames are received by
a message object. The UMask bit in the CANIFnMCTL register enables the Msk bits in the
CANIFnMSKn register to filter which frames are received. The MXtd bit should be set if only 29-bit
extended identifiers should be received by this message object.
414 March 17, 2008
Preliminary
Controller Area Network (CAN) Module
16.4.11 Handling of Received Message Objects
The CPU may read a received message any time via the CAN Interface registers because the data
consistency is guaranteed by the message handler state machine.
Typically, the CPU first writes 0x007F to the CAN IFn Command Mask (CANIFnCMSK) register
and then writes the number of the message object to the CAN IFn Command Request
(CANIFnCRQ) register. That combination transfers the whole received message from the message
RAM into the Message Buffer registers (CANIFnMSKn, CANIFnARBn, and CANIFnMCTL).
Additionally, the NewDat and IntPnd bits are cleared in the message RAM, acknowledging that
the message has been read and clearing the pending interrupt being generated by this message
object.
If the message object uses masks for acceptance filtering, the arbitration bits show which of the
matching messages has been received.
The actual value of NewDat shows whether a new message has been received since the last time
this message object was read. The actual value of MsgLst shows whether more than one message
has been received since the last time this message object was read. MsgLst is not automatically
reset.
Using a remote frame, the CPU may request new data from another CAN node on the CAN bus.
Setting the TxRqst bit of a receive object causes the transmission of a remote frame with the receive
object's identifier. This remote frame triggers the other CAN node to start the transmission of the
matching data frame. If the matching data frame is received before the remote frame could be
transmitted, the TxRqst bit is automatically reset. This prevents the possible loss of data when the
other device on the CAN bus has already transmitted the data slightly earlier than expected.
16.4.12 Handling of Interrupts
If several interrupts are pending, the CAN Interrupt (CANINT) register points to the pending interrupt
with the highest priority, disregarding their chronological order. An interrupt remains pending until
the CPU has cleared it.
The Status Interrupt has the highest priority. Among the message interrupts, the message object's
interrupt priority decreases with increasing message number. A message interrupt is cleared by
clearing the message object's IntPnd bit. The Status Interrupt is cleared by reading the CAN Status
(CANSTS) register.
The interrupt identifier IntId in the CANINT register indicates the cause of the interrupt. When no
interrupt is pending, the register holds the value to 0. If the value of CANINT is different from 0, then
there is an interrupt pending. If the IE bit is set in the CANCTL register, the interrupt line to the CPU
is active. The interrupt line remains active until CANINT is 0, all interrupt sources have been cleared
(the cause of the interrupt is reset), or until IE is reset, which disables interrupts from the CAN
controller.
The value 0x8000 in the CANINT register indicates that an interrupt is pending because the CAN
module has updated, but not necessarily changed, the CANSTS register (Error Interrupt or Status
Interrupt). This indicates that there is either a new Error Interrupt or a new Status Interrupt. A write
access can clear the RxOK, TxOK, and LEC flags in the CANSTS register, however, only a read
access to the CANSTS register will clear the source of the Status Interrupt.
IntId points to the pending message interrupt with the highest interrupt priority. The SIE bit in the
CANCTL register controls whether a change of the status register may cause an interrupt. The EIE
bit in the CANCTL register controls whether any interrupt from the CAN controller actually generates
an interrupt to the microcontroller's interrupt controller. The CANINT interrupt register is updated
even when the IE bit is set to zero.
March 17, 2008 415
Preliminary
LM3S8933 Microcontroller
There are two possibilities when handling the source of a message interrupt. The first is to read the
IntId bit in the CANINT interrupt register to determine the highest priority interrupt that is pending,
and the second is to read the CAN Message Interrupt Pending (CANMSGnINT) register to see
all of the message objects that have pending interrupts.
An interrupt service routine reading the message that is the source of the interrupt may read the
message and reset the message object's IntPnd at the same time by setting the ClrIntPnd bit
in the CAN IFn Command Mask (CANIFnCMSK) register. When the IntPnd bit is cleared, the
CANINT register will contain the message number for the next message object with a pending
interrupt.
16.4.13 Bit Timing Configuration Error Considerations
Even if minor errors in the configuration of the CAN bit timing do not result in immediate failure, the
performance of a CAN network can be reduced significantly. In many cases, the CAN bit
synchronization amends a faulty configuration of the CAN bit timing to such a degree that only
occasionally an error frame is generated. In the case of arbitration, however, when two or more
CAN nodes simultaneously try to transmit a frame, a misplaced sample point may cause one of the
transmitters to become error passive. The analysis of such sporadic errors requires a detailed
knowledge of the CAN bit synchronization inside a CAN node and of the CAN nodes' interaction on
the CAN bus.
16.4.14 Bit Time and Bit Rate
The CAN system supports bit rates in the range of lower than 1 Kbps up to 1000 Kbps. Each member
of the CAN network has its own clock generator. The timing parameter of the bit time can be
configured individually for each CAN node, creating a common bit rate even though the CAN nodes'
oscillator periods may be different.
Because of small variations in frequency caused by changes in temperature or voltage and by
deteriorating components, these oscillators are not absolutely stable. As long as the variations
remain inside a specific oscillator's tolerance range, the CAN nodes are able to compensate for the
different bit rates by periodically resynchronizing to the bit stream.
According to the CAN specification, the bit time is divided into four segments (see Figure
16-2 on page 417): the Synchronization Segment, the Propagation Time Segment, the Phase Buffer
Segment 1, and the Phase Buffer Segment 2. Each segment consists of a specific, programmable
number of time quanta (see Table 16-3 on page 417). The length of the time quantum (tq), which is
the basic time unit of the bit time, is defined by the CAN controller's system clock (fsys) and the
Baud Rate Prescaler (BRP):
tq = BRP / fsys
The CAN module's system clock fsys is the frequency of its CAN module clock input.
The Synchronization Segment Sync_Seg is that part of the bit time where edges of the CAN bus
level are expected to occur; the distance between an edge that occurs outside of Sync_Seg and
the Sync_Seg is called the phase error of that edge.
The Propagation Time Segment Prop_Seg is intended to compensate for the physical delay times
within the CAN network.
The Phase Buffer Segments Phase_Seg1 and Phase_Seg2 surround the Sample Point.
The (Re-)Synchronization Jump Width (SJW) defines how far a resynchronization may move the
Sample Point inside the limits defined by the Phase Buffer Segments to compensate for edge phase
errors.
416 March 17, 2008
Preliminary
Controller Area Network (CAN) Module
A given bit rate may be met by different bit-time configurations, but for the proper function of the
CAN network, the physical delay times and the oscillator's tolerance range have to be considered.
Figure 16-2. CAN Bit Time
Table 16-3. CAN Protocol Rangesa
Parameter Range Remark
BRP [1 .. 32] Defines the length of the time quantum tq
Sync_Seg 1 tq Fixed length, synchronization of bus input to system clock
Prop_Seg [1 .. 8] tq Compensates for the physical delay times
Phase_Seg1 [1 .. 8] tq May be lengthened temporarily by synchronization
Phase_Seg2 [1 .. 8] tq May be shortened temporarily by synchronization
SJW [1 .. 4] tq May not be longer than either Phase Buffer Segment
a. This table describes the minimum programmable ranges required by the CAN protocol.
The bit timing configuration is programmed in two register bytes in the CANBIT register. The sum
of Prop_Seg and Phase_Seg1 (as TSEG1) is combined with Phase_Seg2 (as TSEG2) in one byte,
and SJW and BRP are combined in the other byte.
In these bit timing registers, the four components TSEG1, TSEG2, SJW, and BRP have to be
programmed to a numerical value that is one less than its functional value; so instead of values in
the range of [1..n], values in the range of [0..n-1] are programmed. That way, for example, SJW
(functional range of [1..4]) is represented by only two bits. Therefore, the length of the bit time is
(programmed values):
[TSEG1 + TSEG2 + 3] × tq
or (functional values):
[Sync_Seg + Prop_Seg + Phase_Seg1 + Phase_Seg2] × tq
The data in the bit timing registers are the configuration input of the CAN protocol controller. The
Baud Rate Prescalar (configured by BRP) defines the length of the time quantum, the basic time
unit of the bit time; the Bit Timing Logic (configured by TSEG1, TSEG2, and SJW) defines the number
of time quanta in the bit time.
The processing of the bit time, the calculation of the position of the Sample Point, and occasional
synchronizations are controlled by the CAN controller and are evaluated once per time quantum.
March 17, 2008 417
Preliminary
LM3S8933 Microcontroller
The CAN controller translates messages to and from frames. It generates and discards the enclosing
fixed format bits, inserts and extracts stuff bits, calculates and checks the CRC code, performs the
error management, and decides which type of synchronization is to be used. It is evaluated at the
Sample Point and processes the sampled bus input bit. The time after the Sample Point that is
needed to calculate the next bit to be sent (that is, the data bit, CRC bit, stuff bit, error flag, or idle)
is called the Information Processing Time (IPT).
The IPT is application-specific but may not be longer than 2 tq; the CAN's IPT is 0 tq. Its length is
the lower limit of the programmed length of Phase_Seg2. In case of synchronization, Phase_Seg2
may be shortened to a value less than IPT, which does not affect bus timing.
16.4.15 Calculating the Bit Timing Parameters
Usually, the calculation of the bit timing configuration starts with a desired bit rate or bit time. The
resulting bit time (1/bit rate) must be an integer multiple of the system clock period.
The bit time may consist of 4 to 25 time quanta. Several combinations may lead to the desired bit
time, allowing iterations of the following steps.
The first part of the bit time to be defined is the Prop_Seg. Its length depends on the delay times
measured in the system. A maximum bus length as well as a maximum node delay has to be defined
for expandable CAN bus systems. The resulting time for Prop_Seg is converted into time quanta
(rounded up to the nearest integer multiple of tq).
The Sync_Seg is 1 tq long (fixed), which leaves (bit time - Prop_Seg - 1) tq for the two Phase Buffer
Segments. If the number of remaining tq is even, the Phase Buffer Segments have the same length,
that is, Phase_Seg2 = Phase_Seg1, else Phase_Seg2 = Phase_Seg1 + 1.
The minimum nominal length of Phase_Seg2 has to be regarded as well. Phase_Seg2 may not
be shorter than the CAN controller's Information Processing Time, which is, depending on the actual
implementation, in the range of [0..2] tq.
The length of the Synchronization Jump Width is set to its maximum value, which is the minimum
of 4 and Phase_Seg1.
The oscillator tolerance range necessary for the resulting configuration is calculated by the formula
given below:
(1 -df) x fnom <= fosc <= (1+ df) × fnom
where:
■ df = Maximum tolerance of oscillator frequency
■ fosc = Actual oscillator frequency
■ fnom = Nominal oscillator frequency
Maximum frequency tolerance must take into account the following formulas:
df <= (Phase_Seg1,Phase_Seg2)min/ 2 × (13 × tbit - Phase_Seg2)
dfmax = 2 × df × fnom
where:
■ Phase_Seg1 and Phase_Seg2 are from Table 16-3 on page 417
418 March 17, 2008
Preliminary
Controller Area Network (CAN) Module
■ tbit = Bit Time
■ dfmax = Maximum difference between two oscillators
If more than one configuration is possible, that configuration allowing the highest oscillator tolerance
range should be chosen.
CAN nodes with different system clocks require different configurations to come to the same bit
rate. The calculation of the propagation time in the CAN network, based on the nodes with the
longest delay times, is done once for the whole network.
The CAN system's oscillator tolerance range is limited by the node with the lowest tolerance range.
The calculation may show that bus length or bit rate have to be decreased or that the oscillator
frequencies' stability has to be increased in order to find a protocol-compliant configuration of the
CAN bit timing.
The resulting configuration is written into the CAN Bit Timing (CANBIT) register :
(Phase_Seg2-1)&(Phase_Seg1+Prop_Seg-1)&(SynchronizationJumpWidth-1)&(Prescaler-1)
16.4.15.1 Example for Bit Timing at High Baud Rate
In this example, the frequency of CAN clock is 25 MHz, BRP is 0, and the bit rate is 1 Mbps.
tq 40 ns = 1/((BRP + 1) × CAN Clock)
delay of bus driver 50 ns
delay of receiver circuit 30 ns
delay of bus line (40m) 220 ns
tProp 640 ns = 16 × tq
tSJW 160 ns = 4 × tq
tTSeg1 800 ns = tProp + tSJW
tTSeg2 160 ns = Information Processing Time + 4 × tq
tSync-Seg 40 ns = 1 × tq
bit time 1000 ns = tSync-Seg + tTSeg1 + tTSeg2
tolerance for CAN_CLK 0.39 % =
min(PB1,PB2)/ 2 × (13 x bit time - PB2) =
0.1us/ 2 x (13x 1us - 2us)
In the above example, the parameters for the CANBIT register are: TSeg2=3, TSeg1=15, SJW =3
and BRP=0. This makes the final value programmed into the CANBIT register, 0x3FC0.
16.4.15.2 Example for Bit Timing at Low Baud Rate
In this example, the frequency of CAN clock is 50 MHz, BRP is 25, and the bit rate is 100 Kbps.
tq 500 ns = 1/((BRP + 1) × CAN clock)
delay of bus driver 200 ns
delay of receiver circuit 80 ns
delay of bus line (40m) 220 ns
tProp 4.5 ms = 9 × tq
tSJW 2 ms = 4 × tq
tTSeg1 6.5 ms = tProp + tSJW
tTSeg2 3 ms = Information Processing Time + 6 × tq
tSync-Seg 500 ns = 1 × tq
bit time 10 ms = tSync-Seg + tTSeg1 + tTSeg2
March 17, 2008 419
Preliminary
LM3S8933 Microcontroller
tolerance for CAN_CLK 1.58 % =
min(PB1,PB2)/ 2 x (13 x bit time - PB2) =
4us/ 2 x (13 x 10us - 4us)
In this example, the concatenated bit time parameters are (4-1)3&(5-1)4&(4-1)2&(2-1)6, and CANBIT
is programmed to 0x34C1.
In the above example, the parameters for the CANBIT register are: TSeg2=5, TSeg1=12, SJW =3
and BRP=24. This makes the final value programmed into the CANBIT register, 0x5CD8.
16.5 Controller Area Network Register Map
Table 16-4 on page 420 lists the registers. All addresses given are relative to the CAN base address
of:
■ CAN0: 0x4004.0000
Table 16-4. CAN Register Map
See
Offset Name Type Reset Description page
0x000 CANCTL R/W 0x0000.0001 CAN Control 422
0x004 CANSTS R/W 0x0000.0000 CAN Status 424
0x008 CANERR RO 0x0000.0000 CAN Error Counter 427
0x00C CANBIT R/W 0x0000.2301 CAN Bit Timing 428
0x010 CANINT RO 0x0000.0000 CAN Interrupt 430
0x014 CANTST R/W 0x0000.0000 CAN Test 431
0x018 CANBRPE R/W 0x0000.0000 CAN Baud Rate Prescalar Extension 433
0x020 CANIF1CRQ R/W 0x0000.0001 CAN IF1 Command Request 434
0x024 CANIF1CMSK R/W 0x0000.0000 CAN IF1 Command Mask 435
0x028 CANIF1MSK1 R/W 0x0000.FFFF CAN IF1 Mask 1 438
0x02C CANIF1MSK2 R/W 0x0000.FFFF CAN IF1 Mask 2 439
0x030 CANIF1ARB1 R/W 0x0000.0000 CAN IF1 Arbitration 1 440
0x034 CANIF1ARB2 R/W 0x0000.0000 CAN IF1 Arbitration 2 441
0x038 CANIF1MCTL R/W 0x0000.0000 CAN IF1 Message Control 442
0x03C CANIF1DA1 R/W 0x0000.0000 CAN IF1 Data A1 444
0x040 CANIF1DA2 R/W 0x0000.0000 CAN IF1 Data A2 444
0x044 CANIF1DB1 R/W 0x0000.0000 CAN IF1 Data B1 444
0x048 CANIF1DB2 R/W 0x0000.0000 CAN IF1 Data B2 444
0x080 CANIF2CRQ R/W 0x0000.0001 CAN IF2 Command Request 434
0x084 CANIF2CMSK R/W 0x0000.0000 CAN IF2 Command Mask 435
0x088 CANIF2MSK1 R/W 0x0000.FFFF CAN IF2 Mask 1 438
420 March 17, 2008
Preliminary
Controller Area Network (CAN) Module
See
Offset Name Type Reset Description page
0x08C CANIF2MSK2 R/W 0x0000.FFFF CAN IF2 Mask 2 439
0x090 CANIF2ARB1 R/W 0x0000.0000 CAN IF2 Arbitration 1 440
0x094 CANIF2ARB2 R/W 0x0000.0000 CAN IF2 Arbitration 2 441
0x098 CANIF2MCTL R/W 0x0000.0000 CAN IF2 Message Control 442
0x09C CANIF2DA1 R/W 0x0000.0000 CAN IF2 Data A1 444
0x0A0 CANIF2DA2 R/W 0x0000.0000 CAN IF2 Data A2 444
0x0A4 CANIF2DB1 R/W 0x0000.0000 CAN IF2 Data B1 444
0x0A8 CANIF2DB2 R/W 0x0000.0000 CAN IF2 Data B2 444
0x100 CANTXRQ1 RO 0x0000.0000 CAN Transmission Request 1 445
0x104 CANTXRQ2 RO 0x0000.0000 CAN Transmission Request 2 445
0x120 CANNWDA1 RO 0x0000.0000 CAN New Data 1 446
0x124 CANNWDA2 RO 0x0000.0000 CAN New Data 2 446
0x140 CANMSG1INT RO 0x0000.0000 CAN Message 1 Interrupt Pending 447
0x144 CANMSG2INT RO 0x0000.0000 CAN Message 2 Interrupt Pending 447
0x160 CANMSG1VAL RO 0x0000.0000 CAN Message 1 Valid 448
0x164 CANMSG2VAL RO 0x0000.0000 CAN Message 2 Valid 448
16.6 Register Descriptions
The remainder of this section lists and describes the CAN registers, in numerical order by address
offset. There are two sets of Interface Registers that are used to access the Message Objects in
the Message RAM: CANIF1x and CANIF2x. The function of the two sets are identical and are used
to queue transactions.
March 17, 2008 421
Preliminary
LM3S8933 Microcontroller
Register 1: CAN Control (CANCTL), offset 0x000
This control register initializes the module and enables test mode and interrupts.
The bus-off recovery sequence (see CAN Specification Rev. 2.0) cannot be shortened by setting
or resetting INIT. If the device goes bus-off, it sets INIT, stopping all bus activities. Once INIT
has been cleared by the CPU, the device then waits for 129 occurrences of Bus Idle (129 * 11
consecutive High bits) before resuming normal operations. At the end of the bus-off recovery
sequence, the Error Management Counters are reset.
During the waiting time after INIT is reset, each time a sequence of 11 High bits has been monitored,
a Bit0Error code is written to the CANSTS status register, enabling the CPU to readily check
whether the CAN bus is stuck Low or continuously disturbed, and to monitor the proceeding of the
bus-off recovery sequence.
CAN Control (CANCTL)
CAN0 base: 0x4004.0000
Offset 0x000
Type R/W, reset 0x0000.0001
31 30 29 28 27 26 25 24 23 22 21 20 19 18 17 16
reserved
Type RO RO RO RO RO RO RO RO RO RO RO RO RO RO RO RO
Reset 0 0 0 0 0 0 0 0 0 0 0 0 0 0 0 0
15 14 13 12 11 10 9 8 7 6 5 4 3 2 1 0
reserved Test CCE DAR reserved EIE SIE IE INIT
Type RO RO RO RO RO RO RO RO R/W R/W R/W RO R/W R/W R/W R/W
Reset 0 0 0 0 0 0 0 0 0 0 0 0 0 0 0 1
Bit/Field Name Type Reset Description
Software should not rely on the value of a reserved bit. To provide
compatibility with future products, the value of a reserved bit should be
preserved across a read-modify-write operation.
31:8 reserved RO 0x0000
Test Mode Enable
0: Normal Operation
1: Test Mode
7 Test R/W 0
Configuration Change Enable
0: Do not allow write access to the CANBIT register.
1: Allow write access to the CANBIT register if the INIT bit is 1.
6 CCE R/W 0
Disable Automatic Retransmission
0: Auto retransmission of disturbed messages is enabled.
1: Auto retransmission is disabled.
5 DAR R/W 0
Software should not rely on the value of a reserved bit. To provide
compatibility with future products, the value of a reserved bit should be
preserved across a read-modify-write operation.
4 reserved RO 0
Error Interrupt Enable
0: Disabled. No Error Status interrupt is generated.
1: Enabled. A change in the Boff or EWarn bits in the CANSTS register
generates an interrupt.
3 EIE R/W 0
422 March 17, 2008
Preliminary
Controller Area Network (CAN) Module
Bit/Field Name Type Reset Description
Status Interrupt Enable
0: Disabled. No Status interrupt is generated.
1: Enabled. An interrupt is generated when a message has successfully
been transmitted or received, or a CAN bus error has been detected. A
change in the TxOK or RxOK bits in the CANSTS register generates an
interrupt.
2 SIE R/W 0
CAN Interrupt Enable
0: Interrupts disabled.
1: Interrupts enabled.
1 IE R/W 0
Initialization
0: Normal operation.
1: Initialization started.
0 INIT R/W 1
March 17, 2008 423
Preliminary
LM3S8933 Microcontroller
Register 2: CAN Status (CANSTS), offset 0x004
The status register contains information for interrupt servicing such as Bus-Off, error count threshold,
and error types.
The LEC field holds the code that indicates the type of the last error to occur on the CAN bus. This
field is cleared to 0 when a message has been transferred (reception or transmission) without error.
The unused error code 7 may be written by the CPU to manually set this field to an invalid error so
that it can be checked for a change later.
An Error Interrupt is generated by the BOff and EWarn bits and a Status Interrupt is generated by
the RxOK, TxOK, and LEC bits, assuming that the corresponding enable bits in the CAN Control
(CANCTL) register are set. A change of the EPass bit or a write to the RxOK, TxOK, or LEC bits
does not generate an interrupt.
Reading the CAN Status (CANSTS) register clears the CAN Interrupt (CANINT) register, if it is
pending.
CAN Status (CANSTS)
CAN0 base: 0x4004.0000
Offset 0x004
Type R/W, reset 0x0000.0000
31 30 29 28 27 26 25 24 23 22 21 20 19 18 17 16
reserved
Type RO RO RO RO RO RO RO RO RO RO RO RO RO RO RO RO
Reset 0 0 0 0 0 0 0 0 0 0 0 0 0 0 0 0
15 14 13 12 11 10 9 8 7 6 5 4 3 2 1 0
reserved BOff EWarn EPass RxOK TxOK LEC
Type RO RO RO RO RO RO RO RO RO RO RO R/W R/W R/W R/W R/W
Reset 0 0 0 0 0 0 0 0 0 0 0 0 0 0 0 0
Bit/Field Name Type Reset Description
Software should not rely on the value of a reserved bit. To provide
compatibility with future products, the value of a reserved bit should be
preserved across a read-modify-write operation.
31:8 reserved RO 0x0000
Bus-Off Status
0: Module is not in bus-off state.
1: Module is in bus-off state.
7 BOff RO 0
Warning Status
0: Both error counters are below the error warning limit of 96.
1: At least one of the error counters has reached the error warning limit
of 96.
6 EWarn RO 0
Error Passive
0: The CAN module is in the Error Active state, that is, the receive or
transmit error count is less than or equal to 127.
1: The CAN module is in the Error Passive state, that is, the receive or
transmit error count is greater than 127.
5 EPass RO 0
424 March 17, 2008
Preliminary
Controller Area Network (CAN) Module
Bit/Field Name Type Reset Description
Received a Message Successfully
0: Since this bit was last reset to 0, no message has been successfully
received.
1: Since this bit was last reset to 0, a message has been successfully
received, independent of the result of the acceptance filtering.
This bit is never reset by the CAN module.
4 RxOK R/W 0
Transmitted a Message Successfully
0: Since this bit was last reset to 0, no message has been successfully
transmitted.
1: Since this bit was last reset to 0, a message has been successfully
transmitted error-free and acknowledged by at least one other node.
This bit is never reset by the CAN module.
3 TxOK R/W 0
March 17, 2008 425
Preliminary
LM3S8933 Microcontroller
Bit/Field Name Type Reset Description
Last Error Code
This is the type of the last error to occur on the CAN bus.
Value Definition
0x0 No Error
Stuff Error
More than 5 equal bits in a sequence have occurred in a part
of a received message where this is not allowed.
0x1
Format Error
A fixed format part of the received frame has the wrong format.
0x2
ACK Error
The message transmitted was not acknowledged by another
node.
0x3
Bit 1 Error
When a message is transmitted, the CAN controller monitors
the data lines to detect any conflicts. When the arbitration field
is transmitted, data conflicts are a part of the arbitration protocol.
When other frame fields are transmitted, data conflicts are
considered errors.
A Bit 1 Error indicates that the device wanted to send a High
level (logical 1) but the monitored bus value was Low (logical
0).
0x4
Bit 0 Error
A Bit 0 Error indicates that the device wanted to send a Low
level (logical 0), but the monitored bus value was High (logical
1).
During bus-off recovery, this status is set each time a sequence
of 11 High bits has been monitored. This enables the CPU to
monitor the proceeding of the bus-off recovery sequence without
any disturbances to the bus.
0x5
CRC Error
The CRC checksum was incorrect in the received message,
indicating that the calculated value received did not match the
calculated CRC of the data.
0x6
Unused
When the LEC bit shows this value, no CAN bus event was
detected since the CPU wrote this value to LEC.
0x7
2:0 LEC R/W 0x0
426 March 17, 2008
Preliminary
Controller Area Network (CAN) Module
Register 3: CAN Error Counter (CANERR), offset 0x008
This register contains the error counter values, which can be used to analyze the cause of an error.
CAN Error Counter (CANERR)
CAN0 base: 0x4004.0000
Offset 0x008
Type RO, reset 0x0000.0000
31 30 29 28 27 26 25 24 23 22 21 20 19 18 17 16
reserved
Type RO RO RO RO RO RO RO RO RO RO RO RO RO RO RO RO
Reset 0 0 0 0 0 0 0 0 0 0 0 0 0 0 0 0
15 14 13 12 11 10 9 8 7 6 5 4 3 2 1 0
RP REC TEC
Type RO RO RO RO RO RO RO RO RO RO RO RO RO RO RO RO
Reset 0 0 0 0 0 0 0 0 0 0 0 0 0 0 0 0
Bit/Field Name Type Reset Description
Software should not rely on the value of a reserved bit. To provide
compatibility with future products, the value of a reserved bit should be
preserved across a read-modify-write operation.
31:16 reserved RO 0x0000
Received Error Passive
0: The Receive Error counter is below the Error Passive level (127 or
less).
1: The Receive Error counter has reached the Error Passive level (128
or greater).
15 RP RO 0
Receive Error Counter
State of the receiver error counter (0 to 127).
14:8 REC RO 0x0
Transmit Error Counter
State of the transmit error counter (0 to 255).
7:0 TEC RO 0x0
March 17, 2008 427
Preliminary
LM3S8933 Microcontroller
Register 4: CAN Bit Timing (CANBIT), offset 0x00C
This register is used to program the bit width and bit quantum. Values are to be programmed to the
system clock frequency. This register is write-enabled by the CCE and INIT bits in the CANCTL
register. See “Bit Time and Bit Rate” on page 416 for more information.
CAN Bit Timing (CANBIT)
CAN0 base: 0x4004.0000
Offset 0x00C
Type R/W, reset 0x0000.2301
31 30 29 28 27 26 25 24 23 22 21 20 19 18 17 16
reserved
Type RO RO RO RO RO RO RO RO RO RO RO RO RO RO RO RO
Reset 0 0 0 0 0 0 0 0 0 0 0 0 0 0 0 0
15 14 13 12 11 10 9 8 7 6 5 4 3 2 1 0
reserved TSeg2 TSeg1 SJW BRP
Type RO R/W R/W R/W R/W R/W R/W R/W R/W R/W R/W R/W R/W R/W R/W R/W
Reset 0 0 1 0 0 0 1 1 0 0 0 0 0 0 0 1
Bit/Field Name Type Reset Description
Software should not rely on the value of a reserved bit. To provide
compatibility with future products, the value of a reserved bit should be
preserved across a read-modify-write operation.
31:15 reserved RO 0x0000
Time Segment after Sample Point
0x00-0x07: The actual interpretation by the hardware of this value is
such that one more than the value programmed here is used.
So, for example, a reset value of 0x2 defines that there is 3(2+1) bit
time quanta defined for Phase_Seg2 (see Figure 16-2 on page 417).
The bit time quanta is defined by BRP.
14:12 TSeg2 R/W 0x2
Time Segment Before Sample Point
0x00-0x0F: The actual interpretation by the hardware of this value is
such that one more than the value programmed here is used.
So, for example, the reset value of 0x3 defines that there is 4(3+1) bit
time quanta defined for Phase_Seg1 (see Figure 16-2 on page 417).
The bit time quanta is define by BRP.
11:8 TSeg1 R/W 0x3
(Re)Synchronization Jump Width
0x00-0x03: The actual interpretation by the hardware of this value is
such that one more than the value programmed here is used.
During the start of frame (SOF), if the CAN controller detects a phase
error (misalignment), it can adjust the length of TSeg2 or TSeg1 by the
value in SJW. So the reset value of 0 adjusts the length by 1 bit time
quanta.
7:6 SJW R/W 0x0
428 March 17, 2008
Preliminary
Controller Area Network (CAN) Module
Bit/Field Name Type Reset Description
Baud Rate Prescalar
The value by which the oscillator frequency is divided for generating the
bit time quanta. The bit time is built up from a multiple of this quantum.
0x00-0x03F: The actual interpretation by the hardware of this value is
such that one more than the value programmed here is used.
BRP defines the number of CAN clock periods that make up 1 bit time
quanta, so the reset value is 2 bit time quanta (1+1).
The CANBRPE register can be used to further divide the bit time.
5:0 BRP R/W 0x1
March 17, 2008 429
Preliminary
LM3S8933 Microcontroller
Register 5: CAN Interrupt (CANINT), offset 0x010
This register indicates the source of the interrupt.
If several interrupts are pending, the CAN Interrupt (CANINT) register points to the pending interrupt
with the highest priority, disregarding their chronological order. An interrupt remains pending until
the CPU has cleared it. If the IntId bit is not 0x0000 (the default) and the IE bit in the CANCTL
register is set, the interrupt is active. The interrupt line remains active until the IntId bit is set back
to 0x0000 when the cause of all interrupts are reset, or until IE is reset.
Note: Reading the CAN Status (CANSTS) register clears the CAN Interrupt (CANINT) register,
if it is pending.
CAN Interrupt (CANINT)
CAN0 base: 0x4004.0000
Offset 0x010
Type RO, reset 0x0000.0000
31 30 29 28 27 26 25 24 23 22 21 20 19 18 17 16
reserved
Type RO RO RO RO RO RO RO RO RO RO RO RO RO RO RO RO
Reset 0 0 0 0 0 0 0 0 0 0 0 0 0 0 0 0
15 14 13 12 11 10 9 8 7 6 5 4 3 2 1 0
IntId
Type RO RO RO RO RO RO RO RO RO RO RO RO RO RO RO RO
Reset 0 0 0 0 0 0 0 0 0 0 0 0 0 0 0 0
Bit/Field Name Type Reset Description
Software should not rely on the value of a reserved bit. To provide
compatibility with future products, the value of a reserved bit should be
preserved across a read-modify-write operation.
31:16 reserved RO 0x0000
Interrupt Identifier
The number in this field indicates the source of the interrupt.
Value Definition
0x0000 No interrupt pending
Number of the message object that caused the
interrupt
0x0001-0x0020
0x0021-0x7FFF Unused
0x8000 Status Interrupt
0x8001-0xFFFF Unused
15:0 IntId RO 0x0000
430 March 17, 2008
Preliminary
Controller Area Network (CAN) Module
Register 6: CAN Test (CANTST), offset 0x014
This is the test mode register for self-test and external pin access. It is write-enabled by the Test
bit in the CANCTL register. Different test functions may be combined, however, CAN transfers will
be affected if the Tx bits in this register are not zero.
CAN Test (CANTST)
CAN0 base: 0x4004.0000
Offset 0x014
Type R/W, reset 0x0000.0000
31 30 29 28 27 26 25 24 23 22 21 20 19 18 17 16
reserved
Type RO RO RO RO RO RO RO RO RO RO RO RO RO RO RO RO
Reset 0 0 0 0 0 0 0 0 0 0 0 0 0 0 0 0
15 14 13 12 11 10 9 8 7 6 5 4 3 2 1 0
reserved Rx Tx LBack Silent Basic reserved
Type RO RO RO RO RO RO RO RO RO R/W R/W R/W R/W R/W RO RO
Reset 0 0 0 0 0 0 0 0 0 0 0 0 0 0 0 0
Bit/Field Name Type Reset Description
Software should not rely on the value of a reserved bit. To provide
compatibility with future products, the value of a reserved bit should be
preserved across a read-modify-write operation.
31:8 reserved RO 0x0000
Receive Observation
Displays the value on the CANnRx pin.
7 Rx RO 0
Transmit Control
Overrides control of the CANnTx pin.
Value Description
0x0 CANnTx is controlled by the CAN module
0x1 Sample Point signal driven on the CANnTx pin
0x2 CANnTx drives a Low value
0x3 CANnTx drives a High value
6:5 Tx R/W 0x0
Loopback Mode
0: Disabled.
1: Enabled.
4 LBack R/W 0
Silent Mode
Do not transmit data; monitor the bus. Also known as Bus Monitor mode.
0: Disabled.
1: Enabled.
3 Silent R/W 0
Basic Mode
0: Disabled.
1: Use CANIF1 registers as transmit buffer, and use CANIF2 registers
as receive buffer.
2 Basic R/W 0
March 17, 2008 431
Preliminary
LM3S8933 Microcontroller
Bit/Field Name Type Reset Description
Software should not rely on the value of a reserved bit. To provide
compatibility with future products, the value of a reserved bit should be
preserved across a read-modify-write operation.
1:0 reserved RO 0x0
432 March 17, 2008
Preliminary
Controller Area Network (CAN) Module
Register 7: CAN Baud Rate Prescalar Extension (CANBRPE), offset 0x018
This register is used to further divide the bit time set with the BRP bit in the CANBIT register. It is
write-enabled with the CCE bit in the CANCTL register.
CAN Baud Rate Prescalar Extension (CANBRPE)
CAN0 base: 0x4004.0000
Offset 0x018
Type R/W, reset 0x0000.0000
31 30 29 28 27 26 25 24 23 22 21 20 19 18 17 16
reserved
Type RO RO RO RO RO RO RO RO RO RO RO RO RO RO RO RO
Reset 0 0 0 0 0 0 0 0 0 0 0 0 0 0 0 0
15 14 13 12 11 10 9 8 7 6 5 4 3 2 1 0
reserved BRPE
Type RO RO RO RO RO RO RO RO RO RO RO RO R/W R/W R/W R/W
Reset 0 0 0 0 0 0 0 0 0 0 0 0 0 0 0 0
Bit/Field Name Type Reset Description
Software should not rely on the value of a reserved bit. To provide
compatibility with future products, the value of a reserved bit should be
preserved across a read-modify-write operation.
31:4 reserved RO 0x0000
Baud Rate Prescalar Extension
0x00-0x0F: Extend the BRP bit in the CANBIT register to values up to
1023. The actual interpretation by the hardware is one more than the
value programmed by BRPE (MSBs) and BRP (LSBs).
3:0 BRPE R/W 0x0
March 17, 2008 433
Preliminary
LM3S8933 Microcontroller
Register 8: CAN IF1 Command Request (CANIF1CRQ), offset 0x020
Register 9: CAN IF2 Command Request (CANIF2CRQ), offset 0x080
This register is used to start a transfer when its MNUM bit field is updated. Its Busy bit indicates that
the information is transferring from the CAN Interface Registers to the internal message RAM.
A message transfer is started as soon as there is a write of the message object number with the
MNUM bit. With this write operation, the Busy bit is automatically set to 1 to indicate that a transfer
is in progress. After a wait time of 3 to 6 CAN_CLK periods, the transfer between the interface register
and the message RAM completes, which then sets the Busy bit back to 0.
CAN IF1 Command Request (CANIF1CRQ)
CAN0 base: 0x4004.0000
Offset 0x020
Type R/W, reset 0x0000.0001
31 30 29 28 27 26 25 24 23 22 21 20 19 18 17 16
reserved
Type RO RO RO RO RO RO RO RO RO RO RO RO RO RO RO RO
Reset 0 0 0 0 0 0 0 0 0 0 0 0 0 0 0 0
15 14 13 12 11 10 9 8 7 6 5 4 3 2 1 0
Busy reserved MNUM
Type RO RO RO RO RO RO RO RO RO RO R/W R/W R/W R/W R/W R/W
Reset 0 0 0 0 0 0 0 0 0 0 0 0 0 0 0 1
Bit/Field Name Type Reset Description
Software should not rely on the value of a reserved bit. To provide
compatibility with future products, the value of a reserved bit should be
preserved across a read-modify-write operation.
31:16 reserved RO 0x0000
Busy Flag
0: Reset when read/write action has finished.
1: Set when a write occurs to the message number in this register.
15 Busy RO 0x0
Software should not rely on the value of a reserved bit. To provide
compatibility with future products, the value of a reserved bit should be
preserved across a read-modify-write operation.
14:6 reserved RO 0x00
Message Number
Selects one of the 32 message objects in the message RAM for data
transfer. The message objects are numbered from 1 to 32.
Value Description
0 is not a valid message number; it is interpreted as 0x20,
or object 32.
0x00
0x01-0x20 Indicates specified message object 1 to 32.
Not a valid message number; values are shifted and it is
interpreted as 0x01-0x1F.
0x21-0x3F
5:0 MNUM R/W 0x01
434 March 17, 2008
Preliminary
Controller Area Network (CAN) Module
Register 10: CAN IF1 Command Mask (CANIF1CMSK), offset 0x024
Register 11: CAN IF2 Command Mask (CANIF2CMSK), offset 0x084
The Command Mask registers specify the transfer direction and select which buffer registers are
the source or target of the data transfer.
Read-Only CANIFnCMSK Register
CAN IF1 Command Mask (CANIF1CMSK)
CAN0 base: 0x4004.0000
Offset 0x024
Type R/W, reset 0x0000.0000
31 30 29 28 27 26 25 24 23 22 21 20 19 18 17 16
reserved
Type RO RO RO RO RO RO RO RO RO RO RO RO RO RO RO RO
Reset 0 0 0 0 0 0 0 0 0 0 0 0 0 0 0 0
15 14 13 12 11 10 9 8 7 6 5 4 3 2 1 0
reserved WRNRD Mask Arb Control ClrIntPnd NewDat DataA DataB
Type RO RO RO RO RO RO RO RO R R R R R R R R
Reset 0 0 0 0 0 0 0 0 0 0 0 0 0 0 0 0
Bit/Field Name Type Reset Description
Software should not rely on the value of a reserved bit. To provide
compatibility with future products, the value of a reserved bit should be
preserved across a read-modify-write operation.
31:8 reserved RO 0x0000
Write, Not Read
Transfer the message object address specified by the CAN Command
Request (CANIFnCRQ) register to the CAN message buffer registers
(CANIFnMSK1, CANIFnMSK2, CANIFnARB1, CANIFnARB2,
CANIFnCTL, CANIFnDA1, CANIFnDA2, CANIFnDB1, and
CANIFnDB2).
7 WRNRD R 0
Access Mask Bits
0: Mask bits unchanged.
1: Transfer IDMask + Dir + MXtd of the message object into the
Interface registers.
6 Mask R 0
Access Arbitration Bits
0: Arbitration bits unchanged.
1: Transfer ID + Dir + Xtd + MsgVal of the message object into the
Interface registers.
5 Arb R 0
Access Control Bits
0: Control bits unchanged.
1: Transfer control bits into Interface registers.
4 Control R 0
Clear Interrupt Pending Bit
0: IntPnd bit in CANIFnMCTL register remains unchanged.
1: Clear IntPnd bit in the CANIFnMCTL register in the message object.
3 ClrIntPnd R 0
March 17, 2008 435
Preliminary
LM3S8933 Microcontroller
Bit/Field Name Type Reset Description
Access New Data
0: NewDat bit unchanged.
1: Clear NewDat bit in the message object.
Note: A read access to a message object can be combined with the
reset of the control bits IntPdn and NewDat. The values of
these bits that are transferred to the CANIFnMCTL register
always reflect the status before resetting these bits.
2 NewDat R 0
Access Data Byte 0 to 3
0: Data bytes 0-3 are unchanged.
1: Transfer data bytes 0-3 in message object to CANIFnDA1 and
CANIFnDA2.
1 DataA R 0
Access Data Byte 4 to 7
0: Data bytes 4-7 unchanged.
1: Transfer data bytes 4-7 in message object to CANIFnDB1 and
CANIFnDB2.
0 DataB R 0
Write-Only CANIFnCMSK Register
CAN IF1 Command Mask (CANIF1CMSK)
CAN0 base: 0x4004.0000
Offset 0x024
Type R/W, reset 0x0000.0000
31 30 29 28 27 26 25 24 23 22 21 20 19 18 17 16
reserved
Type RO RO RO RO RO RO RO RO RO RO RO RO RO RO RO RO
Reset 0 0 0 0 0 0 0 0 0 0 0 0 0 0 0 0
15 14 13 12 11 10 9 8 7 6 5 4 3 2 1 0
reserved WRNRD Mask Arb Control reserved TxRqst DataA DataB
Type RO RO RO RO RO RO RO RO W W W W RO W W W
Reset 0 0 0 0 0 0 0 0 0 0 0 0 0 0 0 0
Bit/Field Name Type Reset Description
Software should not rely on the value of a reserved bit. To provide
compatibility with future products, the value of a reserved bit should be
preserved across a read-modify-write operation.
31:8 reserved RO 0x0000
Write, Not Read
0: Read.
1: Write. Transfer data from the message buffer registers to the message
object address specified by the CANIFnCRQ register.
7 WRNRD W 0
Access Mask Bits
0: Mask bits unchanged.
1: Transfer IDMask + Dir + MXtd to message object.
6 Mask W 0
436 March 17, 2008
Preliminary
Controller Area Network (CAN) Module
Bit/Field Name Type Reset Description
Access Arbitration Bits
0: Arbitration bits unchanged.
1: Transfer ID + Dir + Xtd + MsgVal to message object.
5 Arb W 0
Access Control Bits
0: Control bits unchanged.
1: Transfer control bits to message object.
4 Control W 0
Software should not rely on the value of a reserved bit. To provide
compatibility with future products, the value of a reserved bit should be
preserved across a read-modify-write operation.
3 reserved RO 0
Access Transmission Request Bit
0: TxRqst bit unchanged.
1: Set TxRqst bit
Note: If a transmission is requested by programming this TxRqst
bit, the parallel TxRqst in the CANIFnMCTL register is
ignored.
2 TxRqst W 0
Access Data Byte 0 to 3
0: Data bytes 0-3 are unchanged.
1: Transfer data bytes 0-3 (CANIFnDA1 and CANIFnDA2) to message
object.
1 DataA W 0
Access Data Byte 4 to 7
0: Data bytes 4-7 unchanged.
1: Transfer data bytes 4-7 (CANIFnDB1 and CANIFnDB2) to message
object.
0 DataB W 0
March 17, 2008 437
Preliminary
LM3S8933 Microcontroller
Register 12: CAN IF1 Mask 1 (CANIF1MSK1), offset 0x028
Register 13: CAN IF2 Mask 1 (CANIF2MSK1), offset 0x088
The mask information provided in this register accompanies the data (CANIFnDAn), arbitration
information (CANIFnARBn), and control information (CANIFnMCTL) to the message object in the
message RAM. The mask is used with the ID bit in the CANIFnARBn register for acceptance
filtering. Additional mask information is contained in the CANIFnMSK2 register.
CAN IF1 Mask 1 (CANIF1MSK1)
CAN0 base: 0x4004.0000
Offset 0x028
Type R/W, reset 0x0000.FFFF
31 30 29 28 27 26 25 24 23 22 21 20 19 18 17 16
reserved
Type RO RO RO RO RO RO RO RO RO RO RO RO RO RO RO RO
Reset 0 0 0 0 0 0 0 0 0 0 0 0 0 0 0 0
15 14 13 12 11 10 9 8 7 6 5 4 3 2 1 0
Msk
Type R/W R/W R/W R/W R/W R/W R/W R/W R/W R/W R/W R/W R/W R/W R/W R/W
Reset 0 0 0 0 0 0 0 0 1 1 1 1 1 1 1 1
Bit/Field Name Type Reset Description
Software should not rely on the value of a reserved bit. To provide
compatibility with future products, the value of a reserved bit should be
preserved across a read-modify-write operation.
31:16 reserved RO 0x0000
Identifier Mask
0: The corresponding identifier bit (ID) in the message object cannot
inhibit the match in acceptance filtering.
1: The corresponding identifier bit (ID) is used for acceptance filtering.
15:0 Msk R/W 0xFF
438 March 17, 2008
Preliminary
Controller Area Network (CAN) Module
Register 14: CAN IF1 Mask 2 (CANIF1MSK2), offset 0x02C
Register 15: CAN IF2 Mask 2 (CANIF2MSK2), offset 0x08C
This register holds extended mask information that accompanies the CANIFnMSK1 register.
CAN IF1 Mask 2 (CANIF1MSK2)
CAN0 base: 0x4004.0000
Offset 0x02C
Type R/W, reset 0x0000.FFFF
31 30 29 28 27 26 25 24 23 22 21 20 19 18 17 16
reserved
Type RO RO RO RO RO RO RO RO RO RO RO RO RO RO RO RO
Reset 0 0 0 0 0 0 0 0 0 0 0 0 0 0 0 0
15 14 13 12 11 10 9 8 7 6 5 4 3 2 1 0
MXtd MDir reserved Msk
Type R/W R/W RO R/W R/W R/W R/W R/W R/W R/W R/W R/W R/W R/W R/W R/W
Reset 1 1 1 0 0 0 0 0 1 1 1 1 1 1 1 1
Bit/Field Name Type Reset Description
Software should not rely on the value of a reserved bit. To provide
compatibility with future products, the value of a reserved bit should be
preserved across a read-modify-write operation.
31:16 reserved RO 0x0000
Mask Extended Identifier
0: The extended identifier bit (Xtd in the CANIFnARB2 register) has
no effect on the acceptance filtering.
1: The extended identifier bit Xtd is used for acceptance filtering.
15 MXtd R/W 0x1
Mask Message Direction
0: The message direction bit (Dir in the CANIFnARB2 register) has
no effect for acceptance filtering.
1: The message direction bit Dir is used for acceptance filtering.
14 MDir R/W 0x1
Software should not rely on the value of a reserved bit. To provide
compatibility with future products, the value of a reserved bit should be
preserved across a read-modify-write operation.
13 reserved RO 0x1
Identifier Mask
0: The corresponding identifier bit (ID) in the message object cannot
inhibit the match in acceptance filtering.
1: The corresponding identifier bit (ID) is used for acceptance filtering.
12:0 Msk R/W 0xFF
March 17, 2008 439
Preliminary
LM3S8933 Microcontroller
Register 16: CAN IF1 Arbitration 1 (CANIF1ARB1), offset 0x030
Register 17: CAN IF2 Arbitration 1 (CANIF2ARB1), offset 0x090
These registers hold the identifiers for acceptance filtering.
CAN IF1 Arbitration 1 (CANIF1ARB1)
CAN0 base: 0x4004.0000
Offset 0x030
Type R/W, reset 0x0000.0000
31 30 29 28 27 26 25 24 23 22 21 20 19 18 17 16
reserved
Type RO RO RO RO RO RO RO RO RO RO RO RO RO RO RO RO
Reset 0 0 0 0 0 0 0 0 0 0 0 0 0 0 0 0
15 14 13 12 11 10 9 8 7 6 5 4 3 2 1 0
ID
Type R/W R/W R/W R/W R/W R/W R/W R/W R/W R/W R/W R/W R/W R/W R/W R/W
Reset 0 0 0 0 0 0 0 0 0 0 0 0 0 0 0 0
Bit/Field Name Type Reset Description
Software should not rely on the value of a reserved bit. To provide
compatibility with future products, the value of a reserved bit should be
preserved across a read-modify-write operation.
31:16 reserved RO 0x0000
Message Identifier
This bit field is used with the ID field in the CANIFnARB2 register to
create the message identifier. ID[28:0] is the Extended Frame and
ID[28:18] is the Standard Frame.
15:0 ID R/W 0x00
440 March 17, 2008
Preliminary
Controller Area Network (CAN) Module
Register 18: CAN IF1 Arbitration 2 (CANIF1ARB2), offset 0x034
Register 19: CAN IF2 Arbitration 2 (CANIF2ARB2), offset 0x094
These registers hold information for acceptance filtering.
CAN IF1 Arbitration 2 (CANIF1ARB2)
CAN0 base: 0x4004.0000
Offset 0x034
Type R/W, reset 0x0000.0000
31 30 29 28 27 26 25 24 23 22 21 20 19 18 17 16
reserved
Type RO RO RO RO RO RO RO RO RO RO RO RO RO RO RO RO
Reset 0 0 0 0 0 0 0 0 0 0 0 0 0 0 0 0
15 14 13 12 11 10 9 8 7 6 5 4 3 2 1 0
MsgVal Xtd Dir ID
Type R/W R/W R/W R/W R/W R/W R/W R/W R/W R/W R/W R/W R/W R/W R/W R/W
Reset 0 0 0 0 0 0 0 0 0 0 0 0 0 0 0 0
Bit/Field Name Type Reset Description
Software should not rely on the value of a reserved bit. To provide
compatibility with future products, the value of a reserved bit should be
preserved across a read-modify-write operation.
31:16 reserved RO 0x0000
Message Valid
0: The message object is ignored by the message handler.
1: The message object is configured and will be considered by the
message handler within the CAN controller.
All unused message objects should have this bit cleared during
initialization and before clearing the Init bit in the CANCTL register.
The MsgVal bit must also be cleared before any of the following bits
are modified or if the message object is no longer required: the ID bit
fields in the CANIFnARBn registers, the Xtd and Dir bits in the
CANIFnARB2 register, or the DLC bits in the CANIFnMCTL register.
15 MsgVal R/W 0x0
Extended Identifier
0: The 11-bit Standard Identifier will be used for this message object.
1: The 29-bit Extended Identifier will be used for this message object.
14 Xtd R/W 0x0
Message Direction
0: Receive. On TxRqst, a remote frame with the identifier of this
message object is transmitted. On reception of a data frame with
matching identifier, that message is stored in this message object.
1: Transmit. On TxRqst, the respective message object is transmitted
as a data frame. On reception of a remote frame with matching identifier,
TxRqst bit of this message object is set (if RmtEn=1).
13 Dir R/W 0x0
Message Identifier
Used with the ID bit in the CANIFnARB1 register to create the message
identifier. ID[28:0] is the Extended Frame and ID[28:18] is the Standard
Frame.
12:0 ID R/W 0x0
March 17, 2008 441
Preliminary
LM3S8933 Microcontroller
Register 20: CAN IF1 Message Control (CANIF1MCTL), offset 0x038
Register 21: CAN IF2 Message Control (CANIF2MCTL), offset 0x098
This register holds the control information associated with the message object to be sent to the
Message RAM.
CAN IF1 Message Control (CANIF1MCTL)
CAN0 base: 0x4004.0000
Offset 0x038
Type R/W, reset 0x0000.0000
31 30 29 28 27 26 25 24 23 22 21 20 19 18 17 16
reserved
Type RO RO RO RO RO RO RO RO RO RO RO RO RO RO RO RO
Reset 0 0 0 0 0 0 0 0 0 0 0 0 0 0 0 0
15 14 13 12 11 10 9 8 7 6 5 4 3 2 1 0
NewDat MsgLst IntPnd UMask TxIE RxIE RmtEn TxRqst EoB reserved DLC
Type R/W R/W R/W R/W R/W R/W R/W R/W R/W RO RO RO R/W R/W R/W R/W
Reset 0 0 0 0 0 0 0 0 0 0 0 0 0 0 0 0
Bit/Field Name Type Reset Description
Software should not rely on the value of a reserved bit. To provide
compatibility with future products, the value of a reserved bit should be
preserved across a read-modify-write operation.
31:16 reserved RO 0x0000
New Data
0: No new data has been written into the data portion of this message
object by the message handler since the last time this flag was cleared
by the CPU.
1: The message handler or the CPU has written new data into the data
portion of this message object.
15 NewDat R/W 0x0
Message Lost
0 : No message was lost since the last time this bit was reset by the
CPU.
1: The message handler stored a new message into this object when
NewDat was set; the CPU has lost a message.
This bit is only valid for message objects with the Dir bit in the
CANIFnARB2 register set to 0 (receive).
14 MsgLst R/W 0x0
Interrupt Pending
0: This message object is not the source of an interrupt.
1: This message object is the source of an interrupt. The interrupt
identifier in the CAN Interrupt (CANINT) register will point to this
message object if there is not another interrupt source with a higher
priority.
13 IntPnd R/W 0x0
Use Acceptance Mask
0: Mask ignored.
1: Use mask (Msk, MXtd, and MDir) for acceptance filtering.
12 UMask R/W 0x0
442 March 17, 2008
Preliminary
Controller Area Network (CAN) Module
Bit/Field Name Type Reset Description
Transmit Interrupt Enable
0: The IntPnd bit in the CANIFnMCTL register is unchanged after a
successful transmission of a frame.
1: The IntPnd bit in the CANIFnMCTL register is set after a successful
transmission of a frame.
11 TxIE R/W 0x0
Receive Interrupt Enable
0: The IntPnd bit in the CANIFnMCTL register is unchanged after a
successful reception of a frame.
1: The IntPnd bit in the CANIFnMCTL register is set after a successful
reception of a frame.
10 RxIE R/W 0x0
Remote Enable
0: At the reception of a remote frame, the TxRqst bit in the
CANIFnMCTL register is left unchanged.
1: At the reception of a remote frame, the TxRqst bit in the
CANIFnMCTL register is set.
9 RmtEn R/W 0x0
Transmit Request
0: This message object is not waiting for transmission.
1: The transmission of this message object is requested and is not yet
done.
8 TxRqst R/W 0x0
End of Buffer
0: Message object belongs to a FIFO Buffer and is not the last message
object of that FIFO Buffer.
1: Single message object or last message object of a FIFO Buffer.
This bit is used to concatenate two or more message objects (up to 32)
to build a FIFO buffer. For a single message object (thus not belonging
to a FIFO buffer), this bit must be set to 1.
7 EoB R/W 0x0
Software should not rely on the value of a reserved bit. To provide
compatibility with future products, the value of a reserved bit should be
preserved across a read-modify-write operation.
6:4 reserved RO 0x0
Data Length Code
Value Description
0x0-0x8 Specifies the number of bytes in the data frame.
0x9-0xF Defaults to a data frame with 8 bytes.
The DLC bit in the CANIFnMCTL register of a message object must be
defined the same as in all the corresponding objects with the same
identifier at other nodes. When the message handler stores a data frame,
it writes DLC to the value given by the received message.
3:0 DLC R/W 0x0
March 17, 2008 443
Preliminary
LM3S8933 Microcontroller
Register 22: CAN IF1 Data A1 (CANIF1DA1), offset 0x03C
Register 23: CAN IF1 Data A2 (CANIF1DA2), offset 0x040
Register 24: CAN IF1 Data B1 (CANIF1DB1), offset 0x044
Register 25: CAN IF1 Data B2 (CANIF1DB2), offset 0x048
Register 26: CAN IF2 Data A1 (CANIF2DA1), offset 0x09C
Register 27: CAN IF2 Data A2 (CANIF2DA2), offset 0x0A0
Register 28: CAN IF2 Data B1 (CANIF2DB1), offset 0x0A4
Register 29: CAN IF2 Data B2 (CANIF2DB2), offset 0x0A8
These registers contain the data to be sent or that has been received. In a CAN data frame, data
byte 0 is the first byte to be transmitted or received and data byte 7 is the last byte to be transmitted
or received. In CAN's serial bit stream, the MSB of each byte is transmitted first.
CAN IF1 Data A1 (CANIF1DA1)
CAN0 base: 0x4004.0000
Offset 0x03C
Type R/W, reset 0x0000.0000
31 30 29 28 27 26 25 24 23 22 21 20 19 18 17 16
reserved
Type RO RO RO RO RO RO RO RO RO RO RO RO RO RO RO RO
Reset 0 0 0 0 0 0 0 0 0 0 0 0 0 0 0 0
15 14 13 12 11 10 9 8 7 6 5 4 3 2 1 0
Data
Type R/W R/W R/W R/W R/W R/W R/W R/W R/W R/W R/W R/W R/W R/W R/W R/W
Reset 0 0 0 0 0 0 0 0 0 0 0 0 0 0 0 0
Bit/Field Name Type Reset Description
Software should not rely on the value of a reserved bit. To provide
compatibility with future products, the value of a reserved bit should be
preserved across a read-modify-write operation.
31:16 reserved RO 0x0000
Data
The CANIFnDA1 registers contain data bytes 1 and 0; CANIFnDA2
data bytes 3 and 2; CANIFnDB1 data bytes 5 and 4; and CANIFnDB2
data bytes 7 and 6.
15:0 Data R/W 0x00
444 March 17, 2008
Preliminary
Controller Area Network (CAN) Module
Register 30: CAN Transmission Request 1 (CANTXRQ1), offset 0x100
Register 31: CAN Transmission Request 2 (CANTXRQ2), offset 0x104
The CANTXRQ1 and CANTXRQ2 registers hold the TxRqst bits of the 32 message objects. By
reading out these bits, the CPU can check which message object has a transmission request pending.
The TxRqst bit of a specific message object can be changed by three sources: (1) the CPU via the
CAN IFn Message Control (CANIFnMCTL) register, (2) the message handler state machine after
the reception of a remote frame, or (3) the message handler state machine after a successful
transmission.
The CANTXRQ1 register contains the TxRqst bit of the first 16 message objects in the message
RAM; the CANTXRQ2 register contains the TxRqst bit of the second 16 message objects.
CAN Transmission Request 1 (CANTXRQ1)
CAN0 base: 0x4004.0000
Offset 0x100
Type RO, reset 0x0000.0000
31 30 29 28 27 26 25 24 23 22 21 20 19 18 17 16
reserved
Type RO RO RO RO RO RO RO RO RO RO RO RO RO RO RO RO
Reset 0 0 0 0 0 0 0 0 0 0 0 0 0 0 0 0
15 14 13 12 11 10 9 8 7 6 5 4 3 2 1 0
TxRqst
Type RO RO RO RO RO RO RO RO RO RO RO RO RO RO RO RO
Reset 0 0 0 0 0 0 0 0 0 0 0 0 0 0 0 0
Bit/Field Name Type Reset Description
Software should not rely on the value of a reserved bit. To provide
compatibility with future products, the value of a reserved bit should be
preserved across a read-modify-write operation.
31:16 reserved RO 0x0000
Transmission Request Bits
(of all message objects)
0: The message object is not waiting for transmission.
1: The transmission of the message object is requested and is not yet
done.
15:0 TxRqst RO 0x00
March 17, 2008 445
Preliminary
LM3S8933 Microcontroller
Register 32: CAN New Data 1 (CANNWDA1), offset 0x120
Register 33: CAN New Data 2 (CANNWDA2), offset 0x124
The CANNWDA1 and CANNWDA2 registers hold the NewDat bits of the 32 message objects. By
reading these bits, the CPU can check which message object has its data portion updated. The
NewDat bit of a specific message object can be changed by three sources: (1) the CPU via the
CAN IFn Message Control (CANIFnMCTL) register, (2) the message handler state machine after
the reception of a data frame, or (3) the message handler state machine after a successful
transmission.
The CANNWDA1 register contains the NewDat bit of the first 16 message objects in the message
RAM; the CANNWDA2 register contains the NewDat bit of the second 16 message objects.
CAN New Data 1 (CANNWDA1)
CAN0 base: 0x4004.0000
Offset 0x120
Type RO, reset 0x0000.0000
31 30 29 28 27 26 25 24 23 22 21 20 19 18 17 16
reserved
Type RO RO RO RO RO RO RO RO RO RO RO RO RO RO RO RO
Reset 0 0 0 0 0 0 0 0 0 0 0 0 0 0 0 0
15 14 13 12 11 10 9 8 7 6 5 4 3 2 1 0
NewDat
Type RO RO RO RO RO RO RO RO RO RO RO RO RO RO RO RO
Reset 0 0 0 0 0 0 0 0 0 0 0 0 0 0 0 0
Bit/Field Name Type Reset Description
Software should not rely on the value of a reserved bit. To provide
compatibility with future products, the value of a reserved bit should be
preserved across a read-modify-write operation.
31:16 reserved RO 0x0000
New Data Bits
(of all message objects)
0: No new data has been written into the data portion of this message
object by the message handler since the last time this flag was cleared
by the CPU.
1: The message handler or the CPU has written new data into the data
portion of this message object.
15:0 NewDat RO 0x00
446 March 17, 2008
Preliminary
Controller Area Network (CAN) Module
Register 34: CAN Message 1 Interrupt Pending (CANMSG1INT), offset 0x140
Register 35: CAN Message 2 Interrupt Pending (CANMSG2INT), offset 0x144
The CANMSG1INT and CANMSG2INT registers hold the IntPnd bits of the 32 message objects.
By reading these bits, the CPU can check which message object has an interrupt pending. The
IntPnd bit of a specific message object can be changed through two sources: (1) the CPU via the
CAN IFn Message Control (CANIFnMCTL) register, or (2) the message handler state machine
after the reception or transmission of a frame.
This field is also encoded in the CAN Interrupt (CANINT) register.
The CANMSG1INT register contains the IntPnd bit of the first 16 message objects in the message
RAM; the CANMSG2INT register contains the IntPnd bit of the second 16 message objects.
CAN Message 1 Interrupt Pending (CANMSG1INT)
CAN0 base: 0x4004.0000
Offset 0x140
Type RO, reset 0x0000.0000
31 30 29 28 27 26 25 24 23 22 21 20 19 18 17 16
reserved
Type RO RO RO RO RO RO RO RO RO RO RO RO RO RO RO RO
Reset 0 0 0 0 0 0 0 0 0 0 0 0 0 0 0 0
15 14 13 12 11 10 9 8 7 6 5 4 3 2 1 0
IntPnd
Type RO RO RO RO RO RO RO RO RO RO RO RO RO RO RO RO
Reset 0 0 0 0 0 0 0 0 0 0 0 0 0 0 0 0
Bit/Field Name Type Reset Description
Software should not rely on the value of a reserved bit. To provide
compatibility with future products, the value of a reserved bit should be
preserved across a read-modify-write operation.
31:16 reserved RO 0x0000
Interrupt Pending Bits
(of all message objects)
0: This message object is not the source of an interrupt.
1: This message object is the source of an interrupt.
15:0 IntPnd RO 0x00
March 17, 2008 447
Preliminary
LM3S8933 Microcontroller
Register 36: CAN Message 1 Valid (CANMSG1VAL), offset 0x160
Register 37: CAN Message 2 Valid (CANMSG2VAL), offset 0x164
The CANMSG1VAL and CANMSG2VAL registers hold the MsgVal bits of the 32 message objects.
By reading these bits, the CPU can check which message object is valid. The message value of a
specific message object can be changed with the CAN IFn Message Control (CANIFnMCTL)
register.
The CANMSG1VAL register contains the MsgVal bit of the first 16 message objects in the message
RAM; the CANMSG2VAL register contains the MsgVal bit of the second 16 message objects in
the message RAM.
CAN Message 1 Valid (CANMSG1VAL)
CAN0 base: 0x4004.0000
Offset 0x160
Type RO, reset 0x0000.0000
31 30 29 28 27 26 25 24 23 22 21 20 19 18 17 16
reserved
Type RO RO RO RO RO RO RO RO RO RO RO RO RO RO RO RO
Reset 0 0 0 0 0 0 0 0 0 0 0 0 0 0 0 0
15 14 13 12 11 10 9 8 7 6 5 4 3 2 1 0
MsgVal
Type RO RO RO RO RO RO RO RO RO RO RO RO RO RO RO RO
Reset 0 0 0 0 0 0 0 0 0 0 0 0 0 0 0 0
Bit/Field Name Type Reset Description
Software should not rely on the value of a reserved bit. To provide
compatibility with future products, the value of a reserved bit should be
preserved across a read-modify-write operation.
31:16 reserved RO 0x0000
Message Valid Bits
(of all message objects)
0: This message object is not configured and is ignored by the message
handler.
1: This message object is configured and should be considered by the
message handler.
15:0 MsgVal RO 0x00
448 March 17, 2008
Preliminary
Controller Area Network (CAN) Module
17 Ethernet Controller
The Stellaris® Ethernet Controller consists of a fully integrated media access controller (MAC) and
network physical (PHY) interface device. The Ethernet Controller conforms to IEEE 802.3
specifications and fully supports 10BASE-T and 100BASE-TX standards.
The Ethernet Controller module has the following features:
■ Conforms to the IEEE 802.3-2002 specification
– 10BASE-T/100BASE-TX IEEE-802.3 compliant. Requires only a dual 1:1 isolation transformer
interface to the line
– 10BASE-T/100BASE-TX ENDEC, 100BASE-TX scrambler/descrambler
– Full-featured auto-negotiation
■ Multiple operational modes
– Full- and half-duplex 100 Mbps
– Full- and half-duplex 10 Mbps
– Power-saving and power-down modes
■ Highly configurable
– Programmable MAC address
– LED activity selection
– Promiscuous mode support
– CRC error-rejection control
– User-configurable interrupts
■ Physical media manipulation
– Automatic MDI/MDI-X cross-over correction
– Register-programmable transmit amplitude
– Automatic polarity correction and 10BASE-T signal reception
■ IEEE 1588 Precision Time Protocol
March 17, 2008 449
Preliminary
LM3S8933 Microcontroller
17.1 Block Diagram
Figure 17-1. Ethernet Controller Block Diagram
MACISR
MACIACK
MACIMR
Interrupt
Control
MACRCR
MACNPR
Receive
Control
MACTCR
MACITHR
MACTRR
Transmit
Control
Transmit
FIFO
Receive
FIFO
MACIAR0
MACIAR1
Individual
Address
MACMDTX
MACMCR
MACMDVR
MACMAR
MACMDRX
MII
Control
MACDR
Data
Access
MACTSR
Timer
Support
TXOP
TXON
RXIP
RXIN
XTLP
XTLN
MDIX
Clock
Reference
Transmit
Encoding
Pulse
Shaping
Receive
Decoding
Clock
Recovery
Auto
Negotiation
Carrier
Sense
MR3
MR0
MR1
MR2
MR4
Media Independent Interface
Management Register Set
MR5
MR18
MR6
MR16
MR17
MR19
MR23
MR24
Collision
Detect System Clock
Interrupt
17.2 Functional Description
As shown in Figure 17-2 on page 450, the Ethernet Controller is functionally divided into two layers
or modules: the Media Access Controller (MAC) layer and the Network Physical (PHY) layer. These
correspond to the OSI model layers 2 and 1. The primary interface to the Ethernet Controller is a
simple bus interface to the MAC layer. The MAC layer provides transmit and receive processing for
Ethernet frames. The MAC layer also provides the interface to the PHY module via an internal Media
Independent Interface (MII).
Figure 17-2. Ethernet Controller
Cortex M3
Media Access
Controller
MAC
(Layer 2)
Physical
Layer Entity
PHY
(Layer 1)
Magnetics RJ45
Ethernet Controller
17.2.1 Internal MII Operation
For the MII management interface to function properly, the MDIO signal must be connected through
a 10k Ω pull-up resistor to the +3.3 V supply. Failure to connect this pull-up resistor prevents
management transactions on this internal MII to function. Note that it is possible for data transmission
across the MII to still function since the PHY layer auto-negotiates the link parameters by default.
450 March 17, 2008
Preliminary
Ethernet Controller
For the MII management interface to function properly, the internal clock must be divided down from
the system clock to a frequency no greater than 2.5 MHz. The MACMDV register contains the divider
used for scaling down the system clock. See page 470 for more details about the use of this register.
17.2.2 PHY Configuration/Operation
The Physical Layer (PHY) in the Ethernet Controller includes integrated ENDECs,
scrambler/descrambler, dual-speed clock recovery, and full-featured auto-negotiation functions.
The transmitter includes an on-chip pulse shaper and a low-power line driver. The receiver has an
adaptive equalizer and a baseline restoration circuit required for accurate clock and data recovery.
The transceiver interfaces to Category-5 unshielded twisted pair (Cat-5 UTP) cabling for 100BASE-TX
applications, and Category-3 unshielded twisted pair (Cat-3 UTP) for 10BASE-T applications. The
Ethernet Controller is connected to the line media via dual 1:1 isolation transformers. No external
filter is required.
17.2.2.1 Clock Selection
The PHY has an on-chip crystal oscillator which can also be driven by an external oscillator. In this
mode of operation, a 25-MHz crystal should be connected between the XTALPPHY and XTALNPHY
pins. Alternatively, an external 25-MHz clock input can be connected to the XTALPPHY pin. In this
mode of operation, a crystal is not required and the XTALNPHY pin must be tied to ground.
17.2.2.2 Auto-Negotiation
The PHY supports the auto-negotiation functions of Clause 28 of the IEEE 802.3 standard for 10/100
Mbps operation over copper wiring. This function can be enabled via register settings. The
auto-negotiation function defaults to On and the ANEGEN bit in the MR0 register is High after reset.
Software can disable the auto-negotiation function by writing to the ANEGEN bit. The contents of the
MR4 register are sent to the PHY’s link partner during auto-negotiation via fast-link pulse coding.
Once auto-negotiation is complete, the DPLX and RATE bits in the MR18 register reflect the actual
speed and duplex that was chosen. If auto-negotiation fails to establish a link for any reason, the
ANEGF bit in the MR18 register reflects this and auto-negotiation restarts from the beginning. Writing
a 1 to the RANEG bit in the MR0 register also causes auto-negotiation to restart.
17.2.2.3 Polarity Correction
The PHY is capable of either automatic or manual polarity reversal for 10BASE-T and auto-negotiation
functions. Bits 4 and 5 (RVSPOL and APOL) in the MR16 register control this feature. The default is
automatic mode, where APOL is Low and RVSPOL indicates if the detection circuitry has inverted
the input signal. To enter manual mode, APOL should be set High and RVSPOL then controls the
signal polarity.
17.2.2.4 MDI/MDI-X Configuration
The PHY supports the automatic MDI/MDI-X configuration as defined in IEEE 802.3-2002
specification. This eliminates the need for cross-over cables when connecting to another device,
such as a hub. The algorithm is controlled via settings in the MR24 register. Refer to page 493 for
additional details about these settings.
17.2.2.5 LED Indicators
The PHY supports two LED signals that can be used to indicate various states of operation of the
Ethernet Controller. These signals are mapped to the LED0 and LED1 pins. By default, these pins
are configured as GPIO signals (PF3 and PF2). For the PHY layer to drive these signals, they must
be reconfigured to their hardware function. See “General-Purpose Input/Outputs (GPIOs)” on page
March 17, 2008 451
Preliminary
LM3S8933 Microcontroller
162 for additional details. The function of these pins is programmable via the PHY layer MR23 register.
Refer to page 492 for additonal details on how to program these LED functions.
17.2.3 MAC Configuration/Operation
17.2.3.1 Ethernet Frame Format
Ethernet data is carried by Ethernet frames. The basic frame format is shown in Figure
17-3 on page 452.
Figure 17-3. Ethernet Frame
Preamble SFD Destination Address Source Address Length/
Type Data FCS
7
Bytes
6
Bytes
6
Bytes
2
Bytes
1
Byte
4
Bytes
46 - 1500
Bytes
The seven fields of the frame are transmitted from left to right. The bits within the frame are
transmitted from least to most significant bit.
■ Preamble
The Preamble field is used by the physical layer signaling circuitry to synchronize with the received
frame’s timing. The preamble is 7 octets long.
■ Start Frame Delimiter (SFD)
The SFD field follows the preamble pattern and indicates the start of the frame. Its value is
1010.1011.
■ Destination Address (DA)
This field specifies destination addresses for which the frame is intended. The LSB of the DA
determines whether the address is an individual (0), or group/multicast (1) address.
■ Source Address (SA)
The source address field identifies the station from which the frame was initiated.
■ Length/Type Field
The meaning of this field depends on its numeric value. The first of two octets is most significant.
This field can be interpreted as length or type code. The maximum length of the data field is
1500 octets. If the value of the Length/Type field is less than or equal to 1500 decimal, it indicates
the number of MAC client data octets. If the value of this field is greater than or equal to 1536
decimal, then it is type interpretation. The meaning of the Length/Type field when the value is
between 1500 and 1536 decimal is unspecified by the standard. The MAC module assumes
type interpretation if the value of the Length/Type field is greater than 1500 decimal.
■ Data
The data field is a sequence of 0 to 1500 octets. Full data transparency is provided so any values
can appear in this field. A minimum frame size is required to properly meet the IEEE standard.
If necessary, the data field is extended by appending extra bits (a pad). The pad field can have
a size of 0 to 46 octets. The sum of the data and pad lengths must be a minimum of 46 octets.
The MAC module automatically inserts pads if required, though it can be disabled by a register
452 March 17, 2008
Preliminary
Ethernet Controller
write. For the MAC module core, data sent/received can be larger than 1500 bytes, and no Frame
Too Long error is reported. Instead, a FIFO Overrun error is reported when the frame received
is too large to fit into the Ethernet Controller’s RAM.
■ Frame Check Sequence (FCS)
The frame check sequence carries the cyclic redundancy check (CRC) value. The value of this
field is computed over destination address, source address, length/type, data, and pad fields
using the CRC-32 algorithm. The MAC module computes the FCS value one nibble at a time.
For transmitted frames, this field is automatically inserted by the MAC layer, unless disabled by
the CRC bit in the MACTCTL register. For received frames, this field is automatically checked.
If the FCS does not pass, the frame is not placed in the RX FIFO, unless the FCS check is
disabled by the BADCRC bit in the MACRCTL register.
17.2.3.2 MAC Layer FIFOs
For Ethernet frame transmission, a 2 KB TX FIFO is provided that can be used to store a single
frame. While the IEEE 802.3 specification limits the size of an Ethernet frame's payload section to
1500 Bytes, the Ethernet Controller places no such limit. The full buffer can be used, for a payload
of up to 2032 bytes.
For Ethernet frame reception, a 2-KB RX FIFO is provided that can be used to store multiple frames,
up to a maximum of 31 frames. If a frame is received and there is insufficient space in the RX FIFO,
an overflow error is indicated.
For details regarding the TX and RX FIFO layout, refer to Table 17-1 on page 453. Please note the
following difference between TX and RX FIFO layout. For the TX FIFO, the Data Length field in the
first FIFO word refers to the Ethernet frame data payload, as shown in the 5th to nth FIFO positions.
For the RX FIFO, the Frame Length field is the total length of the received Ethernet frame, including
the FCS and Frame Length bytes. Also note that if FCS generation is disabled with the CRC bit in
the MACTCTL register, the last word in the FIFO must be the FCS bytes for the frame that has been
written to the FIFO.
Also note that if the length of the data payload section is not a multiple of 4, the FCS field overlaps
words in the FIFO. However, for the RX FIFO, the beginning of the next frame is always on a word
boundary.
Table 17-1. TX & RX FIFO Organization
FIFO Word Read/Write Word Bit Fields TX FIFO (Write) RX FIFO (Read)
Sequence
1st 7:0 Data Length LSB Frame Length LSB
15:8 Data Length MSB Frame Length MSB
23:16 DA oct 1
31:24 DA oct 2
2nd 7:0 DA oct 3
15:8 DA oct 4
23:16 DA oct 5
31:24 DA oct 6
3rd 7:0 SA oct 1
15:8 SA oct 2
23:16 SA oct 3
31:24 SA oct 4
March 17, 2008 453
Preliminary
LM3S8933 Microcontroller
FIFO Word Read/Write Word Bit Fields TX FIFO (Write) RX FIFO (Read)
Sequence
4th 7:0 SA oct 5
15:8 SA oct 6
23:16 Len/Type MSB
31:24 Len/Type LSB
5th to nth 7:0 data oct n
15:8 data oct n+1
23:16 data oct n+2
31:24 data oct n+3
FCS 1 (if the CRC bit in FCS 1
MACCTL is 0)
last 7:0
FCS 2 (if the CRC bit in FCS 2
MACCTL is 0)
15:8
FCS 3 (if the CRC bit in FCS 3
MACCTL is 0)
23:16
FCS 4 (if the CRC bit in FCS 4
MACCTL is 0)
31:24
17.2.3.3 Ethernet Transmission Options
The Ethernet Controller can automatically generate and insert the Frame Check Sequence (FCS)
at the end of the transmit frame. This is controlled by the CRC bit in the MACTCTL register. For test
purposes, in order to generate a frame with an invalid CRC, this feature can be disabled.
The IEEE 802.3 specification requires that the Ethernet frame payload section be a minimum of 46
bytes. The Ethernet Controller can be configured to automatically pad the data section if the payload
data section loaded into the FIFO is less than the minimum 46 bytes. This feature is controlled by
the PADEN bit in the MACTCTL register.
At the MAC layer, the transmitter can be configured for both full-duplex and half-duplex operation
by using the DUPLEX bit in the MACTCTL register.
17.2.3.4 Ethernet Reception Options
Using the BADCRC bit in the MACRCTL register, the Ethernet Controller can be configured to reject
incoming Ethernet frames with an invalid FCS field.
The Ethernet receiver can also be configured for Promiscuous and Multicast modes using the PRMS
and AMUL fields in the MACRCTL register. If these modes are not enabled, only Ethernet frames
with a broadcast address, or frames matching the MAC address programmed into the MACIA0 and
MACIA1 register is placed into the RX FIFO.
17.2.3.5 Packet Timestamps
Using the TSEN bit in the MACTS register, the MAC transmit and receive interrupts can be used to
trigger edge capture events on General-Purpose Timer 3. The transmit interrupt is routed to the
CCP (even) input of General-Purpose Timer 3, while the receive interrupt is routed to the CCP (odd)
input of General-Purpose Timer 3. This timer can then be configured in 16-bit edge capture mode
and be used with a third 16-bit free-running timer to capture a more accurate timestamp for the
transmit or receive packet. This feature can be used with a protocol such as IEEE-1588 to provide
more accurate timestamps of the synchronization packets, improving the overall accuracy of the
protocol.
454 March 17, 2008
Preliminary
Ethernet Controller
17.2.4 Interrupts
The Ethernet Controller can generate an interrupt for one or more of the following conditions:
■ A frame has been received into an empty RX FIFO
■ A frame transmission error has occurred
■ A frame has been transmitted successfully
■ A frame has been received with no room in the RX FIFO (overrun)
■ A frame has been received with one or more error conditions (for example, FCS failed)
■ An MII management transaction between the MAC and PHY layers has completed
■ One or more of the following PHY layer conditions occurs:
– Auto-Negotiate Complete
– Remote Fault
– Link Status Change
– Link Partner Acknowledge
– Parallel Detect Fault
– Page Received
– Receive Error
– Jabber Event Detected
17.3 Initialization and Configuration
To use the Ethernet Controller, the peripheral must be enabled by setting the EPHY0 and EMAC0
bits in the RCGC2 register. The following steps can then be used to configure the Ethernet Controller
for basic operation.
1. Program the MACDIV register to obtain a 2.5 MHz clock (or less) on the internal MII. Assuming
a 20-MHz system clock, the MACDIV value would be 4.
2. Program the MACIA0 and MACIA1 register for address filtering.
3. Program the MACTCTL register for Auto CRC generation, padding, and full-duplex operation
using a value of 0x16.
4. Program the MACRCTL register to reject frames with bad FCS using a value of 0x08.
5. Enable both the Transmitter and Receive by setting the LSB in both the MACTCTL and
MACRCTL registers.
6. To transmit a frame, write the frame into the TX FIFO using the MACDATA register. Then set
the NEWTX bit in the MACTR register to initiate the transmit process. When the NEWTX bit has
been cleared, the TX FIFO is available for the next transmit frame.
March 17, 2008 455
Preliminary
LM3S8933 Microcontroller
7. To receive a frame, wait for the NPR field in the MACNP register to be non-zero. Then begin
reading the frame from the RX FIFO by using the MACDATA register. When the frame (including
the FCS field) has been read, the NPR field should decrement by one. When there are no more
frames in the RX FIFO, the NPR field reads 0.
17.4 Ethernet Register Map
Table 17-2 on page 456 lists the Ethernet MAC registers. All addresses given are relative to the
Ethernet MAC base address of 0x4004.8000.
The IEEE 802.3 standard specifies a register set for controlling and gathering status from the PHY.
The registers are collectively known as the MII Management registers and are detailed in Section
22.2.4 of the IEEE 802.3 specification. Table 17-2 on page 456 also lists these MII Management
registers. All addresses given are absolute and are written directly to the REGADR field of the
MACMCTL register. The format of registers 0 to 15 are defined by the IEEE specification and are
common to all PHY implementations. The only variance allowed is for features that may or may not
be supported by a specific PHY. Registers 16 to 31 are vendor-specific registers, used to support
features that are specific to a vendors PHY implementation. Vendor-specific registers not listed are
reserved.
Table 17-2. Ethernet Register Map
See
Offset Name Type Reset Description page
Ethernet MAC
0x000 MACRIS RO 0x0000.0000 Ethernet MAC Raw Interrupt Status 458
0x000 MACIACK W1C 0x0000.0000 Ethernet MAC Interrupt Acknowledge 460
0x004 MACIM R/W 0x0000.007F Ethernet MAC Interrupt Mask 461
0x008 MACRCTL R/W 0x0000.0008 Ethernet MAC Receive Control 462
0x00C MACTCTL R/W 0x0000.0000 Ethernet MAC Transmit Control 463
0x010 MACDATA R/W 0x0000.0000 Ethernet MAC Data 464
0x014 MACIA0 R/W 0x0000.0000 Ethernet MAC Individual Address 0 466
0x018 MACIA1 R/W 0x0000.0000 Ethernet MAC Individual Address 1 467
0x01C MACTHR R/W 0x0000.003F Ethernet MAC Threshold 468
0x020 MACMCTL R/W 0x0000.0000 Ethernet MAC Management Control 469
0x024 MACMDV R/W 0x0000.0080 Ethernet MAC Management Divider 470
0x02C MACMTXD R/W 0x0000.0000 Ethernet MAC Management Transmit Data 471
0x030 MACMRXD R/W 0x0000.0000 Ethernet MAC Management Receive Data 472
0x034 MACNP RO 0x0000.0000 Ethernet MAC Number of Packets 473
0x038 MACTR R/W 0x0000.0000 Ethernet MAC Transmission Request 474
0x03C MACTS R/W 0x0000.0000 Ethernet MAC Timer Support 475
MII Management
- MR0 R/W 0x3100 Ethernet PHY Management Register 0 – Control 476
456 March 17, 2008
Preliminary
Ethernet Controller
See
Offset Name Type Reset Description page
- MR1 RO 0x7849 Ethernet PHY Management Register 1 – Status 478
Ethernet PHY Management Register 2 – PHY Identifier 480
- MR2 RO 0x000E 1
Ethernet PHY Management Register 3 – PHY Identifier 481
- MR3 RO 0x7237 2
Ethernet PHYManagement Register 4 – Auto-Negotiation 482
- MR4 R/W 0x01E1 Advertisement
Ethernet PHYManagement Register 5 – Auto-Negotiation 484
- MR5 RO 0x0000 Link Partner Base Page Ability
Ethernet PHYManagement Register 6 – Auto-Negotiation 485
- MR6 RO 0x0000 Expansion
Ethernet PHY Management Register 16 – 486
- MR16 R/W 0x0140 Vendor-Specific
Ethernet PHY Management Register 17 – Interrupt 488
- MR17 R/W 0x0000 Control/Status
- MR18 RO 0x0000 Ethernet PHY Management Register 18 – Diagnostic 490
Ethernet PHY Management Register 19 – Transceiver 491
- MR19 R/W 0x4000 Control
Ethernet PHY Management Register 23 – LED 492
- MR23 R/W 0x0010 Configuration
Ethernet PHY Management Register 24 –MDI/MDIX 493
- MR24 R/W 0x00C0 Control
17.5 Ethernet MAC Register Descriptions
The remainder of this section lists and describes the Ethernet MAC registers, in numerical order by
address offset. Also see “MII Management Register Descriptions” on page 475.
March 17, 2008 457
Preliminary
LM3S8933 Microcontroller
Register 1: Ethernet MAC Raw Interrupt Status (MACRIS), offset 0x000
The MACRIS register is the interrupt status register. On a read, this register gives the current status
value of the corresponding interrupt prior to masking.
Ethernet MAC Raw Interrupt Status (MACRIS)
Base 0x4004.8000
Offset 0x000
Type RO, reset 0x0000.0000
31 30 29 28 27 26 25 24 23 22 21 20 19 18 17 16
reserved
Type RO RO RO RO RO RO RO RO RO RO RO RO RO RO RO RO
Reset 0 0 0 0 0 0 0 0 0 0 0 0 0 0 0 0
15 14 13 12 11 10 9 8 7 6 5 4 3 2 1 0
reserved PHYINT MDINT RXER FOV TXEMP TXER RXINT
Type RO RO RO RO RO RO RO RO RO RO RO RO RO RO RO RO
Reset 0 0 0 0 0 0 0 0 0 0 0 0 0 0 0 0
Bit/Field Name Type Reset Description
Software should not rely on the value of a reserved bit. To provide
compatibility with future products, the value of a reserved bit should be
preserved across a read-modify-write operation.
31:7 reserved RO 0x0
PHY Interrupt
When set, indicates that an enabled interrupt in the PHY layer has
occured. MR17 in the PHY must be read to determine the specific PHY
event that triggered this interrupt.
6 PHYINT RO 0x0
MII Transaction Complete
When set, indicates that a transaction (read or write) on the MII interface
has completed successfully.
5 MDINT RO 0x0
Receive Error
This bit indicates that an error was encountered on the receiver. The
possible errors that can cause this interrupt bit to be set are:
■ A receive error occurs during the reception of a frame (100 Mb/s
only).
■ The frame is not an integer number of bytes (dribble bits) due to an
alignment error.
■ The CRC of the frame does not pass the FCS check.
■ The length/type field is inconsistent with the frame data size when
interpreted as a length field.
4 RXER RO 0x0
FIFO Overrrun
When set, indicates that an overrun was encountered on the receive
FIFO.
3 FOV RO 0x0
Transmit FIFO Empty
When set, indicates that the packet was transmitted and that the TX
FIFO is empty.
2 TXEMP RO 0x0
458 March 17, 2008
Preliminary
Ethernet Controller
Bit/Field Name Type Reset Description
Transmit Error
When set, indicates that an error was encountered on the transmitter.
The possible errors that can cause this interrupt bit to be set are:
■ The data length field stored in the TX FIFO exceeds 2032. The
frame is not sent when this error occurs.
■ The retransmission attempts during the backoff process have
exceeded the maximum limit of 16.
1 TXER RO 0x0
Packet Received
When set, indicates that at least one packet has been received and is
stored in the receiver FIFO.
0 RXINT RO 0x0
March 17, 2008 459
Preliminary
LM3S8933 Microcontroller
Register 2: Ethernet MAC Interrupt Acknowledge (MACIACK), offset 0x000
A write of a 1 to any bit position of this register clears the corresponding interrupt bit in the Ethernet
MAC Raw Interrupt Status (MACRIS) register.
Ethernet MAC Interrupt Acknowledge (MACIACK)
Base 0x4004.8000
Offset 0x000
Type W1C, reset 0x0000.0000
31 30 29 28 27 26 25 24 23 22 21 20 19 18 17 16
reserved
Type RO RO RO RO RO RO RO RO RO RO RO RO RO RO RO RO
Reset 0 0 0 0 0 0 0 0 0 0 0 0 0 0 0 0
15 14 13 12 11 10 9 8 7 6 5 4 3 2 1 0
reserved PHYINT MDINT RXER FOV TXEMP TXER RXINT
Type RO RO RO RO RO RO RO RO RO W1C W1C W1C W1C W1C W1C W1C
Reset 0 0 0 0 0 0 0 0 0 0 0 0 0 0 0 0
Bit/Field Name Type Reset Description
Software should not rely on the value of a reserved bit. To provide
compatibility with future products, the value of a reserved bit should be
preserved across a read-modify-write operation.
31:7 reserved RO 0x0
Clear PHY Interrupt
A write of a 1 clears the PHYINT interrupt read from the MACRIS
register.
6 PHYINT W1C 0x0
Clear MII Transaction Complete
A write of a 1 clears the MDINT interrupt read from the MACRIS register.
5 MDINT W1C 0x0
Clear Receive Error
A write of a 1 clears the RXER interrupt read from the MACRIS register.
4 RXER W1C 0x0
Clear FIFO Overrun
A write of a 1 clears the FOV interrupt read from the MACRIS register.
3 FOV W1C 0x0
Clear Transmit FIFO Empty
A write of a 1 clears the TXEMP interrupt read from the MACRIS register.
2 TXEMP W1C 0x0
Clear Transmit Error
A write of a 1 clears the TXER interrupt read from the MACRIS register
and resets the TX FIFO write pointer.
1 TXER W1C 0x0
Clear Packet Received
A write of a 1 clears the RXINT interrupt read from the MACRIS register.
0 RXINT W1C 0x0
460 March 17, 2008
Preliminary
Ethernet Controller
Register 3: Ethernet MAC Interrupt Mask (MACIM), offset 0x004
This register allows software to enable/disable Ethernet MAC interrupts. Writing a 0 disables the
interrupt, while writing a 1 enables it.
Ethernet MAC Interrupt Mask (MACIM)
Base 0x4004.8000
Offset 0x004
Type R/W, reset 0x0000.007F
31 30 29 28 27 26 25 24 23 22 21 20 19 18 17 16
reserved
Type RO RO RO RO RO RO RO RO RO RO RO RO RO RO RO RO
Reset 0 0 0 0 0 0 0 0 0 0 0 0 0 0 0 0
15 14 13 12 11 10 9 8 7 6 5 4 3 2 1 0
reserved PHYINTM MDINTM RXERM FOVM TXEMPM TXERM RXINTM
Type RO RO RO RO RO RO RO RO RO R/W R/W R/W R/W R/W R/W R/W
Reset 0 0 0 0 0 0 0 0 0 1 1 1 1 1 1 1
Bit/Field Name Type Reset Description
Software should not rely on the value of a reserved bit. To provide
compatibility with future products, the value of a reserved bit should be
preserved across a read-modify-write operation.
31:7 reserved RO 0x0
Mask PHY Interrupt
This bit masks the PHYINT bit in the MACRIS register from being
asserted.
6 PHYINTM R/W 1
Mask MII Transaction Complete
This bit masks the MDINT bit in the MACRIS register from being
asserted.
5 MDINTM R/W 1
Mask Receive Error
This bit masks the RXER bit in the MACRIS register from being asserted.
4 RXERM R/W 1
Mask FIFO Overrrun
This bit masks the FOV bit in the MACRIS register from being asserted.
3 FOVM R/W 1
Mask Transmit FIFO Empty
This bit masks the TXEMP bit in the MACRIS register from being
asserted.
2 TXEMPM R/W 1
Mask Transmit Error
This bit masks the TXER bit in the MACRIS register from being asserted.
1 TXERM R/W 1
Mask Packet Received
This bit masks the RXINT bit in the MACRIS register from being
asserted.
0 RXINTM R/W 1
March 17, 2008 461
Preliminary
LM3S8933 Microcontroller
Register 4: Ethernet MAC Receive Control (MACRCTL), offset 0x008
This register enables software to configure the receive module and control the types of frames that
are received from the physical medium. It is important to note that when the receive module is
enabled, all valid frames with a broadcast address of FF-FF-FF-FF-FF-FF in the Destination Address
field is received and stored in the RX FIFO, even if the AMUL bit is not set.
Ethernet MAC Receive Control (MACRCTL)
Base 0x4004.8000
Offset 0x008
Type R/W, reset 0x0000.0008
31 30 29 28 27 26 25 24 23 22 21 20 19 18 17 16
reserved
Type RO RO RO RO RO RO RO RO RO RO RO RO RO RO RO RO
Reset 0 0 0 0 0 0 0 0 0 0 0 0 0 0 0 0
15 14 13 12 11 10 9 8 7 6 5 4 3 2 1 0
reserved RSTFIFO BADCRC PRMS AMUL RXEN
Type RO RO RO RO RO RO RO RO RO RO RO R/W R/W R/W R/W R/W
Reset 0 0 0 0 0 0 0 0 0 0 0 0 1 0 0 0
Bit/Field Name Type Reset Description
Software should not rely on the value of a reserved bit. To provide
compatibility with future products, the value of a reserved bit should be
preserved across a read-modify-write operation.
31:5 reserved RO 0x0
Clear Receive FIFO
When set, clears the receive FIFO. This should be done when software
initialization is performed.
It is recommended that the receiver be disabled (RXEN = 0), and then
the reset initiated (RSTFIFO = 1). This sequence flushes and resets the
RX FIFO.
4 RSTFIFO R/W 0x0
Enable Reject Bad CRC
The BADCRC bit enables the rejection of frames with an incorrectly
calculated CRC.
3 BADCRC R/W 0x1
Enable Promiscuous Mode
The PRMS bit enables Promiscuous mode, which accepts all valid frames,
regardless of the Destination Address.
2 PRMS R/W 0x0
Enable Multicast Frames
The AMUL bit enables the reception of multicast frames from the physical
medium.
1 AMUL R/W 0x0
Enable Receiver
The RXEN bit enables the Ethernet receiver. When this bit is Low, the
receiver is disabled and all frames on the physical medium are ignored.
0 RXEN R/W 0x0
462 March 17, 2008
Preliminary
Ethernet Controller
Register 5: Ethernet MAC Transmit Control (MACTCTL), offset 0x00C
This register enables software to configure the transmit module, and control frames are placed onto
the physical medium.
Ethernet MAC Transmit Control (MACTCTL)
Base 0x4004.8000
Offset 0x00C
Type R/W, reset 0x0000.0000
31 30 29 28 27 26 25 24 23 22 21 20 19 18 17 16
reserved
Type RO RO RO RO RO RO RO RO RO RO RO RO RO RO RO RO
Reset 0 0 0 0 0 0 0 0 0 0 0 0 0 0 0 0
15 14 13 12 11 10 9 8 7 6 5 4 3 2 1 0
reserved DUPLEX reserved CRC PADEN TXEN
Type RO RO RO RO RO RO RO RO RO RO RO R/W RO R/W R/W R/W
Reset 0 0 0 0 0 0 0 0 0 0 0 0 0 0 0 0
Bit/Field Name Type Reset Description
Software should not rely on the value of a reserved bit. To provide
compatibility with future products, the value of a reserved bit should be
preserved across a read-modify-write operation.
31:5 reserved RO 0x0
Enable Duplex Mode
When set, enables Duplex mode, allowing simultaneous transmission
and reception.
4 DUPLEX R/W 0x0
Software should not rely on the value of a reserved bit. To provide
compatibility with future products, the value of a reserved bit should be
preserved across a read-modify-write operation.
3 reserved RO 0x0
Enable CRC Generation
When set, enables the automatic generation of the CRC and the
placement at the end of the packet. If this bit is not set, the frames placed
in the TX FIFO are sent exactly as they are written into the FIFO.
2 CRC R/W 0x0
Enable Packet Padding
When set, enables the automatic padding of packets that do not meet
the minimum frame size.
1 PADEN R/W 0x0
Enable Transmitter
When set, enables the transmitter. When this bit is 0, the transmitter is
disabled.
0 TXEN R/W 0x0
March 17, 2008 463
Preliminary
LM3S8933 Microcontroller
Register 6: Ethernet MAC Data (MACDATA), offset 0x010
This register enables software to access the TX and RX FIFOs.
Reads from this register return the data stored in the RX FIFO from the location indicated by the
read pointer.
Writes to this register store the data in the TX FIFO at the location indicated by the write pointer.
The write pointer is then auto-incremented to the next TX FIFO location.
There is no mechanism for randomly accessing bytes in either the RX or TX FIFOs. Data must be
read from the RX FIFO sequentially and stored in a buffer for further processing. Once a read has
been performed, the data in the FIFO cannot be re-read. Data must be written to the TX FIFO
sequentially. If an error is made in placing the frame into the TX FIFO, the write pointer can be reset
to the start of the TX FIFO by writing the TXER bit of the MACIACK register and then the data
re-written.
Read-Only Register
Ethernet MAC Data (MACDATA)
Base 0x4004.8000
Offset 0x010
Type RO, reset 0x0000.0000
31 30 29 28 27 26 25 24 23 22 21 20 19 18 17 16
RXDATA
Type RO RO RO RO RO RO RO RO RO RO RO RO RO RO RO RO
Reset 0 0 0 0 0 0 0 0 0 0 0 0 0 0 0 0
15 14 13 12 11 10 9 8 7 6 5 4 3 2 1 0
RXDATA
Type RO RO RO RO RO RO RO RO RO RO RO RO RO RO RO RO
Reset 0 0 0 0 0 0 0 0 0 0 0 0 0 0 0 0
Bit/Field Name Type Reset Description
Receive FIFO Data
The RXDATA bits represent the next four bytes of data stored in the RX
FIFO.
31:0 RXDATA RO 0x0
Write-Only Register
Ethernet MAC Data (MACDATA)
Base 0x4004.8000
Offset 0x010
Type WO, reset 0x0000.0000
31 30 29 28 27 26 25 24 23 22 21 20 19 18 17 16
TXDATA
Type WO WO WO WO WO WO WO WO WO WO WO WO WO WO WO WO
Reset 0 0 0 0 0 0 0 0 0 0 0 0 0 0 0 0
15 14 13 12 11 10 9 8 7 6 5 4 3 2 1 0
TXDATA
Type WO WO WO WO WO WO WO WO WO WO WO WO WO WO WO WO
Reset 0 0 0 0 0 0 0 0 0 0 0 0 0 0 0 0
464 March 17, 2008
Preliminary
Ethernet Controller
Bit/Field Name Type Reset Description
Transmit FIFO Data
The TXDATA bits represent the next four bytes of data to place in the
TX FIFO for transmission.
31:0 TXDATA WO 0x0
March 17, 2008 465
Preliminary
LM3S8933 Microcontroller
Register 7: Ethernet MAC Individual Address 0 (MACIA0), offset 0x014
This register enables software to program the first four bytes of the hardware MAC address of the
Network Interface Card (NIC). (The last two bytes are in MACIA1). The 6-byte IAR is compared
against the incoming Destination Address fields to determine whether the frame should be received.
Ethernet MAC Individual Address 0 (MACIA0)
Base 0x4004.8000
Offset 0x014
Type R/W, reset 0x0000.0000
31 30 29 28 27 26 25 24 23 22 21 20 19 18 17 16
MACOCT4 MACOCT3
Type R/W R/W R/W R/W R/W R/W R/W R/W R/W R/W R/W R/W R/W R/W R/W R/W
Reset 0 0 0 0 0 0 0 0 0 0 0 0 0 0 0 0
15 14 13 12 11 10 9 8 7 6 5 4 3 2 1 0
MACOCT2 MACOCT1
Type R/W R/W R/W R/W R/W R/W R/W R/W R/W R/W R/W R/W R/W R/W R/W R/W
Reset 0 0 0 0 0 0 0 0 0 0 0 0 0 0 0 0
Bit/Field Name Type Reset Description
MAC Address Octet 4
The MACOCT4 bits represent the fourth octet of the MAC address used
to uniquely identify each Ethernet Controller.
31:24 MACOCT4 R/W 0x0
MAC Address Octet 3
The MACOCT3 bits represent the third octet of the MAC address used
to uniquely identify each Ethernet Controller.
23:16 MACOCT3 R/W 0x0
MAC Address Octet 2
The MACOCT2 bits represent the second octet of the MAC address used
to uniquely identify each Ethernet Controller.
15:8 MACOCT2 R/W 0x0
MAC Address Octet 1
The MACOCT1 bits represent the first octet of the MAC address used to
uniquely identify each Ethernet Controller.
7:0 MACOCT1 R/W 0x0
466 March 17, 2008
Preliminary
Ethernet Controller
Register 8: Ethernet MAC Individual Address 1 (MACIA1), offset 0x018
This register enables software to program the last two bytes of the hardware MAC address of the
Network Interface Card (NIC). (The first four bytes are in MACIA0). The 6-byte IAR is compared
against the incoming Destination Address fields to determine whether the frame should be received.
Ethernet MAC Individual Address 1 (MACIA1)
Base 0x4004.8000
Offset 0x018
Type R/W, reset 0x0000.0000
31 30 29 28 27 26 25 24 23 22 21 20 19 18 17 16
reserved
Type RO RO RO RO RO RO RO RO RO RO RO RO RO RO RO RO
Reset 0 0 0 0 0 0 0 0 0 0 0 0 0 0 0 0
15 14 13 12 11 10 9 8 7 6 5 4 3 2 1 0
MACOCT6 MACOCT5
Type R/W R/W R/W R/W R/W R/W R/W R/W R/W R/W R/W R/W R/W R/W R/W R/W
Reset 0 0 0 0 0 0 0 0 0 0 0 0 0 0 0 0
Bit/Field Name Type Reset Description
Software should not rely on the value of a reserved bit. To provide
compatibility with future products, the value of a reserved bit should be
preserved across a read-modify-write operation.
31:16 reserved RO 0x0
MAC Address Octet 6
The MACOCT6 bits represent the sixth octet of the MAC address used
to uniquely identify each Ethernet Controller.
15:8 MACOCT6 R/W 0x0
MAC Address Octet 5
The MACOCT5 bits represent the fifth octet of the MAC address used to
uniquely identify each Ethernet Controller.
7:0 MACOCT5 R/W 0x0
March 17, 2008 467
Preliminary
LM3S8933 Microcontroller
Register 9: Ethernet MAC Threshold (MACTHR), offset 0x01C
This register enables software to set the threshold level at which the transmission of the frame
begins. If the THRESH bits are set to 0x3F, which is the reset value, transmission does not start until
the NEWTX bit is set in the MACTR register. This effectively disables the early transmission feature.
Writing the THRESH bits to any value besides all 1s enables the early transmission feature. Once
the byte count of data in the TX FIFO reaches this level, transmission of the frame begins. When
THRESH is set to all 0s, transmission of the frame begins after 4 bytes (a single write) are stored in
the TX FIFO. Each increment of the THRESH bit field waits for an additional 32 bytes of data (eight
writes) to be stored in the TX FIFO. Therefore, a value of 0x01 would wait for 36 bytes of data to
be written while a value of 0x02 would wait for 68 bytes to be written. In general, early transmission
starts when:
Number of Bytes >= 4 (THRESH x 8 + 1)
Reaching the threshold level has the same effect as setting the NEWTX bit in the MACTR register.
Transmission of the frame begins and then the number of bytes indicated by the Data Length field
is sent out on the physical medium. Because under-run checking is not performed, it is possible
that the tail pointer may reach and pass the write pointer in the TX FIFO. This causes indeterminate
values to be written to the physical medium rather than the end of the frame. Therefore, sufficient
bus bandwidth for writing to the TX FIFO must be guaranteed by the software.
If a frame smaller than the threshold level needs to be sent, the NEWTX bit in the MACTR register
must be set with an explicit write. This initiates the transmission of the frame even though the
threshold limit has not been reached.
If the threshold level is set too small, it is possible for the transmitter to underrun. If this occurs, the
transmit frame is aborted, and a transmit error occurs.
Ethernet MAC Threshold (MACTHR)
Base 0x4004.8000
Offset 0x01C
Type R/W, reset 0x0000.003F
31 30 29 28 27 26 25 24 23 22 21 20 19 18 17 16
reserved
Type RO RO RO RO RO RO RO RO RO RO RO RO RO RO RO RO
Reset 0 0 0 0 0 0 0 0 0 0 0 0 0 0 0 0
15 14 13 12 11 10 9 8 7 6 5 4 3 2 1 0
reserved THRESH
Type RO RO RO RO RO RO RO RO RO RO R/W R/W R/W R/W R/W R/W
Reset 0 0 0 0 0 0 0 0 0 0 1 1 1 1 1 1
Bit/Field Name Type Reset Description
Software should not rely on the value of a reserved bit. To provide
compatibility with future products, the value of a reserved bit should be
preserved across a read-modify-write operation.
31:6 reserved RO 0x0
Threshold Value
The THRESH bits represent the early transmit threshold. Once the amount
of data in the TX FIFO exceeds this value, transmission of the packet
begins.
5:0 THRESH R/W 0x3F
468 March 17, 2008
Preliminary
Ethernet Controller
Register 10: Ethernet MAC Management Control (MACMCTL), offset 0x020
This register enables software to control the transfer of data to and from the MII Management
registers in the Ethernet PHY. The address, name, type, reset configuration, and functional description
of each of these registers can be found in Table 17-2 on page 456 and in “MII Management Register
Descriptions” on page 475.
In order to initiate a read transaction from the MII Management registers, the WRITE bit must be
written with a 0 during the same cycle that the START bit is written with a 1.
In order to initiate a write transaction to the MII Management registers, the WRITE bit must be written
with a 1 during the same cycle that the START bit is written with a 1.
Ethernet MAC Management Control (MACMCTL)
Base 0x4004.8000
Offset 0x020
Type R/W, reset 0x0000.0000
31 30 29 28 27 26 25 24 23 22 21 20 19 18 17 16
reserved
Type RO RO RO RO RO RO RO RO RO RO RO RO RO RO RO RO
Reset 0 0 0 0 0 0 0 0 0 0 0 0 0 0 0 0
15 14 13 12 11 10 9 8 7 6 5 4 3 2 1 0
reserved REGADR reserved WRITE START
Type RO RO RO RO RO RO RO RO R/W R/W R/W R/W R/W RO R/W R/W
Reset 0 0 0 0 0 0 0 0 0 0 0 0 0 0 0 0
Bit/Field Name Type Reset Description
Software should not rely on the value of a reserved bit. To provide
compatibility with future products, the value of a reserved bit should be
preserved across a read-modify-write operation.
31:8 reserved RO 0x0
MII Register Address
The REGADR bit field represents the MII Management register address
for the next MII management interface transaction.
7:3 REGADR R/W 0x0
Software should not rely on the value of a reserved bit. To provide
compatibility with future products, the value of a reserved bit should be
preserved across a read-modify-write operation.
2 reserved RO 0x0
MII Register Transaction Type
The WRITE bit represents the operation of the next MII management
interface transaction. If WRITE is set, the next operation is a write;
otherwise, it is a read.
1 WRITE R/W 0x0
MII Register Transaction Enable
The START bit represents the initiation of the next MII management
interface transaction. When a 1 is written to this bit, the MII register
located at REGADR is read (WRITE=0) or written (WRITE=1).
0 START R/W 0x0
March 17, 2008 469
Preliminary
LM3S8933 Microcontroller
Register 11: Ethernet MAC Management Divider (MACMDV), offset 0x024
This register enables software to set the clock divider for the Management Data Clock (MDC). This
clock is used to synchronize read and write transactions between the system and the MII Management
registers. The frequency of the MDC clock can be calculated from the following formula:
Fmdc = Fipclk / (2 * (MACMDVR + 1 ))
The clock divider must be written with a value that ensures that the MDC clock does not exceed a
frequency of 2.5 MHz.
Ethernet MAC Management Divider (MACMDV)
Base 0x4004.8000
Offset 0x024
Type R/W, reset 0x0000.0080
31 30 29 28 27 26 25 24 23 22 21 20 19 18 17 16
reserved
Type RO RO RO RO RO RO RO RO RO RO RO RO RO RO RO RO
Reset 0 0 0 0 0 0 0 0 0 0 0 0 0 0 0 0
15 14 13 12 11 10 9 8 7 6 5 4 3 2 1 0
reserved DIV
Type RO RO RO RO RO RO RO RO R/W R/W R/W R/W R/W R/W R/W R/W
Reset 0 0 0 0 0 0 0 0 1 0 0 0 0 0 0 0
Bit/Field Name Type Reset Description
Software should not rely on the value of a reserved bit. To provide
compatibility with future products, the value of a reserved bit should be
preserved across a read-modify-write operation.
31:8 reserved RO 0x0
Clock Divider
The DIV bits are used to set the clock divider for the MDC clock used
to transmit data between the MAC and PHY over the serial MII interface.
7:0 DIV R/W 0x80
470 March 17, 2008
Preliminary
Ethernet Controller
Register 12: Ethernet MAC Management Transmit Data (MACMTXD), offset
0x02C
This register holds the next value to be written to the MII Management registers.
Ethernet MAC Management Transmit Data (MACMTXD)
Base 0x4004.8000
Offset 0x02C
Type R/W, reset 0x0000.0000
31 30 29 28 27 26 25 24 23 22 21 20 19 18 17 16
reserved
Type RO RO RO RO RO RO RO RO RO RO RO RO RO RO RO RO
Reset 0 0 0 0 0 0 0 0 0 0 0 0 0 0 0 0
15 14 13 12 11 10 9 8 7 6 5 4 3 2 1 0
MDTX
Type R/W R/W R/W R/W R/W R/W R/W R/W R/W R/W R/W R/W R/W R/W R/W R/W
Reset 0 0 0 0 0 0 0 0 0 0 0 0 0 0 0 0
Bit/Field Name Type Reset Description
Software should not rely on the value of a reserved bit. To provide
compatibility with future products, the value of a reserved bit should be
preserved across a read-modify-write operation.
31:16 reserved RO 0x0
MII Register Transmit Data
The MDTX bits represent the data that will be written in the next MII
management transaction.
15:0 MDTX R/W 0x0
March 17, 2008 471
Preliminary
LM3S8933 Microcontroller
Register 13: Ethernet MAC Management Receive Data (MACMRXD), offset
0x030
This register holds the last value read from the MII Management registers.
Ethernet MAC Management Receive Data (MACMRXD)
Base 0x4004.8000
Offset 0x030
Type R/W, reset 0x0000.0000
31 30 29 28 27 26 25 24 23 22 21 20 19 18 17 16
reserved
Type RO RO RO RO RO RO RO RO RO RO RO RO RO RO RO RO
Reset 0 0 0 0 0 0 0 0 0 0 0 0 0 0 0 0
15 14 13 12 11 10 9 8 7 6 5 4 3 2 1 0
MDRX
Type R/W R/W R/W R/W R/W R/W R/W R/W R/W R/W R/W R/W R/W R/W R/W R/W
Reset 0 0 0 0 0 0 0 0 0 0 0 0 0 0 0 0
Bit/Field Name Type Reset Description
Software should not rely on the value of a reserved bit. To provide
compatibility with future products, the value of a reserved bit should be
preserved across a read-modify-write operation.
31:16 reserved RO 0x0
MII Register Receive Data
The MDRX bits represent the data that was read in the previous MII
management transaction.
15:0 MDRX R/W 0x0
472 March 17, 2008
Preliminary
Ethernet Controller
Register 14: Ethernet MAC Number of Packets (MACNP), offset 0x034
This register holds the number of frames that are currently in the RX FIFO. When NPR is 0, there
are no frames in the RX FIFO and the RXINT bit is not set. When NPR is any other value, there is
at least one frame in the RX FIFO and the RXINT bit in the MACRIS register is set.
Ethernet MAC Number of Packets (MACNP)
Base 0x4004.8000
Offset 0x034
Type RO, reset 0x0000.0000
31 30 29 28 27 26 25 24 23 22 21 20 19 18 17 16
reserved
Type RO RO RO RO RO RO RO RO RO RO RO RO RO RO RO RO
Reset 0 0 0 0 0 0 0 0 0 0 0 0 0 0 0 0
15 14 13 12 11 10 9 8 7 6 5 4 3 2 1 0
reserved NPR
Type RO RO RO RO RO RO RO RO RO RO RO RO RO RO RO RO
Reset 0 0 0 0 0 0 0 0 0 0 0 0 0 0 0 0
Bit/Field Name Type Reset Description
Software should not rely on the value of a reserved bit. To provide
compatibility with future products, the value of a reserved bit should be
preserved across a read-modify-write operation.
31:6 reserved RO 0x0
Number of Packets in Receive FIFO
The NPR bits represent the number of packets stored in the RX FIFO.
While the NPR field is greater than 0, the RXINT interrupt in the MACRIS
register is asserted.
5:0 NPR RO 0x0
March 17, 2008 473
Preliminary
LM3S8933 Microcontroller
Register 15: Ethernet MAC Transmission Request (MACTR), offset 0x038
This register enables software to initiate the transmission of the frame currently located in the TX
FIFO to the physical medium. Once the frame has been transmitted to the medium from the TX
FIFO or a transmission error has been encountered, the NEWTX bit is auto-cleared by the hardware.
Ethernet MAC Transmission Request (MACTR)
Base 0x4004.8000
Offset 0x038
Type R/W, reset 0x0000.0000
31 30 29 28 27 26 25 24 23 22 21 20 19 18 17 16
reserved
Type RO RO RO RO RO RO RO RO RO RO RO RO RO RO RO RO
Reset 0 0 0 0 0 0 0 0 0 0 0 0 0 0 0 0
15 14 13 12 11 10 9 8 7 6 5 4 3 2 1 0
reserved NEWTX
Type RO RO RO RO RO RO RO RO RO RO RO RO RO RO RO R/W
Reset 0 0 0 0 0 0 0 0 0 0 0 0 0 0 0 0
Bit/Field Name Type Reset Description
Software should not rely on the value of a reserved bit. To provide
compatibility with future products, the value of a reserved bit should be
preserved across a read-modify-write operation.
31:1 reserved RO 0x0
New Transmission
When set, the NEWTX bit initiates an Ethernet transmission once the
packet has been placed in the TX FIFO. This bit is cleared once the
transmission has been completed. If early transmission is being used
(see the MACTHR register), this bit does not need to be set.
0 NEWTX R/W 0x0
474 March 17, 2008
Preliminary
Ethernet Controller
Register 16: Ethernet MAC Timer Support (MACTS), offset 0x03C
This register enables software to enable timer support on the transmission and reception of frames.
This register is only applicable for devices that have 1588 hardware support; for all others, a read
returns 0s.
Ethernet MAC Timer Support (MACTS)
Base 0x4004.8000
Offset 0x03C
Type R/W, reset 0x0000.0000
31 30 29 28 27 26 25 24 23 22 21 20 19 18 17 16
reserved
Type RO RO RO RO RO RO RO RO RO RO RO RO RO RO RO RO
Reset 0 0 0 0 0 0 0 0 0 0 0 0 0 0 0 0
15 14 13 12 11 10 9 8 7 6 5 4 3 2 1 0
reserved TSEN
Type RO RO RO RO RO RO RO RO RO RO RO RO RO RO RO R/W
Reset 0 0 0 0 0 0 0 0 0 0 0 0 0 0 0 0
Bit/Field Name Type Reset Description
Software should not rely on the value of a reserved bit. To provide
compatibility with future products, the value of a reserved bit should be
preserved across a read-modify-write operation.
31:1 reserved RO 0x0
Time Stamp Enable
When set, the TSEN bit multiplexes the TX and RX interrupts to the CCP
inputs of General-Purpose Timer 3.
0 TSEN R/W 0x0
17.6 MII Management Register Descriptions
The IEEE 802.3 standard specifies a register set for controlling and gathering status from the PHY.
The registers are collectively known as the MII Management registers. All addresses given are
absolute. Addresses not listed are reserved. Also see “Ethernet MAC Register
Descriptions” on page 457.
March 17, 2008 475
Preliminary
LM3S8933 Microcontroller
Register 17: Ethernet PHY Management Register 0 – Control (MR0), address
0x00
This register enables software to configure the operation of the PHY. The default settings of these
registers are designed to initialize the PHY to a normal operational mode without configuration.
Ethernet PHY Management Register 0 – Control (MR0)
Base 0x4004.8000
Address 0x00
Type R/W, reset 0x3100
15 14 13 12 11 10 9 8 7 6 5 4 3 2 1 0
RESET LOOPBK SPEEDSL ANEGEN PWRDN ISO RANEG DUPLEX COLT reserved
Type R/W R/W R/W R/W R/W R/W R/W R/W R/W R/W R/W R/W R/W R/W R/W R/W
Reset 0 0 1 1 0 0 0 1 0 0 0 0 0 0 0 0
Bit/Field Name Type Reset Description
Reset Registers
When set, resets the registers to their default state and reinitializes
internal state machines. Once the reset operation has completed, this
bit is cleared by hardware.
15 RESET R/W 0
Loopback Mode
When set, enables the Loopback mode of operation. The receive circuitry
is isolated from the physical medium and transmissions are sent back
through the receive circuitry instead of the medium.
14 LOOPBK R/W 0
Speed Select
Value Description
1 Enables the 100 Mb/s mode of operation (100BASE-TX).
0 Enables the 10 Mb/s mode of operation (10BASE-T).
13 SPEEDSL R/W 1
Auto-Negotiation Enable
When set, enables the Auto-Negotiation process.
12 ANEGEN R/W 1
Power Down
When set, places the PHY into a low-power consuming state.
11 PWRDN R/W 0
Isolate
When set, isolates transmit and receive data paths and ignores all
signaling on these buses.
10 ISO R/W 0
Restart Auto-Negotiation
When set, restarts the Auto-Negotiation process. Once the restart has
initiated, this bit is cleared by hardware.
9 RANEG R/W 0
Set Duplex Mode
Value Description
Enables the Full-Duplex mode of operation. This bit can be
set by software in a manual configuration process or by the
Auto-Negotiation process.
1
0 Enables the Half-Duplex mode of operation.
8 DUPLEX R/W 1
476 March 17, 2008
Preliminary
Ethernet Controller
Bit/Field Name Type Reset Description
Collision Test
When set, enables the Collision Test mode of operation. The COLT bit
asserts after the initiation of a transmission and de-asserts once the
transmission is halted.
7 COLT R/W 0
6:0 reserved R/W 0x00 Write as 0, ignore on read.
March 17, 2008 477
Preliminary
LM3S8933 Microcontroller
Register 18: Ethernet PHY Management Register 1 – Status (MR1), address
0x01
This register enables software to determine the capabilities of the PHY and perform its initialization
and operation appropriately.
Ethernet PHY Management Register 1 – Status (MR1)
Base 0x4004.8000
Address 0x01
Type RO, reset 0x7849
15 14 13 12 11 10 9 8 7 6 5 4 3 2 1 0
reserved 100X_F 100X_H 10T_F 10T_H reserved MFPS ANEGC RFAULT ANEGA LINK JAB EXTD
Type RO RO RO RO RO RO RO RO RO RO RO RC RO RO RC RO
Reset 0 1 1 1 1 0 0 0 0 1 0 0 1 0 0 1
Bit/Field Name Type Reset Description
Software should not rely on the value of a reserved bit. To provide
compatibility with future products, the value of a reserved bit should be
preserved across a read-modify-write operation.
15 reserved RO 0
100BASE-TX Full-Duplex Mode
When set, indicates that the PHY is capable of supporting 100BASE-TX
Full-Duplex mode.
14 100X_F RO 1
100BASE-TX Half-Duplex Mode
When set, indicates that the PHY is capable of supporting 100BASE-TX
Half-Duplex mode.
13 100X_H RO 1
10BASE-T Full-Duplex Mode
When set, indicates that the PHY is capable of 10BASE-T Full-Duplex
mode.
12 10T_F RO 1
10BASE-T Half-Duplex Mode
When set, indicates that the PHY is capable of supporting 10BASE-T
Half-Duplex mode.
11 10T_H RO 1
Software should not rely on the value of a reserved bit. To provide
compatibility with future products, the value of a reserved bit should be
preserved across a read-modify-write operation.
10:7 reserved RO 0
Management Frames with Preamble Suppressed
When set, indicates that the Management Interface is capable of
receiving management frames with the preamble suppressed.
6 MFPS RO 1
Auto-Negotiation Complete
When set, indicates that the Auto-Negotiation process has been
completed and that the extended registers defined by the
Auto-Negotiation protocol are valid.
5 ANEGC RO 0
Remote Fault
When set, indicates that a remote fault condition has been detected.
This bit remains set until it is read, even if the condition no longer exists.
4 RFAULT RC 0
478 March 17, 2008
Preliminary
Ethernet Controller
Bit/Field Name Type Reset Description
Auto-Negotiation
When set, indicates that the PHY has the ability to perform
Auto-Negotiation.
3 ANEGA RO 1
Link Made
When set, indicates that a valid link has been established by the PHY.
2 LINK RO 0
Jabber Condition
When set, indicates that a jabber condition has been detected by the
PHY. This bit remains set until it is read, even if the jabber condition no
longer exists.
1 JAB RC 0
Extended Capabilities
When set, indicates that the PHY provides an extended set of capabilities
that can be accessed through the extended register set.
0 EXTD RO 1
March 17, 2008 479
Preliminary
LM3S8933 Microcontroller
Register 19: Ethernet PHY Management Register 2 – PHY Identifier 1 (MR2),
address 0x02
This register, along with MR3, provides a 32-bit value indicating the manufacturer, model, and
revision information.
Ethernet PHY Management Register 2 – PHY Identifier 1 (MR2)
Base 0x4004.8000
Address 0x02
Type RO, reset 0x000E
15 14 13 12 11 10 9 8 7 6 5 4 3 2 1 0
OUI[21:6]
Type RO RO RO RO RO RO RO RO RO RO RO RO RO RO RO RO
Reset 0 0 0 0 0 0 0 0 0 0 0 0 1 1 1 0
Bit/Field Name Type Reset Description
Organizationally Unique Identifier[21:6]
This field, along with the OUI[5:0] field in MR3, makes up the
Organizationally Unique Identifier indicating the PHY manufacturer.
15:0 OUI[21:6] RO 0x000E
480 March 17, 2008
Preliminary
Ethernet Controller
Register 20: Ethernet PHY Management Register 3 – PHY Identifier 2 (MR3),
address 0x03
This register, along with MR2, provides a 32-bit value indicating the manufacturer, model, and
revision information.
Ethernet PHY Management Register 3 – PHY Identifier 2 (MR3)
Base 0x4004.8000
Address 0x03
Type RO, reset 0x7237
15 14 13 12 11 10 9 8 7 6 5 4 3 2 1 0
OUI[5:0] MN RN
Type RO RO RO RO RO RO RO RO RO RO RO RO RO RO RO RO
Reset 0 1 1 1 0 0 1 0 0 0 1 1 0 1 1 1
Bit/Field Name Type Reset Description
Organizationally Unique Identifier[5:0]
This field, along with the OUI[21:6] field in MR2, makes up the
Organizationally Unique Identifier indicating the PHY manufacturer.
15:10 OUI[5:0] RO 0x1C
Model Number
The MN field represents the Model Number of the PHY.
9:4 MN RO 0x23
Revision Number
The RN field represents the Revision Number of the PHY.
3:0 RN RO 0x7
March 17, 2008 481
Preliminary
LM3S8933 Microcontroller
Register 21: Ethernet PHY Management Register 4 – Auto-Negotiation
Advertisement (MR4), address 0x04
This register provides the advertised abilities of the PHY used during Auto-Negotiation. Bits 8:5
represent the Technology Ability Field bits. This field can be overwritten by software to Auto-Negotiate
to an alternate common technology. Writing to this register has no effect until Auto-Negotiation is
re-initiated.
Ethernet PHY Management Register 4 – Auto-Negotiation Advertisement (MR4)
Base 0x4004.8000
Address 0x04
Type R/W, reset 0x01E1
15 14 13 12 11 10 9 8 7 6 5 4 3 2 1 0
NP reserved RF reserved A3 A2 A1 A0 S[4:0]
Type RO RO R/W RO RO RO RO R/W R/W R/W R/W RO RO RO RO RO
Reset 0 0 0 0 0 0 0 1 1 1 1 0 0 0 0 1
Bit/Field Name Type Reset Description
Next Page
When set, indicates the PHY is capable of Next Page exchanges to
provide more detailed information on the PHY’s capabilities.
15 NP RO 0
Software should not rely on the value of a reserved bit. To provide
compatibility with future products, the value of a reserved bit should be
preserved across a read-modify-write operation.
14 reserved RO 0
Remote Fault
When set, indicates to the link partner that a Remote Fault condition
has been encountered.
13 RF R/W 0
Software should not rely on the value of a reserved bit. To provide
compatibility with future products, the value of a reserved bit should be
preserved across a read-modify-write operation.
12:9 reserved RO 0
Technology Ability Field[3]
When set, indicates that the PHY supports the 100Base-TX full-duplex
signaling protocol. If software wants to ensure that this mode is not used,
this bit can be written to 0 and Auto-Negotiation re-initiated with the
RANEG bit in the MR0 register.
8 A3 R/W 1
Technology Ability Field[2]
When set, indicates that the PHY supports the 100Base-T half-duplex
signaling protocol. If software wants to ensure that this mode is not used,
this bit can be written to 0 and Auto-Negotiation re-initiated.
7 A2 R/W 1
Technology Ability Field[1]
When set, indicates that the PHY supports the 10Base-T full-duplex
signaling protocol. If software wants to ensure that this mode is not used,
this bit can be written to 0 and Auto-Negotiation re-initiated.
6 A1 R/W 1
Technology Ability Field[0]
When set, indicates that the PHY supports the 10Base-T half-duplex
signaling protocol. If software wants to ensure that this mode is not used,
this bit can be written to 0 and Auto-Negotiation re-initiated.
5 A0 R/W 1
482 March 17, 2008
Preliminary
Ethernet Controller
Bit/Field Name Type Reset Description
Selector Field
The S[4:0] field encodes 32 possible messages for communicating
between PHYs. This field is hard-coded to 0x01, indicating that the
Stellaris® PHY is IEEE 802.3 compliant.
4:0 S[4:0] RO 0x01
March 17, 2008 483
Preliminary
LM3S8933 Microcontroller
Register 22: Ethernet PHY Management Register 5 – Auto-Negotiation Link
Partner Base Page Ability (MR5), address 0x05
This register provides the advertised abilities of the link partner’s PHY that are received and stored
during Auto-Negotiation.
Ethernet PHY Management Register 5 – Auto-Negotiation Link Partner Base Page Ability (MR5)
Base 0x4004.8000
Address 0x05
Type RO, reset 0x0000
15 14 13 12 11 10 9 8 7 6 5 4 3 2 1 0
NP ACK RF A[7:0] S[4:0]
Type RO RO RO RO RO RO RO RO RO RO RO RO RO RO RO RO
Reset 0 0 0 0 0 0 0 0 0 0 0 0 0 0 0 0
Bit/Field Name Type Reset Description
Next Page
When set, indicates that the link partner’s PHY is capable of Next page
exchanges to provide more detailed information on the PHY’s
capabilities.
15 NP RO 0
Acknowledge
When set, indicates that the device has successfully received the link
partner’s advertised abilities during Auto-Negotiation.
14 ACK RO 0
Remote Fault
Used as a standard transport mechanism for transmitting simple fault
information.
13 RF RO 0
Technology Ability Field
The A[7:0] field encodes individual technologies that are supported
by the PHY. See the MR4 register.
12:5 A[7:0] RO 0x00
Selector Field
The S[4:0] field encodes possible messages for communicating
between PHYs.
Value Description
0x00 Reserved
0x01 IEEE Std 802.3
0x02 IEEE Std 802.9 ISLAN-16T
0x03 IEEE Std 802.5
0x04 IEEE Std 1394
0x05–0x1F Reserved
4:0 S[4:0] RO 0x00
484 March 17, 2008
Preliminary
Ethernet Controller
Register 23: Ethernet PHY Management Register 6 – Auto-Negotiation
Expansion (MR6), address 0x06
This register enables software to determine the Auto-Negotiation and Next Page capabilities of the
PHY and the link partner after Auto-Negotiation.
Ethernet PHY Management Register 6 – Auto-Negotiation Expansion (MR6)
Base 0x4004.8000
Address 0x06
Type RO, reset 0x0000
15 14 13 12 11 10 9 8 7 6 5 4 3 2 1 0
reserved PDF LPNPA reserved PRX LPANEGA
Type RO RO RO RO RO RO RO RO RO RO RO RC RO RO RC RO
Reset 0 0 0 0 0 0 0 0 0 0 0 0 0 0 0 0
Bit/Field Name Type Reset Description
Software should not rely on the value of a reserved bit. To provide
compatibility with future products, the value of a reserved bit should be
preserved across a read-modify-write operation.
15:5 reserved RO 0x000
Parallel Detection Fault
When set, indicates that more than one technology has been detected
at link up. This bit is cleared when read.
4 PDF RC 0
Link Partner is Next Page Able
When set, indicates that the link partner is Next Page Able.
3 LPNPA RO 0
Software should not rely on the value of a reserved bit. To provide
compatibility with future products, the value of a reserved bit should be
preserved across a read-modify-write operation.
2 reserved RO 0x000
New Page Received
When set, indicates that a New Page has been received from the link
partner and stored in the appropriate location. This bit remains set until
the register is read.
1 PRX RC 0
Link Partner is Auto-Negotiation Able
When set, indicates that the Link partner is Auto-Negotiation Able.
0 LPANEGA RO 0
March 17, 2008 485
Preliminary
LM3S8933 Microcontroller
Register 24: Ethernet PHY Management Register 16 – Vendor-Specific (MR16),
address 0x10
This register enables software to configure the operation of vendor-specific modes of the PHY.
Ethernet PHY Management Register 16 – Vendor-Specific (MR16)
Base 0x4004.8000
Address 0x10
Type R/W, reset 0x0140
15 14 13 12 11 10 9 8 7 6 5 4 3 2 1 0
RPTR INPOL reserved TXHIM SQEI NL10 reserved APOL RVSPOL reserved PCSBP RXCC
Type R/W R/W RO R/W R/W R/W RO RO RO RO R/W R/W RO RO R/W R/W
Reset 0 0 0 0 0 0 0 1 0 1 0 0 0 0 0 0
Bit/Field Name Type Reset Description
Repeater Mode
When set, enables the repeater mode of operation. In this mode,
full-duplex is not allowed and the Carrier Sense signal only responds
to receive activity. If the PHY is configured to 10Base-T mode, the SQE
test function is disabled.
15 RPTR R/W 0
Interrupt Polarity
Value Description
1 Sets the polarity of the PHY interrupt to be active High.
0 Sets the polarity of the PHY interrupt to active Low.
Important: Because the Media Access Controller expects active
Low interrupts from the PHY, this bit must always be
written with a 0 to ensure proper operation.
14 INPOL R/W 0
Software should not rely on the value of a reserved bit. To provide
compatibility with future products, the value of a reserved bit should be
preserved across a read-modify-write operation.
13 reserved RO 0
Transmit High Impedance Mode
When set, enables the transmitter High Impedance mode. In this mode,
the TXOP and TXON transmitter pins are put into a high impedance state.
The RXIP and RXIN pins remain fully functional.
12 TXHIM R/W 0
SQE Inhibit Testing
When set, prohibits 10Base-T SQE testing.
When 0, the SQE testing is performed by generating a Collision pulse
following the completion of the transmission of a frame.
11 SQEI R/W 0
Natural Loopback Mode
When set, enables the 10Base-T Natural Loopback mode. This causes
the transmission data received by the PHY to be looped back onto the
receive data path when 10Base-T mode is enabled.
10 NL10 R/W 0
Software should not rely on the value of a reserved bit. To provide
compatibility with future products, the value of a reserved bit should be
preserved across a read-modify-write operation.
9:6 reserved RO 0x05
486 March 17, 2008
Preliminary
Ethernet Controller
Bit/Field Name Type Reset Description
Auto-Polarity Disable
When set, disables the PHY’s auto-polarity function.
If this bit is 0, the PHY automatically inverts the received signal due to
a wrong polarity connection during Auto-Negotiation if the PHY is in
10Base-T mode.
5 APOL R/W 0
Receive Data Polarity
This bit indicates whether the receive data pulses are being inverted.
If the APOL bit is 0, then the RVSPOL bit is read-only and indicates
whether the auto-polarity circuitry is reversing the polarity. In this case,
a 1 in the RVSPOL bit indicates that the receive data is inverted while a
0 indicates that the receive data is not inverted.
If the APOL bit is 1, then the RVSPOL bit is writable and software can
force the receive data to be inverted. Setting RVSPOL to 1 forces the
receive data to be inverted while a 0 does not invert the receive data.
4 RVSPOL R/W 0
Software should not rely on the value of a reserved bit. To provide
compatibility with future products, the value of a reserved bit should be
preserved across a read-modify-write operation.
3:2 reserved RO 0
PCS Bypass
When set, enables the bypass of the PCS and scrambling/descrambling
functions in 100Base-TX mode. This mode is only valid when
Auto-Negotiation is disabled and 100Base-T mode is enabled.
1 PCSBP R/W 0
Receive Clock Control
When set, enables the Receive Clock Control power saving mode if the
PHY is configured in 100Base-TX mode. This mode shuts down the
receive clock when no data is being received from the physical medium
to save power. This mode should not be used when PCSBP is enabled
and is automatically disabled when the LOOPBK bit in the MR0 register
is set.
0 RXCC R/W 0
March 17, 2008 487
Preliminary
LM3S8933 Microcontroller
Register 25: Ethernet PHY Management Register 17 – Interrupt Control/Status
(MR17), address 0x11
This register provides the means for controlling and observing the events, which trigger a PHY
interrupt in the MACRIS register. This register can also be used in a polling mode via the MII Serial
Interface as a means to observe key events within the PHY via one register address. Bits 0 through
7 are status bits, which are each set to logic 1 based on an event. These bits are cleared after the
register is read. Bits 8 through 15 of this register, when set to logic 1, enable their corresponding
bit in the lower byte to signal a PHY interrupt in the MACRIS register.
Ethernet PHY Management Register 17 – Interrupt Control/Status (MR17)
Base 0x4004.8000
Address 0x11
Type R/W, reset 0x0000
15 14 13 12 11 10 9 8 7 6 5 4 3 2 1 0
JABBER_IE RXER_IE PRX_IE PDF_IE LPACK_IELSCHG_IE RFAULT_IE ANEGCOMP_IE JABBER_INTRXER_INT PRX_INT PDF_INT LPACK_INT LSCHG_INT RFAULT_INT ANEGCOMP_INT
Type R/W R/W R/W R/W R/W R/W R/W R/W RC RC RC RC RC RC RC RC
Reset 0 0 0 0 0 0 0 0 0 0 0 0 0 0 0 0
Bit/Field Name Type Reset Description
Jabber Interrupt Enable
When set, enables system interrupts when a Jabber condition is detected
by the PHY.
15 JABBER_IE R/W 0
Receive Error Interrupt Enable
When set, enables system interrupts when a receive error is detected
by the PHY.
14 RXER_IE R/W 0
Page Received Interrupt Enable
When set, enables system interrupts when a new page is received by
the PHY.
13 PRX_IE R/W 0
Parallel Detection Fault Interrupt Enable
When set, enables system interrupts when a Parallel Detection Fault is
detected by the PHY.
12 PDF_IE R/W 0
LP Acknowledge Interrupt Enable
When set, enables system interrupts when FLP bursts are received with
the Acknowledge bit during Auto-Negotiation.
11 LPACK_IE R/W 0
Link Status Change Interrupt Enable
When set, enables system interrupts when the Link Status changes
from OK to FAIL.
10 LSCHG_IE R/W 0
Remote Fault Interrupt Enable
When set, enables system interrupts when a Remote Fault condition is
signaled by the link partner.
9 RFAULT_IE R/W 0
Auto-Negotiation Complete Interrupt Enable
When set, enables system interrupts when the Auto-Negotiation
sequence has completed successfully.
8 ANEGCOMP_IE R/W 0
488 March 17, 2008
Preliminary
Ethernet Controller
Bit/Field Name Type Reset Description
Jabber Event Interrupt
When set, indicates that a Jabber event has been detected by the
10Base-T circuitry.
7 JABBER_INT RC 0
Receive Error Interrupt
When set, indicates that a receive error has been detected by the PHY.
6 RXER_INT RC 0
Page Receive Interrupt
When set, indicates that a new page has been received from the link
partner during Auto-Negotiation.
5 PRX_INT RC 0
Parallel Detection Fault Interrupt
When set, indicates that a Parallel Detection Fault has been detected
by the PHY during the Auto-Negotiation process.
4 PDF_INT RC 0
LP Acknowledge Interrupt
When set, indicates that an FLP burst has been received with the
Acknowledge bit set during Auto-Negotiation.
3 LPACK_INT RC 0
Link Status Change Interrupt
When set, indicates that the link status has changed from OK to FAIL.
2 LSCHG_INT RC 0
Remote Fault Interrupt
When set, indicates that a Remote Fault condition has been signaled
by the link partner.
1 RFAULT_INT RC 0
Auto-Negotiation Complete Interrupt
When set, indicates that the Auto-Negotiation sequence has completed
successfully.
0 ANEGCOMP_INT RC 0
March 17, 2008 489
Preliminary
LM3S8933 Microcontroller
Register 26: Ethernet PHY Management Register 18 – Diagnostic (MR18),
address 0x12
This register enables software to diagnose the results of the previous Auto-Negotiation.
Ethernet PHY Management Register 18 – Diagnostic (MR18)
Base 0x4004.8000
Address 0x12
Type RO, reset 0x0000
15 14 13 12 11 10 9 8 7 6 5 4 3 2 1 0
reserved ANEGF DPLX RATE RXSD RX_LOCK reserved
Type RO RO RO RC RO RO RO RO RO RO RO RO RO RO RO RO
Reset 0 0 0 0 0 0 0 0 0 0 0 0 0 0 0 0
Bit/Field Name Type Reset Description
Software should not rely on the value of a reserved bit. To provide
compatibility with future products, the value of a reserved bit should be
preserved across a read-modify-write operation.
15:13 reserved RO 0
Auto-Negotiation Failure
When set, indicates that no common technology was found during
Auto-Negotiation and has failed. This bit remains set until read.
12 ANEGF RC 0
Duplex Mode
When set, indicates that Full-Duplex was the highest common
denominator found during the Auto-Negotiation process. Otherwise,
Half-Duplex was the highest common denominator found.
11 DPLX RO 0
Rate
When set, indicates that 100Base-TX was the highest common
denominator found during the Auto-Negotiation process. Otherwise,
10Base-TX was the highest common denominator found.
10 RATE RO 0
Receive Detection
When set, indicates that receive signal detection has occurred (in
100Base-TX mode) or that Manchester-encoded data has been detected
(in 10Base-T mode).
9 RXSD RO 0
Receive PLL Lock
When set, indicates that the Receive PLL has locked onto the receive
signal for the selected speed of operation (10Base-T or 100Base-TX).
8 RX_LOCK RO 0
Software should not rely on the value of a reserved bit. To provide
compatibility with future products, the value of a reserved bit should be
preserved across a read-modify-write operation.
7:0 reserved RO 00
490 March 17, 2008
Preliminary
Ethernet Controller
Register 27: Ethernet PHY Management Register 19 – Transceiver Control
(MR19), address 0x13
This register enables software to set the gain of the transmit output to compensate for transformer
loss.
Ethernet PHY Management Register 19 – Transceiver Control (MR19)
Base 0x4004.8000
Address 0x13
Type R/W, reset 0x4000
15 14 13 12 11 10 9 8 7 6 5 4 3 2 1 0
TXO[1:0] reserved
Type R/W R/W RO RO RO RO RO RO RO RO RO RO RO RO RO RO
Reset 0 1 0 0 0 0 0 0 0 0 0 0 0 0 0 0
Bit/Field Name Type Reset Description
Transmit Amplitude Selection
The TXO[1:0] field sets the transmit output amplitude to account for
transmit transformer insertion loss.
Value Description
0x0 Gain set for 0.0dB of insertion loss
0x1 Gain set for 0.4dB of insertion loss
0x2 Gain set for 0.8dB of insertion loss
0x3 Gain set for 1.2dB of insertion loss
15:14 TXO[1:0] R/W 1
Software should not rely on the value of a reserved bit. To provide
compatibility with future products, the value of a reserved bit should be
preserved across a read-modify-write operation.
13:0 reserved RO 0x0
March 17, 2008 491
Preliminary
LM3S8933 Microcontroller
Register 28: Ethernet PHY Management Register 23 – LED Configuration
(MR23), address 0x17
This register enables software to select the source that causes the LEDs to toggle.
Ethernet PHY Management Register 23 – LED Configuration (MR23)
Base 0x4004.8000
Address 0x17
Type R/W, reset 0x0010
15 14 13 12 11 10 9 8 7 6 5 4 3 2 1 0
reserved LED1[3:0] LED0[3:0]
Type RO RO RO RO RO RO RO RO R/W R/W R/W R/W R/W R/W R/W R/W
Reset 0 0 0 0 0 0 0 0 0 0 0 1 0 0 0 0
Bit/Field Name Type Reset Description
Software should not rely on the value of a reserved bit. To provide
compatibility with future products, the value of a reserved bit should be
preserved across a read-modify-write operation.
15:8 reserved RO 0x0
LED1 Source
The LED1 field selects the source that toggles the LED1 signal.
Value Description
0x0 Link OK
0x1 RX or TX Activity (Default LED1)
0x2 TX Activity
0x3 RX Activity
0x4 Collision
0x5 100BASE-TX mode
0x6 10BASE-T mode
0x7 Full-Duplex
0x8 Link OK & Blink=RX or TX Activity
7:4 LED1[3:0] R/W 1
LED0 Source
The LED0 field selects the source that toggles the LED0 signal.
Value Description
0x0 Link OK (Default LED0)
0x1 RX or TX Activity
0x2 TX Activity
0x3 RX Activity
0x4 Collision
0x5 100BASE-TX mode
0x6 10BASE-T mode
0x7 Full-Duplex
0x8 Link OK & Blink=RX or TX Activity
3:0 LED0[3:0] R/W 0
492 March 17, 2008
Preliminary
Ethernet Controller
Register 29: Ethernet PHY Management Register 24 –MDI/MDIX Control (MR24),
address 0x18
This register enables software to control the behavior of the MDI/MDIX mux and its switching
capabilities.
Ethernet PHY Management Register 24 –MDI/MDIX Control (MR24)
Base 0x4004.8000
Address 0x18
Type R/W, reset 0x00C0
15 14 13 12 11 10 9 8 7 6 5 4 3 2 1 0
reserved PD_MODEAUTO_SW MDIX MDIX_CM MDIX_SD
Type RO RO RO RO RO RO RO RO R/W R/W R/W RO R/W R/W R/W R/W
Reset 0 0 0 0 0 0 0 0 0 0 0 0 0 0 0 0
Bit/Field Name Type Reset Description
Software should not rely on the value of a reserved bit. To provide
compatibility with future products, the value of a reserved bit should be
preserved across a read-modify-write operation.
15:8 reserved RO 0x0
Parallel Detection Mode
When set, enables the Parallel Detection mode and allows auto-switching
to work when Auto-Negotiation is not enabled.
7 PD_MODE R/W 0
Auto-Switching Enable
When set, enables Auto-Switching of the MDI/MDIX mux.
6 AUTO_SW R/W 0
Auto-Switching Configuration
When set, indicates that the MDI/MDIX mux is in the crossover (MDIX)
configuration.
When 0, it indicates that the mux is in the pass-through (MDI)
configuration.
When the AUTO_SW bit is 1, the MDIX bit is read-only. When the
AUTO_SW bit is 0, the MDIX bit is read/write and can be configured
manually.
5 MDIX R/W 0
Auto-Switching Complete
When set, indicates that the auto-switching sequence has completed.
If 0, it indicates that the sequence has not completed or that
auto-switching is disabled.
4 MDIX_CM RO 0
Auto-Switching Seed
This field provides the initial seed for the switching algorithm. This seed
directly affects the number of attempts [5,4] respectively to write bits
[3:0].
A 0 sets the seed to 0x5.
3:0 MDIX_SD R/W 0
March 17, 2008 493
Preliminary
LM3S8933 Microcontroller
18 Analog Comparators
An analog comparator is a peripheral that compares two analog voltages, and provides a logical
output that signals the comparison result.
The LM3S8933 controller provides three independent integrated analog comparators that can be
configured to drive an output or generate an interrupt or ADC event.
Note: Not all comparators have the option to drive an output pin. See the Comparator Operating
Mode tables in “Functional Description” on page 495 for more information.
A comparator can compare a test voltage against any one of these voltages:
■ An individual external reference voltage
■ A shared single external reference voltage
■ A shared internal reference voltage
The comparator can provide its output to a device pin, acting as a replacement for an analog
comparator on the board, or it can be used to signal the application via interrupts or triggers to the
ADC to cause it to start capturing a sample sequence. The interrupt generation and ADC triggering
logic is separate. This means, for example, that an interrupt can be generated on a rising edge and
the ADC triggered on a falling edge.
494 March 17, 2008
Preliminary
Analog Comparators
18.1 Block Diagram
Figure 18-1. Analog Comparator Module Block Diagram
C2+
C2-
output
+ve input (alternate)
+ve input
interrupt
-ve input
reference input
Comparator 2
ACSTAT2
ACCTL2
C1-
C1+ output
+ve input (alternate)
+ve input
interrupt
-ve input
reference input
Comparator 1
ACSTAT1
ACCTL1
C1o
Voltage
Ref
ACREFCTL
output
+ve input (alternate)
+ve input
interrupt
-ve input
reference input
Comparator 0
ACSTAT0
ACCTL0
C0+
internal
bus
C0-
C0o
trigger trigger
trigger trigger
trigger trigger
Interrupt Control
ACRIS
ACMIS
ACINTEN
interrupt
18.2 Functional Description
Important: It is recommended that the Digital-Input enable (the GPIODEN bit in the GPIO module)
for the analog input pin be disabled to prevent excessive current draw from the I/O
pads.
The comparator compares the VIN- and VIN+ inputs to produce an output, VOUT.
VIN- < VIN+, VOUT = 1
VIN- > VIN+, VOUT = 0
As shown in Figure 18-2 on page 496, the input source for VIN- is an external input. In addition to
an external input, input sources for VIN+ can be the +ve input of comparator 0 or an internal reference.
March 17, 2008 495
Preliminary
LM3S8933 Microcontroller
Figure 18-2. Structure of Comparator Unit
ACCTL ACSTAT
IntGen
2 TrigGen
1
0
CINV
output
-ve input
+ve input
interrupt
internal
bus
trigger
+ve input (alternate)
reference input
A comparator is configured through two status/control registers (ACCTL and ACSTAT ). The internal
reference is configured through one control register (ACREFCTL). Interrupt status and control is
configured through three registers (ACMIS, ACRIS, and ACINTEN). The operating modes of the
comparators are shown in the Comparator Operating Mode tables.
Typically, the comparator output is used internally to generate controller interrupts. It may also be
used to drive an external pin or generate an analog-to-digital converter (ADC) trigger.
Important: Certain register bit values must be set before using the analog comparators. The proper
pad configuration for the comparator input and output pins are described in the
Comparator Operating Mode tables.
Table 18-1. Comparator 0 Operating Modes
ACCNTL0 Comparator 0
ASRCP VIN- VIN+ Output Interrupt ADCTrigger
00 C0- C0+ C0o yes yes
01 C0- C0+ C0o yes yes
10 C0- Vref C0o yes yes
11 C0- reserved C0o yes yes
Table 18-2. Comparator 1 Operating Modes
ACCNTL1 Comparator 1
ASRCP VIN- VIN+ Output Interrupt ADCTrigger
00 C1- C1o/C1+ C1o/C1+ yes yes
01 C1- C0+ C1o/C1+ yes yes
10 C1- Vref C1o/C1+ yes yes
11 C1- reserved C1o/C1+ yes yes
496 March 17, 2008
Preliminary
Analog Comparators
Table 18-3. Comparator 2 Operating Modes
ACCNTL2 Comparator 2
ASRCP VIN- VIN+ Output Interrupt ADCTrigger
00 C2- C2+ n/a yes yes
01 C2- C0+ n/a yes yes
10 C2- Vref n/a yes yes
11 C2- reserved n/a yes yes
18.2.1 Internal Reference Programming
The structure of the internal reference is shown in Figure 18-3 on page 497. This is controlled by a
single configuration register (ACREFCTL). Table 18-4 on page 497 shows the programming options
to develop specific internal reference values, to compare an external voltage against a particular
voltage generated internally.
Figure 18-3. Comparator Internal Reference Structure
8R R R
8R
R
•••
•••
0
Decoder
15 14 1
AVDD
EN
internal
reference
VREF
RNG
Table 18-4. Internal Reference Voltage and ACREFCTL Field Values
ACREFCTL Register Output Reference Voltage Based on VREF Field Value
EN Bit Value RNG Bit Value
0 V (GND) for any value of VREF; however, it is recommended that RNG=1 and VREF=0
for the least noisy ground reference.
EN=0 RNG=X
March 17, 2008 497
Preliminary
LM3S8933 Microcontroller
ACREFCTL Register Output Reference Voltage Based on VREF Field Value
EN Bit Value RNG Bit Value
Total resistance in ladder is 31 R.
The range of internal reference in this mode is 0.85-2.448 V.
EN=1 RNG=0
Total resistance in ladder is 23 R.
The range of internal reference for this mode is 0-2.152 V.
RNG=1
18.3 Initialization and Configuration
The following example shows how to configure an analog comparator to read back its output value
from an internal register.
1. Enable the analog comparator 0 clock by writing a value of 0x0010.0000 to the RCGC1 register
in the System Control module.
2. In the GPIO module, enable the GPIO port/pin associated with C0- as a GPIO input.
3. Configure the internal voltage reference to 1.65 V by writing the ACREFCTL register with the
value 0x0000.030C.
4. Configure comparator 0 to use the internal voltage reference and to not invert the output on the
C0o pin by writing the ACCTL0 register with the value of 0x0000.040C.
5. Delay for some time.
6. Read the comparator output value by reading the ACSTAT0 register’s OVAL value.
Change the level of the signal input on C0- to see the OVAL value change.
18.4 Register Map
Table 18-5 on page 499 lists the comparator registers. The offset listed is a hexadecimal increment
to the register’s address, relative to the Analog Comparator base address of 0x4003.C000.
498 March 17, 2008
Preliminary
Analog Comparators
Table 18-5. Analog Comparators Register Map
See
Offset Name Type Reset Description page
0x00 ACMIS R/W1C 0x0000.0000 Analog Comparator Masked Interrupt Status 500
0x04 ACRIS RO 0x0000.0000 Analog Comparator Raw Interrupt Status 501
0x08 ACINTEN R/W 0x0000.0000 Analog Comparator Interrupt Enable 502
0x10 ACREFCTL R/W 0x0000.0000 Analog Comparator Reference Voltage Control 503
0x20 ACSTAT0 RO 0x0000.0000 Analog Comparator Status 0 504
0x24 ACCTL0 R/W 0x0000.0000 Analog Comparator Control 0 505
0x40 ACSTAT1 RO 0x0000.0000 Analog Comparator Status 1 504
0x44 ACCTL1 R/W 0x0000.0000 Analog Comparator Control 1 505
0x60 ACSTAT2 RO 0x0000.0000 Analog Comparator Status 2 504
0x64 ACCTL2 R/W 0x0000.0000 Analog Comparator Control 2 505
18.5 Register Descriptions
The remainder of this section lists and describes the Analog Comparator registers, in numerical
order by address offset.
March 17, 2008 499
Preliminary
LM3S8933 Microcontroller
Register 1: Analog Comparator Masked Interrupt Status (ACMIS), offset 0x00
This register provides a summary of the interrupt status (masked) of the comparator.
Analog Comparator Masked Interrupt Status (ACMIS)
Base 0x4003.C000
Offset 0x00
Type R/W1C, reset 0x0000.0000
31 30 29 28 27 26 25 24 23 22 21 20 19 18 17 16
reserved
Type RO RO RO RO RO RO RO RO RO RO RO RO RO RO RO RO
Reset 0 0 0 0 0 0 0 0 0 0 0 0 0 0 0 0
15 14 13 12 11 10 9 8 7 6 5 4 3 2 1 0
reserved IN2 IN1 IN0
Type RO RO RO RO RO RO RO RO RO RO RO RO RO R/W1C R/W1C R/W1C
Reset 0 0 0 0 0 0 0 0 0 0 0 0 0 0 0 0
Bit/Field Name Type Reset Description
Software should not rely on the value of a reserved bit. To provide
compatibility with future products, the value of a reserved bit should be
preserved across a read-modify-write operation.
31:3 reserved RO 0x00
Comparator 2 Masked Interrupt Status
Gives the masked interrupt state of this interrupt. Write 1 to this bit to
clear the pending interrupt.
2 IN2 R/W1C 0
Comparator 1 Masked Interrupt Status
Gives the masked interrupt state of this interrupt. Write 1 to this bit to
clear the pending interrupt.
1 IN1 R/W1C 0
Comparator 0 Masked Interrupt Status
Gives the masked interrupt state of this interrupt. Write 1 to this bit to
clear the pending interrupt.
0 IN0 R/W1C 0
500 March 17, 2008
Preliminary
Analog Comparators
Register 2: Analog Comparator Raw Interrupt Status (ACRIS), offset 0x04
This register provides a summary of the interrupt status (raw) of the comparator.
Analog Comparator Raw Interrupt Status (ACRIS)
Base 0x4003.C000
Offset 0x04
Type RO, reset 0x0000.0000
31 30 29 28 27 26 25 24 23 22 21 20 19 18 17 16
reserved
Type RO RO RO RO RO RO RO RO RO RO RO RO RO RO RO RO
Reset 0 0 0 0 0 0 0 0 0 0 0 0 0 0 0 0
15 14 13 12 11 10 9 8 7 6 5 4 3 2 1 0
reserved IN2 IN1 IN0
Type RO RO RO RO RO RO RO RO RO RO RO RO RO RO RO RO
Reset 0 0 0 0 0 0 0 0 0 0 0 0 0 0 0 0
Bit/Field Name Type Reset Description
Software should not rely on the value of a reserved bit. To provide
compatibility with future products, the value of a reserved bit should be
preserved across a read-modify-write operation.
31:3 reserved RO 0x00
Comparator 2 Interrupt Status
When set, indicates that an interrupt has been generated by comparator
2.
2 IN2 RO 0
Comparator 1 Interrupt Status
When set, indicates that an interrupt has been generated by comparator
1.
1 IN1 RO 0
Comparator 0 Interrupt Status
When set, indicates that an interrupt has been generated by comparator
0.
0 IN0 RO 0
March 17, 2008 501
Preliminary
LM3S8933 Microcontroller
Register 3: Analog Comparator Interrupt Enable (ACINTEN), offset 0x08
This register provides the interrupt enable for the comparator.
Analog Comparator Interrupt Enable (ACINTEN)
Base 0x4003.C000
Offset 0x08
Type R/W, reset 0x0000.0000
31 30 29 28 27 26 25 24 23 22 21 20 19 18 17 16
reserved
Type RO RO RO RO RO RO RO RO RO RO RO RO RO RO RO RO
Reset 0 0 0 0 0 0 0 0 0 0 0 0 0 0 0 0
15 14 13 12 11 10 9 8 7 6 5 4 3 2 1 0
reserved IN2 IN1 IN0
Type RO RO RO RO RO RO RO RO RO RO RO RO RO R/W R/W R/W
Reset 0 0 0 0 0 0 0 0 0 0 0 0 0 0 0 0
Bit/Field Name Type Reset Description
Software should not rely on the value of a reserved bit. To provide
compatibility with future products, the value of a reserved bit should be
preserved across a read-modify-write operation.
31:3 reserved RO 0x00
Comparator 2 Interrupt Enable
When set, enables the controller interrupt from the comparator 2 output
2 IN2 R/W 0
Comparator 1 Interrupt Enable
When set, enables the controller interrupt from the comparator 1 output.
1 IN1 R/W 0
Comparator 0 Interrupt Enable
When set, enables the controller interrupt from the comparator 0 output.
0 IN0 R/W 0
502 March 17, 2008
Preliminary
Analog Comparators
Register 4: Analog Comparator Reference Voltage Control (ACREFCTL), offset
0x10
This register specifies whether the resistor ladder is powered on as well as the range and tap.
Analog Comparator Reference Voltage Control (ACREFCTL)
Base 0x4003.C000
Offset 0x10
Type R/W, reset 0x0000.0000
31 30 29 28 27 26 25 24 23 22 21 20 19 18 17 16
reserved
Type RO RO RO RO RO RO RO RO RO RO RO RO RO RO RO RO
Reset 0 0 0 0 0 0 0 0 0 0 0 0 0 0 0 0
15 14 13 12 11 10 9 8 7 6 5 4 3 2 1 0
reserved EN RNG reserved VREF
Type RO RO RO RO RO RO R/W R/W RO RO RO RO R/W R/W R/W R/W
Reset 0 0 0 0 0 0 0 0 0 0 0 0 0 0 0 0
Bit/Field Name Type Reset Description
Software should not rely on the value of a reserved bit. To provide
compatibility with future products, the value of a reserved bit should be
preserved across a read-modify-write operation.
31:10 reserved RO 0x00
Resistor Ladder Enable
The EN bit specifies whether the resistor ladder is powered on. If 0, the
resistor ladder is unpowered. If 1, the resistor ladder is connected to
the analog VDD.
This bit is reset to 0 so that the internal reference consumes the least
amount of power if not used and programmed.
9 EN R/W 0
Resistor Ladder Range
The RNG bit specifies the range of the resistor ladder. If 0, the resistor
ladder has a total resistance of 31 R. If 1, the resistor ladder has a total
resistance of 23 R.
8 RNG R/W 0
Software should not rely on the value of a reserved bit. To provide
compatibility with future products, the value of a reserved bit should be
preserved across a read-modify-write operation.
7:4 reserved RO 0x00
Resistor Ladder Voltage Ref
The VREF bit field specifies the resistor ladder tap that is passed through
an analog multiplexer. The voltage corresponding to the tap position is
the internal reference voltage available for comparison. See Table
18-4 on page 497 for some output reference voltage examples.
3:0 VREF R/W 0x00
March 17, 2008 503
Preliminary
LM3S8933 Microcontroller
Register 5: Analog Comparator Status 0 (ACSTAT0), offset 0x20
Register 6: Analog Comparator Status 1 (ACSTAT1), offset 0x40
Register 7: Analog Comparator Status 2 (ACSTAT2), offset 0x60
These registers specify the current output value of the comparator.
Analog Comparator Status 0 (ACSTAT0)
Base 0x4003.C000
Offset 0x20
Type RO, reset 0x0000.0000
31 30 29 28 27 26 25 24 23 22 21 20 19 18 17 16
reserved
Type RO RO RO RO RO RO RO RO RO RO RO RO RO RO RO RO
Reset 0 0 0 0 0 0 0 0 0 0 0 0 0 0 0 0
15 14 13 12 11 10 9 8 7 6 5 4 3 2 1 0
reserved OVAL reserved
Type RO RO RO RO RO RO RO RO RO RO RO RO RO RO RO RO
Reset 0 0 0 0 0 0 0 0 0 0 0 0 0 0 0 0
Bit/Field Name Type Reset Description
Software should not rely on the value of a reserved bit. To provide
compatibility with future products, the value of a reserved bit should be
preserved across a read-modify-write operation.
31:2 reserved RO 0x00
Comparator Output Value
The OVAL bit specifies the current output value of the comparator.
1 OVAL RO 0
Software should not rely on the value of a reserved bit. To provide
compatibility with future products, the value of a reserved bit should be
preserved across a read-modify-write operation.
0 reserved RO 0
504 March 17, 2008
Preliminary
Analog Comparators
Register 8: Analog Comparator Control 0 (ACCTL0), offset 0x24
Register 9: Analog Comparator Control 1 (ACCTL1), offset 0x44
Register 10: Analog Comparator Control 2 (ACCTL2), offset 0x64
These registers configure the comparator’s input and output.
Analog Comparator Control 0 (ACCTL0)
Base 0x4003.C000
Offset 0x24
Type R/W, reset 0x0000.0000
31 30 29 28 27 26 25 24 23 22 21 20 19 18 17 16
reserved
Type RO RO RO RO RO RO RO RO RO RO RO RO RO RO RO RO
Reset 0 0 0 0 0 0 0 0 0 0 0 0 0 0 0 0
15 14 13 12 11 10 9 8 7 6 5 4 3 2 1 0
reserved TOEN ASRCP reserved TSLVAL TSEN ISLVAL ISEN CINV reserved
Type RO RO RO RO R/W R/W R/W RO R/W R/W R/W R/W R/W R/W R/W RO
Reset 0 0 0 0 0 0 0 0 0 0 0 0 0 0 0 0
Bit/Field Name Type Reset Description
Software should not rely on the value of a reserved bit. To provide
compatibility with future products, the value of a reserved bit should be
preserved across a read-modify-write operation.
31:12 reserved RO 0x00
Trigger Output Enable
The TOEN bit enables the ADC event transmission to the ADC. If 0, the
event is suppressed and not sent to the ADC. If 1, the event is
transmitted to the ADC.
11 TOEN R/W 0
Analog Source Positive
The ASRCP field specifies the source of input voltage to the VIN+ terminal
of the comparator. The encodings for this field are as follows:
Value Function
0x0 Pin value
0x1 Pin value of C0+
0x2 Internal voltage reference
0x3 Reserved
10:9 ASRCP R/W 0x00
Software should not rely on the value of a reserved bit. To provide
compatibility with future products, the value of a reserved bit should be
preserved across a read-modify-write operation.
8 reserved RO 0
Trigger Sense Level Value
The TSLVAL bit specifies the sense value of the input that generates
an ADC event if in Level Sense mode. If 0, an ADC event is generated
if the comparator output is Low. Otherwise, an ADC event is generated
if the comparator output is High.
7 TSLVAL R/W 0
March 17, 2008 505
Preliminary
LM3S8933 Microcontroller
Bit/Field Name Type Reset Description
Trigger Sense
The TSEN field specifies the sense of the comparator output that
generates an ADC event. The sense conditioning is as follows:
Value Function
0x0 Level sense, see TSLVAL
0x1 Falling edge
0x2 Rising edge
0x3 Either edge
6:5 TSEN R/W 0x0
Interrupt Sense Level Value
The ISLVAL bit specifies the sense value of the input that generates
an interrupt if in Level Sense mode. If 0, an interrupt is generated if the
comparator output is Low. Otherwise, an interrupt is generated if the
comparator output is High.
4 ISLVAL R/W 0
Interrupt Sense
The ISEN field specifies the sense of the comparator output that
generates an interrupt. The sense conditioning is as follows:
Value Function
0x0 Level sense, see ISLVAL
0x1 Falling edge
0x2 Rising edge
0x3 Either edge
3:2 ISEN R/W 0x0
Comparator Output Invert
The CINV bit conditionally inverts the output of the comparator. If 0, the
output of the comparator is unchanged. If 1, the output of the comparator
is inverted prior to being processed by hardware.
1 CINV R/W 0
Software should not rely on the value of a reserved bit. To provide
compatibility with future products, the value of a reserved bit should be
preserved across a read-modify-write operation.
0 reserved RO 0
506 March 17, 2008
Preliminary
Analog Comparators
19 Pin Diagram
The LM3S8933 microcontroller pin diagrams are shown below.
Figure 19-1. 100-Pin LQFP Package Pin Diagram
March 17, 2008 507
Preliminary
LM3S8933 Microcontroller
Figure 19-2. 108-Ball BGA Package Pin Diagram (Top View)
508 March 17, 2008
Preliminary
Pin Diagram
20 Signal Tables
The following tables list the signals available for each pin. Functionality is enabled by software with
the GPIOAFSEL register.
Important: All multiplexed pins are GPIOs by default, with the exception of the five JTAG pins (PB7
and PC[3:0]) which default to the JTAG functionality.
Table 20-1 on page 509 shows the pin-to-signal-name mapping, including functional characteristics
of the signals. Table 20-2 on page 513 lists the signals in alphabetical order by signal name.
Table 20-3 on page 517 groups the signals by functionality, except for GPIOs. Table 20-4 on page
519 lists the GPIO pins and their alternate functionality.
20.1 100-Pin LQFP Package Pin Tables
Table 20-1. Signals by Pin Number
Pin Number Pin Name Pin Type Buffer Type Description
1 ADC0 I Analog Analog-to-digital converter input 0.
2 ADC1 I Analog Analog-to-digital converter input 1.
The positive supply (3.3 V) for the analog
circuits (ADC, Analog Comparators, etc.).
These are separated from VDD to minimize
the electrical noise contained on VDD from
affecting the analog functions.
3 VDDA - Power
The ground reference for the analog circuits
(ADC, Analog Comparators, etc.). These are
separated from GND to minimize the electrical
noise contained on VDD from affecting the
analog functions.
4 GNDA - Power
5 ADC2 I Analog Analog-to-digital converter input 2.
6 ADC3 I Analog Analog-to-digital converter input 3.
Low drop-out regulator output voltage. This
pin requires an external capacitor between
the pin and GND of 1 μF or greater. When the
on-chip LDO is used to provide power to the
logic, the LDO pin must also be connected to
the VDD25 pins at the board level in addition
to the decoupling capacitor(s).
7 LDO - Power
8 VDD - Power Positive supply for I/O and some logic.
9 GND - Power Ground reference for logic and I/O pins.
10 PD0 I/O TTL GPIO port D bit 0
CAN0Rx I TTL CAN module 0 receive
11 PD1 I/O TTL GPIO port D bit 1
CAN0Tx O TTL CAN module 0 transmit
12 PD2 I/O TTL GPIO port D bit 2
UART module 1 receive. When in IrDA mode,
this signal has IrDA modulation.
U1Rx I TTL
13 PD3 I/O TTL GPIO port D bit 3
UART module 1 transmit. When in IrDA mode,
this signal has IrDA modulation.
U1Tx O TTL
March 17, 2008 509
Preliminary
LM3S8933 Microcontroller
Pin Number Pin Name Pin Type Buffer Type Description
Positive supply for most of the logic function,
including the processor core and most
peripherals.
14 VDD25 - Power
15 GND - Power Ground reference for logic and I/O pins.
16 XTALPPHY I TTL XTALP of the Ethernet PHY
17 XTALNPHY O TTL XTALN of the Ethernet PHY
18 NC - - No connect
19 NC - - No connect
20 VDD - Power Positive supply for I/O and some logic.
21 GND - Power Ground reference for logic and I/O pins.
22 PC7 I/O TTL GPIO port C bit 7
23 PC6 I/O TTL GPIO port C bit 6
24 PC5 I/O TTL GPIO port C bit 5
C1o O TTL Analog comparator 1 output
25 PC4 I/O TTL GPIO port C bit 4
26 PA0 I/O TTL GPIO port A bit 0
UART module 0 receive. When in IrDA mode,
this signal has IrDA modulation.
U0Rx I TTL
27 PA1 I/O TTL GPIO port A bit 1
UART module 0 transmit. When in IrDA mode,
this signal has IrDA modulation.
U0Tx O TTL
28 PA2 I/O TTL GPIO port A bit 2
SSI0Clk I/O TTL SSI module 0 clock
29 PA3 I/O TTL GPIO port A bit 3
SSI0Fss I/O TTL SSI module 0 frame
30 PA4 I/O TTL GPIO port A bit 4
SSI0Rx I TTL SSI module 0 receive
31 PA5 I/O TTL GPIO port A bit 5
SSI0Tx O TTL SSI module 0 transmit
32 VDD - Power Positive supply for I/O and some logic.
33 GND - Power Ground reference for logic and I/O pins.
34 PA6 I/O TTL GPIO port A bit 6
CCP1 I/O TTL Capture/Compare/PWM 1
35 PA7 I/O TTL GPIO port A bit 7
36 VCCPHY I TTL VCC of the Ethernet PHY
37 RXIN I Analog RXIN of the Ethernet PHY
Positive supply for most of the logic function,
including the processor core and most
peripherals.
38 VDD25 - Power
39 GND - Power Ground reference for logic and I/O pins.
40 RXIP I Analog RXIP of the Ethernet PHY
41 GNDPHY I TTL GND of the Ethernet PHY
42 GNDPHY I TTL GND of the Ethernet PHY
43 TXOP O Analog TXOP of the Ethernet PHY
510 March 17, 2008
Preliminary
Signal Tables
Pin Number Pin Name Pin Type Buffer Type Description
44 VDD - Power Positive supply for I/O and some logic.
45 GND - Power Ground reference for logic and I/O pins.
46 TXON O Analog TXON of the Ethernet PHY
47 PF0 I/O TTL GPIO port F bit 0
Main oscillator crystal input or an external
clock reference input.
48 OSC0 I Analog
49 OSC1 O Analog Main oscillator crystal output.
An external input that brings the processor out
of hibernate mode when asserted.
50 WAKE I OD
An output that indicates the processor is in
hibernate mode.
51 HIB O TTL
Hibernation Module oscillator crystal input or
an external clock reference input. Note that
this is either a 4.19-MHz crystal or a
32.768-kHz oscillator for the Hibernation
Module RTC. See the CLKSEL bit in the
HIBCTL register.
52 XOSC0 I Analog
53 XOSC1 O Analog Hibernation Module oscillator crystal output.
54 GND - Power Ground reference for logic and I/O pins.
Power source for the Hibernation Module. It
is normally connected to the positive terminal
of a battery and serves as the battery
backup/Hibernation Module power-source
supply.
55 VBAT - Power
56 VDD - Power Positive supply for I/O and some logic.
57 GND - Power Ground reference for logic and I/O pins.
58 MDIO I/O TTL MDIO of the Ethernet PHY
59 PF3 I/O TTL GPIO port F bit 3
LED0 O TTL MII LED 0
60 PF2 I/O TTL GPIO port F bit 2
LED1 O TTL MII LED 1
61 PF1 I/O TTL GPIO port F bit 1
Positive supply for most of the logic function,
including the processor core and most
peripherals.
62 VDD25 - Power
63 GND - Power Ground reference for logic and I/O pins.
64 RST I TTL System reset input.
CPU Mode bit 0. Input must be set to logic 0
(grounded); other encodings reserved.
65 CMOD0 I/O TTL
66 PB0 I/O TTL GPIO port B bit 0
CCP0 I/O TTL Capture/Compare/PWM 0
67 PB1 I/O TTL GPIO port B bit 1
CCP2 I/O TTL Capture/Compare/PWM 2
68 VDD - Power Positive supply for I/O and some logic.
69 GND - Power Ground reference for logic and I/O pins.
70 PB2 I/O TTL GPIO port B bit 2
I2C0SCL I/O OD I2C module 0 clock
March 17, 2008 511
Preliminary
LM3S8933 Microcontroller
Pin Number Pin Name Pin Type Buffer Type Description
71 PB3 I/O TTL GPIO port B bit 3
I2C0SDA I/O OD I2C module 0 data
72 NC - - No connect
73 NC - - No connect
74 NC - - No connect
75 NC - - No connect
CPU Mode bit 1. Input must be set to logic 0
(grounded); other encodings reserved.
76 CMOD1 I/O TTL
77 PC3 I/O TTL GPIO port C bit 3
TDO O TTL JTAG TDO and SWO
SWO O TTL JTAG TDO and SWO
78 PC2 I/O TTL GPIO port C bit 2
TDI I TTL JTAG TDI
79 PC1 I/O TTL GPIO port C bit 1
TMS I/O TTL JTAG TMS and SWDIO
SWDIO I/O TTL JTAG TMS and SWDIO
80 PC0 I/O TTL GPIO port C bit 0
TCK I TTL JTAG/SWD CLK
SWCLK I TTL JTAG/SWD CLK
81 VDD - Power Positive supply for I/O and some logic.
82 GND - Power Ground reference for logic and I/O pins.
83 VCCPHY I TTL VCC of the Ethernet PHY
84 VCCPHY I TTL VCC of the Ethernet PHY
85 GNDPHY I TTL GND of the Ethernet PHY
86 GNDPHY I TTL GND of the Ethernet PHY
87 GND - Power Ground reference for logic and I/O pins.
Positive supply for most of the logic function,
including the processor core and most
peripherals.
88 VDD25 - Power
89 PB7 I/O TTL GPIO port B bit 7
TRST I TTL JTAG TRSTn
90 PB6 I/O TTL GPIO port B bit 6
91 PB5 I/O TTL GPIO port B bit 5
92 PB4 I/O TTL GPIO port B bit 4
93 VDD - Power Positive supply for I/O and some logic.
94 GND - Power Ground reference for logic and I/O pins.
95 PD4 I/O TTL GPIO port D bit 4
CCP3 I/O TTL Capture/Compare/PWM 3
96 PD5 I/O TTL GPIO port D bit 5
The ground reference for the analog circuits
(ADC, Analog Comparators, etc.). These are
separated from GND to minimize the electrical
noise contained on VDD from affecting the
analog functions.
97 GNDA - Power
512 March 17, 2008
Preliminary
Signal Tables
Pin Number Pin Name Pin Type Buffer Type Description
The positive supply (3.3 V) for the analog
circuits (ADC, Analog Comparators, etc.).
These are separated from VDD to minimize
the electrical noise contained on VDD from
affecting the analog functions.
98 VDDA - Power
99 PD6 I/O TTL GPIO port D bit 6
100 PD7 I/O TTL GPIO port D bit 7
C0o O TTL Analog comparator 0 output
Table 20-2. Signals by Signal Name
Pin Name Pin Number Pin Type Buffer Type Description
ADC0 1 I Analog Analog-to-digital converter input 0.
ADC1 2 I Analog Analog-to-digital converter input 1.
ADC2 5 I Analog Analog-to-digital converter input 2.
ADC3 6 I Analog Analog-to-digital converter input 3.
C0o 100 O TTL Analog comparator 0 output
C1o 24 O TTL Analog comparator 1 output
CAN0Rx 10 I TTL CAN module 0 receive
CAN0Tx 11 O TTL CAN module 0 transmit
CCP0 66 I/O TTL Capture/Compare/PWM 0
CCP1 34 I/O TTL Capture/Compare/PWM 1
CCP2 67 I/O TTL Capture/Compare/PWM 2
CCP3 95 I/O TTL Capture/Compare/PWM 3
CPU Mode bit 0. Input must be set to logic 0
(grounded); other encodings reserved.
CMOD0 65 I/O TTL
CPU Mode bit 1. Input must be set to logic 0
(grounded); other encodings reserved.
CMOD1 76 I/O TTL
GND 9 - Power Ground reference for logic and I/O pins.
GND 15 - Power Ground reference for logic and I/O pins.
GND 21 - Power Ground reference for logic and I/O pins.
GND 33 - Power Ground reference for logic and I/O pins.
GND 39 - Power Ground reference for logic and I/O pins.
GND 45 - Power Ground reference for logic and I/O pins.
GND 54 - Power Ground reference for logic and I/O pins.
GND 57 - Power Ground reference for logic and I/O pins.
GND 63 - Power Ground reference for logic and I/O pins.
GND 69 - Power Ground reference for logic and I/O pins.
GND 82 - Power Ground reference for logic and I/O pins.
GND 87 - Power Ground reference for logic and I/O pins.
GND 94 - Power Ground reference for logic and I/O pins.
The ground reference for the analog circuits
(ADC, Analog Comparators, etc.). These are
separated from GND to minimize the electrical
noise contained on VDD from affecting the
analog functions.
GNDA 4 - Power
March 17, 2008 513
Preliminary
LM3S8933 Microcontroller
Pin Name Pin Number Pin Type Buffer Type Description
The ground reference for the analog circuits
(ADC, Analog Comparators, etc.). These are
separated from GND to minimize the electrical
noise contained on VDD from affecting the
analog functions.
GNDA 97 - Power
GNDPHY 41 I TTL GND of the Ethernet PHY
GNDPHY 42 I TTL GND of the Ethernet PHY
GNDPHY 85 I TTL GND of the Ethernet PHY
GNDPHY 86 I TTL GND of the Ethernet PHY
An output that indicates the processor is in
hibernate mode.
HIB 51 O TTL
I2C0SCL 70 I/O OD I2C module 0 clock
I2C0SDA 71 I/O OD I2C module 0 data
Low drop-out regulator output voltage. This
pin requires an external capacitor between
the pin and GND of 1 μF or greater. When the
on-chip LDO is used to provide power to the
logic, the LDO pin must also be connected to
the VDD25 pins at the board level in addition
to the decoupling capacitor(s).
LDO 7 - Power
LED0 59 O TTL MII LED 0
LED1 60 O TTL MII LED 1
MDIO 58 I/O TTL MDIO of the Ethernet PHY
NC 18 - - No connect
NC 19 - - No connect
NC 72 - - No connect
NC 73 - - No connect
NC 74 - - No connect
NC 75 - - No connect
Main oscillator crystal input or an external
clock reference input.
OSC0 48 I Analog
OSC1 49 O Analog Main oscillator crystal output.
PA0 26 I/O TTL GPIO port A bit 0
PA1 27 I/O TTL GPIO port A bit 1
PA2 28 I/O TTL GPIO port A bit 2
PA3 29 I/O TTL GPIO port A bit 3
PA4 30 I/O TTL GPIO port A bit 4
PA5 31 I/O TTL GPIO port A bit 5
PA6 34 I/O TTL GPIO port A bit 6
PA7 35 I/O TTL GPIO port A bit 7
PB0 66 I/O TTL GPIO port B bit 0
PB1 67 I/O TTL GPIO port B bit 1
PB2 70 I/O TTL GPIO port B bit 2
PB3 71 I/O TTL GPIO port B bit 3
PB4 92 I/O TTL GPIO port B bit 4
PB5 91 I/O TTL GPIO port B bit 5
514 March 17, 2008
Preliminary
Signal Tables
Pin Name Pin Number Pin Type Buffer Type Description
PB6 90 I/O TTL GPIO port B bit 6
PB7 89 I/O TTL GPIO port B bit 7
PC0 80 I/O TTL GPIO port C bit 0
PC1 79 I/O TTL GPIO port C bit 1
PC2 78 I/O TTL GPIO port C bit 2
PC3 77 I/O TTL GPIO port C bit 3
PC4 25 I/O TTL GPIO port C bit 4
PC5 24 I/O TTL GPIO port C bit 5
PC6 23 I/O TTL GPIO port C bit 6
PC7 22 I/O TTL GPIO port C bit 7
PD0 10 I/O TTL GPIO port D bit 0
PD1 11 I/O TTL GPIO port D bit 1
PD2 12 I/O TTL GPIO port D bit 2
PD3 13 I/O TTL GPIO port D bit 3
PD4 95 I/O TTL GPIO port D bit 4
PD5 96 I/O TTL GPIO port D bit 5
PD6 99 I/O TTL GPIO port D bit 6
PD7 100 I/O TTL GPIO port D bit 7
PF0 47 I/O TTL GPIO port F bit 0
PF1 61 I/O TTL GPIO port F bit 1
PF2 60 I/O TTL GPIO port F bit 2
PF3 59 I/O TTL GPIO port F bit 3
RST 64 I TTL System reset input.
RXIN 37 I Analog RXIN of the Ethernet PHY
RXIP 40 I Analog RXIP of the Ethernet PHY
SSI0Clk 28 I/O TTL SSI module 0 clock
SSI0Fss 29 I/O TTL SSI module 0 frame
SSI0Rx 30 I TTL SSI module 0 receive
SSI0Tx 31 O TTL SSI module 0 transmit
SWCLK 80 I TTL JTAG/SWD CLK
SWDIO 79 I/O TTL JTAG TMS and SWDIO
SWO 77 O TTL JTAG TDO and SWO
TCK 80 I TTL JTAG/SWD CLK
TDI 78 I TTL JTAG TDI
TDO 77 O TTL JTAG TDO and SWO
TMS 79 I/O TTL JTAG TMS and SWDIO
TRST 89 I TTL JTAG TRSTn
TXON 46 O Analog TXON of the Ethernet PHY
TXOP 43 O Analog TXOP of the Ethernet PHY
UART module 0 receive. When in IrDA mode,
this signal has IrDA modulation.
U0Rx 26 I TTL
UART module 0 transmit. When in IrDA mode,
this signal has IrDA modulation.
U0Tx 27 O TTL
March 17, 2008 515
Preliminary
LM3S8933 Microcontroller
Pin Name Pin Number Pin Type Buffer Type Description
UART module 1 receive. When in IrDA mode,
this signal has IrDA modulation.
U1Rx 12 I TTL
UART module 1 transmit. When in IrDA mode,
this signal has IrDA modulation.
U1Tx 13 O TTL
Power source for the Hibernation Module. It
is normally connected to the positive terminal
of a battery and serves as the battery
backup/Hibernation Module power-source
supply.
VBAT 55 - Power
VCCPHY 36 I TTL VCC of the Ethernet PHY
VCCPHY 83 I TTL VCC of the Ethernet PHY
VCCPHY 84 I TTL VCC of the Ethernet PHY
VDD 8 - Power Positive supply for I/O and some logic.
VDD 20 - Power Positive supply for I/O and some logic.
VDD 32 - Power Positive supply for I/O and some logic.
VDD 44 - Power Positive supply for I/O and some logic.
VDD 56 - Power Positive supply for I/O and some logic.
VDD 68 - Power Positive supply for I/O and some logic.
VDD 81 - Power Positive supply for I/O and some logic.
VDD 93 - Power Positive supply for I/O and some logic.
Positive supply for most of the logic function,
including the processor core and most
peripherals.
VDD25 14 - Power
Positive supply for most of the logic function,
including the processor core and most
peripherals.
VDD25 38 - Power
Positive supply for most of the logic function,
including the processor core and most
peripherals.
VDD25 62 - Power
Positive supply for most of the logic function,
including the processor core and most
peripherals.
VDD25 88 - Power
The positive supply (3.3 V) for the analog
circuits (ADC, Analog Comparators, etc.).
These are separated from VDD to minimize
the electrical noise contained on VDD from
affecting the analog functions.
VDDA 3 - Power
The positive supply (3.3 V) for the analog
circuits (ADC, Analog Comparators, etc.).
These are separated from VDD to minimize
the electrical noise contained on VDD from
affecting the analog functions.
VDDA 98 - Power
An external input that brings the processor out
of hibernate mode when asserted.
WAKE 50 I OD
Hibernation Module oscillator crystal input or
an external clock reference input. Note that
this is either a 4.19-MHz crystal or a
32.768-kHz oscillator for the Hibernation
Module RTC. See the CLKSEL bit in the
HIBCTL register.
XOSC0 52 I Analog
XOSC1 53 O Analog Hibernation Module oscillator crystal output.
516 March 17, 2008
Preliminary
Signal Tables
Pin Name Pin Number Pin Type Buffer Type Description
XTALNPHY 17 O TTL XTALN of the Ethernet PHY
XTALPPHY 16 I TTL XTALP of the Ethernet PHY
Table 20-3. Signals by Function, Except for GPIO
Buffer Description
Type
Pin Pin Type
Number
Function Pin Name
ADC ADC0 1 I Analog Analog-to-digital converter input 0.
ADC1 2 I Analog Analog-to-digital converter input 1.
ADC2 5 I Analog Analog-to-digital converter input 2.
ADC3 6 I Analog Analog-to-digital converter input 3.
Analog C0o 100 O TTL Analog comparator 0 output
Comparators C1o 24 O TTL Analog comparator 1 output
Controller Area CAN0Rx 10 I TTL CAN module 0 receive
Network CAN0Tx 11 O TTL CAN module 0 transmit
Ethernet PHY GNDPHY 41 I TTL GND of the Ethernet PHY
GNDPHY 42 I TTL GND of the Ethernet PHY
GNDPHY 85 I TTL GND of the Ethernet PHY
GNDPHY 86 I TTL GND of the Ethernet PHY
LED0 59 O TTL MII LED 0
LED1 60 O TTL MII LED 1
MDIO 58 I/O TTL MDIO of the Ethernet PHY
RXIN 37 I Analog RXIN of the Ethernet PHY
RXIP 40 I Analog RXIP of the Ethernet PHY
TXON 46 O Analog TXON of the Ethernet PHY
TXOP 43 O Analog TXOP of the Ethernet PHY
VCCPHY 36 I TTL VCC of the Ethernet PHY
VCCPHY 83 I TTL VCC of the Ethernet PHY
VCCPHY 84 I TTL VCC of the Ethernet PHY
XTALNPHY 17 O TTL XTALN of the Ethernet PHY
XTALPPHY 16 I TTL XTALP of the Ethernet PHY
General-Purpose CCP0 66 I/O TTL Capture/Compare/PWM 0
Timers CCP1 34 I/O TTL Capture/Compare/PWM 1
CCP2 67 I/O TTL Capture/Compare/PWM 2
CCP3 95 I/O TTL Capture/Compare/PWM 3
I2C I2C0SCL 70 I/O OD I2C module 0 clock
I2C0SDA 71 I/O OD I2C module 0 data
JTAG/SWD/SWO SWCLK 80 I TTL JTAG/SWD CLK
SWDIO 79 I/O TTL JTAG TMS and SWDIO
SWO 77 O TTL JTAG TDO and SWO
TCK 80 I TTL JTAG/SWD CLK
TDI 78 I TTL JTAG TDI
TDO 77 O TTL JTAG TDO and SWO
TMS 79 I/O TTL JTAG TMS and SWDIO
March 17, 2008 517
Preliminary
LM3S8933 Microcontroller
Buffer Description
Type
Pin Pin Type
Number
Function Pin Name
Power GND 9 - Power Ground reference for logic and I/O pins.
GND 15 - Power Ground reference for logic and I/O pins.
GND 21 - Power Ground reference for logic and I/O pins.
GND 33 - Power Ground reference for logic and I/O pins.
GND 39 - Power Ground reference for logic and I/O pins.
GND 45 - Power Ground reference for logic and I/O pins.
GND 54 - Power Ground reference for logic and I/O pins.
GND 57 - Power Ground reference for logic and I/O pins.
GND 63 - Power Ground reference for logic and I/O pins.
GND 69 - Power Ground reference for logic and I/O pins.
GND 82 - Power Ground reference for logic and I/O pins.
GND 87 - Power Ground reference for logic and I/O pins.
GND 94 - Power Ground reference for logic and I/O pins.
The ground reference for the analog circuits (ADC,
Analog Comparators, etc.). These are separated
from GND to minimize the electrical noise contained
on VDD from affecting the analog functions.
GNDA 4 - Power
The ground reference for the analog circuits (ADC,
Analog Comparators, etc.). These are separated
from GND to minimize the electrical noise contained
on VDD from affecting the analog functions.
GNDA 97 - Power
An output that indicates the processor is in
hibernate mode.
HIB 51 O TTL
Low drop-out regulator output voltage. This pin
requires an external capacitor between the pin and
GND of 1 μF or greater. When the on-chip LDO is
used to provide power to the logic, the LDO pin
must also be connected to the VDD25 pins at the
board level in addition to the decoupling
capacitor(s).
LDO 7 - Power
Power source for the Hibernation Module. It is
normally connected to the positive terminal of a
battery and serves as the battery
backup/Hibernation Module power-source supply.
VBAT 55 - Power
VDD 8 - Power Positive supply for I/O and some logic.
VDD 20 - Power Positive supply for I/O and some logic.
VDD 32 - Power Positive supply for I/O and some logic.
VDD 44 - Power Positive supply for I/O and some logic.
VDD 56 - Power Positive supply for I/O and some logic.
VDD 68 - Power Positive supply for I/O and some logic.
VDD 81 - Power Positive supply for I/O and some logic.
VDD 93 - Power Positive supply for I/O and some logic.
Positive supply for most of the logic function,
including the processor core and most peripherals.
VDD25 14 - Power
Positive supply for most of the logic function,
including the processor core and most peripherals.
VDD25 38 - Power
Positive supply for most of the logic function,
including the processor core and most peripherals.
VDD25 62 - Power
518 March 17, 2008
Preliminary
Signal Tables
Buffer Description
Type
Pin Pin Type
Number
Function Pin Name
VDD25 Positive supply for most of the logic function,
including the processor core and most peripherals.
88 - Power
The positive supply (3.3 V) for the analog circuits
(ADC, Analog Comparators, etc.). These are
separated from VDD to minimize the electrical noise
contained on VDD from affecting the analog
functions.
VDDA 3 - Power
The positive supply (3.3 V) for the analog circuits
(ADC, Analog Comparators, etc.). These are
separated from VDD to minimize the electrical noise
contained on VDD from affecting the analog
functions.
VDDA 98 - Power
An external input that brings the processor out of
hibernate mode when asserted.
WAKE 50 I OD
SSI SSI0Clk 28 I/O TTL SSI module 0 clock
SSI0Fss 29 I/O TTL SSI module 0 frame
SSI0Rx 30 I TTL SSI module 0 receive
SSI0Tx 31 O TTL SSI module 0 transmit
CPU Mode bit 0. Input must be set to logic 0
(grounded); other encodings reserved.
System Control & CMOD0 65 I/O TTL
Clocks
CPU Mode bit 1. Input must be set to logic 0
(grounded); other encodings reserved.
CMOD1 76 I/O TTL
Main oscillator crystal input or an external clock
reference input.
OSC0 48 I Analog
OSC1 49 O Analog Main oscillator crystal output.
RST 64 I TTL System reset input.
TRST 89 I TTL JTAG TRSTn
Hibernation Module oscillator crystal input or an
external clock reference input. Note that this is
either a 4.19-MHz crystal or a 32.768-kHz oscillator
for the Hibernation Module RTC. See the CLKSEL
bit in the HIBCTL register.
XOSC0 52 I Analog
XOSC1 53 O Analog Hibernation Module oscillator crystal output.
UART module 0 receive. When in IrDA mode, this
signal has IrDA modulation.
UART U0Rx 26 I TTL
UART module 0 transmit. When in IrDA mode, this
signal has IrDA modulation.
U0Tx 27 O TTL
UART module 1 receive. When in IrDA mode, this
signal has IrDA modulation.
U1Rx 12 I TTL
UART module 1 transmit. When in IrDA mode, this
signal has IrDA modulation.
U1Tx 13 O TTL
Table 20-4. GPIO Pins and Alternate Functions
GPIO Pin Pin Number Multiplexed Function Multiplexed Function
PA0 26 U0Rx
PA1 27 U0Tx
PA2 28 SSI0Clk
PA3 29 SSI0Fss
March 17, 2008 519
Preliminary
LM3S8933 Microcontroller
GPIO Pin Pin Number Multiplexed Function Multiplexed Function
PA4 30 SSI0Rx
PA5 31 SSI0Tx
PA6 34 CCP1
PA7 35
PB0 66 CCP0
PB1 67 CCP2
PB2 70 I2C0SCL
PB3 71 I2C0SDA
PB4 92
PB5 91
PB6 90
PB7 89 TRST
PC0 80 TCK SWCLK
PC1 79 TMS SWDIO
PC2 78 TDI
PC3 77 TDO SWO
PC4 25
PC5 24 C1o
PC6 23
PC7 22
PD0 10 CAN0Rx
PD1 11 CAN0Tx
PD2 12 U1Rx
PD3 13 U1Tx
PD4 95 CCP3
PD5 96
PD6 99
PD7 100 C0o
PF0 47
PF1 61
PF2 60 LED1
PF3 59 LED0
20.2 108-Pin BGA Package Pin Tables
Table 20-5. Signals by Pin Number
Pin Number Pin Name Pin Type Buffer Type Description
A1 ADC1 I Analog Analog-to-digital converter input 1.
A2 NC - - No connect
A3 NC - - No connect
A4 NC - - No connect
520 March 17, 2008
Preliminary
Signal Tables
Pin Number Pin Name Pin Type Buffer Type Description
The ground reference for the analog circuits
(ADC, Analog Comparators, etc.). These are
separated from GND to minimize the electrical
noise contained on VDD from affecting the
analog functions.
A5 GNDA - Power
A6 PB4 I/O TTL GPIO port B bit 4
C0- I Analog Analog comparator 0 negative input
A7 PB6 I/O TTL GPIO port B bit 6
C0+ I Analog Analog comparator 0 positive input
A8 PB7 I/O TTL GPIO port B bit 7
TRST I TTL JTAG TRSTn
A9 PC0 I/O TTL GPIO port C bit 0
TCK I TTL JTAG/SWD CLK
SWCLK I TTL JTAG/SWD CLK
A10 PC3 I/O TTL GPIO port C bit 3
TDO O TTL JTAG TDO and SWO
SWO O TTL JTAG TDO and SWO
A11 NC - - No connect
A12 NC - - No connect
B1 ADC0 I Analog Analog-to-digital converter input 0.
B2 ADC3 I Analog Analog-to-digital converter input 3.
B3 ADC2 I Analog Analog-to-digital converter input 2.
B4 NC - - No connect
The ground reference for the analog circuits
(ADC, Analog Comparators, etc.). These are
separated from GND to minimize the electrical
noise contained on VDD from affecting the
analog functions.
B5 GNDA - Power
B6 GND - Power Ground reference for logic and I/O pins.
B7 PB5 I/O TTL GPIO port B bit 5
C1- I Analog Analog comparator 1 negative input
B8 PC2 I/O TTL GPIO port C bit 2
TDI I TTL JTAG TDI
B9 PC1 I/O TTL GPIO port C bit 1
TMS I/O TTL JTAG TMS and SWDIO
SWDIO I/O TTL JTAG TMS and SWDIO
CPU Mode bit 1. Input must be set to logic 0
(grounded); other encodings reserved.
B10 CMOD1 I/O TTL
B11 NC - - No connect
B12 NC - - No connect
C1 PE7 I/O TTL GPIO port E bit 7
C2 PE6 I/O TTL GPIO port E bit 6
Positive supply for most of the logic function,
including the processor core and most
peripherals.
C3 VDD25 - Power
C4 GND - Power Ground reference for logic and I/O pins.
March 17, 2008 521
Preliminary
LM3S8933 Microcontroller
Pin Number Pin Name Pin Type Buffer Type Description
C5 GND - Power Ground reference for logic and I/O pins.
The positive supply (3.3 V) for the analog
circuits (ADC, Analog Comparators, etc.).
These are separated from VDD to minimize
the electrical noise contained on VDD from
affecting the analog functions.
C6 VDDA - Power
The positive supply (3.3 V) for the analog
circuits (ADC, Analog Comparators, etc.).
These are separated from VDD to minimize
the electrical noise contained on VDD from
affecting the analog functions.
C7 VDDA - Power
C8 GNDPHY I TTL GND of the Ethernet PHY
C9 GNDPHY I TTL GND of the Ethernet PHY
C10 VCCPHY I TTL VCC of the Ethernet PHY
C11 PB2 I/O TTL GPIO port B bit 2
I2C0SCL I/O OD I2C module 0 clock
C12 PB3 I/O TTL GPIO port B bit 3
I2C0SDA I/O OD I2C module 0 data
D1 PE4 I/O TTL GPIO port E bit 4
D2 PE5 I/O TTL GPIO port E bit 5
Positive supply for most of the logic function,
including the processor core and most
peripherals.
D3 VDD25 - Power
D10 VCCPHY I TTL VCC of the Ethernet PHY
D11 VCCPHY I TTL VCC of the Ethernet PHY
D12 PB1 I/O TTL GPIO port B bit 1
CCP2 I/O TTL Capture/Compare/PWM 2
E1 PD4 I/O TTL GPIO port D bit 4
CCP3 I/O TTL Capture/Compare/PWM 3
E2 PD5 I/O TTL GPIO port D bit 5
Low drop-out regulator output voltage. This
pin requires an external capacitor between
the pin and GND of 1 μF or greater. When the
on-chip LDO is used to provide power to the
logic, the LDO pin must also be connected to
the VDD25 pins at the board level in addition
to the decoupling capacitor(s).
E3 LDO - Power
E10 VDD33 - Power
CPU Mode bit 0. Input must be set to logic 0
(grounded); other encodings reserved.
E11 CMOD0 I/O TTL
E12 PB0 I/O TTL GPIO port B bit 0
CCP0 I/O TTL Capture/Compare/PWM 0
F1 PD7 I/O TTL GPIO port D bit 7
C0o O TTL Analog comparator 0 output
F2 PD6 I/O TTL GPIO port D bit 6
Positive supply for most of the logic function,
including the processor core and most
peripherals.
F3 VDD25 - Power
522 March 17, 2008
Preliminary
Signal Tables
Pin Number Pin Name Pin Type Buffer Type Description
F10 GND - Power Ground reference for logic and I/O pins.
F11 GND - Power Ground reference for logic and I/O pins.
F12 GND - Power Ground reference for logic and I/O pins.
G1 PD0 I/O TTL GPIO port D bit 0
CAN0Rx I TTL CAN module 0 receive
G2 PD1 I/O TTL GPIO port D bit 1
CAN0Tx O TTL CAN module 0 transmit
Positive supply for most of the logic function,
including the processor core and most
peripherals.
G3 VDD25 - Power
G10 VDD33 - Power
G11 VDD33 - Power
G12 VDD33 - Power
H1 PD3 I/O TTL GPIO port D bit 3
UART module 1 transmit. When in IrDA mode,
this signal has IrDA modulation.
U1Tx O TTL
H2 PD2 I/O TTL GPIO port D bit 2
UART module 1 receive. When in IrDA mode,
this signal has IrDA modulation.
U1Rx I TTL
H3 GND - Power Ground reference for logic and I/O pins.
H10 VDD33 - Power
H11 RST I TTL System reset input.
H12 PF1 I/O TTL GPIO port F bit 1
J1 XTALNPHY O TTL XTALN of the Ethernet PHY
J2 XTALPPHY I TTL XTALP of the Ethernet PHY
J3 GND - Power Ground reference for logic and I/O pins.
J10 GND - Power Ground reference for logic and I/O pins.
J11 PF2 I/O TTL GPIO port F bit 2
LED1 O TTL MII LED 1
J12 PF3 I/O TTL GPIO port F bit 3
LED0 O TTL MII LED 0
K1 NC - - No connect
K2 NC - - No connect
K3 GNDPHY I TTL GND of the Ethernet PHY
K4 GNDPHY I TTL GND of the Ethernet PHY
K5 GND - Power Ground reference for logic and I/O pins.
K6 GND - Power Ground reference for logic and I/O pins.
K7 VDD33 - Power
K8 VDD33 - Power
K9 VDD33 - Power
K10 GND - Power Ground reference for logic and I/O pins.
March 17, 2008 523
Preliminary
LM3S8933 Microcontroller
Pin Number Pin Name Pin Type Buffer Type Description
Hibernation Module oscillator crystal input or
an external clock reference input. Note that
this is either a 4.19-MHz crystal or a
32.768-kHz oscillator for the Hibernation
Module RTC. See the CLKSEL bit in the
HIBCTL register.
K11 XOSC0 I Analog
K12 XOSC1 O Analog Hibernation Module oscillator crystal output.
L1 PC4 I/O TTL GPIO port C bit 4
L2 PC7 I/O TTL GPIO port C bit 7
C2- I Analog Analog comparator 2 negative input
L3 PA0 I/O TTL GPIO port A bit 0
UART module 0 receive. When in IrDA mode,
this signal has IrDA modulation.
U0Rx I TTL
L4 PA3 I/O TTL GPIO port A bit 3
SSI0Fss I/O TTL SSI module 0 frame
L5 PA4 I/O TTL GPIO port A bit 4
SSI0Rx I TTL SSI module 0 receive
L6 PA6 I/O TTL GPIO port A bit 6
CCP1 I/O TTL Capture/Compare/PWM 1
L7 RXIN I Analog RXIN of the Ethernet PHY
L8 TXON O Analog TXON of the Ethernet PHY
L9 MDIO I/O TTL MDIO of the Ethernet PHY
L10 GND - Power Ground reference for logic and I/O pins.
Main oscillator crystal input or an external
clock reference input.
L11 OSC0 I Analog
Power source for the Hibernation Module. It
is normally connected to the positive terminal
of a battery and serves as the battery
backup/Hibernation Module power-source
supply.
L12 VBAT - Power
M1 PC5 I/O TTL GPIO port C bit 5
C1+ I Analog Analog comparator positive input
C1o O TTL Analog comparator 1 output
M2 PC6 I/O TTL GPIO port C bit 6
C2+ I Analog Analog comparator positive input
M3 PA1 I/O TTL GPIO port A bit 1
UART module 0 transmit. When in IrDA mode,
this signal has IrDA modulation.
U0Tx O TTL
M4 PA2 I/O TTL GPIO port A bit 2
SSI0Clk I/O TTL SSI module 0 clock
M5 PA5 I/O TTL GPIO port A bit 5
SSI0Tx O TTL SSI module 0 transmit
M6 PA7 I/O TTL GPIO port A bit 7
M7 RXIP I Analog RXIP of the Ethernet PHY
M8 TXOP O Analog TXOP of the Ethernet PHY
M9 PF0 I/O TTL GPIO port F bit 0
524 March 17, 2008
Preliminary
Signal Tables
Pin Number Pin Name Pin Type Buffer Type Description
An external input that brings the processor out
of hibernate mode when asserted.
M10 WAKE I OD
M11 OSC1 O Analog Main oscillator crystal output.
An output that indicates the processor is in
hibernate mode.
M12 HIB O TTL
Table 20-6. Signals by Signal Name
Pin Name Pin Number Pin Type Buffer Type Description
ADC0 B1 I Analog Analog-to-digital converter input 0.
ADC1 A1 I Analog Analog-to-digital converter input 1.
ADC2 B3 I Analog Analog-to-digital converter input 2.
ADC3 B2 I Analog Analog-to-digital converter input 3.
C0+ A7 I Analog Analog comparator 0 positive input
C0- A6 I Analog Analog comparator 0 negative input
C0o F1 O TTL Analog comparator 0 output
C1+ M1 I Analog Analog comparator positive input
C1- B7 I Analog Analog comparator 1 negative input
C1o M1 O TTL Analog comparator 1 output
C2+ M2 I Analog Analog comparator positive input
C2- L2 I Analog Analog comparator 2 negative input
CAN0Rx G1 I TTL CAN module 0 receive
CAN0Tx G2 O TTL CAN module 0 transmit
CCP0 E12 I/O TTL Capture/Compare/PWM 0
CCP1 L6 I/O TTL Capture/Compare/PWM 1
CCP2 D12 I/O TTL Capture/Compare/PWM 2
CCP3 E1 I/O TTL Capture/Compare/PWM 3
CPU Mode bit 0. Input must be set to logic 0
(grounded); other encodings reserved.
CMOD0 E11 I/O TTL
CPU Mode bit 1. Input must be set to logic 0
(grounded); other encodings reserved.
CMOD1 B10 I/O TTL
GND C4 - Power Ground reference for logic and I/O pins.
GND C5 - Power Ground reference for logic and I/O pins.
GND H3 - Power Ground reference for logic and I/O pins.
GND J3 - Power Ground reference for logic and I/O pins.
GND K5 - Power Ground reference for logic and I/O pins.
GND K6 - Power Ground reference for logic and I/O pins.
GND L10 - Power Ground reference for logic and I/O pins.
GND K10 - Power Ground reference for logic and I/O pins.
GND J10 - Power Ground reference for logic and I/O pins.
GND F10 - Power Ground reference for logic and I/O pins.
GND F11 - Power Ground reference for logic and I/O pins.
GND B6 - Power Ground reference for logic and I/O pins.
GND F12 - Power Ground reference for logic and I/O pins.
March 17, 2008 525
Preliminary
LM3S8933 Microcontroller
Pin Name Pin Number Pin Type Buffer Type Description
The ground reference for the analog circuits
(ADC, Analog Comparators, etc.). These are
separated from GND to minimize the electrical
noise contained on VDD from affecting the
analog functions.
GNDA B5 - Power
The ground reference for the analog circuits
(ADC, Analog Comparators, etc.). These are
separated from GND to minimize the electrical
noise contained on VDD from affecting the
analog functions.
GNDA A5 - Power
GNDPHY K3 I TTL GND of the Ethernet PHY
GNDPHY K4 I TTL GND of the Ethernet PHY
GNDPHY C8 I TTL GND of the Ethernet PHY
GNDPHY C9 I TTL GND of the Ethernet PHY
An output that indicates the processor is in
hibernate mode.
HIB M12 O TTL
I2C0SCL C11 I/O OD I2C module 0 clock
I2C0SDA C12 I/O OD I2C module 0 data
Low drop-out regulator output voltage. This
pin requires an external capacitor between
the pin and GND of 1 μF or greater. When the
on-chip LDO is used to provide power to the
logic, the LDO pin must also be connected to
the VDD25 pins at the board level in addition
to the decoupling capacitor(s).
LDO E3 - Power
LED0 J12 O TTL MII LED 0
LED1 J11 O TTL MII LED 1
MDIO L9 I/O TTL MDIO of the Ethernet PHY
NC A2 - - No connect
NC A3 - - No connect
NC B4 - - No connect
NC A4 - - No connect
NC A11 - - No connect
NC B12 - - No connect
NC B11 - - No connect
NC A12 - - No connect
NC K1 - - No connect
NC K2 - - No connect
Main oscillator crystal input or an external
clock reference input.
OSC0 L11 I Analog
OSC1 M11 O Analog Main oscillator crystal output.
PA0 L3 I/O TTL GPIO port A bit 0
PA1 M3 I/O TTL GPIO port A bit 1
PA2 M4 I/O TTL GPIO port A bit 2
PA3 L4 I/O TTL GPIO port A bit 3
PA4 L5 I/O TTL GPIO port A bit 4
PA5 M5 I/O TTL GPIO port A bit 5
526 March 17, 2008
Preliminary
Signal Tables
Pin Name Pin Number Pin Type Buffer Type Description
PA6 L6 I/O TTL GPIO port A bit 6
PA7 M6 I/O TTL GPIO port A bit 7
PB0 E12 I/O TTL GPIO port B bit 0
PB1 D12 I/O TTL GPIO port B bit 1
PB2 C11 I/O TTL GPIO port B bit 2
PB3 C12 I/O TTL GPIO port B bit 3
PB4 A6 I/O TTL GPIO port B bit 4
PB5 B7 I/O TTL GPIO port B bit 5
PB6 A7 I/O TTL GPIO port B bit 6
PB7 A8 I/O TTL GPIO port B bit 7
PC0 A9 I/O TTL GPIO port C bit 0
PC1 B9 I/O TTL GPIO port C bit 1
PC2 B8 I/O TTL GPIO port C bit 2
PC3 A10 I/O TTL GPIO port C bit 3
PC4 L1 I/O TTL GPIO port C bit 4
PC5 M1 I/O TTL GPIO port C bit 5
PC6 M2 I/O TTL GPIO port C bit 6
PC7 L2 I/O TTL GPIO port C bit 7
PD0 G1 I/O TTL GPIO port D bit 0
PD1 G2 I/O TTL GPIO port D bit 1
PD2 H2 I/O TTL GPIO port D bit 2
PD3 H1 I/O TTL GPIO port D bit 3
PD4 E1 I/O TTL GPIO port D bit 4
PD5 E2 I/O TTL GPIO port D bit 5
PD6 F2 I/O TTL GPIO port D bit 6
PD7 F1 I/O TTL GPIO port D bit 7
PE4 D1 I/O TTL GPIO port E bit 4
PE5 D2 I/O TTL GPIO port E bit 5
PE6 C2 I/O TTL GPIO port E bit 6
PE7 C1 I/O TTL GPIO port E bit 7
PF0 M9 I/O TTL GPIO port F bit 0
PF1 H12 I/O TTL GPIO port F bit 1
PF2 J11 I/O TTL GPIO port F bit 2
PF3 J12 I/O TTL GPIO port F bit 3
RST H11 I TTL System reset input.
RXIN L7 I Analog RXIN of the Ethernet PHY
RXIP M7 I Analog RXIP of the Ethernet PHY
SSI0Clk M4 I/O TTL SSI module 0 clock
SSI0Fss L4 I/O TTL SSI module 0 frame
SSI0Rx L5 I TTL SSI module 0 receive
SSI0Tx M5 O TTL SSI module 0 transmit
SWCLK A9 I TTL JTAG/SWD CLK
March 17, 2008 527
Preliminary
LM3S8933 Microcontroller
Pin Name Pin Number Pin Type Buffer Type Description
SWDIO B9 I/O TTL JTAG TMS and SWDIO
SWO A10 O TTL JTAG TDO and SWO
TCK A9 I TTL JTAG/SWD CLK
TDI B8 I TTL JTAG TDI
TDO A10 O TTL JTAG TDO and SWO
TMS B9 I/O TTL JTAG TMS and SWDIO
TRST A8 I TTL JTAG TRSTn
TXON L8 O Analog TXON of the Ethernet PHY
TXOP M8 O Analog TXOP of the Ethernet PHY
UART module 0 receive. When in IrDA mode,
this signal has IrDA modulation.
U0Rx L3 I TTL
UART module 0 transmit. When in IrDA mode,
this signal has IrDA modulation.
U0Tx M3 O TTL
UART module 1 receive. When in IrDA mode,
this signal has IrDA modulation.
U1Rx H2 I TTL
UART module 1 transmit. When in IrDA mode,
this signal has IrDA modulation.
U1Tx H1 O TTL
Power source for the Hibernation Module. It
is normally connected to the positive terminal
of a battery and serves as the battery
backup/Hibernation Module power-source
supply.
VBAT L12 - Power
VCCPHY C10 I TTL VCC of the Ethernet PHY
VCCPHY D10 I TTL VCC of the Ethernet PHY
VCCPHY D11 I TTL VCC of the Ethernet PHY
Positive supply for most of the logic function,
including the processor core and most
peripherals.
VDD25 C3 - Power
Positive supply for most of the logic function,
including the processor core and most
peripherals.
VDD25 D3 - Power
Positive supply for most of the logic function,
including the processor core and most
peripherals.
VDD25 F3 - Power
Positive supply for most of the logic function,
including the processor core and most
peripherals.
VDD25 G3 - Power
VDD33 K7 - Power
VDD33 G12 - Power
VDD33 K8 - Power
VDD33 K9 - Power
VDD33 H10 - Power
VDD33 G10 - Power
VDD33 E10 - Power
VDD33 G11 - Power
528 March 17, 2008
Preliminary
Signal Tables
Pin Name Pin Number Pin Type Buffer Type Description
The positive supply (3.3 V) for the analog
circuits (ADC, Analog Comparators, etc.).
These are separated from VDD to minimize
the electrical noise contained on VDD from
affecting the analog functions.
VDDA C6 - Power
The positive supply (3.3 V) for the analog
circuits (ADC, Analog Comparators, etc.).
These are separated from VDD to minimize
the electrical noise contained on VDD from
affecting the analog functions.
VDDA C7 - Power
An external input that brings the processor out
of hibernate mode when asserted.
WAKE M10 I OD
Hibernation Module oscillator crystal input or
an external clock reference input. Note that
this is either a 4.19-MHz crystal or a
32.768-kHz oscillator for the Hibernation
Module RTC. See the CLKSEL bit in the
HIBCTL register.
XOSC0 K11 I Analog
XOSC1 K12 O Analog Hibernation Module oscillator crystal output.
XTALNPHY J1 O TTL XTALN of the Ethernet PHY
XTALPPHY J2 I TTL XTALP of the Ethernet PHY
Table 20-7. Signals by Function, Except for GPIO
Buffer Description
Type
Pin Pin Type
Number
Function Pin Name
ADC ADC0 B1 I Analog Analog-to-digital converter input 0.
ADC1 A1 I Analog Analog-to-digital converter input 1.
ADC2 B3 I Analog Analog-to-digital converter input 2.
ADC3 B2 I Analog Analog-to-digital converter input 3.
Analog C0+ A7 I Analog Analog comparator 0 positive input
Comparators C0- A6 I Analog Analog comparator 0 negative input
C0o F1 O TTL Analog comparator 0 output
C1+ M1 I Analog Analog comparator positive input
C1- B7 I Analog Analog comparator 1 negative input
C1o M1 O TTL Analog comparator 1 output
C2+ M2 I Analog Analog comparator positive input
C2- L2 I Analog Analog comparator 2 negative input
Controller Area CAN0Rx G1 I TTL CAN module 0 receive
Network CAN0Tx G2 O TTL CAN module 0 transmit
March 17, 2008 529
Preliminary
LM3S8933 Microcontroller
Buffer Description
Type
Pin Pin Type
Number
Function Pin Name
Ethernet PHY GNDPHY K3 I TTL GND of the Ethernet PHY
GNDPHY K4 I TTL GND of the Ethernet PHY
GNDPHY C8 I TTL GND of the Ethernet PHY
GNDPHY C9 I TTL GND of the Ethernet PHY
LED0 J12 O TTL MII LED 0
LED1 J11 O TTL MII LED 1
MDIO L9 I/O TTL MDIO of the Ethernet PHY
RXIN L7 I Analog RXIN of the Ethernet PHY
RXIP M7 I Analog RXIP of the Ethernet PHY
TXON L8 O Analog TXON of the Ethernet PHY
TXOP M8 O Analog TXOP of the Ethernet PHY
VCCPHY C10 I TTL VCC of the Ethernet PHY
VCCPHY D10 I TTL VCC of the Ethernet PHY
VCCPHY D11 I TTL VCC of the Ethernet PHY
XTALNPHY J1 O TTL XTALN of the Ethernet PHY
XTALPPHY J2 I TTL XTALP of the Ethernet PHY
General-Purpose CCP0 E12 I/O TTL Capture/Compare/PWM 0
Timers CCP1 L6 I/O TTL Capture/Compare/PWM 1
CCP2 D12 I/O TTL Capture/Compare/PWM 2
CCP3 E1 I/O TTL Capture/Compare/PWM 3
I2C I2C0SCL C11 I/O OD I2C module 0 clock
I2C0SDA C12 I/O OD I2C module 0 data
JTAG/SWD/SWO SWCLK A9 I TTL JTAG/SWD CLK
SWDIO B9 I/O TTL JTAG TMS and SWDIO
SWO A10 O TTL JTAG TDO and SWO
TCK A9 I TTL JTAG/SWD CLK
TDI B8 I TTL JTAG TDI
TDO A10 O TTL JTAG TDO and SWO
TMS B9 I/O TTL JTAG TMS and SWDIO
530 March 17, 2008
Preliminary
Signal Tables
Buffer Description
Type
Pin Pin Type
Number
Function Pin Name
Power GND C4 - Power Ground reference for logic and I/O pins.
GND C5 - Power Ground reference for logic and I/O pins.
GND H3 - Power Ground reference for logic and I/O pins.
GND J3 - Power Ground reference for logic and I/O pins.
GND K5 - Power Ground reference for logic and I/O pins.
GND K6 - Power Ground reference for logic and I/O pins.
GND L10 - Power Ground reference for logic and I/O pins.
GND K10 - Power Ground reference for logic and I/O pins.
GND J10 - Power Ground reference for logic and I/O pins.
GND F10 - Power Ground reference for logic and I/O pins.
GND F11 - Power Ground reference for logic and I/O pins.
GND B6 - Power Ground reference for logic and I/O pins.
GND F12 - Power Ground reference for logic and I/O pins.
The ground reference for the analog circuits (ADC,
Analog Comparators, etc.). These are separated
from GND to minimize the electrical noise contained
on VDD from affecting the analog functions.
GNDA B5 - Power
The ground reference for the analog circuits (ADC,
Analog Comparators, etc.). These are separated
from GND to minimize the electrical noise contained
on VDD from affecting the analog functions.
GNDA A5 - Power
An output that indicates the processor is in
hibernate mode.
HIB M12 O TTL
Low drop-out regulator output voltage. This pin
requires an external capacitor between the pin and
GND of 1 μF or greater. When the on-chip LDO is
used to provide power to the logic, the LDO pin
must also be connected to the VDD25 pins at the
board level in addition to the decoupling
capacitor(s).
LDO E3 - Power
Power source for the Hibernation Module. It is
normally connected to the positive terminal of a
battery and serves as the battery
backup/Hibernation Module power-source supply.
VBAT L12 - Power
Positive supply for most of the logic function,
including the processor core and most peripherals.
VDD25 C3 - Power
Positive supply for most of the logic function,
including the processor core and most peripherals.
VDD25 D3 - Power
Positive supply for most of the logic function,
including the processor core and most peripherals.
VDD25 F3 - Power
Positive supply for most of the logic function,
including the processor core and most peripherals.
VDD25 G3 - Power
VDD33 K7 - Power
VDD33 G12 - Power
VDD33 K8 - Power
VDD33 K9 - Power
VDD33 H10 - Power
VDD33 G10 - Power
March 17, 2008 531
Preliminary
LM3S8933 Microcontroller
Buffer Description
Type
Pin Pin Type
Number
Function Pin Name
VDD33 E10 - Power
VDD33 G11 - Power
The positive supply (3.3 V) for the analog circuits
(ADC, Analog Comparators, etc.). These are
separated from VDD to minimize the electrical noise
contained on VDD from affecting the analog
functions.
VDDA C6 - Power
The positive supply (3.3 V) for the analog circuits
(ADC, Analog Comparators, etc.). These are
separated from VDD to minimize the electrical noise
contained on VDD from affecting the analog
functions.
VDDA C7 - Power
An external input that brings the processor out of
hibernate mode when asserted.
WAKE M10 I OD
SSI SSI0Clk M4 I/O TTL SSI module 0 clock
SSI0Fss L4 I/O TTL SSI module 0 frame
SSI0Rx L5 I TTL SSI module 0 receive
SSI0Tx M5 O TTL SSI module 0 transmit
CPU Mode bit 0. Input must be set to logic 0
(grounded); other encodings reserved.
System Control & CMOD0 E11 I/O TTL
Clocks
CPU Mode bit 1. Input must be set to logic 0
(grounded); other encodings reserved.
CMOD1 B10 I/O TTL
Main oscillator crystal input or an external clock
reference input.
OSC0 L11 I Analog
OSC1 M11 O Analog Main oscillator crystal output.
RST H11 I TTL System reset input.
TRST A8 I TTL JTAG TRSTn
Hibernation Module oscillator crystal input or an
external clock reference input. Note that this is
either a 4.19-MHz crystal or a 32.768-kHz oscillator
for the Hibernation Module RTC. See the CLKSEL
bit in the HIBCTL register.
XOSC0 K11 I Analog
XOSC1 K12 O Analog Hibernation Module oscillator crystal output.
UART module 0 receive. When in IrDA mode, this
signal has IrDA modulation.
UART U0Rx L3 I TTL
UART module 0 transmit. When in IrDA mode, this
signal has IrDA modulation.
U0Tx M3 O TTL
UART module 1 receive. When in IrDA mode, this
signal has IrDA modulation.
U1Rx H2 I TTL
UART module 1 transmit. When in IrDA mode, this
signal has IrDA modulation.
U1Tx H1 O TTL
Table 20-8. GPIO Pins and Alternate Functions
GPIO Pin Pin Number Multiplexed Function Multiplexed Function
PA0 L3 U0Rx
PA1 M3 U0Tx
PA2 M4 SSI0Clk
PA3 L4 SSI0Fss
532 March 17, 2008
Preliminary
Signal Tables
GPIO Pin Pin Number Multiplexed Function Multiplexed Function
PA4 L5 SSI0Rx
PA5 M5 SSI0Tx
PA6 L6 CCP1
PA7 M6
PB0 E12 CCP0
PB1 D12 CCP2
PB2 C11 I2C0SCL
PB3 C12 I2C0SDA
PB4 A6 C0-
PB5 B7 C1-
PB6 A7 C0+
PB7 A8 TRST
PC0 A9 TCK SWCLK
PC1 B9 TMS SWDIO
PC2 B8 TDI
PC3 A10 TDO SWO
PC4 L1
PC5 M1 C1+ C1o
PC6 M2 C2+
PC7 L2 C2-
PD0 G1 CAN0Rx
PD1 G2 CAN0Tx
PD2 H2 U1Rx
PD3 H1 U1Tx
PD4 E1 CCP3
PD5 E2
PD6 F2
PD7 F1 C0o
PE4 D1
PE5 D2
PE6 C2
PE7 C1
PF0 M9
PF1 H12
PF2 J11 LED1
PF3 J12 LED0
March 17, 2008 533
Preliminary
LM3S8933 Microcontroller
21 Operating Characteristics
Table 21-1. Temperature Characteristics
Characteristica Symbol Value Unit
Industrial operating temperature range TA -40 to +85 °C
Extended operating temperature range TA -40 to +105 °C
a. Maximum storage temperature is 150°C.
Table 21-2. Thermal Characteristics
Characteristic Symbol Value Unit
Thermal resistance (junction to ambient)a ΘJA °C/W
Average junction temperatureb TJ TA + (PAVG • ΘJA) °C
a. Junction to ambient thermal resistance θJA numbers are determined by a package simulator.
b. Power dissipation is a function of temperature.
534 March 17, 2008
Preliminary
Operating Characteristics
22 Electrical Characteristics
22.1 DC Characteristics
22.1.1 Maximum Ratings
The maximum ratings are the limits to which the device can be subjected without permanently
damaging the device.
Note: The device is not guaranteed to operate properly at the maximum ratings.
Table 22-1. Maximum Ratings
Characteristic Symbol Value Unit
a
Min Max
I/O supply voltage (VDD) VDD 0 4 V
Core supply voltage (VDD25) VDD25 0 4 V
Analog supply voltage (VDDA) VDDA 0 4 V
Battery supply voltage (VBAT) VBAT 0 4 V
Ethernet PHY supply voltage (VCCPHY) VCCPHY 0 4 V
Input voltage VIN -0.3 5.5 V
Maximum current per output pins I - 25 mA
a. Voltages are measured with respect to GND.
Important: This device contains circuitry to protect the inputs against damage due to high-static
voltages or electric fields; however, it is advised that normal precautions be taken to
avoid application of any voltage higher than maximum-rated voltages to this
high-impedance circuit. Reliability of operation is enhanced if unused inputs are
connected to an appropriate logic voltage level (for example, either GND or VDD).
22.1.2 Recommended DC Operating Conditions
Table 22-2. Recommended DC Operating Conditions
Parameter Parameter Name Min Nom Max Unit
VDD I/O supply voltage 3.0 3.3 3.6 V
VDD25 Core supply voltage 2.25 2.5 2.75 V
VDDA Analog supply voltage 3.0 3.3 3.6 V
VBAT Battery supply voltage 2.3 3.0 3.6 V
VCCPHY Ethernet PHY supply voltage 3.0 3.3 3.6 V
VIH High-level input voltage 2.0 - 5.0 V
VIL Low-level input voltage -0.3 - 1.3 V
VSIH High-level input voltage for Schmitt trigger inputs 0.8 * VDD - VDD V
VSIL Low-level input voltage for Schmitt trigger inputs 0 - 0.2 * VDD V
VOH High-level output voltage 2.4 - - V
VOL Low-level output voltage - - 0.4 V
March 17, 2008 535
Preliminary
LM3S8933 Microcontroller
Parameter Parameter Name Min Nom Max Unit
IOH High-level source current, VOH=2.4 V
2-mA Drive 2.0 - - mA
4-mA Drive 4.0 - - mA
8-mA Drive 8.0 - - mA
IOL Low-level sink current, VOL=0.4 V
2-mA Drive 2.0 - - mA
4-mA Drive 4.0 - - mA
8-mA Drive 8.0 - - mA
22.1.3 On-Chip Low Drop-Out (LDO) Regulator Characteristics
Table 22-3. LDO Regulator Characteristics
Parameter Parameter Name Min Nom Max Unit
VLDOOUT Programmable internal (logic) power supply output value 2.25 2.5 2.75 V
Output voltage accuracy - 2% - %
tPON Power-on time - - 100 μs
tON Time on - - 200 μs
tOFF Time off - - 100 μs
VSTEP Step programming incremental voltage - 50 - mV
CLDO External filter capacitor size for internal power supply 1.0 - 3.0 μF
22.1.4 Power Specifications
The power measurements specified in the tables that follow are run on the core processor using
SRAM with the following specifications (except as noted):
■ VDD = 3.3 V
■ VDD25 = 2.50 V
■ VBAT = 3.0 V
■ VDDA = 3.3 V
■ VDDPHY = 3.3 V
■ Temperature = 25°C
■ Clock Source (MOSC) =3.579545 MHz Crystal Oscillator
■ Main oscillator (MOSC) = enabled
■ Internal oscillator (IOSC) = disabled
536 March 17, 2008
Preliminary
Electrical Characteristics
Table 22-4. Detailed Power Specifications
3.3 V VDD, VDDA, 2.5 V VDD25 3.0 V VBAT Unit
VDDPHY
Parameter Conditions
Name
Parameter
Nom Max Nom Max Nom Max
VDD25 = 2.50 V 48 pendinga 108 pendinga 0 pendinga mA
Code= while(1){} executed in
Flash
Peripherals = All ON
System Clock = 50 MHz (with
PLL)
Run mode 1
(Flash loop)
IDD_RUN
VDD25 = 2.50 V 5 pendinga 52 pendinga 0 pendinga mA
Code= while(1){} executed in
Flash
Peripherals = All OFF
System Clock = 50 MHz (with
PLL)
Run mode 2
(Flash loop)
VDD25 = 2.50 V 48 pendinga 100 pendinga 0 pendinga mA
Code= while(1){} executed in
SRAM
Peripherals = All ON
System Clock = 50 MHz (with
PLL)
Run mode 1
(SRAM loop)
VDD25 = 2.50 V 5 pendinga 45 pendinga 0 pendinga mA
Code= while(1){} executed in
SRAM
Peripherals = All OFF
System Clock = 50 MHz (with
PLL)
Run mode 2
(SRAM loop)
VDD25 = 2.50 V 5 pendinga 16 pendinga 0 pendinga mA
Peripherals = All OFF
System Clock = 50 MHz (with
PLL)
IDD_SLEEP Sleep mode
LDO = 2.25 V 4.6 pendinga 0.21 pendinga 0 pendinga mA
Peripherals = All OFF
System Clock = IOSC30KHZ/64
Deep-Sleep
mode
IDD_DEEPSLEEP
VBAT = 3.0 V 0 pendinga 0 pendinga 16 pendinga μA
VDD = 0 V
VDD25 = 0 V
VDDA = 0 V
VDDPHY = 0 V
Peripherals = All OFF
System Clock = OFF
Hibernate Module = 32 kHz
Hibernate
mode
IDD_HIBERNATE
a. Pending characterization completion.
March 17, 2008 537
Preliminary
LM3S8933 Microcontroller
22.1.5 Flash Memory Characteristics
Table 22-5. Flash Memory Characteristics
Parameter Parameter Name Min Nom Max Unit
PECYC Number of guaranteed program/erase cycles before failurea 10,000 100,000 - cycles
Data retention at average operating temperature of 85˚C (industrial) or 105˚C 10 - - years
(extended)
TRET
TPROG Word program time 20 - - μs
TERASE Page erase time 20 - - ms
TME Mass erase time 200 - - ms
a. A program/erase cycle is defined as switching the bits from 1-> 0 -> 1.
22.2 AC Characteristics
22.2.1 Load Conditions
Unless otherwise specified, the following conditions are true for all timing measurements. Timing
measurements are for 4-mA drive strength.
Figure 22-1. Load Conditions
CL = 50 pF
GND
pin
22.2.2 Clocks
Table 22-6. Phase Locked Loop (PLL) Characteristics
Parameter Parameter Name Min Nom Max Unit
fref_crystal Crystal referencea 3.579545 - 8.192 MHz
fref_ext External clock referencea 3.579545 - 8.192 MHz
fpll PLL frequencyb - 400 - MHz
TREADY PLL lock time - - 0.5 ms
a. The exact value is determined by the crystal value programmed into the XTAL field of the Run-Mode Clock Configuration
(RCC) register.
b. PLL frequency is automatically calculated by the hardware based on the XTAL field of the RCC register.
Table 22-7. Clock Characteristics
Parameter Parameter Name Min Nom Max Unit
fIOSC Internal 12 MHz oscillator frequency 8.4 12 15.6 MHz
fIOSC30KHZ Internal 30 KHz oscillator frequency 21 30 39 KHz
fXOSC Hibernation module oscillator frequency - 4.194304 - MHz
fXOSC_XTAL Crystal reference for hibernation oscillator - 4.194304 - MHz
fXOSC_EXT External clock reference for hibernation module - 32.768 - KHz
538 March 17, 2008
Preliminary
Electrical Characteristics
Parameter Parameter Name Min Nom Max Unit
fMOSC Main oscillator frequency 1 - 8 MHz
tMOSC_per Main oscillator period 125 - 1000 ns
Crystal reference using the main oscillator (PLL in BYPASS mode) 1 - 8 MHz
a
fref_crystal_bypass
fref_ext_bypass External clock reference (PLL in BYPASS mode)a 0 - 50 MHz
fsystem_clock System clock 0 - 50 MHz
a. The ADC must be clocked from the PLL or directly from a 14-MHz to 18-MHz clock source to operate properly.
Table 22-8. Crystal Characteristics
Parameter Name Value Units
Frequency 8 6 4 3.5 MHz
Frequency tolerance ±50 ±50 ±50 ±50 ppm
Aging ±5 ±5 ±5 ±5 ppm/yr
Oscillation mode Parallel Parallel Parallel Parallel
Temperature stability (-40°C to 85°C) ±25 ±25 ±25 ±25 ppm
Temperature stability (-40°C to 105°C) ±25 ±25 ±25 ±25 ppm
Motional capacitance (typ) 27.8 37.0 55.6 63.5 pF
Motional inductance (typ) 14.3 19.1 28.6 32.7 mH
Equivalent series resistance (max) 120 160 200 220 Ω
Shunt capacitance (max) 10 10 10 10 pF
Load capacitance (typ) 16 16 16 16 pF
Drive level (typ) 100 100 100 100 μW
22.2.3 Analog-to-Digital Converter
Table 22-9. ADC Characteristics
Parameter Parameter Name Min Nom Max Unit
VADCIN Maximum single-ended, full-scale analog input voltage - - 3.0 V
Minimum single-ended, full-scale analog input voltage - - 0 V
Maximum differential, full-scale analog input voltage - - 1.5 V
Minimum differential, full-scale analog input voltage - - -1.5 V
CADCIN Equivalent input capacitance - 1 - pF
N Resolution - 10 - bits
fADC ADC internal clock frequency 14 16 18 MHz
tADCCONV Conversion time - - 16 tADCcyclesa
f ADCCONV Conversion rate 875 1000 1125 k samples/s
INL Integral nonlinearity - - ±1 LSB
DNL Differential nonlinearity - - ±1 LSB
OFF Offset - - ±1 LSB
GAIN Gain - - ±1 LSB
a. tADC= 1/fADC clock
March 17, 2008 539
Preliminary
LM3S8933 Microcontroller
22.2.4 Analog Comparator
Table 22-10. Analog Comparator Characteristics
Parameter Parameter Name Min Nom Max Unit
VOS Input offset voltage - ±10 ±25 mV
VCM Input common mode voltage range 0 - VDD-1.5 V
CMRR Common mode rejection ratio 50 - - dB
TRT Response time - - 1 μs
TMC Comparator mode change to Output Valid - - 10 μs
Table 22-11. Analog Comparator Voltage Reference Characteristics
Parameter Parameter Name Min Nom Max Unit
RHR Resolution high range - VDD/32 - LSB
RLR Resolution low range - VDD/24 - LSB
AHR Absolute accuracy high range - - ±1/2 LSB
ALR Absolute accuracy low range - - ±1/4 LSB
22.2.5 I2C
Table 22-12. I2C Characteristics
Parameter No. Parameter Parameter Name Min Nom Max Unit
I1a tSCH Start condition hold time 36 - - system clocks
I2a tLP Clock Low period 36 - - system clocks
I3b tSRT I2CSCL/I2CSDA rise time (VIL =0.5 V to V IH =2.4 V) - - (see note b) ns
I4a tDH Data hold time 2 - - system clocks
I5c tSFT I2CSCL/I2CSDA fall time (VIH =2.4 V to V IL =0.5 V) - 9 10 ns
I6a tHT Clock High time 24 - - system clocks
I7a tDS Data setup time 18 - - system clocks
Start condition setup time (for repeated start condition 36 - - system clocks
only)
I8a tSCSR
I9a tSCS Stop condition setup time 24 - - system clocks
a. Values depend on the value programmed into the TPR bit in the I2C Master Timer Period (I2CMTPR) register; a TPR
programmed for the maximum I2CSCL frequency (TPR=0x2) results in a minimum output timing as shown in the table
above. The I 2C interface is designed to scale the actual data transition time to move it to the middle of the I2CSCL Low
period. The actual position is affected by the value programmed into the TPR; however, the numbers given in the above
values are minimum values.
b. Because I2CSCL and I2CSDA are open-drain-type outputs, which the controller can only actively drive Low, the time
I2CSCL or I2CSDA takes to reach a high level depends on external signal capacitance and pull-up resistor values.
c. Specified at a nominal 50 pF load.
540 March 17, 2008
Preliminary
Electrical Characteristics
Figure 22-2. I2C Timing
I2CSCL
I2CSDA
I1
I2
I4
I6
I7 I8
I5
I3 I9
22.2.6 Ethernet Controller
Table 22-13. 100BASE-TX Transmitter Characteristicsa
Parameter Name Min Nom Max Unit
Peak output amplitude 950 - 1050 mVpk
Output amplitude symmetry 0.98 - 1.02 mVpk
Output overshoot - - 5 %
Rise/Fall time 3 - 5 ns
Rise/Fall time imbalance - - 500 ps
Duty cycle distortion - - - ps
Jitter - - 1.4 ns
a. Measured at the line side of the transformer.
Table 22-14. 100BASE-TX Transmitter Characteristics (informative)a
Parameter Name Min Nom Max Unit
Return loss 16 - - dB
Open-circuit inductance 350 - - μs
a. The specifications in this table are included for information only. They are mainly a function of the external transformer
and termination resistors used for measurements.
Table 22-15. 100BASE-TX Receiver Characteristics
Parameter Name Min Nom Max Unit
Signal detect assertion threshold 600 700 mVppd
Signal detect de-assertion threshold 350 425 - mVppd
Differential input resistance 20 - - kΩ
Jitter tolerance (pk-pk) 4 - - ns
Baseline wander tracking -75 - +75 %
Signal detect assertion time - - 1000 μs
Signal detect de-assertion time - - 4 μs
Table 22-16. 10BASE-T Transmitter Characteristicsa
Parameter Name Min Nom Max Unit
Peak differential output signal 2.2 - 2.8 V
Harmonic content 27 - - dB
Link pulse width - 100 - ns
March 17, 2008 541
Preliminary
LM3S8933 Microcontroller
Parameter Name Min Nom Max Unit
300 - ns
350
Start-of-idle pulse width -
a. The Manchester-encoded data pulses, the link pulse and the start-of-idle pulse are tested against the templates and using
the procedures found in Clause 14 of IEEE 802.3.
Table 22-17. 10BASE-T Transmitter Characteristics (informative)a
Parameter Name Min Nom Max Unit
Output return loss 15 - - dB
Output impedance balance 29-17log(f/10) - - dB
Peak common-mode output voltage - - 50 mV
Common-mode rejection - - 100 mV
Common-mode rejection jitter - - 1 ns
a. The specifications in this table are included for information only. They are mainly a function of the external transformer
and termination resistors used for measurements.
Table 22-18. 10BASE-T Receiver Characteristics
Parameter Name Min Nom Max Unit
DLL phase acquisition time - 10 - BT
Jitter tolerance (pk-pk) 30 - - ns
Input squelched threshold 500 600 700 mVppd
Input unsquelched threshold 275 350 425 mVppd
Differential input resistance - 20 - kΩ
Bit error ratio - 10-10 - -
Common-mode rejection 25 - - V
Table 22-19. Isolation Transformersa
Name Value Condition
Turns ratio 1 CT : 1 CT +/- 5%
Open-circuit inductance 350 uH (min) @ 10 mV, 10 kHz
Leakage inductance 0.40 uH (max) @ 1 MHz (min)
Inter-winding capacitance 25 pF (max)
DC resistance 0.9 Ohm (max)
Insertion loss 0.4 dB (typ) 0-65 MHz
HIPOT 1500 Vrms
a. Two simple 1:1 isolation transformers are required at the line interface. Transformers with integrated common-mode
chokes are recommended for exceeding FCC requirements. This table gives the recommended line transformer
characteristics.
Note: The 100Base-TX amplitude specifications assume a transformer loss of 0.4 dB. For the
transmit line transformer with higher insertion losses, up to 1.2 dB of insertion loss can be
compensated by selecting the appropriate setting in the Transmit Amplitude Selection (TXO)
bits in the MR19 register.
542 March 17, 2008
Preliminary
Electrical Characteristics
Table 22-20. Ethernet Reference Crystala
Name Value Condition
Frequency 25.00000 MHz
Frequency tolerance ±50 PPM
Aging ±2 PPM/yr
Temperature stability (-40° to 85°) ±5 PPM
Temperature stability (-40° to 105°) ±5 PPM
Oscillation mode Parallel resonance, fundamental mode
Parameters at 25° C ±2° C; Drive level = 0.5 mW
Drive level (typ) 50-100 μW
Shunt capacitance (max) 10 pF
Motional capacitance (min) 10 fF
Serious resistance (max) 60 Ω
Spurious response (max) > 5 dB below main within 500 kHz
a. If the internal crystal oscillator is used, select a crystal with the following characteristics.
Figure 22-3. External XTLP Oscillator Characteristics
Tclkper
Tr
Tclkhi Tclklo
Tf
Table 22-21. External XTLP Oscillator Characteristics
Parameter Name Symbol Min Nom Max Unit
XTLN Input Low Voltage XTLNILV - - 0.8 -
XTLP Frequencya XTLPf - 25.0 - -
XTLP Periodb Tclkper - 40 - -
60 %
60
40 -
40
XTLPDC XTLP Duty Cycle
Rise/Fall Time Tr , Tf - - 4.0 ns
Absolute Jitter - - 0.1 ns
a. IEEE 802.3 frequency tolerance ±50 ppm.
b. IEEE 802.3 frequency tolerance ±50 ppm.
March 17, 2008 543
Preliminary
LM3S8933 Microcontroller
22.2.7 Hibernation Module
The Hibernation Module requires special system implementation considerations since it is intended
to power-down all other sections of its host device. The system power-supply distribution and
interfaces of the system must be driven to 0 VDC or powered down with the same regulator controlled
by HIB.
The regulators controlled by HIB are expected to have a settling time of 250 μs or less.
Table 22-22. Hibernation Module Characteristics
Parameter No Parameter Parameter Name Min Nom Max Unit
H1 tHIB_LOW Internal 32.768 KHz clock reference rising edge to /HIB asserted - 200 - μs
H2 tHIB_HIGH Internal 32.768 KHz clock reference rising edge to /HIB deasserted - 30 - μs
H3 tWAKE_ASSERT /WAKE assertion time 62 - - μs
H4 tWAKETOHIB /WAKE assert to /HIB desassert 62 - 124 μs
H5 tXOSC_SETTLE XOSC settling timea 20 - - ms
H6 tHIB_REG_WRITE Time for a write to non-volatile registers in HIB module to complete 92 - - μs
H7 tHIB_TO_VDD HIB deassert to VDD and VDD25 at minimum operational level - - 250 μs
a. This parameter is highly sensitive to PCB layout and trace lengths, which may make this parameter time longer. Care
must be taken in PCB design to minimize trace lengths and RLC (resistance, inductance, capacitance).
Figure 22-4. Hibernation Module Timing
32.768 KHz
(internal)
/HIB
H4
H1
/WAKE
H2
H3
22.2.8 Synchronous Serial Interface (SSI)
Table 22-23. SSI Characteristics
Parameter No. Parameter Parameter Name Min Nom Max Unit
S1 tclk_per SSIClk cycle time 2 - 65024 system clocks
S2 tclk_high SSIClk high time - 1/2 - t clk_per
S3 tclk_low SSIClk low time - 1/2 - t clk_per
S4 tclkrf SSIClk rise/fall time - 7.4 26 ns
S5 tDMd Data from master valid delay time 0 - 20 ns
S6 tDMs Data from master setup time 20 - - ns
S7 tDMh Data from master hold time 40 - - ns
S8 tDSs Data from slave setup time 20 - - ns
S9 tDSh Data from slave hold time 40 - - ns
544 March 17, 2008
Preliminary
Electrical Characteristics
Figure 22-5. SSI Timing for TI Frame Format (FRF=01), Single Transfer Timing Measurement
SSIClk
SSIFss
SSITx
SSIRx MSB LSB
S2
S3
S1
S4
4 to 16 bits
Figure 22-6. SSI Timing for MICROWIRE Frame Format (FRF=10), Single Transfer
0
SSIClk
SSIFss
SSITx
SSIRx
MSB LSB
MSB LSB
S2
S3
S1
8-bit control
4 to 16 bits output data
March 17, 2008 545
Preliminary
LM3S8933 Microcontroller
Figure 22-7. SSI Timing for SPI Frame Format (FRF=00), with SPH=1
SSIClk
(SPO=1)
SSITx
(master)
SSIRx
(slave) LSB
SSIClk
(SPO=0)
S2
S1
S4
SSIFss
LSB
S3
MSB
S5
S6 S7
S8 S9
MSB
22.2.9 JTAG and Boundary Scan
Table 22-24. JTAG Characteristics
Parameter No. Parameter Parameter Name Min Nom Max Unit
J1 fTCK TCK operational clock frequency 0 - 10 MHz
J2 tTCK TCK operational clock period 100 - - ns
J3 tTCK_LOW TCK clock Low time - tTCK - ns
J4 tTCK_HIGH TCK clock High time - tTCK - ns
J5 tTCK_R TCK rise time 0 - 10 ns
J6 tTCK_F TCK fall time 0 - 10 ns
J7 tTMS_SU TMS setup time to TCK rise 20 - - ns
J8 tTMS_HLD TMS hold time from TCK rise 20 - - ns
J9 tTDI_SU TDI setup time to TCK rise 25 - - ns
J10 tTDI_HLD TDI hold time from TCK rise 25 - - ns
J11 TCK fall to Data Valid from High-Z 2-mA drive - 23 35 ns
t TDO_ZDV 4-mA drive 15 26 ns
8-mA drive 14 25 ns
8-mA drive with slew rate control 18 29 ns
J12 TCK fall to Data Valid from Data Valid 2-mA drive - 21 35 ns
t TDO_DV 4-mA drive 14 25 ns
8-mA drive 13 24 ns
8-mA drive with slew rate control 18 28 ns
546 March 17, 2008
Preliminary
Electrical Characteristics
Parameter No. Parameter Parameter Name Min Nom Max Unit
J13 TCK fall to High-Z from Data Valid 2-mA drive - 9 11 ns
t TDO_DVZ 4-mA drive 7 9 ns
8-mA drive 6 8 ns
8-mA drive with slew rate control 7 9 ns
J14 tTRST TRST assertion time 100 - - ns
J15 tTRST_SU TRST setup time to TCK rise 10 - - ns
Figure 22-8. JTAG Test Clock Input Timing
TCK
J6 J5
J3 J4
J2
Figure 22-9. JTAG Test Access Port (TAP) Timing
TDO Output Valid
TCK
TDO Output Valid
J12
TDO
TDI
TMS
TDI Input Valid TDI Input Valid
J13
J9 J10
TMS Input Valid
J9 J10
TMS Input Valid
J11
J7 J8 J7 J8
Figure 22-10. JTAG TRST Timing
TCK
J14 J15
TRST
22.2.10 General-Purpose I/O
Note: All GPIOs are 5 V-tolerant.
March 17, 2008 547
Preliminary
LM3S8933 Microcontroller
Table 22-25. GPIO Characteristics
Parameter Parameter Name Condition Min Nom Max Unit
tGPIOR GPIO Rise Time (from 20% to 80% of VDD) 2-mA drive - 17 26 ns
4-mA drive 9 13 ns
8-mA drive 6 9 ns
8-mA drive with slew rate control 10 12 ns
tGPIOF GPIO Fall Time (from 80% to 20% of VDD) 2-mA drive - 17 25 ns
4-mA drive 8 12 ns
8-mA drive 6 10 ns
8-mA drive with slew rate control 11 13 ns
22.2.11 Reset
Table 22-26. Reset Characteristics
Parameter No. Parameter Parameter Name Min Nom Max Unit
R1 VTH Reset threshold - 2.0 - V
R2 VBTH Brown-Out threshold 2.85 2.9 2.95 V
R3 TPOR Power-On Reset timeout - 10 - ms
R4 TBOR Brown-Out timeout - 500 - μs
R5 TIRPOR Internal reset timeout after POR 6 - 11 ms
R6 TIRBOR Internal reset timeout after BORa 0 - 1 μs
R7 TIRHWR Internal reset timeout after hardware reset (RST pin) 0 - 1 ms
R8 TIRSWR Internal reset timeout after software-initiated system reset a 2.5 - 20 μs
R9 TIRWDR Internal reset timeout after watchdog reseta 2.5 - 20 μs
R10 TVDDRISE Supply voltage (VDD) rise time (0V-3.3V) - - 100 ms
R11 TMIN Minimum RST pulse width 2 - - μs
a. 20 * t MOSC_per
Figure 22-11. External Reset Timing (RST)
RST
/Reset
(Internal)
R11 R7
548 March 17, 2008
Preliminary
Electrical Characteristics
Figure 22-12. Power-On Reset Timing
VDD
/POR
(Internal)
/Reset
(Internal)
R3
R1
R5
Figure 22-13. Brown-Out Reset Timing
VDD
/BOR
(Internal)
/Reset
(Internal)
R2
R4
R6
Figure 22-14. Software Reset Timing
R8
SW Reset
/Reset
(Internal)
Figure 22-15. Watchdog Reset Timing
WDOG
Reset
(Internal)
/Reset
(Internal)
R9
March 17, 2008 549
Preliminary
LM3S8933 Microcontroller
23 Package Information
Figure 23-1. 100-Pin LQFP Package
Note: The following notes apply to the package drawing.
1. All dimensions shown in mm.
2. Dimensions shown are nominal with tolerances indicated.
3. Foot length 'L' is measured at gage plane 0.25 mm above seating plane.
550 March 17, 2008
Preliminary
Package Information
Body +2.00 mm Footprint, 1.4 mm package thickness
Symbols Leads 100L
A Max. 1.60
A1 0.05 Min./0.15 Max.
A2 ±0.05 1.40
D ±0.20 16.00
D1 ±0.05 14.00
E ±0.20 16.00
E1 ±0.05 14.00
L ±0.15/-0.10 0.60
e Basic 0.50
b ±0.05 0.22
θ === 0˚~7˚
ddd Max. 0.08
ccc Max. 0.08
JEDEC Reference Drawing MS-026
Variation Designator BED
March 17, 2008 551
Preliminary
LM3S8933 Microcontroller
Figure 23-2. 100-Ball BGA Package
552 March 17, 2008
Preliminary
Package Information
Note: The following notes apply to the package drawing.
Symbols MIN NOM MAX
A 1.22 1.36 1.50
A1 0.29 0.34 0.39
A3 0.65 0.70 0.75
c 0.28 0.32 0.36
D 9.85 10.00 10.15
D1 8.80 BSC
E 9.85 10.00 10.15
E1 8.80 BSC
b 0.43 0.48 0.53
bbb .20
ddd .12
e 0.80 BSC
f - 0.60 -
M 12
n 108
REF: JEDEC MO-219F
March 17, 2008 553
Preliminary
LM3S8933 Microcontroller
A Serial Flash Loader
A.1 Serial Flash Loader
The Stellaris® serial flash loader is a preprogrammed flash-resident utility used to download code
to the flash memory of a device without the use of a debug interface. The serial flash loader uses
a simple packet interface to provide synchronous communication with the device. The flash loader
runs off the crystal and does not enable the PLL, so its speed is determined by the crystal used.
The two serial interfaces that can be used are the UART0 and SSI0 interfaces. For simplicity, both
the data format and communication protocol are identical for both serial interfaces.
A.2 Interfaces
Once communication with the flash loader is established via one of the serial interfaces, that interface
is used until the flash loader is reset or new code takes over. For example, once you start
communicating using the SSI port, communications with the flash loader via the UART are disabled
until the device is reset.
A.2.1 UART
The Universal Asynchronous Receivers/Transmitters (UART) communication uses a fixed serial
format of 8 bits of data, no parity, and 1 stop bit. The baud rate used for communication is
automatically detected by the flash loader and can be any valid baud rate supported by the host
and the device. The auto detection sequence requires that the baud rate should be no more than
1/32 the crystal frequency of the board that is running the serial flash loader. This is actually the
same as the hardware limitation for the maximum baud rate for any UART on a Stellaris® device
which is calculated as follows:
Max Baud Rate = System Clock Frequency / 16
In order to determine the baud rate, the serial flash loader needs to determine the relationship
between its own crystal frequency and the baud rate. This is enough information for the flash loader
to configure its UART to the same baud rate as the host. This automatic baud-rate detection allows
the host to use any valid baud rate that it wants to communicate with the device.
The method used to perform this automatic synchronization relies on the host sending the flash
loader two bytes that are both 0x55. This generates a series of pulses to the flash loader that it can
use to calculate the ratios needed to program the UART to match the host’s baud rate. After the
host sends the pattern, it attempts to read back one byte of data from the UART. The flash loader
returns the value of 0xCC to indicate successful detection of the baud rate. If this byte is not received
after at least twice the time required to transfer the two bytes, the host can resend another pattern
of 0x55, 0x55, and wait for the 0xCC byte again until the flash loader acknowledges that it has
received a synchronization pattern correctly. For example, the time to wait for data back from the
flash loader should be calculated as at least 2*(20(bits/sync)/baud rate (bits/sec)). For a baud rate
of 115200, this time is 2*(20/115200) or 0.35 ms.
A.2.2 SSI
The Synchronous Serial Interface (SSI) port also uses a fixed serial format for communications,
with the framing defined as Motorola format with SPH set to 1 and SPO set to 1. See “Frame
Formats” on page 339 in the SSI chapter for more information on formats for this transfer protocol.
Like the UART, this interface has hardware requirements that limit the maximum speed that the SSI
clock can run. This allows the SSI clock to be at most 1/12 the crystal frequency of the board running
554 March 17, 2008
Preliminary
Serial Flash Loader
the flash loader. Since the host device is the master, the SSI on the flash loader device does not
need to determine the clock as it is provided directly by the host.
A.3 Packet Handling
All communications, with the exception of the UART auto-baud, are done via defined packets that
are acknowledged (ACK) or not acknowledged (NAK) by the devices. The packets use the same
format for receiving and sending packets, including the method used to acknowledge successful or
unsuccessful reception of a packet.
A.3.1 Packet Format
All packets sent and received from the device use the following byte-packed format.
struct
{
unsigned char ucSize;
unsigned char ucCheckSum;
unsigned char Data[];
};
ucSize The first byte received holds the total size of the transfer including
the size and checksum bytes.
ucChecksum This holds a simple checksum of the bytes in the data buffer only.
The algorithm is Data[0]+Data[1]+…+ Data[ucSize-3].
Data This is the raw data intended for the device, which is formatted in
some form of command interface. There should be ucSize–2
bytes of data provided in this buffer to or from the device.
A.3.2 Sending Packets
The actual bytes of the packet can be sent individually or all at once; the only limitation is that
commands that cause flash memory access should limit the download sizes to prevent losing bytes
during flash programming. This limitation is discussed further in the section that describes the serial
flash loader command, COMMAND_SEND_DATA (see “COMMAND_SEND_DATA
(0x24)” on page 557).
Once the packet has been formatted correctly by the host, it should be sent out over the UART or
SSI interface. Then the host should poll the UART or SSI interface for the first non-zero data returned
from the device. The first non-zero byte will either be an ACK (0xCC) or a NAK (0x33) byte from
the device indicating the packet was received successfully (ACK) or unsuccessfully (NAK). This
does not indicate that the actual contents of the command issued in the data portion of the packet
were valid, just that the packet was received correctly.
A.3.3 Receiving Packets
The flash loader sends a packet of data in the same format that it receives a packet. The flash loader
may transfer leading zero data before the first actual byte of data is sent out. The first non-zero byte
is the size of the packet followed by a checksum byte, and finally followed by the data itself. There
is no break in the data after the first non-zero byte is sent from the flash loader. Once the device
communicating with the flash loader receives all the bytes, it must either ACK or NAK the packet to
indicate that the transmission was successful. The appropriate response after sending a NAK to
the flash loader is to resend the command that failed and request the data again. If needed, the
host may send leading zeros before sending down the ACK/NAK signal to the flash loader, as the
March 17, 2008 555
Preliminary
LM3S8933 Microcontroller
flash loader only accepts the first non-zero data as a valid response. This zero padding is needed
by the SSI interface in order to receive data to or from the flash loader.
A.4 Commands
The next section defines the list of commands that can be sent to the flash loader. The first byte of
the data should always be one of the defined commands, followed by data or parameters as
determined by the command that is sent.
A.4.1 COMMAND_PING (0X20)
This command simply accepts the command and sets the global status to success. The format of
the packet is as follows:
Byte[0] = 0x03;
Byte[1] = checksum(Byte[2]);
Byte[2] = COMMAND_PING;
The ping command has 3 bytes and the value for COMMAND_PING is 0x20 and the checksum of one
byte is that same byte, making Byte[1] also 0x20. Since the ping command has no real return status,
the receipt of an ACK can be interpreted as a successful ping to the flash loader.
A.4.2 COMMAND_GET_STATUS (0x23)
This command returns the status of the last command that was issued. Typically, this command
should be sent after every command to ensure that the previous command was successful or to
properly respond to a failure. The command requires one byte in the data of the packet and should
be followed by reading a packet with one byte of data that contains a status code. The last step is
to ACK or NAK the received data so the flash loader knows that the data has been read.
Byte[0] = 0x03
Byte[1] = checksum(Byte[2])
Byte[2] = COMMAND_GET_STATUS
A.4.3 COMMAND_DOWNLOAD (0x21)
This command is sent to the flash loader to indicate where to store data and how many bytes will
be sent by the COMMAND_SEND_DATA commands that follow. The command consists of two 32-bit
values that are both transferred MSB first. The first 32-bit value is the address to start programming
data into, while the second is the 32-bit size of the data that will be sent. This command also triggers
an erase of the full area to be programmed so this command takes longer than other commands.
This results in a longer time to receive the ACK/NAK back from the board. This command should
be followed by a COMMAND_GET_STATUS to ensure that the Program Address and Program size
are valid for the device running the flash loader.
The format of the packet to send this command is a follows:
Byte[0] = 11
Byte[1] = checksum(Bytes[2:10])
Byte[2] = COMMAND_DOWNLOAD
Byte[3] = Program Address [31:24]
Byte[4] = Program Address [23:16]
Byte[5] = Program Address [15:8]
Byte[6] = Program Address [7:0]
Byte[7] = Program Size [31:24]
556 March 17, 2008
Preliminary
Serial Flash Loader
Byte[8] = Program Size [23:16]
Byte[9] = Program Size [15:8]
Byte[10] = Program Size [7:0]
A.4.4 COMMAND_SEND_DATA (0x24)
This command should only follow a COMMAND_DOWNLOAD command or another
COMMAND_SEND_DATA command if more data is needed. Consecutive send data commands
automatically increment address and continue programming from the previous location. The caller
should limit transfers of data to a maximum 8 bytes of packet data to allow the flash to program
successfully and not overflow input buffers of the serial interfaces. The command terminates
programming once the number of bytes indicated by the COMMAND_DOWNLOAD command has been
received. Each time this function is called it should be followed by a COMMAND_GET_STATUS to
ensure that the data was successfully programmed into the flash. If the flash loader sends a NAK
to this command, the flash loader does not increment the current address to allow retransmission
of the previous data.
Byte[0] = 11
Byte[1] = checksum(Bytes[2:10])
Byte[2] = COMMAND_SEND_DATA
Byte[3] = Data[0]
Byte[4] = Data[1]
Byte[5] = Data[2]
Byte[6] = Data[3]
Byte[7] = Data[4]
Byte[8] = Data[5]
Byte[9] = Data[6]
Byte[10] = Data[7]
A.4.5 COMMAND_RUN (0x22)
This command is used to tell the flash loader to execute from the address passed as the parameter
in this command. This command consists of a single 32-bit value that is interpreted as the address
to execute. The 32-bit value is transmitted MSB first and the flash loader responds with an ACK
signal back to the host device before actually executing the code at the given address. This allows
the host to know that the command was received successfully and the code is now running.
Byte[0] = 7
Byte[1] = checksum(Bytes[2:6])
Byte[2] = COMMAND_RUN
Byte[3] = Execute Address[31:24]
Byte[4] = Execute Address[23:16]
Byte[5] = Execute Address[15:8]
Byte[6] = Execute Address[7:0]
A.4.6 COMMAND_RESET (0x25)
This command is used to tell the flash loader device to reset. This is useful when downloading a
new image that overwrote the flash loader and wants to start from a full reset. Unlike the
COMMAND_RUN command, this allows the initial stack pointer to be read by the hardware and set
up for the new code. It can also be used to reset the flash loader if a critical error occurs and the
host device wants to restart communication with the flash loader.
March 17, 2008 557
Preliminary
LM3S8933 Microcontroller
Byte[0] = 3
Byte[1] = checksum(Byte[2])
Byte[2] = COMMAND_RESET
The flash loader responds with an ACK signal back to the host device before actually executing the
software reset to the device running the flash loader. This allows the host to know that the command
was received successfully and the part will be reset.
558 March 17, 2008
Preliminary
Serial Flash Loader
B Register Quick Reference
31 30 29 28 27 26 25 24 23 22 21 20 19 18 17 16
15 14 13 12 11 10 9 8 7 6 5 4 3 2 1 0
System Control
Base 0x400F.E000
DID0, type RO, offset 0x000, reset -
VER CLASS
MAJOR MINOR
PBORCTL, type R/W, offset 0x030, reset 0x0000.7FFD
BORIOR
LDOPCTL, type R/W, offset 0x034, reset 0x0000.0000
VADJ
RIS, type RO, offset 0x050, reset 0x0000.0000
PLLLRIS BORRIS
IMC, type R/W, offset 0x054, reset 0x0000.0000
PLLLIM BORIM
MISC, type R/W1C, offset 0x058, reset 0x0000.0000
PLLLMIS BORMIS
RESC, type R/W, offset 0x05C, reset -
LDO SW WDT BOR POR EXT
RCC, type R/W, offset 0x060, reset 0x0780.3AD1
ACG SYSDIV USESYSDIV
PWRDN BYPASS XTAL OSCSRC IOSCDIS MOSCDIS
PLLCFG, type RO, offset 0x064, reset -
F R
RCC2, type R/W, offset 0x070, reset 0x0780.2800
USERCC2 SYSDIV2
PWRDN2 BYPASS2 OSCSRC2
DSLPCLKCFG, type R/W, offset 0x144, reset 0x0780.0000
DSDIVORIDE
DSOSCSRC
DID1, type RO, offset 0x004, reset -
VER FAM PARTNO
PINCOUNT TEMP PKG ROHS QUAL
DC0, type RO, offset 0x008, reset 0x00FF.007F
SRAMSZ
FLASHSZ
DC1, type RO, offset 0x010, reset 0x0101.33FF
CAN0 ADC
MINSYSDIV MAXADCSPD MPU HIB TEMPSNS PLL WDT SWO SWD JTAG
DC2, type RO, offset 0x014, reset 0x070F.1013
COMP2 COMP1 COMP0 TIMER3 TIMER2 TIMER1 TIMER0
I2C0 SSI0 UART1 UART0
DC3, type RO, offset 0x018, reset 0x0F0F.3FC0
CCP3 CCP2 CCP1 CCP0 ADC3 ADC2 ADC1 ADC0
C2PLUS C2MINUS C1O C1PLUS C1MINUS C0O C0PLUS C0MINUS
March 17, 2008 559
Preliminary
LM3S8933 Microcontroller
31 30 29 28 27 26 25 24 23 22 21 20 19 18 17 16
15 14 13 12 11 10 9 8 7 6 5 4 3 2 1 0
DC4, type RO, offset 0x01C, reset 0x5100.007F
EPHY0 EMAC0 E1588
GPIOG GPIOF GPIOE GPIOD GPIOC GPIOB GPIOA
RCGC0, type R/W, offset 0x100, reset 0x00000040
CAN0 ADC
MAXADCSPD HIB WDT
SCGC0, type R/W, offset 0x110, reset 0x00000040
CAN0 ADC
MAXADCSPD HIB WDT
DCGC0, type R/W, offset 0x120, reset 0x00000040
CAN0 ADC
MAXADCSPD HIB WDT
RCGC1, type R/W, offset 0x104, reset 0x00000000
COMP2 COMP1 COMP0 TIMER3 TIMER2 TIMER1 TIMER0
I2C0 SSI0 UART1 UART0
SCGC1, type R/W, offset 0x114, reset 0x00000000
COMP2 COMP1 COMP0 TIMER3 TIMER2 TIMER1 TIMER0
I2C0 SSI0 UART1 UART0
DCGC1, type R/W, offset 0x124, reset 0x00000000
COMP2 COMP1 COMP0 TIMER3 TIMER2 TIMER1 TIMER0
I2C0 SSI0 UART1 UART0
RCGC2, type R/W, offset 0x108, reset 0x00000000
EPHY0 EMAC0
GPIOG GPIOF GPIOE GPIOD GPIOC GPIOB GPIOA
SCGC2, type R/W, offset 0x118, reset 0x00000000
EPHY0 EMAC0
GPIOG GPIOF GPIOE GPIOD GPIOC GPIOB GPIOA
DCGC2, type R/W, offset 0x128, reset 0x00000000
EPHY0 EMAC0
GPIOG GPIOF GPIOE GPIOD GPIOC GPIOB GPIOA
SRCR0, type R/W, offset 0x040, reset 0x00000000
CAN0 ADC
HIB WDT
SRCR1, type R/W, offset 0x044, reset 0x00000000
COMP2 COMP1 COMP0 TIMER3 TIMER2 TIMER1 TIMER0
I2C0 SSI0 UART1 UART0
SRCR2, type R/W, offset 0x048, reset 0x00000000
EPHY0 EMAC0
GPIOG GPIOF GPIOE GPIOD GPIOC GPIOB GPIOA
Hibernation Module
Base 0x400F.C000
HIBRTCC, type RO, offset 0x000, reset 0x0000.0000
RTCC
RTCC
HIBRTCM0, type R/W, offset 0x004, reset 0xFFFF.FFFF
RTCM0
RTCM0
HIBRTCM1, type R/W, offset 0x008, reset 0xFFFF.FFFF
RTCM1
RTCM1
HIBRTCLD, type R/W, offset 0x00C, reset 0xFFFF.FFFF
RTCLD
RTCLD
560 March 17, 2008
Preliminary
Register Quick Reference
31 30 29 28 27 26 25 24 23 22 21 20 19 18 17 16
15 14 13 12 11 10 9 8 7 6 5 4 3 2 1 0
HIBCTL, type R/W, offset 0x010, reset 0x0000.0000
VABORT CLK32EN LOWBATEN PINWEN RTCWEN CLKSEL HIBREQ RTCEN
HIBIM, type R/W, offset 0x014, reset 0x0000.0000
EXTW LOWBAT RTCALT1 RTCALT0
HIBRIS, type RO, offset 0x018, reset 0x0000.0000
EXTW LOWBAT RTCALT1 RTCALT0
HIBMIS, type RO, offset 0x01C, reset 0x0000.0000
EXTW LOWBAT RTCALT1 RTCALT0
HIBIC, type R/W1C, offset 0x020, reset 0x0000.0000
EXTW LOWBAT RTCALT1 RTCALT0
HIBRTCT, type R/W, offset 0x024, reset 0x0000.7FFF
TRIM
HIBDATA, type R/W, offset 0x030-0x12C, reset 0x0000.0000
RTD
RTD
Internal Memory
Flash Control Offset
Base 0x400F.D000
FMA, type R/W, offset 0x000, reset 0x0000.0000
OFFSET
OFFSET
FMD, type R/W, offset 0x004, reset 0x0000.0000
DATA
DATA
FMC, type R/W, offset 0x008, reset 0x0000.0000
WRKEY
COMT MERASE ERASE WRITE
FCRIS, type RO, offset 0x00C, reset 0x0000.0000
PRIS ARIS
FCIM, type R/W, offset 0x010, reset 0x0000.0000
PMASK AMASK
FCMISC, type R/W1C, offset 0x014, reset 0x0000.0000
PMISC AMISC
Internal Memory
System Control Offset
Base 0x400F.E000
USECRL, type R/W, offset 0x140, reset 0x31
USEC
FMPRE0, type R/W, offset 0x130 and 0x200, reset 0xFFFF.FFFF
READ_ENABLE
READ_ENABLE
March 17, 2008 561
Preliminary
LM3S8933 Microcontroller
31 30 29 28 27 26 25 24 23 22 21 20 19 18 17 16
15 14 13 12 11 10 9 8 7 6 5 4 3 2 1 0
FMPPE0, type R/W, offset 0x134 and 0x400, reset 0xFFFF.FFFF
PROG_ENABLE
PROG_ENABLE
USER_DBG, type R/W, offset 0x1D0, reset 0xFFFF.FFFE
NW DATA
DATA DBG1 DBG0
USER_REG0, type R/W, offset 0x1E0, reset 0xFFFF.FFFF
NW DATA
DATA
USER_REG1, type R/W, offset 0x1E4, reset 0xFFFF.FFFF
NW DATA
DATA
FMPRE1, type R/W, offset 0x204, reset 0xFFFF.FFFF
READ_ENABLE
READ_ENABLE
FMPRE2, type R/W, offset 0x208, reset 0xFFFF.FFFF
READ_ENABLE
READ_ENABLE
FMPRE3, type R/W, offset 0x20C, reset 0xFFFF.FFFF
READ_ENABLE
READ_ENABLE
FMPPE1, type R/W, offset 0x404, reset 0xFFFF.FFFF
PROG_ENABLE
PROG_ENABLE
FMPPE2, type R/W, offset 0x408, reset 0xFFFF.FFFF
PROG_ENABLE
PROG_ENABLE
FMPPE3, type R/W, offset 0x40C, reset 0xFFFF.FFFF
PROG_ENABLE
PROG_ENABLE
General-Purpose Input/Outputs (GPIOs)
GPIO Port A base: 0x4000.4000
GPIO Port B base: 0x4000.5000
GPIO Port C base: 0x4000.6000
GPIO Port D base: 0x4000.7000
GPIO Port E base: 0x4002.4000
GPIO Port F base: 0x4002.5000
GPIO Port G base: 0x4002.6000
GPIODATA, type R/W, offset 0x000, reset 0x0000.0000
DATA
GPIODIR, type R/W, offset 0x400, reset 0x0000.0000
DIR
GPIOIS, type R/W, offset 0x404, reset 0x0000.0000
IS
GPIOIBE, type R/W, offset 0x408, reset 0x0000.0000
IBE
GPIOIEV, type R/W, offset 0x40C, reset 0x0000.0000
IEV
562 March 17, 2008
Preliminary
Register Quick Reference
31 30 29 28 27 26 25 24 23 22 21 20 19 18 17 16
15 14 13 12 11 10 9 8 7 6 5 4 3 2 1 0
GPIOIM, type R/W, offset 0x410, reset 0x0000.0000
IME
GPIORIS, type RO, offset 0x414, reset 0x0000.0000
RIS
GPIOMIS, type RO, offset 0x418, reset 0x0000.0000
MIS
GPIOICR, type W1C, offset 0x41C, reset 0x0000.0000
IC
GPIOAFSEL, type R/W, offset 0x420, reset -
AFSEL
GPIODR2R, type R/W, offset 0x500, reset 0x0000.00FF
DRV2
GPIODR4R, type R/W, offset 0x504, reset 0x0000.0000
DRV4
GPIODR8R, type R/W, offset 0x508, reset 0x0000.0000
DRV8
GPIOODR, type R/W, offset 0x50C, reset 0x0000.0000
ODE
GPIOPUR, type R/W, offset 0x510, reset -
PUE
GPIOPDR, type R/W, offset 0x514, reset 0x0000.0000
PDE
GPIOSLR, type R/W, offset 0x518, reset 0x0000.0000
SRL
GPIODEN, type R/W, offset 0x51C, reset -
DEN
GPIOLOCK, type R/W, offset 0x520, reset 0x0000.0001
LOCK
LOCK
GPIOCR, type -, offset 0x524, reset -
CR
GPIOPeriphID4, type RO, offset 0xFD0, reset 0x0000.0000
PID4
GPIOPeriphID5, type RO, offset 0xFD4, reset 0x0000.0000
PID5
March 17, 2008 563
Preliminary
LM3S8933 Microcontroller
31 30 29 28 27 26 25 24 23 22 21 20 19 18 17 16
15 14 13 12 11 10 9 8 7 6 5 4 3 2 1 0
GPIOPeriphID6, type RO, offset 0xFD8, reset 0x0000.0000
PID6
GPIOPeriphID7, type RO, offset 0xFDC, reset 0x0000.0000
PID7
GPIOPeriphID0, type RO, offset 0xFE0, reset 0x0000.0061
PID0
GPIOPeriphID1, type RO, offset 0xFE4, reset 0x0000.0000
PID1
GPIOPeriphID2, type RO, offset 0xFE8, reset 0x0000.0018
PID2
GPIOPeriphID3, type RO, offset 0xFEC, reset 0x0000.0001
PID3
GPIOPCellID0, type RO, offset 0xFF0, reset 0x0000.000D
CID0
GPIOPCellID1, type RO, offset 0xFF4, reset 0x0000.00F0
CID1
GPIOPCellID2, type RO, offset 0xFF8, reset 0x0000.0005
CID2
GPIOPCellID3, type RO, offset 0xFFC, reset 0x0000.00B1
CID3
General-Purpose Timers
Timer0 base: 0x4003.0000
Timer1 base: 0x4003.1000
Timer2 base: 0x4003.2000
Timer3 base: 0x4003.3000
GPTMCFG, type R/W, offset 0x000, reset 0x0000.0000
GPTMCFG
GPTMTAMR, type R/W, offset 0x004, reset 0x0000.0000
TAAMS TACMR TAMR
GPTMTBMR, type R/W, offset 0x008, reset 0x0000.0000
TBAMS TBCMR TBMR
GPTMCTL, type R/W, offset 0x00C, reset 0x0000.0000
TBPWML TBOTE TBEVENT TBSTALL TBEN TAPWML TAOTE RTCEN TAEVENT TASTALL TAEN
GPTMIMR, type R/W, offset 0x018, reset 0x0000.0000
CBEIM CBMIM TBTOIM RTCIM CAEIM CAMIM TATOIM
GPTMRIS, type RO, offset 0x01C, reset 0x0000.0000
CBERIS CBMRIS TBTORIS RTCRIS CAERIS CAMRIS TATORIS
564 March 17, 2008
Preliminary
Register Quick Reference
31 30 29 28 27 26 25 24 23 22 21 20 19 18 17 16
15 14 13 12 11 10 9 8 7 6 5 4 3 2 1 0
GPTMMIS, type RO, offset 0x020, reset 0x0000.0000
CBEMIS CBMMIS TBTOMIS RTCMIS CAEMIS CAMMIS TATOMIS
GPTMICR, type W1C, offset 0x024, reset 0x0000.0000
CBECINT CBMCINT TBTOCINT RTCCINT CAECINT CAMCINT TATOCINT
GPTMTAILR, type R/W, offset 0x028, reset 0x0000.FFFF (16-bit mode) and 0xFFFF.FFFF (32-bit mode)
TAILRH
TAILRL
GPTMTBILR, type R/W, offset 0x02C, reset 0x0000.FFFF
TBILRL
GPTMTAMATCHR, type R/W, offset 0x030, reset 0x0000.FFFF (16-bit mode) and 0xFFFF.FFFF (32-bit mode)
TAMRH
TAMRL
GPTMTBMATCHR, type R/W, offset 0x034, reset 0x0000.FFFF
TBMRL
GPTMTAPR, type R/W, offset 0x038, reset 0x0000.0000
TAPSR
GPTMTBPR, type R/W, offset 0x03C, reset 0x0000.0000
TBPSR
GPTMTAPMR, type R/W, offset 0x040, reset 0x0000.0000
TAPSMR
GPTMTBPMR, type R/W, offset 0x044, reset 0x0000.0000
TBPSMR
GPTMTAR, type RO, offset 0x048, reset 0x0000.FFFF (16-bit mode) and 0xFFFF.FFFF (32-bit mode)
TARH
TARL
GPTMTBR, type RO, offset 0x04C, reset 0x0000.FFFF
TBRL
Watchdog Timer
Base 0x4000.0000
WDTLOAD, type R/W, offset 0x000, reset 0xFFFF.FFFF
WDTLoad
WDTLoad
WDTVALUE, type RO, offset 0x004, reset 0xFFFF.FFFF
WDTValue
WDTValue
WDTCTL, type R/W, offset 0x008, reset 0x0000.0000
RESEN INTEN
WDTICR, type WO, offset 0x00C, reset -
WDTIntClr
WDTIntClr
WDTRIS, type RO, offset 0x010, reset 0x0000.0000
WDTRIS
March 17, 2008 565
Preliminary
LM3S8933 Microcontroller
31 30 29 28 27 26 25 24 23 22 21 20 19 18 17 16
15 14 13 12 11 10 9 8 7 6 5 4 3 2 1 0
WDTMIS, type RO, offset 0x014, reset 0x0000.0000
WDTMIS
WDTTEST, type R/W, offset 0x418, reset 0x0000.0000
STALL
WDTLOCK, type R/W, offset 0xC00, reset 0x0000.0000
WDTLock
WDTLock
WDTPeriphID4, type RO, offset 0xFD0, reset 0x0000.0000
PID4
WDTPeriphID5, type RO, offset 0xFD4, reset 0x0000.0000
PID5
WDTPeriphID6, type RO, offset 0xFD8, reset 0x0000.0000
PID6
WDTPeriphID7, type RO, offset 0xFDC, reset 0x0000.0000
PID7
WDTPeriphID0, type RO, offset 0xFE0, reset 0x0000.0005
PID0
WDTPeriphID1, type RO, offset 0xFE4, reset 0x0000.0018
PID1
WDTPeriphID2, type RO, offset 0xFE8, reset 0x0000.0018
PID2
WDTPeriphID3, type RO, offset 0xFEC, reset 0x0000.0001
PID3
WDTPCellID0, type RO, offset 0xFF0, reset 0x0000.000D
CID0
WDTPCellID1, type RO, offset 0xFF4, reset 0x0000.00F0
CID1
WDTPCellID2, type RO, offset 0xFF8, reset 0x0000.0005
CID2
WDTPCellID3, type RO, offset 0xFFC, reset 0x0000.00B1
CID3
Analog-to-Digital Converter (ADC)
Base 0x4003.8000
ADCACTSS, type R/W, offset 0x000, reset 0x0000.0000
ASEN3 ASEN2 ASEN1 ASEN0
ADCRIS, type RO, offset 0x004, reset 0x0000.0000
INR3 INR2 INR1 INR0
566 March 17, 2008
Preliminary
Register Quick Reference
31 30 29 28 27 26 25 24 23 22 21 20 19 18 17 16
15 14 13 12 11 10 9 8 7 6 5 4 3 2 1 0
ADCIM, type R/W, offset 0x008, reset 0x0000.0000
MASK3 MASK2 MASK1 MASK0
ADCISC, type R/W1C, offset 0x00C, reset 0x0000.0000
IN3 IN2 IN1 IN0
ADCOSTAT, type R/W1C, offset 0x010, reset 0x0000.0000
OV3 OV2 OV1 OV0
ADCEMUX, type R/W, offset 0x014, reset 0x0000.0000
EM3 EM2 EM1 EM0
ADCUSTAT, type R/W1C, offset 0x018, reset 0x0000.0000
UV3 UV2 UV1 UV0
ADCSSPRI, type R/W, offset 0x020, reset 0x0000.3210
SS3 SS2 SS1 SS0
ADCPSSI, type WO, offset 0x028, reset -
SS3 SS2 SS1 SS0
ADCSAC, type R/W, offset 0x030, reset 0x0000.0000
AVG
ADCSSMUX0, type R/W, offset 0x040, reset 0x0000.0000
MUX7 MUX6 MUX5 MUX4
MUX3 MUX2 MUX1 MUX0
ADCSSCTL0, type R/W, offset 0x044, reset 0x0000.0000
TS7 IE7 END7 D7 TS6 IE6 END6 D6 TS5 IE5 END5 D5 TS4 IE4 END4 D4
TS3 IE3 END3 D3 TS2 IE2 END2 D2 TS1 IE1 END1 D1 TS0 IE0 END0 D0
ADCSSFIFO0, type RO, offset 0x048, reset 0x0000.0000
DATA
ADCSSFIFO1, type RO, offset 0x068, reset 0x0000.0000
DATA
ADCSSFIFO2, type RO, offset 0x088, reset 0x0000.0000
DATA
ADCSSFIFO3, type RO, offset 0x0A8, reset 0x0000.0000
DATA
ADCSSFSTAT0, type RO, offset 0x04C, reset 0x0000.0100
FULL EMPTY HPTR TPTR
ADCSSFSTAT1, type RO, offset 0x06C, reset 0x0000.0100
FULL EMPTY HPTR TPTR
ADCSSFSTAT2, type RO, offset 0x08C, reset 0x0000.0100
FULL EMPTY HPTR TPTR
March 17, 2008 567
Preliminary
LM3S8933 Microcontroller
31 30 29 28 27 26 25 24 23 22 21 20 19 18 17 16
15 14 13 12 11 10 9 8 7 6 5 4 3 2 1 0
ADCSSFSTAT3, type RO, offset 0x0AC, reset 0x0000.0100
FULL EMPTY HPTR TPTR
ADCSSMUX1, type R/W, offset 0x060, reset 0x0000.0000
MUX3 MUX2 MUX1 MUX0
ADCSSMUX2, type R/W, offset 0x080, reset 0x0000.0000
MUX3 MUX2 MUX1 MUX0
ADCSSCTL1, type R/W, offset 0x064, reset 0x0000.0000
TS3 IE3 END3 D3 TS2 IE2 END2 D2 TS1 IE1 END1 D1 TS0 IE0 END0 D0
ADCSSCTL2, type R/W, offset 0x084, reset 0x0000.0000
TS3 IE3 END3 D3 TS2 IE2 END2 D2 TS1 IE1 END1 D1 TS0 IE0 END0 D0
ADCSSMUX3, type R/W, offset 0x0A0, reset 0x0000.0000
MUX0
ADCSSCTL3, type R/W, offset 0x0A4, reset 0x0000.0002
TS0 IE0 END0 D0
ADCTMLB, type R/W, offset 0x100, reset 0x0000.0000
LB
Universal Asynchronous Receivers/Transmitters (UARTs)
UART0 base: 0x4000.C000
UART1 base: 0x4000.D000
UARTDR, type R/W, offset 0x000, reset 0x0000.0000
OE BE PE FE DATA
UARTRSR/UARTECR, type RO, offset 0x004, reset 0x0000.0000
OE BE PE FE
UARTRSR/UARTECR, type WO, offset 0x004, reset 0x0000.0000
DATA
UARTFR, type RO, offset 0x018, reset 0x0000.0090
TXFE RXFF TXFF RXFE BUSY
UARTILPR, type R/W, offset 0x020, reset 0x0000.0000
ILPDVSR
UARTIBRD, type R/W, offset 0x024, reset 0x0000.0000
DIVINT
UARTFBRD, type R/W, offset 0x028, reset 0x0000.0000
DIVFRAC
UARTLCRH, type R/W, offset 0x02C, reset 0x0000.0000
SPS WLEN FEN STP2 EPS PEN BRK
568 March 17, 2008
Preliminary
Register Quick Reference
31 30 29 28 27 26 25 24 23 22 21 20 19 18 17 16
15 14 13 12 11 10 9 8 7 6 5 4 3 2 1 0
UARTCTL, type R/W, offset 0x030, reset 0x0000.0300
RXE TXE LBE SIRLP SIREN UARTEN
UARTIFLS, type R/W, offset 0x034, reset 0x0000.0012
RXIFLSEL TXIFLSEL
UARTIM, type R/W, offset 0x038, reset 0x0000.0000
OEIM BEIM PEIM FEIM RTIM TXIM RXIM
UARTRIS, type RO, offset 0x03C, reset 0x0000.000F
OERIS BERIS PERIS FERIS RTRIS TXRIS RXRIS
UARTMIS, type RO, offset 0x040, reset 0x0000.0000
OEMIS BEMIS PEMIS FEMIS RTMIS TXMIS RXMIS
UARTICR, type W1C, offset 0x044, reset 0x0000.0000
OEIC BEIC PEIC FEIC RTIC TXIC RXIC
UARTPeriphID4, type RO, offset 0xFD0, reset 0x0000.0000
PID4
UARTPeriphID5, type RO, offset 0xFD4, reset 0x0000.0000
PID5
UARTPeriphID6, type RO, offset 0xFD8, reset 0x0000.0000
PID6
UARTPeriphID7, type RO, offset 0xFDC, reset 0x0000.0000
PID7
UARTPeriphID0, type RO, offset 0xFE0, reset 0x0000.0011
PID0
UARTPeriphID1, type RO, offset 0xFE4, reset 0x0000.0000
PID1
UARTPeriphID2, type RO, offset 0xFE8, reset 0x0000.0018
PID2
UARTPeriphID3, type RO, offset 0xFEC, reset 0x0000.0001
PID3
UARTPCellID0, type RO, offset 0xFF0, reset 0x0000.000D
CID0
UARTPCellID1, type RO, offset 0xFF4, reset 0x0000.00F0
CID1
UARTPCellID2, type RO, offset 0xFF8, reset 0x0000.0005
CID2
March 17, 2008 569
Preliminary
LM3S8933 Microcontroller
31 30 29 28 27 26 25 24 23 22 21 20 19 18 17 16
15 14 13 12 11 10 9 8 7 6 5 4 3 2 1 0
UARTPCellID3, type RO, offset 0xFFC, reset 0x0000.00B1
CID3
Synchronous Serial Interface (SSI)
SSI0 base: 0x4000.8000
SSICR0, type R/W, offset 0x000, reset 0x0000.0000
SCR SPH SPO FRF DSS
SSICR1, type R/W, offset 0x004, reset 0x0000.0000
SOD MS SSE LBM
SSIDR, type R/W, offset 0x008, reset 0x0000.0000
DATA
SSISR, type RO, offset 0x00C, reset 0x0000.0003
BSY RFF RNE TNF TFE
SSICPSR, type R/W, offset 0x010, reset 0x0000.0000
CPSDVSR
SSIIM, type R/W, offset 0x014, reset 0x0000.0000
TXIM RXIM RTIM RORIM
SSIRIS, type RO, offset 0x018, reset 0x0000.0008
TXRIS RXRIS RTRIS RORRIS
SSIMIS, type RO, offset 0x01C, reset 0x0000.0000
TXMIS RXMIS RTMIS RORMIS
SSIICR, type W1C, offset 0x020, reset 0x0000.0000
RTIC RORIC
SSIPeriphID4, type RO, offset 0xFD0, reset 0x0000.0000
PID4
SSIPeriphID5, type RO, offset 0xFD4, reset 0x0000.0000
PID5
SSIPeriphID6, type RO, offset 0xFD8, reset 0x0000.0000
PID6
SSIPeriphID7, type RO, offset 0xFDC, reset 0x0000.0000
PID7
SSIPeriphID0, type RO, offset 0xFE0, reset 0x0000.0022
PID0
SSIPeriphID1, type RO, offset 0xFE4, reset 0x0000.0000
PID1
SSIPeriphID2, type RO, offset 0xFE8, reset 0x0000.0018
PID2
570 March 17, 2008
Preliminary
Register Quick Reference
31 30 29 28 27 26 25 24 23 22 21 20 19 18 17 16
15 14 13 12 11 10 9 8 7 6 5 4 3 2 1 0
SSIPeriphID3, type RO, offset 0xFEC, reset 0x0000.0001
PID3
SSIPCellID0, type RO, offset 0xFF0, reset 0x0000.000D
CID0
SSIPCellID1, type RO, offset 0xFF4, reset 0x0000.00F0
CID1
SSIPCellID2, type RO, offset 0xFF8, reset 0x0000.0005
CID2
SSIPCellID3, type RO, offset 0xFFC, reset 0x0000.00B1
CID3
Inter-Integrated Circuit (I2C) Interface
I2C Master
I2C Master 0 base: 0x4002.0000
I2CMSA, type R/W, offset 0x000, reset 0x0000.0000
SA R/S
I2CMCS, type RO, offset 0x004, reset 0x0000.0000
BUSBSY IDLE ARBLST DATACK ADRACK ERROR BUSY
I2CMCS, type WO, offset 0x004, reset 0x0000.0000
ACK STOP START RUN
I2CMDR, type R/W, offset 0x008, reset 0x0000.0000
DATA
I2CMTPR, type R/W, offset 0x00C, reset 0x0000.0001
TPR
I2CMIMR, type R/W, offset 0x010, reset 0x0000.0000
IM
I2CMRIS, type RO, offset 0x014, reset 0x0000.0000
RIS
I2CMMIS, type RO, offset 0x018, reset 0x0000.0000
MIS
I2CMICR, type WO, offset 0x01C, reset 0x0000.0000
IC
I2CMCR, type R/W, offset 0x020, reset 0x0000.0000
SFE MFE LPBK
March 17, 2008 571
Preliminary
LM3S8933 Microcontroller
31 30 29 28 27 26 25 24 23 22 21 20 19 18 17 16
15 14 13 12 11 10 9 8 7 6 5 4 3 2 1 0
Inter-Integrated Circuit (I2C) Interface
I2C Slave
I2C Slave 0 base: 0x4002.0800
I2CSOAR, type R/W, offset 0x000, reset 0x0000.0000
OAR
I2CSCSR, type RO, offset 0x004, reset 0x0000.0000
FBR TREQ RREQ
I2CSCSR, type WO, offset 0x004, reset 0x0000.0000
DA
I2CSDR, type R/W, offset 0x008, reset 0x0000.0000
DATA
I2CSIMR, type R/W, offset 0x00C, reset 0x0000.0000
IM
I2CSRIS, type RO, offset 0x010, reset 0x0000.0000
RIS
I2CSMIS, type RO, offset 0x014, reset 0x0000.0000
MIS
I2CSICR, type WO, offset 0x018, reset 0x0000.0000
IC
Controller Area Network (CAN) Module
CAN0 base: 0x4004.0000
CANCTL, type R/W, offset 0x000, reset 0x0000.0001
Test CCE DAR EIE SIE IE INIT
CANSTS, type R/W, offset 0x004, reset 0x0000.0000
BOff EWarn EPass RxOK TxOK LEC
CANERR, type RO, offset 0x008, reset 0x0000.0000
RP REC TEC
CANBIT, type R/W, offset 0x00C, reset 0x0000.2301
TSeg2 TSeg1 SJW BRP
CANINT, type RO, offset 0x010, reset 0x0000.0000
IntId
CANTST, type R/W, offset 0x014, reset 0x0000.0000
Rx Tx LBack Silent Basic
CANBRPE, type R/W, offset 0x018, reset 0x0000.0000
BRPE
572 March 17, 2008
Preliminary
Register Quick Reference
31 30 29 28 27 26 25 24 23 22 21 20 19 18 17 16
15 14 13 12 11 10 9 8 7 6 5 4 3 2 1 0
CANIF1CRQ, type R/W, offset 0x020, reset 0x0000.0001
Busy MNUM
CANIF2CRQ, type R/W, offset 0x080, reset 0x0000.0001
Busy MNUM
CANIF1CMSK, type R/W, offset 0x024, reset 0x0000.0000
WRNRD Mask Arb Control ClrIntPnd NewDat DataA DataB
CANIF2CMSK, type R/W, offset 0x084, reset 0x0000.0000
WRNRD Mask Arb Control ClrIntPnd NewDat DataA DataB
CANIF1CMSK, type R/W, offset 0x024, reset 0x0000.0000
WRNRD Mask Arb Control TxRqst DataA DataB
CANIF2CMSK, type R/W, offset 0x084, reset 0x0000.0000
WRNRD Mask Arb Control TxRqst DataA DataB
CANIF1MSK1, type R/W, offset 0x028, reset 0x0000.FFFF
Msk
CANIF2MSK1, type R/W, offset 0x088, reset 0x0000.FFFF
Msk
CANIF1MSK2, type R/W, offset 0x02C, reset 0x0000.FFFF
MXtd MDir Msk
CANIF2MSK2, type R/W, offset 0x08C, reset 0x0000.FFFF
MXtd MDir Msk
CANIF1ARB1, type R/W, offset 0x030, reset 0x0000.0000
ID
CANIF2ARB1, type R/W, offset 0x090, reset 0x0000.0000
ID
CANIF1ARB2, type R/W, offset 0x034, reset 0x0000.0000
MsgVal Xtd Dir ID
CANIF2ARB2, type R/W, offset 0x094, reset 0x0000.0000
MsgVal Xtd Dir ID
CANIF1MCTL, type R/W, offset 0x038, reset 0x0000.0000
NewDat MsgLst IntPnd UMask TxIE RxIE RmtEn TxRqst EoB DLC
CANIF2MCTL, type R/W, offset 0x098, reset 0x0000.0000
NewDat MsgLst IntPnd UMask TxIE RxIE RmtEn TxRqst EoB DLC
CANIF1DA1, type R/W, offset 0x03C, reset 0x0000.0000
Data
March 17, 2008 573
Preliminary
LM3S8933 Microcontroller
31 30 29 28 27 26 25 24 23 22 21 20 19 18 17 16
15 14 13 12 11 10 9 8 7 6 5 4 3 2 1 0
CANIF1DA2, type R/W, offset 0x040, reset 0x0000.0000
Data
CANIF1DB1, type R/W, offset 0x044, reset 0x0000.0000
Data
CANIF1DB2, type R/W, offset 0x048, reset 0x0000.0000
Data
CANIF2DA1, type R/W, offset 0x09C, reset 0x0000.0000
Data
CANIF2DA2, type R/W, offset 0x0A0, reset 0x0000.0000
Data
CANIF2DB1, type R/W, offset 0x0A4, reset 0x0000.0000
Data
CANIF2DB2, type R/W, offset 0x0A8, reset 0x0000.0000
Data
CANTXRQ1, type RO, offset 0x100, reset 0x0000.0000
TxRqst
CANTXRQ2, type RO, offset 0x104, reset 0x0000.0000
TxRqst
CANNWDA1, type RO, offset 0x120, reset 0x0000.0000
NewDat
CANNWDA2, type RO, offset 0x124, reset 0x0000.0000
NewDat
CANMSG1INT, type RO, offset 0x140, reset 0x0000.0000
IntPnd
CANMSG2INT, type RO, offset 0x144, reset 0x0000.0000
IntPnd
CANMSG1VAL, type RO, offset 0x160, reset 0x0000.0000
MsgVal
CANMSG2VAL, type RO, offset 0x164, reset 0x0000.0000
MsgVal
Ethernet Controller
Ethernet MAC
Base 0x4004.8000
MACRIS, type RO, offset 0x000, reset 0x0000.0000
PHYINT MDINT RXER FOV TXEMP TXER RXINT
574 March 17, 2008
Preliminary
Register Quick Reference
31 30 29 28 27 26 25 24 23 22 21 20 19 18 17 16
15 14 13 12 11 10 9 8 7 6 5 4 3 2 1 0
MACIACK, type W1C, offset 0x000, reset 0x0000.0000
PHYINT MDINT RXER FOV TXEMP TXER RXINT
MACIM, type R/W, offset 0x004, reset 0x0000.007F
PHYINTM MDINTM RXERM FOVM TXEMPM TXERM RXINTM
MACRCTL, type R/W, offset 0x008, reset 0x0000.0008
RSTFIFO BADCRC PRMS AMUL RXEN
MACTCTL, type R/W, offset 0x00C, reset 0x0000.0000
DUPLEX CRC PADEN TXEN
MACDATA, type RO, offset 0x010, reset 0x0000.0000
RXDATA
RXDATA
MACDATA, type WO, offset 0x010, reset 0x0000.0000
TXDATA
TXDATA
MACIA0, type R/W, offset 0x014, reset 0x0000.0000
MACOCT4 MACOCT3
MACOCT2 MACOCT1
MACIA1, type R/W, offset 0x018, reset 0x0000.0000
MACOCT6 MACOCT5
MACTHR, type R/W, offset 0x01C, reset 0x0000.003F
THRESH
MACMCTL, type R/W, offset 0x020, reset 0x0000.0000
REGADR WRITE START
MACMDV, type R/W, offset 0x024, reset 0x0000.0080
DIV
MACMTXD, type R/W, offset 0x02C, reset 0x0000.0000
MDTX
MACMRXD, type R/W, offset 0x030, reset 0x0000.0000
MDRX
MACNP, type RO, offset 0x034, reset 0x0000.0000
NPR
MACTR, type R/W, offset 0x038, reset 0x0000.0000
NEWTX
MACTS, type R/W, offset 0x03C, reset 0x0000.0000
TSEN
March 17, 2008 575
Preliminary
LM3S8933 Microcontroller
31 30 29 28 27 26 25 24 23 22 21 20 19 18 17 16
15 14 13 12 11 10 9 8 7 6 5 4 3 2 1 0
Ethernet Controller
MII Management
Base 0x4004.8000
MR0, type R/W, address 0x00, reset 0x3100
RESET LOOPBK SPEEDSL ANEGEN PWRDN ISO RANEG DUPLEX COLT
MR1, type RO, address 0x01, reset 0x7849
100X_F 100X_H 10T_F 10T_H MFPS ANEGC RFAULT ANEGA LINK JAB EXTD
MR2, type RO, address 0x02, reset 0x000E
OUI[21:6]
MR3, type RO, address 0x03, reset 0x7237
OUI[5:0] MN RN
MR4, type R/W, address 0x04, reset 0x01E1
NP RF A3 A2 A1 A0 S[4:0]
MR5, type RO, address 0x05, reset 0x0000
NP ACK RF A[7:0] S[4:0]
MR6, type RO, address 0x06, reset 0x0000
PDF LPNPA PRX LPANEGA
MR16, type R/W, address 0x10, reset 0x0140
RPTR INPOL TXHIM SQEI NL10 APOL RVSPOL PCSBP RXCC
MR17, type R/W, address 0x11, reset 0x0000
JABBER_IE RXER_IE PRX_IE PDF_IE LPACK_IE LSCHG_IE RFAULT_IE ANEGCOMP_IE JABBER_INT RXER_INT PRX_INT PDF_INT LPACK_INT LSCHG_INT RFAULT_INT ANEGCOMP_INT
MR18, type RO, address 0x12, reset 0x0000
ANEGF DPLX RATE RXSD RX_LOCK
MR19, type R/W, address 0x13, reset 0x4000
TXO[1:0]
MR23, type R/W, address 0x17, reset 0x0010
LED1[3:0] LED0[3:0]
MR24, type R/W, address 0x18, reset 0x00C0
PD_MODE AUTO_SW MDIX MDIX_CM MDIX_SD
Analog Comparators
Base 0x4003.C000
ACMIS, type R/W1C, offset 0x00, reset 0x0000.0000
IN2 IN1 IN0
ACRIS, type RO, offset 0x04, reset 0x0000.0000
IN2 IN1 IN0
ACINTEN, type R/W, offset 0x08, reset 0x0000.0000
IN2 IN1 IN0
ACREFCTL, type R/W, offset 0x10, reset 0x0000.0000
EN RNG VREF
ACSTAT0, type RO, offset 0x20, reset 0x0000.0000
OVAL
ACSTAT1, type RO, offset 0x40, reset 0x0000.0000
OVAL
ACSTAT2, type RO, offset 0x60, reset 0x0000.0000
OVAL
576 March 17, 2008
Preliminary
Register Quick Reference
31 30 29 28 27 26 25 24 23 22 21 20 19 18 17 16
15 14 13 12 11 10 9 8 7 6 5 4 3 2 1 0
ACCTL0, type R/W, offset 0x24, reset 0x0000.0000
TOEN ASRCP TSLVAL TSEN ISLVAL ISEN CINV
ACCTL1, type R/W, offset 0x44, reset 0x0000.0000
TOEN ASRCP TSLVAL TSEN ISLVAL ISEN CINV
ACCTL2, type R/W, offset 0x64, reset 0x0000.0000
TOEN ASRCP TSLVAL TSEN ISLVAL ISEN CINV
March 17, 2008 577
Preliminary
LM3S8933 Microcontroller
C Ordering and Contact Information
C.1 Ordering Information
L M 3 S n n n n – g p p s s – r r m
Part Number
Temperature
Package
Speed
Revision
Shipping Medium
E=-40 C to 105 C
I = -40 C to 85 C
T = Tape-and-reel
Omitted = Default shipping (tray or tube)
Omitted = Default to current shipping
revision
A0 = First all-layer mask
A1 = Metal layers update to A0
A2 = Metal layers update to A1
B0 = Second all-layer mask revision
etc.
BZ = RoHS-compliant 108-ball BGA
QC = RoHS-compliant 100-pin LQFP
QN = RoHS-compliant 48-pin LQFP
RN = RoHS-compliant 28-pin SOIC
20 = 20 MHz
25 = 25 MHz
50 = 50 MHz
Table C-1. Part Ordering Information
Orderable Part Number Description
Stellaris® LM3S8933-IBZ50 LM3S8933 Microcontroller
Stellaris® LM3S8933-IBZ50 (T) LM3S8933 Microcontroller
Stellaris® LM3S8933-EQC50 LM3S8933 Microcontroller
Stellaris® LM3S8933-EQC50 (T) LM3S8933 Microcontroller
Stellaris® LM3S8933-IQC50 LM3S8933 Microcontroller
Stellaris® LM3S8933-IQC50 (T) LM3S8933 Microcontroller
C.2 Kits
The Luminary Micro Stellaris® Family provides the hardware and software tools that engineers need
to begin development quickly.
■ Reference Design Kits accelerate product development by providing ready-to-run hardware, and
comprehensive documentation including hardware design files:
http://www.luminarymicro.com/products/reference_design_kits/
■ Evaluation Kits provide a low-cost and effective means of evaluating Stellaris® microcontrollers
before purchase:
http://www.luminarymicro.com/products/kits.html
■ Development Kits provide you with all the tools you need to develop and prototype embedded
applications right out of the box:
http://www.luminarymicro.com/products/development_kits.html
See the Luminary Micro website for the latest tools available, or ask your Luminary Micro distributor.
578 March 17, 2008
Preliminary
Ordering and Contact Information
C.3 Company Information
Luminary Micro, Inc. designs, markets, and sells ARM Cortex-M3-based microcontrollers (MCUs).
Austin, Texas-based Luminary Micro is the lead partner for the Cortex-M3 processor, delivering the
world's first silicon implementation of the Cortex-M3 processor. Luminary Micro's introduction of the
Stellaris® family of products provides 32-bit performance for the same price as current 8- and 16-bit
microcontroller designs. With entry-level pricing at $1.00 for an ARM technology-based MCU,
Luminary Micro's Stellaris product line allows for standardization that eliminates future architectural
upgrades or software tool changes.
Luminary Micro, Inc.
108 Wild Basin, Suite 350
Austin, TX 78746
Main: +1-512-279-8800
Fax: +1-512-279-8879
http://www.luminarymicro.com
sales@luminarymicro.com
C.4 Support Information
For support on Luminary Micro products, contact:
support@luminarymicro.com +1-512-279-8800, ext. 3
March 17, 2008 579
Preliminary
LM3S8933 Microcontroller
Stellaris® LM3S2965 Microcontroller
DATA SHEET
Copyright © 2007-2011
Texas Instruments Incorporated
DS-LM3S2965-9102
TEXAS INSTRUMENTS-PRODUCTION DATA
Copyright
Copyright © 2007-2011 Texas Instruments Incorporated All rights reserved. Stellaris and StellarisWare are registered trademarks of Texas Instruments
Incorporated. ARM and Thumb are registered trademarks and Cortex is a trademark of ARM Limited. Other names and brands may be claimed as the
property of others.
PRODUCTION DATA information is current as of publication date. Products conform to specifications per the terms of Texas Instruments standard
warranty. Production processing does not necessarily include testing of all parameters.
Please be aware that an important notice concerning availability, standard warranty, and use in critical applications of Texas Instruments semiconductor
products and disclaimers thereto appears at the end of this data sheet.
Texas Instruments Incorporated
108 Wild Basin, Suite 350
Austin, TX 78746
http://www.ti.com/stellaris
http://www-k.ext.ti.com/sc/technical-support/product-information-centers.htm
2 January 08, 2011
Texas Instruments-Production Data
Table of Contents
Revision History ............................................................................................................................. 25
About This Document .................................................................................................................... 31
Audience .............................................................................................................................................. 31
About This Manual ................................................................................................................................ 31
Related Documents ............................................................................................................................... 31
Documentation Conventions .................................................................................................................. 32
1 Architectural Overview .......................................................................................... 34
1.1 Product Features .......................................................................................................... 34
1.2 Target Applications ........................................................................................................ 43
1.3 High-Level Block Diagram ............................................................................................. 43
1.4 Functional Overview ...................................................................................................... 45
1.4.1 ARM Cortex™-M3 ......................................................................................................... 45
1.4.2 Motor Control Peripherals .............................................................................................. 46
1.4.3 Analog Peripherals ........................................................................................................ 47
1.4.4 Serial Communications Peripherals ................................................................................ 47
1.4.5 System Peripherals ....................................................................................................... 49
1.4.6 Memory Peripherals ...................................................................................................... 50
1.4.7 Additional Features ....................................................................................................... 50
1.4.8 Hardware Details .......................................................................................................... 51
2 The Cortex-M3 Processor ...................................................................................... 52
2.1 Block Diagram .............................................................................................................. 53
2.2 Overview ...................................................................................................................... 54
2.2.1 System-Level Interface .................................................................................................. 54
2.2.2 Integrated Configurable Debug ...................................................................................... 54
2.2.3 Trace Port Interface Unit (TPIU) ..................................................................................... 55
2.2.4 Cortex-M3 System Component Details ........................................................................... 55
2.3 Programming Model ...................................................................................................... 56
2.3.1 Processor Mode and Privilege Levels for Software Execution ........................................... 56
2.3.2 Stacks .......................................................................................................................... 56
2.3.3 Register Map ................................................................................................................ 57
2.3.4 Register Descriptions .................................................................................................... 58
2.3.5 Exceptions and Interrupts .............................................................................................. 71
2.3.6 Data Types ................................................................................................................... 71
2.4 Memory Model .............................................................................................................. 71
2.4.1 Memory Regions, Types and Attributes ........................................................................... 73
2.4.2 Memory System Ordering of Memory Accesses .............................................................. 73
2.4.3 Behavior of Memory Accesses ....................................................................................... 73
2.4.4 Software Ordering of Memory Accesses ......................................................................... 74
2.4.5 Bit-Banding ................................................................................................................... 75
2.4.6 Data Storage ................................................................................................................ 77
2.4.7 Synchronization Primitives ............................................................................................. 78
2.5 Exception Model ........................................................................................................... 79
2.5.1 Exception States ........................................................................................................... 80
2.5.2 Exception Types ............................................................................................................ 80
2.5.3 Exception Handlers ....................................................................................................... 83
January 08, 2011 3
Texas Instruments-Production Data
Stellaris® LM3S2965 Microcontroller
2.5.4 Vector Table .................................................................................................................. 83
2.5.5 Exception Priorities ....................................................................................................... 84
2.5.6 Interrupt Priority Grouping .............................................................................................. 85
2.5.7 Exception Entry and Return ........................................................................................... 85
2.6 Fault Handling .............................................................................................................. 87
2.6.1 Fault Types ................................................................................................................... 87
2.6.2 Fault Escalation and Hard Faults .................................................................................... 88
2.6.3 Fault Status Registers and Fault Address Registers ........................................................ 89
2.6.4 Lockup ......................................................................................................................... 89
2.7 Power Management ...................................................................................................... 89
2.7.1 Entering Sleep Modes ................................................................................................... 90
2.7.2 Wake Up from Sleep Mode ............................................................................................ 90
2.8 Instruction Set Summary ............................................................................................... 91
3 Cortex-M3 Peripherals ........................................................................................... 94
3.1 Functional Description ................................................................................................... 94
3.1.1 System Timer (SysTick) ................................................................................................. 94
3.1.2 Nested Vectored Interrupt Controller (NVIC) .................................................................... 95
3.1.3 System Control Block (SCB) .......................................................................................... 97
3.1.4 Memory Protection Unit (MPU) ....................................................................................... 97
3.2 Register Map .............................................................................................................. 102
3.3 System Timer (SysTick) Register Descriptions .............................................................. 104
3.4 NVIC Register Descriptions .......................................................................................... 108
3.5 System Control Block (SCB) Register Descriptions ........................................................ 121
3.6 Memory Protection Unit (MPU) Register Descriptions .................................................... 148
4 JTAG Interface ...................................................................................................... 158
4.1 Block Diagram ............................................................................................................ 159
4.2 Functional Description ................................................................................................. 159
4.2.1 JTAG Interface Pins ..................................................................................................... 159
4.2.2 JTAG TAP Controller ................................................................................................... 161
4.2.3 Shift Registers ............................................................................................................ 162
4.2.4 Operational Considerations .......................................................................................... 162
4.3 Initialization and Configuration ..................................................................................... 165
4.4 Register Descriptions .................................................................................................. 165
4.4.1 Instruction Register (IR) ............................................................................................... 165
4.4.2 Data Registers ............................................................................................................ 167
5 System Control ..................................................................................................... 170
5.1 Functional Description ................................................................................................. 170
5.1.1 Device Identification .................................................................................................... 170
5.1.2 Reset Control .............................................................................................................. 170
5.1.3 Power Control ............................................................................................................. 174
5.1.4 Clock Control .............................................................................................................. 175
5.1.5 System Control ........................................................................................................... 180
5.2 Initialization and Configuration ..................................................................................... 181
5.3 Register Map .............................................................................................................. 181
5.4 Register Descriptions .................................................................................................. 183
6 Hibernation Module .............................................................................................. 236
6.1 Block Diagram ............................................................................................................ 237
4 January 08, 2011
Texas Instruments-Production Data
Table of Contents
6.2 Functional Description ................................................................................................. 237
6.2.1 Register Access Timing ............................................................................................... 237
6.2.2 Clock Source .............................................................................................................. 238
6.2.3 Battery Management ................................................................................................... 239
6.2.4 Real-Time Clock .......................................................................................................... 240
6.2.5 Non-Volatile Memory ................................................................................................... 240
6.2.6 Power Control ............................................................................................................. 240
6.2.7 Initiating Hibernate ...................................................................................................... 241
6.2.8 Interrupts and Status ................................................................................................... 241
6.3 Initialization and Configuration ..................................................................................... 241
6.3.1 Initialization ................................................................................................................. 242
6.3.2 RTC Match Functionality (No Hibernation) .................................................................... 242
6.3.3 RTC Match/Wake-Up from Hibernation ......................................................................... 242
6.3.4 External Wake-Up from Hibernation .............................................................................. 242
6.3.5 RTC/External Wake-Up from Hibernation ...................................................................... 243
6.4 Register Map .............................................................................................................. 243
6.5 Register Descriptions .................................................................................................. 243
7 Internal Memory ................................................................................................... 256
7.1 Block Diagram ............................................................................................................ 256
7.2 Functional Description ................................................................................................. 256
7.2.1 SRAM Memory ............................................................................................................ 256
7.2.2 Flash Memory ............................................................................................................. 257
7.3 Flash Memory Initialization and Configuration ............................................................... 258
7.3.1 Flash Programming ..................................................................................................... 258
7.3.2 Nonvolatile Register Programming ............................................................................... 259
7.4 Register Map .............................................................................................................. 260
7.5 Flash Register Descriptions (Flash Control Offset) ......................................................... 261
7.6 Flash Register Descriptions (System Control Offset) ...................................................... 269
8 General-Purpose Input/Outputs (GPIOs) ........................................................... 282
8.1 Functional Description ................................................................................................. 282
8.1.1 Data Control ............................................................................................................... 283
8.1.2 Interrupt Control .......................................................................................................... 284
8.1.3 Mode Control .............................................................................................................. 285
8.1.4 Commit Control ........................................................................................................... 285
8.1.5 Pad Control ................................................................................................................. 285
8.1.6 Identification ............................................................................................................... 286
8.2 Initialization and Configuration ..................................................................................... 286
8.3 Register Map .............................................................................................................. 287
8.4 Register Descriptions .................................................................................................. 289
9 General-Purpose Timers ...................................................................................... 324
9.1 Block Diagram ............................................................................................................ 325
9.2 Functional Description ................................................................................................. 326
9.2.1 GPTM Reset Conditions .............................................................................................. 326
9.2.2 32-Bit Timer Operating Modes ...................................................................................... 326
9.2.3 16-Bit Timer Operating Modes ...................................................................................... 327
9.3 Initialization and Configuration ..................................................................................... 331
9.3.1 32-Bit One-Shot/Periodic Timer Mode ........................................................................... 331
9.3.2 32-Bit Real-Time Clock (RTC) Mode ............................................................................. 332
January 08, 2011 5
Texas Instruments-Production Data
Stellaris® LM3S2965 Microcontroller
9.3.3 16-Bit One-Shot/Periodic Timer Mode ........................................................................... 332
9.3.4 16-Bit Input Edge Count Mode ..................................................................................... 333
9.3.5 16-Bit Input Edge Timing Mode .................................................................................... 333
9.3.6 16-Bit PWM Mode ....................................................................................................... 334
9.4 Register Map .............................................................................................................. 334
9.5 Register Descriptions .................................................................................................. 335
10 Watchdog Timer ................................................................................................... 360
10.1 Block Diagram ............................................................................................................ 361
10.2 Functional Description ................................................................................................. 361
10.3 Initialization and Configuration ..................................................................................... 362
10.4 Register Map .............................................................................................................. 362
10.5 Register Descriptions .................................................................................................. 363
11 Analog-to-Digital Converter (ADC) ..................................................................... 384
11.1 Block Diagram ............................................................................................................ 384
11.2 Functional Description ................................................................................................. 385
11.2.1 Sample Sequencers .................................................................................................... 385
11.2.2 Module Control ............................................................................................................ 386
11.2.3 Hardware Sample Averaging Circuit ............................................................................. 387
11.2.4 Analog-to-Digital Converter .......................................................................................... 387
11.2.5 Differential Sampling ................................................................................................... 387
11.2.6 Test Modes ................................................................................................................. 389
11.2.7 Internal Temperature Sensor ........................................................................................ 390
11.3 Initialization and Configuration ..................................................................................... 390
11.3.1 Module Initialization ..................................................................................................... 390
11.3.2 Sample Sequencer Configuration ................................................................................. 391
11.4 Register Map .............................................................................................................. 391
11.5 Register Descriptions .................................................................................................. 392
12 Universal Asynchronous Receivers/Transmitters (UARTs) ............................. 420
12.1 Block Diagram ............................................................................................................ 421
12.2 Functional Description ................................................................................................. 421
12.2.1 Transmit/Receive Logic ............................................................................................... 421
12.2.2 Baud-Rate Generation ................................................................................................. 422
12.2.3 Data Transmission ...................................................................................................... 423
12.2.4 Serial IR (SIR) ............................................................................................................. 423
12.2.5 FIFO Operation ........................................................................................................... 424
12.2.6 Interrupts .................................................................................................................... 424
12.2.7 Loopback Operation .................................................................................................... 425
12.2.8 IrDA SIR block ............................................................................................................ 425
12.3 Initialization and Configuration ..................................................................................... 425
12.4 Register Map .............................................................................................................. 426
12.5 Register Descriptions .................................................................................................. 427
13 Synchronous Serial Interface (SSI) .................................................................... 461
13.1 Block Diagram ............................................................................................................ 461
13.2 Functional Description ................................................................................................. 462
13.2.1 Bit Rate Generation ..................................................................................................... 462
13.2.2 FIFO Operation ........................................................................................................... 462
13.2.3 Interrupts .................................................................................................................... 462
6 January 08, 2011
Texas Instruments-Production Data
Table of Contents
13.2.4 Frame Formats ........................................................................................................... 463
13.3 Initialization and Configuration ..................................................................................... 470
13.4 Register Map .............................................................................................................. 471
13.5 Register Descriptions .................................................................................................. 472
14 Inter-Integrated Circuit (I2C) Interface ................................................................ 498
14.1 Block Diagram ............................................................................................................ 499
14.2 Functional Description ................................................................................................. 499
14.2.1 I2C Bus Functional Overview ........................................................................................ 499
14.2.2 Available Speed Modes ............................................................................................... 501
14.2.3 Interrupts .................................................................................................................... 502
14.2.4 Loopback Operation .................................................................................................... 503
14.2.5 Command Sequence Flow Charts ................................................................................ 503
14.3 Initialization and Configuration ..................................................................................... 510
14.4 Register Map .............................................................................................................. 511
14.5 Register Descriptions (I2C Master) ............................................................................... 512
14.6 Register Descriptions (I2C Slave) ................................................................................. 525
15 Controller Area Network (CAN) Module ............................................................. 534
15.1 Block Diagram ............................................................................................................ 535
15.2 Functional Description ................................................................................................. 535
15.2.1 Initialization ................................................................................................................. 536
15.2.2 Operation ................................................................................................................... 537
15.2.3 Transmitting Message Objects ..................................................................................... 538
15.2.4 Configuring a Transmit Message Object ........................................................................ 538
15.2.5 Updating a Transmit Message Object ........................................................................... 539
15.2.6 Accepting Received Message Objects .......................................................................... 540
15.2.7 Receiving a Data Frame .............................................................................................. 540
15.2.8 Receiving a Remote Frame .......................................................................................... 540
15.2.9 Receive/Transmit Priority ............................................................................................. 541
15.2.10 Configuring a Receive Message Object ........................................................................ 541
15.2.11 Handling of Received Message Objects ........................................................................ 542
15.2.12 Handling of Interrupts .................................................................................................. 545
15.2.13 Test Mode ................................................................................................................... 545
15.2.14 Bit Timing Configuration Error Considerations ............................................................... 547
15.2.15 Bit Time and Bit Rate ................................................................................................... 547
15.2.16 Calculating the Bit Timing Parameters .......................................................................... 549
15.3 Register Map .............................................................................................................. 552
15.4 CAN Register Descriptions .......................................................................................... 553
16 Analog Comparators ............................................................................................ 579
16.1 Block Diagram ............................................................................................................ 580
16.2 Functional Description ................................................................................................. 580
16.2.1 Internal Reference Programming .................................................................................. 581
16.3 Initialization and Configuration ..................................................................................... 582
16.4 Register Map .............................................................................................................. 582
16.5 Register Descriptions .................................................................................................. 583
17 Pulse Width Modulator (PWM) ............................................................................ 591
17.1 Block Diagram ............................................................................................................ 592
17.2 Functional Description ................................................................................................. 593
January 08, 2011 7
Texas Instruments-Production Data
Stellaris® LM3S2965 Microcontroller
17.2.1 PWM Timer ................................................................................................................. 593
17.2.2 PWM Comparators ...................................................................................................... 593
17.2.3 PWM Signal Generator ................................................................................................ 594
17.2.4 Dead-Band Generator ................................................................................................. 595
17.2.5 Interrupt/ADC-Trigger Selector ..................................................................................... 595
17.2.6 Synchronization Methods ............................................................................................ 596
17.2.7 Fault Conditions .......................................................................................................... 596
17.2.8 Output Control Block ................................................................................................... 596
17.3 Initialization and Configuration ..................................................................................... 596
17.4 Register Map .............................................................................................................. 597
17.5 Register Descriptions .................................................................................................. 599
18 Quadrature Encoder Interface (QEI) ................................................................... 629
18.1 Block Diagram ............................................................................................................ 629
18.2 Functional Description ................................................................................................. 630
18.3 Initialization and Configuration ..................................................................................... 632
18.4 Register Map .............................................................................................................. 633
18.5 Register Descriptions .................................................................................................. 633
19 Pin Diagram .......................................................................................................... 646
20 Signal Tables ........................................................................................................ 648
20.1 100-Pin LQFP Package Pin Tables ............................................................................... 648
20.2 108-Pin BGA Package Pin Tables ................................................................................ 662
20.3 Connections for Unused Signals ................................................................................... 676
21 Operating Characteristics ................................................................................... 678
22 Electrical Characteristics .................................................................................... 679
22.1 DC Characteristics ...................................................................................................... 679
22.1.1 Maximum Ratings ....................................................................................................... 679
22.1.2 Recommended DC Operating Conditions ...................................................................... 679
22.1.3 On-Chip Low Drop-Out (LDO) Regulator Characteristics ................................................ 680
22.1.4 GPIO Module Characteristics ....................................................................................... 680
22.1.5 Power Specifications ................................................................................................... 680
22.1.6 Flash Memory Characteristics ...................................................................................... 682
22.1.7 Hibernation ................................................................................................................. 682
22.2 AC Characteristics ....................................................................................................... 682
22.2.1 Load Conditions .......................................................................................................... 682
22.2.2 Clocks ........................................................................................................................ 682
22.2.3 JTAG and Boundary Scan ............................................................................................ 684
22.2.4 Reset ......................................................................................................................... 685
22.2.5 Sleep Modes ............................................................................................................... 687
22.2.6 Hibernation Module ..................................................................................................... 687
22.2.7 General-Purpose I/O (GPIO) ........................................................................................ 688
22.2.8 Analog-to-Digital Converter .......................................................................................... 688
22.2.9 Synchronous Serial Interface (SSI) ............................................................................... 690
22.2.10 Inter-Integrated Circuit (I2C) Interface ........................................................................... 691
22.2.11 Analog Comparator ..................................................................................................... 692
A Serial Flash Loader .............................................................................................. 693
A.1 Serial Flash Loader ..................................................................................................... 693
A.2 Interfaces ................................................................................................................... 693
8 January 08, 2011
Texas Instruments-Production Data
Table of Contents
A.2.1 UART ......................................................................................................................... 693
A.2.2 SSI ............................................................................................................................. 693
A.3 Packet Handling .......................................................................................................... 694
A.3.1 Packet Format ............................................................................................................ 694
A.3.2 Sending Packets ......................................................................................................... 694
A.3.3 Receiving Packets ....................................................................................................... 694
A.4 Commands ................................................................................................................. 695
A.4.1 COMMAND_PING (0X20) ............................................................................................ 695
A.4.2 COMMAND_GET_STATUS (0x23) ............................................................................... 695
A.4.3 COMMAND_DOWNLOAD (0x21) ................................................................................. 695
A.4.4 COMMAND_SEND_DATA (0x24) ................................................................................. 696
A.4.5 COMMAND_RUN (0x22) ............................................................................................. 696
A.4.6 COMMAND_RESET (0x25) ......................................................................................... 696
B Register Quick Reference ................................................................................... 698
C Ordering and Contact Information ..................................................................... 723
C.1 Ordering Information .................................................................................................... 723
C.2 Part Markings .............................................................................................................. 723
C.3 Kits ............................................................................................................................. 724
C.4 Support Information ..................................................................................................... 724
D Package Information ............................................................................................ 725
D.1 100-Pin LQFP Package ............................................................................................... 725
D.1.1 Package Dimensions ................................................................................................... 725
D.1.2 Tray Dimensions ......................................................................................................... 727
D.1.3 Tape and Reel Dimensions .......................................................................................... 727
D.2 108-Ball BGA Package ................................................................................................ 729
D.2.1 Package Dimensions ................................................................................................... 729
D.2.2 Tray Dimensions ......................................................................................................... 731
D.2.3 Tape and Reel Dimensions .......................................................................................... 732
January 08, 2011 9
Texas Instruments-Production Data
Stellaris® LM3S2965 Microcontroller
List of Figures
Figure 1-1. Stellaris LM3S2965 Microcontroller High-Level Block Diagram .............................. 44
Figure 2-1. CPU Block Diagram ............................................................................................. 54
Figure 2-2. TPIU Block Diagram ............................................................................................ 55
Figure 2-3. Cortex-M3 Register Set ........................................................................................ 57
Figure 2-4. Bit-Band Mapping ................................................................................................ 77
Figure 2-5. Data Storage ....................................................................................................... 78
Figure 2-6. Vector table ......................................................................................................... 84
Figure 2-7. Exception Stack Frame ........................................................................................ 86
Figure 3-1. SRD Use Example ............................................................................................. 100
Figure 4-1. JTAG Module Block Diagram .............................................................................. 159
Figure 4-2. Test Access Port State Machine ......................................................................... 162
Figure 4-3. IDCODE Register Format ................................................................................... 168
Figure 4-4. BYPASS Register Format ................................................................................... 168
Figure 4-5. Boundary Scan Register Format ......................................................................... 169
Figure 5-1. Basic RST Configuration .................................................................................... 172
Figure 5-2. External Circuitry to Extend Power-On Reset ....................................................... 172
Figure 5-3. Reset Circuit Controlled by Switch ...................................................................... 173
Figure 5-4. Power Architecture ............................................................................................ 175
Figure 5-5. Main Clock Tree ................................................................................................ 177
Figure 6-1. Hibernation Module Block Diagram ..................................................................... 237
Figure 6-2. Clock Source Using Crystal ................................................................................ 239
Figure 6-3. Clock Source Using Dedicated Oscillator ............................................................. 239
Figure 7-1. Flash Block Diagram .......................................................................................... 256
Figure 8-1. GPIO Port Block Diagram ................................................................................... 283
Figure 8-2. GPIODATA Write Example ................................................................................. 284
Figure 8-3. GPIODATA Read Example ................................................................................. 284
Figure 9-1. GPTM Module Block Diagram ............................................................................ 325
Figure 9-2. 16-Bit Input Edge Count Mode Example .............................................................. 329
Figure 9-3. 16-Bit Input Edge Time Mode Example ............................................................... 330
Figure 9-4. 16-Bit PWM Mode Example ................................................................................ 331
Figure 10-1. WDT Module Block Diagram .............................................................................. 361
Figure 11-1. ADC Module Block Diagram ............................................................................... 385
Figure 11-2. Differential Sampling Range, VIN_ODD = 1.5 V ...................................................... 388
Figure 11-3. Differential Sampling Range, VIN_ODD = 0.75 V .................................................... 389
Figure 11-4. Differential Sampling Range, VIN_ODD = 2.25 V .................................................... 389
Figure 11-5. Internal Temperature Sensor Characteristic ......................................................... 390
Figure 12-1. UART Module Block Diagram ............................................................................. 421
Figure 12-2. UART Character Frame ..................................................................................... 422
Figure 12-3. IrDA Data Modulation ......................................................................................... 424
Figure 13-1. SSI Module Block Diagram ................................................................................. 461
Figure 13-2. TI Synchronous Serial Frame Format (Single Transfer) ........................................ 464
Figure 13-3. TI Synchronous Serial Frame Format (Continuous Transfer) ................................ 464
Figure 13-4. Freescale SPI Format (Single Transfer) with SPO=0 and SPH=0 .......................... 465
Figure 13-5. Freescale SPI Format (Continuous Transfer) with SPO=0 and SPH=0 .................. 465
Figure 13-6. Freescale SPI Frame Format with SPO=0 and SPH=1 ......................................... 466
Figure 13-7. Freescale SPI Frame Format (Single Transfer) with SPO=1 and SPH=0 ............... 467
10 January 08, 2011
Texas Instruments-Production Data
Table of Contents
Figure 13-8. Freescale SPI Frame Format (Continuous Transfer) with SPO=1 and SPH=0 ........ 467
Figure 13-9. Freescale SPI Frame Format with SPO=1 and SPH=1 ......................................... 468
Figure 13-10. MICROWIRE Frame Format (Single Frame) ........................................................ 469
Figure 13-11. MICROWIRE Frame Format (Continuous Transfer) ............................................. 470
Figure 13-12. MICROWIRE Frame Format, SSIFss Input Setup and Hold Requirements ............ 470
Figure 14-1. I2C Block Diagram ............................................................................................. 499
Figure 14-2. I2C Bus Configuration ........................................................................................ 499
Figure 14-3. START and STOP Conditions ............................................................................. 500
Figure 14-4. Complete Data Transfer with a 7-Bit Address ....................................................... 500
Figure 14-5. R/S Bit in First Byte ............................................................................................ 500
Figure 14-6. Data Validity During Bit Transfer on the I2C Bus ................................................... 501
Figure 14-7. Master Single SEND .......................................................................................... 504
Figure 14-8. Master Single RECEIVE ..................................................................................... 505
Figure 14-9. Master Burst SEND ........................................................................................... 506
Figure 14-10. Master Burst RECEIVE ...................................................................................... 507
Figure 14-11. Master Burst RECEIVE after Burst SEND ............................................................ 508
Figure 14-12. Master Burst SEND after Burst RECEIVE ............................................................ 509
Figure 14-13. Slave Command Sequence ................................................................................ 510
Figure 15-1. CAN Controller Block Diagram ............................................................................ 535
Figure 15-2. CAN Data/Remote Frame .................................................................................. 536
Figure 15-3. Message Objects in a FIFO Buffer ...................................................................... 544
Figure 15-4. CAN Bit Time .................................................................................................... 548
Figure 16-1. Analog Comparator Module Block Diagram ......................................................... 580
Figure 16-2. Structure of Comparator Unit .............................................................................. 581
Figure 16-3. Comparator Internal Reference Structure ............................................................ 581
Figure 17-1. PWM Unit Diagram ............................................................................................ 592
Figure 17-2. PWM Module Block Diagram .............................................................................. 593
Figure 17-3. PWM Count-Down Mode .................................................................................... 594
Figure 17-4. PWM Count-Up/Down Mode .............................................................................. 594
Figure 17-5. PWM Generation Example In Count-Up/Down Mode ........................................... 595
Figure 17-6. PWM Dead-Band Generator ............................................................................... 595
Figure 18-1. QEI Block Diagram ............................................................................................ 630
Figure 18-2. Quadrature Encoder and Velocity Predivider Operation ........................................ 631
Figure 19-1. 100-Pin LQFP Package Pin Diagram .................................................................. 646
Figure 19-2. 108-Ball BGA Package Pin Diagram (Top View) ................................................... 647
Figure 22-1. Load Conditions ................................................................................................ 682
Figure 22-2. JTAG Test Clock Input Timing ............................................................................. 685
Figure 22-3. JTAG Test Access Port (TAP) Timing .................................................................. 685
Figure 22-4. JTAG TRST Timing ............................................................................................ 685
Figure 22-5. External Reset Timing (RST) .............................................................................. 686
Figure 22-6. Power-On Reset Timing ..................................................................................... 686
Figure 22-7. Brown-Out Reset Timing .................................................................................... 686
Figure 22-8. Software Reset Timing ....................................................................................... 687
Figure 22-9. Watchdog Reset Timing ..................................................................................... 687
Figure 22-10. Hibernation Module Timing ................................................................................. 688
Figure 22-11. ADC Input Equivalency Diagram ......................................................................... 689
Figure 22-12. SSI Timing for TI Frame Format (FRF=01), Single Transfer Timing
Measurement .................................................................................................... 690
January 08, 2011 11
Texas Instruments-Production Data
Stellaris® LM3S2965 Microcontroller
Figure 22-13. SSI Timing for MICROWIRE Frame Format (FRF=10), Single Transfer ................. 691
Figure 22-14. SSI Timing for SPI Frame Format (FRF=00), with SPH=1 ..................................... 691
Figure 22-15. I2C Timing ......................................................................................................... 692
Figure D-1. 100-Pin LQFP Package Dimensions ................................................................... 725
Figure D-2. 100-Pin LQFP Tray Dimensions .......................................................................... 727
Figure D-3. 100-Pin LQFP Tape and Reel Dimensions ........................................................... 728
Figure D-4. 108-Ball BGA Package Dimensions .................................................................... 729
Figure D-5. 108-Ball BGA Tray Dimensions ........................................................................... 731
Figure D-6. 108-Ball BGA Tape and Reel Dimensions ............................................................ 732
12 January 08, 2011
Texas Instruments-Production Data
Table of Contents
List of Tables
Table 1. Revision History .................................................................................................. 25
Table 2. Documentation Conventions ................................................................................ 32
Table 2-1. Summary of Processor Mode, Privilege Level, and Stack Use ................................ 57
Table 2-2. Processor Register Map ....................................................................................... 58
Table 2-3. PSR Register Combinations ................................................................................. 63
Table 2-4. Memory Map ....................................................................................................... 71
Table 2-5. Memory Access Behavior ..................................................................................... 74
Table 2-6. SRAM Memory Bit-Banding Regions .................................................................... 76
Table 2-7. Peripheral Memory Bit-Banding Regions ............................................................... 76
Table 2-8. Exception Types .................................................................................................. 81
Table 2-9. Interrupts ............................................................................................................ 82
Table 2-10. Exception Return Behavior ................................................................................... 87
Table 2-11. Faults ................................................................................................................. 88
Table 2-12. Fault Status and Fault Address Registers .............................................................. 89
Table 2-13. Cortex-M3 Instruction Summary ........................................................................... 91
Table 3-1. Core Peripheral Register Regions ......................................................................... 94
Table 3-2. Memory Attributes Summary ................................................................................ 97
Table 3-3. TEX, S, C, and B Bit Field Encoding ................................................................... 100
Table 3-4. Cache Policy for Memory Attribute Encoding ....................................................... 101
Table 3-5. AP Bit Field Encoding ........................................................................................ 101
Table 3-6. Memory Region Attributes for Stellaris Microcontrollers ........................................ 101
Table 3-7. Peripherals Register Map ................................................................................... 102
Table 3-8. Interrupt Priority Levels ...................................................................................... 127
Table 3-9. Example SIZE Field Values ................................................................................ 155
Table 4-1. JTAG Port Pins Reset State ............................................................................... 160
Table 4-2. JTAG Instruction Register Commands ................................................................. 165
Table 5-1. Reset Sources ................................................................................................... 170
Table 5-2. Clock Source Options ........................................................................................ 176
Table 5-3. Possible System Clock Frequencies Using the SYSDIV Field ............................... 178
Table 5-4. Examples of Possible System Clock Frequencies Using the SYSDIV2 Field .......... 178
Table 5-5. System Control Register Map ............................................................................. 182
Table 5-6. RCC2 Fields that Override RCC fields ................................................................. 197
Table 6-1. Hibernation Module Register Map ....................................................................... 243
Table 7-1. Flash Protection Policy Combinations ................................................................. 257
Table 7-2. User-Programmable Flash Memory Resident Registers ....................................... 259
Table 7-3. Flash Register Map ............................................................................................ 260
Table 8-1. GPIO Pad Configuration Examples ..................................................................... 286
Table 8-2. GPIO Interrupt Configuration Example ................................................................ 286
Table 8-3. GPIO Register Map ........................................................................................... 288
Table 9-1. Available CCP Pins ............................................................................................ 325
Table 9-2. 16-Bit Timer With Prescaler Configurations ......................................................... 328
Table 9-3. Timers Register Map .......................................................................................... 334
Table 10-1. Watchdog Timer Register Map ............................................................................ 362
Table 11-1. Samples and FIFO Depth of Sequencers ............................................................ 385
Table 11-2. Differential Sampling Pairs ................................................................................. 387
Table 11-3. ADC Register Map ............................................................................................. 391
January 08, 2011 13
Texas Instruments-Production Data
Stellaris® LM3S2965 Microcontroller
Table 12-1. UART Register Map ........................................................................................... 427
Table 13-1. SSI Register Map .............................................................................................. 472
Table 14-1. Examples of I2C Master Timer Period versus Speed Mode ................................... 502
Table 14-2. Inter-Integrated Circuit (I2C) Interface Register Map ............................................. 511
Table 14-3. Write Field Decoding for I2CMCS[3:0] Field (Sheet 1 of 3) .................................... 516
Table 15-1. CAN Protocol Ranges ........................................................................................ 548
Table 15-2. CANBIT Register Values .................................................................................... 548
Table 15-3. CAN Register Map ............................................................................................. 552
Table 16-1. Internal Reference Voltage and ACREFCTL Field Values ..................................... 581
Table 16-2. Analog Comparators Register Map ..................................................................... 583
Table 17-1. PWM Register Map ............................................................................................ 598
Table 18-1. QEI Register Map .............................................................................................. 633
Table 20-1. Signals by Pin Number ....................................................................................... 648
Table 20-2. Signals by Signal Name ..................................................................................... 652
Table 20-3. Signals by Function, Except for GPIO ................................................................. 657
Table 20-4. GPIO Pins and Alternate Functions ..................................................................... 660
Table 20-5. Signals by Pin Number ....................................................................................... 662
Table 20-6. Signals by Signal Name ..................................................................................... 666
Table 20-7. Signals by Function, Except for GPIO ................................................................. 671
Table 20-8. GPIO Pins and Alternate Functions ..................................................................... 674
Table 20-9. Connections for Unused Signals (100-pin LQFP) ................................................. 676
Table 20-10. Connections for Unused Signals, 108-pin BGA .................................................... 676
Table 21-1. Temperature Characteristics ............................................................................... 678
Table 21-2. Thermal Characteristics ..................................................................................... 678
Table 21-3. ESD Absolute Maximum Ratings ........................................................................ 678
Table 22-1. Maximum Ratings .............................................................................................. 679
Table 22-2. Recommended DC Operating Conditions ............................................................ 679
Table 22-3. LDO Regulator Characteristics ........................................................................... 680
Table 22-4. GPIO Module DC Characteristics ........................................................................ 680
Table 22-5. Detailed Power Specifications ............................................................................ 681
Table 22-6. Flash Memory Characteristics ............................................................................ 682
Table 22-7. Hibernation Module DC Characteristics ............................................................... 682
Table 22-8. Phase Locked Loop (PLL) Characteristics ........................................................... 682
Table 22-9. Actual PLL Frequency ........................................................................................ 683
Table 22-10. Clock Characteristics ......................................................................................... 683
Table 22-11. Crystal Characteristics ....................................................................................... 683
Table 22-12. System Clock Characteristics with ADC Operation ............................................... 684
Table 22-13. JTAG Characteristics ......................................................................................... 684
Table 22-14. Reset Characteristics ......................................................................................... 685
Table 22-15. Sleep Modes AC Characteristics ......................................................................... 687
Table 22-16. Hibernation Module AC Characteristics ............................................................... 687
Table 22-17. GPIO Characteristics ......................................................................................... 688
Table 22-18. ADC Characteristics ........................................................................................... 688
Table 22-19. ADC Module Internal Reference Characteristics .................................................. 689
Table 22-20. SSI Characteristics ............................................................................................ 690
Table 22-21. I2C Characteristics ............................................................................................. 691
Table 22-22. Analog Comparator Characteristics ..................................................................... 692
Table 22-23. Analog Comparator Voltage Reference Characteristics ........................................ 692
14 January 08, 2011
Texas Instruments-Production Data
Table of Contents
Table C-1. Part Ordering Information ................................................................................... 723
January 08, 2011 15
Texas Instruments-Production Data
Stellaris® LM3S2965 Microcontroller
List of Registers
The Cortex-M3 Processor ............................................................................................................. 52
Register 1: Cortex General-Purpose Register 0 (R0) ........................................................................... 59
Register 2: Cortex General-Purpose Register 1 (R1) ........................................................................... 59
Register 3: Cortex General-Purpose Register 2 (R2) ........................................................................... 59
Register 4: Cortex General-Purpose Register 3 (R3) ........................................................................... 59
Register 5: Cortex General-Purpose Register 4 (R4) ........................................................................... 59
Register 6: Cortex General-Purpose Register 5 (R5) ........................................................................... 59
Register 7: Cortex General-Purpose Register 6 (R6) ........................................................................... 59
Register 8: Cortex General-Purpose Register 7 (R7) ........................................................................... 59
Register 9: Cortex General-Purpose Register 8 (R8) ........................................................................... 59
Register 10: Cortex General-Purpose Register 9 (R9) ........................................................................... 59
Register 11: Cortex General-Purpose Register 10 (R10) ....................................................................... 59
Register 12: Cortex General-Purpose Register 11 (R11) ........................................................................ 59
Register 13: Cortex General-Purpose Register 12 (R12) ....................................................................... 59
Register 14: Stack Pointer (SP) ........................................................................................................... 60
Register 15: Link Register (LR) ............................................................................................................ 61
Register 16: Program Counter (PC) ..................................................................................................... 62
Register 17: Program Status Register (PSR) ........................................................................................ 63
Register 18: Priority Mask Register (PRIMASK) .................................................................................... 67
Register 19: Fault Mask Register (FAULTMASK) .................................................................................. 68
Register 20: Base Priority Mask Register (BASEPRI) ............................................................................ 69
Register 21: Control Register (CONTROL) ........................................................................................... 70
Cortex-M3 Peripherals ................................................................................................................... 94
Register 1: SysTick Control and Status Register (STCTRL), offset 0x010 ........................................... 105
Register 2: SysTick Reload Value Register (STRELOAD), offset 0x014 .............................................. 107
Register 3: SysTick Current Value Register (STCURRENT), offset 0x018 ........................................... 108
Register 4: Interrupt 0-31 Set Enable (EN0), offset 0x100 .................................................................. 109
Register 5: Interrupt 32-43 Set Enable (EN1), offset 0x104 ................................................................ 110
Register 6: Interrupt 0-31 Clear Enable (DIS0), offset 0x180 .............................................................. 111
Register 7: Interrupt 32-43 Clear Enable (DIS1), offset 0x184 ............................................................ 112
Register 8: Interrupt 0-31 Set Pending (PEND0), offset 0x200 ........................................................... 113
Register 9: Interrupt 32-43 Set Pending (PEND1), offset 0x204 ......................................................... 114
Register 10: Interrupt 0-31 Clear Pending (UNPEND0), offset 0x280 ................................................... 115
Register 11: Interrupt 32-43 Clear Pending (UNPEND1), offset 0x284 .................................................. 116
Register 12: Interrupt 0-31 Active Bit (ACTIVE0), offset 0x300 ............................................................. 117
Register 13: Interrupt 32-43 Active Bit (ACTIVE1), offset 0x304 ........................................................... 118
Register 14: Interrupt 0-3 Priority (PRI0), offset 0x400 ......................................................................... 119
Register 15: Interrupt 4-7 Priority (PRI1), offset 0x404 ......................................................................... 119
Register 16: Interrupt 8-11 Priority (PRI2), offset 0x408 ....................................................................... 119
Register 17: Interrupt 12-15 Priority (PRI3), offset 0x40C .................................................................... 119
Register 18: Interrupt 16-19 Priority (PRI4), offset 0x410 ..................................................................... 119
Register 19: Interrupt 20-23 Priority (PRI5), offset 0x414 ..................................................................... 119
Register 20: Interrupt 24-27 Priority (PRI6), offset 0x418 ..................................................................... 119
Register 21: Interrupt 28-31 Priority (PRI7), offset 0x41C .................................................................... 119
Register 22: Interrupt 32-35 Priority (PRI8), offset 0x420 ..................................................................... 119
16 January 08, 2011
Texas Instruments-Production Data
Table of Contents
Register 23: Interrupt 36-39 Priority (PRI9), offset 0x424 ..................................................................... 119
Register 24: Interrupt 40-43 Priority (PRI10), offset 0x428 ................................................................... 119
Register 25: Software Trigger Interrupt (SWTRIG), offset 0xF00 .......................................................... 121
Register 26: CPU ID Base (CPUID), offset 0xD00 ............................................................................... 122
Register 27: Interrupt Control and State (INTCTRL), offset 0xD04 ........................................................ 123
Register 28: Vector Table Offset (VTABLE), offset 0xD08 .................................................................... 126
Register 29: Application Interrupt and Reset Control (APINT), offset 0xD0C ......................................... 127
Register 30: System Control (SYSCTRL), offset 0xD10 ....................................................................... 129
Register 31: Configuration and Control (CFGCTRL), offset 0xD14 ....................................................... 131
Register 32: System Handler Priority 1 (SYSPRI1), offset 0xD18 ......................................................... 133
Register 33: System Handler Priority 2 (SYSPRI2), offset 0xD1C ........................................................ 134
Register 34: System Handler Priority 3 (SYSPRI3), offset 0xD20 ......................................................... 135
Register 35: System Handler Control and State (SYSHNDCTRL), offset 0xD24 .................................... 136
Register 36: Configurable Fault Status (FAULTSTAT), offset 0xD28 ..................................................... 140
Register 37: Hard Fault Status (HFAULTSTAT), offset 0xD2C .............................................................. 146
Register 38: Memory Management Fault Address (MMADDR), offset 0xD34 ........................................ 147
Register 39: Bus Fault Address (FAULTADDR), offset 0xD38 .............................................................. 148
Register 40: MPU Type (MPUTYPE), offset 0xD90 ............................................................................. 149
Register 41: MPU Control (MPUCTRL), offset 0xD94 .......................................................................... 150
Register 42: MPU Region Number (MPUNUMBER), offset 0xD98 ....................................................... 152
Register 43: MPU Region Base Address (MPUBASE), offset 0xD9C ................................................... 153
Register 44: MPU Region Base Address Alias 1 (MPUBASE1), offset 0xDA4 ....................................... 153
Register 45: MPU Region Base Address Alias 2 (MPUBASE2), offset 0xDAC ...................................... 153
Register 46: MPU Region Base Address Alias 3 (MPUBASE3), offset 0xDB4 ....................................... 153
Register 47: MPU Region Attribute and Size (MPUATTR), offset 0xDA0 ............................................... 155
Register 48: MPU Region Attribute and Size Alias 1 (MPUATTR1), offset 0xDA8 .................................. 155
Register 49: MPU Region Attribute and Size Alias 2 (MPUATTR2), offset 0xDB0 .................................. 155
Register 50: MPU Region Attribute and Size Alias 3 (MPUATTR3), offset 0xDB8 .................................. 155
System Control ............................................................................................................................ 170
Register 1: Device Identification 0 (DID0), offset 0x000 ..................................................................... 184
Register 2: Brown-Out Reset Control (PBORCTL), offset 0x030 ........................................................ 186
Register 3: LDO Power Control (LDOPCTL), offset 0x034 ................................................................. 187
Register 4: Raw Interrupt Status (RIS), offset 0x050 .......................................................................... 188
Register 5: Interrupt Mask Control (IMC), offset 0x054 ...................................................................... 189
Register 6: Masked Interrupt Status and Clear (MISC), offset 0x058 .................................................. 190
Register 7: Reset Cause (RESC), offset 0x05C ................................................................................ 191
Register 8: Run-Mode Clock Configuration (RCC), offset 0x060 ......................................................... 192
Register 9: XTAL to PLL Translation (PLLCFG), offset 0x064 ............................................................. 196
Register 10: Run-Mode Clock Configuration 2 (RCC2), offset 0x070 .................................................... 197
Register 11: Deep Sleep Clock Configuration (DSLPCLKCFG), offset 0x144 ........................................ 199
Register 12: Device Identification 1 (DID1), offset 0x004 ..................................................................... 200
Register 13: Device Capabilities 0 (DC0), offset 0x008 ........................................................................ 202
Register 14: Device Capabilities 1 (DC1), offset 0x010 ........................................................................ 203
Register 15: Device Capabilities 2 (DC2), offset 0x014 ........................................................................ 205
Register 16: Device Capabilities 3 (DC3), offset 0x018 ........................................................................ 207
Register 17: Device Capabilities 4 (DC4), offset 0x01C ....................................................................... 209
Register 18: Run Mode Clock Gating Control Register 0 (RCGC0), offset 0x100 ................................... 210
Register 19: Sleep Mode Clock Gating Control Register 0 (SCGC0), offset 0x110 ................................. 212
January 08, 2011 17
Texas Instruments-Production Data
Stellaris® LM3S2965 Microcontroller
Register 20: Deep Sleep Mode Clock Gating Control Register 0 (DCGC0), offset 0x120 ....................... 214
Register 21: Run Mode Clock Gating Control Register 1 (RCGC1), offset 0x104 ................................... 216
Register 22: Sleep Mode Clock Gating Control Register 1 (SCGC1), offset 0x114 ................................. 219
Register 23: Deep Sleep Mode Clock Gating Control Register 1 (DCGC1), offset 0x124 ....................... 222
Register 24: Run Mode Clock Gating Control Register 2 (RCGC2), offset 0x108 ................................... 225
Register 25: Sleep Mode Clock Gating Control Register 2 (SCGC2), offset 0x118 ................................. 227
Register 26: Deep Sleep Mode Clock Gating Control Register 2 (DCGC2), offset 0x128 ....................... 229
Register 27: Software Reset Control 0 (SRCR0), offset 0x040 ............................................................. 231
Register 28: Software Reset Control 1 (SRCR1), offset 0x044 ............................................................. 233
Register 29: Software Reset Control 2 (SRCR2), offset 0x048 ............................................................. 235
Hibernation Module ..................................................................................................................... 236
Register 1: Hibernation RTC Counter (HIBRTCC), offset 0x000 ......................................................... 244
Register 2: Hibernation RTC Match 0 (HIBRTCM0), offset 0x004 ....................................................... 245
Register 3: Hibernation RTC Match 1 (HIBRTCM1), offset 0x008 ....................................................... 246
Register 4: Hibernation RTC Load (HIBRTCLD), offset 0x00C ........................................................... 247
Register 5: Hibernation Control (HIBCTL), offset 0x010 ..................................................................... 248
Register 6: Hibernation Interrupt Mask (HIBIM), offset 0x014 ............................................................. 250
Register 7: Hibernation Raw Interrupt Status (HIBRIS), offset 0x018 .................................................. 251
Register 8: Hibernation Masked Interrupt Status (HIBMIS), offset 0x01C ............................................ 252
Register 9: Hibernation Interrupt Clear (HIBIC), offset 0x020 ............................................................. 253
Register 10: Hibernation RTC Trim (HIBRTCT), offset 0x024 ............................................................... 254
Register 11: Hibernation Data (HIBDATA), offset 0x030-0x12C ............................................................ 255
Internal Memory ........................................................................................................................... 256
Register 1: Flash Memory Address (FMA), offset 0x000 .................................................................... 262
Register 2: Flash Memory Data (FMD), offset 0x004 ......................................................................... 263
Register 3: Flash Memory Control (FMC), offset 0x008 ..................................................................... 264
Register 4: Flash Controller Raw Interrupt Status (FCRIS), offset 0x00C ............................................ 266
Register 5: Flash Controller Interrupt Mask (FCIM), offset 0x010 ........................................................ 267
Register 6: Flash Controller Masked Interrupt Status and Clear (FCMISC), offset 0x014 ..................... 268
Register 7: USec Reload (USECRL), offset 0x140 ............................................................................ 270
Register 8: Flash Memory Protection Read Enable 0 (FMPRE0), offset 0x130 and 0x200 ................... 271
Register 9: Flash Memory Protection Program Enable 0 (FMPPE0), offset 0x134 and 0x400 ............... 272
Register 10: User Debug (USER_DBG), offset 0x1D0 ......................................................................... 273
Register 11: User Register 0 (USER_REG0), offset 0x1E0 .................................................................. 274
Register 12: User Register 1 (USER_REG1), offset 0x1E4 .................................................................. 275
Register 13: Flash Memory Protection Read Enable 1 (FMPRE1), offset 0x204 .................................... 276
Register 14: Flash Memory Protection Read Enable 2 (FMPRE2), offset 0x208 .................................... 277
Register 15: Flash Memory Protection Read Enable 3 (FMPRE3), offset 0x20C ................................... 278
Register 16: Flash Memory Protection Program Enable 1 (FMPPE1), offset 0x404 ............................... 279
Register 17: Flash Memory Protection Program Enable 2 (FMPPE2), offset 0x408 ............................... 280
Register 18: Flash Memory Protection Program Enable 3 (FMPPE3), offset 0x40C ............................... 281
General-Purpose Input/Outputs (GPIOs) ................................................................................... 282
Register 1: GPIO Data (GPIODATA), offset 0x000 ............................................................................ 290
Register 2: GPIO Direction (GPIODIR), offset 0x400 ......................................................................... 291
Register 3: GPIO Interrupt Sense (GPIOIS), offset 0x404 .................................................................. 292
Register 4: GPIO Interrupt Both Edges (GPIOIBE), offset 0x408 ........................................................ 293
Register 5: GPIO Interrupt Event (GPIOIEV), offset 0x40C ................................................................ 294
Register 6: GPIO Interrupt Mask (GPIOIM), offset 0x410 ................................................................... 295
18 January 08, 2011
Texas Instruments-Production Data
Table of Contents
Register 7: GPIO Raw Interrupt Status (GPIORIS), offset 0x414 ........................................................ 296
Register 8: GPIO Masked Interrupt Status (GPIOMIS), offset 0x418 ................................................... 297
Register 9: GPIO Interrupt Clear (GPIOICR), offset 0x41C ................................................................ 298
Register 10: GPIO Alternate Function Select (GPIOAFSEL), offset 0x420 ............................................ 299
Register 11: GPIO 2-mA Drive Select (GPIODR2R), offset 0x500 ........................................................ 301
Register 12: GPIO 4-mA Drive Select (GPIODR4R), offset 0x504 ........................................................ 302
Register 13: GPIO 8-mA Drive Select (GPIODR8R), offset 0x508 ........................................................ 303
Register 14: GPIO Open Drain Select (GPIOODR), offset 0x50C ......................................................... 304
Register 15: GPIO Pull-Up Select (GPIOPUR), offset 0x510 ................................................................ 305
Register 16: GPIO Pull-Down Select (GPIOPDR), offset 0x514 ........................................................... 306
Register 17: GPIO Slew Rate Control Select (GPIOSLR), offset 0x518 ................................................ 307
Register 18: GPIO Digital Enable (GPIODEN), offset 0x51C ................................................................ 308
Register 19: GPIO Lock (GPIOLOCK), offset 0x520 ............................................................................ 309
Register 20: GPIO Commit (GPIOCR), offset 0x524 ............................................................................ 310
Register 21: GPIO Peripheral Identification 4 (GPIOPeriphID4), offset 0xFD0 ....................................... 312
Register 22: GPIO Peripheral Identification 5 (GPIOPeriphID5), offset 0xFD4 ....................................... 313
Register 23: GPIO Peripheral Identification 6 (GPIOPeriphID6), offset 0xFD8 ....................................... 314
Register 24: GPIO Peripheral Identification 7 (GPIOPeriphID7), offset 0xFDC ...................................... 315
Register 25: GPIO Peripheral Identification 0 (GPIOPeriphID0), offset 0xFE0 ....................................... 316
Register 26: GPIO Peripheral Identification 1 (GPIOPeriphID1), offset 0xFE4 ....................................... 317
Register 27: GPIO Peripheral Identification 2 (GPIOPeriphID2), offset 0xFE8 ....................................... 318
Register 28: GPIO Peripheral Identification 3 (GPIOPeriphID3), offset 0xFEC ...................................... 319
Register 29: GPIO PrimeCell Identification 0 (GPIOPCellID0), offset 0xFF0 .......................................... 320
Register 30: GPIO PrimeCell Identification 1 (GPIOPCellID1), offset 0xFF4 .......................................... 321
Register 31: GPIO PrimeCell Identification 2 (GPIOPCellID2), offset 0xFF8 .......................................... 322
Register 32: GPIO PrimeCell Identification 3 (GPIOPCellID3), offset 0xFFC ......................................... 323
General-Purpose Timers ............................................................................................................. 324
Register 1: GPTM Configuration (GPTMCFG), offset 0x000 .............................................................. 336
Register 2: GPTM TimerA Mode (GPTMTAMR), offset 0x004 ............................................................ 337
Register 3: GPTM TimerB Mode (GPTMTBMR), offset 0x008 ............................................................ 339
Register 4: GPTM Control (GPTMCTL), offset 0x00C ........................................................................ 341
Register 5: GPTM Interrupt Mask (GPTMIMR), offset 0x018 .............................................................. 344
Register 6: GPTM Raw Interrupt Status (GPTMRIS), offset 0x01C ..................................................... 346
Register 7: GPTM Masked Interrupt Status (GPTMMIS), offset 0x020 ................................................ 347
Register 8: GPTM Interrupt Clear (GPTMICR), offset 0x024 .............................................................. 348
Register 9: GPTM TimerA Interval Load (GPTMTAILR), offset 0x028 ................................................. 350
Register 10: GPTM TimerB Interval Load (GPTMTBILR), offset 0x02C ................................................ 351
Register 11: GPTM TimerA Match (GPTMTAMATCHR), offset 0x030 ................................................... 352
Register 12: GPTM TimerB Match (GPTMTBMATCHR), offset 0x034 .................................................. 353
Register 13: GPTM TimerA Prescale (GPTMTAPR), offset 0x038 ........................................................ 354
Register 14: GPTM TimerB Prescale (GPTMTBPR), offset 0x03C ....................................................... 355
Register 15: GPTM TimerA Prescale Match (GPTMTAPMR), offset 0x040 ........................................... 356
Register 16: GPTM TimerB Prescale Match (GPTMTBPMR), offset 0x044 ........................................... 357
Register 17: GPTM TimerA (GPTMTAR), offset 0x048 ........................................................................ 358
Register 18: GPTM TimerB (GPTMTBR), offset 0x04C ....................................................................... 359
Watchdog Timer ........................................................................................................................... 360
Register 1: Watchdog Load (WDTLOAD), offset 0x000 ...................................................................... 364
Register 2: Watchdog Value (WDTVALUE), offset 0x004 ................................................................... 365
January 08, 2011 19
Texas Instruments-Production Data
Stellaris® LM3S2965 Microcontroller
Register 3: Watchdog Control (WDTCTL), offset 0x008 ..................................................................... 366
Register 4: Watchdog Interrupt Clear (WDTICR), offset 0x00C .......................................................... 367
Register 5: Watchdog Raw Interrupt Status (WDTRIS), offset 0x010 .................................................. 368
Register 6: Watchdog Masked Interrupt Status (WDTMIS), offset 0x014 ............................................. 369
Register 7: Watchdog Test (WDTTEST), offset 0x418 ....................................................................... 370
Register 8: Watchdog Lock (WDTLOCK), offset 0xC00 ..................................................................... 371
Register 9: Watchdog Peripheral Identification 4 (WDTPeriphID4), offset 0xFD0 ................................. 372
Register 10: Watchdog Peripheral Identification 5 (WDTPeriphID5), offset 0xFD4 ................................. 373
Register 11: Watchdog Peripheral Identification 6 (WDTPeriphID6), offset 0xFD8 ................................. 374
Register 12: Watchdog Peripheral Identification 7 (WDTPeriphID7), offset 0xFDC ................................ 375
Register 13: Watchdog Peripheral Identification 0 (WDTPeriphID0), offset 0xFE0 ................................. 376
Register 14: Watchdog Peripheral Identification 1 (WDTPeriphID1), offset 0xFE4 ................................. 377
Register 15: Watchdog Peripheral Identification 2 (WDTPeriphID2), offset 0xFE8 ................................. 378
Register 16: Watchdog Peripheral Identification 3 (WDTPeriphID3), offset 0xFEC ................................. 379
Register 17: Watchdog PrimeCell Identification 0 (WDTPCellID0), offset 0xFF0 .................................... 380
Register 18: Watchdog PrimeCell Identification 1 (WDTPCellID1), offset 0xFF4 .................................... 381
Register 19: Watchdog PrimeCell Identification 2 (WDTPCellID2), offset 0xFF8 .................................... 382
Register 20: Watchdog PrimeCell Identification 3 (WDTPCellID3 ), offset 0xFFC .................................. 383
Analog-to-Digital Converter (ADC) ............................................................................................. 384
Register 1: ADC Active Sample Sequencer (ADCACTSS), offset 0x000 ............................................. 393
Register 2: ADC Raw Interrupt Status (ADCRIS), offset 0x004 ........................................................... 394
Register 3: ADC Interrupt Mask (ADCIM), offset 0x008 ..................................................................... 395
Register 4: ADC Interrupt Status and Clear (ADCISC), offset 0x00C .................................................. 396
Register 5: ADC Overflow Status (ADCOSTAT), offset 0x010 ............................................................ 397
Register 6: ADC Event Multiplexer Select (ADCEMUX), offset 0x014 ................................................. 398
Register 7: ADC Underflow Status (ADCUSTAT), offset 0x018 ........................................................... 402
Register 8: ADC Sample Sequencer Priority (ADCSSPRI), offset 0x020 ............................................. 403
Register 9: ADC Processor Sample Sequence Initiate (ADCPSSI), offset 0x028 ................................. 405
Register 10: ADC Sample Averaging Control (ADCSAC), offset 0x030 ................................................. 406
Register 11: ADC Sample Sequence Input Multiplexer Select 0 (ADCSSMUX0), offset 0x040 ............... 407
Register 12: ADC Sample Sequence Control 0 (ADCSSCTL0), offset 0x044 ........................................ 409
Register 13: ADC Sample Sequence Result FIFO 0 (ADCSSFIFO0), offset 0x048 ................................ 412
Register 14: ADC Sample Sequence Result FIFO 1 (ADCSSFIFO1), offset 0x068 ................................ 412
Register 15: ADC Sample Sequence Result FIFO 2 (ADCSSFIFO2), offset 0x088 ................................ 412
Register 16: ADC Sample Sequence Result FIFO 3 (ADCSSFIFO3), offset 0x0A8 ............................... 412
Register 17: ADC Sample Sequence FIFO 0 Status (ADCSSFSTAT0), offset 0x04C ............................. 413
Register 18: ADC Sample Sequence FIFO 1 Status (ADCSSFSTAT1), offset 0x06C ............................. 413
Register 19: ADC Sample Sequence FIFO 2 Status (ADCSSFSTAT2), offset 0x08C ............................ 413
Register 20: ADC Sample Sequence FIFO 3 Status (ADCSSFSTAT3), offset 0x0AC ............................ 413
Register 21: ADC Sample Sequence Input Multiplexer Select 1 (ADCSSMUX1), offset 0x060 ............... 414
Register 22: ADC Sample Sequence Input Multiplexer Select 2 (ADCSSMUX2), offset 0x080 ............... 414
Register 23: ADC Sample Sequence Control 1 (ADCSSCTL1), offset 0x064 ........................................ 415
Register 24: ADC Sample Sequence Control 2 (ADCSSCTL2), offset 0x084 ........................................ 415
Register 25: ADC Sample Sequence Input Multiplexer Select 3 (ADCSSMUX3), offset 0x0A0 ............... 417
Register 26: ADC Sample Sequence Control 3 (ADCSSCTL3), offset 0x0A4 ........................................ 418
Register 27: ADC Test Mode Loopback (ADCTMLB), offset 0x100 ....................................................... 419
Universal Asynchronous Receivers/Transmitters (UARTs) ..................................................... 420
Register 1: UART Data (UARTDR), offset 0x000 ............................................................................... 428
20 January 08, 2011
Texas Instruments-Production Data
Table of Contents
Register 2: UART Receive Status/Error Clear (UARTRSR/UARTECR), offset 0x004 ........................... 430
Register 3: UART Flag (UARTFR), offset 0x018 ................................................................................ 432
Register 4: UART IrDA Low-Power Register (UARTILPR), offset 0x020 ............................................. 434
Register 5: UART Integer Baud-Rate Divisor (UARTIBRD), offset 0x024 ............................................ 435
Register 6: UART Fractional Baud-Rate Divisor (UARTFBRD), offset 0x028 ....................................... 436
Register 7: UART Line Control (UARTLCRH), offset 0x02C ............................................................... 437
Register 8: UART Control (UARTCTL), offset 0x030 ......................................................................... 439
Register 9: UART Interrupt FIFO Level Select (UARTIFLS), offset 0x034 ........................................... 441
Register 10: UART Interrupt Mask (UARTIM), offset 0x038 ................................................................. 443
Register 11: UART Raw Interrupt Status (UARTRIS), offset 0x03C ...................................................... 445
Register 12: UART Masked Interrupt Status (UARTMIS), offset 0x040 ................................................. 446
Register 13: UART Interrupt Clear (UARTICR), offset 0x044 ............................................................... 447
Register 14: UART Peripheral Identification 4 (UARTPeriphID4), offset 0xFD0 ..................................... 449
Register 15: UART Peripheral Identification 5 (UARTPeriphID5), offset 0xFD4 ..................................... 450
Register 16: UART Peripheral Identification 6 (UARTPeriphID6), offset 0xFD8 ..................................... 451
Register 17: UART Peripheral Identification 7 (UARTPeriphID7), offset 0xFDC ..................................... 452
Register 18: UART Peripheral Identification 0 (UARTPeriphID0), offset 0xFE0 ...................................... 453
Register 19: UART Peripheral Identification 1 (UARTPeriphID1), offset 0xFE4 ...................................... 454
Register 20: UART Peripheral Identification 2 (UARTPeriphID2), offset 0xFE8 ...................................... 455
Register 21: UART Peripheral Identification 3 (UARTPeriphID3), offset 0xFEC ..................................... 456
Register 22: UART PrimeCell Identification 0 (UARTPCellID0), offset 0xFF0 ........................................ 457
Register 23: UART PrimeCell Identification 1 (UARTPCellID1), offset 0xFF4 ........................................ 458
Register 24: UART PrimeCell Identification 2 (UARTPCellID2), offset 0xFF8 ........................................ 459
Register 25: UART PrimeCell Identification 3 (UARTPCellID3), offset 0xFFC ........................................ 460
Synchronous Serial Interface (SSI) ............................................................................................ 461
Register 1: SSI Control 0 (SSICR0), offset 0x000 .............................................................................. 473
Register 2: SSI Control 1 (SSICR1), offset 0x004 .............................................................................. 475
Register 3: SSI Data (SSIDR), offset 0x008 ...................................................................................... 477
Register 4: SSI Status (SSISR), offset 0x00C ................................................................................... 478
Register 5: SSI Clock Prescale (SSICPSR), offset 0x010 .................................................................. 480
Register 6: SSI Interrupt Mask (SSIIM), offset 0x014 ......................................................................... 481
Register 7: SSI Raw Interrupt Status (SSIRIS), offset 0x018 .............................................................. 483
Register 8: SSI Masked Interrupt Status (SSIMIS), offset 0x01C ........................................................ 484
Register 9: SSI Interrupt Clear (SSIICR), offset 0x020 ....................................................................... 485
Register 10: SSI Peripheral Identification 4 (SSIPeriphID4), offset 0xFD0 ............................................. 486
Register 11: SSI Peripheral Identification 5 (SSIPeriphID5), offset 0xFD4 ............................................. 487
Register 12: SSI Peripheral Identification 6 (SSIPeriphID6), offset 0xFD8 ............................................. 488
Register 13: SSI Peripheral Identification 7 (SSIPeriphID7), offset 0xFDC ............................................ 489
Register 14: SSI Peripheral Identification 0 (SSIPeriphID0), offset 0xFE0 ............................................. 490
Register 15: SSI Peripheral Identification 1 (SSIPeriphID1), offset 0xFE4 ............................................. 491
Register 16: SSI Peripheral Identification 2 (SSIPeriphID2), offset 0xFE8 ............................................. 492
Register 17: SSI Peripheral Identification 3 (SSIPeriphID3), offset 0xFEC ............................................ 493
Register 18: SSI PrimeCell Identification 0 (SSIPCellID0), offset 0xFF0 ............................................... 494
Register 19: SSI PrimeCell Identification 1 (SSIPCellID1), offset 0xFF4 ............................................... 495
Register 20: SSI PrimeCell Identification 2 (SSIPCellID2), offset 0xFF8 ............................................... 496
Register 21: SSI PrimeCell Identification 3 (SSIPCellID3), offset 0xFFC ............................................... 497
Inter-Integrated Circuit (I2C) Interface ........................................................................................ 498
Register 1: I2C Master Slave Address (I2CMSA), offset 0x000 ........................................................... 513
January 08, 2011 21
Texas Instruments-Production Data
Stellaris® LM3S2965 Microcontroller
Register 2: I2C Master Control/Status (I2CMCS), offset 0x004 ........................................................... 514
Register 3: I2C Master Data (I2CMDR), offset 0x008 ......................................................................... 518
Register 4: I2C Master Timer Period (I2CMTPR), offset 0x00C ........................................................... 519
Register 5: I2C Master Interrupt Mask (I2CMIMR), offset 0x010 ......................................................... 520
Register 6: I2C Master Raw Interrupt Status (I2CMRIS), offset 0x014 ................................................. 521
Register 7: I2C Master Masked Interrupt Status (I2CMMIS), offset 0x018 ........................................... 522
Register 8: I2C Master Interrupt Clear (I2CMICR), offset 0x01C ......................................................... 523
Register 9: I2C Master Configuration (I2CMCR), offset 0x020 ............................................................ 524
Register 10: I2C Slave Own Address (I2CSOAR), offset 0x800 ............................................................ 526
Register 11: I2C Slave Control/Status (I2CSCSR), offset 0x804 ........................................................... 527
Register 12: I2C Slave Data (I2CSDR), offset 0x808 ........................................................................... 529
Register 13: I2C Slave Interrupt Mask (I2CSIMR), offset 0x80C ........................................................... 530
Register 14: I2C Slave Raw Interrupt Status (I2CSRIS), offset 0x810 ................................................... 531
Register 15: I2C Slave Masked Interrupt Status (I2CSMIS), offset 0x814 .............................................. 532
Register 16: I2C Slave Interrupt Clear (I2CSICR), offset 0x818 ............................................................ 533
Controller Area Network (CAN) Module ..................................................................................... 534
Register 1: CAN Control (CANCTL), offset 0x000 ............................................................................. 555
Register 2: CAN Status (CANSTS), offset 0x004 ............................................................................... 557
Register 3: CAN Error Counter (CANERR), offset 0x008 ................................................................... 559
Register 4: CAN Bit Timing (CANBIT), offset 0x00C .......................................................................... 560
Register 5: CAN Interrupt (CANINT), offset 0x010 ............................................................................. 561
Register 6: CAN Test (CANTST), offset 0x014 .................................................................................. 562
Register 7: CAN Baud Rate Prescaler Extension (CANBRPE), offset 0x018 ....................................... 564
Register 8: CAN IF1 Command Request (CANIF1CRQ), offset 0x020 ................................................ 565
Register 9: CAN IF2 Command Request (CANIF2CRQ), offset 0x080 ................................................ 565
Register 10: CAN IF1 Command Mask (CANIF1CMSK), offset 0x024 .................................................. 566
Register 11: CAN IF2 Command Mask (CANIF2CMSK), offset 0x084 .................................................. 566
Register 12: CAN IF1 Mask 1 (CANIF1MSK1), offset 0x028 ................................................................ 568
Register 13: CAN IF2 Mask 1 (CANIF2MSK1), offset 0x088 ................................................................ 568
Register 14: CAN IF1 Mask 2 (CANIF1MSK2), offset 0x02C ................................................................ 569
Register 15: CAN IF2 Mask 2 (CANIF2MSK2), offset 0x08C ................................................................ 569
Register 16: CAN IF1 Arbitration 1 (CANIF1ARB1), offset 0x030 ......................................................... 570
Register 17: CAN IF2 Arbitration 1 (CANIF2ARB1), offset 0x090 ......................................................... 570
Register 18: CAN IF1 Arbitration 2 (CANIF1ARB2), offset 0x034 ......................................................... 571
Register 19: CAN IF2 Arbitration 2 (CANIF2ARB2), offset 0x094 ......................................................... 571
Register 20: CAN IF1 Message Control (CANIF1MCTL), offset 0x038 .................................................. 572
Register 21: CAN IF2 Message Control (CANIF2MCTL), offset 0x098 .................................................. 572
Register 22: CAN IF1 Data A1 (CANIF1DA1), offset 0x03C ................................................................. 574
Register 23: CAN IF1 Data A2 (CANIF1DA2), offset 0x040 ................................................................. 574
Register 24: CAN IF1 Data B1 (CANIF1DB1), offset 0x044 ................................................................. 574
Register 25: CAN IF1 Data B2 (CANIF1DB2), offset 0x048 ................................................................. 574
Register 26: CAN IF2 Data A1 (CANIF2DA1), offset 0x09C ................................................................. 574
Register 27: CAN IF2 Data A2 (CANIF2DA2), offset 0x0A0 ................................................................. 574
Register 28: CAN IF2 Data B1 (CANIF2DB1), offset 0x0A4 ................................................................. 574
Register 29: CAN IF2 Data B2 (CANIF2DB2), offset 0x0A8 ................................................................. 574
Register 30: CAN Transmission Request 1 (CANTXRQ1), offset 0x100 ................................................ 575
Register 31: CAN Transmission Request 2 (CANTXRQ2), offset 0x104 ................................................ 575
22 January 08, 2011
Texas Instruments-Production Data
Table of Contents
Register 32: CAN New Data 1 (CANNWDA1), offset 0x120 ................................................................. 576
Register 33: CAN New Data 2 (CANNWDA2), offset 0x124 ................................................................. 576
Register 34: CAN Message 1 Interrupt Pending (CANMSG1INT), offset 0x140 ..................................... 577
Register 35: CAN Message 2 Interrupt Pending (CANMSG2INT), offset 0x144 ..................................... 577
Register 36: CAN Message 1 Valid (CANMSG1VAL), offset 0x160 ....................................................... 578
Register 37: CAN Message 2 Valid (CANMSG2VAL), offset 0x164 ....................................................... 578
Analog Comparators ................................................................................................................... 579
Register 1: Analog Comparator Masked Interrupt Status (ACMIS), offset 0x000 .................................. 584
Register 2: Analog Comparator Raw Interrupt Status (ACRIS), offset 0x004 ....................................... 585
Register 3: Analog Comparator Interrupt Enable (ACINTEN), offset 0x008 ......................................... 586
Register 4: Analog Comparator Reference Voltage Control (ACREFCTL), offset 0x010 ....................... 587
Register 5: Analog Comparator Status 0 (ACSTAT0), offset 0x020 ..................................................... 588
Register 6: Analog Comparator Status 1 (ACSTAT1), offset 0x040 ..................................................... 588
Register 7: Analog Comparator Status 2 (ACSTAT2), offset 0x060 ..................................................... 588
Register 8: Analog Comparator Control 0 (ACCTL0), offset 0x024 ..................................................... 589
Register 9: Analog Comparator Control 1 (ACCTL1), offset 0x044 ..................................................... 589
Register 10: Analog Comparator Control 2 (ACCTL2), offset 0x064 .................................................... 589
Pulse Width Modulator (PWM) .................................................................................................... 591
Register 1: PWM Master Control (PWMCTL), offset 0x000 ................................................................ 600
Register 2: PWM Time Base Sync (PWMSYNC), offset 0x004 ........................................................... 601
Register 3: PWM Output Enable (PWMENABLE), offset 0x008 .......................................................... 602
Register 4: PWM Output Inversion (PWMINVERT), offset 0x00C ....................................................... 603
Register 5: PWM Output Fault (PWMFAULT), offset 0x010 ................................................................ 604
Register 6: PWM Interrupt Enable (PWMINTEN), offset 0x014 ........................................................... 605
Register 7: PWM Raw Interrupt Status (PWMRIS), offset 0x018 ........................................................ 606
Register 8: PWM Interrupt Status and Clear (PWMISC), offset 0x01C ................................................ 607
Register 9: PWM Status (PWMSTATUS), offset 0x020 ...................................................................... 608
Register 10: PWM0 Control (PWM0CTL), offset 0x040 ....................................................................... 609
Register 11: PWM1 Control (PWM1CTL), offset 0x080 ....................................................................... 609
Register 12: PWM2 Control (PWM2CTL), offset 0x0C0 ...................................................................... 609
Register 13: PWM0 Interrupt and Trigger Enable (PWM0INTEN), offset 0x044 .................................... 611
Register 14: PWM1 Interrupt and Trigger Enable (PWM1INTEN), offset 0x084 .................................... 611
Register 15: PWM2 Interrupt and Trigger Enable (PWM2INTEN), offset 0x0C4 .................................... 611
Register 16: PWM0 Raw Interrupt Status (PWM0RIS), offset 0x048 .................................................... 614
Register 17: PWM1 Raw Interrupt Status (PWM1RIS), offset 0x088 .................................................... 614
Register 18: PWM2 Raw Interrupt Status (PWM2RIS), offset 0x0C8 ................................................... 614
Register 19: PWM0 Interrupt Status and Clear (PWM0ISC), offset 0x04C ........................................... 615
Register 20: PWM1 Interrupt Status and Clear (PWM1ISC), offset 0x08C ........................................... 615
Register 21: PWM2 Interrupt Status and Clear (PWM2ISC), offset 0x0CC ........................................... 615
Register 22: PWM0 Load (PWM0LOAD), offset 0x050 ....................................................................... 616
Register 23: PWM1 Load (PWM1LOAD), offset 0x090 ....................................................................... 616
Register 24: PWM2 Load (PWM2LOAD), offset 0x0D0 ....................................................................... 616
Register 25: PWM0 Counter (PWM0COUNT), offset 0x054 ................................................................ 617
Register 26: PWM1 Counter (PWM1COUNT), offset 0x094 ................................................................ 617
Register 27: PWM2 Counter (PWM2COUNT), offset 0x0D4 ............................................................... 617
Register 28: PWM0 Compare A (PWM0CMPA), offset 0x058 ............................................................. 618
Register 29: PWM1 Compare A (PWM1CMPA), offset 0x098 ............................................................. 618
Register 30: PWM2 Compare A (PWM2CMPA), offset 0x0D8 ............................................................. 618
January 08, 2011 23
Texas Instruments-Production Data
Stellaris® LM3S2965 Microcontroller
Register 31: PWM0 Compare B (PWM0CMPB), offset 0x05C ............................................................. 619
Register 32: PWM1 Compare B (PWM1CMPB), offset 0x09C ............................................................. 619
Register 33: PWM2 Compare B (PWM2CMPB), offset 0x0DC ............................................................ 619
Register 34: PWM0 Generator A Control (PWM0GENA), offset 0x060 ................................................ 620
Register 35: PWM1 Generator A Control (PWM1GENA), offset 0x0A0 ................................................ 620
Register 36: PWM2 Generator A Control (PWM2GENA), offset 0x0E0 ................................................ 620
Register 37: PWM0 Generator B Control (PWM0GENB), offset 0x064 ................................................ 623
Register 38: PWM1 Generator B Control (PWM1GENB), offset 0x0A4 ................................................ 623
Register 39: PWM2 Generator B Control (PWM2GENB), offset 0x0E4 ................................................ 623
Register 40: PWM0 Dead-Band Control (PWM0DBCTL), offset 0x068 ................................................ 626
Register 41: PWM1 Dead-Band Control (PWM1DBCTL), offset 0x0A8 ................................................. 626
Register 42: PWM2 Dead-Band Control (PWM2DBCTL), offset 0x0E8 ................................................ 626
Register 43: PWM0 Dead-Band Rising-Edge Delay (PWM0DBRISE), offset 0x06C ............................. 627
Register 44: PWM1 Dead-Band Rising-Edge Delay (PWM1DBRISE), offset 0x0AC ............................. 627
Register 45: PWM2 Dead-Band Rising-Edge Delay (PWM2DBRISE), offset 0x0EC ............................. 627
Register 46: PWM0 Dead-Band Falling-Edge-Delay (PWM0DBFALL), offset 0x070 ............................. 628
Register 47: PWM1 Dead-Band Falling-Edge-Delay (PWM1DBFALL), offset 0x0B0 ............................. 628
Register 48: PWM2 Dead-Band Falling-Edge-Delay (PWM2DBFALL), offset 0x0F0 ............................. 628
Quadrature Encoder Interface (QEI) .......................................................................................... 629
Register 1: QEI Control (QEICTL), offset 0x000 ................................................................................ 634
Register 2: QEI Status (QEISTAT), offset 0x004 ................................................................................ 636
Register 3: QEI Position (QEIPOS), offset 0x008 .............................................................................. 637
Register 4: QEI Maximum Position (QEIMAXPOS), offset 0x00C ....................................................... 638
Register 5: QEI Timer Load (QEILOAD), offset 0x010 ....................................................................... 639
Register 6: QEI Timer (QEITIME), offset 0x014 ................................................................................. 640
Register 7: QEI Velocity Counter (QEICOUNT), offset 0x018 ............................................................. 641
Register 8: QEI Velocity (QEISPEED), offset 0x01C .......................................................................... 642
Register 9: QEI Interrupt Enable (QEIINTEN), offset 0x020 ............................................................... 643
Register 10: QEI Raw Interrupt Status (QEIRIS), offset 0x024 ............................................................. 644
Register 11: QEI Interrupt Status and Clear (QEIISC), offset 0x028 ..................................................... 645
24 January 08, 2011
Texas Instruments-Production Data
Table of Contents
Revision History
The revision history table notes changes made between the indicated revisions of the LM3S2965
data sheet.
Table 1. Revision History
Date Revision Description
■ In Application Interrupt and Reset Control (APINT) register, changed bit name from SYSRESETREQ
to SYSRESREQ.
■ Added DEBUG (Debug Priority) bit field to System Handler Priority 3 (SYSPRI3) register.
■ Added "Reset Sources" table to System Control chapter.
■ Removed mention of false-start bit detection in the UART chapter. This feature is not supported.
■ Added note that specific module clocks must be enabled before that module's registers can be
programmed. There must be a delay of 3 system clocks after the module clock is enabled before
any of that module's registers are accessed.
■ Changed I2C slave register base addresses and offsets to be relative to the I2C module base address
of 0x4002.0000 and 0x4002.1000, so register bases and offsets were changed for all I2C slave
registers. Note that the hw_i2c.h file in the StellarisWare Driver Library uses a base address of
0x4002.0800 and 0x4002.1800 for the I2C slave registers. Be aware when using registers with
offsets between 0x800 and 0x818 that StellarisWare uses the old slave base address for these
offsets.
■ Added GNDPHY and VCCPHY to Connections for Unused Signals tables.
■ Corrected nonlinearity and offset error parameters (EL, ED and EO) in ADC Characteristics table.
■ Added specification for maximum input voltage on a non-power pin when the microcontroller is
unpowered (VNON parameter in Maximum Ratings table).
■ Additional minor data sheet clarifications and corrections.
January 2011 9102
January 08, 2011 25
Texas Instruments-Production Data
Stellaris® LM3S2965 Microcontroller
Table 1. Revision History (continued)
Date Revision Description
■ Reorganized ARM Cortex-M3 Processor Core, Memory Map and Interrupts chapters, creating two
new chapters, The Cortex-M3 Processor and Cortex-M3 Peripherals. Much additional content was
added, including all the Cortex-M3 registers.
■ Changed register names to be consistent with StellarisWare® names: the Cortex-M3 Interrupt
Control and Status (ICSR) register to the Interrupt Control and State (INTCTRL) register, and
the Cortex-M3 Interrupt Set Enable (SETNA) register to the Interrupt 0-31 Set Enable (EN0)
register.
■ Added clarification of instruction execution during Flash operations.
■ Modified Figure 8-1 on page 283 to clarify operation of the GPIO inputs when used as an alternate
function.
■ Corrected GPIOAMSEL bit field in GPIO Analog Mode Select (GPIOAMSEL) register to be eight-bits
wide, bits[7:0].
■ Added caution not to apply a Low value to PB7 when debugging; a Low value on the pin causes
the JTAG controller to be reset, resulting in a loss of JTAG communication.
■ In General-Purpose Timers chapter, clarified operation of the 32-bit RTC mode.
■ In Electrical Characteristics chapter:
– Added ILKG parameter (GPIO input leakage current) to Table 22-4 on page 680.
– Corrected values for tCLKRF parameter (SSIClk rise/fall time) in Table 22-20 on page 690.
■ Added dimensions for Tray and Tape and Reel shipping mediums.
September 2010 7787
■ Corrected base address for SRAM in architectural overview chapter.
■ Clarified system clock operation, adding content to “Clock Control” on page 175.
■ Clarified CAN bit timing examples.
■ In Signal Tables chapter, added table "Connections for Unused Signals."
■ In "Thermal Characteristics" table, corrected thermal resistance value from 34 to 32.
■ In "Reset Characteristics" table, corrected value for supply voltage (VDD) rise time.
■ Additional minor data sheet clarifications and corrections.
June 2010 7393
■ Added caution note to the I2C Master Timer Period (I2CMTPR) register description and changed
field width to 7 bits.
■ Removed erroneous text about restoring the Flash Protection registers.
■ Added note about RST signal routing.
■ Clarified the function of the TnSTALL bit in the GPTMCTL register.
■ Additional minor data sheet clarifications and corrections.
April 2010 7007
26 January 08, 2011
Texas Instruments-Production Data
Revision History
Table 1. Revision History (continued)
Date Revision Description
■ In "System Control" section, clarified Debug Access Port operation after Sleep modes.
■ Clarified wording on Flash memory access errors.
■ Added section on Flash interrupts.
■ Changed the reset value of the ADC Sample Sequence Result FIFO n (ADCSSFIFOn) registers
to be indeterminate.
■ Clarified operation of SSI transmit FIFO.
■ Made these changes to the Operating Characteristics chapter:
– Added storage temperature ratings to "Temperature Characteristics" table
– Added "ESD Absolute Maximum Ratings" table
■ Made these changes to the Electrical Characteristics chapter:
– In "Flash Memory Characteristics" table, corrected Mass erase time
– Added sleep and deep-sleep wake-up times ("Sleep Modes AC Characteristics" table)
– In "Reset Characteristics" table, corrected units for supply voltage (VDD) rise time
January 2010 6712
■ Deleted MAXADCSPD bit field from DCGC0 register as it is not applicable in Deep-Sleep mode.
■ Removed erroneous reference to the WRC bit in the Hibernation chapter.
■ Deleted reset value for 16-bit mode from GPTMTAILR, GPTMTAMATCHR, and GPTMTAR registers
because the module resets in 32-bit mode.
■ Clarified PWM source for ADC triggering.
■ Clarified CAN bit timing and corrected examples.
■ Made these changes to the Electrical Characteristics chapter:
– Removed VSIH and VSIL parameters from Operating Conditions table.
– Added table showing actual PLL frequency depending on input crystal.
– Changed the name of the tHIB_REG_WRITE parameter to tHIB_REG_ACCESS.
– Revised ADC electrical specifications to clarify, including reorganizing and adding new data.
– Changed SSI set up and hold times to be expressed in system clocks, not ns.
October 2009 6462
July 2009 5920 Corrected ordering numbers.
January 08, 2011 27
Texas Instruments-Production Data
Stellaris® LM3S2965 Microcontroller
Table 1. Revision History (continued)
Date Revision Description
■ Clarified Power-on reset and RST pin operation; added new diagrams.
■ Corrected the reset value of the Hibernation Data (HIBDATA) and Hibernation Control (HIBCTL)
registers.
■ Clarified explanation of nonvolatile register programming in Internal Memory chapter.
■ Added explanation of reset value to FMPRE0/1/2/3, FMPPE0/1/2/3, USER_DBG, and USER_REG0/1
registers.
■ Changed buffer type for WAKE pin to TTL and HIB pin to OD.
■ In ADC characteristics table, changed Max value for GAIN parameter from ±1 to ±3 and added EIR
(Internal voltage reference error) parameter.
■ Additional minor data sheet clarifications and corrections.
July 2009 5902
■ Added JTAG/SWD clarification (see “Communication with JTAG/SWD” on page 164).
■ Added clarification that the PLL operates at 400 MHz, but is divided by two prior to the application
of the output divisor.
■ Added "GPIO Module DC Characteristics" table (see Table 22-4 on page 680).
■ Additional minor data sheet clarifications and corrections.
April 2009 5367
■ Corrected bit type for RELOAD bit field in SysTick Reload Value register; changed to R/W.
■ Clarification added as to what happens when the SSI in slave mode is required to transmit but there
is no data in the TX FIFO.
■ Corrected bit timing examples in CAN chapter.
■ Additional minor data sheet clarifications and corrections.
January 2009 4660
■ Revised High-Level Block Diagram.
■ Additional minor data sheet clarifications and corrections were made.
November 2008 4283
■ Corrected values for DSOSCSRC bit field in Deep Sleep Clock Configuration (DSLPCLKCFG)
register.
■ The FMA value for the FMPRE3 register was incorrect in the Flash Resident Registers table in the
Internal Memory chapter. The correct value is 0x0000.0006.
■ In the CAN chapter, major improvements were made including a rewrite of the conceptual information
and the addition of new figures to clarify how to use the Controller Area Network (CAN) module.
■ Incorrect Comparator Operating Modes tables were removed from the Analog Comparators chapter.
October 2008 4149
■ Added note on clearing interrupts to Interrupts chapter.
■ Added Power Architecture diagram to System Control chapter.
■ Additional minor data sheet clarifications and corrections.
August 2008 3447
July 2008 3108 ■ Additional minor data sheet clarifications and corrections.
28 January 08, 2011
Texas Instruments-Production Data
Revision History
Table 1. Revision History (continued)
Date Revision Description
■ The 108-Ball BGA pin diagram and pin tables had an error. The following signals were erroneously
indicated as available and have now been changed to a No Connect (NC):
– Ball C1: Changed PE7 to NC
– Ball C2: Changed PE6 to NC
– Ball D2: Changed PE5 to NC
– Ball D1: Changed PE4 to NC
■ As noted in the PCN, the option to provide VDD25 power from external sources was removed. Use
the LDO output as the source of VDD25 input.
■ Additional minor data sheet clarifications and corrections.
May 2008 2972
April 2008 2881 ■ The ΘJA value was changed from 55.3 to 34 in the "Thermal Characteristics" table in the Operating
Characteristics chapter.
■ Bit 31 of the DC3 register was incorrectly described in prior versions of the data sheet. A reset of
1 indicates that an even CCP pin is present and can be used as a 32-KHz input clock.
■ Values for IDD_HIBERNATE were added to the "Detailed Power Specifications" table in the "Electrical
Characteristics" chapter.
■ The "Hibernation Module DC Electricals" table was added to the "Electrical Characteristics" chapter.
■ The TVDDRISE parameter in the "Reset Characteristics" table in the "Electrical Characteristics" chapter
was changed from a max of 100 to 250.
■ The maximum value on Core supply voltage (VDD25) in the "Maximum Ratings" table in the "Electrical
Characteristics" chapter was changed from 4 to 3.
■ The operational frequency of the internal 30-kHz oscillator clock source is 30 kHz ± 50% (prior data
sheets incorrectly noted it as 30 kHz ± 30%).
■ A value of 0x3 in bits 5:4 of the MISC register (OSCSRC) indicates the 30-KHz internal oscillator is
the input source for the oscillator. Prior data sheets incorrectly noted 0x3 as a reserved value.
■ The reset for bits 6:4 of the RCC2 register (OSCSRC2) is 0x1 (IOSC). Prior data sheets incorrectly
noted the reset was 0x0 (MOSC).
■ Two figures on clock source were added to the "Hibernation Module":
– Clock Source Using Crystal
– Clock Source Using Dedicated Oscillator
■ The following notes on battery management were added to the "Hibernation Module" chapter:
– Battery voltage is not measured while in Hibernate mode.
– System level factors may affect the accuracy of the low battery detect circuit. The designer
should consider battery type, discharge characteristics, and a test load during battery voltage
measurements.
■ A note on high-current applications was added to the GPIO chapter:
For special high-current applications, the GPIO output buffers may be used with the following
restrictions. With the GPIO pins configured as 8-mA output drivers, a total of four GPIO outputs may
be used to sink current loads up to 18 mA each. At 18-mA sink current loading, the VOL value is
specified as 1.2 V. The high-current GPIO package pins must be selected such that there are only
January 08, 2011 29
Texas Instruments-Production Data
Stellaris® LM3S2965 Microcontroller
Table 1. Revision History (continued)
Date Revision Description
a maximum of two per side of the physical package or BGA pin group with the total number of
high-current GPIO outputs not exceeding four for the entire package.
■ A note on Schmitt inputs was added to the GPIO chapter:
Pins configured as digital inputs are Schmitt-triggered.
■ The Buffer type on the WAKE pin changed from OD to - in the Signal Tables.
■ The "Differential Sampling Range" figures in the ADC chapter were clarified.
■ The last revision of the data sheet (revision 2550) introduced two errors that have now been corrected:
– The LQFP pin diagrams and pin tables were missing the comparator positive and negative input
pins.
– The base address was listed incorrectly in the FMPRE0 and FMPPE0 register bit diagrams.
■ Additional minor data sheet clarifications and corrections.
March 2008 2550 Started tracking revision history.
30 January 08, 2011
Texas Instruments-Production Data
Revision History
About This Document
This data sheet provides reference information for the LM3S2965 microcontroller, describing the
functional blocks of the system-on-chip (SoC) device designed around the ARM® Cortex™-M3
core.
Audience
This manual is intended for system software developers, hardware designers, and application
developers.
About This Manual
This document is organized into sections that correspond to each major feature.
Related Documents
The following related documents are available on the Stellaris® web site at www.ti.com/stellaris:
■ Stellaris® Errata
■ ARM® Cortex™-M3 Errata
■ Cortex™-M3 Instruction Set Technical User's Manual
■ Stellaris® Graphics Library User's Guide
■ Stellaris® Peripheral Driver Library User's Guide
The following related documents are also referenced:
■ ARM® Debug Interface V5 Architecture Specification
■ IEEE Standard 1149.1-Test Access Port and Boundary-Scan Architecture
This documentation list was current as of publication date. Please check the web site for additional
documentation, including application notes and white papers.
January 08, 2011 31
Texas Instruments-Production Data
Stellaris® LM3S2965 Microcontroller
Documentation Conventions
This document uses the conventions shown in Table 2 on page 32.
Table 2. Documentation Conventions
Notation Meaning
General Register Notation
APB registers are indicated in uppercase bold. For example, PBORCTL is the Power-On and
Brown-Out Reset Control register. If a register name contains a lowercase n, it represents more
than one register. For example, SRCRn represents any (or all) of the three Software Reset Control
registers: SRCR0, SRCR1 , and SRCR2.
REGISTER
bit A single bit in a register.
bit field Two or more consecutive and related bits.
A hexadecimal increment to a register's address, relative to that module's base address as specified
in Table 2-4 on page 71.
offset 0xnnn
Registers are numbered consecutively throughout the document to aid in referencing them. The
register number has no meaning to software.
Register N
Register bits marked reserved are reserved for future use. In most cases, reserved bits are set to
0; however, user software should not rely on the value of a reserved bit. To provide software
compatibility with future products, the value of a reserved bit should be preserved across a
read-modify-write operation.
reserved
The range of register bits inclusive from xx to yy. For example, 31:15 means bits 15 through 31 in
that register.
yy:xx
This value in the register bit diagram indicates whether software running on the controller can
change the value of the bit field.
Register Bit/Field
Types
RC Software can read this field. The bit or field is cleared by hardware after reading the bit/field.
RO Software can read this field. Always write the chip reset value.
R/W Software can read or write this field.
R/WC Software can read or write this field. Writing to it with any value clears the register.
Software can read or write this field. A write of a 0 to a W1C bit does not affect the bit value in the
register. A write of a 1 clears the value of the bit in the register; the remaining bits remain unchanged.
This register type is primarily used for clearing interrupt status bits where the read operation
provides the interrupt status and the write of the read value clears only the interrupts being reported
at the time the register was read.
R/W1C
Software can read or write a 1 to this field. A write of a 0 to a R/W1S bit does not affect the bit
value in the register.
R/W1S
Software can write this field. A write of a 0 to a W1C bit does not affect the bit value in the register.
A write of a 1 clears the value of the bit in the register; the remaining bits remain unchanged. A
read of the register returns no meaningful data.
This register is typically used to clear the corresponding bit in an interrupt register.
W1C
WO Only a write by software is valid; a read of the register returns no meaningful data.
Register Bit/Field This value in the register bit diagram shows the bit/field value after any reset, unless noted.
Reset Value
0 Bit cleared to 0 on chip reset.
1 Bit set to 1 on chip reset.
- Nondeterministic.
Pin/Signal Notation
[ ] Pin alternate function; a pin defaults to the signal without the brackets.
pin Refers to the physical connection on the package.
signal Refers to the electrical signal encoding of a pin.
32 January 08, 2011
Texas Instruments-Production Data
About This Document
Table 2. Documentation Conventions (continued)
Notation Meaning
Change the value of the signal from the logically False state to the logically True state. For active
High signals, the asserted signal value is 1 (High); for active Low signals, the asserted signal value
is 0 (Low). The active polarity (High or Low) is defined by the signal name (see SIGNAL and SIGNAL
below).
assert a signal
deassert a signal Change the value of the signal from the logically True state to the logically False state.
Signal names are in uppercase and in the Courier font. An overbar on a signal name indicates that
it is active Low. To assert SIGNAL is to drive it Low; to deassert SIGNAL is to drive it High.
SIGNAL
Signal names are in uppercase and in the Courier font. An active High signal has no overbar. To
assert SIGNAL is to drive it High; to deassert SIGNAL is to drive it Low.
SIGNAL
Numbers
An uppercase X indicates any of several values is allowed, where X can be any legal pattern. For
example, a binary value of 0X00 can be either 0100 or 0000, a hex value of 0xX is 0x0 or 0x1, and
so on.
X
Hexadecimal numbers have a prefix of 0x. For example, 0x00FF is the hexadecimal number FF.
All other numbers within register tables are assumed to be binary. Within conceptual information,
binary numbers are indicated with a b suffix, for example, 1011b, and decimal numbers are written
without a prefix or suffix.
0x
January 08, 2011 33
Texas Instruments-Production Data
Stellaris® LM3S2965 Microcontroller
1 Architectural Overview
The Stellaris® family of microcontrollers—the first ARM® Cortex™-M3 based controllers—brings
high-performance 32-bit computing to cost-sensitive embedded microcontroller applications. These
pioneering parts deliver customers 32-bit performance at a cost equivalent to legacy 8- and 16-bit
devices, all in a package with a small footprint.
The Stellaris family offers efficient performance and extensive integration, favorably positioning the
device into cost-conscious applications requiring significant control-processing and connectivity
capabilities. The Stellaris LM3S2000 series, designed for Controller Area Network (CAN) applications,
extends the Stellaris family with Bosch CAN networking technology, the golden standard in short-haul
industrial networks. The Stellaris LM3S2000 series also marks the first integration of CAN capabilities
with the revolutionary Cortex-M3 core.
The LM3S2965 microcontroller is targeted for industrial applications, including remote monitoring,
electronic point-of-sale machines, test and measurement equipment, network appliances and
switches, factory automation, HVAC and building control, gaming equipment, motion control, medical
instrumentation, and fire and security.
For applications requiring extreme conservation of power, the LM3S2965 microcontroller features
a battery-backed Hibernation module to efficiently power down the LM3S2965 to a low-power state
during extended periods of inactivity. With a power-up/power-down sequencer, a continuous time
counter (RTC), a pair of match registers, an APB interface to the system bus, and dedicated
non-volatile memory, the Hibernation module positions the LM3S2965 microcontroller perfectly for
battery applications.
In addition, the LM3S2965 microcontroller offers the advantages of ARM's widely available
development tools, System-on-Chip (SoC) infrastructure IP applications, and a large user community.
Additionally, the microcontroller uses ARM's Thumb®-compatible Thumb-2 instruction set to reduce
memory requirements and, thereby, cost. Finally, the LM3S2965 microcontroller is code-compatible
to all members of the extensive Stellaris family; providing flexibility to fit our customers' precise
needs.
Texas Instruments offers a complete solution to get to market quickly, with evaluation and
development boards, white papers and application notes, an easy-to-use peripheral driver library,
and a strong support, sales, and distributor network. See “Ordering and Contact
Information” on page 723 for ordering information for Stellaris family devices.
1.1 Product Features
The LM3S2965 microcontroller includes the following product features:
■ 32-Bit RISC Performance
– 32-bit ARM® Cortex™-M3 v7M architecture optimized for small-footprint embedded
applications
– System timer (SysTick), providing a simple, 24-bit clear-on-write, decrementing, wrap-on-zero
counter with a flexible control mechanism
– Thumb®-compatible Thumb-2-only instruction set processor core for high code density
– 50-MHz operation
– Hardware-division and single-cycle-multiplication
34 January 08, 2011
Texas Instruments-Production Data
Architectural Overview
– Integrated Nested Vectored Interrupt Controller (NVIC) providing deterministic interrupt
handling
– 42 interrupts with eight priority levels
– Memory protection unit (MPU), providing a privileged mode for protected operating system
functionality
– Unaligned data access, enabling data to be efficiently packed into memory
– Atomic bit manipulation (bit-banding), delivering maximum memory utilization and streamlined
peripheral control
■ ARM® Cortex™-M3 Processor Core
– Compact core.
– Thumb-2 instruction set, delivering the high-performance expected of an ARM core in the
memory size usually associated with 8- and 16-bit devices; typically in the range of a few
kilobytes of memory for microcontroller class applications.
– Rapid application execution through Harvard architecture characterized by separate buses
for instruction and data.
– Exceptional interrupt handling, by implementing the register manipulations required for handling
an interrupt in hardware.
– Deterministic, fast interrupt processing: always 12 cycles, or just 6 cycles with tail-chaining
– Memory protection unit (MPU) to provide a privileged mode of operation for complex
applications.
– Migration from the ARM7™ processor family for better performance and power efficiency.
– Full-featured debug solution
• Serial Wire JTAG Debug Port (SWJ-DP)
• Flash Patch and Breakpoint (FPB) unit for implementing breakpoints
• Data Watchpoint and Trigger (DWT) unit for implementing watchpoints, trigger resources,
and system profiling
• Instrumentation Trace Macrocell (ITM) for support of printf style debugging
• Trace Port Interface Unit (TPIU) for bridging to a Trace Port Analyzer
– Optimized for single-cycle flash usage
– Three sleep modes with clock gating for low power
– Single-cycle multiply instruction and hardware divide
– Atomic operations
– ARM Thumb2 mixed 16-/32-bit instruction set
January 08, 2011 35
Texas Instruments-Production Data
Stellaris® LM3S2965 Microcontroller
– 1.25 DMIPS/MHz
■ JTAG
– IEEE 1149.1-1990 compatible Test Access Port (TAP) controller
– Four-bit Instruction Register (IR) chain for storing JTAG instructions
– IEEE standard instructions: BYPASS, IDCODE, SAMPLE/PRELOAD, EXTEST and INTEST
– ARM additional instructions: APACC, DPACC and ABORT
– Integrated ARM Serial Wire Debug (SWD)
■ Hibernation
– System power control using discrete external regulator
– Dedicated pin for waking from an external signal
– Low-battery detection, signaling, and interrupt generation
– 32-bit real-time clock (RTC)
– Two 32-bit RTC match registers for timed wake-up and interrupt generation
– Clock source from a 32.768-kHz external oscillator or a 4.194304-MHz crystal
– RTC predivider trim for making fine adjustments to the clock rate
– 64 32-bit words of non-volatile memory
– Programmable interrupts for RTC match, external wake, and low battery events
■ Internal Memory
– 256 KB single-cycle flash
• User-managed flash block protection on a 2-KB block basis
• User-managed flash data programming
• User-defined and managed flash-protection block
– 64 KB single-cycle SRAM
■ GPIOs
– 3-56 GPIOs, depending on configuration
– 5-V-tolerant in input configuration
– Programmable control for GPIO interrupts
• Interrupt generation masking
• Edge-triggered on rising, falling, or both
36 January 08, 2011
Texas Instruments-Production Data
Architectural Overview
• Level-sensitive on High or Low values
– Bit masking in both read and write operations through address lines
– Can initiate an ADC sample sequence
– Pins configured as digital inputs are Schmitt-triggered.
– Programmable control for GPIO pad configuration
• Weak pull-up or pull-down resistors
• 2-mA, 4-mA, and 8-mA pad drive for digital communication; up to four pads can be
configured with an 18-mA pad drive for high-current applications
• Slew rate control for the 8-mA drive
• Open drain enables
• Digital input enables
■ General-Purpose Timers
– Four General-Purpose Timer Modules (GPTM), each of which provides two 16-bit
timers/counters. Each GPTM can be configured to operate independently:
• As a single 32-bit timer
• As one 32-bit Real-Time Clock (RTC) to event capture
• For Pulse Width Modulation (PWM)
• To trigger analog-to-digital conversions
– 32-bit Timer modes
• Programmable one-shot timer
• Programmable periodic timer
• Real-Time Clock when using an external 32.768-KHz clock as the input
• User-enabled stalling when the controller asserts CPU Halt flag during debug
• ADC event trigger
– 16-bit Timer modes
• General-purpose timer function with an 8-bit prescaler (for one-shot and periodic modes
only)
• Programmable one-shot timer
• Programmable periodic timer
• User-enabled stalling when the controller asserts CPU Halt flag during debug
January 08, 2011 37
Texas Instruments-Production Data
Stellaris® LM3S2965 Microcontroller
• ADC event trigger
– 16-bit Input Capture modes
• Input edge count capture
• Input edge time capture
– 16-bit PWM mode
• Simple PWM mode with software-programmable output inversion of the PWM signal
■ ARM FiRM-compliant Watchdog Timer
– 32-bit down counter with a programmable load register
– Separate watchdog clock with an enable
– Programmable interrupt generation logic with interrupt masking
– Lock register protection from runaway software
– Reset generation logic with an enable/disable
– User-enabled stalling when the controller asserts the CPU Halt flag during debug
■ ADC
– Four analog input channels
– Single-ended and differential-input configurations
– On-chip internal temperature sensor
– Sample rate of one million samples/second
– Flexible, configurable analog-to-digital conversion
– Four programmable sample conversion sequences from one to eight entries long, with
corresponding conversion result FIFOs
– Flexible trigger control
• Controller (software)
• Timers
• Analog Comparators
• PWM
• GPIO
– Hardware averaging of up to 64 samples for improved accuracy
– Converter uses an internal 3-V reference
38 January 08, 2011
Texas Instruments-Production Data
Architectural Overview
– Power and ground for the analog circuitry is separate from the digital power and ground
■ UART
– Three fully programmable 16C550-type UARTs with IrDA support
– Separate 16x8 transmit (TX) and receive (RX) FIFOs to reduce CPU interrupt service loading
– Programmable baud-rate generator allowing speeds up to 3.125 Mbps
– Programmable FIFO length, including 1-byte deep operation providing conventional
double-buffered interface
– FIFO trigger levels of 1/8, 1/4, 1/2, 3/4, and 7/8
– Standard asynchronous communication bits for start, stop, and parity
– Line-break generation and detection
– Fully programmable serial interface characteristics
• 5, 6, 7, or 8 data bits
• Even, odd, stick, or no-parity bit generation/detection
• 1 or 2 stop bit generation
– IrDA serial-IR (SIR) encoder/decoder providing
• Programmable use of IrDA Serial Infrared (SIR) or UART input/output
• Support of IrDA SIR encoder/decoder functions for data rates up to 115.2 Kbps half-duplex
• Support of normal 3/16 and low-power (1.41-2.23 μs) bit durations
• Programmable internal clock generator enabling division of reference clock by 1 to 256
for low-power mode bit duration
■ Synchronous Serial Interface (SSI)
– Two SSI modules, each with the following features:
– Master or slave operation
– Programmable clock bit rate and prescale
– Separate transmit and receive FIFOs, 16 bits wide, 8 locations deep
– Programmable interface operation for Freescale SPI, MICROWIRE, or Texas Instruments
synchronous serial interfaces
– Programmable data frame size from 4 to 16 bits
– Internal loopback test mode for diagnostic/debug testing
■ I2C
January 08, 2011 39
Texas Instruments-Production Data
Stellaris® LM3S2965 Microcontroller
– Two I2C modules, each with the following features:
– Devices on the I2C bus can be designated as either a master or a slave
• Supports both sending and receiving data as either a master or a slave
• Supports simultaneous master and slave operation
– Four I2C modes
• Master transmit
• Master receive
• Slave transmit
• Slave receive
– Two transmission speeds: Standard (100 Kbps) and Fast (400 Kbps)
– Master and slave interrupt generation
• Master generates interrupts when a transmit or receive operation completes (or aborts
due to an error)
• Slave generates interrupts when data has been sent or requested by a master
– Master with arbitration and clock synchronization, multimaster support, and 7-bit addressing
mode
■ Controller Area Network (CAN)
– Two CAN modules, each with the following features:
– CAN protocol version 2.0 part A/B
– Bit rates up to 1 Mbps
– 32 message objects with individual identifier masks
– Maskable interrupt
– Disable Automatic Retransmission mode for Time-Triggered CAN (TTCAN) applications
– Programmable Loopback mode for self-test operation
– Programmable FIFO mode enables storage of multiple message objects
– Gluelessly attaches to an external CAN interface through the CANnTX and CANnRX signals
■ Analog Comparators
– Three independent integrated analog comparators
– Configurable for output to drive an output pin, generate an interrupt, or initiate an ADC sample
sequence
40 January 08, 2011
Texas Instruments-Production Data
Architectural Overview
– Compare external pin input to external pin input or to internal programmable voltage reference
– Compare a test voltage against any one of these voltages
• An individual external reference voltage
• A shared single external reference voltage
• A shared internal reference voltage
■ PWM
– Three PWM generator blocks, each with one 16-bit counter, two PWM comparators, a PWM
signal generator, a dead-band generator, and an interrupt/ADC-trigger selector
– One fault input in hardware to promote low-latency shutdown
– One 16-bit counter
• Runs in Down or Up/Down mode
• Output frequency controlled by a 16-bit load value
• Load value updates can be synchronized
• Produces output signals at zero and load value
– Two PWM comparators
• Comparator value updates can be synchronized
• Produces output signals on match
– PWM generator
• Output PWM signal is constructed based on actions taken as a result of the counter and
PWM comparator output signals
• Produces two independent PWM signals
– Dead-band generator
• Produces two PWM signals with programmable dead-band delays suitable for driving a
half-H bridge
• Can be bypassed, leaving input PWM signals unmodified
– Flexible output control block with PWM output enable of each PWM signal
• PWM output enable of each PWM signal
• Optional output inversion of each PWM signal (polarity control)
• Optional fault handling for each PWM signal
• Synchronization of timers in the PWM generator blocks
January 08, 2011 41
Texas Instruments-Production Data
Stellaris® LM3S2965 Microcontroller
• Synchronization of timer/comparator updates across the PWM generator blocks
• Interrupt status summary of the PWM generator blocks
– Can initiate an ADC sample sequence
■ QEI
– Two QEI modules, each with the following features:
– Position integrator that tracks the encoder position
– Velocity capture using built-in timer
– The input frequency of the QEI inputs may be as high as 1/4 of the processor frequency (for
example, 12.5 MHz for a 50-MHz system)
– Interrupt generation on:
• Index pulse
• Velocity-timer expiration
• Direction change
• Quadrature error detection
■ Power
– On-chip Low Drop-Out (LDO) voltage regulator, with programmable output user-adjustable
from 2.25 V to 2.75 V
– Hibernation module handles the power-up/down 3.3 V sequencing and control for the core
digital logic and analog circuits
– Low-power options on controller: Sleep and Deep-sleep modes
– Low-power options for peripherals: software controls shutdown of individual peripherals
– 3.3-V supply brown-out detection and reporting via interrupt or reset
■ Flexible Reset Sources
– Power-on reset (POR)
– Reset pin assertion
– Brown-out (BOR) detector alerts to system power drops
– Software reset
– Watchdog timer reset
– Internal low drop-out (LDO) regulator output goes unregulated
■ Industrial and extended temperature 100-pin RoHS-compliant LQFP package
42 January 08, 2011
Texas Instruments-Production Data
Architectural Overview
■ Industrial-range 108-ball RoHS-compliant BGA package
1.2 Target Applications
■ Remote monitoring
■ Electronic point-of-sale (POS) machines
■ Test and measurement equipment
■ Network appliances and switches
■ Factory automation
■ HVAC and building control
■ Gaming equipment
■ Motion control
■ Medical instrumentation
■ Fire and security
■ Power and energy
■ Transportation
1.3 High-Level Block Diagram
Figure 1-1 on page 44 depicts the features on the Stellaris LM3S2965 microcontroller.
January 08, 2011 43
Texas Instruments-Production Data
Stellaris® LM3S2965 Microcontroller
Figure 1-1. Stellaris LM3S2965 Microcontroller High-Level Block Diagram
LM3S2965
ARM®
Cortex™-M3
(50 MHz)
NVIC MPU
Flash
(256 KB)
DCode bus
ICode bus
JTAG/SWD
System
Control and
Clocks
Bus Matrix
System Bus
SRAM
(64 KB)
SYSTEM PERIPHERALS
Watchdog
Timer
(1)
Hibernation
Module
General-
Purpose
Timers (4)
GPIOs
(3-56)
SERIAL PERIPHERALS
UARTs
(3)
I2C
(2)
SSI
(2)
CAN
Controllers
(2)
ANALOG PERIPHERALS
ADC
Channels
(4)
Analog
Comparators
(3)
MOTION CONTROL PERIPHERALS
QEI
(2)
PWM
(6)
Advanced Peripheral Bus (APB)
44 January 08, 2011
Texas Instruments-Production Data
Architectural Overview
1.4 Functional Overview
The following sections provide an overview of the features of the LM3S2965 microcontroller. The
page number in parenthesis indicates where that feature is discussed in detail. Ordering and support
information can be found in “Ordering and Contact Information” on page 723.
1.4.1 ARM Cortex™-M3
1.4.1.1 Processor Core (see page 52)
All members of the Stellaris product family, including the LM3S2965 microcontroller, are designed
around an ARM Cortex™-M3 processor core. The ARM Cortex-M3 processor provides the core for
a high-performance, low-cost platform that meets the needs of minimal memory implementation,
reduced pin count, and low-power consumption, while delivering outstanding computational
performance and exceptional system response to interrupts.
1.4.1.2 Memory Map (see page 71)
A memory map lists the location of instructions and data in memory. The memory map for the
LM3S2965 controller can be found in Table 2-4 on page 71. Register addresses are given as a
hexadecimal increment, relative to the module's base address as shown in the memory map.
1.4.1.3 System Timer (SysTick) (see page 94)
Cortex-M3 includes an integrated system timer, SysTick. SysTick provides a simple, 24-bit
clear-on-write, decrementing, wrap-on-zero counter with a flexible control mechanism. The counter
can be used in several different ways, for example:
■ An RTOS tick timer which fires at a programmable rate (for example, 100 Hz) and invokes a
SysTick routine.
■ A high-speed alarm timer using the system clock.
■ A variable rate alarm or signal timer—the duration is range-dependent on the reference clock
used and the dynamic range of the counter.
■ A simple counter. Software can use this to measure time to completion and time used.
■ An internal clock source control based on missing/meeting durations. The COUNTFLAG bit-field
in the control and status register can be used to determine if an action completed within a set
duration, as part of a dynamic clock management control loop.
1.4.1.4 Nested Vectored Interrupt Controller (NVIC) (see page 95)
The LM3S2965 controller includes the ARM Nested Vectored Interrupt Controller (NVIC) on the
ARM® Cortex™-M3 core. The NVIC and Cortex-M3 prioritize and handle all exceptions. All exceptions
are handled in Handler Mode. The processor state is automatically stored to the stack on an
exception, and automatically restored from the stack at the end of the Interrupt Service Routine
(ISR). The vector is fetched in parallel to the state saving, which enables efficient interrupt entry.
The processor supports tail-chaining, which enables back-to-back interrupts to be performed without
the overhead of state saving and restoration. Software can set eight priority levels on 7 exceptions
(system handlers) and 42 interrupts.
January 08, 2011 45
Texas Instruments-Production Data
Stellaris® LM3S2965 Microcontroller
1.4.1.5 System Control Block (SCB) (see page 97)
The SCB provides system implementation information and system control, including configuration,
control, and reporting of system exceptions.
1.4.1.6 Memory Protection Unit (MPU) (see page 97)
The MPU supports the standard ARMv7 Protected Memory System Architecture (PMSA) model.
The MPU provides full support for protection regions, overlapping protection regions, access
permissions, and exporting memory attributes to the system.
1.4.2 Motor Control Peripherals
To enhance motor control, the LM3S2965 controller features Pulse Width Modulation (PWM) outputs
and the Quadrature Encoder Interface (QEI).
1.4.2.1 PWM
Pulse width modulation (PWM) is a powerful technique for digitally encoding analog signal levels.
High-resolution counters are used to generate a square wave, and the duty cycle of the square
wave is modulated to encode an analog signal. Typical applications include switching power supplies
and motor control.
On the LM3S2965, PWM motion control functionality can be achieved through:
■ Dedicated, flexible motion control hardware using the PWM pins
■ The motion control features of the general-purpose timers using the CCP pins
PWM Pins (see page 591)
The LM3S2965 PWM module consists of three PWM generator blocks and a control block. Each
PWM generator block contains one timer (16-bit down or up/down counter), two comparators, a
PWM signal generator, a dead-band generator, and an interrupt/ADC-trigger selector. The control
block determines the polarity of the PWM signals, and which signals are passed through to the pins.
Each PWM generator block produces two PWM signals that can either be independent signals or
a single pair of complementary signals with dead-band delays inserted. The output of the PWM
generation blocks are managed by the output control block before being passed to the device pins.
CCP Pins (see page 330)
The General-Purpose Timer Module's CCP (Capture Compare PWM) pins are software programmable
to support a simple PWM mode with a software-programmable output inversion of the PWM signal.
Fault Pin (see page 596)
The LM3S2965 PWM module includes one fault-condition handling input to quickly provide low-latency
shutdown and prevent damage to the motor being controlled.
1.4.2.2 QEI (see page 629)
A quadrature encoder, also known as a 2-channel incremental encoder, converts linear displacement
into a pulse signal. By monitoring both the number of pulses and the relative phase of the two signals,
you can track the position, direction of rotation, and speed. In addition, a third channel, or index
signal, can be used to reset the position counter.
The Stellaris quadrature encoder with index (QEI) module interprets the code produced by a
quadrature encoder wheel to integrate position over time and determine direction of rotation. In
46 January 08, 2011
Texas Instruments-Production Data
Architectural Overview
addition, it can capture a running estimate of the velocity of the encoder wheel. The LM3S2965
microcontroller includes two QEI modules, which enables control of two motors at the same time.
1.4.3 Analog Peripherals
To handle analog signals, the LM3S2965 microcontroller offers an Analog-to-Digital Converter
(ADC).
For support of analog signals, the LM3S2965 microcontroller offers three analog comparators.
1.4.3.1 ADC (see page 384)
An analog-to-digital converter (ADC) is a peripheral that converts a continuous analog voltage to a
discrete digital number.
The LM3S2965 ADC module features 10-bit conversion resolution and supports four input channels,
plus an internal temperature sensor. Four buffered sample sequences allow rapid sampling of up
to eight analog input sources without controller intervention. Each sample sequence provides flexible
programming with fully configurable input source, trigger events, interrupt generation, and sequence
priority.
1.4.3.2 Analog Comparators (see page 579)
An analog comparator is a peripheral that compares two analog voltages, and provides a logical
output that signals the comparison result.
The LM3S2965 microcontroller provides three independent integrated analog comparators that can
be configured to drive an output or generate an interrupt or ADC event.
A comparator can compare a test voltage against any one of these voltages:
■ An individual external reference voltage
■ A shared single external reference voltage
■ A shared internal reference voltage
The comparator can provide its output to a device pin, acting as a replacement for an analog
comparator on the board, or it can be used to signal the application via interrupts or triggers to the
ADC to cause it to start capturing a sample sequence. The interrupt generation and ADC triggering
logic is separate. This means, for example, that an interrupt can be generated on a rising edge and
the ADC triggered on a falling edge.
1.4.4 Serial Communications Peripherals
The LM3S2965 controller supports both asynchronous and synchronous serial communications
with:
■ Three fully programmable 16C550-type UARTs
■ Two SSI modules
■ Two I2C modules
■ Two CAN units
January 08, 2011 47
Texas Instruments-Production Data
Stellaris® LM3S2965 Microcontroller
1.4.4.1 UART (see page 420)
A Universal Asynchronous Receiver/Transmitter (UART) is an integrated circuit used for RS-232C
serial communications, containing a transmitter (parallel-to-serial converter) and a receiver
(serial-to-parallel converter), each clocked separately.
The LM3S2965 controller includes three fully programmable 16C550-type UARTs that support data
transfer speeds up to 3.125 Mbps. (Although similar in functionality to a 16C550 UART, it is not
register-compatible.) In addition, each UART is capable of supporting IrDA.
Separate 16x8 transmit (TX) and receive (RX) FIFOs reduce CPU interrupt service loading. The
UART can generate individually masked interrupts from the RX, TX, modem status, and error
conditions. The module provides a single combined interrupt when any of the interrupts are asserted
and are unmasked.
1.4.4.2 SSI (see page 461)
Synchronous Serial Interface (SSI) is a four-wire bi-directional full and low-speed communications
interface.
The LM3S2965 controller includes two SSI modules that provide the functionality for synchronous
serial communications with peripheral devices, and can be configured to use the Freescale SPI,
MICROWIRE, or TI synchronous serial interface frame formats. The size of the data frame is also
configurable, and can be set between 4 and 16 bits, inclusive.
Each SSI module performs serial-to-parallel conversion on data received from a peripheral device,
and parallel-to-serial conversion on data transmitted to a peripheral device. The TX and RX paths
are buffered with internal FIFOs, allowing up to eight 16-bit values to be stored independently.
Each SSI module can be configured as either a master or slave device. As a slave device, the SSI
module can also be configured to disable its output, which allows a master device to be coupled
with multiple slave devices.
Each SSI module also includes a programmable bit rate clock divider and prescaler to generate the
output serial clock derived from the SSI module's input clock. Bit rates are generated based on the
input clock and the maximum bit rate is determined by the connected peripheral.
1.4.4.3 I2C (see page 498)
The Inter-Integrated Circuit (I2C) bus provides bi-directional data transfer through a two-wire design
(a serial data line SDA and a serial clock line SCL).
The I2C bus interfaces to external I2C devices such as serial memory (RAMs and ROMs), networking
devices, LCDs, tone generators, and so on. The I2C bus may also be used for system testing and
diagnostic purposes in product development and manufacture.
The LM3S2965 controller includes two I2C modules that provide the ability to communicate to other
IC devices over an I2C bus. The I2C bus supports devices that can both transmit and receive (write
and read) data.
Devices on the I2C bus can be designated as either a master or a slave. Each I2C module supports
both sending and receiving data as either a master or a slave, and also supports the simultaneous
operation as both a master and a slave. The four I2C modes are: Master Transmit, Master Receive,
Slave Transmit, and Slave Receive.
A Stellaris I2C module can operate at two speeds: Standard (100 Kbps) and Fast (400 Kbps).
48 January 08, 2011
Texas Instruments-Production Data
Architectural Overview
Both the I2C master and slave can generate interrupts. The I2C master generates interrupts when
a transmit or receive operation completes (or aborts due to an error). The I2C slave generates
interrupts when data has been sent or requested by a master.
1.4.4.4 Controller Area Network (see page 534)
Controller Area Network (CAN) is a multicast shared serial-bus standard for connecting electronic
control units (ECUs). CAN was specifically designed to be robust in electromagnetically noisy
environments and can utilize a differential balanced line like RS-485 or a more robust twisted-pair
wire. Originally created for automotive purposes, now it is used in many embedded control
applications (for example, industrial or medical). Bit rates up to 1Mb/s are possible at network lengths
below 40 meters. Decreased bit rates allow longer network distances (for example, 125 Kb/s at
500m).
A transmitter sends a message to all CAN nodes (broadcasting). Each node decides on the basis
of the identifier received whether it should process the message. The identifier also determines the
priority that the message enjoys in competition for bus access. Each CAN message can transmit
from 0 to 8 bytes of user information. The LM3S2965 includes two CAN units.
1.4.5 System Peripherals
1.4.5.1 Programmable GPIOs (see page 282)
General-purpose input/output (GPIO) pins offer flexibility for a variety of connections.
The Stellaris GPIO module is comprised of eight physical GPIO blocks, each corresponding to an
individual GPIO port. The GPIO module is FiRM-compliant (compliant to the ARM Foundation IP
for Real-Time Microcontrollers specification) and supports 3-56 programmable input/output pins.
The number of GPIOs available depends on the peripherals being used (see “Signal
Tables” on page 648 for the signals available to each GPIO pin).
The GPIO module features programmable interrupt generation as either edge-triggered or
level-sensitive on all pins, programmable control for GPIO pad configuration, and bit masking in
both read and write operations through address lines. Pins configured as digital inputs are
Schmitt-triggered.
1.4.5.2 Four Programmable Timers (see page 324)
Programmable timers can be used to count or time external events that drive the Timer input pins.
The Stellaris General-Purpose Timer Module (GPTM) contains four GPTM blocks. Each GPTM
block provides two 16-bit timers/counters that can be configured to operate independently as timers
or event counters, or configured to operate as one 32-bit timer or one 32-bit Real-Time Clock (RTC).
Timers can also be used to trigger analog-to-digital (ADC) conversions.
When configured in 32-bit mode, a timer can run as a Real-Time Clock (RTC), one-shot timer or
periodic timer. When in 16-bit mode, a timer can run as a one-shot timer or periodic timer, and can
extend its precision by using an 8-bit prescaler. A 16-bit timer can also be configured for event
capture or Pulse Width Modulation (PWM) generation.
1.4.5.3 Watchdog Timer (see page 360)
A watchdog timer can generate an interrupt or a reset when a time-out value is reached. The
watchdog timer is used to regain control when a system has failed due to a software error or to the
failure of an external device to respond in the expected way.
The Stellaris Watchdog Timer module consists of a 32-bit down counter, a programmable load
register, interrupt generation logic, and a locking register.
January 08, 2011 49
Texas Instruments-Production Data
Stellaris® LM3S2965 Microcontroller
The Watchdog Timer can be configured to generate an interrupt to the controller on its first time-out,
and to generate a reset signal on its second time-out. Once the Watchdog Timer has been configured,
the lock register can be written to prevent the timer configuration from being inadvertently altered.
1.4.6 Memory Peripherals
The LM3S2965 controller offers both single-cycle SRAM and single-cycle Flash memory.
1.4.6.1 SRAM (see page 256)
The LM3S2965 static random access memory (SRAM) controller supports 64 KB SRAM. The internal
SRAM of the Stellaris devices starts at base address 0x2000.0000 of the device memory map. To
reduce the number of time-consuming read-modify-write (RMW) operations, ARM has introduced
bit-banding technology in the new Cortex-M3 processor. With a bit-band-enabled processor, certain
regions in the memory map (SRAM and peripheral space) can use address aliases to access
individual bits in a single, atomic operation.
1.4.6.2 Flash (see page 257)
The LM3S2965 Flash controller supports 256 KB of flash memory. The flash is organized as a set
of 1-KB blocks that can be individually erased. Erasing a block causes the entire contents of the
block to be reset to all 1s. These blocks are paired into a set of 2-KB blocks that can be individually
protected. The blocks can be marked as read-only or execute-only, providing different levels of code
protection. Read-only blocks cannot be erased or programmed, protecting the contents of those
blocks from being modified. Execute-only blocks cannot be erased or programmed, and can only
be read by the controller instruction fetch mechanism, protecting the contents of those blocks from
being read by either the controller or by a debugger.
1.4.7 Additional Features
1.4.7.1 JTAG TAP Controller (see page 158)
The Joint Test Action Group (JTAG) port is an IEEE standard that defines a Test Access Port and
Boundary Scan Architecture for digital integrated circuits and provides a standardized serial interface
for controlling the associated test logic. The TAP, Instruction Register (IR), and Data Registers (DR)
can be used to test the interconnections of assembled printed circuit boards and obtain manufacturing
information on the components. The JTAG Port also provides a means of accessing and controlling
design-for-test features such as I/O pin observation and control, scan testing, and debugging.
The JTAG port is composed of the standard five pins: TRST, TCK, TMS, TDI, and TDO. Data is
transmitted serially into the controller on TDI and out of the controller on TDO. The interpretation of
this data is dependent on the current state of the TAP controller. For detailed information on the
operation of the JTAG port and TAP controller, please refer to the IEEE Standard 1149.1-Test
Access Port and Boundary-Scan Architecture.
The Stellaris JTAG controller works with the ARM JTAG controller built into the Cortex-M3 core.
This is implemented by multiplexing the TDO outputs from both JTAG controllers. ARM JTAG
instructions select the ARM TDO output while Stellaris JTAG instructions select the Stellaris TDO
outputs. The multiplexer is controlled by the Stellaris JTAG controller, which has comprehensive
programming for the ARM, Stellaris, and unimplemented JTAG instructions.
1.4.7.2 System Control and Clocks (see page 170)
System control determines the overall operation of the device. It provides information about the
device, controls the clocking of the device and individual peripherals, and handles reset detection
and reporting.
50 January 08, 2011
Texas Instruments-Production Data
Architectural Overview
1.4.7.3 Hibernation Module (see page 236)
The Hibernation module provides logic to switch power off to the main processor and peripherals,
and to wake on external or time-based events. The Hibernation module includes power-sequencing
logic, a real-time clock with a pair of match registers, low-battery detection circuitry, and interrupt
signalling to the processor. It also includes 64 32-bit words of non-volatile memory that can be used
for saving state during hibernation.
1.4.8 Hardware Details
Details on the pins and package can be found in the following sections:
■ “Pin Diagram” on page 646
■ “Signal Tables” on page 648
■ “Operating Characteristics” on page 678
■ “Electrical Characteristics” on page 679
■ “Package Information” on page 725
January 08, 2011 51
Texas Instruments-Production Data
Stellaris® LM3S2965 Microcontroller
2 The Cortex-M3 Processor
The ARM® Cortex™-M3 processor provides a high-performance, low-cost platform that meets the
system requirements of minimal memory implementation, reduced pin count, and low power
consumption, while delivering outstanding computational performance and exceptional system
response to interrupts. Features include:
■ Compact core.
■ Thumb-2 instruction set, delivering the high-performance expected of an ARM core in the memory
size usually associated with 8- and 16-bit devices; typically in the range of a few kilobytes of
memory for microcontroller class applications.
■ Rapid application execution through Harvard architecture characterized by separate buses for
instruction and data.
■ Exceptional interrupt handling, by implementing the register manipulations required for handling
an interrupt in hardware.
■ Deterministic, fast interrupt processing: always 12 cycles, or just 6 cycles with tail-chaining
■ Memory protection unit (MPU) to provide a privileged mode of operation for complex applications.
■ Migration from the ARM7™ processor family for better performance and power efficiency.
■ Full-featured debug solution
– Serial Wire JTAG Debug Port (SWJ-DP)
– Flash Patch and Breakpoint (FPB) unit for implementing breakpoints
– Data Watchpoint and Trigger (DWT) unit for implementing watchpoints, trigger resources,
and system profiling
– Instrumentation Trace Macrocell (ITM) for support of printf style debugging
– Trace Port Interface Unit (TPIU) for bridging to a Trace Port Analyzer
■ Optimized for single-cycle flash usage
■ Three sleep modes with clock gating for low power
■ Single-cycle multiply instruction and hardware divide
■ Atomic operations
■ ARM Thumb2 mixed 16-/32-bit instruction set
■ 1.25 DMIPS/MHz
The Stellaris® family of microcontrollers builds on this core to bring high-performance 32-bit computing
to cost-sensitive embedded microcontroller applications, such as factory automation and control,
industrial control power devices, building and home automation, and stepper motor control.
52 January 08, 2011
Texas Instruments-Production Data
The Cortex-M3 Processor
This chapter provides information on the Stellaris implementation of the Cortex-M3 processor,
including the programming model, the memory model, the exception model, fault handling, and
power management.
For technical details on the instruction set, see the Cortex™-M3 Instruction Set Technical User's
Manual.
2.1 Block Diagram
The Cortex-M3 processor is built on a high-performance processor core, with a 3-stage pipeline
Harvard architecture, making it ideal for demanding embedded applications. The processor delivers
exceptional power efficiency through an efficient instruction set and extensively optimized design,
providing high-end processing hardware including single-cycle 32x32 multiplication and dedicated
hardware division.
To facilitate the design of cost-sensitive devices, the Cortex-M3 processor implements tightly coupled
system components that reduce processor area while significantly improving interrupt handling and
system debug capabilities. The Cortex-M3 processor implements a version of the Thumb® instruction
set, ensuring high code density and reduced program memory requirements. The Cortex-M3
instruction set provides the exceptional performance expected of a modern 32-bit architecture, with
the high code density of 8-bit and 16-bit microcontrollers.
The Cortex-M3 processor closely integrates a nested interrupt controller (NVIC), to deliver
industry-leading interrupt performance. The Stellaris NVIC includes a non-maskable interrupt (NMI)
and provides eight interrupt priority levels. The tight integration of the processor core and NVIC
provides fast execution of interrupt service routines (ISRs), dramatically reducing interrupt latency.
The hardware stacking of registers and the ability to suspend load-multiple and store-multiple
operations further reduce interrupt latency. Interrupt handlers do not require any assembler stubs
which removes code overhead from the ISRs. Tail-chaining optimization also significantly reduces
the overhead when switching from one ISR to another. To optimize low-power designs, the NVIC
integrates with the sleep modes, including Deep-sleep mode, which enables the entire device to be
rapidly powered down.
January 08, 2011 53
Texas Instruments-Production Data
Stellaris® LM3S2965 Microcontroller
Figure 2-1. CPU Block Diagram
Private Peripheral
Bus
(internal)
Data
Watchpoint
and Trace
Interrupts
Debug
Sleep
Instrumentation
Trace Macrocell
Trace
Port
Interface
Unit
CM3 Core
Instructions Data
Flash
Patch and
Breakpoint
Memory
Protection
Unit
Debug
Access Port
Nested
Vectored
Interrupt
Controller
Serial Wire JTAG
Debug Port
Bus
Matrix
Adv. Peripheral
Bus
I-code bus
D-code bus
System bus
ROM
Table
Serial
Wire
Output
Trace
Port
(SWO)
ARM
Cortex-M3
2.2 Overview
2.2.1 System-Level Interface
The Cortex-M3 processor provides multiple interfaces using AMBA® technology to provide
high-speed, low-latency memory accesses. The core supports unaligned data accesses and
implements atomic bit manipulation that enables faster peripheral controls, system spinlocks, and
thread-safe Boolean data handling.
The Cortex-M3 processor has a memory protection unit (MPU) that provides fine-grain memory
control, enabling applications to implement security privilege levels and separate code, data and
stack on a task-by-task basis.
2.2.2 Integrated Configurable Debug
The Cortex-M3 processor implements a complete hardware debug solution, providing high system
visibility of the processor and memory through either a traditional JTAG port or a 2-pin Serial Wire
Debug (SWD) port that is ideal for microcontrollers and other small package devices. The Stellaris
implementation replaces the ARM SW-DP and JTAG-DP with the ARM CoreSight™-compliant
Serial Wire JTAG Debug Port (SWJ-DP) interface. The SWJ-DP interface combines the SWD and
JTAG debug ports into one module. See the ARM® Debug Interface V5 Architecture Specification
for details on SWJ-DP.
For system trace, the processor integrates an Instrumentation Trace Macrocell (ITM) alongside data
watchpoints and a profiling unit. To enable simple and cost-effective profiling of the system trace
events, a Serial Wire Viewer (SWV) can export a stream of software-generated messages, data
trace, and profiling information through a single pin.
54 January 08, 2011
Texas Instruments-Production Data
The Cortex-M3 Processor
The Flash Patch and Breakpoint Unit (FPB) provides up to eight hardware breakpoint comparators
that debuggers can use. The comparators in the FPB also provide remap functions of up to eight
words in the program code in the CODE memory region. This enables applications stored in a
read-only area of Flash memory to be patched in another area of on-chip SRAM or Flash memory.
If a patch is required, the application programs the FPB to remap a number of addresses. When
those addresses are accessed, the accesses are redirected to a remap table specified in the FPB
configuration.
For more information on the Cortex-M3 debug capabilities, see theARM® Debug Interface V5
Architecture Specification.
2.2.3 Trace Port Interface Unit (TPIU)
The TPIU acts as a bridge between the Cortex-M3 trace data from the ITM, and an off-chip Trace
Port Analyzer, as shown in Figure 2-2 on page 55.
Figure 2-2. TPIU Block Diagram
ATB
Interface
Asynchronous FIFO
APB
Interface
Trace Out
(serializer)
Debug
ATB
Slave
Port
APB
Slave
Port
Serial Wire
Trace Port
(SWO)
2.2.4 Cortex-M3 System Component Details
The Cortex-M3 includes the following system components:
■ SysTick
A 24-bit count-down timer that can be used as a Real-Time Operating System (RTOS) tick timer
or as a simple counter (see “System Timer (SysTick)” on page 94).
■ Nested Vectored Interrupt Controller (NVIC)
An embedded interrupt controller that supports low latency interrupt processing (see “Nested
Vectored Interrupt Controller (NVIC)” on page 95).
■ System Control Block (SCB)
January 08, 2011 55
Texas Instruments-Production Data
Stellaris® LM3S2965 Microcontroller
The programming model interface to the processor. The SCB provides system implementation
information and system control, including configuration, control, and reporting of system
exceptions( see “System Control Block (SCB)” on page 97).
■ Memory Protection Unit (MPU)
Improves system reliability by defining the memory attributes for different memory regions. The
MPU provides up to eight different regions and an optional predefined background region (see
“Memory Protection Unit (MPU)” on page 97).
2.3 Programming Model
This section describes the Cortex-M3 programming model. In addition to the individual core register
descriptions, information about the processor modes and privilege levels for software execution and
stacks is included.
2.3.1 Processor Mode and Privilege Levels for Software Execution
The Cortex-M3 has two modes of operation:
■ Thread mode
Used to execute application software. The processor enters Thread mode when it comes out of
reset.
■ Handler mode
Used to handle exceptions. When the processor has finished exception processing, it returns to
Thread mode.
In addition, the Cortex-M3 has two privilege levels:
■ Unprivileged
In this mode, software has the following restrictions:
– Limited access to the MSR and MRS instructions and no use of the CPS instruction
– No access to the system timer, NVIC, or system control block
– Possibly restricted access to memory or peripherals
■ Privileged
In this mode, software can use all the instructions and has access to all resources.
In Thread mode, the CONTROL register (see page 70) controls whether software execution is
privileged or unprivileged. In Handler mode, software execution is always privileged.
Only privileged software can write to the CONTROL register to change the privilege level for software
execution in Thread mode. Unprivileged software can use the SVC instruction to make a supervisor
call to transfer control to privileged software.
2.3.2 Stacks
The processor uses a full descending stack, meaning that the stack pointer indicates the last stacked
item on the stack memory. When the processor pushes a new item onto the stack, it decrements
the stack pointer and then writes the item to the new memory location. The processor implements
56 January 08, 2011
Texas Instruments-Production Data
The Cortex-M3 Processor
two stacks: the main stack and the process stack, with independent copies of the stack pointer (see
the SP register on page 60).
In Thread mode, the CONTROL register (see page 70) controls whether the processor uses the
main stack or the process stack. In Handler mode, the processor always uses the main stack. The
options for processor operations are shown in Table 2-1 on page 57.
Table 2-1. Summary of Processor Mode, Privilege Level, and Stack Use
Processor Mode Use Privilege Level Stack Used
Thread Applications Privileged or unprivileged a Main stack or process stack a
Handler Exception handlers Always privileged Main stack
a. See CONTROL (page 70).
2.3.3 Register Map
Figure 2-3 on page 57 shows the Cortex-M3 register set. Table 2-2 on page 58 lists the Core
registers. The core registers are not memory mapped and are accessed by register name, so the
base address is n/a (not applicable) and there is no offset.
Figure 2-3. Cortex-M3 Register Set
SP (R13)
LR (R14)
PC (R15)
R5
R6
R7
R0
R1
R3
R4
R2
R10
R11
R12
R8
R9
Low registers
High registers
PSP‡ MSP‡
PSR
PRIMASK
FAULTMASK
BASEPRI
CONTROL
General-purpose registers
Stack Pointer
Link Register
Program Counter
Program status register
Exception mask registers
CONTROL register
Special registers
‡Banked version of SP
January 08, 2011 57
Texas Instruments-Production Data
Stellaris® LM3S2965 Microcontroller
Table 2-2. Processor Register Map
See
Offset Name Type Reset Description page
- R0 R/W - Cortex General-Purpose Register 0 59
- R1 R/W - Cortex General-Purpose Register 1 59
- R2 R/W - Cortex General-Purpose Register 2 59
- R3 R/W - Cortex General-Purpose Register 3 59
- R4 R/W - Cortex General-Purpose Register 4 59
- R5 R/W - Cortex General-Purpose Register 5 59
- R6 R/W - Cortex General-Purpose Register 6 59
- R7 R/W - Cortex General-Purpose Register 7 59
- R8 R/W - Cortex General-Purpose Register 8 59
- R9 R/W - Cortex General-Purpose Register 9 59
- R10 R/W - Cortex General-Purpose Register 10 59
- R11 R/W - Cortex General-Purpose Register 11 59
- R12 R/W - Cortex General-Purpose Register 12 59
- SP R/W - Stack Pointer 60
- LR R/W 0xFFFF.FFFF Link Register 61
- PC R/W - Program Counter 62
- PSR R/W 0x0100.0000 Program Status Register 63
- PRIMASK R/W 0x0000.0000 Priority Mask Register 67
- FAULTMASK R/W 0x0000.0000 Fault Mask Register 68
- BASEPRI R/W 0x0000.0000 Base Priority Mask Register 69
- CONTROL R/W 0x0000.0000 Control Register 70
2.3.4 Register Descriptions
This section lists and describes the Cortex-M3 registers, in the order shown in Figure 2-3 on page 57.
The core registers are not memory mapped and are accessed by register name rather than offset.
Note: The register type shown in the register descriptions refers to type during program execution
in Thread mode and Handler mode. Debug access can differ.
58 January 08, 2011
Texas Instruments-Production Data
The Cortex-M3 Processor
Register 1: Cortex General-Purpose Register 0 (R0)
Register 2: Cortex General-Purpose Register 1 (R1)
Register 3: Cortex General-Purpose Register 2 (R2)
Register 4: Cortex General-Purpose Register 3 (R3)
Register 5: Cortex General-Purpose Register 4 (R4)
Register 6: Cortex General-Purpose Register 5 (R5)
Register 7: Cortex General-Purpose Register 6 (R6)
Register 8: Cortex General-Purpose Register 7 (R7)
Register 9: Cortex General-Purpose Register 8 (R8)
Register 10: Cortex General-Purpose Register 9 (R9)
Register 11: Cortex General-Purpose Register 10 (R10)
Register 12: Cortex General-Purpose Register 11 (R11)
Register 13: Cortex General-Purpose Register 12 (R12)
The Rn registers are 32-bit general-purpose registers for data operations and can be accessed
from either privileged or unprivileged mode.
Cortex General-Purpose Register 0 (R0)
Type R/W, reset -
31 30 29 28 27 26 25 24 23 22 21 20 19 18 17 16
DATA
Type R/W R/W R/W R/W R/W R/W R/W R/W R/W R/W R/W R/W R/W R/W R/W R/W
Reset - - - - - - - - - - - - - - - -
15 14 13 12 11 10 9 8 7 6 5 4 3 2 1 0
DATA
Type R/W R/W R/W R/W R/W R/W R/W R/W R/W R/W R/W R/W R/W R/W R/W R/W
Reset - - - - - - - - - - - - - - - -
Bit/Field Name Type Reset Description
31:0 DATA R/W - Register data.
January 08, 2011 59
Texas Instruments-Production Data
Stellaris® LM3S2965 Microcontroller
Register 14: Stack Pointer (SP)
The Stack Pointer (SP) is register R13. In Thread mode, the function of this register changes
depending on the ASP bit in the Control Register (CONTROL) register. When the ASP bit is clear,
this register is the Main Stack Pointer (MSP). When the ASP bit is set, this register is the Process
Stack Pointer (PSP). On reset, the ASP bit is clear, and the processor loads the MSP with the value
from address 0x0000.0000. The MSP can only be accessed in privileged mode; the PSP can be
accessed in either privileged or unprivileged mode.
Stack Pointer (SP)
Type R/W, reset -
31 30 29 28 27 26 25 24 23 22 21 20 19 18 17 16
SP
Type R/W R/W R/W R/W R/W R/W R/W R/W R/W R/W R/W R/W R/W R/W R/W R/W
Reset - - - - - - - - - - - - - - - -
15 14 13 12 11 10 9 8 7 6 5 4 3 2 1 0
SP
Type R/W R/W R/W R/W R/W R/W R/W R/W R/W R/W R/W R/W R/W R/W R/W R/W
Reset - - - - - - - - - - - - - - - -
Bit/Field Name Type Reset Description
31:0 SP R/W - This field is the address of the stack pointer.
60 January 08, 2011
Texas Instruments-Production Data
The Cortex-M3 Processor
Register 15: Link Register (LR)
The Link Register (LR) is register R14, and it stores the return information for subroutines, function
calls, and exceptions. LR can be accessed from either privileged or unprivileged mode.
EXC_RETURN is loaded into LR on exception entry. See Table 2-10 on page 87 for the values and
description.
Link Register (LR)
Type R/W, reset 0xFFFF.FFFF
31 30 29 28 27 26 25 24 23 22 21 20 19 18 17 16
LINK
Type R/W R/W R/W R/W R/W R/W R/W R/W R/W R/W R/W R/W R/W R/W R/W R/W
Reset 1 1 1 1 1 1 1 1 1 1 1 1 1 1 1 1
15 14 13 12 11 10 9 8 7 6 5 4 3 2 1 0
LINK
Type R/W R/W R/W R/W R/W R/W R/W R/W R/W R/W R/W R/W R/W R/W R/W R/W
Reset 1 1 1 1 1 1 1 1 1 1 1 1 1 1 1 1
Bit/Field Name Type Reset Description
31:0 LINK R/W 0xFFFF.FFFF This field is the return address.
January 08, 2011 61
Texas Instruments-Production Data
Stellaris® LM3S2965 Microcontroller
Register 16: Program Counter (PC)
The Program Counter (PC) is register R15, and it contains the current program address. On reset,
the processor loads the PC with the value of the reset vector, which is at address 0x0000.0004. Bit
0 of the reset vector is loaded into the THUMB bit of the EPSR at reset and must be 1. The PC register
can be accessed in either privileged or unprivileged mode.
Program Counter (PC)
Type R/W, reset -
31 30 29 28 27 26 25 24 23 22 21 20 19 18 17 16
PC
Type R/W R/W R/W R/W R/W R/W R/W R/W R/W R/W R/W R/W R/W R/W R/W R/W
Reset - - - - - - - - - - - - - - - -
15 14 13 12 11 10 9 8 7 6 5 4 3 2 1 0
PC
Type R/W R/W R/W R/W R/W R/W R/W R/W R/W R/W R/W R/W R/W R/W R/W R/W
Reset - - - - - - - - - - - - - - - -
Bit/Field Name Type Reset Description
31:0 PC R/W - This field is the current program address.
62 January 08, 2011
Texas Instruments-Production Data
The Cortex-M3 Processor
Register 17: Program Status Register (PSR)
Note: This register is also referred to as xPSR.
The Program Status Register (PSR) has three functions, and the register bits are assigned to the
different functions:
■ Application Program Status Register (APSR), bits 31:27,
■ Execution Program Status Register (EPSR), bits 26:24, 15:10
■ Interrupt Program Status Register (IPSR), bits 5:0
The PSR, IPSR, and EPSR registers can only be accessed in privileged mode; the APSR register
can be accessed in either privileged or unprivileged mode.
APSR contains the current state of the condition flags from previous instruction executions.
EPSR contains the Thumb state bit and the execution state bits for the If-Then (IT) instruction or
the Interruptible-Continuable Instruction (ICI) field for an interrupted load multiple or store multiple
instruction. Attempts to read the EPSR directly through application software using the MSR instruction
always return zero. Attempts to write the EPSR using the MSR instruction in application software
are always ignored. Fault handlers can examine the EPSR value in the stacked PSR to determine
the operation that faulted (see “Exception Entry and Return” on page 85).
IPSR contains the exception type number of the current Interrupt Service Routine (ISR).
These registers can be accessed individually or as a combination of any two or all three registers,
using the register name as an argument to the MSR or MRS instructions. For example, all of the
registers can be read using PSR with the MRS instruction, or APSR only can be written to using
APSR with the MSR instruction. page 63 shows the possible register combinations for the PSR. See
the MRS and MSR instruction descriptions in the Cortex™-M3 Instruction Set Technical User's Manual
for more information about how to access the program status registers.
Table 2-3. PSR Register Combinations
Register Type Combination
PSR R/Wa, b APSR, EPSR, and IPSR
IEPSR RO EPSR and IPSR
IAPSR R/Wa APSR and IPSR
EAPSR R/Wb APSR and EPSR
a. The processor ignores writes to the IPSR bits.
b. Reads of the EPSR bits return zero, and the processor ignores writes to these bits.
Program Status Register (PSR)
Type R/W, reset 0x0100.0000
31 30 29 28 27 26 25 24 23 22 21 20 19 18 17 16
N Z C V Q ICI / IT THUMB reserved
Type R/W R/W R/W R/W R/W RO RO RO RO RO RO RO RO RO RO RO
Reset 0 0 0 0 0 0 0 1 0 0 0 0 0 0 0 0
15 14 13 12 11 10 9 8 7 6 5 4 3 2 1 0
ICI / IT reserved ISRNUM
Type RO RO RO RO RO RO RO RO RO RO RO RO RO RO RO RO
Reset 0 0 0 0 0 0 0 0 0 0 0 0 0 0 0 0
January 08, 2011 63
Texas Instruments-Production Data
Stellaris® LM3S2965 Microcontroller
Bit/Field Name Type Reset Description
APSR Negative or Less Flag
Value Description
1 The previous operation result was negative or less than.
The previous operation result was positive, zero, greater than,
or equal.
0
The value of this bit is only meaningful when accessing PSR or APSR.
31 N R/W 0
APSR Zero Flag
Value Description
1 The previous operation result was zero.
0 The previous operation result was non-zero.
The value of this bit is only meaningful when accessing PSR or APSR.
30 Z R/W 0
APSR Carry or Borrow Flag
Value Description
The previous add operation resulted in a carry bit or the previous
subtract operation did not result in a borrow bit.
1
The previous add operation did not result in a carry bit or the
previous subtract operation resulted in a borrow bit.
0
The value of this bit is only meaningful when accessing PSR or APSR.
29 C R/W 0
APSR Overflow Flag
Value Description
1 The previous operation resulted in an overflow.
0 The previous operation did not result in an overflow.
The value of this bit is only meaningful when accessing PSR or APSR.
28 V R/W 0
APSR DSP Overflow and Saturation Flag
Value Description
1 DSP Overflow or saturation has occurred.
DSP overflow or saturation has not occurred since reset or since
the bit was last cleared.
0
The value of this bit is only meaningful when accessing PSR or APSR.
This bit is cleared by software using an MRS instruction.
27 Q R/W 0
64 January 08, 2011
Texas Instruments-Production Data
The Cortex-M3 Processor
Bit/Field Name Type Reset Description
EPSR ICI / IT status
These bits, along with bits 15:10, contain the Interruptible-Continuable
Instruction (ICI) field for an interrupted load multiple or store multiple
instruction or the execution state bits of the IT instruction.
When EPSR holds the ICI execution state, bits 26:25 are zero.
The If-Then block contains up to four instructions following a 16-bit IT
instruction. Each instruction in the block is conditional. The conditions
for the instructions are either all the same, or some can be the inverse
of others. See the Cortex™-M3 Instruction Set Technical User's Manual
for more information.
The value of this field is only meaningful when accessing PSR or EPSR.
26:25 ICI / IT RO 0x0
EPSR Thumb State
This bit indicates the Thumb state and should always be set.
The following can clear the THUMB bit:
■ The BLX, BX and POP{PC} instructions
■ Restoration from the stacked xPSR value on an exception return
■ Bit 0 of the vector value on an exception entry
Attempting to execute instructions when this bit is clear results in a fault
or lockup. See “Lockup” on page 89 for more information.
The value of this bit is only meaningful when accessing PSR or EPSR.
24 THUMB RO 1
Software should not rely on the value of a reserved bit. To provide
compatibility with future products, the value of a reserved bit should be
preserved across a read-modify-write operation.
23:16 reserved RO 0x00
EPSR ICI / IT status
These bits, along with bits 26:25, contain the Interruptible-Continuable
Instruction (ICI) field for an interrupted load multiple or store multiple
instruction or the execution state bits of the IT instruction.
When an interrupt occurs during the execution of an LDM, STM, PUSH
or POP instruction, the processor stops the load multiple or store multiple
instruction operation temporarily and stores the next register operand
in the multiple operation to bits 15:12. After servicing the interrupt, the
processor returns to the register pointed to by bits 15:12 and resumes
execution of the multiple load or store instruction. When EPSR holds
the ICI execution state, bits 11:10 are zero.
The If-Then block contains up to four instructions following a 16-bit IT
instruction. Each instruction in the block is conditional. The conditions
for the instructions are either all the same, or some can be the inverse
of others. See the Cortex™-M3 Instruction Set Technical User's Manual
for more information.
The value of this field is only meaningful when accessing PSR or EPSR.
15:10 ICI / IT RO 0x0
Software should not rely on the value of a reserved bit. To provide
compatibility with future products, the value of a reserved bit should be
preserved across a read-modify-write operation.
9:6 reserved RO 0x0
January 08, 2011 65
Texas Instruments-Production Data
Stellaris® LM3S2965 Microcontroller
Bit/Field Name Type Reset Description
IPSR ISR Number
This field contains the exception type number of the current Interrupt
Service Routine (ISR).
Value Description
0x00 Thread mode
0x01 Reserved
0x02 NMI
0x03 Hard fault
0x04 Memory management fault
0x05 Bus fault
0x06 Usage fault
0x07-0x0A Reserved
0x0B SVCall
0x0C Reserved for Debug
0x0D Reserved
0x0E PendSV
0x0F SysTick
0x10 Interrupt Vector 0
0x11 Interrupt Vector 1
... ...
0x3B Interrupt Vector 43
0x3C-0x3F Reserved
See “Exception Types” on page 80 for more information.
The value of this field is only meaningful when accessing PSR or IPSR.
5:0 ISRNUM RO 0x00
66 January 08, 2011
Texas Instruments-Production Data
The Cortex-M3 Processor
Register 18: Priority Mask Register (PRIMASK)
The PRIMASK register prevents activation of all exceptions with programmable priority. Reset,
non-maskable interrupt (NMI), and hard fault are the only exceptions with fixed priority. Exceptions
should be disabled when they might impact the timing of critical tasks. This register is only accessible
in privileged mode. The MSR and MRS instructions are used to access the PRIMASK register, and
the CPS instruction may be used to change the value of the PRIMASK register. See the Cortex™-M3
Instruction Set Technical User's Manual for more information on these instructions. For more
information on exception priority levels, see “Exception Types” on page 80.
Priority Mask Register (PRIMASK)
Type R/W, reset 0x0000.0000
31 30 29 28 27 26 25 24 23 22 21 20 19 18 17 16
reserved
Type RO RO RO RO RO RO RO RO RO RO RO RO RO RO RO RO
Reset 0 0 0 0 0 0 0 0 0 0 0 0 0 0 0 0
15 14 13 12 11 10 9 8 7 6 5 4 3 2 1 0
reserved PRIMASK
Type RO RO RO RO RO RO RO RO RO RO RO RO RO RO RO R/W
Reset 0 0 0 0 0 0 0 0 0 0 0 0 0 0 0 0
Bit/Field Name Type Reset Description
Software should not rely on the value of a reserved bit. To provide
compatibility with future products, the value of a reserved bit should be
preserved across a read-modify-write operation.
31:1 reserved RO 0x0000.000
Priority Mask
Value Description
Prevents the activation of all exceptions with configurable
priority.
1
0 No effect.
0 PRIMASK R/W 0
January 08, 2011 67
Texas Instruments-Production Data
Stellaris® LM3S2965 Microcontroller
Register 19: Fault Mask Register (FAULTMASK)
The FAULTMASK register prevents activation of all exceptions except for the Non-Maskable Interrupt
(NMI). Exceptions should be disabled when they might impact the timing of critical tasks. This register
is only accessible in privileged mode. The MSR and MRS instructions are used to access the
FAULTMASK register, and the CPS instruction may be used to change the value of the FAULTMASK
register. See the Cortex™-M3 Instruction Set Technical User's Manual for more information on
these instructions. For more information on exception priority levels, see “Exception
Types” on page 80.
Fault Mask Register (FAULTMASK)
Type R/W, reset 0x0000.0000
31 30 29 28 27 26 25 24 23 22 21 20 19 18 17 16
reserved
Type RO RO RO RO RO RO RO RO RO RO RO RO RO RO RO RO
Reset 0 0 0 0 0 0 0 0 0 0 0 0 0 0 0 0
15 14 13 12 11 10 9 8 7 6 5 4 3 2 1 0
reserved FAULTMASK
Type RO RO RO RO RO RO RO RO RO RO RO RO RO RO RO R/W
Reset 0 0 0 0 0 0 0 0 0 0 0 0 0 0 0 0
Bit/Field Name Type Reset Description
Software should not rely on the value of a reserved bit. To provide
compatibility with future products, the value of a reserved bit should be
preserved across a read-modify-write operation.
31:1 reserved RO 0x0000.000
Fault Mask
Value Description
1 Prevents the activation of all exceptions except for NMI.
0 No effect.
The processor clears the FAULTMASK bit on exit from any exception
handler except the NMI handler.
0 FAULTMASK R/W 0
68 January 08, 2011
Texas Instruments-Production Data
The Cortex-M3 Processor
Register 20: Base Priority Mask Register (BASEPRI)
The BASEPRI register defines the minimum priority for exception processing. When BASEPRI is
set to a nonzero value, it prevents the activation of all exceptions with the same or lower priority
level as the BASEPRI value. Exceptions should be disabled when they might impact the timing of
critical tasks. This register is only accessible in privileged mode. For more information on exception
priority levels, see “Exception Types” on page 80.
Base Priority Mask Register (BASEPRI)
Type R/W, reset 0x0000.0000
31 30 29 28 27 26 25 24 23 22 21 20 19 18 17 16
reserved
Type RO RO RO RO RO RO RO RO RO RO RO RO RO RO RO RO
Reset 0 0 0 0 0 0 0 0 0 0 0 0 0 0 0 0
15 14 13 12 11 10 9 8 7 6 5 4 3 2 1 0
reserved BASEPRI reserved
Type RO RO RO RO RO RO RO RO R/W R/W R/W RO RO RO RO RO
Reset 0 0 0 0 0 0 0 0 0 0 0 0 0 0 0 0
Bit/Field Name Type Reset Description
Software should not rely on the value of a reserved bit. To provide
compatibility with future products, the value of a reserved bit should be
preserved across a read-modify-write operation.
31:8 reserved RO 0x0000.00
Base Priority
Any exception that has a programmable priority level with the same or
lower priority as the value of this field is masked. The PRIMASK register
can be used to mask all exceptions with programmable priority levels.
Higher priority exceptions have lower priority levels.
Value Description
0x0 All exceptions are unmasked.
0x1 All exceptions with priority level 1-7 are masked.
0x2 All exceptions with priority level 2-7 are masked.
0x3 All exceptions with priority level 3-7 are masked.
0x4 All exceptions with priority level 4-7 are masked.
0x5 All exceptions with priority level 5-7 are masked.
0x6 All exceptions with priority level 6-7 are masked.
0x7 All exceptions with priority level 7 are masked.
7:5 BASEPRI R/W 0x0
Software should not rely on the value of a reserved bit. To provide
compatibility with future products, the value of a reserved bit should be
preserved across a read-modify-write operation.
4:0 reserved RO 0x0
January 08, 2011 69
Texas Instruments-Production Data
Stellaris® LM3S2965 Microcontroller
Register 21: Control Register (CONTROL)
The CONTROL register controls the stack used and the privilege level for software execution when
the processor is in Thread mode. This register is only accessible in privileged mode.
Handler mode always uses MSP, so the processor ignores explicit writes to the ASP bit of the
CONTROL register when in Handler mode. The exception entry and return mechanisms automatically
update the CONTROL register based on the EXC_RETURN value (see Table 2-10 on page 87).
In an OS environment, threads running in Thread mode should use the process stack and the kernel
and exception handlers should use the main stack. By default, Thread mode uses MSP. To switch
the stack pointer used in Thread mode to PSP, either use the MSR instruction to set the ASP bit, as
detailed in the Cortex™-M3 Instruction Set Technical User's Manual, or perform an exception return
to Thread mode with the appropriate EXC_RETURN value, as shown in Table 2-10 on page 87.
Note: When changing the stack pointer, software must use an ISB instruction immediately after
the MSR instruction, ensuring that instructions after the ISB execute use the new stack
pointer. See the Cortex™-M3 Instruction Set Technical User's Manual.
Control Register (CONTROL)
Type R/W, reset 0x0000.0000
31 30 29 28 27 26 25 24 23 22 21 20 19 18 17 16
reserved
Type RO RO RO RO RO RO RO RO RO RO RO RO RO RO RO RO
Reset 0 0 0 0 0 0 0 0 0 0 0 0 0 0 0 0
15 14 13 12 11 10 9 8 7 6 5 4 3 2 1 0
reserved ASP TMPL
Type RO RO RO RO RO RO RO RO RO RO RO RO RO RO R/W R/W
Reset 0 0 0 0 0 0 0 0 0 0 0 0 0 0 0 0
Bit/Field Name Type Reset Description
Software should not rely on the value of a reserved bit. To provide
compatibility with future products, the value of a reserved bit should be
preserved across a read-modify-write operation.
31:2 reserved RO 0x0000.000
Active Stack Pointer
Value Description
1 PSP is the current stack pointer.
0 MSP is the current stack pointer
In Handler mode, this bit reads as zero and ignores writes. The
Cortex-M3 updates this bit automatically on exception return.
1 ASP R/W 0
Thread Mode Privilege Level
Value Description
1 Unprivileged software can be executed in Thread mode.
0 Only privileged software can be executed in Thread mode.
0 TMPL R/W 0
70 January 08, 2011
Texas Instruments-Production Data
The Cortex-M3 Processor
2.3.5 Exceptions and Interrupts
The Cortex-M3 processor supports interrupts and system exceptions. The processor and the Nested
Vectored Interrupt Controller (NVIC) prioritize and handle all exceptions. An exception changes the
normal flow of software control. The processor uses Handler mode to handle all exceptions except
for reset. See “Exception Entry and Return” on page 85 for more information.
The NVIC registers control interrupt handling. See “Nested Vectored Interrupt Controller
(NVIC)” on page 95 for more information.
2.3.6 Data Types
The Cortex-M3 supports 32-bit words, 16-bit halfwords, and 8-bit bytes. The processor also supports
64-bit data transfer instructions. All instruction and data memory accesses are little endian. See
“Memory Regions, Types and Attributes” on page 73 for more information.
2.4 Memory Model
This section describes the processor memory map, the behavior of memory accesses, and the
bit-banding features. The processor has a fixed memory map that provides up to 4 GB of addressable
memory.
The memory map for the LM3S2965 controller is provided in Table 2-4 on page 71. In this manual,
register addresses are given as a hexadecimal increment, relative to the module’s base address
as shown in the memory map.
The regions for SRAM and peripherals include bit-band regions. Bit-banding provides atomic
operations to bit data (see “Bit-Banding” on page 75).
The processor reserves regions of the Private peripheral bus (PPB) address range for core peripheral
registers (see “Cortex-M3 Peripherals” on page 94).
Note: Within the memory map, all reserved space returns a bus fault when read or written.
Table 2-4. Memory Map
For details,
see page ...
Start End Description
Memory
0x0000.0000 0x0003.FFFF On-chip Flash 257
0x0004.0000 0x1FFF.FFFF Reserved -
0x2000.0000 0x2000.FFFF Bit-banded on-chip SRAM 256
0x2001.0000 0x21FF.FFFF Reserved -
0x2200.0000 0x221F.FFFF Bit-band alias of 0x2000.0000 through 0x200F.FFFF 256
0x2220.0000 0x3FFF.FFFF Reserved -
FiRM Peripherals
0x4000.0000 0x4000.0FFF Watchdog timer 0 363
0x4000.1000 0x4000.3FFF Reserved -
0x4000.4000 0x4000.4FFF GPIO Port A 289
0x4000.5000 0x4000.5FFF GPIO Port B 289
0x4000.6000 0x4000.6FFF GPIO Port C 289
0x4000.7000 0x4000.7FFF GPIO Port D 289
0x4000.8000 0x4000.8FFF SSI0 472
January 08, 2011 71
Texas Instruments-Production Data
Stellaris® LM3S2965 Microcontroller
Table 2-4. Memory Map (continued)
For details,
see page ...
Start End Description
0x4000.9000 0x4000.9FFF SSI1 472
0x4000.A000 0x4000.BFFF Reserved -
0x4000.C000 0x4000.CFFF UART0 427
0x4000.D000 0x4000.DFFF UART1 427
0x4000.E000 0x4000.EFFF UART2 427
0x4000.F000 0x4001.FFFF Reserved -
Peripherals
0x4002.0000 0x4002.0FFF I2C 0 512
0x4002.1000 0x4002.1FFF I2C 1 512
0x4002.2000 0x4002.3FFF Reserved -
0x4002.4000 0x4002.4FFF GPIO Port E 289
0x4002.5000 0x4002.5FFF GPIO Port F 289
0x4002.6000 0x4002.6FFF GPIO Port G 289
0x4002.7000 0x4002.7FFF GPIO Port H 289
0x4002.8000 0x4002.8FFF PWM 599
0x4002.9000 0x4002.BFFF Reserved -
0x4002.C000 0x4002.CFFF QEI0 633
0x4002.D000 0x4002.DFFF QEI1 633
0x4002.E000 0x4002.FFFF Reserved -
0x4003.0000 0x4003.0FFF Timer 0 335
0x4003.1000 0x4003.1FFF Timer 1 335
0x4003.2000 0x4003.2FFF Timer 2 335
0x4003.3000 0x4003.3FFF Timer 3 335
0x4003.4000 0x4003.7FFF Reserved -
0x4003.8000 0x4003.8FFF ADC0 392
0x4003.9000 0x4003.BFFF Reserved -
0x4003.C000 0x4003.CFFF Analog Comparators 579
0x4003.D000 0x4003.FFFF Reserved -
0x4004.0000 0x4004.0FFF CAN0 Controller 553
0x4004.1000 0x4004.1FFF CAN1 Controller 553
0x4004.2000 0x400F.BFFF Reserved -
0x400F.C000 0x400F.CFFF Hibernation Module 243
0x400F.D000 0x400F.DFFF Flash memory control 261
0x400F.E000 0x400F.EFFF System control 183
0x400F.F000 0x41FF.FFFF Reserved -
0x4200.0000 0x43FF.FFFF Bit-banded alias of 0x4000.0000 through 0x400F.FFFF -
0x4400.0000 0xDFFF.FFFF Reserved -
Private Peripheral Bus
0xE000.0000 0xE000.0FFF Instrumentation Trace Macrocell (ITM) 54
0xE000.1000 0xE000.1FFF Data Watchpoint and Trace (DWT) 54
0xE000.2000 0xE000.2FFF Flash Patch and Breakpoint (FPB) 54
72 January 08, 2011
Texas Instruments-Production Data
The Cortex-M3 Processor
Table 2-4. Memory Map (continued)
For details,
see page ...
Start End Description
0xE000.3000 0xE000.DFFF Reserved -
0xE000.E000 0xE000.EFFF Cortex-M3 Peripherals (SysTick, NVIC, SCB, and MPU) 79
0xE000.F000 0xE003.FFFF Reserved -
0xE004.0000 0xE004.0FFF Trace Port Interface Unit (TPIU) 55
0xE004.1000 0xFFFF.FFFF Reserved -
2.4.1 Memory Regions, Types and Attributes
The memory map and the programming of the MPU split the memory map into regions. Each region
has a defined memory type, and some regions have additional memory attributes. The memory
type and attributes determine the behavior of accesses to the region.
The memory types are:
■ Normal: The processor can re-order transactions for efficiency and perform speculative reads.
■ Device: The processor preserves transaction order relative to other transactions to Device or
Strongly Ordered memory.
■ Strongly Ordered: The processor preserves transaction order relative to all other transactions.
The different ordering requirements for Device and Strongly Ordered memory mean that the memory
system can buffer a write to Device memory but must not buffer a write to Strongly Ordered memory.
An additional memory attribute is Execute Never (XN), which means the processor prevents
instruction accesses. A fault exception is generated only on execution of an instruction executed
from an XN region.
2.4.2 Memory System Ordering of Memory Accesses
For most memory accesses caused by explicit memory access instructions, the memory system
does not guarantee that the order in which the accesses complete matches the program order of
the instructions, providing the order does not affect the behavior of the instruction sequence. Normally,
if correct program execution depends on two memory accesses completing in program order,
software must insert a memory barrier instruction between the memory access instructions (see
“Software Ordering of Memory Accesses” on page 74).
However, the memory system does guarantee ordering of accesses to Device and Strongly Ordered
memory. For two memory access instructions A1 and A2, if both A1 and A2 are accesses to either
Device or Strongly Ordered memory, and if A1 occurs before A2 in program order, A1 is always
observed before A2.
2.4.3 Behavior of Memory Accesses
Table 2-5 on page 74 shows the behavior of accesses to each region in the memory map. See
“Memory Regions, Types and Attributes” on page 73 for more information on memory types and
the XN attribute. Stellaris devices may have reserved memory areas within the address ranges
shown below (refer to Table 2-4 on page 71 for more information).
January 08, 2011 73
Texas Instruments-Production Data
Stellaris® LM3S2965 Microcontroller
Table 2-5. Memory Access Behavior
Execute Description
Never
(XN)
Address Range Memory Region Memory Type
This executable region is for program code.
Data can also be stored here.
0x0000.0000 - 0x1FFF.FFFF Code Normal -
This executable region is for data. Code
can also be stored here. This region
includes bit band and bit band alias areas
(see Table 2-6 on page 76).
0x2000.0000 - 0x3FFF.FFFF SRAM Normal -
This region includes bit band and bit band
alias areas (see Table 2-7 on page 76).
0x4000.0000 - 0x5FFF.FFFF Peripheral Device XN
0x6000.0000 - 0x9FFF.FFFF External RAM Normal - This executable region is for data.
0xA000.0000 - 0xDFFF.FFFF External device Device XN This region is for external device memory.
This region includes the NVIC, system
timer, and system control block.
Strongly XN
Ordered
Private peripheral
bus
0xE000.0000- 0xE00F.FFFF
0xE010.0000- 0xFFFF.FFFF Reserved - - -
The Code, SRAM, and external RAM regions can hold programs. However, it is recommended that
programs always use the Code region because the Cortex-M3 has separate buses that can perform
instruction fetches and data accesses simultaneously.
The MPU can override the default memory access behavior described in this section. For more
information, see “Memory Protection Unit (MPU)” on page 97.
The Cortex-M3 prefetches instructions ahead of execution and speculatively prefetches from branch
target addresses.
2.4.4 Software Ordering of Memory Accesses
The order of instructions in the program flow does not always guarantee the order of the
corresponding memory transactions for the following reasons:
■ The processor can reorder some memory accesses to improve efficiency, providing this does
not affect the behavior of the instruction sequence.
■ The processor has multiple bus interfaces.
■ Memory or devices in the memory map have different wait states.
■ Some memory accesses are buffered or speculative.
“Memory System Ordering of Memory Accesses” on page 73 describes the cases where the memory
system guarantees the order of memory accesses. Otherwise, if the order of memory accesses is
critical, software must include memory barrier instructions to force that ordering. The Cortex-M3
has the following memory barrier instructions:
■ The Data Memory Barrier (DMB) instruction ensures that outstanding memory transactions
complete before subsequent memory transactions.
■ The Data Synchronization Barrier (DSB) instruction ensures that outstanding memory transactions
complete before subsequent instructions execute.
■ The Instruction Synchronization Barrier (ISB) instruction ensures that the effect of all completed
memory transactions is recognizable by subsequent instructions.
74 January 08, 2011
Texas Instruments-Production Data
The Cortex-M3 Processor
Memory barrier instructions can be used in the following situations:
■ MPU programming
– If the MPU settings are changed and the change must be effective on the very next instruction,
use a DSB instruction to ensure the effect of the MPU takes place immediately at the end of
context switching.
– Use an ISB instruction to ensure the new MPU setting takes effect immediately after
programming the MPU region or regions, if the MPU configuration code was accessed using
a branch or call. If the MPU configuration code is entered using exception mechanisms, then
an ISB instruction is not required.
■ Vector table
If the program changes an entry in the vector table and then enables the corresponding exception,
use a DMB instruction between the operations. The DMB instruction ensures that if the exception
is taken immediately after being enabled, the processor uses the new exception vector.
■ Self-modifying code
If a program contains self-modifying code, use an ISB instruction immediately after the code
modification in the program. The ISB instruction ensures subsequent instruction execution uses
the updated program.
■ Memory map switching
If the system contains a memory map switching mechanism, use a DSB instruction after switching
the memory map in the program. The DSB instruction ensures subsequent instruction execution
uses the updated memory map.
■ Dynamic exception priority change
When an exception priority has to change when the exception is pending or active, use DSB
instructions after the change. The change then takes effect on completion of the DSB instruction.
Memory accesses to Strongly Ordered memory, such as the System Control Block, do not require
the use of DMB instructions.
For more information on the memory barrier instructions, see the Cortex™-M3 Instruction Set
Technical User's Manual.
2.4.5 Bit-Banding
A bit-band region maps each word in a bit-band alias region to a single bit in the bit-band region.
The bit-band regions occupy the lowest 1 MB of the SRAM and peripheral memory regions. Accesses
to the 32-MB SRAM alias region map to the 1-MB SRAM bit-band region, as shown in Table
2-6 on page 76. Accesses to the 32-MB peripheral alias region map to the 1-MB peripheral bit-band
region, as shown in Table 2-7 on page 76. For the specific address range of the bit-band regions,
see Table 2-4 on page 71.
Note: A word access to the SRAM or the peripheral bit-band alias region maps to a single bit in
the SRAM or peripheral bit-band region.
A word access to a bit band address results in a word access to the underlying memory,
and similarly for halfword and byte accesses. This allows bit band accesses to match the
access requirements of the underlying peripheral.
January 08, 2011 75
Texas Instruments-Production Data
Stellaris® LM3S2965 Microcontroller
Table 2-6. SRAM Memory Bit-Banding Regions
Address Range Memory Region Instruction and Data Accesses
Direct accesses to this memory range behave as SRAM memory
accesses, but this region is also bit addressable through bit-band
alias.
0x2000.0000 - 0x200F.FFFF SRAM bit-band region
Data accesses to this region are remapped to bit band region.
A write operation is performed as read-modify-write. Instruction
accesses are not remapped.
0x2200.0000 - 0x23FF.FFFF SRAM bit-band alias
Table 2-7. Peripheral Memory Bit-Banding Regions
Address Range Memory Region Instruction and Data Accesses
Direct accesses to this memory range behave as peripheral
memory accesses, but this region is also bit addressable through
bit-band alias.
0x4000.0000 - 0x400F.FFFF Peripheral bit-band region
Data accesses to this region are remapped to bit band region.
A write operation is performed as read-modify-write. Instruction
accesses are not permitted.
0x4200.0000 - 0x43FF.FFFF Peripheral bit-band alias
The following formula shows how the alias region maps onto the bit-band region:
bit_word_offset = (byte_offset x 32) + (bit_number x 4)
bit_word_addr = bit_band_base + bit_word_offset
where:
bit_word_offset
The position of the target bit in the bit-band memory region.
bit_word_addr
The address of the word in the alias memory region that maps to the targeted bit.
bit_band_base
The starting address of the alias region.
byte_offset
The number of the byte in the bit-band region that contains the targeted bit.
bit_number
The bit position, 0-7, of the targeted bit.
Figure 2-4 on page 77 shows examples of bit-band mapping between the SRAM bit-band alias
region and the SRAM bit-band region:
■ The alias word at 0x23FF.FFE0 maps to bit 0 of the bit-band byte at 0x200F.FFFF:
0x23FF.FFE0 = 0x2200.0000 + (0x000F.FFFF*32) + (0*4)
■ The alias word at 0x23FF.FFFC maps to bit 7 of the bit-band byte at 0x200F.FFFF:
0x23FF.FFFC = 0x2200.0000 + (0x000F.FFFF*32) + (7*4)
76 January 08, 2011
Texas Instruments-Production Data
The Cortex-M3 Processor
■ The alias word at 0x2200.0000 maps to bit 0 of the bit-band byte at 0x2000.0000:
0x2200.0000 = 0x2200.0000 + (0*32) + (0*4)
■ The alias word at 0x2200.001C maps to bit 7 of the bit-band byte at 0x2000.0000:
0x2200.001C = 0x2200.0000+ (0*32) + (7*4)
Figure 2-4. Bit-Band Mapping
0x23FF.FFE4
0x2200.0004
0x23FF.FFFC 0x23FF.FFF8 0x23FF.FFF4 0x23FF.FFF0 0x23FF.FFEC 0x23FF.FFE8 0x23FF.FFE0
0x2200.001C 0x2200.0018 0x2200.0014 0x2200.0010 0x2200.000C 0x2200.0008 0x2200.0000
32-MB Alias Region
0
7 0
7 0
0x2000.0003 0x2000.0002 0x2000.0001 0x2000.0000
6 5 4 3 2 1 7 6 5 4 3 2 1 0 7 6 5 4 3 2 1 7 6 5 4 3 2 1 0
7 6 5 4 3 2 1 0 7 6 5 4 3 2 1 0 7 6 5 4 3 2 1 0 6 5 4 3 2 1
0x200F.FFFF 0x200F.FFFE 0x200F.FFFD 0x200F.FFFC
1-MB SRAM Bit-Band Region
2.4.5.1 Directly Accessing an Alias Region
Writing to a word in the alias region updates a single bit in the bit-band region.
Bit 0 of the value written to a word in the alias region determines the value written to the targeted
bit in the bit-band region. Writing a value with bit 0 set writes a 1 to the bit-band bit, and writing a
value with bit 0 clear writes a 0 to the bit-band bit.
Bits 31:1 of the alias word have no effect on the bit-band bit. Writing 0x01 has the same effect as
writing 0xFF. Writing 0x00 has the same effect as writing 0x0E.
When reading a word in the alias region, 0x0000.0000 indicates that the targeted bit in the bit-band
region is clear and 0x0000.0001 indicates that the targeted bit in the bit-band region is set.
2.4.5.2 Directly Accessing a Bit-Band Region
“Behavior of Memory Accesses” on page 73 describes the behavior of direct byte, halfword, or word
accesses to the bit-band regions.
2.4.6 Data Storage
The processor views memory as a linear collection of bytes numbered in ascending order from zero.
For example, bytes 0-3 hold the first stored word, and bytes 4-7 hold the second stored word. Data
is stored in little-endian format, with the least-significant byte (lsbyte) of a word stored at the
January 08, 2011 77
Texas Instruments-Production Data
Stellaris® LM3S2965 Microcontroller
lowest-numbered byte, and the most-significant byte (msbyte) stored at the highest-numbered byte.
Figure 2-5 on page 78 illustrates how data is stored.
Figure 2-5. Data Storage
Memory Register
Address A
A+1
lsbyte
msbyte
A+2
A+3
7 0
B3 B2 B1 B0
31 24 23 16 15 8 7 0
B0
B1
B2
B3
2.4.7 Synchronization Primitives
The Cortex-M3 instruction set includes pairs of synchronization primitives which provide a
non-blocking mechanism that a thread or process can use to obtain exclusive access to a memory
location. Software can use these primitives to perform a guaranteed read-modify-write memory
update sequence or for a semaphore mechanism.
A pair of synchronization primitives consists of:
■ A Load-Exclusive instruction, which is used to read the value of a memory location and requests
exclusive access to that location.
■ A Store-Exclusive instruction, which is used to attempt to write to the same memory location and
returns a status bit to a register. If this status bit is clear, it indicates that the thread or process
gained exclusive access to the memory and the write succeeds; if this status bit is set, it indicates
that the thread or process did not gain exclusive access to the memory and no write is performed.
The pairs of Load-Exclusive and Store-Exclusive instructions are:
■ The word instructions LDREX and STREX
■ The halfword instructions LDREXH and STREXH
■ The byte instructions LDREXB and STREXB
Software must use a Load-Exclusive instruction with the corresponding Store-Exclusive instruction.
To perform a guaranteed read-modify-write of a memory location, software must:
1. Use a Load-Exclusive instruction to read the value of the location.
2. Update the value, as required.
3. Use a Store-Exclusive instruction to attempt to write the new value back to the memory location,
and test the returned status bit. If the status bit is clear, the read-modify-write completed
successfully; if the status bit is set, no write was performed, which indicates that the value
returned at step 1 might be out of date. The software must retry the read-modify-write sequence.
Software can use the synchronization primitives to implement a semaphore as follows:
78 January 08, 2011
Texas Instruments-Production Data
The Cortex-M3 Processor
1. Use a Load-Exclusive instruction to read from the semaphore address to check whether the
semaphore is free.
2. If the semaphore is free, use a Store-Exclusive to write the claim value to the semaphore
address.
3. If the returned status bit from step 2 indicates that the Store-Exclusive succeeded, then the
software has claimed the semaphore. However, if the Store-Exclusive failed, another process
might have claimed the semaphore after the software performed step 1.
The Cortex-M3 includes an exclusive access monitor that tags the fact that the processor has
executed a Load-Exclusive instruction. The processor removes its exclusive access tag if:
■ It executes a CLREX instruction.
■ It executes a Store-Exclusive instruction, regardless of whether the write succeeds.
■ An exception occurs, which means the processor can resolve semaphore conflicts between
different threads.
For more information about the synchronization primitive instructions, see the Cortex™-M3 Instruction
Set Technical User's Manual.
2.5 Exception Model
The ARM Cortex-M3 processor and the Nested Vectored Interrupt Controller (NVIC) prioritize and
handle all exceptions in Handler Mode. The processor state is automatically stored to the stack on
an exception and automatically restored from the stack at the end of the Interrupt Service Routine
(ISR). The vector is fetched in parallel to the state saving, enabling efficient interrupt entry. The
processor supports tail-chaining, which enables back-to-back interrupts to be performed without the
overhead of state saving and restoration.
Table 2-8 on page 81 lists all exception types. Software can set eight priority levels on seven of
these exceptions (system handlers) as well as on 42 interrupts (listed in Table 2-9 on page 82).
Priorities on the system handlers are set with the NVIC System Handler Priority n (SYSPRIn)
registers. Interrupts are enabled through the NVIC Interrupt Set Enable n (ENn) register and
prioritized with the NVIC Interrupt Priority n (PRIn) registers. Priorities can be grouped by splitting
priority levels into preemption priorities and subpriorities. All the interrupt registers are described in
“Nested Vectored Interrupt Controller (NVIC)” on page 95.
Internally, the highest user-programmable priority (0) is treated as fourth priority, after a Reset,
Non-Maskable Interrupt (NMI), and a Hard Fault, in that order. Note that 0 is the default priority for
all the programmable priorities.
Important: After a write to clear an interrupt source, it may take several processor cycles for the
NVIC to see the interrupt source de-assert. Thus if the interrupt clear is done as the
last action in an interrupt handler, it is possible for the interrupt handler to complete
while the NVIC sees the interrupt as still asserted, causing the interrupt handler to be
re-entered errantly. This situation can be avoided by either clearing the interrupt source
at the beginning of the interrupt handler or by performing a read or write after the write
to clear the interrupt source (and flush the write buffer).
See “Nested Vectored Interrupt Controller (NVIC)” on page 95 for more information on exceptions
and interrupts.
January 08, 2011 79
Texas Instruments-Production Data
Stellaris® LM3S2965 Microcontroller
2.5.1 Exception States
Each exception is in one of the following states:
■ Inactive. The exception is not active and not pending.
■ Pending. The exception is waiting to be serviced by the processor. An interrupt request from a
peripheral or from software can change the state of the corresponding interrupt to pending.
■ Active. An exception that is being serviced by the processor but has not completed.
Note: An exception handler can interrupt the execution of another exception handler. In this
case, both exceptions are in the active state.
■ Active and Pending. The exception is being serviced by the processor, and there is a pending
exception from the same source.
2.5.2 Exception Types
The exception types are:
■ Reset. Reset is invoked on power up or a warm reset. The exception model treats reset as a
special form of exception. When reset is asserted, the operation of the processor stops, potentially
at any point in an instruction. When reset is deasserted, execution restarts from the address
provided by the reset entry in the vector table. Execution restarts as privileged execution in
Thread mode.
■ NMI. A non-maskable Interrupt (NMI) can be signaled using the NMI signal or triggered by
software using the Interrupt Control and State (INTCTRL) register. This exception has the
highest priority other than reset. NMI is permanently enabled and has a fixed priority of -2. NMIs
cannot be masked or prevented from activation by any other exception or preempted by any
exception other than reset.
■ Hard Fault. A hard fault is an exception that occurs because of an error during exception
processing, or because an exception cannot be managed by any other exception mechanism.
Hard faults have a fixed priority of -1, meaning they have higher priority than any exception with
configurable priority.
■ Memory Management Fault. A memory management fault is an exception that occurs because
of a memory protection related fault, including access violation and no match. The MPU or the
fixed memory protection constraints determine this fault, for both instruction and data memory
transactions. This fault is used to abort instruction accesses to Execute Never (XN) memory
regions, even if the MPU is disabled.
■ Bus Fault. A bus fault is an exception that occurs because of a memory-related fault for an
instruction or data memory transaction such as a prefetch fault or a memory access fault. This
fault can be enabled or disabled.
■ Usage Fault. A usage fault is an exception that occurs because of a fault related to instruction
execution, such as:
– An undefined instruction
– An illegal unaligned access
– Invalid state on instruction execution
80 January 08, 2011
Texas Instruments-Production Data
The Cortex-M3 Processor
– An error on exception return
An unaligned address on a word or halfword memory access or division by zero can cause a
usage fault when the core is properly configured.
■ SVCall. A supervisor call (SVC) is an exception that is triggered by the SVC instruction. In an
OS environment, applications can use SVC instructions to access OS kernel functions and device
drivers.
■ Debug Monitor. This exception is caused by the debug monitor (when not halting). This exception
is only active when enabled. This exception does not activate if it is a lower priority than the
current activation.
■ PendSV. PendSV is a pendable, interrupt-driven request for system-level service. In an OS
environment, use PendSV for context switching when no other exception is active. PendSV is
triggered using the Interrupt Control and State (INTCTRL) register.
■ SysTick. A SysTick exception is an exception that the system timer generates when it reaches
zero when it is enabled to generate an interrupt. Software can also generate a SysTick exception
using the Interrupt Control and State (INTCTRL) register. In an OS environment, the processor
can use this exception as system tick.
■ Interrupt (IRQ). An interrupt, or IRQ, is an exception signaled by a peripheral or generated by
a software request and fed through the NVIC (prioritized). All interrupts are asynchronous to
instruction execution. In the system, peripherals use interrupts to communicate with the processor.
Table 2-9 on page 82 lists the interrupts on the LM3S2965 controller.
For an asynchronous exception, other than reset, the processor can execute another instruction
between when the exception is triggered and when the processor enters the exception handler.
Privileged software can disable the exceptions that Table 2-8 on page 81 shows as having
configurable priority (see the SYSHNDCTRL register on page 136 and the DIS0 register on page 111).
For more information about hard faults, memory management faults, bus faults, and usage faults,
see “Fault Handling” on page 87.
Table 2-8. Exception Types
Vector Address or Activation
Offsetb
Vector Prioritya
Number
Exception Type
Stack top is loaded from the first
entry of the vector table on reset.
- 0 - 0x0000.0000
Reset 1 -3 (highest) 0x0000.0004 Asynchronous
Non-Maskable Interrupt 2 -2 0x0000.0008 Asynchronous
(NMI)
Hard Fault 3 -1 0x0000.000C -
Memory Management 4 programmablec 0x0000.0010 Synchronous
Synchronous when precise and
asynchronous when imprecise
Bus Fault 5 programmablec 0x0000.0014
Usage Fault 6 programmablec 0x0000.0018 Synchronous
- 7-10 - - Reserved
SVCall 11 programmablec 0x0000.002C Synchronous
Debug Monitor 12 programmablec 0x0000.0030 Synchronous
- 13 - - Reserved
January 08, 2011 81
Texas Instruments-Production Data
Stellaris® LM3S2965 Microcontroller
Table 2-8. Exception Types (continued)
Vector Address or Activation
Offsetb
Vector Prioritya
Number
Exception Type
PendSV 14 programmablec 0x0000.0038 Asynchronous
SysTick 15 programmablec 0x0000.003C Asynchronous
Interrupts 16 and above programmabled 0x0000.0040 and above Asynchronous
a. 0 is the default priority for all the programmable priorities.
b. See “Vector Table” on page 83.
c. See SYSPRI1 on page 133.
d. See PRIn registers on page 119.
Table 2-9. Interrupts
Vector Address or Description
Offset
Interrupt Number (Bit
in Interrupt Registers)
Vector Number
0x0000.0000 - Processor exceptions
0x0000.003C
0-15 -
16 0 0x0000.0040 GPIO Port A
17 1 0x0000.0044 GPIO Port B
18 2 0x0000.0048 GPIO Port C
19 3 0x0000.004C GPIO Port D
20 4 0x0000.0050 GPIO Port E
21 5 0x0000.0054 UART0
22 6 0x0000.0058 UART1
23 7 0x0000.005C SSI0
24 8 0x0000.0060 I2C0
25 9 - Reserved
26 10 0x0000.0068 PWM Generator 0
27 11 0x0000.006C PWM Generator 1
28 12 0x0000.0070 PWM Generator 2
29 13 0x0000.0074 QEI0
30 14 0x0000.0078 ADC0 Sequence 0
31 15 0x0000.007C ADC0 Sequence 1
32 16 0x0000.0080 ADC0 Sequence 2
33 17 0x0000.0084 ADC0 Sequence 3
34 18 0x0000.0088 Watchdog Timer 0
35 19 0x0000.008C Timer 0A
36 20 0x0000.0090 Timer 0B
37 21 0x0000.0094 Timer 1A
38 22 0x0000.0098 Timer 1B
39 23 0x0000.009C Timer 2A
40 24 0x0000.00A0 Timer 2B
41 25 0x0000.00A4 Analog Comparator 0
42 26 0x0000.00A8 Analog Comparator 1
43 27 0x0000.00AC Analog Comparator 2
44 28 0x0000.00B0 System Control
82 January 08, 2011
Texas Instruments-Production Data
The Cortex-M3 Processor
Table 2-9. Interrupts (continued)
Vector Address or Description
Offset
Interrupt Number (Bit
in Interrupt Registers)
Vector Number
45 29 0x0000.00B4 Flash Memory Control
46 30 0x0000.00B8 GPIO Port F
47 31 0x0000.00BC GPIO Port G
48 32 0x0000.00C0 GPIO Port H
49 33 0x0000.00C4 UART2
50 34 0x0000.00C8 SSI1
51 35 0x0000.00CC Timer 3A
52 36 0x0000.00D0 Timer 3B
53 37 0x0000.00D4 I2C1
54 38 0x0000.00D8 QEI1
55 39 0x0000.00DC CAN0
56 40 0x0000.00E0 CAN1
57-58 41-42 - Reserved
59 43 0x0000.00EC Hibernation Module
2.5.3 Exception Handlers
The processor handles exceptions using:
■ Interrupt Service Routines (ISRs). Interrupts (IRQx) are the exceptions handled by ISRs.
■ Fault Handlers. Hard fault, memory management fault, usage fault, and bus fault are fault
exceptions handled by the fault handlers.
■ System Handlers. NMI, PendSV, SVCall, SysTick, and the fault exceptions are all system
exceptions that are handled by system handlers.
2.5.4 Vector Table
The vector table contains the reset value of the stack pointer and the start addresses, also called
exception vectors, for all exception handlers. The vector table is constructed using the vector address
or offset shown in Table 2-8 on page 81. Figure 2-6 on page 84 shows the order of the exception
vectors in the vector table. The least-significant bit of each vector must be 1, indicating that the
exception handler is Thumb code
January 08, 2011 83
Texas Instruments-Production Data
Stellaris® LM3S2965 Microcontroller
Figure 2-6. Vector table
Initial SP value
Reset
Hard fault
NMI
Memory management fault
Usage fault
Bus fault
0x0000
0x0004
0x0008
0x000C
0x0010
0x0014
0x0018
Reserved
SVCall
PendSV
Reserved for Debug
Systick
IRQ0
Reserved
0x002C
0x0038
0x003C
0x0040
Exception number Offset
2
3
4
5
6
11
12
14
15
16
18
13
7
10
1
Vector
...
8
9
IRQ1
IRQ2
0x0044
IRQ43
17
0x0048
0x004C
59
...
...
0x00EC
IRQ number
-14
-13
-12
-11
-10
-5
-2
-1
0
2
1
43
On system reset, the vector table is fixed at address 0x0000.0000. Privileged software can write to
the Vector Table Offset (VTABLE) register to relocate the vector table start address to a different
memory location, in the range 0x0000.0100 to 0x3FFF.FF00 (see “Vector Table” on page 83). Note
that when configuring the VTABLE register, the offset must be aligned on a 256-byte boundary.
2.5.5 Exception Priorities
As Table 2-8 on page 81 shows, all exceptions have an associated priority, with a lower priority
value indicating a higher priority and configurable priorities for all exceptions except Reset, Hard
fault, and NMI. If software does not configure any priorities, then all exceptions with a configurable
priority have a priority of 0. For information about configuring exception priorities, see page 133 and
page 119.
Note: Configurable priority values for the Stellaris implementation are in the range 0-7. This means
that the Reset, Hard fault, and NMI exceptions, with fixed negative priority values, always
have higher priority than any other exception.
For example, assigning a higher priority value to IRQ[0] and a lower priority value to IRQ[1] means
that IRQ[1] has higher priority than IRQ[0]. If both IRQ[1] and IRQ[0] are asserted, IRQ[1] is processed
before IRQ[0].
84 January 08, 2011
Texas Instruments-Production Data
The Cortex-M3 Processor
If multiple pending exceptions have the same priority, the pending exception with the lowest exception
number takes precedence. For example, if both IRQ[0] and IRQ[1] are pending and have the same
priority, then IRQ[0] is processed before IRQ[1].
When the processor is executing an exception handler, the exception handler is preempted if a
higher priority exception occurs. If an exception occurs with the same priority as the exception being
handled, the handler is not preempted, irrespective of the exception number. However, the status
of the new interrupt changes to pending.
2.5.6 Interrupt Priority Grouping
To increase priority control in systems with interrupts, the NVIC supports priority grouping. This
grouping divides each interrupt priority register entry into two fields:
■ An upper field that defines the group priority
■ A lower field that defines a subpriority within the group
Only the group priority determines preemption of interrupt exceptions. When the processor is
executing an interrupt exception handler, another interrupt with the same group priority as the
interrupt being handled does not preempt the handler.
If multiple pending interrupts have the same group priority, the subpriority field determines the order
in which they are processed. If multiple pending interrupts have the same group priority and
subpriority, the interrupt with the lowest IRQ number is processed first.
For information about splitting the interrupt priority fields into group priority and subpriority, see
page 127.
2.5.7 Exception Entry and Return
Descriptions of exception handling use the following terms:
■ Preemption. When the processor is executing an exception handler, an exception can preempt
the exception handler if its priority is higher than the priority of the exception being handled. See
“Interrupt Priority Grouping” on page 85 for more information about preemption by an interrupt.
When one exception preempts another, the exceptions are called nested exceptions. See
“Exception Entry” on page 86 more information.
■ Return. Return occurs when the exception handler is completed, and there is no pending
exception with sufficient priority to be serviced and the completed exception handler was not
handling a late-arriving exception. The processor pops the stack and restores the processor
state to the state it had before the interrupt occurred. See “Exception Return” on page 87 for
more information.
■ Tail-Chaining. This mechanism speeds up exception servicing. On completion of an exception
handler, if there is a pending exception that meets the requirements for exception entry, the
stack pop is skipped and control transfers to the new exception handler.
■ Late-Arriving. This mechanism speeds up preemption. If a higher priority exception occurs
during state saving for a previous exception, the processor switches to handle the higher priority
exception and initiates the vector fetch for that exception. State saving is not affected by late
arrival because the state saved is the same for both exceptions. Therefore, the state saving
continues uninterrupted. The processor can accept a late arriving exception until the first instruction
of the exception handler of the original exception enters the execute stage of the processor. On
January 08, 2011 85
Texas Instruments-Production Data
Stellaris® LM3S2965 Microcontroller
return from the exception handler of the late-arriving exception, the normal tail-chaining rules
apply.
2.5.7.1 Exception Entry
Exception entry occurs when there is a pending exception with sufficient priority and either the
processor is in Thread mode or the new exception is of higher priority than the exception being
handled, in which case the new exception preempts the original exception.
When one exception preempts another, the exceptions are nested.
Sufficient priority means the exception has more priority than any limits set by the mask registers
(see PRIMASK on page 67, FAULTMASK on page 68, and BASEPRI on page 69). An exception
with less priority than this is pending but is not handled by the processor.
When the processor takes an exception, unless the exception is a tail-chained or a late-arriving
exception, the processor pushes information onto the current stack. This operation is referred to as
stacking and the structure of eight data words is referred to as stack frame.
Figure 2-7. Exception Stack Frame
Pre-IRQ top of stack
xPSR
PC
LR
R12
R3
R2
R1
R0
{aligner}
IRQ top of stack
...
Immediately after stacking, the stack pointer indicates the lowest address in the stack frame. Unless
stack alignment is disabled, the stack frame is aligned to a double-word address. If the STKALIGN
bit of the Configuration Control (CCR) register is set, stack align adjustment is performed during
stacking.
The stack frame includes the return address, which is the address of the next instruction in the
interrupted program. This value is restored to the PC at exception return so that the interrupted
program resumes.
In parallel to the stacking operation, the processor performs a vector fetch that reads the exception
handler start address from the vector table. When stacking is complete, the processor starts executing
the exception handler. At the same time, the processor writes an EXC_RETURN value to the LR,
indicating which stack pointer corresponds to the stack frame and what operation mode the processor
was in before the entry occurred.
If no higher-priority exception occurs during exception entry, the processor starts executing the
exception handler and automatically changes the status of the corresponding pending interrupt to
active.
If another higher-priority exception occurs during exception entry, known as late arrival, the processor
starts executing the exception handler for this exception and does not change the pending status
of the earlier exception.
86 January 08, 2011
Texas Instruments-Production Data
The Cortex-M3 Processor
2.5.7.2 Exception Return
Exception return occurs when the processor is in Handler mode and executes one of the following
instructions to load the EXC_RETURN value into the PC:
■ An LDM or POP instruction that loads the PC
■ A BX instruction using any register
■ An LDR instruction with the PC as the destination
EXC_RETURN is the value loaded into the LR on exception entry. The exception mechanism relies
on this value to detect when the processor has completed an exception handler. The lowest four
bits of this value provide information on the return stack and processor mode. Table 2-10 on page 87
shows the EXC_RETURN values with a description of the exception return behavior.
EXC_RETURN bits 31:4 are all set. When this value is loaded into the PC, it indicates to the processor
that the exception is complete, and the processor initiates the appropriate exception return sequence.
Table 2-10. Exception Return Behavior
EXC_RETURN[31:0] Description
0xFFFF.FFF0 Reserved
Return to Handler mode.
Exception return uses state from MSP.
Execution uses MSP after return.
0xFFFF.FFF1
0xFFFF.FFF2 - 0xFFFF.FFF8 Reserved
Return to Thread mode.
Exception return uses state from MSP.
Execution uses MSP after return.
0xFFFF.FFF9
0xFFFF.FFFA - 0xFFFF.FFFC Reserved
Return to Thread mode.
Exception return uses state from PSP.
Execution uses PSP after return.
0xFFFF.FFFD
0xFFFF.FFFE - 0xFFFF.FFFF Reserved
2.6 Fault Handling
Faults are a subset of the exceptions (see “Exception Model” on page 79). The following conditions
generate a fault:
■ A bus error on an instruction fetch or vector table load or a data access.
■ An internally detected error such as an undefined instruction or an attempt to change state with
a BX instruction.
■ Attempting to execute an instruction from a memory region marked as Non-Executable (XN).
■ An MPU fault because of a privilege violation or an attempt to access an unmanaged region.
2.6.1 Fault Types
Table 2-11 on page 88 shows the types of fault, the handler used for the fault, the corresponding
fault status register, and the register bit that indicates the fault has occurred. See page 140 for more
information about the fault status registers.
January 08, 2011 87
Texas Instruments-Production Data
Stellaris® LM3S2965 Microcontroller
Table 2-11. Faults
Fault Handler Fault Status Register Bit Name
Bus error on a vector read Hard fault Hard Fault Status (HFAULTSTAT) VECT
Fault escalated to a hard fault Hard fault Hard Fault Status (HFAULTSTAT) FORCED
Memory Management Fault Status IERR a
(MFAULTSTAT)
Memory management
fault
MPU or default memory mismatch on
instruction access
Memory Management Fault Status DERR
(MFAULTSTAT)
Memory management
fault
MPU or default memory mismatch on
data access
Memory Management Fault Status MSTKE
(MFAULTSTAT)
Memory management
fault
MPU or default memory mismatch on
exception stacking
Memory Management Fault Status MUSTKE
(MFAULTSTAT)
Memory management
fault
MPU or default memory mismatch on
exception unstacking
Bus error during exception stacking Bus fault Bus Fault Status (BFAULTSTAT) BSTKE
Bus error during exception unstacking Bus fault Bus Fault Status (BFAULTSTAT) BUSTKE
Bus error during instruction prefetch Bus fault Bus Fault Status (BFAULTSTAT) IBUS
Precise data bus error Bus fault Bus Fault Status (BFAULTSTAT) PRECISE
Imprecise data bus error Bus fault Bus Fault Status (BFAULTSTAT) IMPRE
Attempt to access a coprocessor Usage fault Usage Fault Status (UFAULTSTAT) NOCP
Undefined instruction Usage fault Usage Fault Status (UFAULTSTAT) UNDEF
Attempt to enter an invalid instruction Usage fault Usage Fault Status (UFAULTSTAT) INVSTAT
set state b
Invalid EXC_RETURN value Usage fault Usage Fault Status (UFAULTSTAT) INVPC
Illegal unaligned load or store Usage fault Usage Fault Status (UFAULTSTAT) UNALIGN
Divide by 0 Usage fault Usage Fault Status (UFAULTSTAT) DIV0
a. Occurs on an access to an XN region even if the MPU is disabled.
b. Attempting to use an instruction set other than the Thumb instruction set, or returning to a non load-store-multiple instruction
with ICI continuation.
2.6.2 Fault Escalation and Hard Faults
All fault exceptions except for hard fault have configurable exception priority (see SYSPRI1 on
page 133). Software can disable execution of the handlers for these faults (see SYSHNDCTRL on
page 136).
Usually, the exception priority, together with the values of the exception mask registers, determines
whether the processor enters the fault handler, and whether a fault handler can preempt another
fault handler as described in “Exception Model” on page 79.
In some situations, a fault with configurable priority is treated as a hard fault. This process is called
priority escalation, and the fault is described as escalated to hard fault. Escalation to hard fault
occurs when:
■ A fault handler causes the same kind of fault as the one it is servicing. This escalation to hard
fault occurs because a fault handler cannot preempt itself because it must have the same priority
as the current priority level.
■ A fault handler causes a fault with the same or lower priority as the fault it is servicing. This
situation happens because the handler for the new fault cannot preempt the currently executing
fault handler.
88 January 08, 2011
Texas Instruments-Production Data
The Cortex-M3 Processor
■ An exception handler causes a fault for which the priority is the same as or lower than the currently
executing exception.
■ A fault occurs and the handler for that fault is not enabled.
If a bus fault occurs during a stack push when entering a bus fault handler, the bus fault does not
escalate to a hard fault. Thus if a corrupted stack causes a fault, the fault handler executes even
though the stack push for the handler failed. The fault handler operates but the stack contents are
corrupted.
Note: Only Reset and NMI can preempt the fixed priority hard fault. A hard fault can preempt any
exception other than Reset, NMI, or another hard fault.
2.6.3 Fault Status Registers and Fault Address Registers
The fault status registers indicate the cause of a fault. For bus faults and memory management
faults, the fault address register indicates the address accessed by the operation that caused the
fault, as shown in Table 2-12 on page 89.
Table 2-12. Fault Status and Fault Address Registers
Handler Status Register Name Address Register Name Register Description
Hard fault Hard Fault Status (HFAULTSTAT) - page 146
page 140
page 147
Memory Management Fault
Address (MMADDR)
Memory Management Fault Status
(MFAULTSTAT)
Memory management
fault
page 140
page 148
Bus Fault Address
(FAULTADDR)
Bus fault Bus Fault Status (BFAULTSTAT)
Usage fault Usage Fault Status (UFAULTSTAT) - page 140
2.6.4 Lockup
The processor enters a lockup state if a hard fault occurs when executing the NMI or hard fault
handlers. When the processor is in the lockup state, it does not execute any instructions. The
processor remains in lockup state until it is reset or an NMI occurs.
Note: If the lockup state occurs from the NMI handler, a subsequent NMI does not cause the
processor to leave the lockup state.
2.7 Power Management
The Cortex-M3 processor sleep modes reduce power consumption:
■ Sleep mode stops the processor clock.
■ Deep-sleep mode stops the system clock and switches off the PLL and Flash memory.
The SLEEPDEEP bit of the System Control (SYSCTRL) register selects which sleep mode is used
(see page 129). For more information about the behavior of the sleep modes, see “System
Control” on page 180.
This section describes the mechanisms for entering sleep mode and the conditions for waking up
from sleep mode, both of which apply to Sleep mode and Deep-sleep mode.
January 08, 2011 89
Texas Instruments-Production Data
Stellaris® LM3S2965 Microcontroller
2.7.1 Entering Sleep Modes
This section describes the mechanisms software can use to put the processor into one of the sleep
modes.
The system can generate spurious wake-up events, for example a debug operation wakes up the
processor. Therefore, software must be able to put the processor back into sleep mode after such
an event. A program might have an idle loop to put the processor back to sleep mode.
2.7.1.1 Wait for Interrupt
The wait for interrupt instruction, WFI, causes immediate entry to sleep mode unless the wake-up
condition is true (see “Wake Up from WFI or Sleep-on-Exit” on page 90). When the processor
executes a WFI instruction, it stops executing instructions and enters sleep mode. See the
Cortex™-M3 Instruction Set Technical User's Manual for more information.
2.7.1.2 Wait for Event
The wait for event instruction, WFE, causes entry to sleep mode conditional on the value of a one-bit
event register. When the processor executes a WFE instruction, it checks the event register. If the
register is 0, the processor stops executing instructions and enters sleep mode. If the register is 1,
the processor clears the register and continues executing instructions without entering sleep mode.
If the event register is 1, the processor must not enter sleep mode on execution of a WFE instruction.
Typically, this situation occurs if an SEV instruction has been executed. Software cannot access
this register directly.
See the Cortex™-M3 Instruction Set Technical User's Manual for more information.
2.7.1.3 Sleep-on-Exit
If the SLEEPEXIT bit of the SYSCTRL register is set, when the processor completes the execution
of an exception handler, it returns to Thread mode and immediately enters sleep mode. This
mechanism can be used in applications that only require the processor to run when an exception
occurs.
2.7.2 Wake Up from Sleep Mode
The conditions for the processor to wake up depend on the mechanism that cause it to enter sleep
mode.
2.7.2.1 Wake Up from WFI or Sleep-on-Exit
Normally, the processor wakes up only when it detects an exception with sufficient priority to cause
exception entry. Some embedded systems might have to execute system restore tasks after the
processor wakes up and before executing an interrupt handler. Entry to the interrupt handler can
be delayed by setting the PRIMASK bit and clearing the FAULTMASK bit. If an interrupt arrives that
is enabled and has a higher priority than current exception priority, the processor wakes up but does
not execute the interrupt handler until the processor clears PRIMASK. For more information about
PRIMASK and FAULTMASK, see page 67 and page 68.
2.7.2.2 Wake Up from WFE
The processor wakes up if it detects an exception with sufficient priority to cause exception entry.
In addition, if the SEVONPEND bit in the SYSCTRL register is set, any new pending interrupt triggers
an event and wakes up the processor, even if the interrupt is disabled or has insufficient priority to
cause exception entry. For more information about SYSCTRL, see page 129.
90 January 08, 2011
Texas Instruments-Production Data
The Cortex-M3 Processor
2.8 Instruction Set Summary
The processor implements a version of the Thumb instruction set. Table 2-13 on page 91 lists the
supported instructions.
Note: In Table 2-13 on page 91:
■ Angle brackets, <>, enclose alternative forms of the operand
■ Braces, {}, enclose optional operands
■ The Operands column is not exhaustive
■ Op2 is a flexible second operand that can be either a register or a constant
■ Most instructions can use an optional condition code suffix
For more information on the instructions and operands, see the instruction descriptions in
the Cortex™-M3 Instruction Set Technical User's Manual.
Table 2-13. Cortex-M3 Instruction Summary
Mnemonic Operands Brief Description Flags
ADC, ADCS {Rd,} Rn , Op2 Add with carry N,Z,C,V
ADD, ADDS {Rd,} Rn , Op2 Add N,Z,C,V
ADD, ADDW {Rd,} Rn , #imm12 Add N,Z,C,V
ADR Rd , label Load PC-relative address -
AND, ANDS {Rd ,} Rn , Op2 Logical AND N,Z,C
ASR, ASRS Rd , Rm , Arithmetic shift right N,Z,C
B label Branch -
BFC Rd , #lsb , #width Bit field clear -
BFI Rd , Rn , #lsb , #width Bit field insert -
BIC, BICS {Rd ,} Rn , Op2 Bit clear N,Z,C
BKPT #imm Breakpoint -
BL label Branch with link -
BLX Rm Branch indirect with link -
BX Rm Branch indirect -
CBNZ Rn , label Compare and branch if non-zero -
CBZ Rn , label Compare and branch if zero -
CLREX - Clear exclusive -
CLZ Rd , Rm Count leading zeros -
CMN Rn , Op2 Compare negative N,Z,C,V
CMP Rn , Op2 Compare N,Z,C,V
Change processor state, disable -
interrupts
CPSID iflags
Change processor state, enable -
interrupts
CPSIE iflags
DMB - Data memory barrier -
DSB - Data synchronization barrier -
EOR, EORS {Rd ,} Rn , Op2 Exclusive OR N,Z,C
ISB - Instruction synchronization barrier -
IT - If-Then condition block -
January 08, 2011 91
Texas Instruments-Production Data
Stellaris® LM3S2965 Microcontroller
Table 2-13. Cortex-M3 Instruction Summary (continued)
Mnemonic Operands Brief Description Flags
LDM Rn{!} , reglist Load multiple registers, increment after -
Load multiple registers, decrement -
before
LDMDB, LDMEA Rn{!} , reglist
LDMFD, LDMIA Rn{!} , reglist Load multiple registers, increment after -
LDR Rt , [ Rn {, #offset}] Load register with word -
LDRB, LDRBT Rt , [ Rn {, #offset}] Load register with byte -
LDRD Rt , Rt2 , [ Rn {, #offset}] Load register with two words -
LDREX Rt , [ Rn , #offset ] Load register exclusive -
LDREXB Rt, [Rn] Load register exclusive with byte -
LDREXH Rt , [Rn] Load register exclusive with halfword -
LDRH, LDRHT Rt , [ Rn{ , #offset}] Load register with halfword -
LDRSB, LDRSBT Rt , [ Rn{ , #offset}] Load register with signed byte -
LDRSH, LDRSHT Rt , [ Rn {, #offset}] Load register with signed halfword -
LDRT Rt , [ Rn {, #offset}] Load register with word -
LSL, LSLS Rd , Rm , Logical shift left N,Z,C
LSR, LSRS Rd , Rm , Logical shift right N,Z,C
MLA Rd , Rn , Rm, Ra Multiply with accumulate, 32-bit result -
MLS Rd , Rn , Rm, Ra Multiply and subtract, 32-bit result -
MOV, MOVS Rd , Op2 Move N,Z,C
MOV, MOVW Rd , #imm16 Move 16-bit constant N,Z,C
MOVT Rd , #imm16 Move top -
Move from special register to general -
register
MRS Rd , spec_reg
Move from general register to special N,Z,C,V
register
MSR spec_reg , Rn
MUL, MULS {Rd,}Rn , Rm Multiply, 32-bit result N,Z
MVN, MVNS Rd , Op2 Move NOT N,Z,C
NOP - No operation -
ORN, ORNS {Rd,} Rn , Op2 Logical OR NOT N,Z,C
ORR, ORRS {Rd,} Rn , Op2 Logical OR N,Z,C
POP reglist Pop registers from stack -
PUSH reglist Push registers onto stack -
RBIT Rd , Rn Reverse bits -
REV Rd , Rn Reverse byte order in a word -
REV16 Rd , Rn Reverse byte order in each halfword -
Reverse byte order in bottom halfword -
and sign extend
REVSH Rd , Rn
ROR, RORS Rd , Rm , Rotate right N,Z,C
RRX, RRXS Rd , Rm Rotate right with extend N,Z,C
RSB, RSBS {Rd,} Rn , Op2 Reverse subtract N,Z,C,V
SBC, SBCS {Rd,} Rn , Op2 Subtract with carry N,Z,C,V
SBFX Rd , Rn , #lsb , #width Signed bit field extract -
92 January 08, 2011
Texas Instruments-Production Data
The Cortex-M3 Processor
Table 2-13. Cortex-M3 Instruction Summary (continued)
Mnemonic Operands Brief Description Flags
SDIV {Rd ,} Rn , Rm Signed divide -
SEV - Send event -
Signed multiply with accumulate -
(32x32+64), 64-bit result
SMLAL RdLo, RdHi, Rn, Rm
SMULL RdLo, RdHi, Rn, Rm Signed multiply (32x32), 64-bit result -
SSAT Rd, #n, Rm {,shift #s} Signed saturate Q
STM Rn{!} , reglist Store multiple registers, increment after -
Store multiple registers, decrement -
before
STMDB, STMEA Rn{!} , reglist
STMFD, STMIA Rn{!} , reglist Store multiple registers, increment after -
STR Rt , [ Rn {, #offset}] Store register word -
STRB, STRBT Rt , [ Rn {, #offset}] Store register byte -
STRD Rt , Rt2 , [ Rn {, #offset}] Store register two words -
STREX Rd , Rt , [ Rn , #offset ] Store register exclusive -
STREXB Rd , Rt , [Rn] Store register exclusive byte -
STREXH Rd , Rt , [Rn] Store register exclusive halfword -
STRH, STRHT Rt , [ Rn {, #offset}] Store register halfword -
STRSB, STRSBT Rt , [ Rn {, #offset}] Store register signed byte -
STRSH, STRSHT Rt , [ Rn {, #offset}] Store register signed halfword -
STRT Rt , [ Rn {, #offset}] Store register word -
SUB, SUBS {Rd,} Rn , Op2 Subtract N,Z,C,V
SUB, SUBW {Rd,} Rn , #imm12 Subtract 12-bit constant N,Z,C,V
SVC #imm Supervisor call -
SXTB {Rd,} Rm {,ROR #n} Sign extend a byte -
SXTH {Rd,} Rm {,ROR #n} Sign extend a halfword -
TBB [Rn, Rm] Table branch byte -
TBH [Rn, Rm, LSL #1] Table branch halfword -
TEQ Rn, Op2 Test equivalence N,Z,C
TST Rn, Op2 Test N,Z,C
UBFX Rd , Rn , #lsb , #width Unsigned bit field extract -
UDIV {Rd,} Rn , Rm Unsigned divide -
Unsigned multiply with accumulate -
(32x32+32+32), 64-bit result
UMLAL RdLo, RdHi, Rn, Rm
UMULL RdLo, RdHi, Rn, Rm Unsigned multiply (32x 2), 64-bit result -
USAT Rd, #n, Rm {,shift #s} Unsigned saturate Q
UXTB {Rd,} Rm {,ROR #n} Zero extend a byte -
UXTH {Rd,} Rm {,ROR #n} Zero extend a halfword -
WFE - Wait for event -
WFI - Wait for interrupt -
January 08, 2011 93
Texas Instruments-Production Data
Stellaris® LM3S2965 Microcontroller
3 Cortex-M3 Peripherals
This chapter provides information on the Stellaris® implementation of the Cortex-M3 processor
peripherals, including:
■ SysTick (see page 94)
Provides a simple, 24-bit clear-on-write, decrementing, wrap-on-zero counter with a flexible
control mechanism.
■ Nested Vectored Interrupt Controller (NVIC) (see page 95)
– Facilitates low-latency exception and interrupt handling
– Controls power management
– Implements system control registers
■ System Control Block (SCB) (see page 97)
Provides system implementation information and system control, including configuration, control,
and reporting of system exceptions.
■ Memory Protection Unit (MPU) (see page 97)
Supports the standard ARMv7 Protected Memory System Architecture (PMSA) model. The MPU
provides full support for protection regions, overlapping protection regions, access permissions,
and exporting memory attributes to the system.
Table 3-1 on page 94 shows the address map of the Private Peripheral Bus (PPB). Some peripheral
register regions are split into two address regions, as indicated by two addresses listed.
Table 3-1. Core Peripheral Register Regions
Address Core Peripheral Description (see page ...)
0xE000.E010-0xE000.E01F System Timer 94
0xE000.E100-0xE000.E4EF Nested Vectored Interrupt Controller 95
0xE000.EF00-0xE000.EF03
0xE000.ED00-0xE000.ED3F System Control Block 97
0xE000.ED90-0xE000.EDB8 Memory Protection Unit 97
3.1 Functional Description
This chapter provides information on the Stellaris implementation of the Cortex-M3 processor
peripherals: SysTick, NVIC, SCB and MPU.
3.1.1 System Timer (SysTick)
Cortex-M3 includes an integrated system timer, SysTick, which provides a simple, 24-bit
clear-on-write, decrementing, wrap-on-zero counter with a flexible control mechanism. The counter
can be used in several different ways, for example as:
■ An RTOS tick timer that fires at a programmable rate (for example, 100 Hz) and invokes a SysTick
routine.
■ A high-speed alarm timer using the system clock.
94 January 08, 2011
Texas Instruments-Production Data
Cortex-M3 Peripherals
■ A variable rate alarm or signal timer—the duration is range-dependent on the reference clock
used and the dynamic range of the counter.
■ A simple counter used to measure time to completion and time used.
■ An internal clock source control based on missing/meeting durations. The COUNT bit in the
STCTRL control and status register can be used to determine if an action completed within a
set duration, as part of a dynamic clock management control loop.
The timer consists of three registers:
■ SysTick Control and Status (STCTRL): A control and status counter to configure its clock,
enable the counter, enable the SysTick interrupt, and determine counter status.
■ SysTick Reload Value (STRELOAD): The reload value for the counter, used to provide the
counter's wrap value.
■ SysTick Current Value (STCURRENT): The current value of the counter.
When enabled, the timer counts down on each clock from the reload value to zero, reloads (wraps)
to the value in the STRELOAD register on the next clock edge, then decrements on subsequent
clocks. Clearing the STRELOAD register disables the counter on the next wrap. When the counter
reaches zero, the COUNT status bit is set. The COUNT bit clears on reads.
Writing to the STCURRENT register clears the register and the COUNT status bit. The write does
not trigger the SysTick exception logic. On a read, the current value is the value of the register at
the time the register is accessed.
The SysTick counter runs on the processor clock. If this clock signal is stopped for low power mode,
the SysTick counter stops. Ensure software uses aligned word accesses to access the SysTick
registers.
Note: When the processor is halted for debugging, the counter does not decrement.
3.1.2 Nested Vectored Interrupt Controller (NVIC)
This section describes the Nested Vectored Interrupt Controller (NVIC) and the registers it uses.
The NVIC supports:
■ 42 interrupts.
■ A programmable priority level of 0-7 for each interrupt. A higher level corresponds to a lower
priority, so level 0 is the highest interrupt priority.
■ Low-latency exception and interrupt handling.
■ Level and pulse detection of interrupt signals.
■ Dynamic reprioritization of interrupts.
■ Grouping of priority values into group priority and subpriority fields.
■ Interrupt tail-chaining.
■ An external Non-maskable interrupt (NMI).
January 08, 2011 95
Texas Instruments-Production Data
Stellaris® LM3S2965 Microcontroller
The processor automatically stacks its state on exception entry and unstacks this state on exception
exit, with no instruction overhead, providing low latency exception handling.
3.1.2.1 Level-Sensitive and Pulse Interrupts
The processor supports both level-sensitive and pulse interrupts. Pulse interrupts are also described
as edge-triggered interrupts.
A level-sensitive interrupt is held asserted until the peripheral deasserts the interrupt signal. Typically
this happens because the ISR accesses the peripheral, causing it to clear the interrupt request. A
pulse interrupt is an interrupt signal sampled synchronously on the rising edge of the processor
clock. To ensure the NVIC detects the interrupt, the peripheral must assert the interrupt signal for
at least one clock cycle, during which the NVIC detects the pulse and latches the interrupt.
When the processor enters the ISR, it automatically removes the pending state from the interrupt
(see “Hardware and Software Control of Interrupts” on page 96 for more information). For a
level-sensitive interrupt, if the signal is not deasserted before the processor returns from the ISR,
the interrupt becomes pending again, and the processor must execute its ISR again. As a result,
the peripheral can hold the interrupt signal asserted until it no longer needs servicing.
3.1.2.2 Hardware and Software Control of Interrupts
The Cortex-M3 latches all interrupts. A peripheral interrupt becomes pending for one of the following
reasons:
■ The NVIC detects that the interrupt signal is High and the interrupt is not active.
■ The NVIC detects a rising edge on the interrupt signal.
■ Software writes to the corresponding interrupt set-pending register bit, or to the Software Trigger
Interrupt (SWTRIG) register to make a Software-Generated Interrupt pending. See the INT bit
in the PEND0 register on page 113 or SWTRIG on page 121.
A pending interrupt remains pending until one of the following:
■ The processor enters the ISR for the interrupt, changing the state of the interrupt from pending
to active. Then:
– For a level-sensitive interrupt, when the processor returns from the ISR, the NVIC samples
the interrupt signal. If the signal is asserted, the state of the interrupt changes to pending,
which might cause the processor to immediately re-enter the ISR. Otherwise, the state of the
interrupt changes to inactive.
– For a pulse interrupt, the NVIC continues to monitor the interrupt signal, and if this is pulsed
the state of the interrupt changes to pending and active. In this case, when the processor
returns from the ISR the state of the interrupt changes to pending, which might cause the
processor to immediately re-enter the ISR.
If the interrupt signal is not pulsed while the processor is in the ISR, when the processor
returns from the ISR the state of the interrupt changes to inactive.
■ Software writes to the corresponding interrupt clear-pending register bit
– For a level-sensitive interrupt, if the interrupt signal is still asserted, the state of the interrupt
does not change. Otherwise, the state of the interrupt changes to inactive.
96 January 08, 2011
Texas Instruments-Production Data
Cortex-M3 Peripherals
– For a pulse interrupt, the state of the interrupt changes to inactive, if the state was pending
or to active, if the state was active and pending.
3.1.3 System Control Block (SCB)
The System Control Block (SCB) provides system implementation information and system control,
including configuration, control, and reporting of the system exceptions.
3.1.4 Memory Protection Unit (MPU)
This section describes the Memory protection unit (MPU). The MPU divides the memory map into
a number of regions and defines the location, size, access permissions, and memory attributes of
each region. The MPU supports independent attribute settings for each region, overlapping regions,
and export of memory attributes to the system.
The memory attributes affect the behavior of memory accesses to the region. The Cortex-M3 MPU
defines eight separate memory regions, 0-7, and a background region.
When memory regions overlap, a memory access is affected by the attributes of the region with the
highest number. For example, the attributes for region 7 take precedence over the attributes of any
region that overlaps region 7.
The background region has the same memory access attributes as the default memory map, but is
accessible from privileged software only.
The Cortex-M3 MPU memory map is unified, meaning that instruction accesses and data accesses
have the same region settings.
If a program accesses a memory location that is prohibited by the MPU, the processor generates
a memory management fault, causing a fault exception and possibly causing termination of the
process in an OS environment. In an OS environment, the kernel can update the MPU region setting
dynamically based on the process to be executed. Typically, an embedded OS uses the MPU for
memory protection.
Configuration of MPU regions is based on memory types (see “Memory Regions, Types and
Attributes” on page 73 for more information).
Table 3-2 on page 97 shows the possible MPU region attributes. See the section called “MPU
Configuration for a Stellaris Microcontroller” on page 101 for guidelines for programming a
microcontroller implementation.
Table 3-2. Memory Attributes Summary
Memory Type Description
Strongly Ordered All accesses to Strongly Ordered memory occur in program order.
Device Memory-mapped peripherals
Normal Normal memory
To avoid unexpected behavior, disable the interrupts before updating the attributes of a region that
the interrupt handlers might access.
Ensure software uses aligned accesses of the correct size to access MPU registers:
■ Except for the MPU Region Attribute and Size (MPUATTR) register, all MPU registers must
be accessed with aligned word accesses.
■ The MPUATTR register can be accessed with byte or aligned halfword or word accesses.
January 08, 2011 97
Texas Instruments-Production Data
Stellaris® LM3S2965 Microcontroller
The processor does not support unaligned accesses to MPU registers.
When setting up the MPU, and if the MPU has previously been programmed, disable unused regions
to prevent any previous region settings from affecting the new MPU setup.
3.1.4.1 Updating an MPU Region
To update the attributes for an MPU region, the MPU Region Number (MPUNUMBER), MPU
Region Base Address (MPUBASE) and MPUATTR registers must be updated. Each register can
be programmed separately or with a multiple-word write to program all of these registers. You can
use the MPUBASEx and MPUATTRx aliases to program up to four regions simultaneously using
an STM instruction.
Updating an MPU Region Using Separate Words
This example simple code configures one region:
; R1 = region number
; R2 = size/enable
; R3 = attributes
; R4 = address
LDR R0,=MPUNUMBER ; 0xE000ED98, MPU region number register
STR R1, [R0, #0x0] ; Region Number
STR R4, [R0, #0x4] ; Region Base Address
STRH R2, [R0, #0x8] ; Region Size and Enable
STRH R3, [R0, #0xA] ; Region Attribute
Disable a region before writing new region settings to the MPU if you have previously enabled the
region being changed. For example:
; R1 = region number
; R2 = size/enable
; R3 = attributes
; R4 = address
LDR R0,=MPUNUMBER ; 0xE000ED98, MPU region number register
STR R1, [R0, #0x0] ; Region Number
BIC R2, R2, #1 ; Disable
STRH R2, [R0, #0x8] ; Region Size and Enable
STR R4, [R0, #0x4] ; Region Base Address
STRH R3, [R0, #0xA] ; Region Attribute
ORR R2, #1 ; Enable
STRH R2, [R0, #0x8] ; Region Size and Enable
Software must use memory barrier instructions:
■ Before MPU setup, if there might be outstanding memory transfers, such as buffered writes, that
might be affected by the change in MPU settings.
■ After MPU setup, if it includes memory transfers that must use the new MPU settings.
However, memory barrier instructions are not required if the MPU setup process starts by entering
an exception handler, or is followed by an exception return, because the exception entry and
exception return mechanism cause memory barrier behavior.
Software does not need any memory barrier instructions during MPU setup, because it accesses
the MPU through the Private Peripheral Bus (PPB), which is a Strongly Ordered memory region.
98 January 08, 2011
Texas Instruments-Production Data
Cortex-M3 Peripherals
For example, if all of the memory access behavior is intended to take effect immediately after the
programming sequence, then a DSB instruction and an ISB instruction should be used. A DSB is
required after changing MPU settings, such as at the end of context switch. An ISB is required if
the code that programs the MPU region or regions is entered using a branch or call. If the
programming sequence is entered using a return from exception, or by taking an exception, then
an ISB is not required.
Updating an MPU Region Using Multi-Word Writes
The MPU can be programmed directly using multi-word writes, depending how the information is
divided. Consider the following reprogramming:
; R1 = region number
; R2 = address
; R3 = size, attributes in one
LDR R0, =MPUNUMBER ; 0xE000ED98, MPU region number register
STR R1, [R0, #0x0] ; Region Number
STR R2, [R0, #0x4] ; Region Base Address
STR R3, [R0, #0x8] ; Region Attribute, Size and Enable
An STM instruction can be used to optimize this:
; R1 = region number
; R2 = address
; R3 = size, attributes in one
LDR R0, =MPUNUMBER ; 0xE000ED98, MPU region number register
STM R0, {R1-R3} ; Region number, address, attribute, size and enable
This operation can be done in two words for pre-packed information, meaning that the MPU Region
Base Address (MPUBASE) register (see page 153) contains the required region number and has
the VALID bit set. This method can be used when the data is statically packed, for example in a
boot loader:
; R1 = address and region number in one
; R2 = size and attributes in one
LDR R0, =MPUBASE ; 0xE000ED9C, MPU Region Base register
STR R1, [R0, #0x0] ; Region base address and region number combined
; with VALID (bit 4) set
STR R2, [R0, #0x4] ; Region Attribute, Size and Enable
An STM instruction can be used to optimize this:
; R1 = address and region number in one
; R2 = size and attributes in one
LDR R0,=MPUBASE ; 0xE000ED9C, MPU Region Base register
STM R0, {R1-R2} ; Region base address, region number and VALID bit,
; and Region Attribute, Size and Enable
Subregions
Regions of 256 bytes or more are divided into eight equal-sized subregions. Set the corresponding
bit in the SRD field of the MPU Region Attribute and Size (MPUATTR) register (see page 155) to
disable a subregion. The least-significant bit of the SRD field controls the first subregion, and the
most-significant bit controls the last subregion. Disabling a subregion means another region
January 08, 2011 99
Texas Instruments-Production Data
Stellaris® LM3S2965 Microcontroller
overlapping the disabled range matches instead. If no other enabled region overlaps the disabled
subregion, the MPU issues a fault.
Regions of 32, 64, and 128 bytes do not support subregions. With regions of these sizes, the SRD
field must be configured to 0x00, otherwise the MPU behavior is unpredictable.
Example of SRD Use
Two regions with the same base address overlap. Region one is 128 KB, and region two is 512 KB.
To ensure the attributes from region one apply to the first 128 KB region, configure the SRD field for
region two to 0x03 to disable the first two subregions, as Figure 3-1 on page 100 shows.
Figure 3-1. SRD Use Example
Region 1
Disabled subregion
Disabled subregion
Region 2, with
subregions
Base address of both regions
Offset from
base address
0
64KB
128KB
192KB
256KB
320KB
384KB
448KB
512KB
3.1.4.2 MPU Access Permission Attributes
The access permission bits, TEX, S, C, B, AP, and XN of the MPUATTR register, control access to
the corresponding memory region. If an access is made to an area of memory without the required
permissions, then the MPU generates a permission fault.
Table 3-3 on page 100 shows the encodings for the TEX, C, B, and S access permission bits. All
encodings are shown for completeness, however the current implementation of the Cortex-M3 does
not support the concept of cacheability or shareability. Refer to the section called “MPU Configuration
for a Stellaris Microcontroller” on page 101 for information on programming the MPU for Stellaris
implementations.
Table 3-3. TEX, S, C, and B Bit Field Encoding
TEX S C B Memory Type Shareability Other Attributes
000b xa 0 0 Strongly Ordered Shareable -
000 xa 0 1 Device Shareable -
Outer and inner
write-through. No write
allocate.
000 0 1 0 Normal Not shareable
000 1 1 0 Normal Shareable
000 0 1 1 Normal Not shareable
000 1 1 1 Normal Shareable
Outer and inner
noncacheable.
001 0 0 0 Normal Not shareable
001 1 0 0 Normal Shareable
001 xa 0 1 Reserved encoding - -
001 xa 1 0 Reserved encoding - -
Outer and inner
write-back. Write and
read allocate.
001 0 1 1 Normal Not shareable
001 1 1 1 Normal Shareable
100 January 08, 2011
Texas Instruments-Production Data
Cortex-M3 Peripherals
Table 3-3. TEX, S, C, and B Bit Field Encoding (continued)
TEX S C B Memory Type Shareability Other Attributes
010 xa 0 0 Device Not shareable Nonshared Device.
010 xa 0 1 Reserved encoding - -
010 xa 1 xa Reserved encoding - -
Cached memory (BB =
outer policy, AA = inner
policy).
See Table 3-4 for the
encoding of the AA and
BB bits.
1BB 0 A A Normal Not shareable
1BB 1 A A Normal Shareable
a. The MPU ignores the value of this bit.
Table 3-4 on page 101 shows the cache policy for memory attribute encodings with a TEX value in
the range of 0x4-0x7.
Table 3-4. Cache Policy for Memory Attribute Encoding
Encoding, AA or BB Corresponding Cache Policy
00 Non-cacheable
01 Write back, write and read allocate
10 Write through, no write allocate
11 Write back, no write allocate
Table 3-5 on page 101 shows the AP encodings in the MPUATTR register that define the access
permissions for privileged and unprivileged software.
Table 3-5. AP Bit Field Encoding
Unprivileged Description
Permissions
Privileged
Permissions
AP Bit Field
000 No access No access All accesses generate a permission fault.
001 R/W No access Access from privileged software only.
Writes by unprivileged software generate a
permission fault.
010 R/W RO
011 R/W R/W Full access.
100 Unpredictable Unpredictable Reserved.
101 RO No access Reads by privileged software only.
110 RO RO Read-only, by privileged or unprivileged software.
111 RO RO Read-only, by privileged or unprivileged software.
MPU Configuration for a Stellaris Microcontroller
Stellaris microcontrollers have only a single processor and no caches. As a result, the MPU should
be programmed as shown in Table 3-6 on page 101.
Table 3-6. Memory Region Attributes for Stellaris Microcontrollers
Memory Region TEX S C B Memory Type and Attributes
Flash memory 000b 0 1 0 Normal memory, non-shareable, write-through
Internal SRAM 000b 1 1 0 Normal memory, shareable, write-through
January 08, 2011 101
Texas Instruments-Production Data
Stellaris® LM3S2965 Microcontroller
Table 3-6. Memory Region Attributes for Stellaris Microcontrollers (continued)
Memory Region TEX S C B Memory Type and Attributes
Normal memory, shareable, write-back,
write-allocate
External SRAM 000b 1 1 1
Peripherals 000b 1 0 1 Device memory, shareable
In current Stellaris microcontroller implementations, the shareability and cache policy attributes do
not affect the system behavior. However, using these settings for the MPU regions can make the
application code more portable. The values given are for typical situations.
3.1.4.3 MPU Mismatch
When an access violates the MPU permissions, the processor generates a memory management
fault (see “Exceptions and Interrupts” on page 71 for more information). The MFAULTSTAT register
indicates the cause of the fault. See page 140 for more information.
3.2 Register Map
Table 3-7 on page 102 lists the Cortex-M3 Peripheral SysTick, NVIC, SCB, and MPU registers. The
offset listed is a hexadecimal increment to the register's address, relative to the Core Peripherals
base address of 0xE000.E000.
Note: Register spaces that are not used are reserved for future or internal use. Software should
not modify any reserved memory address.
Table 3-7. Peripherals Register Map
See
Offset Name Type Reset Description page
System Timer (SysTick) Registers
0x010 STCTRL R/W 0x0000.0000 SysTick Control and Status Register 105
0x014 STRELOAD R/W 0x0000.0000 SysTick Reload Value Register 107
0x018 STCURRENT R/WC 0x0000.0000 SysTick Current Value Register 108
Nested Vectored Interrupt Controller (NVIC) Registers
0x100 EN0 R/W 0x0000.0000 Interrupt 0-31 Set Enable 109
0x104 EN1 R/W 0x0000.0000 Interrupt 32-43 Set Enable 110
0x180 DIS0 R/W 0x0000.0000 Interrupt 0-31 Clear Enable 111
0x184 DIS1 R/W 0x0000.0000 Interrupt 32-43 Clear Enable 112
0x200 PEND0 R/W 0x0000.0000 Interrupt 0-31 Set Pending 113
0x204 PEND1 R/W 0x0000.0000 Interrupt 32-43 Set Pending 114
0x280 UNPEND0 R/W 0x0000.0000 Interrupt 0-31 Clear Pending 115
0x284 UNPEND1 R/W 0x0000.0000 Interrupt 32-43 Clear Pending 116
0x300 ACTIVE0 RO 0x0000.0000 Interrupt 0-31 Active Bit 117
0x304 ACTIVE1 RO 0x0000.0000 Interrupt 32-43 Active Bit 118
0x400 PRI0 R/W 0x0000.0000 Interrupt 0-3 Priority 119
102 January 08, 2011
Texas Instruments-Production Data
Cortex-M3 Peripherals
Table 3-7. Peripherals Register Map (continued)
See
Offset Name Type Reset Description page
0x404 PRI1 R/W 0x0000.0000 Interrupt 4-7 Priority 119
0x408 PRI2 R/W 0x0000.0000 Interrupt 8-11 Priority 119
0x40C PRI3 R/W 0x0000.0000 Interrupt 12-15 Priority 119
0x410 PRI4 R/W 0x0000.0000 Interrupt 16-19 Priority 119
0x414 PRI5 R/W 0x0000.0000 Interrupt 20-23 Priority 119
0x418 PRI6 R/W 0x0000.0000 Interrupt 24-27 Priority 119
0x41C PRI7 R/W 0x0000.0000 Interrupt 28-31 Priority 119
0x420 PRI8 R/W 0x0000.0000 Interrupt 32-35 Priority 119
0x424 PRI9 R/W 0x0000.0000 Interrupt 36-39 Priority 119
0x428 PRI10 R/W 0x0000.0000 Interrupt 40-43 Priority 119
0xF00 SWTRIG WO 0x0000.0000 Software Trigger Interrupt 121
System Control Block (SCB) Registers
0xD00 CPUID RO 0x411F.C231 CPU ID Base 122
0xD04 INTCTRL R/W 0x0000.0000 Interrupt Control and State 123
0xD08 VTABLE R/W 0x0000.0000 Vector Table Offset 126
0xD0C APINT R/W 0xFA05.0000 Application Interrupt and Reset Control 127
0xD10 SYSCTRL R/W 0x0000.0000 System Control 129
0xD14 CFGCTRL R/W 0x0000.0000 Configuration and Control 131
0xD18 SYSPRI1 R/W 0x0000.0000 System Handler Priority 1 133
0xD1C SYSPRI2 R/W 0x0000.0000 System Handler Priority 2 134
0xD20 SYSPRI3 R/W 0x0000.0000 System Handler Priority 3 135
0xD24 SYSHNDCTRL R/W 0x0000.0000 System Handler Control and State 136
0xD28 FAULTSTAT R/W1C 0x0000.0000 Configurable Fault Status 140
0xD2C HFAULTSTAT R/W1C 0x0000.0000 Hard Fault Status 146
0xD34 MMADDR R/W - Memory Management Fault Address 147
0xD38 FAULTADDR R/W - Bus Fault Address 148
Memory Protection Unit (MPU) Registers
0xD90 MPUTYPE RO 0x0000.0800 MPU Type 149
0xD94 MPUCTRL R/W 0x0000.0000 MPU Control 150
0xD98 MPUNUMBER R/W 0x0000.0000 MPU Region Number 152
0xD9C MPUBASE R/W 0x0000.0000 MPU Region Base Address 153
0xDA0 MPUATTR R/W 0x0000.0000 MPU Region Attribute and Size 155
January 08, 2011 103
Texas Instruments-Production Data
Stellaris® LM3S2965 Microcontroller
Table 3-7. Peripherals Register Map (continued)
See
Offset Name Type Reset Description page
0xDA4 MPUBASE1 R/W 0x0000.0000 MPU Region Base Address Alias 1 153
0xDA8 MPUATTR1 R/W 0x0000.0000 MPU Region Attribute and Size Alias 1 155
0xDAC MPUBASE2 R/W 0x0000.0000 MPU Region Base Address Alias 2 153
0xDB0 MPUATTR2 R/W 0x0000.0000 MPU Region Attribute and Size Alias 2 155
0xDB4 MPUBASE3 R/W 0x0000.0000 MPU Region Base Address Alias 3 153
0xDB8 MPUATTR3 R/W 0x0000.0000 MPU Region Attribute and Size Alias 3 155
3.3 System Timer (SysTick) Register Descriptions
This section lists and describes the System Timer registers, in numerical order by address offset.
104 January 08, 2011
Texas Instruments-Production Data
Cortex-M3 Peripherals
Register 1: SysTick Control and Status Register (STCTRL), offset 0x010
Note: This register can only be accessed from privileged mode.
The SysTick STCTRL register enables the SysTick features.
SysTick Control and Status Register (STCTRL)
Base 0xE000.E000
Offset 0x010
Type R/W, reset 0x0000.0000
31 30 29 28 27 26 25 24 23 22 21 20 19 18 17 16
reserved COUNT
Type RO RO RO RO RO RO RO RO RO RO RO RO RO RO RO RO
Reset 0 0 0 0 0 0 0 0 0 0 0 0 0 0 0 0
15 14 13 12 11 10 9 8 7 6 5 4 3 2 1 0
reserved CLK_SRC INTEN ENABLE
Type RO RO RO RO RO RO RO RO RO RO RO RO RO R/W R/W R/W
Reset 0 0 0 0 0 0 0 0 0 0 0 0 0 0 0 0
Bit/Field Name Type Reset Description
Software should not rely on the value of a reserved bit. To provide
compatibility with future products, the value of a reserved bit should be
preserved across a read-modify-write operation.
31:17 reserved RO 0x000
Count Flag
Value Description
The SysTick timer has not counted to 0 since the last time
this bit was read.
0
The SysTick timer has counted to 0 since the last time
this bit was read.
1
This bit is cleared by a read of the register or if the STCURRENT register
is written with any value.
If read by the debugger using the DAP, this bit is cleared only if the
MasterType bit in the AHB-AP Control Register is clear. Otherwise,
the COUNT bit is not changed by the debugger read. See the ARM®
Debug Interface V5 Architecture Specification for more information on
MasterType.
16 COUNT RO 0
Software should not rely on the value of a reserved bit. To provide
compatibility with future products, the value of a reserved bit should be
preserved across a read-modify-write operation.
15:3 reserved RO 0x000
Clock Source
Value Description
External reference clock. (Not implemented for Stellaris
microcontrollers.)
0
1 System clock
Because an external reference clock is not implemented, this bit must
be set in order for SysTick to operate.
2 CLK_SRC R/W 0
January 08, 2011 105
Texas Instruments-Production Data
Stellaris® LM3S2965 Microcontroller
Bit/Field Name Type Reset Description
Interrupt Enable
Value Description
Interrupt generation is disabled. Software can use the
COUNT bit to determine if the counter has ever reached 0.
0
An interrupt is generated to the NVIC when SysTick counts
to 0.
1
1 INTEN R/W 0
Enable
Value Description
0 The counter is disabled.
Enables SysTick to operate in a multi-shot way. That is, the
counter loads the RELOAD value and begins counting down.
On reaching 0, the COUNT bit is set and an interrupt is
generated if enabled by INTEN. The counter then loads the
RELOAD value again and begins counting.
1
0 ENABLE R/W 0
106 January 08, 2011
Texas Instruments-Production Data
Cortex-M3 Peripherals
Register 2: SysTick Reload Value Register (STRELOAD), offset 0x014
Note: This register can only be accessed from privileged mode.
Note: This register can only be accessed from privileged mode.
The STRELOAD register specifies the start value to load into the SysTick Current Value
(STCURRENT) register when the counter reaches 0. The start value can be between 0x1 and
0x00FF.FFFF. A start value of 0 is possible but has no effect because the SysTick interrupt and the
COUNT bit are activated when counting from 1 to 0.
SysTick can be configured as a multi-shot timer, repeated over and over, firing every N+1 clock
pulses, where N is any value from 1 to 0x00FF.FFFF. For example, if a tick interrupt is required
every 100 clock pulses, 99 must be written into the RELOAD field.
SysTick Reload Value Register (STRELOAD)
Base 0xE000.E000
Offset 0x014
Type R/W, reset 0x0000.0000
31 30 29 28 27 26 25 24 23 22 21 20 19 18 17 16
reserved RELOAD
Type RO RO RO RO RO RO RO RO R/W R/W R/W R/W R/W R/W R/W R/W
Reset 0 0 0 0 0 0 0 0 0 0 0 0 0 0 0 0
15 14 13 12 11 10 9 8 7 6 5 4 3 2 1 0
RELOAD
Type R/W R/W R/W R/W R/W R/W R/W R/W R/W R/W R/W R/W R/W R/W R/W R/W
Reset 0 0 0 0 0 0 0 0 0 0 0 0 0 0 0 0
Bit/Field Name Type Reset Description
Software should not rely on the value of a reserved bit. To provide
compatibility with future products, the value of a reserved bit should be
preserved across a read-modify-write operation.
31:24 reserved RO 0x00
Reload Value
Value to load into the SysTick Current Value (STCURRENT) register
when the counter reaches 0.
23:0 RELOAD R/W 0x00.0000
January 08, 2011 107
Texas Instruments-Production Data
Stellaris® LM3S2965 Microcontroller
Register 3: SysTick Current Value Register (STCURRENT), offset 0x018
Note: This register can only be accessed from privileged mode.
The STCURRENT register contains the current value of the SysTick counter.
SysTick Current Value Register (STCURRENT)
Base 0xE000.E000
Offset 0x018
Type R/WC, reset 0x0000.0000
31 30 29 28 27 26 25 24 23 22 21 20 19 18 17 16
reserved CURRENT
Type RO RO RO RO RO RO RO RO R/WC R/WC R/WC R/WC R/WC R/WC R/WC R/WC
Reset 0 0 0 0 0 0 0 0 0 0 0 0 0 0 0 0
15 14 13 12 11 10 9 8 7 6 5 4 3 2 1 0
CURRENT
Type R/WC R/WC R/WC R/WC R/WC R/WC R/WC R/WC R/WC R/WC R/WC R/WC R/WC R/WC R/WC R/WC
Reset 0 0 0 0 0 0 0 0 0 0 0 0 0 0 0 0
Bit/Field Name Type Reset Description
Software should not rely on the value of a reserved bit. To provide
compatibility with future products, the value of a reserved bit should be
preserved across a read-modify-write operation.
31:24 reserved RO 0x00
Current Value
This field contains the current value at the time the register is accessed.
No read-modify-write protection is provided, so change with care.
This register is write-clear. Writing to it with any value clears the register.
Clearing this register also clears the COUNT bit of the STCTRL register.
23:0 CURRENT R/WC 0x00.0000
3.4 NVIC Register Descriptions
This section lists and describes the NVIC registers, in numerical order by address offset.
The NVIC registers can only be fully accessed from privileged mode, but interrupts can be pended
while in unprivileged mode by enabling the Configuration and Control (CFGCTRL) register. Any
other unprivileged mode access causes a bus fault.
Ensure software uses correctly aligned register accesses. The processor does not support unaligned
accesses to NVIC registers.
An interrupt can enter the pending state even if it is disabled.
Before programming the VTABLE register to relocate the vector table, ensure the vector table
entries of the new vector table are set up for fault handlers, NMI, and all enabled exceptions such
as interrupts. For more information, see page 126.
108 January 08, 2011
Texas Instruments-Production Data
Cortex-M3 Peripherals
Register 4: Interrupt 0-31 Set Enable (EN0), offset 0x100
Note: This register can only be accessed from privileged mode.
The EN0 register enables interrupts and shows which interrupts are enabled. Bit 0 corresponds to
Interrupt 0; bit 31 corresponds to Interrupt 31.
See Table 2-9 on page 82 for interrupt assignments.
If a pending interrupt is enabled, the NVIC activates the interrupt based on its priority. If an interrupt
is not enabled, asserting its interrupt signal changes the interrupt state to pending, but the NVIC
never activates the interrupt, regardless of its priority.
Interrupt 0-31 Set Enable (EN0)
Base 0xE000.E000
Offset 0x100
Type R/W, reset 0x0000.0000
31 30 29 28 27 26 25 24 23 22 21 20 19 18 17 16
INT
Type R/W R/W R/W R/W R/W R/W R/W R/W R/W R/W R/W R/W R/W R/W R/W R/W
Reset 0 0 0 0 0 0 0 0 0 0 0 0 0 0 0 0
15 14 13 12 11 10 9 8 7 6 5 4 3 2 1 0
INT
Type R/W R/W R/W R/W R/W R/W R/W R/W R/W R/W R/W R/W R/W R/W R/W R/W
Reset 0 0 0 0 0 0 0 0 0 0 0 0 0 0 0 0
Bit/Field Name Type Reset Description
Interrupt Enable
Value Description
On a read, indicates the interrupt is disabled.
On a write, no effect.
0
On a read, indicates the interrupt is enabled.
On a write, enables the interrupt.
1
A bit can only be cleared by setting the corresponding INT[n] bit in
the DISn register.
31:0 INT R/W 0x0000.0000
January 08, 2011 109
Texas Instruments-Production Data
Stellaris® LM3S2965 Microcontroller
Register 5: Interrupt 32-43 Set Enable (EN1), offset 0x104
Note: This register can only be accessed from privileged mode.
The EN1 register enables interrupts and shows which interrupts are enabled. Bit 0 corresponds to
Interrupt 32; bit 11 corresponds to Interrupt 43. See Table 2-9 on page 82 for interrupt assignments.
If a pending interrupt is enabled, the NVIC activates the interrupt based on its priority. If an interrupt
is not enabled, asserting its interrupt signal changes the interrupt state to pending, but the NVIC
never activates the interrupt, regardless of its priority.
Interrupt 32-43 Set Enable (EN1)
Base 0xE000.E000
Offset 0x104
Type R/W, reset 0x0000.0000
31 30 29 28 27 26 25 24 23 22 21 20 19 18 17 16
reserved
Type RO RO RO RO RO RO RO RO RO RO RO RO RO RO RO RO
Reset 0 0 0 0 0 0 0 0 0 0 0 0 0 0 0 0
15 14 13 12 11 10 9 8 7 6 5 4 3 2 1 0
reserved INT
Type RO RO RO RO R/W R/W R/W R/W R/W R/W R/W R/W R/W R/W R/W R/W
Reset 0 0 0 0 0 0 0 0 0 0 0 0 0 0 0 0
Bit/Field Name Type Reset Description
Software should not rely on the value of a reserved bit. To provide
compatibility with future products, the value of a reserved bit should be
preserved across a read-modify-write operation.
31:12 reserved RO 0x0000.0
Interrupt Enable
Value Description
On a read, indicates the interrupt is disabled.
On a write, no effect.
0
On a read, indicates the interrupt is enabled.
On a write, enables the interrupt.
1
A bit can only be cleared by setting the corresponding INT[n] bit in
the DIS1 register.
11:0 INT R/W 0x000
110 January 08, 2011
Texas Instruments-Production Data
Cortex-M3 Peripherals
Register 6: Interrupt 0-31 Clear Enable (DIS0), offset 0x180
Note: This register can only be accessed from privileged mode.
The DIS0 register disables interrupts. Bit 0 corresponds to Interrupt 0; bit 31 corresponds to Interrupt
31.
See Table 2-9 on page 82 for interrupt assignments.
Interrupt 0-31 Clear Enable (DIS0)
Base 0xE000.E000
Offset 0x180
Type R/W, reset 0x0000.0000
31 30 29 28 27 26 25 24 23 22 21 20 19 18 17 16
INT
Type R/W R/W R/W R/W R/W R/W R/W R/W R/W R/W R/W R/W R/W R/W R/W R/W
Reset 0 0 0 0 0 0 0 0 0 0 0 0 0 0 0 0
15 14 13 12 11 10 9 8 7 6 5 4 3 2 1 0
INT
Type R/W R/W R/W R/W R/W R/W R/W R/W R/W R/W R/W R/W R/W R/W R/W R/W
Reset 0 0 0 0 0 0 0 0 0 0 0 0 0 0 0 0
Bit/Field Name Type Reset Description
Interrupt Disable
Value Description
On a read, indicates the interrupt is disabled.
On a write, no effect.
0
On a read, indicates the interrupt is enabled.
On a write, clears the corresponding INT[n] bit in the EN0
register, disabling interrupt [n].
1
31:0 INT R/W 0x0000.0000
January 08, 2011 111
Texas Instruments-Production Data
Stellaris® LM3S2965 Microcontroller
Register 7: Interrupt 32-43 Clear Enable (DIS1), offset 0x184
Note: This register can only be accessed from privileged mode.
The DIS1 register disables interrupts. Bit 0 corresponds to Interrupt 32; bit 11 corresponds to Interrupt
43. See Table 2-9 on page 82 for interrupt assignments.
Interrupt 32-43 Clear Enable (DIS1)
Base 0xE000.E000
Offset 0x184
Type R/W, reset 0x0000.0000
31 30 29 28 27 26 25 24 23 22 21 20 19 18 17 16
reserved
Type RO RO RO RO RO RO RO RO RO RO RO RO RO RO RO RO
Reset 0 0 0 0 0 0 0 0 0 0 0 0 0 0 0 0
15 14 13 12 11 10 9 8 7 6 5 4 3 2 1 0
reserved INT
Type RO RO RO RO R/W R/W R/W R/W R/W R/W R/W R/W R/W R/W R/W R/W
Reset 0 0 0 0 0 0 0 0 0 0 0 0 0 0 0 0
Bit/Field Name Type Reset Description
Software should not rely on the value of a reserved bit. To provide
compatibility with future products, the value of a reserved bit should be
preserved across a read-modify-write operation.
31:12 reserved RO 0x0000.0
Interrupt Disable
Value Description
On a read, indicates the interrupt is disabled.
On a write, no effect.
0
On a read, indicates the interrupt is enabled.
On a write, clears the corresponding INT[n] bit in the EN1
register, disabling interrupt [n].
1
11:0 INT R/W 0x000
112 January 08, 2011
Texas Instruments-Production Data
Cortex-M3 Peripherals
Register 8: Interrupt 0-31 Set Pending (PEND0), offset 0x200
Note: This register can only be accessed from privileged mode.
The PEND0 register forces interrupts into the pending state and shows which interrupts are pending.
Bit 0 corresponds to Interrupt 0; bit 31 corresponds to Interrupt 31.
See Table 2-9 on page 82 for interrupt assignments.
Interrupt 0-31 Set Pending (PEND0)
Base 0xE000.E000
Offset 0x200
Type R/W, reset 0x0000.0000
31 30 29 28 27 26 25 24 23 22 21 20 19 18 17 16
INT
Type R/W R/W R/W R/W R/W R/W R/W R/W R/W R/W R/W R/W R/W R/W R/W R/W
Reset 0 0 0 0 0 0 0 0 0 0 0 0 0 0 0 0
15 14 13 12 11 10 9 8 7 6 5 4 3 2 1 0
INT
Type R/W R/W R/W R/W R/W R/W R/W R/W R/W R/W R/W R/W R/W R/W R/W R/W
Reset 0 0 0 0 0 0 0 0 0 0 0 0 0 0 0 0
Bit/Field Name Type Reset Description
Interrupt Set Pending
Value Description
On a read, indicates that the interrupt is not pending.
On a write, no effect.
0
On a read, indicates that the interrupt is pending.
On a write, the corresponding interrupt is set to pending
even if it is disabled.
1
If the corresponding interrupt is already pending, setting a bit has no
effect.
A bit can only be cleared by setting the corresponding INT[n] bit in
the UNPEND0 register.
31:0 INT R/W 0x0000.0000
January 08, 2011 113
Texas Instruments-Production Data
Stellaris® LM3S2965 Microcontroller
Register 9: Interrupt 32-43 Set Pending (PEND1), offset 0x204
Note: This register can only be accessed from privileged mode.
The PEND1 register forces interrupts into the pending state and shows which interrupts are pending.
Bit 0 corresponds to Interrupt 32; bit 11 corresponds to Interrupt 43. See Table 2-9 on page 82 for
interrupt assignments.
Interrupt 32-43 Set Pending (PEND1)
Base 0xE000.E000
Offset 0x204
Type R/W, reset 0x0000.0000
31 30 29 28 27 26 25 24 23 22 21 20 19 18 17 16
reserved
Type RO RO RO RO RO RO RO RO RO RO RO RO RO RO RO RO
Reset 0 0 0 0 0 0 0 0 0 0 0 0 0 0 0 0
15 14 13 12 11 10 9 8 7 6 5 4 3 2 1 0
reserved INT
Type RO RO RO RO R/W R/W R/W R/W R/W R/W R/W R/W R/W R/W R/W R/W
Reset 0 0 0 0 0 0 0 0 0 0 0 0 0 0 0 0
Bit/Field Name Type Reset Description
Software should not rely on the value of a reserved bit. To provide
compatibility with future products, the value of a reserved bit should be
preserved across a read-modify-write operation.
31:12 reserved RO 0x0000.0
Interrupt Set Pending
Value Description
On a read, indicates that the interrupt is not pending.
On a write, no effect.
0
On a read, indicates that the interrupt is pending.
On a write, the corresponding interrupt is set to pending
even if it is disabled.
1
If the corresponding interrupt is already pending, setting a bit has no
effect.
A bit can only be cleared by setting the corresponding INT[n] bit in
the UNPEND1 register.
11:0 INT R/W 0x000
114 January 08, 2011
Texas Instruments-Production Data
Cortex-M3 Peripherals
Register 10: Interrupt 0-31 Clear Pending (UNPEND0), offset 0x280
Note: This register can only be accessed from privileged mode.
The UNPEND0 register shows which interrupts are pending and removes the pending state from
interrupts. Bit 0 corresponds to Interrupt 0; bit 31 corresponds to Interrupt 31.
See Table 2-9 on page 82 for interrupt assignments.
Interrupt 0-31 Clear Pending (UNPEND0)
Base 0xE000.E000
Offset 0x280
Type R/W, reset 0x0000.0000
31 30 29 28 27 26 25 24 23 22 21 20 19 18 17 16
INT
Type R/W R/W R/W R/W R/W R/W R/W R/W R/W R/W R/W R/W R/W R/W R/W R/W
Reset 0 0 0 0 0 0 0 0 0 0 0 0 0 0 0 0
15 14 13 12 11 10 9 8 7 6 5 4 3 2 1 0
INT
Type R/W R/W R/W R/W R/W R/W R/W R/W R/W R/W R/W R/W R/W R/W R/W R/W
Reset 0 0 0 0 0 0 0 0 0 0 0 0 0 0 0 0
Bit/Field Name Type Reset Description
Interrupt Clear Pending
Value Description
On a read, indicates that the interrupt is not pending.
On a write, no effect.
0
On a read, indicates that the interrupt is pending.
On a write, clears the corresponding INT[n] bit in the PEND0
register, so that interrupt [n] is no longer pending.
Setting a bit does not affect the active state of the corresponding
interrupt.
1
31:0 INT R/W 0x0000.0000
January 08, 2011 115
Texas Instruments-Production Data
Stellaris® LM3S2965 Microcontroller
Register 11: Interrupt 32-43 Clear Pending (UNPEND1), offset 0x284
Note: This register can only be accessed from privileged mode.
The UNPEND1 register shows which interrupts are pending and removes the pending state from
interrupts. Bit 0 corresponds to Interrupt 32; bit 11 corresponds to Interrupt 43. See Table
2-9 on page 82 for interrupt assignments.
Interrupt 32-43 Clear Pending (UNPEND1)
Base 0xE000.E000
Offset 0x284
Type R/W, reset 0x0000.0000
31 30 29 28 27 26 25 24 23 22 21 20 19 18 17 16
reserved
Type RO RO RO RO RO RO RO RO RO RO RO RO RO RO RO RO
Reset 0 0 0 0 0 0 0 0 0 0 0 0 0 0 0 0
15 14 13 12 11 10 9 8 7 6 5 4 3 2 1 0
reserved INT
Type RO RO RO RO R/W R/W R/W R/W R/W R/W R/W R/W R/W R/W R/W R/W
Reset 0 0 0 0 0 0 0 0 0 0 0 0 0 0 0 0
Bit/Field Name Type Reset Description
Software should not rely on the value of a reserved bit. To provide
compatibility with future products, the value of a reserved bit should be
preserved across a read-modify-write operation.
31:12 reserved RO 0x0000.0
Interrupt Clear Pending
Value Description
On a read, indicates that the interrupt is not pending.
On a write, no effect.
0
On a read, indicates that the interrupt is pending.
On a write, clears the corresponding INT[n] bit in the PEND1
register, so that interrupt [n] is no longer pending.
Setting a bit does not affect the active state of the corresponding
interrupt.
1
11:0 INT R/W 0x000
116 January 08, 2011
Texas Instruments-Production Data
Cortex-M3 Peripherals
Register 12: Interrupt 0-31 Active Bit (ACTIVE0), offset 0x300
Note: This register can only be accessed from privileged mode.
The ACTIVE0 register indicates which interrupts are active. Bit 0 corresponds to Interrupt 0; bit 31
corresponds to Interrupt 31.
See Table 2-9 on page 82 for interrupt assignments.
Caution – Do not manually set or clear the bits in this register.
Interrupt 0-31 Active Bit (ACTIVE0)
Base 0xE000.E000
Offset 0x300
Type RO, reset 0x0000.0000
31 30 29 28 27 26 25 24 23 22 21 20 19 18 17 16
INT
Type RO RO RO RO RO RO RO RO RO RO RO RO RO RO RO RO
Reset 0 0 0 0 0 0 0 0 0 0 0 0 0 0 0 0
15 14 13 12 11 10 9 8 7 6 5 4 3 2 1 0
INT
Type RO RO RO RO RO RO RO RO RO RO RO RO RO RO RO RO
Reset 0 0 0 0 0 0 0 0 0 0 0 0 0 0 0 0
Bit/Field Name Type Reset Description
Interrupt Active
Value Description
0 The corresponding interrupt is not active.
1 The corresponding interrupt is active, or active and pending.
31:0 INT RO 0x0000.0000
January 08, 2011 117
Texas Instruments-Production Data
Stellaris® LM3S2965 Microcontroller
Register 13: Interrupt 32-43 Active Bit (ACTIVE1), offset 0x304
Note: This register can only be accessed from privileged mode.
The ACTIVE1 register indicates which interrupts are active. Bit 0 corresponds to Interrupt 32; bit
11 corresponds to Interrupt 43. See Table 2-9 on page 82 for interrupt assignments.
Caution – Do not manually set or clear the bits in this register.
Interrupt 32-43 Active Bit (ACTIVE1)
Base 0xE000.E000
Offset 0x304
Type RO, reset 0x0000.0000
31 30 29 28 27 26 25 24 23 22 21 20 19 18 17 16
reserved
Type RO RO RO RO RO RO RO RO RO RO RO RO RO RO RO RO
Reset 0 0 0 0 0 0 0 0 0 0 0 0 0 0 0 0
15 14 13 12 11 10 9 8 7 6 5 4 3 2 1 0
reserved INT
Type RO RO RO RO RO RO RO RO RO RO RO RO RO RO RO RO
Reset 0 0 0 0 0 0 0 0 0 0 0 0 0 0 0 0
Bit/Field Name Type Reset Description
Software should not rely on the value of a reserved bit. To provide
compatibility with future products, the value of a reserved bit should be
preserved across a read-modify-write operation.
31:12 reserved RO 0x0000.0
Interrupt Active
Value Description
0 The corresponding interrupt is not active.
1 The corresponding interrupt is active, or active and pending.
11:0 INT RO 0x000
118 January 08, 2011
Texas Instruments-Production Data
Cortex-M3 Peripherals
Register 14: Interrupt 0-3 Priority (PRI0), offset 0x400
Register 15: Interrupt 4-7 Priority (PRI1), offset 0x404
Register 16: Interrupt 8-11 Priority (PRI2), offset 0x408
Register 17: Interrupt 12-15 Priority (PRI3), offset 0x40C
Register 18: Interrupt 16-19 Priority (PRI4), offset 0x410
Register 19: Interrupt 20-23 Priority (PRI5), offset 0x414
Register 20: Interrupt 24-27 Priority (PRI6), offset 0x418
Register 21: Interrupt 28-31 Priority (PRI7), offset 0x41C
Register 22: Interrupt 32-35 Priority (PRI8), offset 0x420
Register 23: Interrupt 36-39 Priority (PRI9), offset 0x424
Register 24: Interrupt 40-43 Priority (PRI10), offset 0x428
Note: This register can only be accessed from privileged mode.
The PRIn registers provide 3-bit priority fields for each interrupt. These registers are byte accessible.
Each register holds four priority fields that are assigned to interrupts as follows:
PRIn Register Bit Field Interrupt
Bits 31:29 Interrupt [4n+3]
Bits 23:21 Interrupt [4n+2]
Bits 15:13 Interrupt [4n+1]
Bits 7:5 Interrupt [4n]
See Table 2-9 on page 82 for interrupt assignments.
Each priority level can be split into separate group priority and subpriority fields. The PRIGROUP
field in the Application Interrupt and Reset Control (APINT) register (see page 127) indicates the
position of the binary point that splits the priority and subpriority fields .
These registers can only be accessed from privileged mode.
Interrupt 0-3 Priority (PRI0)
Base 0xE000.E000
Offset 0x400
Type R/W, reset 0x0000.0000
31 30 29 28 27 26 25 24 23 22 21 20 19 18 17 16
INTD reserved INTC reserved
Type R/W R/W R/W RO RO RO RO RO R/W R/W R/W RO RO RO RO RO
Reset 0 0 0 0 0 0 0 0 0 0 0 0 0 0 0 0
15 14 13 12 11 10 9 8 7 6 5 4 3 2 1 0
INTB reserved INTA reserved
Type R/W R/W R/W RO RO RO RO RO R/W R/W R/W RO RO RO RO RO
Reset 0 0 0 0 0 0 0 0 0 0 0 0 0 0 0 0
January 08, 2011 119
Texas Instruments-Production Data
Stellaris® LM3S2965 Microcontroller
Bit/Field Name Type Reset Description
Interrupt Priority for Interrupt [4n+3]
This field holds a priority value, 0-7, for the interrupt with the number
[4n+3], where n is the number of the Interrupt Priority register (n=0 for
PRI0, and so on). The lower the value, the greater the priority of the
corresponding interrupt.
31:29 INTD R/W 0x0
Software should not rely on the value of a reserved bit. To provide
compatibility with future products, the value of a reserved bit should be
preserved across a read-modify-write operation.
28:24 reserved RO 0x0
Interrupt Priority for Interrupt [4n+2]
This field holds a priority value, 0-7, for the interrupt with the number
[4n+2], where n is the number of the Interrupt Priority register (n=0 for
PRI0, and so on). The lower the value, the greater the priority of the
corresponding interrupt.
23:21 INTC R/W 0x0
Software should not rely on the value of a reserved bit. To provide
compatibility with future products, the value of a reserved bit should be
preserved across a read-modify-write operation.
20:16 reserved RO 0x0
Interrupt Priority for Interrupt [4n+1]
This field holds a priority value, 0-7, for the interrupt with the number
[4n+1], where n is the number of the Interrupt Priority register (n=0 for
PRI0, and so on). The lower the value, the greater the priority of the
corresponding interrupt.
15:13 INTB R/W 0x0
Software should not rely on the value of a reserved bit. To provide
compatibility with future products, the value of a reserved bit should be
preserved across a read-modify-write operation.
12:8 reserved RO 0x0
Interrupt Priority for Interrupt [4n]
This field holds a priority value, 0-7, for the interrupt with the number
[4n], where n is the number of the Interrupt Priority register (n=0 for
PRI0, and so on). The lower the value, the greater the priority of the
corresponding interrupt.
7:5 INTA R/W 0x0
Software should not rely on the value of a reserved bit. To provide
compatibility with future products, the value of a reserved bit should be
preserved across a read-modify-write operation.
4:0 reserved RO 0x0
120 January 08, 2011
Texas Instruments-Production Data
Cortex-M3 Peripherals
Register 25: Software Trigger Interrupt (SWTRIG), offset 0xF00
Note: Only privileged software can enable unprivileged access to the SWTRIG register.
Writing an interrupt number to the SWTRIG register generates a Software Generated Interrupt (SGI).
See Table 2-9 on page 82 for interrupt assignments.
When the MAINPEND bit in the Configuration and Control (CFGCTRL) register (see page 131) is
set, unprivileged software can access the SWTRIG register.
Software Trigger Interrupt (SWTRIG)
Base 0xE000.E000
Offset 0xF00
Type WO, reset 0x0000.0000
31 30 29 28 27 26 25 24 23 22 21 20 19 18 17 16
reserved
Type RO RO RO RO RO RO RO RO RO RO RO RO RO RO RO RO
Reset 0 0 0 0 0 0 0 0 0 0 0 0 0 0 0 0
15 14 13 12 11 10 9 8 7 6 5 4 3 2 1 0
reserved INTID
Type RO RO RO RO RO RO RO RO RO RO WO WO WO WO WO WO
Reset 0 0 0 0 0 0 0 0 0 0 0 0 0 0 0 0
Bit/Field Name Type Reset Description
Software should not rely on the value of a reserved bit. To provide
compatibility with future products, the value of a reserved bit should be
preserved across a read-modify-write operation.
31:6 reserved RO 0x0000.00
Interrupt ID
This field holds the interrupt ID of the required SGI. For example, a value
of 0x3 generates an interrupt on IRQ3.
5:0 INTID WO 0x00
3.5 System Control Block (SCB) Register Descriptions
This section lists and describes the System Control Block (SCB) registers, in numerical order by
address offset. The SCB registers can only be accessed from privileged mode.
All registers must be accessed with aligned word accesses except for the FAULTSTAT and
SYSPRI1-SYSPRI3 registers, which can be accessed with byte or aligned halfword or word accesses.
The processor does not support unaligned accesses to system control block registers.
January 08, 2011 121
Texas Instruments-Production Data
Stellaris® LM3S2965 Microcontroller
Register 26: CPU ID Base (CPUID), offset 0xD00
Note: This register can only be accessed from privileged mode.
The CPUID register contains the ARM® Cortex™-M3 processor part number, version, and
implementation information.
CPU ID Base (CPUID)
Base 0xE000.E000
Offset 0xD00
Type RO, reset 0x411F.C231
31 30 29 28 27 26 25 24 23 22 21 20 19 18 17 16
IMP VAR CON
Type R0 R0 R0 R0 R0 R0 R0 R0 RO RO RO RO RO RO RO RO
Reset 0 1 0 0 0 0 0 1 0 0 0 1 1 1 1 1
15 14 13 12 11 10 9 8 7 6 5 4 3 2 1 0
PARTNO REV
Type RO RO RO RO RO RO RO RO RO RO RO RO RO RO RO RO
Reset 1 1 0 0 0 0 1 0 0 0 1 1 0 0 0 1
Bit/Field Name Type Reset Description
Implementer Code
Value Description
0x41 ARM
31:24 IMP R0 0x41
Variant Number
Value Description
The rn value in the rnpn product revision identifier, for example,
the 1 in r1p1.
0x1
23:20 VAR RO 0x1
Constant
Value Description
0xF Always reads as 0xF.
19:16 CON RO 0xF
Part Number
Value Description
0xC23 Cortex-M3 processor.
15:4 PARTNO RO 0xC23
Revision Number
Value Description
The pn value in the rnpn product revision identifier, for example,
the 1 in r1p1.
0x1
3:0 REV RO 0x1
122 January 08, 2011
Texas Instruments-Production Data
Cortex-M3 Peripherals
Register 27: Interrupt Control and State (INTCTRL), offset 0xD04
Note: This register can only be accessed from privileged mode.
The INCTRL register provides a set-pending bit for the NMI exception, and set-pending and
clear-pending bits for the PendSV and SysTick exceptions. In addition, bits in this register indicate
the exception number of the exception being processed, whether there are preempted active
exceptions, the exception number of the highest priority pending exception, and whether any interrupts
are pending.
When writing to INCTRL, the effect is unpredictable when writing a 1 to both the PENDSV and
UNPENDSV bits, or writing a 1 to both the PENDSTSET and PENDSTCLR bits.
Interrupt Control and State (INTCTRL)
Base 0xE000.E000
Offset 0xD04
Type R/W, reset 0x0000.0000
31 30 29 28 27 26 25 24 23 22 21 20 19 18 17 16
NMISET reserved PENDSV UNPENDSV PENDSTSET PENDSTCLR reserved ISRPRE ISRPEND reserved VECPEND
Type R/W RO RO R/W WO R/W WO RO RO RO RO RO RO RO RO RO
Reset 0 0 0 0 0 0 0 0 0 0 0 0 0 0 0 0
15 14 13 12 11 10 9 8 7 6 5 4 3 2 1 0
VECPEND RETBASE reserved VECACT
Type RO RO RO RO RO RO RO RO RO RO RO RO RO RO RO RO
Reset 0 0 0 0 0 0 0 0 0 0 0 0 0 0 0 0
Bit/Field Name Type Reset Description
NMI Set Pending
Value Description
On a read, indicates an NMI exception is not pending.
On a write, no effect.
0
On a read, indicates an NMI exception is pending.
On a write, changes the NMI exception state to pending.
1
Because NMI is the highest-priority exception, normally the processor
enters the NMI exception handler as soon as it registers the setting of
this bit, and clears this bit on entering the interrupt handler. A read of
this bit by the NMI exception handler returns 1 only if the NMI signal is
reasserted while the processor is executing that handler.
31 NMISET R/W 0
Software should not rely on the value of a reserved bit. To provide
compatibility with future products, the value of a reserved bit should be
preserved across a read-modify-write operation.
30:29 reserved RO 0x0
PendSV Set Pending
Value Description
On a read, indicates a PendSV exception is not pending.
On a write, no effect.
0
On a read, indicates a PendSV exception is pending.
On a write, changes the PendSV exception state to pending.
1
Setting this bit is the only way to set the PendSV exception state to
pending. This bit is cleared by writing a 1 to the UNPENDSV bit.
28 PENDSV R/W 0
January 08, 2011 123
Texas Instruments-Production Data
Stellaris® LM3S2965 Microcontroller
Bit/Field Name Type Reset Description
PendSV Clear Pending
Value Description
0 On a write, no effect.
On a write, removes the pending state from the PendSV
exception.
1
This bit is write only; on a register read, its value is unknown.
27 UNPENDSV WO 0
SysTick Set Pending
Value Description
On a read, indicates a SysTick exception is not pending.
On a write, no effect.
0
On a read, indicates a SysTick exception is pending.
On a write, changes the SysTick exception state to pending.
1
This bit is cleared by writing a 1 to the PENDSTCLR bit.
26 PENDSTSET R/W 0
SysTick Clear Pending
Value Description
0 On a write, no effect.
On a write, removes the pending state from the SysTick
exception.
1
This bit is write only; on a register read, its value is unknown.
25 PENDSTCLR WO 0
Software should not rely on the value of a reserved bit. To provide
compatibility with future products, the value of a reserved bit should be
preserved across a read-modify-write operation.
24 reserved RO 0
Debug Interrupt Handling
Value Description
0 The release from halt does not take an interrupt.
1 The release from halt takes an interrupt.
This bit is only meaningful in Debug mode and reads as zero when the
processor is not in Debug mode.
23 ISRPRE RO 0
Interrupt Pending
Value Description
0 No interrupt is pending.
1 An interrupt is pending.
This bit provides status for all interrupts excluding NMI and Faults.
22 ISRPEND RO 0
Software should not rely on the value of a reserved bit. To provide
compatibility with future products, the value of a reserved bit should be
preserved across a read-modify-write operation.
21:18 reserved RO 0x0
124 January 08, 2011
Texas Instruments-Production Data
Cortex-M3 Peripherals
Bit/Field Name Type Reset Description
Interrupt Pending Vector Number
This field contains the exception number of the highest priority pending
enabled exception. The value indicated by this field includes the effect
of the BASEPRI and FAULTMASK registers, but not any effect of the
PRIMASK register.
Value Description
0x00 No exceptions are pending
0x01 Reserved
0x02 NMI
0x03 Hard fault
0x04 Memory management fault
0x05 Bus fault
0x06 Usage fault
0x07-0x0A Reserved
0x0B SVCall
0x0C Reserved for Debug
0x0D Reserved
0x0E PendSV
0x0F SysTick
0x10 Interrupt Vector 0
0x11 Interrupt Vector 1
... ...
0x3B Interrupt Vector 43
0x3C-0x3F Reserved
17:12 VECPEND RO 0x00
Return to Base
Value Description
0 There are preempted active exceptions to execute.
There are no active exceptions, or the currently executing
exception is the only active exception.
1
This bit provides status for all interrupts excluding NMI and Faults. This
bit only has meaning if the processor is currently executing an ISR (the
Interrupt Program Status (IPSR) register is non-zero).
11 RETBASE RO 0
Software should not rely on the value of a reserved bit. To provide
compatibility with future products, the value of a reserved bit should be
preserved across a read-modify-write operation.
10:6 reserved RO 0x0
Interrupt Pending Vector Number
This field contains the active exception number. The exception numbers
can be found in the description for the VECPEND field. If this field is clear,
the processor is in Thread mode. This field contains the same value as
the ISRNUM field in the IPSR register.
Subtract 16 from this value to obtain the IRQ number required to index
into the Interrupt Set Enable (ENn), Interrupt Clear Enable (DISn),
Interrupt Set Pending (PENDn), Interrupt Clear Pending (UNPENDn),
and Interrupt Priority (PRIn) registers (see page 63).
5:0 VECACT RO 0x00
January 08, 2011 125
Texas Instruments-Production Data
Stellaris® LM3S2965 Microcontroller
Register 28: Vector Table Offset (VTABLE), offset 0xD08
Note: This register can only be accessed from privileged mode.
The VTABLE register indicates the offset of the vector table base address from memory address
0x0000.0000.
Vector Table Offset (VTABLE)
Base 0xE000.E000
Offset 0xD08
Type R/W, reset 0x0000.0000
31 30 29 28 27 26 25 24 23 22 21 20 19 18 17 16
reserved BASE OFFSET
Type RO RO R/W R/W R/W R/W R/W R/W R/W R/W R/W R/W R/W R/W R/W R/W
Reset 0 0 0 0 0 0 0 0 0 0 0 0 0 0 0 0
15 14 13 12 11 10 9 8 7 6 5 4 3 2 1 0
OFFSET reserved
Type R/W R/W R/W R/W R/W R/W R/W R/W RO RO RO RO RO RO RO RO
Reset 0 0 0 0 0 0 0 0 0 0 0 0 0 0 0 0
Bit/Field Name Type Reset Description
Software should not rely on the value of a reserved bit. To provide
compatibility with future products, the value of a reserved bit should be
preserved across a read-modify-write operation.
31:30 reserved RO 0x0
Vector Table Base
Value Description
0 The vector table is in the code memory region.
1 The vector table is in the SRAM memory region.
29 BASE R/W 0
Vector Table Offset
When configuring the OFFSET field, the offset must be aligned to the
number of exception entries in the vector table. Because there are 43
interrupts, the minimum alignment is 64 words.
28:8 OFFSET R/W 0x000.00
Software should not rely on the value of a reserved bit. To provide
compatibility with future products, the value of a reserved bit should be
preserved across a read-modify-write operation.
7:0 reserved RO 0x00
126 January 08, 2011
Texas Instruments-Production Data
Cortex-M3 Peripherals
Register 29: Application Interrupt and Reset Control (APINT), offset 0xD0C
Note: This register can only be accessed from privileged mode.
The APINT register provides priority grouping control for the exception model, endian status for
data accesses, and reset control of the system. To write to this register, 0x05FA must be written to
the VECTKEY field, otherwise the write is ignored.
The PRIGROUP field indicates the position of the binary point that splits the INTx fields in the
Interrupt Priority (PRIx) registers into separate group priority and subpriority fields. Table
3-8 on page 127 shows how the PRIGROUP value controls this split. The bit numbers in the Group
Priority Field and Subpriority Field columns in the table refer to the bits in the INTA field. For the
INTB field, the corresponding bits are 15:13; for INTC, 23:21; and for INTD, 31:29.
Note: Determining preemption of an exception uses only the group priority field.
Table 3-8. Interrupt Priority Levels
Group Subpriorities
Priorities
PRIGROUP Bit Field Binary Pointa Group Priority Field Subpriority Field
0x0 - 0x4 bxxx. [7:5] None 8 1
0x5 bxx.y [7:6] [5] 4 2
0x6 bx.yy [7] [6:5] 2 4
0x7 b.yyy None [7:5] 1 8
a. INTx field showing the binary point. An x denotes a group priority field bit, and a y denotes a subpriority field bit.
Application Interrupt and Reset Control (APINT)
Base 0xE000.E000
Offset 0xD0C
Type R/W, reset 0xFA05.0000
31 30 29 28 27 26 25 24 23 22 21 20 19 18 17 16
VECTKEY
Type R/W R/W R/W R/W R/W R/W R/W R/W R/W R/W R/W R/W R/W R/W R/W R/W
Reset 1 1 1 1 1 0 1 0 0 0 0 0 0 1 0 1
15 14 13 12 11 10 9 8 7 6 5 4 3 2 1 0
ENDIANESS reserved PRIGROUP reserved SYSRESREQVECTCLRACT VECTRESET
Type RO RO RO RO RO R/W R/W R/W RO RO RO RO RO WO WO WO
Reset 0 0 0 0 0 0 0 0 0 0 0 0 0 0 0 0
Bit/Field Name Type Reset Description
Register Key
This field is used to guard against accidental writes to this register.
0x05FA must be written to this field in order to change the bits in this
register. On a read, 0xFA05 is returned.
31:16 VECTKEY R/W 0xFA05
Data Endianess
The Stellaris implementation uses only little-endian mode so this is
cleared to 0.
15 ENDIANESS RO 0
Software should not rely on the value of a reserved bit. To provide
compatibility with future products, the value of a reserved bit should be
preserved across a read-modify-write operation.
14:11 reserved RO 0x0
January 08, 2011 127
Texas Instruments-Production Data
Stellaris® LM3S2965 Microcontroller
Bit/Field Name Type Reset Description
Interrupt Priority Grouping
This field determines the split of group priority from subpriority (see
Table 3-8 on page 127 for more information).
10:8 PRIGROUP R/W 0x0
Software should not rely on the value of a reserved bit. To provide
compatibility with future products, the value of a reserved bit should be
preserved across a read-modify-write operation.
7:3 reserved RO 0x0
System Reset Request
Value Description
0 No effect.
Resets the core and all on-chip peripherals except the Debug
interface.
1
This bit is automatically cleared during the reset of the core and reads
as 0.
2 SYSRESREQ WO 0
Clear Active NMI / Fault
This bit is reserved for Debug use and reads as 0. This bit must be
written as a 0, otherwise behavior is unpredictable.
1 VECTCLRACT WO 0
System Reset
This bit is reserved for Debug use and reads as 0. This bit must be
written as a 0, otherwise behavior is unpredictable.
0 VECTRESET WO 0
128 January 08, 2011
Texas Instruments-Production Data
Cortex-M3 Peripherals
Register 30: System Control (SYSCTRL), offset 0xD10
Note: This register can only be accessed from privileged mode.
The SYSCTRL register controls features of entry to and exit from low-power state.
System Control (SYSCTRL)
Base 0xE000.E000
Offset 0xD10
Type R/W, reset 0x0000.0000
31 30 29 28 27 26 25 24 23 22 21 20 19 18 17 16
reserved
Type RO RO RO RO RO RO RO RO RO RO RO RO RO RO RO RO
Reset 0 0 0 0 0 0 0 0 0 0 0 0 0 0 0 0
15 14 13 12 11 10 9 8 7 6 5 4 3 2 1 0
reserved SEVONPEND reserved SLEEPDEEP SLEEPEXIT reserved
Type RO RO RO RO RO RO RO RO RO RO RO R/W RO R/W R/W RO
Reset 0 0 0 0 0 0 0 0 0 0 0 0 0 0 0 0
Bit/Field Name Type Reset Description
Software should not rely on the value of a reserved bit. To provide
compatibility with future products, the value of a reserved bit should be
preserved across a read-modify-write operation.
31:5 reserved RO 0x0000.00
Wake Up on Pending
Value Description
Only enabled interrupts or events can wake up the processor;
disabled interrupts are excluded.
0
Enabled events and all interrupts, including disabled interrupts,
can wake up the processor.
1
When an event or interrupt enters the pending state, the event signal
wakes up the processor from WFE. If the processor is not waiting for an
event, the event is registered and affects the next WFE.
The processor also wakes up on execution of a SEV instruction or an
external event.
4 SEVONPEND R/W 0
Software should not rely on the value of a reserved bit. To provide
compatibility with future products, the value of a reserved bit should be
preserved across a read-modify-write operation.
3 reserved RO 0
Deep Sleep Enable
Value Description
0 Use Sleep mode as the low power mode.
1 Use Deep-sleep mode as the low power mode.
2 SLEEPDEEP R/W 0
January 08, 2011 129
Texas Instruments-Production Data
Stellaris® LM3S2965 Microcontroller
Bit/Field Name Type Reset Description
Sleep on ISR Exit
Value Description
When returning from Handler mode to Thread mode, do not
sleep when returning to Thread mode.
0
When returning from Handler mode to Thread mode, enter sleep
or deep sleep on return from an ISR.
1
Setting this bit enables an interrupt-driven application to avoid returning
to an empty main application.
1 SLEEPEXIT R/W 0
Software should not rely on the value of a reserved bit. To provide
compatibility with future products, the value of a reserved bit should be
preserved across a read-modify-write operation.
0 reserved RO 0
130 January 08, 2011
Texas Instruments-Production Data
Cortex-M3 Peripherals
Register 31: Configuration and Control (CFGCTRL), offset 0xD14
Note: This register can only be accessed from privileged mode.
The CFGCTRL register controls entry to Thread mode and enables: the handlers for NMI, hard fault
and faults escalated by the FAULTMASK register to ignore bus faults; trapping of divide by zero
and unaligned accesses; and access to the SWTRIG register by unprivileged software (see page 121).
Configuration and Control (CFGCTRL)
Base 0xE000.E000
Offset 0xD14
Type R/W, reset 0x0000.0000
31 30 29 28 27 26 25 24 23 22 21 20 19 18 17 16
reserved
Type RO RO RO RO RO RO RO RO RO RO RO RO RO RO RO RO
Reset 0 0 0 0 0 0 0 0 0 0 0 0 0 0 0 0
15 14 13 12 11 10 9 8 7 6 5 4 3 2 1 0
reserved STKALIGN BFHFNMIGN reserved DIV0 UNALIGNED reserved MAINPEND BASETHR
Type RO RO RO RO RO RO R/W R/W RO RO RO R/W R/W RO R/W R/W
Reset 0 0 0 0 0 0 0 0 0 0 0 0 0 0 0 0
Bit/Field Name Type Reset Description
Software should not rely on the value of a reserved bit. To provide
compatibility with future products, the value of a reserved bit should be
preserved across a read-modify-write operation.
31:10 reserved RO 0x0000.00
Stack Alignment on Exception Entry
Value Description
0 The stack is 4-byte aligned.
1 The stack is 8-byte aligned.
On exception entry, the processor uses bit 9 of the stacked PSR to
indicate the stack alignment. On return from the exception, it uses this
stacked bit to restore the correct stack alignment.
9 STKALIGN R/W 0
Ignore Bus Fault in NMI and Fault
This bit enables handlers with priority -1 or -2 to ignore data bus faults
caused by load and store instructions. The setting of this bit applies to
the hard fault, NMI, and FAULTMASK escalated handlers.
Value Description
Data bus faults caused by load and store instructions cause a
lock-up.
0
Handlers running at priority -1 and -2 ignore data bus faults
caused by load and store instructions.
1
Set this bit only when the handler and its data are in absolutely safe
memory. The normal use of this bit is to probe system devices and
bridges to detect control path problems and fix them.
8 BFHFNMIGN R/W 0
Software should not rely on the value of a reserved bit. To provide
compatibility with future products, the value of a reserved bit should be
preserved across a read-modify-write operation.
7:5 reserved RO 0x0
January 08, 2011 131
Texas Instruments-Production Data
Stellaris® LM3S2965 Microcontroller
Bit/Field Name Type Reset Description
Trap on Divide by 0
This bit enables faulting or halting when the processor executes an
SDIV or UDIV instruction with a divisor of 0.
Value Description
Do not trap on divide by 0. A divide by zero returns a quotient
of 0.
0
1 Trap on divide by 0.
4 DIV0 R/W 0
Trap on Unaligned Access
Value Description
0 Do not trap on unaligned halfword and word accesses.
Trap on unaligned halfword and word accesses. An unaligned
access generates a usage fault.
1
Unaligned LDM, STM, LDRD, and STRD instructions always fault
regardless of whether UNALIGNED is set.
3 UNALIGNED R/W 0
Software should not rely on the value of a reserved bit. To provide
compatibility with future products, the value of a reserved bit should be
preserved across a read-modify-write operation.
2 reserved RO 0
Allow Main Interrupt Trigger
Value Description
0 Disables unprivileged software access to the SWTRIG register.
Enables unprivileged software access to the SWTRIG register
(see page 121).
1
1 MAINPEND R/W 0
Thread State Control
Value Description
The processor can enter Thread mode only when no exception
is active.
0
The processor can enter Thread mode from any level under the
control of an EXC_RETURN value (see “Exception
Return” on page 87 for more information).
1
0 BASETHR R/W 0
132 January 08, 2011
Texas Instruments-Production Data
Cortex-M3 Peripherals
Register 32: System Handler Priority 1 (SYSPRI1), offset 0xD18
Note: This register can only be accessed from privileged mode.
The SYSPRI1 register configures the priority level, 0 to 7 of the usage fault, bus fault, and memory
management fault exception handlers. This register is byte-accessible.
System Handler Priority 1 (SYSPRI1)
Base 0xE000.E000
Offset 0xD18
Type R/W, reset 0x0000.0000
31 30 29 28 27 26 25 24 23 22 21 20 19 18 17 16
reserved USAGE reserved
Type RO RO RO RO RO RO RO RO R/W R/W R/W RO RO RO RO RO
Reset 0 0 0 0 0 0 0 0 0 0 0 0 0 0 0 0
15 14 13 12 11 10 9 8 7 6 5 4 3 2 1 0
BUS reserved MEM reserved
Type R/W R/W R/W RO RO RO RO RO R/W R/W R/W RO RO RO RO RO
Reset 0 0 0 0 0 0 0 0 0 0 0 0 0 0 0 0
Bit/Field Name Type Reset Description
Software should not rely on the value of a reserved bit. To provide
compatibility with future products, the value of a reserved bit should be
preserved across a read-modify-write operation.
31:24 reserved RO 0x00
Usage Fault Priority
This field configures the priority level of the usage fault. Configurable
priority values are in the range 0-7, with lower values having higher
priority.
23:21 USAGE R/W 0x0
Software should not rely on the value of a reserved bit. To provide
compatibility with future products, the value of a reserved bit should be
preserved across a read-modify-write operation.
20:16 reserved RO 0x0
Bus Fault Priority
This field configures the priority level of the bus fault. Configurable priority
values are in the range 0-7, with lower values having higher priority.
15:13 BUS R/W 0x0
Software should not rely on the value of a reserved bit. To provide
compatibility with future products, the value of a reserved bit should be
preserved across a read-modify-write operation.
12:8 reserved RO 0x0
Memory Management Fault Priority
This field configures the priority level of the memory management fault.
Configurable priority values are in the range 0-7, with lower values
having higher priority.
7:5 MEM R/W 0x0
Software should not rely on the value of a reserved bit. To provide
compatibility with future products, the value of a reserved bit should be
preserved across a read-modify-write operation.
4:0 reserved RO 0x0
January 08, 2011 133
Texas Instruments-Production Data
Stellaris® LM3S2965 Microcontroller
Register 33: System Handler Priority 2 (SYSPRI2), offset 0xD1C
Note: This register can only be accessed from privileged mode.
The SYSPRI2 register configures the priority level, 0 to 7 of the SVCall handler. This register is
byte-accessible.
System Handler Priority 2 (SYSPRI2)
Base 0xE000.E000
Offset 0xD1C
Type R/W, reset 0x0000.0000
31 30 29 28 27 26 25 24 23 22 21 20 19 18 17 16
SVC reserved
Type R/W R/W R/W RO RO RO RO RO RO RO RO RO RO RO RO RO
Reset 0 0 0 0 0 0 0 0 0 0 0 0 0 0 0 0
15 14 13 12 11 10 9 8 7 6 5 4 3 2 1 0
reserved
Type RO RO RO RO RO RO RO RO RO RO RO RO RO RO RO RO
Reset 0 0 0 0 0 0 0 0 0 0 0 0 0 0 0 0
Bit/Field Name Type Reset Description
SVCall Priority
This field configures the priority level of SVCall. Configurable priority
values are in the range 0-7, with lower values having higher priority.
31:29 SVC R/W 0x0
Software should not rely on the value of a reserved bit. To provide
compatibility with future products, the value of a reserved bit should be
preserved across a read-modify-write operation.
28:0 reserved RO 0x000.0000
134 January 08, 2011
Texas Instruments-Production Data
Cortex-M3 Peripherals
Register 34: System Handler Priority 3 (SYSPRI3), offset 0xD20
Note: This register can only be accessed from privileged mode.
The SYSPRI3 register configures the priority level, 0 to 7 of the SysTick exception and PendSV
handlers. This register is byte-accessible.
System Handler Priority 3 (SYSPRI3)
Base 0xE000.E000
Offset 0xD20
Type R/W, reset 0x0000.0000
31 30 29 28 27 26 25 24 23 22 21 20 19 18 17 16
TICK reserved PENDSV reserved
Type R/W R/W R/W RO RO RO RO RO R/W R/W R/W RO RO RO RO RO
Reset 0 0 0 0 0 0 0 0 0 0 0 0 0 0 0 0
15 14 13 12 11 10 9 8 7 6 5 4 3 2 1 0
reserved DEBUG reserved
Type RO RO RO RO RO RO RO RO R/W R/W R/W RO RO RO RO RO
Reset 0 0 0 0 0 0 0 0 0 0 0 0 0 0 0 0
Bit/Field Name Type Reset Description
SysTick Exception Priority
This field configures the priority level of the SysTick exception.
Configurable priority values are in the range 0-7, with lower values
having higher priority.
31:29 TICK R/W 0x0
Software should not rely on the value of a reserved bit. To provide
compatibility with future products, the value of a reserved bit should be
preserved across a read-modify-write operation.
28:24 reserved RO 0x0
PendSV Priority
This field configures the priority level of PendSV. Configurable priority
values are in the range 0-7, with lower values having higher priority.
23:21 PENDSV R/W 0x0
Software should not rely on the value of a reserved bit. To provide
compatibility with future products, the value of a reserved bit should be
preserved across a read-modify-write operation.
20:8 reserved RO 0x000
Debug Priority
This field configures the priority level of Debug. Configurable priority
values are in the range 0-7, with lower values having higher priority.
7:5 DEBUG R/W 0x0
Software should not rely on the value of a reserved bit. To provide
compatibility with future products, the value of a reserved bit should be
preserved across a read-modify-write operation.
4:0 reserved RO 0x0.0000
January 08, 2011 135
Texas Instruments-Production Data
Stellaris® LM3S2965 Microcontroller
Register 35: System Handler Control and State (SYSHNDCTRL), offset 0xD24
Note: This register can only be accessed from privileged mode.
The SYSHNDCTRL register enables the system handlers, and indicates the pending status of the
usage fault, bus fault, memory management fault, and SVC exceptions as well as the active status
of the system handlers.
If a system handler is disabled and the corresponding fault occurs, the processor treats the fault as
a hard fault.
This register can be modified to change the pending or active status of system exceptions. An OS
kernel can write to the active bits to perform a context switch that changes the current exception
type.
Caution – Software that changes the value of an active bit in this register without correct adjustment
to the stacked content can cause the processor to generate a fault exception. Ensure software that writes
to this register retains and subsequently restores the current active status.
If the value of a bit in this register must be modified after enabling the system handlers, a
read-modify-write procedure must be used to ensure that only the required bit is modified.
System Handler Control and State (SYSHNDCTRL)
Base 0xE000.E000
Offset 0xD24
Type R/W, reset 0x0000.0000
31 30 29 28 27 26 25 24 23 22 21 20 19 18 17 16
reserved USAGE BUS MEM
Type RO RO RO RO RO RO RO RO RO RO RO RO RO R/W R/W R/W
Reset 0 0 0 0 0 0 0 0 0 0 0 0 0 0 0 0
15 14 13 12 11 10 9 8 7 6 5 4 3 2 1 0
SVC BUSP MEMP USAGEP TICK PNDSV reserved MON SVCA reserved USGA reserved BUSA MEMA
Type R/W R/W R/W R/W R/W R/W RO R/W R/W RO RO RO R/W RO R/W R/W
Reset 0 0 0 0 0 0 0 0 0 0 0 0 0 0 0 0
Bit/Field Name Type Reset Description
Software should not rely on the value of a reserved bit. To provide
compatibility with future products, the value of a reserved bit should be
preserved across a read-modify-write operation.
31:19 reserved RO 0x000
Usage Fault Enable
Value Description
0 Disables the usage fault exception.
1 Enables the usage fault exception.
18 USAGE R/W 0
Bus Fault Enable
Value Description
0 Disables the bus fault exception.
1 Enables the bus fault exception.
17 BUS R/W 0
136 January 08, 2011
Texas Instruments-Production Data
Cortex-M3 Peripherals
Bit/Field Name Type Reset Description
Memory Management Fault Enable
Value Description
0 Disables the memory management fault exception.
1 Enables the memory management fault exception.
16 MEM R/W 0
SVC Call Pending
Value Description
0 An SVC call exception is not pending.
1 An SVC call exception is pending.
This bit can be modified to change the pending status of the SVC call
exception.
15 SVC R/W 0
Bus Fault Pending
Value Description
0 A bus fault exception is not pending.
1 A bus fault exception is pending.
This bit can be modified to change the pending status of the bus fault
exception.
14 BUSP R/W 0
Memory Management Fault Pending
Value Description
0 A memory management fault exception is not pending.
1 A memory management fault exception is pending.
This bit can be modified to change the pending status of the memory
management fault exception.
13 MEMP R/W 0
Usage Fault Pending
Value Description
0 A usage fault exception is not pending.
1 A usage fault exception is pending.
This bit can be modified to change the pending status of the usage fault
exception.
12 USAGEP R/W 0
SysTick Exception Active
Value Description
0 A SysTick exception is not active.
1 A SysTick exception is active.
This bit can be modified to change the active status of the SysTick
exception, however, see the Caution above before setting this bit.
11 TICK R/W 0
January 08, 2011 137
Texas Instruments-Production Data
Stellaris® LM3S2965 Microcontroller
Bit/Field Name Type Reset Description
PendSV Exception Active
Value Description
0 A PendSV exception is not active.
1 A PendSV exception is active.
This bit can be modified to change the active status of the PendSV
exception, however, see the Caution above before setting this bit.
10 PNDSV R/W 0
Software should not rely on the value of a reserved bit. To provide
compatibility with future products, the value of a reserved bit should be
preserved across a read-modify-write operation.
9 reserved RO 0
Debug Monitor Active
Value Description
0 The Debug monitor is not active.
1 The Debug monitor is active.
8 MON R/W 0
SVC Call Active
Value Description
0 SVC call is not active.
1 SVC call is active.
This bit can be modified to change the active status of the SVC call
exception, however, see the Caution above before setting this bit.
7 SVCA R/W 0
Software should not rely on the value of a reserved bit. To provide
compatibility with future products, the value of a reserved bit should be
preserved across a read-modify-write operation.
6:4 reserved RO 0x0
Usage Fault Active
Value Description
0 Usage fault is not active.
1 Usage fault is active.
This bit can be modified to change the active status of the usage fault
exception, however, see the Caution above before setting this bit.
3 USGA R/W 0
Software should not rely on the value of a reserved bit. To provide
compatibility with future products, the value of a reserved bit should be
preserved across a read-modify-write operation.
2 reserved RO 0
Bus Fault Active
Value Description
0 Bus fault is not active.
1 Bus fault is active.
This bit can be modified to change the active status of the bus fault
exception, however, see the Caution above before setting this bit.
1 BUSA R/W 0
138 January 08, 2011
Texas Instruments-Production Data
Cortex-M3 Peripherals
Bit/Field Name Type Reset Description
Memory Management Fault Active
Value Description
0 Memory management fault is not active.
1 Memory management fault is active.
This bit can be modified to change the active status of the memory
management fault exception, however, see the Caution above before
setting this bit.
0 MEMA R/W 0
January 08, 2011 139
Texas Instruments-Production Data
Stellaris® LM3S2965 Microcontroller
Register 36: Configurable Fault Status (FAULTSTAT), offset 0xD28
Note: This register can only be accessed from privileged mode.
The FAULTSTAT register indicates the cause of a memory management fault, bus fault, or usage
fault. Each of these functions is assigned to a subregister as follows:
■ Usage Fault Status (UFAULTSTAT), bits 31:16
■ Bus Fault Status (BFAULTSTAT), bits 15:8
■ Memory Management Fault Status (MFAULTSTAT), bits 7:0
FAULTSTAT is byte accessible. FAULTSTAT or its subregisters can be accessed as follows:
■ The complete FAULTSTAT register, with a word access to offset 0xD28
■ The MFAULTSTAT, with a byte access to offset 0xD28
■ The MFAULTSTAT and BFAULTSTAT, with a halfword access to offset 0xD28
■ The BFAULTSTAT, with a byte access to offset 0xD29
■ The UFAULTSTAT, with a halfword access to offset 0xD2A
Bits are cleared by writing a 1 to them.
In a fault handler, the true faulting address can be determined by:
1. Read and save the Memory Management Fault Address (MMADDR) or Bus Fault Address
(FAULTADDR) value.
2. Read the MMARV bit in MFAULTSTAT, or the BFARV bit in BFAULTSTAT to determine if the
MMADDR or FAULTADDR contents are valid.
Software must follow this sequence because another higher priority exception might change the
MMADDR or FAULTADDR value. For example, if a higher priority handler preempts the current
fault handler, the other fault might change the MMADDR or FAULTADDR value.
Configurable Fault Status (FAULTSTAT)
Base 0xE000.E000
Offset 0xD28
Type R/W1C, reset 0x0000.0000
31 30 29 28 27 26 25 24 23 22 21 20 19 18 17 16
reserved DIV0 UNALIGN reserved NOCP INVPC INVSTAT UNDEF
Type RO RO RO RO RO RO R/W1C R/W1C RO RO RO RO R/W1C R/W1C R/W1C R/W1C
Reset 0 0 0 0 0 0 0 0 0 0 0 0 0 0 0 0
15 14 13 12 11 10 9 8 7 6 5 4 3 2 1 0
BFARV reserved BSTKE BUSTKE IMPRE PRECISE IBUS MMARV reserved MSTKE MUSTKE reserved DERR IERR
Type R/W1C RO RO R/W1C R/W1C R/W1C R/W1C R/W1C R/W1C RO RO R/W1C R/W1C RO R/W1C R/W1C
Reset 0 0 0 0 0 0 0 0 0 0 0 0 0 0 0 0
Bit/Field Name Type Reset Description
Software should not rely on the value of a reserved bit. To provide
compatibility with future products, the value of a reserved bit should be
preserved across a read-modify-write operation.
31:26 reserved RO 0x00
140 January 08, 2011
Texas Instruments-Production Data
Cortex-M3 Peripherals
Bit/Field Name Type Reset Description
Divide-by-Zero Usage Fault
Value Description
No divide-by-zero fault has occurred, or divide-by-zero trapping
is not enabled.
0
The processor has executed an SDIV or UDIV instruction with
a divisor of 0.
1
When this bit is set, the PC value stacked for the exception return points
to the instruction that performed the divide by zero.
Trapping on divide-by-zero is enabled by setting the DIV0 bit in the
Configuration and Control (CFGCTRL) register (see page 131).
This bit is cleared by writing a 1 to it.
25 DIV0 R/W1C 0
Unaligned Access Usage Fault
Value Description
No unaligned access fault has occurred, or unaligned access
trapping is not enabled.
0
1 The processor has made an unaligned memory access.
Unaligned LDM, STM, LDRD, and STRD instructions always fault
regardless of the configuration of this bit.
Trapping on unaligned access is enabled by setting the UNALIGNED bit
in the CFGCTRL register (see page 131).
This bit is cleared by writing a 1 to it.
24 UNALIGN R/W1C 0
Software should not rely on the value of a reserved bit. To provide
compatibility with future products, the value of a reserved bit should be
preserved across a read-modify-write operation.
23:20 reserved RO 0x00
No Coprocessor Usage Fault
Value Description
A usage fault has not been caused by attempting to access a
coprocessor.
0
1 The processor has attempted to access a coprocessor.
This bit is cleared by writing a 1 to it.
19 NOCP R/W1C 0
Invalid PC Load Usage Fault
Value Description
A usage fault has not been caused by attempting to load an
invalid PC value.
0
The processor has attempted an illegal load of EXC_RETURN
to the PC as a result of an invalid context or an invalid
EXC_RETURN value.
1
When this bit is set, the PC value stacked for the exception return points
to the instruction that tried to perform the illegal load of the PC.
This bit is cleared by writing a 1 to it.
18 INVPC R/W1C 0
January 08, 2011 141
Texas Instruments-Production Data
Stellaris® LM3S2965 Microcontroller
Bit/Field Name Type Reset Description
Invalid State Usage Fault
Value Description
0 A usage fault has not been caused by an invalid state.
The processor has attempted to execute an instruction that
makes illegal use of the EPSR register.
1
When this bit is set, the PC value stacked for the exception return points
to the instruction that attempted the illegal use of the Execution
Program Status Register (EPSR) register.
This bit is not set if an undefined instruction uses the EPSR register.
This bit is cleared by writing a 1 to it.
17 INVSTAT R/W1C 0
Undefined Instruction Usage Fault
Value Description
0 A usage fault has not been caused by an undefined instruction.
The processor has attempted to execute an undefined
instruction.
1
When this bit is set, the PC value stacked for the exception return points
to the undefined instruction.
An undefined instruction is an instruction that the processor cannot
decode.
This bit is cleared by writing a 1 to it.
16 UNDEF R/W1C 0
Bus Fault Address Register Valid
Value Description
The value in the Bus Fault Address (FAULTADDR) register
is not a valid fault address.
0
1 The FAULTADDR register is holding a valid fault address.
This bit is set after a bus fault, where the address is known. Other faults
can clear this bit, such as a memory management fault occurring later.
If a bus fault occurs and is escalated to a hard fault because of priority,
the hard fault handler must clear this bit. This action prevents problems
if returning to a stacked active bus fault handler whose FAULTADDR
register value has been overwritten.
This bit is cleared by writing a 1 to it.
15 BFARV R/W1C 0
Software should not rely on the value of a reserved bit. To provide
compatibility with future products, the value of a reserved bit should be
preserved across a read-modify-write operation.
14:13 reserved RO 0
Stack Bus Fault
Value Description
0 No bus fault has occurred on stacking for exception entry.
Stacking for an exception entry has caused one or more bus
faults.
1
When this bit is set, the SP is still adjusted but the values in the context
area on the stack might be incorrect. A fault address is not written to
the FAULTADDR register.
This bit is cleared by writing a 1 to it.
12 BSTKE R/W1C 0
142 January 08, 2011
Texas Instruments-Production Data
Cortex-M3 Peripherals
Bit/Field Name Type Reset Description
Unstack Bus Fault
Value Description
No bus fault has occurred on unstacking for a return from
exception.
0
Unstacking for a return from exception has caused one or more
bus faults.
1
This fault is chained to the handler. Thus, when this bit is set, the original
return stack is still present. The SP is not adjusted from the failing return,
a new save is not performed, and a fault address is not written to the
FAULTADDR register.
This bit is cleared by writing a 1 to it.
11 BUSTKE R/W1C 0
Imprecise Data Bus Error
Value Description
0 An imprecise data bus error has not occurred.
A data bus error has occurred, but the return address in the
stack frame is not related to the instruction that caused the error.
1
When this bit is set, a fault address is not written to the FAULTADDR
register.
This fault is asynchronous. Therefore, if the fault is detected when the
priority of the current process is higher than the bus fault priority, the
bus fault becomes pending and becomes active only when the processor
returns from all higher-priority processes. If a precise fault occurs before
the processor enters the handler for the imprecise bus fault, the handler
detects that both the IMPRE bit is set and one of the precise fault status
bits is set.
This bit is cleared by writing a 1 to it.
10 IMPRE R/W1C 0
Precise Data Bus Error
Value Description
0 A precise data bus error has not occurred.
A data bus error has occurred, and the PC value stacked for
the exception return points to the instruction that caused the
fault.
1
When this bit is set, the fault address is written to the FAULTADDR
register.
This bit is cleared by writing a 1 to it.
9 PRECISE R/W1C 0
Instruction Bus Error
Value Description
0 An instruction bus error has not occurred.
1 An instruction bus error has occurred.
The processor detects the instruction bus error on prefetching an
instruction, but sets this bit only if it attempts to issue the faulting
instruction.
When this bit is set, a fault address is not written to the FAULTADDR
register.
This bit is cleared by writing a 1 to it.
8 IBUS R/W1C 0
January 08, 2011 143
Texas Instruments-Production Data
Stellaris® LM3S2965 Microcontroller
Bit/Field Name Type Reset Description
Memory Management Fault Address Register Valid
Value Description
The value in the Memory Management Fault Address
(MMADDR) register is not a valid fault address.
0
1 The MMADDR register is holding a valid fault address.
If a memory management fault occurs and is escalated to a hard fault
because of priority, the hard fault handler must clear this bit. This action
prevents problems if returning to a stacked active memory management
fault handler whose MMADDR register value has been overwritten.
This bit is cleared by writing a 1 to it.
7 MMARV R/W1C 0
Software should not rely on the value of a reserved bit. To provide
compatibility with future products, the value of a reserved bit should be
preserved across a read-modify-write operation.
6:5 reserved RO 0
Stack Access Violation
Value Description
No memory management fault has occurred on stacking for
exception entry.
0
Stacking for an exception entry has caused one or more access
violations.
1
When this bit is set, the SP is still adjusted but the values in the context
area on the stack might be incorrect. A fault address is not written to
the MMADDR register.
This bit is cleared by writing a 1 to it.
4 MSTKE R/W1C 0
Unstack Access Violation
Value Description
No memory management fault has occurred on unstacking for
a return from exception.
0
Unstacking for a return from exception has caused one or more
access violations.
1
This fault is chained to the handler. Thus, when this bit is set, the original
return stack is still present. The SP is not adjusted from the failing return,
a new save is not performed, and a fault address is not written to the
MMADDR register.
This bit is cleared by writing a 1 to it.
3 MUSTKE R/W1C 0
Software should not rely on the value of a reserved bit. To provide
compatibility with future products, the value of a reserved bit should be
preserved across a read-modify-write operation.
2 reserved RO 0
144 January 08, 2011
Texas Instruments-Production Data
Cortex-M3 Peripherals
Bit/Field Name Type Reset Description
Data Access Violation
Value Description
0 A data access violation has not occurred.
The processor attempted a load or store at a location that does
not permit the operation.
1
When this bit is set, the PC value stacked for the exception return points
to the faulting instruction and the address of the attempted access is
written to the MMADDR register.
This bit is cleared by writing a 1 to it.
1 DERR R/W1C 0
Instruction Access Violation
Value Description
0 An instruction access violation has not occurred.
The processor attempted an instruction fetch from a location
that does not permit execution.
1
This fault occurs on any access to an XN region, even when the MPU
is disabled or not present.
When this bit is set, the PC value stacked for the exception return points
to the faulting instruction and the address of the attempted access is
not written to the MMADDR register.
This bit is cleared by writing a 1 to it.
0 IERR R/W1C 0
January 08, 2011 145
Texas Instruments-Production Data
Stellaris® LM3S2965 Microcontroller
Register 37: Hard Fault Status (HFAULTSTAT), offset 0xD2C
Note: This register can only be accessed from privileged mode.
The HFAULTSTAT register gives information about events that activate the hard fault handler.
Bits are cleared by writing a 1 to them.
Hard Fault Status (HFAULTSTAT)
Base 0xE000.E000
Offset 0xD2C
Type R/W1C, reset 0x0000.0000
31 30 29 28 27 26 25 24 23 22 21 20 19 18 17 16
DBG FORCED reserved
Type R/W1C R/W1C RO RO RO RO RO RO RO RO RO RO RO RO RO RO
Reset 0 0 0 0 0 0 0 0 0 0 0 0 0 0 0 0
15 14 13 12 11 10 9 8 7 6 5 4 3 2 1 0
reserved VECT reserved
Type RO RO RO RO RO RO RO RO RO RO RO RO RO RO R/W1C RO
Reset 0 0 0 0 0 0 0 0 0 0 0 0 0 0 0 0
Bit/Field Name Type Reset Description
Debug Event
This bit is reserved for Debug use. This bit must be written as a 0,
otherwise behavior is unpredictable.
31 DBG R/W1C 0
Forced Hard Fault
Value Description
0 No forced hard fault has occurred.
A forced hard fault has been generated by escalation of a fault
with configurable priority that cannot be handled, either because
of priority or because it is disabled.
1
When this bit is set, the hard fault handler must read the other fault
status registers to find the cause of the fault.
This bit is cleared by writing a 1 to it.
30 FORCED R/W1C 0
Software should not rely on the value of a reserved bit. To provide
compatibility with future products, the value of a reserved bit should be
preserved across a read-modify-write operation.
29:2 reserved RO 0x00
Vector Table Read Fault
Value Description
0 No bus fault has occurred on a vector table read.
1 A bus fault occurred on a vector table read.
This error is always handled by the hard fault handler.
When this bit is set, the PC value stacked for the exception return points
to the instruction that was preempted by the exception.
This bit is cleared by writing a 1 to it.
1 VECT R/W1C 0
Software should not rely on the value of a reserved bit. To provide
compatibility with future products, the value of a reserved bit should be
preserved across a read-modify-write operation.
0 reserved RO 0
146 January 08, 2011
Texas Instruments-Production Data
Cortex-M3 Peripherals
Register 38: Memory Management Fault Address (MMADDR), offset 0xD34
Note: This register can only be accessed from privileged mode.
The MMADDR register contains the address of the location that generated a memory management
fault. When an unaligned access faults, the address in the MMADDR register is the actual address
that faulted. Because a single read or write instruction can be split into multiple aligned accesses,
the fault address can be any address in the range of the requested access size. Bits in the Memory
Management Fault Status (MFAULTSTAT) register indicate the cause of the fault and whether
the value in the MMADDR register is valid (see page 140).
Memory Management Fault Address (MMADDR)
Base 0xE000.E000
Offset 0xD34
Type R/W, reset -
31 30 29 28 27 26 25 24 23 22 21 20 19 18 17 16
ADDR
Type R/W R/W R/W R/W R/W R/W R/W R/W R/W R/W R/W R/W R/W R/W R/W R/W
Reset - - - - - - - - - - - - - - - -
15 14 13 12 11 10 9 8 7 6 5 4 3 2 1 0
ADDR
Type R/W R/W R/W R/W R/W R/W R/W R/W R/W R/W R/W R/W R/W R/W R/W R/W
Reset - - - - - - - - - - - - - - - -
Bit/Field Name Type Reset Description
Fault Address
When the MMARV bit of MFAULTSTAT is set, this field holds the address
of the location that generated the memory management fault.
31:0 ADDR R/W -
January 08, 2011 147
Texas Instruments-Production Data
Stellaris® LM3S2965 Microcontroller
Register 39: Bus Fault Address (FAULTADDR), offset 0xD38
Note: This register can only be accessed from privileged mode.
The FAULTADDR register contains the address of the location that generated a bus fault. When
an unaligned access faults, the address in the FAULTADDR register is the one requested by the
instruction, even if it is not the address of the fault. Bits in the Bus Fault Status (BFAULTSTAT)
register indicate the cause of the fault and whether the value in the FAULTADDR register is valid
(see page 140).
Bus Fault Address (FAULTADDR)
Base 0xE000.E000
Offset 0xD38
Type R/W, reset -
31 30 29 28 27 26 25 24 23 22 21 20 19 18 17 16
ADDR
Type R/W R/W R/W R/W R/W R/W R/W R/W R/W R/W R/W R/W R/W R/W R/W R/W
Reset - - - - - - - - - - - - - - - -
15 14 13 12 11 10 9 8 7 6 5 4 3 2 1 0
ADDR
Type R/W R/W R/W R/W R/W R/W R/W R/W R/W R/W R/W R/W R/W R/W R/W R/W
Reset - - - - - - - - - - - - - - - -
Bit/Field Name Type Reset Description
Fault Address
When the FAULTADDRV bit of BFAULTSTAT is set, this field holds the
address of the location that generated the bus fault.
31:0 ADDR R/W -
3.6 Memory Protection Unit (MPU) Register Descriptions
This section lists and describes the Memory Protection Unit (MPU) registers, in numerical order by
address offset.
The MPU registers can only be accessed from privileged mode.
148 January 08, 2011
Texas Instruments-Production Data
Cortex-M3 Peripherals
Register 40: MPU Type (MPUTYPE), offset 0xD90
Note: This register can only be accessed from privileged mode.
The MPUTYPE register indicates whether the MPU is present, and if so, how many regions it
supports.
MPU Type (MPUTYPE)
Base 0xE000.E000
Offset 0xD90
Type RO, reset 0x0000.0800
31 30 29 28 27 26 25 24 23 22 21 20 19 18 17 16
reserved IREGION
Type RO RO RO RO RO RO RO RO RO RO RO RO RO RO RO RO
Reset 0 0 0 0 0 0 0 0 0 0 0 0 0 0 0 0
15 14 13 12 11 10 9 8 7 6 5 4 3 2 1 0
DREGION reserved SEPARATE
Type RO RO RO RO RO RO RO RO RO RO RO RO RO RO RO RO
Reset 0 0 0 0 1 0 0 0 0 0 0 0 0 0 0 0
Bit/Field Name Type Reset Description
Software should not rely on the value of a reserved bit. To provide
compatibility with future products, the value of a reserved bit should be
preserved across a read-modify-write operation.
31:24 reserved RO 0x00
Number of I Regions
This field indicates the number of supported MPU instruction regions.
This field always contains 0x00. The MPU memory map is unified and
is described by the DREGION field.
23:16 IREGION RO 0x00
Number of D Regions
Value Description
0x08 Indicates there are eight supported MPU data regions.
15:8 DREGION RO 0x08
Software should not rely on the value of a reserved bit. To provide
compatibility with future products, the value of a reserved bit should be
preserved across a read-modify-write operation.
7:1 reserved RO 0x00
Separate or Unified MPU
Value Description
0 Indicates the MPU is unified.
0 SEPARATE RO 0
January 08, 2011 149
Texas Instruments-Production Data
Stellaris® LM3S2965 Microcontroller
Register 41: MPU Control (MPUCTRL), offset 0xD94
Note: This register can only be accessed from privileged mode.
The MPUCTRL register enables the MPU, enables the default memory map background region,
and enables use of the MPU when in the hard fault, Non-maskable Interrupt (NMI), and Fault Mask
Register (FAULTMASK) escalated handlers.
When the ENABLE and PRIVDEFEN bits are both set:
■ For privileged accesses, the default memory map is as described in “Memory Model” on page 71.
Any access by privileged software that does not address an enabled memory region behaves
as defined by the default memory map.
■ Any access by unprivileged software that does not address an enabled memory region causes
a memory management fault.
Execute Never (XN) and Strongly Ordered rules always apply to the System Control Space regardless
of the value of the ENABLE bit.
When the ENABLE bit is set, at least one region of the memory map must be enabled for the system
to function unless the PRIVDEFEN bit is set. If the PRIVDEFEN bit is set and no regions are enabled,
then only privileged software can operate.
When the ENABLE bit is clear, the system uses the default memory map, which has the same
memory attributes as if the MPU is not implemented (see Table 2-5 on page 74 for more information).
The default memory map applies to accesses from both privileged and unprivileged software.
When the MPU is enabled, accesses to the System Control Space and vector table are always
permitted. Other areas are accessible based on regions and whether PRIVDEFEN is set.
Unless HFNMIENA is set, the MPU is not enabled when the processor is executing the handler for
an exception with priority –1 or –2. These priorities are only possible when handling a hard fault or
NMI exception or when FAULTMASK is enabled. Setting the HFNMIENA bit enables the MPU when
operating with these two priorities.
MPU Control (MPUCTRL)
Base 0xE000.E000
Offset 0xD94
Type R/W, reset 0x0000.0000
31 30 29 28 27 26 25 24 23 22 21 20 19 18 17 16
reserved
Type RO RO RO RO RO RO RO RO RO RO RO RO RO RO RO RO
Reset 0 0 0 0 0 0 0 0 0 0 0 0 0 0 0 0
15 14 13 12 11 10 9 8 7 6 5 4 3 2 1 0
reserved PRIVDEFEN HFNMIENA ENABLE
Type RO RO RO RO RO RO RO RO RO RO RO RO RO R/W R/W R/W
Reset 0 0 0 0 0 0 0 0 0 0 0 0 0 0 0 0
Bit/Field Name Type Reset Description
Software should not rely on the value of a reserved bit. To provide
compatibility with future products, the value of a reserved bit should be
preserved across a read-modify-write operation.
31:3 reserved RO 0x0000.000
150 January 08, 2011
Texas Instruments-Production Data
Cortex-M3 Peripherals
Bit/Field Name Type Reset Description
MPU Default Region
This bit enables privileged software access to the default memory map.
Value Description
If the MPU is enabled, this bit disables use of the default memory
map. Any memory access to a location not covered by any
enabled region causes a fault.
0
If the MPU is enabled, this bit enables use of the default memory
map as a background region for privileged software accesses.
1
When this bit is set, the background region acts as if it is region number
-1. Any region that is defined and enabled has priority over this default
map.
If the MPU is disabled, the processor ignores this bit.
2 PRIVDEFEN R/W 0
MPU Enabled During Faults
This bit controls the operation of the MPU during hard fault, NMI, and
FAULTMASK handlers.
Value Description
The MPU is disabled during hard fault, NMI, and FAULTMASK
handlers, regardless of the value of the ENABLE bit.
0
The MPU is enabled during hard fault, NMI, and FAULTMASK
handlers.
1
When the MPU is disabled and this bit is set, the resulting behavior is
unpredictable.
1 HFNMIENA R/W 0
MPU Enable
Value Description
0 The MPU is disabled.
1 The MPU is enabled.
When the MPU is disabled and the HFNMIENA bit is set, the resulting
behavior is unpredictable.
0 ENABLE R/W 0
January 08, 2011 151
Texas Instruments-Production Data
Stellaris® LM3S2965 Microcontroller
Register 42: MPU Region Number (MPUNUMBER), offset 0xD98
Note: This register can only be accessed from privileged mode.
The MPUNUMBER register selects which memory region is referenced by the MPU Region Base
Address (MPUBASE) and MPU Region Attribute and Size (MPUATTR) registers. Normally, the
required region number should be written to this register before accessing the MPUBASE or the
MPUATTR register. However, the region number can be changed by writing to the MPUBASE
register with the VALID bit set (see page 153). This write updates the value of the REGION field.
MPU Region Number (MPUNUMBER)
Base 0xE000.E000
Offset 0xD98
Type R/W, reset 0x0000.0000
31 30 29 28 27 26 25 24 23 22 21 20 19 18 17 16
reserved
Type RO RO RO RO RO RO RO RO RO RO RO RO RO RO RO RO
Reset 0 0 0 0 0 0 0 0 0 0 0 0 0 0 0 0
15 14 13 12 11 10 9 8 7 6 5 4 3 2 1 0
reserved NUMBER
Type RO RO RO RO RO RO RO RO RO RO RO RO RO R/W R/W R/W
Reset 0 0 0 0 0 0 0 0 0 0 0 0 0 0 0 0
Bit/Field Name Type Reset Description
Software should not rely on the value of a reserved bit. To provide
compatibility with future products, the value of a reserved bit should be
preserved across a read-modify-write operation.
31:3 reserved RO 0x0000.000
MPU Region to Access
This field indicates the MPU region referenced by the MPUBASE and
MPUATTR registers. The MPU supports eight memory regions.
2:0 NUMBER R/W 0x0
152 January 08, 2011
Texas Instruments-Production Data
Cortex-M3 Peripherals
Register 43: MPU Region Base Address (MPUBASE), offset 0xD9C
Register 44: MPU Region Base Address Alias 1 (MPUBASE1), offset 0xDA4
Register 45: MPU Region Base Address Alias 2 (MPUBASE2), offset 0xDAC
Register 46: MPU Region Base Address Alias 3 (MPUBASE3), offset 0xDB4
Note: This register can only be accessed from privileged mode.
The MPUBASE register defines the base address of the MPU region selected by the MPU Region
Number (MPUNUMBER) register and can update the value of the MPUNUMBER register. To
change the current region number and update the MPUNUMBER register, write the MPUBASE
register with the VALID bit set.
The ADDR field is bits 31:N of the MPUBASE register. Bits (N-1):5 are reserved. The region size,
as specified by the SIZE field in the MPU Region Attribute and Size (MPUATTR) register, defines
the value of N where:
N = Log2(Region size in bytes)
If the region size is configured to 4 GB in the MPUATTR register, there is no valid ADDR field. In
this case, the region occupies the complete memory map, and the base address is 0x0000.0000.
The base address is aligned to the size of the region. For example, a 64-KB region must be aligned
on a multiple of 64 KB, for example, at 0x0001.0000 or 0x0002.0000.
MPU Region Base Address (MPUBASE)
Base 0xE000.E000
Offset 0xD9C
Type R/W, reset 0x0000.0000
31 30 29 28 27 26 25 24 23 22 21 20 19 18 17 16
ADDR
Type R/W R/W R/W R/W R/W R/W R/W R/W R/W R/W R/W R/W R/W R/W R/W R/W
Reset 0 0 0 0 0 0 0 0 0 0 0 0 0 0 0 0
15 14 13 12 11 10 9 8 7 6 5 4 3 2 1 0
ADDR VALID reserved REGION
Type R/W R/W R/W R/W R/W R/W R/W R/W R/W R/W R/W WO RO R/W R/W R/W
Reset 0 0 0 0 0 0 0 0 0 0 0 0 0 0 0 0
Bit/Field Name Type Reset Description
Base Address Mask
Bits 31:N in this field contain the region base address. The value of N
depends on the region size, as shown above. The remaining bits (N-1):5
are reserved.
Software should not rely on the value of a reserved bit. To provide
compatibility with future products, the value of a reserved bit should be
preserved across a read-modify-write operation.
31:5 ADDR R/W 0x0000.000
January 08, 2011 153
Texas Instruments-Production Data
Stellaris® LM3S2965 Microcontroller
Bit/Field Name Type Reset Description
Region Number Valid
Value Description
The MPUNUMBER register is not changed and the processor
updates the base address for the region specified in the
MPUNUMBER register and ignores the value of the REGION
field.
0
The MPUNUMBER register is updated with the value of the
REGION field and the base address is updated for the region
specified in the REGION field.
1
This bit is always read as 0.
4 VALID WO 0
Software should not rely on the value of a reserved bit. To provide
compatibility with future products, the value of a reserved bit should be
preserved across a read-modify-write operation.
3 reserved RO 0
Region Number
On a write, contains the value to be written to the MPUNUMBER register.
On a read, returns the current region number in the MPUNUMBER
register.
2:0 REGION R/W 0x0
154 January 08, 2011
Texas Instruments-Production Data
Cortex-M3 Peripherals
Register 47: MPU Region Attribute and Size (MPUATTR), offset 0xDA0
Register 48: MPU Region Attribute and Size Alias 1 (MPUATTR1), offset 0xDA8
Register 49: MPU Region Attribute and Size Alias 2 (MPUATTR2), offset 0xDB0
Register 50: MPU Region Attribute and Size Alias 3 (MPUATTR3), offset 0xDB8
Note: This register can only be accessed from privileged mode.
The MPUATTR register defines the region size and memory attributes of the MPU region specified
by the MPU Region Number (MPUNUMBER) register and enables that region and any subregions.
The MPUATTR register is accessible using word or halfword accesses with the most-significant
halfword holding the region attributes and the least-significant halfword holds the region size and
the region and subregion enable bits.
The MPU access permission attribute bits, XN, AP, TEX, S, C, and B, control access to the
corresponding memory region. If an access is made to an area of memory without the required
permissions, then the MPU generates a permission fault.
The SIZE field defines the size of the MPU memory region specified by the MPUNUMBER register
as follows:
(Region size in bytes) = 2(SIZE+1)
The smallest permitted region size is 32 bytes, corresponding to a SIZE value of 4. Table
3-9 on page 155 gives example SIZE values with the corresponding region size and value of N in
the MPU Region Base Address (MPUBASE) register.
Table 3-9. Example SIZE Field Values
SIZE Encoding Region Size Value of Na Note
00100b (0x4) 32 B 5 Minimum permitted size
01001b (0x9) 1 KB 10 -
10011b (0x13) 1 MB 20 -
11101b (0x1D) 1 GB 30 -
No valid ADDR field inMPUBASE; the Maximum possible size
region occupies the complete
memory map.
11111b (0x1F) 4 GB
a. Refers to the N parameter in the MPUBASE register (see page 153).
MPU Region Attribute and Size (MPUATTR)
Base 0xE000.E000
Offset 0xDA0
Type R/W, reset 0x0000.0000
31 30 29 28 27 26 25 24 23 22 21 20 19 18 17 16
reserved XN reserved AP reserved TEX S C B
Type RO RO RO R/W RO R/W R/W R/W RO RO R/W R/W R/W R/W R/W R/W
Reset 0 0 0 0 0 0 0 0 0 0 0 0 0 0 0 0
15 14 13 12 11 10 9 8 7 6 5 4 3 2 1 0
SRD reserved SIZE ENABLE
Type R/W R/W R/W R/W R/W R/W R/W R/W RO RO R/W R/W R/W R/W R/W R/W
Reset 0 0 0 0 0 0 0 0 0 0 0 0 0 0 0 0
January 08, 2011 155
Texas Instruments-Production Data
Stellaris® LM3S2965 Microcontroller
Bit/Field Name Type Reset Description
Software should not rely on the value of a reserved bit. To provide
compatibility with future products, the value of a reserved bit should be
preserved across a read-modify-write operation.
31:29 reserved RO 0x00
Instruction Access Disable
Value Description
0 Instruction fetches are enabled.
1 Instruction fetches are disabled.
28 XN R/W 0
Software should not rely on the value of a reserved bit. To provide
compatibility with future products, the value of a reserved bit should be
preserved across a read-modify-write operation.
27 reserved RO 0
Access Privilege
For information on using this bit field, see Table 3-5 on page 101.
26:24 AP R/W 0
Software should not rely on the value of a reserved bit. To provide
compatibility with future products, the value of a reserved bit should be
preserved across a read-modify-write operation.
23:22 reserved RO 0x0
Type Extension Mask
For information on using this bit field, see Table 3-3 on page 100.
21:19 TEX R/W 0x0
Shareable
For information on using this bit, see Table 3-3 on page 100.
18 S R/W 0
Cacheable
For information on using this bit, see Table 3-3 on page 100.
17 C R/W 0
Bufferable
For information on using this bit, see Table 3-3 on page 100.
16 B R/W 0
Subregion Disable Bits
Value Description
0 The corresponding subregion is enabled.
1 The corresponding subregion is disabled.
Region sizes of 128 bytes and less do not support subregions. When
writing the attributes for such a region, configure the SRD field as 0x00.
See the section called “Subregions” on page 99 for more information.
15:8 SRD R/W 0x00
Software should not rely on the value of a reserved bit. To provide
compatibility with future products, the value of a reserved bit should be
preserved across a read-modify-write operation.
7:6 reserved RO 0x0
Region Size Mask
The SIZE field defines the size of the MPU memory region specified by
the MPUNUMBER register. Refer to Table 3-9 on page 155 for more
information.
5:1 SIZE R/W 0x0
156 January 08, 2011
Texas Instruments-Production Data
Cortex-M3 Peripherals
Bit/Field Name Type Reset Description
Region Enable
Value Description
0 The region is disabled.
1 The region is enabled.
0 ENABLE R/W 0
January 08, 2011 157
Texas Instruments-Production Data
Stellaris® LM3S2965 Microcontroller
4 JTAG Interface
The Joint Test Action Group (JTAG) port is an IEEE standard that defines a Test Access Port and
Boundary Scan Architecture for digital integrated circuits and provides a standardized serial interface
for controlling the associated test logic. The TAP, Instruction Register (IR), and Data Registers (DR)
can be used to test the interconnections of assembled printed circuit boards and obtain manufacturing
information on the components. The JTAG Port also provides a means of accessing and controlling
design-for-test features such as I/O pin observation and control, scan testing, and debugging.
The JTAG port is comprised of five pins: TRST, TCK, TMS, TDI, and TDO. Data is transmitted serially
into the controller on TDI and out of the controller on TDO. The interpretation of this data is dependent
on the current state of the TAP controller. For detailed information on the operation of the JTAG
port and TAP controller, please refer to the IEEE Standard 1149.1-Test Access Port and
Boundary-Scan Architecture.
The Stellaris® JTAG controller works with the ARM JTAG controller built into the Cortex-M3 core.
This is implemented by multiplexing the TDO outputs from both JTAG controllers. ARM JTAG
instructions select the ARM TDO output while Stellaris JTAG instructions select the Stellaris TDO
outputs. The multiplexer is controlled by the Stellaris JTAG controller, which has comprehensive
programming for the ARM, Stellaris, and unimplemented JTAG instructions.
The Stellaris JTAG module has the following features:
■ IEEE 1149.1-1990 compatible Test Access Port (TAP) controller
■ Four-bit Instruction Register (IR) chain for storing JTAG instructions
■ IEEE standard instructions: BYPASS, IDCODE, SAMPLE/PRELOAD, EXTEST and INTEST
■ ARM additional instructions: APACC, DPACC and ABORT
■ Integrated ARM Serial Wire Debug (SWD)
See the ARM® Debug Interface V5 Architecture Specification for more information on the ARM
JTAG controller.
158 January 08, 2011
Texas Instruments-Production Data
JTAG Interface
4.1 Block Diagram
Figure 4-1. JTAG Module Block Diagram
Instruction Register (IR)
TAP Controller
BYPASS Data Register
Boundary Scan Data Register
IDCODE Data Register
ABORT Data Register
DPACC Data Register
APACC Data Register
TCK
TMS
TDI
TDO
Cortex-M3
Debug
Port
TRST
4.2 Functional Description
A high-level conceptual drawing of the JTAG module is shown in Figure 4-1 on page 159. The JTAG
module is composed of the Test Access Port (TAP) controller and serial shift chains with parallel
update registers. The TAP controller is a simple state machine controlled by the TRST, TCK and
TMS inputs. The current state of the TAP controller depends on the current value of TRST and the
sequence of values captured on TMS at the rising edge of TCK. The TAP controller determines when
the serial shift chains capture new data, shift data from TDI towards TDO, and update the parallel
load registers. The current state of the TAP controller also determines whether the Instruction
Register (IR) chain or one of the Data Register (DR) chains is being accessed.
The serial shift chains with parallel load registers are comprised of a single Instruction Register (IR)
chain and multiple Data Register (DR) chains. The current instruction loaded in the parallel load
register determines which DR chain is captured, shifted, or updated during the sequencing of the
TAP controller.
Some instructions, like EXTEST and INTEST, operate on data currently in a DR chain and do not
capture, shift, or update any of the chains. Instructions that are not implemented decode to the
BYPASS instruction to ensure that the serial path between TDI and TDO is always connected (see
Table 4-2 on page 165 for a list of implemented instructions).
See “JTAG and Boundary Scan” on page 684 for JTAG timing diagrams.
4.2.1 JTAG Interface Pins
The JTAG interface consists of five standard pins: TRST,TCK, TMS, TDI, and TDO. These pins and
their associated reset state are given in Table 4-1 on page 160. Detailed information on each pin
follows.
January 08, 2011 159
Texas Instruments-Production Data
Stellaris® LM3S2965 Microcontroller
Table 4-1. JTAG Port Pins Reset State
Pin Name Data Direction Internal Pull-Up Internal Pull-Down Drive Strength Drive Value
TRST Input Enabled Disabled N/A N/A
TCK Input Enabled Disabled N/A N/A
TMS Input Enabled Disabled N/A N/A
TDI Input Enabled Disabled N/A N/A
TDO Output Enabled Disabled 2-mA driver High-Z
4.2.1.1 Test Reset Input (TRST)
The TRST pin is an asynchronous active Low input signal for initializing and resetting the JTAG TAP
controller and associated JTAG circuitry. When TRST is asserted, the TAP controller resets to the
Test-Logic-Reset state and remains there while TRST is asserted. When the TAP controller enters
the Test-Logic-Reset state, the JTAG Instruction Register (IR) resets to the default instruction,
IDCODE.
By default, the internal pull-up resistor on the TRST pin is enabled after reset. Changes to the pull-up
resistor settings on GPIO Port B should ensure that the internal pull-up resistor remains enabled
on PB7/TRST; otherwise JTAG communication could be lost.
4.2.1.2 Test Clock Input (TCK)
The TCK pin is the clock for the JTAG module. This clock is provided so the test logic can operate
independently of any other system clocks. In addition, it ensures that multiple JTAG TAP controllers
that are daisy-chained together can synchronously communicate serial test data between
components. During normal operation, TCK is driven by a free-running clock with a nominal 50%
duty cycle. When necessary, TCK can be stopped at 0 or 1 for extended periods of time. While TCK
is stopped at 0 or 1, the state of the TAP controller does not change and data in the JTAG Instruction
and Data Registers is not lost.
By default, the internal pull-up resistor on the TCK pin is enabled after reset. This assures that no
clocking occurs if the pin is not driven from an external source. The internal pull-up and pull-down
resistors can be turned off to save internal power as long as the TCK pin is constantly being driven
by an external source.
4.2.1.3 Test Mode Select (TMS)
The TMS pin selects the next state of the JTAG TAP controller. TMS is sampled on the rising edge
of TCK. Depending on the current TAP state and the sampled value of TMS, the next state is entered.
Because the TMS pin is sampled on the rising edge of TCK, the IEEE Standard 1149.1 expects the
value on TMS to change on the falling edge of TCK.
Holding TMS high for five consecutive TCK cycles drives the TAP controller state machine to the
Test-Logic-Reset state. When the TAP controller enters the Test-Logic-Reset state, the JTAG
Instruction Register (IR) resets to the default instruction, IDCODE. Therefore, this sequence can
be used as a reset mechanism, similar to asserting TRST. The JTAG Test Access Port state machine
can be seen in its entirety in Figure 4-2 on page 162.
By default, the internal pull-up resistor on the TMS pin is enabled after reset. Changes to the pull-up
resistor settings on GPIO Port C should ensure that the internal pull-up resistor remains enabled
on PC1/TMS; otherwise JTAG communication could be lost.
160 January 08, 2011
Texas Instruments-Production Data
JTAG Interface
4.2.1.4 Test Data Input (TDI)
The TDI pin provides a stream of serial information to the IR chain and the DR chains. TDI is
sampled on the rising edge of TCK and, depending on the current TAP state and the current
instruction, presents this data to the proper shift register chain. Because the TDI pin is sampled on
the rising edge of TCK, the IEEE Standard 1149.1 expects the value on TDI to change on the falling
edge of TCK.
By default, the internal pull-up resistor on the TDI pin is enabled after reset. Changes to the pull-up
resistor settings on GPIO Port C should ensure that the internal pull-up resistor remains enabled
on PC2/TDI; otherwise JTAG communication could be lost.
4.2.1.5 Test Data Output (TDO)
The TDO pin provides an output stream of serial information from the IR chain or the DR chains.
The value of TDO depends on the current TAP state, the current instruction, and the data in the
chain being accessed. In order to save power when the JTAG port is not being used, the TDO pin
is placed in an inactive drive state when not actively shifting out data. Because TDO can be connected
to the TDI of another controller in a daisy-chain configuration, the IEEE Standard 1149.1 expects
the value on TDO to change on the falling edge of TCK.
By default, the internal pull-up resistor on the TDO pin is enabled after reset. This assures that the
pin remains at a constant logic level when the JTAG port is not being used. The internal pull-up and
pull-down resistors can be turned off to save internal power if a High-Z output value is acceptable
during certain TAP controller states.
4.2.2 JTAG TAP Controller
The JTAG TAP controller state machine is shown in Figure 4-2 on page 162. The TAP controller
state machine is reset to the Test-Logic-Reset state on the assertion of a Power-On-Reset (POR)
or the assertion of TRST. Asserting the correct sequence on the TMS pin allows the JTAG module
to shift in new instructions, shift in data, or idle during extended testing sequences. For detailed
information on the function of the TAP controller and the operations that occur in each state, please
refer to IEEE Standard 1149.1.
January 08, 2011 161
Texas Instruments-Production Data
Stellaris® LM3S2965 Microcontroller
Figure 4-2. Test Access Port State Machine
Test Logic Reset
Run Test Idle Select DR Scan Select IR Scan
Capture DR Capture IR
Shift DR Shift IR
Exit 1 DR Exit 1 IR
Exit 2 DR Exit 2 IR
Pause DR Pause IR
Update DR Update IR
1 1 1
1 1
1
1 1
1 1
1 1
1 1
1 0 1 0
0 0
0 0
0 0
0 0
0 0
0 0
0
0
4.2.3 Shift Registers
The Shift Registers consist of a serial shift register chain and a parallel load register. The serial shift
register chain samples specific information during the TAP controller’s CAPTURE states and allows
this information to be shifted out of TDO during the TAP controller’s SHIFT states. While the sampled
data is being shifted out of the chain on TDO, new data is being shifted into the serial shift register
on TDI. This new data is stored in the parallel load register during the TAP controller’s UPDATE
states. Each of the shift registers is discussed in detail in “Register Descriptions” on page 165.
4.2.4 Operational Considerations
There are certain operational considerations when using the JTAG module. Because the JTAG pins
can be programmed to be GPIOs, board configuration and reset conditions on these pins must be
considered. In addition, because the JTAG module has integrated ARM Serial Wire Debug, the
method for switching between these two operational modes is described below.
162 January 08, 2011
Texas Instruments-Production Data
JTAG Interface
4.2.4.1 GPIO Functionality
When the controller is reset with either a POR or RST, the JTAG/SWD port pins default to their
JTAG/SWD configurations. The default configuration includes enabling digital functionality (setting
GPIODEN to 1), enabling the pull-up resistors (setting GPIOPUR to 1), and enabling the alternate
hardware function (setting GPIOAFSEL to 1) for the PB7 and PC[3:0] JTAG/SWD pins.
It is possible for software to configure these pins as GPIOs after reset by writing 0s to PB7 and
PC[3:0] in the GPIOAFSEL register. If the user does not require the JTAG/SWD port for debugging
or board-level testing, this provides five more GPIOs for use in the design.
Caution – It is possible to create a software sequence that prevents the debugger from connecting to
the Stellaris microcontroller. If the program code loaded into flash immediately changes the JTAG pins
to their GPIO functionality, the debugger may not have enough time to connect and halt the controller
before the JTAG pin functionality switches. This may lock the debugger out of the part. This can be
avoided with a software routine that restores JTAG functionality based on an external or software
trigger.
The GPIO commit control registers provide a layer of protection against accidental programming of
critical hardware peripherals. Protection is currently provided for the five JTAG/SWD pins (PB7 and
PC[3:0]). Writes to protected bits of the GPIO Alternate Function Select (GPIOAFSEL) register
(see page 299) are not committed to storage unless the GPIO Lock (GPIOLOCK) register (see
page 309) has been unlocked and the appropriate bits of the GPIO Commit (GPIOCR) register (see
page 310) have been set to 1.
Recovering a "Locked" Device
Note: The mass erase of the flash memory caused by the below sequence erases the entire flash
memory, regardless of the settings in the Flash Memory Protection Program Enable n
(FMPPEn) registers. Performing the sequence below does not affect the nonvolatile registers
discussed in “Nonvolatile Register Programming” on page 259.
If software configures any of the JTAG/SWD pins as GPIO and loses the ability to communicate
with the debugger, there is a debug sequence that can be used to recover the device. Performing
a total of ten JTAG-to-SWD and SWD-to-JTAG switch sequences while holding the device in reset
mass erases the flash memory. The sequence to recover the device is:
1. Assert and hold the RST signal.
2. Perform the JTAG-to-SWD switch sequence.
3. Perform the SWD-to-JTAG switch sequence.
4. Perform the JTAG-to-SWD switch sequence.
5. Perform the SWD-to-JTAG switch sequence.
6. Perform the JTAG-to-SWD switch sequence.
7. Perform the SWD-to-JTAG switch sequence.
8. Perform the JTAG-to-SWD switch sequence.
9. Perform the SWD-to-JTAG switch sequence.
10. Perform the JTAG-to-SWD switch sequence.
January 08, 2011 163
Texas Instruments-Production Data
Stellaris® LM3S2965 Microcontroller
11. Perform the SWD-to-JTAG switch sequence.
12. Release the RST signal.
13. Wait 400 ms.
14. Power-cycle the device.
The JTAG-to-SWD and SWD-to-JTAG switch sequences are described in “ARM Serial Wire Debug
(SWD)” on page 164. When performing switch sequences for the purpose of recovering the debug
capabilities of the device, only steps 1 and 2 of the switch sequence in the section called
“JTAG-to-SWD Switching” on page 164 must be performed.
4.2.4.2 Communication with JTAG/SWD
Because the debug clock and the system clock can be running at different frequencies, care must
be taken to maintain reliable communication with the JTAG/SWD interface. In the Capture-DR state,
the result of the previous transaction, if any, is returned, together with a 3-bit ACK response. Software
should check the ACK response to see if the previous operation has completed before initiating a
new transaction. Alternatively, if the system clock is at least 8 times faster than the debug clock
(TCK or SWCLK), the previous operation has enough time to complete and the ACK bits do not have
to be checked.
4.2.4.3 ARM Serial Wire Debug (SWD)
In order to seamlessly integrate the ARM Serial Wire Debug (SWD) functionality, a serial-wire
debugger must be able to connect to the Cortex-M3 core without having to perform, or have any
knowledge of, JTAG cycles. This is accomplished with a SWD preamble that is issued before the
SWD session begins.
The switching preamble used to enable the SWD interface of the SWJ-DP module starts with the
TAP controller in the Test-Logic-Reset state. From here, the preamble sequences the TAP controller
through the following states: Run Test Idle, Select DR, Select IR, Test Logic Reset, Test Logic
Reset, Run Test Idle, Run Test Idle, Select DR, Select IR, Test Logic Reset, Test Logic Reset, Run
Test Idle, Run Test Idle, Select DR, Select IR, and Test Logic Reset states.
Stepping through this sequences of the TAP state machine enables the SWD interface and disables
the JTAG interface. For more information on this operation and the SWD interface, see the ARM®
Debug Interface V5 Architecture Specification.
Because this sequence is a valid series of JTAG operations that could be issued, the ARM JTAG
TAP controller is not fully compliant to the IEEE Standard 1149.1. This is the only instance where
the ARM JTAG TAP controller does not meet full compliance with the specification. Due to the low
probability of this sequence occurring during normal operation of the TAP controller, it should not
affect normal performance of the JTAG interface.
JTAG-to-SWD Switching
To switch the operating mode of the Debug Access Port (DAP) from JTAG to SWD mode, the
external debug hardware must send the switching preamble to the device. The 16-bit switch sequence
for switching to SWD mode is defined as b1110011110011110, transmitted LSB first. This can also
be represented as 16'hE79E when transmitted LSB first. The complete switch sequence should
consist of the following transactions on the TCK/SWCLK and TMS/SWDIO signals:
1. Send at least 50 TCK/SWCLK cycles with TMS/SWDIO set to 1. This ensures that both JTAG and
SWD are in their reset/idle states.
164 January 08, 2011
Texas Instruments-Production Data
JTAG Interface
2. Send the 16-bit JTAG-to-SWD switch sequence, 16'hE79E.
3. Send at least 50 TCK/SWCLK cycles with TMS/SWDIO set to 1. This ensures that if SWJ-DP was
already in SWD mode, before sending the switch sequence, the SWD goes into the line reset
state.
SWD-to-JTAG Switching
To switch the operating mode of the Debug Access Port (DAP) from SWD to JTAG mode, the
external debug hardware must send a switch sequence to the device. The 16-bit switch sequence
for switching to JTAG mode is defined as b1110011100111100, transmitted LSB first. This can also
be represented as 16'hE73C when transmitted LSB first. The complete switch sequence should
consist of the following transactions on the TCK/SWCLK and TMS/SWDIO signals:
1. Send at least 50 TCK/SWCLK cycles with TMS/SWDIO set to 1. This ensures that both JTAG and
SWD are in their reset/idle states.
2. Send the 16-bit SWD-to-JTAG switch sequence, 16'hE73C.
3. Send at least 5 TCK/SWCLK cycles with TMS/SWDIO set to 1. This ensures that if SWJ-DP was
already in JTAG mode, before sending the switch sequence, the JTAG goes into the Test Logic
Reset state.
4.3 Initialization and Configuration
After a Power-On-Reset or an external reset (RST), the JTAG pins are automatically configured for
JTAG communication. No user-defined initialization or configuration is needed. However, if the user
application changes these pins to their GPIO function, they must be configured back to their JTAG
functionality before JTAG communication can be restored. This is done by enabling the five JTAG
pins (PB7 and PC[3:0]) for their alternate function using the GPIOAFSEL register. In addition to
enabling the alternate functions, any other changes to the GPIO pad configurations on the five JTAG
pins (PB7 andPC[3:0]) should be reverted to their default settings.
4.4 Register Descriptions
There are no APB-accessible registers in the JTAG TAP Controller or Shift Register chains. The
registers within the JTAG controller are all accessed serially through the TAP Controller. The registers
can be broken down into two main categories: Instruction Registers and Data Registers.
4.4.1 Instruction Register (IR)
The JTAG TAP Instruction Register (IR) is a four-bit serial scan chain connected between the JTAG
TDI and TDO pins with a parallel load register. When the TAP Controller is placed in the correct
states, bits can be shifted into the Instruction Register. Once these bits have been shifted into the
chain and updated, they are interpreted as the current instruction. The decode of the Instruction
Register bits is shown in Table 4-2 on page 165. A detailed explanation of each instruction, along
with its associated Data Register, follows.
Table 4-2. JTAG Instruction Register Commands
IR[3:0] Instruction Description
Drives the values preloaded into the Boundary Scan Chain by the
SAMPLE/PRELOAD instruction onto the pads.
0000 EXTEST
Drives the values preloaded into the Boundary Scan Chain by the
SAMPLE/PRELOAD instruction into the controller.
0001 INTEST
January 08, 2011 165
Texas Instruments-Production Data
Stellaris® LM3S2965 Microcontroller
Table 4-2. JTAG Instruction Register Commands (continued)
IR[3:0] Instruction Description
Captures the current I/O values and shifts the sampled values out of the
Boundary Scan Chain while new preload data is shifted in.
0010 SAMPLE / PRELOAD
1000 ABORT Shifts data into the ARM Debug Port Abort Register.
1010 DPACC Shifts data into and out of the ARM DP Access Register.
1011 APACC Shifts data into and out of the ARM AC Access Register.
Loads manufacturing information defined by the IEEE Standard 1149.1
into the IDCODE chain and shifts it out.
1110 IDCODE
1111 BYPASS Connects TDI to TDO through a single Shift Register chain.
Defaults to the BYPASS instruction to ensure that TDI is always connected
to TDO.
All Others Reserved
4.4.1.1 EXTEST Instruction
The EXTEST instruction is not associated with its own Data Register chain. The EXTEST instruction
uses the data that has been preloaded into the Boundary Scan Data Register using the
SAMPLE/PRELOAD instruction. When the EXTEST instruction is present in the Instruction Register,
the preloaded data in the Boundary Scan Data Register associated with the outputs and output
enables are used to drive the GPIO pads rather than the signals coming from the core. This allows
tests to be developed that drive known values out of the controller, which can be used to verify
connectivity. While the EXTEST instruction is present in the Instruction Register, the Boundary Scan
Data Register can be accessed to sample and shift out the current data and load new data into the
Boundary Scan Data Register.
4.4.1.2 INTEST Instruction
The INTEST instruction is not associated with its own Data Register chain. The INTEST instruction
uses the data that has been preloaded into the Boundary Scan Data Register using the
SAMPLE/PRELOAD instruction. When the INTEST instruction is present in the Instruction Register,
the preloaded data in the Boundary Scan Data Register associated with the inputs are used to drive
the signals going into the core rather than the signals coming from the GPIO pads. This allows tests
to be developed that drive known values into the controller, which can be used for testing. It is
important to note that although the RST input pin is on the Boundary Scan Data Register chain, it
is only observable. While the INTEXT instruction is present in the Instruction Register, the Boundary
Scan Data Register can be accessed to sample and shift out the current data and load new data
into the Boundary Scan Data Register.
4.4.1.3 SAMPLE/PRELOAD Instruction
The SAMPLE/PRELOAD instruction connects the Boundary Scan Data Register chain between
TDI and TDO. This instruction samples the current state of the pad pins for observation and preloads
new test data. Each GPIO pad has an associated input, output, and output enable signal. When the
TAP controller enters the Capture DR state during this instruction, the input, output, and output-enable
signals to each of the GPIO pads are captured. These samples are serially shifted out of TDO while
the TAP controller is in the Shift DR state and can be used for observation or comparison in various
tests.
While these samples of the inputs, outputs, and output enables are being shifted out of the Boundary
Scan Data Register, new data is being shifted into the Boundary Scan Data Register from TDI.
Once the new data has been shifted into the Boundary Scan Data Register, the data is saved in the
parallel load registers when the TAP controller enters the Update DR state. This update of the
parallel load register preloads data into the Boundary Scan Data Register that is associated with
166 January 08, 2011
Texas Instruments-Production Data
JTAG Interface
each input, output, and output enable. This preloaded data can be used with the EXTEST and
INTEST instructions to drive data into or out of the controller. Please see “Boundary Scan Data
Register” on page 168 for more information.
4.4.1.4 ABORT Instruction
The ABORT instruction connects the associated ABORT Data Register chain between TDI and
TDO. This instruction provides read and write access to the ABORT Register of the ARM Debug
Access Port (DAP). Shifting the proper data into this Data Register clears various error bits or initiates
a DAP abort of a previous request. Please see the “ABORT Data Register” on page 169 for more
information.
4.4.1.5 DPACC Instruction
The DPACC instruction connects the associated DPACC Data Register chain between TDI and
TDO. This instruction provides read and write access to the DPACC Register of the ARM Debug
Access Port (DAP). Shifting the proper data into this register and reading the data output from this
register allows read and write access to the ARM debug and status registers. Please see “DPACC
Data Register” on page 169 for more information.
4.4.1.6 APACC Instruction
The APACC instruction connects the associated APACC Data Register chain between TDI and
TDO. This instruction provides read and write access to the APACC Register of the ARM Debug
Access Port (DAP). Shifting the proper data into this register and reading the data output from this
register allows read and write access to internal components and buses through the Debug Port.
Please see “APACC Data Register” on page 169 for more information.
4.4.1.7 IDCODE Instruction
The IDCODE instruction connects the associated IDCODE Data Register chain between TDI and
TDO. This instruction provides information on the manufacturer, part number, and version of the
ARM core. This information can be used by testing equipment and debuggers to automatically
configure their input and output data streams. IDCODE is the default instruction that is loaded into
the JTAG Instruction Register when a Power-On-Reset (POR) is asserted, TRST is asserted, or the
Test-Logic-Reset state is entered. Please see “IDCODE Data Register” on page 168 for more
information.
4.4.1.8 BYPASS Instruction
The BYPASS instruction connects the associated BYPASS Data Register chain between TDI and
TDO. This instruction is used to create a minimum length serial path between the TDI and TDO ports.
The BYPASS Data Register is a single-bit shift register. This instruction improves test efficiency by
allowing components that are not needed for a specific test to be bypassed in the JTAG scan chain
by loading them with the BYPASS instruction. Please see “BYPASS Data Register” on page 168 for
more information.
4.4.2 Data Registers
The JTAG module contains six Data Registers. These include: IDCODE, BYPASS, Boundary Scan,
APACC, DPACC, and ABORT serial Data Register chains. Each of these Data Registers is discussed
in the following sections.
January 08, 2011 167
Texas Instruments-Production Data
Stellaris® LM3S2965 Microcontroller
4.4.2.1 IDCODE Data Register
The format for the 32-bit IDCODE Data Register defined by the IEEE Standard 1149.1 is shown in
Figure 4-3 on page 168. The standard requires that every JTAG-compliant device implement either
the IDCODE instruction or the BYPASS instruction as the default instruction. The LSB of the IDCODE
Data Register is defined to be a 1 to distinguish it from the BYPASS instruction, which has an LSB
of 0. This allows auto configuration test tools to determine which instruction is the default instruction.
The major uses of the JTAG port are for manufacturer testing of component assembly, and program
development and debug. To facilitate the use of auto-configuration debug tools, the IDCODE
instruction outputs a value of 0x3BA0.0477. This allows the debuggers to automatically configure
themselves to work correctly with the Cortex-M3 during debug.
Figure 4-3. IDCODE Register Format
Version Part Number Manufacturer ID 1
31 28 27 12 11 1 0
TDI TDO
4.4.2.2 BYPASS Data Register
The format for the 1-bit BYPASS Data Register defined by the IEEE Standard 1149.1 is shown in
Figure 4-4 on page 168. The standard requires that every JTAG-compliant device implement either
the BYPASS instruction or the IDCODE instruction as the default instruction. The LSB of the BYPASS
Data Register is defined to be a 0 to distinguish it from the IDCODE instruction, which has an LSB
of 1. This allows auto configuration test tools to determine which instruction is the default instruction.
Figure 4-4. BYPASS Register Format
TDI 0 TDO
0
4.4.2.3 Boundary Scan Data Register
The format of the Boundary Scan Data Register is shown in Figure 4-5 on page 169. Each GPIO
pin, starting with a GPIO pin next to the JTAG port pins, is included in the Boundary Scan Data
Register. Each GPIO pin has three associated digital signals that are included in the chain. These
signals are input, output, and output enable, and are arranged in that order as can be seen in the
figure.
When the Boundary Scan Data Register is accessed with the SAMPLE/PRELOAD instruction, the
input, output, and output enable from each digital pad are sampled and then shifted out of the chain
to be verified. The sampling of these values occurs on the rising edge of TCK in the Capture DR
state of the TAP controller. While the sampled data is being shifted out of the Boundary Scan chain
in the Shift DR state of the TAP controller, new data can be preloaded into the chain for use with
the EXTEST and INTEST instructions. These instructions either force data out of the controller, with
the EXTEST instruction, or into the controller, with the INTEST instruction.
168 January 08, 2011
Texas Instruments-Production Data
JTAG Interface
Figure 4-5. Boundary Scan Register Format
O TDO TDI O IN
E UT
O O IN
U E
T
O O IN
E UT
O O IN
U E
T
I
N ... ...
GPIO PB6 GPIO m RST GPIO m+1 GPIO n
4.4.2.4 APACC Data Register
The format for the 35-bit APACC Data Register defined by ARM is described in the ARM® Debug
Interface V5 Architecture Specification.
4.4.2.5 DPACC Data Register
The format for the 35-bit DPACC Data Register defined by ARM is described in the ARM® Debug
Interface V5 Architecture Specification.
4.4.2.6 ABORT Data Register
The format for the 35-bit ABORT Data Register defined by ARM is described in the ARM® Debug
Interface V5 Architecture Specification.
January 08, 2011 169
Texas Instruments-Production Data
Stellaris® LM3S2965 Microcontroller
5 System Control
System control determines the overall operation of the device. It provides information about the
device, controls the clocking to the core and individual peripherals, and handles reset detection and
reporting.
5.1 Functional Description
The System Control module provides the following capabilities:
■ Device identification (see “Device Identification” on page 170)
■ Local control, such as reset (see “Reset Control” on page 170), power (see “Power
Control” on page 174) and clock control (see “Clock Control” on page 175)
■ System control (Run, Sleep, and Deep-Sleep modes); see “System Control” on page 180
5.1.1 Device Identification
Several read-only registers provide software with information on the microcontroller, such as version,
part number, SRAM size, flash size, and other features. See the DID0, DID1, and DC0-DC4 registers.
5.1.2 Reset Control
This section discusses aspects of hardware functions during reset as well as system software
requirements following the reset sequence.
5.1.2.1 CMOD0 and CMOD1 Test-Mode Control Pins
Two pins, CMOD0 and CMOD1, are defined for internal use for testing the microcontroller during
manufacture. They have no end-user function and should not be used. The CMOD pins should be
connected to ground.
5.1.2.2 Reset Sources
The controller has five sources of reset:
1. External reset input pin (RST) assertion; see “External RST Pin” on page 171.
2. Power-on reset (POR); see “Power-On Reset (POR)” on page 171.
3. Internal brown-out (BOR) detector; see “Brown-Out Reset (BOR)” on page 173.
4. Software-initiated reset (with the software reset registers); see “Software Reset” on page 173.
5. A watchdog timer reset condition violation; see “Watchdog Timer Reset” on page 174.
Table 5-1 provides a summary of results of the various reset operations.
Table 5-1. Reset Sources
Reset Source Core Reset? JTAG Reset? On-Chip Peripherals Reset?
Power-On Reset Yes Yes Yes
RST Yes Pin Config Only Yes
Brown-Out Reset Yes No Yes
170 January 08, 2011
Texas Instruments-Production Data
System Control
Table 5-1. Reset Sources (continued)
Reset Source Core Reset? JTAG Reset? On-Chip Peripherals Reset?
Software System Request Yes No Yes
Reseta
Software Peripheral Reset No No Yesb
Watchdog Reset Yes No Yes
a. By using the SYSRESREQ bit in the ARM Cortex-M3 Application Interrupt and Reset Control (APINT) register
b. Programmable on a module-by-module basis using the Software Reset Control Registers.
After a reset, the Reset Cause (RESC) register is set with the reset cause. The bits in this register
are sticky and maintain their state across multiple reset sequences, except when an internal POR
is the cause, and then all the other bits in the RESC register are cleared except for the POR indicator.
5.1.2.3 Power-On Reset (POR)
Note: The power-on reset also resets the JTAG controller. An external reset does not.
The internal Power-On Reset (POR) circuit monitors the power supply voltage (VDD) and generates
a reset signal to all of the internal logic including JTAG when the power supply ramp reaches a
threshold value (VTH). The microcontroller must be operating within the specified operating parameters
when the on-chip power-on reset pulse is complete. The 3.3-V power supply to the microcontroller
must reach 3.0 V within 10 msec of VDD crossing 2.0 V to guarantee proper operation. For applications
that require the use of an external reset signal to hold the microcontroller in reset longer than the
internal POR, the RST input may be used as discussed in “External RST Pin” on page 171.
The Power-On Reset sequence is as follows:
1. The microcontroller waits for internal POR to go inactive.
2. The internal reset is released and the core loads from memory the initial stack pointer, the initial
program counter, and the first instruction designated by the program counter, and then begins
execution.
The internal POR is only active on the initial power-up of the microcontroller. The Power-On Reset
timing is shown in Figure 22-6 on page 686.
5.1.2.4 External RST Pin
Note: It is recommended that the trace for the RST signal must be kept as short as possible. Be
sure to place any components connected to the RST signal as close to the microcontroller
as possible.
If the application only uses the internal POR circuit, the RST input must be connected to the power
supply (VDD) through an optional pull-up resistor (0 to 100K Ω) as shown in Figure 5-1 on page 172.
January 08, 2011 171
Texas Instruments-Production Data
Stellaris® LM3S2965 Microcontroller
Figure 5-1. Basic RST Configuration
PU
RST
Stellaris®
R
VDD
RPU = 0 to 100 kΩ
The external reset pin (RST) resets the microcontroller including the core and all the on-chip
peripherals except the JTAG TAP controller (see “JTAG Interface” on page 158). The external reset
sequence is as follows:
1. The external reset pin (RST) is asserted for the duration specified by TMIN and then de-asserted
(see “Reset” on page 685).
2. The internal reset is released and the core loads from memory the initial stack pointer, the initial
program counter, and the first instruction designated by the program counter, and then begins
execution.
To improve noise immunity and/or to delay reset at power up, the RST input may be connected to
an RC network as shown in Figure 5-2 on page 172.
Figure 5-2. External Circuitry to Extend Power-On Reset
PU
C1
RST
Stellaris®
R
VDD
RPU = 1 kΩ to 100 kΩ
C1 = 1 nF to 10 μF
If the application requires the use of an external reset switch, Figure 5-3 on page 173 shows the
proper circuitry to use.
172 January 08, 2011
Texas Instruments-Production Data
System Control
Figure 5-3. Reset Circuit Controlled by Switch
PU
C1
RS
RST
Stellaris®
R
VDD
Typical RPU = 10 kΩ
Typical RS = 470 Ω
C1 = 10 nF
The RPU and C1 components define the power-on delay.
The external reset timing is shown in Figure 22-5 on page 686.
5.1.2.5 Brown-Out Reset (BOR)
A drop in the input voltage resulting in the assertion of the internal brown-out detector can be used
to reset the controller. This is initially disabled and may be enabled by software.
The system provides a brown-out detection circuit that triggers if the power supply (VDD) drops
below a brown-out threshold voltage (VBTH). If a brown-out condition is detected, the system may
generate a controller interrupt or a system reset.
Brown-out resets are controlled with the Power-On and Brown-Out Reset Control (PBORCTL)
register. The BORIOR bit in the PBORCTL register must be set for a brown-out condition to trigger
a reset.
The brown-out reset is equivalent to an assertion of the external RST input and the reset is held
active until the proper VDD level is restored. The RESC register can be examined in the reset interrupt
handler to determine if a Brown-Out condition was the cause of the reset, thus allowing software to
determine what actions are required to recover.
The internal Brown-Out Reset timing is shown in Figure 22-7 on page 686.
5.1.2.6 Software Reset
Software can reset a specific peripheral or generate a reset to the entire system .
Peripherals can be individually reset by software via three registers that control reset signals to each
peripheral (see the SRCRn registers). If the bit position corresponding to a peripheral is set and
subsequently cleared, the peripheral is reset. The encoding of the reset registers is consistent with
the encoding of the clock gating control for peripherals and on-chip functions (see “System
Control” on page 180). Note that all reset signals for all clocks of the specified unit are asserted as
a result of a software-initiated reset.
The entire system can be reset by software by setting the SYSRESETREQ bit in the Cortex-M3
Application Interrupt and Reset Control register resets the entire system including the core. The
software-initiated system reset sequence is as follows:
January 08, 2011 173
Texas Instruments-Production Data
Stellaris® LM3S2965 Microcontroller
1. A software system reset is initiated by writing the SYSRESETREQ bit in the ARM Cortex-M3
Application Interrupt and Reset Control register.
2. An internal reset is asserted.
3. The internal reset is deasserted and the controller loads from memory the initial stack pointer,
the initial program counter, and the first instruction designated by the program counter, and
then begins execution.
The software-initiated system reset timing is shown in Figure 22-8 on page 687.
5.1.2.7 Watchdog Timer Reset
The watchdog timer module's function is to prevent system hangs. The watchdog timer can be
configured to generate an interrupt to the controller on its first time-out, and to generate a reset
signal on its second time-out.
After the first time-out event, the 32-bit counter is reloaded with the value of the Watchdog Timer
Load (WDTLOAD) register, and the timer resumes counting down from that value. If the timer counts
down to its zero state again before the first time-out interrupt is cleared, and the reset signal has
been enabled, the watchdog timer asserts its reset signal to the system. The watchdog timer reset
sequence is as follows:
1. The watchdog timer times out for the second time without being serviced.
2. An internal reset is asserted.
3. The internal reset is released and the controller loads from memory the initial stack pointer, the
initial program counter, the first instruction designated by the program counter, and begins
execution.
The watchdog reset timing is shown in Figure 22-9 on page 687.
5.1.3 Power Control
The Stellaris® microcontroller provides an integrated LDO regulator that may be used to provide
power to the majority of the controller's internal logic. For power reduction, the LDO regulator provides
software a mechanism to adjust the regulated value, in small increments (VSTEP), over the range
of 2.25 V to 2.75 V (inclusive)—or 2.5 V ± 10%. The adjustment is made by changing the value of
the VADJ field in the LDO Power Control (LDOPCTL) register.
Figure 5-4 on page 175 shows the power architecture.
Note: On the printed circuit board, use the LDO output as the source of VDD25 input. Do not use
an external regulator to supply the voltage to VDD25. In addition, the LDO requires decoupling
capacitors. See “On-Chip Low Drop-Out (LDO) Regulator Characteristics” on page 680.
VDDA must be supplied with 3.3 V, or the microcontroller does not function properly. VDDA
is the supply for all of the analog circuitry on the device, including the LDO and the clock
circuitry.
174 January 08, 2011
Texas Instruments-Production Data
System Control
Figure 5-4. Power Architecture
I/O Buffers
Analog circuits
Low-noise
LDO
Internal
Logic and PLL
GND
GND
GND
GND
GNDA
GND
GND
GND
GND
VDD
VDD
VDD
VDD
VDDA
VDDA
VDD25
VDD25
VDD25
VDD25
LDO
+3.3V
GNDA
5.1.4 Clock Control
System control determines the control of clocks in this part.
5.1.4.1 Fundamental Clock Sources
There are multiple clock sources for use in the device:
■ Internal Oscillator (IOSC). The internal oscillator is an on-chip clock source. It does not require
the use of any external components. The frequency of the internal oscillator is 12 MHz ± 30%.
Applications that do not depend on accurate clock sources may use this clock source to reduce
system cost. The internal oscillator is the clock source the device uses during and following POR.
If the main oscillator is required, software must enable the main oscillator following reset and
allow the main oscillator to stabilize before changing the clock reference.
■ Main Oscillator (MOSC). The main oscillator provides a frequency-accurate clock source by
one of two means: an external single-ended clock source is connected to the OSC0 input pin, or
an external crystal is connected across the OSC0 input and OSC1 output pins. If the PLL is being
January 08, 2011 175
Texas Instruments-Production Data
Stellaris® LM3S2965 Microcontroller
used, the crystal value must be one of the supported frequencies between 3.579545 MHz through
8.192 MHz (inclusive). If the PLL is not being used, the crystal may be any one of the supported
frequencies between 1 MHz and 8.192 MHz. The single-ended clock source range is from DC
through the specified speed of the device. The supported crystals are listed in the XTAL bit field
in the RCC register (see page 192).
■ Internal 30-kHz Oscillator. The internal 30-kHz oscillator is similar to the internal oscillator,
except that it provides an operational frequency of 30 kHz ± 50%. It is intended for use during
Deep-Sleep power-saving modes. This power-savings mode benefits from reduced internal
switching and also allows the main oscillator to be powered down.
■ External Real-Time Oscillator. The external real-time oscillator provides a low-frequency,
accurate clock reference. It is intended to provide the system with a real-time clock source. The
real-time oscillator is part of the Hibernation Module (see “Hibernation Module” on page 236) and
may also provide an accurate source of Deep-Sleep or Hibernate mode power savings.
The internal system clock (SysClk), is derived from any of the above sources plus two others: the
output of the main internal PLL, and the internal oscillator divided by four (3 MHz ± 30%). The
frequency of the PLL clock reference must be in the range of 3.579545 MHz to 8.192 MHz (inclusive).
Table 5-2 on page 176 shows how the various clock sources can be used in a system.
Table 5-2. Clock Source Options
Clock Source Drive PLL? Used as SysClk?
Internal Oscillator (12 MHz) No BYPASS = 1 Yes BYPASS = 1, OSCSRC = 0x1
Internal Oscillator divide by 4 (3 No BYPASS = 1 Yes BYPASS = 1, OSCSRC = 0x2
MHz)
BYPASS = 0, OSCSRC = Yes BYPASS = 1, OSCSRC = 0x0
0x0
Main Oscillator Yes
Internal 30-kHz Oscillator No BYPASS = 1 Yes BYPASS = 1, OSCSRC = 0x3
External Real-Time Oscillator No BYPASS = 1 Yes BYPASS = 1, OSCSRC2 = 0x7
5.1.4.2 Clock Configuration
The Run-Mode Clock Configuration (RCC) and Run-Mode Clock Configuration 2 (RCC2)
registers provide control for the system clock. The RCC2 register is provided to extend fields that
offer additional encodings over the RCC register. When used, the RCC2 register field values are
used by the logic over the corresponding field in the RCC register. In particular, RCC2 provides for
a larger assortment of clock configuration options. These registers control the following clock
functionality:
■ Source of clocks in sleep and deep-sleep modes
■ System clock derived from PLL or other clock source
■ Enabling/disabling of oscillators and PLL
■ Clock divisors
■ Crystal input selection
Figure 5-5 on page 177 shows the logic for the main clock tree. The peripheral blocks are driven by
the system clock signal and can be individually enabled/disabled. The ADC clock signal is
automatically divided down to 16 MHz for proper ADC operation. The PWM clock signal is a
176 January 08, 2011
Texas Instruments-Production Data
System Control
synchronous divide of the system clock to provide the PWM circuit with more range (set with PWMDIV
in RCC).
Note: When the ADC module is in operation, the system clock must be at least 16 MHz.
Figure 5-5. Main Clock Tree
PLL
Main OSC (400 MHz)
Internal
OSC
(12 MHz)
Internal
OSC
(30 kHz)
÷ 4
Hibernation
Module
(32.768 kHz) ÷ 25
PWRDN
ADC Clock
System Clock
XTALa
PWRDN b
MOSCDIS a
IOSCDISa
OSCSRCb,d
BYPASS b,d
SYSDIVb,d
USESYSDIV a,d
PWMDW a
USEPWMDIV a
PWM Clock
a. Control provided by RCC register bit/field.
b. Control provided by RCC register bit/field or RCC2 register bit/field, if overridden with RCC2 register bit USERCC2.
c. Control provided by RCC2 register bit/field.
d. Also may be controlled by DSLPCLKCFG when in deep sleep mode.
÷ 2
÷ 50 CAN Clock
Note: The figure above shows all features available on all Stellaris® Fury-class devices. Not all peripherals may be
available on this device.
In the RCC register, the SYSDIV field specifies which divisor is used to generate the system clock
from either the PLL output or the oscillator source (depending on how the BYPASS bit in this register
is configured). When using the PLL, the VCO frequency of 400 MHz is predivided by 2 before the
divisor is applied. Table 5-3 shows how the SYSDIV encoding affects the system clock frequency,
depending on whether the PLL is used (BYPASS=0) or another clock source is used (BYPASS=1).
January 08, 2011 177
Texas Instruments-Production Data
Stellaris® LM3S2965 Microcontroller
The divisor is equivalent to the SYSDIV encoding plus 1. For a list of possible clock sources, see
Table 5-2 on page 176.
Table 5-3. Possible System Clock Frequencies Using the SYSDIV Field
Frequency Frequency (BYPASS=1) StellarisWare Parametera
(BYPASS=0)
SYSDIV Divisor
0x0 /1 reserved Clock source frequency/2 SYSCTL_SYSDIV_1b
0x1 /2 reserved Clock source frequency/2 SYSCTL_SYSDIV_2
0x2 /3 reserved Clock source frequency/3 SYSCTL_SYSDIV_3
0x3 /4 50 MHz Clock source frequency/4 SYSCTL_SYSDIV_4
0x4 /5 40 MHz Clock source frequency/5 SYSCTL_SYSDIV_5
0x5 /6 33.33 MHz Clock source frequency/6 SYSCTL_SYSDIV_6
0x6 /7 28.57 MHz Clock source frequency/7 SYSCTL_SYSDIV_7
0x7 /8 25 MHz Clock source frequency/8 SYSCTL_SYSDIV_8
0x8 /9 22.22 MHz Clock source frequency/9 SYSCTL_SYSDIV_9
0x9 /10 20 MHz Clock source frequency/10 SYSCTL_SYSDIV_10
0xA /11 18.18 MHz Clock source frequency/11 SYSCTL_SYSDIV_11
0xB /12 16.67 MHz Clock source frequency/12 SYSCTL_SYSDIV_12
0xC /13 15.38 MHz Clock source frequency/13 SYSCTL_SYSDIV_13
0xD /14 14.29 MHz Clock source frequency/14 SYSCTL_SYSDIV_14
0xE /15 13.33 MHz Clock source frequency/15 SYSCTL_SYSDIV_15
0xF /16 12.5 MHz (default) Clock source frequency/16 SYSCTL_SYSDIV_16
a. This parameter is used in functions such as SysCtlClockSet() in the Stellaris Peripheral Driver Library.
b. SYSCTL_SYSDIV_1 does not set the USESYSDIV bit. As a result, using this parameter without enabling the PLL results
in the system clock having the same frequency as the clock source.
The SYSDIV2 field in the RCC2 register is 2 bits wider than the SYSDIV field in the RCC register
so that additional larger divisors up to /64 are possible, allowing a lower system clock frequency for
improved Deep Sleep power consumption. When using the PLL, the VCO frequency of 400 MHz is
predivided by 2 before the divisor is applied. The divisor is equivalent to the SYSDIV2 encoding
plus 1. Table 5-4 shows how the SYSDIV2 encoding affects the system clock frequency, depending
on whether the PLL is used (BYPASS2=0) or another clock source is used (BYPASS2=1). For a list
of possible clock sources, see Table 5-2 on page 176.
Table 5-4. Examples of Possible System Clock Frequencies Using the SYSDIV2 Field
Frequency Frequency (BYPASS2=1) StellarisWare Parametera
(BYPASS2=0)
SYSDIV2 Divisor
0x00 /1 reserved Clock source frequency/2 SYSCTL_SYSDIV_1b
0x01 /2 reserved Clock source frequency/2 SYSCTL_SYSDIV_2
0x02 /3 reserved Clock source frequency/3 SYSCTL_SYSDIV_3
0x03 /4 50 MHz Clock source frequency/4 SYSCTL_SYSDIV_4
0x04 /5 40 MHz Clock source frequency/5 SYSCTL_SYSDIV_5
0x05 /6 33.33 MHz Clock source frequency/6 SYSCTL_SYSDIV_6
0x06 /7 28.57 MHz Clock source frequency/7 SYSCTL_SYSDIV_7
0x07 /8 25 MHz Clock source frequency/8 SYSCTL_SYSDIV_8
0x08 /9 22.22 MHz Clock source frequency/9 SYSCTL_SYSDIV_9
0x09 /10 20 MHz Clock source frequency/10 SYSCTL_SYSDIV_10
178 January 08, 2011
Texas Instruments-Production Data
System Control
Table 5-4. Examples of Possible System Clock Frequencies Using the SYSDIV2 Field
(continued)
Frequency Frequency (BYPASS2=1) StellarisWare Parametera
(BYPASS2=0)
SYSDIV2 Divisor
... ... ... ... ...
0x3F /64 3.125 MHz Clock source frequency/64 SYSCTL_SYSDIV_64
a. This parameter is used in functions such as SysCtlClockSet() in the Stellaris Peripheral Driver Library.
b. SYSCTL_SYSDIV_1 does not set the USESYSDIV bit. As a result, using this parameter without enabling the PLL results
in the system clock having the same frequency as the clock source.
5.1.4.3 Crystal Configuration for the Main Oscillator (MOSC)
The main oscillator supports the use of a select number of crystals. If the main oscillator is used by
the PLL as a reference clock, the supported range of crystals is 3.579545 to 8.192 MHz, otherwise,
the range of supported crystals is 1 to 8.192 MHz.
The XTAL bit in the RCC register (see page 192) describes the available crystal choices and default
programming values.
Software configures the RCC register XTAL field with the crystal number. If the PLL is used in the
design, the XTAL field value is internally translated to the PLL settings.
5.1.4.4 Main PLL Frequency Configuration
The main PLL is disabled by default during power-on reset and is enabled later by software if
required. Software specifies the output divisor to set the system clock frequency, and enables the
main PLL to drive the output. The PLL operates at 400 MHz, but is divided by two prior to the
application of the output divisor.
If the main oscillator provides the clock reference to the main PLL, the translation provided by
hardware and used to program the PLL is available for software in the XTAL to PLL Translation
(PLLCFG) register (see page 196). The internal translation provides a translation within ± 1% of the
targeted PLL VCO frequency. Table 22-9 on page 683 shows the actual PLL frequency and error for
a given crystal choice.
The Crystal Value field (XTAL) in the Run-Mode Clock Configuration (RCC) register (see page 192)
describes the available crystal choices and default programming of the PLLCFG register. Any time
the XTAL field changes, the new settings are translated and the internal PLL settings are updated.
To configure the external 32-kHz real-time oscillator as the PLL input reference, program the OSCRC2
field in the Run-Mode Clock Configuration 2 (RCC2) register to be 0x7.
5.1.4.5 PLL Modes
The PLL has two modes of operation: Normal and Power-Down
■ Normal: The PLL multiplies the input clock reference and drives the output.
■ Power-Down: Most of the PLL internal circuitry is disabled and the PLL does not drive the output.
The modes are programmed using the RCC/RCC2 register fields (see page 192 and page 197).
5.1.4.6 PLL Operation
If a PLL configuration is changed, the PLL output frequency is unstable until it reconverges (relocks)
to the new setting. The time between the configuration change and relock is TREADY (see Table
22-8 on page 682). During the relock time, the affected PLL is not usable as a clock reference.
January 08, 2011 179
Texas Instruments-Production Data
Stellaris® LM3S2965 Microcontroller
PLL is changed by one of the following:
■ Change to the XTAL value in the RCC register—writes of the same value do not cause a relock.
■ Change in the PLL from Power-Down to Normal mode.
A counter is defined to measure the TREADY requirement. The counter is clocked by the main
oscillator. The range of the main oscillator has been taken into account and the down counter is set
to 0x1200 (that is, ~600 μs at an 8.192 MHz external oscillator clock). Hardware is provided to keep
the PLL from being used as a system clock until the TREADY condition is met after one of the two
changes above. It is the user's responsibility to have a stable clock source (like the main oscillator)
before the RCC/RCC2 register is switched to use the PLL.
If the main PLL is enabled and the system clock is switched to use the PLL in one step, the system
control hardware continues to clock the controller from the oscillator selected by the RCC/RCC2
register until the main PLL is stable (TREADY time met), after which it changes to the PLL. Software
can use many methods to ensure that the system is clocked from the main PLL, including periodically
polling the PLLLRIS bit in the Raw Interrupt Status (RIS) register, and enabling the PLL Lock
interrupt.
5.1.5 System Control
For power-savings purposes, the RCGCn , SCGCn , and DCGCn registers control the clock gating
logic for each peripheral or block in the system while the controller is in Run, Sleep, and Deep-Sleep
mode, respectively.
There are four levels of operation for the device defined as:
■ Run Mode. In Run mode, the controller actively executes code. Run mode provides normal
operation of the processor and all of the peripherals that are currently enabled by the RCGCn
registers. The system clock can be any of the available clock sources including the PLL.
■ Sleep Mode. In Sleep mode, the clock frequency of the active peripherals is unchanged, but the
processor and the memory subsystem are not clocked and therefore no longer execute code.
Sleep mode is entered by the Cortex-M3 core executing a WFI(Wait for Interrupt)
instruction. Any properly configured interrupt event in the system will bring the processor back
into Run mode. See “Power Management” on page 89 for more details.
Peripherals are clocked that are enabled in the SCGCn register when auto-clock gating is enabled
(see the RCC register) or the RCGCn register when the auto-clock gating is disabled. The system
clock has the same source and frequency as that during Run mode.
■ Deep-Sleep Mode. In Deep-Sleep mode, the clock frequency of the active peripherals may
change (depending on the Run mode clock configuration) in addition to the processor clock being
stopped. An interrupt returns the device to Run mode from one of the sleep modes; the sleep
modes are entered on request from the code. Deep-Sleep mode is entered by first writing the
Deep Sleep Enable bit in the ARM Cortex-M3 NVIC system control register and then executing
a WFI instruction. Any properly configured interrupt event in the system will bring the processor
back into Run mode. See “Power Management” on page 89 for more details.
The Cortex-M3 processor core and the memory subsystem are not clocked. Peripherals are
clocked that are enabled in the DCGCn register when auto-clock gating is enabled (see the RCC
register) or the RCGCn register when auto-clock gating is disabled. The system clock source is
the main oscillator by default or the internal oscillator specified in the DSLPCLKCFG register if
one is enabled. When the DSLPCLKCFG register is used, the internal oscillator is powered up,
if necessary, and the main oscillator is powered down. If the PLL is running at the time of the
180 January 08, 2011
Texas Instruments-Production Data
System Control
WFI instruction, hardware will power the PLL down and override the SYSDIV field of the active
RCC/RCC2 register, to be determined by the DSDIVORIDE setting in the DSLPCLKCFG register,
up to /16 or /64 respectively. When the Deep-Sleep exit event occurs, hardware brings the system
clock back to the source and frequency it had at the onset of Deep-Sleep mode before enabling
the clocks that had been stopped during the Deep-Sleep duration.
■ Hibernate Mode. In this mode, the power supplies are turned off to the main part of the device
and only the Hibernation module's circuitry is active. An external wake event or RTC event is
required to bring the device back to Run mode. The Cortex-M3 processor and peripherals outside
of the Hibernation module see a normal "power on" sequence and the processor starts running
code. It can determine that it has been restarted from Hibernate mode by inspecting the
Hibernation module registers.
Caution – If the Cortex-M3 Debug Access Port (DAP) has been enabled, and the device wakes from a
low power sleep or deep-sleep mode, the core may start executing code before all clocks to peripherals
have been restored to their run mode configuration. The DAP is usually enabled by software tools
accessing the JTAG or SWD interface when debugging or flash programming. If this condition occurs,
a Hard Fault is triggered when software accesses a peripheral with an invalid clock.
A software delay loop can be used at the beginning of the interrupt routine that is used to wake up a
system from a WFI (Wait For Interrupt) instruction. This stalls the execution of any code that accesses
a peripheral register that might cause a fault. This loop can be removed for production software as the
DAP is most likely not enabled during normal execution.
Because the DAP is disabled by default (power on reset), the user can also power-cycle the device. The
DAP is not enabled unless it is enabled through the JTAG or SWD interface.
5.2 Initialization and Configuration
The PLL is configured using direct register writes to the RCC/RCC2 register. If the RCC2 register
is being used, the USERCC2 bit must be set and the appropriate RCC2 bit/field is used. The steps
required to successfully change the PLL-based system clock are:
1. Bypass the PLL and system clock divider by setting the BYPASS bit and clearing the USESYS
bit in the RCC register. This configures the system to run off a “raw” clock source and allows
for the new PLL configuration to be validated before switching the system clock to the PLL.
2. Select the crystal value (XTAL) and oscillator source (OSCSRC), and clear the PWRDN bit in
RCC/RCC2. Setting the XTAL field automatically pulls valid PLL configuration data for the
appropriate crystal, and clearing the PWRDN bit powers and enables the PLL and its output.
3. Select the desired system divider (SYSDIV) in RCC/RCC2 and set the USESYS bit in RCC. The
SYSDIV field determines the system frequency for the microcontroller.
4. Wait for the PLL to lock by polling the PLLLRIS bit in the Raw Interrupt Status (RIS) register.
5. Enable use of the PLL by clearing the BYPASS bit in RCC/RCC2.
5.3 Register Map
Table 5-5 on page 182 lists the System Control registers, grouped by function. The offset listed is a
hexadecimal increment to the register's address, relative to the System Control base address of
0x400F.E000.
January 08, 2011 181
Texas Instruments-Production Data
Stellaris® LM3S2965 Microcontroller
Note: Spaces in the System Control register space that are not used are reserved for future or
internal use. Software should not modify any reserved memory address.
Table 5-5. System Control Register Map
See
Offset Name Type Reset Description page
0x000 DID0 RO - Device Identification 0 184
0x004 DID1 RO - Device Identification 1 200
0x008 DC0 RO 0x00FF.007F Device Capabilities 0 202
0x010 DC1 RO 0x0311.33FF Device Capabilities 1 203
0x014 DC2 RO 0x070F.5337 Device Capabilities 2 205
0x018 DC3 RO 0xBF0F.B7FF Device Capabilities 3 207
0x01C DC4 RO 0x0000.00FF Device Capabilities 4 209
0x030 PBORCTL R/W 0x0000.7FFD Brown-Out Reset Control 186
0x034 LDOPCTL R/W 0x0000.0000 LDO Power Control 187
0x040 SRCR0 R/W 0x00000000 Software Reset Control 0 231
0x044 SRCR1 R/W 0x00000000 Software Reset Control 1 233
0x048 SRCR2 R/W 0x00000000 Software Reset Control 2 235
0x050 RIS RO 0x0000.0000 Raw Interrupt Status 188
0x054 IMC R/W 0x0000.0000 Interrupt Mask Control 189
0x058 MISC R/W1C 0x0000.0000 Masked Interrupt Status and Clear 190
0x05C RESC R/W - Reset Cause 191
0x060 RCC R/W 0x078E.3AD1 Run-Mode Clock Configuration 192
0x064 PLLCFG RO - XTAL to PLL Translation 196
0x070 RCC2 R/W 0x0780.2810 Run-Mode Clock Configuration 2 197
0x100 RCGC0 R/W 0x00000040 Run Mode Clock Gating Control Register 0 210
0x104 RCGC1 R/W 0x00000000 Run Mode Clock Gating Control Register 1 216
0x108 RCGC2 R/W 0x00000000 Run Mode Clock Gating Control Register 2 225
0x110 SCGC0 R/W 0x00000040 Sleep Mode Clock Gating Control Register 0 212
0x114 SCGC1 R/W 0x00000000 Sleep Mode Clock Gating Control Register 1 219
0x118 SCGC2 R/W 0x00000000 Sleep Mode Clock Gating Control Register 2 227
0x120 DCGC0 R/W 0x00000040 Deep Sleep Mode Clock Gating Control Register 0 214
0x124 DCGC1 R/W 0x00000000 Deep Sleep Mode Clock Gating Control Register 1 222
0x128 DCGC2 R/W 0x00000000 Deep Sleep Mode Clock Gating Control Register 2 229
0x144 DSLPCLKCFG R/W 0x0780.0000 Deep Sleep Clock Configuration 199
182 January 08, 2011
Texas Instruments-Production Data
System Control
5.4 Register Descriptions
All addresses given are relative to the System Control base address of 0x400F.E000.
January 08, 2011 183
Texas Instruments-Production Data
Stellaris® LM3S2965 Microcontroller
Register 1: Device Identification 0 (DID0), offset 0x000
This register identifies the version of the device.
Device Identification 0 (DID0)
Base 0x400F.E000
Offset 0x000
Type RO, reset -
31 30 29 28 27 26 25 24 23 22 21 20 19 18 17 16
reserved VER reserved CLASS
Type RO RO RO RO RO RO RO RO RO RO RO RO RO RO RO RO
Reset 0 0 0 1 0 0 0 0 0 0 0 0 0 0 0 1
15 14 13 12 11 10 9 8 7 6 5 4 3 2 1 0
MAJOR MINOR
Type RO RO RO RO RO RO RO RO RO RO RO RO RO RO RO RO
Reset - - - - - - - - - - - - - - - -
Bit/Field Name Type Reset Description
Software should not rely on the value of a reserved bit. To provide
compatibility with future products, the value of a reserved bit should be
preserved across a read-modify-write operation.
31 reserved RO 0
DID0 Version
This field defines the DID0 register format version. The version number
is numeric. The value of the VER field is encoded as follows:
Value Description
0x1 Second version of the DID0 register format.
30:28 VER RO 0x1
Software should not rely on the value of a reserved bit. To provide
compatibility with future products, the value of a reserved bit should be
preserved across a read-modify-write operation.
27:24 reserved RO 0x0
Device Class
The CLASS field value identifies the internal design from which all mask
sets are generated for all devices in a particular product line. The CLASS
field value is changed for new product lines, for changes in fab process
(for example, a remap or shrink), or any case where the MAJOR or MINOR
fields require differentiation from prior devices. The value of the CLASS
field is encoded as follows (all other encodings are reserved):
Value Description
0x1 Stellaris® Fury-class devices.
23:16 CLASS RO 0x1
184 January 08, 2011
Texas Instruments-Production Data
System Control
Bit/Field Name Type Reset Description
Major Revision
This field specifies the major revision number of the device. The major
revision reflects changes to base layers of the design. The major revision
number is indicated in the part number as a letter (A for first revision, B
for second, and so on). This field is encoded as follows:
Value Description
0x0 Revision A (initial device)
0x1 Revision B (first base layer revision)
0x2 Revision C (second base layer revision)
and so on.
15:8 MAJOR RO -
Minor Revision
This field specifies the minor revision number of the device. The minor
revision reflects changes to the metal layers of the design. The MINOR
field value is reset when the MAJOR field is changed. This field is numeric
and is encoded as follows:
Value Description
0x0 Initial device, or a major revision update.
0x1 First metal layer change.
0x2 Second metal layer change.
and so on.
7:0 MINOR RO -
January 08, 2011 185
Texas Instruments-Production Data
Stellaris® LM3S2965 Microcontroller
Register 2: Brown-Out Reset Control (PBORCTL), offset 0x030
This register is responsible for controlling reset conditions after initial power-on reset.
Brown-Out Reset Control (PBORCTL)
Base 0x400F.E000
Offset 0x030
Type R/W, reset 0x0000.7FFD
31 30 29 28 27 26 25 24 23 22 21 20 19 18 17 16
reserved
Type RO RO RO RO RO RO RO RO RO RO RO RO RO RO RO RO
Reset 0 0 0 0 0 0 0 0 0 0 0 0 0 0 0 0
15 14 13 12 11 10 9 8 7 6 5 4 3 2 1 0
reserved BORIOR reserved
Type RO RO RO RO RO RO RO RO RO RO RO RO RO RO R/W RO
Reset 0 0 0 0 0 0 0 0 0 0 0 0 0 0 0 0
Bit/Field Name Type Reset Description
Software should not rely on the value of a reserved bit. To provide
compatibility with future products, the value of a reserved bit should be
preserved across a read-modify-write operation.
31:2 reserved RO 0x0
BOR Interrupt or Reset
This bit controls how a BOR event is signaled to the controller. If set, a
reset is signaled. Otherwise, an interrupt is signaled.
1 BORIOR R/W 0
Software should not rely on the value of a reserved bit. To provide
compatibility with future products, the value of a reserved bit should be
preserved across a read-modify-write operation.
0 reserved RO 0
186 January 08, 2011
Texas Instruments-Production Data
System Control
Register 3: LDO Power Control (LDOPCTL), offset 0x034
The VADJ field in this register adjusts the on-chip output voltage (VOUT).
LDO Power Control (LDOPCTL)
Base 0x400F.E000
Offset 0x034
Type R/W, reset 0x0000.0000
31 30 29 28 27 26 25 24 23 22 21 20 19 18 17 16
reserved
Type RO RO RO RO RO RO RO RO RO RO RO RO RO RO RO RO
Reset 0 0 0 0 0 0 0 0 0 0 0 0 0 0 0 0
15 14 13 12 11 10 9 8 7 6 5 4 3 2 1 0
reserved VADJ
Type RO RO RO RO RO RO RO RO RO RO R/W R/W R/W R/W R/W R/W
Reset 0 0 0 0 0 0 0 0 0 0 0 0 0 0 0 0
Bit/Field Name Type Reset Description
Software should not rely on the value of a reserved bit. To provide
compatibility with future products, the value of a reserved bit should be
preserved across a read-modify-write operation.
31:6 reserved RO 0
LDO Output Voltage
This field sets the on-chip output voltage. The programming values for
the VADJ field are provided below.
Value VOUT (V)
0x00 2.50
0x01 2.45
0x02 2.40
0x03 2.35
0x04 2.30
0x05 2.25
0x06-0x3F Reserved
0x1B 2.75
0x1C 2.70
0x1D 2.65
0x1E 2.60
0x1F 2.55
5:0 VADJ R/W 0x0
January 08, 2011 187
Texas Instruments-Production Data
Stellaris® LM3S2965 Microcontroller
Register 4: Raw Interrupt Status (RIS), offset 0x050
Central location for system control raw interrupts. These are set and cleared by hardware.
Raw Interrupt Status (RIS)
Base 0x400F.E000
Offset 0x050
Type RO, reset 0x0000.0000
31 30 29 28 27 26 25 24 23 22 21 20 19 18 17 16
reserved
Type RO RO RO RO RO RO RO RO RO RO RO RO RO RO RO RO
Reset 0 0 0 0 0 0 0 0 0 0 0 0 0 0 0 0
15 14 13 12 11 10 9 8 7 6 5 4 3 2 1 0
reserved PLLLRIS reserved BORRIS reserved
Type RO RO RO RO RO RO RO RO RO RO RO RO RO RO RO RO
Reset 0 0 0 0 0 0 0 0 0 0 0 0 0 0 0 0
Bit/Field Name Type Reset Description
Software should not rely on the value of a reserved bit. To provide
compatibility with future products, the value of a reserved bit should be
preserved across a read-modify-write operation.
31:7 reserved RO 0
PLL Lock Raw Interrupt Status
This bit is set when the PLL TREADY Timer asserts.
6 PLLLRIS RO 0
Software should not rely on the value of a reserved bit. To provide
compatibility with future products, the value of a reserved bit should be
preserved across a read-modify-write operation.
5:2 reserved RO 0
Brown-Out Reset Raw Interrupt Status
This bit is the raw interrupt status for any brown-out conditions. If set,
a brown-out condition is currently active. This is an unregistered signal
from the brown-out detection circuit. An interrupt is reported if the BORIM
bit in the IMC register is set and the BORIOR bit in the PBORCTL register
is cleared.
1 BORRIS RO 0
Software should not rely on the value of a reserved bit. To provide
compatibility with future products, the value of a reserved bit should be
preserved across a read-modify-write operation.
0 reserved RO 0
188 January 08, 2011
Texas Instruments-Production Data
System Control
Register 5: Interrupt Mask Control (IMC), offset 0x054
Central location for system control interrupt masks.
Interrupt Mask Control (IMC)
Base 0x400F.E000
Offset 0x054
Type R/W, reset 0x0000.0000
31 30 29 28 27 26 25 24 23 22 21 20 19 18 17 16
reserved
Type RO RO RO RO RO RO RO RO RO RO RO RO RO RO RO RO
Reset 0 0 0 0 0 0 0 0 0 0 0 0 0 0 0 0
15 14 13 12 11 10 9 8 7 6 5 4 3 2 1 0
reserved PLLLIM reserved BORIM reserved
Type RO RO RO RO RO RO RO RO RO R/W RO RO RO RO R/W RO
Reset 0 0 0 0 0 0 0 0 0 0 0 0 0 0 0 0
Bit/Field Name Type Reset Description
Software should not rely on the value of a reserved bit. To provide
compatibility with future products, the value of a reserved bit should be
preserved across a read-modify-write operation.
31:7 reserved RO 0
PLL Lock Interrupt Mask
This bit specifies whether a PLL Lock interrupt is promoted to a controller
interrupt. If set, an interrupt is generated if PLLLRIS in RIS is set;
otherwise, an interrupt is not generated.
6 PLLLIM R/W 0
Software should not rely on the value of a reserved bit. To provide
compatibility with future products, the value of a reserved bit should be
preserved across a read-modify-write operation.
5:2 reserved RO 0
Brown-Out Reset Interrupt Mask
This bit specifies whether a brown-out condition is promoted to a
controller interrupt. If set, an interrupt is generated if BORRIS is set;
otherwise, an interrupt is not generated.
1 BORIM R/W 0
Software should not rely on the value of a reserved bit. To provide
compatibility with future products, the value of a reserved bit should be
preserved across a read-modify-write operation.
0 reserved RO 0
January 08, 2011 189
Texas Instruments-Production Data
Stellaris® LM3S2965 Microcontroller
Register 6: Masked Interrupt Status and Clear (MISC), offset 0x058
On a read, this register gives the current masked status value of the corresponding interrupt. All of
the bits are R/W1C and this action also clears the corresponding raw interrupt bit in the RIS register
(see page 188).
Masked Interrupt Status and Clear (MISC)
Base 0x400F.E000
Offset 0x058
Type R/W1C, reset 0x0000.0000
31 30 29 28 27 26 25 24 23 22 21 20 19 18 17 16
reserved
Type RO RO RO RO RO RO RO RO RO RO RO RO RO RO RO RO
Reset 0 0 0 0 0 0 0 0 0 0 0 0 0 0 0 0
15 14 13 12 11 10 9 8 7 6 5 4 3 2 1 0
reserved PLLLMIS reserved BORMIS reserved
Type RO RO RO RO RO RO RO RO RO R/W1C RO RO RO RO R/W1C RO
Reset 0 0 0 0 0 0 0 0 0 0 0 0 0 0 0 0
Bit/Field Name Type Reset Description
Software should not rely on the value of a reserved bit. To provide
compatibility with future products, the value of a reserved bit should be
preserved across a read-modify-write operation.
31:7 reserved RO 0
PLL Lock Masked Interrupt Status
This bit is set when the PLL TREADY timer asserts. The interrupt is cleared
by writing a 1 to this bit.
6 PLLLMIS R/W1C 0
Software should not rely on the value of a reserved bit. To provide
compatibility with future products, the value of a reserved bit should be
preserved across a read-modify-write operation.
5:2 reserved RO 0
BOR Masked Interrupt Status
The BORMIS is simply the BORRIS ANDed with the mask value, BORIM.
1 BORMIS R/W1C 0
Software should not rely on the value of a reserved bit. To provide
compatibility with future products, the value of a reserved bit should be
preserved across a read-modify-write operation.
0 reserved RO 0
190 January 08, 2011
Texas Instruments-Production Data
System Control
Register 7: Reset Cause (RESC), offset 0x05C
This register is set with the reset cause after reset. The bits in this register are sticky and maintain
their state across multiple reset sequences, except when an power-on reset is the cause, in which
case, all bits other than POR in the RESC register are cleared.
Reset Cause (RESC)
Base 0x400F.E000
Offset 0x05C
Type R/W, reset -
31 30 29 28 27 26 25 24 23 22 21 20 19 18 17 16
reserved
Type RO RO RO RO RO RO RO RO RO RO RO RO RO RO RO RO
Reset 0 0 0 0 0 0 0 0 0 0 0 0 0 0 0 0
15 14 13 12 11 10 9 8 7 6 5 4 3 2 1 0
reserved SW WDT BOR POR EXT
Type RO RO RO RO RO RO RO RO RO RO RO R/W R/W R/W R/W R/W
Reset 0 0 0 0 0 0 0 0 0 0 0 - - - - -
Bit/Field Name Type Reset Description
Software should not rely on the value of a reserved bit. To provide
compatibility with future products, the value of a reserved bit should be
preserved across a read-modify-write operation.
31:5 reserved RO 0
Software Reset
When set, indicates a software reset is the cause of the reset event.
4 SW R/W -
Watchdog Timer Reset
When set, indicates a watchdog reset is the cause of the reset event.
3 WDT R/W -
Brown-Out Reset
When set, indicates a brown-out reset is the cause of the reset event.
2 BOR R/W -
Power-On Reset
When set, indicates a power-on reset is the cause of the reset event.
1 POR R/W -
External Reset
When set, indicates an external reset (RST assertion) is the cause of
the reset event.
0 EXT R/W -
January 08, 2011 191
Texas Instruments-Production Data
Stellaris® LM3S2965 Microcontroller
Register 8: Run-Mode Clock Configuration (RCC), offset 0x060
This register is defined to provide source control and frequency speed.
Run-Mode Clock Configuration (RCC)
Base 0x400F.E000
Offset 0x060
Type R/W, reset 0x078E.3AD1
31 30 29 28 27 26 25 24 23 22 21 20 19 18 17 16
reserved ACG SYSDIV USESYSDIV reserved USEPWMDIV PWMDIV reserved
Type RO RO RO RO R/W R/W R/W R/W R/W R/W RO R/W R/W R/W R/W RO
Reset 0 0 0 0 0 1 1 1 1 0 0 0 1 1 1 0
15 14 13 12 11 10 9 8 7 6 5 4 3 2 1 0
reserved PWRDN reserved BYPASS reserved XTAL OSCSRC reserved IOSCDIS MOSCDIS
Type RO RO R/W RO R/W RO R/W R/W R/W R/W R/W R/W RO RO R/W R/W
Reset 0 0 1 1 1 0 1 0 1 1 0 1 0 0 0 1
Bit/Field Name Type Reset Description
Software should not rely on the value of a reserved bit. To provide
compatibility with future products, the value of a reserved bit should be
preserved across a read-modify-write operation.
31:28 reserved RO 0x0
Auto Clock Gating
This bit specifies whether the system uses the Sleep-Mode Clock
Gating Control (SCGCn) registers and Deep-Sleep-Mode Clock
Gating Control (DCGCn) registers if the controller enters a Sleep or
Deep-Sleep mode (respectively). If set, the SCGCn or DCGCn registers
are used to control the clocks distributed to the peripherals when the
controller is in a sleep mode. Otherwise, the Run-Mode Clock Gating
Control (RCGCn) registers are used when the controller enters a sleep
mode.
The RCGCn registers are always used to control the clocks in Run
mode.
This allows peripherals to consume less power when the controller is
in a sleep mode and the peripheral is unused.
27 ACG R/W 0
System Clock Divisor
Specifies which divisor is used to generate the system clock from either
the PLL output or the oscillator source (depending on how the BYPASS
bit in this register is configured). See Table 5-3 on page 178 for bit
encodings.
If the SYSDIV value is less than MINSYSDIV (see page 203), and the
PLL is being used, then the MINSYSDIV value is used as the divisor.
If the PLL is not being used, the SYSDIV value can be less than
MINSYSDIV.
26:23 SYSDIV R/W 0xF
Enable System Clock Divider
Use the system clock divider as the source for the system clock. The
system clock divider is forced to be used when the PLL is selected as
the source.
If the USERCC2 bit in the RCC2 register is set, then the SYSDIV2 field
in the RCC2 register is used as the system clock divider rather than the
SYSDIV field in this register.
22 USESYSDIV R/W 0
Software should not rely on the value of a reserved bit. To provide
compatibility with future products, the value of a reserved bit should be
preserved across a read-modify-write operation.
21 reserved RO 0
192 January 08, 2011
Texas Instruments-Production Data
System Control
Bit/Field Name Type Reset Description
Enable PWM Clock Divisor
Use the PWM clock divider as the source for the PWM clock.
20 USEPWMDIV R/W 0
PWM Unit Clock Divisor
This field specifies the binary divisor used to predivide the system clock
down for use as the timing reference for the PWM module. This clock
is only power 2 divide and rising edge is synchronous without phase
shift from the system clock.
Value Divisor
0x0 /2
0x1 /4
0x2 /8
0x3 /16
0x4 /32
0x5 /64
0x6 /64
0x7 /64 (default)
19:17 PWMDIV R/W 0x7
Software should not rely on the value of a reserved bit. To provide
compatibility with future products, the value of a reserved bit should be
preserved across a read-modify-write operation.
16:14 reserved RO 0
PLL Power Down
This bit connects to the PLL PWRDN input. The reset value of 1 powers
down the PLL.
13 PWRDN R/W 1
Software should not rely on the value of a reserved bit. To provide
compatibility with future products, the value of a reserved bit should be
preserved across a read-modify-write operation.
12 reserved RO 1
PLL Bypass
Chooses whether the system clock is derived from the PLL output or
the OSC source. If set, the clock that drives the system is the OSC
source. Otherwise, the clock that drives the system is the PLL output
clock divided by the system divider.
See Table 5-3 on page 178 for programming guidelines.
Note: The ADC must be clocked from the PLL or directly from a
14-MHz to 18-MHz clock source to operate properly. While
the ADC works in a 14-18 MHz range, to maintain a 1 M
sample/second rate, the ADC must be provided a 16-MHz
clock source.
11 BYPASS R/W 1
Software should not rely on the value of a reserved bit. To provide
compatibility with future products, the value of a reserved bit should be
preserved across a read-modify-write operation.
10 reserved RO 0
January 08, 2011 193
Texas Instruments-Production Data
Stellaris® LM3S2965 Microcontroller
Bit/Field Name Type Reset Description
Crystal Value
This field specifies the crystal value attached to the main oscillator. The
encoding for this field is provided below. Depending on the crystal used,
the PLL frequency may not be exactly 400 MHz (see Table
22-9 on page 683 for more information).
Crystal Frequency (MHz) Using
the PLL
Crystal Frequency (MHz) Not
Using the PLL
Value
0x0 1.000 reserved
0x1 1.8432 reserved
0x2 2.000 reserved
0x3 2.4576 reserved
0x4 3.579545 MHz
0x5 3.6864 MHz
0x6 4 MHz
0x7 4.096 MHz
0x8 4.9152 MHz
0x9 5 MHz
0xA 5.12 MHz
0xB 6 MHz (reset value)
0xC 6.144 MHz
0xD 7.3728 MHz
0xE 8 MHz
0xF 8.192 MHz
9:6 XTAL R/W 0xB
Oscillator Source
Selects the input source for the OSC. The values are:
Value Input Source
MOSC
Main oscillator
0x0
IOSC
Internal oscillator (default)
0x1
IOSC/4
Internal oscillator / 4
0x2
30 kHz
30-KHz internal oscillator
0x3
For additional oscillator sources, see the RCC2 register.
5:4 OSCSRC R/W 0x1
Software should not rely on the value of a reserved bit. To provide
compatibility with future products, the value of a reserved bit should be
preserved across a read-modify-write operation.
3:2 reserved RO 0x0
Internal Oscillator Disable
0: Internal oscillator (IOSC) is enabled.
1: Internal oscillator is disabled.
1 IOSCDIS R/W 0
194 January 08, 2011
Texas Instruments-Production Data
System Control
Bit/Field Name Type Reset Description
Main Oscillator Disable
0: Main oscillator is enabled .
1: Main oscillator is disabled (default).
0 MOSCDIS R/W 1
January 08, 2011 195
Texas Instruments-Production Data
Stellaris® LM3S2965 Microcontroller
Register 9: XTAL to PLL Translation (PLLCFG), offset 0x064
This register provides a means of translating external crystal frequencies into the appropriate PLL
settings. This register is initialized during the reset sequence and updated anytime that the XTAL
field changes in the Run-Mode Clock Configuration (RCC) register (see page 192).
The PLL frequency is calculated using the PLLCFG field values, as follows:
PLLFreq = OSCFreq * F / (R + 1)
XTAL to PLL Translation (PLLCFG)
Base 0x400F.E000
Offset 0x064
Type RO, reset -
31 30 29 28 27 26 25 24 23 22 21 20 19 18 17 16
reserved
Type RO RO RO RO RO RO RO RO RO RO RO RO RO RO RO RO
Reset 0 0 0 0 0 0 0 0 0 0 0 0 0 0 0 0
15 14 13 12 11 10 9 8 7 6 5 4 3 2 1 0
reserved F R
Type RO RO RO RO RO RO RO RO RO RO RO RO RO RO RO RO
Reset 0 0 - - - - - - - - - - - - - -
Bit/Field Name Type Reset Description
Software should not rely on the value of a reserved bit. To provide
compatibility with future products, the value of a reserved bit should be
preserved across a read-modify-write operation.
31:14 reserved RO 0x0
PLL F Value
This field specifies the value supplied to the PLL’s F input.
13:5 F RO -
PLL R Value
This field specifies the value supplied to the PLL’s R input.
4:0 R RO -
196 January 08, 2011
Texas Instruments-Production Data
System Control
Register 10: Run-Mode Clock Configuration 2 (RCC2), offset 0x070
This register overrides the RCC equivalent register fields, as shown in Table 5-6, when the USERCC2
bit is set, allowing the extended capabilities of the RCC2 register to be used while also providing a
means to be backward-compatible to previous parts. Each RCC2 field that supersedes an RCC
field is located at the same LSB bit position; however, some RCC2 fields are larger than the
corresponding RCC field.
Table 5-6. RCC2 Fields that Override RCC fields
RCC2 Field... Overrides RCC Field
SYSDIV2, bits[28:23] SYSDIV, bits[26:23]
PWRDN2, bit[13] PWRDN, bit[13]
BYPASS2, bit[11] BYPASS, bit[11]
OSCSRC2, bits[6:4] OSCSRC, bits[5:4]
Run-Mode Clock Configuration 2 (RCC2)
Base 0x400F.E000
Offset 0x070
Type R/W, reset 0x0780.2810
31 30 29 28 27 26 25 24 23 22 21 20 19 18 17 16
USERCC2 reserved SYSDIV2 reserved
Type R/W RO RO R/W R/W R/W R/W R/W R/W RO RO RO RO RO RO RO
Reset 0 0 0 0 0 1 1 1 1 0 0 0 0 0 0 0
15 14 13 12 11 10 9 8 7 6 5 4 3 2 1 0
reserved PWRDN2 reserved BYPASS2 reserved OSCSRC2 reserved
Type RO RO R/W RO R/W RO RO RO RO R/W R/W R/W RO RO RO RO
Reset 0 0 1 0 1 0 0 0 0 0 0 1 0 0 0 0
Bit/Field Name Type Reset Description
Use RCC2
When set, overrides the RCC register fields.
31 USERCC2 R/W 0
Software should not rely on the value of a reserved bit. To provide
compatibility with future products, the value of a reserved bit should be
preserved across a read-modify-write operation.
30:29 reserved RO 0x0
System Clock Divisor
Specifies which divisor is used to generate the system clock from either
the PLL output or the oscillator source (depending on how the BYPASS2
bit is configured). SYSDIV2 is used for the divisor when both the
USESYSDIV bit in the RCC register and the USERCC2 bit in this register
are set. See Table 5-4 on page 178 for programming guidelines.
28:23 SYSDIV2 R/W 0x0F
Software should not rely on the value of a reserved bit. To provide
compatibility with future products, the value of a reserved bit should be
preserved across a read-modify-write operation.
22:14 reserved RO 0x0
Power-Down PLL
When set, powers down the PLL.
13 PWRDN2 R/W 1
Software should not rely on the value of a reserved bit. To provide
compatibility with future products, the value of a reserved bit should be
preserved across a read-modify-write operation.
12 reserved RO 0
January 08, 2011 197
Texas Instruments-Production Data
Stellaris® LM3S2965 Microcontroller
Bit/Field Name Type Reset Description
Bypass PLL
When set, bypasses the PLL for the clock source.
See Table 5-4 on page 178 for programming guidelines.
11 BYPASS2 R/W 1
Software should not rely on the value of a reserved bit. To provide
compatibility with future products, the value of a reserved bit should be
preserved across a read-modify-write operation.
10:7 reserved RO 0x0
Oscillator Source
Selects the input source for the OSC. The values are:
Value Description
MOSC
Main oscillator
0x0
IOSC
Internal oscillator
0x1
IOSC/4
Internal oscillator / 4
0x2
30 kHz
30-kHz internal oscillator
0x3
0x4 Reserved
0x5 Reserved
0x6 Reserved
32 kHz
32.768-kHz external oscillator
0x7
6:4 OSCSRC2 R/W 0x1
Software should not rely on the value of a reserved bit. To provide
compatibility with future products, the value of a reserved bit should be
preserved across a read-modify-write operation.
3:0 reserved RO 0
198 January 08, 2011
Texas Instruments-Production Data
System Control
Register 11: Deep Sleep Clock Configuration (DSLPCLKCFG), offset 0x144
This register provides configuration information for the hardware control of Deep Sleep Mode.
Deep Sleep Clock Configuration (DSLPCLKCFG)
Base 0x400F.E000
Offset 0x144
Type R/W, reset 0x0780.0000
31 30 29 28 27 26 25 24 23 22 21 20 19 18 17 16
reserved DSDIVORIDE reserved
Type RO RO RO R/W R/W R/W R/W R/W R/W RO RO RO RO RO RO RO
Reset 0 0 0 0 0 1 1 1 1 0 0 0 0 0 0 0
15 14 13 12 11 10 9 8 7 6 5 4 3 2 1 0
reserved DSOSCSRC reserved
Type RO RO RO RO RO RO RO RO RO R/W R/W R/W RO RO RO RO
Reset 0 0 0 0 0 0 0 0 0 0 0 0 0 0 0 0
Bit/Field Name Type Reset Description
Software should not rely on the value of a reserved bit. To provide
compatibility with future products, the value of a reserved bit should be
preserved across a read-modify-write operation.
31:29 reserved RO 0x0
Divider Field Override
6-bit system divider field to override when Deep-Sleep occurs with PLL
running.
28:23 DSDIVORIDE R/W 0x0F
Software should not rely on the value of a reserved bit. To provide
compatibility with future products, the value of a reserved bit should be
preserved across a read-modify-write operation.
22:7 reserved RO 0x0
Clock Source
Specifies the clock source during Deep-Sleep mode.
Value Description
MOSC
Use main oscillator as source.
0x0
IOSC
Use internal 12-MHz oscillator as source.
0x1
0x2 Reserved
30 kHz
Use 30-kHz internal oscillator as source.
0x3
0x4 Reserved
0x5 Reserved
0x6 Reserved
32 kHz
Use 32.768-kHz external oscillator as source.
0x7
6:4 DSOSCSRC R/W 0x0
Software should not rely on the value of a reserved bit. To provide
compatibility with future products, the value of a reserved bit should be
preserved across a read-modify-write operation.
3:0 reserved RO 0x0
January 08, 2011 199
Texas Instruments-Production Data
Stellaris® LM3S2965 Microcontroller
Register 12: Device Identification 1 (DID1), offset 0x004
This register identifies the device family, part number, temperature range, pin count, and package
type.
Device Identification 1 (DID1)
Base 0x400F.E000
Offset 0x004
Type RO, reset -
31 30 29 28 27 26 25 24 23 22 21 20 19 18 17 16
VER FAM PARTNO
Type RO RO RO RO RO RO RO RO RO RO RO RO RO RO RO RO
Reset 0 0 0 1 0 0 0 0 0 1 0 1 0 1 0 1
15 14 13 12 11 10 9 8 7 6 5 4 3 2 1 0
PINCOUNT reserved TEMP PKG ROHS QUAL
Type RO RO RO RO RO RO RO RO RO RO RO RO RO RO RO RO
Reset 0 1 0 0 0 0 0 0 - - - - - 1 - -
Bit/Field Name Type Reset Description
DID1 Version
This field defines the DID1 register format version. The version number
is numeric. The value of the VER field is encoded as follows (all other
encodings are reserved):
Value Description
0x1 Second version of the DID1 register format.
31:28 VER RO 0x1
Family
This field provides the family identification of the device within the
Luminary Micro product portfolio. The value is encoded as follows (all
other encodings are reserved):
Value Description
Stellaris family of microcontollers, that is, all devices with
external part numbers starting with LM3S.
0x0
27:24 FAM RO 0x0
Part Number
This field provides the part number of the device within the family. The
value is encoded as follows (all other encodings are reserved):
Value Description
0x55 LM3S2965
23:16 PARTNO RO 0x55
Package Pin Count
This field specifies the number of pins on the device package. The value
is encoded as follows (all other encodings are reserved):
Value Description
0x2 100-pin or 108-ball package
15:13 PINCOUNT RO 0x2
200 January 08, 2011
Texas Instruments-Production Data
System Control
Bit/Field Name Type Reset Description
Software should not rely on the value of a reserved bit. To provide
compatibility with future products, the value of a reserved bit should be
preserved across a read-modify-write operation.
12:8 reserved RO 0
Temperature Range
This field specifies the temperature rating of the device. The value is
encoded as follows (all other encodings are reserved):
Value Description
0x0 Commercial temperature range (0°C to 70°C)
0x1 Industrial temperature range (-40°C to 85°C)
0x2 Extended temperature range (-40°C to 105°C)
7:5 TEMP RO -
Package Type
This field specifies the package type. The value is encoded as follows
(all other encodings are reserved):
Value Description
0x0 SOIC package
0x1 LQFP package
0x2 BGA package
4:3 PKG RO -
RoHS-Compliance
This bit specifies whether the device is RoHS-compliant. A 1 indicates
the part is RoHS-compliant.
2 ROHS RO 1
Qualification Status
This field specifies the qualification status of the device. The value is
encoded as follows (all other encodings are reserved):
Value Description
0x0 Engineering Sample (unqualified)
0x1 Pilot Production (unqualified)
0x2 Fully Qualified
1:0 QUAL RO -
January 08, 2011 201
Texas Instruments-Production Data
Stellaris® LM3S2965 Microcontroller
Register 13: Device Capabilities 0 (DC0), offset 0x008
This register is predefined by the part and can be used to verify features.
Device Capabilities 0 (DC0)
Base 0x400F.E000
Offset 0x008
Type RO, reset 0x00FF.007F
31 30 29 28 27 26 25 24 23 22 21 20 19 18 17 16
SRAMSZ
Type RO RO RO RO RO RO RO RO RO RO RO RO RO RO RO RO
Reset 0 0 0 0 0 0 0 0 1 1 1 1 1 1 1 1
15 14 13 12 11 10 9 8 7 6 5 4 3 2 1 0
FLASHSZ
Type RO RO RO RO RO RO RO RO RO RO RO RO RO RO RO RO
Reset 0 0 0 0 0 0 0 0 0 1 1 1 1 1 1 1
Bit/Field Name Type Reset Description
SRAM Size
Indicates the size of the on-chip SRAM memory.
Value Description
0x00FF 64 KB of SRAM
31:16 SRAMSZ RO 0x00FF
Flash Size
Indicates the size of the on-chip flash memory.
Value Description
0x007F 256 KB of Flash
15:0 FLASHSZ RO 0x007F
202 January 08, 2011
Texas Instruments-Production Data
System Control
Register 14: Device Capabilities 1 (DC1), offset 0x010
This register provides a list of features available in the system. The Stellaris family uses this register
format to indicate the availability of the following family features in the specific device: CANs, PWM,
ADC, Watchdog timer, Hibernation module, and debug capabilities. This register also indicates the
maximum clock frequency and maximum ADC sample rate. The format of this register is consistent
with the RCGC0, SCGC0, and DCGC0 clock control registers and the SRCR0 software reset control
register.
Device Capabilities 1 (DC1)
Base 0x400F.E000
Offset 0x010
Type RO, reset 0x0311.33FF
31 30 29 28 27 26 25 24 23 22 21 20 19 18 17 16
reserved CAN1 CAN0 reserved PWM reserved ADC
Type RO RO RO RO RO RO RO RO RO RO RO RO RO RO RO RO
Reset 0 0 0 0 0 0 1 1 0 0 0 1 0 0 0 1
15 14 13 12 11 10 9 8 7 6 5 4 3 2 1 0
MINSYSDIV reserved MAXADCSPD MPU HIB TEMPSNS PLL WDT SWO SWD JTAG
Type RO RO RO RO RO RO RO RO RO RO RO RO RO RO RO RO
Reset 0 0 1 1 0 0 1 1 1 1 1 1 1 1 1 1
Bit/Field Name Type Reset Description
Software should not rely on the value of a reserved bit. To provide
compatibility with future products, the value of a reserved bit should be
preserved across a read-modify-write operation.
31:26 reserved RO 0
CAN Module 1 Present
When set, indicates that CAN unit 1 is present.
25 CAN1 RO 1
CAN Module 0 Present
When set, indicates that CAN unit 0 is present.
24 CAN0 RO 1
Software should not rely on the value of a reserved bit. To provide
compatibility with future products, the value of a reserved bit should be
preserved across a read-modify-write operation.
23:21 reserved RO 0
PWM Module Present
When set, indicates that the PWM module is present.
20 PWM RO 1
Software should not rely on the value of a reserved bit. To provide
compatibility with future products, the value of a reserved bit should be
preserved across a read-modify-write operation.
19:17 reserved RO 0
ADC Module Present
When set, indicates that the ADC module is present.
16 ADC RO 1
System Clock Divider
Minimum 4-bit divider value for system clock. The reset value is
hardware-dependent. See the RCC register for how to change the
system clock divisor using the SYSDIV bit.
Value Description
0x3 Specifies a 50-MHz CPU clock with a PLL divider of 4.
15:12 MINSYSDIV RO 0x3
January 08, 2011 203
Texas Instruments-Production Data
Stellaris® LM3S2965 Microcontroller
Bit/Field Name Type Reset Description
Software should not rely on the value of a reserved bit. To provide
compatibility with future products, the value of a reserved bit should be
preserved across a read-modify-write operation.
11:10 reserved RO 0
Max ADC Speed
Indicates the maximum rate at which the ADC samples data.
Value Description
0x3 1M samples/second
9:8 MAXADCSPD RO 0x3
MPU Present
When set, indicates that the Cortex-M3 Memory Protection Unit (MPU)
module is present. See the "Cortex-M3 Peripherals" chapter in the
Stellaris Data Sheet for details on the MPU.
7 MPU RO 1
Hibernation Module Present
When set, indicates that the Hibernation module is present.
6 HIB RO 1
Temp Sensor Present
When set, indicates that the on-chip temperature sensor is present.
5 TEMPSNS RO 1
PLL Present
When set, indicates that the on-chip Phase Locked Loop (PLL) is
present.
4 PLL RO 1
Watchdog Timer Present
When set, indicates that a watchdog timer is present.
3 WDT RO 1
SWO Trace Port Present
When set, indicates that the Serial Wire Output (SWO) trace port is
present.
2 SWO RO 1
SWD Present
When set, indicates that the Serial Wire Debugger (SWD) is present.
1 SWD RO 1
JTAG Present
When set, indicates that the JTAG debugger interface is present.
0 JTAG RO 1
204 January 08, 2011
Texas Instruments-Production Data
System Control
Register 15: Device Capabilities 2 (DC2), offset 0x014
This register provides a list of features available in the system. The Stellaris family uses this register
format to indicate the availability of the following family features in the specific device: Analog
Comparators, General-Purpose Timers, I2Cs, QEIs, SSIs, and UARTs. The format of this register
is consistent with the RCGC1, SCGC1, and DCGC1 clock control registers and the SRCR1 software
reset control register.
Device Capabilities 2 (DC2)
Base 0x400F.E000
Offset 0x014
Type RO, reset 0x070F.5337
31 30 29 28 27 26 25 24 23 22 21 20 19 18 17 16
reserved COMP2 COMP1 COMP0 reserved TIMER3 TIMER2 TIMER1 TIMER0
Type RO RO RO RO RO RO RO RO RO RO RO RO RO RO RO RO
Reset 0 0 0 0 0 1 1 1 0 0 0 0 1 1 1 1
15 14 13 12 11 10 9 8 7 6 5 4 3 2 1 0
reserved I2C1 reserved I2C0 reserved QEI1 QEI0 reserved SSI1 SSI0 reserved UART2 UART1 UART0
Type RO RO RO RO RO RO RO RO RO RO RO RO RO RO RO RO
Reset 0 1 0 1 0 0 1 1 0 0 1 1 0 1 1 1
Bit/Field Name Type Reset Description
Software should not rely on the value of a reserved bit. To provide
compatibility with future products, the value of a reserved bit should be
preserved across a read-modify-write operation.
31:27 reserved RO 0
Analog Comparator 2 Present
When set, indicates that analog comparator 2 is present.
26 COMP2 RO 1
Analog Comparator 1 Present
When set, indicates that analog comparator 1 is present.
25 COMP1 RO 1
Analog Comparator 0 Present
When set, indicates that analog comparator 0 is present.
24 COMP0 RO 1
Software should not rely on the value of a reserved bit. To provide
compatibility with future products, the value of a reserved bit should be
preserved across a read-modify-write operation.
23:20 reserved RO 0
Timer 3 Present
When set, indicates that General-Purpose Timer module 3 is present.
19 TIMER3 RO 1
Timer 2 Present
When set, indicates that General-Purpose Timer module 2 is present.
18 TIMER2 RO 1
Timer 1 Present
When set, indicates that General-Purpose Timer module 1 is present.
17 TIMER1 RO 1
Timer 0 Present
When set, indicates that General-Purpose Timer module 0 is present.
16 TIMER0 RO 1
Software should not rely on the value of a reserved bit. To provide
compatibility with future products, the value of a reserved bit should be
preserved across a read-modify-write operation.
15 reserved RO 0
I2C Module 1 Present
When set, indicates that I2C module 1 is present.
14 I2C1 RO 1
January 08, 2011 205
Texas Instruments-Production Data
Stellaris® LM3S2965 Microcontroller
Bit/Field Name Type Reset Description
Software should not rely on the value of a reserved bit. To provide
compatibility with future products, the value of a reserved bit should be
preserved across a read-modify-write operation.
13 reserved RO 0
I2C Module 0 Present
When set, indicates that I2C module 0 is present.
12 I2C0 RO 1
Software should not rely on the value of a reserved bit. To provide
compatibility with future products, the value of a reserved bit should be
preserved across a read-modify-write operation.
11:10 reserved RO 0
QEI1 Present
When set, indicates that QEI module 1 is present.
9 QEI1 RO 1
QEI0 Present
When set, indicates that QEI module 0 is present.
8 QEI0 RO 1
Software should not rely on the value of a reserved bit. To provide
compatibility with future products, the value of a reserved bit should be
preserved across a read-modify-write operation.
7:6 reserved RO 0
SSI1 Present
When set, indicates that SSI module 1 is present.
5 SSI1 RO 1
SSI0 Present
When set, indicates that SSI module 0 is present.
4 SSI0 RO 1
Software should not rely on the value of a reserved bit. To provide
compatibility with future products, the value of a reserved bit should be
preserved across a read-modify-write operation.
3 reserved RO 0
UART2 Present
When set, indicates that UART module 2 is present.
2 UART2 RO 1
UART1 Present
When set, indicates that UART module 1 is present.
1 UART1 RO 1
UART0 Present
When set, indicates that UART module 0 is present.
0 UART0 RO 1
206 January 08, 2011
Texas Instruments-Production Data
System Control
Register 16: Device Capabilities 3 (DC3), offset 0x018
This register provides a list of features available in the system. The Stellaris family uses this register
format to indicate the availability of the following family features in the specific device: Analog
Comparator I/Os, CCP I/Os, ADC I/Os, and PWM I/Os.
Device Capabilities 3 (DC3)
Base 0x400F.E000
Offset 0x018
Type RO, reset 0xBF0F.B7FF
31 30 29 28 27 26 25 24 23 22 21 20 19 18 17 16
32KHZ reserved CCP5 CCP4 CCP3 CCP2 CCP1 CCP0 reserved ADC3 ADC2 ADC1 ADC0
Type RO RO RO RO RO RO RO RO RO RO RO RO RO RO RO RO
Reset 1 0 1 1 1 1 1 1 0 0 0 0 1 1 1 1
15 14 13 12 11 10 9 8 7 6 5 4 3 2 1 0
PWMFAULT reserved C2PLUS C2MINUS reserved C1PLUS C1MINUS C0O C0PLUS C0MINUS PWM5 PWM4 PWM3 PWM2 PWM1 PWM0
Type RO RO RO RO RO RO RO RO RO RO RO RO RO RO RO RO
Reset 1 0 1 1 0 1 1 1 1 1 1 1 1 1 1 1
Bit/Field Name Type Reset Description
32KHz Input Clock Available
When set, indicates an even CCP pin is present and can be used as a
32-KHz input clock.
31 32KHZ RO 1
Software should not rely on the value of a reserved bit. To provide
compatibility with future products, the value of a reserved bit should be
preserved across a read-modify-write operation.
30 reserved RO 0
CCP5 Pin Present
When set, indicates that Capture/Compare/PWM pin 5 is present.
29 CCP5 RO 1
CCP4 Pin Present
When set, indicates that Capture/Compare/PWM pin 4 is present.
28 CCP4 RO 1
CCP3 Pin Present
When set, indicates that Capture/Compare/PWM pin 3 is present.
27 CCP3 RO 1
CCP2 Pin Present
When set, indicates that Capture/Compare/PWM pin 2 is present.
26 CCP2 RO 1
CCP1 Pin Present
When set, indicates that Capture/Compare/PWM pin 1 is present.
25 CCP1 RO 1
CCP0 Pin Present
When set, indicates that Capture/Compare/PWM pin 0 is present.
24 CCP0 RO 1
Software should not rely on the value of a reserved bit. To provide
compatibility with future products, the value of a reserved bit should be
preserved across a read-modify-write operation.
23:20 reserved RO 0
ADC3 Pin Present
When set, indicates that ADC pin 3 is present.
19 ADC3 RO 1
ADC2 Pin Present
When set, indicates that ADC pin 2 is present.
18 ADC2 RO 1
January 08, 2011 207
Texas Instruments-Production Data
Stellaris® LM3S2965 Microcontroller
Bit/Field Name Type Reset Description
ADC1 Pin Present
When set, indicates that ADC pin 1 is present.
17 ADC1 RO 1
ADC0 Pin Present
When set, indicates that ADC pin 0 is present.
16 ADC0 RO 1
PWM Fault Pin Present
When set, indicates that the PWM Fault pin is present.
15 PWMFAULT RO 1
Software should not rely on the value of a reserved bit. To provide
compatibility with future products, the value of a reserved bit should be
preserved across a read-modify-write operation.
14 reserved RO 0
C2+ Pin Present
When set, indicates that the analog comparator 2 (+) input pin is present.
13 C2PLUS RO 1
C2- Pin Present
When set, indicates that the analog comparator 2 (-) input pin is present.
12 C2MINUS RO 1
Software should not rely on the value of a reserved bit. To provide
compatibility with future products, the value of a reserved bit should be
preserved across a read-modify-write operation.
11 reserved RO 0
C1+ Pin Present
When set, indicates that the analog comparator 1 (+) input pin is present.
10 C1PLUS RO 1
C1- Pin Present
When set, indicates that the analog comparator 1 (-) input pin is present.
9 C1MINUS RO 1
C0o Pin Present
When set, indicates that the analog comparator 0 output pin is present.
8 C0O RO 1
C0+ Pin Present
When set, indicates that the analog comparator 0 (+) input pin is present.
7 C0PLUS RO 1
C0- Pin Present
When set, indicates that the analog comparator 0 (-) input pin is present.
6 C0MINUS RO 1
PWM5 Pin Present
When set, indicates that the PWM pin 5 is present.
5 PWM5 RO 1
PWM4 Pin Present
When set, indicates that the PWM pin 4 is present.
4 PWM4 RO 1
PWM3 Pin Present
When set, indicates that the PWM pin 3 is present.
3 PWM3 RO 1
PWM2 Pin Present
When set, indicates that the PWM pin 2 is present.
2 PWM2 RO 1
PWM1 Pin Present
When set, indicates that the PWM pin 1 is present.
1 PWM1 RO 1
PWM0 Pin Present
When set, indicates that the PWM pin 0 is present.
0 PWM0 RO 1
208 January 08, 2011
Texas Instruments-Production Data
System Control
Register 17: Device Capabilities 4 (DC4), offset 0x01C
This register provides a list of features available in the system. The Stellaris family uses this register
format to indicate the availability of the following family features in the specific device: Ethernet MAC
and PHY, GPIOs, and CCP I/Os. The format of this register is consistent with the RCGC2, SCGC2,
and DCGC2 clock control registers and the SRCR2 software reset control register.
Device Capabilities 4 (DC4)
Base 0x400F.E000
Offset 0x01C
Type RO, reset 0x0000.00FF
31 30 29 28 27 26 25 24 23 22 21 20 19 18 17 16
reserved
Type RO RO RO RO RO RO RO RO RO RO RO RO RO RO RO RO
Reset 0 0 0 0 0 0 0 0 0 0 0 0 0 0 0 0
15 14 13 12 11 10 9 8 7 6 5 4 3 2 1 0
reserved GPIOH GPIOG GPIOF GPIOE GPIOD GPIOC GPIOB GPIOA
Type RO RO RO RO RO RO RO RO RO RO RO RO RO RO RO RO
Reset 0 0 0 0 0 0 0 0 1 1 1 1 1 1 1 1
Bit/Field Name Type Reset Description
Software should not rely on the value of a reserved bit. To provide
compatibility with future products, the value of a reserved bit should be
preserved across a read-modify-write operation.
31:8 reserved RO 0
GPIO Port H Present
When set, indicates that GPIO Port H is present.
7 GPIOH RO 1
GPIO Port G Present
When set, indicates that GPIO Port G is present.
6 GPIOG RO 1
GPIO Port F Present
When set, indicates that GPIO Port F is present.
5 GPIOF RO 1
GPIO Port E Present
When set, indicates that GPIO Port E is present.
4 GPIOE RO 1
GPIO Port D Present
When set, indicates that GPIO Port D is present.
3 GPIOD RO 1
GPIO Port C Present
When set, indicates that GPIO Port C is present.
2 GPIOC RO 1
GPIO Port B Present
When set, indicates that GPIO Port B is present.
1 GPIOB RO 1
GPIO Port A Present
When set, indicates that GPIO Port A is present.
0 GPIOA RO 1
January 08, 2011 209
Texas Instruments-Production Data
Stellaris® LM3S2965 Microcontroller
Register 18: Run Mode Clock Gating Control Register 0 (RCGC0), offset 0x100
This register controls the clock gating logic. Each bit controls a clock enable for a given interface,
function, or unit. If set, the unit receives a clock and functions. Otherwise, the unit is unclocked and
disabled (saving power). If the unit is unclocked, reads or writes to the unit will generate a bus fault.
The reset state of these bits is 0 (unclocked) unless otherwise noted, so that all functional units are
disabled. It is the responsibility of software to enable the ports necessary for the application. Note
that these registers may contain more bits than there are interfaces, functions, or units to control.
This is to assure reasonable code compatibility with other family and future parts. RCGC0 is the
clock configuration register for running operation, SCGC0 for Sleep operation, and DCGC0 for
Deep-Sleep operation. Setting the ACG bit in the Run-Mode Clock Configuration (RCC) register
specifies that the system uses sleep modes.
Run Mode Clock Gating Control Register 0 (RCGC0)
Base 0x400F.E000
Offset 0x100
Type R/W, reset 0x00000040
31 30 29 28 27 26 25 24 23 22 21 20 19 18 17 16
reserved CAN1 CAN0 reserved PWM reserved ADC
Type RO RO RO RO RO RO R/W R/W RO RO RO R/W RO RO RO R/W
Reset 0 0 0 0 0 0 0 0 0 0 0 0 0 0 0 0
15 14 13 12 11 10 9 8 7 6 5 4 3 2 1 0
reserved MAXADCSPD reserved HIB reserved WDT reserved
Type RO RO RO RO RO RO R/W R/W RO R/W RO RO R/W RO RO RO
Reset 0 0 0 0 0 0 0 0 0 1 0 0 0 0 0 0
Bit/Field Name Type Reset Description
Software should not rely on the value of a reserved bit. To provide
compatibility with future products, the value of a reserved bit should be
preserved across a read-modify-write operation.
31:26 reserved RO 0
CAN1 Clock Gating Control
This bit controls the clock gating for CAN unit 1. If set, the unit receives
a clock and functions. Otherwise, the unit is unclocked and disabled.
25 CAN1 R/W 0
CAN0 Clock Gating Control
This bit controls the clock gating for CAN unit 0. If set, the unit receives
a clock and functions. Otherwise, the unit is unclocked and disabled.
24 CAN0 R/W 0
Software should not rely on the value of a reserved bit. To provide
compatibility with future products, the value of a reserved bit should be
preserved across a read-modify-write operation.
23:21 reserved RO 0
PWM Clock Gating Control
This bit controls the clock gating for the PWM module. If set, the unit
receives a clock and functions. Otherwise, the unit is unclocked and
disabled. If the unit is unclocked, a read or write to the unit generates
a bus fault.
20 PWM R/W 0
Software should not rely on the value of a reserved bit. To provide
compatibility with future products, the value of a reserved bit should be
preserved across a read-modify-write operation.
19:17 reserved RO 0
210 January 08, 2011
Texas Instruments-Production Data
System Control
Bit/Field Name Type Reset Description
ADC0 Clock Gating Control
This bit controls the clock gating for SAR ADC module 0. If set, the unit
receives a clock and functions. Otherwise, the unit is unclocked and
disabled. If the unit is unclocked, a read or write to the unit generates
a bus fault.
16 ADC R/W 0
Software should not rely on the value of a reserved bit. To provide
compatibility with future products, the value of a reserved bit should be
preserved across a read-modify-write operation.
15:10 reserved RO 0
ADC Sample Speed
This field sets the rate at which the ADC samples data. You cannot set
the rate higher than the maximum rate. You can set the sample rate by
setting the MAXADCSPD bit as follows:
Value Description
0x3 1M samples/second
0x2 500K samples/second
0x1 250K samples/second
0x0 125K samples/second
9:8 MAXADCSPD R/W 0
Software should not rely on the value of a reserved bit. To provide
compatibility with future products, the value of a reserved bit should be
preserved across a read-modify-write operation.
7 reserved RO 0
HIB Clock Gating Control
This bit controls the clock gating for the Hibernation module. If set, the
unit receives a clock and functions. Otherwise, the unit is unclocked and
disabled.
6 HIB R/W 1
Software should not rely on the value of a reserved bit. To provide
compatibility with future products, the value of a reserved bit should be
preserved across a read-modify-write operation.
5:4 reserved RO 0
WDT Clock Gating Control
This bit controls the clock gating for the WDT module. If set, the unit
receives a clock and functions. Otherwise, the unit is unclocked and
disabled. If the unit is unclocked, a read or write to the unit generates
a bus fault.
3 WDT R/W 0
Software should not rely on the value of a reserved bit. To provide
compatibility with future products, the value of a reserved bit should be
preserved across a read-modify-write operation.
2:0 reserved RO 0
January 08, 2011 211
Texas Instruments-Production Data
Stellaris® LM3S2965 Microcontroller
Register 19: Sleep Mode Clock Gating Control Register 0 (SCGC0), offset
0x110
This register controls the clock gating logic. Each bit controls a clock enable for a given interface,
function, or unit. If set, the unit receives a clock and functions. Otherwise, the unit is unclocked and
disabled (saving power). If the unit is unclocked, reads or writes to the unit will generate a bus fault.
The reset state of these bits is 0 (unclocked) unless otherwise noted, so that all functional units are
disabled. It is the responsibility of software to enable the ports necessary for the application. Note
that these registers may contain more bits than there are interfaces, functions, or units to control.
This is to assure reasonable code compatibility with other family and future parts. RCGC0 is the
clock configuration register for running operation, SCGC0 for Sleep operation, and DCGC0 for
Deep-Sleep operation. Setting the ACG bit in the Run-Mode Clock Configuration (RCC) register
specifies that the system uses sleep modes.
Sleep Mode Clock Gating Control Register 0 (SCGC0)
Base 0x400F.E000
Offset 0x110
Type R/W, reset 0x00000040
31 30 29 28 27 26 25 24 23 22 21 20 19 18 17 16
reserved CAN1 CAN0 reserved PWM reserved ADC
Type RO RO RO RO RO RO R/W R/W RO RO RO R/W RO RO RO R/W
Reset 0 0 0 0 0 0 0 0 0 0 0 0 0 0 0 0
15 14 13 12 11 10 9 8 7 6 5 4 3 2 1 0
reserved MAXADCSPD reserved HIB reserved WDT reserved
Type RO RO RO RO RO RO R/W R/W RO R/W RO RO R/W RO RO RO
Reset 0 0 0 0 0 0 0 0 0 1 0 0 0 0 0 0
Bit/Field Name Type Reset Description
Software should not rely on the value of a reserved bit. To provide
compatibility with future products, the value of a reserved bit should be
preserved across a read-modify-write operation.
31:26 reserved RO 0
CAN1 Clock Gating Control
This bit controls the clock gating for CAN unit 1. If set, the unit receives
a clock and functions. Otherwise, the unit is unclocked and disabled.
25 CAN1 R/W 0
CAN0 Clock Gating Control
This bit controls the clock gating for CAN unit 0. If set, the unit receives
a clock and functions. Otherwise, the unit is unclocked and disabled.
24 CAN0 R/W 0
Software should not rely on the value of a reserved bit. To provide
compatibility with future products, the value of a reserved bit should be
preserved across a read-modify-write operation.
23:21 reserved RO 0
PWM Clock Gating Control
This bit controls the clock gating for the PWM module. If set, the unit
receives a clock and functions. Otherwise, the unit is unclocked and
disabled. If the unit is unclocked, a read or write to the unit generates
a bus fault.
20 PWM R/W 0
Software should not rely on the value of a reserved bit. To provide
compatibility with future products, the value of a reserved bit should be
preserved across a read-modify-write operation.
19:17 reserved RO 0
212 January 08, 2011
Texas Instruments-Production Data
System Control
Bit/Field Name Type Reset Description
ADC0 Clock Gating Control
This bit controls the clock gating for SAR ADC module 0. If set, the unit
receives a clock and functions. Otherwise, the unit is unclocked and
disabled. If the unit is unclocked, a read or write to the unit generates
a bus fault.
16 ADC R/W 0
Software should not rely on the value of a reserved bit. To provide
compatibility with future products, the value of a reserved bit should be
preserved across a read-modify-write operation.
15:10 reserved RO 0
ADC Sample Speed
This field sets the rate at which the ADC samples data. You cannot set
the rate higher than the maximum rate. You can set the sample rate by
setting the MAXADCSPD bit as follows:
Value Description
0x3 1M samples/second
0x2 500K samples/second
0x1 250K samples/second
0x0 125K samples/second
9:8 MAXADCSPD R/W 0
Software should not rely on the value of a reserved bit. To provide
compatibility with future products, the value of a reserved bit should be
preserved across a read-modify-write operation.
7 reserved RO 0
HIB Clock Gating Control
This bit controls the clock gating for the Hibernation module. If set, the
unit receives a clock and functions. Otherwise, the unit is unclocked and
disabled.
6 HIB R/W 1
Software should not rely on the value of a reserved bit. To provide
compatibility with future products, the value of a reserved bit should be
preserved across a read-modify-write operation.
5:4 reserved RO 0
WDT Clock Gating Control
This bit controls the clock gating for the WDT module. If set, the unit
receives a clock and functions. Otherwise, the unit is unclocked and
disabled. If the unit is unclocked, a read or write to the unit generates
a bus fault.
3 WDT R/W 0
Software should not rely on the value of a reserved bit. To provide
compatibility with future products, the value of a reserved bit should be
preserved across a read-modify-write operation.
2:0 reserved RO 0
January 08, 2011 213
Texas Instruments-Production Data
Stellaris® LM3S2965 Microcontroller
Register 20: Deep Sleep Mode Clock Gating Control Register 0 (DCGC0),
offset 0x120
This register controls the clock gating logic. Each bit controls a clock enable for a given interface,
function, or unit. If set, the unit receives a clock and functions. Otherwise, the unit is unclocked and
disabled (saving power). If the unit is unclocked, reads or writes to the unit will generate a bus fault.
The reset state of these bits is 0 (unclocked) unless otherwise noted, so that all functional units are
disabled. It is the responsibility of software to enable the ports necessary for the application. Note
that these registers may contain more bits than there are interfaces, functions, or units to control.
This is to assure reasonable code compatibility with other family and future parts. RCGC0 is the
clock configuration register for running operation, SCGC0 for Sleep operation, and DCGC0 for
Deep-Sleep operation. Setting the ACG bit in the Run-Mode Clock Configuration (RCC) register
specifies that the system uses sleep modes.
Deep Sleep Mode Clock Gating Control Register 0 (DCGC0)
Base 0x400F.E000
Offset 0x120
Type R/W, reset 0x00000040
31 30 29 28 27 26 25 24 23 22 21 20 19 18 17 16
reserved CAN1 CAN0 reserved PWM reserved ADC
Type RO RO RO RO RO RO R/W R/W RO RO RO R/W RO RO RO R/W
Reset 0 0 0 0 0 0 0 0 0 0 0 0 0 0 0 0
15 14 13 12 11 10 9 8 7 6 5 4 3 2 1 0
reserved HIB reserved WDT reserved
Type RO RO RO RO RO RO RO RO RO R/W RO RO R/W RO RO RO
Reset 0 0 0 0 0 0 0 0 0 1 0 0 0 0 0 0
Bit/Field Name Type Reset Description
Software should not rely on the value of a reserved bit. To provide
compatibility with future products, the value of a reserved bit should be
preserved across a read-modify-write operation.
31:26 reserved RO 0
CAN1 Clock Gating Control
This bit controls the clock gating for CAN unit 1. If set, the unit receives
a clock and functions. Otherwise, the unit is unclocked and disabled.
25 CAN1 R/W 0
CAN0 Clock Gating Control
This bit controls the clock gating for CAN unit 0. If set, the unit receives
a clock and functions. Otherwise, the unit is unclocked and disabled.
24 CAN0 R/W 0
Software should not rely on the value of a reserved bit. To provide
compatibility with future products, the value of a reserved bit should be
preserved across a read-modify-write operation.
23:21 reserved RO 0
PWM Clock Gating Control
This bit controls the clock gating for the PWM module. If set, the unit
receives a clock and functions. Otherwise, the unit is unclocked and
disabled. If the unit is unclocked, a read or write to the unit generates
a bus fault.
20 PWM R/W 0
Software should not rely on the value of a reserved bit. To provide
compatibility with future products, the value of a reserved bit should be
preserved across a read-modify-write operation.
19:17 reserved RO 0
214 January 08, 2011
Texas Instruments-Production Data
System Control
Bit/Field Name Type Reset Description
ADC0 Clock Gating Control
This bit controls the clock gating for SAR ADC module 0. If set, the unit
receives a clock and functions. Otherwise, the unit is unclocked and
disabled. If the unit is unclocked, a read or write to the unit generates
a bus fault.
16 ADC R/W 0
Software should not rely on the value of a reserved bit. To provide
compatibility with future products, the value of a reserved bit should be
preserved across a read-modify-write operation.
15:7 reserved RO 0
HIB Clock Gating Control
This bit controls the clock gating for the Hibernation module. If set, the
unit receives a clock and functions. Otherwise, the unit is unclocked and
disabled.
6 HIB R/W 1
Software should not rely on the value of a reserved bit. To provide
compatibility with future products, the value of a reserved bit should be
preserved across a read-modify-write operation.
5:4 reserved RO 0
WDT Clock Gating Control
This bit controls the clock gating for the WDT module. If set, the unit
receives a clock and functions. Otherwise, the unit is unclocked and
disabled. If the unit is unclocked, a read or write to the unit generates
a bus fault.
3 WDT R/W 0
Software should not rely on the value of a reserved bit. To provide
compatibility with future products, the value of a reserved bit should be
preserved across a read-modify-write operation.
2:0 reserved RO 0
January 08, 2011 215
Texas Instruments-Production Data
Stellaris® LM3S2965 Microcontroller
Register 21: Run Mode Clock Gating Control Register 1 (RCGC1), offset 0x104
This register controls the clock gating logic. Each bit controls a clock enable for a given interface,
function, or unit. If set, the unit receives a clock and functions. Otherwise, the unit is unclocked and
disabled (saving power). If the unit is unclocked, reads or writes to the unit will generate a bus fault.
The reset state of these bits is 0 (unclocked) unless otherwise noted, so that all functional units are
disabled. It is the responsibility of software to enable the ports necessary for the application. Note
that these registers may contain more bits than there are interfaces, functions, or units to control.
This is to assure reasonable code compatibility with other family and future parts. RCGC1 is the
clock configuration register for running operation, SCGC1 for Sleep operation, and DCGC1 for
Deep-Sleep operation. Setting the ACG bit in the Run-Mode Clock Configuration (RCC) register
specifies that the system uses sleep modes.
Run Mode Clock Gating Control Register 1 (RCGC1)
Base 0x400F.E000
Offset 0x104
Type R/W, reset 0x00000000
31 30 29 28 27 26 25 24 23 22 21 20 19 18 17 16
reserved COMP2 COMP1 COMP0 reserved TIMER3 TIMER2 TIMER1 TIMER0
Type RO RO RO RO RO R/W R/W R/W RO RO RO RO R/W R/W R/W R/W
Reset 0 0 0 0 0 0 0 0 0 0 0 0 0 0 0 0
15 14 13 12 11 10 9 8 7 6 5 4 3 2 1 0
reserved I2C1 reserved I2C0 reserved QEI1 QEI0 reserved SSI1 SSI0 reserved UART2 UART1 UART0
Type RO R/W RO R/W RO RO R/W R/W RO RO R/W R/W RO R/W R/W R/W
Reset 0 0 0 0 0 0 0 0 0 0 0 0 0 0 0 0
Bit/Field Name Type Reset Description
Software should not rely on the value of a reserved bit. To provide
compatibility with future products, the value of a reserved bit should be
preserved across a read-modify-write operation.
31:27 reserved RO 0
Analog Comparator 2 Clock Gating
This bit controls the clock gating for analog comparator 2. If set, the unit
receives a clock and functions. Otherwise, the unit is unclocked and
disabled. If the unit is unclocked, reads or writes to the unit will generate
a bus fault.
26 COMP2 R/W 0
Analog Comparator 1 Clock Gating
This bit controls the clock gating for analog comparator 1. If set, the unit
receives a clock and functions. Otherwise, the unit is unclocked and
disabled. If the unit is unclocked, reads or writes to the unit will generate
a bus fault.
25 COMP1 R/W 0
Analog Comparator 0 Clock Gating
This bit controls the clock gating for analog comparator 0. If set, the unit
receives a clock and functions. Otherwise, the unit is unclocked and
disabled. If the unit is unclocked, reads or writes to the unit will generate
a bus fault.
24 COMP0 R/W 0
Software should not rely on the value of a reserved bit. To provide
compatibility with future products, the value of a reserved bit should be
preserved across a read-modify-write operation.
23:20 reserved RO 0
216 January 08, 2011
Texas Instruments-Production Data
System Control
Bit/Field Name Type Reset Description
Timer 3 Clock Gating Control
This bit controls the clock gating for General-Purpose Timer module 3.
If set, the unit receives a clock and functions. Otherwise, the unit is
unclocked and disabled. If the unit is unclocked, reads or writes to the
unit will generate a bus fault.
19 TIMER3 R/W 0
Timer 2 Clock Gating Control
This bit controls the clock gating for General-Purpose Timer module 2.
If set, the unit receives a clock and functions. Otherwise, the unit is
unclocked and disabled. If the unit is unclocked, reads or writes to the
unit will generate a bus fault.
18 TIMER2 R/W 0
Timer 1 Clock Gating Control
This bit controls the clock gating for General-Purpose Timer module 1.
If set, the unit receives a clock and functions. Otherwise, the unit is
unclocked and disabled. If the unit is unclocked, reads or writes to the
unit will generate a bus fault.
17 TIMER1 R/W 0
Timer 0 Clock Gating Control
This bit controls the clock gating for General-Purpose Timer module 0.
If set, the unit receives a clock and functions. Otherwise, the unit is
unclocked and disabled. If the unit is unclocked, reads or writes to the
unit will generate a bus fault.
16 TIMER0 R/W 0
Software should not rely on the value of a reserved bit. To provide
compatibility with future products, the value of a reserved bit should be
preserved across a read-modify-write operation.
15 reserved RO 0
I2C1 Clock Gating Control
This bit controls the clock gating for I2C module 1. If set, the unit receives
a clock and functions. Otherwise, the unit is unclocked and disabled. If
the unit is unclocked, reads or writes to the unit will generate a bus fault.
14 I2C1 R/W 0
Software should not rely on the value of a reserved bit. To provide
compatibility with future products, the value of a reserved bit should be
preserved across a read-modify-write operation.
13 reserved RO 0
I2C0 Clock Gating Control
This bit controls the clock gating for I2C module 0. If set, the unit receives
a clock and functions. Otherwise, the unit is unclocked and disabled. If
the unit is unclocked, reads or writes to the unit will generate a bus fault.
12 I2C0 R/W 0
Software should not rely on the value of a reserved bit. To provide
compatibility with future products, the value of a reserved bit should be
preserved across a read-modify-write operation.
11:10 reserved RO 0
QEI1 Clock Gating Control
This bit controls the clock gating for QEI module 1. If set, the unit
receives a clock and functions. Otherwise, the unit is unclocked and
disabled. If the unit is unclocked, reads or writes to the unit will generate
a bus fault.
9 QEI1 R/W 0
QEI0 Clock Gating Control
This bit controls the clock gating for QEI module 0. If set, the unit
receives a clock and functions. Otherwise, the unit is unclocked and
disabled. If the unit is unclocked, reads or writes to the unit will generate
a bus fault.
8 QEI0 R/W 0
January 08, 2011 217
Texas Instruments-Production Data
Stellaris® LM3S2965 Microcontroller
Bit/Field Name Type Reset Description
Software should not rely on the value of a reserved bit. To provide
compatibility with future products, the value of a reserved bit should be
preserved across a read-modify-write operation.
7:6 reserved RO 0
SSI1 Clock Gating Control
This bit controls the clock gating for SSI module 1. If set, the unit receives
a clock and functions. Otherwise, the unit is unclocked and disabled. If
the unit is unclocked, reads or writes to the unit will generate a bus fault.
5 SSI1 R/W 0
SSI0 Clock Gating Control
This bit controls the clock gating for SSI module 0. If set, the unit receives
a clock and functions. Otherwise, the unit is unclocked and disabled. If
the unit is unclocked, reads or writes to the unit will generate a bus fault.
4 SSI0 R/W 0
Software should not rely on the value of a reserved bit. To provide
compatibility with future products, the value of a reserved bit should be
preserved across a read-modify-write operation.
3 reserved RO 0
UART2 Clock Gating Control
This bit controls the clock gating for UART module 2. If set, the unit
receives a clock and functions. Otherwise, the unit is unclocked and
disabled. If the unit is unclocked, reads or writes to the unit will generate
a bus fault.
2 UART2 R/W 0
UART1 Clock Gating Control
This bit controls the clock gating for UART module 1. If set, the unit
receives a clock and functions. Otherwise, the unit is unclocked and
disabled. If the unit is unclocked, reads or writes to the unit will generate
a bus fault.
1 UART1 R/W 0
UART0 Clock Gating Control
This bit controls the clock gating for UART module 0. If set, the unit
receives a clock and functions. Otherwise, the unit is unclocked and
disabled. If the unit is unclocked, reads or writes to the unit will generate
a bus fault.
0 UART0 R/W 0
218 January 08, 2011
Texas Instruments-Production Data
System Control
Register 22: Sleep Mode Clock Gating Control Register 1 (SCGC1), offset
0x114
This register controls the clock gating logic. Each bit controls a clock enable for a given interface,
function, or unit. If set, the unit receives a clock and functions. Otherwise, the unit is unclocked and
disabled (saving power). If the unit is unclocked, reads or writes to the unit will generate a bus fault.
The reset state of these bits is 0 (unclocked) unless otherwise noted, so that all functional units are
disabled. It is the responsibility of software to enable the ports necessary for the application. Note
that these registers may contain more bits than there are interfaces, functions, or units to control.
This is to assure reasonable code compatibility with other family and future parts. RCGC1 is the
clock configuration register for running operation, SCGC1 for Sleep operation, and DCGC1 for
Deep-Sleep operation. Setting the ACG bit in the Run-Mode Clock Configuration (RCC) register
specifies that the system uses sleep modes.
Sleep Mode Clock Gating Control Register 1 (SCGC1)
Base 0x400F.E000
Offset 0x114
Type R/W, reset 0x00000000
31 30 29 28 27 26 25 24 23 22 21 20 19 18 17 16
reserved COMP2 COMP1 COMP0 reserved TIMER3 TIMER2 TIMER1 TIMER0
Type RO RO RO RO RO R/W R/W R/W RO RO RO RO R/W R/W R/W R/W
Reset 0 0 0 0 0 0 0 0 0 0 0 0 0 0 0 0
15 14 13 12 11 10 9 8 7 6 5 4 3 2 1 0
reserved I2C1 reserved I2C0 reserved QEI1 QEI0 reserved SSI1 SSI0 reserved UART2 UART1 UART0
Type RO R/W RO R/W RO RO R/W R/W RO RO R/W R/W RO R/W R/W R/W
Reset 0 0 0 0 0 0 0 0 0 0 0 0 0 0 0 0
Bit/Field Name Type Reset Description
Software should not rely on the value of a reserved bit. To provide
compatibility with future products, the value of a reserved bit should be
preserved across a read-modify-write operation.
31:27 reserved RO 0
Analog Comparator 2 Clock Gating
This bit controls the clock gating for analog comparator 2. If set, the unit
receives a clock and functions. Otherwise, the unit is unclocked and
disabled. If the unit is unclocked, reads or writes to the unit will generate
a bus fault.
26 COMP2 R/W 0
Analog Comparator 1 Clock Gating
This bit controls the clock gating for analog comparator 1. If set, the unit
receives a clock and functions. Otherwise, the unit is unclocked and
disabled. If the unit is unclocked, reads or writes to the unit will generate
a bus fault.
25 COMP1 R/W 0
Analog Comparator 0 Clock Gating
This bit controls the clock gating for analog comparator 0. If set, the unit
receives a clock and functions. Otherwise, the unit is unclocked and
disabled. If the unit is unclocked, reads or writes to the unit will generate
a bus fault.
24 COMP0 R/W 0
Software should not rely on the value of a reserved bit. To provide
compatibility with future products, the value of a reserved bit should be
preserved across a read-modify-write operation.
23:20 reserved RO 0
January 08, 2011 219
Texas Instruments-Production Data
Stellaris® LM3S2965 Microcontroller
Bit/Field Name Type Reset Description
Timer 3 Clock Gating Control
This bit controls the clock gating for General-Purpose Timer module 3.
If set, the unit receives a clock and functions. Otherwise, the unit is
unclocked and disabled. If the unit is unclocked, reads or writes to the
unit will generate a bus fault.
19 TIMER3 R/W 0
Timer 2 Clock Gating Control
This bit controls the clock gating for General-Purpose Timer module 2.
If set, the unit receives a clock and functions. Otherwise, the unit is
unclocked and disabled. If the unit is unclocked, reads or writes to the
unit will generate a bus fault.
18 TIMER2 R/W 0
Timer 1 Clock Gating Control
This bit controls the clock gating for General-Purpose Timer module 1.
If set, the unit receives a clock and functions. Otherwise, the unit is
unclocked and disabled. If the unit is unclocked, reads or writes to the
unit will generate a bus fault.
17 TIMER1 R/W 0
Timer 0 Clock Gating Control
This bit controls the clock gating for General-Purpose Timer module 0.
If set, the unit receives a clock and functions. Otherwise, the unit is
unclocked and disabled. If the unit is unclocked, reads or writes to the
unit will generate a bus fault.
16 TIMER0 R/W 0
Software should not rely on the value of a reserved bit. To provide
compatibility with future products, the value of a reserved bit should be
preserved across a read-modify-write operation.
15 reserved RO 0
I2C1 Clock Gating Control
This bit controls the clock gating for I2C module 1. If set, the unit receives
a clock and functions. Otherwise, the unit is unclocked and disabled. If
the unit is unclocked, reads or writes to the unit will generate a bus fault.
14 I2C1 R/W 0
Software should not rely on the value of a reserved bit. To provide
compatibility with future products, the value of a reserved bit should be
preserved across a read-modify-write operation.
13 reserved RO 0
I2C0 Clock Gating Control
This bit controls the clock gating for I2C module 0. If set, the unit receives
a clock and functions. Otherwise, the unit is unclocked and disabled. If
the unit is unclocked, reads or writes to the unit will generate a bus fault.
12 I2C0 R/W 0
Software should not rely on the value of a reserved bit. To provide
compatibility with future products, the value of a reserved bit should be
preserved across a read-modify-write operation.
11:10 reserved RO 0
QEI1 Clock Gating Control
This bit controls the clock gating for QEI module 1. If set, the unit
receives a clock and functions. Otherwise, the unit is unclocked and
disabled. If the unit is unclocked, reads or writes to the unit will generate
a bus fault.
9 QEI1 R/W 0
QEI0 Clock Gating Control
This bit controls the clock gating for QEI module 0. If set, the unit
receives a clock and functions. Otherwise, the unit is unclocked and
disabled. If the unit is unclocked, reads or writes to the unit will generate
a bus fault.
8 QEI0 R/W 0
220 January 08, 2011
Texas Instruments-Production Data
System Control
Bit/Field Name Type Reset Description
Software should not rely on the value of a reserved bit. To provide
compatibility with future products, the value of a reserved bit should be
preserved across a read-modify-write operation.
7:6 reserved RO 0
SSI1 Clock Gating Control
This bit controls the clock gating for SSI module 1. If set, the unit receives
a clock and functions. Otherwise, the unit is unclocked and disabled. If
the unit is unclocked, reads or writes to the unit will generate a bus fault.
5 SSI1 R/W 0
SSI0 Clock Gating Control
This bit controls the clock gating for SSI module 0. If set, the unit receives
a clock and functions. Otherwise, the unit is unclocked and disabled. If
the unit is unclocked, reads or writes to the unit will generate a bus fault.
4 SSI0 R/W 0
Software should not rely on the value of a reserved bit. To provide
compatibility with future products, the value of a reserved bit should be
preserved across a read-modify-write operation.
3 reserved RO 0
UART2 Clock Gating Control
This bit controls the clock gating for UART module 2. If set, the unit
receives a clock and functions. Otherwise, the unit is unclocked and
disabled. If the unit is unclocked, reads or writes to the unit will generate
a bus fault.
2 UART2 R/W 0
UART1 Clock Gating Control
This bit controls the clock gating for UART module 1. If set, the unit
receives a clock and functions. Otherwise, the unit is unclocked and
disabled. If the unit is unclocked, reads or writes to the unit will generate
a bus fault.
1 UART1 R/W 0
UART0 Clock Gating Control
This bit controls the clock gating for UART module 0. If set, the unit
receives a clock and functions. Otherwise, the unit is unclocked and
disabled. If the unit is unclocked, reads or writes to the unit will generate
a bus fault.
0 UART0 R/W 0
January 08, 2011 221
Texas Instruments-Production Data
Stellaris® LM3S2965 Microcontroller
Register 23: Deep Sleep Mode Clock Gating Control Register 1 (DCGC1),
offset 0x124
This register controls the clock gating logic. Each bit controls a clock enable for a given interface,
function, or unit. If set, the unit receives a clock and functions. Otherwise, the unit is unclocked and
disabled (saving power). If the unit is unclocked, reads or writes to the unit will generate a bus fault.
The reset state of these bits is 0 (unclocked) unless otherwise noted, so that all functional units are
disabled. It is the responsibility of software to enable the ports necessary for the application. Note
that these registers may contain more bits than there are interfaces, functions, or units to control.
This is to assure reasonable code compatibility with other family and future parts. RCGC1 is the
clock configuration register for running operation, SCGC1 for Sleep operation, and DCGC1 for
Deep-Sleep operation. Setting the ACG bit in the Run-Mode Clock Configuration (RCC) register
specifies that the system uses sleep modes.
Deep Sleep Mode Clock Gating Control Register 1 (DCGC1)
Base 0x400F.E000
Offset 0x124
Type R/W, reset 0x00000000
31 30 29 28 27 26 25 24 23 22 21 20 19 18 17 16
reserved COMP2 COMP1 COMP0 reserved TIMER3 TIMER2 TIMER1 TIMER0
Type RO RO RO RO RO R/W R/W R/W RO RO RO RO R/W R/W R/W R/W
Reset 0 0 0 0 0 0 0 0 0 0 0 0 0 0 0 0
15 14 13 12 11 10 9 8 7 6 5 4 3 2 1 0
reserved I2C1 reserved I2C0 reserved QEI1 QEI0 reserved SSI1 SSI0 reserved UART2 UART1 UART0
Type RO R/W RO R/W RO RO R/W R/W RO RO R/W R/W RO R/W R/W R/W
Reset 0 0 0 0 0 0 0 0 0 0 0 0 0 0 0 0
Bit/Field Name Type Reset Description
Software should not rely on the value of a reserved bit. To provide
compatibility with future products, the value of a reserved bit should be
preserved across a read-modify-write operation.
31:27 reserved RO 0
Analog Comparator 2 Clock Gating
This bit controls the clock gating for analog comparator 2. If set, the unit
receives a clock and functions. Otherwise, the unit is unclocked and
disabled. If the unit is unclocked, reads or writes to the unit will generate
a bus fault.
26 COMP2 R/W 0
Analog Comparator 1 Clock Gating
This bit controls the clock gating for analog comparator 1. If set, the unit
receives a clock and functions. Otherwise, the unit is unclocked and
disabled. If the unit is unclocked, reads or writes to the unit will generate
a bus fault.
25 COMP1 R/W 0
Analog Comparator 0 Clock Gating
This bit controls the clock gating for analog comparator 0. If set, the unit
receives a clock and functions. Otherwise, the unit is unclocked and
disabled. If the unit is unclocked, reads or writes to the unit will generate
a bus fault.
24 COMP0 R/W 0
Software should not rely on the value of a reserved bit. To provide
compatibility with future products, the value of a reserved bit should be
preserved across a read-modify-write operation.
23:20 reserved RO 0
222 January 08, 2011
Texas Instruments-Production Data
System Control
Bit/Field Name Type Reset Description
Timer 3 Clock Gating Control
This bit controls the clock gating for General-Purpose Timer module 3.
If set, the unit receives a clock and functions. Otherwise, the unit is
unclocked and disabled. If the unit is unclocked, reads or writes to the
unit will generate a bus fault.
19 TIMER3 R/W 0
Timer 2 Clock Gating Control
This bit controls the clock gating for General-Purpose Timer module 2.
If set, the unit receives a clock and functions. Otherwise, the unit is
unclocked and disabled. If the unit is unclocked, reads or writes to the
unit will generate a bus fault.
18 TIMER2 R/W 0
Timer 1 Clock Gating Control
This bit controls the clock gating for General-Purpose Timer module 1.
If set, the unit receives a clock and functions. Otherwise, the unit is
unclocked and disabled. If the unit is unclocked, reads or writes to the
unit will generate a bus fault.
17 TIMER1 R/W 0
Timer 0 Clock Gating Control
This bit controls the clock gating for General-Purpose Timer module 0.
If set, the unit receives a clock and functions. Otherwise, the unit is
unclocked and disabled. If the unit is unclocked, reads or writes to the
unit will generate a bus fault.
16 TIMER0 R/W 0
Software should not rely on the value of a reserved bit. To provide
compatibility with future products, the value of a reserved bit should be
preserved across a read-modify-write operation.
15 reserved RO 0
I2C1 Clock Gating Control
This bit controls the clock gating for I2C module 1. If set, the unit receives
a clock and functions. Otherwise, the unit is unclocked and disabled. If
the unit is unclocked, reads or writes to the unit will generate a bus fault.
14 I2C1 R/W 0
Software should not rely on the value of a reserved bit. To provide
compatibility with future products, the value of a reserved bit should be
preserved across a read-modify-write operation.
13 reserved RO 0
I2C0 Clock Gating Control
This bit controls the clock gating for I2C module 0. If set, the unit receives
a clock and functions. Otherwise, the unit is unclocked and disabled. If
the unit is unclocked, reads or writes to the unit will generate a bus fault.
12 I2C0 R/W 0
Software should not rely on the value of a reserved bit. To provide
compatibility with future products, the value of a reserved bit should be
preserved across a read-modify-write operation.
11:10 reserved RO 0
QEI1 Clock Gating Control
This bit controls the clock gating for QEI module 1. If set, the unit
receives a clock and functions. Otherwise, the unit is unclocked and
disabled. If the unit is unclocked, reads or writes to the unit will generate
a bus fault.
9 QEI1 R/W 0
QEI0 Clock Gating Control
This bit controls the clock gating for QEI module 0. If set, the unit
receives a clock and functions. Otherwise, the unit is unclocked and
disabled. If the unit is unclocked, reads or writes to the unit will generate
a bus fault.
8 QEI0 R/W 0
January 08, 2011 223
Texas Instruments-Production Data
Stellaris® LM3S2965 Microcontroller
Bit/Field Name Type Reset Description
Software should not rely on the value of a reserved bit. To provide
compatibility with future products, the value of a reserved bit should be
preserved across a read-modify-write operation.
7:6 reserved RO 0
SSI1 Clock Gating Control
This bit controls the clock gating for SSI module 1. If set, the unit receives
a clock and functions. Otherwise, the unit is unclocked and disabled. If
the unit is unclocked, reads or writes to the unit will generate a bus fault.
5 SSI1 R/W 0
SSI0 Clock Gating Control
This bit controls the clock gating for SSI module 0. If set, the unit receives
a clock and functions. Otherwise, the unit is unclocked and disabled. If
the unit is unclocked, reads or writes to the unit will generate a bus fault.
4 SSI0 R/W 0
Software should not rely on the value of a reserved bit. To provide
compatibility with future products, the value of a reserved bit should be
preserved across a read-modify-write operation.
3 reserved RO 0
UART2 Clock Gating Control
This bit controls the clock gating for UART module 2. If set, the unit
receives a clock and functions. Otherwise, the unit is unclocked and
disabled. If the unit is unclocked, reads or writes to the unit will generate
a bus fault.
2 UART2 R/W 0
UART1 Clock Gating Control
This bit controls the clock gating for UART module 1. If set, the unit
receives a clock and functions. Otherwise, the unit is unclocked and
disabled. If the unit is unclocked, reads or writes to the unit will generate
a bus fault.
1 UART1 R/W 0
UART0 Clock Gating Control
This bit controls the clock gating for UART module 0. If set, the unit
receives a clock and functions. Otherwise, the unit is unclocked and
disabled. If the unit is unclocked, reads or writes to the unit will generate
a bus fault.
0 UART0 R/W 0
224 January 08, 2011
Texas Instruments-Production Data
System Control
Register 24: Run Mode Clock Gating Control Register 2 (RCGC2), offset 0x108
This register controls the clock gating logic. Each bit controls a clock enable for a given interface,
function, or unit. If set, the unit receives a clock and functions. Otherwise, the unit is unclocked and
disabled (saving power). If the unit is unclocked, reads or writes to the unit will generate a bus fault.
The reset state of these bits is 0 (unclocked) unless otherwise noted, so that all functional units are
disabled. It is the responsibility of software to enable the ports necessary for the application. Note
that these registers may contain more bits than there are interfaces, functions, or units to control.
This is to assure reasonable code compatibility with other family and future parts. RCGC2 is the
clock configuration register for running operation, SCGC2 for Sleep operation, and DCGC2 for
Deep-Sleep operation. Setting the ACG bit in the Run-Mode Clock Configuration (RCC) register
specifies that the system uses sleep modes.
Run Mode Clock Gating Control Register 2 (RCGC2)
Base 0x400F.E000
Offset 0x108
Type R/W, reset 0x00000000
31 30 29 28 27 26 25 24 23 22 21 20 19 18 17 16
reserved
Type RO RO RO RO RO RO RO RO RO RO RO RO RO RO RO RO
Reset 0 0 0 0 0 0 0 0 0 0 0 0 0 0 0 0
15 14 13 12 11 10 9 8 7 6 5 4 3 2 1 0
reserved GPIOH GPIOG GPIOF GPIOE GPIOD GPIOC GPIOB GPIOA
Type RO RO RO RO RO RO RO RO R/W R/W R/W R/W R/W R/W R/W R/W
Reset 0 0 0 0 0 0 0 0 0 0 0 0 0 0 0 0
Bit/Field Name Type Reset Description
Software should not rely on the value of a reserved bit. To provide
compatibility with future products, the value of a reserved bit should be
preserved across a read-modify-write operation.
31:8 reserved RO 0
Port H Clock Gating Control
This bit controls the clock gating for Port H. If set, the unit receives a
clock and functions. Otherwise, the unit is unclocked and disabled. If
the unit is unclocked, reads or writes to the unit will generate a bus fault.
7 GPIOH R/W 0
Port G Clock Gating Control
This bit controls the clock gating for Port G. If set, the unit receives a
clock and functions. Otherwise, the unit is unclocked and disabled. If
the unit is unclocked, reads or writes to the unit will generate a bus fault.
6 GPIOG R/W 0
Port F Clock Gating Control
This bit controls the clock gating for Port F. If set, the unit receives a
clock and functions. Otherwise, the unit is unclocked and disabled. If
the unit is unclocked, reads or writes to the unit will generate a bus fault.
5 GPIOF R/W 0
Port E Clock Gating Control
This bit controls the clock gating for Port E. If set, the unit receives a
clock and functions. Otherwise, the unit is unclocked and disabled. If
the unit is unclocked, reads or writes to the unit will generate a bus fault.
4 GPIOE R/W 0
Port D Clock Gating Control
This bit controls the clock gating for Port D. If set, the unit receives a
clock and functions. Otherwise, the unit is unclocked and disabled. If
the unit is unclocked, reads or writes to the unit will generate a bus fault.
3 GPIOD R/W 0
January 08, 2011 225
Texas Instruments-Production Data
Stellaris® LM3S2965 Microcontroller
Bit/Field Name Type Reset Description
Port C Clock Gating Control
This bit controls the clock gating for Port C. If set, the unit receives a
clock and functions. Otherwise, the unit is unclocked and disabled. If
the unit is unclocked, reads or writes to the unit will generate a bus fault.
2 GPIOC R/W 0
Port B Clock Gating Control
This bit controls the clock gating for Port B. If set, the unit receives a
clock and functions. Otherwise, the unit is unclocked and disabled. If
the unit is unclocked, reads or writes to the unit will generate a bus fault.
1 GPIOB R/W 0
Port A Clock Gating Control
This bit controls the clock gating for Port A. If set, the unit receives a
clock and functions. Otherwise, the unit is unclocked and disabled. If
the unit is unclocked, reads or writes to the unit will generate a bus fault.
0 GPIOA R/W 0
226 January 08, 2011
Texas Instruments-Production Data
System Control
Register 25: Sleep Mode Clock Gating Control Register 2 (SCGC2), offset
0x118
This register controls the clock gating logic. Each bit controls a clock enable for a given interface,
function, or unit. If set, the unit receives a clock and functions. Otherwise, the unit is unclocked and
disabled (saving power). If the unit is unclocked, reads or writes to the unit will generate a bus fault.
The reset state of these bits is 0 (unclocked) unless otherwise noted, so that all functional units are
disabled. It is the responsibility of software to enable the ports necessary for the application. Note
that these registers may contain more bits than there are interfaces, functions, or units to control.
This is to assure reasonable code compatibility with other family and future parts. RCGC2 is the
clock configuration register for running operation, SCGC2 for Sleep operation, and DCGC2 for
Deep-Sleep operation. Setting the ACG bit in the Run-Mode Clock Configuration (RCC) register
specifies that the system uses sleep modes.
Sleep Mode Clock Gating Control Register 2 (SCGC2)
Base 0x400F.E000
Offset 0x118
Type R/W, reset 0x00000000
31 30 29 28 27 26 25 24 23 22 21 20 19 18 17 16
reserved
Type RO RO RO RO RO RO RO RO RO RO RO RO RO RO RO RO
Reset 0 0 0 0 0 0 0 0 0 0 0 0 0 0 0 0
15 14 13 12 11 10 9 8 7 6 5 4 3 2 1 0
reserved GPIOH GPIOG GPIOF GPIOE GPIOD GPIOC GPIOB GPIOA
Type RO RO RO RO RO RO RO RO R/W R/W R/W R/W R/W R/W R/W R/W
Reset 0 0 0 0 0 0 0 0 0 0 0 0 0 0 0 0
Bit/Field Name Type Reset Description
Software should not rely on the value of a reserved bit. To provide
compatibility with future products, the value of a reserved bit should be
preserved across a read-modify-write operation.
31:8 reserved RO 0
Port H Clock Gating Control
This bit controls the clock gating for Port H. If set, the unit receives a
clock and functions. Otherwise, the unit is unclocked and disabled. If
the unit is unclocked, reads or writes to the unit will generate a bus fault.
7 GPIOH R/W 0
Port G Clock Gating Control
This bit controls the clock gating for Port G. If set, the unit receives a
clock and functions. Otherwise, the unit is unclocked and disabled. If
the unit is unclocked, reads or writes to the unit will generate a bus fault.
6 GPIOG R/W 0
Port F Clock Gating Control
This bit controls the clock gating for Port F. If set, the unit receives a
clock and functions. Otherwise, the unit is unclocked and disabled. If
the unit is unclocked, reads or writes to the unit will generate a bus fault.
5 GPIOF R/W 0
Port E Clock Gating Control
This bit controls the clock gating for Port E. If set, the unit receives a
clock and functions. Otherwise, the unit is unclocked and disabled. If
the unit is unclocked, reads or writes to the unit will generate a bus fault.
4 GPIOE R/W 0
Port D Clock Gating Control
This bit controls the clock gating for Port D. If set, the unit receives a
clock and functions. Otherwise, the unit is unclocked and disabled. If
the unit is unclocked, reads or writes to the unit will generate a bus fault.
3 GPIOD R/W 0
January 08, 2011 227
Texas Instruments-Production Data
Stellaris® LM3S2965 Microcontroller
Bit/Field Name Type Reset Description
Port C Clock Gating Control
This bit controls the clock gating for Port C. If set, the unit receives a
clock and functions. Otherwise, the unit is unclocked and disabled. If
the unit is unclocked, reads or writes to the unit will generate a bus fault.
2 GPIOC R/W 0
Port B Clock Gating Control
This bit controls the clock gating for Port B. If set, the unit receives a
clock and functions. Otherwise, the unit is unclocked and disabled. If
the unit is unclocked, reads or writes to the unit will generate a bus fault.
1 GPIOB R/W 0
Port A Clock Gating Control
This bit controls the clock gating for Port A. If set, the unit receives a
clock and functions. Otherwise, the unit is unclocked and disabled. If
the unit is unclocked, reads or writes to the unit will generate a bus fault.
0 GPIOA R/W 0
228 January 08, 2011
Texas Instruments-Production Data
System Control
Register 26: Deep Sleep Mode Clock Gating Control Register 2 (DCGC2),
offset 0x128
This register controls the clock gating logic. Each bit controls a clock enable for a given interface,
function, or unit. If set, the unit receives a clock and functions. Otherwise, the unit is unclocked and
disabled (saving power). If the unit is unclocked, reads or writes to the unit will generate a bus fault.
The reset state of these bits is 0 (unclocked) unless otherwise noted, so that all functional units are
disabled. It is the responsibility of software to enable the ports necessary for the application. Note
that these registers may contain more bits than there are interfaces, functions, or units to control.
This is to assure reasonable code compatibility with other family and future parts. RCGC2 is the
clock configuration register for running operation, SCGC2 for Sleep operation, and DCGC2 for
Deep-Sleep operation. Setting the ACG bit in the Run-Mode Clock Configuration (RCC) register
specifies that the system uses sleep modes.
Deep Sleep Mode Clock Gating Control Register 2 (DCGC2)
Base 0x400F.E000
Offset 0x128
Type R/W, reset 0x00000000
31 30 29 28 27 26 25 24 23 22 21 20 19 18 17 16
reserved
Type RO RO RO RO RO RO RO RO RO RO RO RO RO RO RO RO
Reset 0 0 0 0 0 0 0 0 0 0 0 0 0 0 0 0
15 14 13 12 11 10 9 8 7 6 5 4 3 2 1 0
reserved GPIOH GPIOG GPIOF GPIOE GPIOD GPIOC GPIOB GPIOA
Type RO RO RO RO RO RO RO RO R/W R/W R/W R/W R/W R/W R/W R/W
Reset 0 0 0 0 0 0 0 0 0 0 0 0 0 0 0 0
Bit/Field Name Type Reset Description
Software should not rely on the value of a reserved bit. To provide
compatibility with future products, the value of a reserved bit should be
preserved across a read-modify-write operation.
31:8 reserved RO 0
Port H Clock Gating Control
This bit controls the clock gating for Port H. If set, the unit receives a
clock and functions. Otherwise, the unit is unclocked and disabled. If
the unit is unclocked, reads or writes to the unit will generate a bus fault.
7 GPIOH R/W 0
Port G Clock Gating Control
This bit controls the clock gating for Port G. If set, the unit receives a
clock and functions. Otherwise, the unit is unclocked and disabled. If
the unit is unclocked, reads or writes to the unit will generate a bus fault.
6 GPIOG R/W 0
Port F Clock Gating Control
This bit controls the clock gating for Port F. If set, the unit receives a
clock and functions. Otherwise, the unit is unclocked and disabled. If
the unit is unclocked, reads or writes to the unit will generate a bus fault.
5 GPIOF R/W 0
Port E Clock Gating Control
This bit controls the clock gating for Port E. If set, the unit receives a
clock and functions. Otherwise, the unit is unclocked and disabled. If
the unit is unclocked, reads or writes to the unit will generate a bus fault.
4 GPIOE R/W 0
Port D Clock Gating Control
This bit controls the clock gating for Port D. If set, the unit receives a
clock and functions. Otherwise, the unit is unclocked and disabled. If
the unit is unclocked, reads or writes to the unit will generate a bus fault.
3 GPIOD R/W 0
January 08, 2011 229
Texas Instruments-Production Data
Stellaris® LM3S2965 Microcontroller
Bit/Field Name Type Reset Description
Port C Clock Gating Control
This bit controls the clock gating for Port C. If set, the unit receives a
clock and functions. Otherwise, the unit is unclocked and disabled. If
the unit is unclocked, reads or writes to the unit will generate a bus fault.
2 GPIOC R/W 0
Port B Clock Gating Control
This bit controls the clock gating for Port B. If set, the unit receives a
clock and functions. Otherwise, the unit is unclocked and disabled. If
the unit is unclocked, reads or writes to the unit will generate a bus fault.
1 GPIOB R/W 0
Port A Clock Gating Control
This bit controls the clock gating for Port A. If set, the unit receives a
clock and functions. Otherwise, the unit is unclocked and disabled. If
the unit is unclocked, reads or writes to the unit will generate a bus fault.
0 GPIOA R/W 0
230 January 08, 2011
Texas Instruments-Production Data
System Control
Register 27: Software Reset Control 0 (SRCR0), offset 0x040
Writes to this register are masked by the bits in the Device Capabilities 1 (DC1) register.
Software Reset Control 0 (SRCR0)
Base 0x400F.E000
Offset 0x040
Type R/W, reset 0x00000000
31 30 29 28 27 26 25 24 23 22 21 20 19 18 17 16
reserved CAN1 CAN0 reserved PWM reserved ADC
Type RO RO RO RO RO RO R/W R/W RO RO RO R/W RO RO RO R/W
Reset 0 0 0 0 0 0 0 0 0 0 0 0 0 0 0 0
15 14 13 12 11 10 9 8 7 6 5 4 3 2 1 0
reserved HIB reserved WDT reserved
Type RO RO RO RO RO RO RO RO RO R/W RO RO R/W RO RO RO
Reset 0 0 0 0 0 0 0 0 0 0 0 0 0 0 0 0
Bit/Field Name Type Reset Description
Software should not rely on the value of a reserved bit. To provide
compatibility with future products, the value of a reserved bit should be
preserved across a read-modify-write operation.
31:26 reserved RO 0
CAN1 Reset Control
Reset control for CAN unit 1.
25 CAN1 R/W 0
CAN0 Reset Control
Reset control for CAN unit 0.
24 CAN0 R/W 0
Software should not rely on the value of a reserved bit. To provide
compatibility with future products, the value of a reserved bit should be
preserved across a read-modify-write operation.
23:21 reserved RO 0
PWM Reset Control
Reset control for PWM module.
20 PWM R/W 0
Software should not rely on the value of a reserved bit. To provide
compatibility with future products, the value of a reserved bit should be
preserved across a read-modify-write operation.
19:17 reserved RO 0
ADC0 Reset Control
Reset control for SAR ADC module 0.
16 ADC R/W 0
Software should not rely on the value of a reserved bit. To provide
compatibility with future products, the value of a reserved bit should be
preserved across a read-modify-write operation.
15:7 reserved RO 0
HIB Reset Control
Reset control for the Hibernation module.
6 HIB R/W 0
Software should not rely on the value of a reserved bit. To provide
compatibility with future products, the value of a reserved bit should be
preserved across a read-modify-write operation.
5:4 reserved RO 0
WDT Reset Control
Reset control for Watchdog unit.
3 WDT R/W 0
January 08, 2011 231
Texas Instruments-Production Data
Stellaris® LM3S2965 Microcontroller
Bit/Field Name Type Reset Description
Software should not rely on the value of a reserved bit. To provide
compatibility with future products, the value of a reserved bit should be
preserved across a read-modify-write operation.
2:0 reserved RO 0
232 January 08, 2011
Texas Instruments-Production Data
System Control
Register 28: Software Reset Control 1 (SRCR1), offset 0x044
Writes to this register are masked by the bits in the Device Capabilities 2 (DC2) register.
Software Reset Control 1 (SRCR1)
Base 0x400F.E000
Offset 0x044
Type R/W, reset 0x00000000
31 30 29 28 27 26 25 24 23 22 21 20 19 18 17 16
reserved COMP2 COMP1 COMP0 reserved TIMER3 TIMER2 TIMER1 TIMER0
Type RO RO RO RO RO R/W R/W R/W RO RO RO RO R/W R/W R/W R/W
Reset 0 0 0 0 0 0 0 0 0 0 0 0 0 0 0 0
15 14 13 12 11 10 9 8 7 6 5 4 3 2 1 0
reserved I2C1 reserved I2C0 reserved QEI1 QEI0 reserved SSI1 SSI0 reserved UART2 UART1 UART0
Type RO R/W RO R/W RO RO R/W R/W RO RO R/W R/W RO R/W R/W R/W
Reset 0 0 0 0 0 0 0 0 0 0 0 0 0 0 0 0
Bit/Field Name Type Reset Description
Software should not rely on the value of a reserved bit. To provide
compatibility with future products, the value of a reserved bit should be
preserved across a read-modify-write operation.
31:27 reserved RO 0
Analog Comp 2 Reset Control
Reset control for analog comparator 2.
26 COMP2 R/W 0
Analog Comp 1 Reset Control
Reset control for analog comparator 1.
25 COMP1 R/W 0
Analog Comp 0 Reset Control
Reset control for analog comparator 0.
24 COMP0 R/W 0
Software should not rely on the value of a reserved bit. To provide
compatibility with future products, the value of a reserved bit should be
preserved across a read-modify-write operation.
23:20 reserved RO 0
Timer 3 Reset Control
Reset control for General-Purpose Timer module 3.
19 TIMER3 R/W 0
Timer 2 Reset Control
Reset control for General-Purpose Timer module 2.
18 TIMER2 R/W 0
Timer 1 Reset Control
Reset control for General-Purpose Timer module 1.
17 TIMER1 R/W 0
Timer 0 Reset Control
Reset control for General-Purpose Timer module 0.
16 TIMER0 R/W 0
Software should not rely on the value of a reserved bit. To provide
compatibility with future products, the value of a reserved bit should be
preserved across a read-modify-write operation.
15 reserved RO 0
I2C1 Reset Control
Reset control for I2C unit 1.
14 I2C1 R/W 0
Software should not rely on the value of a reserved bit. To provide
compatibility with future products, the value of a reserved bit should be
preserved across a read-modify-write operation.
13 reserved RO 0
January 08, 2011 233
Texas Instruments-Production Data
Stellaris® LM3S2965 Microcontroller
Bit/Field Name Type Reset Description
I2C0 Reset Control
Reset control for I2C unit 0.
12 I2C0 R/W 0
Software should not rely on the value of a reserved bit. To provide
compatibility with future products, the value of a reserved bit should be
preserved across a read-modify-write operation.
11:10 reserved RO 0
QEI1 Reset Control
Reset control for QEI unit 1.
9 QEI1 R/W 0
QEI0 Reset Control
Reset control for QEI unit 0.
8 QEI0 R/W 0
Software should not rely on the value of a reserved bit. To provide
compatibility with future products, the value of a reserved bit should be
preserved across a read-modify-write operation.
7:6 reserved RO 0
SSI1 Reset Control
Reset control for SSI unit 1.
5 SSI1 R/W 0
SSI0 Reset Control
Reset control for SSI unit 0.
4 SSI0 R/W 0
Software should not rely on the value of a reserved bit. To provide
compatibility with future products, the value of a reserved bit should be
preserved across a read-modify-write operation.
3 reserved RO 0
UART2 Reset Control
Reset control for UART unit 2.
2 UART2 R/W 0
UART1 Reset Control
Reset control for UART unit 1.
1 UART1 R/W 0
UART0 Reset Control
Reset control for UART unit 0.
0 UART0 R/W 0
234 January 08, 2011
Texas Instruments-Production Data
System Control
Register 29: Software Reset Control 2 (SRCR2), offset 0x048
Writes to this register are masked by the bits in the Device Capabilities 4 (DC4) register.
Software Reset Control 2 (SRCR2)
Base 0x400F.E000
Offset 0x048
Type R/W, reset 0x00000000
31 30 29 28 27 26 25 24 23 22 21 20 19 18 17 16
reserved
Type RO RO RO RO RO RO RO RO RO RO RO RO RO RO RO RO
Reset 0 0 0 0 0 0 0 0 0 0 0 0 0 0 0 0
15 14 13 12 11 10 9 8 7 6 5 4 3 2 1 0
reserved GPIOH GPIOG GPIOF GPIOE GPIOD GPIOC GPIOB GPIOA
Type RO RO RO RO RO RO RO RO R/W R/W R/W R/W R/W R/W R/W R/W
Reset 0 0 0 0 0 0 0 0 0 0 0 0 0 0 0 0
Bit/Field Name Type Reset Description
Software should not rely on the value of a reserved bit. To provide
compatibility with future products, the value of a reserved bit should be
preserved across a read-modify-write operation.
31:8 reserved RO 0
Port H Reset Control
Reset control for GPIO Port H.
7 GPIOH R/W 0
Port G Reset Control
Reset control for GPIO Port G.
6 GPIOG R/W 0
Port F Reset Control
Reset control for GPIO Port F.
5 GPIOF R/W 0
Port E Reset Control
Reset control for GPIO Port E.
4 GPIOE R/W 0
Port D Reset Control
Reset control for GPIO Port D.
3 GPIOD R/W 0
Port C Reset Control
Reset control for GPIO Port C.
2 GPIOC R/W 0
Port B Reset Control
Reset control for GPIO Port B.
1 GPIOB R/W 0
Port A Reset Control
Reset control for GPIO Port A.
0 GPIOA R/W 0
January 08, 2011 235
Texas Instruments-Production Data
Stellaris® LM3S2965 Microcontroller
6 Hibernation Module
The Hibernation Module manages removal and restoration of power to provide a means for reducing
power consumption. When the processor and peripherals are idle, power can be completely removed
with only the Hibernation module remaining powered. Power can be restored based on an external
signal, or at a certain time using the built-in Real-Time Clock (RTC). The Hibernation module can
be independently supplied from a battery or an auxiliary power supply.
The Hibernation module has the following features:
■ System power control using discrete external regulator
■ Dedicated pin for waking from an external signal
■ Low-battery detection, signaling, and interrupt generation
■ 32-bit real-time clock (RTC)
■ Two 32-bit RTC match registers for timed wake-up and interrupt generation
■ Clock source from a 32.768-kHz external oscillator or a 4.194304-MHz crystal
■ RTC predivider trim for making fine adjustments to the clock rate
■ 64 32-bit words of non-volatile memory
■ Programmable interrupts for RTC match, external wake, and low battery events
236 January 08, 2011
Texas Instruments-Production Data
Hibernation Module
6.1 Block Diagram
Figure 6-1. Hibernation Module Block Diagram
HIBIM
HIBRIS
HIBMIS
HIBIC
HIBRTCT
Pre-Divider
/128
XOSC0
XOSC1
HIBCTL.CLK32EN
HIBCTL.CLKSEL
HIBRTCC
HIBRTCLD
HIBRTCM0
HIBRTCM1
RTC
Interrupts
Power
Sequence
Logic
MATCH0/1
WAKE
Interrupts
to CPU
Low Battery
Detect
LOWBAT
VDD
VBAT
HIB
HIBCTL.LOWBATEN HIBCTL.PWRCUT
HIBCTL.EXTWEN
HIBCTL.RTCWEN
HIBCTL.VABORT
Non-Volatile
Memory
64 words
HIBDATA
32.768 kHz
4.194304 MHz
6.2 Functional Description
The Hibernation module controls the power to the processor with an enable signal (HIB) that signals
an external voltage regulator to turn off.
The Hibernation module power source is determined dynamically. The supply voltage of the
Hibernation module is the larger of the main voltage source (VDD) or the battery/auxilliary voltage
source (VBAT). A voting circuit indicates the larger and an internal power switch selects the appropriate
voltage source. The Hibernation module also has a separate clock source to maintain a real-time
clock (RTC). Once in hibernation, the module signals an external voltage regulator to turn back on
the power when an external pin (WAKE) is asserted, or when the internal RTC reaches a certain
value. The Hibernation module can also detect when the battery voltage is low, and optionally
prevent hibernation when this occurs.
When waking from hibernation, the HIB signal is deasserted. The return of VDD causes a POR to
be executed. The time from when the WAKE signal is asserted to when code begins execution is
equal to the wake-up time (tWAKE_TO_HIB) plus the power-on reset time (TIRPOR).
6.2.1 Register Access Timing
Because the Hibernation module has an independent clocking domain, certain registers must be
written only with a timing gap between accesses. The delay time is tHIB_REG_WRITE, therefore software
must guarantee that a delay of tHIB_REG_WRITE is inserted between back-to-back writes to certain
Hibernation registers, or between a write followed by a read to those same registers. There is no
January 08, 2011 237
Texas Instruments-Production Data
Stellaris® LM3S2965 Microcontroller
restriction on timing for back-to-back reads from the Hibernation module. The following registers
are subject to this timing restriction:
■ Hibernation RTC Counter (HIBRTCC)
■ Hibernation RTC Match 0 (HIBRTCM0)
■ Hibernation RTC Match 1 (HIBRTCM1)
■ Hibernation RTC Load (HIBRTCLD)
■ Hibernation RTC Trim (HIBRTCT)
■ Hibernation Data (HIBDATA)
6.2.2 Clock Source
The Hibernation module must be clocked by an external source, even if the RTC feature is not used.
An external oscillator or crystal can be used for this purpose. To use a crystal, a 4.194304-MHz
crystal is connected to the XOSC0 and XOSC1 pins. This clock signal is divided by 128 internally to
produce the 32.768-kHz clock reference. For an alternate clock source, a 32.768-kHz oscillator can
be connected to the XOSC0 pin. See Figure 6-2 on page 239 and Figure 6-3 on page 239. Note that
these diagrams only show the connection to the Hibernation pins and not to the full system. See
“Hibernation Module” on page 687 for specific values.
The clock source is enabled by setting the CLK32EN bit of the HIBCTL register. The type of clock
source is selected by setting the CLKSEL bit to 0 for a 4.194304-MHz clock source, and to 1 for a
32.768-kHz clock source. If the bit is set to 0, the 4.194304-MHz input clock is divided by 128,
resulting in a 32.768-kHz clock source. If a crystal is used for the clock source, the software must
leave a delay of tXOSC_SETTLE after setting the CLK32EN bit and before any other accesses to the
Hibernation module registers. The delay allows the crystal to power up and stabilize. If an oscillator
is used for the clock source, no delay is needed.
238 January 08, 2011
Texas Instruments-Production Data
Hibernation Module
Figure 6-2. Clock Source Using Crystal
Open drain
external wake
up circuit
3 V
Battery
GND
C1 C2
X1 RL
VBAT
EN
Input
Voltage
Regulator
or Switch
XOSC1
XOSC0
VDD
HIB
WAKE
IN OUT
Stellaris Microcontroller
RPU
Note: X1 = Crystal frequency is fXOSC_XTAL.
C1,2 = Capacitor value derived from crystal vendor load capacitance specifications.
RL = Load resistor is RXOSC_LOAD.
RPU = Pull-up resistor (1 M½).
See “Hibernation Module” on page 687 for specific parameter values.
Figure 6-3. Clock Source Using Dedicated Oscillator
Open drain
external wake
up circuit
EN
3 V
Battery
GND
Stellaris Microcontroller
Input
Voltage
Regulator
or Switch
Clock
Source
(fEXT_OSC)
N.C. XOSC1
XOSC0
VDD
HIB
WAKE VBAT
IN OUT
RPU
Note: RPU = Pull-up resistor (1 M½).
6.2.3 Battery Management
The Hibernation module can be independently powered by a battery or an auxiliary power source.
The module can monitor the voltage level of the battery and detect when the voltage drops below
VLOWBAT. When this happens, an interrupt can be generated. The module can also be configured
so that it will not go into Hibernate mode if the battery voltage drops below this threshold. Battery
voltage is not measured while in Hibernate mode.
January 08, 2011 239
Texas Instruments-Production Data
Stellaris® LM3S2965 Microcontroller
Important: System level factors may affect the accuracy of the low battery detect circuit. The
designer should consider battery type, discharge characteristics, and a test load during
battery voltage measurements.
Note that the Hibernation module draws power from whichever source (VBAT or VDD) has the higher
voltage. Therefore, it is important to design the circuit to ensure that VDD is higher that VBAT under
nominal conditions or else the Hibernation module draws power from the battery even when VDD is
available.
The Hibernation module can be configured to detect a low battery condition by setting the LOWBATEN
bit of the HIBCTL register. In this configuration, the LOWBAT bit of the HIBRIS register will be set
when the battery level is low. If the VABORT bit is also set, then the module is prevented from entering
Hibernation mode when a low battery is detected. The module can also be configured to generate
an interrupt for the low-battery condition (see “Interrupts and Status” on page 241).
6.2.4 Real-Time Clock
The Hibernation module includes a 32-bit counter that increments once per second with a proper
clock source and configuration (see “Clock Source” on page 238). The 32.768-kHz clock signal is
fed into a predivider register which counts down the 32.768-kHz clock ticks to achieve a once per
second clock rate for the RTC. The rate can be adjusted to compensate for inaccuracies in the clock
source by using the predivider trim register, HIBRTCT. This register has a nominal value of 0x7FFF,
and is used for one second out of every 64 seconds to divide the input clock. This allows the software
to make fine corrections to the clock rate by adjusting the predivider trim register up or down from
0x7FFF. The predivider trim should be adjusted up from 0x7FFF in order to slow down the RTC
rate, and down from 0x7FFF in order to speed up the RTC rate.
The Hibernation module includes two 32-bit match registers that are compared to the value of the
RTC counter. The match registers can be used to wake the processor from hibernation mode, or
to generate an interrupt to the processor if it is not in hibernation.
The RTC must be enabled with the RTCEN bit of the HIBCTL register. The value of the RTC can be
set at any time by writing to the HIBRTCLD register. The predivider trim can be adjusted by reading
and writing the HIBRTCT register. The predivider uses this register once every 64 seconds to adjust
the clock rate. The two match registers can be set by writing to the HIBRTCM0 and HIBRTCM1
registers. The RTC can be configured to generate interrupts by using the interrupt registers (see
“Interrupts and Status” on page 241).
6.2.5 Non-Volatile Memory
The Hibernation module contains 64 32-bit words of memory which are retained during hibernation.
This memory is powered from the battery or auxiliary power supply during hibernation. The processor
software can save state information in this memory prior to hibernation, and can then recover the
state upon waking. The non-volatile memory can be accessed through the HIBDATA registers.
6.2.6 Power Control
Important: The Hibernation Module requires special system implementation considerations when
using HIB to control power, as it is intended to power-down all other sections of its host
device. All system signals and power supplies that connect to the chip must be driven
to 0 VDC or powered down with the same regulator controlled by HIB. See “Hibernation
Module” on page 687 for more details.
The Hibernation module controls power to the microcontroller through the use of the HIB pin. This
pin is intended to be connected to the enable signal of the external regulator(s) providing 3.3 V
240 January 08, 2011
Texas Instruments-Production Data
Hibernation Module
and/or 2.5 V to the microcontroller. When the HIB signal is asserted by the Hibernation module, the
external regulator is turned off and no longer powers the system. The Hibernation module remains
powered from the VBAT supply (which could be a battery or an auxiliary power source) until a Wake
event. Power to the device is restored by deasserting the HIB signal, which causes the external
regulator to turn power back on to the chip.
6.2.7 Initiating Hibernate
Hibernation mode is initiated by the microcontroller setting the HIBREQ bit of the HIBCTL register.
Prior to doing this, a wake-up condition must be configured, either from the external WAKE pin, or
by using an RTC match.
The Hibernation module is configured to wake from the external WAKE pin by setting the PINWEN
bit of the HIBCTL register. It is configured to wake from RTC match by setting the RTCWEN bit. Either
one or both of these bits can be set prior to going into hibernation. The WAKE pin includes a weak
internal pull-up. Note that both the HIB and WAKE pins use the Hibernation module's internal power
supply as the logic 1 reference.
When the Hibernation module wakes, the microcontroller will see a normal power-on reset. Software
can detect that the power-on was due to a wake from hibernation by examining the raw interrupt
status register (see “Interrupts and Status” on page 241) and by looking for state data in the non-volatile
memory (see “Non-Volatile Memory” on page 240).
When the HIB signal deasserts, enabling the external regulator, the external regulator must reach
the operating voltage within tHIB_TO_VDD.
6.2.8 Interrupts and Status
The Hibernation module can generate interrupts when the following conditions occur:
■ Assertion of WAKE pin
■ RTC match
■ Low battery detected
All of the interrupts are ORed together before being sent to the interrupt controller, so the Hibernate
module can only generate a single interrupt request to the controller at any given time. The software
interrupt handler can service multiple interrupt events by reading the HIBMIS register. Software can
also read the status of the Hibernation module at any time by reading the HIBRIS register which
shows all of the pending events. This register can be used at power-on to see if a wake condition
is pending, which indicates to the software that a hibernation wake occurred.
The events that can trigger an interrupt are configured by setting the appropriate bits in the HIBIM
register. Pending interrupts can be cleared by writing the corresponding bit in the HIBIC register.
6.3 Initialization and Configuration
The Hibernation module can be set in several different configurations. The following sections show
the recommended programming sequence for various scenarios. The examples below assume that
a 32.768-kHz oscillator is used, and thus always show bit 2 (CLKSEL) of the HIBCTL register set
to 1. If a 4.194304-MHz crystal is used instead, then the CLKSEL bit remains cleared. Because the
Hibernation module runs at 32.768 kHz and is asynchronous to the rest of the system, software
must allow a delay of tHIB_REG_WRITE after writes to certain registers (see “Register Access
Timing” on page 237). The registers that require a delay are listed in a note in “Register
Map” on page 243 as well as in each register description.
January 08, 2011 241
Texas Instruments-Production Data
Stellaris® LM3S2965 Microcontroller
6.3.1 Initialization
The Hibernation module clock source must be enabled first, even if the RTC feature is not used. If
a 4.194304-MHz crystal is used, perform the following steps:
1. Write 0x40 to the HIBCTL register at offset 0x10 to enable the crystal and select the divide-by-128
input path.
2. Wait for a time of tXOSC_SETTLE for the crystal to power up and stabilize before performing any
other operations with the Hibernation module.
If a 32.678-kHz oscillator is used, then perform the following steps:
1. Write 0x44 to the HIBCTL register at offset 0x10 to enable the oscillator input.
2. No delay is necessary.
The above is only necessary when the entire system is initialized for the first time. If the processor
is powered due to a wake from hibernation, then the Hibernation module has already been powered
up and the above steps are not necessary. The software can detect that the Hibernation module
and clock are already powered by examining the CLK32EN bit of the HIBCTL register.
6.3.2 RTC Match Functionality (No Hibernation)
Use the following steps to implement the RTC match functionality of the Hibernation module:
1. Write the required RTC match value to one of the HIBRTCMn registers at offset 0x004 or 0x008.
2. Write the required RTC load value to the HIBRTCLD register at offset 0x00C.
3. Set the required RTC match interrupt mask in the RTCALT0 and RTCALT1 bits (bits 1:0) in the
HIBIM register at offset 0x014.
4. Write 0x0000.0041 to the HIBCTL register at offset 0x010 to enable the RTC to begin counting.
6.3.3 RTC Match/Wake-Up from Hibernation
Use the following steps to implement the RTC match and wake-up functionality of the Hibernation
module:
1. Write the required RTC match value to the HIBRTCMn registers at offset 0x004 or 0x008.
2. Write the required RTC load value to the HIBRTCLD register at offset 0x00C.
3. Write any data to be retained during power cut to the HIBDATA register at offsets 0x030-0x12C.
4. Set the RTC Match Wake-Up and start the hibernation sequence by writing 0x0000.004F to the
HIBCTL register at offset 0x010.
6.3.4 External Wake-Up from Hibernation
Use the following steps to implement the Hibernation module with the external WAKE pin as the
wake-up source for the microcontroller:
1. Write any data to be retained during power cut to the HIBDATA register at offsets 0x030-0x12C.
242 January 08, 2011
Texas Instruments-Production Data
Hibernation Module
2. Enable the external wake and start the hibernation sequence by writing 0x0000.0056 to the
HIBCTL register at offset 0x010.
6.3.5 RTC/External Wake-Up from Hibernation
1. Write the required RTC match value to the HIBRTCMn registers at offset 0x004 or 0x008.
2. Write the required RTC load value to the HIBRTCLD register at offset 0x00C.
3. Write any data to be retained during power cut to the HIBDATA register at offsets 0x030-0x12C.
4. Set the RTC Match/External Wake-Up and start the hibernation sequence by writing 0x0000.005F
to the HIBCTL register at offset 0x010.
6.4 Register Map
Table 6-1 on page 243 lists the Hibernation registers. All addresses given are relative to the Hibernation
Module base address at 0x400F.C000. Note that the Hibernation module clock must be enabled
before the registers can be programmed (see page 210). There must be a delay of 3 system clocks
after the Hibernation module clock is enabled before any Hibernation module registers are accessed.
Table 6-1. Hibernation Module Register Map
See
Offset Name Type Reset Description page
0x000 HIBRTCC RO 0x0000.0000 Hibernation RTC Counter 244
0x004 HIBRTCM0 R/W 0xFFFF.FFFF Hibernation RTC Match 0 245
0x008 HIBRTCM1 R/W 0xFFFF.FFFF Hibernation RTC Match 1 246
0x00C HIBRTCLD R/W 0xFFFF.FFFF Hibernation RTC Load 247
0x010 HIBCTL R/W 0x8000.0000 Hibernation Control 248
0x014 HIBIM R/W 0x0000.0000 Hibernation Interrupt Mask 250
0x018 HIBRIS RO 0x0000.0000 Hibernation Raw Interrupt Status 251
0x01C HIBMIS RO 0x0000.0000 Hibernation Masked Interrupt Status 252
0x020 HIBIC R/W1C 0x0000.0000 Hibernation Interrupt Clear 253
0x024 HIBRTCT R/W 0x0000.7FFF Hibernation RTC Trim 254
0x030- HIBDATA R/W - Hibernation Data 255
0x12C
6.5 Register Descriptions
The remainder of this section lists and describes the Hibernation module registers, in numerical
order by address offset.
January 08, 2011 243
Texas Instruments-Production Data
Stellaris® LM3S2965 Microcontroller
Register 1: Hibernation RTC Counter (HIBRTCC), offset 0x000
This register is the current 32-bit value of the RTC counter.
Hibernation RTC Counter (HIBRTCC)
Base 0x400F.C000
Offset 0x000
Type RO, reset 0x0000.0000
31 30 29 28 27 26 25 24 23 22 21 20 19 18 17 16
RTCC
Type RO RO RO RO RO RO RO RO RO RO RO RO RO RO RO RO
Reset 0 0 0 0 0 0 0 0 0 0 0 0 0 0 0 0
15 14 13 12 11 10 9 8 7 6 5 4 3 2 1 0
RTCC
Type RO RO RO RO RO RO RO RO RO RO RO RO RO RO RO RO
Reset 0 0 0 0 0 0 0 0 0 0 0 0 0 0 0 0
Bit/Field Name Type Reset Description
RTC Counter
A read returns the 32-bit counter value. This register is read-only. To
change the value, use the HIBRTCLD register.
31:0 RTCC RO 0x0000.0000
244 January 08, 2011
Texas Instruments-Production Data
Hibernation Module
Register 2: Hibernation RTC Match 0 (HIBRTCM0), offset 0x004
This register is the 32-bit match 0 register for the RTC counter.
Hibernation RTC Match 0 (HIBRTCM0)
Base 0x400F.C000
Offset 0x004
Type R/W, reset 0xFFFF.FFFF
31 30 29 28 27 26 25 24 23 22 21 20 19 18 17 16
RTCM0
Type R/W R/W R/W R/W R/W R/W R/W R/W R/W R/W R/W R/W R/W R/W R/W R/W
Reset 1 1 1 1 1 1 1 1 1 1 1 1 1 1 1 1
15 14 13 12 11 10 9 8 7 6 5 4 3 2 1 0
RTCM0
Type R/W R/W R/W R/W R/W R/W R/W R/W R/W R/W R/W R/W R/W R/W R/W R/W
Reset 1 1 1 1 1 1 1 1 1 1 1 1 1 1 1 1
Bit/Field Name Type Reset Description
RTC Match 0
A write loads the value into the RTC match register.
A read returns the current match value.
31:0 RTCM0 R/W 0xFFFF.FFFF
January 08, 2011 245
Texas Instruments-Production Data
Stellaris® LM3S2965 Microcontroller
Register 3: Hibernation RTC Match 1 (HIBRTCM1), offset 0x008
This register is the 32-bit match 1 register for the RTC counter.
Hibernation RTC Match 1 (HIBRTCM1)
Base 0x400F.C000
Offset 0x008
Type R/W, reset 0xFFFF.FFFF
31 30 29 28 27 26 25 24 23 22 21 20 19 18 17 16
RTCM1
Type R/W R/W R/W R/W R/W R/W R/W R/W R/W R/W R/W R/W R/W R/W R/W R/W
Reset 1 1 1 1 1 1 1 1 1 1 1 1 1 1 1 1
15 14 13 12 11 10 9 8 7 6 5 4 3 2 1 0
RTCM1
Type R/W R/W R/W R/W R/W R/W R/W R/W R/W R/W R/W R/W R/W R/W R/W R/W
Reset 1 1 1 1 1 1 1 1 1 1 1 1 1 1 1 1
Bit/Field Name Type Reset Description
RTC Match 1
A write loads the value into the RTC match register.
A read returns the current match value.
31:0 RTCM1 R/W 0xFFFF.FFFF
246 January 08, 2011
Texas Instruments-Production Data
Hibernation Module
Register 4: Hibernation RTC Load (HIBRTCLD), offset 0x00C
This register is the 32-bit value loaded into the RTC counter.
Hibernation RTC Load (HIBRTCLD)
Base 0x400F.C000
Offset 0x00C
Type R/W, reset 0xFFFF.FFFF
31 30 29 28 27 26 25 24 23 22 21 20 19 18 17 16
RTCLD
Type R/W R/W R/W R/W R/W R/W R/W R/W R/W R/W R/W R/W R/W R/W R/W R/W
Reset 1 1 1 1 1 1 1 1 1 1 1 1 1 1 1 1
15 14 13 12 11 10 9 8 7 6 5 4 3 2 1 0
RTCLD
Type R/W R/W R/W R/W R/W R/W R/W R/W R/W R/W R/W R/W R/W R/W R/W R/W
Reset 1 1 1 1 1 1 1 1 1 1 1 1 1 1 1 1
Bit/Field Name Type Reset Description
RTC Load
A write loads the current value into the RTC counter (RTCC).
A read returns the 32-bit load value.
31:0 RTCLD R/W 0xFFFF.FFFF
January 08, 2011 247
Texas Instruments-Production Data
Stellaris® LM3S2965 Microcontroller
Register 5: Hibernation Control (HIBCTL), offset 0x010
This register is the control register for the Hibernation module.
Hibernation Control (HIBCTL)
Base 0x400F.C000
Offset 0x010
Type R/W, reset 0x8000.0000
31 30 29 28 27 26 25 24 23 22 21 20 19 18 17 16
reserved
Type RO RO RO RO RO RO RO RO RO RO RO RO RO RO RO RO
Reset 0 0 0 0 0 0 0 0 0 0 0 0 0 0 0 0
15 14 13 12 11 10 9 8 7 6 5 4 3 2 1 0
reserved VABORT CLK32EN LOWBATEN PINWEN RTCWEN CLKSEL HIBREQ RTCEN
Type RO RO RO RO RO RO RO RO R/W R/W R/W R/W R/W R/W R/W R/W
Reset 0 0 0 0 0 0 0 0 0 0 0 0 0 0 0 0
Bit/Field Name Type Reset Description
Software should not rely on the value of a reserved bit. To provide
compatibility with future products, the value of a reserved bit should be
preserved across a read-modify-write operation.
31:8 reserved RO 0x00
Power Cut Abort Enable
Value Description
0 Power cut occurs during a low-battery alert.
1 Power cut is aborted.
7 VABORT R/W 0
Clocking Enable
Value Description
0 Disabled
1 Enabled
This bit must be enabled to use the Hibernation module. If a crystal is
used, then software should wait 20 ms after setting this bit to allow the
crystal to power up and stabilize.
6 CLK32EN R/W 0
Low Battery Monitoring Enable
Value Description
0 Disabled
1 Enabled
When set, low battery voltage detection is enabled (VBAT < VLOWBAT).
5 LOWBATEN R/W 0
External WAKE Pin Enable
Value Description
0 Disabled
1 Enabled
When set, an external event on the WAKE pin will re-power the device.
4 PINWEN R/W 0
248 January 08, 2011
Texas Instruments-Production Data
Hibernation Module
Bit/Field Name Type Reset Description
RTC Wake-up Enable
Value Description
0 Disabled
1 Enabled
When set, an RTC match event (RTCM0 or RTCM1) will re-power the
device based on the RTC counter value matching the corresponding
match register 0 or 1.
3 RTCWEN R/W 0
Hibernation Module Clock Select
Value Description
Use Divide by 128 output. Use this value for a
4.194304-MHz crystal.
0
Use raw output. Use this value for a 32.768-kHz
oscillator.
1
2 CLKSEL R/W 0
Hibernation Request
Value Description
0 Disabled
1 Hibernation initiated
After a wake-up event, this bit is cleared by hardware.
1 HIBREQ R/W 0
RTC Timer Enable
Value Description
0 Disabled
1 Enabled
0 RTCEN R/W 0
January 08, 2011 249
Texas Instruments-Production Data
Stellaris® LM3S2965 Microcontroller
Register 6: Hibernation Interrupt Mask (HIBIM), offset 0x014
This register is the interrupt mask register for the Hibernation module interrupt sources.
Hibernation Interrupt Mask (HIBIM)
Base 0x400F.C000
Offset 0x014
Type R/W, reset 0x0000.0000
31 30 29 28 27 26 25 24 23 22 21 20 19 18 17 16
reserved
Type RO RO RO RO RO RO RO RO RO RO RO RO RO RO RO RO
Reset 0 0 0 0 0 0 0 0 0 0 0 0 0 0 0 0
15 14 13 12 11 10 9 8 7 6 5 4 3 2 1 0
reserved EXTW LOWBAT RTCALT1 RTCALT0
Type RO RO RO RO RO RO RO RO RO RO RO RO R/W R/W R/W R/W
Reset 0 0 0 0 0 0 0 0 0 0 0 0 0 0 0 0
Bit/Field Name Type Reset Description
Software should not rely on the value of a reserved bit. To provide
compatibility with future products, the value of a reserved bit should be
preserved across a read-modify-write operation.
31:4 reserved RO 0x000.0000
External Wake-Up Interrupt Mask
Value Description
0 Masked
1 Unmasked
3 EXTW R/W 0
Low Battery Voltage Interrupt Mask
Value Description
0 Masked
1 Unmasked
2 LOWBAT R/W 0
RTC Alert1 Interrupt Mask
Value Description
0 Masked
1 Unmasked
1 RTCALT1 R/W 0
RTC Alert0 Interrupt Mask
Value Description
0 Masked
1 Unmasked
0 RTCALT0 R/W 0
250 January 08, 2011
Texas Instruments-Production Data
Hibernation Module
Register 7: Hibernation Raw Interrupt Status (HIBRIS), offset 0x018
This register is the raw interrupt status for the Hibernation module interrupt sources.
Hibernation Raw Interrupt Status (HIBRIS)
Base 0x400F.C000
Offset 0x018
Type RO, reset 0x0000.0000
31 30 29 28 27 26 25 24 23 22 21 20 19 18 17 16
reserved
Type RO RO RO RO RO RO RO RO RO RO RO RO RO RO RO RO
Reset 0 0 0 0 0 0 0 0 0 0 0 0 0 0 0 0
15 14 13 12 11 10 9 8 7 6 5 4 3 2 1 0
reserved EXTW LOWBAT RTCALT1 RTCALT0
Type RO RO RO RO RO RO RO RO RO RO RO RO RO RO RO RO
Reset 0 0 0 0 0 0 0 0 0 0 0 0 0 0 0 0
Bit/Field Name Type Reset Description
Software should not rely on the value of a reserved bit. To provide
compatibility with future products, the value of a reserved bit should be
preserved across a read-modify-write operation.
31:4 reserved RO 0x000.0000
3 EXTW RO 0 External Wake-Up Raw Interrupt Status
2 LOWBAT RO 0 Low Battery Voltage Raw Interrupt Status
1 RTCALT1 RO 0 RTC Alert1 Raw Interrupt Status
0 RTCALT0 RO 0 RTC Alert0 Raw Interrupt Status
January 08, 2011 251
Texas Instruments-Production Data
Stellaris® LM3S2965 Microcontroller
Register 8: Hibernation Masked Interrupt Status (HIBMIS), offset 0x01C
This register is the masked interrupt status for the Hibernation module interrupt sources.
Hibernation Masked Interrupt Status (HIBMIS)
Base 0x400F.C000
Offset 0x01C
Type RO, reset 0x0000.0000
31 30 29 28 27 26 25 24 23 22 21 20 19 18 17 16
reserved
Type RO RO RO RO RO RO RO RO RO RO RO RO RO RO RO RO
Reset 0 0 0 0 0 0 0 0 0 0 0 0 0 0 0 0
15 14 13 12 11 10 9 8 7 6 5 4 3 2 1 0
reserved EXTW LOWBAT RTCALT1 RTCALT0
Type RO RO RO RO RO RO RO RO RO RO RO RO RO RO RO RO
Reset 0 0 0 0 0 0 0 0 0 0 0 0 0 0 0 0
Bit/Field Name Type Reset Description
Software should not rely on the value of a reserved bit. To provide
compatibility with future products, the value of a reserved bit should be
preserved across a read-modify-write operation.
31:4 reserved RO 0x000.0000
3 EXTW RO 0 External Wake-Up Masked Interrupt Status
2 LOWBAT RO 0 Low Battery Voltage Masked Interrupt Status
1 RTCALT1 RO 0 RTC Alert1 Masked Interrupt Status
0 RTCALT0 RO 0 RTC Alert0 Masked Interrupt Status
252 January 08, 2011
Texas Instruments-Production Data
Hibernation Module
Register 9: Hibernation Interrupt Clear (HIBIC), offset 0x020
This register is the interrupt write-one-to-clear register for the Hibernation module interrupt sources.
Hibernation Interrupt Clear (HIBIC)
Base 0x400F.C000
Offset 0x020
Type R/W1C, reset 0x0000.0000
31 30 29 28 27 26 25 24 23 22 21 20 19 18 17 16
reserved
Type RO RO RO RO RO RO RO RO RO RO RO RO RO RO RO RO
Reset 0 0 0 0 0 0 0 0 0 0 0 0 0 0 0 0
15 14 13 12 11 10 9 8 7 6 5 4 3 2 1 0
reserved EXTW LOWBAT RTCALT1 RTCALT0
Type RO RO RO RO RO RO RO RO RO RO RO RO R/W1C R/W1C R/W1C R/W1C
Reset 0 0 0 0 0 0 0 0 0 0 0 0 0 0 0 0
Bit/Field Name Type Reset Description
Software should not rely on the value of a reserved bit. To provide
compatibility with future products, the value of a reserved bit should be
preserved across a read-modify-write operation.
31:4 reserved RO 0x000.0000
External Wake-Up Masked Interrupt Clear
Reads return an indeterminate value.
3 EXTW R/W1C 0
Low Battery Voltage Masked Interrupt Clear
Reads return an indeterminate value.
2 LOWBAT R/W1C 0
RTC Alert1 Masked Interrupt Clear
Reads return an indeterminate value.
1 RTCALT1 R/W1C 0
RTC Alert0 Masked Interrupt Clear
Reads return an indeterminate value.
0 RTCALT0 R/W1C 0
January 08, 2011 253
Texas Instruments-Production Data
Stellaris® LM3S2965 Microcontroller
Register 10: Hibernation RTC Trim (HIBRTCT), offset 0x024
This register contains the value that is used to trim the RTC clock predivider. It represents the
computed underflow value that is used during the trim cycle. It is represented as 0x7FFF ± N clock
cycles.
Hibernation RTC Trim (HIBRTCT)
Base 0x400F.C000
Offset 0x024
Type R/W, reset 0x0000.7FFF
31 30 29 28 27 26 25 24 23 22 21 20 19 18 17 16
reserved
Type RO RO RO RO RO RO RO RO RO RO RO RO RO RO RO RO
Reset 0 0 0 0 0 0 0 0 0 0 0 0 0 0 0 0
15 14 13 12 11 10 9 8 7 6 5 4 3 2 1 0
TRIM
Type R/W R/W R/W R/W R/W R/W R/W R/W R/W R/W R/W R/W R/W R/W R/W R/W
Reset 0 1 1 1 1 1 1 1 1 1 1 1 1 1 1 1
Bit/Field Name Type Reset Description
Software should not rely on the value of a reserved bit. To provide
compatibility with future products, the value of a reserved bit should be
preserved across a read-modify-write operation.
31:16 reserved RO 0x0000
RTC Trim Value
This value is loaded into the RTC predivider every 64 seconds. It is used
to adjust the RTC rate to account for drift and inaccuracy in the clock
source. The compensation is made by software by adjusting the default
value of 0x7FFF up or down.
15:0 TRIM R/W 0x7FFF
254 January 08, 2011
Texas Instruments-Production Data
Hibernation Module
Register 11: Hibernation Data (HIBDATA), offset 0x030-0x12C
This address space is implemented as a 64x32-bit memory (256 bytes). It can be loaded by the
system processor in order to store any non-volatile state data and will not lose power during a power
cut operation.
Hibernation Data (HIBDATA)
Base 0x400F.C000
Offset 0x030-0x12C
Type R/W, reset -
31 30 29 28 27 26 25 24 23 22 21 20 19 18 17 16
RTD
Type R/W R/W R/W R/W R/W R/W R/W R/W R/W R/W R/W R/W R/W R/W R/W R/W
Reset - - - - - - - - - - - - - - - -
15 14 13 12 11 10 9 8 7 6 5 4 3 2 1 0
RTD
Type R/W R/W R/W R/W R/W R/W R/W R/W R/W R/W R/W R/W R/W R/W R/W R/W
Reset - - - - - - - - - - - - - - - -
Bit/Field Name Type Reset Description
31:0 RTD R/W - Hibernation Module NV Registers[63:0]
January 08, 2011 255
Texas Instruments-Production Data
Stellaris® LM3S2965 Microcontroller
7 Internal Memory
The LM3S2965 microcontroller comes with 64 KB of bit-banded SRAM and 256 KB of flash memory.
The flash controller provides a user-friendly interface, making flash programming a simple task.
Flash protection can be applied to the flash memory on a 2-KB block basis.
7.1 Block Diagram
Figure 7-1 on page 256 illustrates the Flash functions. The dashed boxes in the figure indicate
registers residing in the System Control module rather than the Flash Control module.
Figure 7-1. Flash Block Diagram
Flash Control
FMA
FMD
FCIM
FCMISC
Flash Array
Cortex-M3
Bridge
SRAM Array
System
Bus
Icode
Bus
Dcode
Bus
Flash Protection
FMPREn
FMPPEn
Flash Timing
USECRL
User Registers
USER_DBG
USER_REG0
USER_REG1
FMC
FCRIS
7.2 Functional Description
This section describes the functionality of the SRAM and Flash memories.
7.2.1 SRAM Memory
The internal SRAM of the Stellaris® devices is located at address 0x2000.0000 of the device memory
map. To reduce the number of time consuming read-modify-write (RMW) operations, ARM has
introduced bit-banding technology in the Cortex-M3 processor. With a bit-band-enabled processor,
certain regions in the memory map (SRAM and peripheral space) can use address aliases to access
individual bits in a single, atomic operation.
The bit-band alias is calculated by using the formula:
bit-band alias = bit-band base + (byte offset * 32) + (bit number * 4)
For example, if bit 3 at address 0x2000.1000 is to be modified, the bit-band alias is calculated as:
0x2200.0000 + (0x1000 * 32) + (3 * 4) = 0x2202.000C
256 January 08, 2011
Texas Instruments-Production Data
Internal Memory
With the alias address calculated, an instruction performing a read/write to address 0x2202.000C
allows direct access to only bit 3 of the byte at address 0x2000.1000.
For details about bit-banding, see “Bit-Banding” on page 75.
7.2.2 Flash Memory
The flash is organized as a set of 1-KB blocks that can be individually erased. Erasing a block
causes the entire contents of the block to be reset to all 1s. An individual 32-bit word can be
programmed to change bits that are currently 1 to a 0. These blocks are paired into a set of 2-KB
blocks that can be individually protected. The protection allows blocks to be marked as read-only
or execute-only, providing different levels of code protection. Read-only blocks cannot be erased
or programmed, protecting the contents of those blocks from being modified. Execute-only blocks
cannot be erased or programmed, and can only be read by the controller instruction fetch mechanism,
protecting the contents of those blocks from being read by either the controller or by a debugger.
See also “Serial Flash Loader” on page 693 for a preprogrammed flash-resident utility used to
download code to the flash memory of a device without the use of a debug interface.
7.2.2.1 Flash Memory Timing
The timing for the flash is automatically handled by the flash controller. However, in order to do so,
it must know the clock rate of the system in order to time its internal signals properly. The number
of clock cycles per microsecond must be provided to the flash controller for it to accomplish this
timing. It is software's responsibility to keep the flash controller updated with this information via the
USec Reload (USECRL) register.
On reset, the USECRL register is loaded with a value that configures the flash timing so that it works
with the maximum clock rate of the part. If software changes the system operating frequency, the
new operating frequency minus 1 (in MHz) must be loaded into USECRL before any flash
modifications are attempted. For example, if the device is operating at a speed of 20 MHz, a value
of 0x13 (20-1) must be written to the USECRL register.
7.2.2.2 Flash Memory Protection
The user is provided two forms of flash protection per 2-KB flash blocks in four pairs of 32-bit wide
registers. The protection policy for each form is controlled by individual bits (per policy per block)
in the FMPPEn and FMPREn registers.
■ Flash Memory Protection Program Enable (FMPPEn): If set, the block may be programmed
(written) or erased. If cleared, the block may not be changed.
■ Flash Memory Protection Read Enable (FMPREn): If a bit is set, the corresponding block may
be executed or read by software or debuggers. If a bit is cleared, the corresponding block may
only be executed, and contents of the memory block are prohibited from being read as data.
The policies may be combined as shown in Table 7-1 on page 257.
Table 7-1. Flash Protection Policy Combinations
FMPPEn FMPREn Protection
Execute-only protection. The block may only be executed and may not be written or erased.
This mode is used to protect code.
0 0
The block may be written, erased or executed, but not read. This combination is unlikely to
be used.
1 0
January 08, 2011 257
Texas Instruments-Production Data
Stellaris® LM3S2965 Microcontroller
Table 7-1. Flash Protection Policy Combinations (continued)
FMPPEn FMPREn Protection
Read-only protection. The block may be read or executed but may not be written or erased.
This mode is used to lock the block from further modification while allowing any read or
execute access.
0 1
1 1 No protection. The block may be written, erased, executed or read.
A Flash memory access that attempts to read a read-protected block (FMPREn bit is set) is prohibited
and generates a bus fault. A Flash memory access that attempts to program or erase a
program-protected block (FMPPEn bit is set) is prohibited and can optionally generate an interrupt
(by setting the AMASK bit in the Flash Controller Interrupt Mask (FCIM) register) to alert software
developers of poorly behaving software during the development and debug phases.
The factory settings for the FMPREn and FMPPEn registers are a value of 1 for all implemented
banks. These settings create a policy of open access and programmability. The register bits may
be changed by clearing the specific register bit. The changes are not permanent until the register
is committed (saved), at which point the bit change is permanent. If a bit is changed from a 1 to a
0 and not committed, it may be restored by executing a power-on reset sequence. The changes
are committed using the Flash Memory Control (FMC) register. Details on programming these bits
are discussed in “Nonvolatile Register Programming” on page 259.
7.2.2.3 Interrupts
The Flash memory controller can generate interrupts when the following conditions are observed:
■ Programming Interrupt - signals when a program or erase action is complete.
■ Access Interrupt - signals when a program or erase action has been attempted on a 2-kB block
of memory that is protected by its corresponding FMPPEn bit.
The interrupt events that can trigger a controller-level interrupt are defined in the Flash Controller
Masked Interrupt Status (FCMIS) register (see page 267) by setting the corresponding MASK bits.
If interrupts are not used, the raw interrupt status is always visible via the Flash Controller Raw
Interrupt Status (FCRIS) register (see page 266).
Interrupts are always cleared (for both the FCMIS and FCRIS registers) by writing a 1 to the
corresponding bit in the Flash Controller Masked Interrupt Status and Clear (FCMISC) register
(see page 268).
7.3 Flash Memory Initialization and Configuration
7.3.1 Flash Programming
The Stellaris devices provide a user-friendly interface for flash programming. All erase/program
operations are handled via three registers: FMA, FMD, and FMC.
During a Flash memory operation (write, page erase, or mass erase) access to the Flash memory
is inhibited. As a result, instruction and literal fetches are held off until the Flash memory operation
is complete. If instruction execution is required during a Flash memory operation, the code that is
executing must be placed in SRAM and executed from there while the flash operation is in progress.
7.3.1.1 To program a 32-bit word
1. Write source data to the FMD register.
258 January 08, 2011
Texas Instruments-Production Data
Internal Memory
2. Write the target address to the FMA register.
3. Write the flash write key and the WRITE bit (a value of 0xA442.0001) to the FMC register.
4. Poll the FMC register until the WRITE bit is cleared.
7.3.1.2 To perform an erase of a 1-KB page
1. Write the page address to the FMA register.
2. Write the flash write key and the ERASE bit (a value of 0xA442.0002) to the FMC register.
3. Poll the FMC register until the ERASE bit is cleared.
7.3.1.3 To perform a mass erase of the flash
1. Write the flash write key and the MERASE bit (a value of 0xA442.0004) to the FMC register.
2. Poll the FMC register until the MERASE bit is cleared.
7.3.2 Nonvolatile Register Programming
This section discusses how to update registers that are resident within the Flash memory itself.
These registers exist in a separate space from the main Flash memory array and are not affected
by an ERASE or MASS ERASE operation. The bits in these registers can be changed from 1 to 0
with a write operation. Prior to being committed, the register contents are unaffected by any reset
condition except power-on reset, which returns the register contents to the original value. By
committing the register values using the COMT bit in the FMC register, the register contents become
nonvolatile and are therefore retained following power cycling. Once the register contents are
committed, the contents are permanent, and they cannot be restored to their factory default values.
With the exception of the USER_DBG register, the settings in these registers can be tested before
committing them to Flash memory. For the USER_DBG register, the data to be written is loaded
into the FMD register before it is committed. The FMD register is read only and does not allow the
USER_DBG operation to be tried before committing it to nonvolatile memory.
Important: The Flash memory registers can only have bits changed from 1 to 0 by user programming
and can only be committed once. After being committed, these registers cannot be
restored to their factory default values.
In addition, the USER_REG0, USER_REG1, USER_REG2, USER_REG3, and USER_DBG registers
each use bit 31 (NW) to indicate that they have not been committed and bits in the register may be
changed from 1 to 0. These five registers can only be committed once whereas the Flash memory
protection registers may be committed multiple times. Table 7-2 on page 259 provides the FMA
address required for commitment of each of the registers and the source of the data to be written
when the FMC register is written with a value of 0xA442.0008. After writing the COMT bit, the user
may poll the FMC register to wait for the commit operation to complete.
Table 7-2. User-Programmable Flash Memory Resident Registers
Register to be Committed FMA Value Data Source
FMPRE0 0x0000.0000 FMPRE0
FMPRE1 0x0000.0002 FMPRE1
FMPRE2 0x0000.0004 FMPRE2
FMPRE3 0x0000.0006 FMPRE3
January 08, 2011 259
Texas Instruments-Production Data
Stellaris® LM3S2965 Microcontroller
Table 7-2. User-Programmable Flash Memory Resident Registers (continued)
Register to be Committed FMA Value Data Source
FMPPE0 0x0000.0001 FMPPE0
FMPPE1 0x0000.0003 FMPPE1
FMPPE2 0x0000.0005 FMPPE2
FMPPE3 0x0000.0007 FMPPE3
USER_REG0 0x8000.0000 USER_REG0
USER_REG1 0x8000.0001 USER_REG1
USER_REG2 0x8000.0002 USER_REG2
USER_REG3 0x8000.0003 USER_REG3
USER_DBG 0x7510.0000 FMD
7.4 Register Map
Table 7-3 on page 260 lists the Flash memory and control registers. The offset listed is a hexadecimal
increment to the register's address. The FMA, FMD, FMC, FCRIS, FCIM, and FCMISC register
offsets are relative to the Flash memory control base address of 0x400F.D000. The Flash memory
protection register offsets are relative to the System Control base address of 0x400F.E000.
Table 7-3. Flash Register Map
See
Offset Name Type Reset Description page
Flash Memory Control Registers (Flash Control Offset)
0x000 FMA R/W 0x0000.0000 Flash Memory Address 262
0x004 FMD R/W 0x0000.0000 Flash Memory Data 263
0x008 FMC R/W 0x0000.0000 Flash Memory Control 264
0x00C FCRIS RO 0x0000.0000 Flash Controller Raw Interrupt Status 266
0x010 FCIM R/W 0x0000.0000 Flash Controller Interrupt Mask 267
0x014 FCMISC R/W1C 0x0000.0000 Flash Controller Masked Interrupt Status and Clear 268
Flash Memory Protection Registers (System Control Offset)
0x130 FMPRE0 R/W 0xFFFF.FFFF Flash Memory Protection Read Enable 0 271
0x200 FMPRE0 R/W 0xFFFF.FFFF Flash Memory Protection Read Enable 0 271
0x134 FMPPE0 R/W 0xFFFF.FFFF Flash Memory Protection Program Enable 0 272
0x400 FMPPE0 R/W 0xFFFF.FFFF Flash Memory Protection Program Enable 0 272
0x140 USECRL R/W 0x31 USec Reload 270
0x1D0 USER_DBG R/W 0xFFFF.FFFE User Debug 273
0x1E0 USER_REG0 R/W 0xFFFF.FFFF User Register 0 274
0x1E4 USER_REG1 R/W 0xFFFF.FFFF User Register 1 275
0x204 FMPRE1 R/W 0xFFFF.FFFF Flash Memory Protection Read Enable 1 276
0x208 FMPRE2 R/W 0xFFFF.FFFF Flash Memory Protection Read Enable 2 277
260 January 08, 2011
Texas Instruments-Production Data
Internal Memory
Table 7-3. Flash Register Map (continued)
See
Offset Name Type Reset Description page
0x20C FMPRE3 R/W 0xFFFF.FFFF Flash Memory Protection Read Enable 3 278
0x404 FMPPE1 R/W 0xFFFF.FFFF Flash Memory Protection Program Enable 1 279
0x408 FMPPE2 R/W 0xFFFF.FFFF Flash Memory Protection Program Enable 2 280
0x40C FMPPE3 R/W 0xFFFF.FFFF Flash Memory Protection Program Enable 3 281
7.5 Flash Register Descriptions (Flash Control Offset)
This section lists and describes the Flash Memory registers, in numerical order by address offset.
Registers in this section are relative to the Flash control base address of 0x400F.D000.
January 08, 2011 261
Texas Instruments-Production Data
Stellaris® LM3S2965 Microcontroller
Register 1: Flash Memory Address (FMA), offset 0x000
During a write operation, this register contains a 4-byte-aligned address and specifies where the
data is written. During erase operations, this register contains a 1 KB-aligned address and specifies
which page is erased. Note that the alignment requirements must be met by software or the results
of the operation are unpredictable.
Flash Memory Address (FMA)
Base 0x400F.D000
Offset 0x000
Type R/W, reset 0x0000.0000
31 30 29 28 27 26 25 24 23 22 21 20 19 18 17 16
reserved OFFSET
Type RO RO RO RO RO RO RO RO RO RO RO RO RO RO R/W R/W
Reset 0 0 0 0 0 0 0 0 0 0 0 0 0 0 0 0
15 14 13 12 11 10 9 8 7 6 5 4 3 2 1 0
OFFSET
Type R/W R/W R/W R/W R/W R/W R/W R/W R/W R/W R/W R/W R/W R/W R/W R/W
Reset 0 0 0 0 0 0 0 0 0 0 0 0 0 0 0 0
Bit/Field Name Type Reset Description
Software should not rely on the value of a reserved bit. To provide
compatibility with future products, the value of a reserved bit should be
preserved across a read-modify-write operation.
31:18 reserved RO 0x0
Address Offset
Address offset in flash where operation is performed, except for
nonvolatile registers (see “Nonvolatile Register
Programming” on page 259 for details on values for this field).
17:0 OFFSET R/W 0x0
262 January 08, 2011
Texas Instruments-Production Data
Internal Memory
Register 2: Flash Memory Data (FMD), offset 0x004
This register contains the data to be written during the programming cycle or read during the read
cycle. Note that the contents of this register are undefined for a read access of an execute-only
block. This register is not used during the erase cycles.
Flash Memory Data (FMD)
Base 0x400F.D000
Offset 0x004
Type R/W, reset 0x0000.0000
31 30 29 28 27 26 25 24 23 22 21 20 19 18 17 16
DATA
Type R/W R/W R/W R/W R/W R/W R/W R/W R/W R/W R/W R/W R/W R/W R/W R/W
Reset 0 0 0 0 0 0 0 0 0 0 0 0 0 0 0 0
15 14 13 12 11 10 9 8 7 6 5 4 3 2 1 0
DATA
Type R/W R/W R/W R/W R/W R/W R/W R/W R/W R/W R/W R/W R/W R/W R/W R/W
Reset 0 0 0 0 0 0 0 0 0 0 0 0 0 0 0 0
Bit/Field Name Type Reset Description
Data Value
Data value for write operation.
31:0 DATA R/W 0x0
January 08, 2011 263
Texas Instruments-Production Data
Stellaris® LM3S2965 Microcontroller
Register 3: Flash Memory Control (FMC), offset 0x008
When this register is written, the flash controller initiates the appropriate access cycle for the location
specified by the Flash Memory Address (FMA) register (see page 262). If the access is a write
access, the data contained in the Flash Memory Data (FMD) register (see page 263) is written.
This is the final register written and initiates the memory operation. There are four control bits in the
lower byte of this register that, when set, initiate the memory operation. The most used of these
register bits are the ERASE and WRITE bits.
It is a programming error to write multiple control bits and the results of such an operation are
unpredictable.
Flash Memory Control (FMC)
Base 0x400F.D000
Offset 0x008
Type R/W, reset 0x0000.0000
31 30 29 28 27 26 25 24 23 22 21 20 19 18 17 16
WRKEY
Type WO WO WO WO WO WO WO WO WO WO WO WO WO WO WO WO
Reset 0 0 0 0 0 0 0 0 0 0 0 0 0 0 0 0
15 14 13 12 11 10 9 8 7 6 5 4 3 2 1 0
reserved COMT MERASE ERASE WRITE
Type RO RO RO RO RO RO RO RO RO RO RO RO R/W R/W R/W R/W
Reset 0 0 0 0 0 0 0 0 0 0 0 0 0 0 0 0
Bit/Field Name Type Reset Description
Flash Write Key
This field contains a write key, which is used to minimize the incidence
of accidental flash writes. The value 0xA442 must be written into this
field for a write to occur. Writes to the FMC register without this WRKEY
value are ignored. A read of this field returns the value 0.
31:16 WRKEY WO 0x0
Software should not rely on the value of a reserved bit. To provide
compatibility with future products, the value of a reserved bit should be
preserved across a read-modify-write operation.
15:4 reserved RO 0x0
Commit Register Value
Commit (write) of register value to nonvolatile storage. A write of 0 has
no effect on the state of this bit.
If read, the state of the previous commit access is provided. If the
previous commit access is complete, a 0 is returned; otherwise, if the
commit access is not complete, a 1 is returned.
This can take up to 50 μs.
3 COMT R/W 0
Mass Erase Flash Memory
If this bit is set, the flash main memory of the device is all erased. A
write of 0 has no effect on the state of this bit.
If read, the state of the previous mass erase access is provided. If the
previous mass erase access is complete, a 0 is returned; otherwise, if
the previous mass erase access is not complete, a 1 is returned.
This can take up to 250 ms.
2 MERASE R/W 0
264 January 08, 2011
Texas Instruments-Production Data
Internal Memory
Bit/Field Name Type Reset Description
Erase a Page of Flash Memory
If this bit is set, the page of flash main memory as specified by the
contents of FMA is erased. A write of 0 has no effect on the state of this
bit.
If read, the state of the previous erase access is provided. If the previous
erase access is complete, a 0 is returned; otherwise, if the previous
erase access is not complete, a 1 is returned.
This can take up to 25 ms.
1 ERASE R/W 0
Write a Word into Flash Memory
If this bit is set, the data stored in FMD is written into the location as
specified by the contents of FMA. A write of 0 has no effect on the state
of this bit.
If read, the state of the previous write update is provided. If the previous
write access is complete, a 0 is returned; otherwise, if the write access
is not complete, a 1 is returned.
This can take up to 50 μs.
0 WRITE R/W 0
January 08, 2011 265
Texas Instruments-Production Data
Stellaris® LM3S2965 Microcontroller
Register 4: Flash Controller Raw Interrupt Status (FCRIS), offset 0x00C
This register indicates that the flash controller has an interrupt condition. An interrupt is only signaled
if the corresponding FCIM register bit is set.
Flash Controller Raw Interrupt Status (FCRIS)
Base 0x400F.D000
Offset 0x00C
Type RO, reset 0x0000.0000
31 30 29 28 27 26 25 24 23 22 21 20 19 18 17 16
reserved
Type RO RO RO RO RO RO RO RO RO RO RO RO RO RO RO RO
Reset 0 0 0 0 0 0 0 0 0 0 0 0 0 0 0 0
15 14 13 12 11 10 9 8 7 6 5 4 3 2 1 0
reserved PRIS ARIS
Type RO RO RO RO RO RO RO RO RO RO RO RO RO RO RO RO
Reset 0 0 0 0 0 0 0 0 0 0 0 0 0 0 0 0
Bit/Field Name Type Reset Description
Software should not rely on the value of a reserved bit. To provide
compatibility with future products, the value of a reserved bit should be
preserved across a read-modify-write operation.
31:2 reserved RO 0x0
Programming Raw Interrupt Status
This bit provides status on programming cycles which are write or erase
actions generated through the FMC register bits (see page 264).
Value Description
1 The programming cycle has completed.
0 The programming cycle has not completed.
This status is sent to the interrupt controller when the PMASK bit in the
FCIM register is set.
This bit is cleared by writing a 1 to the PMISC bit in the FCMISC register.
1 PRIS RO 0
Access Raw Interrupt Status
Value Description
A program or erase action was attempted on a block of Flash
memory that contradicts the protection policy for that block as
set in the FMPPEn registers.
1
No access has tried to improperly program or erase the Flash
memory.
0
This status is sent to the interrupt controller when the AMASK bit in the
FCIM register is set.
This bit is cleared by writing a 1 to the AMISC bit in the FCMISC register.
0 ARIS RO 0
266 January 08, 2011
Texas Instruments-Production Data
Internal Memory
Register 5: Flash Controller Interrupt Mask (FCIM), offset 0x010
This register controls whether the flash controller generates interrupts to the controller.
Flash Controller Interrupt Mask (FCIM)
Base 0x400F.D000
Offset 0x010
Type R/W, reset 0x0000.0000
31 30 29 28 27 26 25 24 23 22 21 20 19 18 17 16
reserved
Type RO RO RO RO RO RO RO RO RO RO RO RO RO RO RO RO
Reset 0 0 0 0 0 0 0 0 0 0 0 0 0 0 0 0
15 14 13 12 11 10 9 8 7 6 5 4 3 2 1 0
reserved PMASK AMASK
Type RO RO RO RO RO RO RO RO RO RO RO RO RO RO R/W R/W
Reset 0 0 0 0 0 0 0 0 0 0 0 0 0 0 0 0
Bit/Field Name Type Reset Description
Software should not rely on the value of a reserved bit. To provide
compatibility with future products, the value of a reserved bit should be
preserved across a read-modify-write operation.
31:2 reserved RO 0x0
Programming Interrupt Mask
This bit controls the reporting of the programming raw interrupt status
to the interrupt controller.
Value Description
An interrupt is sent to the interrupt controller when the PRIS bit
is set.
1
The PRIS interrupt is suppressed and not sent to the interrupt
controller.
0
1 PMASK R/W 0
Access Interrupt Mask
This bit controls the reporting of the access raw interrupt status to the
interrupt controller.
Value Description
An interrupt is sent to the interrupt controller when the ARIS bit
is set.
1
The ARIS interrupt is suppressed and not sent to the interrupt
controller.
0
0 AMASK R/W 0
January 08, 2011 267
Texas Instruments-Production Data
Stellaris® LM3S2965 Microcontroller
Register 6: Flash Controller Masked Interrupt Status and Clear (FCMISC),
offset 0x014
This register provides two functions. First, it reports the cause of an interrupt by indicating which
interrupt source or sources are signalling the interrupt. Second, it serves as the method to clear the
interrupt reporting.
Flash Controller Masked Interrupt Status and Clear (FCMISC)
Base 0x400F.D000
Offset 0x014
Type R/W1C, reset 0x0000.0000
31 30 29 28 27 26 25 24 23 22 21 20 19 18 17 16
reserved
Type RO RO RO RO RO RO RO RO RO RO RO RO RO RO RO RO
Reset 0 0 0 0 0 0 0 0 0 0 0 0 0 0 0 0
15 14 13 12 11 10 9 8 7 6 5 4 3 2 1 0
reserved PMISC AMISC
Type RO RO RO RO RO RO RO RO RO RO RO RO RO RO R/W1C R/W1C
Reset 0 0 0 0 0 0 0 0 0 0 0 0 0 0 0 0
Bit/Field Name Type Reset Description
Software should not rely on the value of a reserved bit. To provide
compatibility with future products, the value of a reserved bit should be
preserved across a read-modify-write operation.
31:2 reserved RO 0x0
Programming Masked Interrupt Status and Clear
Value Description
When read, a 1 indicates that an unmasked interrupt was
signaled because a programming cycle completed.
Writing a 1 to this bit clears PMISC and also the PRIS bit in the
FCRIS register (see page 266).
1
When read, a 0 indicates that a programming cycle complete
interrupt has not occurred.
A write of 0 has no effect on the state of this bit.
0
1 PMISC R/W1C 0
Access Masked Interrupt Status and Clear
Value Description
When read, a 1 indicates that an unmasked interrupt was
signaled because a program or erase action was attempted on
a block of Flash memory that contradicts the protection policy
for that block as set in the FMPPEn registers.
Writing a 1 to this bit clears AMISC and also the ARIS bit in the
FCRIS register (see page 266).
1
When read, a 0 indicates that no improper accesses have
occurred.
A write of 0 has no effect on the state of this bit.
0
0 AMISC R/W1C 0
268 January 08, 2011
Texas Instruments-Production Data
Internal Memory
7.6 Flash Register Descriptions (System Control Offset)
The remainder of this section lists and describes the Flash Memory registers, in numerical order by
address offset. Registers in this section are relative to the System Control base address of
0x400F.E000.
January 08, 2011 269
Texas Instruments-Production Data
Stellaris® LM3S2965 Microcontroller
Register 7: USec Reload (USECRL), offset 0x140
Note: Offset is relative to System Control base address of 0x400F.E000
This register is provided as a means of creating a 1-μs tick divider reload value for the flash controller.
The internal flash has specific minimum and maximum requirements on the length of time the high
voltage write pulse can be applied. It is required that this register contain the operating frequency
(in MHz -1) whenever the flash is being erased or programmed. The user is required to change this
value if the clocking conditions are changed for a flash erase/program operation.
USec Reload (USECRL)
Base 0x400F.E000
Offset 0x140
Type R/W, reset 0x31
31 30 29 28 27 26 25 24 23 22 21 20 19 18 17 16
reserved
Type RO RO RO RO RO RO RO RO RO RO RO RO RO RO RO RO
Reset 0 0 0 0 0 0 0 0 0 0 0 0 0 0 0 0
15 14 13 12 11 10 9 8 7 6 5 4 3 2 1 0
reserved USEC
Type RO RO RO RO RO RO RO RO R/W R/W R/W R/W R/W R/W R/W R/W
Reset 0 0 0 0 0 0 0 0 0 0 1 1 0 0 0 1
Bit/Field Name Type Reset Description
Software should not rely on the value of a reserved bit. To provide
compatibility with future products, the value of a reserved bit should be
preserved across a read-modify-write operation.
31:8 reserved RO 0x0
Microsecond Reload Value
MHz -1 of the controller clock when the flash is being erased or
programmed.
If the maximum system frequency is being used, USEC should be set to
0x31 (50 MHz) whenever the flash is being erased or programmed.
7:0 USEC R/W 0x31
270 January 08, 2011
Texas Instruments-Production Data
Internal Memory
Register 8: Flash Memory Protection Read Enable 0 (FMPRE0), offset 0x130
and 0x200
Note: This register is aliased for backwards compatability.
Note: Offset is relative to System Control base address of 0x400FE000.
This register stores the read-only protection bits for each 2-KB flash block (FMPPEn stores the
execute-only bits). Flash memory up to a total of 64 KB is controlled by this register. Other FMPREn
registers (if any) provide protection for other 64K blocks. This register is loaded during the power-on
reset sequence. The factory settings for the FMPREn and FMPPEn registers are a value of 1 for
all implemented banks. This achieves a policy of open access and programmability. The register
bits may be changed by writing the specific register bit. However, this register is R/W0; the user can
only change the protection bit from a 1 to a 0 (and may NOT change a 0 to a 1). The changes are
not permanent until the register is committed (saved), at which point the bit change is permanent.
If a bit is changed from a 1 to a 0 and not committed, it may be restored by executing a power-on
reset sequence. The reset value shown only applies to power-on reset; any other type of reset does
not affect this register. For additional information, see the "Flash Memory Protection" section.
Flash Memory Protection Read Enable 0 (FMPRE0)
Base 0x400F.E000
Offset 0x130 and 0x200
Type R/W, reset 0xFFFF.FFFF
31 30 29 28 27 26 25 24 23 22 21 20 19 18 17 16
READ_ENABLE
Type R/W R/W R/W R/W R/W R/W R/W R/W R/W R/W R/W R/W R/W R/W R/W R/W
Reset 1 1 1 1 1 1 1 1 1 1 1 1 1 1 1 1
15 14 13 12 11 10 9 8 7 6 5 4 3 2 1 0
READ_ENABLE
Type R/W R/W R/W R/W R/W R/W R/W R/W R/W R/W R/W R/W R/W R/W R/W R/W
Reset 1 1 1 1 1 1 1 1 1 1 1 1 1 1 1 1
Bit/Field Name Type Reset Description
Flash Read Enable. Enables 2-KB Flash memory blocks to be executed
or read. The policies may be combined as shown in the table “Flash
Protection Policy Combinations”.
Value Description
Bits [31:0] each enable protection on a 2-KB block of
Flash memory up to the total of 64 KB.
0xFFFFFFFF
31:0 READ_ENABLE R/W 0xFFFFFFFF
January 08, 2011 271
Texas Instruments-Production Data
Stellaris® LM3S2965 Microcontroller
Register 9: Flash Memory Protection Program Enable 0 (FMPPE0), offset
0x134 and 0x400
Note: This register is aliased for backwards compatability.
Note: Offset is relative to System Control base address of 0x400FE000.
This register stores the execute-only protection bits for each 2-KB flash block (FMPREn stores the
execute-only bits). Flash memory up to a total of 64 KB is controlled by this register. Other FMPPEn
registers (if any) provide protection for other 64K blocks. This register is loaded during the power-on
reset sequence. The factory settings for the FMPREn and FMPPEn registers are a value of 1 for
all implemented banks. This achieves a policy of open access and programmability. The register
bits may be changed by writing the specific register bit. However, this register is R/W0; the user can
only change the protection bit from a 1 to a 0 (and may NOT change a 0 to a 1). The changes are
not permanent until the register is committed (saved), at which point the bit change is permanent.
If a bit is changed from a 1 to a 0 and not committed, it may be restored by executing a power-on
reset sequence. The reset value shown only applies to power-on reset; any other type of reset does
not affect this register. For additional information, see the "Flash Memory Protection" section.
Flash Memory Protection Program Enable 0 (FMPPE0)
Base 0x400F.E000
Offset 0x134 and 0x400
Type R/W, reset 0xFFFF.FFFF
31 30 29 28 27 26 25 24 23 22 21 20 19 18 17 16
PROG_ENABLE
Type R/W R/W R/W R/W R/W R/W R/W R/W R/W R/W R/W R/W R/W R/W R/W R/W
Reset 1 1 1 1 1 1 1 1 1 1 1 1 1 1 1 1
15 14 13 12 11 10 9 8 7 6 5 4 3 2 1 0
PROG_ENABLE
Type R/W R/W R/W R/W R/W R/W R/W R/W R/W R/W R/W R/W R/W R/W R/W R/W
Reset 1 1 1 1 1 1 1 1 1 1 1 1 1 1 1 1
Bit/Field Name Type Reset Description
Flash Programming Enable
Configures 2-KB flash blocks to be execute only. The policies may be
combined as shown in the table “Flash Protection Policy Combinations”.
Value Description
Bits [31:0] each enable protection on a 2-KB block of
Flash memory up to the total of 64 KB.
0xFFFFFFFF
31:0 PROG_ENABLE R/W 0xFFFFFFFF
272 January 08, 2011
Texas Instruments-Production Data
Internal Memory
Register 10: User Debug (USER_DBG), offset 0x1D0
Note: Offset is relative to System Control base address of 0x400FE000.
This register provides a write-once mechanism to disable external debugger access to the device
in addition to 27 additional bits of user-defined data. The DBG0 bit (bit 0) is set to 0 from the factory
and the DBG1 bit (bit 1) is set to 1, which enables external debuggers. Changing the DBG1 bit to
0 disables any external debugger access to the device permanently, starting with the next power-up
cycle of the device. The NW bit (bit 31) indicates that the register has not yet been committed and
is controlled through hardware to ensure that the register is only committed once. Prior to being
committed, bits can only be changed from 1 to 0. The reset value shown only applies to power-on
reset; any other type of reset does not affect this register. Once committed, this register cannot be
restored to the factory default value.
User Debug (USER_DBG)
Base 0x400F.E000
Offset 0x1D0
Type R/W, reset 0xFFFF.FFFE
31 30 29 28 27 26 25 24 23 22 21 20 19 18 17 16
NW DATA
Type R/W R/W R/W R/W R/W R/W R/W R/W R/W R/W R/W R/W R/W R/W R/W R/W
Reset 1 1 1 1 1 1 1 1 1 1 1 1 1 1 1 1
15 14 13 12 11 10 9 8 7 6 5 4 3 2 1 0
DATA DBG1 DBG0
Type R/W R/W R/W R/W R/W R/W R/W R/W R/W R/W R/W R/W R/W R/W R/W R/W
Reset 1 1 1 1 1 1 1 1 1 1 1 1 1 1 1 0
Bit/Field Name Type Reset Description
User Debug Not Written
When set, this bit indicates that this 32-bit register has not been
committed. When clear, this bit specifies that this register has been
committed and may not be committed again.
31 NW R/W 1
User Data
Contains the user data value. This field is initialized to all 1s and can
only be committed once.
30:2 DATA R/W 0x1FFFFFFF
Debug Control 1
The DBG1 bit must be 1 and DBG0 must be 0 for debug to be available.
1 DBG1 R/W 1
Debug Control 0
The DBG1 bit must be 1 and DBG0 must be 0 for debug to be available.
0 DBG0 R/W 0
January 08, 2011 273
Texas Instruments-Production Data
Stellaris® LM3S2965 Microcontroller
Register 11: User Register 0 (USER_REG0), offset 0x1E0
Note: Offset is relative to System Control base address of 0x400FE000.
This register provides 31 bits of user-defined data that is non-volatile and can only be committed
once. Bit 31 indicates that the register is available to be committed and is controlled through hardware
to ensure that the register is only committed once. Prior to being committed, bits can only be changed
from 1 to 0. The reset value shown only applies to power-on reset; any other type of reset does not
affect this register. The write-once characteristics of this register are useful for keeping static
information like communication addresses that need to be unique per part and would otherwise
require an external EEPROM or other non-volatile device. Once committed, this register cannot be
restored to the factory default value.
User Register 0 (USER_REG0)
Base 0x400F.E000
Offset 0x1E0
Type R/W, reset 0xFFFF.FFFF
31 30 29 28 27 26 25 24 23 22 21 20 19 18 17 16
NW DATA
Type R/W R/W R/W R/W R/W R/W R/W R/W R/W R/W R/W R/W R/W R/W R/W R/W
Reset 1 1 1 1 1 1 1 1 1 1 1 1 1 1 1 1
15 14 13 12 11 10 9 8 7 6 5 4 3 2 1 0
DATA
Type R/W R/W R/W R/W R/W R/W R/W R/W R/W R/W R/W R/W R/W R/W R/W R/W
Reset 1 1 1 1 1 1 1 1 1 1 1 1 1 1 1 1
Bit/Field Name Type Reset Description
Not Written
When set, this bit indicates that this 32-bit register has not been
committed. When clear, this bit specifies that this register has been
committed and may not be committed again.
31 NW R/W 1
User Data
Contains the user data value. This field is initialized to all 1s and can
only be committed once.
30:0 DATA R/W 0x7FFFFFFF
274 January 08, 2011
Texas Instruments-Production Data
Internal Memory
Register 12: User Register 1 (USER_REG1), offset 0x1E4
Note: Offset is relative to System Control base address of 0x400FE000.
This register provides 31 bits of user-defined data that is non-volatile and can only be committed
once. Bit 31 indicates that the register is available to be committed and is controlled through hardware
to ensure that the register is only committed once. Prior to being committed, bits can only be changed
from 1 to 0. The reset value shown only applies to power-on reset; any other type of reset does not
affect this register. The write-once characteristics of this register are useful for keeping static
information like communication addresses that need to be unique per part and would otherwise
require an external EEPROM or other non-volatile device. Once committed, this register cannot be
restored to the factory default value.
User Register 1 (USER_REG1)
Base 0x400F.E000
Offset 0x1E4
Type R/W, reset 0xFFFF.FFFF
31 30 29 28 27 26 25 24 23 22 21 20 19 18 17 16
NW DATA
Type R/W R/W R/W R/W R/W R/W R/W R/W R/W R/W R/W R/W R/W R/W R/W R/W
Reset 1 1 1 1 1 1 1 1 1 1 1 1 1 1 1 1
15 14 13 12 11 10 9 8 7 6 5 4 3 2 1 0
DATA
Type R/W R/W R/W R/W R/W R/W R/W R/W R/W R/W R/W R/W R/W R/W R/W R/W
Reset 1 1 1 1 1 1 1 1 1 1 1 1 1 1 1 1
Bit/Field Name Type Reset Description
Not Written
When set, this bit indicates that this 32-bit register has not been
committed. When clear, this bit specifies that this register has been
committed and may not be committed again.
31 NW R/W 1
User Data
Contains the user data value. This field is initialized to all 1s and can
only be committed once.
30:0 DATA R/W 0x7FFFFFFF
January 08, 2011 275
Texas Instruments-Production Data
Stellaris® LM3S2965 Microcontroller
Register 13: Flash Memory Protection Read Enable 1 (FMPRE1), offset 0x204
Note: Offset is relative to System Control base address of 0x400FE000.
This register stores the read-only protection bits for each 2-KB flash block (FMPPEn stores the
execute-only bits). Flash memory up to a total of 64 KB is controlled by this register. Other FMPREn
registers (if any) provide protection for other 64K blocks. This register is loaded during the power-on
reset sequence. The factory settings for the FMPREn and FMPPEn registers are a value of 1 for
all implemented banks. This achieves a policy of open access and programmability. The register
bits may be changed by writing the specific register bit. However, this register is R/W0; the user can
only change the protection bit from a 1 to a 0 (and may NOT change a 0 to a 1). The changes are
not permanent until the register is committed (saved), at which point the bit change is permanent.
If a bit is changed from a 1 to a 0 and not committed, it may be restored by executing a power-on
reset sequence. The reset value shown only applies to power-on reset; any other type of reset does
not affect this register. If the Flash memory size on the device is less than 64 KB, this register usually
reads as zeroes, but software should not rely on these bits to be zero. For additional information,
see the "Flash Memory Protection" section.
Flash Memory Protection Read Enable 1 (FMPRE1)
Base 0x400F.E000
Offset 0x204
Type R/W, reset 0xFFFF.FFFF
31 30 29 28 27 26 25 24 23 22 21 20 19 18 17 16
READ_ENABLE
Type R/W R/W R/W R/W R/W R/W R/W R/W R/W R/W R/W R/W R/W R/W R/W R/W
Reset 1 1 1 1 1 1 1 1 1 1 1 1 1 1 1 1
15 14 13 12 11 10 9 8 7 6 5 4 3 2 1 0
READ_ENABLE
Type R/W R/W R/W R/W R/W R/W R/W R/W R/W R/W R/W R/W R/W R/W R/W R/W
Reset 1 1 1 1 1 1 1 1 1 1 1 1 1 1 1 1
Bit/Field Name Type Reset Description
Flash Read Enable. Enables 2-KB Flash memory blocks to be executed
or read. The policies may be combined as shown in the table “Flash
Protection Policy Combinations”.
Value Description
Bits [31:0] each enable protection on a 2-KB block of
Flash memory in memory range from 65 to 128 KB.
0xFFFFFFFF
31:0 READ_ENABLE R/W 0xFFFFFFFF
276 January 08, 2011
Texas Instruments-Production Data
Internal Memory
Register 14: Flash Memory Protection Read Enable 2 (FMPRE2), offset 0x208
Note: Offset is relative to System Control base address of 0x400FE000.
This register stores the read-only protection bits for each 2-KB flash block (FMPPEn stores the
execute-only bits). This register is loaded during the power-on reset sequence. The factory settings
for the FMPREn and FMPPEn registers are a value of 1 for all implemented banks. This achieves
a policy of open access and programmability. The register bits may be changed by writing the
specific register bit. However, this register is R/W0; the user can only change the protection bit from
a 1 to a 0 (and may NOT change a 0 to a 1). For additional information, see the "Flash Memory
Protection" section.
Flash Memory Protection Read Enable 2 (FMPRE2)
Base 0x400F.E000
Offset 0x208
Type R/W, reset 0xFFFF.FFFF
31 30 29 28 27 26 25 24 23 22 21 20 19 18 17 16
READ_ENABLE
Type R/W R/W R/W R/W R/W R/W R/W R/W R/W R/W R/W R/W R/W R/W R/W R/W
Reset 1 1 1 1 1 1 1 1 1 1 1 1 1 1 1 1
15 14 13 12 11 10 9 8 7 6 5 4 3 2 1 0
READ_ENABLE
Type R/W R/W R/W R/W R/W R/W R/W R/W R/W R/W R/W R/W R/W R/W R/W R/W
Reset 1 1 1 1 1 1 1 1 1 1 1 1 1 1 1 1
Bit/Field Name Type Reset Description
Flash Read Enable
Enables 2-KB flash blocks to be executed or read. The policies may be
combined as shown in the table “Flash Protection Policy Combinations”.
Value Description
0xFFFFFFFF Enables 256 KB of flash.
31:0 READ_ENABLE R/W 0xFFFFFFFF
January 08, 2011 277
Texas Instruments-Production Data
Stellaris® LM3S2965 Microcontroller
Register 15: Flash Memory Protection Read Enable 3 (FMPRE3), offset 0x20C
Note: Offset is relative to System Control base address of 0x400FE000.
This register stores the read-only protection bits for each 2-KB flash block (FMPPEn stores the
execute-only bits). This register is loaded during the power-on reset sequence. The factory settings
for the FMPREn and FMPPEn registers are a value of 1 for all implemented banks. This achieves
a policy of open access and programmability. The register bits may be changed by writing the
specific register bit. However, this register is R/W0; the user can only change the protection bit from
a 1 to a 0 (and may NOT change a 0 to a 1). The changes are not permanent until the register is
committed (saved), at which point the bit change is permanent. If a bit is changed from a 1 to a 0
and not committed, it may be restored by executing a power-on reset sequence. For additional
information, see the "Flash Memory Protection" section.
Flash Memory Protection Read Enable 3 (FMPRE3)
Base 0x400F.E000
Offset 0x20C
Type R/W, reset 0xFFFF.FFFF
31 30 29 28 27 26 25 24 23 22 21 20 19 18 17 16
READ_ENABLE
Type R/W R/W R/W R/W R/W R/W R/W R/W R/W R/W R/W R/W R/W R/W R/W R/W
Reset 1 1 1 1 1 1 1 1 1 1 1 1 1 1 1 1
15 14 13 12 11 10 9 8 7 6 5 4 3 2 1 0
READ_ENABLE
Type R/W R/W R/W R/W R/W R/W R/W R/W R/W R/W R/W R/W R/W R/W R/W R/W
Reset 1 1 1 1 1 1 1 1 1 1 1 1 1 1 1 1
Bit/Field Name Type Reset Description
Flash Read Enable
Enables 2-KB flash blocks to be executed or read. The policies may be
combined as shown in the table “Flash Protection Policy Combinations”.
Value Description
0xFFFFFFFF Enables 256 KB of flash.
31:0 READ_ENABLE R/W 0xFFFFFFFF
278 January 08, 2011
Texas Instruments-Production Data
Internal Memory
Register 16: Flash Memory Protection Program Enable 1 (FMPPE1), offset
0x404
Note: Offset is relative to System Control base address of 0x400FE000.
This register stores the execute-only protection bits for each 2-KB flash block (FMPREn stores the
execute-only bits). Flash memory up to a total of 64 KB is controlled by this register. Other FMPPEn
registers (if any) provide protection for other 64K blocks. This register is loaded during the power-on
reset sequence. The factory settings for the FMPREn and FMPPEn registers are a value of 1 for
all implemented banks. This achieves a policy of open access and programmability. The register
bits may be changed by writing the specific register bit. However, this register is R/W0; the user can
only change the protection bit from a 1 to a 0 (and may NOT change a 0 to a 1). The changes are
not permanent until the register is committed (saved), at which point the bit change is permanent.
If a bit is changed from a 1 to a 0 and not committed, it may be restored by executing a power-on
reset sequence. The reset value shown only applies to power-on reset; any other type of reset does
not affect this register. If the Flash memory size on the device is less than 64 KB, this register usually
reads as zeroes, but software should not rely on these bits to be zero. For additional information,
see the "Flash Memory Protection" section.
Flash Memory Protection Program Enable 1 (FMPPE1)
Base 0x400F.E000
Offset 0x404
Type R/W, reset 0xFFFF.FFFF
31 30 29 28 27 26 25 24 23 22 21 20 19 18 17 16
PROG_ENABLE
Type R/W R/W R/W R/W R/W R/W R/W R/W R/W R/W R/W R/W R/W R/W R/W R/W
Reset 1 1 1 1 1 1 1 1 1 1 1 1 1 1 1 1
15 14 13 12 11 10 9 8 7 6 5 4 3 2 1 0
PROG_ENABLE
Type R/W R/W R/W R/W R/W R/W R/W R/W R/W R/W R/W R/W R/W R/W R/W R/W
Reset 1 1 1 1 1 1 1 1 1 1 1 1 1 1 1 1
Bit/Field Name Type Reset Description
Flash Programming Enable
Value Description
Bits [31:0] each enable protection on a 2-KB block of
Flash memory in memory range from 65 to 128 KB.
0xFFFFFFFF
31:0 PROG_ENABLE R/W 0xFFFFFFFF
January 08, 2011 279
Texas Instruments-Production Data
Stellaris® LM3S2965 Microcontroller
Register 17: Flash Memory Protection Program Enable 2 (FMPPE2), offset
0x408
Note: Offset is relative to System Control base address of 0x400FE000.
This register stores the execute-only protection bits for each 2-KB flash block (FMPREn stores the
execute-only bits). This register is loaded during the power-on reset sequence. The factory settings
for the FMPREn and FMPPEn registers are a value of 1 for all implemented banks. This achieves
a policy of open access and programmability. The register bits may be changed by writing the
specific register bit. However, this register is R/W0; the user can only change the protection bit from
a 1 to a 0 (and may NOT change a 0 to a 1). The changes are not permanent until the register is
committed (saved), at which point the bit change is permanent. If a bit is changed from a 1 to a 0
and not committed, it may be restored by executing a power-on reset sequence. For additional
information, see the "Flash Memory Protection" section.
Flash Memory Protection Program Enable 2 (FMPPE2)
Base 0x400F.E000
Offset 0x408
Type R/W, reset 0xFFFF.FFFF
31 30 29 28 27 26 25 24 23 22 21 20 19 18 17 16
PROG_ENABLE
Type R/W R/W R/W R/W R/W R/W R/W R/W R/W R/W R/W R/W R/W R/W R/W R/W
Reset 1 1 1 1 1 1 1 1 1 1 1 1 1 1 1 1
15 14 13 12 11 10 9 8 7 6 5 4 3 2 1 0
PROG_ENABLE
Type R/W R/W R/W R/W R/W R/W R/W R/W R/W R/W R/W R/W R/W R/W R/W R/W
Reset 1 1 1 1 1 1 1 1 1 1 1 1 1 1 1 1
Bit/Field Name Type Reset Description
Flash Programming Enable
Configures 2-KB flash blocks to be execute only. The policies may be
combined as shown in the table “Flash Protection Policy Combinations”.
Value Description
0xFFFFFFFF Enables 256 KB of flash.
31:0 PROG_ENABLE R/W 0xFFFFFFFF
280 January 08, 2011
Texas Instruments-Production Data
Internal Memory
Register 18: Flash Memory Protection Program Enable 3 (FMPPE3), offset
0x40C
Note: Offset is relative to System Control base address of 0x400FE000.
This register stores the execute-only protection bits for each 2-KB flash block (FMPREn stores the
execute-only bits). This register is loaded during the power-on reset sequence. The factory settings
for the FMPREn and FMPPEn registers are a value of 1 for all implemented banks. This achieves
a policy of open access and programmability. The register bits may be changed by writing the
specific register bit. However, this register is R/W0; the user can only change the protection bit from
a 1 to a 0 (and may NOT change a 0 to a 1). The changes are not permanent until the register is
committed (saved), at which point the bit change is permanent. If a bit is changed from a 1 to a 0
and not committed, it may be restored by executing a power-on reset sequence. For additional
information, see the "Flash Memory Protection" section.
Flash Memory Protection Program Enable 3 (FMPPE3)
Base 0x400F.E000
Offset 0x40C
Type R/W, reset 0xFFFF.FFFF
31 30 29 28 27 26 25 24 23 22 21 20 19 18 17 16
PROG_ENABLE
Type R/W R/W R/W R/W R/W R/W R/W R/W R/W R/W R/W R/W R/W R/W R/W R/W
Reset 1 1 1 1 1 1 1 1 1 1 1 1 1 1 1 1
15 14 13 12 11 10 9 8 7 6 5 4 3 2 1 0
PROG_ENABLE
Type R/W R/W R/W R/W R/W R/W R/W R/W R/W R/W R/W R/W R/W R/W R/W R/W
Reset 1 1 1 1 1 1 1 1 1 1 1 1 1 1 1 1
Bit/Field Name Type Reset Description
Flash Programming Enable
Configures 2-KB flash blocks to be execute only. The policies may be
combined as shown in the table “Flash Protection Policy Combinations”.
Value Description
0xFFFFFFFF Enables 256 KB of flash.
31:0 PROG_ENABLE R/W 0xFFFFFFFF
January 08, 2011 281
Texas Instruments-Production Data
Stellaris® LM3S2965 Microcontroller
8 General-Purpose Input/Outputs (GPIOs)
The GPIO module is composed of eight physical GPIO blocks, each corresponding to an individual
GPIO port (Port A, Port B, Port C, Port D, Port E, Port F, Port G, Port H). The GPIO module supports
3-56 programmable input/output pins, depending on the peripherals being used.
The GPIO module has the following features:
■ 3-56 GPIOs, depending on configuration
■ 5-V-tolerant in input configuration
■ Programmable control for GPIO interrupts
– Interrupt generation masking
– Edge-triggered on rising, falling, or both
– Level-sensitive on High or Low values
■ Bit masking in both read and write operations through address lines
■ Can initiate an ADC sample sequence
■ Pins configured as digital inputs are Schmitt-triggered.
■ Programmable control for GPIO pad configuration
– Weak pull-up or pull-down resistors
– 2-mA, 4-mA, and 8-mA pad drive for digital communication; up to four pads can be configured
with an 18-mA pad drive for high-current applications
– Slew rate control for the 8-mA drive
– Open drain enables
– Digital input enables
8.1 Functional Description
Important: All GPIO pins are tri-stated by default (GPIOAFSEL=0, GPIODEN=0, GPIOPDR=0,
and GPIOPUR=0), with the exception of the five JTAG/SWD pins (PB7 and PC[3:0]).
The JTAG/SWD pins default to their JTAG/SWD functionality (GPIOAFSEL=1,
GPIODEN=1 and GPIOPUR=1). A Power-On-Reset (POR) or asserting RST puts both
groups of pins back to their default state.
While debugging systems where PB7 is being used as a GPIO, care must be taken to
ensure that a low value is not applied to the pin when the part is reset. Because PB7
reverts to the TRST function after reset, a Low value on the pin causes the JTAG
controller to be reset, resulting in a loss of JTAG communication.
Each GPIO port is a separate hardware instantiation of the same physical block (see Figure
8-1 on page 283). The LM3S2965 microcontroller contains eight ports and thus eight of these physical
GPIO blocks.
282 January 08, 2011
Texas Instruments-Production Data
General-Purpose Input/Outputs (GPIOs)
Figure 8-1. GPIO Port Block Diagram
Alternate Input
Alternate Output
Alternate Output Enable
Interrupt
GPIO Input
GPIO Output
GPIO Output Enable
Pad Output
Pad Output Enable
Package I/O Pin
GPIODATA
GPIODIR
Data
Control
GPIOIS
GPIOIBE
GPIOIEV
GPIOIM
GPIORIS
GPIOMIS
GPIOICR
Interrupt
Control
GPIODR2R
GPIODR4R
GPIODR8R
GPIOSLR
GPIOPUR
GPIOPDR
GPIOODR
GPIODEN
Pad
Control
GPIOPeriphID0
GPIOPeriphID1
GPIOPeriphID2
GPIOPeriphID3
GPIOPeriphID4
GPIOPeriphID5
GPIOPeriphID6
GPIOPeriphID7
GPIOPCellID0
GPIOPCellID1
GPIOPCellID2
GPIOPCellID3
Identification Registers
GPIOAFSEL
Mode
Control
DEMUX MUX MUX
Digital
I/O Pad
Pad Input
GPIOLOCK
Commit
Control
GPIOCR
8.1.1 Data Control
The data control registers allow software to configure the operational modes of the GPIOs. The data
direction register configures the GPIO as an input or an output while the data register either captures
incoming data or drives it out to the pads.
8.1.1.1 Data Direction Operation
The GPIO Direction (GPIODIR) register (see page 291) is used to configure each individual pin as
an input or output. When the data direction bit is set to 0, the GPIO is configured as an input and
the corresponding data register bit will capture and store the value on the GPIO port. When the data
direction bit is set to 1, the GPIO is configured as an output and the corresponding data register bit
will be driven out on the GPIO port.
8.1.1.2 Data Register Operation
To aid in the efficiency of software, the GPIO ports allow for the modification of individual bits in the
GPIO Data (GPIODATA) register (see page 290) by using bits [9:2] of the address bus as a mask.
This allows software drivers to modify individual GPIO pins in a single instruction, without affecting
the state of the other pins. This is in contrast to the "typical" method of doing a read-modify-write
operation to set or clear an individual GPIO pin. To accommodate this feature, the GPIODATA
register covers 256 locations in the memory map.
January 08, 2011 283
Texas Instruments-Production Data
Stellaris® LM3S2965 Microcontroller
During a write, if the address bit associated with that data bit is set to 1, the value of the GPIODATA
register is altered. If it is cleared to 0, it is left unchanged.
For example, writing a value of 0xEB to the address GPIODATA + 0x098 would yield as shown in
Figure 8-2 on page 284, where u is data unchanged by the write.
Figure 8-2. GPIODATA Write Example
0 0 1 0 0 1 1 0 0
u u 1 u u 0 1 u
9 8 7 6 5 4 3 2 1 0
1 1 1 0 1 0 1 1
7 6 5 4 3 2 1 0
GPIODATA
0xEB
0x098
ADDR[9:2]
0
During a read, if the address bit associated with the data bit is set to 1, the value is read. If the
address bit associated with the data bit is set to 0, it is read as a zero, regardless of its actual value.
For example, reading address GPIODATA + 0x0C4 yields as shown in Figure 8-3 on page 284.
Figure 8-3. GPIODATA Read Example
0 0 1 1 0 0 0 1 0 0
0 0 1 1 0 0 0 0
9 8 7 6 5 4 3 2 1 0
1 0 1 1 1 1 1 0
7 6 5 4 3 2 1 0
Returned Value
GPIODATA
0x0C4
ADDR[9:2]
8.1.2 Interrupt Control
The interrupt capabilities of each GPIO port are controlled by a set of seven registers. With these
registers, it is possible to select the source of the interrupt, its polarity, and the edge properties.
When one or more GPIO inputs cause an interrupt, a single interrupt output is sent to the interrupt
controller for the entire GPIO port. For edge-triggered interrupts, software must clear the interrupt
to enable any further interrupts. For a level-sensitive interrupt, it is assumed that the external source
holds the level constant for the interrupt to be recognized by the controller.
Three registers are required to define the edge or sense that causes interrupts:
■ GPIO Interrupt Sense (GPIOIS) register (see page 292)
■ GPIO Interrupt Both Edges (GPIOIBE) register (see page 293)
■ GPIO Interrupt Event (GPIOIEV) register (see page 294)
Interrupts are enabled/disabled via the GPIO Interrupt Mask (GPIOIM) register (see page 295).
When an interrupt condition occurs, the state of the interrupt signal can be viewed in two locations:
the GPIO Raw Interrupt Status (GPIORIS) and GPIO Masked Interrupt Status (GPIOMIS) registers
(see page 296 and page 297). As the name implies, the GPIOMIS register only shows interrupt
284 January 08, 2011
Texas Instruments-Production Data
General-Purpose Input/Outputs (GPIOs)
conditions that are allowed to be passed to the controller. The GPIORIS register indicates that a
GPIO pin meets the conditions for an interrupt, but has not necessarily been sent to the controller.
In addition to providing GPIO functionality, PB4 can also be used as an external trigger for the ADC.
If PB4 is configured as a non-masked interrupt pin (the appropriate bit of GPIOIM is set to 1), not
only is an interrupt for PortB generated, but an external trigger signal is sent to the ADC. If the ADC
Event Multiplexer Select (ADCEMUX) register is configured to use the external trigger, an ADC
conversion is initiated.
If no other PortB pins are being used to generate interrupts, the Interrupt 0-31 Set Enable (EN0)
register can disable the PortB interrupts, and the ADC interrupt can be used to read back the
converted data. Otherwise, the PortB interrupt handler needs to ignore and clear interrupts on PB4,
and wait for the ADC interrupt or the ADC interrupt must be disabled in the EN0 register and the
PortB interrupt handler must poll the ADC registers until the conversion is completed. See page 109
for more information.
Interrupts are cleared by writing a 1 to the appropriate bit of the GPIO Interrupt Clear (GPIOICR)
register (see page 298).
When programming the following interrupt control registers, the interrupts should be masked (GPIOIM
set to 0). Writing any value to an interrupt control register (GPIOIS, GPIOIBE, or GPIOIEV) can
generate a spurious interrupt if the corresponding bits are enabled.
8.1.3 Mode Control
The GPIO pins can be controlled by either hardware or software. When hardware control is enabled
via the GPIO Alternate Function Select (GPIOAFSEL) register (see page 299), the pin state is
controlled by its alternate function (that is, the peripheral). Software control corresponds to GPIO
mode, where the GPIODATA register is used to read/write the corresponding pins.
8.1.4 Commit Control
The GPIO commit control registers provide a layer of protection against accidental programming of
critical hardware peripherals. Protection is currently provided for the five JTAG/SWD pins (PB7 and
PC[3:0]). Writes to protected bits of the GPIO Alternate Function Select (GPIOAFSEL) register
(see page 299) are not committed to storage unless the GPIO Lock (GPIOLOCK) register (see
page 309) has been unlocked and the appropriate bits of the GPIO Commit (GPIOCR) register (see
page 310) have been set to 1.
8.1.5 Pad Control
The pad control registers allow for GPIO pad configuration by software based on the application
requirements. The pad control registers include the GPIODR2R, GPIODR4R, GPIODR8R, GPIOODR,
GPIOPUR, GPIOPDR, GPIOSLR, and GPIODEN registers. These registers control drive strength,
open-drain configuration, pull-up and pull-down resistors, slew-rate control and digital input enable.
For special high-current applications, the GPIO output buffers may be used with the following
restrictions. With the GPIO pins configured as 8-mA output drivers, a total of four GPIO outputs may
be used to sink current loads up to 18 mA each. At 18-mA sink current loading, the VOL value is
specified as 1.2 V. The high-current GPIO package pins must be selected such that there are only
a maximum of two per side of the physical package or BGA pin group with the total number of
high-current GPIO outputs not exceeding four for the entire package.
January 08, 2011 285
Texas Instruments-Production Data
Stellaris® LM3S2965 Microcontroller
8.1.6 Identification
The identification registers configured at reset allow software to detect and identify the module as
a GPIO block. The identification registers include the GPIOPeriphID0-GPIOPeriphID7 registers as
well as the GPIOPCellID0-GPIOPCellID3 registers.
8.2 Initialization and Configuration
To use the GPIO, the peripheral clock must be enabled by setting the appropriate GPIO Port bit
field (GPIOn) in the RCGC2 register.
On reset, all GPIO pins (except for the five JTAG pins) are configured out of reset to be undriven
(tristate): GPIOAFSEL=0, GPIODEN=0, GPIOPDR=0, and GPIOPUR=0. Table 8-1 on page 286
shows all possible configurations of the GPIO pads and the control register settings required to
achieve them. Table 8-2 on page 286 shows how a rising edge interrupt would be configured for pin
2 of a GPIO port.
Table 8-1. GPIO Pad Configuration Examples
GPIO Register Bit Valuea
Configuration
AFSEL DIR ODR DEN PUR PDR DR2R DR4R DR8R SLR
Digital Input (GPIO) 0 0 0 1 ? ? X X X X
Digital Output (GPIO) 0 1 0 1 ? ? ? ? ? ?
Open Drain Output 0 1 1 1 X X ? ? ? ?
(GPIO)
Open Drain 1 X 1 1 X X ? ? ? ?
Input/Output (I2C)
Digital Input (Timer 1 X 0 1 ? ? X X X X
CCP)
Digital Input (QEI) 1 X 0 1 ? ? X X X X
Digital Output (PWM) 1 X 0 1 ? ? ? ? ? ?
Digital Output (Timer 1 X 0 1 ? ? ? ? ? ?
PWM)
Digital Input/Output 1 X 0 1 ? ? ? ? ? ?
(SSI)
Digital Input/Output 1 X 0 1 ? ? ? ? ? ?
(UART)
Analog Input 0 0 0 0 0 0 X X X X
(Comparator)
Digital Output 1 X 0 1 ? ? ? ? ? ?
(Comparator)
a. X=Ignored (don’t care bit)
?=Can be either 0 or 1, depending on the configuration
Table 8-2. GPIO Interrupt Configuration Example
Desired Pin 2 Bit Valuea
Interrupt
Event
Trigger
Register 7 6 5 4 3 2 1 0
0=edge X X X X X 0 X X
1=level
GPIOIS
286 January 08, 2011
Texas Instruments-Production Data
General-Purpose Input/Outputs (GPIOs)
Table 8-2. GPIO Interrupt Configuration Example (continued)
Desired Pin 2 Bit Valuea
Interrupt
Event
Trigger
Register 7 6 5 4 3 2 1 0
0=single X X X X X 0 X X
edge
1=both
edges
GPIOIBE
0=Low level, X X X X X 1 X X
or negative
edge
1=High level,
or positive
edge
GPIOIEV
0=masked 0 0 0 0 0 1 0 0
1=not
masked
GPIOIM
a. X=Ignored (don’t care bit)
8.3 Register Map
Table 8-3 on page 288 lists the GPIO registers. The offset listed is a hexadecimal increment to the
register’s address, relative to that GPIO port’s base address:
■ GPIO Port A: 0x4000.4000
■ GPIO Port B: 0x4000.5000
■ GPIO Port C: 0x4000.6000
■ GPIO Port D: 0x4000.7000
■ GPIO Port E: 0x4002.4000
■ GPIO Port F: 0x4002.5000
■ GPIO Port G: 0x4002.6000
■ GPIO Port H: 0x4002.7000
Note that the GPIO module clock must be enabled before the registers can be programmed (see
page 225). There must be a delay of 3 system clocks after the GPIO module clock is enabled before
any GPIO module registers are accessed.
Important: The GPIO registers in this chapter are duplicated in each GPIO block; however,
depending on the block, all eight bits may not be connected to a GPIO pad. In those
cases, writing to those unconnected bits has no effect, and reading those unconnected
bits returns no meaningful data.
Note: The default reset value for the GPIOAFSEL, GPIOPUR, and GPIODEN registers are
0x0000.0000 for all GPIO pins, with the exception of the five JTAG/SWD pins (PB7 and
PC[3:0]). These five pins default to JTAG/SWD functionality. Because of this, the default
reset value of these registers for GPIO Port B is 0x0000.0080 while the default reset value
for Port C is 0x0000.000F.
The default register type for the GPIOCR register is RO for all GPIO pins with the exception
of the five JTAG/SWD pins (PB7 and PC[3:0]). These five pins are currently the only
GPIOs that are protected by the GPIOCR register. Because of this, the register type for
GPIO Port B7 and GPIO Port C[3:0] is R/W.
January 08, 2011 287
Texas Instruments-Production Data
Stellaris® LM3S2965 Microcontroller
The default reset value for the GPIOCR register is 0x0000.00FF for all GPIO pins, with the
exception of the five JTAG/SWD pins (PB7 and PC[3:0]). To ensure that the JTAG port
is not accidentally programmed as a GPIO, these five pins default to non-committable.
Because of this, the default reset value of GPIOCR for GPIO Port B is 0x0000.007F while
the default reset value of GPIOCR for Port C is 0x0000.00F0.
Table 8-3. GPIO Register Map
See
Offset Name Type Reset Description page
0x000 GPIODATA R/W 0x0000.0000 GPIO Data 290
0x400 GPIODIR R/W 0x0000.0000 GPIO Direction 291
0x404 GPIOIS R/W 0x0000.0000 GPIO Interrupt Sense 292
0x408 GPIOIBE R/W 0x0000.0000 GPIO Interrupt Both Edges 293
0x40C GPIOIEV R/W 0x0000.0000 GPIO Interrupt Event 294
0x410 GPIOIM R/W 0x0000.0000 GPIO Interrupt Mask 295
0x414 GPIORIS RO 0x0000.0000 GPIO Raw Interrupt Status 296
0x418 GPIOMIS RO 0x0000.0000 GPIO Masked Interrupt Status 297
0x41C GPIOICR W1C 0x0000.0000 GPIO Interrupt Clear 298
0x420 GPIOAFSEL R/W - GPIO Alternate Function Select 299
0x500 GPIODR2R R/W 0x0000.00FF GPIO 2-mA Drive Select 301
0x504 GPIODR4R R/W 0x0000.0000 GPIO 4-mA Drive Select 302
0x508 GPIODR8R R/W 0x0000.0000 GPIO 8-mA Drive Select 303
0x50C GPIOODR R/W 0x0000.0000 GPIO Open Drain Select 304
0x510 GPIOPUR R/W - GPIO Pull-Up Select 305
0x514 GPIOPDR R/W 0x0000.0000 GPIO Pull-Down Select 306
0x518 GPIOSLR R/W 0x0000.0000 GPIO Slew Rate Control Select 307
0x51C GPIODEN R/W - GPIO Digital Enable 308
0x520 GPIOLOCK R/W 0x0000.0001 GPIO Lock 309
0x524 GPIOCR - - GPIO Commit 310
0xFD0 GPIOPeriphID4 RO 0x0000.0000 GPIO Peripheral Identification 4 312
0xFD4 GPIOPeriphID5 RO 0x0000.0000 GPIO Peripheral Identification 5 313
0xFD8 GPIOPeriphID6 RO 0x0000.0000 GPIO Peripheral Identification 6 314
0xFDC GPIOPeriphID7 RO 0x0000.0000 GPIO Peripheral Identification 7 315
0xFE0 GPIOPeriphID0 RO 0x0000.0061 GPIO Peripheral Identification 0 316
0xFE4 GPIOPeriphID1 RO 0x0000.0000 GPIO Peripheral Identification 1 317
0xFE8 GPIOPeriphID2 RO 0x0000.0018 GPIO Peripheral Identification 2 318
0xFEC GPIOPeriphID3 RO 0x0000.0001 GPIO Peripheral Identification 3 319
288 January 08, 2011
Texas Instruments-Production Data
General-Purpose Input/Outputs (GPIOs)
Table 8-3. GPIO Register Map (continued)
See
Offset Name Type Reset Description page
0xFF0 GPIOPCellID0 RO 0x0000.000D GPIO PrimeCell Identification 0 320
0xFF4 GPIOPCellID1 RO 0x0000.00F0 GPIO PrimeCell Identification 1 321
0xFF8 GPIOPCellID2 RO 0x0000.0005 GPIO PrimeCell Identification 2 322
0xFFC GPIOPCellID3 RO 0x0000.00B1 GPIO PrimeCell Identification 3 323
8.4 Register Descriptions
The remainder of this section lists and describes the GPIO registers, in numerical order by address
offset.
January 08, 2011 289
Texas Instruments-Production Data
Stellaris® LM3S2965 Microcontroller
Register 1: GPIO Data (GPIODATA), offset 0x000
The GPIODATA register is the data register. In software control mode, values written in the
GPIODATA register are transferred onto the GPIO port pins if the respective pins have been
configured as outputs through the GPIO Direction (GPIODIR) register (see page 291).
In order to write to GPIODATA, the corresponding bits in the mask, resulting from the address bus
bits [9:2], must be High. Otherwise, the bit values remain unchanged by the write.
Similarly, the values read from this register are determined for each bit by the mask bit derived from
the address used to access the data register, bits [9:2]. Bits that are 1 in the address mask cause
the corresponding bits in GPIODATA to be read, and bits that are 0 in the address mask cause the
corresponding bits in GPIODATA to be read as 0, regardless of their value.
A read from GPIODATA returns the last bit value written if the respective pins are configured as
outputs, or it returns the value on the corresponding input pin when these are configured as inputs.
All bits are cleared by a reset.
GPIO Data (GPIODATA)
GPIO Port A base: 0x4000.4000
GPIO Port B base: 0x4000.5000
GPIO Port C base: 0x4000.6000
GPIO Port D base: 0x4000.7000
GPIO Port E base: 0x4002.4000
GPIO Port F base: 0x4002.5000
GPIO Port G base: 0x4002.6000
GPIO Port H base: 0x4002.7000
Offset 0x000
Type R/W, reset 0x0000.0000
31 30 29 28 27 26 25 24 23 22 21 20 19 18 17 16
reserved
Type RO RO RO RO RO RO RO RO RO RO RO RO RO RO RO RO
Reset 0 0 0 0 0 0 0 0 0 0 0 0 0 0 0 0
15 14 13 12 11 10 9 8 7 6 5 4 3 2 1 0
reserved DATA
Type RO RO RO RO RO RO RO RO R/W R/W R/W R/W R/W R/W R/W R/W
Reset 0 0 0 0 0 0 0 0 0 0 0 0 0 0 0 0
Bit/Field Name Type Reset Description
Software should not rely on the value of a reserved bit. To provide
compatibility with future products, the value of a reserved bit should be
preserved across a read-modify-write operation.
31:8 reserved RO 0x00
GPIO Data
This register is virtually mapped to 256 locations in the address space.
To facilitate the reading and writing of data to these registers by
independent drivers, the data read from and the data written to the
registers are masked by the eight address lines ipaddr[9:2]. Reads
from this register return its current state. Writes to this register only affect
bits that are not masked by ipaddr[9:2] and are configured as
outputs. See “Data Register Operation” on page 283 for examples of
reads and writes.
7:0 DATA R/W 0x00
290 January 08, 2011
Texas Instruments-Production Data
General-Purpose Input/Outputs (GPIOs)
Register 2: GPIO Direction (GPIODIR), offset 0x400
The GPIODIR register is the data direction register. Bits set to 1 in the GPIODIR register configure
the corresponding pin to be an output, while bits set to 0 configure the pins to be inputs. All bits are
cleared by a reset, meaning all GPIO pins are inputs by default.
GPIO Direction (GPIODIR)
GPIO Port A base: 0x4000.4000
GPIO Port B base: 0x4000.5000
GPIO Port C base: 0x4000.6000
GPIO Port D base: 0x4000.7000
GPIO Port E base: 0x4002.4000
GPIO Port F base: 0x4002.5000
GPIO Port G base: 0x4002.6000
GPIO Port H base: 0x4002.7000
Offset 0x400
Type R/W, reset 0x0000.0000
31 30 29 28 27 26 25 24 23 22 21 20 19 18 17 16
reserved
Type RO RO RO RO RO RO RO RO RO RO RO RO RO RO RO RO
Reset 0 0 0 0 0 0 0 0 0 0 0 0 0 0 0 0
15 14 13 12 11 10 9 8 7 6 5 4 3 2 1 0
reserved DIR
Type RO RO RO RO RO RO RO RO R/W R/W R/W R/W R/W R/W R/W R/W
Reset 0 0 0 0 0 0 0 0 0 0 0 0 0 0 0 0
Bit/Field Name Type Reset Description
Software should not rely on the value of a reserved bit. To provide
compatibility with future products, the value of a reserved bit should be
preserved across a read-modify-write operation.
31:8 reserved RO 0x00
GPIO Data Direction
The DIR values are defined as follows:
Value Description
0 Pins are inputs.
1 Pins are outputs.
7:0 DIR R/W 0x00
January 08, 2011 291
Texas Instruments-Production Data
Stellaris® LM3S2965 Microcontroller
Register 3: GPIO Interrupt Sense (GPIOIS), offset 0x404
The GPIOIS register is the interrupt sense register. Bits set to 1 in GPIOIS configure the
corresponding pins to detect levels, while bits set to 0 configure the pins to detect edges. All bits
are cleared by a reset.
GPIO Interrupt Sense (GPIOIS)
GPIO Port A base: 0x4000.4000
GPIO Port B base: 0x4000.5000
GPIO Port C base: 0x4000.6000
GPIO Port D base: 0x4000.7000
GPIO Port E base: 0x4002.4000
GPIO Port F base: 0x4002.5000
GPIO Port G base: 0x4002.6000
GPIO Port H base: 0x4002.7000
Offset 0x404
Type R/W, reset 0x0000.0000
31 30 29 28 27 26 25 24 23 22 21 20 19 18 17 16
reserved
Type RO RO RO RO RO RO RO RO RO RO RO RO RO RO RO RO
Reset 0 0 0 0 0 0 0 0 0 0 0 0 0 0 0 0
15 14 13 12 11 10 9 8 7 6 5 4 3 2 1 0
reserved IS
Type RO RO RO RO RO RO RO RO R/W R/W R/W R/W R/W R/W R/W R/W
Reset 0 0 0 0 0 0 0 0 0 0 0 0 0 0 0 0
Bit/Field Name Type Reset Description
Software should not rely on the value of a reserved bit. To provide
compatibility with future products, the value of a reserved bit should be
preserved across a read-modify-write operation.
31:8 reserved RO 0x00
GPIO Interrupt Sense
The IS values are defined as follows:
Value Description
0 Edge on corresponding pin is detected (edge-sensitive).
1 Level on corresponding pin is detected (level-sensitive).
7:0 IS R/W 0x00
292 January 08, 2011
Texas Instruments-Production Data
General-Purpose Input/Outputs (GPIOs)
Register 4: GPIO Interrupt Both Edges (GPIOIBE), offset 0x408
The GPIOIBE register is the interrupt both-edges register. When the corresponding bit in the GPIO
Interrupt Sense (GPIOIS) register (see page 292) is set to detect edges, bits set to High in GPIOIBE
configure the corresponding pin to detect both rising and falling edges, regardless of the
corresponding bit in the GPIO Interrupt Event (GPIOIEV) register (see page 294). Clearing a bit
configures the pin to be controlled by GPIOIEV. All bits are cleared by a reset.
GPIO Interrupt Both Edges (GPIOIBE)
GPIO Port A base: 0x4000.4000
GPIO Port B base: 0x4000.5000
GPIO Port C base: 0x4000.6000
GPIO Port D base: 0x4000.7000
GPIO Port E base: 0x4002.4000
GPIO Port F base: 0x4002.5000
GPIO Port G base: 0x4002.6000
GPIO Port H base: 0x4002.7000
Offset 0x408
Type R/W, reset 0x0000.0000
31 30 29 28 27 26 25 24 23 22 21 20 19 18 17 16
reserved
Type RO RO RO RO RO RO RO RO RO RO RO RO RO RO RO RO
Reset 0 0 0 0 0 0 0 0 0 0 0 0 0 0 0 0
15 14 13 12 11 10 9 8 7 6 5 4 3 2 1 0
reserved IBE
Type RO RO RO RO RO RO RO RO R/W R/W R/W R/W R/W R/W R/W R/W
Reset 0 0 0 0 0 0 0 0 0 0 0 0 0 0 0 0
Bit/Field Name Type Reset Description
Software should not rely on the value of a reserved bit. To provide
compatibility with future products, the value of a reserved bit should be
preserved across a read-modify-write operation.
31:8 reserved RO 0x00
GPIO Interrupt Both Edges
The IBE values are defined as follows:
Value Description
Interrupt generation is controlled by the GPIO Interrupt Event
(GPIOIEV) register (see page 294).
0
1 Both edges on the corresponding pin trigger an interrupt.
Note: Single edge is determined by the corresponding bit
in GPIOIEV.
7:0 IBE R/W 0x00
January 08, 2011 293
Texas Instruments-Production Data
Stellaris® LM3S2965 Microcontroller
Register 5: GPIO Interrupt Event (GPIOIEV), offset 0x40C
The GPIOIEV register is the interrupt event register. Bits set to High in GPIOIEV configure the
corresponding pin to detect rising edges or high levels, depending on the corresponding bit value
in the GPIO Interrupt Sense (GPIOIS) register (see page 292). Clearing a bit configures the pin to
detect falling edges or low levels, depending on the corresponding bit value in GPIOIS. All bits are
cleared by a reset.
GPIO Interrupt Event (GPIOIEV)
GPIO Port A base: 0x4000.4000
GPIO Port B base: 0x4000.5000
GPIO Port C base: 0x4000.6000
GPIO Port D base: 0x4000.7000
GPIO Port E base: 0x4002.4000
GPIO Port F base: 0x4002.5000
GPIO Port G base: 0x4002.6000
GPIO Port H base: 0x4002.7000
Offset 0x40C
Type R/W, reset 0x0000.0000
31 30 29 28 27 26 25 24 23 22 21 20 19 18 17 16
reserved
Type RO RO RO RO RO RO RO RO RO RO RO RO RO RO RO RO
Reset 0 0 0 0 0 0 0 0 0 0 0 0 0 0 0 0
15 14 13 12 11 10 9 8 7 6 5 4 3 2 1 0
reserved IEV
Type RO RO RO RO RO RO RO RO R/W R/W R/W R/W R/W R/W R/W R/W
Reset 0 0 0 0 0 0 0 0 0 0 0 0 0 0 0 0
Bit/Field Name Type Reset Description
Software should not rely on the value of a reserved bit. To provide
compatibility with future products, the value of a reserved bit should be
preserved across a read-modify-write operation.
31:8 reserved RO 0x00
GPIO Interrupt Event
The IEV values are defined as follows:
Value Description
Falling edge or Low levels on corresponding pins trigger
interrupts.
0
Rising edge or High levels on corresponding pins trigger
interrupts.
1
7:0 IEV R/W 0x00
294 January 08, 2011
Texas Instruments-Production Data
General-Purpose Input/Outputs (GPIOs)
Register 6: GPIO Interrupt Mask (GPIOIM), offset 0x410
The GPIOIM register is the interrupt mask register. Bits set to High in GPIOIM allow the corresponding
pins to trigger their individual interrupts and the combined GPIOINTR line. Clearing a bit disables
interrupt triggering on that pin. All bits are cleared by a reset.
GPIO Interrupt Mask (GPIOIM)
GPIO Port A base: 0x4000.4000
GPIO Port B base: 0x4000.5000
GPIO Port C base: 0x4000.6000
GPIO Port D base: 0x4000.7000
GPIO Port E base: 0x4002.4000
GPIO Port F base: 0x4002.5000
GPIO Port G base: 0x4002.6000
GPIO Port H base: 0x4002.7000
Offset 0x410
Type R/W, reset 0x0000.0000
31 30 29 28 27 26 25 24 23 22 21 20 19 18 17 16
reserved
Type RO RO RO RO RO RO RO RO RO RO RO RO RO RO RO RO
Reset 0 0 0 0 0 0 0 0 0 0 0 0 0 0 0 0
15 14 13 12 11 10 9 8 7 6 5 4 3 2 1 0
reserved IME
Type RO RO RO RO RO RO RO RO R/W R/W R/W R/W R/W R/W R/W R/W
Reset 0 0 0 0 0 0 0 0 0 0 0 0 0 0 0 0
Bit/Field Name Type Reset Description
Software should not rely on the value of a reserved bit. To provide
compatibility with future products, the value of a reserved bit should be
preserved across a read-modify-write operation.
31:8 reserved RO 0x00
GPIO Interrupt Mask Enable
The IME values are defined as follows:
Value Description
0 Corresponding pin interrupt is masked.
1 Corresponding pin interrupt is not masked.
7:0 IME R/W 0x00
January 08, 2011 295
Texas Instruments-Production Data
Stellaris® LM3S2965 Microcontroller
Register 7: GPIO Raw Interrupt Status (GPIORIS), offset 0x414
The GPIORIS register is the raw interrupt status register. Bits read High in GPIORIS reflect the
status of interrupt trigger conditions detected (raw, prior to masking), indicating that all the
requirements have been met, before they are finally allowed to trigger by the GPIO Interrupt Mask
(GPIOIM) register (see page 295). Bits read as zero indicate that corresponding input pins have not
initiated an interrupt. All bits are cleared by a reset.
GPIO Raw Interrupt Status (GPIORIS)
GPIO Port A base: 0x4000.4000
GPIO Port B base: 0x4000.5000
GPIO Port C base: 0x4000.6000
GPIO Port D base: 0x4000.7000
GPIO Port E base: 0x4002.4000
GPIO Port F base: 0x4002.5000
GPIO Port G base: 0x4002.6000
GPIO Port H base: 0x4002.7000
Offset 0x414
Type RO, reset 0x0000.0000
31 30 29 28 27 26 25 24 23 22 21 20 19 18 17 16
reserved
Type RO RO RO RO RO RO RO RO RO RO RO RO RO RO RO RO
Reset 0 0 0 0 0 0 0 0 0 0 0 0 0 0 0 0
15 14 13 12 11 10 9 8 7 6 5 4 3 2 1 0
reserved RIS
Type RO RO RO RO RO RO RO RO RO RO RO RO RO RO RO RO
Reset 0 0 0 0 0 0 0 0 0 0 0 0 0 0 0 0
Bit/Field Name Type Reset Description
Software should not rely on the value of a reserved bit. To provide
compatibility with future products, the value of a reserved bit should be
preserved across a read-modify-write operation.
31:8 reserved RO 0x00
GPIO Interrupt Raw Status
Reflects the status of interrupt trigger condition detection on pins (raw,
prior to masking).
The RIS values are defined as follows:
Value Description
0 Corresponding pin interrupt requirements not met.
1 Corresponding pin interrupt has met requirements.
7:0 RIS RO 0x00
296 January 08, 2011
Texas Instruments-Production Data
General-Purpose Input/Outputs (GPIOs)
Register 8: GPIO Masked Interrupt Status (GPIOMIS), offset 0x418
The GPIOMIS register is the masked interrupt status register. Bits read High in GPIOMIS reflect
the status of input lines triggering an interrupt. Bits read as Low indicate that either no interrupt has
been generated, or the interrupt is masked.
In addition to providing GPIO functionality, PB4 can also be used as an external trigger for the ADC.
If PB4 is configured as a non-masked interrupt pin (the appropriate bit of GPIOIM is set to 1), not
only is an interrupt for PortB generated, but an external trigger signal is sent to the ADC. If the ADC
Event Multiplexer Select (ADCEMUX) register is configured to use the external trigger, an ADC
conversion is initiated.
If no other PortB pins are being used to generate interrupts, the Interrupt 0-31 Set Enable (EN0)
register can disable the PortB interrupts, and the ADC interrupt can be used to read back the
converted data. Otherwise, the PortB interrupt handler needs to ignore and clear interrupts on PB4,
and wait for the ADC interrupt or the ADC interrupt must be disabled in the EN0 register and the
PortB interrupt handler must poll the ADC registers until the conversion is completed. See page 109
for more information.
GPIOMIS is the state of the interrupt after masking.
GPIO Masked Interrupt Status (GPIOMIS)
GPIO Port A base: 0x4000.4000
GPIO Port B base: 0x4000.5000
GPIO Port C base: 0x4000.6000
GPIO Port D base: 0x4000.7000
GPIO Port E base: 0x4002.4000
GPIO Port F base: 0x4002.5000
GPIO Port G base: 0x4002.6000
GPIO Port H base: 0x4002.7000
Offset 0x418
Type RO, reset 0x0000.0000
31 30 29 28 27 26 25 24 23 22 21 20 19 18 17 16
reserved
Type RO RO RO RO RO RO RO RO RO RO RO RO RO RO RO RO
Reset 0 0 0 0 0 0 0 0 0 0 0 0 0 0 0 0
15 14 13 12 11 10 9 8 7 6 5 4 3 2 1 0
reserved MIS
Type RO RO RO RO RO RO RO RO RO RO RO RO RO RO RO RO
Reset 0 0 0 0 0 0 0 0 0 0 0 0 0 0 0 0
Bit/Field Name Type Reset Description
Software should not rely on the value of a reserved bit. To provide
compatibility with future products, the value of a reserved bit should be
preserved across a read-modify-write operation.
31:8 reserved RO 0x00
GPIO Masked Interrupt Status
Masked value of interrupt due to corresponding pin.
The MIS values are defined as follows:
Value Description
0 Corresponding GPIO line interrupt not active.
1 Corresponding GPIO line asserting interrupt.
7:0 MIS RO 0x00
January 08, 2011 297
Texas Instruments-Production Data
Stellaris® LM3S2965 Microcontroller
Register 9: GPIO Interrupt Clear (GPIOICR), offset 0x41C
The GPIOICR register is the interrupt clear register. Writing a 1 to a bit in this register clears the
corresponding interrupt edge detection logic register. Writing a 0 has no effect.
GPIO Interrupt Clear (GPIOICR)
GPIO Port A base: 0x4000.4000
GPIO Port B base: 0x4000.5000
GPIO Port C base: 0x4000.6000
GPIO Port D base: 0x4000.7000
GPIO Port E base: 0x4002.4000
GPIO Port F base: 0x4002.5000
GPIO Port G base: 0x4002.6000
GPIO Port H base: 0x4002.7000
Offset 0x41C
Type W1C, reset 0x0000.0000
31 30 29 28 27 26 25 24 23 22 21 20 19 18 17 16
reserved
Type RO RO RO RO RO RO RO RO RO RO RO RO RO RO RO RO
Reset 0 0 0 0 0 0 0 0 0 0 0 0 0 0 0 0
15 14 13 12 11 10 9 8 7 6 5 4 3 2 1 0
reserved IC
Type RO RO RO RO RO RO RO RO W1C W1C W1C W1C W1C W1C W1C W1C
Reset 0 0 0 0 0 0 0 0 0 0 0 0 0 0 0 0
Bit/Field Name Type Reset Description
Software should not rely on the value of a reserved bit. To provide
compatibility with future products, the value of a reserved bit should be
preserved across a read-modify-write operation.
31:8 reserved RO 0x00
GPIO Interrupt Clear
The IC values are defined as follows:
Value Description
0 Corresponding interrupt is unaffected.
1 Corresponding interrupt is cleared.
7:0 IC W1C 0x00
298 January 08, 2011
Texas Instruments-Production Data
General-Purpose Input/Outputs (GPIOs)
Register 10: GPIO Alternate Function Select (GPIOAFSEL), offset 0x420
The GPIOAFSEL register is the mode control select register. Writing a 1 to any bit in this register
selects the hardware control for the corresponding GPIO line. All bits are cleared by a reset, therefore
no GPIO line is set to hardware control by default.
The GPIO commit control registers provide a layer of protection against accidental programming of
critical hardware peripherals. Protection is currently provided for the five JTAG/SWD pins (PB7 and
PC[3:0]). Writes to protected bits of the GPIO Alternate Function Select (GPIOAFSEL) register
(see page 299) are not committed to storage unless the GPIO Lock (GPIOLOCK) register (see
page 309) has been unlocked and the appropriate bits of the GPIO Commit (GPIOCR) register (see
page 310) have been set to 1.
Important: All GPIO pins are tri-stated by default (GPIOAFSEL=0, GPIODEN=0, GPIOPDR=0,
and GPIOPUR=0), with the exception of the five JTAG/SWD pins (PB7 and PC[3:0]).
The JTAG/SWD pins default to their JTAG/SWD functionality (GPIOAFSEL=1,
GPIODEN=1 and GPIOPUR=1). A Power-On-Reset (POR) or asserting RST puts both
groups of pins back to their default state.
While debugging systems where PB7 is being used as a GPIO, care must be taken to
ensure that a low value is not applied to the pin when the part is reset. Because PB7
reverts to the TRST function after reset, a Low value on the pin causes the JTAG
controller to be reset, resulting in a loss of JTAG communication.
Caution – It is possible to create a software sequence that prevents the debugger from connecting to
the Stellaris® microcontroller. If the program code loaded into flash immediately changes the JTAG
pins to their GPIO functionality, the debugger may not have enough time to connect and halt the
controller before the JTAG pin functionality switches. This may lock the debugger out of the part. This
can be avoided with a software routine that restores JTAG functionality based on an external or software
trigger.
GPIO Alternate Function Select (GPIOAFSEL)
GPIO Port A base: 0x4000.4000
GPIO Port B base: 0x4000.5000
GPIO Port C base: 0x4000.6000
GPIO Port D base: 0x4000.7000
GPIO Port E base: 0x4002.4000
GPIO Port F base: 0x4002.5000
GPIO Port G base: 0x4002.6000
GPIO Port H base: 0x4002.7000
Offset 0x420
Type R/W, reset -
31 30 29 28 27 26 25 24 23 22 21 20 19 18 17 16
reserved
Type RO RO RO RO RO RO RO RO RO RO RO RO RO RO RO RO
Reset 0 0 0 0 0 0 0 0 0 0 0 0 0 0 0 0
15 14 13 12 11 10 9 8 7 6 5 4 3 2 1 0
reserved AFSEL
Type RO RO RO RO RO RO RO RO R/W R/W R/W R/W R/W R/W R/W R/W
Reset 0 0 0 0 0 0 0 0 - - - - - - - -
Bit/Field Name Type Reset Description
Software should not rely on the value of a reserved bit. To provide
compatibility with future products, the value of a reserved bit should be
preserved across a read-modify-write operation.
31:8 reserved RO 0x00
January 08, 2011 299
Texas Instruments-Production Data
Stellaris® LM3S2965 Microcontroller
Bit/Field Name Type Reset Description
GPIO Alternate Function Select
The AFSEL values are defined as follows:
Value Description
0 Software control of corresponding GPIO line (GPIO mode).
Hardware control of corresponding GPIO line (alternate
hardware function).
1
Note: The default reset value for the GPIOAFSEL,
GPIOPUR, and GPIODEN registers are 0x0000.0000
for all GPIO pins, with the exception of the five
JTAG/SWD pins (PB7 and PC[3:0]). These five pins
default to JTAG/SWD functionality. Because of this,
the default reset value of these registers for GPIO
Port B is 0x0000.0080 while the default reset value
for Port C is 0x0000.000F.
7:0 AFSEL R/W -
300 January 08, 2011
Texas Instruments-Production Data
General-Purpose Input/Outputs (GPIOs)
Register 11: GPIO 2-mA Drive Select (GPIODR2R), offset 0x500
The GPIODR2R register is the 2-mA drive control register. It allows for each GPIO signal in the port
to be individually configured without affecting the other pads. When writing a DRV2 bit for a GPIO
signal, the corresponding DRV4 bit in the GPIODR4R register and the DRV8 bit in the GPIODR8R
register are automatically cleared by hardware.
GPIO 2-mA Drive Select (GPIODR2R)
GPIO Port A base: 0x4000.4000
GPIO Port B base: 0x4000.5000
GPIO Port C base: 0x4000.6000
GPIO Port D base: 0x4000.7000
GPIO Port E base: 0x4002.4000
GPIO Port F base: 0x4002.5000
GPIO Port G base: 0x4002.6000
GPIO Port H base: 0x4002.7000
Offset 0x500
Type R/W, reset 0x0000.00FF
31 30 29 28 27 26 25 24 23 22 21 20 19 18 17 16
reserved
Type RO RO RO RO RO RO RO RO RO RO RO RO RO RO RO RO
Reset 0 0 0 0 0 0 0 0 0 0 0 0 0 0 0 0
15 14 13 12 11 10 9 8 7 6 5 4 3 2 1 0
reserved DRV2
Type RO RO RO RO RO RO RO RO R/W R/W R/W R/W R/W R/W R/W R/W
Reset 0 0 0 0 0 0 0 0 1 1 1 1 1 1 1 1
Bit/Field Name Type Reset Description
Software should not rely on the value of a reserved bit. To provide
compatibility with future products, the value of a reserved bit should be
preserved across a read-modify-write operation.
31:8 reserved RO 0x00
Output Pad 2-mA Drive Enable
A write of 1 to either GPIODR4[n] or GPIODR8[n] clears the
corresponding 2-mA enable bit. The change is effective on the second
clock cycle after the write.
7:0 DRV2 R/W 0xFF
January 08, 2011 301
Texas Instruments-Production Data
Stellaris® LM3S2965 Microcontroller
Register 12: GPIO 4-mA Drive Select (GPIODR4R), offset 0x504
The GPIODR4R register is the 4-mA drive control register. It allows for each GPIO signal in the port
to be individually configured without affecting the other pads. When writing the DRV4 bit for a GPIO
signal, the corresponding DRV2 bit in the GPIODR2R register and the DRV8 bit in the GPIODR8R
register are automatically cleared by hardware.
GPIO 4-mA Drive Select (GPIODR4R)
GPIO Port A base: 0x4000.4000
GPIO Port B base: 0x4000.5000
GPIO Port C base: 0x4000.6000
GPIO Port D base: 0x4000.7000
GPIO Port E base: 0x4002.4000
GPIO Port F base: 0x4002.5000
GPIO Port G base: 0x4002.6000
GPIO Port H base: 0x4002.7000
Offset 0x504
Type R/W, reset 0x0000.0000
31 30 29 28 27 26 25 24 23 22 21 20 19 18 17 16
reserved
Type RO RO RO RO RO RO RO RO RO RO RO RO RO RO RO RO
Reset 0 0 0 0 0 0 0 0 0 0 0 0 0 0 0 0
15 14 13 12 11 10 9 8 7 6 5 4 3 2 1 0
reserved DRV4
Type RO RO RO RO RO RO RO RO R/W R/W R/W R/W R/W R/W R/W R/W
Reset 0 0 0 0 0 0 0 0 0 0 0 0 0 0 0 0
Bit/Field Name Type Reset Description
Software should not rely on the value of a reserved bit. To provide
compatibility with future products, the value of a reserved bit should be
preserved across a read-modify-write operation.
31:8 reserved RO 0x00
Output Pad 4-mA Drive Enable
A write of 1 to either GPIODR2[n] or GPIODR8[n] clears the
corresponding 4-mA enable bit. The change is effective on the second
clock cycle after the write.
7:0 DRV4 R/W 0x00
302 January 08, 2011
Texas Instruments-Production Data
General-Purpose Input/Outputs (GPIOs)
Register 13: GPIO 8-mA Drive Select (GPIODR8R), offset 0x508
The GPIODR8R register is the 8-mA drive control register. It allows for each GPIO signal in the port
to be individually configured without affecting the other pads. When writing the DRV8 bit for a GPIO
signal, the corresponding DRV2 bit in the GPIODR2R register and the DRV4 bit in the GPIODR4R
register are automatically cleared by hardware.
GPIO 8-mA Drive Select (GPIODR8R)
GPIO Port A base: 0x4000.4000
GPIO Port B base: 0x4000.5000
GPIO Port C base: 0x4000.6000
GPIO Port D base: 0x4000.7000
GPIO Port E base: 0x4002.4000
GPIO Port F base: 0x4002.5000
GPIO Port G base: 0x4002.6000
GPIO Port H base: 0x4002.7000
Offset 0x508
Type R/W, reset 0x0000.0000
31 30 29 28 27 26 25 24 23 22 21 20 19 18 17 16
reserved
Type RO RO RO RO RO RO RO RO RO RO RO RO RO RO RO RO
Reset 0 0 0 0 0 0 0 0 0 0 0 0 0 0 0 0
15 14 13 12 11 10 9 8 7 6 5 4 3 2 1 0
reserved DRV8
Type RO RO RO RO RO RO RO RO R/W R/W R/W R/W R/W R/W R/W R/W
Reset 0 0 0 0 0 0 0 0 0 0 0 0 0 0 0 0
Bit/Field Name Type Reset Description
Software should not rely on the value of a reserved bit. To provide
compatibility with future products, the value of a reserved bit should be
preserved across a read-modify-write operation.
31:8 reserved RO 0x00
Output Pad 8-mA Drive Enable
A write of 1 to either GPIODR2[n] or GPIODR4[n] clears the
corresponding 8-mA enable bit. The change is effective on the second
clock cycle after the write.
7:0 DRV8 R/W 0x00
January 08, 2011 303
Texas Instruments-Production Data
Stellaris® LM3S2965 Microcontroller
Register 14: GPIO Open Drain Select (GPIOODR), offset 0x50C
The GPIOODR register is the open drain control register. Setting a bit in this register enables the
open drain configuration of the corresponding GPIO pad. When open drain mode is enabled, the
corresponding bit should also be set in the GPIO Digital Input Enable (GPIODEN) register (see
page 308). Corresponding bits in the drive strength registers (GPIODR2R, GPIODR4R, GPIODR8R,
and GPIOSLR ) can be set to achieve the desired rise and fall times. The GPIO acts as an open-drain
input if the corresponding bit in the GPIODIR register is cleared. If open drain is selected while the
GPIO is configured as an input, the GPIO will remain an input and the open-drain selection has no
effect until the GPIO is changed to an output.
When using the I2C module, in addition to configuring the pin to open drain, the GPIO Alternate
Function Select (GPIOAFSEL) register bits for the I2C clock and data pins should be set to 1 (see
examples in “Initialization and Configuration” on page 286).
GPIO Open Drain Select (GPIOODR)
GPIO Port A base: 0x4000.4000
GPIO Port B base: 0x4000.5000
GPIO Port C base: 0x4000.6000
GPIO Port D base: 0x4000.7000
GPIO Port E base: 0x4002.4000
GPIO Port F base: 0x4002.5000
GPIO Port G base: 0x4002.6000
GPIO Port H base: 0x4002.7000
Offset 0x50C
Type R/W, reset 0x0000.0000
31 30 29 28 27 26 25 24 23 22 21 20 19 18 17 16
reserved
Type RO RO RO RO RO RO RO RO RO RO RO RO RO RO RO RO
Reset 0 0 0 0 0 0 0 0 0 0 0 0 0 0 0 0
15 14 13 12 11 10 9 8 7 6 5 4 3 2 1 0
reserved ODE
Type RO RO RO RO RO RO RO RO R/W R/W R/W R/W R/W R/W R/W R/W
Reset 0 0 0 0 0 0 0 0 0 0 0 0 0 0 0 0
Bit/Field Name Type Reset Description
Software should not rely on the value of a reserved bit. To provide
compatibility with future products, the value of a reserved bit should be
preserved across a read-modify-write operation.
31:8 reserved RO 0x00
Output Pad Open Drain Enable
The ODE values are defined as follows:
Value Description
0 Open drain configuration is disabled.
1 Open drain configuration is enabled.
7:0 ODE R/W 0x00
304 January 08, 2011
Texas Instruments-Production Data
General-Purpose Input/Outputs (GPIOs)
Register 15: GPIO Pull-Up Select (GPIOPUR), offset 0x510
The GPIOPUR register is the pull-up control register. When a bit is set to 1, it enables a weak pull-up
resistor on the corresponding GPIO signal. Setting a bit in GPIOPUR automatically clears the
corresponding bit in the GPIO Pull-Down Select (GPIOPDR) register (see page 306).
GPIO Pull-Up Select (GPIOPUR)
GPIO Port A base: 0x4000.4000
GPIO Port B base: 0x4000.5000
GPIO Port C base: 0x4000.6000
GPIO Port D base: 0x4000.7000
GPIO Port E base: 0x4002.4000
GPIO Port F base: 0x4002.5000
GPIO Port G base: 0x4002.6000
GPIO Port H base: 0x4002.7000
Offset 0x510
Type R/W, reset -
31 30 29 28 27 26 25 24 23 22 21 20 19 18 17 16
reserved
Type RO RO RO RO RO RO RO RO RO RO RO RO RO RO RO RO
Reset 0 0 0 0 0 0 0 0 0 0 0 0 0 0 0 0
15 14 13 12 11 10 9 8 7 6 5 4 3 2 1 0
reserved PUE
Type RO RO RO RO RO RO RO RO R/W R/W R/W R/W R/W R/W R/W R/W
Reset 0 0 0 0 0 0 0 0 - - - - - - - -
Bit/Field Name Type Reset Description
Software should not rely on the value of a reserved bit. To provide
compatibility with future products, the value of a reserved bit should be
preserved across a read-modify-write operation.
31:8 reserved RO 0x00
Pad Weak Pull-Up Enable
A write of 1 to GPIOPDR[n] clears the corresponding GPIOPUR[n]
enables. The change is effective on the second clock cycle after the
write.
Note: The default reset value for the GPIOAFSEL, GPIOPUR, and
GPIODEN registers are 0x0000.0000 for all GPIO pins, with
the exception of the five JTAG/SWD pins (PB7 and PC[3:0]).
These five pins default to JTAG/SWD functionality. Because
of this, the default reset value of these registers for GPIO Port
B is 0x0000.0080 while the default reset value for Port C is
0x0000.000F.
7:0 PUE R/W -
January 08, 2011 305
Texas Instruments-Production Data
Stellaris® LM3S2965 Microcontroller
Register 16: GPIO Pull-Down Select (GPIOPDR), offset 0x514
The GPIOPDR register is the pull-down control register. When a bit is set to 1, it enables a weak
pull-down resistor on the corresponding GPIO signal. Setting a bit in GPIOPDR automatically clears
the corresponding bit in the GPIO Pull-Up Select (GPIOPUR) register (see page 305).
GPIO Pull-Down Select (GPIOPDR)
GPIO Port A base: 0x4000.4000
GPIO Port B base: 0x4000.5000
GPIO Port C base: 0x4000.6000
GPIO Port D base: 0x4000.7000
GPIO Port E base: 0x4002.4000
GPIO Port F base: 0x4002.5000
GPIO Port G base: 0x4002.6000
GPIO Port H base: 0x4002.7000
Offset 0x514
Type R/W, reset 0x0000.0000
31 30 29 28 27 26 25 24 23 22 21 20 19 18 17 16
reserved
Type RO RO RO RO RO RO RO RO RO RO RO RO RO RO RO RO
Reset 0 0 0 0 0 0 0 0 0 0 0 0 0 0 0 0
15 14 13 12 11 10 9 8 7 6 5 4 3 2 1 0
reserved PDE
Type RO RO RO RO RO RO RO RO R/W R/W R/W R/W R/W R/W R/W R/W
Reset 0 0 0 0 0 0 0 0 0 0 0 0 0 0 0 0
Bit/Field Name Type Reset Description
Software should not rely on the value of a reserved bit. To provide
compatibility with future products, the value of a reserved bit should be
preserved across a read-modify-write operation.
31:8 reserved RO 0x00
Pad Weak Pull-Down Enable
A write of 1 to GPIOPUR[n] clears the corresponding GPIOPDR[n]
enables. The change is effective on the second clock cycle after the
write.
7:0 PDE R/W 0x00
306 January 08, 2011
Texas Instruments-Production Data
General-Purpose Input/Outputs (GPIOs)
Register 17: GPIO Slew Rate Control Select (GPIOSLR), offset 0x518
The GPIOSLR register is the slew rate control register. Slew rate control is only available when
using the 8-mA drive strength option via the GPIO 8-mA Drive Select (GPIODR8R) register (see
page 303).
GPIO Slew Rate Control Select (GPIOSLR)
GPIO Port A base: 0x4000.4000
GPIO Port B base: 0x4000.5000
GPIO Port C base: 0x4000.6000
GPIO Port D base: 0x4000.7000
GPIO Port E base: 0x4002.4000
GPIO Port F base: 0x4002.5000
GPIO Port G base: 0x4002.6000
GPIO Port H base: 0x4002.7000
Offset 0x518
Type R/W, reset 0x0000.0000
31 30 29 28 27 26 25 24 23 22 21 20 19 18 17 16
reserved
Type RO RO RO RO RO RO RO RO RO RO RO RO RO RO RO RO
Reset 0 0 0 0 0 0 0 0 0 0 0 0 0 0 0 0
15 14 13 12 11 10 9 8 7 6 5 4 3 2 1 0
reserved SRL
Type RO RO RO RO RO RO RO RO R/W R/W R/W R/W R/W R/W R/W R/W
Reset 0 0 0 0 0 0 0 0 0 0 0 0 0 0 0 0
Bit/Field Name Type Reset Description
Software should not rely on the value of a reserved bit. To provide
compatibility with future products, the value of a reserved bit should be
preserved across a read-modify-write operation.
31:8 reserved RO 0x00
Slew Rate Limit Enable (8-mA drive only)
The SRL values are defined as follows:
Value Description
0 Slew rate control disabled.
1 Slew rate control enabled.
7:0 SRL R/W 0x00
January 08, 2011 307
Texas Instruments-Production Data
Stellaris® LM3S2965 Microcontroller
Register 18: GPIO Digital Enable (GPIODEN), offset 0x51C
Note: Pins configured as digital inputs are Schmitt-triggered.
The GPIODEN register is the digital enable register. By default, with the exception of the GPIO
signals used for JTAG/SWD function, all other GPIO signals are configured out of reset to be undriven
(tristate). Their digital function is disabled; they do not drive a logic value on the pin and they do not
allow the pin voltage into the GPIO receiver. To use the pin in a digital function (either GPIO or
alternate function), the corresponding GPIODEN bit must be set.
GPIO Digital Enable (GPIODEN)
GPIO Port A base: 0x4000.4000
GPIO Port B base: 0x4000.5000
GPIO Port C base: 0x4000.6000
GPIO Port D base: 0x4000.7000
GPIO Port E base: 0x4002.4000
GPIO Port F base: 0x4002.5000
GPIO Port G base: 0x4002.6000
GPIO Port H base: 0x4002.7000
Offset 0x51C
Type R/W, reset -
31 30 29 28 27 26 25 24 23 22 21 20 19 18 17 16
reserved
Type RO RO RO RO RO RO RO RO RO RO RO RO RO RO RO RO
Reset 0 0 0 0 0 0 0 0 0 0 0 0 0 0 0 0
15 14 13 12 11 10 9 8 7 6 5 4 3 2 1 0
reserved DEN
Type RO RO RO RO RO RO RO RO R/W R/W R/W R/W R/W R/W R/W R/W
Reset 0 0 0 0 0 0 0 0 - - - - - - - -
Bit/Field Name Type Reset Description
Software should not rely on the value of a reserved bit. To provide
compatibility with future products, the value of a reserved bit should be
preserved across a read-modify-write operation.
31:8 reserved RO 0x00
Digital Enable
The DEN values are defined as follows:
Value Description
0 Digital functions disabled.
1 Digital functions enabled.
Note: The default reset value for the GPIOAFSEL,
GPIOPUR, and GPIODEN registers are 0x0000.0000
for all GPIO pins, with the exception of the five
JTAG/SWD pins (PB7 and PC[3:0]). These five pins
default to JTAG/SWD functionality. Because of this,
the default reset value of these registers for GPIO
Port B is 0x0000.0080 while the default reset value
for Port C is 0x0000.000F.
7:0 DEN R/W -
308 January 08, 2011
Texas Instruments-Production Data
General-Purpose Input/Outputs (GPIOs)
Register 19: GPIO Lock (GPIOLOCK), offset 0x520
The GPIOLOCK register enables write access to the GPIOCR register (see page 310). Writing
0x1ACC.E551 to the GPIOLOCK register will unlock the GPIOCR register. Writing any other value
to the GPIOLOCK register re-enables the locked state. Reading the GPIOLOCK register returns
the lock status rather than the 32-bit value that was previously written. Therefore, when write accesses
are disabled, or locked, reading the GPIOLOCK register returns 0x00000001. When write accesses
are enabled, or unlocked, reading the GPIOLOCK register returns 0x00000000.
GPIO Lock (GPIOLOCK)
GPIO Port A base: 0x4000.4000
GPIO Port B base: 0x4000.5000
GPIO Port C base: 0x4000.6000
GPIO Port D base: 0x4000.7000
GPIO Port E base: 0x4002.4000
GPIO Port F base: 0x4002.5000
GPIO Port G base: 0x4002.6000
GPIO Port H base: 0x4002.7000
Offset 0x520
Type R/W, reset 0x0000.0001
31 30 29 28 27 26 25 24 23 22 21 20 19 18 17 16
LOCK
Type R/W R/W R/W R/W R/W R/W R/W R/W R/W R/W R/W R/W R/W R/W R/W R/W
Reset 0 0 0 0 0 0 0 0 0 0 0 0 0 0 0 0
15 14 13 12 11 10 9 8 7 6 5 4 3 2 1 0
LOCK
Type R/W R/W R/W R/W R/W R/W R/W R/W R/W R/W R/W R/W R/W R/W R/W R/W
Reset 0 0 0 0 0 0 0 0 0 0 0 0 0 0 0 1
Bit/Field Name Type Reset Description
GPIO Lock
A write of the value 0x1ACC.E551 unlocks the GPIO Commit (GPIOCR)
register for write access.
A write of any other value or a write to the GPIOCR register reapplies
the lock, preventing any register updates. A read of this register returns
the following values:
Value Description
0x0000.0001 locked
0x0000.0000 unlocked
31:0 LOCK R/W 0x0000.0001
January 08, 2011 309
Texas Instruments-Production Data
Stellaris® LM3S2965 Microcontroller
Register 20: GPIO Commit (GPIOCR), offset 0x524
The GPIOCR register is the commit register. The value of the GPIOCR register determines which
bits of the GPIOAFSEL register are committed when a write to the GPIOAFSEL register is performed.
If a bit in the GPIOCR register is a zero, the data being written to the corresponding bit in the
GPIOAFSEL register will not be committed and will retain its previous value. If a bit in the GPIOCR
register is a one, the data being written to the corresponding bit of the GPIOAFSEL register will be
committed to the register and will reflect the new value.
The contents of the GPIOCR register can only be modified if the GPIOLOCK register is unlocked.
Writes to the GPIOCR register are ignored if the GPIOLOCK register is locked.
Important: This register is designed to prevent accidental programming of the registers that control
connectivity to the JTAG/SWD debug hardware. By initializing the bits of the GPIOCR
register to 0 for PB7 and PC[3:0], the JTAG/SWD debug port can only be converted
to GPIOs through a deliberate set of writes to the GPIOLOCK, GPIOCR, and the
corresponding registers.
Because this protection is currently only implemented on the JTAG/SWD pins on PB7
and PC[3:0], all of the other bits in the GPIOCR registers cannot be written with 0x0.
These bits are hardwired to 0x1, ensuring that it is always possible to commit new
values to the GPIOAFSELregister bits of these other pins.
GPIO Commit (GPIOCR)
GPIO Port A base: 0x4000.4000
GPIO Port B base: 0x4000.5000
GPIO Port C base: 0x4000.6000
GPIO Port D base: 0x4000.7000
GPIO Port E base: 0x4002.4000
GPIO Port F base: 0x4002.5000
GPIO Port G base: 0x4002.6000
GPIO Port H base: 0x4002.7000
Offset 0x524
Type -, reset -
31 30 29 28 27 26 25 24 23 22 21 20 19 18 17 16
reserved
Type RO RO RO RO RO RO RO RO RO RO RO RO RO RO RO RO
Reset 0 0 0 0 0 0 0 0 0 0 0 0 0 0 0 0
15 14 13 12 11 10 9 8 7 6 5 4 3 2 1 0
reserved CR
Type RO RO RO RO RO RO RO RO - - - - - - - -
Reset 0 0 0 0 0 0 0 0 - - - - - - - -
Bit/Field Name Type Reset Description
Software should not rely on the value of a reserved bit. To provide
compatibility with future products, the value of a reserved bit should be
preserved across a read-modify-write operation.
31:8 reserved RO 0x00
310 January 08, 2011
Texas Instruments-Production Data
General-Purpose Input/Outputs (GPIOs)
Bit/Field Name Type Reset Description
GPIO Commit
On a bit-wise basis, any bit set allows the corresponding GPIOAFSEL
bit to be set to its alternate function.
Note: The default register type for the GPIOCR register is RO for
all GPIO pins with the exception of the five JTAG/SWD pins
(PB7 and PC[3:0]). These five pins are currently the only
GPIOs that are protected by the GPIOCR register. Because
of this, the register type for GPIO Port B7 and GPIO Port
C[3:0] is R/W.
The default reset value for the GPIOCR register is
0x0000.00FF for all GPIO pins, with the exception of the five
JTAG/SWD pins (PB7 and PC[3:0]). To ensure that the
JTAG port is not accidentally programmed as a GPIO, these
five pins default to non-committable. Because of this, the
default reset value of GPIOCR for GPIO Port B is
0x0000.007F while the default reset value of GPIOCR for Port
C is 0x0000.00F0.
7:0 CR - -
January 08, 2011 311
Texas Instruments-Production Data
Stellaris® LM3S2965 Microcontroller
Register 21: GPIO Peripheral Identification 4 (GPIOPeriphID4), offset 0xFD0
The GPIOPeriphID4, GPIOPeriphID5, GPIOPeriphID6, and GPIOPeriphID7 registers can
conceptually be treated as one 32-bit register; each register contains eight bits of the 32-bit register,
used by software to identify the peripheral.
GPIO Peripheral Identification 4 (GPIOPeriphID4)
GPIO Port A base: 0x4000.4000
GPIO Port B base: 0x4000.5000
GPIO Port C base: 0x4000.6000
GPIO Port D base: 0x4000.7000
GPIO Port E base: 0x4002.4000
GPIO Port F base: 0x4002.5000
GPIO Port G base: 0x4002.6000
GPIO Port H base: 0x4002.7000
Offset 0xFD0
Type RO, reset 0x0000.0000
31 30 29 28 27 26 25 24 23 22 21 20 19 18 17 16
reserved
Type RO RO RO RO RO RO RO RO RO RO RO RO RO RO RO RO
Reset 0 0 0 0 0 0 0 0 0 0 0 0 0 0 0 0
15 14 13 12 11 10 9 8 7 6 5 4 3 2 1 0
reserved PID4
Type RO RO RO RO RO RO RO RO RO RO RO RO RO RO RO RO
Reset 0 0 0 0 0 0 0 0 0 0 0 0 0 0 0 0
Bit/Field Name Type Reset Description
Software should not rely on the value of a reserved bit. To provide
compatibility with future products, the value of a reserved bit should be
preserved across a read-modify-write operation.
31:8 reserved RO 0x00
7:0 PID4 RO 0x00 GPIO Peripheral ID Register[7:0]
312 January 08, 2011
Texas Instruments-Production Data
General-Purpose Input/Outputs (GPIOs)
Register 22: GPIO Peripheral Identification 5 (GPIOPeriphID5), offset 0xFD4
The GPIOPeriphID4, GPIOPeriphID5, GPIOPeriphID6, and GPIOPeriphID7 registers can
conceptually be treated as one 32-bit register; each register contains eight bits of the 32-bit register,
used by software to identify the peripheral.
GPIO Peripheral Identification 5 (GPIOPeriphID5)
GPIO Port A base: 0x4000.4000
GPIO Port B base: 0x4000.5000
GPIO Port C base: 0x4000.6000
GPIO Port D base: 0x4000.7000
GPIO Port E base: 0x4002.4000
GPIO Port F base: 0x4002.5000
GPIO Port G base: 0x4002.6000
GPIO Port H base: 0x4002.7000
Offset 0xFD4
Type RO, reset 0x0000.0000
31 30 29 28 27 26 25 24 23 22 21 20 19 18 17 16
reserved
Type RO RO RO RO RO RO RO RO RO RO RO RO RO RO RO RO
Reset 0 0 0 0 0 0 0 0 0 0 0 0 0 0 0 0
15 14 13 12 11 10 9 8 7 6 5 4 3 2 1 0
reserved PID5
Type RO RO RO RO RO RO RO RO RO RO RO RO RO RO RO RO
Reset 0 0 0 0 0 0 0 0 0 0 0 0 0 0 0 0
Bit/Field Name Type Reset Description
Software should not rely on the value of a reserved bit. To provide
compatibility with future products, the value of a reserved bit should be
preserved across a read-modify-write operation.
31:8 reserved RO 0x00
7:0 PID5 RO 0x00 GPIO Peripheral ID Register[15:8]
January 08, 2011 313
Texas Instruments-Production Data
Stellaris® LM3S2965 Microcontroller
Register 23: GPIO Peripheral Identification 6 (GPIOPeriphID6), offset 0xFD8
The GPIOPeriphID4, GPIOPeriphID5, GPIOPeriphID6, and GPIOPeriphID7 registers can
conceptually be treated as one 32-bit register; each register contains eight bits of the 32-bit register,
used by software to identify the peripheral.
GPIO Peripheral Identification 6 (GPIOPeriphID6)
GPIO Port A base: 0x4000.4000
GPIO Port B base: 0x4000.5000
GPIO Port C base: 0x4000.6000
GPIO Port D base: 0x4000.7000
GPIO Port E base: 0x4002.4000
GPIO Port F base: 0x4002.5000
GPIO Port G base: 0x4002.6000
GPIO Port H base: 0x4002.7000
Offset 0xFD8
Type RO, reset 0x0000.0000
31 30 29 28 27 26 25 24 23 22 21 20 19 18 17 16
reserved
Type RO RO RO RO RO RO RO RO RO RO RO RO RO RO RO RO
Reset 0 0 0 0 0 0 0 0 0 0 0 0 0 0 0 0
15 14 13 12 11 10 9 8 7 6 5 4 3 2 1 0
reserved PID6
Type RO RO RO RO RO RO RO RO RO RO RO RO RO RO RO RO
Reset 0 0 0 0 0 0 0 0 0 0 0 0 0 0 0 0
Bit/Field Name Type Reset Description
Software should not rely on the value of a reserved bit. To provide
compatibility with future products, the value of a reserved bit should be
preserved across a read-modify-write operation.
31:8 reserved RO 0x00
7:0 PID6 RO 0x00 GPIO Peripheral ID Register[23:16]
314 January 08, 2011
Texas Instruments-Production Data
General-Purpose Input/Outputs (GPIOs)
Register 24: GPIO Peripheral Identification 7 (GPIOPeriphID7), offset 0xFDC
The GPIOPeriphID4, GPIOPeriphID5, GPIOPeriphID6, and GPIOPeriphID7 registers can
conceptually be treated as one 32-bit register; each register contains eight bits of the 32-bit register,
used by software to identify the peripheral.
GPIO Peripheral Identification 7 (GPIOPeriphID7)
GPIO Port A base: 0x4000.4000
GPIO Port B base: 0x4000.5000
GPIO Port C base: 0x4000.6000
GPIO Port D base: 0x4000.7000
GPIO Port E base: 0x4002.4000
GPIO Port F base: 0x4002.5000
GPIO Port G base: 0x4002.6000
GPIO Port H base: 0x4002.7000
Offset 0xFDC
Type RO, reset 0x0000.0000
31 30 29 28 27 26 25 24 23 22 21 20 19 18 17 16
reserved
Type RO RO RO RO RO RO RO RO RO RO RO RO RO RO RO RO
Reset 0 0 0 0 0 0 0 0 0 0 0 0 0 0 0 0
15 14 13 12 11 10 9 8 7 6 5 4 3 2 1 0
reserved PID7
Type RO RO RO RO RO RO RO RO RO RO RO RO RO RO RO RO
Reset 0 0 0 0 0 0 0 0 0 0 0 0 0 0 0 0
Bit/Field Name Type Reset Description
Software should not rely on the value of a reserved bit. To provide
compatibility with future products, the value of a reserved bit should be
preserved across a read-modify-write operation.
31:8 reserved RO 0x00
7:0 PID7 RO 0x00 GPIO Peripheral ID Register[31:24]
January 08, 2011 315
Texas Instruments-Production Data
Stellaris® LM3S2965 Microcontroller
Register 25: GPIO Peripheral Identification 0 (GPIOPeriphID0), offset 0xFE0
The GPIOPeriphID0, GPIOPeriphID1, GPIOPeriphID2, and GPIOPeriphID3 registers can
conceptually be treated as one 32-bit register; each register contains eight bits of the 32-bit register,
used by software to identify the peripheral.
GPIO Peripheral Identification 0 (GPIOPeriphID0)
GPIO Port A base: 0x4000.4000
GPIO Port B base: 0x4000.5000
GPIO Port C base: 0x4000.6000
GPIO Port D base: 0x4000.7000
GPIO Port E base: 0x4002.4000
GPIO Port F base: 0x4002.5000
GPIO Port G base: 0x4002.6000
GPIO Port H base: 0x4002.7000
Offset 0xFE0
Type RO, reset 0x0000.0061
31 30 29 28 27 26 25 24 23 22 21 20 19 18 17 16
reserved
Type RO RO RO RO RO RO RO RO RO RO RO RO RO RO RO RO
Reset 0 0 0 0 0 0 0 0 0 0 0 0 0 0 0 0
15 14 13 12 11 10 9 8 7 6 5 4 3 2 1 0
reserved PID0
Type RO RO RO RO RO RO RO RO RO RO RO RO RO RO RO RO
Reset 0 0 0 0 0 0 0 0 0 1 1 0 0 0 0 1
Bit/Field Name Type Reset Description
Software should not rely on the value of a reserved bit. To provide
compatibility with future products, the value of a reserved bit should be
preserved across a read-modify-write operation.
31:8 reserved RO 0x00
GPIO Peripheral ID Register[7:0]
Can be used by software to identify the presence of this peripheral.
7:0 PID0 RO 0x61
316 January 08, 2011
Texas Instruments-Production Data
General-Purpose Input/Outputs (GPIOs)
Register 26: GPIO Peripheral Identification 1 (GPIOPeriphID1), offset 0xFE4
The GPIOPeriphID0, GPIOPeriphID1, GPIOPeriphID2, and GPIOPeriphID3 registers can
conceptually be treated as one 32-bit register; each register contains eight bits of the 32-bit register,
used by software to identify the peripheral.
GPIO Peripheral Identification 1 (GPIOPeriphID1)
GPIO Port A base: 0x4000.4000
GPIO Port B base: 0x4000.5000
GPIO Port C base: 0x4000.6000
GPIO Port D base: 0x4000.7000
GPIO Port E base: 0x4002.4000
GPIO Port F base: 0x4002.5000
GPIO Port G base: 0x4002.6000
GPIO Port H base: 0x4002.7000
Offset 0xFE4
Type RO, reset 0x0000.0000
31 30 29 28 27 26 25 24 23 22 21 20 19 18 17 16
reserved
Type RO RO RO RO RO RO RO RO RO RO RO RO RO RO RO RO
Reset 0 0 0 0 0 0 0 0 0 0 0 0 0 0 0 0
15 14 13 12 11 10 9 8 7 6 5 4 3 2 1 0
reserved PID1
Type RO RO RO RO RO RO RO RO RO RO RO RO RO RO RO RO
Reset 0 0 0 0 0 0 0 0 0 0 0 0 0 0 0 0
Bit/Field Name Type Reset Description
Software should not rely on the value of a reserved bit. To provide
compatibility with future products, the value of a reserved bit should be
preserved across a read-modify-write operation.
31:8 reserved RO 0x00
GPIO Peripheral ID Register[15:8]
Can be used by software to identify the presence of this peripheral.
7:0 PID1 RO 0x00
January 08, 2011 317
Texas Instruments-Production Data
Stellaris® LM3S2965 Microcontroller
Register 27: GPIO Peripheral Identification 2 (GPIOPeriphID2), offset 0xFE8
The GPIOPeriphID0, GPIOPeriphID1, GPIOPeriphID2, and GPIOPeriphID3 registers can
conceptually be treated as one 32-bit register; each register contains eight bits of the 32-bit register,
used by software to identify the peripheral.
GPIO Peripheral Identification 2 (GPIOPeriphID2)
GPIO Port A base: 0x4000.4000
GPIO Port B base: 0x4000.5000
GPIO Port C base: 0x4000.6000
GPIO Port D base: 0x4000.7000
GPIO Port E base: 0x4002.4000
GPIO Port F base: 0x4002.5000
GPIO Port G base: 0x4002.6000
GPIO Port H base: 0x4002.7000
Offset 0xFE8
Type RO, reset 0x0000.0018
31 30 29 28 27 26 25 24 23 22 21 20 19 18 17 16
reserved
Type RO RO RO RO RO RO RO RO RO RO RO RO RO RO RO RO
Reset 0 0 0 0 0 0 0 0 0 0 0 0 0 0 0 0
15 14 13 12 11 10 9 8 7 6 5 4 3 2 1 0
reserved PID2
Type RO RO RO RO RO RO RO RO RO RO RO RO RO RO RO RO
Reset 0 0 0 0 0 0 0 0 0 0 0 1 1 0 0 0
Bit/Field Name Type Reset Description
Software should not rely on the value of a reserved bit. To provide
compatibility with future products, the value of a reserved bit should be
preserved across a read-modify-write operation.
31:8 reserved RO 0x00
GPIO Peripheral ID Register[23:16]
Can be used by software to identify the presence of this peripheral.
7:0 PID2 RO 0x18
318 January 08, 2011
Texas Instruments-Production Data
General-Purpose Input/Outputs (GPIOs)
Register 28: GPIO Peripheral Identification 3 (GPIOPeriphID3), offset 0xFEC
The GPIOPeriphID0, GPIOPeriphID1, GPIOPeriphID2, and GPIOPeriphID3 registers can
conceptually be treated as one 32-bit register; each register contains eight bits of the 32-bit register,
used by software to identify the peripheral.
GPIO Peripheral Identification 3 (GPIOPeriphID3)
GPIO Port A base: 0x4000.4000
GPIO Port B base: 0x4000.5000
GPIO Port C base: 0x4000.6000
GPIO Port D base: 0x4000.7000
GPIO Port E base: 0x4002.4000
GPIO Port F base: 0x4002.5000
GPIO Port G base: 0x4002.6000
GPIO Port H base: 0x4002.7000
Offset 0xFEC
Type RO, reset 0x0000.0001
31 30 29 28 27 26 25 24 23 22 21 20 19 18 17 16
reserved
Type RO RO RO RO RO RO RO RO RO RO RO RO RO RO RO RO
Reset 0 0 0 0 0 0 0 0 0 0 0 0 0 0 0 0
15 14 13 12 11 10 9 8 7 6 5 4 3 2 1 0
reserved PID3
Type RO RO RO RO RO RO RO RO RO RO RO RO RO RO RO RO
Reset 0 0 0 0 0 0 0 0 0 0 0 0 0 0 0 1
Bit/Field Name Type Reset Description
Software should not rely on the value of a reserved bit. To provide
compatibility with future products, the value of a reserved bit should be
preserved across a read-modify-write operation.
31:8 reserved RO 0x00
GPIO Peripheral ID Register[31:24]
Can be used by software to identify the presence of this peripheral.
7:0 PID3 RO 0x01
January 08, 2011 319
Texas Instruments-Production Data
Stellaris® LM3S2965 Microcontroller
Register 29: GPIO PrimeCell Identification 0 (GPIOPCellID0), offset 0xFF0
The GPIOPCellID0, GPIOPCellID1, GPIOPCellID2, and GPIOPCellID3 registers are four 8-bit wide
registers, that can conceptually be treated as one 32-bit register. The register is used as a standard
cross-peripheral identification system.
GPIO PrimeCell Identification 0 (GPIOPCellID0)
GPIO Port A base: 0x4000.4000
GPIO Port B base: 0x4000.5000
GPIO Port C base: 0x4000.6000
GPIO Port D base: 0x4000.7000
GPIO Port E base: 0x4002.4000
GPIO Port F base: 0x4002.5000
GPIO Port G base: 0x4002.6000
GPIO Port H base: 0x4002.7000
Offset 0xFF0
Type RO, reset 0x0000.000D
31 30 29 28 27 26 25 24 23 22 21 20 19 18 17 16
reserved
Type RO RO RO RO RO RO RO RO RO RO RO RO RO RO RO RO
Reset 0 0 0 0 0 0 0 0 0 0 0 0 0 0 0 0
15 14 13 12 11 10 9 8 7 6 5 4 3 2 1 0
reserved CID0
Type RO RO RO RO RO RO RO RO RO RO RO RO RO RO RO RO
Reset 0 0 0 0 0 0 0 0 0 0 0 0 1 1 0 1
Bit/Field Name Type Reset Description
Software should not rely on the value of a reserved bit. To provide
compatibility with future products, the value of a reserved bit should be
preserved across a read-modify-write operation.
31:8 reserved RO 0x00
GPIO PrimeCell ID Register[7:0]
Provides software a standard cross-peripheral identification system.
7:0 CID0 RO 0x0D
320 January 08, 2011
Texas Instruments-Production Data
General-Purpose Input/Outputs (GPIOs)
Register 30: GPIO PrimeCell Identification 1 (GPIOPCellID1), offset 0xFF4
The GPIOPCellID0, GPIOPCellID1, GPIOPCellID2, and GPIOPCellID3 registers are four 8-bit wide
registers, that can conceptually be treated as one 32-bit register. The register is used as a standard
cross-peripheral identification system.
GPIO PrimeCell Identification 1 (GPIOPCellID1)
GPIO Port A base: 0x4000.4000
GPIO Port B base: 0x4000.5000
GPIO Port C base: 0x4000.6000
GPIO Port D base: 0x4000.7000
GPIO Port E base: 0x4002.4000
GPIO Port F base: 0x4002.5000
GPIO Port G base: 0x4002.6000
GPIO Port H base: 0x4002.7000
Offset 0xFF4
Type RO, reset 0x0000.00F0
31 30 29 28 27 26 25 24 23 22 21 20 19 18 17 16
reserved
Type RO RO RO RO RO RO RO RO RO RO RO RO RO RO RO RO
Reset 0 0 0 0 0 0 0 0 0 0 0 0 0 0 0 0
15 14 13 12 11 10 9 8 7 6 5 4 3 2 1 0
reserved CID1
Type RO RO RO RO RO RO RO RO RO RO RO RO RO RO RO RO
Reset 0 0 0 0 0 0 0 0 1 1 1 1 0 0 0 0
Bit/Field Name Type Reset Description
Software should not rely on the value of a reserved bit. To provide
compatibility with future products, the value of a reserved bit should be
preserved across a read-modify-write operation.
31:8 reserved RO 0x00
GPIO PrimeCell ID Register[15:8]
Provides software a standard cross-peripheral identification system.
7:0 CID1 RO 0xF0
January 08, 2011 321
Texas Instruments-Production Data
Stellaris® LM3S2965 Microcontroller
Register 31: GPIO PrimeCell Identification 2 (GPIOPCellID2), offset 0xFF8
The GPIOPCellID0, GPIOPCellID1, GPIOPCellID2, and GPIOPCellID3 registers are four 8-bit wide
registers, that can conceptually be treated as one 32-bit register. The register is used as a standard
cross-peripheral identification system.
GPIO PrimeCell Identification 2 (GPIOPCellID2)
GPIO Port A base: 0x4000.4000
GPIO Port B base: 0x4000.5000
GPIO Port C base: 0x4000.6000
GPIO Port D base: 0x4000.7000
GPIO Port E base: 0x4002.4000
GPIO Port F base: 0x4002.5000
GPIO Port G base: 0x4002.6000
GPIO Port H base: 0x4002.7000
Offset 0xFF8
Type RO, reset 0x0000.0005
31 30 29 28 27 26 25 24 23 22 21 20 19 18 17 16
reserved
Type RO RO RO RO RO RO RO RO RO RO RO RO RO RO RO RO
Reset 0 0 0 0 0 0 0 0 0 0 0 0 0 0 0 0
15 14 13 12 11 10 9 8 7 6 5 4 3 2 1 0
reserved CID2
Type RO RO RO RO RO RO RO RO RO RO RO RO RO RO RO RO
Reset 0 0 0 0 0 0 0 0 0 0 0 0 0 1 0 1
Bit/Field Name Type Reset Description
Software should not rely on the value of a reserved bit. To provide
compatibility with future products, the value of a reserved bit should be
preserved across a read-modify-write operation.
31:8 reserved RO 0x00
GPIO PrimeCell ID Register[23:16]
Provides software a standard cross-peripheral identification system.
7:0 CID2 RO 0x05
322 January 08, 2011
Texas Instruments-Production Data
General-Purpose Input/Outputs (GPIOs)
Register 32: GPIO PrimeCell Identification 3 (GPIOPCellID3), offset 0xFFC
The GPIOPCellID0, GPIOPCellID1, GPIOPCellID2, and GPIOPCellID3 registers are four 8-bit wide
registers, that can conceptually be treated as one 32-bit register. The register is used as a standard
cross-peripheral identification system.
GPIO PrimeCell Identification 3 (GPIOPCellID3)
GPIO Port A base: 0x4000.4000
GPIO Port B base: 0x4000.5000
GPIO Port C base: 0x4000.6000
GPIO Port D base: 0x4000.7000
GPIO Port E base: 0x4002.4000
GPIO Port F base: 0x4002.5000
GPIO Port G base: 0x4002.6000
GPIO Port H base: 0x4002.7000
Offset 0xFFC
Type RO, reset 0x0000.00B1
31 30 29 28 27 26 25 24 23 22 21 20 19 18 17 16
reserved
Type RO RO RO RO RO RO RO RO RO RO RO RO RO RO RO RO
Reset 0 0 0 0 0 0 0 0 0 0 0 0 0 0 0 0
15 14 13 12 11 10 9 8 7 6 5 4 3 2 1 0
reserved CID3
Type RO RO RO RO RO RO RO RO RO RO RO RO RO RO RO RO
Reset 0 0 0 0 0 0 0 0 1 0 1 1 0 0 0 1
Bit/Field Name Type Reset Description
Software should not rely on the value of a reserved bit. To provide
compatibility with future products, the value of a reserved bit should be
preserved across a read-modify-write operation.
31:8 reserved RO 0x00
GPIO PrimeCell ID Register[31:24]
Provides software a standard cross-peripheral identification system.
7:0 CID3 RO 0xB1
January 08, 2011 323
Texas Instruments-Production Data
Stellaris® LM3S2965 Microcontroller
9 General-Purpose Timers
Programmable timers can be used to count or time external events that drive the Timer input pins.
The Stellaris® General-Purpose Timer Module (GPTM) contains four GPTM blocks (Timer0, Timer1,
Timer 2, and Timer 3). Each GPTM block provides two 16-bit timers/counters (referred to as TimerA
and TimerB) that can be configured to operate independently as timers or event counters, or
configured to operate as one 32-bit timer or one 32-bit Real-Time Clock (RTC).
In addition, timers can be used to trigger analog-to-digital conversions (ADC). The ADC trigger
signals from all of the general-purpose timers are ORed together before reaching the ADC module,
so only one timer should be used to trigger ADC events.
The GPT Module is one timing resource available on the Stellaris microcontrollers. Other timer
resources include the System Timer (SysTick) (see 94) and the PWM timer in the PWM module
(see “PWM Timer” on page 593).
The General-Purpose Timers provide the following features:
■ Four General-Purpose Timer Modules (GPTM), each of which provides two 16-bit timers/counters.
Each GPTM can be configured to operate independently:
– As a single 32-bit timer
– As one 32-bit Real-Time Clock (RTC) to event capture
– For Pulse Width Modulation (PWM)
– To trigger analog-to-digital conversions
■ 32-bit Timer modes
– Programmable one-shot timer
– Programmable periodic timer
– Real-Time Clock when using an external 32.768-KHz clock as the input
– User-enabled stalling when the controller asserts CPU Halt flag during debug
– ADC event trigger
■ 16-bit Timer modes
– General-purpose timer function with an 8-bit prescaler (for one-shot and periodic modes only)
– Programmable one-shot timer
– Programmable periodic timer
– User-enabled stalling when the controller asserts CPU Halt flag during debug
– ADC event trigger
■ 16-bit Input Capture modes
– Input edge count capture
324 January 08, 2011
Texas Instruments-Production Data
General-Purpose Timers
– Input edge time capture
■ 16-bit PWM mode
– Simple PWM mode with software-programmable output inversion of the PWM signal
9.1 Block Diagram
Note: In Figure 9-1 on page 325, the specific CCP pins available depend on the Stellaris device.
See Table 9-1 on page 325 for the available CCPs.
Figure 9-1. GPTM Module Block Diagram
TA Comparator
TB Comparator
GPTMTBR
GPTMAR
Clock / Edge
Detect
RTC Divider
Clock / Edge
Detect
TimerA
Interrupt
TimerB
Interrupt
System
Clock
0x0000 (Down Counter Modes)
0x0000 (Down Counter Modes)
32 KHz or
Even CCP Pin
Odd CCP Pin
En
En
TimerA Control
GPTMTAPMR
GPTMTAILR
GPTMTAMATCHR
GPTMTAPR
GPTMTAMR
TimerB Control
GPTMTBPMR
GPTMTBILR
GPTMTBMATCHR
GPTMTBPR
GPTMTBMR
Interrupt / Config
GPTMCFG
GPTMRIS
GPTMICR
GPTMMIS
GPTMIMR
GPTMCTL
Table 9-1. Available CCP Pins
Timer 16-Bit Up/Down Counter Even CCP Pin Odd CCP Pin
Timer 0 TimerA CCP0 -
TimerB - CCP1
Timer 1 TimerA CCP2 -
TimerB - CCP3
Timer 2 TimerA CCP4 -
TimerB - CCP5
Timer 3 TimerA - -
TimerB - -
January 08, 2011 325
Texas Instruments-Production Data
Stellaris® LM3S2965 Microcontroller
9.2 Functional Description
The main components of each GPTM block are two free-running 16-bit up/down counters (referred
to as TimerA and TimerB), two 16-bit match registers, two prescaler match registers, and two 16-bit
load/initialization registers and their associated control functions. The exact functionality of each
GPTM is controlled by software and configured through the register interface.
Software configures the GPTM using the GPTM Configuration (GPTMCFG) register (see page 336),
the GPTM TimerA Mode (GPTMTAMR) register (see page 337), and the GPTM TimerB Mode
(GPTMTBMR) register (see page 339). When in one of the 32-bit modes, the timer can only act as
a 32-bit timer. However, when configured in 16-bit mode, the GPTM can have its two 16-bit timers
configured in any combination of the 16-bit modes.
9.2.1 GPTM Reset Conditions
After reset has been applied to the GPTM module, the module is in an inactive state, and all control
registers are cleared and in their default states. Counters TimerA and TimerB are initialized to
0xFFFF, along with their corresponding load registers: the GPTM TimerA Interval Load
(GPTMTAILR) register (see page 350) and the GPTM TimerB Interval Load (GPTMTBILR) register
(see page 351). The prescale counters are initialized to 0x00: the GPTM TimerA Prescale
(GPTMTAPR) register (see page 354) and the GPTM TimerB Prescale (GPTMTBPR) register (see
page 355).
9.2.2 32-Bit Timer Operating Modes
This section describes the three GPTM 32-bit timer modes (One-Shot, Periodic, and RTC) and their
configuration.
The GPTM is placed into 32-bit mode by writing a 0 (One-Shot/Periodic 32-bit timer mode) or a 1
(RTC mode) to the GPTM Configuration (GPTMCFG) register. In both configurations, certain GPTM
registers are concatenated to form pseudo 32-bit registers. These registers include:
■ GPTM TimerA Interval Load (GPTMTAILR) register [15:0], see page 350
■ GPTM TimerB Interval Load (GPTMTBILR) register [15:0], see page 351
■ GPTM TimerA (GPTMTAR) register [15:0], see page 358
■ GPTM TimerB (GPTMTBR) register [15:0], see page 359
In the 32-bit modes, the GPTM translates a 32-bit write access to GPTMTAILR into a write access
to both GPTMTAILR and GPTMTBILR. The resulting word ordering for such a write operation is:
GPTMTBILR[15:0]:GPTMTAILR[15:0]
Likewise, a read access to GPTMTAR returns the value:
GPTMTBR[15:0]:GPTMTAR[15:0]
9.2.2.1 32-Bit One-Shot/Periodic Timer Mode
In 32-bit one-shot and periodic timer modes, the concatenated versions of the TimerA and TimerB
registers are configured as a 32-bit down-counter. The selection of one-shot or periodic mode is
determined by the value written to the TAMR field of the GPTM TimerA Mode (GPTMTAMR) register
(see page 337), and there is no need to write to the GPTM TimerB Mode (GPTMTBMR) register.
326 January 08, 2011
Texas Instruments-Production Data
General-Purpose Timers
When software writes the TAEN bit in the GPTM Control (GPTMCTL) register (see page 341), the
timer begins counting down from its preloaded value. Once the 0x0000.0000 state is reached, the
timer reloads its start value from the concatenated GPTMTAILR on the next cycle. If configured to
be a one-shot timer, the timer stops counting and clears the TAEN bit in the GPTMCTL register. If
configured as a periodic timer, it continues counting.
In addition to reloading the count value, the GPTM generates interrupts and triggers when it reaches
the 0x000.0000 state. The GPTM sets the TATORIS bit in the GPTM Raw Interrupt Status
(GPTMRIS) register (see page 346), and holds it until it is cleared by writing the GPTM Interrupt
Clear (GPTMICR) register (see page 348). If the time-out interrupt is enabled in the GPTM Interrupt
Mask (GPTMIMR) register (see page 344), the GPTM also sets the TATOMIS bit in the GPTM Masked
Interrupt Status (GPTMMIS) register (see page 347). The ADC trigger is enabled by setting the
TAOTE bit in GPTMCTL.
If software reloads the GPTMTAILR register while the counter is running, the counter loads the new
value on the next clock cycle and continues counting from the new value.
If the TASTALL bit in the GPTMCTL register is set, the timer freezes counting while the processor
is halted by the debugger. The timer resumes counting when the processor resumes execution.
9.2.2.2 32-Bit Real-Time Clock Timer Mode
In Real-Time Clock (RTC) mode, the concatenated versions of the TimerA and TimerB registers
are configured as a 32-bit up-counter. When RTC mode is selected for the first time, the counter is
loaded with a value of 0x0000.0001. All subsequent load values must be written to the GPTM TimerA
Match (GPTMTAMATCHR) register (see page 352) by the controller.
The input clock on an even CCP input is required to be 32.768 KHz in RTC mode. The clock signal
is then divided down to a 1 Hz rate and is passed along to the input of the 32-bit counter.
When software writes the TAEN bit inthe GPTMCTL register, the counter starts counting up from its
preloaded value of 0x0000.0001. When the current count value matches the preloaded value in the
GPTMTAMATCHR register, it rolls over to a value of 0x0000.0000 and continues counting until
either a hardware reset, or it is disabled by software (clearing the TAEN bit). When a match occurs,
the GPTM asserts the RTCRIS bit in GPTMRIS. If the RTC interrupt is enabled in GPTMIMR, the
GPTM also sets the RTCMIS bit in GPTMMIS and generates a controller interrupt. The status flags
are cleared by writing the RTCCINT bit in GPTMICR.
If the TASTALL and/or TBSTALL bits in the GPTMCTL register are set, the timer does not freeze if
the RTCEN bit is set in GPTMCTL.
9.2.3 16-Bit Timer Operating Modes
The GPTM is placed into global 16-bit mode by writing a value of 0x4 to the GPTM Configuration
(GPTMCFG) register (see page 336). This section describes each of the GPTM 16-bit modes of
operation. TimerA and TimerB have identical modes, so a single description is given using an n to
reference both.
9.2.3.1 16-Bit One-Shot/Periodic Timer Mode
In 16-bit one-shot and periodic timer modes, the timer is configured as a 16-bit down-counter with
an optional 8-bit prescaler that effectively extends the counting range of the timer to 24 bits. The
selection of one-shot or periodic mode is determined by the value written to the TnMR field of the
GPTMTnMR register. The optional prescaler is loaded into the GPTM Timern Prescale (GPTMTnPR)
register.
January 08, 2011 327
Texas Instruments-Production Data
Stellaris® LM3S2965 Microcontroller
When software writes the TnEN bit in the GPTMCTL register, the timer begins counting down from
its preloaded value. Once the 0x0000 state is reached, the timer reloads its start value from
GPTMTnILR and GPTMTnPR on the next cycle. If configured to be a one-shot timer, the timer stops
counting and clears the TnEN bit in the GPTMCTL register. If configured as a periodic timer, it
continues counting.
In addition to reloading the count value, the timer generates interrupts and triggers when it reaches
the 0x0000 state. The GPTM sets the TnTORIS bit in the GPTMRIS register, and holds it until it is
cleared by writing the GPTMICR register. If the time-out interrupt is enabled in GPTMIMR, the GPTM
also sets the TnTOMIS bit in GPTMISR and generates a controller interrupt. The ADC trigger is
enabled by setting the TnOTE bit in the GPTMCTL register.
If software reloads the GPTMTAILR register while the counter is running, the counter loads the new
value on the next clock cycle and continues counting from the new value.
If the TnSTALL bit in the GPTMCTL register is set, the timer freezes counting while the processor
is halted by the debugger. The timer resumes counting when the processor resumes execution.
The following example shows a variety of configurations for a 16-bit free running timer while using
the prescaler. All values assume a 50-MHz clock with Tc=20 ns (clock period).
Table 9-2. 16-Bit Timer With Prescaler Configurations
Prescale #Clock (T c)a Max Time Units
00000000 1 1.3107 mS
00000001 2 2.6214 mS
00000010 3 3.9322 mS
------------ -- -- --
11111101 254 332.9229 mS
11111110 255 334.2336 mS
11111111 256 335.5443 mS
a. Tc is the clock period.
9.2.3.2 16-Bit Input Edge Count Mode
Note: For rising-edge detection, the input signal must be High for at least two system clock periods
following the rising edge. Similarly, for falling-edge detection, the input signal must be Low
for at least two system clock periods following the falling edge. Based on this criteria, the
maximum input frequency for edge detection is 1/4 of the system frequency.
Note: The prescaler is not available in 16-Bit Input Edge Count mode.
In Edge Count mode, the timer is configured as a down-counter capable of capturing three types
of events: rising edge, falling edge, or both. To place the timer in Edge Count mode, the TnCMR bit
of the GPTMTnMR register must be set to 0. The type of edge that the timer counts is determined
by the TnEVENT fields of the GPTMCTL register. During initialization, the GPTM Timern Match
(GPTMTnMATCHR) register is configured so that the difference between the value in the
GPTMTnILR register and the GPTMTnMATCHR register equals the number of edge events that
must be counted.
When software writes the TnEN bit in the GPTM Control (GPTMCTL) register, the timer is enabled
for event capture. Each input event on the CCP pin decrements the counter by 1 until the event count
matches GPTMTnMATCHR. When the counts match, the GPTM asserts the CnMRIS bit in the
GPTMRIS register (and the CnMMIS bit, if the interrupt is not masked).
328 January 08, 2011
Texas Instruments-Production Data
General-Purpose Timers
The counter is then reloaded using the value in GPTMTnILR, and stopped since the GPTM
automatically clears the TnEN bit in the GPTMCTL register. Once the event count has been reached,
all further events are ignored until TnEN is re-enabled by software.
Figure 9-2 on page 329 shows how input edge count mode works. In this case, the timer start value
is set to GPTMTnILR =0x000A and the match value is set to GPTMTnMATCHR =0x0006 so that
four edge events are counted. The counter is configured to detect both edges of the input signal.
Note that the last two edges are not counted since the timer automatically clears the TnEN bit after
the current count matches the value in the GPTMTnMATCHR register.
Figure 9-2. 16-Bit Input Edge Count Mode Example
Input Signal
Timer stops,
flags
asserted
Timer reload
Count on next cycle Ignored Ignored
0x000A
0x0006
0x0007
0x0008
0x0009
9.2.3.3 16-Bit Input Edge Time Mode
Note: For rising-edge detection, the input signal must be High for at least two system clock periods
following the rising edge. Similarly, for falling edge detection, the input signal must be Low
for at least two system clock periods following the falling edge. Based on this criteria, the
maximum input frequency for edge detection is 1/4 of the system frequency.
Note: The prescaler is not available in 16-Bit Input Edge Time mode.
In Edge Time mode, the timer is configured as a free-running down-counter initialized to the value
loaded in the GPTMTnILR register (or 0xFFFF at reset). This mode allows for event capture of
either rising or falling edges, but not both. The timer is placed into Edge Time mode by setting the
TnCMR bit in the GPTMTnMR register, and the type of event that the timer captures is determined
by the TnEVENT fields of the GPTMCTL register.
When software writes the TnEN bit in the GPTMCTL register, the timer is enabled for event capture.
When the selected input event is detected, the current Tn counter value is captured in the GPTMTnR
register and is available to be read by the controller. The GPTM then asserts the CnERIS bit (and
the CnEMIS bit, if the interrupt is not masked).
After an event has been captured, the timer does not stop counting. It continues to count until the
TnEN bit is cleared. When the timer reaches the 0x0000 state, it is reloaded with the value from the
GPTMTnILR register.
January 08, 2011 329
Texas Instruments-Production Data
Stellaris® LM3S2965 Microcontroller
Figure 9-3 on page 330 shows how input edge timing mode works. In the diagram, it is assumed that
the start value of the timer is the default value of 0xFFFF, and the timer is configured to capture
rising edge events.
Each time a rising edge event is detected, the current count value is loaded into the GPTMTnR
register, and is held there until another rising edge is detected (at which point the new count value
is loaded into GPTMTnR).
Figure 9-3. 16-Bit Input Edge Time Mode Example
GPTMTnR=Y
Input Signal
Time
Count
GPTMTnR=X GPTMTnR=Z
Z
X
Y
0xFFFF
9.2.3.4 16-Bit PWM Mode
Note: The prescaler is not available in 16-Bit PWM mode.
The GPTM supports a simple PWM generation mode. In PWM mode, the timer is configured as a
down-counter with a start value (and thus period) defined by GPTMTnILR. In this mode, the PWM
frequency and period are synchronous events and therefore guaranteed to be glitch free. PWM
mode is enabled with the GPTMTnMR register by setting the TnAMS bit to 0x1, the TnCMR bit to
0x0, and the TnMR field to 0x2.
When software writes the TnEN bit in the GPTMCTL register, the counter begins counting down
until it reaches the 0x0000 state. On the next counter cycle, the counter reloads its start value from
GPTMTnILR and continues counting until disabled by software clearing the TnEN bit in the GPTMCTL
register. No interrupts or status bits are asserted in PWM mode.
The output PWM signal asserts when the counter is at the value of the GPTMTnILR register (its
start state), and is deasserted when the counter value equals the value in the GPTM Timern Match
Register (GPTMTnMATCHR). Software has the capability of inverting the output PWM signal by
setting the TnPWML bit in the GPTMCTL register.
Figure 9-4 on page 331 shows how to generate an output PWM with a 1-ms period and a 66% duty
cycle assuming a 50-MHz input clock and TnPWML =0 (duty cycle would be 33% for the TnPWML
=1 configuration). For this example, the start value is GPTMTnIRL=0xC350 and the match value is
GPTMTnMATCHR=0x411A.
330 January 08, 2011
Texas Instruments-Production Data
General-Purpose Timers
Figure 9-4. 16-Bit PWM Mode Example
Output
Signal
Time
Count GPTMTnR=GPTMnMR GPTMTnR=GPTMnMR
0xC350
0x411A
TnPWML = 0
TnPWML = 1
TnEN set
9.3 Initialization and Configuration
To use the general-purpose timers, the peripheral clock must be enabled by setting the TIMER0,
TIMER1, TIMER2, and TIMER3 bits in the RCGC1 register.
This section shows module initialization and configuration examples for each of the supported timer
modes.
9.3.1 32-Bit One-Shot/Periodic Timer Mode
The GPTM is configured for 32-bit One-Shot and Periodic modes by the following sequence:
1. Ensure the timer is disabled (the TAEN bit in the GPTMCTL register is cleared) before making
any changes.
2. Write the GPTM Configuration Register (GPTMCFG) with a value of 0x0.
3. Set the TAMR field in the GPTM TimerA Mode Register (GPTMTAMR):
a. Write a value of 0x1 for One-Shot mode.
b. Write a value of 0x2 for Periodic mode.
4. Load the start value into the GPTM TimerA Interval Load Register (GPTMTAILR).
5. If interrupts are required, set the TATOIM bit in the GPTM Interrupt Mask Register (GPTMIMR).
6. Set the TAEN bit in the GPTMCTL register to enable the timer and start counting.
January 08, 2011 331
Texas Instruments-Production Data
Stellaris® LM3S2965 Microcontroller
7. Poll the TATORIS bit in the GPTMRIS register or wait for the interrupt to be generated (if enabled).
In both cases, the status flags are cleared by writing a 1 to the TATOCINT bit of the GPTM
Interrupt Clear Register (GPTMICR).
In One-Shot mode, the timer stops counting after step 7 on page 332. To re-enable the timer, repeat
the sequence. A timer configured in Periodic mode does not stop counting after it times out.
9.3.2 32-Bit Real-Time Clock (RTC) Mode
To use the RTC mode, the timer must have a 32.768-KHz input signal on an even CCP input. To
enable the RTC feature, follow these steps:
1. Ensure the timer is disabled (the TAEN bit is cleared) before making any changes.
2. Write the GPTM Configuration Register (GPTMCFG) with a value of 0x1.
3. Write the desired match value to the GPTM TimerA Match Register (GPTMTAMATCHR).
4. Set/clear the RTCEN bit in the GPTM Control Register (GPTMCTL) as desired.
5. If interrupts are required, set the RTCIM bit in the GPTM Interrupt Mask Register (GPTMIMR).
6. Set the TAEN bit in the GPTMCTL register to enable the timer and start counting.
When the timer count equals the value in the GPTMTAMATCHR register, the GPTM asserts the
RTCRIS bit in the GPTMRIS register and continues counting until Timer A is disabled or a hardware
reset. The interrupt is cleared by writing the RTCCINT bit in the GPTMICR register.
9.3.3 16-Bit One-Shot/Periodic Timer Mode
A timer is configured for 16-bit One-Shot and Periodic modes by the following sequence:
1. Ensure the timer is disabled (the TnEN bit is cleared) before making any changes.
2. Write the GPTM Configuration Register (GPTMCFG) with a value of 0x4.
3. Set the TnMR field in the GPTM Timer Mode (GPTMTnMR) register:
a. Write a value of 0x1 for One-Shot mode.
b. Write a value of 0x2 for Periodic mode.
4. If a prescaler is to be used, write the prescale value to the GPTM Timern Prescale Register
(GPTMTnPR).
5. Load the start value into the GPTM Timer Interval Load Register (GPTMTnILR).
6. If interrupts are required, set the TnTOIM bit in the GPTM Interrupt Mask Register (GPTMIMR).
7. Set the TnEN bit in the GPTM Control Register (GPTMCTL) to enable the timer and start
counting.
8. Poll the TnTORIS bit in the GPTMRIS register or wait for the interrupt to be generated (if enabled).
In both cases, the status flags are cleared by writing a 1 to the TnTOCINT bit of the GPTM
Interrupt Clear Register (GPTMICR).
332 January 08, 2011
Texas Instruments-Production Data
General-Purpose Timers
In One-Shot mode, the timer stops counting after step 8 on page 332. To re-enable the timer, repeat
the sequence. A timer configured in Periodic mode does not stop counting after it times out.
9.3.4 16-Bit Input Edge Count Mode
A timer is configured to Input Edge Count mode by the following sequence:
1. Ensure the timer is disabled (the TnEN bit is cleared) before making any changes.
2. Write the GPTM Configuration (GPTMCFG) register with a value of 0x4.
3. In the GPTM Timer Mode (GPTMTnMR) register, write the TnCMR field to 0x0 and the TnMR
field to 0x3.
4. Configure the type of event(s) that the timer captures by writing the TnEVENT field of the GPTM
Control (GPTMCTL) register.
5. Load the timer start value into the GPTM Timern Interval Load (GPTMTnILR) register.
6. Load the desired event count into the GPTM Timern Match (GPTMTnMATCHR) register.
7. If interrupts are required, set the CnMIM bit in the GPTM Interrupt Mask (GPTMIMR) register.
8. Set the TnEN bit in the GPTMCTL register to enable the timer and begin waiting for edge events.
9. Poll the CnMRIS bit in the GPTMRIS register or wait for the interrupt to be generated (if enabled).
In both cases, the status flags are cleared by writing a 1 to the CnMCINT bit of the GPTM
Interrupt Clear (GPTMICR) register.
In Input Edge Count Mode, the timer stops after the desired number of edge events has been
detected. To re-enable the timer, ensure that the TnEN bit is cleared and repeat step 4 on page 333
through step 9 on page 333.
9.3.5 16-Bit Input Edge Timing Mode
A timer is configured to Input Edge Timing mode by the following sequence:
1. Ensure the timer is disabled (the TnEN bit is cleared) before making any changes.
2. Write the GPTM Configuration (GPTMCFG) register with a value of 0x4.
3. In the GPTM Timer Mode (GPTMTnMR) register, write the TnCMR field to 0x1 and the TnMR
field to 0x3.
4. Configure the type of event that the timer captures by writing the TnEVENT field of the GPTM
Control (GPTMCTL) register.
5. Load the timer start value into the GPTM Timern Interval Load (GPTMTnILR) register.
6. If interrupts are required, set the CnEIM bit in the GPTM Interrupt Mask (GPTMIMR) register.
7. Set the TnEN bit in the GPTM Control (GPTMCTL) register to enable the timer and start counting.
8. Poll the CnERIS bit in the GPTMRIS register or wait for the interrupt to be generated (if enabled).
In both cases, the status flags are cleared by writing a 1 to the CnECINT bit of the GPTM
January 08, 2011 333
Texas Instruments-Production Data
Stellaris® LM3S2965 Microcontroller
Interrupt Clear (GPTMICR) register. The time at which the event happened can be obtained
by reading the GPTM Timern (GPTMTnR) register.
In Input Edge Timing mode, the timer continues running after an edge event has been detected,
but the timer interval can be changed at any time by writing the GPTMTnILR register. The change
takes effect at the next cycle after the write.
9.3.6 16-Bit PWM Mode
A timer is configured to PWM mode using the following sequence:
1. Ensure the timer is disabled (the TnEN bit is cleared) before making any changes.
2. Write the GPTM Configuration (GPTMCFG) register with a value of 0x4.
3. In the GPTM Timer Mode (GPTMTnMR) register, set the TnAMS bit to 0x1, the TnCMR bit to
0x0, and the TnMR field to 0x2.
4. Configure the output state of the PWM signal (whether or not it is inverted) in the TnPWML field
of the GPTM Control (GPTMCTL) register.
5. Load the timer start value into the GPTM Timern Interval Load (GPTMTnILR) register.
6. Load the GPTM Timern Match (GPTMTnMATCHR) register with the desired value.
7. Set the TnEN bit in the GPTM Control (GPTMCTL) register to enable the timer and begin
generation of the output PWM signal.
In PWM Timing mode, the timer continues running after the PWM signal has been generated. The
PWM period can be adjusted at any time by writing the GPTMTnILR register, and the change takes
effect at the next cycle after the write.
9.4 Register Map
Table 9-3 on page 334 lists the GPTM registers. The offset listed is a hexadecimal increment to the
register’s address, relative to that timer’s base address:
■ Timer0: 0x4003.0000
■ Timer1: 0x4003.1000
■ Timer2: 0x4003.2000
■ Timer3: 0x4003.3000
Note that the Timer module clock must be enabled before the registers can be programmed (see
page 216). There must be a delay of 3 system clocks after the Timer module clock is enabled before
any Timer module registers are accessed.
Table 9-3. Timers Register Map
See
Offset Name Type Reset Description page
0x000 GPTMCFG R/W 0x0000.0000 GPTM Configuration 336
0x004 GPTMTAMR R/W 0x0000.0000 GPTM TimerA Mode 337
0x008 GPTMTBMR R/W 0x0000.0000 GPTM TimerB Mode 339
334 January 08, 2011
Texas Instruments-Production Data
General-Purpose Timers
Table 9-3. Timers Register Map (continued)
See
Offset Name Type Reset Description page
0x00C GPTMCTL R/W 0x0000.0000 GPTM Control 341
0x018 GPTMIMR R/W 0x0000.0000 GPTM Interrupt Mask 344
0x01C GPTMRIS RO 0x0000.0000 GPTM Raw Interrupt Status 346
0x020 GPTMMIS RO 0x0000.0000 GPTM Masked Interrupt Status 347
0x024 GPTMICR W1C 0x0000.0000 GPTM Interrupt Clear 348
0x028 GPTMTAILR R/W 0xFFFF.FFFF GPTM TimerA Interval Load 350
0x02C GPTMTBILR R/W 0x0000.FFFF GPTM TimerB Interval Load 351
0x030 GPTMTAMATCHR R/W 0xFFFF.FFFF GPTM TimerA Match 352
0x034 GPTMTBMATCHR R/W 0x0000.FFFF GPTM TimerB Match 353
0x038 GPTMTAPR R/W 0x0000.0000 GPTM TimerA Prescale 354
0x03C GPTMTBPR R/W 0x0000.0000 GPTM TimerB Prescale 355
0x040 GPTMTAPMR R/W 0x0000.0000 GPTM TimerA Prescale Match 356
0x044 GPTMTBPMR R/W 0x0000.0000 GPTM TimerB Prescale Match 357
0x048 GPTMTAR RO 0xFFFF.FFFF GPTM TimerA 358
0x04C GPTMTBR RO 0x0000.FFFF GPTM TimerB 359
9.5 Register Descriptions
The remainder of this section lists and describes the GPTM registers, in numerical order by address
offset.
January 08, 2011 335
Texas Instruments-Production Data
Stellaris® LM3S2965 Microcontroller
Register 1: GPTM Configuration (GPTMCFG), offset 0x000
This register configures the global operation of the GPTM module. The value written to this register
determines whether the GPTM is in 32- or 16-bit mode.
GPTM Configuration (GPTMCFG)
Timer0 base: 0x4003.0000
Timer1 base: 0x4003.1000
Timer2 base: 0x4003.2000
Timer3 base: 0x4003.3000
Offset 0x000
Type R/W, reset 0x0000.0000
31 30 29 28 27 26 25 24 23 22 21 20 19 18 17 16
reserved
Type RO RO RO RO RO RO RO RO RO RO RO RO RO RO RO RO
Reset 0 0 0 0 0 0 0 0 0 0 0 0 0 0 0 0
15 14 13 12 11 10 9 8 7 6 5 4 3 2 1 0
reserved GPTMCFG
Type RO RO RO RO RO RO RO RO RO RO RO RO RO R/W R/W R/W
Reset 0 0 0 0 0 0 0 0 0 0 0 0 0 0 0 0
Bit/Field Name Type Reset Description
Software should not rely on the value of a reserved bit. To provide
compatibility with future products, the value of a reserved bit should be
preserved across a read-modify-write operation.
31:3 reserved RO 0x00
GPTM Configuration
The GPTMCFG values are defined as follows:
Value Description
0x0 32-bit timer configuration.
0x1 32-bit real-time clock (RTC) counter configuration.
0x2 Reserved
0x3 Reserved
16-bit timer configuration, function is controlled by bits 1:0 of
GPTMTAMR and GPTMTBMR.
0x4-0x7
2:0 GPTMCFG R/W 0x0
336 January 08, 2011
Texas Instruments-Production Data
General-Purpose Timers
Register 2: GPTM TimerA Mode (GPTMTAMR), offset 0x004
This register configures the GPTM based on the configuration selected in the GPTMCFG register.
When in 16-bit PWM mode, set the TAAMS bit to 0x1, the TACMR bit to 0x0, and the TAMR field to
0x2.
GPTM TimerA Mode (GPTMTAMR)
Timer0 base: 0x4003.0000
Timer1 base: 0x4003.1000
Timer2 base: 0x4003.2000
Timer3 base: 0x4003.3000
Offset 0x004
Type R/W, reset 0x0000.0000
31 30 29 28 27 26 25 24 23 22 21 20 19 18 17 16
reserved
Type RO RO RO RO RO RO RO RO RO RO RO RO RO RO RO RO
Reset 0 0 0 0 0 0 0 0 0 0 0 0 0 0 0 0
15 14 13 12 11 10 9 8 7 6 5 4 3 2 1 0
reserved TAAMS TACMR TAMR
Type RO RO RO RO RO RO RO RO RO RO RO RO R/W R/W R/W R/W
Reset 0 0 0 0 0 0 0 0 0 0 0 0 0 0 0 0
Bit/Field Name Type Reset Description
Software should not rely on the value of a reserved bit. To provide
compatibility with future products, the value of a reserved bit should be
preserved across a read-modify-write operation.
31:4 reserved RO 0x00
GPTM TimerA Alternate Mode Select
The TAAMS values are defined as follows:
Value Description
0 Capture mode is enabled.
1 PWM mode is enabled.
Note: To enable PWM mode, you must also clear the TACMR
bit and set the TAMR field to 0x2.
3 TAAMS R/W 0
GPTM TimerA Capture Mode
The TACMR values are defined as follows:
Value Description
0 Edge-Count mode
1 Edge-Time mode
2 TACMR R/W 0
January 08, 2011 337
Texas Instruments-Production Data
Stellaris® LM3S2965 Microcontroller
Bit/Field Name Type Reset Description
GPTM TimerA Mode
The TAMR values are defined as follows:
Value Description
0x0 Reserved
0x1 One-Shot Timer mode
0x2 Periodic Timer mode
0x3 Capture mode
The Timer mode is based on the timer configuration defined by bits 2:0
in the GPTMCFG register (16-or 32-bit).
In 16-bit timer configuration, TAMR controls the 16-bit timer modes for
TimerA.
In 32-bit timer configuration, this register controls the mode and the
contents of GPTMTBMR are ignored.
1:0 TAMR R/W 0x0
338 January 08, 2011
Texas Instruments-Production Data
General-Purpose Timers
Register 3: GPTM TimerB Mode (GPTMTBMR), offset 0x008
This register configures the GPTM based on the configuration selected in the GPTMCFG register.
When in 16-bit PWM mode, set the TBAMS bit to 0x1, the TBCMR bit to 0x0, and the TBMR field to
0x2.
GPTM TimerB Mode (GPTMTBMR)
Timer0 base: 0x4003.0000
Timer1 base: 0x4003.1000
Timer2 base: 0x4003.2000
Timer3 base: 0x4003.3000
Offset 0x008
Type R/W, reset 0x0000.0000
31 30 29 28 27 26 25 24 23 22 21 20 19 18 17 16
reserved
Type RO RO RO RO RO RO RO RO RO RO RO RO RO RO RO RO
Reset 0 0 0 0 0 0 0 0 0 0 0 0 0 0 0 0
15 14 13 12 11 10 9 8 7 6 5 4 3 2 1 0
reserved TBAMS TBCMR TBMR
Type RO RO RO RO RO RO RO RO RO RO RO RO R/W R/W R/W R/W
Reset 0 0 0 0 0 0 0 0 0 0 0 0 0 0 0 0
Bit/Field Name Type Reset Description
Software should not rely on the value of a reserved bit. To provide
compatibility with future products, the value of a reserved bit should be
preserved across a read-modify-write operation.
31:4 reserved RO 0x00
GPTM TimerB Alternate Mode Select
The TBAMS values are defined as follows:
Value Description
0 Capture mode is enabled.
1 PWM mode is enabled.
Note: To enable PWM mode, you must also clear the TBCMR
bit and set the TBMR field to 0x2.
3 TBAMS R/W 0
GPTM TimerB Capture Mode
The TBCMR values are defined as follows:
Value Description
0 Edge-Count mode
1 Edge-Time mode
2 TBCMR R/W 0
January 08, 2011 339
Texas Instruments-Production Data
Stellaris® LM3S2965 Microcontroller
Bit/Field Name Type Reset Description
GPTM TimerB Mode
The TBMR values are defined as follows:
Value Description
0x0 Reserved
0x1 One-Shot Timer mode
0x2 Periodic Timer mode
0x3 Capture mode
The timer mode is based on the timer configuration defined by bits 2:0
in the GPTMCFG register.
In 16-bit timer configuration, these bits control the 16-bit timer modes
for TimerB.
In 32-bit timer configuration, this register’s contents are ignored and
GPTMTAMR is used.
1:0 TBMR R/W 0x0
340 January 08, 2011
Texas Instruments-Production Data
General-Purpose Timers
Register 4: GPTM Control (GPTMCTL), offset 0x00C
This register is used alongside the GPTMCFG and GMTMTnMR registers to fine-tune the timer
configuration, and to enable other features such as timer stall and the output trigger. The output
trigger can be used to initiate transfers on the ADC module.
GPTM Control (GPTMCTL)
Timer0 base: 0x4003.0000
Timer1 base: 0x4003.1000
Timer2 base: 0x4003.2000
Timer3 base: 0x4003.3000
Offset 0x00C
Type R/W, reset 0x0000.0000
31 30 29 28 27 26 25 24 23 22 21 20 19 18 17 16
reserved
Type RO RO RO RO RO RO RO RO RO RO RO RO RO RO RO RO
Reset 0 0 0 0 0 0 0 0 0 0 0 0 0 0 0 0
15 14 13 12 11 10 9 8 7 6 5 4 3 2 1 0
reserved TBPWML TBOTE reserved TBEVENT TBSTALL TBEN reserved TAPWML TAOTE RTCEN TAEVENT TASTALL TAEN
Type RO R/W R/W RO R/W R/W R/W R/W RO R/W R/W R/W R/W R/W R/W R/W
Reset 0 0 0 0 0 0 0 0 0 0 0 0 0 0 0 0
Bit/Field Name Type Reset Description
Software should not rely on the value of a reserved bit. To provide
compatibility with future products, the value of a reserved bit should be
preserved across a read-modify-write operation.
31:15 reserved RO 0x00
GPTM TimerB PWM Output Level
The TBPWML values are defined as follows:
Value Description
0 Output is unaffected.
1 Output is inverted.
14 TBPWML R/W 0
GPTM TimerB Output Trigger Enable
The TBOTE values are defined as follows:
Value Description
0 The output TimerB ADC trigger is disabled.
1 The output TimerB ADC trigger is enabled.
In addition, the ADC must be enabled and the timer selected as a trigger
source with the EMn bit in the ADCEMUX register (see page 398).
13 TBOTE R/W 0
Software should not rely on the value of a reserved bit. To provide
compatibility with future products, the value of a reserved bit should be
preserved across a read-modify-write operation.
12 reserved RO 0
January 08, 2011 341
Texas Instruments-Production Data
Stellaris® LM3S2965 Microcontroller
Bit/Field Name Type Reset Description
GPTM TimerB Event Mode
The TBEVENT values are defined as follows:
Value Description
0x0 Positive edge
0x1 Negative edge
0x2 Reserved
0x3 Both edges
11:10 TBEVENT R/W 0x0
GPTM Timer B Stall Enable
The TBSTALL values are defined as follows:
Value Description
Timer B continues counting while the processor is halted by the
debugger.
0
Timer B freezes counting while the processor is halted by the
debugger.
1
If the processor is executing normally, the TBSTALL bit is ignored.
9 TBSTALL R/W 0
GPTM TimerB Enable
The TBEN values are defined as follows:
Value Description
0 TimerB is disabled.
TimerB is enabled and begins counting or the capture logic is
enabled based on the GPTMCFG register.
1
8 TBEN R/W 0
Software should not rely on the value of a reserved bit. To provide
compatibility with future products, the value of a reserved bit should be
preserved across a read-modify-write operation.
7 reserved RO 0
GPTM TimerA PWM Output Level
The TAPWML values are defined as follows:
Value Description
0 Output is unaffected.
1 Output is inverted.
6 TAPWML R/W 0
GPTM TimerA Output Trigger Enable
The TAOTE values are defined as follows:
Value Description
0 The output TimerA ADC trigger is disabled.
1 The output TimerA ADC trigger is enabled.
In addition, the ADC must be enabled and the timer selected as a trigger
source with the EMn bit in the ADCEMUX register (see page 398).
5 TAOTE R/W 0
342 January 08, 2011
Texas Instruments-Production Data
General-Purpose Timers
Bit/Field Name Type Reset Description
GPTM RTC Enable
The RTCEN values are defined as follows:
Value Description
0 RTC counting is disabled.
1 RTC counting is enabled.
4 RTCEN R/W 0
GPTM TimerA Event Mode
The TAEVENT values are defined as follows:
Value Description
0x0 Positive edge
0x1 Negative edge
0x2 Reserved
0x3 Both edges
3:2 TAEVENT R/W 0x0
GPTM Timer A Stall Enable
The TASTALL values are defined as follows:
Value Description
Timer A continues counting while the processor is halted by the
debugger.
0
Timer A freezes counting while the processor is halted by the
debugger.
1
If the processor is executing normally, the TASTALL bit is ignored.
1 TASTALL R/W 0
GPTM TimerA Enable
The TAEN values are defined as follows:
Value Description
0 TimerA is disabled.
TimerA is enabled and begins counting or the capture logic is
enabled based on the GPTMCFG register.
1
0 TAEN R/W 0
January 08, 2011 343
Texas Instruments-Production Data
Stellaris® LM3S2965 Microcontroller
Register 5: GPTM Interrupt Mask (GPTMIMR), offset 0x018
This register allows software to enable/disable GPTM controller-level interrupts. Writing a 1 enables
the interrupt, while writing a 0 disables it.
GPTM Interrupt Mask (GPTMIMR)
Timer0 base: 0x4003.0000
Timer1 base: 0x4003.1000
Timer2 base: 0x4003.2000
Timer3 base: 0x4003.3000
Offset 0x018
Type R/W, reset 0x0000.0000
31 30 29 28 27 26 25 24 23 22 21 20 19 18 17 16
reserved
Type RO RO RO RO RO RO RO RO RO RO RO RO RO RO RO RO
Reset 0 0 0 0 0 0 0 0 0 0 0 0 0 0 0 0
15 14 13 12 11 10 9 8 7 6 5 4 3 2 1 0
reserved CBEIM CBMIM TBTOIM reserved RTCIM CAEIM CAMIM TATOIM
Type RO RO RO RO RO R/W R/W R/W RO RO RO RO R/W R/W R/W R/W
Reset 0 0 0 0 0 0 0 0 0 0 0 0 0 0 0 0
Bit/Field Name Type Reset Description
Software should not rely on the value of a reserved bit. To provide
compatibility with future products, the value of a reserved bit should be
preserved across a read-modify-write operation.
31:11 reserved RO 0x00
GPTM CaptureB Event Interrupt Mask
The CBEIM values are defined as follows:
Value Description
0 Interrupt is disabled.
1 Interrupt is enabled.
10 CBEIM R/W 0
GPTM CaptureB Match Interrupt Mask
The CBMIM values are defined as follows:
Value Description
0 Interrupt is disabled.
1 Interrupt is enabled.
9 CBMIM R/W 0
GPTM TimerB Time-Out Interrupt Mask
The TBTOIM values are defined as follows:
Value Description
0 Interrupt is disabled.
1 Interrupt is enabled.
8 TBTOIM R/W 0
Software should not rely on the value of a reserved bit. To provide
compatibility with future products, the value of a reserved bit should be
preserved across a read-modify-write operation.
7:4 reserved RO 0
344 January 08, 2011
Texas Instruments-Production Data
General-Purpose Timers
Bit/Field Name Type Reset Description
GPTM RTC Interrupt Mask
The RTCIM values are defined as follows:
Value Description
0 Interrupt is disabled.
1 Interrupt is enabled.
3 RTCIM R/W 0
GPTM CaptureA Event Interrupt Mask
The CAEIM values are defined as follows:
Value Description
0 Interrupt is disabled.
1 Interrupt is enabled.
2 CAEIM R/W 0
GPTM CaptureA Match Interrupt Mask
The CAMIM values are defined as follows:
Value Description
0 Interrupt is disabled.
1 Interrupt is enabled.
1 CAMIM R/W 0
GPTM TimerA Time-Out Interrupt Mask
The TATOIM values are defined as follows:
Value Description
0 Interrupt is disabled.
1 Interrupt is enabled.
0 TATOIM R/W 0
January 08, 2011 345
Texas Instruments-Production Data
Stellaris® LM3S2965 Microcontroller
Register 6: GPTM Raw Interrupt Status (GPTMRIS), offset 0x01C
This register shows the state of the GPTM's internal interrupt signal. These bits are set whether or
not the interrupt is masked in the GPTMIMR register. Each bit can be cleared by writing a 1 to its
corresponding bit in GPTMICR.
GPTM Raw Interrupt Status (GPTMRIS)
Timer0 base: 0x4003.0000
Timer1 base: 0x4003.1000
Timer2 base: 0x4003.2000
Timer3 base: 0x4003.3000
Offset 0x01C
Type RO, reset 0x0000.0000
31 30 29 28 27 26 25 24 23 22 21 20 19 18 17 16
reserved
Type RO RO RO RO RO RO RO RO RO RO RO RO RO RO RO RO
Reset 0 0 0 0 0 0 0 0 0 0 0 0 0 0 0 0
15 14 13 12 11 10 9 8 7 6 5 4 3 2 1 0
reserved CBERIS CBMRIS TBTORIS reserved RTCRIS CAERIS CAMRIS TATORIS
Type RO RO RO RO RO RO RO RO RO RO RO RO RO RO RO RO
Reset 0 0 0 0 0 0 0 0 0 0 0 0 0 0 0 0
Bit/Field Name Type Reset Description
Software should not rely on the value of a reserved bit. To provide
compatibility with future products, the value of a reserved bit should be
preserved across a read-modify-write operation.
31:11 reserved RO 0x00
GPTM CaptureB Event Raw Interrupt
This is the CaptureB Event interrupt status prior to masking.
10 CBERIS RO 0
GPTM CaptureB Match Raw Interrupt
This is the CaptureB Match interrupt status prior to masking.
9 CBMRIS RO 0
GPTM TimerB Time-Out Raw Interrupt
This is the TimerB time-out interrupt status prior to masking.
8 TBTORIS RO 0
Software should not rely on the value of a reserved bit. To provide
compatibility with future products, the value of a reserved bit should be
preserved across a read-modify-write operation.
7:4 reserved RO 0x0
GPTM RTC Raw Interrupt
This is the RTC Event interrupt status prior to masking.
3 RTCRIS RO 0
GPTM CaptureA Event Raw Interrupt
This is the CaptureA Event interrupt status prior to masking.
2 CAERIS RO 0
GPTM CaptureA Match Raw Interrupt
This is the CaptureA Match interrupt status prior to masking.
1 CAMRIS RO 0
GPTM TimerA Time-Out Raw Interrupt
This the TimerA time-out interrupt status prior to masking.
0 TATORIS RO 0
346 January 08, 2011
Texas Instruments-Production Data
General-Purpose Timers
Register 7: GPTM Masked Interrupt Status (GPTMMIS), offset 0x020
This register show the state of the GPTM's controller-level interrupt. If an interrupt is unmasked in
GPTMIMR, and there is an event that causes the interrupt to be asserted, the corresponding bit is
set in this register. All bits are cleared by writing a 1 to the corresponding bit in GPTMICR.
GPTM Masked Interrupt Status (GPTMMIS)
Timer0 base: 0x4003.0000
Timer1 base: 0x4003.1000
Timer2 base: 0x4003.2000
Timer3 base: 0x4003.3000
Offset 0x020
Type RO, reset 0x0000.0000
31 30 29 28 27 26 25 24 23 22 21 20 19 18 17 16
reserved
Type RO RO RO RO RO RO RO RO RO RO RO RO RO RO RO RO
Reset 0 0 0 0 0 0 0 0 0 0 0 0 0 0 0 0
15 14 13 12 11 10 9 8 7 6 5 4 3 2 1 0
reserved CBEMIS CBMMIS TBTOMIS reserved RTCMIS CAEMIS CAMMIS TATOMIS
Type RO RO RO RO RO RO RO RO RO RO RO RO RO RO RO RO
Reset 0 0 0 0 0 0 0 0 0 0 0 0 0 0 0 0
Bit/Field Name Type Reset Description
Software should not rely on the value of a reserved bit. To provide
compatibility with future products, the value of a reserved bit should be
preserved across a read-modify-write operation.
31:11 reserved RO 0x00
GPTM CaptureB Event Masked Interrupt
This is the CaptureB event interrupt status after masking.
10 CBEMIS RO 0
GPTM CaptureB Match Masked Interrupt
This is the CaptureB match interrupt status after masking.
9 CBMMIS RO 0
GPTM TimerB Time-Out Masked Interrupt
This is the TimerB time-out interrupt status after masking.
8 TBTOMIS RO 0
Software should not rely on the value of a reserved bit. To provide
compatibility with future products, the value of a reserved bit should be
preserved across a read-modify-write operation.
7:4 reserved RO 0x0
GPTM RTC Masked Interrupt
This is the RTC event interrupt status after masking.
3 RTCMIS RO 0
GPTM CaptureA Event Masked Interrupt
This is the CaptureA event interrupt status after masking.
2 CAEMIS RO 0
GPTM CaptureA Match Masked Interrupt
This is the CaptureA match interrupt status after masking.
1 CAMMIS RO 0
GPTM TimerA Time-Out Masked Interrupt
This is the TimerA time-out interrupt status after masking.
0 TATOMIS RO 0
January 08, 2011 347
Texas Instruments-Production Data
Stellaris® LM3S2965 Microcontroller
Register 8: GPTM Interrupt Clear (GPTMICR), offset 0x024
This register is used to clear the status bits in the GPTMRIS and GPTMMIS registers. Writing a 1
to a bit clears the corresponding bit in the GPTMRIS and GPTMMIS registers.
GPTM Interrupt Clear (GPTMICR)
Timer0 base: 0x4003.0000
Timer1 base: 0x4003.1000
Timer2 base: 0x4003.2000
Timer3 base: 0x4003.3000
Offset 0x024
Type W1C, reset 0x0000.0000
31 30 29 28 27 26 25 24 23 22 21 20 19 18 17 16
reserved
Type RO RO RO RO RO RO RO RO RO RO RO RO RO RO RO RO
Reset 0 0 0 0 0 0 0 0 0 0 0 0 0 0 0 0
15 14 13 12 11 10 9 8 7 6 5 4 3 2 1 0
reserved CBECINT CBMCINT TBTOCINT reserved RTCCINT CAECINT CAMCINT TATOCINT
Type RO RO RO RO RO W1C W1C W1C RO RO RO RO W1C W1C W1C W1C
Reset 0 0 0 0 0 0 0 0 0 0 0 0 0 0 0 0
Bit/Field Name Type Reset Description
Software should not rely on the value of a reserved bit. To provide
compatibility with future products, the value of a reserved bit should be
preserved across a read-modify-write operation.
31:11 reserved RO 0x00
GPTM CaptureB Event Interrupt Clear
The CBECINT values are defined as follows:
Value Description
0 The interrupt is unaffected.
1 The interrupt is cleared.
10 CBECINT W1C 0
GPTM CaptureB Match Interrupt Clear
The CBMCINT values are defined as follows:
Value Description
0 The interrupt is unaffected.
1 The interrupt is cleared.
9 CBMCINT W1C 0
GPTM TimerB Time-Out Interrupt Clear
The TBTOCINT values are defined as follows:
Value Description
0 The interrupt is unaffected.
1 The interrupt is cleared.
8 TBTOCINT W1C 0
Software should not rely on the value of a reserved bit. To provide
compatibility with future products, the value of a reserved bit should be
preserved across a read-modify-write operation.
7:4 reserved RO 0x0
348 January 08, 2011
Texas Instruments-Production Data
General-Purpose Timers
Bit/Field Name Type Reset Description
GPTM RTC Interrupt Clear
The RTCCINT values are defined as follows:
Value Description
0 The interrupt is unaffected.
1 The interrupt is cleared.
3 RTCCINT W1C 0
GPTM CaptureA Event Interrupt Clear
The CAECINT values are defined as follows:
Value Description
0 The interrupt is unaffected.
1 The interrupt is cleared.
2 CAECINT W1C 0
GPTM CaptureA Match Interrupt Clear
The CAMCINT values are defined as follows:
Value Description
0 The interrupt is unaffected.
1 The interrupt is cleared.
1 CAMCINT W1C 0
GPTM TimerA Time-Out Interrupt Clear
The TATOCINT values are defined as follows:
Value Description
0 The interrupt is unaffected.
1 The interrupt is cleared.
0 TATOCINT W1C 0
January 08, 2011 349
Texas Instruments-Production Data
Stellaris® LM3S2965 Microcontroller
Register 9: GPTM TimerA Interval Load (GPTMTAILR), offset 0x028
This register is used to load the starting count value into the timer. When GPTM is configured to
one of the 32-bit modes, GPTMTAILR appears as a 32-bit register (the upper 16-bits correspond
to the contents of the GPTM TimerB Interval Load (GPTMTBILR) register). In 16-bit mode, the
upper 16 bits of this register read as 0s and have no effect on the state of GPTMTBILR.
GPTM TimerA Interval Load (GPTMTAILR)
Timer0 base: 0x4003.0000
Timer1 base: 0x4003.1000
Timer2 base: 0x4003.2000
Timer3 base: 0x4003.3000
Offset 0x028
Type R/W, reset 0xFFFF.FFFF
31 30 29 28 27 26 25 24 23 22 21 20 19 18 17 16
TAILRH
Type R/W R/W R/W R/W R/W R/W R/W R/W R/W R/W R/W R/W R/W R/W R/W R/W
Reset 1 1 1 1 1 1 1 1 1 1 1 1 1 1 1 1
15 14 13 12 11 10 9 8 7 6 5 4 3 2 1 0
TAILRL
Type R/W R/W R/W R/W R/W R/W R/W R/W R/W R/W R/W R/W R/W R/W R/W R/W
Reset 1 1 1 1 1 1 1 1 1 1 1 1 1 1 1 1
Bit/Field Name Type Reset Description
GPTM TimerA Interval Load Register High
When configured for 32-bit mode via the GPTMCFG register, the GPTM
TimerB Interval Load (GPTMTBILR) register loads this value on a
write. A read returns the current value of GPTMTBILR.
In 16-bit mode, this field reads as 0 and does not have an effect on the
state of GPTMTBILR.
31:16 TAILRH R/W 0xFFFF
GPTM TimerA Interval Load Register Low
For both 16- and 32-bit modes, writing this field loads the counter for
TimerA. A read returns the current value of GPTMTAILR.
15:0 TAILRL R/W 0xFFFF
350 January 08, 2011
Texas Instruments-Production Data
General-Purpose Timers
Register 10: GPTM TimerB Interval Load (GPTMTBILR), offset 0x02C
This register is used to load the starting count value into TimerB. When the GPTM is configured to
a 32-bit mode, GPTMTBILR returns the current value of TimerB and ignores writes.
GPTM TimerB Interval Load (GPTMTBILR)
Timer0 base: 0x4003.0000
Timer1 base: 0x4003.1000
Timer2 base: 0x4003.2000
Timer3 base: 0x4003.3000
Offset 0x02C
Type R/W, reset 0x0000.FFFF
31 30 29 28 27 26 25 24 23 22 21 20 19 18 17 16
reserved
Type RO RO RO RO RO RO RO RO RO RO RO RO RO RO RO RO
Reset 0 0 0 0 0 0 0 0 0 0 0 0 0 0 0 0
15 14 13 12 11 10 9 8 7 6 5 4 3 2 1 0
TBILRL
Type R/W R/W R/W R/W R/W R/W R/W R/W R/W R/W R/W R/W R/W R/W R/W R/W
Reset 1 1 1 1 1 1 1 1 1 1 1 1 1 1 1 1
Bit/Field Name Type Reset Description
Software should not rely on the value of a reserved bit. To provide
compatibility with future products, the value of a reserved bit should be
preserved across a read-modify-write operation.
31:16 reserved RO 0x0000
GPTM TimerB Interval Load Register
When the GPTM is not configured as a 32-bit timer, a write to this field
updates GPTMTBILR. In 32-bit mode, writes are ignored, and reads
return the current value of GPTMTBILR.
15:0 TBILRL R/W 0xFFFF
January 08, 2011 351
Texas Instruments-Production Data
Stellaris® LM3S2965 Microcontroller
Register 11: GPTM TimerA Match (GPTMTAMATCHR), offset 0x030
This register is used in 32-bit Real-Time Clock mode and 16-bit PWM and Input Edge Count modes.
GPTM TimerA Match (GPTMTAMATCHR)
Timer0 base: 0x4003.0000
Timer1 base: 0x4003.1000
Timer2 base: 0x4003.2000
Timer3 base: 0x4003.3000
Offset 0x030
Type R/W, reset 0xFFFF.FFFF
31 30 29 28 27 26 25 24 23 22 21 20 19 18 17 16
TAMRH
Type R/W R/W R/W R/W R/W R/W R/W R/W R/W R/W R/W R/W R/W R/W R/W R/W
Reset 1 1 1 1 1 1 1 1 1 1 1 1 1 1 1 1
15 14 13 12 11 10 9 8 7 6 5 4 3 2 1 0
TAMRL
Type R/W R/W R/W R/W R/W R/W R/W R/W R/W R/W R/W R/W R/W R/W R/W R/W
Reset 1 1 1 1 1 1 1 1 1 1 1 1 1 1 1 1
Bit/Field Name Type Reset Description
GPTM TimerA Match Register High
When configured for 32-bit Real-Time Clock (RTC) mode via the
GPTMCFG register, this value is compared to the upper half of
GPTMTAR, to determine match events.
In 16-bit mode, this field reads as 0 and does not have an effect on the
state of GPTMTBMATCHR.
31:16 TAMRH R/W 0xFFFF
GPTM TimerA Match Register Low
When configured for 32-bit Real-Time Clock (RTC) mode via the
GPTMCFG register, this value is compared to the lower half of
GPTMTAR, to determine match events.
When configured for PWM mode, this value along with GPTMTAILR,
determines the duty cycle of the output PWM signal.
When configured for Edge Count mode, this value along with
GPTMTAILR, determines how many edge events are counted. The total
number of edge events counted is equal to the value in GPTMTAILR
minus this value.
15:0 TAMRL R/W 0xFFFF
352 January 08, 2011
Texas Instruments-Production Data
General-Purpose Timers
Register 12: GPTM TimerB Match (GPTMTBMATCHR), offset 0x034
This register is used in 16-bit PWM and Input Edge Count modes.
GPTM TimerB Match (GPTMTBMATCHR)
Timer0 base: 0x4003.0000
Timer1 base: 0x4003.1000
Timer2 base: 0x4003.2000
Timer3 base: 0x4003.3000
Offset 0x034
Type R/W, reset 0x0000.FFFF
31 30 29 28 27 26 25 24 23 22 21 20 19 18 17 16
reserved
Type RO RO RO RO RO RO RO RO RO RO RO RO RO RO RO RO
Reset 0 0 0 0 0 0 0 0 0 0 0 0 0 0 0 0
15 14 13 12 11 10 9 8 7 6 5 4 3 2 1 0
TBMRL
Type R/W R/W R/W R/W R/W R/W R/W R/W R/W R/W R/W R/W R/W R/W R/W R/W
Reset 1 1 1 1 1 1 1 1 1 1 1 1 1 1 1 1
Bit/Field Name Type Reset Description
Software should not rely on the value of a reserved bit. To provide
compatibility with future products, the value of a reserved bit should be
preserved across a read-modify-write operation.
31:16 reserved RO 0x0000
GPTM TimerB Match Register Low
When configured for PWM mode, this value along with GPTMTBILR,
determines the duty cycle of the output PWM signal.
When configured for Edge Count mode, this value along with
GPTMTBILR, determines how many edge events are counted. The total
number of edge events counted is equal to the value in GPTMTBILR
minus this value.
15:0 TBMRL R/W 0xFFFF
January 08, 2011 353
Texas Instruments-Production Data
Stellaris® LM3S2965 Microcontroller
Register 13: GPTM TimerA Prescale (GPTMTAPR), offset 0x038
This register allows software to extend the range of the 16-bit timers when operating in one-shot or
periodic mode.
GPTM TimerA Prescale (GPTMTAPR)
Timer0 base: 0x4003.0000
Timer1 base: 0x4003.1000
Timer2 base: 0x4003.2000
Timer3 base: 0x4003.3000
Offset 0x038
Type R/W, reset 0x0000.0000
31 30 29 28 27 26 25 24 23 22 21 20 19 18 17 16
reserved
Type RO RO RO RO RO RO RO RO RO RO RO RO RO RO RO RO
Reset 0 0 0 0 0 0 0 0 0 0 0 0 0 0 0 0
15 14 13 12 11 10 9 8 7 6 5 4 3 2 1 0
reserved TAPSR
Type RO RO RO RO RO RO RO RO R/W R/W R/W R/W R/W R/W R/W R/W
Reset 0 0 0 0 0 0 0 0 0 0 0 0 0 0 0 0
Bit/Field Name Type Reset Description
Software should not rely on the value of a reserved bit. To provide
compatibility with future products, the value of a reserved bit should be
preserved across a read-modify-write operation.
31:8 reserved RO 0x00
GPTM TimerA Prescale
The register loads this value on a write. A read returns the current value
of the register.
Refer to Table 9-2 on page 328 for more details and an example.
7:0 TAPSR R/W 0x00
354 January 08, 2011
Texas Instruments-Production Data
General-Purpose Timers
Register 14: GPTM TimerB Prescale (GPTMTBPR), offset 0x03C
This register allows software to extend the range of the 16-bit timers when operating in one-shot or
periodic mode.
GPTM TimerB Prescale (GPTMTBPR)
Timer0 base: 0x4003.0000
Timer1 base: 0x4003.1000
Timer2 base: 0x4003.2000
Timer3 base: 0x4003.3000
Offset 0x03C
Type R/W, reset 0x0000.0000
31 30 29 28 27 26 25 24 23 22 21 20 19 18 17 16
reserved
Type RO RO RO RO RO RO RO RO RO RO RO RO RO RO RO RO
Reset 0 0 0 0 0 0 0 0 0 0 0 0 0 0 0 0
15 14 13 12 11 10 9 8 7 6 5 4 3 2 1 0
reserved TBPSR
Type RO RO RO RO RO RO RO RO R/W R/W R/W R/W R/W R/W R/W R/W
Reset 0 0 0 0 0 0 0 0 0 0 0 0 0 0 0 0
Bit/Field Name Type Reset Description
Software should not rely on the value of a reserved bit. To provide
compatibility with future products, the value of a reserved bit should be
preserved across a read-modify-write operation.
31:8 reserved RO 0x00
GPTM TimerB Prescale
The register loads this value on a write. A read returns the current value
of this register.
Refer to Table 9-2 on page 328 for more details and an example.
7:0 TBPSR R/W 0x00
January 08, 2011 355
Texas Instruments-Production Data
Stellaris® LM3S2965 Microcontroller
Register 15: GPTM TimerA Prescale Match (GPTMTAPMR), offset 0x040
This register effectively extends the range of GPTMTAMATCHR to 24 bits when operating in 16-bit
one-shot or periodic mode.
GPTM TimerA Prescale Match (GPTMTAPMR)
Timer0 base: 0x4003.0000
Timer1 base: 0x4003.1000
Timer2 base: 0x4003.2000
Timer3 base: 0x4003.3000
Offset 0x040
Type R/W, reset 0x0000.0000
31 30 29 28 27 26 25 24 23 22 21 20 19 18 17 16
reserved
Type RO RO RO RO RO RO RO RO RO RO RO RO RO RO RO RO
Reset 0 0 0 0 0 0 0 0 0 0 0 0 0 0 0 0
15 14 13 12 11 10 9 8 7 6 5 4 3 2 1 0
reserved TAPSMR
Type RO RO RO RO RO RO RO RO R/W R/W R/W R/W R/W R/W R/W R/W
Reset 0 0 0 0 0 0 0 0 0 0 0 0 0 0 0 0
Bit/Field Name Type Reset Description
Software should not rely on the value of a reserved bit. To provide
compatibility with future products, the value of a reserved bit should be
preserved across a read-modify-write operation.
31:8 reserved RO 0x00
GPTM TimerA Prescale Match
This value is used alongside GPTMTAMATCHR to detect timer match
events while using a prescaler.
7:0 TAPSMR R/W 0x00
356 January 08, 2011
Texas Instruments-Production Data
General-Purpose Timers
Register 16: GPTM TimerB Prescale Match (GPTMTBPMR), offset 0x044
This register effectively extends the range of GPTMTBMATCHR to 24 bits when operating in 16-bit
one-shot or periodic mode.
GPTM TimerB Prescale Match (GPTMTBPMR)
Timer0 base: 0x4003.0000
Timer1 base: 0x4003.1000
Timer2 base: 0x4003.2000
Timer3 base: 0x4003.3000
Offset 0x044
Type R/W, reset 0x0000.0000
31 30 29 28 27 26 25 24 23 22 21 20 19 18 17 16
reserved
Type RO RO RO RO RO RO RO RO RO RO RO RO RO RO RO RO
Reset 0 0 0 0 0 0 0 0 0 0 0 0 0 0 0 0
15 14 13 12 11 10 9 8 7 6 5 4 3 2 1 0
reserved TBPSMR
Type RO RO RO RO RO RO RO RO R/W R/W R/W R/W R/W R/W R/W R/W
Reset 0 0 0 0 0 0 0 0 0 0 0 0 0 0 0 0
Bit/Field Name Type Reset Description
Software should not rely on the value of a reserved bit. To provide
compatibility with future products, the value of a reserved bit should be
preserved across a read-modify-write operation.
31:8 reserved RO 0x00
GPTM TimerB Prescale Match
This value is used alongside GPTMTBMATCHR to detect timer match
events while using a prescaler.
7:0 TBPSMR R/W 0x00
January 08, 2011 357
Texas Instruments-Production Data
Stellaris® LM3S2965 Microcontroller
Register 17: GPTM TimerA (GPTMTAR), offset 0x048
This register shows the current value of the TimerA counter in all cases except for Input Edge Count
mode. When in this mode, this register contains the number of edges that have occurred.
GPTM TimerA (GPTMTAR)
Timer0 base: 0x4003.0000
Timer1 base: 0x4003.1000
Timer2 base: 0x4003.2000
Timer3 base: 0x4003.3000
Offset 0x048
Type RO, reset 0xFFFF.FFFF
31 30 29 28 27 26 25 24 23 22 21 20 19 18 17 16
TARH
Type RO RO RO RO RO RO RO RO RO RO RO RO RO RO RO RO
Reset 1 1 1 1 1 1 1 1 1 1 1 1 1 1 1 1
15 14 13 12 11 10 9 8 7 6 5 4 3 2 1 0
TARL
Type RO RO RO RO RO RO RO RO RO RO RO RO RO RO RO RO
Reset 1 1 1 1 1 1 1 1 1 1 1 1 1 1 1 1
Bit/Field Name Type Reset Description
GPTM TimerA Register High
If the GPTMCFG is in a 32-bit mode, TimerB value is read. If the
GPTMCFG is in a 16-bit mode, this is read as zero.
31:16 TARH RO 0xFFFF
GPTM TimerA Register Low
A read returns the current value of the GPTM TimerA Count Register,
except in Input Edge-Count mode, when it returns the number of edges
that have occurred.
15:0 TARL RO 0xFFFF
358 January 08, 2011
Texas Instruments-Production Data
General-Purpose Timers
Register 18: GPTM TimerB (GPTMTBR), offset 0x04C
This register shows the current value of the TimerB counter in all cases except for Input Edge Count
mode. When in this mode, this register contains the number of edges that have occurred.
GPTM TimerB (GPTMTBR)
Timer0 base: 0x4003.0000
Timer1 base: 0x4003.1000
Timer2 base: 0x4003.2000
Timer3 base: 0x4003.3000
Offset 0x04C
Type RO, reset 0x0000.FFFF
31 30 29 28 27 26 25 24 23 22 21 20 19 18 17 16
reserved
Type RO RO RO RO RO RO RO RO RO RO RO RO RO RO RO RO
Reset 0 0 0 0 0 0 0 0 0 0 0 0 0 0 0 0
15 14 13 12 11 10 9 8 7 6 5 4 3 2 1 0
TBRL
Type RO RO RO RO RO RO RO RO RO RO RO RO RO RO RO RO
Reset 1 1 1 1 1 1 1 1 1 1 1 1 1 1 1 1
Bit/Field Name Type Reset Description
Software should not rely on the value of a reserved bit. To provide
compatibility with future products, the value of a reserved bit should be
preserved across a read-modify-write operation.
31:16 reserved RO 0x0000
GPTM TimerB
A read returns the current value of the GPTM TimerB Count Register,
except in Input Edge-Count mode, when it returns the number of edges
that have occurred.
15:0 TBRL RO 0xFFFF
January 08, 2011 359
Texas Instruments-Production Data
Stellaris® LM3S2965 Microcontroller
10 Watchdog Timer
A watchdog timer can generate nonmaskable interrupts (NMIs) or a reset when a time-out value is
reached. The watchdog timer is used to regain control when a system has failed due to a software
error or due to the failure of an external device to respond in the expected way.
The Stellaris® Watchdog Timer module has the following features:
■ 32-bit down counter with a programmable load register
■ Separate watchdog clock with an enable
■ Programmable interrupt generation logic with interrupt masking
■ Lock register protection from runaway software
■ Reset generation logic with an enable/disable
■ User-enabled stalling when the controller asserts the CPU Halt flag during debug
The Watchdog Timer can be configured to generate an interrupt to the controller on its first time-out,
and to generate a reset signal on its second time-out. Once the Watchdog Timer has been configured,
the lock register can be written to prevent the timer configuration from being inadvertently altered.
360 January 08, 2011
Texas Instruments-Production Data
Watchdog Timer
10.1 Block Diagram
Figure 10-1. WDT Module Block Diagram
Control / Clock /
Interrupt
Generation
WDTCTL
WDTICR
WDTRIS
WDTMIS
WDTLOCK
WDTTEST
WDTLOAD
WDTVALUE
Comparator
32-Bit Down
Counter
0x00000000
Interrupt
System Clock
Identification Registers
WDTPCellID0 WDTPeriphID0 WDTPeriphID4
WDTPCellID1 WDTPeriphID1 WDTPeriphID5
WDTPCellID2 WDTPeriphID2 WDTPeriphID6
WDTPCellID3 WDTPeriphID3 WDTPeriphID7
10.2 Functional Description
The Watchdog Timer module generates the first time-out signal when the 32-bit counter reaches
the zero state after being enabled; enabling the counter also enables the watchdog timer interrupt.
After the first time-out event, the 32-bit counter is re-loaded with the value of the Watchdog Timer
Load (WDTLOAD) register, and the timer resumes counting down from that value. Once the
Watchdog Timer has been configured, the Watchdog Timer Lock (WDTLOCK) register is written,
which prevents the timer configuration from being inadvertently altered by software.
If the timer counts down to its zero state again before the first time-out interrupt is cleared, and the
reset signal has been enabled (via the WatchdogResetEnable function), the Watchdog timer
asserts its reset signal to the system. If the interrupt is cleared before the 32-bit counter reaches its
second time-out, the 32-bit counter is loaded with the value in the WDTLOAD register, and counting
resumes from that value.
If WDTLOAD is written with a new value while the Watchdog Timer counter is counting, then the
counter is loaded with the new value and continues counting.
January 08, 2011 361
Texas Instruments-Production Data
Stellaris® LM3S2965 Microcontroller
Writing to WDTLOAD does not clear an active interrupt. An interrupt must be specifically cleared
by writing to the Watchdog Interrupt Clear (WDTICR) register.
The Watchdog module interrupt and reset generation can be enabled or disabled as required. When
the interrupt is re-enabled, the 32-bit counter is preloaded with the load register value and not its
last state.
10.3 Initialization and Configuration
To use the WDT, its peripheral clock must be enabled by setting the WDT bit in the RCGC0 register.
The Watchdog Timer is configured using the following sequence:
1. Load the WDTLOAD register with the desired timer load value.
2. If the Watchdog is configured to trigger system resets, set the RESEN bit in the WDTCTL register.
3. Set the INTEN bit in the WDTCTL register to enable the Watchdog and lock the control register.
If software requires that all of the watchdog registers are locked, the Watchdog Timer module can
be fully locked by writing any value to the WDTLOCK register. To unlock the Watchdog Timer, write
a value of 0x1ACC.E551.
10.4 Register Map
Table 10-1 on page 362 lists the Watchdog registers. The offset listed is a hexadecimal increment
to the register’s address, relative to the Watchdog Timer base address of 0x4000.0000.
Table 10-1. Watchdog Timer Register Map
See
Offset Name Type Reset Description page
0x000 WDTLOAD R/W 0xFFFF.FFFF Watchdog Load 364
0x004 WDTVALUE RO 0xFFFF.FFFF Watchdog Value 365
0x008 WDTCTL R/W 0x0000.0000 Watchdog Control 366
0x00C WDTICR WO - Watchdog Interrupt Clear 367
0x010 WDTRIS RO 0x0000.0000 Watchdog Raw Interrupt Status 368
0x014 WDTMIS RO 0x0000.0000 Watchdog Masked Interrupt Status 369
0x418 WDTTEST R/W 0x0000.0000 Watchdog Test 370
0xC00 WDTLOCK R/W 0x0000.0000 Watchdog Lock 371
0xFD0 WDTPeriphID4 RO 0x0000.0000 Watchdog Peripheral Identification 4 372
0xFD4 WDTPeriphID5 RO 0x0000.0000 Watchdog Peripheral Identification 5 373
0xFD8 WDTPeriphID6 RO 0x0000.0000 Watchdog Peripheral Identification 6 374
0xFDC WDTPeriphID7 RO 0x0000.0000 Watchdog Peripheral Identification 7 375
0xFE0 WDTPeriphID0 RO 0x0000.0005 Watchdog Peripheral Identification 0 376
0xFE4 WDTPeriphID1 RO 0x0000.0018 Watchdog Peripheral Identification 1 377
0xFE8 WDTPeriphID2 RO 0x0000.0018 Watchdog Peripheral Identification 2 378
362 January 08, 2011
Texas Instruments-Production Data
Watchdog Timer
Table 10-1. Watchdog Timer Register Map (continued)
See
Offset Name Type Reset Description page
0xFEC WDTPeriphID3 RO 0x0000.0001 Watchdog Peripheral Identification 3 379
0xFF0 WDTPCellID0 RO 0x0000.000D Watchdog PrimeCell Identification 0 380
0xFF4 WDTPCellID1 RO 0x0000.00F0 Watchdog PrimeCell Identification 1 381
0xFF8 WDTPCellID2 RO 0x0000.0005 Watchdog PrimeCell Identification 2 382
0xFFC WDTPCellID3 RO 0x0000.00B1 Watchdog PrimeCell Identification 3 383
10.5 Register Descriptions
The remainder of this section lists and describes the WDT registers, in numerical order by address
offset.
January 08, 2011 363
Texas Instruments-Production Data
Stellaris® LM3S2965 Microcontroller
Register 1: Watchdog Load (WDTLOAD), offset 0x000
This register is the 32-bit interval value used by the 32-bit counter. When this register is written, the
value is immediately loaded and the counter restarts counting down from the new value. If the
WDTLOAD register is loaded with 0x0000.0000, an interrupt is immediately generated.
Watchdog Load (WDTLOAD)
Base 0x4000.0000
Offset 0x000
Type R/W, reset 0xFFFF.FFFF
31 30 29 28 27 26 25 24 23 22 21 20 19 18 17 16
WDTLoad
Type R/W R/W R/W R/W R/W R/W R/W R/W R/W R/W R/W R/W R/W R/W R/W R/W
Reset 1 1 1 1 1 1 1 1 1 1 1 1 1 1 1 1
15 14 13 12 11 10 9 8 7 6 5 4 3 2 1 0
WDTLoad
Type R/W R/W R/W R/W R/W R/W R/W R/W R/W R/W R/W R/W R/W R/W R/W R/W
Reset 1 1 1 1 1 1 1 1 1 1 1 1 1 1 1 1
Bit/Field Name Type Reset Description
31:0 WDTLoad R/W 0xFFFF.FFFF Watchdog Load Value
364 January 08, 2011
Texas Instruments-Production Data
Watchdog Timer
Register 2: Watchdog Value (WDTVALUE), offset 0x004
This register contains the current count value of the timer.
Watchdog Value (WDTVALUE)
Base 0x4000.0000
Offset 0x004
Type RO, reset 0xFFFF.FFFF
31 30 29 28 27 26 25 24 23 22 21 20 19 18 17 16
WDTValue
Type RO RO RO RO RO RO RO RO RO RO RO RO RO RO RO RO
Reset 1 1 1 1 1 1 1 1 1 1 1 1 1 1 1 1
15 14 13 12 11 10 9 8 7 6 5 4 3 2 1 0
WDTValue
Type RO RO RO RO RO RO RO RO RO RO RO RO RO RO RO RO
Reset 1 1 1 1 1 1 1 1 1 1 1 1 1 1 1 1
Bit/Field Name Type Reset Description
Watchdog Value
Current value of the 32-bit down counter.
31:0 WDTValue RO 0xFFFF.FFFF
January 08, 2011 365
Texas Instruments-Production Data
Stellaris® LM3S2965 Microcontroller
Register 3: Watchdog Control (WDTCTL), offset 0x008
This register is the watchdog control register. The watchdog timer can be configured to generate a
reset signal (on second time-out) or an interrupt on time-out.
When the watchdog interrupt has been enabled, all subsequent writes to the control register are
ignored. The only mechanism that can re-enable writes is a hardware reset.
Watchdog Control (WDTCTL)
Base 0x4000.0000
Offset 0x008
Type R/W, reset 0x0000.0000
31 30 29 28 27 26 25 24 23 22 21 20 19 18 17 16
reserved
Type RO RO RO RO RO RO RO RO RO RO RO RO RO RO RO RO
Reset 0 0 0 0 0 0 0 0 0 0 0 0 0 0 0 0
15 14 13 12 11 10 9 8 7 6 5 4 3 2 1 0
reserved RESEN INTEN
Type RO RO RO RO RO RO RO RO RO RO RO RO RO RO R/W R/W
Reset 0 0 0 0 0 0 0 0 0 0 0 0 0 0 0 0
Bit/Field Name Type Reset Description
Software should not rely on the value of a reserved bit. To provide
compatibility with future products, the value of a reserved bit should be
preserved across a read-modify-write operation.
31:2 reserved RO 0x00
Watchdog Reset Enable
The RESEN values are defined as follows:
Value Description
0 Disabled.
1 Enable the Watchdog module reset output.
1 RESEN R/W 0
Watchdog Interrupt Enable
The INTEN values are defined as follows:
Value Description
Interrupt event disabled (once this bit is set, it can only be
cleared by a hardware reset).
0
1 Interrupt event enabled. Once enabled, all writes are ignored.
0 INTEN R/W 0
366 January 08, 2011
Texas Instruments-Production Data
Watchdog Timer
Register 4: Watchdog Interrupt Clear (WDTICR), offset 0x00C
This register is the interrupt clear register. A write of any value to this register clears the Watchdog
interrupt and reloads the 32-bit counter from the WDTLOAD register. Value for a read or reset is
indeterminate.
Watchdog Interrupt Clear (WDTICR)
Base 0x4000.0000
Offset 0x00C
Type WO, reset -
31 30 29 28 27 26 25 24 23 22 21 20 19 18 17 16
WDTIntClr
Type WO WO WO WO WO WO WO WO WO WO WO WO WO WO WO WO
Reset - - - - - - - - - - - - - - - -
15 14 13 12 11 10 9 8 7 6 5 4 3 2 1 0
WDTIntClr
Type WO WO WO WO WO WO WO WO WO WO WO WO WO WO WO WO
Reset - - - - - - - - - - - - - - - -
Bit/Field Name Type Reset Description
31:0 WDTIntClr WO - Watchdog Interrupt Clear
January 08, 2011 367
Texas Instruments-Production Data
Stellaris® LM3S2965 Microcontroller
Register 5: Watchdog Raw Interrupt Status (WDTRIS), offset 0x010
This register is the raw interrupt status register. Watchdog interrupt events can be monitored via
this register if the controller interrupt is masked.
Watchdog Raw Interrupt Status (WDTRIS)
Base 0x4000.0000
Offset 0x010
Type RO, reset 0x0000.0000
31 30 29 28 27 26 25 24 23 22 21 20 19 18 17 16
reserved
Type RO RO RO RO RO RO RO RO RO RO RO RO RO RO RO RO
Reset 0 0 0 0 0 0 0 0 0 0 0 0 0 0 0 0
15 14 13 12 11 10 9 8 7 6 5 4 3 2 1 0
reserved WDTRIS
Type RO RO RO RO RO RO RO RO RO RO RO RO RO RO RO RO
Reset 0 0 0 0 0 0 0 0 0 0 0 0 0 0 0 0
Bit/Field Name Type Reset Description
Software should not rely on the value of a reserved bit. To provide
compatibility with future products, the value of a reserved bit should be
preserved across a read-modify-write operation.
31:1 reserved RO 0x00
Watchdog Raw Interrupt Status
Gives the raw interrupt state (prior to masking) of WDTINTR.
0 WDTRIS RO 0
368 January 08, 2011
Texas Instruments-Production Data
Watchdog Timer
Register 6: Watchdog Masked Interrupt Status (WDTMIS), offset 0x014
This register is the masked interrupt status register. The value of this register is the logical AND of
the raw interrupt bit and the Watchdog interrupt enable bit.
Watchdog Masked Interrupt Status (WDTMIS)
Base 0x4000.0000
Offset 0x014
Type RO, reset 0x0000.0000
31 30 29 28 27 26 25 24 23 22 21 20 19 18 17 16
reserved
Type RO RO RO RO RO RO RO RO RO RO RO RO RO RO RO RO
Reset 0 0 0 0 0 0 0 0 0 0 0 0 0 0 0 0
15 14 13 12 11 10 9 8 7 6 5 4 3 2 1 0
reserved WDTMIS
Type RO RO RO RO RO RO RO RO RO RO RO RO RO RO RO RO
Reset 0 0 0 0 0 0 0 0 0 0 0 0 0 0 0 0
Bit/Field Name Type Reset Description
Software should not rely on the value of a reserved bit. To provide
compatibility with future products, the value of a reserved bit should be
preserved across a read-modify-write operation.
31:1 reserved RO 0x00
Watchdog Masked Interrupt Status
Gives the masked interrupt state (after masking) of the WDTINTR
interrupt.
0 WDTMIS RO 0
January 08, 2011 369
Texas Instruments-Production Data
Stellaris® LM3S2965 Microcontroller
Register 7: Watchdog Test (WDTTEST), offset 0x418
This register provides user-enabled stalling when the microcontroller asserts the CPU halt flag
during debug.
Watchdog Test (WDTTEST)
Base 0x4000.0000
Offset 0x418
Type R/W, reset 0x0000.0000
31 30 29 28 27 26 25 24 23 22 21 20 19 18 17 16
reserved
Type RO RO RO RO RO RO RO RO RO RO RO RO RO RO RO RO
Reset 0 0 0 0 0 0 0 0 0 0 0 0 0 0 0 0
15 14 13 12 11 10 9 8 7 6 5 4 3 2 1 0
reserved STALL reserved
Type RO RO RO RO RO RO RO R/W RO RO RO RO RO RO RO RO
Reset 0 0 0 0 0 0 0 0 0 0 0 0 0 0 0 0
Bit/Field Name Type Reset Description
Software should not rely on the value of a reserved bit. To provide
compatibility with future products, the value of a reserved bit should be
preserved across a read-modify-write operation.
31:9 reserved RO 0x00
Watchdog Stall Enable
When set to 1, if the Stellaris microcontroller is stopped with a debugger,
the watchdog timer stops counting. Once the microcontroller is restarted,
the watchdog timer resumes counting.
8 STALL R/W 0
Software should not rely on the value of a reserved bit. To provide
compatibility with future products, the value of a reserved bit should be
preserved across a read-modify-write operation.
7:0 reserved RO 0x00
370 January 08, 2011
Texas Instruments-Production Data
Watchdog Timer
Register 8: Watchdog Lock (WDTLOCK), offset 0xC00
Writing 0x1ACC.E551 to the WDTLOCK register enables write access to all other registers. Writing
any other value to the WDTLOCK register re-enables the locked state for register writes to all the
other registers. Reading the WDTLOCK register returns the lock status rather than the 32-bit value
written. Therefore, when write accesses are disabled, reading the WDTLOCK register returns
0x0000.0001 (when locked; otherwise, the returned value is 0x0000.0000 (unlocked)).
Watchdog Lock (WDTLOCK)
Base 0x4000.0000
Offset 0xC00
Type R/W, reset 0x0000.0000
31 30 29 28 27 26 25 24 23 22 21 20 19 18 17 16
WDTLock
Type R/W R/W R/W R/W R/W R/W R/W R/W R/W R/W R/W R/W R/W R/W R/W R/W
Reset 0 0 0 0 0 0 0 0 0 0 0 0 0 0 0 0
15 14 13 12 11 10 9 8 7 6 5 4 3 2 1 0
WDTLock
Type R/W R/W R/W R/W R/W R/W R/W R/W R/W R/W R/W R/W R/W R/W R/W R/W
Reset 0 0 0 0 0 0 0 0 0 0 0 0 0 0 0 0
Bit/Field Name Type Reset Description
Watchdog Lock
A write of the value 0x1ACC.E551 unlocks the watchdog registers for
write access. A write of any other value reapplies the lock, preventing
any register updates.
A read of this register returns the following values:
Value Description
0x0000.0001 Locked
0x0000.0000 Unlocked
31:0 WDTLock R/W 0x0000
January 08, 2011 371
Texas Instruments-Production Data
Stellaris® LM3S2965 Microcontroller
Register 9: Watchdog Peripheral Identification 4 (WDTPeriphID4), offset 0xFD0
The WDTPeriphIDn registers are hard-coded and the fields within the register determine the reset
value.
Watchdog Peripheral Identification 4 (WDTPeriphID4)
Base 0x4000.0000
Offset 0xFD0
Type RO, reset 0x0000.0000
31 30 29 28 27 26 25 24 23 22 21 20 19 18 17 16
reserved
Type RO RO RO RO RO RO RO RO RO RO RO RO RO RO RO RO
Reset 0 0 0 0 0 0 0 0 0 0 0 0 0 0 0 0
15 14 13 12 11 10 9 8 7 6 5 4 3 2 1 0
reserved PID4
Type RO RO RO RO RO RO RO RO RO RO RO RO RO RO RO RO
Reset 0 0 0 0 0 0 0 0 0 0 0 0 0 0 0 0
Bit/Field Name Type Reset Description
Software should not rely on the value of a reserved bit. To provide
compatibility with future products, the value of a reserved bit should be
preserved across a read-modify-write operation.
31:8 reserved RO 0x00
7:0 PID4 RO 0x00 WDT Peripheral ID Register[7:0]
372 January 08, 2011
Texas Instruments-Production Data
Watchdog Timer
Register 10: Watchdog Peripheral Identification 5 (WDTPeriphID5), offset
0xFD4
The WDTPeriphIDn registers are hard-coded and the fields within the register determine the reset
value.
Watchdog Peripheral Identification 5 (WDTPeriphID5)
Base 0x4000.0000
Offset 0xFD4
Type RO, reset 0x0000.0000
31 30 29 28 27 26 25 24 23 22 21 20 19 18 17 16
reserved
Type RO RO RO RO RO RO RO RO RO RO RO RO RO RO RO RO
Reset 0 0 0 0 0 0 0 0 0 0 0 0 0 0 0 0
15 14 13 12 11 10 9 8 7 6 5 4 3 2 1 0
reserved PID5
Type RO RO RO RO RO RO RO RO RO RO RO RO RO RO RO RO
Reset 0 0 0 0 0 0 0 0 0 0 0 0 0 0 0 0
Bit/Field Name Type Reset Description
Software should not rely on the value of a reserved bit. To provide
compatibility with future products, the value of a reserved bit should be
preserved across a read-modify-write operation.
31:8 reserved RO 0x00
7:0 PID5 RO 0x00 WDT Peripheral ID Register[15:8]
January 08, 2011 373
Texas Instruments-Production Data
Stellaris® LM3S2965 Microcontroller
Register 11: Watchdog Peripheral Identification 6 (WDTPeriphID6), offset
0xFD8
The WDTPeriphIDn registers are hard-coded and the fields within the register determine the reset
value.
Watchdog Peripheral Identification 6 (WDTPeriphID6)
Base 0x4000.0000
Offset 0xFD8
Type RO, reset 0x0000.0000
31 30 29 28 27 26 25 24 23 22 21 20 19 18 17 16
reserved
Type RO RO RO RO RO RO RO RO RO RO RO RO RO RO RO RO
Reset 0 0 0 0 0 0 0 0 0 0 0 0 0 0 0 0
15 14 13 12 11 10 9 8 7 6 5 4 3 2 1 0
reserved PID6
Type RO RO RO RO RO RO RO RO RO RO RO RO RO RO RO RO
Reset 0 0 0 0 0 0 0 0 0 0 0 0 0 0 0 0
Bit/Field Name Type Reset Description
Software should not rely on the value of a reserved bit. To provide
compatibility with future products, the value of a reserved bit should be
preserved across a read-modify-write operation.
31:8 reserved RO 0x00
7:0 PID6 RO 0x00 WDT Peripheral ID Register[23:16]
374 January 08, 2011
Texas Instruments-Production Data
Watchdog Timer
Register 12: Watchdog Peripheral Identification 7 (WDTPeriphID7), offset
0xFDC
The WDTPeriphIDn registers are hard-coded and the fields within the register determine the reset
value.
Watchdog Peripheral Identification 7 (WDTPeriphID7)
Base 0x4000.0000
Offset 0xFDC
Type RO, reset 0x0000.0000
31 30 29 28 27 26 25 24 23 22 21 20 19 18 17 16
reserved
Type RO RO RO RO RO RO RO RO RO RO RO RO RO RO RO RO
Reset 0 0 0 0 0 0 0 0 0 0 0 0 0 0 0 0
15 14 13 12 11 10 9 8 7 6 5 4 3 2 1 0
reserved PID7
Type RO RO RO RO RO RO RO RO RO RO RO RO RO RO RO RO
Reset 0 0 0 0 0 0 0 0 0 0 0 0 0 0 0 0
Bit/Field Name Type Reset Description
Software should not rely on the value of a reserved bit. To provide
compatibility with future products, the value of a reserved bit should be
preserved across a read-modify-write operation.
31:8 reserved RO 0x00
7:0 PID7 RO 0x00 WDT Peripheral ID Register[31:24]
January 08, 2011 375
Texas Instruments-Production Data
Stellaris® LM3S2965 Microcontroller
Register 13: Watchdog Peripheral Identification 0 (WDTPeriphID0), offset
0xFE0
The WDTPeriphIDn registers are hard-coded and the fields within the register determine the reset
value.
Watchdog Peripheral Identification 0 (WDTPeriphID0)
Base 0x4000.0000
Offset 0xFE0
Type RO, reset 0x0000.0005
31 30 29 28 27 26 25 24 23 22 21 20 19 18 17 16
reserved
Type RO RO RO RO RO RO RO RO RO RO RO RO RO RO RO RO
Reset 0 0 0 0 0 0 0 0 0 0 0 0 0 0 0 0
15 14 13 12 11 10 9 8 7 6 5 4 3 2 1 0
reserved PID0
Type RO RO RO RO RO RO RO RO RO RO RO RO RO RO RO RO
Reset 0 0 0 0 0 0 0 0 0 0 0 0 0 1 0 1
Bit/Field Name Type Reset Description
Software should not rely on the value of a reserved bit. To provide
compatibility with future products, the value of a reserved bit should be
preserved across a read-modify-write operation.
31:8 reserved RO 0x00
7:0 PID0 RO 0x05 Watchdog Peripheral ID Register[7:0]
376 January 08, 2011
Texas Instruments-Production Data
Watchdog Timer
Register 14: Watchdog Peripheral Identification 1 (WDTPeriphID1), offset
0xFE4
The WDTPeriphIDn registers are hard-coded and the fields within the register determine the reset
value.
Watchdog Peripheral Identification 1 (WDTPeriphID1)
Base 0x4000.0000
Offset 0xFE4
Type RO, reset 0x0000.0018
31 30 29 28 27 26 25 24 23 22 21 20 19 18 17 16
reserved
Type RO RO RO RO RO RO RO RO RO RO RO RO RO RO RO RO
Reset 0 0 0 0 0 0 0 0 0 0 0 0 0 0 0 0
15 14 13 12 11 10 9 8 7 6 5 4 3 2 1 0
reserved PID1
Type RO RO RO RO RO RO RO RO RO RO RO RO RO RO RO RO
Reset 0 0 0 0 0 0 0 0 0 0 0 1 1 0 0 0
Bit/Field Name Type Reset Description
Software should not rely on the value of a reserved bit. To provide
compatibility with future products, the value of a reserved bit should be
preserved across a read-modify-write operation.
31:8 reserved RO 0x00
7:0 PID1 RO 0x18 Watchdog Peripheral ID Register[15:8]
January 08, 2011 377
Texas Instruments-Production Data
Stellaris® LM3S2965 Microcontroller
Register 15: Watchdog Peripheral Identification 2 (WDTPeriphID2), offset
0xFE8
The WDTPeriphIDn registers are hard-coded and the fields within the register determine the reset
value.
Watchdog Peripheral Identification 2 (WDTPeriphID2)
Base 0x4000.0000
Offset 0xFE8
Type RO, reset 0x0000.0018
31 30 29 28 27 26 25 24 23 22 21 20 19 18 17 16
reserved
Type RO RO RO RO RO RO RO RO RO RO RO RO RO RO RO RO
Reset 0 0 0 0 0 0 0 0 0 0 0 0 0 0 0 0
15 14 13 12 11 10 9 8 7 6 5 4 3 2 1 0
reserved PID2
Type RO RO RO RO RO RO RO RO RO RO RO RO RO RO RO RO
Reset 0 0 0 0 0 0 0 0 0 0 0 1 1 0 0 0
Bit/Field Name Type Reset Description
Software should not rely on the value of a reserved bit. To provide
compatibility with future products, the value of a reserved bit should be
preserved across a read-modify-write operation.
31:8 reserved RO 0x00
7:0 PID2 RO 0x18 Watchdog Peripheral ID Register[23:16]
378 January 08, 2011
Texas Instruments-Production Data
Watchdog Timer
Register 16: Watchdog Peripheral Identification 3 (WDTPeriphID3), offset
0xFEC
The WDTPeriphIDn registers are hard-coded and the fields within the register determine the reset
value.
Watchdog Peripheral Identification 3 (WDTPeriphID3)
Base 0x4000.0000
Offset 0xFEC
Type RO, reset 0x0000.0001
31 30 29 28 27 26 25 24 23 22 21 20 19 18 17 16
reserved
Type RO RO RO RO RO RO RO RO RO RO RO RO RO RO RO RO
Reset 0 0 0 0 0 0 0 0 0 0 0 0 0 0 0 0
15 14 13 12 11 10 9 8 7 6 5 4 3 2 1 0
reserved PID3
Type RO RO RO RO RO RO RO RO RO RO RO RO RO RO RO RO
Reset 0 0 0 0 0 0 0 0 0 0 0 0 0 0 0 1
Bit/Field Name Type Reset Description
Software should not rely on the value of a reserved bit. To provide
compatibility with future products, the value of a reserved bit should be
preserved across a read-modify-write operation.
31:8 reserved RO 0x00
7:0 PID3 RO 0x01 Watchdog Peripheral ID Register[31:24]
January 08, 2011 379
Texas Instruments-Production Data
Stellaris® LM3S2965 Microcontroller
Register 17: Watchdog PrimeCell Identification 0 (WDTPCellID0), offset 0xFF0
The WDTPCellIDn registers are hard-coded and the fields within the register determine the reset
value.
Watchdog PrimeCell Identification 0 (WDTPCellID0)
Base 0x4000.0000
Offset 0xFF0
Type RO, reset 0x0000.000D
31 30 29 28 27 26 25 24 23 22 21 20 19 18 17 16
reserved
Type RO RO RO RO RO RO RO RO RO RO RO RO RO RO RO RO
Reset 0 0 0 0 0 0 0 0 0 0 0 0 0 0 0 0
15 14 13 12 11 10 9 8 7 6 5 4 3 2 1 0
reserved CID0
Type RO RO RO RO RO RO RO RO RO RO RO RO RO RO RO RO
Reset 0 0 0 0 0 0 0 0 0 0 0 0 1 1 0 1
Bit/Field Name Type Reset Description
Software should not rely on the value of a reserved bit. To provide
compatibility with future products, the value of a reserved bit should be
preserved across a read-modify-write operation.
31:8 reserved RO 0x00
7:0 CID0 RO 0x0D Watchdog PrimeCell ID Register[7:0]
380 January 08, 2011
Texas Instruments-Production Data
Watchdog Timer
Register 18: Watchdog PrimeCell Identification 1 (WDTPCellID1), offset 0xFF4
The WDTPCellIDn registers are hard-coded and the fields within the register determine the reset
value.
Watchdog PrimeCell Identification 1 (WDTPCellID1)
Base 0x4000.0000
Offset 0xFF4
Type RO, reset 0x0000.00F0
31 30 29 28 27 26 25 24 23 22 21 20 19 18 17 16
reserved
Type RO RO RO RO RO RO RO RO RO RO RO RO RO RO RO RO
Reset 0 0 0 0 0 0 0 0 0 0 0 0 0 0 0 0
15 14 13 12 11 10 9 8 7 6 5 4 3 2 1 0
reserved CID1
Type RO RO RO RO RO RO RO RO RO RO RO RO RO RO RO RO
Reset 0 0 0 0 0 0 0 0 1 1 1 1 0 0 0 0
Bit/Field Name Type Reset Description
Software should not rely on the value of a reserved bit. To provide
compatibility with future products, the value of a reserved bit should be
preserved across a read-modify-write operation.
31:8 reserved RO 0x00
7:0 CID1 RO 0xF0 Watchdog PrimeCell ID Register[15:8]
January 08, 2011 381
Texas Instruments-Production Data
Stellaris® LM3S2965 Microcontroller
Register 19: Watchdog PrimeCell Identification 2 (WDTPCellID2), offset 0xFF8
The WDTPCellIDn registers are hard-coded and the fields within the register determine the reset
value.
Watchdog PrimeCell Identification 2 (WDTPCellID2)
Base 0x4000.0000
Offset 0xFF8
Type RO, reset 0x0000.0005
31 30 29 28 27 26 25 24 23 22 21 20 19 18 17 16
reserved
Type RO RO RO RO RO RO RO RO RO RO RO RO RO RO RO RO
Reset 0 0 0 0 0 0 0 0 0 0 0 0 0 0 0 0
15 14 13 12 11 10 9 8 7 6 5 4 3 2 1 0
reserved CID2
Type RO RO RO RO RO RO RO RO RO RO RO RO RO RO RO RO
Reset 0 0 0 0 0 0 0 0 0 0 0 0 0 1 0 1
Bit/Field Name Type Reset Description
Software should not rely on the value of a reserved bit. To provide
compatibility with future products, the value of a reserved bit should be
preserved across a read-modify-write operation.
31:8 reserved RO 0x00
7:0 CID2 RO 0x05 Watchdog PrimeCell ID Register[23:16]
382 January 08, 2011
Texas Instruments-Production Data
Watchdog Timer
Register 20: Watchdog PrimeCell Identification 3 (WDTPCellID3 ), offset 0xFFC
The WDTPCellIDn registers are hard-coded and the fields within the register determine the reset
value.
Watchdog PrimeCell Identification 3 (WDTPCellID3)
Base 0x4000.0000
Offset 0xFFC
Type RO, reset 0x0000.00B1
31 30 29 28 27 26 25 24 23 22 21 20 19 18 17 16
reserved
Type RO RO RO RO RO RO RO RO RO RO RO RO RO RO RO RO
Reset 0 0 0 0 0 0 0 0 0 0 0 0 0 0 0 0
15 14 13 12 11 10 9 8 7 6 5 4 3 2 1 0
reserved CID3
Type RO RO RO RO RO RO RO RO RO RO RO RO RO RO RO RO
Reset 0 0 0 0 0 0 0 0 1 0 1 1 0 0 0 1
Bit/Field Name Type Reset Description
Software should not rely on the value of a reserved bit. To provide
compatibility with future products, the value of a reserved bit should be
preserved across a read-modify-write operation.
31:8 reserved RO 0x00
7:0 CID3 RO 0xB1 Watchdog PrimeCell ID Register[31:24]
January 08, 2011 383
Texas Instruments-Production Data
Stellaris® LM3S2965 Microcontroller
11 Analog-to-Digital Converter (ADC)
An analog-to-digital converter (ADC) is a peripheral that converts a continuous analog voltage to a
discrete digital number.
The Stellaris® ADC module features 10-bit conversion resolution and supports four input channels,
plus an internal temperature sensor. The ADC module contains four programmable sequencer which
allows for the sampling of multiple analog input sources without controller intervention. Each sample
sequence provides flexible programming with fully configurable input source, trigger events, interrupt
generation, and sequence priority.
The Stellaris ADC module provides the following features:
■ Four analog input channels
■ Single-ended and differential-input configurations
■ On-chip internal temperature sensor
■ Sample rate of one million samples/second
■ Flexible, configurable analog-to-digital conversion
■ Four programmable sample conversion sequences from one to eight entries long, with
corresponding conversion result FIFOs
■ Flexible trigger control
– Controller (software)
– Timers
– Analog Comparators
– PWM
– GPIO
■ Hardware averaging of up to 64 samples for improved accuracy
■ Converter uses an internal 3-V reference
■ Power and ground for the analog circuitry is separate from the digital power and ground
11.1 Block Diagram
Figure 11-1 on page 385 provides details on the internal configuration of the ADC controls and data
registers.
384 January 08, 2011
Texas Instruments-Production Data
Analog-to-Digital Converter (ADC)
Figure 11-1. ADC Module Block Diagram
Analog-to-Digital
Converter
ADCSSFSTAT0
ADCSSCTL0
ADCSSMUX0
Sample
Sequencer 0
ADCSSFSTAT1
ADCSSCTL1
ADCSSMUX1
Sample
Sequencer 1
ADCSSFSTAT2
ADCSSCTL2
ADCSSMUX2
Sample
Sequencer 2
ADCSSFSTAT3
ADCSSCTL3
ADCSSMUX3
Sample
Sequencer 3
ADCUSTAT
ADCOSTAT
ADCACTSS
Control/Status
ADCSSPRI
ADCISC
ADCRIS
ADCIM
Interrupt Control
Analog Inputs
SS0 Interrupt
SS1 Interrupt
SS2 Interrupt
SS3 Interrupt
ADCEMUX
ADCPSSI
Trigger Events
SS0
SS1
SS2
SS3
Comparator
GPIO (PB4)
Timer
PWM
Comparator
GPIO (PB4)
Timer
PWM
Comparator
GPIO (PB4)
Timer
PWM
Comparator
GPIO (PB4)
Timer
PWM
ADCSSFIFO0
ADCSSFIFO1
ADCSSFIFO2
ADCSSFIFO3
FIFO Block
Hardware Averager
ADCSAC
11.2 Functional Description
The Stellaris ADC collects sample data by using a programmable sequence-based approach instead
of the traditional single or double-sampling approaches found on many ADC modules. Each sample
sequence is a fully programmed series of consecutive (back-to-back) samples, allowing the ADC
to collect data from multiple input sources without having to be re-configured or serviced by the
controller. The programming of each sample in the sample sequence includes parameters such as
the input source and mode (differential versus single-ended input), interrupt generation on sample
completion, and the indicator for the last sample in the sequence.
11.2.1 Sample Sequencers
The sampling control and data capture is handled by the sample sequencers. All of the sequencers
are identical in implementation except for the number of samples that can be captured and the depth
of the FIFO. Table 11-1 on page 385 shows the maximum number of samples that each sequencer
can capture and its corresponding FIFO depth. In this implementation, each FIFO entry is a 32-bit
word, with the lower 10 bits containing the conversion result.
Table 11-1. Samples and FIFO Depth of Sequencers
Sequencer Number of Samples Depth of FIFO
SS3 1 1
SS2 4 4
SS1 4 4
SS0 8 8
For a given sample sequence, each sample is defined by two 4-bit nibbles in the ADC Sample
Sequence Input Multiplexer Select (ADCSSMUXn) and ADC Sample Sequence Control
(ADCSSCTLn) registers, where "n" corresponds to the sequence number. The ADCSSMUXn
January 08, 2011 385
Texas Instruments-Production Data
Stellaris® LM3S2965 Microcontroller
nibbles select the input pin, while the ADCSSCTLn nibbles contain the sample control bits
corresponding to parameters such as temperature sensor selection, interrupt enable, end of
sequence, and differential input mode. Sample sequencers are enabled by setting the respective
ASENn bit in the ADC Active Sample Sequencer (ADCACTSS) register, and should be configured
before being enabled.
When configuring a sample sequence, multiple uses of the same input pin within the same sequence
is allowed. In the ADCSSCTLn register, the IEn bits can be set for any combination of samples,
allowing interrupts to be generated after every sample in the sequence if necessary. Also, the END
bit can be set at any point within a sample sequence. For example, if Sequencer 0 is used, the END
bit can be set in the nibble associated with the fifth sample, allowing Sequencer 0 to complete
execution of the sample sequence after the fifth sample.
After a sample sequence completes execution, the result data can be retrieved from the ADC
Sample Sequence Result FIFO (ADCSSFIFOn) registers. The FIFOs are simple circular buffers
that read a single address to "pop" result data. For software debug purposes, the positions of the
FIFO head and tail pointers are visible in the ADC Sample Sequence FIFO Status (ADCSSFSTATn)
registers along with FULL and EMPTY status flags. Overflow and underflow conditions are monitored
using the ADCOSTAT and ADCUSTAT registers.
11.2.2 Module Control
Outside of the sample sequencers, the remainder of the control logic is responsible for tasks such
as:
■ Interrupt generation
■ Sequence prioritization
■ Trigger configuration
Most of the ADC control logic runs at the ADC clock rate of 14-18 MHz. The internal ADC divider
is configured automatically by hardware when the system XTAL is selected. The automatic clock
divider configuration targets 16.667 MHz operation for all Stellaris devices.
11.2.2.1 Interrupts
The register configurations of the sample sequencers dictate which events generate raw interrupts,
but do not have control over whether the interrupt is actually sent to the interrupt controller. The
ADC module's interrupt signals are controlled by the state of the MASK bits in the ADC Interrupt
Mask (ADCIM) register. Interrupt status can be viewed at two locations: the ADC Raw Interrupt
Status (ADCRIS) register, which shows the raw status of the various interrupt signals, and the ADC
Interrupt Status and Clear (ADCISC) register, which shows active interrupts that are enabled by
the ADCIM register. Sequencer interrupts are cleared by writing a 1 to the corresponding IN bit in
ADCISC.
11.2.2.2 Prioritization
When sampling events (triggers) happen concurrently, they are prioritized for processing by the
values in the ADC Sample Sequencer Priority (ADCSSPRI) register. Valid priority values are in
the range of 0-3, with 0 being the highest priority and 3 being the lowest. Multiple active sample
sequencer units with the same priority do not provide consistent results, so software must ensure
that all active sample sequencer units have a unique priority value.
386 January 08, 2011
Texas Instruments-Production Data
Analog-to-Digital Converter (ADC)
11.2.2.3 Sampling Events
Sample triggering for each sample sequencer is defined in the ADC Event Multiplexer Select
(ADCEMUX) register. The external peripheral triggering sources vary by Stellaris family member,
but all devices share the "Controller" and "Always" triggers. Software can initiate sampling by setting
the SSx bits in the ADC Processor Sample Sequence Initiate (ADCPSSI) register.
Care must be taken when using the "Always" trigger. If a sequence's priority is too high, it is possible
to starve other lower priority sequences.
11.2.3 Hardware Sample Averaging Circuit
Higher precision results can be generated using the hardware averaging circuit, however, the
improved results are at the cost of throughput. Up to 64 samples can be accumulated and averaged
to form a single data entry in the sequencer FIFO. Throughput is decreased proportionally to the
number of samples in the averaging calculation. For example, if the averaging circuit is configured
to average 16 samples, the throughput is decreased by a factor of 16.
By default the averaging circuit is off and all data from the converter passes through to the sequencer
FIFO. The averaging hardware is controlled by the ADC Sample Averaging Control (ADCSAC)
register (see page 406). There is a single averaging circuit and all input channels receive the same
amount of averaging whether they are single-ended or differential.
11.2.4 Analog-to-Digital Converter
The converter itself generates a 10-bit output value for selected analog input. Special analog pads
are used to minimize the distortion on the input. An internal 3 V reference is used by the converter
resulting in sample values ranging from 0x000 at 0 V input to 0x3FF at 3 V input when in single-ended
input mode.
11.2.5 Differential Sampling
In addition to traditional single-ended sampling, the ADC module supports differential sampling of
two analog input channels. To enable differential sampling, software must set the Dn bit in the
ADCSSCTL0n register in a step's configuration nibble.
When a sequence step is configured for differential sampling, its corresponding value in the
ADCSSMUXn register must be set to one of the four differential pairs, numbered 0-3. Differential
pair 0 samples analog inputs 0 and 1; differential pair 1 samples analog inputs 2 and 3; and so on
(see Table 11-2 on page 387). The ADC does not support other differential pairings such as analog
input 0 with analog input 3. The number of differential pairs supported is dependent on the number
of analog inputs (see Table 11-2 on page 387).
Table 11-2. Differential Sampling Pairs
Differential Pair Analog Inputs
0 0 and 1
1 2 and 3
The voltage sampled in differential mode is the difference between the odd and even channels:
ΔV (differential voltage) = VIN_EVEN (even channels) – VIN_ODD (odd channels), therefore:
■ If ΔV = 0, then the conversion result = 0x1FF
■ If ΔV > 0, then the conversion result > 0x1FF (range is 0x1FF–0x3FF)
January 08, 2011 387
Texas Instruments-Production Data
Stellaris® LM3S2965 Microcontroller
■ If ΔV < 0, then the conversion result < 0x1FF (range is 0–0x1FF)
The differential pairs assign polarities to the analog inputs: the even-numbered input is always
positive, and the odd-numbered input is always negative. In order for a valid conversion result to
appear, the negative input must be in the range of ± 1.5 V of the positive input. If an analog input
is greater than 3 V or less than 0 V (the valid range for analog inputs), the input voltage is clipped,
meaning it appears as either 3 V or 0 V, respectively, to the ADC.
Figure 11-2 on page 388 shows an example of the negative input centered at 1.5 V. In this
configuration, the differential range spans from -1.5 V to 1.5 V. Figure 11-3 on page 389 shows an
example where the negative input is centered at -0.75 V, meaning inputs on the positive input
saturate past a differential voltage of -0.75 V since the input voltage is less than 0 V. Figure
11-4 on page 389 shows an example of the negative input centered at 2.25 V, where inputs on the
positive channel saturate past a differential voltage of 0.75 V since the input voltage would be greater
than 3 V.
Figure 11-2. Differential Sampling Range, VIN_ODD = 1.5 V
0 V 1.5 V 3.0 V
-1.5 V 0 V 1.5 V
VIN_EVEN
DV
VIN_ODD = 1.5 V
0x3FF
0x1FF
ADC Conversion Result
- Input Saturation
388 January 08, 2011
Texas Instruments-Production Data
Analog-to-Digital Converter (ADC)
Figure 11-3. Differential Sampling Range, VIN_ODD = 0.75 V
ADC Conversion Result
0x3FF
0x1FF
0x0FF
0 V +0.75 V +2.25 V VIN_EVEN
-1.5 V -0.75 V +1.5 V DV
- Input Saturation
Figure 11-4. Differential Sampling Range, VIN_ODD = 2.25 V
ADC Conversion Result
0x3FF
0x2FF
0x1FF
0.75 V 2.25 V 3.0 V VIN_EVEN
-1.5 V 0.75 V 1.5 V DV
- Input Saturation
11.2.6 Test Modes
There is a user-available test mode that allows for loopback operation within the digital portion of
the ADC module. This can be useful for debugging software without having to provide actual analog
stimulus. This mode is available through the ADC Test Mode Loopback (ADCTMLB) register (see
page 419).
January 08, 2011 389
Texas Instruments-Production Data
Stellaris® LM3S2965 Microcontroller
11.2.7 Internal Temperature Sensor
The temperature sensor serves two primary purposes: 1) to notify the system that internal temperature
is too high or low for reliable operation, and 2) to provide temperature measurements for calibration
of the Hibernate module RTC trim value.
The temperature sensor does not have a separate enable, since it also contains the bandgap
reference and must always be enabled. The reference is supplied to other analog modules; not just
the ADC.
The internal temperature sensor provides an analog temperature reading as well as a reference
voltage. The voltage at the output terminal SENSO is given by the following equation:
SENSO = 2.7 - ((T + 55) / 75)
This relation is shown in Figure 11-5 on page 390.
Figure 11-5. Internal Temperature Sensor Characteristic
11.3 Initialization and Configuration
In order for the ADC module to be used, the PLL must be enabled and using a supported crystal
frequency (see the RCC register). Using unsupported frequencies can cause faulty operation in the
ADC module.
11.3.1 Module Initialization
Initialization of the ADC module is a simple process with very few steps. The main steps include
enabling the clock to the ADC and reconfiguring the sample sequencer priorities (if needed).
The initialization sequence for the ADC is as follows:
1. Enable the ADC clock by writing a value of 0x0001.0000 to the RCGC0 register (see page 210).
2. If required by the application, reconfigure the sample sequencer priorities in the ADCSSPRI
register. The default configuration has Sample Sequencer 0 with the highest priority, and Sample
Sequencer 3 as the lowest priority.
390 January 08, 2011
Texas Instruments-Production Data
Analog-to-Digital Converter (ADC)
11.3.2 Sample Sequencer Configuration
Configuration of the sample sequencers is slightly more complex than the module initialization since
each sample sequence is completely programmable.
The configuration for each sample sequencer should be as follows:
1. Ensure that the sample sequencer is disabled by writing a 0 to the corresponding ASENn bit in
the ADCACTSS register. Programming of the sample sequencers is allowed without having
them enabled. Disabling the sequencer during programming prevents erroneous execution if a
trigger event were to occur during the configuration process.
2. Configure the trigger event for the sample sequencer in the ADCEMUX register.
3. For each sample in the sample sequence, configure the corresponding input source in the
ADCSSMUXn register.
4. For each sample in the sample sequence, configure the sample control bits in the corresponding
nibble in the ADCSSCTLn register. When programming the last nibble, ensure that the END bit
is set. Failure to set the END bit causes unpredictable behavior.
5. If interrupts are to be used, write a 1 to the corresponding MASK bit in the ADCIM register.
6. Enable the sample sequencer logic by writing a 1 to the corresponding ASENn bit in the
ADCACTSS register.
11.4 Register Map
Table 11-3 on page 391 lists the ADC registers. The offset listed is a hexadecimal increment to the
register’s address, relative to the ADC base address of 0x4003.8000.
Note that the ADC module clock must be enabled before the registers can be programmed (see
page 210). There must be a delay of 3 system clocks after the ADC module clock is enabled before
any ADC module registers are accessed.
Table 11-3. ADC Register Map
See
Offset Name Type Reset Description page
0x000 ADCACTSS R/W 0x0000.0000 ADC Active Sample Sequencer 393
0x004 ADCRIS RO 0x0000.0000 ADC Raw Interrupt Status 394
0x008 ADCIM R/W 0x0000.0000 ADC Interrupt Mask 395
0x00C ADCISC R/W1C 0x0000.0000 ADC Interrupt Status and Clear 396
0x010 ADCOSTAT R/W1C 0x0000.0000 ADC Overflow Status 397
0x014 ADCEMUX R/W 0x0000.0000 ADC Event Multiplexer Select 398
0x018 ADCUSTAT R/W1C 0x0000.0000 ADC Underflow Status 402
0x020 ADCSSPRI R/W 0x0000.3210 ADC Sample Sequencer Priority 403
0x028 ADCPSSI WO - ADC Processor Sample Sequence Initiate 405
0x030 ADCSAC R/W 0x0000.0000 ADC Sample Averaging Control 406
January 08, 2011 391
Texas Instruments-Production Data
Stellaris® LM3S2965 Microcontroller
Table 11-3. ADC Register Map (continued)
See
Offset Name Type Reset Description page
0x040 ADCSSMUX0 R/W 0x0000.0000 ADC Sample Sequence Input Multiplexer Select 0 407
0x044 ADCSSCTL0 R/W 0x0000.0000 ADC Sample Sequence Control 0 409
0x048 ADCSSFIFO0 RO - ADC Sample Sequence Result FIFO 0 412
0x04C ADCSSFSTAT0 RO 0x0000.0100 ADC Sample Sequence FIFO 0 Status 413
0x060 ADCSSMUX1 R/W 0x0000.0000 ADC Sample Sequence Input Multiplexer Select 1 414
0x064 ADCSSCTL1 R/W 0x0000.0000 ADC Sample Sequence Control 1 415
0x068 ADCSSFIFO1 RO - ADC Sample Sequence Result FIFO 1 412
0x06C ADCSSFSTAT1 RO 0x0000.0100 ADC Sample Sequence FIFO 1 Status 413
0x080 ADCSSMUX2 R/W 0x0000.0000 ADC Sample Sequence Input Multiplexer Select 2 414
0x084 ADCSSCTL2 R/W 0x0000.0000 ADC Sample Sequence Control 2 415
0x088 ADCSSFIFO2 RO - ADC Sample Sequence Result FIFO 2 412
0x08C ADCSSFSTAT2 RO 0x0000.0100 ADC Sample Sequence FIFO 2 Status 413
0x0A0 ADCSSMUX3 R/W 0x0000.0000 ADC Sample Sequence Input Multiplexer Select 3 417
0x0A4 ADCSSCTL3 R/W 0x0000.0002 ADC Sample Sequence Control 3 418
0x0A8 ADCSSFIFO3 RO - ADC Sample Sequence Result FIFO 3 412
0x0AC ADCSSFSTAT3 RO 0x0000.0100 ADC Sample Sequence FIFO 3 Status 413
0x100 ADCTMLB R/W 0x0000.0000 ADC Test Mode Loopback 419
11.5 Register Descriptions
The remainder of this section lists and describes the ADC registers, in numerical order by address
offset.
392 January 08, 2011
Texas Instruments-Production Data
Analog-to-Digital Converter (ADC)
Register 1: ADC Active Sample Sequencer (ADCACTSS), offset 0x000
This register controls the activation of the sample sequencers. Each sample sequencer can be
enabled or disabled independently.
ADC Active Sample Sequencer (ADCACTSS)
Base 0x4003.8000
Offset 0x000
Type R/W, reset 0x0000.0000
31 30 29 28 27 26 25 24 23 22 21 20 19 18 17 16
reserved
Type RO RO RO RO RO RO RO RO RO RO RO RO RO RO RO RO
Reset 0 0 0 0 0 0 0 0 0 0 0 0 0 0 0 0
15 14 13 12 11 10 9 8 7 6 5 4 3 2 1 0
reserved ASEN3 ASEN2 ASEN1 ASEN0
Type RO RO RO RO RO RO RO RO RO RO RO RO R/W R/W R/W R/W
Reset 0 0 0 0 0 0 0 0 0 0 0 0 0 0 0 0
Bit/Field Name Type Reset Description
Software should not rely on the value of a reserved bit. To provide
compatibility with future products, the value of a reserved bit should be
preserved across a read-modify-write operation.
31:4 reserved RO 0x0000.000
ADC SS3 Enable
Specifies whether Sample Sequencer 3 is enabled. If set, the sample
sequence logic for Sequencer 3 is active. Otherwise, the sequencer is
inactive.
3 ASEN3 R/W 0
ADC SS2 Enable
Specifies whether Sample Sequencer 2 is enabled. If set, the sample
sequence logic for Sequencer 2 is active. Otherwise, the sequencer is
inactive.
2 ASEN2 R/W 0
ADC SS1 Enable
Specifies whether Sample Sequencer 1 is enabled. If set, the sample
sequence logic for Sequencer 1 is active. Otherwise, the sequencer is
inactive.
1 ASEN1 R/W 0
ADC SS0 Enable
Specifies whether Sample Sequencer 0 is enabled. If set, the sample
sequence logic for Sequencer 0 is active. Otherwise, the sequencer is
inactive.
0 ASEN0 R/W 0
January 08, 2011 393
Texas Instruments-Production Data
Stellaris® LM3S2965 Microcontroller
Register 2: ADC Raw Interrupt Status (ADCRIS), offset 0x004
This register shows the status of the raw interrupt signal of each sample sequencer. These bits may
be polled by software to look for interrupt conditions without having to generate controller interrupts.
ADC Raw Interrupt Status (ADCRIS)
Base 0x4003.8000
Offset 0x004
Type RO, reset 0x0000.0000
31 30 29 28 27 26 25 24 23 22 21 20 19 18 17 16
reserved
Type RO RO RO RO RO RO RO RO RO RO RO RO RO RO RO RO
Reset 0 0 0 0 0 0 0 0 0 0 0 0 0 0 0 0
15 14 13 12 11 10 9 8 7 6 5 4 3 2 1 0
reserved INR3 INR2 INR1 INR0
Type RO RO RO RO RO RO RO RO RO RO RO RO RO RO RO RO
Reset 0 0 0 0 0 0 0 0 0 0 0 0 0 0 0 0
Bit/Field Name Type Reset Description
Software should not rely on the value of a reserved bit. To provide
compatibility with future products, the value of a reserved bit should be
preserved across a read-modify-write operation.
31:4 reserved RO 0x000
SS3 Raw Interrupt Status
This bit is set by hardware when a sample with its respective
ADCSSCTL3 IE bit has completed conversion. This bit is cleared by
setting the IN3 bit in the ADCISC register.
3 INR3 RO 0
SS2 Raw Interrupt Status
This bit is set by hardware when a sample with its respective
ADCSSCTL2 IE bit has completed conversion. This bit is cleared by
setting the IN2 bit in the ADCISC register.
2 INR2 RO 0
SS1 Raw Interrupt Status
This bit is set by hardware when a sample with its respective
ADCSSCTL1 IE bit has completed conversion. This bit is cleared by
setting the IN1 bit in the ADCISC register.
1 INR1 RO 0
SS0 Raw Interrupt Status
This bit is set by hardware when a sample with its respective
ADCSSCTL0 IE bit has completed conversion. This bit is cleared by
setting the IN30 bit in the ADCISC register.
0 INR0 RO 0
394 January 08, 2011
Texas Instruments-Production Data
Analog-to-Digital Converter (ADC)
Register 3: ADC Interrupt Mask (ADCIM), offset 0x008
This register controls whether the sample sequencer raw interrupt signals are promoted to controller
interrupts. Each raw interrupt signal can be masked independently.
ADC Interrupt Mask (ADCIM)
Base 0x4003.8000
Offset 0x008
Type R/W, reset 0x0000.0000
31 30 29 28 27 26 25 24 23 22 21 20 19 18 17 16
reserved
Type RO RO RO RO RO RO RO RO RO RO RO RO RO RO RO RO
Reset 0 0 0 0 0 0 0 0 0 0 0 0 0 0 0 0
15 14 13 12 11 10 9 8 7 6 5 4 3 2 1 0
reserved MASK3 MASK2 MASK1 MASK0
Type RO RO RO RO RO RO RO RO RO RO RO RO R/W R/W R/W R/W
Reset 0 0 0 0 0 0 0 0 0 0 0 0 0 0 0 0
Bit/Field Name Type Reset Description
Software should not rely on the value of a reserved bit. To provide
compatibility with future products, the value of a reserved bit should be
preserved across a read-modify-write operation.
31:4 reserved RO 0x000
SS3 Interrupt Mask
When set, this bit allows the raw interrupt signal from Sample Sequencer
3 (ADCRIS register INR3 bit) to be promoted to a controller interrupt.
When clear, the status of Sample Sequencer 3 does not affect the SS3
interrupt status.
3 MASK3 R/W 0
SS2 Interrupt Mask
When set, this bit allows the raw interrupt signal from Sample Sequencer
2 (ADCRIS register INR2 bit) to be promoted to a controller interrupt.
When clear, the status of Sample Sequencer 2 does not affect the SS2
interrupt status.
2 MASK2 R/W 0
SS1 Interrupt Mask
When set, this bit allows the raw interrupt signal from Sample Sequencer
1 (ADCRIS register INR1 bit) to be promoted to a controller interrupt.
When clear, the status of Sample Sequencer 1 does not affect the SS1
interrupt status.
1 MASK1 R/W 0
SS0 Interrupt Mask
When set, this bit allows the raw interrupt signal from Sample Sequencer
0 (ADCRIS register INR0 bit) to be promoted to a controller interrupt.
When clear, the status of Sample Sequencer 0 does not affect the SS0
interrupt status.
0 MASK0 R/W 0
January 08, 2011 395
Texas Instruments-Production Data
Stellaris® LM3S2965 Microcontroller
Register 4: ADC Interrupt Status and Clear (ADCISC), offset 0x00C
This register provides the mechanism for clearing sample sequence interrupt conditions and shows
the status of controller interrupts generated by the sample sequencers. When read, each bit field
is the logical AND of the respective INR and MASK bits. Sample sequence nterrupts are cleared by
setting the corresponding bit position. If software is polling the ADCRIS instead of generating
interrupts, the sample sequence INR bits are still cleared via the ADCISC register, even if the IN
bit is not set.
ADC Interrupt Status and Clear (ADCISC)
Base 0x4003.8000
Offset 0x00C
Type R/W1C, reset 0x0000.0000
31 30 29 28 27 26 25 24 23 22 21 20 19 18 17 16
reserved
Type RO RO RO RO RO RO RO RO RO RO RO RO RO RO RO RO
Reset 0 0 0 0 0 0 0 0 0 0 0 0 0 0 0 0
15 14 13 12 11 10 9 8 7 6 5 4 3 2 1 0
reserved IN3 IN2 IN1 IN0
Type RO RO RO RO RO RO RO RO RO RO RO RO R/W1C R/W1C R/W1C R/W1C
Reset 0 0 0 0 0 0 0 0 0 0 0 0 0 0 0 0
Bit/Field Name Type Reset Description
Software should not rely on the value of a reserved bit. To provide
compatibility with future products, the value of a reserved bit should be
preserved across a read-modify-write operation.
31:4 reserved RO 0x000
SS3 Interrupt Status and Clear
This bit is set when both the INR3 bit in the ADCRIS register and the
MASK3 bit in the ADCIM register are set, providing a level-based interrupt
to the controller.
This bit is cleared by writing a 1. Clearing this bit also clears the INR3
bit.
3 IN3 R/W1C 0
SS2 Interrupt Status and Clear
This bit is set when both the INR2 bit in the ADCRIS register and the
MASK2 bit in the ADCIM register are set, providing a level-based interrupt
to the controller.
This bit is cleared by writing a 1. Clearing this bit also clears the INR2
bit.
2 IN2 R/W1C 0
SS1 Interrupt Status and Clear
This bit is set when both the INR1 bit in the ADCRIS register and the
MASK1 bit in the ADCIM register are set, providing a level-based interrupt
to the controller.
This bit is cleared by writing a 1. Clearing this bit also clears the INR1
bit.
1 IN1 R/W1C 0
SS0 Interrupt Status and Clear
This bit is set when both the INR0 bit in the ADCRIS register and the
MASK0 bit in the ADCIM register are set, providing a level-based interrupt
to the controller.
This bit is cleared by writing a 1. Clearing this bit also clears the INR0
bit.
0 IN0 R/W1C 0
396 January 08, 2011
Texas Instruments-Production Data
Analog-to-Digital Converter (ADC)
Register 5: ADC Overflow Status (ADCOSTAT), offset 0x010
This register indicates overflow conditions in the sample sequencer FIFOs. Once the overflow
condition has been handled by software, the condition can be cleared by writing a 1 to the
corresponding bit position.
ADC Overflow Status (ADCOSTAT)
Base 0x4003.8000
Offset 0x010
Type R/W1C, reset 0x0000.0000
31 30 29 28 27 26 25 24 23 22 21 20 19 18 17 16
reserved
Type RO RO RO RO RO RO RO RO RO RO RO RO RO RO RO RO
Reset 0 0 0 0 0 0 0 0 0 0 0 0 0 0 0 0
15 14 13 12 11 10 9 8 7 6 5 4 3 2 1 0
reserved OV3 OV2 OV1 OV0
Type RO RO RO RO RO RO RO RO RO RO RO RO R/W1C R/W1C R/W1C R/W1C
Reset 0 0 0 0 0 0 0 0 0 0 0 0 0 0 0 0
Bit/Field Name Type Reset Description
Software should not rely on the value of a reserved bit. To provide
compatibility with future products, the value of a reserved bit should be
preserved across a read-modify-write operation.
31:4 reserved RO 0x0000.000
SS3 FIFO Overflow
When set, this bit specifies that the FIFO for Sample Sequencer 3 has
hit an overflow condition where the FIFO is full and a write was
requested. When an overflow is detected, the most recent write is
dropped.
This bit is cleared by writing a 1.
3 OV3 R/W1C 0
SS2 FIFO Overflow
When set, this bit specifies that the FIFO for Sample Sequencer 2 has
hit an overflow condition where the FIFO is full and a write was
requested. When an overflow is detected, the most recent write is
dropped.
This bit is cleared by writing a 1.
2 OV2 R/W1C 0
SS1 FIFO Overflow
When set, this bit specifies that the FIFO for Sample Sequencer 1 has
hit an overflow condition where the FIFO is full and a write was
requested. When an overflow is detected, the most recent write is
dropped.
This bit is cleared by writing a 1.
1 OV1 R/W1C 0
SS0 FIFO Overflow
When set, this bit specifies that the FIFO for Sample Sequencer 0 has
hit an overflow condition where the FIFO is full and a write was
requested. When an overflow is detected, the most recent write is
dropped.
This bit is cleared by writing a 1.
0 OV0 R/W1C 0
January 08, 2011 397
Texas Instruments-Production Data
Stellaris® LM3S2965 Microcontroller
Register 6: ADC Event Multiplexer Select (ADCEMUX), offset 0x014
The ADCEMUX selects the event (trigger) that initiates sampling for each sample sequencer. Each
sample sequencer can be configured with a unique trigger source.
ADC Event Multiplexer Select (ADCEMUX)
Base 0x4003.8000
Offset 0x014
Type R/W, reset 0x0000.0000
31 30 29 28 27 26 25 24 23 22 21 20 19 18 17 16
reserved
Type RO RO RO RO RO RO RO RO RO RO RO RO RO RO RO RO
Reset 0 0 0 0 0 0 0 0 0 0 0 0 0 0 0 0
15 14 13 12 11 10 9 8 7 6 5 4 3 2 1 0
EM3 EM2 EM1 EM0
Type R/W R/W R/W R/W R/W R/W R/W R/W R/W R/W R/W R/W R/W R/W R/W R/W
Reset 0 0 0 0 0 0 0 0 0 0 0 0 0 0 0 0
Bit/Field Name Type Reset Description
Software should not rely on the value of a reserved bit. To provide
compatibility with future products, the value of a reserved bit should be
preserved across a read-modify-write operation.
31:16 reserved RO 0x0
SS3 Trigger Select
This field selects the trigger source for Sample Sequencer 3.
The valid configurations for this field are:
Value Event
0x0 Controller (default)
0x1 Analog Comparator 0
0x2 Analog Comparator 1
0x3 Analog Comparator 2
0x4 External (GPIO PB4)
Timer
In addition, the trigger must be enabled with the TnOTE bit in
the GPTMCTL register (see page 341).
0x5
PWM0
The PWM module 0 trigger can be configured with the PWM0
Interrupt and Trigger Enable (PWM0INTEN) register, see
page 611.
0x6
PWM1
The PWM module 1 trigger can be configured with the
PWM1INTEN register, see page 611.
0x7
PWM2
The PWM module 2 trigger can be configured with the
PWM2INTEN register, see page 611.
0x8
0x9-0xE reserved
0xF Always (continuously sample)
15:12 EM3 R/W 0x0
398 January 08, 2011
Texas Instruments-Production Data
Analog-to-Digital Converter (ADC)
Bit/Field Name Type Reset Description
SS2 Trigger Select
This field selects the trigger source for Sample Sequencer 2.
The valid configurations for this field are:
Value Event
0x0 Controller (default)
0x1 Analog Comparator 0
0x2 Analog Comparator 1
0x3 Analog Comparator 2
0x4 External (GPIO PB4)
Timer
In addition, the trigger must be enabled with the TnOTE bit in
the GPTMCTL register (see page 341).
0x5
PWM0
The PWM module 0 trigger can be configured with the PWM0
Interrupt and Trigger Enable (PWM0INTEN) register, see
page 611.
0x6
PWM1
The PWM module 1 trigger can be configured with the
PWM1INTEN register, see page 611.
0x7
PWM2
The PWM module 2 trigger can be configured with the
PWM2INTEN register, see page 611.
0x8
0x9-0xE reserved
0xF Always (continuously sample)
11:8 EM2 R/W 0x0
January 08, 2011 399
Texas Instruments-Production Data
Stellaris® LM3S2965 Microcontroller
Bit/Field Name Type Reset Description
SS1 Trigger Select
This field selects the trigger source for Sample Sequencer 1.
The valid configurations for this field are:
Value Event
0x0 Controller (default)
0x1 Analog Comparator 0
0x2 Analog Comparator 1
0x3 Analog Comparator 2
0x4 External (GPIO PB4)
Timer
In addition, the trigger must be enabled with the TnOTE bit in
the GPTMCTL register (see page 341).
0x5
PWM0
The PWM module 0 trigger can be configured with the PWM0
Interrupt and Trigger Enable (PWM0INTEN) register, see
page 611.
0x6
PWM1
The PWM module 1 trigger can be configured with the
PWM1INTEN register, see page 611.
0x7
PWM2
The PWM module 2 trigger can be configured with the
PWM2INTEN register, see page 611.
0x8
0x9-0xE reserved
0xF Always (continuously sample)
7:4 EM1 R/W 0x0
400 January 08, 2011
Texas Instruments-Production Data
Analog-to-Digital Converter (ADC)
Bit/Field Name Type Reset Description
SS0 Trigger Select
This field selects the trigger source for Sample Sequencer 0.
The valid configurations for this field are:
Value Event
0x0 Controller (default)
0x1 Analog Comparator 0
0x2 Analog Comparator 1
0x3 Analog Comparator 2
0x4 External (GPIO PB4)
Timer
In addition, the trigger must be enabled with the TnOTE bit in
the GPTMCTL register (see page 341).
0x5
PWM0
The PWM module 0 trigger can be configured with the PWM0
Interrupt and Trigger Enable (PWM0INTEN) register, see
page 611.
0x6
PWM1
The PWM module 1 trigger can be configured with the
PWM1INTEN register, see page 611.
0x7
PWM2
The PWM module 2 trigger can be configured with the
PWM2INTEN register, see page 611.
0x8
0x9-0xE reserved
0xF Always (continuously sample)
3:0 EM0 R/W 0x0
January 08, 2011 401
Texas Instruments-Production Data
Stellaris® LM3S2965 Microcontroller
Register 7: ADC Underflow Status (ADCUSTAT), offset 0x018
This register indicates underflow conditions in the sample sequencer FIFOs. The corresponding
underflow condition is cleared by writing a 1 to the relevant bit position.
ADC Underflow Status (ADCUSTAT)
Base 0x4003.8000
Offset 0x018
Type R/W1C, reset 0x0000.0000
31 30 29 28 27 26 25 24 23 22 21 20 19 18 17 16
reserved
Type RO RO RO RO RO RO RO RO RO RO RO RO RO RO RO RO
Reset 0 0 0 0 0 0 0 0 0 0 0 0 0 0 0 0
15 14 13 12 11 10 9 8 7 6 5 4 3 2 1 0
reserved UV3 UV2 UV1 UV0
Type RO RO RO RO RO RO RO RO RO RO RO RO R/W1C R/W1C R/W1C R/W1C
Reset 0 0 0 0 0 0 0 0 0 0 0 0 0 0 0 0
Bit/Field Name Type Reset Description
Software should not rely on the value of a reserved bit. To provide
compatibility with future products, the value of a reserved bit should be
preserved across a read-modify-write operation.
31:4 reserved RO 0x0000.000
SS3 FIFO Underflow
When set, this bit specifies that the FIFO for Sample Sequencer 3 has
hit an underflow condition where the FIFO is empty and a read was
requested. The problematic read does not move the FIFO pointers, and
0s are returned.
This bit is cleared by writing a 1.
3 UV3 R/W1C 0
SS2 FIFO Underflow
When set, this bit specifies that the FIFO for Sample Sequencer 2 has
hit an underflow condition where the FIFO is empty and a read was
requested. The problematic read does not move the FIFO pointers, and
0s are returned.
This bit is cleared by writing a 1.
2 UV2 R/W1C 0
SS1 FIFO Underflow
When set, this bit specifies that the FIFO for Sample Sequencer 1 has
hit an underflow condition where the FIFO is empty and a read was
requested. The problematic read does not move the FIFO pointers, and
0s are returned.
This bit is cleared by writing a 1.
1 UV1 R/W1C 0
SS0 FIFO Underflow
When set, this bit specifies that the FIFO for Sample Sequencer 0 has
hit an underflow condition where the FIFO is empty and a read was
requested. The problematic read does not move the FIFO pointers, and
0s are returned.
This bit is cleared by writing a 1.
0 UV0 R/W1C 0
402 January 08, 2011
Texas Instruments-Production Data
Analog-to-Digital Converter (ADC)
Register 8: ADC Sample Sequencer Priority (ADCSSPRI), offset 0x020
This register sets the priority for each of the sample sequencers. Out of reset, Sequencer 0 has the
highest priority, and Sequencer 3 has the lowest priority. When reconfiguring sequence priorities,
each sequence must have a unique priority for the ADC to operate properly.
ADC Sample Sequencer Priority (ADCSSPRI)
Base 0x4003.8000
Offset 0x020
Type R/W, reset 0x0000.3210
31 30 29 28 27 26 25 24 23 22 21 20 19 18 17 16
reserved
Type RO RO RO RO RO RO RO RO RO RO RO RO RO RO RO RO
Reset 0 0 0 0 0 0 0 0 0 0 0 0 0 0 0 0
15 14 13 12 11 10 9 8 7 6 5 4 3 2 1 0
reserved SS3 reserved SS2 reserved SS1 reserved SS0
Type RO RO R/W R/W RO RO R/W R/W RO RO R/W R/W RO RO R/W R/W
Reset 0 0 1 1 0 0 1 0 0 0 0 1 0 0 0 0
Bit/Field Name Type Reset Description
Software should not rely on the value of a reserved bit. To provide
compatibility with future products, the value of a reserved bit should be
preserved across a read-modify-write operation.
31:14 reserved RO 0x0000.0
SS3 Priority
This field contains a binary-encoded value that specifies the priority
encoding of Sample Sequencer 3. A priority encoding of 0 is highest
and 3 is lowest. The priorities assigned to the sequencers must be
uniquely mapped. The ADC may not operate properly if two or more
fields are equal.
13:12 SS3 R/W 0x3
Software should not rely on the value of a reserved bit. To provide
compatibility with future products, the value of a reserved bit should be
preserved across a read-modify-write operation.
11:10 reserved RO 0x0
SS2 Priority
This field contains a binary-encoded value that specifies the priority
encoding of Sample Sequencer 2. A priority encoding of 0 is highest
and 3 is lowest. The priorities assigned to the sequencers must be
uniquely mapped. The ADC may not operate properly if two or more
fields are equal.
9:8 SS2 R/W 0x2
Software should not rely on the value of a reserved bit. To provide
compatibility with future products, the value of a reserved bit should be
preserved across a read-modify-write operation.
7:6 reserved RO 0x0
SS1 Priority
This field contains a binary-encoded value that specifies the priority
encoding of Sample Sequencer 1. A priority encoding of 0 is highest
and 3 is lowest. The priorities assigned to the sequencers must be
uniquely mapped. The ADC may not operate properly if two or more
fields are equal.
5:4 SS1 R/W 0x1
Software should not rely on the value of a reserved bit. To provide
compatibility with future products, the value of a reserved bit should be
preserved across a read-modify-write operation.
3:2 reserved RO 0x0
January 08, 2011 403
Texas Instruments-Production Data
Stellaris® LM3S2965 Microcontroller
Bit/Field Name Type Reset Description
SS0 Priority
This field contains a binary-encoded value that specifies the priority
encoding of Sample Sequencer 0. A priority encoding of 0 is highest
and 3 is lowest. The priorities assigned to the sequencers must be
uniquely mapped. The ADC may not operate properly if two or more
fields are equal.
1:0 SS0 R/W 0x0
404 January 08, 2011
Texas Instruments-Production Data
Analog-to-Digital Converter (ADC)
Register 9: ADC Processor Sample Sequence Initiate (ADCPSSI), offset 0x028
This register provides a mechanism for application software to initiate sampling in the sample
sequencers. Sample sequences can be initiated individually or in any combination. When multiple
sequences are triggered simultaneously, the priority encodings in ADCSSPRI dictate execution
order.
ADC Processor Sample Sequence Initiate (ADCPSSI)
Base 0x4003.8000
Offset 0x028
Type WO, reset -
31 30 29 28 27 26 25 24 23 22 21 20 19 18 17 16
reserved
Type RO RO RO RO RO RO RO RO RO RO RO RO RO RO RO RO
Reset 0 0 0 0 0 0 0 0 0 0 0 0 0 0 0 0
15 14 13 12 11 10 9 8 7 6 5 4 3 2 1 0
reserved SS3 SS2 SS1 SS0
Type RO RO RO RO RO RO RO RO RO RO RO RO WO WO WO WO
Reset 0 0 0 0 0 0 0 0 0 0 0 0 - - - -
Bit/Field Name Type Reset Description
Software should not rely on the value of a reserved bit. To provide
compatibility with future products, the value of a reserved bit should be
preserved across a read-modify-write operation.
31:4 reserved RO 0
SS3 Initiate
When set, this bit triggers sampling on Sample Sequencer 3 if the
sequencer is enabled in the ADCACTSS register.
Only a write by software is valid; a read of this register returns no
meaningful data.
3 SS3 WO -
SS2 Initiate
When set, this bit triggers sampling on Sample Sequencer 2 if the
sequencer is enabled in the ADCACTSS register.
Only a write by software is valid; a read of this register returns no
meaningful data.
2 SS2 WO -
SS1 Initiate
When set, this bit triggers sampling on Sample Sequencer 1 if the
sequencer is enabled in the ADCACTSS register.
Only a write by software is valid; a read of this register returns no
meaningful data.
1 SS1 WO -
SS0 Initiate
When set, this bit triggers sampling on Sample Sequencer 0 if the
sequencer is enabled in the ADCACTSS register.
Only a write by software is valid; a read of this register returns no
meaningful data.
0 SS0 WO -
January 08, 2011 405
Texas Instruments-Production Data
Stellaris® LM3S2965 Microcontroller
Register 10: ADC Sample Averaging Control (ADCSAC), offset 0x030
This register controls the amount of hardware averaging applied to conversion results. The final
conversion result stored in the FIFO is averaged from 2 AVG consecutive ADC samples at the specified
ADC speed. If AVG is 0, the sample is passed directly through without any averaging. If AVG=6,
then 64 consecutive ADC samples are averaged to generate one result in the sequencer FIFO. An
AVG = 7 provides unpredictable results.
ADC Sample Averaging Control (ADCSAC)
Base 0x4003.8000
Offset 0x030
Type R/W, reset 0x0000.0000
31 30 29 28 27 26 25 24 23 22 21 20 19 18 17 16
reserved
Type RO RO RO RO RO RO RO RO RO RO RO RO RO RO RO RO
Reset 0 0 0 0 0 0 0 0 0 0 0 0 0 0 0 0
15 14 13 12 11 10 9 8 7 6 5 4 3 2 1 0
reserved AVG
Type RO RO RO RO RO RO RO RO RO RO RO RO RO R/W R/W R/W
Reset 0 0 0 0 0 0 0 0 0 0 0 0 0 0 0 0
Bit/Field Name Type Reset Description
Software should not rely on the value of a reserved bit. To provide
compatibility with future products, the value of a reserved bit should be
preserved across a read-modify-write operation.
31:3 reserved RO 0x0000.000
Hardware Averaging Control
Specifies the amount of hardware averaging that will be applied to ADC
samples. The AVG field can be any value between 0 and 6. Entering a
value of 7 creates unpredictable results.
Value Description
0x0 No hardware oversampling
0x1 2x hardware oversampling
0x2 4x hardware oversampling
0x3 8x hardware oversampling
0x4 16x hardware oversampling
0x5 32x hardware oversampling
0x6 64x hardware oversampling
0x7 Reserved
2:0 AVG R/W 0x0
406 January 08, 2011
Texas Instruments-Production Data
Analog-to-Digital Converter (ADC)
Register 11: ADC Sample Sequence Input Multiplexer Select 0 (ADCSSMUX0),
offset 0x040
This register defines the analog input configuration for each sample in a sequence executed with
Sample Sequencer 0. This register is 32 bits wide and contains information for eight possible
samples.
ADC Sample Sequence Input Multiplexer Select 0 (ADCSSMUX0)
Base 0x4003.8000
Offset 0x040
Type R/W, reset 0x0000.0000
31 30 29 28 27 26 25 24 23 22 21 20 19 18 17 16
reserved MUX7 reserved MUX6 reserved MUX5 reserved MUX4
Type RO RO R/W R/W RO RO R/W R/W RO RO R/W R/W RO RO R/W R/W
Reset 0 0 0 0 0 0 0 0 0 0 0 0 0 0 0 0
15 14 13 12 11 10 9 8 7 6 5 4 3 2 1 0
reserved MUX3 reserved MUX2 reserved MUX1 reserved MUX0
Type RO RO R/W R/W RO RO R/W R/W RO RO R/W R/W RO RO R/W R/W
Reset 0 0 0 0 0 0 0 0 0 0 0 0 0 0 0 0
Bit/Field Name Type Reset Description
Software should not rely on the value of a reserved bit. To provide
compatibility with future products, the value of a reserved bit should be
preserved across a read-modify-write operation.
31:30 reserved RO 0
8th Sample Input Select
The MUX7 field is used during the eighth sample of a sequence executed
with the sample sequencer. It specifies which of the analog inputs is
sampled for the analog-to-digital conversion. The value set here indicates
the corresponding pin, for example, a value of 1 indicates the input is
ADC1.
29:28 MUX7 R/W 0x0
Software should not rely on the value of a reserved bit. To provide
compatibility with future products, the value of a reserved bit should be
preserved across a read-modify-write operation.
27:26 reserved RO 0
7th Sample Input Select
The MUX6 field is used during the seventh sample of a sequence
executed with the sample sequencer. It specifies which of the analog
inputs is sampled for the analog-to-digital conversion.
25:24 MUX6 R/W 0x0
Software should not rely on the value of a reserved bit. To provide
compatibility with future products, the value of a reserved bit should be
preserved across a read-modify-write operation.
23:22 reserved RO 0
6th Sample Input Select
The MUX5 field is used during the sixth sample of a sequence executed
with the sample sequencer. It specifies which of the analog inputs is
sampled for the analog-to-digital conversion.
21:20 MUX5 R/W 0x0
Software should not rely on the value of a reserved bit. To provide
compatibility with future products, the value of a reserved bit should be
preserved across a read-modify-write operation.
19:18 reserved RO 0
January 08, 2011 407
Texas Instruments-Production Data
Stellaris® LM3S2965 Microcontroller
Bit/Field Name Type Reset Description
5th Sample Input Select
The MUX4 field is used during the fifth sample of a sequence executed
with the sample sequencer. It specifies which of the analog inputs is
sampled for the analog-to-digital conversion.
17:16 MUX4 R/W 0x0
Software should not rely on the value of a reserved bit. To provide
compatibility with future products, the value of a reserved bit should be
preserved across a read-modify-write operation.
15:14 reserved RO 0
4th Sample Input Select
The MUX3 field is used during the fourth sample of a sequence executed
with the sample sequencer. It specifies which of the analog inputs is
sampled for the analog-to-digital conversion.
13:12 MUX3 R/W 0x0
Software should not rely on the value of a reserved bit. To provide
compatibility with future products, the value of a reserved bit should be
preserved across a read-modify-write operation.
11:10 reserved RO 0
3rd Sample Input Select
The MUX72 field is used during the third sample of a sequence executed
with the sample sequencer. It specifies which of the analog inputs is
sampled for the analog-to-digital conversion.
9:8 MUX2 R/W 0x0
Software should not rely on the value of a reserved bit. To provide
compatibility with future products, the value of a reserved bit should be
preserved across a read-modify-write operation.
7:6 reserved RO 0
2nd Sample Input Select
The MUX1 field is used during the second sample of a sequence
executed with the sample sequencer. It specifies which of the analog
inputs is sampled for the analog-to-digital conversion.
5:4 MUX1 R/W 0x0
Software should not rely on the value of a reserved bit. To provide
compatibility with future products, the value of a reserved bit should be
preserved across a read-modify-write operation.
3:2 reserved RO 0
1st Sample Input Select
The MUX0 field is used during the first sample of a sequence executed
with the sample sequencer. It specifies which of the analog inputs is
sampled for the analog-to-digital conversion.
1:0 MUX0 R/W 0x0
408 January 08, 2011
Texas Instruments-Production Data
Analog-to-Digital Converter (ADC)
Register 12: ADC Sample Sequence Control 0 (ADCSSCTL0), offset 0x044
This register contains the configuration information for each sample for a sequence executed with
a sample sequencer. When configuring a sample sequence, the END bit must be set at some point,
whether it be after the first sample, last sample, or any sample in between. This register is 32-bits
wide and contains information for eight possible samples.
ADC Sample Sequence Control 0 (ADCSSCTL0)
Base 0x4003.8000
Offset 0x044
Type R/W, reset 0x0000.0000
31 30 29 28 27 26 25 24 23 22 21 20 19 18 17 16
TS7 IE7 END7 D7 TS6 IE6 END6 D6 TS5 IE5 END5 D5 TS4 IE4 END4 D4
Type R/W R/W R/W R/W R/W R/W R/W R/W R/W R/W R/W R/W R/W R/W R/W R/W
Reset 0 0 0 0 0 0 0 0 0 0 0 0 0 0 0 0
15 14 13 12 11 10 9 8 7 6 5 4 3 2 1 0
TS3 IE3 END3 D3 TS2 IE2 END2 D2 TS1 IE1 END1 D1 TS0 IE0 END0 D0
Type R/W R/W R/W R/W R/W R/W R/W R/W R/W R/W R/W R/W R/W R/W R/W R/W
Reset 0 0 0 0 0 0 0 0 0 0 0 0 0 0 0 0
Bit/Field Name Type Reset Description
8th Sample Temp Sensor Select
This bit is used during the eighth sample of the sample sequence and
and specifies the input source of the sample.
When set, the temperature sensor is read.
When clear, the input pin specified by the ADCSSMUX register is read.
31 TS7 R/W 0
8th Sample Interrupt Enable
This bit is used during the eighth sample of the sample sequence and
specifies whether the raw interrupt signal (INR0 bit) is asserted at the
end of the sample's conversion. If the MASK0 bit in the ADCIM register
is set, the interrupt is promoted to a controller-level interrupt.
When this bit is set, the raw interrupt is asserted.
When this bit is clear, the raw interrupt is not asserted.
It is legal to have multiple samples within a sequence generate interrupts.
30 IE7 R/W 0
8th Sample is End of Sequence
The END7 bit indicates that this is the last sample of the sequence. It is
possible to end the sequence on any sample position. Samples defined
after the sample containing a set END are not requested for conversion
even though the fields may be non-zero. It is required that software write
the END bit somewhere within the sequence. (Sample Sequencer 3,
which only has a single sample in the sequence, is hardwired to have
the END0 bit set.)
Setting this bit indicates that this sample is the last in the sequence.
29 END7 R/W 0
8th Sample Diff Input Select
The D7 bit indicates that the analog input is to be differentially sampled.
The corresponding ADCSSMUXx nibble must be set to the pair number
"i", where the paired inputs are "2i and 2i+1". The temperature sensor
does not have a differential option. When set, the analog inputs are
differentially sampled.
28 D7 R/W 0
7th Sample Temp Sensor Select
Same definition as TS7 but used during the seventh sample.
27 TS6 R/W 0
January 08, 2011 409
Texas Instruments-Production Data
Stellaris® LM3S2965 Microcontroller
Bit/Field Name Type Reset Description
7th Sample Interrupt Enable
Same definition as IE7 but used during the seventh sample.
26 IE6 R/W 0
7th Sample is End of Sequence
Same definition as END7 but used during the seventh sample.
25 END6 R/W 0
7th Sample Diff Input Select
Same definition as D7 but used during the seventh sample.
24 D6 R/W 0
6th Sample Temp Sensor Select
Same definition as TS7 but used during the sixth sample.
23 TS5 R/W 0
6th Sample Interrupt Enable
Same definition as IE7 but used during the sixth sample.
22 IE5 R/W 0
6th Sample is End of Sequence
Same definition as END7 but used during the sixth sample.
21 END5 R/W 0
6th Sample Diff Input Select
Same definition as D7 but used during the sixth sample.
20 D5 R/W 0
5th Sample Temp Sensor Select
Same definition as TS7 but used during the fifth sample.
19 TS4 R/W 0
5th Sample Interrupt Enable
Same definition as IE7 but used during the fifth sample.
18 IE4 R/W 0
5th Sample is End of Sequence
Same definition as END7 but used during the fifth sample.
17 END4 R/W 0
5th Sample Diff Input Select
Same definition as D7 but used during the fifth sample.
16 D4 R/W 0
4th Sample Temp Sensor Select
Same definition as TS7 but used during the fourth sample.
15 TS3 R/W 0
4th Sample Interrupt Enable
Same definition as IE7 but used during the fourth sample.
14 IE3 R/W 0
4th Sample is End of Sequence
Same definition as END7 but used during the fourth sample.
13 END3 R/W 0
4th Sample Diff Input Select
Same definition as D7 but used during the fourth sample.
12 D3 R/W 0
3rd Sample Temp Sensor Select
Same definition as TS7 but used during the third sample.
11 TS2 R/W 0
3rd Sample Interrupt Enable
Same definition as IE7 but used during the third sample.
10 IE2 R/W 0
3rd Sample is End of Sequence
Same definition as END7 but used during the third sample.
9 END2 R/W 0
3rd Sample Diff Input Select
Same definition as D7 but used during the third sample.
8 D2 R/W 0
410 January 08, 2011
Texas Instruments-Production Data
Analog-to-Digital Converter (ADC)
Bit/Field Name Type Reset Description
2nd Sample Temp Sensor Select
Same definition as TS7 but used during the second sample.
7 TS1 R/W 0
2nd Sample Interrupt Enable
Same definition as IE7 but used during the second sample.
6 IE1 R/W 0
2nd Sample is End of Sequence
Same definition as END7 but used during the second sample.
5 END1 R/W 0
2nd Sample Diff Input Select
Same definition as D7 but used during the second sample.
4 D1 R/W 0
1st Sample Temp Sensor Select
Same definition as TS7 but used during the first sample.
3 TS0 R/W 0
1st Sample Interrupt Enable
Same definition as IE7 but used during the first sample.
2 IE0 R/W 0
1st Sample is End of Sequence
Same definition as END7 but used during the first sample.
1 END0 R/W 0
1st Sample Diff Input Select
Same definition as D7 but used during the first sample.
0 D0 R/W 0
January 08, 2011 411
Texas Instruments-Production Data
Stellaris® LM3S2965 Microcontroller
Register 13: ADC Sample Sequence Result FIFO 0 (ADCSSFIFO0), offset 0x048
Register 14: ADC Sample Sequence Result FIFO 1 (ADCSSFIFO1), offset 0x068
Register 15: ADC Sample Sequence Result FIFO 2 (ADCSSFIFO2), offset 0x088
Register 16: ADC Sample Sequence Result FIFO 3 (ADCSSFIFO3), offset
0x0A8
Important: Use caution when reading this register. Performing a read may change bit status.
This register contains the conversion results for samples collected with the sample sequencer (the
ADCSSFIFO0 register is used for Sample Sequencer 0, ADCSSFIFO1 for Sequencer 1,
ADCSSFIFO2 for Sequencer 2, and ADCSSFIFO3 for Sequencer 3). Reads of this register return
conversion result data in the order sample 0, sample 1, and so on, until the FIFO is empty. If the
FIFO is not properly handled by software, overflow and underflow conditions are registered in the
ADCOSTAT and ADCUSTAT registers.
ADC Sample Sequence Result FIFO 0 (ADCSSFIFO0)
Base 0x4003.8000
Offset 0x048
Type RO, reset -
31 30 29 28 27 26 25 24 23 22 21 20 19 18 17 16
reserved
Type RO RO RO RO RO RO RO RO RO RO RO RO RO RO RO RO
Reset - - - - - - - - - - - - - - - -
15 14 13 12 11 10 9 8 7 6 5 4 3 2 1 0
reserved DATA
Type RO RO RO RO RO RO RO RO RO RO RO RO RO RO RO RO
Reset - - - - - - - - - - - - - - - -
Bit/Field Name Type Reset Description
Software should not rely on the value of a reserved bit. To provide
compatibility with future products, the value of a reserved bit should be
preserved across a read-modify-write operation.
31:10 reserved RO -
9:0 DATA RO - Conversion Result Data
412 January 08, 2011
Texas Instruments-Production Data
Analog-to-Digital Converter (ADC)
Register 17: ADC Sample Sequence FIFO 0 Status (ADCSSFSTAT0), offset
0x04C
Register 18: ADC Sample Sequence FIFO 1 Status (ADCSSFSTAT1), offset
0x06C
Register 19: ADC Sample Sequence FIFO 2 Status (ADCSSFSTAT2), offset
0x08C
Register 20: ADC Sample Sequence FIFO 3 Status (ADCSSFSTAT3), offset
0x0AC
This register provides a window into the sample sequencer, providing full/empty status information
as well as the positions of the head and tail pointers. The reset value of 0x100 indicates an empty
FIFO. The ADCSSFSTAT0 register provides status on FIFO0, ADCSSFSTAT1 on FIFO1,
ADCSSFSTAT2 on FIFO2, and ADCSSFSTAT3 on FIFO3.
ADC Sample Sequence FIFO 0 Status (ADCSSFSTAT0)
Base 0x4003.8000
Offset 0x04C
Type RO, reset 0x0000.0100
31 30 29 28 27 26 25 24 23 22 21 20 19 18 17 16
reserved
Type RO RO RO RO RO RO RO RO RO RO RO RO RO RO RO RO
Reset 0 0 0 0 0 0 0 0 0 0 0 0 0 0 0 0
15 14 13 12 11 10 9 8 7 6 5 4 3 2 1 0
reserved FULL reserved EMPTY HPTR TPTR
Type RO RO RO RO RO RO RO RO RO RO RO RO RO RO RO RO
Reset 0 0 0 0 0 0 0 1 0 0 0 0 0 0 0 0
Bit/Field Name Type Reset Description
Software should not rely on the value of a reserved bit. To provide
compatibility with future products, the value of a reserved bit should be
preserved across a read-modify-write operation.
31:13 reserved RO 0x0
FIFO Full
When set, this bit indicates that the FIFO is currently full.
12 FULL RO 0
Software should not rely on the value of a reserved bit. To provide
compatibility with future products, the value of a reserved bit should be
preserved across a read-modify-write operation.
11:9 reserved RO 0x0
FIFO Empty
When set, this bit indicates that the FIFO is currently empty.
8 EMPTY RO 1
FIFO Head Pointer
This field contains the current "head" pointer index for the FIFO, that is,
the next entry to be written.
7:4 HPTR RO 0x0
FIFO Tail Pointer
This field contains the current "tail" pointer index for the FIFO, that is,
the next entry to be read.
3:0 TPTR RO 0x0
January 08, 2011 413
Texas Instruments-Production Data
Stellaris® LM3S2965 Microcontroller
Register 21: ADC Sample Sequence Input Multiplexer Select 1 (ADCSSMUX1),
offset 0x060
Register 22: ADC Sample Sequence Input Multiplexer Select 2 (ADCSSMUX2),
offset 0x080
This register defines the analog input configuration for each sample in a sequence executed with
Sample Sequencer 1 or 2. These registers are 16-bits wide and contain information for four possible
samples. See the ADCSSMUX0 register on page 407 for detailed bit descriptions. The ADCSSMUX1
register affects Sample Sequencer 1 and the ADCSSMUX2 register affects Sample Sequencer 2.
ADC Sample Sequence Input Multiplexer Select 1 (ADCSSMUX1)
Base 0x4003.8000
Offset 0x060
Type R/W, reset 0x0000.0000
31 30 29 28 27 26 25 24 23 22 21 20 19 18 17 16
reserved
Type RO RO RO RO RO RO RO RO RO RO RO RO RO RO RO RO
Reset 0 0 0 0 0 0 0 0 0 0 0 0 0 0 0 0
15 14 13 12 11 10 9 8 7 6 5 4 3 2 1 0
reserved MUX3 reserved MUX2 reserved MUX1 reserved MUX0
Type RO RO R/W R/W RO RO R/W R/W RO RO R/W R/W RO RO R/W R/W
Reset 0 0 0 0 0 0 0 0 0 0 0 0 0 0 0 0
Bit/Field Name Type Reset Description
Software should not rely on the value of a reserved bit. To provide
compatibility with future products, the value of a reserved bit should be
preserved across a read-modify-write operation.
31:14 reserved RO 0x0000
13:12 MUX3 R/W 0x0 4th Sample Input Select
Software should not rely on the value of a reserved bit. To provide
compatibility with future products, the value of a reserved bit should be
preserved across a read-modify-write operation.
11:10 reserved RO 0
9:8 MUX2 R/W 0x0 3rd Sample Input Select
Software should not rely on the value of a reserved bit. To provide
compatibility with future products, the value of a reserved bit should be
preserved across a read-modify-write operation.
7:6 reserved RO 0
5:4 MUX1 R/W 0x0 2nd Sample Input Select
Software should not rely on the value of a reserved bit. To provide
compatibility with future products, the value of a reserved bit should be
preserved across a read-modify-write operation.
3:2 reserved RO 0
1:0 MUX0 R/W 0x0 1st Sample Input Select
414 January 08, 2011
Texas Instruments-Production Data
Analog-to-Digital Converter (ADC)
Register 23: ADC Sample Sequence Control 1 (ADCSSCTL1), offset 0x064
Register 24: ADC Sample Sequence Control 2 (ADCSSCTL2), offset 0x084
These registers contain the configuration information for each sample for a sequence executed with
Sample Sequencer 1 or 2. When configuring a sample sequence, the END bit must be set at some
point, whether it be after the first sample, last sample, or any sample in between. These registers
are 16-bits wide and contain information for four possible samples. See the ADCSSCTL0 register
on page 409 for detailed bit descriptions. The ADCSSCTL1 register configures Sample Sequencer
1 and the ADCSSCTL2 register configures Sample Sequencer 2.
ADC Sample Sequence Control 1 (ADCSSCTL1)
Base 0x4003.8000
Offset 0x064
Type R/W, reset 0x0000.0000
31 30 29 28 27 26 25 24 23 22 21 20 19 18 17 16
reserved
Type RO RO RO RO RO RO RO RO RO RO RO RO RO RO RO RO
Reset 0 0 0 0 0 0 0 0 0 0 0 0 0 0 0 0
15 14 13 12 11 10 9 8 7 6 5 4 3 2 1 0
TS3 IE3 END3 D3 TS2 IE2 END2 D2 TS1 IE1 END1 D1 TS0 IE0 END0 D0
Type R/W R/W R/W R/W R/W R/W R/W R/W R/W R/W R/W R/W R/W R/W R/W R/W
Reset 0 0 0 0 0 0 0 0 0 0 0 0 0 0 0 0
Bit/Field Name Type Reset Description
Software should not rely on the value of a reserved bit. To provide
compatibility with future products, the value of a reserved bit should be
preserved across a read-modify-write operation.
31:16 reserved RO 0x0000
4th Sample Temp Sensor Select
Same definition as TS7 but used during the fourth sample.
15 TS3 R/W 0
4th Sample Interrupt Enable
Same definition as IE7 but used during the fourth sample.
14 IE3 R/W 0
4th Sample is End of Sequence
Same definition as END7 but used during the fourth sample.
13 END3 R/W 0
4th Sample Diff Input Select
Same definition as D7 but used during the fourth sample.
12 D3 R/W 0
3rd Sample Temp Sensor Select
Same definition as TS7 but used during the third sample.
11 TS2 R/W 0
3rd Sample Interrupt Enable
Same definition as IE7 but used during the third sample.
10 IE2 R/W 0
3rd Sample is End of Sequence
Same definition as END7 but used during the third sample.
9 END2 R/W 0
3rd Sample Diff Input Select
Same definition as D7 but used during the third sample.
8 D2 R/W 0
2nd Sample Temp Sensor Select
Same definition as TS7 but used during the second sample.
7 TS1 R/W 0
January 08, 2011 415
Texas Instruments-Production Data
Stellaris® LM3S2965 Microcontroller
Bit/Field Name Type Reset Description
2nd Sample Interrupt Enable
Same definition as IE7 but used during the second sample.
6 IE1 R/W 0
2nd Sample is End of Sequence
Same definition as END7 but used during the second sample.
5 END1 R/W 0
2nd Sample Diff Input Select
Same definition as D7 but used during the second sample.
4 D1 R/W 0
1st Sample Temp Sensor Select
Same definition as TS7 but used during the first sample.
3 TS0 R/W 0
1st Sample Interrupt Enable
Same definition as IE7 but used during the first sample.
2 IE0 R/W 0
1st Sample is End of Sequence
Same definition as END7 but used during the first sample.
1 END0 R/W 0
1st Sample Diff Input Select
Same definition as D7 but used during the first sample.
0 D0 R/W 0
416 January 08, 2011
Texas Instruments-Production Data
Analog-to-Digital Converter (ADC)
Register 25: ADC Sample Sequence Input Multiplexer Select 3 (ADCSSMUX3),
offset 0x0A0
This register defines the analog input configuration for a sample executed with Sample Sequencer
3. This register is 4-bits wide and contains information for one possible sample. See the ADCSSMUX0
register on page 407 for detailed bit descriptions.
ADC Sample Sequence Input Multiplexer Select 3 (ADCSSMUX3)
Base 0x4003.8000
Offset 0x0A0
Type R/W, reset 0x0000.0000
31 30 29 28 27 26 25 24 23 22 21 20 19 18 17 16
reserved
Type RO RO RO RO RO RO RO RO RO RO RO RO RO RO RO RO
Reset 0 0 0 0 0 0 0 0 0 0 0 0 0 0 0 0
15 14 13 12 11 10 9 8 7 6 5 4 3 2 1 0
reserved MUX0
Type RO RO RO RO RO RO RO RO RO RO RO RO RO RO R/W R/W
Reset 0 0 0 0 0 0 0 0 0 0 0 0 0 0 0 0
Bit/Field Name Type Reset Description
Software should not rely on the value of a reserved bit. To provide
compatibility with future products, the value of a reserved bit should be
preserved across a read-modify-write operation.
31:2 reserved RO 0x0000.000
1:0 MUX0 R/W 0 1st Sample Input Select
January 08, 2011 417
Texas Instruments-Production Data
Stellaris® LM3S2965 Microcontroller
Register 26: ADC Sample Sequence Control 3 (ADCSSCTL3), offset 0x0A4
This register contains the configuration information for a sample executed with Sample Sequencer
3. The END bit is always set since there is only one sample in this sequencer. This register is 4-bits
wide and contains information for one possible sample. See the ADCSSCTL0 register on page 409
for detailed bit descriptions.
ADC Sample Sequence Control 3 (ADCSSCTL3)
Base 0x4003.8000
Offset 0x0A4
Type R/W, reset 0x0000.0002
31 30 29 28 27 26 25 24 23 22 21 20 19 18 17 16
reserved
Type RO RO RO RO RO RO RO RO RO RO RO RO RO RO RO RO
Reset 0 0 0 0 0 0 0 0 0 0 0 0 0 0 0 0
15 14 13 12 11 10 9 8 7 6 5 4 3 2 1 0
reserved TS0 IE0 END0 D0
Type RO RO RO RO RO RO RO RO RO RO RO RO R/W R/W R/W R/W
Reset 0 0 0 0 0 0 0 0 0 0 0 0 0 0 1 0
Bit/Field Name Type Reset Description
Software should not rely on the value of a reserved bit. To provide
compatibility with future products, the value of a reserved bit should be
preserved across a read-modify-write operation.
31:4 reserved RO 0x0000.000
1st Sample Temp Sensor Select
Same definition as TS7 but used during the first sample.
3 TS0 R/W 0
1st Sample Interrupt Enable
Same definition as IE7 but used during the first sample.
2 IE0 R/W 0
1st Sample is End of Sequence
Same definition as END7 but used during the first sample.
Since this sequencer has only one entry, this bit must be set.
1 END0 R/W 1
1st Sample Diff Input Select
Same definition as D7 but used during the first sample.
0 D0 R/W 0
418 January 08, 2011
Texas Instruments-Production Data
Analog-to-Digital Converter (ADC)
Register 27: ADC Test Mode Loopback (ADCTMLB), offset 0x100
This register provides loopback operation within the digital logic of the ADC, which can be useful in
debugging software without having to provide actual analog stimulus. This test mode is entered by
writing a value of 0x0000.0001 to this register. When data is read from the FIFO in loopback mode,
the read-only portion of this register is returned.
ADC Test Mode Loopback (ADCTMLB)
Base 0x4003.8000
Offset 0x100
Type R/W, reset 0x0000.0000
31 30 29 28 27 26 25 24 23 22 21 20 19 18 17 16
reserved
Type RO RO RO RO RO RO RO RO RO RO RO RO RO RO RO RO
Reset 0 0 0 0 0 0 0 0 0 0 0 0 0 0 0 0
15 14 13 12 11 10 9 8 7 6 5 4 3 2 1 0
reserved LB
Type RO RO RO RO RO RO RO RO RO RO RO RO RO RO RO R/W
Reset 0 0 0 0 0 0 0 0 0 0 0 0 0 0 0 0
Bit/Field Name Type Reset Description
Software should not rely on the value of a reserved bit. To provide
compatibility with future products, the value of a reserved bit should be
preserved across a read-modify-write operation.
31:1 reserved RO 0x0000.000
Loopback Mode Enable
When set, forces a loopback within the digital block to provide information
on input and unique numbering. The ADCSSFIFOn registers do not
provide sample data, but instead provide the 10-bit loopback data as
shown below.
Bit/Field Name Description
Continuous Sample Counter
Continuous sample counter that is initialized to 0
and counts each sample as it processed. This
helps provide a unique value for the data received.
9:6 CNT
Continuation Sample Indicator
When set, indicates that this is a continuation
sample. For example, if two sequencers were to
run back-to-back, this indicates that the controller
kept continuously sampling at full rate.
5 CONT
Differential Sample Indicator
When set, indicates that this is a differential
sample.
4 DIFF
Temp Sensor Sample Indicator
When set, indicates that this is a temperature
sensor sample.
3 TS
Analog Input Indicator
Indicates which analog input is to be sampled.
2:0 MUX
0 LB R/W 0
January 08, 2011 419
Texas Instruments-Production Data
Stellaris® LM3S2965 Microcontroller
12 Universal Asynchronous Receivers/Transmitters
(UARTs)
Each Stellaris® Universal Asynchronous Receiver/Transmitter (UART) has the following features:
■ Three fully programmable 16C550-type UARTs with IrDA support
■ Separate 16x8 transmit (TX) and receive (RX) FIFOs to reduce CPU interrupt service loading
■ Programmable baud-rate generator allowing speeds up to 3.125 Mbps
■ Programmable FIFO length, including 1-byte deep operation providing conventional
double-buffered interface
■ FIFO trigger levels of 1/8, 1/4, 1/2, 3/4, and 7/8
■ Standard asynchronous communication bits for start, stop, and parity
■ Line-break generation and detection
■ Fully programmable serial interface characteristics
– 5, 6, 7, or 8 data bits
– Even, odd, stick, or no-parity bit generation/detection
– 1 or 2 stop bit generation
■ IrDA serial-IR (SIR) encoder/decoder providing
– Programmable use of IrDA Serial Infrared (SIR) or UART input/output
– Support of IrDA SIR encoder/decoder functions for data rates up to 115.2 Kbps half-duplex
– Support of normal 3/16 and low-power (1.41-2.23 μs) bit durations
– Programmable internal clock generator enabling division of reference clock by 1 to 256 for
low-power mode bit duration
420 January 08, 2011
Texas Instruments-Production Data
Universal Asynchronous Receivers/Transmitters (UARTs)
12.1 Block Diagram
Figure 12-1. UART Module Block Diagram
TxFIFO
16 x 8
...
RxFIFO
16 x 8
...
Identification
Registers
UARTPCellID0
UARTPCellID1
UARTPCellID2
UARTPCellID3
UARTPeriphID0
UARTPeriphID1
UARTPeriphID2
UARTPeriphID3
UARTPeriphID4
UARTPeriphID5
UARTPeriphID6
UARTPeriphID7
Interrupt Control
UARTDR
Control/Status
Transmitter
(with SIR
Transmit
Baud Rate Encoder)
Generator
Receiver
(with SIR
Receive
Decoder)
UnTx
UnRx
System Clock
Interrupt
UARTIFLS
UARTIM
UARTMIS
UARTRIS
UARTICR
UARTIBRD
UARTFBRD
UARTRSR/ECR
UARTFR
UARTLCRH
UARTCTL
UARTILPR
12.2 Functional Description
Each Stellaris UART performs the functions of parallel-to-serial and serial-to-parallel conversions.
It is similar in functionality to a 16C550 UART, but is not register compatible.
The UART is configured for transmit and/or receive via the TXE and RXE bits of the UART Control
(UARTCTL) register (see page 439). Transmit and receive are both enabled out of reset. Before any
control registers are programmed, the UART must be disabled by clearing the UARTEN bit in
UARTCTL. If the UART is disabled during a TX or RX operation, the current transaction is completed
prior to the UART stopping.
The UART peripheral also includes a serial IR (SIR) encoder/decoder block that can be connected
to an infrared transceiver to implement an IrDA SIR physical layer. The SIR function is programmed
using the UARTCTL register.
12.2.1 Transmit/Receive Logic
The transmit logic performs parallel-to-serial conversion on the data read from the transmit FIFO.
The control logic outputs the serial bit stream beginning with a start bit, and followed by the data
January 08, 2011 421
Texas Instruments-Production Data
Stellaris® LM3S2965 Microcontroller
bits (LSB first), parity bit, and the stop bits according to the programmed configuration in the control
registers. See Figure 12-2 on page 422 for details.
The receive logic performs serial-to-parallel conversion on the received bit stream after a valid start
pulse has been detected. Overrun, parity, frame error checking, and line-break detection are also
performed, and their status accompanies the data that is written to the receive FIFO.
Figure 12-2. UART Character Frame
1
0 5-8 data bits
LSB MSB
Parity bit
if enabled
1-2
stop bits
UnTX
n
Start
12.2.2 Baud-Rate Generation
The baud-rate divisor is a 22-bit number consisting of a 16-bit integer and a 6-bit fractional part.
The number formed by these two values is used by the baud-rate generator to determine the bit
period. Having a fractional baud-rate divider allows the UART to generate all the standard baud
rates.
The 16-bit integer is loaded through the UART Integer Baud-Rate Divisor (UARTIBRD) register
(see page 435) and the 6-bit fractional part is loaded with the UART Fractional Baud-Rate Divisor
(UARTFBRD) register (see page 436). The baud-rate divisor (BRD) has the following relationship
to the system clock (where BRDI is the integer part of the BRD and BRDF is the fractional part,
separated by a decimal place.)
BRD = BRDI + BRDF = UARTSysClk / (16 * Baud Rate)
where UARTSysClk is the system clock connected to the UART.
The 6-bit fractional number (that is to be loaded into the DIVFRAC bit field in the UARTFBRD register)
can be calculated by taking the fractional part of the baud-rate divisor, multiplying it by 64, and
adding 0.5 to account for rounding errors:
UARTFBRD[DIVFRAC] = integer(BRDF * 64 + 0.5)
The UART generates an internal baud-rate reference clock at 16x the baud-rate (referred to as
Baud16). This reference clock is divided by 16 to generate the transmit clock, and is used for error
detection during receive operations.
Along with the UART Line Control, High Byte (UARTLCRH) register (see page 437), the UARTIBRD
and UARTFBRD registers form an internal 30-bit register. This internal register is only updated
when a write operation to UARTLCRH is performed, so any changes to the baud-rate divisor must
be followed by a write to the UARTLCRH register for the changes to take effect.
To update the baud-rate registers, there are four possible sequences:
■ UARTIBRD write, UARTFBRD write, and UARTLCRH write
■ UARTFBRD write, UARTIBRD write, and UARTLCRH write
■ UARTIBRD write and UARTLCRH write
■ UARTFBRD write and UARTLCRH write
422 January 08, 2011
Texas Instruments-Production Data
Universal Asynchronous Receivers/Transmitters (UARTs)
12.2.3 Data Transmission
Data received or transmitted is stored in two 16-byte FIFOs, though the receive FIFO has an extra
four bits per character for status information. For transmission, data is written into the transmit FIFO.
If the UART is enabled, it causes a data frame to start transmitting with the parameters indicated
in the UARTLCRH register. Data continues to be transmitted until there is no data left in the transmit
FIFO. The BUSY bit in the UART Flag (UARTFR) register (see page 432) is asserted as soon as
data is written to the transmit FIFO (that is, if the FIFO is non-empty) and remains asserted while
data is being transmitted. The BUSY bit is negated only when the transmit FIFO is empty, and the
last character has been transmitted from the shift register, including the stop bits. The UART can
indicate that it is busy even though the UART may no longer be enabled.
When the receiver is idle (the UnRx is continuously 1) and the data input goes Low (a start bit has
been received), the receive counter begins running and data is sampled on the eighth cycle of
Baud16 (described in “Transmit/Receive Logic” on page 421).
The start bit is valid and recognized if UnRx is still low on the eighth cycle of Baud16, otherwise it
is ignored. After a valid start bit is detected, successive data bits are sampled on every 16th cycle
of Baud16 (that is, one bit period later) according to the programmed length of the data characters.
The parity bit is then checked if parity mode was enabled. Data length and parity are defined in the
UARTLCRH register.
Lastly, a valid stop bit is confirmed if UnRx is High, otherwise a framing error has occurred. When
a full word is received, the data is stored in the receive FIFO, with any error bits associated with
that word.
12.2.4 Serial IR (SIR)
The UART peripheral includes an IrDA serial-IR (SIR) encoder/decoder block. The IrDA SIR block
provides functionality that converts between an asynchronous UART data stream, and half-duplex
serial SIR interface. No analog processing is performed on-chip. The role of the SIR block is to
provide a digital encoded output and decoded input to the UART. The UART signal pins can be
connected to an infrared transceiver to implement an IrDA SIR physical layer link. The SIR block
has two modes of operation:
■ In normal IrDA mode, a zero logic level is transmitted as high pulse of 3/16th duration of the
selected baud rate bit period on the output pin, while logic one levels are transmitted as a static
LOW signal. These levels control the driver of an infrared transmitter, sending a pulse of light
for each zero. On the reception side, the incoming light pulses energize the photo transistor base
of the receiver, pulling its output LOW. This drives the UART input pin LOW.
■ In low-power IrDA mode, the width of the transmitted infrared pulse is set to three times the
period of the internally generated IrLPBaud16 signal (1.63 μs, assuming a nominal 1.8432 MHz
frequency) by changing the appropriate bit in the UARTCR register. See page 434 for more
information on IrDA low-power pulse-duration configuration.
Figure 12-3 on page 424 shows the UART transmit and receive signals, with and without IrDA
modulation.
January 08, 2011 423
Texas Instruments-Production Data
Stellaris® LM3S2965 Microcontroller
Figure 12-3. IrDA Data Modulation
0 1 0 1 0 0 1 1 0 1
Data bits
0 1 0 1 0 0 1 1 0 1
Start Data bits
bit
Start Stop
Bit period 3 Bit period
16
UnTx
UnTx with IrDA
UnRx with IrDA
UnRx
Stop
bit
In both normal and low-power IrDA modes:
■ During transmission, the UART data bit is used as the base for encoding
■ During reception, the decoded bits are transferred to the UART receive logic
The IrDA SIR physical layer specifies a half-duplex communication link, with a minimum 10 ms delay
between transmission and reception. This delay must be generated by software because it is not
automatically supported by the UART. The delay is required because the infrared receiver electronics
might become biased, or even saturated from the optical power coupled from the adjacent transmitter
LED. This delay is known as latency, or receiver setup time.
If the application does not require the use of the UnRx signal, the GPIO pin that has the UnRx signal
as an alternate function must be configured as the UnRx signal and pulled High.
12.2.5 FIFO Operation
The UART has two 16-entry FIFOs; one for transmit and one for receive. Both FIFOs are accessed
via the UART Data (UARTDR) register (see page 428). Read operations of the UARTDR register
return a 12-bit value consisting of 8 data bits and 4 error flags while write operations place 8-bit data
in the transmit FIFO.
Out of reset, both FIFOs are disabled and act as 1-byte-deep holding registers. The FIFOs are
enabled by setting the FEN bit in UARTLCRH (page 437).
FIFO status can be monitored via the UART Flag (UARTFR) register (see page 432) and the UART
Receive Status (UARTRSR) register. Hardware monitors empty, full and overrun conditions. The
UARTFR register contains empty and full flags (TXFE, TXFF, RXFE, and RXFF bits) and the
UARTRSR register shows overrun status via the OE bit.
The trigger points at which the FIFOs generate interrupts is controlled via the UART Interrupt FIFO
Level Select (UARTIFLS) register (see page 441). Both FIFOs can be individually configured to
trigger interrupts at different levels. Available configurations include 1/8, ¼, ½, ¾, and 7/8. For
example, if the ¼ option is selected for the receive FIFO, the UART generates a receive interrupt
after 4 data bytes are received. Out of reset, both FIFOs are configured to trigger an interrupt at the
½ mark.
12.2.6 Interrupts
The UART can generate interrupts when the following conditions are observed:
424 January 08, 2011
Texas Instruments-Production Data
Universal Asynchronous Receivers/Transmitters (UARTs)
■ Overrun Error
■ Break Error
■ Parity Error
■ Framing Error
■ Receive Timeout
■ Transmit (when condition defined in the TXIFLSEL bit in the UARTIFLS register is met)
■ Receive (when condition defined in the RXIFLSEL bit in the UARTIFLS register is met)
All of the interrupt events are ORed together before being sent to the interrupt controller, so the
UART can only generate a single interrupt request to the controller at any given time. Software can
service multiple interrupt events in a single interrupt service routine by reading the UART Masked
Interrupt Status (UARTMIS) register (see page 446).
The interrupt events that can trigger a controller-level interrupt are defined in the UART Interrupt
Mask (UARTIM ) register (see page 443) by setting the corresponding IM bit to 1. If interrupts are
not used, the raw interrupt status is always visible via the UART Raw Interrupt Status (UARTRIS)
register (see page 445).
Interrupts are always cleared (for both the UARTMIS and UARTRIS registers) by setting the
corresponding bit in the UART Interrupt Clear (UARTICR) register (see page 447).
The receive timeout interrupt is asserted when the receive FIFO is not empty, and no further data
is received over a 32-bit period. The receive timeout interrupt is cleared either when the FIFO
becomes empty through reading all the data (or by reading the holding register), or when a 1 is
written to the corresponding bit in the UARTICR register.
12.2.7 Loopback Operation
The UART can be placed into an internal loopback mode for diagnostic or debug work. This is
accomplished by setting the LBE bit in the UARTCTL register (see page 439). In loopback mode,
data transmitted on UnTx is received on the UnRx input.
12.2.8 IrDA SIR block
The IrDA SIR block contains an IrDA serial IR (SIR) protocol encoder/decoder. When enabled, the
SIR block uses the UnTx and UnRx pins for the SIR protocol, which should be connected to an IR
transceiver.
The SIR block can receive and transmit, but it is only half-duplex so it cannot do both at the same
time. Transmission must be stopped before data can be received. The IrDA SIR physical layer
specifies a minimum 10-ms delay between transmission and reception.
12.3 Initialization and Configuration
To use the UARTs, the peripheral clock must be enabled by setting the UART0, UART1, or UART2
bits in the RCGC1 register.
This section discusses the steps that are required to use a UART module. For this example, the
UART clock is assumed to be 20 MHz and the desired UART configuration is:
■ 115200 baud rate
January 08, 2011 425
Texas Instruments-Production Data
Stellaris® LM3S2965 Microcontroller
■ Data length of 8 bits
■ One stop bit
■ No parity
■ FIFOs disabled
■ No interrupts
The first thing to consider when programming the UART is the baud-rate divisor (BRD), since the
UARTIBRD and UARTFBRD registers must be written before the UARTLCRH register. Using the
equation described in “Baud-Rate Generation” on page 422, the BRD can be calculated:
BRD = 20,000,000 / (16 * 115,200) = 10.8507
which means that the DIVINT field of the UARTIBRD register (see page 435) should be set to 10.
The value to be loaded into the UARTFBRD register (see page 436) is calculated by the equation:
UARTFBRD[DIVFRAC] = integer(0.8507 * 64 + 0.5) = 54
With the BRD values in hand, the UART configuration is written to the module in the following order:
1. Disable the UART by clearing the UARTEN bit in the UARTCTL register.
2. Write the integer portion of the BRD to the UARTIBRD register.
3. Write the fractional portion of the BRD to the UARTFBRD register.
4. Write the desired serial parameters to the UARTLCRH register (in this case, a value of
0x0000.0060).
5. Enable the UART by setting the UARTEN bit in the UARTCTL register.
12.4 Register Map
Table 12-1 on page 427 lists the UART registers. The offset listed is a hexadecimal increment to the
register’s address, relative to that UART’s base address:
■ UART0: 0x4000.C000
■ UART1: 0x4000.D000
■ UART2: 0x4000.E000
Note that the UART module clock must be enabled before the registers can be programmed (see
page 216). There must be a delay of 3 system clocks after the UART module clock is enabled before
any UART module registers are accessed.
Note: The UART must be disabled (see the UARTEN bit in the UARTCTL register on page 439)
before any of the control registers are reprogrammed. When the UART is disabled during
a TX or RX operation, the current transaction is completed prior to the UART stopping.
426 January 08, 2011
Texas Instruments-Production Data
Universal Asynchronous Receivers/Transmitters (UARTs)
Table 12-1. UART Register Map
See
Offset Name Type Reset Description page
0x000 UARTDR R/W 0x0000.0000 UART Data 428
0x004 UARTRSR/UARTECR R/W 0x0000.0000 UART Receive Status/Error Clear 430
0x018 UARTFR RO 0x0000.0090 UART Flag 432
0x020 UARTILPR R/W 0x0000.0000 UART IrDA Low-Power Register 434
0x024 UARTIBRD R/W 0x0000.0000 UART Integer Baud-Rate Divisor 435
0x028 UARTFBRD R/W 0x0000.0000 UART Fractional Baud-Rate Divisor 436
0x02C UARTLCRH R/W 0x0000.0000 UART Line Control 437
0x030 UARTCTL R/W 0x0000.0300 UART Control 439
0x034 UARTIFLS R/W 0x0000.0012 UART Interrupt FIFO Level Select 441
0x038 UARTIM R/W 0x0000.0000 UART Interrupt Mask 443
0x03C UARTRIS RO 0x0000.000F UART Raw Interrupt Status 445
0x040 UARTMIS RO 0x0000.0000 UART Masked Interrupt Status 446
0x044 UARTICR W1C 0x0000.0000 UART Interrupt Clear 447
0xFD0 UARTPeriphID4 RO 0x0000.0000 UART Peripheral Identification 4 449
0xFD4 UARTPeriphID5 RO 0x0000.0000 UART Peripheral Identification 5 450
0xFD8 UARTPeriphID6 RO 0x0000.0000 UART Peripheral Identification 6 451
0xFDC UARTPeriphID7 RO 0x0000.0000 UART Peripheral Identification 7 452
0xFE0 UARTPeriphID0 RO 0x0000.0011 UART Peripheral Identification 0 453
0xFE4 UARTPeriphID1 RO 0x0000.0000 UART Peripheral Identification 1 454
0xFE8 UARTPeriphID2 RO 0x0000.0018 UART Peripheral Identification 2 455
0xFEC UARTPeriphID3 RO 0x0000.0001 UART Peripheral Identification 3 456
0xFF0 UARTPCellID0 RO 0x0000.000D UART PrimeCell Identification 0 457
0xFF4 UARTPCellID1 RO 0x0000.00F0 UART PrimeCell Identification 1 458
0xFF8 UARTPCellID2 RO 0x0000.0005 UART PrimeCell Identification 2 459
0xFFC UARTPCellID3 RO 0x0000.00B1 UART PrimeCell Identification 3 460
12.5 Register Descriptions
The remainder of this section lists and describes the UART registers, in numerical order by address
offset.
January 08, 2011 427
Texas Instruments-Production Data
Stellaris® LM3S2965 Microcontroller
Register 1: UART Data (UARTDR), offset 0x000
Important: Use caution when reading this register. Performing a read may change bit status.
This register is the data register (the interface to the FIFOs).
When FIFOs are enabled, data written to this location is pushed onto the transmit FIFO. If FIFOs
are disabled, data is stored in the transmitter holding register (the bottom word of the transmit FIFO).
A write to this register initiates a transmission from the UART.
For received data, if the FIFO is enabled, the data byte and the 4-bit status (break, frame, parity,
and overrun) is pushed onto the 12-bit wide receive FIFO. If FIFOs are disabled, the data byte and
status are stored in the receiving holding register (the bottom word of the receive FIFO). The received
data can be retrieved by reading this register.
UART Data (UARTDR)
UART0 base: 0x4000.C000
UART1 base: 0x4000.D000
UART2 base: 0x4000.E000
Offset 0x000
Type R/W, reset 0x0000.0000
31 30 29 28 27 26 25 24 23 22 21 20 19 18 17 16
reserved
Type RO RO RO RO RO RO RO RO RO RO RO RO RO RO RO RO
Reset 0 0 0 0 0 0 0 0 0 0 0 0 0 0 0 0
15 14 13 12 11 10 9 8 7 6 5 4 3 2 1 0
reserved OE BE PE FE DATA
Type RO RO RO RO RO RO RO RO R/W R/W R/W R/W R/W R/W R/W R/W
Reset 0 0 0 0 0 0 0 0 0 0 0 0 0 0 0 0
Bit/Field Name Type Reset Description
Software should not rely on the value of a reserved bit. To provide
compatibility with future products, the value of a reserved bit should be
preserved across a read-modify-write operation.
31:12 reserved RO 0
UART Overrun Error
The OE values are defined as follows:
Value Description
0 There has been no data loss due to a FIFO overrun.
New data was received when the FIFO was full, resulting in
data loss.
1
11 OE RO 0
UART Break Error
This bit is set to 1 when a break condition is detected, indicating that
the receive data input was held Low for longer than a full-word
transmission time (defined as start, data, parity, and stop bits).
In FIFO mode, this error is associated with the character at the top of
the FIFO. When a break occurs, only one 0 character is loaded into the
FIFO. The next character is only enabled after the received data input
goes to a 1 (marking state) and the next valid start bit is received.
10 BE RO 0
428 January 08, 2011
Texas Instruments-Production Data
Universal Asynchronous Receivers/Transmitters (UARTs)
Bit/Field Name Type Reset Description
UART Parity Error
This bit is set to 1 when the parity of the received data character does
not match the parity defined by bits 2 and 7 of the UARTLCRH register.
In FIFO mode, this error is associated with the character at the top of
the FIFO.
9 PE RO 0
UART Framing Error
This bit is set to 1 when the received character does not have a valid
stop bit (a valid stop bit is 1).
8 FE RO 0
Data Transmitted or Received
When written, the data that is to be transmitted via the UART. When
read, the data that was received by the UART.
7:0 DATA R/W 0
January 08, 2011 429
Texas Instruments-Production Data
Stellaris® LM3S2965 Microcontroller
Register 2: UART Receive Status/Error Clear (UARTRSR/UARTECR), offset
0x004
The UARTRSR/UARTECR register is the receive status register/error clear register.
In addition to the UARTDR register, receive status can also be read from the UARTRSR register.
If the status is read from this register, then the status information corresponds to the entry read from
UARTDR prior to reading UARTRSR. The status information for overrun is set immediately when
an overrun condition occurs.
The UARTRSR register cannot be written.
A write of any value to the UARTECR register clears the framing, parity, break, and overrun errors.
All the bits are cleared to 0 on reset.
Reads
UART Receive Status/Error Clear (UARTRSR/UARTECR)
UART0 base: 0x4000.C000
UART1 base: 0x4000.D000
UART2 base: 0x4000.E000
Offset 0x004
Type RO, reset 0x0000.0000
31 30 29 28 27 26 25 24 23 22 21 20 19 18 17 16
reserved
Type RO RO RO RO RO RO RO RO RO RO RO RO RO RO RO RO
Reset 0 0 0 0 0 0 0 0 0 0 0 0 0 0 0 0
15 14 13 12 11 10 9 8 7 6 5 4 3 2 1 0
reserved OE BE PE FE
Type RO RO RO RO RO RO RO RO RO RO RO RO RO RO RO RO
Reset 0 0 0 0 0 0 0 0 0 0 0 0 0 0 0 0
Bit/Field Name Type Reset Description
Software should not rely on the value of a reserved bit. To provide
compatibility with future products, the value of a reserved bit should be
preserved across a read-modify-write operation.
31:4 reserved RO 0
UART Overrun Error
When this bit is set to 1, data is received and the FIFO is already full.
This bit is cleared to 0 by a write to UARTECR.
The FIFO contents remain valid since no further data is written when
the FIFO is full, only the contents of the shift register are overwritten.
The CPU must now read the data in order to empty the FIFO.
3 OE RO 0
UART Break Error
This bit is set to 1 when a break condition is detected, indicating that
the received data input was held Low for longer than a full-word
transmission time (defined as start, data, parity, and stop bits).
This bit is cleared to 0 by a write to UARTECR.
In FIFO mode, this error is associated with the character at the top of
the FIFO. When a break occurs, only one 0 character is loaded into the
FIFO. The next character is only enabled after the receive data input
goes to a 1 (marking state) and the next valid start bit is received.
2 BE RO 0
430 January 08, 2011
Texas Instruments-Production Data
Universal Asynchronous Receivers/Transmitters (UARTs)
Bit/Field Name Type Reset Description
UART Parity Error
This bit is set to 1 when the parity of the received data character does
not match the parity defined by bits 2 and 7 of the UARTLCRH register.
This bit is cleared to 0 by a write to UARTECR.
1 PE RO 0
UART Framing Error
This bit is set to 1 when the received character does not have a valid
stop bit (a valid stop bit is 1).
This bit is cleared to 0 by a write to UARTECR.
In FIFO mode, this error is associated with the character at the top of
the FIFO.
0 FE RO 0
Writes
UART Receive Status/Error Clear (UARTRSR/UARTECR)
UART0 base: 0x4000.C000
UART1 base: 0x4000.D000
UART2 base: 0x4000.E000
Offset 0x004
Type WO, reset 0x0000.0000
31 30 29 28 27 26 25 24 23 22 21 20 19 18 17 16
reserved
Type WO WO WO WO WO WO WO WO WO WO WO WO WO WO WO WO
Reset 0 0 0 0 0 0 0 0 0 0 0 0 0 0 0 0
15 14 13 12 11 10 9 8 7 6 5 4 3 2 1 0
reserved DATA
Type WO WO WO WO WO WO WO WO WO WO WO WO WO WO WO WO
Reset 0 0 0 0 0 0 0 0 0 0 0 0 0 0 0 0
Bit/Field Name Type Reset Description
Software should not rely on the value of a reserved bit. To provide
compatibility with future products, the value of a reserved bit should be
preserved across a read-modify-write operation.
31:8 reserved WO 0
Error Clear
A write to this register of any data clears the framing, parity, break, and
overrun flags.
7:0 DATA WO 0
January 08, 2011 431
Texas Instruments-Production Data
Stellaris® LM3S2965 Microcontroller
Register 3: UART Flag (UARTFR), offset 0x018
The UARTFR register is the flag register. After reset, the TXFF, RXFF, and BUSY bits are 0, and
TXFE and RXFE bits are 1.
UART Flag (UARTFR)
UART0 base: 0x4000.C000
UART1 base: 0x4000.D000
UART2 base: 0x4000.E000
Offset 0x018
Type RO, reset 0x0000.0090
31 30 29 28 27 26 25 24 23 22 21 20 19 18 17 16
reserved
Type RO RO RO RO RO RO RO RO RO RO RO RO RO RO RO RO
Reset 0 0 0 0 0 0 0 0 0 0 0 0 0 0 0 0
15 14 13 12 11 10 9 8 7 6 5 4 3 2 1 0
reserved TXFE RXFF TXFF RXFE BUSY reserved
Type RO RO RO RO RO RO RO RO RO RO RO RO RO RO RO RO
Reset 0 0 0 0 0 0 0 0 1 0 0 1 0 0 0 0
Bit/Field Name Type Reset Description
Software should not rely on the value of a reserved bit. To provide
compatibility with future products, the value of a reserved bit should be
preserved across a read-modify-write operation.
31:8 reserved RO 0
UART Transmit FIFO Empty
The meaning of this bit depends on the state of the FEN bit in the
UARTLCRH register.
If the FIFO is disabled (FEN is 0), this bit is set when the transmit holding
register is empty.
If the FIFO is enabled (FEN is 1), this bit is set when the transmit FIFO
is empty.
7 TXFE RO 1
UART Receive FIFO Full
The meaning of this bit depends on the state of the FEN bit in the
UARTLCRH register.
If the FIFO is disabled, this bit is set when the receive holding register
is full.
If the FIFO is enabled, this bit is set when the receive FIFO is full.
6 RXFF RO 0
UART Transmit FIFO Full
The meaning of this bit depends on the state of the FEN bit in the
UARTLCRH register.
If the FIFO is disabled, this bit is set when the transmit holding register
is full.
If the FIFO is enabled, this bit is set when the transmit FIFO is full.
5 TXFF RO 0
UART Receive FIFO Empty
The meaning of this bit depends on the state of the FEN bit in the
UARTLCRH register.
If the FIFO is disabled, this bit is set when the receive holding register
is empty.
If the FIFO is enabled, this bit is set when the receive FIFO is empty.
4 RXFE RO 1
432 January 08, 2011
Texas Instruments-Production Data
Universal Asynchronous Receivers/Transmitters (UARTs)
Bit/Field Name Type Reset Description
UART Busy
When this bit is 1, the UART is busy transmitting data. This bit remains
set until the complete byte, including all stop bits, has been sent from
the shift register.
This bit is set as soon as the transmit FIFO becomes non-empty
(regardless of whether UART is enabled).
3 BUSY RO 0
Software should not rely on the value of a reserved bit. To provide
compatibility with future products, the value of a reserved bit should be
preserved across a read-modify-write operation.
2:0 reserved RO 0
January 08, 2011 433
Texas Instruments-Production Data
Stellaris® LM3S2965 Microcontroller
Register 4: UART IrDA Low-Power Register (UARTILPR), offset 0x020
The UARTILPR register is an 8-bit read/write register that stores the low-power counter divisor
value used to derive the low-power SIR pulse width clock by dividing down the system clock (SysClk).
All the bits are cleared to 0 when reset.
The internal IrLPBaud16 clock is generated by dividing down SysClk according to the low-power
divisor value written to UARTILPR. The duration of SIR pulses generated when low-power mode
is enabled is three times the period of the IrLPBaud16 clock. The low-power divisor value is
calculated as follows:
ILPDVSR = SysClk / FIrLPBaud16
where FIrLPBaud16 is nominally 1.8432 MHz.
You must choose the divisor so that 1.42 MHz < FIrLPBaud16 < 2.12 MHz, which results in a low-power
pulse duration of 1.41–2.11 μs (three times the period of IrLPBaud16). The minimum frequency
of IrLPBaud16 ensures that pulses less than one period of IrLPBaud16 are rejected, but that
pulses greater than 1.4 μs are accepted as valid pulses.
Note: Zero is an illegal value. Programming a zero value results in no IrLPBaud16 pulses being
generated.
UART IrDA Low-Power Register (UARTILPR)
UART0 base: 0x4000.C000
UART1 base: 0x4000.D000
UART2 base: 0x4000.E000
Offset 0x020
Type R/W, reset 0x0000.0000
31 30 29 28 27 26 25 24 23 22 21 20 19 18 17 16
reserved
Type RO RO RO RO RO RO RO RO RO RO RO RO RO RO RO RO
Reset 0 0 0 0 0 0 0 0 0 0 0 0 0 0 0 0
15 14 13 12 11 10 9 8 7 6 5 4 3 2 1 0
reserved ILPDVSR
Type RO RO RO RO RO RO RO RO R/W R/W R/W R/W R/W R/W R/W R/W
Reset 0 0 0 0 0 0 0 0 0 0 0 0 0 0 0 0
Bit/Field Name Type Reset Description
Software should not rely on the value of a reserved bit. To provide
compatibility with future products, the value of a reserved bit should be
preserved across a read-modify-write operation.
31:8 reserved RO 0
IrDA Low-Power Divisor
This is an 8-bit low-power divisor value.
7:0 ILPDVSR R/W 0x00
434 January 08, 2011
Texas Instruments-Production Data
Universal Asynchronous Receivers/Transmitters (UARTs)
Register 5: UART Integer Baud-Rate Divisor (UARTIBRD), offset 0x024
The UARTIBRD register is the integer part of the baud-rate divisor value. All the bits are cleared
on reset. The minimum possible divide ratio is 1 (when UARTIBRD=0), in which case the UARTFBRD
register is ignored. When changing the UARTIBRD register, the new value does not take effect until
transmission/reception of the current character is complete. Any changes to the baud-rate divisor
must be followed by a write to the UARTLCRH register. See “Baud-Rate Generation” on page 422
for configuration details.
UART Integer Baud-Rate Divisor (UARTIBRD)
UART0 base: 0x4000.C000
UART1 base: 0x4000.D000
UART2 base: 0x4000.E000
Offset 0x024
Type R/W, reset 0x0000.0000
31 30 29 28 27 26 25 24 23 22 21 20 19 18 17 16
reserved
Type RO RO RO RO RO RO RO RO RO RO RO RO RO RO RO RO
Reset 0 0 0 0 0 0 0 0 0 0 0 0 0 0 0 0
15 14 13 12 11 10 9 8 7 6 5 4 3 2 1 0
DIVINT
Type R/W R/W R/W R/W R/W R/W R/W R/W R/W R/W R/W R/W R/W R/W R/W R/W
Reset 0 0 0 0 0 0 0 0 0 0 0 0 0 0 0 0
Bit/Field Name Type Reset Description
Software should not rely on the value of a reserved bit. To provide
compatibility with future products, the value of a reserved bit should be
preserved across a read-modify-write operation.
31:16 reserved RO 0
15:0 DIVINT R/W 0x0000 Integer Baud-Rate Divisor
January 08, 2011 435
Texas Instruments-Production Data
Stellaris® LM3S2965 Microcontroller
Register 6: UART Fractional Baud-Rate Divisor (UARTFBRD), offset 0x028
The UARTFBRD register is the fractional part of the baud-rate divisor value. All the bits are cleared
on reset. When changing the UARTFBRD register, the new value does not take effect until
transmission/reception of the current character is complete. Any changes to the baud-rate divisor
must be followed by a write to the UARTLCRH register. See “Baud-Rate Generation” on page 422
for configuration details.
UART Fractional Baud-Rate Divisor (UARTFBRD)
UART0 base: 0x4000.C000
UART1 base: 0x4000.D000
UART2 base: 0x4000.E000
Offset 0x028
Type R/W, reset 0x0000.0000
31 30 29 28 27 26 25 24 23 22 21 20 19 18 17 16
reserved
Type RO RO RO RO RO RO RO RO RO RO RO RO RO RO RO RO
Reset 0 0 0 0 0 0 0 0 0 0 0 0 0 0 0 0
15 14 13 12 11 10 9 8 7 6 5 4 3 2 1 0
reserved DIVFRAC
Type RO RO RO RO RO RO RO RO RO RO R/W R/W R/W R/W R/W R/W
Reset 0 0 0 0 0 0 0 0 0 0 0 0 0 0 0 0
Bit/Field Name Type Reset Description
Software should not rely on the value of a reserved bit. To provide
compatibility with future products, the value of a reserved bit should be
preserved across a read-modify-write operation.
31:6 reserved RO 0x00
5:0 DIVFRAC R/W 0x000 Fractional Baud-Rate Divisor
436 January 08, 2011
Texas Instruments-Production Data
Universal Asynchronous Receivers/Transmitters (UARTs)
Register 7: UART Line Control (UARTLCRH), offset 0x02C
The UARTLCRH register is the line control register. Serial parameters such as data length, parity,
and stop bit selection are implemented in this register.
When updating the baud-rate divisor (UARTIBRD and/or UARTIFRD), the UARTLCRH register
must also be written. The write strobe for the baud-rate divisor registers is tied to the UARTLCRH
register.
UART Line Control (UARTLCRH)
UART0 base: 0x4000.C000
UART1 base: 0x4000.D000
UART2 base: 0x4000.E000
Offset 0x02C
Type R/W, reset 0x0000.0000
31 30 29 28 27 26 25 24 23 22 21 20 19 18 17 16
reserved
Type RO RO RO RO RO RO RO RO RO RO RO RO RO RO RO RO
Reset 0 0 0 0 0 0 0 0 0 0 0 0 0 0 0 0
15 14 13 12 11 10 9 8 7 6 5 4 3 2 1 0
reserved SPS WLEN FEN STP2 EPS PEN BRK
Type RO RO RO RO RO RO RO RO R/W R/W R/W R/W R/W R/W R/W R/W
Reset 0 0 0 0 0 0 0 0 0 0 0 0 0 0 0 0
Bit/Field Name Type Reset Description
Software should not rely on the value of a reserved bit. To provide
compatibility with future products, the value of a reserved bit should be
preserved across a read-modify-write operation.
31:8 reserved RO 0
UART Stick Parity Select
When bits 1, 2, and 7 of UARTLCRH are set, the parity bit is transmitted
and checked as a 0. When bits 1 and 7 are set and 2 is cleared, the
parity bit is transmitted and checked as a 1.
When this bit is cleared, stick parity is disabled.
7 SPS R/W 0
UART Word Length
The bits indicate the number of data bits transmitted or received in a
frame as follows:
Value Description
0x3 8 bits
0x2 7 bits
0x1 6 bits
0x0 5 bits (default)
6:5 WLEN R/W 0
UART Enable FIFOs
If this bit is set to 1, transmit and receive FIFO buffers are enabled (FIFO
mode).
When cleared to 0, FIFOs are disabled (Character mode). The FIFOs
become 1-byte-deep holding registers.
4 FEN R/W 0
UART Two Stop Bits Select
If this bit is set to 1, two stop bits are transmitted at the end of a frame.
The receive logic does not check for two stop bits being received.
3 STP2 R/W 0
January 08, 2011 437
Texas Instruments-Production Data
Stellaris® LM3S2965 Microcontroller
Bit/Field Name Type Reset Description
UART Even Parity Select
If this bit is set to 1, even parity generation and checking is performed
during transmission and reception, which checks for an even number
of 1s in data and parity bits.
When cleared to 0, then odd parity is performed, which checks for an
odd number of 1s.
This bit has no effect when parity is disabled by the PEN bit.
2 EPS R/W 0
UART Parity Enable
If this bit is set to 1, parity checking and generation is enabled; otherwise,
parity is disabled and no parity bit is added to the data frame.
1 PEN R/W 0
UART Send Break
If this bit is set to 1, a Low level is continually output on the UnTX output,
after completing transmission of the current character. For the proper
execution of the break command, the software must set this bit for at
least two frames (character periods). For normal use, this bit must be
cleared to 0.
0 BRK R/W 0
438 January 08, 2011
Texas Instruments-Production Data
Universal Asynchronous Receivers/Transmitters (UARTs)
Register 8: UART Control (UARTCTL), offset 0x030
The UARTCTL register is the control register. All the bits are cleared on reset except for the
Transmit Enable (TXE) and Receive Enable (RXE) bits, which are set to 1.
To enable the UART module, the UARTEN bit must be set to 1. If software requires a configuration
change in the module, the UARTEN bit must be cleared before the configuration changes are written.
If the UART is disabled during a transmit or receive operation, the current transaction is completed
prior to the UART stopping.
Note: The UARTCTL register should not be changed while the UART is enabled or else the results
are unpredictable. The following sequence is recommended for making changes to the
UARTCTL register.
1. Disable the UART.
2. Wait for the end of transmission or reception of the current character.
3. Flush the transmit FIFO by disabling bit 4 (FEN) in the line control register (UARTLCRH).
4. Reprogram the control register.
5. Enable the UART.
UART Control (UARTCTL)
UART0 base: 0x4000.C000
UART1 base: 0x4000.D000
UART2 base: 0x4000.E000
Offset 0x030
Type R/W, reset 0x0000.0300
31 30 29 28 27 26 25 24 23 22 21 20 19 18 17 16
reserved
Type RO RO RO RO RO RO RO RO RO RO RO RO RO RO RO RO
Reset 0 0 0 0 0 0 0 0 0 0 0 0 0 0 0 0
15 14 13 12 11 10 9 8 7 6 5 4 3 2 1 0
reserved RXE TXE LBE reserved SIRLP SIREN UARTEN
Type RO RO RO RO RO RO R/W R/W R/W RO RO RO RO R/W R/W R/W
Reset 0 0 0 0 0 0 1 1 0 0 0 0 0 0 0 0
Bit/Field Name Type Reset Description
Software should not rely on the value of a reserved bit. To provide
compatibility with future products, the value of a reserved bit should be
preserved across a read-modify-write operation.
31:10 reserved RO 0
UART Receive Enable
If this bit is set to 1, the receive section of the UART is enabled. When
the UART is disabled in the middle of a receive, it completes the current
character before stopping.
Note: To enable reception, the UARTEN bit must also be set.
9 RXE R/W 1
UART Transmit Enable
If this bit is set to 1, the transmit section of the UART is enabled. When
the UART is disabled in the middle of a transmission, it completes the
current character before stopping.
Note: To enable transmission, the UARTEN bit must also be set.
8 TXE R/W 1
January 08, 2011 439
Texas Instruments-Production Data
Stellaris® LM3S2965 Microcontroller
Bit/Field Name Type Reset Description
UART Loop Back Enable
If this bit is set to 1, the UnTX path is fed through the UnRX path.
7 LBE R/W 0
Software should not rely on the value of a reserved bit. To provide
compatibility with future products, the value of a reserved bit should be
preserved across a read-modify-write operation.
6:3 reserved RO 0
UART SIR Low Power Mode
This bit selects the IrDA encoding mode. If this bit is cleared to 0,
low-level bits are transmitted as an active High pulse with a width of
3/16th of the bit period. If this bit is set to 1, low-level bits are transmitted
with a pulse width which is 3 times the period of the IrLPBaud16 input
signal, regardless of the selected bit rate. Setting this bit uses less power,
but might reduce transmission distances. See page 434 for more
information.
2 SIRLP R/W 0
UART SIR Enable
If this bit is set to 1, the IrDA SIR block is enabled, and the UART will
transmit and receive data using SIR protocol.
1 SIREN R/W 0
UART Enable
If this bit is set to 1, the UART is enabled. When the UART is disabled
in the middle of transmission or reception, it completes the current
character before stopping.
0 UARTEN R/W 0
440 January 08, 2011
Texas Instruments-Production Data
Universal Asynchronous Receivers/Transmitters (UARTs)
Register 9: UART Interrupt FIFO Level Select (UARTIFLS), offset 0x034
The UARTIFLS register is the interrupt FIFO level select register. You can use this register to define
the FIFO level at which the TXRIS and RXRIS bits in the UARTRIS register are triggered.
The interrupts are generated based on a transition through a level rather than being based on the
level. That is, the interrupts are generated when the fill level progresses through the trigger level.
For example, if the receive trigger level is set to the half-way mark, the interrupt is triggered as the
module is receiving the 9th character.
Out of reset, the TXIFLSEL and RXIFLSEL bits are configured so that the FIFOs trigger an interrupt
at the half-way mark.
UART Interrupt FIFO Level Select (UARTIFLS)
UART0 base: 0x4000.C000
UART1 base: 0x4000.D000
UART2 base: 0x4000.E000
Offset 0x034
Type R/W, reset 0x0000.0012
31 30 29 28 27 26 25 24 23 22 21 20 19 18 17 16
reserved
Type RO RO RO RO RO RO RO RO RO RO RO RO RO RO RO RO
Reset 0 0 0 0 0 0 0 0 0 0 0 0 0 0 0 0
15 14 13 12 11 10 9 8 7 6 5 4 3 2 1 0
reserved RXIFLSEL TXIFLSEL
Type RO RO RO RO RO RO RO RO RO RO R/W R/W R/W R/W R/W R/W
Reset 0 0 0 0 0 0 0 0 0 0 0 1 0 0 1 0
Bit/Field Name Type Reset Description
Software should not rely on the value of a reserved bit. To provide
compatibility with future products, the value of a reserved bit should be
preserved across a read-modify-write operation.
31:6 reserved RO 0x00
UART Receive Interrupt FIFO Level Select
The trigger points for the receive interrupt are as follows:
Value Description
0x0 RX FIFO ≥ ⅛ full
0x1 RX FIFO ≥ ¼ full
0x2 RX FIFO ≥ ½ full (default)
0x3 RX FIFO ≥ ¾ full
0x4 RX FIFO ≥ ⅞ full
0x5-0x7 Reserved
5:3 RXIFLSEL R/W 0x2
January 08, 2011 441
Texas Instruments-Production Data
Stellaris® LM3S2965 Microcontroller
Bit/Field Name Type Reset Description
UART Transmit Interrupt FIFO Level Select
The trigger points for the transmit interrupt are as follows:
Value Description
0x0 TX FIFO ≤ ⅞ empty
0x1 TX FIFO ≤ ¾ empty
0x2 TX FIFO ≤ ½ empty (default)
0x3 TX FIFO ≤ ¼ empty
0x4 TX FIFO ≤ ⅛ empty
0x5-0x7 Reserved
2:0 TXIFLSEL R/W 0x2
442 January 08, 2011
Texas Instruments-Production Data
Universal Asynchronous Receivers/Transmitters (UARTs)
Register 10: UART Interrupt Mask (UARTIM), offset 0x038
The UARTIM register is the interrupt mask set/clear register.
On a read, this register gives the current value of the mask on the relevant interrupt. Writing a 1 to
a bit allows the corresponding raw interrupt signal to be routed to the interrupt controller. Writing a
0 prevents the raw interrupt signal from being sent to the interrupt controller.
UART Interrupt Mask (UARTIM)
UART0 base: 0x4000.C000
UART1 base: 0x4000.D000
UART2 base: 0x4000.E000
Offset 0x038
Type R/W, reset 0x0000.0000
31 30 29 28 27 26 25 24 23 22 21 20 19 18 17 16
reserved
Type RO RO RO RO RO RO RO RO RO RO RO RO RO RO RO RO
Reset 0 0 0 0 0 0 0 0 0 0 0 0 0 0 0 0
15 14 13 12 11 10 9 8 7 6 5 4 3 2 1 0
reserved OEIM BEIM PEIM FEIM RTIM TXIM RXIM reserved
Type RO RO RO RO RO R/W R/W R/W R/W R/W R/W R/W RO RO RO RO
Reset 0 0 0 0 0 0 0 0 0 0 0 0 0 0 0 0
Bit/Field Name Type Reset Description
Software should not rely on the value of a reserved bit. To provide
compatibility with future products, the value of a reserved bit should be
preserved across a read-modify-write operation.
31:11 reserved RO 0x00
UART Overrun Error Interrupt Mask
On a read, the current mask for the OEIM interrupt is returned.
Setting this bit to 1 promotes the OEIM interrupt to the interrupt controller.
10 OEIM R/W 0
UART Break Error Interrupt Mask
On a read, the current mask for the BEIM interrupt is returned.
Setting this bit to 1 promotes the BEIM interrupt to the interrupt controller.
9 BEIM R/W 0
UART Parity Error Interrupt Mask
On a read, the current mask for the PEIM interrupt is returned.
Setting this bit to 1 promotes the PEIM interrupt to the interrupt controller.
8 PEIM R/W 0
UART Framing Error Interrupt Mask
On a read, the current mask for the FEIM interrupt is returned.
Setting this bit to 1 promotes the FEIM interrupt to the interrupt controller.
7 FEIM R/W 0
UART Receive Time-Out Interrupt Mask
On a read, the current mask for the RTIM interrupt is returned.
Setting this bit to 1 promotes the RTIM interrupt to the interrupt controller.
6 RTIM R/W 0
UART Transmit Interrupt Mask
On a read, the current mask for the TXIM interrupt is returned.
Setting this bit to 1 promotes the TXIM interrupt to the interrupt controller.
5 TXIM R/W 0
UART Receive Interrupt Mask
On a read, the current mask for the RXIM interrupt is returned.
Setting this bit to 1 promotes the RXIM interrupt to the interrupt controller.
4 RXIM R/W 0
January 08, 2011 443
Texas Instruments-Production Data
Stellaris® LM3S2965 Microcontroller
Bit/Field Name Type Reset Description
Software should not rely on the value of a reserved bit. To provide
compatibility with future products, the value of a reserved bit should be
preserved across a read-modify-write operation.
3:0 reserved RO 0x00
444 January 08, 2011
Texas Instruments-Production Data
Universal Asynchronous Receivers/Transmitters (UARTs)
Register 11: UART Raw Interrupt Status (UARTRIS), offset 0x03C
The UARTRIS register is the raw interrupt status register. On a read, this register gives the current
raw status value of the corresponding interrupt. A write has no effect.
UART Raw Interrupt Status (UARTRIS)
UART0 base: 0x4000.C000
UART1 base: 0x4000.D000
UART2 base: 0x4000.E000
Offset 0x03C
Type RO, reset 0x0000.000F
31 30 29 28 27 26 25 24 23 22 21 20 19 18 17 16
reserved
Type RO RO RO RO RO RO RO RO RO RO RO RO RO RO RO RO
Reset 0 0 0 0 0 0 0 0 0 0 0 0 0 0 0 0
15 14 13 12 11 10 9 8 7 6 5 4 3 2 1 0
reserved OERIS BERIS PERIS FERIS RTRIS TXRIS RXRIS reserved
Type RO RO RO RO RO RO RO RO RO RO RO RO RO RO RO RO
Reset 0 0 0 0 0 0 0 0 0 0 0 0 1 1 1 1
Bit/Field Name Type Reset Description
Software should not rely on the value of a reserved bit. To provide
compatibility with future products, the value of a reserved bit should be
preserved across a read-modify-write operation.
31:11 reserved RO 0x00
UART Overrun Error Raw Interrupt Status
Gives the raw interrupt state (prior to masking) of this interrupt.
10 OERIS RO 0
UART Break Error Raw Interrupt Status
Gives the raw interrupt state (prior to masking) of this interrupt.
9 BERIS RO 0
UART Parity Error Raw Interrupt Status
Gives the raw interrupt state (prior to masking) of this interrupt.
8 PERIS RO 0
UART Framing Error Raw Interrupt Status
Gives the raw interrupt state (prior to masking) of this interrupt.
7 FERIS RO 0
UART Receive Time-Out Raw Interrupt Status
Gives the raw interrupt state (prior to masking) of this interrupt.
6 RTRIS RO 0
UART Transmit Raw Interrupt Status
Gives the raw interrupt state (prior to masking) of this interrupt.
5 TXRIS RO 0
UART Receive Raw Interrupt Status
Gives the raw interrupt state (prior to masking) of this interrupt.
4 RXRIS RO 0
Software should not rely on the value of a reserved bit. To provide
compatibility with future products, the value of a reserved bit should be
preserved across a read-modify-write operation.
3:0 reserved RO 0xF
January 08, 2011 445
Texas Instruments-Production Data
Stellaris® LM3S2965 Microcontroller
Register 12: UART Masked Interrupt Status (UARTMIS), offset 0x040
The UARTMIS register is the masked interrupt status register. On a read, this register gives the
current masked status value of the corresponding interrupt. A write has no effect.
UART Masked Interrupt Status (UARTMIS)
UART0 base: 0x4000.C000
UART1 base: 0x4000.D000
UART2 base: 0x4000.E000
Offset 0x040
Type RO, reset 0x0000.0000
31 30 29 28 27 26 25 24 23 22 21 20 19 18 17 16
reserved
Type RO RO RO RO RO RO RO RO RO RO RO RO RO RO RO RO
Reset 0 0 0 0 0 0 0 0 0 0 0 0 0 0 0 0
15 14 13 12 11 10 9 8 7 6 5 4 3 2 1 0
reserved OEMIS BEMIS PEMIS FEMIS RTMIS TXMIS RXMIS reserved
Type RO RO RO RO RO RO RO RO RO RO RO RO RO RO RO RO
Reset 0 0 0 0 0 0 0 0 0 0 0 0 0 0 0 0
Bit/Field Name Type Reset Description
Software should not rely on the value of a reserved bit. To provide
compatibility with future products, the value of a reserved bit should be
preserved across a read-modify-write operation.
31:11 reserved RO 0x00
UART Overrun Error Masked Interrupt Status
Gives the masked interrupt state of this interrupt.
10 OEMIS RO 0
UART Break Error Masked Interrupt Status
Gives the masked interrupt state of this interrupt.
9 BEMIS RO 0
UART Parity Error Masked Interrupt Status
Gives the masked interrupt state of this interrupt.
8 PEMIS RO 0
UART Framing Error Masked Interrupt Status
Gives the masked interrupt state of this interrupt.
7 FEMIS RO 0
UART Receive Time-Out Masked Interrupt Status
Gives the masked interrupt state of this interrupt.
6 RTMIS RO 0
UART Transmit Masked Interrupt Status
Gives the masked interrupt state of this interrupt.
5 TXMIS RO 0
UART Receive Masked Interrupt Status
Gives the masked interrupt state of this interrupt.
4 RXMIS RO 0
Software should not rely on the value of a reserved bit. To provide
compatibility with future products, the value of a reserved bit should be
preserved across a read-modify-write operation.
3:0 reserved RO 0
446 January 08, 2011
Texas Instruments-Production Data
Universal Asynchronous Receivers/Transmitters (UARTs)
Register 13: UART Interrupt Clear (UARTICR), offset 0x044
The UARTICR register is the interrupt clear register. On a write of 1, the corresponding interrupt
(both raw interrupt and masked interrupt, if enabled) is cleared. A write of 0 has no effect.
UART Interrupt Clear (UARTICR)
UART0 base: 0x4000.C000
UART1 base: 0x4000.D000
UART2 base: 0x4000.E000
Offset 0x044
Type W1C, reset 0x0000.0000
31 30 29 28 27 26 25 24 23 22 21 20 19 18 17 16
reserved
Type RO RO RO RO RO RO RO RO RO RO RO RO RO RO RO RO
Reset 0 0 0 0 0 0 0 0 0 0 0 0 0 0 0 0
15 14 13 12 11 10 9 8 7 6 5 4 3 2 1 0
reserved OEIC BEIC PEIC FEIC RTIC TXIC RXIC reserved
Type RO RO RO RO RO W1C W1C W1C W1C W1C W1C W1C RO RO RO RO
Reset 0 0 0 0 0 0 0 0 0 0 0 0 0 0 0 0
Bit/Field Name Type Reset Description
Software should not rely on the value of a reserved bit. To provide
compatibility with future products, the value of a reserved bit should be
preserved across a read-modify-write operation.
31:11 reserved RO 0x00
Overrun Error Interrupt Clear
The OEIC values are defined as follows:
Value Description
0 No effect on the interrupt.
1 Clears interrupt.
10 OEIC W1C 0
Break Error Interrupt Clear
The BEIC values are defined as follows:
Value Description
0 No effect on the interrupt.
1 Clears interrupt.
9 BEIC W1C 0
Parity Error Interrupt Clear
The PEIC values are defined as follows:
Value Description
0 No effect on the interrupt.
1 Clears interrupt.
8 PEIC W1C 0
Framing Error Interrupt Clear
The FEIC values are defined as follows:
Value Description
0 No effect on the interrupt.
1 Clears interrupt.
7 FEIC W1C 0
January 08, 2011 447
Texas Instruments-Production Data
Stellaris® LM3S2965 Microcontroller
Bit/Field Name Type Reset Description
Receive Time-Out Interrupt Clear
The RTIC values are defined as follows:
Value Description
0 No effect on the interrupt.
1 Clears interrupt.
6 RTIC W1C 0
Transmit Interrupt Clear
The TXIC values are defined as follows:
Value Description
0 No effect on the interrupt.
1 Clears interrupt.
5 TXIC W1C 0
Receive Interrupt Clear
The RXIC values are defined as follows:
Value Description
0 No effect on the interrupt.
1 Clears interrupt.
4 RXIC W1C 0
Software should not rely on the value of a reserved bit. To provide
compatibility with future products, the value of a reserved bit should be
preserved across a read-modify-write operation.
3:0 reserved RO 0x00
448 January 08, 2011
Texas Instruments-Production Data
Universal Asynchronous Receivers/Transmitters (UARTs)
Register 14: UART Peripheral Identification 4 (UARTPeriphID4), offset 0xFD0
The UARTPeriphIDn registers are hard-coded and the fields within the registers determine the
reset values.
UART Peripheral Identification 4 (UARTPeriphID4)
UART0 base: 0x4000.C000
UART1 base: 0x4000.D000
UART2 base: 0x4000.E000
Offset 0xFD0
Type RO, reset 0x0000.0000
31 30 29 28 27 26 25 24 23 22 21 20 19 18 17 16
reserved
Type RO RO RO RO RO RO RO RO RO RO RO RO RO RO RO RO
Reset 0 0 0 0 0 0 0 0 0 0 0 0 0 0 0 0
15 14 13 12 11 10 9 8 7 6 5 4 3 2 1 0
reserved PID4
Type RO RO RO RO RO RO RO RO RO RO RO RO RO RO RO RO
Reset 0 0 0 0 0 0 0 0 0 0 0 0 0 0 0 0
Bit/Field Name Type Reset Description
Software should not rely on the value of a reserved bit. To provide
compatibility with future products, the value of a reserved bit should be
preserved across a read-modify-write operation.
31:8 reserved RO 0x00
UART Peripheral ID Register[7:0]
Can be used by software to identify the presence of this peripheral.
7:0 PID4 RO 0x0000
January 08, 2011 449
Texas Instruments-Production Data
Stellaris® LM3S2965 Microcontroller
Register 15: UART Peripheral Identification 5 (UARTPeriphID5), offset 0xFD4
The UARTPeriphIDn registers are hard-coded and the fields within the registers determine the
reset values.
UART Peripheral Identification 5 (UARTPeriphID5)
UART0 base: 0x4000.C000
UART1 base: 0x4000.D000
UART2 base: 0x4000.E000
Offset 0xFD4
Type RO, reset 0x0000.0000
31 30 29 28 27 26 25 24 23 22 21 20 19 18 17 16
reserved
Type RO RO RO RO RO RO RO RO RO RO RO RO RO RO RO RO
Reset 0 0 0 0 0 0 0 0 0 0 0 0 0 0 0 0
15 14 13 12 11 10 9 8 7 6 5 4 3 2 1 0
reserved PID5
Type RO RO RO RO RO RO RO RO RO RO RO RO RO RO RO RO
Reset 0 0 0 0 0 0 0 0 0 0 0 0 0 0 0 0
Bit/Field Name Type Reset Description
Software should not rely on the value of a reserved bit. To provide
compatibility with future products, the value of a reserved bit should be
preserved across a read-modify-write operation.
31:8 reserved RO 0x00
UART Peripheral ID Register[15:8]
Can be used by software to identify the presence of this peripheral.
7:0 PID5 RO 0x0000
450 January 08, 2011
Texas Instruments-Production Data
Universal Asynchronous Receivers/Transmitters (UARTs)
Register 16: UART Peripheral Identification 6 (UARTPeriphID6), offset 0xFD8
The UARTPeriphIDn registers are hard-coded and the fields within the registers determine the
reset values.
UART Peripheral Identification 6 (UARTPeriphID6)
UART0 base: 0x4000.C000
UART1 base: 0x4000.D000
UART2 base: 0x4000.E000
Offset 0xFD8
Type RO, reset 0x0000.0000
31 30 29 28 27 26 25 24 23 22 21 20 19 18 17 16
reserved
Type RO RO RO RO RO RO RO RO RO RO RO RO RO RO RO RO
Reset 0 0 0 0 0 0 0 0 0 0 0 0 0 0 0 0
15 14 13 12 11 10 9 8 7 6 5 4 3 2 1 0
reserved PID6
Type RO RO RO RO RO RO RO RO RO RO RO RO RO RO RO RO
Reset 0 0 0 0 0 0 0 0 0 0 0 0 0 0 0 0
Bit/Field Name Type Reset Description
Software should not rely on the value of a reserved bit. To provide
compatibility with future products, the value of a reserved bit should be
preserved across a read-modify-write operation.
31:8 reserved RO 0x00
UART Peripheral ID Register[23:16]
Can be used by software to identify the presence of this peripheral.
7:0 PID6 RO 0x0000
January 08, 2011 451
Texas Instruments-Production Data
Stellaris® LM3S2965 Microcontroller
Register 17: UART Peripheral Identification 7 (UARTPeriphID7), offset 0xFDC
The UARTPeriphIDn registers are hard-coded and the fields within the registers determine the
reset values.
UART Peripheral Identification 7 (UARTPeriphID7)
UART0 base: 0x4000.C000
UART1 base: 0x4000.D000
UART2 base: 0x4000.E000
Offset 0xFDC
Type RO, reset 0x0000.0000
31 30 29 28 27 26 25 24 23 22 21 20 19 18 17 16
reserved
Type RO RO RO RO RO RO RO RO RO RO RO RO RO RO RO RO
Reset 0 0 0 0 0 0 0 0 0 0 0 0 0 0 0 0
15 14 13 12 11 10 9 8 7 6 5 4 3 2 1 0
reserved PID7
Type RO RO RO RO RO RO RO RO RO RO RO RO RO RO RO RO
Reset 0 0 0 0 0 0 0 0 0 0 0 0 0 0 0 0
Bit/Field Name Type Reset Description
Software should not rely on the value of a reserved bit. To provide
compatibility with future products, the value of a reserved bit should be
preserved across a read-modify-write operation.
31:8 reserved RO 0
UART Peripheral ID Register[31:24]
Can be used by software to identify the presence of this peripheral.
7:0 PID7 RO 0x0000
452 January 08, 2011
Texas Instruments-Production Data
Universal Asynchronous Receivers/Transmitters (UARTs)
Register 18: UART Peripheral Identification 0 (UARTPeriphID0), offset 0xFE0
The UARTPeriphIDn registers are hard-coded and the fields within the registers determine the
reset values.
UART Peripheral Identification 0 (UARTPeriphID0)
UART0 base: 0x4000.C000
UART1 base: 0x4000.D000
UART2 base: 0x4000.E000
Offset 0xFE0
Type RO, reset 0x0000.0011
31 30 29 28 27 26 25 24 23 22 21 20 19 18 17 16
reserved
Type RO RO RO RO RO RO RO RO RO RO RO RO RO RO RO RO
Reset 0 0 0 0 0 0 0 0 0 0 0 0 0 0 0 0
15 14 13 12 11 10 9 8 7 6 5 4 3 2 1 0
reserved PID0
Type RO RO RO RO RO RO RO RO RO RO RO RO RO RO RO RO
Reset 0 0 0 0 0 0 0 0 0 0 0 1 0 0 0 1
Bit/Field Name Type Reset Description
Software should not rely on the value of a reserved bit. To provide
compatibility with future products, the value of a reserved bit should be
preserved across a read-modify-write operation.
31:8 reserved RO 0x00
UART Peripheral ID Register[7:0]
Can be used by software to identify the presence of this peripheral.
7:0 PID0 RO 0x11
January 08, 2011 453
Texas Instruments-Production Data
Stellaris® LM3S2965 Microcontroller
Register 19: UART Peripheral Identification 1 (UARTPeriphID1), offset 0xFE4
The UARTPeriphIDn registers are hard-coded and the fields within the registers determine the
reset values.
UART Peripheral Identification 1 (UARTPeriphID1)
UART0 base: 0x4000.C000
UART1 base: 0x4000.D000
UART2 base: 0x4000.E000
Offset 0xFE4
Type RO, reset 0x0000.0000
31 30 29 28 27 26 25 24 23 22 21 20 19 18 17 16
reserved
Type RO RO RO RO RO RO RO RO RO RO RO RO RO RO RO RO
Reset 0 0 0 0 0 0 0 0 0 0 0 0 0 0 0 0
15 14 13 12 11 10 9 8 7 6 5 4 3 2 1 0
reserved PID1
Type RO RO RO RO RO RO RO RO RO RO RO RO RO RO RO RO
Reset 0 0 0 0 0 0 0 0 0 0 0 0 0 0 0 0
Bit/Field Name Type Reset Description
Software should not rely on the value of a reserved bit. To provide
compatibility with future products, the value of a reserved bit should be
preserved across a read-modify-write operation.
31:8 reserved RO 0x00
UART Peripheral ID Register[15:8]
Can be used by software to identify the presence of this peripheral.
7:0 PID1 RO 0x00
454 January 08, 2011
Texas Instruments-Production Data
Universal Asynchronous Receivers/Transmitters (UARTs)
Register 20: UART Peripheral Identification 2 (UARTPeriphID2), offset 0xFE8
The UARTPeriphIDn registers are hard-coded and the fields within the registers determine the
reset values.
UART Peripheral Identification 2 (UARTPeriphID2)
UART0 base: 0x4000.C000
UART1 base: 0x4000.D000
UART2 base: 0x4000.E000
Offset 0xFE8
Type RO, reset 0x0000.0018
31 30 29 28 27 26 25 24 23 22 21 20 19 18 17 16
reserved
Type RO RO RO RO RO RO RO RO RO RO RO RO RO RO RO RO
Reset 0 0 0 0 0 0 0 0 0 0 0 0 0 0 0 0
15 14 13 12 11 10 9 8 7 6 5 4 3 2 1 0
reserved PID2
Type RO RO RO RO RO RO RO RO RO RO RO RO RO RO RO RO
Reset 0 0 0 0 0 0 0 0 0 0 0 1 1 0 0 0
Bit/Field Name Type Reset Description
Software should not rely on the value of a reserved bit. To provide
compatibility with future products, the value of a reserved bit should be
preserved across a read-modify-write operation.
31:8 reserved RO 0x00
UART Peripheral ID Register[23:16]
Can be used by software to identify the presence of this peripheral.
7:0 PID2 RO 0x18
January 08, 2011 455
Texas Instruments-Production Data
Stellaris® LM3S2965 Microcontroller
Register 21: UART Peripheral Identification 3 (UARTPeriphID3), offset 0xFEC
The UARTPeriphIDn registers are hard-coded and the fields within the registers determine the
reset values.
UART Peripheral Identification 3 (UARTPeriphID3)
UART0 base: 0x4000.C000
UART1 base: 0x4000.D000
UART2 base: 0x4000.E000
Offset 0xFEC
Type RO, reset 0x0000.0001
31 30 29 28 27 26 25 24 23 22 21 20 19 18 17 16
reserved
Type RO RO RO RO RO RO RO RO RO RO RO RO RO RO RO RO
Reset 0 0 0 0 0 0 0 0 0 0 0 0 0 0 0 0
15 14 13 12 11 10 9 8 7 6 5 4 3 2 1 0
reserved PID3
Type RO RO RO RO RO RO RO RO RO RO RO RO RO RO RO RO
Reset 0 0 0 0 0 0 0 0 0 0 0 0 0 0 0 1
Bit/Field Name Type Reset Description
Software should not rely on the value of a reserved bit. To provide
compatibility with future products, the value of a reserved bit should be
preserved across a read-modify-write operation.
31:8 reserved RO 0x00
UART Peripheral ID Register[31:24]
Can be used by software to identify the presence of this peripheral.
7:0 PID3 RO 0x01
456 January 08, 2011
Texas Instruments-Production Data
Universal Asynchronous Receivers/Transmitters (UARTs)
Register 22: UART PrimeCell Identification 0 (UARTPCellID0), offset 0xFF0
The UARTPCellIDn registers are hard-coded and the fields within the registers determine the reset
values.
UART PrimeCell Identification 0 (UARTPCellID0)
UART0 base: 0x4000.C000
UART1 base: 0x4000.D000
UART2 base: 0x4000.E000
Offset 0xFF0
Type RO, reset 0x0000.000D
31 30 29 28 27 26 25 24 23 22 21 20 19 18 17 16
reserved
Type RO RO RO RO RO RO RO RO RO RO RO RO RO RO RO RO
Reset 0 0 0 0 0 0 0 0 0 0 0 0 0 0 0 0
15 14 13 12 11 10 9 8 7 6 5 4 3 2 1 0
reserved CID0
Type RO RO RO RO RO RO RO RO RO RO RO RO RO RO RO RO
Reset 0 0 0 0 0 0 0 0 0 0 0 0 1 1 0 1
Bit/Field Name Type Reset Description
Software should not rely on the value of a reserved bit. To provide
compatibility with future products, the value of a reserved bit should be
preserved across a read-modify-write operation.
31:8 reserved RO 0x00
UART PrimeCell ID Register[7:0]
Provides software a standard cross-peripheral identification system.
7:0 CID0 RO 0x0D
January 08, 2011 457
Texas Instruments-Production Data
Stellaris® LM3S2965 Microcontroller
Register 23: UART PrimeCell Identification 1 (UARTPCellID1), offset 0xFF4
The UARTPCellIDn registers are hard-coded and the fields within the registers determine the reset
values.
UART PrimeCell Identification 1 (UARTPCellID1)
UART0 base: 0x4000.C000
UART1 base: 0x4000.D000
UART2 base: 0x4000.E000
Offset 0xFF4
Type RO, reset 0x0000.00F0
31 30 29 28 27 26 25 24 23 22 21 20 19 18 17 16
reserved
Type RO RO RO RO RO RO RO RO RO RO RO RO RO RO RO RO
Reset 0 0 0 0 0 0 0 0 0 0 0 0 0 0 0 0
15 14 13 12 11 10 9 8 7 6 5 4 3 2 1 0
reserved CID1
Type RO RO RO RO RO RO RO RO RO RO RO RO RO RO RO RO
Reset 0 0 0 0 0 0 0 0 1 1 1 1 0 0 0 0
Bit/Field Name Type Reset Description
Software should not rely on the value of a reserved bit. To provide
compatibility with future products, the value of a reserved bit should be
preserved across a read-modify-write operation.
31:8 reserved RO 0x00
UART PrimeCell ID Register[15:8]
Provides software a standard cross-peripheral identification system.
7:0 CID1 RO 0xF0
458 January 08, 2011
Texas Instruments-Production Data
Universal Asynchronous Receivers/Transmitters (UARTs)
Register 24: UART PrimeCell Identification 2 (UARTPCellID2), offset 0xFF8
The UARTPCellIDn registers are hard-coded and the fields within the registers determine the reset
values.
UART PrimeCell Identification 2 (UARTPCellID2)
UART0 base: 0x4000.C000
UART1 base: 0x4000.D000
UART2 base: 0x4000.E000
Offset 0xFF8
Type RO, reset 0x0000.0005
31 30 29 28 27 26 25 24 23 22 21 20 19 18 17 16
reserved
Type RO RO RO RO RO RO RO RO RO RO RO RO RO RO RO RO
Reset 0 0 0 0 0 0 0 0 0 0 0 0 0 0 0 0
15 14 13 12 11 10 9 8 7 6 5 4 3 2 1 0
reserved CID2
Type RO RO RO RO RO RO RO RO RO RO RO RO RO RO RO RO
Reset 0 0 0 0 0 0 0 0 0 0 0 0 0 1 0 1
Bit/Field Name Type Reset Description
Software should not rely on the value of a reserved bit. To provide
compatibility with future products, the value of a reserved bit should be
preserved across a read-modify-write operation.
31:8 reserved RO 0x00
UART PrimeCell ID Register[23:16]
Provides software a standard cross-peripheral identification system.
7:0 CID2 RO 0x05
January 08, 2011 459
Texas Instruments-Production Data
Stellaris® LM3S2965 Microcontroller
Register 25: UART PrimeCell Identification 3 (UARTPCellID3), offset 0xFFC
The UARTPCellIDn registers are hard-coded and the fields within the registers determine the reset
values.
UART PrimeCell Identification 3 (UARTPCellID3)
UART0 base: 0x4000.C000
UART1 base: 0x4000.D000
UART2 base: 0x4000.E000
Offset 0xFFC
Type RO, reset 0x0000.00B1
31 30 29 28 27 26 25 24 23 22 21 20 19 18 17 16
reserved
Type RO RO RO RO RO RO RO RO RO RO RO RO RO RO RO RO
Reset 0 0 0 0 0 0 0 0 0 0 0 0 0 0 0 0
15 14 13 12 11 10 9 8 7 6 5 4 3 2 1 0
reserved CID3
Type RO RO RO RO RO RO RO RO RO RO RO RO RO RO RO RO
Reset 0 0 0 0 0 0 0 0 1 0 1 1 0 0 0 1
Bit/Field Name Type Reset Description
Software should not rely on the value of a reserved bit. To provide
compatibility with future products, the value of a reserved bit should be
preserved across a read-modify-write operation.
31:8 reserved RO 0x00
UART PrimeCell ID Register[31:24]
Provides software a standard cross-peripheral identification system.
7:0 CID3 RO 0xB1
460 January 08, 2011
Texas Instruments-Production Data
Universal Asynchronous Receivers/Transmitters (UARTs)
13 Synchronous Serial Interface (SSI)
The Stellaris® microcontroller includes two Synchronous Serial Interface (SSI) modules. Each SSI
is a master or slave interface for synchronous serial communication with peripheral devices that
have either Freescale SPI, MICROWIRE, or Texas Instruments synchronous serial interfaces.
Each Stellaris SSI module has the following features:
■ Two SSI modules, each with the following features:
■ Master or slave operation
■ Programmable clock bit rate and prescale
■ Separate transmit and receive FIFOs, 16 bits wide, 8 locations deep
■ Programmable interface operation for Freescale SPI, MICROWIRE, or Texas Instruments
synchronous serial interfaces
■ Programmable data frame size from 4 to 16 bits
■ Internal loopback test mode for diagnostic/debug testing
13.1 Block Diagram
Figure 13-1. SSI Module Block Diagram
Transmit /
Receive
Logic
Clock
Prescaler
SSICPSR
SSICR0
SSICR1
SSISR
Interrupt Control
SSIIM
SSIMIS
SSIRIS
SSIICR
SSIDR
TxFIFO
8 x16
...
RxFIFO
8 x16
...
System Clock
SSITx
SSIRx
SSIClk
SSIFss
Interrupt
Identification
Registers
SSIPCellID0 0 SSIPeriphID 4
SSIPCellID1 1 SSIPeriphID 5
SSIPCellID2 2 SSIPeriphID 6
SSIPCellID3 SSIPeriphID 3 SSIPeriphID7
Control/ Status
SSIPeriphID
SSIPeriphID
SSIPeriphID
January 08, 2011 461
Texas Instruments-Production Data
Stellaris® LM3S2965 Microcontroller
13.2 Functional Description
The SSI performs serial-to-parallel conversion on data received from a peripheral device. The CPU
accesses data, control, and status information. The transmit and receive paths are buffered with
internal FIFO memories allowing up to eight 16-bit values to be stored independently in both transmit
and receive modes.
13.2.1 Bit Rate Generation
The SSI includes a programmable bit rate clock divider and prescaler to generate the serial output
clock. Bit rates are supported to 2 MHz and higher, although maximum bit rate is determined by
peripheral devices.
The serial bit rate is derived by dividing down the input clock (FSysClk). The clock is first divided
by an even prescale value CPSDVSR from 2 to 254, which is programmed in the SSI Clock Prescale
(SSICPSR) register (see page 480). The clock is further divided by a value from 1 to 256, which is
1 + SCR, where SCR is the value programmed in the SSI Control0 (SSICR0) register (see page 473).
The frequency of the output clock SSIClk is defined by:
SSIClk = FSysClk / (CPSDVSR * (1 + SCR))
Note: For master mode, the system clock must be at least two times faster than the SSIClk. For
slave mode, the system clock must be at least 12 times faster than the SSIClk.
See “Synchronous Serial Interface (SSI)” on page 690 to view SSI timing parameters.
13.2.2 FIFO Operation
13.2.2.1 Transmit FIFO
The common transmit FIFO is a 16-bit wide, 8-locations deep, first-in, first-out memory buffer. The
CPU writes data to the FIFO by writing the SSI Data (SSIDR) register (see page 477), and data is
stored in the FIFO until it is read out by the transmission logic.
When configured as a master or a slave, parallel data is written into the transmit FIFO prior to serial
conversion and transmission to the attached slave or master, respectively, through the SSITx pin.
In slave mode, the SSI transmits data each time the master initiates a transaction. If the transmit
FIFO is empty and the master initiates, the slave transmits the 8th most recent value in the transmit
FIFO. If less than 8 values have been written to the transmit FIFO since the SSI module clock was
enabled using the SSI bit in the RGCG1 register, then 0 is transmitted. Care should be taken to
ensure that valid data is in the FIFO as needed. The SSI can be configured to generate an interrupt
or a μDMA request when the FIFO is empty.
13.2.2.2 Receive FIFO
The common receive FIFO is a 16-bit wide, 8-locations deep, first-in, first-out memory buffer.
Received data from the serial interface is stored in the buffer until read out by the CPU, which
accesses the read FIFO by reading the SSIDR register.
When configured as a master or slave, serial data received through the SSIRx pin is registered
prior to parallel loading into the attached slave or master receive FIFO, respectively.
13.2.3 Interrupts
The SSI can generate interrupts when the following conditions are observed:
462 January 08, 2011
Texas Instruments-Production Data
Synchronous Serial Interface (SSI)
■ Transmit FIFO service
■ Receive FIFO service
■ Receive FIFO time-out
■ Receive FIFO overrun
All of the interrupt events are ORed together before being sent to the interrupt controller, so the SSI
can only generate a single interrupt request to the controller at any given time. You can mask each
of the four individual maskable interrupts by setting the appropriate bits in the SSI Interrupt Mask
(SSIIM) register (see page 481). Setting the appropriate mask bit to 1 enables the interrupt.
Provision of the individual outputs, as well as a combined interrupt output, allows use of either a
global interrupt service routine, or modular device drivers to handle interrupts. The transmit and
receive dynamic dataflow interrupts have been separated from the status interrupts so that data
can be read or written in response to the FIFO trigger levels. The status of the individual interrupt
sources can be read from the SSI Raw Interrupt Status (SSIRIS) and SSI Masked Interrupt Status
(SSIMIS) registers (see page 483 and page 484, respectively).
13.2.4 Frame Formats
Each data frame is between 4 and 16 bits long, depending on the size of data programmed, and is
transmitted starting with the MSB. There are three basic frame types that can be selected:
■ Texas Instruments synchronous serial
■ Freescale SPI
■ MICROWIRE
For all three formats, the serial clock (SSIClk) is held inactive while the SSI is idle, and SSIClk
transitions at the programmed frequency only during active transmission or reception of data. The
idle state of SSIClk is utilized to provide a receive timeout indication that occurs when the receive
FIFO still contains data after a timeout period.
For Freescale SPI and MICROWIRE frame formats, the serial frame (SSIFss ) pin is active Low,
and is asserted (pulled down) during the entire transmission of the frame.
For Texas Instruments synchronous serial frame format, the SSIFss pin is pulsed for one serial
clock period starting at its rising edge, prior to the transmission of each frame. For this frame format,
both the SSI and the off-chip slave device drive their output data on the rising edge of SSIClk, and
latch data from the other device on the falling edge.
Unlike the full-duplex transmission of the other two frame formats, the MICROWIRE format uses a
special master-slave messaging technique, which operates at half-duplex. In this mode, when a
frame begins, an 8-bit control message is transmitted to the off-chip slave. During this transmit, no
incoming data is received by the SSI. After the message has been sent, the off-chip slave decodes
it and, after waiting one serial clock after the last bit of the 8-bit control message has been sent,
responds with the requested data. The returned data can be 4 to 16 bits in length, making the total
frame length anywhere from 13 to 25 bits.
13.2.4.1 Texas Instruments Synchronous Serial Frame Format
Figure 13-2 on page 464 shows the Texas Instruments synchronous serial frame format for a single
transmitted frame.
January 08, 2011 463
Texas Instruments-Production Data
Stellaris® LM3S2965 Microcontroller
Figure 13-2. TI Synchronous Serial Frame Format (Single Transfer)
SSIClk
SSIFss
SSITx/SSIRx MSB LSB
4 to 16 bits
In this mode, SSIClk and SSIFss are forced Low, and the transmit data line SSITx is tristated
whenever the SSI is idle. Once the bottom entry of the transmit FIFO contains data, SSIFss is
pulsed High for one SSIClk period. The value to be transmitted is also transferred from the transmit
FIFO to the serial shift register of the transmit logic. On the next rising edge of SSIClk, the MSB
of the 4 to 16-bit data frame is shifted out on the SSITx pin. Likewise, the MSB of the received data
is shifted onto the SSIRx pin by the off-chip serial slave device.
Both the SSI and the off-chip serial slave device then clock each data bit into their serial shifter on
the falling edge of each SSIClk. The received data is transferred from the serial shifter to the receive
FIFO on the first rising edge of SSIClk after the LSB has been latched.
Figure 13-3 on page 464 shows the Texas Instruments synchronous serial frame format when
back-to-back frames are transmitted.
Figure 13-3. TI Synchronous Serial Frame Format (Continuous Transfer)
MSB LSB
SSIClk
SSIFss
SSITx/SSIRx
4 to 16 bits
13.2.4.2 Freescale SPI Frame Format
The Freescale SPI interface is a four-wire interface where the SSIFss signal behaves as a slave
select. The main feature of the Freescale SPI format is that the inactive state and phase of the
SSIClk signal are programmable through the SPO and SPH bits within the SSISCR0 control register.
SPO Clock Polarity Bit
When the SPO clock polarity control bit is Low, it produces a steady state Low value on the SSIClk
pin. If the SPO bit is High, a steady state High value is placed on the SSIClk pin when data is not
being transferred.
464 January 08, 2011
Texas Instruments-Production Data
Synchronous Serial Interface (SSI)
SPH Phase Control Bit
The SPH phase control bit selects the clock edge that captures data and allows it to change state.
It has the most impact on the first bit transmitted by either allowing or not allowing a clock transition
before the first data capture edge. When the SPH phase control bit is Low, data is captured on the
first clock edge transition. If the SPH bit is High, data is captured on the second clock edge transition.
13.2.4.3 Freescale SPI Frame Format with SPO=0 and SPH=0
Single and continuous transmission signal sequences for Freescale SPI format with SPO=0 and
SPH=0 are shown in Figure 13-4 on page 465 and Figure 13-5 on page 465.
Figure 13-4. Freescale SPI Format (Single Transfer) with SPO=0 and SPH=0
SSIClk
SSIFss
SSIRx Q
SSITx MSB
MSB
LSB
LSB
4 to 16 bits
Note: Q is undefined.
Figure 13-5. Freescale SPI Format (Continuous Transfer) with SPO=0 and SPH=0
SSIClk
SSIFss
SSIRx LSB
SSITx MSB LSB
LSB MSB
MSB
MSB
LSB
4 to16 bits
In this configuration, during idle periods:
■ SSIClk is forced Low
■ SSIFss is forced High
■ The transmit data line SSITx is arbitrarily forced Low
■ When the SSI is configured as a master, it enables the SSIClk pad
■ When the SSI is configured as a slave, it disables the SSIClk pad
If the SSI is enabled and there is valid data within the transmit FIFO, the start of transmission is
signified by the SSIFss master signal being driven Low. This causes slave data to be enabled onto
the SSIRx input line of the master. The master SSITx output pad is enabled.
January 08, 2011 465
Texas Instruments-Production Data
Stellaris® LM3S2965 Microcontroller
One half SSIClk period later, valid master data is transferred to the SSITx pin. Now that both the
master and slave data have been set, the SSIClk master clock pin goes High after one further half
SSIClk period.
The data is now captured on the rising and propagated on the falling edges of the SSIClk signal.
In the case of a single word transmission, after all bits of the data word have been transferred, the
SSIFss line is returned to its idle High state one SSIClk period after the last bit has been captured.
However, in the case of continuous back-to-back transmissions, the SSIFss signal must be pulsed
High between each data word transfer. This is because the slave select pin freezes the data in its
serial peripheral register and does not allow it to be altered if the SPH bit is logic zero. Therefore,
the master device must raise the SSIFss pin of the slave device between each data transfer to
enable the serial peripheral data write. On completion of the continuous transfer, the SSIFss pin
is returned to its idle state one SSIClk period after the last bit has been captured.
13.2.4.4 Freescale SPI Frame Format with SPO=0 and SPH=1
The transfer signal sequence for Freescale SPI format with SPO=0 and SPH=1 is shown in Figure
13-6 on page 466, which covers both single and continuous transfers.
Figure 13-6. Freescale SPI Frame Format with SPO=0 and SPH=1
SSIClk
SSIFss
SSIRx
SSITx
Q
MSB
MQSB
LSB
LSB
4 to 16 bits
Q
Note: Q is undefined.
In this configuration, during idle periods:
■ SSIClk is forced Low
■ SSIFss is forced High
■ The transmit data line SSITx is arbitrarily forced Low
■ When the SSI is configured as a master, it enables the SSIClk pad
■ When the SSI is configured as a slave, it disables the SSIClk pad
If the SSI is enabled and there is valid data within the transmit FIFO, the start of transmission is
signified by the SSIFss master signal being driven Low. The master SSITx output is enabled. After
a further one half SSIClk period, both master and slave valid data is enabled onto their respective
transmission lines. At the same time, the SSIClk is enabled with a rising edge transition.
Data is then captured on the falling edges and propagated on the rising edges of the SSIClk signal.
In the case of a single word transfer, after all bits have been transferred, the SSIFss line is returned
to its idle High state one SSIClk period after the last bit has been captured.
466 January 08, 2011
Texas Instruments-Production Data
Synchronous Serial Interface (SSI)
For continuous back-to-back transfers, the SSIFss pin is held Low between successive data words
and termination is the same as that of the single word transfer.
13.2.4.5 Freescale SPI Frame Format with SPO=1 and SPH=0
Single and continuous transmission signal sequences for Freescale SPI format with SPO=1 and
SPH=0 are shown in Figure 13-7 on page 467 and Figure 13-8 on page 467.
Figure 13-7. Freescale SPI Frame Format (Single Transfer) with SPO=1 and SPH=0
SSIClk
SSIFss
SSIRx
SSITx
MSB Q
MSB LSB
LSB
4 to 16 bits
Note: Q is undefined.
Figure 13-8. Freescale SPI Frame Format (Continuous Transfer) with SPO=1 and SPH=0
SSIClk
SSIFss
SSITx/SSIRx LSB MSB LSB MSB
4 to 16 bits
In this configuration, during idle periods:
■ SSIClk is forced High
■ SSIFss is forced High
■ The transmit data line SSITx is arbitrarily forced Low
■ When the SSI is configured as a master, it enables the SSIClk pad
■ When the SSI is configured as a slave, it disables the SSIClk pad
If the SSI is enabled and there is valid data within the transmit FIFO, the start of transmission is
signified by the SSIFss master signal being driven Low, which causes slave data to be immediately
transferred onto the SSIRx line of the master. The master SSITx output pad is enabled.
One half period later, valid master data is transferred to the SSITx line. Now that both the master
and slave data have been set, the SSIClk master clock pin becomes Low after one further half
SSIClk period. This means that data is captured on the falling edges and propagated on the rising
edges of the SSIClk signal.
In the case of a single word transmission, after all bits of the data word are transferred, the SSIFss
line is returned to its idle High state one SSIClk period after the last bit has been captured.
January 08, 2011 467
Texas Instruments-Production Data
Stellaris® LM3S2965 Microcontroller
However, in the case of continuous back-to-back transmissions, the SSIFss signal must be pulsed
High between each data word transfer. This is because the slave select pin freezes the data in its
serial peripheral register and does not allow it to be altered if the SPH bit is logic zero. Therefore,
the master device must raise the SSIFss pin of the slave device between each data transfer to
enable the serial peripheral data write. On completion of the continuous transfer, the SSIFss pin
is returned to its idle state one SSIClk period after the last bit has been captured.
13.2.4.6 Freescale SPI Frame Format with SPO=1 and SPH=1
The transfer signal sequence for Freescale SPI format with SPO=1 and SPH=1 is shown in Figure
13-9 on page 468, which covers both single and continuous transfers.
Figure 13-9. Freescale SPI Frame Format with SPO=1 and SPH=1
SSIClk
SSIFss
SSIRx
SSITx
Q
MSB
MSB
LSB
LSB
4 to 16 bits
Q
Note: Q is undefined.
In this configuration, during idle periods:
■ SSIClk is forced High
■ SSIFss is forced High
■ The transmit data line SSITx is arbitrarily forced Low
■ When the SSI is configured as a master, it enables the SSIClk pad
■ When the SSI is configured as a slave, it disables the SSIClk pad
If the SSI is enabled and there is valid data within the transmit FIFO, the start of transmission is
signified by the SSIFss master signal being driven Low. The master SSITx output pad is enabled.
After a further one-half SSIClk period, both master and slave data are enabled onto their respective
transmission lines. At the same time, SSIClk is enabled with a falling edge transition. Data is then
captured on the rising edges and propagated on the falling edges of the SSIClk signal.
After all bits have been transferred, in the case of a single word transmission, the SSIFss line is
returned to its idle high state one SSIClk period after the last bit has been captured.
For continuous back-to-back transmissions, the SSIFss pin remains in its active Low state, until
the final bit of the last word has been captured, and then returns to its idle state as described above.
For continuous back-to-back transfers, the SSIFss pin is held Low between successive data words
and termination is the same as that of the single word transfer.
13.2.4.7 MICROWIRE Frame Format
Figure 13-10 on page 469 shows the MICROWIRE frame format, again for a single frame. Figure
13-11 on page 470 shows the same format when back-to-back frames are transmitted.
468 January 08, 2011
Texas Instruments-Production Data
Synchronous Serial Interface (SSI)
Figure 13-10. MICROWIRE Frame Format (Single Frame)
SSIClk
SSIFss
SSIRx 0
SSITx
8-bit control
4 to 16 bits
output data
LSB
MSB
MSB
LSB
MICROWIRE format is very similar to SPI format, except that transmission is half-duplex instead of
full-duplex, using a master-slave message passing technique. Each serial transmission begins with
an 8-bit control word that is transmitted from the SSI to the off-chip slave device. During this
transmission, no incoming data is received by the SSI. After the message has been sent, the off-chip
slave decodes it and, after waiting one serial clock after the last bit of the 8-bit control message has
been sent, responds with the required data. The returned data is 4 to 16 bits in length, making the
total frame length anywhere from 13 to 25 bits.
In this configuration, during idle periods:
■ SSIClk is forced Low
■ SSIFss is forced High
■ The transmit data line SSITx is arbitrarily forced Low
A transmission is triggered by writing a control byte to the transmit FIFO. The falling edge of SSIFss
causes the value contained in the bottom entry of the transmit FIFO to be transferred to the serial
shift register of the transmit logic, and the MSB of the 8-bit control frame to be shifted out onto the
SSITx pin. SSIFss remains Low for the duration of the frame transmission. The SSIRx pin remains
tristated during this transmission.
The off-chip serial slave device latches each control bit into its serial shifter on the rising edge of
each SSIClk. After the last bit is latched by the slave device, the control byte is decoded during a
one clock wait-state, and the slave responds by transmitting data back to the SSI. Each bit is driven
onto the SSIRx line on the falling edge of SSIClk. The SSI in turn latches each bit on the rising
edge of SSIClk. At the end of the frame, for single transfers, the SSIFss signal is pulled High one
clock period after the last bit has been latched in the receive serial shifter, which causes the data
to be transferred to the receive FIFO.
Note: The off-chip slave device can tristate the receive line either on the falling edge of SSIClk
after the LSB has been latched by the receive shifter, or when the SSIFss pin goes High.
For continuous transfers, data transmission begins and ends in the same manner as a single transfer.
However, the SSIFss line is continuously asserted (held Low) and transmission of data occurs
back-to-back. The control byte of the next frame follows directly after the LSB of the received data
from the current frame. Each of the received values is transferred from the receive shifter on the
falling edge of SSIClk, after the LSB of the frame has been latched into the SSI.
January 08, 2011 469
Texas Instruments-Production Data
Stellaris® LM3S2965 Microcontroller
Figure 13-11. MICROWIRE Frame Format (Continuous Transfer)
SSIClk
SSIFss
SSIRx 0 MSB LSB
SSITx LSB LSB
MSB
4 to 16 bits
output data
8-bit control
MSB
In the MICROWIRE mode, the SSI slave samples the first bit of receive data on the rising edge of
SSIClk after SSIFss has gone Low. Masters that drive a free-running SSIClk must ensure that
the SSIFss signal has sufficient setup and hold margins with respect to the rising edge of SSIClk.
Figure 13-12 on page 470 illustrates these setup and hold time requirements. With respect to the
SSIClk rising edge on which the first bit of receive data is to be sampled by the SSI slave, SSIFss
must have a setup of at least two times the period of SSIClk on which the SSI operates. With
respect to the SSIClk rising edge previous to this edge, SSIFss must have a hold of at least one
SSIClk period.
Figure 13-12. MICROWIRE Frame Format, SSIFss Input Setup and Hold Requirements
SSIClk
SSIFss
SSIRx
First RX data to be
sampled by SSI slave
tSetup=(2*tSSIClk)
tHold=tSSIClk
13.3 Initialization and Configuration
To use the SSI, its peripheral clock must be enabled by setting the SSI bit in the RCGC1 register.
For each of the frame formats, the SSI is configured using the following steps:
1. Ensure that the SSE bit in the SSICR1 register is disabled before making any configuration
changes.
2. Select whether the SSI is a master or slave:
a. For master operations, set the SSICR1 register to 0x0000.0000.
b. For slave mode (output enabled), set the SSICR1 register to 0x0000.0004.
c. For slave mode (output disabled), set the SSICR1 register to 0x0000.000C.
3. Configure the clock prescale divisor by writing the SSICPSR register.
4. Write the SSICR0 register with the following configuration:
470 January 08, 2011
Texas Instruments-Production Data
Synchronous Serial Interface (SSI)
■ Serial clock rate (SCR)
■ Desired clock phase/polarity, if using Freescale SPI mode (SPH and SPO)
■ The protocol mode: Freescale SPI, TI SSF, MICROWIRE (FRF)
■ The data size (DSS)
5. Enable the SSI by setting the SSE bit in the SSICR1 register.
As an example, assume the SSI must be configured to operate with the following parameters:
■ Master operation
■ Freescale SPI mode (SPO=1, SPH=1)
■ 1 Mbps bit rate
■ 8 data bits
Assuming the system clock is 20 MHz, the bit rate calculation would be:
FSSIClk = FSysClk / (CPSDVSR * (1 + SCR))
1x106 = 20x106 / (CPSDVSR * (1 + SCR))
In this case, if CPSDVSR=2, SCR must be 9.
The configuration sequence would be as follows:
1. Ensure that the SSE bit in the SSICR1 register is disabled.
2. Write the SSICR1 register with a value of 0x0000.0000.
3. Write the SSICPSR register with a value of 0x0000.0002.
4. Write the SSICR0 register with a value of 0x0000.09C7.
5. The SSI is then enabled by setting the SSE bit in the SSICR1 register to 1.
13.4 Register Map
Table 13-1 on page 472 lists the SSI registers. The offset listed is a hexadecimal increment to the
register’s address, relative to that SSI module’s base address:
■ SSI0: 0x4000.8000
■ SSI1: 0x4000.9000
Note that the SSI module clock must be enabled before the registers can be programmed (see
page 216). There must be a delay of 3 system clocks after the SSI module clock is enabled before
any SSI module registers are accessed.
Note: The SSI must be disabled (see the SSE bit in the SSICR1 register) before any of the control
registers are reprogrammed.
January 08, 2011 471
Texas Instruments-Production Data
Stellaris® LM3S2965 Microcontroller
Table 13-1. SSI Register Map
See
Offset Name Type Reset Description page
0x000 SSICR0 R/W 0x0000.0000 SSI Control 0 473
0x004 SSICR1 R/W 0x0000.0000 SSI Control 1 475
0x008 SSIDR R/W 0x0000.0000 SSI Data 477
0x00C SSISR RO 0x0000.0003 SSI Status 478
0x010 SSICPSR R/W 0x0000.0000 SSI Clock Prescale 480
0x014 SSIIM R/W 0x0000.0000 SSI Interrupt Mask 481
0x018 SSIRIS RO 0x0000.0008 SSI Raw Interrupt Status 483
0x01C SSIMIS RO 0x0000.0000 SSI Masked Interrupt Status 484
0x020 SSIICR W1C 0x0000.0000 SSI Interrupt Clear 485
0xFD0 SSIPeriphID4 RO 0x0000.0000 SSI Peripheral Identification 4 486
0xFD4 SSIPeriphID5 RO 0x0000.0000 SSI Peripheral Identification 5 487
0xFD8 SSIPeriphID6 RO 0x0000.0000 SSI Peripheral Identification 6 488
0xFDC SSIPeriphID7 RO 0x0000.0000 SSI Peripheral Identification 7 489
0xFE0 SSIPeriphID0 RO 0x0000.0022 SSI Peripheral Identification 0 490
0xFE4 SSIPeriphID1 RO 0x0000.0000 SSI Peripheral Identification 1 491
0xFE8 SSIPeriphID2 RO 0x0000.0018 SSI Peripheral Identification 2 492
0xFEC SSIPeriphID3 RO 0x0000.0001 SSI Peripheral Identification 3 493
0xFF0 SSIPCellID0 RO 0x0000.000D SSI PrimeCell Identification 0 494
0xFF4 SSIPCellID1 RO 0x0000.00F0 SSI PrimeCell Identification 1 495
0xFF8 SSIPCellID2 RO 0x0000.0005 SSI PrimeCell Identification 2 496
0xFFC SSIPCellID3 RO 0x0000.00B1 SSI PrimeCell Identification 3 497
13.5 Register Descriptions
The remainder of this section lists and describes the SSI registers, in numerical order by address
offset.
472 January 08, 2011
Texas Instruments-Production Data
Synchronous Serial Interface (SSI)
Register 1: SSI Control 0 (SSICR0), offset 0x000
SSICR0 is control register 0 and contains bit fields that control various functions within the SSI
module. Functionality such as protocol mode, clock rate, and data size are configured in this register.
SSI Control 0 (SSICR0)
SSI0 base: 0x4000.8000
SSI1 base: 0x4000.9000
Offset 0x000
Type R/W, reset 0x0000.0000
31 30 29 28 27 26 25 24 23 22 21 20 19 18 17 16
reserved
Type RO RO RO RO RO RO RO RO RO RO RO RO RO RO RO RO
Reset 0 0 0 0 0 0 0 0 0 0 0 0 0 0 0 0
15 14 13 12 11 10 9 8 7 6 5 4 3 2 1 0
SCR SPH SPO FRF DSS
Type R/W R/W R/W R/W R/W R/W R/W R/W R/W R/W R/W R/W R/W R/W R/W R/W
Reset 0 0 0 0 0 0 0 0 0 0 0 0 0 0 0 0
Bit/Field Name Type Reset Description
Software should not rely on the value of a reserved bit. To provide
compatibility with future products, the value of a reserved bit should be
preserved across a read-modify-write operation.
31:16 reserved RO 0x00
SSI Serial Clock Rate
The value SCR is used to generate the transmit and receive bit rate of
the SSI. The bit rate is:
BR=FSSIClk/(CPSDVSR * (1 + SCR))
where CPSDVSR is an even value from 2-254 programmed in the
SSICPSR register, and SCR is a value from 0-255.
15:8 SCR R/W 0x0000
SSI Serial Clock Phase
This bit is only applicable to the Freescale SPI Format.
The SPH control bit selects the clock edge that captures data and allows
it to change state. It has the most impact on the first bit transmitted by
either allowing or not allowing a clock transition before the first data
capture edge.
When the SPH bit is 0, data is captured on the first clock edge transition.
If SPH is 1, data is captured on the second clock edge transition.
7 SPH R/W 0
SSI Serial Clock Polarity
This bit is only applicable to the Freescale SPI Format.
When the SPO bit is 0, it produces a steady state Low value on the
SSIClk pin. If SPO is 1, a steady state High value is placed on the
SSIClk pin when data is not being transferred.
6 SPO R/W 0
SSI Frame Format Select
The FRF values are defined as follows:
Value Frame Format
0x0 Freescale SPI Frame Format
0x1 Texas Instruments Synchronous Serial Frame Format
0x2 MICROWIRE Frame Format
0x3 Reserved
5:4 FRF R/W 0x0
January 08, 2011 473
Texas Instruments-Production Data
Stellaris® LM3S2965 Microcontroller
Bit/Field Name Type Reset Description
SSI Data Size Select
The DSS values are defined as follows:
Value Data Size
0x0-0x2 Reserved
0x3 4-bit data
0x4 5-bit data
0x5 6-bit data
0x6 7-bit data
0x7 8-bit data
0x8 9-bit data
0x9 10-bit data
0xA 11-bit data
0xB 12-bit data
0xC 13-bit data
0xD 14-bit data
0xE 15-bit data
0xF 16-bit data
3:0 DSS R/W 0x00
474 January 08, 2011
Texas Instruments-Production Data
Synchronous Serial Interface (SSI)
Register 2: SSI Control 1 (SSICR1), offset 0x004
SSICR1 is control register 1 and contains bit fields that control various functions within the SSI
module. Master and slave mode functionality is controlled by this register.
SSI Control 1 (SSICR1)
SSI0 base: 0x4000.8000
SSI1 base: 0x4000.9000
Offset 0x004
Type R/W, reset 0x0000.0000
31 30 29 28 27 26 25 24 23 22 21 20 19 18 17 16
reserved
Type RO RO RO RO RO RO RO RO RO RO RO RO RO RO RO RO
Reset 0 0 0 0 0 0 0 0 0 0 0 0 0 0 0 0
15 14 13 12 11 10 9 8 7 6 5 4 3 2 1 0
reserved SOD MS SSE LBM
Type RO RO RO RO RO RO RO RO RO RO RO RO R/W R/W R/W R/W
Reset 0 0 0 0 0 0 0 0 0 0 0 0 0 0 0 0
Bit/Field Name Type Reset Description
Software should not rely on the value of a reserved bit. To provide
compatibility with future products, the value of a reserved bit should be
preserved across a read-modify-write operation.
31:4 reserved RO 0x00
SSI Slave Mode Output Disable
This bit is relevant only in the Slave mode (MS=1). In multiple-slave
systems, it is possible for the SSI master to broadcast a message to all
slaves in the system while ensuring that only one slave drives data onto
the serial output line. In such systems, the TXD lines from multiple slaves
could be tied together. To operate in such a system, the SOD bit can be
configured so that the SSI slave does not drive the SSITx pin.
The SOD values are defined as follows:
Value Description
0 SSI can drive SSITx output in Slave Output mode.
1 SSI must not drive the SSITx output in Slave mode.
3 SOD R/W 0
SSI Master/Slave Select
This bit selects Master or Slave mode and can be modified only when
SSI is disabled (SSE=0).
The MS values are defined as follows:
Value Description
0 Device configured as a master.
1 Device configured as a slave.
2 MS R/W 0
January 08, 2011 475
Texas Instruments-Production Data
Stellaris® LM3S2965 Microcontroller
Bit/Field Name Type Reset Description
SSI Synchronous Serial Port Enable
Setting this bit enables SSI operation.
The SSE values are defined as follows:
Value Description
0 SSI operation disabled.
1 SSI operation enabled.
Note: This bit must be set to 0 before any control registers
are reprogrammed.
1 SSE R/W 0
SSI Loopback Mode
Setting this bit enables Loopback Test mode.
The LBM values are defined as follows:
Value Description
0 Normal serial port operation enabled.
Output of the transmit serial shift register is connected internally
to the input of the receive serial shift register.
1
0 LBM R/W 0
476 January 08, 2011
Texas Instruments-Production Data
Synchronous Serial Interface (SSI)
Register 3: SSI Data (SSIDR), offset 0x008
Important: Use caution when reading this register. Performing a read may change bit status.
SSIDR is the data register and is 16-bits wide. When SSIDR is read, the entry in the receive FIFO
(pointed to by the current FIFO read pointer) is accessed. As data values are removed by the SSI
receive logic from the incoming data frame, they are placed into the entry in the receive FIFO (pointed
to by the current FIFO write pointer).
When SSIDR is written to, the entry in the transmit FIFO (pointed to by the write pointer) is written
to. Data values are removed from the transmit FIFO one value at a time by the transmit logic. It is
loaded into the transmit serial shifter, then serially shifted out onto the SSITx pin at the programmed
bit rate.
When a data size of less than 16 bits is selected, the user must right-justify data written to the
transmit FIFO. The transmit logic ignores the unused bits. Received data less than 16 bits is
automatically right-justified in the receive buffer.
When the SSI is programmed for MICROWIRE frame format, the default size for transmit data is
eight bits (the most significant byte is ignored). The receive data size is controlled by the programmer.
The transmit FIFO and the receive FIFO are not cleared even when the SSE bit in the SSICR1
register is set to zero. This allows the software to fill the transmit FIFO before enabling the SSI.
SSI Data (SSIDR)
SSI0 base: 0x4000.8000
SSI1 base: 0x4000.9000
Offset 0x008
Type R/W, reset 0x0000.0000
31 30 29 28 27 26 25 24 23 22 21 20 19 18 17 16
reserved
Type RO RO RO RO RO RO RO RO RO RO RO RO RO RO RO RO
Reset 0 0 0 0 0 0 0 0 0 0 0 0 0 0 0 0
15 14 13 12 11 10 9 8 7 6 5 4 3 2 1 0
DATA
Type R/W R/W R/W R/W R/W R/W R/W R/W R/W R/W R/W R/W R/W R/W R/W R/W
Reset 0 0 0 0 0 0 0 0 0 0 0 0 0 0 0 0
Bit/Field Name Type Reset Description
Software should not rely on the value of a reserved bit. To provide
compatibility with future products, the value of a reserved bit should be
preserved across a read-modify-write operation.
31:16 reserved RO 0x0000
SSI Receive/Transmit Data
A read operation reads the receive FIFO. A write operation writes the
transmit FIFO.
Software must right-justify data when the SSI is programmed for a data
size that is less than 16 bits. Unused bits at the top are ignored by the
transmit logic. The receive logic automatically right-justifies the data.
15:0 DATA R/W 0x0000
January 08, 2011 477
Texas Instruments-Production Data
Stellaris® LM3S2965 Microcontroller
Register 4: SSI Status (SSISR), offset 0x00C
SSISR is a status register that contains bits that indicate the FIFO fill status and the SSI busy status.
SSI Status (SSISR)
SSI0 base: 0x4000.8000
SSI1 base: 0x4000.9000
Offset 0x00C
Type RO, reset 0x0000.0003
31 30 29 28 27 26 25 24 23 22 21 20 19 18 17 16
reserved
Type RO RO RO RO RO RO RO RO RO RO RO RO RO RO RO RO
Reset 0 0 0 0 0 0 0 0 0 0 0 0 0 0 0 0
15 14 13 12 11 10 9 8 7 6 5 4 3 2 1 0
reserved BSY RFF RNE TNF TFE
Type RO RO RO RO RO RO RO RO RO RO RO RO RO RO RO R0
Reset 0 0 0 0 0 0 0 0 0 0 0 0 0 0 1 1
Bit/Field Name Type Reset Description
Software should not rely on the value of a reserved bit. To provide
compatibility with future products, the value of a reserved bit should be
preserved across a read-modify-write operation.
31:5 reserved RO 0x00
SSI Busy Bit
The BSY values are defined as follows:
Value Description
0 SSI is idle.
SSI is currently transmitting and/or receiving a frame, or the
transmit FIFO is not empty.
1
4 BSY RO 0
SSI Receive FIFO Full
The RFF values are defined as follows:
Value Description
0 Receive FIFO is not full.
1 Receive FIFO is full.
3 RFF RO 0
SSI Receive FIFO Not Empty
The RNE values are defined as follows:
Value Description
0 Receive FIFO is empty.
1 Receive FIFO is not empty.
2 RNE RO 0
SSI Transmit FIFO Not Full
The TNF values are defined as follows:
Value Description
0 Transmit FIFO is full.
1 Transmit FIFO is not full.
1 TNF RO 1
478 January 08, 2011
Texas Instruments-Production Data
Synchronous Serial Interface (SSI)
Bit/Field Name Type Reset Description
SSI Transmit FIFO Empty
The TFE values are defined as follows:
Value Description
0 Transmit FIFO is not empty.
1 Transmit FIFO is empty.
0 TFE R0 1
January 08, 2011 479
Texas Instruments-Production Data
Stellaris® LM3S2965 Microcontroller
Register 5: SSI Clock Prescale (SSICPSR), offset 0x010
SSICPSR is the clock prescale register and specifies the division factor by which the system clock
must be internally divided before further use.
The value programmed into this register must be an even number between 2 and 254. The
least-significant bit of the programmed number is hard-coded to zero. If an odd number is written
to this register, data read back from this register has the least-significant bit as zero.
SSI Clock Prescale (SSICPSR)
SSI0 base: 0x4000.8000
SSI1 base: 0x4000.9000
Offset 0x010
Type R/W, reset 0x0000.0000
31 30 29 28 27 26 25 24 23 22 21 20 19 18 17 16
reserved
Type RO RO RO RO RO RO RO RO RO RO RO RO RO RO RO RO
Reset 0 0 0 0 0 0 0 0 0 0 0 0 0 0 0 0
15 14 13 12 11 10 9 8 7 6 5 4 3 2 1 0
reserved CPSDVSR
Type RO RO RO RO RO RO RO RO R/W R/W R/W R/W R/W R/W R/W R/W
Reset 0 0 0 0 0 0 0 0 0 0 0 0 0 0 0 0
Bit/Field Name Type Reset Description
Software should not rely on the value of a reserved bit. To provide
compatibility with future products, the value of a reserved bit should be
preserved across a read-modify-write operation.
31:8 reserved RO 0x00
SSI Clock Prescale Divisor
This value must be an even number from 2 to 254, depending on the
frequency of SSIClk. The LSB always returns 0 on reads.
7:0 CPSDVSR R/W 0x00
480 January 08, 2011
Texas Instruments-Production Data
Synchronous Serial Interface (SSI)
Register 6: SSI Interrupt Mask (SSIIM), offset 0x014
The SSIIM register is the interrupt mask set or clear register. It is a read/write register and all bits
are cleared to 0 on reset.
On a read, this register gives the current value of the mask on the relevant interrupt. A write of 1 to
the particular bit sets the mask, enabling the interrupt to be read. A write of 0 clears the corresponding
mask.
SSI Interrupt Mask (SSIIM)
SSI0 base: 0x4000.8000
SSI1 base: 0x4000.9000
Offset 0x014
Type R/W, reset 0x0000.0000
31 30 29 28 27 26 25 24 23 22 21 20 19 18 17 16
reserved
Type RO RO RO RO RO RO RO RO RO RO RO RO RO RO RO RO
Reset 0 0 0 0 0 0 0 0 0 0 0 0 0 0 0 0
15 14 13 12 11 10 9 8 7 6 5 4 3 2 1 0
reserved TXIM RXIM RTIM RORIM
Type RO RO RO RO RO RO RO RO RO RO RO RO R/W R/W R/W R/W
Reset 0 0 0 0 0 0 0 0 0 0 0 0 0 0 0 0
Bit/Field Name Type Reset Description
Software should not rely on the value of a reserved bit. To provide
compatibility with future products, the value of a reserved bit should be
preserved across a read-modify-write operation.
31:4 reserved RO 0x00
SSI Transmit FIFO Interrupt Mask
The TXIM values are defined as follows:
Value Description
0 TX FIFO half-full or less condition interrupt is masked.
1 TX FIFO half-full or less condition interrupt is not masked.
3 TXIM R/W 0
SSI Receive FIFO Interrupt Mask
The RXIM values are defined as follows:
Value Description
0 RX FIFO half-full or more condition interrupt is masked.
1 RX FIFO half-full or more condition interrupt is not masked.
2 RXIM R/W 0
SSI Receive Time-Out Interrupt Mask
The RTIM values are defined as follows:
Value Description
0 RX FIFO time-out interrupt is masked.
1 RX FIFO time-out interrupt is not masked.
1 RTIM R/W 0
January 08, 2011 481
Texas Instruments-Production Data
Stellaris® LM3S2965 Microcontroller
Bit/Field Name Type Reset Description
SSI Receive Overrun Interrupt Mask
The RORIM values are defined as follows:
Value Description
0 RX FIFO overrun interrupt is masked.
1 RX FIFO overrun interrupt is not masked.
0 RORIM R/W 0
482 January 08, 2011
Texas Instruments-Production Data
Synchronous Serial Interface (SSI)
Register 7: SSI Raw Interrupt Status (SSIRIS), offset 0x018
The SSIRIS register is the raw interrupt status register. On a read, this register gives the current
raw status value of the corresponding interrupt prior to masking. A write has no effect.
SSI Raw Interrupt Status (SSIRIS)
SSI0 base: 0x4000.8000
SSI1 base: 0x4000.9000
Offset 0x018
Type RO, reset 0x0000.0008
31 30 29 28 27 26 25 24 23 22 21 20 19 18 17 16
reserved
Type RO RO RO RO RO RO RO RO RO RO RO RO RO RO RO RO
Reset 0 0 0 0 0 0 0 0 0 0 0 0 0 0 0 0
15 14 13 12 11 10 9 8 7 6 5 4 3 2 1 0
reserved TXRIS RXRIS RTRIS RORRIS
Type RO RO RO RO RO RO RO RO RO RO RO RO RO RO RO RO
Reset 0 0 0 0 0 0 0 0 0 0 0 0 1 0 0 0
Bit/Field Name Type Reset Description
Software should not rely on the value of a reserved bit. To provide
compatibility with future products, the value of a reserved bit should be
preserved across a read-modify-write operation.
31:4 reserved RO 0x00
SSI Transmit FIFO Raw Interrupt Status
Indicates that the transmit FIFO is half full or less, when set.
3 TXRIS RO 1
SSI Receive FIFO Raw Interrupt Status
Indicates that the receive FIFO is half full or more, when set.
2 RXRIS RO 0
SSI Receive Time-Out Raw Interrupt Status
Indicates that the receive time-out has occurred, when set.
1 RTRIS RO 0
SSI Receive Overrun Raw Interrupt Status
Indicates that the receive FIFO has overflowed, when set.
0 RORRIS RO 0
January 08, 2011 483
Texas Instruments-Production Data
Stellaris® LM3S2965 Microcontroller
Register 8: SSI Masked Interrupt Status (SSIMIS), offset 0x01C
The SSIMIS register is the masked interrupt status register. On a read, this register gives the current
masked status value of the corresponding interrupt. A write has no effect.
SSI Masked Interrupt Status (SSIMIS)
SSI0 base: 0x4000.8000
SSI1 base: 0x4000.9000
Offset 0x01C
Type RO, reset 0x0000.0000
31 30 29 28 27 26 25 24 23 22 21 20 19 18 17 16
reserved
Type RO RO RO RO RO RO RO RO RO RO RO RO RO RO RO RO
Reset 0 0 0 0 0 0 0 0 0 0 0 0 0 0 0 0
15 14 13 12 11 10 9 8 7 6 5 4 3 2 1 0
reserved TXMIS RXMIS RTMIS RORMIS
Type RO RO RO RO RO RO RO RO RO RO RO RO RO RO RO RO
Reset 0 0 0 0 0 0 0 0 0 0 0 0 0 0 0 0
Bit/Field Name Type Reset Description
Software should not rely on the value of a reserved bit. To provide
compatibility with future products, the value of a reserved bit should be
preserved across a read-modify-write operation.
31:4 reserved RO 0
SSI Transmit FIFO Masked Interrupt Status
Indicates that the transmit FIFO is half full or less, when set.
3 TXMIS RO 0
SSI Receive FIFO Masked Interrupt Status
Indicates that the receive FIFO is half full or more, when set.
2 RXMIS RO 0
SSI Receive Time-Out Masked Interrupt Status
Indicates that the receive time-out has occurred, when set.
1 RTMIS RO 0
SSI Receive Overrun Masked Interrupt Status
Indicates that the receive FIFO has overflowed, when set.
0 RORMIS RO 0
484 January 08, 2011
Texas Instruments-Production Data
Synchronous Serial Interface (SSI)
Register 9: SSI Interrupt Clear (SSIICR), offset 0x020
The SSIICR register is the interrupt clear register. On a write of 1, the corresponding interrupt is
cleared. A write of 0 has no effect.
SSI Interrupt Clear (SSIICR)
SSI0 base: 0x4000.8000
SSI1 base: 0x4000.9000
Offset 0x020
Type W1C, reset 0x0000.0000
31 30 29 28 27 26 25 24 23 22 21 20 19 18 17 16
reserved
Type RO RO RO RO RO RO RO RO RO RO RO RO RO RO RO RO
Reset 0 0 0 0 0 0 0 0 0 0 0 0 0 0 0 0
15 14 13 12 11 10 9 8 7 6 5 4 3 2 1 0
reserved RTIC RORIC
Type RO RO RO RO RO RO RO RO RO RO RO RO RO RO W1C W1C
Reset 0 0 0 0 0 0 0 0 0 0 0 0 0 0 0 0
Bit/Field Name Type Reset Description
Software should not rely on the value of a reserved bit. To provide
compatibility with future products, the value of a reserved bit should be
preserved across a read-modify-write operation.
31:2 reserved RO 0x00
SSI Receive Time-Out Interrupt Clear
The RTIC values are defined as follows:
Value Description
0 No effect on interrupt.
1 Clears interrupt.
1 RTIC W1C 0
SSI Receive Overrun Interrupt Clear
The RORIC values are defined as follows:
Value Description
0 No effect on interrupt.
1 Clears interrupt.
0 RORIC W1C 0
January 08, 2011 485
Texas Instruments-Production Data
Stellaris® LM3S2965 Microcontroller
Register 10: SSI Peripheral Identification 4 (SSIPeriphID4), offset 0xFD0
The SSIPeriphIDn registers are hard-coded and the fields within the register determine the reset
value.
SSI Peripheral Identification 4 (SSIPeriphID4)
SSI0 base: 0x4000.8000
SSI1 base: 0x4000.9000
Offset 0xFD0
Type RO, reset 0x0000.0000
31 30 29 28 27 26 25 24 23 22 21 20 19 18 17 16
reserved
Type RO RO RO RO RO RO RO RO RO RO RO RO RO RO RO RO
Reset 0 0 0 0 0 0 0 0 0 0 0 0 0 0 0 0
15 14 13 12 11 10 9 8 7 6 5 4 3 2 1 0
reserved PID4
Type RO RO RO RO RO RO RO RO RO RO RO RO RO RO RO RO
Reset 0 0 0 0 0 0 0 0 0 0 0 0 0 0 0 0
Bit/Field Name Type Reset Description
Software should not rely on the value of a reserved bit. To provide
compatibility with future products, the value of a reserved bit should be
preserved across a read-modify-write operation.
31:8 reserved RO 0x00
SSI Peripheral ID Register[7:0]
Can be used by software to identify the presence of this peripheral.
7:0 PID4 RO 0x00
486 January 08, 2011
Texas Instruments-Production Data
Synchronous Serial Interface (SSI)
Register 11: SSI Peripheral Identification 5 (SSIPeriphID5), offset 0xFD4
The SSIPeriphIDn registers are hard-coded and the fields within the register determine the reset
value.
SSI Peripheral Identification 5 (SSIPeriphID5)
SSI0 base: 0x4000.8000
SSI1 base: 0x4000.9000
Offset 0xFD4
Type RO, reset 0x0000.0000
31 30 29 28 27 26 25 24 23 22 21 20 19 18 17 16
reserved
Type RO RO RO RO RO RO RO RO RO RO RO RO RO RO RO RO
Reset 0 0 0 0 0 0 0 0 0 0 0 0 0 0 0 0
15 14 13 12 11 10 9 8 7 6 5 4 3 2 1 0
reserved PID5
Type RO RO RO RO RO RO RO RO RO RO RO RO RO RO RO RO
Reset 0 0 0 0 0 0 0 0 0 0 0 0 0 0 0 0
Bit/Field Name Type Reset Description
Software should not rely on the value of a reserved bit. To provide
compatibility with future products, the value of a reserved bit should be
preserved across a read-modify-write operation.
31:8 reserved RO 0x00
SSI Peripheral ID Register[15:8]
Can be used by software to identify the presence of this peripheral.
7:0 PID5 RO 0x00
January 08, 2011 487
Texas Instruments-Production Data
Stellaris® LM3S2965 Microcontroller
Register 12: SSI Peripheral Identification 6 (SSIPeriphID6), offset 0xFD8
The SSIPeriphIDn registers are hard-coded and the fields within the register determine the reset
value.
SSI Peripheral Identification 6 (SSIPeriphID6)
SSI0 base: 0x4000.8000
SSI1 base: 0x4000.9000
Offset 0xFD8
Type RO, reset 0x0000.0000
31 30 29 28 27 26 25 24 23 22 21 20 19 18 17 16
reserved
Type RO RO RO RO RO RO RO RO RO RO RO RO RO RO RO RO
Reset 0 0 0 0 0 0 0 0 0 0 0 0 0 0 0 0
15 14 13 12 11 10 9 8 7 6 5 4 3 2 1 0
reserved PID6
Type RO RO RO RO RO RO RO RO RO RO RO RO RO RO RO RO
Reset 0 0 0 0 0 0 0 0 0 0 0 0 0 0 0 0
Bit/Field Name Type Reset Description
Software should not rely on the value of a reserved bit. To provide
compatibility with future products, the value of a reserved bit should be
preserved across a read-modify-write operation.
31:8 reserved RO 0x00
SSI Peripheral ID Register[23:16]
Can be used by software to identify the presence of this peripheral.
7:0 PID6 RO 0x00
488 January 08, 2011
Texas Instruments-Production Data
Synchronous Serial Interface (SSI)
Register 13: SSI Peripheral Identification 7 (SSIPeriphID7), offset 0xFDC
The SSIPeriphIDn registers are hard-coded and the fields within the register determine the reset
value.
SSI Peripheral Identification 7 (SSIPeriphID7)
SSI0 base: 0x4000.8000
SSI1 base: 0x4000.9000
Offset 0xFDC
Type RO, reset 0x0000.0000
31 30 29 28 27 26 25 24 23 22 21 20 19 18 17 16
reserved
Type RO RO RO RO RO RO RO RO RO RO RO RO RO RO RO RO
Reset 0 0 0 0 0 0 0 0 0 0 0 0 0 0 0 0
15 14 13 12 11 10 9 8 7 6 5 4 3 2 1 0
reserved PID7
Type RO RO RO RO RO RO RO RO RO RO RO RO RO RO RO RO
Reset 0 0 0 0 0 0 0 0 0 0 0 0 0 0 0 0
Bit/Field Name Type Reset Description
Software should not rely on the value of a reserved bit. To provide
compatibility with future products, the value of a reserved bit should be
preserved across a read-modify-write operation.
31:8 reserved RO 0x00
SSI Peripheral ID Register[31:24]
Can be used by software to identify the presence of this peripheral.
7:0 PID7 RO 0x00
January 08, 2011 489
Texas Instruments-Production Data
Stellaris® LM3S2965 Microcontroller
Register 14: SSI Peripheral Identification 0 (SSIPeriphID0), offset 0xFE0
The SSIPeriphIDn registers are hard-coded and the fields within the register determine the reset
value.
SSI Peripheral Identification 0 (SSIPeriphID0)
SSI0 base: 0x4000.8000
SSI1 base: 0x4000.9000
Offset 0xFE0
Type RO, reset 0x0000.0022
31 30 29 28 27 26 25 24 23 22 21 20 19 18 17 16
reserved
Type RO RO RO RO RO RO RO RO RO RO RO RO RO RO RO RO
Reset 0 0 0 0 0 0 0 0 0 0 0 0 0 0 0 0
15 14 13 12 11 10 9 8 7 6 5 4 3 2 1 0
reserved PID0
Type RO RO RO RO RO RO RO RO RO RO RO RO RO RO RO RO
Reset 0 0 0 0 0 0 0 0 0 0 1 0 0 0 1 0
Bit/Field Name Type Reset Description
Software should not rely on the value of a reserved bit. To provide
compatibility with future products, the value of a reserved bit should be
preserved across a read-modify-write operation.
31:8 reserved RO 0
SSI Peripheral ID Register[7:0]
Can be used by software to identify the presence of this peripheral.
7:0 PID0 RO 0x22
490 January 08, 2011
Texas Instruments-Production Data
Synchronous Serial Interface (SSI)
Register 15: SSI Peripheral Identification 1 (SSIPeriphID1), offset 0xFE4
The SSIPeriphIDn registers are hard-coded and the fields within the register determine the reset
value.
SSI Peripheral Identification 1 (SSIPeriphID1)
SSI0 base: 0x4000.8000
SSI1 base: 0x4000.9000
Offset 0xFE4
Type RO, reset 0x0000.0000
31 30 29 28 27 26 25 24 23 22 21 20 19 18 17 16
reserved
Type RO RO RO RO RO RO RO RO RO RO RO RO RO RO RO RO
Reset 0 0 0 0 0 0 0 0 0 0 0 0 0 0 0 0
15 14 13 12 11 10 9 8 7 6 5 4 3 2 1 0
reserved PID1
Type RO RO RO RO RO RO RO RO RO RO RO RO RO RO RO RO
Reset 0 0 0 0 0 0 0 0 0 0 0 0 0 0 0 0
Bit/Field Name Type Reset Description
Software should not rely on the value of a reserved bit. To provide
compatibility with future products, the value of a reserved bit should be
preserved across a read-modify-write operation.
31:8 reserved RO 0x00
SSI Peripheral ID Register [15:8]
Can be used by software to identify the presence of this peripheral.
7:0 PID1 RO 0x00
January 08, 2011 491
Texas Instruments-Production Data
Stellaris® LM3S2965 Microcontroller
Register 16: SSI Peripheral Identification 2 (SSIPeriphID2), offset 0xFE8
The SSIPeriphIDn registers are hard-coded and the fields within the register determine the reset
value.
SSI Peripheral Identification 2 (SSIPeriphID2)
SSI0 base: 0x4000.8000
SSI1 base: 0x4000.9000
Offset 0xFE8
Type RO, reset 0x0000.0018
31 30 29 28 27 26 25 24 23 22 21 20 19 18 17 16
reserved
Type RO RO RO RO RO RO RO RO RO RO RO RO RO RO RO RO
Reset 0 0 0 0 0 0 0 0 0 0 0 0 0 0 0 0
15 14 13 12 11 10 9 8 7 6 5 4 3 2 1 0
reserved PID2
Type RO RO RO RO RO RO RO RO RO RO RO RO RO RO RO RO
Reset 0 0 0 0 0 0 0 0 0 0 0 1 1 0 0 0
Bit/Field Name Type Reset Description
Software should not rely on the value of a reserved bit. To provide
compatibility with future products, the value of a reserved bit should be
preserved across a read-modify-write operation.
31:8 reserved RO 0x00
SSI Peripheral ID Register [23:16]
Can be used by software to identify the presence of this peripheral.
7:0 PID2 RO 0x18
492 January 08, 2011
Texas Instruments-Production Data
Synchronous Serial Interface (SSI)
Register 17: SSI Peripheral Identification 3 (SSIPeriphID3), offset 0xFEC
The SSIPeriphIDn registers are hard-coded and the fields within the register determine the reset
value.
SSI Peripheral Identification 3 (SSIPeriphID3)
SSI0 base: 0x4000.8000
SSI1 base: 0x4000.9000
Offset 0xFEC
Type RO, reset 0x0000.0001
31 30 29 28 27 26 25 24 23 22 21 20 19 18 17 16
reserved
Type RO RO RO RO RO RO RO RO RO RO RO RO RO RO RO RO
Reset 0 0 0 0 0 0 0 0 0 0 0 0 0 0 0 0
15 14 13 12 11 10 9 8 7 6 5 4 3 2 1 0
reserved PID3
Type RO RO RO RO RO RO RO RO RO RO RO RO RO RO RO RO
Reset 0 0 0 0 0 0 0 0 0 0 0 0 0 0 0 1
Bit/Field Name Type Reset Description
Software should not rely on the value of a reserved bit. To provide
compatibility with future products, the value of a reserved bit should be
preserved across a read-modify-write operation.
31:8 reserved RO 0x00
SSI Peripheral ID Register [31:24]
Can be used by software to identify the presence of this peripheral.
7:0 PID3 RO 0x01
January 08, 2011 493
Texas Instruments-Production Data
Stellaris® LM3S2965 Microcontroller
Register 18: SSI PrimeCell Identification 0 (SSIPCellID0), offset 0xFF0
The SSIPCellIDn registers are hard-coded, and the fields within the register determine the reset
value.
SSI PrimeCell Identification 0 (SSIPCellID0)
SSI0 base: 0x4000.8000
SSI1 base: 0x4000.9000
Offset 0xFF0
Type RO, reset 0x0000.000D
31 30 29 28 27 26 25 24 23 22 21 20 19 18 17 16
reserved
Type RO RO RO RO RO RO RO RO RO RO RO RO RO RO RO RO
Reset 0 0 0 0 0 0 0 0 0 0 0 0 0 0 0 0
15 14 13 12 11 10 9 8 7 6 5 4 3 2 1 0
reserved CID0
Type RO RO RO RO RO RO RO RO RO RO RO RO RO RO RO RO
Reset 0 0 0 0 0 0 0 0 0 0 0 0 1 1 0 1
Bit/Field Name Type Reset Description
Software should not rely on the value of a reserved bit. To provide
compatibility with future products, the value of a reserved bit should be
preserved across a read-modify-write operation.
31:8 reserved RO 0x00
SSI PrimeCell ID Register [7:0]
Provides software a standard cross-peripheral identification system.
7:0 CID0 RO 0x0D
494 January 08, 2011
Texas Instruments-Production Data
Synchronous Serial Interface (SSI)
Register 19: SSI PrimeCell Identification 1 (SSIPCellID1), offset 0xFF4
The SSIPCellIDn registers are hard-coded, and the fields within the register determine the reset
value.
SSI PrimeCell Identification 1 (SSIPCellID1)
SSI0 base: 0x4000.8000
SSI1 base: 0x4000.9000
Offset 0xFF4
Type RO, reset 0x0000.00F0
31 30 29 28 27 26 25 24 23 22 21 20 19 18 17 16
reserved
Type RO RO RO RO RO RO RO RO RO RO RO RO RO RO RO RO
Reset 0 0 0 0 0 0 0 0 0 0 0 0 0 0 0 0
15 14 13 12 11 10 9 8 7 6 5 4 3 2 1 0
reserved CID1
Type RO RO RO RO RO RO RO RO RO RO RO RO RO RO RO RO
Reset 0 0 0 0 0 0 0 0 1 1 1 1 0 0 0 0
Bit/Field Name Type Reset Description
Software should not rely on the value of a reserved bit. To provide
compatibility with future products, the value of a reserved bit should be
preserved across a read-modify-write operation.
31:8 reserved RO 0x00
SSI PrimeCell ID Register [15:8]
Provides software a standard cross-peripheral identification system.
7:0 CID1 RO 0xF0
January 08, 2011 495
Texas Instruments-Production Data
Stellaris® LM3S2965 Microcontroller
Register 20: SSI PrimeCell Identification 2 (SSIPCellID2), offset 0xFF8
The SSIPCellIDn registers are hard-coded, and the fields within the register determine the reset
value.
SSI PrimeCell Identification 2 (SSIPCellID2)
SSI0 base: 0x4000.8000
SSI1 base: 0x4000.9000
Offset 0xFF8
Type RO, reset 0x0000.0005
31 30 29 28 27 26 25 24 23 22 21 20 19 18 17 16
reserved
Type RO RO RO RO RO RO RO RO RO RO RO RO RO RO RO RO
Reset 0 0 0 0 0 0 0 0 0 0 0 0 0 0 0 0
15 14 13 12 11 10 9 8 7 6 5 4 3 2 1 0
reserved CID2
Type RO RO RO RO RO RO RO RO RO RO RO RO RO RO RO RO
Reset 0 0 0 0 0 0 0 0 0 0 0 0 0 1 0 1
Bit/Field Name Type Reset Description
Software should not rely on the value of a reserved bit. To provide
compatibility with future products, the value of a reserved bit should be
preserved across a read-modify-write operation.
31:8 reserved RO 0x00
SSI PrimeCell ID Register [23:16]
Provides software a standard cross-peripheral identification system.
7:0 CID2 RO 0x05
496 January 08, 2011
Texas Instruments-Production Data
Synchronous Serial Interface (SSI)
Register 21: SSI PrimeCell Identification 3 (SSIPCellID3), offset 0xFFC
The SSIPCellIDn registers are hard-coded, and the fields within the register determine the reset
value.
SSI PrimeCell Identification 3 (SSIPCellID3)
SSI0 base: 0x4000.8000
SSI1 base: 0x4000.9000
Offset 0xFFC
Type RO, reset 0x0000.00B1
31 30 29 28 27 26 25 24 23 22 21 20 19 18 17 16
reserved
Type RO RO RO RO RO RO RO RO RO RO RO RO RO RO RO RO
Reset 0 0 0 0 0 0 0 0 0 0 0 0 0 0 0 0
15 14 13 12 11 10 9 8 7 6 5 4 3 2 1 0
reserved CID3
Type RO RO RO RO RO RO RO RO RO RO RO RO RO RO RO RO
Reset 0 0 0 0 0 0 0 0 1 0 1 1 0 0 0 1
Bit/Field Name Type Reset Description
Software should not rely on the value of a reserved bit. To provide
compatibility with future products, the value of a reserved bit should be
preserved across a read-modify-write operation.
31:8 reserved RO 0x00
SSI PrimeCell ID Register [31:24]
Provides software a standard cross-peripheral identification system.
7:0 CID3 RO 0xB1
January 08, 2011 497
Texas Instruments-Production Data
Stellaris® LM3S2965 Microcontroller
14 Inter-Integrated Circuit (I2C) Interface
The Inter-Integrated Circuit (I2C) bus provides bi-directional data transfer through a two-wire design
(a serial data line SDA and a serial clock line SCL), and interfaces to external I2C devices such as
serial memory (RAMs and ROMs), networking devices, LCDs, tone generators, and so on. The I2C
bus may also be used for system testing and diagnostic purposes in product development and
manufacture. The LM3S2965 microcontroller includes two I2C modules, providing the ability to
interact (both send and receive) with other I2C devices on the bus.
The Stellaris® I2C interface has the following features:
■ Two I2C modules, each with the following features:
■ Devices on the I2C bus can be designated as either a master or a slave
– Supports both sending and receiving data as either a master or a slave
– Supports simultaneous master and slave operation
■ Four I2C modes
– Master transmit
– Master receive
– Slave transmit
– Slave receive
■ Two transmission speeds: Standard (100 Kbps) and Fast (400 Kbps)
■ Master and slave interrupt generation
– Master generates interrupts when a transmit or receive operation completes (or aborts due
to an error)
– Slave generates interrupts when data has been sent or requested by a master
■ Master with arbitration and clock synchronization, multimaster support, and 7-bit addressing
mode
498 January 08, 2011
Texas Instruments-Production Data
Inter-Integrated Circuit (I2C) Interface
14.1 Block Diagram
Figure 14-1. I2C Block Diagram
I2C I/O Select
I2C Master Core
Interrupt
I2C Slave Core
I2CSCL
I2CSDA
I2CSDA
I2CSCL
I2CSDA
I2CSCL
I2CMSA
I2CMCS
I2CMDR
I2CMTPR
I2CMIMR
I2CMRIS
I2CMICR
I2CMCR
I2CSOAR
I2CSCSR
I2CSDR
I2CSIM
I2CSRIS
I2CSMIS
I2CMMIS I2CSICR
I2C Control
14.2 Functional Description
Each I2C module is comprised of both master and slave functions which are implemented as separate
peripherals. For proper operation, the SDA and SCL pins must be connected to bi-directional
open-drain pads. A typical I2C bus configuration is shown in Figure 14-2 on page 499.
See “Inter-Integrated Circuit (I2C) Interface” on page 691 for I2C timing diagrams.
Figure 14-2. I2C Bus Configuration
RPUP
StellarisTM
I2CSCL I2CSDA
RPUP
3rd Party Device
with I2C Interface
SCL SDA
I2C Bus
SCL
SDA
3rd Party Device
with I2C Interface
SCL SDA
14.2.1 I2C Bus Functional Overview
The I2C bus uses only two signals: SDA and SCL, named I2CSDA and I2CSCL on Stellaris
microcontrollers. SDA is the bi-directional serial data line and SCL is the bi-directional serial clock
line. The bus is considered idle when both lines are High.
Every transaction on the I2C bus is nine bits long, consisting of eight data bits and a single
acknowledge bit. The number of bytes per transfer (defined as the time between a valid START
and STOP condition, described in “START and STOP Conditions” on page 500) is unrestricted, but
each byte has to be followed by an acknowledge bit, and data must be transferred MSB first. When
a receiver cannot receive another complete byte, it can hold the clock line SCL Low and force the
transmitter into a wait state. The data transfer continues when the receiver releases the clock SCL.
January 08, 2011 499
Texas Instruments-Production Data
Stellaris® LM3S2965 Microcontroller
14.2.1.1 START and STOP Conditions
The protocol of the I2C bus defines two states to begin and end a transaction: START and STOP.
A High-to-Low transition on the SDA line while the SCL is High is defined as a START condition,
and a Low-to-High transition on the SDA line while SCL is High is defined as a STOP condition.
The bus is considered busy after a START condition and free after a STOP condition. See Figure
14-3 on page 500.
Figure 14-3. START and STOP Conditions
START
condition
SDA
SCL
STOP
condition
SDA
SCL
14.2.1.2 Data Format with 7-Bit Address
Data transfers follow the format shown in Figure 14-4 on page 500. After the START condition, a
slave address is sent. This address is 7-bits long followed by an eighth bit, which is a data direction
bit (R/S bit in the I2CMSA register). A zero indicates a transmit operation (send), and a one indicates
a request for data (receive). A data transfer is always terminated by a STOP condition generated
by the master, however, a master can initiate communications with another device on the bus by
generating a repeated START condition and addressing another slave without first generating a
STOP condition. Various combinations of receive/send formats are then possible within a single
transfer.
Figure 14-4. Complete Data Transfer with a 7-Bit Address
Slave address Data
SDA MSB LSB R/S ACK MSB LSB ACK
SCL 1 2 7 8 9 1 2 7 8 9
The first seven bits of the first byte make up the slave address (see Figure 14-5 on page 500). The
eighth bit determines the direction of the message. A zero in the R/S position of the first byte means
that the master will write (send) data to the selected slave, and a one in this position means that
the master will receive data from the slave.
Figure 14-5. R/S Bit in First Byte
R/S
LSB
Slave address
MSB
14.2.1.3 Data Validity
The data on the SDA line must be stable during the high period of the clock, and the data line can
only change when SCL is Low (see Figure 14-6 on page 501).
500 January 08, 2011
Texas Instruments-Production Data
Inter-Integrated Circuit (I2C) Interface
Figure 14-6. Data Validity During Bit Transfer on the I2C Bus
Change
of data
allowed
Dataline
stable
SDA
SCL
14.2.1.4 Acknowledge
All bus transactions have a required acknowledge clock cycle that is generated by the master. During
the acknowledge cycle, the transmitter (which can be the master or slave) releases the SDA line.
To acknowledge the transaction, the receiver must pull down SDA during the acknowledge clock
cycle. The data sent out by the receiver during the acknowledge cycle must comply with the data
validity requirements described in “Data Validity” on page 500.
When a slave receiver does not acknowledge the slave address, SDA must be left High by the slave
so that the master can generate a STOP condition and abort the current transfer. If the master
device is acting as a receiver during a transfer, it is responsible for acknowledging each transfer
made by the slave. Since the master controls the number of bytes in the transfer, it signals the end
of data to the slave transmitter by not generating an acknowledge on the last data byte. The slave
transmitter must then release SDA to allow the master to generate the STOP or a repeated START
condition.
14.2.1.5 Arbitration
A master may start a transfer only if the bus is idle. It's possible for two or more masters to generate
a START condition within minimum hold time of the START condition. In these situations, an
arbitration scheme takes place on the SDA line, while SCL is High. During arbitration, the first of
the competing master devices to place a '1' (High) on SDA while another master transmits a '0'
(Low) will switch off its data output stage and retire until the bus is idle again.
Arbitration can take place over several bits. Its first stage is a comparison of address bits, and if
both masters are trying to address the same device, arbitration continues on to the comparison of
data bits.
14.2.2 Available Speed Modes
The I2C clock rate is determined by the parameters: CLK_PRD, TIMER_PRD, SCL_LP, and SCL_HP.
where:
CLK_PRD is the system clock period
SCL_LP is the low phase of SCL (fixed at 6)
SCL_HP is the high phase of SCL (fixed at 4)
TIMER_PRD is the programmed value in the I2C Master Timer Period (I2CMTPR) register (see
page 519).
The I2C clock period is calculated as follows:
SCL_PERIOD = 2*(1 + TIMER_PRD)*(SCL_LP + SCL_HP)*CLK_PRD
For example:
January 08, 2011 501
Texas Instruments-Production Data
Stellaris® LM3S2965 Microcontroller
CLK_PRD = 50 ns
TIMER_PRD = 2
SCL_LP=6
SCL_HP=4
yields a SCL frequency of:
1/T = 333 Khz
Table 14-1 on page 502 gives examples of timer period, system clock, and speed mode (Standard
or Fast).
Table 14-1. Examples of I2C Master Timer Period versus Speed Mode
System Clock Timer Period Standard Mode Timer Period Fast Mode
4 MHz 0x01 100 Kbps - -
6 MHz 0x02 100 Kbps - -
12.5 MHz 0x06 89 Kbps 0x01 312 Kbps
16.7 MHz 0x08 93 Kbps 0x02 278 Kbps
20 MHz 0x09 100 Kbps 0x02 333 Kbps
25 MHz 0x0C 96.2 Kbps 0x03 312 Kbps
33 MHz 0x10 97.1 Kbps 0x04 330 Kbps
40 MHz 0x13 100 Kbps 0x04 400 Kbps
50 MHz 0x18 100 Kbps 0x06 357 Kbps
14.2.3 Interrupts
The I2C can generate interrupts when the following conditions are observed:
■ Master transaction completed
■ Master arbitration lost
■ Master transaction error
■ Slave transaction received
■ Slave transaction requested
There is a separate interrupt signal for the I2C master and I2C slave modules. While both modules
can generate interrupts for multiple conditions, only a single interrupt signal is sent to the interrupt
controller.
14.2.3.1 I2C Master Interrupts
The I2C master module generates an interrupt when a transaction completes (either transmit or
receive), when arbitration is lost, or when an error occurs during a transaction. To enable the I2C
master interrupt, software must set the IM bit in the I2C Master Interrupt Mask (I2CMIMR) register.
When an interrupt condition is met, software must check the ERROR and ARBLST bits in the I2C
Master Control/Status (I2CMCS) register to verify that an error didn't occur during the last transaction
and to ensure that arbitration has not been lost. An error condition is asserted if the last transaction
wasn't acknowledged by the slave. If an error is not detected and the master has not lost arbitration,
502 January 08, 2011
Texas Instruments-Production Data
Inter-Integrated Circuit (I2C) Interface
the application can proceed with the transfer. The interrupt is cleared by writing a 1 to the IC bit in
the I2C Master Interrupt Clear (I2CMICR) register.
If the application doesn't require the use of interrupts, the raw interrupt status is always visible via
the I2C Master Raw Interrupt Status (I2CMRIS) register.
14.2.3.2 I2C Slave Interrupts
The slave module can generate an interrupt when data has been received or requested. This interrupt
is enabled by writing a 1 to the DATAIM bit in the I2C Slave Interrupt Mask (I2CSIMR) register.
Software determines whether the module should write (transmit) or read (receive) data from the I2C
Slave Data (I2CSDR) register, by checking the RREQ and TREQ bits of the I2C Slave Control/Status
(I2CSCSR) register. If the slave module is in receive mode and the first byte of a transfer is received,
the FBR bit is set along with the RREQ bit. The interrupt is cleared by writing a 1 to the DATAIC bit
in the I2C Slave Interrupt Clear (I2CSICR) register.
If the application doesn't require the use of interrupts, the raw interrupt status is always visible via
the I2C Slave Raw Interrupt Status (I2CSRIS) register.
14.2.4 Loopback Operation
The I2C modules can be placed into an internal loopback mode for diagnostic or debug work. This
is accomplished by setting the LPBK bit in the I2C Master Configuration (I2CMCR) register. In
loopback mode, the SDA and SCL signals from the master and slave modules are tied together.
14.2.5 Command Sequence Flow Charts
This section details the steps required to perform the various I2C transfer types in both master and
slave mode.
14.2.5.1 I2C Master Command Sequences
The figures that follow show the command sequences available for the I2C master.
January 08, 2011 503
Texas Instruments-Production Data
Stellaris® LM3S2965 Microcontroller
Figure 14-7. Master Single SEND
Idle
Write Slave
Address to
I2CMSA
Write data to
I2CMDR
Read I2CMCS
Sequence
may be
omitted in a
Single Master
system
BUSBSY bit=0? NO
Write ---0-111 to
I2CMCS
YES
Read I2CMCS
BUSY bit=0?
ERROR bit=0?
YES
Error Service
Idle
YES
NO
NO
504 January 08, 2011
Texas Instruments-Production Data
Inter-Integrated Circuit (I2C) Interface
Figure 14-8. Master Single RECEIVE
Idle
Write Slave
Address to
I2CMSA
Read I2CMCS
Sequence may be
omitted in a Single
Master system
BUSBSY bit=0? NO
Write ---00111 to
I2CMCS
YES
Read I2CMCS
BUSY bit=0?
ERROR bit=0?
YES
Error Service
Idle
NO
NO
Read data from
I2CMDR
YES
January 08, 2011 505
Texas Instruments-Production Data
Stellaris® LM3S2965 Microcontroller
Figure 14-9. Master Burst SEND
Idle
Write Slave
Address to
I2CMSA
Write data to
I2CMDR
Read I2CMCS
BUSBSY bit=0?
YES
Write ---0-011 to
I2CMCS
NO
Read I2CMCS
BUSY bit=0?
YES
ERROR bit=0?
YES
Write data to ARBLST bit=1?
I2CMDR
Write ---0-100 to
Index=n? I2CMCS
NO
Error Service
Idle
YES
Write ---0-001 to
I2CMCS
Write ---0-101 to
I2CMCS
YES
Read I2CMCS
BUSY bit=0?
ERROR bit=0?
YES
NO
Idle
YES
Error Service NO
NO
NO
NO
Sequence
may be
omitted in a
Single Master
system
506 January 08, 2011
Texas Instruments-Production Data
Inter-Integrated Circuit (I2C) Interface
Figure 14-10. Master Burst RECEIVE
Idle
Write Slave
Address to
I2CMSA
Read I2CMCS
BUSBSY bit=0? NO
Write ---01011 to
I2CMCS
YES
Read I2CMCS
BUSY bit=0? NO
ERROR bit=0?
YES
ARBLST bit=1?
Write ---0-100 to
I2CMCS
NO
Error Service
YES
Idle
Read data from
I2CMDR
Index=m-1?
Write ---00101 to
I2CMCS
YES
Idle
Read data from
Error Service I2CMDR
ERROR bit=0?
YES
Write ---01001 to
I2CMCS
Read I2CMCS
BUSY bit=0? NO
YES
Sequence
may be
omitted in a
Single Master
system
NO
NO
NO
January 08, 2011 507
Texas Instruments-Production Data
Stellaris® LM3S2965 Microcontroller
Figure 14-11. Master Burst RECEIVE after Burst SEND
Idle
Master operates in
Master Transmit mode
STOP condition is not
generated
Write Slave
Address to
I2CMSA
Write ---01011 to
I2CMCS
Master operates in
Master Receive mode
Idle
Repeated START
condition is generated
with changing data
direction
508 January 08, 2011
Texas Instruments-Production Data
Inter-Integrated Circuit (I2C) Interface
Figure 14-12. Master Burst SEND after Burst RECEIVE
Idle
Master operates in
Master Receive mode
STOP condition is not
generated
Write Slave
Address to
I2CMSA
Write ---0-011 to
I2CMCS
Master operates in
Master Transmit mode
Idle
Repeated START
condition is generated
with changing data
direction
14.2.5.2 I2C Slave Command Sequences
Figure 14-13 on page 510 presents the command sequence available for the I2C slave.
January 08, 2011 509
Texas Instruments-Production Data
Stellaris® LM3S2965 Microcontroller
Figure 14-13. Slave Command Sequence
Idle
Write OWN Slave
Address to
I2CSOAR
Write -------1 to
I2CSCSR
Read I2CSCSR
RREQ bit=1?
Read data from
I2CSDR
YES
TREQ bit=1? NO
Write data to
I2CSDR
YES
NO
FBR is
also valid
14.3 Initialization and Configuration
The following example shows how to configure the I2C module to send a single byte as a master.
This assumes the system clock is 20 MHz.
1. Enable the I2C clock by writing a value of 0x0000.1000 to the RCGC1 register in the System
Control module.
2. Enable the clock to the appropriate GPIO module via the RCGC2 register in the System Control
module.
3. In the GPIO module, enable the appropriate pins for their alternate function using the
GPIOAFSEL register. Also, be sure to enable the same pins for Open Drain operation.
4. Initialize the I2C Master by writing the I2CMCR register with a value of 0x0000.0020.
5. Set the desired SCL clock speed of 100 Kbps by writing the I2CMTPR register with the correct
value. The value written to the I2CMTPR register represents the number of system clock periods
in one SCL clock period. The TPR value is determined by the following equation:
510 January 08, 2011
Texas Instruments-Production Data
Inter-Integrated Circuit (I2C) Interface
TPR = (System Clock / (2 * (SCL_LP + SCL_HP) * SCL_CLK)) - 1;
TPR = (20MHz / (2 * (6 + 4) * 100000)) - 1;
TPR = 9
Write the I2CMTPR register with the value of 0x0000.0009.
6. Specify the slave address of the master and that the next operation will be a Send by writing
the I2CMSA register with a value of 0x0000.0076. This sets the slave address to 0x3B.
7. Place data (byte) to be sent in the data register by writing the I2CMDR register with the desired
data.
8. Initiate a single byte send of the data from Master to Slave by writing the I2CMCS register with
a value of 0x0000.0007 (STOP, START, RUN).
9. Wait until the transmission completes by polling the I2CMCS register’s BUSBSY bit until it has
been cleared.
14.4 Register Map
Table 14-2 on page 511 lists the I2C registers. All addresses given are relative to the I2C base
addresses for the master and slave:
■ I2C 0: 0x4002.0000
■ I2C 1: 0x4002.1000
Note that the I2C module clock must be enabled before the registers can be programmed (see
page 216). There must be a delay of 3 system clocks after the I2C module clock is enabled before
any I2C module registers are accessed.
The hw_i2c.h file in the StellarisWare® Driver Library uses a base address of 0x800 for the I2C slave
registers. Be aware when using registers with offsets between 0x800 and 0x818 that StellarisWare
uses an offset between 0x000 and 0x018 with the slave base address.
Table 14-2. Inter-Integrated Circuit (I2C) Interface Register Map
See
Offset Name Type Reset Description page
I2C Master
0x000 I2CMSA R/W 0x0000.0000 I2C Master Slave Address 513
0x004 I2CMCS R/W 0x0000.0000 I2C Master Control/Status 514
0x008 I2CMDR R/W 0x0000.0000 I2C Master Data 518
0x00C I2CMTPR R/W 0x0000.0001 I2C Master Timer Period 519
0x010 I2CMIMR R/W 0x0000.0000 I2C Master Interrupt Mask 520
0x014 I2CMRIS RO 0x0000.0000 I2C Master Raw Interrupt Status 521
0x018 I2CMMIS RO 0x0000.0000 I2C Master Masked Interrupt Status 522
0x01C I2CMICR WO 0x0000.0000 I2C Master Interrupt Clear 523
0x020 I2CMCR R/W 0x0000.0000 I2C Master Configuration 524
January 08, 2011 511
Texas Instruments-Production Data
Stellaris® LM3S2965 Microcontroller
Table 14-2. Inter-Integrated Circuit (I2C) Interface Register Map (continued)
See
Offset Name Type Reset Description page
I2C Slave
0x800 I2CSOAR R/W 0x0000.0000 I2C Slave Own Address 526
0x804 I2CSCSR RO 0x0000.0000 I2C Slave Control/Status 527
0x808 I2CSDR R/W 0x0000.0000 I2C Slave Data 529
0x80C I2CSIMR R/W 0x0000.0000 I2C Slave Interrupt Mask 530
0x810 I2CSRIS RO 0x0000.0000 I2C Slave Raw Interrupt Status 531
0x814 I2CSMIS RO 0x0000.0000 I2C Slave Masked Interrupt Status 532
0x818 I2CSICR WO 0x0000.0000 I2C Slave Interrupt Clear 533
14.5 Register Descriptions (I2C Master)
The remainder of this section lists and describes the I2C master registers, in numerical order by
address offset. See also “Register Descriptions (I2C Slave)” on page 525.
512 January 08, 2011
Texas Instruments-Production Data
Inter-Integrated Circuit (I2C) Interface
Register 1: I2C Master Slave Address (I2CMSA), offset 0x000
This register consists of eight bits: seven address bits (A6-A0), and a Receive/Send bit, which
determines if the next operation is a Receive (High), or Send (Low).
I2C Master Slave Address (I2CMSA)
I2C 0 base: 0x4002.0000
I2C 1 base: 0x4002.1000
Offset 0x000
Type R/W, reset 0x0000.0000
31 30 29 28 27 26 25 24 23 22 21 20 19 18 17 16
reserved
Type RO RO RO RO RO RO RO RO RO RO RO RO RO RO RO RO
Reset 0 0 0 0 0 0 0 0 0 0 0 0 0 0 0 0
15 14 13 12 11 10 9 8 7 6 5 4 3 2 1 0
reserved SA R/S
Type RO RO RO RO RO RO RO RO R/W R/W R/W R/W R/W R/W R/W R/W
Reset 0 0 0 0 0 0 0 0 0 0 0 0 0 0 0 0
Bit/Field Name Type Reset Description
Software should not rely on the value of a reserved bit. To provide
compatibility with future products, the value of a reserved bit should be
preserved across a read-modify-write operation.
31:8 reserved RO 0x00
I2C Slave Address
This field specifies bits A6 through A0 of the slave address.
7:1 SA R/W 0
Receive/Send
The R/S bit specifies if the next operation is a Receive (High) or Send
(Low).
Value Description
0 Send.
1 Receive.
0 R/S R/W 0
January 08, 2011 513
Texas Instruments-Production Data
Stellaris® LM3S2965 Microcontroller
Register 2: I2C Master Control/Status (I2CMCS), offset 0x004
This register accesses four control bits when written, and accesses seven status bits when read.
The status register consists of seven bits, which when read determine the state of the I2C bus
controller.
The control register consists of four bits: the RUN, START, STOP, and ACK bits. The START bit causes
the generation of the START, or REPEATED START condition.
The STOP bit determines if the cycle stops at the end of the data cycle, or continues on to a burst.
To generate a single send cycle, the I2C Master Slave Address (I2CMSA) register is written with
the desired address, the R/S bit is set to 0, and the Control register is written with ACK=X (0 or 1),
STOP=1, START=1, and RUN=1 to perform the operation and stop. When the operation is completed
(or aborted due an error), the interrupt pin becomes active and the data may be read from the
I2CMDR register. When the I2C module operates in Master receiver mode, the ACK bit must be set
normally to logic 1. This causes the I2C bus controller to send an acknowledge automatically after
each byte. This bit must be reset when the I2C bus controller requires no further data to be sent
from the slave transmitter.
Reads
I2C Master Control/Status (I2CMCS)
I2C 0 base: 0x4002.0000
I2C 1 base: 0x4002.1000
Offset 0x004
Type RO, reset 0x0000.0000
31 30 29 28 27 26 25 24 23 22 21 20 19 18 17 16
reserved
Type RO RO RO RO RO RO RO RO RO RO RO RO RO RO RO RO
Reset 0 0 0 0 0 0 0 0 0 0 0 0 0 0 0 0
15 14 13 12 11 10 9 8 7 6 5 4 3 2 1 0
reserved BUSBSY IDLE ARBLST DATACK ADRACK ERROR BUSY
Type RO RO RO RO RO RO RO RO RO RO RO RO RO RO RO RO
Reset 0 0 0 0 0 0 0 0 0 0 0 0 0 0 0 0
Bit/Field Name Type Reset Description
Software should not rely on the value of a reserved bit. To provide
compatibility with future products, the value of a reserved bit should be
preserved across a read-modify-write operation.
31:7 reserved RO 0x00
Bus Busy
This bit specifies the state of the I2C bus. If set, the bus is busy;
otherwise, the bus is idle. The bit changes based on the START and
STOP conditions.
6 BUSBSY RO 0
I2C Idle
This bit specifies the I2C controller state. If set, the controller is idle;
otherwise the controller is not idle.
5 IDLE RO 0
Arbitration Lost
This bit specifies the result of bus arbitration. If set, the controller lost
arbitration; otherwise, the controller won arbitration.
4 ARBLST RO 0
514 January 08, 2011
Texas Instruments-Production Data
Inter-Integrated Circuit (I2C) Interface
Bit/Field Name Type Reset Description
Acknowledge Data
This bit specifies the result of the last data operation. If set, the
transmitted data was not acknowledged; otherwise, the data was
acknowledged.
3 DATACK RO 0
Acknowledge Address
This bit specifies the result of the last address operation. If set, the
transmitted address was not acknowledged; otherwise, the address was
acknowledged.
2 ADRACK RO 0
Error
This bit specifies the result of the last bus operation. If set, an error
occurred on the last operation; otherwise, no error was detected. The
error can be from the slave address not being acknowledged or the
transmit data not being acknowledged.
1 ERROR RO 0
I2C Busy
This bit specifies the state of the controller. If set, the controller is busy;
otherwise, the controller is idle. When the BUSY bit is set, the other status
bits are not valid.
0 BUSY RO 0
Writes
I2C Master Control/Status (I2CMCS)
I2C 0 base: 0x4002.0000
I2C 1 base: 0x4002.1000
Offset 0x004
Type WO, reset 0x0000.0000
31 30 29 28 27 26 25 24 23 22 21 20 19 18 17 16
reserved
Type WO WO WO WO WO WO WO WO WO WO WO WO WO WO WO WO
Reset 0 0 0 0 0 0 0 0 0 0 0 0 0 0 0 0
15 14 13 12 11 10 9 8 7 6 5 4 3 2 1 0
reserved ACK STOP START RUN
Type WO WO WO WO WO WO WO WO WO WO WO WO WO WO WO WO
Reset 0 0 0 0 0 0 0 0 0 0 0 0 0 0 0 0
Bit/Field Name Type Reset Description
Software should not rely on the value of a reserved bit. To provide
compatibility with future products, the value of a reserved bit should be
preserved across a read-modify-write operation.
31:4 reserved WO 0x00
Data Acknowledge Enable
When set, causes received data byte to be acknowledged automatically
by the master. See field decoding in Table 14-3 on page 516.
3 ACK WO 0
Generate STOP
When set, causes the generation of the STOP condition. See field
decoding in Table 14-3 on page 516.
2 STOP WO 0
Generate START
When set, causes the generation of a START or repeated START
condition. See field decoding in Table 14-3 on page 516.
1 START WO 0
January 08, 2011 515
Texas Instruments-Production Data
Stellaris® LM3S2965 Microcontroller
Bit/Field Name Type Reset Description
I2C Master Enable
When set, allows the master to send or receive data. See field decoding
in Table 14-3 on page 516.
0 RUN WO 0
Table 14-3. Write Field Decoding for I2CMCS[3:0] Field (Sheet 1 of 3)
Description
Current I2CMSA[0] I2CMCS[3:0]
State R/S ACK STOP START RUN
START condition followed by SEND (master goes to the
Master Transmit state).
0 Xa 0 1 1
Idle
START condition followed by a SEND and STOP
condition (master remains in Idle state).
0 X 1 1 1
START condition followed by RECEIVE operation with
negative ACK (master goes to the Master Receive state).
1 0 0 1 1
START condition followed by RECEIVE and STOP
condition (master remains in Idle state).
1 0 1 1 1
START condition followed by RECEIVE (master goes
to the Master Receive state).
1 1 0 1 1
1 1 1 1 1 Illegal.
All other combinations not listed are non-operations. NOP.
SEND operation (master remains in Master Transmit
state).
X X 0 0 1
Master
Transmit
X X 1 0 0 STOP condition (master goes to Idle state).
SEND followed by STOP condition (master goes to Idle
state).
X X 1 0 1
Repeated START condition followed by a SEND (master
remains in Master Transmit state).
0 X 0 1 1
Repeated START condition followed by SEND and STOP
condition (master goes to Idle state).
0 X 1 1 1
Repeated START condition followed by a RECEIVE
operation with a negative ACK (master goes to Master
Receive state).
1 0 0 1 1
Repeated START condition followed by a SEND and
STOP condition (master goes to Idle state).
1 0 1 1 1
Repeated START condition followed by RECEIVE
(master goes to Master Receive state).
1 1 0 1 1
1 1 1 1 1 Illegal.
All other combinations not listed are non-operations. NOP.
516 January 08, 2011
Texas Instruments-Production Data
Inter-Integrated Circuit (I2C) Interface
Table 14-3. Write Field Decoding for I2CMCS[3:0] Field (Sheet 1 of 3) (continued)
Description
Current I2CMSA[0] I2CMCS[3:0]
State R/S ACK STOP START RUN
RECEIVE operation with negative ACK (master remains
in Master Receive state).
X 0 0 0 1
Master
Receive
X X 1 0 0 STOP condition (master goes to Idle state).b
RECEIVE followed by STOP condition (master goes to
Idle state).
X 0 1 0 1
RECEIVE operation (master remains in Master Receive
state).
X 1 0 0 1
X 1 1 0 1 Illegal.
Repeated START condition followed by RECEIVE
operation with a negative ACK (master remains in Master
Receive state).
1 0 0 1 1
Repeated START condition followed by RECEIVE and
STOP condition (master goes to Idle state).
1 0 1 1 1
Repeated START condition followed by RECEIVE
(master remains in Master Receive state).
1 1 0 1 1
Repeated START condition followed by SEND (master
goes to Master Transmit state).
0 X 0 1 1
Repeated START condition followed by SEND and STOP
condition (master goes to Idle state).
0 X 1 1 1
All other combinations not listed are non-operations. NOP.
a. An X in a table cell indicates the bit can be 0 or 1.
b. In Master Receive mode, a STOP condition should be generated only after a Data Negative Acknowledge executed by
the master or an Address Negative Acknowledge executed by the slave.
January 08, 2011 517
Texas Instruments-Production Data
Stellaris® LM3S2965 Microcontroller
Register 3: I2C Master Data (I2CMDR), offset 0x008
Important: Use caution when reading this register. Performing a read may change bit status.
This register contains the data to be transmitted when in the Master Transmit state, and the data
received when in the Master Receive state.
I2C Master Data (I2CMDR)
I2C 0 base: 0x4002.0000
I2C 1 base: 0x4002.1000
Offset 0x008
Type R/W, reset 0x0000.0000
31 30 29 28 27 26 25 24 23 22 21 20 19 18 17 16
reserved
Type RO RO RO RO RO RO RO RO RO RO RO RO RO RO RO RO
Reset 0 0 0 0 0 0 0 0 0 0 0 0 0 0 0 0
15 14 13 12 11 10 9 8 7 6 5 4 3 2 1 0
reserved DATA
Type RO RO RO RO RO RO RO RO R/W R/W R/W R/W R/W R/W R/W R/W
Reset 0 0 0 0 0 0 0 0 0 0 0 0 0 0 0 0
Bit/Field Name Type Reset Description
Software should not rely on the value of a reserved bit. To provide
compatibility with future products, the value of a reserved bit should be
preserved across a read-modify-write operation.
31:8 reserved RO 0x00
Data Transferred
Data transferred during transaction.
7:0 DATA R/W 0x00
518 January 08, 2011
Texas Instruments-Production Data
Inter-Integrated Circuit (I2C) Interface
Register 4: I2C Master Timer Period (I2CMTPR), offset 0x00C
This register specifies the period of the SCL clock.
Caution – Take care not to set bit 7 when accessing this register as unpredictable behavior can occur.
I2C Master Timer Period (I2CMTPR)
I2C 0 base: 0x4002.0000
I2C 1 base: 0x4002.1000
Offset 0x00C
Type R/W, reset 0x0000.0001
31 30 29 28 27 26 25 24 23 22 21 20 19 18 17 16
reserved
Type RO RO RO RO RO RO RO RO RO RO RO RO RO RO RO RO
Reset 0 0 0 0 0 0 0 0 0 0 0 0 0 0 0 0
15 14 13 12 11 10 9 8 7 6 5 4 3 2 1 0
reserved TPR
Type RO RO RO RO RO RO RO RO RO R/W R/W R/W R/W R/W R/W R/W
Reset 0 0 0 0 0 0 0 0 0 0 0 0 0 0 0 1
Bit/Field Name Type Reset Description
Software should not rely on the value of a reserved bit. To provide
compatibility with future products, the value of a reserved bit should be
preserved across a read-modify-write operation.
31:7 reserved RO 0x00
SCL Clock Period
This field specifies the period of the SCL clock.
SCL_PRD = 2*(1 + TPR)*(SCL_LP + SCL_HP)*CLK_PRD
where:
SCL_PRD is the SCL line period (I2C clock).
TPR is the Timer Period register value (range of 1 to 127).
SCL_LP is the SCL Low period (fixed at 6).
SCL_HP is the SCL High period (fixed at 4).
6:0 TPR R/W 0x1
January 08, 2011 519
Texas Instruments-Production Data
Stellaris® LM3S2965 Microcontroller
Register 5: I2C Master Interrupt Mask (I2CMIMR), offset 0x010
This register controls whether a raw interrupt is promoted to a controller interrupt.
I2C Master Interrupt Mask (I2CMIMR)
I2C 0 base: 0x4002.0000
I2C 1 base: 0x4002.1000
Offset 0x010
Type R/W, reset 0x0000.0000
31 30 29 28 27 26 25 24 23 22 21 20 19 18 17 16
reserved
Type RO RO RO RO RO RO RO RO RO RO RO RO RO RO RO RO
Reset 0 0 0 0 0 0 0 0 0 0 0 0 0 0 0 0
15 14 13 12 11 10 9 8 7 6 5 4 3 2 1 0
reserved IM
Type RO RO RO RO RO RO RO RO RO RO RO RO RO RO RO R/W
Reset 0 0 0 0 0 0 0 0 0 0 0 0 0 0 0 0
Bit/Field Name Type Reset Description
Software should not rely on the value of a reserved bit. To provide
compatibility with future products, the value of a reserved bit should be
preserved across a read-modify-write operation.
31:1 reserved RO 0x00
Interrupt Mask
This bit controls whether a raw interrupt is promoted to a controller
interrupt. If set, the interrupt is not masked and the interrupt is promoted;
otherwise, the interrupt is masked.
0 IM R/W 0
520 January 08, 2011
Texas Instruments-Production Data
Inter-Integrated Circuit (I2C) Interface
Register 6: I2C Master Raw Interrupt Status (I2CMRIS), offset 0x014
This register specifies whether an interrupt is pending.
I2C Master Raw Interrupt Status (I2CMRIS)
I2C 0 base: 0x4002.0000
I2C 1 base: 0x4002.1000
Offset 0x014
Type RO, reset 0x0000.0000
31 30 29 28 27 26 25 24 23 22 21 20 19 18 17 16
reserved
Type RO RO RO RO RO RO RO RO RO RO RO RO RO RO RO RO
Reset 0 0 0 0 0 0 0 0 0 0 0 0 0 0 0 0
15 14 13 12 11 10 9 8 7 6 5 4 3 2 1 0
reserved RIS
Type RO RO RO RO RO RO RO RO RO RO RO RO RO RO RO RO
Reset 0 0 0 0 0 0 0 0 0 0 0 0 0 0 0 0
Bit/Field Name Type Reset Description
Software should not rely on the value of a reserved bit. To provide
compatibility with future products, the value of a reserved bit should be
preserved across a read-modify-write operation.
31:1 reserved RO 0x00
Raw Interrupt Status
This bit specifies the raw interrupt state (prior to masking) of the I2C
master block. If set, an interrupt is pending; otherwise, an interrupt is
not pending.
0 RIS RO 0
January 08, 2011 521
Texas Instruments-Production Data
Stellaris® LM3S2965 Microcontroller
Register 7: I2C Master Masked Interrupt Status (I2CMMIS), offset 0x018
This register specifies whether an interrupt was signaled.
I2C Master Masked Interrupt Status (I2CMMIS)
I2C 0 base: 0x4002.0000
I2C 1 base: 0x4002.1000
Offset 0x018
Type RO, reset 0x0000.0000
31 30 29 28 27 26 25 24 23 22 21 20 19 18 17 16
reserved
Type RO RO RO RO RO RO RO RO RO RO RO RO RO RO RO RO
Reset 0 0 0 0 0 0 0 0 0 0 0 0 0 0 0 0
15 14 13 12 11 10 9 8 7 6 5 4 3 2 1 0
reserved MIS
Type RO RO RO RO RO RO RO RO RO RO RO RO RO RO RO RO
Reset 0 0 0 0 0 0 0 0 0 0 0 0 0 0 0 0
Bit/Field Name Type Reset Description
Software should not rely on the value of a reserved bit. To provide
compatibility with future products, the value of a reserved bit should be
preserved across a read-modify-write operation.
31:1 reserved RO 0x00
Masked Interrupt Status
This bit specifies the raw interrupt state (after masking) of the I2C master
block. If set, an interrupt was signaled; otherwise, an interrupt has not
been generated since the bit was last cleared.
0 MIS RO 0
522 January 08, 2011
Texas Instruments-Production Data
Inter-Integrated Circuit (I2C) Interface
Register 8: I2C Master Interrupt Clear (I2CMICR), offset 0x01C
This register clears the raw interrupt.
I2C Master Interrupt Clear (I2CMICR)
I2C 0 base: 0x4002.0000
I2C 1 base: 0x4002.1000
Offset 0x01C
Type WO, reset 0x0000.0000
31 30 29 28 27 26 25 24 23 22 21 20 19 18 17 16
reserved
Type RO RO RO RO RO RO RO RO RO RO RO RO RO RO RO RO
Reset 0 0 0 0 0 0 0 0 0 0 0 0 0 0 0 0
15 14 13 12 11 10 9 8 7 6 5 4 3 2 1 0
reserved IC
Type RO RO RO RO RO RO RO RO RO RO RO RO RO RO RO WO
Reset 0 0 0 0 0 0 0 0 0 0 0 0 0 0 0 0
Bit/Field Name Type Reset Description
Software should not rely on the value of a reserved bit. To provide
compatibility with future products, the value of a reserved bit should be
preserved across a read-modify-write operation.
31:1 reserved RO 0x00
Interrupt Clear
This bit controls the clearing of the raw interrupt. A write of 1 clears the
interrupt; otherwise, a write of 0 has no affect on the interrupt state. A
read of this register returns no meaningful data.
0 IC WO 0
January 08, 2011 523
Texas Instruments-Production Data
Stellaris® LM3S2965 Microcontroller
Register 9: I2C Master Configuration (I2CMCR), offset 0x020
This register configures the mode (Master or Slave) and sets the interface for test mode loopback.
I2C Master Configuration (I2CMCR)
I2C 0 base: 0x4002.0000
I2C 1 base: 0x4002.1000
Offset 0x020
Type R/W, reset 0x0000.0000
31 30 29 28 27 26 25 24 23 22 21 20 19 18 17 16
reserved
Type RO RO RO RO RO RO RO RO RO RO RO RO RO RO RO RO
Reset 0 0 0 0 0 0 0 0 0 0 0 0 0 0 0 0
15 14 13 12 11 10 9 8 7 6 5 4 3 2 1 0
reserved SFE MFE reserved LPBK
Type RO RO RO RO RO RO RO RO RO RO R/W R/W RO RO RO R/W
Reset 0 0 0 0 0 0 0 0 0 0 0 0 0 0 0 0
Bit/Field Name Type Reset Description
Software should not rely on the value of a reserved bit. To provide
compatibility with future products, the value of a reserved bit should be
preserved across a read-modify-write operation.
31:6 reserved RO 0x00
I2C Slave Function Enable
This bit specifies whether the interface may operate in Slave mode. If
set, Slave mode is enabled; otherwise, Slave mode is disabled.
5 SFE R/W 0
I2C Master Function Enable
This bit specifies whether the interface may operate in Master mode. If
set, Master mode is enabled; otherwise, Master mode is disabled and
the interface clock is disabled.
4 MFE R/W 0
Software should not rely on the value of a reserved bit. To provide
compatibility with future products, the value of a reserved bit should be
preserved across a read-modify-write operation.
3:1 reserved RO 0x00
I2C Loopback
This bit specifies whether the interface is operating normally or in
Loopback mode. If set, the device is put in a test mode loopback
configuration; otherwise, the device operates normally.
0 LPBK R/W 0
524 January 08, 2011
Texas Instruments-Production Data
Inter-Integrated Circuit (I2C) Interface
14.6 Register Descriptions (I2C Slave)
The remainder of this section lists and describes the I2C slave registers, in numerical order by
address offset. See also “Register Descriptions (I2C Master)” on page 512.
January 08, 2011 525
Texas Instruments-Production Data
Stellaris® LM3S2965 Microcontroller
Register 10: I2C Slave Own Address (I2CSOAR), offset 0x800
This register consists of seven address bits that identify the Stellaris I2C device on the I2C bus.
I2C Slave Own Address (I2CSOAR)
I2C 0 base: 0x4002.0000
I2C 1 base: 0x4002.1000
Offset 0x800
Type R/W, reset 0x0000.0000
31 30 29 28 27 26 25 24 23 22 21 20 19 18 17 16
reserved
Type RO RO RO RO RO RO RO RO RO RO RO RO RO RO RO RO
Reset 0 0 0 0 0 0 0 0 0 0 0 0 0 0 0 0
15 14 13 12 11 10 9 8 7 6 5 4 3 2 1 0
reserved OAR
Type RO RO RO RO RO RO RO RO RO R/W R/W R/W R/W R/W R/W R/W
Reset 0 0 0 0 0 0 0 0 0 0 0 0 0 0 0 0
Bit/Field Name Type Reset Description
Software should not rely on the value of a reserved bit. To provide
compatibility with future products, the value of a reserved bit should be
preserved across a read-modify-write operation.
31:7 reserved RO 0x00
I2C Slave Own Address
This field specifies bits A6 through A0 of the slave address.
6:0 OAR R/W 0x00
526 January 08, 2011
Texas Instruments-Production Data
Inter-Integrated Circuit (I2C) Interface
Register 11: I2C Slave Control/Status (I2CSCSR), offset 0x804
This register accesses one control bit when written, and three status bits when read.
The read-only Status register consists of three bits: the FBR, RREQ, and TREQ bits. The First
Byte Received (FBR) bit is set only after the Stellaris device detects its own slave address and
receives the first data byte from the I2C master. The Receive Request (RREQ) bit indicates that
the Stellaris I2C device has received a data byte from an I2C master. Read one data byte from the
I2C Slave Data (I2CSDR) register to clear the RREQ bit. The Transmit Request (TREQ) bit
indicates that the Stellaris I2C device is addressed as a Slave Transmitter. Write one data byte into
the I2C Slave Data (I2CSDR) register to clear the TREQ bit.
The write-only Control register consists of one bit: the DA bit. The DA bit enables and disables the
Stellaris I2C slave operation.
Reads
I2C Slave Control/Status (I2CSCSR)
I2C 0 base: 0x4002.0000
I2C 1 base: 0x4002.1000
Offset 0x804
Type RO, reset 0x0000.0000
31 30 29 28 27 26 25 24 23 22 21 20 19 18 17 16
reserved
Type RO RO RO RO RO RO RO RO RO RO RO RO RO RO RO RO
Reset 0 0 0 0 0 0 0 0 0 0 0 0 0 0 0 0
15 14 13 12 11 10 9 8 7 6 5 4 3 2 1 0
reserved FBR TREQ RREQ
Type RO RO RO RO RO RO RO RO RO RO RO RO RO RO RO RO
Reset 0 0 0 0 0 0 0 0 0 0 0 0 0 0 0 0
Bit/Field Name Type Reset Description
Software should not rely on the value of a reserved bit. To provide
compatibility with future products, the value of a reserved bit should be
preserved across a read-modify-write operation.
31:3 reserved RO 0x00
First Byte Received
Indicates that the first byte following the slave’s own address is received.
This bit is only valid when the RREQ bit is set, and is automatically cleared
when data has been read from the I2CSDR register.
Note: This bit is not used for slave transmit operations.
2 FBR RO 0
Transmit Request
This bit specifies the state of the I2C slave with regards to outstanding
transmit requests. If set, the I2C unit has been addressed as a slave
transmitter and uses clock stretching to delay the master until data has
been written to the I2CSDR register. Otherwise, there is no outstanding
transmit request.
1 TREQ RO 0
Receive Request
This bit specifies the status of the I2C slave with regards to outstanding
receive requests. If set, the I2C unit has outstanding receive data from
the I2C master and uses clock stretching to delay the master until the
data has been read from the I2CSDR register. Otherwise, no receive
data is outstanding.
0 RREQ RO 0
January 08, 2011 527
Texas Instruments-Production Data
Stellaris® LM3S2965 Microcontroller
Writes
I2C Slave Control/Status (I2CSCSR)
I2C 0 base: 0x4002.0000
I2C 1 base: 0x4002.1000
Offset 0x804
Type WO, reset 0x0000.0000
31 30 29 28 27 26 25 24 23 22 21 20 19 18 17 16
reserved
Type RO RO RO RO RO RO RO RO RO RO RO RO RO RO RO RO
Reset 0 0 0 0 0 0 0 0 0 0 0 0 0 0 0 0
15 14 13 12 11 10 9 8 7 6 5 4 3 2 1 0
reserved DA
Type RO RO RO RO RO RO RO RO RO RO RO RO RO RO RO WO
Reset 0 0 0 0 0 0 0 0 0 0 0 0 0 0 0 0
Bit/Field Name Type Reset Description
Software should not rely on the value of a reserved bit. To provide
compatibility with future products, the value of a reserved bit should be
preserved across a read-modify-write operation.
31:1 reserved RO 0x00
Device Active
Value Description
0 Disables the I2C slave operation.
1 Enables the I2C slave operation.
0 DA WO 0
528 January 08, 2011
Texas Instruments-Production Data
Inter-Integrated Circuit (I2C) Interface
Register 12: I2C Slave Data (I2CSDR), offset 0x808
Important: Use caution when reading this register. Performing a read may change bit status.
This register contains the data to be transmitted when in the Slave Transmit state, and the data
received when in the Slave Receive state.
I2C Slave Data (I2CSDR)
I2C 0 base: 0x4002.0000
I2C 1 base: 0x4002.1000
Offset 0x808
Type R/W, reset 0x0000.0000
31 30 29 28 27 26 25 24 23 22 21 20 19 18 17 16
reserved
Type RO RO RO RO RO RO RO RO RO RO RO RO RO RO RO RO
Reset 0 0 0 0 0 0 0 0 0 0 0 0 0 0 0 0
15 14 13 12 11 10 9 8 7 6 5 4 3 2 1 0
reserved DATA
Type RO RO RO RO RO RO RO RO R/W R/W R/W R/W R/W R/W R/W R/W
Reset 0 0 0 0 0 0 0 0 0 0 0 0 0 0 0 0
Bit/Field Name Type Reset Description
Software should not rely on the value of a reserved bit. To provide
compatibility with future products, the value of a reserved bit should be
preserved across a read-modify-write operation.
31:8 reserved RO 0x00
Data for Transfer
This field contains the data for transfer during a slave receive or transmit
operation.
7:0 DATA R/W 0x0
January 08, 2011 529
Texas Instruments-Production Data
Stellaris® LM3S2965 Microcontroller
Register 13: I2C Slave Interrupt Mask (I2CSIMR), offset 0x80C
This register controls whether a raw interrupt is promoted to a controller interrupt.
I2C Slave Interrupt Mask (I2CSIMR)
I2C 0 base: 0x4002.0000
I2C 1 base: 0x4002.1000
Offset 0x80C
Type R/W, reset 0x0000.0000
31 30 29 28 27 26 25 24 23 22 21 20 19 18 17 16
reserved
Type RO RO RO RO RO RO RO RO RO RO RO RO RO RO RO RO
Reset 0 0 0 0 0 0 0 0 0 0 0 0 0 0 0 0
15 14 13 12 11 10 9 8 7 6 5 4 3 2 1 0
reserved DATAIM
Type RO RO RO RO RO RO RO RO RO RO RO RO RO RO RO R/W
Reset 0 0 0 0 0 0 0 0 0 0 0 0 0 0 0 0
Bit/Field Name Type Reset Description
Software should not rely on the value of a reserved bit. To provide
compatibility with future products, the value of a reserved bit should be
preserved across a read-modify-write operation.
31:1 reserved RO 0x00
Data Interrupt Mask
This bit controls whether the raw interrupt for data received and data
requested is promoted to a controller interrupt. If set, the interrupt is not
masked and the interrupt is promoted; otherwise, the interrupt is masked.
0 DATAIM R/W 0
530 January 08, 2011
Texas Instruments-Production Data
Inter-Integrated Circuit (I2C) Interface
Register 14: I2C Slave Raw Interrupt Status (I2CSRIS), offset 0x810
This register specifies whether an interrupt is pending.
I2C Slave Raw Interrupt Status (I2CSRIS)
I2C 0 base: 0x4002.0000
I2C 1 base: 0x4002.1000
Offset 0x810
Type RO, reset 0x0000.0000
31 30 29 28 27 26 25 24 23 22 21 20 19 18 17 16
reserved
Type RO RO RO RO RO RO RO RO RO RO RO RO RO RO RO RO
Reset 0 0 0 0 0 0 0 0 0 0 0 0 0 0 0 0
15 14 13 12 11 10 9 8 7 6 5 4 3 2 1 0
reserved DATARIS
Type RO RO RO RO RO RO RO RO RO RO RO RO RO RO RO RO
Reset 0 0 0 0 0 0 0 0 0 0 0 0 0 0 0 0
Bit/Field Name Type Reset Description
Software should not rely on the value of a reserved bit. To provide
compatibility with future products, the value of a reserved bit should be
preserved across a read-modify-write operation.
31:1 reserved RO 0x00
Data Raw Interrupt Status
This bit specifies the raw interrupt state for data received and data
requested (prior to masking) of the I2C slave block. If set, an interrupt
is pending; otherwise, an interrupt is not pending.
0 DATARIS RO 0
January 08, 2011 531
Texas Instruments-Production Data
Stellaris® LM3S2965 Microcontroller
Register 15: I2C Slave Masked Interrupt Status (I2CSMIS), offset 0x814
This register specifies whether an interrupt was signaled.
I2C Slave Masked Interrupt Status (I2CSMIS)
I2C 0 base: 0x4002.0000
I2C 1 base: 0x4002.1000
Offset 0x814
Type RO, reset 0x0000.0000
31 30 29 28 27 26 25 24 23 22 21 20 19 18 17 16
reserved
Type RO RO RO RO RO RO RO RO RO RO RO RO RO RO RO RO
Reset 0 0 0 0 0 0 0 0 0 0 0 0 0 0 0 0
15 14 13 12 11 10 9 8 7 6 5 4 3 2 1 0
reserved DATAMIS
Type RO RO RO RO RO RO RO RO RO RO RO RO RO RO RO RO
Reset 0 0 0 0 0 0 0 0 0 0 0 0 0 0 0 0
Bit/Field Name Type Reset Description
Software should not rely on the value of a reserved bit. To provide
compatibility with future products, the value of a reserved bit should be
preserved across a read-modify-write operation.
31:1 reserved RO 0x00
Data Masked Interrupt Status
This bit specifies the interrupt state for data received and data requested
(after masking) of the I2C slave block. If set, an interrupt was signaled;
otherwise, an interrupt has not been generated since the bit was last
cleared.
0 DATAMIS RO 0
532 January 08, 2011
Texas Instruments-Production Data
Inter-Integrated Circuit (I2C) Interface
Register 16: I2C Slave Interrupt Clear (I2CSICR), offset 0x818
This register clears the raw interrupt. A read of this register returns no meaningful data.
I2C Slave Interrupt Clear (I2CSICR)
I2C 0 base: 0x4002.0000
I2C 1 base: 0x4002.1000
Offset 0x818
Type WO, reset 0x0000.0000
31 30 29 28 27 26 25 24 23 22 21 20 19 18 17 16
reserved
Type RO RO RO RO RO RO RO RO RO RO RO RO RO RO RO RO
Reset 0 0 0 0 0 0 0 0 0 0 0 0 0 0 0 0
15 14 13 12 11 10 9 8 7 6 5 4 3 2 1 0
reserved DATAIC
Type RO RO RO RO RO RO RO RO RO RO RO RO RO RO RO WO
Reset 0 0 0 0 0 0 0 0 0 0 0 0 0 0 0 0
Bit/Field Name Type Reset Description
Software should not rely on the value of a reserved bit. To provide
compatibility with future products, the value of a reserved bit should be
preserved across a read-modify-write operation.
31:1 reserved RO 0x00
Data Interrupt Clear
This bit controls the clearing of the raw interrupt for data received and
data requested. When set, it clears the DATARIS interrupt bit; otherwise,
it has no effect on the DATARIS bit value.
0 DATAIC WO 0
January 08, 2011 533
Texas Instruments-Production Data
Stellaris® LM3S2965 Microcontroller
15 Controller Area Network (CAN) Module
Controller Area Network (CAN) is a multicast, shared serial bus standard for connecting electronic
control units (ECUs). CAN was specifically designed to be robust in electromagnetically-noisy
environments and can utilize a differential balanced line like RS-485 or a more robust twisted-pair
wire. Originally created for automotive purposes, it is also used in many embedded control
applications (such as industrial and medical). Bit rates up to 1Mbps are possible at network lengths
less than 40 meters. Decreased bit rates allow longer network distances (for example, 125 Kbps at
500 meters).
Each Stellaris® CAN controller supports the following features:
■ Two CAN modules, each with the following features:
■ CAN protocol version 2.0 part A/B
■ Bit rates up to 1 Mbps
■ 32 message objects with individual identifier masks
■ Maskable interrupt
■ Disable Automatic Retransmission mode for Time-Triggered CAN (TTCAN) applications
■ Programmable Loopback mode for self-test operation
■ Programmable FIFO mode enables storage of multiple message objects
■ Gluelessly attaches to an external CAN interface through the CANnTX and CANnRX signals
534 January 08, 2011
Texas Instruments-Production Data
Controller Area Network (CAN) Module
15.1 Block Diagram
Figure 15-1. CAN Controller Block Diagram
CAN Control
CAN Core
Message Object
Registers
CANNWDA2
CANMSG1INT
CANMSG2INT
CANMSG1VAL
CANMSG2VAL
CAN Tx
CANINT
CANTST
CANBRPE
CANBIT
APB
Interface
ABP
Pins
Message RAM
32 Message Objects
CANERR
CANCTL
CANSTS
CANIF2ARB2
CANIF2MCTL
CANIF2DA1
CAN Interface 2
CANIF2DA2
CANIF2DB1
CANIF2DB2
CANIF2ARB1
CANIF2MSK2
CANIF2CRQ
CANIF2CMSK
CANIF2MSK1
CAN Interface 1
CANIF1CRQ
CANIF1CMSK
CANIF1MSK1
CANIF1MSK2
CANIF1ARB1
CANIF1ARB2
CANIF1MCTL
CANIF1DA1
CANIF1DA2
CANIF1DB1
CANIF1DB2
CAN Rx
CANNWDA1
CANTXRQ1
CANTXRQ2
15.2 Functional Description
The Stellaris CAN controller conforms to the CAN protocol version 2.0 (parts A and B). Message
transfers that include data, remote, error, and overload frames with an 11-bit identifier (standard)
or a 29-bit identifier (extended) are supported. Transfer rates can be programmed up to 1 Mbps.
The CAN module consists of three major parts:
■ CAN protocol controller and message handler
■ Message memory
■ CAN register interface
January 08, 2011 535
Texas Instruments-Production Data
Stellaris® LM3S2965 Microcontroller
A data frame contains data for transmission, whereas a remote frame contains no data and is used
to request the transmission of a specific message object. The CAN data/remote frame is constructed
as shown in Figure 15-2 on page 536.
Figure 15-2. CAN Data/Remote Frame
Number
Of Bits
SOF
EOP IFS Bus
Idle
1 11 or 29 1 6 0 . . . 64 15 1 1 1 7 3
ACK
Control Data Field
Field
RTR
Message Delimiter
Bus
Idle
Bit Stuffing
CAN Data Frame
Arbitration Field
CRC Sequence
CRC
Field
Acknowledgement
Field
End of
Frame
Field
Interframe
Field
Start
Of Frame
Remote
Transmission
Request
Delimiter
Bits
CRC
Sequence
The protocol controller transfers and receives the serial data from the CAN bus and passes the data
on to the message handler. The message handler then loads this information into the appropriate
message object based on the current filtering and identifiers in the message object memory. The
message handler is also responsible for generating interrupts based on events on the CAN bus.
The message object memory is a set of 32 identical memory blocks that hold the current configuration,
status, and actual data for each message object. These are accessed via either of the CAN message
object register interfaces.
The message memory is not directly accessible in the Stellaris memory map, so the Stellaris CAN
controller provides an interface to communicate with the message memory via two CAN interface
register sets for communicating with the message objects. As there is no direct access to the
message object memory, these two interfaces must be used to read or write to each message object.
The two message object interfaces allow parallel access to the CAN controller message objects
when multiple objects may have new information that must be processed. In general, one interface
is used for transmit data and one for receive data.
15.2.1 Initialization
Software initialization is started by setting the INIT bit in the CAN Control (CANCTL) register (with
software or by a hardware reset) or by going bus-off, which occurs when the transmitter's error
counter exceeds a count of 255. While INIT is set, all message transfers to and from the CAN bus
are stopped and the CANnTX signal is held High. Entering the initialization state does not change
the configuration of the CAN controller, the message objects, or the error counters. However, some
configuration registers are only accessible while in the initialization state.
To initialize the CAN controller, set the CAN Bit Timing (CANBIT) register and configure each
message object. If a message object is not needed, label it as not valid by clearing the MSGVAL bit
536 January 08, 2011
Texas Instruments-Production Data
Controller Area Network (CAN) Module
in the CAN IFn Arbitration 2 (CANIFnARB2) register. Otherwise, the whole message object must
be initialized, as the fields of the message object may not have valid information, causing unexpected
results. Both the INIT and CCE bits in the CANCTL register must be set in order to access the
CANBIT register and the CAN Baud Rate Prescaler Extension (CANBRPE) register to configure
the bit timing. To leave the initialization state, the INIT bit must be cleared. Afterwards, the internal
Bit Stream Processor (BSP) synchronizes itself to the data transfer on the CAN bus by waiting for
the occurrence of a sequence of 11 consecutive recessive bits (indicating a bus idle condition)
before it takes part in bus activities and starts message transfers. Message object initialization does
not require the CAN to be in the initialization state and can be done on the fly. However, message
objects should all be configured to particular identifiers or set to not valid before message transfer
starts. To change the configuration of a message object during normal operation, clear the MSGVAL
bit in the CANIFnARB2 register to indicate that the message object is not valid during the change.
When the configuration is completed, set the MSGVAL bit again to indicate that the message object
is once again valid.
15.2.2 Operation
There are two sets of CAN Interface Registers (CANIF1x and CANIF2x), which are used to access
the message objects in the Message RAM. The CAN controller coordinates transfers to and from
the Message RAM to and from the registers. The two sets are independent and identical and can
be used to queue transactions. Generally, one interface is used to transmit data and one is used to
receive data.
Once the CAN module is initialized and the INIT bit in the CANCTL register is cleared, the CAN
module synchronizes itself to the CAN bus and starts the message transfer. As each message is
received, it goes through the message handler's filtering process, and if it passes through the filter,
is stored in the message object specified by the MNUM bit in the CAN IFn Command Request
(CANIFnCRQ) register. The whole message (including all arbitration bits, data-length code, and
eight data bytes) is stored in the message object. If the Identifier Mask (the MSK bits in the CAN IFn
Mask 1 and CAN IFn Mask 2 (CANIFnMSKn) registers) is used, the arbitration bits that are masked
to "don't care" may be overwritten in the message object.
The CPU may read or write each message at any time via the CAN Interface Registers. The message
handler guarantees data consistency in case of concurrent accesses.
The transmission of message objects is under the control of the software that is managing the CAN
hardware. These can be message objects used for one-time data transfers, or permanent message
objects used to respond in a more periodic manner. Permanent message objects have all arbitration
and control set up, and only the data bytes are updated. At the start of transmission, the appropriate
TXRQST bit in the CAN Transmission Request n (CANTXRQn) register and the NEWDAT bit in the
CAN New Data n (CANNWDAn) register are set. If several transmit messages are assigned to the
same message object (when the number of message objects is not sufficient), the whole message
object has to be configured before the transmission of this message is requested.
The transmission of any number of message objects may be requested at the same time; they are
transmitted according to their internal priority, which is based on the message identifier (MNUM) for
the message object, with 1 being the highest priority and 32 being the lowest priority. Messages
may be updated or set to not valid any time, even when their requested transmission is still pending.
The old data is discarded when a message is updated before its pending transmission has started.
Depending on the configuration of the message object, the transmission of a message may be
requested autonomously by the reception of a remote frame with a matching identifier.
Transmission can be automatically started by the reception of a matching remote frame. To enable
this mode, set the RMTEN bit in the CAN IFn Message Control (CANIFnMCTL) register. A matching
received remote frame causes the TXRQST bit to be set and the message object automatically
January 08, 2011 537
Texas Instruments-Production Data
Stellaris® LM3S2965 Microcontroller
transfers its data or generates an interrupt indicating a remote frame was requested. This can be
strictly a single message identifier, or it can be a range of values specified in the message object.
The CAN mask registers, CANIFnMSKn, configure which groups of frames are identified as remote
frame requests. The UMASK bit in the CANIFnMCTL register enables the MSK bits in the
CANIFnMSKn register to filter which frames are identified as a remote frame request. The MXTD
bit in the CANIFnMSK2 register should be set if a remote frame request is expected to be triggered
by 29-bit extended identifiers.
15.2.3 Transmitting Message Objects
If the internal transmit shift register of the CAN module is ready for loading, and if there is no data
transfer occurring between the CAN Interface Registers and message RAM, the valid message
object with the highest priority that has a pending transmission request is loaded into the transmit
shift register by the message handler and the transmission is started. The message object's NEWDAT
bit in the CANNWDAn register is cleared. After a successful transmission, and if no new data was
written to the message object since the start of the transmission, the TXRQST bit in the CANTXRQn
register is cleared. If the CAN controller is set up to interrupt upon a successful transmission of a
message object, (the TXIE bit in the CAN IFn Message Control (CANIFnMCTL) register is set),
the INTPND bit in the CANIFnMCTL register is set after a successful transmission. If the CAN
module has lost the arbitration or if an error occurred during the transmission, the message is
re-transmitted as soon as the CAN bus is free again. If, meanwhile, the transmission of a message
with higher priority has been requested, the messages are transmitted in the order of their priority.
15.2.4 Configuring a Transmit Message Object
The following steps illustrate how to configure a transmit message object.
1. In the CAN IFn Command Mask (CANIFnCMASK) register:
■ Set the WRNRD bit to specify a write to the CANIFnCMASK register; specify whether to
transfer the IDMASK, DIR, and MXTD of the message object into the CAN IFn registers using
the MASK bit
■ Specify whether to transfer the ID, DIR, XTD, and MSGVAL of the message object into the
interface registers using the ARB bit
■ Specify whether to transfer the control bits into the interface registers using the CONTROL
bit
■ Specify whether to clear the INTPND bit in the CANIFnMCTL register using the CLRINTPND
bit
■ Specify whether to clear the NEWDAT bit in the CANNWDAn register using the NEWDAT bit
■ Specify which bits to transfer using the DATAA and DATAB bits
2. In the CANIFnMSK1 register, use the MSK[15:0] bits to specify which of the bits in the 29-bit
or 11-bit message identifier are used for acceptance filtering. Note that MSK[15:0] in this
register are used for bits [15:0] of the 29-bit message identifier and are not used for an 11-bit
identifier. A value of 0x00 enables all messages to pass through the acceptance filtering. Also
note that in order for these bits to be used for acceptance filtering, they must be enabled by
setting the UMASK bit in the CANIFnMCTL register.
538 January 08, 2011
Texas Instruments-Production Data
Controller Area Network (CAN) Module
3. In the CANIFnMSK2 register, use the MSK[12:0] bits to specify which of the bits in the 29-bit
or 11-bit message identifier are used for acceptance filtering. Note that MSK[12:0] are used
for bits [28:16] of the 29-bit message identifier; whereas MSK[12:2] are used for bits [10:0] of
the 11-bit message identifier. Use the MXTD and MDIR bits to specify whether to use XTD and
DIR for acceptance filtering. A value of 0x00 enables all messages to pass through the
acceptance filtering. Also note that in order for these bits to be used for acceptance filtering,
they must be enabled by setting the UMASK bit in the CANIFnMCTL register.
4. For a 29-bit identifier, configure ID[15:0] in the CANIFnARB1 register to are used for bits
[15:0] of the message identifier and ID[12:0] in the CANIFnARB2 register to are used for
bits [28:16] of the message identifier. Set the XTD bit to indicate an extended identifier; set the
DIR bit to indicate transmit; and set the MSGVAL bit to indicate that the message object is valid.
5. For an 11-bit identifier, disregard the CANIFnARB1 register and configure ID[12:2] in the
CANIFnARB2 register to are used for bits [10:0] of the message identifier. Clear the XTD bit to
indicate a standard identifier; set the DIR bit to indicate transmit; and set the MSGVAL bit to
indicate that the message object is valid.
6. In the CANIFnMCTL register:
■ Optionally set the UMASK bit to enable the mask (MSK, MXTD, and MDIR specified in the
CANIFnMSK1 and CANIFnMSK2 registers) for acceptance filtering
■ Optionally set the TXIE bit to enable the INTPND bit to be set after a successful transmission
■ Optionally set the RMTEN bit to enable the TXRQST bit to be set upon the reception of a
matching remote frame allowing automatic transmission
■ Set the EOB bit for a single message object;
■ Set the DLC[3:0] field to specify the size of the data frame. Take care during this
configuration not to set the NEWDAT, MSGLST, INTPND or TXRQST bits.
7. Load the data to be transmitted into the CAN IFn Data (CANIFnDA1, CANIFnDA2, CANIFnDB1,
CANIFnDB2) or (CANIFnDATAA and CANIFnDATAB) registers. Byte 0 of the CAN data frame
is stored in DATA[7:0] in the CANIFnDA1 register.
8. Program the number of the message object to be transmitted in the MNUM field in the CAN IFn
Command Request (CANIFnCRQ) register.
9. When everything is properly configured, set the TXRQST bit in the CANIFnMCTL register. Once
this bit is set, the message object is available to be transmitted, depending on priority and bus
availability. Note that setting the RMTEN bit in the CANIFnMCTL register can also start message
transmission if a matching remote frame has been received.
15.2.5 Updating a Transmit Message Object
The CPU may update the data bytes of a Transmit Message Object any time via the CAN Interface
Registers and neither the MSGVAL bit in the CANIFnARB2 register nor the TXRQST bits in the
CANIFnMCTL register have to be cleared before the update.
Even if only some of the data bytes are to be updated, all four bytes of the corresponding
CANIFnDAn/CANIFnDBn register have to be valid before the content of that register is transferred
to the message object. Either the CPU must write all four bytes into the CANIFnDAn/CANIFnDBn
January 08, 2011 539
Texas Instruments-Production Data
Stellaris® LM3S2965 Microcontroller
register or the message object is transferred to the CANIFnDAn/CANIFnDBn register before the
CPU writes the new data bytes.
In order to only update the data in a message object, the WRNRD, DATAA and DATAB bits in the
CANIFnMSKn register are set, followed by writing the updated data into CANIFnDA1, CANIFnDA2,
CANIFnDB1, and CANIFnDB2 registers, and then the number of the message object is written to
the MNUM field in the CAN IFn Command Request (CANIFnCRQ) register. To begin transmission
of the new data as soon as possible, set the TXRQST bit in the CANIFnMSKn register.
To prevent the clearing of the TXRQST bit in the CANIFnMCTL register at the end of a transmission
that may already be in progress while the data is updated, the NEWDAT and TXRQST bits have to be
set at the same time in the CANIFnMCTL register. When these bits are set at the same time, NEWDAT
is cleared as soon as the new transmission has started.
15.2.6 Accepting Received Message Objects
When the arbitration and control field (the ID and XTD bits in the CANIFnARB2 and the RMTEN and
DLC[3:0] bits of the CANIFnMCTL register) of an incoming message is completely shifted into
the CAN controller, the message handling capability of the controller starts scanning the message
RAM for a matching valid message object. To scan the message RAM for a matching message
object, the controller uses the acceptance filtering programmed through the mask bits in the
CANIFnMSKn register and enabled using the UMASK bit in the CANIFnMCTL register. Each valid
message object, starting with object 1, is compared with the incoming message to locate a matching
message object in the message RAM. If a match occurs, the scanning is stopped and the message
handler proceeds depending on whether it is a data frame or remote frame that was received.
15.2.7 Receiving a Data Frame
The message handler stores the message from the CAN controller receive shift register into the
matching message object in the message RAM. The data bytes, all arbitration bits, and the DLC bits
are all stored into the corresponding message object. In this manner, the data bytes are connected
with the identifier even if arbitration masks are used. The NEWDAT bit of the CANIFnMCTL register
is set to indicate that new data has been received. The CPU should clear this bit when it reads the
message object to indicate to the controller that the message has been received, and the buffer is
free to receive more messages. If the CAN controller receives a message and the NEWDAT bit is
already set, the MSGLST bit in the CANIFnMCTL register is set to indicate that the previous data
was lost. If the system requires an interrupt upon successful reception of a frame, the RXIE bit of
the CANIFnMCTL register should be set. In this case, the INTPND bit of the same register is set,
causing the CANINT register to point to the message object that just received a message. The
TXRQST bit of this message object should be cleared to prevent the transmission of a remote frame.
15.2.8 Receiving a Remote Frame
A remote frame contains no data, but instead specifies which object should be transmitted. When
a remote frame is received, three different configurations of the matching message object have to
be considered:
Configuration in CANIFnMCTL Description
At the reception of a matching remote frame, the TXRQST bit of this
message object is set. The rest of the message object remains
unchanged, and the controller automatically transfers the data in
the message object as soon as possible.
■ DIR = 1 (direction = transmit); programmed in the
CANIFnARB2 register
■ RMTEN = 1 (set the TXRQST bit of the
CANIFnMCTL register at reception of the frame
to enable transmission)
■ UMASK = 1 or 0
540 January 08, 2011
Texas Instruments-Production Data
Controller Area Network (CAN) Module
Configuration in CANIFnMCTL Description
At the reception of a matching remote frame, the TXRQST bit of this
message object remains unchanged, and the remote frame is
ignored. This remote frame is disabled, the data is not transferred
and there is no indication that the remote frame ever happened.
■ DIR = 1 (direction = transmit); programmed in the
CANIFnARB2 register
■ RMTEN = 0 (do not change the TXRQST bit of the
CANIFnMCTL register at reception of the frame)
■ UMASK = 0 (ignore mask in the CANIFnMSKn
register)
At the reception of a matching remote frame, the TXRQST bit of this
message object is cleared. The arbitration and control field (ID +
XTD + RMTEN + DLC) from the shift register is stored into the
message object in the message RAM and the NEWDAT bit of this
message object is set. The data field of the message object remains
unchanged; the remote frame is treated similar to a received data
frame. This is useful for a remote data request from another CAN
device for which the Stellaris controller does not have readily
available data. The software must fill the data and answer the frame
manually.
■ DIR = 1 (direction = transmit); programmed in the
CANIFnARB2 register
■ RMTEN = 0 (do not change the TXRQST bit of the
CANIFnMCTL register at reception of the frame)
■ UMASK = 1 (use mask (MSK, MXTD, and MDIR in
the CANIFnMSKn register) for acceptance filtering)
15.2.9 Receive/Transmit Priority
The receive/transmit priority for the message objects is controlled by the message number. Message
object 1 has the highest priority, while message object 32 has the lowest priority. If more than one
transmission request is pending, the message objects are transmitted in order based on the message
object with the lowest message number. This should not be confused with the message identifier
as that priority is enforced by the CAN bus. This means that if message object 1 and message object
2 both have valid messages that need to be transmitted, message object 1 will always be transmitted
first regardless of the message identifier in the message object itself.
15.2.10 Configuring a Receive Message Object
The following steps illustrate how to configure a receive message object.
1. Program the CAN IFn Command Mask (CANIFnCMASK) register as described in the
“Configuring a Transmit Message Object” on page 538 section, except that the WRNRD bit is set
to specify a write to the message RAM.
2. Program the CANIFnMSK1and CANIFnMSK2 registers as described in the “Configuring a
Transmit Message Object” on page 538 section to configure which bits are used for acceptance
filtering. Note that in order for these bits to be used for acceptance filtering, they must be enabled
by setting the UMASK bit in the CANIFnMCTL register.
3. In the CANIFnMSK2 register, use the MSK[12:0] bits to specify which of the bits in the 29-bit
or 11-bit message identifier are used for acceptance filtering. Note that MSK[12:0] are used
for bits [28:16] of the 29-bit message identifier; whereas MSK[12:2] are used for bits [10:0] of
the 11-bit message identifier. Use the MXTD and MDIR bits to specify whether to use XTD and
DIR for acceptance filtering. A value of 0x00 enables all messages to pass through the
acceptance filtering. Also note that in order for these bits to be used for acceptance filtering,
they must be enabled by setting the UMASK bit in the CANIFnMCTL register.
4. Program the CANIFnARB1 and CANIFnARB2 registers as described in the “Configuring a
Transmit Message Object” on page 538 section to program XTD and ID bits for the message
identifier to be received; set the MSGVAL bit to indicate a valid message; and clear the DIR bit
to specify receive.
January 08, 2011 541
Texas Instruments-Production Data
Stellaris® LM3S2965 Microcontroller
5. In the CANIFnMCTL register:
■ Optionally set the UMASK bit to enable the mask (MSK, MXTD, and MDIR specified in the
CANIFnMSK1 and CANIFnMSK2 registers) for acceptance filtering
■ Optionally set the RXIE bit to enable the INTPND bit to be set after a successful reception
■ Clear the RMTEN bit to leave the TXRQST bit unchanged
■ Set the EOB bit for a single message object
■ Set the DLC[3:0] field to specify the size of the data frame
Take care during this configuration not to set the NEWDAT, MSGLST, INTPND or TXRQST bits.
6. Program the number of the message object to be received in the MNUM field in the CAN IFn
Command Request (CANIFnCRQ) register. Reception of the message object begins as soon
as a matching frame is available on the CAN bus.
When the message handler stores a data frame in the message object, it stores the received Data
Length Code and eight data bytes in the CANIFnDA1, CANIFnDA2, CANIFnDB1, and CANIFnDB2
register. Byte 0 of the CAN data frame is stored in DATA[7:0] in the CANIFnDA1 register. If the
Data Length Code is less than 8, the remaining bytes of the message object are overwritten by
unspecified values.
The CAN mask registers can be used to allow groups of data frames to be received by a message
object. The CAN mask registers, CANIFnMSKn, configure which groups of frames are received by
a message object. The UMASK bit in the CANIFnMCTL register enables the MSK bits in the
CANIFnMSKn register to filter which frames are received. The MXTD bit in the CANIFnMSK2 register
should be set if only 29-bit extended identifiers are expected by this message object.
15.2.11 Handling of Received Message Objects
The CPU may read a received message any time via the CAN Interface registers because the data
consistency is guaranteed by the message handler state machine.
Typically, the CPU first writes 0x007F to the CANIFnCMSK register and then writes the number of
the message object to the CANIFnCRQ register. That combination transfers the whole received
message from the message RAM into the Message Buffer registers (CANIFnMSKn, CANIFnARBn,
and CANIFnMCTL). Additionally, the NEWDAT and INTPND bits are cleared in the message RAM,
acknowledging that the message has been read and clearing the pending interrupt generated by
this message object.
If the message object uses masks for acceptance filtering, the CANIFnARBn registers show the
full, unmasked ID for the received message.
The NEWDAT bit in the CANIFnMCTL register shows whether a new message has been received
since the last time this message object was read. The MSGLST bit in the CANIFnMCTL register
shows whether more than one message has been received since the last time this message object
was read. MSGLST is not automatically cleared, and should be cleared by software after reading its
status.
Using a remote frame, the CPU may request new data from another CAN node on the CAN bus.
Setting the TXRQST bit of a receive object causes the transmission of a remote frame with the receive
object's identifier. This remote frame triggers the other CAN node to start the transmission of the
matching data frame. If the matching data frame is received before the remote frame could be
542 January 08, 2011
Texas Instruments-Production Data
Controller Area Network (CAN) Module
transmitted, the TXRQST bit is automatically reset. This prevents the possible loss of data when the
other device on the CAN bus has already transmitted the data slightly earlier than expected.
15.2.11.1 Configuration of a FIFO Buffer
With the exception of the EOB bit in the CANIFnMCTL register, the configuration of receive message
objects belonging to a FIFO buffer is the same as the configuration of a single receive message
object (see “Configuring a Receive Message Object” on page 541). To concatenate two or more
message objects into a FIFO buffer, the identifiers and masks (if used) of these message objects
have to be programmed to matching values. Due to the implicit priority of the message objects, the
message object with the lowest message object number is the first message object in a FIFO buffer.
The EOB bit of all message objects of a FIFO buffer except the last one must be cleared. The EOB
bit of the last message object of a FIFO buffer is set, indicating it is the last entry in the buffer.
15.2.11.2 Reception of Messages with FIFO Buffers
Received messages with identifiers matching to a FIFO buffer are stored starting with the message
object with the lowest message number. When a message is stored into a message object of a
FIFO buffer, the NEWDAT of the CANIFnMCTL register bit of this message object is set. By setting
NEWDAT while EOB is clear, the message object is locked and cannot be written to by the message
handler until the CPU has cleared the NEWDAT bit. Messages are stored into a FIFO buffer until the
last message object of this FIFO buffer is reached. If none of the preceding message objects has
been released by clearing the NEWDAT bit, all further messages for this FIFO buffer will be written
into the last message object of the FIFO buffer and therefore overwrite previous messages.
15.2.11.3 Reading from a FIFO Buffer
When the CPU transfers the contents of a message object from a FIFO buffer by writing its number
to the CANIFnCRQ, the TXRQST and CLRINTPND bits in the CANIFnCMSK register should be set
such that the NEWDAT and INTPEND bits in the CANIFnMCTL register are cleared after the read.
The values of these bits in the CANIFnMCTL register always reflect the status of the message
object before the bits are cleared. To assure the correct function of a FIFO buffer, the CPU should
read out the message objects starting with the message object with the lowest message number.
When reading from the FIFO buffer, the user should be aware that a new received message could
be placed in the location of any message object for which the NEWDAT bit of the CANIFnMCTL
register. As a result, the order of the received messages in the FIFO is not guaranteed. Figure
15-3 on page 544 shows how a set of message objects which are concatenated to a FIFO Buffer
can be handled by the CPU.
January 08, 2011 543
Texas Instruments-Production Data
Stellaris® LM3S2965 Microcontroller
Figure 15-3. Message Objects in a FIFO Buffer
START
No
Yes
Write MNUM to IFn Command Request
(Read Message to IFn Registers,
Reset NEWDAT = 0,
Reset INTPND = 0
MNUM = Interrupt Pointer
Read IFn Message Control
Read Data from IFn Data A,B
NEWDAT = 1
EOB = 1
Read Interrupt Pointer
Status Change
Interrupt Handling
END
Message Interrupt
Yes
MNUM = MNUM + 1
Case Interrupt Pointer else
0x0000 0x8000
No
544 January 08, 2011
Texas Instruments-Production Data
Controller Area Network (CAN) Module
15.2.12 Handling of Interrupts
If several interrupts are pending, the CAN Interrupt (CANINT) register points to the pending interrupt
with the highest priority, disregarding their chronological order. The status interrupt has the highest
priority. Among the message interrupts, the message object's interrupt with the lowest message
number has the highest priority. A message interrupt is cleared by clearing the message object's
INTPND bit in the CANIFnMCTL register or by reading the CAN Status (CANSTS) register. The
status Interrupt is cleared by reading the CANSTS register.
The interrupt identifier INTID in the CANINT register indicates the cause of the interrupt. When no
interrupt is pending, the register reads as 0x0000. If the value of the INTID field is different from 0,
then there is an interrupt pending. If the IE bit is set in the CANCTL register, the interrupt line to
the CPU is active. The interrupt line remains active until the INTID field is 0, meaning that all interrupt
sources have been cleared (the cause of the interrupt is reset), or until IE is cleared, which disables
interrupts from the CAN controller.
The INTID field of the CANINT register points to the pending message interrupt with the highest
interrupt priority. The SIE bit in the CANCTL register controls whether a change of the RXOK, TXOK,
and LEC bits in the CANSTS register can cause an interrupt. The EIE bit in the CANCTLregister
controls whether a change of the BOFF and EWARN bits in the CANSTS can cause an interrupt. The
IE bit in the CANCTL controls whether any interrupt from the CAN controller actually generates an
interrupt to the microcontroller's interrupt controller. The CANINT register is updated even when
the IE bit in the CANCTL register is clear, but the interrupt will not be indicated to the CPU.
A value of 0x8000 in the CANINT register indicates that an interrupt is pending because the CAN
module has updated, but not necessarily changed, the CANSTS , indicating that either an error or
status interrupt has been generated. A write access to the CANSTS register can clear the RXOK,
TXOK, and LEC bits in that same register; however, the only way to clear the source of a status
interrupt is to read the CANSTS register.
There are two ways to determine the source of an interrupt during interrupt handling. The first is to
read the INTID bit in the CANINT register to determine the highest priority interrupt that is pending,
and the second is to read the CAN Message Interrupt Pending (CANMSGnINT) register to see
all of the message objects that have pending interrupts.
An interrupt service routine reading the message that is the source of the interrupt may read the
message and clear the message object's INTPND bit at the same time by setting the CLRINTPND
bit in the CANIFnCMSK register. Once the INTPND bit has been cleared, the CANINT register
contains the message number for the next message object with a pending interrupt.
15.2.13 Test Mode
A Test Mode is provided, which allows various diagnostics to be performed. Test Mode is entered
by setting the TEST bit CANCTL register. Once in Test Mode, the TX[1:0], LBACK, SILENT and
BASIC bits in the CAN Test (CANTST) register can be used to put the CAN controller into the
various diagnostic modes. The RX bit in the CANTST register allows monitoring of the CANnRX
signal. All CANTST register functions are disabled when the TEST bit is cleared.
15.2.13.1 Silent Mode
Silent Mode can be used to analyze the traffic on a CAN bus without affecting it by the transmission
of dominant bits (Acknowledge Bits, Error Frames). The CAN Controller is put in Silent Mode setting
the SILENT bit in the CANTST register. In Silent Mode, the CAN controller is able to receive valid
data frames and valid remote frames, but it sends only recessive bits on the CAN bus and it cannot
start a transmission. If the CAN Controller is required to send a dominant bit (ACK bit, overload flag,
January 08, 2011 545
Texas Instruments-Production Data
Stellaris® LM3S2965 Microcontroller
or active error flag), the bit is rerouted internally so that the CAN Controller monitors this dominant
bit, although the CAN bus remains in recessive state.
15.2.13.2 Loopback Mode
Loopback mode is useful for self-test functions. In Loopback Mode, the CAN Controller internally
routes the CANnTX signal on to the CANnRX signal and treats its own transmitted messages as
received messages and stores them (if they pass acceptance filtering) into the message buffer. The
CAN Controller is put in Loopback Mode by setting the LBACK bit in the CANTST register. To be
independent from external stimulation, the CAN Controller ignores acknowledge errors (a recessive
bit sampled in the acknowledge slot of a data/remote frame) in Loopback Mode. The actual value
of the CANnRX signal is disregarded by the CAN Controller. The transmitted messages can be
monitored on the CANnTX signal.
15.2.13.3 Loopback Combined with Silent Mode
Loopback Mode and Silent Mode can be combined to allow the CAN Controller to be tested without
affecting a running CAN system connected to the CANnTX and CANnRX signals. In this mode, the
CANnRX signal is disconnected from the CAN Controller and the CANnTX signal is held recessive.
This mode is enabled by setting both the LBACK and SILENT bits in the CANTST register.
15.2.13.4 Basic Mode
Basic Mode allows the CAN Controller to be operated without the Message RAM. In Basic Mode,
The CANIF1 registers are used as the transmit buffer. The transmission of the contents of the IF1
registers is requested by setting the BUSY bit of the CANIF1CRQ register. The CANIF1 registers
are locked while the BUSY bit is set. The BUSY bit indicates that a transmission is pending. As soon
the CAN bus is idle, the CANIF1 registers are loaded into the shift register of the CAN Controller
and transmission is started. When the transmission has completed, the BUSY bit is cleared and the
locked CANIF1 registers are released. A pending transmission can be aborted at any time by clearing
the BUSY bit in the CANIF1CRQ register while the CANIF1 registers are locked. If the CPU has
cleared the BUSY bit, a possible retransmission in case of lost arbitration or an error is disabled.
The CANIF2 Registers are used as a receive buffer. After the reception of a message, the contents
of the shift register is stored into the CANIF2 registers, without any acceptance filtering. Additionally,
the actual contents of the shift register can be monitored during the message transfer. Each time a
read message object is initiated by setting the BUSY bit of the CANIF2CRQ register, the contents
of the shift register are stored into the CANIF2 registers.
In Basic Mode, all message-object-related control and status bits and of the control bits of the
CANIFnCMSK registers are not evaluated. The message number of the CANIFnCRQ registers is
also not evaluated. In the CANIF2MCTL register, the NEWDAT and MSGLST bits retain their function,
the DLC[3:0] field shows the received DLC, the other control bits are cleared.
Basic Mode is enabled by setting the BASIC bit in the CANTST register.
15.2.13.5 Transmit Control
Software can directly override control of the CANnTX signal in four different ways.
■ CANnTX is controlled by the CAN Controller
■ The sample point is driven on the CANnTX signal to monitor the bit timing
■ CANnTX drives a low value
546 January 08, 2011
Texas Instruments-Production Data
Controller Area Network (CAN) Module
■ CANnTX drives a high value
The last two functions, combined with the readable CAN receive pin CANnRX, can be used to check
the physical layer of the CAN bus.
The Transmit Control function is enabled by programming the TX[1:0] field in the CANTST register.
The three test functions for the CANnTX signal interfere with all CAN protocol functions. TX[1:0]
must be cleared when CAN message transfer or Loopback Mode, Silent Mode, or Basic Mode are
selected.
15.2.14 Bit Timing Configuration Error Considerations
Even if minor errors in the configuration of the CAN bit timing do not result in immediate failure, the
performance of a CAN network can be reduced significantly. In many cases, the CAN bit
synchronization amends a faulty configuration of the CAN bit timing to such a degree that only
occasionally an error frame is generated. In the case of arbitration, however, when two or more
CAN nodes simultaneously try to transmit a frame, a misplaced sample point may cause one of the
transmitters to become error passive. The analysis of such sporadic errors requires a detailed
knowledge of the CAN bit synchronization inside a CAN node and of the CAN nodes' interaction on
the CAN bus.
15.2.15 Bit Time and Bit Rate
The CAN system supports bit rates in the range of lower than 1 Kbps up to 1000 Kbps. Each member
of the CAN network has its own clock generator. The timing parameter of the bit time can be
configured individually for each CAN node, creating a common bit rate even though the CAN nodes'
oscillator periods may be different.
Because of small variations in frequency caused by changes in temperature or voltage and by
deteriorating components, these oscillators are not absolutely stable. As long as the variations
remain inside a specific oscillator's tolerance range, the CAN nodes are able to compensate for the
different bit rates by periodically resynchronizing to the bit stream.
According to the CAN specification, the bit time is divided into four segments (see Figure
15-4 on page 548): the Synchronization Segment, the Propagation Time Segment, the Phase Buffer
Segment 1, and the Phase Buffer Segment 2. Each segment consists of a specific, programmable
number of time quanta (see Table 15-1 on page 548). The length of the time quantum (tq), which is
the basic time unit of the bit time, is defined by the CAN controller's input clock (fsys) and the Baud
Rate Prescaler (BRP):
tq = BRP / fsys
The fsys input clock is 8 MHz.
The Synchronization Segment Sync is that part of the bit time where edges of the CAN bus level
are expected to occur; the distance between an edge that occurs outside of Sync and the Sync is
called the phase error of that edge.
The Propagation Time Segment Prop is intended to compensate for the physical delay times within
the CAN network.
The Phase Buffer Segments Phase1 and Phase2 surround the Sample Point.
The (Re-)Synchronization Jump Width (SJW) defines how far a resynchronization may move the
Sample Point inside the limits defined by the Phase Buffer Segments to compensate for edge phase
errors.
January 08, 2011 547
Texas Instruments-Production Data
Stellaris® LM3S2965 Microcontroller
A given bit rate may be met by different bit-time configurations, but for the proper function of the
CAN network, the physical delay times and the oscillator's tolerance range have to be considered.
Figure 15-4. CAN Bit Time
Sync Prop Phase2
Sample
Point
1 Time
Quantum
( t qq )
Nominal CAN Bit Time
a. TSEG1 = Prop + Phase1
b. TSEG2 = Phase2
c. Phase1 = Phase2 or Phase1 + 1 = Phase2
TSEG1a TSEG2b
Phase1 c
Table 15-1. CAN Protocol Rangesa
Parameter Range Remark
Defines the length of the time quantum tq. The CANBRPE register can
be used to extend the range to 1024.
BRP [1 .. 64]
Sync 1 tq Fixed length, synchronization of bus input to system clock
Prop [1 .. 8] tq Compensates for the physical delay times
Phase1 [1 .. 8] tq May be lengthened temporarily by synchronization
Phase2 [1 .. 8] tq May be shortened temporarily by synchronization
SJW [1 .. 4] tq May not be longer than either Phase Buffer Segment
a. This table describes the minimum programmable ranges required by the CAN protocol.
The bit timing configuration is programmed in two register bytes in the CANBIT register. In the
CANBIT register, the four components TSEG2, TSEG1, SJW, and BRP have to be programmed to a
numerical value that is one less than its functional value; so instead of values in the range of [1..n],
values in the range of [0..n-1] are programmed. That way, for example, SJW (functional range of
[1..4]) is represented by only two bits in the SJW bit field. Table 15-2 shows the relationship between
the CANBIT register values and the parameters.
Table 15-2. CANBIT Register Values
CANBIT Register Field Setting
TSEG2 Phase2 - 1
TSEG1 Prop + Phase1 - 1
SJW SJW - 1
BRP BRP
Therefore, the length of the bit time is (programmed values):
[TSEG1 + TSEG2 + 3] × tq
or (functional values):
548 January 08, 2011
Texas Instruments-Production Data
Controller Area Network (CAN) Module
[Sync + Prop + Phase1 + Phase2] × tq
The data in the CANBIT register is the configuration input of the CAN protocol controller. The baud
rate prescaler (configured by the BRP field) defines the length of the time quantum, the basic time
unit of the bit time; the bit timing logic (configured by TSEG1, TSEG2, and SJW) defines the number
of time quanta in the bit time.
The processing of the bit time, the calculation of the position of the sample point, and occasional
synchronizations are controlled by the CAN controller and are evaluated once per time quantum.
The CAN controller translates messages to and from frames. In addition, the controller generates
and discards the enclosing fixed format bits, inserts and extracts stuff bits, calculates and checks
the CRC code, performs the error management, and decides which type of synchronization is to be
used. The bit value is received or transmitted at the sample point. The information processing time
(IPT) is the time after the sample point needed to calculate the next bit to be transmitted on the CAN
bus. The IPT includes any of the following: retrieving the next data bit, handling a CRC bit, determining
if bit stuffing is required, generating an error flag or simply going idle.
The IPT is application-specific but may not be longer than 2 tq; the CAN's IPT is 0 tq. Its length is
the lower limit of the programmed length of Phase2. In case of synchronization, Phase2 may be
shortened to a value less than IPT, which does not affect bus timing.
15.2.16 Calculating the Bit Timing Parameters
Usually, the calculation of the bit timing configuration starts with a required bit rate or bit time. The
resulting bit time (1/bit rate) must be an integer multiple of the system clock period.
The bit time may consist of 4 to 25 time quanta. Several combinations may lead to the required bit
time, allowing iterations of the following steps.
The first part of the bit time to be defined is Prop. Its length depends on the delay times measured
in the system. A maximum bus length as well as a maximum node delay has to be defined for
expandable CAN bus systems. The resulting time for Prop is converted into time quanta (rounded
up to the nearest integer multiple of tq).
Sync is 1 tq long (fixed), which leaves (bit time - Prop - 1) tq for the two Phase Buffer Segments. If
the number of remaining tq is even, the Phase Buffer Segments have the same length, that is,
Phase2 = Phase1, else Phase2 = Phase1 + 1.
The minimum nominal length of Phase2 has to be regarded as well. Phase2 may not be shorter
than the CAN controller's Information Processing Time, which is, depending on the actual
implementation, in the range of [0..2] tq.
The length of the synchronization jump width is set to the least of 4, Phase1 or Phase2.
The oscillator tolerance range necessary for the resulting configuration is calculated by the formula
given below:
(1 − df) × fnom ≤ fosc ≤ (1 + df) × fnom
( )
2 (13 _ 2)
_ 1, _ 2 min
tbit Phase Seg
Phase seg Phase seg
df
× × −
≤
df max = 2 × df × fnom
where:
■ df = Maximum tolerance of oscillator frequency
■ fosc = Actual oscillator frequency
January 08, 2011 549
Texas Instruments-Production Data
Stellaris® LM3S2965 Microcontroller
■ fnom = Nominal oscillator frequency
Max(i1mu−mdfrfeq)u×enfcyntoolmera≤ncefomsucst ta≤ke(1int+o adcfco)un×t tfhneofomllowing formulas:
( )
2 (13 _ 2)
_ 1, _ 2 min
tbit Phase Seg
Phase seg Phase seg
df
× × −
≤
df max = 2 × df × fnom
(1 − df) × fnom ≤ fosc ≤ (1 + df) × fnom
( )
2 (13 _ 2)
_ 1, _ 2 min
tbit Phase Seg
Phase seg Phase seg
df
× × −
≤
df max = 2 × df × fnom
where:
■ Phase1 and Phase2 are from Table 15-1 on page 548
■ tbit = Bit Time
■ dfmax = Maximum difference between two oscillators
If more than one configuration is possible, that configuration allowing the highest oscillator tolerance
range should be chosen.
CAN nodes with different system clocks require different configurations to come to the same bit
rate. The calculation of the propagation time in the CAN network, based on the nodes with the
longest delay times, is done once for the whole network.
The CAN system's oscillator tolerance range is limited by the node with the lowest tolerance range.
The calculation may show that bus length or bit rate have to be decreased or that the oscillator
frequencies' stability has to be increased in order to find a protocol-compliant configuration of the
CAN bit timing.
15.2.16.1 Example for Bit Timing at High Baud Rate
In this example, the frequency of CAN clock is 8 MHz, and the bit rate is 1 Mbps.
bit time = 1 μs = n * tq = 8 * tq
tq = 125 ns
tq = (Baud rate Prescaler)/CAN Clock
Baud rate Prescaler = tq * CAN Clock
Baud rate Prescaler = 125E-9 * 8E6 = 1
tSync = 1 * tq = 125 ns \\fixed at 1 time quanta
delay of bus driver 50 ns
delay of receiver circuit 30 ns
delay of bus line (40m) 220 ns
tProp 375 ns = 3 * tq \\375 is next integer multiple of tq
bit time = tSync + tTSeg1 + tTSeg2 = 8 * tq
bit time = tSync + tProp + tPhase 1 + tPhase2
tPhase 1 + tPhase2 = bit time - tSync - tProp
tPhase 1 + tPhase2 = (8 * tq) - (1 * tq) - (3 * tq)
tPhase 1 + tPhase2 = 4 * tq
550 January 08, 2011
Texas Instruments-Production Data
Controller Area Network (CAN) Module
tPhase1 = 2 * tq
tPhase2 = 2 * tq \\tPhase2 = tPhase1
tTSeg1 = tProp + tPhase1
tTSeg1 = (3 * tq) + (2 * tq)
tTSeg1 = 5 * tq
tTSeg2 = tPhase2
tTSeg2 = (Information Processing Time + 2) × tq
tTSeg2 = 2 * tq \\Assumes IPT=0
tSJW = 2 * tq \\Least of 4, Phase1 and Phase2 = 1
In the above example, the bit field values for the CANBIT register are:
= TSeg2 -1
= 2-1
= 1
TSEG2
= TSeg1 -1
= 5-1
= 4
TSEG1
= SJW -1
= 2-1
= 1
SJW
= Baud rate prescaler - 1
= 1-1
=0
BRP
The final value programmed into the CANBIT register = 0x1440.
15.2.16.2 Example for Bit Timing at Low Baud Rate
In this example, the frequency of the CAN clock is 8 MHz, and the bit rate is 100 Kbps.
bit time = 10 μs = n * tq = 10 * tq
tq = 1 μs
tq = (Baud rate Prescaler)/CAN Clock
Baud rate Prescaler = tq * CAN Clock
Baud rate Prescaler = 1E-6 * 8E6 = 8
tSync = 1 * tq = 1 μs \\fixed at 1 time quanta
delay of bus driver 200 ns
delay of receiver circuit 80 ns
delay of bus line (40m) 220 ns
tProp 1 μs = 1 * tq \\1 μs is next integer multiple of tq
bit time = tSync + tTSeg1 + tTSeg2 = 10 * tq
bit time = tSync + tProp + tPhase 1 + tPhase2
tPhase 1 + tPhase2 = bit time - tSync - tProp
tPhase 1 + tPhase2 = (10 * tq) - (1 * tq) - (1 * tq)
tPhase 1 + tPhase2 = 8 * tq
tPhase1 = 4 * tq
tPhase2 = 4 * tq \\tPhase2 = tPhase1
January 08, 2011 551
Texas Instruments-Production Data
Stellaris® LM3S2965 Microcontroller
tTSeg1 = tProp + tPhase1
tTSeg1 = (1 * tq) + (4 * tq)
tTSeg1 = 5 * tq
tTSeg2 = tPhase2
tTSeg2 = (Information Processing Time + 4) * tq
tTSeg2 = 4 * tq \\Assumes IPT=0
tSJW = 4 * tq \\Least of 4, Phase1, and Phase2
= TSeg2 -1
= 4-1
= 3
TSEG2
= TSeg1 -1
= 5-1
= 4
TSEG1
= SJW -1
= 4-1
= 3
SJW
= Baud rate prescaler - 1
= 8-1
= 7
BRP
The final value programmed into the CANBIT register = 0x34C7.
15.3 Register Map
Table 15-3 on page 552 lists the registers. All addresses given are relative to the CAN base address
of:
■ CAN0: 0x4004.0000
■ CAN1: 0x4004.1000
Note that the CAN module clock must be enabled before the registers can be programmed (see
page 210). There must be a delay of 3 system clocks after the CAN module clock is enabled before
any CAN module registers are accessed.
Table 15-3. CAN Register Map
See
Offset Name Type Reset Description page
0x000 CANCTL R/W 0x0000.0001 CAN Control 555
0x004 CANSTS R/W 0x0000.0000 CAN Status 557
0x008 CANERR RO 0x0000.0000 CAN Error Counter 559
0x00C CANBIT R/W 0x0000.2301 CAN Bit Timing 560
0x010 CANINT RO 0x0000.0000 CAN Interrupt 561
0x014 CANTST R/W 0x0000.0000 CAN Test 562
0x018 CANBRPE R/W 0x0000.0000 CAN Baud Rate Prescaler Extension 564
0x020 CANIF1CRQ R/W 0x0000.0001 CAN IF1 Command Request 565
552 January 08, 2011
Texas Instruments-Production Data
Controller Area Network (CAN) Module
Table 15-3. CAN Register Map (continued)
See
Offset Name Type Reset Description page
0x024 CANIF1CMSK R/W 0x0000.0000 CAN IF1 Command Mask 566
0x028 CANIF1MSK1 R/W 0x0000.FFFF CAN IF1 Mask 1 568
0x02C CANIF1MSK2 R/W 0x0000.FFFF CAN IF1 Mask 2 569
0x030 CANIF1ARB1 R/W 0x0000.0000 CAN IF1 Arbitration 1 570
0x034 CANIF1ARB2 R/W 0x0000.0000 CAN IF1 Arbitration 2 571
0x038 CANIF1MCTL R/W 0x0000.0000 CAN IF1 Message Control 572
0x03C CANIF1DA1 R/W 0x0000.0000 CAN IF1 Data A1 574
0x040 CANIF1DA2 R/W 0x0000.0000 CAN IF1 Data A2 574
0x044 CANIF1DB1 R/W 0x0000.0000 CAN IF1 Data B1 574
0x048 CANIF1DB2 R/W 0x0000.0000 CAN IF1 Data B2 574
0x080 CANIF2CRQ R/W 0x0000.0001 CAN IF2 Command Request 565
0x084 CANIF2CMSK R/W 0x0000.0000 CAN IF2 Command Mask 566
0x088 CANIF2MSK1 R/W 0x0000.FFFF CAN IF2 Mask 1 568
0x08C CANIF2MSK2 R/W 0x0000.FFFF CAN IF2 Mask 2 569
0x090 CANIF2ARB1 R/W 0x0000.0000 CAN IF2 Arbitration 1 570
0x094 CANIF2ARB2 R/W 0x0000.0000 CAN IF2 Arbitration 2 571
0x098 CANIF2MCTL R/W 0x0000.0000 CAN IF2 Message Control 572
0x09C CANIF2DA1 R/W 0x0000.0000 CAN IF2 Data A1 574
0x0A0 CANIF2DA2 R/W 0x0000.0000 CAN IF2 Data A2 574
0x0A4 CANIF2DB1 R/W 0x0000.0000 CAN IF2 Data B1 574
0x0A8 CANIF2DB2 R/W 0x0000.0000 CAN IF2 Data B2 574
0x100 CANTXRQ1 RO 0x0000.0000 CAN Transmission Request 1 575
0x104 CANTXRQ2 RO 0x0000.0000 CAN Transmission Request 2 575
0x120 CANNWDA1 RO 0x0000.0000 CAN New Data 1 576
0x124 CANNWDA2 RO 0x0000.0000 CAN New Data 2 576
0x140 CANMSG1INT RO 0x0000.0000 CAN Message 1 Interrupt Pending 577
0x144 CANMSG2INT RO 0x0000.0000 CAN Message 2 Interrupt Pending 577
0x160 CANMSG1VAL RO 0x0000.0000 CAN Message 1 Valid 578
0x164 CANMSG2VAL RO 0x0000.0000 CAN Message 2 Valid 578
15.4 CAN Register Descriptions
The remainder of this section lists and describes the CAN registers, in numerical order by address
offset. There are two sets of Interface Registers that are used to access the Message Objects in
January 08, 2011 553
Texas Instruments-Production Data
Stellaris® LM3S2965 Microcontroller
the Message RAM: CANIF1x and CANIF2x. The function of the two sets are identical and are used
to queue transactions.
554 January 08, 2011
Texas Instruments-Production Data
Controller Area Network (CAN) Module
Register 1: CAN Control (CANCTL), offset 0x000
This control register initializes the module and enables test mode and interrupts.
The bus-off recovery sequence (see CAN Specification Rev. 2.0) cannot be shortened by setting
or clearing INIT. If the device goes bus-off, it sets INIT, stopping all bus activities. Once INIT
has been cleared by the CPU, the device then waits for 129 occurrences of Bus Idle (129 * 11
consecutive High bits) before resuming normal operations. At the end of the bus-off recovery
sequence, the Error Management Counters are reset.
During the waiting time after INIT is cleared, each time a sequence of 11 High bits has been
monitored, a BITERROR0 code is written to the CANSTS register (the LEC field = 0x5), enabling
the CPU to readily check whether the CAN bus is stuck Low or continuously disturbed, and to monitor
the proceeding of the bus-off recovery sequence.
CAN Control (CANCTL)
CAN0 base: 0x4004.0000
CAN1 base: 0x4004.1000
Offset 0x000
Type R/W, reset 0x0000.0001
31 30 29 28 27 26 25 24 23 22 21 20 19 18 17 16
reserved
Type RO RO RO RO RO RO RO RO RO RO RO RO RO RO RO RO
Reset 0 0 0 0 0 0 0 0 0 0 0 0 0 0 0 0
15 14 13 12 11 10 9 8 7 6 5 4 3 2 1 0
reserved TEST CCE DAR reserved EIE SIE IE INIT
Type RO RO RO RO RO RO RO RO R/W R/W R/W RO R/W R/W R/W R/W
Reset 0 0 0 0 0 0 0 0 0 0 0 0 0 0 0 1
Bit/Field Name Type Reset Description
Software should not rely on the value of a reserved bit. To provide
compatibility with future products, the value of a reserved bit should be
preserved across a read-modify-write operation.
31:8 reserved RO 0x0000.00
Test Mode Enable
0: Normal operation
1: Test mode
7 TEST R/W 0
Configuration Change Enable
0: Do not allow write access to the CANBIT register.
1: Allow write access to the CANBIT register if the INIT bit is 1.
6 CCE R/W 0
Disable Automatic-Retransmission
0: Auto-retransmission of disturbed messages is enabled.
1: Auto-retransmission is disabled.
5 DAR R/W 0
Software should not rely on the value of a reserved bit. To provide
compatibility with future products, the value of a reserved bit should be
preserved across a read-modify-write operation.
4 reserved RO 0
Error Interrupt Enable
0: Disabled. No error status interrupt is generated.
1: Enabled. A change in the BOFF or EWARN bits in the CANSTS register
generates an interrupt.
3 EIE R/W 0
January 08, 2011 555
Texas Instruments-Production Data
Stellaris® LM3S2965 Microcontroller
Bit/Field Name Type Reset Description
Status Interrupt Enable
0: Disabled. No status interrupt is generated.
1: Enabled. An interrupt is generated when a message has successfully
been transmitted or received, or a CAN bus error has been detected. A
change in the TXOK, RXOK or LEC bits in the CANSTS register generates
an interrupt.
2 SIE R/W 0
CAN Interrupt Enable
0: Interrupts disabled.
1: Interrupts enabled.
1 IE R/W 0
Initialization
0: Normal operation.
1: Initialization started.
0 INIT R/W 1
556 January 08, 2011
Texas Instruments-Production Data
Controller Area Network (CAN) Module
Register 2: CAN Status (CANSTS), offset 0x004
Important: Use caution when reading this register. Performing a read may change bit status.
The status register contains information for interrupt servicing such as Bus-Off, error count threshold,
and error types.
The LEC field holds the code that indicates the type of the last error to occur on the CAN bus. This
field is cleared when a message has been transferred (reception or transmission) without error. The
unused error code 7 may be written by the CPU to manually set this field to an invalid error so that
it can be checked for a change later.
An error interrupt is generated by the BOFF and EWARN bits and a status interrupt is generated by
the RXOK, TXOK, and LEC bits, if the corresponding enable bits in the CAN Control (CANCTL)
register are set. A change of the EPASS bit or a write to the RXOK, TXOK, or LEC bits does not
generate an interrupt.
Reading the CAN Status (CANSTS) register clears the CAN Interrupt (CANINT) register, if it is
pending.
CAN Status (CANSTS)
CAN0 base: 0x4004.0000
CAN1 base: 0x4004.1000
Offset 0x004
Type R/W, reset 0x0000.0000
31 30 29 28 27 26 25 24 23 22 21 20 19 18 17 16
reserved
Type RO RO RO RO RO RO RO RO RO RO RO RO RO RO RO RO
Reset 0 0 0 0 0 0 0 0 0 0 0 0 0 0 0 0
15 14 13 12 11 10 9 8 7 6 5 4 3 2 1 0
reserved BOFF EWARN EPASS RXOK TXOK LEC
Type RO RO RO RO RO RO RO RO RO RO RO R/W R/W R/W R/W R/W
Reset 0 0 0 0 0 0 0 0 0 0 0 0 0 0 0 0
Bit/Field Name Type Reset Description
Software should not rely on the value of a reserved bit. To provide
compatibility with future products, the value of a reserved bit should be
preserved across a read-modify-write operation.
31:8 reserved RO 0x0000.00
Bus-Off Status
0: CAN controller is not in bus-off state.
1: CAN controller is in bus-off state.
7 BOFF RO 0
Warning Status
0: Both error counters are below the error warning limit of 96.
1: At least one of the error counters has reached the error warning limit
of 96.
6 EWARN RO 0
Error Passive
0: The CAN module is in the Error Active state, that is, the receive or
transmit error count is less than or equal to 127.
1: The CAN module is in the Error Passive state, that is, the receive or
transmit error count is greater than 127.
5 EPASS RO 0
January 08, 2011 557
Texas Instruments-Production Data
Stellaris® LM3S2965 Microcontroller
Bit/Field Name Type Reset Description
Received a Message Successfully
0: Since this bit was last cleared, no message has been successfully
received.
1: Since this bit was last cleared, a message has been successfully
received, independent of the result of the acceptance filtering.
This bit is never cleared by the CAN module.
4 RXOK R/W 0
Transmitted a Message Successfully
0: Since this bit was last cleared, no message has been successfully
transmitted.
1: Since this bit was last cleared, a message has been successfully
transmitted error-free and acknowledged by at least one other node.
This bit is never cleared by the CAN module.
3 TXOK R/W 0
Last Error Code
This is the type of the last error to occur on the CAN bus.
Value Definition
0x0 No Error
Stuff Error
More than 5 equal bits in a sequence have occurred in a part
of a received message where this is not allowed.
0x1
Format Error
A fixed format part of the received frame has the wrong
format.
0x2
ACK Error
The message transmitted was not acknowledged by another
node.
0x3
Bit 1 Error
When a message is transmitted, the CAN controller monitors
the data lines to detect any conflicts. When the arbitration
field is transmitted, data conflicts are a part of the arbitration
protocol. When other frame fields are transmitted, data
conflicts are considered errors.
A Bit 1 Error indicates that the device wanted to send a High
level (logical 1) but the monitored bus value was Low (logical
0).
0x4
Bit 0 Error
A Bit 0 Error indicates that the device wanted to send a Low
level (logical 0), but the monitored bus value was High (logical
1).
During bus-off recovery, this status is set each time a
sequence of 11 High bits has been monitored. This enables
the CPU to monitor the proceeding of the bus-off recovery
sequence without any disturbances to the bus.
0x5
CRC Error
The CRC checksum was incorrect in the received message,
indicating that the calculated value received did not match
the calculated CRC of the data.
0x6
No Event
When the LEC bit shows this value, no CAN bus event was
detected since the CPU wrote this value to LEC.
0x7
2:0 LEC R/W 0x0
558 January 08, 2011
Texas Instruments-Production Data
Controller Area Network (CAN) Module
Register 3: CAN Error Counter (CANERR), offset 0x008
This register contains the error counter values, which can be used to analyze the cause of an error.
CAN Error Counter (CANERR)
CAN0 base: 0x4004.0000
CAN1 base: 0x4004.1000
Offset 0x008
Type RO, reset 0x0000.0000
31 30 29 28 27 26 25 24 23 22 21 20 19 18 17 16
reserved
Type RO RO RO RO RO RO RO RO RO RO RO RO RO RO RO RO
Reset 0 0 0 0 0 0 0 0 0 0 0 0 0 0 0 0
15 14 13 12 11 10 9 8 7 6 5 4 3 2 1 0
RP REC TEC
Type RO RO RO RO RO RO RO RO RO RO RO RO RO RO RO RO
Reset 0 0 0 0 0 0 0 0 0 0 0 0 0 0 0 0
Bit/Field Name Type Reset Description
Software should not rely on the value of a reserved bit. To provide
compatibility with future products, the value of a reserved bit should be
preserved across a read-modify-write operation.
31:16 reserved RO 0x0000
Received Error Passive
0: The Receive Error counter is below the Error Passive level (127 or
less).
1: The Receive Error counter has reached the Error Passive level (128
or greater).
15 RP RO 0
Receive Error Counter
State of the receiver error counter (0 to 127).
14:8 REC RO 0x00
Transmit Error Counter
State of the transmit error counter (0 to 255).
7:0 TEC RO 0x00
January 08, 2011 559
Texas Instruments-Production Data
Stellaris® LM3S2965 Microcontroller
Register 4: CAN Bit Timing (CANBIT), offset 0x00C
This register is used to program the bit width and bit quantum. Values are programmed to the system
clock frequency. This register is write-enabled by setting the CCE and INIT bits in the CANCTL
register. See “Bit Time and Bit Rate” on page 547 for more information.
CAN Bit Timing (CANBIT)
CAN0 base: 0x4004.0000
CAN1 base: 0x4004.1000
Offset 0x00C
Type R/W, reset 0x0000.2301
31 30 29 28 27 26 25 24 23 22 21 20 19 18 17 16
reserved
Type RO RO RO RO RO RO RO RO RO RO RO RO RO RO RO RO
Reset 0 0 0 0 0 0 0 0 0 0 0 0 0 0 0 0
15 14 13 12 11 10 9 8 7 6 5 4 3 2 1 0
reserved TSEG2 TSEG1 SJW BRP
Type RO R/W R/W R/W R/W R/W R/W R/W R/W R/W R/W R/W R/W R/W R/W R/W
Reset 0 0 1 0 0 0 1 1 0 0 0 0 0 0 0 1
Bit/Field Name Type Reset Description
Software should not rely on the value of a reserved bit. To provide
compatibility with future products, the value of a reserved bit should be
preserved across a read-modify-write operation.
31:15 reserved RO 0x0000
Time Segment after Sample Point
0x00-0x07: The actual interpretation by the hardware of this value is
such that one more than the value programmed here is used.
So, for example, a reset value of 0x2 defines that there is 3 (2+1) bit
time quanta defined for Phase_Seg2 (see Figure 15-4 on page 548).
The bit time quanta is defined by the BRP field.
14:12 TSEG2 R/W 0x2
Time Segment Before Sample Point
0x00-0x0F: The actual interpretation by the hardware of this value is
such that one more than the value programmed here is used.
So, for example, the reset value of 0x3 defines that there is 4 (3+1) bit
time quanta defined for Phase_Seg1 (see Figure 15-4 on page 548).
The bit time quanta is define by the BRP field.
11:8 TSEG1 R/W 0x3
(Re)Synchronization Jump Width
0x00-0x03: The actual interpretation by the hardware of this value is
such that one more than the value programmed here is used.
During the start of frame (SOF), if the CAN controller detects a phase
error (misalignment), it can adjust the length of TSEG2 or TSEG1 by the
value in SJW. So the reset value of 0 adjusts the length by 1 bit time
quanta.
7:6 SJW R/W 0x0
Baud Rate Prescaler
The value by which the oscillator frequency is divided for generating the
bit time quanta. The bit time is built up from a multiple of this quantum.
0x00-0x03F: The actual interpretation by the hardware of this value is
such that one more than the value programmed here is used.
BRP defines the number of CAN clock periods that make up 1 bit time
quanta, so the reset value is 2 bit time quanta (1+1).
The CANBRPE register can be used to further divide the bit time.
5:0 BRP R/W 0x1
560 January 08, 2011
Texas Instruments-Production Data
Controller Area Network (CAN) Module
Register 5: CAN Interrupt (CANINT), offset 0x010
This register indicates the source of the interrupt.
If several interrupts are pending, the CAN Interrupt (CANINT) register points to the pending interrupt
with the highest priority, disregarding the order in which the interrupts occurred. An interrupt remains
pending until the CPU has cleared it. If the INTID field is not 0x0000 (the default) and the IE bit in
the CANCTL register is set, the interrupt is active. The interrupt line remains active until the INTID
field is cleared by reading the CANSTS register, or until the IE bit in the CANCTL register is cleared.
Note: Reading the CAN Status (CANSTS) register clears the CAN Interrupt (CANINT) register,
if it is pending.
CAN Interrupt (CANINT)
CAN0 base: 0x4004.0000
CAN1 base: 0x4004.1000
Offset 0x010
Type RO, reset 0x0000.0000
31 30 29 28 27 26 25 24 23 22 21 20 19 18 17 16
reserved
Type RO RO RO RO RO RO RO RO RO RO RO RO RO RO RO RO
Reset 0 0 0 0 0 0 0 0 0 0 0 0 0 0 0 0
15 14 13 12 11 10 9 8 7 6 5 4 3 2 1 0
INTID
Type RO RO RO RO RO RO RO RO RO RO RO RO RO RO RO RO
Reset 0 0 0 0 0 0 0 0 0 0 0 0 0 0 0 0
Bit/Field Name Type Reset Description
Software should not rely on the value of a reserved bit. To provide
compatibility with future products, the value of a reserved bit should be
preserved across a read-modify-write operation.
31:16 reserved RO 0x0000
Interrupt Identifier
The number in this field indicates the source of the interrupt.
Value Definition
0x0000 No interrupt pending
Number of the message object that
caused the interrupt
0x0001-0x0020
0x0021-0x7FFF Reserved
0x8000 Status Interrupt
0x8001-0xFFFF Reserved
15:0 INTID RO 0x0000
January 08, 2011 561
Texas Instruments-Production Data
Stellaris® LM3S2965 Microcontroller
Register 6: CAN Test (CANTST), offset 0x014
This is the test mode register for self-test and external pin access. It is write-enabled by setting the
TEST bit in the CANCTL register. Different test functions may be combined, however, CAN transfers
will be affected if the TX bits in this register are not zero.
CAN Test (CANTST)
CAN0 base: 0x4004.0000
CAN1 base: 0x4004.1000
Offset 0x014
Type R/W, reset 0x0000.0000
31 30 29 28 27 26 25 24 23 22 21 20 19 18 17 16
reserved
Type RO RO RO RO RO RO RO RO RO RO RO RO RO RO RO RO
Reset 0 0 0 0 0 0 0 0 0 0 0 0 0 0 0 0
15 14 13 12 11 10 9 8 7 6 5 4 3 2 1 0
reserved RX TX LBACK SILENT BASIC reserved
Type RO RO RO RO RO RO RO RO RO R/W R/W R/W R/W R/W RO RO
Reset 0 0 0 0 0 0 0 0 0 0 0 0 0 0 0 0
Bit/Field Name Type Reset Description
Software should not rely on the value of a reserved bit. To provide
compatibility with future products, the value of a reserved bit should be
preserved across a read-modify-write operation.
31:8 reserved RO 0x0000.00
Receive Observation
Displays the value on the CANnRx pin.
7 RX RO 0
Transmit Control
Overrides control of the CANnTx pin.
Value Description
CAN Module Control
CANnTx is controlled by the CAN module; default
operation
0x0
Sample Point
The sample point is driven on the CANnTx signal. This
mode is useful to monitor bit timing.
0x1
Driven Low
CANnTx drives a low value. This mode is useful for
checking the physical layer of the CAN bus.
0x2
Driven High
CANnTx drives a high value. This mode is useful for
checking the physical layer of the CAN bus.
0x3
6:5 TX R/W 0x0
Loopback Mode
0: Disabled.
1: Enabled. In loopback mode, the data from the transmitter is routed
into the receiver. Any data on the receive input is ignored.
4 LBACK R/W 0
Silent Mode
Do not transmit data; monitor the bus. Also known as Bus Monitor mode.
0: Disabled.
1: Enabled.
3 SILENT R/W 0
562 January 08, 2011
Texas Instruments-Production Data
Controller Area Network (CAN) Module
Bit/Field Name Type Reset Description
Basic Mode
0: Disabled.
1: Use CANIF1 registers as transmit buffer, and use CANIF2 registers
as receive buffer.
2 BASIC R/W 0
Software should not rely on the value of a reserved bit. To provide
compatibility with future products, the value of a reserved bit should be
preserved across a read-modify-write operation.
1:0 reserved RO 0x0
January 08, 2011 563
Texas Instruments-Production Data
Stellaris® LM3S2965 Microcontroller
Register 7: CAN Baud Rate Prescaler Extension (CANBRPE), offset 0x018
This register is used to further divide the bit time set with the BRP bit in the CANBIT register. It is
write-enabled by setting the CCE bit in the CANCTL register.
CAN Baud Rate Prescaler Extension (CANBRPE)
CAN0 base: 0x4004.0000
CAN1 base: 0x4004.1000
Offset 0x018
Type R/W, reset 0x0000.0000
31 30 29 28 27 26 25 24 23 22 21 20 19 18 17 16
reserved
Type RO RO RO RO RO RO RO RO RO RO RO RO RO RO RO RO
Reset 0 0 0 0 0 0 0 0 0 0 0 0 0 0 0 0
15 14 13 12 11 10 9 8 7 6 5 4 3 2 1 0
reserved BRPE
Type RO RO RO RO RO RO RO RO RO RO RO RO R/W R/W R/W R/W
Reset 0 0 0 0 0 0 0 0 0 0 0 0 0 0 0 0
Bit/Field Name Type Reset Description
Software should not rely on the value of a reserved bit. To provide
compatibility with future products, the value of a reserved bit should be
preserved across a read-modify-write operation.
31:4 reserved RO 0x0000.000
Baud Rate Prescaler Extension
0x00-0x0F: Extend the BRP bit in the CANBIT register to values up to
1023. The actual interpretation by the hardware is one more than the
value programmed by BRPE (MSBs) and BRP (LSBs).
3:0 BRPE R/W 0x0
564 January 08, 2011
Texas Instruments-Production Data
Controller Area Network (CAN) Module
Register 8: CAN IF1 Command Request (CANIF1CRQ), offset 0x020
Register 9: CAN IF2 Command Request (CANIF2CRQ), offset 0x080
A message transfer is started as soon as there is a write of the message object number to the MNUM
field when the TXRQST bit in the CANIF1MCTL register is set. With this write operation, the BUSY
bit is automatically set to indicate that a transfer between the CAN Interface Registers and the
internal message RAM is in progress. After a wait time of 3 to 6 CAN_CLK periods, the transfer
between the interface register and the message RAM completes, which then clears the BUSY bit.
CAN IF1 Command Request (CANIF1CRQ)
CAN0 base: 0x4004.0000
CAN1 base: 0x4004.1000
Offset 0x020
Type R/W, reset 0x0000.0001
31 30 29 28 27 26 25 24 23 22 21 20 19 18 17 16
reserved
Type RO RO RO RO RO RO RO RO RO RO RO RO RO RO RO RO
Reset 0 0 0 0 0 0 0 0 0 0 0 0 0 0 0 0
15 14 13 12 11 10 9 8 7 6 5 4 3 2 1 0
BUSY reserved MNUM
Type RO RO RO RO RO RO RO RO RO RO R/W R/W R/W R/W R/W R/W
Reset 0 0 0 0 0 0 0 0 0 0 0 0 0 0 0 1
Bit/Field Name Type Reset Description
Software should not rely on the value of a reserved bit. To provide
compatibility with future products, the value of a reserved bit should be
preserved across a read-modify-write operation.
31:16 reserved RO 0x0000
Busy Flag
0: Cleared when read/write action has finished.
1: Set when a write occurs to the message number in this register.
15 BUSY RO 0
Software should not rely on the value of a reserved bit. To provide
compatibility with future products, the value of a reserved bit should be
preserved across a read-modify-write operation.
14:6 reserved RO 0x00
Message Number
Selects one of the 32 message objects in the message RAM for data
transfer. The message objects are numbered from 1 to 32.
Value Description
Reserved
0 is not a valid message number; it is interpreted
as 0x20, or object 32.
0x00
Message Number
Indicates specified message object 1 to 32.
0x01-0x20
Reserved
Not a valid message number; values are shifted and
it is interpreted as 0x01-0x1F.
0x21-0x3F
5:0 MNUM R/W 0x01
January 08, 2011 565
Texas Instruments-Production Data
Stellaris® LM3S2965 Microcontroller
Register 10: CAN IF1 Command Mask (CANIF1CMSK), offset 0x024
Register 11: CAN IF2 Command Mask (CANIF2CMSK), offset 0x084
Reading the Command Mask registers provides status for various functions. Writing to the Command
Mask registers specifies the transfer direction and selects which buffer registers are the source or
target of the data transfer.
Note that when a read from the message object buffer occurs when the WRNRD bit is clear and the
CLRINTPND and/or NEWDAT bits are set, the interrupt pending and/or new data flags in the message
object buffer are cleared.
CAN IF1 Command Mask (CANIF1CMSK)
CAN0 base: 0x4004.0000
CAN1 base: 0x4004.1000
Offset 0x024
Type R/W, reset 0x0000.0000
31 30 29 28 27 26 25 24 23 22 21 20 19 18 17 16
reserved
Type RO RO RO RO RO RO RO RO RO RO RO RO RO RO RO RO
Reset 0 0 0 0 0 0 0 0 0 0 0 0 0 0 0 0
15 14 13 12 11 10 9 8 7 6 5 4 3 2 1 0
DATAA DATAB NEWDAT /
TXRQST
reserved WRNRD MASK ARB CONTROL CLRINTPND
Type RO RO RO RO RO RO RO RO R/W R/W R/W R/W R/W R/W R/W R/W
Reset 0 0 0 0 0 0 0 0 0 0 0 0 0 0 0 0
Bit/Field Name Type Reset Description
Software should not rely on the value of a reserved bit. To provide
compatibility with future products, the value of a reserved bit should be
preserved across a read-modify-write operation.
31:8 reserved RO 0x0000.00
Write, Not Read
Transfer the message object address specified by the CAN Command
Request (CANIFnCRQ) register to the CAN message buffer registers.
Note: Interrupt pending and new data conditions in the message
buffer can be cleared by reading from the buffer (WRNRD = 0)
when the CLRINTPND and/or NEWDAT bits are set.
7 WRNRD R/W 0
Access Mask Bits
0: Mask bits unchanged.
1: Transfer IDMASK + DIR + MXTD of the message object into the
Interface registers.
6 MASK R/W 0
Access Arbitration Bits
0: Arbitration bits unchanged.
1: Transfer ID + DIR + XTD + MSGVAL of the message object into the
Interface registers.
5 ARB R/W 0
Access Control Bits
0: Control bits unchanged.
1: Transfer control bits from the CANIFnMCTL register into the Interface
registers.
4 CONTROL R/W 0
566 January 08, 2011
Texas Instruments-Production Data
Controller Area Network (CAN) Module
Bit/Field Name Type Reset Description
Clear Interrupt Pending Bit
If WRNRD is set, this bit controls whether the INTPND bit in the
CANIFnMCTL register is changed.
0: The INTPND bit in the message object remains unchanged.
1: The INTPND bit is cleared in the message object.
If WRNRD is clear and this bit is clear, the interrupt pending status is
transferred from the message buffer into the CANIFnMCTL register.
If WRNRD is clear and this bit is set, the interrupt pending status is cleared
in the message buffer. Note that the value of this bit that is transferred
to the CANIFnMCTL register always reflects the status of the bits before
clearing.
3 CLRINTPND R/W 0
NEWDAT / TXRQST Bit
If WRNRD is set, this bit can act as a TXRQST bit and request a
transmission. Note that when this bit is set, the TXRQST bit in the
CANIFnMCTL register is ignored.
0: Transmission is not requested
1: Begin a transmission
If WRNRD is clear and this bit is clear, the value of the new data status
is transferred from the message buffer into the CANIFnMCTL register.
If WRNRD is clear and this bit is set, the new data status is cleared in the
message buffer. Note that the value of this bit that is transferred to the
CANIFnMCTL register always reflects the status of the bits before
clearing.
2 NEWDAT / TXRQST R/W 0
Access Data Byte 0 to 3
When WRNRD = 1:
0: Data bytes 0-3 are unchanged.
1: Transfer data bytes 0-3 in message object to CANIFnDA1 and
CANIFnDA2.
When WRNRD = 0:
0: Data bytes 0-3 are unchanged.
1: Transfer data bytes 0-3 in CANIFnDA1 and CANIFnDA2 to the
message object.
1 DATAA R/W 0
Access Data Byte 4 to 7
When WRNRD = 1:
0: Data bytes 4-7 are unchanged.
1: Transfer data bytes 4-7 in message object to CANIFnDB1 and
CANIFnDB2.
When WRNRD = 0:
0: Data bytes 4-7 are unchanged.
1: Transfer data bytes 4-7 in CANIFnDB1 and CANIFnDB2 to the
message object.
0 DATAB R/W 0
January 08, 2011 567
Texas Instruments-Production Data
Stellaris® LM3S2965 Microcontroller
Register 12: CAN IF1 Mask 1 (CANIF1MSK1), offset 0x028
Register 13: CAN IF2 Mask 1 (CANIF2MSK1), offset 0x088
The mask information provided in this register accompanies the data (CANIFnDAn), arbitration
information (CANIFnARBn), and control information (CANIFnMCTL) to the message object in the
message RAM. The mask is used with the ID bit in the CANIFnARBn register for acceptance
filtering. Additional mask information is contained in the CANIFnMSK2 register.
CAN IF1 Mask 1 (CANIF1MSK1)
CAN0 base: 0x4004.0000
CAN1 base: 0x4004.1000
Offset 0x028
Type R/W, reset 0x0000.FFFF
31 30 29 28 27 26 25 24 23 22 21 20 19 18 17 16
reserved
Type RO RO RO RO RO RO RO RO RO RO RO RO RO RO RO RO
Reset 0 0 0 0 0 0 0 0 0 0 0 0 0 0 0 0
15 14 13 12 11 10 9 8 7 6 5 4 3 2 1 0
MSK
Type R/W R/W R/W R/W R/W R/W R/W R/W R/W R/W R/W R/W R/W R/W R/W R/W
Reset 1 1 1 1 1 1 1 1 1 1 1 1 1 1 1 1
Bit/Field Name Type Reset Description
Software should not rely on the value of a reserved bit. To provide
compatibility with future products, the value of a reserved bit should be
preserved across a read-modify-write operation.
31:16 reserved RO 0x0000
Identifier Mask
When using a 29-bit identifier, these bits are used for bits [15:0] of the
ID. The MSK field in the CANIFnMSK2 register are used for bits [28:16]
of the ID. When using an 11-bit identifier, these bits are ignored.
0: The corresponding identifier field (ID) in the message object cannot
inhibit the match in acceptance filtering.
1: The corresponding identifier field (ID) is used for acceptance filtering.
15:0 MSK R/W 0xFFFF
568 January 08, 2011
Texas Instruments-Production Data
Controller Area Network (CAN) Module
Register 14: CAN IF1 Mask 2 (CANIF1MSK2), offset 0x02C
Register 15: CAN IF2 Mask 2 (CANIF2MSK2), offset 0x08C
This register holds extended mask information that accompanies the CANIFnMSK1 register.
CAN IF1 Mask 2 (CANIF1MSK2)
CAN0 base: 0x4004.0000
CAN1 base: 0x4004.1000
Offset 0x02C
Type R/W, reset 0x0000.FFFF
31 30 29 28 27 26 25 24 23 22 21 20 19 18 17 16
reserved
Type RO RO RO RO RO RO RO RO RO RO RO RO RO RO RO RO
Reset 0 0 0 0 0 0 0 0 0 0 0 0 0 0 0 0
15 14 13 12 11 10 9 8 7 6 5 4 3 2 1 0
MXTD MDIR reserved MSK
Type R/W R/W RO R/W R/W R/W R/W R/W R/W R/W R/W R/W R/W R/W R/W R/W
Reset 1 1 1 0 0 0 0 0 1 1 1 1 1 1 1 1
Bit/Field Name Type Reset Description
Software should not rely on the value of a reserved bit. To provide
compatibility with future products, the value of a reserved bit should be
preserved across a read-modify-write operation.
31:16 reserved RO 0x0000
Mask Extended Identifier
0: The extended identifier bit (XTD in the CANIFnARB2 register) has
no effect on the acceptance filtering.
1: The extended identifier bit XTD is used for acceptance filtering.
15 MXTD R/W 0x1
Mask Message Direction
0: The message direction bit (DIR in the CANIFnARB2 register) has
no effect for acceptance filtering.
1: The message direction bit DIR is used for acceptance filtering.
14 MDIR R/W 0x1
Software should not rely on the value of a reserved bit. To provide
compatibility with future products, the value of a reserved bit should be
preserved across a read-modify-write operation.
13 reserved RO 0x1
Identifier Mask
When using a 29-bit identifier, these bits are used for bits [28:16] of the
ID. The MSK field in the CANIFnMSK1 register are used for bits [15:0]
of the ID. When using an 11-bit identifier, MSK[12:2] are used for bits
[10:0] of the ID.
0: The corresponding identifier field (ID) in the message object cannot
inhibit the match in acceptance filtering.
1: The corresponding identifier field (ID) is used for acceptance filtering.
12:0 MSK R/W 0xFF
January 08, 2011 569
Texas Instruments-Production Data
Stellaris® LM3S2965 Microcontroller
Register 16: CAN IF1 Arbitration 1 (CANIF1ARB1), offset 0x030
Register 17: CAN IF2 Arbitration 1 (CANIF2ARB1), offset 0x090
These registers hold the identifiers for acceptance filtering.
CAN IF1 Arbitration 1 (CANIF1ARB1)
CAN0 base: 0x4004.0000
CAN1 base: 0x4004.1000
Offset 0x030
Type R/W, reset 0x0000.0000
31 30 29 28 27 26 25 24 23 22 21 20 19 18 17 16
reserved
Type RO RO RO RO RO RO RO RO RO RO RO RO RO RO RO RO
Reset 0 0 0 0 0 0 0 0 0 0 0 0 0 0 0 0
15 14 13 12 11 10 9 8 7 6 5 4 3 2 1 0
ID
Type R/W R/W R/W R/W R/W R/W R/W R/W R/W R/W R/W R/W R/W R/W R/W R/W
Reset 0 0 0 0 0 0 0 0 0 0 0 0 0 0 0 0
Bit/Field Name Type Reset Description
Software should not rely on the value of a reserved bit. To provide
compatibility with future products, the value of a reserved bit should be
preserved across a read-modify-write operation.
31:16 reserved RO 0x0000
Message Identifier
This bit field is used with the ID field in the CANIFnARB2 register to
create the message identifier.
When using a 29-bit identifier, bits 15:0 of the CANIFnARB1 register
are [15:0] of the ID, while bits 12:0 of the CANIFnARB2 register are
[28:16] of the ID.
When using an 11-bit identifier, these bits are not used.
15:0 ID R/W 0x0000
570 January 08, 2011
Texas Instruments-Production Data
Controller Area Network (CAN) Module
Register 18: CAN IF1 Arbitration 2 (CANIF1ARB2), offset 0x034
Register 19: CAN IF2 Arbitration 2 (CANIF2ARB2), offset 0x094
These registers hold information for acceptance filtering.
CAN IF1 Arbitration 2 (CANIF1ARB2)
CAN0 base: 0x4004.0000
CAN1 base: 0x4004.1000
Offset 0x034
Type R/W, reset 0x0000.0000
31 30 29 28 27 26 25 24 23 22 21 20 19 18 17 16
reserved
Type RO RO RO RO RO RO RO RO RO RO RO RO RO RO RO RO
Reset 0 0 0 0 0 0 0 0 0 0 0 0 0 0 0 0
15 14 13 12 11 10 9 8 7 6 5 4 3 2 1 0
MSGVAL XTD DIR ID
Type R/W R/W R/W R/W R/W R/W R/W R/W R/W R/W R/W R/W R/W R/W R/W R/W
Reset 0 0 0 0 0 0 0 0 0 0 0 0 0 0 0 0
Bit/Field Name Type Reset Description
Software should not rely on the value of a reserved bit. To provide
compatibility with future products, the value of a reserved bit should be
preserved across a read-modify-write operation.
31:16 reserved RO 0x0000
Message Valid
0: The message object is ignored by the message handler.
1: The message object is configured and ready to be considered by the
message handler within the CAN controller.
All unused message objects should have this bit cleared during
initialization and before clearing the INIT bit in the CANCTL register.
The MSGVAL bit must also be cleared before any of the following bits
are modified or if the message object is no longer required: the ID fields
in the CANIFnARBn registers, the XTD and DIR bits in the CANIFnARB2
register, or the DLC field in the CANIFnMCTL register.
15 MSGVAL R/W 0
Extended Identifier
0: An 11-bit Standard Identifier is used for this message object.
1: A 29-bit Extended Identifier is used for this message object.
14 XTD R/W 0
Message Direction
0: Receive. When the TXRQST bit in the CANIFnMCTL register is set,
a remote frame with the identifier of this message object is received.
On reception of a data frame with matching identifier, that message is
stored in this message object.
1: Transmit. When the TXRQST bit in the CANIFnMCTL register is set,
the respective message object is transmitted as a data frame. On
reception of a remote frame with matching identifier, the TXRQST bit of
this message object is set (if RMTEN=1).
13 DIR R/W 0
Message Identifier
This bit field is used with the ID field in the CANIFnARB2 register to
create the message identifier.
When using a 29-bit identifier, ID[15:0] of the CANIFnARB1 register
are [15:0] of the ID, while these bits, ID[12:0], are [28:16] of the ID.
When using an 11-bit identifier, ID[12:2] are used for bits [10:0] of
the ID. The ID field in the CANIFnARB1 register is ignored.
12:0 ID R/W 0x000
January 08, 2011 571
Texas Instruments-Production Data
Stellaris® LM3S2965 Microcontroller
Register 20: CAN IF1 Message Control (CANIF1MCTL), offset 0x038
Register 21: CAN IF2 Message Control (CANIF2MCTL), offset 0x098
This register holds the control information associated with the message object to be sent to the
Message RAM.
CAN IF1 Message Control (CANIF1MCTL)
CAN0 base: 0x4004.0000
CAN1 base: 0x4004.1000
Offset 0x038
Type R/W, reset 0x0000.0000
31 30 29 28 27 26 25 24 23 22 21 20 19 18 17 16
reserved
Type RO RO RO RO RO RO RO RO RO RO RO RO RO RO RO RO
Reset 0 0 0 0 0 0 0 0 0 0 0 0 0 0 0 0
15 14 13 12 11 10 9 8 7 6 5 4 3 2 1 0
NEWDAT MSGLST INTPND UMASK TXIE RXIE RMTEN TXRQST EOB reserved DLC
Type R/W R/W R/W R/W R/W R/W R/W R/W R/W RO RO RO R/W R/W R/W R/W
Reset 0 0 0 0 0 0 0 0 0 0 0 0 0 0 0 0
Bit/Field Name Type Reset Description
Software should not rely on the value of a reserved bit. To provide
compatibility with future products, the value of a reserved bit should be
preserved across a read-modify-write operation.
31:16 reserved RO 0x0000
New Data
0: No new data has been written into the data portion of this message
object by the message handler since the last time this flag was cleared
by the CPU.
1: The message handler or the CPU has written new data into the data
portion of this message object.
15 NEWDAT R/W 0
Message Lost
0 : No message was lost since the last time this bit was cleared by the
CPU.
1: The message handler stored a new message into this object when
NEWDAT was set; the CPU has lost a message.
This bit is only valid for message objects when the DIR bit in the
CANIFnARB2 register clear (receive).
14 MSGLST R/W 0
Interrupt Pending
0: This message object is not the source of an interrupt.
1: This message object is the source of an interrupt. The interrupt
identifier in the CANINT register points to this message object if there
is not another interrupt source with a higher priority.
13 INTPND R/W 0
Use Acceptance Mask
0: Mask ignored.
1: Use mask (MSK, MXTD, and MDIR bits in the CANIFnMSKn registers)
for acceptance filtering.
12 UMASK R/W 0
Transmit Interrupt Enable
0: The INTPND bit in the CANIFnMCTL register is unchanged after a
successful transmission of a frame.
1: The INTPND bit in the CANIFnMCTL register is set after a successful
transmission of a frame.
11 TXIE R/W 0
572 January 08, 2011
Texas Instruments-Production Data
Controller Area Network (CAN) Module
Bit/Field Name Type Reset Description
Receive Interrupt Enable
0: The INTPND bit in the CANIFnMCTL register is unchanged after a
successful reception of a frame.
1: The INTPND bit in the CANIFnMCTL register is set after a successful
reception of a frame.
10 RXIE R/W 0
Remote Enable
0: At the reception of a remote frame, the TXRQST bit in the
CANIFnMCTL register is left unchanged.
1: At the reception of a remote frame, the TXRQST bit in the
CANIFnMCTL register is set.
9 RMTEN R/W 0
Transmit Request
0: This message object is not waiting for transmission.
1: The transmission of this message object is requested and is not yet
done.
8 TXRQST R/W 0
End of Buffer
0: Message object belongs to a FIFO Buffer and is not the last message
object of that FIFO Buffer.
1: Single message object or last message object of a FIFO Buffer.
This bit is used to concatenate two or more message objects (up to 32)
to build a FIFO buffer. For a single message object (thus not belonging
to a FIFO buffer), this bit must be set.
7 EOB R/W 0
Software should not rely on the value of a reserved bit. To provide
compatibility with future products, the value of a reserved bit should be
preserved across a read-modify-write operation.
6:4 reserved RO 0x0
Data Length Code
Value Description
0x0-0x8 Specifies the number of bytes in the data frame.
0x9-0xF Defaults to a data frame with 8 bytes.
The DLC field in the CANIFnMCTL register of a message object must
be defined the same as in all the corresponding objects with the same
identifier at other nodes. When the message handler stores a data frame,
it writes DLC to the value given by the received message.
3:0 DLC R/W 0x0
January 08, 2011 573
Texas Instruments-Production Data
Stellaris® LM3S2965 Microcontroller
Register 22: CAN IF1 Data A1 (CANIF1DA1), offset 0x03C
Register 23: CAN IF1 Data A2 (CANIF1DA2), offset 0x040
Register 24: CAN IF1 Data B1 (CANIF1DB1), offset 0x044
Register 25: CAN IF1 Data B2 (CANIF1DB2), offset 0x048
Register 26: CAN IF2 Data A1 (CANIF2DA1), offset 0x09C
Register 27: CAN IF2 Data A2 (CANIF2DA2), offset 0x0A0
Register 28: CAN IF2 Data B1 (CANIF2DB1), offset 0x0A4
Register 29: CAN IF2 Data B2 (CANIF2DB2), offset 0x0A8
These registers contain the data to be sent or that has been received. In a CAN data frame, data
byte 0 is the first byte to be transmitted or received and data byte 7 is the last byte to be transmitted
or received. In CAN's serial bit stream, the MSB of each byte is transmitted first.
CAN IF1 Data A1 (CANIF1DA1)
CAN0 base: 0x4004.0000
CAN1 base: 0x4004.1000
Offset 0x03C
Type R/W, reset 0x0000.0000
31 30 29 28 27 26 25 24 23 22 21 20 19 18 17 16
reserved
Type RO RO RO RO RO RO RO RO RO RO RO RO RO RO RO RO
Reset 0 0 0 0 0 0 0 0 0 0 0 0 0 0 0 0
15 14 13 12 11 10 9 8 7 6 5 4 3 2 1 0
DATA
Type R/W R/W R/W R/W R/W R/W R/W R/W R/W R/W R/W R/W R/W R/W R/W R/W
Reset 0 0 0 0 0 0 0 0 0 0 0 0 0 0 0 0
Bit/Field Name Type Reset Description
Software should not rely on the value of a reserved bit. To provide
compatibility with future products, the value of a reserved bit should be
preserved across a read-modify-write operation.
31:16 reserved RO 0x0000
Data
The CANIFnDA1 registers contain data bytes 1 and 0; CANIFnDA2
data bytes 3 and 2; CANIFnDB1 data bytes 5 and 4; and CANIFnDB2
data bytes 7 and 6.
15:0 DATA R/W 0x0000
574 January 08, 2011
Texas Instruments-Production Data
Controller Area Network (CAN) Module
Register 30: CAN Transmission Request 1 (CANTXRQ1), offset 0x100
Register 31: CAN Transmission Request 2 (CANTXRQ2), offset 0x104
The CANTXRQ1 and CANTXRQ2 registers hold the TXRQST bits of the 32 message objects. By
reading out these bits, the CPU can check which message object has a transmission request pending.
The TXRQST bit of a specific message object can be changed by three sources: (1) the CPU via the
CANIFnMCTL register, (2) the message handler state machine after the reception of a remote
frame, or (3) the message handler state machine after a successful transmission.
The CANTXRQ1 register contains the TXRQST bits of the first 16 message objects in the message
RAM; the CANTXRQ2 register contains the TXRQST bits of the second 16 message objects.
CAN Transmission Request 1 (CANTXRQ1)
CAN0 base: 0x4004.0000
CAN1 base: 0x4004.1000
Offset 0x100
Type RO, reset 0x0000.0000
31 30 29 28 27 26 25 24 23 22 21 20 19 18 17 16
reserved
Type RO RO RO RO RO RO RO RO RO RO RO RO RO RO RO RO
Reset 0 0 0 0 0 0 0 0 0 0 0 0 0 0 0 0
15 14 13 12 11 10 9 8 7 6 5 4 3 2 1 0
TXRQST
Type RO RO RO RO RO RO RO RO RO RO RO RO RO RO RO RO
Reset 0 0 0 0 0 0 0 0 0 0 0 0 0 0 0 0
Bit/Field Name Type Reset Description
Software should not rely on the value of a reserved bit. To provide
compatibility with future products, the value of a reserved bit should be
preserved across a read-modify-write operation.
31:16 reserved RO 0x0000
Transmission Request Bits
0: The corresponding message object is not waiting for transmission.
1: The transmission of the corresponding message object is requested
and is not yet done.
15:0 TXRQST RO 0x0000
January 08, 2011 575
Texas Instruments-Production Data
Stellaris® LM3S2965 Microcontroller
Register 32: CAN New Data 1 (CANNWDA1), offset 0x120
Register 33: CAN New Data 2 (CANNWDA2), offset 0x124
The CANNWDA1 and CANNWDA2 registers hold the NEWDAT bits of the 32 message objects. By
reading these bits, the CPU can check which message object has its data portion updated. The
NEWDAT bit of a specific message object can be changed by three sources: (1) the CPU via the
CANIFnMCTL register, (2) the message handler state machine after the reception of a data frame,
or (3) the message handler state machine after a successful transmission.
The CANNWDA1 register contains the NEWDAT bits of the first 16 message objects in the message
RAM; the CANNWDA2 register contains the NEWDAT bits of the second 16 message objects.
CAN New Data 1 (CANNWDA1)
CAN0 base: 0x4004.0000
CAN1 base: 0x4004.1000
Offset 0x120
Type RO, reset 0x0000.0000
31 30 29 28 27 26 25 24 23 22 21 20 19 18 17 16
reserved
Type RO RO RO RO RO RO RO RO RO RO RO RO RO RO RO RO
Reset 0 0 0 0 0 0 0 0 0 0 0 0 0 0 0 0
15 14 13 12 11 10 9 8 7 6 5 4 3 2 1 0
NEWDAT
Type RO RO RO RO RO RO RO RO RO RO RO RO RO RO RO RO
Reset 0 0 0 0 0 0 0 0 0 0 0 0 0 0 0 0
Bit/Field Name Type Reset Description
Software should not rely on the value of a reserved bit. To provide
compatibility with future products, the value of a reserved bit should be
preserved across a read-modify-write operation.
31:16 reserved RO 0x0000
New Data Bits
0: No new data has been written into the data portion of the
corresponding message object by the message handler since the last
time this flag was cleared by the CPU.
1: The message handler or the CPU has written new data into the data
portion of the corresponding message object.
15:0 NEWDAT RO 0x0000
576 January 08, 2011
Texas Instruments-Production Data
Controller Area Network (CAN) Module
Register 34: CAN Message 1 Interrupt Pending (CANMSG1INT), offset 0x140
Register 35: CAN Message 2 Interrupt Pending (CANMSG2INT), offset 0x144
The CANMSG1INT and CANMSG2INT registers hold the INTPND bits of the 32 message objects.
By reading these bits, the CPU can check which message object has an interrupt pending. The
INTPND bit of a specific message object can be changed through two sources: (1) the CPU via the
CANIFnMCTL register, or (2) the message handler state machine after the reception or transmission
of a frame.
This field is also encoded in the CANINT register.
The CANMSG1INT register contains the INTPND bits of the first 16 message objects in the message
RAM; the CANMSG2INT register contains the INTPND bits of the second 16 message objects.
CAN Message 1 Interrupt Pending (CANMSG1INT)
CAN0 base: 0x4004.0000
CAN1 base: 0x4004.1000
Offset 0x140
Type RO, reset 0x0000.0000
31 30 29 28 27 26 25 24 23 22 21 20 19 18 17 16
reserved
Type RO RO RO RO RO RO RO RO RO RO RO RO RO RO RO RO
Reset 0 0 0 0 0 0 0 0 0 0 0 0 0 0 0 0
15 14 13 12 11 10 9 8 7 6 5 4 3 2 1 0
INTPND
Type RO RO RO RO RO RO RO RO RO RO RO RO RO RO RO RO
Reset 0 0 0 0 0 0 0 0 0 0 0 0 0 0 0 0
Bit/Field Name Type Reset Description
Software should not rely on the value of a reserved bit. To provide
compatibility with future products, the value of a reserved bit should be
preserved across a read-modify-write operation.
31:16 reserved RO 0x0000
Interrupt Pending Bits
0: The corresponding message object is not the source of an interrupt.
1: The corresponding message object is the source of an interrupt.
15:0 INTPND RO 0x0000
January 08, 2011 577
Texas Instruments-Production Data
Stellaris® LM3S2965 Microcontroller
Register 36: CAN Message 1 Valid (CANMSG1VAL), offset 0x160
Register 37: CAN Message 2 Valid (CANMSG2VAL), offset 0x164
The CANMSG1VAL and CANMSG2VAL registers hold the MSGVAL bits of the 32 message objects.
By reading these bits, the CPU can check which message object is valid. The message value of a
specific message object can be changed with the CANIFnMCTL register.
The CANMSG1VAL register contains the MSGVAL bits of the first 16 message objects in the message
RAM; the CANMSG2VAL register contains the MSGVAL bits of the second 16 message objects in
the message RAM.
CAN Message 1 Valid (CANMSG1VAL)
CAN0 base: 0x4004.0000
CAN1 base: 0x4004.1000
Offset 0x160
Type RO, reset 0x0000.0000
31 30 29 28 27 26 25 24 23 22 21 20 19 18 17 16
reserved
Type RO RO RO RO RO RO RO RO RO RO RO RO RO RO RO RO
Reset 0 0 0 0 0 0 0 0 0 0 0 0 0 0 0 0
15 14 13 12 11 10 9 8 7 6 5 4 3 2 1 0
MSGVAL
Type RO RO RO RO RO RO RO RO RO RO RO RO RO RO RO RO
Reset 0 0 0 0 0 0 0 0 0 0 0 0 0 0 0 0
Bit/Field Name Type Reset Description
Software should not rely on the value of a reserved bit. To provide
compatibility with future products, the value of a reserved bit should be
preserved across a read-modify-write operation.
31:16 reserved RO 0x0000
Message Valid Bits
0: The corresponding message object is not configured and is ignored
by the message handler.
1: The corresponding message object is configured and should be
considered by the message handler.
15:0 MSGVAL RO 0x0000
578 January 08, 2011
Texas Instruments-Production Data
Controller Area Network (CAN) Module
16 Analog Comparators
An analog comparator is a peripheral that compares two analog voltages, and provides a logical
output that signals the comparison result.
Note: Not all comparators have the option to drive an output pin.
The comparator can provide its output to a device pin, acting as a replacement for an analog
comparator on the board, or it can be used to signal the application via interrupts or triggers to the
ADC to cause it to start capturing a sample sequence. The interrupt generation and ADC triggering
logic is separate. This means, for example, that an interrupt can be generated on a rising edge and
the ADC triggered on a falling edge.
The Stellaris® Analog Comparators module has the following features:
■ Three independent integrated analog comparators
■ Configurable for output to drive an output pin, generate an interrupt, or initiate an ADC sample
sequence
■ Compare external pin input to external pin input or to internal programmable voltage reference
■ Compare a test voltage against any one of these voltages
– An individual external reference voltage
– A shared single external reference voltage
– A shared internal reference voltage
January 08, 2011 579
Texas Instruments-Production Data
Stellaris® LM3S2965 Microcontroller
16.1 Block Diagram
Figure 16-1. Analog Comparator Module Block Diagram
C2+
C2-
output
+ve input (alternate)
+ve input
interrupt
-ve input
reference input
Comparator 2
ACSTAT2
ACCTL2
C1-
C1+ output
+ve input (alternate)
+ve input
interrupt
-ve input
reference input
Comparator 1
ACSTAT1
ACCTL1
Voltage
Ref
ACREFCTL
output
+ve input (alternate)
+ve input
interrupt
-ve input
reference input
Comparator 0
ACSTAT0
ACCTL0
C0+
internal
bus
C0-
C0o
trigger trigger
trigger trigger
trigger trigger
Interrupt Control
ACRIS
ACMIS
ACINTEN
interrupt
16.2 Functional Description
Important: It is recommended that the Digital-Input enable (the GPIODEN bit in the GPIO module)
for the analog input pin be disabled to prevent excessive current draw from the I/O
pads.
The comparator compares the VIN- and VIN+ inputs to produce an output, VOUT.
VIN- < VIN+, VOUT = 1
VIN- > VIN+, VOUT = 0
As shown in Figure 16-2 on page 581, the input source for VIN- is an external input. In addition to
an external input, input sources for VIN+ can be the +ve input of comparator 0 or an internal reference.
580 January 08, 2011
Texas Instruments-Production Data
Analog Comparators
Figure 16-2. Structure of Comparator Unit
ACCTL
CINV
internal
bus
interrupt
trigger
TrigGen
output
ACSTAT
IntGen
- ve input
1
+ ve input (alternate)
0
+ ve input
2
reference input
A comparator is configured through two status/control registers (ACCTL and ACSTAT ). The internal
reference is configured through one control register (ACREFCTL). Interrupt status and control is
configured through three registers (ACMIS, ACRIS, and ACINTEN).
Typically, the comparator output is used internally to generate controller interrupts. It may also be
used to drive an external pin or generate an analog-to-digital converter (ADC) trigger.
Important: The ASRCP bits in the ACCTLn register must be set before using the analog
comparators.
16.2.1 Internal Reference Programming
The structure of the internal reference is shown in Figure 16-3 on page 581. This is controlled by a
single configuration register (ACREFCTL). Table 16-1 on page 581 shows the programming options
to develop specific internal reference values, to compare an external voltage against a particular
voltage generated internally.
Figure 16-3. Comparator Internal Reference Structure
8R R R
8R
R
•••
•••
0
Decoder
15 14 1
AVDD
EN
internal
reference
VREF
RNG
Table 16-1. Internal Reference Voltage and ACREFCTL Field Values
Output Reference Voltage Based on VREF Field Value
ACREFCTL Register
EN Bit Value RNG Bit Value
0 V (GND) for any value of VREF; however, it is recommended that RNG=1 and
VREF=0 for the least noisy ground reference.
EN=0 RNG=X
January 08, 2011 581
Texas Instruments-Production Data
Stellaris® LM3S2965 Microcontroller
Table 16-1. Internal Reference Voltage and ACREFCTL Field Values (continued)
Output Reference Voltage Based on VREF Field Value
ACREFCTL Register
EN Bit Value RNG Bit Value
Total resistance in ladder is 31 R.
The range of internal reference in this mode is 0.85-2.448 V.
RNG=0
EN=1
Total resistance in ladder is 23 R.
The range of internal reference for this mode is 0-2.152 V.
RNG=1
16.3 Initialization and Configuration
The following example shows how to configure an analog comparator to read back its output value
from an internal register.
1. Enable the analog comparator 0 clock by writing a value of 0x0010.0000 to the RCGC1 register
in the System Control module.
2. In the GPIO module, enable the GPIO port/pin associated with C0- as a GPIO input.
3. Configure the internal voltage reference to 1.65 V by writing the ACREFCTL register with the
value 0x0000.030C.
4. Configure comparator 0 to use the internal voltage reference and to not invert the output by
writing the ACCTL0 register with the value of 0x0000.040C.
5. Delay for some time.
6. Read the comparator output value by reading the ACSTAT0 register’s OVAL value.
Change the level of the signal input on C0- to see the OVAL value change.
16.4 Register Map
Table 16-2 on page 583 lists the comparator registers. The offset listed is a hexadecimal increment
to the register’s address, relative to the Analog Comparator base address of 0x4003.C000.
Note that the analog comparator module clock must be enabled before the registers can be
programmed (see page 216). There must be a delay of 3 system clocks after the ADC module clock
is enabled before any ADC module registers are accessed.
582 January 08, 2011
Texas Instruments-Production Data
Analog Comparators
Table 16-2. Analog Comparators Register Map
See
Offset Name Type Reset Description page
0x000 ACMIS R/W1C 0x0000.0000 Analog Comparator Masked Interrupt Status 584
0x004 ACRIS RO 0x0000.0000 Analog Comparator Raw Interrupt Status 585
0x008 ACINTEN R/W 0x0000.0000 Analog Comparator Interrupt Enable 586
0x010 ACREFCTL R/W 0x0000.0000 Analog Comparator Reference Voltage Control 587
0x020 ACSTAT0 RO 0x0000.0000 Analog Comparator Status 0 588
0x024 ACCTL0 R/W 0x0000.0000 Analog Comparator Control 0 589
0x040 ACSTAT1 RO 0x0000.0000 Analog Comparator Status 1 588
0x044 ACCTL1 R/W 0x0000.0000 Analog Comparator Control 1 589
0x060 ACSTAT2 RO 0x0000.0000 Analog Comparator Status 2 588
0x064 ACCTL2 R/W 0x0000.0000 Analog Comparator Control 2 589
16.5 Register Descriptions
The remainder of this section lists and describes the Analog Comparator registers, in numerical
order by address offset.
January 08, 2011 583
Texas Instruments-Production Data
Stellaris® LM3S2965 Microcontroller
Register 1: Analog Comparator Masked Interrupt Status (ACMIS), offset 0x000
This register provides a summary of the interrupt status (masked) of the comparator.
Analog Comparator Masked Interrupt Status (ACMIS)
Base 0x4003.C000
Offset 0x000
Type R/W1C, reset 0x0000.0000
31 30 29 28 27 26 25 24 23 22 21 20 19 18 17 16
reserved
Type RO RO RO RO RO RO RO RO RO RO RO RO RO RO RO RO
Reset 0 0 0 0 0 0 0 0 0 0 0 0 0 0 0 0
15 14 13 12 11 10 9 8 7 6 5 4 3 2 1 0
reserved IN2 IN1 IN0
Type RO RO RO RO RO RO RO RO RO RO RO RO RO R/W1C R/W1C R/W1C
Reset 0 0 0 0 0 0 0 0 0 0 0 0 0 0 0 0
Bit/Field Name Type Reset Description
Software should not rely on the value of a reserved bit. To provide
compatibility with future products, the value of a reserved bit should be
preserved across a read-modify-write operation.
31:3 reserved RO 0x00
Comparator 2 Masked Interrupt Status
Gives the masked interrupt state of this interrupt. Write 1 to this bit to
clear the pending interrupt.
2 IN2 R/W1C 0
Comparator 1 Masked Interrupt Status
Gives the masked interrupt state of this interrupt. Write 1 to this bit to
clear the pending interrupt.
1 IN1 R/W1C 0
Comparator 0 Masked Interrupt Status
Gives the masked interrupt state of this interrupt. Write 1 to this bit to
clear the pending interrupt.
0 IN0 R/W1C 0
584 January 08, 2011
Texas Instruments-Production Data
Analog Comparators
Register 2: Analog Comparator Raw Interrupt Status (ACRIS), offset 0x004
This register provides a summary of the interrupt status (raw) of the comparator.
Analog Comparator Raw Interrupt Status (ACRIS)
Base 0x4003.C000
Offset 0x004
Type RO, reset 0x0000.0000
31 30 29 28 27 26 25 24 23 22 21 20 19 18 17 16
reserved
Type RO RO RO RO RO RO RO RO RO RO RO RO RO RO RO RO
Reset 0 0 0 0 0 0 0 0 0 0 0 0 0 0 0 0
15 14 13 12 11 10 9 8 7 6 5 4 3 2 1 0
reserved IN2 IN1 IN0
Type RO RO RO RO RO RO RO RO RO RO RO RO RO RO RO RO
Reset 0 0 0 0 0 0 0 0 0 0 0 0 0 0 0 0
Bit/Field Name Type Reset Description
Software should not rely on the value of a reserved bit. To provide
compatibility with future products, the value of a reserved bit should be
preserved across a read-modify-write operation.
31:3 reserved RO 0x00
Comparator 2 Interrupt Status
When set, indicates that an interrupt has been generated by comparator
2.
2 IN2 RO 0
Comparator 1 Interrupt Status
When set, indicates that an interrupt has been generated by comparator
1.
1 IN1 RO 0
Comparator 0 Interrupt Status
When set, indicates that an interrupt has been generated by comparator
0.
0 IN0 RO 0
January 08, 2011 585
Texas Instruments-Production Data
Stellaris® LM3S2965 Microcontroller
Register 3: Analog Comparator Interrupt Enable (ACINTEN), offset 0x008
This register provides the interrupt enable for the comparator.
Analog Comparator Interrupt Enable (ACINTEN)
Base 0x4003.C000
Offset 0x008
Type R/W, reset 0x0000.0000
31 30 29 28 27 26 25 24 23 22 21 20 19 18 17 16
reserved
Type RO RO RO RO RO RO RO RO RO RO RO RO RO RO RO RO
Reset 0 0 0 0 0 0 0 0 0 0 0 0 0 0 0 0
15 14 13 12 11 10 9 8 7 6 5 4 3 2 1 0
reserved IN2 IN1 IN0
Type RO RO RO RO RO RO RO RO RO RO RO RO RO R/W R/W R/W
Reset 0 0 0 0 0 0 0 0 0 0 0 0 0 0 0 0
Bit/Field Name Type Reset Description
Software should not rely on the value of a reserved bit. To provide
compatibility with future products, the value of a reserved bit should be
preserved across a read-modify-write operation.
31:3 reserved RO 0x00
Comparator 2 Interrupt Enable
When set, enables the controller interrupt from the comparator 2 output
2 IN2 R/W 0
Comparator 1 Interrupt Enable
When set, enables the controller interrupt from the comparator 1 output.
1 IN1 R/W 0
Comparator 0 Interrupt Enable
When set, enables the controller interrupt from the comparator 0 output.
0 IN0 R/W 0
586 January 08, 2011
Texas Instruments-Production Data
Analog Comparators
Register 4: Analog Comparator Reference Voltage Control (ACREFCTL), offset
0x010
This register specifies whether the resistor ladder is powered on as well as the range and tap.
Analog Comparator Reference Voltage Control (ACREFCTL)
Base 0x4003.C000
Offset 0x010
Type R/W, reset 0x0000.0000
31 30 29 28 27 26 25 24 23 22 21 20 19 18 17 16
reserved
Type RO RO RO RO RO RO RO RO RO RO RO RO RO RO RO RO
Reset 0 0 0 0 0 0 0 0 0 0 0 0 0 0 0 0
15 14 13 12 11 10 9 8 7 6 5 4 3 2 1 0
reserved EN RNG reserved VREF
Type RO RO RO RO RO RO R/W R/W RO RO RO RO R/W R/W R/W R/W
Reset 0 0 0 0 0 0 0 0 0 0 0 0 0 0 0 0
Bit/Field Name Type Reset Description
Software should not rely on the value of a reserved bit. To provide
compatibility with future products, the value of a reserved bit should be
preserved across a read-modify-write operation.
31:10 reserved RO 0x00
Resistor Ladder Enable
The EN bit specifies whether the resistor ladder is powered on. If 0, the
resistor ladder is unpowered. If 1, the resistor ladder is connected to
the analog VDD.
This bit is reset to 0 so that the internal reference consumes the least
amount of power if not used and programmed.
9 EN R/W 0
Resistor Ladder Range
The RNG bit specifies the range of the resistor ladder. If 0, the resistor
ladder has a total resistance of 31 R. If 1, the resistor ladder has a total
resistance of 23 R.
8 RNG R/W 0
Software should not rely on the value of a reserved bit. To provide
compatibility with future products, the value of a reserved bit should be
preserved across a read-modify-write operation.
7:4 reserved RO 0x00
Resistor Ladder Voltage Ref
The VREF bit field specifies the resistor ladder tap that is passed through
an analog multiplexer. The voltage corresponding to the tap position is
the internal reference voltage available for comparison. See Table
16-1 on page 581 for some output reference voltage examples.
3:0 VREF R/W 0x00
January 08, 2011 587
Texas Instruments-Production Data
Stellaris® LM3S2965 Microcontroller
Register 5: Analog Comparator Status 0 (ACSTAT0), offset 0x020
Register 6: Analog Comparator Status 1 (ACSTAT1), offset 0x040
Register 7: Analog Comparator Status 2 (ACSTAT2), offset 0x060
These registers specify the current output value of the comparator.
Analog Comparator Status 0 (ACSTAT0)
Base 0x4003.C000
Offset 0x020
Type RO, reset 0x0000.0000
31 30 29 28 27 26 25 24 23 22 21 20 19 18 17 16
reserved
Type RO RO RO RO RO RO RO RO RO RO RO RO RO RO RO RO
Reset 0 0 0 0 0 0 0 0 0 0 0 0 0 0 0 0
15 14 13 12 11 10 9 8 7 6 5 4 3 2 1 0
reserved OVAL reserved
Type RO RO RO RO RO RO RO RO RO RO RO RO RO RO RO RO
Reset 0 0 0 0 0 0 0 0 0 0 0 0 0 0 0 0
Bit/Field Name Type Reset Description
Software should not rely on the value of a reserved bit. To provide
compatibility with future products, the value of a reserved bit should be
preserved across a read-modify-write operation.
31:2 reserved RO 0x00
Comparator Output Value
The OVAL bit specifies the current output value of the comparator.
1 OVAL RO 0
Software should not rely on the value of a reserved bit. To provide
compatibility with future products, the value of a reserved bit should be
preserved across a read-modify-write operation.
0 reserved RO 0
588 January 08, 2011
Texas Instruments-Production Data
Analog Comparators
Register 8: Analog Comparator Control 0 (ACCTL0), offset 0x024
Register 9: Analog Comparator Control 1 (ACCTL1), offset 0x044
Register 10: Analog Comparator Control 2 (ACCTL2), offset 0x064
These registers configure the comparator’s input and output.
Analog Comparator Control 0 (ACCTL0)
Base 0x4003.C000
Offset 0x024
Type R/W, reset 0x0000.0000
31 30 29 28 27 26 25 24 23 22 21 20 19 18 17 16
reserved
Type RO RO RO RO RO RO RO RO RO RO RO RO RO RO RO RO
Reset 0 0 0 0 0 0 0 0 0 0 0 0 0 0 0 0
15 14 13 12 11 10 9 8 7 6 5 4 3 2 1 0
reserved TOEN ASRCP reserved TSLVAL TSEN ISLVAL ISEN CINV reserved
Type RO RO RO RO R/W R/W R/W RO R/W R/W R/W R/W R/W R/W R/W RO
Reset 0 0 0 0 0 0 0 0 0 0 0 0 0 0 0 0
Bit/Field Name Type Reset Description
Software should not rely on the value of a reserved bit. To provide
compatibility with future products, the value of a reserved bit should be
preserved across a read-modify-write operation.
31:12 reserved RO 0x00
Trigger Output Enable
The TOEN bit enables the ADC event transmission to the ADC. If 0, the
event is suppressed and not sent to the ADC. If 1, the event is
transmitted to the ADC.
11 TOEN R/W 0
Analog Source Positive
The ASRCP field specifies the source of input voltage to the VIN+ terminal
of the comparator. The encodings for this field are as follows:
Value Function
0x0 Pin value
0x1 Pin value of C0+
0x2 Internal voltage reference
0x3 Reserved
10:9 ASRCP R/W 0x00
Software should not rely on the value of a reserved bit. To provide
compatibility with future products, the value of a reserved bit should be
preserved across a read-modify-write operation.
8 reserved RO 0
Trigger Sense Level Value
The TSLVAL bit specifies the sense value of the input that generates
an ADC event if in Level Sense mode. If 0, an ADC event is generated
if the comparator output is Low. Otherwise, an ADC event is generated
if the comparator output is High.
7 TSLVAL R/W 0
January 08, 2011 589
Texas Instruments-Production Data
Stellaris® LM3S2965 Microcontroller
Bit/Field Name Type Reset Description
Trigger Sense
The TSEN field specifies the sense of the comparator output that
generates an ADC event. The sense conditioning is as follows:
Value Function
0x0 Level sense, see TSLVAL
0x1 Falling edge
0x2 Rising edge
0x3 Either edge
6:5 TSEN R/W 0x0
Interrupt Sense Level Value
The ISLVAL bit specifies the sense value of the input that generates
an interrupt if in Level Sense mode. If 0, an interrupt is generated if the
comparator output is Low. Otherwise, an interrupt is generated if the
comparator output is High.
4 ISLVAL R/W 0
Interrupt Sense
The ISEN field specifies the sense of the comparator output that
generates an interrupt. The sense conditioning is as follows:
Value Function
0x0 Level sense, see ISLVAL
0x1 Falling edge
0x2 Rising edge
0x3 Either edge
3:2 ISEN R/W 0x0
Comparator Output Invert
The CINV bit conditionally inverts the output of the comparator. If 0, the
output of the comparator is unchanged. If 1, the output of the comparator
is inverted prior to being processed by hardware.
1 CINV R/W 0
Software should not rely on the value of a reserved bit. To provide
compatibility with future products, the value of a reserved bit should be
preserved across a read-modify-write operation.
0 reserved RO 0
590 January 08, 2011
Texas Instruments-Production Data
Analog Comparators
17 Pulse Width Modulator (PWM)
Pulse width modulation (PWM) is a powerful technique for digitally encoding analog signal levels.
High-resolution counters are used to generate a square wave, and the duty cycle of the square
wave is modulated to encode an analog signal. Typical applications include switching power supplies
and motor control.
The Stellaris® PWM module consists of three PWM generator blocks and a control block. The control
block determines the polarity of the PWM signals, and which signals are passed through to the pins.
Each PWM generator block produces two PWM signals that can either be independent signals
(other than being based on the same timer and therefore having the same frequency) or a single
pair of complementary signals with dead-band delays inserted. The output of the PWM generation
blocks are managed by the output control block before being passed to the device pins.
The Stellaris PWM module provides a great deal of flexibility. It can generate simple PWM signals,
such as those required by a simple charge pump. It can also generate paired PWM signals with
dead-band delays, such as those required by a half-H bridge driver. Three generator blocks can
also generate the full six channels of gate controls required by a 3-phase inverter bridge.
Each Stellaris PWM module has the following features:
■ Three PWM generator blocks, each with one 16-bit counter, two PWM comparators, a PWM
signal generator, a dead-band generator, and an interrupt/ADC-trigger selector
■ One fault input in hardware to promote low-latency shutdown
■ One 16-bit counter
– Runs in Down or Up/Down mode
– Output frequency controlled by a 16-bit load value
– Load value updates can be synchronized
– Produces output signals at zero and load value
■ Two PWM comparators
– Comparator value updates can be synchronized
– Produces output signals on match
■ PWM generator
– Output PWM signal is constructed based on actions taken as a result of the counter and
PWM comparator output signals
– Produces two independent PWM signals
■ Dead-band generator
– Produces two PWM signals with programmable dead-band delays suitable for driving a half-H
bridge
– Can be bypassed, leaving input PWM signals unmodified
January 08, 2011 591
Texas Instruments-Production Data
Stellaris® LM3S2965 Microcontroller
■ Flexible output control block with PWM output enable of each PWM signal
– PWM output enable of each PWM signal
– Optional output inversion of each PWM signal (polarity control)
– Optional fault handling for each PWM signal
– Synchronization of timers in the PWM generator blocks
– Synchronization of timer/comparator updates across the PWM generator blocks
– Interrupt status summary of the PWM generator blocks
■ Can initiate an ADC sample sequence
17.1 Block Diagram
Figure 17-1 on page 592 provides the Stellaris PWM module unit diagram and Figure 17-2 on page 593
provides a more detailed diagram of a Stellaris PWM generator. The LM3S2965 controller contains
three generator blocks (PWM0, PWM1, and PWM2) and generates six independent PWM signals
or three paired PWM signals with dead-band delays inserted.
Figure 17-1. PWM Unit Diagram
PWMINTEN
Interrupt
PWMRIS
PWMISC
PWMCTL
Control and
Status
PWMSYNC
PWMSTATUS
PWM
Generator 0
PWM
Generator 1
PWM
Generator 2
PWM 0
PWM 1
PWM 2
PWM 3
PWM 4
PWM 5
PWM
Output
Control
Logic
PWM Clock
System Clock
Interrupts
Triggers
PWM0_A
PWM0_B
PWM1_A
PWM1_B
PWM2_A
PWM2_B
PWM0_Fault
PWM1_Fault
PWM2_Fault
Fault
PWMENABLE
Output
PWMINVERT
PWMFAULT
592 January 08, 2011
Texas Instruments-Production Data
Pulse Width Modulator (PWM)
Figure 17-2. PWM Module Block Diagram
PWMnCMPA
Comparators
PWMnCMPB
PWMnLOAD
Timer
PWMnCOUNT
PWMnDBCTL
Dead-Band
Generator
PWMnDBRISE
PWMnDBFALL
PWMnCTL
Control
PWM Clock
PWM Generator Block
Signal
Generator
PWMnGENA
PWMnGENB
PWMnINTEN
Interrupt and
Trigger
Generator
PWMnRIS
PWMnISC
Fault(s)
PWMn_A
PWMn_B
Interrupts /
Triggers
PWMn_Fault
cmp A
cmp B
zero
load
dir
PWMnFLTSRC0
Fault
Condition
PWMnMINFLTPER
PWMnFLTSEN
PWMnFLTSTAT0
17.2 Functional Description
17.2.1 PWM Timer
The timer in each PWM generator runs in one of two modes: Count-Down mode or Count-Up/Down
mode. In Count-Down mode, the timer counts from the load value to zero, goes back to the load
value, and continues counting down. In Count-Up/Down mode, the timer counts from zero up to the
load value, back down to zero, back up to the load value, and so on. Generally, Count-Down mode
is used for generating left- or right-aligned PWM signals, while the Count-Up/Down mode is used
for generating center-aligned PWM signals.
The timers output three signals that are used in the PWM generation process: the direction signal
(this is always Low in Count-Down mode, but alternates between Low and High in Count-Up/Down
mode), a single-clock-cycle-width High pulse when the counter is zero, and a single-clock-cycle-width
High pulse when the counter is equal to the load value. Note that in Count-Down mode, the zero
pulse is immediately followed by the load pulse.
17.2.2 PWM Comparators
There are two comparators in each PWM generator that monitor the value of the counter; when
either match the counter, they output a single-clock-cycle-width High pulse. When in Count-Up/Down
mode, these comparators match both when counting up and when counting down; they are therefore
qualified by the counter direction signal. These qualified pulses are used in the PWM generation
process. If either comparator match value is greater than the counter load value, then that comparator
never outputs a High pulse.
Figure 17-3 on page 594 shows the behavior of the counter and the relationship of these pulses
when the counter is in Count-Down mode. Figure 17-4 on page 594 shows the behavior of the counter
and the relationship of these pulses when the counter is in Count-Up/Down mode.
January 08, 2011 593
Texas Instruments-Production Data
Stellaris® LM3S2965 Microcontroller
Figure 17-3. PWM Count-Down Mode
Load
Zero
CompB
CompA
Load
Zero
B
A
Dir
ADown
BDown
Figure 17-4. PWM Count-Up/Down Mode
Load
Zero
CompB
CompA
Load
Zero
B
A
Dir
BUp
AUp ADown
BDown
17.2.3 PWM Signal Generator
The PWM generator takes these pulses (qualified by the direction signal), and generates two PWM
signals. In Count-Down mode, there are four events that can affect the PWM signal: zero, load,
match A down, and match B down. In Count-Up/Down mode, there are six events that can affect
the PWM signal: zero, load, match A down, match A up, match B down, and match B up. The match
A or match B events are ignored when they coincide with the zero or load events. If the match A
and match B events coincide, the first signal, PWMA, is generated based only on the match A event,
and the second signal, PWMB, is generated based only on the match B event.
For each event, the effect on each output PWM signal is programmable: it can be left alone (ignoring
the event), it can be toggled, it can be driven Low, or it can be driven High. These actions can be
used to generate a pair of PWM signals of various positions and duty cycles, which do or do not
overlap. Figure 17-5 on page 595 shows the use of Count-Up/Down mode to generate a pair of
center-aligned, overlapped PWM signals that have different duty cycles.
594 January 08, 2011
Texas Instruments-Production Data
Pulse Width Modulator (PWM)
Figure 17-5. PWM Generation Example In Count-Up/Down Mode
Load
Zero
CompB
CompA
PWMB
PWMA
In this example, the first generator is set to drive High on match A up, drive Low on match A down,
and ignore the other four events. The second generator is set to drive High on match B up, drive
Low on match B down, and ignore the other four events. Changing the value of comparator A
changes the duty cycle of the PWMA signal, and changing the value of comparator B changes the
duty cycle of the PWMB signal.
17.2.4 Dead-Band Generator
The two PWM signals produced by the PWM generator are passed to the dead-band generator. If
disabled, the PWM signals simply pass through unmodified. If enabled, the second PWM signal is
lost and two PWM signals are generated based on the first PWM signal. The first output PWM signal
is the input signal with the rising edge delayed by a programmable amount. The second output
PWM signal is the inversion of the input signal with a programmable delay added between the falling
edge of the input signal and the rising edge of this new signal.
This is therefore a pair of active High signals where one is always High, except for a programmable
amount of time at transitions where both are Low. These signals are therefore suitable for driving
a half-H bridge, with the dead-band delays preventing shoot-through current from damaging the
power electronics. Figure 17-6 on page 595 shows the effect of the dead-band generator on an input
PWM signal.
Figure 17-6. PWM Dead-Band Generator
Input
PWMA
PWMB
Rising Edge
Delay
Falling Edge
Delay
17.2.5 Interrupt/ADC-Trigger Selector
The PWM generator also takes the same four (or six) counter events and uses them to generate
an interrupt or an ADC trigger. Any of these events or a set of these events can be selected as a
source for an interrupt; when any of the selected events occur, an interrupt is generated. Additionally,
the same event, a different event, the same set of events, or a different set of events can be selected
as a source for an ADC trigger; when any of these selected events occur, an ADC trigger pulse is
generated. The selection of events allows the interrupt or ADC trigger to occur at a specific position
within the PWM signal. Note that interrupts and ADC triggers are based on the raw events; delays
in the PWM signal edges caused by the dead-band generator are not taken into account.
January 08, 2011 595
Texas Instruments-Production Data
Stellaris® LM3S2965 Microcontroller
17.2.6 Synchronization Methods
There is a global reset capability that can synchronously reset any or all of the counters in the PWM
generators. If multiple PWM generators are configured with the same counter load value, this can
be used to guarantee that they also have the same count value (this does imply that the PWM
generators must be configured before they are synchronized). With this, more than two PWM signals
can be produced with a known relationship between the edges of those signals since the counters
always have the same values.
The counter load values and comparator match values of the PWM generator can be updated in
two ways. The first is immediate update mode, where a new value is used as soon as the counter
reaches zero. By waiting for the counter to reach zero, a guaranteed behavior is defined, and overly
short or overly long output PWM pulses are prevented.
The other update method is synchronous, where the new value is not used until a global synchronized
update signal is asserted, at which point the new value is used as soon as the counter reaches
zero. This second mode allows multiple items in multiple PWM generators to be updated
simultaneously without odd effects during the update; everything runs from the old values until a
point at which they all run from the new values. The Update mode of the load and comparator match
values can be individually configured in each PWM generator block. It typically makes sense to use
the synchronous update mechanism across PWM generator blocks when the timers in those blocks
are synchronized, though this is not required in order for this mechanism to function properly.
17.2.7 Fault Conditions
There are two external conditions that affect the PWM block; the signal input on the Fault pin and
the stalling of the controller by a debugger. There are two mechanisms available to handle such
conditions: the output signals can be forced into an inactive state and/or the PWM timers can be
stopped.
Each output signal has a fault bit. If set, a fault input signal causes the corresponding output signal
to go into the inactive state. If the inactive state is a safe condition for the signal to be in for an
extended period of time, this keeps the output signal from driving the outside world in a dangerous
manner during the fault condition. A fault condition can also generate a controller interrupt.
Each PWM generator can also be configured to stop counting during a stall condition. The user can
select for the counters to run until they reach zero then stop, or to continue counting and reloading.
A stall condition does not generate a controller interrupt.
17.2.8 Output Control Block
With each PWM generator block producing two raw PWM signals, the output control block takes
care of the final conditioning of the PWM signals before they go to the pins. Via a single register,
the set of PWM signals that are actually enabled to the pins can be modified; this can be used, for
example, to perform commutation of a brushless DC motor with a single register write (and without
modifying the individual PWM generators, which are modified by the feedback control loop). Similarly,
fault control can disable any of the PWM signals as well. A final inversion can be applied to any of
the PWM signals, making them active Low instead of the default active High.
17.3 Initialization and Configuration
The following example shows how to initialize the PWM Generator 0 with a 25-KHz frequency, and
with a 25% duty cycle on the PWM0 pin and a 75% duty cycle on the PWM1 pin. This example assumes
the system clock is 20 MHz.
596 January 08, 2011
Texas Instruments-Production Data
Pulse Width Modulator (PWM)
1. Enable the PWM clock by writing a value of 0x0010.0000 to the RCGC0 register in the System
Control module.
2. Enable the clock to the appropriate GPIO module via the RCGC2 register in the System Control
module.
3. In the GPIO module, enable the appropriate pins for their alternate function using the
GPIOAFSEL register.
4. Configure the Run-Mode Clock Configuration (RCC) register in the System Control module
to use the PWM divide (USEPWMDIV) and set the divider (PWMDIV) to divide by 2 (000).
5. Configure the PWM generator for countdown mode with immediate updates to the parameters.
■ Write the PWM0CTL register with a value of 0x0000.0000.
■ Write the PWM0GENA register with a value of 0x0000.008C.
■ Write the PWM0GENB register with a value of 0x0000.080C.
6. Set the period. For a 25-KHz frequency, the period = 1/25,000, or 40 microseconds. The PWM
clock source is 10 MHz; the system clock divided by 2. This translates to 400 clock ticks per
period. Use this value to set the PWM0LOAD register. In Count-Down mode, set the Load field
in the PWM0LOAD register to the requested period minus one.
■ Write the PWM0LOAD register with a value of 0x0000.018F.
7. Set the pulse width of the PWM0 pin for a 25% duty cycle.
■ Write the PWM0CMPA register with a value of 0x0000.012B.
8. Set the pulse width of the PWM1 pin for a 75% duty cycle.
■ Write the PWM0CMPB register with a value of 0x0000.0063.
9. Start the timers in PWM generator 0.
■ Write the PWM0CTL register with a value of 0x0000.0001.
10. Enable PWM outputs.
■ Write the PWMENABLE register with a value of 0x0000.0003.
17.4 Register Map
Table 17-1 on page 598 lists the PWM registers. The offset listed is a hexadecimal increment to the
register’s address, relative to the PWM base address of 0x4002.8000. Note that the PWM module
clock must be enabled before the registers can be programmed (see page 210). There must be a
delay of 3 system clocks after the PWM module clock is enabled before any PWM module registers
are accessed.
January 08, 2011 597
Texas Instruments-Production Data
Stellaris® LM3S2965 Microcontroller
Table 17-1. PWM Register Map
See
Offset Name Type Reset Description page
0x000 PWMCTL R/W 0x0000.0000 PWM Master Control 600
0x004 PWMSYNC R/W 0x0000.0000 PWM Time Base Sync 601
0x008 PWMENABLE R/W 0x0000.0000 PWM Output Enable 602
0x00C PWMINVERT R/W 0x0000.0000 PWM Output Inversion 603
0x010 PWMFAULT R/W 0x0000.0000 PWM Output Fault 604
0x014 PWMINTEN R/W 0x0000.0000 PWM Interrupt Enable 605
0x018 PWMRIS RO 0x0000.0000 PWM Raw Interrupt Status 606
0x01C PWMISC R/W1C 0x0000.0000 PWM Interrupt Status and Clear 607
0x020 PWMSTATUS RO 0x0000.0000 PWM Status 608
0x040 PWM0CTL R/W 0x0000.0000 PWM0 Control 609
0x044 PWM0INTEN R/W 0x0000.0000 PWM0 Interrupt and Trigger Enable 611
0x048 PWM0RIS RO 0x0000.0000 PWM0 Raw Interrupt Status 614
0x04C PWM0ISC R/W1C 0x0000.0000 PWM0 Interrupt Status and Clear 615
0x050 PWM0LOAD R/W 0x0000.0000 PWM0 Load 616
0x054 PWM0COUNT RO 0x0000.0000 PWM0 Counter 617
0x058 PWM0CMPA R/W 0x0000.0000 PWM0 Compare A 618
0x05C PWM0CMPB R/W 0x0000.0000 PWM0 Compare B 619
0x060 PWM0GENA R/W 0x0000.0000 PWM0 Generator A Control 620
0x064 PWM0GENB R/W 0x0000.0000 PWM0 Generator B Control 623
0x068 PWM0DBCTL R/W 0x0000.0000 PWM0 Dead-Band Control 626
0x06C PWM0DBRISE R/W 0x0000.0000 PWM0 Dead-Band Rising-Edge Delay 627
0x070 PWM0DBFALL R/W 0x0000.0000 PWM0 Dead-Band Falling-Edge-Delay 628
0x080 PWM1CTL R/W 0x0000.0000 PWM1 Control 609
0x084 PWM1INTEN R/W 0x0000.0000 PWM1 Interrupt and Trigger Enable 611
0x088 PWM1RIS RO 0x0000.0000 PWM1 Raw Interrupt Status 614
0x08C PWM1ISC R/W1C 0x0000.0000 PWM1 Interrupt Status and Clear 615
0x090 PWM1LOAD R/W 0x0000.0000 PWM1 Load 616
0x094 PWM1COUNT RO 0x0000.0000 PWM1 Counter 617
0x098 PWM1CMPA R/W 0x0000.0000 PWM1 Compare A 618
0x09C PWM1CMPB R/W 0x0000.0000 PWM1 Compare B 619
0x0A0 PWM1GENA R/W 0x0000.0000 PWM1 Generator A Control 620
0x0A4 PWM1GENB R/W 0x0000.0000 PWM1 Generator B Control 623
598 January 08, 2011
Texas Instruments-Production Data
Pulse Width Modulator (PWM)
Table 17-1. PWM Register Map (continued)
See
Offset Name Type Reset Description page
0x0A8 PWM1DBCTL R/W 0x0000.0000 PWM1 Dead-Band Control 626
0x0AC PWM1DBRISE R/W 0x0000.0000 PWM1 Dead-Band Rising-Edge Delay 627
0x0B0 PWM1DBFALL R/W 0x0000.0000 PWM1 Dead-Band Falling-Edge-Delay 628
0x0C0 PWM2CTL R/W 0x0000.0000 PWM2 Control 609
0x0C4 PWM2INTEN R/W 0x0000.0000 PWM2 Interrupt and Trigger Enable 611
0x0C8 PWM2RIS RO 0x0000.0000 PWM2 Raw Interrupt Status 614
0x0CC PWM2ISC R/W1C 0x0000.0000 PWM2 Interrupt Status and Clear 615
0x0D0 PWM2LOAD R/W 0x0000.0000 PWM2 Load 616
0x0D4 PWM2COUNT RO 0x0000.0000 PWM2 Counter 617
0x0D8 PWM2CMPA R/W 0x0000.0000 PWM2 Compare A 618
0x0DC PWM2CMPB R/W 0x0000.0000 PWM2 Compare B 619
0x0E0 PWM2GENA R/W 0x0000.0000 PWM2 Generator A Control 620
0x0E4 PWM2GENB R/W 0x0000.0000 PWM2 Generator B Control 623
0x0E8 PWM2DBCTL R/W 0x0000.0000 PWM2 Dead-Band Control 626
0x0EC PWM2DBRISE R/W 0x0000.0000 PWM2 Dead-Band Rising-Edge Delay 627
0x0F0 PWM2DBFALL R/W 0x0000.0000 PWM2 Dead-Band Falling-Edge-Delay 628
17.5 Register Descriptions
The remainder of this section lists and describes the PWM registers, in numerical order by address
offset.
January 08, 2011 599
Texas Instruments-Production Data
Stellaris® LM3S2965 Microcontroller
Register 1: PWM Master Control (PWMCTL), offset 0x000
This register provides master control over the PWM generation blocks.
PWM Master Control (PWMCTL)
Base 0x4002.8000
Offset 0x000
Type R/W, reset 0x0000.0000
31 30 29 28 27 26 25 24 23 22 21 20 19 18 17 16
reserved
Type RO RO RO RO RO RO RO RO RO RO RO RO RO RO RO RO
Reset 0 0 0 0 0 0 0 0 0 0 0 0 0 0 0 0
15 14 13 12 11 10 9 8 7 6 5 4 3 2 1 0
reserved GlobalSync2 GlobalSync1 GlobalSync0
Type RO RO RO RO RO RO RO RO RO RO RO RO RO R/W R/W R/W
Reset 0 0 0 0 0 0 0 0 0 0 0 0 0 0 0 0
Bit/Field Name Type Reset Description
Software should not rely on the value of a reserved bit. To provide
compatibility with future products, the value of a reserved bit should be
preserved across a read-modify-write operation.
31:3 reserved RO 0x00
Update PWM Generator 2
Same as GlobalSync0 but for PWM generator 2.
2 GlobalSync2 R/W 0
Update PWM Generator 1
Same as GlobalSync0 but for PWM generator 1.
1 GlobalSync1 R/W 0
Update PWM Generator 0
Setting this bit causes any queued update to a load or comparator
register in PWM generator 0 to be applied the next time the
corresponding counter becomes zero. This bit automatically clears when
the updates have completed; it cannot be cleared by software.
0 GlobalSync0 R/W 0
600 January 08, 2011
Texas Instruments-Production Data
Pulse Width Modulator (PWM)
Register 2: PWM Time Base Sync (PWMSYNC), offset 0x004
This register provides a method to perform synchronization of the counters in the PWM generation
blocks. Writing a bit in this register to 1 causes the specified counter to reset back to 0; writing
multiple bits resets multiple counters simultaneously. The bits auto-clear after the reset has occurred;
reading them back as zero indicates that the synchronization has completed.
PWM Time Base Sync (PWMSYNC)
Base 0x4002.8000
Offset 0x004
Type R/W, reset 0x0000.0000
31 30 29 28 27 26 25 24 23 22 21 20 19 18 17 16
reserved
Type RO RO RO RO RO RO RO RO RO RO RO RO RO RO RO RO
Reset 0 0 0 0 0 0 0 0 0 0 0 0 0 0 0 0
15 14 13 12 11 10 9 8 7 6 5 4 3 2 1 0
reserved Sync2 Sync1 Sync0
Type RO RO RO RO RO RO RO RO RO RO RO RO RO R/W R/W R/W
Reset 0 0 0 0 0 0 0 0 0 0 0 0 0 0 0 0
Bit/Field Name Type Reset Description
Software should not rely on the value of a reserved bit. To provide
compatibility with future products, the value of a reserved bit should be
preserved across a read-modify-write operation.
31:3 reserved RO 0x00
Reset Generator 2 Counter
Performs a reset of the PWM generator 2 counter.
2 Sync2 R/W 0
Reset Generator 1 Counter
Performs a reset of the PWM generator 1 counter.
1 Sync1 R/W 0
Reset Generator 0 Counter
Performs a reset of the PWM generator 0 counter.
0 Sync0 R/W 0
January 08, 2011 601
Texas Instruments-Production Data
Stellaris® LM3S2965 Microcontroller
Register 3: PWM Output Enable (PWMENABLE), offset 0x008
This register provides a master control of which generated PWM signals are output to device pins.
By disabling a PWM output, the generation process can continue (for example, when the time bases
are synchronized) without driving PWM signals to the pins. When bits in this register are set, the
corresponding PWM signal is passed through to the output stage, which is controlled by the
PWMINVERT register. When bits are not set, the PWM signal is replaced by a zero value which is
also passed to the output stage.
PWM Output Enable (PWMENABLE)
Base 0x4002.8000
Offset 0x008
Type R/W, reset 0x0000.0000
31 30 29 28 27 26 25 24 23 22 21 20 19 18 17 16
reserved
Type RO RO RO RO RO RO RO RO RO RO RO RO RO RO RO RO
Reset 0 0 0 0 0 0 0 0 0 0 0 0 0 0 0 0
15 14 13 12 11 10 9 8 7 6 5 4 3 2 1 0
reserved PWM5En PWM4En PWM3En PWM2En PWM1En PWM0En
Type RO RO RO RO RO RO RO RO RO RO R/W R/W R/W R/W R/W R/W
Reset 0 0 0 0 0 0 0 0 0 0 0 0 0 0 0 0
Bit/Field Name Type Reset Description
Software should not rely on the value of a reserved bit. To provide
compatibility with future products, the value of a reserved bit should be
preserved across a read-modify-write operation.
31:6 reserved RO 0x00
PWM5 Output Enable
When set, allows the generated PWM5 signal to be passed to the device
pin.
5 PWM5En R/W 0
PWM4 Output Enable
When set, allows the generated PWM4 signal to be passed to the device
pin.
4 PWM4En R/W 0
PWM3 Output Enable
When set, allows the generated PWM3 signal to be passed to the device
pin.
3 PWM3En R/W 0
PWM2 Output Enable
When set, allows the generated PWM2 signal to be passed to the device
pin.
2 PWM2En R/W 0
PWM1 Output Enable
When set, allows the generated PWM1 signal to be passed to the device
pin.
1 PWM1En R/W 0
PWM0 Output Enable
When set, allows the generated PWM0 signal to be passed to the device
pin.
0 PWM0En R/W 0
602 January 08, 2011
Texas Instruments-Production Data
Pulse Width Modulator (PWM)
Register 4: PWM Output Inversion (PWMINVERT), offset 0x00C
This register provides a master control of the polarity of the PWM signals on the device pins. The
PWM signals generated by the PWM generator are active High; they can optionally be made active
Low via this register. Disabled PWM channels are also passed through the output inverter (if so
configured) so that inactive channels maintain the correct polarity.
PWM Output Inversion (PWMINVERT)
Base 0x4002.8000
Offset 0x00C
Type R/W, reset 0x0000.0000
31 30 29 28 27 26 25 24 23 22 21 20 19 18 17 16
reserved
Type RO RO RO RO RO RO RO RO RO RO RO RO RO RO RO RO
Reset 0 0 0 0 0 0 0 0 0 0 0 0 0 0 0 0
15 14 13 12 11 10 9 8 7 6 5 4 3 2 1 0
reserved PWM5Inv PWM4Inv PWM3Inv PWM2Inv PWM1Inv PWM0Inv
Type RO RO RO RO RO RO RO RO RO RO R/W R/W R/W R/W R/W R/W
Reset 0 0 0 0 0 0 0 0 0 0 0 0 0 0 0 0
Bit/Field Name Type Reset Description
Software should not rely on the value of a reserved bit. To provide
compatibility with future products, the value of a reserved bit should be
preserved across a read-modify-write operation.
31:6 reserved RO 0x00
Invert PWM5 Signal
When set, the generated PWM5 signal is inverted.
5 PWM5Inv R/W 0
Invert PWM4 Signal
When set, the generated PWM4 signal is inverted.
4 PWM4Inv R/W 0
Invert PWM3 Signal
When set, the generated PWM3 signal is inverted.
3 PWM3Inv R/W 0
Invert PWM2 Signal
When set, the generated PWM2 signal is inverted.
2 PWM2Inv R/W 0
Invert PWM1 Signal
When set, the generated PWM1 signal is inverted.
1 PWM1Inv R/W 0
Invert PWM0 Signal
When set, the generated PWM0 signal is inverted.
0 PWM0Inv R/W 0
January 08, 2011 603
Texas Instruments-Production Data
Stellaris® LM3S2965 Microcontroller
Register 5: PWM Output Fault (PWMFAULT), offset 0x010
This register controls the behavior of the PWM outputs in the presence of fault conditions. Both the
fault inputs and debug events are considered fault conditions. On a fault condition, each PWM signal
can be passed through unmodified or driven Low. For outputs that are configured for pass-through,
the debug event handling on the corresponding PWM generator also determines if the PWM signal
continues to be generated.
Fault condition control occurs before the output inverter, so PWM signals driven Low on fault are
inverted if the channel is configured for inversion (therefore, the pin is driven High on a fault condition).
PWM Output Fault (PWMFAULT)
Base 0x4002.8000
Offset 0x010
Type R/W, reset 0x0000.0000
31 30 29 28 27 26 25 24 23 22 21 20 19 18 17 16
reserved
Type RO RO RO RO RO RO RO RO RO RO RO RO RO RO RO RO
Reset 0 0 0 0 0 0 0 0 0 0 0 0 0 0 0 0
15 14 13 12 11 10 9 8 7 6 5 4 3 2 1 0
reserved Fault5 Fault4 Fault3 Fault2 Fault1 Fault0
Type RO RO RO RO RO RO RO RO RO RO R/W R/W R/W R/W R/W R/W
Reset 0 0 0 0 0 0 0 0 0 0 0 0 0 0 0 0
Bit/Field Name Type Reset Description
Software should not rely on the value of a reserved bit. To provide
compatibility with future products, the value of a reserved bit should be
preserved across a read-modify-write operation.
31:6 reserved RO 0x00
PWM5 Fault
When set, the PWM5 output signal is driven Low on a fault condition.
5 Fault5 R/W 0
PWM4 Fault
When set, the PWM4 output signal is driven Low on a fault condition.
4 Fault4 R/W 0
PWM3 Fault
When set, the PWM3 output signal is driven Low on a fault condition.
3 Fault3 R/W 0
PWM2 Fault
When set, the PWM2 output signal is driven Low on a fault condition.
2 Fault2 R/W 0
PWM1 Fault
When set, the PWM1 output signal is driven Low on a fault condition.
1 Fault1 R/W 0
PWM0 Fault
When set, the PWM0 output signal is driven Low on a fault condition.
0 Fault0 R/W 0
604 January 08, 2011
Texas Instruments-Production Data
Pulse Width Modulator (PWM)
Register 6: PWM Interrupt Enable (PWMINTEN), offset 0x014
This register controls the global interrupt generation capabilities of the PWM module. The events
that can cause an interrupt are the fault input and the individual interrupts from the PWM generators.
PWM Interrupt Enable (PWMINTEN)
Base 0x4002.8000
Offset 0x014
Type R/W, reset 0x0000.0000
31 30 29 28 27 26 25 24 23 22 21 20 19 18 17 16
reserved IntFault
Type RO RO RO RO RO RO RO RO RO RO RO RO RO RO RO R/W
Reset 0 0 0 0 0 0 0 0 0 0 0 0 0 0 0 0
15 14 13 12 11 10 9 8 7 6 5 4 3 2 1 0
reserved IntPWM2 IntPWM1 IntPWM0
Type RO RO RO RO RO RO RO RO RO RO RO RO RO R/W R/W R/W
Reset 0 0 0 0 0 0 0 0 0 0 0 0 0 0 0 0
Bit/Field Name Type Reset Description
Software should not rely on the value of a reserved bit. To provide
compatibility with future products, the value of a reserved bit should be
preserved across a read-modify-write operation.
31:17 reserved RO 0x00
Fault Interrupt Enable
When set, an interrupt occurs when the fault input is asserted.
16 IntFault R/W 0
Software should not rely on the value of a reserved bit. To provide
compatibility with future products, the value of a reserved bit should be
preserved across a read-modify-write operation.
15:3 reserved RO 0x00
PWM2 Interrupt Enable
When set, an interrupt occurs when the PWM generator 2 block asserts
an interrupt.
2 IntPWM2 R/W 0
PWM1 Interrupt Enable
When set, an interrupt occurs when the PWM generator 1 block asserts
an interrupt.
1 IntPWM1 R/W 0
PWM0 Interrupt Enable
When set, an interrupt occurs when the PWM generator 0 block asserts
an interrupt.
0 IntPWM0 R/W 0
January 08, 2011 605
Texas Instruments-Production Data
Stellaris® LM3S2965 Microcontroller
Register 7: PWM Raw Interrupt Status (PWMRIS), offset 0x018
This register provides the current set of interrupt sources that are asserted, regardless of whether
they cause an interrupt to be asserted to the controller. The fault interrupt is latched on detection;
it must be cleared through the PWM Interrupt Status and Clear (PWMISC) register (see page 607).
The PWM generator interrupts simply reflect the status of the PWM generators; they are cleared
via the interrupt status register in the PWM generator blocks. Bits set to 1 indicate the events that
are active; zero bits indicate that the event in question is not active.
PWM Raw Interrupt Status (PWMRIS)
Base 0x4002.8000
Offset 0x018
Type RO, reset 0x0000.0000
31 30 29 28 27 26 25 24 23 22 21 20 19 18 17 16
reserved IntFault
Type RO RO RO RO RO RO RO RO RO RO RO RO RO RO RO RO
Reset 0 0 0 0 0 0 0 0 0 0 0 0 0 0 0 0
15 14 13 12 11 10 9 8 7 6 5 4 3 2 1 0
reserved IntPWM2 IntPWM1 IntPWM0
Type RO RO RO RO RO RO RO RO RO RO RO RO RO RO RO RO
Reset 0 0 0 0 0 0 0 0 0 0 0 0 0 0 0 0
Bit/Field Name Type Reset Description
Software should not rely on the value of a reserved bit. To provide
compatibility with future products, the value of a reserved bit should be
preserved across a read-modify-write operation.
31:17 reserved RO 0x00
Fault Interrupt Asserted
Indicates that the fault input is asserting.
16 IntFault RO 0
Software should not rely on the value of a reserved bit. To provide
compatibility with future products, the value of a reserved bit should be
preserved across a read-modify-write operation.
15:3 reserved RO 0x00
PWM2 Interrupt Asserted
Indicates that the PWM generator 2 block is asserting its interrupt.
2 IntPWM2 RO 0
PWM1 Interrupt Asserted
Indicates that the PWM generator 1 block is asserting its interrupt.
1 IntPWM1 RO 0
PWM0 Interrupt Asserted
Indicates that the PWM generator 0 block is asserting its interrupt.
0 IntPWM0 RO 0
606 January 08, 2011
Texas Instruments-Production Data
Pulse Width Modulator (PWM)
Register 8: PWM Interrupt Status and Clear (PWMISC), offset 0x01C
This register provides a summary of the interrupt status of the individual PWM generator blocks. A
bit set to 1 indicates that the corresponding generator block is asserting an interrupt. The individual
interrupt status registers in each block must be consulted to determine the reason for the interrupt,
and used to clear the interrupt. For the fault interrupt, a write of 1 to that bit position clears the latched
interrupt status.
PWM Interrupt Status and Clear (PWMISC)
Base 0x4002.8000
Offset 0x01C
Type R/W1C, reset 0x0000.0000
31 30 29 28 27 26 25 24 23 22 21 20 19 18 17 16
reserved IntFault
Type RO RO RO RO RO RO RO RO RO RO RO RO RO RO RO R/W1C
Reset 0 0 0 0 0 0 0 0 0 0 0 0 0 0 0 0
15 14 13 12 11 10 9 8 7 6 5 4 3 2 1 0
reserved IntPWM2 IntPWM1 IntPWM0
Type RO RO RO RO RO RO RO RO RO RO RO RO RO RO RO RO
Reset 0 0 0 0 0 0 0 0 0 0 0 0 0 0 0 0
Bit/Field Name Type Reset Description
Software should not rely on the value of a reserved bit. To provide
compatibility with future products, the value of a reserved bit should be
preserved across a read-modify-write operation.
31:17 reserved RO 0x00
Fault Interrupt Asserted
Indicates that the fault input is asserting an interrupt.
16 IntFault R/W1C 0
Software should not rely on the value of a reserved bit. To provide
compatibility with future products, the value of a reserved bit should be
preserved across a read-modify-write operation.
15:3 reserved RO 0x00
PWM2 Interrupt Status
Indicates if the PWM generator 2 block is asserting an interrupt.
2 IntPWM2 RO 0
PWM1 Interrupt Status
Indicates if the PWM generator 1 block is asserting an interrupt.
1 IntPWM1 RO 0
PWM0 Interrupt Status
Indicates if the PWM generator 0 block is asserting an interrupt.
0 IntPWM0 RO 0
January 08, 2011 607
Texas Instruments-Production Data
Stellaris® LM3S2965 Microcontroller
Register 9: PWM Status (PWMSTATUS), offset 0x020
This register provides the status of the FAULT input signal.
PWM Status (PWMSTATUS)
Base 0x4002.8000
Offset 0x020
Type RO, reset 0x0000.0000
31 30 29 28 27 26 25 24 23 22 21 20 19 18 17 16
reserved
Type RO RO RO RO RO RO RO RO RO RO RO RO RO RO RO RO
Reset 0 0 0 0 0 0 0 0 0 0 0 0 0 0 0 0
15 14 13 12 11 10 9 8 7 6 5 4 3 2 1 0
reserved Fault
Type RO RO RO RO RO RO RO RO RO RO RO RO RO RO RO RO
Reset 0 0 0 0 0 0 0 0 0 0 0 0 0 0 0 0
Bit/Field Name Type Reset Description
Software should not rely on the value of a reserved bit. To provide
compatibility with future products, the value of a reserved bit should be
preserved across a read-modify-write operation.
31:1 reserved RO 0x00
Fault Interrupt Status
When set, indicates the fault input is asserted.
0 Fault RO 0
608 January 08, 2011
Texas Instruments-Production Data
Pulse Width Modulator (PWM)
Register 10: PWM0 Control (PWM0CTL), offset 0x040
Register 11: PWM1 Control (PWM1CTL), offset 0x080
Register 12: PWM2 Control (PWM2CTL), offset 0x0C0
These registers configure the PWM signal generation blocks (PWM0CTL controls the PWM generator
0 block, and so on). The Register Update mode, Debug mode, Counting mode, and Block Enable
mode are all controlled via these registers. The blocks produce the PWM signals, which can be
either two independent PWM signals (from the same counter), or a paired set of PWM signals with
dead-band delays added.
The PWM0 block produces the PWM0 and PWM1 outputs, the PWM1 block produces the PWM2 and
PWM3 outputs, and the PWM2 block produces the PWM4 and PWM5 outputs.
PWM0 Control (PWM0CTL)
Base 0x4002.8000
Offset 0x040
Type R/W, reset 0x0000.0000
31 30 29 28 27 26 25 24 23 22 21 20 19 18 17 16
reserved
Type RO RO RO RO RO RO RO RO RO RO RO RO RO RO RO RO
Reset 0 0 0 0 0 0 0 0 0 0 0 0 0 0 0 0
15 14 13 12 11 10 9 8 7 6 5 4 3 2 1 0
reserved CmpBUpd CmpAUpd LoadUpd Debug Mode Enable
Type RO RO RO RO RO RO RO RO RO RO R/W R/W R/W R/W R/W R/W
Reset 0 0 0 0 0 0 0 0 0 0 0 0 0 0 0 0
Bit/Field Name Type Reset Description
Software should not rely on the value of a reserved bit. To provide
compatibility with future products, the value of a reserved bit should be
preserved across a read-modify-write operation.
31:6 reserved RO 0x00
Comparator B Update Mode
Same as CmpAUpd but for the comparator B register.
5 CmpBUpd R/W 0
Comparator A Update Mode
The Update mode for the comparator A register. When not set, updates
to the register are reflected to the comparator the next time the counter
is 0. When set, updates to the register are delayed until the next time
the counter is 0 after a synchronous update has been requested through
the PWM Master Control (PWMCTL) register (see page 600).
4 CmpAUpd R/W 0
Load Register Update Mode
The Update mode for the load register. When not set, updates to the
register are reflected to the counter the next time the counter is 0. When
set, updates to the register are delayed until the next time the counter
is 0 after a synchronous update has been requested through the PWM
Master Control (PWMCTL) register.
3 LoadUpd R/W 0
Debug Mode
The behavior of the counter in Debug mode. When not set, the counter
stops running when it next reaches 0, and continues running again when
no longer in Debug mode. When set, the counter always runs.
2 Debug R/W 0
January 08, 2011 609
Texas Instruments-Production Data
Stellaris® LM3S2965 Microcontroller
Bit/Field Name Type Reset Description
Counter Mode
The mode for the counter. When not set, the counter counts down from
the load value to 0 and then wraps back to the load value (Count-Down
mode). When set, the counter counts up from 0 to the load value, back
down to 0, and then repeats (Count-Up/Down mode).
1 Mode R/W 0
PWM Block Enable
Master enable for the PWM generation block. When not set, the entire
block is disabled and not clocked. When set, the block is enabled and
produces PWM signals.
0 Enable R/W 0
610 January 08, 2011
Texas Instruments-Production Data
Pulse Width Modulator (PWM)
Register 13: PWM0 Interrupt and Trigger Enable (PWM0INTEN), offset 0x044
Register 14: PWM1 Interrupt and Trigger Enable (PWM1INTEN), offset 0x084
Register 15: PWM2 Interrupt and Trigger Enable (PWM2INTEN), offset 0x0C4
These registers control the interrupt and ADC trigger generation capabilities of the PWM generators
(PWM0INTEN controls the PWM generator 0 block, and so on). The events that can cause an
interrupt or an ADC trigger are:
■ The counter being equal to the load register
■ The counter being equal to zero
■ The counter being equal to the comparator A register while counting up
■ The counter being equal to the comparator A register while counting down
■ The counter being equal to the comparator B register while counting up
■ The counter being equal to the comparator B register while counting down
Any combination of these events can generate either an interrupt, or an ADC trigger; though no
determination can be made as to the actual event that caused an ADC trigger if more than one is
specified.
PWM0 Interrupt and Trigger Enable (PWM0INTEN)
Base 0x4002.8000
Offset 0x044
Type R/W, reset 0x0000.0000
31 30 29 28 27 26 25 24 23 22 21 20 19 18 17 16
reserved
Type RO RO RO RO RO RO RO RO RO RO RO RO RO RO RO RO
Reset 0 0 0 0 0 0 0 0 0 0 0 0 0 0 0 0
15 14 13 12 11 10 9 8 7 6 5 4 3 2 1 0
reserved TrCmpBD TrCmpBU TrCmpAD TrCmpAU TrCntLoad TrCntZero reserved IntCmpBD IntCmpBU IntCmpAD IntCmpAU IntCntLoad IntCntZero
Type RO RO R/W R/W R/W R/W R/W R/W RO RO R/W R/W R/W R/W R/W R/W
Reset 0 0 0 0 0 0 0 0 0 0 0 0 0 0 0 0
Bit/Field Name Type Reset Description
Software should not rely on the value of a reserved bit. To provide
compatibility with future products, the value of a reserved bit should be
preserved across a read-modify-write operation.
31:14 reserved RO 0x00
Trigger for Counter=Comparator B Down
Value Description
An ADC trigger pulse is output when the counter matches the
value in the PWMnCMPB register value while counting down.
1
0 No ADC trigger is output.
13 TrCmpBD R/W 0
January 08, 2011 611
Texas Instruments-Production Data
Stellaris® LM3S2965 Microcontroller
Bit/Field Name Type Reset Description
Trigger for Counter=Comparator B Up
Value Description
An ADC trigger pulse is output when the counter matches the
value in the PWMnCMPB register value while counting up.
1
0 No ADC trigger is output.
12 TrCmpBU R/W 0
Trigger for Counter=Comparator A Down
Value Description
An ADC trigger pulse is output when the counter matches the
value in the PWMnCMPA register value while counting down.
1
0 No ADC trigger is output.
11 TrCmpAD R/W 0
Trigger for Counter=Comparator A Up
Value Description
An ADC trigger pulse is output when the counter matches the
value in the PWMnCMPA register value while counting up.
1
0 No ADC trigger is output.
10 TrCmpAU R/W 0
Trigger for Counter=Load
Value Description
An ADC trigger pulse is output when the counter matches the
PWMnLOAD register.
1
0 No ADC trigger is output.
9 TrCntLoad R/W 0
Trigger for Counter=0
Value Description
1 An ADC trigger pulse is output when the counter is 0.
0 No ADC trigger is output.
8 TrCntZero R/W 0
Software should not rely on the value of a reserved bit. To provide
compatibility with future products, the value of a reserved bit should be
preserved across a read-modify-write operation.
7:6 reserved RO 0x0
Interrupt for Counter=Comparator B Down
Value Description
A raw interrupt occurs when the counter matches the value in
the PWMnCMPB register value while counting down.
1
0 No interrupt.
5 IntCmpBD R/W 0
612 January 08, 2011
Texas Instruments-Production Data
Pulse Width Modulator (PWM)
Bit/Field Name Type Reset Description
Interrupt for Counter=Comparator B Up
Value Description
A raw interrupt occurs when the counter matches the value in
the PWMnCMPB register value while counting up.
1
0 No interrupt.
4 IntCmpBU R/W 0
Interrupt for Counter=Comparator A Down
Value Description
A raw interrupt occurs when the counter matches the value in
the PWMnCMPA register value while counting down.
1
0 No interrupt.
3 IntCmpAD R/W 0
Interrupt for Counter=Comparator A Up
Value Description
A raw interrupt occurs when the counter matches the value in
the PWMnCMPA register value while counting up.
1
0 No interrupt.
2 IntCmpAU R/W 0
Interrupt for Counter=Load
Value Description
A raw interrupt occurs when the counter matches the value in
the PWMnLOAD register value.
1
0 No interrupt.
1 IntCntLoad R/W 0
Interrupt for Counter=0
Value Description
1 A raw interrupt occurs when the counter is zero.
0 No interrupt.
0 IntCntZero R/W 0
January 08, 2011 613
Texas Instruments-Production Data
Stellaris® LM3S2965 Microcontroller
Register 16: PWM0 Raw Interrupt Status (PWM0RIS), offset 0x048
Register 17: PWM1 Raw Interrupt Status (PWM1RIS), offset 0x088
Register 18: PWM2 Raw Interrupt Status (PWM2RIS), offset 0x0C8
These registers provide the current set of interrupt sources that are asserted, regardless of whether
they cause an interrupt to be asserted to the controller (PWM0RIS controls the PWM generator 0
block, and so on). Bits set to 1 indicate the latched events that have occurred; bits set to 0 indicate
that the event in question has not occurred.
PWM0 Raw Interrupt Status (PWM0RIS)
Base 0x4002.8000
Offset 0x048
Type RO, reset 0x0000.0000
31 30 29 28 27 26 25 24 23 22 21 20 19 18 17 16
reserved
Type RO RO RO RO RO RO RO RO RO RO RO RO RO RO RO RO
Reset 0 0 0 0 0 0 0 0 0 0 0 0 0 0 0 0
15 14 13 12 11 10 9 8 7 6 5 4 3 2 1 0
reserved IntCmpBD IntCmpBU IntCmpAD IntCmpAU IntCntLoad IntCntZero
Type RO RO RO RO RO RO RO RO RO RO RO RO RO RO RO RO
Reset 0 0 0 0 0 0 0 0 0 0 0 0 0 0 0 0
Bit/Field Name Type Reset Description
Software should not rely on the value of a reserved bit. To provide
compatibility with future products, the value of a reserved bit should be
preserved across a read-modify-write operation.
31:6 reserved RO 0x00
Comparator B Down Interrupt Status
Indicates that the counter has matched the comparator B value while
counting down.
5 IntCmpBD RO 0
Comparator B Up Interrupt Status
Indicates that the counter has matched the comparator B value while
counting up.
4 IntCmpBU RO 0
Comparator A Down Interrupt Status
Indicates that the counter has matched the comparator A value while
counting down.
3 IntCmpAD RO 0
Comparator A Up Interrupt Status
Indicates that the counter has matched the comparator A value while
counting up.
2 IntCmpAU RO 0
Counter=Load Interrupt Status
Indicates that the counter has matched the PWMnLOAD register.
1 IntCntLoad RO 0
Counter=0 Interrupt Status
Indicates that the counter has matched 0.
0 IntCntZero RO 0
614 January 08, 2011
Texas Instruments-Production Data
Pulse Width Modulator (PWM)
Register 19: PWM0 Interrupt Status and Clear (PWM0ISC), offset 0x04C
Register 20: PWM1 Interrupt Status and Clear (PWM1ISC), offset 0x08C
Register 21: PWM2 Interrupt Status and Clear (PWM2ISC), offset 0x0CC
These registers provide the current set of interrupt sources that are asserted to the controller
(PWM0ISC controls the PWM generator 0 block, and so on). Bits set to 1 indicate the latched events
that have occurred; bits set to 0 indicate that the event in question has not occurred. These are
R/W1C registers; writing a 1 to a bit position clears the corresponding interrupt reason.
PWM0 Interrupt Status and Clear (PWM0ISC)
Base 0x4002.8000
Offset 0x04C
Type R/W1C, reset 0x0000.0000
31 30 29 28 27 26 25 24 23 22 21 20 19 18 17 16
reserved
Type RO RO RO RO RO RO RO RO RO RO RO RO RO RO RO RO
Reset 0 0 0 0 0 0 0 0 0 0 0 0 0 0 0 0
15 14 13 12 11 10 9 8 7 6 5 4 3 2 1 0
reserved IntCmpBD IntCmpBU IntCmpAD IntCmpAU IntCntLoad IntCntZero
Type RO RO RO RO RO RO RO RO RO RO R/W1C R/W1C R/W1C R/W1C R/W1C R/W1C
Reset 0 0 0 0 0 0 0 0 0 0 0 0 0 0 0 0
Bit/Field Name Type Reset Description
Software should not rely on the value of a reserved bit. To provide
compatibility with future products, the value of a reserved bit should be
preserved across a read-modify-write operation.
31:6 reserved RO 0x00
Comparator B Down Interrupt
Indicates that the counter has matched the comparator B value while
counting down.
5 IntCmpBD R/W1C 0
Comparator B Up Interrupt
Indicates that the counter has matched the comparator B value while
counting up.
4 IntCmpBU R/W1C 0
Comparator A Down Interrupt
Indicates that the counter has matched the comparator A value while
counting down.
3 IntCmpAD R/W1C 0
Comparator A Up Interrupt
Indicates that the counter has matched the comparator A value while
counting up.
2 IntCmpAU R/W1C 0
Counter=Load Interrupt
Indicates that the counter has matched the PWMnLOAD register.
1 IntCntLoad R/W1C 0
Counter=0 Interrupt
Indicates that the counter has matched 0.
0 IntCntZero R/W1C 0
January 08, 2011 615
Texas Instruments-Production Data
Stellaris® LM3S2965 Microcontroller
Register 22: PWM0 Load (PWM0LOAD), offset 0x050
Register 23: PWM1 Load (PWM1LOAD), offset 0x090
Register 24: PWM2 Load (PWM2LOAD), offset 0x0D0
These registers contain the load value for the PWM counter (PWM0LOAD controls the PWM
generator 0 block, and so on). Based on the counter mode, either this value is loaded into the counter
after it reaches zero, or it is the limit of up-counting after which the counter decrements back to zero.
If the Load Value Update mode is immediate, this value is used the next time the counter reaches
zero; if the mode is synchronous, it is used the next time the counter reaches zero after a synchronous
update has been requested through the PWM Master Control (PWMCTL) register (see page 600).
If this register is re-written before the actual update occurs, the previous value is never used and is
lost.
PWM0 Load (PWM0LOAD)
Base 0x4002.8000
Offset 0x050
Type R/W, reset 0x0000.0000
31 30 29 28 27 26 25 24 23 22 21 20 19 18 17 16
reserved
Type RO RO RO RO RO RO RO RO RO RO RO RO RO RO RO RO
Reset 0 0 0 0 0 0 0 0 0 0 0 0 0 0 0 0
15 14 13 12 11 10 9 8 7 6 5 4 3 2 1 0
Load
Type R/W R/W R/W R/W R/W R/W R/W R/W R/W R/W R/W R/W R/W R/W R/W R/W
Reset 0 0 0 0 0 0 0 0 0 0 0 0 0 0 0 0
Bit/Field Name Type Reset Description
Software should not rely on the value of a reserved bit. To provide
compatibility with future products, the value of a reserved bit should be
preserved across a read-modify-write operation.
31:16 reserved RO 0x00
Counter Load Value
The counter load value.
15:0 Load R/W 0
616 January 08, 2011
Texas Instruments-Production Data
Pulse Width Modulator (PWM)
Register 25: PWM0 Counter (PWM0COUNT), offset 0x054
Register 26: PWM1 Counter (PWM1COUNT), offset 0x094
Register 27: PWM2 Counter (PWM2COUNT), offset 0x0D4
These registers contain the current value of the PWM counter (PWM0COUNT is the value of the
PWM generator 0 block, and so on). When this value matches the load register, a pulse is output;
this can drive the generation of a PWM signal (via the PWMnGENA/PWMnGENB registers, see
page 620 and page 623) or drive an interrupt or ADC trigger (via the PWMnINTEN register, see
page 611). A pulse with the same capabilities is generated when this value is zero.
PWM0 Counter (PWM0COUNT)
Base 0x4002.8000
Offset 0x054
Type RO, reset 0x0000.0000
31 30 29 28 27 26 25 24 23 22 21 20 19 18 17 16
reserved
Type RO RO RO RO RO RO RO RO RO RO RO RO RO RO RO RO
Reset 0 0 0 0 0 0 0 0 0 0 0 0 0 0 0 0
15 14 13 12 11 10 9 8 7 6 5 4 3 2 1 0
Count
Type RO RO RO RO RO RO RO RO RO RO RO RO RO RO RO RO
Reset 0 0 0 0 0 0 0 0 0 0 0 0 0 0 0 0
Bit/Field Name Type Reset Description
Software should not rely on the value of a reserved bit. To provide
compatibility with future products, the value of a reserved bit should be
preserved across a read-modify-write operation.
31:16 reserved RO 0x00
Counter Value
The current value of the counter.
15:0 Count RO 0x00
January 08, 2011 617
Texas Instruments-Production Data
Stellaris® LM3S2965 Microcontroller
Register 28: PWM0 Compare A (PWM0CMPA), offset 0x058
Register 29: PWM1 Compare A (PWM1CMPA), offset 0x098
Register 30: PWM2 Compare A (PWM2CMPA), offset 0x0D8
These registers contain a value to be compared against the counter (PWM0CMPA controls the
PWM generator 0 block, and so on). When this value matches the counter, a pulse is output; this
can drive the generation of a PWM signal (via the PWMnGENA/PWMnGENB registers) or drive an
interrupt or ADC trigger (via the PWMnINTEN register). If the value of this register is greater than
the PWMnLOAD register (see page 616), then no pulse is ever output.
If the comparator A update mode is immediate (based on the CmpAUpd bit in the PWMnCTL register),
this 16-bit CompA value is used the next time the counter reaches zero. If the update mode is
synchronous, it is used the next time the counter reaches zero after a synchronous update has been
requested through the PWM Master Control (PWMCTL) register (see page 600). If this register is
rewritten before the actual update occurs, the previous value is never used and is lost.
PWM0 Compare A (PWM0CMPA)
Base 0x4002.8000
Offset 0x058
Type R/W, reset 0x0000.0000
31 30 29 28 27 26 25 24 23 22 21 20 19 18 17 16
reserved
Type RO RO RO RO RO RO RO RO RO RO RO RO RO RO RO RO
Reset 0 0 0 0 0 0 0 0 0 0 0 0 0 0 0 0
15 14 13 12 11 10 9 8 7 6 5 4 3 2 1 0
CompA
Type R/W R/W R/W R/W R/W R/W R/W R/W R/W R/W R/W R/W R/W R/W R/W R/W
Reset 0 0 0 0 0 0 0 0 0 0 0 0 0 0 0 0
Bit/Field Name Type Reset Description
Software should not rely on the value of a reserved bit. To provide
compatibility with future products, the value of a reserved bit should be
preserved across a read-modify-write operation.
31:16 reserved RO 0x00
Comparator A Value
The value to be compared against the counter.
15:0 CompA R/W 0x00
618 January 08, 2011
Texas Instruments-Production Data
Pulse Width Modulator (PWM)
Register 31: PWM0 Compare B (PWM0CMPB), offset 0x05C
Register 32: PWM1 Compare B (PWM1CMPB), offset 0x09C
Register 33: PWM2 Compare B (PWM2CMPB), offset 0x0DC
These registers contain a value to be compared against the counter (PWM0CMPB controls the
PWM generator 0 block, and so on). When this value matches the counter, a pulse is output; this
can drive the generation of a PWM signal (via the PWMnGENA/PWMnGENB registers) or drive an
interrupt or ADC trigger (via the PWMnINTEN register). If the value of this register is greater than
the PWMnLOAD register, no pulse is ever output.
If the comparator B update mode is immediate (based on the CmpBUpd bit in the PWMnCTL register),
this 16-bit CompB value is used the next time the counter reaches zero. If the update mode is
synchronous, it is used the next time the counter reaches zero after a synchronous update has been
requested through the PWM Master Control (PWMCTL) register (see page 600). If this register is
rewritten before the actual update occurs, the previous value is never used and is lost.
PWM0 Compare B (PWM0CMPB)
Base 0x4002.8000
Offset 0x05C
Type R/W, reset 0x0000.0000
31 30 29 28 27 26 25 24 23 22 21 20 19 18 17 16
reserved
Type RO RO RO RO RO RO RO RO RO RO RO RO RO RO RO RO
Reset 0 0 0 0 0 0 0 0 0 0 0 0 0 0 0 0
15 14 13 12 11 10 9 8 7 6 5 4 3 2 1 0
CompB
Type R/W R/W R/W R/W R/W R/W R/W R/W R/W R/W R/W R/W R/W R/W R/W R/W
Reset 0 0 0 0 0 0 0 0 0 0 0 0 0 0 0 0
Bit/Field Name Type Reset Description
Software should not rely on the value of a reserved bit. To provide
compatibility with future products, the value of a reserved bit should be
preserved across a read-modify-write operation.
31:16 reserved RO 0x00
Comparator B Value
The value to be compared against the counter.
15:0 CompB R/W 0x00
January 08, 2011 619
Texas Instruments-Production Data
Stellaris® LM3S2965 Microcontroller
Register 34: PWM0 Generator A Control (PWM0GENA), offset 0x060
Register 35: PWM1 Generator A Control (PWM1GENA), offset 0x0A0
Register 36: PWM2 Generator A Control (PWM2GENA), offset 0x0E0
These registers control the generation of the PWMnA signal based on the load and zero output pulses
from the counter, as well as the compare A and compare B pulses from the comparators
(PWM0GENA controls the PWM generator 0 block, and so on). When the counter is running in
Count-Down mode, only four of these events occur; when running in Count-Up/Down mode, all six
occur. These events provide great flexibility in the positioning and duty cycle of the PWM signal that
is produced.
The PWM0GENA register controls generation of the PWM0A signal; PWM1GENA, the PWM1A signal;
and PWM2GENA, the PWM2A signal.
If a zero or load event coincides with a compare A or compare B event, the zero or load action is
taken and the compare A or compare B action is ignored. If a compare A event coincides with a
compare B event, the compare A action is taken and the compare B action is ignored.
PWM0 Generator A Control (PWM0GENA)
Base 0x4002.8000
Offset 0x060
Type R/W, reset 0x0000.0000
31 30 29 28 27 26 25 24 23 22 21 20 19 18 17 16
reserved
Type RO RO RO RO RO RO RO RO RO RO RO RO RO RO RO RO
Reset 0 0 0 0 0 0 0 0 0 0 0 0 0 0 0 0
15 14 13 12 11 10 9 8 7 6 5 4 3 2 1 0
reserved ActCmpBD ActCmpBU ActCmpAD ActCmpAU ActLoad ActZero
Type RO RO RO RO R/W R/W R/W R/W R/W R/W R/W R/W R/W R/W R/W R/W
Reset 0 0 0 0 0 0 0 0 0 0 0 0 0 0 0 0
Bit/Field Name Type Reset Description
Software should not rely on the value of a reserved bit. To provide
compatibility with future products, the value of a reserved bit should be
preserved across a read-modify-write operation.
31:12 reserved RO 0x00
Action for Comparator B Down
The action to be taken when the counter matches comparator B while
counting down.
The table below defines the effect of the event on the output signal.
Value Description
0x0 Do nothing.
0x1 Invert the output signal.
0x2 Set the output signal to 0.
0x3 Set the output signal to 1.
11:10 ActCmpBD R/W 0x0
620 January 08, 2011
Texas Instruments-Production Data
Pulse Width Modulator (PWM)
Bit/Field Name Type Reset Description
Action for Comparator B Up
The action to be taken when the counter matches comparator B while
counting up. Occurs only when the Mode bit in the PWMnCTL register
(see page 609) is set to 1.
The table below defines the effect of the event on the output signal.
Value Description
0x0 Do nothing.
0x1 Invert the output signal.
0x2 Set the output signal to 0.
0x3 Set the output signal to 1.
9:8 ActCmpBU R/W 0x0
Action for Comparator A Down
The action to be taken when the counter matches comparator A while
counting down.
The table below defines the effect of the event on the output signal.
Value Description
0x0 Do nothing.
0x1 Invert the output signal.
0x2 Set the output signal to 0.
0x3 Set the output signal to 1.
7:6 ActCmpAD R/W 0x0
Action for Comparator A Up
The action to be taken when the counter matches comparator A while
counting up. Occurs only when the Mode bit in the PWMnCTL register
is set to 1.
The table below defines the effect of the event on the output signal.
Value Description
0x0 Do nothing.
0x1 Invert the output signal.
0x2 Set the output signal to 0.
0x3 Set the output signal to 1.
5:4 ActCmpAU R/W 0x0
Action for Counter=Load
The action to be taken when the counter matches the load value.
The table below defines the effect of the event on the output signal.
Value Description
0x0 Do nothing.
0x1 Invert the output signal.
0x2 Set the output signal to 0.
0x3 Set the output signal to 1.
3:2 ActLoad R/W 0x0
January 08, 2011 621
Texas Instruments-Production Data
Stellaris® LM3S2965 Microcontroller
Bit/Field Name Type Reset Description
Action for Counter=0
The action to be taken when the counter is zero.
The table below defines the effect of the event on the output signal.
Value Description
0x0 Do nothing.
0x1 Invert the output signal.
0x2 Set the output signal to 0.
0x3 Set the output signal to 1.
1:0 ActZero R/W 0x0
622 January 08, 2011
Texas Instruments-Production Data
Pulse Width Modulator (PWM)
Register 37: PWM0 Generator B Control (PWM0GENB), offset 0x064
Register 38: PWM1 Generator B Control (PWM1GENB), offset 0x0A4
Register 39: PWM2 Generator B Control (PWM2GENB), offset 0x0E4
These registers control the generation of the PWMnB signal based on the load and zero output pulses
from the counter, as well as the compare A and compare B pulses from the comparators
(PWM0GENB controls the PWM generator 0 block, and so on). When the counter is running in
Down mode, only four of these events occur; when running in Up/Down mode, all six occur. These
events provide great flexibility in the positioning and duty cycle of the PWM signal that is produced.
The PWM0GENB register controls generation of the PWM0B signal; PWM1GENB, the PWM1B signal;
and PWM2GENB, the PWM2B signal.
If a zero or load event coincides with a compare A or compare B event, the zero or load action is
taken and the compare A or compare B action is ignored. If a compare A event coincides with a
compare B event, the compare B action is taken and the compare A action is ignored.
PWM0 Generator B Control (PWM0GENB)
Base 0x4002.8000
Offset 0x064
Type R/W, reset 0x0000.0000
31 30 29 28 27 26 25 24 23 22 21 20 19 18 17 16
reserved
Type RO RO RO RO RO RO RO RO RO RO RO RO RO RO RO RO
Reset 0 0 0 0 0 0 0 0 0 0 0 0 0 0 0 0
15 14 13 12 11 10 9 8 7 6 5 4 3 2 1 0
reserved ActCmpBD ActCmpBU ActCmpAD ActCmpAU ActLoad ActZero
Type RO RO RO RO R/W R/W R/W R/W R/W R/W R/W R/W R/W R/W R/W R/W
Reset 0 0 0 0 0 0 0 0 0 0 0 0 0 0 0 0
Bit/Field Name Type Reset Description
Software should not rely on the value of a reserved bit. To provide
compatibility with future products, the value of a reserved bit should be
preserved across a read-modify-write operation.
31:12 reserved RO 0x00
Action for Comparator B Down
The action to be taken when the counter matches comparator B while
counting down.
The table below defines the effect of the event on the output signal.
Value Description
0x0 Do nothing.
0x1 Invert the output signal.
0x2 Set the output signal to 0.
0x3 Set the output signal to 1.
11:10 ActCmpBD R/W 0x0
January 08, 2011 623
Texas Instruments-Production Data
Stellaris® LM3S2965 Microcontroller
Bit/Field Name Type Reset Description
Action for Comparator B Up
The action to be taken when the counter matches comparator B while
counting up. Occurs only when the Mode bit in the PWMnCTL register
is set to 1.
The table below defines the effect of the event on the output signal.
Value Description
0x0 Do nothing.
0x1 Invert the output signal.
0x2 Set the output signal to 0.
0x3 Set the output signal to 1.
9:8 ActCmpBU R/W 0x0
Action for Comparator A Down
The action to be taken when the counter matches comparator A while
counting down.
The table below defines the effect of the event on the output signal.
Value Description
0x0 Do nothing.
0x1 Invert the output signal.
0x2 Set the output signal to 0.
0x3 Set the output signal to 1.
7:6 ActCmpAD R/W 0x0
Action for Comparator A Up
The action to be taken when the counter matches comparator A while
counting up. Occurs only when the Mode bit in the PWMnCTL register
is set to 1.
The table below defines the effect of the event on the output signal.
Value Description
0x0 Do nothing.
0x1 Invert the output signal.
0x2 Set the output signal to 0.
0x3 Set the output signal to 1.
5:4 ActCmpAU R/W 0x0
Action for Counter=Load
The action to be taken when the counter matches the load value.
The table below defines the effect of the event on the output signal.
Value Description
0x0 Do nothing.
0x1 Invert the output signal.
0x2 Set the output signal to 0.
0x3 Set the output signal to 1.
3:2 ActLoad R/W 0x0
624 January 08, 2011
Texas Instruments-Production Data
Pulse Width Modulator (PWM)
Bit/Field Name Type Reset Description
Action for Counter=0
The action to be taken when the counter is 0.
The table below defines the effect of the event on the output signal.
Value Description
0x0 Do nothing.
0x1 Invert the output signal.
0x2 Set the output signal to 0.
0x3 Set the output signal to 1.
1:0 ActZero R/W 0x0
January 08, 2011 625
Texas Instruments-Production Data
Stellaris® LM3S2965 Microcontroller
Register 40: PWM0 Dead-Band Control (PWM0DBCTL), offset 0x068
Register 41: PWM1 Dead-Band Control (PWM1DBCTL), offset 0x0A8
Register 42: PWM2 Dead-Band Control (PWM2DBCTL), offset 0x0E8
The PWM0DBCTL register controls the dead-band generator, which produces the PWM0 and PWM1
signals based on the PWM0A and PWM0B signals. When disabled, the PWM0A signal passes through
to the PWM0 signal and the PWM0B signal passes through to the PWM1 signal. When enabled and
inverting the resulting waveform, the PWM0B signal is ignored; the PWM0 signal is generated by
delaying the rising edge(s) of the PWM0A signal by the value in the PWM0DBRISE register (see
page 627), and the PWM1 signal is generated by delaying the falling edge(s) of the PWM0A signal by
the value in the PWM0DBFALL register (see page 628). In a similar manner, PWM2 and PWM3 are
produced from the PWM1A and PWM1B signals, and PWM4 and PWM5 are produced from the PWM2A
and PWM2B signals.
PWM0 Dead-Band Control (PWM0DBCTL)
Base 0x4002.8000
Offset 0x068
Type R/W, reset 0x0000.0000
31 30 29 28 27 26 25 24 23 22 21 20 19 18 17 16
reserved
Type RO RO RO RO RO RO RO RO RO RO RO RO RO RO RO RO
Reset 0 0 0 0 0 0 0 0 0 0 0 0 0 0 0 0
15 14 13 12 11 10 9 8 7 6 5 4 3 2 1 0
reserved Enable
Type RO RO RO RO RO RO RO RO RO RO RO RO RO RO RO R/W
Reset 0 0 0 0 0 0 0 0 0 0 0 0 0 0 0 0
Bit/Field Name Type Reset Description
Software should not rely on the value of a reserved bit. To provide
compatibility with future products, the value of a reserved bit should be
preserved across a read-modify-write operation.
31:1 reserved RO 0x00
Dead-Band Generator Enable
When set, the dead-band generator inserts dead bands into the output
signals; when clear, it simply passes the PWM signals through.
0 Enable R/W 0
626 January 08, 2011
Texas Instruments-Production Data
Pulse Width Modulator (PWM)
Register 43: PWM0 Dead-Band Rising-Edge Delay (PWM0DBRISE), offset
0x06C
Register 44: PWM1 Dead-Band Rising-Edge Delay (PWM1DBRISE), offset
0x0AC
Register 45: PWM2 Dead-Band Rising-Edge Delay (PWM2DBRISE), offset
0x0EC
The PWM0DBRISE register contains the number of clock ticks to delay the rising edge of the PWM0A
signal when generating the PWM0 signal. If the dead-band generator is disabled through the
PWMnDBCTL register, the PWM0DBRISE register is ignored. If the value of this register is larger
than the width of a High pulse on the input PWM signal, the rising-edge delay consumes the entire
High time of the signal, resulting in no High time on the output. Care must be taken to ensure that
the input High time always exceeds the rising-edge delay. In a similar manner, PWM2 is generated
from PWM1A with its rising edge delayed and PWM4 is produced from PWM2A with its rising edge
delayed.
PWM0 Dead-Band Rising-Edge Delay (PWM0DBRISE)
Base 0x4002.8000
Offset 0x06C
Type R/W, reset 0x0000.0000
31 30 29 28 27 26 25 24 23 22 21 20 19 18 17 16
reserved
Type RO RO RO RO RO RO RO RO RO RO RO RO RO RO RO RO
Reset 0 0 0 0 0 0 0 0 0 0 0 0 0 0 0 0
15 14 13 12 11 10 9 8 7 6 5 4 3 2 1 0
reserved RiseDelay
Type RO RO RO RO R/W R/W R/W R/W R/W R/W R/W R/W R/W R/W R/W R/W
Reset 0 0 0 0 0 0 0 0 0 0 0 0 0 0 0 0
Bit/Field Name Type Reset Description
Software should not rely on the value of a reserved bit. To provide
compatibility with future products, the value of a reserved bit should be
preserved across a read-modify-write operation.
31:12 reserved RO 0x00
Dead-Band Rise Delay
The number of clock ticks to delay the rising edge.
11:0 RiseDelay R/W 0
January 08, 2011 627
Texas Instruments-Production Data
Stellaris® LM3S2965 Microcontroller
Register 46: PWM0 Dead-Band Falling-Edge-Delay (PWM0DBFALL), offset
0x070
Register 47: PWM1 Dead-Band Falling-Edge-Delay (PWM1DBFALL), offset
0x0B0
Register 48: PWM2 Dead-Band Falling-Edge-Delay (PWM2DBFALL), offset
0x0F0
The PWM0DBFALL register contains the number of clock ticks to delay the falling edge of the
PWM0A signal when generating the PWM1 signal. If the dead-band generator is disabled, this register
is ignored. If the value of this register is larger than the width of a Low pulse on the input PWM
signal, the falling-edge delay consumes the entire Low time of the signal, resulting in no Low time
on the output. Care must be taken to ensure that the input Low time always exceeds the falling-edge
delay. In a similar manner, PWM3 is generated from PWM1A with its falling edge delayed and PWM5
is produced from PWM2A with its falling edge delayed.
PWM0 Dead-Band Falling-Edge-Delay (PWM0DBFALL)
Base 0x4002.8000
Offset 0x070
Type R/W, reset 0x0000.0000
31 30 29 28 27 26 25 24 23 22 21 20 19 18 17 16
reserved
Type RO RO RO RO RO RO RO RO RO RO RO RO RO RO RO RO
Reset 0 0 0 0 0 0 0 0 0 0 0 0 0 0 0 0
15 14 13 12 11 10 9 8 7 6 5 4 3 2 1 0
reserved FallDelay
Type RO RO RO RO R/W R/W R/W R/W R/W R/W R/W R/W R/W R/W R/W R/W
Reset 0 0 0 0 0 0 0 0 0 0 0 0 0 0 0 0
Bit/Field Name Type Reset Description
Software should not rely on the value of a reserved bit. To provide
compatibility with future products, the value of a reserved bit should be
preserved across a read-modify-write operation.
31:12 reserved RO 0x00
Dead-Band Fall Delay
The number of clock ticks to delay the falling edge.
11:0 FallDelay R/W 0x00
628 January 08, 2011
Texas Instruments-Production Data
Pulse Width Modulator (PWM)
18 Quadrature Encoder Interface (QEI)
A quadrature encoder, also known as a 2-channel incremental encoder, converts linear displacement
into a pulse signal. By monitoring both the number of pulses and the relative phase of the two signals,
you can track the position, direction of rotation, and speed. In addition, a third channel, or index
signal, can be used to reset the position counter.
The LM3S2965 microcontroller includes two quadrature encoder interface (QEI) modules. Each
QEI module interprets the code produced by a quadrature encoder wheel to integrate position over
time and determine direction of rotation. In addition, it can capture a running estimate of the velocity
of the encoder wheel.
Each Stellaris® quadrature encoder has the following features:
■ Two QEI modules, each with the following features:
■ Position integrator that tracks the encoder position
■ Velocity capture using built-in timer
■ The input frequency of the QEI inputs may be as high as 1/4 of the processor frequency (for
example, 12.5 MHz for a 50-MHz system)
■ Interrupt generation on:
– Index pulse
– Velocity-timer expiration
– Direction change
– Quadrature error detection
18.1 Block Diagram
Figure 18-1 on page 630 provides a block diagram of a Stellaris QEI module.
January 08, 2011 629
Texas Instruments-Production Data
Stellaris® LM3S2965 Microcontroller
Figure 18-1. QEI Block Diagram
Quadrature
Encoder
Velocity
Predivider
Interrupt Control
QEIINTEN
QEIRIS
QEIISC
Position Integrator
QEIMAXPOS
QEIPOS
Velocity Accumulator
QEICOUNT
QEISPEED
Velocity Timer
QEILOAD
QEITIME
PhA
PhB
IDX
clk
dir
Interrupt
Control & Status
QEICTL
QEISTAT
18.2 Functional Description
The QEI module interprets the two-bit gray code produced by a quadrature encoder wheel to integrate
position over time and determine direction of rotation. In addition, it can capture a running estimate
of the velocity of the encoder wheel.
The position integrator and velocity capture can be independently enabled, though the position
integrator must be enabled before the velocity capture can be enabled. The two phase signals, PhA
and PhB, can be swapped before being interpreted by the QEI module to change the meaning of
forward and backward, and to correct for miswiring of the system. Alternatively, the phase signals
can be interpreted as a clock and direction signal as output by some encoders.
The QEI module supports two modes of signal operation: quadrature phase mode and clock/direction
mode. In quadrature phase mode, the encoder produces two clocks that are 90 degrees out of
phase; the edge relationship is used to determine the direction of rotation. In clock/direction mode,
the encoder produces a clock signal to indicate steps and a direction signal to indicate the direction
of rotation. This mode is determined by the SigMode bit of the QEI Control (QEICTL) register (see
page 634).
When the QEI module is set to use the quadrature phase mode (SigMode bit equals zero), the
capture mode for the position integrator can be set to update the position counter on every edge of
the PhA signal or to update on every edge of both PhA and PhB. Updating the position counter on
every PhA and PhB provides more positional resolution at the cost of less range in the positional
counter.
When edges on PhA lead edges on PhB , the position counter is incremented. When edges on PhB
lead edges on PhA , the position counter is decremented. When a rising and falling edge pair is
seen on one of the phases without any edges on the other, the direction of rotation has changed.
630 January 08, 2011
Texas Instruments-Production Data
Quadrature Encoder Interface (QEI)
The positional counter is automatically reset on one of two conditions: sensing the index pulse or
reaching the maximum position value. Which mode is determined by the ResMode bit of the QEI
Control (QEICTL) register.
When ResMode is 1, the positional counter is reset when the index pulse is sensed. This limits the
positional counter to the values [0:N-1], where N is the number of phase edges in a full revolution
of the encoder wheel. The QEIMAXPOS register must be programmed with N-1 so that the reverse
direction from position 0 can move the position counter to N-1. In this mode, the position register
contains the absolute position of the encoder relative to the index (or home) position once an index
pulse has been seen.
When ResMode is 0, the positional counter is constrained to the range [0:M], where M is the
programmable maximum value. The index pulse is ignored by the positional counter in this mode.
The velocity capture has a configurable timer and a count register. It counts the number of phase
edges (using the same configuration as for the position integrator) in a given time period. The edge
count from the previous time period is available to the controller via the QEISPEED register, while
the edge count for the current time period is being accumulated in the QEICOUNT register. As soon
as the current time period is complete, the total number of edges counted in that time period is made
available in the QEISPEED register (losing the previous value), the QEICOUNT is reset to 0, and
counting commences on a new time period. The number of edges counted in a given time period
is directly proportional to the velocity of the encoder.
Figure 18-2 on page 631 shows how the Stellaris quadrature encoder converts the phase input signals
into clock pulses, the direction signal, and how the velocity predivider operates (in Divide by 4 mode).
Figure 18-2. Quadrature Encoder and Velocity Predivider Operation
-1 -1 -1 -1 -1 -1 -1 -1 -1 +1 +1 +1 +1 +1 +1 +1 +1 -1 -1 -1 -1 -1 -1 -1 -1 -1 -1 -1 -1 -1 -1 -1
+1 +1 +1 +1 +1 +1 +1 +1
PhA
PhB
clk
clkdiv
dir
pos
rel
The period of the timer is configurable by specifying the load value for the timer in the QEILOAD
register. When the timer reaches zero, an interrupt can be triggered, and the hardware reloads the
timer with the QEILOAD value and continues to count down. At lower encoder speeds, a longer
timer period is needed to be able to capture enough edges to have a meaningful result. At higher
encoder speeds, both a shorter timer period and/or the velocity predivider can be used.
The following equation converts the velocity counter value into an rpm value:
rpm = (clock * (2 ^ VelDiv) * Speed * 60) ÷ (Load * ppr * edges)
where:
clock is the controller clock rate
ppr is the number of pulses per revolution of the physical encoder
edges is 2 or 4, based on the capture mode set in the QEICTL register (2 for CapMode set to 0 and
4 for CapMode set to 1)
For example, consider a motor running at 600 rpm. A 2048 pulse per revolution quadrature encoder
is attached to the motor, producing 8192 phase edges per revolution. With a velocity predivider of
January 08, 2011 631
Texas Instruments-Production Data
Stellaris® LM3S2965 Microcontroller
÷1 (VelDiv set to 0) and clocking on both PhA and PhB edges, this results in 81,920 pulses per
second (the motor turns 10 times per second). If the timer were clocked at 10,000 Hz, and the load
value was 2,500 (¼ of a second), it would count 20,480 pulses per update. Using the above equation:
rpm = (10000 * 1 * 20480 * 60) ÷ (2500 * 2048 * 4) = 600 rpm
Now, consider that the motor is sped up to 3000 rpm. This results in 409,600 pulses per second,
or 102,400 every ¼ of a second. Again, the above equation gives:
rpm = (10000 * 1 * 102400 * 60) ÷ (2500 * 2048 * 4) = 3000 rpm
Care must be taken when evaluating this equation since intermediate values may exceed the capacity
of a 32-bit integer. In the above examples, the clock is 10,000 and the divider is 2,500; both could
be predivided by 100 (at compile time if they are constants) and therefore be 100 and 25. In fact, if
they were compile-time constants, they could also be reduced to a simple multiply by 4, cancelled
by the ÷4 for the edge-count factor.
Important: Reducing constant factors at compile time is the best way to control the intermediate
values of this equation, as well as reducing the processing requirement of computing
this equation.
The division can be avoided by selecting a timer load value such that the divisor is a power of 2; a
simple shift can therefore be done in place of the division. For encoders with a power of 2 pulses
per revolution, this is a simple matter of selecting a power of 2 load value. For other encoders, a
load value must be selected such that the product is very close to a power of two. For example, a
100 pulse per revolution encoder could use a load value of 82, resulting in 32,800 as the divisor,
which is 0.09% above 214; in this case a shift by 15 would be an adequate approximation of the
divide in most cases. If absolute accuracy were required, the controller’s divide instruction could be
used.
The QEI module can produce a controller interrupt on several events: phase error, direction change,
reception of the index pulse, and expiration of the velocity timer. Standard masking, raw interrupt
status, interrupt status, and interrupt clear capabilities are provided.
18.3 Initialization and Configuration
The following example shows how to configure the Quadrature Encoder module to read back an
absolute position:
1. Enable the QEI clock by writing a value of 0x0000.0100 to the RCGC1 register in the System
Control module.
2. Enable the clock to the appropriate GPIO module via the RCGC2 register in the System Control
module.
3. In the GPIO module, enable the appropriate pins for their alternate function using the
GPIOAFSEL register.
4. Configure the quadrature encoder to capture edges on both signals and maintain an absolute
position by resetting on index pulses. Using a 1000-line encoder at four edges per line, there
are 4000 pulses per revolution; therefore, set the maximum position to 3999 (0xF9F) since the
count is zero-based.
■ Write the QEICTL register with the value of 0x0000.0018.
632 January 08, 2011
Texas Instruments-Production Data
Quadrature Encoder Interface (QEI)
■ Write the QEIMAXPOS register with the value of 0x0000.0F9F.
5. Enable the quadrature encoder by setting bit 0 of the QEICTL register.
6. Delay for some time.
7. Read the encoder position by reading the QEIPOS register value.
18.4 Register Map
Table 18-1 on page 633 lists the QEI registers. The offset listed is a hexadecimal increment to the
register’s address, relative to the module’s base address:
■ QEI0: 0x4002.C000
■ QEI1: 0x4002.D000
Note that the QEI module clock must be enabled before the registers can be programmed (see
page 216). There must be a delay of 3 system clocks after the QEI module clock is enabled before
any QEI module registers are accessed.
Table 18-1. QEI Register Map
See
Offset Name Type Reset Description page
0x000 QEICTL R/W 0x0000.0000 QEI Control 634
0x004 QEISTAT RO 0x0000.0000 QEI Status 636
0x008 QEIPOS R/W 0x0000.0000 QEI Position 637
0x00C QEIMAXPOS R/W 0x0000.0000 QEI Maximum Position 638
0x010 QEILOAD R/W 0x0000.0000 QEI Timer Load 639
0x014 QEITIME RO 0x0000.0000 QEI Timer 640
0x018 QEICOUNT RO 0x0000.0000 QEI Velocity Counter 641
0x01C QEISPEED RO 0x0000.0000 QEI Velocity 642
0x020 QEIINTEN R/W 0x0000.0000 QEI Interrupt Enable 643
0x024 QEIRIS RO 0x0000.0000 QEI Raw Interrupt Status 644
0x028 QEIISC R/W1C 0x0000.0000 QEI Interrupt Status and Clear 645
18.5 Register Descriptions
The remainder of this section lists and describes the QEI registers, in numerical order by address
offset.
January 08, 2011 633
Texas Instruments-Production Data
Stellaris® LM3S2965 Microcontroller
Register 1: QEI Control (QEICTL), offset 0x000
This register contains the configuration of the QEI module. Separate enables are provided for the
quadrature encoder and the velocity capture blocks; the quadrature encoder must be enabled in
order to capture the velocity, but the velocity does not need to be captured in applications that do
not need it. The phase signal interpretation, phase swap, Position Update mode, Position Reset
mode, and velocity predivider are all set via this register.
QEI Control (QEICTL)
QEI0 base: 0x4002.C000
QEI1 base: 0x4002.D000
Offset 0x000
Type R/W, reset 0x0000.0000
31 30 29 28 27 26 25 24 23 22 21 20 19 18 17 16
reserved
Type RO RO RO RO RO RO RO RO RO RO RO RO RO RO RO RO
Reset 0 0 0 0 0 0 0 0 0 0 0 0 0 0 0 0
15 14 13 12 11 10 9 8 7 6 5 4 3 2 1 0
reserved STALLEN INVI INVB INVA VelDiv VelEn ResMode CapMode SigMode Swap Enable
Type RO RO RO R/W R/W R/W R/W R/W R/W R/W R/W R/W R/W R/W R/W R/W
Reset 0 0 0 0 0 0 0 0 0 0 0 0 0 0 0 0
Bit/Field Name Type Reset Description
Software should not rely on the value of a reserved bit. To provide
compatibility with future products, the value of a reserved bit should be
preserved across a read-modify-write operation.
31:13 reserved RO 0x00
Stall QEI
When set, the QEI stalls when the microcontroller asserts Halt.
12 STALLEN R/W 0
Invert Index Pulse
When set , the input Index Pulse is inverted.
11 INVI R/W 0
Invert PhB
When set, the PhB input is inverted.
10 INVB R/W 0
Invert PhA
When set, the PhA input is inverted.
9 INVA R/W 0
Predivide Velocity
A predivider of the input quadrature pulses before being applied to the
QEICOUNT accumulator. This field can be set to the following values:
Value Predivider
0x0 ÷1
0x1 ÷2
0x2 ÷4
0x3 ÷8
0x4 ÷16
0x5 ÷32
0x6 ÷64
0x7 ÷128
8:6 VelDiv R/W 0x0
634 January 08, 2011
Texas Instruments-Production Data
Quadrature Encoder Interface (QEI)
Bit/Field Name Type Reset Description
Capture Velocity
When set, enables capture of the velocity of the quadrature encoder.
5 VelEn R/W 0
Reset Mode
The Reset mode for the position counter. When 0, the position counter
is reset when it reaches the maximum; when 1, the position counter is
reset when the index pulse is captured.
4 ResMode R/W 0
Capture Mode
The Capture mode defines the phase edges that are counted in the
position. When 0, only the PhA edges are counted; when 1, the PhA
and PhB edges are counted, providing twice the positional resolution
but half the range.
3 CapMode R/W 0
Signal Mode
When 1, the PhA and PhB signals are clock and direction; when 0, they
are quadrature phase signals.
2 SigMode R/W 0
Swap Signals
Swaps the PhA and PhB signals.
1 Swap R/W 0
Enable QEI
Enables the quadrature encoder module.
0 Enable R/W 0
January 08, 2011 635
Texas Instruments-Production Data
Stellaris® LM3S2965 Microcontroller
Register 2: QEI Status (QEISTAT), offset 0x004
This register provides status about the operation of the QEI module.
QEI Status (QEISTAT)
QEI0 base: 0x4002.C000
QEI1 base: 0x4002.D000
Offset 0x004
Type RO, reset 0x0000.0000
31 30 29 28 27 26 25 24 23 22 21 20 19 18 17 16
reserved
Type RO RO RO RO RO RO RO RO RO RO RO RO RO RO RO RO
Reset 0 0 0 0 0 0 0 0 0 0 0 0 0 0 0 0
15 14 13 12 11 10 9 8 7 6 5 4 3 2 1 0
reserved Direction Error
Type RO RO RO RO RO RO RO RO RO RO RO RO RO RO RO RO
Reset 0 0 0 0 0 0 0 0 0 0 0 0 0 0 0 0
Bit/Field Name Type Reset Description
Software should not rely on the value of a reserved bit. To provide
compatibility with future products, the value of a reserved bit should be
preserved across a read-modify-write operation.
31:2 reserved RO 0x00
Direction of Rotation
Indicates the direction the encoder is rotating.
The Direction values are defined as follows:
Value Description
0 Forward rotation
1 Reverse rotation
1 Direction RO 0
Error Detected
Indicates that an error was detected in the gray code sequence (that is,
both signals changing at the same time).
0 Error RO 0
636 January 08, 2011
Texas Instruments-Production Data
Quadrature Encoder Interface (QEI)
Register 3: QEI Position (QEIPOS), offset 0x008
This register contains the current value of the position integrator. Its value is updated by inputs on
the QEI phase inputs, and can be set to a specific value by writing to it.
QEI Position (QEIPOS)
QEI0 base: 0x4002.C000
QEI1 base: 0x4002.D000
Offset 0x008
Type R/W, reset 0x0000.0000
31 30 29 28 27 26 25 24 23 22 21 20 19 18 17 16
Position
Type R/W R/W R/W R/W R/W R/W R/W R/W R/W R/W R/W R/W R/W R/W R/W R/W
Reset 0 0 0 0 0 0 0 0 0 0 0 0 0 0 0 0
15 14 13 12 11 10 9 8 7 6 5 4 3 2 1 0
Position
Type R/W R/W R/W R/W R/W R/W R/W R/W R/W R/W R/W R/W R/W R/W R/W R/W
Reset 0 0 0 0 0 0 0 0 0 0 0 0 0 0 0 0
Bit/Field Name Type Reset Description
Current Position Integrator Value
The current value of the position integrator.
31:0 Position R/W 0x00
January 08, 2011 637
Texas Instruments-Production Data
Stellaris® LM3S2965 Microcontroller
Register 4: QEI Maximum Position (QEIMAXPOS), offset 0x00C
This register contains the maximum value of the position integrator. When moving forward, the
position register resets to zero when it increments past this value. When moving backward, the
position register resets to this value when it decrements from zero.
QEI Maximum Position (QEIMAXPOS)
QEI0 base: 0x4002.C000
QEI1 base: 0x4002.D000
Offset 0x00C
Type R/W, reset 0x0000.0000
31 30 29 28 27 26 25 24 23 22 21 20 19 18 17 16
MaxPos
Type R/W R/W R/W R/W R/W R/W R/W R/W R/W R/W R/W R/W R/W R/W R/W R/W
Reset 0 0 0 0 0 0 0 0 0 0 0 0 0 0 0 0
15 14 13 12 11 10 9 8 7 6 5 4 3 2 1 0
MaxPos
Type R/W R/W R/W R/W R/W R/W R/W R/W R/W R/W R/W R/W R/W R/W R/W R/W
Reset 0 0 0 0 0 0 0 0 0 0 0 0 0 0 0 0
Bit/Field Name Type Reset Description
Maximum Position Integrator Value
The maximum value of the position integrator.
31:0 MaxPos R/W 0x00
638 January 08, 2011
Texas Instruments-Production Data
Quadrature Encoder Interface (QEI)
Register 5: QEI Timer Load (QEILOAD), offset 0x010
This register contains the load value for the velocity timer. Since this value is loaded into the timer
the clock cycle after the timer is zero, this value should be one less than the number of clocks in
the desired period. So, for example, to have 2000 clocks per timer period, this register should contain
1999.
QEI Timer Load (QEILOAD)
QEI0 base: 0x4002.C000
QEI1 base: 0x4002.D000
Offset 0x010
Type R/W, reset 0x0000.0000
31 30 29 28 27 26 25 24 23 22 21 20 19 18 17 16
Load
Type R/W R/W R/W R/W R/W R/W R/W R/W R/W R/W R/W R/W R/W R/W R/W R/W
Reset 0 0 0 0 0 0 0 0 0 0 0 0 0 0 0 0
15 14 13 12 11 10 9 8 7 6 5 4 3 2 1 0
Load
Type R/W R/W R/W R/W R/W R/W R/W R/W R/W R/W R/W R/W R/W R/W R/W R/W
Reset 0 0 0 0 0 0 0 0 0 0 0 0 0 0 0 0
Bit/Field Name Type Reset Description
Velocity Timer Load Value
The load value for the velocity timer.
31:0 Load R/W 0x00
January 08, 2011 639
Texas Instruments-Production Data
Stellaris® LM3S2965 Microcontroller
Register 6: QEI Timer (QEITIME), offset 0x014
This register contains the current value of the velocity timer. This counter does not increment when
VelEn in QEICTL is 0.
QEI Timer (QEITIME)
QEI0 base: 0x4002.C000
QEI1 base: 0x4002.D000
Offset 0x014
Type RO, reset 0x0000.0000
31 30 29 28 27 26 25 24 23 22 21 20 19 18 17 16
Time
Type RO RO RO RO RO RO RO RO RO RO RO RO RO RO RO RO
Reset 0 0 0 0 0 0 0 0 0 0 0 0 0 0 0 0
15 14 13 12 11 10 9 8 7 6 5 4 3 2 1 0
Time
Type RO RO RO RO RO RO RO RO RO RO RO RO RO RO RO RO
Reset 0 0 0 0 0 0 0 0 0 0 0 0 0 0 0 0
Bit/Field Name Type Reset Description
Velocity Timer Current Value
The current value of the velocity timer.
31:0 Time RO 0x00
640 January 08, 2011
Texas Instruments-Production Data
Quadrature Encoder Interface (QEI)
Register 7: QEI Velocity Counter (QEICOUNT), offset 0x018
This register contains the running count of velocity pulses for the current time period. Since this is
a running total, the time period to which it applies cannot be known with precision (that is, a read of
this register does not necessarily correspond to the time returned by the QEITIME register since
there is a small window of time between the two reads, during which time either value may have
changed). The QEISPEED register should be used to determine the actual encoder velocity; this
register is provided for information purposes only. This counter does not increment when VelEn in
QEICTL is 0.
QEI Velocity Counter (QEICOUNT)
QEI0 base: 0x4002.C000
QEI1 base: 0x4002.D000
Offset 0x018
Type RO, reset 0x0000.0000
31 30 29 28 27 26 25 24 23 22 21 20 19 18 17 16
Count
Type RO RO RO RO RO RO RO RO RO RO RO RO RO RO RO RO
Reset 0 0 0 0 0 0 0 0 0 0 0 0 0 0 0 0
15 14 13 12 11 10 9 8 7 6 5 4 3 2 1 0
Count
Type RO RO RO RO RO RO RO RO RO RO RO RO RO RO RO RO
Reset 0 0 0 0 0 0 0 0 0 0 0 0 0 0 0 0
Bit/Field Name Type Reset Description
Velocity Pulse Count
The running total of encoder pulses during this velocity timer period.
31:0 Count RO 0x00
January 08, 2011 641
Texas Instruments-Production Data
Stellaris® LM3S2965 Microcontroller
Register 8: QEI Velocity (QEISPEED), offset 0x01C
This register contains the most recently measured velocity of the quadrature encoder. This
corresponds to the number of velocity pulses counted in the previous velocity timer period. This
register does not update when VelEn in QEICTL is 0.
QEI Velocity (QEISPEED)
QEI0 base: 0x4002.C000
QEI1 base: 0x4002.D000
Offset 0x01C
Type RO, reset 0x0000.0000
31 30 29 28 27 26 25 24 23 22 21 20 19 18 17 16
Speed
Type RO RO RO RO RO RO RO RO RO RO RO RO RO RO RO RO
Reset 0 0 0 0 0 0 0 0 0 0 0 0 0 0 0 0
15 14 13 12 11 10 9 8 7 6 5 4 3 2 1 0
Speed
Type RO RO RO RO RO RO RO RO RO RO RO RO RO RO RO RO
Reset 0 0 0 0 0 0 0 0 0 0 0 0 0 0 0 0
Bit/Field Name Type Reset Description
Velocity
The measured speed of the quadrature encoder in pulses per period.
31:0 Speed RO 0x00
642 January 08, 2011
Texas Instruments-Production Data
Quadrature Encoder Interface (QEI)
Register 9: QEI Interrupt Enable (QEIINTEN), offset 0x020
This register contains enables for each of the QEI module’s interrupts. An interrupt is asserted to
the controller if its corresponding bit in this register is set to 1.
QEI Interrupt Enable (QEIINTEN)
QEI0 base: 0x4002.C000
QEI1 base: 0x4002.D000
Offset 0x020
Type R/W, reset 0x0000.0000
31 30 29 28 27 26 25 24 23 22 21 20 19 18 17 16
reserved
Type RO RO RO RO RO RO RO RO RO RO RO RO RO RO RO RO
Reset 0 0 0 0 0 0 0 0 0 0 0 0 0 0 0 0
15 14 13 12 11 10 9 8 7 6 5 4 3 2 1 0
reserved IntError IntDir IntTimer IntIndex
Type RO RO RO RO RO RO RO RO RO RO RO RO R/W R/W R/W R/W
Reset 0 0 0 0 0 0 0 0 0 0 0 0 0 0 0 0
Bit/Field Name Type Reset Description
Software should not rely on the value of a reserved bit. To provide
compatibility with future products, the value of a reserved bit should be
preserved across a read-modify-write operation.
31:4 reserved RO 0x00
Phase Error Interrupt Enable
When 1, an interrupt occurs when a phase error is detected.
3 IntError R/W 0
Direction Change Interrupt Enable
When 1, an interrupt occurs when the direction changes.
2 IntDir R/W 0
Timer Expires Interrupt Enable
When 1, an interrupt occurs when the velocity timer expires.
1 IntTimer R/W 0
Index Pulse Detected Interrupt Enable
When 1, an interrupt occurs when the index pulse is detected.
0 IntIndex R/W 0
January 08, 2011 643
Texas Instruments-Production Data
Stellaris® LM3S2965 Microcontroller
Register 10: QEI Raw Interrupt Status (QEIRIS), offset 0x024
This register provides the current set of interrupt sources that are asserted, regardless of whether
they cause an interrupt to be asserted to the controller (this is set through the QEIINTEN register).
Bits set to 1 indicate the latched events that have occurred; a zero bit indicates that the event in
question has not occurred.
QEI Raw Interrupt Status (QEIRIS)
QEI0 base: 0x4002.C000
QEI1 base: 0x4002.D000
Offset 0x024
Type RO, reset 0x0000.0000
31 30 29 28 27 26 25 24 23 22 21 20 19 18 17 16
reserved
Type RO RO RO RO RO RO RO RO RO RO RO RO RO RO RO RO
Reset 0 0 0 0 0 0 0 0 0 0 0 0 0 0 0 0
15 14 13 12 11 10 9 8 7 6 5 4 3 2 1 0
reserved IntError IntDir IntTimer IntIndex
Type RO RO RO RO RO RO RO RO RO RO RO RO RO RO RO RO
Reset 0 0 0 0 0 0 0 0 0 0 0 0 0 0 0 0
Bit/Field Name Type Reset Description
Software should not rely on the value of a reserved bit. To provide
compatibility with future products, the value of a reserved bit should be
preserved across a read-modify-write operation.
31:4 reserved RO 0x00
Phase Error Detected
Indicates that a phase error was detected.
3 IntError RO 0
Direction Change Detected
Indicates that the direction has changed.
2 IntDir RO 0
Velocity Timer Expired
Indicates that the velocity timer has expired.
1 IntTimer RO 0
Index Pulse Asserted
Indicates that the index pulse has occurred.
0 IntIndex RO 0
644 January 08, 2011
Texas Instruments-Production Data
Quadrature Encoder Interface (QEI)
Register 11: QEI Interrupt Status and Clear (QEIISC), offset 0x028
This register provides the current set of interrupt sources that are asserted to the controller. Bits set
to 1 indicate the latched events that have occurred; a zero bit indicates that the event in question
has not occurred. This is a R/W1C register; writing a 1 to a bit position clears the corresponding
interrupt reason.
QEI Interrupt Status and Clear (QEIISC)
QEI0 base: 0x4002.C000
QEI1 base: 0x4002.D000
Offset 0x028
Type R/W1C, reset 0x0000.0000
31 30 29 28 27 26 25 24 23 22 21 20 19 18 17 16
reserved
Type RO RO RO RO RO RO RO RO RO RO RO RO RO RO RO RO
Reset 0 0 0 0 0 0 0 0 0 0 0 0 0 0 0 0
15 14 13 12 11 10 9 8 7 6 5 4 3 2 1 0
reserved IntError IntDir IntTimer IntIndex
Type RO RO RO RO RO RO RO RO RO RO RO RO R/W1C R/W1C R/W1C R/W1C
Reset 0 0 0 0 0 0 0 0 0 0 0 0 0 0 0 0
Bit/Field Name Type Reset Description
Software should not rely on the value of a reserved bit. To provide
compatibility with future products, the value of a reserved bit should be
preserved across a read-modify-write operation.
31:4 reserved RO 0x00
Phase Error Interrupt
Indicates that a phase error was detected.
3 IntError R/W1C 0
Direction Change Interrupt
Indicates that the direction has changed.
2 IntDir R/W1C 0
Velocity Timer Expired Interrupt
Indicates that the velocity timer has expired.
1 IntTimer R/W1C 0
Index Pulse Interrupt
Indicates that the index pulse has occurred.
0 IntIndex R/W1C 0
January 08, 2011 645
Texas Instruments-Production Data
Stellaris® LM3S2965 Microcontroller
19 Pin Diagram
The LM3S2965 microcontroller pin diagrams are shown below.
Figure 19-1. 100-Pin LQFP Package Pin Diagram
646 January 08, 2011
Texas Instruments-Production Data
Pin Diagram
Figure 19-2. 108-Ball BGA Package Pin Diagram (Top View)
January 08, 2011 647
Texas Instruments-Production Data
Stellaris® LM3S2965 Microcontroller
20 Signal Tables
The following tables list the signals available for each pin. Functionality is enabled by software with
the GPIOAFSEL register.
Important: All multiplexed pins are GPIOs by default, with the exception of the five JTAG pins (PB7
and PC[3:0]) which default to the JTAG functionality.
Table 20-1 on page 648 shows the pin-to-signal-name mapping, including functional characteristics
of the signals. Table 20-2 on page 652 lists the signals in alphabetical order by signal name.
Table 20-3 on page 657 groups the signals by functionality, except for GPIOs. Table 20-4 on page 660
lists the GPIO pins and their alternate functionality.
Note: All digital inputs are Schmitt triggered.
20.1 100-Pin LQFP Package Pin Tables
Table 20-1. Signals by Pin Number
Pin Number Pin Name Pin Type Buffer Typea Description
1 ADC0 I Analog Analog-to-digital converter input 0.
2 ADC1 I Analog Analog-to-digital converter input 1.
The positive supply (3.3 V) for the analog circuits (ADC, Analog
Comparators, etc.). These are separated from VDD to minimize
the electrical noise contained on VDD from affecting the analog
functions. VDDA pins must be connected to 3.3 V, regardless of
system implementation.
VDDA - Power
3
The ground reference for the analog circuits (ADC, Analog
Comparators, etc.). These are separated from GND to minimize
the electrical noise contained on VDD from affecting the analog
functions.
GNDA - Power
4
5 ADC2 I Analog Analog-to-digital converter input 2.
6 ADC3 I Analog Analog-to-digital converter input 3.
Low drop-out regulator output voltage. This pin requires an external
capacitor between the pin and GND of 1 μF or greater. When the
on-chip LDO is used to provide power to the logic, the LDO pin
must also be connected to the VDD25 pins at the board level in
addition to the decoupling capacitor(s).
LDO - Power
7
8 VDD - Power Positive supply for I/O and some logic.
9 GND - Power Ground reference for logic and I/O pins.
PD0 I/O TTL GPIO port D bit 0.
10
CAN0Rx I TTL CAN module 0 receive.
PD1 I/O TTL GPIO port D bit 1.
11
CAN0Tx O TTL CAN module 0 transmit.
PD2 I/O TTL GPIO port D bit 2.
12 UART module 1 receive. When in IrDA mode, this signal has IrDA
modulation.
U1Rx I TTL
PD3 I/O TTL GPIO port D bit 3.
13 UART module 1 transmit. When in IrDA mode, this signal has IrDA
modulation.
U1Tx O TTL
648 January 08, 2011
Texas Instruments-Production Data
Signal Tables
Table 20-1. Signals by Pin Number (continued)
Pin Number Pin Name Pin Type Buffer Typea Description
Positive supply for most of the logic function, including the
processor core and most peripherals.
VDD25 - Power 14
15 GND - Power Ground reference for logic and I/O pins.
PG3 I/O TTL GPIO port G bit 3.
16
PWM1 O TTL PWM 1. This signal is controlled by PWM Generator 0.
PG2 I/O TTL GPIO port G bit 2.
17
PWM0 O TTL PWM 0. This signal is controlled by PWM Generator 0.
PG1 I/O TTL GPIO port G bit 1.
18 UART module 2 transmit. When in IrDA mode, this signal has IrDA
modulation.
U2Tx O TTL
PG0 I/O TTL GPIO port G bit 0.
19 UART module 2 receive. When in IrDA mode, this signal has IrDA
modulation.
U2Rx I TTL
20 VDD - Power Positive supply for I/O and some logic.
21 GND - Power Ground reference for logic and I/O pins.
PC7 I/O TTL GPIO port C bit 7.
22
C2- I Analog Analog comparator 2 negative input.
PC6 I/O TTL GPIO port C bit 6.
23
C2+ I Analog Analog comparator 2 positive input.
PC5 I/O TTL GPIO port C bit 5.
24
C1+ I Analog Analog comparator 1 positive input.
PC4 I/O TTL GPIO port C bit 4.
25
PhA0 I TTL QEI module 0 phase A.
PA0 I/O TTL GPIO port A bit 0.
26 UART module 0 receive. When in IrDA mode, this signal has IrDA
modulation.
U0Rx I TTL
PA1 I/O TTL GPIO port A bit 1.
27 UART module 0 transmit. When in IrDA mode, this signal has IrDA
modulation.
U0Tx O TTL
PA2 I/O TTL GPIO port A bit 2.
28
SSI0Clk I/O TTL SSI module 0 clock.
PA3 I/O TTL GPIO port A bit 3.
29
SSI0Fss I/O TTL SSI module 0 frame.
PA4 I/O TTL GPIO port A bit 4.
30
SSI0Rx I TTL SSI module 0 receive.
PA5 I/O TTL GPIO port A bit 5.
31
SSI0Tx O TTL SSI module 0 transmit.
32 VDD - Power Positive supply for I/O and some logic.
33 GND - Power Ground reference for logic and I/O pins.
PA6 I/O TTL GPIO port A bit 6.
34
I2C1SCL I/O OD I2C module 1 clock.
PA7 I/O TTL GPIO port A bit 7.
35
I2C1SDA I/O OD I2C module 1 data.
January 08, 2011 649
Texas Instruments-Production Data
Stellaris® LM3S2965 Microcontroller
Table 20-1. Signals by Pin Number (continued)
Pin Number Pin Name Pin Type Buffer Typea Description
PG7 I/O TTL GPIO port G bit 7.
36
PhB1 I TTL QEI module 1 phase B.
PG6 I/O TTL GPIO port G bit 6.
37
PhA1 I TTL QEI module 1 phase A.
Positive supply for most of the logic function, including the
processor core and most peripherals.
VDD25 - Power 38
39 GND - Power Ground reference for logic and I/O pins.
PG5 I/O TTL GPIO port G bit 5.
40
CCP5 I/O TTL Capture/Compare/PWM 5.
41 PG4 I/O TTL GPIO port G bit 4.
42 PF7 I/O TTL GPIO port F bit 7.
PF6 I/O TTL GPIO port F bit 6.
43
CCP1 I/O TTL Capture/Compare/PWM 1.
44 VDD - Power Positive supply for I/O and some logic.
45 GND - Power Ground reference for logic and I/O pins.
46 PF5 I/O TTL GPIO port F bit 5.
PF0 I/O TTL GPIO port F bit 0.
47
CAN1Rx I TTL CAN module 1 receive.
48 OSC0 I Analog Main oscillator crystal input or an external clock reference input.
Main oscillator crystal output. Leave unconnected when using a
single-ended clock source.
OSC1 O Analog 49
An external input that brings the processor out of Hibernate mode
when asserted.
WAKE I TTL 50
An open-drain output with internal pull-up that indicates the
processor is in Hibernate mode.
HIB O OD 51
Hibernation module oscillator crystal input or an external clock
reference input. Note that this is either a crystal or a 32.768-kHz
oscillator for the Hibernation module RTC.
XOSC0 I Analog
52
Hibernation module oscillator crystal output. Leave unconnected
when using a single-ended clock source.
XOSC1 O Analog 53
54 GND - Power Ground reference for logic and I/O pins.
Power source for the Hibernation module. It is normally connected
to the positive terminal of a battery and serves as the battery
backup/Hibernation module power-source supply.
VBAT - Power
55
56 VDD - Power Positive supply for I/O and some logic.
57 GND - Power Ground reference for logic and I/O pins.
PF4 I/O TTL GPIO port F bit 4.
58
C0o O TTL Analog comparator 0 output.
PF3 I/O TTL GPIO port F bit 3.
59
PWM5 O TTL PWM 5. This signal is controlled by PWM Generator 2.
PF2 I/O TTL GPIO port F bit 2.
60
PWM4 O TTL PWM 4. This signal is controlled by PWM Generator 2.
PF1 I/O TTL GPIO port F bit 1.
61
CAN1Tx O TTL CAN module 1 transmit.
650 January 08, 2011
Texas Instruments-Production Data
Signal Tables
Table 20-1. Signals by Pin Number (continued)
Pin Number Pin Name Pin Type Buffer Typea Description
Positive supply for most of the logic function, including the
processor core and most peripherals.
VDD25 - Power 62
63 GND - Power Ground reference for logic and I/O pins.
64 RST I TTL System reset input.
CPU Mode bit 0. Input must be set to logic 0 (grounded); other
encodings reserved.
CMOD0 I TTL 65
PB0 I/O TTL GPIO port B bit 0.
66
CCP0 I/O TTL Capture/Compare/PWM 0.
PB1 I/O TTL GPIO port B bit 1.
67
CCP2 I/O TTL Capture/Compare/PWM 2.
68 VDD - Power Positive supply for I/O and some logic.
69 GND - Power Ground reference for logic and I/O pins.
PB2 I/O TTL GPIO port B bit 2.
70
I2C0SCL I/O OD I2C module 0 clock.
PB3 I/O TTL GPIO port B bit 3.
71
I2C0SDA I/O OD I2C module 0 data.
PE0 I/O TTL GPIO port E bit 0.
72
SSI1Clk I/O TTL SSI module 1 clock.
PE1 I/O TTL GPIO port E bit 1.
73
SSI1Fss I/O TTL SSI module 1 frame.
PE2 I/O TTL GPIO port E bit 2.
74
SSI1Rx I TTL SSI module 1 receive.
PE3 I/O TTL GPIO port E bit 3.
75
SSI1Tx O TTL SSI module 1 transmit.
CPU Mode bit 1. Input must be set to logic 0 (grounded); other
encodings reserved.
CMOD1 I TTL 76
PC3 I/O TTL GPIO port C bit 3.
77 SWO O TTL JTAG TDO and SWO.
TDO O TTL JTAG TDO and SWO.
PC2 I/O TTL GPIO port C bit 2.
78
TDI I TTL JTAG TDI.
PC1 I/O TTL GPIO port C bit 1.
79 SWDIO I/O TTL JTAG TMS and SWDIO.
TMS I/O TTL JTAG TMS and SWDIO.
PC0 I/O TTL GPIO port C bit 0.
80 SWCLK I TTL JTAG/SWD CLK.
TCK I TTL JTAG/SWD CLK.
81 VDD - Power Positive supply for I/O and some logic.
82 GND - Power Ground reference for logic and I/O pins.
PH3 I/O TTL GPIO port H bit 3.
83
PhB0 I TTL QEI module 0 phase B.
January 08, 2011 651
Texas Instruments-Production Data
Stellaris® LM3S2965 Microcontroller
Table 20-1. Signals by Pin Number (continued)
Pin Number Pin Name Pin Type Buffer Typea Description
PH2 I/O TTL GPIO port H bit 2.
84
IDX1 I TTL QEI module 1 index.
PH1 I/O TTL GPIO port H bit 1.
85
PWM3 O TTL PWM 3. This signal is controlled by PWM Generator 1.
PH0 I/O TTL GPIO port H bit 0.
86
PWM2 O TTL PWM 2. This signal is controlled by PWM Generator 1.
87 GND - Power Ground reference for logic and I/O pins.
Positive supply for most of the logic function, including the
processor core and most peripherals.
VDD25 - Power 88
PB7 I/O TTL GPIO port B bit 7.
89
TRST I TTL JTAG TRST.
PB6 I/O TTL GPIO port B bit 6.
90
C0+ I Analog Analog comparator 0 positive input.
PB5 I/O TTL GPIO port B bit 5.
91
C1- I Analog Analog comparator 1 negative input.
PB4 I/O TTL GPIO port B bit 4.
92
C0- I Analog Analog comparator 0 negative input.
93 VDD - Power Positive supply for I/O and some logic.
94 GND - Power Ground reference for logic and I/O pins.
PD4 I/O TTL GPIO port D bit 4.
95
CCP3 I/O TTL Capture/Compare/PWM 3.
PD5 I/O TTL GPIO port D bit 5.
96
CCP4 I/O TTL Capture/Compare/PWM 4.
The ground reference for the analog circuits (ADC, Analog
Comparators, etc.). These are separated from GND to minimize
the electrical noise contained on VDD from affecting the analog
functions.
GNDA - Power
97
The positive supply (3.3 V) for the analog circuits (ADC, Analog
Comparators, etc.). These are separated from VDD to minimize
the electrical noise contained on VDD from affecting the analog
functions. VDDA pins must be connected to 3.3 V, regardless of
system implementation.
VDDA - Power
98
PD6 I/O TTL GPIO port D bit 6.
99
Fault I TTL PWM Fault.
PD7 I/O TTL GPIO port D bit 7.
100
IDX0 I TTL QEI module 0 index.
a. The TTL designation indicates the pin has TTL-compatible voltage levels.
Table 20-2. Signals by Signal Name
Pin Name Pin Number Pin Type Buffer Typea Description
ADC0 1 I Analog Analog-to-digital converter input 0.
ADC1 2 I Analog Analog-to-digital converter input 1.
ADC2 5 I Analog Analog-to-digital converter input 2.
ADC3 6 I Analog Analog-to-digital converter input 3.
652 January 08, 2011
Texas Instruments-Production Data
Signal Tables
Table 20-2. Signals by Signal Name (continued)
Pin Name Pin Number Pin Type Buffer Typea Description
C0+ 90 I Analog Analog comparator 0 positive input.
C0- 92 I Analog Analog comparator 0 negative input.
C0o 58 O TTL Analog comparator 0 output.
C1+ 24 I Analog Analog comparator 1 positive input.
C1- 91 I Analog Analog comparator 1 negative input.
C2+ 23 I Analog Analog comparator 2 positive input.
C2- 22 I Analog Analog comparator 2 negative input.
CAN0Rx 10 I TTL CAN module 0 receive.
CAN0Tx 11 O TTL CAN module 0 transmit.
CAN1Rx 47 I TTL CAN module 1 receive.
CAN1Tx 61 O TTL CAN module 1 transmit.
CCP0 66 I/O TTL Capture/Compare/PWM 0.
CCP1 43 I/O TTL Capture/Compare/PWM 1.
CCP2 67 I/O TTL Capture/Compare/PWM 2.
CCP3 95 I/O TTL Capture/Compare/PWM 3.
CCP4 96 I/O TTL Capture/Compare/PWM 4.
CCP5 40 I/O TTL Capture/Compare/PWM 5.
CPU Mode bit 0. Input must be set to logic 0 (grounded); other
encodings reserved.
CMOD0 65 I TTL
CPU Mode bit 1. Input must be set to logic 0 (grounded); other
encodings reserved.
CMOD1 76 I TTL
Fault 99 I TTL PWM Fault.
9 - Power Ground reference for logic and I/O pins.
15
21
33
39
45
54
57
63
69
82
87
94
GND
The ground reference for the analog circuits (ADC, Analog
Comparators, etc.). These are separated from GND to
minimize the electrical noise contained on VDD from affecting
the analog functions.
4 - Power
97
GNDA
An open-drain output with internal pull-up that indicates the
processor is in Hibernate mode.
HIB 51 O OD
I2C0SCL 70 I/O OD I2C module 0 clock.
I2C0SDA 71 I/O OD I2C module 0 data.
I2C1SCL 34 I/O OD I2C module 1 clock.
I2C1SDA 35 I/O OD I2C module 1 data.
IDX0 100 I TTL QEI module 0 index.
IDX1 84 I TTL QEI module 1 index.
January 08, 2011 653
Texas Instruments-Production Data
Stellaris® LM3S2965 Microcontroller
Table 20-2. Signals by Signal Name (continued)
Pin Name Pin Number Pin Type Buffer Typea Description
Low drop-out regulator output voltage. This pin requires an
external capacitor between the pin and GND of 1 μF or
greater. When the on-chip LDO is used to provide power to
the logic, the LDO pin must also be connected to the VDD25
pins at the board level in addition to the decoupling
capacitor(s).
LDO 7 - Power
Main oscillator crystal input or an external clock reference
input.
OSC0 48 I Analog
Main oscillator crystal output. Leave unconnected when using
a single-ended clock source.
OSC1 49 O Analog
PA0 26 I/O TTL GPIO port A bit 0.
PA1 27 I/O TTL GPIO port A bit 1.
PA2 28 I/O TTL GPIO port A bit 2.
PA3 29 I/O TTL GPIO port A bit 3.
PA4 30 I/O TTL GPIO port A bit 4.
PA5 31 I/O TTL GPIO port A bit 5.
PA6 34 I/O TTL GPIO port A bit 6.
PA7 35 I/O TTL GPIO port A bit 7.
PB0 66 I/O TTL GPIO port B bit 0.
PB1 67 I/O TTL GPIO port B bit 1.
PB2 70 I/O TTL GPIO port B bit 2.
PB3 71 I/O TTL GPIO port B bit 3.
PB4 92 I/O TTL GPIO port B bit 4.
PB5 91 I/O TTL GPIO port B bit 5.
PB6 90 I/O TTL GPIO port B bit 6.
PB7 89 I/O TTL GPIO port B bit 7.
PC0 80 I/O TTL GPIO port C bit 0.
PC1 79 I/O TTL GPIO port C bit 1.
PC2 78 I/O TTL GPIO port C bit 2.
PC3 77 I/O TTL GPIO port C bit 3.
PC4 25 I/O TTL GPIO port C bit 4.
PC5 24 I/O TTL GPIO port C bit 5.
PC6 23 I/O TTL GPIO port C bit 6.
PC7 22 I/O TTL GPIO port C bit 7.
PD0 10 I/O TTL GPIO port D bit 0.
PD1 11 I/O TTL GPIO port D bit 1.
PD2 12 I/O TTL GPIO port D bit 2.
PD3 13 I/O TTL GPIO port D bit 3.
PD4 95 I/O TTL GPIO port D bit 4.
PD5 96 I/O TTL GPIO port D bit 5.
PD6 99 I/O TTL GPIO port D bit 6.
PD7 100 I/O TTL GPIO port D bit 7.
PE0 72 I/O TTL GPIO port E bit 0.
654 January 08, 2011
Texas Instruments-Production Data
Signal Tables
Table 20-2. Signals by Signal Name (continued)
Pin Name Pin Number Pin Type Buffer Typea Description
PE1 73 I/O TTL GPIO port E bit 1.
PE2 74 I/O TTL GPIO port E bit 2.
PE3 75 I/O TTL GPIO port E bit 3.
PF0 47 I/O TTL GPIO port F bit 0.
PF1 61 I/O TTL GPIO port F bit 1.
PF2 60 I/O TTL GPIO port F bit 2.
PF3 59 I/O TTL GPIO port F bit 3.
PF4 58 I/O TTL GPIO port F bit 4.
PF5 46 I/O TTL GPIO port F bit 5.
PF6 43 I/O TTL GPIO port F bit 6.
PF7 42 I/O TTL GPIO port F bit 7.
PG0 19 I/O TTL GPIO port G bit 0.
PG1 18 I/O TTL GPIO port G bit 1.
PG2 17 I/O TTL GPIO port G bit 2.
PG3 16 I/O TTL GPIO port G bit 3.
PG4 41 I/O TTL GPIO port G bit 4.
PG5 40 I/O TTL GPIO port G bit 5.
PG6 37 I/O TTL GPIO port G bit 6.
PG7 36 I/O TTL GPIO port G bit 7.
PH0 86 I/O TTL GPIO port H bit 0.
PH1 85 I/O TTL GPIO port H bit 1.
PH2 84 I/O TTL GPIO port H bit 2.
PH3 83 I/O TTL GPIO port H bit 3.
PhA0 25 I TTL QEI module 0 phase A.
PhA1 37 I TTL QEI module 1 phase A.
PhB0 83 I TTL QEI module 0 phase B.
PhB1 36 I TTL QEI module 1 phase B.
PWM0 17 O TTL PWM 0. This signal is controlled by PWM Generator 0.
PWM1 16 O TTL PWM 1. This signal is controlled by PWM Generator 0.
PWM2 86 O TTL PWM 2. This signal is controlled by PWM Generator 1.
PWM3 85 O TTL PWM 3. This signal is controlled by PWM Generator 1.
PWM4 60 O TTL PWM 4. This signal is controlled by PWM Generator 2.
PWM5 59 O TTL PWM 5. This signal is controlled by PWM Generator 2.
RST 64 I TTL System reset input.
SSI0Clk 28 I/O TTL SSI module 0 clock.
SSI0Fss 29 I/O TTL SSI module 0 frame.
SSI0Rx 30 I TTL SSI module 0 receive.
SSI0Tx 31 O TTL SSI module 0 transmit.
SSI1Clk 72 I/O TTL SSI module 1 clock.
SSI1Fss 73 I/O TTL SSI module 1 frame.
SSI1Rx 74 I TTL SSI module 1 receive.
January 08, 2011 655
Texas Instruments-Production Data
Stellaris® LM3S2965 Microcontroller
Table 20-2. Signals by Signal Name (continued)
Pin Name Pin Number Pin Type Buffer Typea Description
SSI1Tx 75 O TTL SSI module 1 transmit.
SWCLK 80 I TTL JTAG/SWD CLK.
SWDIO 79 I/O TTL JTAG TMS and SWDIO.
SWO 77 O TTL JTAG TDO and SWO.
TCK 80 I TTL JTAG/SWD CLK.
TDI 78 I TTL JTAG TDI.
TDO 77 O TTL JTAG TDO and SWO.
TMS 79 I/O TTL JTAG TMS and SWDIO.
TRST 89 I TTL JTAG TRST.
UART module 0 receive. When in IrDA mode, this signal has
IrDA modulation.
U0Rx 26 I TTL
UART module 0 transmit. When in IrDA mode, this signal has
IrDA modulation.
U0Tx 27 O TTL
UART module 1 receive. When in IrDA mode, this signal has
IrDA modulation.
U1Rx 12 I TTL
UART module 1 transmit. When in IrDA mode, this signal has
IrDA modulation.
U1Tx 13 O TTL
UART module 2 receive. When in IrDA mode, this signal has
IrDA modulation.
U2Rx 19 I TTL
UART module 2 transmit. When in IrDA mode, this signal has
IrDA modulation.
U2Tx 18 O TTL
Power source for the Hibernation module. It is normally
connected to the positive terminal of a battery and serves as
the battery backup/Hibernation module power-source supply.
VBAT 55 - Power
8 - Power Positive supply for I/O and some logic.
20
32
44
56
68
81
93
VDD
Positive supply for most of the logic function, including the
processor core and most peripherals.
14 - Power
38
62
88
VDD25
The positive supply (3.3 V) for the analog circuits (ADC,
Analog Comparators, etc.). These are separated from VDD
to minimize the electrical noise contained on VDD from
affecting the analog functions. VDDA pins must be connected
to 3.3 V, regardless of system implementation.
3 - Power
98
VDDA
An external input that brings the processor out of Hibernate
mode when asserted.
WAKE 50 I TTL
Hibernation module oscillator crystal input or an external clock
reference input. Note that this is either a crystal or a
32.768-kHz oscillator for the Hibernation module RTC.
XOSC0 52 I Analog
Hibernation module oscillator crystal output. Leave
unconnected when using a single-ended clock source.
XOSC1 53 O Analog
a. The TTL designation indicates the pin has TTL-compatible voltage levels.
656 January 08, 2011
Texas Instruments-Production Data
Signal Tables
Table 20-3. Signals by Function, Except for GPIO
Function Pin Name Pin Number Pin Type Buffer Typea Description
ADC0 1 I Analog Analog-to-digital converter input 0.
ADC
ADC1 2 I Analog Analog-to-digital converter input 1.
ADC2 5 I Analog Analog-to-digital converter input 2.
ADC3 6 I Analog Analog-to-digital converter input 3.
C0+ 90 I Analog Analog comparator 0 positive input.
Analog Comparators
C0- 92 I Analog Analog comparator 0 negative input.
C0o 58 O TTL Analog comparator 0 output.
C1+ 24 I Analog Analog comparator 1 positive input.
C1- 91 I Analog Analog comparator 1 negative input.
C2+ 23 I Analog Analog comparator 2 positive input.
C2- 22 I Analog Analog comparator 2 negative input.
CAN0Rx 10 I TTL CAN module 0 receive.
Controller Area
Network
CAN0Tx 11 O TTL CAN module 0 transmit.
CAN1Rx 47 I TTL CAN module 1 receive.
CAN1Tx 61 O TTL CAN module 1 transmit.
CCP0 66 I/O TTL Capture/Compare/PWM 0.
General-Purpose
Timers
CCP1 43 I/O TTL Capture/Compare/PWM 1.
CCP2 67 I/O TTL Capture/Compare/PWM 2.
CCP3 95 I/O TTL Capture/Compare/PWM 3.
CCP4 96 I/O TTL Capture/Compare/PWM 4.
CCP5 40 I/O TTL Capture/Compare/PWM 5.
An open-drain output with internal pull-up that
indicates the processor is in Hibernate mode.
HIB 51 O OD
Hibernate
Power source for the Hibernation module. It is
normally connected to the positive terminal of a
battery and serves as the battery
backup/Hibernation module power-source supply.
VBAT 55 - Power
An external input that brings the processor out of
Hibernate mode when asserted.
WAKE 50 I TTL
Hibernation module oscillator crystal input or an
external clock reference input. Note that this is
either a crystal or a 32.768-kHz oscillator for the
Hibernation module RTC.
XOSC0 52 I Analog
Hibernation module oscillator crystal output. Leave
unconnected when using a single-ended clock
source.
XOSC1 53 O Analog
I2C0SCL 70 I/O OD I2C module 0 clock.
I2C
I2C0SDA 71 I/O OD I2C module 0 data.
I2C1SCL 34 I/O OD I2C module 1 clock.
I2C1SDA 35 I/O OD I2C module 1 data.
January 08, 2011 657
Texas Instruments-Production Data
Stellaris® LM3S2965 Microcontroller
Table 20-3. Signals by Function, Except for GPIO (continued)
Function Pin Name Pin Number Pin Type Buffer Typea Description
SWCLK 80 I TTL JTAG/SWD CLK.
JTAG/SWD/SWO
SWDIO 79 I/O TTL JTAG TMS and SWDIO.
SWO 77 O TTL JTAG TDO and SWO.
TCK 80 I TTL JTAG/SWD CLK.
TDI 78 I TTL JTAG TDI.
TDO 77 O TTL JTAG TDO and SWO.
TMS 79 I/O TTL JTAG TMS and SWDIO.
TRST 89 I TTL JTAG TRST.
Fault 99 I TTL PWM Fault.
PWM
PWM 0. This signal is controlled by PWM Generator
0.
PWM0 17 O TTL
PWM 1. This signal is controlled by PWM Generator
0.
PWM1 16 O TTL
PWM 2. This signal is controlled by PWM Generator
1.
PWM2 86 O TTL
PWM 3. This signal is controlled by PWM Generator
1.
PWM3 85 O TTL
PWM 4. This signal is controlled by PWM Generator
2.
PWM4 60 O TTL
PWM 5. This signal is controlled by PWM Generator
2.
PWM5 59 O TTL
658 January 08, 2011
Texas Instruments-Production Data
Signal Tables
Table 20-3. Signals by Function, Except for GPIO (continued)
Function Pin Name Pin Number Pin Type Buffer Typea Description
9 - Power Ground reference for logic and I/O pins.
15
21
33
39
45
54
57
63
69
82
87
94
GND
Power
The ground reference for the analog circuits (ADC,
Analog Comparators, etc.). These are separated
from GND to minimize the electrical noise contained
on VDD from affecting the analog functions.
4 - Power
97
GNDA
Low drop-out regulator output voltage. This pin
requires an external capacitor between the pin and
GND of 1 μF or greater. When the on-chip LDO is
used to provide power to the logic, the LDO pin must
also be connected to the VDD25 pins at the board
level in addition to the decoupling capacitor(s).
LDO 7 - Power
8 - Power Positive supply for I/O and some logic.
20
32
44
56
68
81
93
VDD
Positive supply for most of the logic function,
including the processor core and most peripherals.
14 - Power
38
62
88
VDD25
The positive supply (3.3 V) for the analog circuits
(ADC, Analog Comparators, etc.). These are
separated from VDD to minimize the electrical noise
contained on VDD from affecting the analog
functions. VDDA pins must be connected to 3.3 V,
regardless of system implementation.
3 - Power
98
VDDA
IDX0 100 I TTL QEI module 0 index.
QEI
IDX1 84 I TTL QEI module 1 index.
PhA0 25 I TTL QEI module 0 phase A.
PhA1 37 I TTL QEI module 1 phase A.
PhB0 83 I TTL QEI module 0 phase B.
PhB1 36 I TTL QEI module 1 phase B.
January 08, 2011 659
Texas Instruments-Production Data
Stellaris® LM3S2965 Microcontroller
Table 20-3. Signals by Function, Except for GPIO (continued)
Function Pin Name Pin Number Pin Type Buffer Typea Description
SSI0Clk 28 I/O TTL SSI module 0 clock.
SSI
SSI0Fss 29 I/O TTL SSI module 0 frame.
SSI0Rx 30 I TTL SSI module 0 receive.
SSI0Tx 31 O TTL SSI module 0 transmit.
SSI1Clk 72 I/O TTL SSI module 1 clock.
SSI1Fss 73 I/O TTL SSI module 1 frame.
SSI1Rx 74 I TTL SSI module 1 receive.
SSI1Tx 75 O TTL SSI module 1 transmit.
CPU Mode bit 0. Input must be set to logic 0
(grounded); other encodings reserved.
CMOD0 65 I TTL
System Control &
Clocks
CPU Mode bit 1. Input must be set to logic 0
(grounded); other encodings reserved.
CMOD1 76 I TTL
Main oscillator crystal input or an external clock
reference input.
OSC0 48 I Analog
Main oscillator crystal output. Leave unconnected
when using a single-ended clock source.
OSC1 49 O Analog
RST 64 I TTL System reset input.
UART module 0 receive. When in IrDA mode, this
signal has IrDA modulation.
U0Rx 26 I TTL
UART
UART module 0 transmit. When in IrDA mode, this
signal has IrDA modulation.
U0Tx 27 O TTL
UART module 1 receive. When in IrDA mode, this
signal has IrDA modulation.
U1Rx 12 I TTL
UART module 1 transmit. When in IrDA mode, this
signal has IrDA modulation.
U1Tx 13 O TTL
UART module 2 receive. When in IrDA mode, this
signal has IrDA modulation.
U2Rx 19 I TTL
UART module 2 transmit. When in IrDA mode, this
signal has IrDA modulation.
U2Tx 18 O TTL
a. The TTL designation indicates the pin has TTL-compatible voltage levels.
Table 20-4. GPIO Pins and Alternate Functions
IO Pin Number Multiplexed Function Multiplexed Function
PA0 26 U0Rx
PA1 27 U0Tx
PA2 28 SSI0Clk
PA3 29 SSI0Fss
PA4 30 SSI0Rx
PA5 31 SSI0Tx
PA6 34 I2C1SCL
PA7 35 I2C1SDA
PB0 66 CCP0
PB1 67 CCP2
PB2 70 I2C0SCL
PB3 71 I2C0SDA
660 January 08, 2011
Texas Instruments-Production Data
Signal Tables
Table 20-4. GPIO Pins and Alternate Functions (continued)
IO Pin Number Multiplexed Function Multiplexed Function
PB4 92 C0-
PB5 91 C1-
PB6 90 C0+
PB7 89 TRST
PC0 80 TCK SWCLK
PC1 79 TMS SWDIO
PC2 78 TDI
PC3 77 TDO SWO
PC4 25 PhA0
PC5 24 C1+
PC6 23 C2+
PC7 22 C2-
PD0 10 CAN0Rx
PD1 11 CAN0Tx
PD2 12 U1Rx
PD3 13 U1Tx
PD4 95 CCP3
PD5 96 CCP4
PD6 99 Fault
PD7 100 IDX0
PE0 72 SSI1Clk
PE1 73 SSI1Fss
PE2 74 SSI1Rx
PE3 75 SSI1Tx
PF0 47 CAN1Rx
PF1 61 CAN1Tx
PF2 60 PWM4
PF3 59 PWM5
PF4 58 C0o
PF5 46
PF6 43 CCP1
PF7 42
PG0 19 U2Rx
PG1 18 U2Tx
PG2 17 PWM0
PG3 16 PWM1
PG4 41
PG5 40 CCP5
PG6 37 PhA1
PG7 36 PhB1
PH0 86 PWM2
January 08, 2011 661
Texas Instruments-Production Data
Stellaris® LM3S2965 Microcontroller
Table 20-4. GPIO Pins and Alternate Functions (continued)
IO Pin Number Multiplexed Function Multiplexed Function
PH1 85 PWM3
PH2 84 IDX1
PH3 83 PhB0
20.2 108-Pin BGA Package Pin Tables
Table 20-5. Signals by Pin Number
Pin Number Pin Name Pin Type Buffer Typea Description
A1 ADC1 I Analog Analog-to-digital converter input 1.
A2 NC - - No connect. Leave the pin electrically unconnected/isolated.
A3 NC - - No connect. Leave the pin electrically unconnected/isolated.
A4 NC - - No connect. Leave the pin electrically unconnected/isolated.
The ground reference for the analog circuits (ADC, Analog
Comparators, etc.). These are separated from GND to minimize
the electrical noise contained on VDD from affecting the analog
functions.
GNDA - Power
A5
PB4 I/O TTL GPIO port B bit 4.
A6
C0- I Analog Analog comparator 0 negative input.
PB6 I/O TTL GPIO port B bit 6.
A7
C0+ I Analog Analog comparator 0 positive input.
PB7 I/O TTL GPIO port B bit 7.
A8
TRST I TTL JTAG TRST.
PC0 I/O TTL GPIO port C bit 0.
A9 SWCLK I TTL JTAG/SWD CLK.
TCK I TTL JTAG/SWD CLK.
PC3 I/O TTL GPIO port C bit 3.
A10 SWO O TTL JTAG TDO and SWO.
TDO O TTL JTAG TDO and SWO.
PE0 I/O TTL GPIO port E bit 0.
A11
SSI1Clk I/O TTL SSI module 1 clock.
PE3 I/O TTL GPIO port E bit 3.
A12
SSI1Tx O TTL SSI module 1 transmit.
B1 ADC0 I Analog Analog-to-digital converter input 0.
B2 ADC3 I Analog Analog-to-digital converter input 3.
B3 ADC2 I Analog Analog-to-digital converter input 2.
B4 NC - - No connect. Leave the pin electrically unconnected/isolated.
The ground reference for the analog circuits (ADC, Analog
Comparators, etc.). These are separated from GND to minimize
the electrical noise contained on VDD from affecting the analog
functions.
GNDA - Power
B5
B6 GND - Power Ground reference for logic and I/O pins.
PB5 I/O TTL GPIO port B bit 5.
B7
C1- I Analog Analog comparator 1 negative input.
662 January 08, 2011
Texas Instruments-Production Data
Signal Tables
Table 20-5. Signals by Pin Number (continued)
Pin Number Pin Name Pin Type Buffer Typea Description
PC2 I/O TTL GPIO port C bit 2.
B8
TDI I TTL JTAG TDI.
PC1 I/O TTL GPIO port C bit 1.
B9 SWDIO I/O TTL JTAG TMS and SWDIO.
TMS I/O TTL JTAG TMS and SWDIO.
CPU Mode bit 1. Input must be set to logic 0 (grounded); other
encodings reserved.
CMOD1 I TTL B10
PE2 I/O TTL GPIO port E bit 2.
B11
SSI1Rx I TTL SSI module 1 receive.
PE1 I/O TTL GPIO port E bit 1.
B12
SSI1Fss I/O TTL SSI module 1 frame.
C1 NC - - No connect. Leave the pin electrically unconnected/isolated.
C2 NC - - No connect. Leave the pin electrically unconnected/isolated.
Positive supply for most of the logic function, including the
processor core and most peripherals.
VDD25 - Power C3
C4 GND - Power Ground reference for logic and I/O pins.
C5 GND - Power Ground reference for logic and I/O pins.
The positive supply (3.3 V) for the analog circuits (ADC, Analog
Comparators, etc.). These are separated from VDD to minimize
the electrical noise contained on VDD from affecting the analog
functions. VDDA pins must be connected to 3.3 V, regardless of
system implementation.
VDDA - Power
C6
The positive supply (3.3 V) for the analog circuits (ADC, Analog
Comparators, etc.). These are separated from VDD to minimize
the electrical noise contained on VDD from affecting the analog
functions. VDDA pins must be connected to 3.3 V, regardless of
system implementation.
VDDA - Power
C7
PH1 I/O TTL GPIO port H bit 1.
C8
PWM3 O TTL PWM 3. This signal is controlled by PWM Generator 1.
PH0 I/O TTL GPIO port H bit 0.
C9
PWM2 O TTL PWM 2. This signal is controlled by PWM Generator 1.
PG7 I/O TTL GPIO port G bit 7.
C10
PhB1 I TTL QEI module 1 phase B.
PB2 I/O TTL GPIO port B bit 2.
C11
I2C0SCL I/O OD I2C module 0 clock.
PB3 I/O TTL GPIO port B bit 3.
C12
I2C0SDA I/O OD I2C module 0 data.
D1 NC - - No connect. Leave the pin electrically unconnected/isolated.
D2 NC - - No connect. Leave the pin electrically unconnected/isolated.
Positive supply for most of the logic function, including the
processor core and most peripherals.
VDD25 - Power D3
PH3 I/O TTL GPIO port H bit 3.
D10
PhB0 I TTL QEI module 0 phase B.
PH2 I/O TTL GPIO port H bit 2.
D11
IDX1 I TTL QEI module 1 index.
January 08, 2011 663
Texas Instruments-Production Data
Stellaris® LM3S2965 Microcontroller
Table 20-5. Signals by Pin Number (continued)
Pin Number Pin Name Pin Type Buffer Typea Description
PB1 I/O TTL GPIO port B bit 1.
D12
CCP2 I/O TTL Capture/Compare/PWM 2.
PD4 I/O TTL GPIO port D bit 4.
E1
CCP3 I/O TTL Capture/Compare/PWM 3.
PD5 I/O TTL GPIO port D bit 5.
E2
CCP4 I/O TTL Capture/Compare/PWM 4.
Low drop-out regulator output voltage. This pin requires an external
capacitor between the pin and GND of 1 μF or greater. When the
on-chip LDO is used to provide power to the logic, the LDO pin
must also be connected to the VDD25 pins at the board level in
addition to the decoupling capacitor(s).
LDO - Power
E3
E10 VDD33 - Power Positive supply for I/O and some logic.
CPU Mode bit 0. Input must be set to logic 0 (grounded); other
encodings reserved.
CMOD0 I TTL E11
PB0 I/O TTL GPIO port B bit 0.
E12
CCP0 I/O TTL Capture/Compare/PWM 0.
PD7 I/O TTL GPIO port D bit 7.
F1
IDX0 I TTL QEI module 0 index.
PD6 I/O TTL GPIO port D bit 6.
F2
Fault I TTL PWM Fault.
Positive supply for most of the logic function, including the
processor core and most peripherals.
VDD25 - Power F3
F10 GND - Power Ground reference for logic and I/O pins.
F11 GND - Power Ground reference for logic and I/O pins.
F12 GND - Power Ground reference for logic and I/O pins.
PD0 I/O TTL GPIO port D bit 0.
G1
CAN0Rx I TTL CAN module 0 receive.
PD1 I/O TTL GPIO port D bit 1.
G2
CAN0Tx O TTL CAN module 0 transmit.
Positive supply for most of the logic function, including the
processor core and most peripherals.
VDD25 - Power G3
G10 VDD33 - Power Positive supply for I/O and some logic.
G11 VDD33 - Power Positive supply for I/O and some logic.
G12 VDD33 - Power Positive supply for I/O and some logic.
PD3 I/O TTL GPIO port D bit 3.
H1 UART module 1 transmit. When in IrDA mode, this signal has IrDA
modulation.
U1Tx O TTL
PD2 I/O TTL GPIO port D bit 2.
H2 UART module 1 receive. When in IrDA mode, this signal has IrDA
modulation.
U1Rx I TTL
H3 GND - Power Ground reference for logic and I/O pins.
H10 VDD33 - Power Positive supply for I/O and some logic.
H11 RST I TTL System reset input.
664 January 08, 2011
Texas Instruments-Production Data
Signal Tables
Table 20-5. Signals by Pin Number (continued)
Pin Number Pin Name Pin Type Buffer Typea Description
PF1 I/O TTL GPIO port F bit 1.
H12
CAN1Tx O TTL CAN module 1 transmit.
PG2 I/O TTL GPIO port G bit 2.
J1
PWM0 O TTL PWM 0. This signal is controlled by PWM Generator 0.
PG3 I/O TTL GPIO port G bit 3.
J2
PWM1 O TTL PWM 1. This signal is controlled by PWM Generator 0.
J3 GND - Power Ground reference for logic and I/O pins.
J10 GND - Power Ground reference for logic and I/O pins.
PF2 I/O TTL GPIO port F bit 2.
J11
PWM4 O TTL PWM 4. This signal is controlled by PWM Generator 2.
PF3 I/O TTL GPIO port F bit 3.
J12
PWM5 O TTL PWM 5. This signal is controlled by PWM Generator 2.
PG0 I/O TTL GPIO port G bit 0.
K1 UART module 2 receive. When in IrDA mode, this signal has IrDA
modulation.
U2Rx I TTL
PG1 I/O TTL GPIO port G bit 1.
K2 UART module 2 transmit. When in IrDA mode, this signal has IrDA
modulation.
U2Tx O TTL
K3 PG4 I/O TTL GPIO port G bit 4.
K4 PF7 I/O TTL GPIO port F bit 7.
K5 GND - Power Ground reference for logic and I/O pins.
K6 GND - Power Ground reference for logic and I/O pins.
K7 VDD33 - Power Positive supply for I/O and some logic.
K8 VDD33 - Power Positive supply for I/O and some logic.
K9 VDD33 - Power Positive supply for I/O and some logic.
K10 GND - Power Ground reference for logic and I/O pins.
Hibernation module oscillator crystal input or an external clock
reference input. Note that this is either a crystal or a 32.768-kHz
oscillator for the Hibernation module RTC.
XOSC0 I Analog
K11
Hibernation module oscillator crystal output. Leave unconnected
when using a single-ended clock source.
XOSC1 O Analog K12
PC4 I/O TTL GPIO port C bit 4.
L1
PhA0 I TTL QEI module 0 phase A.
PC7 I/O TTL GPIO port C bit 7.
L2
C2- I Analog Analog comparator 2 negative input.
PA0 I/O TTL GPIO port A bit 0.
L3 UART module 0 receive. When in IrDA mode, this signal has IrDA
modulation.
U0Rx I TTL
PA3 I/O TTL GPIO port A bit 3.
L4
SSI0Fss I/O TTL SSI module 0 frame.
PA4 I/O TTL GPIO port A bit 4.
L5
SSI0Rx I TTL SSI module 0 receive.
January 08, 2011 665
Texas Instruments-Production Data
Stellaris® LM3S2965 Microcontroller
Table 20-5. Signals by Pin Number (continued)
Pin Number Pin Name Pin Type Buffer Typea Description
PA6 I/O TTL GPIO port A bit 6.
L6
I2C1SCL I/O OD I2C module 1 clock.
PG6 I/O TTL GPIO port G bit 6.
L7
PhA1 I TTL QEI module 1 phase A.
L8 PF5 I/O TTL GPIO port F bit 5.
PF4 I/O TTL GPIO port F bit 4.
L9
C0o O TTL Analog comparator 0 output.
L10 GND - Power Ground reference for logic and I/O pins.
L11 OSC0 I Analog Main oscillator crystal input or an external clock reference input.
Power source for the Hibernation module. It is normally connected
to the positive terminal of a battery and serves as the battery
backup/Hibernation module power-source supply.
VBAT - Power
L12
PC5 I/O TTL GPIO port C bit 5.
M1
C1+ I Analog Analog comparator 1 positive input.
PC6 I/O TTL GPIO port C bit 6.
M2
C2+ I Analog Analog comparator 2 positive input.
PA1 I/O TTL GPIO port A bit 1.
M3 UART module 0 transmit. When in IrDA mode, this signal has IrDA
modulation.
U0Tx O TTL
PA2 I/O TTL GPIO port A bit 2.
M4
SSI0Clk I/O TTL SSI module 0 clock.
PA5 I/O TTL GPIO port A bit 5.
M5
SSI0Tx O TTL SSI module 0 transmit.
PA7 I/O TTL GPIO port A bit 7.
M6
I2C1SDA I/O OD I2C module 1 data.
PG5 I/O TTL GPIO port G bit 5.
M7
CCP5 I/O TTL Capture/Compare/PWM 5.
PF6 I/O TTL GPIO port F bit 6.
M8
CCP1 I/O TTL Capture/Compare/PWM 1.
PF0 I/O TTL GPIO port F bit 0.
M9
CAN1Rx I TTL CAN module 1 receive.
An external input that brings the processor out of Hibernate mode
when asserted.
WAKE I TTL M10
Main oscillator crystal output. Leave unconnected when using a
single-ended clock source.
OSC1 O Analog M11
An open-drain output with internal pull-up that indicates the
processor is in Hibernate mode.
HIB O OD M12
a. The TTL designation indicates the pin has TTL-compatible voltage levels.
Table 20-6. Signals by Signal Name
Pin Name Pin Number Pin Type Buffer Typea Description
ADC0 B1 I Analog Analog-to-digital converter input 0.
ADC1 A1 I Analog Analog-to-digital converter input 1.
666 January 08, 2011
Texas Instruments-Production Data
Signal Tables
Table 20-6. Signals by Signal Name (continued)
Pin Name Pin Number Pin Type Buffer Typea Description
ADC2 B3 I Analog Analog-to-digital converter input 2.
ADC3 B2 I Analog Analog-to-digital converter input 3.
C0+ A7 I Analog Analog comparator 0 positive input.
C0- A6 I Analog Analog comparator 0 negative input.
C0o L9 O TTL Analog comparator 0 output.
C1+ M1 I Analog Analog comparator 1 positive input.
C1- B7 I Analog Analog comparator 1 negative input.
C2+ M2 I Analog Analog comparator 2 positive input.
C2- L2 I Analog Analog comparator 2 negative input.
CAN0Rx G1 I TTL CAN module 0 receive.
CAN0Tx G2 O TTL CAN module 0 transmit.
CAN1Rx M9 I TTL CAN module 1 receive.
CAN1Tx H12 O TTL CAN module 1 transmit.
CCP0 E12 I/O TTL Capture/Compare/PWM 0.
CCP1 M8 I/O TTL Capture/Compare/PWM 1.
CCP2 D12 I/O TTL Capture/Compare/PWM 2.
CCP3 E1 I/O TTL Capture/Compare/PWM 3.
CCP4 E2 I/O TTL Capture/Compare/PWM 4.
CCP5 M7 I/O TTL Capture/Compare/PWM 5.
CPU Mode bit 0. Input must be set to logic 0 (grounded); other
encodings reserved.
CMOD0 E11 I TTL
CPU Mode bit 1. Input must be set to logic 0 (grounded); other
encodings reserved.
CMOD1 B10 I TTL
Fault F2 I TTL PWM Fault.
B6 - Power Ground reference for logic and I/O pins.
C4
C5
F10
F11
F12
H3
J3
J10
K5
K6
K10
L10
GND
The ground reference for the analog circuits (ADC, Analog
Comparators, etc.). These are separated from GND to
minimize the electrical noise contained on VDD from affecting
the analog functions.
A5 - Power
B5
GNDA
An open-drain output with internal pull-up that indicates the
processor is in Hibernate mode.
HIB M12 O OD
I2C0SCL C11 I/O OD I2C module 0 clock.
I2C0SDA C12 I/O OD I2C module 0 data.
I2C1SCL L6 I/O OD I2C module 1 clock.
I2C1SDA M6 I/O OD I2C module 1 data.
January 08, 2011 667
Texas Instruments-Production Data
Stellaris® LM3S2965 Microcontroller
Table 20-6. Signals by Signal Name (continued)
Pin Name Pin Number Pin Type Buffer Typea Description
IDX0 F1 I TTL QEI module 0 index.
IDX1 D11 I TTL QEI module 1 index.
Low drop-out regulator output voltage. This pin requires an
external capacitor between the pin and GND of 1 μF or
greater. When the on-chip LDO is used to provide power to
the logic, the LDO pin must also be connected to the VDD25
pins at the board level in addition to the decoupling
capacitor(s).
LDO E3 - Power
A2 - - No connect. Leave the pin electrically unconnected/isolated.
A3
A4
B4
C1
C2
D1
D2
NC
Main oscillator crystal input or an external clock reference
input.
OSC0 L11 I Analog
Main oscillator crystal output. Leave unconnected when using
a single-ended clock source.
OSC1 M11 O Analog
PA0 L3 I/O TTL GPIO port A bit 0.
PA1 M3 I/O TTL GPIO port A bit 1.
PA2 M4 I/O TTL GPIO port A bit 2.
PA3 L4 I/O TTL GPIO port A bit 3.
PA4 L5 I/O TTL GPIO port A bit 4.
PA5 M5 I/O TTL GPIO port A bit 5.
PA6 L6 I/O TTL GPIO port A bit 6.
PA7 M6 I/O TTL GPIO port A bit 7.
PB0 E12 I/O TTL GPIO port B bit 0.
PB1 D12 I/O TTL GPIO port B bit 1.
PB2 C11 I/O TTL GPIO port B bit 2.
PB3 C12 I/O TTL GPIO port B bit 3.
PB4 A6 I/O TTL GPIO port B bit 4.
PB5 B7 I/O TTL GPIO port B bit 5.
PB6 A7 I/O TTL GPIO port B bit 6.
PB7 A8 I/O TTL GPIO port B bit 7.
PC0 A9 I/O TTL GPIO port C bit 0.
PC1 B9 I/O TTL GPIO port C bit 1.
PC2 B8 I/O TTL GPIO port C bit 2.
PC3 A10 I/O TTL GPIO port C bit 3.
PC4 L1 I/O TTL GPIO port C bit 4.
PC5 M1 I/O TTL GPIO port C bit 5.
PC6 M2 I/O TTL GPIO port C bit 6.
PC7 L2 I/O TTL GPIO port C bit 7.
PD0 G1 I/O TTL GPIO port D bit 0.
PD1 G2 I/O TTL GPIO port D bit 1.
668 January 08, 2011
Texas Instruments-Production Data
Signal Tables
Table 20-6. Signals by Signal Name (continued)
Pin Name Pin Number Pin Type Buffer Typea Description
PD2 H2 I/O TTL GPIO port D bit 2.
PD3 H1 I/O TTL GPIO port D bit 3.
PD4 E1 I/O TTL GPIO port D bit 4.
PD5 E2 I/O TTL GPIO port D bit 5.
PD6 F2 I/O TTL GPIO port D bit 6.
PD7 F1 I/O TTL GPIO port D bit 7.
PE0 A11 I/O TTL GPIO port E bit 0.
PE1 B12 I/O TTL GPIO port E bit 1.
PE2 B11 I/O TTL GPIO port E bit 2.
PE3 A12 I/O TTL GPIO port E bit 3.
PF0 M9 I/O TTL GPIO port F bit 0.
PF1 H12 I/O TTL GPIO port F bit 1.
PF2 J11 I/O TTL GPIO port F bit 2.
PF3 J12 I/O TTL GPIO port F bit 3.
PF4 L9 I/O TTL GPIO port F bit 4.
PF5 L8 I/O TTL GPIO port F bit 5.
PF6 M8 I/O TTL GPIO port F bit 6.
PF7 K4 I/O TTL GPIO port F bit 7.
PG0 K1 I/O TTL GPIO port G bit 0.
PG1 K2 I/O TTL GPIO port G bit 1.
PG2 J1 I/O TTL GPIO port G bit 2.
PG3 J2 I/O TTL GPIO port G bit 3.
PG4 K3 I/O TTL GPIO port G bit 4.
PG5 M7 I/O TTL GPIO port G bit 5.
PG6 L7 I/O TTL GPIO port G bit 6.
PG7 C10 I/O TTL GPIO port G bit 7.
PH0 C9 I/O TTL GPIO port H bit 0.
PH1 C8 I/O TTL GPIO port H bit 1.
PH2 D11 I/O TTL GPIO port H bit 2.
PH3 D10 I/O TTL GPIO port H bit 3.
PhA0 L1 I TTL QEI module 0 phase A.
PhA1 L7 I TTL QEI module 1 phase A.
PhB0 D10 I TTL QEI module 0 phase B.
PhB1 C10 I TTL QEI module 1 phase B.
PWM0 J1 O TTL PWM 0. This signal is controlled by PWM Generator 0.
PWM1 J2 O TTL PWM 1. This signal is controlled by PWM Generator 0.
PWM2 C9 O TTL PWM 2. This signal is controlled by PWM Generator 1.
PWM3 C8 O TTL PWM 3. This signal is controlled by PWM Generator 1.
PWM4 J11 O TTL PWM 4. This signal is controlled by PWM Generator 2.
PWM5 J12 O TTL PWM 5. This signal is controlled by PWM Generator 2.
RST H11 I TTL System reset input.
January 08, 2011 669
Texas Instruments-Production Data
Stellaris® LM3S2965 Microcontroller
Table 20-6. Signals by Signal Name (continued)
Pin Name Pin Number Pin Type Buffer Typea Description
SSI0Clk M4 I/O TTL SSI module 0 clock.
SSI0Fss L4 I/O TTL SSI module 0 frame.
SSI0Rx L5 I TTL SSI module 0 receive.
SSI0Tx M5 O TTL SSI module 0 transmit.
SSI1Clk A11 I/O TTL SSI module 1 clock.
SSI1Fss B12 I/O TTL SSI module 1 frame.
SSI1Rx B11 I TTL SSI module 1 receive.
SSI1Tx A12 O TTL SSI module 1 transmit.
SWCLK A9 I TTL JTAG/SWD CLK.
SWDIO B9 I/O TTL JTAG TMS and SWDIO.
SWO A10 O TTL JTAG TDO and SWO.
TCK A9 I TTL JTAG/SWD CLK.
TDI B8 I TTL JTAG TDI.
TDO A10 O TTL JTAG TDO and SWO.
TMS B9 I/O TTL JTAG TMS and SWDIO.
TRST A8 I TTL JTAG TRST.
UART module 0 receive. When in IrDA mode, this signal has
IrDA modulation.
U0Rx L3 I TTL
UART module 0 transmit. When in IrDA mode, this signal has
IrDA modulation.
U0Tx M3 O TTL
UART module 1 receive. When in IrDA mode, this signal has
IrDA modulation.
U1Rx H2 I TTL
UART module 1 transmit. When in IrDA mode, this signal has
IrDA modulation.
U1Tx H1 O TTL
UART module 2 receive. When in IrDA mode, this signal has
IrDA modulation.
U2Rx K1 I TTL
UART module 2 transmit. When in IrDA mode, this signal has
IrDA modulation.
U2Tx K2 O TTL
Power source for the Hibernation module. It is normally
connected to the positive terminal of a battery and serves as
the battery backup/Hibernation module power-source supply.
VBAT L12 - Power
Positive supply for most of the logic function, including the
processor core and most peripherals.
C3 - Power
D3
F3
G3
VDD25
E10 - Power Positive supply for I/O and some logic.
G10
G11
G12
H10
K7
K8
K9
VDD33
The positive supply (3.3 V) for the analog circuits (ADC,
Analog Comparators, etc.). These are separated from VDD
to minimize the electrical noise contained on VDD from
affecting the analog functions. VDDA pins must be connected
to 3.3 V, regardless of system implementation.
C6 - Power
C7
VDDA
670 January 08, 2011
Texas Instruments-Production Data
Signal Tables
Table 20-6. Signals by Signal Name (continued)
Pin Name Pin Number Pin Type Buffer Typea Description
An external input that brings the processor out of Hibernate
mode when asserted.
WAKE M10 I TTL
Hibernation module oscillator crystal input or an external clock
reference input. Note that this is either a crystal or a
32.768-kHz oscillator for the Hibernation module RTC.
XOSC0 K11 I Analog
Hibernation module oscillator crystal output. Leave
unconnected when using a single-ended clock source.
XOSC1 K12 O Analog
a. The TTL designation indicates the pin has TTL-compatible voltage levels.
Table 20-7. Signals by Function, Except for GPIO
Function Pin Name Pin Number Pin Type Buffer Typea Description
ADC0 B1 I Analog Analog-to-digital converter input 0.
ADC
ADC1 A1 I Analog Analog-to-digital converter input 1.
ADC2 B3 I Analog Analog-to-digital converter input 2.
ADC3 B2 I Analog Analog-to-digital converter input 3.
C0+ A7 I Analog Analog comparator 0 positive input.
Analog Comparators
C0- A6 I Analog Analog comparator 0 negative input.
C0o L9 O TTL Analog comparator 0 output.
C1+ M1 I Analog Analog comparator 1 positive input.
C1- B7 I Analog Analog comparator 1 negative input.
C2+ M2 I Analog Analog comparator 2 positive input.
C2- L2 I Analog Analog comparator 2 negative input.
CAN0Rx G1 I TTL CAN module 0 receive.
Controller Area
Network
CAN0Tx G2 O TTL CAN module 0 transmit.
CAN1Rx M9 I TTL CAN module 1 receive.
CAN1Tx H12 O TTL CAN module 1 transmit.
CCP0 E12 I/O TTL Capture/Compare/PWM 0.
General-Purpose
Timers
CCP1 M8 I/O TTL Capture/Compare/PWM 1.
CCP2 D12 I/O TTL Capture/Compare/PWM 2.
CCP3 E1 I/O TTL Capture/Compare/PWM 3.
CCP4 E2 I/O TTL Capture/Compare/PWM 4.
CCP5 M7 I/O TTL Capture/Compare/PWM 5.
January 08, 2011 671
Texas Instruments-Production Data
Stellaris® LM3S2965 Microcontroller
Table 20-7. Signals by Function, Except for GPIO (continued)
Function Pin Name Pin Number Pin Type Buffer Typea Description
An open-drain output with internal pull-up that
indicates the processor is in Hibernate mode.
HIB M12 O OD
Hibernate
Power source for the Hibernation module. It is
normally connected to the positive terminal of a
battery and serves as the battery
backup/Hibernation module power-source supply.
VBAT L12 - Power
An external input that brings the processor out of
Hibernate mode when asserted.
WAKE M10 I TTL
Hibernation module oscillator crystal input or an
external clock reference input. Note that this is
either a crystal or a 32.768-kHz oscillator for the
Hibernation module RTC.
XOSC0 K11 I Analog
Hibernation module oscillator crystal output. Leave
unconnected when using a single-ended clock
source.
XOSC1 K12 O Analog
I2C0SCL C11 I/O OD I2C module 0 clock.
I2C
I2C0SDA C12 I/O OD I2C module 0 data.
I2C1SCL L6 I/O OD I2C module 1 clock.
I2C1SDA M6 I/O OD I2C module 1 data.
SWCLK A9 I TTL JTAG/SWD CLK.
JTAG/SWD/SWO
SWDIO B9 I/O TTL JTAG TMS and SWDIO.
SWO A10 O TTL JTAG TDO and SWO.
TCK A9 I TTL JTAG/SWD CLK.
TDI B8 I TTL JTAG TDI.
TDO A10 O TTL JTAG TDO and SWO.
TMS B9 I/O TTL JTAG TMS and SWDIO.
TRST A8 I TTL JTAG TRST.
Fault F2 I TTL PWM Fault.
PWM
PWM 0. This signal is controlled by PWM Generator
0.
PWM0 J1 O TTL
PWM 1. This signal is controlled by PWM Generator
0.
PWM1 J2 O TTL
PWM 2. This signal is controlled by PWM Generator
1.
PWM2 C9 O TTL
PWM 3. This signal is controlled by PWM Generator
1.
PWM3 C8 O TTL
PWM 4. This signal is controlled by PWM Generator
2.
PWM4 J11 O TTL
PWM 5. This signal is controlled by PWM Generator
2.
PWM5 J12 O TTL
672 January 08, 2011
Texas Instruments-Production Data
Signal Tables
Table 20-7. Signals by Function, Except for GPIO (continued)
Function Pin Name Pin Number Pin Type Buffer Typea Description
B6 - Power Ground reference for logic and I/O pins.
C4
C5
F10
F11
F12
H3
J3
J10
K5
K6
K10
L10
GND
Power
The ground reference for the analog circuits (ADC,
Analog Comparators, etc.). These are separated
from GND to minimize the electrical noise contained
on VDD from affecting the analog functions.
A5 - Power
B5
GNDA
Low drop-out regulator output voltage. This pin
requires an external capacitor between the pin and
GND of 1 μF or greater. When the on-chip LDO is
used to provide power to the logic, the LDO pin must
also be connected to the VDD25 pins at the board
level in addition to the decoupling capacitor(s).
LDO E3 - Power
Positive supply for most of the logic function,
including the processor core and most peripherals.
C3 - Power
D3
F3
G3
VDD25
E10 - Power Positive supply for I/O and some logic.
G10
G11
G12
H10
K7
K8
K9
VDD33
The positive supply (3.3 V) for the analog circuits
(ADC, Analog Comparators, etc.). These are
separated from VDD to minimize the electrical noise
contained on VDD from affecting the analog
functions. VDDA pins must be connected to 3.3 V,
regardless of system implementation.
C6 - Power
C7
VDDA
IDX0 F1 I TTL QEI module 0 index.
QEI
IDX1 D11 I TTL QEI module 1 index.
PhA0 L1 I TTL QEI module 0 phase A.
PhA1 L7 I TTL QEI module 1 phase A.
PhB0 D10 I TTL QEI module 0 phase B.
PhB1 C10 I TTL QEI module 1 phase B.
January 08, 2011 673
Texas Instruments-Production Data
Stellaris® LM3S2965 Microcontroller
Table 20-7. Signals by Function, Except for GPIO (continued)
Function Pin Name Pin Number Pin Type Buffer Typea Description
SSI0Clk M4 I/O TTL SSI module 0 clock.
SSI
SSI0Fss L4 I/O TTL SSI module 0 frame.
SSI0Rx L5 I TTL SSI module 0 receive.
SSI0Tx M5 O TTL SSI module 0 transmit.
SSI1Clk A11 I/O TTL SSI module 1 clock.
SSI1Fss B12 I/O TTL SSI module 1 frame.
SSI1Rx B11 I TTL SSI module 1 receive.
SSI1Tx A12 O TTL SSI module 1 transmit.
CPU Mode bit 0. Input must be set to logic 0
(grounded); other encodings reserved.
CMOD0 E11 I TTL
System Control &
Clocks
CPU Mode bit 1. Input must be set to logic 0
(grounded); other encodings reserved.
CMOD1 B10 I TTL
Main oscillator crystal input or an external clock
reference input.
OSC0 L11 I Analog
Main oscillator crystal output. Leave unconnected
when using a single-ended clock source.
OSC1 M11 O Analog
RST H11 I TTL System reset input.
UART module 0 receive. When in IrDA mode, this
signal has IrDA modulation.
U0Rx L3 I TTL
UART
UART module 0 transmit. When in IrDA mode, this
signal has IrDA modulation.
U0Tx M3 O TTL
UART module 1 receive. When in IrDA mode, this
signal has IrDA modulation.
U1Rx H2 I TTL
UART module 1 transmit. When in IrDA mode, this
signal has IrDA modulation.
U1Tx H1 O TTL
UART module 2 receive. When in IrDA mode, this
signal has IrDA modulation.
U2Rx K1 I TTL
UART module 2 transmit. When in IrDA mode, this
signal has IrDA modulation.
U2Tx K2 O TTL
a. The TTL designation indicates the pin has TTL-compatible voltage levels.
Table 20-8. GPIO Pins and Alternate Functions
IO Pin Number Multiplexed Function Multiplexed Function
PA0 L3 U0Rx
PA1 M3 U0Tx
PA2 M4 SSI0Clk
PA3 L4 SSI0Fss
PA4 L5 SSI0Rx
PA5 M5 SSI0Tx
PA6 L6 I2C1SCL
PA7 M6 I2C1SDA
PB0 E12 CCP0
PB1 D12 CCP2
PB2 C11 I2C0SCL
PB3 C12 I2C0SDA
674 January 08, 2011
Texas Instruments-Production Data
Signal Tables
Table 20-8. GPIO Pins and Alternate Functions (continued)
IO Pin Number Multiplexed Function Multiplexed Function
PB4 A6 C0-
PB5 B7 C1-
PB6 A7 C0+
PB7 A8 TRST
PC0 A9 TCK SWCLK
PC1 B9 TMS SWDIO
PC2 B8 TDI
PC3 A10 TDO SWO
PC4 L1 PhA0
PC5 M1 C1+
PC6 M2 C2+
PC7 L2 C2-
PD0 G1 CAN0Rx
PD1 G2 CAN0Tx
PD2 H2 U1Rx
PD3 H1 U1Tx
PD4 E1 CCP3
PD5 E2 CCP4
PD6 F2 Fault
PD7 F1 IDX0
PE0 A11 SSI1Clk
PE1 B12 SSI1Fss
PE2 B11 SSI1Rx
PE3 A12 SSI1Tx
PF0 M9 CAN1Rx
PF1 H12 CAN1Tx
PF2 J11 PWM4
PF3 J12 PWM5
PF4 L9 C0o
PF5 L8
PF6 M8 CCP1
PF7 K4
PG0 K1 U2Rx
PG1 K2 U2Tx
PG2 J1 PWM0
PG3 J2 PWM1
PG4 K3
PG5 M7 CCP5
PG6 L7 PhA1
PG7 C10 PhB1
PH0 C9 PWM2
January 08, 2011 675
Texas Instruments-Production Data
Stellaris® LM3S2965 Microcontroller
Table 20-8. GPIO Pins and Alternate Functions (continued)
IO Pin Number Multiplexed Function Multiplexed Function
PH1 C8 PWM3
PH2 D11 IDX1
PH3 D10 PhB0
20.3 Connections for Unused Signals
Table 20-9 on page 676 show how to handle signals for functions that are not used in a particular
system implementation for devices that are in a 100-pin LQFP package. Two options are shown in
the table: an acceptable practice and a preferred practice for reduced power consumption and
improved EMC characteristics. If a module is not used in a system, and its inputs are grounded, it
is important that the clock to the module is never enabled by setting the corresponding bit in the
RCGCx register.
Table 20-9. Connections for Unused Signals (100-pin LQFP)
Function Signal Name Pin Number Acceptable Practice Preferred Practice
1 NC GNDA
2
3
4
ADC0
ADC1
ADC2
ADC3
ADC
GPIO All unused GPIOs - NC GND
HIB 51 NC NC
Hibernate
VBAT 55 NC GND
WAKE 50 NC GND
XOSC0 52 NC GND
XOSC1 53 NC NC
No Connects NC - NC NC
OSC0 48 NC GND
System Control OSC1 49 NC NC
Connect through a capacitor to
GND as close to pin as possible
Pull up as shown in Figure
5-1 on page 172
RST 48
Table 20-10 on page 676 show how to handle signals for functions that are not used in a particular
system implementation for devices that are in a 108-pin BGA package. Two options are shown in
the table: an acceptable practice and a preferred practice for reduced power consumption and
improved EMC characteristics. If a module is not used in a system, and its inputs are grounded, it
is important that the clock to the module is never enabled by setting the corresponding bit in the
RCGCx register.
Table 20-10. Connections for Unused Signals, 108-pin BGA
Function Signal Name Pin Number Acceptable Practice Preferred Practice
B1 NC GNDA
A1
B3
B2
ADC0
ADC1
ADC2
ADC3
ADC
GPIO All unused GPIOs - NC GND
676 January 08, 2011
Texas Instruments-Production Data
Signal Tables
Table 20-10. Connections for Unused Signals, 108-pin BGA (continued)
Function Signal Name Pin Number Acceptable Practice Preferred Practice
HIB M12 NC NC
Hibernate
VBAT L12 NC GND
WAKE M10 NC GND
XOSC0 K11 NC GND
XOSC1 K12 NC NC
No Connects NC - NC NC
OSC0 L11 NC GND
System Control
OSC1 M11 NC NC
Connect through a capacitor
to GND as close to pin as
possible
Pull up as shown in Figure
5-1 on page 172
RST H11
January 08, 2011 677
Texas Instruments-Production Data
Stellaris® LM3S2965 Microcontroller
21 Operating Characteristics
Table 21-1. Temperature Characteristics
Characteristic Symbol Value Unit
Industrial operating temperature range TA -40 to +85 °C
Extended operating temperature range TA -40 to +105 °C
Unpowered storage temperature range TS -65 to +150 °C
Table 21-2. Thermal Characteristics
Characteristic Symbol Value Unit
Thermal resistance (junction to ambient)a ΘJA 32 °C/W
Junction temperatureb TJ TA + (P • ΘJA) °C
a. Junction to ambient thermal resistance θJA numbers are determined by a package simulator.
b. Power dissipation is a function of temperature.
Table 21-3. ESD Absolute Maximum Ratingsa
Parameter Name Min Nom Max Unit
VESDHBM - - 2.0 kV
VESDCDM - - 1.0 kV
VESDMM - - 100 V
a. All Stellaris parts are ESD tested following the JEDEC standard.
678 January 08, 2011
Texas Instruments-Production Data
Operating Characteristics
22 Electrical Characteristics
22.1 DC Characteristics
22.1.1 Maximum Ratings
The maximum ratings are the limits to which the device can be subjected without permanently
damaging the device.
Note: The device is not guaranteed to operate properly at the maximum ratings.
Table 22-1. Maximum Ratings
Unit
Value
Characteristic Symbol
a
Min Max
I/O supply voltage (VDD) VDD 0 4 V
Core supply voltage (VDD25) VDD25 0 3 V
Analog supply voltage (VDDA) VDDA 0 4 V
Battery supply voltage (VBAT) VBAT 0 4 V
Input voltage VIN -0.3 5.5 V
Maximum current per output pins I - 25 mA
Maximum input voltage on a non-power pin when the VNON - 300 mV
microcontroller is unpowered
a. Voltages are measured with respect to GND.
Important: This device contains circuitry to protect the inputs against damage due to high-static
voltages or electric fields; however, it is advised that normal precautions be taken to
avoid application of any voltage higher than maximum-rated voltages to this
high-impedance circuit. Reliability of operation is enhanced if unused inputs are
connected to an appropriate logic voltage level (for example, either GND or VDD).
22.1.2 Recommended DC Operating Conditions
For special high-current applications, the GPIO output buffers may be used with the following
restrictions. With the GPIO pins configured as 8-mA output drivers, a total of four GPIO outputs may
be used to sink current loads up to 18 mA each. At 18-mA sink current loading, the VOL value is
specified as 1.2 V. The high-current GPIO package pins must be selected such that there are only
a maximum of two per side of the physical package or BGA pin group with the total number of
high-current GPIO outputs not exceeding four for the entire package.
Table 22-2. Recommended DC Operating Conditions
Parameter Parameter Name Min Nom Max Unit
VDD I/O supply voltage 3.0 3.3 3.6 V
VDD25 Core supply voltage 2.25 2.5 2.75 V
VDDA Analog supply voltage 3.0 3.3 3.6 V
VBAT Battery supply voltage 2.3 3.0 3.6 V
VIH High-level input voltage 2.0 - 5.0 V
VIL Low-level input voltage -0.3 - 1.3 V
VOH High-level output voltage 2.4 - - V
a
January 08, 2011 679
Texas Instruments-Production Data
Stellaris® LM3S2965 Microcontroller
Table 22-2. Recommended DC Operating Conditions (continued)
Parameter Parameter Name Min Nom Max Unit
VOL Low-level output voltage - - 0.4 V
a
High-level source current, VOH=2.4 V
IOH
2-mA Drive 2.0 - - mA
4-mA Drive 4.0 - - mA
8-mA Drive 8.0 - - mA
Low-level sink current, VOL=0.4 V
IOL
2-mA Drive 2.0 - - mA
4-mA Drive 4.0 - - mA
8-mA Drive 8.0 - - mA
a. VOL and VOH shift to 1.2 V when using high-current GPIOs.
22.1.3 On-Chip Low Drop-Out (LDO) Regulator Characteristics
Table 22-3. LDO Regulator Characteristics
Parameter Parameter Name Min Nom Max Unit
Programmable internal (logic) power supply 2.25 2.5 2.75 V
VLDOOUT output value
Output voltage accuracy - 2% - %
tPON Power-on time - - 100 μs
tON Time on - - 200 μs
tOFF Time off - - 100 μs
VSTEP Step programming incremental voltage - 50 - mV
External filter capacitor size for internal power 1.0 - 3.0 μF
supply
CLDO
22.1.4 GPIO Module Characteristics
Table 22-4. GPIO Module DC Characteristics
Parameter Parameter Name Min Nom Max Unit
RGPIOPU GPIO internal pull-up resistor 50 - 110 kΩ
RGPIOPD GPIO internal pull-down resistor 55 - 180 kΩ
ILKG GPIO input leakage currenta - - 2 μA
a. The leakage current is measured with GND or VDD applied to the corresponding pin(s). The leakage of digital port pins is
measured individually. The port pin is configured as an input and the pullup/pulldown resistor is disabled.
22.1.5 Power Specifications
The power measurements specified in the tables that follow are run on the core processor using
SRAM with the following specifications (except as noted):
■ VDD = 3.3 V
■ VDD25 = 2.50 V
■ VBAT = 3.0 V
680 January 08, 2011
Texas Instruments-Production Data
Electrical Characteristics
■ VDDA = 3.3 V
■ Temperature = 25°C
■ Clock Source (MOSC) =3.579545 MHz Crystal Oscillator
■ Main oscillator (MOSC) = enabled
■ Internal oscillator (IOSC) = disabled
Table 22-5. Detailed Power Specifications
Unit
3.3 V VDD, 2.5 V VDD25 3.0 V VBAT
Parameter Conditions VDDA
Parameter Name
Nom Max Nom Max Nom Max
VDD25 = 2.50 V 3 pendinga 108 pendinga 0 pendinga mA
Code= while(1){} executed in
Flash
Peripherals = All ON
System Clock = 50 MHz (with
PLL)
Run mode 1
(Flash loop)
IDD_RUN
VDD25 = 2.50 V 0 pendinga 53 pendinga 0 pendinga mA
Code= while(1){} executed in
Flash
Peripherals = All OFF
System Clock = 50 MHz (with
PLL)
Run mode 2
(Flash loop)
VDD25 = 2.50 V 3 pendinga 102 pendinga 0 pendinga mA
Code= while(1){} executed in
SRAM
Peripherals = All ON
System Clock = 50 MHz (with
PLL)
Run mode 1
(SRAM loop)
VDD25 = 2.50 V 0 pendinga 47 pendinga 0 pendinga mA
Code= while(1){} executed in
SRAM
Peripherals = All OFF
System Clock = 50 MHz (with
PLL)
Run mode 2
(SRAM loop)
VDD25 = 2.50 V 0 pendinga 17 pendinga 0 pendinga mA
Peripherals = All OFF
System Clock = 50 MHz (with
PLL)
IDD_SLEEP Sleep mode
LDO = 2.25 V 0.14 pendinga 0.18 pendinga 0 pendinga mA
Peripherals = All OFF
System Clock = IOSC30KHZ/64
Deep-Sleep
mode
IDD_DEEPSLEEP
VBAT = 3.0 V 0 0 0 0 16 pendinga μA
VDD = 0 V
VDD25 = 0 V
VDDA = 0 V
Peripherals = All OFF
System Clock = OFF
Hibernate Module = 32 kHz
Hibernate
mode
IDD_HIBERNATE
a. Pending characterization completion.
January 08, 2011 681
Texas Instruments-Production Data
Stellaris® LM3S2965 Microcontroller
22.1.6 Flash Memory Characteristics
Table 22-6. Flash Memory Characteristics
Parameter Parameter Name Min Nom Max Unit
Number of guaranteed program/erase cycles 10,000 100,000 - cycles
before failurea
PECYC
Data retention at average operating temperature 10 - - years
of 85˚C (industrial) or 105˚C (extended)
TRET
TPROG Word program time 20 - - μs
TERASE Page erase time 20 - - ms
TME Mass erase time - - 250 ms
a. A program/erase cycle is defined as switching the bits from 1-> 0 -> 1.
22.1.7 Hibernation
Table 22-7. Hibernation Module DC Characteristics
Parameter Parameter Name Value Unit
VLOWBAT Low battery detect voltage 2.35 V
RWAKEPU WAKE internal pull-up resistor 200 kΩ
22.2 AC Characteristics
22.2.1 Load Conditions
Unless otherwise specified, the following conditions are true for all timing measurements. Timing
measurements are for 4-mA drive strength.
Figure 22-1. Load Conditions
CL = 50 pF
GND
pin
22.2.2 Clocks
Table 22-8. Phase Locked Loop (PLL) Characteristics
Parameter Parameter Name Min Nom Max Unit
fref_crystal Crystal referencea 3.579545 - 8.192 MHz
fref_ext External clock referencea 3.579545 - 8.192 MHz
fpll PLL frequencyb - 400 - MHz
TREADY PLL lock time - - 0.5 ms
a. The exact value is determined by the crystal value programmed into the XTAL field of the Run-Mode Clock Configuration
(RCC) register.
b. PLL frequency is automatically calculated by the hardware based on the XTAL field of the RCC register.
682 January 08, 2011
Texas Instruments-Production Data
Electrical Characteristics
Table 22-9 on page 683 shows the actual frequency of the PLL based on the crystal frequency used
(defined by the XTAL field in the RCC register).
Table 22-9. Actual PLL Frequency
XTAL Crystal Frequency (MHz) PLL Frequency (MHz) Error
0x4 3.5795 400.904 0.0023%
0x5 3.6864 398.1312 0.0047%
0x6 4.0 400 -
0x7 4.096 401.408 0.0035%
0x8 4.9152 398.1312 0.0047%
0x9 5.0 400 -
0xA 5.12 399.36 0.0016%
0xB 6.0 400 -
0xC 6.144 399.36 0.0016%
0xD 7.3728 398.1312 0.0047%
0xE 8.0 400 0.0047%
0xF 8.192 398.6773333 0.0033%
Table 22-10. Clock Characteristics
Parameter Parameter Name Min Nom Max Unit
fIOSC Internal 12 MHz oscillator frequency 8.4 12 15.6 MHz
fIOSC30KHZ Internal 30 KHz oscillator frequency 15 30 45 KHz
fXOSC Hibernation module oscillator frequency - 4.194304 - MHz
fXOSC_XTAL Crystal reference for hibernation oscillator - 4.194304 - MHz
External clock reference for hibernation - 32.768 - KHz
module
fXOSC_EXT
fMOSC Main oscillator frequency 1 - 8.192 MHz
tMOSC_per Main oscillator period 125 - 1000 ns
Crystal reference using the main oscillator 1 - 8.192 MHz
(PLL in BYPASS mode)a
fref_crystal_bypass
External clock reference (PLL in BYPASS 0 - 50 MHz
mode)a
fref_ext_bypass
fsystem_clock System clock 0 - 50 MHz
a. The ADC must be clocked from the PLL or directly from a 16-MHz clock source to operate properly.
Table 22-11. Crystal Characteristics
Parameter Name Value Units
Frequency 8 6 4 3.5 MHz
Frequency tolerance ±50 ±50 ±50 ±50 ppm
Aging ±5 ±5 ±5 ±5 ppm/yr
Oscillation mode Parallel Parallel Parallel Parallel -
Temperature stability (-40°C to 85°C) ±25 ±25 ±25 ±25 ppm
Temperature stability (-40°C to 105°C) ±25 ±25 ±25 ±25 ppm
Motional capacitance (typ) 27.8 37.0 55.6 63.5 pF
Motional inductance (typ) 14.3 19.1 28.6 32.7 mH
January 08, 2011 683
Texas Instruments-Production Data
Stellaris® LM3S2965 Microcontroller
Table 22-11. Crystal Characteristics (continued)
Parameter Name Value Units
Equivalent series resistance (max) 120 160 200 220 Ω
Shunt capacitance (max) 10 10 10 10 pF
Load capacitance (typ) 16 16 16 16 pF
Drive level (typ) 100 100 100 100 μW
22.2.2.1 System Clock Specifications with ADC Operation
Table 22-12. System Clock Characteristics with ADC Operation
Parameter Parameter Name Min Nom Max Unit
System clock frequency when the ADC module is 16 - - MHz
operating (when PLL is bypassed)
fsysadc
22.2.3 JTAG and Boundary Scan
Table 22-13. JTAG Characteristics
Parameter Parameter Parameter Name Min Nom Max Unit
No.
J1 fTCK TCK operational clock frequency 0 - 10 MHz
J2 tTCK TCK operational clock period 100 - - ns
J3 tTCK_LOW TCK clock Low time - tTCK - ns
J4 tTCK_HIGH TCK clock High time - tTCK - ns
J5 tTCK_R TCK rise time 0 - 10 ns
J6 tTCK_F TCK fall time 0 - 10 ns
J7 tTMS_SU TMS setup time to TCK rise 20 - - ns
J8 tTMS_HLD TMS hold time from TCK rise 20 - - ns
J9 tTDI_SU TDI setup time to TCK rise 25 - - ns
J10 tTDI_HLD TDI hold time from TCK rise 25 - - ns
23 35 ns
-
2-mA drive
TCK fall to Data
Valid from High-Z
J11
t TDO_ZDV
4-mA drive 15 26 ns
8-mA drive 14 25 ns
8-mA drive with slew rate control 18 29 ns
21 35 ns
-
2-mA drive
TCK fall to Data
Valid from Data
Valid
J12
t TDO_DV
4-mA drive 14 25 ns
8-mA drive 13 24 ns
8-mA drive with slew rate control 18 28 ns
9 11 ns
-
2-mA drive
TCK fall to High-Z
from Data Valid
J13
t TDO_DVZ
4-mA drive 7 9 ns
8-mA drive 6 8 ns
8-mA drive with slew rate control 7 9 ns
J14 tTRST TRST assertion time 100 - - ns
J15 tTRST_SU TRST setup time to TCK rise 10 - - ns
684 January 08, 2011
Texas Instruments-Production Data
Electrical Characteristics
Figure 22-2. JTAG Test Clock Input Timing
TCK
J6 J5
J3 J4
J2
Figure 22-3. JTAG Test Access Port (TAP) Timing
TDO Output Valid
TCK
TDO Output Valid
J12
TDO
TDI
TMS
TDI Input Valid TDI Input Valid
J13
J9 J10
TMS Input Valid
J9 J10
TMS Input Valid
J11
J7 J8 J7 J8
Figure 22-4. JTAG TRST Timing
TCK
J14 J15
TRST
22.2.4 Reset
Table 22-14. Reset Characteristics
Parameter Parameter Parameter Name Min Nom Max Unit
No.
R1 VTH Reset threshold - 2.0 - V
R2 VBTH Brown-Out threshold 2.85 2.9 2.95 V
R3 TPOR Power-On Reset timeout - 10 - ms
R4 TBOR Brown-Out timeout - 500 - μs
R5 TIRPOR Internal reset timeout after POR 6 - 11 ms
R6 TIRBOR Internal reset timeout after BORa 0 - 1 μs
January 08, 2011 685
Texas Instruments-Production Data
Stellaris® LM3S2965 Microcontroller
Table 22-14. Reset Characteristics (continued)
Parameter Parameter Parameter Name Min Nom Max Unit
No.
Internal reset timeout after hardware reset 0 - 1 ms
(RST pin)
R7 TIRHWR
Internal reset timeout after software-initiated 2.5 - 20 μs
system reset a
R8 TIRSWR
R9 TIRWDR Internal reset timeout after watchdog reseta 2.5 - 20 μs
Supply voltage (VDD) rise time (0V-3.3V), - - 100 ms
power on reset
R10 TVDDRISE
Supply voltage (VDD) rise time (0V-3.3V), - - 250 μs
waking from hibernation
R11 TMIN Minimum RST pulse width 2 - - μs
a. 20 * t MOSC_per
Figure 22-5. External Reset Timing (RST)
RST
/Reset
(Internal)
R11 R7
Figure 22-6. Power-On Reset Timing
VDD
/POR
(Internal)
/Reset
(Internal)
R3
R1
R5
Figure 22-7. Brown-Out Reset Timing
VDD
/BOR
(Internal)
/Reset
(Internal)
R2
R4
R6
686 January 08, 2011
Texas Instruments-Production Data
Electrical Characteristics
Figure 22-8. Software Reset Timing
R8
SW Reset
/Reset
(Internal)
Figure 22-9. Watchdog Reset Timing
WDOG
Reset
(Internal)
/Reset
(Internal)
R9
22.2.5 Sleep Modes
Table 22-15. Sleep Modes AC Characteristicsa
Parameter No Parameter Parameter Name Min Nom Max Unit
Time to wake from interrupt in sleep or - - 7 system clocks
deep-sleep mode, not using the PLL
D1 tWAKE_S
Time to wake from interrupt in sleep or - - TREADY ms
deep-sleep mode when using the PLL
D2 tWAKE_PLL_S
a. Values in this table assume the IOSC is the clock source during sleep or deep-sleep mode.
22.2.6 Hibernation Module
The Hibernation Module requires special system implementation considerations since it is intended
to power-down all other sections of its host device. The system power-supply distribution and
interfaces to the device must be driven to 0 VDC or powered down with the same external voltage
regulator controlled by HIB.
The external voltage regulators controlled by HIB must have a settling time of 250 μs or less.
Table 22-16. Hibernation Module AC Characteristics
Parameter Parameter Parameter Name Min Nom Max Unit
No
Internal 32.768 KHz clock reference rising - 200 - μs
edge to /HIB asserted
H1 tHIB_LOW
Internal 32.768 KHz clock reference rising - 30 - μs
edge to /HIB deasserted
H2 tHIB_HIGH
H3 tWAKE_ASSERT /WAKE assertion time 62 - - μs
H4 tWAKETOHIB /WAKE assert to /HIB desassert 62 - 124 μs
H5 tXOSC_SETTLE XOSC settling timea 20 - - ms
Access time to or from a non-volatile register 92 - - μs
in HIB module to complete
H6 tHIB_REG_ACCESS
January 08, 2011 687
Texas Instruments-Production Data
Stellaris® LM3S2965 Microcontroller
Table 22-16. Hibernation Module AC Characteristics (continued)
Parameter Parameter Parameter Name Min Nom Max Unit
No
HIB deassert to VDD and VDD25 at minimum - - 250 μs
operational level
H7 tHIB_TO_VDD
a. This parameter is highly sensitive to PCB layout and trace lengths, which may make this parameter time longer. Care
must be taken in PCB design to minimize trace lengths and RLC (resistance, inductance, capacitance).
Figure 22-10. Hibernation Module Timing
32.768 KHz
(internal)
HIB
H4
H1
WAKE
H2
H3
22.2.7 General-Purpose I/O (GPIO)
Note: All GPIOs are 5 V-tolerant.
Table 22-17. GPIO Characteristics
Parameter Parameter Name Condition Min Nom Max Unit
17 26 ns
-
2-mA drive
GPIO Rise Time
(from 20% to 80%
of VDD)
tGPIOR
4-mA drive 9 13 ns
8-mA drive 6 9 ns
8-mA drive with slew rate control 10 12 ns
17 25 ns
-
2-mA drive
GPIO Fall Time
(from 80% to 20%
of VDD)
tGPIOF
4-mA drive 8 12 ns
8-mA drive 6 10 ns
8-mA drive with slew rate control 11 13 ns
22.2.8 Analog-to-Digital Converter
Table 22-18. ADC Characteristicsa
Parameter Parameter Name Min Nom Max Unit
Maximum single-ended, full-scale analog input - - 3.0 V
voltage
VADCIN
Minimum single-ended, full-scale analog input 0.0 - - V
voltage
Maximumdifferential, full-scale analog input voltage - - 1.5 V
Minimum differential, full-scale analog input voltage 0.0 - - V
N Resolution 10 bits
fADC ADC internal clock frequencyb 14 16 18 MHz
tADCCONV Conversion timec μs
688 January 08, 2011
Texas Instruments-Production Data
Electrical Characteristics
Table 22-18. ADC Characteristics (continued)
Parameter Parameter Name Min Nom Max Unit
f ADCCONV Conversion ratec k samples/s
tLT Latency from trigger to start of conversion - 2 - system clocks
IL ADC input leakage - - ±3.0 μA
RADC ADC equivalent resistance - - 10 kΩ
CADC ADC equivalent capacitance 0.9 1.0 1.1 pF
EL Integral nonlinearity error - - ±3 LSB
ED Differential nonlinearity error - - ±2 LSB
EO Offset error - - +6d LSB
EG Full-scale gain error - - ±3 LSB
ETS Temperature sensor accuracy - - ±5 °C
a. The ADC reference voltage is 3.0 V. This reference voltage is internally generated from the 3.3 VDDA supply by a band
gap circuit.
b. The ADC must be clocked from the PLL or directly from an external clock source to operate properly.
c. The conversion time and rate scale from the specified number if the ADC internal clock frequency is any value other than
16 MHz.
d. The offset error listed above is the conversion result with 0 V applied to the ADC input.
Figure 22-11. ADC Input Equivalency Diagram
Stellaris® Microcontroller
Sample and hold
ADC converter
CADC
RADC
VDD
10-bit
converter
VIN IL
Table 22-19. ADC Module Internal Reference Characteristics
Parameter Parameter Name Min Nom Max Unit
VREFI Internal voltage reference for ADC - 3.0 - V
EIR Internal voltage reference error - - ±2.5 %
January 08, 2011 689
Texas Instruments-Production Data
Stellaris® LM3S2965 Microcontroller
22.2.9 Synchronous Serial Interface (SSI)
Table 22-20. SSI Characteristics
Parameter Parameter Parameter Name Min Nom Max Unit
No.
S1 tclk_per SSIClk cycle time 2 - 65024 system clocks
S2 tclk_high SSIClk high time - 0.5 - t clk_per
S3 tclk_low SSIClk low time - 0.5 - t clk_per
S4 tclkrf SSIClk rise/fall timea - 6 10 ns
S5 tDMd Data from master valid delay time 0 - 1 system clocks
S6 tDMs Data from master setup time 1 - - system clocks
S7 tDMh Data from master hold time 2 - - system clocks
S8 tDSs Data from slave setup time 1 - - system clocks
S9 tDSh Data from slave hold time 2 - - system clocks
a. Note that the delays shown are using 8-mA drive strength.
Figure 22-12. SSI Timing for TI Frame Format (FRF=01), Single Transfer Timing Measurement
SSIClk
SSIFss
SSITx
SSIRx MSB LSB
S2
S3
S1
S4
4 to 16 bits
690 January 08, 2011
Texas Instruments-Production Data
Electrical Characteristics
Figure 22-13. SSI Timing for MICROWIRE Frame Format (FRF=10), Single Transfer
0
SSIClk
SSIFss
SSITx
SSIRx
MSB LSB
MSB LSB
S2
S3
S1
8-bit control
4 to 16 bits output data
Figure 22-14. SSI Timing for SPI Frame Format (FRF=00), with SPH=1
SSIClk
(SPO=1)
SSITx
(master)
SSIRx
(slave) LSB
SSIClk
(SPO=0)
S2
S1
S4
SSIFss
LSB
S3
MSB
S5
S6 S7
S8 S9
MSB
22.2.10 Inter-Integrated Circuit (I2C) Interface
Table 22-21. I2C Characteristics
Parameter Parameter Parameter Name Min Nom Max Unit
No.
I1a tSCH Start condition hold time 36 - - system clocks
I2a tLP Clock Low period 36 - - system clocks
(see note ns
b)
I2CSCL/I2CSDA rise time (VIL =0.5 V - -
to V IH =2.4 V)
I3b tSRT
January 08, 2011 691
Texas Instruments-Production Data
Stellaris® LM3S2965 Microcontroller
Table 22-21. I2C Characteristics (continued)
Parameter Parameter Parameter Name Min Nom Max Unit
No.
I4a tDH Data hold time 2 - - system clocks
I2CSCL/I2CSDA fall time (VIH =2.4 V - 9 10 ns
to V IL =0.5 V)
I5c tSFT
I6a tHT Clock High time 24 - - system clocks
I7a tDS Data setup time 18 - - system clocks
Start condition setup time (for repeated 36 - - system clocks
start condition only)
I8a tSCSR
I9a tSCS Stop condition setup time 24 - - system clocks
a. Values depend on the value programmed into the TPR bit in the I2C Master Timer Period (I2CMTPR) register; a TPR
programmed for the maximum I2CSCL frequency (TPR=0x2) results in a minimum output timing as shown in the table
above. The I 2C interface is designed to scale the actual data transition time to move it to the middle of the I2CSCL Low
period. The actual position is affected by the value programmed into the TPR; however, the numbers given in the above
values are minimum values.
b. Because I2CSCL and I2CSDA are open-drain-type outputs, which the controller can only actively drive Low, the time
I2CSCL or I2CSDA takes to reach a high level depends on external signal capacitance and pull-up resistor values.
c. Specified at a nominal 50 pF load.
Figure 22-15. I2C Timing
I2CSCL
I2CSDA
I1
I2
I4
I6
I7 I8
I5
I3 I9
22.2.11 Analog Comparator
Table 22-22. Analog Comparator Characteristics
Parameter Parameter Name Min Nom Max Unit
VOS Input offset voltage - ±10 ±25 mV
VCM Input common mode voltage range 0 - VDD-1.5 V
CMRR Common mode rejection ratio 50 - - dB
TRT Response time - - 1 μs
TMC Comparator mode change to Output Valid - - 10 μs
Table 22-23. Analog Comparator Voltage Reference Characteristics
Parameter Parameter Name Min Nom Max Unit
RHR Resolution high range - VDD/31 - LSB
RLR Resolution low range - VDD/23 - LSB
AHR Absolute accuracy high range - - ±1/2 LSB
ALR Absolute accuracy low range - - ±1/4 LSB
692 January 08, 2011
Texas Instruments-Production Data
Electrical Characteristics
A Serial Flash Loader
A.1 Serial Flash Loader
The Stellaris® serial flash loader is a preprogrammed flash-resident utility used to download code
to the flash memory of a device without the use of a debug interface. The serial flash loader uses
a simple packet interface to provide synchronous communication with the device. The flash loader
runs off the crystal and does not enable the PLL, so its speed is determined by the crystal used.
The two serial interfaces that can be used are the UART0 and SSI0 interfaces. For simplicity, both
the data format and communication protocol are identical for both serial interfaces.
A.2 Interfaces
Once communication with the flash loader is established via one of the serial interfaces, that interface
is used until the flash loader is reset or new code takes over. For example, once you start
communicating using the SSI port, communications with the flash loader via the UART are disabled
until the device is reset.
A.2.1 UART
The Universal Asynchronous Receivers/Transmitters (UART) communication uses a fixed serial
format of 8 bits of data, no parity, and 1 stop bit. The baud rate used for communication is
automatically detected by the flash loader and can be any valid baud rate supported by the host
and the device. The auto detection sequence requires that the baud rate should be no more than
1/32 the crystal frequency of the board that is running the serial flash loader. This is actually the
same as the hardware limitation for the maximum baud rate for any UART on a Stellaris device
which is calculated as follows:
Max Baud Rate = System Clock Frequency / 16
In order to determine the baud rate, the serial flash loader needs to determine the relationship
between its own crystal frequency and the baud rate. This is enough information for the flash loader
to configure its UART to the same baud rate as the host. This automatic baud-rate detection allows
the host to use any valid baud rate that it wants to communicate with the device.
The method used to perform this automatic synchronization relies on the host sending the flash
loader two bytes that are both 0x55. This generates a series of pulses to the flash loader that it can
use to calculate the ratios needed to program the UART to match the host’s baud rate. After the
host sends the pattern, it attempts to read back one byte of data from the UART. The flash loader
returns the value of 0xCC to indicate successful detection of the baud rate. If this byte is not received
after at least twice the time required to transfer the two bytes, the host can resend another pattern
of 0x55, 0x55, and wait for the 0xCC byte again until the flash loader acknowledges that it has
received a synchronization pattern correctly. For example, the time to wait for data back from the
flash loader should be calculated as at least 2*(20(bits/sync)/baud rate (bits/sec)). For a baud rate
of 115200, this time is 2*(20/115200) or 0.35 ms.
A.2.2 SSI
The Synchronous Serial Interface (SSI) port also uses a fixed serial format for communications,
with the framing defined as Motorola format with SPH set to 1 and SPO set to 1. See “Frame
Formats” on page 463 in the SSI chapter for more information on formats for this transfer protocol.
Like the UART, this interface has hardware requirements that limit the maximum speed that the SSI
clock can run. This allows the SSI clock to be at most 1/12 the crystal frequency of the board running
January 08, 2011 693
Texas Instruments-Production Data
Stellaris® LM3S2965 Microcontroller
the flash loader. Since the host device is the master, the SSI on the flash loader device does not
need to determine the clock as it is provided directly by the host.
A.3 Packet Handling
All communications, with the exception of the UART auto-baud, are done via defined packets that
are acknowledged (ACK) or not acknowledged (NAK) by the devices. The packets use the same
format for receiving and sending packets, including the method used to acknowledge successful or
unsuccessful reception of a packet.
A.3.1 Packet Format
All packets sent and received from the device use the following byte-packed format.
struct
{
unsigned char ucSize;
unsigned char ucCheckSum;
unsigned char Data[];
};
ucSize The first byte received holds the total size of the transfer including
the size and checksum bytes.
ucChecksum This holds a simple checksum of the bytes in the data buffer only.
The algorithm is Data[0]+Data[1]+…+ Data[ucSize-3].
Data This is the raw data intended for the device, which is formatted in
some form of command interface. There should be ucSize–2
bytes of data provided in this buffer to or from the device.
A.3.2 Sending Packets
The actual bytes of the packet can be sent individually or all at once; the only limitation is that
commands that cause flash memory access should limit the download sizes to prevent losing bytes
during flash programming. This limitation is discussed further in the section that describes the serial
flash loader command, COMMAND_SEND_DATA (see “COMMAND_SEND_DATA
(0x24)” on page 696).
Once the packet has been formatted correctly by the host, it should be sent out over the UART or
SSI interface. Then the host should poll the UART or SSI interface for the first non-zero data returned
from the device. The first non-zero byte will either be an ACK (0xCC) or a NAK (0x33) byte from
the device indicating the packet was received successfully (ACK) or unsuccessfully (NAK). This
does not indicate that the actual contents of the command issued in the data portion of the packet
were valid, just that the packet was received correctly.
A.3.3 Receiving Packets
The flash loader sends a packet of data in the same format that it receives a packet. The flash loader
may transfer leading zero data before the first actual byte of data is sent out. The first non-zero byte
is the size of the packet followed by a checksum byte, and finally followed by the data itself. There
is no break in the data after the first non-zero byte is sent from the flash loader. Once the device
communicating with the flash loader receives all the bytes, it must either ACK or NAK the packet to
indicate that the transmission was successful. The appropriate response after sending a NAK to
the flash loader is to resend the command that failed and request the data again. If needed, the
host may send leading zeros before sending down the ACK/NAK signal to the flash loader, as the
694 January 08, 2011
Texas Instruments-Production Data
Serial Flash Loader
flash loader only accepts the first non-zero data as a valid response. This zero padding is needed
by the SSI interface in order to receive data to or from the flash loader.
A.4 Commands
The next section defines the list of commands that can be sent to the flash loader. The first byte of
the data should always be one of the defined commands, followed by data or parameters as
determined by the command that is sent.
A.4.1 COMMAND_PING (0X20)
This command simply accepts the command and sets the global status to success. The format of
the packet is as follows:
Byte[0] = 0x03;
Byte[1] = checksum(Byte[2]);
Byte[2] = COMMAND_PING;
The ping command has 3 bytes and the value for COMMAND_PING is 0x20 and the checksum of one
byte is that same byte, making Byte[1] also 0x20. Since the ping command has no real return status,
the receipt of an ACK can be interpreted as a successful ping to the flash loader.
A.4.2 COMMAND_GET_STATUS (0x23)
This command returns the status of the last command that was issued. Typically, this command
should be sent after every command to ensure that the previous command was successful or to
properly respond to a failure. The command requires one byte in the data of the packet and should
be followed by reading a packet with one byte of data that contains a status code. The last step is
to ACK or NAK the received data so the flash loader knows that the data has been read.
Byte[0] = 0x03
Byte[1] = checksum(Byte[2])
Byte[2] = COMMAND_GET_STATUS
A.4.3 COMMAND_DOWNLOAD (0x21)
This command is sent to the flash loader to indicate where to store data and how many bytes will
be sent by the COMMAND_SEND_DATA commands that follow. The command consists of two 32-bit
values that are both transferred MSB first. The first 32-bit value is the address to start programming
data into, while the second is the 32-bit size of the data that will be sent. This command also triggers
an erase of the full area to be programmed so this command takes longer than other commands.
This results in a longer time to receive the ACK/NAK back from the board. This command should
be followed by a COMMAND_GET_STATUS to ensure that the Program Address and Program size
are valid for the device running the flash loader.
The format of the packet to send this command is a follows:
Byte[0] = 11
Byte[1] = checksum(Bytes[2:10])
Byte[2] = COMMAND_DOWNLOAD
Byte[3] = Program Address [31:24]
Byte[4] = Program Address [23:16]
Byte[5] = Program Address [15:8]
Byte[6] = Program Address [7:0]
Byte[7] = Program Size [31:24]
January 08, 2011 695
Texas Instruments-Production Data
Stellaris® LM3S2965 Microcontroller
Byte[8] = Program Size [23:16]
Byte[9] = Program Size [15:8]
Byte[10] = Program Size [7:0]
A.4.4 COMMAND_SEND_DATA (0x24)
This command should only follow a COMMAND_DOWNLOAD command or another
COMMAND_SEND_DATA command if more data is needed. Consecutive send data commands
automatically increment address and continue programming from the previous location. The caller
should limit transfers of data to a maximum 8 bytes of packet data to allow the flash to program
successfully and not overflow input buffers of the serial interfaces. The command terminates
programming once the number of bytes indicated by the COMMAND_DOWNLOAD command has been
received. Each time this function is called it should be followed by a COMMAND_GET_STATUS to
ensure that the data was successfully programmed into the flash. If the flash loader sends a NAK
to this command, the flash loader does not increment the current address to allow retransmission
of the previous data.
Byte[0] = 11
Byte[1] = checksum(Bytes[2:10])
Byte[2] = COMMAND_SEND_DATA
Byte[3] = Data[0]
Byte[4] = Data[1]
Byte[5] = Data[2]
Byte[6] = Data[3]
Byte[7] = Data[4]
Byte[8] = Data[5]
Byte[9] = Data[6]
Byte[10] = Data[7]
A.4.5 COMMAND_RUN (0x22)
This command is used to tell the flash loader to execute from the address passed as the parameter
in this command. This command consists of a single 32-bit value that is interpreted as the address
to execute. The 32-bit value is transmitted MSB first and the flash loader responds with an ACK
signal back to the host device before actually executing the code at the given address. This allows
the host to know that the command was received successfully and the code is now running.
Byte[0] = 7
Byte[1] = checksum(Bytes[2:6])
Byte[2] = COMMAND_RUN
Byte[3] = Execute Address[31:24]
Byte[4] = Execute Address[23:16]
Byte[5] = Execute Address[15:8]
Byte[6] = Execute Address[7:0]
A.4.6 COMMAND_RESET (0x25)
This command is used to tell the flash loader device to reset. This is useful when downloading a
new image that overwrote the flash loader and wants to start from a full reset. Unlike the
COMMAND_RUN command, this allows the initial stack pointer to be read by the hardware and set
up for the new code. It can also be used to reset the flash loader if a critical error occurs and the
host device wants to restart communication with the flash loader.
696 January 08, 2011
Texas Instruments-Production Data
Serial Flash Loader
Byte[0] = 3
Byte[1] = checksum(Byte[2])
Byte[2] = COMMAND_RESET
The flash loader responds with an ACK signal back to the host device before actually executing the
software reset to the device running the flash loader. This allows the host to know that the command
was received successfully and the part will be reset.
January 08, 2011 697
Texas Instruments-Production Data
Stellaris® LM3S2965 Microcontroller
B Register Quick Reference
31 30 29 28 27 26 25 24 23 22 21 20 19 18 17 16
15 14 13 12 11 10 9 8 7 6 5 4 3 2 1 0
The Cortex-M3 Processor
R0, type R/W, , reset - (see page 59)
DATA
DATA
R1, type R/W, , reset - (see page 59)
DATA
DATA
R2, type R/W, , reset - (see page 59)
DATA
DATA
R3, type R/W, , reset - (see page 59)
DATA
DATA
R4, type R/W, , reset - (see page 59)
DATA
DATA
R5, type R/W, , reset - (see page 59)
DATA
DATA
R6, type R/W, , reset - (see page 59)
DATA
DATA
R7, type R/W, , reset - (see page 59)
DATA
DATA
R8, type R/W, , reset - (see page 59)
DATA
DATA
R9, type R/W, , reset - (see page 59)
DATA
DATA
R10, type R/W, , reset - (see page 59)
DATA
DATA
R11, type R/W, , reset - (see page 59)
DATA
DATA
R12, type R/W, , reset - (see page 59)
DATA
DATA
SP, type R/W, , reset - (see page 60)
SP
SP
LR, type R/W, , reset 0xFFFF.FFFF (see page 61)
LINK
LINK
PC, type R/W, , reset - (see page 62)
PC
PC
698 January 08, 2011
Texas Instruments-Production Data
Register Quick Reference
31 30 29 28 27 26 25 24 23 22 21 20 19 18 17 16
15 14 13 12 11 10 9 8 7 6 5 4 3 2 1 0
PSR, type R/W, , reset 0x0100.0000 (see page 63)
N Z C V Q ICI / IT THUMB
ICI / IT ISRNUM
PRIMASK, type R/W, , reset 0x0000.0000 (see page 67)
PRIMASK
FAULTMASK, type R/W, , reset 0x0000.0000 (see page 68)
FAULTMASK
BASEPRI, type R/W, , reset 0x0000.0000 (see page 69)
BASEPRI
CONTROL, type R/W, , reset 0x0000.0000 (see page 70)
ASP TMPL
Cortex-M3 Peripherals
System Timer (SysTick) Registers
Base 0xE000.E000
STCTRL, type R/W, offset 0x010, reset 0x0000.0000
COUNT
CLK_SRC INTEN ENABLE
STRELOAD, type R/W, offset 0x014, reset 0x0000.0000
RELOAD
RELOAD
STCURRENT, type R/WC, offset 0x018, reset 0x0000.0000
CURRENT
CURRENT
Cortex-M3 Peripherals
Nested Vectored Interrupt Controller (NVIC) Registers
Base 0xE000.E000
EN0, type R/W, offset 0x100, reset 0x0000.0000
INT
INT
EN1, type R/W, offset 0x104, reset 0x0000.0000
INT
DIS0, type R/W, offset 0x180, reset 0x0000.0000
INT
INT
DIS1, type R/W, offset 0x184, reset 0x0000.0000
INT
PEND0, type R/W, offset 0x200, reset 0x0000.0000
INT
INT
PEND1, type R/W, offset 0x204, reset 0x0000.0000
INT
UNPEND0, type R/W, offset 0x280, reset 0x0000.0000
INT
INT
January 08, 2011 699
Texas Instruments-Production Data
Stellaris® LM3S2965 Microcontroller
31 30 29 28 27 26 25 24 23 22 21 20 19 18 17 16
15 14 13 12 11 10 9 8 7 6 5 4 3 2 1 0
UNPEND1, type R/W, offset 0x284, reset 0x0000.0000
INT
ACTIVE0, type RO, offset 0x300, reset 0x0000.0000
INT
INT
ACTIVE1, type RO, offset 0x304, reset 0x0000.0000
INT
PRI0, type R/W, offset 0x400, reset 0x0000.0000
INTD INTC
INTB INTA
PRI1, type R/W, offset 0x404, reset 0x0000.0000
INTD INTC
INTB INTA
PRI2, type R/W, offset 0x408, reset 0x0000.0000
INTD INTC
INTB INTA
PRI3, type R/W, offset 0x40C, reset 0x0000.0000
INTD INTC
INTB INTA
PRI4, type R/W, offset 0x410, reset 0x0000.0000
INTD INTC
INTB INTA
PRI5, type R/W, offset 0x414, reset 0x0000.0000
INTD INTC
INTB INTA
PRI6, type R/W, offset 0x418, reset 0x0000.0000
INTD INTC
INTB INTA
PRI7, type R/W, offset 0x41C, reset 0x0000.0000
INTD INTC
INTB INTA
PRI8, type R/W, offset 0x420, reset 0x0000.0000
INTD INTC
INTB INTA
PRI9, type R/W, offset 0x424, reset 0x0000.0000
INTD INTC
INTB INTA
PRI10, type R/W, offset 0x428, reset 0x0000.0000
INTD INTC
INTB INTA
SWTRIG, type WO, offset 0xF00, reset 0x0000.0000
INTID
Cortex-M3 Peripherals
System Control Block (SCB) Registers
Base 0xE000.E000
CPUID, type RO, offset 0xD00, reset 0x411F.C231
IMP VAR CON
PARTNO REV
700 January 08, 2011
Texas Instruments-Production Data
Register Quick Reference
31 30 29 28 27 26 25 24 23 22 21 20 19 18 17 16
15 14 13 12 11 10 9 8 7 6 5 4 3 2 1 0
INTCTRL, type R/W, offset 0xD04, reset 0x0000.0000
NMISET PENDSV UNPENDSV PENDSTSET PENDSTCLR ISRPRE ISRPEND VECPEND
VECPEND RETBASE VECACT
VTABLE, type R/W, offset 0xD08, reset 0x0000.0000
BASE OFFSET
OFFSET
APINT, type R/W, offset 0xD0C, reset 0xFA05.0000
VECTKEY
ENDIANESS PRIGROUP SYSRESREQ VECTCLRACT VECTRESET
SYSCTRL, type R/W, offset 0xD10, reset 0x0000.0000
SEVONPEND SLEEPDEEP SLEEPEXIT
CFGCTRL, type R/W, offset 0xD14, reset 0x0000.0000
STKALIGN BFHFNMIGN DIV0 UNALIGNED MAINPEND BASETHR
SYSPRI1, type R/W, offset 0xD18, reset 0x0000.0000
USAGE
BUS MEM
SYSPRI2, type R/W, offset 0xD1C, reset 0x0000.0000
SVC
SYSPRI3, type R/W, offset 0xD20, reset 0x0000.0000
TICK PENDSV
DEBUG
SYSHNDCTRL, type R/W, offset 0xD24, reset 0x0000.0000
USAGE BUS MEM
SVC BUSP MEMP USAGEP TICK PNDSV MON SVCA USGA BUSA MEMA
FAULTSTAT, type R/W1C, offset 0xD28, reset 0x0000.0000
DIV0 UNALIGN NOCP INVPC INVSTAT UNDEF
BFARV BSTKE BUSTKE IMPRE PRECISE IBUS MMARV MSTKE MUSTKE DERR IERR
HFAULTSTAT, type R/W1C, offset 0xD2C, reset 0x0000.0000
DBG FORCED
VECT
MMADDR, type R/W, offset 0xD34, reset -
ADDR
ADDR
FAULTADDR, type R/W, offset 0xD38, reset -
ADDR
ADDR
Cortex-M3 Peripherals
Memory Protection Unit (MPU) Registers
Base 0xE000.E000
MPUTYPE, type RO, offset 0xD90, reset 0x0000.0800
IREGION
DREGION SEPARATE
MPUCTRL, type R/W, offset 0xD94, reset 0x0000.0000
PRIVDEFEN HFNMIENA ENABLE
MPUNUMBER, type R/W, offset 0xD98, reset 0x0000.0000
NUMBER
January 08, 2011 701
Texas Instruments-Production Data
Stellaris® LM3S2965 Microcontroller
31 30 29 28 27 26 25 24 23 22 21 20 19 18 17 16
15 14 13 12 11 10 9 8 7 6 5 4 3 2 1 0
MPUBASE, type R/W, offset 0xD9C, reset 0x0000.0000
ADDR
ADDR VALID REGION
MPUBASE1, type R/W, offset 0xDA4, reset 0x0000.0000
ADDR
ADDR VALID REGION
MPUBASE2, type R/W, offset 0xDAC, reset 0x0000.0000
ADDR
ADDR VALID REGION
MPUBASE3, type R/W, offset 0xDB4, reset 0x0000.0000
ADDR
ADDR VALID REGION
MPUATTR, type R/W, offset 0xDA0, reset 0x0000.0000
XN AP TEX S C B
SRD SIZE ENABLE
MPUATTR1, type R/W, offset 0xDA8, reset 0x0000.0000
XN AP TEX S C B
SRD SIZE ENABLE
MPUATTR2, type R/W, offset 0xDB0, reset 0x0000.0000
XN AP TEX S C B
SRD SIZE ENABLE
MPUATTR3, type R/W, offset 0xDB8, reset 0x0000.0000
XN AP TEX S C B
SRD SIZE ENABLE
System Control
Base 0x400F.E000
DID0, type RO, offset 0x000, reset - (see page 184)
VER CLASS
MAJOR MINOR
PBORCTL, type R/W, offset 0x030, reset 0x0000.7FFD (see page 186)
BORIOR
LDOPCTL, type R/W, offset 0x034, reset 0x0000.0000 (see page 187)
VADJ
RIS, type RO, offset 0x050, reset 0x0000.0000 (see page 188)
PLLLRIS BORRIS
IMC, type R/W, offset 0x054, reset 0x0000.0000 (see page 189)
PLLLIM BORIM
MISC, type R/W1C, offset 0x058, reset 0x0000.0000 (see page 190)
PLLLMIS BORMIS
RESC, type R/W, offset 0x05C, reset - (see page 191)
SW WDT BOR POR EXT
RCC, type R/W, offset 0x060, reset 0x078E.3AD1 (see page 192)
ACG SYSDIV USESYSDIV USEPWMDIV PWMDIV
PWRDN BYPASS XTAL OSCSRC IOSCDIS MOSCDIS
PLLCFG, type RO, offset 0x064, reset - (see page 196)
F R
702 January 08, 2011
Texas Instruments-Production Data
Register Quick Reference
31 30 29 28 27 26 25 24 23 22 21 20 19 18 17 16
15 14 13 12 11 10 9 8 7 6 5 4 3 2 1 0
RCC2, type R/W, offset 0x070, reset 0x0780.2810 (see page 197)
USERCC2 SYSDIV2
PWRDN2 BYPASS2 OSCSRC2
DSLPCLKCFG, type R/W, offset 0x144, reset 0x0780.0000 (see page 199)
DSDIVORIDE
DSOSCSRC
DID1, type RO, offset 0x004, reset - (see page 200)
VER FAM PARTNO
PINCOUNT TEMP PKG ROHS QUAL
DC0, type RO, offset 0x008, reset 0x00FF.007F (see page 202)
SRAMSZ
FLASHSZ
DC1, type RO, offset 0x010, reset 0x0311.33FF (see page 203)
CAN1 CAN0 PWM ADC
MINSYSDIV MAXADCSPD MPU HIB TEMPSNS PLL WDT SWO SWD JTAG
DC2, type RO, offset 0x014, reset 0x070F.5337 (see page 205)
COMP2 COMP1 COMP0 TIMER3 TIMER2 TIMER1 TIMER0
I2C1 I2C0 QEI1 QEI0 SSI1 SSI0 UART2 UART1 UART0
DC3, type RO, offset 0x018, reset 0xBF0F.B7FF (see page 207)
32KHZ CCP5 CCP4 CCP3 CCP2 CCP1 CCP0 ADC3 ADC2 ADC1 ADC0
PWMFAULT C2PLUS C2MINUS C1PLUS C1MINUS C0O C0PLUS C0MINUS PWM5 PWM4 PWM3 PWM2 PWM1 PWM0
DC4, type RO, offset 0x01C, reset 0x0000.00FF (see page 209)
GPIOH GPIOG GPIOF GPIOE GPIOD GPIOC GPIOB GPIOA
RCGC0, type R/W, offset 0x100, reset 0x00000040 (see page 210)
CAN1 CAN0 PWM ADC
MAXADCSPD HIB WDT
SCGC0, type R/W, offset 0x110, reset 0x00000040 (see page 212)
CAN1 CAN0 PWM ADC
MAXADCSPD HIB WDT
DCGC0, type R/W, offset 0x120, reset 0x00000040 (see page 214)
CAN1 CAN0 PWM ADC
HIB WDT
RCGC1, type R/W, offset 0x104, reset 0x00000000 (see page 216)
COMP2 COMP1 COMP0 TIMER3 TIMER2 TIMER1 TIMER0
I2C1 I2C0 QEI1 QEI0 SSI1 SSI0 UART2 UART1 UART0
SCGC1, type R/W, offset 0x114, reset 0x00000000 (see page 219)
COMP2 COMP1 COMP0 TIMER3 TIMER2 TIMER1 TIMER0
I2C1 I2C0 QEI1 QEI0 SSI1 SSI0 UART2 UART1 UART0
DCGC1, type R/W, offset 0x124, reset 0x00000000 (see page 222)
COMP2 COMP1 COMP0 TIMER3 TIMER2 TIMER1 TIMER0
I2C1 I2C0 QEI1 QEI0 SSI1 SSI0 UART2 UART1 UART0
RCGC2, type R/W, offset 0x108, reset 0x00000000 (see page 225)
GPIOH GPIOG GPIOF GPIOE GPIOD GPIOC GPIOB GPIOA
SCGC2, type R/W, offset 0x118, reset 0x00000000 (see page 227)
GPIOH GPIOG GPIOF GPIOE GPIOD GPIOC GPIOB GPIOA
DCGC2, type R/W, offset 0x128, reset 0x00000000 (see page 229)
GPIOH GPIOG GPIOF GPIOE GPIOD GPIOC GPIOB GPIOA
January 08, 2011 703
Texas Instruments-Production Data
Stellaris® LM3S2965 Microcontroller
31 30 29 28 27 26 25 24 23 22 21 20 19 18 17 16
15 14 13 12 11 10 9 8 7 6 5 4 3 2 1 0
SRCR0, type R/W, offset 0x040, reset 0x00000000 (see page 231)
CAN1 CAN0 PWM ADC
HIB WDT
SRCR1, type R/W, offset 0x044, reset 0x00000000 (see page 233)
COMP2 COMP1 COMP0 TIMER3 TIMER2 TIMER1 TIMER0
I2C1 I2C0 QEI1 QEI0 SSI1 SSI0 UART2 UART1 UART0
SRCR2, type R/W, offset 0x048, reset 0x00000000 (see page 235)
GPIOH GPIOG GPIOF GPIOE GPIOD GPIOC GPIOB GPIOA
Hibernation Module
Base 0x400F.C000
HIBRTCC, type RO, offset 0x000, reset 0x0000.0000 (see page 244)
RTCC
RTCC
HIBRTCM0, type R/W, offset 0x004, reset 0xFFFF.FFFF (see page 245)
RTCM0
RTCM0
HIBRTCM1, type R/W, offset 0x008, reset 0xFFFF.FFFF (see page 246)
RTCM1
RTCM1
HIBRTCLD, type R/W, offset 0x00C, reset 0xFFFF.FFFF (see page 247)
RTCLD
RTCLD
HIBCTL, type R/W, offset 0x010, reset 0x8000.0000 (see page 248)
VABORT CLK32EN LOWBATEN PINWEN RTCWEN CLKSEL HIBREQ RTCEN
HIBIM, type R/W, offset 0x014, reset 0x0000.0000 (see page 250)
EXTW LOWBAT RTCALT1 RTCALT0
HIBRIS, type RO, offset 0x018, reset 0x0000.0000 (see page 251)
EXTW LOWBAT RTCALT1 RTCALT0
HIBMIS, type RO, offset 0x01C, reset 0x0000.0000 (see page 252)
EXTW LOWBAT RTCALT1 RTCALT0
HIBIC, type R/W1C, offset 0x020, reset 0x0000.0000 (see page 253)
EXTW LOWBAT RTCALT1 RTCALT0
HIBRTCT, type R/W, offset 0x024, reset 0x0000.7FFF (see page 254)
TRIM
HIBDATA, type R/W, offset 0x030-0x12C, reset - (see page 255)
RTD
RTD
Internal Memory
Flash Memory Control Registers (Flash Control Offset)
Base 0x400F.D000
FMA, type R/W, offset 0x000, reset 0x0000.0000
OFFSET
OFFSET
704 January 08, 2011
Texas Instruments-Production Data
Register Quick Reference
31 30 29 28 27 26 25 24 23 22 21 20 19 18 17 16
15 14 13 12 11 10 9 8 7 6 5 4 3 2 1 0
FMD, type R/W, offset 0x004, reset 0x0000.0000
DATA
DATA
FMC, type R/W, offset 0x008, reset 0x0000.0000
WRKEY
COMT MERASE ERASE WRITE
FCRIS, type RO, offset 0x00C, reset 0x0000.0000
PRIS ARIS
FCIM, type R/W, offset 0x010, reset 0x0000.0000
PMASK AMASK
FCMISC, type R/W1C, offset 0x014, reset 0x0000.0000
PMISC AMISC
Internal Memory
Flash Memory Protection Registers (System Control Offset)
Base 0x400F.E000
USECRL, type R/W, offset 0x140, reset 0x31
USEC
FMPRE0, type R/W, offset 0x130 and 0x200, reset 0xFFFF.FFFF
READ_ENABLE
READ_ENABLE
FMPPE0, type R/W, offset 0x134 and 0x400, reset 0xFFFF.FFFF
PROG_ENABLE
PROG_ENABLE
USER_DBG, type R/W, offset 0x1D0, reset 0xFFFF.FFFE
NW DATA
DATA DBG1 DBG0
USER_REG0, type R/W, offset 0x1E0, reset 0xFFFF.FFFF
NW DATA
DATA
USER_REG1, type R/W, offset 0x1E4, reset 0xFFFF.FFFF
NW DATA
DATA
FMPRE1, type R/W, offset 0x204, reset 0xFFFF.FFFF
READ_ENABLE
READ_ENABLE
FMPRE2, type R/W, offset 0x208, reset 0xFFFF.FFFF
READ_ENABLE
READ_ENABLE
FMPRE3, type R/W, offset 0x20C, reset 0xFFFF.FFFF
READ_ENABLE
READ_ENABLE
FMPPE1, type R/W, offset 0x404, reset 0xFFFF.FFFF
PROG_ENABLE
PROG_ENABLE
FMPPE2, type R/W, offset 0x408, reset 0xFFFF.FFFF
PROG_ENABLE
PROG_ENABLE
January 08, 2011 705
Texas Instruments-Production Data
Stellaris® LM3S2965 Microcontroller
31 30 29 28 27 26 25 24 23 22 21 20 19 18 17 16
15 14 13 12 11 10 9 8 7 6 5 4 3 2 1 0
FMPPE3, type R/W, offset 0x40C, reset 0xFFFF.FFFF
PROG_ENABLE
PROG_ENABLE
General-Purpose Input/Outputs (GPIOs)
GPIO Port A base: 0x4000.4000
GPIO Port B base: 0x4000.5000
GPIO Port C base: 0x4000.6000
GPIO Port D base: 0x4000.7000
GPIO Port E base: 0x4002.4000
GPIO Port F base: 0x4002.5000
GPIO Port G base: 0x4002.6000
GPIO Port H base: 0x4002.7000
GPIODATA, type R/W, offset 0x000, reset 0x0000.0000 (see page 290)
DATA
GPIODIR, type R/W, offset 0x400, reset 0x0000.0000 (see page 291)
DIR
GPIOIS, type R/W, offset 0x404, reset 0x0000.0000 (see page 292)
IS
GPIOIBE, type R/W, offset 0x408, reset 0x0000.0000 (see page 293)
IBE
GPIOIEV, type R/W, offset 0x40C, reset 0x0000.0000 (see page 294)
IEV
GPIOIM, type R/W, offset 0x410, reset 0x0000.0000 (see page 295)
IME
GPIORIS, type RO, offset 0x414, reset 0x0000.0000 (see page 296)
RIS
GPIOMIS, type RO, offset 0x418, reset 0x0000.0000 (see page 297)
MIS
GPIOICR, type W1C, offset 0x41C, reset 0x0000.0000 (see page 298)
IC
GPIOAFSEL, type R/W, offset 0x420, reset - (see page 299)
AFSEL
GPIODR2R, type R/W, offset 0x500, reset 0x0000.00FF (see page 301)
DRV2
GPIODR4R, type R/W, offset 0x504, reset 0x0000.0000 (see page 302)
DRV4
GPIODR8R, type R/W, offset 0x508, reset 0x0000.0000 (see page 303)
DRV8
GPIOODR, type R/W, offset 0x50C, reset 0x0000.0000 (see page 304)
ODE
706 January 08, 2011
Texas Instruments-Production Data
Register Quick Reference
31 30 29 28 27 26 25 24 23 22 21 20 19 18 17 16
15 14 13 12 11 10 9 8 7 6 5 4 3 2 1 0
GPIOPUR, type R/W, offset 0x510, reset - (see page 305)
PUE
GPIOPDR, type R/W, offset 0x514, reset 0x0000.0000 (see page 306)
PDE
GPIOSLR, type R/W, offset 0x518, reset 0x0000.0000 (see page 307)
SRL
GPIODEN, type R/W, offset 0x51C, reset - (see page 308)
DEN
GPIOLOCK, type R/W, offset 0x520, reset 0x0000.0001 (see page 309)
LOCK
LOCK
GPIOCR, type -, offset 0x524, reset - (see page 310)
CR
GPIOPeriphID4, type RO, offset 0xFD0, reset 0x0000.0000 (see page 312)
PID4
GPIOPeriphID5, type RO, offset 0xFD4, reset 0x0000.0000 (see page 313)
PID5
GPIOPeriphID6, type RO, offset 0xFD8, reset 0x0000.0000 (see page 314)
PID6
GPIOPeriphID7, type RO, offset 0xFDC, reset 0x0000.0000 (see page 315)
PID7
GPIOPeriphID0, type RO, offset 0xFE0, reset 0x0000.0061 (see page 316)
PID0
GPIOPeriphID1, type RO, offset 0xFE4, reset 0x0000.0000 (see page 317)
PID1
GPIOPeriphID2, type RO, offset 0xFE8, reset 0x0000.0018 (see page 318)
PID2
GPIOPeriphID3, type RO, offset 0xFEC, reset 0x0000.0001 (see page 319)
PID3
GPIOPCellID0, type RO, offset 0xFF0, reset 0x0000.000D (see page 320)
CID0
GPIOPCellID1, type RO, offset 0xFF4, reset 0x0000.00F0 (see page 321)
CID1
GPIOPCellID2, type RO, offset 0xFF8, reset 0x0000.0005 (see page 322)
CID2
January 08, 2011 707
Texas Instruments-Production Data
Stellaris® LM3S2965 Microcontroller
31 30 29 28 27 26 25 24 23 22 21 20 19 18 17 16
15 14 13 12 11 10 9 8 7 6 5 4 3 2 1 0
GPIOPCellID3, type RO, offset 0xFFC, reset 0x0000.00B1 (see page 323)
CID3
General-Purpose Timers
Timer0 base: 0x4003.0000
Timer1 base: 0x4003.1000
Timer2 base: 0x4003.2000
Timer3 base: 0x4003.3000
GPTMCFG, type R/W, offset 0x000, reset 0x0000.0000 (see page 336)
GPTMCFG
GPTMTAMR, type R/W, offset 0x004, reset 0x0000.0000 (see page 337)
TAAMS TACMR TAMR
GPTMTBMR, type R/W, offset 0x008, reset 0x0000.0000 (see page 339)
TBAMS TBCMR TBMR
GPTMCTL, type R/W, offset 0x00C, reset 0x0000.0000 (see page 341)
TBPWML TBOTE TBEVENT TBSTALL TBEN TAPWML TAOTE RTCEN TAEVENT TASTALL TAEN
GPTMIMR, type R/W, offset 0x018, reset 0x0000.0000 (see page 344)
CBEIM CBMIM TBTOIM RTCIM CAEIM CAMIM TATOIM
GPTMRIS, type RO, offset 0x01C, reset 0x0000.0000 (see page 346)
CBERIS CBMRIS TBTORIS RTCRIS CAERIS CAMRIS TATORIS
GPTMMIS, type RO, offset 0x020, reset 0x0000.0000 (see page 347)
CBEMIS CBMMIS TBTOMIS RTCMIS CAEMIS CAMMIS TATOMIS
GPTMICR, type W1C, offset 0x024, reset 0x0000.0000 (see page 348)
CBECINT CBMCINT TBTOCINT RTCCINT CAECINT CAMCINT TATOCINT
GPTMTAILR, type R/W, offset 0x028, reset 0xFFFF.FFFF (see page 350)
TAILRH
TAILRL
GPTMTBILR, type R/W, offset 0x02C, reset 0x0000.FFFF (see page 351)
TBILRL
GPTMTAMATCHR, type R/W, offset 0x030, reset 0xFFFF.FFFF (see page 352)
TAMRH
TAMRL
GPTMTBMATCHR, type R/W, offset 0x034, reset 0x0000.FFFF (see page 353)
TBMRL
GPTMTAPR, type R/W, offset 0x038, reset 0x0000.0000 (see page 354)
TAPSR
GPTMTBPR, type R/W, offset 0x03C, reset 0x0000.0000 (see page 355)
TBPSR
GPTMTAPMR, type R/W, offset 0x040, reset 0x0000.0000 (see page 356)
TAPSMR
708 January 08, 2011
Texas Instruments-Production Data
Register Quick Reference
31 30 29 28 27 26 25 24 23 22 21 20 19 18 17 16
15 14 13 12 11 10 9 8 7 6 5 4 3 2 1 0
GPTMTBPMR, type R/W, offset 0x044, reset 0x0000.0000 (see page 357)
TBPSMR
GPTMTAR, type RO, offset 0x048, reset 0xFFFF.FFFF (see page 358)
TARH
TARL
GPTMTBR, type RO, offset 0x04C, reset 0x0000.FFFF (see page 359)
TBRL
Watchdog Timer
Base 0x4000.0000
WDTLOAD, type R/W, offset 0x000, reset 0xFFFF.FFFF (see page 364)
WDTLoad
WDTLoad
WDTVALUE, type RO, offset 0x004, reset 0xFFFF.FFFF (see page 365)
WDTValue
WDTValue
WDTCTL, type R/W, offset 0x008, reset 0x0000.0000 (see page 366)
RESEN INTEN
WDTICR, type WO, offset 0x00C, reset - (see page 367)
WDTIntClr
WDTIntClr
WDTRIS, type RO, offset 0x010, reset 0x0000.0000 (see page 368)
WDTRIS
WDTMIS, type RO, offset 0x014, reset 0x0000.0000 (see page 369)
WDTMIS
WDTTEST, type R/W, offset 0x418, reset 0x0000.0000 (see page 370)
STALL
WDTLOCK, type R/W, offset 0xC00, reset 0x0000.0000 (see page 371)
WDTLock
WDTLock
WDTPeriphID4, type RO, offset 0xFD0, reset 0x0000.0000 (see page 372)
PID4
WDTPeriphID5, type RO, offset 0xFD4, reset 0x0000.0000 (see page 373)
PID5
WDTPeriphID6, type RO, offset 0xFD8, reset 0x0000.0000 (see page 374)
PID6
WDTPeriphID7, type RO, offset 0xFDC, reset 0x0000.0000 (see page 375)
PID7
WDTPeriphID0, type RO, offset 0xFE0, reset 0x0000.0005 (see page 376)
PID0
WDTPeriphID1, type RO, offset 0xFE4, reset 0x0000.0018 (see page 377)
PID1
January 08, 2011 709
Texas Instruments-Production Data
Stellaris® LM3S2965 Microcontroller
31 30 29 28 27 26 25 24 23 22 21 20 19 18 17 16
15 14 13 12 11 10 9 8 7 6 5 4 3 2 1 0
WDTPeriphID2, type RO, offset 0xFE8, reset 0x0000.0018 (see page 378)
PID2
WDTPeriphID3, type RO, offset 0xFEC, reset 0x0000.0001 (see page 379)
PID3
WDTPCellID0, type RO, offset 0xFF0, reset 0x0000.000D (see page 380)
CID0
WDTPCellID1, type RO, offset 0xFF4, reset 0x0000.00F0 (see page 381)
CID1
WDTPCellID2, type RO, offset 0xFF8, reset 0x0000.0005 (see page 382)
CID2
WDTPCellID3, type RO, offset 0xFFC, reset 0x0000.00B1 (see page 383)
CID3
Analog-to-Digital Converter (ADC)
Base 0x4003.8000
ADCACTSS, type R/W, offset 0x000, reset 0x0000.0000 (see page 393)
ASEN3 ASEN2 ASEN1 ASEN0
ADCRIS, type RO, offset 0x004, reset 0x0000.0000 (see page 394)
INR3 INR2 INR1 INR0
ADCIM, type R/W, offset 0x008, reset 0x0000.0000 (see page 395)
MASK3 MASK2 MASK1 MASK0
ADCISC, type R/W1C, offset 0x00C, reset 0x0000.0000 (see page 396)
IN3 IN2 IN1 IN0
ADCOSTAT, type R/W1C, offset 0x010, reset 0x0000.0000 (see page 397)
OV3 OV2 OV1 OV0
ADCEMUX, type R/W, offset 0x014, reset 0x0000.0000 (see page 398)
EM3 EM2 EM1 EM0
ADCUSTAT, type R/W1C, offset 0x018, reset 0x0000.0000 (see page 402)
UV3 UV2 UV1 UV0
ADCSSPRI, type R/W, offset 0x020, reset 0x0000.3210 (see page 403)
SS3 SS2 SS1 SS0
ADCPSSI, type WO, offset 0x028, reset - (see page 405)
SS3 SS2 SS1 SS0
ADCSAC, type R/W, offset 0x030, reset 0x0000.0000 (see page 406)
AVG
ADCSSMUX0, type R/W, offset 0x040, reset 0x0000.0000 (see page 407)
MUX7 MUX6 MUX5 MUX4
MUX3 MUX2 MUX1 MUX0
710 January 08, 2011
Texas Instruments-Production Data
Register Quick Reference
31 30 29 28 27 26 25 24 23 22 21 20 19 18 17 16
15 14 13 12 11 10 9 8 7 6 5 4 3 2 1 0
ADCSSCTL0, type R/W, offset 0x044, reset 0x0000.0000 (see page 409)
TS7 IE7 END7 D7 TS6 IE6 END6 D6 TS5 IE5 END5 D5 TS4 IE4 END4 D4
TS3 IE3 END3 D3 TS2 IE2 END2 D2 TS1 IE1 END1 D1 TS0 IE0 END0 D0
ADCSSFIFO0, type RO, offset 0x048, reset - (see page 412)
DATA
ADCSSFIFO1, type RO, offset 0x068, reset - (see page 412)
DATA
ADCSSFIFO2, type RO, offset 0x088, reset - (see page 412)
DATA
ADCSSFIFO3, type RO, offset 0x0A8, reset - (see page 412)
DATA
ADCSSFSTAT0, type RO, offset 0x04C, reset 0x0000.0100 (see page 413)
FULL EMPTY HPTR TPTR
ADCSSFSTAT1, type RO, offset 0x06C, reset 0x0000.0100 (see page 413)
FULL EMPTY HPTR TPTR
ADCSSFSTAT2, type RO, offset 0x08C, reset 0x0000.0100 (see page 413)
FULL EMPTY HPTR TPTR
ADCSSFSTAT3, type RO, offset 0x0AC, reset 0x0000.0100 (see page 413)
FULL EMPTY HPTR TPTR
ADCSSMUX1, type R/W, offset 0x060, reset 0x0000.0000 (see page 414)
MUX3 MUX2 MUX1 MUX0
ADCSSMUX2, type R/W, offset 0x080, reset 0x0000.0000 (see page 414)
MUX3 MUX2 MUX1 MUX0
ADCSSCTL1, type R/W, offset 0x064, reset 0x0000.0000 (see page 415)
TS3 IE3 END3 D3 TS2 IE2 END2 D2 TS1 IE1 END1 D1 TS0 IE0 END0 D0
ADCSSCTL2, type R/W, offset 0x084, reset 0x0000.0000 (see page 415)
TS3 IE3 END3 D3 TS2 IE2 END2 D2 TS1 IE1 END1 D1 TS0 IE0 END0 D0
ADCSSMUX3, type R/W, offset 0x0A0, reset 0x0000.0000 (see page 417)
MUX0
ADCSSCTL3, type R/W, offset 0x0A4, reset 0x0000.0002 (see page 418)
TS0 IE0 END0 D0
ADCTMLB, type R/W, offset 0x100, reset 0x0000.0000 (see page 419)
LB
January 08, 2011 711
Texas Instruments-Production Data
Stellaris® LM3S2965 Microcontroller
31 30 29 28 27 26 25 24 23 22 21 20 19 18 17 16
15 14 13 12 11 10 9 8 7 6 5 4 3 2 1 0
Universal Asynchronous Receivers/Transmitters (UARTs)
UART0 base: 0x4000.C000
UART1 base: 0x4000.D000
UART2 base: 0x4000.E000
UARTDR, type R/W, offset 0x000, reset 0x0000.0000 (see page 428)
OE BE PE FE DATA
UARTRSR/UARTECR, type RO, offset 0x004, reset 0x0000.0000 (Reads) (see page 430)
OE BE PE FE
UARTRSR/UARTECR, type WO, offset 0x004, reset 0x0000.0000 (Writes) (see page 430)
DATA
UARTFR, type RO, offset 0x018, reset 0x0000.0090 (see page 432)
TXFE RXFF TXFF RXFE BUSY
UARTILPR, type R/W, offset 0x020, reset 0x0000.0000 (see page 434)
ILPDVSR
UARTIBRD, type R/W, offset 0x024, reset 0x0000.0000 (see page 435)
DIVINT
UARTFBRD, type R/W, offset 0x028, reset 0x0000.0000 (see page 436)
DIVFRAC
UARTLCRH, type R/W, offset 0x02C, reset 0x0000.0000 (see page 437)
SPS WLEN FEN STP2 EPS PEN BRK
UARTCTL, type R/W, offset 0x030, reset 0x0000.0300 (see page 439)
RXE TXE LBE SIRLP SIREN UARTEN
UARTIFLS, type R/W, offset 0x034, reset 0x0000.0012 (see page 441)
RXIFLSEL TXIFLSEL
UARTIM, type R/W, offset 0x038, reset 0x0000.0000 (see page 443)
OEIM BEIM PEIM FEIM RTIM TXIM RXIM
UARTRIS, type RO, offset 0x03C, reset 0x0000.000F (see page 445)
OERIS BERIS PERIS FERIS RTRIS TXRIS RXRIS
UARTMIS, type RO, offset 0x040, reset 0x0000.0000 (see page 446)
OEMIS BEMIS PEMIS FEMIS RTMIS TXMIS RXMIS
UARTICR, type W1C, offset 0x044, reset 0x0000.0000 (see page 447)
OEIC BEIC PEIC FEIC RTIC TXIC RXIC
UARTPeriphID4, type RO, offset 0xFD0, reset 0x0000.0000 (see page 449)
PID4
UARTPeriphID5, type RO, offset 0xFD4, reset 0x0000.0000 (see page 450)
PID5
712 January 08, 2011
Texas Instruments-Production Data
Register Quick Reference
31 30 29 28 27 26 25 24 23 22 21 20 19 18 17 16
15 14 13 12 11 10 9 8 7 6 5 4 3 2 1 0
UARTPeriphID6, type RO, offset 0xFD8, reset 0x0000.0000 (see page 451)
PID6
UARTPeriphID7, type RO, offset 0xFDC, reset 0x0000.0000 (see page 452)
PID7
UARTPeriphID0, type RO, offset 0xFE0, reset 0x0000.0011 (see page 453)
PID0
UARTPeriphID1, type RO, offset 0xFE4, reset 0x0000.0000 (see page 454)
PID1
UARTPeriphID2, type RO, offset 0xFE8, reset 0x0000.0018 (see page 455)
PID2
UARTPeriphID3, type RO, offset 0xFEC, reset 0x0000.0001 (see page 456)
PID3
UARTPCellID0, type RO, offset 0xFF0, reset 0x0000.000D (see page 457)
CID0
UARTPCellID1, type RO, offset 0xFF4, reset 0x0000.00F0 (see page 458)
CID1
UARTPCellID2, type RO, offset 0xFF8, reset 0x0000.0005 (see page 459)
CID2
UARTPCellID3, type RO, offset 0xFFC, reset 0x0000.00B1 (see page 460)
CID3
Synchronous Serial Interface (SSI)
SSI0 base: 0x4000.8000
SSI1 base: 0x4000.9000
SSICR0, type R/W, offset 0x000, reset 0x0000.0000 (see page 473)
SCR SPH SPO FRF DSS
SSICR1, type R/W, offset 0x004, reset 0x0000.0000 (see page 475)
SOD MS SSE LBM
SSIDR, type R/W, offset 0x008, reset 0x0000.0000 (see page 477)
DATA
SSISR, type RO, offset 0x00C, reset 0x0000.0003 (see page 478)
BSY RFF RNE TNF TFE
SSICPSR, type R/W, offset 0x010, reset 0x0000.0000 (see page 480)
CPSDVSR
SSIIM, type R/W, offset 0x014, reset 0x0000.0000 (see page 481)
TXIM RXIM RTIM RORIM
January 08, 2011 713
Texas Instruments-Production Data
Stellaris® LM3S2965 Microcontroller
31 30 29 28 27 26 25 24 23 22 21 20 19 18 17 16
15 14 13 12 11 10 9 8 7 6 5 4 3 2 1 0
SSIRIS, type RO, offset 0x018, reset 0x0000.0008 (see page 483)
TXRIS RXRIS RTRIS RORRIS
SSIMIS, type RO, offset 0x01C, reset 0x0000.0000 (see page 484)
TXMIS RXMIS RTMIS RORMIS
SSIICR, type W1C, offset 0x020, reset 0x0000.0000 (see page 485)
RTIC RORIC
SSIPeriphID4, type RO, offset 0xFD0, reset 0x0000.0000 (see page 486)
PID4
SSIPeriphID5, type RO, offset 0xFD4, reset 0x0000.0000 (see page 487)
PID5
SSIPeriphID6, type RO, offset 0xFD8, reset 0x0000.0000 (see page 488)
PID6
SSIPeriphID7, type RO, offset 0xFDC, reset 0x0000.0000 (see page 489)
PID7
SSIPeriphID0, type RO, offset 0xFE0, reset 0x0000.0022 (see page 490)
PID0
SSIPeriphID1, type RO, offset 0xFE4, reset 0x0000.0000 (see page 491)
PID1
SSIPeriphID2, type RO, offset 0xFE8, reset 0x0000.0018 (see page 492)
PID2
SSIPeriphID3, type RO, offset 0xFEC, reset 0x0000.0001 (see page 493)
PID3
SSIPCellID0, type RO, offset 0xFF0, reset 0x0000.000D (see page 494)
CID0
SSIPCellID1, type RO, offset 0xFF4, reset 0x0000.00F0 (see page 495)
CID1
SSIPCellID2, type RO, offset 0xFF8, reset 0x0000.0005 (see page 496)
CID2
SSIPCellID3, type RO, offset 0xFFC, reset 0x0000.00B1 (see page 497)
CID3
Inter-Integrated Circuit (I2C) Interface
I2C Master
I2C 0 base: 0x4002.0000
I2C 1 base: 0x4002.1000
I2CMSA, type R/W, offset 0x000, reset 0x0000.0000
SA R/S
714 January 08, 2011
Texas Instruments-Production Data
Register Quick Reference
31 30 29 28 27 26 25 24 23 22 21 20 19 18 17 16
15 14 13 12 11 10 9 8 7 6 5 4 3 2 1 0
I2CMCS, type RO, offset 0x004, reset 0x0000.0000 (Reads)
BUSBSY IDLE ARBLST DATACK ADRACK ERROR BUSY
I2CMCS, type WO, offset 0x004, reset 0x0000.0000 (Writes)
ACK STOP START RUN
I2CMDR, type R/W, offset 0x008, reset 0x0000.0000
DATA
I2CMTPR, type R/W, offset 0x00C, reset 0x0000.0001
TPR
I2CMIMR, type R/W, offset 0x010, reset 0x0000.0000
IM
I2CMRIS, type RO, offset 0x014, reset 0x0000.0000
RIS
I2CMMIS, type RO, offset 0x018, reset 0x0000.0000
MIS
I2CMICR, type WO, offset 0x01C, reset 0x0000.0000
IC
I2CMCR, type R/W, offset 0x020, reset 0x0000.0000
SFE MFE LPBK
Inter-Integrated Circuit (I2C) Interface
I2C Slave
I2C 0 base: 0x4002.0000
I2C 1 base: 0x4002.1000
I2CSOAR, type R/W, offset 0x800, reset 0x0000.0000
OAR
I2CSCSR, type RO, offset 0x804, reset 0x0000.0000 (Reads)
FBR TREQ RREQ
I2CSCSR, type WO, offset 0x804, reset 0x0000.0000 (Writes)
DA
I2CSDR, type R/W, offset 0x808, reset 0x0000.0000
DATA
I2CSIMR, type R/W, offset 0x80C, reset 0x0000.0000
DATAIM
I2CSRIS, type RO, offset 0x810, reset 0x0000.0000
DATARIS
I2CSMIS, type RO, offset 0x814, reset 0x0000.0000
DATAMIS
January 08, 2011 715
Texas Instruments-Production Data
Stellaris® LM3S2965 Microcontroller
31 30 29 28 27 26 25 24 23 22 21 20 19 18 17 16
15 14 13 12 11 10 9 8 7 6 5 4 3 2 1 0
I2CSICR, type WO, offset 0x818, reset 0x0000.0000
DATAIC
Controller Area Network (CAN) Module
CAN0 base: 0x4004.0000
CAN1 base: 0x4004.1000
CANCTL, type R/W, offset 0x000, reset 0x0000.0001 (see page 555)
TEST CCE DAR EIE SIE IE INIT
CANSTS, type R/W, offset 0x004, reset 0x0000.0000 (see page 557)
BOFF EWARN EPASS RXOK TXOK LEC
CANERR, type RO, offset 0x008, reset 0x0000.0000 (see page 559)
RP REC TEC
CANBIT, type R/W, offset 0x00C, reset 0x0000.2301 (see page 560)
TSEG2 TSEG1 SJW BRP
CANINT, type RO, offset 0x010, reset 0x0000.0000 (see page 561)
INTID
CANTST, type R/W, offset 0x014, reset 0x0000.0000 (see page 562)
RX TX LBACK SILENT BASIC
CANBRPE, type R/W, offset 0x018, reset 0x0000.0000 (see page 564)
BRPE
CANIF1CRQ, type R/W, offset 0x020, reset 0x0000.0001 (see page 565)
BUSY MNUM
CANIF2CRQ, type R/W, offset 0x080, reset 0x0000.0001 (see page 565)
BUSY MNUM
CANIF1CMSK, type R/W, offset 0x024, reset 0x0000.0000 (see page 566)
DATAA DATAB NEWDAT /
TXRQST
WRNRD MASK ARB CONTROL CLRINTPND
CANIF2CMSK, type R/W, offset 0x084, reset 0x0000.0000 (see page 566)
DATAA DATAB NEWDAT /
TXRQST
WRNRD MASK ARB CONTROL CLRINTPND
CANIF1MSK1, type R/W, offset 0x028, reset 0x0000.FFFF (see page 568)
MSK
CANIF2MSK1, type R/W, offset 0x088, reset 0x0000.FFFF (see page 568)
MSK
CANIF1MSK2, type R/W, offset 0x02C, reset 0x0000.FFFF (see page 569)
MXTD MDIR MSK
CANIF2MSK2, type R/W, offset 0x08C, reset 0x0000.FFFF (see page 569)
MXTD MDIR MSK
716 January 08, 2011
Texas Instruments-Production Data
Register Quick Reference
31 30 29 28 27 26 25 24 23 22 21 20 19 18 17 16
15 14 13 12 11 10 9 8 7 6 5 4 3 2 1 0
CANIF1ARB1, type R/W, offset 0x030, reset 0x0000.0000 (see page 570)
ID
CANIF2ARB1, type R/W, offset 0x090, reset 0x0000.0000 (see page 570)
ID
CANIF1ARB2, type R/W, offset 0x034, reset 0x0000.0000 (see page 571)
MSGVAL XTD DIR ID
CANIF2ARB2, type R/W, offset 0x094, reset 0x0000.0000 (see page 571)
MSGVAL XTD DIR ID
CANIF1MCTL, type R/W, offset 0x038, reset 0x0000.0000 (see page 572)
NEWDAT MSGLST INTPND UMASK TXIE RXIE RMTEN TXRQST EOB DLC
CANIF2MCTL, type R/W, offset 0x098, reset 0x0000.0000 (see page 572)
NEWDAT MSGLST INTPND UMASK TXIE RXIE RMTEN TXRQST EOB DLC
CANIF1DA1, type R/W, offset 0x03C, reset 0x0000.0000 (see page 574)
DATA
CANIF1DA2, type R/W, offset 0x040, reset 0x0000.0000 (see page 574)
DATA
CANIF1DB1, type R/W, offset 0x044, reset 0x0000.0000 (see page 574)
DATA
CANIF1DB2, type R/W, offset 0x048, reset 0x0000.0000 (see page 574)
DATA
CANIF2DA1, type R/W, offset 0x09C, reset 0x0000.0000 (see page 574)
DATA
CANIF2DA2, type R/W, offset 0x0A0, reset 0x0000.0000 (see page 574)
DATA
CANIF2DB1, type R/W, offset 0x0A4, reset 0x0000.0000 (see page 574)
DATA
CANIF2DB2, type R/W, offset 0x0A8, reset 0x0000.0000 (see page 574)
DATA
CANTXRQ1, type RO, offset 0x100, reset 0x0000.0000 (see page 575)
TXRQST
CANTXRQ2, type RO, offset 0x104, reset 0x0000.0000 (see page 575)
TXRQST
CANNWDA1, type RO, offset 0x120, reset 0x0000.0000 (see page 576)
NEWDAT
January 08, 2011 717
Texas Instruments-Production Data
Stellaris® LM3S2965 Microcontroller
31 30 29 28 27 26 25 24 23 22 21 20 19 18 17 16
15 14 13 12 11 10 9 8 7 6 5 4 3 2 1 0
CANNWDA2, type RO, offset 0x124, reset 0x0000.0000 (see page 576)
NEWDAT
CANMSG1INT, type RO, offset 0x140, reset 0x0000.0000 (see page 577)
INTPND
CANMSG2INT, type RO, offset 0x144, reset 0x0000.0000 (see page 577)
INTPND
CANMSG1VAL, type RO, offset 0x160, reset 0x0000.0000 (see page 578)
MSGVAL
CANMSG2VAL, type RO, offset 0x164, reset 0x0000.0000 (see page 578)
MSGVAL
Analog Comparators
Base 0x4003.C000
ACMIS, type R/W1C, offset 0x000, reset 0x0000.0000 (see page 584)
IN2 IN1 IN0
ACRIS, type RO, offset 0x004, reset 0x0000.0000 (see page 585)
IN2 IN1 IN0
ACINTEN, type R/W, offset 0x008, reset 0x0000.0000 (see page 586)
IN2 IN1 IN0
ACREFCTL, type R/W, offset 0x010, reset 0x0000.0000 (see page 587)
EN RNG VREF
ACSTAT0, type RO, offset 0x020, reset 0x0000.0000 (see page 588)
OVAL
ACSTAT1, type RO, offset 0x040, reset 0x0000.0000 (see page 588)
OVAL
ACSTAT2, type RO, offset 0x060, reset 0x0000.0000 (see page 588)
OVAL
ACCTL0, type R/W, offset 0x024, reset 0x0000.0000 (see page 589)
TOEN ASRCP TSLVAL TSEN ISLVAL ISEN CINV
ACCTL1, type R/W, offset 0x044, reset 0x0000.0000 (see page 589)
TOEN ASRCP TSLVAL TSEN ISLVAL ISEN CINV
ACCTL2, type R/W, offset 0x064, reset 0x0000.0000 (see page 589)
TOEN ASRCP TSLVAL TSEN ISLVAL ISEN CINV
Pulse Width Modulator (PWM)
Base 0x4002.8000
PWMCTL, type R/W, offset 0x000, reset 0x0000.0000 (see page 600)
GlobalSync2 GlobalSync1 GlobalSync0
718 January 08, 2011
Texas Instruments-Production Data
Register Quick Reference
31 30 29 28 27 26 25 24 23 22 21 20 19 18 17 16
15 14 13 12 11 10 9 8 7 6 5 4 3 2 1 0
PWMSYNC, type R/W, offset 0x004, reset 0x0000.0000 (see page 601)
Sync2 Sync1 Sync0
PWMENABLE, type R/W, offset 0x008, reset 0x0000.0000 (see page 602)
PWM5En PWM4En PWM3En PWM2En PWM1En PWM0En
PWMINVERT, type R/W, offset 0x00C, reset 0x0000.0000 (see page 603)
PWM5Inv PWM4Inv PWM3Inv PWM2Inv PWM1Inv PWM0Inv
PWMFAULT, type R/W, offset 0x010, reset 0x0000.0000 (see page 604)
Fault5 Fault4 Fault3 Fault2 Fault1 Fault0
PWMINTEN, type R/W, offset 0x014, reset 0x0000.0000 (see page 605)
IntFault
IntPWM2 IntPWM1 IntPWM0
PWMRIS, type RO, offset 0x018, reset 0x0000.0000 (see page 606)
IntFault
IntPWM2 IntPWM1 IntPWM0
PWMISC, type R/W1C, offset 0x01C, reset 0x0000.0000 (see page 607)
IntFault
IntPWM2 IntPWM1 IntPWM0
PWMSTATUS, type RO, offset 0x020, reset 0x0000.0000 (see page 608)
Fault
PWM0CTL, type R/W, offset 0x040, reset 0x0000.0000 (see page 609)
CmpBUpd CmpAUpd LoadUpd Debug Mode Enable
PWM1CTL, type R/W, offset 0x080, reset 0x0000.0000 (see page 609)
CmpBUpd CmpAUpd LoadUpd Debug Mode Enable
PWM2CTL, type R/W, offset 0x0C0, reset 0x0000.0000 (see page 609)
CmpBUpd CmpAUpd LoadUpd Debug Mode Enable
PWM0INTEN, type R/W, offset 0x044, reset 0x0000.0000 (see page 611)
TrCmpBD TrCmpBU TrCmpAD TrCmpAU TrCntLoad TrCntZero IntCmpBD IntCmpBU IntCmpAD IntCmpAU IntCntLoad IntCntZero
PWM1INTEN, type R/W, offset 0x084, reset 0x0000.0000 (see page 611)
TrCmpBD TrCmpBU TrCmpAD TrCmpAU TrCntLoad TrCntZero IntCmpBD IntCmpBU IntCmpAD IntCmpAU IntCntLoad IntCntZero
PWM2INTEN, type R/W, offset 0x0C4, reset 0x0000.0000 (see page 611)
TrCmpBD TrCmpBU TrCmpAD TrCmpAU TrCntLoad TrCntZero IntCmpBD IntCmpBU IntCmpAD IntCmpAU IntCntLoad IntCntZero
PWM0RIS, type RO, offset 0x048, reset 0x0000.0000 (see page 614)
IntCmpBD IntCmpBU IntCmpAD IntCmpAU IntCntLoad IntCntZero
PWM1RIS, type RO, offset 0x088, reset 0x0000.0000 (see page 614)
IntCmpBD IntCmpBU IntCmpAD IntCmpAU IntCntLoad IntCntZero
PWM2RIS, type RO, offset 0x0C8, reset 0x0000.0000 (see page 614)
IntCmpBD IntCmpBU IntCmpAD IntCmpAU IntCntLoad IntCntZero
January 08, 2011 719
Texas Instruments-Production Data
Stellaris® LM3S2965 Microcontroller
31 30 29 28 27 26 25 24 23 22 21 20 19 18 17 16
15 14 13 12 11 10 9 8 7 6 5 4 3 2 1 0
PWM0ISC, type R/W1C, offset 0x04C, reset 0x0000.0000 (see page 615)
IntCmpBD IntCmpBU IntCmpAD IntCmpAU IntCntLoad IntCntZero
PWM1ISC, type R/W1C, offset 0x08C, reset 0x0000.0000 (see page 615)
IntCmpBD IntCmpBU IntCmpAD IntCmpAU IntCntLoad IntCntZero
PWM2ISC, type R/W1C, offset 0x0CC, reset 0x0000.0000 (see page 615)
IntCmpBD IntCmpBU IntCmpAD IntCmpAU IntCntLoad IntCntZero
PWM0LOAD, type R/W, offset 0x050, reset 0x0000.0000 (see page 616)
Load
PWM1LOAD, type R/W, offset 0x090, reset 0x0000.0000 (see page 616)
Load
PWM2LOAD, type R/W, offset 0x0D0, reset 0x0000.0000 (see page 616)
Load
PWM0COUNT, type RO, offset 0x054, reset 0x0000.0000 (see page 617)
Count
PWM1COUNT, type RO, offset 0x094, reset 0x0000.0000 (see page 617)
Count
PWM2COUNT, type RO, offset 0x0D4, reset 0x0000.0000 (see page 617)
Count
PWM0CMPA, type R/W, offset 0x058, reset 0x0000.0000 (see page 618)
CompA
PWM1CMPA, type R/W, offset 0x098, reset 0x0000.0000 (see page 618)
CompA
PWM2CMPA, type R/W, offset 0x0D8, reset 0x0000.0000 (see page 618)
CompA
PWM0CMPB, type R/W, offset 0x05C, reset 0x0000.0000 (see page 619)
CompB
PWM1CMPB, type R/W, offset 0x09C, reset 0x0000.0000 (see page 619)
CompB
PWM2CMPB, type R/W, offset 0x0DC, reset 0x0000.0000 (see page 619)
CompB
PWM0GENA, type R/W, offset 0x060, reset 0x0000.0000 (see page 620)
ActCmpBD ActCmpBU ActCmpAD ActCmpAU ActLoad ActZero
PWM1GENA, type R/W, offset 0x0A0, reset 0x0000.0000 (see page 620)
ActCmpBD ActCmpBU ActCmpAD ActCmpAU ActLoad ActZero
720 January 08, 2011
Texas Instruments-Production Data
Register Quick Reference
31 30 29 28 27 26 25 24 23 22 21 20 19 18 17 16
15 14 13 12 11 10 9 8 7 6 5 4 3 2 1 0
PWM2GENA, type R/W, offset 0x0E0, reset 0x0000.0000 (see page 620)
ActCmpBD ActCmpBU ActCmpAD ActCmpAU ActLoad ActZero
PWM0GENB, type R/W, offset 0x064, reset 0x0000.0000 (see page 623)
ActCmpBD ActCmpBU ActCmpAD ActCmpAU ActLoad ActZero
PWM1GENB, type R/W, offset 0x0A4, reset 0x0000.0000 (see page 623)
ActCmpBD ActCmpBU ActCmpAD ActCmpAU ActLoad ActZero
PWM2GENB, type R/W, offset 0x0E4, reset 0x0000.0000 (see page 623)
ActCmpBD ActCmpBU ActCmpAD ActCmpAU ActLoad ActZero
PWM0DBCTL, type R/W, offset 0x068, reset 0x0000.0000 (see page 626)
Enable
PWM1DBCTL, type R/W, offset 0x0A8, reset 0x0000.0000 (see page 626)
Enable
PWM2DBCTL, type R/W, offset 0x0E8, reset 0x0000.0000 (see page 626)
Enable
PWM0DBRISE, type R/W, offset 0x06C, reset 0x0000.0000 (see page 627)
RiseDelay
PWM1DBRISE, type R/W, offset 0x0AC, reset 0x0000.0000 (see page 627)
RiseDelay
PWM2DBRISE, type R/W, offset 0x0EC, reset 0x0000.0000 (see page 627)
RiseDelay
PWM0DBFALL, type R/W, offset 0x070, reset 0x0000.0000 (see page 628)
FallDelay
PWM1DBFALL, type R/W, offset 0x0B0, reset 0x0000.0000 (see page 628)
FallDelay
PWM2DBFALL, type R/W, offset 0x0F0, reset 0x0000.0000 (see page 628)
FallDelay
Quadrature Encoder Interface (QEI)
QEI0 base: 0x4002.C000
QEI1 base: 0x4002.D000
QEICTL, type R/W, offset 0x000, reset 0x0000.0000 (see page 634)
STALLEN INVI INVB INVA VelDiv VelEn ResMode CapMode SigMode Swap Enable
QEISTAT, type RO, offset 0x004, reset 0x0000.0000 (see page 636)
Direction Error
QEIPOS, type R/W, offset 0x008, reset 0x0000.0000 (see page 637)
Position
Position
January 08, 2011 721
Texas Instruments-Production Data
Stellaris® LM3S2965 Microcontroller
31 30 29 28 27 26 25 24 23 22 21 20 19 18 17 16
15 14 13 12 11 10 9 8 7 6 5 4 3 2 1 0
QEIMAXPOS, type R/W, offset 0x00C, reset 0x0000.0000 (see page 638)
MaxPos
MaxPos
QEILOAD, type R/W, offset 0x010, reset 0x0000.0000 (see page 639)
Load
Load
QEITIME, type RO, offset 0x014, reset 0x0000.0000 (see page 640)
Time
Time
QEICOUNT, type RO, offset 0x018, reset 0x0000.0000 (see page 641)
Count
Count
QEISPEED, type RO, offset 0x01C, reset 0x0000.0000 (see page 642)
Speed
Speed
QEIINTEN, type R/W, offset 0x020, reset 0x0000.0000 (see page 643)
IntError IntDir IntTimer IntIndex
QEIRIS, type RO, offset 0x024, reset 0x0000.0000 (see page 644)
IntError IntDir IntTimer IntIndex
QEIISC, type R/W1C, offset 0x028, reset 0x0000.0000 (see page 645)
IntError IntDir IntTimer IntIndex
722 January 08, 2011
Texas Instruments-Production Data
Register Quick Reference
C Ordering and Contact Information
C.1 Ordering Information
L M 3 S n n n n – g p p s s – r r m
Part Number
Temperature
Package Speed
Revision
Shipping Medium
E = –40°C to +105°C
I = –40°C to +85°C
T = Tape-and-reel
Omitted = Default shipping (tray or tube)
BZ = 108-ball BGA
QC = 100-pin LQFP
QN = 48-pin LQFP
QR = 64-pin LQFP
GZ = 48-pin QFN
20 = 20 MHz
25 = 25 MHz
50 = 50 MHz
80 = 80 MHz
nnn = Sandstorm-class parts
nnnn = All other Stellaris® parts
Table C-1. Part Ordering Information
Orderable Part Number Description
Stellaris® LM3S2965-IBZ50-A2 LM3S2965 Microcontroller Industrial Temperature 108-ball BGA
Stellaris LM3S2965 Microcontroller Industrial Temperature 108-ball BGA
Tape-and-reel
LM3S2965-IBZ50-A2T
LM3S2965-EQC50-A2 Stellaris LM3S2965 Microcontroller Extended Temperature 100-pin LQFP
Stellaris LM3S2965 Microcontroller Extended Temperature 100-pin LQFP
Tape-and-reel
LM3S2965-EQC50-A2T
LM3S2965-IQC50-A2 Stellaris LM3S2965 Microcontroller Industrial Temperature 100-pin LQFP
Stellaris LM3S2965 Microcontroller Industrial Temperature 100-pin LQFP
Tape-and-reel
LM3S2965-IQC50-A2T
C.2 Part Markings
The Stellaris microcontrollers are marked with an identifying number. This code contains the following
information:
■ The first line indicates the part number. In the example figure below, this is the LM3S6965.
■ In the second line, the first seven characters indicate the temperature, package, speed, and
revision. In the example below, this is an Industrial temperature (I), 100-pin LQFP package (QC),
50-MHz (50), revision A2 (A2) device.
■ The remaining characters contain internal tracking numbers.
January 08, 2011 723
Texas Instruments-Production Data
Stellaris® LM3S2965 Microcontroller
C.3 Kits
The Stellaris Family provides the hardware and software tools that engineers need to begin
development quickly.
■ Reference Design Kits accelerate product development by providing ready-to-run hardware and
comprehensive documentation including hardware design files
■ Evaluation Kits provide a low-cost and effective means of evaluating Stellaris microcontrollers
before purchase
■ Development Kits provide you with all the tools you need to develop and prototype embedded
applications right out of the box
See the website at www.ti.com/stellaris for the latest tools available, or ask your distributor.
C.4 Support Information
For support on Stellaris products, contact the TI Worldwide Product Information Center nearest you:
http://www-k.ext.ti.com/sc/technical-support/product-information-centers.htm.
724 January 08, 2011
Texas Instruments-Production Data
Ordering and Contact Information
D Package Information
D.1 100-Pin LQFP Package
D.1.1 Package Dimensions
Figure D-1. 100-Pin LQFP Package Dimensions
Note: The following notes apply to the package drawing.
1. All dimensions shown in mm.
2. Dimensions shown are nominal with tolerances indicated.
3. Foot length 'L' is measured at gage plane 0.25 mm above seating plane.
January 08, 2011 725
Texas Instruments-Production Data
Stellaris® LM3S2965 Microcontroller
Body +2.00 mm Footprint, 1.4 mm package thickness
Symbols Leads 100L
A Max. 1.60
A1 - 0.05 Min./0.15 Max.
A2 ±0.05 1.40
D ±0.20 16.00
D1 ±0.05 14.00
E ±0.20 16.00
E1 ±0.05 14.00
L +0.15/-0.10 0.60
e Basic 0.50
b +0.05 0.22
θ - 0˚-7˚
ddd Max. 0.08
ccc Max. 0.08
JEDEC Reference Drawing MS-026
Variation Designator BED
726 January 08, 2011
Texas Instruments-Production Data
Package Information
D.1.2 Tray Dimensions
Figure D-2. 100-Pin LQFP Tray Dimensions
D.1.3 Tape and Reel Dimensions
Note: In the figure that follows, pin 1 is located in the top right corner of the device.
January 08, 2011 727
Texas Instruments-Production Data
Stellaris® LM3S2965 Microcontroller
Figure D-3. 100-Pin LQFP Tape and Reel Dimensions
PRINTED ON
MUST NOT BE REPRODUCED WITHOUT WRITTEN
PERMISSION FROM SUMICARRIER (S) PTE LTD
06.01.2003
THIS IS A COMPUTER GENERATED
UNCONTROLLED DOCUMENT
06.01.2003
06.01.2003
06.01.2003
06.01.2003
728 January 08, 2011
Texas Instruments-Production Data
Package Information
D.2 108-Ball BGA Package
D.2.1 Package Dimensions
Figure D-4. 108-Ball BGA Package Dimensions
January 08, 2011 729
Texas Instruments-Production Data
Stellaris® LM3S2965 Microcontroller
Note: The following notes apply to the package drawing.
Symbols MIN NOM MAX
A 1.22 1.36 1.50
A1 0.29 0.34 0.39
A3 0.65 0.70 0.75
c 0.28 0.32 0.36
D 9.85 10.00 10.15
D1 8.80 BSC
E 9.85 10.00 10.15
E1 8.80 BSC
b 0.43 0.48 0.53
bbb .20
ddd .12
e 0.80 BSC
f - 0.60 -
M 12
n 108
REF: JEDEC MO-219F
730 January 08, 2011
Texas Instruments-Production Data
Package Information
D.2.2 Tray Dimensions
Figure D-5. 108-Ball BGA Tray Dimensions
January 08, 2011 731
Texas Instruments-Production Data
Stellaris® LM3S2965 Microcontroller
D.2.3 Tape and Reel Dimensions
Figure D-6. 108-Ball BGA Tape and Reel Dimensions
C-PAK PTE LTD
732 January 08, 2011
Texas Instruments-Production Data
Package Information
IMPORTANT NOTICE
Texas Instruments Incorporated and its subsidiaries (TI) reserve the right to make corrections, modifications, enhancements, improvements,
and other changes to its products and services at any time and to discontinue any product or service without notice. Customers should
obtain the latest relevant information before placing orders and should verify that such information is current and complete. All products are
sold subject to TI’s terms and conditions of sale supplied at the time of order acknowledgment.
TI warrants performance of its hardware products to the specifications applicable at the time of sale in accordance with TI’s standard
warranty. Testing and other quality control techniques are used to the extent TI deems necessary to support this warranty. Except where
mandated by government requirements, testing of all parameters of each product is not necessarily performed.
TI assumes no liability for applications assistance or customer product design. Customers are responsible for their products and
applications using TI components. To minimize the risks associated with customer products and applications, customers should provide
adequate design and operating safeguards.
TI does not warrant or represent that any license, either express or implied, is granted under any TI patent right, copyright, mask work right,
or other TI intellectual property right relating to any combination, machine, or process in which TI products or services are used. Information
published by TI regarding third-party products or services does not constitute a license from TI to use such products or services or a
warranty or endorsement thereof. Use of such information may require a license from a third party under the patents or other intellectual
property of the third party, or a license from TI under the patents or other intellectual property of TI.
Reproduction of TI information in TI data books or data sheets is permissible only if reproduction is without alteration and is accompanied
by all associated warranties, conditions, limitations, and notices. Reproduction of this information with alteration is an unfair and deceptive
business practice. TI is not responsible or liable for such altered documentation. Information of third parties may be subject to additional
restrictions.
Resale of TI products or services with statements different from or beyond the parameters stated by TI for that product or service voids all
express and any implied warranties for the associated TI product or service and is an unfair and deceptive business practice. TI is not
responsible or liable for any such statements.
TI products are not authorized for use in safety-critical applications (such as life support) where a failure of the TI product would reasonably
be expected to cause severe personal injury or death, unless officers of the parties have executed an agreement specifically governing
such use. Buyers represent that they have all necessary expertise in the safety and regulatory ramifications of their applications, and
acknowledge and agree that they are solely responsible for all legal, regulatory and safety-related requirements concerning their products
and any use of TI products in such safety-critical applications, notwithstanding any applications-related information or support that may be
provided by TI. Further, Buyers must fully indemnify TI and its representatives against any damages arising out of the use of TI products in
such safety-critical applications.
TI products are neither designed nor intended for use in military/aerospace applications or environments unless the TI products are
specifically designated by TI as military-grade or "enhanced plastic." Only products designated by TI as military-grade meet military
specifications. Buyers acknowledge and agree that any such use of TI products which TI has not designated as military-grade is solely at
the Buyer's risk, and that they are solely responsible for compliance with all legal and regulatory requirements in connection with such use.
TI products are neither designed nor intended for use in automotive applications or environments unless the specific TI products are
designated by TI as compliant with ISO/TS 16949 requirements. Buyers acknowledge and agree that, if they use any non-designated
products in automotive applications, TI will not be responsible for any failure to meet such requirements.
Following are URLs where you can obtain information on other Texas Instruments products and application solutions:
Products Applications
Audio www.ti.com/audio Communications and Telecom www.ti.com/communications
Amplifiers amplifier.ti.com Computers and Peripherals www.ti.com/computers
Data Converters dataconverter.ti.com Consumer Electronics www.ti.com/consumer-apps
DLP® Products www.dlp.com Energy and Lighting www.ti.com/energy
DSP dsp.ti.com Industrial www.ti.com/industrial
Clocks and Timers www.ti.com/clocks Medical www.ti.com/medical
Interface interface.ti.com Security www.ti.com/security
Logic logic.ti.com Space, Avionics and Defense www.ti.com/space-avionics-defense
Power Mgmt power.ti.com Transportation and www.ti.com/automotive
Automotive
Microcontrollers microcontroller.ti.com Video and Imaging www.ti.com/video
RFID www.ti-rfid.com Wireless www.ti.com/wireless-apps
RF/IF and ZigBee® Solutions www.ti.com/lprf
TI E2E Community Home Page e2e.ti.com
Mailing Address: Texas Instruments, Post Office Box 655303, Dallas, Texas 75265
Copyright © 2011, Texas Instruments Incorporated
LM3S6110 Microcontroller
DATA SHEET
DS-LM3S6110-1972 Copyright © 2007 Luminary Micro, Inc.
PRELIMINARY
Legal Disclaimers and Trademark Information
INFORMATION IN THIS DOCUMENT IS PROVIDED IN CONNECTION WITH LUMINARY MICRO PRODUCTS. NO LICENSE, EXPRESS OR
IMPLIED, BY ESTOPPEL OR OTHERWISE, TO ANY INTELLECTUAL PROPERTY RIGHTS IS GRANTED BY THIS DOCUMENT. EXCEPT
AS PROVIDED IN LUMINARY MICRO'S TERMS AND CONDITIONS OF SALE FOR SUCH PRODUCTS, LUMINARY MICRO ASSUMES NO
LIABILITY WHATSOEVER, AND LUMINARY MICRO DISCLAIMS ANY EXPRESS OR IMPLIED WARRANTY, RELATING TO SALE AND/OR
USE OF LUMINARY MICRO'S PRODUCTS INCLUDING LIABILITY OR WARRANTIES RELATING TO FITNESS FOR A PARTICULAR
PURPOSE, MERCHANTABILITY, OR INFRINGEMENT OF ANY PATENT, COPYRIGHT OR OTHER INTELLECTUAL PROPERTY RIGHT.
LUMINARY MICRO'S PRODUCTS ARE NOT INTENDED FOR USE IN MEDICAL, LIFE SAVING, OR LIFE-SUSTAINING APPLICATIONS.
Luminary Micro may make changes to specifications and product descriptions at any time, without notice. Contact your local Luminary Micro sales office
or your distributor to obtain the latest specifications before placing your product order.
Designers must not rely on the absence or characteristics of any features or instructions marked "reserved" or "undefined." Luminary Micro reserves these
for future definition and shall have no responsibility whatsoever for conflicts or incompatibilities arising from future changes to them.
Copyright © 2007 Luminary Micro, Inc. All rights reserved. Stellaris, Luminary Micro, and the Luminary Micro logo are registered trademarks of
Luminary Micro, Inc. or its subsidiaries in the United States and other countries. ARM and Thumb are registered trademarks and Cortex is a trademark
of ARM Limited. Other names and brands may be claimed as the property of others.
Luminary Micro, Inc.
108 Wild Basin, Suite 350
Austin, TX 78746
Main: +1-512-279-8800
Fax: +1-512-279-8879
http://www.luminarymicro.com
2 November 30, 2007
Preliminary
Table of Contents
About This Document .................................................................................................................... 17
Audience .............................................................................................................................................. 17
About This Manual ................................................................................................................................ 17
Related Documents ............................................................................................................................... 17
Documentation Conventions .................................................................................................................. 17
1 Architectural Overview ...................................................................................................... 19
1.1 Product Features ...................................................................................................................... 19
1.2 Target Applications .................................................................................................................... 24
1.3 High-Level Block Diagram ......................................................................................................... 24
1.4 Functional Overview .................................................................................................................. 25
1.4.1 ARM Cortex™-M3 ..................................................................................................................... 26
1.4.2 Motor Control Peripherals .......................................................................................................... 26
1.4.3 Analog Peripherals .................................................................................................................... 27
1.4.4 Serial Communications Peripherals ............................................................................................ 27
1.4.5 System Peripherals ................................................................................................................... 28
1.4.6 Memory Peripherals .................................................................................................................. 29
1.4.7 Additional Features ................................................................................................................... 30
1.4.8 Hardware Details ...................................................................................................................... 30
2 ARM Cortex-M3 Processor Core ...................................................................................... 31
2.1 Block Diagram .......................................................................................................................... 32
2.2 Functional Description ............................................................................................................... 32
2.2.1 Serial Wire and JTAG Debug ..................................................................................................... 32
2.2.2 Embedded Trace Macrocell (ETM) ............................................................................................. 33
2.2.3 Trace Port Interface Unit (TPIU) ................................................................................................. 33
2.2.4 ROM Table ............................................................................................................................... 33
2.2.5 Memory Protection Unit (MPU) ................................................................................................... 33
2.2.6 Nested Vectored Interrupt Controller (NVIC) ................................................................................ 33
3 Memory Map ....................................................................................................................... 37
4 Interrupts ............................................................................................................................ 39
5 JTAG Interface .................................................................................................................... 41
5.1 Block Diagram .......................................................................................................................... 42
5.2 Functional Description ............................................................................................................... 42
5.2.1 JTAG Interface Pins .................................................................................................................. 43
5.2.2 JTAG TAP Controller ................................................................................................................. 44
5.2.3 Shift Registers .......................................................................................................................... 45
5.2.4 Operational Considerations ........................................................................................................ 45
5.3 Initialization and Configuration ................................................................................................... 48
5.4 Register Descriptions ................................................................................................................ 48
5.4.1 Instruction Register (IR) ............................................................................................................. 48
5.4.2 Data Registers .......................................................................................................................... 50
6 System Control ................................................................................................................... 52
6.1 Functional Description ............................................................................................................... 52
6.1.1 Device Identification .................................................................................................................. 52
6.1.2 Reset Control ............................................................................................................................ 52
November 30, 2007 3
Preliminary
LM3S6110 Microcontroller
6.1.3 Power Control ........................................................................................................................... 55
6.1.4 Clock Control ............................................................................................................................ 55
6.1.5 System Control ......................................................................................................................... 57
6.2 Initialization and Configuration ................................................................................................... 57
6.3 Register Map ............................................................................................................................ 58
6.4 Register Descriptions ................................................................................................................ 59
7 Internal Memory ............................................................................................................... 107
7.1 Block Diagram ........................................................................................................................ 107
7.2 Functional Description ............................................................................................................. 107
7.2.1 SRAM Memory ........................................................................................................................ 107
7.2.2 Flash Memory ......................................................................................................................... 108
7.3 Flash Memory Initialization and Configuration ........................................................................... 109
7.3.1 Flash Programming ................................................................................................................. 109
7.3.2 Nonvolatile Register Programming ........................................................................................... 110
7.4 Register Map .......................................................................................................................... 110
7.5 Flash Register Descriptions (Flash Control Offset) ..................................................................... 111
7.6 Flash Register Descriptions (System Control Offset) .................................................................. 118
8 General-Purpose Input/Outputs (GPIOs) ....................................................................... 131
8.1 Functional Description ............................................................................................................. 131
8.1.1 Data Control ........................................................................................................................... 132
8.1.2 Interrupt Control ...................................................................................................................... 133
8.1.3 Mode Control .......................................................................................................................... 134
8.1.4 Commit Control ....................................................................................................................... 134
8.1.5 Pad Control ............................................................................................................................. 134
8.1.6 Identification ........................................................................................................................... 134
8.2 Initialization and Configuration ................................................................................................. 134
8.3 Register Map .......................................................................................................................... 135
8.4 Register Descriptions .............................................................................................................. 137
9 General-Purpose Timers ................................................................................................. 172
9.1 Block Diagram ........................................................................................................................ 172
9.2 Functional Description ............................................................................................................. 173
9.2.1 GPTM Reset Conditions .......................................................................................................... 173
9.2.2 32-Bit Timer Operating Modes .................................................................................................. 174
9.2.3 16-Bit Timer Operating Modes .................................................................................................. 175
9.3 Initialization and Configuration ................................................................................................. 179
9.3.1 32-Bit One-Shot/Periodic Timer Mode ....................................................................................... 179
9.3.2 32-Bit Real-Time Clock (RTC) Mode ......................................................................................... 180
9.3.3 16-Bit One-Shot/Periodic Timer Mode ....................................................................................... 180
9.3.4 16-Bit Input Edge Count Mode ................................................................................................. 181
9.3.5 16-Bit Input Edge Timing Mode ................................................................................................ 181
9.3.6 16-Bit PWM Mode ................................................................................................................... 182
9.4 Register Map .......................................................................................................................... 182
9.5 Register Descriptions .............................................................................................................. 183
10 Watchdog Timer ............................................................................................................... 208
10.1 Block Diagram ........................................................................................................................ 208
10.2 Functional Description ............................................................................................................. 208
10.3 Initialization and Configuration ................................................................................................. 209
4 November 30, 2007
Preliminary
Table of Contents
10.4 Register Map .......................................................................................................................... 209
10.5 Register Descriptions .............................................................................................................. 210
11 Universal Asynchronous Receivers/Transmitters (UARTs) ......................................... 231
11.1 Block Diagram ........................................................................................................................ 232
11.2 Functional Description ............................................................................................................. 232
11.2.1 Transmit/Receive Logic ........................................................................................................... 232
11.2.2 Baud-Rate Generation ............................................................................................................. 233
11.2.3 Data Transmission .................................................................................................................. 234
11.2.4 Serial IR (SIR) ......................................................................................................................... 234
11.2.5 FIFO Operation ....................................................................................................................... 235
11.2.6 Interrupts ................................................................................................................................ 235
11.2.7 Loopback Operation ................................................................................................................ 236
11.2.8 IrDA SIR block ........................................................................................................................ 236
11.3 Initialization and Configuration ................................................................................................. 236
11.4 Register Map .......................................................................................................................... 237
11.5 Register Descriptions .............................................................................................................. 238
12 Synchronous Serial Interface (SSI) ................................................................................ 272
12.1 Block Diagram ........................................................................................................................ 272
12.2 Functional Description ............................................................................................................. 272
12.2.1 Bit Rate Generation ................................................................................................................. 273
12.2.2 FIFO Operation ....................................................................................................................... 273
12.2.3 Interrupts ................................................................................................................................ 273
12.2.4 Frame Formats ....................................................................................................................... 274
12.3 Initialization and Configuration ................................................................................................. 281
12.4 Register Map .......................................................................................................................... 282
12.5 Register Descriptions .............................................................................................................. 283
13 Ethernet Controller .......................................................................................................... 309
13.1 Block Diagram ........................................................................................................................ 310
13.2 Functional Description ............................................................................................................. 310
13.2.1 Internal MII Operation .............................................................................................................. 310
13.2.2 PHY Configuration/Operation ................................................................................................... 311
13.2.3 MAC Configuration/Operation .................................................................................................. 312
13.2.4 Interrupts ................................................................................................................................ 314
13.3 Initialization and Configuration ................................................................................................. 315
13.4 Ethernet Register Map ............................................................................................................. 315
13.5 Ethernet MAC Register Descriptions ......................................................................................... 317
13.6 MII Management Register Descriptions ..................................................................................... 334
14 Analog Comparators ....................................................................................................... 353
14.1 Block Diagram ........................................................................................................................ 354
14.2 Functional Description ............................................................................................................. 354
14.2.1 Internal Reference Programming .............................................................................................. 356
14.3 Initialization and Configuration ................................................................................................. 357
14.4 Register Map .......................................................................................................................... 357
14.5 Register Descriptions .............................................................................................................. 358
15 Pulse Width Modulator (PWM) ........................................................................................ 366
15.1 Block Diagram ........................................................................................................................ 366
15.2 Functional Description ............................................................................................................. 366
November 30, 2007 5
Preliminary
LM3S6110 Microcontroller
15.2.1 PWM Timer ............................................................................................................................. 366
15.2.2 PWM Comparators .................................................................................................................. 367
15.2.3 PWM Signal Generator ............................................................................................................ 368
15.2.4 Dead-Band Generator ............................................................................................................. 369
15.2.5 Interrupt Selector ..................................................................................................................... 369
15.2.6 Synchronization Methods ......................................................................................................... 369
15.2.7 Fault Conditions ...................................................................................................................... 369
15.2.8 Output Control Block ............................................................................................................... 370
15.3 Initialization and Configuration ................................................................................................. 370
15.4 Register Map .......................................................................................................................... 371
15.5 Register Descriptions .............................................................................................................. 372
16 Pin Diagram ...................................................................................................................... 401
17 Signal Tables .................................................................................................................... 402
18 Operating Characteristics ............................................................................................... 414
19 Electrical Characteristics ................................................................................................ 415
19.1 DC Characteristics .................................................................................................................. 415
19.1.1 Maximum Ratings ................................................................................................................... 415
19.1.2 Recommended DC Operating Conditions .................................................................................. 415
19.1.3 On-Chip Low Drop-Out (LDO) Regulator Characteristics ............................................................ 416
19.1.4 Power Specifications ............................................................................................................... 416
19.1.5 Flash Memory Characteristics .................................................................................................. 417
19.2 AC Characteristics ................................................................................................................... 418
19.2.1 Load Conditions ...................................................................................................................... 418
19.2.2 Clocks .................................................................................................................................... 418
19.2.3 Analog Comparator ................................................................................................................. 419
19.2.4 Ethernet Controller .................................................................................................................. 419
19.2.5 Synchronous Serial Interface (SSI) ........................................................................................... 422
19.2.6 JTAG and Boundary Scan ........................................................................................................ 424
19.2.7 General-Purpose I/O ............................................................................................................... 425
19.2.8 Reset ..................................................................................................................................... 426
20 Package Information ........................................................................................................ 428
A Serial Flash Loader .......................................................................................................... 430
A.1 Serial Flash Loader ................................................................................................................. 430
A.2 Interfaces ............................................................................................................................... 430
A.2.1 UART ..................................................................................................................................... 430
A.2.2 SSI ......................................................................................................................................... 430
A.3 Packet Handling ...................................................................................................................... 431
A.3.1 Packet Format ........................................................................................................................ 431
A.3.2 Sending Packets ..................................................................................................................... 431
A.3.3 Receiving Packets ................................................................................................................... 431
A.4 Commands ............................................................................................................................. 432
A.4.1 COMMAND_PING (0X20) ........................................................................................................ 432
A.4.2 COMMAND_GET_STATUS (0x23) ........................................................................................... 432
A.4.3 COMMAND_DOWNLOAD (0x21) ............................................................................................. 432
A.4.4 COMMAND_SEND_DATA (0x24) ............................................................................................. 433
A.4.5 COMMAND_RUN (0x22) ......................................................................................................... 433
A.4.6 COMMAND_RESET (0x25) ..................................................................................................... 433
6 November 30, 2007
Preliminary
Table of Contents
B Register Quick Reference ............................................................................................... 435
C Ordering and Contact Information ................................................................................. 449
C.1 Ordering Information ................................................................................................................ 449
C.2 Kits ......................................................................................................................................... 449
C.3 Company Information .............................................................................................................. 449
C.4 Support Information ................................................................................................................. 450
November 30, 2007 7
Preliminary
LM3S6110 Microcontroller
List of Figures
Figure 1-1. Stellaris® 6000 Series High-Level Block Diagram ............................................................... 25
Figure 2-1. CPU Block Diagram ......................................................................................................... 32
Figure 2-2. TPIU Block Diagram ........................................................................................................ 33
Figure 5-1. JTAG Module Block Diagram ............................................................................................ 42
Figure 5-2. Test Access Port State Machine ....................................................................................... 45
Figure 5-3. IDCODE Register Format ................................................................................................. 50
Figure 5-4. BYPASS Register Format ................................................................................................ 51
Figure 5-5. Boundary Scan Register Format ....................................................................................... 51
Figure 6-1. External Circuitry to Extend Reset .................................................................................... 53
Figure 7-1. Flash Block Diagram ...................................................................................................... 107
Figure 8-1. GPIO Port Block Diagram ............................................................................................... 132
Figure 8-2. GPIODATA Write Example ............................................................................................. 133
Figure 8-3. GPIODATA Read Example ............................................................................................. 133
Figure 9-1. GPTM Module Block Diagram ........................................................................................ 173
Figure 9-2. 16-Bit Input Edge Count Mode Example .......................................................................... 177
Figure 9-3. 16-Bit Input Edge Time Mode Example ........................................................................... 178
Figure 9-4. 16-Bit PWM Mode Example ............................................................................................ 179
Figure 10-1. WDT Module Block Diagram .......................................................................................... 208
Figure 11-1. UART Module Block Diagram ......................................................................................... 232
Figure 11-2. UART Character Frame ................................................................................................. 233
Figure 11-3. IrDA Data Modulation ..................................................................................................... 235
Figure 12-1. SSI Module Block Diagram ............................................................................................. 272
Figure 12-2. TI Synchronous Serial Frame Format (Single Transfer) .................................................... 275
Figure 12-3. TI Synchronous Serial Frame Format (Continuous Transfer) ............................................ 275
Figure 12-4. Freescale SPI Format (Single Transfer) with SPO=0 and SPH=0 ...................................... 276
Figure 12-5. Freescale SPI Format (Continuous Transfer) with SPO=0 and SPH=0 .............................. 276
Figure 12-6. Freescale SPI Frame Format with SPO=0 and SPH=1 ..................................................... 277
Figure 12-7. Freescale SPI Frame Format (Single Transfer) with SPO=1 and SPH=0 ........................... 278
Figure 12-8. Freescale SPI Frame Format (Continuous Transfer) with SPO=1 and SPH=0 .................... 278
Figure 12-9. Freescale SPI Frame Format with SPO=1 and SPH=1 ..................................................... 279
Figure 12-10. MICROWIRE Frame Format (Single Frame) .................................................................... 280
Figure 12-11. MICROWIRE Frame Format (Continuous Transfer) ......................................................... 281
Figure 12-12. MICROWIRE Frame Format, SSIFss Input Setup and Hold Requirements ........................ 281
Figure 13-1. Ethernet Controller Block Diagram .................................................................................. 310
Figure 13-2. Ethernet Controller ......................................................................................................... 310
Figure 13-3. Ethernet Frame ............................................................................................................. 312
Figure 14-1. Analog Comparator Module Block Diagram ..................................................................... 354
Figure 14-2. Structure of Comparator Unit .......................................................................................... 355
Figure 14-3. Comparator Internal Reference Structure ........................................................................ 356
Figure 15-1. PWM Module Block Diagram .......................................................................................... 366
Figure 15-2. PWM Count-Down Mode ................................................................................................ 367
Figure 15-3. PWM Count-Up/Down Mode .......................................................................................... 368
Figure 15-4. PWM Generation Example In Count-Up/Down Mode ....................................................... 368
Figure 15-5. PWM Dead-Band Generator ........................................................................................... 369
Figure 16-1. Pin Connection Diagram ................................................................................................ 401
Figure 19-1. Load Conditions ............................................................................................................ 418
8 November 30, 2007
Preliminary
Table of Contents
Figure 19-2. External XTLP Oscillator Characteristics ......................................................................... 422
Figure 19-3. SSI Timing for TI Frame Format (FRF=01), Single Transfer Timing Measurement .............. 423
Figure 19-4. SSI Timing for MICROWIRE Frame Format (FRF=10), Single Transfer ............................. 423
Figure 19-5. SSI Timing for SPI Frame Format (FRF=00), with SPH=1 ................................................. 424
Figure 19-6. JTAG Test Clock Input Timing ......................................................................................... 425
Figure 19-7. JTAG Test Access Port (TAP) Timing .............................................................................. 425
Figure 19-8. JTAG TRST Timing ........................................................................................................ 425
Figure 19-9. External Reset Timing (RST) .......................................................................................... 426
Figure 19-10. Power-On Reset Timing ................................................................................................. 427
Figure 19-11. Brown-Out Reset Timing ................................................................................................ 427
Figure 19-12. Software Reset Timing ................................................................................................... 427
Figure 19-13. Watchdog Reset Timing ................................................................................................. 427
Figure 20-1. 100-Pin LQFP Package .................................................................................................. 428
November 30, 2007 9
Preliminary
LM3S6110 Microcontroller
List of Tables
Table 1. Documentation Conventions ............................................................................................ 17
Table 3-1. Memory Map ................................................................................................................... 37
Table 4-1. Exception Types .............................................................................................................. 39
Table 4-2. Interrupts ........................................................................................................................ 40
Table 5-1. JTAG Port Pins Reset State ............................................................................................. 43
Table 5-2. JTAG Instruction Register Commands ............................................................................... 48
Table 6-1. System Control Register Map ........................................................................................... 58
Table 7-1. Flash Protection Policy Combinations ............................................................................. 109
Table 7-2. Flash Resident Registers ............................................................................................... 110
Table 7-3. Flash Register Map ........................................................................................................ 110
Table 8-1. GPIO Pad Configuration Examples ................................................................................. 134
Table 8-2. GPIO Interrupt Configuration Example ............................................................................ 135
Table 8-3. GPIO Register Map ....................................................................................................... 136
Table 9-1. Available CCP Pins ........................................................................................................ 173
Table 9-2. 16-Bit Timer With Prescaler Configurations ..................................................................... 176
Table 9-3. Timers Register Map ...................................................................................................... 182
Table 10-1. Watchdog Timer Register Map ........................................................................................ 209
Table 11-1. UART Register Map ....................................................................................................... 237
Table 12-1. SSI Register Map .......................................................................................................... 282
Table 13-1. TX & RX FIFO Organization ........................................................................................... 313
Table 13-2. Ethernet Register Map ................................................................................................... 316
Table 14-1. Comparator 0 Operating Modes ...................................................................................... 355
Table 14-2. Comparator 1 Operating Modes ..................................................................................... 355
Table 14-3. Comparator 2 Operating Modes ...................................................................................... 356
Table 14-4. Internal Reference Voltage and ACREFCTL Field Values ................................................. 356
Table 14-5. Analog Comparators Register Map ................................................................................. 358
Table 15-1. PWM Register Map ........................................................................................................ 371
Table 17-1. Signals by Pin Number ................................................................................................... 402
Table 17-2. Signals by Signal Name ................................................................................................. 406
Table 17-3. Signals by Function, Except for GPIO ............................................................................. 409
Table 17-4. GPIO Pins and Alternate Functions ................................................................................. 412
Table 18-1. Temperature Characteristics ........................................................................................... 414
Table 18-2. Thermal Characteristics ................................................................................................. 414
Table 19-1. Maximum Ratings .......................................................................................................... 415
Table 19-2. Recommended DC Operating Conditions ........................................................................ 415
Table 19-3. LDO Regulator Characteristics ....................................................................................... 416
Table 19-4. Detailed Power Specifications ........................................................................................ 417
Table 19-5. Flash Memory Characteristics ........................................................................................ 417
Table 19-6. Phase Locked Loop (PLL) Characteristics ....................................................................... 418
Table 19-7. Clock Characteristics ..................................................................................................... 418
Table 19-8. Crystal Characteristics ................................................................................................... 418
Table 19-9. Analog Comparator Characteristics ................................................................................. 419
Table 19-10. Analog Comparator Voltage Reference Characteristics .................................................... 419
Table 19-11. 100BASE-TX Transmitter Characteristics ........................................................................ 419
Table 19-12. 100BASE-TX Transmitter Characteristics (informative) ..................................................... 419
Table 19-13. 100BASE-TX Receiver Characteristics ............................................................................ 420
10 November 30, 2007
Preliminary
Table of Contents
Table 19-14. 10BASE-T Transmitter Characteristics ............................................................................ 420
Table 19-15. 10BASE-T Transmitter Characteristics (informative) ......................................................... 420
Table 19-16. 10BASE-T Receiver Characteristics ................................................................................ 420
Table 19-17. Isolation Transformers ................................................................................................... 420
Table 19-18. Ethernet Reference Crystal ............................................................................................ 421
Table 19-19. External XTLP Oscillator Characteristics ......................................................................... 422
Table 19-20. SSI Characteristics ........................................................................................................ 422
Table 19-21. JTAG Characteristics ..................................................................................................... 424
Table 19-22. GPIO Characteristics ..................................................................................................... 426
Table 19-23. Reset Characteristics ..................................................................................................... 426
Table C-1. Part Ordering Information ............................................................................................... 449
November 30, 2007 11
Preliminary
LM3S6110 Microcontroller
List of Registers
System Control .............................................................................................................................. 52
Register 1: Device Identification 0 (DID0), offset 0x000 ....................................................................... 60
Register 2: Brown-Out Reset Control (PBORCTL), offset 0x030 .......................................................... 62
Register 3: LDO Power Control (LDOPCTL), offset 0x034 ................................................................... 63
Register 4: Raw Interrupt Status (RIS), offset 0x050 ........................................................................... 64
Register 5: Interrupt Mask Control (IMC), offset 0x054 ........................................................................ 65
Register 6: Masked Interrupt Status and Clear (MISC), offset 0x058 .................................................... 66
Register 7: Reset Cause (RESC), offset 0x05C .................................................................................. 67
Register 8: Run-Mode Clock Configuration (RCC), offset 0x060 .......................................................... 68
Register 9: XTAL to PLL Translation (PLLCFG), offset 0x064 .............................................................. 72
Register 10: Run-Mode Clock Configuration 2 (RCC2), offset 0x070 ...................................................... 73
Register 11: Deep Sleep Clock Configuration (DSLPCLKCFG), offset 0x144 .......................................... 75
Register 12: Device Identification 1 (DID1), offset 0x004 ....................................................................... 76
Register 13: Device Capabilities 0 (DC0), offset 0x008 ......................................................................... 78
Register 14: Device Capabilities 1 (DC1), offset 0x010 ......................................................................... 79
Register 15: Device Capabilities 2 (DC2), offset 0x014 ......................................................................... 81
Register 16: Device Capabilities 3 (DC3), offset 0x018 ......................................................................... 83
Register 17: Device Capabilities 4 (DC4), offset 0x01C ......................................................................... 85
Register 18: Run Mode Clock Gating Control Register 0 (RCGC0), offset 0x100 .................................... 87
Register 19: Sleep Mode Clock Gating Control Register 0 (SCGC0), offset 0x110 .................................. 88
Register 20: Deep Sleep Mode Clock Gating Control Register 0 (DCGC0), offset 0x120 ......................... 89
Register 21: Run Mode Clock Gating Control Register 1 (RCGC1), offset 0x104 .................................... 90
Register 22: Sleep Mode Clock Gating Control Register 1 (SCGC1), offset 0x114 .................................. 92
Register 23: Deep Sleep Mode Clock Gating Control Register 1 (DCGC1), offset 0x124 ......................... 94
Register 24: Run Mode Clock Gating Control Register 2 (RCGC2), offset 0x108 .................................... 96
Register 25: Sleep Mode Clock Gating Control Register 2 (SCGC2), offset 0x118 .................................. 98
Register 26: Deep Sleep Mode Clock Gating Control Register 2 (DCGC2), offset 0x128 ....................... 100
Register 27: Software Reset Control 0 (SRCR0), offset 0x040 ............................................................. 102
Register 28: Software Reset Control 1 (SRCR1), offset 0x044 ............................................................. 103
Register 29: Software Reset Control 2 (SRCR2), offset 0x048 ............................................................. 105
Internal Memory ........................................................................................................................... 107
Register 1: Flash Memory Address (FMA), offset 0x000 .................................................................... 112
Register 2: Flash Memory Data (FMD), offset 0x004 ......................................................................... 113
Register 3: Flash Memory Control (FMC), offset 0x008 ..................................................................... 114
Register 4: Flash Controller Raw Interrupt Status (FCRIS), offset 0x00C ............................................ 116
Register 5: Flash Controller Interrupt Mask (FCIM), offset 0x010 ........................................................ 117
Register 6: Flash Controller Masked Interrupt Status and Clear (FCMISC), offset 0x014 ..................... 118
Register 7: USec Reload (USECRL), offset 0x140 ............................................................................ 119
Register 8: Flash Memory Protection Read Enable 0 (FMPRE0), offset 0x130 and 0x200 ................... 120
Register 9: Flash Memory Protection Program Enable 0 (FMPPE0), offset 0x134 and 0x400 ............... 121
Register 10: User Debug (USER_DBG), offset 0x1D0 ......................................................................... 122
Register 11: User Register 0 (USER_REG0), offset 0x1E0 .................................................................. 123
Register 12: User Register 1 (USER_REG1), offset 0x1E4 .................................................................. 124
Register 13: Flash Memory Protection Read Enable 1 (FMPRE1), offset 0x204 .................................... 125
Register 14: Flash Memory Protection Read Enable 2 (FMPRE2), offset 0x208 .................................... 126
12 November 30, 2007
Preliminary
Table of Contents
Register 15: Flash Memory Protection Read Enable 3 (FMPRE3), offset 0x20C ................................... 127
Register 16: Flash Memory Protection Program Enable 1 (FMPPE1), offset 0x404 ............................... 128
Register 17: Flash Memory Protection Program Enable 2 (FMPPE2), offset 0x408 ............................... 129
Register 18: Flash Memory Protection Program Enable 3 (FMPPE3), offset 0x40C ............................... 130
General-Purpose Input/Outputs (GPIOs) ................................................................................... 131
Register 1: GPIO Data (GPIODATA), offset 0x000 ............................................................................ 138
Register 2: GPIO Direction (GPIODIR), offset 0x400 ......................................................................... 139
Register 3: GPIO Interrupt Sense (GPIOIS), offset 0x404 .................................................................. 140
Register 4: GPIO Interrupt Both Edges (GPIOIBE), offset 0x408 ........................................................ 141
Register 5: GPIO Interrupt Event (GPIOIEV), offset 0x40C ................................................................ 142
Register 6: GPIO Interrupt Mask (GPIOIM), offset 0x410 ................................................................... 143
Register 7: GPIO Raw Interrupt Status (GPIORIS), offset 0x414 ........................................................ 144
Register 8: GPIO Masked Interrupt Status (GPIOMIS), offset 0x418 ................................................... 145
Register 9: GPIO Interrupt Clear (GPIOICR), offset 0x41C ................................................................ 146
Register 10: GPIO Alternate Function Select (GPIOAFSEL), offset 0x420 ............................................ 147
Register 11: GPIO 2-mA Drive Select (GPIODR2R), offset 0x500 ........................................................ 149
Register 12: GPIO 4-mA Drive Select (GPIODR4R), offset 0x504 ........................................................ 150
Register 13: GPIO 8-mA Drive Select (GPIODR8R), offset 0x508 ........................................................ 151
Register 14: GPIO Open Drain Select (GPIOODR), offset 0x50C ......................................................... 152
Register 15: GPIO Pull-Up Select (GPIOPUR), offset 0x510 ................................................................ 153
Register 16: GPIO Pull-Down Select (GPIOPDR), offset 0x514 ........................................................... 154
Register 17: GPIO Slew Rate Control Select (GPIOSLR), offset 0x518 ................................................ 155
Register 18: GPIO Digital Enable (GPIODEN), offset 0x51C ................................................................ 156
Register 19: GPIO Lock (GPIOLOCK), offset 0x520 ............................................................................ 157
Register 20: GPIO Commit (GPIOCR), offset 0x524 ............................................................................ 158
Register 21: GPIO Peripheral Identification 4 (GPIOPeriphID4), offset 0xFD0 ....................................... 160
Register 22: GPIO Peripheral Identification 5 (GPIOPeriphID5), offset 0xFD4 ....................................... 161
Register 23: GPIO Peripheral Identification 6 (GPIOPeriphID6), offset 0xFD8 ....................................... 162
Register 24: GPIO Peripheral Identification 7 (GPIOPeriphID7), offset 0xFDC ...................................... 163
Register 25: GPIO Peripheral Identification 0 (GPIOPeriphID0), offset 0xFE0 ....................................... 164
Register 26: GPIO Peripheral Identification 1 (GPIOPeriphID1), offset 0xFE4 ....................................... 165
Register 27: GPIO Peripheral Identification 2 (GPIOPeriphID2), offset 0xFE8 ....................................... 166
Register 28: GPIO Peripheral Identification 3 (GPIOPeriphID3), offset 0xFEC ...................................... 167
Register 29: GPIO PrimeCell Identification 0 (GPIOPCellID0), offset 0xFF0 .......................................... 168
Register 30: GPIO PrimeCell Identification 1 (GPIOPCellID1), offset 0xFF4 .......................................... 169
Register 31: GPIO PrimeCell Identification 2 (GPIOPCellID2), offset 0xFF8 .......................................... 170
Register 32: GPIO PrimeCell Identification 3 (GPIOPCellID3), offset 0xFFC ......................................... 171
General-Purpose Timers ............................................................................................................. 172
Register 1: GPTM Configuration (GPTMCFG), offset 0x000 .............................................................. 184
Register 2: GPTM TimerA Mode (GPTMTAMR), offset 0x004 ............................................................ 185
Register 3: GPTM TimerB Mode (GPTMTBMR), offset 0x008 ............................................................ 187
Register 4: GPTM Control (GPTMCTL), offset 0x00C ........................................................................ 189
Register 5: GPTM Interrupt Mask (GPTMIMR), offset 0x018 .............................................................. 192
Register 6: GPTM Raw Interrupt Status (GPTMRIS), offset 0x01C ..................................................... 194
Register 7: GPTM Masked Interrupt Status (GPTMMIS), offset 0x020 ................................................ 195
Register 8: GPTM Interrupt Clear (GPTMICR), offset 0x024 .............................................................. 196
Register 9: GPTM TimerA Interval Load (GPTMTAILR), offset 0x028 ................................................. 198
Register 10: GPTM TimerB Interval Load (GPTMTBILR), offset 0x02C ................................................ 199
November 30, 2007 13
Preliminary
LM3S6110 Microcontroller
Register 11: GPTM TimerA Match (GPTMTAMATCHR), offset 0x030 ................................................... 200
Register 12: GPTM TimerB Match (GPTMTBMATCHR), offset 0x034 .................................................. 201
Register 13: GPTM TimerA Prescale (GPTMTAPR), offset 0x038 ........................................................ 202
Register 14: GPTM TimerB Prescale (GPTMTBPR), offset 0x03C ....................................................... 203
Register 15: GPTM TimerA Prescale Match (GPTMTAPMR), offset 0x040 ........................................... 204
Register 16: GPTM TimerB Prescale Match (GPTMTBPMR), offset 0x044 ........................................... 205
Register 17: GPTM TimerA (GPTMTAR), offset 0x048 ........................................................................ 206
Register 18: GPTM TimerB (GPTMTBR), offset 0x04C ....................................................................... 207
Watchdog Timer ........................................................................................................................... 208
Register 1: Watchdog Load (WDTLOAD), offset 0x000 ...................................................................... 211
Register 2: Watchdog Value (WDTVALUE), offset 0x004 ................................................................... 212
Register 3: Watchdog Control (WDTCTL), offset 0x008 ..................................................................... 213
Register 4: Watchdog Interrupt Clear (WDTICR), offset 0x00C .......................................................... 214
Register 5: Watchdog Raw Interrupt Status (WDTRIS), offset 0x010 .................................................. 215
Register 6: Watchdog Masked Interrupt Status (WDTMIS), offset 0x014 ............................................. 216
Register 7: Watchdog Test (WDTTEST), offset 0x418 ....................................................................... 217
Register 8: Watchdog Lock (WDTLOCK), offset 0xC00 ..................................................................... 218
Register 9: Watchdog Peripheral Identification 4 (WDTPeriphID4), offset 0xFD0 ................................. 219
Register 10: Watchdog Peripheral Identification 5 (WDTPeriphID5), offset 0xFD4 ................................. 220
Register 11: Watchdog Peripheral Identification 6 (WDTPeriphID6), offset 0xFD8 ................................. 221
Register 12: Watchdog Peripheral Identification 7 (WDTPeriphID7), offset 0xFDC ................................ 222
Register 13: Watchdog Peripheral Identification 0 (WDTPeriphID0), offset 0xFE0 ................................. 223
Register 14: Watchdog Peripheral Identification 1 (WDTPeriphID1), offset 0xFE4 ................................. 224
Register 15: Watchdog Peripheral Identification 2 (WDTPeriphID2), offset 0xFE8 ................................. 225
Register 16: Watchdog Peripheral Identification 3 (WDTPeriphID3), offset 0xFEC ................................. 226
Register 17: Watchdog PrimeCell Identification 0 (WDTPCellID0), offset 0xFF0 .................................... 227
Register 18: Watchdog PrimeCell Identification 1 (WDTPCellID1), offset 0xFF4 .................................... 228
Register 19: Watchdog PrimeCell Identification 2 (WDTPCellID2), offset 0xFF8 .................................... 229
Register 20: Watchdog PrimeCell Identification 3 (WDTPCellID3 ), offset 0xFFC .................................. 230
Universal Asynchronous Receivers/Transmitters (UARTs) ..................................................... 231
Register 1: UART Data (UARTDR), offset 0x000 ............................................................................... 239
Register 2: UART Receive Status/Error Clear (UARTRSR/UARTECR), offset 0x004 ........................... 241
Register 3: UART Flag (UARTFR), offset 0x018 ................................................................................ 243
Register 4: UART IrDA Low-Power Register (UARTILPR), offset 0x020 ............................................. 245
Register 5: UART Integer Baud-Rate Divisor (UARTIBRD), offset 0x024 ............................................ 246
Register 6: UART Fractional Baud-Rate Divisor (UARTFBRD), offset 0x028 ....................................... 247
Register 7: UART Line Control (UARTLCRH), offset 0x02C ............................................................... 248
Register 8: UART Control (UARTCTL), offset 0x030 ......................................................................... 250
Register 9: UART Interrupt FIFO Level Select (UARTIFLS), offset 0x034 ........................................... 252
Register 10: UART Interrupt Mask (UARTIM), offset 0x038 ................................................................. 254
Register 11: UART Raw Interrupt Status (UARTRIS), offset 0x03C ...................................................... 256
Register 12: UART Masked Interrupt Status (UARTMIS), offset 0x040 ................................................. 257
Register 13: UART Interrupt Clear (UARTICR), offset 0x044 ............................................................... 258
Register 14: UART Peripheral Identification 4 (UARTPeriphID4), offset 0xFD0 ..................................... 260
Register 15: UART Peripheral Identification 5 (UARTPeriphID5), offset 0xFD4 ..................................... 261
Register 16: UART Peripheral Identification 6 (UARTPeriphID6), offset 0xFD8 ..................................... 262
Register 17: UART Peripheral Identification 7 (UARTPeriphID7), offset 0xFDC ..................................... 263
Register 18: UART Peripheral Identification 0 (UARTPeriphID0), offset 0xFE0 ...................................... 264
14 November 30, 2007
Preliminary
Table of Contents
Register 19: UART Peripheral Identification 1 (UARTPeriphID1), offset 0xFE4 ...................................... 265
Register 20: UART Peripheral Identification 2 (UARTPeriphID2), offset 0xFE8 ...................................... 266
Register 21: UART Peripheral Identification 3 (UARTPeriphID3), offset 0xFEC ..................................... 267
Register 22: UART PrimeCell Identification 0 (UARTPCellID0), offset 0xFF0 ........................................ 268
Register 23: UART PrimeCell Identification 1 (UARTPCellID1), offset 0xFF4 ........................................ 269
Register 24: UART PrimeCell Identification 2 (UARTPCellID2), offset 0xFF8 ........................................ 270
Register 25: UART PrimeCell Identification 3 (UARTPCellID3), offset 0xFFC ........................................ 271
Synchronous Serial Interface (SSI) ............................................................................................ 272
Register 1: SSI Control 0 (SSICR0), offset 0x000 .............................................................................. 284
Register 2: SSI Control 1 (SSICR1), offset 0x004 .............................................................................. 286
Register 3: SSI Data (SSIDR), offset 0x008 ...................................................................................... 288
Register 4: SSI Status (SSISR), offset 0x00C ................................................................................... 289
Register 5: SSI Clock Prescale (SSICPSR), offset 0x010 .................................................................. 291
Register 6: SSI Interrupt Mask (SSIIM), offset 0x014 ......................................................................... 292
Register 7: SSI Raw Interrupt Status (SSIRIS), offset 0x018 .............................................................. 294
Register 8: SSI Masked Interrupt Status (SSIMIS), offset 0x01C ........................................................ 295
Register 9: SSI Interrupt Clear (SSIICR), offset 0x020 ....................................................................... 296
Register 10: SSI Peripheral Identification 4 (SSIPeriphID4), offset 0xFD0 ............................................. 297
Register 11: SSI Peripheral Identification 5 (SSIPeriphID5), offset 0xFD4 ............................................. 298
Register 12: SSI Peripheral Identification 6 (SSIPeriphID6), offset 0xFD8 ............................................. 299
Register 13: SSI Peripheral Identification 7 (SSIPeriphID7), offset 0xFDC ............................................ 300
Register 14: SSI Peripheral Identification 0 (SSIPeriphID0), offset 0xFE0 ............................................. 301
Register 15: SSI Peripheral Identification 1 (SSIPeriphID1), offset 0xFE4 ............................................. 302
Register 16: SSI Peripheral Identification 2 (SSIPeriphID2), offset 0xFE8 ............................................. 303
Register 17: SSI Peripheral Identification 3 (SSIPeriphID3), offset 0xFEC ............................................ 304
Register 18: SSI PrimeCell Identification 0 (SSIPCellID0), offset 0xFF0 ............................................... 305
Register 19: SSI PrimeCell Identification 1 (SSIPCellID1), offset 0xFF4 ............................................... 306
Register 20: SSI PrimeCell Identification 2 (SSIPCellID2), offset 0xFF8 ............................................... 307
Register 21: SSI PrimeCell Identification 3 (SSIPCellID3), offset 0xFFC ............................................... 308
Ethernet Controller ...................................................................................................................... 309
Register 1: Ethernet MAC Raw Interrupt Status (MACRIS), offset 0x000 ............................................ 318
Register 2: Ethernet MAC Interrupt Acknowledge (MACIACK), offset 0x000 ....................................... 320
Register 3: Ethernet MAC Interrupt Mask (MACIM), offset 0x004 ....................................................... 321
Register 4: Ethernet MAC Receive Control (MACRCTL), offset 0x008 ................................................ 322
Register 5: Ethernet MAC Transmit Control (MACTCTL), offset 0x00C ............................................... 323
Register 6: Ethernet MAC Data (MACDATA), offset 0x010 ................................................................. 324
Register 7: Ethernet MAC Individual Address 0 (MACIA0), offset 0x014 ............................................. 326
Register 8: Ethernet MAC Individual Address 1 (MACIA1), offset 0x018 ............................................. 327
Register 9: Ethernet MAC Threshold (MACTHR), offset 0x01C .......................................................... 328
Register 10: Ethernet MAC Management Control (MACMCTL), offset 0x020 ........................................ 329
Register 11: Ethernet MAC Management Divider (MACMDV), offset 0x024 .......................................... 330
Register 12: Ethernet MAC Management Transmit Data (MACMTXD), offset 0x02C ............................. 331
Register 13: Ethernet MAC Management Receive Data (MACMRXD), offset 0x030 .............................. 332
Register 14: Ethernet MAC Number of Packets (MACNP), offset 0x034 ............................................... 333
Register 15: Ethernet MAC Transmission Request (MACTR), offset 0x038 ........................................... 334
Register 16: Ethernet PHY Management Register 0 – Control (MR0), address 0x00 ............................. 335
Register 17: Ethernet PHY Management Register 1 – Status (MR1), address 0x01 .............................. 337
Register 18: Ethernet PHY Management Register 2 – PHY Identifier 1 (MR2), address 0x02 ................. 339
November 30, 2007 15
Preliminary
LM3S6110 Microcontroller
Register 19: Ethernet PHY Management Register 3 – PHY Identifier 2 (MR3), address 0x03 ................. 340
Register 20: Ethernet PHY Management Register 4 – Auto-Negotiation Advertisement (MR4), address
0x04 ............................................................................................................................. 341
Register 21: Ethernet PHY Management Register 5 – Auto-Negotiation Link Partner Base Page Ability
(MR5), address 0x05 ..................................................................................................... 343
Register 22: Ethernet PHY Management Register 6 – Auto-Negotiation Expansion (MR6), address
0x06 ............................................................................................................................. 344
Register 23: Ethernet PHY Management Register 16 – Vendor-Specific (MR16), address 0x10 ............. 345
Register 24: Ethernet PHY Management Register 17 – Interrupt Control/Status (MR17), address
0x11 .............................................................................................................................. 347
Register 25: Ethernet PHY Management Register 18 – Diagnostic (MR18), address 0x12 ..................... 349
Register 26: Ethernet PHY Management Register 19 – Transceiver Control (MR19), address 0x13 ....... 350
Register 27: Ethernet PHY Management Register 23 – LED Configuration (MR23), address 0x17 ......... 351
Register 28: Ethernet PHY Management Register 24 –MDI/MDIX Control (MR24), address 0x18 .......... 352
Analog Comparators ................................................................................................................... 353
Register 1: Analog Comparator Masked Interrupt Status (ACMIS), offset 0x00 .................................... 359
Register 2: Analog Comparator Raw Interrupt Status (ACRIS), offset 0x04 ......................................... 360
Register 3: Analog Comparator Interrupt Enable (ACINTEN), offset 0x08 ........................................... 361
Register 4: Analog Comparator Reference Voltage Control (ACREFCTL), offset 0x10 ......................... 362
Register 5: Analog Comparator Status 0 (ACSTAT0), offset 0x20 ....................................................... 363
Register 6: Analog Comparator Status 1 (ACSTAT1), offset 0x40 ....................................................... 363
Register 7: Analog Comparator Status 2 (ACSTAT2), offset 0x60 ....................................................... 363
Register 8: Analog Comparator Control 0 (ACCTL0), offset 0x24 ....................................................... 364
Register 9: Analog Comparator Control 1 (ACCTL1), offset 0x44 ....................................................... 364
Register 10: Analog Comparator Control 2 (ACCTL2), offset 0x64 ...................................................... 364
Pulse Width Modulator (PWM) .................................................................................................... 366
Register 1: PWM Master Control (PWMCTL), offset 0x000 ................................................................ 373
Register 2: PWM Time Base Sync (PWMSYNC), offset 0x004 ........................................................... 374
Register 3: PWM Output Enable (PWMENABLE), offset 0x008 .......................................................... 375
Register 4: PWM Output Inversion (PWMINVERT), offset 0x00C ....................................................... 376
Register 5: PWM Output Fault (PWMFAULT), offset 0x010 ................................................................ 377
Register 6: PWM Interrupt Enable (PWMINTEN), offset 0x014 ........................................................... 378
Register 7: PWM Raw Interrupt Status (PWMRIS), offset 0x018 ........................................................ 379
Register 8: PWM Interrupt Status and Clear (PWMISC), offset 0x01C ................................................ 380
Register 9: PWM Status (PWMSTATUS), offset 0x020 ...................................................................... 381
Register 10: PWM0 Control (PWM0CTL), offset 0x040 ....................................................................... 382
Register 11: PWM0 Interrupt Enable (PWM0INTEN), offset 0x044 ...................................................... 384
Register 12: PWM0 Raw Interrupt Status (PWM0RIS), offset 0x048 .................................................... 386
Register 13: PWM0 Interrupt Status and Clear (PWM0ISC), offset 0x04C ........................................... 387
Register 14: PWM0 Load (PWM0LOAD), offset 0x050 ....................................................................... 388
Register 15: PWM0 Counter (PWM0COUNT), offset 0x054 ................................................................ 389
Register 16: PWM0 Compare A (PWM0CMPA), offset 0x058 ............................................................. 390
Register 17: PWM0 Compare B (PWM0CMPB), offset 0x05C ............................................................. 391
Register 18: PWM0 Generator A Control (PWM0GENA), offset 0x060 ................................................ 392
Register 19: PWM0 Generator B Control (PWM0GENB), offset 0x064 ................................................ 395
Register 20: PWM0 Dead-Band Control (PWM0DBCTL), offset 0x068 ................................................ 398
Register 21: PWM0 Dead-Band Rising-Edge Delay (PWM0DBRISE), offset 0x06C ............................. 399
Register 22: PWM0 Dead-Band Falling-Edge-Delay (PWM0DBFALL), offset 0x070 ............................. 400
16 November 30, 2007
Preliminary
Table of Contents
About This Document
This data sheet provides reference information for the LM3S6110 microcontroller, describing the
functional blocks of the system-on-chip (SoC) device designed around the ARM® Cortex™-M3
core.
Audience
This manual is intended for system software developers, hardware designers, and application
developers.
About This Manual
This document is organized into sections that correspond to each major feature.
Related Documents
The following documents are referenced by the data sheet, and available on the documentation CD
or from the Luminary Micro web site at www.luminarymicro.com:
■ ARM® Cortex™-M3 Technical Reference Manual
■ ARM® CoreSight Technical Reference Manual
■ ARM® v7-M Architecture Application Level Reference Manual
The following related documents are also referenced:
■ IEEE Standard 1149.1-Test Access Port and Boundary-Scan Architecture
This documentation list was current as of publication date. Please check the Luminary Micro web
site for additional documentation, including application notes and white papers.
Documentation Conventions
This document uses the conventions shown in Table 1 on page 17.
Table 1. Documentation Conventions
Notation Meaning
General Register Notation
APB registers are indicated in uppercase bold. For example, PBORCTL is the Power-On and
Brown-Out Reset Control register. If a register name contains a lowercase n, it represents more
than one register. For example, SRCRn represents any (or all) of the three Software Reset Control
registers: SRCR0, SRCR1 , and SRCR2.
REGISTER
bit A single bit in a register.
bit field Two or more consecutive and related bits.
A hexadecimal increment to a register's address, relative to that module's base address as specified
in “Memory Map” on page 37.
offset 0xnnn
Registers are numbered consecutively throughout the document to aid in referencing them. The
register number has no meaning to software.
Register N
November 30, 2007 17
Preliminary
LM3S6110 Microcontroller
Notation Meaning
Register bits marked reserved are reserved for future use. In most cases, reserved bits are set to
0; however, user software should not rely on the value of a reserved bit. To provide software
compatibility with future products, the value of a reserved bit should be preserved across a
read-modify-write operation.
reserved
The range of register bits inclusive from xx to yy. For example, 31:15 means bits 15 through 31 in
that register.
yy:xx
This value in the register bit diagram indicates whether software running on the controller can
change the value of the bit field.
Register Bit/Field
Types
RC Software can read this field. The bit or field is cleared by hardware after reading the bit/field.
RO Software can read this field. Always write the chip reset value.
R/W Software can read or write this field.
Software can read or write this field. A write of a 0 to a W1C bit does not affect the bit value in the
register. A write of a 1 clears the value of the bit in the register; the remaining bits remain unchanged.
This register type is primarily used for clearing interrupt status bits where the read operation
provides the interrupt status and the write of the read value clears only the interrupts being reported
at the time the register was read.
R/W1C
Software can write this field. A write of a 0 to a W1C bit does not affect the bit value in the register.
A write of a 1 clears the value of the bit in the register; the remaining bits remain unchanged. A
read of the register returns no meaningful data.
This register is typically used to clear the corresponding bit in an interrupt register.
W1C
WO Only a write by software is valid; a read of the register returns no meaningful data.
Register Bit/Field This value in the register bit diagram shows the bit/field value after any reset, unless noted.
Reset Value
0 Bit cleared to 0 on chip reset.
1 Bit set to 1 on chip reset.
- Nondeterministic.
Pin/Signal Notation
[ ] Pin alternate function; a pin defaults to the signal without the brackets.
pin Refers to the physical connection on the package.
signal Refers to the electrical signal encoding of a pin.
Change the value of the signal from the logically False state to the logically True state. For active
High signals, the asserted signal value is 1 (High); for active Low signals, the asserted signal value
is 0 (Low). The active polarity (High or Low) is defined by the signal name (see SIGNAL and SIGNAL
below).
assert a signal
deassert a signal Change the value of the signal from the logically True state to the logically False state.
Signal names are in uppercase and in the Courier font. An overbar on a signal name indicates that
it is active Low. To assert SIGNAL is to drive it Low; to deassert SIGNAL is to drive it High.
SIGNAL
Signal names are in uppercase and in the Courier font. An active High signal has no overbar. To
assert SIGNAL is to drive it High; to deassert SIGNAL is to drive it Low.
SIGNAL
Numbers
An uppercase X indicates any of several values is allowed, where X can be any legal pattern. For
example, a binary value of 0X00 can be either 0100 or 0000, a hex value of 0xX is 0x0 or 0x1, and
so on.
X
Hexadecimal numbers have a prefix of 0x. For example, 0x00FF is the hexadecimal number FF.
All other numbers within register tables are assumed to be binary. Within conceptual information,
binary numbers are indicated with a b suffix, for example, 1011b, and decimal numbers are written
without a prefix or suffix.
0x
18 November 30, 2007
Preliminary
About This Document
1 Architectural Overview
The Luminary Micro Stellaris® family of microcontrollers—the first ARM® Cortex™-M3 based
controllers—brings high-performance 32-bit computing to cost-sensitive embedded microcontroller
applications. These pioneering parts deliver customers 32-bit performance at a cost equivalent to
legacy 8- and 16-bit devices, all in a package with a small footprint.
The Stellaris® family offers efficient performance and extensive integration, favorably positioning
the device into cost-conscious applications requiring significant control-processing and connectivity
capabilities. The Stellaris® LM3S1000 series extends the Stellaris® family with larger on-chip
memories, enhanced power management, and expanded I/O and control capabilities. The Stellaris®
LM3S2000 series, designed for Controller Area Network (CAN) applications, extends the Stellaris
family with Bosch CAN networking technology, the golden standard in short-haul industrial networks.
The Stellaris® LM3S2000 series also marks the first integration of CAN capabilities with the
revolutionary Cortex-M3 core. The Stellaris® LM3S6000 series combines both a 10/100 Ethernet
Media Access Control (MAC) and Physical (PHY) layer, marking the first time that integrated
connectivity is available with an ARM Cortex-M3 MCU and the only integrated 10/100 Ethernet MAC
and PHY available in an ARM architecture MCU. The Stellaris® LM3S8000 series combines Bosch
Controller Area Network technology with both a 10/100 Ethernet Media Access Control (MAC) and
Physical (PHY) layer.
The LM3S6110 microcontroller is targeted for industrial applications, including remote monitoring,
electronic point-of-sale machines, test and measurement equipment, network appliances and
switches, factory automation, HVAC and building control, gaming equipment, motion control, medical
instrumentation, and fire and security.
In addition, the LM3S6110 microcontroller offers the advantages of ARM's widely available
development tools, System-on-Chip (SoC) infrastructure IP applications, and a large user community.
Additionally, the microcontroller uses ARM's Thumb®-compatible Thumb-2 instruction set to reduce
memory requirements and, thereby, cost. Finally, the LM3S6110 microcontroller is code-compatible
to all members of the extensive Stellaris® family; providing flexibility to fit our customers' precise
needs.
Luminary Micro offers a complete solution to get to market quickly, with evaluation and development
boards, white papers and application notes, an easy-to-use peripheral driver library, and a strong
support, sales, and distributor network.
1.1 Product Features
The LM3S6110 microcontroller includes the following product features:
■ 32-Bit RISC Performance
– 32-bit ARM® Cortex™-M3 v7M architecture optimized for small-footprint embedded
applications
– System timer (SysTick), providing a simple, 24-bit clear-on-write, decrementing, wrap-on-zero
counter with a flexible control mechanism
– Thumb®-compatible Thumb-2-only instruction set processor core for high code density
– 25-MHz operation
– Hardware-division and single-cycle-multiplication
November 30, 2007 19
Preliminary
LM3S6110 Microcontroller
– Integrated Nested Vectored Interrupt Controller (NVIC) providing deterministic interrupt
handling
– 24 interrupts with eight priority levels
– Memory protection unit (MPU), providing a privileged mode for protected operating system
functionality
– Unaligned data access, enabling data to be efficiently packed into memory
– Atomic bit manipulation (bit-banding), delivering maximum memory utilization and streamlined
peripheral control
■ Internal Memory
– 64 KB single-cycle flash
• User-managed flash block protection on a 2-KB block basis
• User-managed flash data programming
• User-defined and managed flash-protection block
– 16 KB single-cycle SRAM
■ General-Purpose Timers
– Three General-Purpose Timer Modules (GPTM), each of which provides two 16-bit timers.
Each GPTM can be configured to operate independently:
• As a single 32-bit timer
• As one 32-bit Real-Time Clock (RTC) to event capture
• For Pulse Width Modulation (PWM)
– 32-bit Timer modes
• Programmable one-shot timer
• Programmable periodic timer
• Real-Time Clock when using an external 32.768-KHz clock as the input
• User-enabled stalling in periodic and one-shot mode when the controller asserts the CPU
Halt flag during debug
– 16-bit Timer modes
• General-purpose timer function with an 8-bit prescaler
• Programmable one-shot timer
• Programmable periodic timer
• User-enabled stalling when the controller asserts CPU Halt flag during debug
20 November 30, 2007
Preliminary
Architectural Overview
– 16-bit Input Capture modes
• Input edge count capture
• Input edge time capture
– 16-bit PWM mode
• Simple PWM mode with software-programmable output inversion of the PWM signal
■ ARM FiRM-compliant Watchdog Timer
– 32-bit down counter with a programmable load register
– Separate watchdog clock with an enable
– Programmable interrupt generation logic with interrupt masking
– Lock register protection from runaway software
– Reset generation logic with an enable/disable
– User-enabled stalling when the controller asserts the CPU Halt flag during debug
■ 10/100 Ethernet Controller
– Conforms to the IEEE 802.3-2002 Specification
– Full- and half-duplex for both 100 Mbps and 10 Mbps operation
– Integrated 10/100 Mbps Transceiver (PHY)
– Automatic MDI/MDI-X cross-over correction
– Programmable MAC address
– Power-saving and power-down modes
■ Synchronous Serial Interface (SSI)
– Master or slave operation
– Programmable clock bit rate and prescale
– Separate transmit and receive FIFOs, 16 bits wide, 8 locations deep
– Programmable interface operation for Freescale SPI, MICROWIRE, or Texas Instruments
synchronous serial interfaces
– Programmable data frame size from 4 to 16 bits
– Internal loopback test mode for diagnostic/debug testing
■ UART
– Fully programmable 16C550-type UART with IrDA support
November 30, 2007 21
Preliminary
LM3S6110 Microcontroller
– Separate 16x8 transmit (TX) and 16x12 receive (RX) FIFOs to reduce CPU interrupt service
loading
– Programmable baud-rate generator with fractional divider
– Programmable FIFO length, including 1-byte deep operation providing conventional
double-buffered interface
– FIFO trigger levels of 1/8, 1/4, 1/2, 3/4, and 7/8
– Standard asynchronous communication bits for start, stop, and parity
– False-start-bit detection
– Line-break generation and detection
■ Analog Comparators
– Three independent integrated analog comparators
– Configurable for output to: drive an output pin or generate an interrupt
– Compare external pin input to external pin input or to internal programmable voltage reference
■ PWM
– One PWM generator blocks, each with one 16-bit counter, two comparators, a PWM generator,
and a dead-band generator
– One 16-bit counter
• Runs in Down or Up/Down mode
• Output frequency controlled by a 16-bit load value
• Load value updates can be synchronized
• Produces output signals at zero and load value
– Two PWM comparators
• Comparator value updates can be synchronized
• Produces output signals on match
– PWM generator
• Output PWM signal is constructed based on actions taken as a result of the counter and
PWM comparator output signals
• Produces two independent PWM signals
– Dead-band generator
• Produces two PWM signals with programmable dead-band delays suitable for driving a
half-H bridge
22 November 30, 2007
Preliminary
Architectural Overview
• Can be bypassed, leaving input PWM signals unmodified
– Flexible output control block with PWM output enable of each PWM signal
• PWM output enable of each PWM signal
• Optional output inversion of each PWM signal (polarity control)
• Optional fault handling for each PWM signal
• Synchronization of timers in the PWM generator blocks
• Synchronization of timer/comparator updates across the PWM generator blocks
• Interrupt status summary of the PWM generator blocks
■ GPIOs
– 8-35 GPIOs, depending on configuration
– 5-V-tolerant input/outputs
– Programmable interrupt generation as either edge-triggered or level-sensitive
– Bit masking in both read and write operations through address lines
– Programmable control for GPIO pad configuration:
• Weak pull-up or pull-down resistors
• 2-mA, 4-mA, and 8-mA pad drive
• Slew rate control for the 8-mA drive
• Open drain enables
• Digital input enables
■ Power
– On-chip Low Drop-Out (LDO) voltage regulator, with programmable output user-adjustable
from 2.25 V to 2.75 V
– Low-power options on controller: Sleep and Deep-sleep modes
– Low-power options for peripherals: software controls shutdown of individual peripherals
– User-enabled LDO unregulated voltage detection and automatic reset
– 3.3-V supply brown-out detection and reporting via interrupt or reset
■ Flexible Reset Sources
– Power-on reset (POR)
– Reset pin assertion
November 30, 2007 23
Preliminary
LM3S6110 Microcontroller
– Brown-out (BOR) detector alerts to system power drops
– Software reset
– Watchdog timer reset
– Internal low drop-out (LDO) regulator output goes unregulated
■ Additional Features
– Six reset sources
– Programmable clock source control
– Clock gating to individual peripherals for power savings
– IEEE 1149.1-1990 compliant Test Access Port (TAP) controller
– Debug access via JTAG and Serial Wire interfaces
– Full JTAG boundary scan
■ Industrial-range 100-pin RoHS-compliant LQFP package
1.2 Target Applications
■ Remote monitoring
■ Electronic point-of-sale (POS) machines
■ Test and measurement equipment
■ Network appliances and switches
■ Factory automation
■ HVAC and building control
■ Gaming equipment
■ Motion control
■ Medical instrumentation
■ Fire and security
■ Power and energy
■ Transportation
1.3 High-Level Block Diagram
Figure 1-1 on page 25 represents the full set of features in the Stellaris® 6000 series of devices;
not all features may be available on the LM3S6110 microcontroller.
24 November 30, 2007
Preliminary
Architectural Overview
Figure 1-1. Stellaris® 6000 Series High-Level Block Diagram
1.4 Functional Overview
The following sections provide an overview of the features of the LM3S6110 microcontroller. The
page number in parenthesis indicates where that feature is discussed in detail. Ordering and support
information can be found in “Ordering and Contact Information” on page 449.
November 30, 2007 25
Preliminary
LM3S6110 Microcontroller
1.4.1 ARM Cortex™-M3
1.4.1.1 Processor Core (see page 31)
All members of the Stellaris® product family, including the LM3S6110 microcontroller, are designed
around an ARM Cortex™-M3 processor core. The ARM Cortex-M3 processor provides the core for
a high-performance, low-cost platform that meets the needs of minimal memory implementation,
reduced pin count, and low-power consumption, while delivering outstanding computational
performance and exceptional system response to interrupts.
“ARM Cortex-M3 Processor Core” on page 31 provides an overview of the ARM core; the core is
detailed in the ARM® Cortex™-M3 Technical Reference Manual.
1.4.1.2 System Timer (SysTick)
Cortex-M3 includes an integrated system timer, SysTick. SysTick provides a simple, 24-bit
clear-on-write, decrementing, wrap-on-zero counter with a flexible control mechanism. The counter
can be used in several different ways, for example:
■ An RTOS tick timer which fires at a programmable rate (for example, 100 Hz) and invokes a
SysTick routine.
■ A high-speed alarm timer using the system clock.
■ A variable rate alarm or signal timer—the duration is range-dependent on the reference clock
used and the dynamic range of the counter.
■ A simple counter. Software can use this to measure time to completion and time used.
■ An internal clock source control based on missing/meeting durations. The COUNTFLAG bit-field
in the control and status register can be used to determine if an action completed within a set
duration, as part of a dynamic clock management control loop.
1.4.1.3 Nested Vectored Interrupt Controller (NVIC)
The LM3S6110 controller includes the ARM Nested Vectored Interrupt Controller (NVIC) on the
ARM Cortex-M3 core. The NVIC and Cortex-M3 prioritize and handle all exceptions. All exceptions
are handled in Handler Mode. The processor state is automatically stored to the stack on an
exception, and automatically restored from the stack at the end of the Interrupt Service Routine
(ISR). The vector is fetched in parallel to the state saving, which enables efficient interrupt entry.
The processor supports tail-chaining, which enables back-to-back interrupts to be performed without
the overhead of state saving and restoration. Software can set eight priority levels on 7 exceptions
(system handlers) and 24 interrupts.
“Interrupts” on page 39 provides an overview of the NVIC controller and the interrupt map. Exceptions
and interrupts are detailed in the ARM® Cortex™-M3 Technical Reference Manual.
1.4.2 Motor Control Peripherals
To enhance motor control, the LM3S6110 controller features Pulse Width Modulation (PWM) outputs.
1.4.2.1 PWM
Pulse width modulation (PWM) is a powerful technique for digitally encoding analog signal levels.
High-resolution counters are used to generate a square wave, and the duty cycle of the square
wave is modulated to encode an analog signal. Typical applications include switching power supplies
and motor control.
26 November 30, 2007
Preliminary
Architectural Overview
On the LM3S6110, PWM motion control functionality can be achieved through:
■ Dedicated, flexible motion control hardware using the PWM pins
■ The motion control features of the general-purpose timers using the CCP pins
PWM Pins (see page 366)
The LM3S6110 PWM module consists of one PWM generator blocks and a control block. Each
PWM generator block contains one timer (16-bit down or up/down counter), two comparators, a
PWM signal generator, a dead-band generator, and an interrupt. The control block determines the
polarity of the PWM signals, and which signals are passed through to the pins.
Each PWM generator block produces two PWM signals that can either be independent signals or
a single pair of complementary signals with dead-band delays inserted. The output of the PWM
generation blocks are managed by the output control block before being passed to the device pins.
CCP Pins (see page 178)
The General-Purpose Timer Module's CCP (Capture Compare PWM) pins are software programmable
to support a simple PWM mode with a software-programmable output inversion of the PWM signal.
1.4.3 Analog Peripherals
For support of analog signals, the LM3S6110 microcontroller offers three analog comparators.
1.4.3.1 Analog Comparators (see page 353)
An analog comparator is a peripheral that compares two analog voltages, and provides a logical
output that signals the comparison result.
The LM3S6110 microcontroller provides three independent integrated analog comparators that can
be configured to drive an output or generate an interrupt .
A comparator can compare a test voltage against any one of these voltages:
■ An individual external reference voltage
■ A shared single external reference voltage
■ A shared internal reference voltage
The comparator can provide its output to a device pin, acting as a replacement for an analog
comparator on the board, or it can be used to signal the application via interrupts to cause it to start
capturing a sample sequence.
1.4.4 Serial Communications Peripherals
The LM3S6110 controller supports both asynchronous and synchronous serial communications
with:
■ One fully programmable 16C550-type UART
■ One SSI module
■ Ethernet controller
November 30, 2007 27
Preliminary
LM3S6110 Microcontroller
1.4.4.1 UART (see page 231)
A Universal Asynchronous Receiver/Transmitter (UART) is an integrated circuit used for RS-232C
serial communications, containing a transmitter (parallel-to-serial converter) and a receiver
(serial-to-parallel converter), each clocked separately.
The LM3S6110 controller includes one fully programmable 16C550-type UARTthat supports data
transfer speeds up to 460.8 Kbps. (Although similar in functionality to a 16C550 UART, it is not
register-compatible.) In addition, each UART is capable of supporting IrDA.
Separate 16x8 transmit (TX) and 16x12 receive (RX) FIFOs reduce CPU interrupt service loading.
The UART can generate individually masked interrupts from the RX, TX, modem status, and error
conditions. The module provides a single combined interrupt when any of the interrupts are asserted
and are unmasked.
1.4.4.2 SSI (see page 272)
Synchronous Serial Interface (SSI) is a four-wire bi-directional communications interface.
The LM3S6110 controller includes one SSI module that provides the functionality for synchronous
serial communications with peripheral devices, and can be configured to use the Freescale SPI,
MICROWIRE, or TI synchronous serial interface frame formats. The size of the data frame is also
configurable, and can be set between 4 and 16 bits, inclusive.
The SSI module performs serial-to-parallel conversion on data received from a peripheral device,
and parallel-to-serial conversion on data transmitted to a peripheral device. The TX and RX paths
are buffered with internal FIFOs, allowing up to eight 16-bit values to be stored independently.
The SSI module can be configured as either a master or slave device. As a slave device, the SSI
module can also be configured to disable its output, which allows a master device to be coupled
with multiple slave devices.
The SSI module also includes a programmable bit rate clock divider and prescaler to generate the
output serial clock derived from the SSI module's input clock. Bit rates are generated based on the
input clock and the maximum bit rate is determined by the connected peripheral.
1.4.4.3 Ethernet Controller (see page 309)
Ethernet is a frame-based computer networking technology for local area networks (LANs). Ethernet
has been standardized as IEEE 802.3. It defines a number of wiring and signaling standards for the
physical layer, two means of network access at the Media Access Control (MAC)/Data Link Layer,
and a common addressing format.
The Stellaris® Ethernet Controller consists of a fully integrated media access controller (MAC) and
network physical (PHY) interface device. The Ethernet Controller conforms to IEEE 802.3
specifications and fully supports 10BASE-T and 100BASE-TX standards. In addition, the Ethernet
Controller supports automatic MDI/MDI-X cross-over correction.
1.4.5 System Peripherals
1.4.5.1 Programmable GPIOs (see page 131)
General-purpose input/output (GPIO) pins offer flexibility for a variety of connections.
The Stellaris® GPIO module is composed of seven physical GPIO blocks, each corresponding to
an individual GPIO port. The GPIO module is FiRM-compliant (compliant to the ARM Foundation
IP for Real-Time Microcontrollers specification) and supports 8-35 programmable input/output pins.
The number of GPIOs available depends on the peripherals being used (see “Signal Tables” on page
402 for the signals available to each GPIO pin).
28 November 30, 2007
Preliminary
Architectural Overview
The GPIO module features programmable interrupt generation as either edge-triggered or
level-sensitive on all pins, programmable control for GPIO pad configuration, and bit masking in
both read and write operations through address lines.
1.4.5.2 Three Programmable Timers (see page 172)
Programmable timers can be used to count or time external events that drive the Timer input pins.
The Stellaris® General-Purpose Timer Module (GPTM) contains three GPTM blocks. Each GPTM
block provides two 16-bit timers/counters that can be configured to operate independently as timers
or event counters, or configured to operate as one 32-bit timer or one 32-bit Real-Time Clock (RTC).
When configured in 32-bit mode, a timer can run as a Real-Time Clock (RTC), one-shot timer or
periodic timer. When in 16-bit mode, a timer can run as a one-shot timer or periodic timer, and can
extend its precision by using an 8-bit prescaler. A 16-bit timer can also be configured for event
capture or Pulse Width Modulation (PWM) generation.
1.4.5.3 Watchdog Timer (see page 208)
A watchdog timer can generate nonmaskable interrupts (NMIs) or a reset when a time-out value is
reached. The watchdog timer is used to regain control when a system has failed due to a software
error or to the failure of an external device to respond in the expected way.
The Stellaris® Watchdog Timer module consists of a 32-bit down counter, a programmable load
register, interrupt generation logic, and a locking register.
The Watchdog Timer can be configured to generate an interrupt to the controller on its first time-out,
and to generate a reset signal on its second time-out. Once the Watchdog Timer has been configured,
the lock register can be written to prevent the timer configuration from being inadvertently altered.
1.4.6 Memory Peripherals
The LM3S6110 controller offers both single-cycle SRAM and single-cycle Flash memory.
1.4.6.1 SRAM (see page 107)
The LM3S6110 static random access memory (SRAM) controller supports 16 KB SRAM. The internal
SRAM of the Stellaris® devices is located at offset 0x0000.0000 of the device memory map. To
reduce the number of time-consuming read-modify-write (RMW) operations, ARM has introduced
bit-banding technology in the new Cortex-M3 processor. With a bit-band-enabled processor, certain
regions in the memory map (SRAM and peripheral space) can use address aliases to access
individual bits in a single, atomic operation.
1.4.6.2 Flash (see page 108)
The LM3S6110 Flash controller supports 64 KB of flash memory. The flash is organized as a set
of 1-KB blocks that can be individually erased. Erasing a block causes the entire contents of the
block to be reset to all 1s. These blocks are paired into a set of 2-KB blocks that can be individually
protected. The blocks can be marked as read-only or execute-only, providing different levels of code
protection. Read-only blocks cannot be erased or programmed, protecting the contents of those
blocks from being modified. Execute-only blocks cannot be erased or programmed, and can only
be read by the controller instruction fetch mechanism, protecting the contents of those blocks from
being read by either the controller or by a debugger.
November 30, 2007 29
Preliminary
LM3S6110 Microcontroller
1.4.7 Additional Features
1.4.7.1 Memory Map (see page 37)
A memory map lists the location of instructions and data in memory. The memory map for the
LM3S6110 controller can be found in “Memory Map” on page 37. Register addresses are given as
a hexadecimal increment, relative to the module's base address as shown in the memory map.
The ARM® Cortex™-M3 Technical Reference Manual provides further information on the memory
map.
1.4.7.2 JTAG TAP Controller (see page 41)
The Joint Test Action Group (JTAG) port provides a standardized serial interface for controlling the
Test Access Port (TAP) and associated test logic. The TAP, JTAG instruction register, and JTAG
data registers can be used to test the interconnects of assembled printed circuit boards, obtain
manufacturing information on the components, and observe and/or control the inputs and outputs
of the controller during normal operation. The JTAG port provides a high degree of testability and
chip-level access at a low cost.
The JTAG port is comprised of the standard five pins: TRST, TCK, TMS, TDI, and TDO. Data is
transmitted serially into the controller on TDI and out of the controller on TDO. The interpretation of
this data is dependent on the current state of the TAP controller. For detailed information on the
operation of the JTAG port and TAP controller, please refer to the IEEE Standard 1149.1-Test
Access Port and Boundary-Scan Architecture.
The Luminary Micro JTAG controller works with the ARM JTAG controller built into the Cortex-M3
core. This is implemented by multiplexing the TDO outputs from both JTAG controllers. ARM JTAG
instructions select the ARM TDO output while Luminary Micro JTAG instructions select the Luminary
Micro TDO outputs. The multiplexer is controlled by the Luminary Micro JTAG controller, which has
comprehensive programming for the ARM, Luminary Micro, and unimplemented JTAG instructions.
1.4.7.3 System Control and Clocks (see page 52)
System control determines the overall operation of the device. It provides information about the
device, controls the clocking of the device and individual peripherals, and handles reset detection
and reporting.
1.4.8 Hardware Details
Details on the pins and package can be found in the following sections:
■ “Pin Diagram” on page 401
■ “Signal Tables” on page 402
■ “Operating Characteristics” on page 414
■ “Electrical Characteristics” on page 415
■ “Package Information” on page 428
30 November 30, 2007
Preliminary
Architectural Overview
2 ARM Cortex-M3 Processor Core
The ARM Cortex-M3 processor provides the core for a high-performance, low-cost platform that
meets the needs of minimal memory implementation, reduced pin count, and low power consumption,
while delivering outstanding computational performance and exceptional system response to
interrupts. Features include:
■ Compact core.
■ Thumb-2 instruction set, delivering the high-performance expected of an ARM core in the memory
size usually associated with 8- and 16-bit devices; typically in the range of a few kilobytes of
memory for microcontroller class applications.
■ Rapid application execution through Harvard architecture characterized by separate buses for
instruction and data.
■ Exceptional interrupt handling, by implementing the register manipulations required for handling
an interrupt in hardware.
■ Memory protection unit (MPU) to provide a privileged mode of operation for complex applications.
■ Migration from the ARM7™ processor family for better performance and power efficiency.
■ Full-featured debug solution with a:
– Serial Wire JTAG Debug Port (SWJ-DP)
– Flash Patch and Breakpoint (FPB) unit for implementing breakpoints
– Data Watchpoint and Trigger (DWT) unit for implementing watchpoints, trigger resources,
and system profiling
– Instrumentation Trace Macrocell (ITM) for support of printf style debugging
– Trace Port Interface Unit (TPIU) for bridging to a Trace Port Analyzer
The Stellaris® family of microcontrollers builds on this core to bring high-performance 32-bit computing
to cost-sensitive embedded microcontroller applications, such as factory automation and control,
industrial control power devices, building and home automation, and stepper motors.
For more information on the ARM Cortex-M3 processor core, see the ARM® Cortex™-M3 Technical
Reference Manual. For information on SWJ-DP, see the ARM® CoreSight Technical Reference
Manual.
November 30, 2007 31
Preliminary
LM3S6110 Microcontroller
2.1 Block Diagram
Figure 2-1. CPU Block Diagram
Private Peripheral
Bus
(internal)
Data
Watchpoint
and Trace
Interrupts
Debug
Sleep
Instrumentation
Trace Macrocell
Trace
Port
Interface
Unit
CM3 Core
Instructions Data
Flash
Patch and
Breakpoint
Memory
Protection
Unit
Adv. High-
Perf. Bus
Access Port
Nested
Vectored
Interrupt
Controller
Serial Wire JTAG
Debug Port
Bus
Matrix
Adv. Peripheral
Bus
I-code bus
D-code bus
System bus
ROM
Table
Private
Peripheral
Bus
(external)
Serial
Wire
Output
Trace
Port
(SWO)
ARM
Cortex-M3
2.2 Functional Description
Important: The ARM® Cortex™-M3 Technical Reference Manual describes all the features of an
ARM Cortex-M3 in detail. However, these features differ based on the implementation.
This section describes the Stellaris® implementation.
Luminary Micro has implemented the ARM Cortex-M3 core as shown in Figure 2-1 on page 32. As
noted in the ARM® Cortex™-M3 Technical Reference Manual, several Cortex-M3 components are
flexible in their implementation: SW/JTAG-DP, ETM, TPIU, the ROM table, the MPU, and the Nested
Vectored Interrupt Controller (NVIC). Each of these is addressed in the sections that follow.
2.2.1 Serial Wire and JTAG Debug
Luminary Micro has replaced the ARM SW-DP and JTAG-DP with the ARM CoreSight™-compliant
Serial Wire JTAG Debug Port (SWJ-DP) interface. This means Chapter 12, “Debug Port,” of the
ARM® Cortex™-M3 Technical Reference Manual does not apply to Stellaris® devices.
The SWJ-DP interface combines the SWD and JTAG debug ports into one module. See the
CoreSight™ Design Kit Technical Reference Manual for details on SWJ-DP.
32 November 30, 2007
Preliminary
ARM Cortex-M3 Processor Core
2.2.2 Embedded Trace Macrocell (ETM)
ETM was not implemented in the Stellaris® devices. This means Chapters 15 and 16 of the ARM®
Cortex™-M3 Technical Reference Manual can be ignored.
2.2.3 Trace Port Interface Unit (TPIU)
The TPIU acts as a bridge between the Cortex-M3 trace data from the ITM, and an off-chip Trace
Port Analyzer. The Stellaris® devices have implemented TPIU as shown in Figure 2-2 on page 33.
This is similar to the non-ETM version described in the ARM® Cortex™-M3 Technical Reference
Manual, however, SWJ-DP only provides SWV output for the TPIU.
Figure 2-2. TPIU Block Diagram
ATB
Interface
Asynchronous FIFO
APB
Interface
Trace Out
(serializer)
Debug
ATB
Slave
Port
APB
Slave
Port
Serial Wire
Trace Port
(SWO)
2.2.4 ROM Table
The default ROM table was implemented as described in the ARM® Cortex™-M3 Technical
Reference Manual.
2.2.5 Memory Protection Unit (MPU)
The Memory Protection Unit (MPU) is included on the LM3S6110 controller and supports the standard
ARMv7 Protected Memory System Architecture (PMSA) model. The MPU provides full support for
protection regions, overlapping protection regions, access permissions, and exporting memory
attributes to the system.
2.2.6 Nested Vectored Interrupt Controller (NVIC)
The Nested Vectored Interrupt Controller (NVIC):
■ Facilitates low-latency exception and interrupt handling
■ Controls power management
■ Implements system control registers
November 30, 2007 33
Preliminary
LM3S6110 Microcontroller
The NVIC supports up to 240 dynamically reprioritizable interrupts each with up to 256 levels of
priority. The NVIC and the processor core interface are closely coupled, which enables low latency
interrupt processing and efficient processing of late arriving interrupts. The NVIC maintains knowledge
of the stacked (nested) interrupts to enable tail-chaining of interrupts.
You can only fully access the NVIC from privileged mode, but you can pend interrupts in user-mode
if you enable the Configuration Control Register (see the ARM® Cortex™-M3 Technical Reference
Manual). Any other user-mode access causes a bus fault.
All NVIC registers are accessible using byte, halfword, and word unless otherwise stated.
All NVIC registers and system debug registers are little endian regardless of the endianness state
of the processor.
2.2.6.1 Interrupts
The ARM® Cortex™-M3 Technical Reference Manual describes the maximum number of interrupts
and interrupt priorities. The LM3S6110 microcontroller supports 24 interrupts with eight priority
levels.
2.2.6.2 System Timer (SysTick)
Cortex-M3 includes an integrated system timer, SysTick. SysTick provides a simple, 24-bit
clear-on-write, decrementing, wrap-on-zero counter with a flexible control mechanism. The counter
can be used in several different ways, for example:
■ An RTOS tick timer which fires at a programmable rate (for example, 100 Hz) and invokes a
SysTick routine.
■ A high-speed alarm timer using the system clock.
■ A variable rate alarm or signal timer—the duration is range-dependent on the reference clock
used and the dynamic range of the counter.
■ A simple counter. Software can use this to measure time to completion and time used.
■ An internal clock source control based on missing/meeting durations. The COUNTFLAG bit-field
in the control and status register can be used to determine if an action completed within a set
duration, as part of a dynamic clock management control loop.
Functional Description
The timer consists of three registers:
■ A control and status counter to configure its clock, enable the counter, enable the SysTick
interrupt, and determine counter status.
■ The reload value for the counter, used to provide the counter's wrap value.
■ The current value of the counter.
A fourth register, the SysTick Calibration Value Register, is not implemented in the Stellaris® devices.
When enabled, the timer counts down from the reload value to zero, reloads (wraps) to the value
in the SysTick Reload Value register on the next clock edge, then decrements on subsequent clocks.
Writing a value of zero to the Reload Value register disables the counter on the next wrap. When
the counter reaches zero, the COUNTFLAG status bit is set. The COUNTFLAG bit clears on reads.
34 November 30, 2007
Preliminary
ARM Cortex-M3 Processor Core
Writing to the Current Value register clears the register and the COUNTFLAG status bit. The write
does not trigger the SysTick exception logic. On a read, the current value is the value of the register
at the time the register is accessed.
If the core is in debug state (halted), the counter will not decrement. The timer is clocked with respect
to a reference clock. The reference clock can be the core clock or an external clock source.
SysTick Control and Status Register
Use the SysTick Control and Status Register to enable the SysTick features. The reset is
0x0000.0000.
Bit/Field Name Type Reset Description
Software should not rely on the value of a reserved bit. To provide compatibility with
future products, the value of a reserved bit should be preserved across a
read-modify-write operation.
31:17 reserved RO 0
Returns 1 if timer counted to 0 since last time this was read. Clears on read by
application. If read by the debugger using the DAP, this bit is cleared on read-only
if the MasterType bit in the AHB-AP Control Register is set to 0. Otherwise, the
COUNTFLAG bit is not changed by the debugger read.
16 COUNTFLAG R/W 0
Software should not rely on the value of a reserved bit. To provide compatibility with
future products, the value of a reserved bit should be preserved across a
read-modify-write operation.
15:3 reserved RO 0
0 = external reference clock. (Not implemented for Stellaris microcontrollers.)
1 = core clock.
If no reference clock is provided, it is held at 1 and so gives the same time as the
core clock. The core clock must be at least 2.5 times faster than the reference clock.
If it is not, the count values are unpredictable.
2 CLKSOURCE R/W 0
1 = counting down to 0 pends the SysTick handler.
0 = counting down to 0 does not pend the SysTick handler. Software can use the
COUNTFLAG to determine if ever counted to 0.
1 TICKINT R/W 0
1 = counter operates in a multi-shot way. That is, counter loads with the Reload
value and then begins counting down. On reaching 0, it sets the COUNTFLAG to
1 and optionally pends the SysTick handler, based on TICKINT. It then loads the
Reload value again, and begins counting.
0 = counter disabled.
0 ENABLE R/W 0
SysTick Reload Value Register
Use the SysTick Reload Value Register to specify the start value to load into the current value
register when the counter reaches 0. It can be any value between 1 and 0x00FF.FFFF. A start value
of 0 is possible, but has no effect because the SysTick interrupt and COUNTFLAG are activated
when counting from 1 to 0.
Therefore, as a multi-shot timer, repeated over and over, it fires every N+1 clock pulse, where N is
any value from 1 to 0x00FF.FFFF. So, if the tick interrupt is required every 100 clock pulses, 99
must be written into the RELOAD. If a new value is written on each tick interrupt, so treated as single
shot, then the actual count down must be written. For example, if a tick is next required after 400
clock pulses, 400 must be written into the RELOAD.
Bit/Field Name Type Reset Description
Software should not rely on the value of a reserved bit. To provide compatibility with
future products, the value of a reserved bit should be preserved across a read-modify-write
operation.
31:24 reserved RO 0
November 30, 2007 35
Preliminary
LM3S6110 Microcontroller
Bit/Field Name Type Reset Description
23:0 RELOAD W1C - Value to load into the SysTick Current Value Register when the counter reaches 0.
SysTick Current Value Register
Use the SysTick Current Value Register to find the current value in the register.
Bit/Field Name Type Reset Description
Software should not rely on the value of a reserved bit. To provide compatibility with
future products, the value of a reserved bit should be preserved across a
read-modify-write operation.
31:24 reserved RO 0
Current value at the time the register is accessed. No read-modify-write protection is
provided, so change with care.
This register is write-clear. Writing to it with any value clears the register to 0. Clearing
this register also clears the COUNTFLAG bit of the SysTick Control and Status Register.
23:0 CURRENT W1C -
SysTick Calibration Value Register
The SysTick Calibration Value register is not implemented.
36 November 30, 2007
Preliminary
ARM Cortex-M3 Processor Core
3 Memory Map
The memory map for the LM3S6110 controller is provided in Table 3-1 on page 37.
In this manual, register addresses are given as a hexadecimal increment, relative to the module’s
base address as shown in the memory map. See also Chapter 4, “Memory Map” in the ARM®
Cortex™-M3 Technical Reference Manual.
Important: In Table 3-1 on page 37, addresses not listed are reserved.
Table 3-1. Memory Mapa
For details on
registers, see
page ...
Start End Description
Memory
0x0000.0000 0x0000.FFFF On-chip flash b 111
0x2000.0000 0x2000.3FFF Bit-banded on-chip SRAMc 111
0x2010.0000 0x21FF.FFFF Reserved non-bit-banded SRAM space -
0x2200.0000 0x23FF.FFFF Bit-band alias of 0x2000.0000 through 0x200F.FFFF 107
0x2400.0000 0x3FFF.FFFF Reserved non-bit-banded SRAM space -
FiRM Peripherals
0x4000.0000 0x4000.0FFF Watchdog timer 210
0x4000.4000 0x4000.4FFF GPIO Port A 137
0x4000.5000 0x4000.5FFF GPIO Port B 137
0x4000.6000 0x4000.6FFF GPIO Port C 137
0x4000.7000 0x4000.7FFF GPIO Port D 137
0x4000.8000 0x4000.8FFF SSI0 283
0x4000.C000 0x4000.CFFF UART0 238
Peripherals
0x4002.4000 0x4002.4FFF GPIO Port E 137
0x4002.5000 0x4002.5FFF GPIO Port F 137
0x4002.6000 0x4002.6FFF GPIO Port G 137
0x4002.8000 0x4002.8FFF PWM 372
0x4003.0000 0x4003.0FFF Timer0 183
0x4003.1000 0x4003.1FFF Timer1 183
0x4003.2000 0x4003.2FFF Timer2 183
0x4003.C000 0x4003.CFFF Analog Comparators 353
0x4004.8000 0x4004.8FFF Ethernet Controller 317
0x400F.D000 0x400F.DFFF Flash control 111
0x400F.E000 0x400F.EFFF System control 59
0x4200.0000 0x43FF.FFFF Bit-banded alias of 0x4000.0000 through 0x400F.FFFF -
Private Peripheral Bus
November 30, 2007 37
Preliminary
LM3S6110 Microcontroller
For details on
registers, see
page ...
Start End Description
ARM®
Cortex™-M3
Technical
Reference
Manual
0xE000.0000 0xE000.0FFF Instrumentation Trace Macrocell (ITM)
0xE000.1000 0xE000.1FFF Data Watchpoint and Trace (DWT)
0xE000.2000 0xE000.2FFF Flash Patch and Breakpoint (FPB)
0xE000.3000 0xE000.DFFF Reserved
0xE000.E000 0xE000.EFFF Nested Vectored Interrupt Controller (NVIC)
0xE000.F000 0xE003.FFFF Reserved
0xE004.0000 0xE004.0FFF Trace Port Interface Unit (TPIU)
0xE004.1000 0xE004.1FFF Reserved -
0xE004.2000 0xE00F.FFFF Reserved -
0xE010.0000 0xFFFF.FFFF Reserved for vendor peripherals -
a. All reserved space returns a bus fault when read or written.
b. The unavailable flash will bus fault throughout this range.
c. The unavailable SRAM will bus fault throughout this range.
38 November 30, 2007
Preliminary
Memory Map
4 Interrupts
The ARM Cortex-M3 processor and the Nested Vectored Interrupt Controller (NVIC) prioritize and
handle all exceptions. All exceptions are handled in Handler Mode. The processor state is
automatically stored to the stack on an exception, and automatically restored from the stack at the
end of the Interrupt Service Routine (ISR). The vector is fetched in parallel to the state saving, which
enables efficient interrupt entry. The processor supports tail-chaining, which enables back-to-back
interrupts to be performed without the overhead of state saving and restoration.
Table 4-1 on page 39 lists all the exceptions. Software can set eight priority levels on seven of these
exceptions (system handlers) as well as on 24 interrupts (listed in Table 4-2 on page 40).
Priorities on the system handlers are set with the NVIC System Handler Priority registers. Interrupts
are enabled through the NVIC Interrupt Set Enable register and prioritized with the NVIC Interrupt
Priority registers. You can also group priorities by splitting priority levels into pre-emption priorities
and subpriorities. All the interrupt registers are described in Chapter 8, “Nested Vectored Interrupt
Controller” in the ARM® Cortex™-M3 Technical Reference Manual.
Internally, the highest user-settable priority (0) is treated as fourth priority, after a Reset, NMI, and
a Hard Fault. Note that 0 is the default priority for all the settable priorities.
If you assign the same priority level to two or more interrupts, their hardware priority (the lower the
position number) determines the order in which the processor activates them. For example, if both
GPIO Port A and GPIO Port B are priority level 1, then GPIO Port A has higher priority.
See Chapter 5, “Exceptions” and Chapter 8, “Nested Vectored Interrupt Controller” in the ARM®
Cortex™-M3 Technical Reference Manual for more information on exceptions and interrupts.
Note: In Table 4-2 on page 40 interrupts not listed are reserved.
Table 4-1. Exception Types
Exception Type Position Prioritya Description
- 0 - Stack top is loaded from first entry of vector table on reset.
Invoked on power up and warm reset. On first instruction, drops to lowest
priority (and then is called the base level of activation). This is
asynchronous.
Reset 1 -3 (highest)
Cannot be stopped or preempted by any exception but reset. This is
asynchronous.
An NMI is only producible by software, using the NVIC Interrupt Control
State register.
Non-Maskable 2 -2
Interrupt (NMI)
All classes of Fault, when the fault cannot activate due to priority or the
configurable fault handler has been disabled. This is synchronous.
Hard Fault 3 -1
MPU mismatch, including access violation and no match. This is
synchronous.
The priority of this exception can be changed.
Memory Management 4 settable
Pre-fetch fault, memory access fault, and other address/memory related
faults. This is synchronous when precise and asynchronous when
imprecise.
You can enable or disable this fault.
Bus Fault 5 settable
Usage fault, such as undefined instruction executed or illegal state
transition attempt. This is synchronous.
Usage Fault 6 settable
- 7-10 - Reserved.
SVCall 11 settable System service call with SVC instruction. This is synchronous.
November 30, 2007 39
Preliminary
LM3S6110 Microcontroller
Exception Type Position Prioritya Description
Debug monitor (when not halting). This is synchronous, but only active
when enabled. It does not activate if lower priority than the current
activation.
Debug Monitor 12 settable
- 13 - Reserved.
Pendable request for system service. This is asynchronous and only
pended by software.
PendSV 14 settable
SysTick 15 settable System tick timer has fired. This is asynchronous.
Asserted from outside the ARM Cortex-M3 core and fed through the NVIC
(prioritized). These are all asynchronous. Table 4-2 on page 40 lists the
interrupts on the LM3S6110 controller.
16 and settable
above
Interrupts
a. 0 is the default priority for all the settable priorities.
Table 4-2. Interrupts
Interrupt (Bit in Interrupt Registers) Description
0 GPIO Port A
1 GPIO Port B
2 GPIO Port C
3 GPIO Port D
4 GPIO Port E
5 UART0
7 SSI0
9 PWM Fault
10 PWM Generator 0
18 Watchdog timer
19 Timer0 A
20 Timer0 B
21 Timer1 A
22 Timer1 B
23 Timer2 A
24 Timer2 B
25 Analog Comparator 0
26 Analog Comparator 1
27 Analog Comparator 2
28 System Control
29 Flash Control
30 GPIO Port F
31 GPIO Port G
42 Ethernet Controller
40 November 30, 2007
Preliminary
Interrupts
5 JTAG Interface
The Joint Test Action Group (JTAG) port is an IEEE standard that defines a Test Access Port and
Boundary Scan Architecture for digital integrated circuits and provides a standardized serial interface
for controlling the associated test logic. The TAP, Instruction Register (IR), and Data Registers (DR)
can be used to test the interconnections of assembled printed circuit boards and obtain manufacturing
information on the components. The JTAG Port also provides a means of accessing and controlling
design-for-test features such as I/O pin observation and control, scan testing, and debugging.
The JTAG port is comprised of the standard five pins: TRST, TCK, TMS, TDI, and TDO. Data is
transmitted serially into the controller on TDI and out of the controller on TDO. The interpretation of
this data is dependent on the current state of the TAP controller. For detailed information on the
operation of the JTAG port and TAP controller, please refer to the IEEE Standard 1149.1-Test
Access Port and Boundary-Scan Architecture.
The Luminary Micro JTAG controller works with the ARM JTAG controller built into the Cortex-M3
core. This is implemented by multiplexing the TDO outputs from both JTAG controllers. ARM JTAG
instructions select the ARM TDO output while Luminary Micro JTAG instructions select the Luminary
Micro TDO outputs. The multiplexer is controlled by the Luminary Micro JTAG controller, which has
comprehensive programming for the ARM, Luminary Micro, and unimplemented JTAG instructions.
The JTAG module has the following features:
■ IEEE 1149.1-1990 compatible Test Access Port (TAP) controller
■ Four-bit Instruction Register (IR) chain for storing JTAG instructions
■ IEEE standard instructions:
– BYPASS instruction
– IDCODE instruction
– SAMPLE/PRELOAD instruction
– EXTEST instruction
– INTEST instruction
■ ARM additional instructions:
– APACC instruction
– DPACC instruction
– ABORT instruction
■ Integrated ARM Serial Wire Debug (SWD)
See the ARM® Cortex™-M3 Technical Reference Manual for more information on the ARM JTAG
controller.
November 30, 2007 41
Preliminary
LM3S6110 Microcontroller
5.1 Block Diagram
Figure 5-1. JTAG Module Block Diagram
Instruction Register (IR)
TAP Controller
BYPASS Data Register
Boundary Scan Data Register
IDCODE Data Register
ABORT Data Register
DPACC Data Register
APACC Data Register
TRST
TCK
TMS
TDI
TDO
Cortex-M3
Debug
Port
5.2 Functional Description
A high-level conceptual drawing of the JTAG module is shown in Figure 5-1 on page 42. The JTAG
module is composed of the Test Access Port (TAP) controller and serial shift chains with parallel
update registers. The TAP controller is a simple state machine controlled by the TRST, TCK and
TMS inputs. The current state of the TAP controller depends on the current value of TRST and the
sequence of values captured on TMS at the rising edge of TCK. The TAP controller determines when
the serial shift chains capture new data, shift data from TDI towards TDO, and update the parallel
load registers. The current state of the TAP controller also determines whether the Instruction
Register (IR) chain or one of the Data Register (DR) chains is being accessed.
The serial shift chains with parallel load registers are comprised of a single Instruction Register (IR)
chain and multiple Data Register (DR) chains. The current instruction loaded in the parallel load
register determines which DR chain is captured, shifted, or updated during the sequencing of the
TAP controller.
Some instructions, like EXTEST and INTEST, operate on data currently in a DR chain and do not
capture, shift, or update any of the chains. Instructions that are not implemented decode to the
BYPASS instruction to ensure that the serial path between TDI and TDO is always connected (see
Table 5-2 on page 48 for a list of implemented instructions).
See “JTAG and Boundary Scan” on page 424 for JTAG timing diagrams.
42 November 30, 2007
Preliminary
JTAG Interface
5.2.1 JTAG Interface Pins
The JTAG interface consists of five standard pins: TRST, TCK, TMS, TDI, and TDO. These pins and
their associated reset state are given in Table 5-1 on page 43. Detailed information on each pin
follows.
Table 5-1. JTAG Port Pins Reset State
Pin Name Data Direction Internal Pull-Up Internal Pull-Down Drive Strength Drive Value
TRST Input Enabled Disabled N/A N/A
TCK Input Enabled Disabled N/A N/A
TMS Input Enabled Disabled N/A N/A
TDI Input Enabled Disabled N/A N/A
TDO Output Enabled Disabled 2-mA driver High-Z
5.2.1.1 Test Reset Input (TRST)
The TRST pin is an asynchronous active Low input signal for initializing and resetting the JTAG TAP
controller and associated JTAG circuitry. When TRST is asserted, the TAP controller resets to the
Test-Logic-Reset state and remains there while TRST is asserted. When the TAP controller enters
the Test-Logic-Reset state, the JTAG Instruction Register (IR) resets to the default instruction,
IDCODE.
By default, the internal pull-up resistor on the TRST pin is enabled after reset. Changes to the pull-up
resistor settings on GPIO Port B should ensure that the internal pull-up resistor remains enabled
on PB7/TRST; otherwise JTAG communication could be lost.
5.2.1.2 Test Clock Input (TCK)
The TCK pin is the clock for the JTAG module. This clock is provided so the test logic can operate
independently of any other system clocks. In addition, it ensures that multiple JTAG TAP controllers
that are daisy-chained together can synchronously communicate serial test data between
components. During normal operation, TCK is driven by a free-running clock with a nominal 50%
duty cycle. When necessary, TCK can be stopped at 0 or 1 for extended periods of time. While TCK
is stopped at 0 or 1, the state of the TAP controller does not change and data in the JTAG Instruction
and Data Registers is not lost.
By default, the internal pull-up resistor on the TCK pin is enabled after reset. This assures that no
clocking occurs if the pin is not driven from an external source. The internal pull-up and pull-down
resistors can be turned off to save internal power as long as the TCK pin is constantly being driven
by an external source.
5.2.1.3 Test Mode Select (TMS)
The TMS pin selects the next state of the JTAG TAP controller. TMS is sampled on the rising edge
of TCK. Depending on the current TAP state and the sampled value of TMS, the next state is entered.
Because the TMS pin is sampled on the rising edge of TCK, the IEEE Standard 1149.1 expects the
value on TMS to change on the falling edge of TCK.
Holding TMS high for five consecutive TCK cycles drives the TAP controller state machine to the
Test-Logic-Reset state. When the TAP controller enters the Test-Logic-Reset state, the JTAG
Instruction Register (IR) resets to the default instruction, IDCODE. Therefore, this sequence can
be used as a reset mechanism, similar to asserting TRST. The JTAG Test Access Port state machine
can be seen in its entirety in Figure 5-2 on page 45.
November 30, 2007 43
Preliminary
LM3S6110 Microcontroller
By default, the internal pull-up resistor on the TMS pin is enabled after reset. Changes to the pull-up
resistor settings on GPIO Port C should ensure that the internal pull-up resistor remains enabled
on PC1/TMS; otherwise JTAG communication could be lost.
5.2.1.4 Test Data Input (TDI)
The TDI pin provides a stream of serial information to the IR chain and the DR chains. TDI is
sampled on the rising edge of TCK and, depending on the current TAP state and the current
instruction, presents this data to the proper shift register chain. Because the TDI pin is sampled on
the rising edge of TCK, the IEEE Standard 1149.1 expects the value on TDI to change on the falling
edge of TCK.
By default, the internal pull-up resistor on the TDI pin is enabled after reset. Changes to the pull-up
resistor settings on GPIO Port C should ensure that the internal pull-up resistor remains enabled
on PC2/TDI; otherwise JTAG communication could be lost.
5.2.1.5 Test Data Output (TDO)
The TDO pin provides an output stream of serial information from the IR chain or the DR chains.
The value of TDO depends on the current TAP state, the current instruction, and the data in the
chain being accessed. In order to save power when the JTAG port is not being used, the TDO pin
is placed in an inactive drive state when not actively shifting out data. Because TDO can be connected
to the TDI of another controller in a daisy-chain configuration, the IEEE Standard 1149.1 expects
the value on TDO to change on the falling edge of TCK.
By default, the internal pull-up resistor on the TDO pin is enabled after reset. This assures that the
pin remains at a constant logic level when the JTAG port is not being used. The internal pull-up and
pull-down resistors can be turned off to save internal power if a High-Z output value is acceptable
during certain TAP controller states.
5.2.2 JTAG TAP Controller
The JTAG TAP controller state machine is shown in Figure 5-2 on page 45. The TAP controller
state machine is reset to the Test-Logic-Reset state on the assertion of a Power-On-Reset (POR)
or the assertion of TRST. Asserting the correct sequence on the TMS pin allows the JTAG module
to shift in new instructions, shift in data, or idle during extended testing sequences. For detailed
information on the function of the TAP controller and the operations that occur in each state, please
refer to IEEE Standard 1149.1.
44 November 30, 2007
Preliminary
JTAG Interface
Figure 5-2. Test Access Port State Machine
Test Logic Reset
Run Test Idle Select DR Scan Select IR Scan
Capture DR Capture IR
Shift DR Shift IR
Exit 1 DR Exit 1 IR
Exit 2 DR Exit 2 IR
Pause DR Pause IR
Update DR Update IR
1 1 1
1 1
1
1 1
1 1
1 1
1 1
1 0 1 0
0 0
0 0
0 0
0 0
0 0
0 0
0
0
5.2.3 Shift Registers
The Shift Registers consist of a serial shift register chain and a parallel load register. The serial shift
register chain samples specific information during the TAP controller’s CAPTURE states and allows
this information to be shifted out of TDO during the TAP controller’s SHIFT states. While the sampled
data is being shifted out of the chain on TDO, new data is being shifted into the serial shift register
on TDI. This new data is stored in the parallel load register during the TAP controller’s UPDATE
states. Each of the shift registers is discussed in detail in “Register Descriptions” on page 48.
5.2.4 Operational Considerations
There are certain operational considerations when using the JTAG module. Because the JTAG pins
can be programmed to be GPIOs, board configuration and reset conditions on these pins must be
considered. In addition, because the JTAG module has integrated ARM Serial Wire Debug, the
method for switching between these two operational modes is described below.
November 30, 2007 45
Preliminary
LM3S6110 Microcontroller
5.2.4.1 GPIO Functionality
When the controller is reset with either a POR or RST, the JTAG/SWD port pins default to their
JTAG/SWD configurations. The default configuration includes enabling digital functionality (setting
GPIODEN to 1), enabling the pull-up resistors (setting GPIOPUR to 1), and enabling the alternate
hardware function (setting GPIOAFSEL to 1) for the PB7 and PC[3:0] JTAG/SWD pins.
It is possible for software to configure these pins as GPIOs after reset by writing 0s to PB7 and
PC[3:0] in the GPIOAFSEL register. If the user does not require the JTAG/SWD port for debugging
or board-level testing, this provides five more GPIOs for use in the design.
Caution – If the JTAG pins are used as GPIOs in a design, PB7 and PC2 cannot have external pull-down
resistors connected to both of them at the same time. If both pins are pulled Low during reset, the
controller has unpredictable behavior. If this happens, remove one or both of the pull-down resistors,
and apply RST or power-cycle the part.
In addition, it is possible to create a software sequence that prevents the debugger from connecting to
the Stellaris® microcontroller. If the program code loaded into flash immediately changes the JTAG
pins to their GPIO functionality, the debugger may not have enough time to connect and halt the
controller before the JTAG pin functionality switches. This may lock the debugger out of the part. This
can be avoided with a software routine that restores JTAG functionality based on an external or software
trigger.
The commit control registers provide a layer of protection against accidental programming of critical
hardware peripherals. Writes to protected bits of the GPIO Alternate Function Select (GPIOAFSEL)
register (see page 147) are not committed to storage unless the GPIO Lock (GPIOLOCK) register
(see page 157) has been unlocked and the appropriate bits of the GPIO Commit (GPIOCR) register
(see page 158) have been set to 1.
Recovering a "Locked" Device
If software configures any of the JTAG/SWD pins as GPIO and loses the ability to communicate
with the debugger, there is a debug sequence that can be used to recover the device. Performing
a total of ten JTAG-to-SWD and SWD-to-JTAG switch sequences while holding the device in reset
mass erases the flash memory. The sequence to recover the device is:
1. Assert and hold the RST signal.
2. Perform the JTAG-to-SWD switch sequence.
3. Perform the SWD-to-JTAG switch sequence.
4. Perform the JTAG-to-SWD switch sequence.
5. Perform the SWD-to-JTAG switch sequence.
6. Perform the JTAG-to-SWD switch sequence.
7. Perform the SWD-to-JTAG switch sequence.
8. Perform the JTAG-to-SWD switch sequence.
9. Perform the SWD-to-JTAG switch sequence.
10. Perform the JTAG-to-SWD switch sequence.
11. Perform the SWD-to-JTAG switch sequence.
46 November 30, 2007
Preliminary
JTAG Interface
12. Release the RST signal.
The JTAG-to-SWD and SWD-to-JTAG switch sequences are described in “ARM Serial Wire Debug
(SWD)” on page 47. When performing switch sequences for the purpose of recovering the debug
capabilities of the device, only steps 1 and 2 of the switch sequence need to be performed.
5.2.4.2 ARM Serial Wire Debug (SWD)
In order to seamlessly integrate the ARM Serial Wire Debug (SWD) functionality, a serial-wire
debugger must be able to connect to the Cortex-M3 core without having to perform, or have any
knowledge of, JTAG cycles. This is accomplished with a SWD preamble that is issued before the
SWD session begins.
The preamble used to enable the SWD interface of the SWJ-DP module starts with the TAP controller
in the Test-Logic-Reset state. From here, the preamble sequences the TAP controller through the
following states: Run Test Idle, Select DR, Select IR, Test Logic Reset, Test Logic Reset, Run Test
Idle, Run Test Idle, Select DR, Select IR, Test Logic Reset, Test Logic Reset, Run Test Idle, Run
Test Idle, Select DR, Select IR, and Test Logic Reset states.
Stepping through this sequences of the TAP state machine enables the SWD interface and disables
the JTAG interface. For more information on this operation and the SWD interface, see the ARM®
Cortex™-M3 Technical Reference Manual and the ARM® CoreSight Technical Reference Manual.
Because this sequence is a valid series of JTAG operations that could be issued, the ARM JTAG
TAP controller is not fully compliant to the IEEE Standard 1149.1. This is the only instance where
the ARM JTAG TAP controller does not meet full compliance with the specification. Due to the low
probability of this sequence occurring during normal operation of the TAP controller, it should not
affect normal performance of the JTAG interface.
JTAG-to-SWD Switching
To switch the operating mode of the Debug Access Port (DAP) from JTAG to SWD mode, the
external debug hardware must send a switch sequence to the device. The 16-bit switch sequence
for switching to SWD mode is defined as b1110011110011110, transmitted LSB first. This can also
be represented as 16'hE79E when transmitted LSB first. The complete switch sequence should
consist of the following transactions on the TCK/SWCLK and TMS/SWDIO signals:
1. Send at least 50 TCK/SWCLK cycles with TMS/SWDIO set to 1. This ensures that both JTAG and
SWD are in their reset/idle states.
2. Send the 16-bit JTAG-to-SWD switch sequence, 16'hE79E.
3. Send at least 50 TCK/SWCLK cycles with TMS/SWDIO set to 1. This ensures that if SWJ-DP was
already in SWD mode, before sending the switch sequence, the SWD goes into the line reset
state.
SWD-to-JTAG Switching
To switch the operating mode of the Debug Access Port (DAP) from SWD to JTAG mode, the
external debug hardware must send a switch sequence to the device. The 16-bit switch sequence
for switching to JTAG mode is defined as b1110011110011110, transmitted LSB first. This can also
be represented as 16'hE73C when transmitted LSB first. The complete switch sequence should
consist of the following transactions on the TCK/SWCLK and TMS/SWDIO signals:
1. Send at least 50 TCK/SWCLK cycles with TMS/SWDIO set to 1. This ensures that both JTAG and
SWD are in their reset/idle states.
November 30, 2007 47
Preliminary
LM3S6110 Microcontroller
2. Send the 16-bit SWD-to-JTAG switch sequence, 16'hE73C.
3. Send at least 5 TCK/SWCLK cycles with TMS/SWDIO set to 1. This ensures that if SWJ-DP was
already in JTAG mode, before sending the switch sequence, the JTAG goes into the Test Logic
Reset state.
5.3 Initialization and Configuration
After a Power-On-Reset or an external reset (RST), the JTAG pins are automatically configured for
JTAG communication. No user-defined initialization or configuration is needed. However, if the user
application changes these pins to their GPIO function, they must be configured back to their JTAG
functionality before JTAG communication can be restored. This is done by enabling the five JTAG
pins (PB7 and PC[3:0]) for their alternate function using the GPIOAFSEL register.
5.4 Register Descriptions
There are no APB-accessible registers in the JTAG TAP Controller or Shift Register chains. The
registers within the JTAG controller are all accessed serially through the TAP Controller. The registers
can be broken down into two main categories: Instruction Registers and Data Registers.
5.4.1 Instruction Register (IR)
The JTAG TAP Instruction Register (IR) is a four-bit serial scan chain with a parallel load register
connected between the JTAG TDI and TDO pins. When the TAP Controller is placed in the correct
states, bits can be shifted into the Instruction Register. Once these bits have been shifted into the
chain and updated, they are interpreted as the current instruction. The decode of the Instruction
Register bits is shown in Table 5-2 on page 48. A detailed explanation of each instruction, along
with its associated Data Register, follows.
Table 5-2. JTAG Instruction Register Commands
IR[3:0] Instruction Description
Drives the values preloaded into the Boundary Scan Chain by the SAMPLE/PRELOAD
instruction onto the pads.
0000 EXTEST
Drives the values preloaded into the Boundary Scan Chain by the SAMPLE/PRELOAD
instruction into the controller.
0001 INTEST
Captures the current I/O values and shifts the sampled values out of the Boundary Scan
Chain while new preload data is shifted in.
0010 SAMPLE / PRELOAD
1000 ABORT Shifts data into the ARM Debug Port Abort Register.
1010 DPACC Shifts data into and out of the ARM DP Access Register.
1011 APACC Shifts data into and out of the ARM AC Access Register.
Loads manufacturing information defined by the IEEE Standard 1149.1 into the IDCODE
chain and shifts it out.
1110 IDCODE
1111 BYPASS Connects TDI to TDO through a single Shift Register chain.
All Others Reserved Defaults to the BYPASS instruction to ensure that TDI is always connected to TDO.
5.4.1.1 EXTEST Instruction
The EXTEST instruction does not have an associated Data Register chain. The EXTEST instruction
uses the data that has been preloaded into the Boundary Scan Data Register using the
SAMPLE/PRELOAD instruction. When the EXTEST instruction is present in the Instruction Register,
the preloaded data in the Boundary Scan Data Register associated with the outputs and output
enables are used to drive the GPIO pads rather than the signals coming from the core. This allows
48 November 30, 2007
Preliminary
JTAG Interface
tests to be developed that drive known values out of the controller, which can be used to verify
connectivity.
5.4.1.2 INTEST Instruction
The INTEST instruction does not have an associated Data Register chain. The INTEST instruction
uses the data that has been preloaded into the Boundary Scan Data Register using the
SAMPLE/PRELOAD instruction. When the INTEST instruction is present in the Instruction Register,
the preloaded data in the Boundary Scan Data Register associated with the inputs are used to drive
the signals going into the core rather than the signals coming from the GPIO pads. This allows tests
to be developed that drive known values into the controller, which can be used for testing. It is
important to note that although the RST input pin is on the Boundary Scan Data Register chain, it
is only observable.
5.4.1.3 SAMPLE/PRELOAD Instruction
The SAMPLE/PRELOAD instruction connects the Boundary Scan Data Register chain between
TDI and TDO. This instruction samples the current state of the pad pins for observation and preloads
new test data. Each GPIO pad has an associated input, output, and output enable signal. When the
TAP controller enters the Capture DR state during this instruction, the input, output, and output-enable
signals to each of the GPIO pads are captured. These samples are serially shifted out of TDO while
the TAP controller is in the Shift DR state and can be used for observation or comparison in various
tests.
While these samples of the inputs, outputs, and output enables are being shifted out of the Boundary
Scan Data Register, new data is being shifted into the Boundary Scan Data Register from TDI.
Once the new data has been shifted into the Boundary Scan Data Register, the data is saved in the
parallel load registers when the TAP controller enters the Update DR state. This update of the
parallel load register preloads data into the Boundary Scan Data Register that is associated with
each input, output, and output enable. This preloaded data can be used with the EXTEST and
INTEST instructions to drive data into or out of the controller. Please see “Boundary Scan Data
Register” on page 51 for more information.
5.4.1.4 ABORT Instruction
The ABORT instruction connects the associated ABORT Data Register chain between TDI and
TDO. This instruction provides read and write access to the ABORT Register of the ARM Debug
Access Port (DAP). Shifting the proper data into this Data Register clears various error bits or initiates
a DAP abort of a previous request. Please see the “ABORT Data Register” on page 51 for more
information.
5.4.1.5 DPACC Instruction
The DPACC instruction connects the associated DPACC Data Register chain between TDI and
TDO. This instruction provides read and write access to the DPACC Register of the ARM Debug
Access Port (DAP). Shifting the proper data into this register and reading the data output from this
register allows read and write access to the ARM debug and status registers. Please see “DPACC
Data Register” on page 51 for more information.
5.4.1.6 APACC Instruction
The APACC instruction connects the associated APACC Data Register chain between TDI and
TDO. This instruction provides read and write access to the APACC Register of the ARM Debug
Access Port (DAP). Shifting the proper data into this register and reading the data output from this
register allows read and write access to internal components and buses through the Debug Port.
Please see “APACC Data Register” on page 51 for more information.
November 30, 2007 49
Preliminary
LM3S6110 Microcontroller
5.4.1.7 IDCODE Instruction
The IDCODE instruction connects the associated IDCODE Data Register chain between TDI and
TDO. This instruction provides information on the manufacturer, part number, and version of the
ARM core. This information can be used by testing equipment and debuggers to automatically
configure their input and output data streams. IDCODE is the default instruction that is loaded into
the JTAG Instruction Register when a power-on-reset (POR) is asserted, TRST is asserted, or the
Test-Logic-Reset state is entered. Please see “IDCODE Data Register” on page 50 for more
information.
5.4.1.8 BYPASS Instruction
The BYPASS instruction connects the associated BYPASS Data Register chain between TDI and
TDO. This instruction is used to create a minimum length serial path between the TDI and TDO ports.
The BYPASS Data Register is a single-bit shift register. This instruction improves test efficiency by
allowing components that are not needed for a specific test to be bypassed in the JTAG scan chain
by loading them with the BYPASS instruction. Please see “BYPASS Data Register” on page 50 for
more information.
5.4.2 Data Registers
The JTAG module contains six Data Registers. These include: IDCODE, BYPASS, Boundary Scan,
APACC, DPACC, and ABORT serial Data Register chains. Each of these Data Registers is discussed
in the following sections.
5.4.2.1 IDCODE Data Register
The format for the 32-bit IDCODE Data Register defined by the IEEE Standard 1149.1 is shown in
Figure 5-3 on page 50. The standard requires that every JTAG-compliant device implement either
the IDCODE instruction or the BYPASS instruction as the default instruction. The LSB of the IDCODE
Data Register is defined to be a 1 to distinguish it from the BYPASS instruction, which has an LSB
of 0. This allows auto configuration test tools to determine which instruction is the default instruction.
The major uses of the JTAG port are for manufacturer testing of component assembly, and program
development and debug. To facilitate the use of auto-configuration debug tools, the IDCODE
instruction outputs a value of 0x3BA00477. This value indicates an ARM Cortex-M3, Version 1
processor. This allows the debuggers to automatically configure themselves to work correctly with
the Cortex-M3 during debug.
Figure 5-3. IDCODE Register Format
5.4.2.2 BYPASS Data Register
The format for the 1-bit BYPASS Data Register defined by the IEEE Standard 1149.1 is shown in
Figure 5-4 on page 51. The standard requires that every JTAG-compliant device implement either
the BYPASS instruction or the IDCODE instruction as the default instruction. The LSB of the BYPASS
Data Register is defined to be a 0 to distinguish it from the IDCODE instruction, which has an LSB
of 1. This allows auto configuration test tools to determine which instruction is the default instruction.
50 November 30, 2007
Preliminary
JTAG Interface
Figure 5-4. BYPASS Register Format
5.4.2.3 Boundary Scan Data Register
The format of the Boundary Scan Data Register is shown in Figure 5-5 on page 51. Each GPIO
pin, in a counter-clockwise direction from the JTAG port pins, is included in the Boundary Scan Data
Register. Each GPIO pin has three associated digital signals that are included in the chain. These
signals are input, output, and output enable, and are arranged in that order as can be seen in the
figure. In addition to the GPIO pins, the controller reset pin, RST, is included in the chain. Because
the reset pin is always an input, only the input signal is included in the Data Register chain.
When the Boundary Scan Data Register is accessed with the SAMPLE/PRELOAD instruction, the
input, output, and output enable from each digital pad are sampled and then shifted out of the chain
to be verified. The sampling of these values occurs on the rising edge of TCK in the Capture DR
state of the TAP controller. While the sampled data is being shifted out of the Boundary Scan chain
in the Shift DR state of the TAP controller, new data can be preloaded into the chain for use with
the EXTEST and INTEST instructions. These instructions either force data out of the controller, with
the EXTEST instruction, or into the controller, with the INTEST instruction.
Figure 5-5. Boundary Scan Register Format
O TDO TDI O IN
E UT
O O IN
U E
T
O O IN
E UT
O O IN
U E
T
I
N ... ...
GPIO PB6 GPIO m RST GPIO m+1 GPIO n
For detailed information on the order of the input, output, and output enable bits for each of the
GPIO ports, please refer to the Stellaris® Family Boundary Scan Description Language (BSDL) files,
downloadable from www.luminarymicro.com.
5.4.2.4 APACC Data Register
The format for the 35-bit APACC Data Register defined by ARM is described in the ARM®
Cortex™-M3 Technical Reference Manual.
5.4.2.5 DPACC Data Register
The format for the 35-bit DPACC Data Register defined by ARM is described in the ARM®
Cortex™-M3 Technical Reference Manual.
5.4.2.6 ABORT Data Register
The format for the 35-bit ABORT Data Register defined by ARM is described in the ARM®
Cortex™-M3 Technical Reference Manual.
November 30, 2007 51
Preliminary
LM3S6110 Microcontroller
6 System Control
System control determines the overall operation of the device. It provides information about the
device, controls the clocking to the core and individual peripherals, and handles reset detection and
reporting.
6.1 Functional Description
The System Control module provides the following capabilities:
■ Device identification, see “Device Identification” on page 52
■ Local control, such as reset (see “Reset Control” on page 52), power (see “Power
Control” on page 55) and clock control (see “Clock Control” on page 55)
■ System control (Run, Sleep, and Deep-Sleep modes), see “System Control” on page 57
6.1.1 Device Identification
Seven read-only registers provide software with information on the microcontroller, such as version,
part number, SRAM size, flash size, and other features. See the DID0, DID1, and DC0-DC4 registers.
6.1.2 Reset Control
This section discusses aspects of hardware functions during reset as well as system software
requirements following the reset sequence.
6.1.2.1 CMOD0 and CMOD1 Test-Mode Control Pins
Two pins, CMOD0 and CMOD1, are defined for use by Luminary Micro for testing the devices during
manufacture. They have no end-user function and should not be used. The CMOD pins should be
connected to ground.
6.1.2.2 Reset Sources
The controller has five sources of reset:
1. External reset input pin (RST) assertion, see “RST Pin Assertion” on page 52.
2. Power-on reset (POR), see “Power-On Reset (POR)” on page 53.
3. Internal brown-out (BOR) detector, see “Brown-Out Reset (BOR)” on page 53.
4. Software-initiated reset (with the software reset registers), see “Software Reset” on page 54.
5. A watchdog timer reset condition violation, see “Watchdog Timer Reset” on page 54.
After a reset, the Reset Cause (RESC) register is set with the reset cause. The bits in this register
are sticky and maintain their state across multiple reset sequences, except when an internal POR
is the cause, and then all the other bits in the RESC register are cleared except for the POR indicator.
6.1.2.3 RST Pin Assertion
The external reset pin (RST) resets the controller. This resets the core and all the peripherals except
the JTAG TAP controller (see “JTAG Interface” on page 41). The external reset sequence is as
follows:
52 November 30, 2007
Preliminary
System Control
1. The external reset pin (RST) is asserted and then de-asserted.
2. The internal reset is released and the core loads from memory the initial stack pointer, the initial
program counter, the first instruction designated by the program counter, and begins execution.
A few clocks cycles from RST de-assertion to the start of the reset sequence is necessary for
synchronization.
The external reset timing is shown in Figure 19-9 on page 426.
6.1.2.4 Power-On Reset (POR)
The Power-On Reset (POR) circuit monitors the power supply voltage (VDD). The POR circuit
generates a reset signal to the internal logic when the power supply ramp reaches a threshold value
(VTH). If the application only uses the POR circuit, the RST input needs to be connected to the power
supply (VDD) through a pull-up resistor (1K to 10K Ω).
The device must be operating within the specified operating parameters at the point when the on-chip
power-on reset pulse is complete. The 3.3-V power supply to the device must reach 3.0 V within
10 msec of it crossing 2.0 V to guarantee proper operation. For applications that require the use of
an external reset to hold the device in reset longer than the internal POR, the RST input may be
used with the circuit as shown in Figure 6-1 on page 53.
Figure 6-1. External Circuitry to Extend Reset
R1
C1
R2
RST
Stellaris
D1
The R1 and C1 components define the power-on delay. The R2 resistor mitigates any leakage from
the RST input. The diode (D1) discharges C1 rapidly when the power supply is turned off.
The Power-On Reset sequence is as follows:
1. The controller waits for the later of external reset (RST) or internal POR to go inactive.
2. The internal reset is released and the core loads from memory the initial stack pointer, the initial
program counter, the first instruction designated by the program counter, and begins execution.
The internal POR is only active on the initial power-up of the controller. The Power-On Reset timing
is shown in Figure 19-10 on page 427.
Note: The power-on reset also resets the JTAG controller. An external reset does not.
6.1.2.5 Brown-Out Reset (BOR)
A drop in the input voltage resulting in the assertion of the internal brown-out detector can be used
to reset the controller. This is initially disabled and may be enabled by software.
The system provides a brown-out detection circuit that triggers if the power supply (VDD) drops
below a brown-out threshold voltage (VBTH). If a brown-out condition is detected, the system may
generate a controller interrupt or a system reset.
November 30, 2007 53
Preliminary
LM3S6110 Microcontroller
Brown-out resets are controlled with the Power-On and Brown-Out Reset Control (PBORCTL)
register. The BORIOR bit in the PBORCTL register must be set for a brown-out condition to trigger
a reset.
The brown-out reset is equivelent to an assertion of the external RST input and the reset is held
active until the proper VDD level is restored. The RESC register can be examined in the reset interrupt
handler to determine if a Brown-Out condition was the cause of the reset, thus allowing software to
determine what actions are required to recover.
The internal Brown-Out Reset timing is shown in Figure 19-11 on page 427.
6.1.2.6 Software Reset
Software can reset a specific peripheral or generate a reset to the entire system .
Peripherals can be individually reset by software via three registers that control reset signals to each
peripheral (see the SRCRn registers). If the bit position corresponding to a peripheral is set and
subsequently cleared, the peripheral is reset. The encoding of the reset registers is consistent with
the encoding of the clock gating control for peripherals and on-chip functions (see “System
Control” on page 57). Note that all reset signals for all clocks of the specified unit are asserted as
a result of a software-initiated reset.
The entire system can be reset by software by setting the SYSRESETREQ bit in the Cortex-M3
Application Interrupt and Reset Control register resets the entire system including the core. The
software-initiated system reset sequence is as follows:
1. A software system reset is initiated by writing the SYSRESETREQ bit in the ARM Cortex-M3
Application Interrupt and Reset Control register.
2. An internal reset is asserted.
3. The internal reset is deasserted and the controller loads from memory the initial stack pointer,
the initial program counter, and the first instruction designated by the program counter, and
then begins execution.
The software-initiated system reset timing is shown in Figure 19-12 on page 427.
6.1.2.7 Watchdog Timer Reset
The watchdog timer module's function is to prevent system hangs. The watchdog timer can be
configured to generate an interrupt to the controller on its first time-out, and to generate a reset
signal on its second time-out.
After the first time-out event, the 32-bit counter is reloaded with the value of the Watchdog Timer
Load (WDTLOAD) register, and the timer resumes counting down from that value. If the timer counts
down to its zero state again before the first time-out interrupt is cleared, and the reset signal has
been enabled, the watchdog timer asserts its reset signal to the system. The watchdog timer reset
sequence is as follows:
1. The watchdog timer times out for the second time without being serviced.
2. An internal reset is asserted.
3. The internal reset is released and the controller loads from memory the initial stack pointer, the
initial program counter, the first instruction designated by the program counter, and begins
execution.
54 November 30, 2007
Preliminary
System Control
The watchdog reset timing is shown in Figure 19-13 on page 427.
6.1.3 Power Control
The Stellaris® microcontroller provides an integrated LDO regulator that may be used to provide
power to the majority of the controller's internal logic. The LDO regulator provides software a
mechanism to adjust the regulated value, in small increments (VSTEP), over the range of 2.25 V
to 2.75 V (inclusive)—or 2.5 V ± 10%. The adjustment is made by changing the value of the VADJ
field in the LDO Power Control (LDOPCTL) register.
Note: The use of the LDO is optional. The internal logic may be supplied by the on-chip LDO or
by an external regulator. If the LDO is used, the LDO output pin is connected to the VDD25
pins on the printed circuit board. The LDO requires decoupling capacitors on the printed
circuit board. If an external regulator is used, it is strongly recommended that the external
regulator supply the controller only and not be shared with other devices on the printed
circuit board.
6.1.4 Clock Control
System control determines the control of clocks in this part.
6.1.4.1 Fundamental Clock Sources
There are four clock sources for use in the device:
■ Internal Oscillator (IOSC): The internal oscillator is an on-chip clock source. It does not require
the use of any external components. The frequency of the internal oscillator is 12 MHz ± 30%.
Applications that do not depend on accurate clock sources may use this clock source to reduce
system cost. The internal oscillator is the clock source the device uses during and following POR.
If the main oscillator is required, software must enable the main oscillator following reset and
allow the main oscillator to stabilize before changing the clock reference.
■ Main Oscillator: The main oscillator provides a frequency-accurate clock source by one of two
means: an external single-ended clock source is connected to the OSC0 input pin, or an external
crystal is connected across the OSC0 input and OSC1 output pins. The crystal value allowed
depends on whether the main oscillator is used as the clock reference source to the PLL. If so,
the crystal must be one of the supported frequencies between 3.579545 MHz through 8.192
MHz (inclusive). If the PLL is not being used, the crystal may be any one of the supported
frequencies between 1 MHz and 8.192 MHz. The single-ended clock source range is from DC
through the specified speed of the device. The supported crystals are listed in the XTAL bit in
the RCC register (see page 68).
■ Internal 30-kHz Oscillator: The internal 30-kHz oscillator is similar to the internal oscillator,
except that it provides an operational frequency of 30 kHz ± 30%. It is intended for use during
Deep-Sleep power-saving modes. This power-savings mode benefits from reduced internal
switching and also allows the main oscillator to be powered down.
The internal system clock (sysclk), is derived from any of the four sources plus two others: the output
of the internal PLL, and the internal oscillator divided by four (3 MHz ± 30%). The frequency of the
PLL clock reference must be in the range of 3.579545 MHz to 8.192 MHz (inclusive).
The Run-Mode Clock Configuration (RCC) and Run-Mode Clock Configuration 2 (RCC2)
registers provide control for the system clock. The RCC2 register is provided to extend fields that
offer additional encodings over the RCC register. When used, the RCC2 register field values are
November 30, 2007 55
Preliminary
LM3S6110 Microcontroller
used by the logic over the corresponding field in the RCC register. In particular, RCC2 provides for
a larger assortment of clock configuration options.
6.1.4.2 Crystal Configuration for the Main Oscillator (MOSC)
The main oscillator supports the use of a select number of crystals. If the main oscillator is used by
the PLL as a reference clock, the supported range of crystals is 3.579545 to 8.192 MHz, otherwise,
the range of supported crystals is 1 to 8.192 MHz.
The XTAL bit in the RCC register (see page 68) describes the available crystal choices and default
programming values.
Software configures the RCC register XTAL field with the crystal number. If the PLL is used in the
design, the XTAL field value is internally translated to the PLL settings.
6.1.4.3 PLL Frequency Configuration
The PLL is disabled by default during power-on reset and is enabled later by software if required.
Software configures the PLL input reference clock source, specifies the output divisor to set the
system clock frequency, and enables the PLL to drive the output.
If the main oscillator provides the clock reference to the PLL, the translation provided by hardware
and used to program the PLL is available for software in the XTAL to PLL Translation (PLLCFG)
register (see page 72). The internal translation provides a translation within ± 1% of the targeted
PLL VCO frequency.
The Crystal Value field (XTAL) on page 68 describes the available crystal choices and default
programming of the PLLCFG register. The crystal number is written into the XTAL field of the
Run-Mode Clock Configuration (RCC) register. Any time the XTAL field changes, the new settings
are translated and the internal PLL settings are updated.
6.1.4.4 PLL Modes
The PLL has two modes of operation: Normal and Power-Down
■ Normal: The PLL multiplies the input clock reference and drives the output.
■ Power-Down: Most of the PLL internal circuitry is disabled and the PLL does not drive the output.
The modes are programmed using the RCC/RCC2 register fields (see page 68 and page 73).
6.1.4.5 PLL Operation
If the PLL configuration is changed, the PLL output frequency is unstable until it reconverges (relocks)
to the new setting. The time between the configuration change and relock is TREADY (see Table
19-6 on page 418). During this time, the PLL is not usable as a clock reference.
The PLL is changed by one of the following:
■ Change to the XTAL value in the RCC register—writes of the same value do not cause a relock.
■ Change in the PLL from Power-Down to Normal mode.
A counter is defined to measure the TREADY requirement. The counter is clocked by the main
oscillator. The range of the main oscillator has been taken into account and the down counter is set
to 0x1200 (that is, ~600 μs at an 8.192 MHz external oscillator clock). . Hardware is provided to
keep the PLL from being used as a system clock until the TREADY condition is met after one of the
56 November 30, 2007
Preliminary
System Control
two changes above. It is the user's responsibility to have a stable clock source (like the main oscillator)
before the RCC/RCC2 register is switched to use the PLL.
6.1.5 System Control
For power-savings purposes, the RCGCn , SCGCn , and DCGCn registers control the clock gating
logic for each peripheral or block in the system while the controller is in Run, Sleep, and Deep-Sleep
mode, respectively.
In Run mode, the processor executes code. In Sleep mode, the clock frequency of the active
peripherals is unchanged, but the processor is not clocked and therefore no longer executes code.
In Deep-Sleep mode, the clock frequency of the active peripherals may change (depending on the
Run mode clock configuration) in addition to the processor clock being stopped. An interrupt returns
the device to Run mode from one of the sleep modes; the sleep modes are entered on request from
the code. Each mode is described in more detail below.
There are four levels of operation for the device defined as:
■ Run Mode. Run mode provides normal operation of the processor and all of the peripherals that
are currently enabled by the RCGCn registers. The system clock can be any of the available
clock sources including the PLL.
■ Sleep Mode. Sleep mode is entered by the Cortex-M3 core executing a WFI (Wait for
Interrupt) instruction. Any properly configured interrupt event in the system will bring the
processor back into Run mode. See the system control NVIC section of the ARM® Cortex™-M3
Technical Reference Manual for more details.
In Sleep mode, the Cortex-M3 processor core and the memory subsystem are not clocked.
Peripherals are clocked that are enabled in the SCGCn register when auto-clock gating is enabled
(see the RCC register) or the RCGCn register when the auto-clock gating is disabled. The system
clock has the same source and frequency as that during Run mode.
■ Deep-Sleep Mode. Deep-Sleep mode is entered by first writing the Deep Sleep Enable bit in
the ARM Cortex-M3 NVIC system control register and then executing a WFI instruction. Any
properly configured interrupt event in the system will bring the processor back into Run mode.
See the system control NVIC section of the ARM® Cortex™-M3 Technical Reference Manual
for more details.
The Cortex-M3 processor core and the memory subsystem are not clocked. Peripherals are
clocked that are enabled in the DCGCn register when auto-clock gating is enabled (see the RCC
register) or the RCGCn register when auto-clock gating is disabled. The system clock source is
the main oscillator by default or the internal oscillator specified in the DSLPCLKCFG register if
one is enabled. When the DSLPCLKCFG register is used, the internal oscillator is powered up,
if necessary, and the main oscillator is powered down. If the PLL is running at the time of the
WFI instruction, hardware will power the PLL down and override the SYSDIV field of the active
RCC/RCC2 register to be /16 or /64, respectively. When the Deep-Sleep exit event occurs,
hardware brings the system clock back to the source and frequency it had at the onset of
Deep-Sleep mode before enabling the clocks that had been stopped during the Deep-Sleep
duration.
6.2 Initialization and Configuration
The PLL is configured using direct register writes to the RCC/RCC2 register. If the RCC2 register
is being used, the USERCC2 bit must be set and the appropriate RCC2 bit/field is used. The steps
required to successfully change the PLL-based system clock are:
November 30, 2007 57
Preliminary
LM3S6110 Microcontroller
1. Bypass the PLL and system clock divider by setting the BYPASS bit and clearing the USESYS
bit in the RCC register. This configures the system to run off a “raw” clock source (using the
main oscillator or internal oscillator) and allows for the new PLL configuration to be validated
before switching the system clock to the PLL.
2. Select the crystal value (XTAL) and oscillator source (OSCSRC), and clear the PWRDN bit in
RCC/RCC2. Setting the XTAL field automatically pulls valid PLL configuration data for the
appropriate crystal, and clearing the PWRDN bit powers and enables the PLL and its output.
3. Select the desired system divider (SYSDIV) in RCC/RCC2 and set the USESYS bit in RCC. The
SYSDIV field determines the system frequency for the microcontroller.
4. Wait for the PLL to lock by polling the PLLLRIS bit in the Raw Interrupt Status (RIS) register.
5. Enable use of the PLL by clearing the BYPASS bit in RCC/RCC2.
6.3 Register Map
Table 6-1 on page 58 lists the System Control registers, grouped by function. The offset listed is a
hexadecimal increment to the register’s address, relative to the System Control base address of
0x400F.E000.
Note: Spaces in the System Control register space that are not used are reserved for future or
internal use by Luminary Micro, Inc. Software should not modify any reserved memory
address.
Table 6-1. System Control Register Map
See
Offset Name Type Reset Description page
0x000 DID0 RO - Device Identification 0 60
0x004 DID1 RO - Device Identification 1 76
0x008 DC0 RO 0x003F.001F Device Capabilities 0 78
0x010 DC1 RO 0x0010.709F Device Capabilities 1 79
0x014 DC2 RO 0x0707.0011 Device Capabilities 2 81
0x018 DC3 RO 0x0F00.B7C3 Device Capabilities 3 83
0x01C DC4 RO 0x5000.007F Device Capabilities 4 85
0x030 PBORCTL R/W 0x0000.7FFD Brown-Out Reset Control 62
0x034 LDOPCTL R/W 0x0000.0000 LDO Power Control 63
0x040 SRCR0 R/W 0x00000000 Software Reset Control 0 102
0x044 SRCR1 R/W 0x00000000 Software Reset Control 1 103
0x048 SRCR2 R/W 0x00000000 Software Reset Control 2 105
0x050 RIS RO 0x0000.0000 Raw Interrupt Status 64
0x054 IMC R/W 0x0000.0000 Interrupt Mask Control 65
0x058 MISC R/W1C 0x0000.0000 Masked Interrupt Status and Clear 66
0x05C RESC R/W - Reset Cause 67
58 November 30, 2007
Preliminary
System Control
See
Offset Name Type Reset Description page
0x060 RCC R/W 0x07AE.3AD1 Run-Mode Clock Configuration 68
0x064 PLLCFG RO - XTAL to PLL Translation 72
0x070 RCC2 R/W 0x0780.2800 Run-Mode Clock Configuration 2 73
0x100 RCGC0 R/W 0x00000040 Run Mode Clock Gating Control Register 0 87
0x104 RCGC1 R/W 0x00000000 Run Mode Clock Gating Control Register 1 90
0x108 RCGC2 R/W 0x00000000 Run Mode Clock Gating Control Register 2 96
0x110 SCGC0 R/W 0x00000040 Sleep Mode Clock Gating Control Register 0 88
0x114 SCGC1 R/W 0x00000000 Sleep Mode Clock Gating Control Register 1 92
0x118 SCGC2 R/W 0x00000000 Sleep Mode Clock Gating Control Register 2 98
0x120 DCGC0 R/W 0x00000040 Deep Sleep Mode Clock Gating Control Register 0 89
0x124 DCGC1 R/W 0x00000000 Deep Sleep Mode Clock Gating Control Register 1 94
0x128 DCGC2 R/W 0x00000000 Deep Sleep Mode Clock Gating Control Register 2 100
0x144 DSLPCLKCFG R/W 0x0780.0000 Deep Sleep Clock Configuration 75
6.4 Register Descriptions
All addresses given are relative to the System Control base address of 0x400F.E000.
November 30, 2007 59
Preliminary
LM3S6110 Microcontroller
Register 1: Device Identification 0 (DID0), offset 0x000
This register identifies the version of the device.
Device Identification 0 (DID0)
Base 0x400F.E000
Offset 0x000
Type RO, reset -
31 30 29 28 27 26 25 24 23 22 21 20 19 18 17 16
reserved VER reserved CLASS
Type RO RO RO RO RO RO RO RO RO RO RO RO RO RO RO RO
Reset 0 0 0 1 0 0 0 0 0 0 0 0 0 0 0 1
15 14 13 12 11 10 9 8 7 6 5 4 3 2 1 0
MAJOR MINOR
Type RO RO RO RO RO RO RO RO RO RO RO RO RO RO RO RO
Reset - - - - - - - - - - - - - - - -
Bit/Field Name Type Reset Description
Software should not rely on the value of a reserved bit. To provide
compatibility with future products, the value of a reserved bit should be
preserved across a read-modify-write operation.
31 reserved RO 0
DID0 Version
This field defines the DID0 register format version. The version number
is numeric. The value of the VER field is encoded as follows:
Value Description
First revision of the DID0 register format, for Stellaris®
Fury-class devices .
0x1
30:28 VER RO 0x1
Software should not rely on the value of a reserved bit. To provide
compatibility with future products, the value of a reserved bit should be
preserved across a read-modify-write operation.
27:24 reserved RO 0x0
Device Class
The CLASS field value identifies the internal design from which all mask
sets are generated for all devices in a particular product line. The CLASS
field value is changed for new product lines, for changes in fab process
(for example, a remap or shrink), or any case where the MAJOR or MINOR
fields require differentiation from prior devices. The value of the CLASS
field is encoded as follows (all other encodings are reserved):
Value Description
0x0 Stellaris® Sandstorm-class devices.
0x1 Stellaris® Fury-class devices.
23:16 CLASS RO 0x1
60 November 30, 2007
Preliminary
System Control
Bit/Field Name Type Reset Description
Major Revision
This field specifies the major revision number of the device. The major
revision reflects changes to base layers of the design. The major revision
number is indicated in the part number as a letter (A for first revision, B
for second, and so on). This field is encoded as follows:
Value Description
0x0 Revision A (initial device)
0x1 Revision B (first base layer revision)
0x2 Revision C (second base layer revision)
and so on.
15:8 MAJOR RO -
Minor Revision
This field specifies the minor revision number of the device. The minor
revision reflects changes to the metal layers of the design. The MINOR
field value is reset when the MAJOR field is changed. This field is numeric
and is encoded as follows:
Value Description
0x0 Initial device, or a major revision update.
0x1 First metal layer change.
0x2 Second metal layer change.
and so on.
7:0 MINOR RO -
November 30, 2007 61
Preliminary
LM3S6110 Microcontroller
Register 2: Brown-Out Reset Control (PBORCTL), offset 0x030
This register is responsible for controlling reset conditions after initial power-on reset.
Brown-Out Reset Control (PBORCTL)
Base 0x400F.E000
Offset 0x030
Type R/W, reset 0x0000.7FFD
31 30 29 28 27 26 25 24 23 22 21 20 19 18 17 16
reserved
Type RO RO RO RO RO RO RO RO RO RO RO RO RO RO RO RO
Reset 0 0 0 0 0 0 0 0 0 0 0 0 0 0 0 0
15 14 13 12 11 10 9 8 7 6 5 4 3 2 1 0
reserved BORIOR reserved
Type RO RO RO RO RO RO RO RO RO RO RO RO RO RO R/W RO
Reset 0 0 0 0 0 0 0 0 0 0 0 0 0 0 0 0
Bit/Field Name Type Reset Description
Software should not rely on the value of a reserved bit. To provide
compatibility with future products, the value of a reserved bit should be
preserved across a read-modify-write operation.
31:2 reserved RO 0x0
BOR Interrupt or Reset
This bit controls how a BOR event is signaled to the controller. If set, a
reset is signaled. Otherwise, an interrupt is signaled.
1 BORIOR R/W 0
Software should not rely on the value of a reserved bit. To provide
compatibility with future products, the value of a reserved bit should be
preserved across a read-modify-write operation.
0 reserved RO 0
62 November 30, 2007
Preliminary
System Control
Register 3: LDO Power Control (LDOPCTL), offset 0x034
The VADJ field in this register adjusts the on-chip output voltage (VOUT).
LDO Power Control (LDOPCTL)
Base 0x400F.E000
Offset 0x034
Type R/W, reset 0x0000.0000
31 30 29 28 27 26 25 24 23 22 21 20 19 18 17 16
reserved
Type RO RO RO RO RO RO RO RO RO RO RO RO RO RO RO RO
Reset 0 0 0 0 0 0 0 0 0 0 0 0 0 0 0 0
15 14 13 12 11 10 9 8 7 6 5 4 3 2 1 0
reserved VADJ
Type RO RO RO RO RO RO RO RO RO RO R/W R/W R/W R/W R/W R/W
Reset 0 0 0 0 0 0 0 0 0 0 0 0 0 0 0 0
Bit/Field Name Type Reset Description
Software should not rely on the value of a reserved bit. To provide
compatibility with future products, the value of a reserved bit should be
preserved across a read-modify-write operation.
31:6 reserved RO 0
LDO Output Voltage
This field sets the on-chip output voltage. The programming values for
the VADJ field are provided below.
Value VOUT (V)
0x00 2.50
0x01 2.45
0x02 2.40
0x03 2.35
0x04 2.30
0x05 2.25
0x06-0x3F Reserved
0x1B 2.75
0x1C 2.70
0x1D 2.65
0x1E 2.60
0x1F 2.55
5:0 VADJ R/W 0x0
November 30, 2007 63
Preliminary
LM3S6110 Microcontroller
Register 4: Raw Interrupt Status (RIS), offset 0x050
Central location for system control raw interrupts. These are set and cleared by hardware.
Raw Interrupt Status (RIS)
Base 0x400F.E000
Offset 0x050
Type RO, reset 0x0000.0000
31 30 29 28 27 26 25 24 23 22 21 20 19 18 17 16
reserved
Type RO RO RO RO RO RO RO RO RO RO RO RO RO RO RO RO
Reset 0 0 0 0 0 0 0 0 0 0 0 0 0 0 0 0
15 14 13 12 11 10 9 8 7 6 5 4 3 2 1 0
reserved PLLLRIS reserved BORRIS reserved
Type RO RO RO RO RO RO RO RO RO RO RO RO RO RO RO RO
Reset 0 0 0 0 0 0 0 0 0 0 0 0 0 0 0 0
Bit/Field Name Type Reset Description
Software should not rely on the value of a reserved bit. To provide
compatibility with future products, the value of a reserved bit should be
preserved across a read-modify-write operation.
31:7 reserved RO 0
PLL Lock Raw Interrupt Status
This bit is set when the PLL TREADY Timer asserts.
6 PLLLRIS RO 0
Software should not rely on the value of a reserved bit. To provide
compatibility with future products, the value of a reserved bit should be
preserved across a read-modify-write operation.
5:2 reserved RO 0
Brown-Out Reset Raw Interrupt Status
This bit is the raw interrupt status for any brown-out conditions. If set,
a brown-out condition is currently active. This is an unregistered signal
from the brown-out detection circuit. An interrupt is reported if the BORIM
bit in the IMC register is set and the BORIOR bit in the PBORCTL register
is cleared.
1 BORRIS RO 0
Software should not rely on the value of a reserved bit. To provide
compatibility with future products, the value of a reserved bit should be
preserved across a read-modify-write operation.
0 reserved RO 0
64 November 30, 2007
Preliminary
System Control
Register 5: Interrupt Mask Control (IMC), offset 0x054
Central location for system control interrupt masks.
Interrupt Mask Control (IMC)
Base 0x400F.E000
Offset 0x054
Type R/W, reset 0x0000.0000
31 30 29 28 27 26 25 24 23 22 21 20 19 18 17 16
reserved
Type RO RO RO RO RO RO RO RO RO RO RO RO RO RO RO RO
Reset 0 0 0 0 0 0 0 0 0 0 0 0 0 0 0 0
15 14 13 12 11 10 9 8 7 6 5 4 3 2 1 0
reserved PLLLIM reserved BORIM reserved
Type RO RO RO RO RO RO RO RO RO R/W RO RO RO RO R/W RO
Reset 0 0 0 0 0 0 0 0 0 0 0 0 0 0 0 0
Bit/Field Name Type Reset Description
Software should not rely on the value of a reserved bit. To provide
compatibility with future products, the value of a reserved bit should be
preserved across a read-modify-write operation.
31:7 reserved RO 0
PLL Lock Interrupt Mask
This bit specifies whether a current limit detection is promoted to a
controller interrupt. If set, an interrupt is generated if PLLLRIS in RIS
is set; otherwise, an interrupt is not generated.
6 PLLLIM R/W 0
Software should not rely on the value of a reserved bit. To provide
compatibility with future products, the value of a reserved bit should be
preserved across a read-modify-write operation.
5:2 reserved RO 0
Brown-Out Reset Interrupt Mask
This bit specifies whether a brown-out condition is promoted to a
controller interrupt. If set, an interrupt is generated if BORRIS is set;
otherwise, an interrupt is not generated.
1 BORIM R/W 0
Software should not rely on the value of a reserved bit. To provide
compatibility with future products, the value of a reserved bit should be
preserved across a read-modify-write operation.
0 reserved RO 0
November 30, 2007 65
Preliminary
LM3S6110 Microcontroller
Register 6: Masked Interrupt Status and Clear (MISC), offset 0x058
Central location for system control result of RIS AND IMC to generate an interrupt to the controller.
All of the bits are R/W1C and this action also clears the corresponding raw interrupt bit in the RIS
register (see page 64).
Masked Interrupt Status and Clear (MISC)
Base 0x400F.E000
Offset 0x058
Type R/W1C, reset 0x0000.0000
31 30 29 28 27 26 25 24 23 22 21 20 19 18 17 16
reserved
Type RO RO RO RO RO RO RO RO RO RO RO RO RO RO RO RO
Reset 0 0 0 0 0 0 0 0 0 0 0 0 0 0 0 0
15 14 13 12 11 10 9 8 7 6 5 4 3 2 1 0
reserved PLLLMIS reserved BORMIS reserved
Type RO RO RO RO RO RO RO RO RO R/W1C RO RO RO RO R/W1C RO
Reset 0 0 0 0 0 0 0 0 0 0 0 0 0 0 0 0
Bit/Field Name Type Reset Description
Software should not rely on the value of a reserved bit. To provide
compatibility with future products, the value of a reserved bit should be
preserved across a read-modify-write operation.
31:7 reserved RO 0
PLL Lock Masked Interrupt Status
This bit is set when the PLL TREADY timer asserts. The interrupt is cleared
by writing a 1 to this bit.
6 PLLLMIS R/W1C 0
Software should not rely on the value of a reserved bit. To provide
compatibility with future products, the value of a reserved bit should be
preserved across a read-modify-write operation.
5:2 reserved RO 0
BOR Masked Interrupt Status
The BORMIS is simply the BORRIS ANDed with the mask value, BORIM.
1 BORMIS R/W1C 0
Software should not rely on the value of a reserved bit. To provide
compatibility with future products, the value of a reserved bit should be
preserved across a read-modify-write operation.
0 reserved RO 0
66 November 30, 2007
Preliminary
System Control
Register 7: Reset Cause (RESC), offset 0x05C
This register is set with the reset cause after reset. The bits in this register are sticky and maintain
their state across multiple reset sequences, except when an external reset is the cause, and then
all the other bits in the RESC register are cleared.
Reset Cause (RESC)
Base 0x400F.E000
Offset 0x05C
Type R/W, reset -
31 30 29 28 27 26 25 24 23 22 21 20 19 18 17 16
reserved
Type RO RO RO RO RO RO RO RO RO RO RO RO RO RO RO RO
Reset 0 0 0 0 0 0 0 0 0 0 0 0 0 0 0 0
15 14 13 12 11 10 9 8 7 6 5 4 3 2 1 0
reserved LDO SW WDT BOR POR EXT
Type RO RO RO RO RO RO RO RO RO RO R/W R/W R/W R/W R/W R/W
Reset 0 0 0 0 0 0 0 0 0 0 - - - - - -
Bit/Field Name Type Reset Description
Software should not rely on the value of a reserved bit. To provide
compatibility with future products, the value of a reserved bit should be
preserved across a read-modify-write operation.
31:6 reserved RO 0
LDO Reset
When set, indicates the LDO circuit has lost regulation and has
generated a reset event.
5 LDO R/W -
Software Reset
When set, indicates a software reset is the cause of the reset event.
4 SW R/W -
Watchdog Timer Reset
When set, indicates a watchdog reset is the cause of the reset event.
3 WDT R/W -
Brown-Out Reset
When set, indicates a brown-out reset is the cause of the reset event.
2 BOR R/W -
Power-On Reset
When set, indicates a power-on reset is the cause of the reset event.
1 POR R/W -
External Reset
When set, indicates an external reset (RST assertion) is the cause of
the reset event.
0 EXT R/W -
November 30, 2007 67
Preliminary
LM3S6110 Microcontroller
Register 8: Run-Mode Clock Configuration (RCC), offset 0x060
This register is defined to provide source control and frequency speed.
Run-Mode Clock Configuration (RCC)
Base 0x400F.E000
Offset 0x060
Type R/W, reset 0x07AE.3AD1
31 30 29 28 27 26 25 24 23 22 21 20 19 18 17 16
reserved ACG SYSDIV USESYSDIV reserved USEPWMDIV PWMDIV reserved
Type RO RO RO RO R/W R/W R/W R/W R/W R/W RO R/W R/W R/W R/W RO
Reset 0 0 0 0 0 1 1 1 1 0 0 0 1 1 1 0
15 14 13 12 11 10 9 8 7 6 5 4 3 2 1 0
reserved PWRDN reserved BYPASS reserved XTAL OSCSRC reserved IOSCDIS MOSCDIS
Type RO RO R/W RO R/W RO R/W R/W R/W R/W R/W R/W RO RO R/W R/W
Reset 0 0 1 1 1 0 1 0 1 1 0 1 0 0 0 1
Bit/Field Name Type Reset Description
Software should not rely on the value of a reserved bit. To provide
compatibility with future products, the value of a reserved bit should be
preserved across a read-modify-write operation.
31:28 reserved RO 0x0
Auto Clock Gating
This bit specifies whether the system uses the Sleep-Mode Clock
Gating Control (SCGCn) registers and Deep-Sleep-Mode Clock
Gating Control (DCGCn) registers if the controller enters a Sleep or
Deep-Sleep mode (respectively). If set, the SCGCn or DCGCn registers
are used to control the clocks distributed to the peripherals when the
controller is in a sleep mode. Otherwise, the Run-Mode Clock Gating
Control (RCGCn) registers are used when the controller enters a sleep
mode.
The RCGCn registers are always used to control the clocks in Run
mode.
This allows peripherals to consume less power when the controller is
in a sleep mode and the peripheral is unused.
27 ACG R/W 0
68 November 30, 2007
Preliminary
System Control
Bit/Field Name Type Reset Description
System Clock Divisor
Specifies which divisor is used to generate the system clock from the
PLL output.
The PLL VCO frequency is 400 MHz.
Value Divisor (BYPASS=1) Frequency (BYPASS=0)
0x0 reserved reserved
0x1 /2 reserved
0x2 /3 reserved
0x3 /4 reserved
0x4 /5 reserved
0x5 /6 reserved
0x6 /7 reserved
0x7 /8 25 MHz
0x8 /9 22.22 MHz
0x9 /10 20 MHz
0xA /11 18.18 MHz
0xB /12 16.67 MHz
0xC /13 15.38 MHz
0xD /14 14.29 MHz
0xE /15 13.33 MHz
0xF /16 12.5 MHz (default)
When reading the Run-Mode Clock Configuration (RCC) register (see
page 68), the SYSDIV value is MINSYSDIV if a lower divider was
requested and the PLL is being used. This lower value is allowed to
divide a non-PLL source.
26:23 SYSDIV R/W 0xF
Enable System Clock Divider
Use the system clock divider as the source for the system clock. The
system clock divider is forced to be used when the PLL is selected as
the source.
22 USESYSDIV R/W 0
Software should not rely on the value of a reserved bit. To provide
compatibility with future products, the value of a reserved bit should be
preserved across a read-modify-write operation.
21 reserved RO 0
Enable PWM Clock Divisor
Use the PWM clock divider as the source for the PWM clock.
20 USEPWMDIV R/W 0
November 30, 2007 69
Preliminary
LM3S6110 Microcontroller
Bit/Field Name Type Reset Description
PWM Unit Clock Divisor
This field specifies the binary divisor used to predivide the system clock
down for use as the timing reference for the PWM module. This clock
is only power 2 divide and rising edge is synchronous without phase
shift from the system clock.
Value Divisor
0x0 /2
0x1 /4
0x2 /8
0x3 /16
0x4 /32
0x5 /64
0x6 /64
0x7 /64 (default)
19:17 PWMDIV R/W 0x7
Software should not rely on the value of a reserved bit. To provide
compatibility with future products, the value of a reserved bit should be
preserved across a read-modify-write operation.
16:14 reserved RO 0
PLL Power Down
This bit connects to the PLL PWRDN input. The reset value of 1 powers
down the PLL.
13 PWRDN R/W 1
Software should not rely on the value of a reserved bit. To provide
compatibility with future products, the value of a reserved bit should be
preserved across a read-modify-write operation.
12 reserved RO 1
PLL Bypass
Chooses whether the system clock is derived from the PLL output or
the OSC source. If set, the clock that drives the system is the OSC
source. Otherwise, the clock that drives the system is the PLL output
clock divided by the system divider.
11 BYPASS R/W 1
Software should not rely on the value of a reserved bit. To provide
compatibility with future products, the value of a reserved bit should be
preserved across a read-modify-write operation.
10 reserved RO 0
70 November 30, 2007
Preliminary
System Control
Bit/Field Name Type Reset Description
Crystal Value
This field specifies the crystal value attached to the main oscillator. The
encoding for this field is provided below.
Crystal Frequency (MHz)
Using the PLL
Crystal Frequency (MHz)
Not Using the PLL
Value
0x0 1.000 reserved
0x1 1.8432 reserved
0x2 2.000 reserved
0x3 2.4576 reserved
0x4 3.579545 MHz
0x5 3.6864 MHz
0x6 4 MHz
0x7 4.096 MHz
0x8 4.9152 MHz
0x9 5 MHz
0xA 5.12 MHz
0xB 6 MHz (reset value)
0xC 6.144 MHz
0xD 7.3728 MHz
0xE 8 MHz
0xF 8.192 MHz
9:6 XTAL R/W 0xB
Oscillator Source
Picks among the four input sources for the OSC. The values are:
Value Input Source
0x0 Main oscillator (default)
0x1 Internal oscillator (default)
0x2 Internal oscillator / 4 (this is necessary if used as input to PLL)
0x3 reserved
5:4 OSCSRC R/W 0x1
Software should not rely on the value of a reserved bit. To provide
compatibility with future products, the value of a reserved bit should be
preserved across a read-modify-write operation.
3:2 reserved RO 0x0
Internal Oscillator Disable
0: Internal oscillator (IOSC) is enabled.
1: Internal oscillator is disabled.
1 IOSCDIS R/W 0
Main Oscillator Disable
0: Main oscillator is enabled.
1: Main oscillator is disabled (default).
0 MOSCDIS R/W 1
November 30, 2007 71
Preliminary
LM3S6110 Microcontroller
Register 9: XTAL to PLL Translation (PLLCFG), offset 0x064
This register provides a means of translating external crystal frequencies into the appropriate PLL
settings. This register is initialized during the reset sequence and updated anytime that the XTAL
field changes in the Run-Mode Clock Configuration (RCC) register (see page 68).
The PLL frequency is calculated using the PLLCFG field values, as follows:
PLLFreq = OSCFreq * F / (R + 1)
XTAL to PLL Translation (PLLCFG)
Base 0x400F.E000
Offset 0x064
Type RO, reset -
31 30 29 28 27 26 25 24 23 22 21 20 19 18 17 16
reserved
Type RO RO RO RO RO RO RO RO RO RO RO RO RO RO RO RO
Reset 0 0 0 0 0 0 0 0 0 0 0 0 0 0 0 0
15 14 13 12 11 10 9 8 7 6 5 4 3 2 1 0
reserved F R
Type RO RO RO RO RO RO RO RO RO RO RO RO RO RO RO RO
Reset 0 0 - - - - - - - - - - - - - -
Bit/Field Name Type Reset Description
Software should not rely on the value of a reserved bit. To provide
compatibility with future products, the value of a reserved bit should be
preserved across a read-modify-write operation.
31:14 reserved RO 0x0
PLL F Value
This field specifies the value supplied to the PLL’s F input.
13:5 F RO -
PLL R Value
This field specifies the value supplied to the PLL’s R input.
4:0 R RO -
72 November 30, 2007
Preliminary
System Control
Register 10: Run-Mode Clock Configuration 2 (RCC2), offset 0x070
This register overrides the RCC equivalent register fields when the USERCC2 bit is set. This allows
RCC2 to be used to extend the capabilities, while also providing a means to be backward-compatible
to previous parts. The fields within the RCC2 register occupy the same bit positions as they do
within the RCC register as LSB-justified.
The SYSDIV2 field is wider so that additional larger divisors are possible. This allows a lower system
clock frequency for improved Deep Sleep power consumption.
Run-Mode Clock Configuration 2 (RCC2)
Base 0x400F.E000
Offset 0x070
Type R/W, reset 0x0780.2800
31 30 29 28 27 26 25 24 23 22 21 20 19 18 17 16
USERCC2 reserved SYSDIV2 reserved
Type R/W RO RO R/W R/W R/W R/W R/W R/W RO RO RO RO RO RO RO
Reset 0 0 0 0 0 1 1 1 1 0 0 0 0 0 0 0
15 14 13 12 11 10 9 8 7 6 5 4 3 2 1 0
reserved PWRDN2 reserved BYPASS2 reserved OSCSRC2 reserved
Type RO RO R/W RO R/W RO RO RO RO R/W R/W R/W RO RO RO RO
Reset 0 0 1 0 1 0 0 0 0 0 0 0 0 0 0 0
Bit/Field Name Type Reset Description
Use RCC2
When set, overrides the RCC register fields.
31 USERCC2 R/W 0
Software should not rely on the value of a reserved bit. To provide
compatibility with future products, the value of a reserved bit should be
preserved across a read-modify-write operation.
30:29 reserved RO 0x0
System Clock Divisor
Specifies which divisor is used to generate the system clock from the
PLL output.
The PLL VCO frequency is 400 MHz.
This field is wider than the RCC register SYSDIV field in order to provide
additional divisor values. This permits the system clock to be run at
much lower frequencies during Deep Sleep mode. For example, where
the RCC register SYSDIV encoding of 1111 provides /16, the RCC2
register SYSDIV2 encoding of 111111 provides /64.
28:23 SYSDIV2 R/W 0x0F
Software should not rely on the value of a reserved bit. To provide
compatibility with future products, the value of a reserved bit should be
preserved across a read-modify-write operation.
22:14 reserved RO 0x0
Power-Down PLL
When set, powers down the PLL.
13 PWRDN2 R/W 1
Software should not rely on the value of a reserved bit. To provide
compatibility with future products, the value of a reserved bit should be
preserved across a read-modify-write operation.
12 reserved RO 0
Bypass PLL
When set, bypasses the PLL for the clock source.
11 BYPASS2 R/W 1
November 30, 2007 73
Preliminary
LM3S6110 Microcontroller
Bit/Field Name Type Reset Description
Software should not rely on the value of a reserved bit. To provide
compatibility with future products, the value of a reserved bit should be
preserved across a read-modify-write operation.
10:7 reserved RO 0x0
System Clock Source
Value Description
0x0 Main oscillator (MOSC)
0x1 Internal oscillator (IOSC)
0x2 Internal oscillator / 4
0x3 30 kHz internal oscillator
0x7 32 kHz external oscillator
6:4 OSCSRC2 R/W 0x0
Software should not rely on the value of a reserved bit. To provide
compatibility with future products, the value of a reserved bit should be
preserved across a read-modify-write operation.
3:0 reserved RO 0
74 November 30, 2007
Preliminary
System Control
Register 11: Deep Sleep Clock Configuration (DSLPCLKCFG), offset 0x144
This register provides configuration information for the hardware control of Deep Sleep Mode.
Deep Sleep Clock Configuration (DSLPCLKCFG)
Base 0x400F.E000
Offset 0x144
Type R/W, reset 0x0780.0000
31 30 29 28 27 26 25 24 23 22 21 20 19 18 17 16
reserved DSDIVORIDE reserved
Type RO RO RO R/W R/W R/W R/W R/W R/W RO RO RO RO RO RO RO
Reset 0 0 0 0 0 1 1 1 1 0 0 0 0 0 0 0
15 14 13 12 11 10 9 8 7 6 5 4 3 2 1 0
reserved DSOSCSRC reserved
Type RO RO RO RO RO RO RO RO RO R/W R/W R/W RO RO RO RO
Reset 0 0 0 0 0 0 0 0 0 0 0 0 0 0 0 0
Bit/Field Name Type Reset Description
Software should not rely on the value of a reserved bit. To provide
compatibility with future products, the value of a reserved bit should be
preserved across a read-modify-write operation.
31:29 reserved RO 0x0
Divider Field Override
6-bit system divider field to override when Deep-Sleep occurs with PLL
running.
28:23 DSDIVORIDE R/W 0x0F
Software should not rely on the value of a reserved bit. To provide
compatibility with future products, the value of a reserved bit should be
preserved across a read-modify-write operation.
22:7 reserved RO 0x0
Clock Source
When set, forces IOSC to be clock source during Deep Sleep mode.
Value Name Description
0x0 NOORIDE No override to the oscillator clock source is done
0x1 IOSC Use internal 12 MHz oscillator as source
0x3 30kHz Use 30 kHz internal oscillator
0x7 32kHz Use 32 kHz external oscillator
6:4 DSOSCSRC R/W 0x0
Software should not rely on the value of a reserved bit. To provide
compatibility with future products, the value of a reserved bit should be
preserved across a read-modify-write operation.
3:0 reserved RO 0x0
November 30, 2007 75
Preliminary
LM3S6110 Microcontroller
Register 12: Device Identification 1 (DID1), offset 0x004
This register identifies the device family, part number, temperature range, pin count, and package
type.
Device Identification 1 (DID1)
Base 0x400F.E000
Offset 0x004
Type RO, reset -
31 30 29 28 27 26 25 24 23 22 21 20 19 18 17 16
VER FAM PARTNO
Type RO RO RO RO RO RO RO RO RO RO RO RO RO RO RO RO
Reset 0 0 0 1 0 0 0 0 0 1 1 1 0 1 0 0
15 14 13 12 11 10 9 8 7 6 5 4 3 2 1 0
PINCOUNT reserved TEMP PKG ROHS QUAL
Type RO RO RO RO RO RO RO RO RO RO RO RO RO RO RO RO
Reset 0 1 0 0 0 0 0 0 0 0 1 0 1 1 - -
Bit/Field Name Type Reset Description
DID1 Version
This field defines the DID1 register format version. The version number
is numeric. The value of the VER field is encoded as follows (all other
encodings are reserved):
Value Description
First revision of the DID1 register format, indicating a Stellaris
Fury-class device.
0x1
31:28 VER RO 0x1
Family
This field provides the family identification of the device within the
Luminary Micro product portfolio. The value is encoded as follows (all
other encodings are reserved):
Value Description
Stellaris family of microcontollers, that is, all devices with
external part numbers starting with LM3S.
0x0
27:24 FAM RO 0x0
Part Number
This field provides the part number of the device within the family. The
value is encoded as follows (all other encodings are reserved):
Value Description
0x74 LM3S6110
23:16 PARTNO RO 0x74
Package Pin Count
This field specifies the number of pins on the device package. The value
is encoded as follows (all other encodings are reserved):
Value Description
0x2 100-pin package
15:13 PINCOUNT RO 0x2
76 November 30, 2007
Preliminary
System Control
Bit/Field Name Type Reset Description
Software should not rely on the value of a reserved bit. To provide
compatibility with future products, the value of a reserved bit should be
preserved across a read-modify-write operation.
12:8 reserved RO 0
Temperature Range
This field specifies the temperature rating of the device. The value is
encoded as follows (all other encodings are reserved):
Value Description
0x1 Industrial temperature range (-40°C to 85°C)
7:5 TEMP RO 0x1
Package Type
This field specifies the package type. The value is encoded as follows
(all other encodings are reserved):
Value Description
0x1 LQFP package
4:3 PKG RO 0x1
RoHS-Compliance
This bit specifies whether the device is RoHS-compliant. A 1 indicates
the part is RoHS-compliant.
2 ROHS RO 1
Qualification Status
This field specifies the qualification status of the device. The value is
encoded as follows (all other encodings are reserved):
Value Description
0x0 Engineering Sample (unqualified)
0x1 Pilot Production (unqualified)
0x2 Fully Qualified
1:0 QUAL RO -
November 30, 2007 77
Preliminary
LM3S6110 Microcontroller
Register 13: Device Capabilities 0 (DC0), offset 0x008
This register is predefined by the part and can be used to verify features.
Device Capabilities 0 (DC0)
Base 0x400F.E000
Offset 0x008
Type RO, reset 0x003F.001F
31 30 29 28 27 26 25 24 23 22 21 20 19 18 17 16
SRAMSZ
Type RO RO RO RO RO RO RO RO RO RO RO RO RO RO RO RO
Reset 0 0 0 0 0 0 0 0 0 0 1 1 1 1 1 1
15 14 13 12 11 10 9 8 7 6 5 4 3 2 1 0
FLASHSZ
Type RO RO RO RO RO RO RO RO RO RO RO RO RO RO RO RO
Reset 0 0 0 0 0 0 0 0 0 0 0 1 1 1 1 1
Bit/Field Name Type Reset Description
SRAM Size
Indicates the size of the on-chip SRAM memory.
Value Description
0x003F 16 KB of SRAM
31:16 SRAMSZ RO 0x003F
Flash Size
Indicates the size of the on-chip flash memory.
Value Description
0x001F 64 KB of Flash
15:0 FLASHSZ RO 0x001F
78 November 30, 2007
Preliminary
System Control
Register 14: Device Capabilities 1 (DC1), offset 0x010
This register provides a list of features available in the system. The Stellaris family uses this register
format to indicate the availability of the following family features in the specific device: CANs, PWM,
ADC, Watchdog timer, Hibernation module, and debug capabilities. This register also indicates the
maximum clock frequency and maximum ADC sample rate. The format of this register is consistent
with the RCGC0, SCGC0, and DCGC0 clock control registers and the SRCR0 software reset control
register.
Device Capabilities 1 (DC1)
Base 0x400F.E000
Offset 0x010
Type RO, reset 0x0010.709F
31 30 29 28 27 26 25 24 23 22 21 20 19 18 17 16
reserved PWM reserved
Type RO RO RO RO RO RO RO RO RO RO RO RO RO RO RO RO
Reset 0 0 0 0 0 0 0 0 0 0 0 1 0 0 0 0
15 14 13 12 11 10 9 8 7 6 5 4 3 2 1 0
MINSYSDIV reserved MPU reserved PLL WDT SWO SWD JTAG
Type RO RO RO RO RO RO RO RO RO RO RO RO RO RO RO RO
Reset 0 1 1 1 0 0 0 0 1 0 0 1 1 1 1 1
Bit/Field Name Type Reset Description
Software should not rely on the value of a reserved bit. To provide
compatibility with future products, the value of a reserved bit should be
preserved across a read-modify-write operation.
31:21 reserved RO 0
PWM Module Present
When set, indicates that the PWM module is present.
20 PWM RO 1
Software should not rely on the value of a reserved bit. To provide
compatibility with future products, the value of a reserved bit should be
preserved across a read-modify-write operation.
19:16 reserved RO 0
System Clock Divider
Minimum 4-bit divider value for system clock. The reset value is
hardware-dependent. See the RCC register for how to change the
system clock divisor using the SYSDIV bit.
Value Description
0x7 Specifies a 25-MHz clock with a PLL divider of 8.
15:12 MINSYSDIV RO 0x7
Software should not rely on the value of a reserved bit. To provide
compatibility with future products, the value of a reserved bit should be
preserved across a read-modify-write operation.
11:8 reserved RO 0
MPU Present
When set, indicates that the Cortex-M3 Memory Protection Unit (MPU)
module is present. See the ARM Cortex-M3 Technical Reference Manual
for details on the MPU.
7 MPU RO 1
Software should not rely on the value of a reserved bit. To provide
compatibility with future products, the value of a reserved bit should be
preserved across a read-modify-write operation.
6:5 reserved RO 0
November 30, 2007 79
Preliminary
LM3S6110 Microcontroller
Bit/Field Name Type Reset Description
PLL Present
When set, indicates that the on-chip Phase Locked Loop (PLL) is
present.
4 PLL RO 1
Watchdog Timer Present
When set, indicates that a watchdog timer is present.
3 WDT RO 1
SWO Trace Port Present
When set, indicates that the Serial Wire Output (SWO) trace port is
present.
2 SWO RO 1
SWD Present
When set, indicates that the Serial Wire Debugger (SWD) is present.
1 SWD RO 1
JTAG Present
When set, indicates that the JTAG debugger interface is present.
0 JTAG RO 1
80 November 30, 2007
Preliminary
System Control
Register 15: Device Capabilities 2 (DC2), offset 0x014
This register provides a list of features available in the system. The Stellaris family uses this register
format to indicate the availability of the following family features in the specific device: Analog
Comparators, General-Purpose Timers, I2Cs, QEIs, SSIs, and UARTs. The format of this register
is consistent with the RCGC1, SCGC1, and DCGC1 clock control registers and the SRCR1 software
reset control register.
Device Capabilities 2 (DC2)
Base 0x400F.E000
Offset 0x014
Type RO, reset 0x0707.0011
31 30 29 28 27 26 25 24 23 22 21 20 19 18 17 16
reserved COMP2 COMP1 COMP0 reserved TIMER2 TIMER1 TIMER0
Type RO RO RO RO RO RO RO RO RO RO RO RO RO RO RO RO
Reset 0 0 0 0 0 1 1 1 0 0 0 0 0 1 1 1
15 14 13 12 11 10 9 8 7 6 5 4 3 2 1 0
reserved SSI0 reserved UART0
Type RO RO RO RO RO RO RO RO RO RO RO RO RO RO RO RO
Reset 0 0 0 0 0 0 0 0 0 0 0 1 0 0 0 1
Bit/Field Name Type Reset Description
Software should not rely on the value of a reserved bit. To provide
compatibility with future products, the value of a reserved bit should be
preserved across a read-modify-write operation.
31:27 reserved RO 0
Analog Comparator 2 Present
When set, indicates that analog comparator 2 is present.
26 COMP2 RO 1
Analog Comparator 1 Present
When set, indicates that analog comparator 1 is present.
25 COMP1 RO 1
Analog Comparator 0 Present
When set, indicates that analog comparator 0 is present.
24 COMP0 RO 1
Software should not rely on the value of a reserved bit. To provide
compatibility with future products, the value of a reserved bit should be
preserved across a read-modify-write operation.
23:19 reserved RO 0
Timer 2 Present
When set, indicates that General-Purpose Timer module 2 is present.
18 TIMER2 RO 1
Timer 1 Present
When set, indicates that General-Purpose Timer module 1 is present.
17 TIMER1 RO 1
Timer 0 Present
When set, indicates that General-Purpose Timer module 0 is present.
16 TIMER0 RO 1
Software should not rely on the value of a reserved bit. To provide
compatibility with future products, the value of a reserved bit should be
preserved across a read-modify-write operation.
15:5 reserved RO 0
SSI0 Present
When set, indicates that SSI module 0 is present.
4 SSI0 RO 1
November 30, 2007 81
Preliminary
LM3S6110 Microcontroller
Bit/Field Name Type Reset Description
Software should not rely on the value of a reserved bit. To provide
compatibility with future products, the value of a reserved bit should be
preserved across a read-modify-write operation.
3:1 reserved RO 0
UART0 Present
When set, indicates that UART module 0 is present.
0 UART0 RO 1
82 November 30, 2007
Preliminary
System Control
Register 16: Device Capabilities 3 (DC3), offset 0x018
This register provides a list of features available in the system. The Stellaris family uses this register
format to indicate the availability of the following family features in the specific device: Analog
Comparator I/Os, CCP I/Os, ADC I/Os, and PWM I/Os.
Device Capabilities 3 (DC3)
Base 0x400F.E000
Offset 0x018
Type RO, reset 0x0F00.B7C3
31 30 29 28 27 26 25 24 23 22 21 20 19 18 17 16
reserved CCP3 CCP2 CCP1 CCP0 reserved
Type RO RO RO RO RO RO RO RO RO RO RO RO RO RO RO RO
Reset 0 0 0 0 1 1 1 1 0 0 0 0 0 0 0 0
15 14 13 12 11 10 9 8 7 6 5 4 3 2 1 0
PWMFAULT reserved C2PLUS C2MINUS reserved C1PLUS C1MINUS C0O C0PLUS C0MINUS reserved PWM1 PWM0
Type RO RO RO RO RO RO RO RO RO RO RO RO RO RO RO RO
Reset 1 0 1 1 0 1 1 1 1 1 0 0 0 0 1 1
Bit/Field Name Type Reset Description
Software should not rely on the value of a reserved bit. To provide
compatibility with future products, the value of a reserved bit should be
preserved across a read-modify-write operation.
31:28 reserved RO 0
CCP3 Pin Present
When set, indicates that Capture/Compare/PWM pin 3 is present.
27 CCP3 RO 1
CCP2 Pin Present
When set, indicates that Capture/Compare/PWM pin 2 is present.
26 CCP2 RO 1
CCP1 Pin Present
When set, indicates that Capture/Compare/PWM pin 1 is present.
25 CCP1 RO 1
CCP0 Pin Present
When set, indicates that Capture/Compare/PWM pin 0 is present.
24 CCP0 RO 1
Software should not rely on the value of a reserved bit. To provide
compatibility with future products, the value of a reserved bit should be
preserved across a read-modify-write operation.
23:16 reserved RO 0
PWM Fault Pin Present
When set, indicates that the PWM Fault pin is present.
15 PWMFAULT RO 1
Software should not rely on the value of a reserved bit. To provide
compatibility with future products, the value of a reserved bit should be
preserved across a read-modify-write operation.
14 reserved RO 0
C2+ Pin Present
When set, indicates that the analog comparator 2 (+) input pin is present.
13 C2PLUS RO 1
C2- Pin Present
When set, indicates that the analog comparator 2 (-) input pin is present.
12 C2MINUS RO 1
November 30, 2007 83
Preliminary
LM3S6110 Microcontroller
Bit/Field Name Type Reset Description
Software should not rely on the value of a reserved bit. To provide
compatibility with future products, the value of a reserved bit should be
preserved across a read-modify-write operation.
11 reserved RO 0
C1+ Pin Present
When set, indicates that the analog comparator 1 (+) input pin is present.
10 C1PLUS RO 1
C1- Pin Present
When set, indicates that the analog comparator 1 (-) input pin is present.
9 C1MINUS RO 1
C0o Pin Present
When set, indicates that the analog comparator 0 output pin is present.
8 C0O RO 1
C0+ Pin Present
When set, indicates that the analog comparator 0 (+) input pin is present.
7 C0PLUS RO 1
C0- Pin Present
When set, indicates that the analog comparator 0 (-) input pin is present.
6 C0MINUS RO 1
Software should not rely on the value of a reserved bit. To provide
compatibility with future products, the value of a reserved bit should be
preserved across a read-modify-write operation.
5:2 reserved RO 0
PWM1 Pin Present
When set, indicates that the PWM pin 1 is present.
1 PWM1 RO 1
PWM0 Pin Present
When set, indicates that the PWM pin 0 is present.
0 PWM0 RO 1
84 November 30, 2007
Preliminary
System Control
Register 17: Device Capabilities 4 (DC4), offset 0x01C
This register provides a list of features available in the system. The Stellaris family uses this register
format to indicate the availability of the following family features in the specific device: Ethernet MAC
and PHY, GPIOs, and CCP I/Os. The format of this register is consistent with the RCGC2, SCGC2,
and DCGC2 clock control registers and the SRCR2 software reset control register.
Device Capabilities 4 (DC4)
Base 0x400F.E000
Offset 0x01C
Type RO, reset 0x5000.007F
31 30 29 28 27 26 25 24 23 22 21 20 19 18 17 16
reserved EPHY0 reserved EMAC0 reserved
Type RO RO RO RO RO RO RO RO RO RO RO RO RO RO RO RO
Reset 0 1 0 1 0 0 0 0 0 0 0 0 0 0 0 0
15 14 13 12 11 10 9 8 7 6 5 4 3 2 1 0
reserved GPIOG GPIOF GPIOE GPIOD GPIOC GPIOB GPIOA
Type RO RO RO RO RO RO RO RO RO RO RO RO RO RO RO RO
Reset 0 0 0 0 0 0 0 0 0 1 1 1 1 1 1 1
Bit/Field Name Type Reset Description
Software should not rely on the value of a reserved bit. To provide
compatibility with future products, the value of a reserved bit should be
preserved across a read-modify-write operation.
31 reserved RO 0
Ethernet PHY0 Present
When set, indicates that Ethernet PHY module 0 is present.
30 EPHY0 RO 1
Software should not rely on the value of a reserved bit. To provide
compatibility with future products, the value of a reserved bit should be
preserved across a read-modify-write operation.
29 reserved RO 0
Ethernet MAC0 Present
When set, indicates that Ethernet MAC module 0 is present.
28 EMAC0 RO 1
Software should not rely on the value of a reserved bit. To provide
compatibility with future products, the value of a reserved bit should be
preserved across a read-modify-write operation.
27:7 reserved RO 0
GPIO Port G Present
When set, indicates that GPIO Port G is present.
6 GPIOG RO 1
GPIO Port F Present
When set, indicates that GPIO Port F is present.
5 GPIOF RO 1
GPIO Port E Present
When set, indicates that GPIO Port E is present.
4 GPIOE RO 1
GPIO Port D Present
When set, indicates that GPIO Port D is present.
3 GPIOD RO 1
GPIO Port C Present
When set, indicates that GPIO Port C is present.
2 GPIOC RO 1
November 30, 2007 85
Preliminary
LM3S6110 Microcontroller
Bit/Field Name Type Reset Description
GPIO Port B Present
When set, indicates that GPIO Port B is present.
1 GPIOB RO 1
GPIO Port A Present
When set, indicates that GPIO Port A is present.
0 GPIOA RO 1
86 November 30, 2007
Preliminary
System Control
Register 18: Run Mode Clock Gating Control Register 0 (RCGC0), offset 0x100
This register controls the clock gating logic. Each bit controls a clock enable for a given interface,
function, or unit. If set, the unit receives a clock and functions. Otherwise, the unit is unclocked and
disabled (saving power). If the unit is unclocked, reads or writes to the unit will generate a bus fault.
The reset state of these bits is 0 (unclocked) unless otherwise noted, so that all functional units are
disabled. It is the responsibility of software to enable the ports necessary for the application. Note
that these registers may contain more bits than there are interfaces, functions, or units to control.
This is to assure reasonable code compatibility with other family and future parts. RCGC0 is the
clock configuration register for running operation, SCGC0 for Sleep operation, and DCGC0 for
Deep-Sleep operation. Setting the ACG bit in the Run-Mode Clock Configuration (RCC) register
specifies that the system uses sleep modes.
Run Mode Clock Gating Control Register 0 (RCGC0)
Base 0x400F.E000
Offset 0x100
Type R/W, reset 0x00000040
31 30 29 28 27 26 25 24 23 22 21 20 19 18 17 16
reserved PWM reserved
Type RO RO RO RO RO RO RO RO RO RO RO R/W RO RO RO RO
Reset 0 0 0 0 0 0 0 0 0 0 0 0 0 0 0 0
15 14 13 12 11 10 9 8 7 6 5 4 3 2 1 0
reserved WDT reserved
Type RO RO RO RO RO RO RO RO RO RO RO RO R/W RO RO RO
Reset 0 0 0 0 0 0 0 0 0 0 0 0 0 0 0 0
Bit/Field Name Type Reset Description
Software should not rely on the value of a reserved bit. To provide
compatibility with future products, the value of a reserved bit should be
preserved across a read-modify-write operation.
31:21 reserved RO 0
PWM Clock Gating Control
This bit controls the clock gating for the PWM module. If set, the unit
receives a clock and functions. Otherwise, the unit is unclocked and
disabled. If the unit is unclocked, a read or write to the unit generates
a bus fault.
20 PWM R/W 0
Software should not rely on the value of a reserved bit. To provide
compatibility with future products, the value of a reserved bit should be
preserved across a read-modify-write operation.
19:4 reserved RO 0
WDT Clock Gating Control
This bit controls the clock gating for the WDT module. If set, the unit
receives a clock and functions. Otherwise, the unit is unclocked and
disabled. If the unit is unclocked, a read or write to the unit generates
a bus fault.
3 WDT R/W 0
Software should not rely on the value of a reserved bit. To provide
compatibility with future products, the value of a reserved bit should be
preserved across a read-modify-write operation.
2:0 reserved RO 0
November 30, 2007 87
Preliminary
LM3S6110 Microcontroller
Register 19: Sleep Mode Clock Gating Control Register 0 (SCGC0), offset
0x110
This register controls the clock gating logic. Each bit controls a clock enable for a given interface,
function, or unit. If set, the unit receives a clock and functions. Otherwise, the unit is unclocked and
disabled (saving power). If the unit is unclocked, reads or writes to the unit will generate a bus fault.
The reset state of these bits is 0 (unclocked) unless otherwise noted, so that all functional units are
disabled. It is the responsibility of software to enable the ports necessary for the application. Note
that these registers may contain more bits than there are interfaces, functions, or units to control.
This is to assure reasonable code compatibility with other family and future parts. RCGC0 is the
clock configuration register for running operation, SCGC0 for Sleep operation, and DCGC0 for
Deep-Sleep operation. Setting the ACG bit in the Run-Mode Clock Configuration (RCC) register
specifies that the system uses sleep modes.
Sleep Mode Clock Gating Control Register 0 (SCGC0)
Base 0x400F.E000
Offset 0x110
Type R/W, reset 0x00000040
31 30 29 28 27 26 25 24 23 22 21 20 19 18 17 16
reserved PWM reserved
Type RO RO RO RO RO RO RO RO RO RO RO R/W RO RO RO RO
Reset 0 0 0 0 0 0 0 0 0 0 0 0 0 0 0 0
15 14 13 12 11 10 9 8 7 6 5 4 3 2 1 0
reserved WDT reserved
Type RO RO RO RO RO RO RO RO RO RO RO RO R/W RO RO RO
Reset 0 0 0 0 0 0 0 0 0 0 0 0 0 0 0 0
Bit/Field Name Type Reset Description
Software should not rely on the value of a reserved bit. To provide
compatibility with future products, the value of a reserved bit should be
preserved across a read-modify-write operation.
31:21 reserved RO 0
PWM Clock Gating Control
This bit controls the clock gating for the PWM module. If set, the unit
receives a clock and functions. Otherwise, the unit is unclocked and
disabled. If the unit is unclocked, a read or write to the unit generates
a bus fault.
20 PWM R/W 0
Software should not rely on the value of a reserved bit. To provide
compatibility with future products, the value of a reserved bit should be
preserved across a read-modify-write operation.
19:4 reserved RO 0
WDT Clock Gating Control
This bit controls the clock gating for the WDT module. If set, the unit
receives a clock and functions. Otherwise, the unit is unclocked and
disabled. If the unit is unclocked, a read or write to the unit generates
a bus fault.
3 WDT R/W 0
Software should not rely on the value of a reserved bit. To provide
compatibility with future products, the value of a reserved bit should be
preserved across a read-modify-write operation.
2:0 reserved RO 0
88 November 30, 2007
Preliminary
System Control
Register 20: Deep Sleep Mode Clock Gating Control Register 0 (DCGC0),
offset 0x120
This register controls the clock gating logic. Each bit controls a clock enable for a given interface,
function, or unit. If set, the unit receives a clock and functions. Otherwise, the unit is unclocked and
disabled (saving power). If the unit is unclocked, reads or writes to the unit will generate a bus fault.
The reset state of these bits is 0 (unclocked) unless otherwise noted, so that all functional units are
disabled. It is the responsibility of software to enable the ports necessary for the application. Note
that these registers may contain more bits than there are interfaces, functions, or units to control.
This is to assure reasonable code compatibility with other family and future parts. RCGC0 is the
clock configuration register for running operation, SCGC0 for Sleep operation, and DCGC0 for
Deep-Sleep operation. Setting the ACG bit in the Run-Mode Clock Configuration (RCC) register
specifies that the system uses sleep modes.
Deep Sleep Mode Clock Gating Control Register 0 (DCGC0)
Base 0x400F.E000
Offset 0x120
Type R/W, reset 0x00000040
31 30 29 28 27 26 25 24 23 22 21 20 19 18 17 16
reserved PWM reserved
Type RO RO RO RO RO RO RO RO RO RO RO R/W RO RO RO RO
Reset 0 0 0 0 0 0 0 0 0 0 0 0 0 0 0 0
15 14 13 12 11 10 9 8 7 6 5 4 3 2 1 0
reserved WDT reserved
Type RO RO RO RO RO RO RO RO RO RO RO RO R/W RO RO RO
Reset 0 0 0 0 0 0 0 0 0 0 0 0 0 0 0 0
Bit/Field Name Type Reset Description
Software should not rely on the value of a reserved bit. To provide
compatibility with future products, the value of a reserved bit should be
preserved across a read-modify-write operation.
31:21 reserved RO 0
PWM Clock Gating Control
This bit controls the clock gating for the PWM module. If set, the unit
receives a clock and functions. Otherwise, the unit is unclocked and
disabled. If the unit is unclocked, a read or write to the unit generates
a bus fault.
20 PWM R/W 0
Software should not rely on the value of a reserved bit. To provide
compatibility with future products, the value of a reserved bit should be
preserved across a read-modify-write operation.
19:4 reserved RO 0
WDT Clock Gating Control
This bit controls the clock gating for the WDT module. If set, the unit
receives a clock and functions. Otherwise, the unit is unclocked and
disabled. If the unit is unclocked, a read or write to the unit generates
a bus fault.
3 WDT R/W 0
Software should not rely on the value of a reserved bit. To provide
compatibility with future products, the value of a reserved bit should be
preserved across a read-modify-write operation.
2:0 reserved RO 0
November 30, 2007 89
Preliminary
LM3S6110 Microcontroller
Register 21: Run Mode Clock Gating Control Register 1 (RCGC1), offset 0x104
This register controls the clock gating logic. Each bit controls a clock enable for a given interface,
function, or unit. If set, the unit receives a clock and functions. Otherwise, the unit is unclocked and
disabled (saving power). If the unit is unclocked, reads or writes to the unit will generate a bus fault.
The reset state of these bits is 0 (unclocked) unless otherwise noted, so that all functional units are
disabled. It is the responsibility of software to enable the ports necessary for the application. Note
that these registers may contain more bits than there are interfaces, functions, or units to control.
This is to assure reasonable code compatibility with other family and future parts. RCGC1 is the
clock configuration register for running operation, SCGC1 for Sleep operation, and DCGC1 for
Deep-Sleep operation. Setting the ACG bit in the Run-Mode Clock Configuration (RCC) register
specifies that the system uses sleep modes.
Run Mode Clock Gating Control Register 1 (RCGC1)
Base 0x400F.E000
Offset 0x104
Type R/W, reset 0x00000000
31 30 29 28 27 26 25 24 23 22 21 20 19 18 17 16
reserved COMP2 COMP1 COMP0 reserved TIMER2 TIMER1 TIMER0
Type RO RO RO RO RO R/W R/W R/W RO RO RO RO RO R/W R/W R/W
Reset 0 0 0 0 0 0 0 0 0 0 0 0 0 0 0 0
15 14 13 12 11 10 9 8 7 6 5 4 3 2 1 0
reserved SSI0 reserved UART0
Type RO RO RO RO RO RO RO RO RO RO RO R/W RO RO RO R/W
Reset 0 0 0 0 0 0 0 0 0 0 0 0 0 0 0 0
Bit/Field Name Type Reset Description
Software should not rely on the value of a reserved bit. To provide
compatibility with future products, the value of a reserved bit should be
preserved across a read-modify-write operation.
31:27 reserved RO 0
Analog Comparator 2 Clock Gating
This bit controls the clock gating for analog comparator 2. If set, the unit
receives a clock and functions. Otherwise, the unit is unclocked and
disabled. If the unit is unclocked, reads or writes to the unit will generate
a bus fault.
26 COMP2 R/W 0
Analog Comparator 1 Clock Gating
This bit controls the clock gating for analog comparator 1. If set, the unit
receives a clock and functions. Otherwise, the unit is unclocked and
disabled. If the unit is unclocked, reads or writes to the unit will generate
a bus fault.
25 COMP1 R/W 0
Analog Comparator 0 Clock Gating
This bit controls the clock gating for analog comparator 0. If set, the unit
receives a clock and functions. Otherwise, the unit is unclocked and
disabled. If the unit is unclocked, reads or writes to the unit will generate
a bus fault.
24 COMP0 R/W 0
Software should not rely on the value of a reserved bit. To provide
compatibility with future products, the value of a reserved bit should be
preserved across a read-modify-write operation.
23:19 reserved RO 0
90 November 30, 2007
Preliminary
System Control
Bit/Field Name Type Reset Description
Timer 2 Clock Gating Control
This bit controls the clock gating for General-Purpose Timer module 2.
If set, the unit receives a clock and functions. Otherwise, the unit is
unclocked and disabled. If the unit is unclocked, reads or writes to the
unit will generate a bus fault.
18 TIMER2 R/W 0
Timer 1 Clock Gating Control
This bit controls the clock gating for General-Purpose Timer module 1.
If set, the unit receives a clock and functions. Otherwise, the unit is
unclocked and disabled. If the unit is unclocked, reads or writes to the
unit will generate a bus fault.
17 TIMER1 R/W 0
Timer 0 Clock Gating Control
This bit controls the clock gating for General-Purpose Timer module 0.
If set, the unit receives a clock and functions. Otherwise, the unit is
unclocked and disabled. If the unit is unclocked, reads or writes to the
unit will generate a bus fault.
16 TIMER0 R/W 0
Software should not rely on the value of a reserved bit. To provide
compatibility with future products, the value of a reserved bit should be
preserved across a read-modify-write operation.
15:5 reserved RO 0
SSI0 Clock Gating Control
This bit controls the clock gating for SSI module 0. If set, the unit receives
a clock and functions. Otherwise, the unit is unclocked and disabled. If
the unit is unclocked, reads or writes to the unit will generate a bus fault.
4 SSI0 R/W 0
Software should not rely on the value of a reserved bit. To provide
compatibility with future products, the value of a reserved bit should be
preserved across a read-modify-write operation.
3:1 reserved RO 0
UART0 Clock Gating Control
This bit controls the clock gating for UART module 0. If set, the unit
receives a clock and functions. Otherwise, the unit is unclocked and
disabled. If the unit is unclocked, reads or writes to the unit will generate
a bus fault.
0 UART0 R/W 0
November 30, 2007 91
Preliminary
LM3S6110 Microcontroller
Register 22: Sleep Mode Clock Gating Control Register 1 (SCGC1), offset
0x114
This register controls the clock gating logic. Each bit controls a clock enable for a given interface,
function, or unit. If set, the unit receives a clock and functions. Otherwise, the unit is unclocked and
disabled (saving power). If the unit is unclocked, reads or writes to the unit will generate a bus fault.
The reset state of these bits is 0 (unclocked) unless otherwise noted, so that all functional units are
disabled. It is the responsibility of software to enable the ports necessary for the application. Note
that these registers may contain more bits than there are interfaces, functions, or units to control.
This is to assure reasonable code compatibility with other family and future parts. RCGC1 is the
clock configuration register for running operation, SCGC1 for Sleep operation, and DCGC1 for
Deep-Sleep operation. Setting the ACG bit in the Run-Mode Clock Configuration (RCC) register
specifies that the system uses sleep modes.
Sleep Mode Clock Gating Control Register 1 (SCGC1)
Base 0x400F.E000
Offset 0x114
Type R/W, reset 0x00000000
31 30 29 28 27 26 25 24 23 22 21 20 19 18 17 16
reserved COMP2 COMP1 COMP0 reserved TIMER2 TIMER1 TIMER0
Type RO RO RO RO RO R/W R/W R/W RO RO RO RO RO R/W R/W R/W
Reset 0 0 0 0 0 0 0 0 0 0 0 0 0 0 0 0
15 14 13 12 11 10 9 8 7 6 5 4 3 2 1 0
reserved SSI0 reserved UART0
Type RO RO RO RO RO RO RO RO RO RO RO R/W RO RO RO R/W
Reset 0 0 0 0 0 0 0 0 0 0 0 0 0 0 0 0
Bit/Field Name Type Reset Description
Software should not rely on the value of a reserved bit. To provide
compatibility with future products, the value of a reserved bit should be
preserved across a read-modify-write operation.
31:27 reserved RO 0
Analog Comparator 2 Clock Gating
This bit controls the clock gating for analog comparator 2. If set, the unit
receives a clock and functions. Otherwise, the unit is unclocked and
disabled. If the unit is unclocked, reads or writes to the unit will generate
a bus fault.
26 COMP2 R/W 0
Analog Comparator 1 Clock Gating
This bit controls the clock gating for analog comparator 1. If set, the unit
receives a clock and functions. Otherwise, the unit is unclocked and
disabled. If the unit is unclocked, reads or writes to the unit will generate
a bus fault.
25 COMP1 R/W 0
Analog Comparator 0 Clock Gating
This bit controls the clock gating for analog comparator 0. If set, the unit
receives a clock and functions. Otherwise, the unit is unclocked and
disabled. If the unit is unclocked, reads or writes to the unit will generate
a bus fault.
24 COMP0 R/W 0
Software should not rely on the value of a reserved bit. To provide
compatibility with future products, the value of a reserved bit should be
preserved across a read-modify-write operation.
23:19 reserved RO 0
92 November 30, 2007
Preliminary
System Control
Bit/Field Name Type Reset Description
Timer 2 Clock Gating Control
This bit controls the clock gating for General-Purpose Timer module 2.
If set, the unit receives a clock and functions. Otherwise, the unit is
unclocked and disabled. If the unit is unclocked, reads or writes to the
unit will generate a bus fault.
18 TIMER2 R/W 0
Timer 1 Clock Gating Control
This bit controls the clock gating for General-Purpose Timer module 1.
If set, the unit receives a clock and functions. Otherwise, the unit is
unclocked and disabled. If the unit is unclocked, reads or writes to the
unit will generate a bus fault.
17 TIMER1 R/W 0
Timer 0 Clock Gating Control
This bit controls the clock gating for General-Purpose Timer module 0.
If set, the unit receives a clock and functions. Otherwise, the unit is
unclocked and disabled. If the unit is unclocked, reads or writes to the
unit will generate a bus fault.
16 TIMER0 R/W 0
Software should not rely on the value of a reserved bit. To provide
compatibility with future products, the value of a reserved bit should be
preserved across a read-modify-write operation.
15:5 reserved RO 0
SSI0 Clock Gating Control
This bit controls the clock gating for SSI module 0. If set, the unit receives
a clock and functions. Otherwise, the unit is unclocked and disabled. If
the unit is unclocked, reads or writes to the unit will generate a bus fault.
4 SSI0 R/W 0
Software should not rely on the value of a reserved bit. To provide
compatibility with future products, the value of a reserved bit should be
preserved across a read-modify-write operation.
3:1 reserved RO 0
UART0 Clock Gating Control
This bit controls the clock gating for UART module 0. If set, the unit
receives a clock and functions. Otherwise, the unit is unclocked and
disabled. If the unit is unclocked, reads or writes to the unit will generate
a bus fault.
0 UART0 R/W 0
November 30, 2007 93
Preliminary
LM3S6110 Microcontroller
Register 23: Deep Sleep Mode Clock Gating Control Register 1 (DCGC1),
offset 0x124
This register controls the clock gating logic. Each bit controls a clock enable for a given interface,
function, or unit. If set, the unit receives a clock and functions. Otherwise, the unit is unclocked and
disabled (saving power). If the unit is unclocked, reads or writes to the unit will generate a bus fault.
The reset state of these bits is 0 (unclocked) unless otherwise noted, so that all functional units are
disabled. It is the responsibility of software to enable the ports necessary for the application. Note
that these registers may contain more bits than there are interfaces, functions, or units to control.
This is to assure reasonable code compatibility with other family and future parts. RCGC1 is the
clock configuration register for running operation, SCGC1 for Sleep operation, and DCGC1 for
Deep-Sleep operation. Setting the ACG bit in the Run-Mode Clock Configuration (RCC) register
specifies that the system uses sleep modes.
Deep Sleep Mode Clock Gating Control Register 1 (DCGC1)
Base 0x400F.E000
Offset 0x124
Type R/W, reset 0x00000000
31 30 29 28 27 26 25 24 23 22 21 20 19 18 17 16
reserved COMP2 COMP1 COMP0 reserved TIMER2 TIMER1 TIMER0
Type RO RO RO RO RO R/W R/W R/W RO RO RO RO RO R/W R/W R/W
Reset 0 0 0 0 0 0 0 0 0 0 0 0 0 0 0 0
15 14 13 12 11 10 9 8 7 6 5 4 3 2 1 0
reserved SSI0 reserved UART0
Type RO RO RO RO RO RO RO RO RO RO RO R/W RO RO RO R/W
Reset 0 0 0 0 0 0 0 0 0 0 0 0 0 0 0 0
Bit/Field Name Type Reset Description
Software should not rely on the value of a reserved bit. To provide
compatibility with future products, the value of a reserved bit should be
preserved across a read-modify-write operation.
31:27 reserved RO 0
Analog Comparator 2 Clock Gating
This bit controls the clock gating for analog comparator 2. If set, the unit
receives a clock and functions. Otherwise, the unit is unclocked and
disabled. If the unit is unclocked, reads or writes to the unit will generate
a bus fault.
26 COMP2 R/W 0
Analog Comparator 1 Clock Gating
This bit controls the clock gating for analog comparator 1. If set, the unit
receives a clock and functions. Otherwise, the unit is unclocked and
disabled. If the unit is unclocked, reads or writes to the unit will generate
a bus fault.
25 COMP1 R/W 0
Analog Comparator 0 Clock Gating
This bit controls the clock gating for analog comparator 0. If set, the unit
receives a clock and functions. Otherwise, the unit is unclocked and
disabled. If the unit is unclocked, reads or writes to the unit will generate
a bus fault.
24 COMP0 R/W 0
Software should not rely on the value of a reserved bit. To provide
compatibility with future products, the value of a reserved bit should be
preserved across a read-modify-write operation.
23:19 reserved RO 0
94 November 30, 2007
Preliminary
System Control
Bit/Field Name Type Reset Description
Timer 2 Clock Gating Control
This bit controls the clock gating for General-Purpose Timer module 2.
If set, the unit receives a clock and functions. Otherwise, the unit is
unclocked and disabled. If the unit is unclocked, reads or writes to the
unit will generate a bus fault.
18 TIMER2 R/W 0
Timer 1 Clock Gating Control
This bit controls the clock gating for General-Purpose Timer module 1.
If set, the unit receives a clock and functions. Otherwise, the unit is
unclocked and disabled. If the unit is unclocked, reads or writes to the
unit will generate a bus fault.
17 TIMER1 R/W 0
Timer 0 Clock Gating Control
This bit controls the clock gating for General-Purpose Timer module 0.
If set, the unit receives a clock and functions. Otherwise, the unit is
unclocked and disabled. If the unit is unclocked, reads or writes to the
unit will generate a bus fault.
16 TIMER0 R/W 0
Software should not rely on the value of a reserved bit. To provide
compatibility with future products, the value of a reserved bit should be
preserved across a read-modify-write operation.
15:5 reserved RO 0
SSI0 Clock Gating Control
This bit controls the clock gating for SSI module 0. If set, the unit receives
a clock and functions. Otherwise, the unit is unclocked and disabled. If
the unit is unclocked, reads or writes to the unit will generate a bus fault.
4 SSI0 R/W 0
Software should not rely on the value of a reserved bit. To provide
compatibility with future products, the value of a reserved bit should be
preserved across a read-modify-write operation.
3:1 reserved RO 0
UART0 Clock Gating Control
This bit controls the clock gating for UART module 0. If set, the unit
receives a clock and functions. Otherwise, the unit is unclocked and
disabled. If the unit is unclocked, reads or writes to the unit will generate
a bus fault.
0 UART0 R/W 0
November 30, 2007 95
Preliminary
LM3S6110 Microcontroller
Register 24: Run Mode Clock Gating Control Register 2 (RCGC2), offset 0x108
This register controls the clock gating logic. Each bit controls a clock enable for a given interface,
function, or unit. If set, the unit receives a clock and functions. Otherwise, the unit is unclocked and
disabled (saving power). If the unit is unclocked, reads or writes to the unit will generate a bus fault.
The reset state of these bits is 0 (unclocked) unless otherwise noted, so that all functional units are
disabled. It is the responsibility of software to enable the ports necessary for the application. Note
that these registers may contain more bits than there are interfaces, functions, or units to control.
This is to assure reasonable code compatibility with other family and future parts. RCGC2 is the
clock configuration register for running operation, SCGC2 for Sleep operation, and DCGC2 for
Deep-Sleep operation. Setting the ACG bit in the Run-Mode Clock Configuration (RCC) register
specifies that the system uses sleep modes.
Run Mode Clock Gating Control Register 2 (RCGC2)
Base 0x400F.E000
Offset 0x108
Type R/W, reset 0x00000000
31 30 29 28 27 26 25 24 23 22 21 20 19 18 17 16
reserved EPHY0 reserved EMAC0 reserved
Type RO R/W RO R/W RO RO RO RO RO RO RO RO RO RO RO RO
Reset 0 0 0 0 0 0 0 0 0 0 0 0 0 0 0 0
15 14 13 12 11 10 9 8 7 6 5 4 3 2 1 0
reserved GPIOG GPIOF GPIOE GPIOD GPIOC GPIOB GPIOA
Type RO RO RO RO RO RO RO RO RO R/W R/W R/W R/W R/W R/W R/W
Reset 0 0 0 0 0 0 0 0 0 0 0 0 0 0 0 0
Bit/Field Name Type Reset Description
Software should not rely on the value of a reserved bit. To provide
compatibility with future products, the value of a reserved bit should be
preserved across a read-modify-write operation.
31 reserved RO 0
PHY0 Clock Gating Control
This bit controls the clock gating for Ethernet PHY unit 0. If set, the unit
receives a clock and functions. Otherwise, the unit is unclocked and
disabled. If the unit is unclocked, reads or writes to the unit will generate
a bus fault.
30 EPHY0 R/W 0
Software should not rely on the value of a reserved bit. To provide
compatibility with future products, the value of a reserved bit should be
preserved across a read-modify-write operation.
29 reserved RO 0
MAC0 Clock Gating Control
This bit controls the clock gating for Ethernet MAC unit 0. If set, the unit
receives a clock and functions. Otherwise, the unit is unclocked and
disabled. If the unit is unclocked, reads or writes to the unit will generate
a bus fault.
28 EMAC0 R/W 0
Software should not rely on the value of a reserved bit. To provide
compatibility with future products, the value of a reserved bit should be
preserved across a read-modify-write operation.
27:7 reserved RO 0
Port G Clock Gating Control
This bit controls the clock gating for Port G. If set, the unit receives a
clock and functions. Otherwise, the unit is unclocked and disabled. If
the unit is unclocked, reads or writes to the unit will generate a bus fault.
6 GPIOG R/W 0
96 November 30, 2007
Preliminary
System Control
Bit/Field Name Type Reset Description
Port F Clock Gating Control
This bit controls the clock gating for Port F. If set, the unit receives a
clock and functions. Otherwise, the unit is unclocked and disabled. If
the unit is unclocked, reads or writes to the unit will generate a bus fault.
5 GPIOF R/W 0
Port E Clock Gating Control
This bit controls the clock gating for Port E. If set, the unit receives a
clock and functions. Otherwise, the unit is unclocked and disabled. If
the unit is unclocked, reads or writes to the unit will generate a bus fault.
4 GPIOE R/W 0
Port D Clock Gating Control
This bit controls the clock gating for Port D. If set, the unit receives a
clock and functions. Otherwise, the unit is unclocked and disabled. If
the unit is unclocked, reads or writes to the unit will generate a bus fault.
3 GPIOD R/W 0
Port C Clock Gating Control
This bit controls the clock gating for Port C. If set, the unit receives a
clock and functions. Otherwise, the unit is unclocked and disabled. If
the unit is unclocked, reads or writes to the unit will generate a bus fault.
2 GPIOC R/W 0
Port B Clock Gating Control
This bit controls the clock gating for Port B. If set, the unit receives a
clock and functions. Otherwise, the unit is unclocked and disabled. If
the unit is unclocked, reads or writes to the unit will generate a bus fault.
1 GPIOB R/W 0
Port A Clock Gating Control
This bit controls the clock gating for Port A. If set, the unit receives a
clock and functions. Otherwise, the unit is unclocked and disabled. If
the unit is unclocked, reads or writes to the unit will generate a bus fault.
0 GPIOA R/W 0
November 30, 2007 97
Preliminary
LM3S6110 Microcontroller
Register 25: Sleep Mode Clock Gating Control Register 2 (SCGC2), offset
0x118
This register controls the clock gating logic. Each bit controls a clock enable for a given interface,
function, or unit. If set, the unit receives a clock and functions. Otherwise, the unit is unclocked and
disabled (saving power). If the unit is unclocked, reads or writes to the unit will generate a bus fault.
The reset state of these bits is 0 (unclocked) unless otherwise noted, so that all functional units are
disabled. It is the responsibility of software to enable the ports necessary for the application. Note
that these registers may contain more bits than there are interfaces, functions, or units to control.
This is to assure reasonable code compatibility with other family and future parts. RCGC2 is the
clock configuration register for running operation, SCGC2 for Sleep operation, and DCGC2 for
Deep-Sleep operation. Setting the ACG bit in the Run-Mode Clock Configuration (RCC) register
specifies that the system uses sleep modes.
Sleep Mode Clock Gating Control Register 2 (SCGC2)
Base 0x400F.E000
Offset 0x118
Type R/W, reset 0x00000000
31 30 29 28 27 26 25 24 23 22 21 20 19 18 17 16
reserved EPHY0 reserved EMAC0 reserved
Type RO R/W RO R/W RO RO RO RO RO RO RO RO RO RO RO RO
Reset 0 0 0 0 0 0 0 0 0 0 0 0 0 0 0 0
15 14 13 12 11 10 9 8 7 6 5 4 3 2 1 0
reserved GPIOG GPIOF GPIOE GPIOD GPIOC GPIOB GPIOA
Type RO RO RO RO RO RO RO RO RO R/W R/W R/W R/W R/W R/W R/W
Reset 0 0 0 0 0 0 0 0 0 0 0 0 0 0 0 0
Bit/Field Name Type Reset Description
Software should not rely on the value of a reserved bit. To provide
compatibility with future products, the value of a reserved bit should be
preserved across a read-modify-write operation.
31 reserved RO 0
PHY0 Clock Gating Control
This bit controls the clock gating for Ethernet PHY unit 0. If set, the unit
receives a clock and functions. Otherwise, the unit is unclocked and
disabled. If the unit is unclocked, reads or writes to the unit will generate
a bus fault.
30 EPHY0 R/W 0
Software should not rely on the value of a reserved bit. To provide
compatibility with future products, the value of a reserved bit should be
preserved across a read-modify-write operation.
29 reserved RO 0
MAC0 Clock Gating Control
This bit controls the clock gating for Ethernet MAC unit 0. If set, the unit
receives a clock and functions. Otherwise, the unit is unclocked and
disabled. If the unit is unclocked, reads or writes to the unit will generate
a bus fault.
28 EMAC0 R/W 0
Software should not rely on the value of a reserved bit. To provide
compatibility with future products, the value of a reserved bit should be
preserved across a read-modify-write operation.
27:7 reserved RO 0
98 November 30, 2007
Preliminary
System Control
Bit/Field Name Type Reset Description
Port G Clock Gating Control
This bit controls the clock gating for Port G. If set, the unit receives a
clock and functions. Otherwise, the unit is unclocked and disabled. If
the unit is unclocked, reads or writes to the unit will generate a bus fault.
6 GPIOG R/W 0
Port F Clock Gating Control
This bit controls the clock gating for Port F. If set, the unit receives a
clock and functions. Otherwise, the unit is unclocked and disabled. If
the unit is unclocked, reads or writes to the unit will generate a bus fault.
5 GPIOF R/W 0
Port E Clock Gating Control
This bit controls the clock gating for Port E. If set, the unit receives a
clock and functions. Otherwise, the unit is unclocked and disabled. If
the unit is unclocked, reads or writes to the unit will generate a bus fault.
4 GPIOE R/W 0
Port D Clock Gating Control
This bit controls the clock gating for Port D. If set, the unit receives a
clock and functions. Otherwise, the unit is unclocked and disabled. If
the unit is unclocked, reads or writes to the unit will generate a bus fault.
3 GPIOD R/W 0
Port C Clock Gating Control
This bit controls the clock gating for Port C. If set, the unit receives a
clock and functions. Otherwise, the unit is unclocked and disabled. If
the unit is unclocked, reads or writes to the unit will generate a bus fault.
2 GPIOC R/W 0
Port B Clock Gating Control
This bit controls the clock gating for Port B. If set, the unit receives a
clock and functions. Otherwise, the unit is unclocked and disabled. If
the unit is unclocked, reads or writes to the unit will generate a bus fault.
1 GPIOB R/W 0
Port A Clock Gating Control
This bit controls the clock gating for Port A. If set, the unit receives a
clock and functions. Otherwise, the unit is unclocked and disabled. If
the unit is unclocked, reads or writes to the unit will generate a bus fault.
0 GPIOA R/W 0
November 30, 2007 99
Preliminary
LM3S6110 Microcontroller
Register 26: Deep Sleep Mode Clock Gating Control Register 2 (DCGC2),
offset 0x128
This register controls the clock gating logic. Each bit controls a clock enable for a given interface,
function, or unit. If set, the unit receives a clock and functions. Otherwise, the unit is unclocked and
disabled (saving power). If the unit is unclocked, reads or writes to the unit will generate a bus fault.
The reset state of these bits is 0 (unclocked) unless otherwise noted, so that all functional units are
disabled. It is the responsibility of software to enable the ports necessary for the application. Note
that these registers may contain more bits than there are interfaces, functions, or units to control.
This is to assure reasonable code compatibility with other family and future parts. RCGC2 is the
clock configuration register for running operation, SCGC2 for Sleep operation, and DCGC2 for
Deep-Sleep operation. Setting the ACG bit in the Run-Mode Clock Configuration (RCC) register
specifies that the system uses sleep modes.
Deep Sleep Mode Clock Gating Control Register 2 (DCGC2)
Base 0x400F.E000
Offset 0x128
Type R/W, reset 0x00000000
31 30 29 28 27 26 25 24 23 22 21 20 19 18 17 16
reserved EPHY0 reserved EMAC0 reserved
Type RO R/W RO R/W RO RO RO RO RO RO RO RO RO RO RO RO
Reset 0 0 0 0 0 0 0 0 0 0 0 0 0 0 0 0
15 14 13 12 11 10 9 8 7 6 5 4 3 2 1 0
reserved GPIOG GPIOF GPIOE GPIOD GPIOC GPIOB GPIOA
Type RO RO RO RO RO RO RO RO RO R/W R/W R/W R/W R/W R/W R/W
Reset 0 0 0 0 0 0 0 0 0 0 0 0 0 0 0 0
Bit/Field Name Type Reset Description
Software should not rely on the value of a reserved bit. To provide
compatibility with future products, the value of a reserved bit should be
preserved across a read-modify-write operation.
31 reserved RO 0
PHY0 Clock Gating Control
This bit controls the clock gating for Ethernet PHY unit 0. If set, the unit
receives a clock and functions. Otherwise, the unit is unclocked and
disabled. If the unit is unclocked, reads or writes to the unit will generate
a bus fault.
30 EPHY0 R/W 0
Software should not rely on the value of a reserved bit. To provide
compatibility with future products, the value of a reserved bit should be
preserved across a read-modify-write operation.
29 reserved RO 0
MAC0 Clock Gating Control
This bit controls the clock gating for Ethernet MAC unit 0. If set, the unit
receives a clock and functions. Otherwise, the unit is unclocked and
disabled. If the unit is unclocked, reads or writes to the unit will generate
a bus fault.
28 EMAC0 R/W 0
Software should not rely on the value of a reserved bit. To provide
compatibility with future products, the value of a reserved bit should be
preserved across a read-modify-write operation.
27:7 reserved RO 0
100 November 30, 2007
Preliminary
System Control
Bit/Field Name Type Reset Description
Port G Clock Gating Control
This bit controls the clock gating for Port G. If set, the unit receives a
clock and functions. Otherwise, the unit is unclocked and disabled. If
the unit is unclocked, reads or writes to the unit will generate a bus fault.
6 GPIOG R/W 0
Port F Clock Gating Control
This bit controls the clock gating for Port F. If set, the unit receives a
clock and functions. Otherwise, the unit is unclocked and disabled. If
the unit is unclocked, reads or writes to the unit will generate a bus fault.
5 GPIOF R/W 0
Port E Clock Gating Control
This bit controls the clock gating for Port E. If set, the unit receives a
clock and functions. Otherwise, the unit is unclocked and disabled. If
the unit is unclocked, reads or writes to the unit will generate a bus fault.
4 GPIOE R/W 0
Port D Clock Gating Control
This bit controls the clock gating for Port D. If set, the unit receives a
clock and functions. Otherwise, the unit is unclocked and disabled. If
the unit is unclocked, reads or writes to the unit will generate a bus fault.
3 GPIOD R/W 0
Port C Clock Gating Control
This bit controls the clock gating for Port C. If set, the unit receives a
clock and functions. Otherwise, the unit is unclocked and disabled. If
the unit is unclocked, reads or writes to the unit will generate a bus fault.
2 GPIOC R/W 0
Port B Clock Gating Control
This bit controls the clock gating for Port B. If set, the unit receives a
clock and functions. Otherwise, the unit is unclocked and disabled. If
the unit is unclocked, reads or writes to the unit will generate a bus fault.
1 GPIOB R/W 0
Port A Clock Gating Control
This bit controls the clock gating for Port A. If set, the unit receives a
clock and functions. Otherwise, the unit is unclocked and disabled. If
the unit is unclocked, reads or writes to the unit will generate a bus fault.
0 GPIOA R/W 0
November 30, 2007 101
Preliminary
LM3S6110 Microcontroller
Register 27: Software Reset Control 0 (SRCR0), offset 0x040
Writes to this register are masked by the bits in the Device Capabilities 1 (DC1) register.
Software Reset Control 0 (SRCR0)
Base 0x400F.E000
Offset 0x040
Type R/W, reset 0x00000000
31 30 29 28 27 26 25 24 23 22 21 20 19 18 17 16
reserved PWM reserved
Type RO RO RO RO RO RO RO RO RO RO RO R/W RO RO RO RO
Reset 0 0 0 0 0 0 0 0 0 0 0 0 0 0 0 0
15 14 13 12 11 10 9 8 7 6 5 4 3 2 1 0
reserved WDT reserved
Type RO RO RO RO RO RO RO RO RO RO RO RO R/W RO RO RO
Reset 0 0 0 0 0 0 0 0 0 0 0 0 0 0 0 0
Bit/Field Name Type Reset Description
Software should not rely on the value of a reserved bit. To provide
compatibility with future products, the value of a reserved bit should be
preserved across a read-modify-write operation.
31:21 reserved RO 0
PWM Reset Control
Reset control for PWM module.
20 PWM R/W 0
Software should not rely on the value of a reserved bit. To provide
compatibility with future products, the value of a reserved bit should be
preserved across a read-modify-write operation.
19:4 reserved RO 0
WDT Reset Control
Reset control for Watchdog unit.
3 WDT R/W 0
Software should not rely on the value of a reserved bit. To provide
compatibility with future products, the value of a reserved bit should be
preserved across a read-modify-write operation.
2:0 reserved RO 0
102 November 30, 2007
Preliminary
System Control
Register 28: Software Reset Control 1 (SRCR1), offset 0x044
Writes to this register are masked by the bits in the Device Capabilities 2 (DC2) register.
Software Reset Control 1 (SRCR1)
Base 0x400F.E000
Offset 0x044
Type R/W, reset 0x00000000
31 30 29 28 27 26 25 24 23 22 21 20 19 18 17 16
reserved COMP2 COMP1 COMP0 reserved TIMER2 TIMER1 TIMER0
Type RO RO RO RO RO R/W R/W R/W RO RO RO RO RO R/W R/W R/W
Reset 0 0 0 0 0 0 0 0 0 0 0 0 0 0 0 0
15 14 13 12 11 10 9 8 7 6 5 4 3 2 1 0
reserved SSI0 reserved UART0
Type RO RO RO RO RO RO RO RO RO RO RO R/W RO RO RO R/W
Reset 0 0 0 0 0 0 0 0 0 0 0 0 0 0 0 0
Bit/Field Name Type Reset Description
Software should not rely on the value of a reserved bit. To provide
compatibility with future products, the value of a reserved bit should be
preserved across a read-modify-write operation.
31:27 reserved RO 0
Analog Comp 2 Reset Control
Reset control for analog comparator 2.
26 COMP2 R/W 0
Analog Comp 1 Reset Control
Reset control for analog comparator 1.
25 COMP1 R/W 0
Analog Comp 0 Reset Control
Reset control for analog comparator 0.
24 COMP0 R/W 0
Software should not rely on the value of a reserved bit. To provide
compatibility with future products, the value of a reserved bit should be
preserved across a read-modify-write operation.
23:19 reserved RO 0
Timer 2 Reset Control
Reset control for General-Purpose Timer module 2.
18 TIMER2 R/W 0
Timer 1 Reset Control
Reset control for General-Purpose Timer module 1.
17 TIMER1 R/W 0
Timer 0 Reset Control
Reset control for General-Purpose Timer module 0.
16 TIMER0 R/W 0
Software should not rely on the value of a reserved bit. To provide
compatibility with future products, the value of a reserved bit should be
preserved across a read-modify-write operation.
15:5 reserved RO 0
SSI0 Reset Control
Reset control for SSI unit 0.
4 SSI0 R/W 0
Software should not rely on the value of a reserved bit. To provide
compatibility with future products, the value of a reserved bit should be
preserved across a read-modify-write operation.
3:1 reserved RO 0
November 30, 2007 103
Preliminary
LM3S6110 Microcontroller
Bit/Field Name Type Reset Description
UART0 Reset Control
Reset control for UART unit 0.
0 UART0 R/W 0
104 November 30, 2007
Preliminary
System Control
Register 29: Software Reset Control 2 (SRCR2), offset 0x048
Writes to this register are masked by the bits in the Device Capabilities 4 (DC4) register.
Software Reset Control 2 (SRCR2)
Base 0x400F.E000
Offset 0x048
Type R/W, reset 0x00000000
31 30 29 28 27 26 25 24 23 22 21 20 19 18 17 16
reserved EPHY0 reserved EMAC0 reserved
Type RO R/W RO R/W RO RO RO RO RO RO RO RO RO RO RO RO
Reset 0 0 0 0 0 0 0 0 0 0 0 0 0 0 0 0
15 14 13 12 11 10 9 8 7 6 5 4 3 2 1 0
reserved GPIOG GPIOF GPIOE GPIOD GPIOC GPIOB GPIOA
Type RO RO RO RO RO RO RO RO RO R/W R/W R/W R/W R/W R/W R/W
Reset 0 0 0 0 0 0 0 0 0 0 0 0 0 0 0 0
Bit/Field Name Type Reset Description
Software should not rely on the value of a reserved bit. To provide
compatibility with future products, the value of a reserved bit should be
preserved across a read-modify-write operation.
31 reserved RO 0
PHY0 Reset Control
Reset control for Ethernet PHY unit 0.
30 EPHY0 R/W 0
Software should not rely on the value of a reserved bit. To provide
compatibility with future products, the value of a reserved bit should be
preserved across a read-modify-write operation.
29 reserved RO 0
MAC0 Reset Control
Reset control for Ethernet MAC unit 0.
28 EMAC0 R/W 0
Software should not rely on the value of a reserved bit. To provide
compatibility with future products, the value of a reserved bit should be
preserved across a read-modify-write operation.
27:7 reserved RO 0
Port G Reset Control
Reset control for GPIO Port G.
6 GPIOG R/W 0
Port F Reset Control
Reset control for GPIO Port F.
5 GPIOF R/W 0
Port E Reset Control
Reset control for GPIO Port E.
4 GPIOE R/W 0
Port D Reset Control
Reset control for GPIO Port D.
3 GPIOD R/W 0
Port C Reset Control
Reset control for GPIO Port C.
2 GPIOC R/W 0
Port B Reset Control
Reset control for GPIO Port B.
1 GPIOB R/W 0
November 30, 2007 105
Preliminary
LM3S6110 Microcontroller
Bit/Field Name Type Reset Description
Port A Reset Control
Reset control for GPIO Port A.
0 GPIOA R/W 0
106 November 30, 2007
Preliminary
System Control
7 Internal Memory
The LM3S6110 microcontroller comes with 16 KB of bit-banded SRAM and 64 KB of flash memory.
The flash controller provides a user-friendly interface, making flash programming a simple task.
Flash protection can be applied to the flash memory on a 2-KB block basis.
7.1 Block Diagram
Figure 7-1. Flash Block Diagram
Flash Control
FMA
FCMISC
FCIM
FCRIS
FMC
FMD
Flash Timing
USECRL
Flash Protection
FMPREn
FMPPEn
Flash Array
SRAM Array
Bridge
Cortex-M3
ICode
DCode
System Bus
APB
User Registers
USER_REG0
USER_REG1
USER_DBG
7.2 Functional Description
This section describes the functionality of both the flash and SRAM memories.
7.2.1 SRAM Memory
The internal SRAM of the Stellaris® devices is located at address 0x2000.0000 of the device memory
map. To reduce the number of time consuming read-modify-write (RMW) operations, ARM has
introduced bit-banding technology in the Cortex-M3 processor. With a bit-band-enabled processor,
certain regions in the memory map (SRAM and peripheral space) can use address aliases to access
individual bits in a single, atomic operation.
The bit-band alias is calculated by using the formula:
November 30, 2007 107
Preliminary
LM3S6110 Microcontroller
bit-band alias = bit-band base + (byte offset * 32) + (bit number * 4)
For example, if bit 3 at address 0x2000.1000 is to be modified, the bit-band alias is calculated as:
0x2200.0000 + (0x1000 * 32) + (3 * 4) = 0x2202.000C
With the alias address calculated, an instruction performing a read/write to address 0x2202.000C
allows direct access to only bit 3 of the byte at address 0x2000.1000.
For details about bit-banding, please refer to Chapter 4, “Memory Map” in the ARM® Cortex™-M3
Technical Reference Manual.
7.2.2 Flash Memory
The flash is organized as a set of 1-KB blocks that can be individually erased. Erasing a block
causes the entire contents of the block to be reset to all 1s. An individual 32-bit word can be
programmed to change bits that are currently 1 to a 0. These blocks are paired into a set of 2-KB
blocks that can be individually protected. The protection allows blocks to be marked as read-only
or execute-only, providing different levels of code protection. Read-only blocks cannot be erased
or programmed, protecting the contents of those blocks from being modified. Execute-only blocks
cannot be erased or programmed, and can only be read by the controller instruction fetch mechanism,
protecting the contents of those blocks from being read by either the controller or by a debugger.
See also “Serial Flash Loader” on page 430 for a preprogrammed flash-resident utility used to
download code to the flash memory of a device without the use of a debug interface.
7.2.2.1 Flash Memory Timing
The timing for the flash is automatically handled by the flash controller. However, in order to do so,
it must know the clock rate of the system in order to time its internal signals properly. The number
of clock cycles per microsecond must be provided to the flash controller for it to accomplish this
timing. It is software's responsibility to keep the flash controller updated with this information via the
USec Reload (USECRL) register.
On reset, the USECRL register is loaded with a value that configures the flash timing so that it works
with the maximum clock rate of the part. If software changes the system operating frequency, the
new operating frequency minus 1 (in MHz) must be loaded into USECRL before any flash
modifications are attempted. For example, if the device is operating at a speed of 20 MHz, a value
of 0x13 (20-1) must be written to the USECRL register.
7.2.2.2 Flash Memory Protection
The user is provided two forms of flash protection per 2-KB flash blocks in one pair of 32-bit wide
registers. The protection policy for each form is controlled by individual bits (per policy per block)
in the FMPPEn and FMPREn registers.
■ Flash Memory Protection Program Enable (FMPPEn): If set, the block may be programmed
(written) or erased. If cleared, the block may not be changed.
■ Flash Memory Protection Read Enable (FMPREn): If set, the block may be executed or read
by software or debuggers. If cleared, the block may only be executed. The contents of the memory
block are prohibited from being accessed as data and traversing the DCode bus.
The policies may be combined as shown in Table 7-1 on page 109.
108 November 30, 2007
Preliminary
Internal Memory
Table 7-1. Flash Protection Policy Combinations
FMPPEn FMPREn Protection
Execute-only protection. The block may only be executed and may not be written or erased. This mode
is used to protect code.
0 0
1 0 The block may be written, erased or executed, but not read. This combination is unlikely to be used.
Read-only protection. The block may be read or executed but may not be written or erased. This mode
is used to lock the block from further modification while allowing any read or execute access.
0 1
1 1 No protection. The block may be written, erased, executed or read.
An access that attempts to program or erase a PE-protected block is prohibited. A controller interrupt
may be optionally generated (by setting the AMASK bit in the FIM register) to alert software developers
of poorly behaving software during the development and debug phases.
An access that attempts to read an RE-protected block is prohibited. Such accesses return data
filled with all 0s. A controller interrupt may be optionally generated to alert software developers of
poorly behaving software during the development and debug phases.
The factory settings for the FMPREn and FMPPEn registers are a value of 1 for all implemented
banks. This implements a policy of open access and programmability. The register bits may be
changed by writing the specific register bit. The changes are not permanent until the register is
committed (saved), at which point the bit change is permanent. If a bit is changed from a 1 to a 0
and not committed, it may be restored by executing a power-on reset sequence. Details on
programming these bits are discussed in “Nonvolatile Register Programming” on page 110.
7.3 Flash Memory Initialization and Configuration
7.3.1 Flash Programming
The Stellaris® devices provide a user-friendly interface for flash programming. All erase/program
operations are handled via three registers: FMA, FMD, and FMC.
7.3.1.1 To program a 32-bit word
1. Write source data to the FMD register.
2. Write the target address to the FMA register.
3. Write the flash write key and the WRITE bit (a value of 0xA442.0001) to the FMC register.
4. Poll the FMC register until the WRITE bit is cleared.
7.3.1.2 To perform an erase of a 1-KB page
1. Write the page address to the FMA register.
2. Write the flash write key and the ERASE bit (a value of 0xA442.0002) to the FMC register.
3. Poll the FMC register until the ERASE bit is cleared.
7.3.1.3 To perform a mass erase of the flash
1. Write the flash write key and the MERASE bit (a value of 0xA442.0004) to the FMC register.
2. Poll the FMC register until the MERASE bit is cleared.
November 30, 2007 109
Preliminary
LM3S6110 Microcontroller
7.3.2 Nonvolatile Register Programming
This section discusses how to update registers that are resident within the flash memory itself.
These registers exist in a separate space from the main flash array and are not affected by an
ERASE or MASS ERASE operation. These nonvolatile registers are updated by using the COMT bit
in the FMC register to activate a write operation. For the USER_DBG register, the data to be written
must be loaded into the FMD register before it is "committed". All other registers are R/W and can
have their operation tried before committing them to nonvolatile memory.
Important: These registers can only have bits changed from 1 to 0 by the user and there is no
mechanism for the user to erase them back to a 1 value.
In addition, the USER_REG0, USER_REG1, and USER_DBG use bit 31 (NW) of their respective
registers to indicate that they are available for user write. These three registers can only be written
once whereas the flash protection registers may be written multiple times. Table 7-2 on page 110
provides the FMA address required for commitment of each of the registers and the source of the
data to be written when the COMT bit of the FMC register is written with a value of 0xA442.0008.
After writing the COMT bit, the user may poll the FMC register to wait for the commit operation to
complete.
Table 7-2. Flash Resident Registersa
Register to be Committed FMA Value Data Source
FMPRE0 0x0000.0000 FMPRE0
FMPRE1 0x0000.0002 FMPRE1
FMPRE2 0x0000.0004 FMPRE2
FMPRE3 0x0000.0008 FMPRE3
FMPPE0 0x0000.0001 FMPPE0
FMPPE1 0x0000.0003 FMPPE1
FMPPE2 0x0000.0005 FMPPE2
FMPPE3 0x0000.0007 FMPPE3
USER_REG0 0x8000.0000 USER_REG0
USER_REG1 0x8000.0001 USER_REG1
USER_DBG 0x7510.0000 FMD
a. Which FMPREn and FMPPEn registers are available depend on the flash size of your particular Stellaris® device.
7.4 Register Map
Table 7-3 on page 110 lists the Flash memory and control registers. The offset listed is a hexadecimal
increment to the register's address. The FMA, FMD, FMC, FCRIS, FCIM, and FCMISC registers
are relative to the Flash control base address of 0x400F.D000. The FMPREn, FMPPEn, USECRL,
USER_DBG, and USER_REGn registers are relative to the System Control base address of
0x400F.E000.
Table 7-3. Flash Register Map
See
Offset Name Type Reset Description page
Flash Control Offset
0x000 FMA R/W 0x0000.0000 Flash Memory Address 112
110 November 30, 2007
Preliminary
Internal Memory
See
Offset Name Type Reset Description page
0x004 FMD R/W 0x0000.0000 Flash Memory Data 113
0x008 FMC R/W 0x0000.0000 Flash Memory Control 114
0x00C FCRIS RO 0x0000.0000 Flash Controller Raw Interrupt Status 116
0x010 FCIM R/W 0x0000.0000 Flash Controller Interrupt Mask 117
0x014 FCMISC R/W1C 0x0000.0000 Flash Controller Masked Interrupt Status and Clear 118
System Control Offset
0x130 FMPRE0 R/W 0xFFFF.FFFF Flash Memory Protection Read Enable 0 120
0x200 FMPRE0 R/W 0xFFFF.FFFF Flash Memory Protection Read Enable 0 120
0x134 FMPPE0 R/W 0xFFFF.FFFF Flash Memory Protection Program Enable 0 121
0x400 FMPPE0 R/W 0xFFFF.FFFF Flash Memory Protection Program Enable 0 121
0x140 USECRL R/W 0x16 USec Reload 119
0x1D0 USER_DBG R/W 0xFFFF.FFFE User Debug 122
0x1E0 USER_REG0 R/W 0xFFFF.FFFF User Register 0 123
0x1E4 USER_REG1 R/W 0xFFFF.FFFF User Register 1 124
0x204 FMPRE1 R/W 0x0000.0000 Flash Memory Protection Read Enable 1 125
0x208 FMPRE2 R/W 0x0000.0000 Flash Memory Protection Read Enable 2 126
0x20C FMPRE3 R/W 0x0000.0000 Flash Memory Protection Read Enable 3 127
0x404 FMPPE1 R/W 0x0000.0000 Flash Memory Protection Program Enable 1 128
0x408 FMPPE2 R/W 0x0000.0000 Flash Memory Protection Program Enable 2 129
0x40C FMPPE3 R/W 0x0000.0000 Flash Memory Protection Program Enable 3 130
7.5 Flash Register Descriptions (Flash Control Offset)
The remainder of this section lists and describes the Flash Memory registers, in numerical order by
address offset. Registers in this section are relative to the Flash control base address of 0x400F.D000.
November 30, 2007 111
Preliminary
LM3S6110 Microcontroller
Register 1: Flash Memory Address (FMA), offset 0x000
During a write operation, this register contains a 4-byte-aligned address and specifies where the
data is written. During erase operations, this register contains a 1 KB-aligned address and specifies
which page is erased. Note that the alignment requirements must be met by software or the results
of the operation are unpredictable.
Flash Memory Address (FMA)
Base 0x400F.D000
Offset 0x000
Type R/W, reset 0x0000.0000
31 30 29 28 27 26 25 24 23 22 21 20 19 18 17 16
reserved
Type RO RO RO RO RO RO RO RO RO RO RO RO RO RO RO RO
Reset 0 0 0 0 0 0 0 0 0 0 0 0 0 0 0 0
15 14 13 12 11 10 9 8 7 6 5 4 3 2 1 0
OFFSET
Type R/W R/W R/W R/W R/W R/W R/W R/W R/W R/W R/W R/W R/W R/W R/W R/W
Reset 0 0 0 0 0 0 0 0 0 0 0 0 0 0 0 0
Bit/Field Name Type Reset Description
Software should not rely on the value of a reserved bit. To provide
compatibility with future products, the value of a reserved bit should be
preserved across a read-modify-write operation.
31:16 reserved RO 0x0
Address Offset
Address offset in flash where operation is performed, except for
nonvolatile registers (see “Nonvolatile Register Programming” on page
110 for details on values for this field).
15:0 OFFSET R/W 0x0
112 November 30, 2007
Preliminary
Internal Memory
Register 2: Flash Memory Data (FMD), offset 0x004
This register contains the data to be written during the programming cycle or read during the read
cycle. Note that the contents of this register are undefined for a read access of an execute-only
block. This register is not used during the erase cycles.
Flash Memory Data (FMD)
Base 0x400F.D000
Offset 0x004
Type R/W, reset 0x0000.0000
31 30 29 28 27 26 25 24 23 22 21 20 19 18 17 16
DATA
Type R/W R/W R/W R/W R/W R/W R/W R/W R/W R/W R/W R/W R/W R/W R/W R/W
Reset 0 0 0 0 0 0 0 0 0 0 0 0 0 0 0 0
15 14 13 12 11 10 9 8 7 6 5 4 3 2 1 0
DATA
Type R/W R/W R/W R/W R/W R/W R/W R/W R/W R/W R/W R/W R/W R/W R/W R/W
Reset 0 0 0 0 0 0 0 0 0 0 0 0 0 0 0 0
Bit/Field Name Type Reset Description
Data Value
Data value for write operation.
31:0 DATA R/W 0x0
November 30, 2007 113
Preliminary
LM3S6110 Microcontroller
Register 3: Flash Memory Control (FMC), offset 0x008
When this register is written, the flash controller initiates the appropriate access cycle for the location
specified by the Flash Memory Address (FMA) register (see page 112). If the access is a write
access, the data contained in the Flash Memory Data (FMD) register (see page 113) is written.
This is the final register written and initiates the memory operation. There are four control bits in the
lower byte of this register that, when set, initiate the memory operation. The most used of these
register bits are the ERASE and WRITE bits.
It is a programming error to write multiple control bits and the results of such an operation are
unpredictable.
Flash Memory Control (FMC)
Base 0x400F.D000
Offset 0x008
Type R/W, reset 0x0000.0000
31 30 29 28 27 26 25 24 23 22 21 20 19 18 17 16
WRKEY
Type WO WO WO WO WO WO WO WO WO WO WO WO WO WO WO WO
Reset 0 0 0 0 0 0 0 0 0 0 0 0 0 0 0 0
15 14 13 12 11 10 9 8 7 6 5 4 3 2 1 0
reserved COMT MERASE ERASE WRITE
Type RO RO RO RO RO RO RO RO RO RO RO RO R/W R/W R/W R/W
Reset 0 0 0 0 0 0 0 0 0 0 0 0 0 0 0 0
Bit/Field Name Type Reset Description
Flash Write Key
This field contains a write key, which is used to minimize the incidence
of accidental flash writes. The value 0xA442 must be written into this
field for a write to occur. Writes to the FMC register without this WRKEY
value are ignored. A read of this field returns the value 0.
31:16 WRKEY WO 0x0
Software should not rely on the value of a reserved bit. To provide
compatibility with future products, the value of a reserved bit should be
preserved across a read-modify-write operation.
15:4 reserved RO 0x0
Commit Register Value
Commit (write) of register value to nonvolatile storage. A write of 0 has
no effect on the state of this bit.
If read, the state of the previous commit access is provided. If the
previous commit access is complete, a 0 is returned; otherwise, if the
commit access is not complete, a 1 is returned.
This can take up to 50 μs.
3 COMT R/W 0
Mass Erase Flash Memory
If this bit is set, the flash main memory of the device is all erased. A
write of 0 has no effect on the state of this bit.
If read, the state of the previous mass erase access is provided. If the
previous mass erase access is complete, a 0 is returned; otherwise, if
the previous mass erase access is not complete, a 1 is returned.
This can take up to 250 ms.
2 MERASE R/W 0
114 November 30, 2007
Preliminary
Internal Memory
Bit/Field Name Type Reset Description
Erase a Page of Flash Memory
If this bit is set, the page of flash main memory as specified by the
contents of FMA is erased. A write of 0 has no effect on the state of this
bit.
If read, the state of the previous erase access is provided. If the previous
erase access is complete, a 0 is returned; otherwise, if the previous
erase access is not complete, a 1 is returned.
This can take up to 25 ms.
1 ERASE R/W 0
Write a Word into Flash Memory
If this bit is set, the data stored in FMD is written into the location as
specified by the contents of FMA. A write of 0 has no effect on the state
of this bit.
If read, the state of the previous write update is provided. If the previous
write access is complete, a 0 is returned; otherwise, if the write access
is not complete, a 1 is returned.
This can take up to 50 μs.
0 WRITE R/W 0
November 30, 2007 115
Preliminary
LM3S6110 Microcontroller
Register 4: Flash Controller Raw Interrupt Status (FCRIS), offset 0x00C
This register indicates that the flash controller has an interrupt condition. An interrupt is only signaled
if the corresponding FCIM register bit is set.
Flash Controller Raw Interrupt Status (FCRIS)
Base 0x400F.D000
Offset 0x00C
Type RO, reset 0x0000.0000
31 30 29 28 27 26 25 24 23 22 21 20 19 18 17 16
reserved
Type RO RO RO RO RO RO RO RO RO RO RO RO RO RO RO RO
Reset 0 0 0 0 0 0 0 0 0 0 0 0 0 0 0 0
15 14 13 12 11 10 9 8 7 6 5 4 3 2 1 0
reserved PRIS ARIS
Type RO RO RO RO RO RO RO RO RO RO RO RO RO RO RO RO
Reset 0 0 0 0 0 0 0 0 0 0 0 0 0 0 0 0
Bit/Field Name Type Reset Description
Software should not rely on the value of a reserved bit. To provide
compatibility with future products, the value of a reserved bit should be
preserved across a read-modify-write operation.
31:2 reserved RO 0x00
Programming Raw Interrupt Status
This bit indicates the current state of the programming cycle. If set, the
programming cycle completed; if cleared, the programming cycle has
not completed. Programming cycles are either write or erase actions
generated through the Flash Memory Control (FMC) register bits (see
page 114).
1 PRIS RO 0
Access Raw Interrupt Status
This bit indicates if the flash was improperly accessed. If set, the program
tried to access the flash counter to the policy as set in the Flash Memory
Protection Read Enable (FMPREn) and Flash Memory Protection
Program Enable (FMPPEn) registers. Otherwise, no access has tried
to improperly access the flash.
0 ARIS RO 0
116 November 30, 2007
Preliminary
Internal Memory
Register 5: Flash Controller Interrupt Mask (FCIM), offset 0x010
This register controls whether the flash controller generates interrupts to the controller.
Flash Controller Interrupt Mask (FCIM)
Base 0x400F.D000
Offset 0x010
Type R/W, reset 0x0000.0000
31 30 29 28 27 26 25 24 23 22 21 20 19 18 17 16
reserved
Type RO RO RO RO RO RO RO RO RO RO RO RO RO RO RO RO
Reset 0 0 0 0 0 0 0 0 0 0 0 0 0 0 0 0
15 14 13 12 11 10 9 8 7 6 5 4 3 2 1 0
reserved PMASK AMASK
Type RO RO RO RO RO RO RO RO RO RO RO RO RO RO R/W R/W
Reset 0 0 0 0 0 0 0 0 0 0 0 0 0 0 0 0
Bit/Field Name Type Reset Description
Software should not rely on the value of a reserved bit. To provide
compatibility with future products, the value of a reserved bit should be
preserved across a read-modify-write operation.
31:2 reserved RO 0x00
Programming Interrupt Mask
This bit controls the reporting of the programming raw interrupt status
to the controller. If set, a programming-generated interrupt is promoted
to the controller. Otherwise, interrupts are recorded but suppressed from
the controller.
1 PMASK R/W 0
Access Interrupt Mask
This bit controls the reporting of the access raw interrupt status to the
controller. If set, an access-generated interrupt is promoted to the
controller. Otherwise, interrupts are recorded but suppressed from the
controller.
0 AMASK R/W 0
November 30, 2007 117
Preliminary
LM3S6110 Microcontroller
Register 6: Flash Controller Masked Interrupt Status and Clear (FCMISC),
offset 0x014
This register provides two functions. First, it reports the cause of an interrupt by indicating which
interrupt source or sources are signalling the interrupt. Second, it serves as the method to clear the
interrupt reporting.
Flash Controller Masked Interrupt Status and Clear (FCMISC)
Base 0x400F.D000
Offset 0x014
Type R/W1C, reset 0x0000.0000
31 30 29 28 27 26 25 24 23 22 21 20 19 18 17 16
reserved
Type RO RO RO RO RO RO RO RO RO RO RO RO RO RO RO RO
Reset 0 0 0 0 0 0 0 0 0 0 0 0 0 0 0 0
15 14 13 12 11 10 9 8 7 6 5 4 3 2 1 0
reserved PMISC AMISC
Type RO RO RO RO RO RO RO RO RO RO RO RO RO RO R/W1C R/W1C
Reset 0 0 0 0 0 0 0 0 0 0 0 0 0 0 0 0
Bit/Field Name Type Reset Description
Software should not rely on the value of a reserved bit. To provide
compatibility with future products, the value of a reserved bit should be
preserved across a read-modify-write operation.
31:2 reserved RO 0x00
Programming Masked Interrupt Status and Clear
This bit indicates whether an interrupt was signaled because a
programming cycle completed and was not masked. This bit is cleared
by writing a 1. The PRIS bit in the FCRIS register (see page 116) is also
cleared when the PMISC bit is cleared.
1 PMISC R/W1C 0
Access Masked Interrupt Status and Clear
This bit indicates whether an interrupt was signaled because an improper
access was attempted and was not masked. This bit is cleared by writing
a 1. The ARIS bit in the FCRIS register is also cleared when the AMISC
bit is cleared.
0 AMISC R/W1C 0
7.6 Flash Register Descriptions (System Control Offset)
The remainder of this section lists and describes the Flash Memory registers, in numerical order by
address offset. Registers in this section are relative to the System Control base address of
0x400F.E000.
118 November 30, 2007
Preliminary
Internal Memory
Register 7: USec Reload (USECRL), offset 0x140
Note: Offset is relative to System Control base address of 0x400F.E000
This register is provided as a means of creating a 1-μs tick divider reload value for the flash controller.
The internal flash has specific minimum and maximum requirements on the length of time the high
voltage write pulse can be applied. It is required that this register contain the operating frequency
(in MHz -1) whenever the flash is being erased or programmed. The user is required to change this
value if the clocking conditions are changed for a flash erase/program operation.
USec Reload (USECRL)
Base 0x400F.E000
Offset 0x140
Type R/W, reset 0x16
31 30 29 28 27 26 25 24 23 22 21 20 19 18 17 16
reserved
Type RO RO RO RO RO RO RO RO RO RO RO RO RO RO RO RO
Reset 0 0 0 0 0 0 0 0 0 0 0 0 0 0 0 0
15 14 13 12 11 10 9 8 7 6 5 4 3 2 1 0
reserved USEC
Type RO RO RO RO RO RO RO RO R/W R/W R/W R/W R/W R/W R/W R/W
Reset 0 0 0 0 0 0 0 0 0 0 0 1 1 0 0 0
Bit/Field Name Type Reset Description
Software should not rely on the value of a reserved bit. To provide
compatibility with future products, the value of a reserved bit should be
preserved across a read-modify-write operation.
31:8 reserved RO 0x00
Microsecond Reload Value
MHz -1 of the controller clock when the flash is being erased or
programmed.
USEC should be set to 0x18 (24 MHz) whenever the flash is being erased
or programmed.
7:0 USEC R/W 0x18
November 30, 2007 119
Preliminary
LM3S6110 Microcontroller
Register 8: Flash Memory Protection Read Enable 0 (FMPRE0), offset 0x130
and 0x200
Note: This register is aliased for backwards compatability.
Note: Offset is relative to System Control base address of 0x400FE000.
This register stores the read-only protection bits for each 2-KB flash block (FMPPEn stores the
execute-only bits). This register is loaded during the power-on reset sequence. The factory settings
for the FMPREn and FMPPEn registers are a value of 1 for all implemented banks. This achieves
a policy of open access and programmability. The register bits may be changed by writing the
specific register bit. However, this register is R/W0; the user can only change the protection bit from
a 1 to a 0 (and may NOT change a 0 to a 1). The changes are not permanent until the register is
committed (saved), at which point the bit change is permanent. If a bit is changed from a 1 to a 0
and not committed, it may be restored by executing a power-on reset sequence. For additional
information, see the "Flash Memory Protection" section.
Flash Memory Protection Read Enable 0 (FMPRE0)
Base 0x400F.D000
Offset 0x130 and 0x200
Type R/W, reset 0xFFFF.FFFF
31 30 29 28 27 26 25 24 23 22 21 20 19 18 17 16
READ_ENABLE
Type R/W R/W R/W R/W R/W R/W R/W R/W R/W R/W R/W R/W R/W R/W R/W R/W
Reset 1 1 1 1 1 1 1 1 1 1 1 1 1 1 1 1
15 14 13 12 11 10 9 8 7 6 5 4 3 2 1 0
READ_ENABLE
Type R/W R/W R/W R/W R/W R/W R/W R/W R/W R/W R/W R/W R/W R/W R/W R/W
Reset 1 1 1 1 1 1 1 1 1 1 1 1 1 1 1 1
Bit/Field Name Type Reset Description
Flash Read Enable
Enables 2-KB flash blocks to be executed or read. The policies may be
combined as shown in the table “Flash Protection Policy Combinations”.
Value Description
0xFFFFFFFF Enables 64 KB of flash.
31:0 READ_ENABLE R/W 0xFFFFFFFF
120 November 30, 2007
Preliminary
Internal Memory
Register 9: Flash Memory Protection Program Enable 0 (FMPPE0), offset
0x134 and 0x400
Note: This register is aliased for backwards compatability.
Note: Offset is relative to System Control base address of 0x400FE000.
This register stores the execute-only protection bits for each 2-KB flash block (FMPREn stores the
execute-only bits). This register is loaded during the power-on reset sequence. The factory settings
for the FMPREn and FMPPEn registers are a value of 1 for all implemented banks. This achieves
a policy of open access and programmability. The register bits may be changed by writing the
specific register bit. However, this register is R/W0; the user can only change the protection bit from
a 1 to a 0 (and may NOT change a 0 to a 1). The changes are not permanent until the register is
committed (saved), at which point the bit change is permanent. If a bit is changed from a 1 to a 0
and not committed, it may be restored by executing a power-on reset sequence. For additional
information, see the "Flash Memory Protection" section.
Flash Memory Protection Program Enable 0 (FMPPE0)
Base 0x400F.D000
Offset 0x134 and 0x400
Type R/W, reset 0xFFFF.FFFF
31 30 29 28 27 26 25 24 23 22 21 20 19 18 17 16
PROG_ENABLE
Type R/W R/W R/W R/W R/W R/W R/W R/W R/W R/W R/W R/W R/W R/W R/W R/W
Reset 1 1 1 1 1 1 1 1 1 1 1 1 1 1 1 1
15 14 13 12 11 10 9 8 7 6 5 4 3 2 1 0
PROG_ENABLE
Type R/W R/W R/W R/W R/W R/W R/W R/W R/W R/W R/W R/W R/W R/W R/W R/W
Reset 1 1 1 1 1 1 1 1 1 1 1 1 1 1 1 1
Bit/Field Name Type Reset Description
Flash Programming Enable
Configures 2-KB flash blocks to be execute only. The policies may be
combined as shown in the table “Flash Protection Policy Combinations”.
Value Description
0xFFFFFFFF Enables 64 KB of flash.
31:0 PROG_ENABLE R/W 0xFFFFFFFF
November 30, 2007 121
Preliminary
LM3S6110 Microcontroller
Register 10: User Debug (USER_DBG), offset 0x1D0
Note: Offset is relative to System Control base address of 0x400FE000.
This register provides a write-once mechanism to disable external debugger access to the device
in addition to 27 additional bits of user-defined data. The DBG0 bit (bit 0) is set to 0 from the factory
and the DBG1 bit (bit 1) is set to 1, which enables external debuggers. Changing the DBG1 bit to 0
disables any external debugger access to the device permanently, starting with the next power-up
cycle of the device. The NOTWRITTEN bit (bit 31) indicates that the register is available to be written
and is controlled through hardware to ensure that the register is only written once.
User Debug (USER_DBG)
Base 0x400F.E000
Offset 0x1D0
Type R/W, reset 0xFFFF.FFFE
31 30 29 28 27 26 25 24 23 22 21 20 19 18 17 16
NW DATA
Type R/W R/W R/W R/W R/W R/W R/W R/W R/W R/W R/W R/W R/W R/W R/W R/W
Reset 1 1 1 1 1 1 1 1 1 1 1 1 1 1 1 1
15 14 13 12 11 10 9 8 7 6 5 4 3 2 1 0
DATA DBG1 DBG0
Type R/W R/W R/W R/W R/W R/W R/W R/W R/W R/W R/W R/W R/W R/W R/W R/W
Reset 1 1 1 1 1 1 1 1 1 1 1 1 1 1 1 0
Bit/Field Name Type Reset Description
User Debug Not Written
Specifies that this 32-bit dword has not been written.
31 NW R/W 1
User Data
Contains the user data value. This field is initialized to all 1s and can
only be written once.
30:2 DATA R/W 0x1FFFFFFF
Debug Control 1
The DBG1 bit must be 1 and DBG0 must be 0 for debug to be available.
1 DBG1 R/W 1
Debug Control 0
The DBG1 bit must be 1 and DBG0 must be 0 for debug to be available.
0 DBG0 R/W 0
122 November 30, 2007
Preliminary
Internal Memory
Register 11: User Register 0 (USER_REG0), offset 0x1E0
Note: Offset is relative to System Control base address of 0x400FE000.
This register provides 31 bits of user-defined data that is non-volatile and can only be written once.
Bit 31 indicates that the register is available to be written and is controlled through hardware to
ensure that the register is only written once. The write-once characteristics of this register are useful
for keeping static information like communication addresses that need to be unique per part and
would otherwise require an external EEPROM or other non-volatile device.
User Register 0 (USER_REG0)
Base 0x400F.E000
Offset 0x1E0
Type R/W, reset 0xFFFF.FFFF
31 30 29 28 27 26 25 24 23 22 21 20 19 18 17 16
NW DATA
Type R/W R/W R/W R/W R/W R/W R/W R/W R/W R/W R/W R/W R/W R/W R/W R/W
Reset 1 1 1 1 1 1 1 1 1 1 1 1 1 1 1 1
15 14 13 12 11 10 9 8 7 6 5 4 3 2 1 0
DATA
Type R/W R/W R/W R/W R/W R/W R/W R/W R/W R/W R/W R/W R/W R/W R/W R/W
Reset 1 1 1 1 1 1 1 1 1 1 1 1 1 1 1 1
Bit/Field Name Type Reset Description
Not Written
Specifies that this 32-bit dword has not been written.
31 NW R/W 1
User Data
Contains the user data value. This field is initialized to all 1s and can
only be written once.
30:0 DATA R/W 0x7FFFFFFF
November 30, 2007 123
Preliminary
LM3S6110 Microcontroller
Register 12: User Register 1 (USER_REG1), offset 0x1E4
Note: Offset is relative to System Control base address of 0x400FE000.
This register provides 31 bits of user-defined data that is non-volatile and can only be written once.
Bit 31 indicates that the register is available to be written and is controlled through hardware to
ensure that the register is only written once. The write-once characteristics of this register are useful
for keeping static information like communication addresses that need to be unique per part and
would otherwise require an external EEPROM or other non-volatile device.
User Register 1 (USER_REG1)
Base 0x400F.E000
Offset 0x1E4
Type R/W, reset 0xFFFF.FFFF
31 30 29 28 27 26 25 24 23 22 21 20 19 18 17 16
NW DATA
Type R/W R/W R/W R/W R/W R/W R/W R/W R/W R/W R/W R/W R/W R/W R/W R/W
Reset 1 1 1 1 1 1 1 1 1 1 1 1 1 1 1 1
15 14 13 12 11 10 9 8 7 6 5 4 3 2 1 0
DATA
Type R/W R/W R/W R/W R/W R/W R/W R/W R/W R/W R/W R/W R/W R/W R/W R/W
Reset 1 1 1 1 1 1 1 1 1 1 1 1 1 1 1 1
Bit/Field Name Type Reset Description
Not Written
Specifies that this 32-bit dword has not been written.
31 NW R/W 1
User Data
Contains the user data value. This field is initialized to all 1s and can
only be written once.
30:0 DATA R/W 0x7FFFFFFF
124 November 30, 2007
Preliminary
Internal Memory
Register 13: Flash Memory Protection Read Enable 1 (FMPRE1), offset 0x204
Note: Offset is relative to System Control base address of 0x400FE000.
This register stores the read-only protection bits for each 2-KB flash block (FMPPEn stores the
execute-only bits). This register is loaded during the power-on reset sequence. The factory settings
for the FMPREn and FMPPEn registers are a value of 1 for all implemented banks. This achieves
a policy of open access and programmability. The register bits may be changed by writing the
specific register bit. However, this register is R/W0; the user can only change the protection bit from
a 1 to a 0 (and may NOT change a 0 to a 1). The changes are not permanent until the register is
committed (saved), at which point the bit change is permanent. If a bit is changed from a 1 to a 0
and not committed, it may be restored by executing a power-on reset sequence. For additional
information, see the "Flash Memory Protection" section.
Flash Memory Protection Read Enable 1 (FMPRE1)
Base 0x400F.E000
Offset 0x204
Type R/W, reset 0x0000.0000
31 30 29 28 27 26 25 24 23 22 21 20 19 18 17 16
READ_ENABLE
Type R/W R/W R/W R/W R/W R/W R/W R/W R/W R/W R/W R/W R/W R/W R/W R/W
Reset 0 0 0 0 0 0 0 0 0 0 0 0 0 0 0 0
15 14 13 12 11 10 9 8 7 6 5 4 3 2 1 0
READ_ENABLE
Type R/W R/W R/W R/W R/W R/W R/W R/W R/W R/W R/W R/W R/W R/W R/W R/W
Reset 0 0 0 0 0 0 0 0 0 0 0 0 0 0 0 0
Bit/Field Name Type Reset Description
Flash Read Enable
Enables 2-KB flash blocks to be executed or read. The policies may be
combined as shown in the table “Flash Protection Policy Combinations”.
Value Description
0x00000000 Enables 64 KB of flash.
31:0 READ_ENABLE R/W 0x00000000
November 30, 2007 125
Preliminary
LM3S6110 Microcontroller
Register 14: Flash Memory Protection Read Enable 2 (FMPRE2), offset 0x208
Note: Offset is relative to System Control base address of 0x400FE000.
This register stores the read-only protection bits for each 2-KB flash block (FMPPEn stores the
execute-only bits). This register is loaded during the power-on reset sequence. The factory settings
for the FMPREn and FMPPEn registers are a value of 1 for all implemented banks. This achieves
a policy of open access and programmability. The register bits may be changed by writing the
specific register bit. However, this register is R/W0; the user can only change the protection bit from
a 1 to a 0 (and may NOT change a 0 to a 1). The changes are not permanent until the register is
committed (saved), at which point the bit change is permanent. If a bit is changed from a 1 to a 0
and not committed, it may be restored by executing a power-on reset sequence. For additional
information, see the "Flash Memory Protection" section.
Flash Memory Protection Read Enable 2 (FMPRE2)
Base 0x400F.E000
Offset 0x208
Type R/W, reset 0x0000.0000
31 30 29 28 27 26 25 24 23 22 21 20 19 18 17 16
READ_ENABLE
Type R/W R/W R/W R/W R/W R/W R/W R/W R/W R/W R/W R/W R/W R/W R/W R/W
Reset 0 0 0 0 0 0 0 0 0 0 0 0 0 0 0 0
15 14 13 12 11 10 9 8 7 6 5 4 3 2 1 0
READ_ENABLE
Type R/W R/W R/W R/W R/W R/W R/W R/W R/W R/W R/W R/W R/W R/W R/W R/W
Reset 0 0 0 0 0 0 0 0 0 0 0 0 0 0 0 0
Bit/Field Name Type Reset Description
Flash Read Enable
Enables 2-KB flash blocks to be executed or read. The policies may be
combined as shown in the table “Flash Protection Policy Combinations”.
Value Description
0x00000000 Enables 64 KB of flash.
31:0 READ_ENABLE R/W 0x00000000
126 November 30, 2007
Preliminary
Internal Memory
Register 15: Flash Memory Protection Read Enable 3 (FMPRE3), offset 0x20C
Note: Offset is relative to System Control base address of 0x400FE000.
This register stores the read-only protection bits for each 2-KB flash block (FMPPEn stores the
execute-only bits). This register is loaded during the power-on reset sequence. The factory settings
for the FMPREn and FMPPEn registers are a value of 1 for all implemented banks. This achieves
a policy of open access and programmability. The register bits may be changed by writing the
specific register bit. However, this register is R/W0; the user can only change the protection bit from
a 1 to a 0 (and may NOT change a 0 to a 1). The changes are not permanent until the register is
committed (saved), at which point the bit change is permanent. If a bit is changed from a 1 to a 0
and not committed, it may be restored by executing a power-on reset sequence. For additional
information, see the "Flash Memory Protection" section.
Flash Memory Protection Read Enable 3 (FMPRE3)
Base 0x400F.E000
Offset 0x20C
Type R/W, reset 0x0000.0000
31 30 29 28 27 26 25 24 23 22 21 20 19 18 17 16
READ_ENABLE
Type R/W R/W R/W R/W R/W R/W R/W R/W R/W R/W R/W R/W R/W R/W R/W R/W
Reset 0 0 0 0 0 0 0 0 0 0 0 0 0 0 0 0
15 14 13 12 11 10 9 8 7 6 5 4 3 2 1 0
READ_ENABLE
Type R/W R/W R/W R/W R/W R/W R/W R/W R/W R/W R/W R/W R/W R/W R/W R/W
Reset 0 0 0 0 0 0 0 0 0 0 0 0 0 0 0 0
Bit/Field Name Type Reset Description
Flash Read Enable
Enables 2-KB flash blocks to be executed or read. The policies may be
combined as shown in the table “Flash Protection Policy Combinations”.
Value Description
0x00000000 Enables 64 KB of flash.
31:0 READ_ENABLE R/W 0x00000000
November 30, 2007 127
Preliminary
LM3S6110 Microcontroller
Register 16: Flash Memory Protection Program Enable 1 (FMPPE1), offset
0x404
Note: Offset is relative to System Control base address of 0x400FE000.
This register stores the execute-only protection bits for each 2-KB flash block (FMPREn stores the
execute-only bits). This register is loaded during the power-on reset sequence. The factory settings
for the FMPREn and FMPPEn registers are a value of 1 for all implemented banks. This achieves
a policy of open access and programmability. The register bits may be changed by writing the
specific register bit. However, this register is R/W0; the user can only change the protection bit from
a 1 to a 0 (and may NOT change a 0 to a 1). The changes are not permanent until the register is
committed (saved), at which point the bit change is permanent. If a bit is changed from a 1 to a 0
and not committed, it may be restored by executing a power-on reset sequence. For additional
information, see the "Flash Memory Protection" section.
Flash Memory Protection Program Enable 1 (FMPPE1)
Base 0x400F.E000
Offset 0x404
Type R/W, reset 0x0000.0000
31 30 29 28 27 26 25 24 23 22 21 20 19 18 17 16
PROG_ENABLE
Type R/W R/W R/W R/W R/W R/W R/W R/W R/W R/W R/W R/W R/W R/W R/W R/W
Reset 0 0 0 0 0 0 0 0 0 0 0 0 0 0 0 0
15 14 13 12 11 10 9 8 7 6 5 4 3 2 1 0
PROG_ENABLE
Type R/W R/W R/W R/W R/W R/W R/W R/W R/W R/W R/W R/W R/W R/W R/W R/W
Reset 0 0 0 0 0 0 0 0 0 0 0 0 0 0 0 0
Bit/Field Name Type Reset Description
Flash Programming Enable
Configures 2-KB flash blocks to be execute only. The policies may be
combined as shown in the table “Flash Protection Policy Combinations”.
Value Description
0x00000000 Enables 64 KB of flash.
31:0 PROG_ENABLE R/W 0x00000000
128 November 30, 2007
Preliminary
Internal Memory
Register 17: Flash Memory Protection Program Enable 2 (FMPPE2), offset
0x408
Note: Offset is relative to System Control base address of 0x400FE000.
This register stores the execute-only protection bits for each 2-KB flash block (FMPREn stores the
execute-only bits). This register is loaded during the power-on reset sequence. The factory settings
for the FMPREn and FMPPEn registers are a value of 1 for all implemented banks. This achieves
a policy of open access and programmability. The register bits may be changed by writing the
specific register bit. However, this register is R/W0; the user can only change the protection bit from
a 1 to a 0 (and may NOT change a 0 to a 1). The changes are not permanent until the register is
committed (saved), at which point the bit change is permanent. If a bit is changed from a 1 to a 0
and not committed, it may be restored by executing a power-on reset sequence. For additional
information, see the "Flash Memory Protection" section.
Flash Memory Protection Program Enable 2 (FMPPE2)
Base 0x400F.E000
Offset 0x408
Type R/W, reset 0x0000.0000
31 30 29 28 27 26 25 24 23 22 21 20 19 18 17 16
PROG_ENABLE
Type R/W R/W R/W R/W R/W R/W R/W R/W R/W R/W R/W R/W R/W R/W R/W R/W
Reset 0 0 0 0 0 0 0 0 0 0 0 0 0 0 0 0
15 14 13 12 11 10 9 8 7 6 5 4 3 2 1 0
PROG_ENABLE
Type R/W R/W R/W R/W R/W R/W R/W R/W R/W R/W R/W R/W R/W R/W R/W R/W
Reset 0 0 0 0 0 0 0 0 0 0 0 0 0 0 0 0
Bit/Field Name Type Reset Description
Flash Programming Enable
Configures 2-KB flash blocks to be execute only. The policies may be
combined as shown in the table “Flash Protection Policy Combinations”.
Value Description
0x00000000 Enables 64 KB of flash.
31:0 PROG_ENABLE R/W 0x00000000
November 30, 2007 129
Preliminary
LM3S6110 Microcontroller
Register 18: Flash Memory Protection Program Enable 3 (FMPPE3), offset
0x40C
Note: Offset is relative to System Control base address of 0x400FE000.
This register stores the execute-only protection bits for each 2-KB flash block (FMPREn stores the
execute-only bits). This register is loaded during the power-on reset sequence. The factory settings
for the FMPREn and FMPPEn registers are a value of 1 for all implemented banks. This achieves
a policy of open access and programmability. The register bits may be changed by writing the
specific register bit. However, this register is R/W0; the user can only change the protection bit from
a 1 to a 0 (and may NOT change a 0 to a 1). The changes are not permanent until the register is
committed (saved), at which point the bit change is permanent. If a bit is changed from a 1 to a 0
and not committed, it may be restored by executing a power-on reset sequence. For additional
information, see the "Flash Memory Protection" section.
Flash Memory Protection Program Enable 3 (FMPPE3)
Base 0x400F.E000
Offset 0x40C
Type R/W, reset 0x0000.0000
31 30 29 28 27 26 25 24 23 22 21 20 19 18 17 16
PROG_ENABLE
Type R/W R/W R/W R/W R/W R/W R/W R/W R/W R/W R/W R/W R/W R/W R/W R/W
Reset 0 0 0 0 0 0 0 0 0 0 0 0 0 0 0 0
15 14 13 12 11 10 9 8 7 6 5 4 3 2 1 0
PROG_ENABLE
Type R/W R/W R/W R/W R/W R/W R/W R/W R/W R/W R/W R/W R/W R/W R/W R/W
Reset 0 0 0 0 0 0 0 0 0 0 0 0 0 0 0 0
Bit/Field Name Type Reset Description
Flash Programming Enable
Configures 2-KB flash blocks to be execute only. The policies may be
combined as shown in the table “Flash Protection Policy Combinations”.
Value Description
0x00000000 Enables 64 KB of flash.
31:0 PROG_ENABLE R/W 0x00000000
130 November 30, 2007
Preliminary
Internal Memory
8 General-Purpose Input/Outputs (GPIOs)
The GPIO module is composed of seven physical GPIO blocks, each corresponding to an individual
GPIO port (Port A, Port B, Port C, Port D, Port E, Port F, and Port G, ). The GPIO module is
FiRM-compliant and supports 8-35 programmable input/output pins, depending on the peripherals
being used.
The GPIO module has the following features:
■ Programmable control for GPIO interrupts
– Interrupt generation masking
– Edge-triggered on rising, falling, or both
– Level-sensitive on High or Low values
■ 5-V-tolerant input/outputs
■ Bit masking in both read and write operations through address lines
■ Programmable control for GPIO pad configuration
– Weak pull-up or pull-down resistors
– 2-mA, 4-mA, and 8-mA pad drive
– Slew rate control for the 8-mA drive
– Open drain enables
– Digital input enables
8.1 Functional Description
Important: All GPIO pins are tri-stated by default (GPIOAFSEL=0, GPIODEN=0, GPIOPDR=0,
and GPIOPUR=0), with the exception of the five JTAG/SWD pins (PB7 and PC[3:0]).
The JTAG/SWD pins default to their JTAG/SWD functionality (GPIOAFSEL=1,
GPIODEN=1 and GPIOPUR=1). A Power-On-Reset (POR) or asserting RST puts both
groups of pins back to their default state.
Each GPIO port is a separate hardware instantiation of the same physical block (see Figure
8-1 on page 132). The LM3S6110 microcontroller contains seven ports and thus seven of these
physical GPIO blocks.
November 30, 2007 131
Preliminary
LM3S6110 Microcontroller
Figure 8-1. GPIO Port Block Diagram
Alternate Input
Alternate Output
Alternate Output Enable
Interrupt
GPIO Input
GPIO Output
GPIO Output Enable
Pad Output
Pad Output Enable
Package I/O Pin
GPIODATA
GPIODIR
Data
Control
GPIOIS
GPIOIBE
GPIOIEV
GPIOIM
GPIORIS
GPIOMIS
GPIOICR
Interrupt
Control
GPIODR2R
GPIODR4R
GPIODR8R
GPIOSLR
GPIOPUR
GPIOPDR
GPIOODR
GPIODEN
Pad
Control
GPIOPeriphID0
GPIOPeriphID1
GPIOPeriphID2
GPIOPeriphID3
GPIOPeriphID4
GPIOPeriphID5
GPIOPeriphID6
GPIOPeriphID7
GPIOPCellID0
GPIOPCellID1
GPIOPCellID2
GPIOPCellID3
Identification Registers
GPIOAFSEL
Mode
Control
DEMUX MUX MUX
Digital
I/O Pad
Pad Input
GPIOLOCK
Commit
Control
GPIOCR
8.1.1 Data Control
The data control registers allow software to configure the operational modes of the GPIOs. The data
direction register configures the GPIO as an input or an output while the data register either captures
incoming data or drives it out to the pads.
8.1.1.1 Data Direction Operation
The GPIO Direction (GPIODIR) register (see page 139) is used to configure each individual pin as
an input or output. When the data direction bit is set to 0, the GPIO is configured as an input and
the corresponding data register bit will capture and store the value on the GPIO port. When the data
direction bit is set to 1, the GPIO is configured as an output and the corresponding data register bit
will be driven out on the GPIO port.
8.1.1.2 Data Register Operation
To aid in the efficiency of software, the GPIO ports allow for the modification of individual bits in the
GPIO Data (GPIODATA) register (see page 138) by using bits [9:2] of the address bus as a mask.
This allows software drivers to modify individual GPIO pins in a single instruction, without affecting
the state of the other pins. This is in contrast to the "typical" method of doing a read-modify-write
operation to set or clear an individual GPIO pin. To accommodate this feature, the GPIODATA
register covers 256 locations in the memory map.
During a write, if the address bit associated with that data bit is set to 1, the value of the GPIODATA
register is altered. If it is cleared to 0, it is left unchanged.
132 November 30, 2007
Preliminary
General-Purpose Input/Outputs (GPIOs)
For example, writing a value of 0xEB to the address GPIODATA + 0x098 would yield as shown in
Figure 8-2 on page 133, where u is data unchanged by the write.
Figure 8-2. GPIODATA Write Example
0 0 1 0 0 1 1 0 1 0
u u 1 u u 0 1 u
9 8 7 6 5 4 3 2 1 0
1 1 1 0 1 0 1 1
7 6 5 4 3 2 1 0
GPIODATA
0xEB
0x098
ADDR[9:2]
During a read, if the address bit associated with the data bit is set to 1, the value is read. If the
address bit associated with the data bit is set to 0, it is read as a zero, regardless of its actual value.
For example, reading address GPIODATA + 0x0C4 yields as shown in Figure 8-3 on page 133.
Figure 8-3. GPIODATA Read Example
0 0 1 1 0 0 0 1 0 0
0 0 1 1 0 0 0 0
9 8 7 6 5 4 3 2 1 0
1 0 1 1 1 1 1 0
7 6 5 4 3 2 1 0
Returned Value
GPIODATA
0x0C4
ADDR[9:2]
8.1.2 Interrupt Control
The interrupt capabilities of each GPIO port are controlled by a set of seven registers. With these
registers, it is possible to select the source of the interrupt, its polarity, and the edge properties.
When one or more GPIO inputs cause an interrupt, a single interrupt output is sent to the interrupt
controller for the entire GPIO port. For edge-triggered interrupts, software must clear the interrupt
to enable any further interrupts. For a level-sensitive interrupt, it is assumed that the external source
holds the level constant for the interrupt to be recognized by the controller.
Three registers are required to define the edge or sense that causes interrupts:
■ GPIO Interrupt Sense (GPIOIS) register (see page 140)
■ GPIO Interrupt Both Edges (GPIOIBE) register (see page 141)
■ GPIO Interrupt Event (GPIOIEV) register (see page 142)
Interrupts are enabled/disabled via the GPIO Interrupt Mask (GPIOIM) register (see page 143).
When an interrupt condition occurs, the state of the interrupt signal can be viewed in two locations:
the GPIO Raw Interrupt Status (GPIORIS) and GPIO Masked Interrupt Status (GPIOMIS) registers
(see page 144 and page 145). As the name implies, the GPIOMIS register only shows interrupt
conditions that are allowed to be passed to the controller. The GPIORIS register indicates that a
GPIO pin meets the conditions for an interrupt, but has not necessarily been sent to the controller.
Interrupts are cleared by writing a 1 to the GPIO Interrupt Clear (GPIOICR) register (see page 146).
November 30, 2007 133
Preliminary
LM3S6110 Microcontroller
When programming the following interrupt control registers, the interrupts should be masked (GPIOIM
set to 0). Writing any value to an interrupt control register (GPIOIS, GPIOIBE, or GPIOIEV) can
generate a spurious interrupt if the corresponding bits are enabled.
8.1.3 Mode Control
The GPIO pins can be controlled by either hardware or software. When hardware control is enabled
via the GPIO Alternate Function Select (GPIOAFSEL) register (see page 147), the pin state is
controlled by its alternate function (that is, the peripheral). Software control corresponds to GPIO
mode, where the GPIODATA register is used to read/write the corresponding pins.
8.1.4 Commit Control
The commit control registers provide a layer of protection against accidental programming of critical
hardware peripherals. Writes to protected bits of the GPIO Alternate Function Select (GPIOAFSEL)
register (see page 147) are not committed to storage unless the GPIO Lock (GPIOLOCK) register
(see page 157) has been unlocked and the appropriate bits of the GPIO Commit (GPIOCR) register
(see page 158) have been set to 1.
8.1.5 Pad Control
The pad control registers allow for GPIO pad configuration by software based on the application
requirements. The pad control registers include the GPIODR2R, GPIODR4R, GPIODR8R, GPIOODR,
GPIOPUR, GPIOPDR, GPIOSLR, and GPIODEN registers.
8.1.6 Identification
The identification registers configured at reset allow software to detect and identify the module as
a GPIO block. The identification registers include the GPIOPeriphID0-GPIOPeriphID7 registers as
well as the GPIOPCellID0-GPIOPCellID3 registers.
8.2 Initialization and Configuration
To use the GPIO, the peripheral clock must be enabled by setting the appropriate GPIO Port bit
field (GPIOn) in the RCGC2 register.
On reset, all GPIO pins (except for the five JTAG pins) are configured out of reset to be undriven
(tristate): GPIOAFSEL=0, GPIODEN=0, GPIOPDR=0, and GPIOPUR=0. Table 8-1 on page 134
shows all possible configurations of the GPIO pads and the control register settings required to
achieve them. Table 8-2 on page 135 shows how a rising edge interrupt would be configured for pin
2 of a GPIO port.
Table 8-1. GPIO Pad Configuration Examples
Configuration GPIO Register Bit Valuea
AFSEL DIR ODR DEN PUR PDR DR2R DR4R DR8R SLR
Digital Input (GPIO) 0 0 0 1 ? ? X X X X
Digital Output (GPIO) 0 1 0 1 ? ? ? ? ? ?
Open Drain Input 0 0 1 1 X X X X X X
(GPIO)
Open Drain Output 0 1 1 1 X X ? ? ? ?
(GPIO)
Digital Input (Timer 1 X 0 1 ? ? X X X X
CCP)
Digital Output (PWM) 1 X 0 1 ? ? ? ? ? ?
134 November 30, 2007
Preliminary
General-Purpose Input/Outputs (GPIOs)
Configuration GPIO Register Bit Valuea
AFSEL DIR ODR DEN PUR PDR DR2R DR4R DR8R SLR
Digital Output (Timer 1 X 0 1 ? ? ? ? ? ?
PWM)
Digital Input/Output 1 X 0 1 ? ? ? ? ? ?
(SSI)
Digital Input/Output 1 X 0 1 ? ? ? ? ? ?
(UART)
Analog Input 0 0 0 0 0 0 X X X X
(Comparator)
Digital Output 1 X 0 1 ? ? ? ? ? ?
(Comparator)
a. X=Ignored (don’t care bit)
?=Can be either 0 or 1, depending on the configuration
Table 8-2. GPIO Interrupt Configuration Example
Desired Pin 2 Bit Valuea
Interrupt
Event
Trigger
Register
7 6 5 4 3 2 1 0
0=edge X X X X X 0 X X
1=level
GPIOIS
0=single X X X X X 0 X X
edge
1=both
edges
GPIOIBE
0=Low level, X X X X X 1 X X
or negative
edge
1=High level,
or positive
edge
GPIOIEV
0=masked 0 0 0 0 0 1 0 0
1=not
masked
GPIOIM
a. X=Ignored (don’t care bit)
8.3 Register Map
Table 8-3 on page 136 lists the GPIO registers. The offset listed is a hexadecimal increment to the
register’s address, relative to that GPIO port’s base address:
■ GPIO Port A: 0x4000.4000
■ GPIO Port B: 0x4000.5000
■ GPIO Port C: 0x4000.6000
■ GPIO Port D: 0x4000.7000
■ GPIO Port E: 0x4002.4000
November 30, 2007 135
Preliminary
LM3S6110 Microcontroller
■ GPIO Port F: 0x4002.5000
■ GPIO Port G: 0x4002.6000
Important: The GPIO registers in this chapter are duplicated in each GPIO block, however,
depending on the block, all eight bits may not be connected to a GPIO pad. In those
cases, writing to those unconnected bits has no effect and reading those unconnected
bits returns no meaningful data.
Note: The default reset value for the GPIOAFSEL, GPIOPUR, and GPIODEN registers are
0x0000.0000 for all GPIO pins, with the exception of the five JTAG/SWD pins (PB7 and
PC[3:0]). These five pins default to JTAG/SWD functionality. Because of this, the default
reset value of these registers for GPIO Port B is 0x0000.0080 while the default reset value
for Port C is 0x0000.000F.
The default register type for the GPIOCR register is RO for all GPIO pins, with the exception
of the five JTAG/SWD pins (PB7 and PC[3:0]). These five pins are currently the only
GPIOs that are protected by the GPIOCR register. Because of this, the register type for
GPIO Port B7 and GPIO Port C[3:0] is R/W.
The default reset value for the GPIOCR register is 0x0000.00FF for all GPIO pins, with the
exception of the five JTAG/SWD pins (PB7 and PC[3:0]). To ensure that the JTAG port
is not accidentally programmed as a GPIO, these five pins default to non-commitable.
Because of this, the default reset value of GPIOCR for GPIO Port B is 0x0000.007F while
the default reset value of GPIOCR for Port C is 0x0000.00F0.
Table 8-3. GPIO Register Map
See
Offset Name Type Reset Description page
0x000 GPIODATA R/W 0x0000.0000 GPIO Data 138
0x400 GPIODIR R/W 0x0000.0000 GPIO Direction 139
0x404 GPIOIS R/W 0x0000.0000 GPIO Interrupt Sense 140
0x408 GPIOIBE R/W 0x0000.0000 GPIO Interrupt Both Edges 141
0x40C GPIOIEV R/W 0x0000.0000 GPIO Interrupt Event 142
0x410 GPIOIM R/W 0x0000.0000 GPIO Interrupt Mask 143
0x414 GPIORIS RO 0x0000.0000 GPIO Raw Interrupt Status 144
0x418 GPIOMIS RO 0x0000.0000 GPIO Masked Interrupt Status 145
0x41C GPIOICR W1C 0x0000.0000 GPIO Interrupt Clear 146
0x420 GPIOAFSEL R/W - GPIO Alternate Function Select 147
0x500 GPIODR2R R/W 0x0000.00FF GPIO 2-mA Drive Select 149
0x504 GPIODR4R R/W 0x0000.0000 GPIO 4-mA Drive Select 150
0x508 GPIODR8R R/W 0x0000.0000 GPIO 8-mA Drive Select 151
0x50C GPIOODR R/W 0x0000.0000 GPIO Open Drain Select 152
0x510 GPIOPUR R/W - GPIO Pull-Up Select 153
0x514 GPIOPDR R/W 0x0000.0000 GPIO Pull-Down Select 154
136 November 30, 2007
Preliminary
General-Purpose Input/Outputs (GPIOs)
See
Offset Name Type Reset Description page
0x518 GPIOSLR R/W 0x0000.0000 GPIO Slew Rate Control Select 155
0x51C GPIODEN R/W - GPIO Digital Enable 156
0x520 GPIOLOCK R/W 0x0000.0001 GPIO Lock 157
0x524 GPIOCR - - GPIO Commit 158
0xFD0 GPIOPeriphID4 RO 0x0000.0000 GPIO Peripheral Identification 4 160
0xFD4 GPIOPeriphID5 RO 0x0000.0000 GPIO Peripheral Identification 5 161
0xFD8 GPIOPeriphID6 RO 0x0000.0000 GPIO Peripheral Identification 6 162
0xFDC GPIOPeriphID7 RO 0x0000.0000 GPIO Peripheral Identification 7 163
0xFE0 GPIOPeriphID0 RO 0x0000.0061 GPIO Peripheral Identification 0 164
0xFE4 GPIOPeriphID1 RO 0x0000.0000 GPIO Peripheral Identification 1 165
0xFE8 GPIOPeriphID2 RO 0x0000.0018 GPIO Peripheral Identification 2 166
0xFEC GPIOPeriphID3 RO 0x0000.0001 GPIO Peripheral Identification 3 167
0xFF0 GPIOPCellID0 RO 0x0000.000D GPIO PrimeCell Identification 0 168
0xFF4 GPIOPCellID1 RO 0x0000.00F0 GPIO PrimeCell Identification 1 169
0xFF8 GPIOPCellID2 RO 0x0000.0005 GPIO PrimeCell Identification 2 170
0xFFC GPIOPCellID3 RO 0x0000.00B1 GPIO PrimeCell Identification 3 171
8.4 Register Descriptions
The remainder of this section lists and describes the GPIO registers, in numerical order by address
offset.
November 30, 2007 137
Preliminary
LM3S6110 Microcontroller
Register 1: GPIO Data (GPIODATA), offset 0x000
The GPIODATA register is the data register. In software control mode, values written in the
GPIODATA register are transferred onto the GPIO port pins if the respective pins have been
configured as outputs through the GPIO Direction (GPIODIR) register (see page 139).
In order to write to GPIODATA, the corresponding bits in the mask, resulting from the address bus
bits [9:2], must be High. Otherwise, the bit values remain unchanged by the write.
Similarly, the values read from this register are determined for each bit by the mask bit derived from
the address used to access the data register, bits [9:2]. Bits that are 1 in the address mask cause
the corresponding bits in GPIODATA to be read, and bits that are 0 in the address mask cause the
corresponding bits in GPIODATA to be read as 0, regardless of their value.
A read from GPIODATA returns the last bit value written if the respective pins are configured as
outputs, or it returns the value on the corresponding input pin when these are configured as inputs.
All bits are cleared by a reset.
GPIO Data (GPIODATA)
GPIO Port A base: 0x4000.4000
GPIO Port B base: 0x4000.5000
GPIO Port C base: 0x4000.6000
GPIO Port D base: 0x4000.7000
GPIO Port E base: 0x4002.4000
GPIO Port F base: 0x4002.5000
GPIO Port G base: 0x4002.6000
Offset 0x000
Type R/W, reset 0x0000.0000
31 30 29 28 27 26 25 24 23 22 21 20 19 18 17 16
reserved
Type RO RO RO RO RO RO RO RO RO RO RO RO RO RO RO RO
Reset 0 0 0 0 0 0 0 0 0 0 0 0 0 0 0 0
15 14 13 12 11 10 9 8 7 6 5 4 3 2 1 0
reserved DATA
Type RO RO RO RO RO RO RO RO R/W R/W R/W R/W R/W R/W R/W R/W
Reset 0 0 0 0 0 0 0 0 0 0 0 0 0 0 0 0
Bit/Field Name Type Reset Description
Software should not rely on the value of a reserved bit. To provide
compatibility with future products, the value of a reserved bit should be
preserved across a read-modify-write operation.
31:8 reserved RO 0x00
GPIO Data
This register is virtually mapped to 256 locations in the address space.
To facilitate the reading and writing of data to these registers by
independent drivers, the data read from and the data written to the
registers are masked by the eight address lines ipaddr[9:2]. Reads
from this register return its current state. Writes to this register only affect
bits that are not masked by ipaddr[9:2] and are configured as
outputs. See “Data Register Operation” on page 132 for examples of
reads and writes.
7:0 DATA R/W 0x00
138 November 30, 2007
Preliminary
General-Purpose Input/Outputs (GPIOs)
Register 2: GPIO Direction (GPIODIR), offset 0x400
The GPIODIR register is the data direction register. Bits set to 1 in the GPIODIR register configure
the corresponding pin to be an output, while bits set to 0 configure the pins to be inputs. All bits are
cleared by a reset, meaning all GPIO pins are inputs by default.
GPIO Direction (GPIODIR)
GPIO Port A base: 0x4000.4000
GPIO Port B base: 0x4000.5000
GPIO Port C base: 0x4000.6000
GPIO Port D base: 0x4000.7000
GPIO Port E base: 0x4002.4000
GPIO Port F base: 0x4002.5000
GPIO Port G base: 0x4002.6000
Offset 0x400
Type R/W, reset 0x0000.0000
31 30 29 28 27 26 25 24 23 22 21 20 19 18 17 16
reserved
Type RO RO RO RO RO RO RO RO RO RO RO RO RO RO RO RO
Reset 0 0 0 0 0 0 0 0 0 0 0 0 0 0 0 0
15 14 13 12 11 10 9 8 7 6 5 4 3 2 1 0
reserved DIR
Type RO RO RO RO RO RO RO RO R/W R/W R/W R/W R/W R/W R/W R/W
Reset 0 0 0 0 0 0 0 0 0 0 0 0 0 0 0 0
Bit/Field Name Type Reset Description
Software should not rely on the value of a reserved bit. To provide
compatibility with future products, the value of a reserved bit should be
preserved across a read-modify-write operation.
31:8 reserved RO 0x00
GPIO Data Direction
The DIR values are defined as follows:
Value Description
0 Pins are inputs.
1 Pins are outputs.
7:0 DIR R/W 0x00
November 30, 2007 139
Preliminary
LM3S6110 Microcontroller
Register 3: GPIO Interrupt Sense (GPIOIS), offset 0x404
The GPIOIS register is the interrupt sense register. Bits set to 1 in GPIOIS configure the
corresponding pins to detect levels, while bits set to 0 configure the pins to detect edges. All bits
are cleared by a reset.
GPIO Interrupt Sense (GPIOIS)
GPIO Port A base: 0x4000.4000
GPIO Port B base: 0x4000.5000
GPIO Port C base: 0x4000.6000
GPIO Port D base: 0x4000.7000
GPIO Port E base: 0x4002.4000
GPIO Port F base: 0x4002.5000
GPIO Port G base: 0x4002.6000
Offset 0x404
Type R/W, reset 0x0000.0000
31 30 29 28 27 26 25 24 23 22 21 20 19 18 17 16
reserved
Type RO RO RO RO RO RO RO RO RO RO RO RO RO RO RO RO
Reset 0 0 0 0 0 0 0 0 0 0 0 0 0 0 0 0
15 14 13 12 11 10 9 8 7 6 5 4 3 2 1 0
reserved IS
Type RO RO RO RO RO RO RO RO R/W R/W R/W R/W R/W R/W R/W R/W
Reset 0 0 0 0 0 0 0 0 0 0 0 0 0 0 0 0
Bit/Field Name Type Reset Description
Software should not rely on the value of a reserved bit. To provide
compatibility with future products, the value of a reserved bit should be
preserved across a read-modify-write operation.
31:8 reserved RO 0x00
GPIO Interrupt Sense
The IS values are defined as follows:
Value Description
0 Edge on corresponding pin is detected (edge-sensitive).
1 Level on corresponding pin is detected (level-sensitive).
7:0 IS R/W 0x00
140 November 30, 2007
Preliminary
General-Purpose Input/Outputs (GPIOs)
Register 4: GPIO Interrupt Both Edges (GPIOIBE), offset 0x408
The GPIOIBE register is the interrupt both-edges register. When the corresponding bit in the GPIO
Interrupt Sense (GPIOIS) register (see page 140) is set to detect edges, bits set to High in GPIOIBE
configure the corresponding pin to detect both rising and falling edges, regardless of the
corresponding bit in the GPIO Interrupt Event (GPIOIEV) register (see page 142). Clearing a bit
configures the pin to be controlled by GPIOIEV. All bits are cleared by a reset.
GPIO Interrupt Both Edges (GPIOIBE)
GPIO Port A base: 0x4000.4000
GPIO Port B base: 0x4000.5000
GPIO Port C base: 0x4000.6000
GPIO Port D base: 0x4000.7000
GPIO Port E base: 0x4002.4000
GPIO Port F base: 0x4002.5000
GPIO Port G base: 0x4002.6000
Offset 0x408
Type R/W, reset 0x0000.0000
31 30 29 28 27 26 25 24 23 22 21 20 19 18 17 16
reserved
Type RO RO RO RO RO RO RO RO RO RO RO RO RO RO RO RO
Reset 0 0 0 0 0 0 0 0 0 0 0 0 0 0 0 0
15 14 13 12 11 10 9 8 7 6 5 4 3 2 1 0
reserved IBE
Type RO RO RO RO RO RO RO RO R/W R/W R/W R/W R/W R/W R/W R/W
Reset 0 0 0 0 0 0 0 0 0 0 0 0 0 0 0 0
Bit/Field Name Type Reset Description
Software should not rely on the value of a reserved bit. To provide
compatibility with future products, the value of a reserved bit should be
preserved across a read-modify-write operation.
31:8 reserved RO 0x00
GPIO Interrupt Both Edges
The IBE values are defined as follows:
Value Description
Interrupt generation is controlled by the GPIO Interrupt Event
(GPIOIEV) register (see page 142).
0
1 Both edges on the corresponding pin trigger an interrupt.
Note: Single edge is determined by the corresponding bit
in GPIOIEV.
7:0 IBE R/W 0x00
November 30, 2007 141
Preliminary
LM3S6110 Microcontroller
Register 5: GPIO Interrupt Event (GPIOIEV), offset 0x40C
The GPIOIEV register is the interrupt event register. Bits set to High in GPIOIEV configure the
corresponding pin to detect rising edges or high levels, depending on the corresponding bit value
in the GPIO Interrupt Sense (GPIOIS) register (see page 140). Clearing a bit configures the pin to
detect falling edges or low levels, depending on the corresponding bit value in GPIOIS. All bits are
cleared by a reset.
GPIO Interrupt Event (GPIOIEV)
GPIO Port A base: 0x4000.4000
GPIO Port B base: 0x4000.5000
GPIO Port C base: 0x4000.6000
GPIO Port D base: 0x4000.7000
GPIO Port E base: 0x4002.4000
GPIO Port F base: 0x4002.5000
GPIO Port G base: 0x4002.6000
Offset 0x40C
Type R/W, reset 0x0000.0000
31 30 29 28 27 26 25 24 23 22 21 20 19 18 17 16
reserved
Type RO RO RO RO RO RO RO RO RO RO RO RO RO RO RO RO
Reset 0 0 0 0 0 0 0 0 0 0 0 0 0 0 0 0
15 14 13 12 11 10 9 8 7 6 5 4 3 2 1 0
reserved IEV
Type RO RO RO RO RO RO RO RO R/W R/W R/W R/W R/W R/W R/W R/W
Reset 0 0 0 0 0 0 0 0 0 0 0 0 0 0 0 0
Bit/Field Name Type Reset Description
Software should not rely on the value of a reserved bit. To provide
compatibility with future products, the value of a reserved bit should be
preserved across a read-modify-write operation.
31:8 reserved RO 0x00
GPIO Interrupt Event
The IEV values are defined as follows:
Value Description
Falling edge or Low levels on corresponding pins trigger
interrupts.
0
Rising edge or High levels on corresponding pins trigger
interrupts.
1
7:0 IEV R/W 0x00
142 November 30, 2007
Preliminary
General-Purpose Input/Outputs (GPIOs)
Register 6: GPIO Interrupt Mask (GPIOIM), offset 0x410
The GPIOIM register is the interrupt mask register. Bits set to High in GPIOIM allow the corresponding
pins to trigger their individual interrupts and the combined GPIOINTR line. Clearing a bit disables
interrupt triggering on that pin. All bits are cleared by a reset.
GPIO Interrupt Mask (GPIOIM)
GPIO Port A base: 0x4000.4000
GPIO Port B base: 0x4000.5000
GPIO Port C base: 0x4000.6000
GPIO Port D base: 0x4000.7000
GPIO Port E base: 0x4002.4000
GPIO Port F base: 0x4002.5000
GPIO Port G base: 0x4002.6000
Offset 0x410
Type R/W, reset 0x0000.0000
31 30 29 28 27 26 25 24 23 22 21 20 19 18 17 16
reserved
Type RO RO RO RO RO RO RO RO RO RO RO RO RO RO RO RO
Reset 0 0 0 0 0 0 0 0 0 0 0 0 0 0 0 0
15 14 13 12 11 10 9 8 7 6 5 4 3 2 1 0
reserved IME
Type RO RO RO RO RO RO RO RO R/W R/W R/W R/W R/W R/W R/W R/W
Reset 0 0 0 0 0 0 0 0 0 0 0 0 0 0 0 0
Bit/Field Name Type Reset Description
Software should not rely on the value of a reserved bit. To provide
compatibility with future products, the value of a reserved bit should be
preserved across a read-modify-write operation.
31:8 reserved RO 0x00
GPIO Interrupt Mask Enable
The IME values are defined as follows:
Value Description
0 Corresponding pin interrupt is masked.
1 Corresponding pin interrupt is not masked.
7:0 IME R/W 0x00
November 30, 2007 143
Preliminary
LM3S6110 Microcontroller
Register 7: GPIO Raw Interrupt Status (GPIORIS), offset 0x414
The GPIORIS register is the raw interrupt status register. Bits read High in GPIORIS reflect the
status of interrupt trigger conditions detected (raw, prior to masking), indicating that all the
requirements have been met, before they are finally allowed to trigger by the GPIO Interrupt Mask
(GPIOIM) register (see page 143). Bits read as zero indicate that corresponding input pins have not
initiated an interrupt. All bits are cleared by a reset.
GPIO Raw Interrupt Status (GPIORIS)
GPIO Port A base: 0x4000.4000
GPIO Port B base: 0x4000.5000
GPIO Port C base: 0x4000.6000
GPIO Port D base: 0x4000.7000
GPIO Port E base: 0x4002.4000
GPIO Port F base: 0x4002.5000
GPIO Port G base: 0x4002.6000
Offset 0x414
Type RO, reset 0x0000.0000
31 30 29 28 27 26 25 24 23 22 21 20 19 18 17 16
reserved
Type RO RO RO RO RO RO RO RO RO RO RO RO RO RO RO RO
Reset 0 0 0 0 0 0 0 0 0 0 0 0 0 0 0 0
15 14 13 12 11 10 9 8 7 6 5 4 3 2 1 0
reserved RIS
Type RO RO RO RO RO RO RO RO RO RO RO RO RO RO RO RO
Reset 0 0 0 0 0 0 0 0 0 0 0 0 0 0 0 0
Bit/Field Name Type Reset Description
Software should not rely on the value of a reserved bit. To provide
compatibility with future products, the value of a reserved bit should be
preserved across a read-modify-write operation.
31:8 reserved RO 0x00
GPIO Interrupt Raw Status
Reflects the status of interrupt trigger condition detection on pins (raw,
prior to masking).
The RIS values are defined as follows:
Value Description
0 Corresponding pin interrupt requirements not met.
1 Corresponding pin interrupt has met requirements.
7:0 RIS RO 0x00
144 November 30, 2007
Preliminary
General-Purpose Input/Outputs (GPIOs)
Register 8: GPIO Masked Interrupt Status (GPIOMIS), offset 0x418
The GPIOMIS register is the masked interrupt status register. Bits read High in GPIOMIS reflect
the status of input lines triggering an interrupt. Bits read as Low indicate that either no interrupt has
been generated, or the interrupt is masked.
GPIOMIS is the state of the interrupt after masking.
GPIO Masked Interrupt Status (GPIOMIS)
GPIO Port A base: 0x4000.4000
GPIO Port B base: 0x4000.5000
GPIO Port C base: 0x4000.6000
GPIO Port D base: 0x4000.7000
GPIO Port E base: 0x4002.4000
GPIO Port F base: 0x4002.5000
GPIO Port G base: 0x4002.6000
Offset 0x418
Type RO, reset 0x0000.0000
31 30 29 28 27 26 25 24 23 22 21 20 19 18 17 16
reserved
Type RO RO RO RO RO RO RO RO RO RO RO RO RO RO RO RO
Reset 0 0 0 0 0 0 0 0 0 0 0 0 0 0 0 0
15 14 13 12 11 10 9 8 7 6 5 4 3 2 1 0
reserved MIS
Type RO RO RO RO RO RO RO RO RO RO RO RO RO RO RO RO
Reset 0 0 0 0 0 0 0 0 0 0 0 0 0 0 0 0
Bit/Field Name Type Reset Description
Software should not rely on the value of a reserved bit. To provide
compatibility with future products, the value of a reserved bit should be
preserved across a read-modify-write operation.
31:8 reserved RO 0x00
GPIO Masked Interrupt Status
Masked value of interrupt due to corresponding pin.
The MIS values are defined as follows:
Value Description
0 Corresponding GPIO line interrupt not active.
1 Corresponding GPIO line asserting interrupt.
7:0 MIS RO 0x00
November 30, 2007 145
Preliminary
LM3S6110 Microcontroller
Register 9: GPIO Interrupt Clear (GPIOICR), offset 0x41C
The GPIOICR register is the interrupt clear register. Writing a 1 to a bit in this register clears the
corresponding interrupt edge detection logic register. Writing a 0 has no effect.
GPIO Interrupt Clear (GPIOICR)
GPIO Port A base: 0x4000.4000
GPIO Port B base: 0x4000.5000
GPIO Port C base: 0x4000.6000
GPIO Port D base: 0x4000.7000
GPIO Port E base: 0x4002.4000
GPIO Port F base: 0x4002.5000
GPIO Port G base: 0x4002.6000
Offset 0x41C
Type W1C, reset 0x0000.0000
31 30 29 28 27 26 25 24 23 22 21 20 19 18 17 16
reserved
Type RO RO RO RO RO RO RO RO RO RO RO RO RO RO RO RO
Reset 0 0 0 0 0 0 0 0 0 0 0 0 0 0 0 0
15 14 13 12 11 10 9 8 7 6 5 4 3 2 1 0
reserved IC
Type RO RO RO RO RO RO RO RO W1C W1C W1C W1C W1C W1C W1C W1C
Reset 0 0 0 0 0 0 0 0 0 0 0 0 0 0 0 0
Bit/Field Name Type Reset Description
Software should not rely on the value of a reserved bit. To provide
compatibility with future products, the value of a reserved bit should be
preserved across a read-modify-write operation.
31:8 reserved RO 0x00
GPIO Interrupt Clear
The IC values are defined as follows:
Value Description
0 Corresponding interrupt is unaffected.
1 Corresponding interrupt is cleared.
7:0 IC W1C 0x00
146 November 30, 2007
Preliminary
General-Purpose Input/Outputs (GPIOs)
Register 10: GPIO Alternate Function Select (GPIOAFSEL), offset 0x420
The GPIOAFSEL register is the mode control select register. Writing a 1 to any bit in this register
selects the hardware control for the corresponding GPIO line. All bits are cleared by a reset, therefore
no GPIO line is set to hardware control by default.
The commit control registers provide a layer of protection against accidental programming of critical
hardware peripherals. Writes to protected bits of the GPIO Alternate Function Select (GPIOAFSEL)
register (see page 147) are not committed to storage unless the GPIO Lock (GPIOLOCK) register
(see page 157) has been unlocked and the appropriate bits of the GPIO Commit (GPIOCR) register
(see page 158) have been set to 1.
Important: All GPIO pins are tri-stated by default (GPIOAFSEL=0, GPIODEN=0, GPIOPDR=0,
and GPIOPUR=0), with the exception of the five JTAG/SWD pins (PB7 and PC[3:0]).
The JTAG/SWD pins default to their JTAG/SWD functionality (GPIOAFSEL=1,
GPIODEN=1 and GPIOPUR=1). A Power-On-Reset (POR) or asserting RST puts both
groups of pins back to their default state.
Caution – If the JTAG pins are used as GPIOs in a design, PB7 and PC2 cannot have external pull-down
resistors connected to both of them at the same time. If both pins are pulled Low during reset, the
controller has unpredictable behavior. If this happens, remove one or both of the pull-down resistors,
and apply RST or power-cycle the part.
In addition, it is possible to create a software sequence that prevents the debugger from connecting to
the Stellaris® microcontroller. If the program code loaded into flash immediately changes the JTAG
pins to their GPIO functionality, the debugger may not have enough time to connect and halt the
controller before the JTAG pin functionality switches. This may lock the debugger out of the part. This
can be avoided with a software routine that restores JTAG functionality based on an external or software
trigger.
GPIO Alternate Function Select (GPIOAFSEL)
GPIO Port A base: 0x4000.4000
GPIO Port B base: 0x4000.5000
GPIO Port C base: 0x4000.6000
GPIO Port D base: 0x4000.7000
GPIO Port E base: 0x4002.4000
GPIO Port F base: 0x4002.5000
GPIO Port G base: 0x4002.6000
Offset 0x420
Type R/W, reset -
31 30 29 28 27 26 25 24 23 22 21 20 19 18 17 16
reserved
Type RO RO RO RO RO RO RO RO RO RO RO RO RO RO RO RO
Reset 0 0 0 0 0 0 0 0 0 0 0 0 0 0 0 0
15 14 13 12 11 10 9 8 7 6 5 4 3 2 1 0
reserved AFSEL
Type RO RO RO RO RO RO RO RO R/W R/W R/W R/W R/W R/W R/W R/W
Reset 0 0 0 0 0 0 0 0 - - - - - - - -
Bit/Field Name Type Reset Description
Software should not rely on the value of a reserved bit. To provide
compatibility with future products, the value of a reserved bit should be
preserved across a read-modify-write operation.
31:8 reserved RO 0x00
November 30, 2007 147
Preliminary
LM3S6110 Microcontroller
Bit/Field Name Type Reset Description
GPIO Alternate Function Select
The AFSEL values are defined as follows:
Value Description
0 Software control of corresponding GPIO line (GPIO mode).
Hardware control of corresponding GPIO line (alternate
hardware function).
1
Note: The default reset value for the GPIOAFSEL,
GPIOPUR, and GPIODEN registers are 0x0000.0000
for all GPIO pins, with the exception of the five
JTAG/SWD pins (PB7 and PC[3:0]). These five pins
default to JTAG/SWD functionality. Because of this,
the default reset value of these registers for GPIO
Port B is 0x0000.0080 while the default reset value
for Port C is 0x0000.000F.
7:0 AFSEL R/W -
148 November 30, 2007
Preliminary
General-Purpose Input/Outputs (GPIOs)
Register 11: GPIO 2-mA Drive Select (GPIODR2R), offset 0x500
The GPIODR2R register is the 2-mA drive control register. It allows for each GPIO signal in the port
to be individually configured without affecting the other pads. When writing a DRV2 bit for a GPIO
signal, the corresponding DRV4 bit in the GPIODR4R register and the DRV8 bit in the GPIODR8R
register are automatically cleared by hardware.
GPIO 2-mA Drive Select (GPIODR2R)
GPIO Port A base: 0x4000.4000
GPIO Port B base: 0x4000.5000
GPIO Port C base: 0x4000.6000
GPIO Port D base: 0x4000.7000
GPIO Port E base: 0x4002.4000
GPIO Port F base: 0x4002.5000
GPIO Port G base: 0x4002.6000
Offset 0x500
Type R/W, reset 0x0000.00FF
31 30 29 28 27 26 25 24 23 22 21 20 19 18 17 16
reserved
Type RO RO RO RO RO RO RO RO RO RO RO RO RO RO RO RO
Reset 0 0 0 0 0 0 0 0 0 0 0 0 0 0 0 0
15 14 13 12 11 10 9 8 7 6 5 4 3 2 1 0
reserved DRV2
Type RO RO RO RO RO RO RO RO R/W R/W R/W R/W R/W R/W R/W R/W
Reset 0 0 0 0 0 0 0 0 1 1 1 1 1 1 1 1
Bit/Field Name Type Reset Description
Software should not rely on the value of a reserved bit. To provide
compatibility with future products, the value of a reserved bit should be
preserved across a read-modify-write operation.
31:8 reserved RO 0x00
Output Pad 2-mA Drive Enable
A write of 1 to either GPIODR4[n] or GPIODR8[n] clears the
corresponding 2-mA enable bit. The change is effective on the second
clock cycle after the write.
7:0 DRV2 R/W 0xFF
November 30, 2007 149
Preliminary
LM3S6110 Microcontroller
Register 12: GPIO 4-mA Drive Select (GPIODR4R), offset 0x504
The GPIODR4R register is the 4-mA drive control register. It allows for each GPIO signal in the port
to be individually configured without affecting the other pads. When writing the DRV4 bit for a GPIO
signal, the corresponding DRV2 bit in the GPIODR2R register and the DRV8 bit in the GPIODR8R
register are automatically cleared by hardware.
GPIO 4-mA Drive Select (GPIODR4R)
GPIO Port A base: 0x4000.4000
GPIO Port B base: 0x4000.5000
GPIO Port C base: 0x4000.6000
GPIO Port D base: 0x4000.7000
GPIO Port E base: 0x4002.4000
GPIO Port F base: 0x4002.5000
GPIO Port G base: 0x4002.6000
Offset 0x504
Type R/W, reset 0x0000.0000
31 30 29 28 27 26 25 24 23 22 21 20 19 18 17 16
reserved
Type RO RO RO RO RO RO RO RO RO RO RO RO RO RO RO RO
Reset 0 0 0 0 0 0 0 0 0 0 0 0 0 0 0 0
15 14 13 12 11 10 9 8 7 6 5 4 3 2 1 0
reserved DRV4
Type RO RO RO RO RO RO RO RO R/W R/W R/W R/W R/W R/W R/W R/W
Reset 0 0 0 0 0 0 0 0 0 0 0 0 0 0 0 0
Bit/Field Name Type Reset Description
Software should not rely on the value of a reserved bit. To provide
compatibility with future products, the value of a reserved bit should be
preserved across a read-modify-write operation.
31:8 reserved RO 0x00
Output Pad 4-mA Drive Enable
A write of 1 to either GPIODR2[n] or GPIODR8[n] clears the
corresponding 4-mA enable bit. The change is effective on the second
clock cycle after the write.
7:0 DRV4 R/W 0x00
150 November 30, 2007
Preliminary
General-Purpose Input/Outputs (GPIOs)
Register 13: GPIO 8-mA Drive Select (GPIODR8R), offset 0x508
The GPIODR8R register is the 8-mA drive control register. It allows for each GPIO signal in the port
to be individually configured without affecting the other pads. When writing the DRV8 bit for a GPIO
signal, the corresponding DRV2 bit in the GPIODR2R register and the DRV4 bit in the GPIODR4R
register are automatically cleared by hardware.
GPIO 8-mA Drive Select (GPIODR8R)
GPIO Port A base: 0x4000.4000
GPIO Port B base: 0x4000.5000
GPIO Port C base: 0x4000.6000
GPIO Port D base: 0x4000.7000
GPIO Port E base: 0x4002.4000
GPIO Port F base: 0x4002.5000
GPIO Port G base: 0x4002.6000
Offset 0x508
Type R/W, reset 0x0000.0000
31 30 29 28 27 26 25 24 23 22 21 20 19 18 17 16
reserved
Type RO RO RO RO RO RO RO RO RO RO RO RO RO RO RO RO
Reset 0 0 0 0 0 0 0 0 0 0 0 0 0 0 0 0
15 14 13 12 11 10 9 8 7 6 5 4 3 2 1 0
reserved DRV8
Type RO RO RO RO RO RO RO RO R/W R/W R/W R/W R/W R/W R/W R/W
Reset 0 0 0 0 0 0 0 0 0 0 0 0 0 0 0 0
Bit/Field Name Type Reset Description
Software should not rely on the value of a reserved bit. To provide
compatibility with future products, the value of a reserved bit should be
preserved across a read-modify-write operation.
31:8 reserved RO 0x00
Output Pad 8-mA Drive Enable
A write of 1 to either GPIODR2[n] or GPIODR4[n] clears the
corresponding 8-mA enable bit. The change is effective on the second
clock cycle after the write.
7:0 DRV8 R/W 0x00
November 30, 2007 151
Preliminary
LM3S6110 Microcontroller
Register 14: GPIO Open Drain Select (GPIOODR), offset 0x50C
The GPIOODR register is the open drain control register. Setting a bit in this register enables the
open drain configuration of the corresponding GPIO pad. When open drain mode is enabled, the
corresponding bit should also be set in the GPIO Digital Input Enable (GPIODEN) register (see
page 156). Corresponding bits in the drive strength registers (GPIODR2R, GPIODR4R, GPIODR8R,
and GPIOSLR ) can be set to achieve the desired rise and fall times. The GPIO acts as an open
drain input if the corresponding bit in the GPIODIR register is set to 0; and as an open drain output
when set to 1.
GPIO Open Drain Select (GPIOODR)
GPIO Port A base: 0x4000.4000
GPIO Port B base: 0x4000.5000
GPIO Port C base: 0x4000.6000
GPIO Port D base: 0x4000.7000
GPIO Port E base: 0x4002.4000
GPIO Port F base: 0x4002.5000
GPIO Port G base: 0x4002.6000
Offset 0x50C
Type R/W, reset 0x0000.0000
31 30 29 28 27 26 25 24 23 22 21 20 19 18 17 16
reserved
Type RO RO RO RO RO RO RO RO RO RO RO RO RO RO RO RO
Reset 0 0 0 0 0 0 0 0 0 0 0 0 0 0 0 0
15 14 13 12 11 10 9 8 7 6 5 4 3 2 1 0
reserved ODE
Type RO RO RO RO RO RO RO RO R/W R/W R/W R/W R/W R/W R/W R/W
Reset 0 0 0 0 0 0 0 0 0 0 0 0 0 0 0 0
Bit/Field Name Type Reset Description
Software should not rely on the value of a reserved bit. To provide
compatibility with future products, the value of a reserved bit should be
preserved across a read-modify-write operation.
31:8 reserved RO 0x00
Output Pad Open Drain Enable
The ODE values are defined as follows:
Value Description
0 Open drain configuration is disabled.
1 Open drain configuration is enabled.
7:0 ODE R/W 0x00
152 November 30, 2007
Preliminary
General-Purpose Input/Outputs (GPIOs)
Register 15: GPIO Pull-Up Select (GPIOPUR), offset 0x510
The GPIOPUR register is the pull-up control register. When a bit is set to 1, it enables a weak pull-up
resistor on the corresponding GPIO signal. Setting a bit in GPIOPUR automatically clears the
corresponding bit in the GPIO Pull-Down Select (GPIOPDR) register (see page 154).
GPIO Pull-Up Select (GPIOPUR)
GPIO Port A base: 0x4000.4000
GPIO Port B base: 0x4000.5000
GPIO Port C base: 0x4000.6000
GPIO Port D base: 0x4000.7000
GPIO Port E base: 0x4002.4000
GPIO Port F base: 0x4002.5000
GPIO Port G base: 0x4002.6000
Offset 0x510
Type R/W, reset -
31 30 29 28 27 26 25 24 23 22 21 20 19 18 17 16
reserved
Type RO RO RO RO RO RO RO RO RO RO RO RO RO RO RO RO
Reset 0 0 0 0 0 0 0 0 0 0 0 0 0 0 0 0
15 14 13 12 11 10 9 8 7 6 5 4 3 2 1 0
reserved PUE
Type RO RO RO RO RO RO RO RO R/W R/W R/W R/W R/W R/W R/W R/W
Reset 0 0 0 0 0 0 0 0 - - - - - - - -
Bit/Field Name Type Reset Description
Software should not rely on the value of a reserved bit. To provide
compatibility with future products, the value of a reserved bit should be
preserved across a read-modify-write operation.
31:8 reserved RO 0x00
Pad Weak Pull-Up Enable
A write of 1 to GPIOPDR[n] clears the corresponding GPIOPUR[n]
enables. The change is effective on the second clock cycle after the
write.
Note: The default reset value for the GPIOAFSEL, GPIOPUR, and
GPIODEN registers are 0x0000.0000 for all GPIO pins, with
the exception of the five JTAG/SWD pins (PB7 and PC[3:0]).
These five pins default to JTAG/SWD functionality. Because
of this, the default reset value of these registers for GPIO Port
B is 0x0000.0080 while the default reset value for Port C is
0x0000.000F.
7:0 PUE R/W -
November 30, 2007 153
Preliminary
LM3S6110 Microcontroller
Register 16: GPIO Pull-Down Select (GPIOPDR), offset 0x514
The GPIOPDR register is the pull-down control register. When a bit is set to 1, it enables a weak
pull-down resistor on the corresponding GPIO signal. Setting a bit in GPIOPDR automatically clears
the corresponding bit in the GPIO Pull-Up Select (GPIOPUR) register (see page 153).
GPIO Pull-Down Select (GPIOPDR)
GPIO Port A base: 0x4000.4000
GPIO Port B base: 0x4000.5000
GPIO Port C base: 0x4000.6000
GPIO Port D base: 0x4000.7000
GPIO Port E base: 0x4002.4000
GPIO Port F base: 0x4002.5000
GPIO Port G base: 0x4002.6000
Offset 0x514
Type R/W, reset 0x0000.0000
31 30 29 28 27 26 25 24 23 22 21 20 19 18 17 16
reserved
Type RO RO RO RO RO RO RO RO RO RO RO RO RO RO RO RO
Reset 0 0 0 0 0 0 0 0 0 0 0 0 0 0 0 0
15 14 13 12 11 10 9 8 7 6 5 4 3 2 1 0
reserved PDE
Type RO RO RO RO RO RO RO RO R/W R/W R/W R/W R/W R/W R/W R/W
Reset 0 0 0 0 0 0 0 0 0 0 0 0 0 0 0 0
Bit/Field Name Type Reset Description
Software should not rely on the value of a reserved bit. To provide
compatibility with future products, the value of a reserved bit should be
preserved across a read-modify-write operation.
31:8 reserved RO 0x00
Pad Weak Pull-Down Enable
A write of 1 to GPIOPUR[n] clears the corresponding GPIOPDR[n]
enables. The change is effective on the second clock cycle after the
write.
7:0 PDE R/W 0x00
154 November 30, 2007
Preliminary
General-Purpose Input/Outputs (GPIOs)
Register 17: GPIO Slew Rate Control Select (GPIOSLR), offset 0x518
The GPIOSLR register is the slew rate control register. Slew rate control is only available when
using the 8-mA drive strength option via the GPIO 8-mA Drive Select (GPIODR8R) register (see
page 151).
GPIO Slew Rate Control Select (GPIOSLR)
GPIO Port A base: 0x4000.4000
GPIO Port B base: 0x4000.5000
GPIO Port C base: 0x4000.6000
GPIO Port D base: 0x4000.7000
GPIO Port E base: 0x4002.4000
GPIO Port F base: 0x4002.5000
GPIO Port G base: 0x4002.6000
Offset 0x518
Type R/W, reset 0x0000.0000
31 30 29 28 27 26 25 24 23 22 21 20 19 18 17 16
reserved
Type RO RO RO RO RO RO RO RO RO RO RO RO RO RO RO RO
Reset 0 0 0 0 0 0 0 0 0 0 0 0 0 0 0 0
15 14 13 12 11 10 9 8 7 6 5 4 3 2 1 0
reserved SRL
Type RO RO RO RO RO RO RO RO R/W R/W R/W R/W R/W R/W R/W R/W
Reset 0 0 0 0 0 0 0 0 0 0 0 0 0 0 0 0
Bit/Field Name Type Reset Description
Software should not rely on the value of a reserved bit. To provide
compatibility with future products, the value of a reserved bit should be
preserved across a read-modify-write operation.
31:8 reserved RO 0x00
Slew Rate Limit Enable (8-mA drive only)
The SRL values are defined as follows:
Value Description
0 Slew rate control disabled.
1 Slew rate control enabled.
7:0 SRL R/W 0x00
November 30, 2007 155
Preliminary
LM3S6110 Microcontroller
Register 18: GPIO Digital Enable (GPIODEN), offset 0x51C
The GPIODEN register is the digital enable register. By default, with the exception of the GPIO
signals used for JTAG/SWD function, all other GPIO signals are configured out of reset to be undriven
(tristate). Their digital function is disabled; they do not drive a logic value on the pin and they do not
allow the pin voltage into the GPIO receiver. To use the pin in a digital function (either GPIO or
alternate function), the corresponding GPIODEN bit must be set.
GPIO Digital Enable (GPIODEN)
GPIO Port A base: 0x4000.4000
GPIO Port B base: 0x4000.5000
GPIO Port C base: 0x4000.6000
GPIO Port D base: 0x4000.7000
GPIO Port E base: 0x4002.4000
GPIO Port F base: 0x4002.5000
GPIO Port G base: 0x4002.6000
Offset 0x51C
Type R/W, reset -
31 30 29 28 27 26 25 24 23 22 21 20 19 18 17 16
reserved
Type RO RO RO RO RO RO RO RO RO RO RO RO RO RO RO RO
Reset 0 0 0 0 0 0 0 0 0 0 0 0 0 0 0 0
15 14 13 12 11 10 9 8 7 6 5 4 3 2 1 0
reserved DEN
Type RO RO RO RO RO RO RO RO R/W R/W R/W R/W R/W R/W R/W R/W
Reset 0 0 0 0 0 0 0 0 - - - - - - - -
Bit/Field Name Type Reset Description
Software should not rely on the value of a reserved bit. To provide
compatibility with future products, the value of a reserved bit should be
preserved across a read-modify-write operation.
31:8 reserved RO 0x00
Digital Enable
The DEN values are defined as follows:
Value Description
0 Digital functions disabled.
1 Digital functions enabled.
Note: The default reset value for the GPIOAFSEL,
GPIOPUR, and GPIODEN registers are 0x0000.0000
for all GPIO pins, with the exception of the five
JTAG/SWD pins (PB7 and PC[3:0]). These five pins
default to JTAG/SWD functionality. Because of this,
the default reset value of these registers for GPIO
Port B is 0x0000.0080 while the default reset value
for Port C is 0x0000.000F.
7:0 DEN R/W -
156 November 30, 2007
Preliminary
General-Purpose Input/Outputs (GPIOs)
Register 19: GPIO Lock (GPIOLOCK), offset 0x520
The GPIOLOCK register enables write access to the GPIOCR register (see page 158). Writing
0x1ACCE551 to the GPIOLOCK register will unlock the GPIOCR register. Writing any other value
to the GPIOLOCK register re-enables the locked state. Reading the GPIOLOCK register returns
the lock status rather than the 32-bit value that was previously written. Therefore, when write accesses
are disabled, or locked, reading the GPIOLOCK register returns 0x00000001. When write accesses
are enabled, or unlocked, reading the GPIOLOCK register returns 0x00000000.
GPIO Lock (GPIOLOCK)
GPIO Port A base: 0x4000.4000
GPIO Port B base: 0x4000.5000
GPIO Port C base: 0x4000.6000
GPIO Port D base: 0x4000.7000
GPIO Port E base: 0x4002.4000
GPIO Port F base: 0x4002.5000
GPIO Port G base: 0x4002.6000
Offset 0x520
Type R/W, reset 0x0000.0001
31 30 29 28 27 26 25 24 23 22 21 20 19 18 17 16
LOCK
Type R/W R/W R/W R/W R/W R/W R/W R/W R/W R/W R/W R/W R/W R/W R/W R/W
Reset 0 0 0 0 0 0 0 0 0 0 0 0 0 0 0 0
15 14 13 12 11 10 9 8 7 6 5 4 3 2 1 0
LOCK
Type R/W R/W R/W R/W R/W R/W R/W R/W R/W R/W R/W R/W R/W R/W R/W R/W
Reset 0 0 0 0 0 0 0 0 0 0 0 0 0 0 0 1
Bit/Field Name Type Reset Description
GPIO Lock
A write of the value 0x1ACCE551 unlocks the GPIO Commit (GPIOCR)
register for write access. A write of any other value reapplies the lock,
preventing any register updates. A read of this register returns the
following values:
Value Description
0x0000.0001 locked
0x0000.0000 unlocked
31:0 LOCK R/W 0x0000.0001
November 30, 2007 157
Preliminary
LM3S6110 Microcontroller
Register 20: GPIO Commit (GPIOCR), offset 0x524
The GPIOCR register is the commit register. The value of the GPIOCR register determines which
bits of the GPIOAFSEL register will be committed when a write to the GPIOAFSEL register is
performed. If a bit in the GPIOCR register is a zero, the data being written to the corresponding bit
in the GPIOAFSEL register will not be committed and will retain its previous value. If a bit in the
GPIOCR register is a one, the data being written to the corresponding bit of the GPIOAFSEL register
will be committed to the register and will reflect the new value.
The contents of the GPIOCR register can only be modified if the GPIOLOCK register is unlocked.
Writes to the GPIOCR register will be ignored if the GPIOLOCK register is locked.
Important: This register is designed to prevent accidental programming of the GPIOAFSEL registers
that control connectivity to the JTAG/SWD debug hardware. By initializing the bits of
the GPIOCR register to 0 for PB7 and PC[3:0], the JTAG/SWD debug port can only
be converted to GPIOs through a deliberate set of writes to the GPIOLOCK, GPIOCR,
and GPIOAFSEL registers.
Because this protection is currently only implemented on the JTAG/SWD pins on PB7
and PC[3:0], all of the other bits in the GPIOCR registers cannot be written with 0x0.
These bits are hardwired to 0x1, ensuring that it is always possible to commit new
values to the GPIOAFSEL register bits of these other pins.
GPIO Commit (GPIOCR)
GPIO Port A base: 0x4000.4000
GPIO Port B base: 0x4000.5000
GPIO Port C base: 0x4000.6000
GPIO Port D base: 0x4000.7000
GPIO Port E base: 0x4002.4000
GPIO Port F base: 0x4002.5000
GPIO Port G base: 0x4002.6000
Offset 0x524
Type -, reset -
31 30 29 28 27 26 25 24 23 22 21 20 19 18 17 16
reserved
Type RO RO RO RO RO RO RO RO RO RO RO RO RO RO RO RO
Reset 0 0 0 0 0 0 0 0 0 0 0 0 0 0 0 0
15 14 13 12 11 10 9 8 7 6 5 4 3 2 1 0
reserved CR
Type RO RO RO RO RO RO RO RO - - - - - - - -
Reset 0 0 0 0 0 0 0 0 - - - - - - - -
Bit/Field Name Type Reset Description
Software should not rely on the value of a reserved bit. To provide
compatibility with future products, the value of a reserved bit should be
preserved across a read-modify-write operation.
31:8 reserved RO 0x00
158 November 30, 2007
Preliminary
General-Purpose Input/Outputs (GPIOs)
Bit/Field Name Type Reset Description
GPIO Commit
On a bit-wise basis, any bit set allows the corresponding GPIOAFSEL
bit to be set to its alternate function.
Note: The default register type for the GPIOCR register is RO for
all GPIO pins, with the exception of the five JTAG/SWD pins
(PB7 and PC[3:0]). These five pins are currently the only
GPIOs that are protected by the GPIOCR register. Because
of this, the register type for GPIO Port B7 and GPIO Port
C[3:0] is R/W.
The default reset value for the GPIOCR register is
0x0000.00FF for all GPIO pins, with the exception of the five
JTAG/SWD pins (PB7 and PC[3:0]). To ensure that the
JTAG port is not accidentally programmed as a GPIO, these
five pins default to non-commitable. Because of this, the
default reset value of GPIOCR for GPIO Port B is
0x0000.007F while the default reset value of GPIOCR for Port
C is 0x0000.00F0.
7:0 CR - -
November 30, 2007 159
Preliminary
LM3S6110 Microcontroller
Register 21: GPIO Peripheral Identification 4 (GPIOPeriphID4), offset 0xFD0
The GPIOPeriphID4, GPIOPeriphID5, GPIOPeriphID6, and GPIOPeriphID7 registers can
conceptually be treated as one 32-bit register; each register contains eight bits of the 32-bit register,
used by software to identify the peripheral.
GPIO Peripheral Identification 4 (GPIOPeriphID4)
GPIO Port A base: 0x4000.4000
GPIO Port B base: 0x4000.5000
GPIO Port C base: 0x4000.6000
GPIO Port D base: 0x4000.7000
GPIO Port E base: 0x4002.4000
GPIO Port F base: 0x4002.5000
GPIO Port G base: 0x4002.6000
Offset 0xFD0
Type RO, reset 0x0000.0000
31 30 29 28 27 26 25 24 23 22 21 20 19 18 17 16
reserved
Type RO RO RO RO RO RO RO RO RO RO RO RO RO RO RO RO
Reset 0 0 0 0 0 0 0 0 0 0 0 0 0 0 0 0
15 14 13 12 11 10 9 8 7 6 5 4 3 2 1 0
reserved PID4
Type RO RO RO RO RO RO RO RO RO RO RO RO RO RO RO RO
Reset 0 0 0 0 0 0 0 0 0 0 0 0 0 0 0 0
Bit/Field Name Type Reset Description
Software should not rely on the value of a reserved bit. To provide
compatibility with future products, the value of a reserved bit should be
preserved across a read-modify-write operation.
31:8 reserved RO 0x00
7:0 PID4 RO 0x00 GPIO Peripheral ID Register[7:0]
160 November 30, 2007
Preliminary
General-Purpose Input/Outputs (GPIOs)
Register 22: GPIO Peripheral Identification 5 (GPIOPeriphID5), offset 0xFD4
The GPIOPeriphID4, GPIOPeriphID5, GPIOPeriphID6, and GPIOPeriphID7 registers can
conceptually be treated as one 32-bit register; each register contains eight bits of the 32-bit register,
used by software to identify the peripheral.
GPIO Peripheral Identification 5 (GPIOPeriphID5)
GPIO Port A base: 0x4000.4000
GPIO Port B base: 0x4000.5000
GPIO Port C base: 0x4000.6000
GPIO Port D base: 0x4000.7000
GPIO Port E base: 0x4002.4000
GPIO Port F base: 0x4002.5000
GPIO Port G base: 0x4002.6000
Offset 0xFD4
Type RO, reset 0x0000.0000
31 30 29 28 27 26 25 24 23 22 21 20 19 18 17 16
reserved
Type RO RO RO RO RO RO RO RO RO RO RO RO RO RO RO RO
Reset 0 0 0 0 0 0 0 0 0 0 0 0 0 0 0 0
15 14 13 12 11 10 9 8 7 6 5 4 3 2 1 0
reserved PID5
Type RO RO RO RO RO RO RO RO RO RO RO RO RO RO RO RO
Reset 0 0 0 0 0 0 0 0 0 0 0 0 0 0 0 0
Bit/Field Name Type Reset Description
Software should not rely on the value of a reserved bit. To provide
compatibility with future products, the value of a reserved bit should be
preserved across a read-modify-write operation.
31:8 reserved RO 0x00
7:0 PID5 RO 0x00 GPIO Peripheral ID Register[15:8]
November 30, 2007 161
Preliminary
LM3S6110 Microcontroller
Register 23: GPIO Peripheral Identification 6 (GPIOPeriphID6), offset 0xFD8
The GPIOPeriphID4, GPIOPeriphID5, GPIOPeriphID6, and GPIOPeriphID7 registers can
conceptually be treated as one 32-bit register; each register contains eight bits of the 32-bit register,
used by software to identify the peripheral.
GPIO Peripheral Identification 6 (GPIOPeriphID6)
GPIO Port A base: 0x4000.4000
GPIO Port B base: 0x4000.5000
GPIO Port C base: 0x4000.6000
GPIO Port D base: 0x4000.7000
GPIO Port E base: 0x4002.4000
GPIO Port F base: 0x4002.5000
GPIO Port G base: 0x4002.6000
Offset 0xFD8
Type RO, reset 0x0000.0000
31 30 29 28 27 26 25 24 23 22 21 20 19 18 17 16
reserved
Type RO RO RO RO RO RO RO RO RO RO RO RO RO RO RO RO
Reset 0 0 0 0 0 0 0 0 0 0 0 0 0 0 0 0
15 14 13 12 11 10 9 8 7 6 5 4 3 2 1 0
reserved PID6
Type RO RO RO RO RO RO RO RO RO RO RO RO RO RO RO RO
Reset 0 0 0 0 0 0 0 0 0 0 0 0 0 0 0 0
Bit/Field Name Type Reset Description
Software should not rely on the value of a reserved bit. To provide
compatibility with future products, the value of a reserved bit should be
preserved across a read-modify-write operation.
31:8 reserved RO 0x00
7:0 PID6 RO 0x00 GPIO Peripheral ID Register[23:16]
162 November 30, 2007
Preliminary
General-Purpose Input/Outputs (GPIOs)
Register 24: GPIO Peripheral Identification 7 (GPIOPeriphID7), offset 0xFDC
The GPIOPeriphID4, GPIOPeriphID5, GPIOPeriphID6, and GPIOPeriphID7 registers can
conceptually be treated as one 32-bit register; each register contains eight bits of the 32-bit register,
used by software to identify the peripheral.
GPIO Peripheral Identification 7 (GPIOPeriphID7)
GPIO Port A base: 0x4000.4000
GPIO Port B base: 0x4000.5000
GPIO Port C base: 0x4000.6000
GPIO Port D base: 0x4000.7000
GPIO Port E base: 0x4002.4000
GPIO Port F base: 0x4002.5000
GPIO Port G base: 0x4002.6000
Offset 0xFDC
Type RO, reset 0x0000.0000
31 30 29 28 27 26 25 24 23 22 21 20 19 18 17 16
reserved
Type RO RO RO RO RO RO RO RO RO RO RO RO RO RO RO RO
Reset 0 0 0 0 0 0 0 0 0 0 0 0 0 0 0 0
15 14 13 12 11 10 9 8 7 6 5 4 3 2 1 0
reserved PID7
Type RO RO RO RO RO RO RO RO RO RO RO RO RO RO RO RO
Reset 0 0 0 0 0 0 0 0 0 0 0 0 0 0 0 0
Bit/Field Name Type Reset Description
Software should not rely on the value of a reserved bit. To provide
compatibility with future products, the value of a reserved bit should be
preserved across a read-modify-write operation.
31:8 reserved RO 0x00
7:0 PID7 RO 0x00 GPIO Peripheral ID Register[31:24]
November 30, 2007 163
Preliminary
LM3S6110 Microcontroller
Register 25: GPIO Peripheral Identification 0 (GPIOPeriphID0), offset 0xFE0
The GPIOPeriphID0, GPIOPeriphID1, GPIOPeriphID2, and GPIOPeriphID3 registers can
conceptually be treated as one 32-bit register; each register contains eight bits of the 32-bit register,
used by software to identify the peripheral.
GPIO Peripheral Identification 0 (GPIOPeriphID0)
GPIO Port A base: 0x4000.4000
GPIO Port B base: 0x4000.5000
GPIO Port C base: 0x4000.6000
GPIO Port D base: 0x4000.7000
GPIO Port E base: 0x4002.4000
GPIO Port F base: 0x4002.5000
GPIO Port G base: 0x4002.6000
Offset 0xFE0
Type RO, reset 0x0000.0061
31 30 29 28 27 26 25 24 23 22 21 20 19 18 17 16
reserved
Type RO RO RO RO RO RO RO RO RO RO RO RO RO RO RO RO
Reset 0 0 0 0 0 0 0 0 0 0 0 0 0 0 0 0
15 14 13 12 11 10 9 8 7 6 5 4 3 2 1 0
reserved PID0
Type RO RO RO RO RO RO RO RO RO RO RO RO RO RO RO RO
Reset 0 0 0 0 0 0 0 0 0 1 1 0 0 0 0 1
Bit/Field Name Type Reset Description
Software should not rely on the value of a reserved bit. To provide
compatibility with future products, the value of a reserved bit should be
preserved across a read-modify-write operation.
31:8 reserved RO 0x00
GPIO Peripheral ID Register[7:0]
Can be used by software to identify the presence of this peripheral.
7:0 PID0 RO 0x61
164 November 30, 2007
Preliminary
General-Purpose Input/Outputs (GPIOs)
Register 26: GPIO Peripheral Identification 1 (GPIOPeriphID1), offset 0xFE4
The GPIOPeriphID0, GPIOPeriphID1, GPIOPeriphID2, and GPIOPeriphID3 registers can
conceptually be treated as one 32-bit register; each register contains eight bits of the 32-bit register,
used by software to identify the peripheral.
GPIO Peripheral Identification 1 (GPIOPeriphID1)
GPIO Port A base: 0x4000.4000
GPIO Port B base: 0x4000.5000
GPIO Port C base: 0x4000.6000
GPIO Port D base: 0x4000.7000
GPIO Port E base: 0x4002.4000
GPIO Port F base: 0x4002.5000
GPIO Port G base: 0x4002.6000
Offset 0xFE4
Type RO, reset 0x0000.0000
31 30 29 28 27 26 25 24 23 22 21 20 19 18 17 16
reserved
Type RO RO RO RO RO RO RO RO RO RO RO RO RO RO RO RO
Reset 0 0 0 0 0 0 0 0 0 0 0 0 0 0 0 0
15 14 13 12 11 10 9 8 7 6 5 4 3 2 1 0
reserved PID1
Type RO RO RO RO RO RO RO RO RO RO RO RO RO RO RO RO
Reset 0 0 0 0 0 0 0 0 0 0 0 0 0 0 0 0
Bit/Field Name Type Reset Description
Software should not rely on the value of a reserved bit. To provide
compatibility with future products, the value of a reserved bit should be
preserved across a read-modify-write operation.
31:8 reserved RO 0x00
GPIO Peripheral ID Register[15:8]
Can be used by software to identify the presence of this peripheral.
7:0 PID1 RO 0x00
November 30, 2007 165
Preliminary
LM3S6110 Microcontroller
Register 27: GPIO Peripheral Identification 2 (GPIOPeriphID2), offset 0xFE8
The GPIOPeriphID0, GPIOPeriphID1, GPIOPeriphID2, and GPIOPeriphID3 registers can
conceptually be treated as one 32-bit register; each register contains eight bits of the 32-bit register,
used by software to identify the peripheral.
GPIO Peripheral Identification 2 (GPIOPeriphID2)
GPIO Port A base: 0x4000.4000
GPIO Port B base: 0x4000.5000
GPIO Port C base: 0x4000.6000
GPIO Port D base: 0x4000.7000
GPIO Port E base: 0x4002.4000
GPIO Port F base: 0x4002.5000
GPIO Port G base: 0x4002.6000
Offset 0xFE8
Type RO, reset 0x0000.0018
31 30 29 28 27 26 25 24 23 22 21 20 19 18 17 16
reserved
Type RO RO RO RO RO RO RO RO RO RO RO RO RO RO RO RO
Reset 0 0 0 0 0 0 0 0 0 0 0 0 0 0 0 0
15 14 13 12 11 10 9 8 7 6 5 4 3 2 1 0
reserved PID2
Type RO RO RO RO RO RO RO RO RO RO RO RO RO RO RO RO
Reset 0 0 0 0 0 0 0 0 0 0 0 1 1 0 0 0
Bit/Field Name Type Reset Description
Software should not rely on the value of a reserved bit. To provide
compatibility with future products, the value of a reserved bit should be
preserved across a read-modify-write operation.
31:8 reserved RO 0x00
GPIO Peripheral ID Register[23:16]
Can be used by software to identify the presence of this peripheral.
7:0 PID2 RO 0x18
166 November 30, 2007
Preliminary
General-Purpose Input/Outputs (GPIOs)
Register 28: GPIO Peripheral Identification 3 (GPIOPeriphID3), offset 0xFEC
The GPIOPeriphID0, GPIOPeriphID1, GPIOPeriphID2, and GPIOPeriphID3 registers can
conceptually be treated as one 32-bit register; each register contains eight bits of the 32-bit register,
used by software to identify the peripheral.
GPIO Peripheral Identification 3 (GPIOPeriphID3)
GPIO Port A base: 0x4000.4000
GPIO Port B base: 0x4000.5000
GPIO Port C base: 0x4000.6000
GPIO Port D base: 0x4000.7000
GPIO Port E base: 0x4002.4000
GPIO Port F base: 0x4002.5000
GPIO Port G base: 0x4002.6000
Offset 0xFEC
Type RO, reset 0x0000.0001
31 30 29 28 27 26 25 24 23 22 21 20 19 18 17 16
reserved
Type RO RO RO RO RO RO RO RO RO RO RO RO RO RO RO RO
Reset 0 0 0 0 0 0 0 0 0 0 0 0 0 0 0 0
15 14 13 12 11 10 9 8 7 6 5 4 3 2 1 0
reserved PID3
Type RO RO RO RO RO RO RO RO RO RO RO RO RO RO RO RO
Reset 0 0 0 0 0 0 0 0 0 0 0 0 0 0 0 1
Bit/Field Name Type Reset Description
Software should not rely on the value of a reserved bit. To provide
compatibility with future products, the value of a reserved bit should be
preserved across a read-modify-write operation.
31:8 reserved RO 0x00
GPIO Peripheral ID Register[31:24]
Can be used by software to identify the presence of this peripheral.
7:0 PID3 RO 0x01
November 30, 2007 167
Preliminary
LM3S6110 Microcontroller
Register 29: GPIO PrimeCell Identification 0 (GPIOPCellID0), offset 0xFF0
The GPIOPCellID0, GPIOPCellID1, GPIOPCellID2, and GPIOPCellID3 registers are four 8-bit wide
registers, that can conceptually be treated as one 32-bit register. The register is used as a standard
cross-peripheral identification system.
GPIO PrimeCell Identification 0 (GPIOPCellID0)
GPIO Port A base: 0x4000.4000
GPIO Port B base: 0x4000.5000
GPIO Port C base: 0x4000.6000
GPIO Port D base: 0x4000.7000
GPIO Port E base: 0x4002.4000
GPIO Port F base: 0x4002.5000
GPIO Port G base: 0x4002.6000
Offset 0xFF0
Type RO, reset 0x0000.000D
31 30 29 28 27 26 25 24 23 22 21 20 19 18 17 16
reserved
Type RO RO RO RO RO RO RO RO RO RO RO RO RO RO RO RO
Reset 0 0 0 0 0 0 0 0 0 0 0 0 0 0 0 0
15 14 13 12 11 10 9 8 7 6 5 4 3 2 1 0
reserved CID0
Type RO RO RO RO RO RO RO RO RO RO RO RO RO RO RO RO
Reset 0 0 0 0 0 0 0 0 0 0 0 0 1 1 0 1
Bit/Field Name Type Reset Description
Software should not rely on the value of a reserved bit. To provide
compatibility with future products, the value of a reserved bit should be
preserved across a read-modify-write operation.
31:8 reserved RO 0x00
GPIO PrimeCell ID Register[7:0]
Provides software a standard cross-peripheral identification system.
7:0 CID0 RO 0x0D
168 November 30, 2007
Preliminary
General-Purpose Input/Outputs (GPIOs)
Register 30: GPIO PrimeCell Identification 1 (GPIOPCellID1), offset 0xFF4
The GPIOPCellID0, GPIOPCellID1, GPIOPCellID2, and GPIOPCellID3 registers are four 8-bit wide
registers, that can conceptually be treated as one 32-bit register. The register is used as a standard
cross-peripheral identification system.
GPIO PrimeCell Identification 1 (GPIOPCellID1)
GPIO Port A base: 0x4000.4000
GPIO Port B base: 0x4000.5000
GPIO Port C base: 0x4000.6000
GPIO Port D base: 0x4000.7000
GPIO Port E base: 0x4002.4000
GPIO Port F base: 0x4002.5000
GPIO Port G base: 0x4002.6000
Offset 0xFF4
Type RO, reset 0x0000.00F0
31 30 29 28 27 26 25 24 23 22 21 20 19 18 17 16
reserved
Type RO RO RO RO RO RO RO RO RO RO RO RO RO RO RO RO
Reset 0 0 0 0 0 0 0 0 0 0 0 0 0 0 0 0
15 14 13 12 11 10 9 8 7 6 5 4 3 2 1 0
reserved CID1
Type RO RO RO RO RO RO RO RO RO RO RO RO RO RO RO RO
Reset 0 0 0 0 0 0 0 0 1 1 1 1 0 0 0 0
Bit/Field Name Type Reset Description
Software should not rely on the value of a reserved bit. To provide
compatibility with future products, the value of a reserved bit should be
preserved across a read-modify-write operation.
31:8 reserved RO 0x00
GPIO PrimeCell ID Register[15:8]
Provides software a standard cross-peripheral identification system.
7:0 CID1 RO 0xF0
November 30, 2007 169
Preliminary
LM3S6110 Microcontroller
Register 31: GPIO PrimeCell Identification 2 (GPIOPCellID2), offset 0xFF8
The GPIOPCellID0, GPIOPCellID1, GPIOPCellID2, and GPIOPCellID3 registers are four 8-bit wide
registers, that can conceptually be treated as one 32-bit register. The register is used as a standard
cross-peripheral identification system.
GPIO PrimeCell Identification 2 (GPIOPCellID2)
GPIO Port A base: 0x4000.4000
GPIO Port B base: 0x4000.5000
GPIO Port C base: 0x4000.6000
GPIO Port D base: 0x4000.7000
GPIO Port E base: 0x4002.4000
GPIO Port F base: 0x4002.5000
GPIO Port G base: 0x4002.6000
Offset 0xFF8
Type RO, reset 0x0000.0005
31 30 29 28 27 26 25 24 23 22 21 20 19 18 17 16
reserved
Type RO RO RO RO RO RO RO RO RO RO RO RO RO RO RO RO
Reset 0 0 0 0 0 0 0 0 0 0 0 0 0 0 0 0
15 14 13 12 11 10 9 8 7 6 5 4 3 2 1 0
reserved CID2
Type RO RO RO RO RO RO RO RO RO RO RO RO RO RO RO RO
Reset 0 0 0 0 0 0 0 0 0 0 0 0 0 1 0 1
Bit/Field Name Type Reset Description
Software should not rely on the value of a reserved bit. To provide
compatibility with future products, the value of a reserved bit should be
preserved across a read-modify-write operation.
31:8 reserved RO 0x00
GPIO PrimeCell ID Register[23:16]
Provides software a standard cross-peripheral identification system.
7:0 CID2 RO 0x05
170 November 30, 2007
Preliminary
General-Purpose Input/Outputs (GPIOs)
Register 32: GPIO PrimeCell Identification 3 (GPIOPCellID3), offset 0xFFC
The GPIOPCellID0, GPIOPCellID1, GPIOPCellID2, and GPIOPCellID3 registers are four 8-bit wide
registers, that can conceptually be treated as one 32-bit register. The register is used as a standard
cross-peripheral identification system.
GPIO PrimeCell Identification 3 (GPIOPCellID3)
GPIO Port A base: 0x4000.4000
GPIO Port B base: 0x4000.5000
GPIO Port C base: 0x4000.6000
GPIO Port D base: 0x4000.7000
GPIO Port E base: 0x4002.4000
GPIO Port F base: 0x4002.5000
GPIO Port G base: 0x4002.6000
Offset 0xFFC
Type RO, reset 0x0000.00B1
31 30 29 28 27 26 25 24 23 22 21 20 19 18 17 16
reserved
Type RO RO RO RO RO RO RO RO RO RO RO RO RO RO RO RO
Reset 0 0 0 0 0 0 0 0 0 0 0 0 0 0 0 0
15 14 13 12 11 10 9 8 7 6 5 4 3 2 1 0
reserved CID3
Type RO RO RO RO RO RO RO RO RO RO RO RO RO RO RO RO
Reset 0 0 0 0 0 0 0 0 1 0 1 1 0 0 0 1
Bit/Field Name Type Reset Description
Software should not rely on the value of a reserved bit. To provide
compatibility with future products, the value of a reserved bit should be
preserved across a read-modify-write operation.
31:8 reserved RO 0x00
GPIO PrimeCell ID Register[31:24]
Provides software a standard cross-peripheral identification system.
7:0 CID3 RO 0xB1
November 30, 2007 171
Preliminary
LM3S6110 Microcontroller
9 General-Purpose Timers
Programmable timers can be used to count or time external events that drive the Timer input pins.
The Stellaris® General-Purpose Timer Module (GPTM) contains three GPTM blocks (Timer0, Timer1,
and Timer 2). Each GPTM block provides two 16-bit timers/counters (referred to as TimerA and
TimerB) that can be configured to operate independently as timers or event counters, or configured
to operate as one 32-bit timer or one 32-bit Real-Time Clock (RTC).
Note: Timer2 is an internal timer and can only be used to generate internal interrupts.
The General-Purpose Timer Module is one timing resource available on the Stellaris® microcontrollers.
Other timer resources include the System Timer (SysTick) (see “System Timer (SysTick)” on page 34)
and the PWM timer in the PWM module (see “PWM Timer” on page 366).
The following modes are supported:
■ 32-bit Timer modes
– Programmable one-shot timer
– Programmable periodic timer
– Real-Time Clock using 32.768-KHz input clock
– Software-controlled event stalling (excluding RTC mode)
■ 16-bit Timer modes
– General-purpose timer function with an 8-bit prescaler (for one-shot and periodic modes only)
– Programmable one-shot timer
– Programmable periodic timer
– Software-controlled event stalling
■ 16-bit Input Capture modes
– Input edge count capture
– Input edge time capture
■ 16-bit PWM mode
– Simple PWM mode with software-programmable output inversion of the PWM signal
9.1 Block Diagram
Note: In Figure 9-1 on page 173, the specific CCP pins available depend on the Stellaris® device.
See Table 9-1 on page 173 for the available CCPs.
172 November 30, 2007
Preliminary
General-Purpose Timers
Figure 9-1. GPTM Module Block Diagram
TA Comparator
TB Comparator
GPTMTBR
GPTMAR
Clock / Edge
Detect
RTC Divider
Clock / Edge
Detect
TimerA
Interrupt
TimerB
Interrupt
System
Clock
0x0000 (Down Counter Modes)
0x0000 (Down Counter Modes)
32 KHz or
Even CCP Pin
Odd CCP Pin
En
En
TimerA Control
GPTMTAPMR
GPTMTAILR
GPTMTAMATCHR
GPTMTAPR
GPTMTAMR
TimerB Control
GPTMTBPMR
GPTMTBILR
GPTMTBMATCHR
GPTMTBPR
GPTMTBMR
Interrupt / Config
GPTMCFG
GPTMRIS
GPTMICR
GPTMMIS
GPTMIMR
GPTMCTL
Table 9-1. Available CCP Pins
Timer 16-Bit Up/Down Counter Even CCP Pin Odd CCP Pin
Timer 0 TimerA CCP0 -
TimerB - CCP1
Timer 1 TimerA CCP2 -
TimerB - CCP3
Timer 2 TimerA - -
TimerB - -
9.2 Functional Description
The main components of each GPTM block are two free-running 16-bit up/down counters (referred
to as TimerA and TimerB), two 16-bit match registers, two prescaler match registers, and two 16-bit
load/initialization registers and their associated control functions. The exact functionality of each
GPTM is controlled by software and configured through the register interface.
Software configures the GPTM using the GPTM Configuration (GPTMCFG) register (see page 184),
the GPTM TimerA Mode (GPTMTAMR) register (see page 185), and the GPTM TimerB Mode
(GPTMTBMR) register (see page 187). When in one of the 32-bit modes, the timer can only act as
a 32-bit timer. However, when configured in 16-bit mode, the GPTM can have its two 16-bit timers
configured in any combination of the 16-bit modes.
9.2.1 GPTM Reset Conditions
After reset has been applied to the GPTM module, the module is in an inactive state, and all control
registers are cleared and in their default states. Counters TimerA and TimerB are initialized to
0xFFFF, along with their corresponding load registers: the GPTM TimerA Interval Load
November 30, 2007 173
Preliminary
LM3S6110 Microcontroller
(GPTMTAILR) register (see page 198) and the GPTM TimerB Interval Load (GPTMTBILR) register
(see page 199). The prescale counters are initialized to 0x00: the GPTM TimerA Prescale
(GPTMTAPR) register (see page 202) and the GPTM TimerB Prescale (GPTMTBPR) register (see
page 203).
9.2.2 32-Bit Timer Operating Modes
This section describes the three GPTM 32-bit timer modes (One-Shot, Periodic, and RTC) and their
configuration.
The GPTM is placed into 32-bit mode by writing a 0 (One-Shot/Periodic 32-bit timer mode) or a 1
(RTC mode) to the GPTM Configuration (GPTMCFG) register. In both configurations, certain GPTM
registers are concatenated to form pseudo 32-bit registers. These registers include:
■ GPTM TimerA Interval Load (GPTMTAILR) register [15:0], see page 198
■ GPTM TimerB Interval Load (GPTMTBILR) register [15:0], see page 199
■ GPTM TimerA (GPTMTAR) register [15:0], see page 206
■ GPTM TimerB (GPTMTBR) register [15:0], see page 207
In the 32-bit modes, the GPTM translates a 32-bit write access to GPTMTAILR into a write access
to both GPTMTAILR and GPTMTBILR. The resulting word ordering for such a write operation is:
GPTMTBILR[15:0]:GPTMTAILR[15:0]
Likewise, a read access to GPTMTAR returns the value:
GPTMTBR[15:0]:GPTMTAR[15:0]
9.2.2.1 32-Bit One-Shot/Periodic Timer Mode
In 32-bit one-shot and periodic timer modes, the concatenated versions of the TimerA and TimerB
registers are configured as a 32-bit down-counter. The selection of one-shot or periodic mode is
determined by the value written to the TAMR field of the GPTM TimerA Mode (GPTMTAMR) register
(see page 185), and there is no need to write to the GPTM TimerB Mode (GPTMTBMR) register.
When software writes the TAEN bit in the GPTM Control (GPTMCTL) register (see page 189), the
timer begins counting down from its preloaded value. Once the 0x0000.0000 state is reached, the
timer reloads its start value from the concatenated GPTMTAILR on the next cycle. If configured to
be a one-shot timer, the timer stops counting and clears the TAEN bit in the GPTMCTL register. If
configured as a periodic timer, it continues counting.
In addition to reloading the count value, the GPTM generates interrupts and output triggers when
it reaches the 0x0000000 state. The GPTM sets the TATORIS bit in the GPTM Raw Interrupt Status
(GPTMRIS) register (see page 194), and holds it until it is cleared by writing the GPTM Interrupt
Clear (GPTMICR) register (see page 196). If the time-out interrupt is enabled in the GPTM Interrupt
Mask (GPTIMR) register (see page 192), the GPTM also sets the TATOMIS bit in the GPTM Masked
Interrupt Status (GPTMMIS) register (see page 195).
The output trigger is a one-clock-cycle pulse that is asserted when the counter hits the 0x0000.0000
state, and deasserted on the following clock cycle. It is enabled by setting the TAOTE bit in GPTMCTL.
If software reloads the GPTMTAILR register while the counter is running, the counter loads the new
value on the next clock cycle and continues counting from the new value.
174 November 30, 2007
Preliminary
General-Purpose Timers
If the TASTALL bit in the GPTMCTL register is asserted, the timer freezes counting until the signal
is deasserted.
9.2.2.2 32-Bit Real-Time Clock Timer Mode
In Real-Time Clock (RTC) mode, the concatenated versions of the TimerA and TimerB registers
are configured as a 32-bit up-counter. When RTC mode is selected for the first time, the counter is
loaded with a value of 0x0000.0001. All subsequent load values must be written to the GPTM TimerA
Match (GPTMTAMATCHR) register (see page 200) by the controller.
The input clock on the CCP0, CCP2, or CCP4 pins is required to be 32.768 KHz in RTC mode. The
clock signal is then divided down to a 1 Hz rate and is passed along to the input of the 32-bit counter.
When software writes the TAEN bit inthe GPTMCTL register, the counter starts counting up from its
preloaded value of 0x0000.0001. When the current count value matches the preloaded value in the
GPTMTAMATCHR register, it rolls over to a value of 0x0000.0000 and continues counting until
either a hardware reset, or it is disabled by software (clearing the TAEN bit). When a match occurs,
the GPTM asserts the RTCRIS bit in GPTMRIS. If the RTC interrupt is enabled in GPTIMR, the
GPTM also sets the RTCMIS bit in GPTMISR and generates a controller interrupt. The status flags
are cleared by writing the RTCCINT bit in GPTMICR.
If the TASTALL and/or TBSTALL bits in the GPTMCTL register are set, the timer does not freeze if
the RTCEN bit is set in GPTMCTL.
9.2.3 16-Bit Timer Operating Modes
The GPTM is placed into global 16-bit mode by writing a value of 0x4 to the GPTM Configuration
(GPTMCFG) register (see page 184). This section describes each of the GPTM 16-bit modes of
operation. TimerA and TimerB have identical modes, so a single description is given using an n to
reference both.
9.2.3.1 16-Bit One-Shot/Periodic Timer Mode
In 16-bit one-shot and periodic timer modes, the timer is configured as a 16-bit down-counter with
an optional 8-bit prescaler that effectively extends the counting range of the timer to 24 bits. The
selection of one-shot or periodic mode is determined by the value written to the TnMR field of the
GPTMTnMR register. The optional prescaler is loaded into the GPTM Timern Prescale (GPTMTnPR)
register.
When software writes the TnEN bit in the GPTMCTL register, the timer begins counting down from
its preloaded value. Once the 0x0000 state is reached, the timer reloads its start value from
GPTMTnILR and GPTMTnPR on the next cycle. If configured to be a one-shot timer, the timer stops
counting and clears the TnEN bit in the GPTMCTL register. If configured as a periodic timer, it
continues counting.
In addition to reloading the count value, the timer generates interrupts and output triggers when it
reaches the 0x0000 state. The GPTM sets the TnTORIS bit in the GPTMRIS register, and holds it
until it is cleared by writing the GPTMICR register. If the time-out interrupt is enabled in GPTIMR,
the GPTM also sets the TnTOMIS bit in GPTMISR and generates a controller interrupt.
The output trigger is a one-clock-cycle pulse that is asserted when the counter hits the 0x0000 state,
and deasserted on the following clock cycle. It is enabled by setting the TnOTE bit in the GPTMCTL
register, and can trigger SoC-level events.
If software reloads the GPTMTAILR register while the counter is running, the counter loads the new
value on the next clock cycle and continues counting from the new value.
November 30, 2007 175
Preliminary
LM3S6110 Microcontroller
If the TnSTALL bit in the GPTMCTL register is enabled, the timer freezes counting until the signal
is deasserted.
The following example shows a variety of configurations for a 16-bit free running timer while using
the prescaler. All values assume a 25-MHz clock with Tc=20 ns (clock period).
Table 9-2. 16-Bit Timer With Prescaler Configurations
Prescale #Clock (T c)a Max Time Units
00000000 1 2.6214 mS
00000001 2 5.2428 mS
00000010 3 7.8642 mS
------------ -- -- --
11111100 254 665.8458 mS
11111110 255 668.4672 mS
11111111 256 671.0886 mS
a. Tc is the clock period.
9.2.3.2 16-Bit Input Edge Count Mode
In Edge Count mode, the timer is configured as a down-counter capable of capturing three types
of events: rising edge, falling edge, or both. To place the timer in Edge Count mode, the TnCMR bit
of the GPTMTnMR register must be set to 0. The type of edge that the timer counts is determined
by the TnEVENT fields of the GPTMCTL register. During initialization, the GPTM Timern Match
(GPTMTnMATCHR) register is configured so that the difference between the value in the
GPTMTnILR register and the GPTMTnMATCHR register equals the number of edge events that
must be counted.
When software writes the TnEN bit in the GPTM Control (GPTMCTL) register, the timer is enabled
for event capture. Each input event on the CCP pin decrements the counter by 1 until the event count
matches GPTMTnMATCHR. When the counts match, the GPTM asserts the CnMRIS bit in the
GPTMRIS register (and the CnMMIS bit, if the interrupt is not masked). The counter is then reloaded
using the value in GPTMTnILR, and stopped since the GPTM automatically clears the TnEN bit in
the GPTMCTL register. Once the event count has been reached, all further events are ignored until
TnEN is re-enabled by software.
Figure 9-2 on page 177 shows how input edge count mode works. In this case, the timer start value
is set to GPTMnILR =0x000A and the match value is set to GPTMnMATCHR =0x0006 so that four
edge events are counted. The counter is configured to detect both edges of the input signal.
Note that the last two edges are not counted since the timer automatically clears the TnEN bit after
the current count matches the value in the GPTMnMR register.
176 November 30, 2007
Preliminary
General-Purpose Timers
Figure 9-2. 16-Bit Input Edge Count Mode Example
0x000A
0x0006
0x0007
0x0008
0x0009
Input Signal
Timer stops,
flags
asserted
Timer reload
Count on next cycle Ignored Ignored
9.2.3.3 16-Bit Input Edge Time Mode
Note: The prescaler is not available in 16-Bit Input Edge Time mode.
In Edge Time mode, the timer is configured as a free-running down-counter initialized to the value
loaded in the GPTMTnILR register (or 0xFFFF at reset). This mode allows for event capture of both
rising and falling edges. The timer is placed into Edge Time mode by setting the TnCMR bit in the
GPTMTnMR register, and the type of event that the timer captures is determined by the TnEVENT
fields of the GPTMCnTL register.
When software writes the TnEN bit in the GPTMCTL register, the timer is enabled for event capture.
When the selected input event is detected, the current Tn counter value is captured in the GPTMTnR
register and is available to be read by the controller. The GPTM then asserts the CnERIS bit (and
the CnEMIS bit, if the interrupt is not masked).
After an event has been captured, the timer does not stop counting. It continues to count until the
TnEN bit is cleared. When the timer reaches the 0x0000 state, it is reloaded with the value from the
GPTMnILR register.
Figure 9-3 on page 178 shows how input edge timing mode works. In the diagram, it is assumed that
the start value of the timer is the default value of 0xFFFF, and the timer is configured to capture
rising edge events.
Each time a rising edge event is detected, the current count value is loaded into the GPTMTnR
register, and is held there until another rising edge is detected (at which point the new count value
is loaded into GPTMTnR).
November 30, 2007 177
Preliminary
LM3S6110 Microcontroller
Figure 9-3. 16-Bit Input Edge Time Mode Example
GPTMTnR=Y
Input Signal
Time
Count
GPTMTnR=X GPTMTnR=Z
Z
X
Y
0xFFFF
9.2.3.4 16-Bit PWM Mode
The GPTM supports a simple PWM generation mode. In PWM mode, the timer is configured as a
down-counter with a start value (and thus period) defined by GPTMTnILR. PWM mode is enabled
with the GPTMTnMR register by setting the TnAMS bit to 0x1, the TnCMR bit to 0x0, and the TnMR
field to 0x2.
When software writes the TnEN bit in the GPTMCTL register, the counter begins counting down
until it reaches the 0x0000 state. On the next counter cycle, the counter reloads its start value from
GPTMTnILR (and GPTMTnPR if using a prescaler) and continues counting until disabled by software
clearing the TnEN bit in the GPTMCTL register. No interrupts or status bits are asserted in PWM
mode.
The output PWM signal asserts when the counter is at the value of the GPTMTnILR register (its
start state), and is deasserted when the counter value equals the value in the GPTM Timern Match
Register (GPTMnMATCHR). Software has the capability of inverting the output PWM signal by
setting the TnPWML bit in the GPTMCTL register.
Figure 9-4 on page 179 shows how to generate an output PWM with a 1-ms period and a 66% duty
cycle assuming a 50-MHz input clock and TnPWML =0 (duty cycle would be 33% for the TnPWML
=1 configuration). For this example, the start value is GPTMnIRL=0xC350 and the match value is
GPTMnMR=0x411A.
178 November 30, 2007
Preliminary
General-Purpose Timers
Figure 9-4. 16-Bit PWM Mode Example
Output
Signal
Time
Count GPTMTnR=GPTMnMR GPTMTnR=GPTMnMR
0xC350
0x411A
TnPWML = 0
TnPWML = 1
TnEN set
9.3 Initialization and Configuration
To use the general-purpose timers, the peripheral clock must be enabled by setting the TIMER0,
TIMER1, and TIMER2 bits in the RCGC1 register.
This section shows module initialization and configuration examples for each of the supported timer
modes.
9.3.1 32-Bit One-Shot/Periodic Timer Mode
The GPTM is configured for 32-bit One-Shot and Periodic modes by the following sequence:
1. Ensure the timer is disabled (the TAEN bit in the GPTMCTL register is cleared) before making
any changes.
2. Write the GPTM Configuration Register (GPTMCFG) with a value of 0x0.
3. Set the TAMR field in the GPTM TimerA Mode Register (GPTMTAMR):
a. Write a value of 0x1 for One-Shot mode.
b. Write a value of 0x2 for Periodic mode.
4. Load the start value into the GPTM TimerA Interval Load Register (GPTMTAILR).
5. If interrupts are required, set the TATOIM bit in the GPTM Interrupt Mask Register (GPTMIMR).
6. Set the TAEN bit in the GPTMCTL register to enable the timer and start counting.
November 30, 2007 179
Preliminary
LM3S6110 Microcontroller
7. Poll the TATORIS bit in the GPTMRIS register or wait for the interrupt to be generated (if enabled).
In both cases, the status flags are cleared by writing a 1 to the TATOCINT bit of the GPTM
Interrupt Clear Register (GPTMICR).
In One-Shot mode, the timer stops counting after step 7 on page 180. To re-enable the timer, repeat
the sequence. A timer configured in Periodic mode does not stop counting after it times out.
9.3.2 32-Bit Real-Time Clock (RTC) Mode
To use the RTC mode, the timer must have a 32.768-KHz input signal on its CCP0, CCP2, or CCP4
pins. To enable the RTC feature, follow these steps:
1. Ensure the timer is disabled (the TAEN bit is cleared) before making any changes.
2. Write the GPTM Configuration Register (GPTMCFG) with a value of 0x1.
3. Write the desired match value to the GPTM TimerA Match Register (GPTMTAMATCHR).
4. Set/clear the RTCEN bit in the GPTM Control Register (GPTMCTL) as desired.
5. If interrupts are required, set the RTCIM bit in the GPTM Interrupt Mask Register (GPTMIMR).
6. Set the TAEN bit in the GPTMCTL register to enable the timer and start counting.
When the timer count equals the value in the GPTMTAMATCHR register, the counter is re-loaded
with 0x0000.0000 and begins counting. If an interrupt is enabled, it does not have to be cleared.
9.3.3 16-Bit One-Shot/Periodic Timer Mode
A timer is configured for 16-bit One-Shot and Periodic modes by the following sequence:
1. Ensure the timer is disabled (the TnEN bit is cleared) before making any changes.
2. Write the GPTM Configuration Register (GPTMCFG) with a value of 0x4.
3. Set the TnMR field in the GPTM Timer Mode (GPTMTnMR) register:
a. Write a value of 0x1 for One-Shot mode.
b. Write a value of 0x2 for Periodic mode.
4. If a prescaler is to be used, write the prescale value to the GPTM Timern Prescale Register
(GPTMTnPR).
5. Load the start value into the GPTM Timer Interval Load Register (GPTMTnILR).
6. If interrupts are required, set the TnTOIM bit in the GPTM Interrupt Mask Register (GPTMIMR).
7. Set the TnEN bit in the GPTM Control Register (GPTMCTL) to enable the timer and start
counting.
8. Poll the TnTORIS bit in the GPTMRIS register or wait for the interrupt to be generated (if enabled).
In both cases, the status flags are cleared by writing a 1 to the TnTOCINT bit of the GPTM
Interrupt Clear Register (GPTMICR).
180 November 30, 2007
Preliminary
General-Purpose Timers
In One-Shot mode, the timer stops counting after step 8 on page 180. To re-enable the timer, repeat
the sequence. A timer configured in Periodic mode does not stop counting after it times out.
9.3.4 16-Bit Input Edge Count Mode
A timer is configured to Input Edge Count mode by the following sequence:
1. Ensure the timer is disabled (the TnEN bit is cleared) before making any changes.
2. Write the GPTM Configuration (GPTMCFG) register with a value of 0x4.
3. In the GPTM Timer Mode (GPTMTnMR) register, write the TnCMR field to 0x0 and the TnMR
field to 0x3.
4. Configure the type of event(s) that the timer captures by writing the TnEVENT field of the GPTM
Control (GPTMCTL) register.
5. Load the timer start value into the GPTM Timern Interval Load (GPTMTnILR) register.
6. Load the desired event count into the GPTM Timern Match (GPTMTnMATCHR) register.
7. If interrupts are required, set the CnMIM bit in the GPTM Interrupt Mask (GPTMIMR) register.
8. Set the TnEN bit in the GPTMCTL register to enable the timer and begin waiting for edge events.
9. Poll the CnMRIS bit in the GPTMRIS register or wait for the interrupt to be generated (if enabled).
In both cases, the status flags are cleared by writing a 1 to the CnMCINT bit of the GPTM
Interrupt Clear (GPTMICR) register.
In Input Edge Count Mode, the timer stops after the desired number of edge events has been
detected. To re-enable the timer, ensure that the TnEN bit is cleared and repeat step 4 on page 181
through step 9 on page 181.
9.3.5 16-Bit Input Edge Timing Mode
A timer is configured to Input Edge Timing mode by the following sequence:
1. Ensure the timer is disabled (the TnEN bit is cleared) before making any changes.
2. Write the GPTM Configuration (GPTMCFG) register with a value of 0x4.
3. In the GPTM Timer Mode (GPTMTnMR) register, write the TnCMR field to 0x1 and the TnMR
field to 0x3.
4. Configure the type of event that the timer captures by writing the TnEVENT field of the GPTM
Control (GPTMCTL) register.
5. Load the timer start value into the GPTM Timern Interval Load (GPTMTnILR) register.
6. If interrupts are required, set the CnEIM bit in the GPTM Interrupt Mask (GPTMIMR) register.
7. Set the TnEN bit in the GPTM Control (GPTMCTL) register to enable the timer and start counting.
8. Poll the CnERIS bit in the GPTMRIS register or wait for the interrupt to be generated (if enabled).
In both cases, the status flags are cleared by writing a 1 to the CnECINT bit of the GPTM
November 30, 2007 181
Preliminary
LM3S6110 Microcontroller
Interrupt Clear (GPTMICR) register. The time at which the event happened can be obtained
by reading the GPTM Timern (GPTMTnR) register.
In Input Edge Timing mode, the timer continues running after an edge event has been detected,
but the timer interval can be changed at any time by writing the GPTMTnILR register. The change
takes effect at the next cycle after the write.
9.3.6 16-Bit PWM Mode
A timer is configured to PWM mode using the following sequence:
1. Ensure the timer is disabled (the TnEN bit is cleared) before making any changes.
2. Write the GPTM Configuration (GPTMCFG) register with a value of 0x4.
3. In the GPTM Timer Mode (GPTMTnMR) register, set the TnAMS bit to 0x1, the TnCMR bit to
0x0, and the TnMR field to 0x2.
4. Configure the output state of the PWM signal (whether or not it is inverted) in the TnEVENT field
of the GPTM Control (GPTMCTL) register.
5. Load the timer start value into the GPTM Timern Interval Load (GPTMTnILR) register.
6. Load the GPTM Timern Match (GPTMTnMATCHR) register with the desired value.
7. If a prescaler is going to be used, configure the GPTM Timern Prescale (GPTMTnPR) register
and the GPTM Timern Prescale Match (GPTMTnPMR) register.
8. Set the TnEN bit in the GPTM Control (GPTMCTL) register to enable the timer and begin
generation of the output PWM signal.
In PWM Timing mode, the timer continues running after the PWM signal has been generated. The
PWM period can be adjusted at any time by writing the GPTMTnILR register, and the change takes
effect at the next cycle after the write.
9.4 Register Map
Table 9-3 on page 182 lists the GPTM registers. The offset listed is a hexadecimal increment to the
register’s address, relative to that timer’s base address:
■ Timer0: 0x4003.0000
■ Timer1: 0x4003.1000
■ Timer2: 0x4003.2000
Table 9-3. Timers Register Map
See
Offset Name Type Reset Description page
0x000 GPTMCFG R/W 0x0000.0000 GPTM Configuration 184
0x004 GPTMTAMR R/W 0x0000.0000 GPTM TimerA Mode 185
0x008 GPTMTBMR R/W 0x0000.0000 GPTM TimerB Mode 187
182 November 30, 2007
Preliminary
General-Purpose Timers
See
Offset Name Type Reset Description page
0x00C GPTMCTL R/W 0x0000.0000 GPTM Control 189
0x018 GPTMIMR R/W 0x0000.0000 GPTM Interrupt Mask 192
0x01C GPTMRIS RO 0x0000.0000 GPTM Raw Interrupt Status 194
0x020 GPTMMIS RO 0x0000.0000 GPTM Masked Interrupt Status 195
0x024 GPTMICR W1C 0x0000.0000 GPTM Interrupt Clear 196
GPTM TimerA Interval Load 198
0x0000.FFFF
(16-bit mode)
0xFFFF.FFFF
(32-bit mode)
0x028 GPTMTAILR R/W
0x02C GPTMTBILR R/W 0x0000.FFFF GPTM TimerB Interval Load 199
GPTM TimerA Match 200
0x0000.FFFF
(16-bit mode)
0xFFFF.FFFF
(32-bit mode)
0x030 GPTMTAMATCHR R/W
0x034 GPTMTBMATCHR R/W 0x0000.FFFF GPTM TimerB Match 201
0x038 GPTMTAPR R/W 0x0000.0000 GPTM TimerA Prescale 202
0x03C GPTMTBPR R/W 0x0000.0000 GPTM TimerB Prescale 203
0x040 GPTMTAPMR R/W 0x0000.0000 GPTM TimerA Prescale Match 204
0x044 GPTMTBPMR R/W 0x0000.0000 GPTM TimerB Prescale Match 205
GPTM TimerA 206
0x0000.FFFF
(16-bit mode)
0xFFFF.FFFF
(32-bit mode)
0x048 GPTMTAR RO
0x04C GPTMTBR RO 0x0000.FFFF GPTM TimerB 207
9.5 Register Descriptions
The remainder of this section lists and describes the GPTM registers, in numerical order by address
offset.
November 30, 2007 183
Preliminary
LM3S6110 Microcontroller
Register 1: GPTM Configuration (GPTMCFG), offset 0x000
This register configures the global operation of the GPTM module. The value written to this register
determines whether the GPTM is in 32- or 16-bit mode.
GPTM Configuration (GPTMCFG)
Timer0 base: 0x4003.0000
Timer1 base: 0x4003.1000
Timer2 base: 0x4003.2000
Offset 0x000
Type R/W, reset 0x0000.0000
31 30 29 28 27 26 25 24 23 22 21 20 19 18 17 16
reserved
Type RO RO RO RO RO RO RO RO RO RO RO RO RO RO RO RO
Reset 0 0 0 0 0 0 0 0 0 0 0 0 0 0 0 0
15 14 13 12 11 10 9 8 7 6 5 4 3 2 1 0
reserved GPTMCFG
Type RO RO RO RO RO RO RO RO RO RO RO RO RO R/W R/W R/W
Reset 0 0 0 0 0 0 0 0 0 0 0 0 0 0 0 0
Bit/Field Name Type Reset Description
Software should not rely on the value of a reserved bit. To provide
compatibility with future products, the value of a reserved bit should be
preserved across a read-modify-write operation.
31:3 reserved RO 0x00
GPTM Configuration
The GPTMCFG values are defined as follows:
Value Description
0x0 32-bit timer configuration.
0x1 32-bit real-time clock (RTC) counter configuration.
0x2 Reserved.
0x3 Reserved.
16-bit timer configuration, function is controlled by bits 1:0 of
GPTMTAMR and GPTMTBMR.
0x4-0x7
2:0 GPTMCFG R/W 0x0
184 November 30, 2007
Preliminary
General-Purpose Timers
Register 2: GPTM TimerA Mode (GPTMTAMR), offset 0x004
This register configures the GPTM based on the configuration selected in the GPTMCFG register.
When in 16-bit PWM mode, set the TAAMS bit to 0x1, the TACMR bit to 0x0, and the TAMR field to
0x2.
GPTM TimerA Mode (GPTMTAMR)
Timer0 base: 0x4003.0000
Timer1 base: 0x4003.1000
Timer2 base: 0x4003.2000
Offset 0x004
Type R/W, reset 0x0000.0000
31 30 29 28 27 26 25 24 23 22 21 20 19 18 17 16
reserved
Type RO RO RO RO RO RO RO RO RO RO RO RO RO RO RO RO
Reset 0 0 0 0 0 0 0 0 0 0 0 0 0 0 0 0
15 14 13 12 11 10 9 8 7 6 5 4 3 2 1 0
reserved TAAMS TACMR TAMR
Type RO RO RO RO RO RO RO RO RO RO RO RO R/W R/W R/W R/W
Reset 0 0 0 0 0 0 0 0 0 0 0 0 0 0 0 0
Bit/Field Name Type Reset Description
Software should not rely on the value of a reserved bit. To provide
compatibility with future products, the value of a reserved bit should be
preserved across a read-modify-write operation.
31:4 reserved RO 0x00
GPTM TimerA Alternate Mode Select
The TAAMS values are defined as follows:
Value Description
0 Capture mode is enabled.
1 PWM mode is enabled.
Note: To enable PWM mode, you must also clear the TACMR
bit and set the TAMR field to 0x2.
3 TAAMS R/W 0
GPTM TimerA Capture Mode
The TACMR values are defined as follows:
Value Description
0 Edge-Count mode.
1 Edge-Time mode.
2 TACMR R/W 0
November 30, 2007 185
Preliminary
LM3S6110 Microcontroller
Bit/Field Name Type Reset Description
GPTM TimerA Mode
The TAMR values are defined as follows:
Value Description
0x0 Reserved.
0x1 One-Shot Timer mode.
0x2 Periodic Timer mode.
0x3 Capture mode.
The Timer mode is based on the timer configuration defined by bits 2:0
in the GPTMCFG register (16-or 32-bit).
In 16-bit timer configuration, TAMR controls the 16-bit timer modes for
TimerA.
In 32-bit timer configuration, this register controls the mode and the
contents of GPTMTBMR are ignored.
1:0 TAMR R/W 0x0
186 November 30, 2007
Preliminary
General-Purpose Timers
Register 3: GPTM TimerB Mode (GPTMTBMR), offset 0x008
This register configures the GPTM based on the configuration selected in the GPTMCFG register.
When in 16-bit PWM mode, set the TBAMS bit to 0x1, the TBCMR bit to 0x0, and the TBMR field to
0x2.
GPTM TimerB Mode (GPTMTBMR)
Timer0 base: 0x4003.0000
Timer1 base: 0x4003.1000
Timer2 base: 0x4003.2000
Offset 0x008
Type R/W, reset 0x0000.0000
31 30 29 28 27 26 25 24 23 22 21 20 19 18 17 16
reserved
Type RO RO RO RO RO RO RO RO RO RO RO RO RO RO RO RO
Reset 0 0 0 0 0 0 0 0 0 0 0 0 0 0 0 0
15 14 13 12 11 10 9 8 7 6 5 4 3 2 1 0
reserved TBAMS TBCMR TBMR
Type RO RO RO RO RO RO RO RO RO RO RO RO R/W R/W R/W R/W
Reset 0 0 0 0 0 0 0 0 0 0 0 0 0 0 0 0
Bit/Field Name Type Reset Description
Software should not rely on the value of a reserved bit. To provide
compatibility with future products, the value of a reserved bit should be
preserved across a read-modify-write operation.
31:4 reserved RO 0x00
GPTM TimerB Alternate Mode Select
The TBAMS values are defined as follows:
Value Description
0 Capture mode is enabled.
1 PWM mode is enabled.
Note: To enable PWM mode, you must also clear the TBCMR
bit and set the TBMR field to 0x2.
3 TBAMS R/W 0
GPTM TimerB Capture Mode
The TBCMR values are defined as follows:
Value Description
0 Edge-Count mode.
1 Edge-Time mode.
2 TBCMR R/W 0
November 30, 2007 187
Preliminary
LM3S6110 Microcontroller
Bit/Field Name Type Reset Description
GPTM TimerB Mode
The TBMR values are defined as follows:
Value Description
0x0 Reserved.
0x1 One-Shot Timer mode.
0x2 Periodic Timer mode.
0x3 Capture mode.
The timer mode is based on the timer configuration defined by bits 2:0
in the GPTMCFG register.
In 16-bit timer configuration, these bits control the 16-bit timer modes
for TimerB.
In 32-bit timer configuration, this register’s contents are ignored and
GPTMTAMR is used.
1:0 TBMR R/W 0x0
188 November 30, 2007
Preliminary
General-Purpose Timers
Register 4: GPTM Control (GPTMCTL), offset 0x00C
This register is used alongside the GPTMCFG and GMTMTnMR registers to fine-tune the timer
configuration, and to enable other features such as timer stall.
GPTM Control (GPTMCTL)
Timer0 base: 0x4003.0000
Timer1 base: 0x4003.1000
Timer2 base: 0x4003.2000
Offset 0x00C
Type R/W, reset 0x0000.0000
31 30 29 28 27 26 25 24 23 22 21 20 19 18 17 16
reserved
Type RO RO RO RO RO RO RO RO RO RO RO RO RO RO RO RO
Reset 0 0 0 0 0 0 0 0 0 0 0 0 0 0 0 0
15 14 13 12 11 10 9 8 7 6 5 4 3 2 1 0
reserved TBPWML TBOTE reserved TBEVENT TBSTALL TBEN reserved TAPWML TAOTE RTCEN TAEVENT TASTALL TAEN
Type RO R/W R/W RO R/W R/W R/W R/W RO R/W R/W R/W R/W R/W R/W R/W
Reset 0 0 0 0 0 0 0 0 0 0 0 0 0 0 0 0
Bit/Field Name Type Reset Description
Software should not rely on the value of a reserved bit. To provide
compatibility with future products, the value of a reserved bit should be
preserved across a read-modify-write operation.
31:15 reserved RO 0x00
GPTM TimerB PWM Output Level
The TBPWML values are defined as follows:
Value Description
0 Output is unaffected.
1 Output is inverted.
14 TBPWML R/W 0
GPTM TimerB Output Trigger Enable
The TBOTE values are defined as follows:
Value Description
0 The output TimerB trigger is disabled.
1 The output TimerB trigger is enabled.
13 TBOTE R/W 0
Software should not rely on the value of a reserved bit. To provide
compatibility with future products, the value of a reserved bit should be
preserved across a read-modify-write operation.
12 reserved RO 0
GPTM TimerB Event Mode
The TBEVENT values are defined as follows:
Value Description
0x0 Positive edge.
0x1 Negative edge.
0x2 Reserved
0x3 Both edges.
11:10 TBEVENT R/W 0x0
November 30, 2007 189
Preliminary
LM3S6110 Microcontroller
Bit/Field Name Type Reset Description
GPTM TimerB Stall Enable
The TBSTALL values are defined as follows:
Value Description
0 TimerB stalling is disabled.
1 TimerB stalling is enabled.
9 TBSTALL R/W 0
GPTM TimerB Enable
The TBEN values are defined as follows:
Value Description
0 TimerB is disabled.
TimerB is enabled and begins counting or the capture logic is
enabled based on the GPTMCFG register.
1
8 TBEN R/W 0
Software should not rely on the value of a reserved bit. To provide
compatibility with future products, the value of a reserved bit should be
preserved across a read-modify-write operation.
7 reserved RO 0
GPTM TimerA PWM Output Level
The TAPWML values are defined as follows:
Value Description
0 Output is unaffected.
1 Output is inverted.
6 TAPWML R/W 0
GPTM TimerA Output Trigger Enable
The TAOTE values are defined as follows:
Value Description
0 The output TimerA trigger is disabled.
1 The output TimerA trigger is enabled.
5 TAOTE R/W 0
GPTM RTC Enable
The RTCEN values are defined as follows:
Value Description
0 RTC counting is disabled.
1 RTC counting is enabled.
4 RTCEN R/W 0
190 November 30, 2007
Preliminary
General-Purpose Timers
Bit/Field Name Type Reset Description
GPTM TimerA Event Mode
The TAEVENT values are defined as follows:
Value Description
0x0 Positive edge.
0x1 Negative edge.
0x2 Reserved
0x3 Both edges.
3:2 TAEVENT R/W 0x0
GPTM TimerA Stall Enable
The TASTALL values are defined as follows:
Value Description
0 TimerA stalling is disabled.
1 TimerA stalling is enabled.
1 TASTALL R/W 0
GPTM TimerA Enable
The TAEN values are defined as follows:
Value Description
0 TimerA is disabled.
TimerA is enabled and begins counting or the capture logic is
enabled based on the GPTMCFG register.
1
0 TAEN R/W 0
November 30, 2007 191
Preliminary
LM3S6110 Microcontroller
Register 5: GPTM Interrupt Mask (GPTMIMR), offset 0x018
This register allows software to enable/disable GPTM controller-level interrupts. Writing a 1 enables
the interrupt, while writing a 0 disables it.
GPTM Interrupt Mask (GPTMIMR)
Timer0 base: 0x4003.0000
Timer1 base: 0x4003.1000
Timer2 base: 0x4003.2000
Offset 0x018
Type R/W, reset 0x0000.0000
31 30 29 28 27 26 25 24 23 22 21 20 19 18 17 16
reserved
Type RO RO RO RO RO RO RO RO RO RO RO RO RO RO RO RO
Reset 0 0 0 0 0 0 0 0 0 0 0 0 0 0 0 0
15 14 13 12 11 10 9 8 7 6 5 4 3 2 1 0
reserved CBEIM CBMIM TBTOIM reserved RTCIM CAEIM CAMIM TATOIM
Type RO RO RO RO RO R/W R/W R/W RO RO RO RO R/W R/W R/W R/W
Reset 0 0 0 0 0 0 0 0 0 0 0 0 0 0 0 0
Bit/Field Name Type Reset Description
Software should not rely on the value of a reserved bit. To provide
compatibility with future products, the value of a reserved bit should be
preserved across a read-modify-write operation.
31:11 reserved RO 0x00
GPTM CaptureB Event Interrupt Mask
The CBEIM values are defined as follows:
Value Description
0 Interrupt is disabled.
1 Interrupt is enabled.
10 CBEIM R/W 0
GPTM CaptureB Match Interrupt Mask
The CBMIM values are defined as follows:
Value Description
0 Interrupt is disabled.
1 Interrupt is enabled.
9 CBMIM R/W 0
GPTM TimerB Time-Out Interrupt Mask
The TBTOIM values are defined as follows:
Value Description
0 Interrupt is disabled.
1 Interrupt is enabled.
8 TBTOIM R/W 0
Software should not rely on the value of a reserved bit. To provide
compatibility with future products, the value of a reserved bit should be
preserved across a read-modify-write operation.
7:4 reserved RO 0
192 November 30, 2007
Preliminary
General-Purpose Timers
Bit/Field Name Type Reset Description
GPTM RTC Interrupt Mask
The RTCIM values are defined as follows:
Value Description
0 Interrupt is disabled.
1 Interrupt is enabled.
3 RTCIM R/W 0
GPTM CaptureA Event Interrupt Mask
The CAEIM values are defined as follows:
Value Description
0 Interrupt is disabled.
1 Interrupt is enabled.
2 CAEIM R/W 0
GPTM CaptureA Match Interrupt Mask
The CAMIM values are defined as follows:
Value Description
0 Interrupt is disabled.
1 Interrupt is enabled.
1 CAMIM R/W 0
GPTM TimerA Time-Out Interrupt Mask
The TATOIM values are defined as follows:
Value Description
0 Interrupt is disabled.
1 Interrupt is enabled.
0 TATOIM R/W 0
November 30, 2007 193
Preliminary
LM3S6110 Microcontroller
Register 6: GPTM Raw Interrupt Status (GPTMRIS), offset 0x01C
This register shows the state of the GPTM's internal interrupt signal. These bits are set whether or
not the interrupt is masked in the GPTMIMR register. Each bit can be cleared by writing a 1 to its
corresponding bit in GPTMICR.
GPTM Raw Interrupt Status (GPTMRIS)
Timer0 base: 0x4003.0000
Timer1 base: 0x4003.1000
Timer2 base: 0x4003.2000
Offset 0x01C
Type RO, reset 0x0000.0000
31 30 29 28 27 26 25 24 23 22 21 20 19 18 17 16
reserved
Type RO RO RO RO RO RO RO RO RO RO RO RO RO RO RO RO
Reset 0 0 0 0 0 0 0 0 0 0 0 0 0 0 0 0
15 14 13 12 11 10 9 8 7 6 5 4 3 2 1 0
reserved CBERIS CBMRIS TBTORIS reserved RTCRIS CAERIS CAMRIS TATORIS
Type RO RO RO RO RO RO RO RO RO RO RO RO RO RO RO RO
Reset 0 0 0 0 0 0 0 0 0 0 0 0 0 0 0 0
Bit/Field Name Type Reset Description
Software should not rely on the value of a reserved bit. To provide
compatibility with future products, the value of a reserved bit should be
preserved across a read-modify-write operation.
31:11 reserved RO 0x00
GPTM CaptureB Event Raw Interrupt
This is the CaptureB Event interrupt status prior to masking.
10 CBERIS RO 0
GPTM CaptureB Match Raw Interrupt
This is the CaptureB Match interrupt status prior to masking.
9 CBMRIS RO 0
GPTM TimerB Time-Out Raw Interrupt
This is the TimerB time-out interrupt status prior to masking.
8 TBTORIS RO 0
Software should not rely on the value of a reserved bit. To provide
compatibility with future products, the value of a reserved bit should be
preserved across a read-modify-write operation.
7:4 reserved RO 0x0
GPTM RTC Raw Interrupt
This is the RTC Event interrupt status prior to masking.
3 RTCRIS RO 0
GPTM CaptureA Event Raw Interrupt
This is the CaptureA Event interrupt status prior to masking.
2 CAERIS RO 0
GPTM CaptureA Match Raw Interrupt
This is the CaptureA Match interrupt status prior to masking.
1 CAMRIS RO 0
GPTM TimerA Time-Out Raw Interrupt
This the TimerA time-out interrupt status prior to masking.
0 TATORIS RO 0
194 November 30, 2007
Preliminary
General-Purpose Timers
Register 7: GPTM Masked Interrupt Status (GPTMMIS), offset 0x020
This register show the state of the GPTM's controller-level interrupt. If an interrupt is unmasked in
GPTMIMR, and there is an event that causes the interrupt to be asserted, the corresponding bit is
set in this register. All bits are cleared by writing a 1 to the corresponding bit in GPTMICR.
GPTM Masked Interrupt Status (GPTMMIS)
Timer0 base: 0x4003.0000
Timer1 base: 0x4003.1000
Timer2 base: 0x4003.2000
Offset 0x020
Type RO, reset 0x0000.0000
31 30 29 28 27 26 25 24 23 22 21 20 19 18 17 16
reserved
Type RO RO RO RO RO RO RO RO RO RO RO RO RO RO RO RO
Reset 0 0 0 0 0 0 0 0 0 0 0 0 0 0 0 0
15 14 13 12 11 10 9 8 7 6 5 4 3 2 1 0
reserved CBEMIS CBMMIS TBTOMIS reserved RTCMIS CAEMIS CAMMIS TATOMIS
Type RO RO RO RO RO RO RO RO RO RO RO RO RO RO RO RO
Reset 0 0 0 0 0 0 0 0 0 0 0 0 0 0 0 0
Bit/Field Name Type Reset Description
Software should not rely on the value of a reserved bit. To provide
compatibility with future products, the value of a reserved bit should be
preserved across a read-modify-write operation.
31:11 reserved RO 0x00
GPTM CaptureB Event Masked Interrupt
This is the CaptureB event interrupt status after masking.
10 CBEMIS RO 0
GPTM CaptureB Match Masked Interrupt
This is the CaptureB match interrupt status after masking.
9 CBMMIS RO 0
GPTM TimerB Time-Out Masked Interrupt
This is the TimerB time-out interrupt status after masking.
8 TBTOMIS RO 0
Software should not rely on the value of a reserved bit. To provide
compatibility with future products, the value of a reserved bit should be
preserved across a read-modify-write operation.
7:4 reserved RO 0x0
GPTM RTC Masked Interrupt
This is the RTC event interrupt status after masking.
3 RTCMIS RO 0
GPTM CaptureA Event Masked Interrupt
This is the CaptureA event interrupt status after masking.
2 CAEMIS RO 0
GPTM CaptureA Match Masked Interrupt
This is the CaptureA match interrupt status after masking.
1 CAMMIS RO 0
GPTM TimerA Time-Out Masked Interrupt
This is the TimerA time-out interrupt status after masking.
0 TATOMIS RO 0
November 30, 2007 195
Preliminary
LM3S6110 Microcontroller
Register 8: GPTM Interrupt Clear (GPTMICR), offset 0x024
This register is used to clear the status bits in the GPTMRIS and GPTMMIS registers. Writing a 1
to a bit clears the corresponding bit in the GPTMRIS and GPTMMIS registers.
GPTM Interrupt Clear (GPTMICR)
Timer0 base: 0x4003.0000
Timer1 base: 0x4003.1000
Timer2 base: 0x4003.2000
Offset 0x024
Type W1C, reset 0x0000.0000
31 30 29 28 27 26 25 24 23 22 21 20 19 18 17 16
reserved
Type RO RO RO RO RO RO RO RO RO RO RO RO RO RO RO RO
Reset 0 0 0 0 0 0 0 0 0 0 0 0 0 0 0 0
15 14 13 12 11 10 9 8 7 6 5 4 3 2 1 0
reserved CBECINT CBMCINT TBTOCINT reserved RTCCINT CAECINT CAMCINT TATOCINT
Type RO RO RO RO RO W1C W1C W1C RO RO RO RO W1C W1C W1C W1C
Reset 0 0 0 0 0 0 0 0 0 0 0 0 0 0 0 0
Bit/Field Name Type Reset Description
Software should not rely on the value of a reserved bit. To provide
compatibility with future products, the value of a reserved bit should be
preserved across a read-modify-write operation.
31:11 reserved RO 0x00
GPTM CaptureB Event Interrupt Clear
The CBECINT values are defined as follows:
Value Description
0 The interrupt is unaffected.
1 The interrupt is cleared.
10 CBECINT W1C 0
GPTM CaptureB Match Interrupt Clear
The CBMCINT values are defined as follows:
Value Description
0 The interrupt is unaffected.
1 The interrupt is cleared.
9 CBMCINT W1C 0
GPTM TimerB Time-Out Interrupt Clear
The TBTOCINT values are defined as follows:
Value Description
0 The interrupt is unaffected.
1 The interrupt is cleared.
8 TBTOCINT W1C 0
Software should not rely on the value of a reserved bit. To provide
compatibility with future products, the value of a reserved bit should be
preserved across a read-modify-write operation.
7:4 reserved RO 0x0
196 November 30, 2007
Preliminary
General-Purpose Timers
Bit/Field Name Type Reset Description
GPTM RTC Interrupt Clear
The RTCCINT values are defined as follows:
Value Description
0 The interrupt is unaffected.
1 The interrupt is cleared.
3 RTCCINT W1C 0
GPTM CaptureA Event Interrupt Clear
The CAECINT values are defined as follows:
Value Description
0 The interrupt is unaffected.
1 The interrupt is cleared.
2 CAECINT W1C 0
GPTM CaptureA Match Raw Interrupt
This is the CaptureA match interrupt status after masking.
1 CAMCINT W1C 0
GPTM TimerA Time-Out Raw Interrupt
The TATOCINT values are defined as follows:
Value Description
0 The interrupt is unaffected.
1 The interrupt is cleared.
0 TATOCINT W1C 0
November 30, 2007 197
Preliminary
LM3S6110 Microcontroller
Register 9: GPTM TimerA Interval Load (GPTMTAILR), offset 0x028
This register is used to load the starting count value into the timer. When GPTM is configured to
one of the 32-bit modes, GPTMTAILR appears as a 32-bit register (the upper 16-bits correspond
to the contents of the GPTM TimerB Interval Load (GPTMTBILR) register). In 16-bit mode, the
upper 16 bits of this register read as 0s and have no effect on the state of GPTMTBILR.
GPTM TimerA Interval Load (GPTMTAILR)
Timer0 base: 0x4003.0000
Timer1 base: 0x4003.1000
Timer2 base: 0x4003.2000
Offset 0x028
Type R/W, reset 0x0000.FFFF (16-bit mode) and 0xFFFF.FFFF (32-bit mode)
31 30 29 28 27 26 25 24 23 22 21 20 19 18 17 16
TAILRH
Type R/W R/W R/W R/W R/W R/W R/W R/W R/W R/W R/W R/W R/W R/W R/W R/W
Reset 0 1 1 0 1 0 1 1 1 1 0 1 1 1 1 0
15 14 13 12 11 10 9 8 7 6 5 4 3 2 1 0
TAILRL
Type R/W R/W R/W R/W R/W R/W R/W R/W R/W R/W R/W R/W R/W R/W R/W R/W
Reset 1 1 1 1 1 1 1 1 1 1 1 1 1 1 1 1
Bit/Field Name Type Reset Description
GPTM TimerA Interval Load Register High
When configured for 32-bit mode via the GPTMCFG register, the GPTM
TimerB Interval Load (GPTMTBILR) register loads this value on a
write. A read returns the current value of GPTMTBILR.
In 16-bit mode, this field reads as 0 and does not have an effect on the
state of GPTMTBILR.
0xFFFF
(32-bit mode)
0x0000 (16-bit
mode)
31:16 TAILRH R/W
GPTM TimerA Interval Load Register Low
For both 16- and 32-bit modes, writing this field loads the counter for
TimerA. A read returns the current value of GPTMTAILR.
15:0 TAILRL R/W 0xFFFF
198 November 30, 2007
Preliminary
General-Purpose Timers
Register 10: GPTM TimerB Interval Load (GPTMTBILR), offset 0x02C
This register is used to load the starting count value into TimerB. When the GPTM is configured to
a 32-bit mode, GPTMTBILR returns the current value of TimerB and ignores writes.
GPTM TimerB Interval Load (GPTMTBILR)
Timer0 base: 0x4003.0000
Timer1 base: 0x4003.1000
Timer2 base: 0x4003.2000
Offset 0x02C
Type R/W, reset 0x0000.FFFF
31 30 29 28 27 26 25 24 23 22 21 20 19 18 17 16
reserved
Type RO RO RO RO RO RO RO RO RO RO RO RO RO RO RO RO
Reset 0 0 0 0 0 0 0 0 0 0 0 0 0 0 0 0
15 14 13 12 11 10 9 8 7 6 5 4 3 2 1 0
TBILRL
Type R/W R/W R/W R/W R/W R/W R/W R/W R/W R/W R/W R/W R/W R/W R/W R/W
Reset 1 1 1 1 1 1 1 1 1 1 1 1 1 1 1 1
Bit/Field Name Type Reset Description
Software should not rely on the value of a reserved bit. To provide
compatibility with future products, the value of a reserved bit should be
preserved across a read-modify-write operation.
31:16 reserved RO 0x0000
GPTM TimerB Interval Load Register
When the GPTM is not configured as a 32-bit timer, a write to this field
updates GPTMTBILR. In 32-bit mode, writes are ignored, and reads
return the current value of GPTMTBILR.
15:0 TBILRL R/W 0xFFFF
November 30, 2007 199
Preliminary
LM3S6110 Microcontroller
Register 11: GPTM TimerA Match (GPTMTAMATCHR), offset 0x030
This register is used in 32-bit Real-Time Clock mode and 16-bit PWM and Input Edge Count modes.
GPTM TimerA Match (GPTMTAMATCHR)
Timer0 base: 0x4003.0000
Timer1 base: 0x4003.1000
Timer2 base: 0x4003.2000
Offset 0x030
Type R/W, reset 0x0000.FFFF (16-bit mode) and 0xFFFF.FFFF (32-bit mode)
31 30 29 28 27 26 25 24 23 22 21 20 19 18 17 16
TAMRH
Type R/W R/W R/W R/W R/W R/W R/W R/W R/W R/W R/W R/W R/W R/W R/W R/W
Reset 0 1 1 0 1 0 1 1 1 1 0 1 1 1 1 0
15 14 13 12 11 10 9 8 7 6 5 4 3 2 1 0
TAMRL
Type R/W R/W R/W R/W R/W R/W R/W R/W R/W R/W R/W R/W R/W R/W R/W R/W
Reset 1 1 1 1 1 1 1 1 1 1 1 1 1 1 1 1
Bit/Field Name Type Reset Description
GPTM TimerA Match Register High
When configured for 32-bit Real-Time Clock (RTC) mode via the
GPTMCFG register, this value is compared to the upper half of
GPTMTAR, to determine match events.
In 16-bit mode, this field reads as 0 and does not have an effect on the
state of GPTMTBMATCHR.
0xFFFF
(32-bit mode)
0x0000 (16-bit
mode)
31:16 TAMRH R/W
GPTM TimerA Match Register Low
When configured for 32-bit Real-Time Clock (RTC) mode via the
GPTMCFG register, this value is compared to the lower half of
GPTMTAR, to determine match events.
When configured for PWM mode, this value along with GPTMTAILR,
determines the duty cycle of the output PWM signal.
When configured for Edge Count mode, this value along with
GPTMTAILR, determines how many edge events are counted. The total
number of edge events counted is equal to the value in GPTMTAILR
minus this value.
15:0 TAMRL R/W 0xFFFF
200 November 30, 2007
Preliminary
General-Purpose Timers
Register 12: GPTM TimerB Match (GPTMTBMATCHR), offset 0x034
This register is used in 32-bit Real-Time Clock mode and 16-bit PWM and Input Edge Count modes.
GPTM TimerB Match (GPTMTBMATCHR)
Timer0 base: 0x4003.0000
Timer1 base: 0x4003.1000
Timer2 base: 0x4003.2000
Offset 0x034
Type R/W, reset 0x0000.FFFF
31 30 29 28 27 26 25 24 23 22 21 20 19 18 17 16
reserved
Type RO RO RO RO RO RO RO RO RO RO RO RO RO RO RO RO
Reset 0 0 0 0 0 0 0 0 0 0 0 0 0 0 0 0
15 14 13 12 11 10 9 8 7 6 5 4 3 2 1 0
TBMRL
Type R/W R/W R/W R/W R/W R/W R/W R/W R/W R/W R/W R/W R/W R/W R/W R/W
Reset 1 1 1 1 1 1 1 1 1 1 1 1 1 1 1 1
Bit/Field Name Type Reset Description
Software should not rely on the value of a reserved bit. To provide
compatibility with future products, the value of a reserved bit should be
preserved across a read-modify-write operation.
31:16 reserved RO 0x0000
GPTM TimerB Match Register Low
When configured for PWM mode, this value along with GPTMTBILR,
determines the duty cycle of the output PWM signal.
When configured for Edge Count mode, this value along with
GPTMTBILR, determines how many edge events are counted. The total
number of edge events counted is equal to the value in GPTMTBILR
minus this value.
15:0 TBMRL R/W 0xFFFF
November 30, 2007 201
Preliminary
LM3S6110 Microcontroller
Register 13: GPTM TimerA Prescale (GPTMTAPR), offset 0x038
This register allows software to extend the range of the 16-bit timers when operating in one-shot or
periodic mode.
GPTM TimerA Prescale (GPTMTAPR)
Timer0 base: 0x4003.0000
Timer1 base: 0x4003.1000
Timer2 base: 0x4003.2000
Offset 0x038
Type R/W, reset 0x0000.0000
31 30 29 28 27 26 25 24 23 22 21 20 19 18 17 16
reserved
Type RO RO RO RO RO RO RO RO RO RO RO RO RO RO RO RO
Reset 0 0 0 0 0 0 0 0 0 0 0 0 0 0 0 0
15 14 13 12 11 10 9 8 7 6 5 4 3 2 1 0
reserved TAPSR
Type RO RO RO RO RO RO RO RO R/W R/W R/W R/W R/W R/W R/W R/W
Reset 0 0 0 0 0 0 0 0 0 0 0 0 0 0 0 0
Bit/Field Name Type Reset Description
Software should not rely on the value of a reserved bit. To provide
compatibility with future products, the value of a reserved bit should be
preserved across a read-modify-write operation.
31:8 reserved RO 0x00
GPTM TimerA Prescale
The register loads this value on a write. A read returns the current value
of the register.
Refer to Table 9-2 on page 176 for more details and an example.
7:0 TAPSR R/W 0x00
202 November 30, 2007
Preliminary
General-Purpose Timers
Register 14: GPTM TimerB Prescale (GPTMTBPR), offset 0x03C
This register allows software to extend the range of the 16-bit timers when operating in one-shot or
periodic mode.
GPTM TimerB Prescale (GPTMTBPR)
Timer0 base: 0x4003.0000
Timer1 base: 0x4003.1000
Timer2 base: 0x4003.2000
Offset 0x03C
Type R/W, reset 0x0000.0000
31 30 29 28 27 26 25 24 23 22 21 20 19 18 17 16
reserved
Type RO RO RO RO RO RO RO RO RO RO RO RO RO RO RO RO
Reset 0 0 0 0 0 0 0 0 0 0 0 0 0 0 0 0
15 14 13 12 11 10 9 8 7 6 5 4 3 2 1 0
reserved TBPSR
Type RO RO RO RO RO RO RO RO R/W R/W R/W R/W R/W R/W R/W R/W
Reset 0 0 0 0 0 0 0 0 0 0 0 0 0 0 0 0
Bit/Field Name Type Reset Description
Software should not rely on the value of a reserved bit. To provide
compatibility with future products, the value of a reserved bit should be
preserved across a read-modify-write operation.
31:8 reserved RO 0x00
GPTM TimerB Prescale
The register loads this value on a write. A read returns the current value
of this register.
Refer to Table 9-2 on page 176 for more details and an example.
7:0 TBPSR R/W 0x00
November 30, 2007 203
Preliminary
LM3S6110 Microcontroller
Register 15: GPTM TimerA Prescale Match (GPTMTAPMR), offset 0x040
This register effectively extends the range of GPTMTAMATCHR to 24 bits when operating in 16-bit
one-shot or periodic mode.
GPTM TimerA Prescale Match (GPTMTAPMR)
Timer0 base: 0x4003.0000
Timer1 base: 0x4003.1000
Timer2 base: 0x4003.2000
Offset 0x040
Type R/W, reset 0x0000.0000
31 30 29 28 27 26 25 24 23 22 21 20 19 18 17 16
reserved
Type RO RO RO RO RO RO RO RO RO RO RO RO RO RO RO RO
Reset 0 0 0 0 0 0 0 0 0 0 0 0 0 0 0 0
15 14 13 12 11 10 9 8 7 6 5 4 3 2 1 0
reserved TAPSMR
Type RO RO RO RO RO RO RO RO R/W R/W R/W R/W R/W R/W R/W R/W
Reset 0 0 0 0 0 0 0 0 0 0 0 0 0 0 0 0
Bit/Field Name Type Reset Description
Software should not rely on the value of a reserved bit. To provide
compatibility with future products, the value of a reserved bit should be
preserved across a read-modify-write operation.
31:8 reserved RO 0x00
GPTM TimerA Prescale Match
This value is used alongside GPTMTAMATCHR to detect timer match
events while using a prescaler.
7:0 TAPSMR R/W 0x00
204 November 30, 2007
Preliminary
General-Purpose Timers
Register 16: GPTM TimerB Prescale Match (GPTMTBPMR), offset 0x044
This register effectively extends the range of GPTMTBMATCHR to 24 bits when operating in 16-bit
one-shot or periodic mode.
GPTM TimerB Prescale Match (GPTMTBPMR)
Timer0 base: 0x4003.0000
Timer1 base: 0x4003.1000
Timer2 base: 0x4003.2000
Offset 0x044
Type R/W, reset 0x0000.0000
31 30 29 28 27 26 25 24 23 22 21 20 19 18 17 16
reserved
Type RO RO RO RO RO RO RO RO RO RO RO RO RO RO RO RO
Reset 0 0 0 0 0 0 0 0 0 0 0 0 0 0 0 0
15 14 13 12 11 10 9 8 7 6 5 4 3 2 1 0
reserved TBPSMR
Type RO RO RO RO RO RO RO RO R/W R/W R/W R/W R/W R/W R/W R/W
Reset 0 0 0 0 0 0 0 0 0 0 0 0 0 0 0 0
Bit/Field Name Type Reset Description
Software should not rely on the value of a reserved bit. To provide
compatibility with future products, the value of a reserved bit should be
preserved across a read-modify-write operation.
31:8 reserved RO 0x00
GPTM TimerB Prescale Match
This value is used alongside GPTMTBMATCHR to detect timer match
events while using a prescaler.
7:0 TBPSMR R/W 0x00
November 30, 2007 205
Preliminary
LM3S6110 Microcontroller
Register 17: GPTM TimerA (GPTMTAR), offset 0x048
This register shows the current value of the TimerA counter in all cases except for Input Edge Count
mode. When in this mode, this register contains the time at which the last edge event took place.
GPTM TimerA (GPTMTAR)
Timer0 base: 0x4003.0000
Timer1 base: 0x4003.1000
Timer2 base: 0x4003.2000
Offset 0x048
Type RO, reset 0x0000.FFFF (16-bit mode) and 0xFFFF.FFFF (32-bit mode)
31 30 29 28 27 26 25 24 23 22 21 20 19 18 17 16
TARH
Type RO RO RO RO RO RO RO RO RO RO RO RO RO RO RO RO
Reset 0 1 1 0 1 0 1 1 1 1 0 1 1 1 1 0
15 14 13 12 11 10 9 8 7 6 5 4 3 2 1 0
TARL
Type RO RO RO RO RO RO RO RO RO RO RO RO RO RO RO RO
Reset 1 1 1 1 1 1 1 1 1 1 1 1 1 1 1 1
Bit/Field Name Type Reset Description
GPTM TimerA Register High
If the GPTMCFG is in a 32-bit mode, TimerB value is read. If the
GPTMCFG is in a 16-bit mode, this is read as zero.
0xFFFF
(32-bit mode)
0x0000 (16-bit
mode)
31:16 TARH RO
GPTM TimerA Register Low
A read returns the current value of the GPTM TimerA Count Register,
except in Input Edge Count mode, when it returns the timestamp from
the last edge event.
15:0 TARL RO 0xFFFF
206 November 30, 2007
Preliminary
General-Purpose Timers
Register 18: GPTM TimerB (GPTMTBR), offset 0x04C
This register shows the current value of the TimerB counter in all cases except for Input Edge Count
mode. When in this mode, this register contains the time at which the last edge event took place.
GPTM TimerB (GPTMTBR)
Timer0 base: 0x4003.0000
Timer1 base: 0x4003.1000
Timer2 base: 0x4003.2000
Offset 0x04C
Type RO, reset 0x0000.FFFF
31 30 29 28 27 26 25 24 23 22 21 20 19 18 17 16
reserved
Type RO RO RO RO RO RO RO RO RO RO RO RO RO RO RO RO
Reset 0 0 0 0 0 0 0 0 0 0 0 0 0 0 0 0
15 14 13 12 11 10 9 8 7 6 5 4 3 2 1 0
TBRL
Type RO RO RO RO RO RO RO RO RO RO RO RO RO RO RO RO
Reset 1 1 1 1 1 1 1 1 1 1 1 1 1 1 1 1
Bit/Field Name Type Reset Description
Software should not rely on the value of a reserved bit. To provide
compatibility with future products, the value of a reserved bit should be
preserved across a read-modify-write operation.
31:16 reserved RO 0x0000
GPTM TimerB
A read returns the current value of the GPTM TimerB Count Register,
except in Input Edge Count mode, when it returns the timestamp from
the last edge event.
15:0 TBRL RO 0xFFFF
November 30, 2007 207
Preliminary
LM3S6110 Microcontroller
10 Watchdog Timer
A watchdog timer can generate nonmaskable interrupts (NMIs) or a reset when a time-out value is
reached. The watchdog timer is used to regain control when a system has failed due to a software
error or due to the failure of an external device to respond in the expected way.
The Stellaris® Watchdog Timer module consists of a 32-bit down counter, a programmable load
register, interrupt generation logic, a locking register, and user-enabled stalling.
The Watchdog Timer can be configured to generate an interrupt to the controller on its first time-out,
and to generate a reset signal on its second time-out. Once the Watchdog Timer has been configured,
the lock register can be written to prevent the timer configuration from being inadvertently altered.
10.1 Block Diagram
Figure 10-1. WDT Module Block Diagram
Control / Clock /
Interrupt
Generation
WDTCTL
WDTICR
WDTRIS
WDTMIS
WDTLOCK
WDTTEST
WDTLOAD
WDTVALUE
Comparator
32-Bit Down
Counter
0x00000000
Interrupt
System Clock
Identification Registers
WDTPCellID0 WDTPeriphID0 WDTPeriphID4
WDTPCellID1 WDTPeriphID1 WDTPeriphID5
WDTPCellID2 WDTPeriphID2 WDTPeriphID6
WDTPCellID3 WDTPeriphID3 WDTPeriphID7
10.2 Functional Description
The Watchdog Timer module generates the first time-out signal when the 32-bit counter reaches
the zero state after being enabled; enabling the counter also enables the watchdog timer interrupt.
After the first time-out event, the 32-bit counter is re-loaded with the value of the Watchdog Timer
Load (WDTLOAD) register, and the timer resumes counting down from that value. Once the
208 November 30, 2007
Preliminary
Watchdog Timer
Watchdog Timer has been configured, the Watchdog Timer Lock (WDTLOCK) register is written,
which prevents the timer configuration from being inadvertently altered by software.
If the timer counts down to its zero state again before the first time-out interrupt is cleared, and the
reset signal has been enabled (via the WatchdogResetEnable function), the Watchdog timer
asserts its reset signal to the system. If the interrupt is cleared before the 32-bit counter reaches its
second time-out, the 32-bit counter is loaded with the value in the WDTLOAD register, and counting
resumes from that value.
If WDTLOAD is written with a new value while the Watchdog Timer counter is counting, then the
counter is loaded with the new value and continues counting.
Writing to WDTLOAD does not clear an active interrupt. An interrupt must be specifically cleared
by writing to the Watchdog Interrupt Clear (WDTICR) register.
The Watchdog module interrupt and reset generation can be enabled or disabled as required. When
the interrupt is re-enabled, the 32-bit counter is preloaded with the load register value and not its
last state.
10.3 Initialization and Configuration
To use the WDT, its peripheral clock must be enabled by setting the WDT bit in the RCGC0 register.
The Watchdog Timer is configured using the following sequence:
1. Load the WDTLOAD register with the desired timer load value.
2. If the Watchdog is configured to trigger system resets, set the RESEN bit in the WDTCTL register.
3. Set the INTEN bit in the WDTCTL register to enable the Watchdog and lock the control register.
If software requires that all of the watchdog registers are locked, the Watchdog Timer module can
be fully locked by writing any value to the WDTLOCK register. To unlock the Watchdog Timer, write
a value of 0x1ACC.E551.
10.4 Register Map
Table 10-1 on page 209 lists the Watchdog registers. The offset listed is a hexadecimal increment
to the register’s address, relative to the Watchdog Timer base address of 0x4000.0000.
Table 10-1. Watchdog Timer Register Map
See
Offset Name Type Reset Description page
0x000 WDTLOAD R/W 0xFFFF.FFFF Watchdog Load 211
0x004 WDTVALUE RO 0xFFFF.FFFF Watchdog Value 212
0x008 WDTCTL R/W 0x0000.0000 Watchdog Control 213
0x00C WDTICR WO - Watchdog Interrupt Clear 214
0x010 WDTRIS RO 0x0000.0000 Watchdog Raw Interrupt Status 215
0x014 WDTMIS RO 0x0000.0000 Watchdog Masked Interrupt Status 216
0x418 WDTTEST R/W 0x0000.0000 Watchdog Test 217
0xC00 WDTLOCK R/W 0x0000.0000 Watchdog Lock 218
November 30, 2007 209
Preliminary
LM3S6110 Microcontroller
See
Offset Name Type Reset Description page
0xFD0 WDTPeriphID4 RO 0x0000.0000 Watchdog Peripheral Identification 4 219
0xFD4 WDTPeriphID5 RO 0x0000.0000 Watchdog Peripheral Identification 5 220
0xFD8 WDTPeriphID6 RO 0x0000.0000 Watchdog Peripheral Identification 6 221
0xFDC WDTPeriphID7 RO 0x0000.0000 Watchdog Peripheral Identification 7 222
0xFE0 WDTPeriphID0 RO 0x0000.0005 Watchdog Peripheral Identification 0 223
0xFE4 WDTPeriphID1 RO 0x0000.0018 Watchdog Peripheral Identification 1 224
0xFE8 WDTPeriphID2 RO 0x0000.0018 Watchdog Peripheral Identification 2 225
0xFEC WDTPeriphID3 RO 0x0000.0001 Watchdog Peripheral Identification 3 226
0xFF0 WDTPCellID0 RO 0x0000.000D Watchdog PrimeCell Identification 0 227
0xFF4 WDTPCellID1 RO 0x0000.00F0 Watchdog PrimeCell Identification 1 228
0xFF8 WDTPCellID2 RO 0x0000.0005 Watchdog PrimeCell Identification 2 229
0xFFC WDTPCellID3 RO 0x0000.00B1 Watchdog PrimeCell Identification 3 230
10.5 Register Descriptions
The remainder of this section lists and describes the WDT registers, in numerical order by address
offset.
210 November 30, 2007
Preliminary
Watchdog Timer
Register 1: Watchdog Load (WDTLOAD), offset 0x000
This register is the 32-bit interval value used by the 32-bit counter. When this register is written, the
value is immediately loaded and the counter restarts counting down from the new value. If the
WDTLOAD register is loaded with 0x0000.0000, an interrupt is immediately generated.
Watchdog Load (WDTLOAD)
Base 0x4000.0000
Offset 0x000
Type R/W, reset 0xFFFF.FFFF
31 30 29 28 27 26 25 24 23 22 21 20 19 18 17 16
WDTLoad
Type R/W R/W R/W R/W R/W R/W R/W R/W R/W R/W R/W R/W R/W R/W R/W R/W
Reset 1 1 1 1 1 1 1 1 1 1 1 1 1 1 1 1
15 14 13 12 11 10 9 8 7 6 5 4 3 2 1 0
WDTLoad
Type R/W R/W R/W R/W R/W R/W R/W R/W R/W R/W R/W R/W R/W R/W R/W R/W
Reset 1 1 1 1 1 1 1 1 1 1 1 1 1 1 1 1
Bit/Field Name Type Reset Description
31:0 WDTLoad R/W 0xFFFF.FFFF Watchdog Load Value
November 30, 2007 211
Preliminary
LM3S6110 Microcontroller
Register 2: Watchdog Value (WDTVALUE), offset 0x004
This register contains the current count value of the timer.
Watchdog Value (WDTVALUE)
Base 0x4000.0000
Offset 0x004
Type RO, reset 0xFFFF.FFFF
31 30 29 28 27 26 25 24 23 22 21 20 19 18 17 16
WDTValue
Type RO RO RO RO RO RO RO RO RO RO RO RO RO RO RO RO
Reset 1 1 1 1 1 1 1 1 1 1 1 1 1 1 1 1
15 14 13 12 11 10 9 8 7 6 5 4 3 2 1 0
WDTValue
Type RO RO RO RO RO RO RO RO RO RO RO RO RO RO RO RO
Reset 1 1 1 1 1 1 1 1 1 1 1 1 1 1 1 1
Bit/Field Name Type Reset Description
Watchdog Value
Current value of the 32-bit down counter.
31:0 WDTValue RO 0xFFFF.FFFF
212 November 30, 2007
Preliminary
Watchdog Timer
Register 3: Watchdog Control (WDTCTL), offset 0x008
This register is the watchdog control register. The watchdog timer can be configured to generate a
reset signal (on second time-out) or an interrupt on time-out.
When the watchdog interrupt has been enabled, all subsequent writes to the control register are
ignored. The only mechanism that can re-enable writes is a hardware reset.
Watchdog Control (WDTCTL)
Base 0x4000.0000
Offset 0x008
Type R/W, reset 0x0000.0000
31 30 29 28 27 26 25 24 23 22 21 20 19 18 17 16
reserved
Type RO RO RO RO RO RO RO RO RO RO RO RO RO RO RO RO
Reset 0 0 0 0 0 0 0 0 0 0 0 0 0 0 0 0
15 14 13 12 11 10 9 8 7 6 5 4 3 2 1 0
reserved RESEN INTEN
Type RO RO RO RO RO RO RO RO RO RO RO RO RO RO R/W R/W
Reset 0 0 0 0 0 0 0 0 0 0 0 0 0 0 0 0
Bit/Field Name Type Reset Description
Software should not rely on the value of a reserved bit. To provide
compatibility with future products, the value of a reserved bit should be
preserved across a read-modify-write operation.
31:2 reserved RO 0x00
Watchdog Reset Enable
The RESEN values are defined as follows:
Value Description
0 Disabled.
1 Enable the Watchdog module reset output.
1 RESEN R/W 0
Watchdog Interrupt Enable
The INTEN values are defined as follows:
Value Description
Interrupt event disabled (once this bit is set, it can only be
cleared by a hardware reset).
0
1 Interrupt event enabled. Once enabled, all writes are ignored.
0 INTEN R/W 0
November 30, 2007 213
Preliminary
LM3S6110 Microcontroller
Register 4: Watchdog Interrupt Clear (WDTICR), offset 0x00C
This register is the interrupt clear register. A write of any value to this register clears the Watchdog
interrupt and reloads the 32-bit counter from the WDTLOAD register. Value for a read or reset is
indeterminate.
Watchdog Interrupt Clear (WDTICR)
Base 0x4000.0000
Offset 0x00C
Type WO, reset -
31 30 29 28 27 26 25 24 23 22 21 20 19 18 17 16
WDTIntClr
Type WO WO WO WO WO WO WO WO WO WO WO WO WO WO WO WO
Reset - - - - - - - - - - - - - - - -
15 14 13 12 11 10 9 8 7 6 5 4 3 2 1 0
WDTIntClr
Type WO WO WO WO WO WO WO WO WO WO WO WO WO WO WO WO
Reset - - - - - - - - - - - - - - - -
Bit/Field Name Type Reset Description
31:0 WDTIntClr WO - Watchdog Interrupt Clear
214 November 30, 2007
Preliminary
Watchdog Timer
Register 5: Watchdog Raw Interrupt Status (WDTRIS), offset 0x010
This register is the raw interrupt status register. Watchdog interrupt events can be monitored via
this register if the controller interrupt is masked.
Watchdog Raw Interrupt Status (WDTRIS)
Base 0x4000.0000
Offset 0x010
Type RO, reset 0x0000.0000
31 30 29 28 27 26 25 24 23 22 21 20 19 18 17 16
reserved
Type RO RO RO RO RO RO RO RO RO RO RO RO RO RO RO RO
Reset 0 0 0 0 0 0 0 0 0 0 0 0 0 0 0 0
15 14 13 12 11 10 9 8 7 6 5 4 3 2 1 0
reserved WDTRIS
Type RO RO RO RO RO RO RO RO RO RO RO RO RO RO RO RO
Reset 0 0 0 0 0 0 0 0 0 0 0 0 0 0 0 0
Bit/Field Name Type Reset Description
Software should not rely on the value of a reserved bit. To provide
compatibility with future products, the value of a reserved bit should be
preserved across a read-modify-write operation.
31:1 reserved RO 0x00
Watchdog Raw Interrupt Status
Gives the raw interrupt state (prior to masking) of WDTINTR.
0 WDTRIS RO 0
November 30, 2007 215
Preliminary
LM3S6110 Microcontroller
Register 6: Watchdog Masked Interrupt Status (WDTMIS), offset 0x014
This register is the masked interrupt status register. The value of this register is the logical AND of
the raw interrupt bit and the Watchdog interrupt enable bit.
Watchdog Masked Interrupt Status (WDTMIS)
Base 0x4000.0000
Offset 0x014
Type RO, reset 0x0000.0000
31 30 29 28 27 26 25 24 23 22 21 20 19 18 17 16
reserved
Type RO RO RO RO RO RO RO RO RO RO RO RO RO RO RO RO
Reset 0 0 0 0 0 0 0 0 0 0 0 0 0 0 0 0
15 14 13 12 11 10 9 8 7 6 5 4 3 2 1 0
reserved WDTMIS
Type RO RO RO RO RO RO RO RO RO RO RO RO RO RO RO RO
Reset 0 0 0 0 0 0 0 0 0 0 0 0 0 0 0 0
Bit/Field Name Type Reset Description
Software should not rely on the value of a reserved bit. To provide
compatibility with future products, the value of a reserved bit should be
preserved across a read-modify-write operation.
31:1 reserved RO 0x00
Watchdog Masked Interrupt Status
Gives the masked interrupt state (after masking) of the WDTINTR
interrupt.
0 WDTMIS RO 0
216 November 30, 2007
Preliminary
Watchdog Timer
Register 7: Watchdog Test (WDTTEST), offset 0x418
This register provides user-enabled stalling when the microcontroller asserts the CPU halt flag
during debug.
Watchdog Test (WDTTEST)
Base 0x4000.0000
Offset 0x418
Type R/W, reset 0x0000.0000
31 30 29 28 27 26 25 24 23 22 21 20 19 18 17 16
reserved
Type RO RO RO RO RO RO RO RO RO RO RO RO RO RO RO RO
Reset 0 0 0 0 0 0 0 0 0 0 0 0 0 0 0 0
15 14 13 12 11 10 9 8 7 6 5 4 3 2 1 0
reserved STALL reserved
Type RO RO RO RO RO RO RO R/W RO RO RO RO RO RO RO RO
Reset 0 0 0 0 0 0 0 0 0 0 0 0 0 0 0 0
Bit/Field Name Type Reset Description
Software should not rely on the value of a reserved bit. To provide
compatibility with future products, the value of a reserved bit should be
preserved across a read-modify-write operation.
31:9 reserved RO 0x00
Watchdog Stall Enable
When set to 1, if the Stellaris® microcontroller is stopped with a
debugger, the watchdog timer stops counting. Once the microcontroller
is restarted, the watchdog timer resumes counting.
8 STALL R/W 0
Software should not rely on the value of a reserved bit. To provide
compatibility with future products, the value of a reserved bit should be
preserved across a read-modify-write operation.
7:0 reserved RO 0x00
November 30, 2007 217
Preliminary
LM3S6110 Microcontroller
Register 8: Watchdog Lock (WDTLOCK), offset 0xC00
Writing 0x1ACC.E551 to the WDTLOCK register enables write access to all other registers. Writing
any other value to the WDTLOCK register re-enables the locked state for register writes to all the
other registers. Reading the WDTLOCK register returns the lock status rather than the 32-bit value
written. Therefore, when write accesses are disabled, reading the WDTLOCK register returns
0x0000.0001 (when locked; otherwise, the returned value is 0x0000.0000 (unlocked)).
Watchdog Lock (WDTLOCK)
Base 0x4000.0000
Offset 0xC00
Type R/W, reset 0x0000.0000
31 30 29 28 27 26 25 24 23 22 21 20 19 18 17 16
WDTLock
Type R/W R/W R/W R/W R/W R/W R/W R/W R/W R/W R/W R/W R/W R/W R/W R/W
Reset 0 0 0 0 0 0 0 0 0 0 0 0 0 0 0 0
15 14 13 12 11 10 9 8 7 6 5 4 3 2 1 0
WDTLock
Type R/W R/W R/W R/W R/W R/W R/W R/W R/W R/W R/W R/W R/W R/W R/W R/W
Reset 0 0 0 0 0 0 0 0 0 0 0 0 0 0 0 0
Bit/Field Name Type Reset Description
Watchdog Lock
A write of the value 0x1ACC.E551 unlocks the watchdog registers for
write access. A write of any other value reapplies the lock, preventing
any register updates.
A read of this register returns the following values:
Value Description
0x0000.0001 Locked
0x0000.0000 Unlocked
31:0 WDTLock R/W 0x0000
218 November 30, 2007
Preliminary
Watchdog Timer
Register 9: Watchdog Peripheral Identification 4 (WDTPeriphID4), offset 0xFD0
The WDTPeriphIDn registers are hard-coded and the fields within the register determine the reset
value.
Watchdog Peripheral Identification 4 (WDTPeriphID4)
Base 0x4000.0000
Offset 0xFD0
Type RO, reset 0x0000.0000
31 30 29 28 27 26 25 24 23 22 21 20 19 18 17 16
reserved
Type RO RO RO RO RO RO RO RO RO RO RO RO RO RO RO RO
Reset 0 0 0 0 0 0 0 0 0 0 0 0 0 0 0 0
15 14 13 12 11 10 9 8 7 6 5 4 3 2 1 0
reserved PID4
Type RO RO RO RO RO RO RO RO RO RO RO RO RO RO RO RO
Reset 0 0 0 0 0 0 0 0 0 0 0 0 0 0 0 0
Bit/Field Name Type Reset Description
Software should not rely on the value of a reserved bit. To provide
compatibility with future products, the value of a reserved bit should be
preserved across a read-modify-write operation.
31:8 reserved RO 0x00
7:0 PID4 RO 0x00 WDT Peripheral ID Register[7:0]
November 30, 2007 219
Preliminary
LM3S6110 Microcontroller
Register 10: Watchdog Peripheral Identification 5 (WDTPeriphID5), offset
0xFD4
The WDTPeriphIDn registers are hard-coded and the fields within the register determine the reset
value.
Watchdog Peripheral Identification 5 (WDTPeriphID5)
Base 0x4000.0000
Offset 0xFD4
Type RO, reset 0x0000.0000
31 30 29 28 27 26 25 24 23 22 21 20 19 18 17 16
reserved
Type RO RO RO RO RO RO RO RO RO RO RO RO RO RO RO RO
Reset 0 0 0 0 0 0 0 0 0 0 0 0 0 0 0 0
15 14 13 12 11 10 9 8 7 6 5 4 3 2 1 0
reserved PID5
Type RO RO RO RO RO RO RO RO RO RO RO RO RO RO RO RO
Reset 0 0 0 0 0 0 0 0 0 0 0 0 0 0 0 0
Bit/Field Name Type Reset Description
Software should not rely on the value of a reserved bit. To provide
compatibility with future products, the value of a reserved bit should be
preserved across a read-modify-write operation.
31:8 reserved RO 0x00
7:0 PID5 RO 0x00 WDT Peripheral ID Register[15:8]
220 November 30, 2007
Preliminary
Watchdog Timer
Register 11: Watchdog Peripheral Identification 6 (WDTPeriphID6), offset
0xFD8
The WDTPeriphIDn registers are hard-coded and the fields within the register determine the reset
value.
Watchdog Peripheral Identification 6 (WDTPeriphID6)
Base 0x4000.0000
Offset 0xFD8
Type RO, reset 0x0000.0000
31 30 29 28 27 26 25 24 23 22 21 20 19 18 17 16
reserved
Type RO RO RO RO RO RO RO RO RO RO RO RO RO RO RO RO
Reset 0 0 0 0 0 0 0 0 0 0 0 0 0 0 0 0
15 14 13 12 11 10 9 8 7 6 5 4 3 2 1 0
reserved PID6
Type RO RO RO RO RO RO RO RO RO RO RO RO RO RO RO RO
Reset 0 0 0 0 0 0 0 0 0 0 0 0 0 0 0 0
Bit/Field Name Type Reset Description
Software should not rely on the value of a reserved bit. To provide
compatibility with future products, the value of a reserved bit should be
preserved across a read-modify-write operation.
31:8 reserved RO 0x00
7:0 PID6 RO 0x00 WDT Peripheral ID Register[23:16]
November 30, 2007 221
Preliminary
LM3S6110 Microcontroller
Register 12: Watchdog Peripheral Identification 7 (WDTPeriphID7), offset
0xFDC
The WDTPeriphIDn registers are hard-coded and the fields within the register determine the reset
value.
Watchdog Peripheral Identification 7 (WDTPeriphID7)
Base 0x4000.0000
Offset 0xFDC
Type RO, reset 0x0000.0000
31 30 29 28 27 26 25 24 23 22 21 20 19 18 17 16
reserved
Type RO RO RO RO RO RO RO RO RO RO RO RO RO RO RO RO
Reset 0 0 0 0 0 0 0 0 0 0 0 0 0 0 0 0
15 14 13 12 11 10 9 8 7 6 5 4 3 2 1 0
reserved PID7
Type RO RO RO RO RO RO RO RO RO RO RO RO RO RO RO RO
Reset 0 0 0 0 0 0 0 0 0 0 0 0 0 0 0 0
Bit/Field Name Type Reset Description
Software should not rely on the value of a reserved bit. To provide
compatibility with future products, the value of a reserved bit should be
preserved across a read-modify-write operation.
31:8 reserved RO 0x00
7:0 PID7 RO 0x00 WDT Peripheral ID Register[31:24]
222 November 30, 2007
Preliminary
Watchdog Timer
Register 13: Watchdog Peripheral Identification 0 (WDTPeriphID0), offset
0xFE0
The WDTPeriphIDn registers are hard-coded and the fields within the register determine the reset
value.
Watchdog Peripheral Identification 0 (WDTPeriphID0)
Base 0x4000.0000
Offset 0xFE0
Type RO, reset 0x0000.0005
31 30 29 28 27 26 25 24 23 22 21 20 19 18 17 16
reserved
Type RO RO RO RO RO RO RO RO RO RO RO RO RO RO RO RO
Reset 0 0 0 0 0 0 0 0 0 0 0 0 0 0 0 0
15 14 13 12 11 10 9 8 7 6 5 4 3 2 1 0
reserved PID0
Type RO RO RO RO RO RO RO RO RO RO RO RO RO RO RO RO
Reset 0 0 0 0 0 0 0 0 0 0 0 0 0 1 0 1
Bit/Field Name Type Reset Description
Software should not rely on the value of a reserved bit. To provide
compatibility with future products, the value of a reserved bit should be
preserved across a read-modify-write operation.
31:8 reserved RO 0x00
7:0 PID0 RO 0x05 Watchdog Peripheral ID Register[7:0]
November 30, 2007 223
Preliminary
LM3S6110 Microcontroller
Register 14: Watchdog Peripheral Identification 1 (WDTPeriphID1), offset
0xFE4
The WDTPeriphIDn registers are hard-coded and the fields within the register determine the reset
value.
Watchdog Peripheral Identification 1 (WDTPeriphID1)
Base 0x4000.0000
Offset 0xFE4
Type RO, reset 0x0000.0018
31 30 29 28 27 26 25 24 23 22 21 20 19 18 17 16
reserved
Type RO RO RO RO RO RO RO RO RO RO RO RO RO RO RO RO
Reset 0 0 0 0 0 0 0 0 0 0 0 0 0 0 0 0
15 14 13 12 11 10 9 8 7 6 5 4 3 2 1 0
reserved PID1
Type RO RO RO RO RO RO RO RO RO RO RO RO RO RO RO RO
Reset 0 0 0 0 0 0 0 0 0 0 0 1 1 0 0 0
Bit/Field Name Type Reset Description
Software should not rely on the value of a reserved bit. To provide
compatibility with future products, the value of a reserved bit should be
preserved across a read-modify-write operation.
31:8 reserved RO 0x00
7:0 PID1 RO 0x18 Watchdog Peripheral ID Register[15:8]
224 November 30, 2007
Preliminary
Watchdog Timer
Register 15: Watchdog Peripheral Identification 2 (WDTPeriphID2), offset
0xFE8
The WDTPeriphIDn registers are hard-coded and the fields within the register determine the reset
value.
Watchdog Peripheral Identification 2 (WDTPeriphID2)
Base 0x4000.0000
Offset 0xFE8
Type RO, reset 0x0000.0018
31 30 29 28 27 26 25 24 23 22 21 20 19 18 17 16
reserved
Type RO RO RO RO RO RO RO RO RO RO RO RO RO RO RO RO
Reset 0 0 0 0 0 0 0 0 0 0 0 0 0 0 0 0
15 14 13 12 11 10 9 8 7 6 5 4 3 2 1 0
reserved PID2
Type RO RO RO RO RO RO RO RO RO RO RO RO RO RO RO RO
Reset 0 0 0 0 0 0 0 0 0 0 0 1 1 0 0 0
Bit/Field Name Type Reset Description
Software should not rely on the value of a reserved bit. To provide
compatibility with future products, the value of a reserved bit should be
preserved across a read-modify-write operation.
31:8 reserved RO 0x00
7:0 PID2 RO 0x18 Watchdog Peripheral ID Register[23:16]
November 30, 2007 225
Preliminary
LM3S6110 Microcontroller
Register 16: Watchdog Peripheral Identification 3 (WDTPeriphID3), offset
0xFEC
The WDTPeriphIDn registers are hard-coded and the fields within the register determine the reset
value.
Watchdog Peripheral Identification 3 (WDTPeriphID3)
Base 0x4000.0000
Offset 0xFEC
Type RO, reset 0x0000.0001
31 30 29 28 27 26 25 24 23 22 21 20 19 18 17 16
reserved
Type RO RO RO RO RO RO RO RO RO RO RO RO RO RO RO RO
Reset 0 0 0 0 0 0 0 0 0 0 0 0 0 0 0 0
15 14 13 12 11 10 9 8 7 6 5 4 3 2 1 0
reserved PID3
Type RO RO RO RO RO RO RO RO RO RO RO RO RO RO RO RO
Reset 0 0 0 0 0 0 0 0 0 0 0 0 0 0 0 1
Bit/Field Name Type Reset Description
Software should not rely on the value of a reserved bit. To provide
compatibility with future products, the value of a reserved bit should be
preserved across a read-modify-write operation.
31:8 reserved RO 0x00
7:0 PID3 RO 0x01 Watchdog Peripheral ID Register[31:24]
226 November 30, 2007
Preliminary
Watchdog Timer
Register 17: Watchdog PrimeCell Identification 0 (WDTPCellID0), offset 0xFF0
The WDTPCellIDn registers are hard-coded and the fields within the register determine the reset
value.
Watchdog PrimeCell Identification 0 (WDTPCellID0)
Base 0x4000.0000
Offset 0xFF0
Type RO, reset 0x0000.000D
31 30 29 28 27 26 25 24 23 22 21 20 19 18 17 16
reserved
Type RO RO RO RO RO RO RO RO RO RO RO RO RO RO RO RO
Reset 0 0 0 0 0 0 0 0 0 0 0 0 0 0 0 0
15 14 13 12 11 10 9 8 7 6 5 4 3 2 1 0
reserved CID0
Type RO RO RO RO RO RO RO RO RO RO RO RO RO RO RO RO
Reset 0 0 0 0 0 0 0 0 0 0 0 0 1 1 0 1
Bit/Field Name Type Reset Description
Software should not rely on the value of a reserved bit. To provide
compatibility with future products, the value of a reserved bit should be
preserved across a read-modify-write operation.
31:8 reserved RO 0x00
7:0 CID0 RO 0x0D Watchdog PrimeCell ID Register[7:0]
November 30, 2007 227
Preliminary
LM3S6110 Microcontroller
Register 18: Watchdog PrimeCell Identification 1 (WDTPCellID1), offset 0xFF4
The WDTPCellIDn registers are hard-coded and the fields within the register determine the reset
value.
Watchdog PrimeCell Identification 1 (WDTPCellID1)
Base 0x4000.0000
Offset 0xFF4
Type RO, reset 0x0000.00F0
31 30 29 28 27 26 25 24 23 22 21 20 19 18 17 16
reserved
Type RO RO RO RO RO RO RO RO RO RO RO RO RO RO RO RO
Reset 0 0 0 0 0 0 0 0 0 0 0 0 0 0 0 0
15 14 13 12 11 10 9 8 7 6 5 4 3 2 1 0
reserved CID1
Type RO RO RO RO RO RO RO RO RO RO RO RO RO RO RO RO
Reset 0 0 0 0 0 0 0 0 1 1 1 1 0 0 0 0
Bit/Field Name Type Reset Description
Software should not rely on the value of a reserved bit. To provide
compatibility with future products, the value of a reserved bit should be
preserved across a read-modify-write operation.
31:8 reserved RO 0x00
7:0 CID1 RO 0xF0 Watchdog PrimeCell ID Register[15:8]
228 November 30, 2007
Preliminary
Watchdog Timer
Register 19: Watchdog PrimeCell Identification 2 (WDTPCellID2), offset 0xFF8
The WDTPCellIDn registers are hard-coded and the fields within the register determine the reset
value.
Watchdog PrimeCell Identification 2 (WDTPCellID2)
Base 0x4000.0000
Offset 0xFF8
Type RO, reset 0x0000.0005
31 30 29 28 27 26 25 24 23 22 21 20 19 18 17 16
reserved
Type RO RO RO RO RO RO RO RO RO RO RO RO RO RO RO RO
Reset 0 0 0 0 0 0 0 0 0 0 0 0 0 0 0 0
15 14 13 12 11 10 9 8 7 6 5 4 3 2 1 0
reserved CID2
Type RO RO RO RO RO RO RO RO RO RO RO RO RO RO RO RO
Reset 0 0 0 0 0 0 0 0 0 0 0 0 0 1 0 1
Bit/Field Name Type Reset Description
Software should not rely on the value of a reserved bit. To provide
compatibility with future products, the value of a reserved bit should be
preserved across a read-modify-write operation.
31:8 reserved RO 0x00
7:0 CID2 RO 0x05 Watchdog PrimeCell ID Register[23:16]
November 30, 2007 229
Preliminary
LM3S6110 Microcontroller
Register 20: Watchdog PrimeCell Identification 3 (WDTPCellID3 ), offset 0xFFC
The WDTPCellIDn registers are hard-coded and the fields within the register determine the reset
value.
Watchdog PrimeCell Identification 3 (WDTPCellID3)
Base 0x4000.0000
Offset 0xFFC
Type RO, reset 0x0000.00B1
31 30 29 28 27 26 25 24 23 22 21 20 19 18 17 16
reserved
Type RO RO RO RO RO RO RO RO RO RO RO RO RO RO RO RO
Reset 0 0 0 0 0 0 0 0 0 0 0 0 0 0 0 0
15 14 13 12 11 10 9 8 7 6 5 4 3 2 1 0
reserved CID3
Type RO RO RO RO RO RO RO RO RO RO RO RO RO RO RO RO
Reset 0 0 0 0 0 0 0 0 1 0 1 1 0 0 0 1
Bit/Field Name Type Reset Description
Software should not rely on the value of a reserved bit. To provide
compatibility with future products, the value of a reserved bit should be
preserved across a read-modify-write operation.
31:8 reserved RO 0x00
7:0 CID3 RO 0xB1 Watchdog PrimeCell ID Register[31:24]
230 November 30, 2007
Preliminary
Watchdog Timer
11 Universal Asynchronous Receivers/Transmitters
(UARTs)
The Stellaris® Universal Asynchronous Receiver/Transmitter (UART) provides fully programmable,
16C550-type serial interface characteristics. The LM3S6110 controller is equipped with one UART
module.
The UART has the following features:
■ Separate transmit and receive FIFOs
■ Programmable FIFO length, including 1-byte deep operation providing conventional
double-buffered interface
■ FIFO trigger levels of 1/8, 1/4, 1/2, 3/4, and 7/8
■ Programmable baud-rate generator allowing rates up to 1.5625 Mbps
■ Standard asynchronous communication bits for start, stop, and parity
■ False start bit detection
■ Line-break generation and detection
■ Fully programmable serial interface characteristics:
– 5, 6, 7, or 8 data bits
– Even, odd, stick, or no-parity bit generation/detection
– 1 or 2 stop bit generation
■ IrDA serial-IR (SIR) encoder/decoder providing:
– Programmable use of IrDA Serial InfraRed (SIR) or UART input/output
– Support of IrDA SIR encoder/decoder functions for data rates up to 115.2 Kbps half-duplex
– Support of normal 3/16 and low-power (1.41-2.23 μs) bit durations
– Programmable internal clock generator enabling division of reference clock by 1 to 256 for
low-power mode bit duration
November 30, 2007 231
Preliminary
LM3S6110 Microcontroller
11.1 Block Diagram
Figure 11-1. UART Module Block Diagram
Receiver
Transmitter
System Clock
Control / Status
UARTRSR/ECR
UARTFR
UARTLCRH
UARTCTL
UARTILPR
Interrupt Control
UARTIFLS
UARTIM
UARTMIS
UARTRIS
UARTICR
Baud Rate
Generator
UARTIBRD
UARTFBRD
Identification
Registers
UARTPCellID0
UARTPCellID1
UARTPCellID2
UARTPCellID3
UARTPeriphID0
UARTPeriphID1
UARTPeriphID2
UARTPeriphID3
UART PeriphID4
UARTPeriphID5
UARTPeriphID6
UARTPeriphID7
UARTDR
TXFIFO
16x8
...
RXFIFO
16x8
...
Interrupt
UnTx
UnRx
11.2 Functional Description
Each Stellaris® UART performs the functions of parallel-to-serial and serial-to-parallel conversions.
It is similar in functionality to a 16C550 UART, but is not register compatible.
The UART is configured for transmit and/or receive via the TXE and RXE bits of the UART Control
(UARTCTL) register (see page 250). Transmit and receive are both enabled out of reset. Before any
control registers are programmed, the UART must be disabled by clearing the UARTEN bit in
UARTCTL. If the UART is disabled during a TX or RX operation, the current transaction is completed
prior to the UART stopping.
The UART peripheral also includes a serial IR (SIR) encoder/decoder block that can be connected
to an infrared transceiver to implement an IrDA SIR physical layer. The SIR function is programmed
using the UARTCTL register.
11.2.1 Transmit/Receive Logic
The transmit logic performs parallel-to-serial conversion on the data read from the transmit FIFO.
The control logic outputs the serial bit stream beginning with a start bit, and followed by the data
232 November 30, 2007
Preliminary
Universal Asynchronous Receivers/Transmitters (UARTs)
bits (LSB first), parity bit, and the stop bits according to the programmed configuration in the control
registers. See Figure 11-2 on page 233 for details.
The receive logic performs serial-to-parallel conversion on the received bit stream after a valid start
pulse has been detected. Overrun, parity, frame error checking, and line-break detection are also
performed, and their status accompanies the data that is written to the receive FIFO.
Figure 11-2. UART Character Frame
1
0 5-8 data bits
LSB MSB
Parity bit
if enabled
1-2
stop bits
UnTX
n
Start
11.2.2 Baud-Rate Generation
The baud-rate divisor is a 22-bit number consisting of a 16-bit integer and a 6-bit fractional part.
The number formed by these two values is used by the baud-rate generator to determine the bit
period. Having a fractional baud-rate divider allows the UART to generate all the standard baud
rates.
The 16-bit integer is loaded through the UART Integer Baud-Rate Divisor (UARTIBRD) register
(see page 246) and the 6-bit fractional part is loaded with the UART Fractional Baud-Rate Divisor
(UARTFBRD) register (see page 247). The baud-rate divisor (BRD) has the following relationship
to the system clock (where BRDI is the integer part of the BRD and BRDF is the fractional part,
separated by a decimal place.):
BRD = BRDI + BRDF = SysClk / (16 * Baud Rate)
The 6-bit fractional number (that is to be loaded into the DIVFRAC bit field in the UARTFBRD register)
can be calculated by taking the fractional part of the baud-rate divisor, multiplying it by 64, and
adding 0.5 to account for rounding errors:
UARTFBRD[DIVFRAC] = integer(BRDF * 64 + 0.5)
The UART generates an internal baud-rate reference clock at 16x the baud-rate (referred to as
Baud16). This reference clock is divided by 16 to generate the transmit clock, and is used for error
detection during receive operations.
Along with the UART Line Control, High Byte (UARTLCRH) register (see page 248), the UARTIBRD
and UARTFBRD registers form an internal 30-bit register. This internal register is only updated
when a write operation to UARTLCRH is performed, so any changes to the baud-rate divisor must
be followed by a write to the UARTLCRH register for the changes to take effect.
To update the baud-rate registers, there are four possible sequences:
■ UARTIBRD write, UARTFBRD write, and UARTLCRH write
■ UARTFBRD write, UARTIBRD write, and UARTLCRH write
■ UARTIBRD write and UARTLCRH write
■ UARTFBRD write and UARTLCRH write
November 30, 2007 233
Preliminary
LM3S6110 Microcontroller
11.2.3 Data Transmission
Data received or transmitted is stored in two 16-byte FIFOs, though the receive FIFO has an extra
four bits per character for status information. For transmission, data is written into the transmit FIFO.
If the UART is enabled, it causes a data frame to start transmitting with the parameters indicated
in the UARTLCRH register. Data continues to be transmitted until there is no data left in the transmit
FIFO. The BUSY bit in the UART Flag (UARTFR) register (see page 243) is asserted as soon as
data is written to the transmit FIFO (that is, if the FIFO is non-empty) and remains asserted while
data is being transmitted. The BUSY bit is negated only when the transmit FIFO is empty, and the
last character has been transmitted from the shift register, including the stop bits. The UART can
indicate that it is busy even though the UART may no longer be enabled.
When the receiver is idle (the UnRx is continuously 1) and the data input goes Low (a start bit has
been received), the receive counter begins running and data is sampled on the eighth cycle of
Baud16 (described in “Transmit/Receive Logic” on page 232).
The start bit is valid if UnRx is still low on the eighth cycle of Baud16, otherwise a false start bit is
detected and it is ignored. Start bit errors can be viewed in the UART Receive Status (UARTRSR)
register (see page 241). If the start bit was valid, successive data bits are sampled on every 16th
cycle of Baud16 (that is, one bit period later) according to the programmed length of the data
characters. The parity bit is then checked if parity mode was enabled. Data length and parity are
defined in the UARTLCRH register.
Lastly, a valid stop bit is confirmed if UnRx is High, otherwise a framing error has occurred. When
a full word is received, the data is stored in the receive FIFO, with any error bits associated with
that word.
11.2.4 Serial IR (SIR)
The UART peripheral includes an IrDA serial-IR (SIR) encoder/decoder block. The IrDA SIR block
provides functionality that converts between an asynchronous UART data stream, and half-duplex
serial SIR interface. No analog processing is performed on-chip. The role of the SIR block is to
provide a digital encoded output, and decoded input to the UART. The UART signal pins can be
connected to an infrared transceiver to implement an IrDA SIR physical layer link. The SIR block
has two modes of operation:
■ In normal IrDA mode, a zero logic level is transmitted as high pulse of 3/16th duration of the
selected baud rate bit period on the output pin, while logic one levels are transmitted as a static
LOW signal. These levels control the driver of an infrared transmitter, sending a pulse of light
for each zero. On the reception side, the incoming light pulses energize the photo transistor base
of the receiver, pulling its output LOW. This drives the UART input pin LOW.
■ In low-power IrDA mode, the width of the transmitted infrared pulse is set to three times the
period of the internally generated IrLPBaud16 signal (1.63 μs, assuming a nominal 1.8432 MHz
frequency) by changing the appropriate bit in the UARTCR register.
Figure 11-3 on page 235 shows the UART transmit and receive signals, with and without IrDA
modulation.
234 November 30, 2007
Preliminary
Universal Asynchronous Receivers/Transmitters (UARTs)
Figure 11-3. IrDA Data Modulation
0 1 0 1 0 0 1 1 0 1
Data bits
0 1 0 1 0 0 1 1 0 1
Start Data bits
bit
Start Stop
Bit period Bit period
3
16
UnTx
UnTx with IrDA
UnRx with IrDA
UnRx
Stop
bit
In both normal and low-power IrDA modes:
■ During transmission, the UART data bit is used as the base for encoding
■ During reception, the decoded bits are transferred to the UART receive logic
The IrDA SIR physical layer specifies a half-duplex communication link, with a minimum 10 ms delay
between transmission and reception. This delay must be generated by software because it is not
automatically supported by the UART. The delay is required because the infrared receiver electronics
might become biased, or even saturated from the optical power coupled from the adjacent transmitter
LED. This delay is known as latency, or receiver setup time.
11.2.5 FIFO Operation
The UART has two 16-entry FIFOs; one for transmit and one for receive. Both FIFOs are accessed
via the UART Data (UARTDR) register (see page 239). Read operations of the UARTDR register
return a 12-bit value consisting of 8 data bits and 4 error flags while write operations place 8-bit data
in the transmit FIFO.
Out of reset, both FIFOs are disabled and act as 1-byte-deep holding registers. The FIFOs are
enabled by setting the FEN bit in UARTLCRH (page 248).
FIFO status can be monitored via the UART Flag (UARTFR) register (see page 243) and the UART
Receive Status (UARTRSR) register. Hardware monitors empty, full and overrun conditions. The
UARTFR register contains empty and full flags (TXFE, TXFF, RXFE, and RXFF bits) and the
UARTRSR register shows overrun status via the OE bit.
The trigger points at which the FIFOs generate interrupts is controlled via the UART Interrupt FIFO
Level Select (UARTIFLS) register (see page 252). Both FIFOs can be individually configured to
trigger interrupts at different levels. Available configurations include 1/8, ¼, ½, ¾, and 7/8. For
example, if the ¼ option is selected for the receive FIFO, the UART generates a receive interrupt
after 4 data bytes are received. Out of reset, both FIFOs are configured to trigger an interrupt at the
½ mark.
11.2.6 Interrupts
The UART can generate interrupts when the following conditions are observed:
■ Overrun Error
■ Break Error
November 30, 2007 235
Preliminary
LM3S6110 Microcontroller
■ Parity Error
■ Framing Error
■ Receive Timeout
■ Transmit (when condition defined in the TXIFLSEL bit in the UARTIFLS register is met)
■ Receive (when condition defined in the RXIFLSEL bit in the UARTIFLS register is met)
All of the interrupt events are ORed together before being sent to the interrupt controller, so the
UART can only generate a single interrupt request to the controller at any given time. Software can
service multiple interrupt events in a single interrupt service routine by reading the UART Masked
Interrupt Status (UARTMIS) register (see page 257).
The interrupt events that can trigger a controller-level interrupt are defined in the UART Interrupt
Mask (UARTIM ) register (see page 254) by setting the corresponding IM bit to 1. If interrupts are
not used, the raw interrupt status is always visible via the UART Raw Interrupt Status (UARTRIS)
register (see page 256).
Interrupts are always cleared (for both the UARTMIS and UARTRIS registers) by setting the
corresponding bit in the UART Interrupt Clear (UARTICR) register (see page 258).
The receive timeout interrupt is asserted when the receive FIFO is not empty, and no further data
is received over a 32-bit period. The receive timeout interrupt is cleared either when the FIFO
becomes empty through reading all the data (or by reading the holding register), or when a 1 is
written to the corresponding bit in the UARTICR register.
11.2.7 Loopback Operation
The UART can be placed into an internal loopback mode for diagnostic or debug work. This is
accomplished by setting the LBE bit in the UARTCTL register (see page 250). In loopback mode,
data transmitted on UnTx is received on the UnRx input.
11.2.8 IrDA SIR block
The IrDA SIR block contains an IrDA serial IR (SIR) protocol encoder/decoder. When enabled, the
SIR block uses the UnTx and UnRx pins for the SIR protocol, which should be connected to an IR
transceiver.
The SIR block can receive and transmit, but it is only half-duplex so it cannot do both at the same
time. Transmission must be stopped before data can be received. The IrDA SIR physical layer
specifies a minimum 10-ms delay between transmission and reception.
11.3 Initialization and Configuration
To use the UART, the peripheral clock must be enabled by setting the UART0 bit in the RCGC1
register.
This section discusses the steps that are required for using a UART module. For this example, the
system clock is assumed to be 20 MHz and the desired UART configuration is:
■ 115200 baud rate
■ Data length of 8 bits
■ One stop bit
236 November 30, 2007
Preliminary
Universal Asynchronous Receivers/Transmitters (UARTs)
■ No parity
■ FIFOs disabled
■ No interrupts
The first thing to consider when programming the UART is the baud-rate divisor (BRD), since the
UARTIBRD and UARTFBRD registers must be written before the UARTLCRH register. Using the
equation described in “Baud-Rate Generation” on page 233, the BRD can be calculated:
BRD = 20,000,000 / (16 * 115,200) = 10.8507
which means that the DIVINT field of the UARTIBRD register (see page 246) should be set to 10.
The value to be loaded into the UARTFBRD register (see page 247) is calculated by the equation:
UARTFBRD[DIVFRAC] = integer(0.8507 * 64 + 0.5) = 54
With the BRD values in hand, the UART configuration is written to the module in the following order:
1. Disable the UART by clearing the UARTEN bit in the UARTCTL register.
2. Write the integer portion of the BRD to the UARTIBRD register.
3. Write the fractional portion of the BRD to the UARTFBRD register.
4. Write the desired serial parameters to the UARTLCRH register (in this case, a value of
0x0000.0060).
5. Enable the UART by setting the UARTEN bit in the UARTCTL register.
11.4 Register Map
Table 11-1 on page 237 lists the UART registers. The offset listed is a hexadecimal increment to the
register’s address, relative to that UART’s base address:
■ UART0: 0x4000.C000
Note: The UART must be disabled (see the UARTEN bit in the UARTCTL register on page 250)
before any of the control registers are reprogrammed. When the UART is disabled during
a TX or RX operation, the current transaction is completed prior to the UART stopping.
Table 11-1. UART Register Map
See
Offset Name Type Reset Description page
0x000 UARTDR R/W 0x0000.0000 UART Data 239
0x004 UARTRSR/UARTECR R/W 0x0000.0000 UART Receive Status/Error Clear 241
0x018 UARTFR RO 0x0000.0090 UART Flag 243
0x020 UARTILPR R/W 0x0000.0000 UART IrDA Low-Power Register 245
0x024 UARTIBRD R/W 0x0000.0000 UART Integer Baud-Rate Divisor 246
0x028 UARTFBRD R/W 0x0000.0000 UART Fractional Baud-Rate Divisor 247
November 30, 2007 237
Preliminary
LM3S6110 Microcontroller
See
Offset Name Type Reset Description page
0x02C UARTLCRH R/W 0x0000.0000 UART Line Control 248
0x030 UARTCTL R/W 0x0000.0300 UART Control 250
0x034 UARTIFLS R/W 0x0000.0012 UART Interrupt FIFO Level Select 252
0x038 UARTIM R/W 0x0000.0000 UART Interrupt Mask 254
0x03C UARTRIS RO 0x0000.000F UART Raw Interrupt Status 256
0x040 UARTMIS RO 0x0000.0000 UART Masked Interrupt Status 257
0x044 UARTICR W1C 0x0000.0000 UART Interrupt Clear 258
0xFD0 UARTPeriphID4 RO 0x0000.0000 UART Peripheral Identification 4 260
0xFD4 UARTPeriphID5 RO 0x0000.0000 UART Peripheral Identification 5 261
0xFD8 UARTPeriphID6 RO 0x0000.0000 UART Peripheral Identification 6 262
0xFDC UARTPeriphID7 RO 0x0000.0000 UART Peripheral Identification 7 263
0xFE0 UARTPeriphID0 RO 0x0000.0011 UART Peripheral Identification 0 264
0xFE4 UARTPeriphID1 RO 0x0000.0000 UART Peripheral Identification 1 265
0xFE8 UARTPeriphID2 RO 0x0000.0018 UART Peripheral Identification 2 266
0xFEC UARTPeriphID3 RO 0x0000.0001 UART Peripheral Identification 3 267
0xFF0 UARTPCellID0 RO 0x0000.000D UART PrimeCell Identification 0 268
0xFF4 UARTPCellID1 RO 0x0000.00F0 UART PrimeCell Identification 1 269
0xFF8 UARTPCellID2 RO 0x0000.0005 UART PrimeCell Identification 2 270
0xFFC UARTPCellID3 RO 0x0000.00B1 UART PrimeCell Identification 3 271
11.5 Register Descriptions
The remainder of this section lists and describes the UART registers, in numerical order by address
offset.
238 November 30, 2007
Preliminary
Universal Asynchronous Receivers/Transmitters (UARTs)
Register 1: UART Data (UARTDR), offset 0x000
This register is the data register (the interface to the FIFOs).
When FIFOs are enabled, data written to this location is pushed onto the transmit FIFO. If FIFOs
are disabled, data is stored in the transmitter holding register (the bottom word of the transmit FIFO).
A write to this register initiates a transmission from the UART.
For received data, if the FIFO is enabled, the data byte and the 4-bit status (break, frame, parity,
and overrun) is pushed onto the 12-bit wide receive FIFO. If FIFOs are disabled, the data byte and
status are stored in the receiving holding register (the bottom word of the receive FIFO). The received
data can be retrieved by reading this register.
UART Data (UARTDR)
UART0 base: 0x4000.C000
Offset 0x000
Type R/W, reset 0x0000.0000
31 30 29 28 27 26 25 24 23 22 21 20 19 18 17 16
reserved
Type RO RO RO RO RO RO RO RO RO RO RO RO RO RO RO RO
Reset 0 0 0 0 0 0 0 0 0 0 0 0 0 0 0 0
15 14 13 12 11 10 9 8 7 6 5 4 3 2 1 0
reserved OE BE PE FE DATA
Type RO RO RO RO RO RO RO RO R/W R/W R/W R/W R/W R/W R/W R/W
Reset 0 0 0 0 0 0 0 0 0 0 0 0 0 0 0 0
Bit/Field Name Type Reset Description
Software should not rely on the value of a reserved bit. To provide
compatibility with future products, the value of a reserved bit should be
preserved across a read-modify-write operation.
31:12 reserved RO 0
UART Overrun Error
The OE values are defined as follows:
Value Description
0 There has been no data loss due to a FIFO overrun.
New data was received when the FIFO was full, resulting in
data loss.
1
11 OE RO 0
UART Break Error
This bit is set to 1 when a break condition is detected, indicating that
the receive data input was held Low for longer than a full-word
transmission time (defined as start, data, parity, and stop bits).
In FIFO mode, this error is associated with the character at the top of
the FIFO. When a break occurs, only one 0 character is loaded into the
FIFO. The next character is only enabled after the received data input
goes to a 1 (marking state) and the next valid start bit is received.
10 BE RO 0
UART Parity Error
This bit is set to 1 when the parity of the received data character does
not match the parity defined by bits 2 and 7 of the UARTLCRH register.
In FIFO mode, this error is associated with the character at the top of
the FIFO.
9 PE RO 0
November 30, 2007 239
Preliminary
LM3S6110 Microcontroller
Bit/Field Name Type Reset Description
UART Framing Error
This bit is set to 1 when the received character does not have a valid
stop bit (a valid stop bit is 1).
8 FE RO 0
Data Transmitted or Received
When written, the data that is to be transmitted via the UART. When
read, the data that was received by the UART.
7:0 DATA R/W 0
240 November 30, 2007
Preliminary
Universal Asynchronous Receivers/Transmitters (UARTs)
Register 2: UART Receive Status/Error Clear (UARTRSR/UARTECR), offset
0x004
The UARTRSR/UARTECR register is the receive status register/error clear register.
In addition to the UARTDR register, receive status can also be read from the UARTRSR register.
If the status is read from this register, then the status information corresponds to the entry read from
UARTDR prior to reading UARTRSR. The status information for overrun is set immediately when
an overrun condition occurs.
The UARTRSR register cannot be written.
A write of any value to the UARTECR register clears the framing, parity, break, and overrun errors.
All the bits are cleared to 0 on reset.
Read-Only Receive Status (UARTRSR) Register
UART Receive Status/Error Clear (UARTRSR/UARTECR)
UART0 base: 0x4000.C000
Offset 0x004
Type RO, reset 0x0000.0000
31 30 29 28 27 26 25 24 23 22 21 20 19 18 17 16
reserved
Type RO RO RO RO RO RO RO RO RO RO RO RO RO RO RO RO
Reset 0 0 0 0 0 0 0 0 0 0 0 0 0 0 0 0
15 14 13 12 11 10 9 8 7 6 5 4 3 2 1 0
reserved OE BE PE FE
Type RO RO RO RO RO RO RO RO RO RO RO RO RO RO RO RO
Reset 0 0 0 0 0 0 0 0 0 0 0 0 0 0 0 0
Bit/Field Name Type Reset Description
Software should not rely on the value of a reserved bit. To provide
compatibility with future products, the value of a reserved bit should be
preserved across a read-modify-write operation.
31:4 reserved RO 0
UART Overrun Error
When this bit is set to 1, data is received and the FIFO is already full.
This bit is cleared to 0 by a write to UARTECR.
The FIFO contents remain valid since no further data is written when
the FIFO is full, only the contents of the shift register are overwritten.
The CPU must now read the data in order to empty the FIFO.
3 OE RO 0
UART Break Error
This bit is set to 1 when a break condition is detected, indicating that
the received data input was held Low for longer than a full-word
transmission time (defined as start, data, parity, and stop bits).
This bit is cleared to 0 by a write to UARTECR.
In FIFO mode, this error is associated with the character at the top of
the FIFO. When a break occurs, only one 0 character is loaded into the
FIFO. The next character is only enabled after the receive data input
goes to a 1 (marking state) and the next valid start bit is received.
2 BE RO 0
November 30, 2007 241
Preliminary
LM3S6110 Microcontroller
Bit/Field Name Type Reset Description
UART Parity Error
This bit is set to 1 when the parity of the received data character does
not match the parity defined by bits 2 and 7 of the UARTLCRH register.
This bit is cleared to 0 by a write to UARTECR.
1 PE RO 0
UART Framing Error
This bit is set to 1 when the received character does not have a valid
stop bit (a valid stop bit is 1).
This bit is cleared to 0 by a write to UARTECR.
In FIFO mode, this error is associated with the character at the top of
the FIFO.
0 FE RO 0
Write-Only Error Clear (UARTECR) Register
UART Receive Status/Error Clear (UARTRSR/UARTECR)
UART0 base: 0x4000.C000
Offset 0x004
Type WO, reset 0x0000.0000
31 30 29 28 27 26 25 24 23 22 21 20 19 18 17 16
reserved
Type WO WO WO WO WO WO WO WO WO WO WO WO WO WO WO WO
Reset 0 0 0 0 0 0 0 0 0 0 0 0 0 0 0 0
15 14 13 12 11 10 9 8 7 6 5 4 3 2 1 0
reserved DATA
Type WO WO WO WO WO WO WO WO WO WO WO WO WO WO WO WO
Reset 0 0 0 0 0 0 0 0 0 0 0 0 0 0 0 0
Bit/Field Name Type Reset Description
Software should not rely on the value of a reserved bit. To provide
compatibility with future products, the value of a reserved bit should be
preserved across a read-modify-write operation.
31:8 reserved WO 0
Error Clear
A write to this register of any data clears the framing, parity, break, and
overrun flags.
7:0 DATA WO 0
242 November 30, 2007
Preliminary
Universal Asynchronous Receivers/Transmitters (UARTs)
Register 3: UART Flag (UARTFR), offset 0x018
The UARTFR register is the flag register. After reset, the TXFF, RXFF, and BUSY bits are 0, and
TXFE and RXFE bits are 1.
UART Flag (UARTFR)
UART0 base: 0x4000.C000
Offset 0x018
Type RO, reset 0x0000.0090
31 30 29 28 27 26 25 24 23 22 21 20 19 18 17 16
reserved
Type RO RO RO RO RO RO RO RO RO RO RO RO RO RO RO RO
Reset 0 0 0 0 0 0 0 0 0 0 0 0 0 0 0 0
15 14 13 12 11 10 9 8 7 6 5 4 3 2 1 0
reserved TXFE RXFF TXFF RXFE BUSY reserved
Type RO RO RO RO RO RO RO RO RO RO RO RO RO RO RO RO
Reset 0 0 0 0 0 0 0 0 1 0 0 1 0 0 0 0
Bit/Field Name Type Reset Description
Software should not rely on the value of a reserved bit. To provide
compatibility with future products, the value of a reserved bit should be
preserved across a read-modify-write operation.
31:8 reserved RO 0
UART Transmit FIFO Empty
The meaning of this bit depends on the state of the FEN bit in the
UARTLCRH register.
If the FIFO is disabled (FEN is 0), this bit is set when the transmit holding
register is empty.
If the FIFO is enabled (FEN is 1), this bit is set when the transmit FIFO
is empty.
7 TXFE RO 1
UART Receive FIFO Full
The meaning of this bit depends on the state of the FEN bit in the
UARTLCRH register.
If the FIFO is disabled, this bit is set when the receive holding register
is full.
If the FIFO is enabled, this bit is set when the receive FIFO is full.
6 RXFF RO 0
UART Transmit FIFO Full
The meaning of this bit depends on the state of the FEN bit in the
UARTLCRH register.
If the FIFO is disabled, this bit is set when the transmit holding register
is full.
If the FIFO is enabled, this bit is set when the transmit FIFO is full.
5 TXFF RO 0
UART Receive FIFO Empty
The meaning of this bit depends on the state of the FEN bit in the
UARTLCRH register.
If the FIFO is disabled, this bit is set when the receive holding register
is empty.
If the FIFO is enabled, this bit is set when the receive FIFO is empty.
4 RXFE RO 1
November 30, 2007 243
Preliminary
LM3S6110 Microcontroller
Bit/Field Name Type Reset Description
UART Busy
When this bit is 1, the UART is busy transmitting data. This bit remains
set until the complete byte, including all stop bits, has been sent from
the shift register.
This bit is set as soon as the transmit FIFO becomes non-empty
(regardless of whether UART is enabled).
3 BUSY RO 0
Software should not rely on the value of a reserved bit. To provide
compatibility with future products, the value of a reserved bit should be
preserved across a read-modify-write operation.
2:0 reserved RO 0
244 November 30, 2007
Preliminary
Universal Asynchronous Receivers/Transmitters (UARTs)
Register 4: UART IrDA Low-Power Register (UARTILPR), offset 0x020
The UARTILPR register is an 8-bit read/write register that stores the low-power counter divisor
value used to generate the IrLPBaud16 signal by dividing down the system clock (SysClk). All the
bits are cleared to 0 when reset.
The IrLPBaud16 internal signal is generated by dividing down the UARTCLK signal according to
the low-power divisor value written to UARTILPR. The low-power divisor value is calculated as
follows:
ILPDVSR = SysClk / FIrLPBaud16
where FIrLPBaud16 is nominally 1.8432 MHz.
IrLPBaud16 is an internal signal used for SIR pulse generation when low-power mode is used.
You must choose the divisor so that 1.42 MHz < FIrLPBaud16 < 2.12 MHz, which results in a low-power
pulse duration of 1.41–2.11 μs (three times the period of IrLPBaud16). The minimum frequency
of IrLPBaud16 ensures that pulses less than one period of IrLPBaud16 are rejected, but that
pulses greater than 1.4 μs are accepted as valid pulses.
Note: Zero is an illegal value. Programming a zero value results in no IrLPBaud16 pulses being
generated.
UART IrDA Low-Power Register (UARTILPR)
UART0 base: 0x4000.C000
Offset 0x020
Type R/W, reset 0x0000.0000
31 30 29 28 27 26 25 24 23 22 21 20 19 18 17 16
reserved
Type RO RO RO RO RO RO RO RO RO RO RO RO RO RO RO RO
Reset 0 0 0 0 0 0 0 0 0 0 0 0 0 0 0 0
15 14 13 12 11 10 9 8 7 6 5 4 3 2 1 0
reserved ILPDVSR
Type RO RO RO RO RO RO RO RO R/W R/W R/W R/W R/W R/W R/W R/W
Reset 0 0 0 0 0 0 0 0 0 0 0 0 0 0 0 0
Bit/Field Name Type Reset Description
Software should not rely on the value of a reserved bit. To provide
compatibility with future products, the value of a reserved bit should be
preserved across a read-modify-write operation.
31:8 reserved RO 0
IrDA Low-Power Divisor
This is an 8-bit low-power divisor value.
7:0 ILPDVSR R/W 0x00
November 30, 2007 245
Preliminary
LM3S6110 Microcontroller
Register 5: UART Integer Baud-Rate Divisor (UARTIBRD), offset 0x024
The UARTIBRD register is the integer part of the baud-rate divisor value. All the bits are cleared
on reset. The minimum possible divide ratio is 1 (when UARTIBRD=0), in which case the UARTFBRD
register is ignored. When changing the UARTIBRD register, the new value does not take effect until
transmission/reception of the current character is complete. Any changes to the baud-rate divisor
must be followed by a write to the UARTLCRH register. See “Baud-Rate Generation” on page 233
for configuration details.
UART Integer Baud-Rate Divisor (UARTIBRD)
UART0 base: 0x4000.C000
Offset 0x024
Type R/W, reset 0x0000.0000
31 30 29 28 27 26 25 24 23 22 21 20 19 18 17 16
reserved
Type RO RO RO RO RO RO RO RO RO RO RO RO RO RO RO RO
Reset 0 0 0 0 0 0 0 0 0 0 0 0 0 0 0 0
15 14 13 12 11 10 9 8 7 6 5 4 3 2 1 0
DIVINT
Type R/W R/W R/W R/W R/W R/W R/W R/W R/W R/W R/W R/W R/W R/W R/W R/W
Reset 0 0 0 0 0 0 0 0 0 0 0 0 0 0 0 0
Bit/Field Name Type Reset Description
Software should not rely on the value of a reserved bit. To provide
compatibility with future products, the value of a reserved bit should be
preserved across a read-modify-write operation.
31:16 reserved RO 0
15:0 DIVINT R/W 0x0000 Integer Baud-Rate Divisor
246 November 30, 2007
Preliminary
Universal Asynchronous Receivers/Transmitters (UARTs)
Register 6: UART Fractional Baud-Rate Divisor (UARTFBRD), offset 0x028
The UARTFBRD register is the fractional part of the baud-rate divisor value. All the bits are cleared
on reset. When changing the UARTFBRD register, the new value does not take effect until
transmission/reception of the current character is complete. Any changes to the baud-rate divisor
must be followed by a write to the UARTLCRH register. See “Baud-Rate Generation” on page 233
for configuration details.
UART Fractional Baud-Rate Divisor (UARTFBRD)
UART0 base: 0x4000.C000
Offset 0x028
Type R/W, reset 0x0000.0000
31 30 29 28 27 26 25 24 23 22 21 20 19 18 17 16
reserved
Type RO RO RO RO RO RO RO RO RO RO RO RO RO RO RO RO
Reset 0 0 0 0 0 0 0 0 0 0 0 0 0 0 0 0
15 14 13 12 11 10 9 8 7 6 5 4 3 2 1 0
reserved DIVFRAC
Type RO RO RO RO RO RO RO RO RO RO R/W R/W R/W R/W R/W R/W
Reset 0 0 0 0 0 0 0 0 0 0 0 0 0 0 0 0
Bit/Field Name Type Reset Description
Software should not rely on the value of a reserved bit. To provide
compatibility with future products, the value of a reserved bit should be
preserved across a read-modify-write operation.
31:6 reserved RO 0x00
5:0 DIVFRAC R/W 0x000 Fractional Baud-Rate Divisor
November 30, 2007 247
Preliminary
LM3S6110 Microcontroller
Register 7: UART Line Control (UARTLCRH), offset 0x02C
The UARTLCRH register is the line control register. Serial parameters such as data length, parity,
and stop bit selection are implemented in this register.
When updating the baud-rate divisor (UARTIBRD and/or UARTIFRD), the UARTLCRH register
must also be written. The write strobe for the baud-rate divisor registers is tied to the UARTLCRH
register.
UART Line Control (UARTLCRH)
UART0 base: 0x4000.C000
Offset 0x02C
Type R/W, reset 0x0000.0000
31 30 29 28 27 26 25 24 23 22 21 20 19 18 17 16
reserved
Type RO RO RO RO RO RO RO RO RO RO RO RO RO RO RO RO
Reset 0 0 0 0 0 0 0 0 0 0 0 0 0 0 0 0
15 14 13 12 11 10 9 8 7 6 5 4 3 2 1 0
reserved SPS WLEN FEN STP2 EPS PEN BRK
Type RO RO RO RO RO RO RO RO R/W R/W R/W R/W R/W R/W R/W R/W
Reset 0 0 0 0 0 0 0 0 0 0 0 0 0 0 0 0
Bit/Field Name Type Reset Description
Software should not rely on the value of a reserved bit. To provide
compatibility with future products, the value of a reserved bit should be
preserved across a read-modify-write operation.
31:8 reserved RO 0
UART Stick Parity Select
When bits 1, 2, and 7 of UARTLCRH are set, the parity bit is transmitted
and checked as a 0. When bits 1 and 7 are set and 2 is cleared, the
parity bit is transmitted and checked as a 1.
When this bit is cleared, stick parity is disabled.
7 SPS R/W 0
UART Word Length
The bits indicate the number of data bits transmitted or received in a
frame as follows:
Value Description
0x3 8 bits
0x2 7 bits
0x1 6 bits
0x0 5 bits (default)
6:5 WLEN R/W 0
UART Enable FIFOs
If this bit is set to 1, transmit and receive FIFO buffers are enabled (FIFO
mode).
When cleared to 0, FIFOs are disabled (Character mode). The FIFOs
become 1-byte-deep holding registers.
4 FEN R/W 0
UART Two Stop Bits Select
If this bit is set to 1, two stop bits are transmitted at the end of a frame.
The receive logic does not check for two stop bits being received.
3 STP2 R/W 0
248 November 30, 2007
Preliminary
Universal Asynchronous Receivers/Transmitters (UARTs)
Bit/Field Name Type Reset Description
UART Even Parity Select
If this bit is set to 1, even parity generation and checking is performed
during transmission and reception, which checks for an even number
of 1s in data and parity bits.
When cleared to 0, then odd parity is performed, which checks for an
odd number of 1s.
This bit has no effect when parity is disabled by the PEN bit.
2 EPS R/W 0
UART Parity Enable
If this bit is set to 1, parity checking and generation is enabled; otherwise,
parity is disabled and no parity bit is added to the data frame.
1 PEN R/W 0
UART Send Break
If this bit is set to 1, a Low level is continually output on the UnTX output,
after completing transmission of the current character. For the proper
execution of the break command, the software must set this bit for at
least two frames (character periods). For normal use, this bit must be
cleared to 0.
0 BRK R/W 0
November 30, 2007 249
Preliminary
LM3S6110 Microcontroller
Register 8: UART Control (UARTCTL), offset 0x030
The UARTCTL register is the control register. All the bits are cleared on reset except for the
Transmit Enable (TXE) and Receive Enable (RXE) bits, which are set to 1.
To enable the UART module, the UARTEN bit must be set to 1. If software requires a configuration
change in the module, the UARTEN bit must be cleared before the configuration changes are written.
If the UART is disabled during a transmit or receive operation, the current transaction is completed
prior to the UART stopping.
UART Control (UARTCTL)
UART0 base: 0x4000.C000
Offset 0x030
Type R/W, reset 0x0000.0300
31 30 29 28 27 26 25 24 23 22 21 20 19 18 17 16
reserved
Type RO RO RO RO RO RO RO RO RO RO RO RO RO RO RO RO
Reset 0 0 0 0 0 0 0 0 0 0 0 0 0 0 0 0
15 14 13 12 11 10 9 8 7 6 5 4 3 2 1 0
reserved RXE TXE LBE reserved SIRLP SIREN UARTEN
Type RO RO RO RO RO RO R/W R/W R/W RO RO RO RO R/W R/W R/W
Reset 0 0 0 0 0 0 1 1 0 0 0 0 0 0 0 0
Bit/Field Name Type Reset Description
Software should not rely on the value of a reserved bit. To provide
compatibility with future products, the value of a reserved bit should be
preserved across a read-modify-write operation.
31:10 reserved RO 0
UART Receive Enable
If this bit is set to 1, the receive section of the UART is enabled. When
the UART is disabled in the middle of a receive, it completes the current
character before stopping.
Note: To enable reception, the UARTEN bit must also be set.
9 RXE R/W 1
UART Transmit Enable
If this bit is set to 1, the transmit section of the UART is enabled. When
the UART is disabled in the middle of a transmission, it completes the
current character before stopping.
Note: To enable transmission, the UARTEN bit must also be set.
8 TXE R/W 1
UART Loop Back Enable
If this bit is set to 1, the UnTX path is fed through the UnRX path.
7 LBE R/W 0
Software should not rely on the value of a reserved bit. To provide
compatibility with future products, the value of a reserved bit should be
preserved across a read-modify-write operation.
6:3 reserved RO 0
250 November 30, 2007
Preliminary
Universal Asynchronous Receivers/Transmitters (UARTs)
Bit/Field Name Type Reset Description
UART SIR Low Power Mode
This bit selects the IrDA encoding mode. If this bit is cleared to 0,
low-level bits are transmitted as an active High pulse with a width of
3/16th of the bit period. If this bit is set to 1, low-level bits are transmitted
with a pulse width which is 3 times the period of the IrLPBaud16 input
signal, regardless of the selected bit rate. Setting this bit uses less power,
but might reduce transmission distances. See page 245 for more
information.
2 SIRLP R/W 0
UART SIR Enable
If this bit is set to 1, the IrDA SIR block is enabled, and the UART will
transmit and receive data using SIR protocol.
1 SIREN R/W 0
UART Enable
If this bit is set to 1, the UART is enabled. When the UART is disabled
in the middle of transmission or reception, it completes the current
character before stopping.
0 UARTEN R/W 0
November 30, 2007 251
Preliminary
LM3S6110 Microcontroller
Register 9: UART Interrupt FIFO Level Select (UARTIFLS), offset 0x034
The UARTIFLS register is the interrupt FIFO level select register. You can use this register to define
the FIFO level at which the TXRIS and RXRIS bits in the UARTRIS register are triggered.
The interrupts are generated based on a transition through a level rather than being based on the
level. That is, the interrupts are generated when the fill level progresses through the trigger level.
For example, if the receive trigger level is set to the half-way mark, the interrupt is triggered as the
module is receiving the 9th character.
Out of reset, the TXIFLSEL and RXIFLSEL bits are configured so that the FIFOs trigger an interrupt
at the half-way mark.
UART Interrupt FIFO Level Select (UARTIFLS)
UART0 base: 0x4000.C000
Offset 0x034
Type R/W, reset 0x0000.0012
31 30 29 28 27 26 25 24 23 22 21 20 19 18 17 16
reserved
Type RO RO RO RO RO RO RO RO RO RO RO RO RO RO RO RO
Reset 0 0 0 0 0 0 0 0 0 0 0 0 0 0 0 0
15 14 13 12 11 10 9 8 7 6 5 4 3 2 1 0
reserved RXIFLSEL TXIFLSEL
Type RO RO RO RO RO RO RO RO RO RO R/W R/W R/W R/W R/W R/W
Reset 0 0 0 0 0 0 0 0 0 0 0 1 0 0 1 0
Bit/Field Name Type Reset Description
Software should not rely on the value of a reserved bit. To provide
compatibility with future products, the value of a reserved bit should be
preserved across a read-modify-write operation.
31:6 reserved RO 0x00
UART Receive Interrupt FIFO Level Select
The trigger points for the receive interrupt are as follows:
Value Description
0x0 RX FIFO ≥ 1/8 full
0x1 RX FIFO ≥ ¼ full
0x2 RX FIFO ≥ ½ full (default)
0x3 RX FIFO ≥ ¾ full
0x4 RX FIFO ≥ 7/8 full
0x5-0x7 Reserved
5:3 RXIFLSEL R/W 0x2
252 November 30, 2007
Preliminary
Universal Asynchronous Receivers/Transmitters (UARTs)
Bit/Field Name Type Reset Description
UART Transmit Interrupt FIFO Level Select
The trigger points for the transmit interrupt are as follows:
Value Description
0x0 TX FIFO ≤ 1/8 full
0x1 TX FIFO ≤ ¼ full
0x2 TX FIFO ≤ ½ full (default)
0x3 TX FIFO ≤ ¾ full
0x4 TX FIFO ≤ 7/8 full
0x5-0x7 Reserved
2:0 TXIFLSEL R/W 0x2
November 30, 2007 253
Preliminary
LM3S6110 Microcontroller
Register 10: UART Interrupt Mask (UARTIM), offset 0x038
The UARTIM register is the interrupt mask set/clear register.
On a read, this register gives the current value of the mask on the relevant interrupt. Writing a 1 to
a bit allows the corresponding raw interrupt signal to be routed to the interrupt controller. Writing a
0 prevents the raw interrupt signal from being sent to the interrupt controller.
UART Interrupt Mask (UARTIM)
UART0 base: 0x4000.C000
Offset 0x038
Type R/W, reset 0x0000.0000
31 30 29 28 27 26 25 24 23 22 21 20 19 18 17 16
reserved
Type RO RO RO RO RO RO RO RO RO RO RO RO RO RO RO RO
Reset 0 0 0 0 0 0 0 0 0 0 0 0 0 0 0 0
15 14 13 12 11 10 9 8 7 6 5 4 3 2 1 0
reserved OEIM BEIM PEIM FEIM RTIM TXIM RXIM reserved
Type RO RO RO RO RO R/W R/W R/W R/W R/W R/W R/W RO RO RO RO
Reset 0 0 0 0 0 0 0 0 0 0 0 0 0 0 0 0
Bit/Field Name Type Reset Description
Software should not rely on the value of a reserved bit. To provide
compatibility with future products, the value of a reserved bit should be
preserved across a read-modify-write operation.
31:11 reserved RO 0x00
UART Overrun Error Interrupt Mask
On a read, the current mask for the OEIM interrupt is returned.
Setting this bit to 1 promotes the OEIM interrupt to the interrupt controller.
10 OEIM R/W 0
UART Break Error Interrupt Mask
On a read, the current mask for the BEIM interrupt is returned.
Setting this bit to 1 promotes the BEIM interrupt to the interrupt controller.
9 BEIM R/W 0
UART Parity Error Interrupt Mask
On a read, the current mask for the PEIM interrupt is returned.
Setting this bit to 1 promotes the PEIM interrupt to the interrupt controller.
8 PEIM R/W 0
UART Framing Error Interrupt Mask
On a read, the current mask for the FEIM interrupt is returned.
Setting this bit to 1 promotes the FEIM interrupt to the interrupt controller.
7 FEIM R/W 0
UART Receive Time-Out Interrupt Mask
On a read, the current mask for the RTIM interrupt is returned.
Setting this bit to 1 promotes the RTIM interrupt to the interrupt controller.
6 RTIM R/W 0
UART Transmit Interrupt Mask
On a read, the current mask for the TXIM interrupt is returned.
Setting this bit to 1 promotes the TXIM interrupt to the interrupt controller.
5 TXIM R/W 0
254 November 30, 2007
Preliminary
Universal Asynchronous Receivers/Transmitters (UARTs)
Bit/Field Name Type Reset Description
UART Receive Interrupt Mask
On a read, the current mask for the RXIM interrupt is returned.
Setting this bit to 1 promotes the RXIM interrupt to the interrupt controller.
4 RXIM R/W 0
Software should not rely on the value of a reserved bit. To provide
compatibility with future products, the value of a reserved bit should be
preserved across a read-modify-write operation.
3:0 reserved RO 0x00
November 30, 2007 255
Preliminary
LM3S6110 Microcontroller
Register 11: UART Raw Interrupt Status (UARTRIS), offset 0x03C
The UARTRIS register is the raw interrupt status register. On a read, this register gives the current
raw status value of the corresponding interrupt. A write has no effect.
UART Raw Interrupt Status (UARTRIS)
UART0 base: 0x4000.C000
Offset 0x03C
Type RO, reset 0x0000.000F
31 30 29 28 27 26 25 24 23 22 21 20 19 18 17 16
reserved
Type RO RO RO RO RO RO RO RO RO RO RO RO RO RO RO RO
Reset 0 0 0 0 0 0 0 0 0 0 0 0 0 0 0 0
15 14 13 12 11 10 9 8 7 6 5 4 3 2 1 0
reserved OERIS BERIS PERIS FERIS RTRIS TXRIS RXRIS reserved
Type RO RO RO RO RO RO RO RO RO RO RO RO RO RO RO RO
Reset 0 0 0 0 0 0 0 0 0 0 0 0 1 1 1 1
Bit/Field Name Type Reset Description
Software should not rely on the value of a reserved bit. To provide
compatibility with future products, the value of a reserved bit should be
preserved across a read-modify-write operation.
31:11 reserved RO 0x00
UART Overrun Error Raw Interrupt Status
Gives the raw interrupt state (prior to masking) of this interrupt.
10 OERIS RO 0
UART Break Error Raw Interrupt Status
Gives the raw interrupt state (prior to masking) of this interrupt.
9 BERIS RO 0
UART Parity Error Raw Interrupt Status
Gives the raw interrupt state (prior to masking) of this interrupt.
8 PERIS RO 0
UART Framing Error Raw Interrupt Status
Gives the raw interrupt state (prior to masking) of this interrupt.
7 FERIS RO 0
UART Receive Time-Out Raw Interrupt Status
Gives the raw interrupt state (prior to masking) of this interrupt.
6 RTRIS RO 0
UART Transmit Raw Interrupt Status
Gives the raw interrupt state (prior to masking) of this interrupt.
5 TXRIS RO 0
UART Receive Raw Interrupt Status
Gives the raw interrupt state (prior to masking) of this interrupt.
4 RXRIS RO 0
Software should not rely on the value of a reserved bit. To provide
compatibility with future products, the value of a reserved bit should be
preserved across a read-modify-write operation.
3:0 reserved RO 0xF
256 November 30, 2007
Preliminary
Universal Asynchronous Receivers/Transmitters (UARTs)
Register 12: UART Masked Interrupt Status (UARTMIS), offset 0x040
The UARTMIS register is the masked interrupt status register. On a read, this register gives the
current masked status value of the corresponding interrupt. A write has no effect.
UART Masked Interrupt Status (UARTMIS)
UART0 base: 0x4000.C000
Offset 0x040
Type RO, reset 0x0000.0000
31 30 29 28 27 26 25 24 23 22 21 20 19 18 17 16
reserved
Type RO RO RO RO RO RO RO RO RO RO RO RO RO RO RO RO
Reset 0 0 0 0 0 0 0 0 0 0 0 0 0 0 0 0
15 14 13 12 11 10 9 8 7 6 5 4 3 2 1 0
reserved OEMIS BEMIS PEMIS FEMIS RTMIS TXMIS RXMIS reserved
Type RO RO RO RO RO RO RO RO RO RO RO RO RO RO RO RO
Reset 0 0 0 0 0 0 0 0 0 0 0 0 0 0 0 0
Bit/Field Name Type Reset Description
Software should not rely on the value of a reserved bit. To provide
compatibility with future products, the value of a reserved bit should be
preserved across a read-modify-write operation.
31:11 reserved RO 0x00
UART Overrun Error Masked Interrupt Status
Gives the masked interrupt state of this interrupt.
10 OEMIS RO 0
UART Break Error Masked Interrupt Status
Gives the masked interrupt state of this interrupt.
9 BEMIS RO 0
UART Parity Error Masked Interrupt Status
Gives the masked interrupt state of this interrupt.
8 PEMIS RO 0
UART Framing Error Masked Interrupt Status
Gives the masked interrupt state of this interrupt.
7 FEMIS RO 0
UART Receive Time-Out Masked Interrupt Status
Gives the masked interrupt state of this interrupt.
6 RTMIS RO 0
UART Transmit Masked Interrupt Status
Gives the masked interrupt state of this interrupt.
5 TXMIS RO 0
UART Receive Masked Interrupt Status
Gives the masked interrupt state of this interrupt.
4 RXMIS RO 0
Software should not rely on the value of a reserved bit. To provide
compatibility with future products, the value of a reserved bit should be
preserved across a read-modify-write operation.
3:0 reserved RO 0
November 30, 2007 257
Preliminary
LM3S6110 Microcontroller
Register 13: UART Interrupt Clear (UARTICR), offset 0x044
The UARTICR register is the interrupt clear register. On a write of 1, the corresponding interrupt
(both raw interrupt and masked interrupt, if enabled) is cleared. A write of 0 has no effect.
UART Interrupt Clear (UARTICR)
UART0 base: 0x4000.C000
Offset 0x044
Type W1C, reset 0x0000.0000
31 30 29 28 27 26 25 24 23 22 21 20 19 18 17 16
reserved
Type RO RO RO RO RO RO RO RO RO RO RO RO RO RO RO RO
Reset 0 0 0 0 0 0 0 0 0 0 0 0 0 0 0 0
15 14 13 12 11 10 9 8 7 6 5 4 3 2 1 0
reserved OEIC BEIC PEIC FEIC RTIC TXIC RXIC reserved
Type RO RO RO RO RO W1C W1C W1C W1C W1C W1C W1C RO RO RO RO
Reset 0 0 0 0 0 0 0 0 0 0 0 0 0 0 0 0
Bit/Field Name Type Reset Description
Software should not rely on the value of a reserved bit. To provide
compatibility with future products, the value of a reserved bit should be
preserved across a read-modify-write operation.
31:11 reserved RO 0x00
Overrun Error Interrupt Clear
The OEIC values are defined as follows:
Value Description
0 No effect on the interrupt.
1 Clears interrupt.
10 OEIC W1C 0
Break Error Interrupt Clear
The BEIC values are defined as follows:
Value Description
0 No effect on the interrupt.
1 Clears interrupt.
9 BEIC W1C 0
Parity Error Interrupt Clear
The PEIC values are defined as follows:
Value Description
0 No effect on the interrupt.
1 Clears interrupt.
8 PEIC W1C 0
Framing Error Interrupt Clear
The FEIC values are defined as follows:
Value Description
0 No effect on the interrupt.
1 Clears interrupt.
7 FEIC W1C 0
258 November 30, 2007
Preliminary
Universal Asynchronous Receivers/Transmitters (UARTs)
Bit/Field Name Type Reset Description
Receive Time-Out Interrupt Clear
The RTIC values are defined as follows:
Value Description
0 No effect on the interrupt.
1 Clears interrupt.
6 RTIC W1C 0
Transmit Interrupt Clear
The TXIC values are defined as follows:
Value Description
0 No effect on the interrupt.
1 Clears interrupt.
5 TXIC W1C 0
Receive Interrupt Clear
The RXIC values are defined as follows:
Value Description
0 No effect on the interrupt.
1 Clears interrupt.
4 RXIC W1C 0
Software should not rely on the value of a reserved bit. To provide
compatibility with future products, the value of a reserved bit should be
preserved across a read-modify-write operation.
3:0 reserved RO 0x00
November 30, 2007 259
Preliminary
LM3S6110 Microcontroller
Register 14: UART Peripheral Identification 4 (UARTPeriphID4), offset 0xFD0
The UARTPeriphIDn registers are hard-coded and the fields within the registers determine the
reset values.
UART Peripheral Identification 4 (UARTPeriphID4)
UART0 base: 0x4000.C000
Offset 0xFD0
Type RO, reset 0x0000.0000
31 30 29 28 27 26 25 24 23 22 21 20 19 18 17 16
reserved
Type RO RO RO RO RO RO RO RO RO RO RO RO RO RO RO RO
Reset 0 0 0 0 0 0 0 0 0 0 0 0 0 0 0 0
15 14 13 12 11 10 9 8 7 6 5 4 3 2 1 0
reserved PID4
Type RO RO RO RO RO RO RO RO RO RO RO RO RO RO RO RO
Reset 0 0 0 0 0 0 0 0 0 0 0 0 0 0 0 0
Bit/Field Name Type Reset Description
Software should not rely on the value of a reserved bit. To provide
compatibility with future products, the value of a reserved bit should be
preserved across a read-modify-write operation.
31:8 reserved RO 0x00
UART Peripheral ID Register[7:0]
Can be used by software to identify the presence of this peripheral.
7:0 PID4 RO 0x0000
260 November 30, 2007
Preliminary
Universal Asynchronous Receivers/Transmitters (UARTs)
Register 15: UART Peripheral Identification 5 (UARTPeriphID5), offset 0xFD4
The UARTPeriphIDn registers are hard-coded and the fields within the registers determine the
reset values.
UART Peripheral Identification 5 (UARTPeriphID5)
UART0 base: 0x4000.C000
Offset 0xFD4
Type RO, reset 0x0000.0000
31 30 29 28 27 26 25 24 23 22 21 20 19 18 17 16
reserved
Type RO RO RO RO RO RO RO RO RO RO RO RO RO RO RO RO
Reset 0 0 0 0 0 0 0 0 0 0 0 0 0 0 0 0
15 14 13 12 11 10 9 8 7 6 5 4 3 2 1 0
reserved PID5
Type RO RO RO RO RO RO RO RO RO RO RO RO RO RO RO RO
Reset 0 0 0 0 0 0 0 0 0 0 0 0 0 0 0 0
Bit/Field Name Type Reset Description
Software should not rely on the value of a reserved bit. To provide
compatibility with future products, the value of a reserved bit should be
preserved across a read-modify-write operation.
31:8 reserved RO 0x00
UART Peripheral ID Register[15:8]
Can be used by software to identify the presence of this peripheral.
7:0 PID5 RO 0x0000
November 30, 2007 261
Preliminary
LM3S6110 Microcontroller
Register 16: UART Peripheral Identification 6 (UARTPeriphID6), offset 0xFD8
The UARTPeriphIDn registers are hard-coded and the fields within the registers determine the
reset values.
UART Peripheral Identification 6 (UARTPeriphID6)
UART0 base: 0x4000.C000
Offset 0xFD8
Type RO, reset 0x0000.0000
31 30 29 28 27 26 25 24 23 22 21 20 19 18 17 16
reserved
Type RO RO RO RO RO RO RO RO RO RO RO RO RO RO RO RO
Reset 0 0 0 0 0 0 0 0 0 0 0 0 0 0 0 0
15 14 13 12 11 10 9 8 7 6 5 4 3 2 1 0
reserved PID6
Type RO RO RO RO RO RO RO RO RO RO RO RO RO RO RO RO
Reset 0 0 0 0 0 0 0 0 0 0 0 0 0 0 0 0
Bit/Field Name Type Reset Description
Software should not rely on the value of a reserved bit. To provide
compatibility with future products, the value of a reserved bit should be
preserved across a read-modify-write operation.
31:8 reserved RO 0x00
UART Peripheral ID Register[23:16]
Can be used by software to identify the presence of this peripheral.
7:0 PID6 RO 0x0000
262 November 30, 2007
Preliminary
Universal Asynchronous Receivers/Transmitters (UARTs)
Register 17: UART Peripheral Identification 7 (UARTPeriphID7), offset 0xFDC
The UARTPeriphIDn registers are hard-coded and the fields within the registers determine the
reset values.
UART Peripheral Identification 7 (UARTPeriphID7)
UART0 base: 0x4000.C000
Offset 0xFDC
Type RO, reset 0x0000.0000
31 30 29 28 27 26 25 24 23 22 21 20 19 18 17 16
reserved
Type RO RO RO RO RO RO RO RO RO RO RO RO RO RO RO RO
Reset 0 0 0 0 0 0 0 0 0 0 0 0 0 0 0 0
15 14 13 12 11 10 9 8 7 6 5 4 3 2 1 0
reserved PID7
Type RO RO RO RO RO RO RO RO RO RO RO RO RO RO RO RO
Reset 0 0 0 0 0 0 0 0 0 0 0 0 0 0 0 0
Bit/Field Name Type Reset Description
Software should not rely on the value of a reserved bit. To provide
compatibility with future products, the value of a reserved bit should be
preserved across a read-modify-write operation.
31:8 reserved RO 0
UART Peripheral ID Register[31:24]
Can be used by software to identify the presence of this peripheral.
7:0 PID7 RO 0x0000
November 30, 2007 263
Preliminary
LM3S6110 Microcontroller
Register 18: UART Peripheral Identification 0 (UARTPeriphID0), offset 0xFE0
The UARTPeriphIDn registers are hard-coded and the fields within the registers determine the
reset values.
UART Peripheral Identification 0 (UARTPeriphID0)
UART0 base: 0x4000.C000
Offset 0xFE0
Type RO, reset 0x0000.0011
31 30 29 28 27 26 25 24 23 22 21 20 19 18 17 16
reserved
Type RO RO RO RO RO RO RO RO RO RO RO RO RO RO RO RO
Reset 0 0 0 0 0 0 0 0 0 0 0 0 0 0 0 0
15 14 13 12 11 10 9 8 7 6 5 4 3 2 1 0
reserved PID0
Type RO RO RO RO RO RO RO RO RO RO RO RO RO RO RO RO
Reset 0 0 0 0 0 0 0 0 0 0 0 1 0 0 0 1
Bit/Field Name Type Reset Description
Software should not rely on the value of a reserved bit. To provide
compatibility with future products, the value of a reserved bit should be
preserved across a read-modify-write operation.
31:8 reserved RO 0x00
UART Peripheral ID Register[7:0]
Can be used by software to identify the presence of this peripheral.
7:0 PID0 RO 0x11
264 November 30, 2007
Preliminary
Universal Asynchronous Receivers/Transmitters (UARTs)
Register 19: UART Peripheral Identification 1 (UARTPeriphID1), offset 0xFE4
The UARTPeriphIDn registers are hard-coded and the fields within the registers determine the
reset values.
UART Peripheral Identification 1 (UARTPeriphID1)
UART0 base: 0x4000.C000
Offset 0xFE4
Type RO, reset 0x0000.0000
31 30 29 28 27 26 25 24 23 22 21 20 19 18 17 16
reserved
Type RO RO RO RO RO RO RO RO RO RO RO RO RO RO RO RO
Reset 0 0 0 0 0 0 0 0 0 0 0 0 0 0 0 0
15 14 13 12 11 10 9 8 7 6 5 4 3 2 1 0
reserved PID1
Type RO RO RO RO RO RO RO RO RO RO RO RO RO RO RO RO
Reset 0 0 0 0 0 0 0 0 0 0 0 0 0 0 0 0
Bit/Field Name Type Reset Description
Software should not rely on the value of a reserved bit. To provide
compatibility with future products, the value of a reserved bit should be
preserved across a read-modify-write operation.
31:8 reserved RO 0x00
UART Peripheral ID Register[15:8]
Can be used by software to identify the presence of this peripheral.
7:0 PID1 RO 0x00
November 30, 2007 265
Preliminary
LM3S6110 Microcontroller
Register 20: UART Peripheral Identification 2 (UARTPeriphID2), offset 0xFE8
The UARTPeriphIDn registers are hard-coded and the fields within the registers determine the
reset values.
UART Peripheral Identification 2 (UARTPeriphID2)
UART0 base: 0x4000.C000
Offset 0xFE8
Type RO, reset 0x0000.0018
31 30 29 28 27 26 25 24 23 22 21 20 19 18 17 16
reserved
Type RO RO RO RO RO RO RO RO RO RO RO RO RO RO RO RO
Reset 0 0 0 0 0 0 0 0 0 0 0 0 0 0 0 0
15 14 13 12 11 10 9 8 7 6 5 4 3 2 1 0
reserved PID2
Type RO RO RO RO RO RO RO RO RO RO RO RO RO RO RO RO
Reset 0 0 0 0 0 0 0 0 0 0 0 1 1 0 0 0
Bit/Field Name Type Reset Description
Software should not rely on the value of a reserved bit. To provide
compatibility with future products, the value of a reserved bit should be
preserved across a read-modify-write operation.
31:8 reserved RO 0x00
UART Peripheral ID Register[23:16]
Can be used by software to identify the presence of this peripheral.
7:0 PID2 RO 0x18
266 November 30, 2007
Preliminary
Universal Asynchronous Receivers/Transmitters (UARTs)
Register 21: UART Peripheral Identification 3 (UARTPeriphID3), offset 0xFEC
The UARTPeriphIDn registers are hard-coded and the fields within the registers determine the
reset values.
UART Peripheral Identification 3 (UARTPeriphID3)
UART0 base: 0x4000.C000
Offset 0xFEC
Type RO, reset 0x0000.0001
31 30 29 28 27 26 25 24 23 22 21 20 19 18 17 16
reserved
Type RO RO RO RO RO RO RO RO RO RO RO RO RO RO RO RO
Reset 0 0 0 0 0 0 0 0 0 0 0 0 0 0 0 0
15 14 13 12 11 10 9 8 7 6 5 4 3 2 1 0
reserved PID3
Type RO RO RO RO RO RO RO RO RO RO RO RO RO RO RO RO
Reset 0 0 0 0 0 0 0 0 0 0 0 0 0 0 0 1
Bit/Field Name Type Reset Description
Software should not rely on the value of a reserved bit. To provide
compatibility with future products, the value of a reserved bit should be
preserved across a read-modify-write operation.
31:8 reserved RO 0x00
UART Peripheral ID Register[31:24]
Can be used by software to identify the presence of this peripheral.
7:0 PID3 RO 0x01
November 30, 2007 267
Preliminary
LM3S6110 Microcontroller
Register 22: UART PrimeCell Identification 0 (UARTPCellID0), offset 0xFF0
The UARTPCellIDn registers are hard-coded and the fields within the registers determine the reset
values.
UART PrimeCell Identification 0 (UARTPCellID0)
UART0 base: 0x4000.C000
Offset 0xFF0
Type RO, reset 0x0000.000D
31 30 29 28 27 26 25 24 23 22 21 20 19 18 17 16
reserved
Type RO RO RO RO RO RO RO RO RO RO RO RO RO RO RO RO
Reset 0 0 0 0 0 0 0 0 0 0 0 0 0 0 0 0
15 14 13 12 11 10 9 8 7 6 5 4 3 2 1 0
reserved CID0
Type RO RO RO RO RO RO RO RO RO RO RO RO RO RO RO RO
Reset 0 0 0 0 0 0 0 0 0 0 0 0 1 1 0 1
Bit/Field Name Type Reset Description
Software should not rely on the value of a reserved bit. To provide
compatibility with future products, the value of a reserved bit should be
preserved across a read-modify-write operation.
31:8 reserved RO 0x00
UART PrimeCell ID Register[7:0]
Provides software a standard cross-peripheral identification system.
7:0 CID0 RO 0x0D
268 November 30, 2007
Preliminary
Universal Asynchronous Receivers/Transmitters (UARTs)
Register 23: UART PrimeCell Identification 1 (UARTPCellID1), offset 0xFF4
The UARTPCellIDn registers are hard-coded and the fields within the registers determine the reset
values.
UART PrimeCell Identification 1 (UARTPCellID1)
UART0 base: 0x4000.C000
Offset 0xFF4
Type RO, reset 0x0000.00F0
31 30 29 28 27 26 25 24 23 22 21 20 19 18 17 16
reserved
Type RO RO RO RO RO RO RO RO RO RO RO RO RO RO RO RO
Reset 0 0 0 0 0 0 0 0 0 0 0 0 0 0 0 0
15 14 13 12 11 10 9 8 7 6 5 4 3 2 1 0
reserved CID1
Type RO RO RO RO RO RO RO RO RO RO RO RO RO RO RO RO
Reset 0 0 0 0 0 0 0 0 1 1 1 1 0 0 0 0
Bit/Field Name Type Reset Description
Software should not rely on the value of a reserved bit. To provide
compatibility with future products, the value of a reserved bit should be
preserved across a read-modify-write operation.
31:8 reserved RO 0x00
UART PrimeCell ID Register[15:8]
Provides software a standard cross-peripheral identification system.
7:0 CID1 RO 0xF0
November 30, 2007 269
Preliminary
LM3S6110 Microcontroller
Register 24: UART PrimeCell Identification 2 (UARTPCellID2), offset 0xFF8
The UARTPCellIDn registers are hard-coded and the fields within the registers determine the reset
values.
UART PrimeCell Identification 2 (UARTPCellID2)
UART0 base: 0x4000.C000
Offset 0xFF8
Type RO, reset 0x0000.0005
31 30 29 28 27 26 25 24 23 22 21 20 19 18 17 16
reserved
Type RO RO RO RO RO RO RO RO RO RO RO RO RO RO RO RO
Reset 0 0 0 0 0 0 0 0 0 0 0 0 0 0 0 0
15 14 13 12 11 10 9 8 7 6 5 4 3 2 1 0
reserved CID2
Type RO RO RO RO RO RO RO RO RO RO RO RO RO RO RO RO
Reset 0 0 0 0 0 0 0 0 0 0 0 0 0 1 0 1
Bit/Field Name Type Reset Description
Software should not rely on the value of a reserved bit. To provide
compatibility with future products, the value of a reserved bit should be
preserved across a read-modify-write operation.
31:8 reserved RO 0x00
UART PrimeCell ID Register[23:16]
Provides software a standard cross-peripheral identification system.
7:0 CID2 RO 0x05
270 November 30, 2007
Preliminary
Universal Asynchronous Receivers/Transmitters (UARTs)
Register 25: UART PrimeCell Identification 3 (UARTPCellID3), offset 0xFFC
The UARTPCellIDn registers are hard-coded and the fields within the registers determine the reset
values.
UART PrimeCell Identification 3 (UARTPCellID3)
UART0 base: 0x4000.C000
Offset 0xFFC
Type RO, reset 0x0000.00B1
31 30 29 28 27 26 25 24 23 22 21 20 19 18 17 16
reserved
Type RO RO RO RO RO RO RO RO RO RO RO RO RO RO RO RO
Reset 0 0 0 0 0 0 0 0 0 0 0 0 0 0 0 0
15 14 13 12 11 10 9 8 7 6 5 4 3 2 1 0
reserved CID3
Type RO RO RO RO RO RO RO RO RO RO RO RO RO RO RO RO
Reset 0 0 0 0 0 0 0 0 1 0 1 1 0 0 0 1
Bit/Field Name Type Reset Description
Software should not rely on the value of a reserved bit. To provide
compatibility with future products, the value of a reserved bit should be
preserved across a read-modify-write operation.
31:8 reserved RO 0x00
UART PrimeCell ID Register[31:24]
Provides software a standard cross-peripheral identification system.
7:0 CID3 RO 0xB1
November 30, 2007 271
Preliminary
LM3S6110 Microcontroller
12 Synchronous Serial Interface (SSI)
The Stellaris® Synchronous Serial Interface (SSI) is a master or slave interface for synchronous
serial communication with peripheral devices that have either Freescale SPI, MICROWIRE, or Texas
Instruments synchronous serial interfaces.
The Stellaris® SSI module has the following features:
■ Master or slave operation
■ Programmable clock bit rate and prescale
■ Separate transmit and receive FIFOs, 16 bits wide, 8 locations deep
■ Programmable interface operation for Freescale SPI, MICROWIRE, or Texas Instruments
synchronous serial interfaces
■ Programmable data frame size from 4 to 16 bits
■ Internal loopback test mode for diagnostic/debug testing
12.1 Block Diagram
Figure 12-1. SSI Module Block Diagram
Transmit/
Receive
Logic
Clock
Prescaler
SSICPSR
Control / Status
SSICR0
SSICR1
SSISR
Interrupt Control
SSIIM
SSIMIS
SSIRIS
SSIICR
SSIDR
TxFIFO
8 x 16
...
RxFIFO
8 x 16
...
System Clock
SSITx
SSIRx
SSIClk
SSIFss
Interrupt
Identification Registers
SSIPCellID0 SSIPeriphID0 SSIPeriphID4
SSIPCellID1 SSIPeriphID1 SSIPeriphID5
SSIPCellID2 SSIPeriphID2 SSIPeriphID6
SSIPCellID3 SSIPeriphID3 SSIPeriphID7
12.2 Functional Description
The SSI performs serial-to-parallel conversion on data received from a peripheral device. The CPU
accesses data, control, and status information. The transmit and receive paths are buffered with
272 November 30, 2007
Preliminary
Synchronous Serial Interface (SSI)
internal FIFO memories allowing up to eight 16-bit values to be stored independently in both transmit
and receive modes.
12.2.1 Bit Rate Generation
The SSI includes a programmable bit rate clock divider and prescaler to generate the serial output
clock. Bit rates are supported to 2 MHz and higher, although maximum bit rate is determined by
peripheral devices.
The serial bit rate is derived by dividing down the 25-MHz input clock. The clock is first divided by
an even prescale value CPSDVSR from 2 to 254, which is programmed in the SSI Clock Prescale
(SSICPSR) register (see page 291). The clock is further divided by a value from 1 to 256, which is
1 + SCR, where SCR is the value programmed in the SSI Control0 (SSICR0) register (see page 284).
The frequency of the output clock SSIClk is defined by:
FSSIClk = FSysClk / (CPSDVSR * (1 + SCR))
Note that although the SSIClk transmit clock can theoretically be 12.5 MHz, the module may not
be able to operate at that speed. For master mode, the system clock must be at least two times
faster than the SSIClk. For slave mode, the system clock must be at least 12 times faster than the
SSIClk.
See “Synchronous Serial Interface (SSI)” on page 422 to view SSI timing parameters.
12.2.2 FIFO Operation
12.2.2.1 Transmit FIFO
The common transmit FIFO is a 16-bit wide, 8-locations deep, first-in, first-out memory buffer. The
CPU writes data to the FIFO by writing the SSI Data (SSIDR) register (see page 288), and data is
stored in the FIFO until it is read out by the transmission logic.
When configured as a master or a slave, parallel data is written into the transmit FIFO prior to serial
conversion and transmission to the attached slave or master, respectively, through the SSITx pin.
12.2.2.2 Receive FIFO
The common receive FIFO is a 16-bit wide, 8-locations deep, first-in, first-out memory buffer.
Received data from the serial interface is stored in the buffer until read out by the CPU, which
accesses the read FIFO by reading the SSIDR register.
When configured as a master or slave, serial data received through the SSIRx pin is registered
prior to parallel loading into the attached slave or master receive FIFO, respectively.
12.2.3 Interrupts
The SSI can generate interrupts when the following conditions are observed:
■ Transmit FIFO service
■ Receive FIFO service
■ Receive FIFO time-out
■ Receive FIFO overrun
November 30, 2007 273
Preliminary
LM3S6110 Microcontroller
All of the interrupt events are ORed together before being sent to the interrupt controller, so the SSI
can only generate a single interrupt request to the controller at any given time. You can mask each
of the four individual maskable interrupts by setting the appropriate bits in the SSI Interrupt Mask
(SSIIM) register (see page 292). Setting the appropriate mask bit to 1 enables the interrupt.
Provision of the individual outputs, as well as a combined interrupt output, allows use of either a
global interrupt service routine, or modular device drivers to handle interrupts. The transmit and
receive dynamic dataflow interrupts have been separated from the status interrupts so that data
can be read or written in response to the FIFO trigger levels. The status of the individual interrupt
sources can be read from the SSI Raw Interrupt Status (SSIRIS) and SSI Masked Interrupt Status
(SSIMIS) registers (see page 294 and page 295, respectively).
12.2.4 Frame Formats
Each data frame is between 4 and 16 bits long, depending on the size of data programmed, and is
transmitted starting with the MSB. There are three basic frame types that can be selected:
■ Texas Instruments synchronous serial
■ Freescale SPI
■ MICROWIRE
For all three formats, the serial clock (SSIClk) is held inactive while the SSI is idle, and SSIClk
transitions at the programmed frequency only during active transmission or reception of data. The
idle state of SSIClk is utilized to provide a receive timeout indication that occurs when the receive
FIFO still contains data after a timeout period.
For Freescale SPI and MICROWIRE frame formats, the serial frame (SSIFss ) pin is active Low,
and is asserted (pulled down) during the entire transmission of the frame.
For Texas Instruments synchronous serial frame format, the SSIFss pin is pulsed for one serial
clock period starting at its rising edge, prior to the transmission of each frame. For this frame format,
both the SSI and the off-chip slave device drive their output data on the rising edge of SSIClk, and
latch data from the other device on the falling edge.
Unlike the full-duplex transmission of the other two frame formats, the MICROWIRE format uses a
special master-slave messaging technique, which operates at half-duplex. In this mode, when a
frame begins, an 8-bit control message is transmitted to the off-chip slave. During this transmit, no
incoming data is received by the SSI. After the message has been sent, the off-chip slave decodes
it and, after waiting one serial clock after the last bit of the 8-bit control message has been sent,
responds with the requested data. The returned data can be 4 to 16 bits in length, making the total
frame length anywhere from 13 to 25 bits.
12.2.4.1 Texas Instruments Synchronous Serial Frame Format
Figure 12-2 on page 275 shows the Texas Instruments synchronous serial frame format for a single
transmitted frame.
274 November 30, 2007
Preliminary
Synchronous Serial Interface (SSI)
Figure 12-2. TI Synchronous Serial Frame Format (Single Transfer)
SSIClk
4 to 16 bits
SSIFss
SSITx/SSIRx MSB LSB
In this mode, SSIClk and SSIFss are forced Low, and the transmit data line SSITx is tristated
whenever the SSI is idle. Once the bottom entry of the transmit FIFO contains data, SSIFss is
pulsed High for one SSIClk period. The value to be transmitted is also transferred from the transmit
FIFO to the serial shift register of the transmit logic. On the next rising edge of SSIClk, the MSB
of the 4 to 16-bit data frame is shifted out on the SSITx pin. Likewise, the MSB of the received data
is shifted onto the SSIRx pin by the off-chip serial slave device.
Both the SSI and the off-chip serial slave device then clock each data bit into their serial shifter on
the falling edge of each SSIClk. The received data is transferred from the serial shifter to the receive
FIFO on the first rising edge of SSIClk after the LSB has been latched.
Figure 12-3 on page 275 shows the Texas Instruments synchronous serial frame format when
back-to-back frames are transmitted.
Figure 12-3. TI Synchronous Serial Frame Format (Continuous Transfer)
MSB LSB
4 to 16 bits
SSIClk
SSIFss
SSITx/SSIRx
12.2.4.2 Freescale SPI Frame Format
The Freescale SPI interface is a four-wire interface where the SSIFss signal behaves as a slave
select. The main feature of the Freescale SPI format is that the inactive state and phase of the
SSIClk signal are programmable through the SPO and SPH bits within the SSISCR0 control register.
SPO Clock Polarity Bit
When the SPO clock polarity control bit is Low, it produces a steady state Low value on the SSIClk
pin. If the SPO bit is High, a steady state High value is placed on the SSIClk pin when data is not
being transferred.
SPH Phase Control Bit
The SPH phase control bit selects the clock edge that captures data and allows it to change state.
It has the most impact on the first bit transmitted by either allowing or not allowing a clock transition
before the first data capture edge. When the SPH phase control bit is Low, data is captured on the
first clock edge transition. If the SPH bit is High, data is captured on the second clock edge transition.
November 30, 2007 275
Preliminary
LM3S6110 Microcontroller
12.2.4.3 Freescale SPI Frame Format with SPO=0 and SPH=0
Single and continuous transmission signal sequences for Freescale SPI format with SPO=0 and
SPH=0 are shown in Figure 12-4 on page 276 and Figure 12-5 on page 276.
Figure 12-4. Freescale SPI Format (Single Transfer) with SPO=0 and SPH=0
4 to 16 bits
SSIClk
SSIFss
SSIRx Q
SSITx
MSB
MSB
LSB
LSB
Note: Q is undefined.
Figure 12-5. Freescale SPI Format (Continuous Transfer) with SPO=0 and SPH=0
SSIClk
SSIFss
SSIRx LSB
SSITx MSB LSB
4 to 16 bits
LSB MSB
MSB
MSB
LSB
In this configuration, during idle periods:
■ SSIClk is forced Low
■ SSIFss is forced High
■ The transmit data line SSITx is arbitrarily forced Low
■ When the SSI is configured as a master, it enables the SSIClk pad
■ When the SSI is configured as a slave, it disables the SSIClk pad
If the SSI is enabled and there is valid data within the transmit FIFO, the start of transmission is
signified by the SSIFss master signal being driven Low. This causes slave data to be enabled onto
the SSIRx input line of the master. The master SSITx output pad is enabled.
One half SSIClk period later, valid master data is transferred to the SSITx pin. Now that both the
master and slave data have been set, the SSIClk master clock pin goes High after one further half
SSIClk period.
The data is now captured on the rising and propagated on the falling edges of the SSIClk signal.
In the case of a single word transmission, after all bits of the data word have been transferred, the
SSIFss line is returned to its idle High state one SSIClk period after the last bit has been captured.
However, in the case of continuous back-to-back transmissions, the SSIFss signal must be pulsed
High between each data word transfer. This is because the slave select pin freezes the data in its
276 November 30, 2007
Preliminary
Synchronous Serial Interface (SSI)
serial peripheral register and does not allow it to be altered if the SPH bit is logic zero. Therefore,
the master device must raise the SSIFss pin of the slave device between each data transfer to
enable the serial peripheral data write. On completion of the continuous transfer, the SSIFss pin
is returned to its idle state one SSIClk period after the last bit has been captured.
12.2.4.4 Freescale SPI Frame Format with SPO=0 and SPH=1
The transfer signal sequence for Freescale SPI format with SPO=0 and SPH=1 is shown in Figure
12-6 on page 277, which covers both single and continuous transfers.
Figure 12-6. Freescale SPI Frame Format with SPO=0 and SPH=1
4 to 16 bits
SSIClk
SSIFss
SSIRx
SSITx
Q
MSB
Q MSB
LSB
LSB
Note: Q is undefined.
In this configuration, during idle periods:
■ SSIClk is forced Low
■ SSIFss is forced High
■ The transmit data line SSITx is arbitrarily forced Low
■ When the SSI is configured as a master, it enables the SSIClk pad
■ When the SSI is configured as a slave, it disables the SSIClk pad
If the SSI is enabled and there is valid data within the transmit FIFO, the start of transmission is
signified by the SSIFss master signal being driven Low. The master SSITx output is enabled. After
a further one half SSIClk period, both master and slave valid data is enabled onto their respective
transmission lines. At the same time, the SSIClk is enabled with a rising edge transition.
Data is then captured on the falling edges and propagated on the rising edges of the SSIClk signal.
In the case of a single word transfer, after all bits have been transferred, the SSIFss line is returned
to its idle High state one SSIClk period after the last bit has been captured.
For continuous back-to-back transfers, the SSIFss pin is held Low between successive data words
and termination is the same as that of the single word transfer.
12.2.4.5 Freescale SPI Frame Format with SPO=1 and SPH=0
Single and continuous transmission signal sequences for Freescale SPI format with SPO=1 and
SPH=0 are shown in Figure 12-7 on page 278 and Figure 12-8 on page 278.
November 30, 2007 277
Preliminary
LM3S6110 Microcontroller
Figure 12-7. Freescale SPI Frame Format (Single Transfer) with SPO=1 and SPH=0
4 to 16 bits
SSIClk
SSIFss
SSIRx
SSITx
MSB Q
MSB LSB
LSB
Note: Q is undefined.
Figure 12-8. Freescale SPI Frame Format (Continuous Transfer) with SPO=1 and SPH=0
SSIClk
SSIFss
SSITx/SSIRx MSB LSB
4 to 16 bits
LSB MSB
In this configuration, during idle periods:
■ SSIClk is forced High
■ SSIFss is forced High
■ The transmit data line SSITx is arbitrarily forced Low
■ When the SSI is configured as a master, it enables the SSIClk pad
■ When the SSI is configured as a slave, it disables the SSIClk pad
If the SSI is enabled and there is valid data within the transmit FIFO, the start of transmission is
signified by the SSIFss master signal being driven Low, which causes slave data to be immediately
transferred onto the SSIRx line of the master. The master SSITx output pad is enabled.
One half period later, valid master data is transferred to the SSITx line. Now that both the master
and slave data have been set, the SSIClk master clock pin becomes Low after one further half
SSIClk period. This means that data is captured on the falling edges and propagated on the rising
edges of the SSIClk signal.
In the case of a single word transmission, after all bits of the data word are transferred, the SSIFss
line is returned to its idle High state one SSIClk period after the last bit has been captured.
However, in the case of continuous back-to-back transmissions, the SSIFss signal must be pulsed
High between each data word transfer. This is because the slave select pin freezes the data in its
serial peripheral register and does not allow it to be altered if the SPH bit is logic zero. Therefore,
the master device must raise the SSIFss pin of the slave device between each data transfer to
enable the serial peripheral data write. On completion of the continuous transfer, the SSIFss pin
is returned to its idle state one SSIClk period after the last bit has been captured.
278 November 30, 2007
Preliminary
Synchronous Serial Interface (SSI)
12.2.4.6 Freescale SPI Frame Format with SPO=1 and SPH=1
The transfer signal sequence for Freescale SPI format with SPO=1 and SPH=1 is shown in Figure
12-9 on page 279, which covers both single and continuous transfers.
Figure 12-9. Freescale SPI Frame Format with SPO=1 and SPH=1
4 to 16 bits
SSIClk
SSIFss
SSIRx
SSITx
Q Q
MSB
MSB
LSB
LSB
Note: Q is undefined.
In this configuration, during idle periods:
■ SSIClk is forced High
■ SSIFss is forced High
■ The transmit data line SSITx is arbitrarily forced Low
■ When the SSI is configured as a master, it enables the SSIClk pad
■ When the SSI is configured as a slave, it disables the SSIClk pad
If the SSI is enabled and there is valid data within the transmit FIFO, the start of transmission is
signified by the SSIFss master signal being driven Low. The master SSITx output pad is enabled.
After a further one-half SSIClk period, both master and slave data are enabled onto their respective
transmission lines. At the same time, SSIClk is enabled with a falling edge transition. Data is then
captured on the rising edges and propagated on the falling edges of the SSIClk signal.
After all bits have been transferred, in the case of a single word transmission, the SSIFss line is
returned to its idle high state one SSIClk period after the last bit has been captured.
For continuous back-to-back transmissions, the SSIFss pin remains in its active Low state, until
the final bit of the last word has been captured, and then returns to its idle state as described above.
For continuous back-to-back transfers, the SSIFss pin is held Low between successive data words
and termination is the same as that of the single word transfer.
12.2.4.7 MICROWIRE Frame Format
Figure 12-10 on page 280 shows the MICROWIRE frame format, again for a single frame. Figure
12-11 on page 281 shows the same format when back-to-back frames are transmitted.
November 30, 2007 279
Preliminary
LM3S6110 Microcontroller
Figure 12-10. MICROWIRE Frame Format (Single Frame)
SSIClk
SSIFss
SSIRx MSB LSB
4 to 16 bits
output data
0
SSITx MSB LSB
8-bit control
MICROWIRE format is very similar to SPI format, except that transmission is half-duplex instead of
full-duplex, using a master-slave message passing technique. Each serial transmission begins with
an 8-bit control word that is transmitted from the SSI to the off-chip slave device. During this
transmission, no incoming data is received by the SSI. After the message has been sent, the off-chip
slave decodes it and, after waiting one serial clock after the last bit of the 8-bit control message has
been sent, responds with the required data. The returned data is 4 to 16 bits in length, making the
total frame length anywhere from 13 to 25 bits.
In this configuration, during idle periods:
■ SSIClk is forced Low
■ SSIFss is forced High
■ The transmit data line SSITx is arbitrarily forced Low
A transmission is triggered by writing a control byte to the transmit FIFO. The falling edge of SSIFss
causes the value contained in the bottom entry of the transmit FIFO to be transferred to the serial
shift register of the transmit logic, and the MSB of the 8-bit control frame to be shifted out onto the
SSITx pin. SSIFss remains Low for the duration of the frame transmission. The SSIRx pin remains
tristated during this transmission.
The off-chip serial slave device latches each control bit into its serial shifter on the rising edge of
each SSIClk. After the last bit is latched by the slave device, the control byte is decoded during a
one clock wait-state, and the slave responds by transmitting data back to the SSI. Each bit is driven
onto the SSIRx line on the falling edge of SSIClk. The SSI in turn latches each bit on the rising
edge of SSIClk. At the end of the frame, for single transfers, the SSIFss signal is pulled High one
clock period after the last bit has been latched in the receive serial shifter, which causes the data
to be transferred to the receive FIFO.
Note: The off-chip slave device can tristate the receive line either on the falling edge of SSIClk
after the LSB has been latched by the receive shifter, or when the SSIFss pin goes High.
For continuous transfers, data transmission begins and ends in the same manner as a single transfer.
However, the SSIFss line is continuously asserted (held Low) and transmission of data occurs
back-to-back. The control byte of the next frame follows directly after the LSB of the received data
from the current frame. Each of the received values is transferred from the receive shifter on the
falling edge of SSIClk, after the LSB of the frame has been latched into the SSI.
280 November 30, 2007
Preliminary
Synchronous Serial Interface (SSI)
Figure 12-11. MICROWIRE Frame Format (Continuous Transfer)
8-bit control
SSIClk
SSIFss
SSIRx MSB LSB
4 to 16 bits
output data
0
SSITx LSB MSB LSB
MSB
In the MICROWIRE mode, the SSI slave samples the first bit of receive data on the rising edge of
SSIClk after SSIFss has gone Low. Masters that drive a free-running SSIClk must ensure that
the SSIFss signal has sufficient setup and hold margins with respect to the rising edge of SSIClk.
Figure 12-12 on page 281 illustrates these setup and hold time requirements. With respect to the
SSIClk rising edge on which the first bit of receive data is to be sampled by the SSI slave, SSIFss
must have a setup of at least two times the period of SSIClk on which the SSI operates. With
respect to the SSIClk rising edge previous to this edge, SSIFss must have a hold of at least one
SSIClk period.
Figure 12-12. MICROWIRE Frame Format, SSIFss Input Setup and Hold Requirements
SSIClk
SSIFss
SSIRx
First RX data to be
sampled by SSI slave
tSetup=(2*tSSIClk)
tHold=tSSIClk
12.3 Initialization and Configuration
To use the SSI, its peripheral clock must be enabled by setting the SSI bit in the RCGC1 register.
For each of the frame formats, the SSI is configured using the following steps:
1. Ensure that the SSE bit in the SSICR1 register is disabled before making any configuration
changes.
2. Select whether the SSI is a master or slave:
a. For master operations, set the SSICR1 register to 0x0000.0000.
b. For slave mode (output enabled), set the SSICR1 register to 0x0000.0004.
c. For slave mode (output disabled), set the SSICR1 register to 0x0000.000C.
3. Configure the clock prescale divisor by writing the SSICPSR register.
November 30, 2007 281
Preliminary
LM3S6110 Microcontroller
4. Write the SSICR0 register with the following configuration:
■ Serial clock rate (SCR)
■ Desired clock phase/polarity, if using Freescale SPI mode (SPH and SPO)
■ The protocol mode: Freescale SPI, TI SSF, MICROWIRE (FRF)
■ The data size (DSS)
5. Enable the SSI by setting the SSE bit in the SSICR1 register.
As an example, assume the SSI must be configured to operate with the following parameters:
■ Master operation
■ Freescale SPI mode (SPO=1, SPH=1)
■ 1 Mbps bit rate
■ 8 data bits
Assuming the system clock is 20 MHz, the bit rate calculation would be:
FSSIClk = FSysClk / (CPSDVSR * (1 + SCR))
1x106 = 20x106 / (CPSDVSR * (1 + SCR))
In this case, if CPSDVSR=2, SCR must be 9.
The configuration sequence would be as follows:
1. Ensure that the SSE bit in the SSICR1 register is disabled.
2. Write the SSICR1 register with a value of 0x0000.0000.
3. Write the SSICPSR register with a value of 0x0000.0002.
4. Write the SSICR0 register with a value of 0x0000.09C7.
5. The SSI is then enabled by setting the SSE bit in the SSICR1 register to 1.
12.4 Register Map
Table 12-1 on page 282 lists the SSI registers. The offset listed is a hexadecimal increment to the
register’s address, relative to that SSI module’s base address:
■ SSI0: 0x4000.8000
Note: The SSI must be disabled (see the SSE bit in the SSICR1 register) before any of the control
registers are reprogrammed.
Table 12-1. SSI Register Map
See
Offset Name Type Reset Description page
0x000 SSICR0 R/W 0x0000.0000 SSI Control 0 284
282 November 30, 2007
Preliminary
Synchronous Serial Interface (SSI)
See
Offset Name Type Reset Description page
0x004 SSICR1 R/W 0x0000.0000 SSI Control 1 286
0x008 SSIDR R/W 0x0000.0000 SSI Data 288
0x00C SSISR RO 0x0000.0003 SSI Status 289
0x010 SSICPSR R/W 0x0000.0000 SSI Clock Prescale 291
0x014 SSIIM R/W 0x0000.0000 SSI Interrupt Mask 292
0x018 SSIRIS RO 0x0000.0008 SSI Raw Interrupt Status 294
0x01C SSIMIS RO 0x0000.0000 SSI Masked Interrupt Status 295
0x020 SSIICR W1C 0x0000.0000 SSI Interrupt Clear 296
0xFD0 SSIPeriphID4 RO 0x0000.0000 SSI Peripheral Identification 4 297
0xFD4 SSIPeriphID5 RO 0x0000.0000 SSI Peripheral Identification 5 298
0xFD8 SSIPeriphID6 RO 0x0000.0000 SSI Peripheral Identification 6 299
0xFDC SSIPeriphID7 RO 0x0000.0000 SSI Peripheral Identification 7 300
0xFE0 SSIPeriphID0 RO 0x0000.0022 SSI Peripheral Identification 0 301
0xFE4 SSIPeriphID1 RO 0x0000.0000 SSI Peripheral Identification 1 302
0xFE8 SSIPeriphID2 RO 0x0000.0018 SSI Peripheral Identification 2 303
0xFEC SSIPeriphID3 RO 0x0000.0001 SSI Peripheral Identification 3 304
0xFF0 SSIPCellID0 RO 0x0000.000D SSI PrimeCell Identification 0 305
0xFF4 SSIPCellID1 RO 0x0000.00F0 SSI PrimeCell Identification 1 306
0xFF8 SSIPCellID2 RO 0x0000.0005 SSI PrimeCell Identification 2 307
0xFFC SSIPCellID3 RO 0x0000.00B1 SSI PrimeCell Identification 3 308
12.5 Register Descriptions
The remainder of this section lists and describes the SSI registers, in numerical order by address
offset.
November 30, 2007 283
Preliminary
LM3S6110 Microcontroller
Register 1: SSI Control 0 (SSICR0), offset 0x000
SSICR0 is control register 0 and contains bit fields that control various functions within the SSI
module. Functionality such as protocol mode, clock rate, and data size are configured in this register.
SSI Control 0 (SSICR0)
SSI0 base: 0x4000.8000
Offset 0x000
Type R/W, reset 0x0000.0000
31 30 29 28 27 26 25 24 23 22 21 20 19 18 17 16
reserved
Type RO RO RO RO RO RO RO RO RO RO RO RO RO RO RO RO
Reset 0 0 0 0 0 0 0 0 0 0 0 0 0 0 0 0
15 14 13 12 11 10 9 8 7 6 5 4 3 2 1 0
SCR SPH SPO FRF DSS
Type R/W R/W R/W R/W R/W R/W R/W R/W R/W R/W R/W R/W R/W R/W R/W R/W
Reset 0 0 0 0 0 0 0 0 0 0 0 0 0 0 0 0
Bit/Field Name Type Reset Description
Software should not rely on the value of a reserved bit. To provide
compatibility with future products, the value of a reserved bit should be
preserved across a read-modify-write operation.
31:16 reserved RO 0x00
SSI Serial Clock Rate
The value SCR is used to generate the transmit and receive bit rate of
the SSI. The bit rate is:
BR=FSSIClk/(CPSDVSR * (1 + SCR))
where CPSDVSR is an even value from 2-254 programmed in the
SSICPSR register, and SCR is a value from 0-255.
15:8 SCR R/W 0x0000
SSI Serial Clock Phase
This bit is only applicable to the Freescale SPI Format.
The SPH control bit selects the clock edge that captures data and allows
it to change state. It has the most impact on the first bit transmitted by
either allowing or not allowing a clock transition before the first data
capture edge.
When the SPH bit is 0, data is captured on the first clock edge transition.
If SPH is 1, data is captured on the second clock edge transition.
7 SPH R/W 0
SSI Serial Clock Polarity
This bit is only applicable to the Freescale SPI Format.
When the SPO bit is 0, it produces a steady state Low value on the
SSIClk pin. If SPO is 1, a steady state High value is placed on the
SSIClk pin when data is not being transferred.
6 SPO R/W 0
284 November 30, 2007
Preliminary
Synchronous Serial Interface (SSI)
Bit/Field Name Type Reset Description
SSI Frame Format Select
The FRF values are defined as follows:
Value Frame Format
0x0 Freescale SPI Frame Format
0x1 Texas Intruments Synchronous Serial Frame Format
0x2 MICROWIRE Frame Format
0x3 Reserved
5:4 FRF R/W 0x0
SSI Data Size Select
The DSS values are defined as follows:
Value Data Size
0x0-0x2 Reserved
0x3 4-bit data
0x4 5-bit data
0x5 6-bit data
0x6 7-bit data
0x7 8-bit data
0x8 9-bit data
0x9 10-bit data
0xA 11-bit data
0xB 12-bit data
0xC 13-bit data
0xD 14-bit data
0xE 15-bit data
0xF 16-bit data
3:0 DSS R/W 0x00
November 30, 2007 285
Preliminary
LM3S6110 Microcontroller
Register 2: SSI Control 1 (SSICR1), offset 0x004
SSICR1 is control register 1 and contains bit fields that control various functions within the SSI
module. Master and slave mode functionality is controlled by this register.
SSI Control 1 (SSICR1)
SSI0 base: 0x4000.8000
Offset 0x004
Type R/W, reset 0x0000.0000
31 30 29 28 27 26 25 24 23 22 21 20 19 18 17 16
reserved
Type RO RO RO RO RO RO RO RO RO RO RO RO RO RO RO RO
Reset 0 0 0 0 0 0 0 0 0 0 0 0 0 0 0 0
15 14 13 12 11 10 9 8 7 6 5 4 3 2 1 0
reserved SOD MS SSE LBM
Type RO RO RO RO RO RO RO RO RO RO RO RO R/W R/W R/W R/W
Reset 0 0 0 0 0 0 0 0 0 0 0 0 0 0 0 0
Bit/Field Name Type Reset Description
Software should not rely on the value of a reserved bit. To provide
compatibility with future products, the value of a reserved bit should be
preserved across a read-modify-write operation.
31:4 reserved RO 0x00
SSI Slave Mode Output Disable
This bit is relevant only in the Slave mode (MS=1). In multiple-slave
systems, it is possible for the SSI master to broadcast a message to all
slaves in the system while ensuring that only one slave drives data onto
the serial output line. In such systems, the TXD lines from multiple slaves
could be tied together. To operate in such a system, the SOD bit can be
configured so that the SSI slave does not drive the SSITx pin.
The SOD values are defined as follows:
Value Description
0 SSI can drive SSITx output in Slave Output mode.
1 SSI must not drive the SSITx output in Slave mode.
3 SOD R/W 0
SSI Master/Slave Select
This bit selects Master or Slave mode and can be modified only when
SSI is disabled (SSE=0).
The MS values are defined as follows:
Value Description
0 Device configured as a master.
1 Device configured as a slave.
2 MS R/W 0
286 November 30, 2007
Preliminary
Synchronous Serial Interface (SSI)
Bit/Field Name Type Reset Description
SSI Synchronous Serial Port Enable
Setting this bit enables SSI operation.
The SSE values are defined as follows:
Value Description
0 SSI operation disabled.
1 SSI operation enabled.
Note: This bit must be set to 0 before any control registers
are reprogrammed.
1 SSE R/W 0
SSI Loopback Mode
Setting this bit enables Loopback Test mode.
The LBM values are defined as follows:
Value Description
0 Normal serial port operation enabled.
Output of the transmit serial shift register is connected internally
to the input of the receive serial shift register.
1
0 LBM R/W 0
November 30, 2007 287
Preliminary
LM3S6110 Microcontroller
Register 3: SSI Data (SSIDR), offset 0x008
SSIDR is the data register and is 16-bits wide. When SSIDR is read, the entry in the receive FIFO
(pointed to by the current FIFO read pointer) is accessed. As data values are removed by the SSI
receive logic from the incoming data frame, they are placed into the entry in the receive FIFO (pointed
to by the current FIFO write pointer).
When SSIDR is written to, the entry in the transmit FIFO (pointed to by the write pointer) is written
to. Data values are removed from the transmit FIFO one value at a time by the transmit logic. It is
loaded into the transmit serial shifter, then serially shifted out onto the SSITx pin at the programmed
bit rate.
When a data size of less than 16 bits is selected, the user must right-justify data written to the
transmit FIFO. The transmit logic ignores the unused bits. Received data less than 16 bits is
automatically right-justified in the receive buffer.
When the SSI is programmed for MICROWIRE frame format, the default size for transmit data is
eight bits (the most significant byte is ignored). The receive data size is controlled by the programmer.
The transmit FIFO and the receive FIFO are not cleared even when the SSE bit in the SSICR1
register is set to zero. This allows the software to fill the transmit FIFO before enabling the SSI.
SSI Data (SSIDR)
SSI0 base: 0x4000.8000
Offset 0x008
Type R/W, reset 0x0000.0000
31 30 29 28 27 26 25 24 23 22 21 20 19 18 17 16
reserved
Type RO RO RO RO RO RO RO RO RO RO RO RO RO RO RO RO
Reset 0 0 0 0 0 0 0 0 0 0 0 0 0 0 0 0
15 14 13 12 11 10 9 8 7 6 5 4 3 2 1 0
DATA
Type R/W R/W R/W R/W R/W R/W R/W R/W R/W R/W R/W R/W R/W R/W R/W R/W
Reset 0 0 0 0 0 0 0 0 0 0 0 0 0 0 0 0
Bit/Field Name Type Reset Description
Software should not rely on the value of a reserved bit. To provide
compatibility with future products, the value of a reserved bit should be
preserved across a read-modify-write operation.
31:16 reserved RO 0x0000
SSI Receive/Transmit Data
A read operation reads the receive FIFO. A write operation writes the
transmit FIFO.
Software must right-justify data when the SSI is programmed for a data
size that is less than 16 bits. Unused bits at the top are ignored by the
transmit logic. The receive logic automatically right-justifies the data.
15:0 DATA R/W 0x0000
288 November 30, 2007
Preliminary
Synchronous Serial Interface (SSI)
Register 4: SSI Status (SSISR), offset 0x00C
SSISR is a status register that contains bits that indicate the FIFO fill status and the SSI busy status.
SSI Status (SSISR)
SSI0 base: 0x4000.8000
Offset 0x00C
Type RO, reset 0x0000.0003
31 30 29 28 27 26 25 24 23 22 21 20 19 18 17 16
reserved
Type RO RO RO RO RO RO RO RO RO RO RO RO RO RO RO RO
Reset 0 0 0 0 0 0 0 0 0 0 0 0 0 0 0 0
15 14 13 12 11 10 9 8 7 6 5 4 3 2 1 0
reserved BSY RFF RNE TNF TFE
Type RO RO RO RO RO RO RO RO RO RO RO RO RO RO RO R0
Reset 0 0 0 0 0 0 0 0 0 0 0 0 0 0 1 1
Bit/Field Name Type Reset Description
Software should not rely on the value of a reserved bit. To provide
compatibility with future products, the value of a reserved bit should be
preserved across a read-modify-write operation.
31:5 reserved RO 0x00
SSI Busy Bit
The BSY values are defined as follows:
Value Description
0 SSI is idle.
SSI is currently transmitting and/or receiving a frame, or the
transmit FIFO is not empty.
1
4 BSY RO 0
SSI Receive FIFO Full
The RFF values are defined as follows:
Value Description
0 Receive FIFO is not full.
1 Receive FIFO is full.
3 RFF RO 0
SSI Receive FIFO Not Empty
The RNE values are defined as follows:
Value Description
0 Receive FIFO is empty.
1 Receive FIFO is not empty.
2 RNE RO 0
SSI Transmit FIFO Not Full
The TNF values are defined as follows:
Value Description
0 Transmit FIFO is full.
1 Transmit FIFO is not full.
1 TNF RO 1
November 30, 2007 289
Preliminary
LM3S6110 Microcontroller
Bit/Field Name Type Reset Description
SSI Transmit FIFO Empty
The TFE values are defined as follows:
Value Description
0 Transmit FIFO is not empty.
1 Transmit FIFO is empty.
0 TFE R0 1
290 November 30, 2007
Preliminary
Synchronous Serial Interface (SSI)
Register 5: SSI Clock Prescale (SSICPSR), offset 0x010
SSICPSR is the clock prescale register and specifies the division factor by which the system clock
must be internally divided before further use.
The value programmed into this register must be an even number between 2 and 254. The
least-significant bit of the programmed number is hard-coded to zero. If an odd number is written
to this register, data read back from this register has the least-significant bit as zero.
SSI Clock Prescale (SSICPSR)
SSI0 base: 0x4000.8000
Offset 0x010
Type R/W, reset 0x0000.0000
31 30 29 28 27 26 25 24 23 22 21 20 19 18 17 16
reserved
Type RO RO RO RO RO RO RO RO RO RO RO RO RO RO RO RO
Reset 0 0 0 0 0 0 0 0 0 0 0 0 0 0 0 0
15 14 13 12 11 10 9 8 7 6 5 4 3 2 1 0
reserved CPSDVSR
Type RO RO RO RO RO RO RO RO R/W R/W R/W R/W R/W R/W R/W R/W
Reset 0 0 0 0 0 0 0 0 0 0 0 0 0 0 0 0
Bit/Field Name Type Reset Description
Software should not rely on the value of a reserved bit. To provide
compatibility with future products, the value of a reserved bit should be
preserved across a read-modify-write operation.
31:8 reserved RO 0x00
SSI Clock Prescale Divisor
This value must be an even number from 2 to 254, depending on the
frequency of SSIClk. The LSB always returns 0 on reads.
7:0 CPSDVSR R/W 0x00
November 30, 2007 291
Preliminary
LM3S6110 Microcontroller
Register 6: SSI Interrupt Mask (SSIIM), offset 0x014
The SSIIM register is the interrupt mask set or clear register. It is a read/write register and all bits
are cleared to 0 on reset.
On a read, this register gives the current value of the mask on the relevant interrupt. A write of 1 to
the particular bit sets the mask, enabling the interrupt to be read. A write of 0 clears the corresponding
mask.
SSI Interrupt Mask (SSIIM)
SSI0 base: 0x4000.8000
Offset 0x014
Type R/W, reset 0x0000.0000
31 30 29 28 27 26 25 24 23 22 21 20 19 18 17 16
reserved
Type RO RO RO RO RO RO RO RO RO RO RO RO RO RO RO RO
Reset 0 0 0 0 0 0 0 0 0 0 0 0 0 0 0 0
15 14 13 12 11 10 9 8 7 6 5 4 3 2 1 0
reserved TXIM RXIM RTIM RORIM
Type RO RO RO RO RO RO RO RO RO RO RO RO R/W R/W R/W R/W
Reset 0 0 0 0 0 0 0 0 0 0 0 0 0 0 0 0
Bit/Field Name Type Reset Description
Software should not rely on the value of a reserved bit. To provide
compatibility with future products, the value of a reserved bit should be
preserved across a read-modify-write operation.
31:4 reserved RO 0x00
SSI Transmit FIFO Interrupt Mask
The TXIM values are defined as follows:
Value Description
0 TX FIFO half-full or less condition interrupt is masked.
1 TX FIFO half-full or less condition interrupt is not masked.
3 TXIM R/W 0
SSI Receive FIFO Interrupt Mask
The RXIM values are defined as follows:
Value Description
0 RX FIFO half-full or more condition interrupt is masked.
1 RX FIFO half-full or more condition interrupt is not masked.
2 RXIM R/W 0
SSI Receive Time-Out Interrupt Mask
The RTIM values are defined as follows:
Value Description
0 RX FIFO time-out interrupt is masked.
1 RX FIFO time-out interrupt is not masked.
1 RTIM R/W 0
292 November 30, 2007
Preliminary
Synchronous Serial Interface (SSI)
Bit/Field Name Type Reset Description
SSI Receive Overrun Interrupt Mask
The RORIM values are defined as follows:
Value Description
0 RX FIFO overrun interrupt is masked.
1 RX FIFO overrun interrupt is not masked.
0 RORIM R/W 0
November 30, 2007 293
Preliminary
LM3S6110 Microcontroller
Register 7: SSI Raw Interrupt Status (SSIRIS), offset 0x018
The SSIRIS register is the raw interrupt status register. On a read, this register gives the current
raw status value of the corresponding interrupt prior to masking. A write has no effect.
SSI Raw Interrupt Status (SSIRIS)
SSI0 base: 0x4000.8000
Offset 0x018
Type RO, reset 0x0000.0008
31 30 29 28 27 26 25 24 23 22 21 20 19 18 17 16
reserved
Type RO RO RO RO RO RO RO RO RO RO RO RO RO RO RO RO
Reset 0 0 0 0 0 0 0 0 0 0 0 0 0 0 0 0
15 14 13 12 11 10 9 8 7 6 5 4 3 2 1 0
reserved TXRIS RXRIS RTRIS RORRIS
Type RO RO RO RO RO RO RO RO RO RO RO RO RO RO RO RO
Reset 0 0 0 0 0 0 0 0 0 0 0 0 1 0 0 0
Bit/Field Name Type Reset Description
Software should not rely on the value of a reserved bit. To provide
compatibility with future products, the value of a reserved bit should be
preserved across a read-modify-write operation.
31:4 reserved RO 0x00
SSI Transmit FIFO Raw Interrupt Status
Indicates that the transmit FIFO is half full or less, when set.
3 TXRIS RO 1
SSI Receive FIFO Raw Interrupt Status
Indicates that the receive FIFO is half full or more, when set.
2 RXRIS RO 0
SSI Receive Time-Out Raw Interrupt Status
Indicates that the receive time-out has occurred, when set.
1 RTRIS RO 0
SSI Receive Overrun Raw Interrupt Status
Indicates that the receive FIFO has overflowed, when set.
0 RORRIS RO 0
294 November 30, 2007
Preliminary
Synchronous Serial Interface (SSI)
Register 8: SSI Masked Interrupt Status (SSIMIS), offset 0x01C
The SSIMIS register is the masked interrupt status register. On a read, this register gives the current
masked status value of the corresponding interrupt. A write has no effect.
SSI Masked Interrupt Status (SSIMIS)
SSI0 base: 0x4000.8000
Offset 0x01C
Type RO, reset 0x0000.0000
31 30 29 28 27 26 25 24 23 22 21 20 19 18 17 16
reserved
Type RO RO RO RO RO RO RO RO RO RO RO RO RO RO RO RO
Reset 0 0 0 0 0 0 0 0 0 0 0 0 0 0 0 0
15 14 13 12 11 10 9 8 7 6 5 4 3 2 1 0
reserved TXMIS RXMIS RTMIS RORMIS
Type RO RO RO RO RO RO RO RO RO RO RO RO RO RO RO RO
Reset 0 0 0 0 0 0 0 0 0 0 0 0 0 0 0 0
Bit/Field Name Type Reset Description
Software should not rely on the value of a reserved bit. To provide
compatibility with future products, the value of a reserved bit should be
preserved across a read-modify-write operation.
31:4 reserved RO 0
SSI Transmit FIFO Masked Interrupt Status
Indicates that the transmit FIFO is half full or less, when set.
3 TXMIS RO 0
SSI Receive FIFO Masked Interrupt Status
Indicates that the receive FIFO is half full or more, when set.
2 RXMIS RO 0
SSI Receive Time-Out Masked Interrupt Status
Indicates that the receive time-out has occurred, when set.
1 RTMIS RO 0
SSI Receive Overrun Masked Interrupt Status
Indicates that the receive FIFO has overflowed, when set.
0 RORMIS RO 0
November 30, 2007 295
Preliminary
LM3S6110 Microcontroller
Register 9: SSI Interrupt Clear (SSIICR), offset 0x020
The SSIICR register is the interrupt clear register. On a write of 1, the corresponding interrupt is
cleared. A write of 0 has no effect.
SSI Interrupt Clear (SSIICR)
SSI0 base: 0x4000.8000
Offset 0x020
Type W1C, reset 0x0000.0000
31 30 29 28 27 26 25 24 23 22 21 20 19 18 17 16
reserved
Type RO RO RO RO RO RO RO RO RO RO RO RO RO RO RO RO
Reset 0 0 0 0 0 0 0 0 0 0 0 0 0 0 0 0
15 14 13 12 11 10 9 8 7 6 5 4 3 2 1 0
reserved RTIC RORIC
Type RO RO RO RO RO RO RO RO RO RO RO RO RO RO W1C W1C
Reset 0 0 0 0 0 0 0 0 0 0 0 0 0 0 0 0
Bit/Field Name Type Reset Description
Software should not rely on the value of a reserved bit. To provide
compatibility with future products, the value of a reserved bit should be
preserved across a read-modify-write operation.
31:2 reserved RO 0x00
SSI Receive Time-Out Interrupt Clear
The RTIC values are defined as follows:
Value Description
0 No effect on interrupt.
1 Clears interrupt.
1 RTIC W1C 0
SSI Receive Overrun Interrupt Clear
The RORIC values are defined as follows:
Value Description
0 No effect on interrupt.
1 Clears interrupt.
0 RORIC W1C 0
296 November 30, 2007
Preliminary
Synchronous Serial Interface (SSI)
Register 10: SSI Peripheral Identification 4 (SSIPeriphID4), offset 0xFD0
The SSIPeriphIDn registers are hard-coded and the fields within the register determine the reset
value.
SSI Peripheral Identification 4 (SSIPeriphID4)
SSI0 base: 0x4000.8000
Offset 0xFD0
Type RO, reset 0x0000.0000
31 30 29 28 27 26 25 24 23 22 21 20 19 18 17 16
reserved
Type RO RO RO RO RO RO RO RO RO RO RO RO RO RO RO RO
Reset 0 0 0 0 0 0 0 0 0 0 0 0 0 0 0 0
15 14 13 12 11 10 9 8 7 6 5 4 3 2 1 0
reserved PID4
Type RO RO RO RO RO RO RO RO RO RO RO RO RO RO RO RO
Reset 0 0 0 0 0 0 0 0 0 0 0 0 0 0 0 0
Bit/Field Name Type Reset Description
Software should not rely on the value of a reserved bit. To provide
compatibility with future products, the value of a reserved bit should be
preserved across a read-modify-write operation.
31:8 reserved RO 0x00
SSI Peripheral ID Register[7:0]
Can be used by software to identify the presence of this peripheral.
7:0 PID4 RO 0x00
November 30, 2007 297
Preliminary
LM3S6110 Microcontroller
Register 11: SSI Peripheral Identification 5 (SSIPeriphID5), offset 0xFD4
The SSIPeriphIDn registers are hard-coded and the fields within the register determine the reset
value.
SSI Peripheral Identification 5 (SSIPeriphID5)
SSI0 base: 0x4000.8000
Offset 0xFD4
Type RO, reset 0x0000.0000
31 30 29 28 27 26 25 24 23 22 21 20 19 18 17 16
reserved
Type RO RO RO RO RO RO RO RO RO RO RO RO RO RO RO RO
Reset 0 0 0 0 0 0 0 0 0 0 0 0 0 0 0 0
15 14 13 12 11 10 9 8 7 6 5 4 3 2 1 0
reserved PID5
Type RO RO RO RO RO RO RO RO RO RO RO RO RO RO RO RO
Reset 0 0 0 0 0 0 0 0 0 0 0 0 0 0 0 0
Bit/Field Name Type Reset Description
Software should not rely on the value of a reserved bit. To provide
compatibility with future products, the value of a reserved bit should be
preserved across a read-modify-write operation.
31:8 reserved RO 0x00
SSI Peripheral ID Register[15:8]
Can be used by software to identify the presence of this peripheral.
7:0 PID5 RO 0x00
298 November 30, 2007
Preliminary
Synchronous Serial Interface (SSI)
Register 12: SSI Peripheral Identification 6 (SSIPeriphID6), offset 0xFD8
The SSIPeriphIDn registers are hard-coded and the fields within the register determine the reset
value.
SSI Peripheral Identification 6 (SSIPeriphID6)
SSI0 base: 0x4000.8000
Offset 0xFD8
Type RO, reset 0x0000.0000
31 30 29 28 27 26 25 24 23 22 21 20 19 18 17 16
reserved
Type RO RO RO RO RO RO RO RO RO RO RO RO RO RO RO RO
Reset 0 0 0 0 0 0 0 0 0 0 0 0 0 0 0 0
15 14 13 12 11 10 9 8 7 6 5 4 3 2 1 0
reserved PID6
Type RO RO RO RO RO RO RO RO RO RO RO RO RO RO RO RO
Reset 0 0 0 0 0 0 0 0 0 0 0 0 0 0 0 0
Bit/Field Name Type Reset Description
Software should not rely on the value of a reserved bit. To provide
compatibility with future products, the value of a reserved bit should be
preserved across a read-modify-write operation.
31:8 reserved RO 0x00
SSI Peripheral ID Register[23:16]
Can be used by software to identify the presence of this peripheral.
7:0 PID6 RO 0x00
November 30, 2007 299
Preliminary
LM3S6110 Microcontroller
Register 13: SSI Peripheral Identification 7 (SSIPeriphID7), offset 0xFDC
The SSIPeriphIDn registers are hard-coded and the fields within the register determine the reset
value.
SSI Peripheral Identification 7 (SSIPeriphID7)
SSI0 base: 0x4000.8000
Offset 0xFDC
Type RO, reset 0x0000.0000
31 30 29 28 27 26 25 24 23 22 21 20 19 18 17 16
reserved
Type RO RO RO RO RO RO RO RO RO RO RO RO RO RO RO RO
Reset 0 0 0 0 0 0 0 0 0 0 0 0 0 0 0 0
15 14 13 12 11 10 9 8 7 6 5 4 3 2 1 0
reserved PID7
Type RO RO RO RO RO RO RO RO RO RO RO RO RO RO RO RO
Reset 0 0 0 0 0 0 0 0 0 0 0 0 0 0 0 0
Bit/Field Name Type Reset Description
Software should not rely on the value of a reserved bit. To provide
compatibility with future products, the value of a reserved bit should be
preserved across a read-modify-write operation.
31:8 reserved RO 0x00
SSI Peripheral ID Register[31:24]
Can be used by software to identify the presence of this peripheral.
7:0 PID7 RO 0x00
300 November 30, 2007
Preliminary
Synchronous Serial Interface (SSI)
Register 14: SSI Peripheral Identification 0 (SSIPeriphID0), offset 0xFE0
The SSIPeriphIDn registers are hard-coded and the fields within the register determine the reset
value.
SSI Peripheral Identification 0 (SSIPeriphID0)
SSI0 base: 0x4000.8000
Offset 0xFE0
Type RO, reset 0x0000.0022
31 30 29 28 27 26 25 24 23 22 21 20 19 18 17 16
reserved
Type RO RO RO RO RO RO RO RO RO RO RO RO RO RO RO RO
Reset 0 0 0 0 0 0 0 0 0 0 0 0 0 0 0 0
15 14 13 12 11 10 9 8 7 6 5 4 3 2 1 0
reserved PID0
Type RO RO RO RO RO RO RO RO RO RO RO RO RO RO RO RO
Reset 0 0 0 0 0 0 0 0 0 0 1 0 0 0 1 0
Bit/Field Name Type Reset Description
Software should not rely on the value of a reserved bit. To provide
compatibility with future products, the value of a reserved bit should be
preserved across a read-modify-write operation.
31:8 reserved RO 0
SSI Peripheral ID Register[7:0]
Can be used by software to identify the presence of this peripheral.
7:0 PID0 RO 0x22
November 30, 2007 301
Preliminary
LM3S6110 Microcontroller
Register 15: SSI Peripheral Identification 1 (SSIPeriphID1), offset 0xFE4
The SSIPeriphIDn registers are hard-coded and the fields within the register determine the reset
value.
SSI Peripheral Identification 1 (SSIPeriphID1)
SSI0 base: 0x4000.8000
Offset 0xFE4
Type RO, reset 0x0000.0000
31 30 29 28 27 26 25 24 23 22 21 20 19 18 17 16
reserved
Type RO RO RO RO RO RO RO RO RO RO RO RO RO RO RO RO
Reset 0 0 0 0 0 0 0 0 0 0 0 0 0 0 0 0
15 14 13 12 11 10 9 8 7 6 5 4 3 2 1 0
reserved PID1
Type RO RO RO RO RO RO RO RO RO RO RO RO RO RO RO RO
Reset 0 0 0 0 0 0 0 0 0 0 0 0 0 0 0 0
Bit/Field Name Type Reset Description
Software should not rely on the value of a reserved bit. To provide
compatibility with future products, the value of a reserved bit should be
preserved across a read-modify-write operation.
31:8 reserved RO 0x00
SSI Peripheral ID Register [15:8]
Can be used by software to identify the presence of this peripheral.
7:0 PID1 RO 0x00
302 November 30, 2007
Preliminary
Synchronous Serial Interface (SSI)
Register 16: SSI Peripheral Identification 2 (SSIPeriphID2), offset 0xFE8
The SSIPeriphIDn registers are hard-coded and the fields within the register determine the reset
value.
SSI Peripheral Identification 2 (SSIPeriphID2)
SSI0 base: 0x4000.8000
Offset 0xFE8
Type RO, reset 0x0000.0018
31 30 29 28 27 26 25 24 23 22 21 20 19 18 17 16
reserved
Type RO RO RO RO RO RO RO RO RO RO RO RO RO RO RO RO
Reset 0 0 0 0 0 0 0 0 0 0 0 0 0 0 0 0
15 14 13 12 11 10 9 8 7 6 5 4 3 2 1 0
reserved PID2
Type RO RO RO RO RO RO RO RO RO RO RO RO RO RO RO RO
Reset 0 0 0 0 0 0 0 0 0 0 0 1 1 0 0 0
Bit/Field Name Type Reset Description
Software should not rely on the value of a reserved bit. To provide
compatibility with future products, the value of a reserved bit should be
preserved across a read-modify-write operation.
31:8 reserved RO 0x00
SSI Peripheral ID Register [23:16]
Can be used by software to identify the presence of this peripheral.
7:0 PID2 RO 0x18
November 30, 2007 303
Preliminary
LM3S6110 Microcontroller
Register 17: SSI Peripheral Identification 3 (SSIPeriphID3), offset 0xFEC
The SSIPeriphIDn registers are hard-coded and the fields within the register determine the reset
value.
SSI Peripheral Identification 3 (SSIPeriphID3)
SSI0 base: 0x4000.8000
Offset 0xFEC
Type RO, reset 0x0000.0001
31 30 29 28 27 26 25 24 23 22 21 20 19 18 17 16
reserved
Type RO RO RO RO RO RO RO RO RO RO RO RO RO RO RO RO
Reset 0 0 0 0 0 0 0 0 0 0 0 0 0 0 0 0
15 14 13 12 11 10 9 8 7 6 5 4 3 2 1 0
reserved PID3
Type RO RO RO RO RO RO RO RO RO RO RO RO RO RO RO RO
Reset 0 0 0 0 0 0 0 0 0 0 0 0 0 0 0 1
Bit/Field Name Type Reset Description
Software should not rely on the value of a reserved bit. To provide
compatibility with future products, the value of a reserved bit should be
preserved across a read-modify-write operation.
31:8 reserved RO 0x00
SSI Peripheral ID Register [31:24]
Can be used by software to identify the presence of this peripheral.
7:0 PID3 RO 0x01
304 November 30, 2007
Preliminary
Synchronous Serial Interface (SSI)
Register 18: SSI PrimeCell Identification 0 (SSIPCellID0), offset 0xFF0
The SSIPCellIDn registers are hard-coded and the fields within the register determine the reset
value.
SSI PrimeCell Identification 0 (SSIPCellID0)
SSI0 base: 0x4000.8000
Offset 0xFF0
Type RO, reset 0x0000.000D
31 30 29 28 27 26 25 24 23 22 21 20 19 18 17 16
reserved
Type RO RO RO RO RO RO RO RO RO RO RO RO RO RO RO RO
Reset 0 0 0 0 0 0 0 0 0 0 0 0 0 0 0 0
15 14 13 12 11 10 9 8 7 6 5 4 3 2 1 0
reserved CID0
Type RO RO RO RO RO RO RO RO RO RO RO RO RO RO RO RO
Reset 0 0 0 0 0 0 0 0 0 0 0 0 1 1 0 1
Bit/Field Name Type Reset Description
Software should not rely on the value of a reserved bit. To provide
compatibility with future products, the value of a reserved bit should be
preserved across a read-modify-write operation.
31:8 reserved RO 0x00
SSI PrimeCell ID Register [7:0]
Provides software a standard cross-peripheral identification system.
7:0 CID0 RO 0x0D
November 30, 2007 305
Preliminary
LM3S6110 Microcontroller
Register 19: SSI PrimeCell Identification 1 (SSIPCellID1), offset 0xFF4
The SSIPCellIDn registers are hard-coded and the fields within the register determine the reset
value.
SSI PrimeCell Identification 1 (SSIPCellID1)
SSI0 base: 0x4000.8000
Offset 0xFF4
Type RO, reset 0x0000.00F0
31 30 29 28 27 26 25 24 23 22 21 20 19 18 17 16
reserved
Type RO RO RO RO RO RO RO RO RO RO RO RO RO RO RO RO
Reset 0 0 0 0 0 0 0 0 0 0 0 0 0 0 0 0
15 14 13 12 11 10 9 8 7 6 5 4 3 2 1 0
reserved CID1
Type RO RO RO RO RO RO RO RO RO RO RO RO RO RO RO RO
Reset 0 0 0 0 0 0 0 0 1 1 1 1 0 0 0 0
Bit/Field Name Type Reset Description
Software should not rely on the value of a reserved bit. To provide
compatibility with future products, the value of a reserved bit should be
preserved across a read-modify-write operation.
31:8 reserved RO 0x00
SSI PrimeCell ID Register [15:8]
Provides software a standard cross-peripheral identification system.
7:0 CID1 RO 0xF0
306 November 30, 2007
Preliminary
Synchronous Serial Interface (SSI)
Register 20: SSI PrimeCell Identification 2 (SSIPCellID2), offset 0xFF8
The SSIPCellIDn registers are hard-coded and the fields within the register determine the reset
value.
SSI PrimeCell Identification 2 (SSIPCellID2)
SSI0 base: 0x4000.8000
Offset 0xFF8
Type RO, reset 0x0000.0005
31 30 29 28 27 26 25 24 23 22 21 20 19 18 17 16
reserved
Type RO RO RO RO RO RO RO RO RO RO RO RO RO RO RO RO
Reset 0 0 0 0 0 0 0 0 0 0 0 0 0 0 0 0
15 14 13 12 11 10 9 8 7 6 5 4 3 2 1 0
reserved CID2
Type RO RO RO RO RO RO RO RO RO RO RO RO RO RO RO RO
Reset 0 0 0 0 0 0 0 0 0 0 0 0 0 1 0 1
Bit/Field Name Type Reset Description
Software should not rely on the value of a reserved bit. To provide
compatibility with future products, the value of a reserved bit should be
preserved across a read-modify-write operation.
31:8 reserved RO 0x00
SSI PrimeCell ID Register [23:16]
Provides software a standard cross-peripheral identification system.
7:0 CID2 RO 0x05
November 30, 2007 307
Preliminary
LM3S6110 Microcontroller
Register 21: SSI PrimeCell Identification 3 (SSIPCellID3), offset 0xFFC
The SSIPCellIDn registers are hard-coded and the fields within the register determine the reset
value.
SSI PrimeCell Identification 3 (SSIPCellID3)
SSI0 base: 0x4000.8000
Offset 0xFFC
Type RO, reset 0x0000.00B1
31 30 29 28 27 26 25 24 23 22 21 20 19 18 17 16
reserved
Type RO RO RO RO RO RO RO RO RO RO RO RO RO RO RO RO
Reset 0 0 0 0 0 0 0 0 0 0 0 0 0 0 0 0
15 14 13 12 11 10 9 8 7 6 5 4 3 2 1 0
reserved CID3
Type RO RO RO RO RO RO RO RO RO RO RO RO RO RO RO RO
Reset 0 0 0 0 0 0 0 0 1 0 1 1 0 0 0 1
Bit/Field Name Type Reset Description
Software should not rely on the value of a reserved bit. To provide
compatibility with future products, the value of a reserved bit should be
preserved across a read-modify-write operation.
31:8 reserved RO 0x00
SSI PrimeCell ID Register [31:24]
Provides software a standard cross-peripheral identification system.
7:0 CID3 RO 0xB1
308 November 30, 2007
Preliminary
Synchronous Serial Interface (SSI)
13 Ethernet Controller
The Stellaris® Ethernet Controller consists of a fully integrated media access controller (MAC) and
network physical (PHY) interface device. The Ethernet Controller conforms to IEEE 802.3
specifications and fully supports 10BASE-T and 100BASE-TX standards.
The Ethernet Controller module has the following features:
■ Conforms to the IEEE 802.3-2002 specification
– 10BASE-T/100BASE-TX IEEE-802.3 compliant. Requires only a dual 1:1 isolation transformer
interface to the line
– 10BASE-T/100BASE-TX ENDEC, 100BASE-TX scrambler/descrambler
– Full-featured auto-negotiation
■ Multiple operational modes
– Full- and half-duplex 100 Mbps
– Full- and half-duplex 10 Mbps
– Power-saving and power-down modes
■ Highly configurable
– Programmable MAC address
– LED activity selection
– Promiscuous mode support
– CRC error-rejection control
– User-configurable interrupts
■ Physical media manipulation
– Automatic MDI/MDI-X cross-over correction
– Register-programmable transmit amplitude
– Automatic polarity correction and 10BASE-T signal reception
November 30, 2007 309
Preliminary
LM3S6110 Microcontroller
13.1 Block Diagram
Figure 13-1. Ethernet Controller Block Diagram
MACISR
MACIACK
MACIMR
Interrupt
Control
MACRCR
MACNPR
Receive
Control
MACTCR
MACITHR
MACTRR
Transmit
Control
Transmit
FIFO
Receive
FIFO
MACIAR0
MACIAR1
Individual
Address
MACMDTX
MACMCR
MACMDVR
MACMAR
MACMDRX
MII
Control
MACDR
Data
Access
TXOP
TXON
RXIP
RXIN
XTLP
XTLN
MDIX
Clock
Reference
Transmit
Encoding
Pulse
Shaping
Receive
Decoding
Clock
Recovery
Auto
Negotiation
Carrier
Sense
MR3
MR0
MR1
MR2
MR4
Media Independent Interface
Management Register Set
MR5
MR18
MR6
MR16
MR17
MR19
MR23
MR24
Collision
Detect System Clock
Interrupt
13.2 Functional Description
As shown in Figure 13-2 on page 310, the Ethernet Controller is functionally divided into two layers
or modules: the Media Access Controller (MAC) layer and the Network Physical (PHY) layer. These
correspond to the OSI model layers 2 and 1. The primary interface to the Ethernet Controller is a
simple bus interface to the MAC layer. The MAC layer provides transmit and receive processing for
Ethernet frames. The MAC layer also provides the interface to the PHY module via an internal Media
Independent Interface (MII).
Figure 13-2. Ethernet Controller
Cortex M3
Media Access
Controller
MAC
(Layer 2)
Physical
Layer Entity
PHY
(Layer 1)
Magnetics RJ45
Ethernet Controller
13.2.1 Internal MII Operation
For the MII management interface to function properly, the MDIO signal must be connected through
a 10k Ω pull-up resistor to the +3.3 V supply. Failure to connect this pull-up resistor will prevent
management transactions on this internal MII to function. Note that it is possible for data transmission
across the MII to still function since the PHY layer will auto-negotiate the link parameters by default.
310 November 30, 2007
Preliminary
Ethernet Controller
For the MII management interface to function properly, the internal clock must be divided down from
the system clock to a frequency no greater than 2.5 MHz. The MACMDV register contains the divider
used for scaling down the system clock. See page 330 for more details about the use of this register.
13.2.2 PHY Configuration/Operation
The Physical Layer (PHY) in the Ethernet Controller includes integrated ENDECs,
scrambler/descrambler, dual-speed clock recovery, and full-featured auto-negotiation functions.
The transmitter includes an on-chip pulse shaper and a low-power line driver. The receiver has an
adaptive equalizer and a baseline restoration circuit required for accurate clock and data recovery.
The transceiver interfaces to Category-5 unshielded twisted pair (Cat-5 UTP) cabling for 100BASE-TX
applications, and Category-3 unshielded twisted pair (Cat-3 UTP) for 10BASE-T applications. The
Ethernet Controller is connected to the line media via dual 1:1 isolation transformers. No external
filter is required.
13.2.2.1 Clock Selection
The PHY has an on-chip crystal oscillator which can also be driven by an external oscillator. In this
mode of operation, a 25-MHz crystal should be connected between the XTALPPHY and XTALNPHY
pins. Alternatively, an external 25-MHz clock input can be connected to the XTALPPHY pin. In this
mode of operation, a crystal is not required and the XTALNPHY pin must be tied to ground.
13.2.2.2 Auto-Negotiation
The PHY supports the auto-negotiation functions of Clause 28 of the IEEE 802.3 standard for 10/100
Mbps operation over copper wiring. This function can be enabled via register settings. The
auto-negotiation function defaults to On and the ANEGEN bit in the MR0 register is High after reset.
Software can disable the auto-negotiation function by writing to the ANEGEN bit. The contents of the
MR4 register are sent to the PHY’s link partner during auto-negotiation via fast-link pulse coding.
Once auto-negotiation is complete, the DPLX and RATE bits in the MR18 register reflect the actual
speed and duplex that was chosen. If auto-negotiation fails to establish a link for any reason, the
ANEGF bit in the MR18 register reflects this and auto-negotiation restarts from the beginning. Writing
a 1 to the RANEG bit in the MR0 register also causes auto-negotiation to restart.
13.2.2.3 Polarity Correction
The PHY is capable of either automatic or manual polarity reversal for 10BASE-T and auto-negotiation
functions. Bits 4 and 5 (RVSPOL and APOL) in the MR16 register control this feature. The default is
automatic mode, where APOL is Low and RVSPOL indicates if the detection circuitry has inverted
the input signal. To enter manual mode, APOL should be set High and RVSPOL then controls the
signal polarity.
13.2.2.4 MDI/MDI-X Configuration
The PHY supports the automatic MDI/MDI-X configuration as defined in IEEE 802.3-2002
specification. This eliminates the need for cross-over cables when connecting to another device,
such as a hub. The algorithm is controlled via settings in the MR24 register. Refer to page 352 for
additional details about these settings.
13.2.2.5 LED Indicators
The PHY supports two LED signals that can be used to indicate various states of operation of the
Ethernet Controller. These signals are mapped to the LED0 and LED1 pins. By default, these pins
are configured as GPIO signals (PF3 and PF2). For the PHY layer to drive these signals, they must
be reconfigured to their hardware function. See “General-Purpose Input/Outputs (GPIOs)” on page
November 30, 2007 311
Preliminary
LM3S6110 Microcontroller
131 for additional details. The function of these pins is programmable via the PHY layer MR23 register.
Refer to page 351 for additonal details on how to program these LED functions.
13.2.3 MAC Configuration/Operation
13.2.3.1 Ethernet Frame Format
Ethernet data is carried by Ethernet frames. The basic frame format is shown in Figure
13-3 on page 312.
Figure 13-3. Ethernet Frame
Preamble SFD Destination Address Source Address Length/
Type Data FCS
7
Bytes
6
Bytes
6
Bytes
2
Bytes
1
Byte
4
Bytes
46 - 1500
Bytes
The seven fields of the frame are transmitted from left to right. The bits within the frame are
transmitted from least to most significant bit.
■ Preamble
The Preamble field is used by the physical layer signaling circuitry to synchronize with the received
frame’s timing. The preamble is 7 octets long.
■ Start Frame Delimiter (SFD)
The SFD field follows the preamble pattern and indicates the start of the frame. Its value is
1010.1011.
■ Destination Address (DA)
This field specifies destination addresses for which the frame is intended. The LSB of the DA
determines whether the address is an individual (0), or group/multicast (1) address.
■ Source Address (SA)
The source address field identifies the station from which the frame was initiated.
■ Length/Type Field
The meaning of this field depends on its numeric value. The first of two octets is most significant.
This field can be interpreted as length or type code. The maximum length of the data field is
1500 octets. If the value of the Length/Type field is less than or equal to 1500 decimal, it indicates
the number of MAC client data octets. If the value of this field is greater than or equal to 1536
decimal, then it is type interpretation. The meaning of the Length/Type field when the value is
between 1500 and 1536 decimal is unspecified by the standard. The MAC module assumes
type interpretation if the value of the Length/Type field is greater than 1500 decimal.
■ Data
The data field is a sequence of 0 to 1500 octets. Full data transparency is provided so any values
can appear in this field. A minimum frame size is required to properly meet the IEEE standard.
If necessary, the data field is extended by appending extra bits (a pad). The pad field can have
a size of 0 to 46 octets. The sum of the data and pad lengths must be a minimum of 46 octets.
The MAC module automatically inserts pads if required, though it can be disabled by a register
312 November 30, 2007
Preliminary
Ethernet Controller
write. For the MAC module core, data sent/received can be larger than 1500 bytes, and no Frame
Too Long error is reported. Instead, a FIFO Overrun error is reported when the frame received
is too large to fit into the Ethernet Controller’s RAM.
■ Frame Check Sequence (FCS)
The frame check sequence carries the cyclic redundancy check (CRC) value. The value of this
field is computed over destination address, source address, length/type, data, and pad fields
using the CRC-32 algorithm. The MAC module computes the FCS value one nibble at a time.
For transmitted frames, this field is automatically inserted by the MAC layer, unless disabled by
the CRC bit in the MACTCTL register. For received frames, this field is automatically checked.
If the FCS does not pass, the frame will not be placed in the RX FIFO, unless the FCS check is
disabled by the BADCRC bit in the MACRCTL register.
13.2.3.2 MAC Layer FIFOs
For Ethernet frame transmission, a 2 KB TX FIFO is provided that can be used to store a single
frame. While the IEEE 802.3 specification limits the size of an Ethernet frame's payload section to
1500 Bytes, the Ethernet Controller places no such limit. The full buffer can be used, for a payload
of up to 2032 bytes.
For Ethernet frame reception, a 2-KB RX FIFO is provided that can be used to store multiple frames,
up to a maximum of 31 frames. If a frame is received and there is insufficient space in the RX FIFO,
an overflow error will be indicated.
For details regarding the TX and RX FIFO layout, refer to Table 13-1 on page 313. Please note the
following difference between TX and RX FIFO layout. For the TX FIFO, the Data Length field in the
first FIFO word refers to the Ethernet frame data payload, as shown in the 5th to nth FIFO positions.
For the RX FIFO, the Frame Length field is the total length of the received Ethernet frame, including
the FCS and Frame Length bytes. Also note that if FCS generation is disabled with the CRC bit in
the MACTCTL register, the last word in the FIFO must be the FCS bytes for the frame that has been
written to the FIFO.
Also note that if the length of the data payload section is not a multiple of 4, the FCS field will overlap
words in the FIFO. However, for the RX FIFO, the beginning of the next frame will always be on a
word boundary.
Table 13-1. TX & RX FIFO Organization
FIFO Word Read/Write Word Bit Fields TX FIFO (Write) RX FIFO (Read)
Sequence
1st 7:0 Data Length LSB Frame Length LSB
15:8 Data Length MSB Frame Length MSB
23:16 DA oct 1
31:24 DA oct 2
2nd 7:0 DA oct 3
15:8 DA oct 4
23:16 DA oct 5
31:24 DA oct 6
3rd 7:0 SA oct 1
15:8 SA oct 2
23:16 SA oct 3
31:24 SA oct 4
November 30, 2007 313
Preliminary
LM3S6110 Microcontroller
FIFO Word Read/Write Word Bit Fields TX FIFO (Write) RX FIFO (Read)
Sequence
4th 7:0 SA oct 5
15:8 SA oct 6
23:16 Len/Type MSB
31:24 Len/Type LSB
5th to nth 7:0 data oct n
15:8 data oct n+1
23:16 data oct n+2
31:24 data oct n+3
FCS 1 (if the CRC bit in FCS 1
MACCTL is 0)
last 7:0
FCS 2 (if the CRC bit in FCS 2
MACCTL is 0)
15:8
FCS 3 (if the CRC bit in FCS 3
MACCTL is 0)
23:16
FCS 4 (if the CRC bit in FCS 4
MACCTL is 0)
31:24
13.2.3.3 Ethernet Transmission Options
The Ethernet Controller can automatically generate and insert the Frame Check Sequence (FCS)
at the end of the transmit frame. This is controlled by the CRC bit in the MACTCTL register. For test
purposes, in order to generate a frame with an invalid CRC, this feature can be disabled.
The IEEE 802.3 specification requires that the Ethernet frame payload section be a minimum of 46
bytes. The Ethernet Controller can be configured to automatically pad the data section if the payload
data section loaded into the FIFO is less than the minimum 46 bytes. This feature is controlled by
the PADEN bit in the MACTCTL register.
At the MAC layer, the transmitter can be configured for both full-duplex and half-duplex operation
by using the DUPLEX bit in the MACTCTL register.
13.2.3.4 Ethernet Reception Options
Using the BADCRC bit in the MACRCTL register, the Ethernet Controller can be configured to reject
incoming Ethernet frames with an invalid FCS field.
The Ethernet receiver can also be configured for Promiscuous and Multicast modes using the PRMS
and AMUL fields in the MACRCTL register. If these modes are not enabled, only Ethernet frames
with a broadcast address, or frames matching the MAC address programmed into the MACIA0 and
MACIA1 register will be placed into the RX FIFO.
13.2.4 Interrupts
The Ethernet Controller can generate an interrupt for one or more of the following conditions:
■ A frame has been received into an empty RX FIFO
■ A frame transmission error has occurred
■ A frame has been transmitted successfully
■ A frame has been received with no room in the RX FIFO (overrun)
314 November 30, 2007
Preliminary
Ethernet Controller
■ A frame has been received with one or more error conditions (for example, FCS failed)
■ An MII management transaction between the MAC and PHY layers has completed
■ One or more of the following PHY layer conditions occurs:
– Auto-Negotiate Complete
– Remote Fault
– Link Status Change
– Link Partner Acknowledge
– Parallel Detect Fault
– Page Received
– Receive Error
– Jabber Event Detected
13.3 Initialization and Configuration
To use the Ethernet Controller, the peripheral must be enabled by setting the EPHY0 and EMAC0
bits in the RCGC2 register. The following steps can then be used to configure the Ethernet Controller
for basic operation.
1. Program the MACDIV register to obtain a 2.5 MHz clock (or less) on the internal MII. Assuming
a 20-MHz system clock, the MACDIV value would be 4.
2. Program the MACIA0 and MACIA1 register for address filtering.
3. Program the MACTCTL register for Auto CRC generation, padding, and full-duplex operation
using a value of 0x16.
4. Program the MACRCTL register to reject frames with bad FCS using a value of 0x08.
5. Enable both the Transmitter and Receive by setting the LSB in both the MACTCTL and
MACRCTL registers.
6. To transmit a frame, write the frame into the TX FIFO using the MACDATA register. Then set
the NEWTX bit in the MACTR register to initiate the transmit process. When the NEWTX bit has
been cleared, the TX FIFO will be available for the next transmit frame.
7. To receive a frame, wait for the NPR field in the MACNP register to be non-zero. Then begin
reading the frame from the RX FIFO by using the MACDATA register. When the frame (including
the FCS field) has been read, the NPR field should decrement by one. When there are no more
frames in the RX FIFO, the NPR field will read 0.
13.4 Ethernet Register Map
Table 13-2 on page 316 lists the Ethernet MAC registers. All addresses given are relative to the
Ethernet MAC base address of 0x4004.8000.
November 30, 2007 315
Preliminary
LM3S6110 Microcontroller
The IEEE 802.3 standard specifies a register set for controlling and gathering status from the PHY.
The registers are collectively known as the MII Management registers and are detailed in Section
22.2.4 of the IEEE 802.3 specification. Table 13-2 on page 316 also lists these MII Management
registers. All addresses given are absolute and are written directly to the REGADR field of the
MACMCTL register. The format of registers 0 to 15 are defined by the IEEE specification and are
common to all PHY implementations. The only variance allowed is for features that may or may not
be supported by a specific PHY. Registers 16 to 31 are vendor-specific registers, used to support
features that are specific to a vendors PHY implementation. Vendor-specific registers not listed are
reserved.
Table 13-2. Ethernet Register Map
See
Offset Name Type Reset Description page
Ethernet MAC
0x000 MACRIS RO 0x0000.0000 Ethernet MAC Raw Interrupt Status 318
0x000 MACIACK W1C 0x0000.0000 Ethernet MAC Interrupt Acknowledge 320
0x004 MACIM R/W 0x0000.007F Ethernet MAC Interrupt Mask 321
0x008 MACRCTL R/W 0x0000.0008 Ethernet MAC Receive Control 322
0x00C MACTCTL R/W 0x0000.0000 Ethernet MAC Transmit Control 323
0x010 MACDATA R/W 0x0000.0000 Ethernet MAC Data 324
0x014 MACIA0 R/W 0x0000.0000 Ethernet MAC Individual Address 0 326
0x018 MACIA1 R/W 0x0000.0000 Ethernet MAC Individual Address 1 327
0x01C MACTHR R/W 0x0000.003F Ethernet MAC Threshold 328
0x020 MACMCTL R/W 0x0000.0000 Ethernet MAC Management Control 329
0x024 MACMDV R/W 0x0000.0080 Ethernet MAC Management Divider 330
0x02C MACMTXD R/W 0x0000.0000 Ethernet MAC Management Transmit Data 331
0x030 MACMRXD R/W 0x0000.0000 Ethernet MAC Management Receive Data 332
0x034 MACNP RO 0x0000.0000 Ethernet MAC Number of Packets 333
0x038 MACTR R/W 0x0000.0000 Ethernet MAC Transmission Request 334
MII Management
- MR0 R/W 0x3100 Ethernet PHY Management Register 0 – Control 335
- MR1 RO 0x7849 Ethernet PHY Management Register 1 – Status 337
Ethernet PHY Management Register 2 – PHY Identifier 339
- MR2 RO 0x000E 1
Ethernet PHY Management Register 3 – PHY Identifier 340
- MR3 RO 0x7237 2
Ethernet PHYManagement Register 4 – Auto-Negotiation 341
- MR4 R/W 0x01E1 Advertisement
Ethernet PHYManagement Register 5 – Auto-Negotiation 343
- MR5 RO 0x0000 Link Partner Base Page Ability
316 November 30, 2007
Preliminary
Ethernet Controller
See
Offset Name Type Reset Description page
Ethernet PHYManagement Register 6 – Auto-Negotiation 344
- MR6 RO 0x0000 Expansion
Ethernet PHY Management Register 16 – 345
- MR16 R/W 0x0140 Vendor-Specific
Ethernet PHY Management Register 17 – Interrupt 347
- MR17 R/W 0x0000 Control/Status
- MR18 RO 0x0000 Ethernet PHY Management Register 18 – Diagnostic 349
Ethernet PHY Management Register 19 – Transceiver 350
- MR19 R/W 0x4000 Control
Ethernet PHY Management Register 23 – LED 351
- MR23 R/W 0x0010 Configuration
Ethernet PHY Management Register 24 –MDI/MDIX 352
- MR24 R/W 0x00C0 Control
13.5 Ethernet MAC Register Descriptions
The remainder of this section lists and describes the Ethernet MAC registers, in numerical order by
address offset. Also see “MII Management Register Descriptions” on page 334.
November 30, 2007 317
Preliminary
LM3S6110 Microcontroller
Register 1: Ethernet MAC Raw Interrupt Status (MACRIS), offset 0x000
The MACRIS register is the interrupt status register. On a read, this register gives the current status
value of the corresponding interrupt prior to masking.
Ethernet MAC Raw Interrupt Status (MACRIS)
Base 0x4004.8000
Offset 0x000
Type RO, reset 0x0000.0000
31 30 29 28 27 26 25 24 23 22 21 20 19 18 17 16
reserved
Type RO RO RO RO RO RO RO RO RO RO RO RO RO RO RO RO
Reset 0 0 0 0 0 0 0 0 0 0 0 0 0 0 0 0
15 14 13 12 11 10 9 8 7 6 5 4 3 2 1 0
reserved PHYINT MDINT RXER FOV TXEMP TXER RXINT
Type RO RO RO RO RO RO RO RO RO RO RO RO RO RO RO RO
Reset 0 0 0 0 0 0 0 0 0 0 0 0 0 0 0 0
Bit/Field Name Type Reset Description
Software should not rely on the value of a reserved bit. To provide
compatibility with future products, the value of a reserved bit should be
preserved across a read-modify-write operation.
31:7 reserved RO 0x0
PHY Interrupt
When set, indicates that an enabled interrupt in the PHY layer has
occured. MR17 in the PHY must be read to determine the specific PHY
event that triggered this interrupt.
6 PHYINT RO 0x0
MII Transaction Complete
When set, indicates that a transaction (read or write) on the MII interface
has completed successfully.
5 MDINT RO 0x0
Receive Error
This bit indicates that an error was encountered on the receiver. The
possible errors that can cause this interrupt bit to be set are:
■ A receive error occurs during the reception of a frame (100 Mb/s
only).
■ The frame is not an integer number of bytes (dribble bits) due to an
alignment error.
■ The CRC of the frame does not pass the FCS check.
■ The length/type field is inconsistent with the frame data size when
interpreted as a length field.
4 RXER RO 0x0
FIFO Overrrun
When set, indicates that an overrun was encountered on the receive
FIFO.
3 FOV RO 0x0
Transmit FIFO Empty
When set, indicates that the packet was transmitted and that the TX
FIFO is empty.
2 TXEMP RO 0x0
318 November 30, 2007
Preliminary
Ethernet Controller
Bit/Field Name Type Reset Description
Transmit Error
When set, indicates that an error was encountered on the transmitter.
The possible errors that can cause this interrupt bit to be set are:
■ The data length field stored in the TX FIFO exceeds 2032. The
frame is not sent when this error occurs.
■ The retransmission attempts during the backoff process have
exceeded the maximum limit of 16.
1 TXER RO 0x0
Packet Received
When set, indicates that at least one packet has been received and is
stored in the receiver FIFO.
0 RXINT RO 0x0
November 30, 2007 319
Preliminary
LM3S6110 Microcontroller
Register 2: Ethernet MAC Interrupt Acknowledge (MACIACK), offset 0x000
A write of a 1 to any bit position of this register clears the corresponding interrupt bit in the Ethernet
MAC Raw Interrupt Status (MACRIS) register.
Ethernet MAC Interrupt Acknowledge (MACIACK)
Base 0x4004.8000
Offset 0x000
Type W1C, reset 0x0000.0000
31 30 29 28 27 26 25 24 23 22 21 20 19 18 17 16
reserved
Type RO RO RO RO RO RO RO RO RO RO RO RO RO RO RO RO
Reset 0 0 0 0 0 0 0 0 0 0 0 0 0 0 0 0
15 14 13 12 11 10 9 8 7 6 5 4 3 2 1 0
reserved PHYINT MDINT RXER FOV TXEMP TXER RXINT
Type RO RO RO RO RO RO RO RO RO W1C W1C W1C W1C W1C W1C W1C
Reset 0 0 0 0 0 0 0 0 0 0 0 0 0 0 0 0
Bit/Field Name Type Reset Description
Software should not rely on the value of a reserved bit. To provide
compatibility with future products, the value of a reserved bit should be
preserved across a read-modify-write operation.
31:7 reserved RO 0x0
Clear PHY Interrupt
A write of a 1 clears the PHYINT interrupt read from the MACRIS
register.
6 PHYINT W1C 0x0
Clear MII Transaction Complete
A write of a 1 clears the MDINT interrupt read from the MACRIS register.
5 MDINT W1C 0x0
Clear Receive Error
A write of a 1 clears the RXER interrupt read from the MACRIS register.
4 RXER W1C 0x0
Clear FIFO Overrun
A write of a 1 clears the FOV interrupt read from the MACRIS register.
3 FOV W1C 0x0
Clear Transmit FIFO Empty
A write of a 1 clears the TXEMP interrupt read from the MACRIS register.
2 TXEMP W1C 0x0
Clear Transmit Error
A write of a 1 clears the TXER interrupt read from the MACRIS register
and resets the TX FIFO write pointer.
1 TXER W1C 0x0
Clear Packet Received
A write of a 1 clears the RXINT interrupt read from the MACRIS register.
0 RXINT W1C 0x0
320 November 30, 2007
Preliminary
Ethernet Controller
Register 3: Ethernet MAC Interrupt Mask (MACIM), offset 0x004
This register allows software to enable/disable Ethernet MAC interrupts. Writing a 0 disables the
interrupt, while writing a 1 enables it.
Ethernet MAC Interrupt Mask (MACIM)
Base 0x4004.8000
Offset 0x004
Type R/W, reset 0x0000.007F
31 30 29 28 27 26 25 24 23 22 21 20 19 18 17 16
reserved
Type RO RO RO RO RO RO RO RO RO RO RO RO RO RO RO RO
Reset 0 0 0 0 0 0 0 0 0 0 0 0 0 0 0 0
15 14 13 12 11 10 9 8 7 6 5 4 3 2 1 0
reserved PHYINTM MDINTM RXERM FOVM TXEMPM TXERM RXINTM
Type RO RO RO RO RO RO RO RO RO R/W R/W R/W R/W R/W R/W R/W
Reset 0 0 0 0 0 0 0 0 0 1 1 1 1 1 1 1
Bit/Field Name Type Reset Description
Software should not rely on the value of a reserved bit. To provide
compatibility with future products, the value of a reserved bit should be
preserved across a read-modify-write operation.
31:7 reserved RO 0x0
Mask PHY Interrupt
This bit masks the PHYINT bit in the MACRIS register from being
asserted.
6 PHYINTM R/W 1
Mask MII Transaction Complete
This bit masks the MDINT bit in the MACRIS register from being
asserted.
5 MDINTM R/W 1
Mask Receive Error
This bit masks the RXER bit in the MACRIS register from being asserted.
4 RXERM R/W 1
Mask FIFO Overrrun
This bit masks the FOV bit in the MACRIS register from being asserted.
3 FOVM R/W 1
Mask Transmit FIFO Empty
This bit masks the TXEMP bit in the MACRIS register from being
asserted.
2 TXEMPM R/W 1
Mask Transmit Error
This bit masks the TXER bit in the MACRIS register from being asserted.
1 TXERM R/W 1
Mask Packet Received
This bit masks the RXINT bit in the MACRIS register from being
asserted.
0 RXINTM R/W 1
November 30, 2007 321
Preliminary
LM3S6110 Microcontroller
Register 4: Ethernet MAC Receive Control (MACRCTL), offset 0x008
This register enables software to configure the receive module and control the types of frames that
are received from the physical medium. It is important to note that when the receive module is
enabled, all valid frames with a broadcast address of FF-FF-FF-FF-FF-FF in the Destination Address
field will be received and stored in the RX FIFO, even if the AMUL bit is not set.
Ethernet MAC Receive Control (MACRCTL)
Base 0x4004.8000
Offset 0x008
Type R/W, reset 0x0000.0008
31 30 29 28 27 26 25 24 23 22 21 20 19 18 17 16
reserved
Type RO RO RO RO RO RO RO RO RO RO RO RO RO RO RO RO
Reset 0 0 0 0 0 0 0 0 0 0 0 0 0 0 0 0
15 14 13 12 11 10 9 8 7 6 5 4 3 2 1 0
reserved RSTFIFO BADCRC PRMS AMUL RXEN
Type RO RO RO RO RO RO RO RO RO RO RO R/W R/W R/W R/W R/W
Reset 0 0 0 0 0 0 0 0 0 0 0 0 1 0 0 0
Bit/Field Name Type Reset Description
Software should not rely on the value of a reserved bit. To provide
compatibility with future products, the value of a reserved bit should be
preserved across a read-modify-write operation.
31:5 reserved RO 0x0
Clear Receive FIFO
When set, clears the receive FIFO. This should be done when software
initialization is performed.
It is recommended that the receiver be disabled (RXEN = 0), and then
the reset initiated (RSTFIFO = 1). This sequence will flush and reset the
RX FIFO.
4 RSTFIFO R/W 0x0
Enable Reject Bad CRC
The BADCRC bit enables the rejection of frames with an incorrectly
calculated CRC.
3 BADCRC R/W 0x1
Enable Promiscuous Mode
The PRMS bit enables Promiscuous mode, which accepts all valid frames,
regardless of the Destination Address.
2 PRMS R/W 0x0
Enable Multicast Frames
The AMUL bit enables the reception of multicast frames from the physical
medium.
1 AMUL R/W 0x0
Enable Receiver
The RXEN bit enables the Ethernet receiver. When this bit is Low, the
receiver is disabled and all frames on the physical medium are ignored.
0 RXEN R/W 0x0
322 November 30, 2007
Preliminary
Ethernet Controller
Register 5: Ethernet MAC Transmit Control (MACTCTL), offset 0x00C
This register enables software to configure the transmit module, and control frames are placed onto
the physical medium.
Ethernet MAC Transmit Control (MACTCTL)
Base 0x4004.8000
Offset 0x00C
Type R/W, reset 0x0000.0000
31 30 29 28 27 26 25 24 23 22 21 20 19 18 17 16
reserved
Type RO RO RO RO RO RO RO RO RO RO RO RO RO RO RO RO
Reset 0 0 0 0 0 0 0 0 0 0 0 0 0 0 0 0
15 14 13 12 11 10 9 8 7 6 5 4 3 2 1 0
reserved DUPLEX reserved CRC PADEN TXEN
Type RO RO RO RO RO RO RO RO RO RO RO R/W RO R/W R/W R/W
Reset 0 0 0 0 0 0 0 0 0 0 0 0 0 0 0 0
Bit/Field Name Type Reset Description
Software should not rely on the value of a reserved bit. To provide
compatibility with future products, the value of a reserved bit should be
preserved across a read-modify-write operation.
31:5 reserved RO 0x0
Enable Duplex Mode
When set, enables Duplex mode, allowing simultaneous transmission
and reception.
4 DUPLEX R/W 0x0
Software should not rely on the value of a reserved bit. To provide
compatibility with future products, the value of a reserved bit should be
preserved across a read-modify-write operation.
3 reserved RO 0x0
Enable CRC Generation
When set, enables the automatic generation of the CRC and the
placement at the end of the packet. If this bit is not set, the frames placed
in the TX FIFO will be sent exactly as they are written into the FIFO.
2 CRC R/W 0x0
Enable Packet Padding
When set, enables the automatic padding of packets that do not meet
the minimum frame size.
1 PADEN R/W 0x0
Enable Transmitter
When set, enables the transmitter. When this bit is 0, the transmitter is
disabled.
0 TXEN R/W 0x0
November 30, 2007 323
Preliminary
LM3S6110 Microcontroller
Register 6: Ethernet MAC Data (MACDATA), offset 0x010
This register enables software to access the TX and RX FIFOs.
Reads from this register return the data stored in the RX FIFO from the location indicated by the
read pointer.
Writes to this register store the data in the TX FIFO at the location indicated by the write pointer.
The write pointer is then auto-incremented to the next TX FIFO location.
There is no mechanism for randomly accessing bytes in either the RX or TX FIFOs. Data must be
read from the RX FIFO sequentially and stored in a buffer for further processing. Once a read has
been performed, the data in the FIFO cannot be re-read. Data must be written to the TX FIFO
sequentially. If an error is made in placing the frame into the TX FIFO, the write pointer can be reset
to the start of the TX FIFO by writing the TXER bit of the MACIACK register and then the data
re-written.
Read-Only Register
Ethernet MAC Data (MACDATA)
Base 0x4004.8000
Offset 0x010
Type RO, reset 0x0000.0000
31 30 29 28 27 26 25 24 23 22 21 20 19 18 17 16
RXDATA
Type RO RO RO RO RO RO RO RO RO RO RO RO RO RO RO RO
Reset 0 0 0 0 0 0 0 0 0 0 0 0 0 0 0 0
15 14 13 12 11 10 9 8 7 6 5 4 3 2 1 0
RXDATA
Type RO RO RO RO RO RO RO RO RO RO RO RO RO RO RO RO
Reset 0 0 0 0 0 0 0 0 0 0 0 0 0 0 0 0
Bit/Field Name Type Reset Description
Receive FIFO Data
The RXDATA bits represent the next four bytes of data stored in the RX
FIFO.
31:0 RXDATA RO 0x0
Write-Only Register
Ethernet MAC Data (MACDATA)
Base 0x4004.8000
Offset 0x010
Type WO, reset 0x0000.0000
31 30 29 28 27 26 25 24 23 22 21 20 19 18 17 16
TXDATA
Type WO WO WO WO WO WO WO WO WO WO WO WO WO WO WO WO
Reset 0 0 0 0 0 0 0 0 0 0 0 0 0 0 0 0
15 14 13 12 11 10 9 8 7 6 5 4 3 2 1 0
TXDATA
Type WO WO WO WO WO WO WO WO WO WO WO WO WO WO WO WO
Reset 0 0 0 0 0 0 0 0 0 0 0 0 0 0 0 0
324 November 30, 2007
Preliminary
Ethernet Controller
Bit/Field Name Type Reset Description
Transmit FIFO Data
The TXDATA bits represent the next four bytes of data to place in the
TX FIFO for transmission.
31:0 TXDATA WO 0x0
November 30, 2007 325
Preliminary
LM3S6110 Microcontroller
Register 7: Ethernet MAC Individual Address 0 (MACIA0), offset 0x014
This register enables software to program the first four bytes of the hardware MAC address of the
Network Interface Card (NIC). (The last two bytes are in MACIA1). The 6-byte IAR is compared
against the incoming Destination Address fields to determine whether the frame should be received.
Ethernet MAC Individual Address 0 (MACIA0)
Base 0x4004.8000
Offset 0x014
Type R/W, reset 0x0000.0000
31 30 29 28 27 26 25 24 23 22 21 20 19 18 17 16
MACOCT4 MACOCT3
Type R/W R/W R/W R/W R/W R/W R/W R/W R/W R/W R/W R/W R/W R/W R/W R/W
Reset 0 0 0 0 0 0 0 0 0 0 0 0 0 0 0 0
15 14 13 12 11 10 9 8 7 6 5 4 3 2 1 0
MACOCT2 MACOCT1
Type R/W R/W R/W R/W R/W R/W R/W R/W R/W R/W R/W R/W R/W R/W R/W R/W
Reset 0 0 0 0 0 0 0 0 0 0 0 0 0 0 0 0
Bit/Field Name Type Reset Description
MAC Address Octet 4
The MACOCT4 bits represent the fourth octet of the MAC address used
to uniquely identify each Ethernet Controller.
31:24 MACOCT4 R/W 0x0
MAC Address Octet 3
The MACOCT3 bits represent the third octet of the MAC address used
to uniquely identify each Ethernet Controller.
23:16 MACOCT3 R/W 0x0
MAC Address Octet 2
The MACOCT2 bits represent the second octet of the MAC address used
to uniquely identify each Ethernet Controller.
15:8 MACOCT2 R/W 0x0
MAC Address Octet 1
The MACOCT1 bits represent the first octet of the MAC address used to
uniquely identify each Ethernet Controller.
7:0 MACOCT1 R/W 0x0
326 November 30, 2007
Preliminary
Ethernet Controller
Register 8: Ethernet MAC Individual Address 1 (MACIA1), offset 0x018
This register enables software to program the last two bytes of the hardware MAC address of the
Network Interface Card (NIC). (The first four bytes are in MACIA0). The 6-byte IAR is compared
against the incoming Destination Address fields to determine whether the frame should be received.
Ethernet MAC Individual Address 1 (MACIA1)
Base 0x4004.8000
Offset 0x018
Type R/W, reset 0x0000.0000
31 30 29 28 27 26 25 24 23 22 21 20 19 18 17 16
reserved
Type RO RO RO RO RO RO RO RO RO RO RO RO RO RO RO RO
Reset 0 0 0 0 0 0 0 0 0 0 0 0 0 0 0 0
15 14 13 12 11 10 9 8 7 6 5 4 3 2 1 0
MACOCT6 MACOCT5
Type R/W R/W R/W R/W R/W R/W R/W R/W R/W R/W R/W R/W R/W R/W R/W R/W
Reset 0 0 0 0 0 0 0 0 0 0 0 0 0 0 0 0
Bit/Field Name Type Reset Description
Software should not rely on the value of a reserved bit. To provide
compatibility with future products, the value of a reserved bit should be
preserved across a read-modify-write operation.
31:16 reserved RO 0x0
MAC Address Octet 6
The MACOCT6 bits represent the sixth octet of the MAC address used
to uniquely identify each Ethernet Controller.
15:8 MACOCT6 R/W 0x0
MAC Address Octet 5
The MACOCT5 bits represent the fifth octet of the MAC address used to
uniquely identify each Ethernet Controller.
7:0 MACOCT5 R/W 0x0
November 30, 2007 327
Preliminary
LM3S6110 Microcontroller
Register 9: Ethernet MAC Threshold (MACTHR), offset 0x01C
This register enables software to set the threshold level at which the transmission of the frame
begins. If the THRESH bits are set to 0x3F, which is the reset value, transmission does not start until
the NEWTX bit is set in the MACTR register. This effectively disables the early transmission feature.
Writing the THRESH bits to any value besides all 1s enables the early transmission feature. Once
the byte count of data in the TX FIFO reaches this level, transmission of the frame begins. When
THRESH is set to all 0s, transmission of the frame begins after 4 bytes (a single write) are stored in
the TX FIFO. Each increment of the THRESH bit field waits for an additional 32 bytes of data (eight
writes) to be stored in the TX FIFO. Therefore, a value of 0x01 would wait for 36 bytes of data to
be written while a value of 0x02 would wait for 68 bytes to be written. In general, early transmission
starts when:
Number of Bytes >= 4 (THRESH x 8 + 1)
Reaching the threshold level has the same effect as setting the NEWTX bit in the MACTR register.
Transmission of the frame begins and then the number of bytes indicated by the Data Length field
is sent out on the physical medium. Because under-run checking is not performed, it is possible
that the tail pointer may reach and pass the write pointer in the TX FIFO. This causes indeterminate
values to be written to the physical medium rather than the end of the frame. Therefore, sufficient
bus bandwidth for writing to the TX FIFO must be guaranteed by the software.
If a frame smaller than the threshold level needs to be sent, the NEWTX bit in the MACTR register
must be set with an explicit write. This initiates the transmission of the frame even though the
threshold limit has not been reached.
If the threshold level is set too small, it is possible for the transmitter to underrun. If this occurs, the
transmit frame is aborted, and a transmit error occurs.
Ethernet MAC Threshold (MACTHR)
Base 0x4004.8000
Offset 0x01C
Type R/W, reset 0x0000.003F
31 30 29 28 27 26 25 24 23 22 21 20 19 18 17 16
reserved
Type RO RO RO RO RO RO RO RO RO RO RO RO RO RO RO RO
Reset 0 0 0 0 0 0 0 0 0 0 0 0 0 0 0 0
15 14 13 12 11 10 9 8 7 6 5 4 3 2 1 0
reserved THRESH
Type RO RO RO RO RO RO RO RO RO RO R/W R/W R/W R/W R/W R/W
Reset 0 0 0 0 0 0 0 0 0 0 1 1 1 1 1 1
Bit/Field Name Type Reset Description
Software should not rely on the value of a reserved bit. To provide
compatibility with future products, the value of a reserved bit should be
preserved across a read-modify-write operation.
31:6 reserved RO 0x0
Threshold Value
The THRESH bits represent the early transmit threshold. Once the amount
of data in the TX FIFO exceeds this value, transmission of the packet
begins.
5:0 THRESH R/W 0x3F
328 November 30, 2007
Preliminary
Ethernet Controller
Register 10: Ethernet MAC Management Control (MACMCTL), offset 0x020
This register enables software to control the transfer of data to and from the MII Management
registers in the Ethernet PHY. The address, name, type, reset configuration, and functional description
of each of these registers can be found in Table 13-2 on page 316 and in “MII Management Register
Descriptions” on page 334.
In order to initiate a read transaction from the MII Management registers, the WRITE bit must be
written with a 0 during the same cycle that the START bit is written with a 1.
In order to initiate a write transaction to the MII Management registers, the WRITE bit must be written
with a 1 during the same cycle that the START bit is written with a 1.
Ethernet MAC Management Control (MACMCTL)
Base 0x4004.8000
Offset 0x020
Type R/W, reset 0x0000.0000
31 30 29 28 27 26 25 24 23 22 21 20 19 18 17 16
reserved
Type RO RO RO RO RO RO RO RO RO RO RO RO RO RO RO RO
Reset 0 0 0 0 0 0 0 0 0 0 0 0 0 0 0 0
15 14 13 12 11 10 9 8 7 6 5 4 3 2 1 0
reserved REGADR reserved WRITE START
Type RO RO RO RO RO RO RO RO R/W R/W R/W R/W R/W RO R/W R/W
Reset 0 0 0 0 0 0 0 0 0 0 0 0 0 0 0 0
Bit/Field Name Type Reset Description
Software should not rely on the value of a reserved bit. To provide
compatibility with future products, the value of a reserved bit should be
preserved across a read-modify-write operation.
31:8 reserved RO 0x0
MII Register Address
The REGADR bit field represents the MII Management register address
for the next MII management interface transaction.
7:3 REGADR R/W 0x0
Software should not rely on the value of a reserved bit. To provide
compatibility with future products, the value of a reserved bit should be
preserved across a read-modify-write operation.
2 reserved RO 0x0
MII Register Transaction Type
The WRITE bit represents the operation of the next MII management
interface transaction. If WRITE is set, the next operation will be a write;
otherwise, it will be a read.
1 WRITE R/W 0x0
MII Register Transaction Enable
The START bit represents the initiation of the next MII management
interface transaction. When a 1 is written to this bit, the MII register
located at REGADR will be read (WRITE=0) or written (WRITE=1).
0 START R/W 0x0
November 30, 2007 329
Preliminary
LM3S6110 Microcontroller
Register 11: Ethernet MAC Management Divider (MACMDV), offset 0x024
This register enables software to set the clock divider for the Management Data Clock (MDC). This
clock is used to synchronize read and write transactions between the system and the MII Management
registers. The frequency of the MDC clock can be calculated from the following formula:
Fmdc = Fipclk / (2 * (MACMDVR + 1 ))
The clock divider must be written with a value that ensures that the MDC clock will not exceed a
frequency of 2.5 MHz.
Ethernet MAC Management Divider (MACMDV)
Base 0x4004.8000
Offset 0x024
Type R/W, reset 0x0000.0080
31 30 29 28 27 26 25 24 23 22 21 20 19 18 17 16
reserved
Type RO RO RO RO RO RO RO RO RO RO RO RO RO RO RO RO
Reset 0 0 0 0 0 0 0 0 0 0 0 0 0 0 0 0
15 14 13 12 11 10 9 8 7 6 5 4 3 2 1 0
reserved DIV
Type RO RO RO RO RO RO RO RO R/W R/W R/W R/W R/W R/W R/W R/W
Reset 0 0 0 0 0 0 0 0 1 0 0 0 0 0 0 0
Bit/Field Name Type Reset Description
Software should not rely on the value of a reserved bit. To provide
compatibility with future products, the value of a reserved bit should be
preserved across a read-modify-write operation.
31:8 reserved RO 0x0
Clock Divider
The DIV bits are used to set the clock divider for the MDC clock used
to transmit data between the MAC and PHY over the serial MII interface.
7:0 DIV R/W 0x80
330 November 30, 2007
Preliminary
Ethernet Controller
Register 12: Ethernet MAC Management Transmit Data (MACMTXD), offset
0x02C
This register holds the next value to be written to the MII Management registers.
Ethernet MAC Management Transmit Data (MACMTXD)
Base 0x4004.8000
Offset 0x02C
Type R/W, reset 0x0000.0000
31 30 29 28 27 26 25 24 23 22 21 20 19 18 17 16
reserved
Type RO RO RO RO RO RO RO RO RO RO RO RO RO RO RO RO
Reset 0 0 0 0 0 0 0 0 0 0 0 0 0 0 0 0
15 14 13 12 11 10 9 8 7 6 5 4 3 2 1 0
MDTX
Type R/W R/W R/W R/W R/W R/W R/W R/W R/W R/W R/W R/W R/W R/W R/W R/W
Reset 0 0 0 0 0 0 0 0 0 0 0 0 0 0 0 0
Bit/Field Name Type Reset Description
Software should not rely on the value of a reserved bit. To provide
compatibility with future products, the value of a reserved bit should be
preserved across a read-modify-write operation.
31:16 reserved RO 0x0
MII Register Transmit Data
The MDTX bits represent the data that will be written in the next MII
management transaction.
15:0 MDTX R/W 0x0
November 30, 2007 331
Preliminary
LM3S6110 Microcontroller
Register 13: Ethernet MAC Management Receive Data (MACMRXD), offset
0x030
This register holds the last value read from the MII Management registers.
Ethernet MAC Management Receive Data (MACMRXD)
Base 0x4004.8000
Offset 0x030
Type R/W, reset 0x0000.0000
31 30 29 28 27 26 25 24 23 22 21 20 19 18 17 16
reserved
Type RO RO RO RO RO RO RO RO RO RO RO RO RO RO RO RO
Reset 0 0 0 0 0 0 0 0 0 0 0 0 0 0 0 0
15 14 13 12 11 10 9 8 7 6 5 4 3 2 1 0
MDRX
Type R/W R/W R/W R/W R/W R/W R/W R/W R/W R/W R/W R/W R/W R/W R/W R/W
Reset 0 0 0 0 0 0 0 0 0 0 0 0 0 0 0 0
Bit/Field Name Type Reset Description
Software should not rely on the value of a reserved bit. To provide
compatibility with future products, the value of a reserved bit should be
preserved across a read-modify-write operation.
31:16 reserved RO 0x0
MII Register Receive Data
The MDRX bits represent the data that was read in the previous MII
management transaction.
15:0 MDRX R/W 0x0
332 November 30, 2007
Preliminary
Ethernet Controller
Register 14: Ethernet MAC Number of Packets (MACNP), offset 0x034
This register holds the number of frames that are currently in the RX FIFO. When NPR is 0, there
are no frames in the RX FIFO and the RXINT bit is not set. When NPR is any other value, there is
at least one frame in the RX FIFO and the RXINT bit in the MACRIS register is set.
Ethernet MAC Number of Packets (MACNP)
Base 0x4004.8000
Offset 0x034
Type RO, reset 0x0000.0000
31 30 29 28 27 26 25 24 23 22 21 20 19 18 17 16
reserved
Type RO RO RO RO RO RO RO RO RO RO RO RO RO RO RO RO
Reset 0 0 0 0 0 0 0 0 0 0 0 0 0 0 0 0
15 14 13 12 11 10 9 8 7 6 5 4 3 2 1 0
reserved NPR
Type RO RO RO RO RO RO RO RO RO RO RO RO RO RO RO RO
Reset 0 0 0 0 0 0 0 0 0 0 0 0 0 0 0 0
Bit/Field Name Type Reset Description
Software should not rely on the value of a reserved bit. To provide
compatibility with future products, the value of a reserved bit should be
preserved across a read-modify-write operation.
31:6 reserved RO 0x0
Number of Packets in Receive FIFO
The NPR bits represent the number of packets stored in the RX FIFO.
While the NPR field is greater than 0, the RXINT interrupt in the MACRIS
register will be asserted.
5:0 NPR RO 0x0
November 30, 2007 333
Preliminary
LM3S6110 Microcontroller
Register 15: Ethernet MAC Transmission Request (MACTR), offset 0x038
This register enables software to initiate the transmission of the frame currently located in the TX
FIFO to the physical medium. Once the frame has been transmitted to the medium from the TX
FIFO or a transmission error has been encountered, the NEWTX bit is auto-cleared by the hardware.
Ethernet MAC Transmission Request (MACTR)
Base 0x4004.8000
Offset 0x038
Type R/W, reset 0x0000.0000
31 30 29 28 27 26 25 24 23 22 21 20 19 18 17 16
reserved
Type RO RO RO RO RO RO RO RO RO RO RO RO RO RO RO RO
Reset 0 0 0 0 0 0 0 0 0 0 0 0 0 0 0 0
15 14 13 12 11 10 9 8 7 6 5 4 3 2 1 0
reserved NEWTX
Type RO RO RO RO RO RO RO RO RO RO RO RO RO RO RO R/W
Reset 0 0 0 0 0 0 0 0 0 0 0 0 0 0 0 0
Bit/Field Name Type Reset Description
Software should not rely on the value of a reserved bit. To provide
compatibility with future products, the value of a reserved bit should be
preserved across a read-modify-write operation.
31:1 reserved RO 0x0
New Transmission
When set, the NEWTX bit initiates an Ethernet transmission once the
packet has been placed in the TX FIFO. This bit is cleared once the
transmission has been completed. If early transmission is being used
(see the MACTHR register), this bit does not need to be set.
0 NEWTX R/W 0x0
13.6 MII Management Register Descriptions
The IEEE 802.3 standard specifies a register set for controlling and gathering status from the PHY.
The registers are collectively known as the MII Management registers. All addresses given are
absolute. Addresses not listed are reserved. Also see “Ethernet MAC Register
Descriptions” on page 317.
334 November 30, 2007
Preliminary
Ethernet Controller
Register 16: Ethernet PHY Management Register 0 – Control (MR0), address
0x00
This register enables software to configure the operation of the PHY. The default settings of these
registers are designed to initialize the PHY to a normal operational mode without configuration.
Ethernet PHY Management Register 0 – Control (MR0)
Base 0x4004.8000
Address 0x00
Type R/W, reset 0x3100
15 14 13 12 11 10 9 8 7 6 5 4 3 2 1 0
RESET LOOPBK SPEEDSL ANEGEN PWRDN ISO RANEG DUPLEX COLT reserved
Type R/W R/W R/W R/W R/W R/W R/W R/W R/W R/W R/W R/W R/W R/W R/W R/W
Reset 0 0 1 1 0 0 0 1 0 0 0 0 0 0 0 0
Bit/Field Name Type Reset Description
Reset Registers
When set, resets the registers to their default state and reinitializes
internal state machines. Once the reset operation has completed, this
bit is cleared by hardware.
15 RESET R/W 0
Loopback Mode
When set, enables the Loopback mode of operation. The receive circuitry
is isolated from the physical medium and transmissions are sent back
through the receive circuitry instead of the medium.
14 LOOPBK R/W 0
Speed Select
1: Enables the 100 Mb/s mode of operation (100BASE-TX).
0: Enables the 10 Mb/s mode of operation (10BASE-T).
13 SPEEDSL R/W 1
Auto-Negotiation Enable
When set, enables the Auto-Negotiation process.
12 ANEGEN R/W 1
Power Down
When set, places the PHY into a low-power consuming state.
11 PWRDN R/W 0
Isolate
When set, isolates transmit and receive data paths and ignores all
signaling on these buses.
10 ISO R/W 0
Restart Auto-Negotiation
When set, restarts the Auto-Negotiation process. Once the restart has
initiated, this bit is cleared by hardware.
9 RANEG R/W 0
Set Duplex Mode
1: Enables the Full-Duplex mode of operation. This bit can be set by
software in a manual configuration process or by the Auto-Negotiation
process.
0: Enables the Half-Duplex mode of operation.
8 DUPLEX R/W 1
November 30, 2007 335
Preliminary
LM3S6110 Microcontroller
Bit/Field Name Type Reset Description
Collision Test
When set, enables the Collision Test mode of operation. The COLT bit
asserts after the initiation of a transmission and de-asserts once the
transmission is halted.
7 COLT R/W 0
6:0 reserved R/W 0x00 Write as 0, ignore on read.
336 November 30, 2007
Preliminary
Ethernet Controller
Register 17: Ethernet PHY Management Register 1 – Status (MR1), address
0x01
This register enables software to determine the capabilities of the PHY and perform its initialization
and operation appropriately.
Ethernet PHY Management Register 1 – Status (MR1)
Base 0x4004.8000
Address 0x01
Type RO, reset 0x7849
15 14 13 12 11 10 9 8 7 6 5 4 3 2 1 0
reserved 100X_F 100X_H 10T_F 10T_H reserved MFPS ANEGC RFAULT ANEGA LINK JAB EXTD
Type RO RO RO RO RO RO RO RO RO RO RO RC RO RO RC RO
Reset 0 1 1 1 1 0 0 0 0 1 0 0 1 0 0 1
Bit/Field Name Type Reset Description
Software should not rely on the value of a reserved bit. To provide
compatibility with future products, the value of a reserved bit should be
preserved across a read-modify-write operation.
15 reserved RO 0
100BASE-TX Full-Duplex Mode
When set, indicates that the PHY is capable of supporting 100BASE-TX
Full-Duplex mode.
14 100X_F RO 1
100BASE-TX Half-Duplex Mode
When set, indicates that the PHY is capable of supporting 100BASE-TX
Half-Duplex mode.
13 100X_H RO 1
10BASE-T Full-Duplex Mode
When set, indicates that the PHY is capable of 10BASE-T Full-Duplex
mode.
12 10T_F RO 1
10BASE-T Half-Duplex Mode
When set, indicates that the PHY is capable of supporting 10BASE-T
Half-Duplex mode.
11 10T_H RO 1
Software should not rely on the value of a reserved bit. To provide
compatibility with future products, the value of a reserved bit should be
preserved across a read-modify-write operation.
10:7 reserved RO 0
Management Frames with Preamble Suppressed
When set, indicates that the Management Interface is capable of
receiving management frames with the preamble suppressed.
6 MFPS RO 1
Auto-Negotiation Complete
When set, indicates that the Auto-Negotiation process has been
completed and that the extended registers defined by the
Auto-Negotiation protocol are valid.
5 ANEGC RO 0
Remote Fault
When set, indicates that a remote fault condition has been detected.
This bit remains set until it is read, even if the condition no longer exists.
4 RFAULT RC 0
November 30, 2007 337
Preliminary
LM3S6110 Microcontroller
Bit/Field Name Type Reset Description
Auto-Negotiation
When set, indicates that the PHY has the ability to perform
Auto-Negotiation.
3 ANEGA RO 1
Link Made
When set, indicates that a valid link has been established by the PHY.
2 LINK RO 0
Jabber Condition
When set, indicates that a jabber condition has been detected by the
PHY. This bit remains set until it is read, even if the jabber condition no
longer exists.
1 JAB RC 0
Extended Capabilities
When set, indicates that the PHY provides an extended set of capabilities
that can be accessed through the extended register set.
0 EXTD RO 1
338 November 30, 2007
Preliminary
Ethernet Controller
Register 18: Ethernet PHY Management Register 2 – PHY Identifier 1 (MR2),
address 0x02
This register, along with MR3, provides a 32-bit value indicating the manufacturer, model, and
revision information.
Ethernet PHY Management Register 2 – PHY Identifier 1 (MR2)
Base 0x4004.8000
Address 0x02
Type RO, reset 0x000E
15 14 13 12 11 10 9 8 7 6 5 4 3 2 1 0
OUI[21:6]
Type RO RO RO RO RO RO RO RO RO RO RO RO RO RO RO RO
Reset 0 0 0 0 0 0 0 0 0 0 0 0 1 1 1 0
Bit/Field Name Type Reset Description
Organizationally Unique Identifier[21:6]
This field, along with the OUI[5:0] field in MR3, makes up the
Organizationally Unique Identifier indicating the PHY manufacturer.
15:0 OUI[21:6] RO 0x000E
November 30, 2007 339
Preliminary
LM3S6110 Microcontroller
Register 19: Ethernet PHY Management Register 3 – PHY Identifier 2 (MR3),
address 0x03
This register, along with MR2, provides a 32-bit value indicating the manufacturer, model, and
revision information.
Ethernet PHY Management Register 3 – PHY Identifier 2 (MR3)
Base 0x4004.8000
Address 0x03
Type RO, reset 0x7237
15 14 13 12 11 10 9 8 7 6 5 4 3 2 1 0
OUI[5:0] MN RN
Type RO RO RO RO RO RO RO RO RO RO RO RO RO RO RO RO
Reset 0 1 1 1 0 0 1 0 0 0 1 1 0 1 1 1
Bit/Field Name Type Reset Description
Organizationally Unique Identifier[5:0]
This field, along with the OUI[21:6] field in MR2, makes up the
Organizationally Unique Identifier indicating the PHY manufacturer.
15:10 OUI[5:0] RO 0x1C
Model Number
The MN field represents the Model Number of the PHY.
9:4 MN RO 0x23
Revision Number
The RN field represents the Revision Number of the PHY.
3:0 RN RO 0x7
340 November 30, 2007
Preliminary
Ethernet Controller
Register 20: Ethernet PHY Management Register 4 – Auto-Negotiation
Advertisement (MR4), address 0x04
This register provides the advertised abilities of the PHY used during Auto-Negotiation. Bits 8:5
represent the Technology Ability Field bits. This field can be overwritten by software to Auto-Negotiate
to an alternate common technology. Writing to this register has no effect until Auto-Negotiation is
re-initiated.
Ethernet PHY Management Register 4 – Auto-Negotiation Advertisement (MR4)
Base 0x4004.8000
Address 0x04
Type R/W, reset 0x01E1
15 14 13 12 11 10 9 8 7 6 5 4 3 2 1 0
NP reserved RF reserved A3 A2 A1 A0 S[4:0]
Type RO RO R/W RO RO RO RO R/W R/W R/W R/W RO RO RO RO RO
Reset 0 0 0 0 0 0 0 1 1 1 1 0 0 0 0 1
Bit/Field Name Type Reset Description
Next Page
When set, indicates the PHY is capable of Next Page exchanges to
provide more detailed information on the PHY’s capabilities.
15 NP RO 0
Software should not rely on the value of a reserved bit. To provide
compatibility with future products, the value of a reserved bit should be
preserved across a read-modify-write operation.
14 reserved RO 0
Remote Fault
When set, indicates to the link partner that a Remote Fault condition
has been encountered.
13 RF R/W 0
Software should not rely on the value of a reserved bit. To provide
compatibility with future products, the value of a reserved bit should be
preserved across a read-modify-write operation.
12:9 reserved RO 0
Technology Ability Field[3]
When set, indicates that the PHY supports the 100Base-TX full-duplex
signaling protocol. If software wants to ensure that this mode is not used,
this bit can be written to 0 and Auto-Negotiation re-initiated with the
RANEG bit in the MR0 register.
8 A3 R/W 1
Technology Ability Field[2]
When set, indicates that the PHY supports the 100Base-T half-duplex
signaling protocol. If software wants to ensure that this mode is not used,
this bit can be written to 0 and Auto-Negotiation re-initiated.
7 A2 R/W 1
Technology Ability Field[1]
When set, indicates that the PHY supports the 10Base-T full-duplex
signaling protocol. If software wants to ensure that this mode is not used,
this bit can be written to 0 and Auto-Negotiation re-initiated.
6 A1 R/W 1
Technology Ability Field[0]
When set, indicates that the PHY supports the 10Base-T half-duplex
signaling protocol. If software wants to ensure that this mode is not used,
this bit can be written to 0 and Auto-Negotiation re-initiated.
5 A0 R/W 1
November 30, 2007 341
Preliminary
LM3S6110 Microcontroller
Bit/Field Name Type Reset Description
Selector Field
The S[4:0] field encodes 32 possible messages for communicating
between PHYs. This field is hard-coded to 0x01, indicating that the
Stellaris® PHY is IEEE 802.3 compliant.
4:0 S[4:0] RO 0x01
342 November 30, 2007
Preliminary
Ethernet Controller
Register 21: Ethernet PHY Management Register 5 – Auto-Negotiation Link
Partner Base Page Ability (MR5), address 0x05
This register provides the advertised abilities of the link partner’s PHY that are received and stored
during Auto-Negotiation.
Ethernet PHY Management Register 5 – Auto-Negotiation Link Partner Base Page Ability (MR5)
Base 0x4004.8000
Address 0x05
Type RO, reset 0x0000
15 14 13 12 11 10 9 8 7 6 5 4 3 2 1 0
NP ACK RF A[7:0] S[4:0]
Type RO RO RO RO RO RO RO RO RO RO RO RO RO RO RO RO
Reset 0 0 0 0 0 0 0 0 0 0 0 0 0 0 0 0
Bit/Field Name Type Reset Description
Next Page
When set, indicates that the link partner’s PHY is capable of Next page
exchanges to provide more detailed information on the PHY’s
capabilities.
15 NP RO 0
Acknowledge
When set, indicates that the device has successfully received the link
partner’s advertised abilities during Auto-Negotiation.
14 ACK RO 0
Remote Fault
Used as a standard transport mechanism for transmitting simple fault
information.
13 RF RO 0
Technology Ability Field
The A[7:0] field encodes individual technologies that are supported
by the PHY. See the MR4 register.
12:5 A[7:0] RO 0x00
Selector Field
The S[4:0] field encodes possible messages for communicating
between PHYs.
Value Description
0x00 Reserved
0x01 IEEE Std 802.3
0x02 IEEE Std 802.9 ISLAN-16T
0x03 IEEE Std 802.5
0x04 IEEE Std 1394
0x05–0x1F Reserved
4:0 S[4:0] RO 0x00
November 30, 2007 343
Preliminary
LM3S6110 Microcontroller
Register 22: Ethernet PHY Management Register 6 – Auto-Negotiation
Expansion (MR6), address 0x06
This register enables software to determine the Auto-Negotiation and Next Page capabilities of the
PHY and the link partner after Auto-Negotiation.
Ethernet PHY Management Register 6 – Auto-Negotiation Expansion (MR6)
Base 0x4004.8000
Address 0x06
Type RO, reset 0x0000
15 14 13 12 11 10 9 8 7 6 5 4 3 2 1 0
reserved PDF LPNPA reserved PRX LPANEGA
Type RO RO RO RO RO RO RO RO RO RO RO RC RO RO RC RO
Reset 0 0 0 0 0 0 0 0 0 0 0 0 0 0 0 0
Bit/Field Name Type Reset Description
Software should not rely on the value of a reserved bit. To provide
compatibility with future products, the value of a reserved bit should be
preserved across a read-modify-write operation.
15:5 reserved RO 0x000
Parallel Detection Fault
When set, indicates that more than one technology has been detected
at link up. This bit is cleared when read.
4 PDF RC 0
Link Partner is Next Page Able
When set, indicates that the link partner is Next Page Able.
3 LPNPA RO 0
Software should not rely on the value of a reserved bit. To provide
compatibility with future products, the value of a reserved bit should be
preserved across a read-modify-write operation.
2 reserved RO 0x000
New Page Received
When set, indicates that a New Page has been received from the link
partner and stored in the appropriate location. This bit remains set until
the register is read.
1 PRX RC 0
Link Partner is Auto-Negotiation Able
When set, indicates that the Link partner is Auto-Negotiation Able.
0 LPANEGA RO 0
344 November 30, 2007
Preliminary
Ethernet Controller
Register 23: Ethernet PHY Management Register 16 – Vendor-Specific (MR16),
address 0x10
This register enables software to configure the operation of vendor-specific modes of the PHY.
Ethernet PHY Management Register 16 – Vendor-Specific (MR16)
Base 0x4004.8000
Address 0x10
Type R/W, reset 0x0140
15 14 13 12 11 10 9 8 7 6 5 4 3 2 1 0
RPTR INPOL reserved TXHIM SQEI NL10 reserved APOL RVSPOL reserved PCSBP RXCC
Type R/W R/W RO R/W R/W R/W RO RO RO RO R/W R/W RO RO R/W R/W
Reset 0 0 0 0 0 0 0 1 0 1 0 0 0 0 0 0
Bit/Field Name Type Reset Description
Repeater Mode
When set, enables the repeater mode of operation. In this mode,
full-duplex is not allowed and the Carrier Sense signal only responds
to receive activity. If the PHY is configured to 10Base-T mode, the SQE
test function is disabled.
15 RPTR R/W 0
Interrupt Polarity
1: Sets the polarity of the PHY interrupt to be active High.
0: Sets the polarity of the PHY interrupt to active Low.
Important: Because the Media Access Controller expects active
Low interrupts from the PHY, this bit must always be
written with a 0 to ensure proper operation.
14 INPOL R/W 0
Software should not rely on the value of a reserved bit. To provide
compatibility with future products, the value of a reserved bit should be
preserved across a read-modify-write operation.
13 reserved RO 0
Transmit High Impedance Mode
When set, enables the transmitter High Impedance mode. In this mode,
the TXOP and TXON transmitter pins are put into a high impedance state.
The RXIP and RXIN pins remain fully functional.
12 TXHIM R/W 0
SQE Inhibit Testing
When set, prohibits 10Base-T SQE testing.
When 0, the SQE testing is performed by generating a Collision pulse
following the completion of the transmission of a frame.
11 SQEI R/W 0
Natural Loopback Mode
When set, enables the 10Base-T Natural Loopback mode. This causes
the transmission data received by the PHY to be looped back onto the
receive data path when 10Base-T mode is enabled.
10 NL10 R/W 0
Software should not rely on the value of a reserved bit. To provide
compatibility with future products, the value of a reserved bit should be
preserved across a read-modify-write operation.
9:6 reserved RO 0x05
November 30, 2007 345
Preliminary
LM3S6110 Microcontroller
Bit/Field Name Type Reset Description
Auto-Polarity Disable
When set, disables the PHY’s auto-polarity function.
If this bit is 0, the PHY automatically inverts the received signal due to
a wrong polarity connection during Auto-Negotiation if the PHY is in
10Base-T mode.
5 APOL R/W 0
Receive Data Polarity
This bit indicates whether the receive data pulses are being inverted.
If the APOL bit is 0, then the RVSPOL bit is read-only and indicates
whether the auto-polarity circuitry is reversing the polarity. In this case,
a 1 in the RVSPOL bit indicates that the receive data is inverted while a
0 indicates that the receive data is not inverted.
If the APOL bit is 1, then the RVSPOL bit is writable and software can
force the receive data to be inverted. Setting RVSPOL to 1 forces the
receive data to be inverted while a 0 does not invert the receive data.
4 RVSPOL R/W 0
Software should not rely on the value of a reserved bit. To provide
compatibility with future products, the value of a reserved bit should be
preserved across a read-modify-write operation.
3:2 reserved RO 0
PCS Bypass
When set, enables the bypass of the PCS and scrambling/descrambling
functions in 100Base-TX mode. This mode is only valid when
Auto-Negotiation is disabled and 100Base-T mode is enabled.
1 PCSBP R/W 0
Receive Clock Control
When set, enables the Receive Clock Control power saving mode if the
PHY is configured in 100Base-TX mode. This mode shuts down the
receive clock when no data is being received from the physical medium
to save power. This mode should not be used when PCSBP is enabled
and is automatically disabled when the LOOPBK bit in the MR0 register
is set.
0 RXCC R/W 0
346 November 30, 2007
Preliminary
Ethernet Controller
Register 24: Ethernet PHY Management Register 17 – Interrupt Control/Status
(MR17), address 0x11
This register provides the means for controlling and observing the events, which trigger a PHY
interrupt in the MACRIS register. This register can also be used in a polling mode via the MII Serial
Interface as a means to observe key events within the PHY via one register address. Bits 0 through
7 are status bits, which are each set to logic 1 based on an event. These bits are cleared after the
register is read. Bits 8 through 15 of this register, when set to logic 1, enable their corresponding
bit in the lower byte to signal a PHY interrupt in the MACRIS register.
Ethernet PHY Management Register 17 – Interrupt Control/Status (MR17)
Base 0x4004.8000
Address 0x11
Type R/W, reset 0x0000
15 14 13 12 11 10 9 8 7 6 5 4 3 2 1 0
JABBER_IE RXER_IE PRX_IE PDF_IE LPACK_IELSCHG_IE RFAULT_IE ANEGCOMP_IE JABBER_INTRXER_INT PRX_INT PDF_INT LPACK_INT LSCHG_INT RFAULT_INT ANEGCOMP_INT
Type R/W R/W R/W R/W R/W R/W R/W R/W RC RC RC RC RC RC RC RC
Reset 0 0 0 0 0 0 0 0 0 0 0 0 0 0 0 0
Bit/Field Name Type Reset Description
Jabber Interrupt Enable
When set, enables system interrupts when a Jabber condition is detected
by the PHY.
15 JABBER_IE R/W 0
Receive Error Interrupt Enable
When set, enables system interrupts when a receive error is detected
by the PHY.
14 RXER_IE R/W 0
Page Received Interrupt Enable
When set, enables system interrupts when a new page is received by
the PHY.
13 PRX_IE R/W 0
Parallel Detection Fault Interrupt Enable
When set, enables system interrupts when a Parallel Detection Fault is
detected by the PHY.
12 PDF_IE R/W 0
LP Acknowledge Interrupt Enable
When set, enables system interrupts when FLP bursts are received with
the Acknowledge bit during Auto-Negotiation.
11 LPACK_IE R/W 0
Link Status Change Interrupt Enable
When set, enables system interrupts when the Link Status changes
from OK to FAIL.
10 LSCHG_IE R/W 0
Remote Fault Interrupt Enable
When set, enables system interrupts when a Remote Fault condition is
signaled by the link partner.
9 RFAULT_IE R/W 0
Auto-Negotiation Complete Interrupt Enable
When set, enables system interrupts when the Auto-Negotiation
sequence has completed successfully.
8 ANEGCOMP_IE R/W 0
November 30, 2007 347
Preliminary
LM3S6110 Microcontroller
Bit/Field Name Type Reset Description
Jabber Event Interrupt
When set, indicates that a Jabber event has been detected by the
10Base-T circuitry.
7 JABBER_INT RC 0
Receive Error Interrupt
When set, indicates that a receive error has been detected by the PHY.
6 RXER_INT RC 0
Page Receive Interrupt
When set, indicates that a new page has been received from the link
partner during Auto-Negotiation.
5 PRX_INT RC 0
Parallel Detection Fault Interrupt
When set, indicates that a Parallel Detection Fault has been detected
by the PHY during the Auto-Negotiation process.
4 PDF_INT RC 0
LP Acknowledge Interrupt
When set, indicates that an FLP burst has been received with the
Acknowledge bit set during Auto-Negotiation.
3 LPACK_INT RC 0
Link Status Change Interrupt
When set, indicates that the link status has changed from OK to FAIL.
2 LSCHG_INT RC 0
Remote Fault Interrupt
When set, indicates that a Remote Fault condition has been signaled
by the link partner.
1 RFAULT_INT RC 0
Auto-Negotiation Complete Interrupt
When set, indicates that the Auto-Negotiation sequence has completed
successfully.
0 ANEGCOMP_INT RC 0
348 November 30, 2007
Preliminary
Ethernet Controller
Register 25: Ethernet PHY Management Register 18 – Diagnostic (MR18),
address 0x12
This register enables software to diagnose the results of the previous Auto-Negotiation.
Ethernet PHY Management Register 18 – Diagnostic (MR18)
Base 0x4004.8000
Address 0x12
Type RO, reset 0x0000
15 14 13 12 11 10 9 8 7 6 5 4 3 2 1 0
reserved ANEGF DPLX RATE RXSD RX_LOCK reserved
Type RO RO RO RC RO RO RO RO RO RO RO RO RO RO RO RO
Reset 0 0 0 0 0 0 0 0 0 0 0 0 0 0 0 0
Bit/Field Name Type Reset Description
Software should not rely on the value of a reserved bit. To provide
compatibility with future products, the value of a reserved bit should be
preserved across a read-modify-write operation.
15:13 reserved RO 0
Auto-Negotiation Failure
When set, indicates that no common technology was found during
Auto-Negotiation and has failed. This bit remains set until read.
12 ANEGF RC 0
Duplex Mode
When set, indicates that Full-Duplex was the highest common
denominator found during the Auto-Negotiation process. Otherwise,
Half-Duplex was the highest common denominator found.
11 DPLX RO 0
Rate
When set, indicates that 100Base-TX was the highest common
denominator found during the Auto-Negotiation process. Otherwise,
10Base-TX was the highest common denominator found.
10 RATE RO 0
Receive Detection
When set, indicates that receive signal detection has occurred (in
100Base-TX mode) or that Manchester-encoded data has been detected
(in 10Base-T mode).
9 RXSD RO 0
Receive PLL Lock
When set, indicates that the Receive PLL has locked onto the receive
signal for the selected speed of operation (10Base-T or 100Base-TX).
8 RX_LOCK RO 0
Software should not rely on the value of a reserved bit. To provide
compatibility with future products, the value of a reserved bit should be
preserved across a read-modify-write operation.
7:0 reserved RO 00
November 30, 2007 349
Preliminary
LM3S6110 Microcontroller
Register 26: Ethernet PHY Management Register 19 – Transceiver Control
(MR19), address 0x13
This register enables software to set the gain of the transmit output to compensate for transformer
loss.
Ethernet PHY Management Register 19 – Transceiver Control (MR19)
Base 0x4004.8000
Address 0x13
Type R/W, reset 0x4000
15 14 13 12 11 10 9 8 7 6 5 4 3 2 1 0
TXO[1:0] reserved
Type R/W R/W RO RO RO RO RO RO RO RO RO RO RO RO RO RO
Reset 0 1 0 0 0 0 0 0 0 0 0 0 0 0 0 0
Bit/Field Name Type Reset Description
Transmit Amplitude Selection
The TXO[1:0] field sets the transmit output amplitude to account for
transmit transformer insertion loss.
Value Description
0x0 Gain set for 0.0dB of insertion loss
0x1 Gain set for 0.4dB of insertion loss
0x2 Gain set for 0.8dB of insertion loss
0x3 Gain set for 1.2dB of insertion loss
15:14 TXO[1:0] R/W 1
Software should not rely on the value of a reserved bit. To provide
compatibility with future products, the value of a reserved bit should be
preserved across a read-modify-write operation.
13:0 reserved RO 0x0
350 November 30, 2007
Preliminary
Ethernet Controller
Register 27: Ethernet PHY Management Register 23 – LED Configuration
(MR23), address 0x17
This register enables software to select the source that will cause the LEDs to toggle.
Ethernet PHY Management Register 23 – LED Configuration (MR23)
Base 0x4004.8000
Address 0x17
Type R/W, reset 0x0010
15 14 13 12 11 10 9 8 7 6 5 4 3 2 1 0
reserved LED1[3:0] LED0[3:0]
Type RO RO RO RO RO RO RO RO R/W R/W R/W R/W R/W R/W R/W R/W
Reset 0 0 0 0 0 0 0 0 0 0 0 1 0 0 0 0
Bit/Field Name Type Reset Description
Software should not rely on the value of a reserved bit. To provide
compatibility with future products, the value of a reserved bit should be
preserved across a read-modify-write operation.
15:8 reserved RO 0x0
LED1 Source
The LED1 field selects the source that will toggle the LED1 signal.
Value Description
0x0 Link OK
0x1 RX or TX Activity (Default LED1)
0x2 TX Activity
0x3 RX Activity
0x4 Collision
0x5 100BASE-TX mode
0x6 10BASE-T mode
0x7 Full-Duplex
0x8 Link OK & Blink=RX or TX Activity
7:4 LED1[3:0] R/W 1
LED0 Source
The LED0 field selects the source that will toggle the LED0 signal.
Value Description
0x0 Link OK (Default LED0)
0x1 RX or TX Activity
0x2 TX Activity
0x3 RX Activity
0x4 Collision
0x5 100BASE-TX mode
0x6 10BASE-T mode
0x7 Full-Duplex
0x8 Link OK & Blink=RX or TX Activity
3:0 LED0[3:0] R/W 0
November 30, 2007 351
Preliminary
LM3S6110 Microcontroller
Register 28: Ethernet PHY Management Register 24 –MDI/MDIX Control (MR24),
address 0x18
This register enables software to control the behavior of the MDI/MDIX mux and its switching
capabilities.
Ethernet PHY Management Register 24 –MDI/MDIX Control (MR24)
Base 0x4004.8000
Address 0x18
Type R/W, reset 0x00C0
15 14 13 12 11 10 9 8 7 6 5 4 3 2 1 0
reserved PD_MODEAUTO_SW MDIX MDIX_CM MDIX_SD
Type RO RO RO RO RO RO RO RO R/W R/W R/W RO R/W R/W R/W R/W
Reset 0 0 0 0 0 0 0 0 0 0 0 0 0 0 0 0
Bit/Field Name Type Reset Description
Software should not rely on the value of a reserved bit. To provide
compatibility with future products, the value of a reserved bit should be
preserved across a read-modify-write operation.
15:8 reserved RO 0x0
Parallel Detection Mode
When set, enables the Parallel Detection mode and allows auto-switching
to work when Auto-Negotiation is not enabled.
7 PD_MODE R/W 0
Auto-Switching Enable
When set, enables Auto-Switching of the MDI/MDIX mux.
6 AUTO_SW R/W 0
Auto-Switching Configuration
When set, indicates that the MDI/MDIX mux is in the crossover (MDIX)
configuration.
When 0, it indicates that the mux is in the pass-through (MDI)
configuration.
When the AUTO_SW bit is 1, the MDIX bit is read-only. When the
AUTO_SW bit is 0, the MDIX bit is read/write and can be configured
manually.
5 MDIX R/W 0
Auto-Switching Complete
When set, indicates that the auto-switching sequence has completed.
If 0, it indicates that the sequence has not completed or that
auto-switching is disabled.
4 MDIX_CM RO 0
Auto-Switching Seed
This field provides the initial seed for the switching algorithm. This seed
directly affects the number of attempts [5,4] respectively to write bits
[3:0].
A 0 sets the seed to 0x5.
3:0 MDIX_SD R/W 0
352 November 30, 2007
Preliminary
Ethernet Controller
14 Analog Comparators
An analog comparator is a peripheral that compares two analog voltages, and provides a logical
output that signals the comparison result.
The LM3S6110 controller provides three independent integrated analog comparators that can be
configured to drive an output or generate an interrupt.
Note: Not all comparators have the option to drive an output pin. See the Comparator Operating
Mode tables for more information.
A comparator can compare a test voltage against any one of these voltages:
■ An individual external reference voltage
■ A shared single external reference voltage
■ A shared internal reference voltage
The comparator can provide its output to a device pin, acting as a replacement for an analog
comparator on the board, or it can be used to signal the application via interrupts to cause it to start
capturing a sample sequence.
November 30, 2007 353
Preliminary
LM3S6110 Microcontroller
14.1 Block Diagram
Figure 14-1. Analog Comparator Module Block Diagram
interrupt
C2+
C2-
output
+ve input (alternate)
+ve input
interrupt
-ve input
reference input
Comparator 2
ACSTAT2
ACCTL2
interrupt
C1-
C1+ output
+ve input (alternate)
+ve input
interrupt
-ve input
reference input
Comparator 1
ACSTAT1
ACCTL1
Voltage
Ref
ACREFCTL
output
+ve input (alternate)
+ve input
interrupt
-ve input
reference input
Comparator 0
ACSTAT0
ACCTL0
C0+
internal
bus
interrupt
C0-
C0o
14.2 Functional Description
Important: It is recommended that the Digital-Input enable (the GPIODEN bit in the GPIO module)
for the analog input pin be disabled to prevent excessive current draw from the I/O
pads.
The comparator compares the VIN- and VIN+ inputs to produce an output, VOUT.
VIN- < VIN+, VOUT = 1
VIN- > VIN+, VOUT = 0
As shown in Figure 14-2 on page 355, the input source for VIN- is an external input. In addition to
an external input, input sources for VIN+ can be the +ve input of comparator 0 or an internal reference.
354 November 30, 2007
Preliminary
Analog Comparators
Figure 14-2. Structure of Comparator Unit
output
-ve input
+ve input
interrupt
internal
bus
+ve input (alternate)
reference input
ACCTL ACSTAT
IntGen
2
1
0
CINV
A comparator is configured through two status/control registers (ACCTL and ACSTAT ). The internal
reference is configured through one control register (ACREFCTL). Interrupt status and control is
configured through three registers (ACMIS, ACRIS, and ACINTEN). The operating modes of the
comparators are shown in the Comparator Operating Mode tables.
Typically, the comparator output is used internally to generate controller interrupts. It may also be
used to drive an external pin.
Important: Certain register bit values must be set before using the analog comparators. The proper
pad configuration for the comparator input and output pins are described in the
Comparator Operating Mode tables.
Table 14-1. Comparator 0 Operating Modes
ACCNTL0 Comparator 0
ASRCP VIN- VIN+ Output Interrupt
00 C0- C0+ C0o/C1+ yes
01 C0- C0+ C0o/C1+ yes
10 C0- Vref C0o/C1+ yes
11 C0- reserved C0o/C1+ yes
Table 14-2. Comparator 1 Operating Modes
ACCNTL1 Comparator 1
ASRCP VIN- VIN+ Output Interrupt
00 C1- C0o/C1+a n/a yes
01 C1- C0+ n/a yes
10 C1- Vref n/a yes
11 C1- reserved n/a yes
a. C0o and C1+ signals share a single pin and may only be used as one or the other.
November 30, 2007 355
Preliminary
LM3S6110 Microcontroller
Table 14-3. Comparator 2 Operating Modes
ACCNTL2 Comparator 2
ASRCP VIN- VIN+ Output Interrupt
00 C2- C2+ n/a yes
01 C2- C0+ n/a yes
10 C2- Vref n/a yes
11 C2- reserved n/a yes
14.2.1 Internal Reference Programming
The structure of the internal reference is shown in Figure 14-3 on page 356. This is controlled by a
single configuration register (ACREFCTL). Table 14-4 on page 356 shows the programming options
to develop specific internal reference values, to compare an external voltage against a particular
voltage generated internally.
Figure 14-3. Comparator Internal Reference Structure
8R R R
8R
R R
•••
•••
0
Decoder
15 14 1
AVDD
EN
internal
reference
VREF
RNG
Table 14-4. Internal Reference Voltage and ACREFCTL Field Values
ACREFCTL Register Output Reference Voltage Based on VREF Field Value
EN Bit Value RNG Bit Value
0 V (GND) for any value of VREF; however, it is recommended that RNG=1 and VREF=0
for the least noisy ground reference.
EN=0 RNG=X
356 November 30, 2007
Preliminary
Analog Comparators
ACREFCTL Register Output Reference Voltage Based on VREF Field Value
EN Bit Value RNG Bit Value
Total resistance in ladder is 32 R.
VREF AVDD
R V REF
RT
= × ----------------
VREF AVDD
(VREF + 8)
32
= × ------------------------------
VR EF = 0.825 + 0.103 VREF
The range of internal reference in this mode is 0.825-2.37 V.
EN=1 RNG=0
Total resistance in ladder is 24 R.
VREF AVDD
R V REF
RT
= × ----------------
VREF AVDD
(VREF)
24
= × --------------------
VREF = 0.1375 x VREF
The range of internal reference for this mode is 0.0-2.0625 V.
RNG=1
14.3 Initialization and Configuration
The following example shows how to configure an analog comparator to read back its output value
from an internal register.
1. Enable the analog comparator 0 clock by writing a value of 0x0010.0000 to the RCGC1 register
in the System Control module.
2. In the GPIO module, enable the GPIO port/pin associated with C0- as a GPIO input.
3. Configure the internal voltage reference to 1.65 V by writing the ACREFCTL register with the
value 0x0000.030C.
4. Configure comparator 0 to use the internal voltage reference and to not invert the output on the
C0o pin by writing the ACCTL0 register with the value of 0x0000.040C.
5. Delay for some time.
6. Read the comparator output value by reading the ACSTAT0 register’s OVAL value.
Change the level of the signal input on C0- to see the OVAL value change.
14.4 Register Map
Table 14-5 on page 358 lists the comparator registers. The offset listed is a hexadecimal increment
to the register’s address, relative to the Analog Comparator base address of 0x4003.C000.
November 30, 2007 357
Preliminary
LM3S6110 Microcontroller
Table 14-5. Analog Comparators Register Map
See
Offset Name Type Reset Description page
0x00 ACMIS R/W1C 0x0000.0000 Analog Comparator Masked Interrupt Status 359
0x04 ACRIS RO 0x0000.0000 Analog Comparator Raw Interrupt Status 360
0x08 ACINTEN R/W 0x0000.0000 Analog Comparator Interrupt Enable 361
0x10 ACREFCTL R/W 0x0000.0000 Analog Comparator Reference Voltage Control 362
0x20 ACSTAT0 RO 0x0000.0000 Analog Comparator Status 0 363
0x24 ACCTL0 R/W 0x0000.0000 Analog Comparator Control 0 364
0x40 ACSTAT1 RO 0x0000.0000 Analog Comparator Status 1 363
0x44 ACCTL1 R/W 0x0000.0000 Analog Comparator Control 1 364
0x60 ACSTAT2 RO 0x0000.0000 Analog Comparator Status 2 363
0x64 ACCTL2 R/W 0x0000.0000 Analog Comparator Control 2 364
14.5 Register Descriptions
The remainder of this section lists and describes the Analog Comparator registers, in numerical
order by address offset.
358 November 30, 2007
Preliminary
Analog Comparators
Register 1: Analog Comparator Masked Interrupt Status (ACMIS), offset 0x00
This register provides a summary of the interrupt status (masked) of the comparator.
Analog Comparator Masked Interrupt Status (ACMIS)
Base 0x4003.C000
Offset 0x00
Type R/W1C, reset 0x0000.0000
31 30 29 28 27 26 25 24 23 22 21 20 19 18 17 16
reserved
Type RO RO RO RO RO RO RO RO RO RO RO RO RO RO RO RO
Reset 0 0 0 0 0 0 0 0 0 0 0 0 0 0 0 0
15 14 13 12 11 10 9 8 7 6 5 4 3 2 1 0
reserved IN2 IN1 IN0
Type RO RO RO RO RO RO RO RO RO RO RO RO RO R/W1C R/W1C R/W1C
Reset 0 0 0 0 0 0 0 0 0 0 0 0 0 0 0 0
Bit/Field Name Type Reset Description
Software should not rely on the value of a reserved bit. To provide
compatibility with future products, the value of a reserved bit should be
preserved across a read-modify-write operation.
31:3 reserved RO 0x00
Comparator 2 Masked Interrupt Status
Gives the masked interrupt state of this interrupt. Write 1 to this bit to
clear the pending interrupt.
2 IN2 R/W1C 0
Comparator 1 Masked Interrupt Status
Gives the masked interrupt state of this interrupt. Write 1 to this bit to
clear the pending interrupt.
1 IN1 R/W1C 0
Comparator 0 Masked Interrupt Status
Gives the masked interrupt state of this interrupt. Write 1 to this bit to
clear the pending interrupt.
0 IN0 R/W1C 0
November 30, 2007 359
Preliminary
LM3S6110 Microcontroller
Register 2: Analog Comparator Raw Interrupt Status (ACRIS), offset 0x04
This register provides a summary of the interrupt status (raw) of the comparator.
Analog Comparator Raw Interrupt Status (ACRIS)
Base 0x4003.C000
Offset 0x04
Type RO, reset 0x0000.0000
31 30 29 28 27 26 25 24 23 22 21 20 19 18 17 16
reserved
Type RO RO RO RO RO RO RO RO RO RO RO RO RO RO RO RO
Reset 0 0 0 0 0 0 0 0 0 0 0 0 0 0 0 0
15 14 13 12 11 10 9 8 7 6 5 4 3 2 1 0
reserved IN2 IN1 IN0
Type RO RO RO RO RO RO RO RO RO RO RO RO RO RO RO RO
Reset 0 0 0 0 0 0 0 0 0 0 0 0 0 0 0 0
Bit/Field Name Type Reset Description
Software should not rely on the value of a reserved bit. To provide
compatibility with future products, the value of a reserved bit should be
preserved across a read-modify-write operation.
31:3 reserved RO 0x00
Comparator 2 Interrupt Status
When set, indicates that an interrupt has been generated by comparator
2.
2 IN2 RO 0
Comparator 1 Interrupt Status
When set, indicates that an interrupt has been generated by comparator
1.
1 IN1 RO 0
Comparator 0 Interrupt Status
When set, indicates that an interrupt has been generated by comparator
0.
0 IN0 RO 0
360 November 30, 2007
Preliminary
Analog Comparators
Register 3: Analog Comparator Interrupt Enable (ACINTEN), offset 0x08
This register provides the interrupt enable for the comparator.
Analog Comparator Interrupt Enable (ACINTEN)
Base 0x4003.C000
Offset 0x08
Type R/W, reset 0x0000.0000
31 30 29 28 27 26 25 24 23 22 21 20 19 18 17 16
reserved
Type RO RO RO RO RO RO RO RO RO RO RO RO RO RO RO RO
Reset 0 0 0 0 0 0 0 0 0 0 0 0 0 0 0 0
15 14 13 12 11 10 9 8 7 6 5 4 3 2 1 0
reserved IN2 IN1 IN0
Type RO RO RO RO RO RO RO RO RO RO RO RO RO R/W R/W R/W
Reset 0 0 0 0 0 0 0 0 0 0 0 0 0 0 0 0
Bit/Field Name Type Reset Description
Software should not rely on the value of a reserved bit. To provide
compatibility with future products, the value of a reserved bit should be
preserved across a read-modify-write operation.
31:3 reserved RO 0x00
Comparator 2 Interrupt Enable
When set, enables the controller interrupt from the comparator 2 output
2 IN2 R/W 0
Comparator 1 Interrupt Enable
When set, enables the controller interrupt from the comparator 1 output.
1 IN1 R/W 0
Comparator 0 Interrupt Enable
When set, enables the controller interrupt from the comparator 0 output.
0 IN0 R/W 0
November 30, 2007 361
Preliminary
LM3S6110 Microcontroller
Register 4: Analog Comparator Reference Voltage Control (ACREFCTL), offset
0x10
This register specifies whether the resistor ladder is powered on as well as the range and tap.
Analog Comparator Reference Voltage Control (ACREFCTL)
Base 0x4003.C000
Offset 0x10
Type R/W, reset 0x0000.0000
31 30 29 28 27 26 25 24 23 22 21 20 19 18 17 16
reserved
Type RO RO RO RO RO RO RO RO RO RO RO RO RO RO RO RO
Reset 0 0 0 0 0 0 0 0 0 0 0 0 0 0 0 0
15 14 13 12 11 10 9 8 7 6 5 4 3 2 1 0
reserved EN RNG reserved VREF
Type RO RO RO RO RO RO R/W R/W RO RO RO RO R/W R/W R/W R/W
Reset 0 0 0 0 0 0 0 0 0 0 0 0 0 0 0 0
Bit/Field Name Type Reset Description
Software should not rely on the value of a reserved bit. To provide
compatibility with future products, the value of a reserved bit should be
preserved across a read-modify-write operation.
31:10 reserved RO 0x00
Resistor Ladder Enable
The EN bit specifies whether the resistor ladder is powered on. If 0, the
resistor ladder is unpowered. If 1, the resistor ladder is connected to
the analog VDD.
This bit is reset to 0 so that the internal reference consumes the least
amount of power if not used and programmed.
9 EN R/W 0
Resistor Ladder Range
The RNG bit specifies the range of the resistor ladder. If 0, the resistor
ladder has a total resistance of 32 R. If 1, the resistor ladder has a total
resistance of 24 R.
8 RNG R/W 0
Software should not rely on the value of a reserved bit. To provide
compatibility with future products, the value of a reserved bit should be
preserved across a read-modify-write operation.
7:4 reserved RO 0x00
Resistor Ladder Voltage Ref
The VREF bit field specifies the resistor ladder tap that is passed through
an analog multiplexer. The voltage corresponding to the tap position is
the internal reference voltage available for comparison. See Table
14-4 on page 356 for some output reference voltage examples.
3:0 VREF R/W 0x00
362 November 30, 2007
Preliminary
Analog Comparators
Register 5: Analog Comparator Status 0 (ACSTAT0), offset 0x20
Register 6: Analog Comparator Status 1 (ACSTAT1), offset 0x40
Register 7: Analog Comparator Status 2 (ACSTAT2), offset 0x60
These registers specify the current output value of the comparator.
Analog Comparator Status 0 (ACSTAT0)
Base 0x4003.C000
Offset 0x20
Type RO, reset 0x0000.0000
31 30 29 28 27 26 25 24 23 22 21 20 19 18 17 16
reserved
Type RO RO RO RO RO RO RO RO RO RO RO RO RO RO RO RO
Reset 0 0 0 0 0 0 0 0 0 0 0 0 0 0 0 0
15 14 13 12 11 10 9 8 7 6 5 4 3 2 1 0
reserved OVAL reserved
Type RO RO RO RO RO RO RO RO RO RO RO RO RO RO RO RO
Reset 0 0 0 0 0 0 0 0 0 0 0 0 0 0 0 0
Bit/Field Name Type Reset Description
Software should not rely on the value of a reserved bit. To provide
compatibility with future products, the value of a reserved bit should be
preserved across a read-modify-write operation.
31:2 reserved RO 0x00
Comparator Output Value
The OVAL bit specifies the current output value of the comparator.
1 OVAL RO 0
Software should not rely on the value of a reserved bit. To provide
compatibility with future products, the value of a reserved bit should be
preserved across a read-modify-write operation.
0 reserved RO 0
November 30, 2007 363
Preliminary
LM3S6110 Microcontroller
Register 8: Analog Comparator Control 0 (ACCTL0), offset 0x24
Register 9: Analog Comparator Control 1 (ACCTL1), offset 0x44
Register 10: Analog Comparator Control 2 (ACCTL2), offset 0x64
These registers configure the comparator’s input and output.
Analog Comparator Control 0 (ACCTL0)
Base 0x4003.C000
Offset 0x24
Type R/W, reset 0x0000.0000
31 30 29 28 27 26 25 24 23 22 21 20 19 18 17 16
reserved
Type RO RO RO RO RO RO RO RO RO RO RO RO RO RO RO RO
Reset 0 0 0 0 0 0 0 0 0 0 0 0 0 0 0 0
15 14 13 12 11 10 9 8 7 6 5 4 3 2 1 0
reserved ASRCP reserved ISLVAL ISEN CINV reserved
Type RO RO RO RO RO R/W R/W RO RO RO RO R/W R/W R/W R/W RO
Reset 0 0 0 0 0 0 0 0 0 0 0 0 0 0 0 0
Bit/Field Name Type Reset Description
Software should not rely on the value of a reserved bit. To provide
compatibility with future products, the value of a reserved bit should be
preserved across a read-modify-write operation.
31:11 reserved RO 0x00
Analog Source Positive
The ASRCP field specifies the source of input voltage to the VIN+ terminal
of the comparator. The encodings for this field are as follows:
Value Function
0x0 Pin value
0x1 Pin value of C0+
0x2 Internal voltage reference
0x3 Reserved
10:9 ASRCP R/W 0x00
Software should not rely on the value of a reserved bit. To provide
compatibility with future products, the value of a reserved bit should be
preserved across a read-modify-write operation.
8:5 reserved RO 0
Interrupt Sense Level Value
The ISLVAL bit specifies the sense value of the input that generates
an interrupt if in Level Sense mode. If 0, an interrupt is generated if the
comparator output is Low. Otherwise, an interrupt is generated if the
comparator output is High.
4 ISLVAL R/W 0
364 November 30, 2007
Preliminary
Analog Comparators
Bit/Field Name Type Reset Description
Interrupt Sense
The ISEN field specifies the sense of the comparator output that
generates an interrupt. The sense conditioning is as follows:
Value Function
0x0 Level sense, see ISLVAL
0x1 Falling edge
0x2 Rising edge
0x3 Either edge
3:2 ISEN R/W 0x0
Comparator Output Invert
The CINV bit conditionally inverts the output of the comparator. If 0, the
output of the comparator is unchanged. If 1, the output of the comparator
is inverted prior to being processed by hardware.
1 CINV R/W 0
Software should not rely on the value of a reserved bit. To provide
compatibility with future products, the value of a reserved bit should be
preserved across a read-modify-write operation.
0 reserved RO 0
November 30, 2007 365
Preliminary
LM3S6110 Microcontroller
15 Pulse Width Modulator (PWM)
Pulse width modulation (PWM) is a powerful technique for digitally encoding analog signal levels.
High-resolution counters are used to generate a square wave, and the duty cycle of the square
wave is modulated to encode an analog signal. Typical applications include switching power supplies
and motor control.
The Stellaris® PWM module consists of one PWM generator block and a control block. The PWM
generator block contains one timer (16-bit down or up/down counter), two PWM comparators, a
PWM signal generator, a dead-band generator, and an interrupt selector. The control block determines
the polarity of the PWM signals, and which signals are passed through to the pins.
The PWM generator block produces two PWM signals that can either be independent signals (other
than being based on the same timer and therefore having the same frequency) or a single pair of
complementary signals with dead-band delays inserted. The output of the PWM generation block
is managed by the output control block before being passed to the device pins.
The Stellaris® PWM module provides a great deal of flexibility. It can generate simple PWM signals,
such as those required by a simple charge pump. It can also generate paired PWM signals with
dead-band delays, such as those required by a half-H bridge driver.
15.1 Block Diagram
Figure 15-1 on page 366 provides a block diagram of a Stellaris® PWM module. The LM3S6110
controller contains one generator block (PWM0) and generates two independent PWM signals or
one paired PWM signal with dead-band delays inserted.
Figure 15-1. PWM Module Block Diagram
Interrupt and
Trigger Generate
PWMnINTEN
PWMnRIS
PWMnISC
PWM Clock
Interrupt
Dead-Band
Generator
PWMnDBCTL
PWMnDBRISE
PWMnDBFALL
PWM Output
Control
PWMENABLE
PWMINVERT
PWMFAULT
PWM
Generator
PWMnGENA
PWMnGENB
pwma
pwmb
Timer
PWMnLOAD
PWMnCOUNT
Comparator A
PWMnCMPA
Comparator B
PWMnCMPB
zero
load
dir
16
cmpA
cmpB
Fault
PWM Generator Block
15.2 Functional Description
15.2.1 PWM Timer
The timer runs in one of two modes: Count-Down mode or Count-Up/Down mode. In Count-Down
mode, the timer counts from the load value to zero, goes back to the load value, and continues
counting down. In Count-Up/Down mode, the timer counts from zero up to the load value, back
down to zero, back up to the load value, and so on. Generally, Count-Down mode is used for
366 November 30, 2007
Preliminary
Pulse Width Modulator (PWM)
generating left- or right-aligned PWM signals, while the Count-Up/Down mode is used for generating
center-aligned PWM signals.
The timers output three signals that are used in the PWM generation process: the direction signal
(this is always Low in Count-Down mode, but alternates between Low and High in Count-Up/Down
mode), a single-clock-cycle-width High pulse when the counter is zero, and a single-clock-cycle-width
High pulse when the counter is equal to the load value. Note that in Count-Down mode, the zero
pulse is immediately followed by the load pulse.
15.2.2 PWM Comparators
There are two comparators in the PWM generator that monitor the value of the counter; when either
match the counter, they output a single-clock-cycle-width High pulse. When in Count-Up/Down
mode, these comparators match both when counting up and when counting down; they are therefore
qualified by the counter direction signal. These qualified pulses are used in the PWM generation
process. If either comparator match value is greater than the counter load value, then that comparator
never outputs a High pulse.
Figure 15-2 on page 367 shows the behavior of the counter and the relationship of these pulses
when the counter is in Count-Down mode. Figure 15-3 on page 368 shows the behavior of the counter
and the relationship of these pulses when the counter is in Count-Up/Down mode.
Figure 15-2. PWM Count-Down Mode
Load
Zero
CompB
CompA
Load
Zero
B
A
Dir
ADown
BDown
November 30, 2007 367
Preliminary
LM3S6110 Microcontroller
Figure 15-3. PWM Count-Up/Down Mode
Load
Zero
CompB
CompA
Load
Zero
B
A
Dir
BUp
AUp ADown
BDown
15.2.3 PWM Signal Generator
The PWM generator takes these pulses (qualified by the direction signal), and generates two PWM
signals. In Count-Down mode, there are four events that can affect the PWM signal: zero, load,
match A down, and match B down. In Count-Up/Down mode, there are six events that can affect
the PWM signal: zero, load, match A down, match A up, match B down, and match B up. The match
A or match B events are ignored when they coincide with the zero or load events. If the match A
and match B events coincide, the first signal, PWMA, is generated based only on the match A event,
and the second signal, PWMB, is generated based only on the match B event.
For each event, the effect on each output PWM signal is programmable: it can be left alone (ignoring
the event), it can be toggled, it can be driven Low, or it can be driven High. These actions can be
used to generate a pair of PWM signals of various positions and duty cycles, which do or do not
overlap. Figure 15-4 on page 368 shows the use of Count-Up/Down mode to generate a pair of
center-aligned, overlapped PWM signals that have different duty cycles.
Figure 15-4. PWM Generation Example In Count-Up/Down Mode
Load
Zero
CompB
CompA
PWMB
PWMA
In this example, the first generator is set to drive High on match A up, drive Low on match A down,
and ignore the other four events. The second generator is set to drive High on match B up, drive
Low on match B down, and ignore the other four events. Changing the value of comparator A
368 November 30, 2007
Preliminary
Pulse Width Modulator (PWM)
changes the duty cycle of the PWMA signal, and changing the value of comparator B changes the
duty cycle of the PWMB signal.
15.2.4 Dead-Band Generator
The two PWM signals produced by the PWM generator are passed to the dead-band generator. If
disabled, the PWM signals simply pass through unmodified. If enabled, the second PWM signal is
lost and two PWM signals are generated based on the first PWM signal. The first output PWM signal
is the input signal with the rising edge delayed by a programmable amount. The second output
PWM signal is the inversion of the input signal with a programmable delay added between the falling
edge of the input signal and the rising edge of this new signal.
This is therefore a pair of active High signals where one is always High, except for a programmable
amount of time at transitions where both are Low. These signals are therefore suitable for driving
a half-H bridge, with the dead-band delays preventing shoot-through current from damaging the
power electronics. Figure 15-5 on page 369 shows the effect of the dead-band generator on an input
PWM signal.
Figure 15-5. PWM Dead-Band Generator
Input
PWMA
PWMB
Rising Edge
Delay
Falling Edge
Delay
15.2.5 Interrupt Selector
The PWM generator also takes the same four (or six) counter events and uses them to generate
an interrupt. Any of these events or a set of these events can be selected as a source for an interrupt;
when any of the selected events occur, an interrupt is generated. The selection of events allows
the interrupt to occur at a specific position within the PWM signal. Note that interrupts are based on
the raw events; delays in the PWM signal edges caused by the dead-band generator are not taken
into account.
15.2.6 Synchronization Methods
There is a global reset capability that can reset the counter of the PWM generator.
The counter load values and comparator match values of the PWM generator can be updated in
two ways. The first is immediate update mode, where a new value is used as soon as the counter
reaches zero. By waiting for the counter to reach zero, a guaranteed behavior is defined, and overly
short or overly long output PWM pulses are prevented.
The other update method is synchronous, where the new value is not used until a global synchronized
update signal is asserted, at which point the new value is used as soon as the counter reaches
zero. This second mode allows multiple items to be updated simultaneously without odd effects
during the update; everything runs from the old values until a point at which they all run from the
new values.
15.2.7 Fault Conditions
There are two external conditions that affect the PWM block; the signal input on the Fault pin and
the stalling of the controller by a debugger. There are two mechanisms available to handle such
November 30, 2007 369
Preliminary
LM3S6110 Microcontroller
conditions: the output signals can be forced into an inactive state and/or the PWM timers can be
stopped.
Each output signal has a fault bit. If set, a fault input signal causes the corresponding output signal
to go into the inactive state. If the inactive state is a safe condition for the signal to be in for an
extended period of time, this keeps the output signal from driving the outside world in a dangerous
manner during the fault condition. A fault condition can also generate a controller interrupt.
Each PWM generator can also be configured to stop counting during a stall condition. The user can
select for the counters to run until they reach zero then stop, or to continue counting and reloading.
A stall condition does not generate a controller interrupt.
15.2.8 Output Control Block
With the PWM generator block producing two raw PWM signals, the output control block takes care
of the final conditioning of the PWM signals before they go to the pins. Via a single register, the set
of PWM signals that are actually enabled to the pins can be modified; this can be used, for example,
to perform commutation of a brushless DC motor with a single register write (and without modifying
the individual PWM generators, which are modified by the feedback control loop). Similarly, fault
control can disable any of the PWM signals as well. A final inversion can be applied to any of the
PWM signals, making them active Low instead of the default active High.
15.3 Initialization and Configuration
The following example shows how to initialize the PWM Generator 0 with a 25-KHz frequency, and
with a 25% duty cycle on the PWM0 pin and a 75% duty cycle on the PWM1 pin. This example assumes
the system clock is 20 MHz.
1. Enable the PWM clock by writing a value of 0x0010.0000 to the RCGC0 register in the System
Control module.
2. Enable the clock to the appropriate GPIO module via the RCGC2 register in the System Control
module.
3. In the GPIO module, enable the appropriate pins for their alternate function using the
GPIOAFSEL register.
4. Configure the Run-Mode Clock Configuration (RCC) register in the System Control module
to use the PWM divide (USEPWMDIV) and set the divider (PWMDIV) to divide by 2 (000).
5. Configure the PWM generator for countdown mode with immediate updates to the parameters.
■ Write the PWM0CTL register with a value of 0x0000.0000.
■ Write the PWM0GENA register with a value of 0x0000.008C.
■ Write the PWM0GENB register with a value of 0x0000.080C.
6. Set the period. For a 25-KHz frequency, the period = 1/25,000, or 40 microseconds. The PWM
clock source is 10 MHz; the system clock divided by 2. This translates to 400 clock ticks per
period. Use this value to set the PWM0LOAD register. In Count-Down mode, set the Load field
in the PWM0LOAD register to the requested period minus one.
■ Write the PWM0LOAD register with a value of 0x0000.018F.
7. Set the pulse width of the PWM0 pin for a 25% duty cycle.
370 November 30, 2007
Preliminary
Pulse Width Modulator (PWM)
■ Write the PWM0CMPA register with a value of 0x0000.012B.
8. Set the pulse width of the PWM1 pin for a 75% duty cycle.
■ Write the PWM0CMPB register with a value of 0x0000.0063.
9. Start the timers in PWM generator 0.
■ Write the PWM0CTL register with a value of 0x0000.0001.
10. Enable PWM outputs.
■ Write the PWMENABLE register with a value of 0x0000.0003.
15.4 Register Map
Table 15-1 on page 371 lists the PWM registers. The offset listed is a hexadecimal increment to the
register’s address, relative to the PWM base address of 0x4002.8000.
Table 15-1. PWM Register Map
See
Offset Name Type Reset Description page
0x000 PWMCTL R/W 0x0000.0000 PWM Master Control 373
0x004 PWMSYNC R/W 0x0000.0000 PWM Time Base Sync 374
0x008 PWMENABLE R/W 0x0000.0000 PWM Output Enable 375
0x00C PWMINVERT R/W 0x0000.0000 PWM Output Inversion 376
0x010 PWMFAULT R/W 0x0000.0000 PWM Output Fault 377
0x014 PWMINTEN R/W 0x0000.0000 PWM Interrupt Enable 378
0x018 PWMRIS RO 0x0000.0000 PWM Raw Interrupt Status 379
0x01C PWMISC R/W1C 0x0000.0000 PWM Interrupt Status and Clear 380
0x020 PWMSTATUS RO 0x0000.0000 PWM Status 381
0x040 PWM0CTL R/W 0x0000.0000 PWM0 Control 382
0x044 PWM0INTEN R/W 0x0000.0000 PWM0 Interrupt Enable 384
0x048 PWM0RIS RO 0x0000.0000 PWM0 Raw Interrupt Status 386
0x04C PWM0ISC R/W1C 0x0000.0000 PWM0 Interrupt Status and Clear 387
0x050 PWM0LOAD R/W 0x0000.0000 PWM0 Load 388
0x054 PWM0COUNT RO 0x0000.0000 PWM0 Counter 389
0x058 PWM0CMPA R/W 0x0000.0000 PWM0 Compare A 390
0x05C PWM0CMPB R/W 0x0000.0000 PWM0 Compare B 391
0x060 PWM0GENA R/W 0x0000.0000 PWM0 Generator A Control 392
0x064 PWM0GENB R/W 0x0000.0000 PWM0 Generator B Control 395
0x068 PWM0DBCTL R/W 0x0000.0000 PWM0 Dead-Band Control 398
November 30, 2007 371
Preliminary
LM3S6110 Microcontroller
See
Offset Name Type Reset Description page
0x06C PWM0DBRISE R/W 0x0000.0000 PWM0 Dead-Band Rising-Edge Delay 399
0x070 PWM0DBFALL R/W 0x0000.0000 PWM0 Dead-Band Falling-Edge-Delay 400
15.5 Register Descriptions
The remainder of this section lists and describes the PWM registers, in numerical order by address
offset.
372 November 30, 2007
Preliminary
Pulse Width Modulator (PWM)
Register 1: PWM Master Control (PWMCTL), offset 0x000
This register provides master control over the PWM generation block.
PWM Master Control (PWMCTL)
Base 0x4002.8000
Offset 0x000
Type R/W, reset 0x0000.0000
31 30 29 28 27 26 25 24 23 22 21 20 19 18 17 16
reserved
Type RO RO RO RO RO RO RO RO RO RO RO RO RO RO RO RO
Reset 0 0 0 0 0 0 0 0 0 0 0 0 0 0 0 0
15 14 13 12 11 10 9 8 7 6 5 4 3 2 1 0
reserved GlobalSync0
Type RO RO RO RO RO RO RO RO RO RO RO RO RO RO RO R/W
Reset 0 0 0 0 0 0 0 0 0 0 0 0 0 0 0 0
Bit/Field Name Type Reset Description
Software should not rely on the value of a reserved bit. To provide
compatibility with future products, the value of a reserved bit should be
preserved across a read-modify-write operation.
31:1 reserved RO 0x00
Update PWM Generator 0
Setting this bit causes any queued update to a load or comparator
register in PWM generator 0 to be applied the next time the
corresponding counter becomes zero. This bit automatically clears when
the updates have completed; it cannot be cleared by software.
0 GlobalSync0 R/W 0
November 30, 2007 373
Preliminary
LM3S6110 Microcontroller
Register 2: PWM Time Base Sync (PWMSYNC), offset 0x004
This register provides a method to perform synchronization of the counters in the PWM generation
blocks. Writing a bit in this register to 1 causes the specified counter to reset back to 0; writing
multiple bits resets multiple counters simultaneously. The bits auto-clear after the reset has occurred;
reading them back as zero indicates that the synchronization has completed.
PWM Time Base Sync (PWMSYNC)
Base 0x4002.8000
Offset 0x004
Type R/W, reset 0x0000.0000
31 30 29 28 27 26 25 24 23 22 21 20 19 18 17 16
reserved
Type RO RO RO RO RO RO RO RO RO RO RO RO RO RO RO RO
Reset 0 0 0 0 0 0 0 0 0 0 0 0 0 0 0 0
15 14 13 12 11 10 9 8 7 6 5 4 3 2 1 0
reserved Sync0
Type RO RO RO RO RO RO RO RO RO RO RO RO RO RO RO R/W
Reset 0 0 0 0 0 0 0 0 0 0 0 0 0 0 0 0
Bit/Field Name Type Reset Description
Software should not rely on the value of a reserved bit. To provide
compatibility with future products, the value of a reserved bit should be
preserved across a read-modify-write operation.
31:1 reserved RO 0x00
Reset Generator 0 Counter
Performs a reset of the PWM generator 0 counter.
0 Sync0 R/W 0
374 November 30, 2007
Preliminary
Pulse Width Modulator (PWM)
Register 3: PWM Output Enable (PWMENABLE), offset 0x008
This register provides a master control of which generated PWM signals are output to device pins.
By disabling a PWM output, the generation process can continue (for example, when the time bases
are synchronized) without driving PWM signals to the pins. When bits in this register are set, the
corresponding PWM signal is passed through to the output stage, which is controlled by the
PWMINVERT register. When bits are not set, the PWM signal is replaced by a zero value which is
also passed to the output stage.
PWM Output Enable (PWMENABLE)
Base 0x4002.8000
Offset 0x008
Type R/W, reset 0x0000.0000
31 30 29 28 27 26 25 24 23 22 21 20 19 18 17 16
reserved
Type RO RO RO RO RO RO RO RO RO RO RO RO RO RO RO RO
Reset 0 0 0 0 0 0 0 0 0 0 0 0 0 0 0 0
15 14 13 12 11 10 9 8 7 6 5 4 3 2 1 0
reserved PWM1En PWM0En
Type RO RO RO RO RO RO RO RO RO RO RO RO RO RO R/W R/W
Reset 0 0 0 0 0 0 0 0 0 0 0 0 0 0 0 0
Bit/Field Name Type Reset Description
Software should not rely on the value of a reserved bit. To provide
compatibility with future products, the value of a reserved bit should be
preserved across a read-modify-write operation.
31:2 reserved RO 0x00
PWM1 Output Enable
When set, allows the generated PWM1 signal to be passed to the device
pin.
1 PWM1En R/W 0
PWM0 Output Enable
When set, allows the generated PWM0 signal to be passed to the device
pin.
0 PWM0En R/W 0
November 30, 2007 375
Preliminary
LM3S6110 Microcontroller
Register 4: PWM Output Inversion (PWMINVERT), offset 0x00C
This register provides a master control of the polarity of the PWM signals on the device pins. The
PWM signals generated by the PWM generator are active High; they can optionally be made active
Low via this register. Disabled PWM channels are also passed through the output inverter (if so
configured) so that inactive channels maintain the correct polarity.
PWM Output Inversion (PWMINVERT)
Base 0x4002.8000
Offset 0x00C
Type R/W, reset 0x0000.0000
31 30 29 28 27 26 25 24 23 22 21 20 19 18 17 16
reserved
Type RO RO RO RO RO RO RO RO RO RO RO RO RO RO RO RO
Reset 0 0 0 0 0 0 0 0 0 0 0 0 0 0 0 0
15 14 13 12 11 10 9 8 7 6 5 4 3 2 1 0
reserved PWM1Inv PWM0Inv
Type RO RO RO RO RO RO RO RO RO RO RO RO RO RO R/W R/W
Reset 0 0 0 0 0 0 0 0 0 0 0 0 0 0 0 0
Bit/Field Name Type Reset Description
Software should not rely on the value of a reserved bit. To provide
compatibility with future products, the value of a reserved bit should be
preserved across a read-modify-write operation.
31:2 reserved RO 0x00
Invert PWM1 Signal
When set, the generated PWM1 signal is inverted.
1 PWM1Inv R/W 0
Invert PWM0 Signal
When set, the generated PWM0 signal is inverted.
0 PWM0Inv R/W 0
376 November 30, 2007
Preliminary
Pulse Width Modulator (PWM)
Register 5: PWM Output Fault (PWMFAULT), offset 0x010
This register controls the behavior of the PWM outputs in the presence of fault conditions. Both the
fault input and debug events are considered fault conditions. On a fault condition, each PWM signal
can either be passed through unmodified or driven Low. For outputs that are configured for
pass-through, the debug event handling on the corresponding PWM generator also determines if
the PWM signal continues to be generated.
Fault condition control happens before the output inverter, so PWM signals driven Low on fault are
inverted if the channel is configured for inversion (therefore, the pin is driven High on a fault condition).
PWM Output Fault (PWMFAULT)
Base 0x4002.8000
Offset 0x010
Type R/W, reset 0x0000.0000
31 30 29 28 27 26 25 24 23 22 21 20 19 18 17 16
reserved
Type RO RO RO RO RO RO RO RO RO RO RO RO RO RO RO RO
Reset 0 0 0 0 0 0 0 0 0 0 0 0 0 0 0 0
15 14 13 12 11 10 9 8 7 6 5 4 3 2 1 0
reserved Fault1 Fault0
Type RO RO RO RO RO RO RO RO RO RO RO RO RO RO R/W R/W
Reset 0 0 0 0 0 0 0 0 0 0 0 0 0 0 0 0
Bit/Field Name Type Reset Description
Software should not rely on the value of a reserved bit. To provide
compatibility with future products, the value of a reserved bit should be
preserved across a read-modify-write operation.
31:2 reserved RO 0x00
PWM1 Driven Low on Fault
When set, the PWM1 output signal is driven Low on a fault condition.
1 Fault1 R/W 0
PWM0 Driven Low on Fault
When set, the PWM0 output signal is driven Low on a fault condition.
0 Fault0 R/W 0
November 30, 2007 377
Preliminary
LM3S6110 Microcontroller
Register 6: PWM Interrupt Enable (PWMINTEN), offset 0x014
This register controls the global interrupt generation capabilities of the PWM module. The events
that can cause an interrupt are the fault input and the individual interrupts from the PWM generator.
PWM Interrupt Enable (PWMINTEN)
Base 0x4002.8000
Offset 0x014
Type R/W, reset 0x0000.0000
31 30 29 28 27 26 25 24 23 22 21 20 19 18 17 16
reserved IntFault
Type RO RO RO RO RO RO RO RO RO RO RO RO RO RO RO R/W
Reset 0 0 0 0 0 0 0 0 0 0 0 0 0 0 0 0
15 14 13 12 11 10 9 8 7 6 5 4 3 2 1 0
reserved IntPWM0
Type RO RO RO RO RO RO RO RO RO RO RO RO RO RO RO R/W
Reset 0 0 0 0 0 0 0 0 0 0 0 0 0 0 0 0
Bit/Field Name Type Reset Description
Software should not rely on the value of a reserved bit. To provide
compatibility with future products, the value of a reserved bit should be
preserved across a read-modify-write operation.
31:17 reserved RO 0x00
Fault Interrupt Enable
When 1, an interrupt occurs when the fault input is asserted.
16 IntFault R/W 0
Software should not rely on the value of a reserved bit. To provide
compatibility with future products, the value of a reserved bit should be
preserved across a read-modify-write operation.
15:1 reserved RO 0x00
PWM0 Interrupt Enable
When 1, an interrupt occurs when the PWM generator 0 block asserts
an interrupt.
0 IntPWM0 R/W 0
378 November 30, 2007
Preliminary
Pulse Width Modulator (PWM)
Register 7: PWM Raw Interrupt Status (PWMRIS), offset 0x018
This register provides the current set of interrupt sources that are asserted, regardless of whether
they cause an interrupt to be asserted to the controller. The fault interrupt is latched on detection;
it must be cleared through the PWM Interrupt Status and Clear (PWMISC) register (see page 380).
The PWM generator interrupts simply reflect the status of the PWM generator; they are cleared via
the interrupt status register in the PWM generator block. Bits set to 1 indicate the events that are
active; a zero bit indicates that the event in question is not active.
PWM Raw Interrupt Status (PWMRIS)
Base 0x4002.8000
Offset 0x018
Type RO, reset 0x0000.0000
31 30 29 28 27 26 25 24 23 22 21 20 19 18 17 16
reserved IntFault
Type RO RO RO RO RO RO RO RO RO RO RO RO RO RO RO RO
Reset 0 0 0 0 0 0 0 0 0 0 0 0 0 0 0 0
15 14 13 12 11 10 9 8 7 6 5 4 3 2 1 0
reserved IntPWM0
Type RO RO RO RO RO RO RO RO RO RO RO RO RO RO RO RO
Reset 0 0 0 0 0 0 0 0 0 0 0 0 0 0 0 0
Bit/Field Name Type Reset Description
Software should not rely on the value of a reserved bit. To provide
compatibility with future products, the value of a reserved bit should be
preserved across a read-modify-write operation.
31:17 reserved RO 0x00
Fault Interrupt Asserted
Indicates that the fault input has been asserted.
16 IntFault RO 0
Software should not rely on the value of a reserved bit. To provide
compatibility with future products, the value of a reserved bit should be
preserved across a read-modify-write operation.
15:1 reserved RO 0x00
PWM0 Interrupt Asserted
Indicates that the PWM generator 0 block is asserting its interrupt.
0 IntPWM0 RO 0
November 30, 2007 379
Preliminary
LM3S6110 Microcontroller
Register 8: PWM Interrupt Status and Clear (PWMISC), offset 0x01C
This register provides a summary of the interrupt status of the PWM generator block. A bit set to 1
indicates that the generator block is asserting an interrupt. The individual interrupt status registers
must be consulted to determine the reason for the interrupt, and used to clear the interrupt. For the
fault interrupt, a write of 1 to that bit position clears the latched interrupt status.
PWM Interrupt Status and Clear (PWMISC)
Base 0x4002.8000
Offset 0x01C
Type R/W1C, reset 0x0000.0000
31 30 29 28 27 26 25 24 23 22 21 20 19 18 17 16
reserved IntFault
Type RO RO RO RO RO RO RO RO RO RO RO RO RO RO RO R/W1C
Reset 0 0 0 0 0 0 0 0 0 0 0 0 0 0 0 0
15 14 13 12 11 10 9 8 7 6 5 4 3 2 1 0
reserved IntPWM0
Type RO RO RO RO RO RO RO RO RO RO RO RO RO RO RO RO
Reset 0 0 0 0 0 0 0 0 0 0 0 0 0 0 0 0
Bit/Field Name Type Reset Description
Software should not rely on the value of a reserved bit. To provide
compatibility with future products, the value of a reserved bit should be
preserved across a read-modify-write operation.
31:17 reserved RO 0x00
Fault Interrupt Asserted
Indicates if the fault input is asserting an interrupt.
16 IntFault R/W1C 0
Software should not rely on the value of a reserved bit. To provide
compatibility with future products, the value of a reserved bit should be
preserved across a read-modify-write operation.
15:1 reserved RO 0x00
PWM0 Interrupt Status
Indicates if the PWM generator 0 block is asserting an interrupt.
0 IntPWM0 RO 0
380 November 30, 2007
Preliminary
Pulse Width Modulator (PWM)
Register 9: PWM Status (PWMSTATUS), offset 0x020
This register provides the status of the Fault input signal.
PWM Status (PWMSTATUS)
Base 0x4002.8000
Offset 0x020
Type RO, reset 0x0000.0000
31 30 29 28 27 26 25 24 23 22 21 20 19 18 17 16
reserved
Type RO RO RO RO RO RO RO RO RO RO RO RO RO RO RO RO
Reset 0 0 0 0 0 0 0 0 0 0 0 0 0 0 0 0
15 14 13 12 11 10 9 8 7 6 5 4 3 2 1 0
reserved Fault
Type RO RO RO RO RO RO RO RO RO RO RO RO RO RO RO RO
Reset 0 0 0 0 0 0 0 0 0 0 0 0 0 0 0 0
Bit/Field Name Type Reset Description
Software should not rely on the value of a reserved bit. To provide
compatibility with future products, the value of a reserved bit should be
preserved across a read-modify-write operation.
31:1 reserved RO 0x00
Fault Interrupt Status
When set to 1, indicates the fault input is asserted.
0 Fault RO 0
November 30, 2007 381
Preliminary
LM3S6110 Microcontroller
Register 10: PWM0 Control (PWM0CTL), offset 0x040
This register configures the PWM signal generation block. The Register Update mode, Debug mode,
Counting mode, and Block Enable mode are all controlled via this register. The block produces the
PWM signals, which can be either two independent PWM signals (from the same counter), or a
paired set of PWM signals with dead-band delays added.
These registers configure the PWM signal generation blocks (PWM0CTL controls the PWM generator
0 block, and so on). The Register Update mode, Debug mode, Counting mode, and Block Enable
mode are all controlled via these registers. The blocks produce the PWM signals, which can be
either two independent PWM signals (from the same counter), or a paired set of PWM signals with
dead-band delays added.
The PWM0 block produces the PWM0 and PWM1 outputs.
PWM0 Control (PWM0CTL)
Base 0x4002.8000
Offset 0x040
Type R/W, reset 0x0000.0000
31 30 29 28 27 26 25 24 23 22 21 20 19 18 17 16
reserved
Type RO RO RO RO RO RO RO RO RO RO RO RO RO RO RO RO
Reset 0 0 0 0 0 0 0 0 0 0 0 0 0 0 0 0
15 14 13 12 11 10 9 8 7 6 5 4 3 2 1 0
reserved CmpBUpdCmpAUpd LoadUpd Debug Mode Enable
Type RO RO RO RO RO RO RO RO RO RO R/W R/W R/W R/W R/W R/W
Reset 0 0 0 0 0 0 0 0 0 0 0 0 0 0 0 0
Bit/Field Name Type Reset Description
Software should not rely on the value of a reserved bit. To provide
compatibility with future products, the value of a reserved bit should be
preserved across a read-modify-write operation.
31:6 reserved RO 0x00
Comparator B Update Mode
Same as CmpAUpd but for the comparator B register.
5 CmpBUpd R/W 0
Comparator A Update Mode
The Update mode for the comparator A register. If 0, updates to the
register are reflected to the comparator the next time the counter is 0.
If 1, updates to the register are delayed until the next time the counter
is 0 after a synchronous update has been requested through the PWM
Master Control (PWMCTL) register (see page 373).
4 CmpAUpd R/W 0
Load Register Update Mode
The Update mode for the load register. If 0, updates to the register are
reflected to the counter the next time the counter is 0. If 1, updates to
the register are delayed until the next time the counter is 0 after a
synchronous update has been requested through the PWM Master
Control (PWMCTL) register.
3 LoadUpd R/W 0
Debug Mode
The behavior of the counter in Debug mode. If 0, the counter stops
running when it next reaches 0, and continues running again when no
longer in Debug mode. If 1, the counter always runs.
2 Debug R/W 0
382 November 30, 2007
Preliminary
Pulse Width Modulator (PWM)
Bit/Field Name Type Reset Description
Counter Mode
The mode for the counter. If 0, the counter counts down from the load
value to 0 and then wraps back to the load value (Count-Down mode).
If 1, the counter counts up from 0 to the load value, back down to 0, and
then repeats (Count-Up/Down mode).
1 Mode R/W 0
PWM Block Enable
Master enable for the PWM generation block. If 0, the entire block is
disabled and not clocked. If 1, the block is enabled and produces PWM
signals.
0 Enable R/W 0
November 30, 2007 383
Preliminary
LM3S6110 Microcontroller
Register 11: PWM0 Interrupt Enable (PWM0INTEN), offset 0x044
This register controls the interrupt generation capabilities of the PWM generator. The events that
can cause an interrupt are:
■ The counter being equal to the load register
■ The counter being equal to zero
■ The counter being equal to the comparator A register while counting up
■ The counter being equal to the comparator A register while counting down
■ The counter being equal to the comparator B register while counting up
■ The counter being equal to the comparator B register while counting down
Any combination of these events can generate either an interrupt.
PWM0 Interrupt Enable (PWM0INTEN)
Base 0x4002.8000
Offset 0x044
Type R/W, reset 0x0000.0000
31 30 29 28 27 26 25 24 23 22 21 20 19 18 17 16
reserved
Type RO RO RO RO RO RO RO RO RO RO RO RO RO RO RO RO
Reset 0 0 0 0 0 0 0 0 0 0 0 0 0 0 0 0
15 14 13 12 11 10 9 8 7 6 5 4 3 2 1 0
reserved IntCmpBDIntCmpBUIntCmpADIntCmpAU IntCntLoad IntCntZero
Type RO RO RO RO RO RO RO RO RO RO R/W R/W R/W R/W R/W R/W
Reset 0 0 0 0 0 0 0 0 0 0 0 0 0 0 0 0
Bit/Field Name Type Reset Description
Software should not rely on the value of a reserved bit. To provide
compatibility with future products, the value of a reserved bit should be
preserved across a read-modify-write operation.
31:6 reserved RO 0x00
Interrupt for Counter=Comparator B Down
When 1, an interrupt occurs when the counter matches the comparator B
value and the counter is counting down.
5 IntCmpBD R/W 0
Interrupt for Counter=Comparator B Up
When 1, an interrupt occurs when the counter matches the comparator B
value and the counter is counting up.
4 IntCmpBU R/W 0
Interrupt for Counter=Comparator A Down
When 1, an interrupt occurs when the counter matches the comparator A
value and the counter is counting down.
3 IntCmpAD R/W 0
Interrupt for Counter=Comparator A Up
When 1, an interrupt occurs when the counter matches the comparator A
value and the counter is counting up.
2 IntCmpAU R/W 0
384 November 30, 2007
Preliminary
Pulse Width Modulator (PWM)
Bit/Field Name Type Reset Description
Interrupt for Counter=Load
When 1, an interrupt occurs when the counter matches the PWMnLOAD
register.
1 IntCntLoad R/W 0
Interrupt for Counter=0
When 1, an interrupt occurs when the counter is 0.
0 IntCntZero R/W 0
November 30, 2007 385
Preliminary
LM3S6110 Microcontroller
Register 12: PWM0 Raw Interrupt Status (PWM0RIS), offset 0x048
This register provides the current set of interrupt sources that are asserted, regardless of whether
they cause an interrupt to be asserted to the controller. Bits set to 1 indicate the latched events that
have occurred; a 0 bit indicates that the event in question has not occurred.
PWM0 Raw Interrupt Status (PWM0RIS)
Base 0x4002.8000
Offset 0x048
Type RO, reset 0x0000.0000
31 30 29 28 27 26 25 24 23 22 21 20 19 18 17 16
reserved
Type RO RO RO RO RO RO RO RO RO RO RO RO RO RO RO RO
Reset 0 0 0 0 0 0 0 0 0 0 0 0 0 0 0 0
15 14 13 12 11 10 9 8 7 6 5 4 3 2 1 0
reserved IntCmpBDIntCmpBUIntCmpADIntCmpAU IntCntLoad IntCntZero
Type RO RO RO RO RO RO RO RO RO RO RO RO RO RO RO RO
Reset 0 0 0 0 0 0 0 0 0 0 0 0 0 0 0 0
Bit/Field Name Type Reset Description
Software should not rely on the value of a reserved bit. To provide
compatibility with future products, the value of a reserved bit should be
preserved across a read-modify-write operation.
31:6 reserved RO 0x00
Comparator B Down Interrupt Status
Indicates that the counter has matched the comparator B value while
counting down.
5 IntCmpBD RO 0
Comparator B Up Interrupt Status
Indicates that the counter has matched the comparator B value while
counting up.
4 IntCmpBU RO 0
Comparator A Down Interrupt Status
Indicates that the counter has matched the comparator A value while
counting down.
3 IntCmpAD RO 0
Comparator A Up Interrupt Status
Indicates that the counter has matched the comparator A value while
counting up.
2 IntCmpAU RO 0
Counter=Load Interrupt Status
Indicates that the counter has matched the PWMnLOAD register.
1 IntCntLoad RO 0
Counter=0 Interrupt Status
Indicates that the counter has matched 0.
0 IntCntZero RO 0
386 November 30, 2007
Preliminary
Pulse Width Modulator (PWM)
Register 13: PWM0 Interrupt Status and Clear (PWM0ISC), offset 0x04C
This register provides the current set of interrupt sources that are asserted to the controller. Bits set
to 1 indicate the latched events that have occurred; a 0 bit indicates that the event in question has
not occurred. These are R/W1C registers; writing a 1 to a bit position clears the corresponding
interrupt reason.
PWM0 Interrupt Status and Clear (PWM0ISC)
Base 0x4002.8000
Offset 0x04C
Type R/W1C, reset 0x0000.0000
31 30 29 28 27 26 25 24 23 22 21 20 19 18 17 16
reserved
Type RO RO RO RO RO RO RO RO RO RO RO RO RO RO RO RO
Reset 0 0 0 0 0 0 0 0 0 0 0 0 0 0 0 0
15 14 13 12 11 10 9 8 7 6 5 4 3 2 1 0
reserved IntCmpBDIntCmpBUIntCmpADIntCmpAU IntCntLoad IntCntZero
Type RO RO RO RO RO RO RO RO RO RO R/W1C R/W1C R/W1C R/W1C R/W1C R/W1C
Reset 0 0 0 0 0 0 0 0 0 0 0 0 0 0 0 0
Bit/Field Name Type Reset Description
Software should not rely on the value of a reserved bit. To provide
compatibility with future products, the value of a reserved bit should be
preserved across a read-modify-write operation.
31:6 reserved RO 0x00
Comparator B Down Interrupt
Indicates that the counter has matched the comparator B value while
counting down.
5 IntCmpBD R/W1C 0
Comparator B Up Interrupt
Indicates that the counter has matched the comparator B value while
counting up.
4 IntCmpBU R/W1C 0
Comparator A Down Interrupt
Indicates that the counter has matched the comparator A value while
counting down.
3 IntCmpAD R/W1C 0
Comparator A Up Interrupt
Indicates that the counter has matched the comparator A value while
counting up.
2 IntCmpAU R/W1C 0
Counter=Load Interrupt
Indicates that the counter has matched the PWMnLOAD register.
1 IntCntLoad R/W1C 0
Counter=0 Interrupt
Indicates that the counter has matched 0.
0 IntCntZero R/W1C 0
November 30, 2007 387
Preliminary
LM3S6110 Microcontroller
Register 14: PWM0 Load (PWM0LOAD), offset 0x050
This register contains the load value for the PWM counter. Based on the counter mode, either this
value is loaded into the counter after it reaches zero, or it is the limit of up-counting after which the
counter decrements back to zero. If the Load Value Update mode is immediate, this value is used
the next time the counter reaches zero; if the mode is synchronous, it is used the next time the
counter reaches zero after a synchronous update has been requested through the PWM Master
Control (PWMCTL) register (see page 373). If this register is re-written before the actual update
occurs, the previous value is never used and is lost.
PWM0 Load (PWM0LOAD)
Base 0x4002.8000
Offset 0x050
Type R/W, reset 0x0000.0000
31 30 29 28 27 26 25 24 23 22 21 20 19 18 17 16
reserved
Type RO RO RO RO RO RO RO RO RO RO RO RO RO RO RO RO
Reset 0 0 0 0 0 0 0 0 0 0 0 0 0 0 0 0
15 14 13 12 11 10 9 8 7 6 5 4 3 2 1 0
Load
Type R/W R/W R/W R/W R/W R/W R/W R/W R/W R/W R/W R/W R/W R/W R/W R/W
Reset 0 0 0 0 0 0 0 0 0 0 0 0 0 0 0 0
Bit/Field Name Type Reset Description
Software should not rely on the value of a reserved bit. To provide
compatibility with future products, the value of a reserved bit should be
preserved across a read-modify-write operation.
31:16 reserved RO 0x00
Counter Load Value
The counter load value.
15:0 Load R/W 0
388 November 30, 2007
Preliminary
Pulse Width Modulator (PWM)
Register 15: PWM0 Counter (PWM0COUNT), offset 0x054
This register contains the current value of the PWM counter. When this value matches the load
register, a pulse is output; this can drive the generation of a PWM signal (via the
PWMnGENA/PWMnGENB registers, see page 392 and page 395) or drive an interrupt (via the
PWMnINTEN register, see page 384). A pulse with the same capabilities is generated when this
value is zero.
PWM0 Counter (PWM0COUNT)
Base 0x4002.8000
Offset 0x054
Type RO, reset 0x0000.0000
31 30 29 28 27 26 25 24 23 22 21 20 19 18 17 16
reserved
Type RO RO RO RO RO RO RO RO RO RO RO RO RO RO RO RO
Reset 0 0 0 0 0 0 0 0 0 0 0 0 0 0 0 0
15 14 13 12 11 10 9 8 7 6 5 4 3 2 1 0
Count
Type RO RO RO RO RO RO RO RO RO RO RO RO RO RO RO RO
Reset 0 0 0 0 0 0 0 0 0 0 0 0 0 0 0 0
Bit/Field Name Type Reset Description
Software should not rely on the value of a reserved bit. To provide
compatibility with future products, the value of a reserved bit should be
preserved across a read-modify-write operation.
31:16 reserved RO 0x00
Counter Value
The current value of the counter.
15:0 Count RO 0x00
November 30, 2007 389
Preliminary
LM3S6110 Microcontroller
Register 16: PWM0 Compare A (PWM0CMPA), offset 0x058
This register contains a value to be compared against the counter . When this value matches the
counter, a pulse is output; this can drive the generation of a PWM signal (via the
PWMnGENA/PWMnGENB registers) or drive an interrupt (via the PWMnINTEN register). If the
value of this register is greater than the PWMnLOAD register (see page 388), then no pulse is ever
output.
If the comparator A update mode is immediate (based on the CmpAUpd bit in the PWMnCTL register),
then this 16-bit CompA value is used the next time the counter reaches zero. If the update mode is
synchronous, it is used the next time the counter reaches zero after a synchronous update has been
requested through the PWM Master Control (PWMCTL) register (see page 373). If this register is
rewritten before the actual update occurs, the previous value is never used and is lost.
PWM0 Compare A (PWM0CMPA)
Base 0x4002.8000
Offset 0x058
Type R/W, reset 0x0000.0000
31 30 29 28 27 26 25 24 23 22 21 20 19 18 17 16
reserved
Type RO RO RO RO RO RO RO RO RO RO RO RO RO RO RO RO
Reset 0 0 0 0 0 0 0 0 0 0 0 0 0 0 0 0
15 14 13 12 11 10 9 8 7 6 5 4 3 2 1 0
CompA
Type R/W R/W R/W R/W R/W R/W R/W R/W R/W R/W R/W R/W R/W R/W R/W R/W
Reset 0 0 0 0 0 0 0 0 0 0 0 0 0 0 0 0
Bit/Field Name Type Reset Description
Software should not rely on the value of a reserved bit. To provide
compatibility with future products, the value of a reserved bit should be
preserved across a read-modify-write operation.
31:16 reserved RO 0x00
Comparator A Value
The value to be compared against the counter.
15:0 CompA R/W 0x00
390 November 30, 2007
Preliminary
Pulse Width Modulator (PWM)
Register 17: PWM0 Compare B (PWM0CMPB), offset 0x05C
This register contains a value to be compared against the counter. When this value matches the
counter, a pulse is output; this can drive the generation of a PWM signal (via the
PWMnGENA/PWMnGENB registers) or drive an interrupt (via the PWMnINTEN register). If the
value of this register is greater than the PWMnLOAD register, then no pulse is ever output.
IF the comparator B update mode is immediate (based on the CmpBUpd bit in the PWMnCTL
register), then this 16-bit CompB value is used the next time the counter reaches zero. If the update
mode is synchronous, it is used the next time the counter reaches zero after a synchronous update
has been requested through the PWM Master Control (PWMCTL) register (see page 373). If this
register is rewritten before the actual update occurs, the previous value is never used and is lost.
PWM0 Compare B (PWM0CMPB)
Base 0x4002.8000
Offset 0x05C
Type R/W, reset 0x0000.0000
31 30 29 28 27 26 25 24 23 22 21 20 19 18 17 16
reserved
Type RO RO RO RO RO RO RO RO RO RO RO RO RO RO RO RO
Reset 0 0 0 0 0 0 0 0 0 0 0 0 0 0 0 0
15 14 13 12 11 10 9 8 7 6 5 4 3 2 1 0
CompB
Type R/W R/W R/W R/W R/W R/W R/W R/W R/W R/W R/W R/W R/W R/W R/W R/W
Reset 0 0 0 0 0 0 0 0 0 0 0 0 0 0 0 0
Bit/Field Name Type Reset Description
Software should not rely on the value of a reserved bit. To provide
compatibility with future products, the value of a reserved bit should be
preserved across a read-modify-write operation.
31:16 reserved RO 0x00
Comparator B Value
The value to be compared against the counter.
15:0 CompB R/W 0x00
November 30, 2007 391
Preliminary
LM3S6110 Microcontroller
Register 18: PWM0 Generator A Control (PWM0GENA), offset 0x060
This register controls the generation of the PWMnA signal based on the load and zero output pulses
from the counter, as well as the compare A and compare B pulses from the comparators. When the
counter is running in Count-Down mode, only four of these events occur; when running in
Count-Up/Down mode, all six occur. These events provide great flexibility in the positioning and
duty cycle of the PWM signal that is produced.
The PWM0GENA register controls generation of the PWM0A signal.
If a zero or load event coincides with a compare A or compare B event, the zero or load action is
taken and the compare A or compare B action is ignored. If a compare A event coincides with a
compare B event, the compare A action is taken and the compare B action is ignored.
PWM0 Generator A Control (PWM0GENA)
Base 0x4002.8000
Offset 0x060
Type R/W, reset 0x0000.0000
31 30 29 28 27 26 25 24 23 22 21 20 19 18 17 16
reserved
Type RO RO RO RO RO RO RO RO RO RO RO RO RO RO RO RO
Reset 0 0 0 0 0 0 0 0 0 0 0 0 0 0 0 0
15 14 13 12 11 10 9 8 7 6 5 4 3 2 1 0
reserved ActCmpBD ActCmpBU ActCmpAD ActCmpAU ActLoad ActZero
Type RO RO RO RO R/W R/W R/W R/W R/W R/W R/W R/W R/W R/W R/W R/W
Reset 0 0 0 0 0 0 0 0 0 0 0 0 0 0 0 0
Bit/Field Name Type Reset Description
Software should not rely on the value of a reserved bit. To provide
compatibility with future products, the value of a reserved bit should be
preserved across a read-modify-write operation.
31:12 reserved RO 0x00
Action for Comparator B Down
The action to be taken when the counter matches comparator B while
counting down.
The table below defines the effect of the event on the output signal.
Value Description
0x0 Do nothing.
0x1 Invert the output signal.
0x2 Set the output signal to 0.
0x3 Set the output signal to 1.
11:10 ActCmpBD R/W 0x0
392 November 30, 2007
Preliminary
Pulse Width Modulator (PWM)
Bit/Field Name Type Reset Description
Action for Comparator B Up
The action to be taken when the counter matches comparator B while
counting up. Occurs only when the Mode bit in the PWMnCTL register
(see page 382) is set to 1.
The table below defines the effect of the event on the output signal.
Value Description
0x0 Do nothing.
0x1 Invert the output signal.
0x2 Set the output signal to 0.
0x3 Set the output signal to 1.
9:8 ActCmpBU R/W 0x0
Action for Comparator A Down
The action to be taken when the counter matches comparator A while
counting down.
The table below defines the effect of the event on the output signal.
Value Description
0x0 Do nothing.
0x1 Invert the output signal.
0x2 Set the output signal to 0.
0x3 Set the output signal to 1.
7:6 ActCmpAD R/W 0x0
Action for Comparator A Up
The action to be taken when the counter matches comparator A while
counting up. Occurs only when the Mode bit in the PWMnCTL register
is set to 1.
The table below defines the effect of the event on the output signal.
Value Description
0x0 Do nothing.
0x1 Invert the output signal.
0x2 Set the output signal to 0.
0x3 Set the output signal to 1.
5:4 ActCmpAU R/W 0x0
Action for Counter=Load
The action to be taken when the counter matches the load value.
The table below defines the effect of the event on the output signal.
Value Description
0x0 Do nothing.
0x1 Invert the output signal.
0x2 Set the output signal to 0.
0x3 Set the output signal to 1.
3:2 ActLoad R/W 0x0
November 30, 2007 393
Preliminary
LM3S6110 Microcontroller
Bit/Field Name Type Reset Description
Action for Counter=0
The action to be taken when the counter is zero.
The table below defines the effect of the event on the output signal.
Value Description
0x0 Do nothing.
0x1 Invert the output signal.
0x2 Set the output signal to 0.
0x3 Set the output signal to 1.
1:0 ActZero R/W 0x0
394 November 30, 2007
Preliminary
Pulse Width Modulator (PWM)
Register 19: PWM0 Generator B Control (PWM0GENB), offset 0x064
This register controls the generation of the PWMnB signal based on the load and zero output pulses
from the counter, as well as the compare A and compare B pulses from the comparators. When the
counter is running in Down mode, only four of these events occur; when running in Up/Down mode,
all six occur. These events provide great flexibility in the positioning and duty cycle of the PWM
signal that is produced.
The PWM0GENB register controls generation of the PWM0B signal.
If a zero or load event coincides with a compare A or compare B event, the zero or load action is
taken and the compare A or compare B action is ignored. If a compare A event coincides with a
compare B event, the compare B action is taken and the compare A action is ignored.
PWM0 Generator B Control (PWM0GENB)
Base 0x4002.8000
Offset 0x064
Type R/W, reset 0x0000.0000
31 30 29 28 27 26 25 24 23 22 21 20 19 18 17 16
reserved
Type RO RO RO RO RO RO RO RO RO RO RO RO RO RO RO RO
Reset 0 0 0 0 0 0 0 0 0 0 0 0 0 0 0 0
15 14 13 12 11 10 9 8 7 6 5 4 3 2 1 0
reserved ActCmpBD ActCmpBU ActCmpAD ActCmpAU ActLoad ActZero
Type RO RO RO RO R/W R/W R/W R/W R/W R/W R/W R/W R/W R/W R/W R/W
Reset 0 0 0 0 0 0 0 0 0 0 0 0 0 0 0 0
Bit/Field Name Type Reset Description
Software should not rely on the value of a reserved bit. To provide
compatibility with future products, the value of a reserved bit should be
preserved across a read-modify-write operation.
31:12 reserved RO 0x00
Action for Comparator B Down
The action to be taken when the counter matches comparator B while
counting down.
The table below defines the effect of the event on the output signal.
Value Description
0x0 Do nothing.
0x1 Invert the output signal.
0x2 Set the output signal to 0.
0x3 Set the output signal to 1.
11:10 ActCmpBD R/W 0x0
November 30, 2007 395
Preliminary
LM3S6110 Microcontroller
Bit/Field Name Type Reset Description
Action for Comparator B Up
The action to be taken when the counter matches comparator B while
counting up. Occurs only when the Mode bit in the PWMnCTL register
is set to 1.
The table below defines the effect of the event on the output signal.
Value Description
0x0 Do nothing.
0x1 Invert the output signal.
0x2 Set the output signal to 0.
0x3 Set the output signal to 1.
9:8 ActCmpBU R/W 0x0
Action for Comparator A Down
The action to be taken when the counter matches comparator A while
counting down.
The table below defines the effect of the event on the output signal.
Value Description
0x0 Do nothing.
0x1 Invert the output signal.
0x2 Set the output signal to 0.
0x3 Set the output signal to 1.
7:6 ActCmpAD R/W 0x0
Action for Comparator A Up
The action to be taken when the counter matches comparator A while
counting up. Occurs only when the Mode bit in the PWMnCTL register
is set to 1.
The table below defines the effect of the event on the output signal.
Value Description
0x0 Do nothing.
0x1 Invert the output signal.
0x2 Set the output signal to 0.
0x3 Set the output signal to 1.
5:4 ActCmpAU R/W 0x0
Action for Counter=Load
The action to be taken when the counter matches the load value.
The table below defines the effect of the event on the output signal.
Value Description
0x0 Do nothing.
0x1 Invert the output signal.
0x2 Set the output signal to 0.
0x3 Set the output signal to 1.
3:2 ActLoad R/W 0x0
396 November 30, 2007
Preliminary
Pulse Width Modulator (PWM)
Bit/Field Name Type Reset Description
Action for Counter=0
The action to be taken when the counter is 0.
The table below defines the effect of the event on the output signal.
Value Description
0x0 Do nothing.
0x1 Invert the output signal.
0x2 Set the output signal to 0.
0x3 Set the output signal to 1.
1:0 ActZero R/W 0x0
November 30, 2007 397
Preliminary
LM3S6110 Microcontroller
Register 20: PWM0 Dead-Band Control (PWM0DBCTL), offset 0x068
The PWM0DBCTL register controls the dead-band generator, which produces the PWM0 and PWM1
signals based on the PWM0A and PWM0B signals. When disabled, the PWM0A signal passes through
to the PWM0 signal and the PWM0B signal passes through to the PWM1 signal. When enabled and
inverting the resulting waveform, the PWM0B signal is ignored; the PWM0 signal is generated by
delaying the rising edge(s) of the PWM0A signal by the value in the PWM0DBRISE register (see
page 399), and the PWM1 signal is generated by delaying the falling edge(s) of the PWM0A signal by
the value in the PWM0DBFALL register (see page 400).
PWM0 Dead-Band Control (PWM0DBCTL)
Base 0x4002.8000
Offset 0x068
Type R/W, reset 0x0000.0000
31 30 29 28 27 26 25 24 23 22 21 20 19 18 17 16
reserved
Type RO RO RO RO RO RO RO RO RO RO RO RO RO RO RO RO
Reset 0 0 0 0 0 0 0 0 0 0 0 0 0 0 0 0
15 14 13 12 11 10 9 8 7 6 5 4 3 2 1 0
reserved Enable
Type RO RO RO RO RO RO RO RO RO RO RO RO RO RO RO R/W
Reset 0 0 0 0 0 0 0 0 0 0 0 0 0 0 0 0
Bit/Field Name Type Reset Description
Software should not rely on the value of a reserved bit. To provide
compatibility with future products, the value of a reserved bit should be
preserved across a read-modify-write operation.
31:1 reserved RO 0x00
Dead-Band Generator Enable
When set, the dead-band generator inserts dead bands into the output
signals; when clear, it simply passes the PWM signals through.
0 Enable R/W 0
398 November 30, 2007
Preliminary
Pulse Width Modulator (PWM)
Register 21: PWM0 Dead-Band Rising-Edge Delay (PWM0DBRISE), offset
0x06C
The PWM0DBRISE register contains the number of clock ticks to delay the rising edge of the PWM0A
signal when generating the PWM0 signal. If the dead-band generator is disabled through the
PWMnDBCTL register, the PWM0DBRISE register is ignored. If the value of this register is larger
than the width of a High pulse on the input PWM signal, the rising-edge delay consumes the entire
High time of the signal, resulting in no High time on the output. Care must be taken to ensure that
the input High time always exceeds the rising-edge delay.
PWM0 Dead-Band Rising-Edge Delay (PWM0DBRISE)
Base 0x4002.8000
Offset 0x06C
Type R/W, reset 0x0000.0000
31 30 29 28 27 26 25 24 23 22 21 20 19 18 17 16
reserved
Type RO RO RO RO RO RO RO RO RO RO RO RO RO RO RO RO
Reset 0 0 0 0 0 0 0 0 0 0 0 0 0 0 0 0
15 14 13 12 11 10 9 8 7 6 5 4 3 2 1 0
reserved RiseDelay
Type RO RO RO RO R/W R/W R/W R/W R/W R/W R/W R/W R/W R/W R/W R/W
Reset 0 0 0 0 0 0 0 0 0 0 0 0 0 0 0 0
Bit/Field Name Type Reset Description
Software should not rely on the value of a reserved bit. To provide
compatibility with future products, the value of a reserved bit should be
preserved across a read-modify-write operation.
31:12 reserved RO 0x00
Dead-Band Rise Delay
The number of clock ticks to delay the rising edge.
11:0 RiseDelay R/W 0
November 30, 2007 399
Preliminary
LM3S6110 Microcontroller
Register 22: PWM0 Dead-Band Falling-Edge-Delay (PWM0DBFALL), offset
0x070
The PWM0DBFALL register contains the number of clock ticks to delay the falling edge of the
PWM0A signal when generating the PWM1 signal. If the dead-band generator is disabled, this register
is ignored. If the value of this register is larger than the width of a Low pulse on the input PWM
signal, the falling-edge delay consumes the entire Low time of the signal, resulting in no Low time
on the output. Care must be taken to ensure that the input Low time always exceeds the falling-edge
delay.
PWM0 Dead-Band Falling-Edge-Delay (PWM0DBFALL)
Base 0x4002.8000
Offset 0x070
Type R/W, reset 0x0000.0000
31 30 29 28 27 26 25 24 23 22 21 20 19 18 17 16
reserved
Type RO RO RO RO RO RO RO RO RO RO RO RO RO RO RO RO
Reset 0 0 0 0 0 0 0 0 0 0 0 0 0 0 0 0
15 14 13 12 11 10 9 8 7 6 5 4 3 2 1 0
reserved FallDelay
Type RO RO RO RO R/W R/W R/W R/W R/W R/W R/W R/W R/W R/W R/W R/W
Reset 0 0 0 0 0 0 0 0 0 0 0 0 0 0 0 0
Bit/Field Name Type Reset Description
Software should not rely on the value of a reserved bit. To provide
compatibility with future products, the value of a reserved bit should be
preserved across a read-modify-write operation.
31:12 reserved RO 0x00
Dead-Band Fall Delay
The number of clock ticks to delay the falling edge.
11:0 FallDelay R/W 0x00
400 November 30, 2007
Preliminary
Pulse Width Modulator (PWM)
16 Pin Diagram
Figure 16-1 on page 401 shows the pin diagram and pin-to-signal-name mapping.
Figure 16-1. Pin Connection Diagram
LM3S6110
38
39
40
41
42
43
44
45
46
47
48
49
50
1 75
26 100
2
27
5
6
3
4
7
8
11
9
10
99
28 98
29 97
30 96
31 95
32 94
33 93
34 92
35 91
36 90
73
72
74
71
69
68
70
67
65
66
12
13
14
17
18
15
16
19
20
23
21
22
24
25
64
37 89
88
87
86
85
84
83
82
81
80
79
78
77
76
63
61
60
62
59
57
56
58
55
53
54
52
51
NC
NC
VDDA
GNDA
NC
NC
LDO
VDD
GND
PD0/PWM0
PD1/PWM1
PD2
PD3
VDD25
GND
XTALPPHY
XTALNPHY
NC
NC
VDD
GND
PC7/C2-
PC6/C2+
PC5/C1+
PC4
PA0/U0Rx
PA1/U0Tx
PA2/SSI0Clk
PA3/SSI0Fss
PA4/SSI0Rx
PA5/SSI0Tx
VDD
GND
PA6/CCP1
NC
VCCPHY
RXIN
VDD25
GND
RXIP
GNDPHY
GNDPHY
TXOP
VDD
GND
TXON
PF0
OSC0
OSC1
NC
NC
NC
NC
GND
VDD
VDD
GND
MDIO
PF3/LED0
PF2/LED1
PF1
VDD25
GND
RST
CMOD0
PB0/CCP0
PB1/CCP2
VDD
GND
PB2
PB3/Fault
NC
NC
NC
NC
CMOD1
PC3/TDO/SWO
PC2/TDI
PC1/TMS/SWDIO
PC0/TCK/SWCLK
VDD
GND
VCCPHY
VCCPHY
GNDPHY
GNDPHY
GND
VDD25
PB7/TRST
PB6/C0+
PB5/C1-
PB4/C0-
VDD
GND
PD4/CCP3
PD5
GNDA
VDDA
PD6
PD7/C0o
November 30, 2007 401
Preliminary
LM3S6110 Microcontroller
17 Signal Tables
The following tables list the signals available for each pin. Functionality is enabled by software with
the GPIOAFSEL register.
Important: All multiplexed pins are GPIOs by default, with the exception of the five JTAG pins (PB7
and PC[3:0]) which default to the JTAG functionality.
Table 17-1 on page 402 shows the pin-to-signal-name mapping, including functional characteristics
of the signals. Table 17-2 on page 406 lists the signals in alphabetical order by signal name.
Table 17-3 on page 409 groups the signals by functionality, except for GPIOs. Table 17-4 on page
412 lists the GPIO pins and their alternate functionality.
Table 17-1. Signals by Pin Number
Pin Number Pin Name Pin Type Buffer Type Description
1 NC - - No connect
2 NC - - No connect
The positive supply (3.3 V) for the analog
circuits (ADC, Analog Comparators, etc.).
These are separated from VDD to minimize
the electrical noise contained on VDD from
affecting the analog functions.
3 VDDA - Power
The ground reference for the analog circuits
(ADC, Analog Comparators, etc.). These are
separated from GND to minimize the electrical
noise contained on VDD from affecting the
analog functions.
4 GNDA - Power
5 NC - - No connect
6 NC - - No connect
Low drop-out regulator output voltage. This
pin requires an external capacitor between
the pin and GND of 1 μF or greater. When the
on-chip LDO is used to provide power to the
logic, the LDO pin must also be connected to
the VDD25 pins at the board level in addition
to the decoupling capacitor(s).
7 LDO - Power
8 VDD - Power Positive supply for I/O and some logic.
9 GND - Power Ground reference for logic and I/O pins.
10 PD0 I/O TTL GPIO port D bit 0
PWM0 O TTL PWM 0
11 PD1 I/O TTL GPIO port D bit 1
PWM1 O TTL PWM 1
12 PD2 I/O TTL GPIO port D bit 2
13 PD3 I/O TTL GPIO port D bit 3
Positive supply for most of the logic function,
including the processor core and most
peripherals.
14 VDD25 - Power
15 GND - Power Ground reference for logic and I/O pins.
16 XTALPPHY O TTL XTALP of the Ethernet PHY
17 XTALNPHY I TTL XTALN of the Ethernet PHY
402 November 30, 2007
Preliminary
Signal Tables
Pin Number Pin Name Pin Type Buffer Type Description
18 NC - - No connect
19 NC - - No connect
20 VDD - Power Positive supply for I/O and some logic.
21 GND - Power Ground reference for logic and I/O pins.
22 PC7 I/O TTL GPIO port C bit 7
C2- I Analog Analog comparator 2 negative input
23 PC6 I/O TTL GPIO port C bit 6
C2+ I Analog Analog comparator positive input
24 PC5 I/O TTL GPIO port C bit 5
C1+ I Analog Analog comparator positive input
25 PC4 I/O TTL GPIO port C bit 4
26 PA0 I/O TTL GPIO port A bit 0
UART module 0 receive. When in IrDA mode,
this signal has IrDA modulation.
U0Rx I TTL
27 PA1 I/O TTL GPIO port A bit 1
UART module 0 transmit. When in IrDA mode,
this signal has IrDA modulation.
U0Tx O TTL
28 PA2 I/O TTL GPIO port A bit 2
SSI0Clk I/O TTL SSI module 0 clock
29 PA3 I/O TTL GPIO port A bit 3
SSI0Fss I/O TTL SSI module 0 frame
30 PA4 I/O TTL GPIO port A bit 4
SSI0Rx I TTL SSI module 0 receive
31 PA5 I/O TTL GPIO port A bit 5
SSI0Tx O TTL SSI module 0 transmit
32 VDD - Power Positive supply for I/O and some logic.
33 GND - Power Ground reference for logic and I/O pins.
34 PA6 I/O TTL GPIO port A bit 6
CCP1 I/O TTL Capture/Compare/PWM 1
35 NC - - No connect
36 VCCPHY I TTL VCC of the Ethernet PHY
37 RXIN I Analog RXIN of the Ethernet PHY
Positive supply for most of the logic function,
including the processor core and most
peripherals.
38 VDD25 - Power
39 GND - Power Ground reference for logic and I/O pins.
40 RXIP I Analog RXIP of the Ethernet PHY
41 GNDPHY I TTL GND of the Ethernet PHY
42 GNDPHY I TTL GND of the Ethernet PHY
43 TXOP O Analog TXOP of the Ethernet PHY
44 VDD - Power Positive supply for I/O and some logic.
45 GND - Power Ground reference for logic and I/O pins.
46 TXON O Analog TXON of the Ethernet PHY
47 PF0 I/O TTL GPIO port F bit 0
November 30, 2007 403
Preliminary
LM3S6110 Microcontroller
Pin Number Pin Name Pin Type Buffer Type Description
Main oscillator crystal input or an external
clock reference input.
48 OSC0 I Analog
49 OSC1 I Analog Main oscillator crystal output.
50 NC - - No connect
51 NC - - No connect
52 NC - - No connect
53 NC - - No connect
54 GND - Power Ground reference for logic and I/O pins.
55 VDD - Power Positive supply for I/O and some logic.
56 VDD - Power Positive supply for I/O and some logic.
57 GND - Power Ground reference for logic and I/O pins.
58 MDIO I/O TTL MDIO of the Ethernet PHY
59 PF3 I/O TTL GPIO port F bit 3
LED0 O TTL MII LED 0
60 PF2 I/O TTL GPIO port F bit 2
LED1 O TTL MII LED 1
61 PF1 I/O TTL GPIO port F bit 1
Positive supply for most of the logic function,
including the processor core and most
peripherals.
62 VDD25 - Power
63 GND - Power Ground reference for logic and I/O pins.
64 RST I TTL System reset input.
CPU Mode bit 0. Input must be set to logic 0
(grounded); other encodings reserved.
65 CMOD0 I/O TTL
66 PB0 I/O TTL GPIO port B bit 0
CCP0 I/O TTL Capture/Compare/PWM 0
67 PB1 I/O TTL GPIO port B bit 1
CCP2 I/O TTL Capture/Compare/PWM 2
68 VDD - Power Positive supply for I/O and some logic.
69 GND - Power Ground reference for logic and I/O pins.
70 PB2 I/O TTL GPIO port B bit 2
71 PB3 I/O TTL GPIO port B bit 3
Fault I TTL PWM Fault
72 NC - - No connect
73 NC - - No connect
74 NC - - No connect
75 NC - - No connect
CPU Mode bit 1. Input must be set to logic 0
(grounded); other encodings reserved.
76 CMOD1 I/O TTL
77 PC3 I/O TTL GPIO port C bit 3
TDO O TTL JTAG TDO and SWO
SWO O TTL JTAG TDO and SWO
78 PC2 I/O TTL GPIO port C bit 2
TDI I TTL JTAG TDI
404 November 30, 2007
Preliminary
Signal Tables
Pin Number Pin Name Pin Type Buffer Type Description
79 PC1 I/O TTL GPIO port C bit 1
TMS I/O TTL JTAG TMS and SWDIO
SWDIO I/O TTL JTAG TMS and SWDIO
80 PC0 I/O TTL GPIO port C bit 0
TCK I TTL JTAG/SWD CLK
SWCLK I TTL JTAG/SWD CLK
81 VDD - Power Positive supply for I/O and some logic.
82 GND - Power Ground reference for logic and I/O pins.
83 VCCPHY I TTL VCC of the Ethernet PHY
84 VCCPHY I TTL VCC of the Ethernet PHY
85 GNDPHY I TTL GND of the Ethernet PHY
86 GNDPHY I TTL GND of the Ethernet PHY
87 GND - Power Ground reference for logic and I/O pins.
Positive supply for most of the logic function,
including the processor core and most
peripherals.
88 VDD25 - Power
89 PB7 I/O TTL GPIO port B bit 7
TRST I TTL JTAG TRSTn
90 PB6 I/O TTL GPIO port B bit 6
C0+ I Analog Analog comparator 0 positive input
91 PB5 I/O TTL GPIO port B bit 5
C1- I Analog Analog comparator 1 negative input
92 PB4 I/O TTL GPIO port B bit 4
C0- I Analog Analog comparator 0 negative input
93 VDD - Power Positive supply for I/O and some logic.
94 GND - Power Ground reference for logic and I/O pins.
95 PD4 I/O TTL GPIO port D bit 4
CCP3 I/O TTL Capture/Compare/PWM 3
96 PD5 I/O TTL GPIO port D bit 5
The ground reference for the analog circuits
(ADC, Analog Comparators, etc.). These are
separated from GND to minimize the electrical
noise contained on VDD from affecting the
analog functions.
97 GNDA - Power
The positive supply (3.3 V) for the analog
circuits (ADC, Analog Comparators, etc.).
These are separated from VDD to minimize
the electrical noise contained on VDD from
affecting the analog functions.
98 VDDA - Power
99 PD6 I/O TTL GPIO port D bit 6
100 PD7 I/O TTL GPIO port D bit 7
C0o O TTL Analog comparator 0 output
November 30, 2007 405
Preliminary
LM3S6110 Microcontroller
Table 17-2. Signals by Signal Name
Pin Name Pin Number Pin Type Buffer Type Description
C0+ 90 I Analog Analog comparator 0 positive input
C0- 92 I Analog Analog comparator 0 negative input
C0o 100 O TTL Analog comparator 0 output
C1+ 24 I Analog Analog comparator positive input
C1- 91 I Analog Analog comparator 1 negative input
C2+ 23 I Analog Analog comparator positive input
C2- 22 I Analog Analog comparator 2 negative input
CCP0 66 I/O TTL Capture/Compare/PWM 0
CCP1 34 I/O TTL Capture/Compare/PWM 1
CCP2 67 I/O TTL Capture/Compare/PWM 2
CCP3 95 I/O TTL Capture/Compare/PWM 3
CPU Mode bit 0. Input must be set to logic 0
(grounded); other encodings reserved.
CMOD0 65 I/O TTL
CPU Mode bit 1. Input must be set to logic 0
(grounded); other encodings reserved.
CMOD1 76 I/O TTL
Fault 71 I TTL PWM Fault
GND 9 - Power Ground reference for logic and I/O pins.
GND 15 - Power Ground reference for logic and I/O pins.
GND 21 - Power Ground reference for logic and I/O pins.
GND 33 - Power Ground reference for logic and I/O pins.
GND 39 - Power Ground reference for logic and I/O pins.
GND 45 - Power Ground reference for logic and I/O pins.
GND 54 - Power Ground reference for logic and I/O pins.
GND 57 - Power Ground reference for logic and I/O pins.
GND 63 - Power Ground reference for logic and I/O pins.
GND 69 - Power Ground reference for logic and I/O pins.
GND 82 - Power Ground reference for logic and I/O pins.
GND 87 - Power Ground reference for logic and I/O pins.
GND 94 - Power Ground reference for logic and I/O pins.
The ground reference for the analog circuits
(ADC, Analog Comparators, etc.). These are
separated from GND to minimize the electrical
noise contained on VDD from affecting the
analog functions.
GNDA 4 - Power
The ground reference for the analog circuits
(ADC, Analog Comparators, etc.). These are
separated from GND to minimize the electrical
noise contained on VDD from affecting the
analog functions.
GNDA 97 - Power
GNDPHY 41 I TTL GND of the Ethernet PHY
GNDPHY 42 I TTL GND of the Ethernet PHY
GNDPHY 85 I TTL GND of the Ethernet PHY
GNDPHY 86 I TTL GND of the Ethernet PHY
406 November 30, 2007
Preliminary
Signal Tables
Pin Name Pin Number Pin Type Buffer Type Description
Low drop-out regulator output voltage. This
pin requires an external capacitor between
the pin and GND of 1 μF or greater. When the
on-chip LDO is used to provide power to the
logic, the LDO pin must also be connected to
the VDD25 pins at the board level in addition
to the decoupling capacitor(s).
LDO 7 - Power
LED0 59 O TTL MII LED 0
LED1 60 O TTL MII LED 1
MDIO 58 I/O TTL MDIO of the Ethernet PHY
NC 1 - - No connect
NC 2 - - No connect
NC 5 - - No connect
NC 6 - - No connect
NC 18 - - No connect
NC 19 - - No connect
NC 35 - - No connect
NC 50 - - No connect
NC 51 - - No connect
NC 52 - - No connect
NC 53 - - No connect
NC 72 - - No connect
NC 73 - - No connect
NC 74 - - No connect
NC 75 - - No connect
Main oscillator crystal input or an external
clock reference input.
OSC0 48 I Analog
OSC1 49 I Analog Main oscillator crystal output.
PA0 26 I/O TTL GPIO port A bit 0
PA1 27 I/O TTL GPIO port A bit 1
PA2 28 I/O TTL GPIO port A bit 2
PA3 29 I/O TTL GPIO port A bit 3
PA4 30 I/O TTL GPIO port A bit 4
PA5 31 I/O TTL GPIO port A bit 5
PA6 34 I/O TTL GPIO port A bit 6
PB0 66 I/O TTL GPIO port B bit 0
PB1 67 I/O TTL GPIO port B bit 1
PB2 70 I/O TTL GPIO port B bit 2
PB3 71 I/O TTL GPIO port B bit 3
PB4 92 I/O TTL GPIO port B bit 4
PB5 91 I/O TTL GPIO port B bit 5
PB6 90 I/O TTL GPIO port B bit 6
PB7 89 I/O TTL GPIO port B bit 7
PC0 80 I/O TTL GPIO port C bit 0
PC1 79 I/O TTL GPIO port C bit 1
November 30, 2007 407
Preliminary
LM3S6110 Microcontroller
Pin Name Pin Number Pin Type Buffer Type Description
PC2 78 I/O TTL GPIO port C bit 2
PC3 77 I/O TTL GPIO port C bit 3
PC4 25 I/O TTL GPIO port C bit 4
PC5 24 I/O TTL GPIO port C bit 5
PC6 23 I/O TTL GPIO port C bit 6
PC7 22 I/O TTL GPIO port C bit 7
PD0 10 I/O TTL GPIO port D bit 0
PD1 11 I/O TTL GPIO port D bit 1
PD2 12 I/O TTL GPIO port D bit 2
PD3 13 I/O TTL GPIO port D bit 3
PD4 95 I/O TTL GPIO port D bit 4
PD5 96 I/O TTL GPIO port D bit 5
PD6 99 I/O TTL GPIO port D bit 6
PD7 100 I/O TTL GPIO port D bit 7
PF0 47 I/O TTL GPIO port F bit 0
PF1 61 I/O TTL GPIO port F bit 1
PF2 60 I/O TTL GPIO port F bit 2
PF3 59 I/O TTL GPIO port F bit 3
PWM0 10 O TTL PWM 0
PWM1 11 O TTL PWM 1
RST 64 I TTL System reset input.
RXIN 37 I Analog RXIN of the Ethernet PHY
RXIP 40 I Analog RXIP of the Ethernet PHY
SSI0Clk 28 I/O TTL SSI module 0 clock
SSI0Fss 29 I/O TTL SSI module 0 frame
SSI0Rx 30 I TTL SSI module 0 receive
SSI0Tx 31 O TTL SSI module 0 transmit
SWCLK 80 I TTL JTAG/SWD CLK
SWDIO 79 I/O TTL JTAG TMS and SWDIO
SWO 77 O TTL JTAG TDO and SWO
TCK 80 I TTL JTAG/SWD CLK
TDI 78 I TTL JTAG TDI
TDO 77 O TTL JTAG TDO and SWO
TMS 79 I/O TTL JTAG TMS and SWDIO
TRST 89 I TTL JTAG TRSTn
TXON 46 O Analog TXON of the Ethernet PHY
TXOP 43 O Analog TXOP of the Ethernet PHY
UART module 0 receive. When in IrDA mode,
this signal has IrDA modulation.
U0Rx 26 I TTL
UART module 0 transmit. When in IrDA mode,
this signal has IrDA modulation.
U0Tx 27 O TTL
VCCPHY 36 I TTL VCC of the Ethernet PHY
VCCPHY 83 I TTL VCC of the Ethernet PHY
408 November 30, 2007
Preliminary
Signal Tables
Pin Name Pin Number Pin Type Buffer Type Description
VCCPHY 84 I TTL VCC of the Ethernet PHY
VDD 8 - Power Positive supply for I/O and some logic.
VDD 20 - Power Positive supply for I/O and some logic.
VDD 32 - Power Positive supply for I/O and some logic.
VDD 44 - Power Positive supply for I/O and some logic.
VDD 55 - Power Positive supply for I/O and some logic.
VDD 56 - Power Positive supply for I/O and some logic.
VDD 68 - Power Positive supply for I/O and some logic.
VDD 81 - Power Positive supply for I/O and some logic.
VDD 93 - Power Positive supply for I/O and some logic.
Positive supply for most of the logic function,
including the processor core and most
peripherals.
VDD25 14 - Power
Positive supply for most of the logic function,
including the processor core and most
peripherals.
VDD25 38 - Power
Positive supply for most of the logic function,
including the processor core and most
peripherals.
VDD25 62 - Power
Positive supply for most of the logic function,
including the processor core and most
peripherals.
VDD25 88 - Power
The positive supply (3.3 V) for the analog
circuits (ADC, Analog Comparators, etc.).
These are separated from VDD to minimize
the electrical noise contained on VDD from
affecting the analog functions.
VDDA 3 - Power
The positive supply (3.3 V) for the analog
circuits (ADC, Analog Comparators, etc.).
These are separated from VDD to minimize
the electrical noise contained on VDD from
affecting the analog functions.
VDDA 98 - Power
XTALNPHY 17 I TTL XTALN of the Ethernet PHY
XTALPPHY 16 O TTL XTALP of the Ethernet PHY
Table 17-3. Signals by Function, Except for GPIO
Buffer Description
Type
Pin Pin Type
Number
Function Pin Name
Analog C0+ 90 I Analog Analog comparator 0 positive input
Comparators C0- 92 I Analog Analog comparator 0 negative input
C0o 100 O TTL Analog comparator 0 output
C1+ 24 I Analog Analog comparator positive input
C1- 91 I Analog Analog comparator 1 negative input
C2+ 23 I Analog Analog comparator positive input
C2- 22 I Analog Analog comparator 2 negative input
November 30, 2007 409
Preliminary
LM3S6110 Microcontroller
Buffer Description
Type
Pin Pin Type
Number
Function Pin Name
Ethernet PHY GNDPHY 41 I TTL GND of the Ethernet PHY
GNDPHY 42 I TTL GND of the Ethernet PHY
GNDPHY 85 I TTL GND of the Ethernet PHY
GNDPHY 86 I TTL GND of the Ethernet PHY
LED0 59 O TTL MII LED 0
LED1 60 O TTL MII LED 1
MDIO 58 I/O TTL MDIO of the Ethernet PHY
RXIN 37 I Analog RXIN of the Ethernet PHY
RXIP 40 I Analog RXIP of the Ethernet PHY
TXON 46 O Analog TXON of the Ethernet PHY
TXOP 43 O Analog TXOP of the Ethernet PHY
VCCPHY 36 I TTL VCC of the Ethernet PHY
VCCPHY 83 I TTL VCC of the Ethernet PHY
VCCPHY 84 I TTL VCC of the Ethernet PHY
XTALNPHY 17 I TTL XTALN of the Ethernet PHY
XTALPPHY 16 O TTL XTALP of the Ethernet PHY
General-Purpose CCP0 66 I/O TTL Capture/Compare/PWM 0
Timers CCP1 34 I/O TTL Capture/Compare/PWM 1
CCP2 67 I/O TTL Capture/Compare/PWM 2
CCP3 95 I/O TTL Capture/Compare/PWM 3
JTAG/SWD/SWO SWCLK 80 I TTL JTAG/SWD CLK
SWDIO 79 I/O TTL JTAG TMS and SWDIO
SWO 77 O TTL JTAG TDO and SWO
TCK 80 I TTL JTAG/SWD CLK
TDI 78 I TTL JTAG TDI
TDO 77 O TTL JTAG TDO and SWO
TMS 79 I/O TTL JTAG TMS and SWDIO
PWM Fault 71 I TTL PWM Fault
PWM0 10 O TTL PWM 0
PWM1 11 O TTL PWM 1
410 November 30, 2007
Preliminary
Signal Tables
Buffer Description
Type
Pin Pin Type
Number
Function Pin Name
Power GND 9 - Power Ground reference for logic and I/O pins.
GND 15 - Power Ground reference for logic and I/O pins.
GND 21 - Power Ground reference for logic and I/O pins.
GND 33 - Power Ground reference for logic and I/O pins.
GND 39 - Power Ground reference for logic and I/O pins.
GND 45 - Power Ground reference for logic and I/O pins.
GND 54 - Power Ground reference for logic and I/O pins.
GND 57 - Power Ground reference for logic and I/O pins.
GND 63 - Power Ground reference for logic and I/O pins.
GND 69 - Power Ground reference for logic and I/O pins.
GND 82 - Power Ground reference for logic and I/O pins.
GND 87 - Power Ground reference for logic and I/O pins.
GND 94 - Power Ground reference for logic and I/O pins.
The ground reference for the analog circuits (ADC,
Analog Comparators, etc.). These are separated
from GND to minimize the electrical noise contained
on VDD from affecting the analog functions.
GNDA 4 - Power
The ground reference for the analog circuits (ADC,
Analog Comparators, etc.). These are separated
from GND to minimize the electrical noise contained
on VDD from affecting the analog functions.
GNDA 97 - Power
Low drop-out regulator output voltage. This pin
requires an external capacitor between the pin and
GND of 1 μF or greater. When the on-chip LDO is
used to provide power to the logic, the LDO pin
must also be connected to the VDD25 pins at the
board level in addition to the decoupling
capacitor(s).
LDO 7 - Power
VDD 8 - Power Positive supply for I/O and some logic.
VDD 20 - Power Positive supply for I/O and some logic.
VDD 32 - Power Positive supply for I/O and some logic.
VDD 44 - Power Positive supply for I/O and some logic.
VDD 55 - Power Positive supply for I/O and some logic.
VDD 56 - Power Positive supply for I/O and some logic.
VDD 68 - Power Positive supply for I/O and some logic.
VDD 81 - Power Positive supply for I/O and some logic.
VDD 93 - Power Positive supply for I/O and some logic.
Positive supply for most of the logic function,
including the processor core and most peripherals.
VDD25 14 - Power
Positive supply for most of the logic function,
including the processor core and most peripherals.
VDD25 38 - Power
Positive supply for most of the logic function,
including the processor core and most peripherals.
VDD25 62 - Power
Positive supply for most of the logic function,
including the processor core and most peripherals.
VDD25 88 - Power
VDDA 3 - Power
November 30, 2007 411
Preliminary
LM3S6110 Microcontroller
Buffer Description
Type
Pin Pin Type
Number
Function Pin Name
The positive supply (3.3 V) for the analog circuits
(ADC, Analog Comparators, etc.). These are
separated from VDD to minimize the electrical noise
contained on VDD from affecting the analog
functions.
The positive supply (3.3 V) for the analog circuits
(ADC, Analog Comparators, etc.). These are
separated from VDD to minimize the electrical noise
contained on VDD from affecting the analog
functions.
VDDA 98 - Power
SSI SSI0Clk 28 I/O TTL SSI module 0 clock
SSI0Fss 29 I/O TTL SSI module 0 frame
SSI0Rx 30 I TTL SSI module 0 receive
SSI0Tx 31 O TTL SSI module 0 transmit
CPU Mode bit 0. Input must be set to logic 0
(grounded); other encodings reserved.
System Control & CMOD0 65 I/O TTL
Clocks
CPU Mode bit 1. Input must be set to logic 0
(grounded); other encodings reserved.
CMOD1 76 I/O TTL
Main oscillator crystal input or an external clock
reference input.
OSC0 48 I Analog
OSC1 49 I Analog Main oscillator crystal output.
RST 64 I TTL System reset input.
TRST 89 I TTL JTAG TRSTn
UART module 0 receive. When in IrDA mode, this
signal has IrDA modulation.
UART U0Rx 26 I TTL
UART module 0 transmit. When in IrDA mode, this
signal has IrDA modulation.
U0Tx 27 O TTL
Table 17-4. GPIO Pins and Alternate Functions
GPIO Pin Pin Number Multiplexed Function Multiplexed Function
PA0 26 U0Rx
PA1 27 U0Tx
PA2 28 SSI0Clk
PA3 29 SSI0Fss
PA4 30 SSI0Rx
PA5 31 SSI0Tx
PA6 34 CCP1
PB0 66 CCP0
PB1 67 CCP2
PB2 70
PB3 71 Fault
PB4 92 C0-
PB5 91 C1-
PB6 90 C0+
PB7 89 TRST
PC0 80 TCK SWCLK
412 November 30, 2007
Preliminary
Signal Tables
GPIO Pin Pin Number Multiplexed Function Multiplexed Function
PC1 79 TMS SWDIO
PC2 78 TDI
PC3 77 TDO SWO
PC4 25
PC5 24 C1+
PC6 23 C2+
PC7 22 C2-
PD0 10 PWM0
PD1 11 PWM1
PD2 12
PD3 13
PD4 95 CCP3
PD5 96
PD6 99
PD7 100 C0o
PF0 47
PF1 61
PF2 60 LED1
PF3 59 LED0
November 30, 2007 413
Preliminary
LM3S6110 Microcontroller
18 Operating Characteristics
Table 18-1. Temperature Characteristics
Characteristic Symbol Value Unit
Operating temperature rangea TA -40 to +85 °C
a. Maximum storage temperature is 150°C.
Table 18-2. Thermal Characteristics
Characteristic Symbol Value Unit
Thermal resistance (junction to ambient)a ΘJA 55.3 °C/W
Average junction temperatureb TJ TA + (PAVG • ΘJA) °C
a. Junction to ambient thermal resistance θJA numbers are determined by a package simulator.
b. Power dissipation is a function of temperature.
414 November 30, 2007
Preliminary
Operating Characteristics
19 Electrical Characteristics
19.1 DC Characteristics
19.1.1 Maximum Ratings
The maximum ratings are the limits to which the device can be subjected without permanently
damaging the device.
Note: The device is not guaranteed to operate properly at the maximum ratings.
Table 19-1. Maximum Ratings
Characteristic Symbol Value Unit
a
Min Max
I/O supply voltage (VDD) VDD 0 4 V
Core supply voltage (VDD25) VDD25 0 4 V
Analog supply voltage (VDDA) VDDA 0 4 V
Ethernet PHY supply voltage (VCCPHY) VCCPHY 0 4 V
Input voltage VIN -0.3 5.5 V
Maximum current per output pins I - 25 mA
a. Voltages are measured with respect to GND.
Important: This device contains circuitry to protect the inputs against damage due to high-static
voltages or electric fields; however, it is advised that normal precautions be taken to
avoid application of any voltage higher than maximum-rated voltages to this
high-impedance circuit. Reliability of operation is enhanced if unused inputs are
connected to an appropriate logic voltage level (for example, either GND or VDD).
19.1.2 Recommended DC Operating Conditions
Table 19-2. Recommended DC Operating Conditions
Parameter Parameter Name Min Nom Max Unit
VDD I/O supply voltage 3.0 3.3 3.6 V
VDD25 Core supply voltage 2.25 2.5 2.75 V
VDDA Analog supply voltage 3.0 3.3 3.6 V
VCCPHY Ethernet PHY supply voltage 3.0 3.3 3.6 V
VIH High-level input voltage 2.0 - 5.0 V
VIL Low-level input voltage -0.3 - 1.3 V
VSIH High-level input voltage for Schmitt trigger inputs 0.8 * VDD - VDD V
VSIL Low-level input voltage for Schmitt trigger inputs 0 - 0.2 * VDD V
VOH High-level output voltage 2.4 - - V
VOL Low-level output voltage - - 0.4 V
IOH High-level source current, VOH=2.4 V
2-mA Drive 2.0 - - mA
4-mA Drive 4.0 - - mA
8-mA Drive 8.0 - - mA
November 30, 2007 415
Preliminary
LM3S6110 Microcontroller
Parameter Parameter Name Min Nom Max Unit
IOL Low-level sink current, VOL=0.4 V
2-mA Drive 2.0 - - mA
4-mA Drive 4.0 - - mA
8-mA Drive 8.0 - - mA
19.1.3 On-Chip Low Drop-Out (LDO) Regulator Characteristics
Table 19-3. LDO Regulator Characteristics
Parameter Parameter Name Min Nom Max Unit
VLDOOUT Programmable internal (logic) power supply output value 2.25 2.5 2.75 V
Output voltage accuracy - 2% - %
tPON Power-on time - - 100 μs
tON Time on - - 200 μs
tOFF Time off - - 100 μs
VSTEP Step programming incremental voltage - 50 - mV
CLDO External filter capacitor size for internal power supply 1.0 - 3.0 μF
19.1.4 Power Specifications
The power measurements specified in the tables that follow are run on the core processor using
SRAM with the following specifications (except as noted):
■ VDD = 3.3 V
■ VDD25 = 2.50 V
■ VDDA = 3.3 V
■ VDDPHY = 3.3 V
■ Temperature = 25°C
■ Clock Source (MOSC) =3.579545 MHz Crystal Oscillator
■ Main oscillator (MOSC) = enabled
■ Internal oscillator (IOSC) = disabled
416 November 30, 2007
Preliminary
Electrical Characteristics
Table 19-4. Detailed Power Specifications
3.3 V VDD, VDDA, 2.5 V VDD25 Unit
VDDPHY
Parameter Parameter Name Conditions
Nom Max Nom Max
VDD25 = 2.50 V 48 pendinga 64 pendinga mA
Code= while(1){} executed in Flash
Peripherals = All ON
System Clock = 25 MHz (with PLL)
Run mode 1 (Flash
loop)
IDD_RUN
VDD25 = 2.50 V 5 pendinga 33 pendinga mA
Code= while(1){} executed in Flash
Peripherals = All OFF
System Clock = 25 MHz (with PLL)
Run mode 2 (Flash
loop)
VDD25 = 2.50 V 48 pendinga 56 pendinga mA
Code= while(1){} executed in SRAM
Peripherals = All ON
System Clock = 25 MHz (with PLL)
Run mode 1 (SRAM
loop)
VDD25 = 2.50 V 5 pendinga 26 pendinga mA
Code= while(1){} executed in SRAM
Peripherals = All OFF
System Clock = 25 MHz (with PLL)
Run mode 2 (SRAM
loop)
VDD25 = 2.50 V 5 pendinga 12 pendinga mA
Peripherals = All OFF
System Clock = 25 MHz (with PLL)
IDD_SLEEP Sleep mode
LDO = 2.25 V 4.6 pendinga 0.21 pendinga mA
Peripherals = All OFF
System Clock = IOSC30KHZ/64
IDD_DEEPSLEEP Deep-Sleep mode
a. Pending characterization completion.
19.1.5 Flash Memory Characteristics
Table 19-5. Flash Memory Characteristics
Parameter Parameter Name Min Nom Max Unit
PECYC Number of guaranteed program/erase cycles before failurea 10,000 100,000 - cycles
TRET Data retention at average operating temperature of 85˚C 10 - - years
TPROG Word program time 20 - - μs
TERASE Page erase time 20 - - ms
TME Mass erase time 200 - - ms
a. A program/erase cycle is defined as switching the bits from 1-> 0 -> 1.
November 30, 2007 417
Preliminary
LM3S6110 Microcontroller
19.2 AC Characteristics
19.2.1 Load Conditions
Unless otherwise specified, the following conditions are true for all timing measurements. Timing
measurements are for 4-mA drive strength.
Figure 19-1. Load Conditions
CL = 50 pF
GND
pin
19.2.2 Clocks
Table 19-6. Phase Locked Loop (PLL) Characteristics
Parameter Parameter Name Min Nom Max Unit
fref_crystal Crystal referencea 3.579545 - 8.192 MHz
fref_ext External clock referencea 3.579545 - 8.192 MHz
fpll PLL frequencyb - 400 - MHz
TREADY PLL lock time - - 0.5 ms
a. The exact value is determined by the crystal value programmed into the XTAL field of the Run-Mode Clock Configuration
(RCC) register.
b. PLL frequency is automatically calculated by the hardware based on the XTAL field of the RCC register.
Table 19-7. Clock Characteristics
Parameter Parameter Name Min Nom Max Unit
fIOSC Internal 12 MHz oscillator frequency 8.4 12 15.6 MHz
fIOSC30KHZ Internal 30 KHz oscillator frequency 21 30 39 KHz
fMOSC Main oscillator frequency 1 - 8 MHz
tMOSC_per Main oscillator period 125 - 1000 ns
fref_crystal_bypass Crystal reference using the main oscillator (PLL in BYPASS mode) 1 - 8 MHz
fref_ext_bypass External clock reference (PLL in BYPASS mode) 0 - 25 MHz
fsystem_clock System clock 0 - 25 MHz
Table 19-8. Crystal Characteristics
Parameter Name Value Units
Frequency 8 6 4 3.5 MHz
Frequency tolerance ±50 ±50 ±50 ±50 ppm
Aging ±5 ±5 ±5 ±5 ppm/yr
Oscillation mode Parallel Parallel Parallel Parallel
Temperature stability (0 - 85 °C) ±25 ±25 ±25 ±25 ppm
Motional capacitance (typ) 27.8 37.0 55.6 63.5 pF
418 November 30, 2007
Preliminary
Electrical Characteristics
Parameter Name Value Units
Motional inductance (typ) 14.3 19.1 28.6 32.7 mH
Equivalent series resistance (max) 120 160 200 220 Ω
Shunt capacitance (max) 10 10 10 10 pF
Load capacitance (typ) 16 16 16 16 pF
Drive level (typ) 100 100 100 100 μW
19.2.3 Analog Comparator
Table 19-9. Analog Comparator Characteristics
Parameter Parameter Name Min Nom Max Unit
VOS Input offset voltage - ±10 ±25 mV
VCM Input common mode voltage range 0 - VDD-1.5 V
CMRR Common mode rejection ratio 50 - - dB
TRT Response time - - 1 μs
TMC Comparator mode change to Output Valid - - 10 μs
Table 19-10. Analog Comparator Voltage Reference Characteristics
Parameter Parameter Name Min Nom Max Unit
RHR Resolution high range - VDD/32 - LSB
RLR Resolution low range - VDD/24 - LSB
AHR Absolute accuracy high range - - ±1/2 LSB
ALR Absolute accuracy low range - - ±1/4 LSB
19.2.4 Ethernet Controller
Table 19-11. 100BASE-TX Transmitter Characteristicsa
Parameter Name Min Nom Max Unit
Peak output amplitude 950 - 1050 mVpk
Output amplitude symmetry 0.98 - 1.02 mVpk
Output overshoot - - 5 %
Rise/Fall time 3 - 5 ns
Rise/Fall time imbalance - - 500 ps
Duty cycle distortion - - - ps
Jitter - - 1.4 ns
a. Measured at the line side of the transformer.
Table 19-12. 100BASE-TX Transmitter Characteristics (informative)a
Parameter Name Min Nom Max Unit
Return loss 16 - - dB
Open-circuit inductance 350 - - μs
a. The specifications in this table are included for information only. They are mainly a function of the external transformer
and termination resistors used for measurements.
November 30, 2007 419
Preliminary
LM3S6110 Microcontroller
Table 19-13. 100BASE-TX Receiver Characteristics
Parameter Name Min Nom Max Unit
Signal detect assertion threshold 600 700 mVppd
Signal detect de-assertion threshold 350 425 - mVppd
Differential input resistance 20 - - kΩ
Jitter tolerance (pk-pk) 4 - - ns
Baseline wander tracking -75 - +75 %
Signal detect assertion time - - 1000 μs
Signal detect de-assertion time - - 4 μs
Table 19-14. 10BASE-T Transmitter Characteristicsa
Parameter Name Min Nom Max Unit
Peak differential output signal 2.2 - 2.8 V
Harmonic content 27 - - dB
Link pulse width - 100 - ns
300 - ns
350
Start-of-idle pulse width -
a. The Manchester-encoded data pulses, the link pulse and the start-of-idle pulse are tested against the templates and using
the procedures found in Clause 14 of IEEE 802.3.
Table 19-15. 10BASE-T Transmitter Characteristics (informative)a
Parameter Name Min Nom Max Unit
Output return loss 15 - - dB
Output impedance balance 29-17log(f/10) - - dB
Peak common-mode output voltage - - 50 mV
Common-mode rejection - - 100 mV
Common-mode rejection jitter - - 1 ns
a. The specifications in this table are included for information only. They are mainly a function of the external transformer
and termination resistors used for measurements.
Table 19-16. 10BASE-T Receiver Characteristics
Parameter Name Min Nom Max Unit
DLL phase acquisition time - 10 - BT
Jitter tolerance (pk-pk) 30 - - ns
Input squelched threshold 500 600 700 mVppd
Input unsquelched threshold 275 350 425 mVppd
Differential input resistance - 20 - kΩ
Bit error ratio - 10-10 - -
Common-mode rejection 25 - - V
Table 19-17. Isolation Transformersa
Name Value Condition
Turns ratio 1 CT : 1 CT +/- 5%
Open-circuit inductance 350 uH (min) @ 10 mV, 10 kHz
420 November 30, 2007
Preliminary
Electrical Characteristics
Name Value Condition
Leakage inductance 0.40 uH (max) @ 1 MHz (min)
Inter-winding capacitance 25 pF (max)
DC resistance 0.9 Ohm (max)
Insertion loss 0.4 dB (typ) 0-65 MHz
HIPOT 1500 Vrms
a. Two simple 1:1 isolation transformers are required at the line interface. Transformers with integrated common-mode
chokes are recommended for exceeding FCC requirements. This table gives the recommended line transformer
characteristics.
Note: The 100Base-TX amplitude specifications assume a transformer loss of 0.4 dB. For the
transmit line transformer with higher insertion losses, up to 1.2 dB of insertion loss can be
compensated by selecting the appropriate setting in the Transmit Amplitude Selection (TXO)
bits in the MR19 register.
Table 19-18. Ethernet Reference Crystala
Name Value Condition
Frequency 25.00000 MHz
Load capacitanceb 4c pF
Frequency tolerance ±50 PPM
Aging ±2 PPM/yr
Temperature stability (0° to 70°) ±5 PPM
Oscillation mode Parallel resonance, fundamental mode
Parameters at 25° C ±2° C; Drive level = 0.5 mW
Drive level (typ) 50-100 μW
Shunt capacitance (max) 10 pF
Motional capacitance (min) 10 fF
Serious resistance (max) 60 Ω
Spurious response (max) > 5 dB below main within 500 kHz
a. If the internal crystal oscillator is used, select a crystal with the following characteristics.
b. Equivalent differential capacitance across XTLP/XTLN.
c. If crystal with a larger load is used, external shunt capacitors to ground should be added to make up the equivalent
capacitance difference.
November 30, 2007 421
Preliminary
LM3S6110 Microcontroller
Figure 19-2. External XTLP Oscillator Characteristics
Tclkper
Tr
Tclkhi Tclklo
Tf
Table 19-19. External XTLP Oscillator Characteristics
Parameter Name Symbol Min Nom Max Unit
XTLN Input Low Voltage XTLNILV - - 0.8 -
XTLP Frequencya XTLPf - 25.0 - -
XTLP Periodb Tclkper - 40 - -
60 %
60
40 -
40
XTLPDC XTLP Duty Cycle
Rise/Fall Time Tr , Tf - - 4.0 ns
Absolute Jitter - - 0.1 ns
a. IEEE 802.3 frequency tolerance ±50 ppm.
b. IEEE 802.3 frequency tolerance ±50 ppm.
19.2.5 Synchronous Serial Interface (SSI)
Table 19-20. SSI Characteristics
Parameter No. Parameter Parameter Name Min Nom Max Unit
S1 tclk_per SSIClk cycle time 2 - 65024 system clocks
S2 tclk_high SSIClk high time - 1/2 - t clk_per
S3 tclk_low SSIClk low time - 1/2 - t clk_per
S4 tclkrf SSIClk rise/fall time - 7.4 26 ns
S5 tDMd Data from master valid delay time 0 - 20 ns
S6 tDMs Data from master setup time 20 - - ns
S7 tDMh Data from master hold time 40 - - ns
S8 tDSs Data from slave setup time 20 - - ns
S9 tDSh Data from slave hold time 40 - - ns
422 November 30, 2007
Preliminary
Electrical Characteristics
Figure 19-3. SSI Timing for TI Frame Format (FRF=01), Single Transfer Timing Measurement
SSIClk
SSIFss
SSITx
SSIRx MSB LSB
S2
S3
S1
S4
4 to 16 bits
Figure 19-4. SSI Timing for MICROWIRE Frame Format (FRF=10), Single Transfer
0
SSIClk
SSIFss
SSITx
SSIRx
MSB LSB
MSB LSB
S2
S3
S1
8-bit control
4 to 16 bits output data
November 30, 2007 423
Preliminary
LM3S6110 Microcontroller
Figure 19-5. SSI Timing for SPI Frame Format (FRF=00), with SPH=1
SSIClk
(SPO=1)
SSITx
(master)
SSIRx
(slave) LSB
SSIClk
(SPO=0)
S2
S1
S4
SSIFss
LSB
S3
MSB
S5
S6 S7
S8 S9
MSB
19.2.6 JTAG and Boundary Scan
Table 19-21. JTAG Characteristics
Parameter No. Parameter Parameter Name Min Nom Max Unit
J1 fTCK TCK operational clock frequency 0 - 10 MHz
J2 tTCK TCK operational clock period 100 - - ns
J3 tTCK_LOW TCK clock Low time - tTCK - ns
J4 tTCK_HIGH TCK clock High time - tTCK - ns
J5 tTCK_R TCK rise time 0 - 10 ns
J6 tTCK_F TCK fall time 0 - 10 ns
J7 tTMS_SU TMS setup time to TCK rise 20 - - ns
J8 tTMS_HLD TMS hold time from TCK rise 20 - - ns
J9 tTDI_SU TDI setup time to TCK rise 25 - - ns
J10 tTDI_HLD TDI hold time from TCK rise 25 - - ns
J11 TCK fall to Data Valid from High-Z 2-mA drive - 23 35 ns
t TDO_ZDV 4-mA drive 15 26 ns
8-mA drive 14 25 ns
8-mA drive with slew rate control 18 29 ns
J12 TCK fall to Data Valid from Data Valid 2-mA drive - 21 35 ns
t TDO_DV 4-mA drive 14 25 ns
8-mA drive 13 24 ns
8-mA drive with slew rate control 18 28 ns
424 November 30, 2007
Preliminary
Electrical Characteristics
Parameter No. Parameter Parameter Name Min Nom Max Unit
J13 TCK fall to High-Z from Data Valid 2-mA drive - 9 11 ns
t TDO_DVZ 4-mA drive 7 9 ns
8-mA drive 6 8 ns
8-mA drive with slew rate control 7 9 ns
J14 tTRST TRST assertion time 100 - - ns
J15 tTRST_SU TRST setup time to TCK rise 10 - - ns
Figure 19-6. JTAG Test Clock Input Timing
TCK
J6 J5
J3 J4
J2
Figure 19-7. JTAG Test Access Port (TAP) Timing
TDO Output Valid
TCK
TDO Output Valid
J12
TDO
TDI
TMS
TDI Input Valid TDI Input Valid
J13
J9 J10
TMS Input Valid
J9 J10
TMS Input Valid
J11
J7 J8 J7 J8
Figure 19-8. JTAG TRST Timing
TCK
J14 J15
TRST
19.2.7 General-Purpose I/O
Note: All GPIOs are 5 V-tolerant.
November 30, 2007 425
Preliminary
LM3S6110 Microcontroller
Table 19-22. GPIO Characteristics
Parameter Parameter Name Condition Min Nom Max Unit
tGPIOR GPIO Rise Time (from 20% to 80% of VDD) 2-mA drive - 17 26 ns
4-mA drive 9 13 ns
8-mA drive 6 9 ns
8-mA drive with slew rate control 10 12 ns
tGPIOF GPIO Fall Time (from 80% to 20% of VDD) 2-mA drive - 17 25 ns
4-mA drive 8 12 ns
8-mA drive 6 10 ns
8-mA drive with slew rate control 11 13 ns
19.2.8 Reset
Table 19-23. Reset Characteristics
Parameter No. Parameter Parameter Name Min Nom Max Unit
R1 VTH Reset threshold - 2.0 - V
R2 VBTH Brown-Out threshold 2.85 2.9 2.95 V
R3 TPOR Power-On Reset timeout - 10 - ms
R4 TBOR Brown-Out timeout - 500 - μs
R5 TIRPOR Internal reset timeout after POR 6 - 11 ms
R6 TIRBOR Internal reset timeout after BORa 0 - 1 μs
R7 TIRHWR Internal reset timeout after hardware reset (RST pin) 0 - 1 ms
R8 TIRSWR Internal reset timeout after software-initiated system reset a 2.5 - 20 μs
R9 TIRWDR Internal reset timeout after watchdog reseta 2.5 - 20 μs
R10 TVDDRISE Supply voltage (VDD) rise time (0V-3.3V) - - 100 ms
R11 TMIN Minimum RST pulse width 2 - - μs
a. 20 * t MOSC_per
Figure 19-9. External Reset Timing (RST)
RST
/Reset
(Internal)
R11 R7
426 November 30, 2007
Preliminary
Electrical Characteristics
Figure 19-10. Power-On Reset Timing
VDD
/POR
(Internal)
/Reset
(Internal)
R3
R1
R5
Figure 19-11. Brown-Out Reset Timing
VDD
/BOR
(Internal)
/Reset
(Internal)
R2
R4
R6
Figure 19-12. Software Reset Timing
R8
SW Reset
/Reset
(Internal)
Figure 19-13. Watchdog Reset Timing
WDOG
Reset
(Internal)
/Reset
(Internal)
R9
November 30, 2007 427
Preliminary
LM3S6110 Microcontroller
20 Package Information
Figure 20-1. 100-Pin LQFP Package
Note: The following notes apply to the package drawing.
1. All dimensions shown in mm.
2. Dimensions shown are nominal with tolerances indicated.
3. Foot length 'L' is measured at gage plane 0.25 mm above seating plane.
428 November 30, 2007
Preliminary
Package Information
Body +2.00 mm Footprint, 1.4 mm package thickness
Symbols Leads 100L
A Max. 1.60
A1 0.05 Min./0.15 Max.
A2 ±0.05 1.40
D ±0.20 16.00
D1 ±0.05 14.00
E ±0.20 16.00
E1 ±0.05 14.00
L ±0.15/-0.10 0.60
e BASIC 0.50
b ±0.05 0.22
θ === 0˚~7˚
ddd Max. 0.08
ccc Max. 0.08
JEDEC Reference Drawing MS-026
Variation Designator BED
November 30, 2007 429
Preliminary
LM3S6110 Microcontroller
A Serial Flash Loader
A.1 Serial Flash Loader
The Stellaris® serial flash loader is a preprogrammed flash-resident utility used to download code
to the flash memory of a device without the use of a debug interface. The serial flash loader uses
a simple packet interface to provide synchronous communication with the device. The flash loader
runs off the crystal and does not enable the PLL, so its speed is determined by the crystal used.
The two serial interfaces that can be used are the UART0 and SSI0 interfaces. For simplicity, both
the data format and communication protocol are identical for both serial interfaces.
A.2 Interfaces
Once communication with the flash loader is established via one of the serial interfaces, that interface
is used until the flash loader is reset or new code takes over. For example, once you start
communicating using the SSI port, communications with the flash loader via the UART are disabled
until the device is reset.
A.2.1 UART
The Universal Asynchronous Receivers/Transmitters (UART) communication uses a fixed serial
format of 8 bits of data, no parity, and 1 stop bit. The baud rate used for communication is
automatically detected by the flash loader and can be any valid baud rate supported by the host
and the device. The auto detection sequence requires that the baud rate should be no more than
1/32 the crystal frequency of the board that is running the serial flash loader. This is actually the
same as the hardware limitation for the maximum baud rate for any UART on a Stellaris® device
which is calculated as follows:
Max Baud Rate = System Clock Frequency / 16
In order to determine the baud rate, the serial flash loader needs to determine the relationship
between its own crystal frequency and the baud rate. This is enough information for the flash loader
to configure its UART to the same baud rate as the host. This automatic baud-rate detection allows
the host to use any valid baud rate that it wants to communicate with the device.
The method used to perform this automatic synchronization relies on the host sending the flash
loader two bytes that are both 0x55. This generates a series of pulses to the flash loader that it can
use to calculate the ratios needed to program the UART to match the host’s baud rate. After the
host sends the pattern, it attempts to read back one byte of data from the UART. The flash loader
returns the value of 0xCC to indicate successful detection of the baud rate. If this byte is not received
after at least twice the time required to transfer the two bytes, the host can resend another pattern
of 0x55, 0x55, and wait for the 0xCC byte again until the flash loader acknowledges that it has
received a synchronization pattern correctly. For example, the time to wait for data back from the
flash loader should be calculated as at least 2*(20(bits/sync)/baud rate (bits/sec)). For a baud rate
of 115200, this time is 2*(20/115200) or 0.35 ms.
A.2.2 SSI
The Synchronous Serial Interface (SSI) port also uses a fixed serial format for communications,
with the framing defined as Motorola format with SPH set to 1 and SPO set to 1. See “Frame
Formats” on page 274 in the SSI chapter for more information on formats for this transfer protocol.
Like the UART, this interface has hardware requirements that limit the maximum speed that the SSI
clock can run. This allows the SSI clock to be at most 1/12 the crystal frequency of the board running
430 November 30, 2007
Preliminary
Serial Flash Loader
the flash loader. Since the host device is the master, the SSI on the flash loader device does not
need to determine the clock as it is provided directly by the host.
A.3 Packet Handling
All communications, with the exception of the UART auto-baud, are done via defined packets that
are acknowledged (ACK) or not acknowledged (NAK) by the devices. The packets use the same
format for receiving and sending packets, including the method used to acknowledge successful or
unsuccessful reception of a packet.
A.3.1 Packet Format
All packets sent and received from the device use the following byte-packed format.
struct
{
unsigned char ucSize;
unsigned char ucCheckSum;
unsigned char Data[];
};
ucSize The first byte received holds the total size of the transfer including
the size and checksum bytes.
ucChecksum This holds a simple checksum of the bytes in the data buffer only.
The algorithm is Data[0]+Data[1]+…+ Data[ucSize-3].
Data This is the raw data intended for the device, which is formatted in
some form of command interface. There should be ucSize–2
bytes of data provided in this buffer to or from the device.
A.3.2 Sending Packets
The actual bytes of the packet can be sent individually or all at once; the only limitation is that
commands that cause flash memory access should limit the download sizes to prevent losing bytes
during flash programming. This limitation is discussed further in the section that describes the serial
flash loader command, COMMAND_SEND_DATA (see “COMMAND_SEND_DATA
(0x24)” on page 433).
Once the packet has been formatted correctly by the host, it should be sent out over the UART or
SSI interface. Then the host should poll the UART or SSI interface for the first non-zero data returned
from the device. The first non-zero byte will either be an ACK (0xCC) or a NAK (0x33) byte from
the device indicating the packet was received successfully (ACK) or unsuccessfully (NAK). This
does not indicate that the actual contents of the command issued in the data portion of the packet
were valid, just that the packet was received correctly.
A.3.3 Receiving Packets
The flash loader sends a packet of data in the same format that it receives a packet. The flash loader
may transfer leading zero data before the first actual byte of data is sent out. The first non-zero byte
is the size of the packet followed by a checksum byte, and finally followed by the data itself. There
is no break in the data after the first non-zero byte is sent from the flash loader. Once the device
communicating with the flash loader receives all the bytes, it must either ACK or NAK the packet to
indicate that the transmission was successful. The appropriate response after sending a NAK to
the flash loader is to resend the command that failed and request the data again. If needed, the
host may send leading zeros before sending down the ACK/NAK signal to the flash loader, as the
November 30, 2007 431
Preliminary
LM3S6110 Microcontroller
flash loader only accepts the first non-zero data as a valid response. This zero padding is needed
by the SSI interface in order to receive data to or from the flash loader.
A.4 Commands
The next section defines the list of commands that can be sent to the flash loader. The first byte of
the data should always be one of the defined commands, followed by data or parameters as
determined by the command that is sent.
A.4.1 COMMAND_PING (0X20)
This command simply accepts the command and sets the global status to success. The format of
the packet is as follows:
Byte[0] = 0x03;
Byte[1] = checksum(Byte[2]);
Byte[2] = COMMAND_PING;
The ping command has 3 bytes and the value for COMMAND_PING is 0x20 and the checksum of one
byte is that same byte, making Byte[1] also 0x20. Since the ping command has no real return status,
the receipt of an ACK can be interpreted as a successful ping to the flash loader.
A.4.2 COMMAND_GET_STATUS (0x23)
This command returns the status of the last command that was issued. Typically, this command
should be sent after every command to ensure that the previous command was successful or to
properly respond to a failure. The command requires one byte in the data of the packet and should
be followed by reading a packet with one byte of data that contains a status code. The last step is
to ACK or NAK the received data so the flash loader knows that the data has been read.
Byte[0] = 0x03
Byte[1] = checksum(Byte[2])
Byte[2] = COMMAND_GET_STATUS
A.4.3 COMMAND_DOWNLOAD (0x21)
This command is sent to the flash loader to indicate where to store data and how many bytes will
be sent by the COMMAND_SEND_DATA commands that follow. The command consists of two 32-bit
values that are both transferred MSB first. The first 32-bit value is the address to start programming
data into, while the second is the 32-bit size of the data that will be sent. This command also triggers
an erase of the full area to be programmed so this command takes longer than other commands.
This results in a longer time to receive the ACK/NAK back from the board. This command should
be followed by a COMMAND_GET_STATUS to ensure that the Program Address and Program size
are valid for the device running the flash loader.
The format of the packet to send this command is a follows:
Byte[0] = 11
Byte[1] = checksum(Bytes[2:10])
Byte[2] = COMMAND_DOWNLOAD
Byte[3] = Program Address [31:24]
Byte[4] = Program Address [23:16]
Byte[5] = Program Address [15:8]
Byte[6] = Program Address [7:0]
Byte[7] = Program Size [31:24]
432 November 30, 2007
Preliminary
Serial Flash Loader
Byte[8] = Program Size [23:16]
Byte[9] = Program Size [15:8]
Byte[10] = Program Size [7:0]
A.4.4 COMMAND_SEND_DATA (0x24)
This command should only follow a COMMAND_DOWNLOAD command or another
COMMAND_SEND_DATA command if more data is needed. Consecutive send data commands
automatically increment address and continue programming from the previous location. The caller
should limit transfers of data to a maximum 8 bytes of packet data to allow the flash to program
successfully and not overflow input buffers of the serial interfaces. The command terminates
programming once the number of bytes indicated by the COMMAND_DOWNLOAD command has been
received. Each time this function is called it should be followed by a COMMAND_GET_STATUS to
ensure that the data was successfully programmed into the flash. If the flash loader sends a NAK
to this command, the flash loader does not increment the current address to allow retransmission
of the previous data.
Byte[0] = 11
Byte[1] = checksum(Bytes[2:10])
Byte[2] = COMMAND_SEND_DATA
Byte[3] = Data[0]
Byte[4] = Data[1]
Byte[5] = Data[2]
Byte[6] = Data[3]
Byte[7] = Data[4]
Byte[8] = Data[5]
Byte[9] = Data[6]
Byte[10] = Data[7]
A.4.5 COMMAND_RUN (0x22)
This command is used to tell the flash loader to execute from the address passed as the parameter
in this command. This command consists of a single 32-bit value that is interpreted as the address
to execute. The 32-bit value is transmitted MSB first and the flash loader responds with an ACK
signal back to the host device before actually executing the code at the given address. This allows
the host to know that the command was received successfully and the code is now running.
Byte[0] = 7
Byte[1] = checksum(Bytes[2:6])
Byte[2] = COMMAND_RUN
Byte[3] = Execute Address[31:24]
Byte[4] = Execute Address[23:16]
Byte[5] = Execute Address[15:8]
Byte[6] = Execute Address[7:0]
A.4.6 COMMAND_RESET (0x25)
This command is used to tell the flash loader device to reset. This is useful when downloading a
new image that overwrote the flash loader and wants to start from a full reset. Unlike the
COMMAND_RUN command, this allows the initial stack pointer to be read by the hardware and set
up for the new code. It can also be used to reset the flash loader if a critical error occurs and the
host device wants to restart communication with the flash loader.
November 30, 2007 433
Preliminary
LM3S6110 Microcontroller
Byte[0] = 3
Byte[1] = checksum(Byte[2])
Byte[2] = COMMAND_RESET
The flash loader responds with an ACK signal back to the host device before actually executing the
software reset to the device running the flash loader. This allows the host to know that the command
was received successfully and the part will be reset.
434 November 30, 2007
Preliminary
Serial Flash Loader
B Register Quick Reference
31 30 29 28 27 26 25 24 23 22 21 20 19 18 17 16
15 14 13 12 11 10 9 8 7 6 5 4 3 2 1 0
System Control
Base 0x400F.E000
DID0, type RO, offset 0x000, reset -
VER CLASS
MAJOR MINOR
PBORCTL, type R/W, offset 0x030, reset 0x0000.7FFD
BORIOR
LDOPCTL, type R/W, offset 0x034, reset 0x0000.0000
VADJ
RIS, type RO, offset 0x050, reset 0x0000.0000
PLLLRIS BORRIS
IMC, type R/W, offset 0x054, reset 0x0000.0000
PLLLIM BORIM
MISC, type R/W1C, offset 0x058, reset 0x0000.0000
PLLLMIS BORMIS
RESC, type R/W, offset 0x05C, reset -
LDO SW WDT BOR POR EXT
RCC, type R/W, offset 0x060, reset 0x07AE.3AD1
ACG SYSDIV USESYSDIV USEPWMDIV PWMDIV
PWRDN BYPASS XTAL OSCSRC IOSCDIS MOSCDIS
PLLCFG, type RO, offset 0x064, reset -
F R
RCC2, type R/W, offset 0x070, reset 0x0780.2800
USERCC2 SYSDIV2
PWRDN2 BYPASS2 OSCSRC2
DSLPCLKCFG, type R/W, offset 0x144, reset 0x0780.0000
DSDIVORIDE
DSOSCSRC
DID1, type RO, offset 0x004, reset -
VER FAM PARTNO
PINCOUNT TEMP PKG ROHS QUAL
DC0, type RO, offset 0x008, reset 0x003F.001F
SRAMSZ
FLASHSZ
DC1, type RO, offset 0x010, reset 0x0010.709F
PWM
MINSYSDIV MPU PLL WDT SWO SWD JTAG
DC2, type RO, offset 0x014, reset 0x0707.0011
COMP2 COMP1 COMP0 TIMER2 TIMER1 TIMER0
SSI0 UART0
DC3, type RO, offset 0x018, reset 0x0F00.B7C3
CCP3 CCP2 CCP1 CCP0
PWMFAULT C2PLUS C2MINUS C1PLUS C1MINUS C0O C0PLUS C0MINUS PWM1 PWM0
November 30, 2007 435
Preliminary
LM3S6110 Microcontroller
31 30 29 28 27 26 25 24 23 22 21 20 19 18 17 16
15 14 13 12 11 10 9 8 7 6 5 4 3 2 1 0
DC4, type RO, offset 0x01C, reset 0x5000.007F
EPHY0 EMAC0
GPIOG GPIOF GPIOE GPIOD GPIOC GPIOB GPIOA
RCGC0, type R/W, offset 0x100, reset 0x00000040
PWM
WDT
SCGC0, type R/W, offset 0x110, reset 0x00000040
PWM
WDT
DCGC0, type R/W, offset 0x120, reset 0x00000040
PWM
WDT
RCGC1, type R/W, offset 0x104, reset 0x00000000
COMP2 COMP1 COMP0 TIMER2 TIMER1 TIMER0
SSI0 UART0
SCGC1, type R/W, offset 0x114, reset 0x00000000
COMP2 COMP1 COMP0 TIMER2 TIMER1 TIMER0
SSI0 UART0
DCGC1, type R/W, offset 0x124, reset 0x00000000
COMP2 COMP1 COMP0 TIMER2 TIMER1 TIMER0
SSI0 UART0
RCGC2, type R/W, offset 0x108, reset 0x00000000
EPHY0 EMAC0
GPIOG GPIOF GPIOE GPIOD GPIOC GPIOB GPIOA
SCGC2, type R/W, offset 0x118, reset 0x00000000
EPHY0 EMAC0
GPIOG GPIOF GPIOE GPIOD GPIOC GPIOB GPIOA
DCGC2, type R/W, offset 0x128, reset 0x00000000
EPHY0 EMAC0
GPIOG GPIOF GPIOE GPIOD GPIOC GPIOB GPIOA
SRCR0, type R/W, offset 0x040, reset 0x00000000
PWM
WDT
SRCR1, type R/W, offset 0x044, reset 0x00000000
COMP2 COMP1 COMP0 TIMER2 TIMER1 TIMER0
SSI0 UART0
SRCR2, type R/W, offset 0x048, reset 0x00000000
EPHY0 EMAC0
GPIOG GPIOF GPIOE GPIOD GPIOC GPIOB GPIOA
Internal Memory
Flash Control Offset
Base 0x400F.D000
FMA, type R/W, offset 0x000, reset 0x0000.0000
OFFSET
FMD, type R/W, offset 0x004, reset 0x0000.0000
DATA
DATA
FMC, type R/W, offset 0x008, reset 0x0000.0000
WRKEY
COMT MERASE ERASE WRITE
436 November 30, 2007
Preliminary
Register Quick Reference
31 30 29 28 27 26 25 24 23 22 21 20 19 18 17 16
15 14 13 12 11 10 9 8 7 6 5 4 3 2 1 0
FCRIS, type RO, offset 0x00C, reset 0x0000.0000
PRIS ARIS
FCIM, type R/W, offset 0x010, reset 0x0000.0000
PMASK AMASK
FCMISC, type R/W1C, offset 0x014, reset 0x0000.0000
PMISC AMISC
Internal Memory
System Control Offset
Base 0x400F.E000
USECRL, type R/W, offset 0x140, reset 0x16
USEC
FMPRE0, type R/W, offset 0x130 and 0x200, reset 0xFFFF.FFFF
READ_ENABLE
READ_ENABLE
FMPPE0, type R/W, offset 0x134 and 0x400, reset 0xFFFF.FFFF
PROG_ENABLE
PROG_ENABLE
USER_DBG, type R/W, offset 0x1D0, reset 0xFFFF.FFFE
NW DATA
DATA DBG1 DBG0
USER_REG0, type R/W, offset 0x1E0, reset 0xFFFF.FFFF
NW DATA
DATA
USER_REG1, type R/W, offset 0x1E4, reset 0xFFFF.FFFF
NW DATA
DATA
FMPRE1, type R/W, offset 0x204, reset 0x0000.0000
READ_ENABLE
READ_ENABLE
FMPRE2, type R/W, offset 0x208, reset 0x0000.0000
READ_ENABLE
READ_ENABLE
FMPRE3, type R/W, offset 0x20C, reset 0x0000.0000
READ_ENABLE
READ_ENABLE
FMPPE1, type R/W, offset 0x404, reset 0x0000.0000
PROG_ENABLE
PROG_ENABLE
FMPPE2, type R/W, offset 0x408, reset 0x0000.0000
PROG_ENABLE
PROG_ENABLE
FMPPE3, type R/W, offset 0x40C, reset 0x0000.0000
PROG_ENABLE
PROG_ENABLE
General-Purpose Input/Outputs (GPIOs)
November 30, 2007 437
Preliminary
LM3S6110 Microcontroller
31 30 29 28 27 26 25 24 23 22 21 20 19 18 17 16
15 14 13 12 11 10 9 8 7 6 5 4 3 2 1 0
GPIO Port A base: 0x4000.4000
GPIO Port B base: 0x4000.5000
GPIO Port C base: 0x4000.6000
GPIO Port D base: 0x4000.7000
GPIO Port E base: 0x4002.4000
GPIO Port F base: 0x4002.5000
GPIO Port G base: 0x4002.6000
GPIODATA, type R/W, offset 0x000, reset 0x0000.0000
DATA
GPIODIR, type R/W, offset 0x400, reset 0x0000.0000
DIR
GPIOIS, type R/W, offset 0x404, reset 0x0000.0000
IS
GPIOIBE, type R/W, offset 0x408, reset 0x0000.0000
IBE
GPIOIEV, type R/W, offset 0x40C, reset 0x0000.0000
IEV
GPIOIM, type R/W, offset 0x410, reset 0x0000.0000
IME
GPIORIS, type RO, offset 0x414, reset 0x0000.0000
RIS
GPIOMIS, type RO, offset 0x418, reset 0x0000.0000
MIS
GPIOICR, type W1C, offset 0x41C, reset 0x0000.0000
IC
GPIOAFSEL, type R/W, offset 0x420, reset -
AFSEL
GPIODR2R, type R/W, offset 0x500, reset 0x0000.00FF
DRV2
GPIODR4R, type R/W, offset 0x504, reset 0x0000.0000
DRV4
GPIODR8R, type R/W, offset 0x508, reset 0x0000.0000
DRV8
GPIOODR, type R/W, offset 0x50C, reset 0x0000.0000
ODE
GPIOPUR, type R/W, offset 0x510, reset -
PUE
GPIOPDR, type R/W, offset 0x514, reset 0x0000.0000
PDE
438 November 30, 2007
Preliminary
Register Quick Reference
31 30 29 28 27 26 25 24 23 22 21 20 19 18 17 16
15 14 13 12 11 10 9 8 7 6 5 4 3 2 1 0
GPIOSLR, type R/W, offset 0x518, reset 0x0000.0000
SRL
GPIODEN, type R/W, offset 0x51C, reset -
DEN
GPIOLOCK, type R/W, offset 0x520, reset 0x0000.0001
LOCK
LOCK
GPIOCR, type -, offset 0x524, reset -
CR
GPIOPeriphID4, type RO, offset 0xFD0, reset 0x0000.0000
PID4
GPIOPeriphID5, type RO, offset 0xFD4, reset 0x0000.0000
PID5
GPIOPeriphID6, type RO, offset 0xFD8, reset 0x0000.0000
PID6
GPIOPeriphID7, type RO, offset 0xFDC, reset 0x0000.0000
PID7
GPIOPeriphID0, type RO, offset 0xFE0, reset 0x0000.0061
PID0
GPIOPeriphID1, type RO, offset 0xFE4, reset 0x0000.0000
PID1
GPIOPeriphID2, type RO, offset 0xFE8, reset 0x0000.0018
PID2
GPIOPeriphID3, type RO, offset 0xFEC, reset 0x0000.0001
PID3
GPIOPCellID0, type RO, offset 0xFF0, reset 0x0000.000D
CID0
GPIOPCellID1, type RO, offset 0xFF4, reset 0x0000.00F0
CID1
GPIOPCellID2, type RO, offset 0xFF8, reset 0x0000.0005
CID2
GPIOPCellID3, type RO, offset 0xFFC, reset 0x0000.00B1
CID3
General-Purpose Timers
November 30, 2007 439
Preliminary
LM3S6110 Microcontroller
31 30 29 28 27 26 25 24 23 22 21 20 19 18 17 16
15 14 13 12 11 10 9 8 7 6 5 4 3 2 1 0
Timer0 base: 0x4003.0000
Timer1 base: 0x4003.1000
Timer2 base: 0x4003.2000
GPTMCFG, type R/W, offset 0x000, reset 0x0000.0000
GPTMCFG
GPTMTAMR, type R/W, offset 0x004, reset 0x0000.0000
TAAMS TACMR TAMR
GPTMTBMR, type R/W, offset 0x008, reset 0x0000.0000
TBAMS TBCMR TBMR
GPTMCTL, type R/W, offset 0x00C, reset 0x0000.0000
TBPWML TBOTE TBEVENT TBSTALL TBEN TAPWML TAOTE RTCEN TAEVENT TASTALL TAEN
GPTMIMR, type R/W, offset 0x018, reset 0x0000.0000
CBEIM CBMIM TBTOIM RTCIM CAEIM CAMIM TATOIM
GPTMRIS, type RO, offset 0x01C, reset 0x0000.0000
CBERIS CBMRIS TBTORIS RTCRIS CAERIS CAMRIS TATORIS
GPTMMIS, type RO, offset 0x020, reset 0x0000.0000
CBEMIS CBMMIS TBTOMIS RTCMIS CAEMIS CAMMIS TATOMIS
GPTMICR, type W1C, offset 0x024, reset 0x0000.0000
CBECINT CBMCINT TBTOCINT RTCCINT CAECINT CAMCINT TATOCINT
GPTMTAILR, type R/W, offset 0x028, reset 0x0000.FFFF (16-bit mode) and 0xFFFF.FFFF (32-bit mode)
TAILRH
TAILRL
GPTMTBILR, type R/W, offset 0x02C, reset 0x0000.FFFF
TBILRL
GPTMTAMATCHR, type R/W, offset 0x030, reset 0x0000.FFFF (16-bit mode) and 0xFFFF.FFFF (32-bit mode)
TAMRH
TAMRL
GPTMTBMATCHR, type R/W, offset 0x034, reset 0x0000.FFFF
TBMRL
GPTMTAPR, type R/W, offset 0x038, reset 0x0000.0000
TAPSR
GPTMTBPR, type R/W, offset 0x03C, reset 0x0000.0000
TBPSR
GPTMTAPMR, type R/W, offset 0x040, reset 0x0000.0000
TAPSMR
GPTMTBPMR, type R/W, offset 0x044, reset 0x0000.0000
TBPSMR
440 November 30, 2007
Preliminary
Register Quick Reference
31 30 29 28 27 26 25 24 23 22 21 20 19 18 17 16
15 14 13 12 11 10 9 8 7 6 5 4 3 2 1 0
GPTMTAR, type RO, offset 0x048, reset 0x0000.FFFF (16-bit mode) and 0xFFFF.FFFF (32-bit mode)
TARH
TARL
GPTMTBR, type RO, offset 0x04C, reset 0x0000.FFFF
TBRL
Watchdog Timer
Base 0x4000.0000
WDTLOAD, type R/W, offset 0x000, reset 0xFFFF.FFFF
WDTLoad
WDTLoad
WDTVALUE, type RO, offset 0x004, reset 0xFFFF.FFFF
WDTValue
WDTValue
WDTCTL, type R/W, offset 0x008, reset 0x0000.0000
RESEN INTEN
WDTICR, type WO, offset 0x00C, reset -
WDTIntClr
WDTIntClr
WDTRIS, type RO, offset 0x010, reset 0x0000.0000
WDTRIS
WDTMIS, type RO, offset 0x014, reset 0x0000.0000
WDTMIS
WDTTEST, type R/W, offset 0x418, reset 0x0000.0000
STALL
WDTLOCK, type R/W, offset 0xC00, reset 0x0000.0000
WDTLock
WDTLock
WDTPeriphID4, type RO, offset 0xFD0, reset 0x0000.0000
PID4
WDTPeriphID5, type RO, offset 0xFD4, reset 0x0000.0000
PID5
WDTPeriphID6, type RO, offset 0xFD8, reset 0x0000.0000
PID6
WDTPeriphID7, type RO, offset 0xFDC, reset 0x0000.0000
PID7
WDTPeriphID0, type RO, offset 0xFE0, reset 0x0000.0005
PID0
WDTPeriphID1, type RO, offset 0xFE4, reset 0x0000.0018
PID1
WDTPeriphID2, type RO, offset 0xFE8, reset 0x0000.0018
PID2
November 30, 2007 441
Preliminary
LM3S6110 Microcontroller
31 30 29 28 27 26 25 24 23 22 21 20 19 18 17 16
15 14 13 12 11 10 9 8 7 6 5 4 3 2 1 0
WDTPeriphID3, type RO, offset 0xFEC, reset 0x0000.0001
PID3
WDTPCellID0, type RO, offset 0xFF0, reset 0x0000.000D
CID0
WDTPCellID1, type RO, offset 0xFF4, reset 0x0000.00F0
CID1
WDTPCellID2, type RO, offset 0xFF8, reset 0x0000.0005
CID2
WDTPCellID3, type RO, offset 0xFFC, reset 0x0000.00B1
CID3
Universal Asynchronous Receivers/Transmitters (UARTs)
UART0 base: 0x4000.C000
UARTDR, type R/W, offset 0x000, reset 0x0000.0000
OE BE PE FE DATA
UARTRSR/UARTECR, type RO, offset 0x004, reset 0x0000.0000
OE BE PE FE
UARTRSR/UARTECR, type WO, offset 0x004, reset 0x0000.0000
DATA
UARTFR, type RO, offset 0x018, reset 0x0000.0090
TXFE RXFF TXFF RXFE BUSY
UARTILPR, type R/W, offset 0x020, reset 0x0000.0000
ILPDVSR
UARTIBRD, type R/W, offset 0x024, reset 0x0000.0000
DIVINT
UARTFBRD, type R/W, offset 0x028, reset 0x0000.0000
DIVFRAC
UARTLCRH, type R/W, offset 0x02C, reset 0x0000.0000
SPS WLEN FEN STP2 EPS PEN BRK
UARTCTL, type R/W, offset 0x030, reset 0x0000.0300
RXE TXE LBE SIRLP SIREN UARTEN
UARTIFLS, type R/W, offset 0x034, reset 0x0000.0012
RXIFLSEL TXIFLSEL
UARTIM, type R/W, offset 0x038, reset 0x0000.0000
OEIM BEIM PEIM FEIM RTIM TXIM RXIM
UARTRIS, type RO, offset 0x03C, reset 0x0000.000F
OERIS BERIS PERIS FERIS RTRIS TXRIS RXRIS
442 November 30, 2007
Preliminary
Register Quick Reference
31 30 29 28 27 26 25 24 23 22 21 20 19 18 17 16
15 14 13 12 11 10 9 8 7 6 5 4 3 2 1 0
UARTMIS, type RO, offset 0x040, reset 0x0000.0000
OEMIS BEMIS PEMIS FEMIS RTMIS TXMIS RXMIS
UARTICR, type W1C, offset 0x044, reset 0x0000.0000
OEIC BEIC PEIC FEIC RTIC TXIC RXIC
UARTPeriphID4, type RO, offset 0xFD0, reset 0x0000.0000
PID4
UARTPeriphID5, type RO, offset 0xFD4, reset 0x0000.0000
PID5
UARTPeriphID6, type RO, offset 0xFD8, reset 0x0000.0000
PID6
UARTPeriphID7, type RO, offset 0xFDC, reset 0x0000.0000
PID7
UARTPeriphID0, type RO, offset 0xFE0, reset 0x0000.0011
PID0
UARTPeriphID1, type RO, offset 0xFE4, reset 0x0000.0000
PID1
UARTPeriphID2, type RO, offset 0xFE8, reset 0x0000.0018
PID2
UARTPeriphID3, type RO, offset 0xFEC, reset 0x0000.0001
PID3
UARTPCellID0, type RO, offset 0xFF0, reset 0x0000.000D
CID0
UARTPCellID1, type RO, offset 0xFF4, reset 0x0000.00F0
CID1
UARTPCellID2, type RO, offset 0xFF8, reset 0x0000.0005
CID2
UARTPCellID3, type RO, offset 0xFFC, reset 0x0000.00B1
CID3
Synchronous Serial Interface (SSI)
SSI0 base: 0x4000.8000
SSICR0, type R/W, offset 0x000, reset 0x0000.0000
SCR SPH SPO FRF DSS
SSICR1, type R/W, offset 0x004, reset 0x0000.0000
SOD MS SSE LBM
SSIDR, type R/W, offset 0x008, reset 0x0000.0000
DATA
November 30, 2007 443
Preliminary
LM3S6110 Microcontroller
31 30 29 28 27 26 25 24 23 22 21 20 19 18 17 16
15 14 13 12 11 10 9 8 7 6 5 4 3 2 1 0
SSISR, type RO, offset 0x00C, reset 0x0000.0003
BSY RFF RNE TNF TFE
SSICPSR, type R/W, offset 0x010, reset 0x0000.0000
CPSDVSR
SSIIM, type R/W, offset 0x014, reset 0x0000.0000
TXIM RXIM RTIM RORIM
SSIRIS, type RO, offset 0x018, reset 0x0000.0008
TXRIS RXRIS RTRIS RORRIS
SSIMIS, type RO, offset 0x01C, reset 0x0000.0000
TXMIS RXMIS RTMIS RORMIS
SSIICR, type W1C, offset 0x020, reset 0x0000.0000
RTIC RORIC
SSIPeriphID4, type RO, offset 0xFD0, reset 0x0000.0000
PID4
SSIPeriphID5, type RO, offset 0xFD4, reset 0x0000.0000
PID5
SSIPeriphID6, type RO, offset 0xFD8, reset 0x0000.0000
PID6
SSIPeriphID7, type RO, offset 0xFDC, reset 0x0000.0000
PID7
SSIPeriphID0, type RO, offset 0xFE0, reset 0x0000.0022
PID0
SSIPeriphID1, type RO, offset 0xFE4, reset 0x0000.0000
PID1
SSIPeriphID2, type RO, offset 0xFE8, reset 0x0000.0018
PID2
SSIPeriphID3, type RO, offset 0xFEC, reset 0x0000.0001
PID3
SSIPCellID0, type RO, offset 0xFF0, reset 0x0000.000D
CID0
SSIPCellID1, type RO, offset 0xFF4, reset 0x0000.00F0
CID1
SSIPCellID2, type RO, offset 0xFF8, reset 0x0000.0005
CID2
444 November 30, 2007
Preliminary
Register Quick Reference
31 30 29 28 27 26 25 24 23 22 21 20 19 18 17 16
15 14 13 12 11 10 9 8 7 6 5 4 3 2 1 0
SSIPCellID3, type RO, offset 0xFFC, reset 0x0000.00B1
CID3
Ethernet Controller
Ethernet MAC
Base 0x4004.8000
MACRIS, type RO, offset 0x000, reset 0x0000.0000
PHYINT MDINT RXER FOV TXEMP TXER RXINT
MACIACK, type W1C, offset 0x000, reset 0x0000.0000
PHYINT MDINT RXER FOV TXEMP TXER RXINT
MACIM, type R/W, offset 0x004, reset 0x0000.007F
PHYINTM MDINTM RXERM FOVM TXEMPM TXERM RXINTM
MACRCTL, type R/W, offset 0x008, reset 0x0000.0008
RSTFIFO BADCRC PRMS AMUL RXEN
MACTCTL, type R/W, offset 0x00C, reset 0x0000.0000
DUPLEX CRC PADEN TXEN
MACDATA, type RO, offset 0x010, reset 0x0000.0000
RXDATA
RXDATA
MACDATA, type WO, offset 0x010, reset 0x0000.0000
TXDATA
TXDATA
MACIA0, type R/W, offset 0x014, reset 0x0000.0000
MACOCT4 MACOCT3
MACOCT2 MACOCT1
MACIA1, type R/W, offset 0x018, reset 0x0000.0000
MACOCT6 MACOCT5
MACTHR, type R/W, offset 0x01C, reset 0x0000.003F
THRESH
MACMCTL, type R/W, offset 0x020, reset 0x0000.0000
REGADR WRITE START
MACMDV, type R/W, offset 0x024, reset 0x0000.0080
DIV
MACMTXD, type R/W, offset 0x02C, reset 0x0000.0000
MDTX
MACMRXD, type R/W, offset 0x030, reset 0x0000.0000
MDRX
MACNP, type RO, offset 0x034, reset 0x0000.0000
NPR
November 30, 2007 445
Preliminary
LM3S6110 Microcontroller
31 30 29 28 27 26 25 24 23 22 21 20 19 18 17 16
15 14 13 12 11 10 9 8 7 6 5 4 3 2 1 0
MACTR, type R/W, offset 0x038, reset 0x0000.0000
NEWTX
Ethernet Controller
MII Management
Base 0x4004.8000
MR0, type R/W, address 0x00, reset 0x3100
RESET LOOPBK SPEEDSL ANEGEN PWRDN ISO RANEG DUPLEX COLT
MR1, type RO, address 0x01, reset 0x7849
100X_F 100X_H 10T_F 10T_H MFPS ANEGC RFAULT ANEGA LINK JAB EXTD
MR2, type RO, address 0x02, reset 0x000E
OUI[21:6]
MR3, type RO, address 0x03, reset 0x7237
OUI[5:0] MN RN
MR4, type R/W, address 0x04, reset 0x01E1
NP RF A3 A2 A1 A0 S[4:0]
MR5, type RO, address 0x05, reset 0x0000
NP ACK RF A[7:0] S[4:0]
MR6, type RO, address 0x06, reset 0x0000
PDF LPNPA PRX LPANEGA
MR16, type R/W, address 0x10, reset 0x0140
RPTR INPOL TXHIM SQEI NL10 APOL RVSPOL PCSBP RXCC
MR17, type R/W, address 0x11, reset 0x0000
JABBER_IE RXER_IE PRX_IE PDF_IE LPACK_IE LSCHG_IE RFAULT_IE ANEGCOMP_IE JABBER_INT RXER_INT PRX_INT PDF_INT LPACK_INT LSCHG_INT RFAULT_INT ANEGCOMP_INT
MR18, type RO, address 0x12, reset 0x0000
ANEGF DPLX RATE RXSD RX_LOCK
MR19, type R/W, address 0x13, reset 0x4000
TXO[1:0]
MR23, type R/W, address 0x17, reset 0x0010
LED1[3:0] LED0[3:0]
MR24, type R/W, address 0x18, reset 0x00C0
PD_MODE AUTO_SW MDIX MDIX_CM MDIX_SD
Analog Comparators
Base 0x4003.C000
ACMIS, type R/W1C, offset 0x00, reset 0x0000.0000
IN2 IN1 IN0
ACRIS, type RO, offset 0x04, reset 0x0000.0000
IN2 IN1 IN0
ACINTEN, type R/W, offset 0x08, reset 0x0000.0000
IN2 IN1 IN0
ACREFCTL, type R/W, offset 0x10, reset 0x0000.0000
EN RNG VREF
ACSTAT0, type RO, offset 0x20, reset 0x0000.0000
OVAL
ACSTAT1, type RO, offset 0x40, reset 0x0000.0000
OVAL
446 November 30, 2007
Preliminary
Register Quick Reference
31 30 29 28 27 26 25 24 23 22 21 20 19 18 17 16
15 14 13 12 11 10 9 8 7 6 5 4 3 2 1 0
ACSTAT2, type RO, offset 0x60, reset 0x0000.0000
OVAL
ACCTL0, type R/W, offset 0x24, reset 0x0000.0000
ASRCP ISLVAL ISEN CINV
ACCTL1, type R/W, offset 0x44, reset 0x0000.0000
ASRCP ISLVAL ISEN CINV
ACCTL2, type R/W, offset 0x64, reset 0x0000.0000
ASRCP ISLVAL ISEN CINV
Pulse Width Modulator (PWM)
Base 0x4002.8000
PWMCTL, type R/W, offset 0x000, reset 0x0000.0000
GlobalSync0
PWMSYNC, type R/W, offset 0x004, reset 0x0000.0000
Sync0
PWMENABLE, type R/W, offset 0x008, reset 0x0000.0000
PWM1En PWM0En
PWMINVERT, type R/W, offset 0x00C, reset 0x0000.0000
PWM1Inv PWM0Inv
PWMFAULT, type R/W, offset 0x010, reset 0x0000.0000
Fault1 Fault0
PWMINTEN, type R/W, offset 0x014, reset 0x0000.0000
IntFault
IntPWM0
PWMRIS, type RO, offset 0x018, reset 0x0000.0000
IntFault
IntPWM0
PWMISC, type R/W1C, offset 0x01C, reset 0x0000.0000
IntFault
IntPWM0
PWMSTATUS, type RO, offset 0x020, reset 0x0000.0000
Fault
PWM0CTL, type R/W, offset 0x040, reset 0x0000.0000
CmpBUpd CmpAUpd LoadUpd Debug Mode Enable
PWM0INTEN, type R/W, offset 0x044, reset 0x0000.0000
IntCmpBD IntCmpBU IntCmpAD IntCmpAU IntCntLoad IntCntZero
PWM0RIS, type RO, offset 0x048, reset 0x0000.0000
IntCmpBD IntCmpBU IntCmpAD IntCmpAU IntCntLoad IntCntZero
PWM0ISC, type R/W1C, offset 0x04C, reset 0x0000.0000
IntCmpBD IntCmpBU IntCmpAD IntCmpAU IntCntLoad IntCntZero
November 30, 2007 447
Preliminary
LM3S6110 Microcontroller
31 30 29 28 27 26 25 24 23 22 21 20 19 18 17 16
15 14 13 12 11 10 9 8 7 6 5 4 3 2 1 0
PWM0LOAD, type R/W, offset 0x050, reset 0x0000.0000
Load
PWM0COUNT, type RO, offset 0x054, reset 0x0000.0000
Count
PWM0CMPA, type R/W, offset 0x058, reset 0x0000.0000
CompA
PWM0CMPB, type R/W, offset 0x05C, reset 0x0000.0000
CompB
PWM0GENA, type R/W, offset 0x060, reset 0x0000.0000
ActCmpBD ActCmpBU ActCmpAD ActCmpAU ActLoad ActZero
PWM0GENB, type R/W, offset 0x064, reset 0x0000.0000
ActCmpBD ActCmpBU ActCmpAD ActCmpAU ActLoad ActZero
PWM0DBCTL, type R/W, offset 0x068, reset 0x0000.0000
Enable
PWM0DBRISE, type R/W, offset 0x06C, reset 0x0000.0000
RiseDelay
PWM0DBFALL, type R/W, offset 0x070, reset 0x0000.0000
FallDelay
448 November 30, 2007
Preliminary
Register Quick Reference
C Ordering and Contact Information
C.1 Ordering Information
L M 3 S n n n n – g p p s s – r r m
Part Number
Temperature
Package
Speed
Revision
Shipping Medium
I = -40 C to 85 C
T = Tape-and-reel
Omitted = Default shipping (tray or tube)
Omitted = Default to current shipping
revision
A0 = First all-layer mask
A1 = Metal layers update to A0
A2 = Metal layers update to A1
B0 = Second all-layer mask revision
RN = 28-pin SOIC
QN = 48-pin LQFP
QC = 100-pin LQFP
20 = 20 MHz
25 = 25 MHz
50 = 50 MHz
Table C-1. Part Ordering Information
Orderable Part Number Description
Stellaris® LM3S6110-IQC25 LM3S6110 Microcontroller
Stellaris® LM3S6110-IQC25(T) LM3S6110 Microcontroller
C.2 Kits
The Luminary Micro Stellaris® Family provides the hardware and software tools that engineers need
to begin development quickly.
■ Reference Design Kits accelerate product development by providing ready-to-run hardware, and
comprehensive documentation including hardware design files:
http://www.luminarymicro.com/products/reference_design_kits/
■ Evaluation Kits provide a low-cost and effective means of evaluating Stellaris® microcontrollers
before purchase:
http://www.luminarymicro.com/products/evaluation_kits/
■ Development Kits provide you with all the tools you need to develop and prototype embedded
applications right out of the box:
http://www.luminarymicro.com/products/boards.html
See the Luminary Micro website for the latest tools available or ask your Luminary Micro distributor.
C.3 Company Information
Luminary Micro, Inc. designs, markets, and sells ARM Cortex-M3-based microcontrollers (MCUs).
Austin, Texas-based Luminary Micro is the lead partner for the Cortex-M3 processor, delivering the
world's first silicon implementation of the Cortex-M3 processor. Luminary Micro's introduction of the
November 30, 2007 449
Preliminary
LM3S6110 Microcontroller
Stellaris® family of products provides 32-bit performance for the same price as current 8- and 16-bit
microcontroller designs. With entry-level pricing at $1.00 for an ARM technology-based MCU,
Luminary Micro's Stellaris product line allows for standardization that eliminates future architectural
upgrades or software tool changes.
Luminary Micro, Inc.
108 Wild Basin, Suite 350
Austin, TX 78746
Main: +1-512-279-8800
Fax: +1-512-279-8879
http://www.luminarymicro.com
sales@luminarymicro.com
C.4 Support Information
For support on Luminary Micro products, contact:
support@luminarymicro.com +1-512-279-8800, ext. 3
450 November 30, 2007
Preliminary
Ordering and Contact Information
1
EIT Series
FCC-B
U Put Any Serial Device On the IP
Network in Minutes
U Bridge RS232/RS485 to TCP/IP
U Auto-negotiating 10/100 Ethernet Half/
Full Duplex
U Built-in Web Server
U TCP, UDP, SNMP, SMTP, TFTP, ICMP,
Telnet, DHCP, DNS, HTTP, and ARP
U MODBUS® RTU to MODBUS TCP/IP
Bridging
U Email Notifications and SNMP Traps
U 1 to 6 Programmable I/Os
U Firmware Upgrade Over Ethernet
U Custom Firmware/Private Labeling
for OEMs
U TCP Socket with Command Line Interface
U Serial Speed Up to 460 Kb/s
U Authentication and Access Restrictions
U Small Enough to Fit Almost Anywhere
U Free COM Port Redirector
U Free Configuration Software
iServer MicroServerTM
for Serial-to-Ethernet Applications
The 3rd Generation NEWPORT® connects
any Serial Device (RS232, RS485) to an Ethernet
network or the Internet in minutes, including Serial
Modbus to ModbusTCP/IP over Ethernet. The
iServer3G can send notifications by email, and has
SNMP for remote management. Newport offers
custom firmware and private-labeling for OEMs.
EIT-D DIN rail
for industrial
applications,
shown smaller
than actual size.
EIT-W
Wall mount
or benchtop
for commercial
applications,
shown smaller
than actual size.
EIT-PCB Embedded
PC board assembly
for OEMs, shown
smaller than
actual size.
Connect any serial device to
Ethernet LAN and the Internet
Quickly configured
through a web browser
2
To Order Visit newportUS.com/eit for Pricing and Details
Model No. Description
EIT-W
iServer MicroServer™ for Serial-to-Ethernet applications in commercial wall-mount case with
universal AC power adaptor (100 to 240 Vac input, 5 Vdc output); full RS232 serial interface
with 1 input pin
EIT-W-485 Commercial wall-mount case; RS485 (full and half duplex) serial interface with 3 I/Os
EIT-D Industrial DIN rail case with screw terminal serial ports; full RS232 serial interface without I/Os
EIT-D-485 Industrial DIN rail case; RS485 (full and half duplex) serial interface with 3 I/Os
EIT-PCB Printed circuit board for embedded applications; full RS232 serial interface with 3 I/Os
EIT-PCB-485 Printed circuit board; RS485 (full and half duplex) serial interface with 6 I/Os
Ordering Example: EIT-W, one full RS232 serial interface commercial wall-mount iServer MicroServer.
* Volume discounts are available.
Sensor Specifications
Serial Interface
Interface: RS232 or RS485
(2- and 4-wire)
Connector: DB9 male DTE for RS232;
8 position terminal block plug for RS485
Serial Data Rates: 300 to 460.8 Kbps
Characters: 5, 6, 7, or 8 data bits
Parity: odd, even, or none
Stop Bits: 1 or 2
Flow Control: Hardware (RTS/CTS)
and Software (Xon/Xoff)
Digital I/Os: 1 to 6 programmable
input/output lines, depending on model.
Network Interface
Interface: Fixed or auto-negotiating
10/100BASE-T half/full duplex Ethernet
with auto MDI/MDIX
Connector: RJ45
Protocols: TCP, UDP, SNMP, SMTP,
TFTP, ICMP, DHCP, DNS, HTTP, ARP,
Modbus TCP/IP and Telnet
Compliant to Standard: IEEE 802.3
Indicators (LEDs): 100BASE-T,
Network Link/Activity, and Serial
Transmit/Receive
32-Bit Microprocessor:
CPU: ARM7, 72 MHz
Memory: 512 Kbyte Flash,
32 Kbyte SRAM
Embedded Web Server: Serves
dynamic Web pages and Java applets
Management: Web server, Telnet login,
Serial login, iConnect
General
Power (for EIT-PCB):
Input: 5 Vdc @ 200 mA max.
Consumption: 1 W max.
Power (for EIT-W):
Input: 5 Vdc @ 200 mA max
Consumption: 1 W max.
Safety Qualified AC Power Adapter
(included):
Nominal Output: 5 Vdc @ 600 mA;
Input: 100 to 240 Vac, 50/60Hz
Operating Temperature:
0 to 40°C (32 to 104°F)
Power (for EIT-D):
Input: 10 to 32 Vdc
Consumption: 2 W max.
DC Power supply sold separately:
iDRN-PS-1000
Packaging (for EIT-W):
Material: ABS (ChiMei PA-757)
with wall mount bracket
Dimensions: 27.4H x 66.0W x
93.1D mm (1.08 x 2.60 x 3.67 in)
Weight: 77g (0.17 lbs.)
Packaging (for EIT-D):
Material: Polycarbonate case
with DIN Rail mount
Dimensions: 90.2H x 25.1W x
115.0D mm (3.54 x .99 x 4.53 in)
Weight: 113g (0.25 lbs.)
Packaging (for EIT-PCB):
Material: FR4
Board Surface area dimensions:
Approximately 80 sq. mm (3 sq")
Weight: 14g (0.03 lbs.)
Environmental
Operating Temperature:
-40 to 85°C (-40 to 185°F)
Storage Temperature:
-40 to 100°C (-40 to 212°F)
Software
Firmware upgrade from
Ethernet COM Port
redirector (iPort);
Configuration Software utility
(iConnect) Compatible with
Windows 9x/ME/NT/2000/XP
software and related utilities
2.60 [66.0]
1.08
[ 27.4]
3.67
[93.1]
100BASE-T
LINK/ACT
TRANSMIT
RECEIVE
RS232
RS485
0.88
[ 22.4]
COMMUNICATIONS
ETHERNET
DC POWER IN
RECEIVE
TRANSMIT
LINK/ACT
100BASE-T
RESET
N/C
4.53 [115] 0.99
[25.1]
3.54
[90.2]
EIT-D
Material: Polycarbonate
case with DIN rail mount
Weight: 113 g (0.25 lbs)
EIT-W
Material: ABS
(ChiMei PA-757)
with wall mount
Weight: 77 g
(0.17 lbs)
EIT-PCB
Board Surface area:
approximately 3 sq. inches
[80 sq. mm]
Weight: 14 g (0.03 lbs)
EIT-W
READINGS
http://192.168.1.200
Overview
Network
Serial
I/O Pins
Management
Security
Device Query
Device Setup
Readings
Terminal
System
Diagnostics
READINGS
000 Auto Update
1 Boiler 1 92.4 Deg. C
No De vice Name Reading Unit
92.4 Deg. C
Dimensions: in (mm)
ø = diameter
Mechanical
SB520-SB5100 2001 Fairchild Semiconductor Corporation SB520 - SB5100, Rev. C Features •Metal to silicon rectifier, majoritycarrier conduction. •For use in low voltage, highfrequency inverters freewheeling, and polarityprotection applications. • Low power loss, high efficiency. • High current capability, low VF. • High surge capacity. SB520 - SB5100 Schottky Rectifiers Absolute Maximum Ratings* TA = 25°C unless otherwise noted *These ratings are limiting values above which the serviceability of any semiconductor device may be impaired. Electrical Characteristics TA = 25°C unless otherwise noted Symbol Parameter Value Units PD Power Dissipation 5.0 W RθJA Thermal Resistance, Junction to Ambient 25 °C/W Symbol Parameter Device Units 520 530 540 550 560 580 5100 VF Forward Voltage @ 5.0 A 0.55 0.67 0.85 V IR Reverse Current @ rated VR TA = 25°C 0.5 mA TA = 100°C 50 25 mA CT Total Capacitance VR = 4.0 V, f = 1.0 MHz 500 380 pF DO-201AD COLOR BAND DENOTES CATHODE Thermal Characteristics Symbol Parameter Value Units 520 530 540 550 560 580 5100 VRRM Maximum Repetitive Reverse Voltage 20 30 40 50 60 80 100 V IF(AV) Average Rectified Forward Current .375 " lead length @ TA = 75°C 5.0 A IFSM Non-repetitive Peak Forward Surge Current 8.3 ms Single Half-Sine-Wave 150 A Tstg Storage Temperature Range -50 to +150 °C TJ Operating Junction Temperature -50 to +150 °C • Glass passivated SB520-SB5100 2001 Fairchild Semiconductor Corporation SB520 - SB5100, Rev. C Schottky Rectifiers (continued) Typical Characteristics 1 2 5 102050100 0 30 60 90 120 150 Number of Cycles at 60Hz Peak Forward Surge Current, IFSM [A] 0.1110100 100 200 500 1000 2000 5000 Reverse Voltage, VR [V] Total Capacitance, CT [pF] SB520-SB540 SB550-SB5100 0.40.50.60.70.80.911.1 0.1 1 10 40 Forward Voltage, VF [V] Forward Current, IF [A] Pulse Width = 300μS 2% Duty Cycle T = 25 C A º SB520-SB540 SB550-SB560 SB580-SB5100 0 255075100125150175 0 1 2 3 4 5 Ambient Temperature [ºC] Average Rectified Forward Current, IF [A] SINGLE PHASE HALF WAVE 60HZ RESISTIVE OR INDUCTIVE LOAD .375" (9.00mm) LOAD LENGTHS SB520-SB540 SB550-SB5100 0 20406080100120140 0.001 0.01 0.1 1 10 20 Percent of Rated Peak Reverse Voltage [%] Reverse Current, IR [mA] T = 25 C A º T = 75 C A º T = 100 C A º SB520-SB540 SB550-SB5100 SB520-SB540 SB550-SB5100 Figure 1. Forward Current Derating Curve Figure 2. Non-Repetitive Surge Current Figure 3. Forward Voltage Characteristics Figure 4. Reverse Current vs Reverse Voltage Figure 5. Total Capacitance DISCLAIMER FAIRCHILD SEMICONDUCTOR RESERVES THE RIGHT TO MAKE CHANGES WITHOUT FURTHER NOTICE TO ANY PRODUCTS HEREIN TO IMPROVE RELIABILITY, FUNCTION OR DESIGN. FAIRCHILD DOES NOTASSUME ANY LIABILITYARISING OUT OF THE APPLICATION OR USE OF ANY PRODUCT OR CIRCUIT DESCRIBED HEREIN; NEITHER DOES IT CONVEYANY LICENSE UNDER ITS PATENT RIGHTS, NOR THE RIGHTS OF OTHERS. TRADEMARKS The following are registered and unregistered trademarks Fairchild Semiconductor owns or is authorized to use and is not intended to be an exhaustive list of all such trademarks. LIFE SUPPORT POLICY FAIRCHILD’S PRODUCTS ARE NOT AUTHORIZED FOR USE AS CRITICAL COMPONENTS IN LIFE SUPPORT DEVICES OR SYSTEMS WITHOUT THE EXPRESS WRITTEN APPROVAL OF FAIRCHILD SEMICONDUCTOR CORPORATION. As used herein: 1. Life support devices or systems are devices or systems which, (a) are intended for surgical implant into the body, or (b) support or sustain life, or (c) whose failure to perform when properly used in accordance with instructions for use provided in the labeling, can be reasonably expected to result in significant injury to the user. 2. A critical component is any component of a life support device or system whose failure to perform can be reasonably expected to cause the failure of the life support device or system, or to affect its safety or effectiveness. PRODUCT STATUS DEFINITIONS Definition of Terms Datasheet Identification Product Status Definition Advance Information Preliminary No Identification Needed Obsolete This datasheet contains the design specifications for product development. Specifications may change in any manner without notice. This datasheet contains preliminary data, and supplementary data will be published at a later date. Fairchild Semiconductor reserves the right to make changes at any time without notice in order to improve design. This datasheet contains final specifications. Fairchild Semiconductor reserves the right to make changes at any time without notice in order to improve design. This datasheet contains specifications on a product that has been discontinued by Fairchild semiconductor. The datasheet is printed for reference information only. Formative or In Design First Production Full Production Not In Production OPTOLOGIC™ OPTOPLANAR™ PACMAN™ POP™ Power247™ PowerTrench QFET™ QS™ QT Optoelectronics™ Quiet Series™ SILENT SWITCHER FAST FASTr™ FRFET™ GlobalOptoisolator™ GTO™ HiSeC™ ISOPLANAR™ LittleFET™ MicroFET™ MicroPak™ MICROWIRE™ Rev. H4 â ACEx™ Bottomless™ CoolFET™ CROSSVOLT™ DenseTrench™ DOME™ EcoSPARK™ E2CMOSTM EnSignaTM FACT™ FACT Quiet Series™ SMART START™ STAR*POWER™ Stealth™ SuperSOT™-3 SuperSOT™-6 SuperSOT™-8 SyncFET™ TinyLogic™ TruTranslation™ UHC™ â UltraFET â â STAR*POWER is used under license VCX™ RaspiCam Documentation July 2013 This document describes the use of the three Raspberry Pi camera applications as of July 2013. There are three applications provided: raspistill, raspivid and raspistillyuv. Both raspistill and raspistillyuv are very similar and are intended for capturing images, while raspivid is for capturing video. All the applications are command-line driven, written to take advantage of the mmal API which runs over OpenMAX. The mmal API provides an easier to use system than that presented by OpenMAX. Note that mmal is a Broadcom specific API used only on Videocore 4 systems. The applications use up to four OpenMAX(mmal) components - camera, preview, encoder and null_sink. All applications use the camera component: raspistill uses the Image Encode component, raspivid uses the Video Encode component, and raspistillyuv does not use an encoder, and sends its YUV or RGB output direct from camera component to file. The preview display is optional, but can be used full screen or directed to a specific rectangular area on the display. If preview is disabled, the null_sink component is used to 'absorb' the preview frames. It is necessary for the camera to produce preview frames even if not required for display, as they are used for calculating exposure and white balance settings. In addition it is possible to omit the filename option, in which case the preview is displayed but no file is written, or to redirect all output to stdout. Command line help is available by typing just the application name in on the command line. Setting up the camera hardware Please note that camera modules are static-sensitive. Earth yourself prior to handling the PCB: a sink tap/faucet or similar should suffice if you don’t have an earthing strap. The camera board attaches to the Raspberry Pi via a 15-way ribbon cable. There are only two connections to make: the ribbon cable need to be attached to the camera PCB and the Raspberry Pi itself. You need to get it the right way round, or the camera will not work. On the camera PCB, the blue backing on the cable should be facing away from the PCB, and on the Raspberry Pi it should be facing towards the Ethernet connection (or where the Ethernet connector would be if you are using a model A). Although the connectors on the PCB and the Pi are different, they work in a similar way. On the Raspberry Pi, pull up the tabs on each end of the connector. It should slide up easily, and be able to pivot around slightly. Fully insert the ribbon cable into the slot, ensuring it is straight, then gently press down the tabs to clip it into place. The camera PCB itself also requires you to pull the tabs away from the board, gently insert the cable, then push the tabs back. The PCB connector is a little more awkward than the one on the Pi itself. You can watch a video showing you how to attach the connectors at www.raspberrypi.org/archives/3890 (scroll down for the video). Setting up the Camera software Execute the following instructions on the command line to download and install the latest kernel, GPU firmware and applications. You will need an internet connection for this to work correctly. sudo apt-get update sudo apt-get upgrade Now you need to enable camera support, using the raspiconfig program you will have used when you first set up your Raspberry Pi. sudo raspi-config Use the cursor keys to move to the camera option and select enable. On exiting raspi-config it will ask to reboot. The enable option will ensure that on reboot the correct GPU firmware will be running (with the camera driver and tuning), and the GPU memory split is sufficient to allow the camera to acquire enough memory to run correctly. To test that the system is installed and working, try the following command: raspistill -v -o test.jpg The display should show a 5-second preview from the camera and then take a picture, saved to the file test.jpg, while displaying various informational messages. Troubleshooting If the camera is not working correctly, there are number of things to try. • Are the ribbon connectors all firmly seated and the right way round? They must be straight in their sockets. • Is the camera module connector firmly attached to the camera PCB? This is the connection from the smaller black camera module itself to the camera PCB. Sometimes this connection can come loose. Using a fingernail, flip up the connector on the PCB, then reseat it with gentle pressure, it engages with a very slight click. • Have sudo apt-get update and sudo apt-get upgrade been run? • Has raspi-config been run and the camera enabled? If things are still not working, try the following: Error : raspistill/raspivid not found. This probably means your update/upgrade failed in some way. Try it again. Error : ENOMEM displayed. Camera is not starting up. Check all connections again. Error : ENOSPC displayed. Camera is probably running out of GPU memory. Check config.txt in the /boot/ folder. The gpu_mem option should be at least 128. If, after all the above, the camera is still not working, it may have a defect (most likely because it has suffered static shock). Try posting on the Raspberry Pi forum in the camera board section to see if there is any more help available there. Common Command line Options Preview Window --preview, -p Preview window settings <'x,y,w,h'> Allows the user to define the size and location on the screen that the preview window will be placed. Note this will be superimposed over the top of any other windows/graphics. --fullscreen, -f Fullscreen preview mode Forces the preview window to use the whole screen. Note that the aspect ratio of the incoming image will be retained, so there may be bars on some edges. --nopreview, -n, Do not display a preview window Disables the preview window completely. Note that even though the preview is disabled, the camera will still be producing frames, so will be using power. --opacity, -op Set preview window opacity Sets the opacity of the preview windows. 0 = invisible, 255 = fully opaque. Camera Control Options --sharpness, -sh Set image sharpness (-100 to 100) Set the sharpness of the image, 0 is the default. --contrast, -co Set image contrast (-100 to 100) Set the contrast of the image, 0 is the default --brightness, -br Set image brightness (0 to 100) Set the brightness of the image, 50 is the default. 0 is black, 100 is white. --saturation, -sa Set image saturation (-100 to 100) Set the colour saturation of the image. 0 is the default. --ISO, -ISO Set capture ISO Sets the ISO to be used for captures. Range is 100 to 800. --vstab, -vs Turn on video stabilization In video mode only, turn on video stabilization. --ev, -ev Set EV compensation Set the EV compensation of the image. Range is -10 to +10, default is 0. --exposure, -ex Set exposure mode Possible options are: off auto Use automatic exposure mode night Select setting for night shooting nightpreview backlight Select setting for back-lit subject spotlight sports Select setting for sports (fast shutter etc.) snow Select setting optimized for snowy scenery beach Select setting optimized for beach verylong Select setting for long exposures fixedfps Constrain fps to a fixed value antishake Antishake mode fireworks Select setting optimized for fireworks Note that not all of these settings may be implemented, depending on camera tuning. --awb, -awb Set automatic white balance (AWB) off Turn off white balance calculation auto Automatic mode (default) sun Sunny mode cloud shade Cloudy mode tungsten Tungsten lighting mode fluorescent Fluorescent lighting mode incandescent Incandescent lighting mode flash Flash mode horizon Horizon mode --imxfx, -ifx Set image effect none No effect negative Produces a negative image solarise Solarise the image whiteboard Whiteboard effect blackboard Blackboard effect sketch Sketch-style effect denoise Denoise the image emboss Embossed effect oilpaint Oil paint-style effect hatch Cross-hatch sketch style gpen Graphite sketch style pastel Pastel effect watercolour Watercolour effect film Grainy film effect blur Blur the image saturation Colour-saturate the image colourswap Not fully implemented washedout Not fully implemented posterise Not fully implemented colourpoint Not fully implemented colourbalance Not fully implemented cartoon Not fully implemented --colfx, -cfx Set colour effect The supplied U and V parameters (range 0 to 255) are applied to the U and Y channels of the image. For example, --colfx 128:128 should result in a monochrome image. --metering, -mm Set metering mode Specify the metering mode used for the preview and capture. average Average the whole frame for metering spot Spot metering backlit Assume a backlit image matrix Matrix metering --rotation, -rot Set image rotation (0-359) Sets the rotation of the image in viewfinder and resulting image. This can take any value from 0 upwards, but due to hardware constraints only 0, 90, 180 and 270-degree rotations are supported. --hflip, -hf Set horizontal flip Flips the preview and saved image horizontally. --vflip, -vf Set vertical flip Flips the preview and saved image vertically. --roi, -roi Set sensor region of interest Allows the specification of the area of the sensor to be used as the source for the preview and capture. This is defined as x,y for the top left corner, and a width and height, all values in normalised coordinates (0.0-1.0). So to set a ROI at half way across and down the sensor, and an width and height of a quarter of the sensor use : -roi 0.5,0.5,0.25,0.25 Application-‐specific settings raspistill --width, -w Set image width --height, -h Set image height --quality, -q Set jpeg quality <0 to 100> Quality 100 is almost completely uncompressed. 75 is a good allround value. --raw, -r Add raw Bayer data to jpeg metadata This option inserts the raw Bayer data from the camera in to the JPEG metadata. --output -o Output filename Specify the output filename. If not specified, no file is saved. If the filename is '-', then all output is sent to stdout. --verbose, -v Output verbose information during run Outputs debugging/information messages during the program run. --timeout, -t Time before capture and shut down The program will run for this length of time, then take the capture (if output is specified). If not specified, this is set to 5 seconds. --timelapse, -tl Timelapse mode. The specific value is the time between shots in milliseconds. Note you should specify %04d at the point in the filename where you want a frame count number to appear. For example: -t 30000 -tl 2000 -o image%04d.jpg will produce a capture every 2 seconds over a total period of 30s, named image1.jpg, image0002.jpg...image0015.jpg. Note that the %04d indicates a four-digit number with leading zeros added to pad to the required number of digits. So, for example, %08d would result in an eight-digit number. --thumb, -th Set thumbnail parameters (x:y:quality) Allows specification of the thumbnail image inserted in to the JPEG file. If not specified, defaults are a size of 64x48 at quality 35. --demo, -d Run a demo mode This options cycles through range of camera options, and no capture is done. The demo will end at the end of the timeout period, irrespective of whether all the options have been cycled. The time between cycles should be specified as a millisecond value. --encoding, -e Encoding to use as output file Valid options are jpg, bmp, gif and png. Note that unaccelerated image types (gif, png, bmp) will take much longer to save than jpg, which is hardware accelerated. Also note that the filename suffix is completely ignored when encoding a file. --exif, -x EXIF tag to apply to captures (format as 'key=value') Allows the insertion of specific EXIF tags into the JPEG image. You can have up to 32 EXIF tge entries. This is useful for things like adding GPS metadata. For example, to set the longitude: --exif GPS.GPSLongitude=5/1,10/1,15/100 would set the longitude to 5degs, 10 minutes, 15 seconds. See EXIF documentation for more details on the range of tags available; the supported tags are as follows: IFD0.< or IFD1.< ImageWidth, ImageLength, BitsPerSample, Compression, PhotometricInterpretation, ImageDescription, Make, Model, StripOffsets, Orientation, SamplesPerPixel, RowsPerString, StripByteCounts, Xresolution, Yresolution, PlanarConfiguration, ResolutionUnit, TransferFunction, Software, DateTime, Artist, WhitePoint, PrimaryChromaticities, JPEGInterchangeFormat, JPEGInterchangeFormatLength, YcbCrCoefficients, YcbCrSubSampling, YcbCrPositioning, ReferenceBlackWhite, Copyright> EXIF.< ExposureTime, FNumber, ExposureProgram, SpectralSensitivity, a ISOSpeedRatings, OECF, ExifVersion, DateTimeOriginal, DateTimeDigitized, ComponentsConfiguration, CompressedBitsPerPixel, ShutterSpeedValue, ApertureValue, BrightnessValue, ExposureBiasValue, MaxApertureValue, SubjectDistance, MeteringMode, LightSource, Flash, FocalLength, SubjectArea, MakerNote, UserComment, SubSecTime, SubSecTimeOriginal, SubSecTimeDigitized, FlashpixVersion, ColorSpace, PixelXDimension, PixelYDimension, RelatedSoundFile, FlashEnergy, SpacialFrequencyResponse, FocalPlaneXResolution, FocalPlaneYResolution, FocalPlaneResolutionUnit, SubjectLocation, ExposureIndex, SensingMethod, FileSource, SceneType, CFAPattern, CustomRendered, ExposureMode, WhiteBalance, DigitalZoomRatio, FocalLengthIn35mmFilm, SceneCaptureType, GainControl, Contrast, Saturation, Sharpness, DeviceSettingDescription, SubjectDistanceRange, ImageUniqueID> GPS.< GPSVersionID, GPSLatitudeRef, GPSLatitude, GPSLongitudeRef, GPSLongitude, GPSAltitudeRef, GPSAltitude, GPSTimeStamp, GPSSatellites, GPSStatus, GPSMeasureMode, GPSDOP, GPSSpeedRef, GPSSpeed, GPSTrackRef, GPSTrack, GPSImgDirectionRef, GPSImgDirection, GPSMapDatum, GPSDestLatitudeRef, GPSDestLatitude, GPSDestLongitudeRef, GPSDestLongitude, GPSDestBearingRef, GPSDestBearing, GPSDestDistanceRef, GPSDestDistance, GPSProcessingMethod, GPSAreaInformation, GPSDateStamp, GPSDifferential> EINT.< InteroperabilityIndex, InteroperabilityVersion, RelatedImageFileFormat, RelatedImageWidth, RelatedImageLength> Note that a small subset of these tags will be set automatically by the camera system, but will be overridden by any exif options on the command line. --fullpreview, -fp Full Preview mode This runs the preview windows using the full resolution capture mode. Maximum frames per second in this mode is 15fps and the preview will have the same field of view as the capture. Captures should happen more quickly as no mode change should be required. This feature is currently under development. raspistillyuv Many of the options for raspistillyuv are the same as those for raspistill. This section shows the differences. Unsupported Options: --exif, --encoding, --thumb, --raw, --quality Extra Options: --rgb, -rgb Save uncompressed data as RGB888 This option forces the image to be saved as RGB data with 8 bits per channel, rather than YUV420. Note that the image buffers saved in raspistillyuv are padded to a horizontal size divisible by 16 (so there may be unused bytes at the end of each line to made the width divisible by 16). Buffers are also padded vertically to be divisible by 16, and in the YUV mode, each plane of Y,U,V is padded in this way. raspivid --width, -w Set image width Width of resulting video. This should be between 64 and 1920. --height, -h Set image height Height of resulting video. This should be between 64 and 1080. --bitrate, -b Set bitrate Use bits per second, so 10MBits/s would be -b 10000000. For H264, 1080p a high quality bitrate would be 15Mbits/s or more. --output, -o Output filename . Specify the output filename. If not specified, no file is saved. If the filename is '-', then all output is sent to stdout. --verbose, -v Output verbose information during run Outputs debugging/information messages during the program run. --timeout, -t Time before capture and shut down The program will run for this length of time, then take the capture (if output is specified). If not specified, this is set to five seconds. Setting 0 will mean the application will run continuously until stopped with Ctrl-C. --demo, -d Run a demo mode This option cycles through range of camera options, no capture is done, the demo will end at the end of the timeout period, irrespective of whether all the options have been cycled. The time between cycles should be specified as a millisecond value. --framerate, -fps Specify the frames per second to record At present, the minimum frame rate allowed is 2fps, the maximum is 30fps. This is likely to change in the future. --penc, -e Display preview image after encoding Switch on an option to display the preview after compression. This will show any compression artefacts in the preview window. In normal operation, the preview will show the camera output prior to being compressed. This option is not guaranteed to work in future releases. --intra, -g Specify the intra refresh period (key frame rate/GoP) Sets the intra refresh period (GoP) rate for the recorded video. H.264 video uses a complete frame (I-frame) every intra refresh period from which subsequent frames are based. This options specifies the numbers of frames between each I-frame. Larger numbers here will reduce the size of the resulting video, smaller numbers make the stream more robust to error. Examples Still captures By default, captures are done at the highest resolution supported by the sensor. This can be changed using the -w and -h command line options. Taking a default capture after two seconds (note times are specified in milliseconds) on viewfinder, saving in image.jpg raspistill -t 2000 -o image.jpg Take a capture at a different resolution raspistill -t 2000 -o image.jpg -w 640 -h 480 Now reduce the quality considerably to reduce file size raspistill -t 2000 -o image.jpg -q 5 Force the preview to appear at coordinate 100,100, with width 300 and height 200 pixels. raspistill -t 2000 -o image.jpg -p 100,100,300,200 Disable preview entirely. raspistill -t 2000 -o image.jpg -n Save the image as a png file (lossless compression, but slower than JPEG). Note that the filename suffix is ignored when choosing the image encoding. raspistill -t 2000 -o image.png –e png Add some EXIF information to the JPEG. This sets the Artist tag name to Mooncake, and the GPS altitude to 123.5m. Note that if setting GPS tags you should set as a minimum GPSLatitude, GPSLatitudeRef, GPSLongitude, GPSLongitudeRef, GPSAltitude and GPSAltitudeRef. raspistill -t 2000 -o image.jpg -x IFDO.Artist=Mooncake -x GPS.GPSAltitude=1235/10 Set an emboss style image effect. raspistill -t 2000 -o image.jpg -ifx emboss Set the U and V channels of the YUV image to specific values (128:128 produces a greyscale image) raspistill -t 2000 -o image.jpg -cfx 128:128 Run preview ONLY for two seconds, no saved image. raspistill -t 2000 Take timelapse picture, one every 10 seconds for 10 minutes (10 minutes = 600000ms), named image_number_1_today.jpg, image_number_2_today.jpg onwards. raspistill -t 600000 -tl 10000 -o image_num_%d_today.jpg Take a picture and send image data to stdout raspistill -t 2000 -o - Take a picture and send image data to file raspistill -t 2000 -o - > my_file.jpg Video Captures Image size and preview settings are the same as for stills capture. Default size for video recording is 1080p (1920x1080) Record a 5s clip with default settings (1080p30) raspivid -t 5000 -o video.h264 Record a 5s clip at a specified bitrate (3.5MBits/s) raspivid -t 5000 -o video.h264 -b 3500000 Record a 5s clip at a specified framerate (5fps) raspivid -t 5000 -o video.h264 -f 5 Encode a 5s camera stream and send image data to stdout raspivid -t 5000 -o - Encode a 5s camera stream and send image data to file raspivid -t 5000 -o - > my_file.h264 L78S 2 A positive voltage regulator IC Datasheet - production data Features • Output current up to 2 A • Output voltages of 5; 7.5; 9; 10; 12; 15; 18; 24 V • Thermal protection • Short circuit protection • Output transition SOA protection Description The L78S series of three-terminal positive regulators is available in TO-220 package and several fixed output voltages, making it useful in a wide range of applications. These regulators can provide local on-card regulation, eliminating the distribution problems associated with single point regulation. Each type embeds internal current limiting, thermal shut-down and safe area protection, making it essentially indestructible. If adequate heat sinking is provided, they can deliver over 2 A output current. Although designed primarily as fixed voltage regulators, these devices can be used with external components to obtain adjustable voltages and currents. TO-220 Table 1. Device summary Part numbers TO-220 packages Output voltage Dual gauge Single gauge L78S05C L78S05CV-DG L78S05CV 5 V L78S75C L78S75CV-DG L78S75CV 7.5 V L78S09C L78S09CV-DG L78S09CV 9 V L78S10C L78S10CV-DG L78S10CV 10 V L78S12C L78S12CV-DG L78S12CV 12 V L78S15C L78S15CV-DG L78S15CV 15 V L78S18C L78S18CV 18 V L78S24C L78S24CV 24 V www.st.com Contents L78S 2/35 DocID2148 Rev 8 Contents 1 Diagram . . . . . . . . . . . . . . . . . . . . . . . . . . . . . . . . . . . . . . . . . . . . . . . . . . . 5 2 Pin configuration . . . . . . . . . . . . . . . . . . . . . . . . . . . . . . . . . . . . . . . . . . . 6 3 Maximum ratings . . . . . . . . . . . . . . . . . . . . . . . . . . . . . . . . . . . . . . . . . . . . 7 4 Test circuits . . . . . . . . . . . . . . . . . . . . . . . . . . . . . . . . . . . . . . . . . . . . . . . . 8 5 Electrical characteristics . . . . . . . . . . . . . . . . . . . . . . . . . . . . . . . . . . . . . 9 6 Typical performance . . . . . . . . . . . . . . . . . . . . . . . . . . . . . . . . . . . . . . . . 17 7 Package mechanical data . . . . . . . . . . . . . . . . . . . . . . . . . . . . . . . . . . . . 28 8 Packaging mechanical data . . . . . . . . . . . . . . . . . . . . . . . . . . . . . . . . . . 33 9 Revision history . . . . . . . . . . . . . . . . . . . . . . . . . . . . . . . . . . . . . . . . . . . 34 DocID2148 Rev 8 3/35 L78S List of tables 35 List of tables Table 1. Device summary . . . . . . . . . . . . . . . . . . . . . . . . . . . . . . . . . . . . . . . . . . . . . . . . . . . . . . . . . . 1 Table 2. Absolute maximum ratings . . . . . . . . . . . . . . . . . . . . . . . . . . . . . . . . . . . . . . . . . . . . . . . . . . 7 Table 3. Thermal data. . . . . . . . . . . . . . . . . . . . . . . . . . . . . . . . . . . . . . . . . . . . . . . . . . . . . . . . . . . . . 7 Table 4. Electrical characteristics of L78S05C . . . . . . . . . . . . . . . . . . . . . . . . . . . . . . . . . . . . . . . . . . 9 Table 5. Electrical characteristics of L78S75C . . . . . . . . . . . . . . . . . . . . . . . . . . . . . . . . . . . . . . . . . 10 Table 6. Electrical characteristics of L78S09C . . . . . . . . . . . . . . . . . . . . . . . . . . . . . . . . . . . . . . . . . 11 Table 7. Electrical characteristics of L78S10C . . . . . . . . . . . . . . . . . . . . . . . . . . . . . . . . . . . . . . . . . 12 Table 8. Electrical characteristics of L78S12C . . . . . . . . . . . . . . . . . . . . . . . . . . . . . . . . . . . . . . . . . 13 Table 9. Electrical characteristics of L78S15C . . . . . . . . . . . . . . . . . . . . . . . . . . . . . . . . . . . . . . . . . 14 Table 10. Electrical characteristics of L78S18C . . . . . . . . . . . . . . . . . . . . . . . . . . . . . . . . . . . . . . . . . 15 Table 11. Electrical characteristics of L78S24C . . . . . . . . . . . . . . . . . . . . . . . . . . . . . . . . . . . . . . . . . 16 Table 12. TO-220 (dual gauge) mechanical data . . . . . . . . . . . . . . . . . . . . . . . . . . . . . . . . . . . . . . . . 30 Table 13. TO-220 SG (single gauge) mechanical data . . . . . . . . . . . . . . . . . . . . . . . . . . . . . . . . . . . 32 Table 14. Document revision history . . . . . . . . . . . . . . . . . . . . . . . . . . . . . . . . . . . . . . . . . . . . . . . . . 34 List of figures L78S 4/35 DocID2148 Rev 8 List of figures Figure 1. Block diagram. . . . . . . . . . . . . . . . . . . . . . . . . . . . . . . . . . . . . . . . . . . . . . . . . . . . . . . . . . . . 5 Figure 2. Pin connections (top view) . . . . . . . . . . . . . . . . . . . . . . . . . . . . . . . . . . . . . . . . . . . . . . . . . . 6 Figure 3. Schematic diagram. . . . . . . . . . . . . . . . . . . . . . . . . . . . . . . . . . . . . . . . . . . . . . . . . . . . . . . . 6 Figure 4. Application circuits . . . . . . . . . . . . . . . . . . . . . . . . . . . . . . . . . . . . . . . . . . . . . . . . . . . . . . . . 7 Figure 5. DC parameter . . . . . . . . . . . . . . . . . . . . . . . . . . . . . . . . . . . . . . . . . . . . . . . . . . . . . . . . . . . . 8 Figure 6. Load regulation . . . . . . . . . . . . . . . . . . . . . . . . . . . . . . . . . . . . . . . . . . . . . . . . . . . . . . . . . . . 8 Figure 7. Ripple rejection . . . . . . . . . . . . . . . . . . . . . . . . . . . . . . . . . . . . . . . . . . . . . . . . . . . . . . . . . . . 8 Figure 8. Dropout voltage vs. junction temperature . . . . . . . . . . . . . . . . . . . . . . . . . . . . . . . . . . . . . . 17 Figure 9. Peak output current vs. input/output differential voltage. . . . . . . . . . . . . . . . . . . . . . . . . . . 17 Figure 10. Output impedance vs. frequency . . . . . . . . . . . . . . . . . . . . . . . . . . . . . . . . . . . . . . . . . . . . 17 Figure 11. Output voltage vs. junction temperature . . . . . . . . . . . . . . . . . . . . . . . . . . . . . . . . . . . . . . . 17 Figure 12. Supply voltage rejection vs. frequency . . . . . . . . . . . . . . . . . . . . . . . . . . . . . . . . . . . . . . . . 18 Figure 13. Quiescent current vs. junction temperature . . . . . . . . . . . . . . . . . . . . . . . . . . . . . . . . . . . . 18 Figure 14. Load transient response . . . . . . . . . . . . . . . . . . . . . . . . . . . . . . . . . . . . . . . . . . . . . . . . . . . 18 Figure 15. Line transient response . . . . . . . . . . . . . . . . . . . . . . . . . . . . . . . . . . . . . . . . . . . . . . . . . . . 18 Figure 16. Quiescent current vs. input voltage . . . . . . . . . . . . . . . . . . . . . . . . . . . . . . . . . . . . . . . . . . 18 Figure 17. Fixed output regulator . . . . . . . . . . . . . . . . . . . . . . . . . . . . . . . . . . . . . . . . . . . . . . . . . . . . . 19 Figure 18. Constant current regulator . . . . . . . . . . . . . . . . . . . . . . . . . . . . . . . . . . . . . . . . . . . . . . . . . 19 Figure 19. Circuit for increasing output voltage . . . . . . . . . . . . . . . . . . . . . . . . . . . . . . . . . . . . . . . . . . 19 Figure 20. Adjustable output regulator (7 to 30 V) . . . . . . . . . . . . . . . . . . . . . . . . . . . . . . . . . . . . . . . . 20 Figure 21. 0.5 to 10 V regulator . . . . . . . . . . . . . . . . . . . . . . . . . . . . . . . . . . . . . . . . . . . . . . . . . . . . . . 20 Figure 22. High current voltage regulator . . . . . . . . . . . . . . . . . . . . . . . . . . . . . . . . . . . . . . . . . . . . . . 21 Figure 23. High output current with short circuit protection . . . . . . . . . . . . . . . . . . . . . . . . . . . . . . . . . 21 Figure 24. Tracking voltage regulator . . . . . . . . . . . . . . . . . . . . . . . . . . . . . . . . . . . . . . . . . . . . . . . . . 22 Figure 25. Positive and negative regulator . . . . . . . . . . . . . . . . . . . . . . . . . . . . . . . . . . . . . . . . . . . . . 22 Figure 26. Negative output voltage circuit . . . . . . . . . . . . . . . . . . . . . . . . . . . . . . . . . . . . . . . . . . . . . . 23 Figure 27. Switching regulator . . . . . . . . . . . . . . . . . . . . . . . . . . . . . . . . . . . . . . . . . . . . . . . . . . . . . . . 23 Figure 28. High input voltage circuit. . . . . . . . . . . . . . . . . . . . . . . . . . . . . . . . . . . . . . . . . . . . . . . . . . . 23 Figure 29. High input voltage circuit. . . . . . . . . . . . . . . . . . . . . . . . . . . . . . . . . . . . . . . . . . . . . . . . . . . 24 Figure 30. High output voltage regulator . . . . . . . . . . . . . . . . . . . . . . . . . . . . . . . . . . . . . . . . . . . . . . . 24 Figure 31. High input and output voltage . . . . . . . . . . . . . . . . . . . . . . . . . . . . . . . . . . . . . . . . . . . . . . . 24 Figure 32. Reducing power dissipation with dropping resistor. . . . . . . . . . . . . . . . . . . . . . . . . . . . . . . 25 Figure 33. Remote shutdown. . . . . . . . . . . . . . . . . . . . . . . . . . . . . . . . . . . . . . . . . . . . . . . . . . . . . . . . 25 Figure 34. Power AM modulator (unity voltage gain, IO £ 1 A) . . . . . . . . . . . . . . . . . . . . . . . . . . . . . . 26 Figure 35. Adjustable output voltage with temperature compensation . . . . . . . . . . . . . . . . . . . . . . . . 26 Figure 36. Light controllers (VOmin = VXX + VBE) . . . . . . . . . . . . . . . . . . . . . . . . . . . . . . . . . . . . . . . . . 27 Figure 37. Protection against input short-circuit with high capacitance loads . . . . . . . . . . . . . . . . . . . 27 Figure 38. TO-220 (dual gauge) drawing. . . . . . . . . . . . . . . . . . . . . . . . . . . . . . . . . . . . . . . . . . . . . . . 29 Figure 39. TO-220 SG (single gauge) drawing . . . . . . . . . . . . . . . . . . . . . . . . . . . . . . . . . . . . . . . . . . 31 Figure 40. Tube for TO-220 (dual gauge) (mm.) . . . . . . . . . . . . . . . . . . . . . . . . . . . . . . . . . . . . . . . . . 33 Figure 41. Tube for TO-220 (single gauge) (mm.) . . . . . . . . . . . . . . . . . . . . . . . . . . . . . . . . . . . . . . . . 33 DocID2148 Rev 8 5/35 L78S Diagram 35 1 Diagram Figure 1. Block diagram Pin configuration L78S 6/35 DocID2148 Rev 8 2 Pin configuration Figure 2. Pin connections (top view) Figure 3. Schematic diagram DocID2148 Rev 8 7/35 L78S Maximum ratings 35 3 Maximum ratings Note: Absolute maximum ratings are those values beyond which damage to the device may occur. Functional operation under these condition is not implied. Table 2. Absolute maximum ratings Symbol Parameter Value Unit VI DC input voltage for VO= 5 to 18V 35 V for VO= 24V 40 IO Output current Internally limited PD Power dissipation Internally limited TSTG Storage temperature range -65 to 150 °C TOP Operating junction temperature range 0 to 150 °C Table 3. Thermal data Symbol Parameter TO-220 Unit RthJC Thermal resistance junction-case 5 °C/W RthJA Thermal resistance junction-ambient 50 °C/W Figure 4. Application circuits Test circuits L78S 8/35 DocID2148 Rev 8 4 Test circuits Figure 5. DC parameter Figure 6. Load regulation Figure 7. Ripple rejection DocID2148 Rev 8 9/35 L78S Electrical characteristics 35 5 Electrical characteristics Refer to the test circuits, TJ = 25 °C, VI = 10 V, IO = 500 mA, unless otherwise specified. Table 4. Electrical characteristics of L78S05C Symbol Parameter Test conditions Min. Typ. Max. Unit VO Output voltage 4.8 5 5.2 V VO Output voltage IO = 1 A, VI = 7 V 4.75 5 5.25 V ΔVO Line regulation VI = 7 to 25 V 100 mV VI = 8 to 25 V 50 ΔVO Load regulation IO = 20 mA to 1.5 A 100 mV IO = 2 A 80 IQ Quiescent current 8 mA ΔIQ Quiescent current change IO = 20 mA to 1 A 0.5 mA VI = 7 to 25 V, IO = 20 mA 1.3 ΔVO/ΔT Output voltage drift IO = 5 mA, TJ = 0 °C to 70 °C -1.1 mV/°C eN Output noise voltage B = 10 Hz to 100 kHz 40 μV SVR Supply voltage rejection f = 120 Hz 54(1) dB VI Operating input voltage IO ≤ 1 A 8 V RO Output resistance f = 1 kHz 17 mΩ Isc Short circuit current VI = 27 V 500 mA Iscp Short circuit peak current 3 A 1. Guaranteed by design. Electrical characteristics L78S 10/35 DocID2148 Rev 8 Refer to the test circuits, TJ = 25 °C, VI = 12.5 V, IO = 500 mA, unless otherwise specified. Table 5. Electrical characteristics of L78S75C Symbol Parameter Test conditions Min. Typ. Max. Unit VO Output voltage 7.15 7.5 7.9 V VO Output voltage IO = 1 A, VI = 9.5 V 7.1 7.5 7.95 V ΔVO Line regulation VI = 9.5 to 25 V 120 mV VI = 10.5 to 20 V 60 ΔVO Load regulation IO = 20 mA to 1.5 A 140 mV IO = 2 A 100 IQ Quiescent current 8 mA ΔIQ Quiescent current change IO = 20 mA to 1 A 0.5 mA VI = 9.5 to 25 V, IO = 20 mA 1.3 ΔVO/ΔT Output voltage drift IO = 5 mA, TJ = 0 °C to 70 °C -0.8 mV/°C eN Output noise voltage B = 10 Hz to 100 kHz 52 μV SVR Supply voltage rejection f = 120 Hz 48(1) dB VI Operating input voltage IO ≤ 1 A 10.5 V RO Output resistance f = 1 kHz 16 mΩ Isc Short circuit current VI = 27 V 500 mA Iscp Short circuit peak current 3 A 1. Guaranteed by design. DocID2148 Rev 8 11/35 L78S Electrical characteristics 35 Refer to the test circuits, TJ = 25 °C, VI = 14 V, IO = 500 mA, unless otherwise specified. Table 6. Electrical characteristics of L78S09C Symbol Parameter Test conditions Min. Typ. Max. Unit VO Output voltage 8.65 9 9.35 V VO Output voltage IO = 1 A, VI = 11 V 8.6 9 9.4 V ΔVO Line regulation VI = 11 to 25 V 130 mV VI = 11 to 20 V 65 ΔVO Load regulation IO = 20 mA to 1.5 A 170 mV IO = 2 A 100 IQ Quiescent current 8 mA ΔIQ Quiescent current change IO = 20 mA to 1 A 0.5 mA VI = 11 to 25 V, IO = 20 mA 1.3 ΔVO/ΔT Output voltage drift IO = 5 mA, TJ = 0 °C to 70 °C -1 mV/°C eN Output noise voltage B = 10 Hz to 100 kHz 60 μV SVR Supply voltage rejection f = 120 Hz 47(1) dB VI Operating input voltage IO ≤ 1 A 12 V RO Output resistance f = 1 kHz 17 mΩ Isc Short circuit current VI = 27 V 500 mA Iscp Short circuit peak current 3 A 1. Guaranteed by design. Electrical characteristics L78S 12/35 DocID2148 Rev 8 Refer to the test circuits, TJ = 25 °C, VI = 15 V, IO = 500 mA, unless otherwise specified. Table 7. Electrical characteristics of L78S10C Symbol Parameter Test conditions Min. Typ. Max. Unit VO Output voltage 9.5 10 10.5 V VO Output voltage IO = 1 A, VI = 12.5 V 9.4 10 10.6 V ΔVO Line regulation VI = 12.5 to 30 V 200 mV VI = 14 to 22 V 100 ΔVO Load regulation IO = 20 mA to 1.5 A 240 mV IO = 2 A 150 IQ Quiescent current 8 mA ΔIQ Quiescent current change IO = 20 mA to 1 A 0.5 mA VI = 12.5 to 30 V, IO = 20 mA 1 ΔVO/ΔT Output voltage drift IO = 5 mA, TJ = 0 °C to 70 °C -1 mV/°C eN Output noise voltage B = 10 Hz to 100 kHz 65 μV SVR Supply voltage rejection f = 120 Hz 47(1) dB VI Operating input voltage IO ≤ 1 A 13 V RO Output resistance f = 1 kHz 17 mΩ Isc Short circuit current VI = 27 V 500 mA Iscp Short circuit peak current 3 A 1. Guaranteed by design. DocID2148 Rev 8 13/35 L78S Electrical characteristics 35 Refer to the test circuits, TJ = 25 °C, VI = 19 V, IO = 500 mA, unless otherwise specified. Table 8. Electrical characteristics of L78S12C Symbol Parameter Test conditions Min. Typ. Max. Unit VO Output voltage 11.5 12 12.5 V VO Output voltage IO = 1 A, VI = 14.5 V 11.4 12 12.6 V ΔVO Line regulation VI = 14.5 to 30 V 240 mV VI = 16 to 22 V 120 ΔVO Load regulation IO = 20 mA to 1.5 A 240 mV IO = 2 A 150 IQ Quiescent current 8 mA ΔIQ Quiescent current change IO = 20 mA to 1 A 0.5 mA VI = 14.5 to 30 V, IO = 20 mA 1 ΔVO/ΔT Output voltage drift IO = 5 mA, TJ = 0 °C to 70 °C -1 mV/°C eN Output noise voltage B =10 Hz to 100 kHz 75 μV SVR Supply voltage rejection f = 120 Hz 47(1) dB VI Operating input voltage IO ≤ 1 A 15 V RO Output resistance f = 1 kHz 18 mΩ Isc Short circuit current VI = 27 V 500 mA Iscp Short circuit peak current 3 A 1. Guaranteed by design. Electrical characteristics L78S 14/35 DocID2148 Rev 8 Refer to the test circuits, TJ = 25 °C, VI = 23 V, IO = 500 mA, unless otherwise specified. Table 9. Electrical characteristics of L78S15C Symbol Parameter Test conditions Min. Typ. Max. Unit VO Output voltage 14.4 15 15.6 V VO Output voltage IO = 1 A, VI = 17.5 V 14.25 15 15.75 V ΔVO Line regulation VI = 17.5 to 30 V 300 mV VI = 20 to 26 V 150 ΔVO Load regulation IO = 20 mA to 1.5 A 300 mV IO = 2 A 150 IQ Quiescent current 8 mA ΔIQ Quiescent current change IO = 20 mA to 1 A 0.5 mA VI = 17.5 to 30 V, IO = 20 mA 1 ΔVO/ΔT Output voltage drift IO = 5 mA, TJ = 0 °C to 70 °C -1 mV/°C eN Output noise voltage B =10 Hz to 100 kHz 90 μV SVR Supply voltage rejection f = 120 Hz 46(1) dB VI Operating input voltage IO ≤ 1 A 18 V RO Output resistance f = 1 kHz 19 mΩ Isc Short circuit current VI = 27 V 500 mA Iscp Short circuit peak current 3 A 1. Guaranteed by design. DocID2148 Rev 8 15/35 L78S Electrical characteristics 35 Refer to the test circuits, TJ = 25 °C, VI = 26 V, IO = 500 mA, unless otherwise specified. Table 10. Electrical characteristics of L78S18C Symbol Parameter Test conditions Min. Typ. Max. Unit VO Output voltage 17.1 18 18.9 V VO Output voltage IO = 1 A, VI = 20.5 V 17 18 19 V ΔVO Line regulation VI = 20.5 to 30 V 360 mV VI = 22 to 28 V 180 ΔVO Load regulation IO = 20 mA to 1.5 A 360 mV IO = 2 A 200 IQ Quiescent current 8 mA ΔIQ Quiescent current change IO = 20 mA to 1 A 0.5 mA VI = 20.5 to 30 V, IO = 20 mA 1 ΔVO/ΔT Output voltage drift IO = 5 mA, TJ = 0 °C to 70 °C -1 mV/°C eN Output noise voltage B =10 Hz to 100 kHz 110 μV SVR Supply voltage rejection f = 120 Hz 43(1) dB VI Operating input voltage IO ≤ 1 A 21 V RO Output resistance f = 1 kHz 22 mΩ Isc Short circuit current VI = 27 V 500 mA Iscp Short circuit peak current 3 A 1. Guaranteed by design. Electrical characteristics L78S 16/35 DocID2148 Rev 8 Refer to the test circuits, TJ = 25 °C, VI = 33 V, IO = 500 mA, unless otherwise specified. Table 11. Electrical characteristics of L78S24C Symbol Parameter Test conditions Min. Typ. Max. Unit VO Output voltage 23 24 25 V VO Output voltage IO = 1 A, VI = 27 V 22.8 24 25.2 V ΔVO Line regulation VI = 27 to 38 V 480 mV VI = 30 to 36 V 240 ΔVO Load regulation IO = 20 mA to 1.5 A 480 mV IO = 2 A 300 IQ Quiescent current 8 mA ΔIQ Quiescent current change IO = 20 mA to 1 A 0.5 mA VI = 27 to 38 V, IO = 20 mA 1 ΔVO/ΔT Output voltage drift IO = 5 mA, TJ = 0 °C to 70 °C -1.5 mV/°C eN Output noise voltage B = 10 Hz to 100 kHz 170 μV SVR Supply voltage rejection f = 120 Hz 42(1) dB VI Operating input voltage IO ≤ 1 A 27 V RO Output resistance f = 1 kHz 28 mΩ Isc Short circuit current VI = 27 V 500 mA Iscp Short circuit peak current 3 A 1. Guaranteed by design. DocID2148 Rev 8 17/35 L78S Typical performance 35 6 Typical performance Figure 8. Dropout voltage vs. junction temperature Figure 9. Peak output current vs. input/output differential voltage Figure 10. Output impedance vs. frequency Figure 11. Output voltage vs. junction temperature Typical performance L78S 18/35 DocID2148 Rev 8 Figure 12. Supply voltage rejection vs. frequency Figure 13. Quiescent current vs. junction temperature Figure 14. Load transient response Figure 15. Line transient response Figure 16. Quiescent current vs. input voltage DocID2148 Rev 8 19/35 L78S Typical performance 35 1. Although no output capacitor is need for stability, it does improve transient response. 2. Required if regulator is located an appreciable distance from power supply filter. Figure 17. Fixed output regulator Figure 18. Constant current regulator Figure 19. Circuit for increasing output voltage Typical performance L78S 20/35 DocID2148 Rev 8 Figure 20. Adjustable output regulator (7 to 30 V) Figure 21. 0.5 to 10 V regulator VO=VXXR4/R1 DocID2148 Rev 8 21/35 L78S Typical performance 35 Figure 22. High current voltage regulator Figure 23. High output current with short circuit protection Typical performance L78S 22/35 DocID2148 Rev 8 Figure 24. Tracking voltage regulator Figure 25. Positive and negative regulator DocID2148 Rev 8 23/35 L78S Typical performance 35 Figure 26. Negative output voltage circuit Figure 27. Switching regulator Figure 28. High input voltage circuit Typical performance L78S 24/35 DocID2148 Rev 8 Figure 29. High input voltage circuit Figure 30. High output voltage regulator Figure 31. High input and output voltage DocID2148 Rev 8 25/35 L78S Typical performance 35 Figure 32. Reducing power dissipation with dropping resistor Figure 33. Remote shutdown Typical performance L78S 26/35 DocID2148 Rev 8 Note: The circuit performs well up to 100 kHz. Note: Q2 is connected as a diode in order to compensate the variation of the Q1 VBE with the temperature. C allows a slow rise time of the VO. Figure 34. Power AM modulator (unity voltage gain, IO ≤ 1 A) Figure 35. Adjustable output voltage with temperature compensation DocID2148 Rev 8 27/35 L78S Typical performance 35 1. Application with high capacitance loads and an output voltage greater than 6 volts need an external diode (see Figure 30 on page 24) to protect the device against input short circuit. In this case the input voltage falls rapidly while the output voltage decrease slowly. The capacitance discharges by means of the Base- Emitter junction of the series pass transistor in the regulator. If the energy is sufficiently high, the transistor may be destroyed. The external diode by-passes the current from the IC to ground. Figure 36. Light controllers (VOmin = VXX + VBE) Figure 37. Protection against input short-circuit with high capacitance loads Package mechanical data L78S 28/35 DocID2148 Rev 8 7 Package mechanical data In order to meet environmental requirements, ST offers these devices in different grades of ECOPACK® packages, depending on their level of environmental compliance. ECOPACK® specifications, grade definitions and product status are available at: www.st.com. ECOPACK® is an ST trademark. DocID2148 Rev 8 29/35 L78S Package mechanical data 35 Figure 38. TO-220 (dual gauge) drawing Package mechanical data L78S 30/35 DocID2148 Rev 8 Table 12. TO-220 (dual gauge) mechanical data Dim. mm Min. Typ. Max. A 4.40 4.60 b 0.61 0.88 b1 1.14 1.70 c 0.48 0.70 D 15.25 15.75 D1 1.27 E 10 10.40 e 2.40 2.70 e1 4.95 5.15 F 1.23 1.32 H1 6.20 6.60 J1 2.40 2.72 L 13 14 L1 3.50 3.93 L20 16.40 L30 28.90 ∅P 3.75 3.85 Q 2.65 2.95 DocID2148 Rev 8 31/35 L78S Package mechanical data 35 Figure 39. TO-220 SG (single gauge) drawing Package mechanical data L78S 32/35 DocID2148 Rev 8 Table 13. TO-220 SG (single gauge) mechanical data Dim. mm Min. Typ. Max. A 4.40 4.60 b 0.61 0.88 b1 1.14 1.70 c 0.48 0.70 D 15.25 15.75 E 10 10.40 e 2.40 2.70 e1 4.95 5.15 F 0.51 0.60 H1 6.20 6.60 J1 2.40 2.72 L 13 14 L1 3.50 3.93 L20 16.40 L30 28.90 ∅P 3.75 3.85 Q 2.65 2.95 DocID2148 Rev 8 33/35 L78S Packaging mechanical data 35 8 Packaging mechanical data Figure 40. Tube for TO-220 (dual gauge) (mm.) Figure 41. Tube for TO-220 (single gauge) (mm.) Revision history L78S 34/35 DocID2148 Rev 8 9 Revision history Table 14. Document revision history Date Revision Changes 07-Sep-2006 2 Order codes updated. 20-Mar-2008 3 Added: Table 1 on page 1. 22-Mar-2010 4 Added: Table 20 on page 32, Figure 38 on page 33, Figure 39 on page 34, Figure 40 and Figure 41 on page 33. 08-Feb-2012 5 Added: order codes L78S05CV-DG, L78S12CV-DG and L78S15CV-DG Table 13 on page 35. 09-Mar-2012 6 Added: order codes L78S09CV-DG Table 13 on page 35. 15-May-2012 7 Added: order codes L78S75CV-DG and L78S10CV-DG Table 13 on page 35. 10-Mar-2014 8 Part numbers L78Sxx and L78SxxC changed to L78S. Modified the title, the features and the description in cover page. Removed TO-3 package. Updated Table 1: Device summary, Section 2: Pin configuration, Section 3: Maximum ratings, Section 4: Test circuits, Section 5: Electrical characteristics,Section 6: Typical performance, Section 7: Package mechanical data, Section 9: Order codes. Added Section 8: Packaging mechanical data. Minor text changes. DocID2148 Rev 8 35/35 L78S 35 Please Read Carefully: Information in this document is provided solely in connection with ST products. STMicroelectronics NV and its subsidiaries (“ST”) reserve the right to make changes, corrections, modifications or improvements, to this document, and the products and services described herein at any time, without notice. All ST products are sold pursuant to ST’s terms and conditions of sale. Purchasers are solely responsible for the choice, selection and use of the ST products and services described herein, and ST assumes no liability whatsoever relating to the choice, selection or use of the ST products and services described herein. No license, express or implied, by estoppel or otherwise, to any intellectual property rights is granted under this document. If any part of this document refers to any third party products or services it shall not be deemed a license grant by ST for the use of such third party products or services, or any intellectual property contained therein or considered as a warranty covering the use in any manner whatsoever of such third party products or services or any intellectual property contained therein. UNLESS OTHERWISE SET FORTH IN ST’S TERMS AND CONDITIONS OF SALE ST DISCLAIMS ANY EXPRESS OR IMPLIED WARRANTY WITH RESPECT TO THE USE AND/OR SALE OF ST PRODUCTS INCLUDING WITHOUT LIMITATION IMPLIED WARRANTIES OF MERCHANTABILITY, FITNESS FOR A PARTICULAR PURPOSE (AND THEIR EQUIVALENTS UNDER THE LAWS OF ANY JURISDICTION), OR INFRINGEMENT OF ANY PATENT, COPYRIGHT OR OTHER INTELLECTUAL PROPERTY RIGHT. ST PRODUCTS ARE NOT DESIGNED OR AUTHORIZED FOR USE IN: (A) SAFETY CRITICAL APPLICATIONS SUCH AS LIFE SUPPORTING, ACTIVE IMPLANTED DEVICES OR SYSTEMS WITH PRODUCT FUNCTIONAL SAFETY REQUIREMENTS; (B) AERONAUTIC APPLICATIONS; (C) AUTOMOTIVE APPLICATIONS OR ENVIRONMENTS, AND/OR (D) AEROSPACE APPLICATIONS OR ENVIRONMENTS. WHERE ST PRODUCTS ARE NOT DESIGNED FOR SUCH USE, THE PURCHASER SHALL USE PRODUCTS AT PURCHASER’S SOLE RISK, EVEN IF ST HAS BEEN INFORMED IN WRITING OF SUCH USAGE, UNLESS A PRODUCT IS EXPRESSLY DESIGNATED BY ST AS BEING INTENDED FOR “AUTOMOTIVE, AUTOMOTIVE SAFETY OR MEDICAL” INDUSTRY DOMAINS ACCORDING TO ST PRODUCT DESIGN SPECIFICATIONS. PRODUCTS FORMALLY ESCC, QML OR JAN QUALIFIED ARE DEEMED SUITABLE FOR USE IN AEROSPACE BY THE CORRESPONDING GOVERNMENTAL AGENCY. Resale of ST products with provisions different from the statements and/or technical features set forth in this document shall immediately void any warranty granted by ST for the ST product or service described herein and shall not create or extend in any manner whatsoever, any liability of ST. ST and the ST logo are trademarks or registered trademarks of ST in various countries. Information in this document supersedes and replaces all information previously supplied. The ST logo is a registered trademark of STMicroelectronics. All other names are the property of their respective owners. © 2014 STMicroelectronics - All rights reserved STMicroelectronics group of companies Australia - Belgium - Brazil - Canada - China - Czech Republic - Finland - France - Germany - Hong Kong - India - Israel - Italy - Japan - Malaysia - Malta - Morocco - Philippines - Singapore - Spain - Sweden - Switzerland - United Kingdom - United States of America www.st.com BD6xxx Complementary power Darlington transistors Features ■ Good hFE linearity ■ High fT frequency ■ Monolithic Darlington configuration with integrated antiparallel collector-emitter diode Applications ■ Linear and switching industrial equipment Description The devices are manufactured in planar base island technology with monolithic Darlington configuration. . Figure 1. Internal schematic diagram SOT-32 3 2 1 R1 typ.= 15 KΩ R2 typ.= 100 Ω Table 1. Device summary Order codes Marking Package Packaging BD677 BD677 SOT-32 Tube BD677A BD677A BD678 BD678 BD678A BD678A BD679 BD679 BD679A BD679A BD680 BD680 BD680A BD680A BD681 BD681 BD682 BD682 www.st.com Contents BD6xxx 2/12 Contents 1 Absolute maximum ratings . . . . . . . . . . . . . . . . . . . . . . . . . . . . . . . . . . . 3 2 Electrical characteristics . . . . . . . . . . . . . . . . . . . . . . . . . . . . . . . . . . . . . 4 2.1 Typical characteristic (curves) . . . . . . . . . . . . . . . . . . . . . . . . . . . . . . . . . . 6 2.2 Test circuit . . . . . . . . . . . . . . . . . . . . . . . . . . . . . . . . . . . . . . . . . . . . . . . . . 8 3 Package mechanical data . . . . . . . . . . . . . . . . . . . . . . . . . . . . . . . . . . . . . 9 4 Revision history . . . . . . . . . . . . . . . . . . . . . . . . . . . . . . . . . . . . . . . . . . . 11 BD6xxx Absolute maximum ratings 3/12 1 Absolute maximum ratings Note: For PNP types voltage and current values are negative Table 2. Absolute maximum ratings Symbol Parameter Value Unit NPN BD677 BD677A BD679 BD679A BD681 PNP BD678 BD678A BD680 BD680A BD682 VCBO Collector-base voltage (IE = 0) 60 80 100 V VCEO Collector-emitter voltage (IB = 0) VEBO Emitte-base voltage (IC = 0) 5 V IC Collector current 4 A ICM Collector peak current 6 A IB Base current 0.1 A PTOT Total dissipation at Tcase = 25°C 40 W Tstg Storage temperature -65 to 150 °C TJ Max. operating junction temperature 150 °C Electrical characteristics BD6xxx 4/12 2 Electrical characteristics (Tcase = 25°C; unless otherwise specified) Table 3. Electrical characteristics Symbol Parameter Test conditions Min. Typ. Max. Unit ICEO Collector cut-off current (IB = 0) VCE = half rated VCEO 0.5 mA ICBO Collector cut-off current (IE = 0) VCE = rated VCBO VCE = rated VCBO Tc = 100 °C 0.2 2 mA IEBO Emitter cut-off current (IC = 0) VEB = 5 V 2 mA VCEO(sus) (1) Collector-emitter sustaining voltage (IB = 0) for BD677, BD677A, BD678, BD678A IC = 50 mA 60 V for BD679, BD679A, BD680, BD680A IC = 50 mA 80 for BD681, BD682 IC = 50 mA 100 VCE(sat) (1) Collector-emitter saturation voltage for BD677, BD678, BD679, BD680, BD681, BD682 IC = 1.5 A IB = 30 mA 2.5 V for BD677A, BD678A, BD679A, BD680A IC = 2 A IB = 40 mA 2.8 VBE (1) Base-emitter voltage for BD677, BD678, BD679, BD680, BD681, BD682 IC = 1.5 A ___ VCE = 3 V 2.5 V for BD677A, BD678A, BD679A, BD680A IC = 2 A VCE = 3 V BD6xxx Electrical characteristics 5/12 Note: For PNP types voltage e current values are negative. hFE (1) DC current gain for BD677, BD678, BD679, BD680, BD681, BD682 IC = 1.5 A_ _ VCE = 3 V 750 for BD677A, BD678A, BD679A, BD680A IC = 2 A_ _ VCE = 3 V 1. Pulsed duration = 300 ms, duty cycle ≥1.5%. Table 3. Electrical characteristics (continued) Symbol Parameter Test conditions Min. Typ. Max. Unit Electrical characteristics BD6xxx 6/12 2.1 Typical characteristic (curves) Figure 2. DC current gain (NPN) Figure 3. DC current gain (PNP) Figure 4. DC current gain (NPN) Figure 5. DC current gain (PNP) Figure 6. Collector-emitter saturation voltage (NPN) Figure 7. Collector-emitter saturation voltage (PNP) BD6xxx Electrical characteristics 7/12 Figure 8. Base-emitter saturation voltage (NPN) Figure 9. Base-emitter saturation voltage (PNP) Figure 10. Base-emitter voltage (NPN) Figure 11. Base-emitter voltage (PNP) Figure 12. Resistive load switching time (NPN, on) Figure 13. Resistive load switching time (PNP, on) Electrical characteristics BD6xxx 8/12 2.2 Test circuit Note: For PNP types voltage e current values are negative. Figure 14. Resistive load switching time (NPN, off) Figure 15. Resistive load switching time (PNP, off) Figure 16. Resistive load switching test circuit 1) Fast electronic switch 2) Non-inductive resistor BD6xxx Package mechanical data 9/12 3 Package mechanical data In order to meet environmental requirements, ST offers these devices in ECOPACK® packages. These packages have a lead-free second level interconnect . The category of second level interconnect is marked on the package and on the inner box label, in compliance with JEDEC Standard JESD97. The maximum ratings related to soldering conditions are also marked on the inner box label. ECOPACK is an ST trademark. ECOPACK specifications are available at: www.st.com Package mechanical data BD6xxx 10/12 BD6xxx Revision history 11/12 4 Revision history Table 4. Document revision history Date Revision Changes 21-Jun-2004 4 14-Jan-2008 5 1. Technology change from epybase to planar. 2. Updated Section 2.1: Typical characteristic (curves) on page 6 3. Content reworked to improve readability. BD6xxx 12/12 Please Read Carefully: Information in this document is provided solely in connection with ST products. STMicroelectronics NV and its subsidiaries (“ST”) reserve the right to make changes, corrections, modifications or improvements, to this document, and the products and services described herein at any time, without notice. All ST products are sold pursuant to ST’s terms and conditions of sale. Purchasers are solely responsible for the choice, selection and use of the ST products and services described herein, and ST assumes no liability whatsoever relating to the choice, selection or use of the ST products and services described herein. No license, express or implied, by estoppel or otherwise, to any intellectual property rights is granted under this document. If any part of this document refers to any third party products or services it shall not be deemed a license grant by ST for the use of such third party products or services, or any intellectual property contained therein or considered as a warranty covering the use in any manner whatsoever of such third party products or services or any intellectual property contained therein. UNLESS OTHERWISE SET FORTH IN ST’S TERMS AND CONDITIONS OF SALE ST DISCLAIMS ANY EXPRESS OR IMPLIED WARRANTY WITH RESPECT TO THE USE AND/OR SALE OF ST PRODUCTS INCLUDING WITHOUT LIMITATION IMPLIED WARRANTIES OF MERCHANTABILITY, FITNESS FOR A PARTICULAR PURPOSE (AND THEIR EQUIVALENTS UNDER THE LAWS OF ANY JURISDICTION), OR INFRINGEMENT OF ANY PATENT, COPYRIGHT OR OTHER INTELLECTUAL PROPERTY RIGHT. UNLESS EXPRESSLY APPROVED IN WRITING BY AN AUTHORIZED ST REPRESENTATIVE, ST PRODUCTS ARE NOT RECOMMENDED, AUTHORIZED OR WARRANTED FOR USE IN MILITARY, AIR CRAFT, SPACE, LIFE SAVING, OR LIFE SUSTAINING APPLICATIONS, NOR IN PRODUCTS OR SYSTEMS WHERE FAILURE OR MALFUNCTION MAY RESULT IN PERSONAL INJURY, DEATH, OR SEVERE PROPERTY OR ENVIRONMENTAL DAMAGE. ST PRODUCTS WHICH ARE NOT SPECIFIED AS "AUTOMOTIVE GRADE" MAY ONLY BE USED IN AUTOMOTIVE APPLICATIONS AT USER’S OWN RISK. Resale of ST products with provisions different from the statements and/or technical features set forth in this document shall immediately void any warranty granted by ST for the ST product or service described herein and shall not create or extend in any manner whatsoever, any liability of ST. ST and the ST logo are trademarks or registered trademarks of ST in various countries. Information in this document supersedes and replaces all information previously supplied. The ST logo is a registered trademark of STMicroelectronics. All other names are the property of their respective owners. © 2008 STMicroelectronics - All rights reserved STMicroelectronics group of companies Australia - Belgium - Brazil - Canada - China - Czech Republic - Finland - France - Germany - Hong Kong - India - Israel - Italy - Japan - Malaysia - Malta - Morocco - Singapore - Spain - Sweden - Switzerland - United Kingdom - United States of America www.st.com This is information on a product in full production. August 2013 DocID13587 Rev 16 1/105 STM32F103x8 STM32F103xB Medium-density performance line ARM-based 32-bit MCU with 64 or 128 KB Flash, USB, CAN, 7 timers, 2 ADCs, 9 com. interfaces Datasheet - production data Features ARM 32-bit Cortex™-M3 CPU Core – 72 MHz maximum frequency, 1.25 DMIPS/MHz (Dhrystone 2.1) performance at 0 wait state memory access – Single-cycle multiplication and hardware division Memories – 64 or 128 Kbytes of Flash memory – 20 Kbytes of SRAM Clock, reset and supply management – 2.0 to 3.6 V application supply and I/Os – POR, PDR, and programmable voltage detector (PVD) – 4-to-16 MHz crystal oscillator – Internal 8 MHz factory-trimmed RC – Internal 40 kHz RC – PLL for CPU clock – 32 kHz oscillator for RTC with calibration Low power – Sleep, Stop and Standby modes – VBAT supply for RTC and backup registers 2 x 12-bit, 1 μs A/D converters (up to 16 channels) – Conversion range: 0 to 3.6 V – Dual-sample and hold capability – Temperature sensor DMA – 7-channel DMA controller – Peripherals supported: timers, ADC, SPIs, I2Cs and USARTs Up to 80 fast I/O ports – 26/37/51/80 I/Os, all mappable on 16 external interrupt vectors and almost all 5 V-tolerant Debug mode – Serial wire debug (SWD) & JTAG interfaces 7 timers – Three 16-bit timers, each with up to 4 IC/OC/PWM or pulse counter and quadrature (incremental) encoder input – 16-bit, motor control PWM timer with deadtime generation and emergency stop – 2 watchdog timers (Independent and Window) – SysTick timer 24-bit downcounter Up to 9 communication interfaces – Up to 2 x I2C interfaces (SMBus/PMBus) – Up to 3 USARTs (ISO 7816 interface, LIN, IrDA capability, modem control) – Up to 2 SPIs (18 Mbit/s) – CAN interface (2.0B Active) – USB 2.0 full-speed interface CRC calculation unit, 96-bit unique ID Packages are ECOPACK® Table 1. Device summary Reference Part number STM32F103x8 STM32F103C8, STM32F103R8 STM32F103V8, STM32F103T8 STM32F103xB STM32F103RB STM32F103VB, STM32F103CB, STM32F103TB BGA100 10 × 10 mm UFBGA100 7 x 7 mm BGA64 5 × 5 mm VFQFPN36 6 × 6 mm LQFP100 14 × 14 mm LQFP64 10 × 10 mm LQFP48 7 × 7 mm UFQFPN48 7 × 7 mm www.st.com 2012-2013 Dremel Experts: US: 1 (800) 437-3635 Canada: 1 (888) 285-3476 www.dremel.com The M akers o f Scan this code with your phone for product information, videos, and more. Do you like to: REA D Visit Dremel.com and get tips and tricks on projects and products. Plus visit our message board or sign up for our monthly eblast for news on new product introductions. TALK Join the conversation on Facebook at facebook.com/Dremel. BE INSPIRE D Sign up for weekly project inspiration at DremelWeekends.com. SHARE Pin Dremel projects and ideas on Pinterest. STAY UP-TO-DATE Get the latest news from Dremel. Follow us on Twitter, username @Dremel. ROTARY TOOLS Corded.. . . . . . . . . . . . . . . . . . . . . . . . . . . 1-12 Cordless.. . . . . . . . . . . . . . . . . . . . . . . 13-20 At tachments.. . . . . . . . . . . . . . . . . 21-26 Accessories.. . . . . . . . . . . . . . . . . . 27-42 OSCILLATING TOOLS Mul t i-Max™ Corded.. . . . . . 43-48 Mul t i-Max™ Cordless.. . . . 49-50 Accessories.. . . . . . . . . . . . . . . . . . 51-54 At tachments.. . . . . . . . . . . . . . . . . . . . . 54 SPECIALTY TOOLS Saw-Max™ System. . . . . . . . 55-60 Trio™ System.. . . . . . . . . . . . . . . . 61-66 VersaTip™ and Accessories.. . . . . . . . . . . . . . . . . . . . . . 67 Engraver and Accessories.. . . . . . . . . . . . . . . . . . . . . . 67 V ersatile Tool Systems™ INDEX Customer Support A well-prepared staff of Dremel Experts is available to answer questions about our tools. With over 650 total years of combined work experience, the Dremel Experts are ready to serve you. Call: 1-800-4-DREMEL (1-800-437-3635) USA. 1-888-285-3476 CANADA. Cal l for Your Free Dremel DVD 1(800) 437-3635 1 The Makers of Versatile Tool Systems™ ROTARY TOOLS 2 What Is a Rotary Tool ? Rotary tools are hand held power tools that use high-speed and low torque to undertake a variety of useful tasks with control and precision. Since AJ Dremel invented the first rotary tool over 80 years ago, no other brand has worked harder to bring users a more complete and innovative system of rotary tools, accessories and attachments. Over the years Dremel rotary tools have become the gold standard in versatility, performance, and quality by which all other rotary tools are judged. 3 4200, 4000, 8220 3000, 8100 ROTARY TOOL OVERVIEW CORDED VERSATILITY METER Model 4200 4000 3000 200 SERIES 100 SERIES Amps 1.6 1.6 1.2 1.15 1.15 Speed Range [RPM] 5,000— 35,000 5,000— 35,000 5,000— 32,000 15,000 and 35,000 35,000 Versatility Level High High Intermediate Basic + Basic Electronic Feedback Control Yes Yes No No No Number of Speeds Variable Variable Variable 2 1 Soft Grip Yes Yes Yes No No Separate On/Off Speed Control Yes Yes No No No Accessory Change System EZ Change™ EZ Twist™ Nose Cap EZ Twist™ Nose Cap Wrench Wrench Weight [oz.] 25 22.5 20.0 18.0 18.0 Warranty 2 year 2 year 2 year 2 year 2 year High Intermediate Models: Models: Premium Rotary Tools, able t o perform the wide st range o f applications. High Performance Rotary Tools, able to tackle a wider r ange of applications. 4 200 SERIES, STYLUS, 7700 100 SERIES, 7300 ROTARY TOOL OVERVIEW CORDLESS Model 8220 8100 STYLUS™ 7700 7300 Voltage 12Vmax 8Vmax 7.2 7.2 4.8 Battery Type Lithium Ion Lithium Ion Lithium Ion Ni-Cd Ni-Cd Speed Range [RPM] 5,000— 30,000 5,000— 30,000 5,000— 25,000 10,000 and 20,000 6,500 and 13,000 Versatility Level High Intermediate Basic + Basic + Basic Electronic Feedback Control No No No No No Number of Speeds Variable Variable Variable 2 2 Soft Grip Yes Yes Yes No No Separate On/Off Speed Control Yes Yes Yes No No Accessory Change System EZ Twist™ Nose Cap EZ Twist™ Nose Cap Wrench Wrench Wrench Weight [oz.] 22.0 14.0 9.0 12.0 9.0 Warranty 2 year 2 year 2 year 2 year 2 year Basic + Basic Models: Models: Enhanced Level Rotary Tools, with improved control across multiple applications. Entry Level Rotary Tools, ideal for precision applications. 5 1 2 3 NEW! PULL INSERT SECURE Integrated EZ Change™ For the fastest and easiest accessory change. Patented pull lever system Means you'll never need to look for the wrench again. Variable Speed For maximum accessory versatility and precise tool control. Electronic Feedback Auto adjusts power and speed as needed. Can be used with all Dremel accessories and attachments except MS400 and PL400 attachments.* High-Performance Motor For maximum performance at all speeds. Separate On/Off Switch Retains speed setting for ease of use. Increased power and air flow For cooler operation. Limited Warranty CORDED ROTARY TOOLS Versatility * Attachment models 225, 575 and 670 are compatible with the 4200 when used with the 4200 Attachment Adapter found in your Dremel 4200 kit. 6 EZC480 EZC481 EZC482 EZC483 • 4200 High Performance Rotary Tool, Circle Cutter, Safety Shield, Cutting Guide, Lawn Mower Sharpener, Lawn Mower and Garden Tool Sharpener, Sanding/Grinding Guide, Detailers Grip • Storage Case, Accessory Case, Product Reference Sheet, Adapter/Drive Coupling 40 ASSORTED ACCESSORIES Carving/Engraving - 107, 191 Grinding/Sharpening - 932, 8193, 84922 Cutting - EZ409, EZ456, 561 Cleaning/Polishing - 403, 428 Sanding - EZ407, 408 (x6), EZ411 (x3) EZ412 (x3), EZ413 (x3), 432 (x6), 445 (x6) Miscellaneous - 150, EZ402 4200 KIT 4200 - 6/40 The following 4200-specific collets are available for purchase. Call 1-800-4-DREMEL for more information. 2615001034 – EZC480 2615001035 – EZC481 2615001036 – EZC482 2615001037 – EZC483 1/8" 3/32" 1/16" 1/32" 3,2 mm 2,4 mm 1,6 mm 0,8 mm 4200 COLLETS 7 Electronic Feedback Auto adjusts power and speed as needed. EZ Twist™ Nose Cap Wrench for fast accessory changes. Variable Speed For maximum accessory versatility and precise tool control. Can be used with all Dremel accessories and attachments. Does it All, Better.™ Limited Warranty Versatility CORDED ROTARY TOOLS High-Performance Motor For maximum performance at all speeds. Separate On/Off Switch Retains speed setting for ease of use. 360º Grip Zone With soft grip for comfort and control. Quick Collet Lock For fast accessory changes. Integrated nose cap wrench for fast accessory changes. 8 • 4000 High Performance Rotary Tool, Planer, Flex Shaft, Circle Cutter, Sanding/Grinding Guide, Cutting Guide, Detail Nose Piece, Lawn Mower and Garden Tool Sharpener • Storage Case, Accessory Case, Product Reference Sheet, Wrench, 1/8" Collet • 4000 High Performance Rotary Tool, Detailer’s Grip, Sanding/Grinding Guide, Cutting Guide, Circle Cutter • Storage Case, Accessory Case, Product Reference Sheet, Wrench, 1/8" Collet • 4000 High Performance Rotary Tool, Sanding/ Grinding Guide, Circle Cutter • Storage Case, Accessory Case, Product Reference Sheet, Wrench, 1/8" Collet Carving/Engraving - 107, 191, 194 Grinding/Sharpening - 541, 932, 8193, 84922 Cutting - 420 (x4), 540, 561, EZ409, EZ456 (x2), EZ476 (x2) Cleaning/Polishing - 405, 414 (x3), 421, 428, 429, 442, EZ423 Sanding - 407, 408 (x2), 411 (x2), 412 (x2), 413 (x2), 432 (x2), 445 (x2), EZ511, EZ512 Miscellaneous - 150, 401, 402, 481, EZ402 50 ASSORTED ACCESSORIES Carving/Engraving - 107, 191 Grinding/Sharpening - 932, 8193, 84922, 85602 Cutting - 420 (x2), 540, 561, EZ456 Cleaning/Polishing - 403, 414 (x3), 421, 428, 429 (x2), 802 Sanding - 407, 408, 411 (x2), 412, 413, 432 (x3), 445 (x2) Miscellaneous - 401, 402, 481, EZ402 34 ASSORTED ACCESSORIES Carving/Engraving - 191 Grinding/Sharpening - 541, 932, 84922 Cutting - 420 (x2), 426 (x2), 561 Cleaning/Polishing - 403, 414, 421, 428, 429 Sanding - 407, 408 (x3), 411 (x3), 412 (x2), 413 (x2), 432 (x2), 445 (x2) Miscellaneous - 401, 402 30 ASSORTED ACCESSORIES 4000 KIT 4000 - 6/50 4000 KIT 4000 - 4/34 4000 KIT 4000 - 2/30 9 Versatility Does it Better.™ CORDED ROTARY TOOLS Limited Warranty EZ Twist™ Nose Cap Wrench for fast accessory changes. Variable Speed For maximum accessory versatility and precise tool control. Sealed Ball Bearing Motor Runs cool for comfort and longer tool life. Can be used with all Dremel accessories and attachments except MS400 and PL400 attachments. Separate On/Off Switch Retains speed setting for ease of use. Double hull construction Eliminates direct heat transfer to hand. 10 • 3000 Series Variable Speed Rotary Tool, Sanding/Grinding Guide • Storage Case, Accessory Case, Product Reference Sheet • Wrench, 1/8" Collet • 3000 Series Variable Speed Rotary Tool, Cutting Guide • Storage Case, Accessory Case, Product Reference Sheet • Wrench, 1/8" Collet Carving/Engraving - 191 Grinding/Sharpening - 932, 952, 85422 Cutting - 426 (x2) Cleaning/Polishing - 403, 414 (x2), 421, 428, 429 Sanding - 407, 408, 430, 432 (x2), 438, 445 (x2), 446 Miscellaneous - 401, 402, 415 24 ASSORTED ACCESSORIES Carving/Engraving - 107, 191, 7144 Grinding/Sharpening - 932, 952, 953, 84922 Cutting - 426 (x2), 560, 561 Cleaning/Polishing - 403, 404, 405, 414 (x2), 421, 428, 429 (x2) Sanding - 407, 408 (x2), 432 (x2), 445 (x2) Miscellaneous - 150, 401, 402, 415 31 ASSORTED ACCESSORIES 3000 KIT 3000 - 1/24 3000 KIT 3000 - 1/31 11 Versatility Limited Warranty Two Speed control For application versatility and control. Sealed Ball Bearing Motor For cool running and longer tool life. • Two-Speed Rotary Tool, Lawn Mower and Garden Tool Sharpener • Corrugated Storage Case, Product Reference Sheet • Wrench, 1/8" Collet Carving/Engraving - 194 Grinding/Sharpening - 932, 8193, 83322 Cutting - 420, 426 Cleaning/Polishing - 421, 422, 425, 429 Sanding - 407, 408, 432 Miscellaneous - 401, 402 15 ASSORTED ACCESSORIES • Two-Speed Rotary Tool, Cutting Guide • Corrugated Storage Case, Product Reference Sheet • Wrench, 1/8" Collet CORDED ROTARY TOOLS 200 SERIES KIT 200 - 1/15 200 SERIES KIT 200 - 1/21 Carving/Engraving - 194 Grinding/Sharpening - 932, 8193, 83142, 84922 Cutting - 420, 426, 561 Cleaning/Polishing - 414 (x2), 421, 422, 425 (x2), 429 (x2) Sanding - 407, 432, 445 Miscellaneous - 401, 402, 415 21 ASSORTED ACCESSORIES 12 Single Speed control For fulltime 35,000 rpm operation. Sealed Ball Bearing Motor For cool running and longer tool life. Limited Warranty Ideal for sanding, carving and drilling. • Single-Speed Rotary Tool • Product Reference Sheet • Wrench, 1/8" Collet 100 SERIES KIT 100 - N/7 Versatility Grinding/Sharpening - 932, 84922 Cutting - 420 Sanding - 407, 432 Miscellaneous - 402, 415 7 ASSORTED ACCESSORIES 13 Limited Warranty CORDLESS ROTARY TOOLS Does it All, Unplugged.™ Next Generation 12V Max For maximum performance and run time. Removable Lithium-Ion Battery Always ready with no memory effects. EZ Twist™ Nose Cap Wrench for fast accessory changes. Variable Speed For maximum accessory versatility and precise tool control. Versatility High-Performance Motor For maximum performance at all speeds. Can be used with all Dremel accessories and attachments. Separate On/Off Switch Retains speed setting for ease of use. 360º Grip Zone With soft grip for comfort and control. NEW! NEW! LITHIUM-ION TECHNOLOGY • More power in a smaller size • Always ready – holds charge up to 2 years • No memory effects – charge any time * When compared to 8200 while cutting screws 14 B812-01 876 12VMAX Lithium-Ion Battery Pack 12VMAX 1-Hour Lithium-Ion Battery Charger • 8220 Cordless 12VMAX High Performance Rotary Tool, Cutting Guide • 1-Hour Battery Charger, 12VMAX Lithium-Ion Battery Pack (1) • Storage Case, Accessory Case, Product Reference Sheet • Wrench, 1/8" Collet Grinding/Sharpening - 541, 8193 Cutting - 426, 561 Cleaning/Polishing - 414 (X4), 421, 425 (X4), 429 (X4) Sanding - 407, 408 (X2), 432 (X3), 445 (X3) Miscellaneous - 401, 402, 28 ASSORTED ACCESSORIES • 8220 Cordless 12VMAX High Performance Rotary Tool, Shield, Cutting Guide • 1-Hour Battery Charger, 12VMAX Lithium-Ion Battery Packs (2) • Storage Case, Accessory Case, Product Reference Sheet • Wrench, 1/8" Collet Grinding/Sharpening - 541, 8193 Cutting - 561, 426, EZ456 Cleaning/Polishing - 414 (X3), 421, 425 (x4), 429 (x3) Sanding - 407, 408 (X2), 432 (X3), 445 (X3) Miscellaneous - 401, 402, EZ402 28 ASSORTED ACCESSORIES Includes 2 batteries 8220 KIT 8220 - 1/28 8220 KIT 8220 - 2/28 CORDLESS 12VMAX ROTARY TOOL ACCESSORIES 15 Limited Warranty Versatility CORDLESS ROTARY TOOLS NEW! EZ Twist™ Nose Cap Wrench for fast accessory changes. Variable Speed For maximum accessory versatility and precise tool control. 8V Max Lithium-ion For power in a smaller size, always ready and no memory effects. Can be used with all Dremel accessories and attachments except MS400 and PL400 attachments. Separate On/Off Switch Retains speed setting for ease of use. Small and Lightweight For easier handling and less fatigue. 16 B808-01 876 • 8100 Cordless 8VMAX Rotary Tool • 1-Hour Charger, 8VMAX Lithium-Ion Battery Pack (1) • Compact Storage Case • Wrench, 1/8" Collet Grinding/Sharpening - 84922, 932, 952 Cutting - 540 (x3) Cleaning/Polishing - 403, 414 (x2), 421 Sanding - 407, 408 (x3), 432 (x3), 445 (x2) Miscellaneous - 401, 402 21 ASSORTED ACCESSORIES 8100 KIT 8100-N/21 CORDLESS 8VMAX ROTARY TOOL ACCESSORIES 8VMAX Lithium-Ion Battery Pack 8VMAX 1-Hour Lithium-Ion Battery Charger 17 Limited Warranty Versatility Variable Speed For maximum accessory versatility and precise tool control. Rechargeable 7.2V Lithium-ion Battery holds a charge 2 years while in storage. Unique Contoured Grip Designed for superior precision, control, and comfort in your hand. Finger-Tip On/Off Switch For one-handed operation. Compact and Ultra-Lightweight Can be used with most Dremel accessories and no attachments. Docking Station Continually charges so the tool is always fully charged and ready to use. CORDLESS ROTARY TOOLS • Always Ready • Goes Everywhere Created to Fit Your Hand and Your Lifestyle™ 18 • Dremel Stylus Rotary Tool • Charging Base and Accessory Organizer • Accessory Case, Product Reference Sheet • Wrench, 1/8" Collet Carving/Engraving - 105, 107, 191, 194 Grinding/Sharpening - 932, 84922 Cleaning/Polishing - 403, 414 (X4), 421, 425, 429 (X3) Sanding - 430, 431, 438 (X2), 446, 521E Miscellaneous - 401, 402, 481 25 ASSORTED ACCESSORIES STYLUS KIT 1100 - N/25 19 757-01 758-01 Two Speeds For control and accuracy. Removable battery pack Continuous use to finish your projects. 7.2 Volts of Power . . . goes anywhere. Light and Compact Easy to handle and fun to use — anywhere! 3-Hour Charger Quick battery recharge with LED light. Light indicates battery is correctly placed into the charger for proper charging. Versatility Limited Warranty CORDLESS ROTARY TOOLS 3-Hour Battery Charger 7.2V Battery Pack 7700 ACCESSORIES • 7.2V Two-Speed Cordless Rotary Tool, Lawn Mower and Garden Tool Sharpener • Corrugated Storage Case, Accessory Organizer, Product Reference Sheet • 3-Hour Charger • Wrench, 1/8" Collet Carving/Engraving - 191 Grinding/Sharpening - 932, 8193, 83322 Cutting - 420, 426 Cleaning/Polishing - 421, 422, 425, 429 Sanding - 407, 408, 432 Miscellaneous - 401, 402 15 ASSORTED ACCESSORIES 7700 KIT 7700-02 20 755-01 756-01 Two Speeds For control and accuracy. Removable battery pack Continuous use to finish your projects. 4.8 Volts of Power For light duty precision jobs. Light and Compact Easy to handle and fun to use — anywhere! 3-Hour Charger Quick battery recharge with LED light. Light indicates battery is correctly placed into the charger for proper charging. Versatility Limited Warranty 4.8V Battery Pack 7300 ACCESSORIES • 4.8V Two-Speed MINIMITE® • 3-Hour Charger • Wrench, 1/8" Collet Grinding/Sharpening - 84922 Cleaning/Polishing - 414 Sanding - 407, 432 Miscellaneous - 401 5 ASSORTED ACCESSORIES 3-Hour Battery Charger 7300 KIT 750-02 21 220 225 231 335 565 566 568 575 A576 A577 670 675 678-01 1453 2500-01 A550 A679-02 4200 • * • • • • • • * • • * • • • • • 4000 • • • • • • • • • • • • • • • • • 400 • • • • • • • • • • • • • • • • • 3000 • • • • • • • • • • • • • • • • • 300 • • • • • • • • • • • • • • • • • 398 • • • • • • • • • • • • • • • • • 395 • • • • • • • • • • • • • • • • • 285 • • • • • • • • • • • • • • • • • 275 • • • • • • • • • • • • • • • • 200 • • • • • • • • • • • • • • • • • 100 • • • • • • • • • • • • • • • • 8220 • • • • • • • • • • • • • • • • • 8200 • • • • • • • • • • • • • • • • • 8100 • • • • • • • • • • • • • • • 800 • • • • • • • • • • • • • • • 770 • • • • • 750 1100 7300 ROTARY TOOL ATTACHMENT COMPATIBILITY KEY SHIELD KIT MODEL A550 Increased comfort from debris and sparks during cutting, grinding, sanding, and polishing applications. • Easy to Use – Spring friction design allows for quick adjustment and accessibility to accessory. • Compact for greater maneuverability. Use this chart to find out which attachments work with your tool. Adapters may be needed. * This attachment is compatible with the 4200 when used with the 4200 Attachment Adapter found in your Dremel 4200 kit. Grinding/Sharpening - 8193 Cutting - EZ456 4 ASSORTED ACCESSORIES ROTARY TOOL ATTACHMENTS CORDLESS CORDED ATTACHMENT MODEL NUMBER Cleaning/Polishing - 428 Miscellaneous - EZ402 TOOL MODEL NUMBER 22 107 481 Functions as an articulating drill press that rotates 90º, rotary tool holder, and flex-shaft tool stand. • Detents click the tool in place in 15º increments from vertical to horizontal. • “Crow’s Nest” provides on-board storage for Dremel accessories. • Durable, die-cast aluminum base. WORK STATION™ MODEL 220 - 01 Ideal for hard to reach places and fine detail work. • Quick connect attach system. • 36" long cable with new 5" bend radius provides more flexibility. • Comfort grip hand piece. • Integrated shaft lock button. • Holds up to 1/8" shank. • Works with collet system and Dremel chuck. FLEX SHAFT ATTACHMENT MODEL 225 - 01 TOOLS NOT INCLUDED WITH ATTACHMENTS Transfers the weight of the tool to the palm of your hand for improved tool balance and control. • Offers enhanced grip and comfort for detailed applications. • Provides optimal tool control when precision is required. • Attaches onto a rotary tool in place of its nose piece for quick and easy installation. • Includes 107 engraving cutter and tracing stencil. DETAILER'S GRIP MODEL A577 23 • Allows for sturdy controlled cuts with maximum visibility. • Easy depth adjustment. Set to the correct cutting depth for the material you are working on. • Includes cutting guide, 2 drywall cutting bits for cutting drywall for electrical boxes & air vents. • Includes 1 multipurpose cutting bit for making cuts in ceiling tile, wood, plastic, fiberglass, drywall, laminate and vinyl siding. MULTIPURPOSE CUTTING KIT MODEL 565 Converts your corded Rotary Tool into a bench mounted wood shaper. • Features an adjustable fence and large 8" x 6" worktable. • Slot, groove, sand and trim edges. SHAPER/ROUTER TABLE MODEL 231 Converts your corded Rotary Tool into a plunge router. • Clear base. • Two depth stops. • Includes edge guide and circle guide. • Rout circles, parallel to edge, signs and inlay work and decorative edges. PLUNGE ROUTER ATTACHMENT MODEL 335 - 01 Gets a Grip on Anything, Anywhere! • Portable vise holds work piece for projects such as woodworking, home projects, crafts and hobbies. • Clamps to any work surface up to 2-1/2" thick. • Rotates 360º and tilts 50º allowing user to lock the workpiece in any position. • Tool holder turns Dremel Rotary Tools into a stationary sander, grinder or polisher. • Removable clamping jaws creates a stand-alone bar clamp. MULTI-VISE™ MODEL 2500 - 01 24 569 570 • Allows for sturdy controlled cuts with maximum visibility. • Easy depth adjustment. Set to the correct cutting depth for the material you are working on. • Includes cutting guide and tile cutting bit. • Shape ceramic wall tile around fixtures or plumbing pipes. Not for use on ceramic floor tile. • Also available: Model 570 1/8" Grout Removal Bit (Not included with 568). For use on wall and floor grout! • Multiple slide depth adjustment. • 30° angle for controlled cutting. • Guides 180° apart to keep bit centered between tiles. • Easy screw-on mounting. • Excellent cutting visibility. • Includes 1/16" Grout Removal Bit – Model 569. Made of solid carbide, the bit will remove both wall and floor grout. TILE CUTTING KIT MODEL 566 GROUT REMOVAL ATTACHMENT MODEL 568 TOOLS NOT INCLUDED WITH ATTACHMENTS Enhances the versatility of your Dremel Rotary Tool by allowing you to get into hard-to-reach areas. • Quick connect system easily attaches to your rotary tool in place of the housing cap, no wrenches required. • Compact, durable design for those “hard-to-reach” places. RIGHT ANGLE ATTACHMENT MODEL 575 25 561 932 407 Works great on wood and all wood-like materials. • Make clean, straight perpendicular cuts up to 1/4" thick. • Quick connect system attaches to your rotary tool in seconds. • Includes blade. • Long-lasting steel blade. • 1-1/4" diameter, 48 teeth. • One blade per package. • For use with Mini Saw Attachment only. CIRCLE CUTTER AND STRAIGHT EDGE GUIDE MODEL 678 - 01 The simple way to cut circular holes in many types of materials. Convenient measurement guides in both inches and centimeters, so you can cut out the right-sized circle every time. • Makes circles from 3/4" -12" (1.9-30 cm). • Attaches quickly and easily without tools. • Depth adjustment allows easy setting of the correct cutting depth. • Straight Edge Guide allows routing or cutting in a straight line. • Includes 1/8" Multipurpose Cutting Bit – Model 561 (see p. 34). Stabilizes a handheld tool by providing an edge guide or serves as a work platform when the tool is mounted in a secure position. • Increased control during sanding and grinding applications. • Platform provides greater stability during edge sanding and sharpening. • Adjustable depth control for a precise finish. • Attaches onto a rotary tool in place of its nose piece for quick and easy installation. • Includes 407 1/2" 60 grit sanding drum, 932 aluminum oxide grinding stone and instructions. SANDING/GRINDING GUIDE™ MODEL A576 MINI SAW ATTACHMENT MODEL 670 RIP CROSSCUT BLADE MODEL 546 26 932 The Dremel chain saw sharpening attachment as well as the Dremel lawn mower and garden tool sharpening attachment are included together in one kit for your convenience. • Guide provides optimum sharpening angle. • Sharpens all rotary lawn mower blades. • Easily sharpen the dullest of chains. • Garden Tool Sharpening Attachment, Lawn Mower Sharpening Attachment, Chain Saw Sharpening Attachment • Wrench, Gauge • 2 Spacers • Instruction Manual • 4 Sharpening Stones Nos. 453, 454, 455, (see p. 30) and 932 (see p. 31) Easily sharpen the dullest of chains. • Sharpening Attachment • 3 Sharpening Stones Nos. 453, 454 and 455 (see p. 30) • Gauge • 2 Spacers • Wrench • Instruction Manual The fastest, easiest, safest way to sharpen your lawn mower blade and other garden tools. • Guide provides optimum sharpening angle. • Sharpens most rotary lawn mower blades. • Long-wearing ABS plastic material. • Includes grinding stone, #932 (see p.31). LAWN MOWER & GARDEN TOOL SHARPENER MODEL 675 LAWN MOWER, GARDEN TOOL, AND CHAIN SAW SHARPENING KIT MODEL A679 - 02 CHAIN SAW SHARPENING ATTACHMENT MODEL 1453 TOOLS NOT INCLUDED WITH ATTACHMENTS 27 9931 9933 9934 9935 9936 100 114 115 (x2) 116 117 (x2) 118 121 124 125 (x2) 134 144 190 191 192 (x2) 193 194 (x2) 196 (x2) 199 480 1/4" 5/16" 5/16" 5/16" 3/4" 6,4 mm 7,9 mm 7,9 mm 7,9 mm 19,1 mm 1/4" 5/16" 5/16" 1/4" 1/4" 1/8" 1/4" 5/16" 1/4" 6,4 mm 7,9 mm 7,9 mm 6,4 mm 6,4 mm 3,2 mm 6,4 mm 7,9 mm 6,4 5/16" 5/16" 3/32 1/8" 3/16" 5/64" 1/8" 7/32" 3/8" 7,9 mm 7,9 mm 2,4 mm 3,2 mm 4,8 mm 2,0 mm 3,2 mm 5,6 mm 9,5 mm HIGH SPEED CUTTERS High speed cutters can be used for shaping, hollowing, grooving, slotting, making tapered holes in soft metals, plastics and woods. # 199 cutter can be used to make small slits. STRUCTURED TOOTH TUNGSTEN CARBIDE CUTTERS Fast-cutting sharp teeth for greater material removal. Use on fiberglass, wood, plastic, epoxy, rubber, laminates, particle board and ceramic tile. CARVING/ENGRAVING NEW UNIVERSAL SHANK STANDARD ROTARY TOOL ACCESSORIES NO MORE HUNTING FOR THE RIGHT COLLET Over the next year, all Dremel rotary accessories are transitioning to a 1/8" shank standard. This means never having to search for the right collet again. Colet 480 will soon work for all rotary accessories. CARVING SOFT MATERIALS * As this conversion will take some time, please refer to accessory packaging to verify accessory shank size. 1/8" 28 7103 7105 7120 7122 7123 7134 7144 7150 9901 9902 9903 9904 9905 9906 9909 9910 9911 105 (x2) 106 (x2) 107 (x2) 108 109 110 111 113 7103 (x1) 7144 (x1) CARVING/ENGRAVING 5/64" 11/64" 17/64" 3/32" 3/16" 5/64" 3/32" 2,0 mm 4,4 mm 6,7 mm 2,4 mm 4,8 mm 2,0 mm 2,4 mm Dual Package 1/8" 3/32" 1/8" 3/32" 1/8" 1/8" 1/8" 1/8" 1/8" 3,2 mm 2,4 mm 3,2 mm 2,4 mm 3,2 mm 3,2 mm 3,2 mm 3,2 mm 3,2 mm ENGRAVING CUTTERS Quality cutters for detail engraving, carving, routing in wood, fiberglass, plastic and soft metals. DIAMOND WHEEL POINTS For fine detail work, engraving, carving, touch-up and finishing. Use on wood, jade, ceramic, glass, hardened steel, semi precious stones and other hard materials. Bits are covered with diamond particles. 1/32" 1/16" 3/32" 1/32" 1/16" 5/64" 1/32" 1/16" 0,8 mm 1,6 mm 2,4 mm 0,8 mm 1,6 mm 2,0 mm 0,8 mm 1,6 mm ENGRAVING ENGRAVING CARVING HARD MATERIALS SOFT MATERIALS HARD MATERIALS TUNGSTEN CARBIDE CUTTERS Use for shaping, smoothing and material removal. Use on hardened steel, stainless steel, cast iron, nonferrous metals, fired ceramics, plastics, hardwoods and other hard materials. Not for use with floor tile. 29 612 615 617 618 640 650 652 654 655 ROUTER BITS For routing, inlaying, and mortising in wood and other soft materials. Use with Dremel # 330 Router Attachment, # 335 Plunge Router Attachment, and # 231 Shaper/Router Table. Made of high speed steel. 3/32" 2,4 mm Piloted Beading 1/8" 3,2 mm Corner Rounding 1/4" 6,4 mm Core Box 1/2" 12,7 mm Chamfer 1/4" 6,4 mm V-Groove 1/8" 3,2 mm Straight 3/16" 4,8 mm Straight 1/4" 6,4 mm Straight 5/16" 7,9 mm Keyhole ROUTING ROTARY TOOL ACCESSORIES 30 453 (x2) 454 (x2) 455 (x2) 500 516 541 EZ541GR CHAIN SAW SHARPENING STONES – 453, 454, 455 Precision-ground for quick, easy sharpening of chain saw blades. Each package contains 2 stones. ALUMINUM OXIDE ABRASIVE WHEEL – 500 Perfect for cleaning, de-burring, removing rust, and polishing of most metals, including stainless steel. ALUMINUM OXIDE ABRASIVE POINT – 516 Abrasive point is great for finishing work and light de-burring. It can be used for paint and rust removal without removing any of the base material. ALUMINUM OXIDE GRINDING WHEEL – 541 Use for de-burring, rust removal and general purpose grinding. 2 Per Pack. Use 541 with Mandrel 402. EZ Lock™ 1-½" ALUMINUM OXIDE GRINDING WHEEL – EZ541GR For use with EZ Lock™ mandrel EZ402. 5/32" 3/16" 7/32" 4,0 mm 4,8 mm 5,6 mm 1" 25,4 mm 1/2" 12,7 mm 7/8" 22,2 mm 1-1/2" 38,1 mm GRINDING/SHARPENING FERROUS MATERIALS 31 971 997 8153 8175 8193 8215 911 932 941 945 952 953 (x2) 83142 83322 83702 84922 (x2) 85422 85602 85622 ALUMINIUM OXIDE GRINDING STONES (ORANGE/BROWN) Use on metals, castings, welded joints, rivets and rust. Ideal for sharpening, de-burring and general purpose grinding of most materials. 5/8" 1/8" 3/16" 3/8" 5/8" 1" 15,9 mm 3,2 mm 4,8 mm 9,5 mm 15,9 mm 25,4 mm 7/16" 3/8" 5/8" 3/16" 3/8" 1/4" 11,1 mm 9,5 mm 15,9 mm 4,8 mm 9,5 mm 6,4 mm SILICON CARBIDE GRINDING STONES (BLUE/GREEN) Designed to work well on stone, glass, ceramics, porcelain and non-ferrous metals. 9/32" 1/8" 1/8" 3/16" 25/32" 13/32" 1/2" 7,1 mm 3,2 mm 3,2 mm 4,8 mm 19,8 mm 10,3 mm 12,7 mm GRINDING/SHARPENING ROTARY TOOL ACCESSORIES FERROUS MATERIALS NON-FERROUS MATERIALS 32 EZ406 EZ409 EZ426CU EZ456 EZ456B EZ476 1 2 3 EZ L ock™ EZ Lock™ STARTER KIT – EZ406 Includes 1 EZ Lock™ mandrel and 5 reinforced cut-off wheels. EZ Lock™ 1-½" THIN REINFORCED CUT-OFF WHEEL – EZ409 For use with EZ Lock™. Reinforced cut-off wheels for cutting metal. 2X more cuts compared with 409. 5pc. EZ Lock™ 1-¼" REINFORCED CUT-OFF WHEEL – EZ426CU For use with EZ Lock™. Reinforced cut-off wheels for cutting metal. 2X more cuts compared with 420. 3pc. EZ Lock™ 1-½" REINFORCED CUT-OFF WHEEL – EZ456 For use with EZ Lock™. Reinforced cut-off wheels for cutting metal. 2X more cuts compared with 426. 5pc. EZ Lock™ 1-½" REINFORCED CUT-OFF WHEEL BULK PACK – EZ456B For use with EZ Lock™. Reinforced cut-off wheels for cutting metal. 12pc. Bulk pack. EZ Lock™ 1-½" REINFORCED CUT-OFF WHEEL – EZ476 For use with EZ Lock™. Reinforced cut-off wheel makes clean cuts in plastic. 5pc. Faster Accessory Changes – Easy As 1, 2, 3 Pul l – Twist – Release CUTTING 33 409 420 540 426 456 426B 543 EZ544 546 CUT-OFF WHEELS – 409, 420, 540 For slicing and cutting metal, wood and plastic. Cut-off wheels make it easy to cut or slot bolts, screws, sheet metal, thin wood and plastic. The cut-off wheel cuts only along its edge. Do not attempt to sand or cut curved holes with them. Use with mandrel 402. FIBERGLASS REINFORCED CUT-OFF WHEELS – 426, 456 Use with mandrel 402. 456 package includes a washer set only used with 456. Mandrel 402 is sold separately. CARBIDE CUTTING/SHAPING WHEEL – 543 For cutting and shaping on soft and hard woods, fiberglass, plastics and laminates. Do not use on metal. Mandrel included. Thickness .070" (1,8 mm). EZ Lock™ 1-½" CARBIDE CUTTING WHEEL – EZ544 For cutting and shaping on soft and hard woods, fiberglass, plastics and laminates. Do not use on metal. For use with EZ Lock™ mandrel. RIP/CROSSCUT BLADE – 546 For use with Mini Saw Attachment 670 only (page 25). Thickness .023" (0,6 mm). 1 - 1/4" 31,8 mm 1 - 1/2" 38,1 mm 15/16" 23,8 mm .025" thick 36 per pack 15/16" 23,8 mm .040" thick 20 per pack 1-1/4" 31,8 mm .0625" thick 5 per pack 1-1/4" 31,8 mm .045" thick 5 per pack 1-1/2" 38,1 mm .045" thick 10 per pack Cut-off wheel dispenser 20 per pack 1-1/4" 31,8 mm CUTTING ROTARY TOOL ACCESSORIES METAL (Limited use on wood and plastic) WOOD 34 545 EZ545 560 561 562 569 570 DIAMOND WHEEL – 545 Great for cutting, sawing and carving of hard materials such as marble, concrete, brick, porcelain, ceramics, hard epoxy, soft and hard wood. Mandrel 402 is included. Thickness .023" (0,6 mm). Do not run in excess of 20,000 RPM. EZ Lock™ 1-½" DIAMOND WHEEL – EZ545 For use with EZ Lock™. Diamond cutting wheel makes clean cuts in hard materials. 1 - 1/2" 38,1 mm 7/8" 22,2 mm 1/16" 1/8" 1,6 mm 3,2 mm CUTTING DRYWALL CUTTING BIT – 560* Gives you fast clean cuts in drywall. MULTIPURPOSE CUTTING BIT – 561* Cuts hardwood up to 3/8" and softwood up to 5/8". Also cuts plastic, fiberglass, drywall, laminate, aluminum & vinyl siding. TILE CUTTING BIT – 562* Cuts ceramic wall tile, cement board, and plaster. (Not for use on floor tile.) CARBIDE GROUT REMOVAL BITS – 569 AND 570† Ideal for replacing wall and floor grout or removing grout to replace broken tiles. * Use with cutting guide (page 23). † Use with grout removal guide (page 24). DRYWALL, MULTIPURPOSE, TILE AND GROUT HARD MATERIALS 35 414 422 429 423E 421 425 461 462 463 POLISHING ACCESSORIES – 414, 422, 429 Ideal for polishing metals and plastics. Using polishing compound # 421 with wheels produces a high luster. Use 414, 422 and 429 with Mandrel 401. POLISHING CLOTH – 423E Made to take a smooth finish and polish it to a high luster. Use with either EZ402, or with 402. Mandrels sold separately. POLISHING COMPOUND – 421 Use with felt or cloth accessories to polish metals and plastics. Compound will remove a dull oxidized film and/or light surface imperfections. A solid compound. EMERY IMPREGNATED POLISHING WHEEL – 425 Ideal for general polishing of most ferrous metal, stone, glass and ceramic. Use 425 with mandrel 402. RUBBER POLISHING POINTS – 461, 462, 463 Blue points for finishing and polishing all ferrous metals. Removes small burrs and scratch marks left by grinding and sanding, and cleans and defines grooves. Also effective on many stones and ceramics. Felt 1/2" dia. 6 per pack Felt 3/8" dia. Felt 1" dia. Cloth 1" dia. 1" 25,4 mm 1/4" 1/4" 1/4" 6,4 mm 6,4 mm 6,4 mm CLEANING/POLISHING ROTARY TOOL ACCESSORIES 36 520 538 403 404 405 428 442 443 530 531 532 535 536 537 POLISHING WHEEL – 520 Use for light stock removal and high luster polishing of metals and hard plastics. The wheel is impregnated with a silicon carbide abrasive and lubricant, eliminating the need for polishing compound. ABRASIVE BRUSH – 538 Dremel’s strongest and longest lasting brush. Extra-thick nylon bristles are coated with an abrasive grit for material removal on the toughest jobs. Use for de-burring metal or wood and for removing rust and paint. Do not run brush in excess of 20,000 RPM. BRISTLE BRUSHES – 403, 404, 405 Use for light de-burring, cleaning, polishing of silverware, jewelry and other precious metals; can use with polishing compound. CARBON STEEL BRUSHES – 428, 442, 443 Versatile brush for removing rust and corrosion, polish metal surfaces. De-burr and blend surface junctures, clean electrical components. STAINLESS STEEL BRUSHES – 530, 531, 532 Stainless steel brushes do not cause “after-rust” when used on corrosive-resistant materials like pewter, aluminum and stainless steel. BRASS BRUSHES – 535, 536, 537 Brass brushes are non-sparking and softer than steel. They will not scratch soft metals like gold, copper, brass. Do not run brushes in excess of 15,000 RPM. CLEANING/POLISHING 3/4" 1/2" 1/8" 19,1 mm 12,7 mm 3,2 mm 3/4" 1/2" 1/8" 19,1 mm 12,7 mm 3,2 mm 1" 25,4 mm 1/2" 12,7 mm 3/4" 1/2" 1/8" 19,1 mm 12,7 mm 3,2 mm 3/4" 1/2" 1/8" 19,1 mm 12,7 mm 3,2 mm 37 EZ471SA EZ472SA EZ473SA 502 503 504 505 801 511E 512E (x2) DETAIL ABRASIVE BRUSHES – EZ471SA, EZ472SA, EZ473SA Great for detail cleaning and light sanding. Use on metal, glass, wood, aluminum and plastics. Use with either EZ402, or 402. Mandrels sold separately. Not to be used in excess of 15,000 RPM. FINISHING ABRASIVE BUFFS – 511E, 512E Great for cleaning and light sanding. Use on metal, glass, wood, aluminum and plastics. The 512 fine-grit buff is particularly ideal for removing tarnish from brass. Use 511E and 512E with either EZ402, or 402. Mandrels sold separately. Not to be used in excess of 15,000 RPM. FLAPWHEELS – 502, 503, 504, 505 Flapwheels grind and polish flat or contoured surfaces. They are used most effectively as a finishing sander after heavier surface sanding and material removal is completed. CARBIDE SHAPING WHEEL – 801 A powerful shaping tool that quickly and efficiently removes material. Easily creates compound curves and works on a variety of materials including woods, fiberglass, laminates, plastic, and leather. Mandrel included. Not to be used for cutting. Grit: 36 120 220 Coarse Medium Fine Grit: 80 120 80 120 60 3/8" 3/8" 3/16" 3/16" 1-1/4" 9,5 mm 9,5 mm 4,8 mm 4,8 mm 31,8 mm SANDING ROTARY TOOL ACCESSORIES 180 280 Coarse Medium 320 Fine 38 430 431 (x6) 438 (x6) 446 (x6) 407 408 (x6) 432 (x6) 445 (x6) 411 412 413 EZ411SA (x5) EZ412SA (x5) EZ413SA (x5) EZ407SA SANDING BANDS – 407, 408, 430, 431, 432, 438, 445, 446 For rough shaping and smoothing wood and fiberglass; removing rust from metal surfaces; shaping rubber surfaces. Sander bands are easily replaceable on drums, and are available in packages of 6 each. EZ DRUM SANDING MANDREL – EZ407SA Resilient rubber sleeve forms around 4 tabs to keep accessory secure. Contoured collar holds entire assembly in place. Currently sold with one sanding band. More accessories to come! SANDING DISCS – 411, 412, 413, EZ411SA, EZ412SA, EZ413SA For rough shaping and smoothing wood and fiberglass; removing rust from metal surfaces; shaping rubber surfaces. Use 411, 412 and 413 with mandrel 402. 36 pieces per pack. Use EZ411SA, EZ412SA and EZ413SA only with the EZ402 mandrel. 5 pieces per pack. 1/4" diameter 1/2" diameter 3/4" diameter Grit: 60 120 240 60 120 240 Grit: 180 220 240 60 120 240 Coarse Medium Fine Coarse Medium Fine SANDING 39 401 402 EZ402 4486 4485 480 481 482 483 90930-04 90930-04 90931 90935 90826* 90827* 90828* 90936 90930* 90929* 90930* 90937 90940 MANDREL – 401 Use with 414, 422 and 429. MANDREL – 402 Use with 409, 411, 412, 413, 420, 423E, 425, 426, 429, 456, EZ471SA, EZ472SA, EZ473SA, 511E, 512E, 540, and 541. EZ Lock™ MANDREL – EZ402 Use with EZ407SA, EZ409, EZ426CU, EZ456, EZ411SA, EZ412SA, EZ413SA, EZ471SA, EZ472SA, EZ473SA, EZ476, 423E, 511E, 512E, EZ541GR, EZ544 and EZ545. DREMEL CHUCK – 4486 This chuck allows you to quickly and easily change accessories on Dremel Rotary Tools without changing collets. Accepts accessories with 1/32" - 1/8" shanks. Use with rotary tool models 100, 200, 275, 285, 300, 3000, 395, 398, 400, 4000, 750, 770, 780, 800 and 8200. Also use with Dremel attachments 212, 225, 575, and 961. QUICK CHANGE COLLET NUT SET – 4485 Includes Collet Nut and 4 Collets. For use with all Rotary Tools except models 1, 2 & 260, 270, 280 series 1 or earlier. Collets also available separately. 1/8" 3/32" 1/16" 1/32" 3,2 mm 2,4 mm 1,6 mm 0,8 mm MISCELLANEOUS * Available as service part only. ROTARY TOOL ACCESSORIES MANDRELS AND COLLETS CARBON MOTOR BRUSHES 100, 200, 275, 285, 4, 5, 300, 395, 595 & 3000 & 6 6000 1 & 2 398 732 Advantage 9000 400 XPR™ 4000 260 270, 280, 370 & 380 232 & 332 275, 285 & 395 1 & 2 275, 285, 300, 3, 4, 395 & 595 5 & 6 6000 1 & 2 BRUSH TOOLS TYPE BRUSH TOOLS TYPE 40 EZ495 90962 415 631-01 660 661 662DR 663DR 150 628 490 EZ TWIST NOSE CAP – EZ495 Loosen or tighten the collet and replace an accessory quickly and easily without the need for a wrench. WRENCH – 90962 For ease of changing bits. 3/8" x 1" DRESSING STONE – 415 Clean grinding wheels. Shape or reshape for desired applications. Available as service part only. COLLET FAN – 490 Blows dust away for greater visibility to work piece. Great for sanding, engraving, and carving. 1/8" DRILL BIT – 150 Available as service part only. DRILL BIT SET – 628 BRAD POINT DRILL BIT SET – 631-01 Titanium coated brad points stay on center and begin drilling immediately. For use on wood. 1/32" DRILL – 660 4 pc. per pack. *Use with 483 collet. 3/64" DRILL – 661 4 pc. per pack. *Use with 482 collet. GLASS DRILLING BITS – 662DR, 663DR Diamond tipped drill bits for use on glass and ceramic wall tile. Lubricant included. 1/8" 1/32" 3/64" 1/16" 5/64" 3/32" 7/64" 1/8" 3,2 mm 0,8 mm 1,2 mm 1,6 mm 2,0 mm 2,4 mm 2,8 mm 3,2 mm 1/8" 5/32" 3/16" 1/4" 1/32" 3/64" 1/8" 1/4" 3,2 mm 4,0 mm 4,8 mm 6,4 mm 0,8 mm 1,2 mm 3,2 mm 6,4 mm MISCELLANEOUS DRILL BITS OTHER NEW! NEW! use 482 use 483 41 MINI ACCESSORY KITS GENERAL PURPOSE KIT – 687-01 Everything you need to cut, carve, sand, grind, clean, and polish, plus a whole lot more! Carving/Engraving - 194 Grinding/Sharpening - 952, 85422 Cutting - 409 (x36), 426 Cleaning/Polishing - 414 (x2), 421, 428, 429 (x2) Sanding - 407, 408, 432 (x2) Miscellaneous - 401, 402 52 ASSORTED ACCESSORIES ROUTER BIT KIT – 692 For routing, inlaying and mortising in wood and other soft materials. Use with #330 Router Attachment, #335 Plunge Router Attachment, and #231 Shaper/Router Table. CUTTING KIT – 688-01 Reslot a screw, cut conduit, sheet metal, rusted hose clamps, plus a whole lot more! Cutting - 409 (x36), 420 (x24), 426 (x3), 540 (x5) Miscellaneous - 402 69 ASSORTED ACCESSORIES CARVING/ENGRAVING KIT – 689-01 Carve intricate details, etch glass, stoneware, terracotta, plus a whole lot more! Carving/Engraving - 105, 106, 107, 108, 7103, 7134 Grinding/Sharpening - 83142, 83322 , 83702, 84922 Miscellaneous - 481 11 ASSORTED ACCESSORIES SANDING/GRINDING KIT – 686-01 Sharpen lawn tools, remove rust, sand down a sticking door, and engrave on glass, plus a whole lot more! Grinding/Sharpening - 932, 8193, 84922, 85422 Cutting - 426 Sanding - 407, 408 (x4), 432 (x4), 412 (x15), 511 Miscellaneous - 402 18 ASSORTED ACCESSORIES CLEANING/POLISHING KIT – 684-01 Polish a variety of materials to a high luster, clean those tough-to-reach areas, plus a whole lot more! Cleaning/Polishing - 403, 404, 405, 414 (x6), 421, 422, 425 (x2), 428, 429 (x3), 520 Miscellaneous - 401, 402 20 ASSORTED ACCESSORIES Routing - 612, 615, 617, 618, 650, 654 6 ASSORTED ACCESSORIES 42 SUPER ACCESSORY KIT – 709-01 This versatile and re-usable accessory kit includes everything you need to cut, grind, sand, polish, drill, sharpen, clean and more. Carving/Engraving - 191 Grinding/Sharpening - 952, 953, 83142, 84922 Cutting - 409 (x12), 420 (x12), 426, 540 Cleaning/Polishing - 405, 414 (x4), 421, 422, 428, 429 (x4) Sanding - 407, 408 (x6), 432 (x6), 430, 431 (x6), 438 (x6), 411 (x12), 412 (x12), 413 (x12), 511E Miscellaneous - 401, 402, 415, 90962 110 ASSORTED ACCESSORIES ALL-PURPOSE ACCESSORY KIT – 710-05 This versatile and re-usable accessory kit includes everything you need to cut, grind, sand, polish, drill, sharpen, clean and more. Carving/Engraving - 191 Grinding/Sharpening - 8193, 83142 Cutting - EZ409, EZ456, EZ476, 540 Cleaning/Polishing - 414 (x5), 421, 423E, 428, 429 (x4) Sanding - 407, 408 (x15), 432 (x15), 430, 431 (x15), 438 (x15), 411 (x24), 412 (x24), 413 (x24), 511E, 512E Miscellaneous - 401 (x2), 402, EZ402, 90962 160 ASSORTED ACCESSORIES EZ LOCK™ CUTTING KIT – EZ688-01 Reslot a screw, cut conduit, sheet metal, rusted hose clamps, plus a whole lot more! Cutting - EZ409 (x3), EZ456 (x4), EZ476 (x3) Miscellaneous - EZ402 11 ASSORTED ACCESSORIES EZ LOCK™ SANDING/POLISHING KIT – EZ684-01 Polish a variety of materials to a high luster, clean those tough-to-reach areas, remove rust, plus a whole lot more! Cleaning/Polishing - 423E, 421 Sanding - EZ471SA, EZ472SA, 511E, 512E 7 ASSORTED ACCESSORIES EZ LOCK™ SANDING/GRINDING KIT – EZ686-01 Contains all of the sanding and grinding products a consumer needs. Grinding - 952, 84922, EZ541GR Cutting - 426 Sanding - EZ407SA, 408 (x3), 432 (x3), EZ411SA (x2), EZ412SA (x2), EZ413SA (x2) Miscellaneous - EZ402 18 ASSORTED ACCESSORIES 43 The Makers of Versatile Tool Systems™ OSCILLATING TOOLS 44 WHAT IS AN OSCILLATING TOOL? Multi-Max™ oscillating tools, like rotary tools, use a variety of accessories to accomplish a wide range of DIY tasks for repair, remodeling and restoration. However, rather than spinning like a rotary tool, Multi-Max™ oscillating tools use rapid side- to-side motion to cut, scrape, sand, remove grout, grind and more. You can rest assured that a Dremel Multi-Max™ oscillating tool will help you get the job done with superior versatility, durability, and control. 45 1 2 3 Repair. R emodel. R estore. Faster. ™ Limited Warranty CORDED OSCILLATING TOOLS For tool-less and secure accessory changes. Unlock – Inser t – Lock ACCESSORIES Quick Lock™ For tool-less and secure accessory changes. High-Performance 2.5 Amp Motor For the most demanding applications. Variable Speed For optimal performance and control in a variety of materials. Electronic Feedback Auto adjusts power and speed as needed. 65% More Power vs. the 6300 Separate On/Off Switch Retains speed setting for ease of use. Compact design Provides easy access to tight areas. Quick Fit™ Accessory Interface System For fast accessory changes without removing the clamping screw. 46 MULTI-MAX™ KIT MM40-01 • Dremel Multi-Max™ MM40 tool Cutting - MM480, MM482, MM450 Scraping - MM600 Sanding - MM14, MM70W (x10), MM70P (x5) Misc - Storage Case 21 ASSORTED PIECES 47 Repair. R emodel. R estore.™ Limited Warranty Separate On/Off Switch Retains speed setting for ease of use. Compact design Provides easy access to tight areas. CORDED OSCILLATING TOOLS ACCESSORIES Powerful 2.3 Amp Motor Easily tackles the toughest applications. Variable Speed For optimal performance and control in a variety of materials. Quick Fit™ For fast accessory changes without removing the clamping screw. 50% More Power vs. the 6300 Efficient Motor Runs cool and smooth under load. 48 • Dremel Multi-Max™ MM20 tool Cutting - MM450, MM480 Scraping - MM610 Sanding - MM11, MM70W (x8), MM70P (x3) Misc - Storage Case, Allen Wrench 17 ASSORTED PIECES MULTI-MAX™ KIT MM20-03 CORDED OSCILLATING TOOL OVERVIEW Model MM40 MM20 Amps 2.5 2.3 OPM 10,000–21,000 10,000–21,000 Electronic Feedback Control Yes No Number of Speeds Variable Variable Soft Grip Yes Yes Separate On/Off Yes Yes QuickFit™ Accessories Yes Yes Tool-less Accessory Change System Yes No Weight 2 lb. 15 oz. 2 lb. 7 oz. Warranty 2 year 2 year 49 Repair. R emodel. R estore. Unplugg ed.™ Limited Warranty Variable Speed For optimal performance and control in a variety of materials. High Performance Motor Cuts through a 1-1/4" oak door jamb. Quick Fit™ For fast accessory changes without removing the clamping screw. Compact design Provides easy access to tight areas. CORDLESS OSCILLATING TOOLS Separate On/Off Switch Retains speed setting for ease of use. Cordless For added convenience and versatility. ACCESSORIES 50 875 876 12VMAX 1-Hour Lithium-Ion Battery Charger 12VMAX 1-Hour Lithium-Ion Battery Pack • Cordless Dremel Multi-Max™ 8300 Tool • 1-Hour Battery Charger • 12VMAX Lithium-Ion Battery Packs (2) Cutting - MM440, MM450 Sanding - MM11, MM70W (x3) Misc - Storage Case, Allen Wrench 8 ASSORTED PIECES CORDLESS 12VMAX OSCILLATING TOOL ACCESSORIES CORDLESS MULTI-MAX™ KIT 8300-01 51 MM470 MM472 MM480 MM482 MM411 MM422 MM440 MM430 MM435 MM450 MM452 MM460 MM462 3" Wood & Drywall Saw Blade 3.5" Wood & Metal Saw Blade 3/4" Wood & Metal 1-1/4" Wood Flush Cut Blade 1-1/4" Wood & Metal Flush Cut Blade 3/8" Wood Flush Cut Blade Flush cut a baseboard to install new flooring or cut out drywall to install a new light switch. Choose from 13 blades to accomplish a variety of tough cuts. 3/4" Wood & Metal Flush Cut Blade 1-1/8” Wood Flush Cut Blade 3/4" Wood Flush Cut Blade Multi-Knife Drywall Jab Saw 3/4" Wood Flush Cut Blade 1-1/8" Wood & Metal Flush Cut Blade OSCILLATING TOOL ACCESSORIES CUTTING NEW! NEW! Dremel Multi-Max™ accessories undergo rigorous testing so you can feel assured that you are purchasing a product of proven value & performance. 52 MM720/MM725 MM723 MM422B (x3) MM440B (x3) MM450B (x3) MM472B (x3) MM491 MM721 (x3) MM722 (x3) MM900 MM920 Multi-Flex™ Spiral Blade Multi Flex™ Bracket MULTI-FLEX™ ACCESSORIES Multi-Flex™ Saw Blade Multi-Flex™ Carbide Blade 3-Pack Cutting Assortment (MM440, MM450, MM422) Bulk Packs - 3 per pack Carbide Rasp 60 Grit Diamond Paper Prepare surfaces for ceramic floor tile replacement. Use the diamond paper to remove cement, plaster, and thin-set mortar. Use the carbide rasp to grind and shape flat surfaces, cement, tile adhesives, stone and rasp wood. GRINDING 53 MM70P MM80P MM70W MM80W MM14 MM500 MM501 MM600 MM610 SCRAPING Rigid Scraper Blade Flexible Scraper Blade Use the rigid scraper blade for removing stuck vinyl flooring, carpeting and carpet pad, and the flexible scraper blade for projects such as removing old caulking around the tub or shower. 6 per pack: 80(2), 120(2), 240(2) Grit 6 per pack: 60(2), 120(2), 240(2) Grit 18 per pack: 80(6), 120(6), 240(6) Grit 18 per pack: 60(6), 120(6), 240(6) Grit Hook & Loop Pad Restore windows, make stuck doors work, and remove rust from metal. Available in assorted grit for sanding bare or painted wood and metal. Sanding Sheets - Paint Sanding Sheets - Wood SANDING Remove wall and floor grout to free a broken tile. Available in a 1/8" size and a 1/16" size. GROUT REMOVAL 1/16" Grout Removal Blade 1/8" Grout Removal Blade OSCILLATING TOOL ACCESSORIES 54 MM300 MM810 MM820 MM830 MM385-01 MM386 MM388 MM389 MULTI-MAX™ ATTACHMENTS 1-3/16" UNIVERSAL ADAPTER – MM300 Adapters allow use of Dremel accessories on most oscillating tools brands. Cutting Dept h Guide – MM810 Includes Depth Foot and Depth Stop. Dust Extraction COLLAR – MM830 NEW! NEW! ACCESSORY KITS NEW! NEW! ASSIST HANDLE – MM820 Only compatible on Multi-Max™ 6300. 5-Piece Multi-Max™ Cutting Kit MM422, MM440, MM450 (3) 6-Piece Multi-Max™ Cutting Kit MM300, MM462, MM470, MM450 (3) 14-Piece Multi-Max™ Accessory Kit MM300, MM482, MM610, MM450 (2), MM60W(9) 6-Piece Multi-Max™ Cutting Kit MM300, MM480, MM482, MM450 (3) 55 The Makers of Versatile Tool Systems™ SAW-MAX™ TOOL SYSTEM 56 WHAT IS A SAW-MAX™ TOOL? The new Dremel Saw-Max™ tool is reinventing cutting as we know it. This powerful tool performs smooth, precise cuts through a variety of materials including wood, metal, drywall, plastic, laminate flooring and floor and wall tile. Its compact design, adjustable foot and excellent line of sight make accurate one-handed operation simple. Offering two blade positions and a variety of unique attachments and accessories - this versatile tool system can help you make any straight, plunge, flush, angle or bevel cut. 57 Limited Warranty Versatile Cutting System Cuts wood, plastic, metal, tile, masonry & more. Two cutting wheel positions For straight, plunge and flush cuts. Powerful 6 Amp Motor For tough applications. Worm Drive Gearing For durability and power. Excellent line of sight For confident, precise cuts. Compact size and gripping zone For user friendly one handed operation. Adjustable Depth Guide And plunge action for precision and control. Dust Extraction Port For clean work environment. SAW-MAX™ TOOL SYSTEM • SAW-MAX™ SM20 Tool, 2 x 4 Guide, Dust Port Adapter • Storage Case Cutting - SM500, SM510, SM540, SM600 4 ASSORTED ACCESSORIES SAW-MAX™ KIT SM20-02 58 1 2 Interior Position For standard straight cuts. Exterior Position For flush cuts with SM600. Plunge Into Material For clean and precise cuts. One-handed Operation 2 CUTTING WHEEL POSITIONS 59 SM500 SM510 (x3) SM520 (x3) SM540 SM600 SAW-MAX™ ACCESSORIES Wood & Plastic Cutting Blade Metal Cutting Blade Masonry Cutting Blade Tile Cutting Blade Wood & Plastic Flush Cut Blade Dremel Saw-Max™ tool only uses Dremel Saw-Max™ accessories. CUTTING 60 SM842 TRSM810 TRSM800 SM840 SM844 1 2 3 4 SAW-MAX™ ATTACHMENTS Dust Port Adapter Miter Guide 2 x 4 Guide Straight Edge/ Circle Guide Angle cut to create miter joint (SM840) Bevel Cut for Corner Joint (SM840) Straight Cut to Butt Joint Trim at Door Jamb (SM840) Compound Miter Cuts for Crown Molding Joints (SM844) IDEAL FOR TRIMWORK NEW! Crown Moulding Guide 61 The Makers of Versatile Tool Systems™ TRIO™ TOOL SYSTEM 62 WHAT IS A TRIO™ TOOL? The Dremel Trio™ allows users to cut, sand, and rout using one multi-purpose tool. Featuring a system of accessories and attachments to increase versatility, Trio™ users can cut multiple materials including wood, plastic, drywall, sheet metal, wall tile and more without switching tools. The tool’s unique, 360-degree cutting technology and plunge-cut ability allows users to make quick and controlled cuts, while its unique, 90-degree pivoting handle facilitates added comfort, control, and accuracy. 63 Cut. Sand. Rout.™ Limited Warranty Variable Speed For maximum accessory versatility and precise tool control. 90º Pivoting Handle For superior comfort and control. Telescoping Foot For accurate depth control while cutting, sanding and routing. Lock-on Button For comfort during extended use. On Board Dust Extraction Port To maintain a clean workspace. Non-marring Base To protect delicate work pieces. Separate On/Off Switch Retains speed setting for ease of use. TRIO™ TOOL SYSTEM 64 TRSM800 TR820 • Dremel Trio™ Tool, Compact Depth Guide, Dust Port Adapter • Storage Case, Manual, Wrench Straight Edge/ Compact Depth Guide/Dust Port Adapter Circle Guide Cutting - TR563 Sanding - TR407, TR408 (x2), TR432 (x2), TR445 (x2) Routing - TR654 9 ASSORTED ACCESSORIES TRIO™ KIT 6800-02 TRIO™ ATTACHMENTS 65 TR560 TR561 TR562 TR563 TR407 TR408 (x6) TR432 (x6) TR445 (x6) TR451 Trio™ accessories are exclusive to the Dremel Trio™ tool system and not interchangeable with Dremel rotary tools. Dremel Trio™ tool only uses Dremel Trio™ 3/16" shaft accessories. PILOTED CUTTING BIT – TR560 Fast, clean cuts in drywall. MULTIPURPOSE CUTTING BIT (STEEL) – TR561 Softwood, plywood composites, drywall, acoustic tile, plastic and aluminum. WALL TILE CUTTING BIT – TR562 Wall tile, plaster, cement board and backer board. HARDWOOD/SHEET METAL BIT (CARBIDE) – TR563 Wood, plywood composites, laminate/engineered flooring and sheet metal. 1/2" SANDING BANDS – TR407, TR408, TR432, TR445 Shape wood and sand edges and curves. RANDOM ORBITAL SANDING KIT – TR451 Sand wood faces. TRIO™ TOOL ACCESSORIES TRIO™ CUTTING ACCESSORIES TRIO™ SANDING ACCESSORIES Grit: 60 120 240 NEW! 66 TR750 TR770 TR780 STRAIGHT ROUTER BIT KIT – TR750 STARTER ROUTER BIT KIT – TR770 SPECIALTY ROUTER BIT KIT – TR780 1/8" 3,2 mm Straight Router Bit 1/4" 6,4 mm Straight Router Bit 1/2" 12,7 mm Straight Router Bit 1/8" 3,2 mm Roman Ogee Router Bit 1/8" 3,2 mm Corner Rounding Router Bit 1/2" 12,7 mm V-Groove Router Bit 3/8" 9,5 mm Dovetail Router Bit 1/4" 6,4 mm Rabbet Router Bit 3/16" 4,8 mm Beading Router Bit 1/4" 6,4 mm Cove Router Bit 1/4" 6,4 mm Flush Trim Router Bit 1/4" 6,4 mm Chamfer Router Bit 1/4" 6,4 mm Roundnose Router Bit TRIO™ ROUTING ACCESSORIES 67 9924 9929 470 471 473 474 499 Multipurpose tool for wood burning, soldering, hot knife cutting of styrofoam and plastics, cutting and fusing rope. Max. Tip Temp: 1,050º F (565º C) | Volts: 110-120V, AC Watts: 30 | Tool Length: 7-3/8" (187,3 mm) Tool Weight: 2.5 oz. (71 g) • VersaTip™ Tool, Tool Stand, Handy Tip Storage Tube • 5 Tips (470, 471, 473, 474 & 499) VERSATIP™ KIT 1550 Limited Warranty VERSATIP™ MULTIPURPOSE TOOL Limited Warranty Identify and personalize your valuables. Use for decorative engraving. Engraves metal, glass, wood, plastic, and ceramics. Holding area allows for extended use. Soft grip adds extra comfort and control. Motor: 115V, AC/115V, 60Hz, .2 amps/0,2 A Strokes: 7,200/SPM | Tool Weight: 12 oz. (340 g) • Engraver Tool, Letter / Number Template • Carbide Point (9924) ENGRAVER KIT 290-01 Carbide Point – 9924 For most applications Diamond Point – 9929 For continuous use ENGRAVER ACCESSORIES Available only through Service Center. Soldering Tip – 470, General Purpose Tip – 471, Script Tip – 473, Fine Cutting Tip – 474, Hot Knife Tip – 499 VERSATIP™ ACCESSORIES ENGRAVER DP83846A DP83846A DsPHYTER - Single 10/100 Ethernet Transceiver Literature Number: SNLS063E DP83846A DsPHYTER — Single 10/100 Ethernet Transceiver ©2002 National Semiconductor Corporation www.national.com May 2002 DP83846A DsPHYTER — Single 10/100 Ethernet Transceiver General Description The DP83846A is a full feature single Physical Layer device with integrated PMD sublayers to support both 10BASE-T and 100BASE-TX Ethernet protocols over Category 3 (10 Mb/s) or Category 5 Unsheilded twisted pair cables. The DP83846A is designed for easy implementation of 10/100 Mb/s Ethernet home or office solutions. It interfaces to Twisted Pair media via an external transformer. This device interfaces directly to MAC devices through the IEEE 802.3u standard Media Independent Interface (MII) ensuring interoperability between products from different vendors. The DP83846A utilizes on chip Digital Signal Processing (DSP) technology and digital Phase Lock Loops (PLLs) for robust performance under all operating conditions, enhanced noise immunity, and lower external component count when compared to analog solutions. System Diagram Status 10BASE-T or MII 100BASE-TX 25 MHz Typical DsPHYTER application Ethernet MAC Magnetics RJ-45 Clock LEDs DP83846A 10/100 Mb/s DsPHYTER Features ■ IEEE 802.3 ENDEC, 10BASE-T transceivers and filters ■ IEEE 802.3u PCS, 100BASE-TX transceivers and filters ■ IEEE 802.3 compliant Auto-Negotiation ■ Output edge rate control eliminates external filtering for Transmit outputs ■ BaseLine Wander compensation ■ 5V/3.3V MAC interface ■ IEEE 802.3u MII (16 pins/port) ■ LED support (Link, Rx, Tx, Duplex, Speed, Collision) ■ Single register access for complete PHY status ■ 10/100 Mb/s packet loopback BIST (Built in Self Test) ■ Low-power 3.3V, 0.35um CMOS technology ■ Power consumption < 495mW (typical) ■ 5V tolerant I/Os ■ 80-pin LQFP package (12w) x (12l) x (1.4h) mm Applications ■ Network Interface Cards ■ PCMCIA Cards Obsolete 2 www.national.com DP83846A Figure 1. Block Diagram of the 10/100 DSP based core. SERIAL MANAGEMENT MII TX_CLK TXD[3:0] TX_ER TX_EN MDIO MDC COL CRS RX_ER RX_DV RXD[3:0] RX_CLK TRANSMIT CHANNELS & 100 Mb/s 10 Mb/s NRZ TO MANCHESTER ENCODER STATE MACHINES TRANSMIT FILTER LINK PULSE GENERATOR 4B/5B ENCODER PARALLEL TO SCRAMBLER NRZ TO NRZI ENCODER BINARY TO MLT-3 ENCODER 10/100 COMMON RECEIVE CHANNELS & 100 Mb/s 10 Mb/s MANCHESTER TO NRZ DECODER STATE MACHINES RECEIVE FILTER LINK PULSE DETECTOR 4B/5B DECODER DESCRAMBLER SERIAL TO PARALLEL NRZI TO NRZ DECODER MLT-3 TO 10/100 COMMON AUTO-NEGOTIATION STATE MACHINE REGISTERS AUTO 100BASE-TX 10BASE-T MII BASIC MODE PCS CONTROL PHY ADDRESS NEGOTIATION CLOCK CLOCK RECOVERY CLOCK RECOVERY CODE GROUP ALIGNMENT SMART SQUELCH RX_DATA RX_CLK RX_CLK RX_DATA TX_DATA TX_DATA TX_CLK SYSTEM CLOCK REFERENCE OUTPUT DRIVER TD± INPUT BUFFER BINARY DECODER ADAPTIVE RD± LED DRIVERS LEDS HARDWARE CONFIGURATION PINS GENERATION (AN_EN, AN0, AN1) CONTROL MII INTERFACE/CONTROL (PAUSE_EN) (LED_CFG, PHYAD) SERIAL BLW AND EQ COMP Obsolete 3 www.national.com DP83846A Table of Contents 1.0 Pin Descriptions . . . . . . . . . . . . . . . . . . . . . . . . . . . . . . . 5 1.1 MII Interface . . . . . . . . . . . . . . . . . . . . . . . . . . . . . . 5 1.2 10 Mb/s and 100 Mb/s PMD Interface . . . . . . . . . . 6 1.3 Clock Interface . . . . . . . . . . . . . . . . . . . . . . . . . . . . 6 1.4 Special Connections . . . . . . . . . . . . . . . . . . . . . . . 6 1.5 LED Interface . . . . . . . . . . . . . . . . . . . . . . . . . . . . . 7 1.6 Strapping Options/Dual Purpose Pins . . . . . . . . . . 7 1.7 Reset . . . . . . . . . . . . . . . . . . . . . . . . . . . . . . . . . . . 9 1.8 Power and Ground Pins . . . . . . . . . . . . . . . . . . . . . 9 1.9 Package Pin Assignments . . . . . . . . . . . . . . . . . . 10 2.0 Configuration . . . . . . . . . . . . . . . . . . . . . . . . . . . . . . . 11 2.1 Auto-Negotiation . . . . . . . . . . . . . . . . . . . . . . . . . 11 2.2 PHY Address and LEDs . . . . . . . . . . . . . . . . . . . 12 2.3 LED INTERFACES . . . . . . . . . . . . . . . . . . . . . . . 13 2.4 Half Duplex vs. Full Duplex . . . . . . . . . . . . . . . . . 13 2.5 MII Isolate Mode . . . . . . . . . . . . . . . . . . . . . . . . . 14 2.6 Loopback . . . . . . . . . . . . . . . . . . . . . . . . . . . . . . . 14 2.7 BIST . . . . . . . . . . . . . . . . . . . . . . . . . . . . . . . . . . . 14 3.0 Functional Description . . . . . . . . . . . . . . . . . . . . . . . . 15 3.1 802.3u MII . . . . . . . . . . . . . . . . . . . . . . . . . . . . . . 15 3.2 100BASE-TX TRANSMITTER . . . . . . . . . . . . . . . 16 3.3 100BASE-TX RECEIVER . . . . . . . . . . . . . . . . . . 20 3.4 10BASE-T TRANSCEIVER MODULE . . . . . . . . . 23 3.5 TPI Network Circuit . . . . . . . . . . . . . . . . . . . . . . . 24 3.6 ESD Protection . . . . . . . . . . . . . . . . . . . . . . . . . . 25 3.7 Crystal Oscillator Circuit . . . . . . . . . . . . . . . . . . . 26 4.0 Reset Operation . . . . . . . . . . . . . . . . . . . . . . . . . . . . . . 26 4.1 Hardware Reset . . . . . . . . . . . . . . . . . . . . . . . . . . 26 4.2 Software Reset . . . . . . . . . . . . . . . . . . . . . . . . . . 26 5.0 Register Block . . . . . . . . . . . . . . . . . . . . . . . . . . . . . . . 27 5.1 Register Definition . . . . . . . . . . . . . . . . . . . . . . . . 29 5.2 Extended Registers . . . . . . . . . . . . . . . . . . . . . . . 37 6.0 Electrical Specifications . . . . . . . . . . . . . . . . . . . . . . . 44 6.1 Reset Timing . . . . . . . . . . . . . . . . . . . . . . . . . . . . 46 6.2 PGM Clock Timing . . . . . . . . . . . . . . . . . . . . . . . 47 6.3 MII Serial Management Timing . . . . . . . . . . . . . . 47 6.4 100 Mb/s Timing . . . . . . . . . . . . . . . . . . . . . . . . . 48 6.5 10 Mb/s Timing . . . . . . . . . . . . . . . . . . . . . . . . . . 52 6.6 Loopback Timing . . . . . . . . . . . . . . . . . . . . . . . . . 57 6.7 Isolation Timing . . . . . . . . . . . . . . . . . . . . . . . . . . 59 7.0 Physical Dimensions . . . . . . . . . . . . . . . . . . . . . . . . . . 60 Obsolete 4 www.national.com DP83846A Connection Diagram COL TXD_3 TXD_2 IO_VDD IO_GND TXD_1 TXD_0 IO_GND TX_EN TX_CLK TX_ER CORE_VDD CORE_GND RESERVED RX_ER/PAUSE_EN RX_CLK RX_DV IO_VDD IO_GND RXD_0 RESERVED ANA_GND RBIAS ANA_VDD RESERVED ANA_GND ANA_VDD RESERVED ANA_GND RDRD+ ANA_VDD ANA_GND ANA_VDD ANA_GND TD+ TDANA_ GND SUB_GND RESERVED DP83846A DSPHYTER 1 2 3 4 5 6 7 8 9 10 11 12 13 14 15 16 17 18 19 20 61 62 63 64 65 66 67 68 69 70 71 72 73 74 75 76 77 78 79 80 60 59 58 57 56 55 54 53 52 51 50 49 48 47 46 45 44 43 42 41 40 39 38 37 36 35 34 33 32 31 30 29 28 27 26 25 24 23 22 21 CRS/LED_CFG RESET RESERVED IO_GND IO_VDD X2 X1 RESERVED RESERVED RESERVED RESERVED CORE_VDD CORE_GND RESERVED RESERVED SUB_GND RESERVED RESERVED SUB_GND RESERVED RXD_1 RXD_2 RXD_3 MDC MDIO IO_VDD IO_GND LED_DPLX/PHYAD0 LED_COL/PHYAD1 LED_GDLNK/PHYAD2 LED_TX/PHYAD3 LED_RX/PHYAD4 LED_SPEED AN_EN AN_1 AN_0 CORE_VDD CORE_GND RESERVED RESERVED Plastic Quad Flat Pack (LQFP) Order Number DP83846AVHG NS Package Number VHG-80A Obsolete 5 www.national.com DP83846A 1.0 Pin Descriptions The DP83846A pins are classified into the following interface categories (each interface is described in the sections that follow): — MII Interface — 10/100 Mb/s PMD Interface — Clock Interface — Special Connect Pins — LED Interface — Strapping Options/Dual Function pins — Reset — Power and Ground pins Note: Strapping pin option (BOLD) Please see Section 1.6 for strap definitions. Note: All DP83846A signal pins are I/O cells regardless of the particular use. Below definitions define the functionality of the I/O cells for each pin. 1.1 MII Interface Type: I Inputs Type: O Outputs Type: I/O Input/Output Type OD Open Drain Type: PD,PU Internal Pulldown/Pullup Type: S Strapping Pin (All strap pins except PHYAD[ 0:4] have internal pull-ups or pulldowns. If the default strap value is needed to be changed then an external 5 kΩ resistor should be used. Please see Table 1.6 on page 7 for details.) Signal Name Type LQFP Pin # Description MDC I 37 MANAGEMENT DATA CLOCK: Synchronous clock to the MDIO management data input/output serial interface which may be asynchronous to transmit and receive clocks. The maximum clock rate is 25 MHz with no minimum clock rate. MDIO I/O, OD 36 MANAGEMENT DATA I/O: Bi-directional management instruction/ data signal that may be sourced by the station management entity or the PHY. This pin requires a 1.5 kΩ pullup resistor. CRS/LED_CFG O, S 61 CARRIER SENSE: Asserted high to indicate the presence of carrier due to receive or transmit activity in 10BASE-T or 100BASE-TX Half Duplex Modes, while in full duplex mode carrier sense is asserted to indicate the presence of carrier due only to receive activity. COL O 60 COLLISION DETECT: Asserted high to indicate detection of a collision condition (simultaneous transmit and receive activity) in 10 Mb/s and 100 Mb/s Half Duplex Modes. While in 10BASE-T Half Duplex mode with Heartbeat enabled this pin are also asserted for a duration of approximately 1μs at the end of transmission to indicate heartbeat (SQE test). In Full Duplex Mode, for 10 Mb/s or 100 Mb/s operation, this signal is always logic 0. There is no heartbeat function during 10 Mb/s full duplex operation. TX_CLK O 51 TRANSMIT CLOCK: 25 MHz Transmit clock outputs in 100BASETX mode or 2.5 MHz in 10BASE-T mode derived from the 25 MHz reference clock. TXD[3] TXD[2] TXD[1] TXD[0]] I 59, 58, 55, 54 TRANSMIT DATA: Transmit data MII input pins that accept nibble data synchronous to the TX_CLK (2.5 MHz in 10BASE-T Mode or 25 MHz in 100BASE-TX mode. TX_EN I 52 TRANSMIT ENABLE: Active high input indicates the presence of valid nibble data on data inputs, TXD[3:0] for both 100 Mb/s or 10 Mb/s nibble mode. TX_ER I 50 TRANSMIT ERROR: In 100MB/s mode, when this signal is high and the corresponding TX_EN is active the HALT symbol is substituted for data. In 10 Mb/s this input is ignored. RX_CLK O, PU 45 RECEIVE CLOCK: Provides the 25 MHz recovered receive clocks for 100BASE-TX mode and 2.5 MHz for 10BASE-T nibble mode. Obsolete 6 www.national.com DP83846A 1.2 10 Mb/s and 100 Mb/s PMD Interface 1.3 Clock Interface 1.4 Special Connections RXD[3] RXD[2] RXD[1] RXD[0] O, PU/PD 38, 39, 40, 41 RECEIVE DATA: Nibble wide receive data (synchronous to corresponding RX_CLK, 25 MHz for 100BASE-TX mode, 2.5 MHz for 10BASE-T nibble mode). Data is driven on the falling edge of RX_CLK. RXD[2] has an internal pulldown resistor. The remaining RXD pins have pullups. RX_ER/PAUSE_EN S, O, PU 46 RECEIVE ERROR: Asserted high to indicate that an invalid symbol has been detected within a received packet in 100BASE-TX mode. RX_DV O 44 RECEIVE DATA VALID: Asserted high to indicate that valid data is present on the corresponding RXD[3:0] for nibble mode. Data is driven on the falling edge of the corresponding RX_CLK. Signal Name Type LQFP Pin # Description Signal Name Type LQFP Pin # Description TD+, TD- O 16, 17 Differential common driver transmit output. These differential outputs are configurable to either 10BASE-T or 100BASE-TX signaling. The DP83846A will automatically configure the common driver outputs for the proper signal type as a result of either forced configuration or Auto-Negotiation. RD-, RD+ I 10, 11 Differential receive input. These differential inputs can be configured to accept either 100BASE-TX or 10BASE-T signaling. The DP83846A will automatically configure the receive inputs to accept the proper signal type as a result of either forced configuration or Auto-Negotiation. Signal Name Type LQFP Pin # Description X1 I 67 REFERENCE CLOCK INPUT 25 MHz: This pin is the primary clock reference input for the DP83846A and must be connected to a 25 MHz 0.005% (±50 ppm) clock source. The DP83846A supports CMOS-level oscillator sources. X2 O 66 REFERENCE CLOCK OUTPUT 25 MHz: This pin is the primary clock reference output. Signal Name Type LQFP Pin # Description RBIAS I 3 Bias Resistor Connection. A 9.31 kΩ 1% resistor should be connected from RBIAS to ANA_GND. RESERVED I/O 1, 5, 8, 20, 21, 22, 47, 63, 68, 69, 70, 71, 74, 75, 77, 78, 80 RESERVED: These pins must be left unconnected. Obsolete 7 www.national.com DP83846A 1.5 LED Interface 1.6 Strapping Options/Dual Purpose Pins A 5 kΩ resistor should be used for pull-down or pull-up to change the default strap option. If the default option is required, then there is no need for external pull-up or pull down resistors, since the internal pull-up or pull down resistors will set the default value. Please note that the PHYAD[0:4] pins have no internal pull-ups or pull-downs and they must be strapped. Since these pins may have alternate functions after reset is deasserted, they should not be connected directly to Vcc or GND. Signal Name Type LQFP Pin # Description LED_DPLX/PHYAD0 S, O 33 FULL DUPLEX LED STATUS: Indicates Full-Duplex status. LED_COL/PHYAD1 S, O 32 COLLISION LED STATUS: Indicates Collision activity in Half Duplex mode. LED_GDLNK/PHYAD2 S, O 31 GOOD LINK LED STATUS: Indicates Good Link Status for 10BASET and 100BASE-TX. LED_TX/PHYAD3 S, O 30 TRANSMIT LED STATUS: Indicates transmit activity. LED is on for activity, off for no activity. LED_RX/PHYAD4 S, O 29 RECEIVE LED STATUS: Indicates receive activity. LED is on for activity, off for no activity. LED_SPEED O 28 SPEED LED STATUS: Indicates link speed; high for 100 Mb/s, low for 10 Mb/s. Signal Name Type LQFP Pin # Description LED_DPLX/PHYAD0 LED_COL/PHYAD1 LED_GDLNK/PHYAD2 LED_TX/PHYAD3 LED_RX/PHYAD4 S, O 33 32 31 30 29 PHY ADDRESS [4:0]: The DP83846A provides five PHY address pins, the state of which are latched into the PHYCTRL register at system Hardware-Reset. The DP83846A supports PHY Address strapping values 0 (<00000>) through 31 (<11111>). PHY Address 0 puts the part into the MII Isolate Mode. The MII isolate mode must be selected by strapping Phy Address 0; changing to Address 0 by register write will not put the Phy in the MII isolate mode. The status of these pins are latched into the PHY Control Register during Hardware-Reset. (Please note these pins have no internal pull-up or pull-down resistors and they must be strapped high or low using 5 kΩ resistors.) Obsolete 8 www.national.com DP83846A AN_EN AN_1 AN_0 S, O, PU 27 26 25 Auto-Negotiation Enable: When high enables Auto-Negotiation with the capability set by ANO and AN1 pins. When low, puts the part into Forced Mode with the capability set by AN0 and AN1 pins. AN0 / AN1: These input pins control the forced or advertised operating mode of the DP83846A according to the following table. The value on these pins is set by connecting the input pins to GND (0) or VCC (1) through 5 kΩ resistors. These pins should NEVER be connected directly to GND or VCC. The value set at this input is latched into the DP83846A at Hardware- Reset. The float/pull-down status of these pins are latched into the Basic Mode Control Register and the Auto_Negotiation Advertisement Register during Hardware-Reset. After reset is deasserted, these pins may switch to outputs so if pull-ups or pull-downs are implemented, they should be pulled through a 5kΩ resistor. The default is 111 since these pins have pull-ups. RX_ER/PAUSE_EN S, O, PU 46 PAUSE ENABLE: This strapping option allows advertisement of whether or not the DTE(MAC) has implemented both the optional MAC control sublayer and the pause function as specified in clause 31 and annex 31B of the IEEE 802.3x specification (Full Duplex Flow Control). When left floating the Auto-Negotiation Advertisement Register will be set to 0, indicating that Full Duplex Flow Control is not supported. When tied low through a 5 kΩ, the Auto-Negotiation Advertisement Register will be set to 1, indicating that Full Duplex Flow Control is supported. The float/pull-down status of this pin is latched into the Auto-Negotiation Advertisement Register during Hardware-Reset. CRS/LED_CFG S, O, PU 61 LED CONFIGURATION: This strapping option defines the polarity and function of the FDPLX LED pin. See Section 2.3 for further descriptions of this strapping option. Signal Name Type LQFP Pin # Description AN_EN AN1 AN0 Forced Mode 0 0 0 10BASE-T, Half-Duplex 0 0 1 10BASE-T, Full-Duplex 0 1 0 100BASE-TX, Half-Duplex 0 1 1 100BASE-TX, Full-Duplex AN_EN AN1 AN0 Advertised Mode 1 0 0 10BASE-T, Half/Full-Duplex 1 0 1 100BASE-TX, Half/Full-Duplex 1 1 0 10BASE-T Half-Duplex 100BASE-TX, Half-Duplex 1 1 1 10BASE-T, Half/Full-Duplex 100BASE-TX, Half/Full-Duplex Obsolete 9 www.national.com DP83846A 1.7 Reset 1.8 Power and Ground Pins Signal Name Type LQFP Pin # LLP Pin # Description RESET I 62 46 RESET: Active Low input that initializes or re-initializes the DP83846A. Asserting this pin low for at least 160 μs will force a reset process to occur which will result in all internal registers re-initializing to their default states as specified for each bit in the Register Block section and all strapping options are re-initialized. Signal Name LQFP Pin # Description TTL/CMOS INPUT/OUTPUT SUPPLY IO_VDD 35, 43, 57, 65 I/O Supply IO_GND 34, 42, 53, 56, 64 I/O Ground INTERNAL SUPPLY PAIRS CORE_VDD 24, 49, 72 Digital Core Supply CORE_GND 23, 48, 73 Digital Core Ground ANALOG SUPPLY PINS ANA_VDD 4, 7, 12, 14 Analog Supply ANA_GND 2, 6, 9, 13, 15, 18, Analog Ground SUBSTRATE GROUND SUB_GND 19, 76, 79 Bandgap Substrate connection Obsolete 10 www.national.com DP83846A 1.9 Package Pin Assignments LQFP Pin # Pin Name LQFP Pin # Pin Name 1 RESERVED 41 RXD_0 2 ANA_GND 42 IO_GND 3 RBIAS 43 IO_VDD 4 ANA_VDD 44 RX_DV 5 RESERVED 45 RX_CLK 6 ANA_GND 46 RX_ER/PAUSE_EN 7 ANA_VDD 47 RESERVED 8 RESERVED 48 CORE_GND 9 ANA_GND 49 CORE_VDD 10 RD- 50 TX_ER 11 RD+ 51 TX_CLK 12 ANA_VDD 52 TX_EN 13 ANA_GND 53 IO_GND 14 ANA_VDD 54 TXD_0 15 ANA_GND 55 TXD_1 16 TD+ 56 IO_GND 17 TD- 57 IO_VDD 18 ANA_GND 58 TXD_2 19 SUB_GND 59 TXD_3 20 RESERVED 60 COL 21 RESERVED 61 CRS/LED_CFG 22 RESERVED 62 RESET 23 CORE_GND 63 RESERVED 24 CORE_VDD 64 IO_GND 25 AN_0 65 IO_VDD 26 AN_1 66 X2 27 AN_EN 67 X1 28 LED_SPEED 68 RESERVED 29 LED_RX /PHYAD4 69 RESERVED 30 LED_TX /PHYAD3 70 RESERVED 31 LED_GDLNK/PHYAD2 71 RESERVED 32 LED_COL /PHYAD1 72 CORE_VDD 33 LED_FDPLX /PHYAD0 73 CORE_GND 34 IO_GND 74 RESERVED 35 IO_VDD 75 RESERVED 36 MDIO 76 SUB_GND 37 MDC 77 RESERVED 38 RXD_3 78 RESERVED 39 RXD_2 79 SUB_GND 40 RXD_1 80 RESERVED Obsolete 11 www.national.com DP83846A 2.0 Configuration This section includes information on the various configuration options available with the DP83846A. The configuration options described below include: — Device Configuration — Auto-Negotiation — PHY Address and LEDs — Half Duplex vs. Full Duplex — Isolate mode — Loopback mode — BIST 2.1 Auto-Negotiation The Auto-Negotiation function provides a mechanism for exchanging configuration information between two ends of a link segment and automatically selecting the highest performance mode of operation supported by both devices. Fast Link Pulse (FLP) Bursts provide the signalling used to communicate Auto-Negotiation abilities between two devices at each end of a link segment. For further detail regarding Auto-Negotiation, refer to Clause 28 of the IEEE 802.3u specification. The DP83846A supports four different Ethernet protocols (10 Mb/s Half Duplex, 10 Mb/s Full Duplex, 100 Mb/s Half Duplex, and 100 Mb/s Full Duplex), so the inclusion of Auto-Negotiation ensures that the highest performance protocol will be selected based on the advertised ability of the Link Partner. The Auto-Negotiation function within the DP83846A can be controlled either by internal register access or by the use of the AN_EN, AN1 and AN0 pins. 2.1.1 Auto-Negotiation Pin Control The state of AN_EN, AN0 and AN1 determines whether the DP83846A is forced into a specific mode or Auto-Negotiation will advertise a specific ability (or set of abilities) as given in Table 1. These pins allow configuration options to be selected without requiring internal register access. The state of AN_EN, AN0 and AN1, upon power-up/reset, determines the state of bits [8:5] of the ANAR register. The Auto-Negotiation function selected at power-up or reset can be changed at any time by writing to the Basic Mode Control Register (BMCR) at address 00h. 2.1.2 Auto-Negotiation Register Control When Auto-Negotiation is enabled, the DP83846A transmits the abilities programmed into the Auto-Negotiation Advertisement register (ANAR) at address 04h via FLP Bursts. Any combination of 10 Mb/s, 100 Mb/s, Half- Duplex, and Full Duplex modes may be selected. The BMCR provides software with a mechanism to control the operation of the DP83846A. The AN0 and AN1 pins do not affect the contents of the BMCR and cannot be used by software to obtain status of the mode selected. Bits 1 & 2 of the PHYSTS register are only valid if Auto-Negotiation is disabled or after Auto-Negotiation is complete. The Auto- Negotiation protocol compares the contents of the ANLPAR and ANAR registers and uses the results to automatically configure to the highest performance protocol between the local and far-end port. The results of Auto- Negotiation (Auto-Neg Complete, Duplex Status and Speed) may be accessed in the PHYSTS register. Auto-Negotiation Priority Resolution: — (1) 100BASE-TX Full Duplex (Highest Priority) — (2) 100BASE-TX Half Duplex — (3) 10BASE-T Full Duplex — (4) 10BASE-T Half Duplex (Lowest Priority) The Basic Mode Control Register (BMCR) at address 00h provides control for enabling, disabling, and restarting the Auto-Negotiation process. When Auto-Negotiation is disabled the Speed Selection bit in the BMCR controls switching between 10 Mb/s or 100 Mb/s operation, and the Duplex Mode bit controls switching between full duplex operation and half duplex operation. The Speed Selection and Duplex Mode bits have no effect on the mode of operation when the Auto-Negotiation Enable bit is set. The Basic Mode Status Register (BMSR) indicates the set of available abilities for technology types, Auto-Negotiation ability, and Extended Register Capability. These bits are permanently set to indicate the full functionality of the DP83846A (only the 100BASE-T4 bit is not set since the DP83846A does not support that function). Table 1. Auto-Negotiation Modes AN_EN AN1 AN0 Forced Mode 0 0 0 10BASE-T, Half-Duplex 0 0 1 10BASE-T, Full-Duplex 0 1 0 100BASE-TX, Half-Duplex 0 1 1 100BASE-TX, Full-Duplex AN_EN AN1 AN0 Advertised Mode 1 0 0 10BASE-T, Half/Full-Duplex 1 0 1 100BASE-TX, Half/Full-Duplex 1 1 0 10BASE-T Half-Duplex 100BASE-TX, Half-Duplex 1 1 1 10BASE-T, Half/Full-Duplex 100BASE-TX, Half/Full-Duplex Obsolete 12 www.national.com DP83846A The BMSR also provides status on: — Whether Auto-Negotiation is complete — Whether the Link Partner is advertising that a remote fault has occurred — Whether valid link has been established — Support for Management Frame Preamble suppression The Auto-Negotiation Advertisement Register (ANAR) indicates the Auto-Negotiation abilities to be advertised by the DP83846A. All available abilities are transmitted by default, but any ability can be suppressed by writing to the ANAR. Updating the ANAR to suppress an ability is one way for a management agent to change (force) the technology that is used. The Auto-Negotiation Link Partner Ability Register (ANLPAR) at address 05h is used to receive the base link code word as well as all next page code words during the negotiation. Furthermore, the ANLPAR will be updated to either 0081h or 0021h for parallel detection to either 100 Mb/s or 10 Mb/s respectively. The Auto-Negotiation Expansion Register (ANER) indicates additional Auto-Negotiation status. The ANER provides status on: — Whether a Parallel Detect Fault has occurred — Whether the Link Partner supports the Next Page function — Whether the DP83846A supports the Next Page function — Whether the current page being exchanged by Auto-Negotiation has been received — Whether the Link Partner supports Auto-Negotiation 2.1.3 Auto-Negotiation Parallel Detection The DP83846A supports the Parallel Detection function as defined in the IEEE 802.3u specification. Parallel Detection requires both the 10 Mb/s and 100 Mb/s receivers to monitor the receive signal and report link status to the Auto- Negotiation function. Auto-Negotiation uses this information to configure the correct technology in the event that the Link Partner does not support Auto-Negotiation but is transmitting link signals that the 100BASE-TX or 10BASET PMAs recognize as valid link signals. If the DP83846A completes Auto-Negotiation as a result of Parallel Detection, bits 5 and 7 within the ANLPAR register will be set to reflect the mode of operation present in the Link Partner. Note that bits 4:0 of the ANLPAR will also be set to 00001 based on a successful parallel detection to indicate a valid 802.3 selector field. Software may determine that negotiation completed via Parallel Detection by reading a zero in the Link Partner Auto-Negotiation Able bit once the Auto-Negotiation Complete bit is set. If configured for parallel detect mode and any condition other than a single good link occurs then the parallel detect fault bit will set. 2.1.4 Auto-Negotiation Restart Once Auto-Negotiation has completed, it may be restarted at any time by setting bit 9 (Restart Auto-Negotiation) of the BMCR to one. If the mode configured by a successful Auto- Negotiation loses a valid link, then the Auto-Negotiation process will resume and attempt to determine the configuration for the link. This function ensures that a valid configuration is maintained if the cable becomes disconnected. A renegotiation request from any entity, such as a management agent, will cause the DP83846A to halt any transmit data and link pulse activity until the break_link_timer expires (~1500 ms). Consequently, the Link Partner will go into link fail and normal Auto-Negotiation resumes. The DP83846A will resume Auto-Negotiation after the break_link_timer has expired by issuing FLP (Fast Link Pulse) bursts. 2.1.5 Enabling Auto-Negotiation via Software It is important to note that if the DP83846A has been initialized upon power-up as a non-auto-negotiating device (forced technology), and it is then required that Auto-Negotiation or re-Auto-Negotiation be initiated via software, bit 12 (Auto-Negotiation Enable) of the Basic Mode Control Register must first be cleared and then set for any Auto- Negotiation function to take effect. 2.1.6 Auto-Negotiation Complete Time Parallel detection and Auto-Negotiation take approximately 2-3 seconds to complete. In addition, Auto-Negotiation with next page should take approximately 2-3 seconds to complete, depending on the number of next pages sent. Refer to Clause 28 of the IEEE 802.3u standard for a full description of the individual timers related to Auto-Negotiation. 2.2 PHY Address and LEDs The 5 PHY address inputs pins are shared with the LED pins as shown below. The DP83846A can be set to respond to any of 32 possible PHY addresses. Each DP83846A or port sharing an MDIO bus in a system must have a unique physical address. Refer to Section 3.1.4, PHY Address Sensing section for more details. The state of each of the PHYAD inputs latched into the PHYCTRL register bits [4:0] at system power-up/reset depends on whether a pull-up or pull-down resistor has been installed for each pin. For further detail relating to the latch-in timing requirements of the PHY Address pins, as well as the other hardware configuration pins, refer to the Reset summary in Section 4.0. Since the PHYAD strap options share the LED output pins, the external components required for strapping and LED usage must be considered in order to avoid contention. Specifically, when the LED outputs are used to drive LEDs directly, the active state of each output driver is dependent on the logic level sampled by the corresponding PHYAD input upon power-up/reset. For example, if a given PHYAD input is resistively pulled low then the corresponding output will be configured as an active high driver. Conversely, if a given PHYAD input is resistively pulled high, then the corresponding output will be configured as an active low Table 2. PHY Address Mapping Pin # PHYAD Function LED Function 33 PHYAD0 Duplex 32 PHYAD1 COL 31 PHYAD2 Good Link 30 PHYAD3 TX Activity 29 PHYAD4 RX Activity 28 n/a Speed Obsolete 13 www.national.com DP83846A driver. Refer to Figure 2 for an example of a PHYAD connection to external components. In this example, the PHYAD strapping results in address 00011 (03h). The adaptive nature of the LED outputs helps to simplify potential implementation issues of these dual purpose pins. 2.3 LED INTERFACES The DP83846A has 6 Light Emitting Diode (LED) outputs, each capable to drive a maximum of 10 mA, to indicate the status of Link, Transmit, Receive, Collision, Speed, and Full/Half Duplex operation. The LED_CFG strap option is used to configure the LED_FDPLX output for use as an LED driver or more general purpose control pin. See the table below: The LED_FDPLX pin indicates the Half or Full Duplex configuration of the port in both 10 Mb/s and 100 Mb/s operation. Since this pin is also used as the PHY address strap option, the polarity of this indicator may be adjusted so that in the “active” (FULL DUPLEX selected) state it drives against the pullup/pulldown strap. In this configuration it is suitable for use as an LED. When LED_CFG is high this mode is selected and DsPHYTER automatically adjusts the polarity of the output. If LED_CFG is low, the output drives high to indicate the “active” state. In this configuration the output is suitable for use as a control pin. The LED_SPEED pin indicates 10 or 100 Mb/s data rate of the port. The standard CMOS driver goes high when operating in 100 Mb/s operation. Since this pin is not utilized as a strap option, it is not affected by polarity adjustment. The LED_GDLNK pin indicates the link status of the port. Since this pin is also used as the PHY address strap option, the polarity of this indicator is adjusted to be the inverse of the strap value. In 100BASE-T mode, link is established as a result of input receive amplitude compliant with TP-PMD specifications which will result in internal generation of signal detect. 10 Mb/s Link is established as a result of the reception of at least seven consecutive normal Link Pulses or the reception of a valid 10BASE-T packet. This will cause the assertion of GD_LINK. GD_LINK will deassert in accordance with the Link Loss Timer as specified in IEEE 802.3. The Collision LED indicates the presence of collision activity for 10 Mb/s or 100 Mb/s Half Duplex operation. This bit has no meaning in Full Duplex operation and will be deasserted when the port is operating in Full Duplex. Since this pin is also used as the PHY address strap option, the polarity of this indicator is adjusted to be the inverse of the strap value. In 10 Mb/s half duplex mode, the collision LED is based on the COL signal. When in this mode, the user should disable the Heartbeat (SQE) to avoid asserting the COL LED during transmission. See Section 3.4.2 for more information about the Heartbeat signal. The LED_RX and LED_TX pins indicate the presence of transmit and/or receive activity. Since these pins are also used in PHY address strap options, the polarity is adjusted to be the inverse of the respective strap values. 2.4 Half Duplex vs. Full Duplex The DP83846A supports both half and full duplex operation at both 10 Mb/s and 100 Mb/s speeds. Half-duplex is the standard, traditional mode of operation which relies on the CSMA/CD protocol to handle collisions and network access. In Half-Duplex mode, CRS responds to both transmit and receive activity in order to maintain compliance with IEEE 802.3 specification. Since the DP83846A is designed to support simultaneous transmit and receive activity it is capable of supporting fullduplex switched applications with a throughput of up to Figure 2. PHYAD Strapping and LED Loading Example LED_FDPLX LED_COL LED_GDLNK LED_TX LED_RX VCC 10kΩ 1kΩ 1kΩ 10kΩ 1kΩ 10kΩ 1kΩ 10kΩ 1kΩ PHYAD4= 0 PHYAD3 = 0 PHYAD2 = 0 PHYAD1 = 1 PHYAD0 = 1 10kΩ Table 3. LED Mode Select LED_CFG Mode Description 1 LED polarity adjusted 0 Duplex active-high Obsolete 14 www.national.com DP83846A 200 Mb/s per port when operating in 100BASE-TX mode. Because the CSMA/CD protocol does not apply to fullduplex operation, the DP83846A disables its own internal collision sensing and reporting functions and modifies the behavior of Carrier Sense (CRS) such that it indicates only receive activity. This allows a full-duplex capable MAC to operate properly. All modes of operation (100BASE-TX and 10BASE-T) can run either half-duplex or full-duplex. Additionally, other than CRS and Collision reporting, all remaining MII signaling remains the same regardless of the selected duplex mode. It is important to understand that while Auto-Negotiation with the use of Fast Link Pulse code words can interpret and configure to full-duplex operation, parallel detection can not recognize the difference between full and halfduplex from a fixed 10 Mb/s or 100 Mb/s link partner over twisted pair. As specified in 802.3u, if a far-end link partner is transmitting forced full duplex 100BASE-TX for example, the parallel detection state machine in the receiving station would be unable to detect the full duplex capability of the far-end link partner and would negotiate to a half duplex 100BASE-TX configuration (same scenario for 10 Mb/s). 2.5 MII Isolate Mode The DP83846A can be put into MII Isolate mode by writing to bit 10 of the BMCR register. In addition, the MII isolate mode can be selected by strapping in Physical Address 0. It should be noted that selecting Physical Address 0 via an MDIO write to PHYCTRL will not put the device in the MII isolate mode. When in the MII isolate mode, the DP83846A does not respond to packet data present at TXD[3:0], TX_EN, and TX_ER inputs and presents a high impedance on the TX_CLK, RX_CLK, RX_DV, RX_ER, RXD[3:0], COL, and CRS outputs. The DP83846A will continue to respond to all management transactions. While in Isolate mode, the TD± outputs will not transmit packet data but will continue to source 100BASE-TX scrambled idles or 10BASE-T normal link pulses. 2.6 Loopback The DP83846A includes a Loopback Test mode for facilitating system diagnostics. The Loopback mode is selected through bit 14 (Loopback) of the Basic Mode Control Register (BMCR). Writing 1 to this bit enables MII transmit data to be routed to the MII receive outputs. Loopback status may be checked in bit 3 of the PHY Status Register (PHYSTS). While in Loopback mode the data will not be transmitted onto the media in 100 Mb/s mode. To ensure that the desired operating mode is maintained, Auto-Negotiation should be disabled before selecting the Loopback mode. During 10BASE-T operation, in order to be standard compliant, the loopback mode loops MII transmit data to the MII receive data, however, Link Pulses are not looped back. In 100BASE-TX Loopback mode the data is routed through the PCS and PMA layers into the PMD sublayer before it is looped back. In addition to serving as a board diagnostic, this mode serves as a functional verification of the device. 2.7 BIST The DsPHYTER incorporates an internal Built-in Self Test (BIST) circuit to accommodate in-circuit testing or diagnostics. The BIST circuit can be utilized to test the integrity of the transmit and receive data paths. BIST testing can be performed with the part in the internal loopback mode or externally looped back using a loopback cable fixture. The BIST is implemented with independent transmit and receive paths, with the transmit block generating a continuous stream of a pseudo random sequence. The user can select a 9 bit or 15 bit pseudo random sequence from the PSR_15 bit in the PHY Control Register (PHYCTRL). The looped back data is compared to the data generated by the BIST Linear Feedback Shift Register (LFSR, which generates a pseudo random sequence) to determine the BIST pass/fail status. The pass/fail status of the BIST is stored in the BIST status bit in the PHYCTRL register. The status bit defaults to 0 (BIST fail) and will transition on a successful comparison. If an error (mis-compare) occurs, the status bit is latched and is cleared upon a subsequent write to the Start/Stop bit. Obsolete 15 www.national.com DP83846A 3.0 Functional Description 3.1 802.3u MII The DP83846A incorporates the Media Independent Interface (MII) as specified in Clause 22 of the IEEE 802.3u standard. This interface may be used to connect PHY devices to a MAC in 10/100 Mb/s systems. This section describes both the serial MII management interface as well as the nibble wide MII data interface. The serial management interface of the MII allows for the configuration and control of multiple PHY devices, gathering of status, error information, and the determination of the type and capabilities of the attached PHY(s). The nibble wide MII data interface consists of a receive bus and a transmit bus each with control signals to facilitate data transfer between the PHY and the upper layer (MAC). 3.1.1 Serial Management Register Access The serial management MII specification defines a set of thirty-two 16-bit status and control registers that are accessible through the management interface pins MDC and MDIO. The DP83846A implements all the required MII registers as well as several optional registers. These registers are fully described in Section 5. A description of the serial management access protocol follows. 3.1.2 Serial Management Access Protocol The serial control interface consists of two pins, Management Data Clock (MDC) and Management Data Input/Output (MDIO). MDC has a maximum clock rate of 25 MHz and no minimum rate. The MDIO line is bi-directional and may be shared by up to 32 devices. The MDIO frame format is shown below in Table 4: Typical MDIO Frame Format. The MDIO pin requires a pull-up resistor (1.5 kΩ) which, during IDLE and turnaround, will pull MDIO high. In order to initialize the MDIO interface, the station management entity sends a sequence of 32 contiguous logic ones on MDIO to provide the DP83846A with a sequence that can be used to establish synchronization. This preamble may be generated either by driving MDIO high for 32 consecutive MDC clock cycles, or by simply allowing the MDIO pull-up resistor to pull the MDIO pin high during which time 32 MDC clock cycles are provided. In addition 32 MDC clock cycles should be used to re-sync the device if an invalid start, opcode, or turnaround bit is detected. The DP83846A waits until it has received this preamble sequence before responding to any other transaction. Once the DP83846A serial management port has been initialized no further preamble sequencing is required until after a power-on/reset, invalid Start, invalid Opcode, or invalid turnaround bit has occurred. The Start code is indicated by a <01> pattern. This assures the MDIO line transitions from the default idle line state. Turnaround is defined as an idle bit time inserted between the Register Address field and the Data field. To avoid contention during a read transaction, no device shall actively drive the MDIO signal during the first bit of Turnaround. The addressed DP83846A drives the MDIO with a zero for the second bit of turnaround and follows this with the required data. Figure 3 shows the timing relationship between MDC and the MDIO as driven/received by the Station (STA) and the DP83846A (PHY) for a typical register read access. For write transactions, the station management entity writes data to the addressed DP83846A thus eliminating the requirement for MDIO Turnaround. The Turnaround time is filled by the management entity by inserting <10>. Figure 4 shows the timing relationship for a typical MII register write access. 3.1.3 Serial Management Preamble Suppression The DP83846A supports a Preamble Suppression mode as indicated by a one in bit 6 of the Basic Mode Status Register (BMSR, address 01h.) If the station management entity (i.e. MAC or other management controller) determines that all PHYs in the system support Preamble Sup- Table 4. Typical MDIO Frame Format MII Management Serial Protocol Read Operation <01><10> Write Operation <01><01><10> Figure 3. Typical MDC/MDIO Read Operation MDC MDIO 0 1 1 0 0 1 1 0 0 0 0 0 0 0 (STA) Idle Start Opcode (Read) PHY Address (PHYAD = 0Ch) Register Address (00h = BMCR) TA Register Data Z MDIO (PHY) Z Z Z 0 0 0 1 1 0 0 0 1 0 0 0 0 0 0 0 0 Z Idle Z Z Obsolete 16 www.national.com DP83846A pression by returning a one in this bit, then the station management entity need not generate preamble for each management transaction. The DP83846A requires a single initialization sequence of 32 bits of preamble following hardware/software reset. This requirement is generally met by the mandatory pull-up resistor on MDIO in conjunction with a continuous MDC, or the management access made to determine whether Preamble Suppression is supported. While the DP83846A requires an initial preamble sequence of 32 bits for management initialization, it does not require a full 32-bit sequence between each subsequent transaction. A minimum of one idle bit between management transactions is required as specified in IEEE 802.3u. 3.1.4 PHY Address Sensing The DP83846A provides five PHY address pins, the information is latched into the PHYCTRL register (address 19h, bits [4:0]) at device power-up/Hardware reset. The DP83846A supports PHY Address strapping values 0 (<00000>) through 31 (<11111>). Strapping PHY Address 0 puts the part into Isolate Mode. It should also be noted that selecting PHY Address 0 via an MDIO write to PHYCTRL will not put the device in Isolate Mode; Address 0 must be strapped in. 3.1.5 Nibble-wide MII Data Interface Clause 22 of the IEEE 802.3u specification defines the Media Independent Interface. This interface includes a dedicated receive bus and a dedicated transmit bus. These two data buses, along with various control and indicate signals, allow for the simultaneous exchange of data between the DP83846A and the upper layer agent (MAC). The receive interface consists of a nibble wide data bus RXD[3:0], a receive error signal RX_ER, a receive data valid flag RX_DV, and a receive clock RX_CLK for synchronous transfer of the data. The receive clock can operate at either 2.5 MHz to support 10 Mb/s operation modes or at 25 MHz to support 100 Mb/s operational modes. The transmit interface consists of a nibble wide data bus TXD[3:0], a transmit enable control signal TX_EN, and a transmit clock TX_CLK which runs at either 2.5 MHz or 25 MHz. Additionally, the MII includes the carrier sense signal CRS, as well as a collision detect signal COL. The CRS signal asserts to indicate the reception of data from the network or as a function of transmit data in Half Duplex mode. The COL signal asserts as an indication of a collision which can occur during half-duplex operation when both a transmit and receive operation occur simultaneously. 3.1.6 Collision Detect For Half Duplex, a 10BASE-T or 100BASE-TX collision is detected when the receive and transmit channels are active simultaneously. Collisions are reported by the COL signal on the MII. If the DP83846A is transmitting in 10 Mb/s mode when a collision is detected, the collision is not reported until seven bits have been received while in the collision state. This prevents a collision being reported incorrectly due to noise on the network. The COL signal remains set for the duration of the collision. If a collision occurs during a receive operation, it is immediately reported by the COL signal. When heartbeat is enabled (only applicable to 10 Mb/s operation), approximately 1μs after the transmission of each packet, a Signal Quality Error (SQE) signal of approximately 10 bit times is generated (internally) to indicate successful transmission. SQE is reported as a pulse on the COL signal of the MII. 3.1.7 Carrier Sense Carrier Sense (CRS) may be asserted due to receive activity, once valid data is detected via the squelch function during 10 Mb/s operation. During 100 Mb/s operation CRS is asserted when a valid link (SD) and two non-contiguous zeros are detected on the line. For 10 or 100 Mb/s Half Duplex operation, CRS is asserted during either packet transmission or reception. For 10 or 100 Mb/s Full Duplex operation, CRS is asserted only due to receive activity. CRS is deasserted following an end of packet. 3.2 100BASE-TX TRANSMITTER The 100BASE-TX transmitter consists of several functional blocks which convert synchronous 4-bit nibble data, as provided by the MII, to a scrambled MLT-3 125 Mb/s serial data stream. Because the 100BASE-TX TP-PMD is integrated, the differential output pins, TD±, can be directly routed to the magnetics. The block diagram in Figure 5 provides an overview of each functional block within the 100BASE-TX transmit section. The Transmitter section consists of the following functional blocks: — Code-group Encoder and Injection block (bypass option) — Scrambler block (bypass option) — NRZ to NRZI encoder block — Binary to MLT-3 converter / Common Driver Figure 4. Typical MDC/MDIO Write Operation MDC MDIO 0 1 0 1 0 1 1 0 0 0 0 0 0 0 (STA) Idle Start Opcode (Write) PHY Address (PHYAD = 0Ch) Register Address (00h = BMCR) TA Register Data Z 0 0 0 0 0 0 0 0 0 0 0 0 0 0 Z Idle 1 00 0 Z Z Obsolete 17 www.national.com DP83846A The bypass option for the functional blocks within the 100BASE-TX transmitter provides flexibility for applications where data conversion is not always required. The DP83846A implements the 100BASE-TX transmit state machine diagram as specified in the IEEE 802.3u Standard, Clause 24. 3.2.1 Code-group Encoding and Injection The code-group encoder converts 4-bit (4B) nibble data generated by the MAC into 5-bit (5B) code-groups for transmission. This conversion is required to allow control data to be combined with packet data code-groups. Refer to Table 5: 4B5B Code-Group Encoding/Decoding for 4B to 5B code-group mapping details. The code-group encoder substitutes the first 8-bits of the MAC preamble with a J/K code-group pair (11000 10001) upon transmission. The code-group encoder continues to replace subsequent 4B preamble and data nibbles with corresponding 5B code-groups. At the end of the transmit packet, upon the deassertion of Transmit Enable signal from the MAC, the code-group encoder injects the T/R code-group pair (01101 00111) indicating the end of frame. After the T/R code-group pair, the code-group encoder continuously injects IDLEs into the transmit data stream until the next transmit packet is detected (reassertion of Transmit Enable). 3.2.2 Scrambler The scrambler is required to control the radiated emissions at the media connector and on the twisted pair cable (for 100BASE-TX applications). By scrambling the data, the total energy launched onto the cable is randomly distributed over a wide frequency range. Without the scrambler, energy levels at the PMD and on the cable could peak beyond FCC limitations at frequencies related to repeating 5B sequences (i.e., continuous transmission of IDLEs). The scrambler is configured as a closed loop linear feedback shift register (LFSR) with an 11-bit polynomial. The output of the closed loop LFSR is X-ORd with the serial Figure 5. 100BASE-TX Transmit Block Diagram 4B5B Code-group encoder & injector scrambler nrz to nrzi encoder 5B parallel to serial TD± TX_CLK TXD[3:0] / tx_er 100BASE-TX Loopback mux binary to mlt-3 / Common Driver FROM PGM BP_4B5B BP_SCR mux DIV BY 5 Obsolete 18 www.national.com DP83846A NRZ data from the code-group encoder. The result is a scrambled data stream with sufficient randomization to decrease radiated emissions at certain frequencies by as much as 20 dB. The DP83846A uses the PHY_ID (pins PHYAD [4:0]) to set a unique seed value. 3.2.3 NRZ to NRZI Encoder After the transmit data stream has been serialized and scrambled, the data must be NRZI encoded in order to comply with the TP-PMD standard for 100BASE-TX transmission over Category-5 Unsheilded twisted pair cable. 3.2.4 Binary to MLT-3 Convertor / Common Driver The Binary to MLT-3 conversion is accomplished by converting the serial binary data stream output from the NRZI encoder into two binary data streams with alternately phased logic one events. These two binary streams are then fed to the twisted pair output driver which converts the voltage to current and alternately drives either side of the transmit transformer primary winding, resulting in a minimal current (20 mA max) MLT-3 signal. Refer to Figure 6. Figure 6. Binary to MLT-3 conversion D Q Q binary_in binary_plus binary_minus binary_in binary_plus binary_minus COMMON DRIVER MLT-3 differential MLT-3 Obsolete 19 www.national.com DP83846A Table 5. 4B5B Code-Group Encoding/Decoding Name PCS 5B Code-group MII 4B Nibble Code DATA CODES 0 11110 0000 1 01001 0001 2 10100 0010 3 10101 0011 4 01010 0100 5 01011 0101 6 01110 0110 7 01111 0111 8 10010 1000 9 10011 1001 A 10110 1010 B 10111 1011 C 11010 1100 D 11011 1101 E 11100 1110 F 11101 1111 IDLE AND CONTROL CODES H 00100 HALT code-group - Error code I 11111 Inter-Packet IDLE - 0000 (Note 1) J 11000 First Start of Packet - 0101 (Note 1) K 10001 Second Start of Packet - 0101 (Note 1) T 01101 First End of Packet - 0000 (Note 1) R 00111 Second End of Packet - 0000 (Note 1) INVALID CODES V 00000 V 00001 V 00010 V 00011 V 00101 V 00110 V 01000 V 01100 V 10000 V 11001 Note 1: Control code-groups I, J, K, T and R in data fields will be mapped as invalid codes, together with RX_ER asserted. Obsolete 20 www.national.com DP83846A The 100BASE-TX MLT-3 signal sourced by the TD± common driver output pins is slew rate controlled. This should be considered when selecting AC coupling magnetics to ensure TP-PMD Standard compliant transition times (3 ns < Tr < 5 ns). The 100BASE-TX transmit TP-PMD function within the DP83846A is capable of sourcing only MLT-3 encoded data. Binary output from the TD± outputs is not possible in 100 Mb/s mode. 3.3 100BASE-TX RECEIVER The 100BASE-TX receiver consists of several functional blocks which convert the scrambled MLT-3 125 Mb/s serial data stream to synchronous 4-bit nibble data that is provided to the MII. Because the 100BASE-TX TP-PMD is integrated, the differential input pins, RD±, can be directly routed from the AC coupling magnetics. See Figure 8 for a block diagram of the 100BASE-TX receive function. This provides an overview of each functional block within the 100BASE-TX receive section. The Receive section consists of the following functional blocks: — ADC — Input and BLW Compensation — Signal Detect — Digital Adaptive Equalization — MLT-3 to Binary Decoder — Clock Recovery Module — NRZI to NRZ Decoder — Serial to Parallel — DESCRAMBLER (bypass option) — Code Group Alignment — 4B/5B Decoder (bypass option) — Link Integrity Monitor — Bad SSD Detection The bypass option for the functional blocks within the 100BASE-TX receiver provides flexibility for applications where data conversion is not always required. 3.3.1 Input and Base Line Wander Compensation Unlike the DP83223V Twister, the DP83846A requires no external attenuation circuitry at its receive inputs, RD±. It accepts TP-PMD compliant waveforms directly, requiring only a 100Ω termination plus a simple 1:1 transformer. The DP83846A is completely ANSI TP-PMD compliant and includes Base Line Wander (BLW) compensation. The BLW compensation block can successfully recover the TPPMD defined “killer” pattern and pass it to the digital adaptive equalization block. BLW can generally be defined as the change in the average DC content, over time, of an AC coupled digital transmission over a given transmission medium. (i.e., copper wire). BLW results from the interaction between the low frequency components of a transmitted bit stream and the frequency response of the AC coupling component(s) within the transmission system. If the low frequency content of the digital bit stream goes below the low frequency pole of the AC coupling transformers then the droop characteristics of the transformers will dominate resulting in potentially serious BLW. The digital oscilloscope plot provided in Figure 7 illustrates the severity of the BLW event that can theoretically be generated during 100BASE-TX packet transmission. This event consists of approximately 800 mV of DC offset for a Figure 7. 100BASE-TX BLW Event Obsolete 21 www.national.com DP83846A Figure 8. Receive Block Diagram 4b/5b Decoder DEscrambler Digital adaptive Equalization MLT-3 to Binary decoder rd± RX_CLK RXD[3:0] / RX_ER InPUT BLW Compensation BP_4B5B BP_SCR Signal Detect nrzi to nrz decoder Code group alignment Serial to parallel mux mux LINK STATUS Clock Recovery Module CLOCK LINK Monitor ÷5 ADC AGC Obsolete 22 www.national.com DP83846A period of 120 μs. Left uncompensated, events such as this can cause packet loss. 3.3.2 Signal Detect The signal detect function of the DP83846A is incorporated to meet the specifications mandated by the ANSI FDDI TPPMD Standard as well as the IEEE 802.3 100BASE-TX Standard for both voltage thresholds and timing parameters. Note that the reception of normal 10BASE-T link pulses and fast link pulses per IEEE 802.3u Auto-Negotiation by the 100BASE-TX receiver do not cause the DP83846A to assert signal detect. 3.3.3 Digital Adaptive Equalization When transmitting data at high speeds over copper twisted pair cable, frequency dependent attenuation becomes a concern. In high-speed twisted pair signalling, the frequency content of the transmitted signal can vary greatly during normal operation based primarily on the randomness of the scrambled data stream. This variation in signal attenuation caused by frequency variations must be compensated for to ensure the integrity of the transmission. In order to ensure quality transmission when employing MLT-3 encoding, the compensation must be able to adapt to various cable lengths and cable types depending on the installed environment. The selection of long cable lengths for a given implementation, requires significant compensation which will over-compensate for shorter, less attenuating lengths. Conversely, the selection of short or intermediate cable lengths requiring less compensation will cause serious under-compensation for longer length cables. The compensation or equalization must be adaptive to ensure proper conditioning of the received signal independent of the cable length. The DP83846A utilizes a extremely robust equalization scheme referred as ‘Digital Adaptive Equalization’. Traditional designs use a pseudo adaptive equalization scheme that determines the approximate cable length by monitoring signal attenuation at certain frequencies. This attenuation value was compared to the internal receive input reference voltage. This comparison would indicate the amount of equalization to use. Although this scheme is used successfully on the DP83223V twister, it is sensitive to transformer mismatch, resistor variation and process induced offset. The DP83223V also required an external attenuation network to help match the incoming signal amplitude to the internal reference. The Digital Equalizer removes ISI (inter symbol interference) from the receive data stream by continuously adapting to provide a filter with the inverse frequency response of the channel. When used in conjunction with a gain stage, this enables the receive 'eye pattern' to be opened sufficiently to allow very reliable data recovery. Traditionally 'adaptive' equalizers selected 1 of N filters in an attempt to match the cables characteristics. This approach will typically leave holes at certain cable lengths, where the performance of the equalizer is not optimized. The DP83846A equalizer is truly adaptive to any length of cable up to 150m. 3.3.4 Clock Recovery Module The Clock Recovery Module (CRM) accepts 125 Mb/s MLT3 data from the equalizer. The DPLL locks onto the 125 Mb/s data stream and extracts a 125 MHz recovered clock. The extracted and synchronized clock and data are used as required by the synchronous receive operations as generally depicted in Figure 8. The CRM is implemented using an advanced all digital Phase Locked Loop (PLL) architecture that replaces sensitive analog circuitry. Using digital PLL circuitry allows the DP83846A to be manufactured and specified to tighter tolerances. 3.3.5 NRZI to NRZ In a typical application, the NRZI to NRZ decoder is required in order to present NRZ formatted data to the descrambler (or to the code-group alignment block, if the descrambler is bypassed, or directly to the PCS, if the receiver is bypassed). 3.3.6 Serial to Parallel The 100BASE-TX receiver includes a Serial to Parallel converter which supplies 5-bit wide data symbols to the PCS Rx state machine. 3.3.7 Descrambler A serial descrambler is used to de-scramble the received NRZ data. The descrambler has to generate an identical data scrambling sequence (N) in order to recover the original unscrambled data (UD) from the scrambled data (SD) as represented in the equations: Synchronization of the descrambler to the original scrambling sequence (N) is achieved based on the knowledge that the incoming scrambled data stream consists of scrambled IDLE data. After the descrambler has recognized 12 consecutive IDLE code-groups, where an unscrambled IDLE code-group in 5B NRZ is equal to five consecutive ones (11111), it will synchronize to the receive data stream and generate unscrambled data in the form of unaligned 5B code-groups. In order to maintain synchronization, the descrambler must continuously monitor the validity of the unscrambled data that it generates. To ensure this, a line state monitor and a hold timer are used to constantly monitor the synchronization status. Upon synchronization of the descrambler the hold timer starts a 722 μs countdown. Upon detection of sufficient IDLE code-groups (58 bit times) within the 722 μs period, the hold timer will reset and begin a new countdown. This monitoring operation will continue indefinitely given a properly operating network connection with good signal integrity. If the line state monitor does not recognize sufficient unscrambled IDLE code-groups within the 722 μs period, the entire descrambler will be forced out of the current state of synchronization and reset in order to reacquire synchronization. 3.3.8 Code-group Alignment The code-group alignment module operates on unaligned 5-bit data from the descrambler (or, if the descrambler is bypassed, directly from the NRZI/NRZ decoder) and converts it into 5B code-group data (5 bits). Code-group alignment occurs after the J/K code-group pair is detected. Once the J/K code-group pair (11000 10001) is detected, subsequent data is aligned on a fixed boundary. UD= (SD ⊕ N) SD UD N ⊕ ( ) = Obsolete 23 www.national.com DP83846A 3.3.9 4B/5B Decoder The code-group decoder functions as a look up table that translates incoming 5B code-groups into 4B nibbles. The code-group decoder first detects the J/K code-group pair preceded by IDLE code-groups and replaces the J/K with MAC preamble. Specifically, the J/K 10-bit code-group pair is replaced by the nibble pair (0101 0101). All subsequent 5B code-groups are converted to the corresponding 4B nibbles for the duration of the entire packet. This conversion ceases upon the detection of the T/R code-group pair denoting the End of Stream Delimiter (ESD) or with the reception of a minimum of two IDLE code-groups. 3.3.10 100BASE-TX Link Integrity Monitor The 100 Base TX Link monitor ensures that a valid and stable link is established before enabling both the Transmit and Receive PCS layer. Signal detect must be valid for 395us to allow the link monitor to enter the 'Link Up' state, and enable the transmit and receive functions. 3.3.11 Bad SSD Detection A Bad Start of Stream Delimiter (Bad SSD) is any transition from consecutive idle code-groups to non-idle code-groups which is not prefixed by the code-group pair /J/K. If this condition is detected, the DP83846A will assert RX_ER and present RXD[3:0] = 1110 to the MII for the cycles that correspond to received 5B code-groups until at least two IDLE code groups are detected. In addition, the False Carrier Sense Counter register (FCSCR) will be incremented by one. Once at least two IDLE code groups are detected, RX_ER and CRS become de-asserted. 3.4 10BASE-T TRANSCEIVER MODULE The 10BASE-T Transceiver Module is IEEE 802.3 compliant. It includes the receiver, transmitter, collision, heartbeat, loopback, jabber, and link integrity functions, as defined in the standard. An external filter is not required on the 10BASE-T interface since this is integrated inside the DP83846A. This section focuses on the general 10BASE-T system level operation. 3.4.1 Operational Modes The DP83846A has two basic 10BASE-T operational modes: — Half Duplex mode — Full Duplex mode Half Duplex Mode In Half Duplex mode the DP83846A functions as a standard IEEE 802.3 10BASE-T transceiver supporting the CSMA/CD protocol. Full Duplex Mode In Full Duplex mode the DP83846A is capable of simultaneously transmitting and receiving without asserting the collision signal. The DP83846A's 10 Mb/s ENDEC is designed to encode and decode simultaneously. 3.4.2 Collision Detection and SQE When in Half Duplex, a 10BASE-T collision is detected when the receive and transmit channels are active simultaneously. Collisions are reported by the COL signal on the MII. Collisions are also reported when a jabber condition is detected. The COL signal remains set for the duration of the collision. If the ENDEC is receiving when a collision is detected it is reported immediately (through the COL pin). When heartbeat is enabled, approximately 1 μs after the transmission of each packet, a Signal Quality Error (SQE) signal of approximately 10-bit times is generated to indicate successful transmission. SQE is reported as a pulse on the COL signal of the MII. The SQE test is inhibited when the PHY is set in full duplex mode. SQE can also be inhibited by setting the HEARTBEAT_DIS bit in the 10BTSCR register. 3.4.3 Carrier Sense Carrier Sense (CRS) may be asserted due to receive activity once valid data is detected via the squelch function. For 10 Mb/s Half Duplex operation, CRS is asserted during either packet transmission or reception. For 10 Mb/s Full Duplex operation, CRS is asserted only during receive activity. CRS is deasserted following an end of packet. 3.4.4 Normal Link Pulse Detection/Generation The link pulse generator produces pulses as defined in the IEEE 802.3 10BASE-T standard. Each link pulse is nominally 100 ns in duration and transmitted every 16 ms in the absence of transmit data. Link pulses are used to check the integrity of the connection with the remote end. If valid link pulses are not received, the link detector disables the 10BASE-T twisted pair transmitter, receiver and collision detection functions. When the link integrity function is disabled (FORCE_LINK_10 of the 10BTSCR register), good link is forced and the 10BASE-T transceiver will operate regardless of the presence of link pulses. 3.4.5 Jabber Function The jabber function monitors the DP83846A's output and disables the transmitter if it attempts to transmit a packet of longer than legal size. A jabber timer monitors the transmitter and disables the transmission if the transmitter is active beyond the Jab time (20-150 ms). Once disabled by the Jabber function, the transmitter stays disabled for the entire time that the ENDEC module's internal transmit enable is asserted. This signal has to be deasserted for approximately 250-750 ms (the “unjab” time) before the Jabber function re-enables the transmit outputs. The Jabber function is only relevant in 10BASE-T mode. 3.4.6 Automatic Link Polarity Detection and Correction The DP83846A's 10BASE-T transceiver module incorporates an automatic link polarity detection circuit. When seven consecutive inverted link pulses are received, inverted polarity is reported. Obsolete 24 www.national.com DP83846A A polarity reversal can be caused by a wiring error at either end of the cable, usually at the Main Distribution Frame (MDF) or patch panel in the wiring closet. The inverse polarity condition is latched in the 10BTSCR register. The DP83846A's 10BASE-T transceiver module corrects for this error internally and will continue to decode received data correctly. This eliminates the need to correct the wiring error immediately. The user is cautioned that if Auto Polarity Detection and Correction is disabled and inverted Polarity is detected but not corrected, the DsPHYTER may falsely report Good Link status and allow Transmission and Reception of inverted data. It is recommended that Auto Polarity Detection and Correction not be disabled during normal operation. 3.4.7 Transmit and Receive Filtering External 10BASE-T filters are not required when using the DP83846A, as the required signal conditioning is integrated into the device. Only isolation/step-up transformers and impedance matching resistors are required for the 10BASE-T transmit and receive interface. The internal transmit filtering ensures that all the harmonics in the transmit signal are attenuated by at least 30 dB. 3.4.8 Transmitter The encoder begins operation when the Transmit Enable input (TX_EN) goes high and converts NRZ data to preemphasized Manchester data for the transceiver. For the duration of TX_EN, the serialized Transmit Data (TXD) is encoded for the transmit-driver pair (TD±). TXD must be valid on the rising edge of Transmit Clock (TX_CLK). Transmission ends when TX_EN deasserts. The last transition is always positive; it occurs at the center of the bit cell if the last bit is a one, or at the end of the bit cell if the last bit is a zero. 3.4.9 Receiver The decoder consists of a differential receiver and a PLL to separate a Manchester encoded data stream into internal clock signals and data. The differential input must be externally terminated with a differential 100Ω termination network to accommodate UTP cable. The impedance of RD± (typically 1.1KΩ) is in parallel with the two 54.9Ω resistors as is shown in Figure 9 below to approximate the 100Ω termination. The decoder detects the end of a frame when no additional mid-bit transitions are detected. Within one and a half bit times after the last bit, carrier sense is de-asserted. 3.5 TPI Network Circuit Figure 9 shows the recommended circuit for a 10/100 Mb/s twisted pair interface. Below is a partial list of recommended transformers. Is is important that the user realize that variations with PCB and component characteristics requires that the application be tested to ensure that the circuit meets the requirements of the intended application. Pulse H1012B, PE-68515L Halo TG22-S052ND Valor PT4171 BELFUSE S558-5999-K2 BELFUSE S558-5999-46 Figure 9. 10/100 Mb/s Twisted Pair Interface RJ45 RDRD+ TDTD+ RDRD+ TDTD+ 1:1 49.9Ω 49.9 Ω 0.1μF* T1 1:1 Common Mode Chokes may be required. 54.9Ω 54.9Ω 0.1μF 0.1μF* Vdd * Place capacitors close to the transformer center taps Obsolete 25 www.national.com DP83846A 3.6 ESD Protection Typically, ESD precautions are predominantly in effect when handling the devices or board before being installed in a system. In those cases, strict handling procedures can be implemented during the manufacturing process to greatly reduce the occurrences of catastrophic ESD events. After the system is assembled, internal components are usually relatively immune from ESD events. In the case of an installed Ethernet system however, the network interface pins are still susceptible to external ESD events. For example, a category 5 cable being dragged across a carpet has the potential of developing a charge well above the typical ESD rating of a semiconductor device. For applications where high reliability is required, it is recommended that additional ESD protection diodes be added as shown below. There are numerous dual series connected diode pairs that are available specifically for ESD protection. The level of protection will vary dependent upon the diode ratings. The primary parameter that affects the level of ESD protection is peak forward surge current. Typical specifications for diodes intended for ESD protection range from 500mA (Motorola BAV99LT1 single pair diodes) to 12A (STM DA108S1 Quad pair array). The user should also select diodes with low input capacitance to minimize the effect on system performance. Since performance is dependent upon components used, board impedance characteristics, and layout, the circuit should be completely tested to ensure performance to the required levels. Figure 10. Typical DP83846A Network Interface with additional ESD protection RJ-45 DP83846A 10/100 TX± RX± Vcc Pin 1 Pin 2 Pin 3 Pin 6 Diodes placed on the device side of the isolation transformer 3.3V Vcc Vcc Obsolete 26 www.national.com DP83846A 3.7 Crystal Oscillator Circuit The DsPHYTER supports an external CMOS level oscillator source or a crystal resonator device. If an external clock source is used, X1 should be tied to the clock source and X2 should be left floating. In either case, the clock source must be a 25 MHz 0.005% (50 PPM) CMOS oscillator, or a 25 MHz (50 PPM), parallel, 20 pF load crystal resonator. Figure 11 below shows a typical connection for a crystal resonator circuit. The load capacitor values will vary with the crystal vendors; check with the vendor for the recommended loads. The oscillator circuit was designed to drive a parallel resonance AT cut crystal with a maximum drive level of 500μW. If a crystal is specified for a lower drive level, a current limiting resistor should be placed in series between X2 and the crystal. As a starting point for evaluating an oscillator circuit, if the requirements for the crystal are not known, CL1 and CL2 should be set at 22 pF, and R1 should be set at 0Ω. 4.0 Reset Operation The DP83846A can be reset either by hardware or software. A hardware reset may be accomplished by asserting the RESET pin after powering up the device (this is required) or during normal operation when a reset is needed. A software reset is accomplished by setting the reset bit in the Basic Mode Control Register. While either the hardware or software reset can be implemented at any time after device initialization, a hardware reset, as described in Section 4.1 must be provided upon device power-up/initialization. Omitting the hardware reset operation during the device power-up/initialization sequence can result in improper device operation. 4.1 Hardware Reset A hardware reset is accomplished by applying a low pulse (TTL level), with a duration of at least 160 μs, to the RESET pin during normal operation. This will reset the device such that all registers will be reset to default values and the hardware configuration values will be re-latched into the device (similar to the power-up/reset operation). 4.2 Software Reset A software reset is accomplished by setting the reset bit (bit 15) of the Basic Mode Control Register (BMCR). The period from the point in time when the reset bit is set to the point in time when software reset has concluded is approximately 160 μs. The software reset will reset the device such that all registers will be reset to default values and the hardware configuration values will be re-latched into the device (similar to the power-up/reset operation). Software driver code should wait 500 μs following a software reset before allowing further serial MII operations with the DP83846A. Figure 11. Crystal Oscillator Circuit X1 X2 CL1 CL2 R1 Obsolete 27 www.national.com DP83846A 5.0 Register Block Table 6. Register Map Offset Access Tag Description Hex Decimal 00h 0 RW BMCR Basic Mode Control Register 01h 1 RO BMSR Basic Mode Status Register 02h 2 RO PHYIDR1 PHY Identifier Register #1 03h 3 RO PHYIDR2 PHY Identifier Register #2 04h 4 RW ANAR Auto-Negotiation Advertisement Register 05h 5 RW ANLPAR Auto-Negotiation Link Partner Ability Register (Base Page) 05h 5 RW ANLPARNP Auto-Negotiation Link Partner Ability Register (Next Page) 06h 6 RW ANER Auto-Negotiation Expansion Register 07h 7 RW ANNPTR Auto-Negotiation Next Page TX 08h-Fh 8-15 RESERVED RESERVED Extended Registers 10h 16 RO PHYSTS PHY Status Register 11h-13h 17-19 RESERVED RESERVED 14h 20 RW FCSCR False Carrier Sense Counter Register 15h 21 RW RECR Receive Error Counter Register 16h 22 RW PCSR PCS Sub-Layer Configuration and Status Register 17h 23 RW RESERVED RESERVED 18h 24 RW RESERVED RESERVED 19h 25 RW PHYCTRL PHY Control Register 1Ah 26 RW 10BTSCR 10Base-T Status/Control Register 1Bh 27 RW CDCTRL CD Test Control Register 1Ch-1Fh 28 RW RESERVED RESERVED Obsolete 28 www.national.com DP83846A Register Name Addr Tag Bit 15 Bit 14 Bit 13 Bit 12 Bit 11 Bit 10 Bit 9 Bit 8 Bit 7 Bit 6 Bit 5 Bit 4 Bit 3 Bit 2 Bit 1 Bit 0 Basic Mode Control Register 00h BMCR Reset Loopback Speed Select Auto-Neg Enable Power down Isolate Restart Auto-Neg Duplex Collision Test Reserved Reserved Reserved Reserved Reserved Reserved Reserved Basic Mode Status Register 01h BMSR 100Base- T4 100Base- TX FDX 100Base- TX HDX 10Base- T FDXx 10Base- T HDX Reserved Reserved Reserved Reserved MF Preamble Suppress Auto-Neg Complete Remote Fault Auto-Neg Ability Link Status Jabber Detect Extended Capability PHY Identifier Register 1 02h PHYIDR1 OUI MSB OUI MSB OUI MSB OUI MSB OUI MSB OUI MSB OUI MSB OUI MSB OUI MSB OUI MSB OUI MSB OUI MSB OUI MSB OUI MSB OUI MSB OUI MSB PHY Identifier Register 2 03h PHYIDR2 OUI LSB OUI LSB OUI LSB OUI LSB OUI LSB OUI LSB VNDR_ MDL VNDR_ MDL VNDR_ MDL VNDR_ MDL VNDR_ MDL VNDR_ MDL MDL_ REV MDL_ REV MDL_ REV MDL_ REV Auto-Negotiation Advertisement Register 04h ANAR Next Page Ind Reserved Remote Fault Reserved Reserved PAUSE T4 TX_FD TX 10_FD 10 Protocol Selection Protocol Selection Protocol Selection Protocol Selection Protocol Selection Auto-Negotiation Link Partner Ability Register (Base Page) 05h ANLPAR Next Page Ind ACK Remote Fault Reserved Reserved Reserved T4 TX_FD TX 10_FD 10 Protocol Selection Protocol Selection Protocol Selection Protocol Selection Protocol Selection Auto-Negotiation Link Partner Ability Register Next Page 05h ANLPARNP Next Page Ind ACK Message Page ACK2 Toggle Code Code Code Code Code Code Code Code Code Code Code Auto-Negotiation Expansion Register 06h ANER Reserved Reserved Reserved Reserved Reserved Reserved Reserved Reserved Reserved Reserved Reserved PDF LP_NP_ ABLE NP_ ABLE PAGE_ RX LP_AN_ ABLE Auto-Negotiation Next Page TX Register 07h ANNPTR Next Page Ind Reserved Message Page ACK2 TOG_TX CODE CODE CODE CODE CODE CODE CODE CODE CODE CODE CODE RESERVED 08-0fh Reserved Reserved Reserved Reserved Reserved Reserved Reserved Reserved Reserved Reserved Reserved Reserved Reserved Reserved Reserved Reserved Reserved EXTENDED REGISTERS PHY Status Register 10h PHYSTS Reserved Reserved Rx Err Latch Polarity Status False Carrier Sense Signal Detect Descram Lock Page Receive Reserved Remote Fault Jabber Detect Auto-Neg Complete Loopback Status Duplex Status Speed Status Link Status RESERVED 11-13h Reserved Reserved Reserved Reserved Reserved Reserved Reserved Reserved Reserved Reserved Reserved Reserved Reserved Reserved Reserved Reserved Reserved False Carrier Sense Counter Register 14h FCSCR Reserved Reserved Reserved Reserved Reserved Reserved Reserved Reserved FCSCNT FCSCNT FCSCNT FCSCNT FCSCNT FCSCNT FCSCNT FCSCNT Receive Error Counter Register 15h RECR Reserved Reserved Reserved Reserved Reserved Reserved Reserved Reserved RXERCNT RXERCNT RXERCNT RXERCNT RXERCNT RXERCNT RXERCNT RXERCNT PCS Sub-Layer Configuration and Status Register 16h PCSR Reserved Reserved Reserved BYP_ 4B5B FREE_ CLK TQ_EN SD_FOR CE_PMA SD_ OPTION Unused Reserved FORCE_ 100_OK Reserved Reserved NRZI_ BYPASS SCRAM_ BYPASS DE SCRAM_ BYPASS RESERVED 17-18h Reserved Reserved Reserved Reserved Reserved Reserved Reserved Reserved Reserved Reserved Reserved Reserved Reserved Reserved Reserved Reserved Reserved PHY Control Register 19h PHYCTRL Unused Unused Unused Unused PSR_15 BIST_ STATUS BIST_ START BP_ STRETC H PAUSE_ STS LED_ CNFG LED_ CNFG PHY ADDR PHY ADDR PHY ADDR PHY ADDR PHY ADDR 10Base-T Status/Control Register 1Ah 10BTSCR Unused Unused Unused Unused Unused Unused Unused Loopback _10_dis LP_DIS Force_ Link_10 Force_ Pol_Cor Polarity Autopol _Dis Reserved Hrtbeat _Dis Jabber _Dis CD Test Control Register 1Bh CDCTRL CD_Enabl e DCD_ Comp FIL_TTL rise- Time[1] rise- Time[0] fallTime[1] fallTime[0] cdTestEn Reserved Reserved Reserved cdPattEn_ 10 cdPatEn_ 100 10meg_ patt_gap cdPatt- Sel[1] cdPatt- Sel[0] RESERVED 1C-1Fh Reserved Reserved Reserved Reserved Reserved Reserved Reserved Reserved Reserved Reserved Reserved Reserved Reserved Reserved Reserved Reserved Reserved Obsolete 29 www.national.com DP83846A 5.1 Register Definition In the register definitions under the ‘Default’ heading, the following definitions hold true: — RW=Read Write access — SC=Register sets on event occurrence and Self-Clears when event ends — RW/SC =Read Write access/Self Clearing bit — RO=Read Only access — COR = Clear on Read — RO/COR=Read Only, Clear on Read — RO/P=Read Only, Permanently set to a default value — LL=Latched Low and held until read, based upon the occurrence of the corresponding event — LH=Latched High and held until read, based upon the occurrence of the corresponding event Obsolete 30 www.national.com DP83846A Table 7. Basic Mode Control Register (BMCR), Address 0x00 Bit Bit Name Default Description 15 Reset 0, RW/SC Reset: 1 = Initiate software Reset / Reset in Process. 0 = Normal operation. This bit, which is self-clearing, returns a value of one until the reset process is complete. The configuration is re-strapped. 14 Loopback 0, RW Loopback: 1 = Loopback enabled. 0 = Normal operation. The loopback function enables MII transmit data to be routed to the MII receive data path. Setting this bit may cause the descrambler to lose synchronization and produce a 500 μs “dead time” before any valid data will appear at the MII receive outputs. 13 Speed Selection Strap, RW Speed Select: When auto-negotiation is disabled writing to this bit allows the port speed to be selected. 1 = 100 Mb/s. 0 = 10 Mb/s. 12 Auto-Negotiation Enable Strap, RW Auto-Negotiation Enable: Strap controls initial value at reset. 1 = Auto-Negotiation Enabled - bits 8 and 13 of this register are ignored when this bit is set. 0 = Auto-Negotiation Disabled - bits 8 and 13 determine the port speed and duplex mode. 11 Power Down 0, RW Power Down: 1 = Power down. 0 = Normal operation. Setting this bit powers down the PHY. Only the register block is enabled during a power down condition. 10 Isolate 0, RW Isolate: 1 = Isolates the Port from the MII with the exception of the serial management. 0 = Normal operation. 9 Restart Auto- Negotiation 0, RW/SC Restart Auto-Negotiation: 1 = Restart Auto-Negotiation. Re-initiates the Auto-Negotiation process. If Auto- Negotiation is disabled (bit 12 = 0), this bit is ignored. This bit is self-clearing and will return a value of 1 until Auto-Negotiation is initiated, whereupon it will selfclear. Operation of the Auto-Negotiation process is not affected by the management entity clearing this bit. 0 = Normal operation. 8 Duplex Mode Strap, RW Duplex Mode: When auto-negotiation is disabled writing to this bit allows the port Duplex capability to be selected. 1 = Full Duplex operation. 0 = Half Duplex operation. 7 Collision Test 0, RW Collision Test: 1 = Collision test enabled. 0 = Normal operation. When set, this bit will cause the COL signal to be asserted in response to the assertion of TX_EN within 512-bit times. The COL signal will be de-asserted within 4-bit times in response to the de-assertion of TX_EN. 6:0 RESERVED 0, RO RESERVED: Write ignored, read as 0. Obsolete 31 www.national.com DP83846A Table 8. Basic Mode Status Register (BMSR), address 0x01 Bit Bit Name Default Description 15 100BASE-T4 0, RO/P 100BASE-T4 Capable: 0 = Device not able to perform 100BASE-T4 mode. 14 100BASE-TX Full Duplex 1, RO/P 100BASE-TX Full Duplex Capable: 1 = Device able to perform 100BASE-TX in full duplex mode. 13 100BASE-TX Half Duplex 1, RO/P 100BASE-TX Half Duplex Capable: 1 = Device able to perform 100BASE-TX in half duplex mode. 12 10BASE-T Full Duplex 1, RO/P 10BASE-T Full Duplex Capable: 1 = Device able to perform 10BASE-T in full duplex mode. 11 10BASE-T Half Duplex 1, RO/P 10BASE-T Half Duplex Capable: 1 = Device able to perform 10BASE-T in half duplex mode. 10:7 RESERVED 0, RO RESERVED: Write as 0, read as 0. 6 MF P reamble Suppression 1, RO/P Preamble suppression Capable: 1 = Device able to perform management transaction with preamble suppressed, 32-bits of preamble needed only once after reset, invalid opcode or invalid turnaround. 0 = Normal management operation. 5 Auto-Negotiation Complete 0, RO Auto-Negotiation Complete: 1 = Auto-Negotiation process complete. 0 = Auto-Negotiation process not complete. 4 Remote Fault 0, RO/LH Remote Fault: 1 = Remote Fault condition detected (cleared on read or by reset). Fault criteria: Far End Fault Indication or notification from Link Partner of Remote Fault. 0 = No remote fault condition detected. 3 Auto-Negotiation Ability 1, RO/P Auto Negotiation Ability: 1 = Device is able to perform Auto-Negotiation. 0 = Device is not able to perform Auto-Negotiation. 2 Link Status 0, RO/LL Link Status: 1 = Valid link established (for either 10 or 100 Mb/s operation). 0 = Link not established. The criteria for link validity is implementation specific. The occurrence of a link failure condition will causes the Link Status bit to clear. Once cleared, this bit may only be set by establishing a good link condition and a read via the management interface. 1 Jabber Detect 0, RO/LH Jabber Detect: This bit only has meaning in 10 Mb/s mode. 1 = Jabber condition detected. 0 = No Jabber. This bit is implemented with a latching function, such that the occurrence of a jabber condition causes it to set until it is cleared by a read to this register by the management interface or by a reset. 0 Extended Capability 1, RO/P Extended Capability: 1 = Extended register capabilities. 0 = Basic register set capabilities only. Obsolete 32 www.national.com DP83846A The PHY Identifier Registers #1 and #2 together form a unique identifier for the DP83846A. The Identifier consists of a concatenation of the Organizationally Unique Identifier (OUI), the vendor's model number and the model revision number. A PHY may return a value of zero in each of the 32 bits of the PHY Identifier if desired. The PHY Identifier is intended to support network management. National's IEEE assigned OUI is 080017h. Table 9. PHY Identifier Register #1 (PHYIDR1), address 0x02 Bit Bit Name Default Description 15:0 OUI_MSB <0010 0000 0000 0000>, RO/P OUI Most Significant Bits: Bits 3 to 18 of the OUI (080017h) are stored in bits 15 to 0 of this register. The most significant two bits of the OUI are ignored (the IEEE standard refers to these as bits 1 and 2). Table 10. PHY Identifier Register #2 (PHYIDR2), address 0x03 Bit Bit Name Default Description 15:10 OUI_LSB <01 0111>, RO/P OUI Least Significant Bits: Bits 19 to 24 of the OUI (080017h) are mapped to bits 15 to 10 of this register respectively. 9:4 VNDR_MDL <00 0010>, RO/P Vendor Model Number: The six bits of vendor model number are mapped to bits 9 to 4 (most significant bit to bit 9). 3:0 MDL_REV <0011>, RO/P Model Revision Number: Four bits of the vendor model revision number are mapped to bits 3 to 0 (most significant bit to bit 3). This field will be incremented for all major device changes. Obsolete 33 www.national.com DP83846A This register contains the advertised abilities of this device as they will be transmitted to its link partner during Auto-Negotiation. Table 11. Auto-Negotiation Advertisement Register (ANAR), address 0x04 Bit Bit Name Default Description 15 NP 0, RW Next Page Indication: 0 = Next Page Transfer not desired. 1 = Next Page Transfer desired. 14 RESERVED 0, RO/P RESERVED by IEEE: Writes ignored, Read as 0. 13 RF 0, RW Remote Fault: 1 = Advertises that this device has detected a Remote Fault. 0 = No Remote Fault detected. 12:11 RESERVED 0, RW RESERVED for Future IEEE use: Write as 0, Read as 0 10 PAUSE Strap, RW PAUSE: The default is set by the strap option for PAUSE_EN pin. 1 = Advertise that the DTE (MAC) has implemented both the optional MAC control sublayer and the pause function as specified in clause 31 and annex 31B of 802.3u. 0= No MAC based full duplex flow control. 9 T4 0, RO/P 100BASE-T4 Support: 1= 100BASE-T4 is supported by the local device. 0 = 100BASE-T4 not supported. 8 TX_FD Strap, RW 100BASE-TX Full Duplex Support: 1 = 100BASE-TX Full Duplex is supported by the local device. 0 = 100BASE-TX Full Duplex not supported. 7 TX Strap, RW 100BASE-TX Support: 1 = 100BASE-TX is supported by the local device. 0 = 100BASE-TX not supported. 6 10_FD Strap, RW 10BASE-T Full Duplex Support: 1 = 10BASE-T Full Duplex is supported by the local device. 0 = 10BASE-T Full Duplex not supported. 5 10 Strap, RW 10BASE-T Support: 1 = 10BASE-T is supported by the local device. 0 = 10BASE-T not supported. 4:0 Selector <00001>, RW Protocol Selection Bits: These bits contain the binary encoded protocol selector supported by this port. <00001> indicates that this device supports IEEE 802.3u. Obsolete 34 www.national.com DP83846A This register contains the advertised abilities of the Link Partner as received during Auto-Negotiation. The content changes after the successful auto negotiation if Next-pages are supported. Table 12. Auto-Negotiation Link Partner Ability Register (ANLPAR) (BASE Page), address 0x05 Bit Bit Name Default Description 15 NP 0, RO Next Page Indication: 0 = Link Partner does not desire Next Page Transfer. 1 = Link Partner desires Next Page Transfer. 14 ACK 0, RO Acknowledge: 1 = Link Partner acknowledges reception of the ability data word. 0 = Not acknowledged. The Device's Auto-Negotiation state machine will automatically control the this bit based on the incoming FLP bursts. 13 RF 0, RO Remote Fault: 1 = Remote Fault indicated by Link Partner. 0 = No Remote Fault indicated by Link Partner. 12:10 RESERVED 0, RO RESERVED for Future IEEE use: Write as 0, read as 0. 9 T4 0, RO 100BASE-T4 Support: 1 = 100BASE-T4 is supported by the Link Partner. 0 = 100BASE-T4 not supported by the Link Partner. 8 TX_FD 0, RO 100BASE-TX Full Duplex Support: 1 = 100BASE-TX Full Duplex is supported by the Link Partner. 0 = 100BASE-TX Full Duplex not supported by the Link Partner. 7 TX 0, RO 100BASE-TX Support: 1 = 100BASE-TX is supported by the Link Partner. 0 = 100BASE-TX not supported by the Link Partner. 6 10_FD 0, RO 10BASE-T Full Duplex Support: 1 = 10BASE-T Full Duplex is supported by the Link Partner. 0 = 10BASE-T Full Duplex not supported by the Link Partner. 5 10 0, RO 10BASE-T Support: 1 = 10BASE-T is supported by the Link Partner. 0 = 10BASE-T not supported by the Link Partner. 4:0 Selector <0 0000>, RO Protocol Selection Bits: Link Partner’s binary encoded protocol selector. Obsolete 35 www.national.com DP83846A This register contains additional Local Device and Link Partner status information. Table 13. Auto-Negotiation Link Partner Ability Register (ANLPAR) Next Page, address 0x05 Bit Bit Name Default Description 15 NP 0, RO Next Page Indication: 1 = Link Partner desires Next Page Transfer. 0 = Link Partner does not desire Next Page Transfer. 14 ACK 0, RO Acknowledge: 1 = Link Partner acknowledges reception of the ability data word. 0 = Not acknowledged. The Device's Auto-Negotiation state machine will automatically control the this bit based on the incoming FLP bursts. Software should not attempt to write to this bit. 13 MP 0, RO Message Page: 1 = Message Page. 0 = Unformatted Page. 12 ACK2 0, RO Acknowledge 2: 1 = Link Partner does have the ability to comply to next page message. 0 = Link Partner does not have the ability to comply to next page message. 11 Toggle 0, RO Toggle: 1 = Previous value of the transmitted Link Code word equalled 0. 0 = Previous value of the transmitted Link Code word equalled 1. 10:0 CODE <000 0000 0000>, RO Code: This field represents the code field of the next page transmission. If the MP bit is set (bit 13 of this register), then the code shall be interpreted as a “Message Page”, as defined in annex 28C of Clause 28. Otherwise, the code shall be interpreted as an “Unformatted Page”, and the interpretation is application specific. Table 14. Auto-Negotiate Expansion Register (ANER), address 0x06 Bit Bit Name Default Description 15:5 RESERVED 0, RO RESERVED: Writes ignored, Read as 0. 4 PDF 0, RO/LH/COR Parallel Detection Fault: 1 = A fault has been detected via the Parallel Detection function. 0 = A fault has not been detected. 3 LP_NP_ABLE 0, RO Link Partner Next Page Able: 1 = Link Partner does support Next Page. 0 = Link Partner does not support Next Page. 2 NP_ABLE 1, RO/P Next Page Able: 1 = Indicates local device is able to send additional “Next Pages”. 1 PAGE_RX 0, RO/LH/COR Link Code Word Page Received: 1 = Link Code Word has been received, cleared on a read. 0 = Link Code Word has not been received. 0 LP_AN_ABLE 0, RO Link Partner Auto-Negotiation Able: 1 = indicates that the Link Partner supports Auto-Negotiation. 0 = indicates that the Link Partner does not support Auto-Negotiation. Obsolete 36 www.national.com DP83846A This register contains the next page information sent by this device to its Link Partner during Auto-Negotiation. Table 15. Auto-Negotiation Next Page Transmit Register (ANNPTR), address 0x07 Bit Bit Name Default Description 15 NP 0, RW Next Page Indication: 0 = No other Next Page Transfer desired. 1 = Another Next Page desired. 14 RESERVED 0, RO RESERVED: Writes ignored, read as 0. 13 MP 1, RW Message Page: 1 = Message Page. 0 = Unformatted Page. 12 ACK2 0, RW Acknowledge2: 1 = Will comply with message. 0 = Cannot comply with message. Acknowledge2 is used by the next page function to indicate that Local Device has the ability to comply with the message received. 11 TOG_TX 0, RO Toggle: 1 = Value of toggle bit in previously transmitted Link Code Word was 0. 0 = Value of toggle bit in previously transmitted Link Code Word was 1. Toggle is used by the Arbitration function within Auto-Negotiation to ensure synchronization with the Link Partner during Next Page exchange. This bit shall always take the opposite value of the Toggle bit in the previously exchanged Link Code Word. 10:0 CODE <000 0000 0001>, RW This field represents the code field of the next page transmission. If the MP bit is set (bit 13 of this register), then the code shall be interpreted as a "Message Page”, as defined in annex 28C of IEEE 802.3u. Otherwise, the code shall be interpreted as an "Unformatted Page”, and the interpretation is application specific. The default value of the CODE represents a Null Page as defined in Annex 28C of IEEE 802.3u. Obsolete 37 www.national.com DP83846A 5.2 Extended Registers This register provides a single location within the register set for quick access to commonly accessed information. Table 16. PHY Status Register (PHYSTS), address 0x10 Bit Bit Name Default Description 15:14 RESERVED 0, RO RESERVED: Write ignored, read as 0. 13 Receive Error Latch 0, RO/LH Receive Error Latch: This bit will be cleared upon a read of the RECR register. 1 = Receive error event has occurred since last read of RXERCNT (address 0x15, Page 0). 0 = No receive error event has occurred. 12 Polarity Status 0, RO Polarity Status: This bit is a duplication of bit 4 in the 10BTSCR register. This bit will be cleared upon a read of the 10BTSCR register, but not upon a read of the PHYSTS register. 1 = Inverted Polarity detected. 0 = Correct Polarity detected. 11 False Carrier Sense Latch 0, RO/LH False Carrier Sense Latch: This bit will be cleared upon a read of the FCSR register. 1 = False Carrier event has occurred since last read of FCSCR (address 0x14). 0 = No False Carrier event has occurred. 10 Signal Detect 0, RO/LL 100Base-TX unconditional Signal Detect from PMD. 9 Descrambler Lock 0, RO/LL 100Base-TX Descrambler Lock from PMD. 8 Page Received 0, RO Link Code Word Page Received: This is a duplicate of the Page Received bit in the ANER register, but this bit will not be cleared upon a read of the PHYSTS register. 1 = A new Link Code Word Page has been received. Cleared on read of the ANER (address 0x06, bit 1). 0 = Link Code Word Page has not been received. Obsolete 38 www.national.com DP83846A 7 RESERVED 0, RO RESERVED: Writes ignored, Read as 0. 6 Remote Fault 0, RO Remote Fault: 1 = Remote Fault condition detected (cleared on read of BMSR (address 01h) register or by reset). Fault criteria: notification from Link Partner of Remote Fault via Auto-Negotiation. 0 = No remote fault condition detected. 5 Jabber Detect 0, RO Jabber Detect: This bit only has meaning in 10 Mb/s mode This bit is a duplicate of the Jabber Detect bit in the BMSR register, except that it is not cleared upon a read of the PHYSTS register. 1 = Jabber condition detected. 0 = No Jabber. 4 Auto-Neg Complete 0, RO Auto-Negotiation Complete: 1 = Auto-Negotiation complete. 0 = Auto-Negotiation not complete. 3 Loopback Status 0, RO Loopback: 1 = Loopback enabled. 0 = Normal operation. 2 Duplex Status 0, RO Duplex: This bit indicates duplex status and is determined from Auto-Negotiation or Forced Modes. 1 = Full duplex mode. 0 = Half duplex mode. Note: This bit is only valid if Auto-Negotiation is enabled and complete and there is a valid link or if Auto-Negotiation is disabled and there is a valid link. 1 Speed Status 0, RO Speed10: This bit indicates the status of the speed and is determined from Auto-Negotiation or Forced Modes. 1 = 10 Mb/s mode. 0 = 100 Mb/s mode. Note: This bit is only valid if Auto-Negotiation is enabled and complete and there is a valid link or if Auto-Negotiation is disabled and there is a valid link. 0 Link Status 0, RO Link Status: This bit is a duplicate of the Link Status bit in the BMSR register, except that it will no be cleared upon a read of the PHYSTS register. 1 = Valid link established (for either 10 or 100 Mb/s operation). 0 = Link not established. Table 16. PHY Status Register (PHYSTS), address 0x10 (Continued) Bit Bit Name Default Description Obsolete 39 www.national.com DP83846A This counter provides information required to implement the “FalseCarriers” attribute within the MAU managed object class of Clause 30 of the IEEE 802.3u specification. This counter provides information required to implement the “SymbolErrorDuringCarrier” attribute within the PHY managed object class of Clause 30 of the IEEE 802.3u specification. Table 17. False Carrier Sense Counter Register (FCSCR), address 0x14 Bit Bit Name Default Description 15:8 RESERVED 0, RO RESERVED: Writes ignored, Read as 0. 7:0 FCSCNT[7:0] 0, RW / COR False Carrier Event Counter: This 8-bit counter increments on every false carrier event. This counter sticks when it reaches its max count (FFh). Table 18. Receiver Error Counter Register (RECR), address 0x15 Bit Bit Name Default Description 15:8 RESERVED 0, RO RESERVED: Writes ignored, Read as 0 7:0 RXERCNT[7:0] 0, RW / COR RX_ER Counter: This 8-bit counter increments for each receive error detected. When a valid carrier is present and there is at least one occurrence of an invalid data symbol. This event can increment only once per valid carrier event. If a collision is present, the attribute will not increment. The counter sticks when it reaches its max count. Table 19. 100 Mb/s PCS Configuration and Status Register (PCSR), address 0x16 Bit Bit Name Default Description 15:13 RESERVED <00>, RO RESERVED: Writes ignored, Read as 0. 12 BYP_4B5B 0, RW Bypass 4B/5B Encoding: 1 = 4B5B encoder functions bypassed. 0 = Normal 4B5B operation. 11 FREE_CLK 0, RW Receive Clock: 1 = RX_CK is free-running. 0 = RX_CK phase adjusted based on alignment. 10 TQ_EN 0, RW 100Mbs True Quiet Mode Enable: 1 = Transmit True Quiet Mode. 0 = Normal Transmit Mode. 9 SD FORCE PMA 0, RW Signal Detect Force PMA: 1 = Forces Signal Detection in PMA. 0 = Normal SD operation. 8 SD_OPTION 1, RW Signal Detect Option: 1 = Enhanced signal detect algorithm. 0 = Reduced signal detect algorithm. Obsolete 40 www.national.com DP83846A 7 Unused 0,RO 6 RESERVED 0 RESERVED: Must be zero. 5 FORCE_100_OK 0, RW Force 100Mb/s Good Link: 1 = Forces 100Mb/s Good Link. 0 = Normal 100Mb/s operation. 4 RESERVED 0 RESERVED: Must be zero. 3 RESERVED 0 RESERVED: Must be zero. 2 NRZI_BYPASS 0, RW NRZI Bypass Enable: 1 = NRZI Bypass Enabled. 0 = NRZI Bypass Disabled. 1 SCRAM_BYPASS 0, RW Scrambler Bypass Enable: 1 = Scrambler Bypass Enabled. 0 = Scrambler Bypass Disabled. 0 DESCRAM_BYPA SS 0, RW Descrambler Bypass Enable: 1 = Descrambler Bypass Enabled. 0 = Descrambler Bypass Disabled. Table 20. Reserved Registers, addresses 0x17, 0x18 Bit Bit Name Default Description 15:0 RESERVED none, RW RESERVED: Must not be written to during normal operation. Table 19. 100 Mb/s PCS Configuration and Status Register (PCSR), address 0x16 (Continued) Bit Bit Name Default Description Obsolete 41 www.national.com DP83846A Table 21. PHY Control Register (PHYCTRL), address 0x19 Bit Bit Name Default Description 15:12 Unused 0, RO 11 PSR_15 0, RW BIST Sequence select: 1 = PSR15 selected. 0 = PSR9 selected. 10 BIST_STATUS 0, RO/LL BIST Test Status: 1 = BIST pass. 0 = BIST fail. Latched, cleared by write to BIST_ START bit. 9 BIST_START 0, RW BIST Start: 1 = BIST start. 0 = BIST stop. 8 BP_STRETCH 0, RW Bypass LED Stretching: This will bypass the LED stretching for the Receive, Transmit and Collision LEDs. 1 = Bypass LED stretching. 0 = Normal operation. 7 PAUSE_STS 0, RO Pause Compare Status: 0 = Local Device and the Link Partner are not Pause capable. 1 = Local Device and the Link Partner are both Pause capable. 6 RESERVED 1, RO/P Reserved: Must be 1. 5 LED_CNFG Strap, RW This bit is used to bypass the selective inversion on the LED output for DPLX - this enables its use in non-LED applications. Mode Description 1 = Led polarity adjusted - DPLX selected. 0 = DPLX active HIGH. 4:0 PHYADDR[4:0] Strap, RW PHY Address: PHY address for port. Obsolete 42 www.national.com DP83846A Table 22. 10Base-T Status/Control Register (10BTSCR), Address 0x1A Bit Bit Name Default Description 15:9 Unused 0, RO 8 LOOPBACK_10_DIS 0, RW 10BASE-T Loopback Disable: If bit 14 (Loopback) in the BMCR is 0: 1 = 10 Mb/s Loopback is disabled. If bit 14 (Loopback) in the BMCR is 1: 1 = 10 Mb/s Loopback is enabled. 7 LP_DIS 0, RW Normal Link Pulse Disable: 1 = Transmission of NLPs is disabled. 0 = Transmission of NLPs is enabled. 6 FORCE_LINK_10 0, RW Force 10Mb Good Link: 1 = Forced Good 10Mb Link. 0 = Normal Link Status. 5 FORCE_POL_COR 0, RW Force 10Mb Polarity Correction: 1 = Force inverted polarity. 0 = Normal polarity. 4 POLARITY RO/LH 10Mb Polarity Status: This bit is a duplication of bit 12 in the PHYSTS register. Both bits will be cleared upon a read of 10BTSCR register, but not upon a read of the PHYSIS register. 1 = Inverted Polarity detected. 0 = Correct Polarity detected. 3 AUTOPOL_DIS 0, RW Auto Polarity Detection & Correction Disable: 1 = Polarity Sense & Correction disabled. 0 = Polarity Sense & Correction enabled. 2 RESERVED 1, RW RESERVED: Must be set to one. 1 HEARTBEAT_DIS 0, RW Heartbeat Disable: This bit only has influence in half-duplex 10Mb mode. 1 = Heartbeat function disabled. 0 = Heartbeat function enabled. When the device is operating at 100Mb or configured for full duplex operation, this bit will be ignored - the heartbeat function is disabled. 0 JABBER_DIS 0, RW Jabber Disable: Applicable only in 10BASE-T. 1 = Jabber function disabled. 0 = Jabber function enabled. Obsolete 43 www.national.com DP83846A Table 23. CD Test Register (CDCTRL), Address 0x1B Bit Bit Name Default Description 15 CD_ENABLE 1, RW CD Enable: 1 = CD Enabled - power-down mode, outputs high impedance. 0 = CD Disabled. 14 DCDCOMP 0, RW Duty Cycle Distortion Compensation: 1 = Increases the amount of DCD compensation. 13 FIL_TTL 0, RW Waveshaper Current Source Test: To check ability of waveshaper current sources to switch on/off. 1 = Test mode; waveshaping is done, but the output is a square wave. All sources are either on or off. 0 = Normal mode; sinusoidal. 12 RESERVED none, RW Reserved: This bit should be written with a 0 if write access is required on this register. 11 RISETIME Strap, RW CD Rise Time Control: 10 RESERVED none, RW Reserved: This bit should be written with a 0 if write access is required on this register. 9 FALLTIME Strap, RW CD Fall Time Control: 8 CDTESTEN 0, RW CD Test Mode Enable: 1 = Enable CD test mode - differs based on speed of operation (10/100Mb). 0 = Normal operation. 7:5 RESERVED[2:0] 000, RW RESERVED: Must be zero. 4 CDPATTEN_10 0, RW CD Pattern Enable for 10meg: 1 = Enabled. 0 = Disabled. 3 CDPATTEN_100 0, RW CD Pattern Enable for 100meg: 1 = Enabled. 0 = Disabled. 2 10MEG_PATT_GAP 0, RW Defines gap between data or NLP test sequences: 1 = 15 μs. 0 = 10 μs. 1:0 CDPATTSEL[1:0] 00, RW CD Pattern Select[1:0]: If CDPATTEN_100 = 1: 00 = All 0’s (True quiet) 01 = All 1’s 10 = 2 1’s, 2 0’s repeating pattern 11 = 14 1’s, 6 0’s repeating pattern If CDPATTEN_10 = 1: 00 = Data, EOP0 sequence 01 = Data, EOP1 sequence 10 = NLPs 11 = Constant Manchester 1s (10mhz sine wave) for harmonic distortion testing. Obsolete 44 www.national.com DP83846A 6.0 Electrical Specifications Absolute Maximum Ratings Recommended Operating Conditions Absolute maximum ratings are those values beyond which the safety of the device cannot be guaranteed. They are not meant to imply that the device should be operated at these limits. Note:0 DC Electrical Specification Supply Voltage (VCC) -0.5 V to 4.2 V DC Input Voltage (VIN) -0.5V to 5.5V DC Output Voltage (VOUT) -0.5V to 5.5V Storage Temperature (TSTG) -65oC to 150°C Lead Temp. (TL) (Soldering, 10 sec) 260°C ESD Rating (RZAP = 1.5k, CZAP = 120 pF) 1.0 kV Supply voltage (VCC) 3.3 Volts + 0.3V Ambient Temperature (TA) 0 to 70 °C Max. die temperature (Tj) 107°C Max case temp 96°C Thermal Characteristic Max Units Theta Junction to Case (Tjc) 15 °C / W Theta Junction to Ambient (Tja) degrees Celsius/Watt - No Airflow @ 1.0W 51 °C / W Theta Junction to Ambient (Tja) degrees Celsius/Watt - 225 LFPM Airflow @ 1.0W 42 °C / W Theta Junction to Ambient (Tja) degrees Celsius/Watt - 500 LFPM Airflow @ 1.0W 37 °C / W Theta Junction to Ambient (Tja) degrees Celsius/Watt - 900 LFPM Airflow @ 1.0W 33 °C / W Symbol Pin Types Parameter Conditions Min Typ Max Units VIH I I/O Input High Voltage Nominal VCC 2.0 V VIL I I/O Input Low Voltage 0.8 V IIH I I/O Input High Current VIN = VCC 10 μA IIL I I/O Input Low Current VIN = GND 10 μA VOL O, I/O Output Low Voltage IOL = 4 mA 0.4 V VOH O, I/O Output High Voltage IOH = -4 mA VCC - 0.5 V VledOL LED Output Low Voltage * IOL = 2.5 mA 0.4 V VledOH LED Output High Voltage IOH = -2.5 mA VCC - 0.5 V IOZH I/O, O TRI-STATE Leakage VOUT = VCC 10 μA I5IH I/O, O 5 Volt Tolerant MII Leakage VIN = 5.25 V 10 μA I5OZH I/O, O 5 Volt Tolerant MII Leakage VOUT = 5.25 V 10 μA RINdiff RD+/− Differential Input Resistance 1.1 kΩ VTPTD_100 TD+/− 100M Transmit Voltage .95 1 1.05 V Obsolete 45 www.national.com DP83846A Note: For Idd Measurements, outputs are not loaded. VTPTDsym TD+/− 100M Transmit Voltage Symmetry ±2 % VTPTD_10 TD+/− 10M Transmit Voltage 2.2 2.5 2.8 V CIN1 I CMOS Input Capacitance Parameter is not 100% tested 8 pF SDTHon RD+/− 100BASE-TX Signal detect turnon threshold 1000 mV diff pk-pk SDTHoff RD+/− 100BASE-TX Signal detect turnoff threshold 200 mV diff pk-pk VTH1 RD+/− 10BASE-T Receive Threshold 300 585 mV Idd100 Supply 100BASE-TX (Full Duplex) IOUT = 0 mA See Note 150 200 mA Idd10 Supply 10BASE-T (Full Duplex) IOUT = 0 mA See Note 100 130 mA Symbol Pin Types Parameter Conditions Min Typ Max Units Obsolete 46 www.national.com DP83846A 6.1 Reset Timing Note1: Software Reset should be initiated no sooner then 500 μs after power-up or the deassertion of hardware reset. Note2: It is important to choose pull-up and/or pull-down resistors for each of the hardware configuration pins that provide fast RC time constants in order to latch-in the proper value prior to the pin transitioning to an output driver. Parameter Description Notes Min Typ Max Units T1.0.1 Post RESET Stabilization time prior to MDC preamble for register accesses MDIO is pulled high for 32-bit serial management initialization 3 μs T1.0.2 Hardware Configuration Latch-in Time from the Deassertion of RESET (either soft or hard) Hardware Configuration Pins are described in the Pin Description section 3 μs T1.0.3 Hardware Configuration pins transition to output drivers 3.5 μs T1.0.4 RESET pulse width X1 Clock must be stable for a minimum of 160us during RESET pulse low time. 160 μs VCC HARDWARE RSTN MDC 32 CLOCKS Latch-In of Hardware Configuration Pins Dual Function Pins Become Enabled As Outputs INPUT OUTPUT T1.0.3 T1.0.2 T1.0.1 T1.0.4 X1 Clock Obsolete 47 www.national.com DP83846A 6.2 PGM Clock Timing 6.3 MII Serial Management Timing Parameter Description Notes Min Typ Max Units T2.0.1 TX_CLK Duty Cycle 35 65 % Parameter Description Notes Min Typ Max Units T3.0.1 MDC to MDIO (Output) Delay Time 0 300 ns T3.0.2 MDIO (Input) to MDC Setup Time 10 ns T3.0.3 MDIO (Input) to MDC Hold Time 10 ns T3.0.4 MDC Frequency 2.5 MHz TX_CLK X1 T2.0.1 MDC MDC MDIO (output) MDIO (input) Valid Data T3.0.1 T3.0.2 T3.0.3 T3.0.4 Obsolete 48 www.national.com DP83846A 6.4 100 Mb/s Timing 6.4.1 100 Mb/s MII Transmit Timing 6.4.2 100 Mb/s MII Receive Timing Parameter Description Notes Min Typ Max Units T4.1.1 TXD[3:0], TX_EN, TX_ER Data Setup to TX_CLK 10 ns T4.1.2 TXD[3:0], TX_EN, TX_ER Data Hold from TX_CLK 5 ns Parameter Description Notes Min Typ Max Units T4.2.1 RX_CLK Duty Cycle 35 65 % T4.2.2 RX_CLK to RXD[3:0], RX_DV, RX_ER Delay 10 30 ns TX_CLK TXD[3:0] TX_EN TX_ER Valid Data T4.1.1 T4.1.2 RX_CLK RXD[3:0] RX_DV RX_ER Valid Data T4.2.2 T4.2.1 Obsolete 49 www.national.com DP83846A 6.4.3 100BASE-TX Transmit Packet Latency Timing Note: Latency is determined by measuring the time from the first rising edge of TX_CLK occurring after the assertion of TX_EN to the first bit of the “J” code group as output from the TD± pins. 6.4.4 100BASE-TX Transmit Packet Deassertion Timing Note: Deassertion is determined by measuring the time from the first rising edge of TX_CLK occurring after the deassertion of TX_EN to the first bit of the “T” code group as output from the TD± pins. Parameter Description Notes Min Typ Max Units T4.3.1 TX_CLK to TD± Latency 6.0 bit times Parameter Description Notes Min Typ Max Units T4.4.1 TX_CLK to TD± Deassertion 6.0 bit times TX_CLK TX_EN TXD TD± IDLE (J/K) DATA T4.3.1 TX_CLK TXD TX_EN TD± DATA (T/R) IDLE T4.4.1 DATA (T/R) IDLE Obsolete 50 www.national.com DP83846A 6.4.5 100BASE-TX Transmit Timing (tR/F & Jitter) Note1: Normal Mismatch is the difference between the maximum and minimum of all rise and fall times. Note2: Rise and fall times taken at 10% and 90% of the +1 or -1 amplitude. Parameter Description Notes Min Typ Max Units T4.5.1 100 Mb/s TD± tR and tF 3 4 5 ns 100 Mb/s tR and tF Mismatch 500 ps T4.5.2 100 Mb/s TD± Transmit Jitter 1.4 ns TD± T4.5.1 T4.5.1 T4.5.1 T4.5.1 +1 rise +1 fall -1 fall -1 rise TD± eye pattern T4.5.2 T4.5.2 90% 10% 10% 90% Obsolete 51 www.national.com DP83846A 6.4.6 100BASE-TX Receive Packet Latency Timing Note: Carrier Sense On Delay is determined by measuring the time from the first bit of the “J” code group to the assertion of Carrier Sense. Note: RD± voltage amplitude is greater than the Signal Detect Turn-On Threshold Value. 6.4.7 100BASE-TX Receive Packet Deassertion Timing Note: Carrier Sense Off Delay is determined by measuring the time from the first bit of the “T” code group to the deassertion of Carrier Sense. Parameter Description Notes Min Typ Max Units T4.6.1 Carrier Sense ON Delay 17.5 bit times T4.6.2 Receive Data Latency 21 bit times Parameter Description Notes Min Typ Max Units T4.7.1 Carrier Sense OFF Delay 21.5 bit times CRS RXD[3:0] RD± RX_DV RX_ER/RXD[4] IDLE Data T4.6.1 T4.6.2 (J/K) CRS T4.7.1 RXD[3:0] RX_DV RX_ER/RXD[4] RD± DATA IDLE (T/R) Obsolete 52 www.national.com DP83846A 6.5 10 Mb/s Timing 6.5.1 10 Mb/s MII Transmit Timing 6.5.2 10 Mb/s MII Receive Timing Parameter Description Notes Min Typ Max Units T5.1.1 TXD[3:0], TX_EN Data Setup to TX_CLK 25 ns T5.1.2 TXD[3:0], TX_EN Data Hold from TX_CLK 5 ns Parameter Description Notes Min Typ Max Units T5.2.1 RX_CLK Duty Cycle 35 65 % T5.2.2 RX_CLK to RXD[3:0], RX_DV 190 210 ns TX_CLK TXD[3:0] TX_EN Valid Data T5.1.1 T5.1.2 RX_CLK RXD[3:0] Valid Data T5.2.2 T5.2.1 RX_DV Obsolete 53 www.national.com DP83846A 6.5.3 10BASE-T Transmit Timing (Start of Packet) 6.5.4 10BASE-T Transmit Timing (End of Packet) Parameter Description Notes Min Typ Max Units T5.3.1 Transmit Enable Setup Time from the Falling Edge of TX_CLK 25 ns T5.3.2 Transmit Data Setup Time from the Falling Edge of TX_CLK 25 ns T5.3.3 Transmit Data Hold Time from the Falling Edge of TX_CLK 5 ns T5.3.4 Transmit Output Delay from the Falling Edge of TX_CLK 6.8 bit times Parameter Description Notes Min Typ Max Units T5.4.1 Transmit Enable Hold Time from the Falling Edge of TX_CLK 5 ns T5.4.2 End of Packet High Time (with ‘0’ ending bit) 250 ns T5.4.3 End of Packet High Time (with ‘1’ ending bit) 250 ns TX_CLK TX_EN TXD[0] TPTD± T5.3.1 T5.3.2 T5.3.3 T5.3.4 TX_CLK TX_EN TPTD± 0 0 1 1 TPTD± T5.4.2 T5.4.3 T5.4.1 Obsolete 54 www.national.com DP83846A 6.5.5 10BASE-T Receive Timing (Start of Packet) Note: 10BASE-T receive Data Latency is measured from first bit of preamble on the wire to the assertion of RX_DV. 6.5.6 10BASE-T Receive Timing (End of Packet) Parameter Description Notes Min Typ Max Units T5.5.1 Carrier Sense Turn On Delay (TPRD± to CRS) 1 μs T5.5.2 Decoder Acquisition Time 3.6 μs T5.5.3 Receive Data Latency 17.3 bit times T5.5.4 SFD Propagation Delay 10 bit times Parameter Description Notes Min Typ Max Units T5.6.1 Carrier Sense Turn Off Delay 1.1 μs 1 0 1 TPRD± CRS RX_CLK RXD[0] 1st SFD bit decoded RX_DV T5.5.1 T5.5.2 T5.5.3 T5.5.4 1 0 1 TPRD± RX_CLK CRS IDLE T5.6.1 Obsolete 55 www.national.com DP83846A 6.5.7 10 Mb/s Heartbeat Timing 6.5.8 10 Mb/s Jabber Timing 6.5.9 10BASE-T Normal Link Pulse Timing Parameter Description Notes Min Typ Max Units T5.7.1 CD Heartbeat Delay 600 1600 ns T5.7.2 CD Heartbeat Duration 500 1500 ns Parameter Description Notes Min Typ Max Units T5.8.1 Jabber Activation Time 20 150 ms T5.8.2 Jabber Deactivation Time 250 750 ms Parameter Description Notes Min Typ Max Units T5.9.1 Pulse Width 100 ns T5.9.2 Pulse Period 8 16 24 ms TXC TXE COL T5.7.1 T5.7.2 TXE TPTD± COL T5.8.2 T5.8.1 T5.9.2 T5.9.1 Normal Link Pulse(s)Obsolete 56 www.national.com DP83846A 6.5.10 Auto-Negotiation Fast Link Pulse (FLP) Timing 6.5.11 100BASE-TX Signal Detect Timing Note: The signal amplitude at RD± is TP-PMD compliant. Parameter Description Notes Min Typ Max Units T5.10.1 Clock, Data Pulse Width 100 ns T5.10.2 Clock Pulse to Clock Pulse Period 111 125 139 μs T5.10.3 Clock Pulse to Data Pulse Period Data = 1 55.5 69.5 μs T5.10.4 Number of Pulses in a Burst 17 33 # T5.10.5 Burst Width 2 ms T5.10.6 FLP Burst to FLP Burst Period 8 24 ms Parameter Description Notes Min Typ Max Units T5.11.1 SD Internal Turn-on Time 1 ms T5.11.2 SD Internal Turn-off Time 300 μs clock pulse data pulse clock pulse FLP Burst FLP Burst Fast Link Pulse(s) T5.10.1 T5.10.1 T5.10.2 T5.10.3 T5.10.4 T5.10.5 T5.10.6 T5.11.1 SD+ internal T5.11.2 RD± Obsolete 57 www.national.com DP83846A 6.6 Loopback Timing 6.6.1 100 Mb/s Internal Loopback Mode Note1: Due to the nature of the descrambler function, all 100BASE-TX Loopback modes will cause an initial “dead-time” of up to 550 μs during which time no data will be present at the receive MII outputs. The 100BASE-TX timing specified is based on device delays after the initial 550μs “dead-time”. Note2: Measurement is made from the first rising edge of TX_CLK after assertion of TX_EN. Parameter Description Notes Min Typ Max Units T6.1.1 TX_EN to RX_DV Loopback 240 ns TX_CLK TX_EN TXD[3:0] CRS RX_CLK RXD[3:0] RX_DV T6.1.1 Obsolete 58 www.national.com DP83846A 6.6.2 10 Mb/s Internal Loopback Mode Note: Measurement is made from the first falling edge of TX_CLK after assertion of TX_EN. Parameter Description Notes Min Typ Max Units T6.2.1 TX_EN to RX_DV Loopback 2 μs TX_CLK TX_EN TXD[3:0] CRS RX_CLK RXD[3:0] RX_DV T6.2.1 Obsolete 59 www.national.com DP83846A 6.7 Isolation Timing Parameter Description Notes Min Typ Max Units T7.0.1 From software clear of bit 10 in the BMCR register to the transition from Isolate to Normal Mode 100 μs T7.0.2 From Deassertion of S/W or H/W Reset to transition from Isolate to Normal mode 500 μs Clear bit 10 of BMCR (return to normal operation from Isolate mode) H/W or S/W Reset (with PHYAD = 00000) MODE ISOLATE NORMAL T7.0.2 T7.0.1 Obsolete DP83846A DsPHYTER — Single 10/100 Ethernet Transceiver National does not assume any responsibility for use of any circuitry described, no circuit patent licenses are implied and National reserves the right at any time without notice to change said circuitry and specifications. LIFE SUPPORT POLICY NATIONAL’S PRODUCTS ARE NOT AUTHORIZED FOR USE AS CRITICAL COMPONENTS IN LIFE SUPPORT DEVICES OR SYSTEMS WITHOUT THE EXPRESS WRITTEN APPROVAL OF THE PRESIDENT AND GENERAL COUNSEL OF NATIONAL SEMICONDUCTOR CORPORATION. As used herein: 1. Life support devices or systems are devices or systems which, (a) are intended for surgical implant into the body, or (b) support or sustain life, and whose failure to perform when properly used in accordance with instructions for use provided in the labeling, can be reasonably expected to result in a significant injury to the user. 2. A critical component is any component of a life support device or system whose failure to perform can be reasonably expected to cause the failure of the life support device or system, or to affect its safety or effectiveness. National Semiconductor Corporation Americas Tel: 1-800-272-9959 Fax: 1-800-737-7018 Email: support@nsc.com National Semiconductor Europe Fax: +49 (0) 180-530 85 86 Email: europe.support@nsc.com Deutsch Tel: +49 (0) 69 9508 6208 English Tel: +44 (0) 870 24 0 2171 Francais Tel: +33 (0) 1 41 91 8790 National Semiconductor Japan Ltd. Tel: 81-3-5639-7560 Fax: 81-3-5639-7507 National Semiconductor Asia Pacific Customer Response Group Tel: 65-2544466 Fax: 65-2504466 Email: ap.support@nsc.com www.national.com 7.0 Physical Dimensions Plastic Quad Flat Pack (LQFP) Order Number DP83846AVHG NS Package Number VHG-80A Obsolete IMPORTANT NOTICE Texas Instruments Incorporated and its subsidiaries (TI) reserve the right to make corrections, modifications, enhancements, improvements, and other changes to its products and services at any time and to discontinue any product or service without notice. Customers should obtain the latest relevant information before placing orders and should verify that such information is current and complete. All products are sold subject to TI’s terms and conditions of sale supplied at the time of order acknowledgment. TI warrants performance of its hardware products to the specifications applicable at the time of sale in accordance with TI’s standard warranty. Testing and other quality control techniques are used to the extent TI deems necessary to support this warranty. Except where mandated by government requirements, testing of all parameters of each product is not necessarily performed. TI assumes no liability for applications assistance or customer product design. Customers are responsible for their products and applications using TI components. To minimize the risks associated with customer products and applications, customers should provide adequate design and operating safeguards. TI does not warrant or represent that any license, either express or implied, is granted under any TI patent right, copyright, mask work right, or other TI intellectual property right relating to any combination, machine, or process in which TI products or services are used. Information published by TI regarding third-party products or services does not constitute a license from TI to use such products or services or a warranty or endorsement thereof. Use of such information may require a license from a third party under the patents or other intellectual property of the third party, or a license from TI under the patents or other intellectual property of TI. Reproduction of TI information in TI data books or data sheets is permissible only if reproduction is without alteration and is accompanied by all associated warranties, conditions, limitations, and notices. Reproduction of this information with alteration is an unfair and deceptive business practice. TI is not responsible or liable for such altered documentation. Information of third parties may be subject to additional restrictions. Resale of TI products or services with statements different from or beyond the parameters stated by TI for that product or service voids all express and any implied warranties for the associated TI product or service and is an unfair and deceptive business practice. TI is not responsible or liable for any such statements. TI products are not authorized for use in safety-critical applications (such as life support) where a failure of the TI product would reasonably be expected to cause severe personal injury or death, unless officers of the parties have executed an agreement specifically governing such use. Buyers represent that they have all necessary expertise in the safety and regulatory ramifications of their applications, and acknowledge and agree that they are solely responsible for all legal, regulatory and safety-related requirements concerning their products and any use of TI products in such safety-critical applications, notwithstanding any applications-related information or support that may be provided by TI. Further, Buyers must fully indemnify TI and its representatives against any damages arising out of the use of TI products in such safety-critical applications. TI products are neither designed nor intended for use in military/aerospace applications or environments unless the TI products are specifically designated by TI as military-grade or "enhanced plastic." Only products designated by TI as military-grade meet military specifications. Buyers acknowledge and agree that any such use of TI products which TI has not designated as military-grade is solely at the Buyer's risk, and that they are solely responsible for compliance with all legal and regulatory requirements in connection with such use. TI products are neither designed nor intended for use in automotive applications or environments unless the specific TI products are designated by TI as compliant with ISO/TS 16949 requirements. Buyers acknowledge and agree that, if they use any non-designated products in automotive applications, TI will not be responsible for any failure to meet such requirements. Following are URLs where you can obtain information on other Texas Instruments products and application solutions: Products Applications Audio www.ti.com/audio Communications and Telecom www.ti.com/communications Amplifiers amplifier.ti.com Computers and Peripherals www.ti.com/computers Data Converters dataconverter.ti.com Consumer Electronics www.ti.com/consumer-apps DLP® Products www.dlp.com Energy and Lighting www.ti.com/energy DSP dsp.ti.com Industrial www.ti.com/industrial Clocks and Timers www.ti.com/clocks Medical www.ti.com/medical Interface interface.ti.com Security www.ti.com/security Logic logic.ti.com Space, Avionics and Defense www.ti.com/space-avionics-defense Power Mgmt power.ti.com Transportation and Automotive www.ti.com/automotive Microcontrollers microcontroller.ti.com Video and Imaging www.ti.com/video RFID www.ti-rfid.com OMAP Mobile Processors www.ti.com/omap Wireless Connectivity www.ti.com/wirelessconnectivity TI E2E Community Home Page e2e.ti.com Mailing Address: Texas Instruments, Post Office Box 655303, Dallas, Texas 75265 Copyright © 2011, Texas Instruments Incorporated The information provided in this documentation contains general descriptions and/or technical characteristics of the performance of the products contained herein. This documentation is not intended as a substitute for and is not to be used for determining suitability or reliability of these products for specific user applications. It is the duty of any such user or integrator to perform the appropriate and complete risk analysis, evaluation and testing of the products with respect to the relevant specific application or use thereof. Neither Schneider Electric Industries SAS nor any of its affiliates or subsidiaries shall be responsible or liable for misuse of the information contained herein. Mar 9, 2013 1 Product data sheet Characteristics XPSAF5130 module XPSAF - Emergency stop - 24 V AC DC Main Range of product Preventa Safety automation Product or component type Preventa safety module Safety module name XPSAF Safety module application For emergency stop and switch monitoring Function of module Monitoring of a movable guard Emergency stop monitoring 1-channel wiring Emergency stop monitoring 2-channel wiring Safety level Can reach SILCL 3 conforming to EN/IEC 62061 Can reach PL e/category 4 conforming to EN/ISO 13849-1 Safety reliability data PFHd = 4.62E-9 1/h conforming to EN/IEC 62061 MTTFd = 243 years conforming to EN/ISO 13849-1 DC > 99 % conforming to EN/ISO 13849-1 Type of start Configurable Connections - terminals Captive screw clamp terminals (2 x 0.5...2 x 1.5 mm²)flexible cable with cable end, with double bezel Captive screw clamp terminals (2 x 0.25...2 x 1 mm²)flexible cable with cable end, with double bezel Captive screw clamp terminals (2 x 0.14...2 x 0.75 mm²)solid cable with cable end, with double bezel Captive screw clamp terminals (2 x 0.14...2 x 0.75 mm²)flexible cable with cable end, with double bezel Captive screw clamp terminals (1 x 0.25...1 x 2.5 mm²)flexible cable with cable end, with double bezel Captive screw clamp terminals (1 x 0.25...1 x 1.5 mm²)flexible cable with cable end, with double bezel Captive screw clamp terminals (1 x 0.14...1 x 2.5 mm²)solid cable with cable end, with double bezel Captive screw clamp terminals (1 x 0.14...1 x 2.5 mm²)flexible cable with cable end, with double bezel Output type Relay instantaneous opening 3 NO, volt-free Number of additional circuits 0 [Us] rated supply voltage 24 V DC (- 15...10 %) 24 V AC (- 15...10 %) Complementary Synchronisation time between inputs Unlimited Supply frequency 50/60 Hz Power consumption in VA <= 5 VA AC Input protection type Internal, electronic Control circuit voltage 24 V Line resistance 90 Ohm Breaking capacity C300: 1800 VA, AC-15 (inrush) for relay output C300: 180 VA, AC-15 (holding) for relay output Breaking capacity 1.5 A at 24 V (DC-13) time constant: 50 ms for relay output Output thermal current 6 A per relay for relay output [Ith] conventional free air thermal current 18 A Associated fuse rating 6 A fuse type fast blow for relay output conforming to EN/IEC 60947-5-1, DIN VDE 0660 part 200 4 A fuse type gG or gL for relay output conforming to EN/IEC 60947-5-1, DIN VDE 0660 part 200 Minimum output current 10 mA for relay output Minimum output voltage 17 V for relay output 2 Response time on input open <= 40 ms [Ui] rated insulation voltage 300 V (degree of pollution: 2) conforming to IEC 60647-5-1, DIN VDE 0110 part 1 [Uimp] rated impulse withstand voltage 4 kV overvoltage category III conforming to IEC 60647-5-1, DIN VDE 0110 part 1 Local signalling 3 LEDs Current consumption 30 mA at 24 V AC (on power supply) Mounting support 35 mm symmetrical DIN rail Product weight 0.25 kg Environment Standards EN 1088/ISO 14119 EN 60204-1 EN/IEC 60947-5-1 EN/ISO 13850 Product certifications CSA TÜV UL IP degree of protection IP40 (enclosure) conforming to EN/IEC 60529 IP20 (terminals) conforming to EN/IEC 60529 Ambient air temperature for operation -25...60 °C Ambient air temperature for storage -40...85 °C 3 Product data sheet Dimensions Drawings XPSAF5130 Dimensions 4 Product data sheet Connections and Schema XPSAF5130 Wiring Diagrams Refer to the Instruction Sheet To download the instruction sheet, follow below procedure: 1 Click on Download & Documents. 2 Click on Instruction sheet. General Description The MAX1365/MAX1367 low-power, 4.5- and 3.5-digit, panel meters feature an integrated sigma-delta analogto- digital converter (ADC), LED display drivers, voltage digital-to-analog converter (DAC), and a 4–20mA (or 0 to 16mA) current driver. The MAX1365/MAX1367’s analog input voltage range is programmable to either ±2V or ±200mV. The MAX1367 drives a 3.5-digit (±1999 count) display and the MAX1365 drives a 4.5-digit (±19,999 count) display. The ADC output directly drives the LED display as well as the voltage DAC, which in turn drives the 4–20mA (or 0 to 16mA) current-loop output. In normal operation, the 0 to 16mA/4–20mA currentloop output follows the ±2V or ±200mV analog input to drive remote panel-meter displays, data loggers, and other industrial controllers. For added flexibility, the MAX1365/MAX1367 allow direct access to the DAC output and the V/I converter input. The sigma-delta ADC does not require external precision integrating capacitors, autozero capacitors, crystal oscillators, charge pumps, or other circuitry commonly required in dual-slope ADC panel-meter circuits. Onchip analog input and reference buffers allow direct interface with high-impedance signal sources. Excellent common-mode rejection and digital filtering provide greater than 100dB rejection of simultaneous 50Hz and 60Hz line noise. Other features include data hold, peak detection, and overrange/underrange detection. The MAX1365/MAX1367 require a 2.7V to 5.25V supply, a 4.75V to 5.25V V/I supply, and a 7V to 30V loop supply. They are available in a space-saving (7mm x 7mm), 48-pin TQFP package and operate over the extended (-40°C to +85°C) temperature range. Applications Automated Test Equipment Data-Acquisition Systems Digital Multimeters Digital Panel Meters Digital Voltmeters Industrial Process Control Features ♦ Stand-Alone, Digital Panel Meter 20-Bit Sigma-Delta ADC 4.5-Digit Resolution (±19,999 Count, MAX1365) 3.5-Digit Resolution (±1999 Count, MAX1367) No Integrating/Autozeroing Capacitors 100MΩ Input Impedance ±200mV or ±2.000V Input Range ♦ LED Display Common-Cathode 7-Segment LED Driver Programmable LED Current (0 to 20mA) 2.5Hz Update Rate ♦ Output DAC and Current Driver ±15-Bit DAC with 14-Bit Linear V/I Converter Selectable 0 to 16mA or 4–20mA Current Output Unipolar/Bipolar Modes ±50μA Zero Scale, ±40ppmFS/°C (typ) ±0.5% Gain Error, ±25ppmFS/°C (typ) Separate 7V to 30V Supply for Current-Loop Output ♦ 2.7V to 5.25V ADC/DAC Supply ♦ 4.75V to 5.25V V/I Converter Supply ♦ Internal 2.048V Reference or External Reference ♦ 48-Pin, 7mm x 7mm TQFP Package MAX1365/MAX1367 Stand-Alone, 4.5-/3.5-Digit Panel Meters with 4–20mA Output ________________________________________________________________ Maxim Integrated Products 1 Selector Guide 19-3889; Rev 1; 1/06 For pricing, delivery, and ordering information, please contact Maxim/Dallas Direct! at 1-888-629-4642, or visit Maxim’s website at www.maxim-ic.com. PART TEMP RANGE PIN-PACKAGE MAX1365ECM -40°C to +85°C 48 TQFP MAX1367ECM -40°C to +85°C 48 TQFP Ordering Information PART RESOLUTION (DIGITS) PKG CODE MAX1365ECM 4.5 C48-6 MAX1367ECM 3.5 C48-6 Pin Configuration appears at end of datasheet. Typical Operating Circuits appear at end of datasheet. MAX1365/MAX1367 Stand-Alone, 4.5-/3.5-Digit Panel Meters with 4–20mA Output 2 _______________________________________________________________________________________ ABSOLUTE MAXIMUM RATINGS ELECTRICAL CHARACTERISTICS (AVDD = DVDD = DAC_VDD = +2.7V to +5.25V, GND = 0, VLEDV = +2.7V to +5.25V, LEDG = 0, VREF+ - VREF- = 2.048V (external reference), 4-20OUT = 7V, VREG_AMP = +5.0V, CREF+ = 0.1μF, REF- = GND, CNEGV = 0.1μF. Internal clock mode, unless otherwise noted. All specifications are at TA = TMIN to TMAX. Typical values are at TA = +25°C, unless otherwise noted.) Stresses beyond those listed under “Absolute Maximum Ratings” may cause permanent damage to the device. These are stress ratings only, and functional operation of the device at these or any other conditions beyond those indicated in the operational sections of the specifications is not implied. Exposure to absolute maximum rating conditions for extended periods may affect device reliability. AVDD, DVDD ....................................................................-0.3V to +6.0V AIN+, AIN-, REF+, REF-.........................VNEGV to (AVDD + 0.3V) REG_FORCE, CMP, DAC_VDD, DACVOUT, CONV_IN, 4-20OUT.............................-0.3V to (AVDD + 0.3V) EN_BPM, EN_I, REFSELE, DACDATA_SEL, INTREF, RANGE, DPSET1, DPSET2, HOLD, PEAK, DPON, CS_DAC...............................................-0.3V to (DVDD + 0.3V) NEGV .......................................................-2.6V to (AVDD + 0.3V) LED_EN....................................................-0.3V to (DVDD + 0.3V) SET...........................................................-0.3V to (AVDD + 0.3V) REG_AMP, REG_VDD ...........................................-0.3V to +6.0V LEDV......................................................................-0.3V to +6.0V LEDG.....................................................................-0.3V to +0.3V GND_DAC .............................................................-0.3V to +0.3V GND_V/I.................................................................-0.3V to +0.3V SEG_ to LEDG.........................................-0.3V to (VLEDV + 0.3V) DIG_ to LEDG..........................................-0.3V to (VLEDV + 0.3V) REF_DAC .................................................-0.3V to (AVDD + 0.3V) DIG_ Sink Current .............................................................300mA DIG_ Source Current...........................................................50mA SEG_ Sink Current . ............................................................50mA SEG_ Source Current..........................................................50mA Maximum Current Input into Any Other Pin . ......................50mA Continuous Power Dissipation (TA = +70°C) 48-Pin TQFP (derate 22.7mW/°C above +70°C).....1818.2mW Operating Temperature Range ...........................-40°C to +85°C Storage Temperature Range .............................-60°C to +150°C Junction Temperature......................................................+150°C Lead Temperature (soldering, 10s) .................................+300°C PARAMETER SYMBOL CONDITIONS MIN TYP MAX UNITS ADC ACCURACY MAX1365 -19,999 +19,999 Noise-Free Resolution MAX1367 -1999 +1999 Counts 2.000V range ±1 Integral Nonlinearity (Note 1) INL 200mV range ±1 Counts Range Change Ratio (VAIN+ - VAIN- = 0.100V) on 200mV range; (VAIN+ - VAIN- = 0.100V) on 2.0V range 10:1 Ratio Rollover Error VAIN+ - VAIN- = full scale ±1 Counts Output Noise 10 μVP-P Offset Error (Zero Input Reading) VAIN+ - VAIN- = 0 (Note 2) -0 +0 Counts Gain Error (Note 3) -0.5 +0.5 %FSR Offset Drift (Zero Reading Drift) VAIN+ - VAIN- = 0 (Note 4) 0.1 μV/°C Gain Drift ±1 ppm/°C INPUT CONVERSION RATE Update Rate 5 Hz ANALOG INPUTS (AIN+, AIN-) (bypass to GND with 0.1μF or greater capacitors) RANGE = GND -2.0 +2.0 AIN Input Voltage Range (Note 5) RANGE = DVDD -0.2 +0.2 V AIN Absolute Input Voltage Range to GND -2.2 +2.2 V Normal-Mode 50Hz and 60Hz Rejection (Simultaneously) 50Hz and 60Hz ±2% 100 dB MAX1365/MAX1367 Stand-Alone, 4.5-/3.5-Digit Panel Meters with 4–20mA Output _______________________________________________________________________________________ 3 PARAMETER SYMBOL CONDITIONS MIN TYP MAX UNITS Common-Mode 50Hz and 60Hz Rejection (Simultaneously) CMR For 50Hz and 60Hz ±2%, RSOURCE < 10kΩ 150 dB Common-Mode Rejection CMR At DC 100 dB Input Leakage Current 10 nA Input Capacitance 10 pF Average Dynamic Input Current -20 +20 nA INTERNAL REFERENCE (REF- = GND, INTREF = DVDD) REF Input Voltage VREF 2.007 2.048 2.089 V REF Output Short-Circuit Current 1 mA REF Output Temperature Coefficient TCVREF 40 ppm/°C Load Regulation ISOURCE = 0 to 300μA, ISINK = 0 to 30μA 6 μV/μA Line Regulation 50 μV/V 0.1Hz to 10Hz 25 Noise Voltage 10Hz to 10kHz 400 μVP-P EXTERNAL REFERENCE (INTREF = GND) REF Input Voltage Differential (VREF+ - VREF-) 2.048 V Absolute REF+, REF- Input Voltage to GND (VREF+ Must Be Greater Than VREF-) -2.2 +2.2 V Normal-Mode 50Hz and 60Hz Rejection (Simultaneously) 50Hz and 60Hz ±2% 100 dB Common-Mode 50Hz and 60Hz Rejection (Simultaneously) CMR For 50Hz and 60Hz ±2%, RSOURCE < 10kΩ 150 dB Common-Mode Rejection CMR At DC 100 dB Input Leakage Current 10 nA Input Capacitance 10 pF Average Dynamic Input Current (Note 6) -20 +20 nA CHARGE PUMP Output Voltage NEGV CNEGV = 0.1μF to GND -2.60 -2.42 -2.30 V DIGITAL INPUTS (INTREF, RANGE, PEAK, HOLD, DPSET1, DPSET2) Input Current IIN VIN = 0 or DVDD -10 +10 μA Input Low Voltage VINL 0.3 x DVDD V Input High Voltage VINH 0.7 x DVDD V Input Hysteresis VHYS DVDD = 3V 200 mV ELECTRICAL CHARACTERISTICS (continued) (AVDD = DVDD = DAC_VDD = +2.7V to +5.25V, GND = 0, VLEDV = +2.7V to +5.25V, LEDG = 0, VREF+ - VREF- = 2.048V (external reference), 4-20OUT = 7V, VREG_AMP = +5.0V, CREF+ = 0.1μF, REF- = GND, CNEGV = 0.1μF. Internal clock mode, unless otherwise noted. All specifications are at TA = TMIN to TMAX. Typical values are at TA = +25°C, unless otherwise noted.) MAX1365/MAX1367 Stand-Alone, 4.5-/3.5-Digit Panel Meters with 4–20mA Output 4 _______________________________________________________________________________________ ELECTRICAL CHARACTERISTICS (continued) (AVDD = DVDD = DAC_VDD = +2.7V to +5.25V, GND = 0, VLEDV = +2.7V to +5.25V, LEDG = 0, VREF+ - VREF- = 2.048V (external reference), 4-20OUT = 7V, VREG_AMP = +5.0V, CREF+ = 0.1μF, REF- = GND, CNEGV = 0.1μF. Internal clock mode, unless otherwise noted. All specifications are at TA = TMIN to TMAX. Typical values are at TA = +25°C, unless otherwise noted.) PARAMETER SYMBOL CONDITIONS MIN TYP MAX UNITS ADC POWER SUPPLY (Note 7) AVDD Voltage AVDD 2.70 5.25 V DVDD Voltage DVDD 2.70 5.25 V Power-Supply Rejection AVDD PSRA (Note 8) 80 dB Power-Supply Rejection DVDD PSRD (Note 8) 100 dB 640 AVDD Current (Note 9) IAVDD Standby mode 305 μA DVDD = +5.25V 320 DVDD Current (Note 9) IDVDD DVDD = +3.3V 180 Standby mode 20 μA DAC POWER SUPPLY DAC Supply Voltage VDAC_VDD 2.70 5.25 V DAC Supply Current 0.10 0.21 mA LINEAR REGULATOR AND V/I CONVERTER POWER REQUIREMENTS REG_AMP Supply Voltage VREG_AMP 4.75 5.25 V REG_AMP Supply Current 0.19 0.30 mA REG_VDD Supply Voltage VREG_VDD 5.20 V REG_VDD Supply Current Includes 20mA programmed current 25.2 27.4 mA LED DRIVERS LED Supply Voltage VLEDV 2.70 5.25 V LED Shutdown Supply Current ISHDN 10 μA LED Supply Current ILEDV 176 180 mA MAX1365 512 Display Scan Rate fOSC MAX1367 640 Hz Segment Current Slew Rate ISEG/Δt 25 mA/μs DIG_ Voltage Low VDIG 0.178 0.300 V Segment-Drive Source-Current Matching ΔISEG 3 ±12 % Segment-Drive Source Current ISEG VLEDV - VSEG = 0.6V, RSET = 25kΩ 15.0 21.5 25.5 mA LED Drivers Bias Current From AVDD 120 μA Interdigit Blanking Time 4 μs MAX1365/MAX1367 Stand-Alone, 4.5-/3.5-Digit Panel Meters with 4–20mA Output _______________________________________________________________________________________ 5 ELECTRICAL CHARACTERISTICS (continued) (AVDD = DVDD = DAC_VDD = +2.7V to +5.25V, GND = 0, VLEDV = +2.7V to +5.25V, LEDG = 0, VREF+ - VREF- = 2.048V (external reference), 4-20OUT = 7V, VREG_AMP = +5.0V, CREF+ = 0.1μF, REF- = GND, CNEGV = 0.1μF. Internal clock mode, unless otherwise noted. All specifications are at TA = TMIN to TMAX. Typical values are at TA = +25°C, unless otherwise noted.) PARAMETER SYMBOL CONDITIONS MIN TYP MAX UNITS DAC OUTPUT ACCURACY Zero-Scale Error 4–20mA or 0 to 16mA mode, TA = +25°C ±50 μA Zero-Scale Error Tempco ±40 p p mFS /° C Gain Error 4–20mA or 0 to 16mA mode, TA = +25°C ±0.5 %FS Gain-Error Tempco ±25 p p mFS /° C Span Linearity ±2 ±4 μA Power-Supply Rejection PSR VEXT = 7V to 30V 4 μA/V Signal Path Noise 10pF to GND on 4-20OUT 2.0 μARMS 4–20mA Current Limit Limited to 12.5 x VREF / 1.28kΩ 20 mA Note 1: Integral nonlinearity is the deviation of the analog value at any code from its theoretical value after nulling the gain error and offset error. Note 2: Offset calibrated. Note 3: Offset nulled. Note 4: Drift error is eliminated by recalibration at the new temperature. Note 5: The input voltage range for the analog inputs is given with respect to the voltage on the negative input of the differential pair. Note 6: VAIN+ or VAIN- = -2.2V to +2.2V. VREF+ or VREF- = -2.2V to +2.2V. All input structures are identical. Production tested on AIN+ and REF+ only. VREF+ must always be greater than VREF-. Note 7: Power-supply currents are measured with all digital inputs at either GND or DVDD. Note 8: Measured at DC by changing the power-supply voltage from 2.7V to 5.25V and measuring the effect on the conversion error with external reference. PSRR at 50Hz and 60Hz exceeds 120dB with filter notches at 50Hz and 60Hz (Figure 1). Note 9: LED drivers are disabled. MAX1365/MAX1367 Stand-Alone, 4.5-/3.5-Digit Panel Meters with 4–20mA Output 6 _______________________________________________________________________________________ 0 300 200 100 400 500 600 700 800 900 1000 2.7 3.2 3.7 4.2 4.7 5.2 SUPPLY CURRENT vs. SUPPLY VOLTAGE MAX1365/67 toc01 SUPPLY VOLTAGE (V) SUPPLY CURRENT (μA) DAC_VDD AVDD DVDD 0 200 100 400 300 600 500 700 -40 -15 10 35 60 85 SUPPLY CURRENT vs. TEMPERATURE MAX1365/67 toc02 TEMPERATURE (°C) SUPPLY CURRENT (μA) AVDD DVDD DAC_VDD MAX1365 OFFSET ERROR vs. SUPPLY VOLTAGE MAX1365/67 toc03 SUPPLY VOLTAGE (V) OFFSET ERROR (LSB) 3.25 3.75 4.25 4.75 -0.11 -0.06 -0.01 0.04 0.09 0.14 0.19 -0.16 2.75 5.25 MAX1365 OFFSET ERROR vs. TEMPERATURE MAX1365/67 toc04 TEMPERATURE (°C) OFFSET ERROR (LSB) 10 20 30 40 50 60 -0.1 0 0.1 0.2 0.3 0.4 0.5 0.6 -0.2 0 70 MAX1365 GAIN ERROR vs. SUPPLY VOLTAGE MAX1365/67 toc05 SUPPLY VOLTAGE (V) GAIN ERROR (% FULL SCALE) 3.25 3.75 4.25 4.75 -0.08 -0.04 -0.06 -0.02 0 0.02 0.04 0.06 0.08 -0.10 2.75 5.25 MAX1365 GAIN ERROR vs. TEMPERATURE MAX1365/67 toc06 TEMPERATURE (°C) GAIN ERROR (% FULL SCALE) 10 20 30 40 50 60 -0.09 -0.08 -0.07 -0.06 -0.05 -0.04 -0.03 -0.02 -0.01 0 -0.10 0 70 MAX1365 INL (±200mV INPUT RANGE) vs. OUTPUT CODE MAX1365/67 toc07 OUTPUT CODE INL (COUNTS) -10,000 0 10,000 -0.5 0 0.5 1.0 -1.0 -20,000 20,000 MAX1365 INL (±2V INPUT RANGE) vs. OUTPUT CODE MAX1365/67 toc08 OUTPUT CODE INL (COUNTS) -10,000 0 10,000 -0.5 0 0.5 1.0 -1.0 -20,000 20,000 NOISE DISTRIBUTION MAX1365/67 toc09 NOISE (LSB) PERCENTAGE OF UNITS (%) -0.1 0 0.1 0.2 0.3 0.4 0.5 0.6 0.7 0.8 5 10 15 20 25 0 -0.2 Typical Operating Characteristics (AVDD = DVDD = +5V, VDAC_VDD = +5.0V, GND = 0, LEDG = 0, VLEDV = +2.7V to +5.25V, VREF+ - VREF- = 2.048V (external reference), VEXT = 7V, CREF+ = CREF- = 0.1μF, CNEGV = 0.1μF. Internal clock mode, unless otherwise noted. TA = +25°C, unless otherwise noted.) MAX1365/MAX1367 Stand-Alone, 4.5-/3.5-Digit Panel Meters with 4–20mA Output _______________________________________________________________________________________ 7 INTERNAL REFERENCE VOLTAGE vs. TEMPERATURE MAX1365/67 toc10 TEMPERATURE (°C) REFERENCE VOLTAGE (V) 10 20 30 40 50 60 2.046 2.045 2.047 2.049 2.048 2.051 2.050 2.053 2.052 2.054 2.044 0 70 INTERNAL REFERENCE VOLTAGE vs. ANALOG SUPPLY VOLTAGE MAX1365/67 toc11 SUPPLY VOLTAGE (V) REFERENCE VOLTAGE (V) 3.25 3.75 4.25 4.75 2.045 2.046 2.047 2.048 2.049 2.050 2.044 2.75 5.25 DATA OUTPUT RATE vs. TEMPERATURE MAX1365/67 toc12 TEMPERATURE (°C) DATA OUTPUT RATE (Hz) -15 10 35 60 4.92 4.98 4.96 4.94 5.00 5.02 5.04 5.06 5.08 5.10 4.90 -40 85 DATA OUTPUT RATE vs. SUPPLY VOLTAGE MAX1365/67 toc13 SUPPLY VOLTAGE (V) DATA OUTPUT RATE (Hz) 3.21 3.72 4.23 4.74 4.995 4.990 4.985 5.000 5.005 5.010 5.015 5.020 4.980 2.70 5.25 OFFSET ERROR vs. COMMON-MODE VOLTAGE MAX1365/67 toc14 COMMON-MODE VOLTAGE (V) OFFSET ERROR (LSB) -1.5 -1.0 -0.5 0 0.5 1.0 1.5 -0.15 -0.10 -0.05 0 0.05 0.10 0.15 0.20 -0.20 -2.0 2.0 VNEG STARTUP SCOPE SHOT MAX1365/67 toc15 20ms/div 2V/div 1V/div VDD VNEG CHARGE-PUMP OUTPUT VOLTAGE vs. ANALOG SUPPLY VOLTAGE MAX1365/67 toc16 SUPPLY VOLTAGE (V) VNEG VOLTAGE (V) 3.25 3.75 4.25 4.75 -2.48 -2.46 -2.44 -2.42 -2.40 -2.50 2.75 5.25 SEGMENT CURRENT vs. SUPPLY VOLTAGE MAX1365/67 toc17 SUPPLY VOLTAGE (V) SEGMENT CURRENT (μA) 3.21 3.72 4.23 4.74 5 10 15 20 25 30 0 2.70 5.25 RISET = 25kΩ -0.2 0 -0.1 0.2 0.1 0.3 0.4 -40 -15 10 35 60 85 DAC ZERO-CODE OFFSET ERROR vs. TEMPERATURE MAX1365/67 toc18 TEMPERATURE (°C) OFFSET ERROR (LSB) Typical Operating Characteristics (continued) (AVDD = DVDD = +5V, VDAC_VDD = +5.0V, GND = 0, LEDG = 0, VLEDV = +2.7V to +5.25V, VREF+ - VREF- = 2.048V (external reference), VEXT = 7V, CREF+ = CREF- = 0.1μF, CNEGV = 0.1μF. Internal clock mode, unless otherwise noted. TA = +25°C, unless otherwise noted.) Stand-Alone, 4.5-/3.5-Digit Panel Meters with 4–20mA Output 8 _______________________________________________________________________________________ Typical Operating Characteristics (continued) (AVDD = DVDD = +5V, VDAC_VDD = +5.0V, GND = 0, LEDG = 0, VLEDV = +2.7V to +5.25V, VREF+ - VREF- = 2.048V (external reference), VEXT = 7V, CREF+ = CREF- = 0.1μF, CNEGV = 0.1μF. Internal clock mode, unless otherwise noted. TA = +25°C, unless otherwise noted.) -0.30 -0.20 -0.25 -0.10 -0.15 -0.05 0 -40 -15 10 35 60 85 DAC GAIN ERROR vs. TEMPERATURE MAX1365/67 toc19 TEMPERATURE (°C) GAIN ERROR (LSB) 4–20OUT = 21.7mA CONV_IN = 1V 10mA/div 500mV/div STEP RESPONSE MAX1365/67 toc20 100μs/div -50 -20 -30 -40 0 -10 40 30 20 10 50 -40 -20 0 20 40 60 80 4–20OUT ZERO-SCALE ERROR vs. TEMPERATURE MAX1365/67 toc21 TEMPERATURE (°C) CURRENT OUTPUT (μA) EXTERNAL REFERENCE = 2.048V -50 -20 -30 -40 0 -10 40 30 20 10 50 -40 -20 0 20 40 60 80 4–20OUT GAIN ERROR vs. TEMPERATURE MAX1365/67 toc22 TEMPERATURE (°C) GAIN ERROR (%) EXTERNAL REFERENCE = 2.048V 4–20mA MODE 0 TO 16mA MODE -0.5 0 0.5 1.0 1.5 2.0 2.5 -20,000 -10,000 0 10,000 20,000 4–20OUT vs. DAC CODE (4–20OUT SPAN LINEARITY) MAX1365/67 toc24 DAC CODE (COUNTS) SPAN LINEARITY (μA) OFFSET ENABLED (EN_I = HIGH) -150 -100 -50 0 50 100 150 4 6 8 10 12 14 16 18 20 POWER-SUPPLY REJECTION vs. CURRENT OUTPUT (4-20OUT) MAX1365/67 toc23 4-20OUT OUTPUT CURRENT (mA) POWER-SUPPLY REJECTION (nA/V) MAX1365/MAX1367 Stand-Alone, 4.5-/3.5-Digit Panel Meters with 4–20mA Output _______________________________________________________________________________________ 9 PIN NAME FUNCTION 1 AIN+ Positive Analog Input. Positive side of fully differential analog input. Bypass AIN+ to GND with a 0.1μF or greater capacitor. 2 AINNegative Analog Input. Negative side of fully differential analog input. Bypass AIN- to GND with a 0.1μF or greater capacitor. 3 GND Ground. Connect to star ground. 4 AVDD Analog Positive Supply Voltage. Connect AVDD to a +2.7V to +5.25V power supply. Bypass AVDD to GND with a 0.1μF capacitor. 5 DVDD Digital Positive Supply Voltage. Connect DVDD to a +2.7V to +5.25V power supply. Bypass DVDD to GND with a 0.1μF capacitor. 6 SET Segment Current Set. Connect to ground through a resistor to set the segment current. See Table 7 for segment-current selection. 7 REG_VDD V/I Converter Regulated Supply Output (5.2V typ) 8 REG_FORCE REG_VDD Control. Drives the gate of external depletion-mode FET. 9 REG_AMP Regulator/Reference Buffer Supply. Connect to a 4.75V to 5.25V power supply. 10 CMP Regulator Compensation Node. Connect a 0.1μF capacitor from CMP to REG_FORCE. 11 DAC_VDD DAC Analog Supply. Connect DAC_VDD to a +2.7V to +5.25V power supply. 12 DACVOUT DAC Voltage Output. DAC output impedance is typically 6.2kΩ. 13 CONV_IN V/I Converter Input 14 4-20OUT 4–20mA (0 to 16mA) Current-Loop Output. Referenced to GND. 15 GND_DAC DAC Analog Ground. Connect to star ground. 16 GND_V/I V/I Converter Analog Ground. Connect to star ground. 17 REF_DAC V-to-I Converter/DAC Reference Input. Connect a voltage source for external reference operation or leave floating for internal reference. Bypass REF_DAC with a 0.1μF capacitor to GND for either internal or external reference operation. 18 EN_BPM Acti ve- H i g h V /I- C onver ter Bi p ol ar - M od e E nab l e. S et hi g h for b i p ol ar m od e. S et l ow for uni p ol ar m od e. 19 EN_I Acti ve- H i g h V /I- C onver ter 4m A O ffset E nab l e. S et l ow for 0 to 16m A outp ut. S et hi g h for 4–20m A. 20 REFSELE DAC External Reference Selection. Set low for internal reference. Set high for external reference. Leave REF_DAC unconnected when REFSELE is low. 21 DACDATA_SEL DAC Data-Source Select. Connect to logic high for the MAX1365/MAX1367. 22 CS_DAC DAC Chip Select. Connect to logic high for the MAX1365/MAX1367. 23 INTREF ADC Reference Selection. Set INTREF high to select the internal ADC reference. Set INTREF low to select external ADC reference. 24 RANGE ADC Range Select. Set RANGE low for ±2V analog input voltage range. Set RANGE high for ±200mV analog input voltage range. 25 PEAK Peak Logic Input. Connect PEAK to DVDD to display the highest ADC value on the LED. Connect PEAK to GND to disable the PEAK function (see Table 1). Pin Description MAX1365/MAX1367 Stand-Alone, 4.5-/3.5-Digit Panel Meters with 4–20mA Output 10 ______________________________________________________________________________________ PIN NAME FUNCTION 26 HOLD Hold Logic Input. Connect HOLD to DVDD to hold the current ADC value on the LED. Connect HOLD to GND to update the LED at a rate of 2.5Hz and disable the hold function. Placing the device into hold mode initiates an offset mismatch calibration. Assert HOLD high for a minimum of 2s to ensure the completion of offset mismatch calibration (see Table 1). 27 DPSET2 Display Decimal-Point Logic-Input 2. Controls the decimal point of the LED. See the Decimal-Point Control section. 28 DPSET1 Display Decimal-Point Logic-Input 1. Controls the decimal point of the LED. See the Decimal-Point Control section. 29 LEDG LED Segment-Drivers Ground 30 DIG0 Digit 0 Driver Out (Connected to GLED for the MAX1367) 31 DIG1 Digit 1 Driver Out 32 DIG2 Digit 2 Driver Out 33 DIG3 Digit 3 Driver Out 34 DIG4 Digit 4 Driver Out 35 SEGA Segment A Driver 36 SEGB Segment B Driver 37 LEDV LED-Display Segment-Driver Supply. Connect to a +2.7V to +5.25V supply. Bypass with a 0.1μF capacitor to LEDG. 38 SEGC Segment C Driver 39 SEGD Segment D Driver 40 SEGE Segment E Driver 41 SEGF Segment F Driver 42 SEGG Segment G Driver 43 SEGDP Segment DP Driver 44 LED_EN Active-High LED Enable. The MAX1365/MAX1367 display driver turns off when LED_EN is low. The MAX1365/MAX1367 LED-display driver turns on when LED_EN is high. 45 NEGV -2.5V Charge-Pump Voltage Output. Connect a 0.1μF capacitor to GND. 46 DPON Decimal-Point Enable Input. Controls the decimal point of the LED. See the Decimal-Point Control section. Connect DPON to DVDD to enable the decimal point. 47 REFADC Negative Reference Voltage Input. For internal reference operation, connect REF- to GND. For external reference operation, bypass REF- to GND with a 0.1μF capacitor and set VREF- from -2.2V to +2.2V (VREF+ > VREF-). 48 REF+ ADC Positive Reference Voltage Input. For internal reference operation, connect a 4.7μF capacitor from REF+ to GND. For external reference operation, bypass REF+ to GND with a 0.1μF capacitor and set VREF+ from -2.2V to +2.2V (VREF+ > VREF-). Pin Description (continued) Detailed Description The MAX1365/MAX1367 low-power, highly integrated ADCs with LED drivers convert a ±2V differential input voltage (one count is equal to 100μV for the MAX1365 and 1mV for the MAX1367) with a sigma-delta ADC and output the result to an LED display. An additional ±200mV input range (one count is equal to 10μV for the MAX1365 and 100μV for the MAX1367) is available to measure small signals with finer resolution. In addition to displaying the results on an LED display, these devices feature a DAC and V-to-I converter for 4–20mA (or 0 to 16mA) current output that proportionally follows the ADC input. The MAX1365/MAX1367 use an external depletion-mode NMOS transistor to regulate 7V to 30V for the V/I converter. Use the 4–20mA (or 0 to 16mA) output to drive a remote display, data logger, PLC input, or other 4–20mA devices in a current loop. The MAX1365/MAX1367 include a 2.048V reference, internal charge pump, and a high-accuracy on-chip oscillator. The devices feature on-chip buffers for the differential input signal and external-reference inputs, allowing direct interface with high-impedance signal sources. In addition, they use continuous internal offsetcalibration and offer > 100dB of 50Hz and 60Hz linenoise rejection. Other features include data hold and peak detection and overrange/underrange detection. Analog Input Protection The MAX1365/MAX1367 provide internal protection diodes that limit the analog input range on AIN+, AIN-, REF+, and REF- from NEGV to (AVDD + 0.3V). If the analog input exceeds this range, limit the input current to 10mA. Internal Analog Input/Reference Buffers The MAX1365/MAX1367 analog input/reference buffers allow the use of high-impedance signal sources. The input buffers’ common-mode input range allows the analog inputs and the reference to range from -2.2V to +2.2V. Modulator The MAX1365/MAX1367 perform analog-to-digital conversions using a single-bit, 3rd-order, sigma-delta modulator. The sigma-delta modulator converts the input MAX1365/MAX1367 Stand-Alone, 4.5-/3.5-Digit Panel Meters with 4–20mA Output ______________________________________________________________________________________ 11 LED DRIVER LEDG SEGA SEGG DIG0(1) DIG4(4) LED_EN MAX1365 MAX1367 ADC INPUT BUFFER -2.5V AIN+ AINREF+ REFNEGV +2.5V 2.048V BANDGAP REFERENCE LOGIC GND CHARGE PUMP -2.5V OUTPUT DAC DAC REF BUFFER AVDD DVDD INTREF RANGE 5V REGULATOR V/I CONVERTER CURRENT SUMMER AND AMPLIFIER OFFSET GENERATOR EN_BPM EN_I DACVOUT 4-20OUT REG_FORCE CS_DAC DACDATA_SEL SET REFSELE REF_DAC REG_AMP CONV_IN CMP REG_VDD DAC_VDD PEAK DPON DPSET1 DPSET 2 HOLD LEDV Functional Diagram MAX1365/MAX1367 Stand-Alone, 4.5-/3.5-Digit Panel Meters with 4–20mA Output 12 ______________________________________________________________________________________ signal into a digital pulse train whose average duty cycle represents the digitized signal information. The modulator quantizes the input signal at a much higher sample rate than the bandwidth of the input. The MAX1365/MAX1367 modulator provides 3rd-order frequency shaping of the quantization noise resulting from the single-bit quantizer. The modulator is fully differential for maximum signal-to-noise ratio and minimum susceptibility to power-supply noise. A single-bit data stream is then presented to the digital filter to remove the frequency-shaped quantization noise. Digital Filtering The MAX1365/MAX1367 contain an on-chip digital lowpass filter that processes the data stream from the modulator using a SINC4 response: The SINC4 filter has a settling time of four output data periods (4 x 200ms). The MAX1365/MAX1367 have 25% overrange capability built into the modulator and digital filter. The digital filter is optimized for the fCLK equal to 4.9152MHz. The frequency response of the SINC4 filter is calculated as follows: where N is the oversampling ratio, and fm = N x output data rate = 5Hz. Filter Characteristics Figure 1 shows the filter frequency response. The SINC4 characteristic -3dB cutoff frequency is 0.228 times the first notch frequency (5Hz). The oversampling ratio (OSR) for the MAX1367 is 128 and the OSR for the MAX1365 is 1024. The output data rate for the digital filter corresponds to the positioning of the first notch of the filter’s frequency response. The notches of the SINC4 filter are repeated at multiples of the first notch frequency. The SINC4 filter provides an attenuation of better than 100dB at these notches. For example, 50Hz is equal to 10 times the first notch frequency and 60Hz is equal to 12 times the first notch frequency. For large step changes at the input, allow a settling time of 800ms before valid data is read. Internal Clock The MAX1365/MAX1367 contain an internal oscillator. Using the internal oscillator saves board space by removing the need for an external clock source. The oscillator is optimized to give 50Hz and 60Hz powersupply and common-mode rejection. Charge Pump The MAX1365/MAX1367 contain an internal charge pump to provide the negative supply voltage for the internal analog input/reference buffers. The bipolar input range of the analog input/reference buffers allows this device to accept negative inputs with high source impedances. Connect a 0.1μF capacitor from NEGV to GND. LED Driver (Table 1) The MAX1365 has a 4.5-digit common-cathode display driver, and the MAX1367 has a 3.5-digit common-cathode display driver. In addition, the LED drivers of the MAX1365/MAX1367 feature peak-detection and datahold circuitry. Figures 2 and 3 show the connection schemes for a standard seven-segment LED display. The LED update rate is 2.5Hz. Figure 4 shows a typical common-cathode configuration for two digits. In common-cathode configuration, the cathodes of all LEDs in a digit are connected together. Each segment driver of the MAX1365/MAX1367 connects to its corresponding LED’s anodes. For example, segment driver SEGA connects to all LED segments designated as A. Similar configurations are used for other segment drivers. H z Z N H f N N f f f f N Z m m ( ) ( ) ( ) sin sin ( ) = − = − − − 11 1 1 4 4 1 π π sin(x) x 4 FREQUENCY (Hz) GAIN (dB) 10 20 30 40 50 -160 -120 -80 -40 0 -200 0 60 Figure 1. Frequency Response of the SINC4 Filter (Notch at 60Hz) The MAX1365/MAX1367 use a multiplexing scheme to drive one digit at a time. The scan rate is fast enough to make the digits appear to be lit. Figure 5 shows the data-timing diagram for the MAX1365/MAX1367 where T is the display scan period (typically around 1/512Hz or 1.9531ms). TON in Figure 5 denotes the amount of time each digit is on and is calculated as follows: Decimal-Point Control The MAX1365/MAX1367 allow for full decimal-point control and feature leading-zero suppression. Use the DPON, DPSET1, and DPSET2 bits in the control register to set the value of the decimal point (Tables 2 and 3). The MAX1365/MAX1367 overrange and underrange display is shown in Table 4. Leading-Zero Suppression The MAX1365/MAX1367 include a leading-zero suppression circuitry to turn off unnecessary zeros. For example, when DPSET1 and DPSET2 = [0,0], 0.0 is displayed instead of 000.0 (MAX1365). This feature saves a substantial amount of power by not lighting unnecessary LEDs. Interdigit Blanking The MAX1365/MAX1367 also include an interdigitblanking circuitry. Without this feature, it is possible to see a faint digit next to a digit that is completely on. The interdigit-blanking circuitry prevents ghosting over into the next digit for a short period of time. The typical interdigit blanking time is 4μs. T T ms ON = = = s 5 1 95312 5 390 60 . . μ MAX1365/MAX1367 Stand-Alone, 4.5-/3.5-Digit Panel Meters with 4–20mA Output ______________________________________________________________________________________ 13 A B C A A A A D DIGIT 4 DIGIT 3 DIGIT 2 DIGIT 1 DIGIT 0 D D D D E G F E E E F G B F G B F G B F G B C C C C DP DP DP DP DP Figure 2. Segment Connection for the MAX1365 (4.5 Digits) A B A A A D DIGIT 4 DIGIT 3 DIGIT 2 DIGIT 1 D D D E G F E E F G B F G B F G B C C C DP DP DP DP C Figure 3. Segment Connection for the MAX1367 (3.5 Digits) HOLD PEAK DISPLAY VALUES FORM 1 X Hold value 0 1 Peak value 0 0 Latest ADC result Table 1. LED Priority Table X = Don’t care. DPON DPSET1 DPSET2 DISPLAY OUTPUT ZERO INPUT READING 1 0 0 1888. 0. 1 0 1 188.8 0.0 1 1 0 18.88 0.00 1 1 1 1.888 0.000 Table 3. Decimal-Point Control Table— MAX1367 CONDITION MAX1367 MAX1365 Overrange 1--- 1---- Underrange -1--- -1---- Table 4. LED During Overrange and Underrange Conditions DPON DPSET1 DPSET2 DISPLAY OUTPUT ZERO INPUT READING 0 0 0 18888 0 0 0 1 18888 0 0 1 0 18888 0 0 1 1 18888 0 1 0 0 1888.8 0.0 1 0 1 188.88 0.00 1 1 0 18.888 0.000 1 1 1 1.8888 0.0000 Table 2. Decimal-Point Control Table— MAX1365 Current Output The MAX1365/MAX1367 feature a 4–20mA (0 to 16mA) current output for driving remote panel meters, data loggers, and process controllers in industrial applications. The DAC output is proportional to the input of the ADC and LED display. In the simplest configuration, connect DAC_VOUT directly to CONV_IN to have the current output (4–20mA or 0 to 16mA) follow the analog inputs. Custom signal conditioning can be inserted between DAC_VOUT and CONV_IN, or CONV_IN can be driven independently by a voltage source if desired. See Figures 11–14 for the transfer functions of the DAC and V/I converter. Note: The MAX1365/MAX1367 expect a 6kΩ (typ) source impedance from the external voltage source driving CONV_IN. Current Offset Set EN_I high for a current span of 4–20mA. Set EN_I low for a current span of 0 to 16mA. See Table 5 for current output. Unipolar Mode Set EN_BPM low to engage unipolar operation. In unipolar mode, the current output at 4-20OUT (4–20mA or 0 to 16mA) maps the analog input voltage (0 to 2V or 0 to 200mV). Negative voltages at the analog input result in a 4mA or 0mA output, depending on the EN_I setting. See Table 5 for current output. See Figures 12 and 13. MAX1365/MAX1367 Stand-Alone, 4.5-/3.5-Digit Panel Meters with 4–20mA Output 14 ______________________________________________________________________________________ A A A DIGIT 1 DIGIT 2 SEGDP SEGG SEGF SEGE SEGD SEGC SEGB SEGA D D E E F G B F G B C C DP DP B C D E F G DP A B C D E F G DP Figure 4. 2-Digit Common-Cathode Configuration 4 3 2 1 0 4 3 2 1 0 4 T TON DIGIT 4 (MSD) DIGIT 3 INTERDIGIT BLANKING TIME DIGIT 2 DIGIT 1 DIGIT 0 (LSD) DATA MSD LSD Figure 5. LED Voltage Waveform Bipolar Mode Set EN_BPM high to engage bipolar operation. In bipolar mode, the current output at 4–20OUT (4–20mA or 0 to 16mA) maps the analog input voltage (±2V or ±200mV). In bipolar mode, a 0V analog input maps to midscale (12mA). See Table 5 for current output (see Figures 12 and 13). 5.2V Linear Regulator with Compensation The MAX1365/MAX1367 feature a 5.2V linear regulator. The 5.2V regulator consists of an op amp and connections to an external depletion-mode FET. The 5.2V regulator regulates the loop voltage that powers the voltage-to-current converter and the rest of the transmitter circuitry. The regulator output voltage is available at REG_VDD and is given by the equation: VREG_VDD = 2.54 x VREF+ The FET breakdown and saturation voltages determine the usable range of loop voltages (VEXT). The external FET parameters such as VGS (off), IDSS, and transconductance must be chosen so that the op amp output on the REG_FORCE pin can control the FET operating point while swinging in the range from VREG_AMP to REG_VDD. See the Selecting Depletion-Mode FET section in the Applications Information section. Connect a 0.1μF capacitor between CMP and REG_FORCE to ensure stable operation of the regulator. Applications Information Power-On Reset At power-on, the digital filter and modulator circuits reset. The MAX1365 allows 6s for the reference to stabilize before performing enhanced offset calibration. MAX1365/MAX1367 Stand-Alone, 4.5-/3.5-Digit Panel Meters with 4–20mA Output ______________________________________________________________________________________ 15 CURRENT OUTPUT (mA) ANALOG INPUT UNIPOLAR MODE (EN_I = LOW) UNIPOLAR MODE (EN_I = HIGH) BIPOLAR MODE (EN_I = LOW) BIPOLAR MODE (EN_I = HIGH) Negative Full Scale 0 4 0 4 0V 0 4 8 12 Positive Full Scale 16 20 16 20 Table 5. Current Output Table MAX1365 MAX1367 AVDD DVDD 10μF 10μF 0.1μF 0.1μF 0.1μF 0.1μF ANALOG SUPPLY FERRITE BEAD RREF R R ACTIVE GAUGE DUMMY GAUGE REF+ REFNEGV AIN+ AIN- 4-20OUT 4–20mA/0 TO 16mA CURRENT-LOOP OUTPUT GND 0.1μF 0.1μF Figure 6. Strain-Gauge Application with the MAX1365/MAX1367 MAX1365/MAX1367 During these 6s, the MAX1365 displays 1.2V to 1.5V when a stable reference is detected. If a valid reference is not found, the MAX1365 times out after 6s and begins enhanced offset calibration. Enhanced offset calibration typically lasts 2s. The MAX1365 begins converting after enhanced offset calibration. Reference ADC Reference The MAX1365/MAX1367 reference sets the full-scale range of the ADC transfer function. With a nominal 2.048V reference, the ADC full-scale range is ±2V with RANGE = GND. With RANGE = DVDD, the full-scale range is ±200mV. A decreased reference voltage decreases full-scale range (see the Transfer Functions section). The ADC of the MAX1365/MAX1367 can accept either an external reference or an internal reference (INTREF). The INTREF logic selects the reference mode. For internal- reference operation, set INTREF to DVDD, connect REF- to GND, and bypass REF+ to GND with a 4.7μF capacitor. The internal reference provides a nominal 2.048V source between REF+ and GND. The internalreference temperature coefficient is typically 40ppm/°C. For external-reference operation, set INTREF to GND. REF+ and REF- are fully differential. For a valid external- reference input, VREF+ must be greater than VREF-. Bypass REF+ and REF- with a 0.1μF or greater capacitor to GND in external-reference mode. Figure 6 shows the MAX1365/MAX1367 operating with an external differential reference. In this figure, REF- is connected to the top of the strain gauge and REF+ is connected to the midpoint of the resistor-divider of the supply. DAC Reference The DAC of the MAX1365/MAX1367 accept either an external reference or an internal reference. The REFSELE enables or disables the internal reference. For externalreference operation, disable the DAC reference buffer by setting REFSELE to DVDD and connect a voltage source to REF_DAC. For internal-reference operation, enable the DAC reference buffer by setting REFSELE to GND. In this mode, leave REFDAC floating. In either internal or external reference operation, bypass REF_DAC with a 0.1μF capacitor to GND. Choose a reference with output impedance (load regulation equivalent) of 100mΩ or less, such as the MAX6126. For best performance, use an external reference source for the ADC and DAC. DAC Operation For the MAX1365/MAX1367, a voltage proportional to the ADC input is available at DACVOUT. Connect DACVOUT to CONV_IN for normal operation. See Figure 11 for the DAC transfer function. Offset Calibration The MAX1365/MAX1367 offer on-chip offset calibration. The device offset calibrates during every conversion cycle. Enhanced Offset Calibration Enhanced offset calibration is a more accurate calibration method that is needed in the case of the ±200mV range and 4.5-digit resolution. In addition to enhanced offset calibration at power-up, the MAX1365/MAX1367 perform enhanced calibration on demand by connecting HOLD to AVDD for > 2s. Peak The MAX1365/MAX1367 feature peak-detection circuitry. When activated, the devices display only the highest voltage measured to the LED. First, the current ADC result is displayed. The new ADC conversion result is compared to the current result. If the new value is larger than the previous peak value, the new value is displayed. If the new value is less than the previous peak value, the display remains unchanged. Connect PEAK to GND to clear the peak value and disable the peak function. See Table 1 for LED Display priority. Hold The MAX1365/MAX1367 feature data-hold circuitry. When activated, the device holds the current reading on the LED. Strain-Gauge Measurement Connect the differential inputs of the MAX1365/ MAX1367 to the bridge network of the strain gauge. In Figure 6, the analog supply voltage powers the bridge network and the MAX1365/MAX1367, along with the reference voltage. The MAX1365/MAX1367 handle an analog input voltage range of ±200mV and ±2V full scale. The analog/reference inputs of the parts allow the analog input range to have an absolute value of anywhere between -2.2V and +2.2V. Stand-Alone, 4.5-/3.5-Digit Panel Meters with 4–20mA Output 16 ______________________________________________________________________________________ Transfer Functions ADC Transfer Functions Figures 7–10 show the transfer functions of the MAX1365/MAX1367. The output data is stored in the ADC data register in two’s complement. The transfer function for the MAX1365 with AIN+ - AIN- ≥ 0 and RANGE = GND is: The transfer function for the MAX1365 with AIN+ - AIN- < 0 and RANGE = GND is: The transfer function for the MAX1367 with AIN+ - AIN- ≥ 0 and RANGE = GND is: (3) COUNT 1.024 2000 V V V V AIN AIN x REF REF = + − − + − − (2) COUNT 1.024 20,000 1 V V V V AIN AIN x REF REF = + − − + + − − (1) COUNT 1.024 20,000 V V V V AIN AIN x REF REF = + − − + − − MAX1365/MAX1367 Stand-Alone, 4.5-/3.5-Digit Panel Meters with 4–20mA Output ______________________________________________________________________________________ 17 -2V 0 ANALOG INPUT VOLTAGE +2V LED 1 - - - - 19,999 2 1 0 - 0 - 1 - 2 -19,999 - 1 - - - - -100μV 100μV Figure 7. MAX1365 Transfer Function—±2V Range -200mV 0 ANALOG INPUT VOLTAGE +200mV LED 1 - - - - 19,999 2 1 0 - 0 - 1 - 2 -19,999 - 1 - - - - -10μV 10μV Figure 8. MAX1365 Transfer Function—±200mV Range -2V 0 ANALOG INPUT VOLTAGE +2V LED 1 - - - 1999 2 1 0 - 0 - 1 - 2 -1999 - 1 - - - -1mV 1mV Figure 10. MAX1367 Transfer Function—±2V Range -200mV 0 ANALOG INPUT VOLTAGE +200mV LED 1 - - - 1999 2 1 0 - 0 - 1 - 2 -1999 - 1 - - - -100μV 100μV Figure 9. MAX1367 Transfer Function—±200mV Range MAX1365/MAX1367 The transfer function for the MAX1367 with AIN+ - AIN- < 0 and RANGE = GND is: The transfer function for the MAX1365 with AIN+ - AIN- ≥ 0 and RANGE = DVDD is: The transfer function for the MAX1365 with AIN+ - AIN- < 0 and RANGE = DVDD is: (6) COUNT 1.024 20,000 10 1 V V V V AIN AIN x x REF REF = + − − + + − − (5) COUNT 1.024 20,000 10 V V V V AIN AIN x x REF REF = + − − + − − (4) COUNT 1.024 2000 1 V V V V AIN AIN x REF REF = + − − + + − − Stand-Alone, 4.5-/3.5-Digit Panel Meters with 4–20mA Output 18 ______________________________________________________________________________________ - FS + FS ADC OUTPUT CODE 0 DAC OUTPUT VOLTAGE (V) 0 1. 25 UNIPOLAR : BIPLOLAR : FS = FULL SCALE Figure 11. DAC Output Voltage vs. ADC Output Code UNIPOLAR : BIPLOLAR : ADC OUTPUT CODE 4-20OUT (mA) 20 FS = FULL SCALE 0 16 4 - FS 0 + FS CURRENT OFFSET ENABLED (EN_I = 1) 12 Figure 12. Output Current (4-20OUT) vs. ADC Output Code (Current Offset Enabled) OFFSET ENABLED : OFFSET DISABLED : V/I CONVERTER INPUT ( V ) 0 4-20OUT (mA) 20 0 16 4 1. 25 Figure 14. 4-20OUT Output Current vs. V/I Converter Input Voltage UNIPOLAR : BIPLOLAR : ADC OUTPUT CODE 4-20OUT (mA) 16 FS = FULL SCALE 0 - FS 0 + FS CURRENT OFFSET DISABLED (EN_I = 0) 8 Figure 13. Output Current (4-20OUT) vs. ADC Output Code (Current Offset Disabled) The transfer function for the MAX1367 with AIN+ - AIN- ≥ 0 and RANGE = DVDD is: The transfer function for the MAX1367 with AIN+ - AIN- < 0 and RANGE = DVDD is: DAC Transfer Functions Figure 11 shows the DAC transfer function for the MAX1365/MAX1367 in unipolar and bipolar modes. The transfer function for the DAC in the MAX1365/ MAX1367 unipolar mode is: where N = two’s complement ADC output code. In unipolar mode, VDACVOUT is equal to 0V for all two’s complement ADC codes less than zero (see Figure 12). The transfer function for the DAC in the MAX1365/ MAX1367 in bipolar mode is: where N = two’s complement ADC output. Voltage-to-Current Transfer Function Figures 12 and 13 show the MAX1365/MAX1367 transfer function of the output current (4-20OUT) versus the ADC input code. The transfer function for the MAX1365/MAX1367 with the current offset enabled (EN_I is high) is: The transfer function for the MAX1365/MAX1367 with the current offset disabled (EN_I is low) is: Supplies, Layout, and Bypassing Power up AVDD and DVDD before applying an analog input and external-reference voltage to the device. If this is not possible, limit the current into these inputs to 50mA. When the analog and digital supplies come from the same source, isolate the digital supply from the analog supply with a low-value resistor (10Ω) or ferrite bead. For best performance, ground the MAX1365/ MAX1367 to the analog ground plane of the circuit board. Avoid running digital lines under the device as this can couple noise onto the IC. Run the analog ground plane under the MAX1365/MAX1367 to minimize coupling of digital noise. Make the power-supply lines to the MAX1365/MAX1367 as wide as possible to provide low-impedance paths and reduce the effects of glitches on the power-supply line. Shield fast-switching signals, such as clocks, with digital ground to avoid radiating noise to other sections of the board. Avoid running clock signals near the analog inputs. Avoid crossover of digital and analog signals. Running traces that are on opposite sides of the board at right angles to each other reduces feedthrough effects. Good decoupling is important when using high-resolution ADCs. Decouple the supplies with 0.1μF ceramic capacitors to GND. Place these components as close to the device as possible to achieve the best decoupling. Selecting Segment Current A resistor from ISET to ground sets the current for each LED segment. See Table 6 for more detail. Use the following formula to set the segment current: RISET values below 25kΩ increase the ISEG. However, the internal current-limit circuit limits the ISEG to less than 30mA. At higher ISEG values, proper operation of the device is not guaranteed. In addition, the power dissipated may exceed the package power-dissipation limit. Choosing Supply Voltage to Minimize Power Dissipation The MAX1365/MAX1367 drive a peak current of 25.5mA into LEDs with a 2.2V forward voltage drop when operated from a supply voltage of at least 3.0V. Therefore, the minimum voltage drop across the internal LED drivers is 0.8V (3.0V - 2.2V = 0.8V). The MAX1365/MAX1367 sink when the outputs are operating and the LED segment drivers are at full current (8 x 25.5mA = 204mA). For a 3.3V supply, the MAX1365/MAX1367 dissipate 224.4mW ((3.3V - 2.2V) x 204 = 224.4mW). If a higher supply voltage is used, the driver absorbs a higher voltage, and the driver’s power dissipation increases accordingly. I V R SEG x ISET = 1 20 450 . IOUT mA ≅ x VCONV IN 16 1.25 _ IOUT mA ≅ x VCONV IN + mA 16 1 25 4 . _ V N DACVOUT = x VREF +19 999 65 536 , , V N DACVOUT = x VREF 32,768−1 (8) COUNT 1.024 2000 10 1 V V V V AIN AIN x x REF REF = + − − + + − − (7) COUNT 1.024 2000 10 V V V V AIN AIN x x REF REF = + − − + − − MAX1365/MAX1367 Stand-Alone, 4.5-/3.5-Digit Panel Meters with 4–20mA Output ______________________________________________________________________________________ 19 Note: The input at VCONV_IN expects a source impedance of typically 6kΩ when driving VCONV_IN externally. MAX1365/MAX1367 However, if the LEDs used have a higher forward voltage drop than 2.2V, the supply voltage must be raised accordingly to ensure that the driver always has at least 0.8V headroom. For a LEDV supply voltage of 2.7V, the maximum LED forward voltage is 1.9V to ensure 0.8V driver headroom. The voltage drop across the drivers with a nominal +5V supply (5.0V - 2.2V = 2.8V) is almost three times the drop across the drivers with a nominal 3.3V supply (3.3V - 2.2V = 1.1V). Therefore, the driver’s power dissipation increases three times. The power dissipation in the part causes the junction temperature to rise accordingly. In the high ambient temperature case, the total junction temperature may be very high (> +125°C). At higher junction temperatures, the ADC performance degrades. To ensure the dissipation limit for the MAX1365/MAX1367 is not exceeded and the ADC performance is not degraded; a diode can be inserted between the power supply and LEDV. Selecting Depletion-Mode FET An external depletion-mode FET (DMOS) works in conjunction with the regulator circuit to supply the V/I converter with loop power. REG_FORCE regulates the gate of the DMOS so that the drain voltage is 5.2V (typ) and allows the 4–20mA (0 to 16mA) loop to be directly powered from a 7V to 30V supply. DMOS IDS consists of the current output at 4-20OUT, a 4mA offset current, and 1mA (typ) consumed by the V/I converter. For offset-enabled mode (EN_I = 1): IDS = I4-20OUT + 4mA + 1mA where IDS is the current in the DMOS. For offset-disabled mode (EN_I = 0): IDS = I4-20OUT + 1mA where IDS is the current in the DMOS. Table 7 provides the FET characteristics for selecting an external DMOS transistor. The DN25D FET transistor from Supertex meets all the requirements of Table 7. Other suitable transistors include ND2020L and ND2410L from Siliconix. Connect a 0.1μF capacitor between CMP and REG_FORCE to ensure stable regulator compensation. Definitions Integral Nonlinearity (INL) INL is the deviation of the values on an actual transfer function from a straight line. This straight line is either a best-straight-line fit or a line drawn between the end points of the transfer function, once offset and gain errors have been nullified. INL for the MAX1365/ MAX1367 is measured using the end-point method. Differential Nonlinearity (DNL) DNL is the difference between an actual step width and the ideal value of ±1 LSB. A DNL error specification of less than ±1 LSB guarantees no missing codes and a monotonic transfer function. Rollover Error Rollover error is defined as the absolute-value difference between a near positive full-scale reading and near negative full-scale reading. Rollover error is tested by applying a full-scale positive voltage, swapping AIN+ and AIN-, and adding the results. Zero-Input Reading Ideally, with AIN+ connected to AIN-, the MAX1365/ MAX1367 LED displays zero. Zero-input reading is the measured deviation from the ideal zero and the actual measured point. Gain Error Gain error is the amount of deviation between the measured full-scale transition point and the ideal full-scale transition point. Common-Mode Rejection (CMR) CMR is the ability of a device to reject a signal that is common to both input terminals. The common-mode signal can be either an AC or a DC signal or a combination of the two. CMR is often expressed in decibels. Normal-Mode 50Hz and 60Hz Rejection (Simultaneously) Normal-mode rejection is a measure of how much output changes when 50Hz and 60Hz signals are injected into only one of the differential inputs. The MAX1365/ MAX1367 sigma-delta converter uses its internal digital filter to provide normal-mode rejection to both 50Hz and 60Hz power-line frequencies simultaneously. Stand-Alone, 4.5-/3.5-Digit Panel Meters with 4–20mA Output 20 ______________________________________________________________________________________ Power-Supply Rejection (PSR)—ADC PSR is a measure of the data converter’s level of immunity to power-supply fluctuations. PSR assumes that the converter’s linearity is unaffected by changes in the power-supply voltage. Power-supply rejection ratio (PSRR) is the ratio of the input signal change to the change in the converter output. PSRR is typically measured in dB. Power-Supply Rejection—V/I Converter PSR is a measure of the data converter’s level of immunity to power-supply fluctuations. PSR assumes that the converter’s linearity is unaffected by changes in the power-supply voltage. Note: The V/I converter current output (4–20mA) power-supply rejection is with respect to the 7V to 30V loop supply. MAX1365/MAX1367 Stand-Alone, 4.5-/3.5-Digit Panel Meters with 4–20mA Output ______________________________________________________________________________________ 21 RSET (kΩ) ISEG (mA) 25 21.6 50 10.8 100 5.4 500 1.1 > 2500 LED driver disabled Table 6. Segment-Current Selection FET TYPE N-CHANNEL DEPLETION MODE IDS 30mA BVDS (VEXT* - REG_VDD) min VPINCHOFF REG_VDD max Power dissipation 30mA x (VEXT - REG_VDD) min Table 7. FET Characteristics *VEXT is the 7V to 30V loop voltage. MAX1365/MAX1367 Stand-Alone, 4.5-/3.5-Digit Panel Meters with 4–20mA Output 22 ______________________________________________________________________________________ MAX1365 MAX6126 0.1μF 10μF 10μF 0.1μF 0.1μF 10μF 10μF LISO RL 2.7V TO 5.25V 4.75V TO 5.25V DEPLETIONMODE FET VEXT 7V TO 30V 4-20mA PLC INPUT ADC AIN+ IN DAC_VDD SUPPLY VOLTAGE 0.1μF AINLEDV 4-20mA/0 TO 16mA CURRENT-LOOP OUTPUT LED_EN DVDD AVDD DAC_VDD GND_DAC REF_DAC SET NEGV GND REF- REF+ LEDG GND_V/I DACVOUT OUTF OUTS CONV_IN EN_BPM EN_I TO DVDD DACDATA_SEL CS_DAC REFSELE INTREF RANGE PEAK HOLD DPON DPSET2 DPSET1 DIG0–DIG4 DIGIT CONNECTIONS SEGA–SEGDP SEGMENT CONNECTIONS VIN CMP GNDS GND REG_FORCE REG_VDD REG_AMP 4-20OUT 25kΩ 0.1μF 0.1μF MAX1365 Typical Operating Circuit MAX1365/MAX1367 Stand-Alone, 4.5-/3.5-Digit Panel Meters with 4–20mA Output ______________________________________________________________________________________ 23 MAX1367 MAX6126 0.1μF 10μF 10μF 0.1μF 0.1μF 10μF 10μF LISO RL 2.7V TO 5.25V 4.75V TO 5.25V DEPLETIONMODE FET VEXT 7V TO 30V 4-20mA PLC INPUT ADC AIN+ IN DAC_VDD SUPPLY VOLTAGE 0.1μF AINLEDV 4-20mA/0 TO 16mA CURRENT-LOOP OUTPUT LED_EN DVDD AVDD DAC_VDD DIGO GND_DAC REF_DAC SET NEGV GND REF- REF+ LEDG GND_V/I DACVOUT OUTF OUTS CONV_IN EN_BPM EN_I TO DVDD DACDATA_SEL CS_DAC REFSELE INTREF RANGE PEAK HOLD DPON DPSET2 DPSET1 DIG1–DIG4 DIGIT CONNECTIONS SEGA–SEGDP SEGMENT CONNECTIONS VIN CMP GNDS GND REG_FORCE REG_VDD REG_AMP 4-20OUT 25kΩ 0.1μF 0.1μF MAX1367 Typical Operating Circuit MAX1365/MAX1367 Stand-Alone, 4.5-/3.5-Digit Panel Meters with 4–20mA Output 24 ______________________________________________________________________________________ TOP VIEW MAX1365 MAX1367 TQFP 13 14 15 16 17 18 19 20 21 22 23 24 CONV_IN 4-200UT GDN_DAC GND_V/I REF_DAC EN_BPM EN_I REFSELE DACDATA_SEL CS_DAC INTREF RANGE 48 47 46 45 44 43 42 41 40 39 38 37 1 2 3 4 5 6 7 8 9 10 11 12 REF+ REFDPON NEGV LED_EN SEGDP SEGG SEGF SEGE SEGD SEGC LEDV DACVOUT DAC_VDD CMP REG_AMP REG_FORCE REG_VDD SET DVDD AVDD GND AINAIN+ 36 35 34 33 32 31 30 29 28 27 26 25 PEAK HOLD DPSET2 DPSET1 LEDG DIG0 DIG1 DIG2 DIG3 DIG4 SEGA SEGB Pin Configuration Chip Information TRANSISTOR COUNT: 83,463 PROCESS: CMOS MAX1365/MAX1367 Stand-Alone, 4.5-/3.5-Digit Panel Meters with 4–20mA Output Maxim cannot assume responsibility for use of any circuitry other than circuitry entirely embodied in a Maxim product. No circuit patent licenses are implied. Maxim reserves the right to change the circuitry and specifications without notice at any time. Maxim Integrated Products, 120 San Gabriel Drive, Sunnyvale, CA 94086 408-737-7600 ____________________ 25 © 2006 Maxim Integrated Products Printed USA is a registered trademark of Maxim Integrated Products, Inc. Package Information (The package drawing(s) in this data sheet may not reflect the most current specifications. For the latest package outline information, go to www.maxim-ic.com/packages.) 32L/48L,TQFP.EPS E 1 21-0054 2 PACKAGE OUTLINE, 32/48L TQFP, 7x7x1.4mm E 2 21-0054 2 PACKAGE OUTLINE, 32/48L TQFP, 7x7x1.4mm 1 623345fc LT6233/LT6233-10 LT6234/LT6235 Typical Application Features Description 60MHz, Rail-to-Rail Output, 1.9nV/√Hz, 1.2mA Op Amp Family Low Noise Low Power Instrumentation Amplifier Applications n Low Noise Voltage: 1.9nV/√Hz n Low Supply Current: 1.2mA/Amp Max n Low Offset Voltage: 350μV Max n Gain-Bandwidth Product: LT6233: 60MHz; AV ≥ 1 LT6233-10: 375MHz; AV ≥ 10 n Wide Supply Range: 3V to 12.6V n Output Swings Rail-to-Rail n Common Mode Rejection Ratio: 115dB Typ n Output Current: 30mA n Operating Temperature Range: –40°C to 85°C n LT6233 Shutdown to 10μA Maximum n LT6233/LT6233-10 in a Low Profile (1mm) ThinSOT™ Package n Dual LT6234 in 8-Pin SO and Tiny DFN Packages n LT6235 in a 16-Pin SSOP Package n Ultrasound Amplifiers n Low Noise, Low Power Signal Processing n Active Filters n Driving A/D Converters n Rail-to-Rail Buffer Amplifiers L, LT, LTC, LTM, Linear Technology and the Linear logo are registered trademarks of Linear Technology Corporation. ThinSOT is a trademark of Linear Technology Corporation. All other trademarks are the property of their respective owners. Noise Voltage and Unbalanced Noise Current vs Frequency The LT®6233/LT6234/LT6235 are single/dual/quad low noise, rail-to-rail output unity-gain stable op amps that feature 1.9nV/√Hz noise voltage and draw only 1.2mA of supply current per amplifier. These amplifiers combine very low noise and supply current with a 60MHz gainbandwidth product, a 17V/μs slew rate and are optimized for low supply voltage signal conditioning systems. The LT6233-10 is a single amplifier optimized for higher gain applications resulting in higher gain bandwidth and slew rate. The LT6233 and LT6233-10 include an enable pin that can be used to reduce the supply current to less than 10μA. The amplifier family has an output that swings within 50mV of either supply rail to maximize the signal dynamic range in low supply applications and is specified on 3.3V, 5V and ±5V supplies. The en • √ISUPPLY product of 2.1 per amplifier is among the most noise efficient of any op amp. The LT6233/LT6233-10 are available in the 6-lead SOT‑23 package and the LT6234 dual is available in the 8-pin SO package with standard pinouts. For compact layouts, the dual is also available in a tiny dual fine pitch leadless package (DFN). The LT6235 is available in the 16-pin SSOP package. R6 499 VS + AV = 20 BW = 2.8MHz VS = ±1.5V to ±5V VOUT VS – IN+ IN– VS – VS + R7 499 R4 499 R2 475 R1 49.9 R3 475 R5 499 EN IS = 3mA EN = 8μVRMS INPUT REFERRED, MEASUREMENT BW = 4MHz 623345 TA01a – + LT6233 1/2 LT6234 1/2 LT6234 FREQUENCY (Hz) NOISE VOLTAGE (nV/Hz) 6 5 4 3 2 1 0 10 1k 10k 100k 623345 TA01b 100 VS = ±2.5V TA = 25°C VCM = 0V NOISE VOLTAGE NOISE CURRENT UNBALANCED NOISE CURRENT (pA/Hz) 6 5 4 3 2 1 0 LT6233/LT6233-10 LT6234/LT6235 2 623345fc Absolute Maximum Ratings Total Supply Voltage (V+ to V–)............................... 12.6V Input Current (Note 2).......................................... ±40mA Output Short-Circuit Duration (Note 3)............. Indefinite Operating Temperature Range (Note 4)....–40°C to 85°C Specified Temperature Range (Note 5).....–40°C to 85°C Junction Temperature............................................ 150°C (Note 1) 6 V+ 5 ENABLE 4 –IN OUT 1 TOP VIEW S6 PACKAGE 6-LEAD PLASTIC TSOT-23 V– 2 +IN 3 TJMAX = 150°C, θJA = 250°C/W TOP VIEW DD PACKAGE 8-LEAD (3mm × 3mm) PLASTIC DFN 5 6 7 8 4 3 2 OUT A 1 –IN A +IN A V– V+ OUT B –IN B +IN B + – + – TJMAX = 125°C, θJA = 160°C/W UNDERSIDE METAL CONNECTED TO V– (PCB CONNECTION OPTIONAL) TOP VIEW V+ OUT B –IN B +IN B OUT A –IN A +IN A V– S8 PACKAGE 8-LEAD PLASTIC SO 1 2 3 4 8 7 6 5 + – + – TJMAX = 150°C, θJA = 190°C/W TOP VIEW GN PACKAGE 16-LEAD NARROW PLASTIC SSOP 1 2 3 4 5 6 7 8 16 15 14 13 12 11 10 9 OUT A –IN A +IN A V+ +IN B –IN B OUT B NC OUT D –IN D +IN D V– +IN C –IN C OUT C NC + – + – + – + – A D B C TJMAX = 150°C, θJA = 135°C/W Pin Configuration Junction Temperature (DD Package)..................... 125°C Storage Temperature Range................... –65°C to 150°C Storage Temperature Range (DD Package)......................................... –65°C to 125°C Lead Temperature (Soldering, 10 sec)....................300°C 3 623345fc LT6233/LT6233-10 LT6234/LT6235 Electrical Characteristics TA = 25°C, VS = 5V, 0V; VS = 3.3V, 0V; VCM = VOUT = half supply, ENABLE = 0V, unless otherwise noted. Order Information LEAD FREE FINISH TAPE AND REEL PART MARKING* PACKAGE DESCRIPTION SPECIFIED TEMPERATURE RANGE LT6233CS6#PBF LT6233CS6#TRPBF LTAFL 6-Lead Plastic TS0T-23 0°C to 70°C LT6233IS6#PBF LT6233IS6#TRPBF LTAFL 6-Lead Plastic TS0T-23 –40°C to 85°C LT6233CS6-10#PBF LT6233CS6-10#TRPBF LTAFM 6-Lead Plastic TS0T-23 0°C to 70°C LT6233IS6-10#PBF LT6233IS6-10#TRPBF LTAFM 6-Lead Plastic TS0T-23 –40°C to 85°C LT6234CS8#PBF LT6234CS8#TRPBF 6234 8-Lead Plastic SO 0°C to 70°C LT6234IS8#PBF LT6234IS8#TRPBF 6234I 8-Lead Plastic SO –40°C to 85°C LT6234CDD#PBF LT6234CDD#TRPBF LAET 8-Lead (3mm × 3mm) Plastic DFN 0°C to 70°C LT6234IDD#PBF LT6234IDD#TRPBF LAET 8-Lead (3mm × 3mm) Plastic DFN –40°C to 85°C LT6235CGN#PBF LT6235CGN#TRPBF 6235 16-Lead Narrow Plastic SSOP 0°C to 70°C LT6235IGN#PBF LT6235IGN#TRPBF 6235I 16-Lead Narrow Plastic SSOP –40°C to 85°C Consult LTC Marketing for parts specified with wider operating temperature ranges. *The temperature grade is identified by a label on the shipping container. Consult LTC Marketing for information on non-standard lead based finish parts. For more information on lead free part marking, go to: http://www.linear.com/leadfree/ For more information on tape and reel specifications, go to: http://www.linear.com/tapeandreel/ SYMBOL PARAMETER CONDITIONS MIN TYP MAX UNITS VOS Input Offset Voltage LT6233S6, LT6233S6-10 LT6234S8, LT6235GN LT6234DD 100 50 75 500 350 450 μV μV μV Input Offset Voltage Match (Channel-to-Channel) (Note 6) 80 600 μV IB Input Bias Current 1.5 3 μA IB Match (Channel-to-Channel) (Note 6) 0.04 0.3 μA IOS Input Offset Current 0.04 0.3 μA Input Noise Voltage 0.1Hz to 10Hz 220 nVP-P en Input Noise Voltage Density f = 10kHz, VS = 5V 1.9 3 nV/√Hz in Input Noise Current Density, Balanced Source Input Noise Current Density, Unbalanced Source f = 10kHz, VS = 5V, RS = 10k f = 10kHz, VS = 5V, RS = 10k 0.43 0.78 pA/√Hz pA/√Hz Input Resistance Common Mode Differential Mode 22 25 MΩ kΩ CIN Input Capacitance Common Mode Differential Mode 2.5 4.2 pF pF AVOL Large-Signal Gain VS = 5V, VO = 0.5V to 4.5V, RL = 10k to VS/2 VS = 5V, VO = 0.5V to 4.5V, RL = 1k to VS/2 73 18 140 35 V/mV V/mV VS = 3.3V, VO = 0.65V to 2.65V, RL = 10k to VS/2 VS = 3.3V, VO = 0.65V to 2.65V, RL = 1k to VS/2 53 11 100 20 V/mV V/mV VCM Input Voltage Range Guaranteed by CMRR, VS = 5V, 0V Guaranteed by CMRR, VS = 3.3V, 0V 1.5 1.15 4 2.65 V V CMRR Common Mode Rejection Ratio VS = 5V, VCM = 1.5V to 4V VS = 3.3V, VCM = 1.15V to 2.65V 90 85 115 110 dB dB CMRR Match (Channel-to-Channel) (Note 6) VS = 5V, VCM = 1.5V to 4V 84 115 dB LT6233/LT6233-10 LT6234/LT6235 4 623345fc Electrical Characteristics TA = 25°C, VS = 5V, 0V; VS = 3.3V, 0V; VCM = VOUT = half supply, ENABLE = 0V, unless otherwise noted. SYMBOL PARAMETER CONDITIONS MIN TYP MAX UNITS PSRR Power Supply Rejection Ratio VS = 3V to 10V 90 115 dB PSRR Match (Channel-to-Channel) (Note 6) VS = 3V to 10V 84 115 dB Minimum Supply Voltage (Note 7) 3 V VOL Output Voltage Swing Low (Note 8) No Load ISINK = 5mA VS = 5V, ISINK = 15mA VS = 3.3V, ISINK = 10mA 4 75 165 125 40 180 320 240 mV mV mV mV VOH Output Voltage Swing High (Note 8) No Load ISOURCE = 5mA VS = 5V, ISOURCE = 15mA VS = 3.3V, ISOURCE = 10mA 5 85 220 165 50 195 410 310 mV mV mV mV ISC Short-Circuit Current VS = 5V VS = 3.3V ±40 ±35 ±55 ±50 mA mA IS Supply Current per Amplifier Disabled Supply Current per Amplifier ENABLE = V+ – 0.35V 1.05 0.2 1.2 10 mA μA IENABLE ENABLE Pin Current ENABLE = 0.3V –25 –75 μA VL ENABLE Pin Input Voltage Low 0.3 V VH ENABLE Pin Input Voltage High V+ – 0.35 V Output Leakage Current ENABLE = V+ – 0.35V, VO = 1.5V to 3.5V 0.2 10 μA tON Turn-On Time ENABLE = 5V to 0V, RL = 1k, VS = 5V 500 ns tOFF Turn-Off Time ENABLE = 0V to 5V, RL = 1k, VS = 5V 76 μs GBW Gain-Bandwidth Product Frequency = 1MHz, VS = 5V LT6233-10 55 320 MHz MHz SR Slew Rate VS = 5V, A V = –1, RL = 1k, VO = 1.5V to 3.5V 10 15 V/μs LT6233-10, VS = 5V, AV = –10, RL = 1k, VO = 1.5V to 3.5V 80 V/μs FPBW Full-Power Bandwidth VS = 5V, VOUT = 3VP-P (Note 9) 1.06 1.6 MHz LT6233-10, HD2 = HD3 ≤ 1% 2.2 MHz tS Settling Time (LT6233, LT6234, LT6235) 0.1%, VS = 5V, VSTEP = 2V, AV = –1, RL = 1k 175 ns 5 623345fc LT6233/LT6233-10 LT6234/LT6235 SYMBOL PARAMETER CONDITIONS MIN TYP MAX UNIT VOS Input Offset Voltage LT6233CS6, LT6233CS6-10 LT6234CS8, LT6235CGN LT6234CDD l l l 600 450 550 μV μV μV Input Offset Voltage Match (Channel-to-Channel) (Note 6) l 800 μV VOS TC Input Offset Voltage Drift (Note 10) VCM = Half Supply l 0.5 3.0 μV/°C IB Input Bias Current l 3.5 μA IB Match (Channel-to-Channel) (Note 6) l 0.4 μA IOS Input Offset Current l 0.4 μA AVOL Large-Signal Gain VS = 5V, VO = 0.5V to 4.5V, RL = 10k to VS/2 VS = 5V, VO = 0.5V to 4.5V, RL = 1k to VS/2 l l 47 12 V/mV V/mV VS = 3.3V, VO = 0.65V to 2.65V, RL = 10k to VS/2 VS = 3.3V, VO = 0.65V to 2.65V, RL = 1k to VS/2 l l 40 7.5 V/mV V/mV VCM Input Voltage Range Guaranteed by CMRR VS = 5V, 0V Vs = 3.3V, 0V l l 1.5 1.15 4 2.65 V V CMRR Common Mode Rejection Ratio VS = 5V, VCM = 1.5V to 4V VS = 3.3V, VCM = 1.15V to 2.65V l l 90 85 dB dB CMRR Match (Channel-to-Channel) (Note 6) VS = 5V, VCM = 1.5V to 4V l 84 dB PSRR Power Supply Rejection Ratio VS = 3V to 10V l 90 dB PSRR Match (Channel-to-Channel) (Note 6) VS = 3V to 10V l 84 dB Minimum Supply Voltage (Note 7) l 3 V VOL Output Voltage Swing Low (Note 8) No Load ISINK = 5mA VS = 5V, ISINK = 15mA VS = 3.3V, ISINK = 10mA l l l l 50 195 360 265 mV mV mV mV VOH Output Voltage Swing High (Note 8) No Load ISOURCE = 5mA VS = 5V, ISOURCE = 15mA VS = 3.3V, ISOURCE = 10mA l l l l 60 205 435 330 mV mV mV mV ISC Short-Circuit Current VS = 5V VS = 3.3V l l ±35 ±30 mA mA IS Supply Current per Amplifier Disabled Supply Current per Amplifier ENABLE = V+ – 0.25V l l 1 1.45 mA μA IENABLE ENABLE Pin Current ENABLE = 0.3V l –85 μA VL ENABLE Pin Input Voltage Low l 0.3 V VH ENABLE Pin Input Voltage High l V+ – 0.25 V Output Leakage Current ENABLE = V+ – 0.25V, VO = 1.5V to 3.5V l 1 μA tON Turn-On Time ENABLE = 5V to 0V, RL = 1k, VS = 5V l 500 ns tOFF Turn-Off Time ENABLE = 0V to 5V, RL = 1k, VS = 5V l 120 μs SR Slew Rate VS = 5V, AV = –1, RL = 1k, VO = 1.5V to 3.5V l 9 V/μs LT6233-10, AV = –10, RL = 1k, VO = 1.5V to 3.5V l 75 V/μs FPBW Full-Power Bandwidth (Note 9) VS = 5V, VOUT = 3VP-P; LT6233C, LT6234C, LT6235C l 955 kHz Electrical Characteristics The l denotes the specifications which apply over the 0°C < TA < 70°C temperature range. VS = 5V, 0V; VS = 3.3V, 0V; VCM = VOUT = half supply, ENABLE = 0V, unless otherwise noted. LT6233/LT6233-10 LT6234/LT6235 6 623345fc Electrical Characteristics The l denotes the specifications which apply over the –40°C < TA < 85°C temperature range. VS = 5V, 0V; VS = 3.3V, 0V; VCM = VOUT = half supply, ENABLE = 0V, unless otherwise noted. (Note 5) SYMBOL PARAMETER CONDITIONS MIN TYP MAX UNITS VOS Input Offset Voltage LT6233IS6, LT6233IS6-10 LT6234IS8, LT6235IGN LT6234IDD l l l 700 550 650 μV μV μV Input Offset Voltage Match (Channel-to-Channel) (Note 6) l 1000 μV VOS TC Input Offset Voltage Drift (Note 10) VCM = Half Supply l 0.5 3 μV/°C IB Input Bias Current l 4 μA IB Match (Channel-to-Channel) (Note 6) l 0.4 μA IOS Input Offset Current l 0.5 μA AVOL Large-Signal Gain VS = 5V, VO = 0.5V to 4.5V, RL = 10k to VS/2 VS = 5V, VO = 0.5V to 4.5V, RL = 1k to VS/2 l l 45 11 V/mV V/mV VS = 3.3V, VO = 0.65V to 2.65V, RL = 10k to VS/2 VS = 3.3V, VO = 0.65V to 2.65V, RL = 1k to VS/2 l l 38 7 V/mV V/mV VCM Input Voltage Range Guaranteed by CMRR VS = 5V, 0V VS = 3.3V, 0V l l 1.5 1.15 4 2.65 V V CMRR Common Mode Rejection Ratio VS = 5V, VCM = 1.5V to 4V VS = 3.3V, VCM = 1.15V to 2.65V l l 90 85 dB dB CMRR Match (Channel-to-Channel) (Note 6) VS = 5V, VCM = 1.5V to 4V l 84 dB PSRR Power Supply Rejection Ratio VS = 3V to 10V l 90 dB PSRR Match (Channel-to-Channel) (Note 6) VS = 3V to 10V l 84 dB Minimum Supply Voltage (Note 7) l 3 V VOL Output Voltage Swing Low (Note 8) No Load ISINK = 5mA VS = 5V, ISINK = 15mA VS = 3.3V, ISINK = 10mA l l l l 50 195 370 275 mV mV mV mV VOH Output Voltage Swing High (Note 6) No Load ISOURCE = 5mA VS = 5V, ISOURCE = 15mA VS = 3.3V, ISOURCE = 10mA l l l l 60 210 445 335 mV mV mV mV ISC Short-Circuit Current VS = 5V VS = 3.3V l l ±30 ±20 mA mA IS Supply Current per Amplifier Disabled Supply Current per Amplifier ENABLE = V+ – 0.2V l l 1 1.5 mA μA IENABLE ENABLE Pin Current ENABLE = 0.3V l –100 μA VL ENABLE Pin Input Voltage Low l 0.3 V VH ENABLE Pin Input Voltage High l V+ – 0.2 V Output Leakage Current ENABLE = V+ – 0.2V, VO = 1.5V to 3.5V l 1 μA tON Turn-On Time ENABLE = 5V to 0V, RL = 1k, VS = 5V l 500 ns tOFF Turn-Off Time ENABLE = 0V to 5V, RL = 1k, VS = 5V l 135 μs SR Slew Rate VS = 5V, AV = –1, RL = 1k, VO = 1.5V to 3.5V l 8 V/μs LT6233-10, AV = –10, RL = 1k, VO = 1.5V to 3.5V l 70 V/μs FPBW Full-Power Bandwidth (Note 9) VS = 5V, VOUT = 3VP-P; LT6233I, LT6234I, LT6235I l 848 kHz 7 623345fc LT6233/LT6233-10 LT6234/LT6235 Electrical Characteristics TA = 25°C, VS = ±5V, VCM = VOUT = 0V, ENABLE = 0V, unless otherwise noted. SYMBOL PARAMETER CONDITIONS MIN TYP MAX UNITS VOS Input Offset Voltage LT6233S6, LT6233S6-10 LT6234S8, LT6235GN LT6234DD 100 50 75 500 350 450 μV μV μV Input Offset Voltage Match (Channel-to-Channel) (Note 6) 100 600 μV IB Input Bias Current 1.5 3 μA IB Match (Channel-to-Channel) (Note 6) 0.04 0.3 μA IOS Input Offset Current 0.04 0.3 μA Input Noise Voltage 0.1Hz to 10Hz 220 nVP-P en Input Noise Voltage Density f = 10kHz 1.9 3.0 nV/√Hz in Input Noise Current Density, Balanced Source Input Noise Current Density, Unbalanced Source f = 10kHz, RS = 10k f = 10kHz, RS = 10k 0.43 0.78 pA/√Hz pA/√Hz Input Resistance Common Mode Differential Mode 22 25 MΩ kΩ CIN Input Capacitance Common Mode Differential Mode 2.1 3.7 pF pF AVOL Large-Signal Gain VO = ±4.5V, RL = 10k VO = ±4.5V, RL = 1k 97 28 180 55 V/mV V/mV VCM Input Voltage Range Guaranteed by CMRR –3 4 V CMRR Common Mode Rejection Ratio VCM = –3V to 4V 90 110 dB CMRR Match (Channel-to-Channel) (Note 6) VCM = –3V to 4V 84 120 dB PSRR Power Supply Rejection Ratio VS = ±1.5V to ±5V 90 115 dB PSRR Match (Channel-to-Channel) (Note 6) VS = ±1.5V to ±5V 84 115 dB VOL Output Voltage Swing Low (Note 8) No Load ISINK = 5mA ISINK = 15mA 4 75 165 40 180 320 mV mV mV VOH Output Voltage Swing High (Note 8) No Load ISOURCE = 5mA ISOURCE = 15mA 5 85 220 50 195 410 mV mV mV ISC Short-Circuit Current ±40 ±55 mA IS Supply Current per Amplifier Disabled Supply Current per Amplifier ENABLE = 4.65V 1.15 0.2 1.4 10 mA μA IENABLE ENABLE Pin Current ENABLE = 0.3V –35 –85 μA VL ENABLE Pin Input Voltage Low 0.3 V VH ENABLE Pin Input Voltage High 4.65 V Output Leakage Current ENABLE = 4.65V, VO = ±1V 0.2 10 μA tON Turn-On Time ENABLE = 5V to 0V, RL = 1k 900 ns tOFF Turn-Off Time ENABLE = 0V to 5V, RL = 1k 100 μs GBW Gain-Bandwidth Product Frequency = 1MHz LT6233-10 42 260 60 375 MHz MHz SR Slew Rate AV = –1, RL = 1k, VO = –2V to 2V 12 17 V/μs LT6233-10, AV = –10, RL = 1k, VO = –2V to 2V 115 V/μs FPBW Full-Power Bandwidth VOUT = 3VP-P (Note 9) 1.27 1.8 MHz LT6233-10, HD2 = HD3 ≤ 1% 2.2 MHz tS Settling Time (LT6233, LT6234, LT6235) 0.1%, VSTEP = 2V, AV = –1, RL = 1k 170 ns LT6233/LT6233-10 LT6234/LT6235 8 623345fc Electrical Characteristics The l denotes the specifications which apply over the 0°C < TA < 70°C temperature range. VS = ±5V, VCM = VOUT = 0V, ENABLE = 0V, unless otherwise noted. SYMBOL PARAMETER CONDITIONS MIN TYP MAX UNITS VOS Input Offset Voltage LT6233CS6, LT6233CS6-10 LT6234CS8, LT6235CGN LT6234CDD l l l 600 450 550 μV μV μV Input Offset Voltage Match (Channel-to-Channel) (Note 6) l 800 μV VOS TC Input Offset Voltage Drift (Note 10) l 0.5 3 μV/°C IB Input Bias Current l 3.5 μA IB Match (Channel-to-Channel) (Note 6) l 0.4 μA IOS Input Offset Current l 0.4 μA AVOL Large-Signal Gain VO = ±4.5V, RL = 10k VO = ±4.5V, RL = 1k l l 75 22 V/mV V/mV VCM Input Voltage Range Guaranteed by CMRR l –3 4 V CMRR Common Mode Rejection Ratio VCM = –3V to 4V l 90 dB CMRR Match (Channel-to-Channel) (Note 6) VCM = –3V to 4V l 84 dB PSRR Power Supply Rejection Ratio VS = ±1.5V to ±5V l 90 dB PSRR Match (Channel-to-Channel) (Note 6) VS = ±1.5V to ±5V l 84 dB VOL Output Voltage Swing Low (Note 8) No Load ISINK = 5mA ISINK = 15mA l l l 50 195 360 mV mV mV VOH Output Voltage Swing High (Note 8) No Load ISOURCE = 5mA ISOURCE = 15mA l l l 60 205 435 mV mV mV ISC Short-Circuit Current l ±35 mA IS Supply Current per Amplifier Disabled Supply Current per Amplifier ENABLE = 4.75V l l 1 1.7 mA μA IENABLE ENABLE Pin Current ENABLE = 0.3V l –95 μA VL ENABLE Pin Input Voltage Low l 0.3 V VH ENABLE Pin Input Voltage High l 4.75 V Output Leakage Current ENABLE = 4.75V, VO = ±1V l 1 μA tON Turn-On Time ENABLE = 5V to 0V, RL = 1k l 900 ns tOFF Turn-Off Time ENABLE = 0V to 5V, RL = 1k l 150 μs SR Slew Rate AV = –1, RL = 1k, VO = –2V to 2V l 11 V/μs LT6233-10, AV = –10, RL = 1k, VO = –2V to 2V l 105 V/μs FPBW Full-Power Bandwidth (Note 9) VOUT = 3VP-P ; LT6233C, LT6234C, LT6235C l 1.16 MHz 9 623345fc LT6233/LT6233-10 LT6234/LT6235 Electrical Characteristics The l denotes the specifications which apply over the –40°C < TA < 85°C temperature range. VS = ±5V, VCM = VOUT = 0V, ENABLE = 0V, unless otherwise noted. (Note 5) SYMBOL PARAMETER CONDITIONS MIN TYP MAX UNITS VOS Input Offset Voltage LT6233IS6, LT6233IS6-10 LT6234IS8, LT6235IGN LT6234IDD l l l 700 550 650 μV μV μV Input Offset Voltage Match (Channel-to-Channel) (Note 6) l 1000 μV VOS TC Input Offset Voltage Drift (Note 10) l 0.5 3 μV/°C IB Input Bias Current l 4 μA IB Match (Channel-to-Channel) (Note 6) l 0.4 μA IOS Input Offset Current l 0.5 μA AVOL Large-Signal Gain VO = ±4.5V, RL = 10k VO = ±4.5V, RL = 1k l l 68 20 V/mV V/mV VCM Input Voltage Range Guaranteed by CMRR l –3 4 V CMRR Common Mode Rejection Ratio VCM = –3V to 4V l 90 dB CMRR Match (Channel-to-Channel) (Note 6) VCM = –3V to 4V l 84 dB PSRR Power Supply Rejection Ratio VS = ±1.5V to ±5V l 90 dB PSRR Match (Channel-to-Channel) (Note 6) VS = ±1.5V to ±5V l 84 dB VOL Output Voltage Swing Low (Note 8) No Load ISINK = 5mA ISINK = 15mA l l l 50 195 370 mV mV mV VOH Output Voltage Swing High (Note 8) No Load ISOURCE = 5mA ISOURCE = 15mA l l l 70 210 445 mV mV mV ISC Short-Circuit Current l ±30 mA IS Supply Current per Amplifier Disabled Supply Current per Amplifier ENABLE = 4.8V l l 1 1.75 mA μA IENABLE ENABLE Pin Current ENABLE = 0.3V l –110 μA VL ENABLE Pin Input Voltage Low l 0.3 V VH ENABLE Pin Input Voltage High l 4.8 V Output Leakage Current ENABLE = 4.8V, VO = ±1V l 1 μA tON Turn-On Time ENABLE = 5V to 0V, RL = 1k l 900 ns tOFF Turn-Off Time ENABLE = 0V to 5V, RL = 1k l 160 μs SR Slew Rate AV = –1, RL = 1k, VO = –2V to 2V l 10 V/μs LT6233-10, AV = –10, RL = 1k, VO = –2V to 2V l 95 V/μs FPBW Full-Power Bandwidth (Note 9) VOUT = 3VP-P; LT6233I, LT6234I, LT6235I l 1.06 MHz Note 1: Stresses beyond those listed under Absolute Maximum Ratings may cause permanent damage to the device. Exposure to any Absolute Maximum Rating condition for extended periods may affect device reliability and lifetime. Note 2: Inputs are protected by back-to-back diodes. If the differential input voltage exceeds 0.7V, the input current must be limited to less than 40mA. Note 3: A heat sink may be required to keep the junction temperature below the absolute maximum rating when the output is shorted indefinitely. Note 4: The LT6233C/LT6233I the LT6234C/LT6234I, and LT6235C/LT6235I are guaranteed functional over the temperature range of –40°C to 85°C. Note 5: The LT6233C/LT6234C/LT6235C are guaranteed to meet specified performance from 0°C to 70°C. The LT6233C/LT6234C/LT6235C are designed, characterized and expected to meet specified performance from –40°C to 85°C, but are not tested or QA sampled at these temperatures. The LT6233I/LT6234I/LT6235I are guaranteed to meet specified performance from –40°C to 85°C. Note 6: Matching parameters are the difference between the two amplifiers A and D and between B and C of the LT6235; between the two amplifiers of the LT6234. CMRR and PSRR match are defined as follows: CMRR and PSRR are measured in μV/V on the matched amplifiers. The difference is calculated between the matching sides in μV/V. The result is converted to dB. LT6233/LT6233-10 LT6234/LT6235 10 623345fc Note 7: Minimum supply voltage is guaranteed by power supply rejection ratio test. Note 8: Output voltage swings are measured between the output and power supply rails. Electrical Characteristics Note 9: Full-power bandwidth is calculated from the slew rate: FPBW = SR/2πVP Note 10: This parameter is not 100% tested. Typical Performance Characteristics Input Bias Current vs Common Mode Voltage Input Bias Current vs Temperature Output Saturation Voltage vs Load Current (Output Low) VOS Distribution Supply Current vs Supply Voltage (Per Amplifier) Offset Voltage vs Input Common Mode Voltage (LT6233/LT6234/LT6235) INPUT OFFSET VOLTAGE (μV) –200 0 NUMBER OF UNITS 10 20 30 40 –100 0 100 200 623345 GO1 50 60 –150 –50 50 150 VS = 5V, 0V VCM = V+/2 S8 TOTAL SUPPLY VOLTAGE (V) 0 SUPPLY CURRENT (mA) 6 623345 GO2 2 4 8 2.0 1.5 1.0 0.5 0 10 12 14 TA = 125°C TA = 25°C TA = –55°C INPUT COMMON MODE VOLTAGE (V) 0 OFFSET VOLTAGE (μV) 1.5 623345 GO3 0.5 1 2 500 400 300 200 100 0 –100 –200 –300 –400 –500 2.5 3 3.5 4 4.5 5 TA = –55°C TA = 25°C TA = 125°C VS = 5V, 0V COMMON MODE VOLTAGE (V) –1 INPUT BIAS CURRENT (μA) 2 623345 GO4 0 1 3 6 5 4 3 2 1 0 –2 –1 4 5 6 TA = 125°C TA = –55°C TA = 25°C VS = 5V, 0V TEMPERATURE (°C) –50 INPUT BIAS CURRENT (μA) 25 623345 GO5 –25 0 50 6 5 4 3 2 1 0 –1 75 100 125 VCM = 4V VCM = 1.5V VS = 5V, 0V LOAD CURRENT (mA) 0.01 0.1 0.0001 OUTPUT SATURATION VOLTAGE (V) 0.01 10 1 10 100 623345 GO6 0.001 0.1 1 VS = 5V, 0V TA = –55°C TA = 125°C TA = 25°C 11 623345fc LT6233/LT6233-10 LT6234/LT6235 Typical Performance Characteristics Open-Loop Gain Open-Loop Gain Open-Loop Gain Offset Voltage vs Output Current Warm-Up Drift vs Time Total Noise vs Total Source Resistance Output Saturation Voltage vs Load Current (Output High) Minimum Supply Voltage Output Short-Circuit Current vs Power Supply Voltage (LT6233/LT6234/LT6235) LOAD CURRENT (mA) OUTPUT SATURATION VOLTAGE (V) 623345 G07 0.01 0.1 0.01 10 1 10 100 0.001 0.1 1 VS = 5V, 0V TA = –55°C TA = 125°C TA = 25°C TOTAL SUPPLY VOLTAGE (V) 0 OFFSET VOLTAGE (mV) 1.5 623345 G08 0.5 1 2 1.0 0.8 0.6 0.4 0.2 0 –0.2 –0.4 –0.6 –0.8 –1.0 2.5 3 3.5 4 4.5 5 TA = –55°C TA = 125°C TA = 25°C VCM = VS/2 POWER SUPPLY VOLTAGE (±V) 1.5 OUTPUT SHORT-CIRCUIT CURRENT (mA) 3.0 623345 GO9 2.0 2.5 3.5 80 60 40 20 0 –20 –40 –80 –60 4.0 4.5 5.0 TA = 125°C TA = –55°C TA = –55°C TA = 25°C SINKING SOURCING TA = 25°C TA = 125°C OUTPUT VOLTAGE (V) 0 INPUT VOLTAGE (mV) 1.5 623345 G10 0.5 1.0 2.0 2.5 2.0 1.5 1.0 0.5 0 –0.5 –1.0 –1.5 –2.0 –2.5 2.5 3.0 RL = 100 RL = 1k VS = 3V, 0V TA = 25°C OUTPUT VOLTAGE (V) 0 INPUT VOLTAGE (mV) 1.5 623345 G11 0.5 1 2 0 2.5 3 3.5 4 4.5 5 RL = 100 RL = 1k VS = 5V, 0V TA = 25°C 2.5 2.0 1.5 1.0 0.5 –0.5 –1.0 –1.5 –2.0 –2.5 OUTPUT VOLTAGE (V) –5 INPUT VOLTAGE (mV) –2 623345 G12 –4 –3 –1 0 0 1 2 3 4 5 RL = 100 RL = 1k VS = ±5V TA = 25°C 2.5 2.0 1.5 1.0 0.5 –0.5 –1.0 –1.5 –2.0 –2.5 OUTPUT CURRENT (mA) –90 OFFSET VOLTAGE (mV) 623345 G13 –60 –30 2.0 1.5 1.0 0.5 0 –0.5 –1.0 –1.5 –2.0 0 30 60 90 TA = –55°C TA = 125°C VS = ±5V TA = 25°C TIME AFTER POWER-UP (s) 0 CHANGE IN OFFSET VOLTAGE (μV) 20 623345 G14 10 30 40 35 30 25 20 15 10 0 40 50 TA = 25°C VS = ±5V VS = ±2.5V VS = ±1.5V TOTAL SOURCE RESISTANCE () 1 TOTAL NOISE (nV/Hz) 10 10 1k 10k 100k 623345 G15 0.1 100 100 VS = ±2.5V VCM = 0V f = 100kHz UNBALANCED SOURCE RESISTORS TOTAL NOISE RESISTOR NOISE AMPLIFIER NOISE VOLTAGE LT6233/LT6233-10 LT6234/LT6235 12 623345fc Typical Performance Characteristics Open-Loop Gain vs Frequency Gain Bandwidth and Phase Margin vs Supply Voltage Slew Rate vs Temperature Output Impedance vs Frequency Common Mode Rejection Ratio vs Frequency Channel Separation vs Frequency Noise Voltage and Unbalanced Noise Current vs Frequency 0.1Hz to 10Hz Output Voltage Noise Gain Bandwidth and Phase Margin vs Temperature (LT6233/LT6234/LT6235) FREQUENCY (Hz) NOISE VOLTAGE (nV/Hz) 6 5 4 3 2 1 0 10 1k 10k 100k 623345 G16 100 VS = ±2.5V TA = 25°C VCM = 0V NOISE VOLTAGE NOISE CURRENT UNBALANCED NOISE CURRENT (pA/Hz) 6 5 4 3 2 1 0 5s/DIV 623345 G17 100nV 100nV/DIV –100nV VS = ±2.5V TEMPERATURE (°C) –55 GAIN BANDWIDTH (MHz) 5 623345 G18 –25 35 90 80 70 60 40 50 PHASE MARGIN (DEG) 70 60 50 40 65 95 125 VS = ±5V VS = 3V, 0V VS = ±5V VS = 3V, 0V PHASE MARGIN GAIN BANDWIDTH CL = 5pF RL = 1k VCM = VS/2 FREQUENCY (Hz) GAIN (dB) 80 70 50 30 0 –10 60 40 10 20 –20 PHASE (DEG) 120 100 60 20 –60 80 40 –20 –40 0 –80 100k 10M 100M 1G 623345 G19 1M CL = 5pF RL = 1k VCM = VS/2 PHASE GAIN VS = ±5V VS = 3V, 0V V VS = ±5V S = 3V, 0V TOTAL SUPPLY VOLTAGE (V) 0 GAIN BANDWIDTH (MHz) 6 623345 G20 2 4 8 70 60 50 30 40 PHASE MARGIN (DEG) 80 70 60 50 40 10 12 14 PHASE MARGIN GAIN BANDWIDTH TA = 25°C CL = 5pF RL = 1k TEMPERATURE (°C) –55 SLEW RATE (V/μs) 5 623345 G21 –35 –15 45 20 22 24 26 18 16 14 10 12 25 65 85 105 125 VS = ±5V FALLING VS = ±2.5V RISING AV = –1 RF = RG = 1k VS = ±2.5V FALLING VS = ±5V RISING FREQUENCY (Hz) 1 OUTPUT IMPEDANCE () 10 100k 10M 100M 623345 G22 0.1 1M 1k 100 VS = 5V, 0V AV = 10 AV = 1 AV = 2 FREQUENCY (Hz) 20 COMMON MODE REJECTION RATIO (dB) 40 60 80 120 100 10k 100k 10M 100M 1G 623345 G23 0 1M VS = 5V, 0V VCM = VS/2 FREQUENCY (Hz) 100k CHANNEL SEPARATION (dB) –40 –50 –60 –70 –80 –90 –100 –110 –120 –130 –140 1M 10M 100M 623345 G24 AV = 1 TA = 25°C VS = ±5V 13 623345fc LT6233/LT6233-10 LT6234/LT6235 Typical Performance Characteristics Settling Time vs Output Step (Noninverting) Settling Time vs Output Step (Inverting) Maximum Undistorted Output Signal vs Frequency Distortion vs Frequency Distortion vs Frequency Distortion vs Frequency Power Supply Rejection Ratio vs Frequency Series Output Resistance and Overshoot vs Capacitive Load Series Output Resistance and Overshoot vs Capacitive Load (LT6233/LT6234/LT6235) FREQUENCY (Hz) 20 POWER SUPPLY REJECTION RATIO (dB) 40 60 80 120 100 1k 10k 100k 10M 100M 623345 G25 0 1M VS = 5V, 0V TA = 25°C VCM = VS/2 NEGATIVE SUPPLY POSITIVE SUPPLY CAPACITIVE LOAD (pF) 10 OVERSHOOT (%) 50 45 40 35 30 25 20 15 10 5 0 100 1000 623345 G26 VS = 5V, 0V AV = 1 RS = 10 RS = 20 RS = 50 RL = 50 CAPACITIVE LOAD (pF) 10 OVERSHOOT (%) 50 45 40 35 30 25 20 15 10 5 0 100 1000 623345 G27 VS = 5V, 0V AV = 2 RS = 10 RS = 20 RS = 50 RL = 50 OUTPUT STEP (V) –4 SETTLING TIME (ns) 0 623345 G28 –3 –2 –1 1 300 400 350 250 200 150 50 100 2 3 4 1mV 10mV 1mV 10mV VS = ±5V TA = 25°C AV = 1 + – 500 VOUT VIN OUTPUT STEP (V) –4 SETTLING TIME (ns) 0 623345 G29 –3 –2 –1 1 300 400 350 250 200 150 50 100 2 3 4 1mV 10mV 1mV 10mV VS = ±5V TA = 25°C AV = –1 + – 500 500 VOUT VIN FREQUENCY (Hz) 10k OUTPUT VOLTAGE SWING (VP-P) 10 9 8 7 6 5 4 3 2 100k 1M 10M 623345 G30 VS = ±5V TA = 25°C HD2, HD3 < –40dBc AV = –1 AV = 2 FREQUENCY (Hz) 10k DISTORTION (dBc) –40 –50 –60 –70 –80 –90 –100 100k 1M 10M 623345 G31 VS = ±2.5V AV = 1 VOUT = 2VP-P RL = 100, 3RD RL = 1k, 3RD RL = 1k, 2ND RL = 100, 2ND FREQUENCY (Hz) 10k DISTORTION (dBc) – 40 –50 –60 –70 –80 –90 –100 100k 1M 10M 623345 G32 VS = ±5V AV = 1 VOUT = 2VP-P RL = 100, 3RD RL = 1k, 3RD RL = 1k, 2ND RL = 100, 2ND FREQUENCY (Hz) 10k DISTORTION (dBc) –30 –40 –50 –60 –70 –80 –90 –100 100k 1M 10M 623345 G33 VS = ±2.5V AV = 2 VOUT = 2VP-P RL = 100, 3RD RL = 1k, 3RD RL = 1k, 2ND RL = 100, 2ND LT6233/LT6233-10 LT6234/LT6235 14 623345fc Typical Performance Characteristics Distortion vs Frequency Large-Signal Response Small-Signal Response (LT6233/LT6234/LT6235) Large-Signal Response Output Overdrive Recovery (LT6233) ENABLE Characteristics Supply Current vs ENABLE Pin Voltage ENABLE Pin Current vs ENABLE Pin Voltage ENABLE Pin Response Time FREQUENCY (Hz) 10k DISTORTION (dBc) –30 –40 –50 –60 –70 –80 –90 –100 100k 1M 10M 623345 G34 VS = ±5V AV = 2 VOUT = 2VP-P RL = 100, 3RD RL = 1k, 3RD RL = 1k, 2ND RL = 100, 2ND 2V 0V –2V 200ns/DIV 623345 G35 VS = ±2.5V AV = –1 RL = 1k 1V/DIV 0V 200ns/DIV 623345 G36 VS = ±2.5V AV = 1 RL = 1k 50mV/DIV 0V 5V –5V 200ns/DIV 623345 G37 VS = ±5V AV = 1 RL = 1k 2V/DIV 0V 0V 200ns/DIV 623345 G38 VS = ±2.5V AV = 3 VIN 1V/DIV VOUT 2V/DIV PIN VOLTAGE (V) SUPPLY CURRENT (mA) –1.0 623345 G39 –2.0 0 1.4 1.2 1.0 0.8 0.6 0.4 0.2 0 1.0 2.0 TA = 125°C VS = ±2.5V TA = 25°C TA = –55°C PIN VOLTAGE (V) ENABLE PIN CURRENT (μA) 623345 G40 35 30 25 20 15 10 5 0 TA = 125°C VS = ±2.5V AV = 1 TA = 25°C TA = –55°C –2.0 –1.0 0 1.0 2.0 0V 5V 0.5V 0V 200μs/DIV 623345 G41 VS = ±2.5V VIN = 0.5V AV = 1 RL = 1k VOUT ENABLE 15 623345fc LT6233/LT6233-10 LT6234/LT6235 Typical Performance Characteristics Open-Loop Gain and Phase vs Frequency Gain Bandwidth and Phase Margin vs Supply Voltage Gain Bandwidth vs Resistor Load Common Mode Rejection Ratio vs Frequency Maximum Undistorted Output vs Frequency 2nd and 3rd Harmonic Distortion vs Frequency Gain Bandwidth and Phase Margin vs Temperature Slew Rate vs Temperature Series Output Resistor and Overshoot vs Capacitive Load (LT6233-10) TEMPERATURE (°C) –50 GAIN BANDWIDTH (MHz) 25 623345 G42 –25 0 50 450 400 350 300 200 250 PHASE MARGIN (DEG) 70 60 50 40 75 100 125 VS = ±5V VS = 3V, 0V VS = ±5V VS = 3V, 0V PHASE MARGIN GAIN BANDWIDTH AV = 10 TEMPERATURE (°C) –55 SLEW RATE (V/μs) 5 623345 G43 –35 –15 45 140 160 180 200 120 100 60 0 20 80 40 25 65 85 105 125 VS = ±5V FALLING VS = ±2.5V RISING AV = –10 RF = 1k RG = 100 VS = ±2.5V FALLING VS = ±5V RISING CAPACITIVE LOAD (pF) 10 OVERSHOOT (%) 70 60 50 40 30 20 10 0 100 1000 10000 623345 G44 VS = 5V, 0V AV = 10 RS = 10 RS = 20 RS = 50 FREQUENCY (Hz) GAIN (dB) 80 70 60 50 40 30 20 10 0 –10 –20 PHASE (DEG) 120 100 80 60 40 20 0 –20 –40 –60 –80 100k 10M 100M 1G 623345 G45 1M AV = 10 CL = 5pF RL = 1k VCM = VS/2 VS = 3V, 0V VS = ±5V PHASE GAIN VS = ±5V VS = 3V, 0V TOTAL SUPPLY VOLTAGE (V) 0 GAIN BANDWIDTH (MHz) 6 623345 G46 2 4 8 450 375 300 225 PHASE MARGIN (DEG) 100 50 0 10 12 PHASE MARGIN GAIN BANDWIDTH TA = 25°C AV = 10 CL = 5pF RL = 1k TOTAL RESISTOR LOAD () (INCLUDES FEEDBACK R) 0 GAIN BANDWIDTH (MHz) 600 623345 G47 200 400 800 400 350 300 200 150 100 50 0 250 1000 AVSV = 1±05V TA = 25°C RF = 1k RG = 100 FREQUENCY (Hz) 20 COMMON MODE REJECTION RATIO (dB) 40 60 80 120 100 10k 100k 10M 100M 1G 623345 G48 0 1M VS = 5V, 0V VCM = VS/2 FREQUENCY (Hz) 10k OUTPUT VOLTAGE SWING (VP-P) 10 9 8 7 6 5 4 3 2 1 0 100k 1M 10M 623345 G49 VS = ±5V TA = 25°C AV = 10 HD2, HD3 40dBc FREQUENCY (Hz) 10k DISTORTION (dBc) –30 –40 –50 –60 –70 –80 –90 –100 100k 1M 10M 623345 G50 VS = ±2.5V AV = 10 VOUT = 2VP-P RL = 100, 3RD RL = 100, 2ND RL = 1k, 3RD RL = 1k, 2ND LT6233/LT6233-10 LT6234/LT6235 16 623345fc Typical Performance Characteristics 2nd and 3rd Harmonic Distortion vs Frequency Large-Signal Response Output-Overload Recovery (LT6233-10) Small-Signal Response Input Referred High Frequency Noise Spectrum FREQUENCY (Hz) 10k DISTORTION (dBc) –30 –40 –50 –60 –70 –80 –90 –100 100k 1M 10M 623345 G51 VS = ±5V AV = 10 VOUT = 2VP-P RL = 100, 3RD RL = 100, 2ND RL = 1k, 3RD RL = 1k, 2ND 0V 100ns/DIV 623345 G52 VS = ±5V AV = 10 RF = 900 RG = 100 VOUT 2V/DIV 0V 100ns/DIV 623345 G53 VS = 5V, 0V AV = 10 RF = 900 RG = 100 VOUT 2V/DIV 0V VIN 0.5V/DIV 2.5V 100ns/DIV 623345 G54 VS = 5V, 0V AV = 10 RF = 900 RG = 100 VOUT 100mV/DIV 10 0 2MHz/DIV 623345 G55 100kHz 20MHz 1nV/Hz/DIV 17 623345fc LT6233/LT6233-10 LT6234/LT6235 Applications Information Figure 1. Simplified Schematic Figure 2. VS = ±2.5V, AV = 1 with Large Overdrive ENABLE DESD6 DESD5 –V +V +VIN –VIN +V 623345 F01 BIAS DIFFERENTIAL DRIVE GENERATOR VOUT +V CM I1 –V DESD3 –V –V DESD4 +V DESD1 –V DESD2 +V D1 C1 D2 Q5 Q6 Q4 Q2 Q3 Q1 2.5V –2.5V 0V 500μs/DIV 623345 F02 1V/DIV Amplifier Characteristics Figure 1 is a simplified schematic of the LT6233/LT6234/ LT6235, which has a pair of low noise input transistors Q1 and Q2. A simple current mirror Q3/Q4 converts the differential signal to a single-ended output, and these transistors are degenerated to reduce their contribution to the overall noise. Capacitor C1 reduces the unity-cross frequency and improves the frequency stability without degrading the gain bandwidth of the amplifier. Capacitor CM sets the overall amplifier gain bandwidth. The differential drive generator supplies current to transistors Q5 and Q6 that swing the output from rail-to-rail. Input Protection There are back-to-back diodes, D1 and D2 across the + and – inputs of these amplifiers to limit the differential input voltage to ±0.7V. The inputs of the LT6233/LT6234/LT6235 do not have internal resistors in series with the input transistors. This technique is often used to protect the input devices from overvoltage that causes excessive current to flow. The addition of these resistors would significantly degrade the low noise voltage of these amplifiers. For instance, a 100Ω resistor in series with each input would generate 1.8nV/√Hz of noise, and the total amplifier noise voltage would rise from 1.9nV/√Hz to 2.6nV/√Hz. Once the input differential voltage exceeds ±0.7V, steady-state current conducted through the protection diodes should be limited to ±40mA. This implies 25Ω of protection resistance is necessary per volt of overdrive beyond ±0.7V. These input diodes are rugged enough to handle transient currents due to amplifier slew rate overdrive and clipping without protection resistors. The photo of Figure 2 shows the output response to an input overdrive with the amplifier connected as a voltage follower. With the input signal low, current source I1 saturates and the differential drive generator drives Q6 into saturation so the output voltage swings all the way to V–. The input can swing positive until transistor Q2 saturates into current mirror Q3/Q4. When saturation occurs, the output tries to phase invert, but diode D2 conducts current from the signal source to the output through the feedback connection. The output is clamped a diode drop below the input. In this photo, the input signal generator is limiting at about 20mA. LT6233/LT6233-10 LT6234/LT6235 18 623345fc Applications Information With the amplifier connected in a gain of AV ≥ 2, the output can invert with very heavy overdrive. To avoid this inversion, limit the input overdrive to 0.5V beyond the power supply rails. ESD The LT6233/LT6234/LT6235 have reverse-biased ESD protection diodes on all inputs and outputs as shown in Figure 1. If these pins are forced beyond either supply, unlimited current will flow through these diodes. If the current is transient and limited to one hundred milliamps or less, no damage to the device will occur. Noise The noise voltage of the LT6233/LT6234/LT6235 is equivalent to that of a 225Ω resistor, and for the lowest possible noise it is desirable to keep the source and feedback resistance at or below this value, i.e., RS + RG||RFB ≤ 225Ω. With RS + RG||RFB = 225Ω the total noise of the amplifier is: eN = √(1.9nV)2 + (1.9nV)2 = 2.69nV/√Hz Below this resistance value, the amplifier dominates the noise, but in the region between 225Ω and about 30k, the noise is dominated by the resistor thermal noise. As the total resistance is further increased beyond 30k, the amplifier noise current multiplied by the total resistance eventually dominates the noise. The product of eN • √ISUPPLY is an interesting way to gauge low noise amplifiers. Most low noise amplifiers with low eN have high ISUPPLY current. In applications that require low noise voltage with the lowest possible supply current, this product can prove to be enlightening. The LT6233/LT6234/LT6235 have an eN • √ISUPPLY product of only 2.1 per amplifier, yet it is common to see amplifiers with similar noise specifications to have eN • √ISUPPLY as high as 13.5. For a complete discussion of amplifier noise, see the LT1028 data sheet. Enable Pin The LT6233 and LT6233-10 include an ENABLE pin that shuts down the amplifier to 10μA maximum supply current. The ENABLE pin must be driven low to operate the amplifier with normal supply current. The ENABLE pin must be driven high to within 0.35V of V+ to shut down the supply current. This can be accomplished with simple gate logic; however care must be taken if the logic and the LT6233 operate from different supplies. If this is the case, then open-drain logic can be used with a pull-up resistor to ensure that the amplifier remains off. See Typical Performance Characteristics. The output leakage current when disabled is very low; however, current can flow into the input protection diodes D1 and D2 if the output voltage exceeds the input voltage by a diode drop. 19 623345fc LT6233/LT6233-10 LT6234/LT6235 Typical Applications Single Supply, Low Noise, Low Power, Bandpass Filter with Gain = 10 Frequency Response Plot of Bandpass Filter Low Power, Low Noise, Single Supply, Instrumentation Amplifier with Gain = 100 R2 732 R4 10k C3 0.1μF EN f0 = 1 = 1MHz C = C1,C2 R = R1 = R2 f0 = (732)MHz, MAXIMUM f0 = 1MHz f–3dB = f0 AV = 20dB at f0 EN = 6μVRMS INPUT REFERRED IS = 1.5mA FOR V+ = 5V 623345 F03 0.1μF C2 47pF C1 1000pF R3 10k R1 732 VOUT V+ VIN 2πRC R 2.5 + – LT6233 FREQUENCY (Hz) 100k GAIN (dB) 23 3 –7 1M 10M 623345 F04 + – R14 2k EN U3 LT6233 VOUT = 100 (VIN2 – VIN1) GAIN = (R2 + 1) (R10) INPUT RESISTANCE = R5 = R6 f–3dB = 310Hz TO 2.5MHz EN = 10μVRMS INPUT REFERRED IS = 4.7mA FOR VS = 5V, 0V 623345 F05 C8 68pF C3 1μF R13 2k R10 511 R15 88.7 R16 88.7 R4 511 R3 30.9 R1 30.9 R2 511 VOUT VIN1 VIN2 V+ R1 R15 C9 68pF R12 511 + – EN U2 LT6233-10 V+ C1 1μF C2 2200pF + – EN U1 LT6233-10 V+ R5 511 R6 511 C4 10μF R1 = R3 R2 = R4 R10 = R12 R15 = R16 LT6233/LT6233-10 LT6234/LT6235 20 623345fc Package Description S6 Package 6-Lead Plastic TSOT-23 (Reference LTC DWG # 05-08-1636) 1.50 – 1.75 (NOTE 4) 2.80 BSC 0.30 – 0.45 6 PLCS (NOTE 3) DATUM ‘A’ 0.09 – 0.20 (NOTE 3) S6 TSOT-23 0302 2.90 BSC (NOTE 4) 0.95 BSC 1.90 BSC 0.80 – 0.90 1.00 MAX 0.01 – 0.10 0.20 BSC 0.30 – 0.50 REF PIN ONE ID NOTE: 1. DIMENSIONS ARE IN MILLIMETERS 2. DRAWING NOT TO SCALE 3. DIMENSIONS ARE INCLUSIVE OF PLATING 4. DIMENSIONS ARE EXCLUSIVE OF MOLD FLASH AND METAL BURR 5. MOLD FLASH SHALL NOT EXCEED 0.254mm 6. JEDEC PACKAGE REFERENCE IS MO-193 3.85 MAX 0.62 MAX 0.95 REF RECOMMENDED SOLDER PAD LAYOUT PER IPC CALCULATOR 2.62 REF 1.4 MIN 1.22 REF 21 623345fc LT6233/LT6233-10 LT6234/LT6235 Package Description DD Package 8-Lead Plastic DFN (3mm × 3mm) (Reference LTC DWG # 05-08-1698 Rev C) 3.00 ±0.10 (4 SIDES) NOTE: 1. DRAWING TO BE MADE A JEDEC PACKAGE OUTLINE M0-229 VARIATION OF (WEED-1) 2. DRAWING NOT TO SCALE 3. ALL DIMENSIONS ARE IN MILLIMETERS 4. DIMENSIONS OF EXPOSED PAD ON BOTTOM OF PACKAGE DO NOT INCLUDE MOLD FLASH. MOLD FLASH, IF PRESENT, SHALL NOT EXCEED 0.15mm ON ANY SIDE 5. EXPOSED PAD SHALL BE SOLDER PLATED 6. SHADED AREA IS ONLY A REFERENCE FOR PIN 1 LOCATION ON TOP AND BOTTOM OF PACKAGE 0.40 ± 0.10 BOTTOM VIEW—EXPOSED PAD 1.65 ± 0.10 (2 SIDES) 0.75 ±0.05 R = 0.125 TYP 2.38 ±0.10 4 1 5 8 PIN 1 TOP MARK (NOTE 6) 0.200 REF 0.00 – 0.05 (DD8) DFN 0509 REV C 0.25 ± 0.05 2.38 ±0.05 RECOMMENDED SOLDER PAD PITCH AND DIMENSIONS APPLY SOLDER MASK TO AREAS THAT ARE NOT SOLDERED 1.65 ±0.05 2.10 ±0.05 (2 SIDES) 0.50 BSC 0.70 ±0.05 3.5 ±0.05 PACKAGE OUTLINE 0.25 ± 0.05 0.50 BSC LT6233/LT6233-10 LT6234/LT6235 22 623345fc Package Description S8 Package 8-Lead Plastic Small Outline (Narrow .150 Inch) (Reference LTC DWG # 05-08-1610) .016 – .050 (0.406 – 1.270) .010 – .020 (0.254 – 0.508) × 45° 0°– 8° TYP .008 – .010 (0.203 – 0.254) SO8 0303 .053 – .069 (1.346 – 1.752) .014 – .019 (0.355 – 0.483) TYP .004 – .010 (0.101 – 0.254) .050 (1.270) BSC 1 2 3 4 .150 – .157 (3.810 – 3.988) NOTE 3 8 7 6 5 .189 – .197 (4.801 – 5.004) NOTE 3 .228 – .244 (5.791 – 6.197) .245 MIN .160 ±.005 RECOMMENDED SOLDER PAD LAYOUT .045 ±.005 .050 BSC .030 ±.005 TYP INCHES (MILLIMETERS) NOTE: 1. DIMENSIONS IN 2. DRAWING NOT TO SCALE 3. THESE DIMENSIONS DO NOT INCLUDE MOLD FLASH OR PROTRUSIONS. MOLD FLASH OR PROTRUSIONS SHALL NOT EXCEED .006" (0.15mm) GN Package 16-Lead Plastic SSOP (Narrow .150 Inch) (Reference LTC DWG # 05-08-1641) GN16 (SSOP) 0204 1 2 3 4 5 6 7 8 .229 – .244 (5.817 – 6.198) .150 – .157** (3.810 – 3.988) 16 15 14 13 .189 – .196* (4.801 – 4.978) 12 11 10 9 .016 – .050 (0.406 – 1.270) .015 ± .004 (0.38 ± 0.10) × 45° .007 – .0098 0° – 8° TYP (0.178 – 0.249) .0532 – .0688 (1.35 – 1.75) .008 – .012 (0.203 – 0.305) TYP .004 – .0098 (0.102 – 0.249) .0250 (0.635) BSC .009 (0.229) REF .254 MIN RECOMMENDED SOLDER PAD LAYOUT .150 – .165 .0165 ±.0015 .0250 BSC .045 ±.005 * DIMENSION DOES NOT INCLUDE MOLD FLASH. MOLD FLASH SHALL NOT EXCEED 0.006" (0.152mm) PER SIDE ** DIMENSION DOES NOT INCLUDE INTERLEAD FLASH. INTERLEAD FLASH SHALL NOT EXCEED 0.010" (0.254mm) PER SIDE INCHES (MILLIMETERS) NOTE: 1. CONTROLLING DIMENSION: INCHES 2. DIMENSIONS ARE IN 3. DRAWING NOT TO SCALE 23 623345fc LT6233/LT6233-10 LT6234/LT6235 Information furnished by Linear Technology Corporation is believed to be accurate and reliable. However, no responsibility is assumed for its use. Linear Technology Corporation makes no representation that the interconnection of its circuits as described herein will not infringe on existing patent rights. Revision History REV DATE DESCRIPTION PAGE NUMBER C 1/11 Revised y-axis lable on curve G40 in Typical Performance Characteristics Updated ENABLE Pin section in Applications Information 14 18 (Revision history begins at Rev C) LT6233/LT6233-10 LT6234/LT6235 24 623345fc Linear Technology Corporation 1630 McCarthy Blvd., Milpitas, CA 95035-7417 (408) 432-1900 ● FAX: (408) 434-0507 ● www.linear.com LINEAR TECHNOLOGY CORPORATION 2003 LT 0111 REV C • PRINTED IN USA Related Parts Typical Applications Low Power Avalanche Photodiode Transimpedance Amplifier IS = 1.2mA Photodiode Amplifier Time Domain Response PART NUMBER DESCRIPTION COMMENTS LT1028 Single, Ultralow Noise 50MHz Op Amp 0.85nV/√Hz LT1677 Single, Low Noise Rail-to-Rail Amplifier 3V Operation, 2.5mA, 4.5nV/√Hz, 60μV Max VOS LT1806/LT1807 Single/Dual, Low Noise 325MHz Rail-to-Rail Amplifier 2.5V Operation, 550μV Max VOS, 3.5nV/√Hz LT6200/LT6201 Single/Dual, Low Noise 165MHz 0.95nV√Hz, Rail-to-Rail Input and Output LT6202/LT6203/LT6204 Single/Dual/Quad, Low Noise, Rail-to-Rail Amplifier 1.9nV/√Hz, 3mA Max, 100MHz Gain Bandwidth The LT6233 is applied as a transimpedance amplifier with an I-to-V conversion gain of 10kΩ set by R1. The LT6233 is ideally suited to this application because of its low input offset voltage and current, and its low noise. This is because the 10k resistor has an inherent thermal noise of 13nV/√Hz or 1.3pA/√Hz at room temperature, while the LT6233 contributes only 2nV and 0.8pA/√Hz. So, with respect to both voltage and current noises, the LT6233 is actually quieter than the gain resistor. The circuit uses an avalanche photodiode with the cathode biased to approximately 200V. When light is incident on the photodiode, it induces a current IPD which flows into the amplifier circuit. The amplifier output falls negative to maintain balance at its inputs. The transfer function is therefore VOUT = –IPD • 10k. C1 ensures stability and good settling characteristics. Output offset was measured at better than 500μV, so low in part because R2 serves to cancel the DC effects of bias current. Output noise was measured at below 1mVP-P on a 20MHz measurement bandwidth, with C2 shunting R2’s thermal noise. As shown in the scope photo, the rise time is 45ns, indicating a signal bandwidth of 7.8MHz. + – R1 10k R2 10k C2 0.1μF 5V –5V ENABLE LT6233 200V BIAS ADVANCED PHOTONIX 012-70-62-541 WWW.ADVANCEDPHOTONIX.COM OUTPUT OFFSET = 500μV TYPICAL BANDWIDTH = 7.8MHz OUTPUT NOISE = 1mVP-P (20MHz MEASUREMENT BW) 623345 TA02a C1 2.7pF 100ns/DIV 623345 TA02b 50mV/DIV REV. A Information furnished by Analog Devices is believed to be accurate and reliable. However, no responsibility is assumed by Analog Devices for its use, nor for any infringements of patents or other rights of third parties which may result from its use. No license is granted by implication or otherwise under any patent or patent rights of Analog Devices. a AD8300 One Technology Way, P.O. Box 9106, Norwood, MA 02062-9106, U.S.A. Tel: 781/329-4700 World Wide Web Site: http://www.analog.com Fax: 781/326-8703 © Analog Devices, Inc., 1999 FUNCTIONAL BLOCK DIAGRAM VDD VOUT GND CLR LD CS CLK SDI AD8300 12 12 12-BIT REF DAC DAC REGISTER EN SERIAL REGISTER +3 Volt, Serial Input Complete 12-Bit DAC FEATURES Complete 12-Bit DAC No External Components Single +3 Volt Operation 0.5 mV/Bit with 2.0475 V Full Scale 6 ms Output Voltage Settling Time Low Power: 3.6 mW Compact SO-8 1.5 mm Height Package APPLICATIONS Portable Communications Digitally Controlled Calibration Servo Controls PC Peripherals GENERAL DESCRIPTION The AD8300 is a complete 12-bit, voltage-output digital-toanalog converter designed to operate from a single +3 volt supply. Built using a CBCMOS process, this monolithic DAC offers the user low cost, and ease-of-use in single-supply +3 volt systems. Operation is guaranteed over the supply voltage range of +2.7 V to +5.5 V making this device ideal for battery operated applications. The 2.0475 V full-scale voltage output is laser trimmed to maintain accuracy over the operating temperature range of the device. The binary input data format provides an easy-to-use one-half-millivolt-per-bit software programmability. The voltage outputs are capable of sourcing 5 mA. A double buffered serial data interface offers high speed, threewire, DSP and microcontroller compatible inputs using data in (SDI), clock (CLK) and load strobe (LD) pins. A chip select (CS) pin simplifies connection of multiple DAC packages by enabling the clock input when active low. Additionally, a CLR input sets the output to zero scale at power on or upon user demand. The AD8300 is specified over the extended industrial (–40°C to +85°C) temperature range. AD8300s are available in plastic DIP, and low profile 1.5 mm height SO-8 surface mount packages. 3.0 2.8 2.0 0.01 0.1 1.0 10 2.6 2.4 2.2 OUTPUT LOAD CURRENT – mA MINIMUM SUPPLY VOLTAGE – Volts PROPER OPERATION WHEN VDD SUPPLY VOLTAGE ABOVE CURVE DVFS 1 LSB DATA = FFFH TA = +258C Figure 1. Minimum Supply Voltage vs. Load 1.00 0.75 –1.00 0 1024 2048 4096 0.50 3072 0.25 0.00 –0.25 –0.50 –0.75 DIGITAL INPUT CODE – Decimal INL LINEARITY ERROR – LSB VDD = +2.7V TA = –408C, +258C, +1258C = –408C = +258C = +1258C Figure 2. Linearity Error vs. Digital Code and Temperature –2– REV. A AD8300–SPECIFICATIONS +3 V OPERATION Parameter Symbol Condition Min Typ Max Units STATIC PERFORMANCE Resolution N [Note 1] 12 Bits Relative Accuracy INL –2 ±1/2 +2 LSB Differential Nonlinearity2 DNL Monotonic –1 ±1/2 +1 LSB Zero-Scale Error VZSE Data = 000H +1/2 +3 mV Full-Scale Voltage3 VFS Data = FFFH 2.039 2.0475 2.056 Volts Full-Scale Tempco TCVFS [Notes 3, 4] 16 ppm/°C ANALOG OUTPUT Output Current (Source) IOUT Data = 800H, DVOUT = 5 LSB 5 mA Output Current (Sink) IOUT Data = 800H, DVOUT = 5 LSB 2 mA Load Regulation LREG RL = 200 W to ¥, Data = 800H 1.5 5 LSB Output Resistance to GND ROUT Data = 000H 30 W Capacitive Load CL No Oscillation4 500 pF LOGIC INPUTS Logic Input Low Voltage VIL 0.6 V Logic Input High Voltage VIH 2.1 V Input Leakage Current IIL 10 mA Input Capacitance CIL 10 pF INTERFACE TIMING SPECIFICATIONS4, 5 Clock Width High tCH 40 ns Clock Width Low tCL 40 ns Load Pulsewidth tLDW 50 ns Data Setup tDS 15 ns Data Hold tDH 15 ns Clear Pulsewidth tCLRW 40 ns Load Setup tLD1 15 ns Load Hold tLD2 40 ns Select tCSS 40 ns Deselect tCSH 40 ns AC CHARACTERISTICS4 Voltage Output Settling Time tS To ±0.2% of Full Scale 7 ms To ±1 LSB of Final Value6 14 ms Output Slew Rate SR Data = 000H to FFFH to 000H 2.0 V/ms DAC Glitch 15 nV/s Digital Feedthrough 15 nV/s SUPPLY CHARACTERISTICS Power Supply Range VDD RANGE DNL < ±1 LSB 2.7 5.5 V Positive Supply Current IDD VDD = 3 V, VIL = 0 V, Data = 000H 1.2 1.7 mA VDD = 3.6 V, VIH = 2.3 V, Data = FFFH 1.9 3.0 mA Power Dissipation PDISS VDD = 3 V, VIL = 0 V, Data = 000H 3.6 5.1 mW Power Supply Sensitivity PSS DVDD = ±5% 0.001 0.005 %/% NOTES 1LSB = 0.5 mV for 0 V to +2.0475 V output range. 2The first two codes (000H, 001H) are excluded from the linearity error measurement. 3Includes internal voltage reference error. 4These parameters are guaranteed by design and not subject to production testing. 5All input control signals are specified with tR = tF = 2 ns (10% to 90% of +3 V) and timed from a voltage level of 1.6 V. 6The settling time specification does not apply for negative going transitions within the last 6 LSBs of ground. Some devices exhibit double the typical settling time in this 6 LSB region. Specifications subject to change without notice. (@ VDD = +5 V 6 10%, –408C £ TA £ +858C, unless otherwise noted) REV. A –3– AD8300 +5 V OPERATION Parameter Symbol Condition Min Typ Max Units STATIC PERFORMANCE Resolution N [Note 1] 12 Bits Relative Accuracy INL –2 ±1/2 +2 LSB Differential Nonlinearity2 DNL Monotonic –1 ±1/2 +1 LSB Zero-Scale Error VZSE Data = 000H +1/2 +3 mV Full-Scale Voltage3 VFS Data = FFFH 2.039 2.0475 2.056 Volts Full-Scale Tempco TCVFS [Notes 3, 4] 16 ppm/°C ANALOG OUTPUT Output Current (Source) IOUT Data = 800H, DVOUT = 5 LSB 5 mA Output Current (Sink) IOUT Data = 800H, DVOUT = 5 LSB 2 mA Load Regulation LREG RL = 200 W to ¥, Data = 800H 1.5 5 LSB Output Resistance to GND ROUT Data = 000H 30 W Capacitive Load CL No Oscillation4 500 pF LOGIC INPUTS Logic Input Low Voltage VIL 0.8 V Logic Input High Voltage VIH 2.4 V Input Leakage Current IIL 10 mA Input Capacitance CIL 10 pF INTERFACE TIMING SPECIFICATIONS4, 5 Clock Width High tCH 30 ns Clock Width Low tCL 30 ns Load Pulsewidth tLDW 30 ns Data Setup tDS 15 ns Data Hold tDH 15 ns Clear Pulsewidth tCLWR 30 ns Load Setup tLD1 15 ns Load Hold tLD2 30 ns Select tCSS 30 ns Deselect tCSH 30 ns AC CHARACTERISTICS4 Voltage Output Settling Time tS To ±0.2% of Full Scale 6 ms To ±1 LSB of Final Value6 13 ms Output Slew Rate SR Data = 000H to FFFH to 000H 2.2 V/ms DAC Glitch 15 nV/s Digital Feedthrough 15 nV/s SUPPLY CHARACTERISTICS Power Supply Range VDD RANGE DNL < ±1 LSB 2.7 5.5 V Positive Supply Current IDD VDD = 5 V, VIL = 0 V, Data = 000H 1.2 1.7 mA VDD = 5.5 V, VIH = 2.3 V, Data = FFFH 2.8 4.0 mA Power Dissipation PDISS VDD = 5 V, VIL = 0 V, Data = 000H 6 5.1 mW Power Supply Sensitivity PSS DVDD = ±10% 0.001 0.006 %/% NOTES 11 LSB = 0.5 mV for 0 V to +2.0475 V output range. 2The first two codes (000H, 001H) are excluded from the linearity error measurement. 3Includes internal voltage reference error. 4These parameters are guaranteed by design and not subject to production testing. 5All input control signals are specified with tR = tF = 2 ns (10% to 90% of +5 V) and timed from a voltage level of 1.6 V. 6The settling time specification does not apply for negative going transitions within the last 6 LSBs of ground. Some devices exhibit double the typical settling time in this 6 LSB region. Specifications subject to change without notice. (@ VDD = +5 V 6 10%, –408C £ TA £ +858C, unless otherwise noted) REV. A AD8300 –4– CAUTION ESD (electrostatic discharge) sensitive device. Electrostatic charges as high as 4000 V readily accumulate on the human body and test equipment and can discharge without detection. Although the AD8300 features proprietary ESD protection circuitry, permanent damage may occur on devices subjected to high energy electrostatic discharges. Therefore, proper ESD precautions are recommended to avoid performance degradation or loss of functionality. WARNING! ESD SENSITIVE DEVICE ABSOLUTE MAXIMUM RATINGS* VDD to GND . . . . . . . . . . . . . . . . . . . . . . . . . . . . –0.3 V, +7 V Logic Inputs to GND . . . . . . . . . . . . . . . . . . . . . –0.3 V, +7 V VOUT to GND . . . . . . . . . . . . . . . . . . . . . . –0.3 V, VDD + 0.3 V IOUT Short Circuit to GND . . . . . . . . . . . . . . . . . . . . . . 50 mA Package Power Dissipation . . . . . . . . . . . . . (TJ Max – TA)/qJA Thermal Resistance qJA 8-Lead Plastic DIP Package (N-8) . . . . . . . . . . . . . 103°C/W 8-Lead SOIC Package (SO-8) . . . . . . . . . . . . . . . . 158°C/W Maximum Junction Temperature (TJ Max) . . . . . . . . . . 150°C Operating Temperature Range . . . . . . . . . . . . –40°C to +85°C Storage Temperature Range . . . . . . . . . . . . . –65°C to +150°C Lead Temperature (Soldering, 10 secs) . . . . . . . . . . . . +300°C *Stresses above those listed under Absolute Maximum Ratings may cause permanent damage to the device. This is a stress rating only; functional operation of the device at these or any other conditions above those indicated in the operational sections of this specification is not implied. Exposure to absolute maximum rating conditions for extended periods may affect device reliability. PIN CONFIGURATIONS SO-8 Plastic DIP 1 2 3 4 TOP VIEW (Not to Scale) 8 7 6 5 AD8300 VDD CS CLK SDI VOUT GND LD CLR 1 4 8 5 ORDERING GUIDE Package Package Model INL Temp Description Options AD8300AN ±2 XIND 8-Lead P-DIP N-8 AD8300AR ±2 XIND 8-Lead SOIC SO-8 NOTES XIND = –40°C to +85°C. The AD8300 contains 630 transistors. The die size measures 72 mil ´ 65 mil. PIN DESCRIPTIONS Pin # Name Function 1 VDD Positive power supply input. Specified range of operation +2.7 V to +5.5 V. 2 CS Chip Select, active low input. Disables shift register loading when high. Does not affect LD operation. 3 CLK Clock input, positive edge clocks data into shift register. 4 SDI Serial Data Input, input data loads directly into the shift register, MSB first. 5 LD Load DAC register strobes, active low. Transfers shift register data to DAC register. See Truth Table I for operation. Asynchronous active low input. 6 CLR Resets DAC register to zero condition. Asynchronous active low input. 7 GND Analog and Digital Ground. 8 VOUT DAC voltage output, 2.0475 V full scale with 0.5 mV per bit. An internal temperature stabilized reference maintains a fixed full-scale voltage independent of time, temperature and power supply variations. SDI D11 D10 D9 D8 D7 D6 D5 D4 D3 D2 D1 D0 tCSS tLD1 tCSH tLD2 CLK CS LD SDI CLK CLR LD 61LSB ERROR BAND FS ZS tDS tDH tCL tCH tLDW tS tCLRW tS VOUT Figure 3. Timing Diagram REV. A AD8300 –5– 2.5 2.0 0 0 1 4 5 6 0.5 1.0 1.5 2 3 VDD SUPPLY VOLTAGE – Volts LOGIC THRESHOLD VOLTAGE TA = –40 TO +858C Figure 5. Logic Input Threshold Voltage vs. VDD 50 45 0 10 100 10k 100k 1M 40 35 30 25 20 15 10 5 1k FREQUENCY – Hz POWER SUPPLY REJECTION – dB VDD = +3V 610% VDD = +5V 610% TA = +258C DATA = FFFH Figure 8. Power Supply Rejection vs. Frequency CODE 800H TO 7FFH Figure 11. Midscale Transition Performance 80 40 –80 0 1 2 –40 0 60 20 –60 –20 OUTPUT VOLTAGE – Volts OUTPUT CURRENT – mA VDD = +3V VDD = +5V VDD = +3V POSITIVE VDD = +5V CURRENT LIMIT NEGATIVE CURRENT LIMIT DATA = 800H RL TIED TO +1.024V Figure 4. IOUT vs. VOUT TIME = 100ms/DIV BROADBAND NOISE – 200mV/DIV Figure 7. Broadband Noise 3.5 3.0 0 0 1 3 4 5 1.5 2.5 2.0 2 LOGIC VOLTAGE – Volts SUPPLY CURRENT – mA VDD = +5V VDD = +3V TA = +258C DATA = FFFH 1.0 0.5 Figure 10. Supply Current vs. Logic Input Voltage HORIZONTAL = 1ms/DIV Figure 6. Detail Settling Time HORIZONTAL = 20ms/DIV Figure 9. Large Signal Settling Time 0.5ms/DIV Figure 12. Digital Feedthrough vs. Time Typical Performance Characteristics– REV. A AD8300 –6– 1.5 1.0 –1.5 –55 –35 –15 5 25 45 65 85 105 125 0.5 0 –0.5 –1.0 VOUT DRIFT – mV TEMPERATURE – 8C VDD = +2.7V VDD = +5V NO LOAD ss = 300 UNITS NORMALIZED TO +258C Figure 14. Zero-Scale Voltage Drift vs. Temperature 10 1 0.01 1 10 100 1k 10k 100k 0.1 FREQUENCY – Hz NOISE DENSITY – mV/Hz VDD = +3V DATA = FFFH Figure 17. Output Voltage Noise Density vs. Frequency 2.4 2.0 0 0 100 200 300 500 600 0.8 1.2 1.6 0.4 400 HOURS OF OPERATION AT +1508C NOMINAL VOLTAGE CHANGE – mV FULL SCALE (DATA = FFFH) ZERO SCALE (DATA = 000H) VDD = +2.7V ss = 135 UNITS Figure 19. Long Term Drift Accelerated by Burn-In 60 50 0 10 30 40 20 –1 0 1 2 3 4 5 6 TOTAL UNADJUSTED ERROR – mV FREQUENCY TUE = SINL+ZS+FS ss = 300 UNITS VDD = +3V TA = +258C Figure 13. Total Unadjusted Error Histogram 1.5 1.0 –1.5 –55 –35 –15 5 25 45 65 85 105 125 0.5 0 –0.5 –1.0 VOUT DRIFT – mV TEMPERATURE – 8C VDD = +2.7V VDD = +5.5V NO LOAD ss = 300 UNITS NORMALIZED TO +258C Figure 16. Full-Scale Voltage Drift vs. Temperature 3.0 1.0 –60 –20 20 60 100 140 2.2 2.6 1.8 TEMPERATURE – 8C IDD SUPPLY CURRENT – mA DATA = FFFH VIH = +2.4V VIL = 0V VDD = +5.5V VDD = +5.0V 1.4 VDD = +4.5V VDD = +2.7, 3.0, 3.3V Figure 15. Supply Current vs. Temperature 70 60 0 –50 –40 –20 –10 40 50 –30 40 30 20 10 0 10 20 30 TEMPERATURE COEFFICIENT – ppm/8C FREQUENCY VDD = +3V DATA FFFH TA = –40 TO +858C Figure 18. Full-Scale Output Tempco Histogram REV. A AD8300 –7– Table I. Control Logic Truth Table CS CLK CLR LD Serial Shift Register Function DAC Register Function H X H H No Effect Latched L L H H No Effect Latched L H H H No Effect Latched L H H Shift-Register-Data Advanced One Bit Latched L H H No Effect Latched H X H ¯ No Effect Updated with Current Shift Register Contents H X H L No Effect Transparent H X L X No Effect Loaded with All Zeros H X H No Effect Latched All Zeros NOTES 1. = Positive Logic Transition; ¯ = Negative Logic Transition; X = Don’t Care. 2. Do not clock in serial data while LD is LOW. 3. Data loads MSB first. OPERATION The AD8300 is a complete ready to use 12-bit digital-to-analog converter. Only one +3 V power supply is necessary for operation. It contains a 12-bit laser-trimmed digital-to-analog converter, a curvature-corrected bandgap reference, rail-to-rail output op amp, serial-input register, and DAC register. The serial data interface consists of a serial-data-input (SDI) clock (CLK), and load strobe pins (LD) with an active low CS strobe. In addition an asynchronous CLR pin will set all DAC register bits to zero causing the VOUT to become zero volts. This function is useful for power on reset or system failure recovery to a known state. D/A CONVERTER SECTION The internal DAC is a 12-bit device with an output that swings from GND potential to 0.4 volt generated from the internal bandgap voltage, see Figure 20. It uses a laser-trimmed segmented R-2R ladder which is switched by N-channel MOSFETs. The output voltage of the DAC has a constant resistance independent of digital input code. The DAC output is internally connected to the rail-to-rail output op amp. AMPLIFIER SECTION The internal DAC’s output is buffered by a low power consumption precision amplifier. This low power amplifier contains a differential PNP pair input stage that provides low offset voltage and low noise, as well as the ability to amplify the zero-scale DAC output voltages. The rail-to-rail amplifier is configured with a gain of approximately five in order to set the 2.0475 volt full-scale output (0.5 mV/LSB). See Figure 20 for an equivalent circuit schematic of the analog section. 12-BIT DAC R1 R2 VOUT 2.047V FS 1.2V 0.4V 0.4V FS BANDGAP REF Figure 20. Equivalent AD8300 Schematic of Analog Portion The op amp has a 2 ms typical settling time to 0.4% of full scale. There are slight differences in settling time for negative slewing signals versus positive. Also negative transition settling time to within the last 6 LSB of zero volts has an extended settling time. See the oscilloscope photos in the typical performances section of this data sheet. OUTPUT SECTION The rail-to-rail output stage of this amplifier has been designed to provide precision performance while operating near either power supply. Figure 21 shows an equivalent output schematic of the rail-to-rail amplifier with its N-channel pull-down FETs that will pull an output load directly to GND. The output sourcing current is provided by a P-channel pull-up device that can source current to GND terminated loads. P-CH N-CH VDD VOUT AGND Figure 21. Equivalent Analog Output Circuit The rail-to-rail output stage achieves the minimum operating supply voltage capability shown in Figure 2. The N-channel output pull-down MOSFET shown in Figure 21 has a 35 W on resistance which sets the sink current capability near ground. In addition to resistive load driving capability, the amplifier has also been carefully designed and characterized for up to 500 pF capacitive load driving capability. REFERENCE SECTION The internal curvature-corrected bandgap voltage reference is laser trimmed for both initial accuracy and low temperature coefficient. Figure 18 provides a histogram of total output performance of full-scale vs. temperature which is dominated by the reference performance. POWER SUPPLY The very low power consumption of the AD8300 is a direct result of a circuit design optimizing use of a CBCMOS process. By using the low power characteristics of the CMOS for the logic, and the low noise, tight matching of the complementary bipolar transistors, good analog accuracy is achieved. For power-consumption sensitive applications it is important to note that the internal power consumption of the AD8300 is strongly dependent on the actual logic input voltage levels present on the SDI, CLK, CS, LD, and CLR pins. Since these inputs are standard CMOS logic structures, they contribute static power dissipation dependent on the actual driving logic REV. A AD8300 –8– PRINTED IN U.S.A. C1968a–0–5/99 OUTLINE DIMENSIONS Dimensions shown in inches and (mm). 8-Lead SOIC (SO-8) 8 5 1 4 0.1968 (5.00) 0.1890 (4.80) 0.2440 (6.20) 0.2284 (5.80) PIN 1 0.1574 (4.00) 0.1497 (3.80) 0.0500 (1.27) BSC 0.0688 (1.75) 0.0532 (1.35) SEATING PLANE 0.0098 (0.25) 0.0040 (0.10) 0.0192 (0.49) 0.0138 (0.35) 0.0098 (0.25) 0.0075 (0.19) 0.0500 (1.27) 0.0160 (0.41) 88 08 0.0196 (0.50) 0.0099 (0.25) 3 458 8-Lead Plastic DIP (N-8) SEATING PLANE 0.015 (0.381) 0.210 TYP (5.33) MAX 0.022 (0.558) 0.014 (0.356) 0.160 (4.06) 0.115 (2.93) 0.070 (1.77) 0.045 (1.15) 0.130 (3.30) MIN 8 1 4 5 PIN 1 0.280 (7.11) 0.240 (6.10) 0.100 (2.54) BSC 0.430 (10.92) 0.348 (8.84) 0.195 (4.95) 0.115 (2.93) 0.015 (0.381) 0.008 (0.204) 0.325 (8.25) 0.300 (7.62) 158 08 VOH and VOL voltage levels. Consequently, for optimum dissipation use of CMOS logic versus TTL provides minimal dissipation in the static state. A VINL = 0 V on the logic input pins provides the lowest standby dissipation of 1.2 mA with a +3.3 V power supply. As with any analog system, it is recommended that the AD8300 power supply be bypassed on the same PC card that contains the chip. Figure 8 shows the power supply rejection versus frequency performance. This should be taken into account when using higher frequency switched-mode power supplies with ripple frequencies of 100 kHz and higher. One advantage of the rail-to-rail output amplifiers used in the AD8300 is the wide range of usable supply voltage. The part is fully specified and tested over temperature for operation from +2.7 V to +5.5 V. If reduced linearity and source current capability near full scale can be tolerated, operation of the AD8300 is possible down to +2.1 volts. The minimum operating supply voltage versus load current plot in Figure 2 provides information for operation below VDD = +2.7 V. TIMING AND CONTROL The AD8300 has a separate serial-input register from the 12-bit DAC register that allows preloading of a new data value MSB first into the serial register without disturbing the present DAC output voltage value. Data can only be loaded when the CS pin is active low. After the new value is fully loaded in the serialinput register, it can be asynchronously transferred to the DAC register by strobing the LD pin. The DAC register uses a level sensitive LD strobe that should be returned high before any new data is loaded into the serial-input register. At any time the contents of the DAC resister can be reset to zero by strobing the CLR pin which causes the DAC output voltage to go to zero volts. All of the timing requirements are detailed in Figure 3 along with Table I. Control Logic Truth Table. All digital inputs are protected with a Zener type ESD protection structure (Figure 22) that allows logic input voltages to exceed the VDD supply voltage. This feature can be useful if the user is loading one or more of the digital inputs with a 5 V CMOS logic input voltage level while operating the AD8300 on a +3.3 V power supply. If this mode of interface is used, make sure that the VOL of the +5 V CMOS meets the VIL input requirement of the AD8300 operating at 3 V. See Figure 5 for the effect on digital logic input threshold versus operating VDD supply voltage. VDD LOGIC IN GND Figure 22. Equivalent Digital Input ESD Protection Unipolar Output Operation This is the basic mode of operation for the AD8300. The AD8300 has been designed to drive loads as low as 400 W in parallel with 500 pF. The code table for this operation is shown in Table II. APPLICATIONS INFORMATION See DAC8512 data sheet for additional application circuit ideas. Table II. Unipolar Code Table Hexadecimal Decimal Number in Number in Analog Output DAC Register DAC Register Voltage (V) FFF 4095 +2.0475 801 2049 +1.0245 800 2048 +1.0240 7FF 2047 +1.0235 000 0 +0.0000 DATA RDS 80 Microprocessor-Controlled Digital 80 Watt Soldering Station The digital soldering station ERSA RDS 80, offers the established and proven ERSA Res istr onic heating technology with a generous 80 watts of power. With this unique temperature control technology, the ceramic PTC heating element (Positive Temperature Coefficient) replaces the function of the thermocouple. This guarantees very fast preheating due to high initial power and fast heat recovery for a stable soldering process. The very high heating power and the largest range of soldering tips allow for great flexibility in handling all applications. The heating system with interior heated soldering tips has the highest thermal efficiency. The newly constructed ergonomic handle, the new design of the housing, and the big digital multi-function display leave nothing to be desired! Precise temperatures can be selected between 150°C and 450°C (302°F - 842°F), and with a touch of a button, 3 fixed temperatures or 2 fixed temperatures and one stand-by temperature can be programmed and selected. I n addition, the station offers a power bar graph display, a calibration capability, and an automatic power-off function. Finally, the potential equalization jack (with integraded 220 kΩ resistor) allows the system to be grounded to the desired resistance of the working environment. Power, Precision, Comfort and Safety- the ERSA RDS 80 offers the best Bang for your Buck! The digital power soldering station with microprocessor control and fantastic price/performance ratio ! Fig.: Microprocessor-controlled digital power soldering station Fig.: Microprocessor-controlled digital power soldering station ERSA product range Soldering tools • Soldering / desoldering stations • SMD equipment • Hand soldering tools • Gas soldering irons • Solder baths • Special tools • Accessories BGA/SMT Rework I R Rework Center • IR/PL 550 A • IR/PL 650 A Hybrid Tool HR 100 A Inspection Systems • ERSASCOPE • ImageDoc Software Soldering Systems Wave soldering • ETS series • EWS series • N-Wave series • POWERFLOW series Reflow soldering • HOTFLOW series Selective soldering • Versaflow ersaflow ersaflow series Process Software • EPOS • CAD Assistant Paste Printing • VERSAPRINT series Accessories • Solder bar & wire • Solder paste • Flux Other Services • Know-how seminars • In-house training • Test soldering • Installation and main- tenance assistance • Process support DATA RDS 80 49263-0507 • subject to changes • © by ERSA Microprocessor-Controlled Digital 80 Watt Soldering Station 832 BD 832 YD 832 CD 832 ED 832 VD 832 GD 832 LD 832 MD 842 BD 842 YD 842 CD 842 ED Technical data: Electronic station RDS 803 Supply voltage: 230 V / 50 Hz Secondary voltage: 24 V ~ Power: 80 VA C ontrol technology: Res istr onic temperature regulation Temperature range: 150°C - 459°C 302°F - 842°F Temperature accuracy: 0°C after calibration Display resolution: 1°C / 1°F C able: 2 m PVC Fuse: 0.63 A delayed action Station dimensions: 110 x 105 x 147 mm (W x H x D) Permissible ambient temperature: 0 - 40°C / 32 - 104°F Weight: approx. 2 kg Soldering iron RT 80 with soldering tip 842 CD Voltage: 24 V ~ Power: 80 W at 350°C (662°F) Preheating power: 290 W Preheating time: approx. 40 s (to 280°C / 536°F) C able: 1.5 m PVC, Weight: approx. 130 g Holder RH 80 Weight: approx. 400 g Fig.: Soldering iron RT 80 with optional soldering tips Excerpt of 832/842 soldering tip series actual size Europe (Headquarters): ERSA GmbH Leonhard-Karl-Str. 24 97877 Wertheim / Germany Phone: +49 (0) 9342 / 800-0 Fax: +49 (0) 9342 / 800-127 e-mail: info@ersa.de www.ersa.com General Description The DS3231 is a low-cost, extremely accurate I2C realtime clock (RTC) with an integrated temperaturecompensated crystal oscillator (TCXO) and crystal. The device incorporates a battery input, and maintains accurate timekeeping when main power to the device is interrupted. The integration of the crystal resonator enhances the long-term accuracy of the device as well as reduces the piece-part count in a manufacturing line. The DS3231 is available in commercial and industrial temperature ranges, and is offered in a 16-pin, 300-mil SO package. The RTC maintains seconds, minutes, hours, day, date, month, and year information. The date at the end of the month is automatically adjusted for months with fewer than 31 days, including corrections for leap year. The clock operates in either the 24-hour or 12-hour format with an AM/PM indicator. Two programmable time-ofday alarms and a programmable square-wave output are provided. Address and data are transferred serially through an I2C bidirectional bus. A precision temperature-compensated voltage reference and comparator circuit monitors the status of VCC to detect power failures, to provide a reset output, and to automatically switch to the backup supply when necessary. Additionally, the RST pin is monitored as a pushbutton input for generating a reset externally. Applications Servers Utility Power Meters Telematics GPS Features ♦ Accuracy ±2ppm from 0°C to +40°C ♦ Accuracy ±3.5ppm from -40°C to +85°C ♦ Battery Backup Input for Continuous Timekeeping ♦ Operating Temperature Ranges Commercial: 0°C to +70°C Industrial: -40°C to +85°C ♦ Low-Power Consumption ♦ Real-Time Clock Counts Seconds, Minutes, Hours, Day, Date, Month, and Year with Leap Year Compensation Valid Up to 2100 ♦ Two Time-of-Day Alarms ♦ Programmable Square-Wave Output ♦ Fast (400kHz) I2C Interface ♦ 3.3V Operation ♦ Digital Temp Sensor Output: ±3°C Accuracy ♦ Register for Aging Trim ♦ RST Output/Pushbutton Reset Debounce Input ♦ Underwriters Laboratories (UL) Recognized DS3231 Extremely Accurate I2C-Integrated RTC/TCXO/Crystal ______________________________________________ Maxim Integrated Products 1 Rev 5; 4/08 Ordering Information PART TEMP RANGE PIN-PACKAGE TOP MARK DS3231S 0°C to +70°C 16 SO DS3231 DS3231SN -40°C to +85°C 16 SO DS3231N DS3231S# 0°C to +70°C 16 SO DS3231S DS3231SN# -40°C to +85°C 16 SO DS3231SN Pin Configuration appears at end of data sheet. DS3231 VCC SCL RPU RPU = tR/CB RPU INT/SQW 32kHz VBAT PUSHBUTTON RESET SDA RST N.C. N.C. N.C. N.C. VCC VCC GND VCC CPU N.C. N.C. N.C. N.C. Typical Operating Circuit # Denotes a RoHS-compliant device that may include lead that is exempt under RoHS requirements. The lead finish is JESD97 category e3, and is compatible with both lead-based and leadfree soldering processes. A "#" anywhere on the top mark denotes a RoHS-compliant device. For pricing, delivery, and ordering information, please contact Maxim Direct at 1-888-629-4642, or visit Maxim’s website at www.maxim-ic.com. DS3231 Extremely Accurate I2C-Integrated RTC/TCXO/Crystal 2 _____________________________________________________________________ ABSOLUTE MAXIMUM RATINGS RECOMMENDED DC OPERATING CONDITIONS (TA = TMIN to TMAX, unless otherwise noted.) (Notes 1, 2) Stresses beyond those listed under “Absolute Maximum Ratings” may cause permanent damage to the device. These are stress ratings only, and functional operation of the device at these or any other conditions beyond those indicated in the operational sections of the specifications is not implied. Exposure to absolute maximum rating conditions for extended periods may affect device reliability. Voltage Range on VCC, VBAT, 32kHz, SCL, SDA, RST, INT/SQW Relative to Ground.............................-0.3V to +6.0V Operating Temperature Range (noncondensing) .............................................-40°C to +85°C Junction Temperature......................................................+125°C Storage Temperature Range ...............................-40°C to +85°C Lead Temperature (Soldering, 10s).....................................................+260°C/10s Soldering Temperature....................................See the Handling, PC Board Layout, and Assembly section. PARAMETER SYMBOL CONDITIONS MIN TYP MAX UNITS VCC 2.3 3.3 5.5 V Supply Voltage VBAT 2.3 3.0 5.5 V Logic 1 Input SDA, SCL VIH 0.7 x VCC VCC + 0.3 V Logic 0 Input SDA, SCL VIL -0.3 +0.3 x VCC V Pullup Voltage (SDA, SCL, 32kHz, INT/SQW) VPU VCC = 0V 5.5V V ELECTRICAL CHARACTERISTICS (VCC = 2.3V to 5.5V, VCC = Active Supply (see Table 1), TA = TMIN to TMAX, unless otherwise noted.) (Typical values are at VCC = 3.3V, VBAT = 3.0V, and TA = +25°C, unless otherwise noted.) (Notes 1, 2) PARAMETER SYMBOL CONDITIONS MIN TYP MAX UNITS VCC = 3.63V 200 Active Supply Current ICCA (Notes 3, 4) VCC = 5.5V 300 μA VCC = 3.63V 110 Standby Supply Current ICCS I2C bus inactive, 32kHz output on, SQW output off (Note 4) VCC = 5.5V 170 μA VCC = 3.63V 575 Temperature Conversion Current ICCSCONV I2C bus inactive, 32kHz output on, SQW output off VCC = 5.5V 650 μA Power-Fail Voltage VPF 2.45 2.575 2.70 V Logic 0 Output, 32kHz, INT/SQW, SDA VOL IOL = 3mA 0.4 V Logic 0 Output, RST VOL IOL = 1mA 0.4 V Output Leakage Current 32kHz, INT/SQW, SDA ILO Output high impedance -1 0 +1 μA Input Leakage SCL ILI -1 +1 μA RST Pin I/O Leakage IOL RST high impedance (Note 5) -200 +10 μA VBAT Leakage Current (VCC Active) IBATLKG 25 100 nA DS3231 Extremely Accurate I2C-Integrated RTC/TCXO/Crystal _____________________________________________________________________ 3 ELECTRICAL CHARACTERISTICS (continued) (VCC = 2.3V to 5.5V, VCC = Active Supply (see Table 1), TA = TMIN to TMAX, unless otherwise noted.) (Typical values are at VCC = 3.3V, VBAT = 3.0V, and TA = +25°C, unless otherwise noted.) (Notes 1, 2) PARAMETER SYMBOL CONDITIONS MIN TYP MAX UNITS Output Frequency fOUT VCC = 3.3V or VBAT = 3.3V 32.768 kHz Frequency Stability vs. 0°C to +40°C ±2 Temperature (Commercial) f/fOUT VCC = 3.3V or VBAT = 3.3V, aging offset = 00h >40°C to +70°C ±3.5 ppm -40°C to <0°C ±3.5 0°C to +40°C ±2 Frequency Stability vs. Temperature (Industrial) f/fOUT VCC = 3.3V or VBAT = 3.3V, aging offset = 00h >40°C to +85°C ±3.5 ppm Frequency Stability vs. Voltage f/V 1 ppm/V -40°C 0.7 +25°C 0.1 +70°C 0.4 Trim Register Frequency Sensitivity per LSB f/LSB Specified at: +85°C 0.8 ppm Temperature Accuracy Temp VCC = 3.3V or VBAT = 3.3V -3 +3 °C First year ±1.0 Crystal Aging f/fO After reflow, not production tested 0–10 years ±5.0 ppm ELECTRICAL CHARACTERISTICS (VCC = 0V, VBAT = 2.3V to 5.5V, TA = TMIN to TMAX, unless otherwise noted.) (Note 1) PARAMETER SYMBOL CONDITIONS MIN TYP MAX UNITS VBAT = 3.63V 70 Active Battery Current IBATA EOSC = 0, BBSQW = 0, SCL = 400kHz (Note 4) VBAT = 5.5V 150 μA VBAT = 3.63V 0.84 3.0 Timekeeping Battery Current IBATT EOSC = 0, BBSQW = 0, EN32kHz = 1, SCL = SDA = 0V or SCL = SDA = VBAT (Note 4) VBAT = 5.5V 1.0 3.5 μA VBAT = 3.63V 575 Temperature Conversion Current IBATTC EOSC = 0, BBSQW = 0, SCL = SDA = 0V or SCL = SDA = VBAT VBAT = 5.5V 650 μA Data-Retention Current IBATTDR EOSC = 1, SCL = SDA = 0V, +25°C 100 nA DS3231 Extremely Accurate I2C-Integrated RTC/TCXO/Crystal 4 _____________________________________________________________________ AC ELECTRICAL CHARACTERISTICS (VCC = VCC(MIN) to VCC(MAX) or VBAT = VBAT(MIN) to VBAT(MAX), VBAT > VCC, TA = TMIN to TMAX, unless otherwise noted.) (Note 1) PARAMETER SYMBOL CONDITIONS MIN TYP MAX UNITS Fast mode 100 400 SCL Clock Frequency fSCL Standard mode 0 100 kHz Bus Free Time Between STOP Fast mode 1.3 and START Conditions tBUF Standard mode 4.7 μs Hold Time (Repeated) START Fast mode 0.6 Condition (Note 6) tHD:STA Standard mode 4.0 μs Fast mode 1.3 Low Period of SCL Clock tLOW Standard mode 4.7 μs Fast mode 0.6 High Period of SCL Clock tHIGH Standard mode 4.0 μs Fast mode 0 0.9 Data Hold Time (Notes 7, 8) tHD:DAT Standard mode 0 0.9 μs Fast mode 100 Data Setup Time (Note 9) tSU:DAT Standard mode 250 ns Fast mode 0.6 START Setup Time tSU:STA Standard mode 4.7 μs Rise Time of Both SDA and SCL Fast mode 300 Signals (Note 10) tR Standard mode 20 + 0.1CB 1000 ns Fall Time of Both SDA and SCL Fast mode 300 Signals (Note 10) tF Standard mode 20 + 0.1CB 300 ns Fast mode 0.6 Setup Time for STOP Condition tSU:STO Standard mode 4.7 μs Capacitive Load for Each Bus Line (Note 10) CB 400 pF Capacitance for SDA, SCL CI/O 10 pF Pulse Width of Spikes That Must Be Suppressed by the Input Filter tSP 30 ns Pushbutton Debounce PBDB 250 ms Reset Active Time tRST 250 ms Oscillator Stop Flag (OSF) Delay tOSF (Note 11) 100 ms Temperature Conversion Time tCONV 125 200 ms POWER-SWITCH CHARACTERISTICS (TA = TMIN to TMAX) PARAMETER SYMBOL CONDITIONS MIN TYP MAX UNITS VCC Fall Time; VPF(MAX) to VPF(MIN) tVCCF 300 μs VCC Rise Time; VPF(MIN) to VPF(MAX) tVCCR 0 μs Recovery at Power-Up tREC (Note 12) 250 300 ms DS3231 Extremely Accurate I2C-Integrated RTC/TCXO/Crystal _____________________________________________________________________ 5 Pushbutton Reset Timing PBDB tRST RST Power-Switch Timing VCC tVCCF tVCCR tREC VPF(MAX) VPF VPF VPF(MIN) RST DS3231 Extremely Accurate I2C-Integrated RTC/TCXO/Crystal 6 _____________________________________________________________________ Data Transfer on I2C Serial Bus SDA SCL tHD:STA tLOW tHIGH tR tF tBUF tHD:DAT tSU:DAT REPEATED START tSU:STA tHD:STA tSU:STO tSP STOP START WARNING: Negative undershoots below -0.3V while the part is in battery-backed mode may cause loss of data. Note 1: Limits at -40°C are guaranteed by design and not production tested. Note 2: All voltages are referenced to ground. Note 3: ICCA—SCL clocking at max frequency = 400kHz. Note 4: Current is the averaged input current, which includes the temperature conversion current. Note 5: The RST pin has an internal 50kΩ (nominal) pullup resistor to VCC. Note 6: After this period, the first clock pulse is generated. Note 7: A device must internally provide a hold time of at least 300ns for the SDA signal (referred to the VIH(MIN) of the SCL signal) to bridge the undefined region of the falling edge of SCL. Note 8: The maximum tHD:DAT needs only to be met if the device does not stretch the low period (tLOW) of the SCL signal. Note 9: A fast-mode device can be used in a standard-mode system, but the requirement tSU:DAT ≥ 250ns must then be met. This is automatically the case if the device does not stretch the low period of the SCL signal. If such a device does stretch the low period of the SCL signal, it must output the next data bit to the SDA line tR(MAX) + tSU:DAT = 1000 + 250 = 1250ns before the SCL line is released. Note 10: CB—total capacitance of one bus line in pF. Note 11: The parameter tOSF is the period of time the oscillator must be stopped for the OSF flag to be set over the voltage range of 0.0V ≤ VCC ≤ VCC(MAX) and 2.3V ≤ VBAT ≤ 3.4V. Note 12: This delay applies only if the oscillator is enabled and running. If the EOSC bit is a 1, tREC is bypassed and RST immediately goes high. The state of RST does not affect the I2C interface, RTC, or TCXO. DS3231 Extremely Accurate I2C-Integrated RTC/TCXO/Crystal _____________________________________________________________________ 7 Typical Operating Characteristics (VCC = +3.3V, TA = +25°C, unless otherwise noted.) STANDBY SUPPLY CURRENT vs. SUPPLY VOLTAGE DS3231 toc01 VCC (V) ICCS (μA) 2.5 3.0 3.5 4.0 4.5 5.0 25 50 75 100 125 150 0 2.0 5.5 RST ACTIVE BSY = 0, SCL = SDA = VCC SUPPLY CURRENT vs. SUPPLY VOLTAGE DS3231 toc02 VBAT (V) IBAT (μA) 3.3 4.3 5.3 0.7 0.8 0.9 1.0 1.1 1.2 0.6 2.3 VCC = 0V, BSY = 0, SDA = SCL = VBAT OR VCC EN32kHz = 1 EN32kHz = 0 SUPPLY CURRENT vs. TEMPERATURE DS3231 toc03 TEMPERATURE (°C) IBAT (μA) -15 10 35 60 0.7 0.8 0.9 1.0 0.6 -40 85 VCC = 0, EN32kHz = 1, BSY = 0, SDA = SCL = VBAT OR GND FREQUENCY DEVIATION vs. TEMPERATURE vs. AGING VALUE DS3231 toc04 TEMPERATURE (°C) FREQUENCY DEVIATION (ppm) -15 10 35 60 -30 -20 -10 0 10 20 30 40 50 60 -40 -40 85 127 32 0 -33 8 DS3231 Extremely Accurate I2C-Integrated RTC/TCXO/Crystal 8 _____________________________________________________________________ Block Diagram N N N RST VCC 32kHz INT/SQW CLOCK AND CALENDAR REGISTERS USER BUFFER (7 BYTES) I2C INTERFACE AND ADDRESS REGISTER DECODE POWER CONTROL VCC VBAT GND SCL SDA TEMPERATURE SENSOR CONTROL LOGIC/ DIVIDER PUSHBUTTON RESET; SQUARE-WAVE BUFFER; INT/SQW CONTROL CONTROL AND STATUS REGISTERS OSCILLATOR AND CAPACITOR ARRAY X1 X2 DS3231 DS3231 Extremely Accurate I2C-Integrated RTC/TCXO/Crystal _____________________________________________________________________ 9 Pin Description PIN NAME FUNCTION 1 32kHz 32kHz Output. This open-drain pin requires an external pullup resistor. When enabled, the output operates on either power supply. It may be left open if not used. 2 VCC DC Power Pin for Primary Power Supply. This pin should be decoupled using a 0.1μF to 1.0μF capacitor. If not used, connect to ground. 3 INT/SQW Active-Low Interrupt or Square-Wave Output. This open-drain pin requires an external pullup resistor connected to a supply at 5.5V or less. It may be left open if not used. This multifunction pin is determined by the state of the INTCN bit in the Control Register (0Eh). When INTCN is set to logic 0, this pin outputs a square wave and its frequency is determined by RS2 and RS1 bits. When INTCN is set to logic 1, then a match between the timekeeping registers and either of the alarm registers activates the INT/SQW pin (if the alarm is enabled). Because the INTCN bit is set to logic 1 when power is first applied, the pin defaults to an interrupt output with alarms disabled. 4 RST Active-Low Reset. This pin is an open-drain input/output. It indicates the status of VCC relative to the VPF specification. As VCC falls below VPF, the RST pin is driven low. When VCC exceeds VPF, for tRST, the RST pin is pulled high by the internal pullup resistor. The active-low, open-drain output is combined with a debounced pushbutton input function. This pin can be activated by a pushbutton reset request. It has an internal 50k nominal value pullup resistor to VCC. No external pullup resistors should be connected. If the oscillator is disabled, tREC is bypassed and RST immediately goes high. 5–12 N.C. No Connection. Must be connected to ground. 13 GND Ground 14 VBAT Backup Power-Supply Input. This pin should be decoupled using a 0.1μF to 1.0μF low-leakage capacitor. If the I2C interface is inactive whenever the device is powered by the VBAT input, the decoupling capacitor is not required. If VBAT is not used, connect to ground. UL recognized to ensure against reverse charging when used with a lithium battery. Go to www.maxim-ic.com/qa/info/ul. 15 SDA Serial Data Input/Output. This pin is the data input/output for the I2C serial interface. This open-drain pin requires an external pullup resistor. 16 SCL Serial Clock Input. This pin is the clock input for the I2C serial interface and is used to synchronize data movement on the serial interface. Detailed Description The DS3231 is a serial RTC driven by a temperaturecompensated 32kHz crystal oscillator. The TCXO provides a stable and accurate reference clock, and maintains the RTC to within ±2 minutes per year accuracy from -40°C to +85°C. The TCXO frequency output is available at the 32kHz pin. The RTC is a low-power clock/calendar with two programmable time-of-day alarms and a programmable square-wave output. The INT/SQW provides either an interrupt signal due to alarm conditions or a square-wave output. The clock/calendar provides seconds, minutes, hours, day, date, month, and year information. The date at the end of the month is automatically adjusted for months with fewer than 31 days, including corrections for leap year. The clock operates in either the 24-hour or 12-hour format with an AM/PM indicator. The internal registers are accessible though an I2C bus interface. A temperature-compensated voltage reference and comparator circuit monitors the level of VCC to detect power failures and to automatically switch to the backup supply when necessary. The RST pin provides an external pushbutton function and acts as an indicator of a power-fail event. DS3231 Operation The block diagram shows the main elements of the DS3231. The eight blocks can be grouped into four functional groups: TCXO, power control, pushbutton function, and RTC. Their operations are described separately in the following sections. 32kHz TCXO The temperature sensor, oscillator, and control logic form the TCXO. The controller reads the output of the on-chip temperature sensor and uses a lookup table to determine the capacitance required, adds the aging correction in AGE register, and then sets the capacitance selection registers. New values, including changes to the AGE register, are loaded only when a change in the temperature value occurs, or when a user-initiated temperature conversion is completed. The temperature is read on initial application of VCC and once every 64 seconds afterwards. Power Control This function is provided by a temperature-compensated voltage reference and a comparator circuit that monitors the VCC level. When VCC is greater than VPF, the part is powered by VCC. When VCC is less than VPF but greater than VBAT, the DS3231 is powered by VCC. If VCC is less than VPF and is less than VBAT, the device is powered by VBAT. See Table 1. To preserve the battery, the first time VBAT is applied to the device, the oscillator will not start up until VCC exceeds VPF, or until a valid I2C address is written to the part. Typical oscillator startup time is less than one second. Approximately 2 seconds after VCC is applied, or a valid I2C address is written, the device makes a temperature measurement and applies the calculated correction to the oscillator. Once the oscillator is running, it continues to run as long as a valid power source is available (VCC or VBAT), and the device continues to measure the temperature and correct the oscillator frequency every 64 seconds. On the first application of power (VCC) or when a valid I2C address is written to the part (VBAT), the time and date registers are reset to 01/01/00 01 00:00:00 (MM/DD/YY DOW HH:MM:SS). Pushbutton Reset Function The DS3231 provides for a pushbutton switch to be connected to the RST output pin. When the DS3231 is not in a reset cycle, it continuously monitors the RST signal for a low going edge. If an edge transition is detected, the DS3231 debounces the switch by pulling the RST low. After the internal timer has expired (PBDB), the DS3231 continues to monitor the RST line. If the line is still low, the DS3231 continuously monitors the line looking for a rising edge. Upon detecting release, the DS3231 forces the RST pin low and holds it low for tRST. RST is also used to indicate a power-fail condition. When VCC is lower than VPF, an internal power-fail signal is generated, which forces the RST pin low. When VCC returns to a level above VPF, the RST pin is held low for approximately 250ms (tREC) to allow the power supply to stabilize. If the oscillator is not running (see the Power Control section) when VCC is applied, tREC is bypassed and RST immediately goes high. The state of RST does not affect the operation of the TCXO, I2C interface, or RTC functions. Real-Time Clock With the clock source from the TCXO, the RTC provides seconds, minutes, hours, day, date, month, and year information. The date at the end of the month is automatically adjusted for months with fewer than 31 days, including corrections for leap year. The clock operates in either the 24-hour or 12-hour format with an AM/PM indicator. The clock provides two programmable time-of-day alarms and a programmable square-wave output. The INT/SQW pin either generates an interrupt due to alarm condition or outputs a square-wave signal and the selection is controlled by the bit INTCN. Address Map Figure 1 shows the address map for the DS3231 timekeeping registers. During a multibyte access, when the address pointer reaches the end of the register space (12h), it wraps around to location 00h. On an I2C START or address pointer incrementing to location 00h, the current time is transferred to a second set of registers. The time information is read from these secondary registers, while the clock may continue to run. This eliminates the need to reread the registers in case the main registers update during a read. I2C Interface The I2C interface is accessible whenever either VCC or VBAT is at a valid level. If a microcontroller connected to the DS3231 resets because of a loss of VCC or other event, it is possible that the microcontroller and DS3231 I2C communications could become unsynchronized, Extremely Accurate I2C-Integrated RTC/TCXO/Crystal 10 ____________________________________________________________________ SUPPLY CONDITION ACTIVE SUPPLY VCC < VPF, VCC < VBAT VBAT VCC < VPF, VCC > VBAT VCC VCC > VPF, VCC < VBAT VCC VCC > VPF, VCC > VBAT VCC Table 1. Power Control e.g., the microcontroller resets while reading data from the DS3231. When the microcontroller resets, the DS3231 I2C interface may be placed into a known state by toggling SCL until SDA is observed to be at a high level. At that point the microcontroller should pull SDA low while SCL is high, generating a START condition. Clock and Calendar The time and calendar information is obtained by reading the appropriate register bytes. Figure 1 illustrates the RTC registers. The time and calendar data are set or initialized by writing the appropriate register bytes. The contents of the time and calendar registers are in the binary-coded decimal (BCD) format. The DS3231 can be run in either 12-hour or 24-hour mode. Bit 6 of the hours register is defined as the 12- or 24-hour mode select bit. When high, the 12-hour mode is selected. In the 12-hour mode, bit 5 is the AM/PM bit with logic-high being PM. In the 24-hour mode, bit 5 is the second 10-hour bit (20–23 hours). The century bit (bit 7 of the month register) is toggled when the years register overflows from 99 to 00. The day-of-week register increments at midnight. Values that correspond to the day of week are userdefined but must be sequential (i.e., if 1 equals Sunday, then 2 equals Monday, and so on). Illogical time and date entries result in undefined operation. When reading or writing the time and date registers, secondary (user) buffers are used to prevent errors when the internal registers update. When reading the time and date registers, the user buffers are synchronized to the internal registers on any START and when the register pointer rolls over to zero. The time information is read DS3231 Extremely Accurate I2C-Integrated RTC/TCXO/Crystal ____________________________________________________________________ 11 Figure 1. Timekeeing Registers Note: Unless otherwise specified, the registers’ state is not defined when power is first applied. ADDRESS BIT 7 MSB BIT 6 BIT 5 BIT 4 BIT 3 BIT 2 BIT 1 BIT 0 LSB FUNCTION RANGE 00h 0 10 Seconds Seconds Seconds 00–59 01h 0 10 Minutes Minutes Minutes 00–59 AM/PM 02h 0 12/24 10 Hour 10 Hour Hour Hours 1–12 + AM/PM 00–23 03h 0 0 0 0 0 Day Day 1–7 04h 0 0 10 Date Date Date 01–31 05h Century 0 0 10 Month Month Month/ Century 01–12 + Century 06h 10 Year Year Year 00–99 07h A1M1 10 Seconds Seconds Alarm 1 Seconds 00–59 08h A1M2 10 Minutes Minutes Alarm 1 Minutes 00–59 AM/PM 09h A1M3 12/24 10 Hour 10 Hour Hour Alarm 1 Hours 1–12 + AM/PM 00–23 Day Alarm 1 Day 1–7 0Ah A1M4 DY/DT 10 Date Date Alarm 1 Date 1–31 0Bh A2M2 10 Minutes Minutes Alarm 2 Minutes 00–59 AM/PM 0Ch A2M3 12/24 10 Hour 10 Hour Hour Alarm 2 Hours 1–12 + AM/PM 00–23 Day Alarm 2 Day 1–7 0Dh A2M4 DY/DT 10 Date Date Alarm 2 Date 1–31 0Eh EOSC BBSQW CONV RS2 RS1 INTCN A2IE A1IE Control — 0Fh OSF 0 0 0 EN32kHz BSY A2F A1F Control/Status — 10h SIGN DATA DATA DATA DATA DATA DATA DATA Aging Offset — 11h SIGN DATA DATA DATA DATA DATA DATA DATA MSB of Temp — 12h DATA DATA 0 0 0 0 0 0 LSB of Temp — DS3231 from these secondary registers, while the clock continues to run. This eliminates the need to reread the registers in case the main registers update during a read. The countdown chain is reset whenever the seconds register is written. Write transfers occur on the acknowledge from the DS3231. Once the countdown chain is reset, to avoid rollover issues the remaining time and date registers must be written within 1 second. The 1Hz square-wave output, if enabled, transitions high 500ms after the seconds data transfer, provided the oscillator is already running. Alarms The DS3231 contains two time-of-day/date alarms. Alarm 1 can be set by writing to registers 07h to 0Ah. Alarm 2 can be set by writing to registers 0Bh to 0Dh. The alarms can be programmed (by the alarm enable and INTCN bits of the control register) to activate the INT/SQW output on an alarm match condition. Bit 7 of each of the time-of-day/date alarm registers are mask bits (Table 2). When all the mask bits for each alarm are logic 0, an alarm only occurs when the values in the timekeeping registers match the corresponding values stored in the time-of-day/date alarm registers. The alarms can also be programmed to repeat every second, minute, hour, day, or date. Table 2 shows the possible settings. Configurations not listed in the table will result in illogical operation. The DY/DT bits (bit 6 of the alarm day/date registers) control whether the alarm value stored in bits 0 to 5 of that register reflects the day of the week or the date of the month. If DY/DT is written to logic 0, the alarm will be the result of a match with date of the month. If DY/DT is written to logic 1, the alarm will be the result of a match with day of the week. When the RTC register values match alarm register settings, the corresponding Alarm Flag ‘A1F’ or ‘A2F’ bit is set to logic 1. If the corresponding Alarm Interrupt Enable ‘A1IE’ or ‘A2IE’ is also set to logic 1 and the INTCN bit is set to logic 1, the alarm condition will activate the INT/SQW signal. The match is tested on the once-per-second update of the time and date registers. Extremely Accurate I2C-Integrated RTC/TCXO/Crystal 12 ____________________________________________________________________ Table 2. Alarm Mask Bits ALARM 1 REGISTER MASK BITS (BIT 7) DY/DT A1M4 A1M3 A1M2 A1M1 ALARM RATE X 1 1 1 1 Alarm once per second X 1 1 1 0 Alarm when seconds match X 1 1 0 0 Alarm when minutes and seconds match X 1 0 0 0 Alarm when hours, minutes, and seconds match 0 0 0 0 0 Alarm when date, hours, minutes, and seconds match 1 0 0 0 0 Alarm when day, hours, minutes, and seconds match ALARM 2 REGISTER MASK BITS (BIT 7) DY/DT A2M4 A2M3 A2M2 ALARM RATE X 1 1 1 Alarm once per minute (00 seconds of every minute) X 1 1 0 Alarm when minutes match X 1 0 0 Alarm when hours and minutes match 0 0 0 0 Alarm when date, hours, and minutes match 1 0 0 0 Alarm when day, hours, and minutes match Special-Purpose Registers The DS3231 has two additional registers (control and status) that control the real-time clock, alarms, and square-wave output. Control Register (0Eh) Bit 7: Enable Oscillator (EOSC). When set to logic 0, the oscillator is started. When set to logic 1, the oscillator is stopped when the DS3231 switches to VBAT. This bit is clear (logic 0) when power is first applied. When the DS3231 is powered by VCC, the oscillator is always on regardless of the status of the EOSC bit. Bit 6: Battery-Backed Square-Wave Enable (BBSQW). When set to logic 1 and the DS3231 is being powered by the VBAT pin, this bit enables the squarewave or interrupt output when VCC is absent. When BBSQW is logic 0, the INT/SQW pin goes high impedance when VCC falls below the power-fail trip point. This bit is disabled (logic 0) when power is first applied. Bit 5: Convert Temperature (CONV). Setting this bit to 1 forces the temperature sensor to convert the temperature into digital code and execute the TCXO algorithm to update the capacitance array to the oscillator. This can only happen when a conversion is not already in progress. The user should check the status bit BSY before forcing the controller to start a new TCXO execution. A user-initiated temperature conversion does not affect the internal 64-second update cycle. A user-initiated temperature conversion does not affect the BSY bit for approximately 2ms. The CONV bit remains at a 1 from the time it is written until the conversion is finished, at which time both CONV and BSY go to 0. The CONV bit should be used when monitoring the status of a user-initiated conversion. Bits 4 and 3: Rate Select (RS2 and RS1). These bits control the frequency of the square-wave output when the square wave has been enabled. The following table shows the square-wave frequencies that can be selected with the RS bits. These bits are both set to logic 1 (8.192kHz) when power is first applied. Bit 2: Interrupt Control (INTCN). This bit controls the INT/SQW signal. When the INTCN bit is set to logic 0, a square wave is output on the INT/SQW pin. When the INTCN bit is set to logic 1, then a match between the timekeeping registers and either of the alarm registers activates the INT/SQW output (if the alarm is also enabled). The corresponding alarm flag is always set regardless of the state of the INTCN bit. The INTCN bit is set to logic 1 when power is first applied. Bit 1: Alarm 2 Interrupt Enable (A2IE). When set to logic 1, this bit permits the alarm 2 flag (A2F) bit in the status register to assert INT/SQW (when INTCN = 1). When the A2IE bit is set to logic 0 or INTCN is set to logic 0, the A2F bit does not initiate an interrupt signal. The A2IE bit is disabled (logic 0) when power is first applied. Bit 0: Alarm 1 Interrupt Enable (A1IE). When set to logic 1, this bit permits the alarm 1 flag (A1F) bit in the status register to assert INT/SQW (when INTCN = 1). When the A1IE bit is set to logic 0 or INTCN is set to logic 0, the A1F bit does not initiate the INT/SQW signal. The A1IE bit is disabled (logic 0) when power is first applied. DS3231 Extremely Accurate I2C-Integrated RTC/TCXO/Crystal ____________________________________________________________________ 13 BIT 7 BIT 6 BIT 5 BIT 4 BIT 3 BIT 2 BIT 1 BIT 0 EOSC BBSQW CONV RS2 RS1 INTCN A2IE A1IE RS2 RS1 SQUARE-WAVE OUTPUT FREQUENCY 0 0 1Hz 0 1 1.024kHz 1 0 4.096kHz 1 1 8.192kHz SQUARE-WAVE OUTPUT FREQUENCY Control Register (0Eh) DS3231 Status Register (0Fh) Bit 7: Oscillator Stop Flag (OSF). A logic 1 in this bit indicates that the oscillator either is stopped or was stopped for some period and may be used to judge the validity of the timekeeping data. This bit is set to logic 1 any time that the oscillator stops. The following are examples of conditions that can cause the OSF bit to be set: 1) The first time power is applied. 2) The voltages present on both VCC and VBAT are insufficient to support oscillation. 3) The EOSC bit is turned off in battery-backed mode. 4) External influences on the crystal (i.e., noise, leakage, etc.). This bit remains at logic 1 until written to logic 0. Bit 3: Enable 32kHz Output (EN32kHz). This bit controls the status of the 32kHz pin. When set to logic 1, the 32kHz pin is enabled and outputs a 32.768kHz square-wave signal. When set to logic 0, the 32kHz pin goes to a high-impedance state. The initial power-up state of this bit is logic 1, and a 32.768kHz square-wave signal appears at the 32kHz pin after a power source is applied to the DS3231 (if the oscillator is running). Bit 2: Busy (BSY). This bit indicates the device is busy executing TCXO functions. It goes to logic 1 when the conversion signal to the temperature sensor is asserted and then is cleared when the device is in the 1-minute idle state. Bit 1: Alarm 2 Flag (A2F). A logic 1 in the alarm 2 flag bit indicates that the time matched the alarm 2 registers. If the A2IE bit is logic 1 and the INTCN bit is set to logic 1, the INT/SQW pin is also asserted. A2F is cleared when written to logic 0. This bit can only be written to logic 0. Attempting to write to logic 1 leaves the value unchanged. Bit 0: Alarm 1 Flag (A1F). A logic 1 in the alarm 1 flag bit indicates that the time matched the alarm 1 registers. If the A1IE bit is logic 1 and the INTCN bit is set to logic 1, the INT/SQW pin is also asserted. A1F is cleared when written to logic 0. This bit can only be written to logic 0. Attempting to write to logic 1 leaves the value unchanged. Aging Offset The crystal aging offset register provides an 8-bit code to add to the codes in the capacitance array registers. The code is encoded in two’s complement. One LSB represents one small capacitor to be switched in or out of the capacitance array at the crystal pins. The offset register is added to the capacitance array register under the following conditions: during a normal temperature conversion, if the temperature changes from the previous conversion, or during a manual user conversion (setting the CONV bit). To see the effects of the aging register on the 32kHz output frequency immediately, a manual conversion should be started after each aging register change. Positive aging values add capacitance to the array, slowing the oscillator frequency. Negative values remove capacitance from the array, increasing the oscillator frequency. The change in ppm per LSB is different at different temperatures. The frequency vs. temperature curve is shifted by the values used in this register. At +25°C, one LSB typically provides about 0.1ppm change in frequency. Extremely Accurate I2C-Integrated RTC/TCXO/Crystal 14 ____________________________________________________________________ BIT 7 BIT 6 BIT 5 BIT 4 BIT 3 BIT 2 BIT 1 BIT 0 Sign Data Data Data Data Data Data Data Aging Offset (10h) BIT 7 BIT 6 BIT 5 BIT 4 BIT 3 BIT 2 BIT 1 BIT 0 OSF 0 0 0 EN32kHz BSY A2F A1F Status Register (0Fh) Temperature Registers (11h–12h) Temperature is represented as a 10-bit code with a resolution of +0.25°C and is accessible at location 11h and 12h. The temperature is encoded in two’s complement format. The upper 8 bits are at location 11h and the lower 2 bits are in the upper nibble at location 12h. Upon power reset, the registers are set to a default temperature of 0°C and the controller starts a temperature conversion. New temperature readings are stored in this register. I2C Serial Data Bus The DS3231 supports a bidirectional I2C bus and data transmission protocol. A device that sends data onto the bus is defined as a transmitter and a device receiving data is defined as a receiver. The device that controls the message is called a master. The devices that are controlled by the master are slaves. The bus must be controlled by a master device that generates the serial clock (SCL), controls the bus access, and generates the START and STOP conditions. The DS3231 operates as a slave on the I2C bus. Connections to the bus are made through the SCL input and open-drain SDA I/O lines. Within the bus specifications, a standard mode (100kHz maximum clock rate) and a fast mode (400kHz maximum clock rate) are defined. The DS3231 works in both modes. The following bus protocol has been defined (Figure 2): • Data transfer may be initiated only when the bus is not busy. • During data transfer, the data line must remain stable whenever the clock line is high. Changes in the data line while the clock line is high are interpreted as control signals. Accordingly, the following bus conditions have been defined: Bus not busy: Both data and clock lines remain high. START data transfer: A change in the state of the data line from high to low, while the clock line is high, defines a START condition. STOP data transfer: A change in the state of the data line from low to high, while the clock line is high, defines a STOP condition. Data valid: The state of the data line represents valid data when, after a START condition, the data line is stable for the duration of the high period of the clock signal. The data on the line must be changed during the low period of the clock signal. There is one clock pulse per bit of data. Each data transfer is initiated with a START condition and terminated with a STOP condition. The number of data bytes transferred between the START and the STOP conditions is not limited, and is determined by the master device. The information is transferred byte-wise and each receiver acknowledges with a ninth bit. Acknowledge: Each receiving device, when addressed, is obliged to generate an acknowledge after the reception of each byte. The master device must generate an extra clock pulse, which is associated with this acknowledge bit. A device that acknowledges must pull down the SDA line during the acknowledge clock pulse in such a way that the SDA line is stable low during the high period of the acknowledge-related clock pulse. Of course, setup and hold times must be taken into account. A master must signal an end of data to the slave by not generating an acknowledge bit on the last byte that has been clocked out of the slave. In this case, the slave must leave the data line high to enable the master to generate the STOP condition. DS3231 Extremely Accurate I2C-Integrated RTC/TCXO/Crystal ____________________________________________________________________ 15 BIT 7 BIT 6 BIT 5 BIT 4 BIT 3 BIT 2 BIT 1 BIT 0 Sign Data Data Data Data Data Data Data Temperature Register (Upper Byte) (11h) BIT 7 BIT 6 BIT 5 BIT 4 BIT 3 BIT 2 BIT 1 BIT 0 Data Data 0 0 0 0 0 0 Temperature Register (Lower Byte) (12h) DS3231 Figures 3 and 4 detail how data transfer is accomplished on the I2C bus. Depending upon the state of the R/W bit, two types of data transfer are possible: Data transfer from a master transmitter to a slave receiver. The first byte transmitted by the master is the slave address. Next follows a number of data bytes. The slave returns an acknowledge bit after each received byte. Data is transferred with the most significant bit (MSB) first. Data transfer from a slave transmitter to a master receiver. The first byte (the slave address) is transmitted by the master. The slave then returns an acknowledge bit. Next follows a number of data bytes transmitted by the slave to the master. The master returns an acknowledge bit after all received bytes other than the last byte. At the end of the last received byte, a not acknowledge is returned. The master device generates all the serial clock pulses and the START and STOP conditions. A transfer is ended with a STOP condition or with a repeated START condition. Since a repeated START condition is also the beginning of the next serial transfer, the bus will not be released. Data is transferred with the most significant bit (MSB) first. The DS3231 can operate in the following two modes: Slave receiver mode (DS3231 write mode): Serial data and clock are received through SDA and SCL. After each byte is received, an acknowledge bit is transmitted. START and STOP conditions are recognized as the beginning and end of a serial transfer. Address recognition is performed by hardware after reception of the slave address and direction bit. The slave address byte is the first byte received after the master generates the START condition. The slave address byte contains the 7-bit DS3231 address, which is 1101000, followed by the direction bit (R/W), which is 0 for a write. After receiving and decoding the slave address byte, the DS3231 outputs an Extremely Accurate I2C-Integrated RTC/TCXO/Crystal 16 ____________________________________________________________________ STOP CONDITION OR REPEATED START CONDITION REPEATED IF MORE BYTES ARE TRANSFERED ACK START CONDITION ACK ACKNOWLEDGEMENT SIGNAL FROM RECEIVER ACKNOWLEDGEMENT SIGNAL FROM RECEIVER SLAVE ADDRESS MSB SCL SDA R/W DIRECTION BIT 1 2 6 7 8 9 1 2 3–7 8 9 Figure 2. I2C Data Transfer Overview S 1101000 0 A XXXXXXXX A XXXXXXXX A XXXXXXXX A XXXXXXXX A P S = START A = ACKNOWLEDGE P = STOP R/W = READ/WRITE OR DIRECTION BIT ADDRESS = D0h DATA TRANSFERRED (X + 1 BYTES + ACKNOWLEDGE) Figure 3. Slave Receiver Mode (Write Mode) S 1101000 1 A XXXXXXXX A XXXXXXXX A XXXXXXXX A XXXXXXXX A P S = START A = ACKNOWLEDGE P = STOP A = NOT ACKNOWLEDGE R/W = READ/WRITE OR DIRECTION BIT ADDRESS = D1h DATA TRANSFERRED (X + 1 BYTES + ACKNOWLEDGE) NOTE: LAST DATA BYTE IS FOLLOWED BY A NOT ACKNOWLEDGE (A) SIGNAL Figure 4. Slave Transmitter Mode (Read Mode) acknowledge on SDA. After the DS3231 acknowledges the slave address + write bit, the master transmits a word address to the DS3231. This sets the register pointer on the DS3231, with the DS3231 acknowledging the transfer. The master may then transmit zero or more bytes of data, with the DS3231 acknowledging each byte received. The register pointer increments after each data byte is transferred. The master generates a STOP condition to terminate the data write. Slave transmitter mode (DS3231 read mode): The first byte is received and handled as in the slave receiver mode. However, in this mode, the direction bit indicates that the transfer direction is reversed. Serial data is transmitted on SDA by the DS3231 while the serial clock is input on SCL. START and STOP conditions are recognized as the beginning and end of a serial transfer. Address recognition is performed by hardware after reception of the slave address and direction bit. The slave address byte is the first byte received after the master generates a START condition. The slave address byte contains the 7-bit DS3231 address, which is 1101000, followed by the direction bit (R/W), which is 1 for a read. After receiving and decoding the slave address byte, the DS3231 outputs an acknowledge on SDA. The DS3231 then begins to transmit data starting with the register address pointed to by the register pointer. If the register pointer is not written to before the initiation of a read mode, the first address that is read is the last one stored in the register pointer. The DS3231 must receive a not acknowledge to end a read. Handling, PC Board Layout, and Assembly The DS3231 package contains a quartz tuning-fork crystal. Pick-and-place equipment can be used, but precautions should be taken to ensure that excessive shocks are avoided. Ultrasonic cleaning should be avoided to prevent damage to the crystal. Avoid running signal traces under the package, unless a ground plane is placed between the package and the signal line. All N.C. (no connect) pins must be connected to ground. Moisture-sensitive packages are shipped from the factory dry packed. Handling instructions listed on the package label must be followed to prevent damage during reflow. Refer to the IPC/JEDEC J-STD-020 standard for moisture-sensitive device (MSD) classifications and reflow profiles. Exposure to reflow is limited to 2 times maximum. DS3231 Extremely Accurate I2C-Integrated RTC/TCXO/Crystal ____________________________________________________________________ 17 DS3231 Extremely Accurate I2C-Integrated RTC/TCXO/Crystal 18 ____________________________________________________________________ Chip Information TRANSISTOR COUNT: 33,000 SUBSTRATE CONNECTED TO GROUND PROCESS: CMOS Thermal Information Theta-JA: +73°C/W Theta-JC: +23°C/W 16 15 14 13 12 11 10 9 1 2 3 4 5 6 7 8 32kHz SCL SDA VBAT GND N.C. N.C. N.C. N.C. TOP VIEW SO VCC INT/SQW N.C. RST N.C. N.C. N.C. DS3231S Pin Configuration PACKAGE TYPE PACKAGE CODE DOCUMENT NO. 16 SO — 56-G4009-001 Package Information For the latest package outline information, go to www.maxim-ic.com/DallasPackInfo. DS3231 Extremely Accurate I2C-Integrated RTC/TCXO/Crystal Maxim cannot assume responsibility for use of any circuitry other than circuitry entirely embodied in a Maxim product. No circuit patent licenses are implied. Maxim reserves the right to change the circuitry and specifications without notice at any time. Maxim Integrated Products, 120 San Gabriel Drive, Sunnyvale, CA 94086 408-737-7600 ____________________ 19 © 2008 Maxim Integrated Products is a registered trademark of Maxim Integrated Products, Inc. is a registered trademark of Dallas Semiconductor Corporation. Revision History REVISION NUMBER REVISION DATE DESCRIPTION PAGES CHANGED 0 1/05 Initial release. — Changed Digital Temp Sensor Output from ±2°C to ±3°C. 1, 3 Updated Typical Operating Circuit. 1 Changed TA = -40°C to +85°C to TA = TMIN to TMAX. 2, 3, 4 1 2/05 Updated Block Diagram. 8 Added “UL Recognized” to Features; added lead-free packages and removed S from top mark info in Ordering Information table; added ground connections to the N.C. pin in the Typical Operating Circuit. 1 Added “noncondensing” to operating temperature range; changed VPF MIN from 2.35V to 2.45V. 2 Added aging offset specification. 3 Relabeled TOC4. 7 Added arrow showing input on X1 in the Block Diagram. 8 Updated pin descriptions for VCC and VBAT. 9 Added the I2C Interface section. 10 Figure 1: Added sign bit to aging and temperature registers; added MSB and LSB. 11 Corrected title for rate select bits frequency table. 13 Added note that frequency stability over temperature spec is with aging offset register = 00h; changed bit 7 from Data to Sign (Crystal Aging Offset Register). 14 Changed bit 7 from Data to Sign (Temperature Register); correct pin definitions in I2C Serial Data Bus section. 15 2 6/05 Modified the Handing, PC Board Layout, and Assembly section to refer to J-STD-020 for reflow profiles for lead-free and leaded packages. 17 3 11/05 Changed lead-free packages to RoHS-compliant packages. 1 Changed RST and UL bullets in Features. 1 Changed EC condition “VCC > VBAT” to “VCC = Active Supply (see Table 1).” 2, 3 Modified Note 12 to correct tREC operation. 6 Added various conditions text to TOCs 1, 2, and 3. 7 Added text to pin descriptions for 32kHz, VCC, and RST. 9 Table 1: Changed column heading “Powered By” to “Active Supply”; changed “applied” to “exceeds VPF” in the Power Control section. 10 Indicated BBSQW applies to both SQW and interrupts; simplified temp convert description (bit 5); added “output” to INT\SQW (bit 2). 13 4 10/06 Changed the Crystal Aging section to the Aging Offset section; changed “this bit indicates” to “this bit controls” for the enable 32kHz output bit. 14 Added Warning note to EC table notes; updated Note 12. 6 Updated the Typical Operating Characteristics graphs. 7 In the Power Control section, added information about the POR state of the time and date registers; in the Real-Time Clock section, added to the description of the RST function. 10 5 4/08 In Figure 1, corrected the months date range for 04h from 00–31 to 01–31. 11 © 2007 Microchip Technology Inc. Preliminary DS39631B PIC18F2420/2520/4420/4520 Data Sheet Enhanced Flash Microcontrollers with 10-Bit A/D and nanoWatt Technology DS39631B-page ii Preliminary © 2007 Microchip Technology Inc. Information contained in this publication regarding device applications and the like is provided only for your convenience and may be superseded by updates. It is your responsibility to ensure that your application meets with your specifications. MICROCHIP MAKES NO REPRESENTATIONS OR WARRANTIES OF ANY KIND WHETHER EXPRESS OR IMPLIED, WRITTEN OR ORAL, STATUTORY OR OTHERWISE, RELATED TO THE INFORMATION, INCLUDING BUT NOT LIMITED TO ITS CONDITION, QUALITY, PERFORMANCE, MERCHANTABILITY OR FITNESS FOR PURPOSE. Microchip disclaims all liability arising from this information and its use. Use of Microchip devices in life support and/or safety applications is entirely at the buyer’s risk, and the buyer agrees to defend, indemnify and hold harmless Microchip from any and all damages, claims, suits, or expenses resulting from such use. No licenses are conveyed, implicitly or otherwise, under any Microchip intellectual property rights. Trademarks The Microchip name and logo, the Microchip logo, Accuron, dsPIC, KEELOQ, microID, MPLAB, PIC, PICmicro, PICSTART, PRO MATE, PowerSmart, rfPIC and SmartShunt are registered trademarks of Microchip Technology Incorporated in the U.S.A. and other countries. AmpLab, FilterLab, Migratable Memory, MXDEV, MXLAB, SEEVAL, SmartSensor and The Embedded Control Solutions Company are registered trademarks of Microchip Technology Incorporated in the U.S.A. Analog-for-the-Digital Age, Application Maestro, CodeGuard, dsPICDEM, dsPICDEM.net, dsPICworks, ECAN, ECONOMONITOR, FanSense, FlexROM, fuzzyLAB, In-Circuit Serial Programming, ICSP, ICEPIC, Linear Active Thermistor, Mindi, MiWi, MPASM, MPLIB, MPLINK, PICkit, PICDEM, PICDEM.net, PICLAB, PICtail, PowerCal, PowerInfo, PowerMate, PowerTool, REAL ICE, rfLAB, rfPICDEM, Select Mode, Smart Serial, SmartTel, Total Endurance, UNI/O, WiperLock and ZENA are trademarks of Microchip Technology Incorporated in the U.S.A. and other countries. SQTP is a service mark of Microchip Technology Incorporated in the U.S.A. All other trademarks mentioned herein are property of their respective companies. © 2007, Microchip Technology Incorporated, Printed in the U.S.A., All Rights Reserved. Printed on recycled paper. Note the following details of the code protection feature on Microchip devices: • Microchip products meet the specification contained in their particular Microchip Data Sheet. • Microchip believes that its family of products is one of the most secure families of its kind on the market today, when used in the intended manner and under normal conditions. • There are dishonest and possibly illegal methods used to breach the code protection feature. All of these methods, to our knowledge, require using the Microchip products in a manner outside the operating specifications contained in Microchip’s Data Sheets. Most likely, the person doing so is engaged in theft of intellectual property. • Microchip is willing to work with the customer who is concerned about the integrity of their code. • Neither Microchip nor any other semiconductor manufacturer can guarantee the security of their code. Code protection does not mean that we are guaranteeing the product as “unbreakable.” Code protection is constantly evolving. We at Microchip are committed to continuously improving the code protection features of our products. Attempts to break Microchip’s code protection feature may be a violation of the Digital Millennium Copyright Act. If such acts allow unauthorized access to your software or other copyrighted work, you may have a right to sue for relief under that Act. Microchip received ISO/TS-16949:2002 certification for its worldwide headquarters, design and wafer fabrication facilities in Chandler and Tempe, Arizona, Gresham, Oregon and Mountain View, California. The Company’s quality system processes and procedures are for its PIC® MCUs and dsPIC DSCs, KEELOQ® code hopping devices, Serial EEPROMs, microperipherals, nonvolatile memory and analog products. In addition, Microchip’s quality system for the design and manufacture of development systems is ISO 9001:2000 certified. © 2007 Microchip Technology Inc. Preliminary DS39631B-page 1 PIC18F2420/2520/4420/4520 Power Managed Modes: • Run: CPU on, peripherals on • Idle: CPU off, peripherals on • Sleep: CPU off, peripherals off • Idle mode currents down to 5.8 μA typical • Sleep mode current down to 0.1 μA typical • Timer1 Oscillator: 1.8 μA, 32 kHz, 2V • Watchdog Timer: 2.1 μA • Two-Speed Oscillator Start-up Peripheral Highlights: • High-current sink/source 25 mA/25 mA • Three programmable external interrupts • Four input change interrupts • Up to 2 Capture/Compare/PWM (CCP) modules, one with Auto-Shutdown (28-pin devices) • Enhanced Capture/Compare/PWM (ECCP) module (40/44-pin devices only): - One, two or four PWM outputs - Selectable polarity - Programmable dead time - Auto-Shutdown and Auto-Restart • Master Synchronous Serial Port (MSSP) module supporting 3-wire SPI™ (all 4 modes) and I2C™ Master and Slave Modes • Enhanced Addressable USART module: - Supports RS-485, RS-232 and LIN 1.2 - RS-232 operation using internal oscillator block (no external crystal required) - Auto-Wake-up on Start bit - Auto-Baud Detect • 10-bit, up to 13-channel Analog-to-Digital Converter module (A/D): - Auto-acquisition capability - Conversion available during Sleep • Dual analog comparators with input multiplexing) Flexible Oscillator Structure: • Four Crystal modes, up to 40 MHz • 4X Phase Lock Loop (available for crystal and internal oscillators) • Two External RC modes, up to 4 MHz • Two External Clock modes, up to 40 MHz • Internal oscillator block: - 8 user selectable frequencies, from 31 kHz to 8 MHz - Provides a complete range of clock speeds from 31 kHz to 32 MHz when used with PLL - User tunable to compensate for frequency drift • Secondary oscillator using Timer1 @ 32 kHz • Fail-Safe Clock Monitor: - Allows for safe shutdown if peripheral clock stops Special Microcontroller Features: • C compiler optimized architecture: - Optional extended instruction set designed to optimize re-entrant code • 100,000 erase/write cycle Enhanced Flash program memory typical • 1,000,000 erase/write cycle Data EEPROM memory typical • Flash/Data EEPROM Retention: 100 years typical • Self-programmable under software control • Priority levels for interrupts • 8 x 8 Single-Cycle Hardware Multiplier • Extended Watchdog Timer (WDT): - Programmable period from 4 ms to 131s • Single-supply 5V In-Circuit Serial Programming™ (ICSP™) via two pins • In-Circuit Debug (ICD) via two pins • Wide operating voltage range: 2.0V to 5.5V • Programmable 16-level High/Low-Voltage Detection (HLVD) module: - Supports interrupt on High/Low-Voltage Detection • Programmable Brown-out Reset (BOR - With software enable option 28/40/44-Pin Enhanced Flash Microcontrollers with 10-Bit A/D and nanoWatt Technology PIC18F2420/2520/4420/4520 DS39631B-page 2 Preliminary © 2007 Microchip Technology Inc. - Device Program Memory Data Memory I/O 10-bit A/D (ch) CCP/ ECCP (PWM) MSSP EUSART Comp. Timers Flash 8/16-bit (bytes) # Single-Word Instructions SRAM (bytes) EEPROM (bytes) SPI Master I2C PIC18F2420 16K 8192 768 256 25 10 2/0 Y Y 1 2 1/3 PIC18F2520 32K 16384 1536 256 25 10 2/0 Y Y 1 2 1/3 PIC18F4420 16K 8192 768 256 36 13 1/1 Y Y 1 2 1/3 PIC18F4520 32K 16384 1536 256 36 13 1/1 Y Y 1 2 1/3 © 2007 Microchip Technology Inc. Preliminary DS39631B-page 3 PIC18F2420/2520/4420/4520 Pin Diagrams RB7/KBI3/PGD RB6/KBI2/PGC RB5/KBI1/PGM RB4/KBI0/AN11 RB3/AN9/CCP2(1) RB2/INT2/AN8 RB1/INT1/AN10 RB0/INT0/FLT0/AN12 VDD VSS RD7/PSP7/P1D RD6/PSP6/P1C RD5/PSP5/P1B RD4/PSP4 RC7/RX/DT RC6/TX/CK RC5/SDO RC4/SDI/SDA RD3/PSP3 RD2/PSP2 MCLR/VPP/RE3 RA0/AN0 RA1/AN1 RA2/AN2/VREF-/CVREF RA3/AN3/VREF+ RA4/T0CKI/C1OUT RA5/AN4/SS/HLVDIN/C2OUT RE0/RD/AN5 RE1/WR/AN6 RE2/CS/AN7 VDD VSS OSC1/CLKI/RA7 OSC2/CLKO/RA6 RC0/T1OSO/T13CKI RC1/T1OSI/CCP2(1) RC2/CCP1/P1A RC3/SCK/SCL RD0/PSP0 RD1/PSP1 1 2 3 4 5 6 7 8 9 10 11 12 13 14 15 16 17 18 19 20 40 39 38 37 36 35 34 33 32 31 30 29 28 27 26 25 24 23 22 21 PIC18F4520 PIC18F2520 10 11 2 3 4 5 6 1 8 7 9 12 13 14 15 16 17 18 19 20 23 24 25 26 27 28 22 21 MCLR/VPP/RE3 RA0/AN0 RA1/AN1 RA2/AN2/VREF-/CVREF RA3/AN3/VREF+ RA4/T0CKI/C1OUT RA5/AN4/SS/HLVDIN/C2OUT VSS OSC1/CLKI/RA7 OSC2/CLKO/RA6 RC0/T1OSO/T13CKI RC1/T1OSI/CCP2(1) RC2/CCP1 RC3/SCK/SCL RB7/KBI3/PGD RB6//KBI2/PGC RB5/KBI1/PGM RB4/KBI0/AN11 RB3/AN9/CCP2(1) RB2/INT2/AN8 RB1/INT1/AN10 RB0/INT0/FLT0/AN12 VDD VSS RC7/RX/DT RC6/TX/CK RC5/SDO RC4/SDI/SDA 40-pin PDIP 28-pin PDIP, SOIC PIC18F4420 PIC18F2420 Note 1: RB3 is the alternate pin for CCP2 multiplexing. 1011 2 3 6 1 18 19 20 21 22 12 13 14 15 8 7 16 17 2827 2625 2423 9 PIC18F2420 RC0/T1OSO/T13CKI 5 4 RB7/KBI3/PGD RB6/KBI2/PGC RB5/KBI1/PGM RB4KBI0/AN11 RB3/AN9/CCP2(1) RB2/INT2/AN8 RB1/INT1/AN10 RB0/INT0/FLT0/AN12 VDD VSS RC7/RX/DT RC6/TX/CK RC5/SDO RC4/SDI/SDA MCLR/VPP/RE3 RA0/AN0 RA1/AN1 RA2/AN2/VREF-/CVREF RA3/AN3/VREF+ RA4/T0CKI/C1OUT RA5/AN4/SS/HLVDIN/C2OUT VSS OSC1/CLKI/RA7 OSC2/CLKO/RA6 RC1/T1OSI/CCP2(1) RC2/CCP1 RC3/SCK/SCL PIC18F2520 28-pin QFN PIC18F2420/2520/4420/4520 DS39631B-page 4 Preliminary © 2007 Microchip Technology Inc. Pin Diagrams (Cont.’d) Note 1: RB3 is the alternate pin for CCP2 multiplexing. 10 11 2 345 6 1 18 19 20 21 22 12 13 14 15 38 8 7 44 43 42 41 40 39 16 17 29 30 31 32 33 23 24 25 26 27 28 36 34 35 9 PIC18F4420 37 RA3/AN3/VREF+ RA2/AN2/VREF-/CVREF RA1/AN1 RA0/AN0 MCLR/VPP/RE3 RB3/AN9/CCP2(1) RB7/KBI3/PGD RB6/KBI2/PGC RB5/KBI1/PGM RB4/KBI0/AN11 NC RC6/TX/CK RC5/SDO RC4/SDI/SDA RD3/PSP3 RD2/PSP2 RD1/PSP1 RD0/PSP0 RC3/SCK/SCL RC2/CCP1/P1A RC1/T1OSI/CCP2(1) RC0/T1OSO/T13CKI OSC2/CLKO/RA6 OSC1/CLKI/RA7 VSS VSS VDD VDD RE2/CS/AN7 RE1/WR/AN6 RE0/RD/AN5 RA5/AN4/SS/HLVDIN/C2OUT RA4/T0CKI/C1OUT RC7/RX/DT RD4/PSP4 RD5/PSP5/P1B RD6/PSP6/P1C RD7/PSP7/P1D VSS VDD VDD RB0/INT0/FLT0/AN12 RB1/INT1/AN10 RB2/INT2/AN8 44-pin QFN PIC18F4520 10 11 2 345 6 1 18 19 20 21 22 12 13 14 15 38 8 7 44 43 42 41 40 39 16 17 29 30 31 32 33 23 24 25 26 27 28 36 34 35 9 PIC18F4420 37 RA3/AN3/VREF+ RA2/AN2/VREF-/CVREF RA1/AN1 RA0/AN0 MCLR/VPP/RE3 NC RB7/KBI3/PGD RB6/KBI2/PGC RB5/KBI1/PGM RB4/KBI0/AN11 NC RC6/TX/CK RC5/SDO RC4/SDI/SDA RD3/PSP3 RD2/PSP2 RD1/PSP1 RD0/PSP0 RC3/SCK/SCL RC2/CCP1/P1A RC1/T1OSI/CCP2(1) NC NC RC0/T1OSO/T13CKI OSC2/CLKO/RA6 OSC1/CLKI/RA7 VSS VDD RE2/CS/AN7 RE1/WR/AN6 RE0/RD/AN5 RA5/AN4/SS/HLVDIN/C2OUT RA4/T0CKI/C1OUT RC7/RX/DT RD4/PSP4 RD5/PSP5/P1B RD6/PSP6/P1C RD7/PSP7/P1D VSS VDD RB0/INT0/FLT0/AN12 RB1/INT1/AN10 RB2/INT2/AN8 RB3/AN9/CCP2(1) 44-pin TQFP PIC18F4520 © 2007 Microchip Technology Inc. Preliminary DS39631B-page 5 PIC18F2420/2520/4420/4520 Table of Contents 1.0 Device Overview .......................................................................................................................................................................... 7 2.0 Oscillator Configurations ............................................................................................................................................................ 23 3.0 Power Managed Modes ............................................................................................................................................................. 33 4.0 Reset .......................................................................................................................................................................................... 41 5.0 Memory Organization................................................................................................................................................................. 53 6.0 Flash Program Memory.............................................................................................................................................................. 73 7.0 Data EEPROM Memory ............................................................................................................................................................. 83 8.0 8 x 8 Hardware Multiplier............................................................................................................................................................ 89 9.0 Interrupts .................................................................................................................................................................................... 91 10.0 I/O Ports ................................................................................................................................................................................... 105 11.0 Timer0 Module ......................................................................................................................................................................... 123 12.0 Timer1 Module ......................................................................................................................................................................... 127 13.0 Timer2 Module ......................................................................................................................................................................... 133 14.0 Timer3 Module ......................................................................................................................................................................... 135 15.0 Capture/Compare/Pwm (CCP) Modules .................................................................................................................................. 139 16.0 Enhanced Capture/Compare/PWM (ECCP) Module................................................................................................................ 147 17.0 Master Synchronous Serial Port (MSSP) Module .................................................................................................................... 161 18.0 Enhanced Universal Synchronous Receiver Transmitter (EUSART)....................................................................................... 201 19.0 10-Bit Analog-to-Digital Converter (A/D) Module ..................................................................................................................... 223 20.0 Comparator Module.................................................................................................................................................................. 233 21.0 Comparator Voltage Reference Module................................................................................................................................... 239 22.0 High/Low-Voltage Detect (HLVD)............................................................................................................................................. 243 23.0 Special Features of the CPU.................................................................................................................................................... 249 24.0 Instruction Set Summary .......................................................................................................................................................... 267 25.0 Development Support............................................................................................................................................................... 317 26.0 Electrical Characteristics .......................................................................................................................................................... 323 27.0 DC and AC Characteristics Graphs and Tables....................................................................................................................... 361 28.0 Packaging Information.............................................................................................................................................................. 363 Appendix A: Revision History............................................................................................................................................................. 371 Appendix B: Device Differences ........................................................................................................................................................ 371 Appendix C: Conversion Considerations ........................................................................................................................................... 372 Appendix D: Migration from Baseline to Enhanced Devices.............................................................................................................. 372 Appendix E: Migration from Mid-Range to Enhanced Devices .......................................................................................................... 373 Appendix F: Migration from High-End to Enhanced Devices............................................................................................................. 373 Index .................................................................................................................................................................................................. 375 On-Line Support................................................................................................................................................................................. 385 Systems Information and Upgrade Hot Line ...................................................................................................................................... 385 Reader Response .............................................................................................................................................................................. 386 PIC18F2420/2520/4420/4520 Product Identification System ............................................................................................................ 387 PIC18F2420/2520/4420/4520 DS39631B-page 6 Preliminary © 2007 Microchip Technology Inc. TO OUR VALUED CUSTOMERS It is our intention to provide our valued customers with the best documentation possible to ensure successful use of your Microchip products. To this end, we will continue to improve our publications to better suit your needs. Our publications will be refined and enhanced as new volumes and updates are introduced. If you have any questions or comments regarding this publication, please contact the Marketing Communications Department via E-mail at docerrors@microchip.com or fax the Reader Response Form in the back of this data sheet to (480) 792-4150. We welcome your feedback. Most Current Data Sheet To obtain the most up-to-date version of this data sheet, please register at our Worldwide Web site at: http://www.microchip.com You can determine the version of a data sheet by examining its literature number found on the bottom outside corner of any page. The last character of the literature number is the version number, (e.g., DS30000A is version A of document DS30000). Errata An errata sheet, describing minor operational differences from the data sheet and recommended workarounds, may exist for current devices. As device/documentation issues become known to us, we will publish an errata sheet. The errata will specify the revision of silicon and revision of document to which it applies. To determine if an errata sheet exists for a particular device, please check with one of the following: • Microchip’s Worldwide Web site; http://www.microchip.com • Your local Microchip sales office (see last page) When contacting a sales office, please specify which device, revision of silicon and data sheet (include literature number) you are using. Customer Notification System Register on our web site at www.microchip.com to receive the most current information on all of our products. © 2007 Microchip Technology Inc. Preliminary DS39631B-page 7 PIC18F2420/2520/4420/4520 1.0 DEVICE OVERVIEW This document contains device specific information for the following devices: This family offers the advantages of all PIC18 microcontrollers – namely, high computational performance at an economical price – with the addition of highendurance, Enhanced Flash program memory. On top of these features, the PIC18F2420/2520/4420/4520 family introduces design enhancements that make these microcontrollers a logical choice for many highperformance, power sensitive applications. 1.1 New Core Features 1.1.1 nanoWatt TECHNOLOGY All of the devices in the PIC18F2420/2520/4420/4520 family incorporate a range of features that can significantly reduce power consumption during operation. Key items include: • Alternate Run Modes: By clocking the controller from the Timer1 source or the internal oscillator block, power consumption during code execution can be reduced by as much as 90%. • Multiple Idle Modes: The controller can also run with its CPU core disabled but the peripherals still active. In these states, power consumption can be reduced even further, to as little as 4% of normal operation requirements. • On-the-fly Mode Switching: The power managed modes are invoked by user code during operation, allowing the user to incorporate powersaving ideas into their application’s software design. • Low Consumption in Key Modules: The power requirements for both Timer1 and the Watchdog Timer are minimized. See Section 26.0 “Electrical Characteristics” for values. 1.1.2 MULTIPLE OSCILLATOR OPTIONS AND FEATURES All of the devices in the PIC18F2420/2520/4420/4520 family offer ten different oscillator options, allowing users a wide range of choices in developing application hardware. These include: • Four Crystal modes, using crystals or ceramic resonators • Two External Clock modes, offering the option of using two pins (oscillator input and a divide-by-4 clock output) or one pin (oscillator input, with the second pin reassigned as general I/O) • Two External RC Oscillator modes with the same pin options as the External Clock modes • An internal oscillator block which provides an 8 MHz clock and an INTRC source (approximately 31 kHz), as well as a range of 6 user selectable clock frequencies, between 125 kHz to 4 MHz, for a total of 8 clock frequencies. This option frees the two oscillator pins for use as additional general purpose I/O. • A Phase Lock Loop (PLL) frequency multiplier, available to both the high-speed crystal and internal oscillator modes, which allows clock speeds of up to 40 MHz. Used with the internal oscillator, the PLL gives users a complete selection of clock speeds, from 31 kHz to 32 MHz – all without using an external crystal or clock circuit. Besides its availability as a clock source, the internal oscillator block provides a stable reference source that gives the family additional features for robust operation: • Fail-Safe Clock Monitor: This option constantly monitors the main clock source against a reference signal provided by the internal oscillator. If a clock failure occurs, the controller is switched to the internal oscillator block, allowing for continued low-speed operation or a safe application shutdown. • Two-Speed Start-up: This option allows the internal oscillator to serve as the clock source from Power-on Reset, or wake-up from Sleep mode, until the primary clock source is available. • PIC18F2420 • PIC18LF2420 • PIC18F2520 • PIC18LF2520 • PIC18F4420 • PIC18LF4420 • PIC18F4520 • PIC18LF4520 PIC18F2420/2520/4420/4520 DS39631B-page 8 Preliminary © 2007 Microchip Technology Inc. 1.2 Other Special Features • Memory Endurance: The Enhanced Flash cells for both program memory and data EEPROM are rated to last for many thousands of erase/write cycles – up to 100,000 for program memory and 1,000,000 for EEPROM. Data retention without refresh is conservatively estimated to be greater than 40 years. • Self-programmability: These devices can write to their own program memory spaces under internal software control. By using a bootloader routine located in the protected Boot Block at the top of program memory, it becomes possible to create an application that can update itself in the field. • Extended Instruction Set: The PIC18F2420/ 2520/4420/4520 family introduces an optional extension to the PIC18 instruction set, which adds 8 new instructions and an Indexed Addressing mode. This extension, enabled as a device configuration option, has been specifically designed to optimize re-entrant application code originally developed in high-level languages, such as C. • Enhanced CCP module: In PWM mode, this module provides 1, 2 or 4 modulated outputs for controlling half-bridge and full-bridge drivers. Other features include Auto-Shutdown, for disabling PWM outputs on interrupt or other select conditions and Auto-Restart, to reactivate outputs once the condition has cleared. • Enhanced Addressable USART: This serial communication module is capable of standard RS-232 operation and provides support for the LIN bus protocol. Other enhancements include automatic baud rate detection and a 16-bit Baud Rate Generator for improved resolution. When the microcontroller is using the internal oscillator block, the USART provides stable operation for applications that talk to the outside world without using an external crystal (or its accompanying power requirement). • 10-bit A/D Converter: This module incorporates programmable acquisition time, allowing for a channel to be selected and a conversion to be initiated without waiting for a sampling period and thus, reduce code overhead. • Extended Watchdog Timer (WDT): This enhanced version incorporates a 16-bit prescaler, allowing an extended time-out range that is stable across operating voltage and temperature. See Section 26.0 “Electrical Characteristics” for time-out periods. 1.3 Details on Individual Family Members Devices in the PIC18F2420/2520/4420/4520 family are available in 28-pin and 40/44-pin packages. Block diagrams for the two groups are shown in Figure 1-1 and Figure 1-2. The devices are differentiated from each other in five ways: 1. Flash program memory (16 Kbytes for PIC18F2420/4420 devices and 32 Kbytes for PIC18F2520/4520). 2. A/D channels (10 for 28-pin devices, 13 for 40/44-pin devices). 3. I/O ports (3 bidirectional ports on 28-pin devices, 5 bidirectional ports on 40/44-pin devices). 4. CCP and Enhanced CCP implementation (28-pin devices have 2 standard CCP modules, 40/44-pin devices have one standard CCP module and one ECCP module). 5. Parallel Slave Port (present only on 40/44-pin devices). All other features for devices in this family are identical. These are summarized in Table 1-1. The pinouts for all devices are listed in Table 1-2 and Table 1-3. Like all Microchip PIC18 devices, members of the PIC18F2420/2520/4420/4520 family are available as both standard and low-voltage devices. Standard devices with Enhanced Flash memory, designated with an “F” in the part number (such as PIC18F2420), accommodate an operating VDD range of 4.2V to 5.5V. Low-voltage parts, designated by “LF” (such as PIC18LF2420), function over an extended VDD range of 2.0V to 5.5V. © 2007 Microchip Technology Inc. Preliminary DS39631B-page 9 PIC18F2420/2520/4420/4520 TABLE 1-1: DEVICE FEATURES Features PIC18F2420 PIC18F2520 PIC18F4420 PIC18F4520 Operating Frequency DC – 40 MHz DC – 40 MHz DC – 40 MHz DC – 40 MHz Program Memory (Bytes) 16384 32768 16384 32768 Program Memory (Instructions) 8192 16384 8192 16384 Data Memory (Bytes) 768 1536 768 1536 Data EEPROM Memory (Bytes) 256 256 256 256 Interrupt Sources 19 19 20 20 I/O Ports Ports A, B, C, (E) Ports A, B, C, (E) Ports A, B, C, D, E Ports A, B, C, D, E Timers 4 4 4 4 Capture/Compare/PWM Modules 2 2 1 1 Enhanced Capture/Compare/PWM Modules 0 0 1 1 Serial Communications MSSP, Enhanced USART MSSP, Enhanced USART MSSP, Enhanced USART MSSP, Enhanced USART Parallel Communications (PSP) No No Yes Yes 10-bit Analog-to-Digital Module 10 Input Channels 10 Input Channels 13 Input Channels 13 Input Channels Resets (and Delays) POR, BOR, RESET Instruction, Stack Full, Stack Underflow (PWRT, OST), MCLR (optional), WDT POR, BOR, RESET Instruction, Stack Full, Stack Underflow (PWRT, OST), MCLR (optional), WDT POR, BOR, RESET Instruction, Stack Full, Stack Underflow (PWRT, OST), MCLR (optional), WDT POR, BOR, RESET Instruction, Stack Full, Stack Underflow (PWRT, OST), MCLR (optional), WDT Programmable High/Low-Voltage Detect Yes Yes Yes Yes Programmable Brown-out Reset Yes Yes Yes Yes Instruction Set 75 Instructions; 83 with Extended Instruction Set enabled 75 Instructions; 83 with Extended Instruction Set enabled 75 Instructions; 83 with Extended Instruction Set enabled 75 Instructions; 83 with Extended Instruction Set enabled Packages 28-pin PDIP 28-pin SOIC 28-pin QFN 28-pin PDIP 28-pin SOIC 28-pin QFN 40-pin PDIP 44-pin QFN 44-pin TQFP 40-pin PDIP 44-pin QFN 44-pin TQFP PIC18F2420/2520/4420/4520 DS39631B-page 10 Preliminary © 2007 Microchip Technology Inc. FIGURE 1-1: PIC18F2420/2520 (28-PIN) BLOCK DIAGRAM Instruction Decode and Control PORTA PORTB PORTC RA4/T0CKI/C1OUT RA5/AN4/SS/HLVDIN/C2OUT RB0/INT0/FLT0/AN12 RC0/T1OSO/T13CKI RC1/T1OSI/CCP2(1) RC2/CCP1 RC3/SCK/SCL RC4/SDI/SDA RC5/SDO RC6/TX/CK RC7/RX/DT RA3/AN3/VREF+ RA2/AN2/VREF-/CVREF RA1/AN1 RA0/AN0 RB1/INT1/AN10 Data Latch Data Memory ( 3.9 Kbytes ) Address Latch Data Address<12> 12 BSR FSR0 Access FSR1 FSR2 inc/dec logic Address 4 12 4 PCH PCL PCLATH 8 31 Level Stack Program Counter PRODH PRODL 8 x 8 Multiply 8 BITOP 8 8 ALU<8> Address Latch Program Memory (16/32 Kbytes) Data Latch 20 8 8 Table Pointer<21> inc/dec logic 21 8 Data Bus<8> Table Latch 8 IR 12 3 ROM Latch RB2/INT2/AN8 RB3/AN9/CCP2(1) PCLATU PCU OSC2/CLKO(3)/RA6 Note 1: CCP2 is multiplexed with RC1 when configuration bit CCP2MX is set, or RB3 when CCP2MX is not set. 2: RE3 is only available when MCLR functionality is disabled. 3: OSC1/CLKI and OSC2/CLKO are only available in select oscillator modes and when these pins are not being used as digital I/O. Refer to Section 2.0 “Oscillator Configurations” for additional information. RB4/KBI0/AN11 RB5/KBI1/PGM RB6/KBI2/PGC RB7/KBI3/PGD Comparator MSSP EUSART 10-bit ADC Timer0 Timer1 Timer2 Timer3 CCP2 HLVD CCP1 BOR Data EEPROM W Instruction Bus <16> STKPTR Bank 8 State machine control signals Decode 8 8 Power-up Timer Oscillator Start-up Timer Power-on Reset Watchdog Timer OSC1(3) OSC2(3) VDD, Brown-out Reset Internal Oscillator Fail-Safe Clock Monitor Precision Reference Band Gap VSS MCLR(2) Block INTRC Oscillator 8 MHz Oscillator Single-Supply Programming In-Circuit Debugger T1OSO OSC1/CLKI(3)/RA7 T1OSI PORTE MCLR/VPP/RE3(2) © 2007 Microchip Technology Inc. Preliminary DS39631B-page 11 PIC18F2420/2520/4420/4520 FIGURE 1-2: PIC18F4420/4520 (40/44-PIN) BLOCK DIAGRAM Instruction Decode and Control Data Latch Data Memory ( 3.9 Kbytes ) Address Latch Data Address<12> 12 BSR FSR0 Access FSR1 FSR2 inc/dec logic Address 4 12 4 PCH PCL PCLATH 8 31 Level Stack Program Counter PRODH PRODL 8 x 8 Multiply 8 BITOP 8 8 ALU<8> Address Latch Program Memory (16/32 Kbytes) Data Latch 20 8 8 Table Pointer<21> inc/dec logic 21 8 Data Bus<8> Table Latch 8 IR 12 3 ROM Latch PORTD RD0/PSP0 PCLATU PCU PORTE MCLR/VPP/RE3(2) RE2/CS/AN7 RE0/RD/AN5 RE1/WR/AN6 Note 1: CCP2 is multiplexed with RC1 when configuration bit CCP2MX is set, or RB3 when CCP2MX is not set. 2: RE3 is only available when MCLR functionality is disabled. 3: OSC1/CLKI and OSC2/CLKO are only available in select oscillator modes and when these pins are not being used as digital I/O. Refer to Section 2.0 “Oscillator Configurations” for additional information. :RD4/PSP4 Comparator MSSP EUSART 10-bit ADC Timer0 Timer1 Timer2 Timer3 CCP2 HLVD ECCP1 BOR Data EEPROM W Instruction Bus <16> STKPTR Bank 8 State machine control signals Decode 8 8 Power-up Timer Oscillator Start-up Timer Power-on Reset Watchdog Timer OSC1(3) OSC2(3) VDD, Brown-out Reset Internal Oscillator Fail-Safe Clock Monitor Precision Reference Band Gap VSS MCLR(2) Block INTRC Oscillator 8 MHz Oscillator Single-Supply Programming In-Circuit Debugger T1OSI T1OSO RD5/PSP5/P1B RD6/PSP6/P1C RD7/PSP7/P1D PORTA PORTB PORTC RA4/T0CKI/C1OUT RA5/AN4/SS/HLVDIN/C2OUT RB0/INT0/FLT0/AN12 RC0/T1OSO/T13CKI RC1/T1OSI/CCP2(1) RC2/CCP1/P1A RC3/SCK/SCL RC4/SDI/SDA RC5/SDO RC6/TX/CK RC7/RX/DT RA3/AN3/VREF+ RA2/AN2/VREF-/CVREF RA1/AN1 RA0/AN0 RB1/INT1/AN10 RB2/INT2/AN8 RB3/AN9/CCP2(1) OSC2/CLKO(3)/RA6 RB4/KBI0/AN11 RB5/KBI1/PGM RB6/KBI2/PGC RB7/KBI3/PGD OSC1/CLKI(3)/RA7 PIC18F2420/2520/4420/4520 DS39631B-page 12 Preliminary © 2007 Microchip Technology Inc. TABLE 1-2: PIC18F2420/2520 PINOUT I/O DESCRIPTIONS Pin Name Pin Number Pin Type Buffer Type PDIP, Description SOIC QFN MCLR/VPP/RE3 MCLR VPP RE3 1 26 I P I ST ST Master Clear (input) or programming voltage (input). Master Clear (Reset) input. This pin is an active-low Reset to the device. Programming voltage input. Digital input. OSC1/CLKI/RA7 OSC1 CLKI RA7 9 6 I I I/O ST CMOS TTL Oscillator crystal or external clock input. Oscillator crystal input or external clock source input. ST buffer when configured in RC mode; CMOS otherwise. External clock source input. Always associated with pin function OSC1. (See related OSC1/CLKI, OSC2/CLKO pins.) General purpose I/O pin. OSC2/CLKO/RA6 OSC2 CLKO RA6 10 7 O O I/O — — TTL Oscillator crystal or clock output. Oscillator crystal output. Connects to crystal or resonator in Crystal Oscillator mode. In RC mode, OSC2 pin outputs CLKO which has 1/4 the frequency of OSC1 and denotes the instruction cycle rate. General purpose I/O pin. Legend: TTL = TTL compatible input CMOS = CMOS compatible input or output ST = Schmitt Trigger input with CMOS levels I = Input O = Output P = Power Note 1: Default assignment for CCP2 when configuration bit CCP2MX is set. 2: Alternate assignment for CCP2 when configuration bit CCP2MX is cleared. © 2007 Microchip Technology Inc. Preliminary DS39631B-page 13 PIC18F2420/2520/4420/4520 PORTA is a bidirectional I/O port. RA0/AN0 RA0 AN0 2 27 I/O I TTL Analog Digital I/O. Analog input 0. RA1/AN1 RA1 AN1 3 28 I/O I TTL Analog Digital I/O. Analog input 1. RA2/AN2/VREF-/CVREF RA2 AN2 VREFCVREF 4 1 I/O I I O TTL Analog Analog Analog Digital I/O. Analog input 2. A/D reference voltage (low) input. Comparator reference voltage output. RA3/AN3/VREF+ RA3 AN3 VREF+ 5 2 I/O I I TTL Analog Analog Digital I/O. Analog input 3. A/D reference voltage (high) input. RA4/T0CKI/C1OUT RA4 T0CKI C1OUT 6 3 I/O I O ST ST — Digital I/O. Timer0 external clock input. Comparator 1 output. RA5/AN4/SS/HLVDIN/ C2OUT RA5 AN4 SS HLVDIN C2OUT 7 4 I/O I I I O TTL Analog TTL Analog — Digital I/O. Analog input 4. SPI™ slave select input. High/Low-Voltage Detect input. Comparator 2 output. RA6 See the OSC2/CLKO/RA6 pin. RA7 See the OSC1/CLKI/RA7 pin. TABLE 1-2: PIC18F2420/2520 PINOUT I/O DESCRIPTIONS (CONTINUED) Pin Name Pin Number Pin Type Buffer Type PDIP, Description SOIC QFN Legend: TTL = TTL compatible input CMOS = CMOS compatible input or output ST = Schmitt Trigger input with CMOS levels I = Input O = Output P = Power Note 1: Default assignment for CCP2 when configuration bit CCP2MX is set. 2: Alternate assignment for CCP2 when configuration bit CCP2MX is cleared. PIC18F2420/2520/4420/4520 DS39631B-page 14 Preliminary © 2007 Microchip Technology Inc. PORTB is a bidirectional I/O port. PORTB can be software programmed for internal weak pull-ups on all inputs. RB0/INT0/FLT0/AN12 RB0 INT0 FLT0 AN12 21 18 I/O I I I TTL ST ST Analog Digital I/O. External interrupt 0. PWM Fault input for CCP1. Analog input 12. RB1/INT1/AN10 RB1 INT1 AN10 22 19 I/O I I TTL ST Analog Digital I/O. External interrupt 1. Analog input 10. RB2/INT2/AN8 RB2 INT2 AN8 23 20 I/O I I TTL ST Analog Digital I/O. External interrupt 2. Analog input 8. RB3/AN9/CCP2 RB3 AN9 CCP2(1) 24 21 I/O I I/O TTL Analog ST Digital I/O. Analog input 9. Capture 2 input/Compare 2 output/PWM 2 output. RB4/KBI0/AN11 RB4 KBI0 AN11 25 22 I/O I I TTL TTL Analog Digital I/O. Interrupt-on-change pin. Analog input 11. RB5/KBI1/PGM RB5 KBI1 PGM 26 23 I/O I I/O TTL TTL ST Digital I/O. Interrupt-on-change pin. Low-Voltage ICSP™ Programming enable pin. RB6/KBI2/PGC RB6 KBI2 PGC 27 24 I/O I I/O TTL TTL ST Digital I/O. Interrupt-on-change pin. In-Circuit Debugger and ICSP programming clock pin. RB7/KBI3/PGD RB7 KBI3 PGD 28 25 I/O I I/O TTL TTL ST Digital I/O. Interrupt-on-change pin. In-Circuit Debugger and ICSP programming data pin. TABLE 1-2: PIC18F2420/2520 PINOUT I/O DESCRIPTIONS (CONTINUED) Pin Name Pin Number Pin Type Buffer Type PDIP, Description SOIC QFN Legend: TTL = TTL compatible input CMOS = CMOS compatible input or output ST = Schmitt Trigger input with CMOS levels I = Input O = Output P = Power Note 1: Default assignment for CCP2 when configuration bit CCP2MX is set. 2: Alternate assignment for CCP2 when configuration bit CCP2MX is cleared. © 2007 Microchip Technology Inc. Preliminary DS39631B-page 15 PIC18F2420/2520/4420/4520 PORTC is a bidirectional I/O port. RC0/T1OSO/T13CKI RC0 T1OSO T13CKI 11 8 I/O O I ST — ST Digital I/O. Timer1 oscillator output. Timer1/Timer3 external clock input. RC1/T1OSI/CCP2 RC1 T1OSI CCP2(2) 12 9 I/O I I/O ST Analog ST Digital I/O. Timer1 oscillator input. Capture 2 input/Compare 2 output/PWM 2 output. RC2/CCP1 RC2 CCP1 13 10 I/O I/O ST ST Digital I/O. Capture 1 input/Compare 1 output/PWM 1 output. RC3/SCK/SCL RC3 SCK SCL 14 11 I/O I/O I/O ST ST ST Digital I/O. Synchronous serial clock input/output for SPI™ mode. Synchronous serial clock input/output for I2C™ mode. RC4/SDI/SDA RC4 SDI SDA 15 12 I/O I I/O ST ST ST Digital I/O. SPI data in. I2C data I/O. RC5/SDO RC5 SDO 16 13 I/O O ST — Digital I/O. SPI data out. RC6/TX/CK RC6 TX CK 17 14 I/O O I/O ST — ST Digital I/O. EUSART asynchronous transmit. EUSART synchronous clock (see related RX/DT). RC7/RX/DT RC7 RX DT 18 15 I/O I I/O ST ST ST Digital I/O. EUSART asynchronous receive. EUSART synchronous data (see related TX/CK). RE3 — — — — See MCLR/VPP/RE3 pin. VSS 8, 19 5, 16 P — Ground reference for logic and I/O pins. VDD 20 17 P — Positive supply for logic and I/O pins. TABLE 1-2: PIC18F2420/2520 PINOUT I/O DESCRIPTIONS (CONTINUED) Pin Name Pin Number Pin Type Buffer Type PDIP, Description SOIC QFN Legend: TTL = TTL compatible input CMOS = CMOS compatible input or output ST = Schmitt Trigger input with CMOS levels I = Input O = Output P = Power Note 1: Default assignment for CCP2 when configuration bit CCP2MX is set. 2: Alternate assignment for CCP2 when configuration bit CCP2MX is cleared. PIC18F2420/2520/4420/4520 DS39631B-page 16 Preliminary © 2007 Microchip Technology Inc. TABLE 1-3: PIC18F4420/4520 PINOUT I/O DESCRIPTIONS Pin Name Pin Number Pin Type Buffer Type Description PDIP QFN TQFP MCLR/VPP/RE3 MCLR VPP RE3 1 18 18 I P I ST ST Master Clear (input) or programming voltage (input). Master Clear (Reset) input. This pin is an active-low Reset to the device. Programming voltage input. Digital input. OSC1/CLKI/RA7 OSC1 CLKI RA7 13 32 30 I I I/O ST CMOS TTL Oscillator crystal or external clock input. Oscillator crystal input or external clock source input. ST buffer when configured in RC mode; analog otherwise. External clock source input. Always associated with pin function OSC1. (See related OSC1/CLKI, OSC2/CLKO pins.) General purpose I/O pin. OSC2/CLKO/RA6 OSC2 CLKO RA6 14 33 31 O O I/O — — TTL Oscillator crystal or clock output. Oscillator crystal output. Connects to crystal or resonator in Crystal Oscillator mode. In RC mode, OSC2 pin outputs CLKO which has 1/4 the frequency of OSC1 and denotes the instruction cycle rate. General purpose I/O pin. Legend: TTL = TTL compatible input CMOS = CMOS compatible input or output ST = Schmitt Trigger input with CMOS levels I = Input O = Output P = Power Note 1: Default assignment for CCP2 when configuration bit CCP2MX is set. 2: Alternate assignment for CCP2 when configuration bit CCP2MX is cleared. © 2007 Microchip Technology Inc. Preliminary DS39631B-page 17 PIC18F2420/2520/4420/4520 PORTA is a bidirectional I/O port. RA0/AN0 RA0 AN0 2 19 19 I/O I TTL Analog Digital I/O. Analog input 0. RA1/AN1 RA1 AN1 3 20 20 I/O I TTL Analog Digital I/O. Analog input 1. RA2/AN2/VREF-/CVREF RA2 AN2 VREFCVREF 4 21 21 I/O I I O TTL Analog Analog Analog Digital I/O. Analog input 2. A/D reference voltage (low) input. Comparator reference voltage output. RA3/AN3/VREF+ RA3 AN3 VREF+ 5 22 22 I/O I I TTL Analog Analog Digital I/O. Analog input 3. A/D reference voltage (high) input. RA4/T0CKI/C1OUT RA4 T0CKI C1OUT 6 23 23 I/O I O ST ST — Digital I/O. Timer0 external clock input. Comparator 1 output. RA5/AN4/SS/HLVDIN/ C2OUT RA5 AN4 SS HLVDIN C2OUT 7 24 24 I/O I I I O TTL Analog TTL Analog — Digital I/O. Analog input 4. SPI slave select input. High/Low-Voltage Detect input. Comparator 2 output. RA6 See the OSC2/CLKO/RA6 pin. RA7 See the OSC1/CLKI/RA7 pin. TABLE 1-3: PIC18F4420/4520 PINOUT I/O DESCRIPTIONS (CONTINUED) Pin Name Pin Number Pin Type Buffer Type Description PDIP QFN TQFP Legend: TTL = TTL compatible input CMOS = CMOS compatible input or output ST = Schmitt Trigger input with CMOS levels I = Input O = Output P = Power Note 1: Default assignment for CCP2 when configuration bit CCP2MX is set. 2: Alternate assignment for CCP2 when configuration bit CCP2MX is cleared. PIC18F2420/2520/4420/4520 DS39631B-page 18 Preliminary © 2007 Microchip Technology Inc. PORTB is a bidirectional I/O port. PORTB can be software programmed for internal weak pull-ups on all inputs. RB0/INT0/FLT0/AN12 RB0 INT0 FLT0 AN12 33 9 8 I/O I I I TTL ST ST Analog Digital I/O. External interrupt 0. PWM Fault input for Enhanced CCP1. Analog input 12. RB1/INT1/AN10 RB1 INT1 AN10 34 10 9 I/O I I TTL ST Analog Digital I/O. External interrupt 1. Analog input 10. RB2/INT2/AN8 RB2 INT2 AN8 35 11 10 I/O I I TTL ST Analog Digital I/O. External interrupt 2. Analog input 8. RB3/AN9/CCP2 RB3 AN9 CCP2(1) 36 12 11 I/O I I/O TTL Analog ST Digital I/O. Analog input 9. Capture 2 input/Compare 2 output/PWM 2 output. RB4/KBI0/AN11 RB4 KBI0 AN11 37 14 14 I/O I I TTL TTL Analog Digital I/O. Interrupt-on-change pin. Analog input 11. RB5/KBI1/PGM RB5 KBI1 PGM 38 15 15 I/O I I/O TTL TTL ST Digital I/O. Interrupt-on-change pin. Low-Voltage ICSP™ Programming enable pin. RB6/KBI2/PGC RB6 KBI2 PGC 39 16 16 I/O I I/O TTL TTL ST Digital I/O. Interrupt-on-change pin. In-Circuit Debugger and ICSP programming clock pin. RB7/KBI3/PGD RB7 KBI3 PGD 40 17 17 I/O I I/O TTL TTL ST Digital I/O. Interrupt-on-change pin. In-Circuit Debugger and ICSP programming data pin. TABLE 1-3: PIC18F4420/4520 PINOUT I/O DESCRIPTIONS (CONTINUED) Pin Name Pin Number Pin Type Buffer Type Description PDIP QFN TQFP Legend: TTL = TTL compatible input CMOS = CMOS compatible input or output ST = Schmitt Trigger input with CMOS levels I = Input O = Output P = Power Note 1: Default assignment for CCP2 when configuration bit CCP2MX is set. 2: Alternate assignment for CCP2 when configuration bit CCP2MX is cleared. © 2007 Microchip Technology Inc. Preliminary DS39631B-page 19 PIC18F2420/2520/4420/4520 PORTC is a bidirectional I/O port. RC0/T1OSO/T13CKI RC0 T1OSO T13CKI 15 34 32 I/O O I ST — ST Digital I/O. Timer1 oscillator output. Timer1/Timer3 external clock input. RC1/T1OSI/CCP2 RC1 T1OSI CCP2(2) 16 35 35 I/O I I/O ST CMOS ST Digital I/O. Timer1 oscillator input. Capture 2 input/Compare 2 output/PWM 2 output. RC2/CCP1/P1A RC2 CCP1 P1A 17 36 36 I/O I/O O ST ST — Digital I/O. Capture 1 input/Compare 1 output/PWM 1 output. Enhanced CCP1 output. RC3/SCK/SCL RC3 SCK SCL 18 37 37 I/O I/O I/O ST ST ST Digital I/O. Synchronous serial clock input/output for SPI™ mode. Synchronous serial clock input/output for I2C™ mode. RC4/SDI/SDA RC4 SDI SDA 23 42 42 I/O I I/O ST ST ST Digital I/O. SPI data in. I2C data I/O. RC5/SDO RC5 SDO 24 43 43 I/O O ST — Digital I/O. SPI data out. RC6/TX/CK RC6 TX CK 25 44 44 I/O O I/O ST — ST Digital I/O. EUSART asynchronous transmit. EUSART synchronous clock (see related RX/DT). RC7/RX/DT RC7 RX DT 26 1 1 I/O I I/O ST ST ST Digital I/O. EUSART asynchronous receive. EUSART synchronous data (see related TX/CK). TABLE 1-3: PIC18F4420/4520 PINOUT I/O DESCRIPTIONS (CONTINUED) Pin Name Pin Number Pin Type Buffer Type Description PDIP QFN TQFP Legend: TTL = TTL compatible input CMOS = CMOS compatible input or output ST = Schmitt Trigger input with CMOS levels I = Input O = Output P = Power Note 1: Default assignment for CCP2 when configuration bit CCP2MX is set. 2: Alternate assignment for CCP2 when configuration bit CCP2MX is cleared. PIC18F2420/2520/4420/4520 DS39631B-page 20 Preliminary © 2007 Microchip Technology Inc. PORTD is a bidirectional I/O port or a Parallel Slave Port (PSP) for interfacing to a microprocessor port. These pins have TTL input buffers when PSP module is enabled. RD0/PSP0 RD0 PSP0 19 38 38 I/O I/O ST TTL Digital I/O. Parallel Slave Port data. RD1/PSP1 RD1 PSP1 20 39 39 I/O I/O ST TTL Digital I/O. Parallel Slave Port data. RD2/PSP2 RD2 PSP2 21 40 40 I/O I/O ST TTL Digital I/O. Parallel Slave Port data. RD3/PSP3 RD3 PSP3 22 41 41 I/O I/O ST TTL Digital I/O. Parallel Slave Port data. RD4/PSP4 RD4 PSP4 27 2 2 I/O I/O ST TTL Digital I/O. Parallel Slave Port data. RD5/PSP5/P1B RD5 PSP5 P1B 28 3 3 I/O I/O O ST TTL — Digital I/O. Parallel Slave Port data. Enhanced CCP1 output. RD6/PSP6/P1C RD6 PSP6 P1C 29 4 4 I/O I/O O ST TTL — Digital I/O. Parallel Slave Port data. Enhanced CCP1 output. RD7/PSP7/P1D RD7 PSP7 P1D 30 5 5 I/O I/O O ST TTL — Digital I/O. Parallel Slave Port data. Enhanced CCP1 output. TABLE 1-3: PIC18F4420/4520 PINOUT I/O DESCRIPTIONS (CONTINUED) Pin Name Pin Number Pin Type Buffer Type Description PDIP QFN TQFP Legend: TTL = TTL compatible input CMOS = CMOS compatible input or output ST = Schmitt Trigger input with CMOS levels I = Input O = Output P = Power Note 1: Default assignment for CCP2 when configuration bit CCP2MX is set. 2: Alternate assignment for CCP2 when configuration bit CCP2MX is cleared. © 2007 Microchip Technology Inc. Preliminary DS39631B-page 21 PIC18F2420/2520/4420/4520 PORTE is a bidirectional I/O port. RE0/RD/AN5 RE0 RD AN5 8 25 25 I/O I I ST TTL Analog Digital I/O. Read control for Parallel Slave Port (see also WR and CS pins). Analog input 5. RE1/WR/AN6 RE1 WR AN6 9 26 26 I/O I I ST TTL Analog Digital I/O. Write control for Parallel Slave Port (see CS and RD pins). Analog input 6. RE2/CS/AN7 RE2 CS AN7 10 27 27 I/O I I ST TTL Analog Digital I/O. Chip Select control for Parallel Slave Port (see related RD and WR). Analog input 7. RE3 — — — — — See MCLR/VPP/RE3 pin. VSS 12, 31 6, 30, 31 6, 29 P — Ground reference for logic and I/O pins. VDD 11, 32 7, 8, 28, 29 7, 28 P — Positive supply for logic and I/O pins. NC — 13 12, 13, 33, 34 — — No connect. TABLE 1-3: PIC18F4420/4520 PINOUT I/O DESCRIPTIONS (CONTINUED) Pin Name Pin Number Pin Type Buffer Type Description PDIP QFN TQFP Legend: TTL = TTL compatible input CMOS = CMOS compatible input or output ST = Schmitt Trigger input with CMOS levels I = Input O = Output P = Power Note 1: Default assignment for CCP2 when configuration bit CCP2MX is set. 2: Alternate assignment for CCP2 when configuration bit CCP2MX is cleared. PIC18F2420/2520/4420/4520 DS39631B-page 22 Preliminary © 2007 Microchip Technology Inc. NOTES: © 2007 Microchip Technology Inc. Preliminary DS39631B-page 23 PIC18F2420/2520/4420/4520 2.0 OSCILLATOR CONFIGURATIONS 2.1 Oscillator Types PIC18F2420/2520/4420/4520 devices can be operated in ten different oscillator modes. The user can program the configuration bits, FOSC3:FOSC0, in Configuration Register 1H to select one of these ten modes: 1. LP Low-Power Crystal 2. XT Crystal/Resonator 3. HS High-Speed Crystal/Resonator 4. HSPLL High-Speed Crystal/Resonator with PLL enabled 5. RC External Resistor/Capacitor with FOSC/4 output on RA6 6. RCIO External Resistor/Capacitor with I/O on RA6 7. INTIO1 Internal Oscillator with FOSC/4 output on RA6 and I/O on RA7 8. INTIO2 Internal Oscillator with I/O on RA6 and RA7 9. EC External Clock with FOSC/4 output 10. ECIO External Clock with I/O on RA6 2.2 Crystal Oscillator/Ceramic Resonators In XT, LP, HS or HSPLL Oscillator modes, a crystal or ceramic resonator is connected to the OSC1 and OSC2 pins to establish oscillation. Figure 2-1 shows the pin connections. The oscillator design requires the use of a parallel cut crystal. FIGURE 2-1: CRYSTAL/CERAMIC RESONATOR OPERATION (XT, LP, HS OR HSPLL CONFIGURATION) TABLE 2-1: CAPACITOR SELECTION FOR CERAMIC RESONATORS Note: Use of a series cut crystal may give a frequency out of the crystal manufacturer’s specifications. Typical Capacitor Values Used: Mode Freq OSC1 OSC2 XT 3.58 MHz 4.19 MHz 4 MHz 4 MHz 15 pF 15 pF 30 pF 50 pF 15 pF 15 pF 30 pF 50 pF Capacitor values are for design guidance only. Different capacitor values may be required to produce acceptable oscillator operation. The user should test the performance of the oscillator over the expected VDD and temperature range for the application. See the notes following Table 2-2 for additional information. Note: When using resonators with frequencies above 3.5 MHz, the use of HS mode, rather than XT mode, is recommended. HS mode may be used at any VDD for which the controller is rated. If HS is selected, it is possible that the gain of the oscillator will overdrive the resonator. Therefore, a series resistor should be placed between the OSC2 pin and the resonator. As a good starting point, the recommended value of RS is 330Ω. Note 1: See Table 2-1 and Table 2-2 for initial values of C1 and C2. 2: A series resistor (RS) may be required for AT strip cut crystals. 3: RF varies with the oscillator mode chosen. C1(1) C2(1) XTAL OSC2 OSC1 RF(3) Sleep To Logic PIC18FXXXX RS(2) Internal PIC18F2420/2520/4420/4520 DS39631B-page 24 Preliminary © 2007 Microchip Technology Inc. TABLE 2-2: CAPACITOR SELECTION FOR CRYSTAL OSCILLATOR An external clock source may also be connected to the OSC1 pin in the HS mode, as shown in Figure 2-2. FIGURE 2-2: EXTERNAL CLOCK INPUT OPERATION (HS OSC CONFIGURATION) 2.3 External Clock Input The EC and ECIO Oscillator modes require an external clock source to be connected to the OSC1 pin. There is no oscillator start-up time required after a Power-on Reset or after an exit from Sleep mode. In the EC Oscillator mode, the oscillator frequency divided by 4 is available on the OSC2 pin. This signal may be used for test purposes or to synchronize other logic. Figure 2-3 shows the pin connections for the EC Oscillator mode. FIGURE 2-3: EXTERNAL CLOCK INPUT OPERATION (EC CONFIGURATION) The ECIO Oscillator mode functions like the EC mode, except that the OSC2 pin becomes an additional general purpose I/O pin. The I/O pin becomes bit 6 of PORTA (RA6). Figure 2-4 shows the pin connections for the ECIO Oscillator mode. FIGURE 2-4: EXTERNAL CLOCK INPUT OPERATION (ECIO CONFIGURATION) Osc Type Crystal Freq Typical Capacitor Values Tested: C1 C2 LP 32 kHz 30 pF 30 pF XT 1 MHz 4 MHz 15 pF 15 pF 15 pF 15 pF HS 4 MHz 10 MHz 20 MHz 25 MHz 25 MHz 15 pF 15 pF 15 pF 0 pF 15 pF 15 pF 15 pF 15 pF 5 pF 15 pF Capacitor values are for design guidance only. These capacitors were tested with the crystals listed below for basic start-up and operation. These values are not optimized. Different capacitor values may be required to produce acceptable oscillator operation. The user should test the performance of the oscillator over the expected VDD and temperature range for the application. See the notes following this table for additional information. Crystals Used: 32 kHz 4 MHz 25 MHz 10 MHz 1 MHz 20 MHz Note 1: Higher capacitance increases the stability of the oscillator but also increases the start-up time. 2: When operating below 3V VDD, or when using certain ceramic resonators at any voltage, it may be necessary to use the HS mode or switch to a crystal oscillator. 3: Since each resonator/crystal has its own characteristics, the user should consult the resonator/crystal manufacturer for appropriate values of external components. 4: Rs may be required to avoid overdriving crystals with low drive level specification. 5: Always verify oscillator performance over the VDD and temperature range that is expected for the application. OSC1 Open OSC2 Clock from Ext. System PIC18FXXXX (HS Mode) OSC1/CLKI FOSC/4 OSC2/CLKO Clock from Ext. System PIC18FXXXX OSC1/CLKI RA6 I/O (OSC2) Clock from Ext. System PIC18FXXXX © 2007 Microchip Technology Inc. Preliminary DS39631B-page 25 PIC18F2420/2520/4420/4520 2.4 RC Oscillator For timing insensitive applications, the “RC” and “RCIO” device options offer additional cost savings. The actual oscillator frequency is a function of several factors: • supply voltage • values of the external resistor (REXT) and capacitor (CEXT) • operating temperature Given the same device, operating voltage and temperature and component values, there will also be unit-to-unit frequency variations. These are due to factors such as: • normal manufacturing variation • difference in lead frame capacitance between package types (especially for low CEXT values) • variations within the tolerance of limits of REXT and CEXT In the RC Oscillator mode, the oscillator frequency divided by 4 is available on the OSC2 pin. This signal may be used for test purposes or to synchronize other logic. Figure 2-5 shows how the R/C combination is connected. FIGURE 2-5: RC OSCILLATOR MODE The RCIO Oscillator mode (Figure 2-6) functions like the RC mode, except that the OSC2 pin becomes an additional general purpose I/O pin. The I/O pin becomes bit 6 of PORTA (RA6). FIGURE 2-6: RCIO OSCILLATOR MODE 2.5 PLL Frequency Multiplier A Phase Locked Loop (PLL) circuit is provided as an option for users who wish to use a lower frequency oscillator circuit or to clock the device up to its highest rated frequency from a crystal oscillator. This may be useful for customers who are concerned with EMI due to high-frequency crystals or users who require higher clock speeds from an internal oscillator. 2.5.1 HSPLL OSCILLATOR MODE The HSPLL mode makes use of the HS mode oscillator for frequencies up to 10 MHz. A PLL then multiplies the oscillator output frequency by 4 to produce an internal clock frequency up to 40 MHz. The PLLEN bit is not available in this oscillator mode. The PLL is only available to the crystal oscillator when the FOSC3:FOSC0 configuration bits are programmed for HSPLL mode (= 0110). FIGURE 2-7: PLL BLOCK DIAGRAM (HS MODE) 2.5.2 PLL AND INTOSC The PLL is also available to the internal oscillator block in selected oscillator modes. In this configuration, the PLL is enabled in software and generates a clock output of up to 32 MHz. The operation of INTOSC with the PLL is described in Section 2.6.4 “PLL in INTOSC Modes”. OSC2/CLKO CEXT REXT PIC18FXXXX OSC1 FOSC/4 Internal Clock VDD VSS Recommended values: 3 kΩ ≤ REXT ≤ 100 kΩ CEXT > 20 pF CEXT REXT PIC18FXXXX OSC1 Internal Clock VDD VSS Recommended values: 3 kΩ ≤ REXT ≤ 100 kΩ CEXT > 20 pF RA6 I/O (OSC2) MUX VCO Loop Filter Crystal Osc OSC2 OSC1 PLL Enable FIN FOUT SYSCLK Phase Comparator HS Oscillator Enable ÷4 (from Configuration Register 1H) HS Mode PIC18F2420/2520/4420/4520 DS39631B-page 26 Preliminary © 2007 Microchip Technology Inc. 2.6 Internal Oscillator Block The PIC18F2420/2520/4420/4520 devices include an internal oscillator block which generates two different clock signals; either can be used as the microcontroller’s clock source. This may eliminate the need for external oscillator circuits on the OSC1 and/or OSC2 pins. The main output (INTOSC) is an 8 MHz clock source, which can be used to directly drive the device clock. It also drives a postscaler, which can provide a range of clock frequencies from 31 kHz to 4 MHz. The INTOSC output is enabled when a clock frequency from 125 kHz to 8 MHz is selected. The other clock source is the internal RC oscillator (INTRC), which provides a nominal 31 kHz output. INTRC is enabled if it is selected as the device clock source; it is also enabled automatically when any of the following are enabled: • Power-up Timer • Fail-Safe Clock Monitor • Watchdog Timer • Two-Speed Start-up These features are discussed in greater detail in Section 23.0 “Special Features of the CPU”. The clock source frequency (INTOSC direct, INTRC direct or INTOSC postscaler) is selected by configuring the IRCF bits of the OSCCON register (page 30). 2.6.1 INTIO MODES Using the internal oscillator as the clock source eliminates the need for up to two external oscillator pins, which can then be used for digital I/O. Two distinct configurations are available: • In INTIO1 mode, the OSC2 pin outputs FOSC/4, while OSC1 functions as RA7 for digital input and output. • In INTIO2 mode, OSC1 functions as RA7 and OSC2 functions as RA6, both for digital input and output. 2.6.2 INTOSC OUTPUT FREQUENCY The internal oscillator block is calibrated at the factory to produce an INTOSC output frequency of 8.0 MHz. The INTRC oscillator operates independently of the INTOSC source. Any changes in INTOSC across voltage and temperature are not necessarily reflected by changes in INTRC and vice versa. 2.6.3 OSCTUNE REGISTER The internal oscillator’s output has been calibrated at the factory but can be adjusted in the user’s application. This is done by writing to the OSCTUNE register (Register 2-1). When the OSCTUNE register is modified, the INTOSC frequency will begin shifting to the new frequency. The INTRC clock will reach the new frequency within 8 clock cycles (approximately 8 * 32 μs = 256 μs). The INTOSC clock will stabilize within 1 ms. Code execution continues during this shift. There is no indication that the shift has occurred. The OSCTUNE register also implements the INTSRC and PLLEN bits, which control certain features of the internal oscillator block. The INTSRC bit allows users to select which internal oscillator provides the clock source when the 31 kHz frequency option is selected. This is covered in greater detail in Section 2.7.1 “Oscillator Control Register”. The PLLEN bit controls the operation of the frequency multiplier, PLL, in internal oscillator modes. 2.6.4 PLL IN INTOSC MODES The 4x frequency multiplier can be used with the internal oscillator block to produce faster device clock speeds than are normally possible with an internal oscillator. When enabled, the PLL produces a clock speed of up to 32 MHz. Unlike HSPLL mode, the PLL is controlled through software. The control bit, PLLEN (OSCTUNE<6>), is used to enable or disable its operation. The PLL is available when the device is configured to use the internal oscillator block as its primary clock source (FOSC3:FOSC0 = 1001 or 1000). Additionally, the PLL will only function when the selected output frequency is either 4 MHz or 8 MHz (OSCCON<6:4> = 111 or 110). If both of these conditions are not met, the PLL is disabled. The PLLEN control bit is only functional in those internal oscillator modes where the PLL is available. In all other modes, it is forced to ‘0’ and is effectively unavailable. 2.6.5 INTOSC FREQUENCY DRIFT The factory calibrates the internal oscillator block output (INTOSC) for 8 MHz. However, this frequency may drift as VDD or temperature changes, which can affect the controller operation in a variety of ways. It is possible to adjust the INTOSC frequency by modifying the value in the OSCTUNE register. This has no effect on the INTRC clock source frequency. Tuning the INTOSC source requires knowing when to make the adjustment, in which direction it should be made and in some cases, how large a change is needed. Three compensation techniques are discussed in Section 2.6.5.1 “Compensating with the USART”, Section 2.6.5.2 “Compensating with the Timers” and Section 2.6.5.3 “Compensating with the CCP Module in Capture Mode”, but other techniques may be used. © 2007 Microchip Technology Inc. Preliminary DS39631B-page 27 PIC18F2420/2520/4420/4520 REGISTER 2-1: OSCTUNE: OSCILLATOR TUNING REGISTER 2.6.5.1 Compensating with the USART An adjustment may be required when the USART begins to generate framing errors or receives data with errors while in Asynchronous mode. Framing errors indicate that the device clock frequency is too high; to adjust for this, decrement the value in OSCTUNE to reduce the clock frequency. On the other hand, errors in data may suggest that the clock speed is too low; to compensate, increment OSCTUNE to increase the clock frequency. 2.6.5.2 Compensating with the Timers This technique compares device clock speed to some reference clock. Two timers may be used; one timer is clocked by the peripheral clock, while the other is clocked by a fixed reference source, such as the Timer1 oscillator. Both timers are cleared, but the timer clocked by the reference generates interrupts. When an interrupt occurs, the internally clocked timer is read and both timers are cleared. If the internally clocked timer value is greater than expected, then the internal oscillator block is running too fast. To adjust for this, decrement the OSCTUNE register. 2.6.5.3 Compensating with the CCP Module in Capture Mode A CCP module can use free running Timer1 (or Timer3), clocked by the internal oscillator block and an external event with a known period (i.e., AC power frequency). The time of the first event is captured in the CCPRxH:CCPRxL registers and is recorded for use later. When the second event causes a capture, the time of the first event is subtracted from the time of the second event. Since the period of the external event is known, the time difference between events can be calculated. If the measured time is much greater than the calculated time, the internal oscillator block is running too fast; to compensate, decrement the OSCTUNE register. If the measured time is much less than the calculated time, the internal oscillator block is running too slow; to compensate, increment the OSCTUNE register. R/W-0 R/W-0(1) U-0 R/W-0 R/W-0 R/W-0 R/W-0 R/W-0 INTSRC PLLEN(1) — TUN4 TUN3 TUN2 TUN1 TUN0 bit 7 bit 0 bit 7 INTSRC: Internal Oscillator Low-Frequency Source Select bit 1 = 31.25 kHz device clock derived from 8 MHz INTOSC source (divide-by-256 enabled) 0 = 31 kHz device clock derived directly from INTRC internal oscillator bit 6 PLLEN: Frequency Multiplier PLL for INTOSC Enable bit(1) 1 = PLL enabled for INTOSC (4 MHz and 8 MHz only) 0 = PLL disabled Note 1: Available only in certain oscillator configurations; otherwise, this bit is unavailable and reads as ‘0’. See Section 2.6.4 “PLL in INTOSC Modes” for details. bit 5 Unimplemented: Read as ‘0’ bit 4-0 TUN4:TUN0: Frequency Tuning bits 01111 = Maximum frequency • • • • 00001 00000 = Center frequency. Oscillator module is running at the calibrated frequency. 11111 • • • • 10000 = Minimum frequency Legend: R = Readable bit W = Writable bit U = Unimplemented bit, read as ‘0’ -n = Value at POR ‘1’ = Bit is set ‘0’ = Bit is cleared x = Bit is unknown PIC18F2420/2520/4420/4520 DS39631B-page 28 Preliminary © 2007 Microchip Technology Inc. 2.7 Clock Sources and Oscillator Switching Like previous PIC18 devices, the PIC18F2420/2520/ 4420/4520 family includes a feature that allows the device clock source to be switched from the main oscillator to an alternate low-frequency clock source. PIC18F2420/2520/4420/4520 devices offer two alternate clock sources. When an alternate clock source is enabled, the various power managed operating modes are available. Essentially, there are three clock sources for these devices: • Primary oscillators • Secondary oscillators • Internal oscillator block The primary oscillators include the External Crystal and Resonator modes, the External RC modes, the External Clock modes and the internal oscillator block. The particular mode is defined by the FOSC3:FOSC0 configuration bits. The details of these modes are covered earlier in this chapter. The secondary oscillators are those external sources not connected to the OSC1 or OSC2 pins. These sources may continue to operate even after the controller is placed in a power managed mode. PIC18F2420/2520/4420/4520 devices offer the Timer1 oscillator as a secondary oscillator. This oscillator, in all power managed modes, is often the time base for functions such as a real-time clock. Most often, a 32.768 kHz watch crystal is connected between the RC0/T1OSO/T13CKI and RC1/T1OSI pins. Like the LP mode oscillator circuit, loading capacitors are also connected from each pin to ground. The Timer1 oscillator is discussed in greater detail in Section 12.3 “Timer1 Oscillator”. In addition to being a primary clock source, the internal oscillator block is available as a power managed mode clock source. The INTRC source is also used as the clock source for several special features, such as the WDT and Fail-Safe Clock Monitor. The clock sources for the PIC18F2420/2520/4420/4520 devices are shown in Figure 2-8. See Section 23.0 “Special Features of the CPU” for Configuration register details. FIGURE 2-8: PIC18F2420/2520/4420/4520 CLOCK DIAGRAM PIC18F2420/2520/4420/4520 4 x PLL FOSC3:FOSC0 Secondary Oscillator T1OSCEN Enable Oscillator T1OSO T1OSI Clock Source Option for other Modules OSC1 OSC2 Sleep HSPLL, INTOSC/PLL LP, XT, HS, RC, EC T1OSC CPU Peripherals IDLEN Postscaler MUX MUX 8 MHz 4 MHz 2 MHz 1 MHz 500 kHz 125 kHz 250 kHz OSCCON<6:4> 111 110 101 100 011 010 001 000 31 kHz INTRC Source Internal Oscillator Block WDT, PWRT, FSCM 8 MHz Internal Oscillator (INTOSC) OSCCON<6:4> Clock Control OSCCON<1:0> Source 8 MHz 31 kHz (INTRC) OSCTUNE<6> 0 1 OSCTUNE<7> and Two-Speed Start-up Primary Oscillator © 2007 Microchip Technology Inc. Preliminary DS39631B-page 29 PIC18F2420/2520/4420/4520 2.7.1 OSCILLATOR CONTROL REGISTER The OSCCON register (Register 2-2) controls several aspects of the device clock’s operation, both in full power operation and in power managed modes. The System Clock Select bits, SCS1:SCS0, select the clock source. The available clock sources are the primary clock (defined by the FOSC3:FOSC0 configuration bits), the secondary clock (Timer1 oscillator) and the internal oscillator block. The clock source changes immediately after one or more of the bits is written to, following a brief clock transition interval. The SCS bits are cleared on all forms of Reset. The Internal Oscillator Frequency Select bits (IRCF2:IRCF0) select the frequency output of the internal oscillator block to drive the device clock. The choices are the INTRC source, the INTOSC source (8 MHz) or one of the frequencies derived from the INTOSC postscaler (31.25 kHz to 4 MHz). If the internal oscillator block is supplying the device clock, changing the states of these bits will have an immediate change on the internal oscillator’s output. On device Resets, the default output frequency of the internal oscillator block is set at 1 MHz. When a nominal output frequency of 31 kHz is selected (IRCF2:IRCF0 = 000), users may choose which internal oscillator acts as the source. This is done with the INTSRC bit in the OSCTUNE register (OSCTUNE<7>). Setting this bit selects INTOSC as a 31.25 kHz clock source by enabling the divide-by-256 output of the INTOSC postscaler. Clearing INTSRC selects INTRC (nominally 31 kHz) as the clock source. This option allows users to select the tunable and more precise INTOSC as a clock source, while maintaining power savings with a very low clock speed. Regardless of the setting of INTSRC, INTRC always remains the clock source for features such as the Watchdog Timer and the Fail-Safe Clock Monitor. The OSTS, IOFS and T1RUN bits indicate which clock source is currently providing the device clock. The OSTS bit indicates that the Oscillator Start-up Timer has timed out and the primary clock is providing the device clock in primary clock modes. The IOFS bit indicates when the internal oscillator block has stabilized and is providing the device clock in RC Clock modes. The T1RUN bit (T1CON<6>) indicates when the Timer1 oscillator is providing the device clock in secondary clock modes. In power managed modes, only one of these three bits will be set at any time. If none of these bits are set, the INTRC is providing the clock or the internal oscillator block has just started and is not yet stable. The IDLEN bit determines if the device goes into Sleep mode or one of the Idle modes when the SLEEP instruction is executed. The use of the flag and control bits in the OSCCON register is discussed in more detail in Section 3.0 “Power Managed Modes”. 2.7.2 OSCILLATOR TRANSITIONS PIC18F2420/2520/4420/4520 devices contain circuitry to prevent clock “glitches” when switching between clock sources. A short pause in the device clock occurs during the clock switch. The length of this pause is the sum of two cycles of the old clock source and three to four cycles of the new clock source. This formula assumes that the new clock source is stable. Clock transitions are discussed in greater detail in Section 3.1.2 “Entering Power Managed Modes”. Note 1: The Timer1 oscillator must be enabled to select the secondary clock source. The Timer1 oscillator is enabled by setting the T1OSCEN bit in the Timer1 Control register (T1CON<3>). If the Timer1 oscillator is not enabled, then any attempt to select a secondary clock source will be ignored. 2: It is recommended that the Timer1 oscillator be operating and stable before selecting the secondary clock source or a very long delay may occur while the Timer1 oscillator starts. PIC18F2420/2520/4420/4520 DS39631B-page 30 Preliminary © 2007 Microchip Technology Inc. REGISTER 2-2: OSCCON REGISTER R/W-0 R/W-1 R/W-0 R/W-0 R(1) R-0 R/W-0 R/W-0 IDLEN IRCF2 IRCF1 IRCF0 OSTS IOFS SCS1 SCS0 bit 7 bit 0 bit 7 IDLEN: Idle Enable bit 1 = Device enters Idle mode on SLEEP instruction 0 = Device enters Sleep mode on SLEEP instruction bit 6-4 IRCF2:IRCF0: Internal Oscillator Frequency Select bits 111 = 8 MHz (INTOSC drives clock directly) 110 = 4 MHz 101 = 2 MHz 100 = 1 MHz(3) 011 = 500 kHz 010 = 250 kHz 001 = 125 kHz 000 = 31 kHz (from either INTOSC/256 or INTRC directly)(2) bit 3 OSTS: Oscillator Start-up Time-out Status bit(1) 1 = Oscillator start-up time-out timer has expired; primary oscillator is running 0 = Oscillator start-up time-out timer is running; primary oscillator is not ready bit 2 IOFS: INTOSC Frequency Stable bit 1 = INTOSC frequency is stable 0 = INTOSC frequency is not stable bit 1-0 SCS1:SCS0: System Clock Select bits 1x = Internal oscillator block 01 = Secondary (Timer1) oscillator 00 = Primary oscillator Note 1: Reset state depends on state of the IESO configuration bit. 2: Source selected by the INTSRC bit (OSCTUNE<7>), see text. 3: Default output frequency of INTOSC on Reset. Legend: R = Readable bit W = Writable bit U = Unimplemented bit, read as ‘0’ -n = Value at POR ‘1’ = Bit is set ‘0’ = Bit is cleared x = Bit is unknown © 2007 Microchip Technology Inc. Preliminary DS39631B-page 31 PIC18F2420/2520/4420/4520 2.8 Effects of Power Managed Modes on the Various Clock Sources When PRI_IDLE mode is selected, the designated primary oscillator continues to run without interruption. For all other power managed modes, the oscillator using the OSC1 pin is disabled. The OSC1 pin (and OSC2 pin, if used by the oscillator) will stop oscillating. In secondary clock modes (SEC_RUN and SEC_IDLE), the Timer1 oscillator is operating and providing the device clock. The Timer1 oscillator may also run in all power managed modes if required to clock Timer1 or Timer3. In internal oscillator modes (RC_RUN and RC_IDLE), the internal oscillator block provides the device clock source. The 31 kHz INTRC output can be used directly to provide the clock and may be enabled to support various special features, regardless of the power managed mode (see Section 23.2 “Watchdog Timer (WDT)”, Section 23.3 “Two-Speed Start-up” and Section 23.4 “Fail-Safe Clock Monitor” for more information on WDT, Fail-Safe Clock Monitor and Two- Speed Start-up). The INTOSC output at 8 MHz may be used directly to clock the device or may be divided down by the postscaler. The INTOSC output is disabled if the clock is provided directly from the INTRC output. If the Sleep mode is selected, all clock sources are stopped. Since all the transistor switching currents have been stopped, Sleep mode achieves the lowest current consumption of the device (only leakage currents). Enabling any on-chip feature that will operate during Sleep will increase the current consumed during Sleep. The INTRC is required to support WDT operation. The Timer1 oscillator may be operating to support a realtime clock. Other features may be operating that do not require a device clock source (i.e., SSP slave, PSP, INTn pins and others). Peripherals that may add significant current consumption are listed in Section 26.2 “DC Characteristics”. 2.9 Power-up Delays Power-up delays are controlled by two timers, so that no external Reset circuitry is required for most applications. The delays ensure that the device is kept in Reset until the device power supply is stable under normal circumstances and the primary clock is operating and stable. For additional information on power-up delays, see Section 4.5 “Device Reset Timers”. The first timer is the Power-up Timer (PWRT), which provides a fixed delay on power-up (parameter 33, Table 26-10). It is enabled by clearing (= 0) the PWRTEN configuration bit. The second timer is the Oscillator Start-up Timer (OST), intended to keep the chip in Reset until the crystal oscillator is stable (LP, XT and HS modes). The OST does this by counting 1024 oscillator cycles before allowing the oscillator to clock the device. When the HSPLL Oscillator mode is selected, the device is kept in Reset for an additional 2 ms, following the HS mode OST delay, so the PLL can lock to the incoming clock frequency. There is a delay of interval TCSD (parameter 38, Table 26-10), following POR, while the controller becomes ready to execute instructions. This delay runs concurrently with any other delays. This may be the only delay that occurs when any of the EC, RC or INTIO modes are used as the primary clock source. TABLE 2-3: OSC1 AND OSC2 PIN STATES IN SLEEP MODE OSC Mode OSC1 Pin OSC2 Pin RC, INTIO1 Floating, external resistor should pull high At logic low (clock/4 output) RCIO Floating, external resistor should pull high Configured as PORTA, bit 6 INTIO2 Configured as PORTA, bit 7 Configured as PORTA, bit 6 ECIO Floating, pulled by external clock Configured as PORTA, bit 6 EC Floating, pulled by external clock At logic low (clock/4 output) LP, XT and HS Feedback inverter disabled at quiescent voltage level Feedback inverter disabled at quiescent voltage level Note: See Table 4-2 in Section 4.0 “Reset” for time-outs due to Sleep and MCLR Reset. PIC18F2420/2520/4420/4520 DS39631B-page 32 Preliminary © 2007 Microchip Technology Inc. NOTES: © 2007 Microchip Technology Inc. DS39631B-page 33 PIC18F2420/2520/4420/4520 3.0 POWER MANAGED MODES PIC18F2420/2520/4420/4520 devices offer a total of seven operating modes for more efficient power management. These modes provide a variety of options for selective power conservation in applications where resources may be limited (i.e., battery-powered devices). There are three categories of power managed modes: • Run modes • Idle modes • Sleep mode These categories define which portions of the device are clocked and sometimes, what speed. The Run and Idle modes may use any of the three available clock sources (primary, secondary or internal oscillator block); the Sleep mode does not use a clock source. The power managed modes include several powersaving features offered on previous PIC® devices. One is the clock switching feature, offered in other PIC18 devices, allowing the controller to use the Timer1 oscillator in place of the primary oscillator. Also included is the Sleep mode, offered by all PIC devices, where all device clocks are stopped. 3.1 Selecting Power Managed Modes Selecting a power managed mode requires two decisions: if the CPU is to be clocked or not and the selection of a clock source. The IDLEN bit (OSCCON<7>) controls CPU clocking, while the SCS1:SCS0 bits (OSCCON<1:0>) select the clock source. The individual modes, bit settings, clock sources and affected modules are summarized in Table 3-1. 3.1.1 CLOCK SOURCES The SCS1:SCS0 bits allow the selection of one of three clock sources for power managed modes. They are: • the primary clock, as defined by the FOSC3:FOSC0 configuration bits • the secondary clock (the Timer1 oscillator) • the internal oscillator block (for RC modes) 3.1.2 ENTERING POWER MANAGED MODES Switching from one power managed mode to another begins by loading the OSCCON register. The SCS1:SCS0 bits select the clock source and determine which Run or Idle mode is to be used. Changing these bits causes an immediate switch to the new clock source, assuming that it is running. The switch may also be subject to clock transition delays. These are discussed in Section 3.1.3 “Clock Transitions and Status Indicators” and subsequent sections. Entry to the Power Managed Idle or Sleep modes is triggered by the execution of a SLEEP instruction. The actual mode that results depends on the status of the IDLEN bit. Depending on the current mode and the mode being switched to, a change to a power managed mode does not always require setting all of these bits. Many transitions may be done by changing the oscillator select bits, or changing the IDLEN bit, prior to issuing a SLEEP instruction. If the IDLEN bit is already configured correctly, it may only be necessary to perform a SLEEP instruction to switch to the desired mode. TABLE 3-1: POWER MANAGED MODES Mode OSCCON Bits Module Clocking IDLEN(1) Available Clock and Oscillator Source <7> SCS1:SCS0 <1:0> CPU Peripherals Sleep 0 N/A Off Off None – All clocks are disabled PRI_RUN N/A 00 Clocked Clocked Primary – LP, XT, HS, HSPLL, RC, EC and Internal Oscillator Block(2). This is the normal full power execution mode. SEC_RUN N/A 01 Clocked Clocked Secondary – Timer1 Oscillator RC_RUN N/A 1x Clocked Clocked Internal Oscillator Block(2) PRI_IDLE 1 00 Off Clocked Primary – LP, XT, HS, HSPLL, RC, EC SEC_IDLE 1 01 Off Clocked Secondary – Timer1 Oscillator RC_IDLE 1 1x Off Clocked Internal Oscillator Block(2) Note 1: IDLEN reflects its value when the SLEEP instruction is executed. 2: Includes INTOSC and INTOSC postscaler, as well as the INTRC source. PIC18F2420/2520/4420/4520 DS39631B-page 34 © 2007 Microchip Technology Inc. 3.1.3 CLOCK TRANSITIONS AND STATUS INDICATORS The length of the transition between clock sources is the sum of two cycles of the old clock source and three to four cycles of the new clock source. This formula assumes that the new clock source is stable. Three bits indicate the current clock source and its status. They are: • OSTS (OSCCON<3>) • IOFS (OSCCON<2>) • T1RUN (T1CON<6>) In general, only one of these bits will be set while in a given power managed mode. When the OSTS bit is set, the primary clock is providing the device clock. When the IOFS bit is set, the INTOSC output is providing a stable 8 MHz clock source to a divider that actually drives the device clock. When the T1RUN bit is set, the Timer1 oscillator is providing the clock. If none of these bits are set, then either the INTRC clock source is clocking the device, or the INTOSC source is not yet stable. If the internal oscillator block is configured as the primary clock source by the FOSC3:FOSC0 configuration bits, then both the OSTS and IOFS bits may be set when in PRI_RUN or PRI_IDLE modes. This indicates that the primary clock (INTOSC output) is generating a stable 8 MHz output. Entering another RC Power Managed mode at the same frequency would clear the OSTS bit. 3.1.4 MULTIPLE SLEEP COMMANDS The power managed mode that is invoked with the SLEEP instruction is determined by the setting of the IDLEN bit at the time the instruction is executed. If another SLEEP instruction is executed, the device will enter the power managed mode specified by IDLEN at that time. If IDLEN has changed, the device will enter the new power managed mode specified by the new setting. 3.2 Run Modes In the Run modes, clocks to both the core and peripherals are active. The difference between these modes is the clock source. 3.2.1 PRI_RUN MODE The PRI_RUN mode is the normal, full power execution mode of the microcontroller. This is also the default mode upon a device Reset, unless Two-Speed Start-up is enabled (see Section 23.3 “Two-Speed Start-up” for details). In this mode, the OSTS bit is set. The IOFS bit may be set if the internal oscillator block is the primary clock source (see Section 2.7.1 “Oscillator Control Register”). 3.2.2 SEC_RUN MODE The SEC_RUN mode is the compatible mode to the “clock switching” feature offered in other PIC18 devices. In this mode, the CPU and peripherals are clocked from the Timer1 oscillator. This gives users the option of lower power consumption while still using a high accuracy clock source. SEC_RUN mode is entered by setting the SCS1:SCS0 bits to ‘01’. The device clock source is switched to the Timer1 oscillator (see Figure 3-1), the primary oscillator is shut down, the T1RUN bit (T1CON<6>) is set and the OSTS bit is cleared. On transitions from SEC_RUN mode to PRI_RUN, the peripherals and CPU continue to be clocked from the Timer1 oscillator while the primary clock is started. When the primary clock becomes ready, a clock switch back to the primary clock occurs (see Figure 3-2). When the clock switch is complete, the T1RUN bit is cleared, the OSTS bit is set and the primary clock is providing the clock. The IDLEN and SCS bits are not affected by the wake-up; the Timer1 oscillator continues to run. Note 1: Caution should be used when modifying a single IRCF bit. If VDD is less than 3V, it is possible to select a higher clock speed than is supported by the low VDD. Improper device operation may result if the VDD/FOSC specifications are violated. 2: Executing a SLEEP instruction does not necessarily place the device into Sleep mode. It acts as the trigger to place the controller into either the Sleep mode or one of the Idle modes, depending on the setting of the IDLEN bit. Note: The Timer1 oscillator should already be running prior to entering SEC_RUN mode. If the T1OSCEN bit is not set when the SCS1:SCS0 bits are set to ‘01’, entry to SEC_RUN mode will not occur. If the Timer1 oscillator is enabled, but not yet running, device clocks will be delayed until the oscillator has started; in such situations, initial oscillator operation is far from stable and unpredictable operation may result. © 2007 Microchip Technology Inc. DS39631B-page 35 PIC18F2420/2520/4420/4520 FIGURE 3-1: TRANSITION TIMING FOR ENTRY TO SEC_RUN MODE FIGURE 3-2: TRANSITION TIMING FROM SEC_RUN MODE TO PRI_RUN MODE (HSPLL) 3.2.3 RC_RUN MODE In RC_RUN mode, the CPU and peripherals are clocked from the internal oscillator block using the INTOSC multiplexer. In this mode, the primary clock is shut down. When using the INTRC source, this mode provides the best power conservation of all the Run modes, while still executing code. It works well for user applications which are not highly timing sensitive or do not require high-speed clocks at all times. If the primary clock source is the internal oscillator block (either INTRC or INTOSC), there are no distinguishable differences between PRI_RUN and RC_RUN modes during execution. However, a clock switch delay will occur during entry to and exit from RC_RUN mode. Therefore, if the primary clock source is the internal oscillator block, the use of RC_RUN mode is not recommended. This mode is entered by setting the SCS1 bit to ‘1’. Although it is ignored, it is recommended that the SCS0 bit also be cleared; this is to maintain software compatibility with future devices. When the clock source is switched to the INTOSC multiplexer (see Figure 3-3), the primary oscillator is shut down and the OSTS bit is cleared. The IRCF bits may be modified at any time to immediately change the clock speed. Q2 Q3 Q4 OSC1 Peripheral Program Q1 T1OSI Q1 Counter Clock CPU Clock PC PC + 2 1 2 3 n-1 n Clock Transition(1) Q2 Q3 Q4 Q1 Q2 Q3 PC + 4 Note 1: Clock transition typically occurs within 2-4 TOSC. Q1 Q3 Q4 OSC1 Peripheral Program PC T1OSI PLL Clock Q1 PC + 4 Q2 Output Q3 Q4 Q1 CPU Clock PC + 2 Clock Counter Q2 Q2 Q3 Note1: TOST = 1024 TOSC; TPLL = 2 ms (approx). These intervals are not shown to scale. 2: Clock transition typically occurs within 2-4 TOSC. SCS1:SCS0 bits changed TPLL(1) 1 2 n-1 n Clock OSTS bit set Transition(2) TOST(1) Note: Caution should be used when modifying a single IRCF bit. If VDD is less than 3V, it is possible to select a higher clock speed than is supported by the low VDD. Improper device operation may result if the VDD/FOSC specifications are violated. PIC18F2420/2520/4420/4520 DS39631B-page 36 © 2007 Microchip Technology Inc. If the IRCF bits and the INTSRC bit are all clear, the INTOSC output is not enabled and the IOFS bit will remain clear; there will be no indication of the current clock source. The INTRC source is providing the device clocks. If the IRCF bits are changed from all clear (thus, enabling the INTOSC output) or if INTSRC is set, the IOFS bit becomes set after the INTOSC output becomes stable. Clocks to the device continue while the INTOSC source stabilizes after an interval of TIOBST. If the IRCF bits were previously at a non-zero value, or if INTSRC was set before setting SCS1 and the INTOSC source was already stable, the IOFS bit will remain set. On transitions from RC_RUN mode to PRI_RUN mode, the device continues to be clocked from the INTOSC multiplexer while the primary clock is started. When the primary clock becomes ready, a clock switch to the primary clock occurs (see Figure 3-4). When the clock switch is complete, the IOFS bit is cleared, the OSTS bit is set and the primary clock is providing the device clock. The IDLEN and SCS bits are not affected by the switch. The INTRC source will continue to run if either the WDT or the Fail-Safe Clock Monitor is enabled. FIGURE 3-3: TRANSITION TIMING TO RC_RUN MODE FIGURE 3-4: TRANSITION TIMING FROM RC_RUN MODE TO PRI_RUN MODE Q2 Q3 Q4 OSC1 Peripheral Program Q1 INTRC Q1 Counter Clock CPU Clock PC PC + 2 1 2 3 n-1 n Clock Transition(1) Q2 Q3 Q4 Q1 Q2 Q3 PC + 4 Note 1: Clock transition typically occurs within 2-4 TOSC. Q1 Q3 Q4 OSC1 Peripheral Program PC INTOSC PLL Clock Q1 PC + 4 Q2 Output Q3 Q4 Q1 CPU Clock PC + 2 Clock Counter Q2 Q2 Q3 Note1: TOST = 1024 TOSC; TPLL = 2 ms (approx). These intervals are not shown to scale. 2: Clock transition typically occurs within 2-4 TOSC. SCS1:SCS0 bits changed TPLL(1) 1 2 n-1 n Clock OSTS bit set Transition(2) Multiplexer TOST(1) © 2007 Microchip Technology Inc. DS39631B-page 37 PIC18F2420/2520/4420/4520 3.3 Sleep Mode The Power Managed Sleep mode in the PIC18F2420/ 2520/4420/4520 devices is identical to the legacy Sleep mode offered in all other PIC devices. It is entered by clearing the IDLEN bit (the default state on device Reset) and executing the SLEEP instruction. This shuts down the selected oscillator (Figure 3-5). All clock source status bits are cleared. Entering the Sleep mode from any other mode does not require a clock switch. This is because no clocks are needed once the controller has entered Sleep. If the WDT is selected, the INTRC source will continue to operate. If the Timer1 oscillator is enabled, it will also continue to run. When a wake event occurs in Sleep mode (by interrupt, Reset or WDT time-out), the device will not be clocked until the clock source selected by the SCS1:SCS0 bits becomes ready (see Figure 3-6), or it will be clocked from the internal oscillator block if either the Two- Speed Start-up or the Fail-Safe Clock Monitor are enabled (see Section 23.0 “Special Features of the CPU”). In either case, the OSTS bit is set when the primary clock is providing the device clocks. The IDLEN and SCS bits are not affected by the wake-up. 3.4 Idle Modes The Idle modes allow the controller’s CPU to be selectively shut down while the peripherals continue to operate. Selecting a particular Idle mode allows users to further manage power consumption. If the IDLEN bit is set to a ‘1’ when a SLEEP instruction is executed, the peripherals will be clocked from the clock source selected using the SCS1:SCS0 bits; however, the CPU will not be clocked. The clock source status bits are not affected. Setting IDLEN and executing a SLEEP instruction provides a quick method of switching from a given Run mode to its corresponding Idle mode. If the WDT is selected, the INTRC source will continue to operate. If the Timer1 oscillator is enabled, it will also continue to run. Since the CPU is not executing instructions, the only exits from any of the Idle modes are by interrupt, WDT time-out or a Reset. When a wake event occurs, CPU execution is delayed by an interval of TCSD (parameter 38, Table 26-10) while it becomes ready to execute code. When the CPU begins executing code, it resumes with the same clock source for the current Idle mode. For example, when waking from RC_IDLE mode, the internal oscillator block will clock the CPU and peripherals (in other words, RC_RUN mode). The IDLEN and SCS bits are not affected by the wake-up. While in any Idle mode or the Sleep mode, a WDT time-out will result in a WDT wake-up to the Run mode currently specified by the SCS1:SCS0 bits. FIGURE 3-5: TRANSITION TIMING FOR ENTRY TO SLEEP MODE FIGURE 3-6: TRANSITION TIMING FOR WAKE FROM SLEEP (HSPLL) Q2 Q3 Q4 OSC1 Peripheral Sleep Program Q1 Q1 Counter Clock CPU Clock PC PC + 2 Q3 Q4 Q1 Q2 OSC1 Peripheral Program PC PLL Clock Q3 Q4 Output CPU Clock Q1 Q2 Q3 Q4 Q1 Q2 Clock Counter PC + 6 PC + 4 Q1 Q2 Q3 Q4 Wake Event Note1: TOST = 1024 TOSC; TPLL = 2 ms (approx). These intervals are not shown to scale. TOST(1) TPLL(1) OSTS bit set PC + 2 PIC18F2420/2520/4420/4520 DS39631B-page 38 © 2007 Microchip Technology Inc. 3.4.1 PRI_IDLE MODE This mode is unique among the three Low-Power Idle modes, in that it does not disable the primary device clock. For timing sensitive applications, this allows for the fastest resumption of device operation with its more accurate primary clock source, since the clock source does not have to “warm-up” or transition from another oscillator. PRI_IDLE mode is entered from PRI_RUN mode by setting the IDLEN bit and executing a SLEEP instruction. If the device is in another Run mode, set IDLEN first, then clear the SCS bits and execute SLEEP. Although the CPU is disabled, the peripherals continue to be clocked from the primary clock source specified by the FOSC3:FOSC0 configuration bits. The OSTS bit remains set (see Figure 3-7). When a wake event occurs, the CPU is clocked from the primary clock source. A delay of interval TCSD is required between the wake event and when code execution starts. This is required to allow the CPU to become ready to execute instructions. After the wakeup, the OSTS bit remains set. The IDLEN and SCS bits are not affected by the wake-up (see Figure 3-8). 3.4.2 SEC_IDLE MODE In SEC_IDLE mode, the CPU is disabled but the peripherals continue to be clocked from the Timer1 oscillator. This mode is entered from SEC_RUN by setting the IDLEN bit and executing a SLEEP instruction. If the device is in another Run mode, set the IDLEN bit first, then set the SCS1:SCS0 bits to ‘01’ and execute SLEEP. When the clock source is switched to the Timer1 oscillator, the primary oscillator is shut down, the OSTS bit is cleared and the T1RUN bit is set. When a wake event occurs, the peripherals continue to be clocked from the Timer1 oscillator. After an interval of TCSD following the wake event, the CPU begins executing code being clocked by the Timer1 oscillator. The IDLEN and SCS bits are not affected by the wake-up; the Timer1 oscillator continues to run (see Figure 3-8). FIGURE 3-7: TRANSITION TIMING FOR ENTRY TO IDLE MODE FIGURE 3-8: TRANSITION TIMING FOR WAKE FROM IDLE TO RUN MODE Note: The Timer1 oscillator should already be running prior to entering SEC_IDLE mode. If the T1OSCEN bit is not set when the SLEEP instruction is executed, the SLEEP instruction will be ignored and entry to SEC_IDLE mode will not occur. If the Timer1 oscillator is enabled but not yet running, peripheral clocks will be delayed until the oscillator has started. In such situations, initial oscillator operation is far from stable and unpredictable operation may result. Q1 Peripheral Program PC PC + 2 OSC1 Q3 Q4 Q1 CPU Clock Clock Counter Q2 OSC1 Peripheral Program PC CPU Clock Q1 Q3 Q4 Clock Counter Q2 Wake Event TCSD © 2007 Microchip Technology Inc. DS39631B-page 39 PIC18F2420/2520/4420/4520 3.4.3 RC_IDLE MODE In RC_IDLE mode, the CPU is disabled but the peripherals continue to be clocked from the internal oscillator block using the INTOSC multiplexer. This mode allows for controllable power conservation during Idle periods. From RC_RUN, this mode is entered by setting the IDLEN bit and executing a SLEEP instruction. If the device is in another Run mode, first set IDLEN, then set the SCS1 bit and execute SLEEP. Although its value is ignored, it is recommended that SCS0 also be cleared; this is to maintain software compatibility with future devices. The INTOSC multiplexer may be used to select a higher clock frequency by modifying the IRCF bits before executing the SLEEP instruction. When the clock source is switched to the INTOSC multiplexer, the primary oscillator is shut down and the OSTS bit is cleared. If the IRCF bits are set to any non-zero value, or the INTSRC bit is set, the INTOSC output is enabled. The IOFS bit becomes set, after the INTOSC output becomes stable, after an interval of TIOBST (parameter 39, Table 26-10). Clocks to the peripherals continue while the INTOSC source stabilizes. If the IRCF bits were previously at a non-zero value, or INTSRC was set before the SLEEP instruction was executed and the INTOSC source was already stable, the IOFS bit will remain set. If the IRCF bits and INTSRC are all clear, the INTOSC output will not be enabled, the IOFS bit will remain clear and there will be no indication of the current clock source. When a wake event occurs, the peripherals continue to be clocked from the INTOSC multiplexer. After a delay of TCSD following the wake event, the CPU begins executing code being clocked by the INTOSC multiplexer. The IDLEN and SCS bits are not affected by the wakeup. The INTRC source will continue to run if either the WDT or the Fail-Safe Clock Monitor is enabled. 3.5 Exiting Idle and Sleep Modes An exit from Sleep mode or any of the Idle modes is triggered by an interrupt, a Reset or a WDT time-out. This section discusses the triggers that cause exits from power managed modes. The clocking subsystem actions are discussed in each of the power managed modes (see Section 3.2 “Run Modes”, Section 3.3 “Sleep Mode” and Section 3.4 “Idle Modes”). 3.5.1 EXIT BY INTERRUPT Any of the available interrupt sources can cause the device to exit from an Idle mode or the Sleep mode to a Run mode. To enable this functionality, an interrupt source must be enabled by setting its enable bit in one of the INTCON or PIE registers. The exit sequence is initiated when the corresponding interrupt flag bit is set. On all exits from Idle or Sleep modes by interrupt, code execution branches to the interrupt vector if the GIE/ GIEH bit (INTCON<7>) is set. Otherwise, code execution continues or resumes without branching (see Section 9.0 “Interrupts”). A fixed delay of interval TCSD following the wake event is required when leaving Sleep and Idle modes. This delay is required for the CPU to prepare for execution. Instruction execution resumes on the first clock cycle following this delay. 3.5.2 EXIT BY WDT TIME-OUT A WDT time-out will cause different actions depending on which power managed mode the device is in when the time-out occurs. If the device is not executing code (all Idle modes and Sleep mode), the time-out will result in an exit from the power managed mode (see Section 3.2 “Run Modes” and Section 3.3 “Sleep Mode”). If the device is executing code (all Run modes), the time-out will result in a WDT Reset (see Section 23.2 “Watchdog Timer (WDT)”). The WDT timer and postscaler are cleared by executing a SLEEP or CLRWDT instruction, the loss of a currently selected clock source (if the Fail-Safe Clock Monitor is enabled) and modifying the IRCF bits in the OSCCON register if the internal oscillator block is the device clock source. 3.5.3 EXIT BY RESET Normally, the device is held in Reset by the Oscillator Start-up Timer (OST) until the primary clock becomes ready. At that time, the OSTS bit is set and the device begins executing code. If the internal oscillator block is the new clock source, the IOFS bit is set instead. The exit delay time from Reset to the start of code execution depends on both the clock sources before and after the wake-up and the type of oscillator if the new clock source is the primary clock. Exit delays are summarized in Table 3-2. Code execution can begin before the primary clock becomes ready. If either the Two-Speed Start-up (see Section 23.3 “Two-Speed Start-up”) or Fail-Safe Clock Monitor (see Section 23.4 “Fail-Safe Clock Monitor”) is enabled, the device may begin execution as soon as the Reset source has cleared. Execution is clocked by the INTOSC multiplexer driven by the internal oscillator block. Execution is clocked by the internal oscillator block until either the primary clock becomes ready or a power managed mode is entered before the primary clock becomes ready; the primary clock is then shut down. PIC18F2420/2520/4420/4520 DS39631B-page 40 © 2007 Microchip Technology Inc. 3.5.4 EXIT WITHOUT AN OSCILLATOR START-UP DELAY Certain exits from power managed modes do not invoke the OST at all. There are two cases: • PRI_IDLE mode, where the primary clock source is not stopped and • the primary clock source is not any of the LP, XT, HS or HSPLL modes. In these instances, the primary clock source either does not require an oscillator start-up delay since it is already running (PRI_IDLE), or normally does not require an oscillator start-up delay (RC, EC and INTIO Oscillator modes). However, a fixed delay of interval TCSD following the wake event is still required when leaving Sleep and Idle modes to allow the CPU to prepare for execution. Instruction execution resumes on the first clock cycle following this delay. TABLE 3-2: EXIT DELAY ON WAKE-UP BY RESET FROM SLEEP MODE OR ANY IDLE MODE (BY CLOCK SOURCES) Clock Source before Wake-up Clock Source after Wake-up Exit Delay Clock Ready Status Bit (OSCCON) Primary Device Clock (PRI_IDLE mode) LP, XT, HS TCSD HSPLL (1) OSTS EC, RC INTOSC(2) IOFS T1OSC or INTRC(1) LP, XT, HS TOST(3) HSPLL TOST + trc OSTS (3) EC, RC TCSD(1) INTOSC(1) TIOBST(4) IOFS INTOSC(2) LP, XT, HS TOST(4) HSPLL TOST + trc OSTS (3) EC, RC TCSD(1) INTOSC(1) None IOFS None (Sleep mode) LP, XT, HS TOST(3) HSPLL TOST + trc OSTS (3) EC, RC TCSD(1) INTOSC(1) TIOBST(4) IOFS Note 1: TCSD (parameter 38) is a required delay when waking from Sleep and all Idle modes and runs concurrently with any other required delays (see Section 3.4 “Idle Modes”). On Reset, INTOSC defaults to 1 MHz. 2: Includes both the INTOSC 8 MHz source and postscaler derived frequencies. 3: TOST is the Oscillator Start-up Timer (parameter 32). trc is the PLL Lock-out Timer (parameter F12); it is also designated as TPLL. 4: Execution continues during TIOBST (parameter 39), the INTOSC stabilization period. © 2007 Microchip Technology Inc. Preliminary DS39631B-page 41 PIC18F2420/2520/4420/4520 4.0 RESET The PIC18F2420/2520/4420/4520 devices differentiate between various kinds of Reset: a) Power-on Reset (POR) b) MCLR Reset during normal operation c) MCLR Reset during power managed modes d) Watchdog Timer (WDT) Reset (during execution) e) Programmable Brown-out Reset (BOR) f) RESET Instruction g) Stack Full Reset h) Stack Underflow Reset This section discusses Resets generated by MCLR, POR and BOR and covers the operation of the various start-up timers. Stack Reset events are covered in Section 5.1.2.4 “Stack Full and Underflow Resets”. WDT Resets are covered in Section 23.2 “Watchdog Timer (WDT)”. A simplified block diagram of the On-Chip Reset Circuit is shown in Figure 4-1. 4.1 RCON Register Device Reset events are tracked through the RCON register (Register 4-1). The lower five bits of the register indicate that a specific Reset event has occurred. In most cases, these bits can only be cleared by the event and must be set by the application after the event. The state of these flag bits, taken together, can be read to indicate the type of Reset that just occurred. This is described in more detail in Section 4.6 “Reset State of Registers”. The RCON register also has control bits for setting interrupt priority (IPEN) and software control of the BOR (SBOREN). Interrupt priority is discussed in Section 9.0 “Interrupts”. BOR is covered in Section 4.4 “Brown-out Reset (BOR)”. FIGURE 4-1: SIMPLIFIED BLOCK DIAGRAM OF ON-CHIP RESET CIRCUIT External Reset MCLR VDD OSC1 WDT Time-out VDD Rise Detect OST/PWRT INTRC(1) POR Pulse OST 10-bit Ripple Counter PWRT 11-bit Ripple Counter Enable OST(2) Enable PWRT Note 1: This is the INTRC source from the internal oscillator block and is separate from the RC oscillator of the CLKI pin. 2: See Table 4-2 for time-out situations. Brown-out Reset BOREN RESET Instruction Stack Pointer Stack Full/Underflow Reset Sleep ( )_IDLE 1024 Cycles 32 μs 65.5 ms MCLRE S R Q Chip_Reset PIC18F2420/2520/4420/4520 DS39631B-page 42 Preliminary © 2007 Microchip Technology Inc. REGISTER 4-1: RCON REGISTER R/W-0 R/W-1(1) U-0 R/W-1 R-1 R-1 R/W-0(2) R/W-0 IPEN SBOREN — RI TO PD POR BOR bit 7 bit 0 bit 7 IPEN: Interrupt Priority Enable bit 1 = Enable priority levels on interrupts 0 = Disable priority levels on interrupts (PIC16CXXX Compatibility mode) bit 6 SBOREN: BOR Software Enable bit(1) If BOREN1:BOREN0 = 01: 1 = BOR is enabled 0 = BOR is disabled If BOREN1:BOREN0 = 00, 10 or 11: Bit is disabled and read as ‘0’. bit 5 Unimplemented: Read as ‘0’ bit 4 RI: RESET Instruction Flag bit 1 = The RESET instruction was not executed (set by firmware only) 0 = The RESET instruction was executed causing a device Reset (must be set in software after a Brown-out Reset occurs) bit 3 TO: Watchdog Time-out Flag bit 1 = Set by power-up, CLRWDT instruction or SLEEP instruction 0 = A WDT time-out occurred bit 2 PD: Power-down Detection Flag bit 1 = Set by power-up or by the CLRWDT instruction 0 = Set by execution of the SLEEP instruction bit 1 POR: Power-on Reset Status bit(2) 1 = A Power-on Reset has not occurred (set by firmware only) 0 = A Power-on Reset occurred (must be set in software after a Power-on Reset occurs) bit 0 BOR: Brown-out Reset Status bit 1 = A Brown-out Reset has not occurred (set by firmware only) 0 = A Brown-out Reset occurred (must be set in software after a Brown-out Reset occurs) Note 1: If SBOREN is enabled, its Reset state is ‘1’; otherwise, it is ‘0’. 2: The actual Reset value of POR is determined by the type of device Reset. See the notes following this register and Section 4.6 “Reset State of Registers” for additional information. Legend: R = Readable bit W = Writable bit U = Unimplemented bit, read as ‘0’ -n = Value at POR ‘1’ = Bit is set ‘0’ = Bit is cleared x = Bit is unknown Note 1: It is recommended that the POR bit be set after a Power-on Reset has been detected so that subsequent Power-on Resets may be detected. 2: Brown-out Reset is said to have occurred when BOR is ‘0’ and POR is ‘1’ (assuming that POR was set to ‘1’ by software immediately after POR). © 2007 Microchip Technology Inc. Preliminary DS39631B-page 43 PIC18F2420/2520/4420/4520 4.2 Master Clear (MCLR) The MCLR pin provides a method for triggering an external Reset of the device. A Reset is generated by holding the pin low. These devices have a noise filter in the MCLR Reset path which detects and ignores small pulses. The MCLR pin is not driven low by any internal Resets, including the WDT. In PIC18F2420/2520/4420/4520 devices, the MCLR input can be disabled with the MCLRE configuration bit. When MCLR is disabled, the pin becomes a digital input. See Section 10.5 “PORTE, TRISE and LATE Registers” for more information. 4.3 Power-on Reset (POR) A Power-on Reset pulse is generated on-chip whenever VDD rises above a certain threshold. This allows the device to start in the initialized state when VDD is adequate for operation. To take advantage of the POR circuitry, tie the MCLR pin through a resistor (1 kΩ to 10 kΩ) to VDD. This will eliminate external RC components usually needed to create a Power-on Reset delay. A minimum rise rate for VDD is specified (parameter D004). For a slow rise time, see Figure 4-2. When the device starts normal operation (i.e., exits the Reset condition), device operating parameters (voltage, frequency, temperature, etc.) must be met to ensure operation. If these conditions are not met, the device must be held in Reset until the operating conditions are met. POR events are captured by the POR bit (RCON<1>). The state of the bit is set to ‘0’ whenever a POR occurs; it does not change for any other Reset event. POR is not reset to ‘1’ by any hardware event. To capture multiple events, the user manually resets the bit to ‘1’ in software following any POR. FIGURE 4-2: EXTERNAL POWER-ON RESET CIRCUIT (FOR SLOW VDD POWER-UP) Note 1: External Power-on Reset circuit is required only if the VDD power-up slope is too slow. The diode D helps discharge the capacitor quickly when VDD powers down. 2: R < 40 kΩ is recommended to make sure that the voltage drop across R does not violate the device’s electrical specification. 3: R1 ≥ 1 kΩ will limit any current flowing into MCLR from external capacitor C, in the event of MCLR/VPP pin breakdown, due to Electrostatic Discharge (ESD) or Electrical Overstress (EOS). C R1 D R VDD MCLR PIC18FXXXX VDD PIC18F2420/2520/4420/4520 DS39631B-page 44 Preliminary © 2007 Microchip Technology Inc. 4.4 Brown-out Reset (BOR) PIC18F2420/2520/4420/4520 devices implement a BOR circuit that provides the user with a number of configuration and power-saving options. The BOR is controlled by the BORV1:BORV0 and BOREN1:BOREN0 configuration bits. There are a total of four BOR configurations which are summarized in Table 4-1. The BOR threshold is set by the BORV1:BORV0 bits. If BOR is enabled (any values of BOREN1:BOREN0, except ‘00’), any drop of VDD below VBOR (parameter D005) for greater than TBOR (parameter 35) will reset the device. A Reset may or may not occur if VDD falls below VBOR for less than TBOR. The chip will remain in Brown-out Reset until VDD rises above VBOR. If the Power-up Timer is enabled, it will be invoked after VDD rises above VBOR; it then will keep the chip in Reset for an additional time delay, TPWRT (parameter 33). If VDD drops below VBOR while the Power-up Timer is running, the chip will go back into a Brown-out Reset and the Power-up Timer will be initialized. Once VDD rises above VBOR, the Power-up Timer will execute the additional time delay. BOR and the Power-on Timer (PWRT) are independently configured. Enabling BOR Reset does not automatically enable the PWRT. 4.4.1 SOFTWARE ENABLED BOR When BOREN1:BOREN0 = 01, the BOR can be enabled or disabled by the user in software. This is done with the control bit, SBOREN (RCON<6>). Setting SBOREN enables the BOR to function as previously described. Clearing SBOREN disables the BOR entirely. The SBOREN bit operates only in this mode; otherwise it is read as ‘0’. Placing the BOR under software control gives the user the additional flexibility of tailoring the application to its environment without having to reprogram the device to change BOR configuration. It also allows the user to tailor device power consumption in software by eliminating the incremental current that the BOR consumes. While the BOR current is typically very small, it may have some impact in low-power applications. 4.4.2 DETECTING BOR When BOR is enabled, the BOR bit always resets to ‘0’ on any BOR or POR event. This makes it difficult to determine if a BOR event has occurred just by reading the state of BOR alone. A more reliable method is to simultaneously check the state of both POR and BOR. This assumes that the POR bit is reset to ‘1’ in software immediately after any POR event. If BOR is ‘0’ while POR is ‘1’, it can be reliably assumed that a BOR event has occurred. 4.4.3 DISABLING BOR IN SLEEP MODE When BOREN1:BOREN0 = 10, the BOR remains under hardware control and operates as previously described. Whenever the device enters Sleep mode, however, the BOR is automatically disabled. When the device returns to any other operating mode, BOR is automatically re-enabled. This mode allows for applications to recover from brown-out situations, while actively executing code, when the device requires BOR protection the most. At the same time, it saves additional power in Sleep mode by eliminating the small incremental BOR current. TABLE 4-1: BOR CONFIGURATIONS Note: Even when BOR is under software control, the BOR Reset voltage level is still set by the BORV1:BORV0 configuration bits. It cannot be changed in software. BOR Configuration Status of SBOREN (RCON<6>) BOR Operation BOREN1 BOREN0 0 0 Unavailable BOR disabled; must be enabled by reprogramming the configuration bits. 0 1 Available BOR enabled in software; operation controlled by SBOREN. 1 0 Unavailable BOR enabled in hardware in Run and Idle modes, disabled during Sleep mode. 1 1 Unavailable BOR enabled in hardware; must be disabled by reprogramming the configuration bits. © 2007 Microchip Technology Inc. Preliminary DS39631B-page 45 PIC18F2420/2520/4420/4520 4.5 Device Reset Timers PIC18F2420/2520/4420/4520 devices incorporate three separate on-chip timers that help regulate the Power-on Reset process. Their main function is to ensure that the device clock is stable before code is executed. These timers are: • Power-up Timer (PWRT) • Oscillator Start-up Timer (OST) • PLL Lock Time-out 4.5.1 POWER-UP TIMER (PWRT) The Power-up Timer (PWRT) of PIC18F2420/2520/ 4420/4520 devices is an 11-bit counter which uses the INTRC source as the clock input. This yields an approximate time interval of 2048 x 32 μs = 65.6ms. While the PWRT is counting, the device is held in Reset. The power-up time delay depends on the INTRC clock and will vary from chip to chip due to temperature and process variation. See DC parameter 33 for details. The PWRT is enabled by clearing the PWRTEN configuration bit. 4.5.2 OSCILLATOR START-UP TIMER (OST) The Oscillator Start-up Timer (OST) provides a 1024 oscillator cycle (from OSC1 input) delay after the PWRT delay is over (parameter 33). This ensures that the crystal oscillator or resonator has started and stabilized. The OST time-out is invoked only for XT, LP, HS and HSPLL modes and only on Power-on Reset, or on exit from most power managed modes. 4.5.3 PLL LOCK TIME-OUT With the PLL enabled in its PLL mode, the time-out sequence following a Power-on Reset is slightly different from other oscillator modes. A separate timer is used to provide a fixed time-out that is sufficient for the PLL to lock to the main oscillator frequency. This PLL lock time-out (TPLL) is typically 2 ms and follows the oscillator start-up time-out. 4.5.4 TIME-OUT SEQUENCE On power-up, the time-out sequence is as follows: 1. After the POR pulse has cleared, PWRT time-out is invoked (if enabled). 2. Then, the OST is activated. The total time-out will vary based on oscillator configuration and the status of the PWRT. Figure 4-3, Figure 4-4, Figure 4-5, Figure 4-6 and Figure 4-7 all depict time-out sequences on power-up, with the Power-up Timer enabled and the device operating in HS Oscillator mode. Figures 4-3 through 4-6 also apply to devices operating in XT or LP modes. For devices in RC mode and with the PWRT disabled, on the other hand, there will be no time-out at all. Since the time-outs occur from the POR pulse, if MCLR is kept low long enough, all time-outs will expire. Bringing MCLR high will begin execution immediately (Figure 4-5). This is useful for testing purposes or to synchronize more than one PIC18FXXXX device operating in parallel. TABLE 4-2: TIME-OUT IN VARIOUS SITUATIONS Oscillator Configuration Power-up(2) and Brown-out Exit from PWRTEN = 0 PWRTEN = 1 Power Managed Mode HSPLL 66 ms(1) + 1024 TOSC + 2 ms(2) 1024 TOSC + 2 ms(2) 1024 TOSC + 2 ms(2) HS, XT, LP 66 ms(1) + 1024 TOSC 1024 TOSC 1024 TOSC EC, ECIO 66 ms(1) — — RC, RCIO 66 ms(1) — — INTIO1, INTIO2 66 ms(1) — — Note 1: 66 ms (65.5 ms) is the nominal Power-up Timer (PWRT) delay. 2: 2 ms is the nominal time required for the PLL to lock. PIC18F2420/2520/4420/4520 DS39631B-page 46 Preliminary © 2007 Microchip Technology Inc. FIGURE 4-3: TIME-OUT SEQUENCE ON POWER-UP (MCLR TIED TO VDD, VDD RISE < TPWRT) FIGURE 4-4: TIME-OUT SEQUENCE ON POWER-UP (MCLR NOT TIED TO VDD): CASE 1 FIGURE 4-5: TIME-OUT SEQUENCE ON POWER-UP (MCLR NOT TIED TO VDD): CASE 2 TPWRT TOST VDD MCLR INTERNAL POR PWRT TIME-OUT OST TIME-OUT INTERNAL RESET TPWRT TOST VDD MCLR INTERNAL POR PWRT TIME-OUT OST TIME-OUT INTERNAL RESET VDD MCLR INTERNAL POR PWRT TIME-OUT OST TIME-OUT INTERNAL RESET TPWRT TOST © 2007 Microchip Technology Inc. Preliminary DS39631B-page 47 PIC18F2420/2520/4420/4520 FIGURE 4-6: SLOW RISE TIME (MCLR TIED TO VDD, VDD RISE > TPWRT) FIGURE 4-7: TIME-OUT SEQUENCE ON POR W/PLL ENABLED (MCLR TIED TO VDD) VDD MCLR INTERNAL POR PWRT TIME-OUT OST TIME-OUT INTERNAL RESET 0V 5V TPWRT TOST TPWRT TOST VDD MCLR INTERNAL POR PWRT TIME-OUT OST TIME-OUT INTERNAL RESET PLL TIME-OUT TPLL Note: TOST = 1024 clock cycles. TPLL ≈ 2 ms max. First three stages of the PWRT timer. PIC18F2420/2520/4420/4520 DS39631B-page 48 Preliminary © 2007 Microchip Technology Inc. 4.6 Reset State of Registers Most registers are unaffected by a Reset. Their status is unknown on POR and unchanged by all other Resets. The other registers are forced to a “Reset state” depending on the type of Reset that occurred. Most registers are not affected by a WDT wake-up, since this is viewed as the resumption of normal operation. Status bits from the RCON register, RI, TO, PD, POR and BOR, are set or cleared differently in different Reset situations, as indicated in Table 4-3. These bits are used in software to determine the nature of the Reset. Table 4-4 describes the Reset states for all of the Special Function Registers. These are categorized by Power-on and Brown-out Resets, Master Clear and WDT Resets and WDT wake-ups. TABLE 4-3: STATUS BITS, THEIR SIGNIFICANCE AND THE INITIALIZATION CONDITION FOR RCON REGISTER Condition Program Counter RCON Register STKPTR Register SBOREN RI TO PD POR BOR STKFUL STKUNF Power-on Reset 0000h 1 1 1 1 0 0 0 0 RESET Instruction 0000h u(2) 0 u u u u u u Brown-out Reset 0000h u(2) 1 1 1 u 0 u u MCLR during Power Managed Run Modes 0000h u(2) u 1 u u u u u MCLR during Power Managed Idle Modes and Sleep Mode 0000h u(2) u 1 0 u u u u WDT Time-out during Full Power or Power Managed Run Mode 0000h u(2) u 0 u u u u u MCLR during Full Power Execution 0000h u(2) u u u u u u u Stack Full Reset (STVREN = 1) 0000h u(2) u u u u u 1 u Stack Underflow Reset (STVREN = 1) 0000h u(2) u u u u u u 1 Stack Underflow Error (not an actual Reset, STVREN = 0) 0000h u(2) u u u u u u 1 WDT Time-out during Power Managed Idle or Sleep Modes PC + 2 u(2) u 0 0 u u u u Interrupt Exit from Power Managed Modes PC + 2(1) u(2) u u 0 u u u u Legend: u = unchanged Note 1: When the wake-up is due to an interrupt and the GIEH or GIEL bits are set, the PC is loaded with the interrupt vector (008h or 0018h). 2: Reset state is ‘1’ for POR and unchanged for all other Resets when software BOR is enabled (BOREN1:BOREN0 configuration bits = 01 and SBOREN = 1). Otherwise, the Reset state is ‘0’. © 2007 Microchip Technology Inc. Preliminary DS39631B-page 49 PIC18F2420/2520/4420/4520 TABLE 4-4: INITIALIZATION CONDITIONS FOR ALL REGISTERS Register Applicable Devices Power-on Reset, Brown-out Reset MCLR Resets, WDT Reset, RESET Instruction, Stack Resets Wake-up via WDT or Interrupt TOSU 2420 2520 4420 4520 ---0 0000 ---0 0000 ---0 uuuu(3) TOSH 2420 2520 4420 4520 0000 0000 0000 0000 uuuu uuuu(3) TOSL 2420 2520 4420 4520 0000 0000 0000 0000 uuuu uuuu(3) STKPTR 2420 2520 4420 4520 00-0 0000 uu-0 0000 uu-u uuuu(3) PCLATU 2420 2520 4420 4520 ---0 0000 ---0 0000 ---u uuuu PCLATH 2420 2520 4420 4520 0000 0000 0000 0000 uuuu uuuu PCL 2420 2520 4420 4520 0000 0000 0000 0000 PC + 2(2) TBLPTRU 2420 2520 4420 4520 --00 0000 --00 0000 --uu uuuu TBLPTRH 2420 2520 4420 4520 0000 0000 0000 0000 uuuu uuuu TBLPTRL 2420 2520 4420 4520 0000 0000 0000 0000 uuuu uuuu TABLAT 2420 2520 4420 4520 0000 0000 0000 0000 uuuu uuuu PRODH 2420 2520 4420 4520 xxxx xxxx uuuu uuuu uuuu uuuu PRODL 2420 2520 4420 4520 xxxx xxxx uuuu uuuu uuuu uuuu INTCON 2420 2520 4420 4520 0000 000x 0000 000u uuuu uuuu(1) INTCON2 2420 2520 4420 4520 1111 -1-1 1111 -1-1 uuuu -u-u(1) INTCON3 2420 2520 4420 4520 11-0 0-00 11-0 0-00 uu-u u-uu(1) INDF0 2420 2520 4420 4520 N/A N/A N/A POSTINC0 2420 2520 4420 4520 N/A N/A N/A POSTDEC0 2420 2520 4420 4520 N/A N/A N/A PREINC0 2420 2520 4420 4520 N/A N/A N/A PLUSW0 2420 2520 4420 4520 N/A N/A N/A FSR0H 2420 2520 4420 4520 ---- 0000 ---- 0000 ---- uuuu FSR0L 2420 2520 4420 4520 xxxx xxxx uuuu uuuu uuuu uuuu WREG 2420 2520 4420 4520 xxxx xxxx uuuu uuuu uuuu uuuu INDF1 2420 2520 4420 4520 N/A N/A N/A POSTINC1 2420 2520 4420 4520 N/A N/A N/A POSTDEC1 2420 2520 4420 4520 N/A N/A N/A PREINC1 2420 2520 4420 4520 N/A N/A N/A PLUSW1 2420 2520 4420 4520 N/A N/A N/A Legend: u = unchanged, x = unknown, - = unimplemented bit, read as ‘0’, q = value depends on condition. Shaded cells indicate conditions do not apply for the designated device. Note 1: One or more bits in the INTCONx or PIRx registers will be affected (to cause wake-up). 2: When the wake-up is due to an interrupt and the GIEL or GIEH bit is set, the PC is loaded with the interrupt vector (0008h or 0018h). 3: When the wake-up is due to an interrupt and the GIEL or GIEH bit is set, the TOSU, TOSH and TOSL are updated with the current value of the PC. The STKPTR is modified to point to the next location in the hardware stack. 4: See Table 4-3 for Reset value for specific condition. 5: Bits 6 and 7 of PORTA, LATA and TRISA are enabled, depending on the oscillator mode selected. When not enabled as PORTA pins, they are disabled and read ‘0’. PIC18F2420/2520/4420/4520 DS39631B-page 50 Preliminary © 2007 Microchip Technology Inc. FSR1H 2420 2520 4420 4520 ---- 0000 ---- 0000 ---- uuuu FSR1L 2420 2520 4420 4520 xxxx xxxx uuuu uuuu uuuu uuuu BSR 2420 2520 4420 4520 ---- 0000 ---- 0000 ---- uuuu INDF2 2420 2520 4420 4520 N/A N/A N/A POSTINC2 2420 2520 4420 4520 N/A N/A N/A POSTDEC2 2420 2520 4420 4520 N/A N/A N/A PREINC2 2420 2520 4420 4520 N/A N/A N/A PLUSW2 2420 2520 4420 4520 N/A N/A N/A FSR2H 2420 2520 4420 4520 ---- 0000 ---- 0000 ---- uuuu FSR2L 2420 2520 4420 4520 xxxx xxxx uuuu uuuu uuuu uuuu STATUS 2420 2520 4420 4520 ---x xxxx ---u uuuu ---u uuuu TMR0H 2420 2520 4420 4520 0000 0000 0000 0000 uuuu uuuu TMR0L 2420 2520 4420 4520 xxxx xxxx uuuu uuuu uuuu uuuu T0CON 2420 2520 4420 4520 1111 1111 1111 1111 uuuu uuuu OSCCON 2420 2520 4420 4520 0100 q000 0100 q000 uuuu uuqu HLVDCON 2420 2520 4420 4520 0-00 0101 0-00 0101 u-uu uuuu WDTCON 2420 2520 4420 4520 ---- ---0 ---- ---0 ---- ---u RCON(4) 2420 2520 4420 4520 0q-1 11q0 0q-q qquu uq-u qquu TMR1H 2420 2520 4420 4520 xxxx xxxx uuuu uuuu uuuu uuuu TMR1L 2420 2520 4420 4520 xxxx xxxx uuuu uuuu uuuu uuuu T1CON 2420 2520 4420 4520 0000 0000 u0uu uuuu uuuu uuuu TMR2 2420 2520 4420 4520 0000 0000 0000 0000 uuuu uuuu PR2 2420 2520 4420 4520 1111 1111 1111 1111 1111 1111 T2CON 2420 2520 4420 4520 -000 0000 -000 0000 -uuu uuuu SSPBUF 2420 2520 4420 4520 xxxx xxxx uuuu uuuu uuuu uuuu SSPADD 2420 2520 4420 4520 0000 0000 0000 0000 uuuu uuuu SSPSTAT 2420 2520 4420 4520 0000 0000 0000 0000 uuuu uuuu SSPCON1 2420 2520 4420 4520 0000 0000 0000 0000 uuuu uuuu SSPCON2 2420 2520 4420 4520 0000 0000 0000 0000 uuuu uuuu TABLE 4-4: INITIALIZATION CONDITIONS FOR ALL REGISTERS (CONTINUED) Register Applicable Devices Power-on Reset, Brown-out Reset MCLR Resets, WDT Reset, RESET Instruction, Stack Resets Wake-up via WDT or Interrupt Legend: u = unchanged, x = unknown, - = unimplemented bit, read as ‘0’, q = value depends on condition. Shaded cells indicate conditions do not apply for the designated device. Note 1: One or more bits in the INTCONx or PIRx registers will be affected (to cause wake-up). 2: When the wake-up is due to an interrupt and the GIEL or GIEH bit is set, the PC is loaded with the interrupt vector (0008h or 0018h). 3: When the wake-up is due to an interrupt and the GIEL or GIEH bit is set, the TOSU, TOSH and TOSL are updated with the current value of the PC. The STKPTR is modified to point to the next location in the hardware stack. 4: See Table 4-3 for Reset value for specific condition. 5: Bits 6 and 7 of PORTA, LATA and TRISA are enabled, depending on the oscillator mode selected. When not enabled as PORTA pins, they are disabled and read ‘0’. © 2007 Microchip Technology Inc. Preliminary DS39631B-page 51 PIC18F2420/2520/4420/4520 ADRESH 2420 2520 4420 4520 xxxx xxxx uuuu uuuu uuuu uuuu ADRESL 2420 2520 4420 4520 xxxx xxxx uuuu uuuu uuuu uuuu ADCON0 2420 2520 4420 4520 --00 0000 --00 0000 --uu uuuu ADCON1 2420 2520 4420 4520 --00 0qqq --00 0qqq --uu uuuu ADCON2 2420 2520 4420 4520 0-00 0000 0-00 0000 u-uu uuuu CCPR1H 2420 2520 4420 4520 xxxx xxxx uuuu uuuu uuuu uuuu CCPR1L 2420 2520 4420 4520 xxxx xxxx uuuu uuuu uuuu uuuu CCP1CON 2420 2520 4420 4520 0000 0000 0000 0000 uuuu uuuu 2420 2520 4420 4520 --00 0000 --00 0000 --uu uuuu CCPR2H 2420 2520 4420 4520 xxxx xxxx uuuu uuuu uuuu uuuu CCPR2L 2420 2520 4420 4520 xxxx xxxx uuuu uuuu uuuu uuuu CCP2CON 2420 2520 4420 4520 --00 0000 --00 0000 --uu uuuu BAUDCON 2420 2520 4420 4520 01-0 0-00 01-0 0-00 --uu uuuu PWM1CON 2420 2520 4420 4520 0000 0000 0000 0000 uuuu uuuu ECCP1AS 2420 2520 4420 4520 0000 0000 0000 0000 uuuu uuuu 2420 2520 4420 4520 0000 00-- 0000 00-- uuuu uu-- CVRCON 2420 2520 4420 4520 0000 0000 0000 0000 uuuu uuuu CMCON 2420 2520 4420 4520 0000 0111 0000 0111 uuuu uuuu TMR3H 2420 2520 4420 4520 xxxx xxxx uuuu uuuu uuuu uuuu TMR3L 2420 2520 4420 4520 xxxx xxxx uuuu uuuu uuuu uuuu T3CON 2420 2520 4420 4520 0000 0000 uuuu uuuu uuuu uuuu SPBRGH 2420 2520 4420 4520 0000 0000 0000 0000 uuuu uuuu SPBRG 2420 2520 4420 4520 0000 0000 0000 0000 uuuu uuuu RCREG 2420 2520 4420 4520 0000 0000 0000 0000 uuuu uuuu TXREG 2420 2520 4420 4520 0000 0000 0000 0000 uuuu uuuu TXSTA 2420 2520 4420 4520 0000 0010 0000 0010 uuuu uuuu RCSTA 2420 2520 4420 4520 0000 000x 0000 000x uuuu uuuu EEADR 2420 2520 4420 4520 0000 0000 0000 0000 uuuu uuuu EEDATA 2420 2520 4420 4520 0000 0000 0000 0000 uuuu uuuu EECON2 2420 2520 4420 4520 0000 0000 0000 0000 0000 0000 EECON1 2420 2520 4420 4520 xx-0 x000 uu-0 u000 uu-0 u000 TABLE 4-4: INITIALIZATION CONDITIONS FOR ALL REGISTERS (CONTINUED) Register Applicable Devices Power-on Reset, Brown-out Reset MCLR Resets, WDT Reset, RESET Instruction, Stack Resets Wake-up via WDT or Interrupt Legend: u = unchanged, x = unknown, - = unimplemented bit, read as ‘0’, q = value depends on condition. Shaded cells indicate conditions do not apply for the designated device. Note 1: One or more bits in the INTCONx or PIRx registers will be affected (to cause wake-up). 2: When the wake-up is due to an interrupt and the GIEL or GIEH bit is set, the PC is loaded with the interrupt vector (0008h or 0018h). 3: When the wake-up is due to an interrupt and the GIEL or GIEH bit is set, the TOSU, TOSH and TOSL are updated with the current value of the PC. The STKPTR is modified to point to the next location in the hardware stack. 4: See Table 4-3 for Reset value for specific condition. 5: Bits 6 and 7 of PORTA, LATA and TRISA are enabled, depending on the oscillator mode selected. When not enabled as PORTA pins, they are disabled and read ‘0’. PIC18F2420/2520/4420/4520 DS39631B-page 52 Preliminary © 2007 Microchip Technology Inc. IPR2 2420 2520 4420 4520 11-1 1111 11-1 1111 uu-u uuuu PIR2 2420 2520 4420 4520 00-0 0000 00-0 0000 uu-u uuuu(1) PIE2 2420 2520 4420 4520 00-0 0000 00-0 0000 uu-u uuuu IPR1 2420 2520 4420 4520 1111 1111 1111 1111 uuuu uuuu 2420 2520 4420 4520 -111 1111 -111 1111 -uuu uuuu PIR1 2420 2520 4420 4520 0000 0000 0000 0000 uuuu uuuu(1) 2420 2520 4420 4520 -000 0000 -000 0000 -uuu uuuu(1) PIE1 2420 2520 4420 4520 0000 0000 0000 0000 uuuu uuuu 2420 2520 4420 4520 -000 0000 -000 0000 -uuu uuuu OSCTUNE 2420 2520 4420 4520 00-0 0000 00-0 0000 uu-u uuuu TRISE 2420 2520 4420 4520 0000 -111 0000 -111 uuuu -uuu TRISD 2420 2520 4420 4520 1111 1111 1111 1111 uuuu uuuu TRISC 2420 2520 4420 4520 1111 1111 1111 1111 uuuu uuuu TRISB 2420 2520 4420 4520 1111 1111 1111 1111 uuuu uuuu TRISA(5) 2420 2520 4420 4520 1111 1111(5) 1111 1111(5) uuuu uuuu(5) LATE 2420 2520 4420 4520 ---- -xxx ---- -uuu ---- -uuu LATD 2420 2520 4420 4520 xxxx xxxx uuuu uuuu uuuu uuuu LATC 2420 2520 4420 4520 xxxx xxxx uuuu uuuu uuuu uuuu LATB 2420 2520 4420 4520 xxxx xxxx uuuu uuuu uuuu uuuu LATA(5) 2420 2520 4420 4520 xxxx xxxx(5) uuuu uuuu(5) uuuu uuuu(5) PORTE 2420 2520 4420 4520 ---- xxxx ---- uuuu ---- uuuu PORTD 2420 2520 4420 4520 xxxx xxxx uuuu uuuu uuuu uuuu PORTC 2420 2520 4420 4520 xxxx xxxx uuuu uuuu uuuu uuuu PORTB 2420 2520 4420 4520 xxxx xxxx uuuu uuuu uuuu uuuu PORTA(5) 2420 2520 4420 4520 xx0x 0000(5) uu0u 0000(5) uuuu uuuu(5) TABLE 4-4: INITIALIZATION CONDITIONS FOR ALL REGISTERS (CONTINUED) Register Applicable Devices Power-on Reset, Brown-out Reset MCLR Resets, WDT Reset, RESET Instruction, Stack Resets Wake-up via WDT or Interrupt Legend: u = unchanged, x = unknown, - = unimplemented bit, read as ‘0’, q = value depends on condition. Shaded cells indicate conditions do not apply for the designated device. Note 1: One or more bits in the INTCONx or PIRx registers will be affected (to cause wake-up). 2: When the wake-up is due to an interrupt and the GIEL or GIEH bit is set, the PC is loaded with the interrupt vector (0008h or 0018h). 3: When the wake-up is due to an interrupt and the GIEL or GIEH bit is set, the TOSU, TOSH and TOSL are updated with the current value of the PC. The STKPTR is modified to point to the next location in the hardware stack. 4: See Table 4-3 for Reset value for specific condition. 5: Bits 6 and 7 of PORTA, LATA and TRISA are enabled, depending on the oscillator mode selected. When not enabled as PORTA pins, they are disabled and read ‘0’. © 2007 Microchip Technology Inc. Preliminary DS39631B-page 53 PIC18F2420/2520/4420/4520 5.0 MEMORY ORGANIZATION There are three types of memory in PIC18 Enhanced microcontroller devices: • Program Memory • Data RAM • Data EEPROM As Harvard architecture devices, the data and program memories use separate busses; this allows for concurrent access of the two memory spaces. The data EEPROM, for practical purposes, can be regarded as a peripheral device, since it is addressed and accessed through a set of control registers. Additional detailed information on the operation of the Flash program memory is provided in Section 6.0 “Flash Program Memory”. Data EEPROM is discussed separately in Section 7.0 “Data EEPROM Memory”. 5.1 Program Memory Organization PIC18 microcontrollers implement a 21-bit program counter, which is capable of addressing a 2-Mbyte program memory space. Accessing a location between the upper boundary of the physically implemented memory and the 2-Mbyte address will return all ‘0’s (a NOP instruction). The PIC18F2420 and PIC18F4420 each have 16 Kbytes of Flash memory and can store up to 8,192 single-word instructions. The PIC18F2520 and PIC18F4520 each have 32 Kbytes of Flash memory and can store up to 16,384 single-word instructions. PIC18 devices have two interrupt vectors. The Reset vector address is at 0000h and the interrupt vector addresses are at 0008h and 0018h. The program memory map for PIC18F2420/2520/ 4420/4520 devices is shown in Figure 5-1. FIGURE 5-1: PROGRAM MEMORY MAP AND STACK FOR PIC18F2420/2520/4420/4520 DEVICES PC<20:0> Stack Level 1 • Stack Level 31 Reset Vector Low Priority Interrupt Vector •• CALL,RCALL,RETURN RETFIE,RETLW 21 0000h 0018h On-Chip Program Memory High Priority Interrupt Vector 0008h User Memory Space 1FFFFFh 4000h 3FFFh Read ‘0’ 200000h PIC18FX4X0 PIC18FX5X0 8000h 7FFFh On-Chip Program Memory Read ‘0’ PIC18F2420/2520/4420/4520 DS39631B-page 54 Preliminary © 2007 Microchip Technology Inc. 5.1.1 PROGRAM COUNTER The Program Counter (PC) specifies the address of the instruction to fetch for execution. The PC is 21 bits wide and is contained in three separate 8-bit registers. The low byte, known as the PCL register, is both readable and writable. The high byte, or PCH register, contains the PC<15:8> bits; it is not directly readable or writable. Updates to the PCH register are performed through the PCLATH register. The upper byte is called PCU. This register contains the PC<20:16> bits; it is also not directly readable or writable. Updates to the PCU register are performed through the PCLATU register. The contents of PCLATH and PCLATU are transferred to the program counter by any operation that writes PCL. Similarly, the upper two bytes of the program counter are transferred to PCLATH and PCLATU by an operation that reads PCL. This is useful for computed offsets to the PC (see Section 5.1.4.1 “Computed GOTO”). The PC addresses bytes in the program memory. To prevent the PC from becoming misaligned with word instructions, the Least Significant bit of PCL is fixed to a value of ‘0’. The PC increments by 2 to address sequential instructions in the program memory. The CALL, RCALL, GOTO and program branch instructions write to the program counter directly. For these instructions, the contents of PCLATH and PCLATU are not transferred to the program counter. 5.1.2 RETURN ADDRESS STACK The return address stack allows any combination of up to 31 program calls and interrupts to occur. The PC is pushed onto the stack when a CALL or RCALL instruction is executed or an interrupt is Acknowledged. The PC value is pulled off the stack on a RETURN, RETLW or a RETFIE instruction. PCLATU and PCLATH are not affected by any of the RETURN or CALL instructions. The stack operates as a 31-word by 21-bit RAM and a 5-bit stack pointer, STKPTR. The stack space is not part of either program or data space. The stack pointer is readable and writable and the address on the top of the stack is readable and writable through the top-ofstack Special File Registers. Data can also be pushed to, or popped from the stack, using these registers. A CALL type instruction causes a push onto the stack; the stack pointer is first incremented and the location pointed to by the stack pointer is written with the contents of the PC (already pointing to the instruction following the CALL). A RETURN type instruction causes a pop from the stack; the contents of the location pointed to by the STKPTR are transferred to the PC and then the stack pointer is decremented. The stack pointer is initialized to ‘00000’ after all Resets. There is no RAM associated with the location corresponding to a stack pointer value of ‘00000’; this is only a Reset value. Status bits indicate if the stack is full or has overflowed or has underflowed. 5.1.2.1 Top-of-Stack Access Only the top of the return address stack (TOS) is readable and writable. A set of three registers, TOSU:TOSH:TOSL, hold the contents of the stack location pointed to by the STKPTR register (Figure 5-2). This allows users to implement a software stack if necessary. After a CALL, RCALL or interrupt, the software can read the pushed value by reading the TOSU:TOSH:TOSL registers. These values can be placed on a user defined software stack. At return time, the software can return these values to TOSU:TOSH:TOSL and do a return. The user must disable the global interrupt enable bits while accessing the stack to prevent inadvertent stack corruption. FIGURE 5-2: RETURN ADDRESS STACK AND ASSOCIATED REGISTERS 00011 001A34h 11111 11110 11101 00010 00001 00000 00010 Return Address Stack <20:0> Top-of-Stack 000D58h TOSU TOSH TOSL 00h 1Ah 34h STKPTR<4:0> Top-of-Stack Registers Stack Pointer © 2007 Microchip Technology Inc. Preliminary DS39631B-page 55 PIC18F2420/2520/4420/4520 5.1.2.2 Return Stack Pointer (STKPTR) The STKPTR register (Register 5-1) contains the stack pointer value, the STKFUL (stack full) status bit and the STKUNF (stack underflow) status bits. The value of the stack pointer can be 0 through 31. The stack pointer increments before values are pushed onto the stack and decrements after values are popped off the stack. On Reset, the stack pointer value will be zero. The user may read and write the stack pointer value. This feature can be used by a Real-Time Operating System (RTOS) for return stack maintenance. After the PC is pushed onto the stack 31 times (without popping any values off the stack), the STKFUL bit is set. The STKFUL bit is cleared by software or by a POR. The action that takes place when the stack becomes full depends on the state of the STVREN (Stack Overflow Reset Enable) configuration bit. (Refer to Section 23.1 “Configuration Bits” for a description of the device configuration bits.) If STVREN is set (default), the 31st push will push the (PC + 2) value onto the stack, set the STKFUL bit and reset the device. The STKFUL bit will remain set and the stack pointer will be set to zero. If STVREN is cleared, the STKFUL bit will be set on the 31st push and the stack pointer will increment to 31. Any additional pushes will not overwrite the 31st push and STKPTR will remain at 31. When the stack has been popped enough times to unload the stack, the next pop will return a value of zero to the PC and sets the STKUNF bit, while the stack pointer remains at zero. The STKUNF bit will remain set until cleared by software or until a POR occurs. 5.1.2.3 PUSH and POP Instructions Since the Top-of-Stack is readable and writable, the ability to push values onto the stack and pull values off the stack without disturbing normal program execution is a desirable feature. The PIC18 instruction set includes two instructions, PUSH and POP, that permit the TOS to be manipulated under software control. TOSU, TOSH and TOSL can be modified to place data or a return address on the stack. The PUSH instruction places the current PC value onto the stack. This increments the stack pointer and loads the current PC value onto the stack. The POP instruction discards the current TOS by decrementing the stack pointer. The previous value pushed onto the stack then becomes the TOS value. REGISTER 5-1: STKPTR REGISTER Note: Returning a value of zero to the PC on an underflow has the effect of vectoring the program to the Reset vector, where the stack conditions can be verified and appropriate actions can be taken. This is not the same as a Reset, as the contents of the SFRs are not affected. R/C-0 R/C-0 U-0 R/W-0 R/W-0 R/W-0 R/W-0 R/W-0 STKFUL(1) STKUNF(1) — SP4 SP3 SP2 SP1 SP0 bit 7 bit 0 bit 7 STKFUL: Stack Full Flag bit(1) 1 = Stack became full or overflowed 0 = Stack has not become full or overflowed bit 6 STKUNF: Stack Underflow Flag bit(1) 1 = Stack underflow occurred 0 = Stack underflow did not occur bit 5 Unimplemented: Read as ‘0’ bit 4-0 SP4:SP0: Stack Pointer Location bits Note 1: Bit 7 and bit 6 are cleared by user software or by a POR. Legend: R = Readable bit W = Writable bit U = Unimplemented C = Clearable only bit -n = Value at POR ‘1’ = Bit is set ‘0’ = Bit is cleared x = Bit is unknown PIC18F2420/2520/4420/4520 DS39631B-page 56 Preliminary © 2007 Microchip Technology Inc. 5.1.2.4 Stack Full and Underflow Resets Device Resets on stack overflow and stack underflow conditions are enabled by setting the STVREN bit in Configuration Register 4L. When STVREN is set, a full or underflow will set the appropriate STKFUL or STKUNF bit and then cause a device Reset. When STVREN is cleared, a full or underflow condition will set the appropriate STKFUL or STKUNF bit but not cause a device Reset. The STKFUL or STKUNF bits are cleared by the user software or a Power-on Reset. 5.1.3 FAST REGISTER STACK A fast register stack is provided for the Status, WREG and BSR registers, to provide a “fast return” option for interrupts. The stack for each register is only one level deep and is neither readable nor writable. It is loaded with the current value of the corresponding register when the processor vectors for an interrupt. All interrupt sources will push values into the stack registers. The values in the registers are then loaded back into their associated registers if the RETFIE, FAST instruction is used to return from the interrupt. If both low and high priority interrupts are enabled, the stack registers cannot be used reliably to return from low priority interrupts. If a high priority interrupt occurs while servicing a low priority interrupt, the stack register values stored by the low priority interrupt will be overwritten. In these cases, users must save the key registers in software during a low priority interrupt. If interrupt priority is not used, all interrupts may use the fast register stack for returns from interrupt. If no interrupts are used, the fast register stack can be used to restore the Status, WREG and BSR registers at the end of a subroutine call. To use the fast register stack for a subroutine call, a CALL label, FAST instruction must be executed to save the Status, WREG and BSR registers to the fast register stack. A RETURN, FAST instruction is then executed to restore these registers from the fast register stack. Example 5-1 shows a source code example that uses the fast register stack during a subroutine call and return. EXAMPLE 5-1: FAST REGISTER STACK CODE EXAMPLE 5.1.4 LOOK-UP TABLES IN PROGRAM MEMORY There may be programming situations that require the creation of data structures, or look-up tables, in program memory. For PIC18 devices, look-up tables can be implemented in two ways: • Computed GOTO • Table Reads 5.1.4.1 Computed GOTO A computed GOTO is accomplished by adding an offset to the program counter. An example is shown in Example 5-2. A look-up table can be formed with an ADDWF PCL instruction and a group of RETLW nn instructions. The W register is loaded with an offset into the table before executing a call to that table. The first instruction of the called routine is the ADDWF PCL instruction. The next instruction executed will be one of the RETLW nn instructions that returns the value ‘nn’ to the calling function. The offset value (in WREG) specifies the number of bytes that the program counter should advance and should be multiples of 2 (LSb = 0). In this method, only one data byte may be stored in each instruction location and room on the return address stack is required. EXAMPLE 5-2: COMPUTED GOTO USING AN OFFSET VALUE 5.1.4.2 Table Reads and Table Writes A better method of storing data in program memory allows two bytes of data to be stored in each instruction location. Look-up table data may be stored two bytes per program word by using table reads and writes. The Table Pointer (TBLPTR) register specifies the byte address and the Table Latch (TABLAT) register contains the data that is read from or written to program memory. Data is transferred to or from program memory one byte at a time. Table read and table write operations are discussed further in Section 6.1 “Table Reads and Table Writes”. CALL SUB1, FAST ;STATUS, WREG, BSR ;SAVED IN FAST REGISTER ;STACK •• SUB1 •• RETURN, FAST ;RESTORE VALUES SAVED ;IN FAST REGISTER STACK MOVF OFFSET, W CALL TABLE ORG nn00h TABLE ADDWF PCL RETLW nnh RETLW nnh RETLW nnh . . . © 2007 Microchip Technology Inc. Preliminary DS39631B-page 57 PIC18F2420/2520/4420/4520 5.2 PIC18 Instruction Cycle 5.2.1 CLOCKING SCHEME The microcontroller clock input, whether from an internal or external source, is internally divided by four to generate four non-overlapping quadrature clocks (Q1, Q2, Q3 and Q4). Internally, the program counter is incremented on every Q1; the instruction is fetched from the program memory and latched into the instruction register during Q4. The instruction is decoded and executed during the following Q1 through Q4. The clocks and instruction execution flow are shown in Figure 5-3. 5.2.2 INSTRUCTION FLOW/PIPELINING An “Instruction Cycle” consists of four Q cycles: Q1 through Q4. The instruction fetch and execute are pipelined in such a manner that a fetch takes one instruction cycle, while the decode and execute take another instruction cycle. However, due to the pipelining, each instruction effectively executes in one cycle. If an instruction causes the program counter to change (e.g., GOTO), then two cycles are required to complete the instruction (Example 5-3). A fetch cycle begins with the Program Counter (PC) incrementing in Q1. In the execution cycle, the fetched instruction is latched into the Instruction Register (IR) in cycle Q1. This instruction is then decoded and executed during the Q2, Q3 and Q4 cycles. Data memory is read during Q2 (operand read) and written during Q4 (destination write). FIGURE 5-3: CLOCK/INSTRUCTION CYCLE EXAMPLE 5-3: INSTRUCTION PIPELINE FLOW Q1 Q2 Q3 Q4 Q1 Q2 Q3 Q4 Q1 Q2 Q3 Q4 OSC1 Q1 Q2 Q3 Q4 PC OSC2/CLKO (RC mode) PC PC + 2 PC + 4 Fetch INST (PC) Execute INST (PC – 2) Fetch INST (PC + 2) Execute INST (PC) Fetch INST (PC + 4) Execute INST (PC + 2) Internal Phase Clock All instructions are single cycle, except for any program branches. These take two cycles since the fetch instruction is “flushed” from the pipeline while the new instruction is being fetched and then executed. TCY0 TCY1 TCY2 TCY3 TCY4 TCY5 1. MOVLW 55h Fetch 1 Execute 1 2. MOVWF PORTB Fetch 2 Execute 2 3. BRA SUB_1 Fetch 3 Execute 3 4. BSF PORTA, BIT3 (Forced NOP) Fetch 4 Flush (NOP) 5. Instruction @ address SUB_1 Fetch SUB_1 Execute SUB_1 PIC18F2420/2520/4420/4520 DS39631B-page 58 Preliminary © 2007 Microchip Technology Inc. 5.2.3 INSTRUCTIONS IN PROGRAM MEMORY The program memory is addressed in bytes. Instructions are stored as two bytes or four bytes in program memory. The Least Significant Byte of an instruction word is always stored in a program memory location with an even address (LSb = 0). To maintain alignment with instruction boundaries, the PC increments in steps of 2 and the LSb will always read ‘0’ (see Section 5.1.1 “Program Counter”). Figure 5-4 shows an example of how instruction words are stored in the program memory. The CALL and GOTO instructions have the absolute program memory address embedded into the instruction. Since instructions are always stored on word boundaries, the data contained in the instruction is a word address. The word address is written to PC<20:1>, which accesses the desired byte address in program memory. Instruction #2 in Figure 5-4 shows how the instruction GOTO 0006h is encoded in the program memory. Program branch instructions, which encode a relative address offset, operate in the same manner. The offset value stored in a branch instruction represents the number of single-word instructions that the PC will be offset by. Section 24.0 “Instruction Set Summary” provides further details of the instruction set. FIGURE 5-4: INSTRUCTIONS IN PROGRAM MEMORY 5.2.4 TWO-WORD INSTRUCTIONS The standard PIC18 instruction set has four two-word instructions: CALL, MOVFF, GOTO and LSFR. In all cases, the second word of the instructions always has ‘1111’ as its four Most Significant bits; the other 12 bits are literal data, usually a data memory address. The use of ‘1111’ in the 4 MSbs of an instruction specifies a special form of NOP. If the instruction is executed in proper sequence – immediately after the first word – the data in the second word is accessed and used by the instruction sequence. If the first word is skipped for some reason and the second word is executed by itself, a NOP is executed instead. This is necessary for cases when the two-word instruction is preceded by a conditional instruction that changes the PC. Example 5-4 shows how this works. EXAMPLE 5-4: TWO-WORD INSTRUCTIONS Word Address LSB = 1 LSB = 0 ↓ Program Memory Byte Locations → 000000h 000002h 000004h 000006h Instruction 1: MOVLW 055h 0Fh 55h 000008h Instruction 2: GOTO 0006h EFh 03h 00000Ah F0h 00h 00000Ch Instruction 3: MOVFF 123h, 456h C1h 23h 00000Eh F4h 56h 000010h 000012h 000014h Note: See Section 5.6 “PIC18 Instruction Execution and the Extended Instruction Set” for information on two-word instructions in the extended instruction set. CASE 1: Object Code Source Code 0110 0110 0000 0000 TSTFSZ REG1 ; is RAM location 0? 1100 0001 0010 0011 MOVFF REG1, REG2 ; No, skip this word 1111 0100 0101 0110 ; Execute this word as a NOP 0010 0100 0000 0000 ADDWF REG3 ; continue code CASE 2: Object Code Source Code 0110 0110 0000 0000 TSTFSZ REG1 ; is RAM location 0? 1100 0001 0010 0011 MOVFF REG1, REG2 ; Yes, execute this word 1111 0100 0101 0110 ; 2nd word of instruction 0010 0100 0000 0000 ADDWF REG3 ; continue code © 2007 Microchip Technology Inc. Preliminary DS39631B-page 59 PIC18F2420/2520/4420/4520 5.3 Data Memory Organization The data memory in PIC18 devices is implemented as static RAM. Each register in the data memory has a 12-bit address, allowing up to 4096 bytes of data memory. The memory space is divided into as many as 16 banks that contain 256 bytes each; PIC18F2420/ 2520/4420/4520 devices implement all 16 banks. Figure 5-5 shows the data memory organization for the PIC18F2420/2520/4420/4520 devices. The data memory contains Special Function Registers (SFRs) and General Purpose Registers (GPRs). The SFRs are used for control and status of the controller and peripheral functions, while GPRs are used for data storage and scratchpad operations in the user’s application. Any read of an unimplemented location will read as ‘0’s. The instruction set and architecture allow operations across all banks. The entire data memory may be accessed by Direct, Indirect or Indexed Addressing modes. Addressing modes are discussed later in this subsection. To ensure that commonly used registers (SFRs and select GPRs) can be accessed in a single cycle, PIC18 devices implement an Access Bank. This is a 256-byte memory space that provides fast access to SFRs and the lower portion of GPR Bank 0 without using the BSR. Section 5.3.2 “Access Bank” provides a detailed description of the Access RAM. 5.3.1 BANK SELECT REGISTER (BSR) Large areas of data memory require an efficient addressing scheme to make rapid access to any address possible. Ideally, this means that an entire address does not need to be provided for each read or write operation. For PIC18 devices, this is accomplished with a RAM banking scheme. This divides the memory space into 16 contiguous banks of 256 bytes. Depending on the instruction, each location can be addressed directly by its full 12-bit address, or an 8-bit low-order address and a 4-bit bank pointer. Most instructions in the PIC18 instruction set make use of the bank pointer, known as the Bank Select Register (BSR). This SFR holds the 4 Most Significant bits of a location’s address; the instruction itself includes the 8 Least Significant bits. Only the four lower bits of the BSR are implemented (BSR3:BSR0). The upper four bits are unused; they will always read ‘0’ and cannot be written to. The BSR can be loaded directly by using the MOVLB instruction. The value of the BSR indicates the bank in data memory; the 8 bits in the instruction show the location in the bank and can be thought of as an offset from the bank’s lower boundary. The relationship between the BSR’s value and the bank division in data memory is shown in Figure 5-7. Since up to 16 registers may share the same low-order address, the user must always be careful to ensure that the proper bank is selected before performing a data read or write. For example, writing what should be program data to an 8-bit address of F9h while the BSR is 0Fh will end up resetting the program counter. While any bank can be selected, only those banks that are actually implemented can be read or written to. Writes to unimplemented banks are ignored, while reads from unimplemented banks will return ‘0’s. Even so, the Status register will still be affected as if the operation was successful. The data memory map in Figure 5-5 indicates which banks are implemented. In the core PIC18 instruction set, only the MOVFF instruction fully specifies the 12-bit address of the source and target registers. This instruction ignores the BSR completely when it executes. All other instructions include only the low-order address as an operand and must use either the BSR or the Access Bank to locate their target registers. Note: The operation of some aspects of data memory are changed when the PIC18 extended instruction set is enabled. See Section 5.5 “Data Memory and the Extended Instruction Set” for more information. PIC18F2420/2520/4420/4520 DS39631B-page 60 Preliminary © 2007 Microchip Technology Inc. FIGURE 5-5: DATA MEMORY MAP FOR PIC18F2420/4420 DEVICES Bank 0 Bank 1 Bank 14 Bank 15 BSR<3:0> Data Memory Map = 0000 = 0001 = 1111 080h 07Fh F80h FFFh 00h 7Fh 80h FFh Access Bank When ‘a’ = 0: The BSR is ignored and the Access Bank is used. The first 128 bytes are general purpose RAM (from Bank 0). The second 128 bytes are Special Function Registers (from Bank 15). When ‘a’ = 1: The BSR specifies the Bank used by the instruction. F7Fh F00h EFFh 1FFh 100h 0FFh Access RAM 000h FFh 00h FFh 00h FFh 00h GPR GPR SFR Access RAM High Access RAM Low Bank 2 = 0110 = 0010 (SFRs) 2FFh 200h 3FFh 300h 4FFh 400h 5FFh 500h 6FFh 600h 7FFh 700h 8FFh 800h 9FFh 900h AFFh A00h BFFh B00h CFFh C00h DFFh D00h E00h Bank 3 Bank 4 Bank 5 Bank 6 Bank 7 Bank 8 Bank 9 Bank 10 Bank 11 Bank 12 Bank 13 FFh 00h FFh 00h FFh 00h FFh 00h FFh 00h FFh 00h FFh 00h FFh 00h FFh 00h FFh 00h FFh 00h FFh 00h GPR FFh 00h = 0011 = 0100 = 0101 = 0111 = 1000 = 1001 = 1010 = 1011 = 1100 = 1101 = 1110 Unused Read 00h Unused © 2007 Microchip Technology Inc. Preliminary DS39631B-page 61 PIC18F2420/2520/4420/4520 FIGURE 5-6: DATA MEMORY MAP FOR PIC18F2520/4520 DEVICES Bank 0 Bank 1 Bank 14 Bank 15 BSR<3:0> Data Memory Map = 0000 = 0001 = 1111 080h 07Fh F80h FFFh 00h 7Fh 80h FFh Access Bank When ‘a’ = 0: The BSR is ignored and the Access Bank is used. The first 128 bytes are general purpose RAM (from Bank 0). The second 128 bytes are Special Function Registers (from Bank 15). When ‘a’ = 1: The BSR specifies the Bank used by the instruction. F7Fh F00h EFFh 1FFh 100h 0FFh Access RAM 000h FFh 00h FFh 00h FFh 00h GPR GPR SFR Access RAM High Access RAM Low Bank 2 = 0110 = 0010 (SFRs) 2FFh 200h 3FFh 300h 4FFh 400h 5FFh 500h 6FFh 600h 7FFh 700h 8FFh 800h 9FFh 900h AFFh A00h BFFh B00h CFFh C00h DFFh D00h E00h Bank 3 Bank 4 Bank 5 Bank 6 Bank 7 Bank 8 Bank 9 Bank 10 Bank 11 Bank 12 Bank 13 FFh 00h FFh 00h FFh 00h FFh 00h FFh 00h FFh 00h FFh 00h FFh 00h FFh 00h FFh 00h FFh 00h FFh 00h GPR FFh 00h = 0011 = 0100 = 0101 = 0111 = 1000 = 1001 = 1010 = 1011 = 1100 = 1101 = 1110 Unused Read 00h Unused GPR GPR GPR PIC18F2420/2520/4420/4520 DS39631B-page 62 Preliminary © 2007 Microchip Technology Inc. FIGURE 5-7: USE OF THE BANK SELECT REGISTER (DIRECT ADDRESSING) 5.3.2 ACCESS BANK While the use of the BSR with an embedded 8-bit address allows users to address the entire range of data memory, it also means that the user must always ensure that the correct bank is selected. Otherwise, data may be read from or written to the wrong location. This can be disastrous if a GPR is the intended target of an operation, but an SFR is written to instead. Verifying and/or changing the BSR for each read or write to data memory can become very inefficient. To streamline access for the most commonly used data memory locations, the data memory is configured with an Access Bank, which allows users to access a mapped block of memory without specifying a BSR. The Access Bank consists of the first 128 bytes of memory (00h-7Fh) in Bank 0 and the last 128 bytes of memory (80h-FFh) in Block 15. The lower half is known as the “Access RAM” and is composed of GPRs. This upper half is also where the device’s SFRs are mapped. These two areas are mapped contiguously in the Access Bank and can be addressed in a linear fashion by an 8-bit address (Figure 5-5). The Access Bank is used by core PIC18 instructions that include the Access RAM bit (the ‘a’ parameter in the instruction). When ‘a’ is equal to ‘1’, the instruction uses the BSR and the 8-bit address included in the opcode for the data memory address. When ‘a’ is ‘0’, however, the instruction is forced to use the Access Bank address map; the current value of the BSR is ignored entirely. Using this “forced” addressing allows the instruction to operate on a data address in a single cycle, without updating the BSR first. For 8-bit addresses of 80h and above, this means that users can evaluate and operate on SFRs more efficiently. The Access RAM below 80h is a good place for data values that the user might need to access rapidly, such as immediate computational results or common program variables. Access RAM also allows for faster and more code efficient context saving and switching of variables. The mapping of the Access Bank is slightly different when the extended instruction set is enabled (XINST configuration bit = 1). This is discussed in more detail in Section 5.5.3 “Mapping the Access Bank in Indexed Literal Offset Mode”. 5.3.3 GENERAL PURPOSE REGISTER FILE PIC18 devices may have banked memory in the GPR area. This is data RAM, which is available for use by all instructions. GPRs start at the bottom of Bank 0 (address 000h) and grow upwards towards the bottom of the SFR area. GPRs are not initialized by a Power-on Reset and are unchanged on all other Resets. Note 1: The Access RAM bit of the instruction can be used to force an override of the selected bank (BSR<3:0>) to the registers of the Access Bank. 2: The MOVFF instruction embeds the entire 12-bit address in the instruction. Data Memory Bank Select(2) 7 0 From Opcode(2) 0 0 0 0 000h 100h 200h 300h F00h E00h FFFh Bank 0 Bank 1 Bank 2 Bank 14 Bank 15 00h FFh 00h FFh 00h FFh 00h FFh 00h FFh 00h FFh Bank 3 through Bank 13 0 0 1 1 1 1 1 1 1 1 1 1 7 0 BSR(1) © 2007 Microchip Technology Inc. Preliminary DS39631B-page 63 PIC18F2420/2520/4420/4520 5.3.4 SPECIAL FUNCTION REGISTERS The Special Function Registers (SFRs) are registers used by the CPU and peripheral modules for controlling the desired operation of the device. These registers are implemented as static RAM. SFRs start at the top of data memory (FFFh) and extend downward to occupy the top half of Bank 15 (F80h to FFFh). A list of these registers is given in Table 5-1 and Table 5-2. The SFRs can be classified into two sets: those associated with the “core” device functionality (ALU, Resets and interrupts) and those related to the peripheral functions. The reset and interrupt registers are described in their respective chapters, while the ALU’s Status register is described later in this section. Registers related to the operation of a peripheral feature are described in the chapter for that peripheral. The SFRs are typically distributed among the peripherals whose functions they control. Unused SFR locations are unimplemented and read as ‘0’s. TABLE 5-1: SPECIAL FUNCTION REGISTER MAP FOR PIC18F2420/2520/4420/4520 DEVICES Address Name Address Name Address Name Address Name FFFh TOSU FDFh INDF2(1) FBFh CCPR1H F9Fh IPR1 FFEh TOSH FDEh POSTINC2(1) FBEh CCPR1L F9Eh PIR1 FFDh TOSL FDDh POSTDEC2(1) FBDh CCP1CON F9Dh PIE1 FFCh STKPTR FDCh PREINC2(1) FBCh CCPR2H F9Ch —(2) FFBh PCLATU FDBh PLUSW2(1) FBBh CCPR2L F9Bh OSCTUNE FFAh PCLATH FDAh FSR2H FBAh CCP2CON F9Ah —(2) FF9h PCL FD9h FSR2L FB9h —(2) F99h —(2) FF8h TBLPTRU FD8h STATUS FB8h BAUDCON F98h —(2) FF7h TBLPTRH FD7h TMR0H FB7h PWM1CON(3) F97h —(2) FF6h TBLPTRL FD6h TMR0L FB6h ECCP1AS(3) F96h TRISE(3) FF5h TABLAT FD5h T0CON FB5h CVRCON F95h TRISD(3) FF4h PRODH FD4h —(2) FB4h CMCON F94h TRISC FF3h PRODL FD3h OSCCON FB3h TMR3H F93h TRISB FF2h INTCON FD2h HLVDCON FB2h TMR3L F92h TRISA FF1h INTCON2 FD1h WDTCON FB1h T3CON F91h —(2) FF0h INTCON3 FD0h RCON FB0h SPBRGH F90h —(2) FEFh INDF0(1) FCFh TMR1H FAFh SPBRG F8Fh —(2) FEEh POSTINC0(1) FCEh TMR1L FAEh RCREG F8Eh —(2) FEDh POSTDEC0(1) FCDh T1CON FADh TXREG F8Dh LATE(3) FECh PREINC0(1) FCCh TMR2 FACh TXSTA F8Ch LATD(3) FEBh PLUSW0(1) FCBh PR2 FABh RCSTA F8Bh LATC FEAh FSR0H FCAh T2CON FAAh —(2) F8Ah LATB FE9h FSR0L FC9h SSPBUF FA9h EEADR F89h LATA FE8h WREG FC8h SSPADD FA8h EEDATA F88h —(2) FE7h INDF1(1) FC7h SSPSTAT FA7h EECON2(1) F87h —(2) FE6h POSTINC1(1) FC6h SSPCON1 FA6h EECON1 F86h —(2) FE5h POSTDEC1(1) FC5h SSPCON2 FA5h —(2) F85h —(2) FE4h PREINC1(1) FC4h ADRESH FA4h —(2) F84h PORTE(3) FE3h PLUSW1(1) FC3h ADRESL FA3h —(2) F83h PORTD(3) FE2h FSR1H FC2h ADCON0 FA2h IPR2 F82h PORTC FE1h FSR1L FC1h ADCON1 FA1h PIR2 F81h PORTB FE0h BSR FC0h ADCON2 FA0h PIE2 F80h PORTA Note 1: This is not a physical register. 2: Unimplemented registers are read as ‘0’. 3: This register is not available on 28-pin devices. PIC18F2420/2520/4420/4520 DS39631B-page 64 Preliminary © 2007 Microchip Technology Inc. TABLE 5-2: REGISTER FILE SUMMARY (PIC18F2420/2520/4420/4520) File Name Bit 7 Bit 6 Bit 5 Bit 4 Bit 3 Bit 2 Bit 1 Bit 0 Value on POR, BOR Details on page: TOSU — — — Top-of-Stack Upper Byte (TOS<20:16>) ---0 0000 49, 54 TOSH Top-of-Stack, High Byte (TOS<15:8>) 0000 0000 49, 54 TOSL Top-of-Stack, Low Byte (TOS<7:0>) 0000 0000 49, 54 STKPTR STKFUL STKUNF — SP4 SP3 SP2 SP1 SP0 00-0 0000 49, 55 PCLATU — — — Holding Register for PC<20:16> ---0 0000 49, 54 PCLATH Holding Register for PC<15:8> 0000 0000 49, 54 PCL PC, Low Byte (PC<7:0>) 0000 0000 49, 54 TBLPTRU — — bit 21 Program Memory Table Pointer Upper Byte (TBLPTR<20:16>) --00 0000 49, 76 TBLPTRH Program Memory Table Pointer, High Byte (TBLPTR<15:8>) 0000 0000 49, 76 TBLPTRL Program Memory Table Pointer, Low Byte (TBLPTR<7:0>) 0000 0000 49, 76 TABLAT Program Memory Table Latch 0000 0000 49, 76 PRODH Product Register, High Byte xxxx xxxx 49, 89 PRODL Product Register, Low Byte xxxx xxxx 49, 89 INTCON GIE/GIEH PEIE/GIEL TMR0IE INT0IE RBIE TMR0IF INT0IF RBIF 0000 000x 49, 93 INTCON2 RBPU INTEDG0 INTEDG1 INTEDG2 — TMR0IP — RBIP 1111 -1-1 49, 94 INTCON3 INT2IP INT1IP — INT2IE INT1IE — INT2IF INT1IF 11-0 0-00 49, 95 INDF0 Uses contents of FSR0 to address data memory – value of FSR0 not changed (not a physical register) N/A 49, 69 POSTINC0 Uses contents of FSR0 to address data memory – value of FSR0 post-incremented (not a physical register) N/A 49, 69 POSTDEC0 Uses contents of FSR0 to address data memory – value of FSR0 post-decremented (not a physical register) N/A 49, 69 PREINC0 Uses contents of FSR0 to address data memory – value of FSR0 pre-incremented (not a physical register) N/A 49, 69 PLUSW0 Uses contents of FSR0 to address data memory – value of FSR0 pre-incremented (not a physical register) – value of FSR0 offset by W N/A 49, 69 FSR0H — — — — Indirect Data Memory Address Pointer 0, High Byte ---- 0000 49, 69 FSR0L Indirect Data Memory Address Pointer 0, Low Byte xxxx xxxx 49, 69 WREG Working Register xxxx xxxx 49 INDF1 Uses contents of FSR1 to address data memory – value of FSR1 not changed (not a physical register) N/A 49, 69 POSTINC1 Uses contents of FSR1 to address data memory – value of FSR1 post-incremented (not a physical register) N/A 49, 69 POSTDEC1 Uses contents of FSR1 to address data memory – value of FSR1 post-decremented (not a physical register) N/A 49, 69 PREINC1 Uses contents of FSR1 to address data memory – value of FSR1 pre-incremented (not a physical register) N/A 49, 69 PLUSW1 Uses contents of FSR1 to address data memory – value of FSR1 pre-incremented (not a physical register) – value of FSR1 offset by W N/A 49, 69 FSR1H — — — — Indirect Data Memory Address Pointer 1, High Byte ---- 0000 50, 69 FSR1L Indirect Data Memory Address Pointer 1, Low Byte xxxx xxxx 50, 69 BSR — — — — Bank Select Register ---- 0000 50, 59 INDF2 Uses contents of FSR2 to address data memory – value of FSR2 not changed (not a physical register) N/A 50, 69 POSTINC2 Uses contents of FSR2 to address data memory – value of FSR2 post-incremented (not a physical register) N/A 50, 69 POSTDEC2 Uses contents of FSR2 to address data memory – value of FSR2 post-decremented (not a physical register) N/A 50, 69 PREINC2 Uses contents of FSR2 to address data memory – value of FSR2 pre-incremented (not a physical register) N/A 50, 69 PLUSW2 Uses contents of FSR2 to address data memory – value of FSR2 pre-incremented (not a physical register) – value of FSR2 offset by W N/A 50, 69 FSR2H — — — — Indirect Data Memory Address Pointer 2, High Byte ---- 0000 50, 69 FSR2L Indirect Data Memory Address Pointer 2, Low Byte xxxx xxxx 50, 69 STATUS — — — N OV Z DC C ---x xxxx 50, 67 Legend: x = unknown, u = unchanged, — = unimplemented, q = value depends on condition Note 1: The SBOREN bit is only available when the BOREN1:BOREN0 configuration bits = 01; otherwise it is disabled and reads as ‘0’. See Section 4.4 “Brown-out Reset (BOR)”. 2: These registers and/or bits are not implemented on 28-pin devices and are read as ‘0’. Reset values are shown for 40/44-pin devices; individual unimplemented bits should be interpreted as ‘-’. 3: The PLLEN bit is only available in specific oscillator configuration; otherwise it is disabled and reads as ‘0’. See Section 2.6.4 “PLL in INTOSC Modes”. 4: The RE3 bit is only available when Master Clear Reset is disabled (MCLRE configuration bit = 0). Otherwise, RE3 reads as ‘0’. This bit is read-only. 5: RA6/RA7 and their associated latch and direction bits are individually configured as port pins based on various primary oscillator modes. When disabled, these bits read as ‘0’. © 2007 Microchip Technology Inc. Preliminary DS39631B-page 65 PIC18F2420/2520/4420/4520 TMR0H Timer0 Register, High Byte 0000 0000 50, 125 TMR0L Timer0 Register, Low Byte xxxx xxxx 50, 125 T0CON TMR0ON T08BIT T0CS T0SE PSA T0PS2 T0PS1 T0PS0 1111 1111 50, 123 OSCCON IDLEN IRCF2 IRCF1 IRCF0 OSTS IOFS SCS1 SCS0 0100 q000 30, 50 HLVDCON VDIRMAG — IRVST HLVDEN HLVDL3 HLVDL2 HLVDL1 HLVDL0 0-00 0101 50, 245 WDTCON — — — — — — — SWDTEN --- ---0 50, 259 RCON IPEN SBOREN(1) — RI TO PD POR BOR 0q-1 11q0 42, 48, 102 TMR1H Timer1 Register, High Byte xxxx xxxx 50, 131 TMR1L Timer1 Register, Low Bytes xxxx xxxx 50, 131 T1CON RD16 T1RUN T1CKPS1 T1CKPS0 T1OSCEN T1SYNC TMR1CS TMR1ON 0000 0000 50, 127 TMR2 Timer2 Register 0000 0000 50, 134 PR2 Timer2 Period Register 1111 1111 50, 134 T2CON — T2OUTPS3 T2OUTPS2 T2OUTPS1 T2OUTPS0 TMR2ON T2CKPS1 T2CKPS0 -000 0000 50, 133 SSPBUF SSP Receive Buffer/Transmit Register xxxx xxxx 50, 169, 170 SSPADD SSP Address Register in I2C Slave Mode. SSP Baud Rate Reload Register in I2C Master Mode. 0000 0000 50, 170 SSPSTAT SMP CKE D/A P S R/W UA BF 0000 0000 50, 162, 171 SSPCON1 WCOL SSPOV SSPEN CKP SSPM3 SSPM2 SSPM1 SSPM0 0000 0000 50, 163, 172 SSPCON2 GCEN ACKSTAT ACKDT ACKEN RCEN PEN RSEN SEN 0000 0000 50, 173 ADRESH A/D Result Register, High Byte xxxx xxxx 51, 232 ADRESL A/D Result Register, Low Byte xxxx xxxx 51, 232 ADCON0 — — CHS3 CHS2 CHS1 CHS0 GO/DONE ADON --00 0000 51, 223 ADCON1 — — VCFG1 VCFG0 PCFG3 PCFG2 PCFG1 PCFG0 --00 0qqq 51, 224 ADCON2 ADFM — ACQT2 ACQT1 ACQT0 ADCS2 ADCS1 ADCS0 0-00 0000 51, 225 CCPR1H Capture/Compare/PWM Register 1, High Byte xxxx xxxx 51, 140 CCPR1L Capture/Compare/PWM Register 1, Low Byte xxxx xxxx 51, 140 CCP1CON P1M1(2) P1M0(2) DC1B1 DC1B0 CCP1M3 CCP1M2 CCP1M1 CCP1M0 0000 0000 51, 139, 147 CCPR2H Capture/Compare/PWM Register 2, High Byte xxxx xxxx 51, 140 CCPR2L Capture/Compare/PWM Register 2, Low Byte xxxx xxxx 51, 140 CCP2CON — — DC2B1 DC2B0 CCP2M3 CCP2M2 CCP2M1 CCP2M0 --00 0000 51, 139 BAUDCON ABDOVF RCIDL — SCKP BRG16 — WUE ABDEN 01-0 0-00 51, 204 PWM1CON PRSEN PDC6(2) PDC5(2) PDC4(2) PDC3(2) PDC2(2) PDC1(2) PDC0(2) 0000 0000 51, 156 ECCP1AS ECCPASE ECCPAS2 ECCPAS1 ECCPAS0 PSSAC1 PSSAC0 PSSBD1(2) PSSBD0(2) 0000 0000 51, 157 CVRCON CVREN CVROE CVRR CVRSS CVR3 CVR2 CVR1 CVR0 0000 0000 51, 239 CMCON C2OUT C1OUT C2INV C1INV CIS CM2 CM1 CM0 0000 0111 51, 233 TMR3H Timer3 Register, High Byte xxxx xxxx 51, 137 TMR3L Timer3 Register, Low Byte xxxx xxxx 51, 137 T3CON RD16 T3CCP2 T3CKPS1 T3CKPS0 T3CCP1 T3SYNC TMR3CS TMR3ON 0000 0000 51, 135 TABLE 5-2: REGISTER FILE SUMMARY (PIC18F2420/2520/4420/4520) (CONTINUED) File Name Bit 7 Bit 6 Bit 5 Bit 4 Bit 3 Bit 2 Bit 1 Bit 0 Value on POR, BOR Details on page: Legend: x = unknown, u = unchanged, — = unimplemented, q = value depends on condition Note 1: The SBOREN bit is only available when the BOREN1:BOREN0 configuration bits = 01; otherwise it is disabled and reads as ‘0’. See Section 4.4 “Brown-out Reset (BOR)”. 2: These registers and/or bits are not implemented on 28-pin devices and are read as ‘0’. Reset values are shown for 40/44-pin devices; individual unimplemented bits should be interpreted as ‘-’. 3: The PLLEN bit is only available in specific oscillator configuration; otherwise it is disabled and reads as ‘0’. See Section 2.6.4 “PLL in INTOSC Modes”. 4: The RE3 bit is only available when Master Clear Reset is disabled (MCLRE configuration bit = 0). Otherwise, RE3 reads as ‘0’. This bit is read-only. 5: RA6/RA7 and their associated latch and direction bits are individually configured as port pins based on various primary oscillator modes. When disabled, these bits read as ‘0’. PIC18F2420/2520/4420/4520 DS39631B-page 66 Preliminary © 2007 Microchip Technology Inc. SPBRGH EUSART Baud Rate Generator Register, High Byte 0000 0000 51, 206 SPBRG EUSART Baud Rate Generator Register, Low Byte 0000 0000 51, 206 RCREG EUSART Receive Register 0000 0000 51, 213 TXREG EUSART Transmit Register 0000 0000 51, 211 TXSTA CSRC TX9 TXEN SYNC SENDB BRGH TRMT TX9D 0000 0010 51, 202 RCSTA SPEN RX9 SREN CREN ADDEN FERR OERR RX9D 0000 000x 51, 203 EEADR EEPROM Address Register 0000 0000 51, 74, 83 EEDATA EEPROM Data Register 0000 0000 51, 74, 83 EECON2 EEPROM Control Register 2 (not a physical register) 0000 0000 51, 74, 83 EECON1 EEPGD CFGS — FREE WRERR WREN WR RD xx-0 x000 51, 75, 84 IPR2 OSCFIP CMIP — EEIP BCLIP HLVDIP TMR3IP CCP2IP 11-1 1111 52, 101 PIR2 OSCFIF CMIF — EEIF BCLIF HLVDIF TMR3IF CCP2IF 00-0 0000 52, 97 PIE2 OSCFIE CMIE — EEIE BCLIE HLVDIE TMR3IE CCP2IE 00-0 0000 52, 99 IPR1 PSPIP(2) ADIP RCIP TXIP SSPIP CCP1IP TMR2IP TMR1IP 1111 1111 52, 100 PIR1 PSPIF(2) ADIF RCIF TXIF SSPIF CCP1IF TMR2IF TMR1IF 0000 0000 52, 96 PIE1 PSPIE(2) ADIE RCIE TXIE SSPIE CCP1IE TMR2IE TMR1IE 0000 0000 52, 98 OSCTUNE INTSRC PLLEN(3) — TUN4 TUN3 TUN2 TUN1 TUN0 0q-0 0000 27, 52 TRISE(2) IBF OBF IBOV PSPMODE — TRISE2 TRISE1 TRISE0 0000 -111 52, 118 TRISD(2) PORTD Data Direction Control Register 1111 1111 52, 114 TRISC PORTC Data Direction Control Register 1111 1111 52, 111 TRISB PORTB Data Direction Control Register 1111 1111 52, 108 TRISA TRISA7(5) TRISA6(5) Data Direction Control Register for PORTA 1111 1111 52, 105 LATE(2) — — — — — PORTE Data Latch Register (Read and Write to Data Latch) ---- -xxx 52, 117 LATD(2) PORTD Data Latch Register (Read and Write to Data Latch) xxxx xxxx 52, 114 LATC PORTC Data Latch Register (Read and Write to Data Latch) xxxx xxxx 52, 111 LATB PORTB Data Latch Register (Read and Write to Data Latch) xxxx xxxx 52, 108 LATA LATA7(5) LATA6(5) PORTA Data Latch Register (Read and Write to Data Latch) xxxx xxxx 52, 105 PORTE — — — — RE3(4) RE2(2) RE1(2) RE0(2) ---- xxxx 52, 117 PORTD(2) RD7 RD6 RD5 RD4 RD3 RD2 RD1 RD0 xxxx xxxx 52, 114 PORTC RC7 RC6 RC5 RC4 RC3 RC2 RC1 RC0 xxxx xxxx 52, 111 PORTB RB7 RB6 RB5 RB4 RB3 RB2 RB1 RB0 xxxx xxxx 52, 108 PORTA RA7(5) RA6(5) RA5 RA4 RA3 RA2 RA1 RA0 xx0x 0000 52, 105 TABLE 5-2: REGISTER FILE SUMMARY (PIC18F2420/2520/4420/4520) (CONTINUED) File Name Bit 7 Bit 6 Bit 5 Bit 4 Bit 3 Bit 2 Bit 1 Bit 0 Value on POR, BOR Details on page: Legend: x = unknown, u = unchanged, — = unimplemented, q = value depends on condition Note 1: The SBOREN bit is only available when the BOREN1:BOREN0 configuration bits = 01; otherwise it is disabled and reads as ‘0’. See Section 4.4 “Brown-out Reset (BOR)”. 2: These registers and/or bits are not implemented on 28-pin devices and are read as ‘0’. Reset values are shown for 40/44-pin devices; individual unimplemented bits should be interpreted as ‘-’. 3: The PLLEN bit is only available in specific oscillator configuration; otherwise it is disabled and reads as ‘0’. See Section 2.6.4 “PLL in INTOSC Modes”. 4: The RE3 bit is only available when Master Clear Reset is disabled (MCLRE configuration bit = 0). Otherwise, RE3 reads as ‘0’. This bit is read-only. 5: RA6/RA7 and their associated latch and direction bits are individually configured as port pins based on various primary oscillator modes. When disabled, these bits read as ‘0’. © 2007 Microchip Technology Inc. Preliminary DS39631B-page 67 PIC18F2420/2520/4420/4520 5.3.5 STATUS REGISTER The Status register, shown in Register 5-2, contains the arithmetic status of the ALU. As with any other SFR, it can be the operand for any instruction. If the Status register is the destination for an instruction that affects the Z, DC, C, OV or N bits, the results of the instruction are not written; instead, the Status register is updated according to the instruction performed. Therefore, the result of an instruction with the Status register as its destination may be different than intended. As an example, CLRF STATUS will set the Z bit and leave the remaining status bits unchanged (‘000u u1uu’). It is recommended that only BCF, BSF, SWAPF, MOVFF and MOVWF instructions are used to alter the Status register, because these instructions do not affect the Z, C, DC, OV or N bits in the Status register. For other instructions that do not affect Status bits, see the instruction set summaries in Table 24-2 and Table 24-3. REGISTER 5-2: STATUS REGISTER Note: The C and DC bits operate as the borrow and digit borrow bits, respectively, in subtraction. U-0 U-0 U-0 R/W-x R/W-x R/W-x R/W-x R/W-x — — — N OV Z DC C bit 7 bit 0 bit 7-5 Unimplemented: Read as ‘0’ bit 4 N: Negative bit This bit is used for signed arithmetic (2’s complement). It indicates whether the result was negative (ALU MSB = 1). 1 = Result was negative 0 = Result was positive bit 3 OV: Overflow bit This bit is used for signed arithmetic (2’s complement). It indicates an overflow of the 7-bit magnitude which causes the sign bit (bit 7 of the result) to change state. 1 = Overflow occurred for signed arithmetic (in this arithmetic operation) 0 = No overflow occurred bit 2 Z: Zero bit 1 = The result of an arithmetic or logic operation is zero 0 = The result of an arithmetic or logic operation is not zero bit 1 DC: Digit Carry/borrow bit For ADDWF, ADDLW, SUBLW and SUBWF instructions: 1 = A carry-out from the 4th low-order bit of the result occurred 0 = No carry-out from the 4th low-order bit of the result Note: For borrow, the polarity is reversed. A subtraction is executed by adding the 2’s complement of the second operand. For rotate (RRF, RLF) instructions, this bit is loaded with either bit 4 or bit 3 of the source register. bit 0 C: Carry/borrow bit For ADDWF, ADDLW, SUBLW and SUBWF instructions: 1 = A carry-out from the Most Significant bit of the result occurred 0 = No carry-out from the Most Significant bit of the result occurred Note: For borrow, the polarity is reversed. A subtraction is executed by adding the 2’s complement of the second operand. For rotate (RRF, RLF) instructions, this bit is loaded with either the high or low-order bit of the source register. Legend: R = Readable bit W = Writable bit U = Unimplemented bit, read as ‘0’ -n = Value at POR ‘1’ = Bit is set ‘0’ = Bit is cleared x = Bit is unknown PIC18F2420/2520/4420/4520 DS39631B-page 68 Preliminary © 2007 Microchip Technology Inc. 5.4 Data Addressing Modes While the program memory can be addressed in only one way – through the program counter – information in the data memory space can be addressed in several ways. For most instructions, the addressing mode is fixed. Other instructions may use up to three modes, depending on which operands are used and whether or not the extended instruction set is enabled. The addressing modes are: • Inherent • Literal • Direct • Indirect An additional addressing mode, Indexed Literal Offset, is available when the extended instruction set is enabled (XINST configuration bit = 1). Its operation is discussed in greater detail in Section 5.5.1 “Indexed Addressing with Literal Offset”. 5.4.1 INHERENT AND LITERAL ADDRESSING Many PIC18 control instructions do not need any argument at all; they either perform an operation that globally affects the device or they operate implicitly on one register. This addressing mode is known as Inherent Addressing. Examples include SLEEP, RESET and DAW. Other instructions work in a similar way but require an additional explicit argument in the opcode. This is known as Literal Addressing mode because they require some literal value as an argument. Examples include ADDLW and MOVLW, which respectively, add or move a literal value to the W register. Other examples include CALL and GOTO, which include a 20-bit program memory address. 5.4.2 DIRECT ADDRESSING Direct addressing specifies all or part of the source and/or destination address of the operation within the opcode itself. The options are specified by the arguments accompanying the instruction. In the core PIC18 instruction set, bit-oriented and byteoriented instructions use some version of direct addressing by default. All of these instructions include some 8-bit literal address as their Least Significant Byte. This address specifies either a register address in one of the banks of data RAM (Section 5.3.3 “General Purpose Register File”) or a location in the Access Bank (Section 5.3.2 “Access Bank”) as the data source for the instruction. The Access RAM bit ‘a’ determines how the address is interpreted. When ‘a’ is ‘1’, the contents of the BSR (Section 5.3.1 “Bank Select Register (BSR)”) are used with the address to determine the complete 12-bit address of the register. When ‘a’ is ‘0’, the address is interpreted as being a register in the Access Bank. Addressing that uses the Access RAM is sometimes also known as Direct Forced Addressing mode. A few instructions, such as MOVFF, include the entire 12-bit address (either source or destination) in their opcodes. In these cases, the BSR is ignored entirely. The destination of the operation’s results is determined by the destination bit ‘d’. When ‘d’ is ‘1’, the results are stored back in the source register, overwriting its original contents. When ‘d’ is ‘0’, the results are stored in the W register. Instructions without the ‘d’ argument have a destination that is implicit in the instruction; their destination is either the target register being operated on or the W register. 5.4.3 INDIRECT ADDRESSING Indirect addressing allows the user to access a location in data memory without giving a fixed address in the instruction. This is done by using File Select Registers (FSRs) as pointers to the locations to be read or written to. Since the FSRs are themselves located in RAM as Special File Registers, they can also be directly manipulated under program control. This makes FSRs very useful in implementing data structures, such as tables and arrays in data memory. The registers for indirect addressing are also implemented with Indirect File Operands (INDFs) that permit automatic manipulation of the pointer value with auto-incrementing, auto-decrementing or offsetting with another value. This allows for efficient code, using loops, such as the example of clearing an entire RAM bank in Example 5-5. EXAMPLE 5-5: HOW TO CLEAR RAM (BANK 1) USING INDIRECT ADDRESSING Note: The execution of some instructions in the core PIC18 instruction set are changed when the PIC18 extended instruction set is enabled. See Section 5.5 “Data Memory and the Extended Instruction Set” for more information. LFSR FSR0, 100h ; NEXT CLRF POSTINC0 ; Clear INDF ; register then ; inc pointer BTFSS FSR0H, 1 ; All done with ; Bank1? BRA NEXT ; NO, clear next CONTINUE ; YES, continue © 2007 Microchip Technology Inc. Preliminary DS39631B-page 69 PIC18F2420/2520/4420/4520 5.4.3.1 FSR Registers and the INDF Operand At the core of indirect addressing are three sets of registers: FSR0, FSR1 and FSR2. Each represents a pair of 8-bit registers, FSRnH and FSRnL. The four upper bits of the FSRnH register are not used so each FSR pair holds a 12-bit value. This represents a value that can address the entire range of the data memory in a linear fashion. The FSR register pairs, then, serve as pointers to data memory locations. Indirect addressing is accomplished with a set of Indirect File Operands, INDF0 through INDF2. These can be thought of as “virtual” registers: they are mapped in the SFR space but are not physically implemented. Reading or writing to a particular INDF register actually accesses its corresponding FSR register pair. A read from INDF1, for example, reads the data at the address indicated by FSR1H:FSR1L. Instructions that use the INDF registers as operands actually use the contents of their corresponding FSR as a pointer to the instruction’s target. The INDF operand is just a convenient way of using the pointer. Because indirect addressing uses a full 12-bit address, data RAM banking is not necessary. Thus, the current contents of the BSR and the Access RAM bit have no effect on determining the target address. 5.4.3.2 FSR Registers and POSTINC, POSTDEC, PREINC and PLUSW In addition to the INDF operand, each FSR register pair also has four additional indirect operands. Like INDF, these are “virtual” registers that cannot be indirectly read or written to. Accessing these registers actually accesses the associated FSR register pair, but also performs a specific action on it stored value. They are: • POSTDEC: accesses the FSR value, then automatically decrements it by 1 afterwards • POSTINC: accesses the FSR value, then automatically increments it by 1 afterwards • PREINC: increments the FSR value by 1, then uses it in the operation • PLUSW: adds the signed value of the W register (range of -127 to 128) to that of the FSR and uses the new value in the operation. In this context, accessing an INDF register uses the value in the FSR registers without changing them. Similarly, accessing a PLUSW register gives the FSR value offset by that in the W register; neither value is actually changed in the operation. Accessing the other virtual registers changes the value of the FSR registers. Operations on the FSRs with POSTDEC, POSTINC and PREINC affect the entire register pair; that is, rollovers of the FSRnL register from FFh to 00h carry over to the FSRnH register. On the other hand, results of these operations do not change the value of any flags in the Status register (e.g., Z, N, OV, etc.). FIGURE 5-8: INDIRECT ADDRESSING FSR1H:FSR1L 7 0 Data Memory 000h 100h 200h 300h F00h E00h FFFh Bank 0 Bank 1 Bank 2 Bank 14 Bank 15 Bank 3 through Bank 13 ADDWF, INDF1, 1 7 0 Using an instruction with one of the indirect addressing registers as the operand.... ...uses the 12-bit address stored in the FSR pair associated with that register.... ...to determine the data memory location to be used in that operation. In this case, the FSR1 pair contains ECCh. This means the contents of location ECCh will be added to that of the W register and stored back in ECCh. x x x x 1 1 1 0 1 1 0 0 1 1 0 0 PIC18F2420/2520/4420/4520 DS39631B-page 70 Preliminary © 2007 Microchip Technology Inc. The PLUSW register can be used to implement a form of indexed addressing in the data memory space. By manipulating the value in the W register, users can reach addresses that are fixed offsets from pointer addresses. In some applications, this can be used to implement some powerful program control structure, such as software stacks, inside of data memory. 5.4.3.3 Operations by FSRs on FSRs Indirect addressing operations that target other FSRs or virtual registers represent special cases. For example, using an FSR to point to one of the virtual registers will not result in successful operations. As a specific case, assume that FSR0H:FSR0L contains FE7h, the address of INDF1. Attempts to read the value of the INDF1 using INDF0 as an operand will return 00h. Attempts to write to INDF1 using INDF0 as the operand will result in a NOP. On the other hand, using the virtual registers to write to an FSR pair may not occur as planned. In these cases, the value will be written to the FSR pair but without any incrementing or decrementing. Thus, writing to INDF2 or POSTDEC2 will write the same value to the FSR2H:FSR2L. Since the FSRs are physical registers mapped in the SFR space, they can be manipulated through all direct operations. Users should proceed cautiously when working on these registers, particularly if their code uses indirect addressing. Similarly, operations by indirect addressing are generally permitted on all other SFRs. Users should exercise the appropriate caution that they do not inadvertently change settings that might affect the operation of the device. 5.5 Data Memory and the Extended Instruction Set Enabling the PIC18 extended instruction set (XINST configuration bit = 1) significantly changes certain aspects of data memory and its addressing. Specifically, the use of the Access Bank for many of the core PIC18 instructions is different; this is due to the introduction of a new addressing mode for the data memory space. What does not change is just as important. The size of the data memory space is unchanged, as well as its linear addressing. The SFR map remains the same. Core PIC18 instructions can still operate in both Direct and Indirect Addressing mode; inherent and literal instructions do not change at all. Indirect addressing with FSR0 and FSR1 also remain unchanged. 5.5.1 INDEXED ADDRESSING WITH LITERAL OFFSET Enabling the PIC18 extended instruction set changes the behavior of indirect addressing using the FSR2 register pair within Access RAM. Under the proper conditions, instructions that use the Access Bank – that is, most bit-oriented and byte-oriented instructions – can invoke a form of indexed addressing using an offset specified in the instruction. This special addressing mode is known as Indexed Addressing with Literal Offset, or Indexed Literal Offset mode. When using the extended instruction set, this addressing mode requires the following: • The use of the Access Bank is forced (‘a’ = 0) and • The file address argument is less than or equal to 5Fh. Under these conditions, the file address of the instruction is not interpreted as the lower byte of an address (used with the BSR in direct addressing), or as an 8-bit address in the Access Bank. Instead, the value is interpreted as an offset value to an address pointer, specified by FSR2. The offset and the contents of FSR2 are added to obtain the target address of the operation. 5.5.2 INSTRUCTIONS AFFECTED BY INDEXED LITERAL OFFSET MODE Any of the core PIC18 instructions that can use direct addressing are potentially affected by the Indexed Literal Offset Addressing mode. This includes all byte-oriented and bit-oriented instructions, or almost one-half of the standard PIC18 instruction set. Instructions that only use Inherent or Literal Addressing modes are unaffected. Additionally, byte-oriented and bit-oriented instructions are not affected if they do not use the Access Bank (Access RAM bit is ‘1’), or include a file address of 60h or above. Instructions meeting these criteria will continue to execute as before. A comparison of the different possible addressing modes when the extended instruction set is enabled in shown in Figure 5-9. Those who desire to use byte-oriented or bit-oriented instructions in the Indexed Literal Offset mode should note the changes to assembler syntax for this mode. This is described in more detail in Section 24.2.1 “Extended Instruction Syntax”. © 2007 Microchip Technology Inc. Preliminary DS39631B-page 71 PIC18F2420/2520/4420/4520 FIGURE 5-9: COMPARING ADDRESSING OPTIONS FOR BIT-ORIENTED AND BYTE-ORIENTED INSTRUCTIONS (EXTENDED INSTRUCTION SET ENABLED) EXAMPLE INSTRUCTION: ADDWF, f, d, a (Opcode: 0010 01da ffff ffff) When ‘a’ = 0 and f ≥ 60h: The instruction executes in Direct Forced mode. ‘f’ is interpreted as a location in the Access RAM between 060h and 0FFh. This is the same as locations 060h to 07Fh (Bank 0) and F80h to FFFh (Bank 15) of data memory. Locations below 60h are not available in this addressing mode. When ‘a’ = 0 and f ≤ 5Fh: The instruction executes in Indexed Literal Offset mode. ‘f’ is interpreted as an offset to the address value in FSR2. The two are added together to obtain the address of the target register for the instruction. The address can be anywhere in the data memory space. Note that in this mode, the correct syntax is now: ADDWF [k], d where ‘k’ is the same as ‘f’. When ‘a’ = 1 (all values of f): The instruction executes in Direct mode (also known as Direct Long mode). ‘f’ is interpreted as a location in one of the 16 banks of the data memory space. The bank is designated by the Bank Select Register (BSR). The address can be in any implemented bank in the data memory space. 000h 060h 100h F00h F80h FFFh Valid range 00h 60h 80h FFh Data Memory Access RAM Bank 0 Bank 1 through Bank 14 Bank 15 SFRs 000h 080h 100h F00h F80h FFFh Data Memory Bank 0 Bank 1 through Bank 14 Bank 15 SFRs FSR2H FSR2L 001001da ffffffff 001001da ffffffff 000h 080h 100h F00h F80h FFFh Data Memory Bank 0 Bank 1 through Bank 14 Bank 15 SFRs for ‘f’ BSR 00000000 080h PIC18F2420/2520/4420/4520 DS39631B-page 72 Preliminary © 2007 Microchip Technology Inc. 5.5.3 MAPPING THE ACCESS BANK IN INDEXED LITERAL OFFSET MODE The use of Indexed Literal Offset Addressing mode effectively changes how the first 96 locations of Access RAM (00h to 5Fh) are mapped. Rather than containing just the contents of the bottom half of Bank 0, this mode maps the contents from Bank 0 and a user defined “window” that can be located anywhere in the data memory space. The value of FSR2 establishes the lower boundary of the addresses mapped into the window, while the upper boundary is defined by FSR2 plus 95 (5Fh). Addresses in the Access RAM above 5Fh are mapped as previously described (see Section 5.3.2 “Access Bank”). An example of Access Bank remapping in this addressing mode is shown in Figure 5-10. Remapping of the Access Bank applies only to operations using the Indexed Literal Offset mode. Operations that use the BSR (Access RAM bit is ‘1’) will continue to use direct addressing as before. 5.6 PIC18 Instruction Execution and the Extended Instruction Set Enabling the extended instruction set adds eight additional commands to the existing PIC18 instruction set. These instructions are executed as described in Section 24.2 “Extended Instruction Set”. FIGURE 5-10: REMAPPING THE ACCESS BANK WITH INDEXED LITERAL OFFSET ADDRESSING Data Memory 000h 100h 200h F80h F00h FFFh Bank 1 Bank 15 Bank 2 through Bank 14 SFRs 05Fh ADDWF f, d, a FSR2H:FSR2L = 120h Locations in the region from the FSR2 pointer (120h) to the pointer plus 05Fh (17Fh) are mapped to the bottom of the Access RAM (000h-05Fh). Locations in Bank 0 from 060h to 07Fh are mapped, as usual, to the middle half of the Access Bank. Special File Registers at F80h through FFFh are mapped to 80h through FFh, as usual. Bank 0 addresses below 5Fh can still be addressed by using the BSR. Access Bank 00h 80h FFh 7Fh Bank 0 SFRs Bank 1 “Window” Bank 0 Bank 0 Window Example Situation: 07Fh 120h 17Fh 5Fh Bank 1 © 2007 Microchip Technology Inc. Preliminary DS39631B-page 73 PIC18F2420/2520/4420/4520 6.0 FLASH PROGRAM MEMORY The Flash program memory is readable, writable and erasable during normal operation over the entire VDD range. A read from program memory is executed on one byte at a time. A write to program memory is executed on blocks of 64 bytes at a time. Program memory is erased in blocks of 64 bytes at a time. A bulk erase operation may not be issued from user code. Writing or erasing program memory will cease instruction fetches until the operation is complete. The program memory cannot be accessed during the write or erase, therefore, code cannot execute. An internal programming timer terminates program memory writes and erases. A value written to program memory does not need to be a valid instruction. Executing a program memory location that forms an invalid instruction results in a NOP. 6.1 Table Reads and Table Writes In order to read and write program memory, there are two operations that allow the processor to move bytes between the program memory space and the data RAM: • Table Read (TBLRD) • Table Write (TBLWT) The program memory space is 16 bits wide, while the data RAM space is 8 bits wide. Table reads and table writes move data between these two memory spaces through an 8-bit register (TABLAT). Table read operations retrieve data from program memory and places it into the data RAM space. Figure 6-1 shows the operation of a table read with program memory and data RAM. Table write operations store data from the data memory space into holding registers in program memory. The procedure to write the contents of the holding registers into program memory is detailed in Section 6.5 “Writing to Flash Program Memory”. Figure 6-2 shows the operation of a table write with program memory and data RAM. Table operations work with byte entities. A table block containing data, rather than program instructions, is not required to be word aligned. Therefore, a table block can start and end at any byte address. If a table write is being used to write executable code into program memory, program instructions will need to be word aligned. FIGURE 6-1: TABLE READ OPERATION Table Pointer(1) Table Latch (8-bit) Program Memory TBLPTRH TBLPTRL TABLAT TBLPTRU Instruction: TBLRD* Note 1: Table Pointer register points to a byte in program memory. Program Memory (TBLPTR) PIC18F2420/2520/4420/4520 DS39631B-page 74 Preliminary © 2007 Microchip Technology Inc. FIGURE 6-2: TABLE WRITE OPERATION 6.2 Control Registers Several control registers are used in conjunction with the TBLRD and TBLWT instructions. These include the: • EECON1 register • EECON2 register • TABLAT register • TBLPTR registers 6.2.1 EECON1 AND EECON2 REGISTERS The EECON1 register (Register 6-1) is the control register for memory accesses. The EECON2 register is not a physical register; it is used exclusively in the memory write and erase sequences. Reading EECON2 will read all ‘0’s. The EEPGD control bit determines if the access will be a program or data EEPROM memory access. When clear, any subsequent operations will operate on the data EEPROM memory. When set, any subsequent operations will operate on the program memory. The CFGS control bit determines if the access will be to the configuration/calibration registers or to program memory/data EEPROM memory. When set, subsequent operations will operate on configuration registers regardless of EEPGD (see Section 23.0 “Special Features of the CPU”). When clear, memory selection access is determined by EEPGD. The FREE bit, when set, will allow a program memory erase operation. When FREE is set, the erase operation is initiated on the next WR command. When FREE is clear, only writes are enabled. The WREN bit, when set, will allow a write operation. On power-up, the WREN bit is clear. The WRERR bit is set in hardware when the WR bit is set and cleared when the internal programming timer expires and the write operation is complete. The WR control bit initiates write operations. The bit cannot be cleared, only set, in software; it is cleared in hardware at the completion of the write operation. Table Pointer(1) Table Latch (8-bit) TBLPTRH TBLPTRL TABLAT Program Memory (TBLPTR) TBLPTRU Instruction: TBLWT* Note 1: Table Pointer actually points to one of 64 holding registers, the address of which is determined by TBLPTRL<5:0>. The process for physically writing data to the program memory array is discussed in Section 6.5 “Writing to Flash Program Memory”. Holding Registers Program Memory Note: During normal operation, the WRERR is read as ‘1’. This can indicate that a write operation was prematurely terminated by a Reset, or a write operation was attempted improperly. Note: The EEIF interrupt flag bit (PIR2<4>) is set when the write is complete. It must be cleared in software. © 2007 Microchip Technology Inc. Preliminary DS39631B-page 75 PIC18F2420/2520/4420/4520 REGISTER 6-1: EECON1 REGISTER R/W-x R/W-x U-0 R/W-0 R/W-x R/W-0 R/S-0 R/S-0 EEPGD CFGS — FREE WRERR WREN WR RD bit 7 bit 0 bit 7 EEPGD: Flash Program or Data EEPROM Memory Select bit 1 = Access Flash program memory 0 = Access data EEPROM memory bit 6 CFGS: Flash Program/Data EEPROM or Configuration Select bit 1 = Access Configuration registers 0 = Access Flash program or data EEPROM memory bit 5 Unimplemented: Read as ‘0’ bit 4 FREE: Flash Row Erase Enable bit 1 = Erase the program memory row addressed by TBLPTR on the next WR command (cleared by completion of erase operation) 0 = Perform write only bit 3 WRERR: Flash Program/Data EEPROM Error Flag bit 1 = A write operation is prematurely terminated (any Reset during self-timed programming in normal operation, or an improper write attempt) 0 = The write operation completed Note: When a WRERR occurs, the EEPGD and CFGS bits are not cleared. This allows tracing of the error condition. bit 2 WREN: Flash Program/Data EEPROM Write Enable bit 1 = Allows write cycles to Flash program/data EEPROM 0 = Inhibits write cycles to Flash program/data EEPROM bit 1 WR: Write Control bit 1 = Initiates a data EEPROM erase/write cycle or a program memory erase cycle or write cycle. (The operation is self-timed and the bit is cleared by hardware once write is complete. The WR bit can only be set (not cleared) in software.) 0 = Write cycle to the EEPROM is complete bit 0 RD: Read Control bit 1 = Initiates an EEPROM read (Read takes one cycle. RD is cleared in hardware. The RD bit can only be set (not cleared) in software. RD bit cannot be set when EEPGD = 1 or CFGS = 1.) 0 = Does not initiate an EEPROM read Legend: R = Readable bit W = Writable bit S = Bit can be set by software, but not cleared U = Unimplemented bit, read as ‘0’ -n = Value at POR ‘1’ = Bit is set ‘0’ = Bit is cleared x = Bit is unknown PIC18F2420/2520/4420/4520 DS39631B-page 76 Preliminary © 2007 Microchip Technology Inc. 6.2.2 TABLAT – TABLE LATCH REGISTER The Table Latch (TABLAT) is an 8-bit register mapped into the SFR space. The Table Latch register is used to hold 8-bit data during data transfers between program memory and data RAM. 6.2.3 TBLPTR – TABLE POINTER REGISTER The Table Pointer (TBLPTR) register addresses a byte within the program memory. The TBLPTR is comprised of three SFR registers: Table Pointer Upper Byte, Table Pointer High Byte and Table Pointer Low Byte (TBLPTRU:TBLPTRH:TBLPTRL). These three registers join to form a 22-bit wide pointer. The low-order 21 bits allow the device to address up to 2 Mbytes of program memory space. The 22nd bit allows access to the device ID, the user ID and the configuration bits. The Table Pointer register, TBLPTR, is used by the TBLRD and TBLWT instructions. These instructions can update the TBLPTR in one of four ways based on the table operation. These operations are shown in Table 6-1. These operations on the TBLPTR only affect the low-order 21 bits. 6.2.4 TABLE POINTER BOUNDARIES TBLPTR is used in reads, writes and erases of the Flash program memory. When a TBLRD is executed, all 22 bits of the TBLPTR determine which byte is read from program memory into TABLAT. When a TBLWT is executed, the six LSbs of the Table Pointer register (TBLPTR<5:0>) determine which of the 64 program memory holding registers is written to. When the timed write to program memory begins (via the WR bit), the 16 MSbs of the TBLPTR (TBLPTR<21:6>) determine which program memory block of 64 bytes is written to. For more detail, see Section 6.5 “Writing to Flash Program Memory”. When an erase of program memory is executed, the 16 MSbs of the Table Pointer register (TBLPTR<21:6>) point to the 64-byte block that will be erased. The Least Significant bits (TBLPTR<5:0>) are ignored. Figure 6-3 describes the relevant boundaries of TBLPTR based on Flash program memory operations. TABLE 6-1: TABLE POINTER OPERATIONS WITH TBLRD AND TBLWT INSTRUCTIONS FIGURE 6-3: TABLE POINTER BOUNDARIES BASED ON OPERATION Example Operation on Table Pointer TBLRD* TBLWT* TBLPTR is not modified TBLRD*+ TBLWT*+ TBLPTR is incremented after the read/write TBLRD*- TBLWT*- TBLPTR is decremented after the read/write TBLRD+* TBLWT+* TBLPTR is incremented before the read/write 21 16 15 8 7 0 TABLE ERASE/WRITE TABLE WRITE TABLE READ – TBLPTR<21:0> TBLPTRU TBLPTRH TBLPTRL TBLPTR<21:6> TBLPTR<5:0> © 2007 Microchip Technology Inc. Preliminary DS39631B-page 77 PIC18F2420/2520/4420/4520 6.3 Reading the Flash Program Memory The TBLRD instruction is used to retrieve data from program memory and places it into data RAM. Table reads from program memory are performed one byte at a time. TBLPTR points to a byte address in program space. Executing TBLRD places the byte pointed to into TABLAT. In addition, TBLPTR can be modified automatically for the next table read operation. The internal program memory is typically organized by words. The Least Significant bit of the address selects between the high and low bytes of the word. Figure 6-4 shows the interface between the internal program memory and the TABLAT. FIGURE 6-4: READS FROM FLASH PROGRAM MEMORY EXAMPLE 6-1: READING A FLASH PROGRAM MEMORY WORD (Even Byte Address) Program Memory (Odd Byte Address) TBLRD TABLAT TBLPTR = xxxxx1 FETCH Instruction Register (IR) Read Register TBLPTR = xxxxx0 MOVLW CODE_ADDR_UPPER ; Load TBLPTR with the base MOVWF TBLPTRU ; address of the word MOVLW CODE_ADDR_HIGH MOVWF TBLPTRH MOVLW CODE_ADDR_LOW MOVWF TBLPTRL READ_WORD TBLRD*+ ; read into TABLAT and increment MOVF TABLAT, W ; get data MOVWF WORD_EVEN TBLRD*+ ; read into TABLAT and increment MOVFW TABLAT, W ; get data MOVF WORD_ODD PIC18F2420/2520/4420/4520 DS39631B-page 78 Preliminary © 2007 Microchip Technology Inc. 6.4 Erasing Flash Program Memory The minimum erase block is 32 words or 64 bytes. Only through the use of an external programmer, or through ICSP control, can larger blocks of program memory be bulk erased. Word erase in the Flash array is not supported. When initiating an erase sequence from the microcontroller itself, a block of 64 bytes of program memory is erased. The Most Significant 16 bits of the TBLPTR<21:6> point to the block being erased. TBLPTR<5:0> are ignored. The EECON1 register commands the erase operation. The EEPGD bit must be set to point to the Flash program memory. The WREN bit must be set to enable write operations. The FREE bit is set to select an erase operation. For protection, the write initiate sequence for EECON2 must be used. A long write is necessary for erasing the internal Flash. Instruction execution is halted while in a long write cycle. The long write will be terminated by the internal programming timer. 6.4.1 FLASH PROGRAM MEMORY ERASE SEQUENCE The sequence of events for erasing a block of internal program memory location is: 1. Load Table Pointer register with address of row being erased. 2. Set the EECON1 register for the erase operation: • set EEPGD bit to point to program memory; • clear the CFGS bit to access program memory; • set WREN bit to enable writes; • set FREE bit to enable the erase. 3. Disable interrupts. 4. Write 55h to EECON2. 5. Write 0AAh to EECON2. 6. Set the WR bit. This will begin the row erase cycle. 7. The CPU will stall for duration of the erase (about 2 ms using internal timer). 8. Re-enable interrupts. EXAMPLE 6-2: ERASING A FLASH PROGRAM MEMORY ROW MOVLW CODE_ADDR_UPPER ; load TBLPTR with the base MOVWF TBLPTRU ; address of the memory block MOVLW CODE_ADDR_HIGH MOVWF TBLPTRH MOVLW CODE_ADDR_LOW MOVWF TBLPTRL ERASE_ROW BSF EECON1, EEPGD ; point to Flash program memory BCF EECON1, CFGS ; access Flash program memory BSF EECON1, WREN ; enable write to memory BSF EECON1, FREE ; enable Row Erase operation BCF INTCON, GIE ; disable interrupts Required MOVLW 55h Sequence MOVWF EECON2 ; write 55h MOVLW 0AAh MOVWF EECON2 ; write 0AAh BSF EECON1, WR ; start erase (CPU stall) BSF INTCON, GIE ; re-enable interrupts © 2007 Microchip Technology Inc. Preliminary DS39631B-page 79 PIC18F2420/2520/4420/4520 6.5 Writing to Flash Program Memory The minimum programming block is 32 words or 64 bytes. Word or byte programming is not supported. Table writes are used internally to load the holding registers needed to program the Flash memory. There are 64 holding registers used by the table writes for programming. Since the Table Latch (TABLAT) is only a single byte, the TBLWT instruction may need to be executed 64 times for each programming operation. All of the table write operations will essentially be short writes because only the holding registers are written. At the end of updating the 64 holding registers, the EECON1 register must be written to in order to start the programming operation with a long write. The long write is necessary for programming the internal Flash. Instruction execution is halted while in a long write cycle. The long write will be terminated by the internal programming timer. The EEPROM on-chip timer controls the write time. The write/erase voltages are generated by an on-chip charge pump, rated to operate over the voltage range of the device. FIGURE 6-5: TABLE WRITES TO FLASH PROGRAM MEMORY 6.5.1 FLASH PROGRAM MEMORY WRITE SEQUENCE The sequence of events for programming an internal program memory location should be: 1. Read 64 bytes into RAM. 2. Update data values in RAM as necessary. 3. Load Table Pointer register with address being erased. 4. Execute the row erase procedure. 5. Load Table Pointer register with address of first byte being written. 6. Write the 64 bytes into the holding registers with auto-increment. 7. Set the EECON1 register for the write operation: • set EEPGD bit to point to program memory; • clear the CFGS bit to access program memory; • set WREN to enable byte writes. 8. Disable interrupts. 9. Write 55h to EECON2. 10. Write 0AAh to EECON2. 11. Set the WR bit. This will begin the write cycle. 12. The CPU will stall for duration of the write (about 2 ms using internal timer). 13. Re-enable interrupts. 14. Verify the memory (table read). This procedure will require about 6 ms to update one row of 64 bytes of memory. An example of the required code is given in Example 6-3. Note: The default value of the holding registers on device Resets and after write operations is FFh. A write of FFh to a holding register does not modify that byte. This means that individual bytes of program memory may be modified, provided that the change does not attempt to change any bit from a ‘0’ to a ‘1’. When modifying individual bytes, it is not necessary to load all 64 holding registers before executing a write operation. TABLAT TBLPTR = xxxxx0 TBLPTR = xxxxx1 TBLPTR = xxxx3F Write Register TBLPTR = xxxxx2 Program Memory Holding Register Holding Register Holding Register Holding Register 8 8 8 8 Note: Before setting the WR bit, the Table Pointer address needs to be within the intended address range of the 64 bytes in the holding register. PIC18F2420/2520/4420/4520 DS39631B-page 80 Preliminary © 2007 Microchip Technology Inc. EXAMPLE 6-3: WRITING TO FLASH PROGRAM MEMORY MOVLW D'64 ; number of bytes in erase block MOVWF COUNTER MOVLW BUFFER_ADDR_HIGH ; point to buffer MOVWF FSR0H MOVLW BUFFER_ADDR_LOW MOVWF FSR0L MOVLW CODE_ADDR_UPPER ; Load TBLPTR with the base MOVWF TBLPTRU ; address of the memory block MOVLW CODE_ADDR_HIGH MOVWF TBLPTRH MOVLW CODE_ADDR_LOW MOVWF TBLPTRL READ_BLOCK TBLRD*+ ; read into TABLAT, and inc MOVF TABLAT, W ; get data MOVWF POSTINC0 ; store data DECFSZ COUNTER ; done? BRA READ_BLOCK ; repeat MODIFY_WORD MOVLW DATA_ADDR_HIGH ; point to buffer MOVWF FSR0H MOVLW DATA_ADDR_LOW MOVWF FSR0L MOVLW NEW_DATA_LOW ; update buffer word MOVWF POSTINC0 MOVLW NEW_DATA_HIGH MOVWF INDF0 ERASE_BLOCK MOVLW CODE_ADDR_UPPER ; load TBLPTR with the base MOVWF TBLPTRU ; address of the memory block MOVLW CODE_ADDR_HIGH MOVWF TBLPTRH MOVLW CODE_ADDR_LOW MOVWF TBLPTRL BSF EECON1, EEPGD ; point to Flash program memory BCF EECON1, CFGS ; access Flash program memory BSF EECON1, WREN ; enable write to memory BSF EECON1, FREE ; enable Row Erase operation BCF INTCON, GIE ; disable interrupts MOVLW 55h Required MOVWF EECON2 ; write 55h Sequence MOVLW 0AAh MOVWF EECON2 ; write 0AAh BSF EECON1, WR ; start erase (CPU stall) BSF INTCON, GIE ; re-enable interrupts TBLRD*- ; dummy read decrement MOVLW BUFFER_ADDR_HIGH ; point to buffer MOVWF FSR0H MOVLW BUFFER_ADDR_LOW MOVWF FSR0L WRITE_BUFFER_BACK MOVLW D’64 ; number of bytes in holding register MOVWF COUNTER WRITE_BYTE_TO_HREGS MOVFF POSTINC0, WREG ; get low byte of buffer data MOVWF TABLAT ; present data to table latch TBLWT+* ; write data, perform a short write ; to internal TBLWT holding register. DECFSZ COUNTER ; loop until buffers are full BRA WRITE_WORD_TO_HREGS © 2007 Microchip Technology Inc. Preliminary DS39631B-page 81 PIC18F2420/2520/4420/4520 EXAMPLE 6-3: WRITING TO FLASH PROGRAM MEMORY (CONTINUED) 6.5.2 WRITE VERIFY Depending on the application, good programming practice may dictate that the value written to the memory should be verified against the original value. This should be used in applications where excessive writes can stress bits near the specification limit. 6.5.3 UNEXPECTED TERMINATION OF WRITE OPERATION If a write is terminated by an unplanned event, such as loss of power or an unexpected Reset, the memory location just programmed should be verified and reprogrammed if needed. If the write operation is interrupted by a MCLR Reset or a WDT Time-out Reset during normal operation, the user can check the WRERR bit and rewrite the location(s) as needed. 6.5.4 PROTECTION AGAINST SPURIOUS WRITES To protect against spurious writes to Flash program memory, the write initiate sequence must also be followed. See Section 23.0 “Special Features of the CPU” for more detail. 6.6 Flash Program Operation During Code Protection See Section 23.5 “Program Verification and Code Protection” for details on code protection of Flash program memory. TABLE 6-2: REGISTERS ASSOCIATED WITH PROGRAM FLASH MEMORY PROGRAM_MEMORY BSF EECON1, EEPGD ; point to Flash program memory BCF EECON1, CFGS ; access Flash program memory BSF EECON1, WREN ; enable write to memory BCF INTCON, GIE ; disable interrupts MOVLW 55h Required MOVWF EECON2 ; write 55h Sequence MOVLW 0AAh MOVWF EECON2 ; write 0AAh BSF EECON1, WR ; start program (CPU stall) BSF INTCON, GIE ; re-enable interrupts BCF EECON1, WREN ; disable write to memory Name Bit 7 Bit 6 Bit 5 Bit 4 Bit 3 Bit 2 Bit 1 Bit 0 Reset Values on page TBLPTRU — — bit 21 Program Memory Table Pointer Upper Byte (TBLPTR<20:16>) 49 TBPLTRH Program Memory Table Pointer High Byte (TBLPTR<15:8>) 49 TBLPTRL Program Memory Table Pointer Low Byte (TBLPTR<7:0>) 49 TABLAT Program Memory Table Latch 49 INTCON GIE/GIEH PEIE/GIEL TMR0IE INT0IE RBIE TMR0IF INT0IF RBIF 49 EECON2 EEPROM Control Register 2 (not a physical register) 51 EECON1 EEPGD CFGS — FREE WRERR WREN WR RD 51 IPR2 OSCFIP CMIP — EEIP BCLIP HLVDIP TMR3IP CCP2IP 52 PIR2 OSCFIF CMIF — EEIF BCLIF HLVDIF TMR3IF CCP2IF 52 PIE2 OSCFIE CMIE — EEIE BCLIE HLVDIE TMR3IE CCP2IE 52 Legend: — = unimplemented, read as ‘0’. Shaded cells are not used during Flash/EEPROM access. PIC18F2420/2520/4420/4520 DS39631B-page 82 Preliminary © 2007 Microchip Technology Inc. NOTES: © 2007 Microchip Technology Inc. Preliminary DS39631B-page 83 PIC18F2420/2520/4420/4520 7.0 DATA EEPROM MEMORY The data EEPROM is a nonvolatile memory array, separate from the data RAM and program memory, that is used for long-term storage of program data. It is not directly mapped in either the register file or program memory space but is indirectly addressed through the Special Function Registers (SFRs). The EEPROM is readable and writable during normal operation over the entire VDD range. Five SFRs are used to read and write to the data EEPROM as well as the program memory. They are: • EECON1 • EECON2 • EEDATA • EEADR The data EEPROM allows byte read and write. When interfacing to the data memory block, EEDATA holds the 8-bit data for read/write and the EEADR register holds the address of the EEPROM location being accessed. The EEPROM data memory is rated for high erase/write cycle endurance. A byte write automatically erases the location and writes the new data (erase-before-write). The write time is controlled by an on-chip timer; it will vary with voltage and temperature as well as from chip to chip. Please refer to parameter D122 (Table 26-1 in Section 26.0 “Electrical Characteristics”) for exact limits. 7.1 EEADR Register The EEADR register is used to address the data EEPROM for read and write operations. The 8-bit range of the register can address a memory range of 256 bytes (00h to FFh). 7.2 EECON1 and EECON2 Registers Access to the data EEPROM is controlled by two registers: EECON1 and EECON2. These are the same registers which control access to the program memory and are used in a similar manner for the data EEPROM. The EECON1 register (Register 7-1) is the control register for data and program memory access. Control bit EEPGD determines if the access will be to program or data EEPROM memory. When clear, operations will access the data EEPROM memory. When set, program memory is accessed. Control bit, CFGS, determines if the access will be to the configuration registers or to program memory/data EEPROM memory. When set, subsequent operations access configuration registers. When CFGS is clear, the EEPGD bit selects either program Flash or data EEPROM memory. The WREN bit, when set, will allow a write operation. On power-up, the WREN bit is clear. The WRERR bit is set in hardware when the WR bit is set and cleared when the internal programming timer expires and the write operation is complete. The WR control bit initiates write operations. The bit can be set but not cleared in software. It is only cleared in hardware at the completion of the write operation. Control bits, RD and WR, start read and erase/write operations, respectively. These bits are set by firmware and cleared by hardware at the completion of the operation. The RD bit cannot be set when accessing program memory (EEPGD = 1). Program memory is read using table read instructions. See Section 6.1 “Table Reads and Table Writes” regarding table reads. The EECON2 register is not a physical register. It is used exclusively in the memory write and erase sequences. Reading EECON2 will read all ‘0’s. Note: During normal operation, the WRERR may read as ‘1’. This can indicate that a write operation was prematurely terminated by a Reset, or a write operation was attempted improperly. Note: The EEIF interrupt flag bit (PIR2<4>) is set when the write is complete. It must be cleared in software. PIC18F2420/2520/4420/4520 DS39631B-page 84 Preliminary © 2007 Microchip Technology Inc. REGISTER 7-1: EECON1 REGISTER R/W-x R/W-x U-0 R/W-0 R/W-x R/W-0 R/S-0 R/S-0 EEPGD CFGS — FREE WRERR WREN WR RD bit 7 bit 0 bit 7 EEPGD: Flash Program or Data EEPROM Memory Select bit 1 = Access Flash program memory 0 = Access data EEPROM memory bit 6 CFGS: Flash Program/Data EEPROM or Configuration Select bit 1 = Access configuration registers 0 = Access Flash program or data EEPROM memory bit 5 Unimplemented: Read as ‘0’ bit 4 FREE: Flash Row Erase Enable bit 1 = Erase the program memory row addressed by TBLPTR on the next WR command (cleared by completion of erase operation) 0 = Perform write only bit 3 WRERR: Flash Program/Data EEPROM Error Flag bit 1 = A write operation is prematurely terminated (any Reset during self-timed programming in normal operation, or an improper write attempt) 0 = The write operation completed Note: When a WRERR occurs, the EEPGD and CFGS bits are not cleared. This allows tracing of the error condition. bit 2 WREN: Flash Program/Data EEPROM Write Enable bit 1 = Allows write cycles to Flash program/data EEPROM 0 = Inhibits write cycles to Flash program/data EEPROM bit 1 WR: Write Control bit 1 = Initiates a data EEPROM erase/write cycle or a program memory erase cycle or write cycle (The operation is self-timed and the bit is cleared by hardware once write is complete. The WR bit can only be set (not cleared) in software.) 0 = Write cycle to the EEPROM is complete bit 0 RD: Read Control bit 1 = Initiates an EEPROM read (Read takes one cycle. RD is cleared in hardware. The RD bit can only be set (not cleared) in software. RD bit cannot be set when EEPGD = 1 or CFGS = 1.) 0 = Does not initiate an EEPROM read Legend: R = Readable bit W = Writable bit S = Bit can be set by software, but not cleared U = Unimplemented bit, read as ‘0’ -n = Value at POR ‘1’ = Bit is set ‘0’ = Bit is cleared x = Bit is unknown © 2007 Microchip Technology Inc. Preliminary DS39631B-page 85 PIC18F2420/2520/4420/4520 7.3 Reading the Data EEPROM Memory To read a data memory location, the user must write the address to the EEADR register, clear the EEPGD control bit (EECON1<7>) and then set control bit, RD (EECON1<0>). The data is available on the very next instruction cycle; therefore, the EEDATA register can be read by the next instruction. EEDATA will hold this value until another read operation, or until it is written to by the user (during a write operation). The basic process is shown in Example 7-1. 7.4 Writing to the Data EEPROM Memory To write an EEPROM data location, the address must first be written to the EEADR register and the data written to the EEDATA register. The sequence in Example 7-2 must be followed to initiate the write cycle. The write will not begin if this sequence is not exactly followed (write 55h to EECON2, write 0AAh to EECON2, then set WR bit) for each byte. It is strongly recommended that interrupts be disabled during this code segment. Additionally, the WREN bit in EECON1 must be set to enable writes. This mechanism prevents accidental writes to data EEPROM due to unexpected code execution (i.e., runaway programs). The WREN bit should be kept clear at all times, except when updating the EEPROM. The WREN bit is not cleared by hardware. After a write sequence has been initiated, EECON1, EEADR and EEDATA cannot be modified. The WR bit will be inhibited from being set unless the WREN bit is set. Both WR and WREN cannot be set with the same instruction. At the completion of the write cycle, the WR bit is cleared in hardware and the EEPROM Interrupt Flag bit, EEIF, is set. The user may either enable this interrupt or poll this bit. EEIF must be cleared by software. 7.5 Write Verify Depending on the application, good programming practice may dictate that the value written to the memory should be verified against the original value. This should be used in applications where excessive writes can stress bits near the specification limit. EXAMPLE 7-1: DATA EEPROM READ EXAMPLE 7-2: DATA EEPROM WRITE MOVLW DATA_EE_ADDR ; MOVWF EEADR ; Data Memory Address to read BCF EECON1, EEPGD ; Point to DATA memory BCF EECON1, CFGS ; Access EEPROM BSF EECON1, RD ; EEPROM Read MOVF EEDATA, W ; W = EEDATA MOVLW DATA_EE_ADDR ; MOVWF EEADR ; Data Memory Address to write MOVLW DATA_EE_DATA ; MOVWF EEDATA ; Data Memory Value to write BCF EECON1, EEPGD ; Point to DATA memory BCF EECON1, CFGS ; Access EEPROM BSF EECON1, WREN ; Enable writes BCF INTCON, GIE ; Disable Interrupts MOVLW 55h ; Required MOVWF EECON2 ; Write 55h Sequence MOVLW 0AAh ; MOVWF EECON2 ; Write 0AAh BSF EECON1, WR ; Set WR bit to begin write BSF INTCON, GIE ; Enable Interrupts ; User code execution BCF EECON1, WREN ; Disable writes on write complete (EEIF set) PIC18F2420/2520/4420/4520 DS39631B-page 86 Preliminary © 2007 Microchip Technology Inc. 7.6 Operation During Code-Protect Data EEPROM memory has its own code-protect bits in configuration words. External read and write operations are disabled if code protection is enabled. The microcontroller itself can both read and write to the internal data EEPROM, regardless of the state of the code-protect configuration bit. Refer to Section 23.0 “Special Features of the CPU” for additional information. 7.7 Protection Against Spurious Write There are conditions when the user may not want to write to the data EEPROM memory. To protect against spurious EEPROM writes, various mechanisms have been implemented. On power-up, the WREN bit is cleared. In addition, writes to the EEPROM are blocked during the Power-up Timer period (TPWRT, parameter 33). The write initiate sequence and the WREN bit together help prevent an accidental write during brown-out, power glitch or software malfunction. 7.8 Using the Data EEPROM The data EEPROM is a high endurance, byte addressable array that has been optimized for the storage of frequently changing information (e.g., program variables or other data that are updated often). Frequently changing values will typically be updated more often than specification D124. If this is not the case, an array refresh must be performed. For this reason, variables that change infrequently (such as constants, IDs, calibration, etc.) should be stored in Flash program memory. A simple data EEPROM refresh routine is shown in Example 7-3. EXAMPLE 7-3: DATA EEPROM REFRESH ROUTINE Note: If data EEPROM is only used to store constants and/or data that changes rarely, an array refresh is likely not required. See specification D124. CLRF EEADR ; Start at address 0 BCF EECON1, CFGS ; Set for memory BCF EECON1, EEPGD ; Set for Data EEPROM BCF INTCON, GIE ; Disable interrupts BSF EECON1, WREN ; Enable writes Loop ; Loop to refresh array BSF EECON1, RD ; Read current address MOVLW 55h ; MOVWF EECON2 ; Write 55h MOVLW 0AAh ; MOVWF EECON2 ; Write 0AAh BSF EECON1, WR ; Set WR bit to begin write BTFSC EECON1, WR ; Wait for write to complete BRA $-2 INCFSZ EEADR, F ; Increment address BRA LOOP ; Not zero, do it again BCF EECON1, WREN ; Disable writes BSF INTCON, GIE ; Enable interrupts © 2007 Microchip Technology Inc. Preliminary DS39631B-page 87 PIC18F2420/2520/4420/4520 TABLE 7-1: REGISTERS ASSOCIATED WITH DATA EEPROM MEMORY Name Bit 7 Bit 6 Bit 5 Bit 4 Bit 3 Bit 2 Bit 1 Bit 0 Reset Values on page INTCON GIE/GIEH PEIE/GIEL TMR0IE INT0IE RBIE TMR0IF INT0IF RBIF 49 EEADR EEPROM Address Register 51 EEDATA EEPROM Data Register 51 EECON2 EEPROM Control Register 2 (not a physical register) 51 EECON1 EEPGD CFGS — FREE WRERR WREN WR RD 51 IPR2 OSCFIP CMIP — EEIP BCLIP HLVDIP TMR3IP CCP2IP 52 PIR2 OSCFIF CMIF — EEIF BCLIF HLVDIF TMR3IF CCP2IF 52 PIE2 OSCFIE CMIE — EEIE BCLIE HLVDIE TMR3IE CCP2IE 52 Legend: — = unimplemented, read as ‘0’. Shaded cells are not used during Flash/EEPROM access. PIC18F2420/2520/4420/4520 DS39631B-page 88 Preliminary © 2007 Microchip Technology Inc. NOTES: © 2007 Microchip Technology Inc. Preliminary DS39631B-page 89 PIC18F2420/2520/4420/4520 8.0 8 x 8 HARDWARE MULTIPLIER 8.1 Introduction All PIC18 devices include an 8 x 8 hardware multiplier as part of the ALU. The multiplier performs an unsigned operation and yields a 16-bit result that is stored in the product register pair, PRODH:PRODL. The multiplier’s operation does not affect any flags in the Status register. Making multiplication a hardware operation allows it to be completed in a single instruction cycle. This has the advantages of higher computational throughput and reduced code size for multiplication algorithms and allows the PIC18 devices to be used in many applications previously reserved for digital signal processors. A comparison of various hardware and software multiply operations, along with the savings in memory and execution time, is shown in Table 8-1. 8.2 Operation Example 8-1 shows the instruction sequence for an 8 x 8 unsigned multiplication. Only one instruction is required when one of the arguments is already loaded in the WREG register. Example 8-2 shows the sequence to do an 8 x 8 signed multiplication. To account for the sign bits of the arguments, each argument’s Most Significant bit (MSb) is tested and the appropriate subtractions are done. EXAMPLE 8-1: 8 x 8 UNSIGNED MULTIPLY ROUTINE EXAMPLE 8-2: 8 x 8 SIGNED MULTIPLY ROUTINE TABLE 8-1: PERFORMANCE COMPARISON FOR VARIOUS MULTIPLY OPERATIONS MOVF ARG1, W ; MULWF ARG2 ; ARG1 * ARG2 -> ; PRODH:PRODL MOVF ARG1, W MULWF ARG2 ; ARG1 * ARG2 -> ; PRODH:PRODL BTFSC ARG2, SB ; Test Sign Bit SUBWF PRODH, F ; PRODH = PRODH ; - ARG1 MOVF ARG2, W BTFSC ARG1, SB ; Test Sign Bit SUBWF PRODH, F ; PRODH = PRODH ; - ARG2 Routine Multiply Method Program Memory (Words) Cycles (Max) Time @ 40 MHz @ 10 MHz @ 4 MHz 8 x 8 unsigned Without hardware multiply 13 69 6.9 μs 27.6 μs 69 μs Hardware multiply 1 1 100 ns 400 ns 1 μs 8 x 8 signed Without hardware multiply 33 91 9.1 μs 36.4 μs 91 μs Hardware multiply 6 6 600 ns 2.4 μs 6 μs 16 x 16 unsigned Without hardware multiply 21 242 24.2 μs 96.8 μs 242 μs Hardware multiply 28 28 2.8 μs 11.2 μs 28 μs 16 x 16 signed Without hardware multiply 52 254 25.4 μs 102.6 μs 254 μs Hardware multiply 35 40 4.0 μs 16.0 μs 40 μs PIC18F2420/2520/4420/4520 DS39631B-page 90 Preliminary © 2007 Microchip Technology Inc. Example 8-3 shows the sequence to do a 16 x 16 unsigned multiplication. Equation 8-1 shows the algorithm that is used. The 32-bit result is stored in four registers (RES3:RES0). EQUATION 8-1: 16 x 16 UNSIGNED MULTIPLICATION ALGORITHM EXAMPLE 8-3: 16 x 16 UNSIGNED MULTIPLY ROUTINE Example 8-4 shows the sequence to do a 16 x 16 signed multiply. Equation 8-2 shows the algorithm used. The 32-bit result is stored in four registers (RES3:RES0). To account for the sign bits of the arguments, the MSb for each argument pair is tested and the appropriate subtractions are done. EQUATION 8-2: 16 x 16 SIGNED MULTIPLICATION ALGORITHM EXAMPLE 8-4: 16 x 16 SIGNED MULTIPLY ROUTINE RES3:RES0 = ARG1H:ARG1L • ARG2H:ARG2L = (ARG1H • ARG2H • 216) + (ARG1H • ARG2L • 28) + (ARG1L • ARG2H • 28) + (ARG1L • ARG2L) MOVF ARG1L, W MULWF ARG2L ; ARG1L * ARG2L-> ; PRODH:PRODL MOVFF PRODH, RES1 ; MOVFF PRODL, RES0 ; ; MOVF ARG1H, W MULWF ARG2H ; ARG1H * ARG2H-> ; PRODH:PRODL MOVFF PRODH, RES3 ; MOVFF PRODL, RES2 ; ; MOVF ARG1L, W MULWF ARG2H ; ARG1L * ARG2H-> ; PRODH:PRODL MOVF PRODL, W ; ADDWF RES1, F ; Add cross MOVF PRODH, W ; products ADDWFC RES2, F ; CLRF WREG ; ADDWFC RES3, F ; ; MOVF ARG1H, W ; MULWF ARG2L ; ARG1H * ARG2L-> ; PRODH:PRODL MOVF PRODL, W ; ADDWF RES1, F ; Add cross MOVF PRODH, W ; products ADDWFC RES2, F ; CLRF WREG ; ADDWFC RES3, F ; RES3:RES0 = ARG1H:ARG1L • ARG2H:ARG2L = (ARG1H • ARG2H • 216) + (ARG1H • ARG2L • 28) + (ARG1L • ARG2H • 28) + (ARG1L • ARG2L) + (-1 • ARG2H<7> • ARG1H:ARG1L • 216) + (-1 • ARG1H<7> • ARG2H:ARG2L • 216) MOVF ARG1L, W MULWF ARG2L ; ARG1L * ARG2L -> ; PRODH:PRODL MOVFF PRODH, RES1 ; MOVFF PRODL, RES0 ; ; MOVF ARG1H, W MULWF ARG2H ; ARG1H * ARG2H -> ; PRODH:PRODL MOVFF PRODH, RES3 ; MOVFF PRODL, RES2 ; ; MOVF ARG1L, W MULWF ARG2H ; ARG1L * ARG2H -> ; PRODH:PRODL MOVF PRODL, W ; ADDWF RES1, F ; Add cross MOVF PRODH, W ; products ADDWFC RES2, F ; CLRF WREG ; ADDWFC RES3, F ; ; MOVF ARG1H, W ; MULWF ARG2L ; ARG1H * ARG2L -> ; PRODH:PRODL MOVF PRODL, W ; ADDWF RES1, F ; Add cross MOVF PRODH, W ; products ADDWFC RES2, F ; CLRF WREG ; ADDWFC RES3, F ; ; BTFSS ARG2H, 7 ; ARG2H:ARG2L neg? BRA SIGN_ARG1 ; no, check ARG1 MOVF ARG1L, W ; SUBWF RES2 ; MOVF ARG1H, W ; SUBWFB RES3 ; SIGN_ARG1 BTFSS ARG1H, 7 ; ARG1H:ARG1L neg? BRA CONT_CODE ; no, done MOVF ARG2L, W ; SUBWF RES2 ; MOVF ARG2H, W ; SUBWFB RES3 ; CONT_CODE : © 2007 Microchip Technology Inc. Preliminary DS39631B-page 91 PIC18F2420/2520/4420/4520 9.0 INTERRUPTS The PIC18F2420/2520/4420/4520 devices have multiple interrupt sources and an interrupt priority feature that allows most interrupt sources to be assigned a high priority level or a low priority level. The high priority interrupt vector is at 0008h and the low priority interrupt vector is at 0018h. High priority interrupt events will interrupt any low priority interrupts that may be in progress. There are ten registers which are used to control interrupt operation. These registers are: • RCON • INTCON • INTCON2 • INTCON3 • PIR1, PIR2 • PIE1, PIE2 • IPR1, IPR2 It is recommended that the Microchip header files supplied with MPLAB® IDE be used for the symbolic bit names in these registers. This allows the assembler/ compiler to automatically take care of the placement of these bits within the specified register. In general, interrupt sources have three bits to control their operation. They are: • Flag bit to indicate that an interrupt event occurred • Enable bit that allows program execution to branch to the interrupt vector address when the flag bit is set • Priority bit to select high priority or low priority The interrupt priority feature is enabled by setting the IPEN bit (RCON<7>). When interrupt priority is enabled, there are two bits which enable interrupts globally. Setting the GIEH bit (INTCON<7>) enables all interrupts that have the priority bit set (high priority). Setting the GIEL bit (INTCON<6>) enables all interrupts that have the priority bit cleared (low priority). When the interrupt flag, enable bit and appropriate global interrupt enable bit are set, the interrupt will vector immediately to address 0008h or 0018h, depending on the priority bit setting. Individual interrupts can be disabled through their corresponding enable bits. When the IPEN bit is cleared (default state), the interrupt priority feature is disabled and interrupts are compatible with PIC® mid-range devices. In Compatibility mode, the interrupt priority bits for each source have no effect. INTCON<6> is the PEIE bit, which enables/disables all peripheral interrupt sources. INTCON<7> is the GIE bit, which enables/disables all interrupt sources. All interrupts branch to address 0008h in Compatibility mode. When an interrupt is responded to, the global interrupt enable bit is cleared to disable further interrupts. If the IPEN bit is cleared, this is the GIE bit. If interrupt priority levels are used, this will be either the GIEH or GIEL bit. High priority interrupt sources can interrupt a low priority interrupt. Low priority interrupts are not processed while high priority interrupts are in progress. The return address is pushed onto the stack and the PC is loaded with the interrupt vector address (0008h or 0018h). Once in the Interrupt Service Routine, the source(s) of the interrupt can be determined by polling the interrupt flag bits. The interrupt flag bits must be cleared in software before re-enabling interrupts to avoid recursive interrupts. The “return from interrupt” instruction, RETFIE, exits the interrupt routine and sets the GIE bit (GIEH or GIEL if priority levels are used), which re-enables interrupts. For external interrupt events, such as the INT pins or the PORTB input change interrupt, the interrupt latency will be three to four instruction cycles. The exact latency is the same for one or two-cycle instructions. Individual interrupt flag bits are set, regardless of the status of their corresponding enable bit or the GIE bit. Note: Do not use the MOVFF instruction to modify any of the interrupt control registers while any interrupt is enabled. Doing so may cause erratic microcontroller behavior. PIC18F2420/2520/4420/4520 DS39631B-page 92 Preliminary © 2007 Microchip Technology Inc. FIGURE 9-1: PIC18 INTERRUPT LOGIC TMR0IE GIEH/GIE GIEL/PEIE Wake-up if in Interrupt to CPU Vector to Location 0008h INT2IF INT2IE INT2IP INT1IF INT1IE INT1IP TMR0IF TMR0IE TMR0IP RBIF RBIE RBIP IPEN TMR0IF TMR0IP INT1IF INT1IE INT1IP INT2IF INT2IE INT2IP RBIF RBIE RBIP INT0IF INT0IE GIEL/PEIE Interrupt to CPU Vector to Location IPEN IPEN 0018h SSPIF SSPIE SSPIP SSPIF SSPIE SSPIP ADIF ADIE ADIP RCIF RCIE RCIP Additional Peripheral Interrupts ADIF ADIE ADIP High Priority Interrupt Generation Low Priority Interrupt Generation RCIF RCIE RCIP Additional Peripheral Interrupts Idle or Sleep modes GIEH/GIE © 2007 Microchip Technology Inc. Preliminary DS39631B-page 93 PIC18F2420/2520/4420/4520 9.1 INTCON Registers The INTCON registers are readable and writable registers, which contain various enable, priority and flag bits. REGISTER 9-1: INTCON REGISTER Note: Interrupt flag bits are set when an interrupt condition occurs, regardless of the state of its corresponding enable bit or the global enable bit. User software should ensure the appropriate interrupt flag bits are clear prior to enabling an interrupt. This feature allows for software polling. R/W-0 R/W-0 R/W-0 R/W-0 R/W-0 R/W-0 R/W-0 R/W-x GIE/GIEH PEIE/GIEL TMR0IE INT0IE RBIE TMR0IF INT0IF RBIF bit 7 bit 0 bit 7 GIE/GIEH: Global Interrupt Enable bit When IPEN = 0: 1 = Enables all unmasked interrupts 0 = Disables all interrupts When IPEN = 1: 1 = Enables all high priority interrupts 0 = Disables all interrupts bit 6 PEIE/GIEL: Peripheral Interrupt Enable bit When IPEN = 0: 1 = Enables all unmasked peripheral interrupts 0 = Disables all peripheral interrupts When IPEN = 1: 1 = Enables all low priority peripheral interrupts 0 = Disables all low priority peripheral interrupts bit 5 TMR0IE: TMR0 Overflow Interrupt Enable bit 1 = Enables the TMR0 overflow interrupt 0 = Disables the TMR0 overflow interrupt bit 4 INT0IE: INT0 External Interrupt Enable bit 1 = Enables the INT0 external interrupt 0 = Disables the INT0 external interrupt bit 3 RBIE: RB Port Change Interrupt Enable bit 1 = Enables the RB port change interrupt 0 = Disables the RB port change interrupt bit 2 TMR0IF: TMR0 Overflow Interrupt Flag bit 1 = TMR0 register has overflowed (must be cleared in software) 0 = TMR0 register did not overflow bit 1 INT0IF: INT0 External Interrupt Flag bit 1 = The INT0 external interrupt occurred (must be cleared in software) 0 = The INT0 external interrupt did not occur bit 0 RBIF: RB Port Change Interrupt Flag bit 1 = At least one of the RB7:RB4 pins changed state (must be cleared in software) 0 = None of the RB7:RB4 pins have changed state Note: A mismatch condition will continue to set this bit. Reading PORTB will end the mismatch condition and allow the bit to be cleared. Legend: R = Readable bit W = Writable bit U = Unimplemented bit, read as ‘0’ -n = Value at POR ‘1’ = Bit is set ‘0’ = Bit is cleared x = Bit is unknown PIC18F2420/2520/4420/4520 DS39631B-page 94 Preliminary © 2007 Microchip Technology Inc. REGISTER 9-2: INTCON2 REGISTER R/W-1 R/W-1 R/W-1 R/W-1 U-0 R/W-1 U-0 R/W-1 RBPU INTEDG0 INTEDG1 INTEDG2 — TMR0IP — RBIP bit 7 bit 0 bit 7 RBPU: PORTB Pull-up Enable bit 1 = All PORTB pull-ups are disabled 0 = PORTB pull-ups are enabled by individual port latch values bit 6 INTEDG0: External Interrupt 0 Edge Select bit 1 = Interrupt on rising edge 0 = Interrupt on falling edge bit 5 INTEDG1: External Interrupt 1 Edge Select bit 1 = Interrupt on rising edge 0 = Interrupt on falling edge bit 4 INTEDG2: External Interrupt 2 Edge Select bit 1 = Interrupt on rising edge 0 = Interrupt on falling edge bit 3 Unimplemented: Read as ‘0’ bit 2 TMR0IP: TMR0 Overflow Interrupt Priority bit 1 = High priority 0 = Low priority bit 1 Unimplemented: Read as ‘0’ bit 0 RBIP: RB Port Change Interrupt Priority bit 1 = High priority 0 = Low priority Legend: R = Readable bit W = Writable bit U = Unimplemented bit, read as ‘0’ -n = Value at POR ‘1’ = Bit is set ‘0’ = Bit is cleared x = Bit is unknown Note: Interrupt flag bits are set when an interrupt condition occurs, regardless of the state of its corresponding enable bit or the global enable bit. User software should ensure the appropriate interrupt flag bits are clear prior to enabling an interrupt. This feature allows for software polling. © 2007 Microchip Technology Inc. Preliminary DS39631B-page 95 PIC18F2420/2520/4420/4520 REGISTER 9-3: INTCON3 REGISTER R/W-1 R/W-1 U-0 R/W-0 R/W-0 U-0 R/W-0 R/W-0 INT2IP INT1IP — INT2IE INT1IE — INT2IF INT1IF bit 7 bit 0 bit 7 INT2IP: INT2 External Interrupt Priority bit 1 = High priority 0 = Low priority bit 6 INT1IP: INT1 External Interrupt Priority bit 1 = High priority 0 = Low priority bit 5 Unimplemented: Read as ‘0’ bit 4 INT2IE: INT2 External Interrupt Enable bit 1 = Enables the INT2 external interrupt 0 = Disables the INT2 external interrupt bit 3 INT1IE: INT1 External Interrupt Enable bit 1 = Enables the INT1 external interrupt 0 = Disables the INT1 external interrupt bit 2 Unimplemented: Read as ‘0’ bit 1 INT2IF: INT2 External Interrupt Flag bit 1 = The INT2 external interrupt occurred (must be cleared in software) 0 = The INT2 external interrupt did not occur bit 0 INT1IF: INT1 External Interrupt Flag bit 1 = The INT1 external interrupt occurred (must be cleared in software) 0 = The INT1 external interrupt did not occur Legend: R = Readable bit W = Writable bit U = Unimplemented bit, read as ‘0’ -n = Value at POR ‘1’ = Bit is set ‘0’ = Bit is cleared x = Bit is unknown Note: Interrupt flag bits are set when an interrupt condition occurs, regardless of the state of its corresponding enable bit or the global enable bit. User software should ensure the appropriate interrupt flag bits are clear prior to enabling an interrupt. This feature allows for software polling. PIC18F2420/2520/4420/4520 DS39631B-page 96 Preliminary © 2007 Microchip Technology Inc. 9.2 PIR Registers The PIR registers contain the individual flag bits for the peripheral interrupts. Due to the number of peripheral interrupt sources, there are two Peripheral Interrupt Request Flag registers (PIR1 and PIR2). REGISTER 9-4: PIR1: PERIPHERAL INTERRUPT REQUEST (FLAG) REGISTER 1 Note 1: Interrupt flag bits are set when an interrupt condition occurs, regardless of the state of its corresponding enable bit or the Global Interrupt Enable bit, GIE (INTCON<7>). 2: User software should ensure the appropriate interrupt flag bits are cleared prior to enabling an interrupt and after servicing that interrupt. R/W-0 R/W-0 R-0 R-0 R/W-0 R/W-0 R/W-0 R/W-0 PSPIF(1) ADIF RCIF TXIF SSPIF CCP1IF TMR2IF TMR1IF bit 7 bit 0 bit 7 PSPIF: Parallel Slave Port Read/Write Interrupt Flag bit(1) 1 = A read or a write operation has taken place (must be cleared in software) 0 = No read or write has occurred Note 1: This bit is unimplemented on 28-pin devices and will read as ‘0’. bit 6 ADIF: A/D Converter Interrupt Flag bit 1 = An A/D conversion completed (must be cleared in software) 0 = The A/D conversion is not complete bit 5 RCIF: EUSART Receive Interrupt Flag bit 1 = The EUSART receive buffer, RCREG, is full (cleared when RCREG is read) 0 = The EUSART receive buffer is empty bit 4 TXIF: EUSART Transmit Interrupt Flag bit 1 = The EUSART transmit buffer, TXREG, is empty (cleared when TXREG is written) 0 = The EUSART transmit buffer is full bit 3 SSPIF: Master Synchronous Serial Port Interrupt Flag bit 1 = The transmission/reception is complete (must be cleared in software) 0 = Waiting to transmit/receive bit 2 CCP1IF: CCP1 Interrupt Flag bit Capture mode: 1 = A TMR1 register capture occurred (must be cleared in software) 0 = No TMR1 register capture occurred Compare mode: 1 = A TMR1 register compare match occurred (must be cleared in software) 0 = No TMR1 register compare match occurred PWM mode: Unused in this mode. bit 1 TMR2IF: TMR2 to PR2 Match Interrupt Flag bit 1 = TMR2 to PR2 match occurred (must be cleared in software) 0 = No TMR2 to PR2 match occurred bit 0 TMR1IF: TMR1 Overflow Interrupt Flag bit 1 = TMR1 register overflowed (must be cleared in software) 0 = TMR1 register did not overflow Legend: R = Readable bit W = Writable bit U = Unimplemented bit, read as ‘0’ -n = Value at POR ‘1’ = Bit is set ‘0’ = Bit is cleared x = Bit is unknown © 2007 Microchip Technology Inc. Preliminary DS39631B-page 97 PIC18F2420/2520/4420/4520 REGISTER 9-5: PIR2: PERIPHERAL INTERRUPT REQUEST (FLAG) REGISTER 2 R/W-0 R/W-0 U-0 R/W-0 R/W-0 R/W-0 R/W-0 R/W-0 OSCFIF CMIF — EEIF BCLIF HLVDIF TMR3IF CCP2IF bit 7 bit 0 bit 7 OSCFIF: Oscillator Fail Interrupt Flag bit 1 = Device oscillator failed, clock input has changed to INTOSC (must be cleared in software) 0 = Device clock operating bit 6 CMIF: Comparator Interrupt Flag bit 1 = Comparator input has changed (must be cleared in software) 0 = Comparator input has not changed bit 5 Unimplemented: Read as ‘0’ bit 4 EEIF: Data EEPROM/Flash Write Operation Interrupt Flag bit 1 = The write operation is complete (must be cleared in software) 0 = The write operation is not complete or has not been started bit 3 BCLIF: Bus Collision Interrupt Flag bit 1 = A bus collision occurred (must be cleared in software) 0 = No bus collision occurred bit 2 HLVDIF: High/Low-Voltage Detect Interrupt Flag bit 1 = A high/low-voltage condition occurred (direction determined by VDIRMAG bit, HLVDCON<7>) 0 = A high/low-voltage condition has not occurred bit 1 TMR3IF: TMR3 Overflow Interrupt Flag bit 1 = TMR3 register overflowed (must be cleared in software) 0 = TMR3 register did not overflow bit 0 CCP2IF: CCPx Interrupt Flag bit Capture mode: 1 = A TMR1 register capture occurred (must be cleared in software) 0 = No TMR1 register capture occurred Compare mode: 1 = A TMR1 register compare match occurred (must be cleared in software) 0 = No TMR1 register compare match occurred PWM mode: Unused in this mode. Legend: R = Readable bit W = Writable bit U = Unimplemented bit, read as ‘0’ -n = Value at POR ‘1’ = Bit is set ‘0’ = Bit is cleared x = Bit is unknown PIC18F2420/2520/4420/4520 DS39631B-page 98 Preliminary © 2007 Microchip Technology Inc. 9.3 PIE Registers The PIE registers contain the individual enable bits for the peripheral interrupts. Due to the number of peripheral interrupt sources, there are two Peripheral Interrupt Enable registers (PIE1 and PIE2). When IPEN = 0, the PEIE bit must be set to enable any of these peripheral interrupts. REGISTER 9-6: PIE1: PERIPHERAL INTERRUPT ENABLE REGISTER 1 R/W-0 R/W-0 R/W-0 R/W-0 R/W-0 R/W-0 R/W-0 R/W-0 PSPIE(1) ADIE RCIE TXIE SSPIE CCP1IE TMR2IE TMR1IE bit 7 bit 0 bit 7 PSPIE: Parallel Slave Port Read/Write Interrupt Enable bit(1) 1 = Enables the PSP read/write interrupt 0 = Disables the PSP read/write interrupt Note 1: This bit is unimplemented on 28-pin devices and will read as ‘0’. bit 6 ADIE: A/D Converter Interrupt Enable bit 1 = Enables the A/D interrupt 0 = Disables the A/D interrupt bit 5 RCIE: EUSART Receive Interrupt Enable bit 1 = Enables the EUSART receive interrupt 0 = Disables the EUSART receive interrupt bit 4 TXIE: EUSART Transmit Interrupt Enable bit 1 = Enables the EUSART transmit interrupt 0 = Disables the EUSART transmit interrupt bit 3 SSPIE: Master Synchronous Serial Port Interrupt Enable bit 1 = Enables the MSSP interrupt 0 = Disables the MSSP interrupt bit 2 CCP1IE: CCP1 Interrupt Enable bit 1 = Enables the CCP1 interrupt 0 = Disables the CCP1 interrupt bit 1 TMR2IE: TMR2 to PR2 Match Interrupt Enable bit 1 = Enables the TMR2 to PR2 match interrupt 0 = Disables the TMR2 to PR2 match interrupt bit 0 TMR1IE: TMR1 Overflow Interrupt Enable bit 1 = Enables the TMR1 overflow interrupt 0 = Disables the TMR1 overflow interrupt Legend: R = Readable bit W = Writable bit U = Unimplemented bit, read as ‘0’ -n = Value at POR ‘1’ = Bit is set ‘0’ = Bit is cleared x = Bit is unknown © 2007 Microchip Technology Inc. Preliminary DS39631B-page 99 PIC18F2420/2520/4420/4520 REGISTER 9-7: PIE2: PERIPHERAL INTERRUPT ENABLE REGISTER 2 R/W-0 R/W-0 U-0 R/W-0 R/W-0 R/W-0 R/W-0 R/W-0 OSCFIE CMIE — EEIE BCLIE HLVDIE TMR3IE CCP2IE bit 7 bit 0 bit 7 OSCFIE: Oscillator Fail Interrupt Enable bit 1 = Enabled 0 = Disabled bit 6 CMIE: Comparator Interrupt Enable bit 1 = Enabled 0 = Disabled bit 5 Unimplemented: Read as ‘0’ bit 4 EEIE: Data EEPROM/Flash Write Operation Interrupt Enable bit 1 = Enabled 0 = Disabled bit 3 BCLIE: Bus Collision Interrupt Enable bit 1 = Enabled 0 = Disabled bit 2 HLVDIE: High/Low-Voltage Detect Interrupt Enable bit 1 = Enabled 0 = Disabled bit 1 TMR3IE: TMR3 Overflow Interrupt Enable bit 1 = Enabled 0 = Disabled bit 0 CCP2IE: CCP2 Interrupt Enable bit 1 = Enabled 0 = Disabled Legend: R = Readable bit W = Writable bit U = Unimplemented bit, read as ‘0’ -n = Value at POR ‘1’ = Bit is set ‘0’ = Bit is cleared x = Bit is unknown PIC18F2420/2520/4420/4520 DS39631B-page 100 Preliminary © 2007 Microchip Technology Inc. 9.4 IPR Registers The IPR registers contain the individual priority bits for the peripheral interrupts. Due to the number of peripheral interrupt sources, there are two Peripheral Interrupt Priority registers (IPR1 and IPR2). Using the priority bits requires that the Interrupt Priority Enable (IPEN) bit be set. REGISTER 9-8: IPR1: PERIPHERAL INTERRUPT PRIORITY REGISTER 1 R/W-1 R/W-1 R/W-1 R/W-1 R/W-1 R/W-1 R/W-1 R/W-1 PSPIP(1) ADIP RCIP TXIP SSPIP CCP1IP TMR2IP TMR1IP bit 7 bit 0 bit 7 PSPIP: Parallel Slave Port Read/Write Interrupt Priority bit(1) 1 = High priority 0 = Low priority Note 1: This bit is unimplemented on 28-pin devices and will read as ‘0’. bit 6 ADIP: A/D Converter Interrupt Priority bit 1 = High priority 0 = Low priority bit 5 RCIP: EUSART Receive Interrupt Priority bit 1 = High priority 0 = Low priority bit 4 TXIP: EUSART Transmit Interrupt Priority bit 1 = High priority 0 = Low priority bit 3 SSPIP: Master Synchronous Serial Port Interrupt Priority bit 1 = High priority 0 = Low priority bit 2 CCP1IP: CCP1 Interrupt Priority bit 1 = High priority 0 = Low priority bit 1 TMR2IP: TMR2 to PR2 Match Interrupt Priority bit 1 = High priority 0 = Low priority bit 0 TMR1IP: TMR1 Overflow Interrupt Priority bit 1 = High priority 0 = Low priority Legend: R = Readable bit W = Writable bit U = Unimplemented bit, read as ‘0’ -n = Value at POR ‘1’ = Bit is set ‘0’ = Bit is cleared x = Bit is unknown © 2007 Microchip Technology Inc. Preliminary DS39631B-page 101 PIC18F2420/2520/4420/4520 REGISTER 9-9: IPR2: PERIPHERAL INTERRUPT PRIORITY REGISTER 2 R/W-1 R/W-1 U-0 R/W-1 R/W-1 R/W-1 R/W-1 R/W-1 OSCFIP CMIP — EEIP BCLIP HLVDIP TMR3IP CCP2IP bit 7 bit 0 bit 7 OSCFIP: Oscillator Fail Interrupt Priority bit 1 = High priority 0 = Low priority bit 6 CMIP: Comparator Interrupt Priority bit 1 = High priority 0 = Low priority bit 5 Unimplemented: Read as ‘0’ bit 4 EEIP: Data EEPROM/Flash Write Operation Interrupt Priority bit 1 = High priority 0 = Low priority bit 3 BCLIP: Bus Collision Interrupt Priority bit 1 = High priority 0 = Low priority bit 2 HLVDIP: High/Low-Voltage Detect Interrupt Priority bit 1 = High priority 0 = Low priority bit 1 TMR3IP: TMR3 Overflow Interrupt Priority bit 1 = High priority 0 = Low priority bit 0 CCP2IP: CCP2 Interrupt Priority bit 1 = High priority 0 = Low priority Legend: R = Readable bit W = Writable bit U = Unimplemented bit, read as ‘0’ -n = Value at POR ‘1’ = Bit is set ‘0’ = Bit is cleared x = Bit is unknown PIC18F2420/2520/4420/4520 DS39631B-page 102 Preliminary © 2007 Microchip Technology Inc. 9.5 RCON Register The RCON register contains flag bits which are used to determine the cause of the last Reset or wake-up from Idle or Sleep modes. RCON also contains the IPEN bit which enables interrupt priorities. The operation of the SBOREN bit and the Reset flag bits is discussed in more detail in Section 4.1 “RCON Register”. REGISTER 9-10: RCON REGISTER R/W-0 R/W-1(1) U-0 R/W-1 R-1 R-1 R/W-0(1) R/W-0 IPEN SBOREN — RI TO PD POR BOR bit 7 bit 0 bit 7 IPEN: Interrupt Priority Enable bit 1 = Enable priority levels on interrupts 0 = Disable priority levels on interrupts (PIC16XXX Compatibility mode) bit 6 SBOREN: Software BOR Enable bit(1) For details of bit operation, see Register 4-1. Note 1: Actual Reset values are determined by device configuration and the nature of the device Reset. See Register 4-1 for additional information. bit 5 Unimplemented: Read as ‘0’ bit 4 RI: RESET Instruction Flag bit For details of bit operation, see Register 4-1. bit 3 TO: Watchdog Time-out Flag bit For details of bit operation, see Register 4-1. bit 2 PD: Power-down Detection Flag bit For details of bit operation, see Register 4-1. bit 1 POR: Power-on Reset Status bit For details of bit operation, see Register 4-1. bit 0 BOR: Brown-out Reset Status bit For details of bit operation, see Register 4-1. Legend: R = Readable bit W = Writable bit U = Unimplemented bit, read as ‘0’ -n = Value at POR ‘1’ = Bit is set ‘0’ = Bit is cleared x = Bit is unknown © 2007 Microchip Technology Inc. Preliminary DS39631B-page 103 PIC18F2420/2520/4420/4520 9.6 INTn Pin Interrupts External interrupts on the RB0/INT0, RB1/INT1 and RB2/INT2 pins are edge-triggered. If the corresponding INTEDGx bit in the INTCON2 register is set (= 1), the interrupt is triggered by a rising edge; if the bit is clear, the trigger is on the falling edge. When a valid edge appears on the RBx/INTx pin, the corresponding flag bit, INTxF, is set. This interrupt can be disabled by clearing the corresponding enable bit, INTxE. Flag bit, INTxF, must be cleared in software in the Interrupt Service Routine before re-enabling the interrupt. All external interrupts (INT0, INT1 and INT2) can wakeup the processor from Idle or Sleep modes if bit INTxE was set prior to going into those modes. If the Global Interrupt Enable bit, GIE, is set, the processor will branch to the interrupt vector following wake-up. Interrupt priority for INT1 and INT2 is determined by the value contained in the interrupt priority bits, INT1IP (INTCON3<6>) and INT2IP (INTCON3<7>). There is no priority bit associated with INT0. It is always a high priority interrupt source. 9.7 TMR0 Interrupt In 8-bit mode (which is the default), an overflow in the TMR0 register (FFh → 00h) will set flag bit, TMR0IF. In 16-bit mode, an overflow in the TMR0H:TMR0L register pair (FFFFh → 0000h) will set TMR0IF. The interrupt can be enabled/disabled by setting/clearing enable bit, TMR0IE (INTCON<5>). Interrupt priority for Timer0 is determined by the value contained in the interrupt priority bit, TMR0IP (INTCON2<2>). See Section 11.0 “Timer0 Module” for further details on the Timer0 module. 9.8 PORTB Interrupt-on-Change An input change on PORTB<7:4> sets flag bit, RBIF (INTCON<0>). The interrupt can be enabled/disabled by setting/clearing enable bit, RBIE (INTCON<3>). Interrupt priority for PORTB interrupt-on-change is determined by the value contained in the interrupt priority bit, RBIP (INTCON2<0>). 9.9 Context Saving During Interrupts During interrupts, the return PC address is saved on the stack. Additionally, the WREG, Status and BSR registers are saved on the fast return stack. If a fast return from interrupt is not used (see Section 5.3 “Data Memory Organization”), the user may need to save the WREG, Status and BSR registers on entry to the Interrupt Service Routine. Depending on the user’s application, other registers may also need to be saved. Example 9-1 saves and restores the WREG, Status and BSR registers during an Interrupt Service Routine. EXAMPLE 9-1: SAVING STATUS, WREG AND BSR REGISTERS IN RAM MOVWF W_TEMP ; W_TEMP is in virtual bank MOVFF STATUS, STATUS_TEMP ; STATUS_TEMP located anywhere MOVFF BSR, BSR_TEMP ; BSR_TMEP located anywhere ; ; USER ISR CODE ; MOVFF BSR_TEMP, BSR ; Restore BSR MOVF W_TEMP, W ; Restore WREG MOVFF STATUS_TEMP, STATUS ; Restore STATUS PIC18F2420/2520/4420/4520 DS39631B-page 104 Preliminary © 2007 Microchip Technology Inc. NOTES: © 2007 Microchip Technology Inc. Preliminary DS39631B-page 105 PIC18F2420/2520/4420/4520 10.0 I/O PORTS Depending on the device selected and features enabled, there are up to five ports available. Some pins of the I/O ports are multiplexed with an alternate function from the peripheral features on the device. In general, when a peripheral is enabled, that pin may not be used as a general purpose I/O pin. Each port has three registers for its operation. These registers are: • TRIS register (data direction register) • PORT register (reads the levels on the pins of the device) • LAT register (output latch) The Data Latch (LAT register) is useful for read-modifywrite operations on the value that the I/O pins are driving. A simplified model of a generic I/O port, without the interfaces to other peripherals, is shown in Figure 10-1. FIGURE 10-1: GENERIC I/O PORT OPERATION 10.1 PORTA, TRISA and LATA Registers PORTA is a 8-bit wide, bidirectional port. The corresponding data direction register is TRISA. Setting a TRISA bit (= 1) will make the corresponding PORTA pin an input (i.e., put the corresponding output driver in a high-impedance mode). Clearing a TRISA bit (= 0) will make the corresponding PORTA pin an output (i.e., put the contents of the output latch on the selected pin). Reading the PORTA register reads the status of the pins, whereas writing to it, will write to the port latch. The Data Latch (LATA) register is also memory mapped. Read-modify-write operations on the LATA register read and write the latched output value for PORTA. The RA4 pin is multiplexed with the Timer0 module clock input and one of the comparator outputs to become the RA4/T0CKI/C1OUT pin. Pins RA6 and RA7 are multiplexed with the main oscillator pins; they are enabled as oscillator or I/O pins by the selection of the main oscillator in the configuration register (see Section 23.1 “Configuration Bits” for details). When they are not used as port pins, RA6 and RA7 and their associated TRIS and LAT bits are read as ‘0’. The other PORTA pins are multiplexed with analog inputs, the analog VREF+ and VREF- inputs and the comparator voltage reference output. The operation of pins RA3:RA0 and RA5 as A/D converter inputs is selected by clearing or setting the control bits in the ADCON1 register (A/D Control Register 1). Pins RA0 through RA5 may also be used as comparator inputs or outputs by setting the appropriate bits in the CMCON register. To use RA3:RA0 as digital inputs, it is also necessary to turn off the comparators. The RA4/T0CKI/C1OUT pin is a Schmitt Trigger input. All other PORTA pins have TTL input levels and full CMOS output drivers. The TRISA register controls the direction of the PORTA pins, even when they are being used as analog inputs. The user must ensure the bits in the TRISA register are maintained set when using them as analog inputs. EXAMPLE 10-1: INITIALIZING PORTA Data Bus WR LAT WR TRIS RD Port Data Latch TRIS Latch RD TRIS Input Buffer I/O pin(1) D Q CK D Q CK EN Q D EN RD LAT or Port Note 1: I/O pins have diode protection to VDD and VSS. Note: On a Power-on Reset, RA5 and RA3:RA0 are configured as analog inputs and read as ‘0’. RA4 is configured as a digital input. CLRF PORTA ; Initialize PORTA by ; clearing output ; data latches CLRF LATA ; Alternate method ; to clear output ; data latches MOVLW 07h ; Configure A/D MOVWF ADCON1 ; for digital inputs MOVWF 07h ; Configure comparators MOVWF CMCON ; for digital input MOVLW 0CFh ; Value used to ; initialize data ; direction MOVWF TRISA ; Set RA<3:0> as inputs ; RA<5:4> as outputs PIC18F2420/2520/4420/4520 DS39631B-page 106 Preliminary © 2007 Microchip Technology Inc. TABLE 10-1: PORTA I/O SUMMARY Pin Function TRIS Setting I/O I/O Type Description RA0/AN0 RA0 0 O DIG LATA<0> data output; not affected by analog input. 1 I TTL PORTA<0> data input; disabled when analog input enabled. AN0 1 I ANA A/D input channel 0 and Comparator C1- input. Default input configuration on POR; does not affect digital output. RA1/AN1 RA1 0 O DIG LATA<1> data output; not affected by analog input. 1 I TTL PORTA<1> data input; disabled when analog input enabled. AN1 1 I ANA A/D input channel 1 and Comparator C2- input. Default input configuration on POR; does not affect digital output. RA2/AN2/ VREF-/CVREF RA2 0 O DIG LATA<2> data output; not affected by analog input. Disabled when CVREF output enabled. 1 I TTL PORTA<2> data input. Disabled when analog functions enabled; disabled when CVREF output enabled. AN2 1 I ANA A/D input channel 2 and Comparator C2+ input. Default input configuration on POR; not affected by analog output. VREF- 1 I ANA A/D and comparator voltage reference low input. CVREF x O ANA Comparator voltage reference output. Enabling this feature disables digital I/O. RA3/AN3/VREF+ RA3 0 O DIG LATA<3> data output; not affected by analog input. 1 I TTL PORTA<3> data input; disabled when analog input enabled. AN3 1 I ANA A/D input channel 3 and Comparator C1+ input. Default input configuration on POR. VREF+ 1 I ANA A/D and comparator voltage reference high input. RA4/T0CKI/C1OUT RA4 0 O DIG LATA<4> data output. 1 I ST PORTA<4> data input; default configuration on POR. T0CKI 1 I ST Timer0 clock input. C1OUT 0 O DIG Comparator 1 output; takes priority over port data. RA5/AN4/SS/ HLVDIN/C2OUT RA5 0 O DIG LATA<5> data output; not affected by analog input. 1 I TTL PORTA<5> data input; disabled when analog input enabled. AN4 1 I ANA A/D input channel 4. Default configuration on POR. SS 1 I TTL Slave select input for SSP (MSSP module). HLVDIN 1 I ANA High/Low-Voltage Detect external trip point input. C2OUT 0 O DIG Comparator 2 output; takes priority over port data. OSC2/CLKO/RA6 RA6 0 O DIG LATA<6> data output. Enabled in RCIO, INTIO2 and ECIO modes only. 1 I TTL PORTA<6> data input. Enabled in RCIO, INTIO2 and ECIO modes only. OSC2 x O ANA Main oscillator feedback output connection (XT, HS and LP modes). CLKO x O DIG System cycle clock output (FOSC/4) in RC, INTIO1 and EC Oscillator modes. OSC1/CLKI/RA7 RA7 0 O DIG LATA<7> data output. Disabled in external oscillator modes. 1 I TTL PORTA<7> data input. Disabled in external oscillator modes. OSC1 x I ANA Main oscillator input connection. CLKI x I ANA Main clock input connection. Legend: DIG = Digital level output; TTL = TTL input buffer; ST = Schmitt Trigger input buffer; ANA = Analog level input/output; x = Don’t care (TRIS bit does not affect port direction or is overridden for this option). © 2007 Microchip Technology Inc. Preliminary DS39631B-page 107 PIC18F2420/2520/4420/4520 TABLE 10-2: SUMMARY OF REGISTERS ASSOCIATED WITH PORTA Name Bit 7 Bit 6 Bit 5 Bit 4 Bit 3 Bit 2 Bit 1 Bit 0 Reset Values on page PORTA RA7(1) RA6(1) RA5 RA4 RA3 RA2 RA1 RA0 52 LATA LATA7(1) LATA6(1) PORTA Data Latch Register (Read and Write to Data Latch) 52 TRISA TRISA7(1) TRISA6(1) PORTA Data Direction Control Register 52 ADCON1 — — VCFG1 VCFG0 PCFG3 PCFG2 PCFG1 PCFG0 51 CMCON C2OUT C1OUT C2INV C1INV CIS CM2 CM1 CM0 51 CVRCON CVREN CVROE CVRR CVRSS CVR3 CVR2 CVR1 CVR0 51 Legend: — = unimplemented, read as ‘0’. Shaded cells are not used by PORTA. Note 1: RA7:RA6 and their associated latch and data direction bits are enabled as I/O pins based on oscillator configuration; otherwise, they are read as ‘0’. PIC18F2420/2520/4420/4520 DS39631B-page 108 Preliminary © 2007 Microchip Technology Inc. 10.2 PORTB, TRISB and LATB Registers PORTB is an 8-bit wide, bidirectional port. The corresponding data direction register is TRISB. Setting a TRISB bit (= 1) will make the corresponding PORTB pin an input (i.e., put the corresponding output driver in a high-impedance mode). Clearing a TRISB bit (= 0) will make the corresponding PORTB pin an output (i.e., put the contents of the output latch on the selected pin). The Data Latch register (LATB) is also memory mapped. Read-modify-write operations on the LATB register read and write the latched output value for PORTB. EXAMPLE 10-2: INITIALIZING PORTB Each of the PORTB pins has a weak internal pull-up. A single control bit can turn on all the pull-ups. This is performed by clearing bit, RBPU (INTCON2<7>). The weak pull-up is automatically turned off when the port pin is configured as an output. The pull-ups are disabled on a Power-on Reset. Four of the PORTB pins (RB7:RB4) have an interrupton- change feature. Only pins configured as inputs can cause this interrupt to occur (i.e., any RB7:RB4 pin configured as an output is excluded from the interrupton- change comparison). The input pins (of RB7:RB4) are compared with the old value latched on the last read of PORTB. The “mismatch” outputs of RB7:RB4 are ORed together to generate the RB Port Change Interrupt with Flag bit, RBIF (INTCON<0>). This interrupt can wake the device from the Sleep mode, or any of the Idle modes. The user, in the Interrupt Service Routine, can clear the interrupt in the following manner: a) Any read or write of PORTB (except with the MOVFF (ANY), PORTB instruction). b) Clear flag bit, RBIF. A mismatch condition will continue to set flag bit, RBIF. Reading PORTB will end the mismatch condition and allow flag bit, RBIF, to be cleared. The interrupt-on-change feature is recommended for wake-up on key depression operation and operations where PORTB is only used for the interrupt-on-change feature. Polling of PORTB is not recommended while using the interrupt-on-change feature. RB3 can be configured by the configuration bit, CCP2MX, as the alternate peripheral pin for the CCP2 module (CCP2MX = 0). Note: On a Power-on Reset, RB4:RB0 are configured as analog inputs by default and read as ‘0’; RB7:RB5 are configured as digital inputs. By programming the configuration bit, PBADEN, RB4:RB0 will alternatively be configured as digital inputs on POR. CLRF PORTB ; Initialize PORTB by ; clearing output ; data latches CLRF LATB ; Alternate method ; to clear output ; data latches MOVLW 0Fh ; Set RB<4:0> as MOVWF ADCON1 ; digital I/O pins ; (required if config bit ; PBADEN is set) MOVLW 0CFh ; Value used to ; initialize data ; direction MOVWF TRISB ; Set RB<3:0> as inputs ; RB<5:4> as outputs ; RB<7:6> as inputs © 2007 Microchip Technology Inc. Preliminary DS39631B-page 109 PIC18F2420/2520/4420/4520 TABLE 10-3: PORTB I/O SUMMARY Pin Function TRIS Setting I/O I/O Type Description RB0/INT0/FLT0/ AN12 RB0 0 O DIG LATB<0> data output; not affected by analog input. 1 I TTL PORTB<0> data input; weak pull-up when RBPU bit is cleared. Disabled when analog input enabled.(1) INT0 1 I ST External interrupt 0 input. FLT0 1 I ST Enhanced PWM Fault input (ECCP1 module); enabled in software. AN12 1 I ANA A/D input channel 12.(1) RB1/INT1/AN10 RB1 0 O DIG LATB<1> data output; not affected by analog input. 1 I TTL PORTB<1> data input; weak pull-up when RBPU bit is cleared. Disabled when analog input enabled.(1) INT1 1 I ST External Interrupt 1 input. AN10 1 I ANA A/D input channel 10.(1) RB2/INT2/AN8 RB2 0 O DIG LATB<2> data output; not affected by analog input. 1 I TTL PORTB<2> data input; weak pull-up when RBPU bit is cleared. Disabled when analog input enabled.(1) INT2 1 I ST External interrupt 2 input. AN8 1 I ANA A/D input channel 8.(1) RB3/AN9/CCP2 RB3 0 O DIG LATB<3> data output; not affected by analog input. 1 I TTL PORTB<3> data input; weak pull-up when RBPU bit is cleared. Disabled when analog input enabled.(1) AN9 1 I ANA A/D input channel 9.(1) CCP2(2) 0 O DIG CCP2 compare and PWM output. 1 I ST CCP2 capture input RB4/KBI0/AN11 RB4 0 O DIG LATB<4> data output; not affected by analog input. 1 I TTL PORTB<4> data input; weak pull-up when RBPU bit is cleared. Disabled when analog input enabled.(1) KBI0 1 I TTL Interrupt on pin change. AN11 1 I ANA A/D input channel 11.(1) RB5/KBI1/PGM RB5 0 O DIG LATB<5> data output. 1 I TTL PORTB<5> data input; weak pull-up when RBPU bit is cleared. KBI1 1 I TTL Interrupt on pin change. PGM x I ST Single-Supply Programming mode entry (ICSP™). Enabled by LVP configuration bit; all other pin functions disabled. RB6/KBI2/PGC RB6 0 O DIG LATB<6> data output. 1 I TTL PORTB<6> data input; weak pull-up when RBPU bit is cleared. KBI2 1 I TTL Interrupt on pin change. PGC x I ST Serial execution (ICSP) clock input for ICSP and ICD operation.(3) RB7/KBI3/PGD RB7 0 O DIG LATB<7> data output. 1 I TTL PORTB<7> data input; weak pull-up when RBPU bit is cleared. KBI3 1 I TTL Interrupt on pin change. PGD x O DIG Serial execution data output for ICSP and ICD operation.(3) x I ST Serial execution data input for ICSP and ICD operation.(3) Legend: DIG = Digital level output; TTL = TTL input buffer; ST = Schmitt Trigger input buffer; ANA = Analog level input/output; x = Don’t care (TRIS bit does not affect port direction or is overridden for this option). Note 1: Configuration on POR is determined by the PBADEN configuration bit. Pins are configured as analog inputs by default when PBADEN is set and digital inputs when PBADEN is cleared. 2: Alternate assignment for CCP2 when the CCP2MX configuration bit is ‘0’. Default assignment is RC1. 3: All other pin functions are disabled when ICSP or ICD are enabled. PIC18F2420/2520/4420/4520 DS39631B-page 110 Preliminary © 2007 Microchip Technology Inc. TABLE 10-4: SUMMARY OF REGISTERS ASSOCIATED WITH PORTB Name Bit 7 Bit 6 Bit 5 Bit 4 Bit 3 Bit 2 Bit 1 Bit 0 Reset Values on page PORTB RB7 RB6 RB5 RB4 RB3 RB2 RB1 RB0 52 LATB PORTB Data Latch Register (Read and Write to Data Latch) 52 TRISB PORTB Data Direction Control Register 52 INTCON GIE/GIEH PEIE/GIEL TMR0IE INT0IE RBIE TMR0IF INT0IF RBIF 49 INTCON2 RBPU INTEDG0 INTEDG1 INTEDG2 — TMR0IP — RBIP 49 INTCON3 INT2IP INT1IP — INT2IE INT1IE — INT2IF INT1IF 49 ADCON1 — — VCFG1 VCFG0 PCFG3 PCFG2 PCFG1 PCFG0 51 Legend: — = unimplemented, read as ‘0’. Shaded cells are not used by PORTB. © 2007 Microchip Technology Inc. Preliminary DS39631B-page 111 PIC18F2420/2520/4420/4520 10.3 PORTC, TRISC and LATC Registers PORTC is an 8-bit wide, bidirectional port. The corresponding data direction register is TRISC. Setting a TRISC bit (= 1) will make the corresponding PORTC pin an input (i.e., put the corresponding output driver in a high-impedance mode). Clearing a TRISC bit (= 0) will make the corresponding PORTC pin an output (i.e., put the contents of the output latch on the selected pin). The Data Latch register (LATC) is also memory mapped. Read-modify-write operations on the LATC register read and write the latched output value for PORTC. PORTC is multiplexed with several peripheral functions (Table 10-5). The pins have Schmitt Trigger input buffers. RC1 is normally configured by configuration bit, CCP2MX, as the default peripheral pin of the CCP2 module (default/erased state, CCP2MX = 1). When enabling peripheral functions, care should be taken in defining TRIS bits for each PORTC pin. Some peripherals override the TRIS bit to make a pin an output, while other peripherals override the TRIS bit to make a pin an input. The user should refer to the corresponding peripheral section for additional information. The contents of the TRISC register are affected by peripheral overrides. Reading TRISC always returns the current contents, even though a peripheral device may be overriding one or more of the pins. EXAMPLE 10-3: INITIALIZING PORTC Note: On a Power-on Reset, these pins are configured as digital inputs. CLRF PORTC ; Initialize PORTC by ; clearing output ; data latches CLRF LATC ; Alternate method ; to clear output ; data latches MOVLW 0CFh ; Value used to ; initialize data ; direction MOVWF TRISC ; Set RC<3:0> as inputs ; RC<5:4> as outputs ; RC<7:6> as inputs PIC18F2420/2520/4420/4520 DS39631B-page 112 Preliminary © 2007 Microchip Technology Inc. TABLE 10-5: PORTC I/O SUMMARY Pin Function TRIS Setting I/O I/O Type Description RC0/T1OSO/ T13CKI RC0 0 O DIG LATC<0> data output. 1 I ST PORTC<0> data input. T1OSO x O ANA Timer1 oscillator output; enabled when Timer1 oscillator enabled. Disables digital I/O. T13CKI 1 I ST Timer1/Timer3 counter input. RC1/T1OSI/CCP2 RC1 0 O DIG LATC<1> data output. 1 I ST PORTC<1> data input. T1OSI x I ANA Timer1 oscillator input; enabled when Timer1 oscillator enabled. Disables digital I/O. CCP2(1) 0 O DIG CCP2 compare and PWM output; takes priority over port data. 1 I ST CCP2 capture input. RC2/CCP1/P1A RC2 0 O DIG LATC<2> data output. 1 I ST PORTC<2> data input. CCP1 0 O DIG ECCP1 compare or PWM output; takes priority over port data. 1 I ST ECCP1 capture input. P1A(2) 0 O DIG ECCP1 Enhanced PWM output, channel A. May be configured for tri-state during Enhanced PWM shutdown events. Takes priority over port data. RC3/SCK/SCL RC3 0 O DIG LATC<3> data output. 1 I ST PORTC<3> data input. SCK 0 O DIG SPI™ clock output (MSSP module); takes priority over port data. 1 I ST SPI clock input (MSSP module). SCL 0 O DIG I2 C™ clock output (MSSP module); takes priority over port data. 1 I I2C/SMB I2C clock input (MSSP module); input type depends on module setting. RC4/SDI/SDA RC4 0 O DIG LATC<4> data output. 1 I ST PORTC<4> data input. SDI 1 I ST SPI data input (MSSP module). SDA 1 O DIG I2 C data output (MSSP module); takes priority over port data. 1 I I2C/SMB I2C data input (MSSP module); input type depends on module setting. RC5/SDO RC5 0 O DIG LATC<5> data output. 1 I ST PORTC<5> data input. SDO 0 O DIG SPI data output (MSSP module); takes priority over port data. RC6/TX/CK RC6 0 O DIG LATC<6> data output. 1 I ST PORTC<6> data input. TX 1 O DIG Asynchronous serial transmit data output (USART module); takes priority over port data. User must configure as output. CK 1 O DIG Synchronous serial clock output (USART module); takes priority over port data. 1 I ST Synchronous serial clock input (USART module). RC7/RX/DT RC7 0 O DIG LATC<7> data output. 1 I ST PORTC<7> data input. RX 1 I ST Asynchronous serial receive data input (USART module). DT 1 O DIG Synchronous serial data output (USART module); takes priority over port data. 1 I ST Synchronous serial data input (USART module). User must configure as an input. Legend: DIG = Digital level output; TTL = TTL input buffer; ST = Schmitt Trigger input buffer; ANA = Analog level input/output; I2C/SMB = I2C/SMBus input buffer; x = Don’t care (TRIS bit does not affect port direction or is overridden for this option). Note 1: Default assignment for CCP2 when the CCP2MX configuration bit is set. Alternate assignment is RB3. 2: Enhanced PWM output is available only on PIC18F4520 devices. © 2007 Microchip Technology Inc. Preliminary DS39631B-page 113 PIC18F2420/2520/4420/4520 TABLE 10-6: SUMMARY OF REGISTERS ASSOCIATED WITH PORTC Name Bit 7 Bit 6 Bit 5 Bit 4 Bit 3 Bit 2 Bit 1 Bit 0 Reset Values on page PORTC RC7 RC6 RC5 RC4 RC3 RC2 RC1 RC0 52 LATC PORTC Data Latch Register (Read and Write to Data Latch) 52 TRISC PORTC Data Direction Control Register 52 PIC18F2420/2520/4420/4520 DS39631B-page 114 Preliminary © 2007 Microchip Technology Inc. 10.4 PORTD, TRISD and LATD Registers PORTD is an 8-bit wide, bidirectional port. The corresponding data direction register is TRISD. Setting a TRISD bit (= 1) will make the corresponding PORTD pin an input (i.e., put the corresponding output driver in a high-impedance mode). Clearing a TRISD bit (= 0) will make the corresponding PORTD pin an output (i.e., put the contents of the output latch on the selected pin). The Data Latch register (LATD) is also memory mapped. Read-modify-write operations on the LATD register read and write the latched output value for PORTD. All pins on PORTD are implemented with Schmitt Trigger input buffers. Each pin is individually configurable as an input or output. Three of the PORTD pins are multiplexed with outputs P1B, P1C and P1D of the enhanced CCP module. The operation of these additional PWM output pins is covered in greater detail in Section 16.0 “Enhanced Capture/Compare/PWM (ECCP) Module”. PORTD can also be configured as an 8-bit wide microprocessor port (Parallel Slave Port) by setting control bit, PSPMODE (TRISE<4>). In this mode, the input buffers are TTL. See Section 10.6 “Parallel Slave Port” for additional information on the Parallel Slave Port (PSP). EXAMPLE 10-4: INITIALIZING PORTD Note: PORTD is only available on 40/44-pin devices. Note: On a Power-on Reset, these pins are configured as digital inputs. Note: When the enhanced PWM mode is used with either dual or quad outputs, the PSP functions of PORTD are automatically disabled. CLRF PORTD ; Initialize PORTD by ; clearing output ; data latches CLRF LATD ; Alternate method ; to clear output ; data latches MOVLW 0CFh ; Value used to ; initialize data ; direction MOVWF TRISD ; Set RD<3:0> as inputs ; RD<5:4> as outputs ; RD<7:6> as inputs © 2007 Microchip Technology Inc. Preliminary DS39631B-page 115 PIC18F2420/2520/4420/4520 TABLE 10-7: PORTD I/O SUMMARY Pin Function TRIS Setting I/O I/O Type Description RD0/PSP0 RD0 0 O DIG LATD<0> data output. 1 I ST PORTD<0> data input. PSP0 x O DIG PSP read data output (LATD<0>); takes priority over port data. x I TTL PSP write data input. RD1/PSP1 RD1 0 O DIG LATD<1> data output. 1 I ST PORTD<1> data input. PSP1 x O DIG PSP read data output (LATD<1>); takes priority over port data. x I TTL PSP write data input. RD2/PSP2 RD2 0 O DIG LATD<2> data output. 1 I ST PORTD<2> data input. PSP2 x O DIG PSP read data output (LATD<2>); takes priority over port data. x I TTL PSP write data input. RD3/PSP3 RD3 0 O DIG LATD<3> data output. 1 I ST PORTD<3> data input. PSP3 x O DIG PSP read data output (LATD<3>); takes priority over port data. x I TTL PSP write data input. RD4/PSP4 RD4 0 O DIG LATD<4> data output. 1 I ST PORTD<4> data input. PSP4 x O DIG PSP read data output (LATD<4>); takes priority over port data. x I TTL PSP write data input. RD5/PSP5/P1B RD5 0 O DIG LATD<5> data output. 1 I ST PORTD<5> data input. PSP5 x O DIG PSP read data output (LATD<5>); takes priority over port data. x I TTL PSP write data input. P1B 0 O DIG ECCP1 Enhanced PWM output, channel B; takes priority over port and PSP data. May be configured for tri-state during Enhanced PWM shutdown events. RD6/PSP6/P1C RD6 0 O DIG LATD<6> data output. 1 I ST PORTD<6> data input. PSP6 x O DIG PSP read data output (LATD<6>); takes priority over port data. x I TTL PSP write data input. P1C 0 O DIG ECCP1 Enhanced PWM output, channel C; takes priority over port and PSP data. May be configured for tri-state during Enhanced PWM shutdown events. RD7/PSP7/P1D RD7 0 O DIG LATD<7> data output. 1 I ST PORTD<7> data input. PSP7 x O DIG PSP read data output (LATD<7>); takes priority over port data. x I TTL PSP write data input. P1D 0 O DIG ECCP1 Enhanced PWM output, channel D; takes priority over port and PSP data. May be configured for tri-state during Enhanced PWM shutdown events. Legend: DIG = Digital level output; TTL = TTL input buffer; ST = Schmitt Trigger input buffer; x = Don’t care (TRIS bit does not affect port direction or is overridden for this option). PIC18F2420/2520/4420/4520 DS39631B-page 116 Preliminary © 2007 Microchip Technology Inc. TABLE 10-8: SUMMARY OF REGISTERS ASSOCIATED WITH PORTD Name Bit 7 Bit 6 Bit 5 Bit 4 Bit 3 Bit 2 Bit 1 Bit 0 Reset Values on page PORTD RD7 RD6 RD5 RD4 RD3 RD2 RD1 RD0 52 LATD PORTD Data Latch Register (Read and Write to Data Latch) 52 TRISD PORTD Data Direction Control Register 52 TRISE IBF OBF IBOV PSPMODE — TRISE2 TRISE1 TRISE0 52 CCP1CON P1M1 P1M0 DC1B1 DC1B0 CCP1M3 CCP1M2 CCP1M1 CCP1M0 51 Legend: — = unimplemented, read as ‘0’. Shaded cells are not used by PORTD. © 2007 Microchip Technology Inc. Preliminary DS39631B-page 117 PIC18F2420/2520/4420/4520 10.5 PORTE, TRISE and LATE Registers Depending on the particular PIC18F2420/2520/4420/ 4520 device selected, PORTE is implemented in two different ways. For 40/44-pin devices, PORTE is a 4-bit wide port. Three pins (RE0/RD/AN5, RE1/WR/AN6 and RE2/CS/ AN7) are individually configurable as inputs or outputs. These pins have Schmitt Trigger input buffers. When selected as an analog input, these pins will read as ‘0’s. The corresponding data direction register is TRISE. Setting a TRISE bit (= 1) will make the corresponding PORTE pin an input (i.e., put the corresponding output driver in a high-impedance mode). Clearing a TRISE bit (= 0) will make the corresponding PORTE pin an output (i.e., put the contents of the output latch on the selected pin). TRISE controls the direction of the RE pins, even when they are being used as analog inputs. The user must make sure to keep the pins configured as inputs when using them as analog inputs. The upper four bits of the TRISE register also control the operation of the Parallel Slave Port. Their operation is explained in Register 10-1. The Data Latch register (LATE) is also memory mapped. Read-modify-write operations on the LATE register, read and write the latched output value for PORTE. The fourth pin of PORTE (MCLR/VPP/RE3) is an input only pin. Its operation is controlled by the MCLRE configuration bit. When selected as a port pin (MCLRE = 0), it functions as a digital input only pin; as such, it does not have TRIS or LAT bits associated with its operation. Otherwise, it functions as the device’s Master Clear input. In either configuration, RE3 also functions as the programming voltage input during programming. EXAMPLE 10-5: INITIALIZING PORTE 10.5.1 PORTE IN 28-PIN DEVICES For 28-pin devices, PORTE is only available when Master Clear functionality is disabled (MCLRE = 0). In these cases, PORTE is a single bit, input only port comprised of RE3 only. The pin operates as previously described. Note: On a Power-on Reset, RE2:RE0 are configured as analog inputs. Note: On a Power-on Reset, RE3 is enabled as a digital input only if Master Clear functionality is disabled. CLRF PORTE ; Initialize PORTE by ; clearing output ; data latches CLRF LATE ; Alternate method ; to clear output ; data latches MOVLW 0Ah ; Configure A/D MOVWF ADCON1 ; for digital inputs MOVLW 03h ; Value used to ; initialize data ; direction MOVWF TRISE ; Set RE<0> as inputs ; RE<1> as outputs ; RE<2> as inputs PIC18F2420/2520/4420/4520 DS39631B-page 118 Preliminary © 2007 Microchip Technology Inc. REGISTER 10-1: TRISE REGISTER (40/44-PIN DEVICES ONLY) R-0 R-0 R/W-0 R/W-0 U-0 R/W-1 R/W-1 R/W-1 IBF OBF IBOV PSPMODE — TRISE2 TRISE1 TRISE0 bit 7 bit 0 bit 7 IBF: Input Buffer Full Status bit 1 = A word has been received and waiting to be read by the CPU 0 = No word has been received bit 6 OBF: Output Buffer Full Status bit 1 = The output buffer still holds a previously written word 0 = The output buffer has been read bit 5 IBOV: Input Buffer Overflow Detect bit (in Microprocessor mode) 1 = A write occurred when a previously input word has not been read (must be cleared in software) 0 = No overflow occurred bit 4 PSPMODE: Parallel Slave Port Mode Select bit 1 = Parallel Slave Port mode 0 = General purpose I/O mode bit 3 Unimplemented: Read as ‘0’ bit 2 TRISE2: RE2 Direction Control bit 1 = Input 0 = Output bit 1 TRISE1: RE1 Direction Control bit 1 = Input 0 = Output bit 0 TRISE0: RE0 Direction Control bit 1 = Input 0 = Output Legend: R = Readable bit W = Writable bit U = Unimplemented bit, read as ‘0’ -n = Value at POR ‘1’ = Bit is set ‘0’ = Bit is cleared x = Bit is unknown © 2007 Microchip Technology Inc. Preliminary DS39631B-page 119 PIC18F2420/2520/4420/4520 TABLE 10-9: PORTE I/O SUMMARY TABLE 10-10: SUMMARY OF REGISTERS ASSOCIATED WITH PORTE Pin Function TRIS Setting I/O I/O Type Description RE0/RD/AN5 RE0 0 O DIG LATE<0> data output; not affected by analog input. 1 I ST PORTE<0> data input; disabled when analog input enabled. RD 1 I TTL PSP read enable input (PSP enabled). AN5 1 I ANA A/D input channel 5; default input configuration on POR. RE1/WR/AN6 RE1 0 O DIG LATE<1> data output; not affected by analog input. 1 I ST PORTE<1> data input; disabled when analog input enabled. WR 1 I TTL PSP write enable input (PSP enabled). AN6 1 I ANA A/D input channel 6; default input configuration on POR. RE2/CS/AN7 RE2 0 O DIG LATE<2> data output; not affected by analog input. 1 I ST PORTE<2> data input; disabled when analog input enabled. CS 1 I TTL PSP write enable input (PSP enabled). AN7 1 I ANA A/D input channel 7; default input configuration on POR. MCLR/VPP/RE3(1) MCLR — I ST External Master Clear input; enabled when MCLRE configuration bit is set. VPP — I ANA High-voltage detection; used for ICSP™ mode entry detection. Always available, regardless of pin mode. RE3 —(2) I ST PORTE<3> data input; enabled when MCLRE configuration bit is clear. Legend: DIG = Digital level output; TTL = TTL input buffer; ST = Schmitt Trigger input buffer; ANA = Analog level input/output; x = Don’t care (TRIS bit does not affect port direction or is overridden for this option). Note 1: RE3 is available on both 28-pin and 40/44-pin devices. All other PORTE pins are only implemented on 40/44-pin devices. 2: RE3 does not have a corresponding TRIS bit to control data direction. Name Bit 7 Bit 6 Bit 5 Bit 4 Bit 3 Bit 2 Bit 1 Bit 0 Reset Values on page PORTE — — — — RE3(1,2) RE2 RE1 RE0 52 LATE(2) — — — — — LATE Data Output Register 52 TRISE IBF OBF IBOV PSPMODE — TRISE2 TRISE1 TRISE0 52 ADCON1 — — VCFG1 VCFG0 PCFG3 PCFG2 PCFG1 PCFG0 51 Legend: — = unimplemented, read as ‘0’. Shaded cells are not used by PORTE. Note 1: Implemented only when Master Clear functionality is disabled (MCLRE configuration bit = 0). 2: RE3 is the only PORTE bit implemented on both 28-pin and 40/44-pin devices. All other bits are implemented only when PORTE is implemented (i.e., 40/44-pin devices). PIC18F2420/2520/4420/4520 DS39631B-page 120 Preliminary © 2007 Microchip Technology Inc. 10.6 Parallel Slave Port In addition to its function as a general I/O port, PORTD can also operate as an 8-bit wide Parallel Slave Port (PSP) or microprocessor port. PSP operation is controlled by the 4 upper bits of the TRISE register (Register 10-1). Setting control bit, PSPMODE (TRISE<4>), enables PSP operation as long as the enhanced CCP module is not operating in dual output or quad output PWM mode. In Slave mode, the port is asynchronously readable and writable by the external world. The PSP can directly interface to an 8-bit microprocessor data bus. The external microprocessor can read or write the PORTD latch as an 8-bit latch. Setting the control bit, PSPMODE, enables the PORTE I/O pins to become control inputs for the microprocessor port. When set, port pin RE0 is the RD input, RE1 is the WR input and RE2 is the CS (Chip Select) input. For this functionality, the corresponding data direction bits of the TRISE register (TRISE<2:0>) must be configured as inputs (set). The A/D port configuration bits, PFCG3:PFCG0 (ADCON1<3:0>), must also be set to a value in the range of ‘1010’ through ‘1111’. A write to the PSP occurs when both the CS and WR lines are first detected low and ends when either are detected high. The PSPIF and IBF flag bits are both set when the write ends. A read from the PSP occurs when both the CS and RD lines are first detected low. The data in PORTD is read out and the OBF bit is clear. If the user writes new data to PORTD to set OBF, the data is immediately read out; however, the OBF bit is not set. When either the CS or RD lines are detected high, the PORTD pins return to the input state and the PSPIF bit is set. User applications should wait for PSPIF to be set before servicing the PSP; when this happens, the IBF and OBF bits can be polled and the appropriate action taken. The timing for the control signals in Write and Read modes is shown in Figure 10-3 and Figure 10-4, respectively. FIGURE 10-2: PORTD AND PORTE BLOCK DIAGRAM (PARALLEL SLAVE PORT) Note: The Parallel Slave Port is only available on 40/44-pin devices. Data Bus WR LATD RDx pin D Q CK EN Q D RD PORTD EN One bit of PORTD Set Interrupt Flag PSPIF (PIR1<7>) Read Chip Select Write RD CS WR TTL TTL TTL TTL or WR PORTD RD LATD Data Latch Note: I/O pins have diode protection to VDD and VSS. PORTE Pins © 2007 Microchip Technology Inc. Preliminary DS39631B-page 121 PIC18F2420/2520/4420/4520 FIGURE 10-3: PARALLEL SLAVE PORT WRITE WAVEFORMS FIGURE 10-4: PARALLEL SLAVE PORT READ WAVEFORMS TABLE 10-11: REGISTERS ASSOCIATED WITH PARALLEL SLAVE PORT Name Bit 7 Bit 6 Bit 5 Bit 4 Bit 3 Bit 2 Bit 1 Bit 0 Reset Values on page PORTD RD7 RD6 RD5 RD4 RD3 RD2 RD1 RD0 52 LATD PORTD Data Latch Register (Read and Write to Data Latch) 52 TRISD PORTD Data Direction Control Register 52 PORTE — — — — RE3 RE2 RE1 RE0 52 LATE — — — — — LATE Data Output bits 52 TRISE IBF OBF IBOV PSPMODE — TRISE2 TRISE1 TRISE0 52 INTCON GIE/GIEH PEIE/GIEL TMR0IF INT0IE RBIE TMR0IF INT0IF RBIF 49 PIR1 PSPIF ADIF RCIF TXIF SSPIF CCP1IF TMR2IF TMR1IF 52 PIE1 PSPIE ADIE RCIE TXIE SSPIE CCP1IE TMR2IE TMR1IE 52 IPR1 PSPIP ADIP RCIP TXIP SSPIP CCP1IP TMR2IP TMR1IP 52 ADCON1 — — VCFG1 VCFG0 PCFG3 PCFG2 PCFG1 PCFG0 51 Legend: — = unimplemented, read as ‘0’. Shaded cells are not used by the Parallel Slave Port. Q1 Q2 Q3 Q4 CS Q1 Q2 Q3 Q4 Q1 Q2 Q3 Q4 WR RD IBF OBF PSPIF PORTD<7:0> Q1 Q2 Q3 Q4 CS Q1 Q2 Q3 Q4 Q1 Q2 Q3 Q4 WR IBF PSPIF RD OBF PORTD<7:0> PIC18F2420/2520/4420/4520 DS39631B-page 122 Preliminary © 2007 Microchip Technology Inc. NOTES: © 2007 Microchip Technology Inc. Preliminary DS39631B-page 123 PIC18F2420/2520/4420/4520 11.0 TIMER0 MODULE The Timer0 module incorporates the following features: • Software selectable operation as a timer or counter in both 8-bit or 16-bit modes • Readable and writable registers • Dedicated 8-bit, software programmable prescaler • Selectable clock source (internal or external) • Edge select for external clock • Interrupt-on-overflow The T0CON register (Register 11-1) controls all aspects of the module’s operation, including the prescale selection. It is both readable and writable. A simplified block diagram of the Timer0 module in 8-bit mode is shown in Figure 11-1. Figure 11-2 shows a simplified block diagram of the Timer0 module in 16-bit mode. REGISTER 11-1: T0CON: TIMER0 CONTROL REGISTER R/W-1 R/W-1 R/W-1 R/W-1 R/W-1 R/W-1 R/W-1 R/W-1 TMR0ON T08BIT T0CS T0SE PSA T0PS2 T0PS1 T0PS0 bit 7 bit 0 bit 7 TMR0ON: Timer0 On/Off Control bit 1 = Enables Timer0 0 = Stops Timer0 bit 6 T08BIT: Timer0 8-bit/16-bit Control bit 1 = Timer0 is configured as an 8-bit timer/counter 0 = Timer0 is configured as a 16-bit timer/counter bit 5 T0CS: Timer0 Clock Source Select bit 1 = Transition on T0CKI pin 0 = Internal instruction cycle clock (CLKO) bit 4 T0SE: Timer0 Source Edge Select bit 1 = Increment on high-to-low transition on T0CKI pin 0 = Increment on low-to-high transition on T0CKI pin bit 3 PSA: Timer0 Prescaler Assignment bit 1 = TImer0 prescaler is NOT assigned. Timer0 clock input bypasses prescaler. 0 = Timer0 prescaler is assigned. Timer0 clock input comes from prescaler output. bit 2-0 T0PS2:T0PS0: Timer0 Prescaler Select bits 111 = 1:256 prescale value 110 = 1:128 prescale value 101 = 1:64 prescale value 100 = 1:32 prescale value 011 = 1:16 prescale value 010 = 1:8 prescale value 001 = 1:4 prescale value 000 = 1:2 prescale value Legend: R = Readable bit W = Writable bit U = Unimplemented bit, read as ‘0’ -n = Value at POR ‘1’ = Bit is set ‘0’ = Bit is cleared x = Bit is unknown PIC18F2420/2520/4420/4520 DS39631B-page 124 Preliminary © 2007 Microchip Technology Inc. 11.1 Timer0 Operation Timer0 can operate as either a timer or a counter; the mode is selected with the T0CS bit (T0CON<5>). In Timer mode (T0CS = 0), the module increments on every clock by default unless a different prescaler value is selected (see Section 11.3 “Prescaler”). If the TMR0 register is written to, the increment is inhibited for the following two instruction cycles. The user can work around this by writing an adjusted value to the TMR0 register. The Counter mode is selected by setting the T0CS bit (= 1). In this mode, Timer0 increments either on every rising or falling edge of pin RA4/T0CKI. The incrementing edge is determined by the Timer0 Source Edge Select bit, T0SE (T0CON<4>); clearing this bit selects the rising edge. Restrictions on the external clock input are discussed below. An external clock source can be used to drive Timer0; however, it must meet certain requirements to ensure that the external clock can be synchronized with the internal phase clock (TOSC). There is a delay between synchronization and the onset of incrementing the timer/counter. 11.2 Timer0 Reads and Writes in 16-Bit Mode TMR0H is not the actual high byte of Timer0 in 16-bit mode; it is actually a buffered version of the real high byte of Timer0 which is not directly readable nor writable (refer to Figure 11-2). TMR0H is updated with the contents of the high byte of Timer0 during a read of TMR0L. This provides the ability to read all 16 bits of Timer0 without having to verify that the read of the high and low byte were valid, due to a rollover between successive reads of the high and low byte. Similarly, a write to the high byte of Timer0 must also take place through the TMR0H Buffer register. The high byte is updated with the contents of TMR0H when a write occurs to TMR0L. This allows all 16 bits of Timer0 to be updated at once. FIGURE 11-1: TIMER0 BLOCK DIAGRAM (8-BIT MODE) FIGURE 11-2: TIMER0 BLOCK DIAGRAM (16-BIT MODE) Note: Upon Reset, Timer0 is enabled in 8-bit mode with clock input from T0CKI max. prescale. T0CKI pin T0SE 0 1 0 1 T0CS FOSC/4 Programmable Prescaler Sync with Internal Clocks TMR0L (2 TCY Delay) PSA Internal Data Bus T0PS2:T0PS0 Set TMR0IF on Overflow 3 8 8 Note: Upon Reset, Timer0 is enabled in 8-bit mode with clock input from T0CKI max. prescale. T0CKI pin T0SE 0 1 0 1 T0CS FOSC/4 Programmable Prescaler Sync with Internal Clocks TMR0L (2 TCY Delay) Internal Data Bus 8 PSA T0PS2:T0PS0 Set TMR0IF on Overflow 3 TMR0 TMR0H High Byte 8 8 8 Read TMR0L Write TMR0L 8 © 2007 Microchip Technology Inc. Preliminary DS39631B-page 125 PIC18F2420/2520/4420/4520 11.3 Prescaler An 8-bit counter is available as a prescaler for the Timer0 module. The prescaler is not directly readable or writable; its value is set by the PSA and T0PS2:T0PS0 bits (T0CON<3:0>) which determine the prescaler assignment and prescale ratio. Clearing the PSA bit assigns the prescaler to the Timer0 module. When it is assigned, prescale values from 1:2 through 1:256 in power-of-2 increments are selectable. When assigned to the Timer0 module, all instructions writing to the TMR0 register (e.g., CLRF TMR0, MOVWF TMR0, BSF TMR0, etc.) clear the prescaler count. 11.3.1 SWITCHING PRESCALER ASSIGNMENT The prescaler assignment is fully under software control and can be changed “on-the-fly” during program execution. 11.4 Timer0 Interrupt The TMR0 interrupt is generated when the TMR0 register overflows from FFh to 00h in 8-bit mode, or from FFFFh to 0000h in 16-bit mode. This overflow sets the TMR0IF flag bit. The interrupt can be masked by clearing the TMR0IE bit (INTCON<5>). Before re-enabling the interrupt, the TMR0IF bit must be cleared in software by the Interrupt Service Routine. Since Timer0 is shut down in Sleep mode, the TMR0 interrupt cannot awaken the processor from Sleep. TABLE 11-1: REGISTERS ASSOCIATED WITH TIMER0 Note: Writing to TMR0 when the prescaler is assigned to Timer0 will clear the prescaler count but will not change the prescaler assignment. Name Bit 7 Bit 6 Bit 5 Bit 4 Bit 3 Bit 2 Bit 1 Bit 0 Reset Values on page TMR0L Timer0 Register, Low Byte 50 TMR0H Timer0 Register, High Byte 50 INTCON GIE/GIEH PEIE/GIEL TMR0IE INT0IE RBIE TMR0IF INT0IF RBIF 49 T0CON TMR0ON T08BIT T0CS T0SE PSA T0PS2 T0PS1 T0PS0 50 TRISA RA7(1) RA6(1) RA5 RA4 RA3 RA2 RA1 RA0 52 Legend: Shaded cells are not used by Timer0. Note 1: PORTA<7:6> and their direction bits are individually configured as port pins based on various primary oscillator modes. When disabled, these bits read as ‘0’. PIC18F2420/2520/4420/4520 DS39631B-page 126 Preliminary © 2007 Microchip Technology Inc. NOTES: © 2007 Microchip Technology Inc. Preliminary DS39631B-page 127 PIC18F2420/2520/4420/4520 12.0 TIMER1 MODULE The Timer1 timer/counter module incorporates these features: • Software selectable operation as a 16-bit timer or counter • Readable and writable 8-bit registers (TMR1H and TMR1L) • Selectable clock source (internal or external) with device clock or Timer1 oscillator internal options • Interrupt-on-overflow • Reset on CCP Special Event Trigger • Device clock status flag (T1RUN) A simplified block diagram of the Timer1 module is shown in Figure 12-1. A block diagram of the module’s operation in Read/Write mode is shown in Figure 12-2. The module incorporates its own low-power oscillator to provide an additional clocking option. The Timer1 oscillator can also be used as a low-power clock source for the microcontroller in power managed operation. Timer1 can also be used to provide Real-Time Clock (RTC) functionality to applications with only a minimal addition of external components and code overhead. Timer1 is controlled through the T1CON Control register (Register 12-1). It also contains the Timer1 Oscillator Enable bit (T1OSCEN). Timer1 can be enabled or disabled by setting or clearing control bit, TMR1ON (T1CON<0>). REGISTER 12-1: T1CON: TIMER1 CONTROL REGISTER R/W-0 R-0 R/W-0 R/W-0 R/W-0 R/W-0 R/W-0 R/W-0 RD16 T1RUN T1CKPS1 T1CKPS0 T1OSCEN T1SYNC TMR1CS TMR1ON bit 7 bit 0 bit 7 RD16: 16-bit Read/Write Mode Enable bit 1 = Enables register read/write of TImer1 in one 16-bit operation 0 = Enables register read/write of Timer1 in two 8-bit operations bit 6 T1RUN: Timer1 System Clock Status bit 1 = Device clock is derived from Timer1 oscillator 0 = Device clock is derived from another source bit 5-4 T1CKPS1:T1CKPS0: Timer1 Input Clock Prescale Select bits 11 = 1:8 Prescale value 10 = 1:4 Prescale value 01 = 1:2 Prescale value 00 = 1:1 Prescale value bit 3 T1OSCEN: Timer1 Oscillator Enable bit 1 = Timer1 oscillator is enabled 0 = Timer1 oscillator is shut off The oscillator inverter and feedback resistor are turned off to eliminate power drain. bit 2 T1SYNC: Timer1 External Clock Input Synchronization Select bit When TMR1CS = 1: 1 = Do not synchronize external clock input 0 = Synchronize external clock input When TMR1CS = 0: This bit is ignored. Timer1 uses the internal clock when TMR1CS = 0. bit 1 TMR1CS: Timer1 Clock Source Select bit 1 = External clock from pin RC0/T1OSO/T13CKI (on the rising edge) 0 = Internal clock (FOSC/4) bit 0 TMR1ON: Timer1 On bit 1 = Enables Timer1 0 = Stops Timer1 Legend: R = Readable bit W = Writable bit U = Unimplemented bit, read as ‘0’ -n = Value at POR ‘1’ = Bit is set ‘0’ = Bit is cleared x = Bit is unknown PIC18F2420/2520/4420/4520 DS39631B-page 128 Preliminary © 2007 Microchip Technology Inc. 12.1 Timer1 Operation Timer1 can operate in one of these modes: • Timer • Synchronous Counter • Asynchronous Counter The operating mode is determined by the clock select bit, TMR1CS (T1CON<1>). When TMR3CS is cleared (= 0), Timer1 increments on every internal instruction cycle (Fosc/4). When the bit is set, Timer1 increments on every rising edge of the Timer1 external clock input or the Timer1 oscillator, if enabled. When Timer1 is enabled, the RC1/T1OSI and RC0/ T1OSO/T13CKI pins become inputs. This means the values of TRISC<1:0> are ignored and the pins are read as ‘0’. FIGURE 12-1: TIMER1 BLOCK DIAGRAM FIGURE 12-2: TIMER1 BLOCK DIAGRAM (16-BIT READ/WRITE MODE) T1SYNC TMR1CS T1CKPS1:T1CKPS0 Sleep Input T1OSCEN(1) FOSC/4 Internal Clock On/Off Prescaler 1, 2, 4, 8 Synchronize Detect 1 0 2 T1OSO/T13CKI T1OSI 1 0 TMR1ON TMR1L Set TMR1IF on Overflow TMR1 Clear TMR1 High Byte (CCP Special Event Trigger) Timer1 Oscillator Note 1: When enable bit, T1OSCEN, is cleared, the inverter and feedback resistor are turned off to eliminate power drain. On/Off Timer1 Timer1 Clock Input T1SYNC TMR1CS T1CKPS1:T1CKPS0 Sleep Input T1OSCEN(1) FOSC/4 Internal Clock Prescaler 1, 2, 4, 8 Synchronize Detect 1 0 2 T1OSO/T13CKI T1OSI Note 1: When enable bit, T1OSCEN, is cleared, the inverter and feedback resistor are turned off to eliminate power drain. 1 0 TMR1L Internal Data Bus 8 Set TMR1IF on Overflow TMR1 TMR1H High Byte 8 8 8 Read TMR1L Write TMR1L 8 TMR1ON Clear TMR1 (CCP Special Event Trigger) Timer1 Oscillator On/Off Timer1 Timer1 Clock Input © 2007 Microchip Technology Inc. Preliminary DS39631B-page 129 PIC18F2420/2520/4420/4520 12.2 Timer1 16-Bit Read/Write Mode Timer1 can be configured for 16-bit reads and writes (see Figure 12-2). When the RD16 control bit (T1CON<7>) is set, the address for TMR1H is mapped to a buffer register for the high byte of Timer1. A read from TMR1L will load the contents of the high byte of Timer1 into the Timer1 high byte buffer. This provides the user with the ability to accurately read all 16 bits of Timer1 without having to determine whether a read of the high byte, followed by a read of the low byte, has become invalid due to a rollover between reads. A write to the high byte of Timer1 must also take place through the TMR1H Buffer register. The Timer1 high byte is updated with the contents of TMR1H when a write occurs to TMR1L. This allows a user to write all 16 bits to both the high and low bytes of Timer1 at once. The high byte of Timer1 is not directly readable or writable in this mode. All reads and writes must take place through the Timer1 High Byte Buffer register. Writes to TMR1H do not clear the Timer1 prescaler. The prescaler is only cleared on writes to TMR1L. 12.3 Timer1 Oscillator An on-chip crystal oscillator circuit is incorporated between pins T1OSI (input) and T1OSO (amplifier output). It is enabled by setting the Timer1 Oscillator Enable bit, T1OSCEN (T1CON<3>). The oscillator is a lowpower circuit rated for 32 kHz crystals. It will continue to run during all power managed modes. The circuit for a typical LP oscillator is shown in Figure 12-3. Table 12-1 shows the capacitor selection for the Timer1 oscillator. The user must provide a software time delay to ensure proper start-up of the Timer1 oscillator. FIGURE 12-3: EXTERNAL COMPONENTS FOR THE TIMER1 LP OSCILLATOR TABLE 12-1: CAPACITOR SELECTION FOR THE TIMER OSCILLATOR 12.3.1 USING TIMER1 AS A CLOCK SOURCE The Timer1 oscillator is also available as a clock source in power managed modes. By setting the clock select bits, SCS1:SCS0 (OSCCON<1:0>), to ‘01’, the device switches to SEC_RUN mode; both the CPU and peripherals are clocked from the Timer1 oscillator. If the IDLEN bit (OSCCON<7>) is cleared and a SLEEP instruction is executed, the device enters SEC_IDLE mode. Additional details are available in Section 3.0 “Power Managed Modes”. Whenever the Timer1 oscillator is providing the clock source, the Timer1 system clock status flag, T1RUN (T1CON<6>), is set. This can be used to determine the controller’s current clocking mode. It can also indicate the clock source being currently used by the Fail-Safe Clock Monitor. If the Clock Monitor is enabled and the Timer1 oscillator fails while providing the clock, polling the T1RUN bit will indicate whether the clock is being provided by the Timer1 oscillator or another source. 12.3.2 LOW-POWER TIMER1 OPTION The Timer1 oscillator can operate at two distinct levels of power consumption based on device configuration. When the LPT1OSC configuration bit is set, the Timer1 oscillator operates in a low-power mode. When LPT1OSC is not set, Timer1 operates at a higher power level. Power consumption for a particular mode is relatively constant, regardless of the device’s operating mode. The default Timer1 configuration is the higher power mode. As the low-power Timer1 mode tends to be more sensitive to interference, high noise environments may cause some oscillator instability. The low-power option is, therefore, best suited for low noise applications where power conservation is an important design consideration. Note: See the Notes with Table 12-1 for additional information about capacitor selection. C1 C2 XTAL PIC18FXXXX T1OSI T1OSO 32.768 kHz 27 pF 27 pF Osc Type Freq C1 C2 LP 32 kHz 27 pF(1) 27 pF(1) Note 1: Microchip suggests these values as a starting point in validating the oscillator circuit. 2: Higher capacitance increases the stability of the oscillator but also increases the start-up time. 3: Since each resonator/crystal has its own characteristics, the user should consult the resonator/crystal manufacturer for appropriate values of external components. 4: Capacitor values are for design guidance only. PIC18F2420/2520/4420/4520 DS39631B-page 130 Preliminary © 2007 Microchip Technology Inc. 12.3.3 TIMER1 OSCILLATOR LAYOUT CONSIDERATIONS The Timer1 oscillator circuit draws very little power during operation. Due to the low-power nature of the oscillator, it may also be sensitive to rapidly changing signals in close proximity. The oscillator circuit, shown in Figure 12-3, should be located as close as possible to the microcontroller. There should be no circuits passing within the oscillator circuit boundaries other than VSS or VDD. If a high-speed circuit must be located near the oscillator (such as the CCP1 pin in Output Compare or PWM mode, or the primary oscillator using the OSC2 pin), a grounded guard ring around the oscillator circuit, as shown in Figure 12-4, may be helpful when used on a single-sided PCB or in addition to a ground plane. FIGURE 12-4: OSCILLATOR CIRCUIT WITH GROUNDED GUARD RING 12.4 Timer1 Interrupt The TMR1 register pair (TMR1H:TMR1L) increments from 0000h to FFFFh and rolls over to 0000h. The Timer1 interrupt, if enabled, is generated on overflow, which is latched in interrupt flag bit, TMR1IF (PIR1<0>). This interrupt can be enabled or disabled by setting or clearing the Timer1 Interrupt Enable bit, TMR1IE (PIE1<0>). 12.5 Resetting Timer1 Using the CCP Special Event Trigger If either of the CCP modules is configured to use Timer1 and generate a Special Event Trigger in Compare mode (CCP1M3:CCP1M0 or CCP2M3:CCP2M0 = 1011), this signal will reset Timer1. The trigger from CCP2 will also start an A/D conversion if the A/D module is enabled (see Section 15.3.4 “Special Event Trigger” for more information). The module must be configured as either a timer or a synchronous counter to take advantage of this feature. When used this way, the CCPRH:CCPRL register pair effectively becomes a period register for Timer1. If Timer1 is running in Asynchronous Counter mode, this Reset operation may not work. In the event that a write to Timer1 coincides with a special Event Trigger, the write operation will take precedence. 12.6 Using Timer1 as a Real-Time Clock Adding an external LP oscillator to Timer1 (such as the one described in Section 12.3 “Timer1 Oscillator” above) gives users the option to include RTC functionality to their applications. This is accomplished with an inexpensive watch crystal to provide an accurate time base and several lines of application code to calculate the time. When operating in Sleep mode and using a battery or supercapacitor as a power source, it can completely eliminate the need for a separate RTC device and battery backup. The application code routine, RTCisr, shown in Example 12-1, demonstrates a simple method to increment a counter at one-second intervals using an Interrupt Service Routine. Incrementing the TMR1 register pair to overflow triggers the interrupt and calls the routine, which increments the seconds counter by one; additional counters for minutes and hours are incremented as the previous counter overflow. Since the register pair is 16 bits wide, counting up to overflow the register directly from a 32.768 kHz clock would take 2 seconds. To force the overflow at the required one-second intervals, it is necessary to preload it; the simplest method is to set the MSb of TMR1H with a BSF instruction. Note that the TMR1L register is never preloaded or altered; doing so may introduce cumulative error over many cycles. For this method to be accurate, Timer1 must operate in Asynchronous mode and the Timer1 overflow interrupt must be enabled (PIE1<0> = 1), as shown in the routine, RTCinit. The Timer1 oscillator must also be enabled and running at all times. VDD OSC1 VSS OSC2 RC0 RC1 RC2 Note: Not drawn to scale. Note: The Special Event Triggers from the CCP2 module will not set the TMR1IF interrupt flag bit (PIR1<0>). © 2007 Microchip Technology Inc. Preliminary DS39631B-page 131 PIC18F2420/2520/4420/4520 EXAMPLE 12-1: IMPLEMENTING A REAL-TIME CLOCK USING A TIMER1 INTERRUPT SERVICE TABLE 12-2: REGISTERS ASSOCIATED WITH TIMER1 AS A TIMER/COUNTER RTCinit MOVLW 80h ; Preload TMR1 register pair MOVWF TMR1H ; for 1 second overflow CLRF TMR1L MOVLW b’00001111’ ; Configure for external clock, MOVWF T1CON ; Asynchronous operation, external oscillator CLRF secs ; Initialize timekeeping registers CLRF mins ; MOVLW .12 MOVWF hours BSF PIE1, TMR1IE ; Enable Timer1 interrupt RETURN RTCisr BSF TMR1H, 7 ; Preload for 1 sec overflow BCF PIR1, TMR1IF ; Clear interrupt flag INCF secs, F ; Increment seconds MOVLW .59 ; 60 seconds elapsed? CPFSGT secs RETURN ; No, done CLRF secs ; Clear seconds INCF mins, F ; Increment minutes MOVLW .59 ; 60 minutes elapsed? CPFSGT mins RETURN ; No, done CLRF mins ; clear minutes INCF hours, F ; Increment hours MOVLW .23 ; 24 hours elapsed? CPFSGT hours RETURN ; No, done CLRF hours ; Reset hours RETURN ; Done Name Bit 7 Bit 6 Bit 5 Bit 4 Bit 3 Bit 2 Bit 1 Bit 0 Reset Values on page INTCON GIE/GIEH PEIE/GIEL TMR0IE INT0IE RBIE TMR0IF INT0IF RBIF 49 PIR1 PSPIF(1) ADIF RCIF TXIF SSPIF CCP1IF TMR2IF TMR1IF 52 PIE1 PSPIE(1) ADIE RCIE TXIE SSPIE CCP1IE TMR2IE TMR1IE 52 IPR1 PSPIP(1) ADIP RCIP TXIP SSPIP CCP1IP TMR2IP TMR1IP 52 TMR1L Timer1 Register, Low Byte 50 TMR1H Timer1 Register, High Byte 50 T1CON RD16 T1RUN T1CKPS1 T1CKPS0 T1OSCEN T1SYNC TMR1CS TMR1ON 50 Legend: Shaded cells are not used by the Timer1 module. Note 1: These bits are unimplemented on 28-pin devices; always maintain these bits clear. PIC18F2420/2520/4420/4520 DS39631B-page 132 Preliminary © 2007 Microchip Technology Inc. NOTES: © 2007 Microchip Technology Inc. Preliminary DS39631B-page 133 PIC18F2420/2520/4420/4520 13.0 TIMER2 MODULE The Timer2 module timer incorporates the following features: • 8-bit timer and period registers (TMR2 and PR2, respectively) • Readable and writable (both registers) • Software programmable prescaler (1:1, 1:4 and 1:16) • Software programmable postscaler (1:1 through 1:16) • Interrupt on TMR2-to-PR2 match • Optional use as the shift clock for the MSSP module The module is controlled through the T2CON register (Register 13-1), which enables or disables the timer and configures the prescaler and postscaler. Timer2 can be shut off by clearing control bit, TMR2ON (T2CON<2>), to minimize power consumption. A simplified block diagram of the module is shown in Figure 13-1. 13.1 Timer2 Operation In normal operation, TMR2 is incremented from 00h on each clock (FOSC/4). A 4-bit counter/prescaler on the clock input gives direct input, divide-by-4 and divide-by- 16 prescale options; these are selected by the prescaler control bits, T2CKPS1:T2CKPS0 (T2CON<1:0>). The value of TMR2 is compared to that of the period register, PR2, on each clock cycle. When the two values match, the comparator generates a match signal as the timer output. This signal also resets the value of TMR2 to 00h on the next cycle and drives the output counter/ postscaler (see Section 13.2 “Timer2 Interrupt”). The TMR2 and PR2 registers are both directly readable and writable. The TMR2 register is cleared on any device Reset, while the PR2 register initializes at FFh. Both the prescaler and postscaler counters are cleared on the following events: • a write to the TMR2 register • a write to the T2CON register • any device Reset (Power-on Reset, MCLR Reset, Watchdog Timer Reset or Brown-out Reset) TMR2 is not cleared when T2CON is written. REGISTER 13-1: T2CON: TIMER2 CONTROL REGISTER U-0 R/W-0 R/W-0 R/W-0 R/W-0 R/W-0 R/W-0 R/W-0 — T2OUTPS3 T2OUTPS2 T2OUTPS1 T2OUTPS0 TMR2ON T2CKPS1 T2CKPS0 bit 7 bit 0 bit 7 Unimplemented: Read as ‘0’ bit 6-3 T2OUTPS3:T2OUTPS0: Timer2 Output Postscale Select bits 0000 = 1:1 Postscale 0001 = 1:2 Postscale • • • 1111 = 1:16 Postscale bit 2 TMR2ON: Timer2 On bit 1 = Timer2 is on 0 = Timer2 is off bit 1-0 T2CKPS1:T2CKPS0: Timer2 Clock Prescale Select bits 00 = Prescaler is 1 01 = Prescaler is 4 1x = Prescaler is 16 Legend: R = Readable bit W = Writable bit U = Unimplemented bit, read as ‘0’ -n = Value at POR ‘1’ = Bit is set ‘0’ = Bit is cleared x = Bit is unknown PIC18F2420/2520/4420/4520 DS39631B-page 134 Preliminary © 2007 Microchip Technology Inc. 13.2 Timer2 Interrupt Timer2 also can generate an optional device interrupt. The Timer2 output signal (TMR2-to-PR2 match) provides the input for the 4-bit output counter/postscaler. This counter generates the TMR2 match interrupt flag which is latched in TMR2IF (PIR1<1>). The interrupt is enabled by setting the TMR2 Match Interrupt Enable bit, TMR2IE (PIE1<1>). A range of 16 postscale options (from 1:1 through 1:16 inclusive) can be selected with the postscaler control bits, T2OUTPS3:T2OUTPS0 (T2CON<6:3>). 13.3 Timer2 Output The unscaled output of TMR2 is available primarily to the CCP modules, where it is used as a time base for operations in PWM mode. Timer2 can be optionally used as the shift clock source for the MSSP module operating in SPI mode. Additional information is provided in Section 17.0 “Master Synchronous Serial Port (MSSP) Module”. FIGURE 13-1: TIMER2 BLOCK DIAGRAM TABLE 13-1: REGISTERS ASSOCIATED WITH TIMER2 AS A TIMER/COUNTER Name Bit 7 Bit 6 Bit 5 Bit 4 Bit 3 Bit 2 Bit 1 Bit 0 Reset Values on page INTCON GIE/GIEH PEIE/GIEL TMR0IE INT0IE RBIE TMR0IF INT0IF RBIF 49 PIR1 PSPIF(1) ADIF RCIF TXIF SSPIF CCP1IF TMR2IF TMR1IF 52 PIE1 PSPIE(1) ADIE RCIE TXIE SSPIE CCP1IE TMR2IE TMR1IE 52 IPR1 PSPIP(1) ADIP RCIP TXIP SSPIP CCP1IP TMR2IP TMR1IP 52 TMR2 Timer2 Register 50 T2CON — T2OUTPS3 T2OUTPS2 T2OUTPS1 T2OUTPS0 TMR2ON T2CKPS1 T2CKPS0 50 PR2 Timer2 Period Register 50 Legend: — = unimplemented, read as ‘0’. Shaded cells are not used by the Timer2 module. Note 1: These bits are unimplemented on 28-pin devices; always maintain these bits clear. Comparator TMR2 Output TMR2 Postscaler Prescaler PR2 2 FOSC/4 1:1 to 1:16 1:1, 1:4, 1:16 4 T2OUTPS3:T2OUTPS0 T2CKPS1:T2CKPS0 Set TMR2IF Internal Data Bus 8 Reset TMR2/PR2 8 8 (to PWM or MSSP) Match © 2007 Microchip Technology Inc. Preliminary DS39631B-page 135 PIC18F2420/2520/4420/4520 14.0 TIMER3 MODULE The Timer3 module timer/counter incorporates these features: • Software selectable operation as a 16-bit timer or counter • Readable and writable 8-bit registers (TMR3H and TMR3L) • Selectable clock source (internal or external) with device clock or Timer1 oscillator internal options • Interrupt-on-overflow • Module Reset on CCP Special Event Trigger A simplified block diagram of the Timer3 module is shown in Figure 14-1. A block diagram of the module’s operation in Read/Write mode is shown in Figure 14-2. The Timer3 module is controlled through the T3CON register (Register 14-1). It also selects the clock source options for the CCP modules (see Section 15.1.1 “CCP Modules and Timer Resources” for more information). REGISTER 14-1: T3CON: TIMER3 CONTROL REGISTER R/W-0 R/W-0 R/W-0 R/W-0 R/W-0 R/W-0 R/W-0 R/W-0 RD16 T3CCP2 T3CKPS1 T3CKPS0 T3CCP1 T3SYNC TMR3CS TMR3ON bit 7 bit 0 bit 7 RD16: 16-bit Read/Write Mode Enable bit 1 = Enables register read/write of Timer3 in one 16-bit operation 0 = Enables register read/write of Timer3 in two 8-bit operations bit 6,3 T3CCP2:T3CCP1: Timer3 and Timer1 to CCPx Enable bits 1x = Timer3 is the capture/compare clock source for the CCP modules 01 = Timer3 is the capture/compare clock source for CCP2; Timer1 is the capture/compare clock source for CCP1 00 = Timer1 is the capture/compare clock source for the CCP modules bit 5-4 T3CKPS1:T3CKPS0: Timer3 Input Clock Prescale Select bits 11 = 1:8 Prescale value 10 = 1:4 Prescale value 01 = 1:2 Prescale value 00 = 1:1 Prescale value bit 2 T3SYNC: Timer3 External Clock Input Synchronization Control bit (Not usable if the device clock comes from Timer1/Timer3.) When TMR3CS = 1: 1 = Do not synchronize external clock input 0 = Synchronize external clock input When TMR3CS = 0: This bit is ignored. Timer3 uses the internal clock when TMR3CS = 0. bit 1 TMR3CS: Timer3 Clock Source Select bit 1 = External clock input from Timer1 oscillator or T13CKI (on the rising edge after the first falling edge) 0 = Internal clock (FOSC/4) bit 0 TMR3ON: Timer3 On bit 1 = Enables Timer3 0 = Stops Timer3 Legend: R = Readable bit W = Writable bit U = Unimplemented bit, read as ‘0’ -n = Value at POR ‘1’ = Bit is set ‘0’ = Bit is cleared x = Bit is unknown PIC18F2420/2520/4420/4520 DS39631B-page 136 Preliminary © 2007 Microchip Technology Inc. 14.1 Timer3 Operation Timer3 can operate in one of three modes: • Timer • Synchronous Counter • Asynchronous Counter The operating mode is determined by the clock select bit, TMR3CS (T3CON<1>). When TMR3CS is cleared (= 0), Timer3 increments on every internal instruction cycle (FOSC/4). When the bit is set, Timer3 increments on every rising edge of the Timer1 external clock input or the Timer1 oscillator, if enabled. As with Timer1, the RC1/T1OSI and RC0/T1OSO/ T13CKI pins become inputs when the Timer1 oscillator is enabled. This means the values of TRISC<1:0> are ignored and the pins are read as ‘0’. FIGURE 14-1: TIMER3 BLOCK DIAGRAM FIGURE 14-2: TIMER3 BLOCK DIAGRAM (16-BIT READ/WRITE MODE) T3SYNC TMR3CS T3CKPS1:T3CKPS0 Sleep Input T1OSCEN(1) FOSC/4 Internal Clock Prescaler 1, 2, 4, 8 Synchronize Detect 1 0 2 T1OSO/T13CKI T1OSI 1 0 TMR3ON TMR3L Set TMR3IF on Overflow TMR3 High Byte Timer1 Oscillator Note 1: When enable bit, T1OSCEN, is cleared, the inverter and feedback resistor are turned off to eliminate power drain. On/Off Timer3 CCP1/CCP2 Special Event Trigger CCP1/CCP2 Select from T3CON<6,3> Clear TMR3 Timer1 Clock Input T3SYNC TMR3CS T3CKPS1:T3CKPS0 Sleep Input T1OSCEN(1) FOSC/4 Internal Clock Prescaler 1, 2, 4, 8 Synchronize Detect 1 0 2 T13CKI/T1OSO T1OSI Note 1: When enable bit, T1OSCEN, is cleared, the inverter and feedback resistor are turned off to eliminate power drain. 1 0 TMR3L Internal Data Bus 8 Set TMR3IF on Overflow TMR3 TMR3H High Byte 8 8 8 Read TMR1L Write TMR1L 8 TMR3ON CCP1/CCP2 Special Event Trigger Timer1 Oscillator On/Off Timer3 Timer1 Clock Input CCP1/CCP2 Select from T3CON<6,3> Clear TMR3 © 2007 Microchip Technology Inc. Preliminary DS39631B-page 137 PIC18F2420/2520/4420/4520 14.2 Timer3 16-Bit Read/Write Mode Timer3 can be configured for 16-bit reads and writes (see Figure 14-2). When the RD16 control bit (T3CON<7>) is set, the address for TMR3H is mapped to a buffer register for the high byte of Timer3. A read from TMR3L will load the contents of the high byte of Timer3 into the Timer3 High Byte Buffer register. This provides the user with the ability to accurately read all 16 bits of Timer1 without having to determine whether a read of the high byte, followed by a read of the low byte, has become invalid due to a rollover between reads. A write to the high byte of Timer3 must also take place through the TMR3H Buffer register. The Timer3 high byte is updated with the contents of TMR3H when a write occurs to TMR3L. This allows a user to write all 16 bits to both the high and low bytes of Timer3 at once. The high byte of Timer3 is not directly readable or writable in this mode. All reads and writes must take place through the Timer3 High Byte Buffer register. Writes to TMR3H do not clear the Timer3 prescaler. The prescaler is only cleared on writes to TMR3L. 14.3 Using the Timer1 Oscillator as the Timer3 Clock Source The Timer1 internal oscillator may be used as the clock source for Timer3. The Timer1 oscillator is enabled by setting the T1OSCEN (T1CON<3>) bit. To use it as the Timer3 clock source, the TMR3CS bit must also be set. As previously noted, this also configures Timer3 to increment on every rising edge of the oscillator source. The Timer1 oscillator is described in Section 12.0 “Timer1 Module”. 14.4 Timer3 Interrupt The TMR3 register pair (TMR3H:TMR3L) increments from 0000h to FFFFh and overflows to 0000h. The Timer3 interrupt, if enabled, is generated on overflow and is latched in interrupt flag bit, TMR3IF (PIR2<1>). This interrupt can be enabled or disabled by setting or clearing the Timer3 Interrupt Enable bit, TMR3IE (PIE2<1>). 14.5 Resetting Timer3 Using the CCP Special Event Trigger If either of the CCP modules is configured to use Timer3 and to generate a Special Event Trigger in Compare mode (CCP1M3:CCP1M0 or CCP2M3:CCP2M0 = 1011), this signal will reset Timer3. It will also start an A/D conversion if the A/D module is enabled (see Section 15.3.4 “Special Event Trigger” for more information). The module must be configured as either a timer or synchronous counter to take advantage of this feature. When used this way, the CCPR2H:CCPR2L register pair effectively becomes a period register for Timer3. If Timer3 is running in Asynchronous Counter mode, the Reset operation may not work. In the event that a write to Timer3 coincides with a Special Event Trigger from a CCP module, the write will take precedence. TABLE 14-1: REGISTERS ASSOCIATED WITH TIMER3 AS A TIMER/COUNTER Note: The Special Event Triggers from the CCP2 module will not set the TMR3IF interrupt flag bit (PIR1<0>). Name Bit 7 Bit 6 Bit 5 Bit 4 Bit 3 Bit 2 Bit 1 Bit 0 Reset Values on page INTCON GIE/GIEH PEIE/GIEL TMR0IE INT0IE RBIE TMR0IF INT0IF RBIF 49 PIR2 OSCFIF CMIF — EEIF BCLIF HLVDIF TMR3IF CCP2IF 52 PIE2 OSCFIE CMIE — EEIE BCLIE HLVDIE TMR3IE CCP2IE 52 IPR2 OSCFIP CMIP — EEIP BCLIP HLVDIP TMR3IP CCP2IP 52 TMR3L Timer3 Register, Low Byte 51 TMR3H Timer3 Register, High Byte 51 T1CON RD16 T1RUN T1CKPS1 T1CKPS0 T1OSCEN T1SYNC TMR1CS TMR1ON 50 T3CON RD16 T3CCP2 T3CKPS1 T3CKPS0 T3CCP1 T3SYNC TMR3CS TMR3ON 51 Legend: — = unimplemented, read as ‘0’. Shaded cells are not used by the Timer3 module. PIC18F2420/2520/4420/4520 DS39631B-page 138 Preliminary © 2007 Microchip Technology Inc. NOTES: © 2007 Microchip Technology Inc. Preliminary DS39631B-page 139 PIC18F2420/2520/4420/4520 15.0 CAPTURE/COMPARE/PWM (CCP) MODULES PIC18F2420/2520/4420/4520 devices all have two CCP (Capture/Compare/PWM) modules. Each module contains a 16-bit register which can operate as a 16-bit Capture register, a 16-bit Compare register or a PWM Master/Slave Duty Cycle register. In 28-pin devices, the two standard CCP modules (CCP1 and CCP2) operate as described in this chapter. In 40/ 44-pin devices, CCP1 is implemented as an enhanced CCP module with standard Capture and Compare modes and enhanced PWM modes. The ECCP implementation is discussed in Section 16.0 “Enhanced Capture/Compare/PWM (ECCP) Module”. The Capture and Compare operations described in this chapter apply to all standard and enhanced CCP modules. REGISTER 15-1: CCPXCON REGISTER (CCP2 MODULE, CCP1 MODULE IN 28-PIN DEVICES) Note: Throughout this section and Section 16.0 “Enhanced Capture/Compare/PWM (ECCP) Module”, references to the register and bit names for CCP modules are referred to generically by the use of ‘x’ or ‘y’ in place of the specific module number. Thus, “CCPxCON” might refer to the control register for CCP1, CCP2 or ECCP1. “CCPxCON” is used throughout these sections to refer to the module control register, regardless of whether the CCP module is a standard or enhanced implementation. U-0 U-0 R/W-0 R/W-0 R/W-0 R/W-0 R/W-0 R/W-0 — — DCxB1 DCxB0 CCPxM3 CCPxM2 CCPxM1 CCPxM0 bit 7 bit 0 bit 7-6 Unimplemented: Read as ‘0’ bit 5-4 DCxB1:DCxB0: PWM Duty Cycle bit 1 and bit 0 for CCP Module x Capture mode: Unused. Compare mode: Unused. PWM mode: These bits are the two LSbs (bit 1 and bit 0) of the 10-bit PWM duty cycle. The eight MSbs (DCx9:DCx2) of the duty cycle are found in CCPRxL. bit 3-0 CCPxM3:CCPxM0: CCP Module x Mode Select bits 0000 = Capture/Compare/PWM disabled (resets CCP module) 0001 = Reserved 0010 = Compare mode, toggle output on match (CCPxIF bit is set) 0011 = Reserved 0100 = Capture mode, every falling edge 0101 = Capture mode, every rising edge 0110 = Capture mode, every 4th rising edge 0111 = Capture mode, every 16th rising edge 1000 = Compare mode: initialize CCP pin low; on compare match, force CCP pin high (CCPIF bit is set) 1001 = Compare mode: initialize CCP pin high; on compare match, force CCP pin low (CCPIF bit is set) 1010 = Compare mode: generate software interrupt on compare match (CCPxIF bit is set, CCP pin reflects I/O state) 1011 = Compare mode: trigger special event, reset timer, start A/D conversion on CCP2 match (CCPxIF bit is set) 11xx = PWM mode Legend: R = Readable bit W = Writable bit U = Unimplemented bit, read as ‘0’ -n = Value at POR ‘1’ = Bit is set ‘0’ = Bit is cleared x = Bit is unknown PIC18F2420/2520/4420/4520 DS39631B-page 140 Preliminary © 2007 Microchip Technology Inc. 15.1 CCP Module Configuration Each Capture/Compare/PWM module is associated with a control register (generically, CCPxCON) and a data register (CCPRx). The data register, in turn, is comprised of two 8-bit registers: CCPRxL (low byte) and CCPRxH (high byte). All registers are both readable and writable. 15.1.1 CCP MODULES AND TIMER RESOURCES The CCP modules utilize Timers 1, 2 or 3, depending on the mode selected. Timer1 and Timer3 are available to modules in Capture or Compare modes, while Timer2 is available for modules in PWM mode. TABLE 15-1: CCP MODE – TIMER RESOURCE The assignment of a particular timer to a module is determined by the Timer-to-CCP enable bits in the T3CON register (Register 14-1). Both modules may be active at any given time and may share the same timer resource if they are configured to operate in the same mode (Capture/Compare or PWM) at the same time. The interactions between the two modules are summarized in Figure 15-1 and Figure 15-2. In Timer1 in Asynchronous Counter mode, the capture operation will not work. 15.1.2 CCP2 PIN ASSIGNMENT The pin assignment for CCP2 (Capture input, Compare and PWM output) can change, based on device configuration. The CCP2MX configuration bit determines which pin CCP2 is multiplexed to. By default, it is assigned to RC1 (CCP2MX = 1). If the configuration bit is cleared, CCP2 is multiplexed with RB3. Changing the pin assignment of CCP2 does not automatically change any requirements for configuring the port pin. Users must always verify that the appropriate TRIS register is configured correctly for CCP2 operation, regardless of where it is located. TABLE 15-2: INTERACTIONS BETWEEN CCP1 AND CCP2 FOR TIMER RESOURCES CCP/ECCP Mode Timer Resource Capture Compare PWM Timer1 or Timer3 Timer1 or Timer3 Timer2 CCP1 Mode CCP2 Mode Interaction Capture Capture Each module can use TMR1 or TMR3 as the time base. The time base can be different for each CCP. Capture Compare CCP2 can be configured for the Special Event Trigger to reset TMR1 or TMR3 (depending upon which time base is used). Automatic A/D conversions on trigger event can also be done. Operation of CCP1 could be affected if it is using the same timer as a time base. Compare Capture CCP1 can be configured for the Special Event Trigger to reset TMR1 or TMR3 (depending upon which time base is used). Operation of CCP2 could be affected if it is using the same timer as a time base. Compare Compare Either module can be configured for the Special Event Trigger to reset the time base. Automatic A/D conversions on CCP2 trigger event can be done. Conflicts may occur if both modules are using the same time base. Capture PWM(1) None Compare PWM(1) None PWM(1) Capture None PWM(1) Compare None PWM(1) PWM Both PWMs will have the same frequency and update rate (TMR2 interrupt). Note 1: Includes standard and enhanced PWM operation. © 2007 Microchip Technology Inc. Preliminary DS39631B-page 141 PIC18F2420/2520/4420/4520 15.2 Capture Mode In Capture mode, the CCPRxH:CCPRxL register pair captures the 16-bit value of the TMR1 or TMR3 registers when an event occurs on the corresponding CCPx pin. An event is defined as one of the following: • every falling edge • every rising edge • every 4th rising edge • every 16th rising edge The event is selected by the mode select bits, CCPxM3:CCPxM0 (CCPxCON<3:0>). When a capture is made, the interrupt request flag bit, CCPxIF, is set; it must be cleared in software. If another capture occurs before the value in register CCPRx is read, the old captured value is overwritten by the new captured value. 15.2.1 CCP PIN CONFIGURATION In Capture mode, the appropriate CCPx pin should be configured as an input by setting the corresponding TRIS direction bit. 15.2.2 TIMER1/TIMER3 MODE SELECTION The timers that are to be used with the capture feature (Timer1 and/or Timer3) must be running in Timer mode or Synchronized Counter mode. In Asynchronous Counter mode, the capture operation will not work. The timer to be used with each CCP module is selected in the T3CON register (see Section 15.1.1 “CCP Modules and Timer Resources”). 15.2.3 SOFTWARE INTERRUPT When the Capture mode is changed, a false capture interrupt may be generated. The user should keep the CCPxIE interrupt enable bit clear to avoid false interrupts. The interrupt flag bit, CCPxIF, should also be cleared following any such change in operating mode. 15.2.4 CCP PRESCALER There are four prescaler settings in Capture mode; they are specified as part of the operating mode selected by the mode select bits (CCPxM3:CCPxM0). Whenever the CCP module is turned off or Capture mode is disabled, the prescaler counter is cleared. This means that any Reset will clear the prescaler counter. Switching from one capture prescaler to another may generate an interrupt. Also, the prescaler counter will not be cleared; therefore, the first capture may be from a non-zero prescaler. Example 15-1 shows the recommended method for switching between capture prescalers. This example also clears the prescaler counter and will not generate the “false” interrupt. EXAMPLE 15-1: CHANGING BETWEEN CAPTURE PRESCALERS (CCP2 SHOWN) FIGURE 15-1: CAPTURE MODE OPERATION BLOCK DIAGRAM Note: If RB3/CCP2 or RC1/CCP2 is configured as an output, a write to the port can cause a capture condition. CLRF CCP2CON ; Turn CCP module off MOVLW NEW_CAPT_PS ; Load WREG with the ; new prescaler mode ; value and CCP ON MOVWF CCP2CON ; Load CCP2CON with ; this value CCPR1H CCPR1L TMR1H TMR1L Set CCP1IF TMR3 Enable Q1:Q4 CCP1CON<3:0> CCP1 pin Prescaler ÷ 1, 4, 16 and Edge Detect TMR1 Enable T3CCP2 T3CCP2 CCPR2H CCPR2L TMR1H TMR1L Set CCP2IF TMR3 Enable CCP2CON<3:0> CCP2 pin Prescaler ÷ 1, 4, 16 TMR3H TMR3L TMR1 Enable T3CCP2 T3CCP1 T3CCP2 T3CCP1 TMR3H TMR3L and Edge Detect 4 4 4 PIC18F2420/2520/4420/4520 DS39631B-page 142 Preliminary © 2007 Microchip Technology Inc. 15.3 Compare Mode In Compare mode, the 16-bit CCPRx register value is constantly compared against either the TMR1 or TMR3 register pair value. When a match occurs, the CCPx pin can be: • driven high • driven low • toggled (high-to-low or low-to-high) • remain unchanged (that is, reflects the state of the I/O latch) The action on the pin is based on the value of the mode select bits (CCPxM3:CCPxM0). At the same time, the interrupt flag bit, CCPxIF, is set. 15.3.1 CCP PIN CONFIGURATION The user must configure the CCPx pin as an output by clearing the appropriate TRIS bit. 15.3.2 TIMER1/TIMER3 MODE SELECTION Timer1 and/or Timer3 must be running in Timer mode or Synchronized Counter mode if the CCP module is using the compare feature. In Asynchronous Counter mode, the compare operation may not work. 15.3.3 SOFTWARE INTERRUPT MODE When the Generate Software Interrupt mode is chosen (CCPxM3:CCPxM0 = 1010), the corresponding CCPx pin is not affected. Only a CCP interrupt is generated, if enabled and the CCPxIE bit is set. 15.3.4 SPECIAL EVENT TRIGGER Both CCP modules are equipped with a Special Event Trigger. This is an internal hardware signal generated in Compare mode to trigger actions by other modules. The Special Event Trigger is enabled by selecting the Compare Special Event Trigger mode (CCPxM3:CCPxM0 = 1011). For either CCP module, the Special Event Trigger resets the timer register pair for whichever timer resource is currently assigned as the module’s time base. This allows the CCPRx registers to serve as a programmable period register for either timer. The Special Event Trigger for CCP2 can also start an A/D conversion. In order to do this, the A/D converter must already be enabled. FIGURE 15-2: COMPARE MODE OPERATION BLOCK DIAGRAM Note: Clearing the CCP2CON register will force the RB3 or RC1 compare output latch (depending on device configuration) to the default low level. This is not the PORTB or PORTC I/O data latch. CCPR1H CCPR1L TMR1H TMR1L Comparator S Q R Output Logic Special Event Trigger Set CCP1IF CCP1 pin TRIS CCP1CON<3:0> Output Enable TMR3H TMR3L CCPR2H CCPR2L Comparator 1 0 T3CCP2 T3CCP1 Set CCP2IF 1 0 Compare 4 (Timer1/Timer3 Reset) S Q R Output Logic Special Event Trigger CCP2 pin TRIS CCP2CON<3:0> 4 Output Enable (Timer1/Timer3 Reset, A/D Trigger) Match Compare Match © 2007 Microchip Technology Inc. Preliminary DS39631B-page 143 PIC18F2420/2520/4420/4520 TABLE 15-3: REGISTERS ASSOCIATED WITH CAPTURE, COMPARE, TIMER1 AND TIMER3 Name Bit 7 Bit 6 Bit 5 Bit 4 Bit 3 Bit 2 Bit 1 Bit 0 Reset Values on page INTCON GIE/GIEH PEIE/GIEL TMR0IE INT0IE RBIE TMR0IF INT0IF RBIF 49 RCON IPEN SBOREN — RI TO PD POR BOR 48 PIR1 PSPIF(1) ADIF RCIF TXIF SSPIF CCP1IF TMR2IF TMR1IF 52 PIE1 PSPIE(1) ADIE RCIE TXIE SSPIE CCP1IE TMR2IE TMR1IE 52 IPR1 PSPIP(1) ADIP RCIP TXIP SSPIP CCP1IP TMR2IP TMR1IP 52 PIR2 OSCFIF CMIF — EEIF BCLIF HLVDIF TMR3IF CCP2IF 52 PIE2 OSCFIE CMIE — EEIE BCLIE HLVDIE TMR3IE CCP2IE 52 IPR2 OSCFIP CMIP — EEIP BCLIP HLVDIP TMR3IP CCP2IP 52 TRISB PORTB Data Direction Control Register 52 TRISC PORTC Data Direction Control Register 52 TMR1L Timer1 Register, Low Byte 50 TMR1H Timer1 Register, High Byte 50 T1CON RD16 T1RUN T1CKPS1 T1CKPS0 T1OSCEN T1SYNC TMR1CS TMR1ON 50 TMR3H Timer3 Register, High Byte 51 TMR3L Timer3 Register, Low Byte 51 T3CON RD16 T3CCP2 T3CKPS1 T3CKPS0 T3CCP1 T3SYNC TMR3CS TMR3ON 51 CCPR1L Capture/Compare/PWM Register 1, Low Byte 51 CCPR1H Capture/Compare/PWM Register 1, High Byte 51 CCP1CON P1M1(1) P1M0(1) DC1B1 DC1B0 CCP1M3 CCP1M2 CCP1M1 CCP1M0 51 CCPR2L Capture/Compare/PWM Register 2, Low Byte 51 CCPR2H Capture/Compare/PWM Register 2, High Byte 51 CCP2CON — — DC2B1 DC2B0 CCP2M3 CCP2M2 CCP2M1 CCP2M0 51 Legend: — = unimplemented, read as ‘0’. Shaded cells are not used by Capture/Compare, Timer1 or Timer3. Note 1: These bits are unimplemented on 28-pin devices; always maintain these bits clear. PIC18F2420/2520/4420/4520 DS39631B-page 144 Preliminary © 2007 Microchip Technology Inc. 15.4 PWM Mode In Pulse Width Modulation (PWM) mode, the CCPx pin produces up to a 10-bit resolution PWM output. Since the CCP2 pin is multiplexed with a PORTB or PORTC data latch, the appropriate TRIS bit must be cleared to make the CCP2 pin an output. Figure 15-3 shows a simplified block diagram of the CCP module in PWM mode. For a step-by-step procedure on how to set up the CCP module for PWM operation, see Section 15.4.4 “Setup for PWM Operation”. FIGURE 15-3: SIMPLIFIED PWM BLOCK DIAGRAM A PWM output (Figure 15-4) has a time base (period) and a time that the output stays high (duty cycle). The frequency of the PWM is the inverse of the period (1/period). FIGURE 15-4: PWM OUTPUT 15.4.1 PWM PERIOD The PWM period is specified by writing to the PR2 register. The PWM period can be calculated using the following formula: EQUATION 15-1: PWM frequency is defined as 1/[PWM period]. When TMR2 is equal to PR2, the following three events occur on the next increment cycle: • TMR2 is cleared • The CCPx pin is set (exception: if PWM duty cycle = 0%, the CCPx pin will not be set) • The PWM duty cycle is latched from CCPRxL into CCPRxH 15.4.2 PWM DUTY CYCLE The PWM duty cycle is specified by writing to the CCPRxL register and to the CCPxCON<5:4> bits. Up to 10-bit resolution is available. The CCPRxL contains the eight MSbs and the CCPxCON<5:4> contains the two LSbs. This 10-bit value is represented by CCPRxL:CCPxCON<5:4>. The following equation is used to calculate the PWM duty cycle in time: EQUATION 15-2: CCPRxL and CCPxCON<5:4> can be written to at any time, but the duty cycle value is not latched into CCPRxH until after a match between PR2 and TMR2 occurs (i.e., the period is complete). In PWM mode, CCPRxH is a read-only register. Note: Clearing the CCP2CON register will force the RB3 or RC1 output latch (depending on device configuration) to the default low level. This is not the PORTB or PORTC I/O data latch. CCPRxL CCPRxH (Slave) Comparator TMR2 Comparator PR2 (Note 1) R Q S Duty Cycle Registers CCPxCON<5:4> Clear Timer, CCP1 pin and latch D.C. Note 1: The 8-bit TMR2 value is concatenated with the 2-bit internal Q clock, or 2 bits of the prescaler, to create the 10-bit time base. CCPx Output Corresponding TRIS bit Period Duty Cycle TMR2 = PR2 TMR2 = Duty Cycle TMR2 = PR2 Note: The Timer2 postscalers (see Section 13.0 “Timer2 Module”) are not used in the determination of the PWM frequency. The postscaler could be used to have a servo update rate at a different frequency than the PWM output. PWM Period = [(PR2) + 1] • 4 • TOSC • (TMR2 Prescale Value) PWM Duty Cycle = (CCPRXL:CCPXCON<5:4>) • TOSC • (TMR2 Prescale Value) © 2007 Microchip Technology Inc. Preliminary DS39631B-page 145 PIC18F2420/2520/4420/4520 The CCPRxH register and a 2-bit internal latch are used to double-buffer the PWM duty cycle. This double-buffering is essential for glitchless PWM operation. When the CCPRxH and 2-bit latch match TMR2, concatenated with an internal 2-bit Q clock or 2 bits of the TMR2 prescaler, the CCPx pin is cleared. The maximum PWM resolution (bits) for a given PWM frequency is given by the equation: EQUATION 15-3: TABLE 15-4: EXAMPLE PWM FREQUENCIES AND RESOLUTIONS AT 40 MHz 15.4.3 PWM AUTO-SHUTDOWN (CCP1 ONLY) The PWM auto-shutdown features of the enhanced CCP module are also available to CCP1 in 28-pin devices. The operation of this feature is discussed in detail in Section 16.4.7 “Enhanced PWM Auto-Shutdown”. Auto-shutdown features are not available for CCP2. 15.4.4 SETUP FOR PWM OPERATION The following steps should be taken when configuring the CCP module for PWM operation: 1. Set the PWM period by writing to the PR2 register. 2. Set the PWM duty cycle by writing to the CCPRxL register and CCPxCON<5:4> bits. 3. Make the CCPx pin an output by clearing the appropriate TRIS bit. 4. Set the TMR2 prescale value, then enable Timer2 by writing to T2CON. 5. Configure the CCPx module for PWM operation. Note: If the PWM duty cycle value is longer than the PWM period, the CCP2 pin will not be cleared. FOSC FPWM ⎝---------------⎠ log⎛ ⎞ log(2) PWM Resolution (max) = -----------------------------bits PWM Frequency 2.44 kHz 9.77 kHz 39.06 kHz 156.25 kHz 312.50 kHz 416.67 kHz Timer Prescaler (1, 4, 16) 16 4 1 1 1 1 PR2 Value FFh FFh FFh 3Fh 1Fh 17h Maximum Resolution (bits) 10 10 10 8 7 6.58 PIC18F2420/2520/4420/4520 DS39631B-page 146 Preliminary © 2007 Microchip Technology Inc. TABLE 15-5: REGISTERS ASSOCIATED WITH PWM AND TIMER2 Name Bit 7 Bit 6 Bit 5 Bit 4 Bit 3 Bit 2 Bit 1 Bit 0 Reset Values on page INTCON GIE/GIEH PEIE/GIEL TMR0IE INT0IE RBIE TMR0IF INT0IF RBIF 49 RCON IPEN SBOREN — RI TO PD POR BOR 48 PIR1 PSPIF(1) ADIF RCIF TXIF SSPIF CCP1IF TMR2IF TMR1IF 52 PIE1 PSPIE(1) ADIE RCIE TXIE SSPIE CCP1IE TMR2IE TMR1IE 52 IPR1 PSPIP(1) ADIP RCIP TXIP SSPIP CCP1IP TMR2IP TMR1IP 52 TRISB PORTB Data Direction Control Register 52 TRISC PORTC Data Direction Control Register 52 TMR2 Timer2 Register 50 PR2 Timer2 Period Register 50 T2CON — T2OUTPS3 T2OUTPS2 T2OUTPS1 T2OUTPS0 TMR2ON T2CKPS1 T2CKPS0 50 CCPR1L Capture/Compare/PWM Register 1, Low Byte 51 CCPR1H Capture/Compare/PWM Register 1, High Byte 51 CCP1CON P1M1(1) P1M0(1) DC1B1 DC1B0 CCP1M3 CCP1M2 CCP1M1 CCP1M0 51 CCPR2L Capture/Compare/PWM Register 2, Low Byte 51 CCPR2H Capture/Compare/PWM Register 2, High Byte 51 CCP2CON — — DC2B1 DC2B0 CCP2M3 CCP2M2 CCP2M1 CCP2M0 51 ECCP1AS ECCPASE ECCPAS2 ECCPAS1 ECCPAS0 PSSAC1 PSSAC0 PSSBD1(1) PSSBD0(1) 51 PWM1CON PRSEN PDC6(1) PDC5(1) PDC4(1) PDC3(1) PDC2(1) PDC1(1) PDC0(1) 51 Legend: — = unimplemented, read as ‘0’. Shaded cells are not used by PWM or Timer2. Note 1: These bits are unimplemented on 28-pin devices; always maintain these bits clear. © 2007 Microchip Technology Inc. Preliminary DS39631B-page 147 PIC18F2420/2520/4420/4520 16.0 ENHANCED CAPTURE/ COMPARE/PWM (ECCP) MODULE In PIC18F4420/4520 devices, CCP1 is implemented as a standard CCP module with enhanced PWM capabilities. These include the provision for 2 or 4 output channels, user selectable polarity, dead-band control and automatic shutdown and restart. The enhanced features are discussed in detail in Section 16.4 “Enhanced PWM Mode”. Capture, Compare and single-output PWM functions of the ECCP module are the same as described for the standard CCP module. The control register for the enhanced CCP module is shown in Register 16-1. It differs from the CCPxCON registers in PIC18F2420/2520 devices in that the two Most Significant bits are implemented to control PWM functionality. REGISTER 16-1: CCP1CON REGISTER (ECCP1 MODULE, 40/44-PIN DEVICES) Note: The ECCP module is implemented only in 40/44-pin devices. R/W-0 R/W-0 R/W-0 R/W-0 R/W-0 R/W-0 R/W-0 R/W-0 P1M1 P1M0 DC1B1 DC1B0 CCP1M3 CCP1M2 CCP1M1 CCP1M0 bit 7 bit 0 bit 7-6 P1M1:P1M0: Enhanced PWM Output Configuration bits If CCP1M3:CCP1M2 = 00, 01, 10: xx = P1A assigned as Capture/Compare input/output; P1B, P1C, P1D assigned as port pins If CCP1M3:CCP1M2 = 11: 00 = Single output: P1A modulated; P1B, P1C, P1D assigned as port pins 01 = Full-bridge output forward: P1D modulated; P1A active; P1B, P1C inactive 10 = Half-bridge output: P1A, P1B modulated with dead-band control; P1C, P1D assigned as port pins 11 = Full-bridge output reverse: P1B modulated; P1C active; P1A, P1D inactive bit 5-4 DC1B1:DC1B0: PWM Duty Cycle bit 1 and bit 0 Capture mode: Unused. Compare mode: Unused. PWM mode: These bits are the two LSbs of the 10-bit PWM duty cycle. The eight MSbs of the duty cycle are found in CCPR1L. bit 3-0 CCP1M3:CCP1M0: Enhanced CCP Mode Select bits 0000 = Capture/Compare/PWM off (resets ECCP module) 0001 = Reserved 0010 = Compare mode, toggle output on match 0011 = Capture mode 0100 = Capture mode, every falling edge 0101 = Capture mode, every rising edge 0110 = Capture mode, every 4th rising edge 0111 = Capture mode, every 16th rising edge 1000 = Compare mode, initialize CCP1 pin low, set output on compare match (set CCP1IF) 1001 = Compare mode, initialize CCP1 pin high, clear output on compare match (set CCP1IF) 1010 = Compare mode, generate software interrupt only, CCP1 pin reverts to I/O state 1011 = Compare mode, trigger special event (ECCP resets TMR1 or TMR3, sets CC1IF bit) 1100 = PWM mode; P1A, P1C active-high; P1B, P1D active-high 1101 = PWM mode; P1A, P1C active-high; P1B, P1D active-low 1110 = PWM mode; P1A, P1C active-low; P1B, P1D active-high 1111 = PWM mode; P1A, P1C active-low; P1B, P1D active-low Legend: R = Readable bit W = Writable bit U = Unimplemented bit, read as ‘0’ -n = Value at POR ‘1’ = Bit is set ‘0’ = Bit is cleared x = Bit is unknown PIC18F2420/2520/4420/4520 DS39631B-page 148 Preliminary © 2007 Microchip Technology Inc. In addition to the expanded range of modes available through the CCP1CON register and ECCP1AS register, the ECCP module has an additional register associated with Enhanced PWM operation and auto-shutdown features. It is: • PWM1CON (Dead-band delay) 16.1 ECCP Outputs and Configuration The enhanced CCP module may have up to four PWM outputs, depending on the selected operating mode. These outputs, designated P1A through P1D, are multiplexed with I/O pins on PORTC and PORTD. The outputs that are active depend on the CCP operating mode selected. The pin assignments are summarized in Table 16-1. To configure the I/O pins as PWM outputs, the proper PWM mode must be selected by setting the P1M1:P1M0 and CCP1M3:CCP1M0 bits. The appropriate TRISC and TRISD direction bits for the port pins must also be set as outputs. 16.1.1 ECCP MODULES AND TIMER RESOURCES Like the standard CCP modules, the ECCP module can utilize Timers 1, 2 or 3, depending on the mode selected. Timer1 and Timer3 are available for modules in Capture or Compare modes, while Timer2 is available for modules in PWM mode. Interactions between the standard and enhanced CCP modules are identical to those described for standard CCP modules. Additional details on timer resources are provided in Section 15.1.1 “CCP Modules and Timer Resources”. 16.2 Capture and Compare Modes Except for the operation of the Special Event Trigger discussed below, the Capture and Compare modes of the ECCP module are identical in operation to that of CCP2. These are discussed in detail in Section 15.2 “Capture Mode” and Section 15.3 “Compare Mode”. No changes are required when moving between 28-pin and 40/44-pin devices. 16.2.1 SPECIAL EVENT TRIGGER The Special Event Trigger output of ECCP1 resets the TMR1 or TMR3 register pair, depending on which timer resource is currently selected. This allows the CCPR1 register to effectively be a 16-bit programmable period register for Timer1 or Timer3. 16.3 Standard PWM Mode When configured in Single Output mode, the ECCP module functions identically to the standard CCP module in PWM mode, as described in Section 15.4 “PWM Mode”. This is also sometimes referred to as “Compatible CCP” mode, as in Table 16-1. TABLE 16-1: PIN ASSIGNMENTS FOR VARIOUS ECCP1 MODES Note: When setting up single output PWM operations, users are free to use either of the processes described in Section 15.4.4 “Setup for PWM Operation” or Section 16.4.9 “Setup for PWM Operation”. The latter is more generic and will work for either single or multi-output PWM. ECCP Mode CCP1CON Configuration RC2 RD5 RD6 RD7 All 40/44-pin devices: Compatible CCP 00xx 11xx CCP1 RD5/PSP5 RD6/PSP6 RD7/PSP7 Dual PWM 10xx 11xx P1A P1B RD6/PSP6 RD7/PSP7 Quad PWM x1xx 11xx P1A P1B P1C P1D Legend: x = Don’t care. Shaded cells indicate pin assignments not used by ECCP1 in a given mode. © 2007 Microchip Technology Inc. Preliminary DS39631B-page 149 PIC18F2420/2520/4420/4520 16.4 Enhanced PWM Mode The Enhanced PWM mode provides additional PWM output options for a broader range of control applications. The module is a backward compatible version of the standard CCP module and offers up to four outputs, designated P1A through P1D. Users are also able to select the polarity of the signal (either active-high or active-low). The module’s output mode and polarity are configured by setting the P1M1:P1M0 and CCP1M3:CCP1M0 bits of the CCP1CON register. Figure 16-1 shows a simplified block diagram of PWM operation. All control registers are double-buffered and are loaded at the beginning of a new PWM cycle (the period boundary when Timer2 resets) in order to prevent glitches on any of the outputs. The exception is the PWM Delay register, PWM1CON, which is loaded at either the duty cycle boundary or the period boundary (whichever comes first). Because of the buffering, the module waits until the assigned timer resets, instead of starting immediately. This means that enhanced PWM waveforms do not exactly match the standard PWM waveforms, but are instead offset by one full instruction cycle (4 TOSC). As before, the user must manually configure the appropriate TRIS bits for output. 16.4.1 PWM PERIOD The PWM period is specified by writing to the PR2 register. The PWM period can be calculated using the following equation. EQUATION 16-1: PWM frequency is defined as 1/[PWM period]. When TMR2 is equal to PR2, the following three events occur on the next increment cycle: • TMR2 is cleared • The CCP1 pin is set (if PWM duty cycle = 0%, the CCP1 pin will not be set) • The PWM duty cycle is copied from CCPR1L into CCPR1H FIGURE 16-1: SIMPLIFIED BLOCK DIAGRAM OF THE ENHANCED PWM MODULE Note: The Timer2 postscaler (see Section 13.0 “Timer2 Module”) is not used in the determination of the PWM frequency. The postscaler could be used to have a servo update rate at a different frequency than the PWM output. PWM Period = [(PR2) + 1] • 4 • TOSC • (TMR2 Prescale Value) CCPR1L CCPR1H (Slave) Comparator TMR2 Comparator PR2 (Note 1) R Q S Duty Cycle Registers CCP1CON<5:4> Clear Timer, set CCP1 pin and latch D.C. Note: The 8-bit TMR2 register is concatenated with the 2-bit internal Q clock, or 2 bits of the prescaler, to create the 10-bit time base. TRISx CCP1/P1A TRISx P1B TRISx TRISx P1D Output Controller P1M1<1:0> 2 CCP1M<3:0> 4 PWM1CON CCP1/P1A P1B P1C P1D P1C PIC18F2420/2520/4420/4520 DS39631B-page 150 Preliminary © 2007 Microchip Technology Inc. 16.4.2 PWM DUTY CYCLE The PWM duty cycle is specified by writing to the CCPR1L register and to the CCP1CON<5:4> bits. Up to 10-bit resolution is available. The CCPR1L contains the eight MSbs and the CCP1CON<5:4> contains the two LSbs. This 10-bit value is represented by CCPR1L:CCP1CON<5:4>. The PWM duty cycle is calculated by the following equation. EQUATION 16-2: CCPR1L and CCP1CON<5:4> can be written to at any time, but the duty cycle value is not copied into CCPR1H until a match between PR2 and TMR2 occurs (i.e., the period is complete). In PWM mode, CCPR1H is a read-only register. The CCPR1H register and a 2-bit internal latch are used to double-buffer the PWM duty cycle. This double-buffering is essential for glitchless PWM operation. When the CCPR1H and 2-bit latch match TMR2, concatenated with an internal 2-bit Q clock or two bits of the TMR2 prescaler, the CCP1 pin is cleared. The maximum PWM resolution (bits) for a given PWM frequency is given by the following equation. EQUATION 16-3: 16.4.3 PWM OUTPUT CONFIGURATIONS The P1M1:P1M0 bits in the CCP1CON register allow one of four configurations: • Single Output • Half-Bridge Output • Full-Bridge Output, Forward mode • Full-Bridge Output, Reverse mode The Single Output mode is the standard PWM mode discussed in Section 16.4 “Enhanced PWM Mode”. The Half-Bridge and Full-Bridge Output modes are covered in detail in the sections that follow. The general relationship of the outputs in all configurations is summarized in Figure 16-2. TABLE 16-2: EXAMPLE PWM FREQUENCIES AND RESOLUTIONS AT 40 MHz PWM Duty Cycle = (CCPR1L:CCP1CON<5:4>) • TOSC • (TMR2 Prescale Value) Note: If the PWM duty cycle value is longer than the PWM period, the CCP1 pin will not be cleared. ( ) PWM Resolution (max) = FOSC FPWM log log(2) bits PWM Frequency 2.44 kHz 9.77 kHz 39.06 kHz 156.25 kHz 312.50 kHz 416.67 kHz Timer Prescaler (1, 4, 16) 16 4 1 1 1 1 PR2 Value FFh FFh FFh 3Fh 1Fh 17h Maximum Resolution (bits) 10 10 10 8 7 6.58 © 2007 Microchip Technology Inc. Preliminary DS39631B-page 151 PIC18F2420/2520/4420/4520 FIGURE 16-2: PWM OUTPUT RELATIONSHIPS (ACTIVE-HIGH STATE) FIGURE 16-3: PWM OUTPUT RELATIONSHIPS (ACTIVE-LOW STATE) 0 Period 00 10 01 11 SIGNAL PR2 + 1 CCP1CON <7:6> P1A Modulated P1A Modulated P1B Modulated P1A Active P1B Inactive P1C Inactive P1D Modulated P1A Inactive P1B Modulated P1C Active P1D Inactive Duty Cycle (Single Output) (Half-Bridge) (Full-Bridge, Forward) (Full-Bridge, Reverse) Delay(1) Delay(1) 0 Period 00 10 01 11 SIGNAL PR2 + 1 CCP1CON <7:6> P1A Modulated P1A Modulated P1B Modulated P1A Active P1B Inactive P1C Inactive P1D Modulated P1A Inactive P1B Modulated P1C Active P1D Inactive Duty Cycle (Single Output) (Half-Bridge) (Full-Bridge, Forward) (Full-Bridge, Reverse) Delay(1) Delay(1) Relationships: • Period = 4 * TOSC * (PR2 + 1) * (TMR2 Prescale Value) • Duty Cycle = TOSC * (CCPR1L<7:0>:CCP1CON<5:4>) * (TMR2 Prescale Value) • Delay = 4 * TOSC * (PWM1CON<6:0>) Note 1: Dead-band delay is programmed using the PWM1CON register (see Section 16.4.6 “Programmable Dead-Band Delay”). PIC18F2420/2520/4420/4520 DS39631B-page 152 Preliminary © 2007 Microchip Technology Inc. 16.4.4 HALF-BRIDGE MODE In the Half-Bridge Output mode, two pins are used as outputs to drive push-pull loads. The PWM output signal is output on the P1A pin, while the complementary PWM output signal is output on the P1B pin (Figure 16-4). This mode can be used for half-bridge applications, as shown in Figure 16-5, or for full-bridge applications where four power switches are being modulated with two PWM signals. In Half-Bridge Output mode, the programmable deadband delay can be used to prevent shoot-through current in half-bridge power devices. The value of bits, PDC6:PDC0, sets the number of instruction cycles before the output is driven active. If the value is greater than the duty cycle, the corresponding output remains inactive during the entire cycle. See Section 16.4.6 “Programmable Dead-Band Delay” for more details of the dead-band delay operations. Since the P1A and P1B outputs are multiplexed with the PORTC<2> and PORTD<5> data latches, the TRISC<2> and TRISD<5> bits must be cleared to configure P1A and P1B as outputs. FIGURE 16-4: HALF-BRIDGE PWM OUTPUT FIGURE 16-5: EXAMPLES OF HALF-BRIDGE OUTPUT MODE APPLICATIONS Period Duty Cycle td td (1) P1A(2) P1B(2) td = Dead-Band Delay Period (1) (1) Note 1: At this time, the TMR2 register is equal to the PR2 register. 2: Output signals are shown as active-high. PIC18F4X2X P1A P1B FET Driver FET Driver V+ VLoad + V- + VFET Driver FET Driver V+ VLoad FET Driver FET Driver PIC18F4X2X P1A P1B Standard Half-Bridge Circuit (“Push-Pull”) Half-Bridge Output Driving a Full-Bridge Circuit © 2007 Microchip Technology Inc. Preliminary DS39631B-page 153 PIC18F2420/2520/4420/4520 16.4.5 FULL-BRIDGE MODE In Full-Bridge Output mode, four pins are used as outputs; however, only two outputs are active at a time. In the Forward mode, pin P1A is continuously active and pin P1D is modulated. In the Reverse mode, pin P1C is continuously active and pin P1B is modulated. These are illustrated in Figure 16-6. P1A, P1B, P1C and P1D outputs are multiplexed with the PORTC<2> and PORTD<7:5> data latches. The TRISC<2> and TRISD<7:5> bits must be cleared to make the P1A, P1B, P1C and P1D pins outputs. FIGURE 16-6: FULL-BRIDGE PWM OUTPUT Period Duty Cycle P1A(2) P1B(2) P1C(2) P1D(2) Forward Mode (1) Period Duty Cycle P1A(2) P1C(2) P1D(2) P1B(2) Reverse Mode (1) (1) (1) Note 1: At this time, the TMR2 register is equal to the PR2 register. Note 2: Output signal is shown as active-high. PIC18F2420/2520/4420/4520 DS39631B-page 154 Preliminary © 2007 Microchip Technology Inc. FIGURE 16-7: EXAMPLE OF FULL-BRIDGE APPLICATION 16.4.5.1 Direction Change in Full-Bridge Mode In the Full-Bridge Output mode, the P1M1 bit in the CCP1CON register allows user to control the forward/ reverse direction. When the application firmware changes this direction control bit, the module will assume the new direction on the next PWM cycle. Just before the end of the current PWM period, the modulated outputs (P1B and P1D) are placed in their inactive state, while the unmodulated outputs (P1A and P1C) are switched to drive in the opposite direction. This occurs in a time interval of 4 TOSC * (Timer2 Prescale Value) before the next PWM period begins. The Timer2 prescaler will be either 1, 4 or 16, depending on the value of the T2CKPS1:T2CKPS0 bits (T2CON<1:0>). During the interval from the switch of the unmodulated outputs to the beginning of the next period, the modulated outputs (P1B and P1D) remain inactive. This relationship is shown in Figure 16-8. Note that in the Full-Bridge Output mode, the CCP1 module does not provide any dead-band delay. In general, since only one output is modulated at all times, dead-band delay is not required. However, there is a situation where a dead-band delay might be required. This situation occurs when both of the following conditions are true: 1. The direction of the PWM output changes when the duty cycle of the output is at or near 100%. 2. The turn-off time of the power switch, including the power device and driver circuit, is greater than the turn-on time. Figure 16-9 shows an example where the PWM direction changes from forward to reverse at a near 100% duty cycle. At time t1, the outputs P1A and P1D become inactive, while output P1C becomes active. In this example, since the turn-off time of the power devices is longer than the turn-on time, a shoot-through current may flow through power devices, QC and QD (see Figure 16-7), for the duration of ‘t’. The same phenomenon will occur to power devices, QA and QB, for PWM direction change from reverse to forward. If changing PWM direction at high duty cycle is required for an application, one of the following requirements must be met: 1. Reduce PWM for a PWM period before changing directions. 2. Use switch drivers that can drive the switches off faster than they can drive them on. Other options to prevent shoot-through current may exist. P1A P1C FET Driver FET Driver V+ VLoad FET Driver FET Driver P1B P1D QA QB QD PIC18F4X2X QC © 2007 Microchip Technology Inc. Preliminary DS39631B-page 155 PIC18F2420/2520/4420/4520 FIGURE 16-8: PWM DIRECTION CHANGE FIGURE 16-9: PWM DIRECTION CHANGE AT NEAR 100% DUTY CYCLE DC Period(1) SIGNAL Note 1: The direction bit in the CCP1 Control register (CCP1CON<7>) is written any time during the PWM cycle. 2: When changing directions, the P1A and P1C signals switch before the end of the current PWM cycle at intervals of 4 TOSC, 16 TOSC or 64 TOSC, depending on the Timer2 prescaler value. The modulated P1B and P1D signals are inactive at this time. Period (Note 2) P1A (Active-High) P1B (Active-High) P1C (Active-High) P1D (Active-High) DC Forward Period Reverse Period P1A(1) tON (2) tOFF (3) t = tOFF – tON (2,3) P1B(1) P1C(1) P1D(1) External Switch D(1) Potential Shoot-Through Current(1) Note 1: All signals are shown as active-high. 2: tON is the turn-on delay of power switch QC and its driver. 3: tOFF is the turn-off delay of power switch QD and its driver. External Switch C(1) t1 DC DC PIC18F2420/2520/4420/4520 DS39631B-page 156 Preliminary © 2007 Microchip Technology Inc. 16.4.6 PROGRAMMABLE DEAD-BAND DELAY In half-bridge applications where all power switches are modulated at the PWM frequency at all times, the power switches normally require more time to turn off than to turn on. If both the upper and lower power switches are switched at the same time (one turned on and the other turned off), both switches may be on for a short period of time until one switch completely turns off. During this brief interval, a very high current (shootthrough current) may flow through both power switches, shorting the bridge supply. To avoid this potentially destructive shoot-through current from flowing during switching, turning on either of the power switches is normally delayed to allow the other switch to completely turn off. In the Half-Bridge Output mode, a digitally programmable dead-band delay is available to avoid shoot-through current from destroying the bridge power switches. The delay occurs at the signal transition from the nonactive state to the active state. See Figure 16-4 for illustration. Bits PDC6:PDC0 of the PWM1CON register (Register 16-2) set the delay period in terms of microcontroller instruction cycles (TCY or 4 TOSC). These bits are not available on 28-pin devices as the standard CCP module does not support half-bridge operation. 16.4.7 ENHANCED PWM AUTO-SHUTDOWN When the CCP1 is programmed for any of the enhanced PWM modes, the active output pins may be configured for auto-shutdown. Auto-shutdown immediately places the enhanced PWM output pins into a defined shutdown state when a shutdown event occurs. A shutdown event can be caused by either of the comparator modules, a low level on the Fault input pin (FLT0) or any combination of these three sources. The comparators may be used to monitor a voltage input proportional to a current being monitored in the bridge circuit. If the voltage exceeds a threshold, the comparator switches state and triggers a shutdown. Alternatively, a low digital signal on FLT0 can also trigger a shutdown. The auto-shutdown feature can be disabled by not selecting any auto-shutdown sources. The autoshutdown sources to be used are selected using the ECCPAS2:ECCPAS0 bits (bits<6:4> of the ECCP1AS register). When a shutdown occurs, the output pins are asynchronously placed in their shutdown states, specified by the PSSAC1:PSSAC0 and PSSBD1:PSSBD0 bits (ECCPAS2:ECCPAS0). Each pin pair (P1A/P1C and P1B/P1D) may be set to drive high, drive low or be tristated (not driving). The ECCPASE bit (ECCP1AS<7>) is also set to hold the enhanced PWM outputs in their shutdown states. The ECCPASE bit is set by hardware when a shutdown event occurs. If automatic restarts are not enabled, the ECCPASE bit is cleared by firmware when the cause of the shutdown clears. If automatic restarts are enabled, the ECCPASE bit is automatically cleared when the cause of the auto-shutdown has cleared. If the ECCPASE bit is set when a PWM period begins, the PWM outputs remain in their shutdown state for that entire PWM period. When the ECCPASE bit is cleared, the PWM outputs will return to normal operation at the beginning of the next PWM period. REGISTER 16-2: PWM1CON: PWM CONFIGURATION REGISTER Note: Programmable dead-band delay is not implemented in 28-pin devices with standard CCP modules. Note: Writing to the ECCPASE bit is disabled while a shutdown condition is active. R/W-0 R/W-0 R/W-0 R/W-0 R/W-0 R/W-0 R/W-0 R/W-0 PRSEN PDC6(1) PDC5(1) PDC4(1) PDC3(1) PDC2(1) PDC1(1) PDC0(1) bit 7 bit 0 bit 7 PRSEN: PWM Restart Enable bit 1 = Upon auto-shutdown, the ECCPASE bit clears automatically once the shutdown event goes away; the PWM restarts automatically 0 = Upon auto-shutdown, ECCPASE must be cleared in software to restart the PWM bit 6-0 PDC6:PDC0: PWM Delay Count bits(1) Delay time, in number of FOSC/4 (4 * TOSC) cycles, between the scheduled and actual time for a PWM signal to transition to active. Note 1: Reserved on 28-pin devices; maintain these bits clear. Legend: R = Readable bit W = Writable bit U = Unimplemented bit, read as ‘0’ -n = Value at POR ‘1’ = Bit is set ‘0’ = Bit is cleared x = Bit is unknown © 2007 Microchip Technology Inc. Preliminary DS39631B-page 157 PIC18F2420/2520/4420/4520 REGISTER 16-3: ECCP1AS: ENHANCED CAPTURE/COMPARE/PWM AUTO-SHUTDOWN CONTROL REGISTER R/W-0 R/W-0 R/W-0 R/W-0 R/W-0 R/W-0 R/W-0 R/W-0 ECCPASE ECCPAS2 ECCPAS1 ECCPAS0 PSSAC1 PSSAC0 PSSBD1(1) PSSBD0(1) bit 7 bit 0 bit 7 ECCPASE: ECCP Auto-Shutdown Event Status bit 1 = A shutdown event has occurred; ECCP outputs are in shutdown state 0 = ECCP outputs are operating bit 6-4 ECCPAS2:ECCPAS0: ECCP Auto-Shutdown Source Select bits 111 = FLT0 or Comparator 1 or Comparator 2 110 = FLT0 or Comparator 2 101 = FLT0 or Comparator 1 100 = FLT0 011 = Either Comparator 1 or 2 010 = Comparator 2 output 001 = Comparator 1 output 000 = Auto-shutdown is disabled bit 3-2 PSSAC1:PSSAC0: Pins A and C Shutdown State Control bits 1x = Pins A and C are tri-state (40/44-pin devices); PWM output is tri-state (28-pin devices) 01 = Drive Pins A and C to ‘1’ 00 = Drive Pins A and C to ‘0’ bit 1-0 PSSBD1:PSSBD0: Pins B and D Shutdown State Control bits(1) 1x = Pins B and D tri-state 01 = Drive Pins B and D to ‘1’ 00 = Drive Pins B and D to ‘0’ Note 1: Reserved on 28-pin devices; maintain these bits clear. Legend: R = Readable bit W = Writable bit U = Unimplemented bit, read as ‘0’ -n = Value at POR ‘1’ = Bit is set ‘0’ = Bit is cleared x = Bit is unknown PIC18F2420/2520/4420/4520 DS39631B-page 158 Preliminary © 2007 Microchip Technology Inc. 16.4.7.1 Auto-Shutdown and Automatic Restart The auto-shutdown feature can be configured to allow automatic restarts of the module following a shutdown event. This is enabled by setting the PRSEN bit of the PWM1CON register (PWM1CON<7>). In Shutdown mode with PRSEN = 1 (Figure 16-10), the ECCPASE bit will remain set for as long as the cause of the shutdown continues. When the shutdown condition clears, the ECCP1ASE bit is cleared. If PRSEN = 0 (Figure 16-11), once a shutdown condition occurs, the ECCPASE bit will remain set until it is cleared by firmware. Once ECCPASE is cleared, the enhanced PWM will resume at the beginning of the next PWM period. Independent of the PRSEN bit setting, if the autoshutdown source is one of the comparators, the shutdown condition is a level. The ECCPASE bit cannot be cleared as long as the cause of the shutdown persists. The Auto-Shutdown mode can be forced by writing a ‘1’ to the ECCPASE bit. 16.4.8 START-UP CONSIDERATIONS When the ECCP module is used in the PWM mode, the application hardware must use the proper external pullup and/or pull-down resistors on the PWM output pins. When the microcontroller is released from Reset, all of the I/O pins are in the high-impedance state. The external circuits must keep the power switch devices in the off state until the microcontroller drives the I/O pins with the proper signal levels, or activates the PWM output(s). The CCP1M1:CCP1M0 bits (CCP1CON<1:0>) allow the user to choose whether the PWM output signals are active-high or active-low for each pair of PWM output pins (P1A/P1C and P1B/P1D). The PWM output polarities must be selected before the PWM pins are configured as outputs. Changing the polarity configuration while the PWM pins are configured as outputs is not recommended, since it may result in damage to the application circuits. The P1A, P1B, P1C and P1D output latches may not be in the proper states when the PWM module is initialized. Enabling the PWM pins for output at the same time as the ECCP module may cause damage to the application circuit. The ECCP module must be enabled in the proper output mode and complete a full PWM cycle before configuring the PWM pins as outputs. The completion of a full PWM cycle is indicated by the TMR2IF bit being set as the second PWM period begins. FIGURE 16-10: PWM AUTO-SHUTDOWN (PRSEN = 1, AUTO-RESTART ENABLED) FIGURE 16-11: PWM AUTO-SHUTDOWN (PRSEN = 0, AUTO-RESTART DISABLED) Note: Writing to the ECCPASE bit is disabled while a shutdown condition is active. Shutdown PWM ECCPASE bit Activity Event Shutdown Event Occurs Shutdown Event Clears PWM Resumes Normal PWM Start of PWM Period PWM Period Shutdown PWM ECCPASE bit Activity Event Shutdown Event Occurs Shutdown Event Clears PWM Resumes Normal PWM Start of PWM Period ECCPASE Cleared by Firmware PWM Period © 2007 Microchip Technology Inc. Preliminary DS39631B-page 159 PIC18F2420/2520/4420/4520 16.4.9 SETUP FOR PWM OPERATION The following steps should be taken when configuring the ECCP module for PWM operation: 1. Configure the PWM pins, P1A and P1B (and P1C and P1D, if used), as inputs by setting the corresponding TRIS bits. 2. Set the PWM period by loading the PR2 register. 3. If auto-shutdown is required: • Disable auto-shutdown (ECCP1AS = 0) • Configure source (FLT0, Comparator 1 or Comparator 2) • Wait for non-shutdown condition 4. Configure the ECCP module for the desired PWM mode and configuration by loading the CCP1CON register with the appropriate values: • Select one of the available output configurations and direction with the P1M1:P1M0 bits. • Select the polarities of the PWM output signals with the CCP1M3:CCP1M0 bits. 5. Set the PWM duty cycle by loading the CCPR1L register and CCP1CON<5:4> bits. 6. For Half-Bridge Output mode, set the deadband delay by loading PWM1CON<6:0> with the appropriate value. 7. If auto-shutdown operation is required, load the ECCP1AS register: • Select the auto-shutdown sources using the ECCPAS2:ECCPAS0 bits. • Select the shutdown states of the PWM output pins using the PSSAC1:PSSAC0 and PSSBD1:PSSBD0 bits. • Set the ECCPASE bit (ECCP1AS<7>). • Configure the comparators using the CMCON register. • Configure the comparator inputs as analog inputs. 8. If auto-restart operation is required, set the PRSEN bit (PWM1CON<7>). 9. Configure and start TMR2: • Clear the TMR2 interrupt flag bit by clearing the TMR2IF bit (PIR1<1>). • Set the TMR2 prescale value by loading the T2CKPS bits (T2CON<1:0>). • Enable Timer2 by setting the TMR2ON bit (T2CON<2>). 10. Enable PWM outputs after a new PWM cycle has started: • Wait until TMRn overflows (TMRnIF bit is set). • Enable the CCP1/P1A, P1B, P1C and/or P1D pin outputs by clearing the respective TRIS bits. • Clear the ECCPASE bit (ECCP1AS<7>). 16.4.10 OPERATION IN POWER MANAGED MODES In Sleep mode, all clock sources are disabled. Timer2 will not increment and the state of the module will not change. If the ECCP pin is driving a value, it will continue to drive that value. When the device wakes up, it will continue from this state. If Two-Speed Start-ups are enabled, the initial start-up frequency from INTOSC and the postscaler may not be stable immediately. In PRI_IDLE mode, the primary clock will continue to clock the ECCP module without change. In all other power managed modes, the selected power managed mode clock will clock Timer2. Other power managed mode clocks will most likely be different than the primary clock frequency. 16.4.10.1 Operation with Fail-Safe Clock Monitor If the Fail-Safe Clock Monitor is enabled, a clock failure will force the device into the RC_RUN Power Managed mode and the OSCFIF bit (PIR2<7>) will be set. The ECCP will then be clocked from the internal oscillator clock source, which may have a different clock frequency than the primary clock. See the previous section for additional details. 16.4.11 EFFECTS OF A RESET Both Power-on Reset and subsequent Resets will force all ports to Input mode and the CCP registers to their Reset states. This forces the enhanced CCP module to reset to a state compatible with the standard CCP module. PIC18F2420/2520/4420/4520 DS39631B-page 160 Preliminary © 2007 Microchip Technology Inc. TABLE 16-3: REGISTERS ASSOCIATED WITH ECCP1 MODULE AND TIMER1 TO TIMER3 Name Bit 7 Bit 6 Bit 5 Bit 4 Bit 3 Bit 2 Bit 1 Bit 0 Reset Values on page INTCON GIE/GIEH PEIE/GIEL TMR0IE INT0IE RBIE TMR0IF INT0IF RBIF 49 RCON IPEN SBOREN — RI TO PD POR BOR 48 PIR1 PSPIF ADIF RCIF TXIF SSPIF CCP1IF TMR2IF TMR1IF 52 PIE1 PSPIE ADIE RCIE TXIE SSPIE CCP1IE TMR2IE TMR1IE 52 IPR1 PSPIP ADIP RCIP TXIP SSPIP CCP1IP TMR2IP TMR1IP 52 PIR2 OSCFIF CMIF — EEIF BCLIF HLVDIF TMR3IF CCP2IF 52 PIE2 OSCFIE CMIE — EEIE BCLIE HLVDIE TMR3IE CCP2IE 52 IPR2 OSCFIP CMIP — EEIP BCLIP HLVDIP TMR3IP CCP2IP 52 TRISB PORTB Data Direction Control Register 52 TRISC PORTC Data Direction Control Register 52 TRISD PORTD Data Direction Control Register 52 TMR1L Timer1 Register, Low Byte 50 TMR1H Timer1 Register, High Byte 50 T1CON RD16 T1RUN T1CKPS1 T1CKPS0 T1OSCEN T1SYNC TMR1CS TMR1ON 50 TMR2 Timer2 Register 50 T2CON — T2OUTPS3 T2OUTPS2 T2OUTPS1 T2OUTPS0 TMR2ON T2CKPS1 T2CKPS0 50 PR2 Timer2 Period Register 50 TMR3L Timer3 Register, Low Byte 51 TMR3H Timer3 Register, High Byte 51 T3CON RD16 T3CCP2 T3CKPS1 T3CKPS0 T3CCP1 T3SYNC TMR3CS TMR3ON 51 CCPR1L Capture/Compare/PWM Register 1, Low Byte 51 CCPR1H Capture/Compare/PWM Register 1, High Byte 51 CCP1CON P1M1(1) P1M0(1) DC1B1 DC1B0 CCP1M3 CCP1M2 CCP1M1 CCP1M0 51 ECCP1AS ECCPASE ECCPAS2 ECCPAS1 ECCPAS0 PSSAC1 PSSAC0 PSSBD1(1) PSSBD0(1) 51 PWM1CON PRSEN PDC6(1) PDC5(1) PDC4(1) PDC3(1) PDC2(1) PDC1(1) PDC0(1) 51 Legend: — = unimplemented, read as ‘0’. Shaded cells are not used during ECCP operation. Note 1: These bits are unimplemented on 28-pin devices; always maintain these bits clear. © 2007 Microchip Technology Inc. Preliminary DS39631B-page 161 PIC18F2420/2520/4420/4520 17.0 MASTER SYNCHRONOUS SERIAL PORT (MSSP) MODULE 17.1 Master SSP (MSSP) Module Overview The Master Synchronous Serial Port (MSSP) module is a serial interface, useful for communicating with other peripheral or microcontroller devices. These peripheral devices may be serial EEPROMs, shift registers, display drivers, A/D converters, etc. The MSSP module can operate in one of two modes: • Serial Peripheral Interface (SPI) • Inter-Integrated Circuit (I2C) - Full Master mode - Slave mode (with general address call) The I2C interface supports the following modes in hardware: • Master mode • Multi-Master mode • Slave mode 17.2 Control Registers The MSSP module has three associated registers. These include a status register (SSPSTAT) and two control registers (SSPCON1 and SSPCON2). The use of these registers and their individual configuration bits differ significantly depending on whether the MSSP module is operated in SPI or I2C mode. Additional details are provided under the individual sections. 17.3 SPI Mode The SPI mode allows 8 bits of data to be synchronously transmitted and received simultaneously. All four modes of SPI are supported. To accomplish communication, typically three pins are used: • Serial Data Out (SDO) – RC5/SDO • Serial Data In (SDI) – RC4/SDI/SDA • Serial Clock (SCK) – RC3/SCK/SCL Additionally, a fourth pin may be used when in a Slave mode of operation: • Slave Select (SS) – RA5/SS Figure 17-1 shows the block diagram of the MSSP module when operating in SPI mode. FIGURE 17-1: MSSP BLOCK DIAGRAM (SPI MODE) ( ) Read Write Internal Data Bus SSPSR reg SSPM3:SSPM0 bit 0 Shift Clock SS Control Enable Edge Select Clock Select TMR2 Output Prescaler TOSC 4, 16, 64 2 Edge Select 2 4 Data to TX/RX in SSPSR TRIS bit 2 SMP:CKE RC5/SDO SSPBUF reg RC4/SDI/SDA RA5/AN4/SS/ RC3/SCK/ SCL HLVDIN/C2OUT PIC18F2420/2520/4420/4520 DS39631B-page 162 Preliminary © 2007 Microchip Technology Inc. 17.3.1 REGISTERS The MSSP module has four registers for SPI mode operation. These are: • MSSP Control Register 1 (SSPCON1) • MSSP Status Register (SSPSTAT) • Serial Receive/Transmit Buffer Register (SSPBUF) • MSSP Shift Register (SSPSR) – Not directly accessible SSPCON1 and SSPSTAT are the control and status registers in SPI mode operation. The SSPCON1 register is readable and writable. The lower 6 bits of the SSPSTAT are read-only. The upper two bits of the SSPSTAT are read/write. SSPSR is the shift register used for shifting data in or out. SSPBUF is the buffer register to which data bytes are written to or read from. In receive operations, SSPSR and SSPBUF together create a double-buffered receiver. When SSPSR receives a complete byte, it is transferred to SSPBUF and the SSPIF interrupt is set. During transmission, the SSPBUF is not doublebuffered. A write to SSPBUF will write to both SSPBUF and SSPSR. REGISTER 17-1: SSPSTAT: MSSP STATUS REGISTER (SPI MODE) R/W-0 R/W-0 R-0 R-0 R-0 R-0 R-0 R-0 SMP CKE D/A P S R/W UA BF bit 7 bit 0 bit 7 SMP: Sample bit SPI Master mode: 1 = Input data sampled at end of data output time 0 = Input data sampled at middle of data output time SPI Slave mode: SMP must be cleared when SPI is used in Slave mode. bit 6 CKE: SPI Clock Select bit 1 = Transmit occurs on transition from active to Idle clock state 0 = Transmit occurs on transition from Idle to active clock state Note: Polarity of clock state is set by the CKP bit (SSPCON1<4>). bit 5 D/A: Data/Address bit Used in I2C mode only. bit 4 P: Stop bit Used in I2C mode only. This bit is cleared when the MSSP module is disabled, SSPEN is cleared. bit 3 S: Start bit Used in I2C mode only. bit 2 R/W: Read/Write Information bit Used in I2C mode only. bit 1 UA: Update Address bit Used in I2C mode only. bit 0 BF: Buffer Full Status bit (Receive mode only) 1 = Receive complete, SSPBUF is full 0 = Receive not complete, SSPBUF is empty Legend: R = Readable bit W = Writable bit U = Unimplemented bit, read as ‘0’ -n = Value at POR ‘1’ = Bit is set ‘0’ = Bit is cleared x = Bit is unknown © 2007 Microchip Technology Inc. Preliminary DS39631B-page 163 PIC18F2420/2520/4420/4520 REGISTER 17-2: SSPCON1: MSSP CONTROL REGISTER 1 (SPI MODE) R/W-0 R/W-0 R/W-0 R/W-0 R/W-0 R/W-0 R/W-0 R/W-0 WCOL SSPOV SSPEN CKP SSPM3 SSPM2 SSPM1 SSPM0 bit 7 bit 0 bit 7 WCOL: Write Collision Detect bit (Transmit mode only) 1 = The SSPBUF register is written while it is still transmitting the previous word (must be cleared in software) 0 = No collision bit 6 SSPOV: Receive Overflow Indicator bit SPI Slave mode: 1 = A new byte is received while the SSPBUF register is still holding the previous data. In case of overflow, the data in SSPSR is lost. Overflow can only occur in Slave mode. The user must read the SSPBUF, even if only transmitting data, to avoid setting overflow (must be cleared in software). 0 = No overflow Note: In Master mode, the overflow bit is not set since each new reception (and transmission) is initiated by writing to the SSPBUF register. bit 5 SSPEN: Synchronous Serial Port Enable bit 1 = Enables serial port and configures SCK, SDO, SDI and SS as serial port pins 0 = Disables serial port and configures these pins as I/O port pins Note: When enabled, these pins must be properly configured as input or output. bit 4 CKP: Clock Polarity Select bit 1 = Idle state for clock is a high level 0 = Idle state for clock is a low level bit 3-0 SSPM3:SSPM0: Synchronous Serial Port Mode Select bits 0101 = SPI Slave mode, clock = SCK pin, SS pin control disabled, SS can be used as I/O pin 0100 = SPI Slave mode, clock = SCK pin, SS pin control enabled 0011 = SPI Master mode, clock = TMR2 output/2 0010 = SPI Master mode, clock = FOSC/64 0001 = SPI Master mode, clock = FOSC/16 0000 = SPI Master mode, clock = FOSC/4 Note: Bit combinations not specifically listed here are either reserved or implemented in I2C mode only. Legend: R = Readable bit W = Writable bit U = Unimplemented bit, read as ‘0’ -n = Value at POR ‘1’ = Bit is set ‘0’ = Bit is cleared x = Bit is unknown PIC18F2420/2520/4420/4520 DS39631B-page 164 Preliminary © 2007 Microchip Technology Inc. 17.3.2 OPERATION When initializing the SPI, several options need to be specified. This is done by programming the appropriate control bits (SSPCON1<5:0> and SSPSTAT<7:6>). These control bits allow the following to be specified: • Master mode (SCK is the clock output) • Slave mode (SCK is the clock input) • Clock Polarity (Idle state of SCK) • Data Input Sample Phase (middle or end of data output time) • Clock Edge (output data on rising/falling edge of SCK) • Clock Rate (Master mode only) • Slave Select mode (Slave mode only) The MSSP consists of a transmit/receive shift register (SSPSR) and a buffer register (SSPBUF). The SSPSR shifts the data in and out of the device, MSb first. The SSPBUF holds the data that was written to the SSPSR until the received data is ready. Once the 8 bits of data have been received, that byte is moved to the SSPBUF register. Then, the Buffer Full detect bit, BF (SSPSTAT<0>) and the interrupt flag bit, SSPIF, are set. This double-buffering of the received data (SSPBUF) allows the next byte to start reception before reading the data that was just received. Any write to the SSPBUF register during transmission/reception of data will be ignored and the write collision detect bit, WCOL (SSPCON1<7>), will be set. User software must clear the WCOL bit so that it can be determined if the following write(s) to the SSPBUF register completed successfully. When the application software is expecting to receive valid data, the SSPBUF should be read before the next byte of data to transfer is written to the SSPBUF. The Buffer Full bit, BF (SSPSTAT<0>), indicates when SSPBUF has been loaded with the received data (transmission is complete). When the SSPBUF is read, the BF bit is cleared. This data may be irrelevant if the SPI is only a transmitter. Generally, the MSSP interrupt is used to determine when the transmission/reception has completed. The SSPBUF must be read and/or written. If the interrupt method is not going to be used, then software polling can be done to ensure that a write collision does not occur. Example 17-1 shows the loading of the SSPBUF (SSPSR) for data transmission. The SSPSR is not directly readable or writable and can only be accessed by addressing the SSPBUF register. Additionally, the MSSP status register (SSPSTAT) indicates the various status conditions. EXAMPLE 17-1: LOADING THE SSPBUF (SSPSR) REGISTER LOOP BTFSS SSPSTAT, BF ;Has data been received (transmit complete)? BRA LOOP ;No MOVF SSPBUF, W ;WREG reg = contents of SSPBUF MOVWF RXDATA ;Save in user RAM, if data is meaningful MOVF TXDATA, W ;W reg = contents of TXDATA MOVWF SSPBUF ;New data to xmit © 2007 Microchip Technology Inc. Preliminary DS39631B-page 165 PIC18F2420/2520/4420/4520 17.3.3 ENABLING SPI I/O To enable the serial port, SSP Enable bit, SSPEN (SSPCON1<5>), must be set. To reset or reconfigure SPI mode, clear the SSPEN bit, reinitialize the SSPCON registers and then set the SSPEN bit. This configures the SDI, SDO, SCK and SS pins as serial port pins. For the pins to behave as the serial port function, some must have their data direction bits (in the TRIS register) appropriately programmed as follows: • SDI is automatically controlled by the SPI module • SDO must have TRISC<5> bit cleared • SCK (Master mode) must have TRISC<3> bit cleared • SCK (Slave mode) must have TRISC<3> bit set • SS must have TRISA<5> bit set Any serial port function that is not desired may be overridden by programming the corresponding data direction (TRIS) register to the opposite value. 17.3.4 TYPICAL CONNECTION Figure 17-2 shows a typical connection between two microcontrollers. The master controller (Processor 1) initiates the data transfer by sending the SCK signal. Data is shifted out of both shift registers on their programmed clock edge and latched on the opposite edge of the clock. Both processors should be programmed to the same Clock Polarity (CKP), then both controllers would send and receive data at the same time. Whether the data is meaningful (or dummy data) depends on the application software. This leads to three scenarios for data transmission: • Master sends data – Slave sends dummy data • Master sends data – Slave sends data • Master sends dummy data – Slave sends data FIGURE 17-2: SPI MASTER/SLAVE CONNECTION Serial Input Buffer (SSPBUF) Shift Register (SSPSR) MSb LSb SDO SDI PROCESSOR 1 SCK SPI Master SSPM3:SSPM0 = 00xxb Serial Input Buffer (SSPBUF) Shift Register (SSPSR) MSb LSb SDI SDO PROCESSOR 2 SCK SPI Slave SSPM3:SSPM0 = 010xb Serial Clock PIC18F2420/2520/4420/4520 DS39631B-page 166 Preliminary © 2007 Microchip Technology Inc. 17.3.5 MASTER MODE The master can initiate the data transfer at any time because it controls the SCK. The master determines when the slave (Processor 2, Figure 17-2) is to broadcast data by the software protocol. In Master mode, the data is transmitted/received as soon as the SSPBUF register is written to. If the SPI is only going to receive, the SDO output could be disabled (programmed as an input). The SSPSR register will continue to shift in the signal present on the SDI pin at the programmed clock rate. As each byte is received, it will be loaded into the SSPBUF register as if a normal received byte (interrupts and status bits appropriately set). This could be useful in receiver applications as a “Line Activity Monitor” mode. The clock polarity is selected by appropriately programming the CKP bit (SSPCON1<4>). This then, would give waveforms for SPI communication as shown in Figure 17-3, Figure 17-5 and Figure 17-6, where the MSB is transmitted first. In Master mode, the SPI clock rate (bit rate) is user programmable to be one of the following: • FOSC/4 (or TCY) • FOSC/16 (or 4 • TCY) • FOSC/64 (or 16 • TCY) • Timer2 output/2 This allows a maximum data rate (at 40 MHz) of 10.00 Mbps. Figure 17-3 shows the waveforms for Master mode. When the CKE bit is set, the SDO data is valid before there is a clock edge on SCK. The change of the input sample is shown based on the state of the SMP bit. The time when the SSPBUF is loaded with the received data is shown. FIGURE 17-3: SPI MODE WAVEFORM (MASTER MODE) SCK (CKP = 0 SCK (CKP = 1 SCK (CKP = 0 SCK (CKP = 1 4 Clock Modes Input Sample Input Sample SDI bit 7 bit 0 SDO bit 7 bit 6 bit 5 bit 4 bit 3 bit 2 bit 1 bit 0 bit 7 SDI SSPIF (SMP = 1) (SMP = 0) (SMP = 1) CKE = 1) CKE = 0) CKE = 1) CKE = 0) (SMP = 0) Write to SSPBUF SSPSR to SSPBUF SDO bit 7 bit 6 bit 5 bit 4 bit 3 bit 2 bit 1 bit 0 (CKE = 0) (CKE = 1) Next Q4 Cycle after Q2↓ bit 0 © 2007 Microchip Technology Inc. Preliminary DS39631B-page 167 PIC18F2420/2520/4420/4520 17.3.6 SLAVE MODE In Slave mode, the data is transmitted and received as the external clock pulses appear on SCK. When the last bit is latched, the SSPIF interrupt flag bit is set. Before enabling the module in SPI Slave mode, the clock line must match the proper Idle state. The clock line can be observed by reading the SCK pin. The Idle state is determined by the CKP bit (SSPCON1<4>). While in Slave mode, the external clock is supplied by the external clock source on the SCK pin. This external clock must meet the minimum high and low times as specified in the electrical specifications. While in Sleep mode, the slave can transmit/receive data. When a byte is received, the device will wake-up from Sleep. 17.3.7 SLAVE SELECT SYNCHRONIZATION The SS pin allows a Synchronous Slave mode. The SPI must be in Slave mode with SS pin control enabled (SSPCON1<3:0> = 04h). The pin must not be driven low for the SS pin to function as an input. The data latch must be high. When the SS pin is low, transmission and reception are enabled and the SDO pin is driven. When the SS pin goes high, the SDO pin is no longer driven, even if in the middle of a transmitted byte and becomes a floating output. External pull-up/pull-down resistors may be desirable depending on the application. When the SPI module resets, the bit counter is forced to ‘0’. This can be done by either forcing the SS pin to a high level or clearing the SSPEN bit. To emulate two-wire communication, the SDO pin can be connected to the SDI pin. When the SPI needs to operate as a receiver, the SDO pin can be configured as an input. This disables transmissions from the SDO. The SDI can always be left as an input (SDI function) since it cannot create a bus conflict. FIGURE 17-4: SLAVE SYNCHRONIZATION WAVEFORM Note 1: When the SPI is in Slave mode with SS pin control enabled (SSPCON<3:0> = 0100), the SPI module will reset if the SS pin is set to VDD. 2: If the SPI is used in Slave mode with CKE set, then the SS pin control must be enabled. SCK (CKP = 1 SCK (CKP = 0 Input Sample SDI bit 7 SDO bit 7 bit 6 bit 7 SSPIF Interrupt (SMP = 0) CKE = 0) CKE = 0) (SMP = 0) Write to SSPBUF SSPSR to SSPBUF SS Flag bit 0 bit 7 bit 0 Next Q4 Cycle after Q2↓ PIC18F2420/2520/4420/4520 DS39631B-page 168 Preliminary © 2007 Microchip Technology Inc. FIGURE 17-5: SPI MODE WAVEFORM (SLAVE MODE WITH CKE = 0) FIGURE 17-6: SPI MODE WAVEFORM (SLAVE MODE WITH CKE = 1) SCK (CKP = 1 SCK (CKP = 0 Input Sample SDI bit 7 SDO bit 7 bit 6 bit 5 bit 4 bit 3 bit 2 bit 1 bit 0 SSPIF Interrupt (SMP = 0) CKE = 0) CKE = 0) (SMP = 0) Write to SSPBUF SSPSR to SSPBUF SS Flag Optional Next Q4 Cycle after Q2↓ bit 0 SCK (CKP = 1 SCK (CKP = 0 Input Sample SDI bit 7 bit 0 SDO bit 7 bit 6 bit 5 bit 4 bit 3 bit 2 bit 1 bit 0 SSPIF Interrupt (SMP = 0) CKE = 1) CKE = 1) (SMP = 0) Write to SSPBUF SSPSR to SSPBUF SS Flag Not Optional Next Q4 Cycle after Q2↓ © 2007 Microchip Technology Inc. Preliminary DS39631B-page 169 PIC18F2420/2520/4420/4520 17.3.8 OPERATION IN POWER MANAGED MODES In SPI Master mode, module clocks may be operating at a different speed than when in full power mode; in the case of the Sleep mode, all clocks are halted. In most Idle modes, a clock is provided to the peripherals. That clock should be from the primary clock source, the secondary clock (Timer1 oscillator at 32.768 kHz) or the INTOSC source. See Section 2.7 “Clock Sources and Oscillator Switching” for additional information. In most cases, the speed that the master clocks SPI data is not important; however, this should be evaluated for each system. If MSSP interrupts are enabled, they can wake the controller from Sleep mode, or one of the Idle modes, when the master completes sending data. If an exit from Sleep or Idle mode is not desired, MSSP interrupts should be disabled. If the Sleep mode is selected, all module clocks are halted and the transmission/reception will remain in that state until the devices wakes. After the device returns to Run mode, the module will resume transmitting and receiving data. In SPI Slave mode, the SPI Transmit/Receive Shift register operates asynchronously to the device. This allows the device to be placed in any power managed mode and data to be shifted into the SPI Transmit/ Receive Shift register. When all 8 bits have been received, the MSSP interrupt flag bit will be set and if enabled, will wake the device. 17.3.9 EFFECTS OF A RESET A Reset disables the MSSP module and terminates the current transfer. 17.3.10 BUS MODE COMPATIBILITY Table 17-1 shows the compatibility between the standard SPI modes and the states of the CKP and CKE control bits. TABLE 17-1: SPI BUS MODES There is also an SMP bit which controls when the data is sampled. TABLE 17-2: REGISTERS ASSOCIATED WITH SPI OPERATION Standard SPI Mode Terminology Control Bits State CKP CKE 0, 0 0 1 0, 1 0 0 1, 0 1 1 1, 1 1 0 Name Bit 7 Bit 6 Bit 5 Bit 4 Bit 3 Bit 2 Bit 1 Bit 0 Reset Values on page INTCON GIE/GIEH PEIE/GIEL TMR0IE INT0IE RBIE TMR0IF INT0IF RBIF 49 PIR1 PSPIF(1) ADIF RCIF TXIF SSPIF CCP1IF TMR2IF TMR1IF 52 PIE1 PSPIE(1) ADIE RCIE TXIE SSPIE CCP1IE TMR2IE TMR1IE 52 IPR1 PSPIP(1) ADIP RCIP TXIP SSPIP CCP1IP TMR2IP TMR1IP 52 TRISA TRISA7(2) TRISA6(2) PORTA Data Direction Control Register 52 TRISC PORTC Data Direction Control Register 52 SSPBUF SSP Receive Buffer/Transmit Register 50 SSPCON1 WCOL SSPOV SSPEN CKP SSPM3 SSPM2 SSPM1 SSPM0 50 SSPSTAT SMP CKE D/A P S R/W UA BF 50 Legend: Shaded cells are not used by the MSSP in SPI mode. Note 1: These bits are unimplemented in 28-pin devices; always maintain these bits clear. 2: PORTA<7:6> and their direction bits are individually configured as port pins based on various primary oscillator modes. When disabled, these bits read as ‘0’. PIC18F2420/2520/4420/4520 DS39631B-page 170 Preliminary © 2007 Microchip Technology Inc. 17.4 I2C Mode The MSSP module in I2C mode fully implements all master and slave functions (including general call support) and provides interrupts on Start and Stop bits in hardware to determine a free bus (multi-master function). The MSSP module implements the standard mode specifications as well as 7-bit and 10-bit addressing. Two pins are used for data transfer: • Serial clock (SCL) – RC3/SCK/SCL • Serial data (SDA) – RC4/SDI/SDA The user must configure these pins as inputs or outputs through the TRISC<4:3> bits. FIGURE 17-7: MSSP BLOCK DIAGRAM (I2C MODE) 17.4.1 REGISTERS The MSSP module has six registers for I2C operation. These are: • MSSP Control Register 1 (SSPCON1) • MSSP Control Register 2 (SSPCON2) • MSSP Status Register (SSPSTAT) • Serial Receive/Transmit Buffer Register (SSPBUF) • MSSP Shift Register (SSPSR) – Not directly accessible • MSSP Address Register (SSPADD) SSPCON1, SSPCON2 and SSPSTAT are the control and status registers in I2C mode operation. The SSPCON1 and SSPCON2 registers are readable and writable. The lower 6 bits of the SSPSTAT are read-only. The upper two bits of the SSPSTAT are read/write. SSPSR is the shift register used for shifting data in or out. SSPBUF is the buffer register to which data bytes are written to or read from. SSPADD register holds the slave device address when the SSP is configured in I2C Slave mode. When the SSP is configured in Master mode, the lower seven bits of SSPADD act as the Baud Rate Generator reload value. In receive operations, SSPSR and SSPBUF together create a double-buffered receiver. When SSPSR receives a complete byte, it is transferred to SSPBUF and the SSPIF interrupt is set. During transmission, the SSPBUF is not doublebuffered. A write to SSPBUF will write to both SSPBUF and SSPSR. Read Write SSPSR reg Match Detect SSPADD reg Start and Stop bit Detect SSPBUF reg Internal Data Bus Addr Match Set, Reset S, P bits (SSPSTAT reg) RC3/SCK/SCL RC4/SDI/ Shift Clock MSb SDA LSb © 2007 Microchip Technology Inc. Preliminary DS39631B-page 171 PIC18F2420/2520/4420/4520 REGISTER 17-3: SSPSTAT: MSSP STATUS REGISTER (I2C MODE) R/W-0 R/W-0 R-0 R-0 R-0 R-0 R-0 R-0 SMP CKE D/A P S R/W UA BF bit 7 bit 0 bit 7 SMP: Slew Rate Control bit In Master or Slave mode: 1 = Slew rate control disabled for standard speed mode (100 kHz and 1 MHz) 0 = Slew rate control enabled for high-speed mode (400 kHz) bit 6 CKE: SMBus Select bit In Master or Slave mode: 1 = Enable SMBus specific inputs 0 = Disable SMBus specific inputs bit 5 D/A: Data/Address bit In Master mode: Reserved. In Slave mode: 1 = Indicates that the last byte received or transmitted was data 0 = Indicates that the last byte received or transmitted was address bit 4 P: Stop bit 1 = Indicates that a Stop bit has been detected last 0 = Stop bit was not detected last Note: This bit is cleared on Reset and when SSPEN is cleared. bit 3 S: Start bit 1 = Indicates that a Start bit has been detected last 0 = Start bit was not detected last Note: This bit is cleared on Reset and when SSPEN is cleared. bit 2 R/W: Read/Write Information bit (I2C mode only) In Slave mode: 1 = Read 0 = Write Note: This bit holds the R/W bit information following the last address match. This bit is only valid from the address match to the next Start bit, Stop bit or not ACK bit. In Master mode: 1 = Transmit is in progress 0 = Transmit is not in progress Note: ORing this bit with SEN, RSEN, PEN, RCEN or ACKEN will indicate if the MSSP is in Active mode. bit 1 UA: Update Address bit (10-bit Slave mode only) 1 = Indicates that the user needs to update the address in the SSPADD register 0 = Address does not need to be updated bit 0 BF: Buffer Full Status bit In Transmit mode: 1 = SSPBUF is full 0 = SSPBUF is empty In Receive mode: 1 = SSPBUF is full (does not include the ACK and Stop bits) 0 = SSPBUF is empty (does not include the ACK and Stop bits) Legend: R = Readable bit W = Writable bit U = Unimplemented bit, read as ‘0’ -n = Value at POR ‘1’ = Bit is set ‘0’ = Bit is cleared x = Bit is unknown PIC18F2420/2520/4420/4520 DS39631B-page 172 Preliminary © 2007 Microchip Technology Inc. REGISTER 17-4: SSPCON1: MSSP CONTROL REGISTER 1 (I2C MODE) R/W-0 R/W-0 R/W-0 R/W-0 R/W-0 R/W-0 R/W-0 R/W-0 WCOL SSPOV SSPEN CKP SSPM3 SSPM2 SSPM1 SSPM0 bit 7 bit 0 bit 7 WCOL: Write Collision Detect bit In Master Transmit mode: 1 = A write to the SSPBUF register was attempted while the I2C conditions were not valid for a transmission to be started (must be cleared in software) 0 = No collision In Slave Transmit mode: 1 = The SSPBUF register is written while it is still transmitting the previous word (must be cleared in software) 0 = No collision In Receive mode (Master or Slave modes): This is a “don’t care” bit. bit 6 SSPOV: Receive Overflow Indicator bit In Receive mode: 1 = A byte is received while the SSPBUF register is still holding the previous byte (must be cleared in software) 0 = No overflow In Transmit mode: This is a “don’t care” bit in Transmit mode. bit 5 SSPEN: Synchronous Serial Port Enable bit 1 = Enables the serial port and configures the SDA and SCL pins as the serial port pins 0 = Disables serial port and configures these pins as I/O port pins Note: When enabled, the SDA and SCL pins must be properly configured as input or output. bit 4 CKP: SCK Release Control bit In Slave mode: 1 = Release clock 0 = Holds clock low (clock stretch), used to ensure data setup time In Master mode: Unused in this mode. bit 3-0 SSPM3:SSPM0: Synchronous Serial Port Mode Select bits 1111 = I2C Slave mode, 10-bit address with Start and Stop bit interrupts enabled 1110 = I2C Slave mode, 7-bit address with Start and Stop bit interrupts enabled 1011 = I2C Firmware Controlled Master mode (Slave Idle) 1000 = I2C Master mode, clock = FOSC/(4 * (SSPADD + 1)) 0111 = I2C Slave mode, 10-bit address 0110 = I2C Slave mode, 7-bit address Bit combinations not specifically listed here are either reserved or implemented in SPI mode only. Legend: R = Readable bit W = Writable bit U = Unimplemented bit, read as ‘0’ -n = Value at POR ‘1’ = Bit is set ‘0’ = Bit is cleared x = Bit is unknown © 2007 Microchip Technology Inc. Preliminary DS39631B-page 173 PIC18F2420/2520/4420/4520 REGISTER 17-5: SSPCON2: MSSP CONTROL REGISTER 2 (I2C MODE) R/W-0 R/W-0 R/W-0 R/W-0 R/W-0 R/W-0 R/W-0 R/W-0 GCEN ACKSTAT ACKDT ACKEN(1) RCEN(1) PEN(1) RSEN(1) SEN(1) bit 7 bit 0 bit 7 GCEN: General Call Enable bit (Slave mode only) 1 = Enable interrupt when a general call address (0000h) is received in the SSPSR 0 = General call address disabled bit 6 ACKSTAT: Acknowledge Status bit (Master Transmit mode only) 1 = Acknowledge was not received from slave 0 = Acknowledge was received from slave bit 5 ACKDT: Acknowledge Data bit (Master Receive mode only) 1 = Not Acknowledge 0 = Acknowledge Note: Value that will be transmitted when the user initiates an Acknowledge sequence at the end of a receive. bit 4 ACKEN: Acknowledge Sequence Enable bit (Master Receive mode only)(1) 1 = Initiate Acknowledge sequence on SDA and SCL pins and transmit ACKDT data bit. Automatically cleared by hardware. 0 = Acknowledge sequence Idle bit 3 RCEN: Receive Enable bit (Master mode only)(1) 1 = Enables Receive mode for I2C 0 = Receive Idle bit 2 PEN: Stop Condition Enable bit (Master mode only)(1) 1 = Initiate Stop condition on SDA and SCL pins. Automatically cleared by hardware. 0 = Stop condition Idle bit 1 RSEN: Repeated Start Condition Enable bit (Master mode only)(1) 1 = Initiate Repeated Start condition on SDA and SCL pins. Automatically cleared by hardware. 0 = Repeated Start condition Idle bit 0 SEN: Start Condition Enable/Stretch Enable bit(1) In Master mode: 1 = Initiate Start condition on SDA and SCL pins. Automatically cleared by hardware. 0 = Start condition Idle In Slave mode: 1 = Clock stretching is enabled for both slave transmit and slave receive (stretch enabled) 0 = Clock stretching is disabled Note 1: For bits ACKEN, RCEN, PEN, RSEN, SEN: If the I2C module is not in the Idle mode, these bits may not be set (no spooling) and the SSPBUF may not be written (or writes to the SSPBUF are disabled). Legend: R = Readable bit W = Writable bit U = Unimplemented bit, read as ‘0’ -n = Value at POR ‘1’ = Bit is set ‘0’ = Bit is cleared x = Bit is unknown PIC18F2420/2520/4420/4520 DS39631B-page 174 Preliminary © 2007 Microchip Technology Inc. 17.4.2 OPERATION The MSSP module functions are enabled by setting MSSP Enable bit, SSPEN (SSPCON<5>). The SSPCON1 register allows control of the I2C operation. Four mode selection bits (SSPCON<3:0>) allow one of the following I2C modes to be selected: • I2C Master mode, clock = (FOSC/4) x (SSPADD + 1) • I2C Slave mode (7-bit address) • I2C Slave mode (10-bit address) • I2C Slave mode (7-bit address) with Start and Stop bit interrupts enabled • I2C Slave mode (10-bit address) with Start and Stop bit interrupts enabled • I2C Firmware Controlled Master mode, slave is Idle Selection of any I2C mode with the SSPEN bit set, forces the SCL and SDA pins to be open-drain, provided these pins are programmed to inputs by setting the appropriate TRISC bits. To ensure proper operation of the module, pull-up resistors must be provided externally to the SCL and SDA pins. 17.4.3 SLAVE MODE In Slave mode, the SCL and SDA pins must be configured as inputs (TRISC<4:3> set). The MSSP module will override the input state with the output data when required (slave-transmitter). The I2C Slave mode hardware will always generate an interrupt on an address match. Through the mode select bits, the user can also choose to interrupt on Start and Stop bits When an address is matched, or the data transfer after an address match is received, the hardware automatically will generate the Acknowledge (ACK) pulse and load the SSPBUF register with the received value currently in the SSPSR register. Any combination of the following conditions will cause the MSSP module not to give this ACK pulse: • The Buffer Full bit, BF (SSPSTAT<0>), was set before the transfer was received. • The overflow bit, SSPOV (SSPCON<6>), was set before the transfer was received. In this case, the SSPSR register value is not loaded into the SSPBUF, but bit SSPIF (PIR1<3>) is set. The BF bit is cleared by reading the SSPBUF register, while bit SSPOV is cleared through software. The SCL clock input must have a minimum high and low for proper operation. The high and low times of the I2C specification, as well as the requirement of the MSSP module, are shown in timing parameter 100 and parameter 101. 17.4.3.1 Addressing Once the MSSP module has been enabled, it waits for a Start condition to occur. Following the Start condition, the 8 bits are shifted into the SSPSR register. All incoming bits are sampled with the rising edge of the clock (SCL) line. The value of register SSPSR<7:1> is compared to the value of the SSPADD register. The address is compared on the falling edge of the eighth clock (SCL) pulse. If the addresses match and the BF and SSPOV bits are clear, the following events occur: 1. The SSPSR register value is loaded into the SSPBUF register. 2. The Buffer Full bit, BF, is set. 3. An ACK pulse is generated. 4. MSSP Interrupt Flag bit, SSPIF (PIR1<3>), is set (interrupt is generated, if enabled) on the falling edge of the ninth SCL pulse. In 10-bit Address mode, two address bytes need to be received by the slave. The five Most Significant bits (MSbs) of the first address byte specify if this is a 10-bit address. Bit R/W (SSPSTAT<2>) must specify a write so the slave device will receive the second address byte. For a 10-bit address, the first byte would equal ‘11110 A9 A8 0’, where ‘A9’ and ‘A8’ are the two MSbs of the address. The sequence of events for 10-bit address is as follows, with steps 7 through 9 for the slave-transmitter: 1. Receive first (high) byte of address (bits SSPIF, BF and UA (SSPSTAT<1>) are set). 2. Update the SSPADD register with second (low) byte of address (clears bit UA and releases the SCL line). 3. Read the SSPBUF register (clears bit BF) and clear flag bit, SSPIF. 4. Receive second (low) byte of address (bits SSPIF, BF and UA are set). 5. Update the SSPADD register with the first (high) byte of address. If match releases SCL line, this will clear bit UA. 6. Read the SSPBUF register (clears bit BF) and clear flag bit, SSPIF. 7. Receive Repeated Start condition. 8. Receive first (high) byte of address (bits SSPIF and BF are set). 9. Read the SSPBUF register (clears bit BF) and clear flag bit, SSPIF. © 2007 Microchip Technology Inc. Preliminary DS39631B-page 175 PIC18F2420/2520/4420/4520 17.4.3.2 Reception When the R/W bit of the address byte is clear and an address match occurs, the R/W bit of the SSPSTAT register is cleared. The received address is loaded into the SSPBUF register and the SDA line is held low (ACK). When the address byte overflow condition exists, then the no Acknowledge (ACK) pulse is given. An overflow condition is defined as either bit BF (SSPSTAT<0>) is set, or bit SSPOV (SSPCON1<6>) is set. An MSSP interrupt is generated for each data transfer byte. Flag bit, SSPIF (PIR1<3>), must be cleared in software. The SSPSTAT register is used to determine the status of the byte. If SEN is enabled (SSPCON2<0> = 1), RC3/SCK/SCL will be held low (clock stretch) following each data transfer. The clock must be released by setting bit, CKP (SSPCON<4>). See Section 17.4.4 “Clock Stretching” for more detail. 17.4.3.3 Transmission When the R/W bit of the incoming address byte is set and an address match occurs, the R/W bit of the SSPSTAT register is set. The received address is loaded into the SSPBUF register. The ACK pulse will be sent on the ninth bit and pin RC3/SCK/SCL is held low regardless of SEN (see Section 17.4.4 “Clock Stretching” for more detail). By stretching the clock, the master will be unable to assert another clock pulse until the slave is done preparing the transmit data. The transmit data must be loaded into the SSPBUF register which also loads the SSPSR register. Then pin RC3/ SCK/SCL should be enabled by setting bit, CKP (SSPCON1<4>). The eight data bits are shifted out on the falling edge of the SCL input. This ensures that the SDA signal is valid during the SCL high time (Figure 17-9). The ACK pulse from the master-receiver is latched on the rising edge of the ninth SCL input pulse. If the SDA line is high (not ACK), then the data transfer is complete. In this case, when the ACK is latched by the slave, the slave logic is reset (resets SSPSTAT register) and the slave monitors for another occurrence of the Start bit. If the SDA line was low (ACK), the next transmit data must be loaded into the SSPBUF register. Again, pin RC3/SCK/SCL must be enabled by setting bit CKP. An MSSP interrupt is generated for each data transfer byte. The SSPIF bit must be cleared in software and the SSPSTAT register is used to determine the status of the byte. The SSPIF bit is set on the falling edge of the ninth clock pulse. PIC18F2420/2520/4420/4520 DS39631B-page 176 Preliminary © 2007 Microchip Technology Inc. FIGURE 17-8: I2C™ SLAVE MODE TIMING WITH SEN = 0 (RECEPTION, 7-BIT ADDRESS) SDA SCL SSPIF BF (SSPSTAT<0>) SSPOV (SSPCON1<6>) S 1 2 3 4 5 6 7 8 9 1 2 3 4 5 6 7 8 9 1 2 3 4 5 7 8 9 P A7 A6 A5 A4 A3 A2 A1 D7 D6 D5 D4 D3 D2 D1 D0 D7 D6 D5 D4 D3 D1 D0 R/W = 0 Receiving Data ACK Receiving Data ACK ACK Receiving Address Cleared in software SSPBUF is read Bus master terminates transfer SSPOV is set because SSPBUF is still full. ACK is not sent. D2 6 (PIR1<3>) CKP (CKP does not reset to ‘0’ when SEN = 0) © 2007 Microchip Technology Inc. Preliminary DS39631B-page 177 PIC18F2420/2520/4420/4520 FIGURE 17-9: I2C™ SLAVE MODE TIMING (TRANSMISSION, 7-BIT ADDRESS) SDA SCL SSPIF (PIR1<3>) BF (SSPSTAT<0>) A6 A5 A4 A3 A2 A1 D6 D5 D4 D3 D2 D1 D0 1 2 3 4 5 6 7 8 2 3 4 5 6 7 8 9 SSPBUF is written in software Cleared in software From SSPIF ISR Data in sampled S ACK R/W = 0 Transmitting Data ACK Receiving Address A7 D7 9 1 D6 D5 D4 D3 D2 D1 D0 2 3 4 5 6 7 8 9 SSPBUF is written in software Cleared in software From SSPIF ISR Transmitting Data D7 1 CKP P ACK CKP is set in software CKP is set in software SCL held low while CPU responds to SSPIF PIC18F2420/2520/4420/4520 DS39631B-page 178 Preliminary © 2007 Microchip Technology Inc. FIGURE 17-10: I2C™ SLAVE MODE TIMING WITH SEN = 0 (RECEPTION, 10-BIT ADDRESS) SDA SCL SSPIF BF (SSPSTAT<0>) S 1 2 3 4 5 6 7 8 9 1 2 3 4 5 6 7 8 9 1 2 3 4 5 7 8 9 P 1 1 1 1 0 A9 A8 A7 A6 A5 A4 A3 A2 A1 A0 D7 D6 D5 D4 D3 D1 D0 Receive Data Byte ACK R/W = 0 ACK Receive First Byte of Address Cleared in software D2 6 (PIR1<3>) Cleared in software Receive Second Byte of Address Cleared by hardware when SSPADD is updated with low byte of address UA (SSPSTAT<1>) Clock is held low until update of SSPADD has taken place UA is set indicating that the SSPADD needs to be updated UA is set indicating that SSPADD needs to be updated Cleared by hardware when SSPADD is updated with high byte of address SSPBUF is written with contents of SSPSR Dummy read of SSPBUF to clear BF flag ACK CKP 1 2 3 4 5 7 8 9 D7 D6 D5 D4 D3 D1 D0 Receive Data Byte Bus master terminates transfer D2 6 ACK Cleared in software Cleared in software SSPOV (SSPCON1<6>) SSPOV is set because SSPBUF is still full. ACK is not sent. (CKP does not reset to ‘0’ when SEN = 0) Clock is held low until update of SSPADD has taken place © 2007 Microchip Technology Inc. Preliminary DS39631B-page 179 PIC18F2420/2520/4420/4520 FIGURE 17-11: I2C™ SLAVE MODE TIMING (TRANSMISSION, 10-BIT ADDRESS) SDA SCL SSPIF BF (SSPSTAT<0>) S 1 2 3 4 5 6 7 8 9 1 2 3 4 5 6 7 8 9 1 2 3 4 5 7 8 9 P 1 1 1 1 0 A9 A8 A7 A6 A5 A4 A3 A2 A1 A0 1 1 1 1 0 A8 R/W=1 ACK ACK R/W = 0 ACK Receive First Byte of Address Cleared in software Bus master terminates transfer A9 6 (PIR1<3>) Receive Second Byte of Address Cleared by hardware when SSPADD is updated with low byte of address UA (SSPSTAT<1>) Clock is held low until update of SSPADD has taken place UA is set indicating that the SSPADD needs to be updated UA is set indicating that SSPADD needs to be updated Cleared by hardware when SSPADD is updated with high byte of address. SSPBUF is written with contents of SSPSR Dummy read of SSPBUF to clear BF flag Receive First Byte of Address 1 2 3 4 5 7 8 9 D7 D6 D5 D4 D3 D1 ACK D2 6 Transmitting Data Byte D0 Dummy read of SSPBUF to clear BF flag Sr Cleared in software Write of SSPBUF initiates transmit Cleared in software Completion of clears BF flag CKP (SSPCON1<4>) CKP is set in software CKP is automatically cleared in hardware, holding SCL low Clock is held low until update of SSPADD has taken place data transmission Clock is held low until CKP is set to ‘1’ third address sequence BF flag is clear at the end of the PIC18F2420/2520/4420/4520 DS39631B-page 180 Preliminary © 2007 Microchip Technology Inc. 17.4.4 CLOCK STRETCHING Both 7-bit and 10-bit Slave modes implement automatic clock stretching during a transmit sequence. The SEN bit (SSPCON2<0>) allows clock stretching to be enabled during receives. Setting SEN will cause the SCL pin to be held low at the end of each data receive sequence. 17.4.4.1 Clock Stretching for 7-bit Slave Receive Mode (SEN = 1) In 7-bit Slave Receive mode, on the falling edge of the ninth clock at the end of the ACK sequence if the BF bit is set, the CKP bit in the SSPCON1 register is automatically cleared, forcing the SCL output to be held low. The CKP being cleared to ‘0’ will assert the SCL line low. The CKP bit must be set in the user’s ISR before reception is allowed to continue. By holding the SCL line low, the user has time to service the ISR and read the contents of the SSPBUF before the master device can initiate another receive sequence. This will prevent buffer overruns from occurring (see Figure 17-13). 17.4.4.2 Clock Stretching for 10-bit Slave Receive Mode (SEN = 1) In 10-bit Slave Receive mode during the address sequence, clock stretching automatically takes place but CKP is not cleared. During this time, if the UA bit is set after the ninth clock, clock stretching is initiated. The UA bit is set after receiving the upper byte of the 10-bit address and following the receive of the second byte of the 10-bit address with the R/W bit cleared to ‘0’. The release of the clock line occurs upon updating SSPADD. Clock stretching will occur on each data receive sequence as described in 7-bit mode. 17.4.4.3 Clock Stretching for 7-bit Slave Transmit Mode 7-bit Slave Transmit mode implements clock stretching by clearing the CKP bit after the falling edge of the ninth clock if the BF bit is clear. This occurs regardless of the state of the SEN bit. The user’s ISR must set the CKP bit before transmission is allowed to continue. By holding the SCL line low, the user has time to service the ISR and load the contents of the SSPBUF before the master device can initiate another transmit sequence (see Figure 17-9). 17.4.4.4 Clock Stretching for 10-bit Slave Transmit Mode In 10-bit Slave Transmit mode, clock stretching is controlled during the first two address sequences by the state of the UA bit, just as it is in 10-bit Slave Receive mode. The first two addresses are followed by a third address sequence which contains the high-order bits of the 10-bit address and the R/W bit set to ‘1’. After the third address sequence is performed, the UA bit is not set, the module is now configured in Transmit mode and clock stretching is controlled by the BF flag as in 7-bit Slave Transmit mode (see Figure 17-11). Note 1: If the user reads the contents of the SSPBUF before the falling edge of the ninth clock, thus clearing the BF bit, the CKP bit will not be cleared and clock stretching will not occur. 2: The CKP bit can be set in software regardless of the state of the BF bit. The user should be careful to clear the BF bit in the ISR before the next receive sequence in order to prevent an overflow condition. Note: If the user polls the UA bit and clears it by updating the SSPADD register before the falling edge of the ninth clock occurs and if the user hasn’t cleared the BF bit by reading the SSPBUF register before that time, then the CKP bit will still NOT be asserted low. Clock stretching on the basis of the state of the BF bit only occurs during a data sequence, not an address sequence. Note 1: If the user loads the contents of SSPBUF, setting the BF bit before the falling edge of the ninth clock, the CKP bit will not be cleared and clock stretching will not occur. 2: The CKP bit can be set in software regardless of the state of the BF bit. © 2007 Microchip Technology Inc. Preliminary DS39631B-page 181 PIC18F2420/2520/4420/4520 17.4.4.5 Clock Synchronization and the CKP bit When the CKP bit is cleared, the SCL output is forced to ‘0’. However, clearing the CKP bit will not assert the SCL output low until the SCL output is already sampled low. Therefore, the CKP bit will not assert the SCL line until an external I2C master device has already asserted the SCL line. The SCL output will remain low until the CKP bit is set and all other devices on the I2C bus have deasserted SCL. This ensures that a write to the CKP bit will not violate the minimum high time requirement for SCL (see Figure 17-12). FIGURE 17-12: CLOCK SYNCHRONIZATION TIMING SDA SCL DX DX – 1 WR Q1 Q2 Q3 Q4 Q1 Q2 Q3 Q4 Q1 Q2 Q3 Q4 Q1 Q2 Q3 Q4 Q1 Q2 Q3 Q4 Q1 Q2 Q3 Q4 Q1 Q2 Q3 Q4 SSPCON CKP Master device deasserts clock Master device asserts clock PIC18F2420/2520/4420/4520 DS39631B-page 182 Preliminary © 2007 Microchip Technology Inc. FIGURE 17-13: I2C™ SLAVE MODE TIMING WITH SEN = 1 (RECEPTION, 7-BIT ADDRESS) SDA SCL SSPIF BF (SSPSTAT<0>) SSPOV (SSPCON1<6>) S 1 2 3 4 5 6 7 8 9 1 2 3 4 5 6 7 8 9 1 2 3 4 5 7 8 9 P A7 A6 A5 A4 A3 A2 A1 D7 D6 D5 D4 D3 D2 D1 D0 D7 D6 D5 D4 D3 D1 D0 R/W = 0 Receiving Data ACK Receiving Data ACK ACK Receiving Address Cleared in software SSPBUF is read Bus master terminates transfer SSPOV is set because SSPBUF is still full. ACK is not sent. D2 6 (PIR1<3>) CKP CKP written to ‘1’ in If BF is cleared prior to the falling edge of the 9th clock, CKP will not be reset to ‘0’ and no clock stretching will occur software Clock is held low until CKP is set to ‘1’ Clock is not held low because buffer full bit is clear prior to falling edge of 9th clock Clock is not held low because ACK = 1 BF is set after falling edge of the 9th clock, CKP is reset to ‘0’ and clock stretching occurs © 2007 Microchip Technology Inc. Preliminary DS39631B-page 183 PIC18F2420/2520/4420/4520 FIGURE 17-14: I2C™ SLAVE MODE TIMING WITH SEN = 1 (RECEPTION, 10-BIT ADDRESS) SDA SCL SSPIF BF (SSPSTAT<0>) S 1 2 3 4 5 6 7 8 9 1 2 3 4 5 6 7 8 9 1 2 3 4 5 7 8 9 P 1 1 1 1 0 A9 A8 A7 A6 A5 A4 A3 A2 A1 A0 D7 D6 D5 D4 D3 D1 D0 Receive Data Byte ACK R/W = 0 ACK Receive First Byte of Address Cleared in software D2 6 (PIR1<3>) Cleared in software Receive Second Byte of Address Cleared by hardware when SSPADD is updated with low byte of address after falling edge UA (SSPSTAT<1>) Clock is held low until update of SSPADD has taken place UA is set indicating that the SSPADD needs to be updated UA is set indicating that SSPADD needs to be updated Cleared by hardware when SSPADD is updated with high byte of address after falling edge SSPBUF is written with contents of SSPSR Dummy read of SSPBUF to clear BF flag ACK CKP 1 2 3 4 5 7 8 9 D7 D6 D5 D4 D3 D1 D0 Receive Data Byte Bus master terminates transfer D2 6 ACK Cleared in software Cleared in software SSPOV (SSPCON1<6>) CKP written to ‘1’ Note: An update of the SSPADD register before the falling edge of the ninth clock will have no effect on UA and UA will remain set. Note: An update of the SSPADD register before the falling edge of the ninth clock will have no effect on UA and UA will remain set. in software Clock is held low until update of SSPADD has taken place of ninth clock of ninth clock SSPOV is set because SSPBUF is still full. ACK is not sent. Dummy read of SSPBUF to clear BF flag Clock is held low until CKP is set to ‘1’ Clock is not held low because ACK = 1 PIC18F2420/2520/4420/4520 DS39631B-page 184 Preliminary © 2007 Microchip Technology Inc. 17.4.5 GENERAL CALL ADDRESS SUPPORT The addressing procedure for the I2C bus is such that the first byte after the Start condition usually determines which device will be the slave addressed by the master. The exception is the general call address which can address all devices. When this address is used, all devices should, in theory, respond with an Acknowledge. The general call address is one of eight addresses reserved for specific purposes by the I2C protocol. It consists of all ‘0’s with R/W = 0. The general call address is recognized when the General Call Enable bit, GCEN, is enabled (SSPCON2<7> is set). Following a Start bit detect, 8 bits are shifted into the SSPSR and the address is compared against the SSPADD. It is also compared to the general call address and fixed in hardware. If the general call address matches, the SSPSR is transferred to the SSPBUF, the BF flag bit is set (eighth bit) and on the falling edge of the ninth bit (ACK bit), the SSPIF interrupt flag bit is set. When the interrupt is serviced, the source for the interrupt can be checked by reading the contents of the SSPBUF. The value can be used to determine if the address was device specific or a general call address. In 10-bit mode, the SSPADD is required to be updated for the second half of the address to match and the UA bit is set (SSPSTAT<1>). If the general call address is sampled when the GCEN bit is set, while the slave is configured in 10-bit Address mode, then the second half of the address is not necessary, the UA bit will not be set and the slave will begin receiving data after the Acknowledge (Figure 17-15). FIGURE 17-15: SLAVE MODE GENERAL CALL ADDRESS SEQUENCE (7 OR 10-BIT ADDRESS MODE) SDA SCL S SSPIF BF (SSPSTAT<0>) SSPOV (SSPCON1<6>) Cleared in software SSPBUF is read R/W = 0 General Call Address ACK Address is compared to General Call Address GCEN (SSPCON2<7>) Receiving Data ACK 1 2 3 4 5 6 7 8 9 1 2 3 4 5 6 7 8 9 D7 D6 D5 D4 D3 D2 D1 D0 after ACK, set interrupt ‘0’ ‘1’ © 2007 Microchip Technology Inc. Preliminary DS39631B-page 185 PIC18F2420/2520/4420/4520 17.4.6 MASTER MODE Master mode is enabled by setting and clearing the appropriate SSPM bits in SSPCON1 and by setting the SSPEN bit. In Master mode, the SCL and SDA lines are manipulated by the MSSP hardware. Master mode of operation is supported by interrupt generation on the detection of the Start and Stop conditions. The Stop (P) and Start (S) bits are cleared from a Reset or when the MSSP module is disabled. Control of the I2C bus may be taken when the P bit is set, or the bus is Idle, with both the S and P bits clear. In Firmware Controlled Master mode, user code conducts all I2C bus operations based on Start and Stop bit conditions. Once Master mode is enabled, the user has six options. 1. Assert a Start condition on SDA and SCL. 2. Assert a Repeated Start condition on SDA and SCL. 3. Write to the SSPBUF register initiating transmission of data/address. 4. Configure the I2C port to receive data. 5. Generate an Acknowledge condition at the end of a received byte of data. 6. Generate a Stop condition on SDA and SCL. The following events will cause the SSP Interrupt Flag bit, SSPIF, to be set (SSP interrupt, if enabled): • Start condition • Stop condition • Data transfer byte transmitted/received • Acknowledge transmit • Repeated Start FIGURE 17-16: MSSP BLOCK DIAGRAM (I2C MASTER MODE) Note: The MSSP module, when configured in I2C Master mode, does not allow queueing of events. For instance, the user is not allowed to initiate a Start condition and immediately write the SSPBUF register to initiate transmission before the Start condition is complete. In this case, the SSPBUF will not be written to and the WCOL bit will be set, indicating that a write to the SSPBUF did not occur. Read Write SSPSR Start bit, Stop bit, SSPBUF Internal Data Bus Set/Reset, S, P, WCOL (SSPSTAT) Shift Clock MSb LSb SDA Acknowledge Generate Stop bit Detect Write Collision Detect Clock Arbitration State Counter for end of XMIT/RCV SCL SCL In Bus Collision SDA In Receive Enable Clock Cntl Clock Arbitrate/WCOL Detect (hold off clock source) SSPADD<6:0> Baud Set SSPIF, BCLIF Reset ACKSTAT, PEN (SSPCON2) Rate Generator SSPM3:SSPM0 Start bit Detect PIC18F2420/2520/4420/4520 DS39631B-page 186 Preliminary © 2007 Microchip Technology Inc. 17.4.6.1 I2C Master Mode Operation The master device generates all of the serial clock pulses and the Start and Stop conditions. A transfer is ended with a Stop condition or with a Repeated Start condition. Since the Repeated Start condition is also the beginning of the next serial transfer, the I2C bus will not be released. In Master Transmitter mode, serial data is output through SDA, while SCL outputs the serial clock. The first byte transmitted contains the slave address of the receiving device (7 bits) and the Read/Write (R/W) bit. In this case, the R/W bit will be logic ‘0’. Serial data is transmitted 8 bits at a time. After each byte is transmitted, an Acknowledge bit is received. Start and Stop conditions are output to indicate the beginning and the end of a serial transfer. In Master Receive mode, the first byte transmitted contains the slave address of the transmitting device (7 bits) and the R/W bit. In this case, the R/W bit will be logic ‘1’. Thus, the first byte transmitted is a 7-bit slave address followed by a ‘1’ to indicate the receive bit. Serial data is received via SDA, while SCL outputs the serial clock. Serial data is received 8 bits at a time. After each byte is received, an Acknowledge bit is transmitted. Start and Stop conditions indicate the beginning and end of transmission. The Baud Rate Generator used for the SPI mode operation is used to set the SCL clock frequency for either 100 kHz, 400 kHz or 1 MHz I2C operation. See Section 17.4.7 “Baud Rate” for more detail. A typical transmit sequence would go as follows: 1. The user generates a Start condition by setting the Start Enable bit, SEN (SSPCON2<0>). 2. SSPIF is set. The MSSP module will wait the required start time before any other operation takes place. 3. The user loads the SSPBUF with the slave address to transmit. 4. Address is shifted out the SDA pin until all 8 bits are transmitted. 5. The MSSP module shifts in the ACK bit from the slave device and writes its value into the SSPCON2 register (SSPCON2<6>). 6. The MSSP module generates an interrupt at the end of the ninth clock cycle by setting the SSPIF bit. 7. The user loads the SSPBUF with eight bits of data. 8. Data is shifted out the SDA pin until all 8 bits are transmitted. 9. The MSSP module shifts in the ACK bit from the slave device and writes its value into the SSPCON2 register (SSPCON2<6>). 10. The MSSP module generates an interrupt at the end of the ninth clock cycle by setting the SSPIF bit. 11. The user generates a Stop condition by setting the Stop Enable bit, PEN (SSPCON2<2>). 12. Interrupt is generated once the Stop condition is complete. © 2007 Microchip Technology Inc. Preliminary DS39631B-page 187 PIC18F2420/2520/4420/4520 17.4.7 BAUD RATE In I2C Master mode, the Baud Rate Generator (BRG) reload value is placed in the lower 7 bits of the SSPADD register (Figure 17-17). When a write occurs to SSPBUF, the Baud Rate Generator will automatically begin counting. The BRG counts down to ‘0’ and stops until another reload has taken place. The BRG count is decremented twice per instruction cycle (TCY) on the Q2 and Q4 clocks. In I2C Master mode, the BRG is reloaded automatically. Once the given operation is complete (i.e., transmission of the last data bit is followed by ACK), the internal clock will automatically stop counting and the SCL pin will remain in its last state. Table 17-3 demonstrates clock rates based on instruction cycles and the BRG value loaded into SSPADD. FIGURE 17-17: BAUD RATE GENERATOR BLOCK DIAGRAM TABLE 17-3: I2C CLOCK RATE W/BRG SSPM3:SSPM0 CLKO BRG Down Counter FOSC/4 SSPADD<6:0> SSPM3:SSPM0 SCL Reload Control Reload FCY FCY*2 BRG Value FSCL (2 Rollovers of BRG) 10 MHz 20 MHz 18h 400 kHz(1) 10 MHz 20 MHz 1Fh 312.5 kHz 10 MHz 20 MHz 63h 100 kHz 4 MHz 8 MHz 09h 400 kHz(1) 4 MHz 8 MHz 0Ch 308 kHz 4 MHz 8 MHz 27h 100 kHz 1 MHz 2 MHz 02h 333 kHz(1) 1 MHz 2 MHz 09h 100 kHz 1 MHz 2 MHz 00h 1 MHz(1) Note 1: The I2C interface does not conform to the 400 kHz I2C specification (which applies to rates greater than 100 kHz) in all details, but may be used with care where higher rates are required by the application. PIC18F2420/2520/4420/4520 DS39631B-page 188 Preliminary © 2007 Microchip Technology Inc. 17.4.7.1 Clock Arbitration Clock arbitration occurs when the master, during any receive, transmit or Repeated Start/Stop condition, deasserts the SCL pin (SCL allowed to float high). When the SCL pin is allowed to float high, the Baud Rate Generator (BRG) is suspended from counting until the SCL pin is actually sampled high. When the SCL pin is sampled high, the Baud Rate Generator is reloaded with the contents of SSPADD<6:0> and begins counting. This ensures that the SCL high time will always be at least one BRG rollover count in the event that the clock is held low by an external device (Figure 17-18). FIGURE 17-18: BAUD RATE GENERATOR TIMING WITH CLOCK ARBITRATION SDA SCL SCL deasserted but slave holds DX DX – 1 BRG SCL is sampled high, reload takes place and BRG starts its count 03h 02h 01h 00h (hold off) 03h 02h Reload BRG Value SCL low (clock arbitration) SCL allowed to transition high BRG decrements on Q2 and Q4 cycles © 2007 Microchip Technology Inc. Preliminary DS39631B-page 189 PIC18F2420/2520/4420/4520 17.4.8 I2C MASTER MODE START CONDITION TIMING To initiate a Start condition, the user sets the Start Enable bit, SEN (SSPCON2<0>). If the SDA and SCL pins are sampled high, the Baud Rate Generator is reloaded with the contents of SSPADD<6:0> and starts its count. If SCL and SDA are both sampled high when the Baud Rate Generator times out (TBRG), the SDA pin is driven low. The action of the SDA being driven low while SCL is high is the Start condition and causes the S bit (SSPSTAT<3>) to be set. Following this, the Baud Rate Generator is reloaded with the contents of SSPADD<6:0> and resumes its count. When the Baud Rate Generator times out (TBRG), the SEN bit (SSPCON2<0>) will be automatically cleared by hardware; the Baud Rate Generator is suspended, leaving the SDA line held low and the Start condition is complete. 17.4.8.1 WCOL Status Flag If the user writes the SSPBUF when a Start sequence is in progress, the WCOL is set and the contents of the buffer are unchanged (the write doesn’t occur). FIGURE 17-19: FIRST START BIT TIMING Note: If at the beginning of the Start condition, the SDA and SCL pins are already sampled low, or if during the Start condition, the SCL line is sampled low before the SDA line is driven low, a bus collision occurs, the Bus Collision Interrupt Flag, BCLIF, is set, the Start condition is aborted and the I2C module is reset into its Idle state. Note: Because queueing of events is not allowed, writing to the lower 5 bits of SSPCON2 is disabled until the Start condition is complete. SDA SCL S TBRG 1st bit 2nd bit TBRG SDA = 1, SCL = At completion of Start bit, 1 TBRG Write to SSPBUF occurs here hardware clears SEN bit TBRG Write to SEN bit occurs here Set S bit (SSPSTAT<3>) and sets SSPIF bit PIC18F2420/2520/4420/4520 DS39631B-page 190 Preliminary © 2007 Microchip Technology Inc. 17.4.9 I2C MASTER MODE REPEATED START CONDITION TIMING A Repeated Start condition occurs when the RSEN bit (SSPCON2<1>) is programmed high and the I2C logic module is in the Idle state. When the RSEN bit is set, the SCL pin is asserted low. When the SCL pin is sampled low, the Baud Rate Generator is loaded with the contents of SSPADD<5:0> and begins counting. The SDA pin is released (brought high) for one Baud Rate Generator count (TBRG). When the Baud Rate Generator times out, if SDA is sampled high, the SCL pin will be deasserted (brought high). When SCL is sampled high, the Baud Rate Generator is reloaded with the contents of SSPADD<6:0> and begins counting. SDA and SCL must be sampled high for one TBRG. This action is then followed by assertion of the SDA pin (SDA = 0) for one TBRG while SCL is high. Following this, the RSEN bit (SSPCON2<1>) will be automatically cleared and the Baud Rate Generator will not be reloaded, leaving the SDA pin held low. As soon as a Start condition is detected on the SDA and SCL pins, the S bit (SSPSTAT<3>) will be set. The SSPIF bit will not be set until the Baud Rate Generator has timed out. Immediately following the SSPIF bit getting set, the user may write the SSPBUF with the 7-bit address in 7-bit mode or the default first address in 10-bit mode. After the first eight bits are transmitted and an ACK is received, the user may then transmit an additional eight bits of address (10-bit mode) or eight bits of data (7-bit mode). 17.4.9.1 WCOL Status Flag If the user writes the SSPBUF when a Repeated Start sequence is in progress, the WCOL is set and the contents of the buffer are unchanged (the write doesn’t occur). FIGURE 17-20: REPEAT START CONDITION WAVEFORM Note 1: If RSEN is programmed while any other event is in progress, it will not take effect. 2: A bus collision during the Repeated Start condition occurs if: • SDA is sampled low when SCL goes from low-to-high. • SCL goes low before SDA is asserted low. This may indicate that another master is attempting to transmit a data ‘1’. Note: Because queueing of events is not allowed, writing of the lower 5 bits of SSPCON2 is disabled until the Repeated Start condition is complete. SDA SCL Sr = Repeated Start Write to SSPCON2 on falling edge of ninth clock, Write to SSPBUF occurs here end of Xmit At completion of Start bit, hardware clears RSEN bit 1st bit S bit set by hardware TBRG TBRG SDA = 1, SDA = 1, SCL (no change). SCL = 1 occurs here. TBRG TBRG TBRG and sets SSPIF RSEN bit set by hardware © 2007 Microchip Technology Inc. Preliminary DS39631B-page 191 PIC18F2420/2520/4420/4520 17.4.10 I2C MASTER MODE TRANSMISSION Transmission of a data byte, a 7-bit address or the other half of a 10-bit address is accomplished by simply writing a value to the SSPBUF register. This action will set the Buffer Full flag bit, BF and allow the Baud Rate Generator to begin counting and start the next transmission. Each bit of address/data will be shifted out onto the SDA pin after the falling edge of SCL is asserted (see data hold time specification parameter 106). SCL is held low for one Baud Rate Generator rollover count (TBRG). Data should be valid before SCL is released high (see data setup time specification parameter 107). When the SCL pin is released high, it is held that way for TBRG. The data on the SDA pin must remain stable for that duration and some hold time after the next falling edge of SCL. After the eighth bit is shifted out (the falling edge of the eighth clock), the BF flag is cleared and the master releases SDA. This allows the slave device being addressed to respond with an ACK bit during the ninth bit time if an address match occurred, or if data was received properly. The status of ACK is written into the ACKDT bit on the falling edge of the ninth clock. If the master receives an Acknowledge, the Acknowledge Status bit, ACKSTAT, is cleared. If not, the bit is set. After the ninth clock, the SSPIF bit is set and the master clock (Baud Rate Generator) is suspended until the next data byte is loaded into the SSPBUF, leaving SCL low and SDA unchanged (Figure 17-21). After the write to the SSPBUF, each bit of the address will be shifted out on the falling edge of SCL until all seven address bits and the R/W bit are completed. On the falling edge of the eighth clock, the master will deassert the SDA pin, allowing the slave to respond with an Acknowledge. On the falling edge of the ninth clock, the master will sample the SDA pin to see if the address was recognized by a slave. The status of the ACK bit is loaded into the ACKSTAT status bit (SSPCON2<6>). Following the falling edge of the ninth clock transmission of the address, the SSPIF is set, the BF flag is cleared and the Baud Rate Generator is turned off until another write to the SSPBUF takes place, holding SCL low and allowing SDA to float. 17.4.10.1 BF Status Flag In Transmit mode, the BF bit (SSPSTAT<0>) is set when the CPU writes to SSPBUF and is cleared when all 8 bits are shifted out. 17.4.10.2 WCOL Status Flag If the user writes the SSPBUF when a transmit is already in progress (i.e., SSPSR is still shifting out a data byte), the WCOL is set and the contents of the buffer are unchanged (the write doesn’t occur). WCOL must be cleared in software. 17.4.10.3 ACKSTAT Status Flag In Transmit mode, the ACKSTAT bit (SSPCON2<6>) is cleared when the slave has sent an Acknowledge (ACK = 0) and is set when the slave does not Acknowledge (ACK = 1). A slave sends an Acknowledge when it has recognized its address (including a general call), or when the slave has properly received its data. 17.4.11 I2C MASTER MODE RECEPTION Master mode reception is enabled by programming the Receive Enable bit, RCEN (SSPCON2<3>). The Baud Rate Generator begins counting and on each rollover, the state of the SCL pin changes (high-to-low/ low-to-high) and data is shifted into the SSPSR. After the falling edge of the eighth clock, the receive enable flag is automatically cleared, the contents of the SSPSR are loaded into the SSPBUF, the BF flag bit is set, the SSPIF flag bit is set and the Baud Rate Generator is suspended from counting, holding SCL low. The MSSP is now in Idle state awaiting the next command. When the buffer is read by the CPU, the BF flag bit is automatically cleared. The user can then send an Acknowledge bit at the end of reception by setting the Acknowledge Sequence Enable bit, ACKEN (SSPCON2<4>). 17.4.11.1 BF Status Flag In receive operation, the BF bit is set when an address or data byte is loaded into SSPBUF from SSPSR. It is cleared when the SSPBUF register is read. 17.4.11.2 SSPOV Status Flag In receive operation, the SSPOV bit is set when 8 bits are received into the SSPSR and the BF flag bit is already set from a previous reception. 17.4.11.3 WCOL Status Flag If the user writes the SSPBUF when a receive is already in progress (i.e., SSPSR is still shifting in a data byte), the WCOL bit is set and the contents of the buffer are unchanged (the write doesn’t occur). Note: The MSSP module must be in an Idle state before the RCEN bit is set or the RCEN bit will be disregarded. PIC18F2420/2520/4420/4520 DS39631B-page 192 Preliminary © 2007 Microchip Technology Inc. FIGURE 17-21: I2C MASTER MODE WAVEFORM (TRANSMISSION, 7 OR 10-BIT ADDRESS) SDA SCL SSPIF BF (SSPSTAT<0>) SEN A7 A6 A5 A4 A3 A2 A1 ACK = ‘0’ D7 D6 D5 D4 D3 D2 D1 D0 ACK Transmitting Data or Second Half Transmit Address to Slave R/W = 0 1 2 3 4 5 6 7 8 9 1 2 3 4 5 6 7 8 9 P Cleared in software service routine SSPBUF is written in software from SSP interrupt After Start condition, SEN cleared by hardware S SSPBUF written with 7-bit address and R/W start transmit SCL held low while CPU responds to SSPIF SEN = 0 of 10-bit Address Write SSPCON2<0> SEN = 1 Start condition begins From slave, clear ACKSTAT bit SSPCON2<6> ACKSTAT in SSPCON2 = 1 Cleared in software SSPBUF written PEN R/W Cleared in software © 2007 Microchip Technology Inc. Preliminary DS39631B-page 193 PIC18F2420/2520/4420/4520 FIGURE 17-22: I2C MASTER MODE WAVEFORM (RECEPTION, 7-BIT ADDRESS) P 5 6 7 8 9 D7 D6 D5 D4 D3 D2 D1 D0 S SDA A7 A6 A5 A4 A3 A2 A1 SCL 1 2 3 4 5 6 7 8 9 1 2 3 4 5 6 7 8 9 1 2 3 4 Bus master terminates transfer ACK Receiving Data from Slave Receiving Data from Slave ACK D7 D6 D5 D4 D3 D2 D1 D0 Transmit Address to Slave R/W = 0 SSPIF BF ACK is not sent Write to SSPCON2<0> (SEN = 1), Write to SSPBUF occurs here, ACK from Slave Master configured as a receiver by programming SSPCON2<3> (RCEN = 1) PEN bit = 1 written here Data shifted in on falling edge of CLK Cleared in software start XMIT SEN = 0 SSPOV SDA = 0, SCL = 1 while CPU (SSPSTAT<0>) ACK Cleared in software Cleared in software Set SSPIF interrupt at end of receive Set P bit (SSPSTAT<4>) and SSPIF Cleared in software ACK from Master Set SSPIF at end Set SSPIF interrupt at end of Acknowledge sequence Set SSPIF interrupt at end of Acknowledge sequence of receive Set ACKEN, start Acknowledge sequence SSPOV is set because SSPBUF is still full SDA = ACKDT = 1 RCEN cleared automatically RCEN = 1, start next receive Write to SSPCON2<4> to start Acknowledge sequence SDA = ACKDT (SSPCON2<5>) = 0 RCEN cleared automatically responds to SSPIF ACKEN begin Start condition Cleared in software SDA = ACKDT = 0 Last bit is shifted into SSPSR and contents are unloaded into SSPBUF PIC18F2420/2520/4420/4520 DS39631B-page 194 Preliminary © 2007 Microchip Technology Inc. 17.4.12 ACKNOWLEDGE SEQUENCE TIMING An Acknowledge sequence is enabled by setting the Acknowledge Sequence Enable bit, ACKEN (SSPCON2<4>). When this bit is set, the SCL pin is pulled low and the contents of the Acknowledge data bit are presented on the SDA pin. If the user wishes to generate an Acknowledge, then the ACKDT bit should be cleared. If not, the user should set the ACKDT bit before starting an Acknowledge sequence. The Baud Rate Generator then counts for one rollover period (TBRG) and the SCL pin is deasserted (pulled high). When the SCL pin is sampled high (clock arbitration), the Baud Rate Generator counts for TBRG. The SCL pin is then pulled low. Following this, the ACKEN bit is automatically cleared, the Baud Rate Generator is turned off and the MSSP module then goes into Idle mode (Figure 17-23). 17.4.12.1 WCOL Status Flag If the user writes the SSPBUF when an Acknowledge sequence is in progress, then WCOL is set and the contents of the buffer are unchanged (the write doesn’t occur). 17.4.13 STOP CONDITION TIMING A Stop bit is asserted on the SDA pin at the end of a receive/transmit by setting the Stop Sequence Enable bit, PEN (SSPCON2<2>). At the end of a receive/ transmit, the SCL line is held low after the falling edge of the ninth clock. When the PEN bit is set, the master will assert the SDA line low. When the SDA line is sampled low, the Baud Rate Generator is reloaded and counts down to ‘0’. When the Baud Rate Generator times out, the SCL pin will be brought high and one TBRG (Baud Rate Generator rollover count) later, the SDA pin will be deasserted. When the SDA pin is sampled high while SCL is high, the P bit (SSPSTAT<4>) is set. A TBRG later, the PEN bit is cleared and the SSPIF bit is set (Figure 17-24). 17.4.13.1 WCOL Status Flag If the user writes the SSPBUF when a Stop sequence is in progress, then the WCOL bit is set and the contents of the buffer are unchanged (the write doesn’t occur). FIGURE 17-23: ACKNOWLEDGE SEQUENCE WAVEFORM FIGURE 17-24: STOP CONDITION RECEIVE OR TRANSMIT MODE Note: TBRG = one Baud Rate Generator period. SDA SCL SSPIF set at Acknowledge sequence starts here, write to SSPCON2 ACKEN automatically cleared Cleared in TBRG TBRG the end of receive 8 ACKEN = 1, ACKDT = 0 D0 9 SSPIF software SSPIF set at the end of Acknowledge sequence Cleared in software ACK SCL SDA SDA asserted low before rising edge of clock Write to SSPCON2, set PEN Falling edge of SCL = 1 for TBRG, followed by SDA = 1 for TBRG 9th clock SCL brought high after TBRG Note: TBRG = one Baud Rate Generator period. TBRG TBRG after SDA sampled high. P bit (SSPSTAT<4>) is set. TBRG to setup Stop condition ACK P TBRG PEN bit (SSPCON2<2>) is cleared by hardware and the SSPIF bit is set © 2007 Microchip Technology Inc. Preliminary DS39631B-page 195 PIC18F2420/2520/4420/4520 17.4.14 SLEEP OPERATION While in Sleep mode, the I2C module can receive addresses or data and when an address match or complete byte transfer occurs, wake the processor from Sleep (if the MSSP interrupt is enabled). 17.4.15 EFFECTS OF A RESET A Reset disables the MSSP module and terminates the current transfer. 17.4.16 MULTI-MASTER MODE In Multi-Master mode, the interrupt generation on the detection of the Start and Stop conditions allows the determination of when the bus is free. The Stop (P) and Start (S) bits are cleared from a Reset or when the MSSP module is disabled. Control of the I2C bus may be taken when the P bit (SSPSTAT<4>) is set, or the bus is Idle, with both the S and P bits clear. When the bus is busy, enabling the SSP interrupt will generate the interrupt when the Stop condition occurs. In multi-master operation, the SDA line must be monitored for arbitration to see if the signal level is the expected output level. This check is performed in hardware with the result placed in the BCLIF bit. The states where arbitration can be lost are: • Address Transfer • Data Transfer • A Start Condition • A Repeated Start Condition • An Acknowledge Condition 17.4.17 MULTI -MASTER COMMUNICATION, BUS COLLISION AND BUS ARBITRATION Multi-Master mode support is achieved by bus arbitration. When the master outputs address/data bits onto the SDA pin, arbitration takes place when the master outputs a ‘1’ on SDA, by letting SDA float high and another master asserts a ‘0’. When the SCL pin floats high, data should be stable. If the expected data on SDA is a ‘1’ and the data sampled on the SDA pin = 0, then a bus collision has taken place. The master will set the Bus Collision Interrupt Flag, BCLIF and reset the I2C port to its Idle state (Figure 17-25). If a transmit was in progress when the bus collision occurred, the transmission is halted, the BF flag is cleared, the SDA and SCL lines are deasserted and the SSPBUF can be written to. When the user services the bus collision Interrupt Service Routine and if the I2C bus is free, the user can resume communication by asserting a Start condition. If a Start, Repeated Start, Stop or Acknowledge condition was in progress when the bus collision occurred, the condition is aborted, the SDA and SCL lines are deasserted and the respective control bits in the SSPCON2 register are cleared. When the user services the bus collision Interrupt Service Routine and if the I2C bus is free, the user can resume communication by asserting a Start condition. The master will continue to monitor the SDA and SCL pins. If a Stop condition occurs, the SSPIF bit will be set. A write to the SSPBUF will start the transmission of data at the first data bit, regardless of where the transmitter left off when the bus collision occurred. In Multi-Master mode, the interrupt generation on the detection of Start and Stop conditions allows the determination of when the bus is free. Control of the I2C bus can be taken when the P bit is set in the SSPSTAT register, or the bus is Idle and the S and P bits are cleared. FIGURE 17-25: BUS COLLISION TIMING FOR TRANSMIT AND ACKNOWLEDGE SDA SCL BCLIF SDA released SDA line pulled low by another source Sample SDA. While SCL is high, data doesn’t match what is driven Bus collision has occurred. Set bus collision interrupt (BCLIF) by the master. by master Data changes while SCL = 0 PIC18F2420/2520/4420/4520 DS39631B-page 196 Preliminary © 2007 Microchip Technology Inc. 17.4.17.1 Bus Collision During a Start Condition During a Start condition, a bus collision occurs if: a) SDA or SCL are sampled low at the beginning of the Start condition (Figure 17-26). b) SCL is sampled low before SDA is asserted low (Figure 17-27). During a Start condition, both the SDA and the SCL pins are monitored. If the SDA pin is already low, or the SCL pin is already low, then all of the following occur: • the Start condition is aborted, • the BCLIF flag is set and • the MSSP module is reset to its Idle state (Figure 17-26). The Start condition begins with the SDA and SCL pins deasserted. When the SDA pin is sampled high, the Baud Rate Generator is loaded from SSPADD<6:0> and counts down to 0. If the SCL pin is sampled low while SDA is high, a bus collision occurs because it is assumed that another master is attempting to drive a data ‘1’ during the Start condition. If the SDA pin is sampled low during this count, the BRG is reset and the SDA line is asserted early (Figure 17-28). If, however, a ‘1’ is sampled on the SDA pin, the SDA pin is asserted low at the end of the BRG count. The Baud Rate Generator is then reloaded and counts down to 0; if the SCL pin is sampled as ‘0’ during this time, a bus collision does not occur. At the end of the BRG count, the SCL pin is asserted low. FIGURE 17-26: BUS COLLISION DURING START CONDITION (SDA ONLY) Note: The reason that bus collision is not a factor during a Start condition is that no two bus masters can assert a Start condition at the exact same time. Therefore, one master will always assert SDA before the other. This condition does not cause a bus collision because the two masters must be allowed to arbitrate the first address following the Start condition. If the address is the same, arbitration must be allowed to continue into the data portion, Repeated Start or Stop conditions. SDA SCL SEN SDA sampled low before SDA goes low before the SEN bit is set. S bit and SSPIF set because SSP module reset into Idle state. SEN cleared automatically because of bus collision. S bit and SSPIF set because Set SEN, enable Start condition if SDA = 1, SCL = 1 SDA = 0, SCL = 1. BCLIF S SSPIF SDA = 0, SCL = 1. SSPIF and BCLIF are cleared in software SSPIF and BCLIF are cleared in software Set BCLIF, Start condition. Set BCLIF. © 2007 Microchip Technology Inc. Preliminary DS39631B-page 197 PIC18F2420/2520/4420/4520 FIGURE 17-27: BUS COLLISION DURING START CONDITION (SCL = 0) FIGURE 17-28: BRG RESET DUE TO SDA ARBITRATION DURING START CONDITION SDA SCL SEN bus collision occurs. Set BCLIF. SCL = 0 before SDA = 0, Set SEN, enable Start sequence if SDA = 1, SCL = 1 TBRG TBRG SDA = 0, SCL = 1 BCLIF S SSPIF Interrupt cleared in software bus collision occurs. Set BCLIF. SCL = 0 before BRG time-out, ‘0’ ‘0’ ‘0’ ‘0’ SDA SCL SEN Set S Less than TBRG TBRG SDA = 0, SCL = 1 BCLIF S SSPIF S Interrupts cleared set SSPIF in software SDA = 0, SCL = 1, SCL pulled low after BRG time-out Set SSPIF ‘0’ SDA pulled low by other master. Reset BRG and assert SDA. Set SEN, enable START sequence if SDA = 1, SCL = 1 PIC18F2420/2520/4420/4520 DS39631B-page 198 Preliminary © 2007 Microchip Technology Inc. 17.4.17.2 Bus Collision During a Repeated Start Condition During a Repeated Start condition, a bus collision occurs if: a) A low level is sampled on SDA when SCL goes from low level to high level. b) SCL goes low before SDA is asserted low, indicating that another master is attempting to transmit a data ‘1’. When the user deasserts SDA and the pin is allowed to float high, the BRG is loaded with SSPADD<6:0> and counts down to 0. The SCL pin is then deasserted and when sampled high, the SDA pin is sampled. If SDA is low, a bus collision has occurred (i.e., another master is attempting to transmit a data ‘0’, Figure 17-29). If SDA is sampled high, the BRG is reloaded and begins counting. If SDA goes from high-to-low before the BRG times out, no bus collision occurs because no two masters can assert SDA at exactly the same time. If SCL goes from high-to-low before the BRG times out and SDA has not already been asserted, a bus collision occurs. In this case, another master is attempting to transmit a data ‘1’ during the Repeated Start condition, see Figure 17-30. If, at the end of the BRG time-out, both SCL and SDA are still high, the SDA pin is driven low and the BRG is reloaded and begins counting. At the end of the count, regardless of the status of the SCL pin, the SCL pin is driven low and the Repeated Start condition is complete. FIGURE 17-29: BUS COLLISION DURING A REPEATED START CONDITION (CASE 1) FIGURE 17-30: BUS COLLISION DURING REPEATED START CONDITION (CASE 2) SDA SCL RSEN BCLIF S SSPIF Sample SDA when SCL goes high. If SDA = 0, set BCLIF and release SDA and SCL. Cleared in software ‘0’ ‘0’ SDA SCL BCLIF RSEN S SSPIF Interrupt cleared in software SCL goes low before SDA, set BCLIF. Release SDA and SCL. TBRG TBRG ‘0’ © 2007 Microchip Technology Inc. Preliminary DS39631B-page 199 PIC18F2420/2520/4420/4520 17.4.17.3 Bus Collision During a Stop Condition Bus collision occurs during a Stop condition if: a) After the SDA pin has been deasserted and allowed to float high, SDA is sampled low after the BRG has timed out. b) After the SCL pin is deasserted, SCL is sampled low before SDA goes high. The Stop condition begins with SDA asserted low. When SDA is sampled low, the SCL pin is allowed to float. When the pin is sampled high (clock arbitration), the Baud Rate Generator is loaded with SSPADD<6:0> and counts down to 0. After the BRG times out, SDA is sampled. If SDA is sampled low, a bus collision has occurred. This is due to another master attempting to drive a data ‘0’ (Figure 17-31). If the SCL pin is sampled low before SDA is allowed to float high, a bus collision occurs. This is another case of another master attempting to drive a data ‘0’ (Figure 17-32). FIGURE 17-31: BUS COLLISION DURING A STOP CONDITION (CASE 1) FIGURE 17-32: BUS COLLISION DURING A STOP CONDITION (CASE 2) SDA SCL BCLIF PEN P SSPIF TBRG TBRG TBRG SDA asserted low SDA sampled low after TBRG, set BCLIF ‘0’ ‘0’ SDA SCL BCLIF PEN P SSPIF TBRG TBRG TBRG Assert SDA SCL goes low before SDA goes high, set BCLIF ‘0’ ‘0’ PIC18F2420/2520/4420/4520 DS39631B-page 200 Preliminary © 2007 Microchip Technology Inc. NOTES: © 2007 Microchip Technology Inc. Preliminary DS39631B-page 201 PIC18F2420/2520/4420/4520 18.0 ENHANCED UNIVERSAL SYNCHRONOUS RECEIVER TRANSMITTER (EUSART) The Enhanced Universal Synchronous Asynchronous Receiver Transmitter (EUSART) module is one of the two serial I/O modules. (Generically, the USART is also known as a Serial Communications Interface or SCI.) The EUSART can be configured as a full-duplex asynchronous system that can communicate with peripheral devices, such as CRT terminals and personal computers. It can also be configured as a halfduplex synchronous system that can communicate with peripheral devices, such as A/D or D/A integrated circuits, serial EEPROMs, etc. The Enhanced USART module implements additional features, including automatic baud rate detection and calibration, automatic wake-up on Sync Break reception and 12-bit Break character transmit. These make it ideally suited for use in Local Interconnect Network bus (LIN bus) systems. The EUSART can be configured in the following modes: • Asynchronous (full duplex) with: - Auto-wake-up on character reception - Auto-baud calibration - 12-bit Break character transmission • Synchronous – Master (half duplex) with selectable clock polarity • Synchronous – Slave (half duplex) with selectable clock polarity The pins of the Enhanced USART are multiplexed with PORTC. In order to configure RC6/TX/CK and RC7/RX/DT as a USART: • bit SPEN (RCSTA<7>) must be set (= 1) • bit TRISC<7> must be set (= 1) • bit TRISC<6> must be set (= 1) The operation of the Enhanced USART module is controlled through three registers: • Transmit Status and Control (TXSTA) • Receive Status and Control (RCSTA) • Baud Rate Control (BAUDCON) These are detailed on the following pages in Register 18-1, Register 18-2 and Register 18-3, respectively. Note: The EUSART control will automatically reconfigure the pin from input to output as needed. PIC18F2420/2520/4420/4520 DS39631B-page 202 Preliminary © 2007 Microchip Technology Inc. REGISTER 18-1: TXSTA: TRANSMIT STATUS AND CONTROL REGISTER R/W-0 R/W-0 R/W-0 R/W-0 R/W-0 R/W-0 R-1 R/W-0 CSRC TX9 TXEN SYNC SENDB BRGH TRMT TX9D bit 7 bit 0 bit 7 CSRC: Clock Source Select bit Asynchronous mode: Don’t care. Synchronous mode: 1 = Master mode (clock generated internally from BRG) 0 = Slave mode (clock from external source) bit 6 TX9: 9-bit Transmit Enable bit 1 = Selects 9-bit transmission 0 = Selects 8-bit transmission bit 5 TXEN: Transmit Enable bit 1 = Transmit enabled 0 = Transmit disabled Note: SREN/CREN overrides TXEN in Sync mode. bit 4 SYNC: EUSART Mode Select bit 1 = Synchronous mode 0 = Asynchronous mode bit 3 SENDB: Send Break Character bit Asynchronous mode: 1 = Send Sync Break on next transmission (cleared by hardware upon completion) 0 = Sync Break transmission completed Synchronous mode: Don’t care. bit 2 BRGH: High Baud Rate Select bit Asynchronous mode: 1 = High speed 0 = Low speed Synchronous mode: Unused in this mode. bit 1 TRMT: Transmit Shift Register Status bit 1 = TSR empty 0 = TSR full bit 0 TX9D: 9th bit of Transmit Data Can be address/data bit or a parity bit. Legend: R = Readable bit W = Writable bit U = Unimplemented bit, read as ‘0’ -n = Value at POR ‘1’ = Bit is set ‘0’ = Bit is cleared x = Bit is unknown © 2007 Microchip Technology Inc. Preliminary DS39631B-page 203 PIC18F2420/2520/4420/4520 REGISTER 18-2: RCSTA: RECEIVE STATUS AND CONTROL REGISTER R/W-0 R/W-0 R/W-0 R/W-0 R/W-0 R-0 R-0 R-x SPEN RX9 SREN CREN ADDEN FERR OERR RX9D bit 7 bit 0 bit 7 SPEN: Serial Port Enable bit 1 = Serial port enabled (configures RX/DT and TX/CK pins as serial port pins) 0 = Serial port disabled (held in Reset) bit 6 RX9: 9-bit Receive Enable bit 1 = Selects 9-bit reception 0 = Selects 8-bit reception bit 5 SREN: Single Receive Enable bit Asynchronous mode: Don’t care. Synchronous mode – Master: 1 = Enables single receive 0 = Disables single receive This bit is cleared after reception is complete. Synchronous mode – Slave: Don’t care. bit 4 CREN: Continuous Receive Enable bit Asynchronous mode: 1 = Enables receiver 0 = Disables receiver Synchronous mode: 1 = Enables continuous receive until enable bit CREN is cleared (CREN overrides SREN) 0 = Disables continuous receive bit 3 ADDEN: Address Detect Enable bit Asynchronous mode 9-bit (RX9 = 1): 1 = Enables address detection, enables interrupt and loads the receive buffer when RSR<8> is set 0 = Disables address detection, all bytes are received and ninth bit can be used as parity bit Asynchronous mode 9-bit (RX9 = 0): Don’t care. bit 2 FERR: Framing Error bit 1 = Framing error (can be updated by reading RCREG register and receiving next valid byte) 0 = No framing error bit 1 OERR: Overrun Error bit 1 = Overrun error (can be cleared by clearing bit CREN) 0 = No overrun error bit 0 RX9D: 9th bit of Received Data This can be address/data bit or a parity bit and must be calculated by user firmware. Legend: R = Readable bit W = Writable bit U = Unimplemented bit, read as ‘0’ -n = Value at POR ‘1’ = Bit is set ‘0’ = Bit is cleared x = Bit is unknown PIC18F2420/2520/4420/4520 DS39631B-page 204 Preliminary © 2007 Microchip Technology Inc. REGISTER 18-3: BAUDCON: BAUD RATE CONTROL REGISTER R/W-0 R-1 U-0 R/W-0 R/W-0 U-0 R/W-0 R/W-0 ABDOVF RCIDL — SCKP BRG16 — WUE ABDEN bit 7 bit 0 bit 7 ABDOVF: Auto-Baud Acquisition Rollover Status bit 1 = A BRG rollover has occurred during Auto-Baud Rate Detect mode (must be cleared in software) 0 = No BRG rollover has occurred bit 6 RCIDL: Receive Operation Idle Status bit 1 = Receive operation is Idle 0 = Receive operation is active bit 5 Unimplemented: Read as ‘0’ bit 4 SCKP: Synchronous Clock Polarity Select bit Asynchronous mode: Unused in this mode. Synchronous mode: 1 = Idle state for clock (CK) is a high level 0 = Idle state for clock (CK) is a low level bit 3 BRG16: 16-bit Baud Rate Register Enable bit 1 = 16-bit Baud Rate Generator – SPBRGH and SPBRG 0 = 8-bit Baud Rate Generator – SPBRG only (Compatible mode), SPBRGH value ignored bit 2 Unimplemented: Read as ‘0’ bit 1 WUE: Wake-up Enable bit Asynchronous mode: 1 = EUSART will continue to sample the RX pin – interrupt generated on falling edge; bit cleared in hardware on following rising edge 0 = RX pin not monitored or rising edge detected Synchronous mode: Unused in this mode. bit 0 ABDEN: Auto-Baud Detect Enable bit Asynchronous mode: 1 = Enable baud rate measurement on the next character. Requires reception of a Sync field (55h); cleared in hardware upon completion 0 = Baud rate measurement disabled or completed Synchronous mode: Unused in this mode. Legend: R = Readable bit W = Writable bit U = Unimplemented bit, read as ‘0’ -n = Value at POR ‘1’ = Bit is set ‘0’ = Bit is cleared x = Bit is unknown © 2007 Microchip Technology Inc. Preliminary DS39631B-page 205 PIC18F2420/2520/4420/4520 18.1 Baud Rate Generator (BRG) The BRG is a dedicated 8-bit or 16-bit generator that supports both the Asynchronous and Synchronous modes of the EUSART. By default, the BRG operates in 8-bit mode; setting the BRG16 bit (BAUDCON<3>) selects 16-bit mode. The SPBRGH:SPBRG register pair controls the period of a free running timer. In Asynchronous mode, bits BRGH (TXSTA<2>) and BRG16 (BAUDCON<3>) also control the baud rate. In Synchronous mode, BRGH is ignored. Table 18-1 shows the formula for computation of the baud rate for different EUSART modes which only apply in Master mode (internally generated clock). Given the desired baud rate and FOSC, the nearest integer value for the SPBRGH:SPBRG registers can be calculated using the formulas in Table 18-1. From this, the error in baud rate can be determined. An example calculation is shown in Example 18-1. Typical baud rates and error values for the various Asynchronous modes are shown in Table 18-2. It may be advantageous to use the high baud rate (BRGH = 1) or the 16-bit BRG to reduce the baud rate error, or achieve a slow baud rate for a fast oscillator frequency. Writing a new value to the SPBRGH:SPBRG registers causes the BRG timer to be reset (or cleared). This ensures the BRG does not wait for a timer overflow before outputting the new baud rate. 18.1.1 OPERATION IN POWER MANAGED MODES The device clock is used to generate the desired baud rate. When one of the power managed modes is entered, the new clock source may be operating at a different frequency. This may require an adjustment to the value in the SPBRG register pair. 18.1.2 SAMPLING The data on the RX pin is sampled three times by a majority detect circuit to determine if a high or a low level is present at the RX pin. TABLE 18-1: BAUD RATE FORMULAS Configuration Bits BRG/EUSART Mode Baud Rate Formula SYNC BRG16 BRGH 0 0 0 8-bit/Asynchronous FOSC/[64 (n + 1)] 0 0 1 8-bit/Asynchronous FOSC/[16 (n + 1)] 0 1 0 16-bit/Asynchronous 0 1 1 16-bit/Asynchronous 1 0 x 8-bit/Synchronous FOSC/[4 (n + 1)] 1 1 x 16-bit/Synchronous Legend: x = Don’t care, n = value of SPBRGH:SPBRG register pair PIC18F2420/2520/4420/4520 DS39631B-page 206 Preliminary © 2007 Microchip Technology Inc. EXAMPLE 18-1: CALCULATING BAUD RATE ERROR TABLE 18-2: REGISTERS ASSOCIATED WITH BAUD RATE GENERATOR For a device with FOSC of 16 MHz, desired baud rate of 9600, Asynchronous mode, 8-bit BRG: Desired Baud Rate = FOSC/(64 ([SPBRGH:SPBRG] + 1)) Solving for SPBRGH:SPBRG: X = ((FOSC/Desired Baud Rate)/64) – 1 = ((16000000/9600)/64) – 1 = [25.042] = 25 Calculated Baud Rate = 16000000/(64 (25 + 1)) = 9615 Error = (Calculated Baud Rate – Desired Baud Rate)/Desired Baud Rate = (9615 – 9600)/9600 = 0.16% Name Bit 7 Bit 6 Bit 5 Bit 4 Bit 3 Bit 2 Bit 1 Bit 0 Reset Values on page TXSTA CSRC TX9 TXEN SYNC SENDB BRGH TRMT TX9D 51 RCSTA SPEN RX9 SREN CREN ADDEN FERR OERR RX9D 51 BAUDCON ABDOVF RCIDL — SCKP BRG16 — WUE ABDEN 51 SPBRGH EUSART Baud Rate Generator Register, High Byte 51 SPBRG EUSART Baud Rate Generator Register, Low Byte 51 Legend: — = unimplemented, read as ‘0’. Shaded cells are not used by the BRG. © 2007 Microchip Technology Inc. Preliminary DS39631B-page 207 PIC18F2420/2520/4420/4520 TABLE 18-3: BAUD RATES FOR ASYNCHRONOUS MODES BAUD RATE (K) SYNC = 0, BRGH = 0, BRG16 = 0 FOSC = 40.000 MHz FOSC = 20.000 MHz FOSC = 10.000 MHz FOSC = 8.000 MHz Actual Rate (K) % Error SPBRG value (decimal) Actual Rate (K) % Error SPBRG value (decimal) Actual Rate (K) % Error SPBRG value (decimal) Actual Rate (K) % Error SPBRG value (decimal) 0.3 — — — — — — — — — — — — 1.2 — — — 1.221 1.73 255 1.202 0.16 129 1201 -0.16 103 2.4 2.441 1.73 255 2.404 0.16 129 2.404 0.16 64 2403 -0.16 51 9.6 9.615 0.16 64 9.766 1.73 31 9.766 1.73 15 9615 -0.16 12 19.2 19.531 1.73 31 19.531 1.73 15 19.531 1.73 7 — — — 57.6 56.818 -1.36 10 62.500 8.51 4 52.083 -9.58 2 — — — 115.2 125.000 8.51 4 104.167 -9.58 2 78.125 -32.18 1 — — — BAUD RATE (K) SYNC = 0, BRGH = 0, BRG16 = 0 FOSC = 4.000 MHz FOSC = 2.000 MHz FOSC = 1.000 MHz Actual Rate (K) % Error SPBRG value (decimal) Actual Rate (K) % Error SPBRG value (decimal) Actual Rate (K) % Error SPBRG value (decimal) 0.3 0.300 0.16 207 300 -0.16 103 300 -0.16 51 1.2 1.202 0.16 51 1201 -0.16 25 1201 -0.16 12 2.4 2.404 0.16 25 2403 -0.16 12 — — — 9.6 8.929 -6.99 6 — — — — — — 19.2 20.833 8.51 2 — — — — — — 57.6 62.500 8.51 0 — — — — — — 115.2 62.500 -45.75 0 — — — — — — BAUD RATE (K) SYNC = 0, BRGH = 1, BRG16 = 0 FOSC = 40.000 MHz FOSC = 20.000 MHz FOSC = 10.000 MHz FOSC = 8.000 MHz Actual Rate (K) % Error SPBRG value (decimal) Actual Rate (K) % Error SPBRG value (decimal) Actual Rate (K) % Error SPBRG value (decimal) Actual Rate (K) % Error SPBRG value (decimal) 0.3 — — — — — — — — — — — — 1.2 — — — — — — — — — — — — 2.4 — — — — — — 2.441 1.73 255 2403 -0.16 207 9.6 9.766 1.73 255 9.615 0.16 129 9.615 0.16 64 9615 -0.16 51 19.2 19.231 0.16 129 19.231 0.16 64 19.531 1.73 31 19230 -0.16 25 57.6 58.140 0.94 42 56.818 -1.36 21 56.818 -1.36 10 55555 3.55 8 115.2 113.636 -1.36 21 113.636 -1.36 10 125.000 8.51 4 — — — BAUD RATE (K) SYNC = 0, BRGH = 1, BRG16 = 0 FOSC = 4.000 MHz FOSC = 2.000 MHz FOSC = 1.000 MHz Actual Rate (K) % Error SPBRG value (decimal) Actual Rate (K) % Error SPBRG value (decimal) Actual Rate (K) % Error SPBRG value (decimal) 0.3 — — — — — — 300 -0.16 207 1.2 1.202 0.16 207 1201 -0.16 103 1201 -0.16 51 2.4 2.404 0.16 103 2403 -0.16 51 2403 -0.16 25 9.6 9.615 0.16 25 9615 -0.16 12 — — — 19.2 19.231 0.16 12 — — — — — — 57.6 62.500 8.51 3 — — — — — — 115.2 125.000 8.51 1 — — — — — — PIC18F2420/2520/4420/4520 DS39631B-page 208 Preliminary © 2007 Microchip Technology Inc. BAUD RATE (K) SYNC = 0, BRGH = 0, BRG16 = 1 FOSC = 40.000 MHz FOSC = 20.000 MHz FOSC = 10.000 MHz FOSC = 8.000 MHz Actual Rate (K) % Error SPBRG value (decimal) Actual Rate (K) % Error SPBRG value (decimal) Actual Rate (K) % Error SPBRG value (decimal) Actual Rate (K) % Error SPBRG value (decimal) 0.3 0.300 0.00 8332 0.300 0.02 4165 0.300 0.02 2082 300 -0.04 1665 1.2 1.200 0.02 2082 1.200 -0.03 1041 1.200 -0.03 520 1201 -0.16 415 2.4 2.402 0.06 1040 2.399 -0.03 520 2.404 0.16 259 2403 -0.16 207 9.6 9.615 0.16 259 9.615 0.16 129 9.615 0.16 64 9615 -0.16 51 19.2 19.231 0.16 129 19.231 0.16 64 19.531 1.73 31 19230 -0.16 25 57.6 58.140 0.94 42 56.818 -1.36 21 56.818 -1.36 10 55555 3.55 8 115.2 113.636 -1.36 21 113.636 -1.36 10 125.000 8.51 4 — — — BAUD RATE (K) SYNC = 0, BRGH = 0, BRG16 = 1 FOSC = 4.000 MHz FOSC = 2.000 MHz FOSC = 1.000 MHz Actual Rate (K) % Error SPBRG value (decimal) Actual Rate (K) % Error SPBRG value (decimal) Actual Rate (K) % Error SPBRG value (decimal) 0.3 0.300 0.04 832 300 -0.16 415 300 -0.16 207 1.2 1.202 0.16 207 1201 -0.16 103 1201 -0.16 51 2.4 2.404 0.16 103 2403 -0.16 51 2403 -0.16 25 9.6 9.615 0.16 25 9615 -0.16 12 — — — 19.2 19.231 0.16 12 — — — — — — 57.6 62.500 8.51 3 — — — — — — 115.2 125.000 8.51 1 — — — — — — BAUD RATE (K) SYNC = 0, BRGH = 1, BRG16 = 1 or SYNC = 1, BRG16 = 1 FOSC = 40.000 MHz FOSC = 20.000 MHz FOSC = 10.000 MHz FOSC = 8.000 MHz Actual Rate (K) % Error SPBRG value (decimal) Actual Rate (K) % Error SPBRG value (decimal) Actual Rate (K) % Error SPBRG value (decimal) Actual Rate (K) % Error SPBRG value (decimal) 0.3 0.300 0.00 33332 0.300 0.00 16665 0.300 0.00 8332 300 -0.01 6665 1.2 1.200 0.00 8332 1.200 0.02 4165 1.200 0.02 2082 1200 -0.04 1665 2.4 2.400 0.02 4165 2.400 0.02 2082 2.402 0.06 1040 2400 -0.04 832 9.6 9.606 0.06 1040 9.596 -0.03 520 9.615 0.16 259 9615 -0.16 207 19.2 19.193 -0.03 520 19.231 0.16 259 19.231 0.16 129 19230 -0.16 103 57.6 57.803 0.35 172 57.471 -0.22 86 58.140 0.94 42 57142 0.79 34 115.2 114.943 -0.22 86 116.279 0.94 42 113.636 -1.36 21 117647 -2.12 16 BAUD RATE (K) SYNC = 0, BRGH = 1, BRG16 = 1 or SYNC = 1, BRG16 = 1 FOSC = 4.000 MHz FOSC = 2.000 MHz FOSC = 1.000 MHz Actual Rate (K) % Error SPBRG value (decimal) Actual Rate (K) % Error SPBRG value (decimal) Actual Rate (K) % Error SPBRG value (decimal) 0.3 0.300 0.01 3332 300 -0.04 1665 300 -0.04 832 1.2 1.200 0.04 832 1201 -0.16 415 1201 -0.16 207 2.4 2.404 0.16 415 2403 -0.16 207 2403 -0.16 103 9.6 9.615 0.16 103 9615 -0.16 51 9615 -0.16 25 19.2 19.231 0.16 51 19230 -0.16 25 19230 -0.16 12 57.6 58.824 2.12 16 55555 3.55 8 — — — 115.2 111.111 -3.55 8 — — — — — — TABLE 18-3: BAUD RATES FOR ASYNCHRONOUS MODES (CONTINUED) © 2007 Microchip Technology Inc. Preliminary DS39631B-page 209 PIC18F2420/2520/4420/4520 18.1.3 AUTO-BAUD RATE DETECT The enhanced USART module supports the automatic detection and calibration of baud rate. This feature is active only in Asynchronous mode and while the WUE bit is clear. The automatic baud rate measurement sequence (Figure 18-1) begins whenever a Start bit is received and the ABDEN bit is set. The calculation is self-averaging. In the Auto-Baud Rate Detect (ABD) mode, the clock to the BRG is reversed. Rather than the BRG clocking the incoming RX signal, the RX signal is timing the BRG. In ABD mode, the internal Baud Rate Generator is used as a counter to time the bit period of the incoming serial byte stream. Once the ABDEN bit is set, the state machine will clear the BRG and look for a Start bit. The Auto-Baud Rate Detect must receive a byte with the value 55h (ASCII “U”, which is also the LIN bus Sync character) in order to calculate the proper bit rate. The measurement is taken over both a low and a high bit time in order to minimize any effects caused by asymmetry of the incoming signal. After a Start bit, the SPBRG begins counting up, using the preselected clock source on the first rising edge of RX. After eight bits on the RX pin or the fifth rising edge, an accumulated value totalling the proper BRG period is left in the SPBRGH:SPBRG register pair. Once the 5th edge is seen (this should correspond to the Stop bit), the ABDEN bit is automatically cleared. If a rollover of the BRG occurs (an overflow from FFFFh to 0000h), the event is trapped by the ABDOVF status bit (BAUDCON<7>). It is set in hardware by BRG rollovers and can be set or cleared by the user in software. ABD mode remains active after rollover events and the ABDEN bit remains set (Figure 18-2). While calibrating the baud rate period, the BRG registers are clocked at 1/8th the preconfigured clock rate. Note that the BRG clock will be configured by the BRG16 and BRGH bits. Independent of the BRG16 bit setting, both the SPBRG and SPBRGH will be used as a 16-bit counter. This allows the user to verify that no carry occurred for 8-bit modes by checking for 00h in the SPBRGH register. Refer to Table 18-4 for counter clock rates to the BRG. While the ABD sequence takes place, the EUSART state machine is held in Idle. The RCIF interrupt is set once the fifth rising edge on RX is detected. The value in the RCREG needs to be read to clear the RCIF interrupt. The contents of RCREG should be discarded. TABLE 18-4: BRG COUNTER CLOCK RATES 18.1.3.1 ABD and EUSART Transmission Since the BRG clock is reversed during ABD acquisition, the EUSART transmitter cannot be used during ABD. This means that whenever the ABDEN bit is set, TXREG cannot be written to. Users should also ensure that ABDEN does not become set during a transmit sequence. Failing to do this may result in unpredictable EUSART operation. Note 1: If the WUE bit is set with the ABDEN bit, Auto-Baud Rate Detection will occur on the byte following the Break character. 2: It is up to the user to determine that the incoming character baud rate is within the range of the selected BRG clock source. Some combinations of oscillator frequency and EUSART baud rates are not possible due to bit error rates. Overall system timing and communication baud rates must be taken into consideration when using the Auto-Baud Rate Detection feature. BRG16 BRGH BRG Counter Clock 0 0 FOSC/512 0 1 FOSC/128 1 0 FOSC/128 1 1 FOSC/32 Note: During the ABD sequence, SPBRG and SPBRGH are both used as a 16-bit counter, independent of BRG16 setting. PIC18F2420/2520/4420/4520 DS39631B-page 210 Preliminary © 2007 Microchip Technology Inc. FIGURE 18-1: AUTOMATIC BAUD RATE CALCULATION FIGURE 18-2: BRG OVERFLOW SEQUENCE BRG Value RX pin ABDEN bit RCIF bit Bit 0 Bit 1 (Interrupt) Read RCREG BRG Clock Start Set by User Auto-Cleared XXXXh 0000h Edge #1 Bit 2 Bit 3 Edge #2 Bit 4 Bit 5 Edge #3 Bit 6 Bit 7 Edge #4 Stop Bit Edge #5 001Ch Note: The ABD sequence requires the EUSART module to be configured in Asynchronous mode and WUE = 0. SPBRG XXXXh 1Ch SPBRGH XXXXh 00h Start Bit 0 XXXXh 0000h 0000h FFFFh BRG Clock ABDEN bit RX pin ABDOVF bit BRG Value © 2007 Microchip Technology Inc. Preliminary DS39631B-page 211 PIC18F2420/2520/4420/4520 18.2 EUSART Asynchronous Mode The Asynchronous mode of operation is selected by clearing the SYNC bit (TXSTA<4>). In this mode, the EUSART uses standard Non-Return-to-Zero (NRZ) format (one Start bit, eight or nine data bits and one Stop bit). The most common data format is 8 bits. An on-chip dedicated 8-bit/16-bit Baud Rate Generator can be used to derive standard baud rate frequencies from the oscillator. The EUSART transmits and receives the LSb first. The EUSART’s transmitter and receiver are functionally independent but use the same data format and baud rate. The Baud Rate Generator produces a clock, either x16 or x64 of the bit shift rate depending on the BRGH and BRG16 bits (TXSTA<2> and BAUDCON<3>). Parity is not supported by the hardware but can be implemented in software and stored as the 9th data bit. When operating in Asynchronous mode, the EUSART module consists of the following important elements: • Baud Rate Generator • Sampling Circuit • Asynchronous Transmitter • Asynchronous Receiver • Auto-Wake-up on Sync Break Character • 12-bit Break Character Transmit • Auto-Baud Rate Detection 18.2.1 EUSART ASYNCHRONOUS TRANSMITTER The EUSART transmitter block diagram is shown in Figure 18-3. The heart of the transmitter is the Transmit (Serial) Shift Register (TSR). The Shift register obtains its data from the Read/Write Transmit Buffer register, TXREG. The TXREG register is loaded with data in software. The TSR register is not loaded until the Stop bit has been transmitted from the previous load. As soon as the Stop bit is transmitted, the TSR is loaded with new data from the TXREG register (if available). Once the TXREG register transfers the data to the TSR register (occurs in one TCY), the TXREG register is empty and the TXIF flag bit (PIR1<4>) is set. This interrupt can be enabled or disabled by setting or clearing the interrupt enable bit, TXIE (PIE1<4>). TXIF will be set regardless of the state of TXIE; it cannot be cleared in software. TXIF is also not cleared immediately upon loading TXREG, but becomes valid in the second instruction cycle following the load instruction. Polling TXIF immediately following a load of TXREG will return invalid results. While TXIF indicates the status of the TXREG register, another bit, TRMT (TXSTA<1>), shows the status of the TSR register. TRMT is a read-only bit which is set when the TSR register is empty. No interrupt logic is tied to this bit so the user has to poll this bit in order to determine if the TSR register is empty. To set up an Asynchronous Transmission: 1. Initialize the SPBRGH:SPBRG registers for the appropriate baud rate. Set or clear the BRGH and BRG16 bits, as required, to achieve the desired baud rate. 2. Enable the asynchronous serial port by clearing bit SYNC and setting bit SPEN. 3. If interrupts are desired, set enable bit TXIE. 4. If 9-bit transmission is desired, set transmit bit TX9. Can be used as address/data bit. 5. Enable the transmission by setting bit TXEN which will also set bit TXIF. 6. If 9-bit transmission is selected, the ninth bit should be loaded in bit TX9D. 7. Load data to the TXREG register (starts transmission). 8. If using interrupts, ensure that the GIE and PEIE bits in the INTCON register (INTCON<7:6>) are set. FIGURE 18-3: EUSART TRANSMIT BLOCK DIAGRAM Note 1: The TSR register is not mapped in data memory so it is not available to the user. 2: Flag bit TXIF is set when enable bit TXEN is set. TXIF TXIE Interrupt TXEN Baud Rate CLK SPBRG Baud Rate Generator TX9D MSb LSb Data Bus TXREG Register TSR Register (8) 0 TX9 TRMT SPEN TX pin Pin Buffer and Control 8 • • • BRG16 SPBRGH PIC18F2420/2520/4420/4520 DS39631B-page 212 Preliminary © 2007 Microchip Technology Inc. FIGURE 18-4: ASYNCHRONOUS TRANSMISSION FIGURE 18-5: ASYNCHRONOUS TRANSMISSION (BACK TO BACK) TABLE 18-5: REGISTERS ASSOCIATED WITH ASYNCHRONOUS TRANSMISSION Word 1 Word 1 Transmit Shift Reg Start bit bit 0 bit 1 bit 7/8 Write to TXREG BRG Output (Shift Clock) TX (pin) TXIF bit (Transmit Buffer Reg. Empty Flag) TRMT bit (Transmit Shift Reg. Empty Flag) 1 TCY Stop bit Word 1 Transmit Shift Reg. Write to TXREG BRG Output (Shift Clock) TX (pin) TXIF bit (Interrupt Reg. Flag) TRMT bit (Transmit Shift Reg. Empty Flag) Word 1 Word 2 Word 1 Word 2 Stop bit Start bit Transmit Shift Reg. Word 1 Word 2 bit 0 bit 1 bit 7/8 bit 0 Note: This timing diagram shows two consecutive transmissions. 1 TCY 1 TCY Start bit Name Bit 7 Bit 6 Bit 5 Bit 4 Bit 3 Bit 2 Bit 1 Bit 0 Reset Values on page INTCON GIE/GIEH PEIE/GIEL TMR0IE INT0IE RBIE TMR0IF INT0IF RBIF 49 PIR1 PSPIF(1) ADIF RCIF TXIF SSPIF CCP1IF TMR2IF TMR1IF 52 PIE1 PSPIE(1) ADIE RCIE TXIE SSPIE CCP1IE TMR2IE TMR1IE 52 IPR1 PSPIP(1) ADIP RCIP TXIP SSPIP CCP1IP TMR2IP TMR1IP 52 RCSTA SPEN RX9 SREN CREN ADDEN FERR OERR RX9D 51 TXREG EUSART Transmit Register 51 TXSTA CSRC TX9 TXEN SYNC SENDB BRGH TRMT TX9D 51 BAUDCON ABDOVF RCIDL — SCKP BRG16 — WUE ABDEN 51 SPBRGH EUSART Baud Rate Generator Register, High Byte 51 SPBRG EUSART Baud Rate Generator Register, Low Byte 51 Legend: — = unimplemented locations read as ‘0’. Shaded cells are not used for asynchronous transmission. Note 1: Reserved in 28-pin devices; always maintain these bits clear. © 2007 Microchip Technology Inc. Preliminary DS39631B-page 213 PIC18F2420/2520/4420/4520 18.2.2 EUSART ASYNCHRONOUS RECEIVER The receiver block diagram is shown in Figure 18-6. The data is received on the RX pin and drives the data recovery block. The data recovery block is actually a high-speed shifter operating at x16 times the baud rate, whereas the main receive serial shifter operates at the bit rate or at FOSC. This mode would typically be used in RS-232 systems. To set up an Asynchronous Reception: 1. Initialize the SPBRGH:SPBRG registers for the appropriate baud rate. Set or clear the BRGH and BRG16 bits, as required, to achieve the desired baud rate. 2. Enable the asynchronous serial port by clearing bit SYNC and setting bit SPEN. 3. If interrupts are desired, set enable bit RCIE. 4. If 9-bit reception is desired, set bit RX9. 5. Enable the reception by setting bit CREN. 6. Flag bit, RCIF, will be set when reception is complete and an interrupt will be generated if enable bit, RCIE, was set. 7. Read the RCSTA register to get the 9th bit (if enabled) and determine if any error occurred during reception. 8. Read the 8-bit received data by reading the RCREG register. 9. If any error occurred, clear the error by clearing enable bit CREN. 10. If using interrupts, ensure that the GIE and PEIE bits in the INTCON register (INTCON<7:6>) are set. 18.2.3 SETTING UP 9-BIT MODE WITH ADDRESS DETECT This mode would typically be used in RS-485 systems. To set up an Asynchronous Reception with Address Detect Enable: 1. Initialize the SPBRGH:SPBRG registers for the appropriate baud rate. Set or clear the BRGH and BRG16 bits, as required, to achieve the desired baud rate. 2. Enable the asynchronous serial port by clearing the SYNC bit and setting the SPEN bit. 3. If interrupts are required, set the RCEN bit and select the desired priority level with the RCIP bit. 4. Set the RX9 bit to enable 9-bit reception. 5. Set the ADDEN bit to enable address detect. 6. Enable reception by setting the CREN bit. 7. The RCIF bit will be set when reception is complete. The interrupt will be Acknowledged if the RCIE and GIE bits are set. 8. Read the RCSTA register to determine if any error occurred during reception, as well as read bit 9 of data (if applicable). 9. Read RCREG to determine if the device is being addressed. 10. If any error occurred, clear the CREN bit. 11. If the device has been addressed, clear the ADDEN bit to allow all received data into the receive buffer and interrupt the CPU. FIGURE 18-6: EUSART RECEIVE BLOCK DIAGRAM x64 Baud Rate CLK Baud Rate Generator RX Pin Buffer and Control SPEN Data Recovery CREN OERR FERR MSb RSR Register LSb RX9D RCREG Register FIFO Interrupt RCIF RCIE Data Bus 8 ÷ 64 ÷ 16 or Stop (8) 7 1 0 Start RX9 • • • BRG16 SPBRGH SPBRG or ÷ 4 PIC18F2420/2520/4420/4520 DS39631B-page 214 Preliminary © 2007 Microchip Technology Inc. FIGURE 18-7: ASYNCHRONOUS RECEPTION TABLE 18-6: REGISTERS ASSOCIATED WITH ASYNCHRONOUS RECEPTION 18.2.4 AUTO-WAKE-UP ON SYNC BREAK CHARACTER During Sleep mode, all clocks to the EUSART are suspended. Because of this, the Baud Rate Generator is inactive and a proper byte reception cannot be performed. The auto-wake-up feature allows the controller to wake-up due to activity on the RX/DT line while the EUSART is operating in Asynchronous mode. The auto-wake-up feature is enabled by setting the WUE bit (BAUDCON<1>). Once set, the typical receive sequence on RX/DT is disabled and the EUSART remains in an Idle state, monitoring for a wake-up event independent of the CPU mode. A wake-up event consists of a high-to-low transition on the RX/DT line. (This coincides with the start of a Sync Break or a Wake-up Signal character for the LIN protocol.) Following a wake-up event, the module generates an RCIF interrupt. The interrupt is generated synchronously to the Q clocks in normal operating modes (Figure 18-8) and asynchronously, if the device is in Sleep mode (Figure 18-9). The interrupt condition is cleared by reading the RCREG register. The WUE bit is automatically cleared once a low-tohigh transition is observed on the RX line following the wake-up event. At this point, the EUSART module is in Idle mode and returns to normal operation. This signals to the user that the Sync Break event is over. Name Bit 7 Bit 6 Bit 5 Bit 4 Bit 3 Bit 2 Bit 1 Bit 0 Reset Values on page INTCON GIE/GIEH PEIE/GIEL TMR0IE INT0IE RBIE TMR0IF INT0IF RBIF 49 PIR1 PSPIF(1) ADIF RCIF TXIF SSPIF CCP1IF TMR2IF TMR1IF 52 PIE1 PSPIE(1) ADIE RCIE TXIE SSPIE CCP1IE TMR2IE TMR1IE 52 IPR1 PSPIP(1) ADIP RCIP TXIP SSPIP CCP1IP TMR2IP TMR1IP 52 RCSTA SPEN RX9 SREN CREN ADDEN FERR OERR RX9D 51 RCREG EUSART Receive Register 51 TXSTA CSRC TX9 TXEN SYNC SENDB BRGH TRMT TX9D 51 BAUDCON ABDOVF RCIDL — SCKP BRG16 — WUE ABDEN 51 SPBRGH EUSART Baud Rate Generator Register, High Byte 51 SPBRG EUSART Baud Rate Generator Register, Low Byte 51 Legend: — = unimplemented locations read as ‘0’. Shaded cells are not used for asynchronous reception. Note 1: Reserved in 28-pin devices; always maintain these bits clear. Start bit bit 0 bit 1 bit 7/8 Stop bit 0 bit 7/8 bit Start bit Start bit 7/8 Stop bit bit RX (pin) Rcv Buffer Reg Rcv Shift Reg Read Rcv Buffer Reg RCREG RCIF (Interrupt Flag) OERR bit CREN Word 1 RCREG Word 2 RCREG Stop bit Note: This timing diagram shows three words appearing on the RX input. The RCREG (receive buffer) is read after the third word causing the OERR (overrun) bit to be set. © 2007 Microchip Technology Inc. Preliminary DS39631B-page 215 PIC18F2420/2520/4420/4520 18.2.4.1 Special Considerations Using Auto-Wake-up Since auto-wake-up functions by sensing rising edge transitions on RX/DT, information with any state changes before the Stop bit may signal a false end-ofcharacter and cause data or framing errors. To work properly, therefore, the initial character in the transmission must be all ‘0’s. This can be 00h (8 bytes) for standard RS-232 devices or 000h (12 bits) for LIN bus. Oscillator start-up time must also be considered, especially in applications using oscillators with longer start-up intervals (i.e., XT or HS mode). The Sync Break (or Wake-up Signal) character must be of sufficient length and be followed by a sufficient interval to allow enough time for the selected oscillator to start and provide proper initialization of the EUSART. 18.2.4.2 Special Considerations Using the WUE Bit The timing of WUE and RCIF events may cause some confusion when it comes to determining the validity of received data. As noted, setting the WUE bit places the EUSART in an Idle mode. The wake-up event causes a receive interrupt by setting the RCIF bit. The WUE bit is cleared after this when a rising edge is seen on RX/DT. The interrupt condition is then cleared by reading the RCREG register. Ordinarily, the data in RCREG will be dummy data and should be discarded. The fact that the WUE bit has been cleared (or is still set) and the RCIF flag is set should not be used as an indicator of the integrity of the data in RCREG. Users should consider implementing a parallel method in firmware to verify received data integrity. To assure that no actual data is lost, check the RCIDL bit to verify that a receive operation is not in process. If a receive operation is not occurring, the WUE bit may then be set just prior to entering the Sleep mode. FIGURE 18-8: AUTO-WAKE-UP BIT (WUE) TIMINGS DURING NORMAL OPERATION FIGURE 18-9: AUTO-WAKE-UP BIT (WUE) TIMINGS DURING SLEEP Q1 Q2 Q3 Q4 Q1 Q2 Q3 Q4 Q1 Q2 Q3 Q4 Q1 Q2 Q3 Q4 Q1 Q2 Q3 Q4 Q1 Q2 Q3 Q4 Q1 Q2 Q3 Q4 Q1 Q2 Q3 Q4 Q1 Q2 Q3 Q4 Q1 Q2 Q3 Q4 OSC1 WUE bit(1) RX/DT Line RCIF Note 1: The EUSART remains in Idle while the WUE bit is set. Bit set by user Cleared due to user read of RCREG Auto-Cleared Q1 Q2 Q3 Q4 Q1 Q2 Q3 Q4 Q1 Q2 Q3 Q4 Q1 Q2 Q3 Q4 Q1 Q2 Q3 Q4 Q1 Q2 Q3 Q4 Q1 Q2 Q3 Q4 Q1 Q2 Q3 Q4 OSC1 WUE bit(2) RX/DT Line RCIF Bit set by user Cleared due to user read of RCREG Sleep Command Executed Note 1: If the wake-up event requires long oscillator warm-up time, the auto-clear of the WUE bit can occur before the oscillator is ready. This sequence should not depend on the presence of Q clocks. 2: The EUSART remains in Idle while the WUE bit is set. Sleep Ends Note 1 Auto-Cleared PIC18F2420/2520/4420/4520 DS39631B-page 216 Preliminary © 2007 Microchip Technology Inc. 18.2.5 BREAK CHARACTER SEQUENCE The EUSART module has the capability of sending the special Break character sequences that are required by the LIN bus standard. The Break character transmit consists of a Start bit, followed by twelve ‘0’ bits and a Stop bit. The frame Break character is sent whenever the SENDB and TXEN bits (TXSTA<3> and TXSTA<5>) are set while the Transmit Shift register is loaded with data. Note that the value of data written to TXREG will be ignored and all ‘0’s will be transmitted. The SENDB bit is automatically reset by hardware after the corresponding Stop bit is sent. This allows the user to preload the transmit FIFO with the next transmit byte following the Break character (typically, the Sync character in the LIN specification). Note that the data value written to the TXREG for the Break character is ignored. The write simply serves the purpose of initiating the proper sequence. The TRMT bit indicates when the transmit operation is active or Idle, just as it does during normal transmission. See Figure 18-10 for the timing of the Break character sequence. 18.2.5.1 Break and Sync Transmit Sequence The following sequence will send a message frame header made up of a Break, followed by an Auto-Baud Sync byte. This sequence is typical of a LIN bus master. 1. Configure the EUSART for the desired mode. 2. Set the TXEN and SENDB bits to set up the Break character. 3. Load the TXREG with a dummy character to initiate transmission (the value is ignored). 4. Write ‘55h’ to TXREG to load the Sync character into the transmit FIFO buffer. 5. After the Break has been sent, the SENDB bit is reset by hardware. The Sync character now transmits in the preconfigured mode. When the TXREG becomes empty, as indicated by the TXIF, the next data byte can be written to TXREG. 18.2.6 RECEIVING A BREAK CHARACTER The enhanced USART module can receive a Break character in two ways. The first method forces configuration of the baud rate at a frequency of 9/13 the typical speed. This allows for the Stop bit transition to be at the correct sampling location (13 bits for Break versus Start bit and 8 data bits for typical data). The second method uses the auto-wake-up feature described in Section 18.2.4 “Auto-Wake-up on Sync Break Character”. By enabling this feature, the EUSART will sample the next two transitions on RX/DT, cause an RCIF interrupt and receive the next data byte followed by another interrupt. Note that following a Break character, the user will typically want to enable the Auto-Baud Rate Detect feature. For both methods, the user can set the ABD bit once the TXIF interrupt is observed. FIGURE 18-10: SEND BREAK CHARACTER SEQUENCE Write to TXREG BRG Output (Shift Clock) Start Bit Bit 0 Bit 1 Bit 11 Stop Bit Break TXIF bit (Transmit Buffer Reg. Empty Flag) TX (pin) TRMT bit (Transmit Shift Reg. Empty Flag) SENDB (Transmit Shift Reg. Empty Flag) SENDB sampled here Auto-Cleared Dummy Write © 2007 Microchip Technology Inc. Preliminary DS39631B-page 217 PIC18F2420/2520/4420/4520 18.3 EUSART Synchronous Master Mode The Synchronous Master mode is entered by setting the CSRC bit (TXSTA<7>). In this mode, the data is transmitted in a half-duplex manner (i.e., transmission and reception do not occur at the same time). When transmitting data, the reception is inhibited and vice versa. Synchronous mode is entered by setting bit SYNC (TXSTA<4>). In addition, enable bit SPEN (RCSTA<7>) is set in order to configure the TX and RX pins to CK (clock) and DT (data) lines, respectively. The Master mode indicates that the processor transmits the master clock on the CK line. Clock polarity is selected with the SCKP bit (BAUDCON<4>); setting SCKP sets the Idle state on CK as high, while clearing the bit sets the Idle state as low. This option is provided to support Microwire devices with this module. 18.3.1 EUSART SYNCHRONOUS MASTER TRANSMISSION The EUSART transmitter block diagram is shown in Figure 18-3. The heart of the transmitter is the Transmit (Serial) Shift Register (TSR). The Shift register obtains its data from the Read/Write Transmit Buffer register, TXREG. The TXREG register is loaded with data in software. The TSR register is not loaded until the last bit has been transmitted from the previous load. As soon as the last bit is transmitted, the TSR is loaded with new data from the TXREG (if available). Once the TXREG register transfers the data to the TSR register (occurs in one TCY), the TXREG is empty and the TXIF flag bit (PIR1<4>) is set. The interrupt can be enabled or disabled by setting or clearing the interrupt enable bit, TXIE (PIE1<4>). TXIF is set regardless of the state of enable bit TXIE; it cannot be cleared in software. It will reset only when new data is loaded into the TXREG register. While flag bit TXIF indicates the status of the TXREG register, another bit, TRMT (TXSTA<1>), shows the status of the TSR register. TRMT is a read-only bit which is set when the TSR is empty. No interrupt logic is tied to this bit so the user has to poll this bit in order to determine if the TSR register is empty. The TSR is not mapped in data memory so it is not available to the user. To set up a Synchronous Master Transmission: 1. Initialize the SPBRGH:SPBRG registers for the appropriate baud rate. Set or clear the BRG16 bit, as required, to achieve the desired baud rate. 2. Enable the synchronous master serial port by setting bits SYNC, SPEN and CSRC. 3. If interrupts are desired, set enable bit TXIE. 4. If 9-bit transmission is desired, set bit TX9. 5. Enable the transmission by setting bit TXEN. 6. If 9-bit transmission is selected, the ninth bit should be loaded in bit TX9D. 7. Start transmission by loading data to the TXREG register. 8. If using interrupts, ensure that the GIE and PEIE bits in the INTCON register (INTCON<7:6>) are set. FIGURE 18-11: SYNCHRONOUS TRANSMISSION bit 0 bit 1 bit 7 Word 1 Q1 Q2 Q3Q4 Q1 Q2 Q3Q4 Q1Q2 Q3 Q4 Q1Q2 Q3 Q4Q1 Q2 Q3 Q4 Q3Q4 Q1Q2 Q3Q4 Q1Q2 Q3Q4 Q1 Q2Q3Q4 Q1 Q2Q3 Q4Q1 Q2 Q3 Q4 Q1 Q2 Q3 Q4 bit 2 bit 0 bit 1 bit 7 RC7/RX/DT RC6/TX/CK pin Write to TXREG Reg TXIF bit (Interrupt Flag) TXEN bit ‘1’ ‘1’ Word 2 TRMT bit Write Word 1 Write Word 2 Note: Sync Master mode, SPBRG = 0, continuous transmission of two 8-bit words. RC6/TX/CK pin (SCKP = 0) (SCKP = 1) PIC18F2420/2520/4420/4520 DS39631B-page 218 Preliminary © 2007 Microchip Technology Inc. FIGURE 18-12: SYNCHRONOUS TRANSMISSION (THROUGH TXEN) TABLE 18-7: REGISTERS ASSOCIATED WITH SYNCHRONOUS MASTER TRANSMISSION RC7/RX/DT pin RC6/TX/CK pin Write to TXREG reg TXIF bit TRMT bit bit 0 bit 1 bit 2 bit 6 bit 7 TXEN bit Name Bit 7 Bit 6 Bit 5 Bit 4 Bit 3 Bit 2 Bit 1 Bit 0 Reset Values on page INTCON GIE/GIEH PEIE/GIEL TMR0IE INT0IE RBIE TMR0IF INT0IF RBIF 49 PIR1 PSPIF(1) ADIF RCIF TXIF SSPIF CCP1IF TMR2IF TMR1IF 52 PIE1 PSPIE(1) ADIE RCIE TXIE SSPIE CCP1IE TMR2IE TMR1IE 52 IPR1 PSPIP(1) ADIP RCIP TXIP SSPIP CCP1IP TMR2IP TMR1IP 52 RCSTA SPEN RX9 SREN CREN ADDEN FERR OERR RX9D 51 TXREG EUSART Transmit Register 51 TXSTA CSRC TX9 TXEN SYNC SENDB BRGH TRMT TX9D 51 BAUDCON ABDOVF RCIDL — SCKP BRG16 — WUE ABDEN 51 SPBRGH EUSART Baud Rate Generator Register, High Byte 51 SPBRG EUSART Baud Rate Generator Register, Low Byte 51 Legend: — = unimplemented, read as ‘0’. Shaded cells are not used for synchronous master transmission. Note 1: Reserved in 28-pin devices; always maintain these bits clear. © 2007 Microchip Technology Inc. Preliminary DS39631B-page 219 PIC18F2420/2520/4420/4520 18.3.2 EUSART SYNCHRONOUS MASTER RECEPTION Once Synchronous mode is selected, reception is enabled by setting either the Single Receive Enable bit, SREN (RCSTA<5>), or the Continuous Receive Enable bit, CREN (RCSTA<4>). Data is sampled on the RX pin on the falling edge of the clock. If enable bit SREN is set, only a single word is received. If enable bit CREN is set, the reception is continuous until CREN is cleared. If both bits are set, then CREN takes precedence. To set up a Synchronous Master Reception: 1. Initialize the SPBRGH:SPBRG registers for the appropriate baud rate. Set or clear the BRG16 bit, as required, to achieve the desired baud rate. 2. Enable the synchronous master serial port by setting bits SYNC, SPEN and CSRC. 3. Ensure bits CREN and SREN are clear. 4. If interrupts are desired, set enable bit RCIE. 5. If 9-bit reception is desired, set bit RX9. 6. If a single reception is required, set bit SREN. For continuous reception, set bit CREN. 7. Interrupt flag bit, RCIF, will be set when reception is complete and an interrupt will be generated if the enable bit, RCIE, was set. 8. Read the RCSTA register to get the 9th bit (if enabled) and determine if any error occurred during reception. 9. Read the 8-bit received data by reading the RCREG register. 10. If any error occurred, clear the error by clearing bit CREN. 11. If using interrupts, ensure that the GIE and PEIE bits in the INTCON register (INTCON<7:6>) are set. FIGURE 18-13: SYNCHRONOUS RECEPTION (MASTER MODE, SREN) TABLE 18-8: REGISTERS ASSOCIATED WITH SYNCHRONOUS MASTER RECEPTION Name Bit 7 Bit 6 Bit 5 Bit 4 Bit 3 Bit 2 Bit 1 Bit 0 Reset Values on page INTCON GIE/GIEH PEIE/GIEL TMR0IE INT0IE RBIE TMR0IF INT0IF RBIF 49 PIR1 PSPIF(1) ADIF RCIF TXIF SSPIF CCP1IF TMR2IF TMR1IF 52 PIE1 PSPIE(1) ADIE RCIE TXIE SSPIE CCP1IE TMR2IE TMR1IE 52 IPR1 PSPIP(1) ADIP RCIP TXIP SSPIP CCP1IP TMR2IP TMR1IP 52 RCSTA SPEN RX9 SREN CREN ADDEN FERR OERR RX9D 51 RCREG EUSART Receive Register 51 TXSTA CSRC TX9 TXEN SYNC SENDB BRGH TRMT TX9D 51 BAUDCON ABDOVF RCIDL — SCKP BRG16 — WUE ABDEN 51 SPBRGH EUSART Baud Rate Generator Register, High Byte 51 SPBRG EUSART Baud Rate Generator Register, Low Byte 51 Legend: — = unimplemented, read as ‘0’. Shaded cells are not used for synchronous master reception. Note 1: Reserved in 28-pin devices; always maintain these bits clear. CREN bit RC7/RX/DT RC6/TX/CK pin Write to bit SREN SREN bit RCIF bit (Interrupt) Read RXREG Q2 Q3 Q4 Q1 Q2 Q3 Q4 Q1 Q2 Q3 Q4 Q1 Q2 Q3 Q4 Q1 Q2 Q3 Q4 Q1 Q2 Q3 Q4Q1 Q2 Q3 Q4 Q1Q2 Q3 Q4 Q1 Q2Q3 Q4 Q1 Q2 Q3 Q4 ‘0’ bit 0 bit 1 bit 2 bit 3 bit 4 bit 5 bit 6 bit 7 ‘0’ Q1 Q2 Q3 Q4 Note: Timing diagram demonstrates Sync Master mode with bit SREN = 1 and bit BRGH = 0. RC6/TX/CK pin pin (SCKP = 0) (SCKP = 1) PIC18F2420/2520/4420/4520 DS39631B-page 220 Preliminary © 2007 Microchip Technology Inc. 18.4 EUSART Synchronous Slave Mode Synchronous Slave mode is entered by clearing bit, CSRC (TXSTA<7>). This mode differs from the Synchronous Master mode in that the shift clock is supplied externally at the CK pin (instead of being supplied internally in Master mode). This allows the device to transfer or receive data while in any low-power mode. 18.4.1 EUSART SYNCHRONOUS SLAVE TRANSMISSION The operation of the Synchronous Master and Slave modes are identical, except in the case of the Sleep mode. If two words are written to the TXREG and then the SLEEP instruction is executed, the following will occur: a) The first word will immediately transfer to the TSR register and transmit. b) The second word will remain in the TXREG register. c) Flag bit, TXIF, will not be set. d) When the first word has been shifted out of TSR, the TXREG register will transfer the second word to the TSR and flag bit, TXIF, will now be set. e) If enable bit TXIE is set, the interrupt will wake the chip from Sleep. If the global interrupt is enabled, the program will branch to the interrupt vector. To set up a Synchronous Slave Transmission: 1. Enable the synchronous slave serial port by setting bits SYNC and SPEN and clearing bit CSRC. 2. Clear bits CREN and SREN. 3. If interrupts are desired, set enable bit TXIE. 4. If 9-bit transmission is desired, set bit TX9. 5. Enable the transmission by setting enable bit TXEN. 6. If 9-bit transmission is selected, the ninth bit should be loaded in bit TX9D. 7. Start transmission by loading data to the TXREGx register. 8. If using interrupts, ensure that the GIE and PEIE bits in the INTCON register (INTCON<7:6>) are set. TABLE 18-9: REGISTERS ASSOCIATED WITH SYNCHRONOUS SLAVE TRANSMISSION Name Bit 7 Bit 6 Bit 5 Bit 4 Bit 3 Bit 2 Bit 1 Bit 0 Reset Values on page INTCON GIE/GIEH PEIE/GIEL TMR0IE INT0IE RBIE TMR0IF INT0IF RBIF 49 PIR1 PSPIF(1) ADIF RCIF TXIF SSPIF CCP1IF TMR2IF TMR1IF 52 PIE1 PSPIE(1) ADIE RCIE TXIE SSPIE CCP1IE TMR2IE TMR1IE 52 IPR1 PSPIP(1) ADIP RCIP TXIP SSPIP CCP1IP TMR2IP TMR1IP 52 RCSTA SPEN RX9 SREN CREN ADDEN FERR OERR RX9D 51 TXREG EUSART Transmit Register 51 TXSTA CSRC TX9 TXEN SYNC SENDB BRGH TRMT TX9D 51 BAUDCON ABDOVF RCIDL — SCKP BRG16 — WUE ABDEN 51 SPBRGH EUSART Baud Rate Generator Register, High Byte 51 SPBRG EUSART Baud Rate Generator Register, Low Byte 51 Legend: — = unimplemented, read as ‘0’. Shaded cells are not used for synchronous slave transmission. Note 1: Reserved in 28-pin devices; always maintain these bits clear. © 2007 Microchip Technology Inc. Preliminary DS39631B-page 221 PIC18F2420/2520/4420/4520 18.4.2 EUSART SYNCHRONOUS SLAVE RECEPTION The operation of the Synchronous Master and Slave modes is identical, except in the case of Sleep, or any Idle mode and bit SREN, which is a “don’t care” in Slave mode. If receive is enabled by setting the CREN bit prior to entering Sleep or any Idle mode, then a word may be received while in this low-power mode. Once the word is received, the RSR register will transfer the data to the RCREG register; if the RCIE enable bit is set, the interrupt generated will wake the chip from the low-power mode. If the global interrupt is enabled, the program will branch to the interrupt vector. To set up a Synchronous Slave Reception: 1. Enable the synchronous master serial port by setting bits SYNC and SPEN and clearing bit CSRC. 2. If interrupts are desired, set enable bit RCIE. 3. If 9-bit reception is desired, set bit RX9. 4. To enable reception, set enable bit CREN. 5. Flag bit, RCIF, will be set when reception is complete. An interrupt will be generated if enable bit, RCIE, was set. 6. Read the RCSTA register to get the 9th bit (if enabled) and determine if any error occurred during reception. 7. Read the 8-bit received data by reading the RCREG register. 8. If any error occurred, clear the error by clearing bit CREN. 9. If using interrupts, ensure that the GIE and PEIE bits in the INTCON register (INTCON<7:6>) are set. TABLE 18-10: REGISTERS ASSOCIATED WITH SYNCHRONOUS SLAVE RECEPTION Name Bit 7 Bit 6 Bit 5 Bit 4 Bit 3 Bit 2 Bit 1 Bit 0 Reset Values on page INTCON GIE/GIEH PEIE/GIEL TMR0IE INT0IE RBIE TMR0IF INT0IF RBIF 49 PIR1 PSPIF(1) ADIF RCIF TXIF SSPIF CCP1IF TMR2IF TMR1IF 52 PIE1 PSPIE(1) ADIE RCIE TXIE SSPIE CCP1IE TMR2IE TMR1IE 52 IPR1 PSPIP(1) ADIP RCIP TXIP SSPIP CCP1IP TMR2IP TMR1IP 52 RCSTA SPEN RX9 SREN CREN ADDEN FERR OERR RX9D 51 RCREG EUSART Receive Register 51 TXSTA CSRC TX9 TXEN SYNC SENDB BRGH TRMT TX9D 51 BAUDCON ABDOVF RCIDL — SCKP BRG16 — WUE ABDEN 51 SPBRGH EUSART Baud Rate Generator Register, High Byte 51 SPBRG EUSART Baud Rate Generator Register, Low Byte 51 Legend: — = unimplemented, read as ‘0’. Shaded cells are not used for synchronous slave reception. Note 1: Reserved in 28-pin devices; always maintain these bits clear. PIC18F2420/2520/4420/4520 DS39631B-page 222 Preliminary © 2007 Microchip Technology Inc. NOTES: © 2007 Microchip Technology Inc. Preliminary DS39631B-page 223 PIC18F2420/2520/4420/4520 19.0 10-BIT ANALOG-TO-DIGITAL CONVERTER (A/D) MODULE The Analog-to-Digital (A/D) converter module has 10 inputs for the 28-pin devices and 13 for the 40/44-pin devices. This module allows conversion of an analog input signal to a corresponding 10-bit digital number. The module has five registers: • A/D Result High Register (ADRESH) • A/D Result Low Register (ADRESL) • A/D Control Register 0 (ADCON0) • A/D Control Register 1 (ADCON1) • A/D Control Register 2 (ADCON2) The ADCON0 register, shown in Register 19-1, controls the operation of the A/D module. The ADCON1 register, shown in Register 19-2, configures the functions of the port pins. The ADCON2 register, shown in Register 19-3, configures the A/D clock source, programmed acquisition time and justification. REGISTER 19-1: ADCON0 REGISTER U-0 U-0 R/W-0 R/W-0 R/W-0 R/W-0 R/W-0 R/W-0 — — CHS3 CHS2 CHS1 CHS0 GO/DONE ADON bit 7 bit 0 bit 7-6 Unimplemented: Read as ‘0’ bit 5-2 CHS3:CHS0: Analog Channel Select bits 0000 = Channel 0 (AN0) 0001 = Channel 1 (AN1) 0010 = Channel 2 (AN2) 0011 = Channel 3 (AN3) 0100 = Channel 4 (AN4) 0101 = Channel 5 (AN5)(1,2) 0110 = Channel 6 (AN6)(1,2) 0111 = Channel 7 (AN7)(1,2) 1000 = Channel 8 (AN8) 1001 = Channel 9 (AN9) 1010 = Channel 10 (AN10) 1011 = Channel 11 (AN11) 1100 = Channel 12 (AN12 1101 = Unimplemented(2) 1110 = Unimplemented(2) 1111 = Unimplemented(2) Note 1: These channels are not implemented on 28-pin devices. 2: Performing a conversion on unimplemented channels will return a floating input measurement. bit 1 GO/DONE: A/D Conversion Status bit When ADON = 1: 1 = A/D conversion in progress 0 = A/D Idle bit 0 ADON: A/D On bit 1 = A/D converter module is enabled 0 = A/D converter module is disabled Legend: R = Readable bit W = Writable bit U = Unimplemented bit, read as ‘0’ -n = Value at POR ‘1’ = Bit is set ‘0’ = Bit is cleared x = Bit is unknown PIC18F2420/2520/4420/4520 DS39631B-page 224 Preliminary © 2007 Microchip Technology Inc. REGISTER 19-2: ADCON1 REGISTER U-0 U-0 R/W-0 R/W-0 R/W-0(1) R/W(1) R/W(1) R/W(1) — — VCFG1 VCFG0 PCFG3 PCFG2 PCFG1 PCFG0 bit 7 bit 0 bit 7-6 Unimplemented: Read as ‘0’ bit 5 VCFG1: Voltage Reference Configuration bit (VREF- source) 1 = VREF- (AN2) 0 = VSS bit 4 VCFG0: Voltage Reference Configuration bit (VREF+ source) 1 = VREF+ (AN3) 0 = VDD bit 3-0 PCFG3:PCFG0: A/D Port Configuration Control bits: Legend: R = Readable bit W = Writable bit U = Unimplemented bit, read as ‘0’ -n = Value at POR ‘1’ = Bit is set ‘0’ = Bit is cleared x = Bit is unknown A = Analog input D = Digital I/O Note 1: The POR value of the PCFG bits depends on the value of the PBADEN configuration bit. When PBADEN = 1, PCFG<3:0> = 0000; when PBADEN = 0, PCFG<3:0> = 0111. 2: AN5 through AN7 are available only on 40/44-pin devices. PCFG3: PCFG0 AN12 AN11 AN10 AN9 AN8 AN7(2) AN6(2) AN5(2) AN4 AN3 AN2 AN1 AN0 0000(1) A A A A A A A A A A A A A 0001 A A A A A A A A A A A A A 0010 A A A A A A A A A A A A A 0011 D A A A A A A A A A A A A 0100 D D A A A A A A A A A A A 0101 D D D A A A A A A A A A A 0110 D D D D A A A A A A A A A 0111(1) D D D D D A A A A A A A A 1000 D D D D D D A A A A A A A 1001 D D D D D D D A A A A A A 1010 D D D D D D D D A A A A A 1011 D D D D D D D D D A A A A 1100 D D D D D D D D D D A A A 1101 D D D D D D D D D D D A A 1110 D D D D D D D D D D D D A 1111 D D D D D D D D D D D D D © 2007 Microchip Technology Inc. Preliminary DS39631B-page 225 PIC18F2420/2520/4420/4520 REGISTER 19-3: ADCON2 REGISTER R/W-0 U-0 R/W-0 R/W-0 R/W-0 R/W-0 R/W-0 R/W-0 ADFM — ACQT2 ACQT1 ACQT0 ADCS2 ADCS1 ADCS0 bit 7 bit 0 bit 7 ADFM: A/D Result Format Select bit 1 = Right justified 0 = Left justified bit 6 Unimplemented: Read as ‘0’ bit 5-3 ACQT2:ACQT0: A/D Acquisition Time Select bits 111 = 20 TAD 110 = 16 TAD 101 = 12 TAD 100 = 8 TAD 011 = 6 TAD 010 = 4 TAD 001 = 2 TAD 000 = 0 TAD(1) bit 2-0 ADCS2:ADCS0: A/D Conversion Clock Select bits 111 = FRC (clock derived from A/D RC oscillator)(1) 110 = FOSC/64 101 = FOSC/16 100 = FOSC/4 011 = FRC (clock derived from A/D RC oscillator)(1) 010 = FOSC/32 001 = FOSC/8 000 = FOSC/2 Note 1: If the A/D FRC clock source is selected, a delay of one TCY (instruction cycle) is added before the A/D clock starts. This allows the SLEEP instruction to be executed before starting a conversion. Legend: R = Readable bit W = Writable bit U = Unimplemented bit, read as ‘0’ -n = Value at POR ‘1’ = Bit is set ‘0’ = Bit is cleared x = Bit is unknown PIC18F2420/2520/4420/4520 DS39631B-page 226 Preliminary © 2007 Microchip Technology Inc. The analog reference voltage is software selectable to either the device’s positive and negative supply voltage (VDD and VSS), or the voltage level on the RA3/AN3/ VREF+ and RA2/AN2/VREF-/CVREF pins. The A/D converter has a unique feature of being able to operate while the device is in Sleep mode. To operate in Sleep, the A/D conversion clock must be derived from the A/D’s internal RC oscillator. The output of the sample and hold is the input into the converter, which generates the result via successive approximation. A device Reset forces all registers to their Reset state. This forces the A/D module to be turned off and any conversion in progress is aborted. Each port pin associated with the A/D converter can be configured as an analog input, or as a digital I/O. The ADRESH and ADRESL registers contain the result of the A/D conversion. When the A/D conversion is complete, the result is loaded into the ADRESH:ADRESL register pair, the GO/DONE bit (ADCON0 register) is cleared and A/D Interrupt Flag bit, ADIF, is set. The block diagram of the A/D module is shown in Figure 19-1. FIGURE 19-1: A/D BLOCK DIAGRAM (Input Voltage) VAIN VREF+ Reference Voltage VDD VCFG1:VCFG0 CHS3:CHS0 AN7(1) AN6(1) AN5(1) AN4 AN3 AN2 AN1 AN0 0111 0110 0101 0100 0011 0010 0001 0000 10-Bit Converter VREFVSS A/D AN12 AN11 AN10 AN9 AN8 1100 1011 1010 1001 1000 Note 1: Channels AN5 through AN7 are not available on 28-pin devices. 2: I/O pins have diode protection to VDD and VSS. 0X 1X X1 X0 © 2007 Microchip Technology Inc. Preliminary DS39631B-page 227 PIC18F2420/2520/4420/4520 The value in the ADRESH:ADRESL registers is not modified for a Power-on Reset. The ADRESH:ADRESL registers will contain unknown data after a Power-on Reset. After the A/D module has been configured as desired, the selected channel must be acquired before the conversion is started. The analog input channels must have their corresponding TRIS bits selected as an input. To determine acquisition time, see Section 19.1 “A/D Acquisition Requirements”. After this acquisition time has elapsed, the A/D conversion can be started. An acquisition time can be programmed to occur between setting the GO/DONE bit and the actual start of the conversion. The following steps should be followed to perform an A/D conversion: 1. Configure the A/D module: • Configure analog pins, voltage reference and digital I/O (ADCON1) • Select A/D input channel (ADCON0) • Select A/D acquisition time (ADCON2) • Select A/D conversion clock (ADCON2) • Turn on A/D module (ADCON0) 2. Configure A/D interrupt (if desired): • Clear ADIF bit • Set ADIE bit • Set GIE bit 3. Wait the required acquisition time (if required). 4. Start conversion: • Set GO/DONE bit (ADCON0 register) 5. Wait for A/D conversion to complete, by either: • Polling for the GO/DONE bit to be cleared OR • Waiting for the A/D interrupt 6. Read A/D Result registers (ADRESH:ADRESL); clear bit ADIF, if required. 7. For next conversion, go to step 1 or step 2, as required. The A/D conversion time per bit is defined as TAD. A minimum wait of 2 TAD is required before the next acquisition starts. FIGURE 19-2: A/D TRANSFER FUNCTION FIGURE 19-3: ANALOG INPUT MODEL Digital Code Output 3FEh 003h 002h 001h 000h 0.5 LSB 1 LSB 1.5 LSB 2 LSB 2.5 LSB 1022 LSB 1022.5 LSB 3 LSB Analog Input Voltage 3FFh 1023 LSB 1023.5 LSB VAIN CPIN Rs ANx 5 pF VT = 0.6V VT = 0.6V ILEAKAGE RIC ≤ 1k Sampling Switch SS RSS CHOLD = 25 pF VSS VDD ± 100 nA Legend: CPIN VT ILEAKAGE RIC SS CHOLD = input capacitance = threshold voltage = leakage current at the pin due to = interconnect resistance = sampling switch = sample/hold capacitance (from DAC) various junctions RSS = sampling switch resistance VDD 6 V Sampling Switch 5 V 4 V 3 V 2 V 1 2 3 4 (kΩ) PIC18F2420/2520/4420/4520 DS39631B-page 228 Preliminary © 2007 Microchip Technology Inc. 19.1 A/D Acquisition Requirements For the A/D converter to meet its specified accuracy, the charge holding capacitor (CHOLD) must be allowed to fully charge to the input channel voltage level. The analog input model is shown in Figure 19-3. The source impedance (RS) and the internal sampling switch (RSS) impedance directly affect the time required to charge the capacitor CHOLD. The sampling switch (RSS) impedance varies over the device voltage (VDD). The source impedance affects the offset voltage at the analog input (due to pin leakage current). The maximum recommended impedance for analog sources is 2.5 kΩ. After the analog input channel is selected (changed), the channel must be sampled for at least the minimum acquisition time before starting a conversion. To calculate the minimum acquisition time, Equation 19-1 may be used. This equation assumes that 1/2 LSb error is used (1024 steps for the A/D). The 1/2 LSb error is the maximum error allowed for the A/D to meet its specified resolution. Example 19-3 shows the calculation of the minimum required acquisition time TACQ. This calculation is based on the following application system assumptions: CHOLD = 25 pF Rs = 2.5 kΩ Conversion Error ≤ 1/2 LSb VDD = 5V → Rss = 2 kΩ Temperature = 85°C (system max.) EQUATION 19-1: ACQUISITION TIME EQUATION 19-2: A/D MINIMUM CHARGING TIME EQUATION 19-3: CALCULATING THE MINIMUM REQUIRED ACQUISITION TIME Note: When the conversion is started, the holding capacitor is disconnected from the input pin. TACQ = Amplifier Settling Time + Holding Capacitor Charging Time + Temperature Coefficient = TAMP + TC + TCOFF VHOLD = (VREF – (VREF/2048)) • (1 – e(-TC/CHOLD(RIC + RSS + RS))) or TC = -(CHOLD)(RIC + RSS + RS) ln(1/2048) TACQ = TAMP + TC + TCOFF TAMP = 0.2 μs TCOFF = (Temp – 25°C)(0.02 μs/°C) (85°C – 25°C)(0.02 μs/°C) 1.2 μs Temperature coefficient is only required for temperatures > 25°C. Below 25°C, TCOFF = 0 ms. TC = -(CHOLD)(RIC + RSS + RS) ln(1/2047) μs -(25 pF) (1 kΩ + 2 kΩ + 2.5 kΩ) ln(0.0004883) μs 1.05 μs TACQ = 0.2 μs + 1 μs + 1.2 μs 2.4 μs © 2007 Microchip Technology Inc. Preliminary DS39631B-page 229 PIC18F2420/2520/4420/4520 19.2 Selecting and Configuring Acquisition Time The ADCON2 register allows the user to select an acquisition time that occurs each time the GO/DONE bit is set. It also gives users the option to use an automatically determined acquisition time. Acquisition time may be set with the ACQT2:ACQT0 bits (ADCON2<5:3>), which provides a range of 2 to 20 TAD. When the GO/DONE bit is set, the A/D module continues to sample the input for the selected acquisition time, then automatically begins a conversion. Since the acquisition time is programmed, there may be no need to wait for an acquisition time between selecting a channel and setting the GO/DONE bit. Manual acquisition is selected when ACQT2:ACQT0 = 000. When the GO/DONE bit is set, sampling is stopped and a conversion begins. The user is responsible for ensuring the required acquisition time has passed between selecting the desired input channel and setting the GO/DONE bit. This option is also the default Reset state of the ACQT2:ACQT0 bits and is compatible with devices that do not offer programmable acquisition times. In either case, when the conversion is completed, the GO/DONE bit is cleared, the ADIF flag is set and the A/D begins sampling the currently selected channel again. If an acquisition time is programmed, there is nothing to indicate if the acquisition time has ended or if the conversion has begun. 19.3 Selecting the A/D Conversion Clock The A/D conversion time per bit is defined as TAD. The A/D conversion requires 11 TAD per 10-bit conversion. The source of the A/D conversion clock is software selectable. There are seven possible options for TAD: • 2 TOSC • 4 TOSC • 8 TOSC • 16 TOSC • 32 TOSC • 64 TOSC • Internal RC Oscillator For correct A/D conversions, the A/D conversion clock (TAD) must be as short as possible, but greater than the minimum TAD (see parameter 130 for more information). Table 19-1 shows the resultant TAD times derived from the device operating frequencies and the A/D clock source selected. TABLE 19-1: TAD vs. DEVICE OPERATING FREQUENCIES AD Clock Source (TAD) Maximum Device Frequency Operation ADCS2:ADCS0 PIC18F2X20/4X20 PIC18LF2X20/4X20(4) 2 TOSC 000 2.86 MHz 1.43 kHz 4 TOSC 100 5.71 MHz 2.86 MHz 8 TOSC 001 11.43 MHz 5.72 MHz 16 TOSC 101 22.86 MHz 11.43 MHz 32 TOSC 010 40.0 MHz 22.86 MHz 64 TOSC 110 40.0 MHz 22.86 MHz RC(3) x11 1.00 MHz(1) 1.00 MHz(2) Note 1: The RC source has a typical TAD time of 1.2 μs. 2: The RC source has a typical TAD time of 2.5 μs. 3: For device frequencies above 1 MHz, the device must be in Sleep for the entire conversion or the A/D accuracy may be out of specification. 4: Low-power (PIC18LFXXXX) devices only. PIC18F2420/2520/4420/4520 DS39631B-page 230 Preliminary © 2007 Microchip Technology Inc. 19.4 Operation in Power Managed Modes The selection of the automatic acquisition time and A/D conversion clock is determined in part by the clock source and frequency while in a power managed mode. If the A/D is expected to operate while the device is in a power managed mode, the ACQT2:ACQT0 and ADCS2:ADCS0 bits in ADCON2 should be updated in accordance with the clock source to be used in that mode. After entering the mode, an A/D acquisition or conversion may be started. Once started, the device should continue to be clocked by the same clock source until the conversion has been completed. If desired, the device may be placed into the corresponding Idle mode during the conversion. If the device clock frequency is less than 1 MHz, the A/D RC clock source should be selected. Operation in the Sleep mode requires the A/D FRC clock to be selected. If bits ACQT2:ACQT0 are set to ‘000’ and a conversion is started, the conversion will be delayed one instruction cycle to allow execution of the SLEEP instruction and entry to Sleep mode. The IDLEN bit (OSCCON<7>) must have already been cleared prior to starting the conversion. 19.5 Configuring Analog Port Pins The ADCON1, TRISA, TRISB and TRISE registers all configure the A/D port pins. The port pins needed as analog inputs must have their corresponding TRIS bits set (input). If the TRIS bit is cleared (output), the digital output level (VOH or VOL) will be converted. The A/D operation is independent of the state of the CHS3:CHS0 bits and the TRIS bits. Note 1: When reading the Port register, all pins configured as analog input channels will read as cleared (a low level). Pins configured as digital inputs will convert as analog inputs. Analog levels on a digitally configured input will be accurately converted. 2: Analog levels on any pin defined as a digital input may cause the digital input buffer to consume current out of the device’s specification limits. 3: The PBADEN bit in Configuration Register 3H configures PORTB pins to reset as analog or digital pins by controlling how the PCFG0 bits in ADCON1 are reset. © 2007 Microchip Technology Inc. Preliminary DS39631B-page 231 PIC18F2420/2520/4420/4520 19.6 A/D Conversions Figure 19-4 shows the operation of the A/D converter after the GO bit has been set and the ACQT2:ACQT0 bits are cleared. A conversion is started after the following instruction to allow entry into Sleep mode before the conversion begins. Figure 19-5 shows the operation of the A/D converter after the GO bit has been set and the ACQT2:ACQT0 bits are set to ‘010’ and selecting a 4 TAD acquisition time before the conversion starts. Clearing the GO/DONE bit during a conversion will abort the current conversion. The A/D Result register pair will NOT be updated with the partially completed A/D conversion sample. This means the ADRESH:ADRESL registers will continue to contain the value of the last completed conversion (or the last value written to the ADRESH:ADRESL registers). After the A/D conversion is completed or aborted, a 2 TAD wait is required before the next acquisition can be started. After this wait, acquisition on the selected channel is automatically started. 19.7 Discharge The discharge phase is used to initialize the value of the capacitor array. The array is discharged before every sample. This feature helps to optimize the unitygain amplifier, as the circuit always needs to charge the capacitor array, rather than charge/discharge based on previous measure values. FIGURE 19-4: A/D CONVERSION TAD CYCLES (ACQT<2:0> = 000, TACQ = 0) FIGURE 19-5: A/D CONVERSION TAD CYCLES (ACQT<2:0> = 010, TACQ = 4 TAD) Note: The GO/DONE bit should NOT be set in the same instruction that turns on the A/D. TAD1 TAD2 TAD3 TAD4 TAD5 TAD6 TAD7 TAD8 TAD11 Set GO bit Holding capacitor is disconnected from analog input (typically 100 ns) TCY - TAD TAD9 TAD10 ADRESH:ADRESL is loaded, GO bit is cleared, ADIF bit is set, holding capacitor is connected to analog input. Conversion starts b9 b8 b7 b6 b5 b4 b3 b2 b1 b0 On the following cycle: TAD1 Discharge 1 2 3 4 5 6 7 8 11 Set GO bit (Holding capacitor is disconnected) 9 10 Conversion starts 1 2 3 4 (Holding capacitor continues acquiring input) TACQT Cycles TAD Cycles Automatic Acquisition Time b9 b8 b7 b6 b5 b4 b3 b2 b1 b0 ADRESH:ADRESL is loaded, GO bit is cleared, ADIF bit is set, holding capacitor is connected to analog input. On the following cycle: TAD1 Discharge PIC18F2420/2520/4420/4520 DS39631B-page 232 Preliminary © 2007 Microchip Technology Inc. 19.8 Use of the CCP2 Trigger An A/D conversion can be started by the Special Event Trigger of the CCP2 module. This requires that the CCP2M3:CCP2M0 bits (CCP2CON<3:0>) be programmed as ‘1011’ and that the A/D module is enabled (ADON bit is set). When the trigger occurs, the GO/DONE bit will be set, starting the A/D acquisition and conversion and the Timer1 (or Timer3) counter will be reset to zero. Timer1 (or Timer3) is reset to automatically repeat the A/D acquisition period with minimal software overhead (moving ADRESH:ADRESL to the desired location). The appropriate analog input channel must be selected and the minimum acquisition period is either timed by the user, or an appropriate TACQ time selected before the Special Event Trigger sets the GO/DONE bit (starts a conversion). If the A/D module is not enabled (ADON is cleared), the Special Event Trigger will be ignored by the A/D module, but will still reset the Timer1 (or Timer3) counter. TABLE 19-2: REGISTERS ASSOCIATED WITH A/D OPERATION Name Bit 7 Bit 6 Bit 5 Bit 4 Bit 3 Bit 2 Bit 1 Bit 0 Reset Values on page INTCON GIE/GIEH PEIE/GIEL TMR0IE INT0IE RBIE TMR0IF INT0IF RBIF 49 PIR1 PSPIF(1) ADIF RCIF TXIF SSPIF CCP1IF TMR2IF TMR1IF 52 PIE1 PSPIE(1) ADIE RCIE TXIE SSPIE CCP1IE TMR2IE TMR1IE 52 IPR1 PSPIP(1) ADIP RCIP TXIP SSPIP CCP1IP TMR2IP TMR1IP 52 PIR2 OSCFIF CMIF — EEIF BCLIF HLVDIF TMR3IF CCP2IF 52 PIE2 OSCFIE CMIE — EEIE BCLIE HLVDIE TMR3IE CCP2IE 52 IPR2 OSCFIP CMIP — EEIP BCLIP HLVDIP TMR3IP CCP2IP 52 ADRESH A/D Result Register, High Byte 51 ADRESL A/D Result Register, Low Byte 51 ADCON0 — — CHS3 CHS2 CHS1 CHS0 GO/DONE ADON 51 ADCON1 — — VCFG1 VCFG0 PCFG3 PCFG2 PCFG1 PCFG0 51 ADCON2 ADFM — ACQT2 ACQT1 ACQT0 ADCS2 ADCS1 ADCS0 51 PORTA RA7(1) RA6(1) RA5 RA4 RA3 RA2 RA1 RA0 52 TRISA TRISA7(2) TRISA6(2) PORTA Data Direction Control Register 52 PORTB RB7 RB6 RB5 RB4 RB3 RB2 RB1 RB0 52 TRISB PORTB Data Direction Control Register 52 LATB PORTB Data Latch Register (Read and Write to Data Latch) 52 PORTE(4) — — — — RE3(3) RE2 RE1 RE0 52 TRISE(4) IBF OBF IBOV PSPMODE — TRISE2 TRISE1 TRISE0 52 LATE(4) — — — — — PORTE Data Latch Register 52 Legend: — = unimplemented, read as ‘0’. Shaded cells are not used for A/D conversion. Note 1: These bits are unimplemented on 28-pin devices; always maintain these bits clear. 2: PORTA<7:6> and their direction bits are individually configured as port pins based on various primary oscillator modes. When disabled, these bits read as ‘0’. 3: RE3 port bit is available only as an input pin when the MCLRE configuration bit is ‘0’. 4: These registers are not implemented on 28-pin devices. © 2007 Microchip Technology Inc. Preliminary DS39631B-page 233 PIC18F2420/2520/4420/4520 20.0 COMPARATOR MODULE The analog comparator module contains two comparators that can be configured in a variety of ways. The inputs can be selected from the analog inputs multiplexed with pins RA0 through RA5, as well as the on-chip voltage reference (see Section 21.0 “Comparator Voltage Reference Module”). The digital outputs (normal or inverted) are available at the pin level and can also be read through the control register. The CMCON register (Register 20-1) selects the comparator input and output configuration. Block diagrams of the various comparator configurations are shown in Figure 20-1. REGISTER 20-1: CMCON REGISTER R-0 R-0 R/W-0 R/W-0 R/W-0 R/W-1 R/W-1 R/W-1 C2OUT C1OUT C2INV C1INV CIS CM2 CM1 CM0 bit 7 bit 0 bit 7 C2OUT: Comparator 2 Output bit When C2INV = 0: 1 = C2 VIN+ > C2 VIN- 0 = C2 VIN+ < C2 VINWhen C2INV = 1: 1 = C2 VIN+ < C2 VIN- 0 = C2 VIN+ > C2 VINbit 6 C1OUT: Comparator 1 Output bit When C1INV = 0: 1 = C1 VIN+ > C1 VIN- 0 = C1 VIN+ < C1 VINWhen C1INV = 1: 1 = C1 VIN+ < C1 VIN- 0 = C1 VIN+ > C1 VINbit 5 C2INV: Comparator 2 Output Inversion bit 1 = C2 output inverted 0 = C2 output not inverted bit 4 C1INV: Comparator 1 Output Inversion bit 1 = C1 output inverted 0 = C1 output not inverted bit 3 CIS: Comparator Input Switch bit When CM2:CM0 = 110: 1 = C1 VIN- connects to RA3/AN3/VREF+ C2 VIN- connects to RA2/AN2/VREF-/CVREF 0 = C1 VIN- connects to RA0/AN0 C2 VIN- connects to RA1/AN1 bit 2-0 CM2:CM0: Comparator Mode bits Figure 20-1 shows the Comparator modes and the CM2:CM0 bit settings. Legend: R = Readable bit W = Writable bit U = Unimplemented bit, read as ‘0’ -n = Value at POR ‘1’ = Bit is set ‘0’ = Bit is cleared x = Bit is unknown PIC18F2420/2520/4420/4520 DS39631B-page 234 Preliminary © 2007 Microchip Technology Inc. 20.1 Comparator Configuration There are eight modes of operation for the comparators, shown in Figure 20-1. Bits CM2:CM0 of the CMCON register are used to select these modes. The TRISA register controls the data direction of the comparator pins for each mode. If the Comparator mode is changed, the comparator output level may not be valid for the specified mode change delay shown in Section 26.0 “Electrical Characteristics”. FIGURE 20-1: COMPARATOR I/O OPERATING MODES Note: Comparator interrupts should be disabled during a Comparator mode change; otherwise, a false interrupt may occur. C1 RA0/AN0 VINRA3/ AN3/ VIN+ Off (Read as ‘0’) Comparators Reset A A CM2:CM0 = 000 C2 RA1/AN1 VINRA2/ AN2/ VIN+ Off (Read as ‘0’) A A C1 VINVIN+ C1OUT Two Independent Comparators A A CM2:CM0 = 010 C2 VINVIN+ C2OUT A A C1 VINVIN+ C1OUT Two Common Reference Comparators A A CM2:CM0 = 100 C2 VINVIN+ C2OUT A D C2 VINVIN+ Off (Read as ‘0’) One Independent Comparator with Output D D CM2:CM0 = 001 C1 VINVIN+ C1OUT A A C1 VINVIN+ Off (Read as ‘0’) Comparators Off (POR Default Value) D D CM2:CM0 = 111 C2 VINVIN+ Off (Read as ‘0’) D D C1 VINVIN+ C1OUT Four Inputs Multiplexed to Two Comparators A A CM2:CM0 = 110 C2 VINVIN+ C2OUT A A From VREF Module CIS = 0 CIS = 1 CIS = 0 CIS = 1 C1 VINVIN+ C1OUT Two Common Reference Comparators with Outputs A A CM2:CM0 = 101 C2 VINVIN+ C2OUT A D A = Analog Input, port reads zeros always D = Digital Input CIS (CMCON<3>) is the Comparator Input Switch CVREF C1 VINVIN+ C1OUT Two Independent Comparators with Outputs A A CM2:CM0 = 011 C2 VINVIN+ C2OUT A A RA5/AN4/SS/HLVDIN/C2OUT* RA4/T0CKI/C1OUT* VREF+ VREF-/CVREF RA0/AN0 RA3/AN3/ RA1/AN1 RA2/AN2/ VREF+ VREF-/CVREF RA0/AN0 RA3/AN3/ RA1/AN1 RA2/AN2/ VREF+ VREF-/CVREF RA0/AN0 RA3/AN3/ RA1/AN1 RA2/AN2/ VREF+ VREF-/CVREF RA0/AN0 RA3/AN3/ RA1/AN1 RA2/AN2/ VREF+ VREF-/CVREF RA0/AN0 RA3/AN3/ RA1/AN1 RA2/AN2/ VREF+ VREF-/CVREF RA0/AN0 RA3/AN3/ VREF+ RA1/AN1 RA2/AN2/ VREF-/CVREF RA4/T0CKI/C1OUT* RA5/AN4/SS/HLVDIN/C2OUT* RA0/AN0 RA3/AN3/ VREF+ RA1/AN1 RA2/AN2/ VREF-/CVREF RA4/T0CKI/C1OUT* * Setting the TRISA<5:4> bits will disable the comparator outputs by configuring the pins as inputs. © 2007 Microchip Technology Inc. Preliminary DS39631B-page 235 PIC18F2420/2520/4420/4520 20.2 Comparator Operation A single comparator is shown in Figure 20-2, along with the relationship between the analog input levels and the digital output. When the analog input at VIN+ is less than the analog input VIN-, the output of the comparator is a digital low level. When the analog input at VIN+ is greater than the analog input VIN-, the output of the comparator is a digital high level. The shaded areas of the output of the comparator in Figure 20-2 represent the uncertainty, due to input offsets and response time. 20.3 Comparator Reference Depending on the comparator operating mode, either an external or internal voltage reference may be used. The analog signal present at VIN- is compared to the signal at VIN+ and the digital output of the comparator is adjusted accordingly (Figure 20-2). FIGURE 20-2: SINGLE COMPARATOR 20.3.1 EXTERNAL REFERENCE SIGNAL When external voltage references are used, the comparator module can be configured to have the comparators operate from the same or different reference sources. However, threshold detector applications may require the same reference. The reference signal must be between VSS and VDD and can be applied to either pin of the comparator(s). 20.3.2 INTERNAL REFERENCE SIGNAL The comparator module also allows the selection of an internally generated voltage reference from the comparator voltage reference module. This module is described in more detail in Section 21.0 “Comparator Voltage Reference Module”. The internal reference is only available in the mode where four inputs are multiplexed to two comparators (CM2:CM0 = 110). In this mode, the internal voltage reference is applied to the VIN+ pin of both comparators. 20.4 Comparator Response Time Response time is the minimum time, after selecting a new reference voltage or input source, before the comparator output has a valid level. If the internal reference is changed, the maximum delay of the internal voltage reference must be considered when using the comparator outputs. Otherwise, the maximum delay of the comparators should be used (see Section 26.0 “Electrical Characteristics”). 20.5 Comparator Outputs The comparator outputs are read through the CMCON register. These bits are read-only. The comparator outputs may also be directly output to the RA4 and RA5 I/O pins. When enabled, multiplexors in the output path of the RA4 and RA5 pins will switch and the output of each pin will be the unsynchronized output of the comparator. The uncertainty of each of the comparators is related to the input offset voltage and the response time given in the specifications. Figure 20-3 shows the comparator output block diagram. The TRISA bits will still function as an output enable/ disable for the RA4 and RA5 pins while in this mode. The polarity of the comparator outputs can be changed using the C2INV and C1INV bits (CMCON<4:5>). – VIN+ + VINOutput Output VINVIN+ Note 1: When reading the Port register, all pins configured as analog inputs will read as a ‘0’. Pins configured as digital inputs will convert an analog input according to the Schmitt Trigger input specification. 2: Analog levels on any pin defined as a digital input may cause the input buffer to consume more current than is specified. PIC18F2420/2520/4420/4520 DS39631B-page 236 Preliminary © 2007 Microchip Technology Inc. FIGURE 20-3: COMPARATOR OUTPUT BLOCK DIAGRAM 20.6 Comparator Interrupts The comparator interrupt flag is set whenever there is a change in the output value of either comparator. Software will need to maintain information about the status of the output bits, as read from CMCON<7:6>, to determine the actual change that occurred. The CMIF bit (PIR2<6>) is the Comparator Interrupt Flag. The CMIF bit must be reset by clearing it. Since it is also possible to write a ‘1’ to this register, a simulated interrupt may be initiated. Both the CMIE bit (PIE2<6>) and the PEIE bit (INTCON<6>) must be set to enable the interrupt. In addition, the GIE bit (INTCON<7>) must also be set. If any of these bits are clear, the interrupt is not enabled, though the CMIF bit will still be set if an interrupt condition occurs. The user, in the Interrupt Service Routine, can clear the interrupt in the following manner: a) Any read or write of CMCON will end the mismatch condition. b) Clear flag bit CMIF. A mismatch condition will continue to set flag bit CMIF. Reading CMCON will end the mismatch condition and allow flag bit CMIF to be cleared. 20.7 Comparator Operation During Sleep When a comparator is active and the device is placed in Sleep mode, the comparator remains active and the interrupt is functional if enabled. This interrupt will wake-up the device from Sleep mode, when enabled. Each operational comparator will consume additional current, as shown in the comparator specifications. To minimize power consumption while in Sleep mode, turn off the comparators (CM2:CM0 = 111) before entering Sleep. If the device wakes up from Sleep, the contents of the CMCON register are not affected. 20.8 Effects of a Reset A device Reset forces the CMCON register to its Reset state, causing the comparator modules to be turned off (CM2:CM0 = 111). However, the input pins (RA0 through RA3) are configured as analog inputs by default on device Reset. The I/O configuration for these pins is determined by the setting of the PCFG3:PCFG0 bits (ADCON1<3:0>). Therefore, device current is minimized when analog inputs are present at Reset time. D Q EN To RA4 or RA5 pin Bus Data Set MULTIPLEX CMIF bit - + Port pins Read CMCON Reset From other Comparator CxINV D Q EN CL Note: If a change in the CMCON register (C1OUT or C2OUT) should occur when a read operation is being executed (start of the Q2 cycle), then the CMIF (PIR registers) interrupt flag may not get set. © 2007 Microchip Technology Inc. Preliminary DS39631B-page 237 PIC18F2420/2520/4420/4520 20.9 Analog Input Connection Considerations A simplified circuit for an analog input is shown in Figure 20-4. Since the analog pins are connected to a digital output, they have reverse biased diodes to VDD and VSS. The analog input, therefore, must be between VSS and VDD. If the input voltage deviates from this range by more than 0.6V in either direction, one of the diodes is forward biased and a latch-up condition may occur. A maximum source impedance of 10 kΩ is recommended for the analog sources. Any external component connected to an analog input pin, such as a capacitor or a Zener diode, should have very little leakage current. FIGURE 20-4: COMPARATOR ANALOG INPUT MODEL TABLE 20-1: REGISTERS ASSOCIATED WITH COMPARATOR MODULE VA RS < 10k AIN CPIN 5 pF VDD VT = 0.6V VT = 0.6V RIC ILEAKAGE ±500 nA VSS Legend: CPIN = Input Capacitance VT = Threshold Voltage ILEAKAGE = Leakage Current at the pin due to various junctions RIC = Interconnect Resistance RS = Source Impedance VA = Analog Voltage Comparator Input Name Bit 7 Bit 6 Bit 5 Bit 4 Bit 3 Bit 2 Bit 1 Bit 0 Reset Values on page CMCON C2OUT C1OUT C2INV C1INV CIS CM2 CM1 CM0 51 CVRCON CVREN CVROE CVRR CVRSS CVR3 CVR2 CVR1 CVR0 51 INTCON GIE/GIEH PEIE/GIEL TMR0IE INT0IE RBIE TMR0IF INT0IF RBIF 52 PIR2 OSCFIF CMIF — EEIF BCLIF HLVDIF TMR3IF CCP2IF 52 PIE2 OSCFIE CMIE — EEIE BCLIE HLVDIE TMR3IE CCP2IE 52 IPR2 OSCFIP CMIP — EEIP BCLIP HLVDIP TMR3IP CCP2IP 52 PORTA RA7(1) RA6(1) RA5 RA4 RA3 RA2 RA1 RA0 52 LATA LATA7(1) LATA6(1) PORTA Data Latch Register (Read and Write to Data Latch) 52 TRISA TRISA7(1) TRISA6(1) PORTA Data Direction Control Register 52 Legend: — = unimplemented, read as ‘0’. Shaded cells are unused by the comparator module. Note 1: PORTA<7:6> and their direction and latch bits are individually configured as port pins based on various primary oscillator modes. When disabled, these bits read as ‘0’. PIC18F2420/2520/4420/4520 DS39631B-page 238 Preliminary © 2007 Microchip Technology Inc. NOTES: © 2007 Microchip Technology Inc. Preliminary DS39631B-page 239 PIC18F2420/2520/4420/4520 21.0 COMPARATOR VOLTAGE REFERENCE MODULE The comparator voltage reference is a 16-tap resistor ladder network that provides a selectable reference voltage. Although its primary purpose is to provide a reference for the analog comparators, it may also be used independently of them. A block diagram of the module is shown in Figure 21-1. The resistor ladder is segmented to provide two ranges of CVREF values and has a power-down function to conserve power when the reference is not being used. The module’s supply reference can be provided from either device VDD/VSS or an external voltage reference. 21.1 Configuring the Comparator Voltage Reference The voltage reference module is controlled through the CVRCON register (Register 21-1). The comparator voltage reference provides two ranges of output voltage, each with 16 distinct levels. The range to be used is selected by the CVRR bit (CVRCON<5>). The primary difference between the ranges is the size of the steps selected by the CVREF Selection bits (CVR3:CVR0), with one range offering finer resolution. The equations used to calculate the output of the comparator voltage reference are as follows: If CVRR = 1: CVREF = ((CVR3:CVR0)/24) x CVRSRC If CVRR = 0: CVREF = (CVRSRC x 1/4) + (((CVR3:CVR0)/32) x CVRSRC) The comparator reference supply voltage can come from either VDD and VSS, or the external VREF+ and VREF- that are multiplexed with RA2 and RA3. The voltage source is selected by the CVRSS bit (CVRCON<4>). The settling time of the comparator voltage reference must be considered when changing the CVREF output (see Table 26-3 in Section 26.0 “Electrical Characteristics”). REGISTER 21-1: CVRCON REGISTER R/W-0 R/W-0 R/W-0 R/W-0 R/W-0 R/W-0 R/W-0 R/W-0 CVREN CVROE(1) CVRR CVRSS CVR3 CVR2 CVR1 CVR0 bit 7 bit 0 bit 7 CVREN: Comparator Voltage Reference Enable bit 1 = CVREF circuit powered on 0 = CVREF circuit powered down bit 6 CVROE: Comparator VREF Output Enable bit(1) 1 = CVREF voltage level is also output on the RA2/AN2/VREF-/CVREF pin 0 = CVREF voltage is disconnected from the RA2/AN2/VREF-/CVREF pin Note 1: CVROE overrides the TRISA<2> bit setting. bit 5 CVRR: Comparator VREF Range Selection bit 1 = 0 to 0.667 CVRSRC, with CVRSRC/24 step size (low range) 0 = 0.25 CVRSRC to 0.75 CVRSRC, with CVRSRC/32 step size (high range) bit 4 CVRSS: Comparator VREF Source Selection bit 1 = Comparator reference source, CVRSRC = (VREF+) – (VREF-) 0 = Comparator reference source, CVRSRC = VDD – VSS bit 3-0 CVR3:CVR0: Comparator VREF Value Selection bits (0 ≤ (CVR3:CVR0) ≤ 15) When CVRR = 1: CVREF = ((CVR3:CVR0)/24) • (CVRSRC) When CVRR = 0: CVREF = (CVRSRC/4) + ((CVR3:CVR0)/32) • (CVRSRC) Legend: R = Readable bit W = Writable bit U = Unimplemented bit, read as ‘0’ -n = Value at POR ‘1’ = Bit is set ‘0’ = Bit is cleared x = Bit is unknown PIC18F2420/2520/4420/4520 DS39631B-page 240 Preliminary © 2007 Microchip Technology Inc. FIGURE 21-1: VOLTAGE REFERENCE BLOCK DIAGRAM 21.2 Voltage Reference Accuracy/Error The full range of voltage reference cannot be realized due to the construction of the module. The transistors on the top and bottom of the resistor ladder network (Figure 21-1) keep CVREF from approaching the reference source rails. The voltage reference is derived from the reference source; therefore, the CVREF output changes with fluctuations in that source. The tested absolute accuracy of the voltage reference can be found in Section 26.0 “Electrical Characteristics”. 21.3 Operation During Sleep When the device wakes up from Sleep through an interrupt or a Watchdog Timer time-out, the contents of the CVRCON register are not affected. To minimize current consumption in Sleep mode, the voltage reference should be disabled. 21.4 Effects of a Reset A device Reset disables the voltage reference by clearing bit, CVREN (CVRCON<7>). This Reset also disconnects the reference from the RA2 pin by clearing bit, CVROE (CVRCON<6>) and selects the high-voltage range by clearing bit, CVRR (CVRCON<5>). The CVR value select bits are also cleared. 21.5 Connection Considerations The voltage reference module operates independently of the comparator module. The output of the reference generator may be connected to the RA2 pin if the CVROE bit is set. Enabling the voltage reference output onto RA2 when it is configured as a digital input will increase current consumption. Connecting RA2 as a digital output with CVRSS enabled will also increase current consumption. The RA2 pin can be used as a simple D/A output with limited drive capability. Due to the limited current drive capability, a buffer must be used on the voltage reference output for external connections to VREF. Figure 21-2 shows an example buffering technique. 16-to-1 MUX CVR3:CVR0 8R CVREN R CVRSS = 0 VDD VREF+ CVRSS = 1 8R CVRSS = 0 VREFCVRSS = 1 R R R R R R 16 Steps CVRR CVREF © 2007 Microchip Technology Inc. Preliminary DS39631B-page 241 PIC18F2420/2520/4420/4520 FIGURE 21-2: VOLTAGE REFERENCE OUTPUT BUFFER EXAMPLE TABLE 21-1: REGISTERS ASSOCIATED WITH COMPARATOR VOLTAGE REFERENCE CVREF Output + – CVREF Module Voltage Reference Output Impedance R(1) RA2 Note 1: R is dependent upon the voltage reference configuration bits, CVRCON<3:0> and CVRCON<5>. PIC18FXXXX Name Bit 7 Bit 6 Bit 5 Bit 4 Bit 3 Bit 2 Bit 1 Bit 0 Reset Values on page CVRCON CVREN CVROE CVRR CVRSS CVR3 CVR2 CVR1 CVR0 51 CMCON C2OUT C1OUT C2INV C1INV CIS CM2 CM1 CM0 51 TRISA TRISA7(1) TRISA6(1) PORTA Data Direction Control Register 52 Legend: Shaded cells are not used with the comparator voltage reference. Note 1: PORTA pins are enabled based on oscillator configuration. PIC18F2420/2520/4420/4520 DS39631B-page 242 Preliminary © 2007 Microchip Technology Inc. NOTES: © 2007 Microchip Technology Inc. DS39631B-page 243 PIC18F2420/2520/4420/4520 22.0 HIGH/LOW-VOLTAGE DETECT (HLVD) PIC18F2420/2520/4420/4520 devices have a High/Low-Voltage Detect module (HLVD). This is a programmable circuit that allows the user to specify both a device voltage trip point and the direction of change from that point. If the device experiences an excursion past the trip point in that direction, an interrupt flag is set. If the interrupt is enabled, the program execution will branch to the interrupt vector address and the software can then respond to the interrupt. The High/Low-Voltage Detect Control register (Register 22-1) completely controls the operation of the HLVD module. This allows the circuitry to be “turned off” by the user under software control, which minimizes the current consumption for the device. The block diagram for the HLVD module is shown in Figure 22-1. REGISTER 22-1: HLVDCON REGISTER (HIGH/LOW-VOLTAGE DETECT CONTROL) R/W-0 U-0 R-0 R/W-0 R/W-0 R/W-1 R/W-0 R/W-1 VDIRMAG — IRVST HLVDEN HLVDL3(1) HLVDL2(1) HLVDL1(1) HLVDL0(1) bit 7 bit 0 bit 7 VDIRMAG: Voltage Direction Magnitude Select bit 1 = Event occurs when voltage equals or exceeds trip point (HLVDL3:HLDVL0) 0 = Event occurs when voltage equals or falls below trip point (HLVDL3:HLVDL0) bit 6 Unimplemented: Read as ‘0’ bit 5 IRVST: Internal Reference Voltage Stable Flag bit 1 = Indicates that the voltage detect logic will generate the interrupt flag at the specified voltage range 0 = Indicates that the voltage detect logic will not generate the interrupt flag at the specified voltage range and the HLVD interrupt should not be enabled bit 4 HLVDEN: High/Low-Voltage Detect Power Enable bit 1 = HLVD enabled 0 = HLVD disabled bit 3-0 HLVDL3:HLVDL0: Voltage Detection Limit bits(1) 1111 = External analog input is used (input comes from the HLVDIN pin) 1110 = Maximum setting . . . 0000 = Minimum setting Note 1: See Table 26-4 for specifications. Legend: R = Readable bit W = Writable bit U = Unimplemented bit, read as ‘0’ -n = Value at POR ‘1’ = Bit is set ‘0’ = Bit is cleared x = Bit is unknown PIC18F2420/2520/4420/4520 DS39631B-page 244 © 2007 Microchip Technology Inc. The module is enabled by setting the HLVDEN bit. Each time that the HLVD module is enabled, the circuitry requires some time to stabilize. The IRVST bit is a read-only bit and is used to indicate when the circuit is stable. The module can only generate an interrupt after the circuit is stable and IRVST is set. The VDIRMAG bit determines the overall operation of the module. When VDIRMAG is cleared, the module monitors for drops in VDD below a predetermined set point. When the bit is set, the module monitors for rises in VDD above the set point. 22.1 Operation When the HLVD module is enabled, a comparator uses an internally generated reference voltage as the set point. The set point is compared with the trip point, where each node in the resistor divider represents a trip point voltage. The “trip point” voltage is the voltage level at which the device detects a high or low-voltage event, depending on the configuration of the module. When the supply voltage is equal to the trip point, the voltage tapped off of the resistor array is equal to the internal reference voltage generated by the voltage reference module. The comparator then generates an interrupt signal by setting the HLVDIF bit. The trip point voltage is software programmable to any one of 16 values. The trip point is selected by programming the HLVDL3:HLVDL0 bits (HLVDCON<3:0>). The HLVD module has an additional feature that allows the user to supply the trip voltage to the module from an external source. This mode is enabled when bits HLVDL3:HLVDL0 are set to ‘1111’. In this state, the comparator input is multiplexed from the external input pin, HLVDIN. This gives users flexibility because it allows them to configure the High/Low-Voltage Detect interrupt to occur at any voltage in the valid operating range. FIGURE 22-1: HLVD MODULE BLOCK DIAGRAM (WITH EXTERNAL INPUT) Set VDD 16 to 1 MUX HLVDEN HLVDCON HLVDIN HLVDL3:HLVDL0 Register HLVDIN VDD Externally Generated Trip Point HLVDIF HLVDEN BOREN Internal Voltage Reference VDIRMAG © 2007 Microchip Technology Inc. DS39631B-page 245 PIC18F2420/2520/4420/4520 22.2 HLVD Setup The following steps are needed to set up the HLVD module: 1. Write the value to the HLVDL3:HLVDL0 bits that selects the desired HLVD trip point. 2. Set the VDIRMAG bit to detect high voltage (VDIRMAG = 1) or low voltage (VDIRMAG = 0). 3. Enable the HLVD module by setting the HLVDEN bit. 4. Clear the HLVD interrupt flag (PIR2<2>), which may have been set from a previous interrupt. 5. Enable the HLVD interrupt if interrupts are desired by setting the HLVDIE and GIE bits (PIE2<2> and INTCON<7>). An interrupt will not be generated until the IRVST bit is set. 22.3 Current Consumption When the module is enabled, the HLVD comparator and voltage divider are enabled and will consume static current. The total current consumption, when enabled, is specified in electrical specification parameter D022B. Depending on the application, the HLVD module does not need to be operating constantly. To decrease the current requirements, the HLVD circuitry may only need to be enabled for short periods where the voltage is checked. After doing the check, the HLVD module may be disabled. 22.4 HLVD Start-up Time The internal reference voltage of the HLVD module, specified in electrical specification parameter D420, may be used by other internal circuitry, such as the Programmable Brown-out Reset. If the HLVD or other circuits using the voltage reference are disabled to lower the device’s current consumption, the reference voltage circuit will require time to become stable before a low or high-voltage condition can be reliably detected. This start-up time, TIRVST, is an interval that is independent of device clock speed. It is specified in electrical specification parameter 36. The HLVD interrupt flag is not enabled until TIRVST has expired and a stable reference voltage is reached. For this reason, brief excursions beyond the set point may not be detected during this interval. Refer to Figure 22-2 or Figure 22-3. FIGURE 22-2: LOW-VOLTAGE DETECT OPERATION (VDIRMAG = 0) VLVD VDD HLVDIF VLVD VDD Enable HLVD TIVRST HLVDIF may not be set Enable HLVD HLVDIF HLVDIF cleared in software HLVDIF cleared in software HLVDIF cleared in software, CASE 1: CASE 2: HLVDIF remains set since HLVD condition still exists TIVRST Internal Reference is stable Internal Reference is stable IRVST IRVST PIC18F2420/2520/4420/4520 DS39631B-page 246 © 2007 Microchip Technology Inc. FIGURE 22-3: HIGH-VOLTAGE DETECT OPERATION (VDIRMAG = 1) 22.5 Applications In many applications, the ability to detect a drop below or rise above a particular threshold is desirable. For example, the HLVD module could be periodically enabled to detect Universal Serial Bus (USB) attach or detach. This assumes the device is powered by a lower voltage source than the USB when detached. An attach would indicate a high-voltage detect from, for example, 3.3V to 5V (the voltage on USB) and vice versa for a detach. This feature could save a design a few extra components and an attach signal (input pin). For general battery applications, Figure 22-4 shows a possible voltage curve. Over time, the device voltage decreases. When the device voltage reaches voltage VA, the HLVD logic generates an interrupt at time TA. The interrupt could cause the execution of an ISR, which would allow the application to perform “housekeeping tasks” and perform a controlled shutdown before the device voltage exits the valid operating range at TB. The HLVD, thus, would give the application a time window, represented by the difference between TA and TB, to safely exit. FIGURE 22-4: TYPICAL LOW-VOLTAGE DETECT APPLICATION VLVD VDD HLVDIF VLVD VDD Enable HLVD TIVRST HLVDIF may not be set Enable HLVD HLVDIF HLVDIF cleared in software HLVDIF cleared in software HLVDIF cleared in software, CASE 1: CASE 2: HLVDIF remains set since HLVD condition still exists TIVRST IRVST Internal Reference is stable Internal Reference is stable IRVST Time Voltage VA VB TA TB VA = HLVD trip point VB = Minimum valid device operating voltage Legend: © 2007 Microchip Technology Inc. DS39631B-page 247 PIC18F2420/2520/4420/4520 22.6 Operation During Sleep When enabled, the HLVD circuitry continues to operate during Sleep. If the device voltage crosses the trip point, the HLVDIF bit will be set and the device will wake-up from Sleep. Device execution will continue from the interrupt vector address if interrupts have been globally enabled. 22.7 Effects of a Reset A device Reset forces all registers to their Reset state. This forces the HLVD module to be turned off. TABLE 22-1: REGISTERS ASSOCIATED WITH HIGH/LOW-VOLTAGE DETECT MODULE Name Bit 7 Bit 6 Bit 5 Bit 4 Bit 3 Bit 2 Bit 1 Bit 0 Reset Values on Page HLVDCON VDIRMAG — IRVST HLVDEN HLVDL3 HLVDL2 HLVDL1 HLVDL0 50 INTCON GIE/GIEH PEIE/GIEL TMR0IE INT0IE RBIE TMR0IF INT0IF RBIF 49 PIR2 OSCFIF CMIF — EEIF BCLIF HLVDIF TMR3IF CCP2IF 52 PIE2 OCSFIE CMIE — EEIE BCLIE HLVDIE TMR3IE CCP2IE 52 IPR2 OSCFIP CMIP — EEIP BCLIP HLVDIP TMR3IP CCP2IP 52 Legend: — = unimplemented, read as ‘0’. Shaded cells are unused by the HLVD module. PIC18F2420/2520/4420/4520 DS39631B-page 248 © 2007 Microchip Technology Inc. NOTES: © 2007 Microchip Technology Inc. Preliminary DS39631B-page 249 PIC18F2420/2520/4420/4520 23.0 SPECIAL FEATURES OF THE CPU PIC18F2420/2520/4420/4520 devices include several features intended to maximize reliability and minimize cost through elimination of external components. These are: • Oscillator Selection • Resets: - Power-on Reset (POR) - Power-up Timer (PWRT) - Oscillator Start-up Timer (OST) - Brown-out Reset (BOR) • Interrupts • Watchdog Timer (WDT) • Fail-Safe Clock Monitor • Two-Speed Start-up • Code Protection • ID Locations • In-Circuit Serial Programming The oscillator can be configured for the application depending on frequency, power, accuracy and cost. All of the options are discussed in detail in Section 2.0 “Oscillator Configurations”. A complete discussion of device Resets and interrupts is available in previous sections of this data sheet. In addition to their Power-up and Oscillator Start-up Timers provided for Resets, PIC18F2420/2520/4420/ 4520 devices have a Watchdog Timer, which is either permanently enabled via the configuration bits or software controlled (if configured as disabled). The inclusion of an internal RC oscillator also provides the additional benefits of a Fail-Safe Clock Monitor (FSCM) and Two-Speed Start-up. FSCM provides for background monitoring of the peripheral clock and automatic switchover in the event of its failure. Two- Speed Start-up enables code to be executed almost immediately on start-up, while the primary clock source completes its start-up delays. All of these features are enabled and configured by setting the appropriate configuration register bits. 23.1 Configuration Bits The configuration bits can be programmed (read as ‘0’) or left unprogrammed (read as ‘1’) to select various device configurations. These bits are mapped starting at program memory location 300000h. The user will note that address 300000h is beyond the user program memory space. In fact, it belongs to the configuration memory space (300000h-3FFFFFh), which can only be accessed using table reads and table writes. Programming the configuration registers is done in a manner similar to programming the Flash memory. The WR bit in the EECON1 register starts a self-timed write to the configuration register. In normal operation mode, a TBLWT instruction with the TBLPTR pointing to the configuration register sets up the address and the data for the configuration register write. Setting the WR bit starts a long write to the configuration register. The configuration registers are written a byte at a time. To write or erase a configuration cell, a TBLWT instruction can write a ‘1’ or a ‘0’ into the cell. For additional details on Flash programming, refer to Section 6.5 “Writing to Flash Program Memory”. TABLE 23-1: CONFIGURATION BITS AND DEVICE IDs File Name Bit 7 Bit 6 Bit 5 Bit 4 Bit 3 Bit 2 Bit 1 Bit 0 Default/ Unprogrammed Value 300001h CONFIG1H IESO FCMEN — — FOSC3 FOSC2 FOSC1 FOSC0 00-- 0111 300002h CONFIG2L — — — BORV1 BORV0 BOREN1 BOREN0 PWRTEN ---1 1111 300003h CONFIG2H — — — WDTPS3 WDTPS2 WDTPS1 WDTPS0 WDTEN ---1 1111 300005h CONFIG3H MCLRE — — — — LPT1OSC PBADEN CCP2MX 1--- -011 300006h CONFIG4L DEBUG XINST — — — LVP — STVREN 10-- -1-1 300008h CONFIG5L — — — — CP3(1) CP2(1) CP1 CP0 ---- 1111 300009h CONFIG5H CPD CPB — — — — — — 11-- ---- 30000Ah CONFIG6L — — — — WRT3(1) WRT2(1) WRT1 WRT0 ---- 1111 30000Bh CONFIG6H WRTD WRTB WRTC — — — — — 111- ---- 30000Ch CONFIG7L — — — — EBTR3(1) EBTR2(1) EBTR1 EBTR0 ---- 1111 30000Dh CONFIG7H — EBTRB — — — — — — -1-- ---- 3FFFFEh DEVID1(1) DEV2 DEV1 DEV0 REV4 REV3 REV2 REV1 REV0 xxxx xxxx(2) 3FFFFFh DEVID2(1) DEV10 DEV9 DEV8 DEV7 DEV6 DEV5 DEV4 DEV3 0000 1100 Legend: x = unknown, u = unchanged, — = unimplemented, q = value depends on condition. Shaded cells are unimplemented, read as ‘0’. Note 1: Unimplemented in PIC18F2420/4420 devices; maintain this bit set. 2: See Register 23-14 for DEVID1 values. DEVID registers are read-only and cannot be programmed by the user. PIC18F2420/2520/4420/4520 DS39631B-page 250 Preliminary © 2007 Microchip Technology Inc. REGISTER 23-1: CONFIG1H: CONFIGURATION REGISTER 1 HIGH (BYTE ADDRESS 300001h) R/P-0 R/P-0 U-0 U-0 R/P-0 R/P-1 R/P-1 R/P-1 IESO FCMEN — — FOSC3 FOSC2 FOSC1 FOSC0 bit 7 bit 0 bit 7 IESO: Internal/External Oscillator Switchover bit 1 = Oscillator Switchover mode enabled 0 = Oscillator Switchover mode disabled bit 6 FCMEN: Fail-Safe Clock Monitor Enable bit 1 = Fail-Safe Clock Monitor enabled 0 = Fail-Safe Clock Monitor disabled bit 5-4 Unimplemented: Read as ‘0’ bit 3-0 FOSC3:FOSC0: Oscillator Selection bits 11xx = External RC oscillator, CLKO function on RA6 101x = External RC oscillator, CLKO function on RA6 1001 = Internal oscillator block, CLKO function on RA6, port function on RA7 1000 = Internal oscillator block, port function on RA6 and RA7 0111 = External RC oscillator, port function on RA6 0110 = HS oscillator, PLL enabled (Clock Frequency = 4 x FOSC1) 0101 = EC oscillator, port function on RA6 0100 = EC oscillator, CLKO function on RA6 0011 = External RC oscillator, CLKO function on RA6 0010 = HS oscillator 0001 = XT oscillator 0000 = LP oscillator Legend: R = Readable bit P = Programmable bit U = Unimplemented bit, read as ‘0’ -n = Value when device is unprogrammed u = Unchanged from programmed state © 2007 Microchip Technology Inc. Preliminary DS39631B-page 251 PIC18F2420/2520/4420/4520 REGISTER 23-2: CONFIG2L: CONFIGURATION REGISTER 2 LOW (BYTE ADDRESS 300002h) U-0 U-0 U-0 R/P-1 R/P-1 R/P-1 R/P-1 R/P-1 — — — BORV1(1) BORV0(1) BOREN1(2) BOREN0(2) PWRTEN(2) bit 7 bit 0 bit 7-5 Unimplemented: Read as ‘0’ bit 4-3 BORV1:BORV0: Brown-out Reset Voltage bits(1) 11 = Maximum setting . . . 00 = Minimum setting bit 2-1 BOREN1:BOREN0: Brown-out Reset Enable bits(2) 11 = Brown-out Reset enabled in hardware only (SBOREN is disabled) 10 = Brown-out Reset enabled in hardware only and disabled in Sleep mode (SBOREN is disabled) 01 = Brown-out Reset enabled and controlled by software (SBOREN is enabled) 00 = Brown-out Reset disabled in hardware and software bit 0 PWRTEN: Power-up Timer Enable bit(2) 1 = PWRT disabled 0 = PWRT enabled Note 1: See Section 26.1 “DC Characteristics: Supply Voltage” for specifications. 2: The Power-up Timer is decoupled from Brown-out Reset, allowing these features to be independently controlled. Legend: R = Readable bit P = Programmable bit U = Unimplemented bit, read as ‘0’ -n = Value when device is unprogrammed u = Unchanged from programmed state PIC18F2420/2520/4420/4520 DS39631B-page 252 Preliminary © 2007 Microchip Technology Inc. REGISTER 23-3: CONFIG2H: CONFIGURATION REGISTER 2 HIGH (BYTE ADDRESS 300003h) U-0 U-0 U-0 R/P-1 R/P-1 R/P-1 R/P-1 R/P-1 — — — WDTPS3 WDTPS2 WDTPS1 WDTPS0 WDTEN bit 7 bit 0 bit 7-5 Unimplemented: Read as ‘0’ bit 4-1 WDTPS3:WDTPS0: Watchdog Timer Postscale Select bits 1111 = 1:32,768 1110 = 1:16,384 1101 = 1:8,192 1100 = 1:4,096 1011 = 1:2,048 1010 = 1:1,024 1001 = 1:512 1000 = 1:256 0111 = 1:128 0110 = 1:64 0101 = 1:32 0100 = 1:16 0011 = 1:8 0010 = 1:4 0001 = 1:2 0000 = 1:1 bit 0 WDTEN: Watchdog Timer Enable bit 1 = WDT enabled 0 = WDT disabled (control is placed on the SWDTEN bit) Legend: R = Readable bit P = Programmable bit U = Unimplemented bit, read as ‘0’ -n = Value when device is unprogrammed u = Unchanged from programmed state © 2007 Microchip Technology Inc. Preliminary DS39631B-page 253 PIC18F2420/2520/4420/4520 REGISTER 23-4: CONFIG3H: CONFIGURATION REGISTER 3 HIGH (BYTE ADDRESS 300005h) REGISTER 23-5: CONFIG4L: CONFIGURATION REGISTER 4 LOW (BYTE ADDRESS 300006h) R/P-1 U-0 U-0 U-0 U-0 R/P-0 R/P-1 R/P-1 MCLRE — — — — LPT1OSC PBADEN CCP2MX bit 7 bit 0 bit 7 MCLRE: MCLR Pin Enable bit 1 = MCLR pin enabled; RE3 input pin disabled 0 = RE3 input pin enabled; MCLR disabled bit 6-3 Unimplemented: Read as ‘0’ bit 2 LPT1OSC: Low-Power Timer1 Oscillator Enable bit 1 = Timer1 configured for low-power operation 0 = Timer1 configured for higher power operation bit 1 PBADEN: PORTB A/D Enable bit (Affects ADCON1 Reset state. ADCON1 controls PORTB<4:0> pin configuration.) 1 = PORTB<4:0> pins are configured as analog input channels on Reset 0 = PORTB<4:0> pins are configured as digital I/O on Reset bit 0 CCP2MX: CCP2 Mux bit 1 = CCP2 input/output is multiplexed with RC1 0 = CCP2 input/output is multiplexed with RB3 Legend: R = Readable bit P = Programmable bit U = Unimplemented bit, read as ‘0’ -n = Value when device is unprogrammed u = Unchanged from programmed state R/P-1 R/P-0 U-0 U-0 U-0 R/P-1 U-0 R/P-1 DEBUG XINST — — — LVP — STVREN bit 7 bit 0 bit 7 DEBUG: Background Debugger Enable bit 1 = Background debugger disabled, RB6 and RB7 configured as general purpose I/O pins 0 = Background debugger enabled, RB6 and RB7 are dedicated to In-Circuit Debug bit 6 XINST: Extended Instruction Set Enable bit 1 = Instruction set extension and Indexed Addressing mode enabled 0 = Instruction set extension and Indexed Addressing mode disabled (Legacy mode) bit 5-3 Unimplemented: Read as ‘0’ bit 2 LVP: Single-Supply ICSP Enable bit 1 = Single-Supply ICSP enabled 0 = Single-Supply ICSP disabled bit 1 Unimplemented: Read as ‘0’ bit 0 STVREN: Stack Full/Underflow Reset Enable bit 1 = Stack full/underflow will cause Reset 0 = Stack full/underflow will not cause Reset Legend: R = Readable bit C = Clearable bit U = Unimplemented bit, read as ‘0’ -n = Value when device is unprogrammed u = Unchanged from programmed state PIC18F2420/2520/4420/4520 DS39631B-page 254 Preliminary © 2007 Microchip Technology Inc. REGISTER 23-6: CONFIG5L: CONFIGURATION REGISTER 5 LOW (BYTE ADDRESS 300008h) REGISTER 23-7: CONFIG5H: CONFIGURATION REGISTER 5 HIGH (BYTE ADDRESS 300009h) U-0 U-0 U-0 U-0 R/C-1 R/C-1 R/C-1 R/C-1 — — — — CP3(1,2) CP2(1) CP1 CP0 bit 7 bit 0 bit 7-4 Unimplemented: Read as ‘0’ bit 3 CP3: Code Protection bit(1,2) 1 = Block 3 (006000-007FFFh) not code-protected 0 = Block 3 (006000-007FFFh) code-protected bit 2 CP2: Code Protection bit(1) 1 = Block 2 (004000-005FFFh) not code-protected 0 = Block 2 (004000-005FFFh) code-protected bit 1 CP1: Code Protection bit 1 = Block 1 (002000-003FFFh) not code-protected 0 = Block 1 (002000-003FFFh) code-protected bit 0 CP0: Code Protection bit 1 = Block 0 (000800-001FFFh) not code-protected 0 = Block 0 (000800-001FFFh) code-protected Note 1: Unimplemented in PIC18F2420/4420 devices; maintain this bit set. 2: Unimplemented in PIC18F2425/4425 devices; maintain this bit set. Legend: R = Readable bit C = Clearable bit U = Unimplemented bit, read as ‘0’ -n = Value when device is unprogrammed u = Unchanged from programmed state R/C-1 R/C-1 U-0 U-0 U-0 U-0 U-0 U-0 CPD CPB — — — — — — bit 7 bit 0 bit 7 CPD: Data EEPROM Code Protection bit 1 = Data EEPROM not code-protected 0 = Data EEPROM code-protected bit 6 CPB: Boot Block Code Protection bit 1 = Boot block (000000-0007FFh) not code-protected 0 = Boot block (000000-0007FFh) code-protected bit 5-0 Unimplemented: Read as ‘0’ Legend: R = Readable bit C = Clearable bit U = Unimplemented bit, read as ‘0’ -n = Value when device is unprogrammed u = Unchanged from programmed state © 2007 Microchip Technology Inc. Preliminary DS39631B-page 255 PIC18F2420/2520/4420/4520 REGISTER 23-8: CONFIG6L: CONFIGURATION REGISTER 6 LOW (BYTE ADDRESS 30000Ah) REGISTER 23-9: CONFIG6H: CONFIGURATION REGISTER 6 HIGH (BYTE ADDRESS 30000Bh) U-0 U-0 U-0 U-0 R/C-1 R/C-1 R/C-1 R/C-1 — — — — WRT3(1,2) WRT2(1) WRT1 WRT0 bit 7 bit 0 bit 7-4 Unimplemented: Read as ‘0’ bit 3 WRT3: Write Protection bit(1,2) 1 = Block 3 (006000-007FFFh) not write-protected 0 = Block 3 (006000-007FFFh) write-protected bit 2 WRT2: Write Protection bit(1) 1 = Block 2 (004000-005FFFh) not write-protected 0 = Block 2 (004000-005FFFh) write-protected bit 1 WRT1: Write Protection bit 1 = Block 1 (002000-003FFFh) not write-protected 0 = Block 1 (002000-003FFFh) write-protected bit 0 WRT0: Write Protection bit 1 = Block 0 (000800-001FFFh) not write-protected 0 = Block 0 (000800-001FFFh) write-protected Note 1: Unimplemented in PIC18F2420/4420 devices; maintain this bit set. 2: Unimplemented in PIC18F2425/4425 devices; maintain this bit set. Legend: R = Readable bit C = Clearable bit U = Unimplemented bit, read as ‘0’ -n = Value when device is unprogrammed u = Unchanged from programmed state R/C-1 R/C-1 R-1 U-0 U-0 U-0 U-0 U-0 WRTD WRTB WRTC(1) — — — — — bit 7 bit 0 bit 7 WRTD: Data EEPROM Write Protection bit 1 = Data EEPROM not write-protected 0 = Data EEPROM write-protected bit 6 WRTB: Boot Block Write Protection bit 1 = Boot block (000000-0007FFh) not write-protected 0 = Boot block (000000-0007FFh) write-protected bit 5 WRTC: Configuration Register Write Protection bit(1) 1 = Configuration registers (300000-3000FFh) not write-protected 0 = Configuration registers (300000-3000FFh) write-protected Note 1: This bit is read-only in normal execution mode; it can be written only in Program mode. bit 4-0 Unimplemented: Read as ‘0’ Legend: R = Readable bit C = Clearable bit U = Unimplemented bit, read as ‘0’ - n = Value when device is unprogrammed u = Unchanged from programmed state PIC18F2420/2520/4420/4520 DS39631B-page 256 Preliminary © 2007 Microchip Technology Inc. REGISTER 23-10: CONFIG7L: CONFIGURATION REGISTER 7 LOW (BYTE ADDRESS 30000Ch) REGISTER 23-11: CONFIG7H: CONFIGURATION REGISTER 7 HIGH (BYTE ADDRESS 30000Dh) U-0 U-0 U-0 U-0 R/C-1 R/C-1 R/C-1 R/C-1 — — — — EBTR3(1,2) EBTR2(1) EBTR1 EBTR0 bit 7 bit 0 bit 7-4 Unimplemented: Read as ‘0’ bit 3 EBTR3: Table Read Protection bit(1,2) 1 = Block 3 (006000-007FFFh) not protected from table reads executed in other blocks 0 = Block 3 (006000-007FFFh) protected from table reads executed in other blocks bit 2 EBTR2: Table Read Protection bit(1) 1 = Block 2 (004000-005FFFh) not protected from table reads executed in other blocks 0 = Block 2 (004000-005FFFh) protected from table reads executed in other blocks bit 1 EBTR1: Table Read Protection bit 1 = Block 1 (002000-003FFFh) not protected from table reads executed in other blocks 0 = Block 1 (002000-003FFFh) protected from table reads executed in other blocks bit 0 EBTR0: Table Read Protection bit 1 = Block 0 (000800-001FFFh) not protected from table reads executed in other blocks 0 = Block 0 (000800-001FFFh) protected from table reads executed in other blocks Note 1: Unimplemented in PIC18F2420/4420 devices; maintain this bit set. 2: Unimplemented in PIC18F2425/4425 devices; maintain this bit set. Legend: R = Readable bit C = Clearable bit U = Unimplemented bit, read as ‘0’ -n = Value when device is unprogrammed u = Unchanged from programmed state U-0 R/C-1 U-0 U-0 U-0 U-0 U-0 U-0 — EBTRB — — — — — — bit 7 bit 0 bit 7 Unimplemented: Read as ‘0’ bit 6 EBTRB: Boot Block Table Read Protection bit 1 = Boot block (000000-0007FFh) not protected from table reads executed in other blocks 0 = Boot block (000000-0007FFh) protected from table reads executed in other blocks bit 5-0 Unimplemented: Read as ‘0’ Legend: R = Readable bit C = Clearable bit U = Unimplemented bit, read as ‘0’ -n = Value when device is unprogrammed u = Unchanged from programmed state © 2007 Microchip Technology Inc. Preliminary DS39631B-page 257 PIC18F2420/2520/4420/4520 REGISTER 23-12: DEVID1: DEVICE ID REGISTER 1 FOR PIC18F2420/2520/4420/4520 REGISTER 23-13: DEVID2: DEVICE ID REGISTER 2 FOR PIC18F2420/2520/4420/4520 R R R R R R R R DEV2 DEV1 DEV0 REV4 REV3 REV2 REV1 REV0 bit 7 bit 0 bit 7-5 DEV2:DEV0: Device ID bits 000 = PIC18F4520 010 = PIC18F4420 100 = PIC18F2520 110 = PIC18F2420 bit 4-0 REV4:REV0: Revision ID bits These bits are used to indicate the device revision. Legend: R = Read-only bit P = Programmable bit U = Unimplemented bit, read as ‘0’ -n = Value when device is unprogrammed u = Unchanged from programmed state R R R R R R R R DEV10 DEV9 DEV8 DEV7 DEV6 DEV5 DEV4 DEV3 bit 7 bit 0 bit 7-0 DEV10:DEV3: Device ID bits These bits are used with the DEV2:DEV0 bits in the Device ID Register 1 to identify the part number. 0000 1100 = PIC18F2420/2520/4420/4520 devices Note: These values for DEV10:DEV3 may be shared with other devices. The specific device is always identified by using the entire DEV10:DEV0 bit sequence. Legend: R = Read-only bit P = Programmable bit U = Unimplemented bit, read as ‘0’ -n = Value when device is unprogrammed u = Unchanged from programmed state PIC18F2420/2520/4420/4520 DS39631B-page 258 Preliminary © 2007 Microchip Technology Inc. 23.2 Watchdog Timer (WDT) For PIC18F2420/2520/4420/4520 devices, the WDT is driven by the INTRC source. When the WDT is enabled, the clock source is also enabled. The nominal WDT period is 4 ms and has the same stability as the INTRC oscillator. The 4 ms period of the WDT is multiplied by a 16-bit postscaler. Any output of the WDT postscaler is selected by a multiplexer, controlled by bits in Configuration Register 2H. Available periods range from 4 ms to 131.072 seconds (2.18 minutes). The WDT and postscaler are cleared when any of the following events occur: a SLEEP or CLRWDT instruction is executed, the IRCF bits (OSCCON<6:4>) are changed or a clock failure has occurred. 23.2.1 CONTROL REGISTER Register 23-14 shows the WDTCON register. This is a readable and writable register which contains a control bit that allows software to override the WDT enable configuration bit, but only if the configuration bit has disabled the WDT. FIGURE 23-1: WDT BLOCK DIAGRAM Note 1: The CLRWDT and SLEEP instructions clear the WDT and postscaler counts when executed. 2: Changing the setting of the IRCF bits (OSCCON<6:4>) clears the WDT and postscaler counts. 3: When a CLRWDT instruction is executed, the postscaler count will be cleared. INTRC Source WDT Wake-up Reset WDT Counter Programmable Postscaler 1:1 to 1:32,768 Enable WDT WDTPS<3:0> SWDTEN WDTEN CLRWDT 4 from Power Reset All Device Resets Sleep ÷128 Change on IRCF bits Managed Modes © 2007 Microchip Technology Inc. Preliminary DS39631B-page 259 PIC18F2420/2520/4420/4520 REGISTER 23-14: WDTCON REGISTER TABLE 23-2: SUMMARY OF WATCHDOG TIMER REGISTERS U-0 U-0 U-0 U-0 U-0 U-0 U-0 R/W-0 — — — — — — — SWDTEN(1) bit 7 bit 0 bit 7-1 Unimplemented: Read as ‘0’ bit 0 SWDTEN: Software Controlled Watchdog Timer Enable bit(1) 1 = Watchdog Timer is on 0 = Watchdog Timer is off Note 1: This bit has no effect if the configuration bit, WDTEN, is enabled. Legend: R = Readable bit W = Writable bit U = Unimplemented bit, read as ‘0’ -n = Value at POR Name Bit 7 Bit 6 Bit 5 Bit 4 Bit 3 Bit 2 Bit 1 Bit 0 Reset Values on page RCON IPEN SBOREN — RI TO PD POR BOR 48 WDTCON — — — — — — — SWDTEN 50 Legend: — = unimplemented, read as ‘0’. Shaded cells are not used by the Watchdog Timer. PIC18F2420/2520/4420/4520 DS39631B-page 260 Preliminary © 2007 Microchip Technology Inc. 23.3 Two-Speed Start-up The Two-Speed Start-up feature helps to minimize the latency period from oscillator start-up to code execution by allowing the microcontroller to use the INTOSC oscillator as a clock source until the primary clock source is available. It is enabled by setting the IESO configuration bit. Two-Speed Start-up should be enabled only if the primary oscillator mode is LP, XT, HS or HSPLL (crystal-based modes). Other sources do not require an OST start-up delay; for these, Two-Speed Start-up should be disabled. When enabled, Resets and wake-ups from Sleep mode cause the device to configure itself to run from the internal oscillator block as the clock source, following the time-out of the Power-up Timer after a Power-on Reset is enabled. This allows almost immediate code execution while the primary oscillator starts and the OST is running. Once the OST times out, the device automatically switches to PRI_RUN mode. To use a higher clock speed on wake-up, the INTOSC or postscaler clock sources can be selected to provide a higher clock speed by setting bits IRCF2:IRCF0 immediately after Reset. For wake-ups from Sleep, the INTOSC or postscaler clock sources can be selected by setting the IRCF2:IRCF0 bits prior to entering Sleep mode. In all other power managed modes, Two-Speed Startup is not used. The device will be clocked by the currently selected clock source until the primary clock source becomes available. The setting of the IESO bit is ignored. 23.3.1 SPECIAL CONSIDERATIONS FOR USING TWO-SPEED START-UP While using the INTOSC oscillator in Two-Speed Startup, the device still obeys the normal command sequences for entering power managed modes, including multiple SLEEP instructions (refer to Section 3.1.4 “Multiple Sleep Commands”). In practice, this means that user code can change the SCS1:SCS0 bit settings or issue SLEEP instructions before the OST times out. This would allow an application to briefly wake-up, perform routine “housekeeping” tasks and return to Sleep before the device starts to operate from the primary oscillator. User code can also check if the primary clock source is currently providing the device clocking by checking the status of the OSTS bit (OSCCON<3>). If the bit is set, the primary oscillator is providing the clock. Otherwise, the internal oscillator block is providing the clock during wake-up from Reset or Sleep mode. FIGURE 23-2: TIMING TRANSITION FOR TWO-SPEED START-UP (INTOSC TO HSPLL) Q1 Q3 Q4 OSC1 Peripheral Program PC PC + 2 INTOSC PLL Clock Q1 PC + 6 Q2 Output Q3 Q4 Q1 CPU Clock PC + 4 Clock Counter Q2 Q2 Q3 Note 1: TOST = 1024 TOSC; TPLL = 2 ms (approx). These intervals are not shown to scale. 2: Clock transition typically occurs within 2-4 TOSC. Wake from Interrupt Event TPLL(1) 1 2 n-1 n Clock OSTS bit Set Transition(2) Multiplexer TOST(1) © 2007 Microchip Technology Inc. Preliminary DS39631B-page 261 PIC18F2420/2520/4420/4520 23.4 Fail-Safe Clock Monitor The Fail-Safe Clock Monitor (FSCM) allows the microcontroller to continue operation in the event of an external oscillator failure by automatically switching the device clock to the internal oscillator block. The FSCM function is enabled by setting the FCMEN configuration bit. When FSCM is enabled, the INTRC oscillator runs at all times to monitor clocks to peripherals and provide a backup clock in the event of a clock failure. Clock monitoring (shown in Figure 23-3) is accomplished by creating a sample clock signal, which is the INTRC output divided by 64. This allows ample time between FSCM sample clocks for a peripheral clock edge to occur. The peripheral device clock and the sample clock are presented as inputs to the Clock Monitor latch (CM). The CM is set on the falling edge of the device clock source, but cleared on the rising edge of the sample clock. FIGURE 23-3: FSCM BLOCK DIAGRAM Clock failure is tested for on the falling edge of the sample clock. If a sample clock falling edge occurs while CM is still set, a clock failure has been detected (Figure 23-4). This causes the following: • the FSCM generates an oscillator fail interrupt by setting bit, OSCFIF (PIR2<7>); • the device clock source is switched to the internal oscillator block (OSCCON is not updated to show the current clock source – this is the fail-safe condition) and • the WDT is reset. During switchover, the postscaler frequency from the internal oscillator block may not be sufficiently stable for timing sensitive applications. In these cases, it may be desirable to select another clock configuration and enter an alternate power managed mode. This can be done to attempt a partial recovery or execute a controlled shutdown. See Section 3.1.4 “Multiple Sleep Commands” and Section 23.3.1 “Special Considerations for Using Two-Speed Start-up” for more details. To use a higher clock speed on wake-up, the INTOSC or postscaler clock sources can be selected to provide a higher clock speed by setting bits, IRCF2:IRCF0, immediately after Reset. For wake-ups from Sleep, the INTOSC or postscaler clock sources can be selected by setting the IRCF2:IRCF0 bits prior to entering Sleep mode. The FSCM will detect failures of the primary or secondary clock sources only. If the internal oscillator block fails, no failure would be detected, nor would any action be possible. 23.4.1 FSCM AND THE WATCHDOG TIMER Both the FSCM and the WDT are clocked by the INTRC oscillator. Since the WDT operates with a separate divider and counter, disabling the WDT has no effect on the operation of the INTRC oscillator when the FSCM is enabled. As already noted, the clock source is switched to the INTOSC clock when a clock failure is detected. Depending on the frequency selected by the IRCF2:IRCF0 bits, this may mean a substantial change in the speed of code execution. If the WDT is enabled with a small prescale value, a decrease in clock speed allows a WDT time-out to occur and a subsequent device Reset. For this reason, fail-safe clock events also reset the WDT and postscaler, allowing it to start timing from when execution speed was changed and decreasing the likelihood of an erroneous time-out. 23.4.2 EXITING FAIL-SAFE OPERATION The fail-safe condition is terminated by either a device Reset or by entering a power managed mode. On Reset, the controller starts the primary clock source specified in Configuration Register 1H (with any required start-up delays that are required for the oscillator mode, such as OST or PLL timer). The INTOSC multiplexer provides the device clock until the primary clock source becomes ready (similar to a Two-Speed Start-up). The clock source is then switched to the primary clock (indicated by the OSTS bit in the OSCCON register becoming set). The Fail-Safe Clock Monitor then resumes monitoring the peripheral clock. The primary clock source may never become ready during start-up. In this case, operation is clocked by the INTOSC multiplexer. The OSCCON register will remain in its Reset state until a power managed mode is entered. Peripheral INTRC ÷ 64 S C Q (32 μs) 488 Hz (2.048 ms) Clock Monitor Latch (CM) (edge-triggered) Clock Failure Detected Source Clock Q PIC18F2420/2520/4420/4520 DS39631B-page 262 Preliminary © 2007 Microchip Technology Inc. FIGURE 23-4: FSCM TIMING DIAGRAM 23.4.3 FSCM INTERRUPTS IN POWER MANAGED MODES By entering a power managed mode, the clock multiplexer selects the clock source selected by the OSCCON register. Fail-Safe Monitoring of the power managed clock source resumes in the power managed mode. If an oscillator failure occurs during power managed operation, the subsequent events depend on whether or not the oscillator failure interrupt is enabled. If enabled (OSCFIF = 1), code execution will be clocked by the INTOSC multiplexer. An automatic transition back to the failed clock source will not occur. If the interrupt is disabled, subsequent interrupts while in Idle mode will cause the CPU to begin executing instructions while being clocked by the INTOSC source. 23.4.4 POR OR WAKE FROM SLEEP The FSCM is designed to detect oscillator failure at any point after the device has exited Power-on Reset (POR) or low-power Sleep mode. When the primary device clock is EC, RC or INTRC modes, monitoring can begin immediately following these events. For oscillator modes involving a crystal or resonator (HS, HSPLL, LP or XT), the situation is somewhat different. Since the oscillator may require a start-up time considerably longer than the FCSM sample clock time, a false clock failure may be detected. To prevent this, the internal oscillator block is automatically configured as the device clock and functions until the primary clock is stable (the OST and PLL timers have timed out). This is identical to Two-Speed Start-up mode. Once the primary clock is stable, the INTRC returns to its role as the FSCM source. As noted in Section 23.3.1 “Special Considerations for Using Two-Speed Start-up”, it is also possible to select another clock configuration and enter an alternate power managed mode while waiting for the primary clock to become stable. When the new power managed mode is selected, the primary clock is disabled. OSCFIF CM Output Device Clock Output Sample Clock Failure Detected Oscillator Failure Note: The device clock is normally at a much higher frequency than the sample clock. The relative frequencies in this example have been chosen for clarity. (Q) CM Test CM Test CM Test Note: The same logic that prevents false oscillator failure interrupts on POR, or wake from Sleep, will also prevent the detection of the oscillator’s failure to start at all following these events. This can be avoided by monitoring the OSTS bit and using a timing routine to determine if the oscillator is taking too long to start. Even so, no oscillator failure interrupt will be flagged. © 2007 Microchip Technology Inc. Preliminary DS39631B-page 263 PIC18F2420/2520/4420/4520 23.5 Program Verification and Code Protection The overall structure of the code protection on the PIC18 Flash devices differs significantly from other PIC® devices. The user program memory is divided into five blocks. One of these is a boot block of 2 Kbytes. The remainder of the memory is divided into four blocks on binary boundaries. Each of the five blocks has three code protection bits associated with them. They are: • Code-Protect bit (CPn) • Write-Protect bit (WRTn) • External Block Table Read bit (EBTRn) Figure 23-5 shows the program memory organization for 16 and 32-Kbyte devices and the specific code protection bit associated with each block. The actual locations of the bits are summarized in Table 23-3. FIGURE 23-5: CODE-PROTECTED PROGRAM MEMORY FOR PIC18F2420/2520/4420/4520 TABLE 23-3: SUMMARY OF CODE PROTECTION REGISTERS File Name Bit 7 Bit 6 Bit 5 Bit 4 Bit 3 Bit 2 Bit 1 Bit 0 300008h CONFIG5L — — — — CP3(1,2) CP2(1) CP1 CP0 300009h CONFIG5H CPD CPB — — — — — — 30000Ah CONFIG6L — — — — WRT3(1,2) WRT2(1) WRT1 WRT0 30000Bh CONFIG6H WRTD WRTB WRTC — — — — — 30000Ch CONFIG7L — — — — EBTR3(1,2) EBTR2(1) EBTR1 EBTR0 30000Dh CONFIG7H — EBTRB — — — — — — Legend: Shaded cells are unimplemented. Note 1: Unimplemented in PIC18F2420/4420 devices; maintain this bit set. 2: Unimplemented in PIC18F2425/4425 devices; maintain this bit set. MEMORY SIZE/DEVICE Block Code Protection 16 Kbytes Controlled By: (PIC18F2420/4420) 32 Kbytes (PIC18F2520/4520) Address Range Boot Block Boot Block 000000h 0007FFh CPB, WRTB, EBTRB Block 0 Block 0 000800h 001FFFh CP0, WRT0, EBTR0 Block 1 Block 1 002000h 003FFFh CP1, WRT1, EBTR1 Unimplemented Read ‘0’s Block 2 004000h 005FFFh CP2, WRT2, EBTR2 Block 3 006000h 007FFFh CP3, WRT3, EBTR3 Unimplemented Read ‘0’s 1FFFFFh (Unimplemented Memory Space) PIC18F2420/2520/4420/4520 DS39631B-page 264 Preliminary © 2007 Microchip Technology Inc. 23.5.1 PROGRAM MEMORY CODE PROTECTION The program memory may be read to or written from any location using the table read and table write instructions. The device ID may be read with table reads. The configuration registers may be read and written with the table read and table write instructions. In normal execution mode, the CPn bits have no direct effect. CPn bits inhibit external reads and writes. A block of user memory may be protected from table writes if the WRTn configuration bit is ‘0’. The EBTRn bits control table reads. For a block of user memory with the EBTRn bit set to ‘0’, a table read instruction that executes from within that block is allowed to read. A table read instruction that executes from a location outside of that block is not allowed to read and will result in reading ‘0’s. Figures 23-6 through 23-8 illustrate table write and table read protection. FIGURE 23-6: TABLE WRITE (WRTn) DISALLOWED Note: Code protection bits may only be written to a ‘0’ from a ‘1’ state. It is not possible to write a ‘1’ to a bit in the ‘0’ state. Code protection bits are only set to ‘1’ by a full chip erase or block erase function. The full chip erase and block erase functions can only be initiated via ICSP or an external programmer. 000000h 0007FFh 000800h 001FFFh 002000h 003FFFh 004000h 005FFFh 006000h 007FFFh WRTB, EBTRB = 11 WRT0, EBTR0 = 01 WRT1, EBTR1 = 11 WRT2, EBTR2 = 11 WRT3, EBTR3 = 11 TBLWT* TBLPTR = 0008FFh PC = 001FFEh PC = 005FFEh TBLWT* Register Values Program Memory Configuration Bit Settings Results: All table writes disabled to Blockn whenever WRTn = 0. © 2007 Microchip Technology Inc. Preliminary DS39631B-page 265 PIC18F2420/2520/4420/4520 FIGURE 23-7: EXTERNAL BLOCK TABLE READ (EBTRn) DISALLOWED FIGURE 23-8: EXTERNAL BLOCK TABLE READ (EBTRn) ALLOWED WRTB, EBTRB = 11 WRT0, EBTR0 = 10 WRT1, EBTR1 = 11 WRT2, EBTR2 = 11 WRT3, EBTR3 = 11 TBLRD* TBLPTR = 0008FFh PC = 003FFEh Results: All table reads from external blocks to Blockn are disabled whenever EBTRn = 0. TABLAT register returns a value of ‘0’. Register Values Program Memory Configuration Bit Settings 000000h 0007FFh 000800h 001FFFh 002000h 003FFFh 004000h 005FFFh 006000h 007FFFh WRTB, EBTRB = 11 WRT0, EBTR0 = 10 WRT1, EBTR1 = 11 WRT2, EBTR2 = 11 WRT3, EBTR3 = 11 TBLRD* TBLPTR = 0008FFh PC = 001FFEh Register Values Program Memory Configuration Bit Settings Results: Table reads permitted within Blockn, even when EBTRBn = 0. TABLAT register returns the value of the data at the location TBLPTR. 000000h 0007FFh 000800h 001FFFh 002000h 003FFFh 004000h 005FFFh 006000h 007FFFh PIC18F2420/2520/4420/4520 DS39631B-page 266 Preliminary © 2007 Microchip Technology Inc. 23.5.2 DATA EEPROM CODE PROTECTION The entire data EEPROM is protected from external reads and writes by two bits: CPD and WRTD. CPD inhibits external reads and writes of data EEPROM. WRTD inhibits internal and external writes to data EEPROM. The CPU can always read data EEPROM under normal operation, regardless of the protection bit settings. 23.5.3 CONFIGURATION REGISTER PROTECTION The configuration registers can be write-protected. The WRTC bit controls protection of the configuration registers. In normal execution mode, the WRTC bit is readable only. WRTC can only be written via ICSP or an external programmer. 23.6 ID Locations Eight memory locations (200000h-200007h) are designated as ID locations, where the user can store checksum or other code identification numbers. These locations are both readable and writable during normal execution through the TBLRD and TBLWT instructions or during program/verify. The ID locations can be read when the device is code-protected. 23.7 In-Circuit Serial Programming PIC18F2420/2520/4420/4520 devices can be serially programmed while in the end application circuit. This is simply done with two lines for clock and data and three other lines for power, ground and the programming voltage. This allows customers to manufacture boards with unprogrammed devices and then program the microcontroller just before shipping the product. This also allows the most recent firmware or a custom firmware to be programmed. 23.8 In-Circuit Debugger When the DEBUG configuration bit is programmed to a ‘0’, the In-Circuit Debugger functionality is enabled. This function allows simple debugging functions when used with MPLAB® IDE. When the microcontroller has this feature enabled, some resources are not available for general use. Table 23-4 shows which resources are required by the background debugger. TABLE 23-4: DEBUGGER RESOURCES To use the In-Circuit Debugger function of the microcontroller, the design must implement In-Circuit Serial Programming connections to MCLR/VPP/RE3, VDD, VSS, RB7 and RB6. This will interface to the In-Circuit Debugger module available from Microchip or one of the third party development tool companies. 23.9 Single-Supply ICSP Programming The LVP configuration bit enables Single-Supply ICSP Programming (formerly known as Low-Voltage ICSP Programming or LVP). When Single-Supply Programming is enabled, the microcontroller can be programmed without requiring high voltage being applied to the MCLR/VPP/RE3 pin, but the RB5/KBI1/PGM pin is then dedicated to controlling Program mode entry and is not available as a general purpose I/O pin. While programming, using Single-Supply Programming mode, VDD is applied to the MCLR/VPP/RE3 pin as in normal execution mode. To enter Programming mode, VDD is applied to the PGM pin. If Single-Supply ICSP Programming mode will not be used, the LVP bit can be cleared. RB5/KBI1/PGM then becomes available as the digital I/O pin, RB5. The LVP bit may be set or cleared only when using standard high-voltage programming (VIHH applied to the MCLR/ VPP/RE3 pin). Once LVP has been disabled, only the standard high-voltage programming is available and must be used to program the device. Memory that is not code-protected can be erased using either a block erase, or erased row by row, then written at any specified VDD. If code-protected memory is to be erased, a block erase is required. If a block erase is to be performed when using Low-Voltage Programming, the device must be supplied with VDD of 4.5V to 5.5V. I/O pins: RB6, RB7 Stack: 2 levels Program Memory: 512 bytes Data Memory: 10 bytes Note 1: High-voltage programming is always available, regardless of the state of the LVP bit or the PGM pin, by applying VIHH to the MCLR pin. 2: By default, Single-Supply ICSP is enabled in unprogrammed devices (as supplied from Microchip) and erased devices. 3: When Single-Supply Programming is enabled, the RB5 pin can no longer be used as a general purpose I/O pin. 4: When LVP is enabled, externally pull the PGM pin to VSS to allow normal program execution. © 2007 Microchip Technology Inc. Preliminary DS39631B-page 267 PIC18F2420/2520/4420/4520 24.0 INSTRUCTION SET SUMMARY PIC18F2420/2520/4420/4520 devices incorporate the standard set of 75 PIC18 core instructions, as well as an extended set of 8 new instructions, for the optimization of code that is recursive or that utilizes a software stack. The extended set is discussed later in this section. 24.1 Standard Instruction Set The standard PIC18 instruction set adds many enhancements to the previous PIC® instruction sets, while maintaining an easy migration from these PIC instruction sets. Most instructions are a single program memory word (16 bits), but there are four instructions that require two program memory locations. Each single-word instruction is a 16-bit word divided into an opcode, which specifies the instruction type and one or more operands, which further specify the operation of the instruction. The instruction set is highly orthogonal and is grouped into four basic categories: • Byte-oriented operations • Bit-oriented operations • Literal operations • Control operations The PIC18 instruction set summary in Table 24-2 lists byte-oriented, bit-oriented, literal and control operations. Table 24-1 shows the opcode field descriptions. Most byte-oriented instructions have three operands: 1. The file register (specified by ‘f’) 2. The destination of the result (specified by ‘d’) 3. The accessed memory (specified by ‘a’) The file register designator ‘f’ specifies which file register is to be used by the instruction. The destination designator ‘d’ specifies where the result of the operation is to be placed. If ‘d’ is zero, the result is placed in the WREG register. If ‘d’ is one, the result is placed in the file register specified in the instruction. All bit-oriented instructions have three operands: 1. The file register (specified by ‘f’) 2. The bit in the file register (specified by ‘b’) 3. The accessed memory (specified by ‘a’) The bit field designator ‘b’ selects the number of the bit affected by the operation, while the file register designator ‘f’ represents the number of the file in which the bit is located. The literal instructions may use some of the following operands: • A literal value to be loaded into a file register (specified by ‘k’) • The desired FSR register to load the literal value into (specified by ‘f’) • No operand required (specified by ‘—’) The control instructions may use some of the following operands: • A program memory address (specified by ‘n’) • The mode of the CALL or RETURN instructions (specified by ‘s’) • The mode of the table read and table write instructions (specified by ‘m’) • No operand required (specified by ‘—’) All instructions are a single word, except for four double-word instructions. These instructions were made double-word to contain the required information in 32 bits. In the second word, the 4 MSbs are ‘1’s. If this second word is executed as an instruction (by itself), it will execute as a NOP. All single-word instructions are executed in a single instruction cycle, unless a conditional test is true or the program counter is changed as a result of the instruction. In these cases, the execution takes two instruction cycles, with the additional instruction cycle(s) executed as a NOP. The double-word instructions execute in two instruction cycles. One instruction cycle consists of four oscillator periods. Thus, for an oscillator frequency of 4 MHz, the normal instruction execution time is 1 μs. If a conditional test is true, or the program counter is changed as a result of an instruction, the instruction execution time is 2 μs. Two-word branch instructions (if true) would take 3 μs. Figure 24-1 shows the general formats that the instructions can have. All examples use the convention ‘nnh’ to represent a hexadecimal number. The Instruction Set Summary, shown in Table 24-2, lists the standard instructions recognized by the Microchip Assembler (MPASMTM). Section 24.1.1 “Standard Instruction Set” provides a description of each instruction. PIC18F2420/2520/4420/4520 DS39631B-page 268 Preliminary © 2007 Microchip Technology Inc. TABLE 24-1: OPCODE FIELD DESCRIPTIONS Field Description a RAM access bit a = 0: RAM location in Access RAM (BSR register is ignored) a = 1: RAM bank is specified by BSR register bbb Bit address within an 8-bit file register (0 to 7). BSR Bank Select Register. Used to select the current RAM bank. C, DC, Z, OV, N ALU Status bits: Carry, Digit Carry, Zero, Overflow, Negative. d Destination select bit d = 0: store result in WREG d = 1: store result in file register f dest Destination: either the WREG register or the specified register file location. f 8-bit Register file address (00h to FFh) or 2-bit FSR designator (0h to 3h). fs 12-bit Register file address (000h to FFFh). This is the source address. fd 12-bit Register file address (000h to FFFh). This is the destination address. GIE Global Interrupt Enable bit. k Literal field, constant data or label (may be either an 8-bit, 12-bit or a 20-bit value). label Label name. mm The mode of the TBLPTR register for the table read and table write instructions. Only used with table read and table write instructions: * No change to register (such as TBLPTR with table reads and writes) *+ Post-Increment register (such as TBLPTR with table reads and writes) *- Post-Decrement register (such as TBLPTR with table reads and writes) +* Pre-Increment register (such as TBLPTR with table reads and writes) n The relative address (2’s complement number) for relative branch instructions or the direct address for Call/Branch and Return instructions. PC Program Counter. PCL Program Counter Low Byte. PCH Program Counter High Byte. PCLATH Program Counter High Byte Latch. PCLATU Program Counter Upper Byte Latch. PD Power-down bit. PRODH Product of Multiply High Byte. PRODL Product of Multiply Low Byte. s Fast Call/Return mode select bit s = 0: do not update into/from shadow registers s = 1: certain registers loaded into/from shadow registers (Fast mode) TBLPTR 21-bit Table Pointer (points to a Program Memory location). TABLAT 8-bit Table Latch. TO Time-out bit. TOS Top-of-Stack. u Unused or unchanged. WDT Watchdog Timer. WREG Working register (accumulator). x Don’t care (‘0’ or ‘1’). The assembler will generate code with x = 0. It is the recommended form of use for compatibility with all Microchip software tools. zs 7-bit offset value for indirect addressing of register files (source). zd 7-bit offset value for indirect addressing of register files (destination). { } Optional argument. [text] Indicates an indexed address. (text) The contents of text. [expr] Specifies bit n of the register indicated by the pointer expr. → Assigned to. < > Register bit field. ∈ In the set of. italics User defined term (font is Courier). © 2007 Microchip Technology Inc. Preliminary DS39631B-page 269 PIC18F2420/2520/4420/4520 FIGURE 24-1: GENERAL FORMAT FOR INSTRUCTIONS Byte-oriented file register operations 15 10 9 8 7 0 d = 0 for result destination to be WREG register OPCODE d a f (FILE #) d = 1 for result destination to be file register (f) a = 0 to force Access Bank Bit-oriented file register operations 15 12 11 9 8 7 0 OPCODE b (BIT #) a f (FILE #) b = 3-bit position of bit in file register (f) Literal operations 15 8 7 0 OPCODE k (literal) k = 8-bit immediate value Byte to Byte move operations (2-word) 15 12 11 0 OPCODE f (Source FILE #) CALL, GOTO and Branch operations 15 8 7 0 OPCODE n<7:0> (literal) n = 20-bit immediate value a = 1 for BSR to select bank f = 8-bit file register address a = 0 to force Access Bank a = 1 for BSR to select bank f = 8-bit file register address 15 12 11 0 1111 n<19:8> (literal) 15 12 11 0 1111 f (Destination FILE #) f = 12-bit file register address Control operations Example Instruction ADDWF MYREG, W, B MOVFF MYREG1, MYREG2 BSF MYREG, bit, B MOVLW 7Fh GOTO Label 15 8 7 0 OPCODE n<7:0> (literal) 15 12 11 0 1111 n<19:8> (literal) CALL MYFUNC 15 11 10 0 OPCODE n<10:0> (literal) S = Fast bit BRA MYFUNC 15 8 7 0 OPCODE n<7:0> (literal) BC MYFUNC S PIC18F2420/2520/4420/4520 DS39631B-page 270 Preliminary © 2007 Microchip Technology Inc. TABLE 24-2: PIC18FXXXX INSTRUCTION SET Mnemonic, Operands Description Cycles 16-Bit Instruction Word Status Affected Notes MSb LSb BYTE-ORIENTED OPERATIONS ADDWF ADDWFC ANDWF CLRF COMF CPFSEQ CPFSGT CPFSLT DECF DECFSZ DCFSNZ INCF INCFSZ INFSNZ IORWF MOVF MOVFF MOVWF MULWF NEGF RLCF RLNCF RRCF RRNCF SETF SUBFWB SUBWF SUBWFB SWAPF TSTFSZ XORWF f, d, a f, d, a f, d, a f, a f, d, a f, a f, a f, a f, d, a f, d, a f, d, a f, d, a f, d, a f, d, a f, d, a f, d, a fs, fd f, a f, a f, a f, d, a f, d, a f, d, a f, d, a f, a f, d, a f, d, a f, d, a f, d, a f, a f, d, a Add WREG and f Add WREG and CARRY bit to f AND WREG with f Clear f Complement f Compare f with WREG, skip = Compare f with WREG, skip > Compare f with WREG, skip < Decrement f Decrement f, Skip if 0 Decrement f, Skip if Not 0 Increment f Increment f, Skip if 0 Increment f, Skip if Not 0 Inclusive OR WREG with f Move f Move fs (source) to 1st word fd (destination) 2nd word Move WREG to f Multiply WREG with f Negate f Rotate Left f through Carry Rotate Left f (No Carry) Rotate Right f through Carry Rotate Right f (No Carry) Set f Subtract f from WREG with borrow Subtract WREG from f Subtract WREG from f with borrow Swap nibbles in f Test f, skip if 0 Exclusive OR WREG with f 1 1 1 1 1 1 (2 or 3) 1 (2 or 3) 1 (2 or 3) 1 1 (2 or 3) 1 (2 or 3) 1 1 (2 or 3) 1 (2 or 3) 1 1 2 1 1 1 1 1 1 1 1 1 1 1 1 1 (2 or 3) 1 0010 0010 0001 0110 0001 0110 0110 0110 0000 0010 0100 0010 0011 0100 0001 0101 1100 1111 0110 0000 0110 0011 0100 0011 0100 0110 0101 0101 0101 0011 0110 0001 01da0 0da 01da 101a 11da 001a 010a 000a 01da 11da 11da 10da 11da 10da 00da 00da ffff ffff 111a 001a 110a 01da 01da 00da 00da 100a 01da 11da 10da 10da 011a 10da ffff ffff ffff ffff ffff ffff ffff ffff ffff ffff ffff ffff ffff ffff ffff ffff ffff ffff ffff ffff ffff ffff ffff ffff ffff ffff ffff ffff ffff ffff ffff ffff ffff ffff ffff ffff ffff ffff ffff ffff ffff ffff ffff ffff ffff ffff ffff ffff ffff ffff ffff ffff ffff ffff ffff ffff ffff ffff ffff ffff ffff ffff ffff ffff C, DC, Z, OV, N C, DC, Z, OV, N Z, N Z Z, N None None None C, DC, Z, OV, N None None C, DC, Z, OV, N None None Z, N Z, N None None None C, DC, Z, OV, N C, Z, N Z, N C, Z, N Z, N None C, DC, Z, OV, N C, DC, Z, OV, N C, DC, Z, OV, N None None Z, N 1, 2 1, 2 1,2 2 1, 2 4 4 1, 2 1, 2, 3, 4 1, 2, 3, 4 1, 2 1, 2, 3, 4 4 1, 2 1, 2 1 1, 2 1, 2 1, 2 1, 2 4 1, 2 Note 1: When a Port register is modified as a function of itself (e.g., MOVF PORTB, 1, 0), the value used will be that value present on the pins themselves. For example, if the data latch is ‘1’ for a pin configured as input and is driven low by an external device, the data will be written back with a ‘0’. 2: If this instruction is executed on the TMR0 register (and where applicable, ‘d’ = 1), the prescaler will be cleared if assigned. 3: If Program Counter (PC) is modified or a conditional test is true, the instruction requires two cycles. The second cycle is executed as a NOP. 4: Some instructions are two-word instructions. The second word of these instructions will be executed as a NOP unless the first word of the instruction retrieves the information embedded in these 16 bits. This ensures that all program memory locations have a valid instruction. © 2007 Microchip Technology Inc. Preliminary DS39631B-page 271 PIC18F2420/2520/4420/4520 BIT-ORIENTED OPERATIONS BCF BSF BTFSC BTFSS BTG f, b, a f, b, a f, b, a f, b, a f, d, a Bit Clear f Bit Set f Bit Test f, Skip if Clear Bit Test f, Skip if Set Bit Toggle f 1 1 1 (2 or 3) 1 (2 or 3) 1 1001 1000 1011 1010 0111 bbba bbba bbba bbba bbba ffff ffff ffff ffff ffff ffff ffff ffff ffff ffff None None None None None 1, 2 1, 2 3, 4 3, 4 1, 2 CONTROL OPERATIONS BC BN BNC BNN BNOV BNZ BOV BRA BZ CALL CLRWDT DAW GOTO NOP NOP POP PUSH RCALL RESET RETFIE RETLW RETURN SLEEP n n n n n n n n n n, s — — n — — — — n s k s — Branch if Carry Branch if Negative Branch if Not Carry Branch if Not Negative Branch if Not Overflow Branch if Not Zero Branch if Overflow Branch Unconditionally Branch if Zero Call subroutine 1st word 2nd word Clear Watchdog Timer Decimal Adjust WREG Go to address 1st word 2nd word No Operation No Operation Pop top of return stack (TOS) Push top of return stack (TOS) Relative Call Software device Reset Return from interrupt enable Return with literal in WREG Return from Subroutine Go into Standby mode 1 (2) 1 (2) 1 (2) 1 (2) 1 (2) 1 (2) 1 (2) 2 1 (2) 2 1 1 2 1 1 1 1 2 1 2 2 2 1 1110 1110 1110 1110 1110 1110 1110 1101 1110 1110 1111 0000 0000 1110 1111 0000 1111 0000 0000 1101 0000 0000 0000 0000 0000 0010 0110 0011 0111 0101 0001 0100 0nnn 0000 110s kkkk 0000 0000 1111 kkkk 0000 xxxx 0000 0000 1nnn 0000 0000 1100 0000 0000 nnnn nnnn nnnn nnnn nnnn nnnn nnnn nnnn nnnn kkkk kkkk 0000 0000 kkkk kkkk 0000 xxxx 0000 0000 nnnn 1111 0001 kkkk 0001 0000 nnnn nnnn nnnn nnnn nnnn nnnn nnnn nnnn nnnn kkkk kkkk 0100 0111 kkkk kkkk 0000 xxxx 0110 0101 nnnn 1111 000s kkkk 001s 0011 None None None None None None None None None None TO, PD C None None None None None None All GIE/GIEH, PEIE/GIEL None None TO, PD 4 TABLE 24-2: PIC18FXXXX INSTRUCTION SET (CONTINUED) Mnemonic, Operands Description Cycles 16-Bit Instruction Word Status Affected Notes MSb LSb Note 1: When a Port register is modified as a function of itself (e.g., MOVF PORTB, 1, 0), the value used will be that value present on the pins themselves. For example, if the data latch is ‘1’ for a pin configured as input and is driven low by an external device, the data will be written back with a ‘0’. 2: If this instruction is executed on the TMR0 register (and where applicable, ‘d’ = 1), the prescaler will be cleared if assigned. 3: If Program Counter (PC) is modified or a conditional test is true, the instruction requires two cycles. The second cycle is executed as a NOP. 4: Some instructions are two-word instructions. The second word of these instructions will be executed as a NOP unless the first word of the instruction retrieves the information embedded in these 16 bits. This ensures that all program memory locations have a valid instruction. PIC18F2420/2520/4420/4520 DS39631B-page 272 Preliminary © 2007 Microchip Technology Inc. LITERAL OPERATIONS ADDLW ANDLW IORLW LFSR MOVLB MOVLW MULLW RETLW SUBLW XORLW k k k f, k k k k k k k Add literal and WREG AND literal with WREG Inclusive OR literal with WREG Move literal (12-bit) 2nd word to FSR(f) 1st word Move literal to BSR<3:0> Move literal to WREG Multiply literal with WREG Return with literal in WREG Subtract WREG from literal Exclusive OR literal with WREG 1 1 1 2 1 1 1 2 1 1 0000 0000 0000 1110 1111 0000 0000 0000 0000 0000 0000 1111 1011 1001 1110 0000 0001 1110 1101 1100 1000 1010 kkkk kkkk kkkk 00ff kkkk 0000 kkkk kkkk kkkk kkkk kkkk kkkk kkkk kkkk kkkk kkkk kkkk kkkk kkkk kkkk kkkk kkkk C, DC, Z, OV, N Z, N Z, N None None None None None C, DC, Z, OV, N Z, N DATA MEMORY ↔ PROGRAM MEMORY OPERATIONS TBLRD* TBLRD*+ TBLRD*- TBLRD+* TBLWT* TBLWT*+ TBLWT*- TBLWT+* Table Read Table Read with post-increment Table Read with post-decrement Table Read with pre-increment Table Write Table Write with post-increment Table Write with post-decrement Table Write with pre-increment 2 2 0000 0000 0000 0000 0000 0000 0000 0000 0000 0000 0000 0000 0000 0000 0000 0000 0000 0000 0000 0000 0000 0000 0000 0000 1000 1001 1010 1011 1100 1101 1110 1111 None None None None None None None None TABLE 24-2: PIC18FXXXX INSTRUCTION SET (CONTINUED) Mnemonic, Operands Description Cycles 16-Bit Instruction Word Status Affected Notes MSb LSb Note 1: When a Port register is modified as a function of itself (e.g., MOVF PORTB, 1, 0), the value used will be that value present on the pins themselves. For example, if the data latch is ‘1’ for a pin configured as input and is driven low by an external device, the data will be written back with a ‘0’. 2: If this instruction is executed on the TMR0 register (and where applicable, ‘d’ = 1), the prescaler will be cleared if assigned. 3: If Program Counter (PC) is modified or a conditional test is true, the instruction requires two cycles. The second cycle is executed as a NOP. 4: Some instructions are two-word instructions. The second word of these instructions will be executed as a NOP unless the first word of the instruction retrieves the information embedded in these 16 bits. This ensures that all program memory locations have a valid instruction. © 2007 Microchip Technology Inc. Preliminary DS39631B-page 273 PIC18F2420/2520/4420/4520 24.1.1 STANDARD INSTRUCTION SET ADDLW ADD literal to W Syntax: ADDLW k Operands: 0 ≤ k ≤ 255 Operation: (W) + k → W Status Affected: N, OV, C, DC, Z Encoding: 0000 1111 kkkk kkkk Description: The contents of W are added to the 8-bit literal ‘k’ and the result is placed in W. Words: 1 Cycles: 1 Q Cycle Activity: Q1 Q2 Q3 Q4 Decode Read literal ‘k’ Process Data Write to W Example: ADDLW 15h Before Instruction W = 10h After Instruction W = 25h ADDWF ADD W to f Syntax: ADDWF f {,d {,a}} Operands: 0 ≤ f ≤ 255 d ∈ [0,1] a ∈ [0,1] Operation: (W) + (f) → dest Status Affected: N, OV, C, DC, Z Encoding: 0010 01da ffff ffff Description: Add W to register ‘f’. If ‘d’ is ‘0’, the result is stored in W. If ‘d’ is ‘1’, the result is stored back in register ‘f’ (default). If ‘a’ is ‘0’, the Access Bank is selected. If ‘a’ is ‘1’, the BSR is used to select the GPR bank (default). If ‘a’ is ‘0’ and the extended instruction set is enabled, this instruction operates in Indexed Literal Offset Addressing mode whenever f ≤ 95 (5Fh). See Section 24.2.3 “Byte-Oriented and Bit-Oriented Instructions in Indexed Literal Offset Mode” for details. Words: 1 Cycles: 1 Q Cycle Activity: Q1 Q2 Q3 Q4 Decode Read register ‘f’ Process Data Write to destination Example: ADDWF REG, 0, 0 Before Instruction W = 17h REG = 0C2h After Instruction W = 0D9h REG = 0C2h Note: All PIC18 instructions may take an optional label argument preceding the instruction mnemonic for use in symbolic addressing. If a label is used, the instruction format then becomes: {label} instruction argument(s). PIC18F2420/2520/4420/4520 DS39631B-page 274 Preliminary © 2007 Microchip Technology Inc. ADDWFC ADD W and CARRY bit to f Syntax: ADDWFC f {,d {,a}} Operands: 0 ≤ f ≤ 255 d ∈ [0,1] a ∈ [0,1] Operation: (W) + (f) + (C) → dest Status Affected: N,OV, C, DC, Z Encoding: 0010 00da ffff ffff Description: Add W, the CARRY flag and data memory location ‘f’. If ‘d’ is ‘0’, the result is placed in W. If ‘d’ is ‘1’, the result is placed in data memory location ‘f’. If ‘a’ is ‘0’, the Access Bank is selected. If ‘a’ is ‘1’, the BSR is used to select the GPR bank (default). If ‘a’ is ‘0’ and the extended instruction set is enabled, this instruction operates in Indexed Literal Offset Addressing mode whenever f ≤ 95 (5Fh). See Section 24.2.3 “Byte-Oriented and Bit-Oriented Instructions in Indexed Literal Offset Mode” for details. Words: 1 Cycles: 1 Q Cycle Activity: Q1 Q2 Q3 Q4 Decode Read register ‘f’ Process Data Write to destination Example: ADDWFC REG, 0, 1 Before Instruction CARRY bit = 1 REG = 02h W = 4Dh After Instruction CARRY bit = 0 REG = 02h W = 50h ANDLW AND literal with W Syntax: ANDLW k Operands: 0 ≤ k ≤ 255 Operation: (W) .AND. k → W Status Affected: N, Z Encoding: 0000 1011 kkkk kkkk Description: The contents of W are AND’ed with the 8-bit literal ‘k’. The result is placed in W. Words: 1 Cycles: 1 Q Cycle Activity: Q1 Q2 Q3 Q4 Decode Read literal ‘k’ Process Data Write to W Example: ANDLW 05Fh Before Instruction W = A3h After Instruction W = 03h © 2007 Microchip Technology Inc. Preliminary DS39631B-page 275 PIC18F2420/2520/4420/4520 ANDWF AND W with f Syntax: ANDWF f {,d {,a}} Operands: 0 ≤ f ≤ 255 d ∈ [0,1] a ∈ [0,1] Operation: (W) .AND. (f) → dest Status Affected: N, Z Encoding: 0001 01da ffff ffff Description: The contents of W are AND’ed with register ‘f’. If ‘d’ is ‘0’, the result is stored in W. If ‘d’ is ‘1’, the result is stored back in register ‘f’ (default). If ‘a’ is ‘0’, the Access Bank is selected. If ‘a’ is ‘1’, the BSR is used to select the GPR bank (default). If ‘a’ is ‘0’ and the extended instruction set is enabled, this instruction operates in Indexed Literal Offset Addressing mode whenever f ≤ 95 (5Fh). See Section 24.2.3 “Byte-Oriented and Bit-Oriented Instructions in Indexed Literal Offset Mode” for details. Words: 1 Cycles: 1 Q Cycle Activity: Q1 Q2 Q3 Q4 Decode Read register ‘f’ Process Data Write to destination Example: ANDWF REG, 0, 0 Before Instruction W = 17h REG = C2h After Instruction W = 02h REG = C2h BC Branch if Carry Syntax: BC n Operands: -128 ≤ n ≤ 127 Operation: if CARRY bit is ‘1’ (PC) + 2 + 2n → PC Status Affected: None Encoding: 1110 0010 nnnn nnnn Description: If the CARRY bit is ‘1’, then the program will branch. The 2’s complement number ‘2n’ is added to the PC. Since the PC will have incremented to fetch the next instruction, the new address will be PC + 2 + 2n. This instruction is then a two-cycle instruction. Words: 1 Cycles: 1(2) Q Cycle Activity: If Jump: Q1 Q2 Q3 Q4 Decode Read literal ‘n’ Process Data Write to PC No operation No operation No operation No operation If No Jump: Q1 Q2 Q3 Q4 Decode Read literal ‘n’ Process Data No operation Example: HERE BC 5 Before Instruction PC = address (HERE) After Instruction If CARRY = 1; PC = address (HERE + 12) If CARRY = 0; PC = address (HERE + 2) PIC18F2420/2520/4420/4520 DS39631B-page 276 Preliminary © 2007 Microchip Technology Inc. BCF Bit Clear f Syntax: BCF f, b {,a} Operands: 0 ≤ f ≤ 255 0 ≤ b ≤ 7 a ∈ [0,1] Operation: 0 → f Status Affected: None Encoding: 1001 bbba ffff ffff Description: Bit ‘b’ in register ‘f’ is cleared. If ‘a’ is ‘0’, the Access Bank is selected. If ‘a’ is ‘1’, the BSR is used to select the GPR bank (default). If ‘a’ is ‘0’ and the extended instruction set is enabled, this instruction operates in Indexed Literal Offset Addressing mode whenever f ≤ 95 (5Fh). See Section 24.2.3 “Byte-Oriented and Bit-Oriented Instructions in Indexed Literal Offset Mode” for details. Words: 1 Cycles: 1 Q Cycle Activity: Q1 Q2 Q3 Q4 Decode Read register ‘f’ Process Data Write register ‘f’ Example: BCF FLAG_REG, 7, 0 Before Instruction FLAG_REG = C7h After Instruction FLAG_REG = 47h BN Branch if Negative Syntax: BN n Operands: -128 ≤ n ≤ 127 Operation: if NEGATIVE bit is ‘1’ (PC) + 2 + 2n → PC Status Affected: None Encoding: 1110 0110 nnnn nnnn Description: If the NEGATIVE bit is ‘1’, then the program will branch. The 2’s complement number ‘2n’ is added to the PC. Since the PC will have incremented to fetch the next instruction, the new address will be PC + 2 + 2n. This instruction is then a two-cycle instruction. Words: 1 Cycles: 1(2) Q Cycle Activity: If Jump: Q1 Q2 Q3 Q4 Decode Read literal ‘n’ Process Data Write to PC No operation No operation No operation No operation If No Jump: Q1 Q2 Q3 Q4 Decode Read literal ‘n’ Process Data No operation Example: HERE BN Jump Before Instruction PC = address (HERE) After Instruction If NEGATIVE = 1; PC = address (Jump) If NEGATIVE = 0; PC = address (HERE + 2) © 2007 Microchip Technology Inc. Preliminary DS39631B-page 277 PIC18F2420/2520/4420/4520 BNC Branch if Not Carry Syntax: BNC n Operands: -128 ≤ n ≤ 127 Operation: if CARRY bit is ‘0’ (PC) + 2 + 2n → PC Status Affected: None Encoding: 1110 0011 nnnn nnnn Description: If the CARRY bit is ‘0’, then the program will branch. The 2’s complement number ‘2n’ is added to the PC. Since the PC will have incremented to fetch the next instruction, the new address will be PC + 2 + 2n. This instruction is then a two-cycle instruction. Words: 1 Cycles: 1(2) Q Cycle Activity: If Jump: Q1 Q2 Q3 Q4 Decode Read literal ‘n’ Process Data Write to PC No operation No operation No operation No operation If No Jump: Q1 Q2 Q3 Q4 Decode Read literal ‘n’ Process Data No operation Example: HERE BNC Jump Before Instruction PC = address (HERE) After Instruction If CARRY = 0; PC = address (Jump) If CARRY = 1; PC = address (HERE + 2) BNN Branch if Not Negative Syntax: BNN n Operands: -128 ≤ n ≤ 127 Operation: if NEGATIVE bit is ‘0’ (PC) + 2 + 2n → PC Status Affected: None Encoding: 1110 0111 nnnn nnnn Description: If the NEGATIVE bit is ‘0’, then the program will branch. The 2’s complement number ‘2n’ is added to the PC. Since the PC will have incremented to fetch the next instruction, the new address will be PC + 2 + 2n. This instruction is then a two-cycle instruction. Words: 1 Cycles: 1(2) Q Cycle Activity: If Jump: Q1 Q2 Q3 Q4 Decode Read literal ‘n’ Process Data Write to PC No operation No operation No operation No operation If No Jump: Q1 Q2 Q3 Q4 Decode Read literal ‘n’ Process Data No operation Example: HERE BNN Jump Before Instruction PC = address (HERE) After Instruction If NEGATIVE = 0; PC = address (Jump) If NEGATIVE = 1; PC = address (HERE + 2) PIC18F2420/2520/4420/4520 DS39631B-page 278 Preliminary © 2007 Microchip Technology Inc. BNOV Branch if Not Overflow Syntax: BNOV n Operands: -128 ≤ n ≤ 127 Operation: if OVERFLOW bit is ‘0’ (PC) + 2 + 2n → PC Status Affected: None Encoding: 1110 0101 nnnn nnnn Description: If the OVERFLOW bit is ‘0’, then the program will branch. The 2’s complement number ‘2n’ is added to the PC. Since the PC will have incremented to fetch the next instruction, the new address will be PC + 2 + 2n. This instruction is then a two-cycle instruction. Words: 1 Cycles: 1(2) Q Cycle Activity: If Jump: Q1 Q2 Q3 Q4 Decode Read literal ‘n’ Process Data Write to PC No operation No operation No operation No operation If No Jump: Q1 Q2 Q3 Q4 Decode Read literal ‘n’ Process Data No operation Example: HERE BNOV Jump Before Instruction PC = address (HERE) After Instruction If OVERFLOW= 0; PC = address (Jump) If OVERFLOW= 1; PC = address (HERE + 2) BNZ Branch if Not Zero Syntax: BNZ n Operands: -128 ≤ n ≤ 127 Operation: if ZERO bit is ‘0’ (PC) + 2 + 2n → PC Status Affected: None Encoding: 1110 0001 nnnn nnnn Description: If the ZERO bit is ‘0’, then the program will branch. The 2’s complement number ‘2n’ is added to the PC. Since the PC will have incremented to fetch the next instruction, the new address will be PC + 2 + 2n. This instruction is then a two-cycle instruction. Words: 1 Cycles: 1(2) Q Cycle Activity: If Jump: Q1 Q2 Q3 Q4 Decode Read literal ‘n’ Process Data Write to PC No operation No operation No operation No operation If No Jump: Q1 Q2 Q3 Q4 Decode Read literal ‘n’ Process Data No operation Example: HERE BNZ Jump Before Instruction PC = address (HERE) After Instruction If ZERO = 0; PC = address (Jump) If ZERO = 1; PC = address (HERE + 2) © 2007 Microchip Technology Inc. Preliminary DS39631B-page 279 PIC18F2420/2520/4420/4520 BRA Unconditional Branch Syntax: BRA n Operands: -1024 ≤ n ≤ 1023 Operation: (PC) + 2 + 2n → PC Status Affected: None Encoding: 1101 0nnn nnnn nnnn Description: Add the 2’s complement number ‘2n’ to the PC. Since the PC will have incremented to fetch the next instruction, the new address will be PC + 2 + 2n. This instruction is a two-cycle instruction. Words: 1 Cycles: 2 Q Cycle Activity: Q1 Q2 Q3 Q4 Decode Read literal ‘n’ Process Data Write to PC No operation No operation No operation No operation Example: HERE BRA Jump Before Instruction PC = address (HERE) After Instruction PC = address (Jump) BSF Bit Set f Syntax: BSF f, b {,a} Operands: 0 ≤ f ≤ 255 0 ≤ b ≤ 7 a ∈ [0,1] Operation: 1 → f Status Affected: None Encoding: 1000 bbba ffff ffff Description: Bit ‘b’ in register ‘f’ is set. If ‘a’ is ‘0’, the Access Bank is selected. If ‘a’ is ‘1’, the BSR is used to select the GPR bank (default). If ‘a’ is ‘0’ and the extended instruction set is enabled, this instruction operates in Indexed Literal Offset Addressing mode whenever f ≤ 95 (5Fh). See Section 24.2.3 “Byte-Oriented and Bit-Oriented Instructions in Indexed Literal Offset Mode” for details. Words: 1 Cycles: 1 Q Cycle Activity: Q1 Q2 Q3 Q4 Decode Read register ‘f’ Process Data Write register ‘f’ Example: BSF FLAG_REG, 7, 1 Before Instruction FLAG_REG = 0Ah After Instruction FLAG_REG = 8Ah PIC18F2420/2520/4420/4520 DS39631B-page 280 Preliminary © 2007 Microchip Technology Inc. BTFSC Bit Test File, Skip if Clear Syntax: BTFSC f, b {,a} Operands: 0 ≤ f ≤ 255 0 ≤ b ≤ 7 a ∈ [0,1] Operation: skip if (f) = 0 Status Affected: None Encoding: 1011 bbba ffff ffff Description: If bit ‘b’ in register ‘f’ is ‘0’, then the next instruction is skipped. If bit ‘b’ is ‘0’, then the next instruction fetched during the current instruction execution is discarded and a NOP is executed instead, making this a two-cycle instruction. If ‘a’ is ‘0’, the Access Bank is selected. If ‘a’ is ‘1’, the BSR is used to select the GPR bank (default). If ‘a’ is ‘0’ and the extended instruction set is enabled, this instruction operates in Indexed Literal Offset Addressing mode whenever f ≤ 95 (5Fh). See Section 24.2.3 “Byte-Oriented and Bit-Oriented Instructions in Indexed Literal Offset Mode” for details. Words: 1 Cycles: 1(2) Note: 3 cycles if skip and followed by a 2-word instruction. Q Cycle Activity: Q1 Q2 Q3 Q4 Decode Read register ‘f’ Process Data No operation If skip: Q1 Q2 Q3 Q4 No operation No operation No operation No operation If skip and followed by 2-word instruction: Q1 Q2 Q3 Q4 No operation No operation No operation No operation No operation No operation No operation No operation Example: HERE FALSE TRUE BTFSC : : FLAG, 1, 0 Before Instruction PC = address (HERE) After Instruction If FLAG<1> = 0; PC = address (TRUE) If FLAG<1> = 1; PC = address (FALSE) BTFSS Bit Test File, Skip if Set Syntax: BTFSS f, b {,a} Operands: 0 ≤ f ≤ 255 0 ≤ b < 7 a ∈ [0,1] Operation: skip if (f) = 1 Status Affected: None Encoding: 1010 bbba ffff ffff Description: If bit ‘b’ in register ‘f’ is ‘1’, then the next instruction is skipped. If bit ‘b’ is ‘1’, then the next instruction fetched during the current instruction execution is discarded and a NOP is executed instead, making this a two-cycle instruction. If ‘a’ is ‘0’, the Access Bank is selected. If ‘a’ is ‘1’, the BSR is used to select the GPR bank (default). If ‘a’ is ‘0’ and the extended instruction set is enabled, this instruction operates in Indexed Literal Offset Addressing mode whenever f ≤ 95 (5Fh). See Section 24.2.3 “Byte-Oriented and Bit-Oriented Instructions in Indexed Literal Offset Mode” for details. Words: 1 Cycles: 1(2) Note: 3 cycles if skip and followed by a 2-word instruction. Q Cycle Activity: Q1 Q2 Q3 Q4 Decode Read register ‘f’ Process Data No operation If skip: Q1 Q2 Q3 Q4 No operation No operation No operation No operation If skip and followed by 2-word instruction: Q1 Q2 Q3 Q4 No operation No operation No operation No operation No operation No operation No operation No operation Example: HERE FALSE TRUE BTFSS : : FLAG, 1, 0 Before Instruction PC = address (HERE) After Instruction If FLAG<1> = 0; PC = address (FALSE) If FLAG<1> = 1; PC = address (TRUE) © 2007 Microchip Technology Inc. Preliminary DS39631B-page 281 PIC18F2420/2520/4420/4520 BTG Bit Toggle f Syntax: BTG f, b {,a} Operands: 0 ≤ f ≤ 255 0 ≤ b < 7 a ∈ [0,1] Operation: (f) → f Status Affected: None Encoding: 0111 bbba ffff ffff Description: Bit ‘b’ in data memory location ‘f’ is inverted. If ‘a’ is ‘0’, the Access Bank is selected. If ‘a’ is ‘1’, the BSR is used to select the GPR bank (default). If ‘a’ is ‘0’ and the extended instruction set is enabled, this instruction operates in Indexed Literal Offset Addressing mode whenever f ≤ 95 (5Fh). See Section 24.2.3 “Byte-Oriented and Bit-Oriented Instructions in Indexed Literal Offset Mode” for details. Words: 1 Cycles: 1 Q Cycle Activity: Q1 Q2 Q3 Q4 Decode Read register ‘f’ Process Data Write register ‘f’ Example: BTG PORTC, 4, 0 Before Instruction: PORTC = 0111 0101 [75h] After Instruction: PORTC = 0110 0101 [65h] BOV Branch if Overflow Syntax: BOV n Operands: -128 ≤ n ≤ 127 Operation: if OVERFLOW bit is ‘1’ (PC) + 2 + 2n → PC Status Affected: None Encoding: 1110 0100 nnnn nnnn Description: If the OVERFLOW bit is ‘1’, then the program will branch. The 2’s complement number ‘2n’ is added to the PC. Since the PC will have incremented to fetch the next instruction, the new address will be PC + 2 + 2n. This instruction is then a two-cycle instruction. Words: 1 Cycles: 1(2) Q Cycle Activity: If Jump: Q1 Q2 Q3 Q4 Decode Read literal ‘n’ Process Data Write to PC No operation No operation No operation No operation If No Jump: Q1 Q2 Q3 Q4 Decode Read literal ‘n’ Process Data No operation Example: HERE BOV Jump Before Instruction PC = address (HERE) After Instruction If OVERFLOW= 1; PC = address (Jump) If OVERFLOW= 0; PC = address (HERE + 2) PIC18F2420/2520/4420/4520 DS39631B-page 282 Preliminary © 2007 Microchip Technology Inc. BZ Branch if Zero Syntax: BZ n Operands: -128 ≤ n ≤ 127 Operation: if ZERO bit is ‘1’ (PC) + 2 + 2n → PC Status Affected: None Encoding: 1110 0000 nnnn nnnn Description: If the ZERO bit is ‘1’, then the program will branch. The 2’s complement number ‘2n’ is added to the PC. Since the PC will have incremented to fetch the next instruction, the new address will be PC + 2 + 2n. This instruction is then a two-cycle instruction. Words: 1 Cycles: 1(2) Q Cycle Activity: If Jump: Q1 Q2 Q3 Q4 Decode Read literal ‘n’ Process Data Write to PC No operation No operation No operation No operation If No Jump: Q1 Q2 Q3 Q4 Decode Read literal ‘n’ Process Data No operation Example: HERE BZ Jump Before Instruction PC = address (HERE) After Instruction If ZERO = 1; PC = address (Jump) If ZERO = 0; PC = address (HERE + 2) CALL Subroutine Call Syntax: CALL k {,s} Operands: 0 ≤ k ≤ 1048575 s ∈ [0,1] Operation: (PC) + 4 → TOS, k → PC<20:1>, if s = 1 (W) → WS, (Status) → STATUSS, (BSR) → BSRS Status Affected: None Encoding: 1st word (k<7:0>) 2nd word(k<19:8>) 1110 1111 110s k19kkk k7kkk kkkk kkkk0 kkkk8 Description: Subroutine call of entire 2-Mbyte memory range. First, return address (PC + 4) is pushed onto the return stack. If ‘s’ = 1, the W, Status and BSR registers are also pushed into their respective shadow registers, WS, STATUSS and BSRS. If ‘s’ = 0, no update occurs (default). Then, the 20-bit value ‘k’ is loaded into PC<20:1>. CALL is a two-cycle instruction. Words: 2 Cycles: 2 Q Cycle Activity: Q1 Q2 Q3 Q4 Decode Read literal ‘k’<7:0>, PUSH PC to stack Read literal ‘k’<19:8>, Write to PC No operation No operation No operation No operation Example: HERE CALL THERE, 1 Before Instruction PC = address (HERE) After Instruction PC = address (THERE) TOS = address (HERE + 4) WS = W BSRS = BSR STATUSS= Status © 2007 Microchip Technology Inc. Preliminary DS39631B-page 283 PIC18F2420/2520/4420/4520 CLRF Clear f Syntax: CLRF f {,a} Operands: 0 ≤ f ≤ 255 a ∈ [0,1] Operation: 000h → f 1 → Z Status Affected: Z Encoding: 0110 101a ffff ffff Description: Clears the contents of the specified register. If ‘a’ is ‘0’, the Access Bank is selected. If ‘a’ is ‘1’, the BSR is used to select the GPR bank (default). If ‘a’ is ‘0’ and the extended instruction set is enabled, this instruction operates in Indexed Literal Offset Addressing mode whenever f ≤ 95 (5Fh). See Section 24.2.3 “Byte-Oriented and Bit-Oriented Instructions in Indexed Literal Offset Mode” for details. Words: 1 Cycles: 1 Q Cycle Activity: Q1 Q2 Q3 Q4 Decode Read register ‘f’ Process Data Write register ‘f’ Example: CLRF FLAG_REG, 1 Before Instruction FLAG_REG = 5Ah After Instruction FLAG_REG = 00h CLRWDT Clear Watchdog Timer Syntax: CLRWDT Operands: None Operation: 000h → WDT, 000h → WDT postscaler, 1 → TO, 1 → PD Status Affected: TO, PD Encoding: 0000 0000 0000 0100 Description: CLRWDT instruction resets the Watchdog Timer. It also resets the postscaler of the WDT. Status bits, TO and PD, are set. Words: 1 Cycles: 1 Q Cycle Activity: Q1 Q2 Q3 Q4 Decode No operation Process Data No operation Example: CLRWDT Before Instruction WDT Counter = ? After Instruction WDT Counter = 00h WDT Postscaler = 0 TO = 1 PD = 1 PIC18F2420/2520/4420/4520 DS39631B-page 284 Preliminary © 2007 Microchip Technology Inc. COMF Complement f Syntax: COMF f {,d {,a}} Operands: 0 ≤ f ≤ 255 d ∈ [0,1] a ∈ [0,1] Operation: (f) → dest Status Affected: N, Z Encoding: 0001 11da ffff ffff Description: The contents of register ‘f’ are complemented. If ‘d’ is ‘0’, the result is stored in W. If ‘d’ is ‘1’, the result is stored back in register ‘f’ (default). If ‘a’ is ‘0’, the Access Bank is selected. If ‘a’ is ‘1’, the BSR is used to select the GPR bank (default). If ‘a’ is ‘0’ and the extended instruction set is enabled, this instruction operates in Indexed Literal Offset Addressing mode whenever f ≤ 95 (5Fh). See Section 24.2.3 “Byte-Oriented and Bit-Oriented Instructions in Indexed Literal Offset Mode” for details. Words: 1 Cycles: 1 Q Cycle Activity: Q1 Q2 Q3 Q4 Decode Read register ‘f’ Process Data Write to destination Example: COMF REG, 0, 0 Before Instruction REG = 13h After Instruction REG = 13h W = ECh CPFSEQ Compare f with W, skip if f = W Syntax: CPFSEQ f {,a} Operands: 0 ≤ f ≤ 255 a ∈ [0,1] Operation: (f) – (W), skip if (f) = (W) (unsigned comparison) Status Affected: None Encoding: 0110 001a ffff ffff Description: Compares the contents of data memory location ‘f’ to the contents of W by performing an unsigned subtraction. If ‘f’ = W, then the fetched instruction is discarded and a NOP is executed instead, making this a two-cycle instruction. If ‘a’ is ‘0’, the Access Bank is selected. If ‘a’ is ‘1’, the BSR is used to select the GPR bank (default). If ‘a’ is ‘0’ and the extended instruction set is enabled, this instruction operates in Indexed Literal Offset Addressing mode whenever f ≤ 95 (5Fh). See Section 24.2.3 “Byte-Oriented and Bit-Oriented Instructions in Indexed Literal Offset Mode” for details. Words: 1 Cycles: 1(2) Note: 3 cycles if skip and followed by a 2-word instruction. Q Cycle Activity: Q1 Q2 Q3 Q4 Decode Read register ‘f’ Process Data No operation If skip: Q1 Q2 Q3 Q4 No operation No operation No operation No operation If skip and followed by 2-word instruction: Q1 Q2 Q3 Q4 No operation No operation No operation No operation No operation No operation No operation No operation Example: HERE CPFSEQ REG, 0 NEQUAL : EQUAL : Before Instruction PC Address = HERE W = ? REG = ? After Instruction If REG = W; PC = Address (EQUAL) If REG ≠ W; PC = Address (NEQUAL) © 2007 Microchip Technology Inc. Preliminary DS39631B-page 285 PIC18F2420/2520/4420/4520 CPFSGT Compare f with W, skip if f > W Syntax: CPFSGT f {,a} Operands: 0 ≤ f ≤ 255 a ∈ [0,1] Operation: (f) – (W), skip if (f) > (W) (unsigned comparison) Status Affected: None Encoding: 0110 010a ffff ffff Description: Compares the contents of data memory location ‘f’ to the contents of the W by performing an unsigned subtraction. If the contents of ‘f’ are greater than the contents of WREG, then the fetched instruction is discarded and a NOP is executed instead, making this a two-cycle instruction. If ‘a’ is ‘0’, the Access Bank is selected. If ‘a’ is ‘1’, the BSR is used to select the GPR bank (default). If ‘a’ is ‘0’ and the extended instruction set is enabled, this instruction operates in Indexed Literal Offset Addressing mode whenever f ≤ 95 (5Fh). See Section 24.2.3 “Byte-Oriented and Bit-Oriented Instructions in Indexed Literal Offset Mode” for details. Words: 1 Cycles: 1(2) Note: 3 cycles if skip and followed by a 2-word instruction. Q Cycle Activity: Q1 Q2 Q3 Q4 Decode Read register ‘f’ Process Data No operation If skip: Q1 Q2 Q3 Q4 No operation No operation No operation No operation If skip and followed by 2-word instruction: Q1 Q2 Q3 Q4 No operation No operation No operation No operation No operation No operation No operation No operation Example: HERE CPFSGT REG, 0 NGREATER : GREATER : Before Instruction PC = Address (HERE) W = ? After Instruction If REG > W; PC = Address (GREATER) If REG ≤ W; PC = Address (NGREATER) CPFSLT Compare f with W, skip if f < W Syntax: CPFSLT f {,a} Operands: 0 ≤ f ≤ 255 a ∈ [0,1] Operation: (f) – (W), skip if (f) < (W) (unsigned comparison) Status Affected: None Encoding: 0110 000a ffff ffff Description: Compares the contents of data memory location ‘f’ to the contents of W by performing an unsigned subtraction. If the contents of ‘f’ are less than the contents of W, then the fetched instruction is discarded and a NOP is executed instead, making this a two-cycle instruction. If ‘a’ is ‘0’, the Access Bank is selected. If ‘a’ is ‘1’, the BSR is used to select the GPR bank (default). Words: 1 Cycles: 1(2) Note: 3 cycles if skip and followed by a 2-word instruction. Q Cycle Activity: Q1 Q2 Q3 Q4 Decode Read register ‘f’ Process Data No operation If skip: Q1 Q2 Q3 Q4 No operation No operation No operation No operation If skip and followed by 2-word instruction: Q1 Q2 Q3 Q4 No operation No operation No operation No operation No operation No operation No operation No operation Example: HERE CPFSLT REG, 1 NLESS : LESS : Before Instruction PC = Address (HERE) W = ? After Instruction If REG < W; PC = Address (LESS) If REG ≥ W; PC = Address (NLESS) PIC18F2420/2520/4420/4520 DS39631B-page 286 Preliminary © 2007 Microchip Technology Inc. DAW Decimal Adjust W Register Syntax: DAW Operands: None Operation: If [W<3:0> > 9] or [DC = 1] then (W<3:0>) + 6 → W<3:0>; else (W<3:0>) → W<3:0>; If [W<7:4> + DC > 9] or [C = 1] then (W<7:4>) + 6 + DC → W<7:4> ; else (W<7:4>) + DC → W<7:4> Status Affected: C Encoding: 0000 0000 0000 0111 Description: DAW adjusts the eight-bit value in W, resulting from the earlier addition of two variables (each in packed BCD format) and produces a correct packed BCD result. Words: 1 Cycles: 1 Q Cycle Activity: Q1 Q2 Q3 Q4 Decode Read register W Process Data Write W Example1: DAW Before Instruction W = A5h C = 0 DC = 0 After Instruction W = 05h C = 1 DC = 0 Example 2: Before Instruction W = CEh C = 0 DC = 0 After Instruction W = 34h C = 1 DC = 0 DECF Decrement f Syntax: DECF f {,d {,a}} Operands: 0 ≤ f ≤ 255 d ∈ [0,1] a ∈ [0,1] Operation: (f) – 1 → dest Status Affected: C, DC, N, OV, Z Encoding: 0000 01da ffff ffff Description: Decrement register ‘f’. If ‘d’ is ‘0’, the result is stored in W. If ‘d’ is ‘1’, the result is stored back in register ‘f’ (default). If ‘a’ is ‘0’, the Access Bank is selected. If ‘a’ is ‘1’, the BSR is used to select the GPR bank (default). If ‘a’ is ‘0’ and the extended instruction set is enabled, this instruction operates in Indexed Literal Offset Addressing mode whenever f ≤ 95 (5Fh). See Section 24.2.3 “Byte-Oriented and Bit-Oriented Instructions in Indexed Literal Offset Mode” for details. Words: 1 Cycles: 1 Q Cycle Activity: Q1 Q2 Q3 Q4 Decode Read register ‘f’ Process Data Write to destination Example: DECF CNT, 1, 0 Before Instruction CNT = 01h Z = 0 After Instruction CNT = 00h Z = 1 © 2007 Microchip Technology Inc. Preliminary DS39631B-page 287 PIC18F2420/2520/4420/4520 DECFSZ Decrement f, skip if 0 Syntax: DECFSZ f {,d {,a}} Operands: 0 ≤ f ≤ 255 d ∈ [0,1] a ∈ [0,1] Operation: (f) – 1 → dest, skip if result = 0 Status Affected: None Encoding: 0010 11da ffff ffff Description: The contents of register ‘f’ are decremented. If ‘d’ is ‘0’, the result is placed in W. If ‘d’ is ‘1’, the result is placed back in register ‘f’ (default). If the result is ‘0’, the next instruction, which is already fetched, is discarded and a NOP is executed instead, making it a two-cycle instruction. If ‘a’ is ‘0’, the Access Bank is selected. If ‘a’ is ‘1’, the BSR is used to select the GPR bank (default). If ‘a’ is ‘0’ and the extended instruction set is enabled, this instruction operates in Indexed Literal Offset Addressing mode whenever f ≤ 95 (5Fh). See Section 24.2.3 “Byte-Oriented and Bit-Oriented Instructions in Indexed Literal Offset Mode” for details. Words: 1 Cycles: 1(2) Note: 3 cycles if skip and followed by a 2-word instruction. Q Cycle Activity: Q1 Q2 Q3 Q4 Decode Read register ‘f’ Process Data Write to destination If skip: Q1 Q2 Q3 Q4 No operation No operation No operation No operation If skip and followed by 2-word instruction: Q1 Q2 Q3 Q4 No operation No operation No operation No operation No operation No operation No operation No operation Example: HERE DECFSZ CNT, 1, 1 GOTO LOOP CONTINUE Before Instruction PC = Address (HERE) After Instruction CNT = CNT - 1 If CNT = 0; PC = Address (CONTINUE) If CNT ≠ 0; PC = Address (HERE + 2) DCFSNZ Decrement f, skip if not 0 Syntax: DCFSNZ f {,d {,a}} Operands: 0 ≤ f ≤ 255 d ∈ [0,1] a ∈ [0,1] Operation: (f) – 1 → dest, skip if result ≠ 0 Status Affected: None Encoding: 0100 11da ffff ffff Description: The contents of register ‘f’ are decremented. If ‘d’ is ‘0’, the result is placed in W. If ‘d’ is ‘1’, the result is placed back in register ‘f’ (default). If the result is not ‘0’, the next instruction, which is already fetched, is discarded and a NOP is executed instead, making it a two-cycle instruction. If ‘a’ is ‘0’, the Access Bank is selected. If ‘a’ is ‘1’, the BSR is used to select the GPR bank (default). If ‘a’ is ‘0’ and the extended instruction set is enabled, this instruction operates in Indexed Literal Offset Addressing mode whenever f ≤ 95 (5Fh). See Section 24.2.3 “Byte-Oriented and Bit-Oriented Instructions in Indexed Literal Offset Mode” for details. Words: 1 Cycles: 1(2) Note: 3 cycles if skip and followed by a 2-word instruction. Q Cycle Activity: Q1 Q2 Q3 Q4 Decode Read register ‘f’ Process Data Write to destination If skip: Q1 Q2 Q3 Q4 No operation No operation No operation No operation If skip and followed by 2-word instruction: Q1 Q2 Q3 Q4 No operation No operation No operation No operation No operation No operation No operation No operation Example: HERE DCFSNZ TEMP, 1, 0 ZERO : NZERO : Before Instruction TEMP = ? After Instruction TEMP = TEMP – 1, If TEMP = 0; PC = Address (ZERO) If TEMP ≠ 0; PC = Address (NZERO) PIC18F2420/2520/4420/4520 DS39631B-page 288 Preliminary © 2007 Microchip Technology Inc. GOTO Unconditional Branch Syntax: GOTO k Operands: 0 ≤ k ≤ 1048575 Operation: k → PC<20:1> Status Affected: None Encoding: 1st word (k<7:0>) 2nd word(k<19:8>) 1110 1111 1111 k19kkk k7kkk kkkk kkkk0 kkkk8 Description: GOTO allows an unconditional branch anywhere within entire 2-Mbyte memory range. The 20-bit value ‘k’ is loaded into PC<20:1>. GOTO is always a two-cycle instruction. Words: 2 Cycles: 2 Q Cycle Activity: Q1 Q2 Q3 Q4 Decode Read literal ‘k’<7:0>, No operation Read literal ‘k’<19:8>, Write to PC No operation No operation No operation No operation Example: GOTO THERE After Instruction PC = Address (THERE) INCF Increment f Syntax: INCF f {,d {,a}} Operands: 0 ≤ f ≤ 255 d ∈ [0,1] a ∈ [0,1] Operation: (f) + 1 → dest Status Affected: C, DC, N, OV, Z Encoding: 0010 10da ffff ffff Description: The contents of register ‘f’ are incremented. If ‘d’ is ‘0’, the result is placed in W. If ‘d’ is ‘1’, the result is placed back in register ‘f’ (default). If ‘a’ is ‘0’, the Access Bank is selected. If ‘a’ is ‘1’, the BSR is used to select the GPR bank (default). If ‘a’ is ‘0’ and the extended instruction set is enabled, this instruction operates in Indexed Literal Offset Addressing mode whenever f ≤ 95 (5Fh). See Section 24.2.3 “Byte-Oriented and Bit-Oriented Instructions in Indexed Literal Offset Mode” for details. Words: 1 Cycles: 1 Q Cycle Activity: Q1 Q2 Q3 Q4 Decode Read register ‘f’ Process Data Write to destination Example: INCF CNT, 1, 0 Before Instruction CNT = FFh Z = 0 C = ? DC = ? After Instruction CNT = 00h Z = 1 C = 1 DC = 1 © 2007 Microchip Technology Inc. Preliminary DS39631B-page 289 PIC18F2420/2520/4420/4520 INCFSZ Increment f, skip if 0 Syntax: INCFSZ f {,d {,a}} Operands: 0 ≤ f ≤ 255 d ∈ [0,1] a ∈ [0,1] Operation: (f) + 1 → dest, skip if result = 0 Status Affected: None Encoding: 0011 11da ffff ffff Description: The contents of register ‘f’ are incremented. If ‘d’ is ‘0’, the result is placed in W. If ‘d’ is ‘1’, the result is placed back in register ‘f’ (default). If the result is ‘0’, the next instruction, which is already fetched, is discarded and a NOP is executed instead, making it a two-cycle instruction. If ‘a’ is ‘0’, the Access Bank is selected. If ‘a’ is ‘1’, the BSR is used to select the GPR bank (default). If ‘a’ is ‘0’ and the extended instruction set is enabled, this instruction operates in Indexed Literal Offset Addressing mode whenever f ≤ 95 (5Fh). See Section 24.2.3 “Byte-Oriented and Bit-Oriented Instructions in Indexed Literal Offset Mode” for details. Words: 1 Cycles: 1(2) Note: 3 cycles if skip and followed by a 2-word instruction. Q Cycle Activity: Q1 Q2 Q3 Q4 Decode Read register ‘f’ Process Data Write to destination If skip: Q1 Q2 Q3 Q4 No operation No operation No operation No operation If skip and followed by 2-word instruction: Q1 Q2 Q3 Q4 No operation No operation No operation No operation No operation No operation No operation No operation Example: HERE INCFSZ CNT, 1, 0 NZERO : ZERO : Before Instruction PC = Address (HERE) After Instruction CNT = CNT + 1 If CNT = 0; PC = Address (ZERO) If CNT ≠ 0; PC = Address (NZERO) INFSNZ Increment f, skip if not 0 Syntax: INFSNZ f {,d {,a}} Operands: 0 ≤ f ≤ 255 d ∈ [0,1] a ∈ [0,1] Operation: (f) + 1 → dest, skip if result ≠ 0 Status Affected: None Encoding: 0100 10da ffff ffff Description: The contents of register ‘f’ are incremented. If ‘d’ is ‘0’, the result is placed in W. If ‘d’ is ‘1’, the result is placed back in register ‘f’ (default). If the result is not ‘0’, the next instruction, which is already fetched, is discarded and a NOP is executed instead, making it a two-cycle instruction. If ‘a’ is ‘0’, the Access Bank is selected. If ‘a’ is ‘1’, the BSR is used to select the GPR bank (default). If ‘a’ is ‘0’ and the extended instruction set is enabled, this instruction operates in Indexed Literal Offset Addressing mode whenever f ≤ 95 (5Fh). See Section 24.2.3 “Byte-Oriented and Bit-Oriented Instructions in Indexed Literal Offset Mode” for details. Words: 1 Cycles: 1(2) Note: 3 cycles if skip and followed by a 2-word instruction. Q Cycle Activity: Q1 Q2 Q3 Q4 Decode Read register ‘f’ Process Data Write to destination If skip: Q1 Q2 Q3 Q4 No operation No operation No operation No operation If skip and followed by 2-word instruction: Q1 Q2 Q3 Q4 No operation No operation No operation No operation No operation No operation No operation No operation Example: HERE INFSNZ REG, 1, 0 ZERO NZERO Before Instruction PC = Address (HERE) After Instruction REG = REG + 1 If REG ≠ 0; PC = Address (NZERO) If REG = 0; PC = Address (ZERO) PIC18F2420/2520/4420/4520 DS39631B-page 290 Preliminary © 2007 Microchip Technology Inc. IORLW Inclusive OR literal with W Syntax: IORLW k Operands: 0 ≤ k ≤ 255 Operation: (W) .OR. k → W Status Affected: N, Z Encoding: 0000 1001 kkkk kkkk Description: The contents of W are ORed with the eight-bit literal ‘k’. The result is placed in W. Words: 1 Cycles: 1 Q Cycle Activity: Q1 Q2 Q3 Q4 Decode Read literal ‘k’ Process Data Write to W Example: IORLW 35h Before Instruction W = 9Ah After Instruction W = BFh IORWF Inclusive OR W with f Syntax: IORWF f {,d {,a}} Operands: 0 ≤ f ≤ 255 d ∈ [0,1] a ∈ [0,1] Operation: (W) .OR. (f) → dest Status Affected: N, Z Encoding: 0001 00da ffff ffff Description: Inclusive OR W with register ‘f’. If ‘d’ is ‘0’, the result is placed in W. If ‘d’ is ‘1’, the result is placed back in register ‘f’ (default). If ‘a’ is ‘0’, the Access Bank is selected. If ‘a’ is ‘1’, the BSR is used to select the GPR bank (default). If ‘a’ is ‘0’ and the extended instruction set is enabled, this instruction operates in Indexed Literal Offset Addressing mode whenever f ≤ 95 (5Fh). See Section 24.2.3 “Byte-Oriented and Bit-Oriented Instructions in Indexed Literal Offset Mode” for details. Words: 1 Cycles: 1 Q Cycle Activity: Q1 Q2 Q3 Q4 Decode Read register ‘f’ Process Data Write to destination Example: IORWF RESULT, 0, 1 Before Instruction RESULT = 13h W = 91h After Instruction RESULT = 13h W = 93h © 2007 Microchip Technology Inc. Preliminary DS39631B-page 291 PIC18F2420/2520/4420/4520 LFSR Load FSR Syntax: LFSR f, k Operands: 0 ≤ f ≤ 2 0 ≤ k ≤ 4095 Operation: k → FSRf Status Affected: None Encoding: 1110 1111 1110 0000 00ff k7kkk k11kkk kkkk Description: The 12-bit literal ‘k’ is loaded into the File Select Register pointed to by ‘f’. Words: 2 Cycles: 2 Q Cycle Activity: Q1 Q2 Q3 Q4 Decode Read literal ‘k’ MSB Process Data Write literal ‘k’ MSB to FSRfH Decode Read literal ‘k’ LSB Process Data Write literal ‘k’ to FSRfL Example: LFSR 2, 3ABh After Instruction FSR2H = 03h FSR2L = ABh MOVF Move f Syntax: MOVF f {,d {,a}} Operands: 0 ≤ f ≤ 255 d ∈ [0,1] a ∈ [0,1] Operation: f → dest Status Affected: N, Z Encoding: 0101 00da ffff ffff Description: The contents of register ‘f’ are moved to a destination dependent upon the status of ‘d’. If ‘d’ is ‘0’, the result is placed in W. If ‘d’ is ‘1’, the result is placed back in register ‘f’ (default). Location ‘f’ can be anywhere in the 256-byte bank. If ‘a’ is ‘0’, the Access Bank is selected. If ‘a’ is ‘1’, the BSR is used to select the GPR bank (default). If ‘a’ is ‘0’ and the extended instruction set is enabled, this instruction operates in Indexed Literal Offset Addressing mode whenever f ≤ 95 (5Fh). See Section 24.2.3 “Byte-Oriented and Bit-Oriented Instructions in Indexed Literal Offset Mode” for details. Words: 1 Cycles: 1 Q Cycle Activity: Q1 Q2 Q3 Q4 Decode Read register ‘f’ Process Data Write W Example: MOVF REG, 0, 0 Before Instruction REG = 22h W = FFh After Instruction REG = 22h W = 22h PIC18F2420/2520/4420/4520 DS39631B-page 292 Preliminary © 2007 Microchip Technology Inc. MOVFF Move f to f Syntax: MOVFF fs,fd Operands: 0 ≤ fs ≤ 4095 0 ≤ fd ≤ 4095 Operation: (fs) → fd Status Affected: None Encoding: 1st word (source) 2nd word (destin.) 1100 1111 ffff ffff ffff ffff ffffs ffffd Description: The contents of source register ‘fs’ are moved to destination register ‘fd’. Location of source ‘fs’ can be anywhere in the 4096-byte data space (000h to FFFh) and location of destination ‘fd’ can also be anywhere from 000h to FFFh. Either source or destination can be W (a useful special situation). MOVFF is particularly useful for transferring a data memory location to a peripheral register (such as the transmit buffer or an I/O port). The MOVFF instruction cannot use the PCL, TOSU, TOSH or TOSL as the destination register. Words: 2 Cycles: 2 (3) Q Cycle Activity: Q1 Q2 Q3 Q4 Decode Read register ‘f’ (src) Process Data No operation Decode No operation No dummy read No operation Write register ‘f’ (dest) Example: MOVFF REG1, REG2 Before Instruction REG1 = 33h REG2 = 11h After Instruction REG1 = 33h REG2 = 33h MOVLB Move literal to low nibble in BSR Syntax: MOVLW k Operands: 0 ≤ k ≤ 255 Operation: k → BSR Status Affected: None Encoding: 0000 0001 kkkk kkkk Description: The eight-bit literal ‘k’ is loaded into the Bank Select Register (BSR). The value of BSR<7:4> always remains ‘0’, regardless of the value of k7:k4. Words: 1 Cycles: 1 Q Cycle Activity: Q1 Q2 Q3 Q4 Decode Read literal ‘k’ Process Data Write literal ‘k’ to BSR Example: MOVLB 5 Before Instruction BSR Register = 02h After Instruction BSR Register = 05h © 2007 Microchip Technology Inc. Preliminary DS39631B-page 293 PIC18F2420/2520/4420/4520 MOVLW Move literal to W Syntax: MOVLW k Operands: 0 ≤ k ≤ 255 Operation: k → W Status Affected: None Encoding: 0000 1110 kkkk kkkk Description: The eight-bit literal ‘k’ is loaded into W. Words: 1 Cycles: 1 Q Cycle Activity: Q1 Q2 Q3 Q4 Decode Read literal ‘k’ Process Data Write to W Example: MOVLW 5Ah After Instruction W = 5Ah MOVWF Move W to f Syntax: MOVWF f {,a} Operands: 0 ≤ f ≤ 255 a ∈ [0,1] Operation: (W) → f Status Affected: None Encoding: 0110 111a ffff ffff Description: Move data from W to register ‘f’. Location ‘f’ can be anywhere in the 256-byte bank. If ‘a’ is ‘0’, the Access Bank is selected. If ‘a’ is ‘1’, the BSR is used to select the GPR bank (default). If ‘a’ is ‘0’ and the extended instruction set is enabled, this instruction operates in Indexed Literal Offset Addressing mode whenever f ≤ 95 (5Fh). See Section 24.2.3 “Byte-Oriented and Bit-Oriented Instructions in Indexed Literal Offset Mode” for details. Words: 1 Cycles: 1 Q Cycle Activity: Q1 Q2 Q3 Q4 Decode Read register ‘f’ Process Data Write register ‘f’ Example: MOVWF REG, 0 Before Instruction W = 4Fh REG = FFh After Instruction W = 4Fh REG = 4Fh PIC18F2420/2520/4420/4520 DS39631B-page 294 Preliminary © 2007 Microchip Technology Inc. MULLW Multiply literal with W Syntax: MULLW k Operands: 0 ≤ k ≤ 255 Operation: (W) x k → PRODH:PRODL Status Affected: None Encoding: 0000 1101 kkkk kkkk Description: An unsigned multiplication is carried out between the contents of W and the 8-bit literal ‘k’. The 16-bit result is placed in the PRODH:PRODL register pair. PRODH contains the high byte. W is unchanged. None of the Status flags are affected. Note that neither overflow nor carry is possible in this operation. A zero result is possible but not detected. Words: 1 Cycles: 1 Q Cycle Activity: Q1 Q2 Q3 Q4 Decode Read literal ‘k’ Process Data Write registers PRODH: PRODL Example: MULLW 0C4h Before Instruction W = E2h PRODH = ? PRODL = ? After Instruction W = E2h PRODH = ADh PRODL = 08h MULWF Multiply W with f Syntax: MULWF f {,a} Operands: 0 ≤ f ≤ 255 a ∈ [0,1] Operation: (W) x (f) → PRODH:PRODL Status Affected: None Encoding: 0000 001a ffff ffff Description: An unsigned multiplication is carried out between the contents of W and the register file location ‘f’. The 16-bit result is stored in the PRODH:PRODL register pair. PRODH contains the high byte. Both W and ‘f’ are unchanged. None of the Status flags are affected. Note that neither overflow nor carry is possible in this operation. A zero result is possible but not detected. If ‘a’ is ‘0’, the Access Bank is selected. If ‘a’ is ‘1’, the BSR is used to select the GPR bank (default). If ‘a’ is ‘0’ and the extended instruction set is enabled, this instruction operates in Indexed Literal Offset Addressing mode whenever f ≤ 95 (5Fh). See Section 24.2.3 “Byte-Oriented and Bit-Oriented Instructions in Indexed Literal Offset Mode” for details. Words: 1 Cycles: 1 Q Cycle Activity: Q1 Q2 Q3 Q4 Decode Read register ‘f’ Process Data Write registers PRODH: PRODL Example: MULWF REG, 1 Before Instruction W = C4h REG = B5h PRODH = ? PRODL = ? After Instruction W = C4h REG = B5h PRODH = 8Ah PRODL = 94h © 2007 Microchip Technology Inc. Preliminary DS39631B-page 295 PIC18F2420/2520/4420/4520 NEGF Negate f Syntax: NEGF f {,a} Operands: 0 ≤ f ≤ 255 a ∈ [0,1] Operation: ( f ) + 1 → f Status Affected: N, OV, C, DC, Z Encoding: 0110 110a ffff ffff Description: Location ‘f’ is negated using two’s complement. The result is placed in the data memory location ‘f’. If ‘a’ is ‘0’, the Access Bank is selected. If ‘a’ is ‘1’, the BSR is used to select the GPR bank (default). If ‘a’ is ‘0’ and the extended instruction set is enabled, this instruction operates in Indexed Literal Offset Addressing mode whenever f ≤ 95 (5Fh). See Section 24.2.3 “Byte-Oriented and Bit-Oriented Instructions in Indexed Literal Offset Mode” for details. Words: 1 Cycles: 1 Q Cycle Activity: Q1 Q2 Q3 Q4 Decode Read register ‘f’ Process Data Write register ‘f’ Example: NEGF REG, 1 Before Instruction REG = 0011 1010 [3Ah] After Instruction REG = 1100 0110 [C6h] NOP No Operation Syntax: NOP Operands: None Operation: No operation Status Affected: None Encoding: 0000 1111 0000 xxxx 0000 xxxx 0000 xxxx Description: No operation. Words: 1 Cycles: 1 Q Cycle Activity: Q1 Q2 Q3 Q4 Decode No operation No operation No operation Example: None. PIC18F2420/2520/4420/4520 DS39631B-page 296 Preliminary © 2007 Microchip Technology Inc. POP Pop Top of Return Stack Syntax: POP Operands: None Operation: (TOS) → bit bucket Status Affected: None Encoding: 0000 0000 0000 0110 Description: The TOS value is pulled off the return stack and is discarded. The TOS value then becomes the previous value that was pushed onto the return stack. This instruction is provided to enable the user to properly manage the return stack to incorporate a software stack. Words: 1 Cycles: 1 Q Cycle Activity: Q1 Q2 Q3 Q4 Decode No operation POP TOS value No operation Example: POP GOTO NEW Before Instruction TOS = 0031A2h Stack (1 level down) = 014332h After Instruction TOS = 014332h PC = NEW PUSH Push Top of Return Stack Syntax: PUSH Operands: None Operation: (PC + 2) → TOS Status Affected: None Encoding: 0000 0000 0000 0101 Description: The PC + 2 is pushed onto the top of the return stack. The previous TOS value is pushed down on the stack. This instruction allows implementing a software stack by modifying TOS and then pushing it onto the return stack. Words: 1 Cycles: 1 Q Cycle Activity: Q1 Q2 Q3 Q4 Decode PUSH PC + 2 onto return stack No operation No operation Example: PUSH Before Instruction TOS = 345Ah PC = 0124h After Instruction PC = 0126h TOS = 0126h Stack (1 level down) = 345Ah © 2007 Microchip Technology Inc. Preliminary DS39631B-page 297 PIC18F2420/2520/4420/4520 RCALL Relative Call Syntax: RCALL n Operands: -1024 ≤ n ≤ 1023 Operation: (PC) + 2 → TOS, (PC) + 2 + 2n → PC Status Affected: None Encoding: 1101 1nnn nnnn nnnn Description: Subroutine call with a jump up to 1K from the current location. First, return address (PC + 2) is pushed onto the stack. Then, add the 2’s complement number ‘2n’ to the PC. Since the PC will have incremented to fetch the next instruction, the new address will be PC + 2 + 2n. This instruction is a two-cycle instruction. Words: 1 Cycles: 2 Q Cycle Activity: Q1 Q2 Q3 Q4 Decode Read literal ‘n’ PUSH PC to stack Process Data Write to PC No operation No operation No operation No operation Example: HERE RCALL Jump Before Instruction PC = Address (HERE) After Instruction PC = Address (Jump) TOS = Address (HERE + 2) RESET Reset Syntax: RESET Operands: None Operation: Reset all registers and flags that are affected by a MCLR Reset. Status Affected: All Encoding: 0000 0000 1111 1111 Description: This instruction provides a way to execute a MCLR Reset in software. Words: 1 Cycles: 1 Q Cycle Activity: Q1 Q2 Q3 Q4 Decode Start Reset No operation No operation Example: RESET After Instruction Registers = Reset Value Flags* = Reset Value PIC18F2420/2520/4420/4520 DS39631B-page 298 Preliminary © 2007 Microchip Technology Inc. RETFIE Return from Interrupt Syntax: RETFIE {s} Operands: s ∈ [0,1] Operation: (TOS) → PC, 1 → GIE/GIEH or PEIE/GIEL, if s = 1 (WS) → W, (STATUSS) → Status, (BSRS) → BSR, PCLATU, PCLATH are unchanged. Status Affected: GIE/GIEH, PEIE/GIEL. Encoding: 0000 0000 0001 000s Description: Return from interrupt. Stack is popped and Top-of-Stack (TOS) is loaded into the PC. Interrupts are enabled by setting either the high or low priority global interrupt enable bit. If ‘s’ = 1, the contents of the shadow registers, WS, STATUSS and BSRS, are loaded into their corresponding registers, W, Status and BSR. If ‘s’ = 0, no update of these registers occurs (default). Words: 1 Cycles: 2 Q Cycle Activity: Q1 Q2 Q3 Q4 Decode No operation No operation POP PC from stack Set GIEH or GIEL No operation No operation No operation No operation Example: RETFIE 1 After Interrupt PC = TOS W = WS BSR = BSRS Status = STATUSS GIE/GIEH, PEIE/GIEL = 1 RETLW Return literal to W Syntax: RETLW k Operands: 0 ≤ k ≤ 255 Operation: k → W, (TOS) → PC, PCLATU, PCLATH are unchanged Status Affected: None Encoding: 0000 1100 kkkk kkkk Description: W is loaded with the eight-bit literal ‘k’. The program counter is loaded from the top of the stack (the return address). The high address latch (PCLATH) remains unchanged. Words: 1 Cycles: 2 Q Cycle Activity: Q1 Q2 Q3 Q4 Decode Read literal ‘k’ Process Data POP PC from stack, Write to W No operation No operation No operation No operation Example: CALL TABLE ; W contains table ; offset value ; W now has ; table value : TABLE ADDWF PCL ; W = offset RETLW k0 ; Begin table RETLW k1 ; : : RETLW kn ; End of table Before Instruction W = 07h After Instruction W = value of kn © 2007 Microchip Technology Inc. Preliminary DS39631B-page 299 PIC18F2420/2520/4420/4520 RETURN Return from Subroutine Syntax: RETURN {s} Operands: s ∈ [0,1] Operation: (TOS) → PC, if s = 1 (WS) → W, (STATUSS) → Status, (BSRS) → BSR, PCLATU, PCLATH are unchanged Status Affected: None Encoding: 0000 0000 0001 001s Description: Return from subroutine. The stack is popped and the top of the stack (TOS) is loaded into the program counter. If ‘s’= 1, the contents of the shadow registers, WS, STATUSS and BSRS, are loaded into their corresponding registers, W, Status and BSR. If ‘s’ = 0, no update of these registers occurs (default). Words: 1 Cycles: 2 Q Cycle Activity: Q1 Q2 Q3 Q4 Decode No operation Process Data POP PC from stack No operation No operation No operation No operation Example: RETURN After Instruction: PC = TOS RLCF Rotate Left f through Carry Syntax: RLCF f {,d {,a}} Operands: 0 ≤ f ≤ 255 d ∈ [0,1] a ∈ [0,1] Operation: (f) → dest, (f<7>) → C, (C) → dest<0> Status Affected: C, N, Z Encoding: 0011 01da ffff ffff Description: The contents of register ‘f’ are rotated one bit to the left through the CARRY flag. If ‘d’ is ‘0’, the result is placed in W. If ‘d’ is ‘1’, the result is stored back in register ‘f’ (default). If ‘a’ is ‘0’, the Access Bank is selected. If ‘a’ is ‘1’, the BSR is used to select the GPR bank (default). If ‘a’ is ‘0’ and the extended instruction set is enabled, this instruction operates in Indexed Literal Offset Addressing mode whenever f ≤ 95 (5Fh). See Section 24.2.3 “Byte-Oriented and Bit-Oriented Instructions in Indexed Literal Offset Mode” for details. Words: 1 Cycles: 1 Q Cycle Activity: Q1 Q2 Q3 Q4 Decode Read register ‘f’ Process Data Write to destination Example: RLCF REG, 0, 0 Before Instruction REG = 1110 0110 C = 0 After Instruction REG = 1110 0110 W = 1100 1100 C = 1 C register f PIC18F2420/2520/4420/4520 DS39631B-page 300 Preliminary © 2007 Microchip Technology Inc. RLNCF Rotate Left f (No Carry) Syntax: RLNCF f {,d {,a}} Operands: 0 ≤ f ≤ 255 d ∈ [0,1] a ∈ [0,1] Operation: (f) → dest, (f<7>) → dest<0> Status Affected: N, Z Encoding: 0100 01da ffff ffff Description: The contents of register ‘f’ are rotated one bit to the left. If ‘d’ is ‘0’, the result is placed in W. If ‘d’ is ‘1’, the result is stored back in register ‘f’ (default). If ‘a’ is ‘0’, the Access Bank is selected. If ‘a’ is ‘1’, the BSR is used to select the GPR bank (default). If ‘a’ is ‘0’ and the extended instruction set is enabled, this instruction operates in Indexed Literal Offset Addressing mode whenever f ≤ 95 (5Fh). See Section 24.2.3 “Byte-Oriented and Bit-Oriented Instructions in Indexed Literal Offset Mode” for details. Words: 1 Cycles: 1 Q Cycle Activity: Q1 Q2 Q3 Q4 Decode Read register ‘f’ Process Data Write to destination Example: RLNCF REG, 1, 0 Before Instruction REG = 1010 1011 After Instruction REG = 0101 0111 register f RRCF Rotate Right f through Carry Syntax: RRCF f {,d {,a}} Operands: 0 ≤ f ≤ 255 d ∈ [0,1] a ∈ [0,1] Operation: (f) → dest, (f<0>) → C, (C) → dest<7> Status Affected: C, N, Z Encoding: 0011 00da ffff ffff Description: The contents of register ‘f’ are rotated one bit to the right through the CARRY flag. If ‘d’ is ‘0’, the result is placed in W. If ‘d’ is ‘1’, the result is placed back in register ‘f’ (default). If ‘a’ is ‘0’, the Access Bank is selected. If ‘a’ is ‘1’, the BSR is used to select the GPR bank (default). If ‘a’ is ‘0’ and the extended instruction set is enabled, this instruction operates in Indexed Literal Offset Addressing mode whenever f ≤ 95 (5Fh). See Section 24.2.3 “Byte-Oriented and Bit-Oriented Instructions in Indexed Literal Offset Mode” for details. Words: 1 Cycles: 1 Q Cycle Activity: Q1 Q2 Q3 Q4 Decode Read register ‘f’ Process Data Write to destination Example: RRCF REG, 0, 0 Before Instruction REG = 1110 0110 C = 0 After Instruction REG = 1110 0110 W = 0111 0011 C = 0 C register f © 2007 Microchip Technology Inc. Preliminary DS39631B-page 301 PIC18F2420/2520/4420/4520 RRNCF Rotate Right f (No Carry) Syntax: RRNCF f {,d {,a}} Operands: 0 ≤ f ≤ 255 d ∈ [0,1] a ∈ [0,1] Operation: (f) → dest, (f<0>) → dest<7> Status Affected: N, Z Encoding: 0100 00da ffff ffff Description: The contents of register ‘f’ are rotated one bit to the right. If ‘d’ is ‘0’, the result is placed in W. If ‘d’ is ‘1’, the result is placed back in register ‘f’ (default). If ‘a’ is ‘0’, the Access Bank will be selected, overriding the BSR value. If ‘a’ is ‘1’, then the bank will be selected as per the BSR value (default). If ‘a’ is ‘0’ and the extended instruction set is enabled, this instruction operates in Indexed Literal Offset Addressing mode whenever f ≤ 95 (5Fh). See Section 24.2.3 “Byte-Oriented and Bit-Oriented Instructions in Indexed Literal Offset Mode” for details. Words: 1 Cycles: 1 Q Cycle Activity: Q1 Q2 Q3 Q4 Decode Read register ‘f’ Process Data Write to destination Example 1: RRNCF REG, 1, 0 Before Instruction REG = 1101 0111 After Instruction REG = 1110 1011 Example 2: RRNCF REG, 0, 0 Before Instruction W = ? REG = 1101 0111 After Instruction W = 1110 1011 REG = 1101 0111 register f SETF Set f Syntax: SETF f {,a} Operands: 0 ≤ f ≤ 255 a ∈ [0,1] Operation: FFh → f Status Affected: None Encoding: 0110 100a ffff ffff Description: The contents of the specified register are set to FFh. If ‘a’ is ‘0’, the Access Bank is selected. If ‘a’ is ‘1’, the BSR is used to select the GPR bank (default). If ‘a’ is ‘0’ and the extended instruction set is enabled, this instruction operates in Indexed Literal Offset Addressing mode whenever f ≤ 95 (5Fh). See Section 24.2.3 “Byte-Oriented and Bit-Oriented Instructions in Indexed Literal Offset Mode” for details. Words: 1 Cycles: 1 Q Cycle Activity: Q1 Q2 Q3 Q4 Decode Read register ‘f’ Process Data Write register ‘f’ Example: SETF REG, 1 Before Instruction REG = 5Ah After Instruction REG = FFh PIC18F2420/2520/4420/4520 DS39631B-page 302 Preliminary © 2007 Microchip Technology Inc. SLEEP Enter Sleep mode Syntax: SLEEP Operands: None Operation: 00h → WDT, 0 → WDT postscaler, 1 → TO, 0 → PD Status Affected: TO, PD Encoding: 0000 0000 0000 0011 Description: The Power-down status bit (PD) is cleared. The Time-out status bit (TO) is set. Watchdog Timer and its postscaler are cleared. The processor is put into Sleep mode with the oscillator stopped. Words: 1 Cycles: 1 Q Cycle Activity: Q1 Q2 Q3 Q4 Decode No operation Process Data Go to Sleep Example: SLEEP Before Instruction TO = ? PD = ? After Instruction TO = 1 † PD = 0 † If WDT causes wake-up, this bit is cleared. SUBFWB Subtract f from W with borrow Syntax: SUBFWB f {,d {,a}} Operands: 0 ≤ f ≤ 255 d ∈ [0,1] a ∈ [0,1] Operation: (W) – (f) – (C) → dest Status Affected: N, OV, C, DC, Z Encoding: 0101 01da ffff ffff Description: Subtract register ‘f’ and CARRY flag (borrow) from W (2’s complement method). If ‘d’ is ‘0’, the result is stored in W. If ‘d’ is ‘1’, the result is stored in register ‘f’ (default). If ‘a’ is ‘0’, the Access Bank is selected. If ‘a’ is ‘1’, the BSR is used to select the GPR bank (default). If ‘a’ is ‘0’ and the extended instruction set is enabled, this instruction operates in Indexed Literal Offset Addressing mode whenever f ≤ 95 (5Fh). See Section 24.2.3 “Byte-Oriented and Bit-Oriented Instructions in Indexed Literal Offset Mode” for details. Words: 1 Cycles: 1 Q Cycle Activity: Q1 Q2 Q3 Q4 Decode Read register ‘f’ Process Data Write to destination Example 1: SUBFWB REG, 1, 0 Before Instruction REG = 3 W = 2 C = 1 After Instruction REG = FF W = 2 C = 0 Z = 0 N = 1 ; result is negative Example 2: SUBFWB REG, 0, 0 Before Instruction REG = 2 W = 5 C = 1 After Instruction REG = 2 W = 3 C = 1 Z = 0 N = 0 ; result is positive Example 3: SUBFWB REG, 1, 0 Before Instruction REG = 1 W = 2 C = 0 After Instruction REG = 0 W = 2 C = 1 Z = 1 ; result is zero N = 0 © 2007 Microchip Technology Inc. Preliminary DS39631B-page 303 PIC18F2420/2520/4420/4520 SUBLW Subtract W from literal Syntax: SUBLW k Operands: 0 ≤ k ≤ 255 Operation: k – (W) → W Status Affected: N, OV, C, DC, Z Encoding: 0000 1000 kkkk kkkk Description W is subtracted from the eight-bit literal ‘k’. The result is placed in W. Words: 1 Cycles: 1 Q Cycle Activity: Q1 Q2 Q3 Q4 Decode Read literal ‘k’ Process Data Write to W Example 1: SUBLW 02h Before Instruction W = 01h C = ? After Instruction W = 01h C = 1 ; result is positive Z = 0 N = 0 Example 2: SUBLW 02h Before Instruction W = 02h C = ? After Instruction W = 00h C = 1 ; result is zero Z = 1 N = 0 Example 3: SUBLW 02h Before Instruction W = 03h C = ? After Instruction W = FFh ; (2’s complement) C = 0 ; result is negative Z = 0 N = 1 SUBWF Subtract W from f Syntax: SUBWF f {,d {,a}} Operands: 0 ≤ f ≤ 255 d ∈ [0,1] a ∈ [0,1] Operation: (f) – (W) → dest Status Affected: N, OV, C, DC, Z Encoding: 0101 11da ffff ffff Description: Subtract W from register ‘f’ (2’s complement method). If ‘d’ is ‘0’, the result is stored in W. If ‘d’ is ‘1’, the result is stored back in register ‘f’ (default). If ‘a’ is ‘0’, the Access Bank is selected. If ‘a’ is ‘1’, the BSR is used to select the GPR bank (default). If ‘a’ is ‘0’ and the extended instruction set is enabled, this instruction operates in Indexed Literal Offset Addressing mode whenever f ≤ 95 (5Fh). See Section 24.2.3 “Byte-Oriented and Bit-Oriented Instructions in Indexed Literal Offset Mode” for details. Words: 1 Cycles: 1 Q Cycle Activity: Q1 Q2 Q3 Q4 Decode Read register ‘f’ Process Data Write to destination Example 1: SUBWF REG, 1, 0 Before Instruction REG = 3 W = 2 C = ? After Instruction REG = 1 W = 2 C = 1 ; result is positive Z = 0 N = 0 Example 2: SUBWF REG, 0, 0 Before Instruction REG = 2 W = 2 C = ? After Instruction REG = 2 W = 0 C = 1 ; result is zero Z = 1 N = 0 Example 3: SUBWF REG, 1, 0 Before Instruction REG = 1 W = 2 C = ? After Instruction REG = FFh ;(2’s complement) W = 2 C = 0 ; result is negative Z = 0 N = 1 PIC18F2420/2520/4420/4520 DS39631B-page 304 Preliminary © 2007 Microchip Technology Inc. SUBWFB Subtract W from f with Borrow Syntax: SUBWFB f {,d {,a}} Operands: 0 ≤ f ≤ 255 d ∈ [0,1] a ∈ [0,1] Operation: (f) – (W) – (C) → dest Status Affected: N, OV, C, DC, Z Encoding: 0101 10da ffff ffff Description: Subtract W and the CARRY flag (borrow) from register ‘f’ (2’s complement method). If ‘d’ is ‘0’, the result is stored in W. If ‘d’ is ‘1’, the result is stored back in register ‘f’ (default). If ‘a’ is ‘0’, the Access Bank is selected. If ‘a’ is ‘1’, the BSR is used to select the GPR bank (default). If ‘a’ is ‘0’ and the extended instruction set is enabled, this instruction operates in Indexed Literal Offset Addressing mode whenever f ≤ 95 (5Fh). See Section 24.2.3 “Byte-Oriented and Bit-Oriented Instructions in Indexed Literal Offset Mode” for details. Words: 1 Cycles: 1 Q Cycle Activity: Q1 Q2 Q3 Q4 Decode Read register ‘f’ Process Data Write to destination Example 1: SUBWFB REG, 1, 0 Before Instruction REG = 19h (0001 1001) W = 0Dh (0000 1101) C = 1 After Instruction REG = 0Ch (0000 1011) W = 0Dh (0000 1101) C = 1 Z = 0 N = 0 ; result is positive Example 2: SUBWFB REG, 0, 0 Before Instruction REG = 1Bh (0001 1011) W = 1Ah (0001 1010) C = 0 After Instruction REG = 1Bh (0001 1011) W = 00h C = 1 Z = 1 ; result is zero N = 0 Example 3: SUBWFB REG, 1, 0 Before Instruction REG = 03h (0000 0011) W = 0Eh (0000 1101) C = 1 After Instruction REG = F5h (1111 0100) ; [2’s comp] W = 0Eh (0000 1101) C = 0 Z = 0 N = 1 ; result is negative SWAPF Swap f Syntax: SWAPF f {,d {,a}} Operands: 0 ≤ f ≤ 255 d ∈ [0,1] a ∈ [0,1] Operation: (f<3:0>) → dest<7:4>, (f<7:4>) → dest<3:0> Status Affected: None Encoding: 0011 10da ffff ffff Description: The upper and lower nibbles of register ‘f’ are exchanged. If ‘d’ is ‘0’, the result is placed in W. If ‘d’ is ‘1’, the result is placed in register ‘f’ (default). If ‘a’ is ‘0’, the Access Bank is selected. If ‘a’ is ‘1’, the BSR is used to select the GPR bank (default). If ‘a’ is ‘0’ and the extended instruction set is enabled, this instruction operates in Indexed Literal Offset Addressing mode whenever f ≤ 95 (5Fh). See Section 24.2.3 “Byte-Oriented and Bit-Oriented Instructions in Indexed Literal Offset Mode” for details. Words: 1 Cycles: 1 Q Cycle Activity: Q1 Q2 Q3 Q4 Decode Read register ‘f’ Process Data Write to destination Example: SWAPF REG, 1, 0 Before Instruction REG = 53h After Instruction REG = 35h © 2007 Microchip Technology Inc. Preliminary DS39631B-page 305 PIC18F2420/2520/4420/4520 TBLRD Table Read Syntax: TBLRD ( *; *+; *-; +*) Operands: None Operation: if TBLRD *, (Prog Mem (TBLPTR)) → TABLAT; TBLPTR – No Change; if TBLRD *+, (Prog Mem (TBLPTR)) → TABLAT; (TBLPTR) + 1 → TBLPTR; if TBLRD *-, (Prog Mem (TBLPTR)) → TABLAT; (TBLPTR) – 1 → TBLPTR; if TBLRD +*, (TBLPTR) + 1 → TBLPTR; (Prog Mem (TBLPTR)) → TABLAT; Status Affected: None Encoding: 0000 0000 0000 10nn nn=0 * =1 *+ =2 *- =3 +* Description: This instruction is used to read the contents of Program Memory (P.M.). To address the program memory, a pointer called Table Pointer (TBLPTR) is used. The TBLPTR (a 21-bit pointer) points to each byte in the program memory. TBLPTR has a 2-Mbyte address range. TBLPTR[0] = 0: Least Significant Byte of Program Memory Word TBLPTR[0] = 1: Most Significant Byte of Program Memory Word The TBLRD instruction can modify the value of TBLPTR as follows: • no change • post-increment • post-decrement • pre-increment Words: 1 Cycles: 2 Q Cycle Activity: Q1 Q2 Q3 Q4 Decode No operation No operation No operation No operation No operation (Read Program Memory) No operation No operation (Write TABLAT) TBLRD Table Read (Continued) Example1: TBLRD *+ ; Before Instruction TABLAT = 55h TBLPTR = 00A356h MEMORY (00A356h) = 34h After Instruction TABLAT = 34h TBLPTR = 00A357h Example2: TBLRD +* ; Before Instruction TABLAT = AAh TBLPTR = 01A357h MEMORY (01A357h) = 12h MEMORY (01A358h) = 34h After Instruction TABLAT = 34h TBLPTR = 01A358h PIC18F2420/2520/4420/4520 DS39631B-page 306 Preliminary © 2007 Microchip Technology Inc. TBLWT Table Write Syntax: TBLWT ( *; *+; *-; +*) Operands: None Operation: if TBLWT*, (TABLAT) → Holding Register; TBLPTR – No Change; if TBLWT*+, (TABLAT) → Holding Register; (TBLPTR) + 1 → TBLPTR; if TBLWT*-, (TABLAT) → Holding Register; (TBLPTR) – 1 → TBLPTR; if TBLWT+*, (TBLPTR) + 1 → TBLPTR; (TABLAT) → Holding Register; Status Affected: None Encoding: 0000 0000 0000 11nn nn=0 * =1 *+ =2 *- =3 +* Description: This instruction uses the 3 LSBs of TBLPTR to determine which of the 8 holding registers the TABLAT is written to. The holding registers are used to program the contents of Program Memory (P.M.). (Refer to Section 6.0 “Flash Program Memory” for additional details on programming Flash memory.) The TBLPTR (a 21-bit pointer) points to each byte in the program memory. TBLPTR has a 2-MByte address range. The LSb of the TBLPTR selects which byte of the program memory location to access. TBLPTR[0] = 0: Least Significant Byte of Program Memory Word TBLPTR[0] = 1: Most Significant Byte of Program Memory Word The TBLWT instruction can modify the value of TBLPTR as follows: • no change • post-increment • post-decrement • pre-increment Words: 1 Cycles: 2 Q Cycle Activity: Q1 Q2 Q3 Q4 Decode No operation No operation No operation No operation No operation (Read TABLAT) No operation No operation (Write to Holding Register ) TBLWT Table Write (Continued) Example1: TBLWT *+; Before Instruction TABLAT = 55h TBLPTR = 00A356h HOLDING REGISTER (00A356h) = FFh After Instructions (table write completion) TABLAT = 55h TBLPTR = 00A357h HOLDING REGISTER (00A356h) = 55h Example 2: TBLWT +*; Before Instruction TABLAT = 34h TBLPTR = 01389Ah HOLDING REGISTER (01389Ah) = FFh HOLDING REGISTER (01389Bh) = FFh After Instruction (table write completion) TABLAT = 34h TBLPTR = 01389Bh HOLDING REGISTER (01389Ah) = FFh HOLDING REGISTER (01389Bh) = 34h © 2007 Microchip Technology Inc. Preliminary DS39631B-page 307 PIC18F2420/2520/4420/4520 TSTFSZ Test f, skip if 0 Syntax: TSTFSZ f {,a} Operands: 0 ≤ f ≤ 255 a ∈ [0,1] Operation: skip if f = 0 Status Affected: None Encoding: 0110 011a ffff ffff Description: If ‘f’ = 0, the next instruction fetched during the current instruction execution is discarded and a NOP is executed, making this a two-cycle instruction. If ‘a’ is ‘0’, the Access Bank is selected. If ‘a’ is ‘1’, the BSR is used to select the GPR bank (default). If ‘a’ is ‘0’ and the extended instruction set is enabled, this instruction operates in Indexed Literal Offset Addressing mode whenever f ≤ 95 (5Fh). See Section 24.2.3 “Byte-Oriented and Bit-Oriented Instructions in Indexed Literal Offset Mode” for details. Words: 1 Cycles: 1(2) Note: 3 cycles if skip and followed by a 2-word instruction. Q Cycle Activity: Q1 Q2 Q3 Q4 Decode Read register ‘f’ Process Data No operation If skip: Q1 Q2 Q3 Q4 No operation No operation No operation No operation If skip and followed by 2-word instruction: Q1 Q2 Q3 Q4 No operation No operation No operation No operation No operation No operation No operation No operation Example: HERE TSTFSZ CNT, 1 NZERO : ZERO : Before Instruction PC = Address (HERE) After Instruction If CNT = 00h, PC = Address (ZERO) If CNT ≠ 00h, PC = Address (NZERO) XORLW Exclusive OR literal with W Syntax: XORLW k Operands: 0 ≤ k ≤ 255 Operation: (W) .XOR. k → W Status Affected: N, Z Encoding: 0000 1010 kkkk kkkk Description: The contents of W are XORed with the 8-bit literal ‘k’. The result is placed in W. Words: 1 Cycles: 1 Q Cycle Activity: Q1 Q2 Q3 Q4 Decode Read literal ‘k’ Process Data Write to W Example: XORLW 0AFh Before Instruction W = B5h After Instruction W = 1Ah PIC18F2420/2520/4420/4520 DS39631B-page 308 Preliminary © 2007 Microchip Technology Inc. XORWF Exclusive OR W with f Syntax: XORWF f {,d {,a}} Operands: 0 ≤ f ≤ 255 d ∈ [0,1] a ∈ [0,1] Operation: (W) .XOR. (f) → dest Status Affected: N, Z Encoding: 0001 10da ffff ffff Description: Exclusive OR the contents of W with register ‘f’. If ‘d’ is ‘0’, the result is stored in W. If ‘d’ is ‘1’, the result is stored back in the register ‘f’ (default). If ‘a’ is ‘0’, the Access Bank is selected. If ‘a’ is ‘1’, the BSR is used to select the GPR bank (default). If ‘a’ is ‘0’ and the extended instruction set is enabled, this instruction operates in Indexed Literal Offset Addressing mode whenever f ≤ 95 (5Fh). See Section 24.2.3 “Byte-Oriented and Bit-Oriented Instructions in Indexed Literal Offset Mode” for details. Words: 1 Cycles: 1 Q Cycle Activity: Q1 Q2 Q3 Q4 Decode Read register ‘f’ Process Data Write to destination Example: XORWF REG, 1, 0 Before Instruction REG = AFh W = B5h After Instruction REG = 1Ah W = B5h © 2007 Microchip Technology Inc. Preliminary DS39631B-page 309 PIC18F2420/2520/4420/4520 24.2 Extended Instruction Set In addition to the standard 75 instructions of the PIC18 instruction set, PIC18F2420/2520/4420/4520 devices also provide an optional extension to the core CPU functionality. The added features include eight additional instructions that augment indirect and indexed addressing operations and the implementation of Indexed Literal Offset Addressing mode for many of the standard PIC18 instructions. The additional features of the extended instruction set are disabled by default. To enable them, users must set the XINST configuration bit. The instructions in the extended set can all be classified as literal operations, which either manipulate the File Select Registers, or use them for indexed addressing. Two of the instructions, ADDFSR and SUBFSR, each have an additional special instantiation for using FSR2. These versions (ADDULNK and SUBULNK) allow for automatic return after execution. The extended instructions are specifically implemented to optimize re-entrant program code (that is, code that is recursive or that uses a software stack) written in high-level languages, particularly C. Among other things, they allow users working in high-level languages to perform certain operations on data structures more efficiently. These include: • dynamic allocation and deallocation of software stack space when entering and leaving subroutines • function pointer invocation • software stack pointer manipulation • manipulation of variables located in a software stack A summary of the instructions in the extended instruction set is provided in Table 24-3. Detailed descriptions are provided in Section 24.2.2 “Extended Instruction Set”. The opcode field descriptions in Table 24-1 (page 268) apply to both the standard and extended PIC18 instruction sets. 24.2.1 EXTENDED INSTRUCTION SYNTAX Most of the extended instructions use indexed arguments, using one of the File Select Registers and some offset to specify a source or destination register. When an argument for an instruction serves as part of indexed addressing, it is enclosed in square brackets (“[ ]”). This is done to indicate that the argument is used as an index or offset. MPASM™ Assembler will flag an error if it determines that an index or offset value is not bracketed. When the extended instruction set is enabled, brackets are also used to indicate index arguments in byteoriented and bit-oriented instructions. This is in addition to other changes in their syntax. For more details, see Section 24.2.3.1 “Extended Instruction Syntax with Standard PIC18 Commands”. TABLE 24-3: EXTENSIONS TO THE PIC18 INSTRUCTION SET Note: The instruction set extension and the Indexed Literal Offset Addressing mode were designed for optimizing applications written in C; the user may likely never use these instructions directly in assembler. The syntax for these commands is provided as a reference for users who may be reviewing code that has been generated by a compiler. Note: In the past, square brackets have been used to denote optional arguments in the PIC18 and earlier instruction sets. In this text and going forward, optional arguments are denoted by braces (“{ }”). Mnemonic, Operands Description Cycles 16-Bit Instruction Word Status MSb LSb Affected ADDFSR ADDULNK CALLW MOVSF MOVSS PUSHL SUBFSR SUBULNK f, k k zs, fd zs, zd k f, k k Add literal to FSR Add literal to FSR2 and return Call subroutine using WREG Move zs (source) to 1st word fd (destination) 2nd word Move zs (source) to 1st word zd (destination) 2nd word Store literal at FSR2, decrement FSR2 Subtract literal from FSR Subtract literal from FSR2 and return 1 2 2 2 2 1 1 2 1110 1110 0000 1110 1111 1110 1111 1110 1110 1110 1000 1000 0000 1011 ffff 1011 xxxx 1010 1001 1001 ffkk 11kk 0001 0zzz ffff 1zzz xzzz kkkk ffkk 11kk kkkk kkkk 0100 zzzz ffff zzzz zzzz kkkk kkkk kkkk None None None None None None None None PIC18F2420/2520/4420/4520 DS39631B-page 310 Preliminary © 2007 Microchip Technology Inc. 24.2.2 EXTENDED INSTRUCTION SET ADDFSR Add Literal to FSR Syntax: ADDFSR f, k Operands: 0 ≤ k ≤ 63 f ∈ [ 0, 1, 2 ] Operation: FSR(f) + k → FSR(f) Status Affected: None Encoding: 1110 1000 ffkk kkkk Description: The 6-bit literal ‘k’ is added to the contents of the FSR specified by ‘f’. Words: 1 Cycles: 1 Q Cycle Activity: Q1 Q2 Q3 Q4 Decode Read literal ‘k’ Process Data Write to FSR Example: ADDFSR 2, 23h Before Instruction FSR2 = 03FFh After Instruction FSR2 = 0422h ADDULNK Add Literal to FSR2 and Return Syntax: ADDULNK k Operands: 0 ≤ k ≤ 63 Operation: FSR2 + k → FSR2, (TOS) → PC Status Affected: None Encoding: 1110 1000 11kk kkkk Description: The 6-bit literal ‘k’ is added to the contents of FSR2. A RETURN is then executed by loading the PC with the TOS. The instruction takes two cycles to execute; a NOP is performed during the second cycle. This may be thought of as a special case of the ADDFSR instruction, where f = 3 (binary ‘11’); it operates only on FSR2. Words: 1 Cycles: 2 Q Cycle Activity: Q1 Q2 Q3 Q4 Decode Read literal ‘k’ Process Data Write to FSR No Operation No Operation No Operation No Operation Example: ADDULNK 23h Before Instruction FSR2 = 03FFh PC = 0100h After Instruction FSR2 = 0422h PC = (TOS) Note: All PIC18 instructions may take an optional label argument preceding the instruction mnemonic for use in symbolic addressing. If a label is used, the instruction syntax then becomes: {label} instruction argument(s). © 2007 Microchip Technology Inc. Preliminary DS39631B-page 311 PIC18F2420/2520/4420/4520 CALLW Subroutine Call Using WREG Syntax: CALLW Operands: None Operation: (PC + 2) → TOS, (W) → PCL, (PCLATH) → PCH, (PCLATU) → PCU Status Affected: None Encoding: 0000 0000 0001 0100 Description First, the return address (PC + 2) is pushed onto the return stack. Next, the contents of W are written to PCL; the existing value is discarded. Then, the contents of PCLATH and PCLATU are latched into PCH and PCU, respectively. The second cycle is executed as a NOP instruction while the new next instruction is fetched. Unlike CALL, there is no option to update W, Status or BSR. Words: 1 Cycles: 2 Q Cycle Activity: Q1 Q2 Q3 Q4 Decode Read WREG PUSH PC to stack No operation No operation No operation No operation No operation Example: HERE CALLW Before Instruction PC = address (HERE) PCLATH = 10h PCLATU = 00h W = 06h After Instruction PC = 001006h TOS = address (HERE + 2) PCLATH = 10h PCLATU = 00h W = 06h MOVSF Move Indexed to f Syntax: MOVSF [zs], fd Operands: 0 ≤ zs ≤ 127 0 ≤ fd ≤ 4095 Operation: ((FSR2) + zs) → fd Status Affected: None Encoding: 1st word (source) 2nd word (destin.) 1110 1111 1011 ffff 0zzz ffff zzzzs ffffd Description: The contents of the source register are moved to destination register ‘fd’. The actual address of the source register is determined by adding the 7-bit literal offset ‘zs’ in the first word to the value of FSR2. The address of the destination register is specified by the 12-bit literal ‘fd’ in the second word. Both addresses can be anywhere in the 4096-byte data space (000h to FFFh). The MOVSF instruction cannot use the PCL, TOSU, TOSH or TOSL as the destination register. If the resultant source address points to an indirect addressing register, the value returned will be 00h. Words: 2 Cycles: 2 Q Cycle Activity: Q1 Q2 Q3 Q4 Decode Determine source addr Determine source addr Read source reg Decode No operation No dummy read No operation Write register ‘f’ (dest) Example: MOVSF [05h], REG2 Before Instruction FSR2 = 80h Contents of 85h = 33h REG2 = 11h After Instruction FSR2 = 80h Contents of 85h = 33h REG2 = 33h PIC18F2420/2520/4420/4520 DS39631B-page 312 Preliminary © 2007 Microchip Technology Inc. MOVSS Move Indexed to Indexed Syntax: MOVSS [zs], [zd] Operands: 0 ≤ zs ≤ 127 0 ≤ zd ≤ 127 Operation: ((FSR2) + zs) → ((FSR2) + zd) Status Affected: None Encoding: 1st word (source) 2nd word (dest.) 1110 1111 1011 xxxx 1zzz xzzz zzzzs zzzzd Description The contents of the source register are moved to the destination register. The addresses of the source and destination registers are determined by adding the 7-bit literal offsets ‘zs’ or ‘zd’, respectively, to the value of FSR2. Both registers can be located anywhere in the 4096-byte data memory space (000h to FFFh). The MOVSS instruction cannot use the PCL, TOSU, TOSH or TOSL as the destination register. If the resultant source address points to an indirect addressing register, the value returned will be 00h. If the resultant destination address points to an indirect addressing register, the instruction will execute as a NOP. Words: 2 Cycles: 2 Q Cycle Activity: Q1 Q2 Q3 Q4 Decode Determine source addr Determine source addr Read source reg Decode Determine dest addr Determine dest addr Write to dest reg Example: MOVSS [05h], [06h] Before Instruction FSR2 = 80h Contents of 85h = 33h Contents of 86h = 11h After Instruction FSR2 = 80h Contents of 85h = 33h Contents of 86h = 33h PUSHL Store Literal at FSR2, Decrement FSR2 Syntax: PUSHL k Operands: 0 ≤ k ≤ 255 Operation: k → (FSR2), FSR2 – 1 → FSR2 Status Affected: None Encoding: 1111 1010 kkkk kkkk Description: The 8-bit literal ‘k’ is written to the data memory address specified by FSR2. FSR2 is decremented by 1 after the operation. This instruction allows users to push values onto a software stack. Words: 1 Cycles: 1 Q Cycle Activity: Q1 Q2 Q3 Q4 Decode Read ‘k’ Process data Write to destination Example: PUSHL 08h Before Instruction FSR2H:FSR2L = 01ECh Memory (01ECh) = 00h After Instruction FSR2H:FSR2L = 01EBh Memory (01ECh) = 08h © 2007 Microchip Technology Inc. Preliminary DS39631B-page 313 PIC18F2420/2520/4420/4520 SUBFSR Subtract Literal from FSR Syntax: SUBFSR f, k Operands: 0 ≤ k ≤ 63 f ∈ [ 0, 1, 2 ] Operation: FSR(f) – k → FSRf Status Affected: None Encoding: 1110 1001 ffkk kkkk Description: The 6-bit literal ‘k’ is subtracted from the contents of the FSR specified by ‘f’. Words: 1 Cycles: 1 Q Cycle Activity: Q1 Q2 Q3 Q4 Decode Read register ‘f’ Process Data Write to destination Example: SUBFSR 2, 23h Before Instruction FSR2 = 03FFh After Instruction FSR2 = 03DCh SUBULNK Subtract Literal from FSR2 and Return Syntax: SUBULNK k Operands: 0 ≤ k ≤ 63 Operation: FSR2 – k → FSR2 (TOS) → PC Status Affected: None Encoding: 1110 1001 11kk kkkk Description: The 6-bit literal ‘k’ is subtracted from the contents of the FSR2. A RETURN is then executed by loading the PC with the TOS. The instruction takes two cycles to execute; a NOP is performed during the second cycle. This may be thought of as a special case of the SUBFSR instruction, where f = 3 (binary ‘11’); it operates only on FSR2. Words: 1 Cycles: 2 Q Cycle Activity: Q1 Q2 Q3 Q4 Decode Read register ‘f’ Process Data Write to destination No Operation No Operation No Operation No Operation Example: SUBULNK 23h Before Instruction FSR2 = 03FFh PC = 0100h After Instruction FSR2 = 03DCh PC = (TOS) PIC18F2420/2520/4420/4520 DS39631B-page 314 Preliminary © 2007 Microchip Technology Inc. 24.2.3 BYTE-ORIENTED AND BIT-ORIENTED INSTRUCTIONS IN INDEXED LITERAL OFFSET MODE In addition to eight new commands in the extended set, enabling the extended instruction set also enables Indexed Literal Offset Addressing mode (Section 5.5.1 “Indexed Addressing with Literal Offset”). This has a significant impact on the way that many commands of the standard PIC18 instruction set are interpreted. When the extended set is disabled, addresses embedded in opcodes are treated as literal memory locations: either as a location in the Access Bank (‘a’ = 0), or in a GPR bank designated by the BSR (‘a’ = 1). When the extended instruction set is enabled and ‘a’ = 0, however, a file register argument of 5Fh or less is interpreted as an offset from the pointer value in FSR2 and not as a literal address. For practical purposes, this means that all instructions that use the Access RAM bit as an argument – that is, all byte-oriented and bitoriented instructions, or almost half of the core PIC18 instructions – may behave differently when the extended instruction set is enabled. When the content of FSR2 is 00h, the boundaries of the Access RAM are essentially remapped to their original values. This may be useful in creating backward compatible code. If this technique is used, it may be necessary to save the value of FSR2 and restore it when moving back and forth between C and assembly routines in order to preserve the stack pointer. Users must also keep in mind the syntax requirements of the extended instruction set (see Section 24.2.3.1 “Extended Instruction Syntax with Standard PIC18 Commands”). Although the Indexed Literal Offset Addressing mode can be very useful for dynamic stack and pointer manipulation, it can also be very annoying if a simple arithmetic operation is carried out on the wrong register. Users who are accustomed to the PIC18 programming must keep in mind that, when the extended instruction set is enabled, register addresses of 5Fh or less are used for Indexed Literal Offset Addressing. Representative examples of typical byte-oriented and bit-oriented instructions in the Indexed Literal Offset Addressing mode are provided on the following page to show how execution is affected. The operand conditions shown in the examples are applicable to all instructions of these types. 24.2.3.1 Extended Instruction Syntax with Standard PIC18 Commands When the extended instruction set is enabled, the file register argument, ‘f’, in the standard byte-oriented and bit-oriented commands is replaced with the literal offset value, ‘k’. As already noted, this occurs only when ‘f’ is less than or equal to 5Fh. When an offset value is used, it must be indicated by square brackets (“[ ]”). As with the extended instructions, the use of brackets indicates to the compiler that the value is to be interpreted as an index or an offset. Omitting the brackets, or using a value greater than 5Fh within brackets, will generate an error in the MPASM Assembler. If the index argument is properly bracketed for Indexed Literal Offset Addressing, the Access RAM argument is never specified; it will automatically be assumed to be ‘0’. This is in contrast to standard operation (extended instruction set disabled) when ‘a’ is set on the basis of the target address. Declaring the Access RAM bit in this mode will also generate an error in the MPASM Assembler. The destination argument, ‘d’, functions as before. In the latest versions of the MPASM assembler, language support for the extended instruction set must be explicitly invoked. This is done with either the command line option, /y, or the PE directive in the source listing. 24.2.4 CONSIDERATIONS WHEN ENABLING THE EXTENDED INSTRUCTION SET It is important to note that the extensions to the instruction set may not be beneficial to all users. In particular, users who are not writing code that uses a software stack may not benefit from using the extensions to the instruction set. Additionally, the Indexed Literal Offset Addressing mode may create issues with legacy applications written to the PIC18 assembler. This is because instructions in the legacy code may attempt to address registers in the Access Bank below 5Fh. Since these addresses are interpreted as literal offsets to FSR2 when the instruction set extension is enabled, the application may read or write to the wrong data addresses. When porting an application to the PIC18F2420/2520/ 4420/4520, it is very important to consider the type of code. A large, re-entrant application that is written in ‘C’ and would benefit from efficient compilation will do well when using the instruction set extensions. Legacy applications that heavily use the Access Bank will most likely not benefit from using the extended instruction set. Note: Enabling the PIC18 instruction set extension may cause legacy applications to behave erratically or fail entirely. © 2007 Microchip Technology Inc. Preliminary DS39631B-page 315 PIC18F2420/2520/4420/4520 ADDWF ADD W to Indexed (Indexed Literal Offset mode) Syntax: ADDWF [k] {,d} Operands: 0 ≤ k ≤ 95 d ∈ [0,1] Operation: (W) + ((FSR2) + k) → dest Status Affected: N, OV, C, DC, Z Encoding: 0010 01d0 kkkk kkkk Description: The contents of W are added to the contents of the register indicated by FSR2, offset by the value ‘k’. If ‘d’ is ‘0’, the result is stored in W. If ‘d’ is ‘1’, the result is stored back in register ‘f’ (default). Words: 1 Cycles: 1 Q Cycle Activity: Q1 Q2 Q3 Q4 Decode Read ‘k’ Process Data Write to destination Example: ADDWF [OFST] , 0 Before Instruction W = 17h OFST = 2Ch FSR2 = 0A00h Contents of 0A2Ch = 20h After Instruction W = 37h Contents of 0A2Ch = 20h BSF Bit Set Indexed (Indexed Literal Offset mode) Syntax: BSF [k], b Operands: 0 ≤ f ≤ 95 0 ≤ b ≤ 7 Operation: 1 → ((FSR2) + k) Status Affected: None Encoding: 1000 bbb0 kkkk kkkk Description: Bit ‘b’ of the register indicated by FSR2, offset by the value ‘k’, is set. Words: 1 Cycles: 1 Q Cycle Activity: Q1 Q2 Q3 Q4 Decode Read register ‘f’ Process Data Write to destination Example: BSF [FLAG_OFST], 7 Before Instruction FLAG_OFST = 0Ah FSR2 = 0A00h Contents of 0A0Ah = 55h After Instruction Contents of 0A0Ah = D5h SETF Set Indexed (Indexed Literal Offset mode) Syntax: SETF [k] Operands: 0 ≤ k ≤ 95 Operation: FFh → ((FSR2) + k) Status Affected: None Encoding: 0110 1000 kkkk kkkk Description: The contents of the register indicated by FSR2, offset by ‘k’, are set to FFh. Words: 1 Cycles: 1 Q Cycle Activity: Q1 Q2 Q3 Q4 Decode Read ‘k’ Process Data Write register Example: SETF [OFST] Before Instruction OFST = 2Ch FSR2 = 0A00h Contents of 0A2Ch = 00h After Instruction Contents of 0A2Ch = FFh PIC18F2420/2520/4420/4520 DS39631B-page 316 Preliminary © 2007 Microchip Technology Inc. 24.2.5 SPECIAL CONSIDERATIONS WITH MICROCHIP MPLAB® IDE TOOLS The latest versions of Microchip’s software tools have been designed to fully support the extended instruction set of the PIC18F2420/2520/4420/4520 family of devices. This includes the MPLAB C18 C compiler, MPASM assembly language and MPLAB Integrated Development Environment (IDE). When selecting a target device for software development, MPLAB IDE will automatically set default configuration bits for that device. The default setting for the XINST configuration bit is ‘0’, disabling the extended instruction set and Indexed Literal Offset Addressing mode. For proper execution of applications developed to take advantage of the extended instruction set, XINST must be set during programming. To develop software for the extended instruction set, the user must enable support for the instructions and the Indexed Addressing mode in their language tool(s). Depending on the environment being used, this may be done in several ways: • A menu option, or dialog box within the environment, that allows the user to configure the language tool and its settings for the project • A command line option • A directive in the source code These options vary between different compilers, assemblers and development environments. Users are encouraged to review the documentation accompanying their development systems for the appropriate information. © 2007 Microchip Technology Inc. Preliminary DS39631B-page 317 PIC18F2420/2520/4420/4520 25.0 DEVELOPMENT SUPPORT The PIC® microcontrollers are supported with a full range of hardware and software development tools: • Integrated Development Environment - MPLAB® IDE Software • Assemblers/Compilers/Linkers - MPASMTM Assembler - MPLAB C17 and MPLAB C18 C Compilers - MPLINKTM Object Linker/ MPLIBTM Object Librarian - MPLAB C30 C Compiler - MPLAB ASM30 Assembler/Linker/Library • Simulators - MPLAB SIM Software Simulator - MPLAB dsPIC30 Software Simulator • Emulators - MPLAB ICE 2000 In-Circuit Emulator - MPLAB ICE 4000 In-Circuit Emulator • In-Circuit Debugger - MPLAB ICD 2 • Device Programmers - PRO MATE® II Universal Device Programmer - PICSTART® Plus Development Programmer - MPLAB PM3 Device Programmer • Low-Cost Demonstration Boards - PICDEMTM 1 Demonstration Board - PICDEM.netTM Demonstration Board - PICDEM 2 Plus Demonstration Board - PICDEM 3 Demonstration Board - PICDEM 4 Demonstration Board - PICDEM 17 Demonstration Board - PICDEM 18R Demonstration Board - PICDEM LIN Demonstration Board - PICDEM USB Demonstration Board • Evaluation Kits - KEELOQ® Evaluation and Programming Tools - PICDEM MSC - microID® Developer Kits - CAN - PowerSmart® Developer Kits - Analog 25.1 MPLAB Integrated Development Environment Software The MPLAB IDE software brings an ease of software development previously unseen in the 8/16-bit microcontroller market. The MPLAB IDE is a Windows® based application that contains: • An interface to debugging tools - simulator - programmer (sold separately) - emulator (sold separately) - in-circuit debugger (sold separately) • A full-featured editor with color coded context • A multiple project manager • Customizable data windows with direct edit of contents • High-level source code debugging • Mouse over variable inspection • Extensive on-line help The MPLAB IDE allows you to: • Edit your source files (either assembly or C) • One touch assemble (or compile) and download to PIC emulator and simulator tools (automatically updates all project information) • Debug using: - source files (assembly or C) - mixed assembly and C - machine code MPLAB IDE supports multiple debugging tools in a single development paradigm, from the cost effective simulators, through low-cost in-circuit debuggers, to full-featured emulators. This eliminates the learning curve when upgrading to tools with increasing flexibility and power. 25.2 MPASM Assembler The MPASM assembler is a full-featured, universal macro assembler for all PIC MCUs. The MPASM assembler generates relocatable object files for the MPLINK object linker, Intel® standard HEX files, MAP files to detail memory usage and symbol reference, absolute LST files that contain source lines and generated machine code and COFF files for debugging. The MPASM assembler features include: • Integration into MPLAB IDE projects • User defined macros to streamline assembly code • Conditional assembly for multi-purpose source files • Directives that allow complete control over the assembly process PIC18F2420/2520/4420/4520 DS39631B-page 318 Preliminary © 2007 Microchip Technology Inc. 25.3 MPLAB C17 and MPLAB C18 C Compilers The MPLAB C17 and MPLAB C18 Code Development Systems are complete ANSI C compilers for Microchip’s PIC17CXXX and PIC18CXXX family of microcontrollers. These compilers provide powerful integration capabilities, superior code optimization and ease of use not found with other compilers. For easy source level debugging, the compilers provide symbol information that is optimized to the MPLAB IDE debugger. 25.4 MPLINK Object Linker/ MPLIB Object Librarian The MPLINK object linker combines relocatable objects created by the MPASM assembler and the MPLAB C17 and MPLAB C18 C compilers. It can link relocatable objects from precompiled libraries, using directives from a linker script. The MPLIB object librarian manages the creation and modification of library files of precompiled code. When a routine from a library is called from a source file, only the modules that contain that routine will be linked in with the application. This allows large libraries to be used efficiently in many different applications. The object linker/library features include: • Efficient linking of single libraries instead of many smaller files • Enhanced code maintainability by grouping related modules together • Flexible creation of libraries with easy module listing, replacement, deletion and extraction 25.5 MPLAB C30 C Compiler The MPLAB C30 C compiler is a full-featured, ANSI compliant, optimizing compiler that translates standard ANSI C programs into dsPIC30F assembly language source. The compiler also supports many command line options and language extensions to take full advantage of the dsPIC30F device hardware capabilities and afford fine control of the compiler code generator. MPLAB C30 is distributed with a complete ANSI C standard library. All library functions have been validated and conform to the ANSI C library standard. The library includes functions for string manipulation, dynamic memory allocation, data conversion, timekeeping and math functions (trigonometric, exponential and hyperbolic). The compiler provides symbolic information for high-level source debugging with the MPLAB IDE. 25.6 MPLAB ASM30 Assembler, Linker and Librarian MPLAB ASM30 assembler produces relocatable machine code from symbolic assembly language for dsPIC30F devices. MPLAB C30 compiler uses the assembler to produce it’s object file. The assembler generates relocatable object files that can then be archived or linked with other relocatable object files and archives to create an executable file. Notable features of the assembler include: • Support for the entire dsPIC30F instruction set • Support for fixed-point and floating-point data • Command line interface • Rich directive set • Flexible macro language • MPLAB IDE compatibility 25.7 MPLAB SIM Software Simulator The MPLAB SIM software simulator allows code development in a PC hosted environment by simulating the PIC series microcontrollers on an instruction level. On any given instruction, the data areas can be examined or modified and stimuli can be applied from a file, or user defined key press, to any pin. The execution can be performed in Single-Step, Execute Until Break or Trace mode. The MPLAB SIM simulator fully supports symbolic debugging using the MPLAB C17 and MPLAB C18 C Compilers, as well as the MPASM assembler. The software simulator offers the flexibility to develop and debug code outside of the laboratory environment, making it an excellent, economical software development tool. 25.8 MPLAB SIM30 Software Simulator The MPLAB SIM30 software simulator allows code development in a PC hosted environment by simulating the dsPIC30F series microcontrollers on an instruction level. On any given instruction, the data areas can be examined or modified and stimuli can be applied from a file, or user defined key press, to any of the pins. The MPLAB SIM30 simulator fully supports symbolic debugging using the MPLAB C30 C Compiler and MPLAB ASM30 assembler. The simulator runs in either a Command Line mode for automated tasks, or from MPLAB IDE. This high-speed simulator is designed to debug, analyze and optimize time intensive DSP routines. © 2007 Microchip Technology Inc. Preliminary DS39631B-page 319 PIC18F2420/2520/4420/4520 25.9 MPLAB ICE 2000 High-Performance Universal In-Circuit Emulator The MPLAB ICE 2000 universal in-circuit emulator is intended to provide the product development engineer with a complete microcontroller design tool set for PIC microcontrollers. Software control of the MPLAB ICE 2000 in-circuit emulator is advanced by the MPLAB Integrated Development Environment, which allows editing, building, downloading and source debugging from a single environment. The MPLAB ICE 2000 is a full-featured emulator system with enhanced trace, trigger and data monitoring features. Interchangeable processor modules allow the system to be easily reconfigured for emulation of different processors. The universal architecture of the MPLAB ICE in-circuit emulator allows expansion to support new PIC microcontrollers. The MPLAB ICE 2000 in-circuit emulator system has been designed as a real-time emulation system with advanced features that are typically found on more expensive development tools. The PC platform and Microsoft® Windows 32-bit operating system were chosen to best make these features available in a simple, unified application. 25.10 MPLAB ICE 4000 High-Performance Universal In-Circuit Emulator The MPLAB ICE 4000 universal in-circuit emulator is intended to provide the product development engineer with a complete microcontroller design tool set for highend PIC microcontrollers. Software control of the MPLAB ICE in-circuit emulator is provided by the MPLAB Integrated Development Environment, which allows editing, building, downloading and source debugging from a single environment. The MPLAB ICD 4000 is a premium emulator system, providing the features of MPLAB ICE 2000, but with increased emulation memory and high-speed performance for dsPIC30F and PIC18XXXX devices. Its advanced emulator features include complex triggering and timing, up to 2 Mb of emulation memory and the ability to view variables in real-time. The MPLAB ICE 4000 in-circuit emulator system has been designed as a real-time emulation system with advanced features that are typically found on more expensive development tools. The PC platform and Microsoft Windows 32-bit operating system were chosen to best make these features available in a simple, unified application. 25.11 MPLAB ICD 2 In-Circuit Debugger Microchip’s In-Circuit Debugger, MPLAB ICD 2, is a powerful, low-cost, run-time development tool, connecting to the host PC via an RS-232 or high-speed USB interface. This tool is based on the Flash PIC MCUs and can be used to develop for these and other PIC microcontrollers. The MPLAB ICD 2 utilizes the incircuit debugging capability built into the Flash devices. This feature, along with Microchip’s In-Circuit Serial ProgrammingTM (ICSPTM) protocol, offers cost effective in-circuit Flash debugging from the graphical user interface of the MPLAB Integrated Development Environment. This enables a designer to develop and debug source code by setting breakpoints, singlestepping and watching variables, CPU status and peripheral registers. Running at full speed enables testing hardware and applications in real-time. MPLAB ICD 2 also serves as a development programmer for selected PIC devices. 25.12 PRO MATE II Universal Device Programmer The PRO MATE II is a universal, CE compliant device programmer with programmable voltage verification at VDDMIN and VDDMAX for maximum reliability. It features an LCD display for instructions and error messages and a modular detachable socket assembly to support various package types. In Stand-Alone mode, the PRO MATE II device programmer can read, verify and program PIC devices without a PC connection. It can also set code protection in this mode. 25.13 MPLAB PM3 Device Programmer The MPLAB PM3 is a universal, CE compliant device programmer with programmable voltage verification at VDDMIN and VDDMAX for maximum reliability. It features a large LCD display (128 x 64) for menus and error messages and a modular detachable socket assembly to support various package types. The ICSP™ cable assembly is included as a standard item. In Stand- Alone mode, the MPLAB PM3 device programmer can read, verify and program PIC devices without a PC connection. It can also set code protection in this mode. MPLAB PM3 connects to the host PC via an RS-232 or USB cable. MPLAB PM3 has high-speed communications and optimized algorithms for quick programming of large memory devices and incorporates an SD/MMC card for file storage and secure data applications. PIC18F2420/2520/4420/4520 DS39631B-page 320 Preliminary © 2007 Microchip Technology Inc. 25.14 PICSTART Plus Development Programmer The PICSTART Plus development programmer is an easy-to-use, low-cost, prototype programmer. It connects to the PC via a COM (RS-232) port. MPLAB Integrated Development Environment software makes using the programmer simple and efficient. The PICSTART Plus development programmer supports most PIC devices up to 40 pins. Larger pin count devices, such as the PIC16C92X and PIC17C76X, may be supported with an adapter socket. The PICSTART Plus development programmer is CE compliant. 25.15 PICDEM 1 PIC Demonstration Board The PICDEM 1 demonstration board demonstrates the capabilities of the PIC16C5X (PIC16C54 to PIC16C58A), PIC16C61, PIC16C62X, PIC16C71, PIC16C8X, PIC17C42, PIC17C43 and PIC17C44. All necessary hardware and software is included to run basic demo programs. The sample microcontrollers provided with the PICDEM 1 demonstration board can be programmed with a PRO MATE II device programmer or a PICSTART Plus development programmer. The PICDEM 1 demonstration board can be connected to the MPLAB ICE in-circuit emulator for testing. A prototype area extends the circuitry for additional application components. Features include an RS-232 interface, a potentiometer for simulated analog input, push button switches and eight LEDs. 25.16 PICDEM.net Internet/Ethernet Demonstration Board The PICDEM.net demonstration board is an Internet/ Ethernet demonstration board using the PIC18F452 microcontroller and TCP/IP firmware. The board supports any 40-pin DIP device that conforms to the standard pinout used by the PIC16F877 or PIC18C452. This kit features a user friendly TCP/IP stack, web server with HTML, a 24L256 Serial EEPROM for Xmodem download to web pages into Serial EEPROM, ICSP/MPLAB ICD 2 interface connector, an Ethernet interface, RS-232 interface and a 16 x 2 LCD display. Also included is the book and CD-ROM “TCP/IP Lean, Web Servers for Embedded Systems,” by Jeremy Bentham 25.17 PICDEM 2 Plus Demonstration Board The PICDEM 2 Plus demonstration board supports many 18, 28 and 40-pin microcontrollers, including PIC16F87X and PIC18FXX2 devices. All the necessary hardware and software is included to run the demonstration programs. The sample microcontrollers provided with the PICDEM 2 demonstration board can be programmed with a PRO MATE II device programmer, PICSTART Plus development programmer, or MPLAB ICD 2 with a Universal Programmer Adapter. The MPLAB ICD 2 and MPLAB ICE in-circuit emulators may also be used with the PICDEM 2 demonstration board to test firmware. A prototype area extends the circuitry for additional application components. Some of the features include an RS-232 interface, a 2 x 16 LCD display, a piezo speaker, an on-board temperature sensor, four LEDs and sample PIC18F452 and PIC16F877 Flash microcontrollers. 25.18 PICDEM 3 PIC16C92X Demonstration Board The PICDEM 3 demonstration board supports the PIC16C923 and PIC16C924 in the PLCC package. All the necessary hardware and software is included to run the demonstration programs. 25.19 PICDEM 4 8/14/18-Pin Demonstration Board The PICDEM 4 can be used to demonstrate the capabilities of the 8, 14 and 18-pin PIC16XXXX and PIC18XXXX MCUs, including the PIC16F818/819, PIC16F87/88, PIC16F62XA and the PIC18F1320 family of microcontrollers. PICDEM 4 is intended to showcase the many features of these low pin count parts, including LIN and Motor Control using ECCP. Special provisions are made for low-power operation with the supercapacitor circuit and jumpers allow onboard hardware to be disabled to eliminate current draw in this mode. Included on the demo board are provisions for Crystal, RC or Canned Oscillator modes, a five volt regulator for use with a nine volt wall adapter or battery, DB-9 RS-232 interface, ICD connector for programming via ICSP and development with MPLAB ICD 2, 2 x 16 liquid crystal display, PCB footprints for H-Bridge motor driver, LIN transceiver and EEPROM. Also included are: header for expansion, eight LEDs, four potentiometers, three push buttons and a prototyping area. Included with the kit is a PIC16F627A and a PIC18F1320. Tutorial firmware is included along with the User’s Guide. © 2007 Microchip Technology Inc. Preliminary DS39631B-page 321 PIC18F2420/2520/4420/4520 25.20 PICDEM 17 Demonstration Board The PICDEM 17 demonstration board is an evaluation board that demonstrates the capabilities of several Microchip microcontrollers, including PIC17C752, PIC17C756A, PIC17C762 and PIC17C766. A programmed sample is included. The PRO MATE II device programmer, or the PICSTART Plus development programmer, can be used to reprogram the device for user tailored application development. The PICDEM 17 demonstration board supports program download and execution from external on-board Flash memory. A generous prototype area is available for user hardware expansion. 25.21 PICDEM 18R PIC18C601/801 Demonstration Board The PICDEM 18R demonstration board serves to assist development of the PIC18C601/801 family of Microchip microcontrollers. It provides hardware implementation of both 8-bit Multiplexed/Demultiplexed and 16-bit Memory modes. The board includes 2 Mb external Flash memory and 128 Kb SRAM memory, as well as serial EEPROM, allowing access to the wide range of memory types supported by the PIC18C601/801. 25.22 PICDEM LIN PIC16C43X Demonstration Board The powerful LIN hardware and software kit includes a series of boards and three PIC microcontrollers. The small footprint PIC16C432 and PIC16C433 are used as slaves in the LIN communication and feature onboard LIN transceivers. A PIC16F874 Flash microcontroller serves as the master. All three microcontrollers are programmed with firmware to provide LIN bus communication. 25.23 PICkitTM 1 Flash Starter Kit A complete “development system in a box”, the PICkit™ Flash Starter Kit includes a convenient multi-section board for programming, evaluation and development of 8/14-pin Flash PIC® microcontrollers. Powered via USB, the board operates under a simple Windows GUI. The PICkit 1 Starter Kit includes the User’s Guide (on CD ROM), PICkit 1 tutorial software and code for various applications. Also included are MPLAB® IDE (Integrated Development Environment) software, software and hardware “Tips 'n Tricks for 8-pin Flash PIC® Microcontrollers” Handbook and a USB interface cable. Supports all current 8/14-pin Flash PIC microcontrollers, as well as many future planned devices. 25.24 PICDEM USB PIC16C7X5 Demonstration Board The PICDEM USB Demonstration Board shows off the capabilities of the PIC16C745 and PIC16C765 USB microcontrollers. This board provides the basis for future USB products. 25.25 Evaluation and Programming Tools In addition to the PICDEM series of circuits, Microchip has a line of evaluation kits and demonstration software for these products. • KEELOQ evaluation and programming tools for Microchip’s HCS Secure Data Products • CAN developers kit for automotive network applications • Analog design boards and filter design software • PowerSmart battery charging evaluation/ calibration kits • IrDA® development kit • microID development and rfLabTM development software • SEEVAL® designer kit for memory evaluation and endurance calculations • PICDEM MSC demo boards for Switching mode power supply, high-power IR driver, delta sigma ADC and flow rate sensor Check the Microchip web page and the latest Product Selector Guide for the complete list of demonstration and evaluation kits. PIC18F2420/2520/4420/4520 DS39631B-page 322 Preliminary © 2007 Microchip Technology Inc. NOTES: © 2007 Microchip Technology Inc. Preliminary DS39631B-page 323 PIC18F2420/2520/4420/4520 26.0 ELECTRICAL CHARACTERISTICS Absolute Maximum Ratings (†) Ambient temperature under bias.............................................................................................................-40°C to +125°C Storage temperature .............................................................................................................................. -65°C to +150°C Voltage on any pin with respect to VSS (except VDD, MCLR and RA4) .......................................... -0.3V to (VDD + 0.3V) Voltage on VDD with respect to VSS ......................................................................................................... -0.3V to +7.5V Voltage on MCLR with respect to VSS (Note 2) ......................................................................................... 0V to +13.25V Total power dissipation (Note 1) ...............................................................................................................................1.0W Maximum current out of VSS pin ...........................................................................................................................300 mA Maximum current into VDD pin ..............................................................................................................................250 mA Input clamp current, IIK (VI < 0 or VI > VDD)...................................................................................................................... ±20 mA Output clamp current, IOK (VO < 0 or VO > VDD) .............................................................................................................. ±20 mA Maximum output current sunk by any I/O pin..........................................................................................................25 mA Maximum output current sourced by any I/O pin ....................................................................................................25 mA Maximum current sunk by all ports .......................................................................................................................200 mA Maximum current sourced by all ports ..................................................................................................................200 mA Note 1: Power dissipation is calculated as follows: Pdis = VDD x {IDD – Σ IOH} + Σ {(VDD – VOH) x IOH} + Σ(VOL x IOL) 2: Voltage spikes below VSS at the MCLR/VPP/RE3 pin, inducing currents greater than 80 mA, may cause latch-up. Thus, a series resistor of 50-100Ω should be used when applying a “low” level to the MCLR/VPP/ RE3 pin, rather than pulling this pin directly to VSS. † NOTICE: Stresses above those listed under “Absolute Maximum Ratings” may cause permanent damage to the device. This is a stress rating only and functional operation of the device at those or any other conditions above those indicated in the operation listings of this specification is not implied. Exposure to maximum rating conditions for extended periods may affect device reliability. PIC18F2420/2520/4420/4520 DS39631B-page 324 Preliminary © 2007 Microchip Technology Inc. FIGURE 26-1: PIC18F2420/2520/4420/4520 VOLTAGE-FREQUENCY GRAPH (INDUSTRIAL) FIGURE 26-2: PIC18LF2X1X/4X1X VOLTAGE-FREQUENCY GRAPH (INDUSTRIAL) Frequency Voltage 6.0V 5.5V 4.5V 4.0V 2.0V 40 MHz 5.0V 3.5V 3.0V 2.5V PIC18FX42X/X52X 4.2V Frequency Voltage 6.0V 5.5V 4.5V 4.0V 2.0V 40 MHz 5.0V 3.5V 3.0V 2.5V PIC18LFX42X/X52X FMAX = (16.36 MHz/V) (VDDAPPMIN – 2.0V) + 4 MHz Note: VDDAPPMIN is the minimum voltage of the PIC® device in the application. 4 MHz 4.2V © 2007 Microchip Technology Inc. Preliminary DS39631B-page 325 PIC18F2420/2520/4420/4520 26.1 DC Characteristics:Supply Voltage PIC18F2420/2520/4420/4520 (Industrial) PIC18LF2X1X/4X1X (Industrial) PIC18LF2X1X/4X1X (Industrial) Standard Operating Conditions (unless otherwise stated) Operating temperature -40°C ≤ TA ≤ +85°C for industrial PIC18FX42X/X52X (Industrial) Standard Operating Conditions (unless otherwise stated) Operating temperature -40°C ≤ TA ≤ +85°C for industrial Param No. Symbol Characteristic Min Typ Max Units Conditions D001 VDD Supply Voltage 2.0 — 5.5 V HS, XT, RC and LP Oscillator modes D002 VDR RAM Data Retention Voltage(1) 1.5 — — V D003 VPOR VDD Start Voltage to ensure internal Power-on Reset signal — — 0.7 V See section on Power-on Reset for details D004 SVDD VDD Rise Rate to ensure internal Power-on Reset signal 0.05 — — V/ms See section on Power-on Reset for details D005 VBOR Brown-out Reset Voltage BORV1:BORV0 = 11 1.94 2.05 2.16 V BORV1:BORV0 = 10 2.65 2.79 2.93 V BORV1:BORV0 = 01 4.11 4.33 4.55 V BORV1:BORV0 = 00 4.36 4.59 4.82 V Legend: Shading of rows is to assist in readability of the table. Note 1: This is the limit to which VDD can be lowered in Sleep mode, or during a device Reset, without losing RAM data. PIC18F2420/2520/4420/4520 DS39631B-page 326 Preliminary © 2007 Microchip Technology Inc. 26.2 DC Characteristics: Power-Down and Supply Current PIC18F2420/2520/4420/4520 (Industrial) PIC18LF2X1X/4X1X (Industrial) PIC18LF2X1X/4X1X (Industrial) Standard Operating Conditions (unless otherwise stated) Operating temperature -40°C ≤ TA ≤ +85°C for industrial PIC18FX42X/X52X (Industrial) Standard Operating Conditions (unless otherwise stated) Operating temperature -40°C ≤ TA ≤ +85°C for industrial ParamNo. Device Typ Max Units Conditions Power-down Current (IPD)(1) PIC18LF2X1X/4X1X 20 950 nA -40°C VDD = 2.0V, (Sleep mode) 0.02 1.0 μA +25°C 0.6 1.1 μA +85°C PIC18LF2X1X/4X1X 0.03 1.4 μA -40°C VDD = 3.0V, (Sleep mode) 0.03 1.5 μA +25°C 0.8 1.6 μA +85°C All devices 0.04 1.9 μA -40°C VDD = 5.0V, (Sleep mode) 0.04 2.0 μA +25°C 1.7 2.1 μA +85°C Legend: Shading of rows is to assist in readability of the table. Note 1: The power-down current in Sleep mode does not depend on the oscillator type. Power-down current is measured with the part in Sleep mode, with all I/O pins in high-impedance state and tied to VDD or VSS and all features that add delta current disabled (such as WDT, Timer1 Oscillator, BOR, etc.). 2: The supply current is mainly a function of operating voltage, frequency and mode. Other factors, such as I/O pin loading and switching rate, oscillator type and circuit, internal code execution pattern and temperature, also have an impact on the current consumption. The test conditions for all IDD measurements in active operation mode are: OSC1 = external square wave, from rail-to-rail; all I/O pins tri-stated, pulled to VDD; MCLR = VDD; WDT enabled/disabled as specified. 3: For RC oscillator configurations, current through REXT is not included. The current through the resistor can be estimated by the formula Ir = VDD/2REXT (mA) with REXT in kΩ. 4: Standard low-cost 32 kHz crystals have an operating temperature range of -10°C to +70°C. Extended temperature crystals are available at a much higher cost. 5: BOR and HLVD enable internal band gap reference. With both modules enabled, current consumption will be less than the sum of both specifications. © 2007 Microchip Technology Inc. Preliminary DS39631B-page 327 PIC18F2420/2520/4420/4520 Supply Current (IDD)(2,3) PIC18LF2X1X/4X1X 15 31.5 μA -40°C FOSC = 31 kHz (RC_RUN mode, INTRC source) 15 30 μA +25°C VDD = 2.0V 15 28.5 μA +85°C PIC18LF2X1X/4X1X 40 63 μA -40°C 35 60 μA +25°C VDD = 3.0V 30 57 μA +85°C All devices 105 168 μA -40°C 90 160 μA +25°C VDD = 5.0V 80 152 μA +85°C PIC18LF2X1X/4X1X 0.32 630 μA -40°C FOSC = 1 MHz (RC_RUN mode, INTOSC source) 0.33 600 μA +25°C VDD = 2.0V 0.33 570 μA +85°C PIC18LF2X1X/4X1X 0.6 1.3 mA -40°C 0.55 1.2 mA +25°C VDD = 3.0V 0.6 1.1 mA +85°C All devices 1.1 2.3 mA -40°C 1.1 2.2 mA +25°C VDD = 5.0V 1.0 2.1 mA +85°C 26.2 DC Characteristics: Power-Down and Supply Current PIC18F2420/2520/4420/4520 (Industrial) PIC18LF2X1X/4X1X (Industrial) (Continued) PIC18LF2X1X/4X1X (Industrial) Standard Operating Conditions (unless otherwise stated) Operating temperature -40°C ≤ TA ≤ +85°C for industrial PIC18FX42X/X52X (Industrial) Standard Operating Conditions (unless otherwise stated) Operating temperature -40°C ≤ TA ≤ +85°C for industrial ParamNo. Device Typ Max Units Conditions Legend: Shading of rows is to assist in readability of the table. Note 1: The power-down current in Sleep mode does not depend on the oscillator type. Power-down current is measured with the part in Sleep mode, with all I/O pins in high-impedance state and tied to VDD or VSS and all features that add delta current disabled (such as WDT, Timer1 Oscillator, BOR, etc.). 2: The supply current is mainly a function of operating voltage, frequency and mode. Other factors, such as I/O pin loading and switching rate, oscillator type and circuit, internal code execution pattern and temperature, also have an impact on the current consumption. The test conditions for all IDD measurements in active operation mode are: OSC1 = external square wave, from rail-to-rail; all I/O pins tri-stated, pulled to VDD; MCLR = VDD; WDT enabled/disabled as specified. 3: For RC oscillator configurations, current through REXT is not included. The current through the resistor can be estimated by the formula Ir = VDD/2REXT (mA) with REXT in kΩ. 4: Standard low-cost 32 kHz crystals have an operating temperature range of -10°C to +70°C. Extended temperature crystals are available at a much higher cost. 5: BOR and HLVD enable internal band gap reference. With both modules enabled, current consumption will be less than the sum of both specifications. PIC18F2420/2520/4420/4520 DS39631B-page 328 Preliminary © 2007 Microchip Technology Inc. Supply Current (IDD)(2,3) PIC18LF2X1X/4X1X 0.8 2.1 μA -40°C FOSC = 4 MHz (RC_RUN mode, INTRC source) 0.8 2.0 μA +25°C VDD = 2.0V 0.8 1.9 μA +85°C PIC18LF2X1X/4X1X 1.3 2.7 mA -40°C 1.3 2.6 mA +25°C VDD = 3.0V 1.3 2.5 mA +85°C All devices 2.5 5.3 mA -40°C 2.5 5.0 mA +25°C VDD = 5.0V 2.5 4.8 mA +85°C PIC18LF2X1X/4X1X 2.9 6.5 μA -40°C FOSC = 31 kHz (RC_IDLE mode, INTRC source) 3.1 6.2 μA +25°C VDD = 2.0V 3.6 5.9 μA +85°C PIC18LF2X1X/4X1X 4.5 10.1 μA -40°C 4.8 9.6 μA +25°C VDD = 3.0V 5.8 9.1 μA +85°C All devices 9.2 15.8 μA -40°C 9.8 15 μA +25°C VDD = 5.0V 11.4 14.3 μA +85°C 26.2 DC Characteristics: Power-Down and Supply Current PIC18F2420/2520/4420/4520 (Industrial) PIC18LF2X1X/4X1X (Industrial) (Continued) PIC18LF2X1X/4X1X (Industrial) Standard Operating Conditions (unless otherwise stated) Operating temperature -40°C ≤ TA ≤ +85°C for industrial PIC18FX42X/X52X (Industrial) Standard Operating Conditions (unless otherwise stated) Operating temperature -40°C ≤ TA ≤ +85°C for industrial ParamNo. Device Typ Max Units Conditions Legend: Shading of rows is to assist in readability of the table. Note 1: The power-down current in Sleep mode does not depend on the oscillator type. Power-down current is measured with the part in Sleep mode, with all I/O pins in high-impedance state and tied to VDD or VSS and all features that add delta current disabled (such as WDT, Timer1 Oscillator, BOR, etc.). 2: The supply current is mainly a function of operating voltage, frequency and mode. Other factors, such as I/O pin loading and switching rate, oscillator type and circuit, internal code execution pattern and temperature, also have an impact on the current consumption. The test conditions for all IDD measurements in active operation mode are: OSC1 = external square wave, from rail-to-rail; all I/O pins tri-stated, pulled to VDD; MCLR = VDD; WDT enabled/disabled as specified. 3: For RC oscillator configurations, current through REXT is not included. The current through the resistor can be estimated by the formula Ir = VDD/2REXT (mA) with REXT in kΩ. 4: Standard low-cost 32 kHz crystals have an operating temperature range of -10°C to +70°C. Extended temperature crystals are available at a much higher cost. 5: BOR and HLVD enable internal band gap reference. With both modules enabled, current consumption will be less than the sum of both specifications. © 2007 Microchip Technology Inc. Preliminary DS39631B-page 329 PIC18F2420/2520/4420/4520 Supply Current (IDD)(2,3) PIC18LF2X1X/4X1X 165 315 μA -40°C FOSC = 1 MHz (RC_IDLE mode, INTOSC source) 175 300 μA +25°C VDD = 2.0V 190 285 μA +85°C PIC18LF2X1X/4X1X 250 470 μA -40°C 270 450 μA +25°C VDD = 3.0V 290 430 μA +85°C All devices 500 840 μA -40°C 520 800 μA +25°C VDD = 5.0V 550 760 μA +85°C PIC18LF2X1X/4X1X 340 525 μA -40°C FOSC = 4 MHz (RC_IDLE mode, INTOSC source) 350 500 μA +25°C VDD = 2.0V 360 475 μA +85°C PIC18LF2X1X/4X1X 520 735 μA -40°C 540 700 μA +25°C VDD = 3.0V 580 665 μA +85°C All devices 1.0 1.6 mA -40°C 1.1 1.5 mA +25°C VDD = 5.0V 1.1 1.4 mA +85°C 26.2 DC Characteristics: Power-Down and Supply Current PIC18F2420/2520/4420/4520 (Industrial) PIC18LF2X1X/4X1X (Industrial) (Continued) PIC18LF2X1X/4X1X (Industrial) Standard Operating Conditions (unless otherwise stated) Operating temperature -40°C ≤ TA ≤ +85°C for industrial PIC18FX42X/X52X (Industrial) Standard Operating Conditions (unless otherwise stated) Operating temperature -40°C ≤ TA ≤ +85°C for industrial ParamNo. Device Typ Max Units Conditions Legend: Shading of rows is to assist in readability of the table. Note 1: The power-down current in Sleep mode does not depend on the oscillator type. Power-down current is measured with the part in Sleep mode, with all I/O pins in high-impedance state and tied to VDD or VSS and all features that add delta current disabled (such as WDT, Timer1 Oscillator, BOR, etc.). 2: The supply current is mainly a function of operating voltage, frequency and mode. Other factors, such as I/O pin loading and switching rate, oscillator type and circuit, internal code execution pattern and temperature, also have an impact on the current consumption. The test conditions for all IDD measurements in active operation mode are: OSC1 = external square wave, from rail-to-rail; all I/O pins tri-stated, pulled to VDD; MCLR = VDD; WDT enabled/disabled as specified. 3: For RC oscillator configurations, current through REXT is not included. The current through the resistor can be estimated by the formula Ir = VDD/2REXT (mA) with REXT in kΩ. 4: Standard low-cost 32 kHz crystals have an operating temperature range of -10°C to +70°C. Extended temperature crystals are available at a much higher cost. 5: BOR and HLVD enable internal band gap reference. With both modules enabled, current consumption will be less than the sum of both specifications. PIC18F2420/2520/4420/4520 DS39631B-page 330 Preliminary © 2007 Microchip Technology Inc. Supply Current (IDD)(2,3) PIC18LF2X1X/4X1X 250 420 μA -40°C FOSC = 1 MHZ (PRI_RUN, EC oscillator) 260 400 μA +25°C VDD = 2.0V 250 380 μA +85°C PIC18LF2X1X/4X1X 550 740 μA -40°C 480 700 μA +25°C VDD = 3.0V 460 670 μA +85°C All devices 1.2 1.6 mA -40°C 1.1 1.5 mA +25°C VDD = 5.0V 1.0 1.4 mA +85°C PIC18LF2X1X/4X1X 0.72 1.6 mA -40°C FOSC = 4 MHz (PRI_RUN, EC oscillator) 0.74 1.5 mA +25°C VDD = 2.0V 0.74 1.4 mA +85°C PIC18LF2X1X/4X1X 1.3 2.6 mA -40°C 1.3 2.5 mA +25°C VDD = 3.0V 1.3 2.4 mA +85°C All devices 2.7 4.7 mA -40°C 2.6 4.5 mA +25°C VDD = 5.0V 2.5 4.3 mA +85°C All devices 15 26 mA -40°C FOSC = 40 MHZ (PRI_RUN, EC oscillator) 16 25 mA +25°C VDD = 4.2V 16 24 mA +85°C All devices 21 32 mA -40°C 21 30 mA +25°C VDD = 5.0V 21 28 mA +85°C 26.2 DC Characteristics: Power-Down and Supply Current PIC18F2420/2520/4420/4520 (Industrial) PIC18LF2X1X/4X1X (Industrial) (Continued) PIC18LF2X1X/4X1X (Industrial) Standard Operating Conditions (unless otherwise stated) Operating temperature -40°C ≤ TA ≤ +85°C for industrial PIC18FX42X/X52X (Industrial) Standard Operating Conditions (unless otherwise stated) Operating temperature -40°C ≤ TA ≤ +85°C for industrial ParamNo. Device Typ Max Units Conditions Legend: Shading of rows is to assist in readability of the table. Note 1: The power-down current in Sleep mode does not depend on the oscillator type. Power-down current is measured with the part in Sleep mode, with all I/O pins in high-impedance state and tied to VDD or VSS and all features that add delta current disabled (such as WDT, Timer1 Oscillator, BOR, etc.). 2: The supply current is mainly a function of operating voltage, frequency and mode. Other factors, such as I/O pin loading and switching rate, oscillator type and circuit, internal code execution pattern and temperature, also have an impact on the current consumption. The test conditions for all IDD measurements in active operation mode are: OSC1 = external square wave, from rail-to-rail; all I/O pins tri-stated, pulled to VDD; MCLR = VDD; WDT enabled/disabled as specified. 3: For RC oscillator configurations, current through REXT is not included. The current through the resistor can be estimated by the formula Ir = VDD/2REXT (mA) with REXT in kΩ. 4: Standard low-cost 32 kHz crystals have an operating temperature range of -10°C to +70°C. Extended temperature crystals are available at a much higher cost. 5: BOR and HLVD enable internal band gap reference. With both modules enabled, current consumption will be less than the sum of both specifications. © 2007 Microchip Technology Inc. Preliminary DS39631B-page 331 PIC18F2420/2520/4420/4520 Supply Current (IDD)(2,3) All devices 7.5 16 mA -40°C VDD = 4.2V FOSC = 4 MHZ (PRI_RUN HS+PLL) 7.4 15 mA +25°C 7.3 14 mA +85°C All devices 10 21 mA -40°C VDD = 5.0V FOSC = 4 MHZ 10 20 mA +25°C (PRI_RUN HS+PLL) 9.7 19 mA +85°C All devices 17 35 mA -40°C VDD = 4.2V FOSC = 10 MHZ 17 34 mA +25°C (PRI_RUN HS+PLL) 17 33 mA +85°C All devices 23 46 mA -40°C VDD = 5.0V FOSC = 10 MHZ 23 45 mA +25°C (PRI_RUN HS+PLL) 23 43 mA +85°C 26.2 DC Characteristics: Power-Down and Supply Current PIC18F2420/2520/4420/4520 (Industrial) PIC18LF2X1X/4X1X (Industrial) (Continued) PIC18LF2X1X/4X1X (Industrial) Standard Operating Conditions (unless otherwise stated) Operating temperature -40°C ≤ TA ≤ +85°C for industrial PIC18FX42X/X52X (Industrial) Standard Operating Conditions (unless otherwise stated) Operating temperature -40°C ≤ TA ≤ +85°C for industrial ParamNo. Device Typ Max Units Conditions Legend: Shading of rows is to assist in readability of the table. Note 1: The power-down current in Sleep mode does not depend on the oscillator type. Power-down current is measured with the part in Sleep mode, with all I/O pins in high-impedance state and tied to VDD or VSS and all features that add delta current disabled (such as WDT, Timer1 Oscillator, BOR, etc.). 2: The supply current is mainly a function of operating voltage, frequency and mode. Other factors, such as I/O pin loading and switching rate, oscillator type and circuit, internal code execution pattern and temperature, also have an impact on the current consumption. The test conditions for all IDD measurements in active operation mode are: OSC1 = external square wave, from rail-to-rail; all I/O pins tri-stated, pulled to VDD; MCLR = VDD; WDT enabled/disabled as specified. 3: For RC oscillator configurations, current through REXT is not included. The current through the resistor can be estimated by the formula Ir = VDD/2REXT (mA) with REXT in kΩ. 4: Standard low-cost 32 kHz crystals have an operating temperature range of -10°C to +70°C. Extended temperature crystals are available at a much higher cost. 5: BOR and HLVD enable internal band gap reference. With both modules enabled, current consumption will be less than the sum of both specifications. PIC18F2420/2520/4420/4520 DS39631B-page 332 Preliminary © 2007 Microchip Technology Inc. Supply Current (IDD)(2,3) PIC18LF2X1X/4X1X 65 130 μA -40°C FOSC = 1 MHz (PRI_IDLE mode, EC oscillator) 65 120 μA +25°C VDD = 2.0V 70 115 μA +85°C PIC18LF2X1X/4X1X 120 270 μA -40°C 120 250 μA +25°C VDD = 3.0V 130 240 μA +85°C All devices 300 480 μA -40°C 240 450 μA +25°C VDD = 5.0V 300 430 μA +85°C PIC18LF2X1X/4X1X 260 475 μA -40°C FOSC = 4 MHz (PRI_IDLE mode, EC oscillator) 255 450 μA +25°C VDD = 2.0V 270 430 μA +85°C PIC18LF2X1X/4X1X 420 900 μA -40°C 430 850 μA +25°C VDD = 3.0V 450 810 μA +85°C All devices 0.9 1.5 mA -40°C 0.9 1.4 mA +25°C VDD = 5.0V 0.9 1.3 mA +85°C All devices 6.0 9.5 mA -40°C FOSC = 40 MHz (PRI_IDLE mode, EC oscillator) 6.2 9.0 mA +25°C VDD = 4.2 V 6.6 8.6 mA +85°C All devices 8.1 12.6 mA -40°C 9.1 12.0 mA +25°C VDD = 5.0V 8.3 11.4 mA +85°C 26.2 DC Characteristics: Power-Down and Supply Current PIC18F2420/2520/4420/4520 (Industrial) PIC18LF2X1X/4X1X (Industrial) (Continued) PIC18LF2X1X/4X1X (Industrial) Standard Operating Conditions (unless otherwise stated) Operating temperature -40°C ≤ TA ≤ +85°C for industrial PIC18FX42X/X52X (Industrial) Standard Operating Conditions (unless otherwise stated) Operating temperature -40°C ≤ TA ≤ +85°C for industrial ParamNo. Device Typ Max Units Conditions Legend: Shading of rows is to assist in readability of the table. Note 1: The power-down current in Sleep mode does not depend on the oscillator type. Power-down current is measured with the part in Sleep mode, with all I/O pins in high-impedance state and tied to VDD or VSS and all features that add delta current disabled (such as WDT, Timer1 Oscillator, BOR, etc.). 2: The supply current is mainly a function of operating voltage, frequency and mode. Other factors, such as I/O pin loading and switching rate, oscillator type and circuit, internal code execution pattern and temperature, also have an impact on the current consumption. The test conditions for all IDD measurements in active operation mode are: OSC1 = external square wave, from rail-to-rail; all I/O pins tri-stated, pulled to VDD; MCLR = VDD; WDT enabled/disabled as specified. 3: For RC oscillator configurations, current through REXT is not included. The current through the resistor can be estimated by the formula Ir = VDD/2REXT (mA) with REXT in kΩ. 4: Standard low-cost 32 kHz crystals have an operating temperature range of -10°C to +70°C. Extended temperature crystals are available at a much higher cost. 5: BOR and HLVD enable internal band gap reference. With both modules enabled, current consumption will be less than the sum of both specifications. © 2007 Microchip Technology Inc. Preliminary DS39631B-page 333 PIC18F2420/2520/4420/4520 Supply Current (IDD)(2,3) PIC18LF2X1X/4X1X 14 31.5 μA -10°C FOSC = 32 kHz(4) (SEC_RUN mode, Timer1 as clock) 15 30 μA +25°C VDD = 2.0V 16 29 μA +70°C PIC18LF2X1X/4X1X 40 74 μA -10°C 35 70 μA +25°C VDD = 3.0V 31 67 μA +70°C All devices 99 126 μA -10°C 81 120 μA +25°C VDD = 5.0V 75 114 μA +70°C PIC18LF2X1X/4X1X 2.5 7.4 μA -10°C FOSC = 32 kHz(4) (SEC_IDLE mode, Timer1 as clock) 3.7 7.0 μA +25°C VDD = 2.0V 4.5 6.7 μA +70°C PIC18LF2X1X/4X1X 5.0 10.5 μA -10°C 5.4 10 μA +25°C VDD = 3.0V 6.3 9.5 μA +70°C All devices 8.5 17 μA -10°C 9.0 16 μA +25°C VDD = 5.0V 10.5 15 μA +70°C 26.2 DC Characteristics: Power-Down and Supply Current PIC18F2420/2520/4420/4520 (Industrial) PIC18LF2X1X/4X1X (Industrial) (Continued) PIC18LF2X1X/4X1X (Industrial) Standard Operating Conditions (unless otherwise stated) Operating temperature -40°C ≤ TA ≤ +85°C for industrial PIC18FX42X/X52X (Industrial) Standard Operating Conditions (unless otherwise stated) Operating temperature -40°C ≤ TA ≤ +85°C for industrial ParamNo. Device Typ Max Units Conditions Legend: Shading of rows is to assist in readability of the table. Note 1: The power-down current in Sleep mode does not depend on the oscillator type. Power-down current is measured with the part in Sleep mode, with all I/O pins in high-impedance state and tied to VDD or VSS and all features that add delta current disabled (such as WDT, Timer1 Oscillator, BOR, etc.). 2: The supply current is mainly a function of operating voltage, frequency and mode. Other factors, such as I/O pin loading and switching rate, oscillator type and circuit, internal code execution pattern and temperature, also have an impact on the current consumption. The test conditions for all IDD measurements in active operation mode are: OSC1 = external square wave, from rail-to-rail; all I/O pins tri-stated, pulled to VDD; MCLR = VDD; WDT enabled/disabled as specified. 3: For RC oscillator configurations, current through REXT is not included. The current through the resistor can be estimated by the formula Ir = VDD/2REXT (mA) with REXT in kΩ. 4: Standard low-cost 32 kHz crystals have an operating temperature range of -10°C to +70°C. Extended temperature crystals are available at a much higher cost. 5: BOR and HLVD enable internal band gap reference. With both modules enabled, current consumption will be less than the sum of both specifications. PIC18F2420/2520/4420/4520 DS39631B-page 334 Preliminary © 2007 Microchip Technology Inc. Module Differential Currents (ΔIWDT, ΔIBOR, ΔILVD, ΔIOSCB, ΔIAD) D022 (ΔIWDT) Watchdog Timer 1.3 7.6 μA -40°C 1.4 8.0 μA +25°C VDD = 2.0V 2.0 8.4 μA +85°C 1.9 11.4 μA -40°C 2.0 12.0 μA +25°C VDD = 3.0V 2.8 12.6 μA +85°C 4.0 14.3 μA -40°C 5.5 15.0 μA +25°C VDD = 5.0V 5.6 15.8 μA +85°C D022A (ΔIBOR) Brown-out Reset(5) 35 52 μA -40°C to +85°C VDD = 3.0V 40 63 μA -40°C to +85°C VDD = 5.0V 40 63 μA -40°C to +85°C VDD = 5.0V Sleep mode, BOREN1:BOREN0 = 10 D022B (ΔILVD) High/Low-Voltage Detect(5) 22 47 μA -40°C to +85°C VDD = 2.0V 25 58 μA -40°C to +85°C VDD = 3.0V 29 69 μA -40°C to +85°C VDD = 5.0V D025 (ΔIOSCB) Timer1 Oscillator 0.01 4.8 μA -10°C 0.01 5.0 μA +25°C VDD = 2.0V 32 kHz on Timer1(4) 0.01 5.3 μA +70°C 0.01 7.6 μA -10°C 0.01 8.0 μA +25°C VDD = 3.0V 32 kHz on Timer1(4) 0.01 8.4 μA +70°C 0.01 9.5 μA -10°C 0.01 10.0 μA +25°C VDD = 5.0V 32 kHz on Timer1(4) 0.01 10.5 μA +70°C D026 (ΔIAD) A/D Converter 1.0 2.0 μA VDD = 2.0V 1.0 2.0 μA VDD = 3.0V A/D on, not converting 1.0 2.0 μA VDD = 5.0V 26.2 DC Characteristics: Power-Down and Supply Current PIC18F2420/2520/4420/4520 (Industrial) PIC18LF2X1X/4X1X (Industrial) (Continued) PIC18LF2X1X/4X1X (Industrial) Standard Operating Conditions (unless otherwise stated) Operating temperature -40°C ≤ TA ≤ +85°C for industrial PIC18FX42X/X52X (Industrial) Standard Operating Conditions (unless otherwise stated) Operating temperature -40°C ≤ TA ≤ +85°C for industrial ParamNo. Device Typ Max Units Conditions Legend: Shading of rows is to assist in readability of the table. Note 1: The power-down current in Sleep mode does not depend on the oscillator type. Power-down current is measured with the part in Sleep mode, with all I/O pins in high-impedance state and tied to VDD or VSS and all features that add delta current disabled (such as WDT, Timer1 Oscillator, BOR, etc.). 2: The supply current is mainly a function of operating voltage, frequency and mode. Other factors, such as I/O pin loading and switching rate, oscillator type and circuit, internal code execution pattern and temperature, also have an impact on the current consumption. The test conditions for all IDD measurements in active operation mode are: OSC1 = external square wave, from rail-to-rail; all I/O pins tri-stated, pulled to VDD; MCLR = VDD; WDT enabled/disabled as specified. 3: For RC oscillator configurations, current through REXT is not included. The current through the resistor can be estimated by the formula Ir = VDD/2REXT (mA) with REXT in kΩ. 4: Standard low-cost 32 kHz crystals have an operating temperature range of -10°C to +70°C. Extended temperature crystals are available at a much higher cost. 5: BOR and HLVD enable internal band gap reference. With both modules enabled, current consumption will be less than the sum of both specifications. © 2007 Microchip Technology Inc. Preliminary DS39631B-page 335 PIC18F2420/2520/4420/4520 26.3 DC Characteristics: PIC18F2420/2520/4420/4520 (Industrial) PIC18LF2X1X/4X1X (Industrial) DC CHARACTERISTICS Standard Operating Conditions (unless otherwise stated) Operating temperature -40°C ≤ TA ≤ +85°C for industrial Param No. Symbol Characteristic Min Max Units Conditions VIL Input Low Voltage I/O ports: D030 with TTL buffer VSS 0.15 VDD V VDD < 4.5V D030A — 0.8 V 4.5V ≤ VDD ≤ 5.5V D031 with Schmitt Trigger buffer RC3 and RC4 VSS VSS 0.2 VDD 0.3 VDD V V D032 MCLR VSS 0.2 VDD V D033 OSC1 VSS 0.3 VDD V HS, HSPLL modes D033A D033B D034 OSC1 OSC1 T13CKI VSS VSS VSS 0.2 VDD 0.3 VDD 0.3 VDD V V V RC, EC modes(1) XT, LP modes VIH Input High Voltage I/O ports: D040 with TTL buffer 0.25 VDD + 0.8V VDD V VDD < 4.5V D040A 2.0 VDD V 4.5V ≤ VDD ≤ 5.5V D041 with Schmitt Trigger buffer RC3 and RC4 0.8 VDD 0.7 VDD VDD VDD V V D042 MCLR 0.8 VDD VDD V D043 OSC1 0.7 VDD VDD V HS, HSPLL modes D043A D043B D043C D044 OSC1 OSC1 OSC1 T13CKI 0.8 VDD 0.9 VDD 1.6 1.6 VDD VDD VDD VDD V V V V EC mode RC mode(1) XT, LP modes IIL Input Leakage Current(2,3) D060 I/O ports — ±1 μA VSS ≤ VPIN ≤ VDD, Pin at high-impedance D061 MCLR — ±5 μA Vss ≤ VPIN ≤ VDD D063 OSC1 — ±5 μA Vss ≤ VPIN ≤ VDD IPU Weak Pull-up Current D070 IPURB PORTB weak pull-up current 50 400 μA VDD = 5V, VPIN = VSS Note 1: In RC oscillator configuration, the OSC1/CLKI pin is a Schmitt Trigger input. It is not recommended that the PIC® device be driven with an external clock while in RC mode. 2: The leakage current on the MCLR pin is strongly dependent on the applied voltage level. The specified levels represent normal operating conditions. Higher leakage current may be measured at different input voltages. 3: Negative current is defined as current sourced by the pin. 4: Parameter is characterized but not tested. PIC18F2420/2520/4420/4520 DS39631B-page 336 Preliminary © 2007 Microchip Technology Inc. VOL Output Low Voltage D080 I/O ports — 0.6 V IOL = 8.5 mA, VDD = 4.5V, -40°C to +85°C D083 OSC2/CLKO (RC, RCIO, EC, ECIO modes) — 0.6 V IOL = 1.6 mA, VDD = 4.5V, -40°C to +85°C VOH Output High Voltage(3) D090 I/O ports VDD – 0.7 — V IOH = -3.0 mA, VDD = 4.5V, -40°C to +85°C D092 OSC2/CLKO (RC, RCIO, EC, ECIO modes) VDD – 0.7 — V IOH = -1.3 mA, VDD = 4.5V, -40°C to +85°C Capacitive Loading Specs on Output Pins D100(4) COSC2 OSC2 pin — 15 pF In XT, HS and LP modes when external clock is used to drive OSC1 D101 CIO All I/O pins and OSC2 (in RC mode) — 50 pF To meet the AC Timing Specifications D102 CB SCL, SDA — 400 pF I2C™ Specification 26.3 DC Characteristics: PIC18F2420/2520/4420/4520 (Industrial) PIC18LF2X1X/4X1X (Industrial) (Continued) DC CHARACTERISTICS Standard Operating Conditions (unless otherwise stated) Operating temperature -40°C ≤ TA ≤ +85°C for industrial Param No. Symbol Characteristic Min Max Units Conditions Note 1: In RC oscillator configuration, the OSC1/CLKI pin is a Schmitt Trigger input. It is not recommended that the PIC® device be driven with an external clock while in RC mode. 2: The leakage current on the MCLR pin is strongly dependent on the applied voltage level. The specified levels represent normal operating conditions. Higher leakage current may be measured at different input voltages. 3: Negative current is defined as current sourced by the pin. 4: Parameter is characterized but not tested. © 2007 Microchip Technology Inc. Preliminary DS39631B-page 337 PIC18F2420/2520/4420/4520 TABLE 26-1: MEMORY PROGRAMMING REQUIREMENTS DC CHARACTERISTICS Standard Operating Conditions (unless otherwise stated) Operating temperature -40°C ≤ TA ≤ +85°C for industrial Param No. Sym Characteristic Min Typ† Max Units Conditions Internal Program Memory Programming Specifications(1) D110 VPP Voltage on MCLR/VPP/RE3 pin 9.00 — 13.25 V (Note 3) D113 IDDP Supply Current during Programming — — 10 mA Data EEPROM Memory D120 ED Byte Endurance 100K 1M — E/W -40°C to +85°C D121 VDRW VDD for Read/Write VMIN — 5.5 V Using EECON to read/write VMIN = Minimum operating voltage D122 TDEW Erase/Write Cycle Time — 4 — ms D123 TRETD Characteristic Retention 40 — — Year Provided no other specifications are violated D124 TREF Number of Total Erase/Write Cycles before Refresh(2) 1M 10M — E/W -40°C to +85°C Program Flash Memory D130 EP Cell Endurance 10K 100K — E/W -40°C to +85°C D131 VPR VDD for Read VMIN — 5.5 V VMIN = Minimum operating voltage D132 VIE VDD for Block Erase 4.5 — 5.5 V Using ICSP port D132A VIW VDD for Externally Timed Erase or Write 4.5 — 5.5 V Using ICSP port D132B VPEW VDD for Self-timed Write VMIN — 5.5 V VMIN = Minimum operating voltage D133 TIE ICSP Block Erase Cycle Time — 4 — ms VDD > 4.5V D133A TIW ICSP Erase or Write Cycle Time (externally timed) 1 — — ms VDD > 4.5V D133A TIW Self-timed Write Cycle Time — 2 — ms D134 TRETD Characteristic Retention 40 100 — Year Provided no other specifications are violated † Data in “Typ” column is at 5.0V, 25°C unless otherwise stated. These parameters are for design guidance only and are not tested. Note 1: These specifications are for programming the on-chip program memory through the use of table write instructions. 2: Refer to Section 7.8 “Using the Data EEPROM” for a more detailed discussion on data EEPROM endurance. 3: Required only if single-supply programming is disabled. PIC18F2420/2520/4420/4520 DS39631B-page 338 Preliminary © 2007 Microchip Technology Inc. TABLE 26-2: COMPARATOR SPECIFICATIONS TABLE 26-3: VOLTAGE REFERENCE SPECIFICATIONS Operating Conditions: 3.0V < VDD < 5.5V, -40°C < TA < +85°C (unless otherwise stated). Param No. Sym Characteristics Min Typ Max Units Comments D300 VIOFF Input Offset Voltage — ±5.0 ±10 mV D301 VICM Input Common Mode Voltage* 0 — VDD – 1.5 V D302 CMRR Common Mode Rejection Ratio* 55 — — dB 300 TRESP Response Time(1)* — 150 400 ns PIC18FXXXX 300A — 150 600 ns PIC18LFXXXX, VDD = 2.0V 301 TMC2OV Comparator Mode Change to Output Valid* — — 10 μs * These parameters are characterized but not tested. Note 1: Response time measured with one comparator input at (VDD – 1.5)/2, while the other input transitions from VSS to VDD. Operating Conditions: 3.0V < VDD < 5.5V, -40°C < TA < +85°C (unless otherwise stated). Param No. Sym Characteristics Min Typ Max Units Comments D310 VRES Resolution VDD/24 — VDD/32 LSb D311 VRAA Absolute Accuracy — — 1/2 LSb Low Range (CVRR = 1) D312 VRUR Unit Resistor Value (R)* — 2k — Ω 310 TSET Settling Time(1)* — — 10 μs * These parameters are characterized but not tested. Note 1: Settling time measured while CVRR = 1 and CVR3:CVR0 transitions from ‘0000’ to ‘1111’. © 2007 Microchip Technology Inc. Preliminary DS39631B-page 339 PIC18F2420/2520/4420/4520 FIGURE 26-3: HIGH/LOW-VOLTAGE DETECT CHARACTERISTICS TABLE 26-4: HIGH/LOW-VOLTAGE DETECT CHARACTERISTICS VLVD HLVDIF VDD (HLVDIF set by hardware) (HLVDIF can be cleared in software) Standard Operating Conditions (unless otherwise stated) Operating temperature -40°C ≤ TA ≤ +85°C for industrial Param No. Symbol Characteristic Min Typ† Max Units Conditions D420 HLVD Voltage on VDD Transition High-to-Low LVV = 0000 2.12 2.17 2.22 V LVV = 0001 2.18 2.23 2.28 V LVV = 0010 2.31 2.36 2.42 V LVV = 0011 2.38 2.44 2.49 V LVV = 0100 2.54 2.60 2.66 V LVV = 0101 2.72 2.79 2.85 V LVV = 0110 2.82 2.89 2.95 V LVV = 0111 3.05 3.12 3.19 V LVV = 1000 3.31 3.39 3.47 V LVV = 1001 3.46 3.55 3.63 V LVV = 1010 3.63 3.71 3.80 V LVV = 1011 3.81 3.90 3.99 V LVV = 1100 4.01 4.11 4.20 V LVV = 1101 4.23 4.33 4.43 V LVV = 1110 4.48 4.59 4.69 V † Production tested at TAMB = 25°C. Specifications over temperature limits ensured by characterization. PIC18F2420/2520/4420/4520 DS39631B-page 340 Preliminary © 2007 Microchip Technology Inc. 26.4 AC (Timing) Characteristics 26.4.1 TIMING PARAMETER SYMBOLOGY The timing parameter symbols have been created using one of the following formats: 1. TppS2ppS 3. TCC:ST (I2C specifications only) 2. TppS 4. Ts (I2C specifications only) T F Frequency T Time Lowercase letters (pp) and their meanings: pp cc CCP1 osc OSC1 ck CLKO rd RD cs CS rw RD or WR di SDI sc SCK do SDO ss SS dt Data in t0 T0CKI io I/O port t1 T13CKI mc MCLR wr WR Uppercase letters and their meanings: S F Fall P Period H High R Rise I Invalid (High-impedance) V Valid L Low Z High-impedance I2C only AA output access High High BUF Bus free Low Low TCC:ST (I2C specifications only) CC HD Hold SU Setup ST DAT DATA input hold STO Stop condition STA Start condition © 2007 Microchip Technology Inc. Preliminary DS39631B-page 341 PIC18F2420/2520/4420/4520 26.4.2 TIMING CONDITIONS The temperature and voltages specified in Table 26-5 apply to all timing specifications unless otherwise noted. Figure 26-4 specifies the load conditions for the timing specifications. TABLE 26-5: TEMPERATURE AND VOLTAGE SPECIFICATIONS – AC FIGURE 26-4: LOAD CONDITIONS FOR DEVICE TIMING SPECIFICATIONS Note: Because of space limitations, the generic terms “PIC18FXXXX” and “PIC18LFXXXX” are used throughout this section to refer to the PIC18F2420/2520/4420/4520 and PIC18LF2X1X/4X1X families of devices specifically and only those devices. AC CHARACTERISTICS Standard Operating Conditions (unless otherwise stated) Operating temperature -40°C ≤ TA ≤ +85°C for industrial Operating voltage VDD range as described in DC spec Section 26.1 and Section 26.3. LF parts operate for industrial temperatures only. VDD/2 CL RL Pin Pin VSS VSS CL RL = 464Ω CL = 50 pF for all pins except OSC2/CLKO and including D and E outputs as ports Load Condition 1 Load Condition 2 PIC18F2420/2520/4420/4520 DS39631B-page 342 Preliminary © 2007 Microchip Technology Inc. 26.4.3 TIMING DIAGRAMS AND SPECIFICATIONS FIGURE 26-5: EXTERNAL CLOCK TIMING (ALL MODES EXCEPT PLL) TABLE 26-6: EXTERNAL CLOCK TIMING REQUIREMENTS OSC1 CLKO Q4 Q1 Q2 Q3 Q4 Q1 1 2 3 3 4 4 Param. No. Symbol Characteristic Min Max Units Conditions 1A FOSC External CLKI Frequency(1) DC 40 MHz EC, ECIO Oscillator mode Oscillator Frequency(1) DC 4 MHz RC Oscillator mode 0.1 4 MHz XT Oscillator mode 4 25 MHz HS Oscillator mode 4 10 MHz HS + PLL Oscillator mode 5 33 kHz LP Oscillator mode 1 TOSC External CLKI Period(1) 25 — ns EC, ECIO Oscillator mode Oscillator Period(1) 250 — ns RC Oscillator mode 250 10,000 ns XT Oscillator mode 40 100 250 250 ns ns HS Oscillator mode HS + PLL Oscillator mode 30 — μs LP Oscillator mode 2 TCY Instruction Cycle Time(1) 100 — ns TCY = 4/FOSC 3 TOSL, TOSH External Clock in (OSC1) High or Low Time 30 — ns XT Oscillator mode 2.5 — μs LP Oscillator mode 10 — ns HS Oscillator mode 4 TOSR, TOSF External Clock in (OSC1) Rise or Fall Time — 20 ns XT Oscillator mode — 50 ns LP Oscillator mode — 7.5 ns HS Oscillator mode Note 1: Instruction cycle period (TCY) equals four times the input oscillator time base period for all configurations except PLL. All specified values are based on characterization data for that particular oscillator type under standard operating conditions with the device executing code. Exceeding these specified limits may result in an unstable oscillator operation and/or higher than expected current consumption. All devices are tested to operate at “min.” values with an external clock applied to the OSC1/CLKI pin. When an external clock input is used, the “max.” cycle time limit is “DC” (no clock) for all devices. © 2007 Microchip Technology Inc. Preliminary DS39631B-page 343 PIC18F2420/2520/4420/4520 TABLE 26-7: PLL CLOCK TIMING SPECIFICATIONS (VDD = 4.2V TO 5.5V) TABLE 26-8: AC CHARACTERISTICS: INTERNAL RC ACCURACY PIC18F2420/2520/4420/4520 (INDUSTRIAL) PIC18LF2X1X/4X1X (INDUSTRIAL) Param No. Sym Characteristic Min Typ† Max Units Conditions F10 FOSC Oscillator Frequency Range 4 — 10 MHz HS mode only F11 FSYS On-Chip VCO System Frequency 16 — 40 MHz HS mode only F12 trc PLL Start-up Time (Lock Time) — — 2 ms F13 ΔCLK CLKO Stability (Jitter) -2 — +2 % † Data in “Typ” column is at 5V, 25°C unless otherwise stated. These parameters are for design guidance only and are not tested. PIC18LF2X1X/4X1X (Industrial) Standard Operating Conditions (unless otherwise stated) Operating temperature -40°C ≤ TA ≤ +85°C for industrial PIC18FX42X/X52X (Industrial) Standard Operating Conditions (unless otherwise stated) Operating temperature -40°C ≤ TA ≤ +85°C for industrial Param No. Device Min Typ Max Units Conditions INTOSC Accuracy @ Freq = 8 MHz, 4 MHz, 2 MHz, 1 MHz, 500 kHz, 250 kHz, 125 kHz(1) PIC18LF2X1X/4X1X -2 +/-1 2 % +25°C VDD = 2.7-3.3V -5 — 5 % -10°C to +85°C VDD = 2.7-3.3V -10 +/-1 10 % -40°C to +85°C VDD = 2.7-3.3V PIC18FX42X/X52X -2 +/-1 2 % +25°C VDD = 4.5-5.5V -5 — 5 % -10°C to +85°C VDD = 4.5-5.5V -10 +/-1 10 % -40°C to +85°C VDD = 4.5-5.5V INTRC Accuracy @ Freq = 31 kHz(2) PIC18LF2X1X/4X1X 26.562 — 35.938 kHz -40°C to +85°C VDD = 2.7-3.3V PIC18FX42X/X52X 26.562 — 35.938 kHz -40°C to +85°C VDD = 4.5-5.5V Legend: Shading of rows is to assist in readability of the table. Note 1: Frequency calibrated at 25°C. OSCTUNE register can be used to compensate for temperature drift. 2: INTRC frequency after calibration. 3: Change of INTRC frequency as VDD changes. PIC18F2420/2520/4420/4520 DS39631B-page 344 Preliminary © 2007 Microchip Technology Inc. FIGURE 26-6: CLKO AND I/O TIMING TABLE 26-9: CLKO AND I/O TIMING REQUIREMENTS Note: Refer to Figure 26-4 for load conditions. OSC1 CLKO I/O pin (Input) I/O pin (Output) Q4 Q1 Q2 Q3 10 13 14 17 20, 21 19 18 15 11 12 16 Old Value New Value Param No. Symbol Characteristic Min Typ Max Units Conditions 10 TosH2ckL OSC1 ↑ to CLKO ↓ — 75 200 ns (Note 1) 11 TosH2ckH OSC1 ↑ to CLKO ↑ — 75 200 ns (Note 1) 12 TckR CLKO Rise Time — 35 100 ns (Note 1) 13 TckF CLKO Fall Time — 35 100 ns (Note 1) 14 TckL2ioV CLKO ↓ to Port Out Valid — — 0.5 TCY + 20 ns (Note 1) 15 TioV2ckH Port In Valid before CLKO ↑ 0.25 TCY + 25 — — ns (Note 1) 16 TckH2ioI Port In Hold after CLKO ↑ 0 — — ns (Note 1) 17 TosH2ioV OSC1 ↑ (Q1 cycle) to Port Out Valid — 50 150 ns 18 TosH2ioI OSC1 ↑ (Q2 cycle) to Port Input Invalid (I/O in hold time) PIC18FXXXX 100 — — ns 18A PIC18LFXXXX 200 — — ns VDD = 2.0V 19 TioV2osH Port Input Valid to OSC1 ↑ (I/O in setup time) 0 — — ns 20 TioR Port Output Rise Time PIC18FXXXX — 10 25 ns 20A PIC18LFXXXX — — 60 ns VDD = 2.0V 21 TioF Port Output Fall Time PIC18FXXXX — 10 25 ns 21A PIC18LFXXXX — — 60 ns VDD = 2.0V 22† TINP INT pin High or Low Time TCY — — ns 23† TRBP RB7:RB4 Change INT High or Low Time TCY — — ns 24† TRCP RC7:RC4 Change INT High or Low Time 20 ns † These parameters are asynchronous events not related to any internal clock edges. Note 1: Measurements are taken in RC mode, where CLKO output is 4 x TOSC. © 2007 Microchip Technology Inc. Preliminary DS39631B-page 345 PIC18F2420/2520/4420/4520 FIGURE 26-7: RESET, WATCHDOG TIMER, OSCILLATOR START-UP TIMER AND POWER-UP TIMER TIMING FIGURE 26-8: BROWN-OUT RESET TIMING TABLE 26-10: RESET, WATCHDOG TIMER, OSCILLATOR START-UP TIMER, POWER-UP TIMER AND BROWN-OUT RESET REQUIREMENTS Param. No. Symbol Characteristic Min Typ Max Units Conditions 30 TmcL MCLR Pulse Width (low) 2 — — μs 31 TWDT Watchdog Timer Time-out Period (no postscaler) — 4.00 TBD ms 32 TOST Oscillation Start-up Timer Period 1024 TOSC — 1024 TOSC — TOSC = OSC1 period 33 TPWRT Power-up Timer Period — 65.5 TBD ms 34 TIOZ I/O High-Impedance from MCLR Low or Watchdog Timer Reset — 2 — μs 35 TBOR Brown-out Reset Pulse Width 200 — — μs VDD ≤ BVDD (see D005) 36 TIVRST Time for Internal Reference Voltage to become Stable — 20 50 μs 37 TLVD High/Low-Voltage Detect Pulse Width 200 — — μs VDD ≤ VLVD 38 TCSD CPU Start-up Time 5 — 10 μs 39 TIOBST Time for INTOSC to Stabilize — 1 — ms Legend: TBD = To Be Determined VDD MCLR Internal POR PWRT Time-out OSC Time-out Internal Reset Watchdog Timer Reset 33 32 30 31 34 I/O pins 34 Note: Refer to Figure 26-4 for load conditions. VDD BVDD 35 VBGAP = 1.2V VIRVST Enable Internal Internal Reference 36 Reference Voltage Voltage Stable PIC18F2420/2520/4420/4520 DS39631B-page 346 Preliminary © 2007 Microchip Technology Inc. FIGURE 26-9: TIMER0 AND TIMER1 EXTERNAL CLOCK TIMINGS TABLE 26-11: TIMER0 AND TIMER1 EXTERNAL CLOCK REQUIREMENTS Note: Refer to Figure 26-4 for load conditions. 46 47 45 48 41 42 40 T0CKI T1OSO/T13CKI TMR0 or TMR1 Param No. Symbol Characteristic Min Max Units Conditions 40 Tt0H T0CKI High Pulse Width No prescaler 0.5 TCY + 20 — ns With prescaler 10 — ns 41 Tt0L T0CKI Low Pulse Width No prescaler 0.5 TCY + 20 — ns With prescaler 10 — ns 42 Tt0P T0CKI Period No prescaler TCY + 10 — ns With prescaler Greater of: 20 ns or (TCY + 40)/N — ns N = prescale value (1, 2, 4,..., 256) 45 Tt1H T13CKI High Time Synchronous, no prescaler 0.5 TCY + 20 — ns Synchronous, with prescaler PIC18FXXXX 10 — ns PIC18LFXXXX 25 — ns VDD = 2.0V Asynchronous PIC18FXXXX 30 — ns PIC18LFXXXX 50 — ns VDD = 2.0V 46 Tt1L T13CKI Low Time Synchronous, no prescaler 0.5 TCY + 5 — ns Synchronous, with prescaler PIC18FXXXX 10 — ns PIC18LFXXXX 25 — ns VDD = 2.0V Asynchronous PIC18FXXXX 30 — ns PIC18LFXXXX 50 — ns VDD = 2.0V 47 Tt1P T13CKI Input Period Synchronous Greater of: 20 ns or (TCY + 40)/N — ns N = prescale value (1, 2, 4, 8) Asynchronous 60 — ns Ft1 T13CKI Oscillator Input Frequency Range DC 50 kHz 48 Tcke2tmrI Delay from External T13CKI Clock Edge to Timer Increment 2 TOSC 7 TOSC — © 2007 Microchip Technology Inc. Preliminary DS39631B-page 347 PIC18F2420/2520/4420/4520 FIGURE 26-10: CAPTURE/COMPARE/PWM TIMINGS (ALL CCP MODULES) TABLE 26-12: CAPTURE/COMPARE/PWM REQUIREMENTS (ALL CCP MODULES) Note: Refer to Figure 26-4 for load conditions. CCPx (Capture Mode) 50 51 52 CCPx 53 54 (Compare or PWM Mode) Param No. Symbol Characteristic Min Max Units Conditions 50 TccL CCPx Input Low Time No prescaler 0.5 TCY + 20 — ns With prescaler PIC18FXXXX 10 — ns PIC18LFXXXX 20 — ns VDD = 2.0V 51 TccH CCPx Input High Time No prescaler 0.5 TCY + 20 — ns With prescaler PIC18FXXXX 10 — ns PIC18LFXXXX 20 — ns VDD = 2.0V 52 TccP CCPx Input Period 3 TCY + 40 N — ns N = prescale value (1, 4 or 16) 53 TccR CCPx Output Fall Time PIC18FXXXX — 25 ns PIC18LFXXXX — 45 ns VDD = 2.0V 54 TccF CCPx Output Fall Time PIC18FXXXX — 25 ns PIC18LFXXXX — 45 ns VDD = 2.0V PIC18F2420/2520/4420/4520 DS39631B-page 348 Preliminary © 2007 Microchip Technology Inc. FIGURE 26-11: PARALLEL SLAVE PORT TIMING (PIC18F4420/4520) TABLE 26-13: PARALLEL SLAVE PORT REQUIREMENTS (PIC18F4420/4520) Note: Refer to Figure 26-4 for load conditions. RE2/CS RE0/RD RE1/WR RD7:RD0 62 63 64 65 Param. No. Symbol Characteristic Min Max Units Conditions 62 TdtV2wrH Data In Valid before WR ↑ or CS ↑ (setup time) 20 — ns 63 TwrH2dtI WR ↑ or CS ↑ to Data–In Invalid (hold time) PIC18FXXXX 20 — ns PIC18LFXXXX 35 — ns VDD = 2.0V 64 TrdL2dtV RD ↓ and CS ↓ to Data–Out Valid — 80 ns 65 TrdH2dtI RD ↑ or CS ↓ to Data–Out Invalid 10 30 ns 66 TibfINH Inhibit of the IBF Flag bit being Cleared from WR ↑ or CS ↑ — 3 TCY © 2007 Microchip Technology Inc. Preliminary DS39631B-page 349 PIC18F2420/2520/4420/4520 FIGURE 26-12: EXAMPLE SPI MASTER MODE TIMING (CKE = 0) TABLE 26-14: EXAMPLE SPI MODE REQUIREMENTS (MASTER MODE, CKE = 0) SS SCK (CKP = 0) SCK (CKP = 1) SDO SDI 70 71 72 73 74 75, 76 79 78 80 78 79 MSb bit 6 - - - - - -1 LSb MSb In bit 6 - - - -1 LSb In Note: Refer to Figure 26-4 for load conditions. Param No. Symbol Characteristic Min Max Units Conditions 70 TssL2scH, TssL2scL SS ↓ to SCK ↓ or SCK ↑ Input TCY — ns 71 TscH SCK Input High Time (Slave mode) Continuous 1.25 TCY + 30 — ns 71A Single Byte 40 — ns (Note 1) 72 TscL SCK Input Low Time (Slave mode) Continuous 1.25 TCY + 30 — ns 72A Single Byte 40 — ns (Note 1) 73 TdiV2scH, TdiV2scL Setup Time of SDI Data Input to SCK Edge 100 — ns 73A Tb2b Last Clock Edge of Byte 1 to the 1st Clock Edge of Byte 2 1.5 TCY + 40 — ns (Note 2) 74 TscH2diL, TscL2diL Hold Time of SDI Data Input to SCK Edge 100 — ns 75 TdoR SDO Data Output Rise Time PIC18FXXXX — 25 ns PIC18LFXXXX — 45 ns VDD = 2.0V 76 TdoF SDO Data Output Fall Time — 25 ns 78 TscR SCK Output Rise Time (Master mode) PIC18FXXXX — 25 ns PIC18LFXXXX — 45 ns VDD = 2.0V 79 TscF SCK Output Fall Time (Master mode) — 25 ns 80 TscH2doV, TscL2doV SDO Data Output Valid after SCK Edge PIC18FXXXX — 50 ns PIC18LFXXXX — 100 ns VDD = 2.0V Note 1: Requires the use of Parameter #73A. 2: Only if Parameter #71A and #72A are used. PIC18F2420/2520/4420/4520 DS39631B-page 350 Preliminary © 2007 Microchip Technology Inc. FIGURE 26-13: EXAMPLE SPI MASTER MODE TIMING (CKE = 1) TABLE 26-15: EXAMPLE SPI MODE REQUIREMENTS (MASTER MODE, CKE = 1) SS SCK (CKP = 0) SCK (CKP = 1) SDO SDI 81 71 72 74 75, 76 78 80 MSb 79 73 MSb In bit 6 - - - - - -1 bit 6 - - - -1 LSb In LSb Note: Refer to Figure 26-4 for load conditions. Param. No. Symbol Characteristic Min Max Units Conditions 71 TscH SCK Input High Time (Slave mode) Continuous 1.25 TCY + 30 — ns 71A Single Byte 40 — ns (Note 1) 72 TscL SCK Input Low Time (Slave mode) Continuous 1.25 TCY + 30 — ns 72A Single Byte 40 — ns (Note 1) 73 TdiV2scH, TdiV2scL Setup Time of SDI Data Input to SCK Edge 100 — ns 73A Tb2b Last Clock Edge of Byte 1 to the 1st Clock Edge of Byte 2 1.5 TCY + 40 — ns (Note 2) 74 TscH2diL, TscL2diL Hold Time of SDI Data Input to SCK Edge 100 — ns 75 TdoR SDO Data Output Rise Time PIC18FXXXX — 25 ns PIC18LFXXXX 45 ns VDD = 2.0V 76 TdoF SDO Data Output Fall Time — 25 ns 78 TscR SCK Output Rise Time (Master mode) PIC18FXXXX — 25 ns PIC18LFXXXX 45 ns VDD = 2.0V 79 TscF SCK Output Fall Time (Master mode) — 25 ns 80 TscH2doV, TscL2doV SDO Data Output Valid after SCK Edge PIC18FXXXX — 50 ns PIC18LFXXXX 100 ns VDD = 2.0V 81 TdoV2scH, TdoV2scL SDO Data Output Setup to SCK Edge TCY — ns Note 1: Requires the use of Parameter #73A. 2: Only if Parameter #71A and #72A are used. © 2007 Microchip Technology Inc. Preliminary DS39631B-page 351 PIC18F2420/2520/4420/4520 FIGURE 26-14: EXAMPLE SPI SLAVE MODE TIMING (CKE = 0) TABLE 26-16: EXAMPLE SPI MODE REQUIREMENTS (SLAVE MODE TIMING, CKE = 0) Param No. Symbol Characteristic Min Max Units Conditions 70 TssL2scH, TssL2scL SS ↓ to SCK ↓ or SCK ↑ Input TCY — ns 71 TscH SCK Input High Time (Slave mode) Continuous 1.25 TCY + 30 — ns 71A Single Byte 40 — ns (Note 1) 72 TscL SCK Input Low Time (Slave mode) Continuous 1.25 TCY + 30 — ns 72A Single Byte 40 — ns (Note 1) 73 TdiV2scH, TdiV2scL Setup Time of SDI Data Input to SCK Edge 100 — ns 73A Tb2b Last Clock Edge of Byte 1 to the First Clock Edge of Byte 2 1.5 TCY + 40 — ns (Note 2) 74 TscH2diL, TscL2diL Hold Time of SDI Data Input to SCK Edge 100 — ns 75 TdoR SDO Data Output Rise Time PIC18FXXXX — 25 ns PIC18LFXXXX 45 ns VDD = 2.0V 76 TdoF SDO Data Output Fall Time — 25 ns 77 TssH2doZ SS↑ to SDO Output High-Impedance 10 50 ns 78 TscR SCK Output Rise Time (Master mode) PIC18FXXXX — 25 ns PIC18LFXXXX 45 ns VDD = 2.0V 79 TscF SCK Output Fall Time (Master mode) — 25 ns 80 TscH2doV, TscL2doV SDO Data Output Valid after SCK Edge PIC18FXXXX — 50 ns PIC18LFXXXX 100 ns VDD = 2.0V 83 TscH2ssH, TscL2ssH SS ↑ after SCK edge 1.5 TCY + 40 — ns Note 1: Requires the use of Parameter #73A. 2: Only if Parameter #71A and #72A are used. SS SCK (CKP = 0) SCK (CKP = 1) SDO 70 71 72 73 74 75, 76 77 79 78 80 78 79 SDI MSb bit 6 - - - - - -1 LSb MSb In bit 6 - - - -1 LSb In 83 Note: Refer to Figure 26-4 for load conditions. PIC18F2420/2520/4420/4520 DS39631B-page 352 Preliminary © 2007 Microchip Technology Inc. FIGURE 26-15: EXAMPLE SPI SLAVE MODE TIMING (CKE = 1) TABLE 26-17: EXAMPLE SPI SLAVE MODE REQUIREMENTS (CKE = 1) Param No. Symbol Characteristic Min Max Units Conditions 70 TssL2scH, TssL2scL SS ↓ to SCK ↓ or SCK ↑ Input TCY — ns 71 TscH SCK Input High Time (Slave mode) Continuous 1.25 TCY + 30 — ns 71A Single Byte 40 — ns (Note 1) 72 TscL SCK Input Low Time (Slave mode) Continuous 1.25 TCY + 30 — ns 72A Single Byte 40 — ns (Note 1) 73A Tb2b Last Clock Edge of Byte 1 to the First Clock Edge of Byte 2 1.5 TCY + 40 — ns (Note 2) 74 TscH2diL, TscL2diL Hold Time of SDI Data Input to SCK Edge 100 — ns 75 TdoR SDO Data Output Rise Time PIC18FXXXX — 25 ns PIC18LFXXXX 45 ns VDD = 2.0V 76 TdoF SDO Data Output Fall Time — 25 ns 77 TssH2doZ SS↑ to SDO Output High-Impedance 10 50 ns 78 TscR SCK Output Rise Time (Master mode) PIC18FXXXX — 25 ns PIC18LFXXXX — 45 ns VDD = 2.0V 79 TscF SCK Output Fall Time (Master mode) — 25 ns 80 TscH2doV, TscL2doV SDO Data Output Valid after SCK Edge PIC18FXXXX — 50 ns PIC18LFXXXX — 100 ns VDD = 2.0V 82 TssL2doV SDO Data Output Valid after SS ↓ Edge PIC18FXXXX — 50 ns PIC18LFXXXX — 100 ns VDD = 2.0V 83 TscH2ssH, TscL2ssH SS ↑ after SCK Edge 1.5 TCY + 40 — ns Note 1: Requires the use of Parameter #73A. 2: Only if Parameter #71A and #72A are used. SS SCK (CKP = 0) SCK (CKP = 1) SDO 70 71 72 82 SDI 74 75, 76 MSb bit 6 - - - - - -1 LSb 77 MSb In bit 6 - - - -1 LSb In 80 83 Note: Refer to Figure 26-4 for load conditions. © 2007 Microchip Technology Inc. Preliminary DS39631B-page 353 PIC18F2420/2520/4420/4520 FIGURE 26-16: I2C BUS START/STOP BITS TIMING TABLE 26-18: I2C BUS START/STOP BITS REQUIREMENTS (SLAVE MODE) FIGURE 26-17: I2C BUS DATA TIMING Note: Refer to Figure 26-4 for load conditions. 91 92 93 SCL SDA Start Condition Stop Condition 90 Param. No. Symbol Characteristic Min Max Units Conditions 90 TSU:STA Start Condition 100 kHz mode 4700 — ns Only relevant for Repeated Setup Time 400 kHz mode 600 — Start condition 91 THD:STA Start Condition 100 kHz mode 4000 — ns After this period, the first Hold Time 400 kHz mode 600 — clock pulse is generated 92 TSU:STO Stop Condition 100 kHz mode 4700 — ns Setup Time 400 kHz mode 600 — 93 THD:STO Stop Condition 100 kHz mode 4000 — ns Hold Time 400 kHz mode 600 — Note: Refer to Figure 26-4 for load conditions. 90 91 92 100 101 103 106 107 109 109 110 102 SCL SDA In SDA Out PIC18F2420/2520/4420/4520 DS39631B-page 354 Preliminary © 2007 Microchip Technology Inc. TABLE 26-19: I2C BUS DATA REQUIREMENTS (SLAVE MODE) Param. No. Symbol Characteristic Min Max Units Conditions 100 THIGH Clock High Time 100 kHz mode 4.0 — μs PIC18FXXXX must operate at a minimum of 1.5 MHz 400 kHz mode 0.6 — μs PIC18FXXXX must operate at a minimum of 10 MHz SSP Module 1.5 TCY — 101 TLOW Clock Low Time 100 kHz mode 4.7 — μs PIC18FXXXX must operate at a minimum of 1.5 MHz 400 kHz mode 1.3 — μs PIC18FXXXX must operate at a minimum of 10 MHz SSP Module 1.5 TCY — 102 TR SDA and SCL Rise Time 100 kHz mode — 1000 ns 400 kHz mode 20 + 0.1 CB 300 ns CB is specified to be from 10 to 400 pF 103 TF SDA and SCL Fall Time 100 kHz mode — 300 ns 400 kHz mode 20 + 0.1 CB 300 ns CB is specified to be from 10 to 400 pF 90 TSU:STA Start Condition Setup Time 100 kHz mode 4.7 — μs Only relevant for Repeated 400 kHz mode 0.6 — μs Start condition 91 THD:STA Start Condition Hold Time 100 kHz mode 4.0 — μs After this period, the first 400 kHz mode 0.6 — μs clock pulse is generated 106 THD:DAT Data Input Hold Time 100 kHz mode 0 — ns 400 kHz mode 0 0.9 μs 107 TSU:DAT Data Input Setup Time 100 kHz mode 250 — ns (Note 2) 400 kHz mode 100 — ns 92 TSU:STO Stop Condition Setup Time 100 kHz mode 4.7 — μs 400 kHz mode 0.6 — μs 109 TAA Output Valid from Clock 100 kHz mode — 3500 ns (Note 1) 400 kHz mode — — ns 110 TBUF Bus Free Time 100 kHz mode 4.7 — μs Time the bus must be free before a new transmission can start 400 kHz mode 1.3 — μs D102 CB Bus Capacitive Loading — 400 pF Note 1: As a transmitter, the device must provide this internal minimum delay time to bridge the undefined region (min. 300 ns) of the falling edge of SCL to avoid unintended generation of Start or Stop conditions. 2: A fast mode I2C bus device can be used in a standard mode I2C bus system but the requirement, TSU:DAT ≥ 250 ns, must then be met. This will automatically be the case if the device does not stretch the LOW period of the SCL signal. If such a device does stretch the LOW period of the SCL signal, it must output the next data bit to the SDA line, TR max. + TSU:DAT = 1000 + 250 = 1250 ns (according to the standard mode I2C bus specification), before the SCL line is released. © 2007 Microchip Technology Inc. Preliminary DS39631B-page 355 PIC18F2420/2520/4420/4520 FIGURE 26-18: MASTER SSP I2C BUS START/STOP BITS TIMING WAVEFORMS TABLE 26-20: MASTER SSP I2C BUS START/STOP BITS REQUIREMENTS FIGURE 26-19: MASTER SSP I2C BUS DATA TIMING Note: Refer to Figure 26-4 for load conditions. 91 93 SCL SDA Start Condition Stop Condition 90 92 Param. No. Symbol Characteristic Min Max Units Conditions 90 TSU:STA Start Condition 100 kHz mode 2(TOSC)(BRG + 1) — ns Only relevant for Repeated Start condition Setup Time 400 kHz mode 2(TOSC)(BRG + 1) — 1 MHz mode(1) 2(TOSC)(BRG + 1) — 91 THD:STA Start Condition 100 kHz mode 2(TOSC)(BRG + 1) — ns After this period, the first clock pulse is generated Hold Time 400 kHz mode 2(TOSC)(BRG + 1) — 1 MHz mode(1) 2(TOSC)(BRG + 1) — 92 TSU:STO Stop Condition 100 kHz mode 2(TOSC)(BRG + 1) — ns Setup Time 400 kHz mode 2(TOSC)(BRG + 1) — 1 MHz mode(1) 2(TOSC)(BRG + 1) — 93 THD:STO Stop Condition 100 kHz mode 2(TOSC)(BRG + 1) — ns Hold Time 400 kHz mode 2(TOSC)(BRG + 1) — 1 MHz mode(1) 2(TOSC)(BRG + 1) — Note 1: Maximum pin capacitance = 10 pF for all I2C pins. Note: Refer to Figure 26-4 for load conditions. 90 91 92 100 101 103 106 107 109 109 110 102 SCL SDA In SDA Out PIC18F2420/2520/4420/4520 DS39631B-page 356 Preliminary © 2007 Microchip Technology Inc. TABLE 26-21: MASTER SSP I2C BUS DATA REQUIREMENTS Param. No. Symbol Characteristic Min Max Units Conditions 100 THIGH Clock High Time 100 kHz mode 2(TOSC)(BRG + 1) — ms 400 kHz mode 2(TOSC)(BRG + 1) — ms 1 MHz mode(1) 2(TOSC)(BRG + 1) — ms 101 TLOW Clock Low Time 100 kHz mode 2(TOSC)(BRG + 1) — ms 400 kHz mode 2(TOSC)(BRG + 1) — ms 1 MHz mode(1) 2(TOSC)(BRG + 1) — ms 102 TR SDA and SCL Rise Time 100 kHz mode — 1000 ns CB is specified to be from 400 kHz mode 20 + 0.1 CB 300 ns 10 to 400 pF 1 MHz mode(1) — 300 ns 103 TF SDA and SCL Fall Time 100 kHz mode — 300 ns CB is specified to be from 400 kHz mode 20 + 0.1 CB 300 ns 10 to 400 pF 1 MHz mode(1) — 100 ns 90 TSU:STA Start Condition Setup Time 100 kHz mode 2(TOSC)(BRG + 1) — ms Only relevant for Repeated Start condition 400 kHz mode 2(TOSC)(BRG + 1) — ms 1 MHz mode(1) 2(TOSC)(BRG + 1) — ms 91 THD:STA Start Condition Hold Time 100 kHz mode 2(TOSC)(BRG + 1) — ms After this period, the first 400 kHz mode 2(TOSC)(BRG + 1) — ms clock pulse is generated 1 MHz mode(1) 2(TOSC)(BRG + 1) — ms 106 THD:DAT Data Input Hold Time 100 kHz mode 0 — ns 400 kHz mode 0 0.9 ms 107 TSU:DAT Data Input Setup Time 100 kHz mode 250 — ns (Note 2) 400 kHz mode 100 — ns 92 TSU:STO Stop Condition Setup Time 100 kHz mode 2(TOSC)(BRG + 1) — ms 400 kHz mode 2(TOSC)(BRG + 1) — ms 1 MHz mode(1) 2(TOSC)(BRG + 1) — ms 109 TAA Output Valid from Clock 100 kHz mode — 3500 ns 400 kHz mode — 1000 ns 1 MHz mode(1) — — ns 110 TBUF Bus Free Time 100 kHz mode 4.7 — ms Time the bus must be free before a new transmission can start 400 kHz mode 1.3 — ms D102 CB Bus Capacitive Loading — 400 pF Note 1: Maximum pin capacitance = 10 pF for all I2C pins. 2: A fast mode I2C bus device can be used in a standard mode I2C bus system, but parameter 107 ≥ 250 ns must then be met. This will automatically be the case if the device does not stretch the LOW period of the SCL signal. If such a device does stretch the LOW period of the SCL signal, it must output the next data bit to the SDA line, parameter 102 + parameter 107 = 1000 + 250 = 1250 ns (for 100 kHz mode), before the SCL line is released. © 2007 Microchip Technology Inc. Preliminary DS39631B-page 357 PIC18F2420/2520/4420/4520 FIGURE 26-20: USART SYNCHRONOUS TRANSMISSION (MASTER/SLAVE) TIMING TABLE 26-22: USART SYNCHRONOUS TRANSMISSION REQUIREMENTS FIGURE 26-21: USART SYNCHRONOUS RECEIVE (MASTER/SLAVE) TIMING TABLE 26-23: USART SYNCHRONOUS RECEIVE REQUIREMENTS 121 121 120 122 RC6/TX/CK RC7/RX/DT pin pin Note: Refer to Figure 26-4 for load conditions. Param No. Symbol Characteristic Min Max Units Conditions 120 TckH2dtV SYNC XMIT (MASTER & SLAVE) Clock High to Data Out Valid PIC18FXXXX — 40 ns PIC18LFXXXX — 100 ns VDD = 2.0V 121 Tckrf Clock Out Rise Time and Fall Time (Master mode) PIC18FXXXX — 20 ns PIC18LFXXXX — 50 ns VDD = 2.0V 122 Tdtrf Data Out Rise Time and Fall Time PIC18FXXXX — 20 ns PIC18LFXXXX — 50 ns VDD = 2.0V 125 126 RC6/TX/CK RC7/RX/DT pin pin Note: Refer to Figure 26-4 for load conditions. Param. No. Symbol Characteristic Min Max Units Conditions 125 TdtV2ckl SYNC RCV (MASTER & SLAVE) Data Hold before CK ↓ (DT hold time) 10 — ns 126 TckL2dtl Data Hold after CK ↓ (DT hold time) 15 — ns PIC18F2420/2520/4420/4520 DS39631B-page 358 Preliminary © 2007 Microchip Technology Inc. TABLE 26-24: A/D CONVERTER CHARACTERISTICS: PIC18FX42X/X52X (INDUSTRIAL) PIC18LF2X1X/4X1X (INDUSTRIAL) Param No. Symbol Characteristic Min Typ Max Units Conditions A01 NR Resolution — — 10 bit ΔVREF ≥ 3.0V A03 EIL Integral Linearity Error — — <±1 LSb ΔVREF ≥ 3.0V A04 EDL Differential Linearity Error — — <±1 LSb ΔVREF ≥ 3.0V A06 EOFF Offset Error — — <±1 LSb ΔVREF ≥ 3.0V A07 EGN Gain Error — — <±1 LSb ΔVREF ≥ 3.0V A10 — Monotonicity Guaranteed(1) — VSS ≤ VAIN ≤ VREF A20 ΔVREF Reference Voltage Range (VREFH – VREFL) 1.8 3 — — — — V V VDD < 3.0V VDD ≥ 3.0V A21 VREFH Reference Voltage High VSS — VREFH V A22 VREFL Reference Voltage Low VSS – 0.3V — VDD – 3.0V V A25 VAIN Analog Input Voltage VREFL — VREFH V A30 ZAIN Recommended Impedance of Analog Voltage Source — — 2.5 kΩ A50 IREF VREF Input Current(2) — — — — 5 150 μA μA During VAIN acquisition. During A/D conversion cycle. Note 1: The A/D conversion result never decreases with an increase in the input voltage and has no missing codes. 2: VREFH current is from RA3/AN3/VREF+ pin or VDD, whichever is selected as the VREFH source. VREFL current is from RA2/AN2/VREF-/CVREF pin or VSS, whichever is selected as the VREFL source. © 2007 Microchip Technology Inc. Preliminary DS39631B-page 359 PIC18F2420/2520/4420/4520 FIGURE 26-22: A/D CONVERSION TIMING TABLE 26-25: A/D CONVERSION REQUIREMENTS 131 130 132 BSF ADCON0, GO Q4 A/D CLK A/D DATA ADRES ADIF GO SAMPLE OLD_DATA SAMPLING STOPPED DONE NEW_DATA (Note 2) 9 8 7 2 1 0 Note 1: If the A/D clock source is selected as RC, a time of TCY is added before the A/D clock starts. This allows the SLEEP instruction to be executed. 2: This is a minimal RC delay (typically 100 ns), which also disconnects the holding capacitor from the analog input. . . . . . . TCY Param No. Symbol Characteristic Min Max Units Conditions 130 TAD A/D Clock Period PIC18FXXXX 0.7 25.0(1) μs TOSC based, VREF ≥ 3.0V PIC18LFXXXX 1.4 25.0(1) μs VDD = 2.0V; TOSC based, VREF full range PIC18FXXXX TBD 1 μs A/D RC mode PIC18LFXXXX TBD 3 μs VDD = 2.0V; A/D RC mode 131 TCNV Conversion Time (not including acquisition time) (Note 2) 11 12 TAD 132 TACQ Acquisition Time (Note 3) 1.4 TBD — — μs μs -40°C to +85°C 0°C ≤ to ≤ +85°C 135 TSWC Switching Time from Convert → Sample — (Note 4) TBD TDIS Discharge Time 0.2 — μs Legend: TBD = To Be Determined Note 1: The time of the A/D clock period is dependent on the device frequency and the TAD clock divider. 2: ADRES register may be read on the following TCY cycle. 3: The time for the holding capacitor to acquire the “New” input voltage when the voltage changes full scale after the conversion (VDD to VSS or VSS to VDD). The source impedance (RS) on the input channels is 50Ω. 4: On the following cycle of the device clock. PIC18F2420/2520/4420/4520 DS39631B-page 360 Preliminary © 2007 Microchip Technology Inc. NOTES: © 2007 Microchip Technology Inc. Preliminary DS39631B-page 361 PIC18F2420/2520/4420/4520 27.0 DC AND AC CHARACTERISTICS GRAPHS AND TABLES Graphs and tables are not available at this time. PIC18F2420/2520/4420/4520 DS39631B-page 362 Preliminary © 2007 Microchip Technology Inc. NOTES: © 2007 Microchip Technology Inc. Preliminary DS39631B-page 363 PIC18F2420/2520/4420/4520 28.0 PACKAGING INFORMATION 28.1 Package Marking Information 28-Lead PDIP XXXXXXXXXXXXXXXXX XXXXXXXXXXXXXXXXX YYWWNNN Example PIC18F2520-I/SP 0710017 28-Lead SOIC XXXXXXXXXXXXXXXXXXXX XXXXXXXXXXXXXXXXXXXX XXXXXXXXXXXXXXXXXXXX YYWWNNN Example PIC18F2520-E/SO 0710017 40-Lead PDIP XXXXXXXXXXXXXXXXXX XXXXXXXXXXXXXXXXXX XXXXXXXXXXXXXXXXXX YYWWNNN Example PIC18F4420-I/P 0710017 Legend: XX...X Customer-specific information Y Year code (last digit of calendar year) YY Year code (last 2 digits of calendar year) WW Week code (week of January 1 is week ‘01’) NNN Alphanumeric traceability code Pb-free JEDEC designator for Matte Tin (Sn) * This package is Pb-free. The Pb-free JEDEC designator ( ) can be found on the outer packaging for this package. Note: In the event the full Microchip part number cannot be marked on one line, it will be carried over to the next line, thus limiting the number of available characters for customer-specific information. e3 e3 e3 e3 e3 PIC18F2420/2520/4420/4520 DS39631B-page 364 Preliminary © 2007 Microchip Technology Inc. Package Marking Information (Continued) 44-Lead TQFP XXXXXXXXXX XXXXXXXXXX XXXXXXXXXX YYWWNNN Example PIC18F4420 -I/PT 0710017 XXXXXXXXXX 44-Lead QFN XXXXXXXXXX XXXXXXXXXX YYWWNNN PIC18F4520 Example -I/ML 0710017 28-Lead QFN XXXXXXXX XXXXXXXX YYWWNNN Example 18F2420 -I/ML 0710017 e3 e3 e3 © 2007 Microchip Technology Inc. Preliminary DS39631B-page 365 PIC18F2420/2520/4420/4520 28.2 Package Details The following sections give the technical details of the packages. 28-Lead Skinny Plastic Dual In-Line (SP) – 300 mil Body [SPDIP] Notes: 1. Pin 1 visual index feature may vary, but must be located within the hatched area. 2. § Significant Characteristic. 3. Dimensions D and E1 do not include mold flash or protrusions. Mold flash or protrusions shall not exceed .010" per side. 4. Dimensioning and tolerancing per ASME Y14.5M. BSC: Basic Dimension. Theoretically exact value shown without tolerances. Note: For the most current package drawings, please see the Microchip Packaging Specification located at http://www.microchip.com/packaging Units INCHES Dimension Limits MIN NOM MAX Number of Pins N 28 Pitch e .100 BSC Top to Seating Plane A – – .200 Molded Package Thickness A2 .120 .135 .150 Base to Seating Plane A1 .015 – – Shoulder to Shoulder Width E .290 .310 .335 Molded Package Width E1 .240 .285 .295 Overall Length D 1.345 1.365 1.400 Tip to Seating Plane L .110 .130 .150 Lead Thickness c .008 .010 .015 Upper Lead Width b1 .040 .050 .070 Lower Lead Width b .014 .018 .022 Overall Row Spacing § eB – – .430 NOTE 1 N 1 2 D E1 eB c E L A2 b e A1 b1 A 3 Microchip Technology Drawing C04-070B PIC18F2420/2520/4420/4520 DS39631B-page 366 Preliminary © 2007 Microchip Technology Inc. 28-Lead Plastic Small Outline (SO) – Wide, 7.50 mm Body [SOIC] Notes: 1. Pin 1 visual index feature may vary, but must be located within the hatched area. 2. § Significant Characteristic. 3. Dimensions D and E1 do not include mold flash or protrusions. Mold flash or protrusions shall not exceed 0.15 mm per side. 4. Dimensioning and tolerancing per ASME Y14.5M. BSC: Basic Dimension. Theoretically exact value shown without tolerances. REF: Reference Dimension, usually without tolerance, for information purposes only. Note: For the most current package drawings, please see the Microchip Packaging Specification located at http://www.microchip.com/packaging Units MILLMETERS Dimension Limits MIN NOM MAX Number of Pins N 28 Pitch e 1.27 BSC Overall Height A – – 2.65 Molded Package Thickness A2 2.05 – – Standoff § A1 0.10 – 0.30 Overall Width E 10.30 BSC Molded Package Width E1 7.50 BSC Overall Length D 17.90 BSC Chamfer (optional) h 0.25 – 0.75 Foot Length L 0.40 – 1.27 Footprint L1 1.40 REF Foot Angle Top φ 0° – 8° Lead Thickness c 0.18 – 0.33 Lead Width b 0.31 – 0.51 Mold Draft Angle Top α 5° – 15° Mold Draft Angle Bottom β 5° – 15° c h h L L1 A2 A1 A NOTE 1 1 2 3 b e E E1 D φ β α N Microchip Technology Drawing C04-052B © 2007 Microchip Technology Inc. Preliminary DS39631B-page 367 PIC18F2420/2520/4420/4520 40-Lead Plastic Dual In-Line (P) – 600 mil Body [PDIP] Notes: 1. Pin 1 visual index feature may vary, but must be located within the hatched area. 2. § Significant Characteristic. 3. Dimensions D and E1 do not include mold flash or protrusions. Mold flash or protrusions shall not exceed .010" per side. 4. Dimensioning and tolerancing per ASME Y14.5M. BSC: Basic Dimension. Theoretically exact value shown without tolerances. Note: For the most current package drawings, please see the Microchip Packaging Specification located at http://www.microchip.com/packaging Units INCHES Dimension Limits MIN NOM MAX Number of Pins N 40 Pitch e .100 BSC Top to Seating Plane A – – .250 Molded Package Thickness A2 .125 – .195 Base to Seating Plane A1 .015 – – Shoulder to Shoulder Width E .590 – .625 Molded Package Width E1 .485 – .580 Overall Length D 1.980 – 2.095 Tip to Seating Plane L .115 – .200 Lead Thickness c .008 – .015 Upper Lead Width b1 .030 – .070 Lower Lead Width b .014 – .023 Overall Row Spacing § eB – – .700 N NOTE 1 E1 D 1 2 3 A A1 b1 b e c eB E L A2 Microchip Technology Drawing C04-016B PIC18F2420/2520/4420/4520 DS39631B-page 368 Preliminary © 2007 Microchip Technology Inc. 28-Lead Plastic Quad Flat, No Lead Package (ML) – 6x6 mm Body [QFN] with 0.55 mm Contact Length Notes: 1. Pin 1 visual index feature may vary, but must be located within the hatched area. 2. Package is saw singulated. 3. Dimensioning and tolerancing per ASME Y14.5M. BSC: Basic Dimension. Theoretically exact value shown without tolerances. REF: Reference Dimension, usually without tolerance, for information purposes only. Note: For the most current package drawings, please see the Microchip Packaging Specification located at http://www.microchip.com/packaging Units MILLIMETERS Dimension Limits MIN NOM MAX Number of Pins N 28 Pitch e 0.65 BSC Overall Height A 0.80 0.90 1.00 Standoff A1 0.00 0.02 0.05 Contact Thickness A3 0.20 REF Overall Width E 6.00 BSC Exposed Pad Width E2 3.65 3.70 4.20 Overall Length D 6.00 BSC Exposed Pad Length D2 3.65 3.70 4.20 Contact Width b 0.23 0.30 0.35 Contact Length L 0.50 0.55 0.70 Contact-to-Exposed Pad K 0.20 – – D EXPOSED D2 e b K E2 E L N NOTE 1 1 2 2 1 N A A3 A1 TOP VIEW BOTTOM VIEW PAD Microchip Technology Drawing C04-105B © 2007 Microchip Technology Inc. Preliminary DS39631B-page 369 PIC18F2420/2520/4420/4520 44-Lead Plastic Quad Flat, No Lead Package (ML) – 8x8 mm Body [QFN] Notes: 1. Pin 1 visual index feature may vary, but must be located within the hatched area. 2. Package is saw singulated. 3. Dimensioning and tolerancing per ASME Y14.5M. BSC: Basic Dimension. Theoretically exact value shown without tolerances. REF: Reference Dimension, usually without tolerance, for information purposes only. Note: For the most current package drawings, please see the Microchip Packaging Specification located at http://www.microchip.com/packaging Units MILLIMETERS Dimension Limits MIN NOM MAX Number of Pins N 44 Pitch e 0.65 BSC Overall Height A 0.80 0.90 1.00 Standoff A1 0.00 0.02 0.05 Contact Thickness A3 0.20 REF Overall Width E 8.00 BSC Exposed Pad Width E2 6.30 6.45 6.80 Overall Length D 8.00 BSC Exposed Pad Length D2 6.30 6.45 6.80 Contact Width b 0.25 0.30 0.38 Contact Length L 0.30 0.40 0.50 Contact-to-Exposed Pad K 0.20 – – D EXPOSED PAD D2 e b K L E2 2 1 N NOTE 1 2 1 E N TOP VIEW BOTTOM VIEW A3 A1 A Microchip Technology Drawing C04-103B PIC18F2420/2520/4420/4520 DS39631B-page 370 Preliminary © 2007 Microchip Technology Inc. 44-Lead Plastic Thin Quad Flatpack (PT) – 10x10x1 mm Body, 2.00 mm Footprint [TQFP] Notes: 1. Pin 1 visual index feature may vary, but must be located within the hatched area. 2. Chamfers at corners are optional; size may vary. 3. Dimensions D1 and E1 do not include mold flash or protrusions. Mold flash or protrusions shall not exceed 0.25 mm per side. 4. Dimensioning and tolerancing per ASME Y14.5M. BSC: Basic Dimension. Theoretically exact value shown without tolerances. REF: Reference Dimension, usually without tolerance, for information purposes only. Note: For the most current package drawings, please see the Microchip Packaging Specification located at http://www.microchip.com/packaging Units MILLIMETERS Dimension Limits MIN NOM MAX Number of Leads N 44 Lead Pitch e 0.80 BSC Overall Height A – – 1.20 Molded Package Thickness A2 0.95 1.00 1.05 Standoff A1 0.05 – 0.15 Foot Length L 0.45 0.60 0.75 Footprint L1 1.00 REF Foot Angle φ 0° 3.5° 7° Overall Width E 12.00 BSC Overall Length D 12.00 BSC Molded Package Width E1 10.00 BSC Molded Package Length D1 10.00 BSC Lead Thickness c 0.09 – 0.20 Lead Width b 0.30 0.37 0.45 Mold Draft Angle Top α 11° 12° 13° Mold Draft Angle Bottom β 11° 12° 13° A E E1 D D1 e b NOTE 1 NOTE 2 N 1 2 3 c A1 L A2 L1 α φ β Microchip Technology Drawing C04-076B © 2007 Microchip Technology Inc. Preliminary DS39631B-page 371 PIC18F2420/2520/4420/4520 APPENDIX A: REVISION HISTORY Revision A (June 2004) Original data sheet for PIC18F2420/2520/4420/4520 devices. Revision B (January 2007) This revision includes updates to the packaging diagrams. APPENDIX B: DEVICE DIFFERENCES The differences between the devices listed in this data sheet are shown in Table B-1. TABLE B-1: DEVICE DIFFERENCES Features PIC18F2420 PIC18F2520 PIC18F4420 PIC18F4520 Program Memory (Bytes) 16384 32768 16384 32768 Program Memory (Instructions) 8192 16384 8192 16384 Interrupt Sources 19 19 20 20 I/O Ports Ports A, B, C, (E) Ports A, B, C, (E) Ports A, B, C, D, E Ports A, B, C, D, E Capture/Compare/PWM Modules 2 2 1 1 Enhanced Capture/Compare/PWM Modules 0 0 1 1 Parallel Communications (PSP) No No Yes Yes 10-bit Analog-to-Digital Module 10 input channels 10 input channels 13 input channels 13 input channels Packages 28-pin PDIP 28-pin SOIC 28-pin QFN 28-pin PDIP 28-pin SOIC 28-pin QFN 40-pin PDIP 44-pin TQFP 44-pin QFN 40-pin PDIP 44-pin TQFP 44-pin QFN PIC18F2420/2520/4420/4520 DS39631B-page 372 Preliminary © 2007 Microchip Technology Inc. APPENDIX C: CONVERSION CONSIDERATIONS This appendix discusses the considerations for converting from previous versions of a device to the ones listed in this data sheet. Typically, these changes are due to the differences in the process technology used. An example of this type of conversion is from a PIC16C74A to a PIC16C74B. Not Applicable APPENDIX D: MIGRATION FROM BASELINE TO ENHANCED DEVICES This section discusses how to migrate from a Baseline device (i.e., PIC16C5X) to an Enhanced MCU device (i.e., PIC18FXXX). The following are the list of modifications over the PIC16C5X microcontroller family: Not Currently Available © 2007 Microchip Technology Inc. Preliminary DS39631B-page 373 PIC18F2420/2520/4420/4520 APPENDIX E: MIGRATION FROM MID-RANGE TO ENHANCED DEVICES A detailed discussion of the differences between the mid-range MCU devices (i.e., PIC16CXXX) and the enhanced devices (i.e., PIC18FXXX) is provided in AN716, “Migrating Designs from PIC16C74A/74B to PIC18C442”. The changes discussed, while device specific, are generally applicable to all mid-range to enhanced device migrations. This Application Note is available as Literature Number DS00716. APPENDIX F: MIGRATION FROM HIGH-END TO ENHANCED DEVICES A detailed discussion of the migration pathway and differences between the high-end MCU devices (i.e., PIC17CXXX) and the enhanced devices (i.e., PIC18FXXX) is provided in AN726, “PIC17CXXX to PIC18CXXX Migration”. This Application Note is available as Literature Number DS00726. PIC18F2420/2520/4420/4520 DS39631B-page 374 Preliminary © 2007 Microchip Technology Inc. NOTES: © 2007 Microchip Technology Inc. Preliminary DS39631B-page 375 PIC18F2420/2520/4420/4520 INDEX A A/D ................................................................................... 223 A/D Converter Interrupt, Configuring ....................... 227 Acquisition Requirements ........................................ 228 ADCON0 Register .................................................... 223 ADCON1 Register .................................................... 223 ADCON2 Register .................................................... 223 ADRESH Register ............................................ 223, 226 ADRESL Register .................................................... 223 Analog Port Pins, Configuring .................................. 230 Associated Registers ............................................... 232 Calculating the Minimum Required Acquisition Time .............................................. 228 Configuring the Module ............................................ 227 Conversion Clock (TAD) ........................................... 229 Conversion Status (GO/DONE Bit) .......................... 226 Conversions ............................................................. 231 Converter Characteristics ........................................ 358 Discharge ................................................................. 231 Operation in Power Managed Modes ...................... 230 Selecting and Configuring Acquisition Time ............ 229 Special Event Trigger (CCP) .................................... 232 Special Event Trigger (ECCP) ................................. 148 Use of the CCP2 Trigger .......................................... 232 Absolute Maximum Ratings ............................................. 323 AC (Timing) Characteristics ............................................. 340 Load Conditions for Device Timing Specifications ....................................... 341 Parameter Symbology ............................................. 340 Temperature and Voltage Specifications ................. 341 Timing Conditions .................................................... 341 AC Characteristics Internal RC Accuracy ............................................... 343 Access Bank Mapping with Indexed Literal Offset Mode ................. 72 ACKSTAT ........................................................................ 191 ACKSTAT Status Flag ..................................................... 191 ADCON0 Register ............................................................ 223 GO/DONE Bit ........................................................... 226 ADCON1 Register ............................................................ 223 ADCON2 Register ............................................................ 223 ADDFSR .......................................................................... 310 ADDLW ............................................................................ 273 ADDULNK ........................................................................ 310 ADDWF ............................................................................ 273 ADDWFC ......................................................................... 274 ADRESH Register ............................................................ 223 ADRESL Register .................................................... 223, 226 Analog-to-Digital Converter. See A/D. ANDLW ............................................................................ 274 ANDWF ............................................................................ 275 Assembler MPASM Assembler .................................................. 317 Auto-Wake-up on Sync Break Character ......................... 214 B Bank Select Register (BSR) ............................................... 59 Baud Rate Generator ....................................................... 187 BC .................................................................................... 275 BCF .................................................................................. 276 BF .................................................................................... 191 BF Status Flag ................................................................. 191 Block Diagrams A/D ........................................................................... 226 Analog Input Model .................................................. 227 Baud Rate Generator .............................................. 187 Capture Mode Operation ......................................... 141 Comparator Analog Input Model .............................. 237 Comparator I/O Operating Modes ........................... 234 Comparator Output .................................................. 236 Comparator Voltage Reference ............................... 240 Compare Mode Operation ....................................... 142 Device Clock .............................................................. 28 Enhanced PWM ....................................................... 149 EUSART Receive .................................................... 213 EUSART Transmit ................................................... 211 External Power-on Reset Circuit (Slow VDD Power-up) ........................................ 43 Fail-Safe Clock Monitor (FSCM) .............................. 261 Generic I/O Port ....................................................... 105 High/Low-Voltage Detect with External Input .......... 244 Interrupt Logic ............................................................ 92 MSSP (I2C Master Mode) ........................................ 185 MSSP (I2C Mode) .................................................... 170 MSSP (SPI Mode) ................................................... 161 On-Chip Reset Circuit ................................................ 41 PIC18F2420/2520 ..................................................... 10 PIC18F4420/4520 ..................................................... 11 PLL (HS Mode) .......................................................... 25 PORTD and PORTE (Parallel Slave Port) ............... 120 PWM Operation (Simplified) .................................... 144 Reads from Flash Program Memory ......................... 77 Single Comparator ................................................... 235 Table Read Operation ............................................... 73 Table Write Operation ............................................... 74 Table Writes to Flash Program Memory .................... 79 Timer0 in 16-Bit Mode ............................................. 124 Timer0 in 8-Bit Mode ............................................... 124 Timer1 ..................................................................... 128 Timer1 (16-Bit Read/Write Mode) ............................ 128 Timer2 ..................................................................... 134 Timer3 ..................................................................... 136 Timer3 (16-Bit Read/Write Mode) ............................ 136 Voltage Reference Output Buffer Example ............. 241 Watchdog Timer ...................................................... 258 BN .................................................................................... 276 BNC ................................................................................. 277 BNN ................................................................................. 277 BNOV .............................................................................. 278 BNZ ................................................................................. 278 BOR. See Brown-out Reset. BOV ................................................................................. 281 BRA ................................................................................. 279 Break Character (12-Bit) Transmit and Receive .............. 216 BRG. See Baud Rate Generator. Brown-out Reset (BOR) ..................................................... 44 Detecting ................................................................... 44 Disabling in Sleep Mode ............................................ 44 Software Enabled ...................................................... 44 BSF .................................................................................. 279 BTFSC ............................................................................. 280 BTFSS ............................................................................. 280 BTG ................................................................................. 281 BZ .................................................................................... 282 PIC18F2420/2520/4420/4520 DS39631B-page 376 Preliminary © 2007 Microchip Technology Inc. C C Compilers MPLAB C17 ............................................................. 318 MPLAB C18 ............................................................. 318 MPLAB C30 ............................................................. 318 CALL ................................................................................ 282 CALLW ............................................................................. 311 Capture (CCP Module) ..................................................... 141 Associated Registers ...............................................143 CCP Pin Configuration ............................................. 141 CCPRxH:CCPRxL Registers ................................... 141 Prescaler .................................................................. 141 Software Interrupt .................................................... 141 Timer1/Timer3 Mode Selection ................................ 141 Capture (ECCP Module) .................................................. 148 Capture/Compare/PWM (CCP) ........................................ 139 Capture Mode. See Capture. CCP Mode and Timer Resources ............................140 CCPRxH Register .................................................... 140 CCPRxL Register ..................................................... 140 Compare Mode. See Compare. Interaction of Two CCP Modules ............................. 140 Module Configuration ...............................................140 Clock Sources .................................................................... 28 Selecting the 31 kHz Source ...................................... 29 Selection Using OSCCON Register ........................... 29 CLRF ................................................................................ 283 CLRWDT .......................................................................... 283 Code Examples 16 x 16 Signed Multiply Routine ................................90 16 x 16 Unsigned Multiply Routine ............................90 8 x 8 Signed Multiply Routine .................................... 89 8 x 8 Unsigned Multiply Routine ................................89 Changing Between Capture Prescalers ................... 141 Computed GOTO Using an Offset Value ................... 56 Data EEPROM Read .................................................85 Data EEPROM Refresh Routine ................................86 Data EEPROM Write .................................................85 Erasing a Flash Program Memory Row ..................... 78 Fast Register Stack .................................................... 56 How to Clear RAM (Bank 1) Using Indirect Addressing ............................................ 68 Implementing a Real-Time Clock Using a Timer1 Interrupt Service ............................... 131 Initializing PORTA .................................................... 105 Initializing PORTB .................................................... 108 Initializing PORTC .................................................... 111 Initializing PORTD .................................................... 114 Initializing PORTE .................................................... 117 Loading the SSPBUF (SSPSR) Register ................. 164 Reading a Flash Program Memory Word .................. 77 Saving Status, WREG and BSR Registers in RAM ..................................... 103 Writing to Flash Program Memory ....................... 80–81 Code Protection ............................................................... 249 COMF ............................................................................... 284 Comparator ......................................................................233 Analog Input Connection Considerations ................. 237 Associated Registers ...............................................237 Configuration ............................................................ 234 Effects of a Reset ..................................................... 236 Interrupts .................................................................. 236 Operation ................................................................. 235 Operation During Sleep ........................................... 236 Outputs ....................................................................235 Reference ................................................................ 235 External Signal ................................................ 235 Internal Signal .................................................. 235 Response Time ........................................................ 235 Comparator Specifications ............................................... 338 Comparator Voltage Reference ....................................... 239 Accuracy and Error .................................................. 240 Associated Registers ............................................... 241 Configuring .............................................................. 239 Connection Considerations ...................................... 240 Effects of a Reset .................................................... 240 Operation During Sleep ........................................... 240 Compare (CCP Module) .................................................. 142 Associated Registers ............................................... 143 CCPRx Register ...................................................... 142 Pin Configuration ..................................................... 142 Software Interrupt .................................................... 142 Special Event Trigger .............................. 137, 142, 232 Timer1/Timer3 Mode Selection ................................ 142 Compare (ECCP Module) ................................................ 148 Special Event Trigger .............................................. 148 Computed GOTO ............................................................... 56 Configuration Bits ............................................................ 249 Configuration Register Protection .................................... 266 Context Saving During Interrupts ..................................... 103 Conversion Considerations .............................................. 372 CPFSEQ .......................................................................... 284 CPFSGT .......................................................................... 285 CPFSLT ........................................................................... 285 Crystal Oscillator/Ceramic Resonator ................................ 23 D Data Addressing Modes .................................................... 68 Comparing Addressing Modes with the Extended Instruction Set Enabled ..................... 71 Direct ......................................................................... 68 Indexed Literal Offset ................................................ 70 Instructions Affected .......................................... 70 Indirect ....................................................................... 68 Inherent and Literal .................................................... 68 Data EEPROM Code Protection ....................................................... 266 Data EEPROM Memory ..................................................... 83 Associated Registers ................................................. 87 EEADR Register ........................................................ 83 EECON1 and EECON2 Registers ............................. 83 Operation During Code-Protect ................................. 86 Protection Against Spurious Write ............................. 86 Reading ..................................................................... 85 Using ......................................................................... 86 Write Verify ................................................................ 85 Writing ....................................................................... 85 Data Memory ..................................................................... 59 Access Bank .............................................................. 62 and the Extended Instruction Set .............................. 70 Bank Select Register (BSR) ...................................... 59 General Purpose Registers ....................................... 62 Map for PIC18F2420/4420 ........................................ 60 Map for PIC18F2520/4520 ........................................ 61 Special Function Registers ........................................ 63 DAW ................................................................................ 286 DC and AC Characteristics Graphs and Tables .................................................. 361 © 2007 Microchip Technology Inc. Preliminary DS39631B-page 377 PIC18F2420/2520/4420/4520 DC Characteristics ........................................................... 335 Power-Down and Supply Current ............................ 326 Supply Voltage ......................................................... 325 DCFSNZ .......................................................................... 287 DECF ............................................................................... 286 DECFSZ ........................................................................... 287 Demonstration Boards PICDEM 1 ................................................................ 320 PICDEM 17 .............................................................. 321 PICDEM 18R ........................................................... 321 PICDEM 2 Plus ........................................................ 320 PICDEM 3 ................................................................ 320 PICDEM 4 ................................................................ 320 PICDEM LIN ............................................................ 321 PICDEM USB ........................................................... 321 PICDEM.net Internet/Ethernet ................................. 320 Development Support ...................................................... 317 Device Differences ........................................................... 371 Device Overview .................................................................. 7 Details on Individual Family Members ......................... 8 Features (table) ............................................................ 9 New Core Features ...................................................... 7 Other Special Features ................................................ 8 Device Reset Timers .......................................................... 45 Oscillator Start-up Timer (OST) ................................. 45 PLL Lock Time-out ..................................................... 45 Power-up Timer (PWRT) ........................................... 45 Time-out Sequence .................................................... 45 Direct Addressing ............................................................... 69 E Effect on Standard PIC Instructions ................................. 314 Effects of Power Managed Modes on Various Clock Sources ............................................... 31 Electrical Characteristics .................................................. 323 Enhanced Capture/Compare/PWM (ECCP) .................... 147 Associated Registers ............................................... 160 Capture and Compare Modes .................................. 148 Capture Mode. See Capture (ECCP Module). Outputs and Configuration ....................................... 148 Pin Configurations for ECCP1 ................................. 148 PWM Mode. See PWM (ECCP Module). Standard PWM Mode ............................................... 148 Timer Resources ...................................................... 148 Enhanced PWM Mode. See PWM (ECCP Module). Enhanced Universal Synchronous Asynchronous Receiver Transmitter (EUSART). See EUSART. Equations A/D Acquisition Time ................................................ 228 A/D Minimum Charging Time ................................... 228 Errata ................................................................................... 6 EUSART Asynchronous Mode ................................................ 211 12-Bit Break Transmit and Receive ................. 216 Associated Registers, Receive ........................ 214 Associated Registers, Transmit ....................... 212 Auto-Wake-up on Sync Break ......................... 214 Receiver ........................................................... 213 Setting up 9-Bit Mode with Address Detect ........................................ 213 Transmitter ....................................................... 211 Baud Rate Generator Operation in Power Managed Mode ................ 205 Baud Rate Generator (BRG) ................................... 205 Associated Registers ....................................... 206 Auto-Baud Rate Detect .................................... 209 Baud Rate Error, Calculating ........................... 206 Baud Rates, Asynchronous Modes ................. 207 High Baud Rate Select (BRGH Bit) ................. 205 Sampling ......................................................... 205 Synchronous Master Mode ...................................... 217 Associated Registers, Receive ........................ 219 Associated Registers, Transmit ....................... 218 Reception ........................................................ 219 Transmission ................................................... 217 Synchronous Slave Mode ........................................ 220 Associated Registers, Receive ........................ 221 Associated Registers, Transmit ....................... 220 Reception ........................................................ 221 Transmission ................................................... 220 Evaluation and Programming Tools ................................. 321 Extended Instruction Set ADDFSR .................................................................. 310 ADDULNK ............................................................... 310 and Using MPLAB Tools ......................................... 316 CALLW .................................................................... 311 Considerations for Use ............................................ 314 MOVSF .................................................................... 311 MOVSS .................................................................... 312 PUSHL ..................................................................... 312 SUBFSR .................................................................. 313 SUBULNK ................................................................ 313 Syntax ...................................................................... 309 External Clock Input ........................................................... 24 F Fail-Safe Clock Monitor ........................................... 249, 261 Exiting Operation ..................................................... 261 Interrupts in Power Managed Modes ....................... 262 POR or Wake from Sleep ........................................ 262 WDT During Oscillator Failure ................................. 261 Fast Register Stack ........................................................... 56 Firmware Instructions ...................................................... 267 Flash Program Memory ..................................................... 73 Associated Registers ................................................. 81 Control Registers ....................................................... 74 EECON1 and EECON2 ..................................... 74 TABLAT (Table Latch) Register ........................ 76 TBLPTR (Table Pointer) Register ...................... 76 Erase Sequence ........................................................ 78 Erasing ...................................................................... 78 Operation During Code-Protect ................................. 81 Reading ..................................................................... 77 Table Pointer Boundaries Based on Operation ....................... 76 Table Pointer Boundaries .......................................... 76 Table Reads and Table Writes .................................. 73 Write Sequence ......................................................... 79 Writing To .................................................................. 79 Protection Against Spurious Writes ................... 81 Unexpected Termination ................................... 81 Write Verify ........................................................ 81 FSCM. See Fail-Safe Clock Monitor. G General Call Address Support ......................................... 184 GOTO .............................................................................. 288 PIC18F2420/2520/4420/4520 DS39631B-page 378 Preliminary © 2007 Microchip Technology Inc. H Hardware Multiplier ............................................................ 89 Introduction ................................................................ 89 Operation ................................................................... 89 Performance Comparison .......................................... 89 High/Low-Voltage Detect .................................................243 Applications .............................................................. 246 Associated Registers ...............................................247 Characteristics ......................................................... 339 Current Consumption ...............................................245 Effects of a Reset ..................................................... 247 Operation ................................................................. 244 During Sleep .................................................... 247 Setup ........................................................................245 Start-up Time ........................................................... 245 Typical Application ...................................................246 HLVD. See High/Low-Voltage Detect. I I/O Ports ........................................................................... 105 I2C Mode (MSSP) Acknowledge Sequence Timing ............................... 194 Baud Rate Generator ...............................................187 Bus Collision During a Repeated Start Condition .................. 198 During a Stop Condition ................................... 199 Clock Arbitration ....................................................... 188 Clock Stretching ....................................................... 180 10-Bit Slave Receive Mode (SEN = 1) ............. 180 10-Bit Slave Transmit Mode ............................. 180 7-Bit Slave Receive Mode (SEN = 1) ............... 180 7-Bit Slave Transmit Mode ............................... 180 Clock Synchronization and the CKP Bit (SEN = 1) .. 181 Effects of a Reset ..................................................... 195 General Call Address Support ................................. 184 I2C Clock Rate w/BRG ............................................. 187 Master Mode ............................................................ 185 Operation ......................................................... 186 Reception ......................................................... 191 Repeated Start Condition Timing ..................... 190 Start Condition Timing ..................................... 189 Transmission .................................................... 191 Multi-Master Communication, Bus Collision and Arbitration .................................................. 195 Multi-Master Mode ...................................................195 Operation ................................................................. 174 Read/Write Bit Information (R/W Bit) ............... 174, 175 Registers .................................................................. 170 Serial Clock (RC3/SCK/SCL) ................................... 175 Slave Mode .............................................................. 174 Addressing ....................................................... 174 Reception ......................................................... 175 Transmission .................................................... 175 Sleep Operation ....................................................... 195 Stop Condition Timing .............................................. 194 ID Locations ............................................................. 249, 266 INCF ................................................................................. 288 INCFSZ ............................................................................ 289 In-Circuit Debugger .......................................................... 266 In-Circuit Serial Programming (ICSP) ...................... 249, 266 Indexed Literal Offset Addressing and Standard PIC18 Instructions ............................. 314 Indexed Literal Offset Mode ............................................. 314 Indirect Addressing ............................................................ 69 INFSNZ ............................................................................ 289 Initialization Conditions for all Registers ...................... 49–52 Instruction Cycle ................................................................ 57 Clocking Scheme ....................................................... 57 Instruction Flow/Pipelining ................................................. 57 Instruction Set .................................................................. 267 ADDLW .................................................................... 273 ADDWF .................................................................... 273 ADDWF (Indexed Literal Offset Mode) .................... 315 ADDWFC ................................................................. 274 ANDLW .................................................................... 274 ANDWF .................................................................... 275 BC ............................................................................ 275 BCF ......................................................................... 276 BN ............................................................................ 276 BNC ......................................................................... 277 BNN ......................................................................... 277 BNOV ...................................................................... 278 BNZ ......................................................................... 278 BOV ......................................................................... 281 BRA ......................................................................... 279 BSF .......................................................................... 279 BSF (Indexed Literal Offset Mode) .......................... 315 BTFSC ..................................................................... 280 BTFSS ..................................................................... 280 BTG ......................................................................... 281 BZ ............................................................................ 282 CALL ........................................................................ 282 CLRF ....................................................................... 283 CLRWDT ................................................................. 283 COMF ...................................................................... 284 CPFSEQ .................................................................. 284 CPFSGT .................................................................. 285 CPFSLT ................................................................... 285 DAW ........................................................................ 286 DCFSNZ .................................................................. 287 DECF ....................................................................... 286 DECFSZ .................................................................. 287 Extended Instruction Set ......................................... 309 General Format ........................................................ 269 GOTO ...................................................................... 288 INCF ........................................................................ 288 INCFSZ .................................................................... 289 INFSNZ .................................................................... 289 IORLW ..................................................................... 290 IORWF ..................................................................... 290 LFSR ....................................................................... 291 MOVF ...................................................................... 291 MOVFF .................................................................... 292 MOVLB .................................................................... 292 MOVLW ................................................................... 293 MOVWF ................................................................... 293 MULLW .................................................................... 294 MULWF .................................................................... 294 NEGF ....................................................................... 295 NOP ......................................................................... 295 Opcode Field Descriptions ....................................... 268 POP ......................................................................... 296 PUSH ....................................................................... 296 RCALL ..................................................................... 297 RESET ..................................................................... 297 RETFIE .................................................................... 298 RETLW .................................................................... 298 RETURN .................................................................. 299 RLCF ....................................................................... 299 RLNCF ..................................................................... 300 © 2007 Microchip Technology Inc. Preliminary DS39631B-page 379 PIC18F2420/2520/4420/4520 RRCF ....................................................................... 300 RRNCF .................................................................... 301 SETF ........................................................................ 301 SETF (Indexed Literal Offset Mode) ........................ 315 SLEEP ..................................................................... 302 SUBFWB .................................................................. 302 SUBLW .................................................................... 303 SUBWF .................................................................... 303 SUBWFB .................................................................. 304 SWAPF .................................................................... 304 TBLRD ..................................................................... 305 TBLWT ..................................................................... 306 TSTFSZ ................................................................... 307 XORLW .................................................................... 307 XORWF .................................................................... 308 INTCON Registers ....................................................... 93–95 Inter-Integrated Circuit. See I2C. Internal Oscillator Block ..................................................... 26 Adjustment ................................................................. 26 INTIO Modes .............................................................. 26 INTOSC Frequency Drift ............................................ 26 INTOSC Output Frequency ........................................ 26 OSCTUNE Register ................................................... 26 PLL in INTOSC Modes .............................................. 26 Internal RC Oscillator Use with WDT .......................................................... 258 Interrupt Sources ............................................................. 249 A/D Conversion Complete ....................................... 227 Capture Complete (CCP) ......................................... 141 Compare Complete (CCP) ....................................... 142 Interrupt-on-Change (RB7:RB4) .............................. 108 INTn Pin ................................................................... 103 PORTB, Interrupt-on-Change .................................. 103 TMR0 ....................................................................... 103 TMR0 Overflow ........................................................ 125 TMR1 Overflow ........................................................ 127 TMR2 to PR2 Match (PWM) ............................ 144, 149 TMR3 Overflow ................................................ 135, 137 Interrupts ............................................................................ 91 Interrupts, Flag Bits Interrupt-on-Change (RB7:RB4) Flag (RBIF Bit) ......................................................... 108 INTOSC, INTRC. See Internal Oscillator Block. IORLW ............................................................................. 290 IORWF ............................................................................. 290 IPR Registers ................................................................... 100 L LFSR ................................................................................ 291 Low-Voltage ICSP Programming. See Single-Supply ICSP Programming M Master Clear (MCLR) ......................................................... 43 Master Synchronous Serial Port (MSSP). See MSSP. Memory Organization ......................................................... 53 Data Memory ............................................................. 59 Program Memory ....................................................... 53 Memory Programming Requirements .............................. 337 Migration from Baseline to Enhanced Devices ................ 372 Migration from High-End to Enhanced Devices ............... 373 Migration from Mid-Range to Enhanced Devices ............ 373 MOVF ............................................................................... 291 MOVFF ............................................................................ 292 MOVLB ............................................................................ 292 MOVLW ........................................................................... 293 MOVSF ............................................................................ 311 MOVSS ............................................................................ 312 MOVWF ........................................................................... 293 MPLAB ASM30 Assembler, Linker, Librarian .................. 318 MPLAB ICD 2 In-Circuit Debugger .................................. 319 MPLAB ICE 2000 High-Performance Universal In-Circuit Emulator ................................... 319 MPLAB ICE 4000 High-Performance Universal In-Circuit Emulator ................................... 319 MPLAB Integrated Development Environment Software ............................................. 317 MPLAB PM3 Device Programmer ................................... 319 MPLINK Object Linker/MPLIB Object Librarian ............... 318 MSSP ACK Pulse ....................................................... 174, 175 Control Registers (general) ..................................... 161 I2C Mode. See I2C Mode. Module Overview ..................................................... 161 SPI Master/Slave Connection .................................. 165 SPI Mode. See SPI Mode. SSPBUF Register .................................................... 166 SSPSR Register ...................................................... 166 MULLW ............................................................................ 294 MULWF ............................................................................ 294 N NEGF ............................................................................... 295 NOP ................................................................................. 295 O Oscillator Configuration ..................................................... 23 EC .............................................................................. 23 ECIO .......................................................................... 23 HS .............................................................................. 23 HSPLL ....................................................................... 23 Internal Oscillator Block ............................................. 26 INTIO1 ....................................................................... 23 INTIO2 ....................................................................... 23 LP .............................................................................. 23 RC ............................................................................. 23 RCIO .......................................................................... 23 XT .............................................................................. 23 Oscillator Selection .......................................................... 249 Oscillator Start-up Timer (OST) ................................... 31, 45 Oscillator Switching ........................................................... 28 Oscillator Transitions ......................................................... 29 Oscillator, Timer1 ..................................................... 127, 137 Oscillator, Timer3 ............................................................. 135 P Packaging Information ..................................................... 363 Marking .................................................................... 363 Parallel Slave Port (PSP) ......................................... 114, 120 Associated Registers ............................................... 121 CS (Chip Select) ...................................................... 120 PORTD .................................................................... 120 RD (Read Input) ...................................................... 120 Select (PSPMODE Bit) .................................... 114, 120 WR (Write Input) ...................................................... 120 PICkit 1 Flash Starter Kit ................................................. 321 PICSTART Plus Development Programmer .................... 320 PIE Registers ..................................................................... 98 PIC18F2420/2520/4420/4520 DS39631B-page 380 Preliminary © 2007 Microchip Technology Inc. Pin Functions MCLR/VPP/RE3 .................................................... 12, 16 OSC1/CLKI/RA7 .................................................. 12, 16 OSC2/CLKO/RA6 ................................................ 12, 16 RA0/AN0 .............................................................. 13, 17 RA1/AN1 .............................................................. 13, 17 RA2/AN2/VREF-/CVREF ........................................ 13, 17 RA3/AN3/VREF+ ................................................... 13, 17 RA4/T0CKI/C1OUT .............................................. 13, 17 RA5/AN4/SS/HLVDIN/C2OUT ............................. 13, 17 RB0/INT0/FLT0/AN12 .......................................... 14, 18 RB1/INT1/AN10 ................................................... 14, 18 RB2/INT2/AN8 ..................................................... 14, 18 RB3/AN9/CCP2 ................................................... 14, 18 RB4/KBI0/AN11 ................................................... 14, 18 RB5/KBI1/PGM .................................................... 14, 18 RB6/KBI2/PGC .................................................... 14, 18 RB7/KBI3/PGD .................................................... 14, 18 RC0/T1OSO/T13CKI ........................................... 15, 19 RC1/T1OSI/CCP2 ................................................ 15, 19 RC2/CCP1 ................................................................. 15 RC2/CCP1/P1A ......................................................... 19 RC3/SCK/SCL ..................................................... 15, 19 RC4/SDI/SDA ...................................................... 15, 19 RC5/SDO ............................................................. 15, 19 RC6/TX/CK .......................................................... 15, 19 RC7/RX/DT .......................................................... 15, 19 RD0/PSP0 .................................................................. 20 RD1/PSP1 .................................................................. 20 RD2/PSP2 .................................................................. 20 RD3/PSP3 .................................................................. 20 RD4/PSP4 .................................................................. 20 RD5/PSP5/P1B .......................................................... 20 RD6/PSP6/P1C .......................................................... 20 RD7/PSP7/P1D .......................................................... 20 RE0/RD/AN5 .............................................................. 21 RE1/WR/AN6 ............................................................. 21 RE2/CS/AN7 .............................................................. 21 VDD ....................................................................... 15, 21 VSS ....................................................................... 15, 21 Pinout I/O Descriptions PIC18F2420/2520 ...................................................... 12 PIC18F4420/4520 ...................................................... 16 PIR Registers ..................................................................... 96 PLL Frequency Multiplier ...................................................25 HSPLL Oscillator Mode .............................................. 25 Use with INTOSC ....................................................... 25 POP .................................................................................. 296 POR. See Power-on Reset. PORTA Associated Registers ...............................................107 LATA Register .......................................................... 105 PORTA Register ...................................................... 105 TRISA Register ........................................................ 105 PORTB Associated Registers ...............................................110 LATB Register .......................................................... 108 PORTB Register ...................................................... 108 RB7:RB4 Interrupt-on-Change Flag (RBIF Bit) ......................................................... 108 TRISB Register ........................................................ 108 PORTC Associated Registers ............................................... 113 LATC Register ......................................................... 111 PORTC Register ...................................................... 111 RC3/SCK/SCL Pin ................................................... 175 TRISC Register ........................................................ 111 PORTD Associated Registers ............................................... 116 LATD Register ......................................................... 114 Parallel Slave Port (PSP) Function .......................... 114 PORTD Register ...................................................... 114 TRISD Register ........................................................ 114 PORTE Associated Registers ............................................... 119 LATE Register ......................................................... 117 PORTE Register ...................................................... 117 PSP Mode Select (PSPMODE Bit) .......................... 114 TRISE Register ........................................................ 117 Power Managed Modes ..................................................... 33 and A/D Operation ................................................... 230 and EUSART Operation .......................................... 205 and Multiple Sleep Commands .................................. 34 and PWM Operation ................................................ 159 and SPI Operation ................................................... 169 Clock Transitions and Status Indicators .................... 34 Effects on Clock Sources ........................................... 31 Entering ..................................................................... 33 Exiting Idle and Sleep Modes .................................... 39 by Interrupt ........................................................ 39 by Reset ............................................................ 39 by WDT Time-out .............................................. 39 Without a Start-up Delay ................................... 40 Idle Modes ................................................................. 37 PRI_IDLE ........................................................... 38 RC_IDLE ........................................................... 39 SEC_IDLE ......................................................... 38 Run Modes ................................................................ 34 PRI_RUN ........................................................... 34 RC_RUN ............................................................ 35 SEC_RUN ......................................................... 34 Selecting .................................................................... 33 Sleep Mode ............................................................... 37 Summary (table) ........................................................ 33 Power-on Reset (POR) ...................................................... 43 Power-up Timer (PWRT) ........................................... 45 Time-out Sequence ................................................... 45 Power-up Delays ............................................................... 31 Power-up Timer (PWRT) ................................................... 31 Prescaler Timer2 ..................................................................... 150 Prescaler, Timer0 ............................................................ 125 Prescaler, Timer2 ............................................................ 145 PRI_IDLE Mode ................................................................. 38 PRI_RUN Mode ................................................................. 34 PRO MATE II Universal Device Programmer .................. 319 Program Counter ............................................................... 54 PCL, PCH and PCU Registers .................................. 54 PCLATH and PCLATU Registers .............................. 54 © 2007 Microchip Technology Inc. Preliminary DS39631B-page 381 PIC18F2420/2520/4420/4520 Program Memory and Extended Instruction Set ..................................... 72 Code Protection ....................................................... 264 Instructions ................................................................. 58 Two-Word .......................................................... 58 Interrupt Vector .......................................................... 53 Look-up Tables .......................................................... 56 Map and Stack (diagram) ........................................... 53 Reset Vector .............................................................. 53 Program Verification and Code Protection ....................... 263 Associated Registers ............................................... 263 Programming, Device Instructions ................................... 267 PSP. See Parallel Slave Port. Pulse-Width Modulation. See PWM (CCP Module) and PWM (ECCP Module). PUSH ............................................................................... 296 PUSH and POP Instructions .............................................. 55 PUSHL ............................................................................. 312 PWM (CCP Module) Associated Registers ............................................... 146 Auto-Shutdown (CCP1 only) .................................... 145 CCPR1H:CCPR1L Registers ................................... 149 Duty Cycle ........................................................ 144, 150 Example Frequencies/Resolutions .................. 145, 150 Period ............................................................... 144, 149 Setup for PWM Operation ........................................ 145 TMR2 to PR2 Match ........................................ 144, 149 PWM (ECCP Module) ...................................................... 149 Direction Change in Full-Bridge Output Mode .................................................... 154 Effects of a Reset ..................................................... 159 Enhanced PWM Auto-Shutdown ............................. 156 Full-Bridge Application Example .............................. 154 Full-Bridge Mode ...................................................... 153 Half-Bridge Mode ..................................................... 152 Half-Bridge Output Mode Applications Example ...................................... 152 Operation in Power Managed Modes ...................... 159 Operation with Fail-Safe Clock Monitor ................... 159 Output Configurations .............................................. 150 Output Relationships (Active-High) .......................... 151 Output Relationships (Active-Low) ........................... 151 Programmable Dead-Band Delay ............................ 156 Setup for PWM Operation ........................................ 159 Start-up Considerations ........................................... 158 Q Q Clock .................................................................... 145, 150 R RAM. See Data Memory. RBIF Bit ............................................................................ 108 RC Oscillator ...................................................................... 25 RCIO Oscillator Mode ................................................ 25 RC_IDLE Mode .................................................................. 39 RC_RUN Mode .................................................................. 35 RCALL ............................................................................. 297 RCON Register Bit Status During Initialization .................................... 48 Register File ....................................................................... 62 Register File Summary ................................................ 64–66 Registers ADCON0 (A/D Control 0) ......................................... 223 ADCON1 (A/D Control 1) ......................................... 224 ADCON2 (A/D Control 2) ......................................... 225 BAUDCON (Baud Rate Control) .............................. 204 CCP1CON (Enhanced Capture/Compare/PWM Control 1) ................. 147 CCPxCON (Standard Capture/Compare/PWM Control) .................... 139 CMCON (Comparator Control) ................................ 233 CONFIG1H (Configuration 1 High) .......................... 250 CONFIG2H (Configuration 2 High) .......................... 252 CONFIG2L (Configuration 2 Low) ........................... 251 CONFIG3H (Configuration 3 High) .......................... 253 CONFIG4L (Configuration 4 Low) ........................... 253 CONFIG5H (Configuration 5 High) .......................... 254 CONFIG5L (Configuration 5 Low) ........................... 254 CONFIG6H (Configuration 6 High) .......................... 255 CONFIG6L (Configuration 6 Low) ........................... 255 CONFIG7H (Configuration 7 High) .......................... 256 CONFIG7L (Configuration 7 Low) ........................... 256 CVRCON (Comparator Voltage Reference Control) .......................................... 239 DEVID1 (Device ID 1) .............................................. 257 DEVID2 (Device ID 2) .............................................. 257 ECCP1AS (ECCP Auto-Shutdown Control) ............ 157 EECON1 (Data EEPROM Control 1) ................... 75, 84 HLVDCON (High/Low-Voltage Detect Control) ....... 243 INTCON (Interrupt Control) ....................................... 93 INTCON2 (Interrupt Control 2) .................................. 94 INTCON3 (Interrupt Control 3) .................................. 95 IPR1 (Peripheral Interrupt Priority 1) ....................... 100 IPR2 (Peripheral Interrupt Priority 2) ....................... 101 OSCCON (Oscillator Control) .................................... 30 OSCTUNE (Oscillator Tuning) ................................... 27 PIE1 (Peripheral Interrupt Enable 1) ......................... 98 PIE2 (Peripheral Interrupt Enable 2) ......................... 99 PIR1 (Peripheral Interrupt Request (Flag) 1) ............. 96 PIR2 (Peripheral Interrupt Request (Flag) 2) ............. 97 PWM1CON (PWM Configuration) ........................... 156 RCON (Reset Control) ....................................... 42, 102 RCSTA (Receive Status and Control) ..................... 203 SSPCON1 (MSSP Control 1, I2C Mode) ................. 172 SSPCON1 (MSSP Control 1, SPI Mode) ................ 163 SSPCON2 (MSSP Control 2, I2C Mode) ................. 173 SSPSTAT (MSSP Status, I2C Mode) ...................... 171 SSPSTAT (MSSP Status, SPI Mode) ...................... 162 Status ........................................................................ 67 STKPTR (Stack Pointer) ............................................ 55 T0CON (Timer0 Control) ......................................... 123 T1CON (Timer1 Control) ......................................... 127 T2CON (Timer2 Control) ......................................... 133 T3CON (Timer3 Control) ......................................... 135 TRISE (PORTE/PSP Control) ................................. 118 TXSTA (Transmit Status and Control) ..................... 202 WDTCON (Watchdog Timer Control) ...................... 259 RESET ............................................................................. 297 Reset State of Registers .................................................... 48 Resets ....................................................................... 41, 249 Brown-out Reset (BOR) ........................................... 249 Oscillator Start-up Timer (OST) ............................... 249 Power-on Reset (POR) ............................................ 249 Power-up Timer (PWRT) ......................................... 249 PIC18F2420/2520/4420/4520 DS39631B-page 382 Preliminary © 2007 Microchip Technology Inc. RETFIE ............................................................................ 298 RETLW ............................................................................. 298 RETURN .......................................................................... 299 Return Address Stack ........................................................ 54 Return Stack Pointer (STKPTR) ........................................ 55 Revision History ............................................................... 371 RLCF ................................................................................ 299 RLNCF ............................................................................. 300 RRCF ............................................................................... 300 RRNCF ............................................................................. 301 S SCK .................................................................................. 161 SDI ................................................................................... 161 SDO ................................................................................. 161 SEC_IDLE Mode ................................................................ 38 SEC_RUN Mode ................................................................ 34 Serial Clock, SCK ............................................................. 161 Serial Data In (SDI) .......................................................... 161 Serial Data Out (SDO) ..................................................... 161 Serial Peripheral Interface. See SPI Mode. SETF ................................................................................ 301 Single-Supply ICSP Programming. Slave Select (SS) ............................................................. 161 Slave Select Synchronization ........................................... 167 SLEEP .............................................................................. 302 Sleep OSC1 and OSC2 Pin States ...................................... 31 Sleep Mode ........................................................................37 Software Simulator (MPLAB SIM) .................................... 318 Software Simulator (MPLAB SIM30) ................................ 318 Special Event Trigger. See Compare (ECCP Mode). Special Event Trigger. See Compare (ECCP Module). Special Features of the CPU ............................................ 249 Special Function Registers ................................................ 63 Map ............................................................................ 63 SPI Mode (MSSP) Associated Registers ...............................................169 Bus Mode Compatibility ........................................... 169 Effects of a Reset ..................................................... 169 Enabling SPI I/O ...................................................... 165 Master Mode ............................................................ 166 Master/Slave Connection ......................................... 165 Operation ................................................................. 164 Operation in Power Managed Modes ...................... 169 Serial Clock .............................................................. 161 Serial Data In ........................................................... 161 Serial Data Out ........................................................ 161 Slave Mode .............................................................. 167 Slave Select ............................................................. 161 Slave Select Synchronization .................................. 167 SPI Clock ................................................................. 166 Typical Connection .................................................. 165 SS .................................................................................... 161 SSPOV ............................................................................. 191 SSPOV Status Flag .......................................................... 191 SSPSTAT Register R/W Bit ............................................................. 174, 175 Stack Full/Underflow Resets .............................................. 56 Standard Instructions ....................................................... 267 SUBFSR ........................................................................... 313 SUBFWB .......................................................................... 302 SUBLW ............................................................................ 303 SUBULNK ........................................................................ 313 SUBWF ............................................................................ 303 SUBWFB ......................................................................... 304 SWAPF ............................................................................ 304 T Table Pointer Operations (table) ........................................ 76 Table Reads/Table Writes ................................................. 56 TBLRD ............................................................................. 305 TBLWT ............................................................................. 306 Time-out in Various Situations (table) ................................ 45 Timer0 .............................................................................. 123 Associated Registers ............................................... 125 Operation ................................................................. 124 Overflow Interrupt .................................................... 125 Prescaler ................................................................. 125 Prescaler Assignment (PSA Bit) .............................. 125 Prescaler Select (T0PS2:T0PS0 Bits) ..................... 125 Prescaler. See Prescaler, Timer0. Reads and Writes in 16-Bit Mode ............................ 124 Source Edge Select (T0SE Bit) ............................... 124 Source Select (T0CS Bit) ......................................... 124 Switching Prescaler Assignment ............................. 125 Timer1 .............................................................................. 127 16-Bit Read/Write Mode .......................................... 129 Associated Registers ............................................... 131 Interrupt ................................................................... 130 Operation ................................................................. 128 Oscillator .......................................................... 127, 129 Oscillator Layout Considerations ............................. 130 Overflow Interrupt .................................................... 127 Resetting, Using the CCP Special Event Trigger ...................................... 130 Special Event Trigger (ECCP) ................................. 148 TMR1H Register ...................................................... 127 TMR1L Register ....................................................... 127 Use as a Real-Time Clock ....................................... 130 Timer2 .............................................................................. 133 Associated Registers ............................................... 134 Interrupt ................................................................... 134 Operation ................................................................. 133 Output ...................................................................... 134 PR2 Register ................................................... 144, 149 TMR2 to PR2 Match Interrupt .......................... 144, 149 Timer3 .............................................................................. 135 16-Bit Read/Write Mode .......................................... 137 Associated Registers ............................................... 137 Operation ................................................................. 136 Oscillator .......................................................... 135, 137 Overflow Interrupt ............................................ 135, 137 Special Event Trigger (CCP) ................................... 137 TMR3H Register ...................................................... 135 TMR3L Register ....................................................... 135 Timing Diagrams A/D Conversion ........................................................ 359 Acknowledge Sequence .......................................... 194 Asynchronous Reception ......................................... 214 Asynchronous Transmission .................................... 212 Asynchronous Transmission (Back to Back) ........... 212 Automatic Baud Rate Calculation ............................ 210 Auto-Wake-up Bit (WUE) During Normal Operation ............................................ 215 Auto-Wake-up Bit (WUE) During Sleep ................... 215 © 2007 Microchip Technology Inc. Preliminary DS39631B-page 383 PIC18F2420/2520/4420/4520 Baud Rate Generator with Clock Arbitration ............ 188 BRG Overflow Sequence ......................................... 210 BRG Reset Due to SDA Arbitration During Start Condition ..................................... 197 Brown-out Reset (BOR) ........................................... 345 Bus Collision During a Repeated Start Condition (Case 1) .................................. 198 Bus Collision During a Repeated Start Condition (Case 2) .................................. 198 Bus Collision During a Start Condition (SCL = 0) ......................................................... 197 Bus Collision During a Stop Condition (Case 1) ........................................................... 199 Bus Collision During a Stop Condition (Case 2) ........................................................... 199 Bus Collision During Start Condition (SDA only) ....................................................... 196 Bus Collision for Transmit and Acknowledge ........... 195 Capture/Compare/PWM (CCP) ................................ 347 CLKO and I/O .......................................................... 344 Clock Synchronization ............................................. 181 Clock/Instruction Cycle .............................................. 57 Example SPI Master Mode (CKE = 0) ..................... 349 Example SPI Master Mode (CKE = 1) ..................... 350 Example SPI Slave Mode (CKE = 0) ....................... 351 Example SPI Slave Mode (CKE = 1) ....................... 352 External Clock (All Modes except PLL) .................... 342 Fail-Safe Clock Monitor (FSCM) .............................. 262 First Start Bit Timing ................................................ 189 Full-Bridge PWM Output .......................................... 153 Half-Bridge PWM Output ......................................... 152 High/Low-Voltage Detect Characteristics ................ 339 High/Low-Voltage Detect Operation (VDIRMAG = 0) ................................................ 245 High/Low-Voltage Detect Operation (VDIRMAG = 1) ................................................ 246 I2C Bus Data ............................................................ 353 I2C Bus Start/Stop Bits ............................................. 353 I2C Master Mode (7 or 10-Bit Transmission) ........... 192 I2C Master Mode (7-Bit Reception) .......................... 193 I2C Slave Mode (10-Bit Reception, SEN = 0) .......... 178 I2C Slave Mode (10-Bit Reception, SEN = 1) .......... 183 I2C Slave Mode (10-Bit Transmission) ..................... 179 I2C Slave Mode (7-bit Reception, SEN = 0) ............. 176 I2C Slave Mode (7-Bit Reception, SEN = 1) ............ 182 I2C Slave Mode (7-Bit Transmission) ....................... 177 I2C Slave Mode General Call Address Sequence (7 or 10-Bit Address Mode) ............ 184 I2C Stop Condition Receive or Transmit Mode ................................................. 194 Master SSP I2C Bus Data ........................................ 355 Master SSP I2C Bus Start/Stop Bits ........................ 355 Parallel Slave Port (PIC18F4420/4520) ................... 348 Parallel Slave Port (PSP) Read ............................... 121 Parallel Slave Port (PSP) Write ............................... 121 PWM Auto-Shutdown (PRSEN = 0, Auto-Restart Disabled) .................................... 158 PWM Auto-Shutdown (PRSEN = 1, Auto-Restart Enabled) ..................................... 158 PWM Direction Change ........................................... 155 PWM Direction Change at Near 100% Duty Cycle ............................................. 155 PWM Output ............................................................ 144 Repeat Start Condition ............................................ 190 Reset, Watchdog Timer (WDT), Oscillator Start-up Timer (OST), Power-up Timer (PWRT) ................................. 345 Send Break Character Sequence ............................ 216 Slave Synchronization ............................................. 167 Slow Rise Time (MCLR Tied to VDD, VDD Rise > TPWRT) ............................................ 47 SPI Mode (Master Mode) ........................................ 166 SPI Mode (Slave Mode, CKE = 0) ........................... 168 SPI Mode (Slave Mode, CKE = 1) ........................... 168 Synchronous Reception (Master Mode, SREN) ..................................... 219 Synchronous Transmission ..................................... 217 Synchronous Transmission (Through TXEN) .......... 218 Time-out Sequence on POR w/PLL Enabled (MCLR Tied to VDD) .......................................... 47 Time-out Sequence on Power-up (MCLR Not Tied to VDD, Case 1) ...................... 46 Time-out Sequence on Power-up (MCLR Not Tied to VDD, Case 2) ...................... 46 Time-out Sequence on Power-up (MCLR Tied to VDD, VDD Rise < TPWRT) ........... 46 Timer0 and Timer1 External Clock .......................... 346 Transition for Entry to SEC_RUN Mode .................... 35 Transition for Entry to Sleep Mode ............................ 37 Transition for Two-Speed Start-up (INTOSC to HSPLL) ........................................ 260 Transition for Wake from Sleep (HSPLL) .................. 37 Transition from RC_RUN Mode to PRI_RUN Mode ................................................. 36 Transition from SEC_RUN Mode to PRI_RUN Mode (HSPLL) .................................. 35 Transition Timing for Entry to Idle Mode .................... 38 Transition Timing for Wake from Idle to Run Mode ............................................... 38 Transition to RC_RUN Mode ..................................... 36 USART Synchronous Receive (Master/Slave) ................................................. 357 USART Synchronous Transmission (Master/Slave) ................................................. 357 Timing Diagrams and Specifications ............................... 342 A/D Conversion Requirements ................................ 359 Capture/Compare/PWM Requirements ................... 347 CLKO and I/O Requirements ................................... 344 Example SPI Mode Requirements (Master Mode, CKE = 0) .................................. 349 Example SPI Mode Requirements (Master Mode, CKE = 1) .................................. 350 Example SPI Mode Requirements (Slave Mode, CKE = 0) .................................... 351 Example SPI Mode Requirements (Slave Mode, CKE = 1) .................................... 352 External Clock Requirements .................................. 342 I2C Bus Data Requirements (Slave Mode) .............. 354 I2C Bus Start/Stop Bits Requirements (Slave Mode) ................................................... 353 Master SSP I2C Bus Data Requirements ................ 356 Master SSP I2C Bus Start/Stop Bits Requirements .................................................. 355 Parallel Slave Port Requirements (PIC18F4420/4520) ......................................... 348 PIC18F2420/2520/4420/4520 DS39631B-page 384 Preliminary © 2007 Microchip Technology Inc. PLL Clock ................................................................. 343 Reset, Watchdog Timer, Oscillator Start-up Timer, Power-up Timer and Brown-out Reset Requirements ...................................................345 Timer0 and Timer1 External Clock Requirements ......................................... 346 USART Synchronous Receive Requirements .........357 USART Synchronous Transmission Requirements ...................................................357 Top-of-Stack Access .......................................................... 54 TRISE Register PSPMODE Bit .......................................................... 114 TSTFSZ ............................................................................ 307 Two-Speed Start-up ................................................. 249, 260 Two-Word Instructions Example Cases .......................................................... 58 TXSTA Register BRGH Bit ................................................................. 205 V Voltage Reference Specifications .................................... 338 W Watchdog Timer (WDT) ........................................... 249, 258 Associated Registers ............................................... 259 Control Register ....................................................... 258 During Oscillator Failure .......................................... 261 Programming Considerations .................................. 258 WCOL ...................................................... 189, 190, 191, 194 WCOL Status Flag ................................... 189, 190, 191, 194 WWW, On-Line Support ...................................................... 6 X XORLW ............................................................................ 307 XORWF ........................................................................... 308 © 2007 Microchip Technology Inc. Preliminary DS39631B-page 385 PIC18F2420/2520/4420/4520 THE MICROCHIP WEB SITE Microchip provides online support via our WWW site at www.microchip.com. This web site is used as a means to make files and information easily available to customers. Accessible by using your favorite Internet browser, the web site contains the following information: • Product Support – Data sheets and errata, application notes and sample programs, design resources, user’s guides and hardware support documents, latest software releases and archived software • General Technical Support – Frequently Asked Questions (FAQ), technical support requests, online discussion groups, Microchip consultant program member listing • Business of Microchip – Product selector and ordering guides, latest Microchip press releases, listing of seminars and events, listings of Microchip sales offices, distributors and factory representatives CUSTOMER CHANGE NOTIFICATION SERVICE Microchip’s customer notification service helps keep customers current on Microchip products. Subscribers will receive e-mail notification whenever there are changes, updates, revisions or errata related to a specified product family or development tool of interest. To register, access the Microchip web site at www.microchip.com, click on Customer Change Notification and follow the registration instructions. CUSTOMER SUPPORT Users of Microchip products can receive assistance through several channels: • Distributor or Representative • Local Sales Office • Field Application Engineer (FAE) • Technical Support • Development Systems Information Line Customers should contact their distributor, representative or field application engineer (FAE) for support. Local sales offices are also available to help customers. A listing of sales offices and locations is included in the back of this document. Technical support is available through the web site at: http://support.microchip.com PIC18F2420/2520/4420/4520 DS39631B-page 386 Preliminary © 2007 Microchip Technology Inc. READER RESPONSE It is our intention to provide you with the best documentation possible to ensure successful use of your Microchip product. If you wish to provide your comments on organization, clarity, subject matter, and ways in which our documentation can better serve you, please FAX your comments to the Technical Publications Manager at (480) 792-4150. Please list the following information, and use this outline to provide us with your comments about this document. To: Technical Publications Manager RE: Reader Response Total Pages Sent ________ From: Name Company Address City / State / ZIP / Country Telephone: (_______) _________ - _________ Application (optional): Would you like a reply? Y N Device: Literature Number: Questions: FAX: (______) _________ - _________ PIC18F2420/2520/4420/4520 DS39631B 1. What are the best features of this document? 2. How does this document meet your hardware and software development needs? 3. Do you find the organization of this document easy to follow? If not, why? 4. What additions to the document do you think would enhance the structure and subject? 5. What deletions from the document could be made without affecting the overall usefulness? 6. Is there any incorrect or misleading information (what and where)? 7. How would you improve this document? © 2007 Microchip Technology Inc. Preliminary DS39631B-page 387 PIC18F2420/2520/4420/4520 PIC18F2420/2520/4420/4520 PRODUCT IDENTIFICATION SYSTEM To order or obtain information, e.g., on pricing or delivery, refer to the factory or the listed sales office. PART NO. X /XX XXX Temperature Package Pattern Range Device Device PIC18F2420/2520(1), PIC18F4420/4520(1), PIC18F2420/2520T(2), PIC18F4420/4520T(2); VDD range 4.2V to 5.5V PIC18LF2420/2520(1), PIC18LF4420/4520(1), PIC18LF2420/2520T(2), PIC18LF4420/4520T(2); VDD range 2.0V to 5.5V Temperature Range I = -40°C to +85°C (Industrial) E = -40°C to +125°C (Extended) Package PT = TQFP (Thin Quad Flatpack) SO = SOIC SP = Skinny Plastic DIP P = PDIP ML = QFN Pattern QTP, SQTP, Code or Special Requirements (blank otherwise) Examples: a) PIC18LF4520-I/P 301 = Industrial temp., PDIP package, Extended VDD limits, QTP pattern #301. b) PIC18LF2420-I/SO = Industrial temp., SOIC package, Extended VDD limits. c) PIC18F4420-I/P = Industrial temp., PDIP package, normal VDD limits. Note 1: F = Standard Voltage Range LF = Wide Voltage Range 2: T = in tape and reel TQFP packages only. DS39631B-page 388 © 2007 Microchip Technology Inc. AMERICAS Corporate Office 2355 West Chandler Blvd. Chandler, AZ 85224-6199 Tel: 480-792-7200 Fax: 480-792-7277 Technical Support: http://support.microchip.com Web Address: www.microchip.com Atlanta Duluth, GA Tel: 678-957-9614 Fax: 678-957-1455 Boston Westborough, MA Tel: 774-760-0087 Fax: 774-760-0088 Chicago Itasca, IL Tel: 630-285-0071 Fax: 630-285-0075 Dallas Addison, TX Tel: 972-818-7423 Fax: 972-818-2924 Detroit Farmington Hills, MI Tel: 248-538-2250 Fax: 248-538-2260 Kokomo Kokomo, IN Tel: 765-864-8360 Fax: 765-864-8387 Los Angeles Mission Viejo, CA Tel: 949-462-9523 Fax: 949-462-9608 Santa Clara Santa Clara, CA Tel: 408-961-6444 Fax: 408-961-6445 Toronto Mississauga, Ontario, Canada Tel: 905-673-0699 Fax: 905-673-6509 ASIA/PACIFIC Asia Pacific Office Suites 3707-14, 37th Floor Tower 6, The Gateway Habour City, Kowloon Hong Kong Tel: 852-2401-1200 Fax: 852-2401-3431 Australia - Sydney Tel: 61-2-9868-6733 Fax: 61-2-9868-6755 China - Beijing Tel: 86-10-8528-2100 Fax: 86-10-8528-2104 China - Chengdu Tel: 86-28-8665-5511 Fax: 86-28-8665-7889 China - Fuzhou Tel: 86-591-8750-3506 Fax: 86-591-8750-3521 China - Hong Kong SAR Tel: 852-2401-1200 Fax: 852-2401-3431 China - Qingdao Tel: 86-532-8502-7355 Fax: 86-532-8502-7205 China - Shanghai Tel: 86-21-5407-5533 Fax: 86-21-5407-5066 China - Shenyang Tel: 86-24-2334-2829 Fax: 86-24-2334-2393 China - Shenzhen Tel: 86-755-8203-2660 Fax: 86-755-8203-1760 China - Shunde Tel: 86-757-2839-5507 Fax: 86-757-2839-5571 China - Wuhan Tel: 86-27-5980-5300 Fax: 86-27-5980-5118 China - Xian Tel: 86-29-8833-7250 Fax: 86-29-8833-7256 ASIA/PACIFIC India - Bangalore Tel: 91-80-4182-8400 Fax: 91-80-4182-8422 India - New Delhi Tel: 91-11-4160-8631 Fax: 91-11-4160-8632 India - Pune Tel: 91-20-2566-1512 Fax: 91-20-2566-1513 Japan - Yokohama Tel: 81-45-471- 6166 Fax: 81-45-471-6122 Korea - Gumi Tel: 82-54-473-4301 Fax: 82-54-473-4302 Korea - Seoul Tel: 82-2-554-7200 Fax: 82-2-558-5932 or 82-2-558-5934 Malaysia - Penang Tel: 60-4-646-8870 Fax: 60-4-646-5086 Philippines - Manila Tel: 63-2-634-9065 Fax: 63-2-634-9069 Singapore Tel: 65-6334-8870 Fax: 65-6334-8850 Taiwan - Hsin Chu Tel: 886-3-572-9526 Fax: 886-3-572-6459 Taiwan - Kaohsiung Tel: 886-7-536-4818 Fax: 886-7-536-4803 Taiwan - Taipei Tel: 886-2-2500-6610 Fax: 886-2-2508-0102 Thailand - Bangkok Tel: 66-2-694-1351 Fax: 66-2-694-1350 EUROPE Austria - Wels Tel: 43-7242-2244-39 Fax: 43-7242-2244-393 Denmark - Copenhagen Tel: 45-4450-2828 Fax: 45-4485-2829 France - Paris Tel: 33-1-69-53-63-20 Fax: 33-1-69-30-90-79 Germany - Munich Tel: 49-89-627-144-0 Fax: 49-89-627-144-44 Italy - Milan Tel: 39-0331-742611 Fax: 39-0331-466781 Netherlands - Drunen Tel: 31-416-690399 Fax: 31-416-690340 Spain - Madrid Tel: 34-91-708-08-90 Fax: 34-91-708-08-91 UK - Wokingham Tel: 44-118-921-5869 Fax: 44-118-921-5820 WORLDWIDE SALES AND SERVICE 12/08/06 1 LT1961 1961fa FEATURES DESCRIPTIO U APPLICATIOU S TYPICAL APPLICATIO U 1.5A, 1.25MHz Step-Up Switching Regulator ■ 1.5A Switch in a Small MSOP Package ■ Constant 1.25MHz Switching Frequency ■ Wide Operating Voltage Range: 3V to 25V ■ High Efficiency 0.2Ω Switch ■ 1.2V Feedback Reference Voltage ■ ±2% Overall Output Voltage Tolerance ■ Uses Low Profile Surface Mount External Components ■ Low Shutdown Current: 6μA ■ Synchronizable from 1.5MHz to 2MHz ■ Current-Mode Loop Control ■ Constant Maximum Switch Current Rating at All Duty Cycles* ■ Thermally Enhanced Exposed Pad 8-Lead Plastic MSOP Package The LT®1961 is a 1.25MHz monolithic boost switching regulator. A high efficiency 1.5A, 0.2Ω switch is included on the die together with all the control circuitry required to complete a high frequency, current-mode switching regulator. Current-mode control provides fast transient response and excellent loop stability. New design techniques achieve high efficiency at high switching frequencies over a wide operating voltage range. A low dropout internal regulator maintains consistent performance over a wide range of inputs from 24V systems to Li-Ion batteries. An operating supply current of 1mA maintains high efficiency, especially at lower output currents. Shutdown reduces quiescent current to 6μA. Maximum switch current remains constant at all duty cycles. Synchronization allows an external logic level signal to increase the internal oscillator from 1.5MHz to 2MHz. The LT1961 is available in an exposed pad, 8-pin MSOP package. Full cycle-by-cycle switch current limit protection and thermal shutdown are provided. High frequency operation allows the reduction of input and output filtering components and permits the use of chip inductors. ■ DSL Modems ■ Portable Computers ■ Battery-Powered Systems ■ Distributed Power Efficiency vs Load Current 5V to 12V Boost Converter LT1961 VIN VOUT 12V 0.5A* VIN 5V 1961 TA01 6800pF 100pF 6.8k 10k 1% 90.9k UPS120 10μF CERAMIC 2.2μF CERAMIC VSW SHDN FB OPEN OR HIGH = ON SYNC GND VC *MAXIMUM OUTPUT CURRENT IS SUBJECT TO THERMAL DERATING. 6.8μH 2 6 8 3,4 7 5 1 LOAD CURRENT (mA) 0 EFFICIENCY (%) 90 85 80 75 70 65 60 100 200 300 400 1961 TA01a 500 VIN = 5V VOUT = 12V , LT, LTC and LTM are registered trademarks of Linear Technology Corporation. All other trademarks are the property of their respective owners. *Patent Pending 2 LT1961 1961fa ABSOLUTE MAXIMUM RATINGS W W W U Input Voltage .......................................................... 25V Switch Voltage ......................................................... 35V SHDN Pin ............................................................... 25V FB Pin Current ....................................................... 1mA SYNC Pin Current .................................................. 1mA Operating Junction Temperature Range (Note 2) LT1961E, LT1961I ........................... – 40°C to 125°C Storage Temperature Range ................ – 65°C to 150°C Lead Temperature (Soldering, 10 sec)................. 300°C (Note 1) TJMAX = 125°C, θJA = 50°C/W GROUND PAD CONNECTED TO LARGE COPPER AREA 1234 VIN SW GND GND 8765 SYNC VC FB SHDN TOP VIEW MS8E PACKAGE 8-LEAD PLASTIC MSOP PI CO FIGURATIOU U U PARAMETER CONDITION MIN TYP MAX UNITS Recommended Operating Voltage ● 3 25 V Maximum Switch Current Limit ● 1.5 2 3 A Oscillator Frequency 3.3V < VIN < 25V ● 1 1.5 MHz Switch On Voltage Drop ISW = 1.5A ● 310 500 mV VIN Undervoltage Lockout (Note 3) ● 2.47 2.6 2.73 V VIN Supply Current ISW = 0A ● 0.9 1.3 mA VIN Supply Current/ISW ISW = 1.5A 27 mA/A Shutdown Supply Current VSHDN = 0V, VIN = 25V, VSW = 25V 6 20 μA ● 45 μA Feedback Voltage 3V < VIN < 25V, 0.4V < VC < 0.9V 1.182 1.2 1.218 V ● 1.176 1.224 V ELECTRICAL CHARACTERISTICS The ● denotes the specifications which apply over the full operating temperature range, otherwise specifications are at TA = 25°C. VIN = 15V, VC = 0.8V, SHDN, SYNC and switch open unless otherwise noted. LEAD FREE FINISH TAPE AND REEL PART MARKING* PACKAGE DESCRIPTION TEMPERATURE RANGE LT1961EMS8E#PBF LT1961EMS8E#TRPBF LTQY 8-Lead Plastic MSOP –40°C to 125°C LT1961IMS8E#PBF LT1961IMS8E#TRPBF LTQY 8-Lead Plastic MSOP –40°C to 125°C LEAD BASED FINISH TAPE AND REEL PART MARKING* PACKAGE DESCRIPTION TEMPERATURE RANGE LT1961EMS8E LT1961EMS8E#TR LTQY 8-Lead Plastic MSOP –40°C to 125°C LT1961IMS8E LT1961IMS8E#TR LTQY 8-Lead Plastic MSOP –40°C to 125°C ORDER IUFORWATIOU Consult LTC Marketing for parts specified with wider operating temperature ranges. *Temperature grades are identified by a label on the shipping container. For more information on lead free part marking, go to: http://www.linear.com/leadfree/ For more information on tape and reel specifications, go to: http://www.linear.com/tapeandreel/ 3 LT1961 1961fa ELECTRICAL CHARACTERISTICS PARAMETER CONDITION MIN TYP MAX UNITS FB Input Current ● 0 –0.2 –0.4 μA FB to VC Voltage Gain 0.4V < VC < 0.9V 150 350 FB to VC Transconductance ΔIVC = ±10μA ● 500 850 1300 μMho VC Pin Source Current VFB = 1V ● – 85 –120 –165 μA VC Pin Sink Current VFB = 1.4V ● 70 110 165 μA VC Pin to Switch Current Transconductance 2.4 A/V VC Pin Minimum Switching Threshold Duty Cycle = 0% 0.3 V VC Pin 1.5A ISW Threshold 0.9 V Maximum Switch Duty Cycle VC = 1.2V, ISW = 100mA ● 80 90 % VC = 1.2V, ISW = 1A, 25°C ≤ TA ≤ 125°C 75 80 % VC = 1.2V, ISW = 1A, TA ≤ 25°C 70 75 % SHDN Threshold Voltage ● 1.28 1.35 1.42 V SHDN Input Current (Shutting Down) SHDN = 60mV Above Threshold ● –7 –10 –13 μA SHDN Threshold Current Hysteresis SHDN = 100mV Below Threshold 4 7 10 μA SYNC Threshold Voltage 1.5 2.2 V SYNC Input Frequency 1.5 2 MHz SYNC Pin Resistance ISYNC = 1mA 20 kΩ The ● denotes the specifications which apply over the full operating temperature range, otherwise specifications are at TA = 25°C. VIN = 15V, VC = 0.8V, SHDN, SYNC and switch open unless otherwise noted. Note 1: Stresses beyond those listed under Absolute Maximum Ratings may cause permanent damage to the device. Exposure to any Absolute Maximum Rating condition for extended periods may affect device reliability and lifetime. Note 2: The LT1961E is guaranteed to meet performance specifications from 0°C to 125°C junction temperature. Specifications over the –40°C to 125°C operating junction temperature range are assured by design, characterization and correlation with statistical process controls. The LT1961I is guaranteed over the – 40ºC to 125ºC operating junction temperature range. Note 3: Minimum input voltage is defined as the voltage where the internal regulator enters lockout. Actual minimum input voltage to maintain a regulated output will depend on output voltage and load current. See Applications Information. 4 LT1961 1961fa TYPICAL PERFORMANCE CHARACTERISTICS U W FB vs Temperature Switch On Voltage Drop Oscillator Frequency SHDN Threshold vs Temperature SHDN Supply Current vs VIN SHDN IP Current vs Temperature TEMPERATURE (°C) –50 –25 0 25 50 75 100 125 FB VOLTAGE (V) 1961 G01 1.22 1.21 1.20 1.19 1.18 SWITCH CURRENT (A) 0 0.5 1 1.5 SWITCH VOLTAGE (mV) 1961 G02 400 350 300 250 200 150 100 50 0 125°C 25°C –40°C TEMPERATURE (°C) –50 –25 0 25 50 75 100 125 FREQUENCY (MHz) 1961 G03 1.5 1.4 1.3 1.2 1.1 TA = 25°C TEMPERATURE (°C) –50 –25 0 25 50 75 100 125 SHDN THRESHOLD (V) 1961 G04 1.40 1.38 1.36 1.34 1.32 1.30 VIN (V) 0 5 10 15 20 25 30 VIN CURRENT (μA) 1961 G05 7 6 5 4 3 2 1 0 TA = 25°C SHDN = 0V TEMPERATURE (°C) –50 –25 0 25 50 75 100 125 SHDN INPUT (μA) 1961G06 –12 –10 –8 –6 –4 –2 0 STARTING UP SHUTTING DOWN SHDN Supply Current Input Supply Current Current Limit Foldback SHUTDOWN VOLTAGE (V) 0 0.2 0.4 0.6 0.8 1 1.2 1.4 VIN CURRENT (μA) 1961 G07 300 250 200 150 100 50 0 TA = 25°C VIN = 15V INPUT VOLTAGE (V) 0 5 10 15 20 25 30 VIN CURRENT (μA) 1961 G08 1200 1000 800 600 400 200 0 MINIMUM INPUT VOLTAGE TA = 25°C FEEDBACK VOLTAGE (V) 0 0.2 0.4 0.6 0.8 1 1.2 SWITCH PEAK CURRENT (A) 1961 G09 2.0 1.5 1.0 0.5 0 FB INPUT CURRENT (μA) 40 30 20 10 0 FB CURRENT SWITCH CURRENT TA = 25°C 5 LT1961 1961fa FB: The feedback pin is used to set output voltage using an external voltage divider that generates 1.2V at the pin with the desired output voltage. If required, the current limit can be reduced during start up when the FB pin is below 0.5V (see the Current Limit Foldback graph in the Typical Performance Characteristics section). An impedance of less than 5kΩ at the FB pin is needed for this feature to operate. VIN: This pin powers the internal circuitry and internal regulator. Keep the external bypass capacitor close to this pin. GND: Short GND pins 3 and 4 and the exposed pad on the PCB. The GND is the reference for the regulated output, so load regulation will suffer if the “ground” end of the load is not at the same voltage as the GND of the IC. This condition occurs when the load current flows through the metal path between the GND pins and the load ground point. Keep the ground path short between the GND pins and the load and use a ground plane when possible. Keep the path between the input bypass and the GND pins short. The exposed pad should be attached to a large copper area to improve thermal resistance. VSW: The switch pin is the collector of the on-chip power NPN switch and has large currents flowing through it. Keep the traces to the switching components as short as possible to minimize radiation and voltage spikes. SYNC: The sync pin is used to synchronize the internal oscillator to an external signal. It is directly logic compatible and can be driven with any signal between 20% and 80% duty cycle. The synchronizing range is equal to initial operating frequency, up to 2MHz. See Synchronization section in Applications Information for details. When not in use, this pin should be grounded. SHDN: The shutdown pin is used to turn off the regulator and to reduce input drain current to a few microamperes. The 1.35V threshold can function as an accurate undervoltage lockout (UVLO), preventing the regulator from operating until the input voltage has reached a predetermined level. Float or pull high to put the regulator in the operating mode. VC: The VC pin is the output of the error amplifier and the input of the peak switch current comparator. It is normally used for frequency compensation, but can do double duty as a current clamp or control loop override. This pin sits at about 0.3V for very light loads and 0.9V at maximum load. PIN FUNCTIONSU U U 6 LT1961 1961fa amplifier commands current to be delivered to the output rather than voltage. A voltage fed system will have low phase shift up to the resonant frequency of the inductor and output capacitor, then an abrupt 180° shift will occur. The current fed system will have 90° phase shift at a much lower frequency, but will not have the additional 90° shift until well beyond the LC resonant frequency. This makes it much easier to frequency compensate the feedback loop and also gives much quicker transient response. A comparator connected to the shutdown pin disables the internal regulator, reducing supply current. The LT1961 is a constant frequency, current-mode boost converter. This means that there is an internal clock and two feedback loops that control the duty cycle of the power switch. In addition to the normal error amplifier, there is a current sense amplifier that monitors switch current on a cycle-by-cycle basis. A switch cycle starts with an oscillator pulse which sets the RS flip-flop to turn the switch on. When switch current reaches a level set by the inverting input of the comparator, the flip-flop is reset and the switch turns off. Output voltage control is obtained by using the output of the error amplifier to set the switch current trip point. This technique means that the error Figure 1. Block Diagram BLOCK DIAGRAMW – + – + Σ VIN 2.5V BIAS REGULATOR 1.25MHz OSCILLATOR SW FB VC GND GND 1767 F01 SLOPE COMP 0.01Ω INTERNAL VCC CURRENT SENSE AMPLIFIER VOLTAGE GAIN = 40 SYNC SHDN SHUTDOWN COMPARATOR CURRENT COMPARATOR ERROR AMPLIFIER gm = 850μMho RS FLIP-FLOP DRIVER CIRCUITRY S R 0.3V Q1 POWER SWITCH 1.2V – + + – 1.35V 3μA 7μA 1 8 5 7 6 3 4 2 7 LT1961 1961fa APPLICATIONS INFORMATION W U U U FB RESISTOR NETWORK The suggested resistance (R2) from FB to ground is 10k 1%. This reduces the contribution of FB input bias current to output voltage to less than 0.2%. The formula for the resistor (R1) from VOUT to FB is: R R V R A OUT 1 2 12 1 2 2 0 2 = ( − ) − μ . . (. ) defines the pole frequency of the output stage, an X7R or X5R type ceramic, which have good temperature stability, is recommended. Tantalum capacitors are usually chosen for their bulk capacitance properties, useful in high transient load applications. ESR rather than absolute value defines output ripple at 1.25MHz. Values in the 22μF to 100μF range are generally needed to minimize ESR and meet ripple current ratings. Care should be taken to ensure the ripple ratings are not exceeded. Table 1. Surface Mount Solid Tantalum Capacitor ESR and Ripple Current E Case Size ESR (Max, Ω) Ripple Current (A) AVX TPS, Sprague 593D 0.1 to 0.3 0.7 to 1.1 AVX TAJ 0.7 to 0.9 0.4 D Case Size AVX TPS, Sprague 593D 0.1 to 0.3 0.7 to 1.1 C Case Size AVX TPS 0.2 (typ) 0.5 (typ) INPUT CAPACITOR Unlike the output capacitor, RMS ripple current in the input capacitor is normally low enough that ripple current rating is not an issue. The current waveform is triangular, with an RMS value given by: I V V V L f V RIPPLE RMS IN OUT IN OUT ( )= ( )( − ) ( )( )( ) 0.29 At higher switching frequency, the energy storage requirement of the input capacitor is reduced so values in the range of 1μF to 4.7μF are suitable for most applications. Y5V or similar type ceramics can be used since the absolute value of capacitance is less important and has no significant effect on loop stability. If operation is required close to the minimum input voltage required by either the output or the LT1961, a larger value may be necessary. This is to prevent excessive ripple causing dips below the minimum operating voltage resulting in erratic operation. Figure 2. Feedback Network OUTPUT CAPACITOR Step-up regulators supply current to the output in pulses. The rise and fall times of these pulses are very fast. The output capacitor is required to reduce the voltage ripple this causes. The RMS ripple current can be calculated from: IRIPPLE(RMS) =IOUT (VOUT − VIN) / VIN The LT1961 will operate with both ceramic and tantalum output capacitors. Ceramic capacitors are generally chosen for their small size, very low ESR (effective series resistance), and good high frequency operation, reducing output ripple voltage. Their low ESR removes a useful zero in the loop frequency response, common to tantalum capacitors. To compensate for this, the VC loop compensation pole frequency must typically be reduced by a factor of 10. Typical ceramic output capacitors are in the 1μF to 10μF range. Since the absolute value of capacitance – + 1.2V VSW VC GND 1961 F02 R1 R2 10k OUTPUT ERROR AMPLIFIER FB LT1961 + 8 LT1961 1961fa APPLICATIONS INFORMATION W U U U INDUCTOR CHOICE AND MAXIMUM OUTPUT CURRENT When choosing an inductor, there are 2 conditions that limit the minimum inductance; required output current, and avoidance of subharmonic oscillation. The maximum output current for the LT1961 in a standard boost converter configuration with an infinitely large inductor is: I A V V OUT MAX IN OUT ( ) . • = 1 5 η Where η = converter efficiency (typically 0.87 at high current). As the value of inductance is reduced, ripple current increases and IOUT(MAX) is reduced. The minimum inductance for a required output current is given by: L V V V V f V I V MIN IN OUT IN OUT OUT OUT IN = ⎛ ⎝ ⎜ ⎞ ⎠ ⎟ ( – ) ( ) . – ( )( ) • 2 15 η The second condition, avoidance of subharmonic oscillation, must be met if the operating duty cycle is greater than 50%. The slope compensation circuit within the LT1961 prevents subharmonic oscillation for inductor ripple currents of up to 0.7AP-P, defining the minimum inductor value to be: L V V V V f MIN IN OUT IN OUT = ( – ) 0.7 ( ) These conditions define the absolute minimum inductance. However, it is generally recommended that to prevent excessive output noise, and difficulty in obtaining stability, the ripple current is no more than 40% of the average inductor current. Since inductor ripple is: I V V V V L f P P RIPPLE IN OUT IN OUT − = ( – ) ( )( ) The recommended minimum inductance is: L V V V V I f MIN IN OUT IN OUT OUT = ( ) ( – ) . ( ) ( )( ) 2 0 4 2 The inductor value may need further adjustment for other factors such as output voltage ripple and filtering requirements. Remember also, inductance can drop significantly with DC current and manufacturing tolerance. The inductor must have a rating greater than its peak operating current to prevent saturation resulting in efficiency loss. Peak inductor current is given by: I V I V V V V V L f LPEAK OUT OUT IN IN OUT IN OUT = ( )( ) + − • ( ) η 2 ( )( ) Also, consideration should be given to the DC resistance of the inductor. Inductor resistance contributes directly to the efficiency losses in the overall converter. Suitable inductors are available from Coilcraft, Coiltronics, Dale, Sumida, Toko, Murata, Panasonic and other manufactures. Table 2 PART NUMBER VALUE (uH) ISAT(DC) (Amps) DCR (Ω) HEIGHT (mm) Coiltronics TP1-2R2 2.2 1.3 0.188 1.8 TP2-2R2 2.2 1.5 0.111 2.2 TP3-4R7 4.7 1.5 0.181 2.2 TP4- 100 10 1.5 0.146 3.0 Murata LQH1C1R0M04 1.0 0.51 0.28 1.8 LQH3C1R0M24 1.0 1.0 0.06 2.0 LQH3C2R2M24 2.2 0.79 0.1 2.0 LQH4C1R5M04 1.5 1 0.09 2.6 Sumida CD73- 100 10 1.44 0.080 3.5 CDRH4D18-2R2 2.2 1.32 0.058 1.8 CDRH5D18-6R2 6.2 1.4 0.071 1.8 CDRH5D28-100 10 1.3 0.048 2.8 Coilcraft 1008PS-272M 2.7 1.3 0.14 2.7 LPO1704-222M 2.2 1.6 0.12 1.0 LPO1704-332M 3.3 1.3 0.16 1.0 9 LT1961 1961fa APPLICATIONS INFORMATION W U U U shutdown pin can be used. The threshold voltage of the shutdown pin comparator is 1.35V. A 3μA internal current source defaults the open pin condition to be operating (see Typical Performance Graphs). Current hysteresis is added above the SHDN threshold. This can be used to set voltage hysteresis of the UVLO using the following: R V V A R V V V R A H L H 1 7 2 1 35 1 35 1 3 = − μ = ( − ) + μ . . VH – Turn-on threshold VL – Turn-off threshold Example: switching should not start until the input is above 4.75V and is to stop if the input falls below 3.75V. VH = 4.75V VL = 3.75V R V V A k R V V V k A k 1 4 75 3 75 7 143 2 1 35 4 75 1 35 143 3 50 4 = − μ = = ( − ) + μ = . . . . . . Keep the connections from the resistors to the SHDN pin short and make sure that the interplane or surface capacitance to the switching nodes are minimized. If high resistor values are used, the SHDN pin should be bypassed with a 1nF capacitor to prevent coupling problems from the switch node. CATCH DIODE The suggested catch diode (D1) is a UPS120 or 1N5818 Schottky. It is rated at 1A average forward current and 20V/30V reverse voltage. Typical forward voltage is 0.5V at 1A. The diode conducts current only during switch off time. Peak reverse voltage is equal to regulator output voltage. Average forward current in normal operation is equal to output current. SHUTDOWN AND UNDERVOLTAGE LOCKOUT Figure 4 shows how to add undervoltage lockout (UVLO) to the LT1961. Typically, UVLO is used in situations where the input supply is current limited, or has a relatively high source resistance. A switching regulator draws constant power from the source, so source current increases as source voltage drops. This looks like a negative resistance load to the source and can cause the source to current limit or latch low under low source voltage conditions. UVLO prevents the regulator from operating at source voltages where these problems might occur. Figure 4. Undervoltage Lockout 1.35V GND INPUT R1 1961 F04 SHDN VCC IN LT1961 3μA C1 R2 7μA An internal comparator will force the part into shutdown below the minimum VIN of 2.6V. This feature can be used to prevent excessive discharge of battery-operated systems. If an adjustable UVLO threshold is required, the 10 LT1961 1961fa SYNCHRONIZATION The SYNC pin, is used to synchronize the internal oscillator to an external signal. The SYNC input must pass from a logic level low, through the maximum synchronization threshold with a duty cycle between 20% and 80%. The input can be driven directly from a logic level output. The synchronizing range is equal to initial operating frequency up to 2MHz. This means that minimum practical sync frequency is equal to the worst-case high self-oscillating frequency (1.5MHz), not the typical operating frequency of 1.25MHz. Caution should be used when synchronizing above 1.7MHz because at higher sync frequencies the amplitude of the internal slope compensation used to prevent subharmonic switching is reduced. Higher inductor values will tend to eliminate this problem. See Frequency Compensation section for a discussion of an entirely different cause of subharmonic switching before assuming that the cause is insufficient slope compensation. Application Note 19 has more details on the theory of slope compensation. LAYOUT CONSIDERATIONS As with all high frequency switchers, when considering layout, care must be taken to achieve optimal electrical, thermal and noise performance. For maximum efficiency, switch rise and fall times are typically in the nanosecond range. To prevent noise both radiated and conducted, the APPLICATIONS INFORMATION W U U U high speed switching current path, shown in Figure 5, must be kept as short as possible. This is implemented in the suggested layout of Figure 6. Shortening this path will also reduce the parasitic trace inductance of approximately 25nH/inch. At switch off, this parasitic inductance produces a flyback spike across the LT1961 switch. When operating at higher currents and output voltages, with poor layout, this spike can generate voltages across the LT1961 that may exceed its absolute maximum rating. A ground plane should always be used under the switcher circuitry to prevent interplane coupling and overall noise. The VC and FB components should be kept as far away as possible from the switch node. The LT1961 pinout has been designed to aid in this. The ground for these components should be separated from the switch current path. Failure to do so will result in poor stability or subharmonic like oscillation. Board layout also has a significant effect on thermal resistance. The exposed pad is the copper plate that runs under the LT1961 die. This is the best thermal path for heat out of the package. Soldering the pad onto the board will reduce die temperature and increase the power capability of the LT1961. Provide as much copper area as possible around this pad. Adding multiple solder filled feedthroughs under and around the pad to the ground plane will also help. Similar treatment to the catch diode and inductor terminations will reduce any additional heating effects. 1961 F05 VOUT L1 SW GND LT1961 D1 C1 C3 VIN HIGH FREQUENCY SWITCHING PATH LOAD Figure 5. High Speed Switching Path 11 LT1961 1961fa Figure 6. Typical Application and Suggested Layout (Topside Only Shown) LT1961 VIN OUTPUT 12V 0.5A* INPUT 5V C2 6800pF C4 R3 100pF 6.8k R2 10k 1% R1 90.9k D1 UPS120 C1 10μF CERAMIC C3 2.2μF CERAMIC VSW SHDN FB OPEN OR HIGH = ON SYNC GND VC *MAXIMUM OUTPUT CURRENT IS SUBJECT TO THERMAL DERATING. L1 6.8μH VOUT INPUT GND C3 C1 R2 R1 L1 D1 KELVIN SENSE VOUT MINIMIZE LT1961, C1, D1 LOOP KEEP FB AND VC COMPONENTS AWAY FROM HIGH FREQUENCY, HIGH INPUT COMPONENTS PLACE FEEDTHROUGHS AROUND GROUND PIN FOR GOOD THERMAL CONDUCTIVITY LT1961EMS8E GND C4 U1 SOLDER EXPOSED GROUND PAD TO BOARD R3 C2 APPLICATIONS INFORMATION W U U U 12 LT1961 1961fa APPLICATIONS INFORMATION W U U U THERMAL CALCULATIONS Power dissipation in the LT1961 chip comes from four sources: switch DC loss, switch AC loss, drive current, and input quiescent current. The following formulas show how to calculate each of these losses. These formulas assume continuous mode operation, so they should not be used for calculating efficiency at light load currents. DC duty cycle V V V I V I V OUT IN OUT SW OUT OUT IN , ( ) ( )( ) = − = Switch loss: PSW = (DC)(ISW)2(RSW)+ 17n(ISW)(VOUT )(f) VIN loss: P V I DC VIN mA V IN SW = + IN ( )( )( ) ( ) 50 1 RSW = Switch resistance (≈ 0.27Ω hot) Example: VIN = 5V, VOUT = 12V and IOUT = 0.5A Total power dissipation = 0.23 + 0.31 + 0.07 + 0.005 = 0.62W Thermal resistance for LT1961 package is influenced by the presence of internal or backside planes. With a full plane under the package, thermal resistance will be about 50°C/W. To calculate die temperature, use the appropriate thermal resistance number and add in worst-case ambient temperature: TJ = TA + θJA (PTOT) If a true die temperature is required, a measurement of the SYNC to GND pin resistance can be used. The SYNC pin resistance across temperature must first be calibrated, with no device power, in an oven. The same measurement can then be used in operation to indicate the die temperature. FREQUENCY COMPENSATION Loop frequency compensation is performed on the output of the error amplifier (VC pin) with a series RC network. The main pole is formed by the series capacitor and the output impedance (≈500kΩ) of the error amplifier. The pole falls in the range of 2Hz to 20Hz. The series resistor creates a “zero” at 1kHz to 5kHz, which improves loop stability and transient response. A second capacitor, typically one-tenth the size of the main compensation capacitor, is sometimes used to reduce the switching frequency ripple on the VC pin. VC pin ripple is caused by output voltage ripple attenuated by the output divider and multiplied by the error amplifier. Without the second capacitor, VC pin ripple is: VC Pin Ripple = VRIPPLE = Output ripple (VP–P) gm = Error amplifier transconductance (≈850μmho) RC = Series resistor on VC pin VOUT = DC output voltage 1.2(VRIPPLE)(gm)(RC) (VOUT) To prevent irregular switching, VC pin ripple should be kept below 50mVP–P. Worst-case VC pin ripple occurs at maximum output load current and will also be increased if poor quality (high ESR) output capacitors are used. The addition of a 47pF capacitor on the VC pin reduces switching frequency ripple to only a few millivolts. A low value for RC will also reduce VC pin ripple, but loop phase margin may be inadequate. 13 LT1961 1961fa LT1961 FB VIN VC VIN 5V TO 10V *DALE LPE-4841-100MB GND LT1961 • TA02 S/S VSW P6KE-20A 1N4148 UPS140 UPS140 C1 4.7μF R2 10k 1% R1 115k 1% C2 2.2nF C3 100pF R3 10k –VOUT –15V VOUT 15V C4 47μF C5 47μF ON OFF 2, 3 8, 9 7 T1* 4 10 1 • • • + + + Dual Output Flyback Converter TYPICAL APPLICATIO SU LT1961 VIN GND VIN** 4V TO 9V VC FB LT1961 • TA03 S/S VSW C1 4.7μF 20V C4 2.2nF C5 100pF R1 10k R3 10k 1% R2 31.6k 1% VOUT † 5V C3 47μF 10V ON OFF L1A* 10μH • • L1B* 10μH C2 4.7μF BH ELECTRONICS 511-1012 INPUT VOLTAGE MAY BE GREATER OR LESS THAN OUTPUT VOLTAGE D1 UPS120 VIN 4V 5V 6V 7V 9V IOUT 0.59A 0.65A 0.70A 0.74A 0.80A †MAX IOUT * ** + + 4V-9VIN to 5VOUT SEPIC Converter** 14 LT1961 1961fa LT1961 VIN GND VC FB LT1961 • TA04 S/S VSW L1 4.7μH C1 10μF SINGLE Li-Ion CELL C4 47μF 10V C2 2.2nF C3 100pF R3 10k R2 10k 1% R1 31.6k 1% VOUT 5V D1 UPS120 ON OFF + + + VIN 2.7V 3.3V 3.6V IOUT 0.75A 0.93A 1.0A Single Li-Ion Cell to 5V TYPICAL APPLICATIO SU 15 LT1961 1961fa PACKAGE DESCRIPTIONU Information furnished by Linear Technology Corporation is believed to be accurate and reliable. However, no responsibility is assumed for its use. Linear Technology Corporation makes no representation that the interconnection of its circuits as described herein will not infringe on existing patent rights. MSOP (MS8E) 0307 REV D 0.53 ± 0.152 (.021 ± .006) SEATING PLANE NOTE: 1. DIMENSIONS IN MILLIMETER/(INCH) 2. DRAWING NOT TO SCALE 3. DIMENSION DOES NOT INCLUDE MOLD FLASH, PROTRUSIONS OR GATE BURRS. MOLD FLASH, PROTRUSIONS OR GATE BURRS SHALL NOT EXCEED 0.152mm (.006") PER SIDE 4. DIMENSION DOES NOT INCLUDE INTERLEAD FLASH OR PROTRUSIONS. INTERLEAD FLASH OR PROTRUSIONS SHALL NOT EXCEED 0.152mm (.006") PER SIDE 5. LEAD COPLANARITY (BOTTOM OF LEADS AFTER FORMING) SHALL BE 0.102mm (.004") MAX 0.18 (.007) 0.254 (.010) 1.10 (.043) MAX 0.22 – 0.38 (.009 – .015) TYP 0.86 (.034) REF 0.65 (.0256) BSC 0° – 6° TYP DETAIL “A” DETAIL “A” GAUGE PLANE 1 2 3 4 4.90 ± 0.152 (.193 ± .006) 8 8 1 BOTTOM VIEW OF EXPOSED PAD OPTION 7 6 5 3.00 ± 0.102 (.118 ± .004) (NOTE 3) 3.00 ± 0.102 (.118 ± .004) (NOTE 4) 0.52 (.0205) REF 1.83 ± 0.102 (.072 ± .004) 2.06 ± 0.102 (.081 ± .004) 5.23 (.206) MIN 3.20 – 3.45 (.126 – .136) 2.083 ± 0.102 (.082 ± .004) 2.794 ± 0.102 (.110 ± .004) 0.889 ± 0.127 (.035 ± .005) RECOMMENDED SOLDER PAD LAYOUT 0.42 ± 0.038 (.0165 ± .0015) TYP 0.65 (.0256) BSC 0.1016 ± 0.0508 (.004 ± .002) MS8E Package 8-Lead Plastic MSOP, Exposed Die Pad (Reference LTC DWG # 05-08-1662 Rev D) 16 LT1961 1961fa PART NUMBER DESCRIPTION COMMENTS LT1308A 600kHz, 2A, Step-Up Regulator 30V Switch, VIN = 1V to 6V, Low Battery Comparator, S8 Package LT1310 4.5MHz, 1.5A Step-Up with Phase Lock Loop 34V Switch, VIN = 2.75V to 18V, VOUT up to 35V, MS10E Package LT1370 High Efficiency DC/DC Converter 42V Switch, 6A, 500kHz Switch, DD-Pak, TO-220 Package LT1371 High Efficiency DC/DC Converter 35V Switch, 3A, 500kHz Switch, DD-Pak, TO-220 Package LT1372/LT1377 500kHz and 1MHz High Efficiency 1.5A Switching Regulators Boost Topology, VIN(MIN) = 2.7V, S8 Package LT1946/LT1946A 1.2MHz/2.7MHz, 1.5A, Monolithic Step-Up Regulator VIN = 2.6V to 16V, VOUT up to 34V, Integrated SS, MS8 Package LTC3400/ 1.2MHz, 600mA, Synchronous Step-Up VIN = 0.85V to 5V, VOUT to 5.5V, Up to 95% Efficiency, LTC3400B ThinSOT Package LTC3401 Single Cell, High Current (1A), Micropower, Synchronous 3MHz VIN = 0.85V to 5V, VOUT to 5.5V, Up to 97% Efficiency Step-Up DC/DC Converter Synchronizable, Oscillator from 100kHz to 3MHz, MS10 Package LTC3402 Single Cell, High Current (2A), Micropower, Synchronous 3MHz VIN = 0.85V to 5V, VOUT to 5.5V, Up to 95% Efficiency Step-Up DC/DC Converter Synchronizable, Oscillator from 100kHz to 3MHz, MS10 Package LTC3405/ 1.5MHz High Efficiency, IOUT = 300mA, Monolithic Synchronous VIN = 2.5V to 5.5V, VOUT to 0.8V, Up to 95% Efficiency, 100% LTC3405A Step-Down Regulator Duty Cycle, IQ = 20μA, ThinSOT Package ThinSOT is a trademark of Linear Technology Corporation. LT 0707 REV A • PRINTED IN USA © LINEAR TECHNOLOGY CORPORATION 2001 RELATED PARTS Linear Technology Corporation 1630 McCarthy Blvd., Milpitas, CA 95035-7417 (408) 432-1900 ● FAX: (408) 434-0507 ● www.linear.com LASER 190Ω 1% 1N4002 0.1μF (ALL) 10k VIN 10μF VC VIN FB GND 2.2μF VIN 12V TO 25V 150Ω MUR405 L2 10μH LT1961 L1 5 4 1 3 2 11 8 HV DIODES 1800pF 10kV 0.01μF 5kV 1800pF 10kV 47k 5W 2.2μF 0.47μF L1 = Q1, Q2 = 0.47μF = HV DIODES = LASER = COILTRONICS CTX02-11128 ZETEX ZTX849 WIMA 3X 0.15μF TYPE MKP-20 SEMTECH-FM-50 HUGHES 3121H-P 10k LT1961 • TA05 VSW Q1 Q2 + + + COILTRONICS (407) 241-7876 U TYPICAL APPLICATIO High Voltage Laser Power Supply LT3757/LT3757A 1 3757afd n Wide Input Voltage Range: 2.9V to 40V n Positive or Negative Output Voltage Programming with a Single Feedback Pin n Current Mode Control Provides Excellent Transient Response n Programmable Operating Frequency (100kHz to 1MHz) with One External Resistor n Synchronizable to an External Clock n Low Shutdown Current < 1μA n Internal 7.2V Low Dropout Voltage Regulator n Programmable Input Undervoltage Lockout with Hysteresis n Programmable Soft-Start n Small 10-Lead DFN (3mm × 3mm) and Thermally Enhanced 10-Pin MSOP Packages Typical Application Description Boost, Flyback, SEPIC and Inverting Controller The LT®3757/LT3757A are wide input range, current mode, DC/DC controllers which are capable of generating either positive or negative output voltages. They can be configured as either a boost, flyback, SEPIC or inverting converter. The LT3757/LT3757A drive a low side external N-channel power MOSFET from an internal regulated 7.2V supply. The fixed frequency, current-mode architecture results in stable operation over a wide range of supply and output voltages. The operating frequency of LT3757/LT3757A can be set with an external resistor over a 100kHz to 1MHz range, and can be synchronized to an external clock using the SYNC pin. A low minimum operating supply voltage of 2.9V, and a low shutdown quiescent current of less than 1μA, make the LT3757/LT3757A ideally suited for batteryoperated systems. The LT3757/LT3757A feature soft-start and frequency foldback functions to limit inductor current during start-up and output short-circuit. The LT3757A has improved load transient performance compared to the LT3757. High Efficiency Boost Converter Features Applications n Automotive and Industrial Boost, Flyback, SEPIC and Inverting Converters n Telecom Power Supplies n Portable Electronic Equipment Efficiency SENSE LT3757 VIN VIN 8V TO 16V 10μF 25V X5R VOUT 24V 2A 0.01 41.2k 300kHz GATE FBX GND INTVCC SHDN/UVLO SYNC RT SS VC 200k 43.2k 0.1μF 22k 6.8nF 10μH 3757 TA01a 226k 16.2k 4.7μF 10V X5R 10μF 25V X5R 47μF 35V ×2 + OUTPUT CURRENT (A) 0.001 EFFICIENCY (%) 30 50 40 60 70 80 90 100 0.01 0.1 1 3757 TA01b 10 VIN = 8V VIN = 16V L, LT, LTC, LTM, Linear Technology, the Linear logo and Burst Mode are registered trademarks and No RSENSE and ThinSOT are trademarks of Linear Technology Corporation. All other trademarks are the property of their respective owners. LT3757/LT3757A 2 3757afd Pin Configuration Absolute Maximum Ratings VIN, SHDN/UVLO (Note 6)..........................................40V INTVCC.....................................................VIN + 0.3V, 20V GATE......................................................... INTVCC + 0.3V SYNC...........................................................................8V VC, SS..........................................................................3V RT.............................................................................1.5V SENSE.....................................................................±0.3V FBX.................................................................. –6V to 6V (Note 1) TOP VIEW DD PACKAGE 10-LEAD (3mm × 3mm) PLASTIC DFN 10 9 6 7 8 4 5 3 11 2 1 VIN SHDN/UVLO INTVCC GATE SENSE VC FBX SS RT SYNC TJMAX = 125°C, θJA = 43°C/W EXPOSED PAD (PIN 11) IS GND, MUST BE SOLDERED TO PCB 12345 VC FBX SS RT SYNC 10 9876 VIN SHDN/UVLO INTVCC GATE SENSE TOP VIEW MSE PACKAGE 10-LEAD PLASTIC MSOP 11 TJMAX = 150°C, θJA = 40°C/W EXPOSED PAD (PIN 11) IS GND, MUST BE SOLDERED TO PCB Order Information LEAD FREE FINISH TAPE AND REEL PART MARKING* PACKAGE DESCRIPTION TEMPERATURE RANGE LT3757EDD#PBF LT3757EDD#TRPBF LDYW 10-Lead (3mm × 3mm) Plastic DFN –40°C to 125°C LT3757IDD#PBF LT3757IDD#TRPBF LDYW 10-Lead (3mm × 3mm) Plastic DFN –40°C to 125°C LT3757EMSE#PBF LT3757EMSE#TRPBF LTDYX 10-Lead (3mm × 3mm) Plastic MSOP –40°C to 125°C LT3757IMSE#PBF LT3757IMSE#TRPBF LTDYX 10-Lead (3mm × 3mm) Plastic MSOP –40°C to 125°C LT3757HMSE#PBF LT3757HMSE#TRPBF LTDYX 10-Lead (3mm × 3mm) Plastic MSOP –40°C to 150°C LT3757MPMSE#PBF LT3757MPMSE#TRPBF LTDYX 10-Lead (3mm × 3mm) Plastic MSOP –55°C to 150°C LT3757AEDD#PBF LT3757AEDD#TRPBF LGGR 10-Lead (3mm × 3mm) Plastic DFN –40°C to 125°C LT3757AIDD#PBF LT3757AIDD#TRPBF LGGR 10-Lead (3mm × 3mm) Plastic DFN –40°C to 125°C LT3757AEMSE#PBF LT3757AEMSE#TRPBF LTGGM 10-Lead (3mm × 3mm) Plastic MSOP –40°C to 125°C LT3757AIMSE#PBF LT3757AIMSE#TRPBF LTGGM 10-Lead (3mm × 3mm) Plastic MSOP –40°C to 125°C LT3757AHMSE#PBF LT3757AHMSE#TRPBF LTGGM 10-Lead (3mm × 3mm) Plastic MSOP –40°C to 150°C LT3757AMPMSE#PBF LT3757AMPMSE#TRPBF LTGGM 10-Lead (3mm × 3mm) Plastic MSOP –55°C to 150°C Consult LTC Marketing for parts specified with wider operating temperature ranges. *The temperature grade is identified by a label on the shipping container. For more information on lead free part marking, go to: http://www.linear.com/leadfree/ For more information on tape and reel specifications, go to: http://www.linear.com/tapeandreel/ Operating Temperature Range (Notes 2, 8) LT3757E/LT3757AE............................ –40°C to 125°C LT3757I/LT3757AI.............................. –40°C to 125°C LT3757H/LT3757AH............................ –40°C to 150°C LT3757MP/LT3757AMP...................... –55°C to 150°C Storage Temperature Range DFN..................................................... –65°C to 125°C MSOP................................................. –65°C to 150°C Lead Temperature (Soldering, 10 sec) MSOP................................................................300°C LT3757/LT3757A 3 3757afd E lectrical Characteristics The l denotes the specifications which apply over the full operating temperature range, otherwise specifications are at TA = 25°C. VIN = 24V, SHDN/UVLO = 24V, SENSE = 0V, unless otherwise noted. PARAMETER CONDITIONS MIN TYP MAX UNITS VIN Operating Range 2.9 40 V VIN Shutdown IQ SHDN/UVLO = 0V SHDN/UVLO = 1.15V 0.1 1 6 μA μA VIN Operating IQ VC = 0.3V, RT = 41.2k 1.6 2.2 mA VIN Operating IQ with Internal LDO Disabled VC = 0.3V, RT = 41.2k, INTVCC = 7.5V 280 400 μA SENSE Current Limit Threshold l 100 110 120 mV SENSE Input Bias Current Current Out of Pin –65 μA Error Amplifier FBX Regulation Voltage (VFBX(REG)) VFBX > 0V (Note 3) VFBX < 0V (Note 3) l l 1.569 –0.816 1.6 –0.80 1.631 –0.784 V V FBX Overvoltage Lockout VFBX > 0V (Note 4) VFBX < 0V (Note 4) 6 7 8 11 10 14 % % FBX Pin Input Current VFBX = 1.6V (Note 3) VFBX = –0.8V (Note 3) –10 70 100 10 nA nA Transconductance gm (ΔIVC/ΔVFBX) (Note 3) 230 μS VC Output Impedance (Note 3) 5 MΩ VFBX Line Regulation [ΔVFBX /(ΔVIN • VFBX(REG))] VFBX > 0V, 2.9V < VIN < 40V (Notes 3, 7) VFBX < 0V, 2.9V < VIN < 40V (Notes 3, 7) 0.002 0.0025 0.056 0.05 %/V %/V VC Current Mode Gain (ΔVVC /ΔVSENSE) 5.5 V/V VC Source Current VFBX = 0V, VC = 1.5V –15 μA VC Sink Current VFBX = 1.7V VFBX = –0.85V 12 11 μA μA Oscillator Switching Frequency RT = 41.2k to GND, VFBX = 1.6V RT = 140k to GND, VFBX = 1.6V RT = 10.5k to GND, VFBX = 1.6V 270 300 100 1000 330 kHz kHz kHz RT Voltage VFBX = 1.6V 1.2 V Minimum Off-Time 220 ns Minimum On-Time 220 ns SYNC Input Low 0.4 V SYNC Input High 1.5 V SS Pull-Up Current SS = 0V, Current Out of Pin –10 μA Low Dropout Regulator INTVCC Regulation Voltage l 7 7.2 7.4 V INTVCC Undervoltage Lockout Threshold Falling INTVCC UVLO Hysteresis 2.6 2.7 0.1 2.8 V V INTVCC Overvoltage Lockout Threshold 16 17.5 V INTVCC Current Limit VIN = 40V VIN = 15V 30 40 95 55 mA mA INTVCC Load Regulation (ΔVINTVCC/ VINTVCC) 0 < IINTVCC < 20mA, VIN = 8V –0.9 –0.5 % INTVCC Line Regulation ΔVINTVCC/(VINTVCC • ΔVIN) 8V < VIN < 40V 0.008 0.03 %/V Dropout Voltage (VIN – VINTVCC) VIN = 6V, IINTVCC = 20mA 400 mV INTVCC Current in Shutdown SHDN/UVLO = 0V, INTVCC = 8V 16 μA LT3757/LT3757A 4 3757afd TEMPERATURE (°C) –75 –50 1580 1585 REGULATED FEEDBACK VOLTAGE (mV) 1590 1605 1600 0 50 75 1595 –25 25 100 125 150 3757 G01 VIN = 40V VIN = 24V VIN = 8V VIN = INTVCC = 2.9V SHDN/UVLO = 1.33V TEMPERATURE (°C) REGULATED FEEDBACK VOLTAGE (mV) –802 –800 –798 –788 –790 –792 –794 –804 –796 3757 G02 –75 –50 –25 0 25 50 75 100 125 150 VIN = 40V VIN = 24V VIN = 8V VIN = INTVCC = 2.9V SHDN/UVLO = 1.33V Typical Performance Characteristics Positive Feedback Voltage vs Temperature, VIN Negative Feedback Voltage vs Temperature, VIN Quiescent Current vs Temperature, VIN TA = 25°C, unless otherwise noted. E lectrical Characteristics The l denotes the specifications which apply over the full operating temperature range, otherwise specifications are at TA = 25°C. VIN = 24V, SHDN/UVLO = 24V, SENSE = 0V, unless otherwise noted. PARAMETER CONDITIONS MIN TYP MAX UNITS INTVCC Voltage to Bypass Internal LDO 7.5 V Logic Inputs SHDN/UVLO Threshold Voltage Falling VIN = INTVCC = 8V l 1.17 1.22 1.27 V SHDN/UVLO Input Low Voltage I(VIN) Drops Below 1μA 0.4 V SHDN/UVLO Pin Bias Current Low SHDN/UVLO = 1.15V 1.7 2 2.5 μA SHDN/UVLO Pin Bias Current High SHDN/UVLO = 1.30V 10 100 nA Gate Driver tr Gate Driver Output Rise Time CL = 3300pF (Note 5), INTVCC = 7.5V 22 ns tf Gate Driver Output Fall Time CL = 3300pF (Note 5), INTVCC = 7.5V 20 ns Gate VOL 0.05 V Gate VOH INTVCC –0.05 V Note 1: Stresses beyond those listed under Absolute Maximum Ratings may cause permanent damage to the device. Exposure to any Absolute Maximum Rating condition for extended periods may affect device reliability and lifetime. Note 2: The LT3757E/LT3757AE are guaranteed to meet performance specifications from the 0°C to 125°C junction temperature. Specifications over the –40°C to 125°C operating junction temperature range are assured by design, characterization and correlation with statistical process controls. The LT3757I/LT3757AI are guaranteed over the full –40°C to 125°C operating junction temperature range. The LT3757H/LT3757AH are guaranteed over the full –40°C to 150°C operating junction temperature range. High junction temperatures degrade operating lifetimes. Operating lifetime is derated at junction temperatures greater than 125°C. The LT3757MP/LT3757AMP are 100% tested and guaranteed over the full –55°C to 150°C operating junction temperature range. Note 3: The LT3757/LT3757A are tested in a feedback loop which servos VFBX to the reference voltages (1.6V and –0.8V) with the VC pin forced to 1.3V. Note 4: FBX overvoltage lockout is measured at VFBX(OVERVOLTAGE) relative to regulated VFBX(REG). Note 5: Rise and fall times are measured at 10% and 90% levels. Note 6: For VIN below 6V, the SHDN/UVLO pin must not exceed VIN. Note 7: SHDN/UVLO = 1.33V when VIN = 2.9V. Note 8: The LT3757/LT3757A include overtemperature protection that is intended to protect the device during momentary overload conditions. Junction temperature will exceed the maximum operating junction temperature when overtemperature protection is active. Continuous operation above the specified maximum operating junction temperature may impair device reliability. –75 –50 –25 0 25 50 75 100 125 150 TEMPERATURE (°C) 1.4 QUIESCENT CURRENT (mA) 1.6 1.8 1.5 1.7 3757 G03 VIN = 40V VIN = 24V VIN = INTVCC = 2.9V LT3757/LT3757A 5 3757afd Typical Performance Characteristics Switching Frequency vs Temperature SENSE Current Limit Threshold vs Temperature SENSE Current Limit Threshold vs Duty Cycle SHDN/UVLO Threshold vs Temperature SHDN/UVLO Current vs Voltage SHDN/UVLO Hysteresis Current vs Temperature Dynamic Quiescent Current vs Switching Frequency RT vs Switching Frequency Normalized Switching Frequency vs FBX TA = 25°C, unless otherwise noted. FBX VOLTAGE (V) –0.8 0 NORMALIZED FREQUENCY (%) 20 40 60 80 120 –0.4 0 0.4 0.8 3757 G06 1.2 1.6 100 –75 –50 –25 0 25 50 75 100 125 150 TEMPERATURE (°C) 100 SENSE THRESHOLD (mV) 105 110 115 120 3757 G08 DUTY CYCLE (%) 0 95 SENSE THRESHOLD (mV) 105 20 40 60 80 115 100 110 100 3757 G09 SHDN/UVLO VOLTAGE (V) 0 0 SHDN/UVLO CURRENT (μA) 20 10 20 30 40 10 30 40 3757 G11 –75 –50 –25 0 25 50 75 100 125 150 TEMPERATURE (°C) 1.6 ISHDN/UVLO (μA) 1.8 2.0 2.2 2.4 3757 G12 SWITCHING FREQUENCY (KHz) 0 0 IQ(mA) 15 20 35 300 500 600 700 10 5 25 30 100 200 400 800 900 1000 3757 G04 CL = 3300pF SWITCHING FREQUENCY (KHz) 0 10 RT (k) 100 1000 100 200 300 400 500 600 700 800 900 1000 3757 G05 –75 –50 –25 0 25 50 75 100 125 150 TEMPERATURE (°C) 270 SWITCHING FREQUENCY (kHz) 280 290 300 310 330 3757 G07 320 RT = 41.2K –75 –50 –25 0 25 50 75 100 125 150 TEMPERATURE (°C) 1.18 SHDN/UVLO VOLTAGE (V) 1.22 1.24 1.26 1.28 1.20 3757 G10 SHDN/UVLO FALLING SHDN/UVLO RISING LT3757/LT3757A 6 3757afd Typical Performance Characteristics INTVCC Line Regulation INTVCC Dropout Voltage vs Current, Temperature Gate Drive Rise and Fall Time vs INTVCC Typical Start-Up Waveforms INTVCC vs Temperature INTVCC Minimum Output Current vs VIN INTVCC Load Regulation TA = 25°C, unless otherwise noted. Gate Drive Rise and Fall Time vs CL FBX Frequency Foldback Waveforms During Overcurrent –75 –50 –25 0 25 50 75 100 125 150 TEMPERATURE (°C) 7.0 INTVCC (V) 7.1 7.2 7.3 7.4 3757 G13 VIN (V) 0 INTVCC VOLTAGE (V) 35 7.25 7.20 5 10 15 20 25 30 40 7.15 7.10 7.30 3757 G16 CL (nF) 0 TIME (ns) 60 70 80 50 40 5 10 15 20 25 30 10 0 30 90 20 3757 G18 RISE TIME INTVCC = 7.2V FALL TIME INTVCC (V) 3 TIME (ns) 20 25 15 10 6 9 12 15 5 0 30 3757 G19 CL = 3300pF RISE TIME FALL TIME 2ms/DIV VOUT 5V/DIV IL1A + IL1B 5A/DIV 3757 G20 VIN = 12V PAGE 31 CIRCUIT 50μs/DIV PAGE 31 CIRCUIT VOUT 10V/DIV VSW 20V/DIV IL1A + IL1B 5A/DIV 3757 G21 VIN = 12V INTVCC LOAD (mA) 0 6.8 7 7.1 7.2 7.3 20 40 50 60 6.9 10 30 70 3757 G15 INTVCC VOLTAGE (V) VIN = 8V INTVCC LOAD (mA) 0 DROPOUT VOLTAGE (mV) 500 600 300 400 200 5 10 15 20 100 0 700 3757 G17 150°C 125°C 25°C 0°C –55°C 75°C VIN = 6V VIN (V) 0 INTVCC CURRENT (mA) 50 60 70 40 3757 G14 40 30 0 10 5 10 15 20 25 30 35 20 90 80 TJ = 150°C INTVCC = 6V INTVCC = 4.5V LT3757/LT3757A 7 3757afd Pin Functions VC (Pin 1): Error Amplifier Compensation Pin. Used to stabilize the voltage loop with an external RC network. FBX (Pin 2): Positive and Negative Feedback Pin. Receives the feedback voltage from the external resistor divider across the output. Also modulates the frequency during start-up and fault conditions when FBX is close to GND. SS (Pin 3): Soft-Start Pin. This pin modulates compensation pin voltage (VC) clamp. The soft-start interval is set with an external capacitor. The pin has a 10μA (typical) pull-up current source to an internal 2.5V rail. The soft-start pin is reset to GND by an undervoltage condition at SHDN/ UVLO, an INTVCC undervoltage or overvoltage condition or an internal thermal lockout. RT (Pin 4): Switching Frequency Adjustment Pin. Set the frequency using a resistor to GND. Do not leave this pin open. SYNC (Pin 5): Frequency Synchronization Pin. Used to synchronize the switching frequency to an outside clock. If this feature is used, an RT resistor should be chosen to program a switching frequency 20% slower than the SYNC pulse frequency. Tie the SYNC pin to GND if this feature is not used. SYNC is ignored when FBX is close to GND. SENSE (Pin 6): The Current Sense Input for the Control Loop. Kelvin connect this pin to the positive terminal of the switch current sense resistor in the source of the N-channel MOSFET. The negative terminal of the current sense resistor should be connected to GND plane close to the IC. GATE (Pin 7): N-Channel MOSFET Gate Driver Output. Switches between INTVCC and GND. Driven to GND when IC is shut down, during thermal lockout or when INTVCC is above or below the OV or UV thresholds, respectively. INTVCC (Pin 8): Regulated Supply for Internal Loads and Gate Driver. Supplied from VIN and regulated to 7.2V (typical). INTVCC must be bypassed with a minimum of 4.7μF capacitor placed close to pin. INTVCC can be connected directly to VIN, if VIN is less than 17.5V. INTVCC can also be connected to a power supply whose voltage is higher than 7.5V, and lower than VIN, provided that supply does not exceed 17.5V. SHDN/UVLO (Pin 9): Shutdown and Undervoltage Detect Pin. An accurate 1.22V (nominal) falling threshold with externally programmable hysteresis detects when power is okay to enable switching. Rising hysteresis is generated by the external resistor divider and an accurate internal 2μA pull-down current. An undervoltage condition resets sort-start. Tie to 0.4V, or less, to disable the device and reduce VIN quiescent current below 1μA. VIN (Pin 10): Input Supply Pin. Must be locally bypassed with a 0.22μF, or larger, capacitor placed close to the pin. Exposed Pad (Pin 11): Ground. This pin also serves as the negative terminal of the current sense resistor. The Exposed Pad must be soldered directly to the local ground plane. LT3757/LT3757A 8 3757afd Block Diagram Figure 1. LT3757 Block Diagram Working as a SEPIC Converter L1 R1 R4 R3 M1 L2 R2 FBX 1.22V 2.5V CDC D1 CIN VOUT COUT2 COUT1 CVCC INTVCC VIN RSENSE VISENSE • + + VIN IS1 2μA 10 8 7 1 9 SHDN/UVLO INTERNAL REGULATOR AND UVLO TSD 165°C A10 Q3 VC VC 17.5V 2.7V UP 2.6V DOWN A8 UVLO IS2 10μA IS3 CC1 CC2 RC DRIVER SLOPE SENSE GND GATE 108mV SR1 + – + – CURRENT LIMIT RAMP GENERATOR 7.2V LDO • + – + – R O S 2.5V G1 RT RT SS CSS SYNC 1.25V 1.25V FBX FBX 1.6V –0.8V + – + – + – 2 3 5 4 + – + – 6 11 RAMP PWM COMPARATOR FREQUENCY FOLDBACK 100kHz-1MHz OSCILLATOR FREQ FOLDBACK FREQ PROG 3757 F01 – ++ Q1 A1 A2 1.72V –0.88V + – + – A11 A12 A3 A4 A5 A6 G5 G2 G6 A7 A9 Q2 D2 R5 8k D3 G4 G3 LT3757/LT3757A 9 3757afd Applications Information Main Control Loop The LT3757 uses a fixed frequency, current mode control scheme to provide excellent line and load regulation. Operation can be best understood by referring to the Block Diagram in Figure 1. The start of each oscillator cycle sets the SR latch (SR1) and turns on the external power MOSFET switch M1 through driver G2. The switch current flows through the external current sensing resistor RSENSE and generates a voltage proportional to the switch current. This current sense voltage VISENSE (amplified by A5) is added to a stabilizing slope compensation ramp and the resulting sum (SLOPE) is fed into the positive terminal of the PWM comparator A7. When SLOPE exceeds the level at the negative input of A7 (VC pin), SR1 is reset, turning off the power switch. The level at the negative input of A7 is set by the error amplifier A1 (or A2) and is an amplified version of the difference between the feedback voltage (FBX pin) and the reference voltage (1.6V or –0.8V, depending on the configuration). In this manner, the error amplifier sets the correct peak switch current level to keep the output in regulation. The LT3757 has a switch current limit function. The current sense voltage is input to the current limit comparator A6. If the SENSE pin voltage is higher than the sense current limit threshold VSENSE(MAX) (110mV, typical), A6 will reset SR1 and turn off M1 immediately. The LT3757 is capable of generating either positive or negative output voltage with a single FBX pin. It can be configured as a boost, flyback or SEPIC converter to generate positive output voltage, or as an inverting converter to generate negative output voltage. When configured as a SEPIC converter, as shown in Figure 1, the FBX pin is pulled up to the internal bias voltage of 1.6V by a voltage divider (R1 and R2) connected from VOUT to GND. Comparator A2 becomes inactive and comparator A1 performs the inverting amplification from FBX to VC. When the LT3757 is in an inverting configuration, the FBX pin is pulled down to –0.8V by a voltage divider connected from VOUT to GND. Comparator A1 becomes inactive and comparator A2 performs the noninverting amplification from FBX to VC. The LT3757 has overvoltage protection functions to protect the converter from excessive output voltage overshoot during start-up or recovery from a short-circuit condition. An overvoltage comparator A11 (with 20mV hysteresis) senses when the FBX pin voltage exceeds the positive regulated voltage (1.6V) by 8% and provides a reset pulse. Similarly, an overvoltage comparator A12 (with 10mV hysteresis) senses when the FBX pin voltage exceeds the negative regulated voltage (–0.8V) by 11% and provides a reset pulse. Both reset pulses are sent to the main RS latch (SR1) through G6 and G5. The power MOSFET switch M1 is actively held off for the duration of an output overvoltage condition. Programming Turn-On and Turn-Off Thresholds with the SHDN/UVLO Pin The SHDN/UVLO pin controls whether the LT3757 is enabled or is in shutdown state. A micropower 1.22V reference, a comparator A10 and a controllable current source IS1 allow the user to accurately program the supply voltage at which the IC turns on and off. The falling value can be accurately set by the resistor dividers R3 and R4. When SHDN/UVLO is above 0.7V, and below the 1.22V threshold, the small pull-down current source IS1 (typical 2μA) is active. The purpose of this current is to allow the user to program the rising hysteresis. The Block Diagram of the comparator and the external resistors is shown in Figure 1. The typical falling threshold voltage and rising threshold voltage can be calculated by the following equations: VVIN,FALLING = 1.22 • (R3 +R4) R4 VVIN,RISING = 2μA •R3+ VIN,FALLING For applications where the SHDN/UVLO pin is only used as a logic input, the SHDN/UVLO pin can be connected directly to the input voltage VIN for always-on operation. LT3757/LT3757A 10 3757afd Applications Information INTVCC Regulator Bypassing and Operation An internal, low dropout (LDO) voltage regulator produces the 7.2V INTVCC supply which powers the gate driver, as shown in Figure 1. If a low input voltage operation is expected (e.g., supplying power from a lithium-ion battery or a 3.3V logic supply), low threshold MOSFETs should be used. The LT3757 contains an undervoltage lockout comparator A8 and an overvoltage lockout comparator A9 for the INTVCC supply. The INTVCC undervoltage (UV) threshold is 2.7V (typical), with 100mV hysteresis, to ensure that the MOSFETs have sufficient gate drive voltage before turning on. The logic circuitry within the LT3757 is also powered from the internal INTVCC supply. The INTVCC overvoltage (OV) threshold is set to be 17.5V (typical) to protect the gate of the power MOSFET. When INTVCC is below the UV threshold, or above the OV threshold, the GATE pin will be forced to GND and the soft-start operation will be triggered. The INTVCC regulator must be bypassed to ground immediately adjacent to the IC pins with a minimum of 4.7μF ceramic capacitor. Good bypassing is necessary to supply the high transient currents required by the MOSFET gate driver. In an actual application, most of the IC supply current is used to drive the gate capacitance of the power MOSFET. The on-chip power dissipation can be a significant concern when a large power MOSFET is being driven at a high frequency and the VIN voltage is high. It is important to limit the power dissipation through selection of MOSFET and/ or operating frequency so the LT3757 does not exceed its maximum junction temperature rating. The junction temperature TJ can be estimated using the following equations: TJ = TA + PIC • θJA TA = ambient temperature θJA = junction-to-ambient thermal resistance PIC = IC power consumption = VIN • (IQ + IDRIVE) IQ = VIN operation IQ = 1.6mA IDRIVE = average gate drive current = f • QG f = switching frequency QG = power MOSFET total gate charge The LT3757 uses packages with an Exposed Pad for enhanced thermal conduction. With proper soldering to the Exposed Pad on the underside of the package and a full copper plane underneath the device, thermal resistance (θJA) will be about 43°C/W for the DD package and 40°C/W for the MSE package. For an ambient board temperature of TA = 70°C and maximum junction temperature of 125°C, the maximum IDRIVE (IDRIVE(MAX)) of the DD package can be calculated as: IDRIVE(MAX) = (TJ − TA) (θJA • VIN) −IQ = 1.28W VIN − 1.6mA The LT3757 has an internal INTVCC IDRIVE current limit function to protect the IC from excessive on-chip power dissipation. The IDRIVE current limit decreases as the VIN increases (see the INTVCC Minimum Output Current vs VIN graph in the Typical Performance Characteristics section). If IDRIVE reaches the current limit, INTVCC voltage will fall and may trigger the soft-start. Based on the preceding equation and the INTVCC Minimum Output Current vs VIN graph, the user can calculate the maximum MOSFET gate charge the LT3757 can drive at a given VIN and switch frequency. A plot of the maximum QG vs VIN at different frequencies to guarantee a minimum 4.5V INTVCC is shown in Figure 2. As illustrated in Figure 2, a trade-off between the operating frequency and the size of the power MOSFET may be needed in order to maintain a reliable IC junction temperature. Figure 2. Recommended Maximum QG vs VIN at Different Frequencies to Ensure INTVCC Higher Than 4.5V VIN (V) 0 QG (nC) 200 250 150 100 5 10 15 20 25 30 35 40 50 0 300 3757 F02 300kHz 1MHz LT3757/LT3757A 11 3757afd Applications Information Prior to lowering the operating frequency, however, be sure to check with power MOSFET manufacturers for their most recent low QG, low RDS(ON) devices. Power MOSFET manufacturing technologies are continually improving, with newer and better performance devices being introduced almost yearly. An effective approach to reduce the power consumption of the internal LDO for gate drive is to tie the INTVCC pin to an external voltage source high enough to turn off the internal LDO regulator. If the input voltage VIN does not exceed the absolute maximum rating of both the power MOSFET gate-source voltage (VGS) and the INTVCC overvoltage lockout threshold voltage (17.5V), the INTVCC pin can be shorted directly to the VIN pin. In this condition, the internal LDO will be turned off and the gate driver will be powered directly from the input voltage, VIN. With the INTVCC pin shorted to VIN, however, a small current (around 16μA) will load the INTVCC in shutdown mode. For applications that require the lowest shutdown mode input supply current, do not connect the INTVCC pin to VIN. In SEPIC or flyback applications, the INTVCC pin can be connected to the output voltage VOUT through a blocking diode, as shown in Figure 3, if VOUT meets the following conditions: 1. VOUT < VIN (pin voltage) 2. VOUT < 17.5V 3. VOUT < maximum VGS rating of power MOSFET A resistor RVCC can be connected, as shown in Figure 3, to limit the inrush current from VOUT. Regardless of whether or not the INTVCC pin is connected to an external voltage source, it is always necessary to have the driver circuitry bypassed with a 4.7μF low ESR ceramic capacitor to ground immediately adjacent to the INTVCC and GND pins. Figure 3. Connecting INTVCC to VOUT CVCC 4.7μF VOUT 3757 F03 INTVCC GND LT3757 RVCC DVCC Operating Frequency and Synchronization The choice of operating frequency may be determined by on-chip power dissipation, otherwise it is a trade-off between efficiency and component size. Low frequency operation improves efficiency by reducing gate drive current and MOSFET and diode switching losses. However, lower frequency operation requires a physically larger inductor. Switching frequency also has implications for loop compensation. The LT3757 uses a constant-frequency architecture that can be programmed over a 100kHz to 1000kHz range with a single external resistor from the RT pin to ground, as shown in Figure 1. The RT pin must have an external resistor to GND for proper operation of the LT3757. A table for selecting the value of RT for a given operating frequency is shown in Table 1. Table 1. Timing Resistor (RT) Value OSCILLATOR FREQUENCY (kHz) RT (kΩ) 100 140 200 63.4 300 41.2 400 30.9 500 24.3 600 19.6 700 16.5 800 14 900 12.1 1000 10.5 The operating frequency of the LT3757 can be synchronized to an external clock source. By providing a digital clock signal into the SYNC pin, the LT3757 will operate at the SYNC clock frequency. If this feature is used, an RT resistor should be chosen to program a switching frequency 20% slower than SYNC pulse frequency. The SYNC pulse should have a minimum pulse width of 200ns. Tie the SYNC pin to GND if this feature is not used. LT3757/LT3757A 12 3757afd Applications Information Duty Cycle Consideration Switching duty cycle is a key variable defining converter operation. As such, its limits must be considered. Minimum on-time is the smallest time duration that the LT3757 is capable of turning on the power MOSFET. This time is generally about 220ns (typical) (see Minimum On-Time in the Electrical Characteristics table). In each switching cycle, the LT3757 keeps the power switch off for at least 220ns (typical) (see Minimum Off-Time in the Electrical Characteristics table). The minimum on-time and minimum off-time and the switching frequency define the minimum and maximum switching duty cycles a converter is able to generate: Minimum duty cycle = minimum on-time • frequency Maximum duty cycle = 1 – (minimum off-time • frequency) Programming the Output Voltage The output voltage (VOUT) is set by a resistor divider, as shown in Figure 1. The positive and negative VOUT are set by the following equations: VOUT,POSITIVE = 1.6V • 1+ R2 R1 VOUT,NEGATIVE = –0.8V • 1+ R2 R1 The resistors R1 and R2 are typically chosen so that the error caused by the current flowing into the FBX pin during normal operation is less than 1% (this translates to a maximum value of R1 at about 158k). In the applications where VOUT is pulled up by an external positive power supply, the FBX pin is also pulled up through the R2 and R1 network. Make sure the FBX does not exceed its absolute maximum rating (6V). The R5, D2, and D3 in Figure 1 provide a resistive clamp in the positive direction. To ensure FBX is lower than 6V, choose sufficiently large R1 and R2 to meet the following condition: 6V • 1+ R2 R1 + 3.5V • R2 8kΩ > VOUT(MAX) where VOUT(MAX) is the maximum VOUT that is pulled up by an external power supply. Soft-Start The LT3757 contains several features to limit peak switch currents and output voltage (VOUT) overshoot during start-up or recovery from a fault condition. The primary purpose of these features is to prevent damage to external components or the load. High peak switch currents during start-up may occur in switching regulators. Since VOUT is far from its final value, the feedback loop is saturated and the regulator tries to charge the output capacitor as quickly as possible, resulting in large peak currents. A large surge current may cause inductor saturation or power switch failure. The LT3757 addresses this mechanism with the SS pin. As shown in Figure 1, the SS pin reduces the power MOSFET current by pulling down the VC pin through Q2. In this way the SS allows the output capacitor to charge gradually toward its final value while limiting the start-up peak currents. The typical start-up waveforms are shown in the Typical Performance Characteristics section. The inductor current IL slewing rate is limited by the soft-start function. Besides start-up, soft-start can also be triggered by the following faults: 1. INTVCC > 17.5V 2. INTVCC < 2.6V 3. Thermal lockout Any of these three faults will cause the LT3757 to stop switching immediately. The SS pin will be discharged by Q3. When all faults are cleared and the SS pin has been discharged below 0.2V, a 10μA current source IS2 starts charging the SS pin, initiating a soft-start operation. The soft-start interval is set by the soft-start capacitor selection according to the equation: TSS =CSS • 1.25V 10μA LT3757/LT3757A 13 3757afd Applications Information FBX Frequency Foldback When VOUT is very low during start-up or a short-circuit fault on the output, the switching regulator must operate at low duty cycles to maintain the power switch current within the current limit range, since the inductor current decay rate is very low during switch off time. The minimum on-time limitation may prevent the switcher from attaining a sufficiently low duty cycle at the programmed switching frequency. So, the switch current will keep increasing through each switch cycle, exceeding the programmed current limit. To prevent the switch peak currents from exceeding the programmed value, the LT3757 contains a frequency foldback function to reduce the switching frequency when the FBX voltage is low (see the Normalized Switching Frequency vs FBX graph in the Typical Performance Characteristics section). The typical frequency foldback waveforms are shown in the Typical Performance Characteristics section. The frequency foldback function prevents IL from exceeding the programmed limits because of the minimum on-time. During frequency foldback, external clock synchronization is disabled to prevent interference with frequency reducing operation. Thermal Lockout If LT3757 die temperature reaches 165°C (typical), the part will go into thermal lockout. The power switch will be turned off. A soft-start operation will be triggered. The part will be enabled again when the die temperature has dropped by 5°C (nominal). Loop Compensation Loop compensation determines the stability and transient performance. The LT3757/LT3757A use current mode control to regulate the output which simplifies loop compensation. The LT3757A improves the no-load to heavy load transient response, when compared to the LT3757. New internal circuits ensure that the transient from not switching to switching at high current can be made in a few cycles. The optimum values depend on the converter topology, the component values and the operating conditions (including the input voltage, load current, etc.). To compensate the feedback loop of the LT3757/LT3757A, a series resistorcapacitor network is usually connected from the VC pin to GND. Figure 1 shows the typical VC compensation network. For most applications, the capacitor should be in the range of 470pF to 22nF, and the resistor should be in the range of 5k to 50k. A small capacitor is often connected in parallel with the RC compensation network to attenuate the VC voltage ripple induced from the output voltage ripple through the internal error amplifier. The parallel capacitor usually ranges in value from 10pF to 100pF. A practical approach to design the compensation network is to start with one of the circuits in this data sheet that is similar to your application, and tune the compensation network to optimize the performance. Stability should then be checked across all operating conditions, including load current, input voltage and temperature. SENSE Pin Programming For control and protection, the LT3757 measures the power MOSFET current by using a sense resistor (RSENSE) between GND and the MOSFET source. Figure 4 shows a typical waveform of the sense voltage (VSENSE) across the sense resistor. It is important to use Kelvin traces between the SENSE pin and RSENSE, and to place the IC GND as close as possible to the GND terminal of the RSENSE for proper operation. Figure 4. The Sense Voltage During a Switching Cycle 3757 F04 VSENSE(PEAK) ΔVSENSE = χ • VSENSE(MAX) VSENSE DT t S VSENSE(MAX) TS LT3757/LT3757A 14 3757afd Applications Information Due to the current limit function of the SENSE pin, RSENSE should be selected to guarantee that the peak current sense voltage VSENSE(PEAK) during steady state normal operation is lower than the SENSE current limit threshold (see the Electrical Characteristics table). Given a 20% margin, VSENSE(PEAK) is set to be 80mV. Then, the maximum switch ripple current percentage can be calculated using the following equation: c = ΔVSENSE 80mV − 0.5 • ΔVSENSE c is used in subsequent design examples to calculate inductor value. ΔVSENSE is the ripple voltage across RSENSE. The LT3757 switching controller incorporates 100ns timing interval to blank the ringing on the current sense signal immediately after M1 is turned on. This ringing is caused by the parasitic inductance and capacitance of the PCB trace, the sense resistor, the diode, and the MOSFET. The 100ns timing interval is adequate for most of the LT3757 applications. In the applications that have very large and long ringing on the current sense signal, a small RC filter can be added to filter out the excess ringing. Figure 5 shows the RC filter on SENSE pin. It is usually sufficient to choose 22Ω for RFLT and 2.2nF to 10nF for CFLT. Keep RFLT’s resistance low. Remember that there is 65μA (typical) flowing out of the SENSE pin. Adding RFLT will affect the SENSE current limit threshold: VSENSE_ILIM = 108mV – 65μA • RFLT Application Circuits The LT3757 can be configured as different topologies. The first topology to be analyzed will be the boost converter, followed by the flyback, SEPIC and inverting converters. Boost Converter: Switch Duty Cycle and Frequency The LT3757 can be configured as a boost converter for the applications where the converter output voltage is higher than the input voltage. Remember that boost converters are not short-circuit protected. Under a shorted output condition, the inductor current is limited only by the input supply capability. For applications requiring a step-up converter that is short-circuit protected, please refer to the Applications Information section covering SEPIC converters. The conversion ratio as a function of duty cycle is VOUT VIN = 1 1−D in continuous conduction mode (CCM). For a boost converter operating in CCM, the duty cycle of the main switch can be calculated based on the output voltage (VOUT) and the input voltage (VIN). The maximum duty cycle (DMAX) occurs when the converter has the minimum input voltage: DMAX = VOUT − VIN(MIN) VOUT Discontinuous conduction mode (DCM) provides higher conversion ratios at a given frequency at the cost of reduced efficiencies and higher switching currents. Figure 5. The RC Filter on SENSE Pin CFLT 3757 F05 LT3757 RFLT RSENSE M1 SENSE GATE GND LT3757/LT3757A 15 3757afd Applications Information Boost Converter: Inductor and Sense Resistor Selection For the boost topology, the maximum average inductor current is: IL(MAX) =IO(MAX) • 1 1−DMAX Then, the ripple current can be calculated by: ΔIL = c •IL(MAX) = c •IO(MAX) • 1 1−DMAX The constant c in the preceding equation represents the percentage peak-to-peak ripple current in the inductor, relative to IL(MAX). The inductor ripple current has a direct effect on the choice of the inductor value. Choosing smaller values of ΔIL requires large inductances and reduces the current loop gain (the converter will approach voltage mode). Accepting larger values of ΔIL provides fast transient response and allows the use of low inductances, but results in higher input current ripple and greater core losses. It is recommended that c fall within the range of 0.2 to 0.6. Given an operating input voltage range, and having chosen the operating frequency and ripple current in the inductor, the inductor value of the boost converter can be determined using the following equation: L = VIN(MIN) ΔIL • f •DMAX The peak and RMS inductor current are: IL(PEAK) =IL(MAX) • 1+ c 2 IL(RMS) =IL(MAX) • 1+ c2 12 Based on these equations, the user should choose the inductors having sufficient saturation and RMS current ratings. Set the sense voltage at IL(PEAK) to be the minimum of the SENSE current limit threshold with a 20% margin. The sense resistor value can then be calculated to be: RSENSE = 80mV IL(PEAK) Boost Converter: Power MOSFET Selection Important parameters for the power MOSFET include the drain-source voltage rating (VDS), the threshold voltage (VGS(TH)), the on-resistance (RDS(ON)), the gate to source and gate to drain charges (QGS and QGD), the maximum drain current (ID(MAX)) and the MOSFET’s thermal resistances (RθJC and RθJA). The power MOSFET will see full output voltage, plus a diode forward voltage, and any additional ringing across its drain-to-source during its off-time. It is recommended to choose a MOSFET whose BVDSS is higher than VOUT by a safety margin (a 10V safety margin is usually sufficient). The power dissipated by the MOSFET in a boost converter is: PFET = I2 L(MAX) • RDS(ON) • DMAX + 2 • V2 OUT • IL(MAX) • CRSS • f /1A The first term in the preceding equation represents the conduction losses in the device, and the second term, the switching loss. CRSS is the reverse transfer capacitance, which is usually specified in the MOSFET characteristics. For maximum efficiency, RDS(ON) and CRSS should be minimized. From a known power dissipated in the power MOSFET, its junction temperature can be obtained using the following equation: TJ = TA + PFET • θJA = TA + PFET • (θJC + θCA) TJ must not exceed the MOSFET maximum junction temperature rating. It is recommended to measure the MOSFET temperature in steady state to ensure that absolute maximum ratings are not exceeded. LT3757/LT3757A 16 3757afd Applications Information Figure 6. The Output Ripple Waveform of a Boost Converter VOUT (AC) tON ΔVESR RINGING DUE TO TOTAL INDUCTANCE (BOARD + CAP) ΔVCOUT 3757 F05 tOFF Boost Converter: Output Diode Selection To maximize efficiency, a fast switching diode with low forward drop and low reverse leakage is desirable. The peak reverse voltage that the diode must withstand is equal to the regulator output voltage plus any additional ringing across its anode-to-cathode during the on-time. The average forward current in normal operation is equal to the output current, and the peak current is equal to: ID(PEAK) =IL(PEAK) = 1+ c 2 •IL(MAX) It is recommended that the peak repetitive reverse voltage rating VRRM is higher than VOUT by a safety margin (a 10V safety margin is usually sufficient). The power dissipated by the diode is: PD = IO(MAX) • VD and the diode junction temperature is: TJ = TA + PD • RθJA The RθJA to be used in this equation normally includes the RθJC for the device plus the thermal resistance from the board to the ambient temperature in the enclosure. TJ must not exceed the diode maximum junction temperature rating. Boost Converter: Output Capacitor Selection Contributions of ESR (equivalent series resistance), ESL (equivalent series inductance) and the bulk capacitance must be considered when choosing the correct output capacitors for a given output ripple voltage. The effect of The choice of component(s) begins with the maximum acceptable ripple voltage (expressed as a percentage of the output voltage), and how this ripple should be divided between the ESR step ΔVESR and the charging/discharging ΔVCOUT. For the purpose of simplicity, we will choose 2% for the maximum output ripple, to be divided equally between ΔVESR and ΔVCOUT. This percentage ripple will change, depending on the requirements of the application, and the following equations can easily be modified. For a 1% contribution to the total ripple voltage, the ESR of the output capacitor can be determined using the following equation: ESRCOUT ≤ 0.01• VOUT ID(PEAK) these three parameters (ESR, ESL and bulk C) on the output voltage ripple waveform for a typical boost converter is illustrated in Figure 6. LT3757/LT3757A 17 3757afd Applications Information For the bulk C component, which also contributes 1% to the total ripple: COUT ≥ IO(MAX) 0.01• VOUT • f The output capacitor in a boost regulator experiences high RMS ripple currents, as shown in Figure 6. The RMS ripple current rating of the output capacitor can be determined using the following equation: IRMS(COUT) ≥IO(MAX) • DMAX 1−DMAX Multiple capacitors are often paralleled to meet ESR requirements. Typically, once the ESR requirement is satisfied, the capacitance is adequate for filtering and has the required RMS current rating. Additional ceramic capacitors in parallel are commonly used to reduce the effect of parasitic inductance in the output capacitor, which reduces high frequency switching noise on the converter output. Boost Converter: Input Capacitor Selection The input capacitor of a boost converter is less critical than the output capacitor, due to the fact that the inductor is in series with the input, and the input current waveform is continuous. The input voltage source impedance determines the size of the input capacitor, which is typically in the range of 10μF to 100μF. A low ESR capacitor is recommended, although it is not as critical as for the output capacitor. The RMS input capacitor ripple current for a boost converter is: IRMS(CIN) = 0.3 • ΔIL Flyback Converter Applications The LT3757 can be configured as a flyback converter for the applications where the converters have multiple outputs, high output voltages or isolated outputs. Figure 7 shows a simplified flyback converter. The flyback converter has a very low parts count for multiple outputs, and with prudent selection of turns ratio, can have high output/input voltage conversion ratios with a desirable duty cycle. However, it has low efficiency due to the high peak currents, high peak voltages and consequent power loss. The flyback converter is commonly used for an output power of less than 50W. The flyback converter can be designed to operate either in continuous or discontinuous mode. Compared to continuous mode, discontinuous mode has the advantage of smaller transformer inductances and easy loop compensation, and the disadvantage of higher peak-to-average current and lower efficiency. In the high output voltage applications, the flyback converters can be designed to operate in discontinuous mode to avoid using large transformers. Figure 7. A Simplified Flyback Converter RSENSE NP:NS VIN CIN CSN VSN LP D SUGGESTED RCD SNUBBER ID ISW VDS 3757 F06 GATE GND LT3757 SENSE LS M + – + – RSN DSN – + + COUT + LT3757/LT3757A 18 3757afd Applications Information Flyback Converter: Switch Duty Cycle and Turns Ratio The flyback converter conversion ratio in the continuous mode operation is: VOUT VIN = NS NP • D 1−D where NS/NP is the second to primary turns ratio. Figure 8 shows the waveforms of the flyback converter in discontinuous mode operation. During each switching period TS, three subintervals occur: DTS, D2TS, D3TS. During DTS, M is on, and D is reverse-biased. During D2TS, M is off, and LS is conducting current. Both LP and LS currents are zero during D3TS. The flyback converter conversion ratio in the discontinuous mode operation is: VOUT VIN = NS NP • D D2 According to the preceding equations, the user has relative freedom in selecting the switch duty cycle or turns ratio to suit a given application. The selections of the duty cycle and the turns ratio are somewhat iterative processes, due to the number of variables involved. The user can choose either a duty cycle or a turns ratio as the start point. The following trade-offs should be considered when selecting the switch duty cycle or turns ratio, to optimize the converter performance. A higher duty cycle affects the flyback converter in the following aspects: • Lower MOSFET RMS current ISW(RMS), but higher MOSFET VDS peak voltage • Lower diode peak reverse voltage, but higher diode RMS current ID(RMS) • Higher transformer turns ratio (NP/NS) The choice, D D+D2 = 1 3 (for discontinuous mode operation with a given D3) gives the power MOSFET the lowest power stress (the product of RMS current and peak voltage). However, in the high output voltage applications, a higher duty cycle may be adopted to limit the large peak reverse voltage of the diode. The choice, D D+D2 = 2 3 (for discontinuous mode operation with a given D3) gives the diode the lowest power stress (the product of RMS current and peak voltage). An extreme high or low duty cycle results in high power stress on the MOSFET or diode, and reduces efficiency. It is recommended to choose a duty cycle, D, between 20% and 80%. Figure 8. Waveforms of the Flyback Converter in Discontinuous Mode Operation 3757 F07 ISW VDS ID DTS D2TS D3TS t ISW(MAX) ID(MAX) TS LT3757/LT3757A 19 3757afd Applications Information Flyback Converter: Transformer Design for Discontinuous Mode Operation The transformer design for discontinuous mode of operation is chosen as presented here. According to Figure 8, the minimum D3 (D3MIN) occurs when the converter has the minimum VIN and the maximum output power (POUT). Choose D3MIN to be equal to or higher than 10% to guarantee the converter is always in discontinuous mode operation (choosing higher D3 allows the use of low inductances, but results in a higher switch peak current). The user can choose a DMAX as the start point. Then, the maximum average primary currents can be calculated by the following equation: ILP(MAX) =ISW(MAX) = POUT(MAX) DMAX • VIN(MIN) • h where h is the converter efficiency. If the flyback converter has multiple outputs, POUT(MAX) is the sum of all the output power. The maximum average secondary current is: ILS(MAX) =ID(MAX) = IOUT(MAX) D2 where: D2 = 1 – DMAX – D3 the primary and secondary RMS currents are: ILP(RMS) = 2 •ILP(MAX) • DMAX 3 ILS(RMS) = 2 •ILS(MAX) • D2 3 According to Figure 8, the primary and secondary peak currents are: ILP(PEAK) = ISW(PEAK) = 2 • ILP(MAX) ILS(PEAK) = ID(PEAK) = 2 • ILS(MAX) The primary and second inductor values of the flyback converter transformer can be determined using the following equations: LP = D2 MAX • V2 IN(MIN) • h 2 • POUT(MAX) • f LS = D22 • (VOUT + VD) 2 • IOUT(MAX) • f The primary to second turns ratio is: NP NS = LP LS Flyback Converter: Snubber Design Transformer leakage inductance (on either the primary or secondary) causes a voltage spike to occur after the MOSFET turn-off. This is increasingly prominent at higher load currents, where more stored energy must be dissipated. In some cases a snubber circuit will be required to avoid overvoltage breakdown at the MOSFET’s drain node. There are different snubber circuits, and Application Note 19 is a good reference on snubber design. An RCD snubber is shown in Figure 7. The snubber resistor value (RSN) can be calculated by the following equation: RSN = 2 • V2 SN − VSN • VOUT • NP NS I2 SW(PEAK) •LLK • f LT3757/LT3757A 20 3757afd Applications Information where VSN is the snubber capacitor voltage. A smaller VSN results in a larger snubber loss. A reasonable VSN is 2 to 2.5 times of: VOUT •NP NS LLK is the leakage inductance of the primary winding, which is usually specified in the transformer characteristics. LLK can be obtained by measuring the primary inductance with the secondary windings shorted. The snubber capacitor value (CCN) can be determined using the following equation: CCN = VSN ΔVSN •RCN • f where ΔVSN is the voltage ripple across CCN. A reasonable ΔVSN is 5% to 10% of VSN. The reverse voltage rating of DSN should be higher than the sum of VSN and VIN(MAX). Flyback Converter: Sense Resistor Selection In a flyback converter, when the power switch is turned on, the current flowing through the sense resistor (ISENSE) is: ISENSE = ILP Set the sense voltage at ILP(PEAK) to be the minimum of the SENSE current limit threshold with a 20% margin. The sense resistor value can then be calculated to be: RSENSE = 80mV ILP(PEAK) Flyback Converter: Power MOSFET Selection For the flyback configuration, the MOSFET is selected with a VDC rating high enough to handle the maximum VIN, the reflected secondary voltage and the voltage spike due to the leakage inductance. Approximate the required MOSFET VDC rating using: BVDSS > VDS(PEAK) where: VDS(PEAK) = VIN(MAX) + VSN The power dissipated by the MOSFET in a flyback converter is: PFET = I2 M(RMS) • RDS(ON) + 2 • V2 DS(PEAK) • IL(MAX) • CRSS • f /1A The first term in this equation represents the conduction losses in the device, and the second term, the switching loss. CRSS is the reverse transfer capacitance, which is usually specified in the MOSFET characteristics. From a known power dissipated in the power MOSFET, its junction temperature can be obtained using the following equation: TJ = TA + PFET • θJA = TA + PFET • (θJC + θCA) TJ must not exceed the MOSFET maximum junction temperature rating. It is recommended to measure the MOSFET temperature in steady state to ensure that absolute maximum ratings are not exceeded. LT3757/LT3757A 21 3757afd Applications Information Flyback Converter: Output Diode Selection The output diode in a flyback converter is subject to large RMS current and peak reverse voltage stresses. A fast switching diode with a low forward drop and a low reverse leakage is desired. Schottky diodes are recommended if the output voltage is below 100V. Approximate the required peak repetitive reverse voltage rating VRRM using: VRRM > NS NP • VIN(MAX) + VOUT The power dissipated by the diode is: PD = IO(MAX) • VD and the diode junction temperature is: TJ = TA + PD • RθJA The RθJA to be used in this equation normally includes the RθJC for the device, plus the thermal resistance from the board to the ambient temperature in the enclosure. TJ must not exceed the diode maximum junction temperature rating. Flyback Converter: Output Capacitor Selection The output capacitor of the flyback converter has a similar operation condition as that of the boost converter. Refer to the Boost Converter: Output Capacitor Selection section for the calculation of COUT and ESRCOUT. The RMS ripple current rating of the output capacitors in discontinuous operation can be determined using the following equation: IRMS(COUT),DISCONTINUOUS ≥ IO(MAX) • 4 − (3 •D2) 3 •D2 Flyback Converter: Input Capacitor Selection The input capacitor in a flyback converter is subject to a large RMS current due to the discontinuous primary current. To prevent large voltage transients, use a low ESR input capacitor sized for the maximum RMS current. The RMS ripple current rating of the input capacitors in discontinuous operation can be determined using the following equation: IRMS(CIN),DISCONTINUOUS ≥ POUT(MAX) VIN(MIN) • h • 4 − (3 •DMAX ) 3 •DMAX SEPIC Converter Applications The LT3757 can be configured as a SEPIC (single-ended primary inductance converter), as shown in Figure 1. This topology allows for the input to be higher, equal, or lower than the desired output voltage. The conversion ratio as a function of duty cycle is: VOUT + VD VIN = D 1−D in continuous conduction mode (CCM). In a SEPIC converter, no DC path exists between the input and output. This is an advantage over the boost converter for applications requiring the output to be disconnected from the input source when the circuit is in shutdown. Compared to the flyback converter, the SEPIC converter has the advantage that both the power MOSFET and the output diode voltages are clamped by the capacitors (CIN, CDC and COUT), therefore, there is less voltage ringing across the power MOSFET and the output diodes. The SEPIC converter requires much smaller input capacitors than those of the flyback converter. This is due to the fact that, in the SEPIC converter, the inductor L1 is in series with the input, and the ripple current flowing through the input capacitor is continuous. LT3757/LT3757A 22 3757afd Applications Information Figure 9. The Switch Current Waveform of the SEPIC Converter 3757 F08 ΔISW = χ • ISW(MAX) ISW DT t S ISW(MAX) TS SEPIC Converter: Switch Duty Cycle and Frequency For a SEPIC converter operating in CCM, the duty cycle of the main switch can be calculated based on the output voltage (VOUT), the input voltage (VIN) and the diode forward voltage (VD). The maximum duty cycle (DMAX) occurs when the converter has the minimum input voltage: DMAX = VOUT + VD VIN(MIN) + VOUT + VD SEPIC Converter: Inductor and Sense Resistor Selection As shown in Figure 1, the SEPIC converter contains two inductors: L1 and L2. L1 and L2 can be independent, but can also be wound on the same core, since identical voltages are applied to L1 and L2 throughout the switching cycle. For the SEPIC topology, the current through L1 is the converter input current. Based on the fact that, ideally, the output power is equal to the input power, the maximum average inductor currents of L1 and L2 are: IL1(MAX) = IIN(MAX) = IO(MAX) • DMAX 1− DMAX IL2(MAX) = IO(MAX) In a SEPIC converter, the switch current is equal to IL1 + IL2 when the power switch is on, therefore, the maximum average switch current is defined as: ISW(MAX) =IL1(MAX) +IL2(MAX) =IO(MAX) • 1 1−DMAX and the peak switch current is: ISW(PEAK) = 1+ c 2 •IO(MAX) • 1 1−DMAX The constant c in the preceding equations represents the percentage peak-to-peak ripple current in the switch, relative to ISW(MAX), as shown in Figure 9. Then, the switch ripple current ΔISW can be calculated by: ΔISW = c • ISW(MAX) The inductor ripple currents ΔIL1 and ΔIL2 are identical: ΔIL1 = ΔIL2 = 0.5 • ΔISW The inductor ripple current has a direct effect on the choice of the inductor value. Choosing smaller values of ΔIL requires large inductances and reduces the current loop gain (the converter will approach voltage mode). Accepting larger values of ΔIL allows the use of low inductances, but results in higher input current ripple and greater core losses. It is recommended that c falls in the range of 0.2 to 0.4. LT3757/LT3757A 23 3757afd Given an operating input voltage range, and having chosen the operating frequency and ripple current in the inductor, the inductor value (L1 and L2 are independent) of the SEPIC converter can be determined using the following equation: L1=L2 = VIN(MIN) 0.5 • ΔISW • f •DMAX For most SEPIC applications, the equal inductor values will fall in the range of 1μH to 100μH. By making L1 = L2, and winding them on the same core, the value of inductance in the preceding equation is replaced by 2L, due to mutual inductance: L = VIN(MIN) ΔISW • f •DMAX This maintains the same ripple current and energy storage in the inductors. The peak inductor currents are: IL1(PEAK) = IL1(MAX) + 0.5 • ΔIL1 IL2(PEAK) = IL2(MAX) + 0.5 • ΔIL2 The RMS inductor currents are: IL1(RMS) =IL1(MAX) • 1+ c2 L1 12 where: cL1 = ΔIL1 IL1(MAX) IL2(RMS) =IL2(MAX) • 1+ c2 L2 12 where: cL2 = ΔIL2 IL2 (MAX) Based on the preceding equations, the user should choose the inductors having sufficient saturation and RMS current ratings. In a SEPIC converter, when the power switch is turned on, the current flowing through the sense resistor (ISENSE) is the switch current. Set the sense voltage at ISENSE(PEAK) to be the minimum of the SENSE current limit threshold with a 20% margin. The sense resistor value can then be calculated to be: RSENSE = 80mV ISW(PEAK) SEPIC Converter: Power MOSFET Selection For the SEPIC configuration, choose a MOSFET with a VDC rating higher than the sum of the output voltage and input voltage by a safety margin (a 10V safety margin is usually sufficient). The power dissipated by the MOSFET in a SEPIC converter is: PFET = I2 SW(MAX) • RDS(ON) • DMAX + 2 • (VIN(MIN) + VOUT)2 • IL(MAX) • CRSS • f /1A The first term in this equation represents the conduction losses in the device, and the second term, the switching loss. CRSS is the reverse transfer capacitance, which is usually specified in the MOSFET characteristics. For maximum efficiency, RDS(ON) and CRSS should be minimized. From a known power dissipated in the power MOSFET, its junction temperature can be obtained using the following equation: TJ = TA + PFET • θJA = TA + PFET • (θJC + θCA) TJ must not exceed the MOSFET maximum junction temperature rating. It is recommended to measure the MOSFET temperature in steady state to ensure that absolute maximum ratings are not exceeded. Applications Information LT3757/LT3757A 24 3757afd Applications Information Figure 10. A Simplified Inverting Converter RSENSE CDC VIN CIN L1 D1 COUT VOUT 3757 F09 GATE + GND LT3757 SENSE L2 M1 + – + – + SEPIC Converter: Output Diode Selection To maximize efficiency, a fast switching diode with a low forward drop and low reverse leakage is desirable. The average forward current in normal operation is equal to the output current, and the peak current is equal to: ID(PEAK) = 1+ c 2 •IO(MAX) • 1 1−DMAX It is recommended that the peak repetitive reverse voltage rating VRRM is higher than VOUT + VIN(MAX) by a safety margin (a 10V safety margin is usually sufficient). The power dissipated by the diode is: PD = IO(MAX) • VD and the diode junction temperature is: TJ = TA + PD • RθJA The RθJA used in this equation normally includes the RθJC for the device, plus the thermal resistance from the board, to the ambient temperature in the enclosure. TJ must not exceed the diode maximum junction temperature rating. SEPIC Converter: Output and Input Capacitor Selection The selections of the output and input capacitors of the SEPIC converter are similar to those of the boost converter. Please refer to the Boost Converter, Output Capacitor Selection and Boost Converter, Input Capacitor Selection sections. SEPIC Converter: Selecting the DC Coupling Capacitor The DC voltage rating of the DC coupling capacitor (CDC, as shown in Figure 1) should be larger than the maximum input voltage: VCDC > VIN(MAX) CDC has nearly a rectangular current waveform. During the switch off-time, the current through CDC is IIN, while approximately –IO flows during the on-time. The RMS rating of the coupling capacitor is determined by the following equation: IRMS(CDC) > IO(MAX) • VOUT + VD VIN(MIN) A low ESR and ESL, X5R or X7R ceramic capacitor works well for CDC. Inverting Converter Applications The LT3757 can be configured as a dual-inductor inverting topology, as shown in Figure 10. The VOUT to VIN ratio is: VOUT − VD VIN = − D 1−D in continuous conduction mode (CCM). LT3757/LT3757A 25 3757afd Inverting Converter: Switch Duty Cycle and Frequency For an inverting converter operating in CCM, the duty cycle of the main switch can be calculated based on the negative output voltage (VOUT) and the input voltage (VIN). The maximum duty cycle (DMAX) occurs when the converter has the minimum input voltage: DMAX = VOUT − VD VOUT − VD − VIN(MIN) Inverting Converter: Inductor, Sense Resistor, Power MOSFET, Output Diode and Input Capacitor Selections The selections of the inductor, sense resistor, power MOSFET, output diode and input capacitor of an inverting converter are similar to those of the SEPIC converter. Please refer to the corresponding SEPIC converter sections. Inverting Converter: Output Capacitor Selection The inverting converter requires much smaller output capacitors than those of the boost, flyback and SEPIC converters for similar output ripples. This is due to the fact that, in the inverting converter, the inductor L2 is in series with the output, and the ripple current flowing through the output capacitors are continuous. The output ripple voltage is produced by the ripple current of L2 flowing through the ESR and bulk capacitance of the output capacitor: ΔVOUT(P–P) = ΔIL2 • ESRCOUT + 1 8 • f •COUT After specifying the maximum output ripple, the user can select the output capacitors according to the preceding equation. The ESR can be minimized by using high quality X5R or X7R dielectric ceramic capacitors. In many applications, ceramic capacitors are sufficient to limit the output voltage ripple. The RMS ripple current rating of the output capacitor needs to be greater than: IRMS(COUT) > 0.3 • ΔIL2 Inverting Converter: Selecting the DC Coupling Capacitor The DC voltage rating of the DC coupling capacitor (CDC, as shown in Figure 10) should be larger than the maximum input voltage minus the output voltage (negative voltage): VCDC > VIN(MAX) – VOUT CDC has nearly a rectangular current waveform. During the switch off-time, the current through CDC is IIN, while approximately –IO flows during the on-time. The RMS rating of the coupling capacitor is determined by the following equation: IRMS(CDC) >IO(MAX) • DMAX 1−DMAX A low ESR and ESL, X5R or X7R ceramic capacitor works well for CDC. Applications Information LT3757/LT3757A 26 3757afd Applications Information Figure 11. 8V to 16V Input, 24V/2A Output Boost Converter Suggested Layout VIN 3757 F10 VOUT L1 VIAS TO GROUND PLANE C D1 COUT2 OUT1 1 2 8 7 3 4 6 5 M1 CIN R4 RC R1 R2 RSS RT R3 CVCC CC1 CC2 LT3757 1 2 3 4 5 9 10 6 7 8 RS Board Layout The high speed operation of the LT3757 demands careful attention to board layout and component placement. The Exposed Pad of the package is the only GND terminal of the IC, and is important for thermal management of the IC. Therefore, it is crucial to achieve a good electrical and thermal contact between the Exposed Pad and the ground plane of the board. For the LT3757 to deliver its full output power, it is imperative that a good thermal path be provided to dissipate the heat generated within the package. It is recommended that multiple vias in the printed circuit board be used to conduct heat away from the IC and into a copper plane with as much area as possible. To prevent radiation and high frequency resonance problems, proper layout of the components connected to the IC is essential, especially the power paths with higher di/ dt. The following high di/dt loops of different topologies should be kept as tight as possible to reduce inductive ringing: • In boost configuration, the high di/dt loop contains the output capacitor, the sensing resistor, the power MOSFET and the Schottky diode. • In flyback configuration, the high di/dt primary loop contains the input capacitor, the primary winding, the power MOSFET and the sensing resistor. The high di/ dt secondary loop contains the output capacitor, the secondary winding and the output diode. • In SEPIC configuration, the high di/dt loop contains the power MOSFET, sense resistor, output capacitor, Schottky diode and the coupling capacitor. • In inverting configuration, the high di/dt loop contains power MOSFET, sense resistor, Schottky diode and the coupling capacitor. LT3757/LT3757A 27 3757afd Table 2. Recommended Component Manufacturers VENDOR COMPONENTS WEB ADDRESS AVX Capacitors avx.com BH Electronics Inductors, Transformers bhelectronics.com Coilcraft Inductors coilcraft.com Cooper Bussmann Inductors bussmann.com Diodes, Inc Diodes diodes.com Fairchild MOSFETs fairchildsemi.com General Semiconductor Diodes generalsemiconductor.com International Rectifier MOSFETs, Diodes irf.com IRC Sense Resistors irctt.com Kemet Capacitors kemet.com Magnetics Inc Toroid Cores mag-inc.com Microsemi Diodes microsemi.com Murata-Erie Inductors, Capacitors murata.co.jp Nichicon Capacitors nichicon.com On Semiconductor Diodes onsemi.com Panasonic Capacitors panasonic.com Sanyo Capacitors sanyo.co.jp Sumida Inductors sumida.com Taiyo Yuden Capacitors t-yuden.com TDK Capacitors, Inductors component.tdk.com Thermalloy Heat Sinks aavidthermalloy.com Tokin Capacitors nec-tokinamerica.com Toko Inductors tokoam.com United Chemi-Con Capacitors chemi-con.com Vishay/Dale Resistors vishay.com Vishay/Siliconix MOSFETs vishay.com Vishay/Sprague Capacitors vishay.com Würth Elektronik Inductors we-online.com Zetex Small-Signal Discretes zetex.com Applications Information Check the stress on the power MOSFET by measuring its drain-to-source voltage directly across the device terminals (reference the ground of a single scope probe directly to the source pad on the PC board). Beware of inductive ringing, which can exceed the maximum specified voltage rating of the MOSFET. If this ringing cannot be avoided, and exceeds the maximum rating of the device, either choose a higher voltage device or specify an avalancherated power MOSFET. The small-signal components should be placed away from high frequency switching nodes. For optimum load regulation and true remote sensing, the top of the output voltage sensing resistor divider should connect independently to the top of the output capacitor (Kelvin connection), staying away from any high dV/dt traces. Place the divider resistors near the LT3757 in order to keep the high impedance FBX node short. Figure 11 shows the suggested layout of the 8V to 16V Input, 24V/2A Output Boost Converter. Recommended Component Manufacturers Some of the recommended component manufacturers are listed in Table 2. LT3757/LT3757A 28 3757afd Typical Applications 3.3V Input, 5V/10A Output Boost Converter Boost Preregulator for Automotive Stop-Start/Idle Efficiency vs Output Current Transient VIN and VOUT Waveforms SENSE LT3757 VIN VIN 3.3V CIN 22μF 6.3V ×2 VOUT 5V 10A 0.004 1W M1 41.2k 300kHz GATE FBX GND INTVCC SHDN/UVLO SYNC RT SS VC 49.9k 34k 0.1μF 6.8k 22nF 2.2nF 22 L1 0.5μH D1 3757 TA02a 34k 1% 15.8k 1% COUT1 150μF 6.3V ×4 COUT2 22μF 6.3V X5R ×4 + CVCC 4.7μF 10V X5R CIN: TAIYO YUDEN JMK325BJ226MM COUT1: PANASONIC EEFUEOJ151R COUT2: TAIYO YUDEN JMK325BJ226MM D1: MBRB2515L L1: VISHAY SILICONIX IHLP-5050FD-01 M1: VISHAY SILICONIX SI4448DY OUTPUT CURRENT (A) EFFICIENCY (%) 3757 TA02b 0.001 20 30 40 50 60 70 80 90 100 0.01 0.1 1 10 SENSE LT3757A VIN VIN 3V TO 36V 10μF 50V X5R ×2 VOUT 9VMIN 2A 41.2k 300kHz GATE FBX GND INTVCC SHDN/UVLO SYNC RT SS VC 1M 698k 0.1μF 10k 10nF 4.7μF L1 3.3μH D1 3757 TA03a M1 75k 8m 16.2k C1 10μF 50V ×4 + 10μF 50V X5R L1: COILTRONIX DR127-3R3 M1: VISHAY SILICONIX Si7848BDP D1: VISHAY SILICONIX 50SQ04FN C1: KEMET T495X106K050A 10ms/DIV VOUT 5V/DIV VIN 5V/DIV 0V 3757 TA03b OUTPUT POWER = 10W LT3757/LT3757A 29 3757afd Typical Applications 8V to 16V Input, 24V/2A Output Boost Converter Efficiency vs Output Current Load Step Response at VIN = 12V SENSE LT3757 VIN VIN 8V TO 16V CIN 10μF 25V X5R CVCC 4.7μF 10V X5R VOUT 24V 2A RS 0.01 1W M1 RT 41.2k 300kHz GATE FBX GND INTVCC SHDN/UVLO SYNC RT SS VC R3 200k R4 43.2k CSS 0.1μF CC2 100pF RC 22k CC1 6.8nF L1 10μH D1 3757 TA04a R2 226k 1% R1 16.2k 1% COUT1 47μF 35V ×4 COUT2 10μF 25V X5R + CIN, COUT2: MURATA GRM31CR61E106KA12 COUT1: KEMET T495X476K035AS D1: ON SEMI MBRS340T3G L1: VISHAY SILICONIX IHLP-5050FD-01 10μH M1: VISHAY SILICONIX Si4840BDP OUTPUT CURRENT (A) 0.001 EFFICIENCY (%) 30 50 40 60 70 80 90 100 0.01 0.1 1 3757 TA04b 10 VIN = 8V VIN = 16V 500μs/DIV VOUT 500mV/DIV (AC) 1.6A 0.4A IOUT 1A/DIV 3757 TA04c LT3757/LT3757A 30 3757afd 2ms/DIV VOUT 100V/DIV 3757 TA05b 5μs/DIV VOUT 5V/DIV (AC) VSW 20V/DIV 3757 TA05c Typical Applications High Voltage Flyback Power Supply Start-Up Waveforms Switching Waveforms SENSE LT3757 VIN VSW VIN 5V TO 12V CIN 47μF 16V ×4 INTVCC COUT 68nF ×2 VOUT 350V 10mA 0.02 22 M1 140k 100kHz GATE GND FBX SHDN/UVLO DANGER! HIGH VOLTAGE OPERATION BY HIGH VOLTAGE TRAINED PERSONNEL ONLY SYNC RT SS VC • 105k • 46.4k 0.1μF 220pF 100pF 6.8k 22nF T1 1:10 D1 CIN: MURATA GRM32ER61C476K COUT: TDK C3225X7R2J683K D1: VISHAY SILICONIX GSD2004S DUAL DIODE CONNECTED IN SERIES M1: VISHAY SILICONIX Si7850DP T1: TDK DCT15EFD-U44S003 3757 TA05a 1M 1% 1M 1% 1.50M 1% 16.2k 1% 10nF CVCC 47μF 25V X5R 22 LT3757/LT3757A 31 3757afd Typical Applications 5.5V to 36V Input, 12V/2A Output SEPIC Converter Efficiency vs Output Current Load Step Waveforms Start-Up Waveforms Frequency Foldback Waveforms When Output Short-Circuits SENSE LT3757A VIN VIN 5.5V TO 36V CIN1 4.7μF 50V ×2 CDC 4.7μF 50V, X5R, ×2 4.7μF 10V X5R VOUT 12V 2A 0.01 1W M1 41.2k 300kHz GATE FBX GND INTVCC SHDN/UVLO SYNC RT SS CIN2 4.7μF 50V ×2 • • 105k 46.4k 0.1μF 6.8nF 10k L1A IL1B L1B D1 CIN1, CDC: TAIYO YUDEN UMK316BJ475KL CIN2: KEMET T495X475K050AS COUT1: KEMET T495X476K020AS COUT2: TAIYO YUDEN TMK432BJ106MM D1: ON SEMI MBRS360T3G L1A, L1B: COILTRONICS DRQ127-4R7 (*COUPLED INDUCTORS) M1: VISHAY SILICONIX Si7460DP 3757 TA06a 105k 1% 15.8k 1% COUT1 47μF 20V ×4 COUT2 10μF 25V X5R + VSW IL1A VC + 2ms/DIV VOUT 5V/DIV IL1A + IL1B 5A/DIV 3757 TA06d VIN = 12V 50μs/DIV VOUT 10V/DIV VSW 20V/DIV IL1A + IL1B 5A/DIV 3757 TA06e VIN = 12V OUTPUT CURRENT (A) 0.001 20 EFFICIENCY (%) 30 40 50 60 70 80 90 100 0.01 0.1 1 3757 TA06b 10 VIN = 16V VIN = 8V 500μs/DIV VOUT 2V/DIV AC-COUPLED IOUT 2A/DIV 0A 2A 3757 TA06c VIN = 12V LT3757/LT3757A 32 3757afd Typical Applications 5V to 12V Input, ±12V/0.4A Output SEPIC Converter Nonisolated Inverting SLIC Supply SENSE LT3757 VIN VIN 5V TO 12V CIN1 1μF 16V, X5R CIN2 47μF 16V CDC1 4.7μF 16V, X5R CDC2 4.7μF 16V X5R COUT2 4.7μF 16V, X5R ×3 VOUT1 12V 0.4A VOUT2 –12V 0.4A COUT2 4.7μF 16V, X5R ×3 CVCC 4.7μF 10V X5R 0.02 M1 30.9k 400kHz D1, D2: MBRS140T3 T1: COILTRONICS VP1-0076 (*PRIMARY = 4 WINDINGS IN PARALLEL) M1: SILICONIX/VISHAY Si4840BDY GATE FBX GND INTVCC SHDN/UVLO SYNC RT SS + 105k • 46.4k 0.1μF 100pF 22k 6.8nF T1 1,2,3,4 D1 GND 1.05k 1% 158 1% D2 5 6 • • 3757 TA07 VC SENSE LT3757 VIN VIN 5V TO 16V CIN 22μF 25V, X5R ×2 C2 10μF 50V X5R D1 DFLS160 CVCC 4.7μF 10V, X5R C3 22μF 25V X5R C4 22μF 25V X5R COUT 3.3μF 100V GND C5 22μF 25V X5R VOUT1 –24V 200mA VOUT1 –72V 200mA 0.012 0.5W M1 Si7850DP 63.4k 200kHz GATE FBX GND INTVCC SHDN/UVLO SYNC RT SS • • • R2 • 105k R1 46.4k 0.1μF 100pF 15.8k 464k 9.1k 10nF T1 1,2,3 4 D2 DFLS160 5 D3 DFLS160 6 VP5-0155 (PRIMARY = 3 WINDINGS IN PARALLEL) 3757 TA08 VC LT3757/LT3757A 33 3757afd Package Description 3.00 ±0.10 (4 SIDES) NOTE: 1. DRAWING TO BE MADE A JEDEC PACKAGE OUTLINE M0-229 VARIATION OF (WEED-2). CHECK THE LTC WEBSITE DATA SHEET FOR CURRENT STATUS OF VARIATION ASSIGNMENT 2. DRAWING NOT TO SCALE 3. ALL DIMENSIONS ARE IN MILLIMETERS 4. DIMENSIONS OF EXPOSED PAD ON BOTTOM OF PACKAGE DO NOT INCLUDE MOLD FLASH. MOLD FLASH, IF PRESENT, SHALL NOT EXCEED 0.15mm ON ANY SIDE 5. EXPOSED PAD SHALL BE SOLDER PLATED 6. SHADED AREA IS ONLY A REFERENCE FOR PIN 1 LOCATION ON THE TOP AND BOTTOM OF PACKAGE 0.40 ± 0.10 BOTTOM VIEW—EXPOSED PAD 1.65 ± 0.10 (2 SIDES) 0.75 ±0.05 R = 0.125 TYP 2.38 ±0.10 (2 SIDES) 5 1 6 10 PIN 1 TOP MARK (SEE NOTE 6) 0.200 REF 0.00 – 0.05 (DD) DFN REV C 0310 0.25 ± 0.05 2.38 ±0.05 (2 SIDES) RECOMMENDED SOLDER PAD PITCH AND DIMENSIONS 1.65 ±0.05 2.15 ±0.05 (2 SIDES) 0.50 BSC 0.70 ±0.05 3.55 ±0.05 PACKAGE OUTLINE 0.25 ± 0.05 0.50 BSC DD Package 10-Lead Plastic DFN (3mm × 3mm) (Reference LTC DWG # 05-08-1699 Rev C) PIN 1 NOTCH R = 0.20 OR 0.35 × 45° CHAMFER LT3757/LT3757A 34 3757afd Package Description MSOP (MSE) 0911 REV H 0.53 ±0.152 (.021 ±.006) SEATING PLANE 0.18 (.007) 1.10 (.043) MAX 0.17 –0.27 (.007 – .011) TYP 0.86 (.034) REF 0.50 (.0197) BSC 1 2 3 4 5 4.90 ±0.152 (.193 ±.006) 0.497 ±0.076 (.0196 ±.003) REF 10 9 8 10 1 7 6 3.00 ±0.102 (.118 ±.004) (NOTE 3) 3.00 ±0.102 (.118 ±.004) (NOTE 4) NOTE: 1. DIMENSIONS IN MILLIMETER/(INCH) 2. DRAWING NOT TO SCALE 3. DIMENSION DOES NOT INCLUDE MOLD FLASH, PROTRUSIONS OR GATE BURRS. MOLD FLASH, PROTRUSIONS OR GATE BURRS SHALL NOT EXCEED 0.152mm (.006") PER SIDE 4. DIMENSION DOES NOT INCLUDE INTERLEAD FLASH OR PROTRUSIONS. INTERLEAD FLASH OR PROTRUSIONS SHALL NOT EXCEED 0.152mm (.006") PER SIDE 5. LEAD COPLANARITY (BOTTOM OF LEADS AFTER FORMING) SHALL BE 0.102mm (.004") MAX 6. EXPOSED PAD DIMENSION DOES INCLUDE MOLD FLASH. MOLD FLASH ON E-PAD SHALL NOT EXCEED 0.254mm (.010") PER SIDE. 0.254 (.010) 0° – 6° TYP DETAIL “A” DETAIL “A” GAUGE PLANE 5.23 (.206) MIN 3.20 – 3.45 (.126 – .136) 0.889 ±0.127 (.035 ±.005) RECOMMENDED SOLDER PAD LAYOUT 1.68 ±0.102 (.066 ±.004) 1.88 ±0.102 (.074 ±.004) 0.50 (.0197) BSC 0.305 ± 0.038 (.0120 ±.0015) TYP BOTTOM VIEW OF EXPOSED PAD OPTION 1.68 (.066) 1.88 (.074) 0.1016 ±0.0508 (.004 ±.002) DETAIL “B” DETAIL “B” CORNER TAIL IS PART OF THE LEADFRAME FEATURE. FOR REFERENCE ONLY NO MEASUREMENT PURPOSE 0.05 REF 0.29 REF MSE Package 10-Lead Plastic MSOP, Exposed Die Pad (Reference LTC DWG # 05-08-1664 Rev H) LT3757/LT3757A 35 3757afd Information furnished by Linear Technology Corporation is believed to be accurate and reliable. However, no responsibility is assumed for its use. Linear Technology Corporation makes no representation that the interconnection of its circuits as described herein will not infringe on existing patent rights. Revision History REV DATE DESCRIPTION PAGE NUMBER B 3/10 Deleted Bullet from Features and Last Line of Description Updated Entire Page to Add H-Grade and Military Grade Updated Electrical Characteristics Notes and Typical Performance Characteristics for H-Grade and Military Grade Revised TA04a and Replaced TA04c in Typical Applications Updated Related Parts 1 2 4 to 6 30 36 C 5/11 Revised MP-grade temperature range in Absolute Maximum Ratings and Order Information sections Revised Note 2 Revised formula in Applications Information Updated Typical Application drawing TA04a values Revised Typical Application title TA06 2 4 19 30 32 D 07/12 Added LT3757A version Throughout Updated Block Diagram 8 Updated Programming the Output Voltage section 12 Updated Loop Compensation section 13 Added an application circuit in the Typical Applications section 28 Updated the schematic and Load Step Waveforms in the Typical Applications section 31 (Revision history begins at Rev B) LT3757/LT3757A 36 3757afd Linear Technology Corporation 1630 McCarthy Blvd., Milpitas, CA 95035-7417 (408) 432-1900 ● FAX: (408) 434-0507 ● www.linear.com LINEAR TECHNOLOGY CORPORATION 2008 LT 0712 REV D • PRINTED IN USA Related Parts Typical Application PART NUMBER DESCRIPTION COMMENTS LT3758A Boost, Flyback, SEPIC and Inverting Controller 5.5V ≤ VIN ≤ 100V, Current Mode Control, 100kHz to 1MHz Programmable Operation Frequency, 3mm × 3mm DFN-10 and MSOP-10E Packages LT3759 Boost, SEPIC and Inverting Controller 1.6V ≤ VIN ≤ 42V, Current Mode Control, 100kHz to 1MHz Programmable Operation Frequency, MSOP-12E Packages LT3957A Boost, Flyback, SEPIC and Inverting Controller with 5A, 40V Switch 3V ≤ VIN ≤ 40V, Current Mode Control, 100kHz to 1MHz Programmable Operation Frequency, 5mm × 6mm QFN Package LT3958 Boost, Flyback, SEPIC and Inverting Controller with 3.3A, 84V Switch 5V ≤ VIN ≤ 80V, Current Mode Control, 100kHz to 1MHz Programmable Operation Frequency, 5mm × 6mm QFN Package LT3573/LT3574/ LT3575 40V Isolated Flyback Converters Monolithic No-Opto Flybacks with Integrated 1.25A/0.65A/2.5A Switch LT3511/LT3512 100V Isolated Flyback Converters Monolithic No-Opto Flybacks with Integrated 240mA/420mA Switch LT3798 Offline Isolated No Opto-Coupler Flyback Controller with Active PFC VIN and VOUT Limited Only by External Components, MSOP-16 Package LT3799/LT3799-1 Offline Isolated Flyback LED Controllers with Active PFC VIN and VOUT Limited Only by External Components, MSOP-16 Package High Efficiency Inverting Power Supply Efficiency vs Output Current OUTPUT CURRENT (A) 0.001 10 EFFICIENCY (%) 20 30 40 50 60 70 80 90 100 0.01 0.1 1 3757 TA09b 10 VIN = 16V VIN = 5V SENSE LT3757 VIN VIN 5V TO 15V CIN 47μF 16V X5R CDC 47μF 25V, X5R VOUT –5V 3A to 5A 0.006 1W M1 Si7848BDP 41.2k 300kHz GATE FBX GND INTVCC SHDN/UVLO SYNC RT SS • R2 • 105k R1 46.4k 0.1μF 9.1k 10nF L1 L2 D1 MBRD835L L1, L2: COILTRONICS DRQ127-3R3 (*COUPLED INDUCTORS) 3757 TA09a 84.5k CVCC 16k 4.7μF 10V X5R COUT 100μF 6.3V, X5R ×2 VC Photoelectric proximity switches HGA Photoelectric proximity switches ener. Photoelectric proximity switches V Photoelectric reflex switches T W 9-2: A Versatile, Complete and Compact Series D A T A S H E E T The W 9-2 series is as versatile as the tasks in automation. The standardized, compact housing model makes it possible to use high-performance sensors that operate reliably even in cramped mounting conditions. All W 9-2 models have red light transmitters as a standard feature. The sensor can be aligned on the object quickly and precisely using the visible light spot. In the models with Teach-In function, the sensor optimizes its sensitivity automatically to the given operating conditions at the push of a button. Depending on the job, the most suitable sensor can be selected from the W 9-2 series. Overview of the sensors: WT 9-2, with adjustable background suppression, max. scanning distance 250 mm, WT 9-2, energetic, max. scanning distance 450 mm, WT 9-2, V model, max. scanning distance 20 mm, WL 9-2, basic model, max. scanning range 4 m, WL 9-2, Teach-In model, max. scanning range 4 m, WL 9-2, focus, max. scanning range 0.4 m. There are multifaceted applications in the targeted main branches thanks to this great variety of products: Storage and handling engineering Packaging industry Electronics industry Elevator construction. 2 SENSICK WT 9-2 Photoelectric Proximity Switch with Background Suppression Setting options Dimension illustration LED light source, visible red light Background suppression Scanning distance adjustable Switching frequency 1500/s Outputs short-circuit protected Scanning distance 30 ... 250 mm 12 22 40 20 3 3 1.5 1 3 2 3 18.5 10.5 11 4 5 7 Axis of the sender optics Axis of the receiver optics Mounting hole Ø 3.2 mm LED signal strength indicator Plug M 12 or M 8, 4 pin, 2 m connection cable or 120 mm cable with plug M 12, 4 pin Scanning distance adjuster Standard direction of the material to be scanned 1 2 3 4 5 Photoelectric proximity switch 6 7 WT 9-2P130 WT 9-2P430 WT 9-2N130 WT 9-2N430 4 6 Cable receptacles Adapter plate Mounting bracket Accessories Connection type L+ Q Q M brn wht blu blk 4 pin, M 12 WT 9-2P330 WT 9-2P630 WT 9-2P430 WT 9-2N430 1 L+ Q Q 4 2 3 M brn wht blu blk 4 pin, M 8 1 L+ Q Q 4 2 3 M brn wht blu blk 4 x 0,14 mm2 1 L+ Q Q 4 2 3 M brn wht blu blk 4 pin, M 12 with 120 mm cable WT 9-2P330 WT 9-2P130 WT 9-2N130 WT 9-2P630 Scanning distance adjustable 1) 30 ... 250 mm Scanning range 5 ... 250 mm Supply voltage VS 2) DC 10 ... 30 V Ripple 3) ≤ 5 VPP Current consumption 4) ≤ 40 mA Light source LED, visible red light 5) Light spot diameter 15 x 15 mm at a distance of 200 mm Switching outputs Q and Q– PNP NPN Signal voltage HIGH VS – 2.9 V VS Signal voltage LOW 6) Approx. 0 V ≤ 1.5 V Output current IA max. ≤ 100 mA Response time 7) ≤ 333 μs Switching frequency max. 8) 1500/s Connection technology Connection cable, 2 m Cable, 120 mm, with plug M 12, 4 pin Plug M 12, 4 pin Plug M 8, 4 pin VDE protection class M 12 9) VDE protection class M 8 9) III Protection type IP 67 Protection circuits 10) A, B, C Ambient temperature 11) Operation –40 ... +60 °C Storage –40 ... +75 °C Weight with connection cable 2 m/120 mm Approx. 80 g with equipment plug M 12/M 8, 4 pin Approx. 20 g SENSICK 3 WT 9-2 Scanning distance Ordering information Technical data WT 9-2 P130 P430 N130 N430 P330 P630 1) Object with 90% reflectance (referred to standard white DIN 5033) 2) Limit values 3) Must be within VS tolerances 4) Without load 5) Average service life at room temperature 100,000 h 6) At TU = +25 °C and 100 mA output current 7) With resistive load 8) With light/dark ratio 1:1 9) Withstand voltage 50 V 10) A = supply connections reverse polarity protected B = outputs short-circuit protected C = interference suppression 11) Do not distort cable below 0 °C Type WT 9-2P130 WT 9-2P430 WT 9-2N130 WT 9-2N430 WT 9-2P330 WT 9-2P630 Order no. 1 018 293 1 018 295 1 018 294 1 018 296 1 019 026 1 019 272 (mm) 50 100 150 200 250 30 15 20 25 10 0 5 % of scanning distance 1 3 2 WT 9-2 HGA 90%/90% 18%/90% 6%/90% Scanning range on gray, white background, Black = 6% reflectance 1 Scanning range on black ), white background, 2 White = 90% reflectance Scanning range on white, white background, Gray = 18% reflectance 3 0(mm) 50 100 150 200 250 3 1 2 Operating distance 30 150 30 220 30 250 4 SENSICK WT 9-2 Photoelectric Proximity Switch, Energetic, Teach-In Setting options Dimension illustration Red-light emitter LED as alignment aid Scanning distance adjustable Switching frequency 800/s Outputs short-circuit protected Teach-In Scanning distance 18 ... 450 mm 12 22 40 20 3 3 1.5 1 3 2 3 25.55 6.5 11 4 5 Axis of the receiver optics Axis of the sender optics Mounting hole Ø 3.2 mm LED signal strength indicator Plug M 12 or M 8, 4 pin, 2 m connection cable or 120 mm cable with plug M 12, 4 pin Scanning distance adjuster, teachable 1 2 3 4 5 Photoelectric proximity switch 6 WT 9-2P151 WT 9-2P451 WT 9-2N151 WT 9-2N451 4 6 Cable receptacles Adapter plate Mounting bracket Accessories Connection type L+ Q Q M brn wht blu blk 4 pin, M 12 WT 9-2P351 WT 9-2P651 WT 9-2P451 WT 9-2N451 1 L+ Q Q 4 2 3 M brn wht blu blk 4 pin, M 8 1 L+ Q Q 4 2 3 M brn wht blu blk 4 x 0,14 mm2 1 L+ Q Q 4 2 3 M brn wht blu blk 4 pin, M 12 with 120 mm cable WT 9-2P351 WT 9-2P151 WT 9-2N151 WT 9-2P651 SENSICK 5 Scanning distance adjustable 1) 10 ... 450 mm Supply voltage VS 2) DC 10 ... 30 V Ripple 3) ≤ 5 VPP Current consumption 4) ≤ 30 mA Light source LED, visible red light 5) Light spot diameter 80 x 80 mm at a distance of 500 mm Switching outputs Q and Q– PNP NPN Signal voltage HIGH VS – 2.9 V VS Signal voltage LOW6) Approx. 0 V ≤ 2.9 V Output current IA max. ≤ 100 mA Response time 7) ≤ 625 μs Switching frequency max. 8) 800/s Connection technology Connection cable, 2 m Cable, 120 mm, with plug M 12, 4 pin Plug M 12, 4 pin Plug M 8, 4 pin VDE protection class M 12 9) VDE protection class M 8 9) III Protection type IP 67 Protection circuits 10) A, B, C Ambient temperature 11) Operation –40 ... +60 °C Storage –40 ... +75 °C Weight with connection cable 2 m/120 mm Approx. 80 g with equipment plug M 12/M 8, 4 pin Approx. 20 g WT 9-2 Scanning distance Ordering information Technical data WT 9-2 P151 P451 N151 N451 P351 P651 1) Object with 90% reflectance (referred to standard white DIN 5033) 2) Limit values 3) Must be within VS tolerances 4) Without load 5) Average service life at room temperature 50,000 h 6) At TU = +25 °C and 100 mA output current 7) With resistive load 8) With light/dark ratio 1:1 9) Withstand voltage 50 V 10) A = supply connections reverse polarity protected B = outputs short-circuit protected C = interference suppression 11) Do not distort cable below 0 °C Type WT 9-2P151 WT 9-2P451 WT 9-2N151 WT 9-2N451 WT 9-2P351 WT 9-2P651 Order no. 1 018 297 1 018 299 1 018 298 1 018 300 1 019 027 1 019 273 (mm) 100 200 1000 10 100 1 300 400 500 Function reserve Operating distance Limiting scanning distance WT 9-2 energetic 3 90% 2 18% 1 6% Programming via Teach-In button. Simple programming: Position object in the beam and push the button: finished; LED confirms the Teach-In procedure. Teach-In values can be stored. Teach-In function Two operating modes: Default setting: short Teach-In time (< 8 s); for standard applications; approx. double reserve via switching threshold; LED lights continuously. Precise setting: long Teach-In time (> 8 s); for precise applications; small switching hysteresis; LED blinks. Scanning range on white, 90 % reflectance Scanning range on gray, 18% reflectance 1 Scanning range on black, 6% reflectance 2 3 0(mm) 100 200 300 400 500 1 2 3 Operating distance Limiting scanning distance 10 180 220 10/100 130 10 350 450 6 SENSICK WT 9-2 Photoelectric Proximity Switch, V-type, Teach-In Setting options Dimension illustration Red-light emitter LED as alignment aid Scanning distance adjustable Switching frequency 800/s Outputs short-circuit protected Teach-In Scanning distance 10 ... 20 mm 12 22 40 20 3 3 1.5 1 3 2 3 26.45 4.7 11 4 5 Axis of the receiver optics Axis of the receiver optics Mounting hole Ø 3.2 mm LED signal strength indicator Plug M 12 or M 8, 4 pin, 2 m connection cable or 120 mm cable with plug M 12, 4 pin Scanning distance adjuster, teachable 1 2 3 4 5 Photoelectric proximity switch 6 WT 9-2P141 WT 9-2P441 WT 9-2N141 WT 9-2N441 4 6 Cable receptacles Adapter plate Mounting bracket Accessories Connection type L+ Q Q M brn wht blu blk 4 pin, M 12 WT 9-2P341 WT 9-2P641 WT 9-2P441 WT 9-2N441 1 L+ Q Q 4 2 3 M brn wht blu blk 4 pin, M 8 1 L+ Q Q 4 2 3 M brn wht blu blk 4 x 0,14 mm2 1 L+ Q Q 4 2 3 M brn wht blu blk 4 pin, M 12 with 120 mm cable WT 9-2P341 WT 9-2P141 WT 9-2N141 WT 9-2P641 SENSICK 7 Scanning distance adjustable 1) 10 ... 20 mm Supply voltage VS 2) DC 10 ... 30 V Ripple 3) ≤ 5 VPP Current consumption 4) ≤ 30 mA Light source LED, visible red light 5) Light spot diameter 3 mm at a distance of 20 mm Switching outputs Q and Q– PNP NPN Signal voltage HIGH VS – 2.9 V VS Signal voltage LOW6) Approx. 0 V ≤ 2.9 V Output current IA max. ≤ 100 mA Response time 7) ≤ 625 μs Switching frequency max. 8) 800/s Connection technology Connection cable, 2 m Cable, 120 mm, with plug M 12, 4 pin Plug M 12, 4 pin Plug M 8, 4 pin VDE protection class M 12 9) VDE protection class M 8 9) III Protection type IP 67 Protection circuits 10) A, B, C Ambient temperature 11) Operation –40 ... +60 °C Storage –40 ... +75 °C Weight with connection cable 2 m/120 mm Approx. 80 g with equipment plug M 12/M 8, 4 pin Approx. 20 g WT 9-2 Scanning distance Ordering information Technical data WT 9-2 P141 P441 N141 N441 P341 P641 1) Object with 90% reflectance (referred to standard white DIN 5033) 2) Limit values 3) Must be within VS tolerances 4) Without load 5) Average service life at room temperature 100,000 h 6) At TU = +25 °C and 100 mA output current 7) With resistive load 8) With light/dark ratio 1:1 9) Withstand voltage 50 V 10) A = supply connections reverse polarity protected B = outputs short-circuit protected C = interference suppression 11) Do not distort cable below 0 °C Type WT 9-2P141 WT 9-2P441 WT 9-2N141 WT 9-2N441 WT 9-2P341 WT 9-2P641 Order no. 1 018 301 1 018 303 1 018 302 1 018 304 1 019 274 1 019 275 Programming via Teach-In button. Simple programming: Position object in the beam and push the button: finished; LED confirms the Teach-In procedure. Teach-In values can be stored. Teach-In function Two operating modes: Default setting: short Teach-In time (< 8 s); for standard applications; approx. double reserve via switching threshold; LED lights continuously. Precise setting: long Teach-In time (> 8 s); for precise applications; small switching hysteresis; LED blinks. (mm) 4 1 10 100 8 12 16 20 24 28 Function reserve 1 3 2 6% 18% 90% Operating distance WT 9-2 0(mm) 10 20 30 1 2 3 Scanning distance 10 22 10 20 10 24 Scanning range on white, 90 % reflectance Scanning range on gray, 18% reflectance 1 Scanning range on black, 6% reflectance 2 3 8 SENSICK WL 9-2 Photoelectric Reflex Switch, Standard Without setting options Dimension illustration Red-light emitter LED as alignment aid Switching frequency 800/s Outputs short-circuit protected Scanning range 0 ... 4 m 12 22 40 20 3 3 1.5 1 2 2 29.5 11 3 4 Middle of optic axis Mounting hole Ø 3.2 mm LED signal strength indicator Plug M 12 or M 8, 4 pin, 2 m connection cable or 120 mm cable with plug M 12, 4 pin 1 2 3 4 Photoelectric reflex switch WL 9-2P130 WL 9-2P430 WL 9-2N130 WL 9-2N430 3 Cable receptacles Adapter plate Mounting bracket Reflectors Accessories Connection type L+ Q Q M brn wht blu blk 4 pin, M 12 WT 9-2P330 WT 9-2P630 WT 9-2P430 WT 9-2N430 1 L+ Q Q 4 2 3 M brn wht blu blk 4 pin, M 8 1 L+ Q Q 4 2 3 M brn wht blu blk 4 x 0,14 mm2 1 L+ Q Q 4 2 3 M brn wht blu blk 4 pin, M 12 with 120 mm cable WT 9-2P330 WT 9-2P130 WT 9-2N130 WT 9-2P630 SENSICK 9 Scanning range typ. max./on reflector 4 m/PL 80 A Supply voltage VS 1) DC 10 ... 30 V Ripple 2) ≤ 5 VPP Current consumption 3) ≤ 30 mA Light source LED, visible red light 4) Angle of dispersion 2.5° Light spot diameter 120 x 120 mm at a distance of 3 m Switching outputs Q and Q– PNP NPN Signal voltage HIGH VS – 2.9 V VS Signal voltage LOW5) Approx. 0 V ≤ 2.9 V Output current IA max. ≤ 100 mA Response time 6) ≤ 625 μs Max. switching frequency 7) 800/s Connection technology Connection cable, 2 m Cable, 120 mm, with plug M 12, 4 pin Plug M 12, 4 pin Plug M 8, 4 pin VDE protection class M 12 8) VDE protection class M 8 8) III Protection type IP 67 Protection circuits 9) A, B, C Ambient temperature 10) Operation –40 ... +60 °C Storage –40 ... +75 °C Weight with connection cable 2 m/120 mm Approx. 80 g with equipment plug M 12/M 8, 4 pin Approx. 20 g WL 9-2 Scanning range Ordering information Technical data WL 9-2 P130 P430 N130 N430 P330 P630 1) Limit values 2) Must be within VS tolerances 3) Without load 4) Average service life at room temperature 100,000 h 5) At TU = +25 °C and 100 mA output current 6) With resistive load 7) With light/dark ratio 1:1 8) Withstand voltage 50 V 19) A = supply connections reverse polarity protected B = outputs short-circuit protected C = interference suppression 10) Do not distort cable below 0 °C Type WL 9-2P130 WL 9-2P430 WL 9-2N130 WL 9-2N430 WL 9-2P330 WL 9-2P630 Order no. 1 018 281 1 018 283 1 018 282 1 018 284 1 019 024 1 019 268 (m) 1 2 3 4 5 100 10 1 Function reserve 1 3 2 Operating range WL 9-2 Limiting scanning range 0(m) 1 2 3 4 5 1 2 3 Operating range Scanning range typ. max. 0 3.0 4.0 0 2.0 3.0 0 0.6/1.0 Reflective tape 0 ... 0.6 m Diamond Grade* 3 2 PL 40 A 0 ... 2 m 1 PL 80 A 0 ... 3 m Reflector type Operating range * 100 x 100 mm2 10 SENSICK WL 9-2 Photoelectric Reflex Switch, Standard, Teach-In Setting options Dimension illustration Red-light emitter LED as alignment aid Switching frequency 800/s Outputs short-circuit protected Teach-In Scanning range 0 ... 4 m 12 22 40 20 3 3 1.5 1 2 2 29.5 11 3 4 Middle of optic axis Mounting hole Ø 3.2 mm LED signal strength indicator Plug M 12 or M 8, 4 pin, 2 m connection cable or 120 mm cable with plug M 12, 4 pin Sensitivity control, teachable 1 2 3 4 5 Photoelectric reflex switch WL 9-2P131 WL 9-2P431 WL 9-2N131 WL 9-2N431 3 5 Cable receptacles Adapter plate Mounting bracket Reflectors Accessories Connection type L+ Q Q M brn wht blu blk 4 pin, M 12 WT 9-2P331 WT 9-2P631 WT 9-2P431 WT 9-2N431 1 L+ Q Q 4 2 3 M brn wht blu blk 4 pin, M 8 1 L+ Q Q 4 2 3 M brn wht blu blk 4 x 0,14 mm2 1 L+ Q Q 4 2 3 M brn wht blu blk 4 pin, M 12 with 120 mm cable WT 9-2P331 WT 9-2P131 WT 9-2N131 WT 9-2P631 SENSICK 11 Scanning range typ. max./on reflector 4 m/PL 80 A Supply voltage VS 1) DC 10 ... 30 V Ripple 2) ≤ 5 VPP Current consumption 3) ≤ 30 mA Light source LED, visible red light 4) Angle of dispersion 2.5° Light spot diameter 120 x 120 mm at a distance of 3 m Switching outputs Q and Q– PNP NPN Signal voltage HIGH VS – 2.9 V VS Signal voltage LOW5) Approx. 0 V ≤ 2.9 V Output current IA max. ≤ 100 mA Response time 6) ≤ 625 μs Max. switching frequency 7) 800/s Connection technology Connection cable, 2 m Cable, 120 mm, with plug M 12, 4 pin Plug M 12, 4 pin Plug M 8, 4 pin VDE protection class M 12 8) VDE protection class M 8 8) III Protection type IP 67 Protection circuits 9) A, B, C Ambient temperature 10) Operation –40 ... +60 °C Storage –40 ... +75 °C Weight with connection cable 2 m/120 mm Approx. 80 g with equipment plug M 12/M 8, 4 pin Approx. 20 g WL 9-2 Scanning range Ordering information Technical data WL 9-2 P131 P431 N131 N431 P331 P631 1) Limit values 2) Must be within VS tolerances 3) Without load 4) Average service life at room temperature 100,000 h 5) At TU = +25 °C and 100 mA output current 6) With resistive load 7) With light/dark ratio 1:1 8) Withstand voltage 50 V 19) A = supply connections reverse polarity protected B = outputs short-circuit protected C = interference suppreasion 10) Do not distort cable below 0 °C Type WL 9-2P131 WL 9-2P431 WL 9-2N131 WL 9-2N431 WL 9-2P331 WL 9-2P631 Order no. 1 018 285 1 018 287 1 018 286 1 018 288 1 019 025 1 019 269 Programming via Teach-In button. Simple programming: Position reflector in the beam and push the button: finished; LED confirms the Teach-In procedure. Teach-In values can be stored. Teach-In function Two operating modes: Default setting: short Teach-In time (< 8 s); for standard applications; approx. double reserve via switching threshold; LED lights continuously. Precise setting: long Teach-In time (> 8 s); for precise applications; small switching hysteresis; LED blinks. (m) 1 2 3 4 5 100 10 1 Function reserve 1 3 2 Operating range WL 9-2 Limiting scanning range 0(m) 1 2 3 4 5 1 2 3 Operating range Scanning range typ. max. 0 3.0 4.0 0 2.0 3.0 0 0.6/1.0 Reflective tape 0 ... 0.6 m Diamond Grade* 3 2 PL 40 A 0 ... 2 m 1 PL 80 A 0 ... 3 m Reflector type Operating range * 100 x 100 mm2 12 SENSICK WL 9-2 Photoelectric Reflex Switch, Focus 35 mm, Teach-In Setting options Dimension illustration LED light source, visible red light Sensitivity adjustment using the Teach-In method Switching frequency 800/s Outputs short-circuit protected Scanning range 0 ... 0.4 m 12 22 40 20 3 3 1.5 1 2 2 29.5 11 3 4 Middle of optic axis Mounting hole Ø 3.2 mm LED signal strength indicator Plug M 12 or M 8, 4 pin, 2 m connection cable or 120 mm cable with plug M 12, 4 pin Sensitivity control, teachable 1 2 3 4 5 Photoelectric reflex switch WL 9-2P121 WL 9-2P421 WL 9-2N121 WL 9-2N421 3 5 Cable receptacles Adapter plate Mounting bracket Reflectors Accessories Connection type L+ Q Q M brn wht blu blk 4 pin, M 12 WT 9-2P321 WT 9-2P621 WT 9-2P421 WT 9-2N421 1 L+ Q Q 4 2 3 M brn wht blu blk 4 pin, M 8 1 L+ Q Q 4 2 3 M brn wht blu blk 4 x 0,14 mm2 1 L+ Q Q 4 2 3 M brn wht blu blk 4 pin, M 12 with 120 mm cable WT 9-2P321 WT 9-2P121 WT 9-2N121 WT 9-2P621 SENSICK 13 Scanning range typ. max./on reflector 0.4 m/PL 80 A Supply voltage VS 1) DC 10 ... 30 V Ripple 2) ≤ 5 VPP Current consumption 3) ≤ 30 mA Light source LED, visible red light 4) Light spot diameter 1.5 x 1.5 mm at a distance of 35 mm Switching outputs Q and Q– PNP NPN Signal voltage HIGH VS – 2.9 V VS Signal voltage LOW5) Approx. 0 V ≤ 2.9 V Output current IA max. ≤ 100 mA Response time 6) ≤ 625 μs Max. switching frequency 7) 800/s Connection technology Connection cable, 2 m Cable, 120 mm, with plug M 12, 4 pin Plug M 12, 4 pin Plug M 8, 4 pin VDE protection class M 12 8) VDE protection class M 8 8) III Protection type IP 67 Protection circuits 9) A, B, C Ambient temperature 10) Operation –40 ... +60 °C Storage –40 ... +75 °C Weight with connection cable 2 m/120 mm Approx. 80 g with equipment plug M 12/M 8, 4 pin Approx. 20 g WL 9-2 Scanning range Ordering information Technical data WL 9-2 P121 P421 N121 N421 P321 P621 1) Limit values 2) Must be within VS tolerances 3) Without load 4) Average service life at room temperature 100,000 h 5) At TU = +25 °C and 100 mA output current 6) With resistive load 7) With light/dark ratio 1:1 8) Withstand voltage 50 V 19) A = supply connections reverse polarity protected B = outputs short-circuit protected C = interference suppression 10) Do not distort cable below 0 °C Type WL 9-2P121 WL 9-2P421 WL 9-2N121 WL 9-2N421 WL 9-2P321 WL 9-2P621 Order no. 1 018 289 1 018 291 1 018 290 1 018 292 1 019 270 1 019 271 Programming via Teach-In button. Simple programming: Position reflector in the beam and push the button: finished; LED confirms the Teach-In procedure. Teach-In values can be stored. Teach-In function Two operating modes: Default setting: short Teach-In time (< 8 s); for standard applications; approx. double reserve via switching threshold; LED lights continuously. Precise setting: long Teach-In time (> 8 s); for precise applications; small switching hysteresis; LED blinks. (m) 0.1 0.2 0.3 0.4 0.5 0.6 100 10 1 Function reserve Limiting scanning range Operating range WL 9-2 2 1 3 0(m) 0.1 0.2 0.3 0.4 0.5 1 2 3 Operating range Limiting scanning range 0 0.3 0.4 0 0.2 0.3 0 0,.1 0.2 Reflective tape 0 ... 0.25 m Diamond Grade* 3 2 PL 40 A 0 ... 0.3 m 1 PL 80 A 0 ... 0.5 m Reflector type Operating range * 100 x 100 mm2 14 Accessoires SENSICK Dimension illustrations of reflectors Reflector 20 x 40 mm Order no. 1 012 719 Type PL 20 A Reflector 30 x 50 mm Order no. 1 002 314 Type PL 30 A 15 18 38 ø8 ø4.6 50 60 4.2 7.3 3.4 ø4.5 ø8 71 82 29.8 7.2 Reflector 40 x 60 mm Order no. 1 012 720 Type PL 40 A Reflector hexagonal, SW 48 mm Order no. 1 000 132 Type PL 50 A 34 38 7.8 40.2 52 56.6 59.8 ø8.5 ø4.5 8 78 68 59 Reflector 80 x 80 mm Order no. 1 003 865 Type PL 80 A Reflector ø 83 mm, center hole mounting Order no. 5 304 549 Type C 110 84 68 71 84 4.5 8 8.5 2.5 ø4.8 83 9 Also available as heatable model: Continuous heating: PL 50HK, Order no. 1 001 545 Regulated heating: PL 50HS, Order no. 1 009 871 Reflective tape fabricated sheet 749 x 914 mm Order no. 4 019 634 5 304 334 Type REF-DG-K REF-DG Dimension illustrations and ordering information 15 Accessoires SENSICK Contact assignments according to EN 50044 DC coding Dimension illustrations of cable receptacles Cable receptacles M 12, 4 pin, straight Order no. 6 007 302 Cable lengths – 5 ø18 M12x1 54 5 ø10.5 ø8.8 1.5 12 M12x1 14.5 27 25.5 42 Rmin 571) Rmin 571) 38.3 12 45° M12x1 26.5 14.5 12 1.5 ø8.8 ø10.5 Pin assignments Pin 1 = brown Pin 2 = white Pin 3 = blue Pin 4 = black 3 2 4 1 Pins 4 Type DOS-1204-G Cable receptacles M 12, 4 pin, angled Order no. 6 007 303 Cable lengths – 36 25 5 14.8 M12x1 ø18 36 5 20.5 Pins 4 Type DOS-1204-W Cable receptacles M 12, 4 pin, straight Pins 4 4 4 Type DOS-1204-G02M DOS-1204-G05M DOS-1204-G10M Order no. 6 009 382 6 009 866 6 010 543 Cable lengths 2 m 5 m 10 m Cable receptacles M 12, 4 pin, angled Pins 4 4 4 Type DOS-1204-W02M DOS-1204-W05M DOS-1204-W10M Order no. 6 009 383 6 009 867 6 010 541 Cable lengths 2 m 5 m 10 m Can be self-made for cables Ø 4.5 to 6.5 mm 1) Minimum bending radius with dynamic use Can be self-made for cables Ø 4.5 to 6.5 mm 1) Minimum bending radius with dynamic use Dimension illustrations and ordering information 16 Accessoires SENSICK Dimension illustrations and ordering information ø 11.6 M 8x1 38.4 Cable diameter max. 5.0 mm 28.0 ø 11.6 M 8x1 12.5 Cable diameter max. 5.0 mm SENSICK circular screwing system, M 8 plug, 4 pin, enclosure rating IP 67 M 8 cable receptacle, 4 pin, straight Type DOS-0804-G Order no. 6 009 974 M 8 cable receptacles, 4 pin, angled Type DOS-0804-W Order no. 6 009 975 2/wht 1/brn 4/blk 3/blu ø 10 30.5 Rmin1) M 8x1 3/blu 6 26 M 8x1 16.5 ø 10 Rmin1) 1/brn 4/blk 2/wht M 8 cable receptacle, 4 pin, straight M 8 cable receptacles, 4 pin, angled Cable diameter 5 mm, 4 x 0.25 mm2, PVC coating Cable diameter 5 mm, 4 x 0.25 mm2, PVC coating Cable length 2 m 5 m 10 m Type DOL-0804-G02M DOL-0804-G05M DOL-0804-G10M Order no. 6 009 870 6 009 872 6 010 754 Cable length 2 m 5 m 10 m Type DOL-0804-W02M DOL-0804-W05M DOL-0804-W10M Order no. 6 009 871 6 009 873 6 010 755 1) Minimum bending radius with dynamic use Rmin= 20x cable diameter SENSICK 17 Dimension illustration adapter plate Adapter plate Order no. 4 033 145 Type BEF-AP-W9 22 63.25 1 8.25 5 3.25 20 3 M 3 ø 3.2 Dimension illustration mounting bracket Mounting bracket Order no. 4 033 146 Type BEF-WN-W9-2 44 1 4 4 3.5 5 6 14.8 12 6.4 8 14.8 16 17 17 Accessoires Dimension illustrations and ordering information 8 008 988.0700 HJS • SM • Printed in Germany • We reserve the right to make changes Contact: Au s t r a l i a Phone +61 3 94 97 41 00 0 08 33 48 02 – toll free Fax +61 3 94 97 11 87 Au s t r i a Phone +43 2 23 66 22 88-0 Fax +43 2 23 66 22 88-5 Bel g i u m / Luxembourg Phone +32 24 66 55 66 Fax +32 24 63 35 07 Br a z i l Phone +55 11 55 61 26 83 Fax +55 11 5 35 41 53 C h i n a / Ho n g Kong Phone +8 52 27 63 69 66 Fax +8 52 27 63 63 11 Czech Re p u b l i c Phone +42 02 57 81 05 61 Fax +42 02 57 81 05 59 Denmark Phone +45 45 82 64 00 Fax +45 45 82 64 01 F i n l a n d Phone +3 58 9-7 28 85 00 Fax +3 58 9-72 88 50 55 Fr a n c e Phone +33 1-64 62 35 00 Fax +33 1-64 62 35 77 Germany Phone +49 76 81 2 02-0 Fax +49 76 81 2 02-36 09 G re a t B r i t a i n Phone +44 17 27-83 11 21 Fax +44 17 27-85 67 67 I t a l y Phone +390 2-92 14 20 62 Fax +390 2-92 14 20 67 Japan Phone +813 33 58-13 41 Fax +813 33 58-05 86 Ne t h e r l a n d s Phone +31 3 02 29 25 44 Fax +31 3 02 29 39 94 Nor w a y Phone +47 67 56 75 00 Fax +47 67 56 66 10 P o l a n d Phone +48 2 26 44-83 45 Fax +48 2 26 44-83 42 Si n g a p o re Phone +65 7 44 37 32 Fax +65 8 41 77 47 Sp a i n Phone +34 9 34 80 31 00 Fax +34 9 34 73 44 69 Sweden Phone +46 8-6 80 64 50 Fax +46 8-7 10 18 75 S w i t z e r l a n d Phone +41 4 16 19 29 39 Fax +41 4 16 19 29 21 Ta i w a n Phone +88 62 23 65 62 92 Fax +88 62 23 68 73 97 USA Phone +1 9 52 9 41-67 80 Fax +1 9 52 9 41-92 87 Representatives and agencies in all major industrial nations. SICK AG • Industrial Sensors • Sebastian-Kneipp-Straße 1 • D-79183 Waldkirch Phone +49/76 81/2 02-0 • Fax +49/76 81/2 02-36 09 • www.sick.de 1. Product profile 1.1 General description The BGA7124 MMIC is a one-stage amplifier, available in a low-cost leadless surface-mount package. It delivers 25 dBm output power at 1 dB gain compression and superior performance up to 2700 MHz. Its power saving features include easy quiescent current adjustment enabling class-AB operation and logic-level shutdown control to reduce the supply current to 4 μA. 1.2 Features and benefits 400 MHz to 2700 MHz frequency operating range 16 dB small signal gain at 2 GHz 25 dBm output power at 1 dB gain compression Integrated active biasing External matching allows broad application optimization of the electrical performance 3.3 V or 5 V single supply operation All pins ESD protected 1.3 Applications 1.4 Quick reference data [1] The supply current is adjustable; see Section 8.1 “Supply current adjustment”. [2] Operation outside this range is possible but not guaranteed. [3] PL = 11 dBm per tone; spacing = 1 MHz. BGA7124 400 MHz to 2700 MHz 0.25 W high linearity silicon amplifier Rev. 3 — 9 September 2010 Product data sheet Wireless infrastructure (base station, repeater, backhaul systems) E-metering Broadband CPE/MoCA Satellite Master Antenna TV (SMATV) Industrial applications WLAN/ISM/RFID Table 1. Quick reference data Input and output impedances matched to 50 Ω, SHDN = HIGH (shutdown disabled). Typical values at VCC = 5 V; ICC = 130 mA; Tcase = 25 °C; unless otherwise specified. Symbol Parameter Conditions Min Typ Max Unit ICC supply current VCC = 5.0 V [1] 50 - 170 mA f frequency [2] 400 - 2700 MHz Gp power gain f = 2140 MHz 14.5 16 17.5 dB PL(1dB) output power at 1 dB gain compression f = 2140 MHz 23.5 24.5 - dBm IP3O output third-order intercept point f = 2140 MHz [3] 34.5 37.5 - dBm BGA7124 All information provided in this document is subject to legal disclaimers. © NXP B.V. 2010. All rights reserved. Product data sheet Rev. 3 — 9 September 2010 2 of 33 NXP Semiconductors BGA7124 400 MHz to 2700 MHz 0.25 W high linearity silicon amplifier 2. Pinning information 2.1 Pinning 2.2 Pin description [1] This pin is DC-coupled and requires an external DC-blocking capacitor. [2] RF decoupled. [3] The center metal base of the SOT908-1 also functions as heatsink for the power amplifier. 3. Ordering information Fig 1. HVSON8 package pin configuration 014aab046 VCC(BIAS) VCC(RF) SHDN VCC(RF) RF_IN ICQ_ADJ GND PAD n.c. Transparent top view 4 5 3 6 2 7 1 8 terminal 1 index area BGA7124 n.c. Table 2. Pin description Symbol Pin Description n.c. 1, 4 not connected VCC(RF) 2, 3 RF output for the power amplifier and DC supply input for the RF transistor collector [1] VCC(BIAS) 5 bias supply voltage [2] SHDN 6 shutdown control function enabled/disabled RF_IN 7 RF input for the power amplifier [1] ICQ_ADJ 8 quiescent collector current adjustment controlled by an external resistor GND GND pad RF and DC ground[3] Table 3. Ordering information Type number Package Name Description Version BGA7124 HVSON8 plastic thermal enhanced very thin small outline package; no leads; 8 terminals; body 3 × 3 × 0.85 mm SOT908-1 BGA7124 All information provided in this document is subject to legal disclaimers. © NXP B.V. 2010. All rights reserved. Product data sheet Rev. 3 — 9 September 2010 3 of 33 NXP Semiconductors BGA7124 400 MHz to 2700 MHz 0.25 W high linearity silicon amplifier 4. Functional diagram 5. Shutdown control Fig 2. Functional diagram BANDGAP INPUT MATCH OUTPUT MATCH BIAS ENABLE V/I CONVERTER RF_OUT GND R1 R2 RF_IN SHDN VCC ICQ_ADJ 6 7 5 8 2, 3 014aab047 VCC(BIAS) VCC(RF) Table 4. Shutdown control settings Mode Mode description Function description Pin SHDN Vctrl(sd) (V) Ictrl(sd) (μA) Min Max Min Max Idle medium power MMIC fully off; minimal supply current shutdown control enabled 0 0 0.7 - 2 TX medium power MMIC transmit mode shutdown control disabled 1 2.5 VCC(BIAS)- 9 BGA7124 All information provided in this document is subject to legal disclaimers. © NXP B.V. 2010. All rights reserved. Product data sheet Rev. 3 — 9 September 2010 4 of 33 NXP Semiconductors BGA7124 400 MHz to 2700 MHz 0.25 W high linearity silicon amplifier 6. Limiting values [1] See Figure 3 for safe operating area. [2] The supply current is adjustable; see Section 8.1 “Supply current adjustment”. [3] If Vctrl(sd) exceeds VCC(BIAS), the internal ESD circuit can be damaged. To prevent this, it is recommended that the Ictrl(sd) is limited to 20 mA. If the SHDN function is not used, the SHDN pin should be connected to the VCC(BIAS) pin. Table 5. Limiting values In accordance with the Absolute Maximum Rating System (IEC 60134). Symbol Parameter Conditions Min Max Unit VCC(RF) RF supply voltage [1]- 6.0 V VCC(BIAS) bias supply voltage [1]- 6.0 V ICC supply current [1][2] 50 200 mA Vctrl(sd) shutdown control voltage [3] 0.0 VCC(BIAS) V Pi(RF) RF input power - 20 dBm Tcase case temperature −40 +85 °C Tj junction temperature - 150 °C VESD electrostatic discharge voltage Human Body Model (HBM); According JEDEC standard 22-A114E - 2000 V Charged Device Model (CDM); According JEDEC standard 22-C101B - 500 V Exceeding the safe operating area limits may cause serious damage to the product. The impact on ICC due to the spread of the external ICQ resistor (R2) should be taken into account. The product-spread on ICC should be taken into account (see Section 8 “Static characteristics”). Fig 3. BGA7124 DC safe operating area VCC(RF) (V) 2 3 4 5 6 7 014aab048 150 100 200 250 ICC (mA) 50 BGA7124 All information provided in this document is subject to legal disclaimers. © NXP B.V. 2010. All rights reserved. Product data sheet Rev. 3 — 9 September 2010 5 of 33 NXP Semiconductors BGA7124 400 MHz to 2700 MHz 0.25 W high linearity silicon amplifier 7. Thermal characteristics [1] defined as thermal resistance from junction to GND paddle. 8. Static characteristics [1] The supply current is adjustable; see Section 8.1 “Supply current adjustment”. [2] See Section 12 “Application information”. 8.1 Supply current adjustment The supply current can be adjusted by changing the value of external ICQ resistor (R2); (see Figure 4). Table 6. Thermal characteristics Symbol Parameter Conditions Typ Max Unit Rth(j-mb) thermal resistance from junction to mounting base Tcase = 85 °C; VCC = 5 V; ICC = 130 mA [1] 32 - K/W Table 7. Characteristics Input and output impedances matched to 50 Ω, pin SHDN = HIGH (shutdown disabled). Typical values at VCC = 3.3 V or VCC = 5 V; Tcase = 25°C; unless otherwise specified. Symbol Parameter Conditions Min Typ Max Unit ICC supply current VCC = 3.3 V [1] 50 - 200 mA R1 = 0 Ω; R2 = 1330 Ω [2] 115 130 145 mA R1 = 2.2 Ω; R2 = 1070 Ω [2] 135 160 185 mA VCC = 5.0 V [1] 50 - 170 mA R1 = 0 Ω; R2 = 1960 Ω [2] 110 130 150 mA R1 = 2.2 Ω; R2 = 1650 Ω [2] 125 150 175 mA during shutdown; pin SHDN = LOW (shutdown enabled) - 4 6 μA BGA7124 All information provided in this document is subject to legal disclaimers. © NXP B.V. 2010. All rights reserved. Product data sheet Rev. 3 — 9 September 2010 6 of 33 NXP Semiconductors BGA7124 400 MHz to 2700 MHz 0.25 W high linearity silicon amplifier 9. Dynamic characteristics a. 5 V supply voltage. b. 3.3 V supply voltage Fig 4. Supply current as a function of the value of R2 VCC = 5 V; R1 = 0 R2 (kΩ) 1.6 2.0 2.4 2.8 3.2 3.6 4.0 4.4 014aab049 90 130 170 ICC (mA) 50 VCC = 3.3 V; R1 = 0 R2 (kΩ) 0.9 1.4 1.9 2.4 2.9 3.4 014aab050 110 140 80 170 200 ICC (mA) 50 Table 8. Characteristics at VCC = 5 V Input and output impedances matched to 50 Ω, pin SHDN = HIGH (shutdown disabled). Typical values at VCC = 5 V; ICC = 130 mA; Tcase = 25°C; see Section 12 “Application information”; unless otherwise specified. Symbol Parameter Conditions Min Typ Max Unit f frequency [1] 400 - 2700 MHz Gp power gain for small signals f = 940 MHz - 22.7 - dB f = 1960 MHz - 16.4 - dB f = 2140 MHz 14.5 16.0 17.5 dB f = 2445 MHz [2] - 14.2 - dB PL(1dB) output power at 1 dB gain compression f = 940 MHz - 25.0 - dBm f = 1960 MHz - 24.5 - dBm f = 2140 MHz 23.5 24.5 - dBm f = 2445 MHz [2] - 23.5 - dBm IP3O output third-order intercept point f = 940 MHz [3] - 38.5 - dBm f = 1960 MHz [3] - 38.0 - dBm f = 2140 MHz [3] 34.5 37.5 - dBm f = 2445 MHz [2][3] - 36.0 - dBm NF noise figure f = 940 MHz [4]- 5.2 - dB f = 1960 MHz [4]- 4.6 - dB f = 2140 MHz [4]- 4.8 6.5 dB f = 2445 MHz [2][4]- 5.4 - dB BGA7124 All information provided in this document is subject to legal disclaimers. © NXP B.V. 2010. All rights reserved. Product data sheet Rev. 3 — 9 September 2010 7 of 33 NXP Semiconductors BGA7124 400 MHz to 2700 MHz 0.25 W high linearity silicon amplifier [1] Operation outside this range is possible but not guaranteed. [2] ICC = 150 mA; see Section 12 “Application information”. [3] PL = 11 dBm per tone; spacing = 1 MHz. [4] Defined at Pi = −40 dBm; small signal conditions. RLin input return loss f = 940 MHz - −15 - dB f = 1960 MHz - −11 - dB f = 2140 MHz - −17 - dB f = 2445 MHz [2] - −13 - dB RLout output return loss f = 940 MHz - −8 - dB f = 1960 MHz - −12 - dB f = 2140 MHz - −15 - dB f = 2445 MHz [2] - −25 - dB Table 8. Characteristics at VCC = 5 V …continued Input and output impedances matched to 50 Ω, pin SHDN = HIGH (shutdown disabled). Typical values at VCC = 5 V; ICC = 130 mA; Tcase = 25°C; see Section 12 “Application information”; unless otherwise specified. Symbol Parameter Conditions Min Typ Max Unit BGA7124 All information provided in this document is subject to legal disclaimers. © NXP B.V. 2010. All rights reserved. Product data sheet Rev. 3 — 9 September 2010 8 of 33 NXP Semiconductors BGA7124 400 MHz to 2700 MHz 0.25 W high linearity silicon amplifier [1] Operation outside this range is possible but not guaranteed. [2] ICC = 160 mA; see Section 12 “Application information”. [3] PL= 11 dBm per tone; spacing = 1 MHz. [4] Defined at Pi = −40 dBm; small signal conditions. Table 9. Characteristics at VCC = 3.3 V Input and output impedances matched to 50 Ω, pin SHDN = HIGH (shutdown disabled). Typical values at VCC = 3.3 V; ICC = 130 mA; Tcase = 25°C, see Section 12 “Application information”; unless otherwise specified. Symbol Parameter Conditions Min Typ Max Unit f frequency [1] 400 - 2700 MHz Gp power gain for small signals f = 940 MHz - 22.5 - dB f = 2445 MHz [2]- 13.8 - dB PL(1dB) output power at 1 dB gain compression f = 940 MHz - 23.5 - dBm f = 2445 MHz [2]- 22.0 - dBm IP3O output third-order intercept point f = 940 MHz [3]- 36.4 - dBm f = 2445 MHz [2][3]- 35.2 - dBm NF noise figure f = 940 MHz [4]- 5.5 - dB f = 2445 MHz [2][4]- 5.5 - dB RLin input return loss f = 940 MHz - −15 - dB f = 2445 MHz [2] - −10 - dB RLout output return loss f = 940 MHz - −9 - dB f = 2445 MHz [2] - −25 - dB BGA7124 All information provided in this document is subject to legal disclaimers. © NXP B.V. 2010. All rights reserved. Product data sheet Rev. 3 — 9 September 2010 9 of 33 NXP Semiconductors BGA7124 400 MHz to 2700 MHz 0.25 W high linearity silicon amplifier 9.1 Scattering parameters Table 10. Scattering parameters at 5 V, MMIC only VCC = 5 V; ICC = 130mA; Tcase = 25°C. f (MHz) s11 s21 s12 s22 Magnitude (ratio) Angle (degree) Magnitude (ratio) Angle (degree) Magnitude (ratio) Angle (degree) Magnitude (ratio) Angle (degree) 400 0.85 161.56 22.94 82.35 0.01 17.02 0.46 −156.50 500 0.90 159.44 11.82 82.58 0.01 27.08 0.63 176.13 600 0.90 152.15 9.98 73.86 0.01 24.10 0.64 169.61 700 0.89 145.75 8.59 66.00 0.01 21.41 0.64 164.34 800 0.88 139.33 7.55 58.86 0.02 18.47 0.65 159.29 900 0.87 133.19 6.74 51.66 0.02 14.00 0.65 154.44 1000 0.87 127.07 6.14 45.11 0.02 11.25 0.65 149.58 1100 0.87 120.67 5.61 38.20 0.02 7.99 0.65 144.25 1200 0.87 114.18 5.19 31.60 0.02 4.20 0.64 139.60 1300 0.86 107.68 4.82 25.08 0.02 0.31 0.64 134.85 1400 0.86 100.86 4.51 18.49 0.02 −4.01 0.63 130.13 1500 0.86 94.14 4.23 11.74 0.02 −8.65 0.63 125.02 1600 0.86 87.48 3.99 5.25 0.03 −13.15 0.63 120.13 1700 0.86 80.83 3.77 −1.50 0.03 −18.16 0.62 114.98 1800 0.86 74.14 3.56 −8.13 0.03 −23.28 0.62 109.78 1900 0.86 67.39 3.37 −14.94 0.03 −28.54 0.62 104.46 2000 0.86 60.70 3.19 −21.68 0.03 −33.68 0.63 99.01 2100 0.86 53.97 3.02 −28.68 0.03 −39.37 0.63 93.58 2200 0.86 47.78 2.85 −35.14 0.03 −44.84 0.63 88.17 2300 0.86 41.57 2.69 −41.70 0.03 −50.27 0.64 83.06 2400 0.86 35.43 2.54 −48.11 0.03 −55.62 0.64 78.10 2500 0.86 29.74 2.39 −54.19 0.04 −60.71 0.65 73.31 2600 0.86 24.79 2.27 −60.06 0.04 −65.48 0.65 68.64 2700 0.85 19.58 2.15 −66.14 0.04 −70.66 0.66 64.16 BGA7124 All information provided in this document is subject to legal disclaimers. © NXP B.V. 2010. All rights reserved. Product data sheet Rev. 3 — 9 September 2010 10 of 33 NXP Semiconductors BGA7124 400 MHz to 2700 MHz 0.25 W high linearity silicon amplifier 10. Reliability information 11. Moisture sensitivity Table 11. Scattering parameters at 3.3 V, MMIC only VCC = 3.3 V; ICC = 130mA; Tcase = 25°C. f (MHz) s11 s21 s12 s22 Magnitude (ratio) Angle (degree) Magnitude (ratio) Angle (degree) Magnitude (ratio) Angle (degree) Magnitude (ratio) Angle (degree) 400 0.84 161.94 21.25 73.81 0.01 17.66 0.57 −154.41 500 0.91 159.25 11.56 79.01 0.01 28.15 0.65 178.05 600 0.90 151.98 9.67 70.71 0.01 24.80 0.66 171.32 700 0.90 145.57 8.29 63.37 0.01 21.89 0.66 165.59 800 0.89 139.18 7.26 56.54 0.02 19.04 0.66 160.37 900 0.88 132.87 6.48 49.74 0.02 15.35 0.66 155.28 1000 0.88 126.78 5.90 43.30 0.02 11.89 0.66 150.23 1100 0.87 120.46 5.39 36.53 0.02 8.33 0.66 144.88 1200 0.87 113.94 4.97 30.05 0.02 4.50 0.65 140.03 1300 0.87 107.48 4.62 23.62 0.02 0.35 0.65 135.35 1400 0.87 100.69 4.32 17.15 0.02 −3.92 0.64 130.48 1500 0.86 93.93 4.05 10.48 0.02 −8.62 0.64 125.46 1600 0.86 87.28 3.81 4.05 0.03 −13.28 0.64 120.31 1700 0.86 80.71 3.61 −2.66 0.03 −18.26 0.64 115.13 1800 0.86 74.00 3.40 −9.21 0.03 −23.51 0.64 109.99 1900 0.86 67.27 3.22 −15.97 0.03 −28.87 0.63 104.66 2000 0.86 60.64 3.05 −22.71 0.03 −34.22 0.64 99.36 2100 0.86 53.84 2.89 −29.68 0.03 −39.95 0.64 93.93 2200 0.86 47.60 2.72 −36.12 0.03 −45.44 0.64 88.55 2300 0.86 41.43 2.57 −42.66 0.03 −51.06 0.65 83.38 2400 0.86 35.35 2.42 −49.01 0.04 −56.53 0.65 78.44 2500 0.85 29.64 2.28 −55.12 0.04 −61.72 0.66 73.56 2600 0.85 24.72 2.16 −60.91 0.04 −66.76 0.66 68.80 2700 0.85 19.59 2.04 −66.91 0.04 −71.84 0.67 64.30 Table 12. Reliability Life test Conditions Intrinsic failure rate HTOL According JESD85; confidence level 60 %; Tj = 55 °C; activation energy = 0.7 eV; acceleration factor determined according Arrhenius 4 Table 13. Moisture sensitivity level Test methodology Class JESD-22-A113 1 BGA7124 All information provided in this document is subject to legal disclaimers. © NXP B.V. 2010. All rights reserved. Product data sheet Rev. 3 — 9 September 2010 11 of 33 NXP Semiconductors BGA7124 400 MHz to 2700 MHz 0.25 W high linearity silicon amplifier 12. Application information 12.1 5 V applications 12.1.1 920 MHz to 960 MHz See Table 14 for a list of components. PCB board specification: Rogers RO4003C; Height = 0.508 mm; εr = 3.38; Copper thickness = 35 μm. Fig 5. 5 V/130 mA application schematic; 920 MHz to 960 MHz C3 C10 C4 C6 C8 C9 C7 R1 R2 ICQ_ADJ SHDN enable L1 L2 C2 MSL1 C1 MSL2 MSL3 MSL5 MSL6 MSL7 MSL8 RF_IN J1 J3 J2 RF_OUT BGA7124 50 Ω 50 Ω VCC C5 014aab051 V MSL4 CC(RF) VCC(BIAS) (1) Tcase = −40 °C. (2) Tcase = 25 °C. (3) Tcase = 85 °C. (1) Tcase = −40 °C. (2) Tcase = 25 °C. (3) Tcase = 85 °C. Fig 6. Output power at 1 dB gain compression as a function of frequency Fig 7. Power gain as a function of frequency f (GHz) 0.92 0.93 0.94 0.95 0.96 014aab052 24 26 22 28 30 PL(1dB) (dBm) 20 (1) (2) (3) f (GHz) 0.92 0.93 0.94 0.95 0.96 014aab053 22 24 20 26 28 Gp (dB) 18 (1) (2) (3) BGA7124 All information provided in this document is subject to legal disclaimers. © NXP B.V. 2010. All rights reserved. Product data sheet Rev. 3 — 9 September 2010 12 of 33 NXP Semiconductors BGA7124 400 MHz to 2700 MHz 0.25 W high linearity silicon amplifier Tcase = 25 °C. (1) Tcase = −40 °C. (2) Tcase = 25 °C. (3) Tcase = 85 °C. Fig 8. Input return loss, output return loss and isolation as a function of frequency Fig 9. Output third-order intercept point as a function of frequency RLout RLin ISL f (GHz) 0.92 0.93 0.94 0.95 0.96 014aab054 −20 −10 0 RLin, RLout, ISL (dB) −30 f (GHz) 0.92 0.93 0.94 0.95 0.96 014aab055 38 40 42 IP3O (dBm) 36 (1) (3) (2) See Table 14 for a list of components. Fig 10. 5 V/130 mA application reference board; 920 MHz to 960 MHz J3 GND VCC GND n.c. enable GND C9 C10 C8 C6 C4 C5 L2 C1 C3 R2 C2 L1 C7 R1 MSL6 MSL7 MSL4 MSL5 MSL1 MSL3 MSL8 MSL2 J1 J I HG F E D C B A 1 2 3 4 5 6 7 8 910 11 12 13 RF in J2 RF out 014aab056 BGA7124 All information provided in this document is subject to legal disclaimers. © NXP B.V. 2010. All rights reserved. Product data sheet Rev. 3 — 9 September 2010 13 of 33 NXP Semiconductors BGA7124 400 MHz to 2700 MHz 0.25 W high linearity silicon amplifier [1] MSL1 to MSL8 dimensions specified as Width (W), Spacing (S) and Length (L). Table 14. 5 V/130 mA application list of components; 920 MHz to 960 MHz See Figure 5 and Figure 10 for component layout. Printed-Circuit Board (PCB): Rogers RO4003C stack; height = 0.508 mm; copper plating thickness = 35 μm. Component Description Value Function Remarks C1, C6 capacitor 68 pF DC blocking Murata GRM1885C1H680JA01D C2, C3 capacitor 3.3 pF input match Murata GRM1885C1H3R3CZ01D C4 capacitor 3.9 pF output match Murata GRM1885C1H3R9CZ01D C5 capacitor 1.0 pF output match Murata GRM1885C1H1R0CZ01D C7 capacitor 68 pF RF decoupling Murata GRM1885C1H680JA01D C8 capacitor 100 nF DC decoupling AVX 0603YC104KAT2A C9 capacitor 10 μF DC decoupling AVX 1206ZG106ZAT2A C10 capacitor 12 pF noise decoupling Murata GRM1555C1H120JZ01D J1, J2 RF connector SMA Emerson Network Power 142-0701-841 J3 DC connector 6-pins MOLEX L1 inductor 2.2 nH output match Tyco electronics 36501J2N2JTDG L2 inductor 22 nH DC feed Tyco electronics 36501J022JTDG MSL1[1] micro stripline 1.14 mm × 0.8 mm × 10.95 mm input match MSL2[1] micro stripline 1.14 mm × 0.8 mm × 2.95 mm input match MSL3[1] micro stripline 1.14 mm × 0.8 mm × 7.75 mm input match MSL4[1] micro stripline 1.14 mm × 0.8 mm × 23.4 mm output match MSL5[1] micro stripline 1.14 mm × 0.8 mm × 2.2 mm output match MSL6[1] micro stripline 1.14 mm × 0.8 mm × 3.15 mm output match MSL7[1] micro stripline 1.14 mm × 0.8 mm × 2.3 mm output match MSL8[1] micro stripline 1.14 mm × 0.8 mm × 10.95 mm output match R1 resistor 0 Ω Multicomp MC 0.063W 0603 0R R2 resistor (trimmer) 2 kΩ bias adjustment Bourns 3214W-1-202E BGA7124 All information provided in this document is subject to legal disclaimers. © NXP B.V. 2010. All rights reserved. Product data sheet Rev. 3 — 9 September 2010 14 of 33 NXP Semiconductors BGA7124 400 MHz to 2700 MHz 0.25 W high linearity silicon amplifier 12.1.2 1930 MHz to 1990 MHz See Table 15 for a list of components. PCB board specification: Rogers RO4003C; Height = 0.508 mm; εr = 3.38; Copper thickness = 35 μm. Fig 11. 5 V/130 mA application schematic; 1930 MHz to 1990 MHz C3 C4 C6 C7 C5 R1 R2 ICQ_ADJ SHDN enable L1 C2 MSL1 C1 MSL2 MSL4 MSL5 MSL6 RF_IN RF_OUT BGA7124 50 Ω 50 Ω VCC 014aab057 MSL3 VCC(BIAS) VCC(RF) J1 J3 J2 (1) Tcase = −40 °C. (2) Tcase = 25 °C. (3) Tcase = 85 °C. (1) Tcase = −40 °C. (2) Tcase = 25 °C. (3) Tcase = 85 °C. Fig 12. Output power at 1 dB gain compression as a function of frequency Fig 13. Power gain as a function of frequency 014aab058 f (GHz) 1.93 1.95 1.97 1.99 24 26 22 28 30 PL(1dB) (dBm) 20 (1) (2) (3) 014aab059 f (GHz) 1.93 1.95 1.97 1.99 14 16 12 18 20 Gp (dB) 10 (1) (2) (3) BGA7124 All information provided in this document is subject to legal disclaimers. © NXP B.V. 2010. All rights reserved. Product data sheet Rev. 3 — 9 September 2010 15 of 33 NXP Semiconductors BGA7124 400 MHz to 2700 MHz 0.25 W high linearity silicon amplifier Tcase = 25 °C. (1) Tcase = −40 °C. (2) Tcase = 25 °C. (3) Tcase = 85 °C. Fig 14. Input return loss, output return loss and isolation as a function of frequency Fig 15. Output third-order intercept point as a function of frequency RLout RLin ISL f (GHz) 1.93 1.95 1.97 1.99 014aab060 −20 −10 0 RLin, RLout, ISL (dB) −30 f (GHz) 1.93 1.95 1.97 1.99 014aab061 36 38 40 34 IP3O (dBm) (2) (1) (3) See Table 15 for a list of components. Fig 16. 5 V/130 mA application reference board; 1930 MHz to 1990 MHz J3 GND VCC GND n.c. enable GND C7 C6 C4 C2 C3 C1 R2 L1 C5 R1 MSL6 MSL4 MSL5 MSL1 MSL2 MSL3 J1 J I HG F E D C B A 1 2 3 4 5 6 7 8 910 11 12 13 RF in J2 RF out 014aab062 BGA7124 All information provided in this document is subject to legal disclaimers. © NXP B.V. 2010. All rights reserved. Product data sheet Rev. 3 — 9 September 2010 16 of 33 NXP Semiconductors BGA7124 400 MHz to 2700 MHz 0.25 W high linearity silicon amplifier [1] MSL1 to MSL6 dimensions specified as Width (W), Spacing (S) and Length (L). 12.1.3 2110 MHz to 2170 MHz Table 15. 5 V/130 mA application list of components; 1930 MHz to 1990 MHz See Figure 11 and Figure 16 for component layout. Printed-Circuit Board (PCB): Rogers RO4003C stack; height = 0.508 mm; copper plating thickness = 35 μm. Component Description Value Function Remarks C1, C4 capacitor 15 pF DC blocking Murata GRM1885C1H150JA01D C2 capacitor 2.2 pF input match Murata GRM1885C1H2R2CZ01D C3 capacitor 1.2 pF output match Murata GRM1885C1H1R2CZ01D C5 capacitor 15 pF RF decoupling Murata GRM1885C1H150JA01D C6 capacitor 100 nF DC decoupling AVX 0603YC104KAT2A C7 capacitor 10 μF DC decoupling AVX 1206ZG106ZAT2A J1, J2 RF connector SMA Emerson Network Power 142-0701-841 J3 DC connector 6-pins MOLEX L1 inductor 22 nH DC feed Tyco electronics 36501J022JTDG MSL1[1] micro stripline 1.14 mm × 0.8 mm × 10.95 mm input match MSL2[1] micro stripline 1.14 mm × 0.8 mm × 10.8 mm input match MSL3[1] micro stripline 1.14 mm × 0.8 mm × 5.8 mm output match MSL4[1] micro stripline 1.14 mm × 0.8 mm × 2.2 mm output match MSL5[1] micro stripline 1.14 mm × 0.8 mm × 3.7 mm output match MSL6[1] micro stripline 1.14 mm × 0.8 mm × 10.95 mm output match R1 resistor 0 Ω Multicomp MC 0.063W 0603 0R R2 resistor (trimmer) 2 kΩ bias adjustment Bourns 3214W-1-202E See Table 16 for a list of components. PCB board specification: Rogers RO4003C; Height = 0.508 mm; εr = 3.38; Copper thickness = 35 μm. Fig 17. 5 V/130 mA application schematic; 2110 MHz to 2170 MHz RF_OUT C3 C4 C6 C7 C5 R1 R2 ICQ_ADJ SHDN enable L1 C2 MSL1 C1 MSL2 MSL4 MSL5 MSL6 RF_IN BGA7124 50 Ω 50 Ω VCC 014aab063 MSL3 VCC(BIAS) VCC(RF) J1 J3 J2 BGA7124 All information provided in this document is subject to legal disclaimers. © NXP B.V. 2010. All rights reserved. Product data sheet Rev. 3 — 9 September 2010 17 of 33 NXP Semiconductors BGA7124 400 MHz to 2700 MHz 0.25 W high linearity silicon amplifier (1) Tcase = −40 °C. (2) Tcase = 25 °C. (3) Tcase = 85 °C. (1) Tcase = −40 °C. (2) Tcase = 25 °C. (3) Tcase = 85 °C. Fig 18. Output power at 1 dB gain compression as a function of frequency Fig 19. Power gain as a function of frequency 014aab064 f (GHz) 2.11 2.13 2.15 2.17 24 26 22 28 30 PL(1dB) (dBm) 20 (1) (2) (3) 014aab065 f (GHz) 2.11 2.13 2.15 2.17 14 16 12 18 20 Gp (dB) 10 (1) (2) (3) Tcase = 25 °C. (1) Tcase = −40 °C. (2) Tcase = 25 °C. (3) Tcase = 85 °C. Fig 20. Input return loss, output return loss and isolation as a function of frequency Fig 21. Output third-order intercept point as a function of frequency RLout RLin ISL f (GHz) 2.11 2.13 2.15 2.17 014aab066 −20 −10 0 RLin, RLout, ISL (dB) −30 (3) (2) (1) f (GHz) 2.11 2.13 2.15 2.17 014aab067 36 38 40 IP3O (dBm) 34 BGA7124 All information provided in this document is subject to legal disclaimers. © NXP B.V. 2010. All rights reserved. Product data sheet Rev. 3 — 9 September 2010 18 of 33 NXP Semiconductors BGA7124 400 MHz to 2700 MHz 0.25 W high linearity silicon amplifier See Table 16 for a list of components. Fig 22. 5 V/130 mA application reference board; 2110 MHz to 2170 MHz J3 GND VCC GND n.c. enable GND C7 C6 C4 C2 C3 C1 R2 L1 C5 R1 MSL6 MSL4 MSL5 MSL1 MSL2 MSL3 J1 J I HG F E D C B A 1 2 3 4 5 6 7 8 910 11 12 13 RF in J2 RF out 014aab068 Table 16. 5 V/130 mA application list of components; 2110 MHz to 2170 MHz See Figure 17 and Figure 22 for component layout. Printed-Circuit Board (PCB): Rogers RO4003C stack; height = 0.508 mm; copper plating thickness = 35 μm. Component Description Value Function Remarks C1, C4 capacitor 15 pF DC blocking Murata GRM1885C1H150JA01D C2 capacitor 2.7 pF input match Murata GRM1885C1H2R7CZ01D C3 capacitor 1.5 pF output match Murata GRM1885C1H1R5CZ01D C5 capacitor 15 pF RF decoupling Murata GRM1885C1H150JA01D C6 capacitor 100 nF DC decoupling AVX 0603YC104KAT2A C7 capacitor 10 μF DC decoupling AVX 1206ZG106ZAT2A J1, J2 RF connector SMA Emerson Network Power 142-0701-841 J3 DC connector 6-pins MOLEX L1 inductor 22 nH DC feed Tyco electronics 36501J022JTDG MSL1[1] micro stripline 1.14 mm × 0.8 mm × 10.95 mm input match MSL2[1] micro stripline 1.14 mm × 0.8 mm × 10.8 mm input match MSL3[1] micro stripline 1.14 mm × 0.8 mm × 5.8 mm output match MSL4[1] micro stripline 1.14 mm × 0.8 mm × 2.5 mm output match MSL5[1] micro stripline 1.14 mm × 0.8 mm × 3.5 mm output match BGA7124 All information provided in this document is subject to legal disclaimers. © NXP B.V. 2010. All rights reserved. Product data sheet Rev. 3 — 9 September 2010 19 of 33 NXP Semiconductors BGA7124 400 MHz to 2700 MHz 0.25 W high linearity silicon amplifier [1] MSL1 to MSL6 dimensions specified as Width (W), Spacing (S) and Length (L). 12.1.4 2405 MHz to 2485 MHz MSL6[1] micro stripline 1.14 mm × 0.8 mm × 10.95 mm output match R1 resistor 0 Ω Multicomp MC 0.063W 0603 0R R2 resistor (trimmer) 2 kΩ bias adjustment Bourns 3214W-1-202E Table 16. 5 V/130 mA application list of components; 2110 MHz to 2170 MHz …continued See Figure 17 and Figure 22 for component layout. Printed-Circuit Board (PCB): Rogers RO4003C stack; height = 0.508 mm; copper plating thickness = 35 μm. Component Description Value Function Remarks See Table 17 for a list of components. PCB board specification: Rogers RO4003C; Height = 0.508 mm; εr = 3.38; Copper thickness = 35 μm. Fig 23. 5 V/130 mA application schematic; 2405 MHz to 2485 MHz C3 C4 C5 C7 C8 C6 R1 R2 ICQ_ADJ SHDN enable L1 C2 MSL1 C1 MSL2 MSL3 MSL4 MSL5 RF_IN RF_OUT BGA7124 50 Ω 50 Ω VCC 014aab069 VCC(BIAS) VCC(RF) J1 J3 J2 BGA7124 All information provided in this document is subject to legal disclaimers. © NXP B.V. 2010. All rights reserved. Product data sheet Rev. 3 — 9 September 2010 20 of 33 NXP Semiconductors BGA7124 400 MHz to 2700 MHz 0.25 W high linearity silicon amplifier (1) Tcase = −40 °C. (2) Tcase = 25 °C. (3) Tcase = 85 °C. (1) Tcase = −40 °C. (2) Tcase = 25 °C. (3) Tcase = 85 °C. Fig 24. Output power at 1 dB gain compression as a function of frequency Fig 25. Power gain as a function of frequency (3) (2) (1) f (GHz) 2.405 2.425 2.445 2.465 2.485 014aab070 20 22 18 24 26 PL(1dB) (dBm) 16 (3) (2) (1) f (GHz) 2.405 2.425 2.445 2.465 2.485 014aab071 14 16 12 18 20 Gp (dB) 10 Tcase = 25 °C. (1) Tcase = −40 °C. (2) Tcase = 25 °C. (3) Tcase = 85 °C. Fig 26. Input return loss, output return loss and isolation as a function of frequency Fig 27. Output third-order intercept point as a function of frequency RLout RLin ISL f (GHz) 2.405 2.425 2.445 2.465 2.485 014aab072 −20 −10 0 RLin, RLout, ISL (dB) −30 f (GHz) 2.405 2.425 2.445 2.465 2.485 014aab073 34 36 38 32 IP3O (dBm) (1) (2) (3) BGA7124 All information provided in this document is subject to legal disclaimers. © NXP B.V. 2010. All rights reserved. Product data sheet Rev. 3 — 9 September 2010 21 of 33 NXP Semiconductors BGA7124 400 MHz to 2700 MHz 0.25 W high linearity silicon amplifier See Table 17 for a list of components. Fig 28. 5 V/130 mA application reference board; 2405 MHz to 2485 MHz J3 GND VCC GND n.c. enable GND C8 C7 C5 C2 C3 C4 C1 R2 L1 C6 R1 MSL1 MSL2 MSL3 MSL4 MSL5 J1 J I HG F E D C B A 1 2 3 4 5 6 7 8 910 11 12 13 RF in J2 RF out 014aab074 Table 17. 5 V/130 mA application list of components; 2405 MHz to 2485 MHz See Figure 23 and Figure 28 for component layout. Printed-Circuit Board (PCB): Rogers RO4003C stack; height = 0.508 mm; copper plating thickness = 35 μm. Component Description Value Function Remarks C1, C5 capacitor 12 pF DC blocking Murata GRM1885C1H120JA01D C2 capacitor 2.2 pF input match Murata GRM1885C1H2R2CZ01D C3 capacitor 0.82 pF output match Murata GRM1885C1HR82CZ01D C4 capacitor 0.68 pF output match Murata GRM1885C1HR68CZ01D C6 capacitor 12 pF RF decoupling Murata GRM1885C1H120JA01D C7 capacitor 100 nF DC decoupling AVX 0603YC104KAT2A C8 capacitor 10 μF DC decoupling AVX 1206ZG106ZAT2A J1, J2 RF connector SMA Emerson Network Power 142-0701-841 J3 DC connector 6-pins MOLEX L1 inductor 22 nH DC feed Tyco electronics 36501J022JTDG MSL1[1] micro stripline 1.14 mm × 0.8 mm × 10.95 mm input match MSL2[1] micro stripline 1.14 mm × 0.8 mm × 10.8 mm input match MSL3[1] micro stripline 1.14 mm × 0.8 mm × 7.3 mm output match MSL4[1] micro stripline 1.14 mm × 0.8 mm × 4.3 mm output match BGA7124 All information provided in this document is subject to legal disclaimers. © NXP B.V. 2010. All rights reserved. Product data sheet Rev. 3 — 9 September 2010 22 of 33 NXP Semiconductors BGA7124 400 MHz to 2700 MHz 0.25 W high linearity silicon amplifier [1] MSL1 to MSL5 dimensions specified as Width (W), Spacing (S) and Length (L). 12.2 3.3 V applications 12.2.1 920 MHz to 960 MHz MSL5[1] micro stripline 1.14 mm × 0.8 mm × 10.95 mm output match R1 resistor 2.2 Ω Multicomp MC 0.063W 0603 2R2 R2 resistor (trimmer) 2 kΩ bias adjustment Bourns 3214W-1-202E Table 17. 5 V/130 mA application list of components; 2405 MHz to 2485 MHz …continued See Figure 23 and Figure 28 for component layout. Printed-Circuit Board (PCB): Rogers RO4003C stack; height = 0.508 mm; copper plating thickness = 35 μm. Component Description Value Function Remarks See Table 18 for a list of components. PCB board specification: Rogers RO4003C; Height = 0.508 mm; εr = 3.38; Copper thickness = 35 μm. Fig 29. 3.3 V/130 mA application schematic; 920 MHz to 960 MHz C3 C4 C6 C8 C9 C7 R1 R2 ICQ_ADJ SHDN enable L1 L2 C2 MSL1 C1 MSL2 MSL3 RF_IN MSL4 MSL5 MSL6 MSL7 MSL8 RF_OUT BGA7124 50 Ω 50 Ω VCC C5 014aab075 VCC(BIAS) VCC(RF) J1 J3 J2 BGA7124 All information provided in this document is subject to legal disclaimers. © NXP B.V. 2010. All rights reserved. Product data sheet Rev. 3 — 9 September 2010 23 of 33 NXP Semiconductors BGA7124 400 MHz to 2700 MHz 0.25 W high linearity silicon amplifier (1) Tcase = −40 °C. (2) Tcase = 25 °C. (3) Tcase = 85 °C. (1) Tcase = −40 °C. (2) Tcase = 25 °C. (3) Tcase = 85 °C. Fig 30. Output power at 1 dB gain compression as a function of frequency Fig 31. Power gain as a function of frequency f (GHz) 0.92 0.93 0.94 0.95 0.96 014aab076 24 26 22 28 30 PL(1dB) (dBm) 20 (1) (2) (3) f (GHz) 0.92 0.93 0.94 0.95 0.96 014aab077 22 24 20 26 28 Gp (dB) 18 (1) (2) (3) Tcase = 25 °C. (1) Tcase = −40 °C. (2) Tcase = 25 °C. (3) Tcase = 85 °C. Fig 32. Input return loss, output return loss and isolation as a function of frequency Fig 33. Output third-order intercept point as a function of frequency RLout RLin ISL f (GHz) 0.92 0.93 0.94 0.95 0.96 014aab078 −20 −10 0 RLin, RLout, ISL (dB) −30 f (GHz) 0.92 0.93 0.94 0.95 0.96 014aab079 36 38 40 IP3O (dBm) 34 (1) (3) (2) BGA7124 All information provided in this document is subject to legal disclaimers. © NXP B.V. 2010. All rights reserved. Product data sheet Rev. 3 — 9 September 2010 24 of 33 NXP Semiconductors BGA7124 400 MHz to 2700 MHz 0.25 W high linearity silicon amplifier See Table 18 for a list of components. Fig 34. 3.3 V/130 mA application reference board; 920 MHz to 960 MHz J3 GND VCC GND n.c. enable GND C9 C8 C6 C2 C3 C4 C5 C1 R2 L2 L1 C7 R1 MSL1 MSL3 MSL8 MSL2 MSL4 MSL6 MSL7 MSL5 J1 J I HG F E D C B A 1 2 3 4 5 6 7 8 910 11 12 13 RF in J2 RF out 014aab080 Table 18. 3.3 V/130 mA application list of components; 920 MHz to 960 MHz See Figure 29 and Figure 34 for component layout. Printed-Circuit Board (PCB): Rogers RO4003C stack; height = 0.508 mm; copper plating thickness = 35 μm. Component Description Value Function Remarks C1, C6 capacitor 68 pF DC blocking Murata GRM1885C1H680JA01D C2, C3 capacitor 3.3 pF input match Murata GRM1885C1H3R3CZ01D C4 capacitor 3.9 pF output match Murata GRM1885C1H3R9CZ01D C5 capacitor 1.0 pF output match Murata GRM1885C1H1R0CZ01D C7 capacitor 68 pF RF decoupling Murata GRM1885C1H680JA01D C8 capacitor 100 nF DC decoupling AVX 0603YC104KAT2A C9 capacitor 10 μF DC decoupling AVX 1206ZG106ZAT2A J1, J2 RF connector SMA Emerson Network Power 142-0701-841 J3 DC connector 6-pins MOLEX L1 inductor 2.2 nH output match Tyco electronics 36501J2N2JTDG L2 inductor 22 nH DC feed Tyco electronics 36501J022JTDG MSL1[1] micro stripline 1.14 mm × 0.8 mm × 10.95 mm input match MSL2[1] micro stripline 1.14 mm × 0.8 mm × 2.95 mm input match MSL3[1] micro stripline 1.14 mm × 0.8 mm × 7.75 mm input match MSL4[1] micro stripline 1.14 mm × 0.8 mm × 23.4 mm output match MSL5[1] micro stripline 1.14 mm × 0.8 mm × 2.2 mm output match BGA7124 All information provided in this document is subject to legal disclaimers. © NXP B.V. 2010. All rights reserved. Product data sheet Rev. 3 — 9 September 2010 25 of 33 NXP Semiconductors BGA7124 400 MHz to 2700 MHz 0.25 W high linearity silicon amplifier [1] MSL1 to MSL8 dimensions specified as Width (W), Spacing (S) and Length (L). 12.2.2 2405 MHz to 2485 MHz MSL6[1] micro stripline 1.14 mm × 0.8 mm × 2.4 mm output match MSL7[1] micro stripline 1.14 mm × 0.8 mm × 2.3 mm output match MSL8[1] micro stripline 1.14 mm × 0.8 mm × 10.95 mm output match R1 resistor 0 Ω Multicomp MC 0.063W 0603 0R R2 resistor (trimmer) 2 kΩ bias adjustment Bourns 3214W-1-202E Table 18. 3.3 V/130 mA application list of components; 920 MHz to 960 MHz …continued See Figure 29 and Figure 34 for component layout. Printed-Circuit Board (PCB): Rogers RO4003C stack; height = 0.508 mm; copper plating thickness = 35 μm. Component Description Value Function Remarks See Table 19 for a list of components. PCB board specification: Rogers RO4003C; Height = 0.508 mm; εr = 3.38; Copper thickness = 35 μm Fig 35. 3.3 V/130 mA application schematic; 2405 MHz to 2485 MHz RF_OUT C3 C5 C7 C8 C6 R1 R2 ICQ_ADJ SHDN enable L1 C2 MSL1 C1 MSL2 MSL3 MSL4 MSL5 RF_IN BGA7124 50 Ω 50 Ω VCC C4 014aab081 VCC(BIAS) VCC(RF) J1 J3 J2 BGA7124 All information provided in this document is subject to legal disclaimers. © NXP B.V. 2010. All rights reserved. Product data sheet Rev. 3 — 9 September 2010 26 of 33 NXP Semiconductors BGA7124 400 MHz to 2700 MHz 0.25 W high linearity silicon amplifier (1) Tcase = −40 °C. (2) Tcase = 25 °C. (3) Tcase = 85 °C. (1) Tcase = −40 °C. (2) Tcase = 25 °C. (3) Tcase = 85 °C. Fig 36. Output power at 1 dB gain compression as a function of frequency Fig 37. Power gain as a function of frequency f (GHz) 2.405 2.425 2.445 2.465 2.485 014aab082 20 22 18 24 26 PL(1dB) (dBm) 16 (3) (1) (2) f (GHz) 2.405 2.425 2.445 2.465 2.485 014aab083 14 16 12 18 20 Gp (dB) 10 (1) (2) (3) Tcase = 25 °C. (1) Tcase = −40 °C. (2) Tcase = 25 °C. (3) Tcase = 85 °C. Fig 38. Input return loss, output return loss and isolation as a function of frequency Fig 39. Output third-order intercept point as a function of frequency RLout RLin ISL f (GHz) 2.405 2.425 2.445 2.465 2.485 014aab084 −20 −10 0 RLin, RLout, ISL (dB) −30 (2) (1) (3) f (GHz) 2.405 2.425 2.445 2.465 2.485 014aab085 34 36 38 IP3O (dBm) 32 BGA7124 All information provided in this document is subject to legal disclaimers. © NXP B.V. 2010. All rights reserved. Product data sheet Rev. 3 — 9 September 2010 27 of 33 NXP Semiconductors BGA7124 400 MHz to 2700 MHz 0.25 W high linearity silicon amplifier See Table 19 for a list of components. Fig 40. 3.3 V/130 mA application reference board; 2405 MHz to 2485 MHz J3 GND VCC GND n.c. enable GND C8 C7 C5 C2 C3 C4 C1 R2 L1 C6 R1 MSL1 MSL2 MSL3 MSL4 MSL5 J1 J I HG F E D C B A 1 2 3 4 5 6 7 8 910 11 12 13 RF in J2 RF out 014aab086 Table 19. 3.3 V/130 mA application list of components; 2405 MHz to 2485 MHz See Figure 35 and Figure 40 for component layout. Printed-Circuit Board (PCB): Rogers RO4003C stack; height = 0.508 mm; copper plating thickness = 35 μm. Component Description Value Function Remarks C1, C5 capacitor 12 pF DC blocking Murata GRM1885C1H120JA01D C2 capacitor 2.2 pF input match Murata GRM1885C1H2R2CZ01D C3 capacitor 0.82 pF output match Murata GRM1885C1HR82CZ01D C4 capacitor 0.68 pF output match Murata GRM1885C1HR68CZ01D C6 capacitor 12 pF RF decoupling Murata GRM1885C1H120JA01D C7 capacitor 100 nF DC decoupling AVX 0603YC104KAT2A C8 capacitor 10 μF DC decoupling AVX 1206ZG106ZAT2A J1, J2 RF connector SMA Emerson Network Power 142-0701-841 J3 DC connector 6-pins MOLEX L1 inductor 22 nH DC feed Tyco electronics 36501J022JTDG MSL1[1] micro stripline 1.14 mm × 0.8 mm × 10.95 mm input match MSL2[1] micro stripline 1.14 mm × 0.8 mm × 10.8 mm input match MSL3[1] micro stripline 1.14 mm × 0.8 mm × 7.3 mm output match MSL4[1] micro stripline 1.14 mm × 0.8 mm × 4.3 mm output match BGA7124 All information provided in this document is subject to legal disclaimers. © NXP B.V. 2010. All rights reserved. Product data sheet Rev. 3 — 9 September 2010 28 of 33 NXP Semiconductors BGA7124 400 MHz to 2700 MHz 0.25 W high linearity silicon amplifier [1] MSL1 to MSL5 dimensions specified as Width (W), Spacing (S) and Length (L). 12.3 PCB stack MSL5[1] micro stripline 1.14 mm × 0.8 mm × 10.95 mm output match R1 resistor 2.2 Ω Multicomp MC 0.063W 0603 2R2 R2 resistor (trimmer) 2 kΩ bias adjustment Bourns 3214W-1-202E Table 19. 3.3 V/130 mA application list of components; 2405 MHz to 2485 MHz …continued See Figure 35 and Figure 40 for component layout. Printed-Circuit Board (PCB): Rogers RO4003C stack; height = 0.508 mm; copper plating thickness = 35 μm. Component Description Value Function Remarks (1) Pre-pregnated RO4003Cdielectric constant εr = 3.38 Fig 41. PCB stack through via RF and analog ground RF and analog routing analog routing RF and analog ground 35 μm (1 oz.) copper + 0.3 μm gold plating RO4003C, 0.51 mm (20 mil) 35 μm (1 oz.) copper (1) 0.2 mm (8 mil) FR4, 0.15 mm (6 mil) 35 μm (1 oz.) copper 35 μm (1 oz.) copper 014aab087 BGA7124 All information provided in this document is subject to legal disclaimers. © NXP B.V. 2010. All rights reserved. Product data sheet Rev. 3 — 9 September 2010 29 of 33 NXP Semiconductors BGA7124 400 MHz to 2700 MHz 0.25 W high linearity silicon amplifier 13. Package outline Fig 42. Package outline SOT908-1 (HVSON8) 1 0.2 0.5 0.05 0.00 UNIT A1 b D(1) Eh e y 1.5 e1 OUTLINE REFERENCES VERSION EUROPEAN PROJECTION ISSUE DATE IEC JEDEC JEITA mm 3.1 2.9 c Dh 1.65 1.35 y1 3.1 2.9 2.25 1.95 0.3 0.2 0.05 0.1 DIMENSIONS (mm are the original dimensions) SOT908-1 MO-229 E(1) 0.5 0.3 L 0.1 v 0.05 w SOT908-1 HVSON8: plastic thermal enhanced very thin small outline package; no leads; 8 terminals; body 3 x 3 x 0.85 mm A(1) max. 05-09-26 05-10-05 Note 1. Plastic or metal protrusions of 0.075 mm maximum per side are not included. X terminal 1 index area D B A E detail X A A1 c C y1 C y exposed tie bar (4×) exposed tie bar (4×) b terminal 1 index area e1 e v M C A B w M C Eh Dh L 1 4 8 5 0 1 2 mm scale BGA7124 All information provided in this document is subject to legal disclaimers. © NXP B.V. 2010. All rights reserved. Product data sheet Rev. 3 — 9 September 2010 30 of 33 NXP Semiconductors BGA7124 400 MHz to 2700 MHz 0.25 W high linearity silicon amplifier 14. Abbreviations 15. Revision history Table 20. Abbreviations Acronym Description CPE Customer-Premises Equipment DC Direct Current ESD ElectroStatic Discharge HTOL High Temperature Operating Life ISM Industrial, Scientific and Medical MMIC Monolithic Microwave Integrated Circuit MoCA Multimedia over Coax Alliance RFID Radio Frequency IDentification SMA SubMiniature version A TX Transmit WLAN Wireless Local Area Network Table 21. Revision history Document ID Release date Data sheet status Change notice Supersedes BGA7124 v.3 20100909 Product data sheet - BGA7124 v.2 Modifications: • Figure 5 on page 11: MSL symbols have been corrected. • Figure 11 on page 14: MSL symbols have been corrected. • Figure 17 on page 16: MSL symbols have been corrected. • Figure 23 on page 19: MSL symbols have been corrected. • Figure 29 on page 22: MSL symbols have been corrected. • Figure 35 on page 25: MSL symbols have been corrected. BGA7124 v.2 20100623 Product data sheet - BGA7124 v.1 BGA7124 v.1 20100421 Product data sheet - - BGA7124 All information provided in this document is subject to legal disclaimers. © NXP B.V. 2010. All rights reserved. Product data sheet Rev. 3 — 9 September 2010 31 of 33 NXP Semiconductors BGA7124 400 MHz to 2700 MHz 0.25 W high linearity silicon amplifier 16. Legal information 16.1 Data sheet status [1] Please consult the most recently issued document before initiating or completing a design. [2] The term ‘short data sheet’ is explained in section “Definitions”. [3] The product status of device(s) described in this document may have changed since this document was published and may differ in case of multiple devices. The latest product status information is available on the Internet at URL http://www.nxp.com. 16.2 Definitions Draft — The document is a draft version only. The content is still under internal review and subject to formal approval, which may result in modifications or additions. NXP Semiconductors does not give any representations or warranties as to the accuracy or completeness of information included herein and shall have no liability for the consequences of use of such information. Short data sheet — A short data sheet is an extract from a full data sheet with the same product type number(s) and title. A short data sheet is intended for quick reference only and should not be relied upon to contain detailed and full information. For detailed and full information see the relevant full data sheet, which is available on request via the local NXP Semiconductors sales office. In case of any inconsistency or conflict with the short data sheet, the full data sheet shall prevail. Product specification — The information and data provided in a Product data sheet shall define the specification of the product as agreed between NXP Semiconductors and its customer, unless NXP Semiconductors and customer have explicitly agreed otherwise in writing. In no event however, shall an agreement be valid in which the NXP Semiconductors product is deemed to offer functions and qualities beyond those described in the Product data sheet. 16.3 Disclaimers Limited warranty and liability — Information in this document is believed to be accurate and reliable. However, NXP Semiconductors does not give any representations or warranties, expressed or implied, as to the accuracy or completeness of such information and shall have no liability for the consequences of use of such information. In no event shall NXP Semiconductors be liable for any indirect, incidental, punitive, special or consequential damages (including - without limitation - lost profits, lost savings, business interruption, costs related to the removal or replacement of any products or rework charges) whether or not such damages are based on tort (including negligence), warranty, breach of contract or any other legal theory. Notwithstanding any damages that customer might incur for any reason whatsoever, NXP Semiconductors’ aggregate and cumulative liability towards customer for the products described herein shall be limited in accordance with the Terms and conditions of commercial sale of NXP Semiconductors. Right to make changes — NXP Semiconductors reserves the right to make changes to information published in this document, including without limitation specifications and product descriptions, at any time and without notice. This document supersedes and replaces all information supplied prior to the publication hereof. Suitability for use — NXP Semiconductors products are not designed, authorized or warranted to be suitable for use in life support, life-critical or safety-critical systems or equipment, nor in applications where failure or malfunction of an NXP Semiconductors product can reasonably be expected to result in personal injury, death or severe property or environmental damage. NXP Semiconductors accepts no liability for inclusion and/or use of NXP Semiconductors products in such equipment or applications and therefore such inclusion and/or use is at the customer’s own risk. Applications — Applications that are described herein for any of these products are for illustrative purposes only. NXP Semiconductors makes no representation or warranty that such applications will be suitable for the specified use without further testing or modification. Customers are responsible for the design and operation of their applications and products using NXP Semiconductors products, and NXP Semiconductors accepts no liability for any assistance with applications or customer product design. It is customer’s sole responsibility to determine whether the NXP Semiconductors product is suitable and fit for the customer’s applications and products planned, as well as for the planned application and use of customer’s third party customer(s). Customers should provide appropriate design and operating safeguards to minimize the risks associated with their applications and products. NXP Semiconductors does not accept any liability related to any default, damage, costs or problem which is based on any weakness or default in the customer’s applications or products, or the application or use by customer’s third party customer(s). Customer is responsible for doing all necessary testing for the customer’s applications and products using NXP Semiconductors products in order to avoid a default of the applications and the products or of the application or use by customer’s third party customer(s). NXP does not accept any liability in this respect. Limiting values — Stress above one or more limiting values (as defined in the Absolute Maximum Ratings System of IEC 60134) will cause permanent damage to the device. Limiting values are stress ratings only and (proper) operation of the device at these or any other conditions above those given in the Recommended operating conditions section (if present) or the Characteristics sections of this document is not warranted. Constant or repeated exposure to limiting values will permanently and irreversibly affect the quality and reliability of the device. Terms and conditions of commercial sale — NXP Semiconductors products are sold subject to the general terms and conditions of commercial sale, as published at http://www.nxp.com/profile/terms, unless otherwise agreed in a valid written individual agreement. In case an individual agreement is concluded only the terms and conditions of the respective agreement shall apply. NXP Semiconductors hereby expressly objects to applying the customer’s general terms and conditions with regard to the purchase of NXP Semiconductors products by customer. No offer to sell or license — Nothing in this document may be interpreted or construed as an offer to sell products that is open for acceptance or the grant, conveyance or implication of any license under any copyrights, patents or other industrial or intellectual property rights. Export control — This document as well as the item(s) described herein may be subject to export control regulations. Export might require a prior authorization from national authorities. Document status[1][2] Product status[3] Definition Objective [short] data sheet Development This document contains data from the objective specification for product development. Preliminary [short] data sheet Qualification This document contains data from the preliminary specification. Product [short] data sheet Production This document contains the product specification. BGA7124 All information provided in this document is subject to legal disclaimers. © NXP B.V. 2010. All rights reserved. Product data sheet Rev. 3 — 9 September 2010 32 of 33 NXP Semiconductors BGA7124 400 MHz to 2700 MHz 0.25 W high linearity silicon amplifier Non-automotive qualified products — Unless this data sheet expressly states that this specific NXP Semiconductors product is automotive qualified, the product is not suitable for automotive use. It is neither qualified nor tested in accordance with automotive testing or application requirements. NXP Semiconductors accepts no liability for inclusion and/or use of non-automotive qualified products in automotive equipment or applications. In the event that customer uses the product for design-in and use in automotive applications to automotive specifications and standards, customer (a) shall use the product without NXP Semiconductors’ warranty of the product for such automotive applications, use and specifications, and (b) whenever customer uses the product for automotive applications beyond NXP Semiconductors’ specifications such use shall be solely at customer’s own risk, and (c) customer fully indemnifies NXP Semiconductors for any liability, damages or failed product claims resulting from customer design and use of the product for automotive applications beyond NXP Semiconductors’ standard warranty and NXP Semiconductors’ product specifications. Export control — This document as well as the item(s) described herein may be subject to export control regulations. Export might require a prior authorization from national authorities. 16.4 Trademarks Notice: All referenced brands, product names, service names and trademarks are the property of their respective owners. 17. Contact information For more information, please visit: http://www.nxp.com For sales office addresses, please send an email to: salesaddresses@nxp.com NXP Semiconductors BGA7124 400 MHz to 2700 MHz 0.25 W high linearity silicon amplifier © NXP B.V. 2010. All rights reserved. For more information, please visit: http://www.nxp.com For sales office addresses, please send an email to: salesaddresses@nxp.com Date of release: 9 September 2010 Document identifier: BGA7124 Please be aware that important notices concerning this document and the product(s) described herein, have been included in section ‘Legal information’. 18. Contents 1 Product profile . . . . . . . . . . . . . . . . . . . . . . . . . . 1 1.1 General description . . . . . . . . . . . . . . . . . . . . . 1 1.2 Features and benefits. . . . . . . . . . . . . . . . . . . . 1 1.3 Applications . . . . . . . . . . . . . . . . . . . . . . . . . . . 1 1.4 Quick reference data . . . . . . . . . . . . . . . . . . . . 1 2 Pinning information. . . . . . . . . . . . . . . . . . . . . . 2 2.1 Pinning . . . . . . . . . . . . . . . . . . . . . . . . . . . . . . . 2 2.2 Pin description . . . . . . . . . . . . . . . . . . . . . . . . . 2 3 Ordering information. . . . . . . . . . . . . . . . . . . . . 2 4 Functional diagram . . . . . . . . . . . . . . . . . . . . . . 3 5 Shutdown control . . . . . . . . . . . . . . . . . . . . . . . 3 6 Limiting values. . . . . . . . . . . . . . . . . . . . . . . . . . 4 7 Thermal characteristics . . . . . . . . . . . . . . . . . . 5 8 Static characteristics. . . . . . . . . . . . . . . . . . . . . 5 8.1 Supply current adjustment . . . . . . . . . . . . . . . . 5 9 Dynamic characteristics . . . . . . . . . . . . . . . . . . 6 9.1 Scattering parameters . . . . . . . . . . . . . . . . . . . 9 10 Reliability information . . . . . . . . . . . . . . . . . . . 10 11 Moisture sensitivity . . . . . . . . . . . . . . . . . . . . . 10 12 Application information. . . . . . . . . . . . . . . . . . 11 12.1 5 V applications . . . . . . . . . . . . . . . . . . . . . . . 11 12.1.1 920 MHz to 960 MHz . . . . . . . . . . . . . . . . . . . 11 12.1.2 1930 MHz to 1990 MHz . . . . . . . . . . . . . . . . . 14 12.1.3 2110 MHz to 2170 MHz . . . . . . . . . . . . . . . . . 16 12.1.4 2405 MHz to 2485 MHz . . . . . . . . . . . . . . . . . 19 12.2 3.3 V applications . . . . . . . . . . . . . . . . . . . . . . 22 12.2.1 920 MHz to 960 MHz . . . . . . . . . . . . . . . . . . . 22 12.2.2 2405 MHz to 2485 MHz . . . . . . . . . . . . . . . . . 25 12.3 PCB stack. . . . . . . . . . . . . . . . . . . . . . . . . . . . 28 13 Package outline . . . . . . . . . . . . . . . . . . . . . . . . 29 14 Abbreviations. . . . . . . . . . . . . . . . . . . . . . . . . . 30 15 Revision history. . . . . . . . . . . . . . . . . . . . . . . . 30 16 Legal information. . . . . . . . . . . . . . . . . . . . . . . 31 16.1 Data sheet status . . . . . . . . . . . . . . . . . . . . . . 31 16.2 Definitions. . . . . . . . . . . . . . . . . . . . . . . . . . . . 31 16.3 Disclaimers . . . . . . . . . . . . . . . . . . . . . . . . . . . 31 16.4 Trademarks. . . . . . . . . . . . . . . . . . . . . . . . . . . 32 17 Contact information. . . . . . . . . . . . . . . . . . . . . 32 18 Contents . . . . . . . . . . . . . . . . . . . . . . . . . . . . . . 33 REV. C Information furnished by Analog Devices is believed to be accurate and reliable. However, no responsibility is assumed by Analog Devices for its use, nor for any infringements of patents or other rights of third parties which may result from its use. No license is granted by implication or otherwise under any patent or patent rights of Analog Devices. a 12-Bit Serial Daisy-Chain CMOS D/A Converter DAC8143 FUNCTIONAL BLOCK DIAGRAM INPUT 12-BIT SHIFT REGISTER DAC REGISTER 12-BIT D/A CONVERTER DAC8143 LOAD IN OUT CLK VDD RFB IOUT1 IOUT2 AGND SRO DGND SRI STB2 STB3 STB4 STB1 LD2 LD1 VREF CLR ADDRESS BUS ADDRESS DECODER STROBE LOAD SRI SRO DAC8143 STROBE LOAD SRI SRO DAC8143 STROBE LOAD SRI SRO DAC8143 STROBE LOAD SRI SRO DAC8143 WR DBX mP Figure 1. Multiple DAC8143s with Three-Wire Interface FEATURES Fast, Flexible, Microprocessor Interfacing in Serially Controlled Systems Buffered Digital Output Pin for Daisy-Chaining Multiple DACs Minimizes Address-Decoding in Multiple DAC Systems—Three-Wire Interface for Any Number of DACs One Data Line One CLK Line One Load Line Improved Resistance to ESD –408C to +858C for the Extended Industrial Temperature Range APPLICATIONS Multiple-Channel Data Acquisition Systems Process Control and Industrial Automation Test Equipment Remote Microprocessor-Controlled Systems GENERAL INFORMATION The DAC8143 is a 12-bit serial-input daisy-chain CMOS D/A converter that features serial data input and buffered serial data output. It was designed for multiple serial DAC systems, where serially daisy-chaining one DAC after another is greatly simplified. The DAC8143 also minimizes address decoding lines enabling simpler logic interfacing. It allows three-wire interface for any number of DACs: one data line, one CLK line and one load line. Serial data in the input register (MSB first) is sequentially clocked out to the SRO pin as the new data word (MSB first) is simultaneously clocked in from the SRI pin. The strobe inputs are used to clock in/out data on the rising or falling (user selected) strobe edges (STB1, STB2, STB3, STB4). When the shift register’s data has been updated, the new data word is transferred to the DAC register with use of LD1 and LD2 inputs. Separate LOAD control inputs allow simultaneous output updating of multiple DACs. An asynchronous CLEAR input resets the DAC register without altering data in the input register. Improved linearity and gain error performance permits reduced circuit parts count through the elimination of trimming components. Fast interface timing reduces timing design considerations while minimizing microprocessor wait states. The DAC8143 is available in plastic packages that are compatible with autoinsertion equipment. Plastic packaged devices come in the extended industrial temperature range of –40°C to +85°C. One Technology Way, P.O. Box 9106, Norwood, MA 02062-9106, U.S.A. Tel: 781/329-4700 World Wide Web Site: http://www.analog.com Fax: 781/326-8703 © Analog Devices, Inc., 1999 ELECTRICAL CHARACTERISTICS Parameter Symbol Conditions Min Typ Max Units STATIC ACCURACY Resolution N 12 Bits Nonlinearity INL ±1 LSB Differential Nonlinearity1 DNL ±1 LSB Gain Error2 GFSE ±2 LSB Gain Tempco (DGain/DTemp)3 TCGFS ±5 ppm/°C Power Supply Rejection Ratio (DGain/DVDD) PSRR DVDD = ±5% ±0.0006 ±0.002 %/% Output Leakage Current4 ILKG TA = +25°C ±5 nA TA = Full Temperature Range ±25 nA Zero Scale Error5, 6 IZSE TA = +25°C ±0.002 ±0.03 LSB TA = Full Temperature Range ±0.01 ±0.15 LSB Input Resistance7 RIN VREF Pin 7 11 15 kW AC PERFORMANCE Output Current Settling Time3, 8 tS 0.380 1 ms AC Feedthrough Error (VREF to IOUT1)3, 9 FT VREF = 20 V p-p @ f = 10 kHz, TA = +25°C 2.0 mV p-p Digital-to-Analog Glitch Energy3, 10 Q VREF = 0 V, IOUT Load = 100 W, CEXT = 13 pF 20 nVs Total Harmonic Distortion3 THD VREF = 6 V rms @ 1 kHz DAC Register Loaded with All 1s –92 dB Output Noise Voltage Density3, 11 en 10 Hz to 100 kHz Between RFB and IOUT 13 nV/ÖHz DIGITAL INPUTS/OUTPUT Digital Input HIGH VIH 2.4 V Digital Input LOW VIL 0.8 V Input Leakage Current12 IIN VIN = 0 V to +5 V ±1 mA Input Capacitance CIN VIN = 0 V 8 pF Digital Output High VOH IOH = –200 mA 4 V Digital Output Low VOL IOL = 1.6 mA 0.4 V ANALOG OUTPUTS Output Capacitance3 COUT1 Digital Inputs = All 1s 90 pF COUT2 Digital Inputs = All 0s 90 pF Output Capacitance3 COUT1 Digital Inputs = All 0s 60 pF COUT2 Digital Inputs = All 1s 60 pF TIMING CHARACTERISTICS3 Serial Input to Strobe Setup Times tDS1 STB1 Used as the Strobe 50 ns (tSTB = 80 ns) tDS2 STB2 Used as the Strobe 20 ns tDS3 STB3 Used as the Strobe TA = +25°C 10 ns TA = Full Temperature Range 20 ns tDS4 STB4 Used as the Strobe 20 ns tDH1 STB1 Used as the Strobe TA = +25°C 40 ns TA = Full Temperature Range 50 ns tDH2 STB2 Used as the Strobe TA = +25°C 50 ns TA = Full Temperature Range 60 ns Serial Input to Strobe Hold Times (tSTB = 80 ns) tDH3 STB3 Used as the Strobe 80 ns tDH4 STB4 Used as the Strobe 80 ns –2– REV. C (@ VDD = +5 V; VREF = +10 V; VOUT1 = VOUT2 = VAGND = VDGND = 0 V; TA = Full Temperature Range specified under Absolute Maximum Ratings, unless otherwise noted.) DAC8143–SPECIFICATIONS ELECTRICAL CHARACTERISTICS DAC8143 Parameter Symbol Conditions Min Typ Max Units STB to SRO Propagation Delay13 tPD TA = +25°C 220 ns TA = Full Temperature Range 300 ns SRI Data Pulsewidth tSRI 100 ns STB1 Pulsewidth (STB1 = 80 ns)14 tSTB1 80 ns STB2 Pulsewidth (STB2 = 100 ns)14 tSTB2 80 ns STB3 Pulsewidth (STB3 = 80 ns)14 tSTB3 80 ns STB4 Pulsewidth (STB4 = 80 ns)14 tSTB4 80 ns Load Pulsewidth tLD1, tLD2 TA = +25°C 140 ns TA = Full Temperature Range 180 ns LSB Strobe into Input Register to Load DAC Register Time tASB 0 ns CLR Pulsewidth tCLR 80 ns POWER SUPPLY Supply Voltage VDD 4.75 5 5.25 V Supply Current IDD All Digital Inputs = VIH or VIL 2 mA All Digital Inputs = 0 V or VDD 0.1 mA Power Dissipation PD Digital Inputs = 0 V or VDD 0.5 mW 5 V ´ 0.1 mA Digital Inputs = VIH or VIL 10 mW 5 V ´ 2 mA NOTES 11All grades are monotonic to 12 bits over temperature. 12Using internal feedback resistor. 13Guaranteed by design and not tested. 14Applies to IOUT1; all digital inputs = VIL, VREF = +10 V; specification also applies for IOUT2 when all digital inputs = VIH. 15VREF = +10 V, all digital inputs = 0 V. 16Calculated from worst case RREF: IZSE (in LSBs) = (RREF ´ ILKG ´ 4096) /VREF. 17Absolute temperature coefficient is less than +300 ppm/°C. 18IOUT, Load = 100 W. CEXT = 13 pF, digital input = 0 V to VDD or VDD to 0 V. Extrapolated to 1/2 LSB: tS = propagation delay (tPD) +9 t, where t equals measured time constant of the final RC decay. 19All digital inputs = 0 V. 10VREF = 0 V, all digital inputs = 0 V to VDD or VDD to 0 V. 11Calculations from en = Ö4K TRB where: K = Boltzmann constant, J/KR = resistance W T = resistor temperature, K B = bandwidth, Hz 12Digital inputs are CMOS gates; IIN typically 1 nA at +25°C. 13Measured from active strobe edge (STB) to new data output at SRO; CL = 50 pF. 14Minimum low time pulsewidth for STB1, STB2, and STB4, and minimum high time pulsewidth for STB3. Specifications subject to change without notice. (@ VDD = +5 V; VREF = +10 V; VOUT1 = V0UT2 = VAGND = VDGND = 0 V; TA = Full Temperature Range specified under Absolute Maximum Ratings, unless otherwise noted.) DAC8143 REV. C –3– DAC8143 –4– REV. C PIN CONNECTIONS 16-Lead Epoxy Plastic DIP 16-Lead SOIC TOP VIEW (Not to Scale) 16 15 14 13 12 11 10 9 1 2 3 4 5 6 7 8 IOUT1 RFB DAC8143 IOUT2 VREF AGND VDD STB1 CLR LD1 DGND SRO STB4 SRI STB3 STB2 LD2 ABSOLUTE MAXIMUM RATINGS (TA = +25°C, unless otherwise noted.) VDD to DGND . . . . . . . . . . . . . . . . . . . . . . . . . . . . . . . . +17 V VREF to DGND . . . . . . . . . . . . . . . . . . . . . . . . . . . . . . . ±25 V VRFB to DGND . . . . . . . . . . . . . . . . . . . . . . . . . . . . . . . ±25 V AGND to DGND . . . . . . . . . . . . . . . . . . . . . . . . VDD + 0.3 V DGND to AGND . . . . . . . . . . . . . . . . . . . . . . . . VDD + 0.3 V Digital Input Voltage Range . . . . . . . . . . . . . . . –0.3 V to VDD Output Voltage (Pin 1, Pin 2) . . . . . . . . . . . . . . –0.3 V to VDD Operating Temperature Range FP/FS Versions . . . . . . . . . . . . . . . . . . . . . –40°C to +85°C Junction Temperature . . . . . . . . . . . . . . . . . . . . . . . . .+150°C Storage Temperature . . . . . . . . . . . . . . . . . . –65°C to +150°C Lead Temperature (Soldering, 60 sec) . . . . . . . . . . . .+300°C Package Type uJA* uJC Units 16-Lead Plastic DIP 76 33 °C/W 16-Lead SOIC 92 27 °C/W *qJA is specified for worst case mounting conditions, i.e., qJA is specified for device in socket for P-DIP package; qJA is specified for device soldered to printed circuit board for SOIC package. CAUTION 1. Do not apply voltage higher than VDD or less than DGND potential on any terminal except VREF (Pin 15) and RFB (Pin 16). 2. The digital control inputs are Zener-protected; however, permanent damage may occur on unprotected units from high energy electrostatic fields. Keep units in conductive foam at all times until ready to use. 3. Use proper antistatic handling procedures. 4. Absolute Maximum Ratings apply to packaged devices. Stresses above those listed under Absolute Maximum Ratings may cause permanent damage to the device. ORDERING GUIDE Gain Temperature Package Package Model Nonlinearity Error Range Descriptions Options DAC8143FP ±1 LSB ±2 LSB –40°C to +85°C 16-Lead Plastic DIP N-16 DAC8143FS ±1 LSB ±2 LSB –40°C to +85°C 16-Lead SOIC R-16W Die Size: 99 ´ 107 mil, 10,543 sq. mils. CAUTION ESD (electrostatic discharge) sensitive device. Electrostatic charges as high as 4000 V readily accumulate on the human body and test equipment and can discharge without detection. Although the DAC8143 features proprietary ESD protection circuitry, permanent damage may occur on devices subjected to high energy electrostatic discharges. Therefore, proper ESD precautions are recommended to avoid performance degradation or loss of functionality. WARNING! ESD SENSITIVE DEVICE DAC8143 REV. C –5– 10 FREQUENCY – Hz THD – dB –90 0.032 THD – % 0.010 –85 –80 –75 –70 –95 0.018 0.0056 0.0032 0.0018 100 1k 10k 100k VIN = 5V rms OUTPUT OP AMP: OP-42 Figure 3. Multiplying Mode Total Harmonic Distortion vs. Frequency Typical Performance Characteristics– ALL BITS ON 100 FREQUENCY – Hz B10 0 ATTENUATION – dB (MSB) B11 B9 B8 B7 B6 B5 B4 B3 B2 B1 (LSB) B0 DATA BITS "ON" (ALL OTHER DATA BITS "OFF") 1k 10k 100k 1M 10M 12 24 36 48 60 72 84 96 108 Figure 2. Multiplying Mode Frequency Response vs. Digital Code 3 0 VIN – Volts IDD – mA 2 1 0 1 2 3 4 5 Figure 4. Supply Current vs. Logic Input Voltage 4 1 VDD – Volts THRESHOLD VOLTAGE – Volts 3 2 0 1 2.4 –0.8 3 5 7 9 11 13 15 17 Figure 7. Logic Threshold Voltage vs. Supply Voltage 0.5 0 DIGITAL INPUT CODE – Decimal LINEARITY ERROR – LSB 0.4 0.3 0.2 0.1 0.0 –0.1 –0.2 –0.3 –0.4 –0.5 512 1024 1536 2048 2560 3072 3584 4095 Figure 5. Linearity Error vs. Digital Code 0.5 2 VREF – Volts DNL – LSB 4 6 8 10 0.25 0 –0.25 –0.5 Figure 8. DNL Error vs. Reference Voltage 0.5 2 VREF – Volts INL – LSB 4 6 8 10 0.25 0 –0.25 –0.5 Figure 6. Linearity Error vs. Reference Voltage 40 0 SRO – VOLTAGE OUT – Volts SINK 30 20 10 0 –10 –20 –30 –40 1 2 3 4 5 SOURCE OUTPUT CURRENT – mA TA = +258C LOGIC 1 LOGIC 0 Figure 9. Digital Output Voltage vs. Output Current DAC8143 –6– REV. C DEFINITION OF SPECIFICATIONS RESOLUTION The resolution of a DAC is the number of states (2n) into which the full-scale range (FSR) is divided (or resolved), where “n” is equal to the number of bits. SETTLING TIME Time required for the analog output of the DAC to settle to within 1/2 LSB of its final value for a given digital input stimulus; i.e., zero to full-scale. GAIN Ratio of the DAC’s external operational amplifier output voltage to the VREF input voltage when all digital inputs are HIGH. FEEDTHROUGH ERROR Error caused by capacitive coupling from VREF to output. Feedthrough error limits are specified with all switches off. OUTPUT CAPACITANCE Capacitance from IOUT1 to ground. OUTPUT LEAKAGE CURRENT Current appearing at IOUT1 when all digital inputs are LOW, or at IOUT2 terminal when all inputs are HIGH. GENERAL CIRCUIT INFORMATION The DAC8143 is a 12-bit serial-input, buffered serial-output, multiplying CMOS D/A converter. It has an R-2R resistor ladder network, a 12-bit input shift register, 12-bit DAC register, control logic circuitry, and a buffered digital output stage. The control logic forms an interface in which serial data is loaded, under microprocessor control, into the input shift register and then transferred, in parallel, to the DAC register. In addition, buffered serial output data is present at the SRO pin when input data is loaded into the input register. This buffered data follows the digital input data (SRI) by 12 clock cycles and is available for daisy-chaining additional DACs. An asynchronous CLEAR function allows resetting the DAC register to a zero code (0000 0000 0000) without altering data stored in the registers. A simplified circuit of the DAC8143 is shown in Figure 10. An inversed R-2R ladder network consisting of silicon-chrome, thin-film resistors, and twelve pairs of NMOS current-steering switches. These switches steer binarily weighted currents into either IOUT1 or IOUT2. Switching current to IOUT1 or IOUT2 yields a constant current in each ladder leg, regardless of digital input code. This constant current results in a constant input resistance at VREF equal to R (typically 11 kW). The VREF input may be driven by any reference voltage or current, ac or dc, that is within the limits stated in the Absolute Maximum Ratings chart. The twelve output current-steering switches are in series with the R-2R resistor ladder, and therefore, can introduce bit errors. It was essential to design these switches such that the switch “ON” resistance be binarily scaled so that the voltage drop across each switch remains constant. If, for example, Switch 1 of Figure 10 was designed with an “ON” resistance of 10 W, Switch 2 for 20 W, etc., a constant 5 mV drop would then be maintained across each switch. To further ensure accuracy across the full temperature range, permanently “ON” MOS switches were included in series with the feedback resistor and the R-2R ladder’s terminating resistor. The Simplified DAC Circuit, Figure 10, shows the location of these switches. These series switches are equivalently scaled to two times Switch 1 (MSB) and top Switch 12 (LSB) to maintain constant relative voltage drops with varying temperature. During any testing of the resistor ladder or RFEEDBACK (such as incoming inspection), VDD must be present to turn “ON” these series switches. VREF RFEEDBACK IOUT2 IOUT1 10kV 10kV 10kV 20kV 20kV 20kV 20kV 20kV S1 S2 S3 S12 10kV BIT 1 (MSB) BIT 2 BIT 3 BIT 12 (LSB) DIGITAL INPUTS (SWITCHES SHOWN FOR DIGITAL INPUTS "HIGH") * * *THESE SWITCHES PERMANENTLY "ON" Figure 10. Simplified DAC Circuit DAC8143 REV. C –7– ESD PROTECTION The DAC8143 digital inputs have been designed with ESD resistance incorporated through careful layout and the inclusion of input protection circuitry. Figure 11 shows the input protection diodes. High voltage static charges applied to the digital inputs are shunted to the supply and ground rails through forward biased diodes. These protection diodes were designed to clamp the inputs well below dangerous levels during static discharge conditions. VDD DTL/TTL/CMOS INPUTS Figure 11. Digital Input Protection EQUIVALENT CIRCUIT ANALYSIS Figures 12 and 13 show equivalent circuits for the DAC8143’s internal DAC with all bits LOW and HIGH, respectively. The reference current is switched to IOUT2 when all data bits are LOW, and to IOUT1 when all bits are HIGH. The ILEAKAGE current source is the combination of surface and junction leakages to the substrate. The 1/4096 current source represents the constant 1-bit current drain through the ladder’s terminating resistor. Output capacitance is dependent upon the digital input code. This is because the capacitance of a MOS transistor changes with applied gate voltage. This output capacitance varies between the low and high values. RFEEDBACK IOUT1 IOUT2 R = 10kV ILEAKAGE 60pF 1/4096 ILEAKAGE 90pF R = 10kV IREF VREF Figure 12. Equivalent Circuit (All Inputs LOW) IOUT2 ILEAKAGE 60pF RFEEDBACK IOUT1 R = 10kV 1/4096 ILEAKAGE 90pF R = 10kV IREF VREF Figure 13. Equivalent Circuit (All Inputs HIGH) DYNAMIC PERFORMANCE ANALOG OUTPUT IMPEDANCE The output resistance, as in the case of the output capacitance, varies with the digital input code. This resistance, looking back into the IOUT1 terminal, varies between 11 kW (the feedback resistor alone when all digital input are LOW) and 7.5 kW (the feedback resistor in parallel with approximately 30 kW of the R-2R ladder network resistance when any single bit logic is HIGH). Static accuracy and dynamic performance will be affected by these variations. The gain and phase stability of the output amplifier, board layout, and power supply decoupling will all affect the dynamic performance of the DAC8143. The use of a small compensation capacitor may be required when high speed operational amplifiers are used. It may be connected across the amplifier’s feedback resistor to provide the necessary phase compensation to critically damp the output. The considerations when using high speed amplifiers are: 1. Phase compensation (see Figures 16 and 17). 2. Power supply decoupling at the device socket and use of proper grounding techniques. OUTPUT AMPLIFIER CONSIDERATIONS When using high speed op amps, a small feedback capacitor (typically 5 pF–30 pF) should be used across the amplifiers to minimize overshoot and ringing. For low speed or static applications, ac specifications of the amplifier are not very critical. In high speed applications, slew rate, settling time, openloop gain and gain/phase margin specifications of the amplifier should be selected for the desired performance. It has already been noted that an offset can be caused by including the usual bias current compensation resistor in the amplifier’s noninverting input terminal. This resistor should not be used. Instead, the amplifier should have a bias current that is low over the temperature range of interest. Static accuracy is affected by the variation in the DAC’s output resistance. This variation is best illustrated by using the circuit of Figure 14 and the equation: VERROR = VOS 1+RFB RO æ è ç ö ø ÷ VOS VREF R R R ETC RFB R2 R2 R2 OP-77 Figure 14. Simplified Circuit DAC8143 –8– REV. C Where RO is a function of the digital code, and: RO = 10 kW for more than four bits of Logic 1, RO = 30 kW for any single bit of Logic 1. Therefore, the offset gain varies as follows: at code 0011 1111 1111, VERROR1 = VOS 1+10 kW 10 kW æ è ç ö ø ÷ = 2 VOS at code 0100 0000 0000, VERROR2 = VOS 1+10 kW 30 kW æ è ç ö ø ÷ = 4/3 VOS The error difference is 2/3 VOS. Since one LSB has a weight (for VREF = +10 V) of 2.4 mV for the DAC8143, it is clearly important that VOS be minimized, using either the amplifier’s pulling pins, an external pulling network, or by selection of an amplifier with inherently low VOS. Amplifiers with sufficiently low VOS include OP77, OP97, OP07, OP27, and OP42. INTERFACE LOGIC OPERATION The microprocessor interface of the DAC8143 has been designed with multiple STROBE and LOAD inputs to maximize interfacing options. Control signals decoding may be done on chip or with the use of external decoding circuitry (see Figure 21). Serial data is clocked into the input register and buffered output stage with STB1, STB2, or STB4. The strobe inputs are active on the rising edge. STB3 may be used with a falling edge clock data. WORD N –1 WORD N WORD N –2 WORD N –1 WORD N BIT 2 BIT 11 BIT 12 LSB BIT 1 MSB BIT 12 LSB BIT 1 BIT 2 SRI MSB BIT 1 BIT 2 MSB BIT 1 MSB BIT 2 BIT 12 LSB BIT 1 LSB tDS1, tDS2, tDS3, tDS4 SRO tDH1, tDH2, tDH3, tDH4 tPD tSTB1 tSTB2 tSTB3 tSTB4 tSTB1 tSTB2 tSTB3 tSTB4 * STROBE (STB1, STB2, STB4) 1 2 12 1 2 tLD1 tLD2 tSR1 11 12 tASB LD1 AND LD2 LOAD NEW 12-BIT WORD INTO INPUT REGISTER AND SHIFT OUT PREVIOUS WORD LOAD INPUT REGISTER'S DATA INTO DAC REGISTER NOTES: * STROBE WAVEFORM IS INVERTED IF STB3 IS USED TO STROBE SERIAL DATA BITS INTO INPUT REGISTER. ** DATA IS STROBED INTO AND OUT OF THE INPUT SHIFT REGISTER MSB FIRST. Figure 15. Timing Diagram Serial data output (SRO) follows the serial data input (SRI) by 12 clocked bits. Holding any STROBE input at its selected state (i.e., STB1, STB2 or STB4 at logic HIGH or STB3 at logic LOW) will act to prevent any further data input. When a new data word has been entered into the input register, it is transferred to the DAC register by asserting both LOAD inputs. The CLR input allows asynchronous resetting of the DAC register to 0000 0000 0000. This reset does not affect data held in the input registers. While in unipolar mode, a CLEAR will result in the analog output going to 0 V. In bipolar mode, the output will go to –VREF. INTERFACE INPUT DESCRIPTION STB1 (Pin 4), STB2 (Pin 8), STB4 (Pin 11)—Input Register and Buffered Output Strobe. Inputs Active on Rising Edge. Selected to load serial data into input register and buffered output stage. See Table I for details. STB3 (Pin 10)—Input Register and Buffered Output Strobe Input. Active on Falling Edge. Selected to load serial data into input register and buffered output stage. See Table I for details. LD1 (Pin 5), LD2 (Pin 9)—Load DAC Register Inputs. Active Low. Selected together to load contents of input register into DAC register. CLR (Pin 13)—Clear Input. Active Low. Asynchronous. When LOW, 12-bit DAC register is forced to a zero code (0000 0000 0000) regardless of other interface inputs. DAC8143 REV. C –9– Table I. Truth Table DAC8143 Logic Inputs Input Register/ Digital Output Control Inputs DAC Register Control Inputs STB4 STB3 STB2 STB1 CLR LD2 LD1 DAC8143 Operation Notes 0 1 0 g X X X 0 1 g 0 X X X Serial Data Bit Loaded from SRI 0 f 0 0 X X X into Input Register and Digital Output 2, 3 g 1 0 0 X X X (SRO Pin) after 12 Clocked Bits. 1 X X X X 0 X X No Operation (Input Register and SRO) 3 X X 1 X X X X 1 Reset DAC Register to Zero Code 0 X X (Code: 0000 0000 0000) 1, 3 (Asynchronous Operation) 1 1 X No Operation (DAC Register and SRO) 3 1 X 1 1 0 0 Load DAC Register with the Contents 3 of Input Register NOTES 1CLR = 0 asynchronously resets DAC Register to 0000 0000 0000, but has no effect on Input Register. 2Serial data is loaded into Input Register MSB first, on edges shown. g is positive edge, f is negative edge. 30 = Logic LOW, 1 = Logic HIGH, X = Don’t Care. APPLICATIONS INFORMATION UNIPOLAR OPERATION (2-QUADRANT) The circuit shown in Figures 16 and 17 may be used with an ac or dc reference voltage. The circuit’s output will range between 0 V and +10(4095/4096) V depending upon the digital input code. The relationship between the digital input and the analog output is shown in Table II. The VREF voltage range is the maximum input voltage range of the op amp or ±25 V, whichever is lowest. Table II. Unipolar Code Table Digital Input Nominal Analog Output (VOUT as Shown MSB LSB in Figures 16 and 17) 1 1 1 1 1 1 1 1 1 1 1 1 –VREF 4095 4096 æ è ç ö ø ÷ 1 0 0 0 0 0 0 0 0 0 0 1 –VREF 2049 4096 æèöø 1 0 0 0 0 0 0 0 0 0 0 0 –VREF 2048 4096 æè öø = – VREF 2 0 1 1 1 1 1 1 1 1 1 1 1 –VREF 2047 4096 æè öø 0 0 0 0 0 0 0 0 0 0 0 1 –VREF 1 4096 æè öø 0 0 0 0 0 0 0 0 0 0 0 0 –VREF 0 4096 æè öø = 0 NOTES 1Nominal full scale for the circuits of Figures 16 and 17 is given by FS = –VREF 4095 4096 æ è ç ö ø ÷ . 2Nominal LSB magnitude for the circuits of Figures 16 and 17 is given by LSB = VREF 1 4096 æ è ç ö ø ÷ or VREF(2–n). OP-77 +5V VREF VDD RFEEDBACK IOUT1 IOUT2 AGND DGND SRO (BUFFERED DIGITAL DATA OUT) 15pF +15V –15V VOUT 7 6 4 3 2 15 14 13 4, 5 8–11 7 1 2 3 6 12 CONTROL DAC8143 INPUTS SRI (SERIAL DATA IN) VREF –10V CLR Figure 16. Unipolar Operation with High Accuracy Op Amp (2-Quadrant) OP-42 +5V VREF VDD RFEEDBACK IOUT1 IOUT2 AGND DGND SRO (BUFFERED DIGITAL DATA OUT) 15pF +15V –15V VOUT 7 6 4 3 2 15 14 13 4, 5 8–11 7 1 2 3 6 12 CONTROL DAC8143 INPUTS SRI (SERIAL DATA IN) VREF –10V R2 50V R1 100V CLR Figure 17. Unipolar Operation with Fast Op Amp and Gain Error Trimming (2-Quadrant) DAC8143 –10– REV. C In many applications, the DAC8143’s zero scale error and low gain error, permit the elimination of external trimming components without adverse effects on circuit performance. For applications requiring a tighter gain error than 0.024% at 25°C for the top grade part, or 0.048% for the lower grade part, the circuit in Figure 17 may be used. Gain error may be trimmed by adjusting R1. The DAC register must first be loaded with all 1s. R1 is then adjusted until VOUT = –VREF (4095/4096). In the case of an adjustable VREF, R1 and RFEEDBACK may be omitted, with VREF adjusted to yield the desired full-scale output. BIPOLAR OPERATION (4-QUADRANT) Figure 18 details a suggested circuit for bipolar, or offset binary, operation. Table III shows the digital input-to-analog output relationship. The circuit uses offset binary coding. Twos complement code can be converted to offset binary by software inversion of the MSB or by the addition of an external inverter to the MSB input. Resistor R3, R4 and R5 must be selected to match within 0.01% and must all be of the same (preferably metal foil) type to assure temperature coefficient match. Mismatching between R3 and R4 causes offset and full-scale error. Calibration is performed by loading the DAC register with 1000 0000 0000 and adjusting R1 until VOUT = 0 V. R1 and R2 may be omitted by adjusting the ratio of R3 to R4 to yield VOUT = 0 V. Full scale can be adjusted by loading the DAC register with 1111 1111 1111 and adjusting either the amplitude of VREF or the value of R5 until the desired VOUT is achieved. Table III. Bipolar (Offset Binary) Code Table Digital Input Nominal Analog Output MSB LSB (VOUT as Shown in Figure 18) 1 1 1 1 1 1 1 1 1 1 1 1 +VREF 2047 2048 æè öø 1 0 0 0 0 0 0 0 0 0 0 1 +VREF 1 2048 æè öø 1 0 0 0 0 0 0 0 0 0 0 0 0 0 1 1 1 1 1 1 1 1 1 1 1 –VREF 1 2048 æè öø 0 0 0 0 0 0 0 0 0 0 0 1 –VREF 2047 2048 æè öø 0 0 0 0 0 0 0 0 0 0 0 0 –VREF 2048 2048 æè öø NOTES 1Nominal full scale for the circuits of Figure 18 is given by FS = VREF 2047 2048 æè öø . 2Nominal LSB magnitude for the circuits of Figure 18 is given by LSB = VREF 1 2048 æè öø . DAISY-CHAINING DAC8143s Many applications use multiple serial input DACs that use numerous interconnecting lines for address decoding and data lines. In addition, they use some type of buffering to reduce loading on the bus. The DAC8143 is ideal for just such an application. It not only reduces the number of interconnecting lines, but also reduces bus loading. The DAC8143 can be daisychained with only three lines: one data line, one CLK line and one load line, see Figure 19. VOUT 1/2 OP200 +5V R2 50V 12 15 7 R1 100V SERIAL DATA INPUT