Consent Manager Tag v2.0 (for TCF 2.0) -->
Farnell PDF
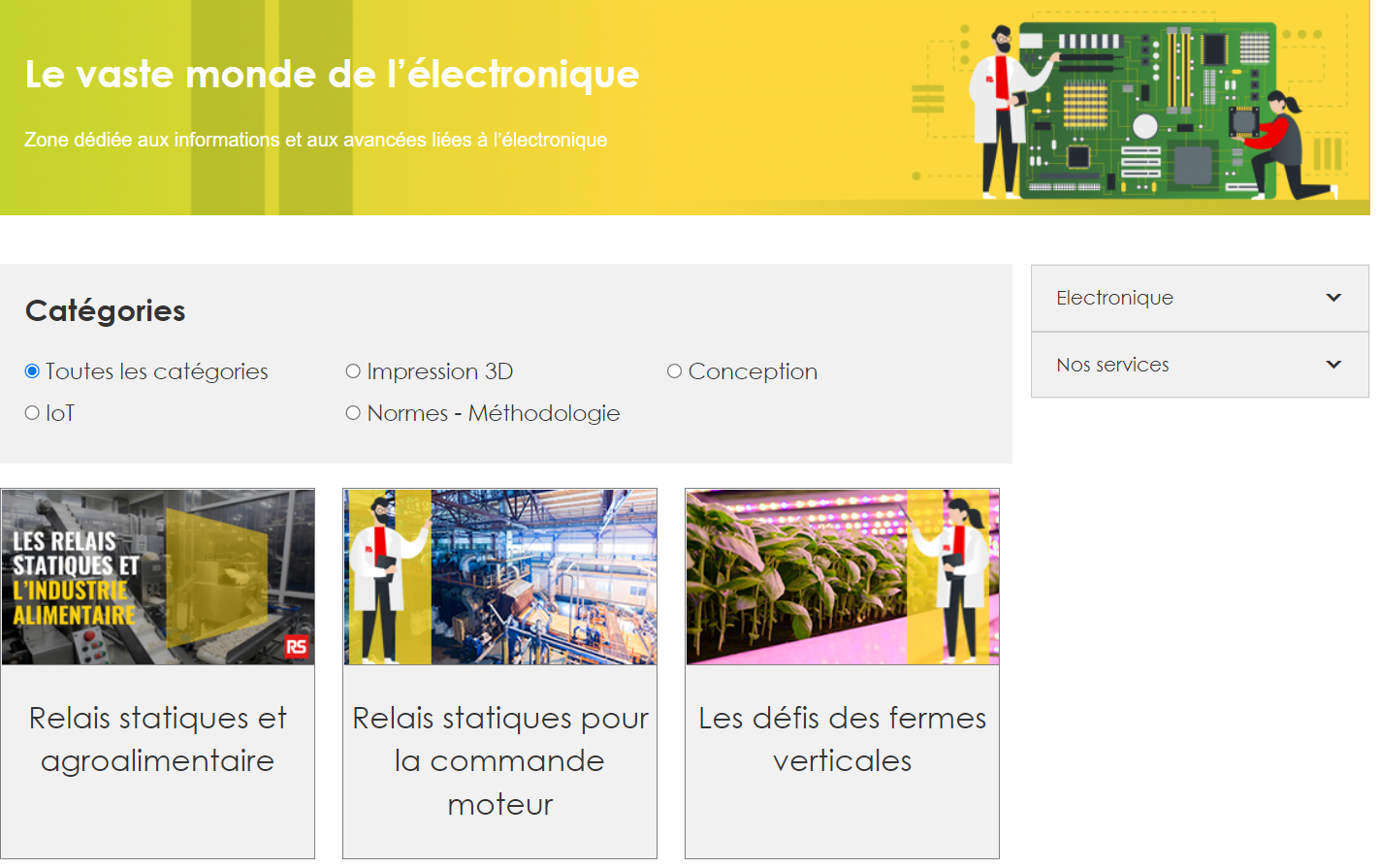
AD8307 Data Sheet - Analog Devices - Farnell Element 14
AD8307 Data Sheet - Analog Devices - Farnell Element 14
- Revenir à l'accueil

Farnell Element 14 :
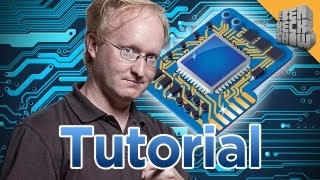
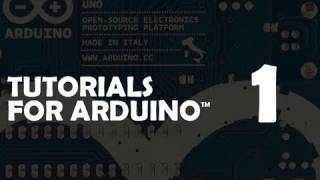
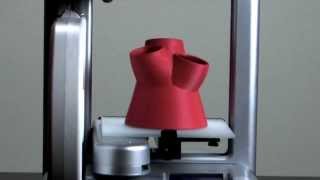
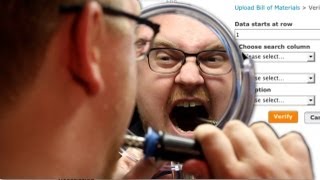
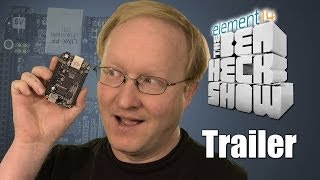
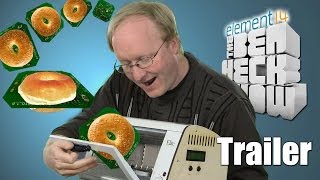
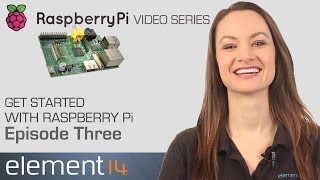
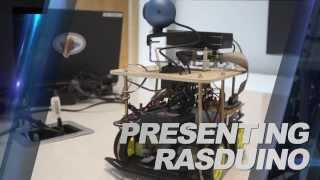
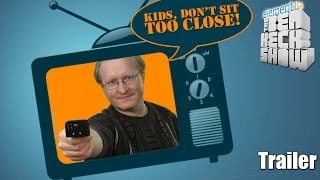
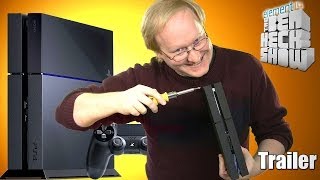
See the trailer for the next exciting episode of The Ben Heck show. Check back on Friday to be among the first to see the exclusive full show on element…
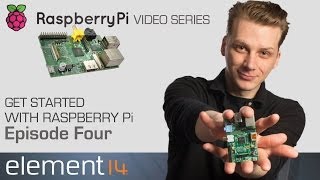
Connect your Raspberry Pi to a breadboard, download some code and create a push-button audio play project.

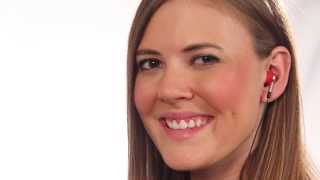
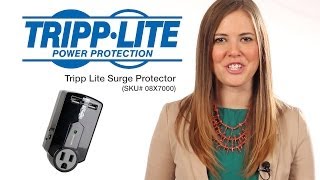
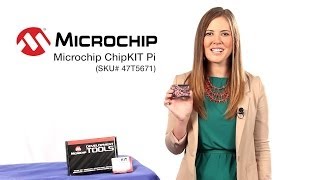
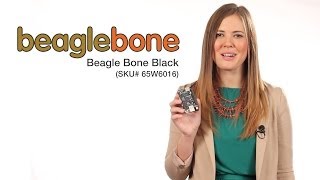
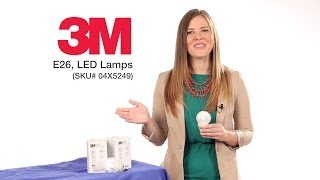
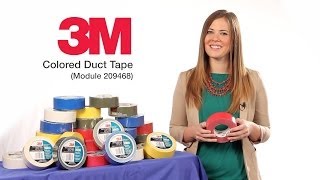
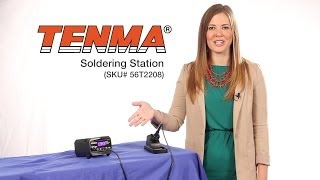
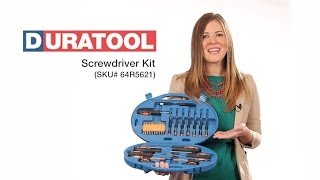
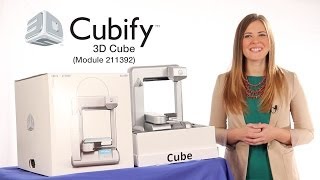
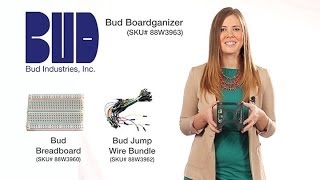
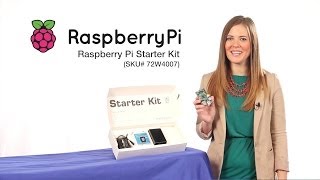
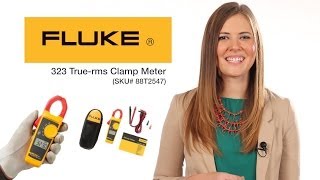
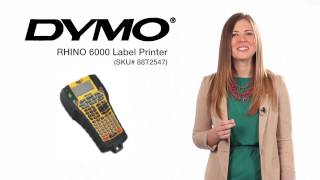
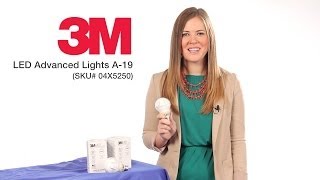
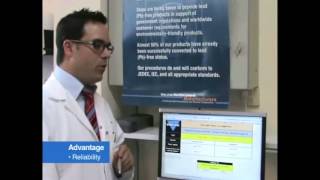
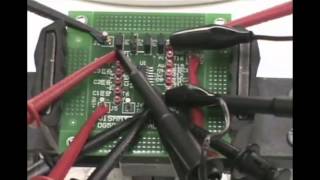
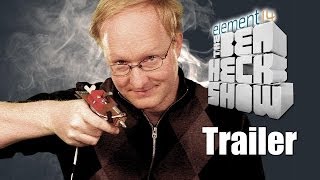
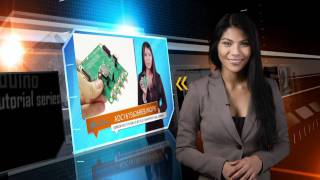
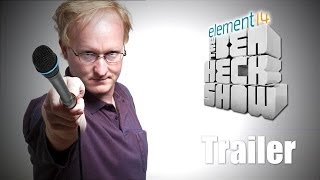
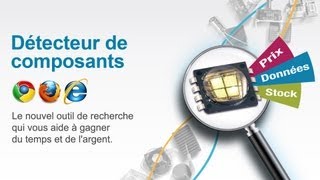
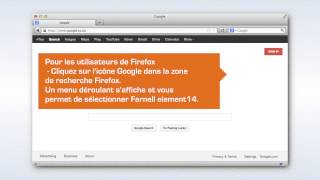
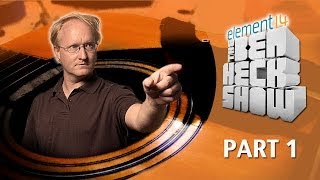
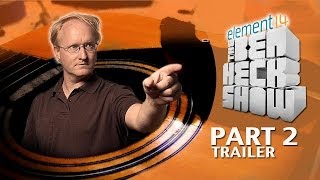

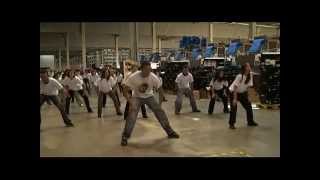
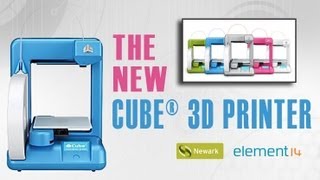










Puce électronique / Microchip :
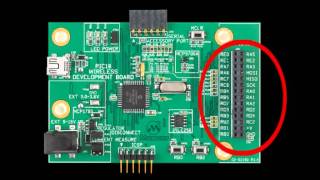
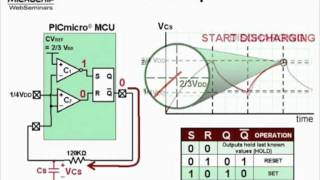
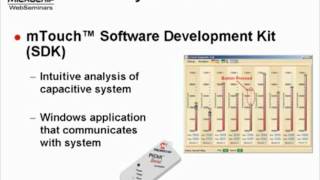
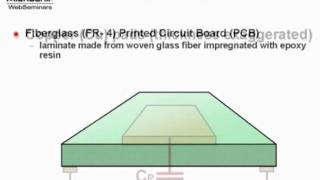
Sans fil - Wireless :
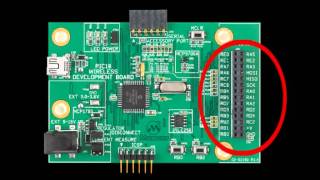
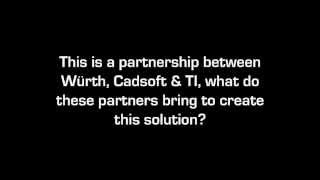
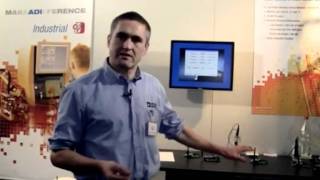
Texas instrument :
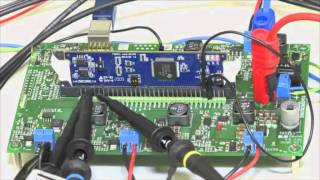
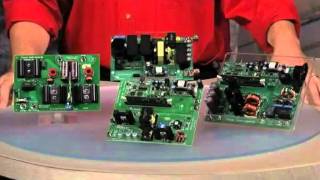
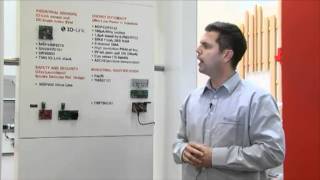
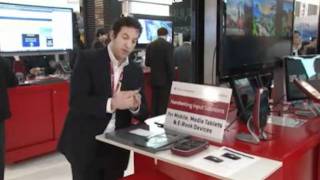
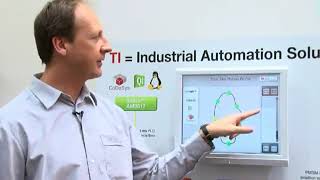
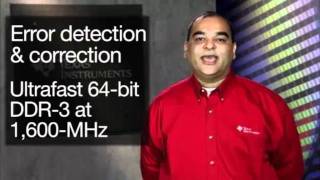
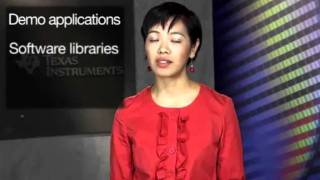

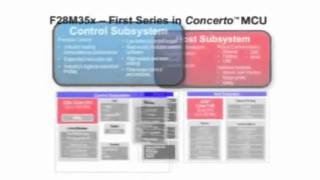
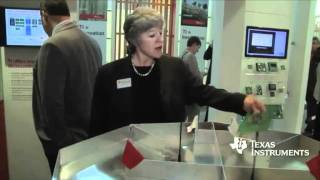
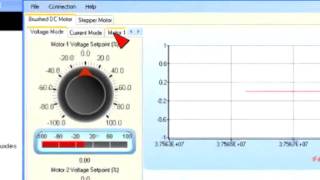
Ordinateurs :
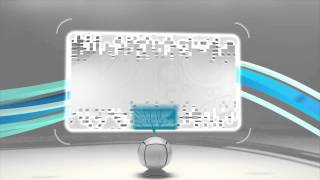
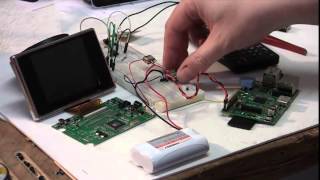
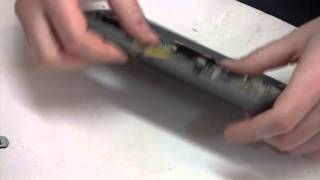
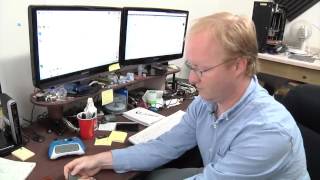
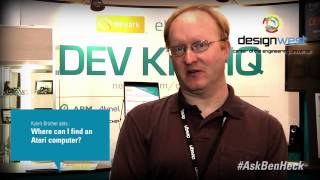
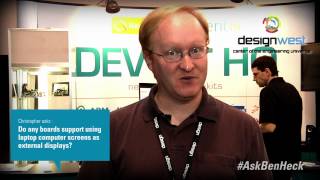
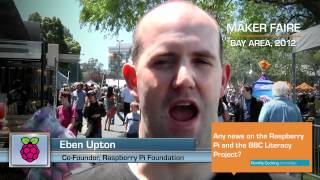
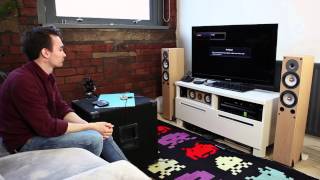
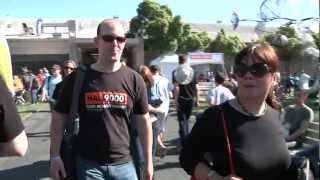
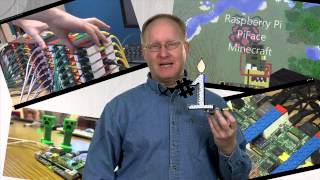
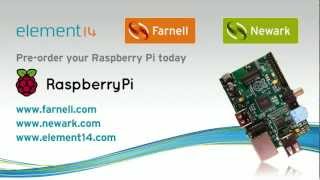
Logiciels :
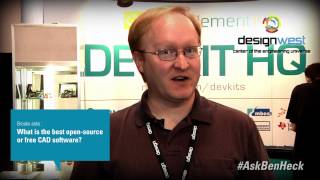
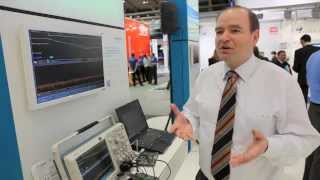
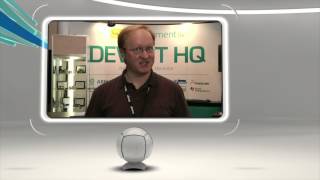
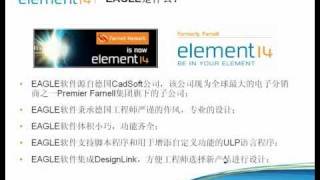
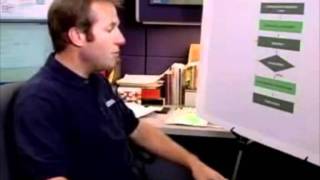
Tutoriels :
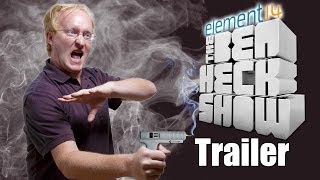
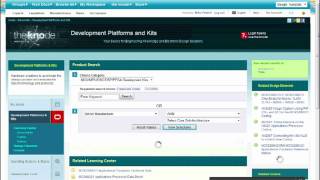
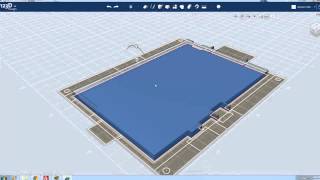
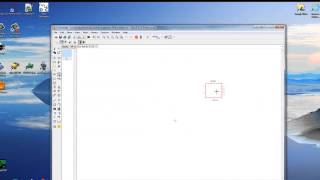
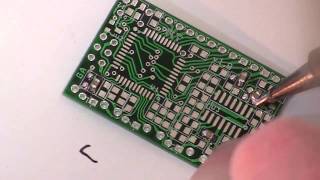
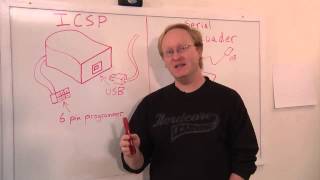
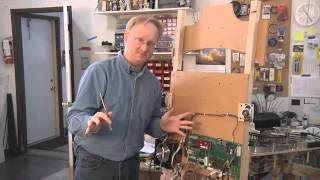
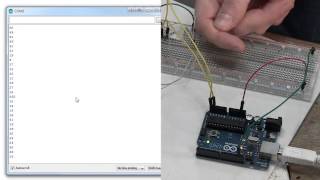

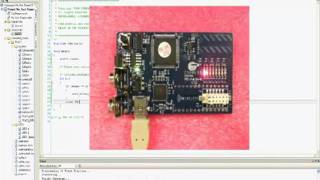
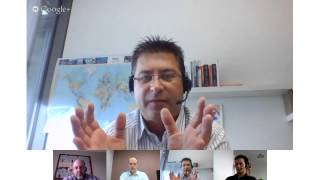
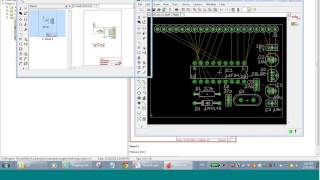
Autres documentations :
Farnell-MSP430-Hardw..> 29-Jul-2014 10:36 1.1M
![[TXT]](http://www.audentia-gestion.fr/icons/text.gif)
Farnell-LM324-Texas-..> 29-Jul-2014 10:32 1.5M
![[TXT]](http://www.audentia-gestion.fr/icons/text.gif)
Farnell-LM386-Low-Vo..> 29-Jul-2014 10:32 1.5M
![[TXT]](http://www.audentia-gestion.fr/icons/text.gif)
Farnell-NE5532-Texas..> 29-Jul-2014 10:32 1.5M
![[TXT]](http://www.audentia-gestion.fr/icons/text.gif)
Farnell-Hex-Inverter..> 29-Jul-2014 10:31 875K
![[TXT]](http://www.audentia-gestion.fr/icons/text.gif)
Farnell-AT90USBKey-H..> 29-Jul-2014 10:31 902K
![[TXT]](http://www.audentia-gestion.fr/icons/text.gif)
Farnell-AT89C5131-Ha..> 29-Jul-2014 10:31 1.2M
![[TXT]](http://www.audentia-gestion.fr/icons/text.gif)
Farnell-MSP-EXP430F5..> 29-Jul-2014 10:31 1.2M
![[TXT]](http://www.audentia-gestion.fr/icons/text.gif)
Farnell-Explorer-16-..> 29-Jul-2014 10:31 1.3M
![[TXT]](http://www.audentia-gestion.fr/icons/text.gif)
Farnell-TMP006EVM-Us..> 29-Jul-2014 10:30 1.3M
![[TXT]](http://www.audentia-gestion.fr/icons/text.gif)
Farnell-Gertboard-Us..> 29-Jul-2014 10:30 1.4M
![[TXT]](http://www.audentia-gestion.fr/icons/text.gif)
Farnell-LMP91051-Use..> 29-Jul-2014 10:30 1.4M
![[TXT]](http://www.audentia-gestion.fr/icons/text.gif)
Farnell-Thermometre-..> 29-Jul-2014 10:30 1.4M
![[TXT]](http://www.audentia-gestion.fr/icons/text.gif)
Farnell-user-manuel-..> 29-Jul-2014 10:29 1.5M
![[TXT]](http://www.audentia-gestion.fr/icons/text.gif)
Farnell-fx-3650P-fx-..> 29-Jul-2014 10:29 1.5M
![[TXT]](http://www.audentia-gestion.fr/icons/text.gif)
Farnell-2-GBPS-Diffe..> 28-Jul-2014 17:42 2.7M
![[TXT]](http://www.audentia-gestion.fr/icons/text.gif)
Farnell-LMT88-2.4V-1..> 28-Jul-2014 17:42 2.8M
![[TXT]](http://www.audentia-gestion.fr/icons/text.gif)
Farnell-Octal-Genera..> 28-Jul-2014 17:42 2.8M
![[TXT]](http://www.audentia-gestion.fr/icons/text.gif)
Farnell-Dual-MOSFET-..> 28-Jul-2014 17:41 2.8M
![[TXT]](http://www.audentia-gestion.fr/icons/text.gif)
Farnell-TLV320AIC325..> 28-Jul-2014 17:41 2.9M
![[TXT]](http://www.audentia-gestion.fr/icons/text.gif)
Farnell-SN54LV4053A-..> 28-Jul-2014 17:20 5.9M
![[TXT]](http://www.audentia-gestion.fr/icons/text.gif)
Farnell-TAS1020B-USB..> 28-Jul-2014 17:19 6.2M
![[TXT]](http://www.audentia-gestion.fr/icons/text.gif)
Farnell-TPS40060-Wid..> 28-Jul-2014 17:19 6.3M
![[TXT]](http://www.audentia-gestion.fr/icons/text.gif)
Farnell-TL082-Wide-B..> 28-Jul-2014 17:16 6.3M
![[TXT]](http://www.audentia-gestion.fr/icons/text.gif)
Farnell-RF-short-tra..> 28-Jul-2014 17:16 6.3M
![[TXT]](http://www.audentia-gestion.fr/icons/text.gif)
Farnell-maxim-integr..> 28-Jul-2014 17:14 6.4M
![[TXT]](http://www.audentia-gestion.fr/icons/text.gif)
Farnell-TSV6390-TSV6..> 28-Jul-2014 17:14 6.4M
![[TXT]](http://www.audentia-gestion.fr/icons/text.gif)
Farnell-Fast-Charge-..> 28-Jul-2014 17:12 6.4M
![[TXT]](http://www.audentia-gestion.fr/icons/text.gif)
Farnell-NVE-datashee..> 28-Jul-2014 17:12 6.5M
![[TXT]](http://www.audentia-gestion.fr/icons/text.gif)
Farnell-Excalibur-Hi..> 28-Jul-2014 17:10 2.4M
![[TXT]](http://www.audentia-gestion.fr/icons/text.gif)
Farnell-Excalibur-Hi..> 28-Jul-2014 17:10 2.4M
![[TXT]](http://www.audentia-gestion.fr/icons/text.gif)
Farnell-REF102-10V-P..> 28-Jul-2014 17:09 2.4M
![[TXT]](http://www.audentia-gestion.fr/icons/text.gif)
Farnell-TMS320F28055..> 28-Jul-2014 17:09 2.7M
![[TXT]](http://www.audentia-gestion.fr/icons/text.gif)
Farnell-MULTICOMP-Ra..> 22-Jul-2014 12:35 5.9M
![[TXT]](http://www.audentia-gestion.fr/icons/text.gif)
Farnell-RASPBERRY-PI..> 22-Jul-2014 12:35 5.9M
![[TXT]](http://www.audentia-gestion.fr/icons/text.gif)
Farnell-Dremel-Exper..> 22-Jul-2014 12:34 1.6M
![[TXT]](http://www.audentia-gestion.fr/icons/text.gif)
Farnell-STM32F103x8-..> 22-Jul-2014 12:33 1.6M
![[TXT]](http://www.audentia-gestion.fr/icons/text.gif)
Farnell-BD6xxx-PDF.htm 22-Jul-2014 12:33 1.6M
![[TXT]](http://www.audentia-gestion.fr/icons/text.gif)
Farnell-L78S-STMicro..> 22-Jul-2014 12:32 1.6M
![[TXT]](http://www.audentia-gestion.fr/icons/text.gif)
Farnell-RaspiCam-Doc..> 22-Jul-2014 12:32 1.6M
![[TXT]](http://www.audentia-gestion.fr/icons/text.gif)
Farnell-SB520-SB5100..> 22-Jul-2014 12:32 1.6M
![[TXT]](http://www.audentia-gestion.fr/icons/text.gif)
Farnell-iServer-Micr..> 22-Jul-2014 12:32 1.6M
![[TXT]](http://www.audentia-gestion.fr/icons/text.gif)
Farnell-LUMINARY-MIC..> 22-Jul-2014 12:31 3.6M
![[TXT]](http://www.audentia-gestion.fr/icons/text.gif)
Farnell-TEXAS-INSTRU..> 22-Jul-2014 12:31 2.4M
![[TXT]](http://www.audentia-gestion.fr/icons/text.gif)
Farnell-TEXAS-INSTRU..> 22-Jul-2014 12:30 4.6M
![[TXT]](http://www.audentia-gestion.fr/icons/text.gif)
Farnell-CLASS 1-or-2..> 22-Jul-2014 12:30 4.7M
![[TXT]](http://www.audentia-gestion.fr/icons/text.gif)
Farnell-TEXAS-INSTRU..> 22-Jul-2014 12:29 4.8M
![[TXT]](http://www.audentia-gestion.fr/icons/text.gif)
Farnell-Evaluating-t..> 22-Jul-2014 12:28 4.9M
![[TXT]](http://www.audentia-gestion.fr/icons/text.gif)
Farnell-LM3S6952-Mic..> 22-Jul-2014 12:27 5.9M
![[TXT]](http://www.audentia-gestion.fr/icons/text.gif)
Farnell-Keyboard-Mou..> 22-Jul-2014 12:27 5.9M
Farnell-Full-Datashe..> 15-Jul-2014 17:08 951K
![[TXT]](http://www.audentia-gestion.fr/icons/text.gif)
Farnell-pmbta13_pmbt..> 15-Jul-2014 17:06 959K
![[TXT]](http://www.audentia-gestion.fr/icons/text.gif)
Farnell-EE-SPX303N-4..> 15-Jul-2014 17:06 969K
![[TXT]](http://www.audentia-gestion.fr/icons/text.gif)
Farnell-Datasheet-NX..> 15-Jul-2014 17:06 1.0M
![[TXT]](http://www.audentia-gestion.fr/icons/text.gif)
Farnell-Datasheet-Fa..> 15-Jul-2014 17:05 1.0M
![[TXT]](http://www.audentia-gestion.fr/icons/text.gif)
Farnell-MIDAS-un-tra..> 15-Jul-2014 17:05 1.0M
![[TXT]](http://www.audentia-gestion.fr/icons/text.gif)
Farnell-SERIAL-TFT-M..> 15-Jul-2014 17:05 1.0M
![[TXT]](http://www.audentia-gestion.fr/icons/text.gif)
Farnell-MCOC1-Farnel..> 15-Jul-2014 17:05 1.0M
![[TXT]](http://www.audentia-gestion.fr/icons/text.gif)
Farnell-TMR-2-series..> 15-Jul-2014 16:48 787K
![[TXT]](http://www.audentia-gestion.fr/icons/text.gif)
Farnell-DC-DC-Conver..> 15-Jul-2014 16:48 781K
![[TXT]](http://www.audentia-gestion.fr/icons/text.gif)
Farnell-Full-Datashe..> 15-Jul-2014 16:47 803K
![[TXT]](http://www.audentia-gestion.fr/icons/text.gif)
Farnell-TMLM-Series-..> 15-Jul-2014 16:47 810K
![[TXT]](http://www.audentia-gestion.fr/icons/text.gif)
Farnell-TEL-5-Series..> 15-Jul-2014 16:47 814K
![[TXT]](http://www.audentia-gestion.fr/icons/text.gif)
Farnell-TXL-series-t..> 15-Jul-2014 16:47 829K
![[TXT]](http://www.audentia-gestion.fr/icons/text.gif)
Farnell-TEP-150WI-Se..> 15-Jul-2014 16:47 837K
![[TXT]](http://www.audentia-gestion.fr/icons/text.gif)
Farnell-AC-DC-Power-..> 15-Jul-2014 16:47 845K
![[TXT]](http://www.audentia-gestion.fr/icons/text.gif)
Farnell-TIS-Instruct..> 15-Jul-2014 16:47 845K
![[TXT]](http://www.audentia-gestion.fr/icons/text.gif)
Farnell-TOS-tracopow..> 15-Jul-2014 16:47 852K
![[TXT]](http://www.audentia-gestion.fr/icons/text.gif)
Farnell-TCL-DC-traco..> 15-Jul-2014 16:46 858K
![[TXT]](http://www.audentia-gestion.fr/icons/text.gif)
Farnell-TIS-series-t..> 15-Jul-2014 16:46 875K
![[TXT]](http://www.audentia-gestion.fr/icons/text.gif)
Farnell-TMR-2-Series..> 15-Jul-2014 16:46 897K
![[TXT]](http://www.audentia-gestion.fr/icons/text.gif)
Farnell-TMR-3-WI-Ser..> 15-Jul-2014 16:46 939K
![[TXT]](http://www.audentia-gestion.fr/icons/text.gif)
Farnell-TEN-8-WI-Ser..> 15-Jul-2014 16:46 939K
![[TXT]](http://www.audentia-gestion.fr/icons/text.gif)
Farnell-Full-Datashe..> 15-Jul-2014 16:46 947K
Farnell-HIP4081A-Int..> 07-Jul-2014 19:47 1.0M
![[TXT]](http://www.audentia-gestion.fr/icons/text.gif)
Farnell-ISL6251-ISL6..> 07-Jul-2014 19:47 1.1M
![[TXT]](http://www.audentia-gestion.fr/icons/text.gif)
Farnell-DG411-DG412-..> 07-Jul-2014 19:47 1.0M
![[TXT]](http://www.audentia-gestion.fr/icons/text.gif)
Farnell-3367-ARALDIT..> 07-Jul-2014 19:46 1.2M
![[TXT]](http://www.audentia-gestion.fr/icons/text.gif)
Farnell-ICM7228-Inte..> 07-Jul-2014 19:46 1.1M
![[TXT]](http://www.audentia-gestion.fr/icons/text.gif)
Farnell-Data-Sheet-K..> 07-Jul-2014 19:46 1.2M
![[TXT]](http://www.audentia-gestion.fr/icons/text.gif)
Farnell-Silica-Gel-M..> 07-Jul-2014 19:46 1.2M
![[TXT]](http://www.audentia-gestion.fr/icons/text.gif)
Farnell-TKC2-Dusters..> 07-Jul-2014 19:46 1.2M
![[TXT]](http://www.audentia-gestion.fr/icons/text.gif)
Farnell-CRC-HANDCLEA..> 07-Jul-2014 19:46 1.2M
![[TXT]](http://www.audentia-gestion.fr/icons/text.gif)
Farnell-760G-French-..> 07-Jul-2014 19:45 1.2M
![[TXT]](http://www.audentia-gestion.fr/icons/text.gif)
Farnell-Decapant-KF-..> 07-Jul-2014 19:45 1.2M
![[TXT]](http://www.audentia-gestion.fr/icons/text.gif)
Farnell-1734-ARALDIT..> 07-Jul-2014 19:45 1.2M
![[TXT]](http://www.audentia-gestion.fr/icons/text.gif)
Farnell-Araldite-Fus..> 07-Jul-2014 19:45 1.2M
![[TXT]](http://www.audentia-gestion.fr/icons/text.gif)
Farnell-fiche-de-don..> 07-Jul-2014 19:44 1.4M
![[TXT]](http://www.audentia-gestion.fr/icons/text.gif)
Farnell-safety-data-..> 07-Jul-2014 19:44 1.4M
![[TXT]](http://www.audentia-gestion.fr/icons/text.gif)
Farnell-A-4-Hardener..> 07-Jul-2014 19:44 1.4M
![[TXT]](http://www.audentia-gestion.fr/icons/text.gif)
Farnell-CC-Debugger-..> 07-Jul-2014 19:44 1.5M
![[TXT]](http://www.audentia-gestion.fr/icons/text.gif)
Farnell-MSP430-Hardw..> 07-Jul-2014 19:43 1.8M
![[TXT]](http://www.audentia-gestion.fr/icons/text.gif)
Farnell-SmartRF06-Ev..> 07-Jul-2014 19:43 1.6M
![[TXT]](http://www.audentia-gestion.fr/icons/text.gif)
Farnell-CC2531-USB-H..> 07-Jul-2014 19:43 1.8M
![[TXT]](http://www.audentia-gestion.fr/icons/text.gif)
Farnell-Alimentation..> 07-Jul-2014 19:43 1.8M
![[TXT]](http://www.audentia-gestion.fr/icons/text.gif)
Farnell-BK889B-PONT-..> 07-Jul-2014 19:42 1.8M
![[TXT]](http://www.audentia-gestion.fr/icons/text.gif)
Farnell-User-Guide-M..> 07-Jul-2014 19:41 2.0M
![[TXT]](http://www.audentia-gestion.fr/icons/text.gif)
Farnell-T672-3000-Se..> 07-Jul-2014 19:41 2.0M
Farnell-0050375063-D..> 18-Jul-2014 17:03 2.5M
![[TXT]](http://www.audentia-gestion.fr/icons/text.gif)
Farnell-Mini-Fit-Jr-..> 18-Jul-2014 17:03 2.5M
![[TXT]](http://www.audentia-gestion.fr/icons/text.gif)
Farnell-43031-0002-M..> 18-Jul-2014 17:03 2.5M
![[TXT]](http://www.audentia-gestion.fr/icons/text.gif)
Farnell-0433751001-D..> 18-Jul-2014 17:02 2.5M
![[TXT]](http://www.audentia-gestion.fr/icons/text.gif)
Farnell-Cube-3D-Prin..> 18-Jul-2014 17:02 2.5M
![[TXT]](http://www.audentia-gestion.fr/icons/text.gif)
Farnell-MTX-Compact-..> 18-Jul-2014 17:01 2.5M
![[TXT]](http://www.audentia-gestion.fr/icons/text.gif)
Farnell-MTX-3250-MTX..> 18-Jul-2014 17:01 2.5M
![[TXT]](http://www.audentia-gestion.fr/icons/text.gif)
Farnell-ATtiny26-L-A..> 18-Jul-2014 17:00 2.6M
![[TXT]](http://www.audentia-gestion.fr/icons/text.gif)
Farnell-MCP3421-Micr..> 18-Jul-2014 17:00 1.2M
![[TXT]](http://www.audentia-gestion.fr/icons/text.gif)
Farnell-LM19-Texas-I..> 18-Jul-2014 17:00 1.2M
![[TXT]](http://www.audentia-gestion.fr/icons/text.gif)
Farnell-Data-Sheet-S..> 18-Jul-2014 17:00 1.2M
![[TXT]](http://www.audentia-gestion.fr/icons/text.gif)
Farnell-LMH6518-Texa..> 18-Jul-2014 16:59 1.3M
![[TXT]](http://www.audentia-gestion.fr/icons/text.gif)
Farnell-AD7719-Low-V..> 18-Jul-2014 16:59 1.4M
![[TXT]](http://www.audentia-gestion.fr/icons/text.gif)
Farnell-DAC8143-Data..> 18-Jul-2014 16:59 1.5M
![[TXT]](http://www.audentia-gestion.fr/icons/text.gif)
Farnell-BGA7124-400-..> 18-Jul-2014 16:59 1.5M
![[TXT]](http://www.audentia-gestion.fr/icons/text.gif)
Farnell-SICK-OPTIC-E..> 18-Jul-2014 16:58 1.5M
![[TXT]](http://www.audentia-gestion.fr/icons/text.gif)
Farnell-LT3757-Linea..> 18-Jul-2014 16:58 1.6M
![[TXT]](http://www.audentia-gestion.fr/icons/text.gif)
Farnell-LT1961-Linea..> 18-Jul-2014 16:58 1.6M
![[TXT]](http://www.audentia-gestion.fr/icons/text.gif)
Farnell-PIC18F2420-2..> 18-Jul-2014 16:57 2.5M
![[TXT]](http://www.audentia-gestion.fr/icons/text.gif)
Farnell-DS3231-DS-PD..> 18-Jul-2014 16:57 2.5M
![[TXT]](http://www.audentia-gestion.fr/icons/text.gif)
Farnell-RDS-80-PDF.htm 18-Jul-2014 16:57 1.3M
![[TXT]](http://www.audentia-gestion.fr/icons/text.gif)
Farnell-AD8300-Data-..> 18-Jul-2014 16:56 1.3M
![[TXT]](http://www.audentia-gestion.fr/icons/text.gif)
Farnell-LT6233-Linea..> 18-Jul-2014 16:56 1.3M
![[TXT]](http://www.audentia-gestion.fr/icons/text.gif)
Farnell-MAX1365-MAX1..> 18-Jul-2014 16:56 1.4M
![[TXT]](http://www.audentia-gestion.fr/icons/text.gif)
Farnell-XPSAF5130-PD..> 18-Jul-2014 16:56 1.4M
![[TXT]](http://www.audentia-gestion.fr/icons/text.gif)
Farnell-DP83846A-DsP..> 18-Jul-2014 16:55 1.5M
![[TXT]](http://www.audentia-gestion.fr/icons/text.gif)
Farnell-Dremel-Exper..> 18-Jul-2014 16:55 1.6M
![[TXT]](http://www.audentia-gestion.fr/icons/text.gif)
Farnell-MCOC1-Farnel..> 16-Jul-2014 09:04 1.0M
![[TXT]](http://www.audentia-gestion.fr/icons/text.gif)
Farnell-SL3S1203_121..> 16-Jul-2014 09:04 1.1M
![[TXT]](http://www.audentia-gestion.fr/icons/text.gif)
Farnell-PN512-Full-N..> 16-Jul-2014 09:03 1.4M
![[TXT]](http://www.audentia-gestion.fr/icons/text.gif)
Farnell-SL3S4011_402..> 16-Jul-2014 09:03 1.1M
![[TXT]](http://www.audentia-gestion.fr/icons/text.gif)
Farnell-LPC408x-7x 3..> 16-Jul-2014 09:03 1.6M
![[TXT]](http://www.audentia-gestion.fr/icons/text.gif)
Farnell-PCF8574-PCF8..> 16-Jul-2014 09:03 1.7M
![[TXT]](http://www.audentia-gestion.fr/icons/text.gif)
Farnell-LPC81xM-32-b..> 16-Jul-2014 09:02 2.0M
![[TXT]](http://www.audentia-gestion.fr/icons/text.gif)
Farnell-LPC1769-68-6..> 16-Jul-2014 09:02 1.9M
![[TXT]](http://www.audentia-gestion.fr/icons/text.gif)
Farnell-Download-dat..> 16-Jul-2014 09:02 2.2M
![[TXT]](http://www.audentia-gestion.fr/icons/text.gif)
Farnell-LPC3220-30-4..> 16-Jul-2014 09:02 2.2M
![[TXT]](http://www.audentia-gestion.fr/icons/text.gif)
Farnell-LPC11U3x-32-..> 16-Jul-2014 09:01 2.4M
![[TXT]](http://www.audentia-gestion.fr/icons/text.gif)
Farnell-SL3ICS1002-1..> 16-Jul-2014 09:01 2.5M
![[TXT]](http://www.audentia-gestion.fr/icons/text.gif)
Farnell-T672-3000-Se..> 08-Jul-2014 18:59 2.0M
![[TXT]](http://www.audentia-gestion.fr/icons/text.gif)
Farnell-tesa®pack63..> 08-Jul-2014 18:56 2.0M
![[TXT]](http://www.audentia-gestion.fr/icons/text.gif)
Farnell-Encodeur-USB..> 08-Jul-2014 18:56 2.0M
![[TXT]](http://www.audentia-gestion.fr/icons/text.gif)
Farnell-CC2530ZDK-Us..> 08-Jul-2014 18:55 2.1M
![[TXT]](http://www.audentia-gestion.fr/icons/text.gif)
Farnell-2020-Manuel-..> 08-Jul-2014 18:55 2.1M
![[TXT]](http://www.audentia-gestion.fr/icons/text.gif)
Farnell-Synchronous-..> 08-Jul-2014 18:54 2.1M
![[TXT]](http://www.audentia-gestion.fr/icons/text.gif)
Farnell-Arithmetic-L..> 08-Jul-2014 18:54 2.1M
![[TXT]](http://www.audentia-gestion.fr/icons/text.gif)
Farnell-NA555-NE555-..> 08-Jul-2014 18:53 2.2M
![[TXT]](http://www.audentia-gestion.fr/icons/text.gif)
Farnell-4-Bit-Magnit..> 08-Jul-2014 18:53 2.2M
![[TXT]](http://www.audentia-gestion.fr/icons/text.gif)
Farnell-LM555-Timer-..> 08-Jul-2014 18:53 2.2M
![[TXT]](http://www.audentia-gestion.fr/icons/text.gif)
Farnell-L293d-Texas-..> 08-Jul-2014 18:53 2.2M
![[TXT]](http://www.audentia-gestion.fr/icons/text.gif)
Farnell-SN54HC244-SN..> 08-Jul-2014 18:52 2.3M
![[TXT]](http://www.audentia-gestion.fr/icons/text.gif)
Farnell-MAX232-MAX23..> 08-Jul-2014 18:52 2.3M
![[TXT]](http://www.audentia-gestion.fr/icons/text.gif)
Farnell-High-precisi..> 08-Jul-2014 18:51 2.3M
![[TXT]](http://www.audentia-gestion.fr/icons/text.gif)
Farnell-SMU-Instrume..> 08-Jul-2014 18:51 2.3M
![[TXT]](http://www.audentia-gestion.fr/icons/text.gif)
Farnell-900-Series-B..> 08-Jul-2014 18:50 2.3M
![[TXT]](http://www.audentia-gestion.fr/icons/text.gif)
Farnell-BA-Series-Oh..> 08-Jul-2014 18:50 2.3M
![[TXT]](http://www.audentia-gestion.fr/icons/text.gif)
Farnell-UTS-Series-S..> 08-Jul-2014 18:49 2.5M
![[TXT]](http://www.audentia-gestion.fr/icons/text.gif)
Farnell-270-Series-O..> 08-Jul-2014 18:49 2.3M
![[TXT]](http://www.audentia-gestion.fr/icons/text.gif)
Farnell-UTS-Series-S..> 08-Jul-2014 18:49 2.8M
![[TXT]](http://www.audentia-gestion.fr/icons/text.gif)
Farnell-Tiva-C-Serie..> 08-Jul-2014 18:49 2.6M
![[TXT]](http://www.audentia-gestion.fr/icons/text.gif)
Farnell-UTO-Souriau-..> 08-Jul-2014 18:48 2.8M
![[TXT]](http://www.audentia-gestion.fr/icons/text.gif)
Farnell-Clipper-Seri..> 08-Jul-2014 18:48 2.8M
![[TXT]](http://www.audentia-gestion.fr/icons/text.gif)
Farnell-SOURIAU-Cont..> 08-Jul-2014 18:47 3.0M
![[TXT]](http://www.audentia-gestion.fr/icons/text.gif)
Farnell-851-Series-P..> 08-Jul-2014 18:47 3.0M
Farnell-SL59830-Inte..> 06-Jul-2014 10:07 1.0M
![[TXT]](http://www.audentia-gestion.fr/icons/text.gif)
Farnell-ALF1210-PDF.htm 06-Jul-2014 10:06 4.0M
![[TXT]](http://www.audentia-gestion.fr/icons/text.gif)
Farnell-AD7171-16-Bi..> 06-Jul-2014 10:06 1.0M
![[TXT]](http://www.audentia-gestion.fr/icons/text.gif)
Farnell-Low-Noise-24..> 06-Jul-2014 10:05 1.0M
![[TXT]](http://www.audentia-gestion.fr/icons/text.gif)
Farnell-ESCON-Featur..> 06-Jul-2014 10:05 938K
![[TXT]](http://www.audentia-gestion.fr/icons/text.gif)
Farnell-74LCX573-Fai..> 06-Jul-2014 10:05 1.9M
![[TXT]](http://www.audentia-gestion.fr/icons/text.gif)
Farnell-1N4148WS-Fai..> 06-Jul-2014 10:04 1.9M
![[TXT]](http://www.audentia-gestion.fr/icons/text.gif)
Farnell-FAN6756-Fair..> 06-Jul-2014 10:04 850K
![[TXT]](http://www.audentia-gestion.fr/icons/text.gif)
Farnell-Datasheet-Fa..> 06-Jul-2014 10:04 861K
![[TXT]](http://www.audentia-gestion.fr/icons/text.gif)
Farnell-ES1F-ES1J-fi..> 06-Jul-2014 10:04 867K
![[TXT]](http://www.audentia-gestion.fr/icons/text.gif)
Farnell-QRE1113-Fair..> 06-Jul-2014 10:03 879K
![[TXT]](http://www.audentia-gestion.fr/icons/text.gif)
Farnell-2N7002DW-Fai..> 06-Jul-2014 10:03 886K
![[TXT]](http://www.audentia-gestion.fr/icons/text.gif)
Farnell-FDC2512-Fair..> 06-Jul-2014 10:03 886K
![[TXT]](http://www.audentia-gestion.fr/icons/text.gif)
Farnell-FDV301N-Digi..> 06-Jul-2014 10:03 886K
![[TXT]](http://www.audentia-gestion.fr/icons/text.gif)
Farnell-S1A-Fairchil..> 06-Jul-2014 10:03 896K
![[TXT]](http://www.audentia-gestion.fr/icons/text.gif)
Farnell-BAV99-Fairch..> 06-Jul-2014 10:03 896K
![[TXT]](http://www.audentia-gestion.fr/icons/text.gif)
Farnell-74AC00-74ACT..> 06-Jul-2014 10:03 911K
![[TXT]](http://www.audentia-gestion.fr/icons/text.gif)
Farnell-NaPiOn-Panas..> 06-Jul-2014 10:02 911K
![[TXT]](http://www.audentia-gestion.fr/icons/text.gif)
Farnell-LQ-RELAYS-AL..> 06-Jul-2014 10:02 924K
![[TXT]](http://www.audentia-gestion.fr/icons/text.gif)
Farnell-ev-relays-ae..> 06-Jul-2014 10:02 926K
![[TXT]](http://www.audentia-gestion.fr/icons/text.gif)
Farnell-ESCON-Featur..> 06-Jul-2014 10:02 931K
![[TXT]](http://www.audentia-gestion.fr/icons/text.gif)
Farnell-Amplifier-In..> 06-Jul-2014 10:02 940K
![[TXT]](http://www.audentia-gestion.fr/icons/text.gif)
Farnell-Serial-File-..> 06-Jul-2014 10:02 941K
![[TXT]](http://www.audentia-gestion.fr/icons/text.gif)
Farnell-Both-the-Del..> 06-Jul-2014 10:01 948K
![[TXT]](http://www.audentia-gestion.fr/icons/text.gif)
Farnell-Videk-PDF.htm 06-Jul-2014 10:01 948K
![[TXT]](http://www.audentia-gestion.fr/icons/text.gif)
Farnell-EPCOS-173438..> 04-Jul-2014 10:43 3.3M
![[TXT]](http://www.audentia-gestion.fr/icons/text.gif)
Farnell-Sensorless-C..> 04-Jul-2014 10:42 3.3M
![[TXT]](http://www.audentia-gestion.fr/icons/text.gif)
Farnell-197.31-KB-Te..> 04-Jul-2014 10:42 3.3M
![[TXT]](http://www.audentia-gestion.fr/icons/text.gif)
Farnell-PIC12F609-61..> 04-Jul-2014 10:41 3.7M
![[TXT]](http://www.audentia-gestion.fr/icons/text.gif)
Farnell-PADO-semi-au..> 04-Jul-2014 10:41 3.7M
![[TXT]](http://www.audentia-gestion.fr/icons/text.gif)
Farnell-03-iec-runds..> 04-Jul-2014 10:40 3.7M
![[TXT]](http://www.audentia-gestion.fr/icons/text.gif)
Farnell-ACC-Silicone..> 04-Jul-2014 10:40 3.7M
![[TXT]](http://www.audentia-gestion.fr/icons/text.gif)
Farnell-Series-TDS10..> 04-Jul-2014 10:39 4.0M
![[TXT]](http://www.audentia-gestion.fr/icons/text.gif)
Farnell-03-iec-runds..> 04-Jul-2014 10:40 3.7M
![[TXT]](http://www.audentia-gestion.fr/icons/text.gif)
Farnell-0430300011-D..> 14-Jun-2014 18:13 2.0M
![[TXT]](http://www.audentia-gestion.fr/icons/text.gif)
Farnell-06-6544-8-PD..> 26-Mar-2014 17:56 2.7M
![[TXT]](http://www.audentia-gestion.fr/icons/text.gif)
Farnell-3M-Polyimide..> 21-Mar-2014 08:09 3.9M
![[TXT]](http://www.audentia-gestion.fr/icons/text.gif)
Farnell-3M-VolitionT..> 25-Mar-2014 08:18 3.3M
![[TXT]](http://www.audentia-gestion.fr/icons/text.gif)
Farnell-10BQ060-PDF.htm 14-Jun-2014 09:50 2.4M
![[TXT]](http://www.audentia-gestion.fr/icons/text.gif)
Farnell-10TPB47M-End..> 14-Jun-2014 18:16 3.4M
![[TXT]](http://www.audentia-gestion.fr/icons/text.gif)
Farnell-12mm-Size-In..> 14-Jun-2014 09:50 2.4M
![[TXT]](http://www.audentia-gestion.fr/icons/text.gif)
Farnell-24AA024-24LC..> 23-Jun-2014 10:26 3.1M
![[TXT]](http://www.audentia-gestion.fr/icons/text.gif)
Farnell-50A-High-Pow..> 20-Mar-2014 17:31 2.9M
![[TXT]](http://www.audentia-gestion.fr/icons/text.gif)
Farnell-197.31-KB-Te..> 04-Jul-2014 10:42 3.3M
![[TXT]](http://www.audentia-gestion.fr/icons/text.gif)
Farnell-1907-2006-PD..> 26-Mar-2014 17:56 2.7M
![[TXT]](http://www.audentia-gestion.fr/icons/text.gif)
Farnell-5910-PDF.htm 25-Mar-2014 08:15 3.0M
![[TXT]](http://www.audentia-gestion.fr/icons/text.gif)
Farnell-6517b-Electr..> 29-Mar-2014 11:12 3.3M
![[TXT]](http://www.audentia-gestion.fr/icons/text.gif)
Farnell-A-True-Syste..> 29-Mar-2014 11:13 3.3M
![[TXT]](http://www.audentia-gestion.fr/icons/text.gif)
Farnell-ACC-Silicone..> 04-Jul-2014 10:40 3.7M
![[TXT]](http://www.audentia-gestion.fr/icons/text.gif)
Farnell-AD524-PDF.htm 20-Mar-2014 17:33 2.8M
![[TXT]](http://www.audentia-gestion.fr/icons/text.gif)
Farnell-ADL6507-PDF.htm 14-Jun-2014 18:19 3.4M
![[TXT]](http://www.audentia-gestion.fr/icons/text.gif)
Farnell-ADSP-21362-A..> 20-Mar-2014 17:34 2.8M
![[TXT]](http://www.audentia-gestion.fr/icons/text.gif)
Farnell-ALF1210-PDF.htm 04-Jul-2014 10:39 4.0M
![[TXT]](http://www.audentia-gestion.fr/icons/text.gif)
Farnell-ALF1225-12-V..> 01-Apr-2014 07:40 3.4M
![[TXT]](http://www.audentia-gestion.fr/icons/text.gif)
Farnell-ALF2412-24-V..> 01-Apr-2014 07:39 3.4M
![[TXT]](http://www.audentia-gestion.fr/icons/text.gif)
Farnell-AN10361-Phil..> 23-Jun-2014 10:29 2.1M
![[TXT]](http://www.audentia-gestion.fr/icons/text.gif)
Farnell-ARADUR-HY-13..> 26-Mar-2014 17:55 2.8M
![[TXT]](http://www.audentia-gestion.fr/icons/text.gif)
Farnell-ARALDITE-201..> 21-Mar-2014 08:12 3.7M
![[TXT]](http://www.audentia-gestion.fr/icons/text.gif)
Farnell-ARALDITE-CW-..> 26-Mar-2014 17:56 2.7M
![[TXT]](http://www.audentia-gestion.fr/icons/text.gif)
Farnell-ATMEL-8-bit-..> 19-Mar-2014 18:04 2.1M
![[TXT]](http://www.audentia-gestion.fr/icons/text.gif)
Farnell-ATMEL-8-bit-..> 11-Mar-2014 07:55 2.1M
![[TXT]](http://www.audentia-gestion.fr/icons/text.gif)
Farnell-ATmega640-VA..> 14-Jun-2014 09:49 2.5M
![[TXT]](http://www.audentia-gestion.fr/icons/text.gif)
Farnell-ATtiny20-PDF..> 25-Mar-2014 08:19 3.6M
![[TXT]](http://www.audentia-gestion.fr/icons/text.gif)
Farnell-ATtiny26-L-A..> 13-Jun-2014 18:40 1.8M
![[TXT]](http://www.audentia-gestion.fr/icons/text.gif)
Farnell-Alimentation..> 14-Jun-2014 18:24 2.5M
![[TXT]](http://www.audentia-gestion.fr/icons/text.gif)
Farnell-Alimentation..> 01-Apr-2014 07:42 3.4M
![[TXT]](http://www.audentia-gestion.fr/icons/text.gif)
Farnell-Amplificateu..> 29-Mar-2014 11:11 3.3M
![[TXT]](http://www.audentia-gestion.fr/icons/text.gif)
Farnell-An-Improved-..> 14-Jun-2014 09:49 2.5M
![[TXT]](http://www.audentia-gestion.fr/icons/text.gif)
Farnell-Atmel-ATmega..> 19-Mar-2014 18:03 2.2M
![[TXT]](http://www.audentia-gestion.fr/icons/text.gif)
Farnell-Avvertenze-e..> 14-Jun-2014 18:20 3.3M
![[TXT]](http://www.audentia-gestion.fr/icons/text.gif)
Farnell-BC846DS-NXP-..> 13-Jun-2014 18:42 1.6M
![[TXT]](http://www.audentia-gestion.fr/icons/text.gif)
Farnell-BC847DS-NXP-..> 23-Jun-2014 10:24 3.3M
![[TXT]](http://www.audentia-gestion.fr/icons/text.gif)
Farnell-BF545A-BF545..> 23-Jun-2014 10:28 2.1M
![[TXT]](http://www.audentia-gestion.fr/icons/text.gif)
Farnell-BK2650A-BK26..> 29-Mar-2014 11:10 3.3M
![[TXT]](http://www.audentia-gestion.fr/icons/text.gif)
Farnell-BT151-650R-N..> 13-Jun-2014 18:40 1.7M
![[TXT]](http://www.audentia-gestion.fr/icons/text.gif)
Farnell-BTA204-800C-..> 13-Jun-2014 18:42 1.6M
![[TXT]](http://www.audentia-gestion.fr/icons/text.gif)
Farnell-BUJD203AX-NX..> 13-Jun-2014 18:41 1.7M
![[TXT]](http://www.audentia-gestion.fr/icons/text.gif)
Farnell-BYV29F-600-N..> 13-Jun-2014 18:42 1.6M
![[TXT]](http://www.audentia-gestion.fr/icons/text.gif)
Farnell-BYV79E-serie..> 10-Mar-2014 16:19 1.6M
![[TXT]](http://www.audentia-gestion.fr/icons/text.gif)
Farnell-BZX384-serie..> 23-Jun-2014 10:29 2.1M
![[TXT]](http://www.audentia-gestion.fr/icons/text.gif)
Farnell-Battery-GBA-..> 14-Jun-2014 18:13 2.0M
![[TXT]](http://www.audentia-gestion.fr/icons/text.gif)
Farnell-C.A-6150-C.A..> 14-Jun-2014 18:24 2.5M
![[TXT]](http://www.audentia-gestion.fr/icons/text.gif)
Farnell-C.A 8332B-C...> 01-Apr-2014 07:40 3.4M
![[TXT]](http://www.audentia-gestion.fr/icons/text.gif)
Farnell-CC2560-Bluet..> 29-Mar-2014 11:14 2.8M
![[TXT]](http://www.audentia-gestion.fr/icons/text.gif)
Farnell-CD4536B-Type..> 14-Jun-2014 18:13 2.0M
![[TXT]](http://www.audentia-gestion.fr/icons/text.gif)
Farnell-CIRRUS-LOGIC..> 10-Mar-2014 17:20 2.1M
![[TXT]](http://www.audentia-gestion.fr/icons/text.gif)
Farnell-CS5532-34-BS..> 01-Apr-2014 07:39 3.5M
![[TXT]](http://www.audentia-gestion.fr/icons/text.gif)
Farnell-Cannon-ZD-PD..> 11-Mar-2014 08:13 2.8M
![[TXT]](http://www.audentia-gestion.fr/icons/text.gif)
Farnell-Ceramic-tran..> 14-Jun-2014 18:19 3.4M
![[TXT]](http://www.audentia-gestion.fr/icons/text.gif)
Farnell-Circuit-Note..> 26-Mar-2014 18:00 2.8M
![[TXT]](http://www.audentia-gestion.fr/icons/text.gif)
Farnell-Circuit-Note..> 26-Mar-2014 18:00 2.8M
![[TXT]](http://www.audentia-gestion.fr/icons/text.gif)
Farnell-Cles-electro..> 21-Mar-2014 08:13 3.9M
![[TXT]](http://www.audentia-gestion.fr/icons/text.gif)
Farnell-Conception-d..> 11-Mar-2014 07:49 2.4M
![[TXT]](http://www.audentia-gestion.fr/icons/text.gif)
Farnell-Connectors-N..> 14-Jun-2014 18:12 2.1M
![[TXT]](http://www.audentia-gestion.fr/icons/text.gif)
Farnell-Construction..> 14-Jun-2014 18:25 2.5M
![[TXT]](http://www.audentia-gestion.fr/icons/text.gif)
Farnell-Controle-de-..> 11-Mar-2014 08:16 2.8M
![[TXT]](http://www.audentia-gestion.fr/icons/text.gif)
Farnell-Cordless-dri..> 14-Jun-2014 18:13 2.0M
![[TXT]](http://www.audentia-gestion.fr/icons/text.gif)
Farnell-Current-Tran..> 26-Mar-2014 17:58 2.7M
![[TXT]](http://www.audentia-gestion.fr/icons/text.gif)
Farnell-Current-Tran..> 26-Mar-2014 17:58 2.7M
![[TXT]](http://www.audentia-gestion.fr/icons/text.gif)
Farnell-Current-Tran..> 26-Mar-2014 17:59 2.7M
![[TXT]](http://www.audentia-gestion.fr/icons/text.gif)
Farnell-Current-Tran..> 26-Mar-2014 17:59 2.7M
![[TXT]](http://www.audentia-gestion.fr/icons/text.gif)
Farnell-DC-Fan-type-..> 14-Jun-2014 09:48 2.5M
![[TXT]](http://www.audentia-gestion.fr/icons/text.gif)
Farnell-DC-Fan-type-..> 14-Jun-2014 09:51 1.8M
![[TXT]](http://www.audentia-gestion.fr/icons/text.gif)
Farnell-Davum-TMC-PD..> 14-Jun-2014 18:27 2.4M
![[TXT]](http://www.audentia-gestion.fr/icons/text.gif)
Farnell-De-la-puissa..> 29-Mar-2014 11:10 3.3M
![[TXT]](http://www.audentia-gestion.fr/icons/text.gif)
Farnell-Directive-re..> 25-Mar-2014 08:16 3.0M
![[TXT]](http://www.audentia-gestion.fr/icons/text.gif)
Farnell-Documentatio..> 14-Jun-2014 18:26 2.5M
![[TXT]](http://www.audentia-gestion.fr/icons/text.gif)
Farnell-Download-dat..> 13-Jun-2014 18:40 1.8M
![[TXT]](http://www.audentia-gestion.fr/icons/text.gif)
Farnell-ECO-Series-T..> 20-Mar-2014 08:14 2.5M
![[TXT]](http://www.audentia-gestion.fr/icons/text.gif)
Farnell-ELMA-PDF.htm 29-Mar-2014 11:13 3.3M
![[TXT]](http://www.audentia-gestion.fr/icons/text.gif)
Farnell-EMC1182-PDF.htm 25-Mar-2014 08:17 3.0M
![[TXT]](http://www.audentia-gestion.fr/icons/text.gif)
Farnell-EPCOS-173438..> 04-Jul-2014 10:43 3.3M
![[TXT]](http://www.audentia-gestion.fr/icons/text.gif)
Farnell-EPCOS-Sample..> 11-Mar-2014 07:53 2.2M
![[TXT]](http://www.audentia-gestion.fr/icons/text.gif)
Farnell-ES2333-PDF.htm 11-Mar-2014 08:14 2.8M
![[TXT]](http://www.audentia-gestion.fr/icons/text.gif)
Farnell-Ed.081002-DA..> 19-Mar-2014 18:02 2.5M
![[TXT]](http://www.audentia-gestion.fr/icons/text.gif)
Farnell-F28069-Picco..> 14-Jun-2014 18:14 2.0M
![[TXT]](http://www.audentia-gestion.fr/icons/text.gif)
Farnell-F42202-PDF.htm 19-Mar-2014 18:00 2.5M
![[TXT]](http://www.audentia-gestion.fr/icons/text.gif)
Farnell-FDS-ITW-Spra..> 14-Jun-2014 18:22 3.3M
![[TXT]](http://www.audentia-gestion.fr/icons/text.gif)
Farnell-FICHE-DE-DON..> 10-Mar-2014 16:17 1.6M
![[TXT]](http://www.audentia-gestion.fr/icons/text.gif)
Farnell-Fastrack-Sup..> 23-Jun-2014 10:25 3.3M
![[TXT]](http://www.audentia-gestion.fr/icons/text.gif)
Farnell-Ferric-Chlor..> 29-Mar-2014 11:14 2.8M
![[TXT]](http://www.audentia-gestion.fr/icons/text.gif)
Farnell-Fiche-de-don..> 14-Jun-2014 09:47 2.5M
![[TXT]](http://www.audentia-gestion.fr/icons/text.gif)
Farnell-Fiche-de-don..> 14-Jun-2014 18:26 2.5M
![[TXT]](http://www.audentia-gestion.fr/icons/text.gif)
Farnell-Fluke-1730-E..> 14-Jun-2014 18:23 2.5M
![[TXT]](http://www.audentia-gestion.fr/icons/text.gif)
Farnell-GALVA-A-FROI..> 26-Mar-2014 17:56 2.7M
![[TXT]](http://www.audentia-gestion.fr/icons/text.gif)
Farnell-GALVA-MAT-Re..> 26-Mar-2014 17:57 2.7M
![[TXT]](http://www.audentia-gestion.fr/icons/text.gif)
Farnell-GN-RELAYS-AG..> 20-Mar-2014 08:11 2.6M
![[TXT]](http://www.audentia-gestion.fr/icons/text.gif)
Farnell-HC49-4H-Crys..> 14-Jun-2014 18:20 3.3M
![[TXT]](http://www.audentia-gestion.fr/icons/text.gif)
Farnell-HFE1600-Data..> 14-Jun-2014 18:22 3.3M
![[TXT]](http://www.audentia-gestion.fr/icons/text.gif)
Farnell-HI-70300-Sol..> 14-Jun-2014 18:27 2.4M
![[TXT]](http://www.audentia-gestion.fr/icons/text.gif)
Farnell-HUNTSMAN-Adv..> 10-Mar-2014 16:17 1.7M
![[TXT]](http://www.audentia-gestion.fr/icons/text.gif)
Farnell-Haute-vitess..> 11-Mar-2014 08:17 2.4M
![[TXT]](http://www.audentia-gestion.fr/icons/text.gif)
Farnell-IP4252CZ16-8..> 13-Jun-2014 18:41 1.7M
![[TXT]](http://www.audentia-gestion.fr/icons/text.gif)
Farnell-Instructions..> 19-Mar-2014 18:01 2.5M
![[TXT]](http://www.audentia-gestion.fr/icons/text.gif)
Farnell-KSZ8851SNL-S..> 23-Jun-2014 10:28 2.1M
![[TXT]](http://www.audentia-gestion.fr/icons/text.gif)
Farnell-L-efficacite..> 11-Mar-2014 07:52 2.3M
![[TXT]](http://www.audentia-gestion.fr/icons/text.gif)
Farnell-LCW-CQ7P.CC-..> 25-Mar-2014 08:19 3.2M
![[TXT]](http://www.audentia-gestion.fr/icons/text.gif)
Farnell-LME49725-Pow..> 14-Jun-2014 09:49 2.5M
![[TXT]](http://www.audentia-gestion.fr/icons/text.gif)
Farnell-LOCTITE-542-..> 25-Mar-2014 08:15 3.0M
![[TXT]](http://www.audentia-gestion.fr/icons/text.gif)
Farnell-LOCTITE-3463..> 25-Mar-2014 08:19 3.0M
![[TXT]](http://www.audentia-gestion.fr/icons/text.gif)
Farnell-LUXEON-Guide..> 11-Mar-2014 07:52 2.3M
![[TXT]](http://www.audentia-gestion.fr/icons/text.gif)
Farnell-Leaded-Trans..> 23-Jun-2014 10:26 3.2M
![[TXT]](http://www.audentia-gestion.fr/icons/text.gif)
Farnell-Les-derniers..> 11-Mar-2014 07:50 2.3M
![[TXT]](http://www.audentia-gestion.fr/icons/text.gif)
Farnell-Loctite3455-..> 25-Mar-2014 08:16 3.0M
![[TXT]](http://www.audentia-gestion.fr/icons/text.gif)
Farnell-Low-cost-Enc..> 13-Jun-2014 18:42 1.7M
![[TXT]](http://www.audentia-gestion.fr/icons/text.gif)
Farnell-Lubrifiant-a..> 26-Mar-2014 18:00 2.7M
![[TXT]](http://www.audentia-gestion.fr/icons/text.gif)
Farnell-MC3510-PDF.htm 25-Mar-2014 08:17 3.0M
![[TXT]](http://www.audentia-gestion.fr/icons/text.gif)
Farnell-MC21605-PDF.htm 11-Mar-2014 08:14 2.8M
![[TXT]](http://www.audentia-gestion.fr/icons/text.gif)
Farnell-MCF532x-7x-E..> 29-Mar-2014 11:14 2.8M
![[TXT]](http://www.audentia-gestion.fr/icons/text.gif)
Farnell-MICREL-KSZ88..> 11-Mar-2014 07:54 2.2M
![[TXT]](http://www.audentia-gestion.fr/icons/text.gif)
Farnell-MICROCHIP-PI..> 19-Mar-2014 18:02 2.5M
![[TXT]](http://www.audentia-gestion.fr/icons/text.gif)
Farnell-MOLEX-39-00-..> 10-Mar-2014 17:19 1.9M
![[TXT]](http://www.audentia-gestion.fr/icons/text.gif)
Farnell-MOLEX-43020-..> 10-Mar-2014 17:21 1.9M
![[TXT]](http://www.audentia-gestion.fr/icons/text.gif)
Farnell-MOLEX-43160-..> 10-Mar-2014 17:21 1.9M
![[TXT]](http://www.audentia-gestion.fr/icons/text.gif)
Farnell-MOLEX-87439-..> 10-Mar-2014 17:21 1.9M
![[TXT]](http://www.audentia-gestion.fr/icons/text.gif)
Farnell-MPXV7002-Rev..> 20-Mar-2014 17:33 2.8M
![[TXT]](http://www.audentia-gestion.fr/icons/text.gif)
Farnell-MX670-MX675-..> 14-Jun-2014 09:46 2.5M
![[TXT]](http://www.audentia-gestion.fr/icons/text.gif)
Farnell-Microchip-MC..> 13-Jun-2014 18:27 1.8M
![[TXT]](http://www.audentia-gestion.fr/icons/text.gif)
Farnell-Microship-PI..> 11-Mar-2014 07:53 2.2M
![[TXT]](http://www.audentia-gestion.fr/icons/text.gif)
Farnell-Midas-Active..> 14-Jun-2014 18:17 3.4M
![[TXT]](http://www.audentia-gestion.fr/icons/text.gif)
Farnell-Midas-MCCOG4..> 14-Jun-2014 18:11 2.1M
![[TXT]](http://www.audentia-gestion.fr/icons/text.gif)
Farnell-Miniature-Ci..> 26-Mar-2014 17:55 2.8M
![[TXT]](http://www.audentia-gestion.fr/icons/text.gif)
Farnell-Mistral-PDF.htm 14-Jun-2014 18:12 2.1M
![[TXT]](http://www.audentia-gestion.fr/icons/text.gif)
Farnell-Molex-83421-..> 14-Jun-2014 18:17 3.4M
![[TXT]](http://www.audentia-gestion.fr/icons/text.gif)
Farnell-Molex-COMMER..> 14-Jun-2014 18:16 3.4M
![[TXT]](http://www.audentia-gestion.fr/icons/text.gif)
Farnell-Molex-Crimp-..> 10-Mar-2014 16:27 1.7M
![[TXT]](http://www.audentia-gestion.fr/icons/text.gif)
Farnell-Multi-Functi..> 20-Mar-2014 17:38 3.0M
![[TXT]](http://www.audentia-gestion.fr/icons/text.gif)
Farnell-NTE_SEMICOND..> 11-Mar-2014 07:52 2.3M
![[TXT]](http://www.audentia-gestion.fr/icons/text.gif)
Farnell-NXP-74VHC126..> 10-Mar-2014 16:17 1.6M
![[TXT]](http://www.audentia-gestion.fr/icons/text.gif)
Farnell-NXP-BT136-60..> 11-Mar-2014 07:52 2.3M
![[TXT]](http://www.audentia-gestion.fr/icons/text.gif)
Farnell-NXP-PBSS9110..> 10-Mar-2014 17:21 1.9M
![[TXT]](http://www.audentia-gestion.fr/icons/text.gif)
Farnell-NXP-PCA9555 ..> 11-Mar-2014 07:54 2.2M
![[TXT]](http://www.audentia-gestion.fr/icons/text.gif)
Farnell-NXP-PMBFJ620..> 10-Mar-2014 16:16 1.7M
![[TXT]](http://www.audentia-gestion.fr/icons/text.gif)
Farnell-NXP-PSMN1R7-..> 10-Mar-2014 16:17 1.6M
![[TXT]](http://www.audentia-gestion.fr/icons/text.gif)
Farnell-NXP-PSMN7R0-..> 10-Mar-2014 17:19 2.1M
![[TXT]](http://www.audentia-gestion.fr/icons/text.gif)
Farnell-NXP-TEA1703T..> 11-Mar-2014 08:15 2.8M
![[TXT]](http://www.audentia-gestion.fr/icons/text.gif)
Farnell-Nilï¬-sk-E-..> 14-Jun-2014 09:47 2.5M
![[TXT]](http://www.audentia-gestion.fr/icons/text.gif)
Farnell-Novembre-201..> 20-Mar-2014 17:38 3.3M
![[TXT]](http://www.audentia-gestion.fr/icons/text.gif)
Farnell-OMRON-Master..> 10-Mar-2014 16:26 1.8M
![[TXT]](http://www.audentia-gestion.fr/icons/text.gif)
Farnell-OSLON-SSL-Ce..> 19-Mar-2014 18:03 2.1M
![[TXT]](http://www.audentia-gestion.fr/icons/text.gif)
Farnell-OXPCIE958-FB..> 13-Jun-2014 18:40 1.8M
![[TXT]](http://www.audentia-gestion.fr/icons/text.gif)
Farnell-PADO-semi-au..> 04-Jul-2014 10:41 3.7M
![[TXT]](http://www.audentia-gestion.fr/icons/text.gif)
Farnell-PBSS5160T-60..> 19-Mar-2014 18:03 2.1M
![[TXT]](http://www.audentia-gestion.fr/icons/text.gif)
Farnell-PDTA143X-ser..> 20-Mar-2014 08:12 2.6M
![[TXT]](http://www.audentia-gestion.fr/icons/text.gif)
Farnell-PDTB123TT-NX..> 13-Jun-2014 18:43 1.5M
![[TXT]](http://www.audentia-gestion.fr/icons/text.gif)
Farnell-PESD5V0F1BL-..> 13-Jun-2014 18:43 1.5M
![[TXT]](http://www.audentia-gestion.fr/icons/text.gif)
Farnell-PESD9X5.0L-P..> 13-Jun-2014 18:43 1.6M
![[TXT]](http://www.audentia-gestion.fr/icons/text.gif)
Farnell-PIC12F609-61..> 04-Jul-2014 10:41 3.7M
![[TXT]](http://www.audentia-gestion.fr/icons/text.gif)
Farnell-PIC18F2455-2..> 23-Jun-2014 10:27 3.1M
![[TXT]](http://www.audentia-gestion.fr/icons/text.gif)
Farnell-PIC24FJ256GB..> 14-Jun-2014 09:51 2.4M
![[TXT]](http://www.audentia-gestion.fr/icons/text.gif)
Farnell-PMBT3906-PNP..> 13-Jun-2014 18:44 1.5M
![[TXT]](http://www.audentia-gestion.fr/icons/text.gif)
Farnell-PMBT4403-PNP..> 23-Jun-2014 10:27 3.1M
![[TXT]](http://www.audentia-gestion.fr/icons/text.gif)
Farnell-PMEG4002EL-N..> 14-Jun-2014 18:18 3.4M
![[TXT]](http://www.audentia-gestion.fr/icons/text.gif)
Farnell-PMEG4010CEH-..> 13-Jun-2014 18:43 1.6M
![[TXT]](http://www.audentia-gestion.fr/icons/text.gif)
Farnell-Panasonic-15..> 23-Jun-2014 10:29 2.1M
![[TXT]](http://www.audentia-gestion.fr/icons/text.gif)
Farnell-Panasonic-EC..> 20-Mar-2014 17:36 2.6M
![[TXT]](http://www.audentia-gestion.fr/icons/text.gif)
Farnell-Panasonic-EZ..> 20-Mar-2014 08:10 2.6M
![[TXT]](http://www.audentia-gestion.fr/icons/text.gif)
Farnell-Panasonic-Id..> 20-Mar-2014 17:35 2.6M
![[TXT]](http://www.audentia-gestion.fr/icons/text.gif)
Farnell-Panasonic-Ne..> 20-Mar-2014 17:36 2.6M
![[TXT]](http://www.audentia-gestion.fr/icons/text.gif)
Farnell-Panasonic-Ra..> 20-Mar-2014 17:37 2.6M
![[TXT]](http://www.audentia-gestion.fr/icons/text.gif)
Farnell-Panasonic-TS..> 20-Mar-2014 08:12 2.6M
![[TXT]](http://www.audentia-gestion.fr/icons/text.gif)
Farnell-Panasonic-Y3..> 20-Mar-2014 08:11 2.6M
![[TXT]](http://www.audentia-gestion.fr/icons/text.gif)
Farnell-Pico-Spox-Wi..> 10-Mar-2014 16:16 1.7M
![[TXT]](http://www.audentia-gestion.fr/icons/text.gif)
Farnell-Pompes-Charg..> 24-Apr-2014 20:23 3.3M
![[TXT]](http://www.audentia-gestion.fr/icons/text.gif)
Farnell-Ponts-RLC-po..> 14-Jun-2014 18:23 3.3M
![[TXT]](http://www.audentia-gestion.fr/icons/text.gif)
Farnell-Portable-Ana..> 29-Mar-2014 11:16 2.8M
![[TXT]](http://www.audentia-gestion.fr/icons/text.gif)
Farnell-Premier-Farn..> 21-Mar-2014 08:11 3.8M
![[TXT]](http://www.audentia-gestion.fr/icons/text.gif)
Farnell-Produit-3430..> 14-Jun-2014 09:48 2.5M
![[TXT]](http://www.audentia-gestion.fr/icons/text.gif)
Farnell-Proskit-SS-3..> 10-Mar-2014 16:26 1.8M
![[TXT]](http://www.audentia-gestion.fr/icons/text.gif)
Farnell-Puissance-ut..> 11-Mar-2014 07:49 2.4M
![[TXT]](http://www.audentia-gestion.fr/icons/text.gif)
Farnell-Q48-PDF.htm 23-Jun-2014 10:29 2.1M
![[TXT]](http://www.audentia-gestion.fr/icons/text.gif)
Farnell-Radial-Lead-..> 20-Mar-2014 08:12 2.6M
![[TXT]](http://www.audentia-gestion.fr/icons/text.gif)
Farnell-Realiser-un-..> 11-Mar-2014 07:51 2.3M
![[TXT]](http://www.audentia-gestion.fr/icons/text.gif)
Farnell-Reglement-RE..> 21-Mar-2014 08:08 3.9M
![[TXT]](http://www.audentia-gestion.fr/icons/text.gif)
Farnell-Repartiteurs..> 14-Jun-2014 18:26 2.5M
![[TXT]](http://www.audentia-gestion.fr/icons/text.gif)
Farnell-S-TRI-SWT860..> 21-Mar-2014 08:11 3.8M
![[TXT]](http://www.audentia-gestion.fr/icons/text.gif)
Farnell-SB175-Connec..> 11-Mar-2014 08:14 2.8M
![[TXT]](http://www.audentia-gestion.fr/icons/text.gif)
Farnell-SMBJ-Transil..> 29-Mar-2014 11:12 3.3M
![[TXT]](http://www.audentia-gestion.fr/icons/text.gif)
Farnell-SOT-23-Multi..> 11-Mar-2014 07:51 2.3M
![[TXT]](http://www.audentia-gestion.fr/icons/text.gif)
Farnell-SPLC780A1-16..> 14-Jun-2014 18:25 2.5M
![[TXT]](http://www.audentia-gestion.fr/icons/text.gif)
Farnell-SSC7102-Micr..> 23-Jun-2014 10:25 3.2M
![[TXT]](http://www.audentia-gestion.fr/icons/text.gif)
Farnell-SVPE-series-..> 14-Jun-2014 18:15 2.0M
![[TXT]](http://www.audentia-gestion.fr/icons/text.gif)
Farnell-Sensorless-C..> 04-Jul-2014 10:42 3.3M
![[TXT]](http://www.audentia-gestion.fr/icons/text.gif)
Farnell-Septembre-20..> 20-Mar-2014 17:46 3.7M
![[TXT]](http://www.audentia-gestion.fr/icons/text.gif)
Farnell-Serie-PicoSc..> 19-Mar-2014 18:01 2.5M
![[TXT]](http://www.audentia-gestion.fr/icons/text.gif)
Farnell-Serie-Standa..> 14-Jun-2014 18:23 3.3M
![[TXT]](http://www.audentia-gestion.fr/icons/text.gif)
Farnell-Series-2600B..> 20-Mar-2014 17:30 3.0M
![[TXT]](http://www.audentia-gestion.fr/icons/text.gif)
Farnell-Series-TDS10..> 04-Jul-2014 10:39 4.0M
![[TXT]](http://www.audentia-gestion.fr/icons/text.gif)
Farnell-Signal-PCB-R..> 14-Jun-2014 18:11 2.1M
![[TXT]](http://www.audentia-gestion.fr/icons/text.gif)
Farnell-Strangkuhlko..> 21-Mar-2014 08:09 3.9M
![[TXT]](http://www.audentia-gestion.fr/icons/text.gif)
Farnell-Supercapacit..> 26-Mar-2014 17:57 2.7M
![[TXT]](http://www.audentia-gestion.fr/icons/text.gif)
Farnell-TDK-Lambda-H..> 14-Jun-2014 18:21 3.3M
![[TXT]](http://www.audentia-gestion.fr/icons/text.gif)
Farnell-TEKTRONIX-DP..> 10-Mar-2014 17:20 2.0M
![[TXT]](http://www.audentia-gestion.fr/icons/text.gif)
Farnell-Tektronix-AC..> 13-Jun-2014 18:44 1.5M
![[TXT]](http://www.audentia-gestion.fr/icons/text.gif)
Farnell-Telemetres-l..> 20-Mar-2014 17:46 3.7M
![[TXT]](http://www.audentia-gestion.fr/icons/text.gif)
Farnell-Termometros-..> 14-Jun-2014 18:14 2.0M
![[TXT]](http://www.audentia-gestion.fr/icons/text.gif)
Farnell-The-essentia..> 10-Mar-2014 16:27 1.7M
![[TXT]](http://www.audentia-gestion.fr/icons/text.gif)
Farnell-U2270B-PDF.htm 14-Jun-2014 18:15 3.4M
![[TXT]](http://www.audentia-gestion.fr/icons/text.gif)
Farnell-USB-Buccanee..> 14-Jun-2014 09:48 2.5M
![[TXT]](http://www.audentia-gestion.fr/icons/text.gif)
Farnell-USB1T11A-PDF..> 19-Mar-2014 18:03 2.1M
![[TXT]](http://www.audentia-gestion.fr/icons/text.gif)
Farnell-V4N-PDF.htm 14-Jun-2014 18:11 2.1M
![[TXT]](http://www.audentia-gestion.fr/icons/text.gif)
Farnell-WetTantalum-..> 11-Mar-2014 08:14 2.8M
![[TXT]](http://www.audentia-gestion.fr/icons/text.gif)
Farnell-XPS-AC-Octop..> 14-Jun-2014 18:11 2.1M
![[TXT]](http://www.audentia-gestion.fr/icons/text.gif)
Farnell-XPS-MC16-XPS..> 11-Mar-2014 08:15 2.8M
![[TXT]](http://www.audentia-gestion.fr/icons/text.gif)
Farnell-YAGEO-DATA-S..> 11-Mar-2014 08:13 2.8M
![[TXT]](http://www.audentia-gestion.fr/icons/text.gif)
Farnell-ZigBee-ou-le..> 11-Mar-2014 07:50 2.4M
![[TXT]](http://www.audentia-gestion.fr/icons/text.gif)
Farnell-celpac-SUL84..> 21-Mar-2014 08:11 3.8M
![[TXT]](http://www.audentia-gestion.fr/icons/text.gif)
Farnell-china_rohs_o..> 21-Mar-2014 10:04 3.9M
![[TXT]](http://www.audentia-gestion.fr/icons/text.gif)
Farnell-cree-Xlamp-X..> 20-Mar-2014 17:34 2.8M
![[TXT]](http://www.audentia-gestion.fr/icons/text.gif)
Farnell-cree-Xlamp-X..> 20-Mar-2014 17:35 2.7M
![[TXT]](http://www.audentia-gestion.fr/icons/text.gif)
Farnell-cree-Xlamp-X..> 20-Mar-2014 17:31 2.9M
![[TXT]](http://www.audentia-gestion.fr/icons/text.gif)
Farnell-cree-Xlamp-m..> 20-Mar-2014 17:32 2.9M
![[TXT]](http://www.audentia-gestion.fr/icons/text.gif)
Farnell-cree-Xlamp-m..> 20-Mar-2014 17:32 2.9M
![[TXT]](http://www.audentia-gestion.fr/icons/text.gif)
Farnell-ir1150s_fr.p..> 29-Mar-2014 11:11 3.3M
![[TXT]](http://www.audentia-gestion.fr/icons/text.gif)
Farnell-manual-bus-p..> 10-Mar-2014 16:29 1.9M
![[TXT]](http://www.audentia-gestion.fr/icons/text.gif)
Farnell-propose-plus..> 11-Mar-2014 08:19 2.8M
![[TXT]](http://www.audentia-gestion.fr/icons/text.gif)
Farnell-techfirst_se..> 21-Mar-2014 08:08 3.9M
![[TXT]](http://www.audentia-gestion.fr/icons/text.gif)
Farnell-testo-205-20..> 20-Mar-2014 17:37 3.0M
![[TXT]](http://www.audentia-gestion.fr/icons/text.gif)
Farnell-testo-470-Fo..> 20-Mar-2014 17:38 3.0M
![[TXT]](http://www.audentia-gestion.fr/icons/text.gif)
Farnell-uC-OS-III-Br..> 10-Mar-2014 17:20 2.0M
![[TXT]](http://www.audentia-gestion.fr/icons/text.gif)
Sefram-7866HD.pdf-PD..> 29-Mar-2014 11:46 472K
![[TXT]](http://www.audentia-gestion.fr/icons/text.gif)
Sefram-CAT_ENREGISTR..> 29-Mar-2014 11:46 461K
![[TXT]](http://www.audentia-gestion.fr/icons/text.gif)
Sefram-CAT_MESUREURS..> 29-Mar-2014 11:46 435K
![[TXT]](http://www.audentia-gestion.fr/icons/text.gif)
Sefram-GUIDE_SIMPLIF..> 29-Mar-2014 11:46 481K
![[TXT]](http://www.audentia-gestion.fr/icons/text.gif)
Sefram-GUIDE_SIMPLIF..> 29-Mar-2014 11:46 442K
![[TXT]](http://www.audentia-gestion.fr/icons/text.gif)
Sefram-GUIDE_SIMPLIF..> 29-Mar-2014 11:46 422K
![[TXT]](http://www.audentia-gestion.fr/icons/text.gif)
Sefram-SP270.pdf-PDF..> 29-Mar-2014 11:46 464K
Low Cost, Low Power,
True RMS-to-DC Converter
Data Sheet AD736
Rev. I
Information furnished by Analog Devices is believed to be accurate and reliable. However, no
responsibility is assumed by Analog Devices for its use, nor for any infringements of patents or other
rights of third parties that may result from its use. Specifications subject to change without notice. No
license is granted by implication or otherwise under any patent or patent rights of Analog Devices.
Trademarks and registered trademarks are the property of their respective owners.
One Technology Way, P.O. Box 9106, Norwood, MA 02062-9106, U.S.A.
Tel: 781.329.4700 www.analog.com
Fax: 781.461.3113 ©1988–2012 Analog Devices, Inc. All rights reserved.
FEATURES
Converts an ac voltage waveform to a dc voltage and then converts to the true rms, average rectified, or absolute value
200 mV rms full-scale input range (larger inputs with input attenuator)
High input impedance: 1012 Ω
Low input bias current: 25 pA maximum
High accuracy: ±0.3 mV ± 0.3% of reading
RMS conversion with signal crest factors up to 5
Wide power supply range: +2.8 V, −3.2 V to ±16.5 V
Low power: 200 μA maximum supply current
Buffered voltage output
No external trims needed for specified accuracy
Related device: the AD737—features a power-down control with standby current of only 25 μA; the dc output voltage is negative and the output impedance is 8 kΩ
GENERAL DESCRIPTION
The AD736 is a low power, precision, monolithic true rms-to-dc converter. It is laser trimmed to provide a maximum error of ±0.3 mV ± 0.3% of reading with sine wave inputs. Furthermore, it maintains high accuracy while measuring a wide range of input waveforms, including variable duty-cycle pulses and triac (phase)-controlled sine waves. The low cost and small size of this converter make it suitable for upgrading the performance of non-rms precision rectifiers in many applications. Compared to these circuits, the AD736 offers higher accuracy at an equal or lower cost.
The AD736 can compute the rms value of both ac and dc input voltages. It can also be operated as an ac-coupled device by adding one external capacitor. In this mode, the AD736 can resolve input signal levels of 100 μV rms or less, despite variations in temperature or supply voltage. High accuracy is also maintained for input waveforms with crest factors of 1 to 3. In addition, crest factors as high as 5 can be measured (introducing only 2.5% additional error) at the 200 mV full-scale input level.
The AD736 has its own output buffer amplifier, thereby pro-viding a great deal of design flexibility. Requiring only 200 μA of power supply current, the AD736 is optimized for use in portable multimeters and other battery-powered applications.
FUNCTIONAL BLOCK DIAGRAM
CC8kΩ–VSCAVCOMVINCAVOUTFULL WAVERECTIFIERRMSCORE8kΩCF(OPT)CFBIASSECTION+VS00834-001
Figure 1.
The AD736 allows the choice of two signal input terminals: a high impedance FET input (1012 Ω) that directly interfaces with High-Z input attenuators and a low impedance input (8 kΩ) that allows the measurement of 300 mV input levels while operating from the minimum power supply voltage of +2.8 V, −3.2 V. The two inputs can be used either single ended or differentially.
The AD736 has a 1% reading error bandwidth that exceeds 10 kHz for the input amplitudes from 20 mV rms to 200 mV rms while consuming only 1 mW.
The AD736 is available in four performance grades. The AD736J and AD736K grades are rated over the 0°C to +70°C and −20°C to +85°C commercial temperature ranges. The AD736A and AD736B grades are rated over the −40°C to +85°C industrial temperature range. The AD736 is available in three low cost, 8-lead packages: PDIP, SOIC, and CERDIP.
PRODUCT HIGHLIGHTS
1. The AD736 is capable of computing the average rectified value, absolute value, or true rms value of various input signals.
2. Only one external component, an averaging capacitor, is required for the AD736 to perform true rms measurement.
3. The low power consumption of 1 mW makes the AD736 suitable for many battery-powered applications.
4. A high input impedance of 1012 Ω eliminates the need for an external buffer when interfacing with input attenuators.
5. A low impedance input is available for those applications that require an input signal up to 300 mV rms operating from low power supply voltages.
MSP430F15x, MSP430F16x, MSP430F161x
MIXED SIGNAL MICROCONTROLLER
SLAS368G − OCTOBER 2002 − REVISED MARCH 2011
POST OFFICE BOX 655303 • DALLAS, TEXAS 75265 1
Low Supply-Voltage Range: 1.8 V to 3.6 V
Ultralow Power Consumption
− Active Mode: 330 μA at 1 MHz, 2.2 V
− Standby Mode: 1.1 μA
− Off Mode (RAM Retention): 0.2 μA
Five Power-Saving Modes
Wake-Up From Standby Mode in
Less Than 6 μs
16-Bit RISC Architecture,
125-ns Instruction Cycle Time
Three-Channel Internal DMA
12-Bit Analog-to-Digital (A/D) Converter
With Internal Reference, Sample-and-Hold,
and Autoscan Feature
Dual 12-Bit Digital-to-Analog (D/A)
Converters With Synchronization
16-Bit Timer_A With Three
Capture/Compare Registers
16-Bit Timer_B With Three or Seven
Capture/Compare-With-Shadow Registers
On-Chip Comparator
Serial Communication Interface (USART0),
Functions as Asynchronous UART or
Synchronous SPI or I2CTM Interface
Serial Communication Interface (USART1),
Functions as Asynchronous UART or
Synchronous SPI Interface
Supply Voltage Supervisor/Monitor With
Programmable Level Detection
Brownout Detector
Bootstrap Loader
I2C is a registered trademark of Philips Incorporated.
Serial Onboard Programming,
No External Programming Voltage Needed,
Programmable Code Protection by Security
Fuse
Family Members Include
− MSP430F155
16KB+256B Flash Memory
512B RAM
− MSP430F156
24KB+256B Flash Memory
1KB RAM
− MSP430F157
32KB+256B Flash Memory,
1KB RAM
− MSP430F167
32KB+256B Flash Memory,
1KB RAM
− MSP430F168
48KB+256B Flash Memory,
2KB RAM
− MSP430F169
60KB+256B Flash Memory,
2KB RAM
− MSP430F1610
32KB+256B Flash Memory
5KB RAM
− MSP430F1611
48KB+256B Flash Memory
10KB RAM
− MSP430F1612
55KB+256B Flash Memory
5KB RAM
Available in 64-Pin QFP Package (PM) and
64-Pin QFN Package (RTD)
For Complete Module Descriptions, See the
MSP430x1xx Family User’s Guide,
Literature Number SLAU049
description
The Texas Instruments MSP430 family of ultralow power microcontrollers consist of several devices featuring
different sets of peripherals targeted for various applications. The architecture, combined with five low power
modes is optimized to achieve extended battery life in portable measurement applications. The device features
a powerful 16-bit RISC CPU, 16-bit registers, and constant generators that contribute to maximum code
efficiency. The digitally controlled oscillator (DCO) allows wake-up from low-power modes to active mode in less
than 6 μs.
This integrated circuit can be damaged by ESD. Texas Instruments recommends that all integrated circuits be handled with
appropriate precautions. Failure to observe proper handling and installation procedures can cause damage. ESD damage can range
from subtle performance degradation to complete device failure. Precision integrated circuits may be more susceptible to damage
because very small parametric changes could cause the device not to meet its published specifications. These devices have limited
built-in ESD protection.
PRODUCTION DATA information is current as of publication date. Copyright © 2011, Texas Instruments Incorporated
Products conform to specifications per the terms of Texas Instruments
standard warranty. Production processing does not necessarily include
testing of all parameters.
Please be aware that an important notice concerning availability, standard warranty, and use in critical applications of
Texas Instruments semiconductor products and disclaimers thereto appears at the end of this data sheet.
MSP430F15x, MSP430F16x, MSP430F161x
MIXED SIGNAL MICROCONTROLLER
SLAS368G − OCTOBER 2002 − REVISED MARCH 2011
2 POST OFFICE BOX 655303 • DALLAS, TEXAS 75265
description (continued)
The MSP430F15x/16x/161x series are microcontroller configurations with two built-in 16-bit timers, a fast 12-bit
A/D converter, dual 12-bit D/A converter, one or two universal serial synchronous/asynchronous
communication interfaces (USART), I2C, DMA, and 48 I/O pins. In addition, the MSP430F161x series offers
extended RAM addressing for memory-intensive applications and large C-stack requirements.
Typical applications include sensor systems, industrial control applications, hand-held meters, etc.
AVAILABLE OPTIONS
T
PACKAGED DEVICES
TA PLASTIC 64-PIN QFP (PM) PLASTIC 64-PIN QFN (RTD)
−40°C to 85°C
MSP430F155IPM
MSP430F156IPM
MSP430F157IPM
MSP430F167IPM
MSP430F168IPM
MSP430F169IPM
MSP430F1610IPM
MSP430F1611IPM
MSP430F1612IPM
MSP430F155IRTD
MSP430F156IRTD
MSP430F157IRTD
MSP430F167IRTD
MSP430F168IRTD
MSP430F169IRTD
MSP430F1610IRTD
MSP430F1611IRTD
MSP430F1612IRTD
† For the most current package and ordering information, see the Package Option Addendum at the end of this
document, or see the TI web site at www.ti.com.
‡ Package drawings, thermal data, and symbolization are available at www.ti.com/packaging.
DEVELOPMENT TOOL SUPPORT
All MSP430 microcontrollers include an Embedded Emulation Module (EEM) allowing advanced debugging
and programming through easy to use development tools. Recommended hardware options include the
following:
Debugging and Programming Interface
− MSP-FET430UIF (USB)
− MSP-FET430PIF (Parallel Port)
Debugging and Programming Interface with Target Board
− MSP-FET430U64 (PM package)
Standalone Target Board
− MSP-TS430PM64 (PM package)
Production Programmer
− MSP-GANG430
MSP430F15x, MSP430F16x, MSP430F161x
MIXED SIGNAL MICROCONTROLLER
SLAS368G − OCTOBER 2002 − REVISED MARCH 2011
POST OFFICE BOX 655303 • DALLAS, TEXAS 75265 3
pin designation, MSP430F155, MSP430F156, and MSP430F157
17 18 19
P5.4/MCLK
P5.3
P5.2
P5.1
P5.0
P4.7/TBCLK
P4.6
P4.5
P4.4
P4.3
P4.2/TB2
P4.1/TB1
P4.0/TB0
P3.7
P3.6
P3.5/URXD0
48
47
46
45
44
43
42
41
40
39
38
37
36
35
34
33
20
1
2
3
4
5
6
7
8
9
10
11
12
13
14
15
16
DVCC
P6.3/A3
P6.4/A4
P6.5/A5
P6.6/A6/DAC0
P6.7/A7/DAC1/SVSIN
VREF+
XIN
XOUT
VeREF+
VREF−/VeREF−
P1.0/TACLK
P1.1/TA0
P1.2/TA1
P1.3/TA2
P1.4/SMCLK
21 22 23 24
64 63 62 61 60 59 58 57 56 55 54
25 26 27 28 29
53 52 51 50 49
30 31 32
PM, RTD PACKAGE
(TOP VIEW)
AVCC
DVSS
AVSS
P6.2/A2
P6.1/A1
P6.0/A0
RST/NMI
TCK
TMS
TDI/TCLK
TDO/TDI
XT2IN
XT2OUT
P5.7/TBOUTH/SVSOUT
P5.6/ACLK
P5.5/SMCLK
P1.5/TA0
P1.6/TA1
P1.7/TA2
P2.0/ACLK
P2.1/TAINCLK
P2.2/CAOUT/TA0
P2.3/CA0/TA1
P2.4/CA1/TA2
P2.5/ROSC
P2.6/ADC12CLK/DMAE0
P2.7/TA0
P3.0/STE0
P3.1/SIMO0/SDA
P3.2/SOMI0
P3.3/UCLK0/SCL
P3.4/UTXD0
MSP430F15x, MSP430F16x, MSP430F161x
MIXED SIGNAL MICROCONTROLLER
SLAS368G − OCTOBER 2002 − REVISED MARCH 2011
4 POST OFFICE BOX 655303 • DALLAS, TEXAS 75265
pin designation, MSP430F167, MSP430F168, MSP430F169
17 18 19
P5.4/MCLK
P5.3/UCLK1
P5.2/SOMI1
P5.1/SIMO1
P5.0/STE1
P4.7/TBCLK
P4.6/TB6
P4.5/TB5
P4.4/TB4
P4.3/TB3
P4.2/TB2
P4.1/TB1
P4.0/TB0
P3.7/URXD1
P3.6/UTXD1
P3.5/URXD0
48
47
46
45
44
43
42
41
40
39
38
37
36
35
34
33
20
1
2
3
4
5
6
7
8
9
10
11
12
13
14
15
16
DVCC
P6.3/A3
P6.4/A4
P6.5/A5
P6.6/A6/DAC0
P6.7/A7/DAC1/SVSIN
VREF+
XIN
XOUT
VeREF+
VREF−/VeREF−
P1.0/TACLK
P1.1/TA0
P1.2/TA1
P1.3/TA2
P1.4/SMCLK
21 22 23 24
64 63 62 61 60 59 58 57 56 55 54
25 26 27 28 29
53 52 51 50 49
30 31 32
PM, RTD PACKAGE
(TOP VIEW)
AVCC
DVSS
AVSS
P6.2/A2
P6.1/A1
P6.0/A0
RST/NMI
TCK
TMS
TDI/TCLK
TDO/TDI
XT2IN
XT2OUT
P5.7/TBOUTH/SVSOUT
P5.6/ACLK
P5.5/SMCLK
P1.5/TA0
P1.6/TA1
P1.7/TA2
P2.0/ACLK
P2.1/TAINCLK
P2.2/CAOUT/TA0
P2.3/CA0/TA1
P2.4/CA1/TA2
P2.5/ROSC
P2.6/ADC12CLK/DMAE0
P2.7/TA0
P3.0/STE0
P3.1/SIMO0/SDA
P3.2/SOMI0
P3.3/UCLK0/SCL
P3.4/UTXD0
MSP430F15x, MSP430F16x, MSP430F161x
MIXED SIGNAL MICROCONTROLLER
SLAS368G − OCTOBER 2002 − REVISED MARCH 2011
POST OFFICE BOX 655303 • DALLAS, TEXAS 75265 5
pin designation, MSP430F1610, MSP430F1611, MSP430F1612
17 18 19
P5.4/MCLK
P5.3/UCLK1
P5.2/SOMI1
P5.1/SIMO1
P5.0/STE1
P4.7/TBCLK
P4.6/TB6
P4.5/TB5
P4.4/TB4
P4.3/TB3
P4.2/TB2
P4.1/TB1
P4.0/TB0
P3.7/URXD1
P3.6/UTXD1
P3.5/URXD0
48
47
46
45
44
43
42
41
40
39
38
37
36
35
34
33
20
1
2
3
4
5
6
7
8
9
10
11
12
13
14
15
16
DVCC
P6.3/A3
P6.4/A4
P6.5/A5
P6.6/A6/DAC0
P6.7/A7/DAC1/SVSIN
VREF+
XIN
XOUT
VeREF+
VREF−/VeREF−
P1.0/TACLK
P1.1/TA0
P1.2/TA1
P1.3/TA2
P1.4/SMCLK
21 22 23 24
64 63 62 61 60 59 58 57 56 55 54
25 26 27 28 29
53 52 51 50 49
30 31 32
PM, RTD PACKAGE
(TOP VIEW)
AVCC
DVSS
AVSS
P6.2/A2
P6.1/A1
P6.0/A0
RST/NMI
TCK
TMS
TDI/TCLK
TDO/TDI
XT2IN
XT2OUT
P5.7/TBOUTH/SVSOUT
P5.6/ACLK
P5.5/SMCLK
P1.5/TA0
P1.6/TA1
P1.7/TA2
P2.0/ACLK
P2.1/TAINCLK
P2.2/CAOUT/TA0
P2.3/CA0/TA1
P2.4/CA1/TA2
P2.5/ROSC
P2.6/ADC12CLK/DMAE0
P2.7/TA0
P3.0/STE0
P3.1/SIMO0/SDA
P3.2/SOMI0
P3.3/UCLK0/SCL
P3.4/UTXD0
MSP430F15x, MSP430F16x, MSP430F161x
MIXED SIGNAL MICROCONTROLLER
SLAS368G − OCTOBER 2002 − REVISED MARCH 2011
6 POST OFFICE BOX 655303 • DALLAS, TEXAS 75265
functional block diagram, MSP430F15x
Oscillator ACLK
SMCLK
CPU
Incl. 16 Reg.
Bus
Conv
MCB
XIN XOUT P2 P3 P4
XT2IN
XT2OUT
TMS
TCK
MDB, 16 Bit
MAB, 16 Bit
MCLK
4
TDI/TCLK
TDO/TDI
P5 P6
MAB,
4 Bit
DVCC DVSS AVCC AVSS RST/NMI
System
Clock
ROSC
P1
32KB Flash
24KB Flash
16KB Flash
1KB RAM
1KB RAM
512B RAM
ADC12
12-Bit
8 Channels
<10μs Conv.
DAC12
12-Bit
2 Channels
Voltage out
DMA
Controller
3 Channels
Watchdog
Timer
15/16-Bit
Timer_B3
3 CC Reg
Shadow
Reg
Timer_A3
3 CC Reg
Test
JTAG
Emulation
Module
I/O Port 1/2
16 I/Os,
with
Interrupt
Capability
I/O Port 3/4
16 I/Os
POR
SVS
Brownout
Comparator
A
USART0
UART Mode
SPI Mode
I2C Mode
I/O Port 5/6
16 I/Os
MDB, 16-Bit MDB, 8 Bit
MAB, 16-Bit
8 8 8 8 8 8
functional block diagram, MSP430F16x
Oscillator ACLK
SMCLK
CPU
Incl. 16 Reg.
Bus
Conv
MCB
XIN XOUT P2 P3 P4
XT2IN
XT2OUT
TMS
TCK
MDB, 16 Bit
MAB, 16 Bit
MCLK
4
TDI/TCLK
TDO/TDI
P5 P6
MAB,
4 Bit
DVCC DVSS AVCC AVSS RST/NMI
System
Clock
ROSC
P1
Hardware
Multiplier
MPY, MPYS
MAC,MACS
60KB Flash
48KB Flash
32KB Flash
2KB RAM
2KB RAM
1KB RAM
ADC12
12-Bit
8 Channels
<10μs Conv.
DAC12
12-Bit
2 Channels
Voltage out
DMA
Controller
3 Channels
Watchdog
Timer
15/16-Bit
Timer_B7
7 CC Reg
Shadow
Reg
Timer_A3
3 CC Reg
Test
JTAG
Emulation
Module
I/O Port 1/2
16 I/Os,
with
Interrupt
Capability
I/O Port 3/4
16 I/Os
POR
SVS
Brownout
Comparator
A
USART0
UART Mode
SPI Mode
I2C Mode
USART1
UART Mode
SPI Mode
I/O Port 5/6
16 I/Os
MDB, 16-Bit MDB, 8 Bit
MAB, 16-Bit
8 8 8 8 8 8
MSP430F15x, MSP430F16x, MSP430F161x
MIXED SIGNAL MICROCONTROLLER
SLAS368G − OCTOBER 2002 − REVISED MARCH 2011
POST OFFICE BOX 655303 • DALLAS, TEXAS 75265 7
functional block diagram, MSP430F161x
Oscillator ACLK
SMCLK
CPU
Incl. 16 Reg.
Bus
Conv
MCB
XIN XOUT P2 P3 P4
XT2IN
XT2OUT
TMS
TCK
MDB, 16 Bit
MAB, 16 Bit
MCLK
4
TDI/TCLK
TDO/TDI
P5 P6
MAB,
4 Bit
DVCC DVSS AVCC AVSS RST/NMI
System
Clock
ROSC
P1
Hardware
Multiplier
MPY, MPYS
MAC,MACS
55KB Flash
48KB Flash
32KB Flash
5KB RAM
10KB RAM
5KB RAM
ADC12
12-Bit
8 Channels
<10μs Conv.
DAC12
12-Bit
2 Channels
Voltage out
DMA
Controller
3 Channels
Watchdog
Timer
15/16-Bit
Timer_B7
7 CC Reg
Shadow
Reg
Timer_A3
3 CC Reg
Test
JTAG
Emulation
Module
I/O Port 1/2
16 I/Os,
with
Interrupt
Capability
I/O Port 3/4
16 I/Os
POR
SVS
Brownout
Comparator
A
USART0
UART Mode
SPI Mode
I2C Mode
USART1
UART Mode
SPI Mode
I/O Port 5/6
16 I/Os
MDB, 16-Bit MDB, 8 Bit
MAB, 16-Bit
8 8 8 8 8 8
MSP430F15x, MSP430F16x, MSP430F161x
MIXED SIGNAL MICROCONTROLLER
SLAS368G − OCTOBER 2002 − REVISED MARCH 2011
8 POST OFFICE BOX 655303 • DALLAS, TEXAS 75265
Terminal Functions
TERMINAL
DESCRIPTION
NAME NO.
I/O AVCC 64 Analog supply voltage, positive terminal. Supplies only the analog portion of ADC12 and DAC12.
AVSS 62 Analog supply voltage, negative terminal. Supplies only the analog portion of ADC12 and DAC12.
DVCC 1 Digital supply voltage, positive terminal. Supplies all digital parts.
DVSS 63 Digital supply voltage, negative terminal. Supplies all digital parts.
P1.0/TACLK 12 I/O General-purpose digital I/O pin/Timer_A, clock signal TACLK input
P1.1/TA0 13 I/O General-purpose digital I/O pin/Timer_A, capture: CCI0A input, compare: Out0 output/BSL transmit
P1.2/TA1 14 I/O General-purpose digital I/O pin/Timer_A, capture: CCI1A input, compare: Out1 output
P1.3/TA2 15 I/O General-purpose digital I/O pin/Timer_A, capture: CCI2A input, compare: Out2 output
P1.4/SMCLK 16 I/O General-purpose digital I/O pin/SMCLK signal output
P1.5/TA0 17 I/O General-purpose digital I/O pin/Timer_A, compare: Out0 output
P1.6/TA1 18 I/O General-purpose digital I/O pin/Timer_A, compare: Out1 output
P1.7/TA2 19 I/O General-purpose digital I/O pin/Timer_A, compare: Out2 output
P2.0/ACLK 20 I/O General-purpose digital I/O pin/ACLK output
P2.1/TAINCLK 21 I/O General-purpose digital I/O pin/Timer_A, clock signal at INCLK
P2.2/CAOUT/TA0 22 I/O General-purpose digital I/O pin/Timer_A, capture: CCI0B input/Comparator_A output/BSL receive
P2.3/CA0/TA1 23 I/O General-purpose digital I/O pin/Timer_A, compare: Out1 output/Comparator_A input
P2.4/CA1/TA2 24 I/O General-purpose digital I/O pin/Timer_A, compare: Out2 output/Comparator_A input
P2.5/Rosc 25 I/O General-purpose digital I/O pin/input for external resistor defining the DCO nominal frequency
P2.6/ADC12CLK/
DMAE0
26 I/O General-purpose digital I/O pin/conversion clock – 12-bit ADC/DMA channel 0 external trigger
P2.7/TA0 27 I/O General-purpose digital I/O pin/Timer_A, compare: Out0 output
P3.0/STE0 28 I/O General-purpose digital I/O pin/slave transmit enable – USART0/SPI mode
P3.1/SIMO0/SDA 29 I/O General-purpose digital I/O pin/slave in/master out of USART0/SPI mode, I2C data − USART0/I2C mode
P3.2/SOMI0 30 I/O General-purpose digital I/O pin/slave out/master in of USART0/SPI mode
P3.3/UCLK0/SCL 31 I/O General-purpose digital I/O pin/external clock input − USART0/UART or SPI mode, clock output –
USART0/SPI mode, I2C clock − USART0/I2C mode
P3.4/UTXD0 32 I/O General-purpose digital I/O pin/transmit data out – USART0/UART mode
P3.5/URXD0 33 I/O General-purpose digital I/O pin/receive data in – USART0/UART mode
P3.6/UTXD1† 34 I/O General-purpose digital I/O pin/transmit data out – USART1/UART mode
P3.7/URXD1† 35 I/O General-purpose digital I/O pin/receive data in – USART1/UART mode
P4.0/TB0 36 I/O General-purpose digital I/O pin/Timer_B, capture: CCI0A/B input, compare: Out0 output
P4.1/TB1 37 I/O General-purpose digital I/O pin/Timer_B, capture: CCI1A/B input, compare: Out1 output
P4.2/TB2 38 I/O General-purpose digital I/O pin/Timer_B, capture: CCI2A/B input, compare: Out2 output
P4.3/TB3† 39 I/O General-purpose digital I/O pin/Timer_B, capture: CCI3A/B input, compare: Out3 output
P4.4/TB4† 40 I/O General-purpose digital I/O pin/Timer_B, capture: CCI4A/B input, compare: Out4 output
P4.5/TB5† 41 I/O General-purpose digital I/O pin/Timer_B, capture: CCI5A/B input, compare: Out5 output
P4.6/TB6† 42 I/O General-purpose digital I/O pin/Timer_B, capture: CCI6A input, compare: Out6 output
P4.7/TBCLK 43 I/O General-purpose digital I/O pin/Timer_B, clock signal TBCLK input
P5.0/STE1† 44 I/O General-purpose digital I/O pin/slave transmit enable – USART1/SPI mode
P5.1/SIMO1† 45 I/O General-purpose digital I/O pin/slave in/master out of USART1/SPI mode
P5.2/SOMI1† 46 I/O General-purpose digital I/O pin/slave out/master in of USART1/SPI mode
P5.3/UCLK1† 47 I/O General-purpose digital I/O pin/external clock input – USART1/UART or SPI mode, clock output –
USART1/SPI mode
† 16x, 161x devices only
MSP430F15x, MSP430F16x, MSP430F161x
MIXED SIGNAL MICROCONTROLLER
SLAS368G − OCTOBER 2002 − REVISED MARCH 2011
POST OFFICE BOX 655303 • DALLAS, TEXAS 75265 9
Terminal Functions (Continued)
TERMINAL
DESCRIPTION
NAME NO.
I/O P5.4/MCLK 48 I/O General-purpose digital I/O pin/main system clock MCLK output
P5.5/SMCLK 49 I/O General-purpose digital I/O pin/submain system clock SMCLK output
P5.6/ACLK 50 I/O General-purpose digital I/O pin/auxiliary clock ACLK output
P5.7/TBOUTH/
SVSOUT
51 I/O General-purpose digital I/O pin/switch all PWM digital output ports to high impedance − Timer_B TB0 to
TB6/SVS comparator output
P6.0/A0 59 I/O General-purpose digital I/O pin/analog input a0 – 12-bit ADC
P6.1/A1 60 I/O General-purpose digital I/O pin/analog input a1 – 12-bit ADC
P6.2/A2 61 I/O General-purpose digital I/O pin/analog input a2 – 12-bit ADC
P6.3/A3 2 I/O General-purpose digital I/O pin/analog input a3 – 12-bit ADC
P6.4/A4 3 I/O General-purpose digital I/O pin/analog input a4 – 12-bit ADC
P6.5/A5 4 I/O General-purpose digital I/O pin/analog input a5 – 12-bit ADC
P6.6/A6/DAC0 5 I/O General-purpose digital I/O pin/analog input a6 – 12-bit ADC/DAC12.0 output
P6.7/A7/DAC1/
SVSIN
6 I/O General-purpose digital I/O pin/analog input a7 – 12-bit ADC/DAC12.1 output/SVS input
RST/NMI 58 I Reset input, nonmaskable interrupt input port, or bootstrap loader start (in Flash devices).
TCK 57 I Test clock. TCK is the clock input port for device programming test and bootstrap loader start
TDI/TCLK 55 I Test data input or test clock input. The device protection fuse is connected to TDI/TCLK.
TDO/TDI 54 I/O Test data output port. TDO/TDI data output or programming data input terminal
TMS 56 I Test mode select. TMS is used as an input port for device programming and test.
VeREF+ 10 I Input for an external reference voltage
VREF+ 7 O Output of positive terminal of the reference voltage in the ADC12
VREF−/VeREF− 11 I Negative terminal for the reference voltage for both sources, the internal reference voltage, or an external
applied reference voltage
XIN 8 I Input port for crystal oscillator XT1. Standard or watch crystals can be connected.
XOUT 9 O Output terminal of crystal oscillator XT1
XT2IN 53 I Input port for crystal oscillator XT2. Only standard crystals can be connected.
XT2OUT 52 O Output terminal of crystal oscillator XT2
QFN Pad NA NA QFN package pad connection to DVSS recommended (RTD package only)
General-Purpose Register
Program Counter
Stack Pointer
Status Register
Constant Generator
General-Purpose Register
General-Purpose Register
General-Purpose Register
PC/R0
SP/R1
SR/CG1/R2
CG2/R3
R4
R5
R12
R13
General-Purpose Register
General-Purpose Register
R6
R7
General-Purpose Register
General-Purpose Register
R8
R9
General-Purpose Register
General-Purpose Register
R10
R11
General-Purpose Register
General-Purpose Register
R14
R15
MSP430F15x, MSP430F16x, MSP430F161x
MIXED SIGNAL MICROCONTROLLER
SLAS368G − OCTOBER 2002 − REVISED MARCH 2011
10 POST OFFICE BOX 655303 • DALLAS, TEXAS 75265
short-form description
CPU
The MSP430 CPU has a 16-bit RISC architecture
that is highly transparent to the application. All
operations, other than program-flow instructions,
are performed as register operations in
conjunction with seven addressing modes for
source operand and four addressing modes for
destination operand.
The CPU is integrated with 16 registers that
provide reduced instruction execution time. The
register-to-register operation execution time is
one cycle of the CPU clock.
Four of the registers, R0 to R3, are dedicated as
program counter, stack pointer, status register,
and constant generator, respectively. The
remaining registers are general-purpose
registers.
Peripherals are connected to the CPU using data,
address, and control buses, and can be handled
with all instructions.
instruction set
The instruction set consists of 51 instructions with
three formats and seven address modes. Each
instruction can operate on word and byte data.
Table 1 shows examples of the three types of
instruction formats; Table 2 shows the address
modes.
Table 1. Instruction Word Formats
Dual operands, source-destination e.g., ADD R4,R5 R4 + R5 −−−> R5
Single operands, destination only e.g., CALL R8 PC −−>(TOS), R8−−> PC
Relative jump, un/conditional e.g., JNE Jump-on-equal bit = 0
Table 2. Address Mode Descriptions
ADDRESS MODE S D SYNTAX EXAMPLE OPERATION
Register MOV Rs,Rd MOV R10,R11 R10 −−> R11
Indexed MOV X(Rn),Y(Rm) MOV 2(R5),6(R6) M(2+R5)−−> M(6+R6)
Symbolic (PC relative) MOV EDE,TONI M(EDE) −−> M(TONI)
Absolute MOV &MEM,&TCDAT M(MEM) −−> M(TCDAT)
Indirect MOV @Rn,Y(Rm) MOV @R10,Tab(R6) M(R10) −−> M(Tab+R6)
Indirect
autoincrement
MOV @Rn+,Rm MOV @R10+,R11
M(R10) −−> R11
R10 + 2−−> R10
Immediate MOV #X,TONI MOV #45,TONI #45 −−> M(TONI)
NOTE: S = source D = destination
MSP430F15x, MSP430F16x, MSP430F161x
MIXED SIGNAL MICROCONTROLLER
SLAS368G − OCTOBER 2002 − REVISED MARCH 2011
POST OFFICE BOX 655303 • DALLAS, TEXAS 75265 11
operating modes
The MSP430 has one active mode and five software selectable low-power modes of operation. An interrupt
event can wake up the device from any of the five low-power modes, service the request, and restore back to
the low-power mode on return from the interrupt program.
The following six operating modes can be configured by software:
Active mode AM
− All clocks are active
Low-power mode 0 (LPM0)
− CPU is disabled
− ACLK and SMCLK remain active. MCLK is disabled
Low-power mode 1 (LPM1)
− CPU is disabled
− ACLK and SMCLK remain active. MCLK is disabled
− DCO’s dc generator is disabled if DCO not used in active mode
Low-power mode 2 (LPM2)
− CPU is disabled
− MCLK and SMCLK are disabled
− DCO’s dc generator remains enabled
− ACLK remains active
Low-power mode 3 (LPM3)
− CPU is disabled
− MCLK and SMCLK are disabled
− DCO’s dc generator is disabled
− ACLK remains active
Low-power mode 4 (LPM4)
− CPU is disabled
− ACLK is disabled
− MCLK and SMCLK are disabled
− DCO’s dc generator is disabled
− Crystal oscillator is stopped
MSP430F15x, MSP430F16x, MSP430F161x
MIXED SIGNAL MICROCONTROLLER
SLAS368G − OCTOBER 2002 − REVISED MARCH 2011
12 POST OFFICE BOX 655303 • DALLAS, TEXAS 75265
interrupt vector addresses
The interrupt vectors and the power-up starting address are located in the address range 0FFFFh to 0FFE0h.
The vector contains the 16-bit address of the appropriate interrupt-handler instruction sequence.
INTERRUPT SOURCE INTERRUPT FLAG SYSTEM INTERRUPT WORD ADDRESS PRIORITY
Power-up
External Reset
Watchdog
Flash memory
WDTIFG
KEYV
(see Note 1)
Reset 0FFFEh 15, highest
NMI
Oscillator Fault
Flash memory access violation
NMIIFG (see Notes 1 and 3)
OFIFG (see Notes 1 and 3)
ACCVIFG (see Notes 1 and 3)
(Non)maskable
(Non)maskable
(Non)maskable
0FFFCh 14
Timer_B7 (see Note 5) TBCCR0 CCIFG
(see Note 2)
Maskable 0FFFAh 13
Timer_B7 (see Note 5)
TBCCR1 to TBCCR6 CCIFGs,
TBIFG
(see Notes 1 and 2)
Maskable 0FFF8h 12
Comparator_A CAIFG Maskable 0FFF6h 11
Watchdog timer WDTIFG Maskable 0FFF4h 10
USART0 receive URXIFG0 Maskable 0FFF2h 9
USART0 transmit
I2C transmit/receive/others
UTXIFG0
I2CIFG (see Note 4)
Maskable 0FFF0h 8
ADC12 ADC12IFG
(see Notes 1 and 2)
Maskable 0FFEEh 7
Timer_A3 TACCR0 CCIFG
(see Note 2)
Maskable 0FFECh 6
Timer_A3
TACCR1 and TACCR2 CCIFGs,
TAIFG
(see Notes 1 and 2)
Maskable 0FFEAh 5
I/O port P1 (eight flags)
P1IFG.0 to P1IFG.7
(see Notes 1 and 2)
Maskable 0FFE8h 4
USART1 receive URXIFG1 Maskable 0FFE6h 3
USART1 transmit UTXIFG1 Maskable 0FFE4h 2
I/O port P2 (eight flags)
P2IFG.0 to P2IFG.7
(see Notes 1 and 2)
Maskable 0FFE2h 1
DAC12
DMA
DAC12_0IFG, DAC12_1IFG
DMA0IFG, DMA1IFG, DMA2IFG
(see Notes 1 and 2)
Maskable 0FFE0h 0, lowest
NOTES: 1. Multiple source flags
2. Interrupt flags are located in the module.
3. (Non)maskable: the individual interrupt-enable bit can disable an interrupt event, but the general-interrupt enable cannot disable it.
4. I2C interrupt flags located in the module
5. Timer_B7 in MSP430F16x/161x family has 7 CCRs; Timer_B3 in MSP430F15x family has 3 CCRs; in Timer_B3 there are only
interrupt flags TBCCR0, 1 and 2 CCIFGs and the interrupt-enable bits TBCCR0, 1 and 2 CCIEs.
MSP430F15x, MSP430F16x, MSP430F161x
MIXED SIGNAL MICROCONTROLLER
SLAS368G − OCTOBER 2002 − REVISED MARCH 2011
POST OFFICE BOX 655303 • DALLAS, TEXAS 75265 13
special function registers
Most interrupt and module-enable bits are collected in the lowest address space. Special-function register bits
not allocated to a functional purpose are not physically present in the device. This arrangement provides simple
software access.
interrupt enable 1 and 2
7 6 5 4 0
UTXIE0 OFIE WDTIE
3 2 1
rw-0 rw-0 rw-0
Address
0h URXIE0 ACCVIE NMIIE
rw-0 rw-0 rw-0
WDTIE: Watchdog timer interrupt enable. Inactive if watchdog mode is selected.
Active if watchdog timer is configured as general-purpose timer.
OFIE: Oscillator fault interrupt enable
NMIIE: Nonmaskable interrupt enable
ACCVIE: Flash memory access violation interrupt enable
URXIE0: USART0: UART and SPI receive-interrupt enable
UTXIE0: USART0: UART and SPI transmit-interrupt enable
7 6 5 4 0
UTXIE1
3 2 1
rw-0 rw-0
Address
01h URXIE1
URXIE1†: USART1: UART and SPI receive interrupt enable
UTXIE1†: USART1: UART and SPI transmit interrupt enable
† URXIE1 and UTXIE1 are not present in MSP430F15x devices.
interrupt flag register 1 and 2
7 6 5 4 0
UTXIFG0 OFIFG WDTIFG
3 2 1
rw-0 rw-1 rw-(0)
Address
02h URXIFG0 NMIIFG
rw-1 rw-0
WDTIFG: Set on watchdog-timer overflow (in watchdog mode) or security key violation
Reset on VCC power-on, or a reset condition at the RST/NMI pin in reset mode
OFIFG: Flag set on oscillator fault
NMIIFG: Set via RST/NMI pin
URXIFG0: USART0: UART and SPI receive flag
UTXIFG0: USART0: UART and SPI transmit flag
7 6 5 4 0
UTXIFG1
3 2 1
rw-1 rw-0
Address
03h URXIFG1
URXIFG1‡: USART1: UART and SPI receive flag
UTXIFG1‡: USART1: UART and SPI transmit flag
‡ URXIFG1 and UTXIFG1 are not present in MSP430F15x devices.
MSP430F15x, MSP430F16x, MSP430F161x
MIXED SIGNAL MICROCONTROLLER
SLAS368G − OCTOBER 2002 − REVISED MARCH 2011
14 POST OFFICE BOX 655303 • DALLAS, TEXAS 75265
module enable registers 1 and 2
7 6 5 4 0
UTXE0
3 2 1
rw-0 rw-0
Address
04h URXE0
USPIE0
URXE0: USART0: UART mode receive enable
UTXE0: USART0: UART mode transmit enable
USPIE0: USART0: SPI mode transmit and receive enable
7 6 5 4 0
UTXE1
3 2 1
rw-0 rw-0
Address
05h URXE1
USPIE1
URXE1†: USART1: UART mode receive enable
UTXE1†: USART1: UART mode transmit enable
USPIE1†: USART1: SPI mode transmit and receive enable
† URXE1, UTXE1, and USPIE1 are not present in MSP430F15x devices.
rw-0:
Legend: rw: Bit Can Be Read and Written
Bit Can Be Read and Written. It Is Reset by PUC.
SFR Bit Not Present in Device
MSP430F15x, MSP430F16x, MSP430F161x
MIXED SIGNAL MICROCONTROLLER
SLAS368G − OCTOBER 2002 − REVISED MARCH 2011
POST OFFICE BOX 655303 • DALLAS, TEXAS 75265 15
memory organization, MSP430F15x
MSP430F155 MSP430F156 MSP430F157
Memory
Main: interrupt vector
Main: code memory
Size
Flash
Flash
16KB
0FFFFh − 0FFE0h
0FFFFh − 0C000h
24KB
0FFFFh − 0FFE0h
0FFFFh − 0A000h
32KB
0FFFFh − 0FFE0h
0FFFFh − 08000h
Information memory Size
Flash
256 Byte
010FFh − 01000h
256 Byte
010FFh − 01000h
256 Byte
010FFh − 01000h
Boot memory Size
ROM
1KB
0FFFh − 0C00h
1KB
0FFFh − 0C00h
1KB
0FFFh − 0C00h
RAM Size 512B
03FFh − 0200h
1KB
05FFh − 0200h
1KB
05FFh − 0200h
Peripherals 16-bit
8-bit
8-bit SFR
01FFh − 0100h
0FFh − 010h
0Fh − 00h
01FFh − 0100h
0FFh − 010h
0Fh − 00h
01FFh − 0100h
0FFh − 010h
0Fh − 00h
memory organization, MSP430F16x
MSP430F167 MSP430F168 MSP430F169
Memory
Main: interrupt vector
Main: code memory
Size
Flash
Flash
32KB
0FFFFh − 0FFE0h
0FFFFh − 08000h
48KB
0FFFFh − 0FFE0h
0FFFFh − 04000h
60KB
0FFFFh − 0FFE0h
0FFFFh − 01100h
Information memory Size
Flash
256 Byte
010FFh − 01000h
256 Byte
010FFh − 01000h
256 Byte
010FFh − 01000h
Boot memory Size
ROM
1KB
0FFFh − 0C00h
1KB
0FFFh − 0C00h
1KB
0FFFh − 0C00h
RAM Size 1KB
05FFh − 0200h
2KB
09FFh − 0200h
2KB
09FFh − 0200h
Peripherals 16-bit
8-bit
8-bit SFR
01FFh − 0100h
0FFh − 010h
0Fh − 00h
01FFh − 0100h
0FFh − 010h
0Fh − 00h
01FFh − 0100h
0FFh − 010h
0Fh − 00h
memory organization, MSP430F161x
MSP430F1610 MSP430F1611 MSP430F1612
Memory
Main: interrupt vector
Main: code memory
Size
Flash
Flash
32KB
0FFFFh − 0FFE0h
0FFFFh − 08000h
48KB
0FFFFh − 0FFE0h
0FFFFh − 04000h
55KB
0FFFFh − 0FFE0h
0FFFFh − 02500h
RAM (Total) Size 5KB
024FFh − 01100h
10KB
038FFh − 01100h
5KB
024FFh − 01100h
Extended Size 3KB
024FFh − 01900h
8KB
038FFh − 01900h
3KB
024FFh − 01900h
Mirrored Size 2KB
018FFh − 01100h
2KB
018FFh − 01100h
2KB
018FFh − 01100h
Information memory Size
Flash
256 Byte
010FFh − 01000h
256 Byte
010FFh − 01000h
256 Byte
010FFh − 01000h
Boot memory Size
ROM
1KB
0FFFh − 0C00h
1KB
0FFFh − 0C00h
1KB
0FFFh − 0C00h
RAM
(mirrored at
018FFh - 01100h)
Size 2KB
09FFh − 0200h
2KB
09FFh − 0200h
2KB
09FFh − 0200h
Peripherals 16-bit
8-bit
8-bit SFR
01FFh − 0100h
0FFh − 010h
0Fh − 00h
01FFh − 0100h
0FFh − 010h
0Fh − 00h
01FFh − 0100h
0FFh − 010h
0Fh − 00h
MSP430F15x, MSP430F16x, MSP430F161x
MIXED SIGNAL MICROCONTROLLER
SLAS368G − OCTOBER 2002 − REVISED MARCH 2011
16 POST OFFICE BOX 655303 • DALLAS, TEXAS 75265
bootstrap loader (BSL)
The MSP430 bootstrap loader (BSL) enables users to program the flash memory or RAM using a UART serial
interface. Access to the MSP430 memory via the BSL is protected by user-defined password. For complete
description of the features of the BSL and its implementation, see the Application report Features of the MSP430
Bootstrap Loader, Literature Number SLAA089.
BSL FUNCTION PM, RTD PACKAGE PINS
Data Transmit 13 - P1.1
Data Receive 22 - P2.2
flash memory
The flash memory can be programmed via the JTAG port, the bootstrap loader, or in-system by the CPU. The
CPU can perform single-byte and single-word writes to the flash memory. Features of the flash memory include:
Flash memory has n segments of main memory and two segments of information memory (A and B) of
128 bytes each. Each segment in main memory is 512 bytes in size.
Segments 0 to n may be erased in one step, or each segment may be individually erased.
Segments A and B can be erased individually, or as a group with segments 0 to n.
Segments A and B are also called information memory.
New devices may have some bytes programmed in the information memory (needed for test during
manufacturing). The user should perform an erase of the information memory prior to the first use.
Segment 0
w/ Interrupt Vectors
Segment 1
Segment 2
Segment n-1
Segment n†
Segment A
Segment B
Main
Memory
Info
Memory
32KB
0FFFFh
0FE00h
0FDFFh
0FC00h
0FBFFh
0FA00h
0F9FFh
48KB
0FFFFh
0FE00h
0FDFFh
0FC00h
0FBFFh
0FA00h
0F9FFh
08400h
083FFh
08200h
081FFh
08000h
024FFh
01100h
010FFh
01080h
0107Fh
01000h
04400h
043FFh
04200h
041FFh
04000h
038FFh
01100h
010FFh
01080h
0107Fh
01000h
RAM
(’F161x
only)
48KB
0FFFFh
0FE00h
0FDFFh
0FC00h
0FBFFh
0FA00h
0F9FFh
60KB
0FFFFh
0FE00h
0FDFFh
0FC00h
0FBFFh
0FA00h
0F9FFh
04400h
043FFh
04200h
041FFh
04000h
010FFh
01080h
0107Fh
01000h
01400h
013FFh
01200h
011FFh
01100h
010FFh
01080h
0107Fh
01000h
24KB
0FFFFh
0FE00h
0FDFFh
0FC00h
0FBFFh
0FA00h
0F9FFh
32KB
0FFFFh
0FE00h
0FDFFh
0FC00h
0FBFFh
0FA00h
0F9FFh
0A400h
0A3FFh
0A200h
0A1FFh
0A000h
010FFh
01080h
0107Fh
01000h
08400h
083FFh
08200h
081FFh
08000h
010FFh
01080h
0107Fh
01000h
16KB
0FFFFh
0FE00h
0FDFFh
0FC00h
0FBFFh
0FA00h
0F9FFh
0C400h
0C3FFh
0C200h
0C1FFh
0C000h
010FFh
01080h
0107Fh
01000h
MSP430F15x and MSP430F16x MSP430F161x
55KB
0FFFFh
0FE00h
0FDFFh
0FC00h
0FBFFh
0FA00h
0F9FFh
02800h
027FFh
02600h
025FFh
02500h
024FFh
01100h
010FFh
01080h
0107Fh
01000h
† MSP430F169 and MSP430F1612 flash segment n = 256 bytes.
MSP430F15x, MSP430F16x, MSP430F161x
MIXED SIGNAL MICROCONTROLLER
SLAS368G − OCTOBER 2002 − REVISED MARCH 2011
POST OFFICE BOX 655303 • DALLAS, TEXAS 75265 17
peripherals
Peripherals are connected to the CPU through data, address, and control busses and can be handled using
all instructions. For complete module descriptions, see the MSP430x1xx Family User’s Guide, literature number
SLAU049.
DMA controller
The DMA controller allows movement of data from one memory address to another without CPU intervention.
For example, the DMA controller can be used to move data from the ADC12 conversion memory to RAM. Using
the DMA controller can increase the throughput of peripheral modules. The DMA controller reduces system
power consumption by allowing the CPU to remain in sleep mode without having to awaken to move data to
or from a peripheral.
oscillator and system clock
The clock system in the MSP430F15x and MSP430F16x(x) family of devices is supported by the basic clock
module that includes support for a 32768-Hz watch crystal oscillator, an internal digitally-controlled oscillator
(DCO) and a high frequency crystal oscillator. The basic clock module is designed to meet the requirements
of both low system cost and low-power consumption. The internal DCO provides a fast turn-on clock source
and stabilizes in less than 6 μs. The basic clock module provides the following clock signals:
Auxiliary clock (ACLK), sourced from a 32768-Hz watch crystal or a high frequency crystal.
Main clock (MCLK), the system clock used by the CPU.
Sub-Main clock (SMCLK), the sub-system clock used by the peripheral modules.
brownout, supply voltage supervisor (SVS)
The brownout circuit is implemented to provide the proper internal reset signal to the device during power on
and power off. The supply voltage supervisor (SVS) circuitry detects if the supply voltage drops below a user
selectable level and supports both supply voltage supervision (the device is automatically reset) and supply
voltage monitoring (SVM, the device is not automatically reset).
The CPU begins code execution after the brownout circuit releases the device reset. However, VCC may not
have ramped to VCC(min) at that time. The user must insure the default DCO settings are not changed until VCC
reaches VCC(min). If desired, the SVS circuit can be used to determine when VCC reaches VCC(min).
digital I/O
There are six 8-bit I/O ports implemented—ports P1 through P6:
All individual I/O bits are independently programmable.
Any combination of input, output, and interrupt conditions is possible.
Edge-selectable interrupt input capability for all the eight bits of ports P1 and P2.
Read/write access to port-control registers is supported by all instructions.
watchdog timer
The primary function of the watchdog timer (WDT) module is to perform a controlled system restart after a
software problem occurs. If the selected time interval expires, a system reset is generated. If the watchdog
function is not needed in an application, the module can be configured as an interval timer and can generate
interrupts at selected time intervals.
hardware multiplier (MSP430F16x/161x only)
The multiplication operation is supported by a dedicated peripheral module. The module performs 1616,
168, 816, and 88 bit operations. The module is capable of supporting signed and unsigned multiplication
as well as signed and unsigned multiply and accumulate operations. The result of an operation can be accessed
immediately after the operands have been loaded into the peripheral registers. No additional clock cycles are
required.
MSP430F15x, MSP430F16x, MSP430F161x
MIXED SIGNAL MICROCONTROLLER
SLAS368G − OCTOBER 2002 − REVISED MARCH 2011
18 POST OFFICE BOX 655303 • DALLAS, TEXAS 75265
USART0
The MSP430F15x and the MSP430F16x(x) have one hardware universal synchronous/asynchronous receive
transmit (USART0) peripheral module that is used for serial data communication. The USART supports
synchronous SPI (3 or 4 pin), asynchronous UART and I2C communication protocols using double-buffered
transmit and receive channels.
The I2C support is compliant with the Philips I2C specification version 2.1 and supports standard mode (up to
100 kbps) and fast mode (up to 400 kbps). In addition, 7-bit and 10-bit device addressing modes are supported,
as well as master and slave modes. The USART0 also supports 16-bit-wide I2C data transfers and has two
dedicated DMA channels to maximize bus throughput. Extensive interrupt capability is also given in the I2C
mode.
USART1 (MSP430F16x/161x only)
The MSP430F16x(x) devices have a second hardware universal synchronous/asynchronous receive transmit
(USART1) peripheral module that is used for serial data communication. The USART supports synchronous
SPI (3 or 4 pin) and asynchronous UART communication protocols, using double-buffered transmit and receive
channels. With the exception of I2C support, operation of USART1 is identical to USART0.
Timer_A3
Timer_A3 is a 16-bit timer/counter with three capture/compare registers. Timer_A3 can support multiple
capture/compares, PWM outputs, and interval timing. Timer_A3 also has extensive interrupt capabilities.
Interrupts may be generated from the counter on overflow conditions and from each of the capture/compare
registers.
TIMER_A3 SIGNAL CONNECTIONS
INPUT PIN
NUMBER
DEVICE INPUT
SIGNAL
MODULE INPUT
NAME MODULE BLOCK
MODULE OUTPUT
SIGNAL
OUTPUT PIN
NUMBER
12 - P1.0 TACLK TACLK
ACLK ACLK
Timer NA
SMCLK SMCLK
21 - P2.1 TAINCLK INCLK
13 - P1.1 TA0 CCI0A 13 - P1.1
22 - P2.2 TA0 CCI0B
CCR0 TA0
17 - P1.5
DVSS GND
27 - P2.7
DVCC VCC
14 - P1.2 TA1 CCI1A 14 - P1.2
CAOUT (internal) CCI1B
CCR1 TA1
18 - P1.6
DVSS GND
23 - P2.3
DVCC VCC ADC12 (internal)
15 - P1.3 TA2 CCI2A 15 - P1.3
ACLK (internal) CCI2B
CCR2 TA2
19 - P1.7
DVSS GND
24 - P2.4
DVCC VCC
Timer_B3 (MSP430F15x only)
Timer_B3 is a 16-bit timer/counter with three capture/compare registers. Timer_B3 can support multiple
capture/compares, PWM outputs, and interval timing. Timer_B3 also has extensive interrupt capabilities.
Interrupts may be generated from the counter on overflow conditions and from each of the capture/compare
registers.
MSP430F15x, MSP430F16x, MSP430F161x
MIXED SIGNAL MICROCONTROLLER
SLAS368G − OCTOBER 2002 − REVISED MARCH 2011
POST OFFICE BOX 655303 • DALLAS, TEXAS 75265 19
Timer_B7 (MSP430F16x/161x only)
Timer_B7 is a 16-bit timer/counter with seven capture/compare registers. Timer_B7 can support multiple
capture/compares, PWM outputs, and interval timing. Timer_B7 also has extensive interrupt capabilities.
Interrupts may be generated from the counter on overflow conditions and from each of the capture/compare
registers.
TIMER_B3/B7 SIGNAL CONNECTIONS†
INPUT PIN
NUMBER
DEVICE INPUT
SIGNAL
MODULE INPUT
NAME MODULE BLOCK
MODULE OUTPUT
SIGNAL
OUTPUT PIN
NUMBER
43 - P4.7 TBCLK TBCLK
ACLK ACLK
Timer NA
SMCLK SMCLK
43 - P4.7 TBCLK INCLK
36 - P4.0 TB0 CCI0A 36 - P4.0
36 - P4.0 TB0 CCI0B
CCR0 TB0
ADC12 (internal)
DVSS GND
DVCC VCC
37 - P4.1 TB1 CCI1A 37 - P4.1
37 - P4.1 TB1 CCI1B
CCR1 TB1
ADC12 (internal)
DVSS GND
DVCC VCC
38 - P4.2 TB2 CCI2A 38 - P4.2
38 - P4.2 TB2 CCI2B
CCR2 TB2
DVSS GND
DVCC VCC
39 - P4.3 TB3 CCI3A 39 - P4.3
39 - P4.3 TB3 CCI3B
CCR3 TB3
DVSS GND
DVCC VCC
40 - P4.4 TB4 CCI4A 40 - P4.4
40 - P4.4 TB4 CCI4B
CCR4 TB4
DVSS GND
DVCC VCC
41 - P4.5 TB5 CCI5A 41 - P4.5
41 - P4.5 TB5 CCI5B
CCR5 TB5
DVSS GND
DVCC VCC
42 - P4.6 TB6 CCI6A 42 - P4.6
ACLK (internal) CCI6B
CCR6 TB6
DVSS GND
DVCC VCC
† Timer_B3 implements three capture/compare blocks (CCR0, CCR1 and CCR2 only).
MSP430F15x, MSP430F16x, MSP430F161x
MIXED SIGNAL MICROCONTROLLER
SLAS368G − OCTOBER 2002 − REVISED MARCH 2011
20 POST OFFICE BOX 655303 • DALLAS, TEXAS 75265
Comparator_A
The primary function of the comparator_A module is to support precision slope analog−to−digital conversions,
battery−voltage supervision, and monitoring of external analog signals.
ADC12
The ADC12 module supports fast, 12-bit analog-to-digital conversions. The module implements a 12-bit SAR
core, sample select control, reference generator and a 16 word conversion-and-control buffer. The
conversion-and-control buffer allows up to 16 independent ADC samples to be converted and stored without
any CPU intervention.
DAC12
The DAC12 module is a 12-bit, R-ladder, voltage output DAC. The DAC12 may be used in 8- or 12-bit mode,
and may be used in conjunction with the DMA controller. When multiple DAC12 modules are present, they may
be grouped together for synchronous operation.
MSP430F15x, MSP430F16x, MSP430F161x
MIXED SIGNAL MICROCONTROLLER
SLAS368G − OCTOBER 2002 − REVISED MARCH 2011
POST OFFICE BOX 655303 • DALLAS, TEXAS 75265 21
peripheral file map
PERIPHERAL FILE MAP
DMA DMA channel 2 transfer size DMA2SZ 01F6h
DMA channel 2 destination address DMA2DA 01F4h
DMA channel 2 source address DMA2SA 01F2h
DMA channel 2 control DMA2CTL 01F0h
DMA channel 1 transfer size DMA1SZ 01EEh
DMA channel 1 destination address DMA1DA 01ECh
DMA channel 1 source address DMA1SA 01EAh
DMA channel 1 control DMA1CTL 01E8h
DMA channel 0 transfer size DMA0SZ 01E6h
DMA channel 0 destination address DMA0DA 01E4h
DMA channel 0 source address DMA0SA 01E2h
DMA channel 0 control DMA0CTL 01E0h
DMA module control 1 DMACTL1 0124h
DMA module control 0 DMACTL0 0122h
DAC12 DAC12_1 data DAC12_1DAT 01CAh
DAC12_1 control DAC12_1CTL 01C2h
DAC12_0 data DAC12_0DAT 01C8h
DAC12_0 control DAC12_0CTL 01C0h
ADC12 Interrupt-vector-word register ADC12IV 01A8h
Inerrupt-enable register ADC12IE 01A6h
Inerrupt-flag register ADC12IFG 01A4h
Control register 1 ADC12CTL1 01A2h
Control register 0 ADC12CTL0 01A0h
Conversion memory 15 ADC12MEM15 015Eh
Conversion memory 14 ADC12MEM14 015Ch
Conversion memory 13 ADC12MEM13 015Ah
Conversion memory 12 ADC12MEM12 0158h
Conversion memory 11 ADC12MEM11 0156h
Conversion memory 10 ADC12MEM10 0154h
Conversion memory 9 ADC12MEM9 0152h
Conversion memory 8 ADC12MEM8 0150h
Conversion memory 7 ADC12MEM7 014Eh
Conversion memory 6 ADC12MEM6 014Ch
Conversion memory 5 ADC12MEM5 014Ah
Conversion memory 4 ADC12MEM4 0148h
Conversion memory 3 ADC12MEM3 0146h
Conversion memory 2 ADC12MEM2 0144h
Conversion memory 1 ADC12MEM1 0142h
Conversion memory 0 ADC12MEM0 0140h
MSP430F15x, MSP430F16x, MSP430F161x
MIXED SIGNAL MICROCONTROLLER
SLAS368G − OCTOBER 2002 − REVISED MARCH 2011
22 POST OFFICE BOX 655303 • DALLAS, TEXAS 75265
peripheral file map (continued)
PERIPHERAL FILE MAP (CONTINUED)
ADC12 ADC memory-control register15 ADC12MCTL15 08Fh
(continued) ADC memory-control register14 ADC12MCTL14 08Eh
ADC memory-control register13 ADC12MCTL13 08Dh
ADC memory-control register12 ADC12MCTL12 08Ch
ADC memory-control register11 ADC12MCTL11 08Bh
ADC memory-control register10 ADC12MCTL10 08Ah
ADC memory-control register9 ADC12MCTL9 089h
ADC memory-control register8 ADC12MCTL8 088h
ADC memory-control register7 ADC12MCTL7 087h
ADC memory-control register6 ADC12MCTL6 086h
ADC memory-control register5 ADC12MCTL5 085h
ADC memory-control register4 ADC12MCTL4 084h
ADC memory-control register3 ADC12MCTL3 083h
ADC memory-control register2 ADC12MCTL2 082h
ADC memory-control register1 ADC12MCTL1 081h
ADC memory-control register0 ADC12MCTL0 080h
Timer_B7/ Capture/compare register 6 TBCCR6 019Eh
Timer_B3
(see Note 1)
Capture/compare register 5 TBCCR5 019Ch
Capture/compare register 4 TBCCR4 019Ah
Capture/compare register 3 TBCCR3 0198h
Capture/compare register 2 TBCCR2 0196h
Capture/compare register 1 TBCCR1 0194h
Capture/compare register 0 TBCCR0 0192h
Timer_B register TBR 0190h
Capture/compare control 6 TBCCTL6 018Eh
Capture/compare control 5 TBCCTL5 018Ch
Capture/compare control 4 TBCCTL4 018Ah
Capture/compare control 3 TBCCTL3 0188h
Capture/compare control 2 TBCCTL2 0186h
Capture/compare control 1 TBCCTL1 0184h
Capture/compare control 0 TBCCTL0 0182h
Timer_B control TBCTL 0180h
Timer_B interrupt vector TBIV 011Eh
Timer_A3 Reserved 017Eh
Reserved 017Ch
Reserved 017Ah
Reserved 0178h
Capture/compare register 2 TACCR2 0176h
Capture/compare register 1 TACCR1 0174h
Capture/compare register 0 TACCR0 0172h
Timer_A register TAR 0170h
Reserved 016Eh
Reserved 016Ch
Reserved 016Ah
Reserved 0168h
NOTE 1: Timer_B7 in MSP430F16x/161x family has seven CCRs, Timer_B3 in MSP430F15x family has three CCRs.
MSP430F15x, MSP430F16x, MSP430F161x
MIXED SIGNAL MICROCONTROLLER
SLAS368G − OCTOBER 2002 − REVISED MARCH 2011
POST OFFICE BOX 655303 • DALLAS, TEXAS 75265 23
peripheral file map (continued)
PERIPHERAL FILE MAP (CONTINUED)
Timer_A3 Capture/compare control 2 TACCTL2 0166h
(continued) Capture/compare control 1 TACCTL1 0164h
Capture/compare control 0 TACCTL0 0162h
Timer_A control TACTL 0160h
Timer_A interrupt vector TAIV 012Eh
Hardware Sum extend SUMEXT 013Eh
Multiplier
(MSP430F16x and
Result high word RESHI 013Ch
MSP430F161x Result low word RESLO 013Ah
only) Second operand OP2 0138h
Multiply signed +accumulate/operand1 MACS 0136h
Multiply+accumulate/operand1 MAC 0134h
Multiply signed/operand1 MPYS 0132h
Multiply unsigned/operand1 MPY 0130h
Flash Flash control 3 FCTL3 012Ch
Flash control 2 FCTL2 012Ah
Flash control 1 FCTL1 0128h
Watchdog Watchdog Timer control WDTCTL 0120h
USART1 Transmit buffer U1TXBUF 07Fh
(MSP430F16x and
MSP430F161x
Receive buffer U1RXBUF 07Eh
only) Baud rate U1BR1 07Dh
Baud rate U1BR0 07Ch
Modulation control U1MCTL 07Bh
Receive control U1RCTL 07Ah
Transmit control U1TCTL 079h
USART control U1CTL 078h
USART0 Transmit buffer U0TXBUF 077h
(UART or
SPI mode)
Receive buffer U0RXBUF 076h
Baud rate U0BR1 075h
Baud rate U0BR0 074h
Modulation control U0MCTL 073h
Receive control U0RCTL 072h
Transmit control U0TCTL 071h
USART control U0CTL 070h
USART0
2
I2C interrupt vector I2CIV 011Ch
(I2C mode) I2C slave address I2CSA 011Ah
I2C own address I2COA 0118h
I2C data I2CDR 076h
I2C SCLL I2CSCLL 075h
I2C SCLH I2CSCLH 074h
I2C PSC I2CPSC 073h
I2C data control I2CDCTL 072h
I2C transfer control I2CTCTL 071h
USART control U0CTL 070h
I2C data count I2CNDAT 052h
I2C interrupt flag I2CIFG 051h
I2C interrupt enable I2CIE 050h
MSP430F15x, MSP430F16x, MSP430F161x
MIXED SIGNAL MICROCONTROLLER
SLAS368G − OCTOBER 2002 − REVISED MARCH 2011
24 POST OFFICE BOX 655303 • DALLAS, TEXAS 75265
peripheral file map (continued)
PERIPHERAL FILE MAP (CONTINUED)
Comparator_A Comparator_A port disable CAPD 05Bh
Comparator_A control2 CACTL2 05Ah
Comparator_A control1 CACTL1 059h
Basic Clock Basic clock system control2 BCSCTL2 058h
Basic clock system control1 BCSCTL1 057h
DCO clock frequency control DCOCTL 056h
BrownOUT, SVS SVS control register (reset by brownout signal) SVSCTL 055h
Port P6 Port P6 selection P6SEL 037h
Port P6 direction P6DIR 036h
Port P6 output P6OUT 035h
Port P6 input P6IN 034h
Port P5 Port P5 selection P5SEL 033h
Port P5 direction P5DIR 032h
Port P5 output P5OUT 031h
Port P5 input P5IN 030h
Port P4 Port P4 selection P4SEL 01Fh
Port P4 direction P4DIR 01Eh
Port P4 output P4OUT 01Dh
Port P4 input P4IN 01Ch
Port P3 Port P3 selection P3SEL 01Bh
Port P3 direction P3DIR 01Ah
Port P3 output P3OUT 019h
Port P3 input P3IN 018h
Port P2 Port P2 selection P2SEL 02Eh
Port P2 interrupt enable P2IE 02Dh
Port P2 interrupt-edge select P2IES 02Ch
Port P2 interrupt flag P2IFG 02Bh
Port P2 direction P2DIR 02Ah
Port P2 output P2OUT 029h
Port P2 input P2IN 028h
Port P1 Port P1 selection P1SEL 026h
Port P1 interrupt enable P1IE 025h
Port P1 interrupt-edge select P1IES 024h
Port P1 interrupt flag P1IFG 023h
Port P1 direction P1DIR 022h
Port P1 output P1OUT 021h
Port P1 input P1IN 020h
Special Functions SFR module enable 2 ME2 005h
SFR module enable 1 ME1 004h
SFR interrupt flag2 IFG2 003h
SFR interrupt flag1 IFG1 002h
SFR interrupt enable2 IE2 001h
SFR interrupt enable1 IE1 000h
MSP430F15x, MSP430F16x, MSP430F161x
MIXED SIGNAL MICROCONTROLLER
SLAS368G − OCTOBER 2002 − REVISED MARCH 2011
POST OFFICE BOX 655303 • DALLAS, TEXAS 75265 25
absolute maximum ratings over operating free-air temperature (unless otherwise noted)†
Voltage applied at VCC to VSS . . . . . . . . . . . . . . . . . . . . . . . . . . . . . . . . . . . . . . . . . . . . . . . . . . . . . . −0.3 V to 4.1 V
Voltage applied to any pin (see Note) . . . . . . . . . . . . . . . . . . . . . . . . . . . . . . . . . . . . . . . . . . −0.3 V to VCC + 0.3 V
Diode current at any device terminal . . . . . . . . . . . . . . . . . . . . . . . . . . . . . . . . . . . . . . . . . . . . . . . . . . . . . . . ±2 mA
Storage temperature, Tstg: Unprogrammed device . . . . . . . . . . . . . . . . . . . . . . . . . . . . . . . . . . . −55°C to 150°C
Programmed device . . . . . . . . . . . . . . . . . . . . . . . . . . . . . . . . . . . . . . . −55°C to 85°C
† Stresses beyond those listed under “absolute maximum ratings” may cause permanent damage to the device. These are stress ratings only, and
functional operation of the device at these or any other conditions beyond those indicated under “recommended operating conditions” is not
implied. Exposure to absolute-maximum-rated conditions for extended periods may affect device reliability.
NOTE: All voltages referenced to VSS. The JTAG fuse-blow voltage, VFB, is allowed to exceed the absolute maximum rating. The voltage is applied
to the TDI/TCLK pin when blowing the JTAG fuse.
recommended operating conditions
MIN NOM MAX UNIT
Supply voltage during program execution,
VCC (AVCC = DVCC = VCC)
MSP430F15x/16x/161x 1.8 3.6 V
Supply voltage during flash memory programming, VCC
(AVCC = DVCC = VCC)
MSP430F15x/16x/161x 2.7 3.6 V
Supply voltage during program execution, SVS enabled
(see Note 1), VCC (AVCC = DVCC = VCC)
MSP430F15x/16x/161x 2 3.6 V
Supply voltage, VSS (AVSS = DVSS = VSS) 0 0 V
Operating free-air temperature range, TA MSP430F15x/16x/161x −40 85 °C
LFXT1 t l f f
LF selected, XTS=0 Watch crystal 32.768 kHz
crystal frequency, f(LFXT1)
XT1 selected, XTS=1 Ceramic resonator 450 8000 kHz
(see Notes 2 and 3)
XT1 selected, XTS=1 Crystal 1000 8000 kHz
XT2 crystal frequency f
Ceramic resonator 450 8000
frequency, f(XT2) kHz
Crystal 1000 8000
Processor frequency (signal MCLK) f
VCC = 1.8 V DC 4.15
MCLK), f(System) MHz
VCC = 3.6 V DC 8
NOTES: 1. The minimum operating supply voltage is defined according to the trip point where POR is going active by decreasing the supply
voltage. POR is going inactive when the VCC is raised above the minimum supply voltage plus the hysteresis of the SVS circuitry.
2. In LF mode, the LFXT1 oscillator requires a watch crystal. A 5.1-MΩ resistor from XOUT to VSS is recommended when
VCC < 2.5 V. In XT1 mode, the LFXT1 and XT2 oscillators accept a ceramic resonator or crystal up to 4.15 MHz at VCC ≥ 2.2 V. In
XT1 mode, the LFXT1 and XT2 oscillators accept a ceramic resonator or crystal up to 8 MHz at VCC ≥ 2.8 V.
3. In LF mode, the LFXT1 oscillator requires a watch crystal. In XT1 mode, LFXT1 accepts a ceramic resonator or a crystal.
f (MHz)
1.8 V 2.7 V 3 V 3.6 V
ÎÎÎÎÎ
ÎÎÎÎÎ
ÎÎÎÎÎ
ÎÎÎÎÎ
ÎÎÎÎÎ
ÎÎÎÎÎ
ÎÎÎÎÎ
ÎÎÎÎÎ
4.15 MHz
8.0 MHz
Supply Voltage − V
Supply voltage range,
’F15x/16x/161x,
during flash memory programming
Supply voltage range,
’F15x/16x/161x, during
program execution
Figure 1. Frequency vs Supply Voltage, MSP430F15x/16x/161x
MSP430F15x, MSP430F16x, MSP430F161x
MIXED SIGNAL MICROCONTROLLER
SLAS368G − OCTOBER 2002 − REVISED MARCH 2011
26 POST OFFICE BOX 655303 • DALLAS, TEXAS 75265
electrical characteristics over recommended operating free-air temperature (unless otherwise
noted)
MSP430F15x/16x supply current into AVCC + DVCC excluding external current (AVCC = DVCC = VCC)
PARAMETER TEST CONDITIONS VCC MIN TYP MAX UNIT
Active mode, (see Note 1)
f(MCLK) = f(SMCLK) = 1 MHz,
T 40°C to 85°C
2.2 V 330 400
A
I
f(ACLK) = 32,768 Hz
XTS=0, SELM=(0,1)
TA = −3 V 500 600
μA
I(AM) Active mode, (see Note 1)
f(MCLK) = f(SMCLK) = 4,096 Hz,
T 40°C to 85°C
2.2 V 2.5 7
A
f(ACLK) = 4,096 Hz
XTS=0, SELM=3
TA = −3 V 9 20
μA
I
Low-power mode, (LPM0)
f(MCLK) = 0 MHz, f(SMCLK) = 1 MHz,
f 32 768 Hz
T 40°C to 85°C
2.2 V 50 60
I(LPM0) A
( ) ( )
f(ACLK) = 32,768 XTS=0, SELM=(0,1)
(see Note 1)
TA = −3 V 75 90
μA
I
Low-power mode, (LPM2),
f f 0 MHz T 40°C to 85°C
2.2 V 11 14
I(LPM2) f(MCLK) = f(SMCLK) = MHz, A
f(ACLK) = 32.768 Hz, SCG0 = 0
TA = −3 V 17 22
μA
TA = −40°C 1.1 1.6
Low-power mode (LPM3)
TA = 25°C 2.2 V
1.1 1.6
I
mode, f(MCLK) = f(SMCLK) = 0 MHz,
TA = 85°C
2.2 3.0
I(LPM3) A
f(ACLK)
= 32,768 Hz, SCG0 = 1
( Nt 2)
TA = −40°C 2.2 2.8
μA
(see Note TA = 25°C 3 V
2.0 2.6
TA = 85°C
3.0 4.3
Low-power mode, (LPM4)
TA = −40°C 0.1 0.5
I(LPM4)
f(MCLK) = 0 MHz, f(SMCLK) = 0 MHz, TA = 25°C 2.2V / 3 V
0.2 0.5 μA
f(ACLK) = 0 Hz, SCG0 = 1 TA = 85°C
1.3 2.5
NOTES: 1. Timer_B is clocked by f(DCOCLK) = 1 MHz. All inputs are tied to 0 V or to VCC. Outputs do not source or sink any current.
2. WDT is clocked by f(ACLK) = 32,768 Hz. All inputs are tied to 0 V or to VCC. Outputs do not source or sink any current. The current
consumption in LPM2 and LPM3 are measured with ACLK selected.
Current consumption of active mode versus system frequency
I(AM) = I(AM) [1 MHz] × f(System) [MHz]
Current consumption of active mode versus supply voltage
I(AM) = I(AM) [3 V] + 210 μA/V × (VCC – 3 V)
MSP430F15x, MSP430F16x, MSP430F161x
MIXED SIGNAL MICROCONTROLLER
SLAS368G − OCTOBER 2002 − REVISED MARCH 2011
POST OFFICE BOX 655303 • DALLAS, TEXAS 75265 27
electrical characteristics over recommended operating free-air temperature (unless otherwise
noted)
MSP430F161x supply current into AVCC + DVCC excluding external current (AVCC = DVCC = VCC)
PARAMETER TEST CONDITIONS VCC MIN TYP MAX UNIT
Active mode, (see Note 1)
f(MCLK) = f(SMCLK) = 1 MHz,
T 40°C to 85°C
2.2 V 330 400
A
I
f(ACLK) = 32,768 Hz
XTS=0, SELM=(0,1)
TA = −3 V 500 600
μA
I(AM) Active mode, (see Note 1)
f(MCLK) = f(SMCLK) = 4,096 Hz,
T 40°C to 85°C
2.2 V 2.5 7
A
f(ACLK) = 4,096 Hz
XTS=0, SELM=3
TA = −3 V 9 20
μA
I
Low-power mode, (LPM0)
f(MCLK) = 0 MHz, f(SMCLK) = 1 MHz,
f 32 768 Hz
T 40°C to 85°C
2.2 V 50 60
I(LPM0) A
( ) ( )
f(ACLK) = 32,768 XTS=0, SELM=(0,1)
(see Note 1)
TA = −3 V 75 95
μA
I
Low-power mode, (LPM2),
f f 0 MHz T 40°C to 85°C
2.2 V 11 14
I(LPM2) f(MCLK) = f(SMCLK) = MHz, A
f(ACLK) = 32.768 Hz, SCG0 = 0
TA = −3 V 17 22
μA
TA = −40°C 1.3 1.6
Low-power mode (LPM3)
TA = 25°C 2.2 V
1.3 1.6
I
mode, f(MCLK) = f(SMCLK) = 0 MHz,
TA = 85°C
3.0 6.0
I(LPM3) A
f(ACLK)
= 32,768 Hz, SCG0 = 1
( Nt 2)
TA = −40°C 2.6 3.0
μA
(see Note TA = 25°C 3 V
2.6 3.0
TA = 85°C
4.4 8.0
Low-power mode, (LPM4)
TA = −40°C 0.2 0.5
I(LPM4)
f(MCLK) = 0 MHz, f(SMCLK) = 0 MHz, TA = 25°C 2.2V / 3 V
0.2 0.5 μA
f(ACLK) = 0 Hz, SCG0 = 1 TA = 85°C
2.0 5.0
NOTES: 1. Timer_B is clocked by f(DCOCLK) = 1 MHz. All inputs are tied to 0 V or to VCC. Outputs do not source or sink any current.
2. WDT is clocked by f(ACLK) = 32,768 Hz. All inputs are tied to 0 V or to VCC. Outputs do not source or sink any current. The current
consumption in LPM2 and LPM3 are measured with ACLK selected.
Current consumption of active mode versus system frequency
I(AM) = I(AM) [1 MHz] × f(System) [MHz]
Current consumption of active mode versus supply voltage
I(AM) = I(AM) [3 V] + 210 μA/V × (VCC – 3 V)
MSP430F15x, MSP430F16x, MSP430F161x
MIXED SIGNAL MICROCONTROLLER
SLAS368G − OCTOBER 2002 − REVISED MARCH 2011
28 POST OFFICE BOX 655303 • DALLAS, TEXAS 75265
electrical characteristics over recommended operating free-air temperature (unless otherwise
noted) (continued)
Schmitt-trigger inputs − ports P1, P2, P3, P4, P5, P6, RST/NMI, JTAG (TCK, TMS, TDI/TCLK, TDO/TDI)
PARAMETER VCC MIN TYP MAX UNIT
V Positive going input threshold voltage
2.2 V 1.1 1.5
VIT+ Positive-V
3 V 1.5 1.98
V Negative going input threshold voltage
2.2 V 0.4 0.9
VIT− Negative-V
3 V 0.9 1.3
V Input voltage hysteresis (V V )
2.2 V 0.3 1.1
Vhys VIT+ − VIT−) V
3 V 0.5 1
inputs Px.x, TAx, TBx
PARAMETER TEST CONDITIONS VCC MIN TYP MAX UNIT
t External interrupt timing
Port P1, P2: P1.x to P2.x, external trigger
2.2 V 62
t(int) ns
signal for the interrupt flag (see Note 1) 3 V 50
TA0, TA1, TA2 2.2 V 62
t(cap) Timer_A, Timer_B capture timing TB0, TB1, TB2, TB3, TB4, TB5, TB6
(see Note 2)
3 V 50
ns
f(TAext) Timer_A, Timer_B clock frequency
TACLK TBCLK INCLK: t = t
2.2 V 8
MHz
f(TBext)
externally applied to pin
TACLK, TBCLK, t(H) t(L) 3 V 10
f(TAint)
Timer A Timer B clock frequency SMCLK or ACLK signal selected
2.2 V 8
MHz
f(TBint)
Timer_A, Timer_3 V 10
NOTES: 1. The external signal sets the interrupt flag every time the minimum t(int) parameters are met. It may be set even with trigger signals
shorter than t(int).
2. Seven capture/compare registers in ’F16x/161x and three capture/compare registers in ’F15x.
leakage current − ports P1, P2, P3, P4, P5, P6 (see Note 1)
PARAMETER TEST CONDITIONS VCC MIN TYP MAX UNIT
Ilkg(Px.y)
Leakage
current Port Px V(Px.y) (see Note 2) 2.2 V/3 V ±50 nA
NOTES: 1. The leakage current is measured with VSS or VCC applied to the corresponding pin(s), unless otherwise noted.
2. The port pin must be selected as input.
MSP430F15x, MSP430F16x, MSP430F161x
MIXED SIGNAL MICROCONTROLLER
SLAS368G − OCTOBER 2002 − REVISED MARCH 2011
POST OFFICE BOX 655303 • DALLAS, TEXAS 75265 29
electrical characteristics over recommended operating free-air temperature (unless otherwise
noted) (continued)
outputs − ports P1, P2, P3, P4, P5, P6
PARAMETER TEST CONDITIONS MIN TYP MAX UNIT
IOH(max) = −1.5 mA, VCC = 2.2 V, See Note 1 VCC−0.25 VCC
V High level output voltage
IOH(max) = −6 mA, VCC = 2.2 V, See Note 2 VCC−0.6 VCC
VOH High-V
IOH(max) = −1.5 mA, VCC = 3 V, See Note 1 VCC−0.25 VCC
IOH(max) = −6 mA, VCC = 3 V, See Note 2 VCC−0.6 VCC
IOL(max) = 1.5 mA, VCC = 2.2 V, See Note 1 VSS VSS+0.25
V Low level output voltage
IOL(max) = 6 mA, VCC = 2.2 V, See Note 2 VSS VSS+0.6
VOL Low-V
IOL(max) = 1.5 mA, VCC = 3 V, See Note 1 VSS VSS+0.25
IOL(max) = 6 mA, VCC = 3 V, See Note 2 VSS VSS+0.6
NOTES: 1. The maximum total current, IOH(max) and IOL(max), for all outputs combined, should not exceed ±12 mA to satisfy the maximum
specified voltage drop.
2. The maximum total current, IOH(max) and IOL(max), for all outputs combined, should not exceed ±48 mA to satisfy the maximum
specified voltage drop.
output frequency
PARAMETER TEST CONDITIONS MIN TYP MAX UNIT
f (1 ≤ x ≤ 6 0≤ y ≤ 7)
CL = 20 pF,
f(Px.y) 6, 0 ≤ V 2 2 V / 3 V DC f MHz
IL = ±1.5 mA VCC = 2.2 fSystem f(ACLK)
f
P2.0/ACLK, P5.6/ACLK
P5 4/MCLK C 20 pF V 2 2 V / 3 V
fSystem MHz
f(MCLK)
f(SMCLK)
P5.4/MCLK,
P1.4/SMCLK, P5.5/SMCLK
CL = VCC = 2.2 P1.0/TACLK f(ACLK) = f(LFXT1) = f(XT1) 40% 60%
CL = 20 pF f(ACLK) = f(LFXT1) = f(LF) 30% 70%
VCC = 2.2 V / 3 V f(ACLK) = f(LFXT1) 50%
P1.1/TA0/MCLK,
f(MCLK) = f(XT1) 40% 60%
t(Xdc) Duty cycle of output frequency
CL = 20 pF,
VCC = 2.2 V / 3 V f(MCLK) = f(DCOCLK)
50%−
15 ns
50%
50%+
15 ns
P1.4/TBCLK/SMCLK, f(SMCLK) = f(XT2) 40% 60%
CL = 20 pF,
VCC = 2.2 V / 3 V f(SMCLK) = f(DCOCLK)
50%−
15 ns
50%
50%+
15 ns
MSP430F15x, MSP430F16x, MSP430F161x
MIXED SIGNAL MICROCONTROLLER
SLAS368G − OCTOBER 2002 − REVISED MARCH 2011
30 POST OFFICE BOX 655303 • DALLAS, TEXAS 75265
electrical characteristics over recommended operating free-air temperature (unless otherwise
noted) (continued)
outputs − ports P1, P2, P3, P4, P5, P6 (continued)
Figure 2
VOL − Low-Level Output Voltage − V
0
5
10
15
20
25
0.0 0.5 1.0 1.5 2.0 2.5
VCC = 2.2 V
P3.5
TYPICAL LOW-LEVEL OUTPUT CURRENT
vs
LOW-LEVEL OUTPUT VOLTAGE
TA = 25°C
TA = 85°C
IOL − Low-Level Output Current − mA
Figure 3
VOL − Low-Level Output Voltage − V
0
10
20
30
40
0.0 0.5 1.0 1.5 2.0 2.5 3.0 3.5
VCC = 3 V
P3.5
TYPICAL LOW-LEVEL OUTPUT CURRENT
vs
LOW-LEVEL OUTPUT VOLTAGE
TA = 25°C
TA = 85°C
IOL − Low-Level Output Current − mA
Figure 4
VOH − High-Level Output Voltage − V
−25
−20
−15
−10
−5
0
0.0 0.5 1.0 1.5 2.0 2.5
VCC = 2.2 V
P3.5
TYPICAL HIGH-LEVEL OUTPUT CURRENT
vs
HIGH-LEVEL OUTPUT VOLTAGE
TA = 25°C
TA = 85°C
IOH− High-Level Output Current − mA
Figure 5
VOH − High-Level Output Voltage − V
−45
−35
−25
−15
−5
0.0 0.5 1.0 1.5 2.0 2.5 3.0 3.5
VCC = 3 V
P3.5
TYPICAL HIGH-LEVEL OUTPUT CURRENT
vs
HIGH-LEVEL OUTPUT VOLTAGE
TA = 25°C
TA = 85°C
IOH− High-Level Output Current − mA
MSP430F15x, MSP430F16x, MSP430F161x
MIXED SIGNAL MICROCONTROLLER
SLAS368G − OCTOBER 2002 − REVISED MARCH 2011
POST OFFICE BOX 655303 • DALLAS, TEXAS 75265 31
electrical characteristics over recommended operating free-air temperature (unless otherwise
noted) (continued)
wake-up LPM3
PARAMETER TEST CONDITIONS MIN TYP MAX UNIT
t(LPM3) Delay time VCC = 2.2 V/3 V, fDCO ≥ fDCO43 6 μs
RAM
PARAMETER TEST CONDITIONS MIN TYP MAX UNIT
VRAMh See Note 1 CPU HALTED 1.6 V
NOTE 1: This parameter defines the minimum supply voltage when the data in program memory RAM remain unchanged. No program execution
should take place during this supply voltage condition.
Comparator_A (see Note 1)
PARAMETER TEST CONDITIONS VCC MIN TYP MAX UNIT
I CAON=1 CARSEL=0 CAREF=0
2.2 V 25 40
I(DD) 1, 0, μA
3 V 45 60
I
CAON=1, CARSEL=0,
CAREF 1/2/3 no load at
2.2 V 30 50
I(Refladder/Refdiode) CAREF=3, μA
P2.3/CA0/TA1 and P2.4/CA1/TA2 3 V 45 71
V(IC)
Common-mode input
voltage
CAON =1 2.2 V/3 V 0 VCC−1 V
V(Ref025)
Voltage @ 0.25 VCC node
VCC
PCA0=1, CARSEL=1, CAREF=1,
no load at P2.3/CA0/TA1 and
P2.4/CA1/TA2
2.2 V/3 V 0.23 0.24 0.25
V(Ref050)
Voltage @ 0.5VCC node
VCC
PCA0=1, CARSEL=1, CAREF=2,
no load at P2.3/CA0/TA1 and
P2.4/CA1/TA2
2.2 V/3 V 0.47 0.48 0.5
V (see Figure 6 and Figure 7)
PCA0=1, CARSEL=1, CAREF=3,
no load at P2 3/CA0/TA1 and
2.2 V 390 480 540
V(RefVT) P2.3/mV
P2.4/CA1/TA2 TA = 85°C 3 V 400 490 550
V(offset) Offset voltage See Note 2 2.2 V/3 V −30 30 mV
Vhys Input hysteresis CAON=1 2.2 V/3 V 0 0.7 1.4 mV
TA = 25°C, Overdrive 10 mV,
2.2 V 130 210 300
ns
t
25 Without filter: CAF=0 3 V 80 150 240
t(response LH)
TA = 25°C, Overdrive 10 mV,
2.2 V 1.4 1.9 3.4
μs
25 With filter: CAF=1 3 V 0.9 1.5 2.6
TA = 25°C, Overdrive 10 mV,
2.2 V 130 210 300
ns
t
25 Without filter: CAF=0 3 V 80 150 240
t(response HL)
TA = 25°C, Overdrive 10 mV,
2.2 V 1.4 1.9 3.4
μs
25 With filter: CAF=1 3 V 0.9 1.5 2.6
NOTES: 1. The leakage current for the Comparator_A terminals is identical to Ilkg(Px.x) specification.
2. The input offset voltage can be cancelled by using the CAEX bit to invert the Comparator_A inputs on successive measurements.
The two successive measurements are then summed together.
MSP430F15x, MSP430F16x, MSP430F161x
MIXED SIGNAL MICROCONTROLLER
SLAS368G − OCTOBER 2002 − REVISED MARCH 2011
32 POST OFFICE BOX 655303 • DALLAS, TEXAS 75265
electrical characteristics over recommended operating free-air temperature (unless otherwise
noted) (continued)
TA − Free-Air Temperature − °C
400
450
500
550
600
650
−45 −25 −5 15 35 55 75 95
VCC = 3 V
Figure 6. V(RefVT) vs Temperature, VCC = 3 V
V(REFVT) − Reference Volts −mV
Typical
Figure 7. V(RefVT) vs Temperature, VCC = 2.2 V
TA − Free-Air Temperature − °C
400
450
500
550
600
650
−45 −25 −5 15 35 55 75 95
VCC = 2.2 V
V(REFVT) − Reference Volts −mV
Typical
_
+
CAON
0
1
V+
0
1
CAF
Low Pass Filter
τ ≈ 2.0 μs
To Internal
Modules
Set CAIFG
Flag
CAOUT
V−
VCC
1
0 V
0
Figure 8. Block Diagram of Comparator_A Module
Overdrive VCAOUT
V+ t(response)
V−
400 mV
Figure 9. Overdrive Definition
MSP430F15x, MSP430F16x, MSP430F161x
MIXED SIGNAL MICROCONTROLLER
SLAS368G − OCTOBER 2002 − REVISED MARCH 2011
POST OFFICE BOX 655303 • DALLAS, TEXAS 75265 33
electrical characteristics over recommended operating free-air temperature (unless otherwise
noted) (continued)
POR/brownout reset (BOR) (see Notes 1 and 2)
PARAMETER TEST CONDITIONS MIN TYP MAX UNIT
td(BOR) 2000 μs
VCC(Start) dVCC/dt ≤ 3 V/s (see Figure 10) 0.7 × V(B_IT−) V
V(B_IT−) Brownout
dVCC/dt ≤ 3 V/s (see Figure 10 through Figure 12) 1.71 V
Vhys(B_IT−)
dVCC/dt ≤ 3 V/s (see Figure 10) 70 130 180 mV
t(reset)
Pulse length needed at RST/NMI pin to accepted reset internally,
VCC = 2.2 V/3 V
2 μs
NOTES: 1. The current consumption of the brownout module is already included in the ICC current consumption data. The voltage level V(B_IT−)
+ Vhys(B_IT−) is ≤ 1.8 V.
2. During power up, the CPU begins code execution following a period of tBOR(delay) after VCC = V(B_IT−) + Vhys(B_IT−). The
default DCO settings must not be changed until VCC ≥ VCC(min), where VCC(min) is the minimum supply voltage for the desired
operating frequency. See the MSP430x1xx Family User’s Guide (SLAU049) for more information on the brownout/SVS circuit.
typical characteristics
0
1
t d(BOR)
VCC
V(B_IT−)
Vhys(B_IT−)
VCC(Start)
BOR
Figure 10. POR/Brownout Reset (BOR) vs Supply Voltage
MSP430F15x, MSP430F16x, MSP430F161x
MIXED SIGNAL MICROCONTROLLER
SLAS368G − OCTOBER 2002 − REVISED MARCH 2011
34 POST OFFICE BOX 655303 • DALLAS, TEXAS 75265
typical characteristics (continued)
VCC(min)
VCC
3 V
tpw
0
0.5
1
1.5
2
0.001 1 1000
Vcc = 3 V
typical conditions
1 ns 1 ns
tpw − Pulse Width − μs
VCC(min)− V
tpw − Pulse Width − μs
Figure 11. VCC(min) Level With a Square Voltage Drop to Generate a POR/Brownout Signal
VCC
0
0.5
1
1.5
2
Vcc = 3 V
typical conditions
VCC(min)
tpw
tpw − Pulse Width − μs
VCC(min)− V
3 V
0.001 1 1000 tf tr
tpw − Pulse Width − μs
tf = tr
Figure 12. VCC(min) Level With a Triangle Voltage Drop to Generate a POR/Brownout Signal
MSP430F15x, MSP430F16x, MSP430F161x
MIXED SIGNAL MICROCONTROLLER
SLAS368G − OCTOBER 2002 − REVISED MARCH 2011
POST OFFICE BOX 655303 • DALLAS, TEXAS 75265 35
electrical characteristics over recommended operating free-air temperature (unless otherwise
noted)
SVS (supply voltage supervisor/monitor)
PARAMETER TEST CONDITIONS MIN NOM MAX UNIT
t
dVCC/dt > 30 V/ms (see Figure 13) 5 150
t(SVSR) μs
dVCC/dt ≤ 30 V/ms 2000
td(SVSon) SVSON, switch from VLD = 0 to VLD ≠ 0, VCC = 3 V 150 300 μs
tsettle VLD ≠ 0‡ 12 μs
V(SVSstart) VLD ≠ 0, VCC/dt ≤ 3 V/s (see Figure 13) 1.55 1.7 V
VLD = 1 70 120 155 mV
Vhys(SVS_IT−)
VCC/dt ≤ 3 V/s (see Figure 13)
VLD = 2 to 14
V(SVS_IT−)
x 0.004
V(SVS_IT−)
x 0.008
VCC/dt ≤ 3 V/s (see Figure 13),
External voltage applied on A7
VLD = 15 4.4 10.4 mV
VLD = 1 1.8 1.9 2.05
VLD = 2 1.94 2.1 2.25
VLD = 3 2.05 2.2 2.37
VLD = 4 2.14 2.3 2.48
VLD = 5 2.24 2.4 2.6
VLD = 6 2.33 2.5 2.71
VCC/dt ≤ 3 V/s (see Figure 13 and Figure 14)
VLD = 7 2.46 2.65 2.86
V(SVS IT )
VLD = 8 2.58 2.8 3
SVS_IT−) V
VLD = 9 2.69 2.9 3.13
VLD = 10 2.83 3.05 3.29
VLD = 11 2.94 3.2 3.42
VLD = 12 3.11 3.35 3.61†
VLD = 13 3.24 3.5 3.76†
VLD = 14 3.43 3.7† 3.99†
VCC/dt ≤ 3 V/s (see Figure 13 and Figure 14),
External voltage applied on A7
VLD = 15 1.1 1.2 1.3
ICC(SVS)
(see Note 1)
VLD ≠ 0, VCC = 2.2 V/3 V 10 15 μA
† The recommended operating voltage range is limited to 3.6 V.
‡ tsettle is the settling time that the comparator o/p needs to have a stable level after VLD is switched VLD ≠ 0 to a different VLD value somewhere
between 2 and 15. The overdrive is assumed to be > 50 mV.
NOTE 1: The current consumption of the SVS module is not included in the ICC current consumption data.
MSP430F15x, MSP430F16x, MSP430F161x
MIXED SIGNAL MICROCONTROLLER
SLAS368G − OCTOBER 2002 − REVISED MARCH 2011
36 POST OFFICE BOX 655303 • DALLAS, TEXAS 75265
typical characteristics
VCC(start)
AVCC
V(B_IT−)
Brownout
Region
V(SVSstart)
V(SVS_IT−)
Software sets VLD >0:
SVS is active
td(SVSR)
undefined
Vhys(SVS_IT−)
0
1
td(BOR)
Brownout
0
1
td(SVSon)
td(BOR)
0
1
Set POR
Brownout
Region
SVS Circuit is Active From VLD > to VCC < V(B_IT−)
SVS out
Vhys(B_IT−)
Figure 13. SVS Reset (SVSR) vs Supply Voltage
0
0.5
1
1.5
2
VCC
VCC
1 ns 1 ns
VCC(min)
tpw
tpw − Pulse Width − μs
VCC(min)− V
3 V
1 10 1000
tf tr
t − Pulse Width − μs
100
tpw
3 V
tf = tr
Rectangular Drop
Triangular Drop
VCC(min)
Figure 14. VCC(min): Square Voltage Drop and Triangle Voltage Drop to Generate an SVS Signal (VLD = 1)
MSP430F15x, MSP430F16x, MSP430F161x
MIXED SIGNAL MICROCONTROLLER
SLAS368G − OCTOBER 2002 − REVISED MARCH 2011
POST OFFICE BOX 655303 • DALLAS, TEXAS 75265 37
electrical characteristics over recommended operating free-air temperature (unless otherwise
noted) (continued)
DCO (see Note 1)
PARAMETER TEST CONDITIONS VCC MIN TYP MAX UNIT
f R 0 DCO 3 MOD 0 DCOR 0 T 25°C
2.2 V 0.08 0.12 0.15
f(DCO03) Rsel = 0, = 3, = 0, = 0, TA = MHz
3 V 0.08 0.13 0.16
f R 1 DCO 3 MOD 0 DCOR 0 T 25°C
2.2 V 0.14 0.19 0.23
f(DCO13) Rsel = 1, = 3, = 0, = 0, TA = MHz
3 V 0.14 0.18 0.22
f R 2 DCO 3 MOD 0 DCOR 0 T 25°C
2.2 V 0.22 0.30 0.36
f(DCO23) Rsel = 2, = 3, = 0, = 0, TA = MHz
3 V 0.22 0.28 0.34
f R 3 DCO 3 MOD 0 DCOR 0 T 25°C
2.2 V 0.37 0.49 0.59
f(DCO33) Rsel = 3, = 3, = 0, = 0, TA = MHz
3 V 0.37 0.47 0.56
f R 4 DCO 3 MOD 0 DCOR 0 T 25°C
2.2 V 0.61 0.77 0.93
f(DCO43) Rsel = 4, = 3, = 0, = 0, TA = MHz
3 V 0.61 0.75 0.90
f R 5 DCO 3 MOD 0 DCOR 0 T 25°C
2.2 V 1 1.2 1.5
f(DCO53) Rsel = 5, = 3, = 0, = 0, TA = MHz
3 V 1 1.3 1.5
f R 6 DCO 3 MOD 0 DCOR 0 T 25°C
2.2 V 1.6 1.9 2.2
f(DCO63) Rsel = 6, = 3, = 0, = 0, TA = MHz
3 V 1.69 2.0 2.29
f R 7 DCO 3 MOD 0 DCOR 0 T 25°C
2.2 V 2.4 2.9 3.4
f(DCO73) Rsel = 7, = 3, = 0, = 0, TA = MHz
3 V 2.7 3.2 3.65
f(DCO47) Rsel = 4, DCO = 7, MOD = 0, DCOR = 0, TA = 25°C 2.2 V/3 V
fDCO40
× 1.7
fDCO40
× 2.1
fDCO40
× 2.5
MHz
f R 7 DCO 7 MOD 0 DCOR 0 T 25°C
2.2 V 4 4.5 4.9
f(DCO77) Rsel = 7, = 7, = 0, = 0, TA = MHz
3 V 4.4 4.9 5.4
SRsel SR = fRsel+1 / fRsel 2.2 V/3 V 1.35 1.65 2
SDCO SDCO = f(DCO+1) / f(DCO) 2.2 V/3 V 1.07 1.12 1.16
D Temperature drift R 4 DCO 3 MOD 0 (see Note 2)
2.2 V −0.31 −0.36 −0.40
Dt drift, Rsel = 4, = 3, = %/°C
3 V −0.33 −0.38 −0.43
DV
Drift with VCC variation, Rsel = 4, DCO = 3, MOD = 0
(see Note 2)
2.2 V/3 V 0 5 10 %/V
NOTES: 1. The DCO frequency may not exceed the maximum system frequency defined by parameter processor frequency, f(System).
2. This parameter is not production tested.
2.2 3
fDCO_0
Max
Min
ÎÎÎÎÎÎÎ
ÎÎÎÎÎÎÎ
Max
Min
fDCO_7
0 1 2 3 4 5 6 7 DCO
f DCOCLK
1
ÎÎÎÎÎÎÎ
ÎÎÎÎÎÎÎ
VCC − V
Frequency Variance
Figure 15. DCO Characteristics
MSP430F15x, MSP430F16x, MSP430F161x
MIXED SIGNAL MICROCONTROLLER
SLAS368G − OCTOBER 2002 − REVISED MARCH 2011
38 POST OFFICE BOX 655303 • DALLAS, TEXAS 75265
electrical characteristics over recommended operating free-air temperature (unless otherwise
noted) (continued)
main DCO characteristics
Individual devices have a minimum and maximum operation frequency. The specified parameters for
f(DCOx0) to f(DCOx7) are valid for all devices.
All ranges selected by Rsel(n) overlap with Rsel(n+1): Rsel0 overlaps Rsel1, ... Rsel6 overlaps Rsel7.
DCO control bits DCO0, DCO1, and DCO2 have a step size as defined by parameter SDCO.
Modulation control bits MOD0 to MOD4 select how often f(DCO+1) is used within the period of 32 DCOCLK
cycles. The frequency f(DCO) is used for the remaining cycles. The frequency is an average equal to:
faverage
32f(DCO)
f(DCO1)
MODf(DCO)
(32MOD)f(DCO1)
DCO when using ROSC (see Note 1)
PARAMETER TEST CONDITIONS VCC MIN TYP MAX UNIT
f DCO output frequency
Rsel = 4, DCO = 3, MOD = 0, DCOR = 1,
2.2 V 1.8±15% MHz
fDCO, TA = 25°C 3 V 1.95±15% MHz
Dt, Temperature drift Rsel = 4, DCO = 3, MOD = 0, DCOR = 1 2.2 V/3 V ±0.1 %/°C
Dv, Drift with VCC variation Rsel = 4, DCO = 3, MOD = 0, DCOR = 1 2.2 V/3 V 10 %/V
NOTES: 1. ROSC = 100kΩ. Metal film resistor, type 0257. 0.6 watt with 1% tolerance and TK = ±50ppm/°C.
crystal oscillator, LFXT1 oscillator (see Note 1)
PARAMETER TEST CONDITIONS MIN TYP MAX UNIT
C Integrated input capacitance
XTS=0; LF oscillator selected, VCC = 2.2 V/3 V 12
CXIN pF
XTS=1; XT1 oscillator selected, VCC = 2.2 V/3 V 2
C Integrated output capacitance
XTS=0; LF oscillator selected, VCC = 2.2 V/3 V 12
CXOUT pF
XTS=1; XT1 oscillator selected, VCC = 2.2 V/3 V 2
VIL
I t l l t XIN
VCC = 2.2 V/3 V
( N 2)
XTS = 0 or 1
XT1 or LF modes
VSS 0.2 × VCC
V
V
Input levels at CC
see Note XTS = 0, LF mode 0.9 × VCC VCC
VIH XTS = 1, XT1 mode 0.8 × VCC VCC
NOTES: 1. The oscillator needs capacitors at both terminals, with values specified by the crystal manufacturer.
2. Applies only when using an external logic-level clock source. Not applicable when using a crystal or resonator.
crystal oscillator, XT2 oscillator (see Note 1)
PARAMETER TEST CONDITIONS MIN TYP MAX UNIT
CXIN Integrated input capacitance VCC = 2.2 V/3 V 2 pF
CXOUT Integrated output capacitance VCC = 2.2 V/3 V 2 pF
VIL Input levels at XIN V = 2 2 V/3 V (see Note 2)
VSS 0.2 × VCC V
VIH
VCC 2.2 0.8 × VCC VCC V
NOTES: 1. The oscillator needs capacitors at both terminals, with values specified by the crystal manufacturer.
2. Applies only when using an external logic-level clock source. Not applicable when using a crystal or resonator.
USART0, USART1 (see Note 1)
PARAMETER TEST CONDITIONS MIN TYP MAX UNIT
t( ) USART0/USART1: deglitch time
VCC = 2.2 V 200 430 800
τ) ns
VCC = 3 V 150 280 500
NOTE 1: The signal applied to the USART0/USART1 receive signal/terminal (URXD0/1) should meet the timing requirements of t(τ) to ensure
that the URXS flip-flop is set. The URXS flip-flop is set with negative pulses meeting the minimum-timing condition of t(τ). The operating
conditions to set the flag must be met independently from this timing constraint. The deglitch circuitry is active only on negative
transitions on the URXD0/1 line.
MSP430F15x, MSP430F16x, MSP430F161x
MIXED SIGNAL MICROCONTROLLER
SLAS368G − OCTOBER 2002 − REVISED MARCH 2011
POST OFFICE BOX 655303 • DALLAS, TEXAS 75265 39
electrical characteristics over recommended operating free-air temperature (unless otherwise
noted) (continued)
12-bit ADC, power supply and input range conditions (see Note 1)
PARAMETER TEST CONDITIONS MIN TYP MAX UNIT
AVCC Analog supply voltage
AVCC and DVCC are connected together
AVSS and DVSS are connected together
V(AVSS) = V(DVSS) = 0 V
2.2 3.6 V
V(P6.x/Ax)
Analog input voltage
range (see Note 2)
All P6.0/A0 to P6.7/A7 terminals. Analog inputs
selected in ADC12MCTLx register and P6Sel.x=1
0 ≤ x ≤ 7; V(AVSS) ≤ VP6.x/Ax ≤ V(AVCC)
0 VAVCC V
I
Operating supply current
into AV terminal
fADC12CLK = 5.0 MHz
ADC12ON 1 REFON 0
2.2 V 0.65 1.3
IADC12 AVCC mA
(see Note 3)
= 1, = SHT0=0, SHT1=0, ADC12DIV=0 3 V 0.8 1.6
I
Operating supply current
i t AV t i l
fADC12CLK = 5.0 MHz
ADC12ON = 0,
REFON = 1, REF2_5V = 1
3 V 0.5 0.8 mA
IREF+ into AVCC terminal
(see Note 4)
fADC12CLK = 5.0 MHz
ADC12ON 0
2.2 V 0.5 0.8
mA
= 0,
REFON = 1, REF2_5V = 0 3 V 0.5 0.8
CI
† Input capacitance
Only one terminal can be selected
at one time, P6.x/Ax
2.2 V 40 pF
RI
† Input MUX ON resistance 0V ≤ VAx ≤ VAVCC 3 V 2000 Ω
† Not production tested, limits verified by design
NOTES: 1. The leakage current is defined in the leakage current table with P6.x/Ax parameter.
2. The analog input voltage range must be within the selected reference voltage range VR+ to VR− for valid conversion results.
3. The internal reference supply current is not included in current consumption parameter IADC12.
4. The internal reference current is supplied via terminal AVCC. Consumption is independent of the ADC12ON control bit, unless a
conversion is active. The REFON bit enables to settle the built-in reference before starting an A/D conversion.
12-bit ADC, external reference (see Note 1)
PARAMETER TEST CONDITIONS MIN TYP MAX UNIT
VeREF+
Positive external
reference voltage input
VeREF+ > VREF−/VeREF− (see Note 2) 1.4 VAVCC V
VREF− /VeREF−
Negative external
reference voltage input
VeREF+ > VREF−/VeREF− (see Note 3) 0 1.2 V
(VeREF+ −
VREF−/VeREF−)
Differential external
reference voltage input
VeREF+ > VREF−/VeREF− (see Note 4) 1.4 VAVCC V
IVeREF+ Static input current 0V ≤VeREF+ ≤ VAVCC 2.2 V/3 V ±1 μA
IVREF−/VeREF− Static input current 0V ≤ VeREF− ≤ VAVCC 2.2 V/3 V ±1 μA
NOTES: 1. The external reference is used during conversion to charge and discharge the capacitance array. The input capacitance, Ci, is also
the dynamic load for an external reference during conversion. The dynamic impedance of the reference supply should follow the
recommendations on analog-source impedance to allow the charge to settle for 12-bit accuracy.
2. The accuracy limits the minimum positive external reference voltage. Lower reference voltage levels may be applied with reduced
accuracy requirements.
3. The accuracy limits the maximum negative external reference voltage. Higher reference voltage levels may be applied with reduced
accuracy requirements.
4. The accuracy limits minimum external differential reference voltage. Lower differential reference voltage levels may be applied with
reduced accuracy requirements.
MSP430F15x, MSP430F16x, MSP430F161x
MIXED SIGNAL MICROCONTROLLER
SLAS368G − OCTOBER 2002 − REVISED MARCH 2011
40 POST OFFICE BOX 655303 • DALLAS, TEXAS 75265
electrical characteristics over recommended operating free-air temperature (unless otherwise
noted) (continued)
12-bit ADC, built-in reference
PARAMETER TEST CONDITIONS MIN TYP MAX UNIT
V
built-REF2_5V = 1 for 2.5 V
IVREF+max ≤ IVREF+≤ IVREF+min
VCC = 3 V 2.4 2.5 2.6
VREF+ V
Positive built in reference
voltage output REF2_5V = 0 for 1.5 V
IVREF+max ≤ IVREF+≤ IVREF+min
VCC = 2.2 V/3 V 1.44 1.5 1.56
AVCC minimum voltage,
REF2_5V = 0, IVREF+max ≤ IVREF+≤ IVREF+min 2.2
AVCC(min)
Positive built-in reference REF2_5V = 1, −0.5mA ≤ IVREF+≤ IVREF+min 2.8 V
active REF2_5V = 1, −1mA ≤ IVREF+≤ IVREF+min 2.9
I
Load current out of VREF+
VCC = 2.2 V 0.01 −0.5
IVREF+ mA
terminal VCC = 3 V 0.01 −1
IVREF+ = 500 μA +/− 100 μA
Analog input voltage 0 75 V
VCC = 2.2 V ±2
LSB
I Load-current regulation
~0.75 V,
REF2_5V = 0 VCC = 3 V ±2
IL(VREF)+
† Load VREF+ terminal IVREF+ = 500 μA ± 100 μA
Analog input voltage ~1.25 V,
REF2_5V = 1
VCC = 3 V ±2 LSB
I Load current regulation
IVREF+ =100 μA → 900 μA,
IDL(VREF) + C 5 μF ax 0 5 x V V 3 V 20 ns
‡ VREF+ terminal
CVREF+=μF, ~0.5 VREF+ ,
Error of conversion result ≤ 1 LSB
VCC = CVREF+
Capacitance at pin VREF+
(see Note 1)
REFON =1,
0 mA ≤ IVREF+ ≤ IVREF+max
VCC = 2.2 V/3 V 5 10 μF
TREF+
† Temperature coefficient of
built-in reference
IVREF+ is a constant in the range of
0 mA ≤ IVREF+ ≤ 1 mA
VCC = 2.2 V/3 V ±100 ppm/°C
tREFON
†
Settle time of internal
reference voltage (see
Figure 16 and Note 2)
IVREF+ = 0.5 mA, CVREF+ = 10 μF, VREF+ = 1.5 V,
VAVCC = 2.2 V
17 ms
† Not production tested, limits characterized
‡ Not production tested, limits verified by design
NOTES: 1. The internal buffer operational amplifier and the accuracy specifications require an external capacitor. All INL and DNL tests uses
two capacitors between pins VREF+ and AVSS and VREF−/VeREF− and AVSS: 10 μF tantalum and 100 nF ceramic.
2. The condition is that the error in a conversion started after tREFON is less than ±0.5 LSB. The settling time depends on the external
capacitive load.
CVREF+
1 μF
0
1 ms 10 ms 100 ms tREFON
tREFON ≈ .66 x CVREF+ [ms] with CVREF+ in μF
100 μF
10 μF
Figure 16. Typical Settling Time of Internal Reference tREFON vs External Capacitor on VREF+
MSP430F15x, MSP430F16x, MSP430F161x
MIXED SIGNAL MICROCONTROLLER
SLAS368G − OCTOBER 2002 − REVISED MARCH 2011
POST OFFICE BOX 655303 • DALLAS, TEXAS 75265 41
+
−
10 μF 100 nF
AVSS
MSP430F15x
MSP430F16x
+
−
+
−
10 μF 100 nF
10 μF 100 nF
AVCC
10 μF 100 nF
DVSS
From DVCC
Power
Supply
Apply
External
Reference
+
−
Apply External Reference [VeREF+]
or Use Internal Reference [VREF+] VREF+ or VeREF+
VREF−/VeREF−
MSP430F161x
Figure 17. Supply Voltage and Reference Voltage Design VREF−/VeREF− External Supply
+
−
10 μF 100 nF
AVSS
MSP430F15x
MSP430F16x
+
−
10 μF 100 nF
AVCC
10 μF 100 nF
DVSS
From DVCC
Power
Supply
+
−
Apply External Reference [VeREF+]
or Use Internal Reference [VREF+] VREF+ or VeREF+
Reference Is Internally VREF−/VeREF−
Switched to AVSS
MSP430F161x
Figure 18. Supply Voltage and Reference Voltage Design VREF−/VeREF− = AVSS, Internally Connected
MSP430F15x, MSP430F16x, MSP430F161x
MIXED SIGNAL MICROCONTROLLER
SLAS368G − OCTOBER 2002 − REVISED MARCH 2011
42 POST OFFICE BOX 655303 • DALLAS, TEXAS 75265
electrical characteristics over recommended operating free-air temperature (unless otherwise
noted) (continued)
12-bit ADC, timing parameters
PARAMETER TEST CONDITIONS MIN TYP MAX UNIT
fADC12CLK
For specified performance of ADC12
linearity parameters
2.2V/3 V 0.45 5 6.3 MHz
fADC12OSC
Internal ADC12
oscillator
ADC12DIV=0,
fADC12CLK=fADC12OSC
2.2 V/ 3 V 3.7 5 6.3 MHz
t Conversion time
CVREF+ ≥ 5 μF, Internal oscillator,
fADC12OSC = 3.7 MHz to 6.3 MHz
2.2 V/ 3 V 2.06 3.51 μs
tCONVERT External fADC12CLK from ACLK, MCLK or SMCLK:
ADC12SSEL ≠ 0
13×ADC12DIV×
1/fADC12CLK
μs
tADC12ON
‡ Turn on settling time of
the ADC
(see Note 1) 100 ns
t ‡ Sampling time
RS = 400 Ω, RI = 1000 Ω,
C 30 pF
3 V 1220
tSample ns
CI = τ = [RS + RI] x CI;(see Note 2) 2.2 V 1400
† Not production tested, limits characterized
‡ Not production tested, limits verified by design
NOTES: 1. The condition is that the error in a conversion started after tADC12ON is less than ±0.5 LSB. The reference and input signal are already
settled.
2. Approximately ten Tau (τ) are needed to get an error of less than ±0.5 LSB:
tSample = ln(2n+1) x (RS + RI) x CI+ 800 ns where n = ADC resolution = 12, RS = external source resistance.
12-bit ADC, linearity parameters
PARAMETER TEST CONDITIONS MIN TYP MAX UNIT
E Integral linearity error
1.4 V ≤ (VeREF+ − VREF−/VeREF−) min ≤ 1.6 V
2 2 V/3 V
±2
EI LSB
1.6 V < (VeREF+ − VREF−/VeREF−) min ≤ [VAVCC]
2.2 ±1.7
ED
Differential linearity
error
(VeREF+ − VREF−/VeREF−)min ≤ (VeREF+ − VREF−/VeREF−),
CVREF+ = 10 μF (tantalum) and 100 nF (ceramic)
2.2 V/3 V ±1 LSB
EO Offset error
(VeREF+ − VREF−/VeREF−)min ≤ (VeREF+ − VREF−/VeREF−),
Internal impedance of source RS < 100 Ω,
CVREF+ = 10 μF (tantalum) and 100 nF (ceramic)
2.2 V/3 V ±2 ±4 LSB
EG Gain error
(VeREF+ − VREF−/VeREF−)min ≤ (VeREF+ − VREF−/VeREF−),
CVREF+ = 10 μF (tantalum) and 100 nF (ceramic)
2.2 V/3 V ±1.1 ±2 LSB
ET
Total unadjusted
error
(VeREF+ − VREF−/VeREF−)min ≤ (VeREF+ − VREF−/VeREF−),
CVREF+ = 10 μF (tantalum) and 100 nF (ceramic)
2.2 V/3 V ±2 ±5 LSB
MSP430F15x, MSP430F16x, MSP430F161x
MIXED SIGNAL MICROCONTROLLER
SLAS368G − OCTOBER 2002 − REVISED MARCH 2011
POST OFFICE BOX 655303 • DALLAS, TEXAS 75265 43
electrical characteristics over recommended operating free-air temperature (unless otherwise
noted) (continued)
12-bit ADC, temperature sensor and built-in VMID
PARAMETER TEST CONDITIONS MIN TYP MAX UNIT
I
Operating supply current into
REFON = 0, INCH = 0Ah,
2.2 V 40 120
ISENSOR A
AVCC terminal (see Note 1)
ADC12ON=NA, TA = 25C 3 V 60 160
μA
V (see Note 2)
ADC12ON = 1, INCH = 0Ah,
2.2 V 986
VSENSOR mV
† TA = 0°C 3 V 986
TC † ADC12ON 1 INCH 0Ah
2.2 V 3.55 3.55±3%
TCSENSOR mV/°C
= 1, = 3 V 3.55 3.55±3%
t Sample time required if channel
ADC12ON = 1, INCH = 0Ah,
Error of conversion result ≤ 1
2.2 V 30
tSENSOR(sample) s
† 10 is selected (see Note 3)
LSB 3 V 30
μs
I
Current into divider at channel 11
ADC12ON 1 INCH 0Bh
2.2 V NA
IVMID A
(see Note 4) = 1, = 0Bh,
3 V NA
μA
V AV divider at channel 11
ADC12ON = 1, INCH = 0Bh,
2.2 V 1.1 1.1±0.04
VMID AVCC V
VMID is ~0.5 x VAVCC 3 V 1.5 1.50±0.04
t
Sample time required if channel
ADC12ON = 1, INCH = 0Bh,
Error of conversion result ≤ 1
2.2 V 1400
tVMID(sample) ns
11 is selected (see Note 5)
LSB 3 V 1220
† Not production tested, limits characterized
NOTES: 1. The sensor current ISENSOR is consumed if (ADC12ON = 1 and REFON=1), or (ADC12ON=1 AND INCH=0Ah and sample signal
is high). When REFON = 1, ISENSOR is already included in IREF+.
2. The temperature sensor offset can be as much as ±20C. A single-point calibration is recommended in order to minimize the offset
error of the built-in temperature sensor.
3. The typical equivalent impedance of the sensor is 51 kΩ. The sample time required includes the sensor-on time tSENSOR(on)
4. No additional current is needed. The VMID is used during sampling.
5. The on-time tVMID(on) is included in the sampling time tVMID(sample); no additional on time is needed.
12-bit DAC, supply specifications
PARAMETER TEST CONDITIONS VCC MIN TYP MAX UNIT
AVCC Analog supply voltage
AVCC = DVCC,
AVSS = DVSS =0 V
2.20 3.60 V
DAC12AMPx=2, DAC12IR=0,
DAC12_xDAT=0800h
2.2V/3V 50 110
I
Supply Current:
DAC12AMPx=2, DAC12IR=1,
DAC12_xDAT=0800h , VeREF+=VREF+= AVCC
2.2V/3V 50 110
IDD Single DAC Channel
A
(see Notes 1 and 2)
DAC12AMPx=5, DAC12IR=1,
DAC12_xDAT=0800h, VeREF+=VREF+= AVCC
2.2V/3V 200 440
μA
DAC12AMPx=7, DAC12IR=1,
DAC12_xDAT=0800h, VeREF+=VREF+= AVCC
2.2V/3V 700 1500
PSRR
Power supply
DAC12_xDAT = 800h, VREF = 1.5 V
ΔAVCC = 100mV
2.2V
rejection ratio
70 dB
(see Notes 3 and 4)
DAC12_xDAT = 800h, VREF = 1.5 V or 2.5 V
ΔAVCC = 100mV
3V
NOTES: 1. No load at the output pin, DAC12_0 or DAC12_1, assuming that the control bits for the shared pins are set properly.
2. Current into reference terminals not included. If DAC12IR = 1 current flows through the input divider; see Reference Input
specifications.
3. PSRR = 20*log{ΔAVCC/ΔVDAC12_xOUT}.
4. VREF is applied externally. The internal reference is not used.
MSP430F15x, MSP430F16x, MSP430F161x
MIXED SIGNAL MICROCONTROLLER
SLAS368G − OCTOBER 2002 − REVISED MARCH 2011
44 POST OFFICE BOX 655303 • DALLAS, TEXAS 75265
electrical characteristics over recommended operating free-air temperature (unless otherwise
noted) (continued)
12-bit DAC, linearity specifications (see Figure 19)
PARAMETER TEST CONDITIONS VCC MIN TYP MAX UNIT
Resolution (12-bit Monotonic) 12 bits
INL
Vref = 1.5 V
DAC12AMPx = 7, DAC12IR = 1
2.2V
±2 0 ±8 0 LSB
Integral nonlinearity
(see Note 1) Vref = 2.5 V
DAC12AMPx = 7, DAC12IR = 1
3V
2.0 8.0 DNL
Vref = 1.5 V
DAC12AMPx = 7, DAC12IR = 1
2.2V
±0 4 ±1 0 LSB
Differential nonlinearity
(see Note 1) Vref = 2.5 V
DAC12AMPx = 7, DAC12IR = 1
3V
0.4 1.0 Offset voltage w/o
Vref = 1.5 V
DAC12AMPx = 7, DAC12IR = 1
2.2V
±21
EO
calibration
(see Notes 1, 2)
Vref = 2.5 V
DAC12AMPx = 7, DAC12IR = 1
3V
mV
Offset voltage with
Vref = 1.5 V
DAC12AMPx = 7, DAC12IR = 1
2.2V
±2 5
calibration
(see Notes 1, 2)
Vref = 2.5 V
DAC12AMPx = 7, DAC12IR = 1
3V
2.5
dE(O)/dT
Offset error
temperature coefficient
(see Note 1)
2.2V/3V 30 uV/C
E Gain error (see Note 1)
VREF = 1.5 V 2.2V
EG ±3 50 % FSR
VREF = 2.5 V 3V
3.50 dE(G)/dT
Gain temperature
coefficient (see Note 1)
2.2V/3V 10
ppm of
FSR/°C
Time for offset calibration
DAC12AMPx=2 2.2V/3V 100
tOffset_Cal
DAC12AMPx=3,5 2.2V/3V 32 ms
(see Note 3)
DAC12AMPx=4,6,7 2.2V/3V 6
NOTES: 1. Parameters calculated from the best-fit curve from 0x0A to 0xFFF. The best-fit curve method is used to deliver coefficients “a” and
“b” of the first order equation: y = a + b*x. VDAC12_xOUT = EO + (1 + EG) * (VeREF+/4095) * DAC12_xDAT, DAC12IR = 1.
2. The offset calibration works on the output operational amplifier. Offset Calibration is triggered setting bit DAC12CALON
3. The offset calibration can be done if DAC12AMPx = {2, 3, 4, 5, 6, 7}. The output operational amplifier is switched off with DAC12AMPx
={0, 1}. It is recommended that the DAC12 module be configured prior to initiating calibration. Port activity during calibration may
effect accuracy and is not recommended.
Positive
Negative
VR+
Offset Error Gain Error
DAC Code
DAC VOUT
Ideal transfer
function
RLoad =
AVCC
CLoad = 100pF
2
DAC Output
Figure 19. Linearity Test Load Conditions and Gain/Offset Definition
MSP430F15x, MSP430F16x, MSP430F161x
MIXED SIGNAL MICROCONTROLLER
SLAS368G − OCTOBER 2002 − REVISED MARCH 2011
POST OFFICE BOX 655303 • DALLAS, TEXAS 75265 45
electrical characteristics over recommended operating free-air temperature (unless otherwise
noted) (continued)
12-bit DAC, linearity specifications (continued)
DAC12_xDAT − Digital Code
−4
−3
−2
−1
0
1
2
3
4
0 512 1024 1536 2048 2560 3072 3584
VCC = 2.2 V, VREF = 1.5V
DAC12AMPx = 7
DAC12IR = 1
TYPICAL INL ERROR
vs
DIGITAL INPUT DATA
4095
INL − Integral Nonlinearity Error − LSB
DAC12_xDAT − Digital Code
−2.0
−1.5
−1.0
−0.5
0.0
0.5
1.0
1.5
2.0
0 512 1024 1536 2048 2560 3072 3584
VCC = 2.2 V, VREF = 1.5V
DAC12AMPx = 7
DAC12IR = 1
TYPICAL DNL ERROR
vs
DIGITAL INPUT DATA
4095
DNL − Differential Nonlinearity Error − LSB
MSP430F15x, MSP430F16x, MSP430F161x
MIXED SIGNAL MICROCONTROLLER
SLAS368G − OCTOBER 2002 − REVISED MARCH 2011
46 POST OFFICE BOX 655303 • DALLAS, TEXAS 75265
electrical characteristics over recommended operating free-air temperature (unless otherwise
noted) (continued)
12-bit DAC, output specifications
PARAMETER TEST CONDITIONS VCC MIN TYP MAX UNIT
No Load, VeREF+ = AVCC,
DAC12_xDAT = 0h, DAC12IR = 1,
DAC12AMPx = 7
2.2V/3V 0 0.005
V
V
Output voltage
range
No Load, VeREF+ = AVCC,
DAC12_xDAT = 0FFFh, DAC12IR = 1,
DAC12AMPx = 7
2.2V/3V AVCC−0.05 AVCC
VO
(see Note 1,
Figure 22)
RLoad= 3 kΩ, VeREF+ = AVCC,
DAC12_xDAT = 0h, DAC12IR = 1,
DAC12AMPx = 7
2.2V/3V 0 0.1 V
RLoad= 3 kΩ, VeREF+ = AVCC,
DAC12_xDAT = 0FFFh, DAC12IR = 1,
DAC12AMPx = 7
2.2V/3V AVCC−0.13 AVCC V
CL(DAC12)
Max DAC12
load
capacitance
2.2V/3V 100 pF
I
Max DAC12
2.2V −0.5 +0.5 mA
IL(DAC12)
load current 3V −1.0 +1.0 mA
RLoad= 3 kΩ
VO/P(DAC12) = 0 V
DAC12AMPx = 7
DAC12_xDAT = 0h
2.2V/3V 150 250
RO/P(DAC12)
Output
resistance
(see Figure 22)
RLoad= 3 kΩ
VO/P(DAC12) = AVCC
DAC12AMPx = 7
DAC12_xDAT = 0FFFh
2.2V/3V 150 250 Ω
RLoad= 3 kΩ
0.3 V < VO/P(DAC12) < AVCC − 0.3 V
DAC12AMPx = 7
2.2V/3V 1 4
NOTES: 1. Data is valid after the offset calibration of the output amplifier.
RO/P(DAC12_x)
Max
0.3
AVCC
AVCC −0.3V VOUT
Min
RLoad
AVCC
CLoad = 100pF
2
ILoad
DAC12
O/P(DAC12_x)
Figure 22. DAC12_x Output Resistance Tests
MSP430F15x, MSP430F16x, MSP430F161x
MIXED SIGNAL MICROCONTROLLER
SLAS368G − OCTOBER 2002 − REVISED MARCH 2011
POST OFFICE BOX 655303 • DALLAS, TEXAS 75265 47
electrical characteristics over recommended operating free-air temperature (unless otherwise
noted)
12-bit DAC, reference input specifications
PARAMETER TEST CONDITIONS VCC MIN TYP MAX UNIT
Ve
Reference input
DAC12IR=0 (see Notes 1 and 2) 2.2V/3V AVCC/3 AVCC+0.2
VeREF+ V
voltage range DAC12IR=1 (see Notes 3 and 4) 2.2V/3V AVcc AVcc+0.2
DAC12_0 IR = DAC12_1 IR = 0 2.2V/3V 20 MΩ
DAC12_0 IR = 1, DAC12_1 IR = 0 2.2V/3V
40 48 56 kΩ
Ri(VREF+),
Ri
Reference input
i t
DAC12_0 IR = 0, DAC12_1 IR = 1 2.2V/3V
(VREF+)
Ri(VeREF+)
p
resistance DAC12_0 IR = DAC12_1 IR =1,
DAC12_0 SREFx = DAC12_1 SREFx
(see Note 5)
2.2V/3V 20 24 28 kΩ
NOTES: 1. For a full-scale output, the reference input voltage can be as high as 1/3 of the maximum output voltage swing (AVCC).
2. The maximum voltage applied at reference input voltage terminal VeREF+ = [AVCC − VE(O)] / [3*(1 + EG)].
3. For a full-scale output, the reference input voltage can be as high as the maximum output voltage swing (AVCC).
4. The maximum voltage applied at reference input voltage terminal VeREF+ = [AVCC − VE(O)] / (1 + EG).
5. When DAC12IR = 1 and DAC12SREFx = 0 or 1 for both channels, the reference input resistive dividers for each DAC are in parallel
reducing the reference input resistance.
12-bit DAC, dynamic specifications; Vref = VCC, DAC12IR = 1 (see Figure 23 and Figure 24)
PARAMETER TEST CONDITIONS VCC MIN TYP MAX UNIT
DAC12_xDAT = 800h, DAC12AMPx = 0 → {2, 3, 4} 2.2V/3V 60 120
tON
DAC12
_ ,
ErrorV(O) < ±0.5 LSB
(see Note
ON DAC12AMPx = 0 → {5, 6} 2.2V/3V 15 30 μs on-time
1,Figure 23) DAC12AMPx = 0 → 7 2.2V/3V 6 12
μ
S ttli ti DAC12 DAT
DAC12AMPx = 2 2.2V/3V 100 200
tS(FS)
Settling time,
DAC12_xDAT =
DAC12AMPx = 3,5 2.2V/3V 40 80 μs
full-scale
80h→ F7Fh→ 80h
DAC12AMPx = 4,6,7 2.2V/3V 15 30
S ttli ti
DAC12 xDAT =
DAC12AMPx = 2 2.2V/3V 5
tS(C-C)
Settling time,
code to code
DAC12_3F8h→ 408h→ 3F8h
DAC12AMPx = 3,5 2.2V/3V 2 μs
BF8h→ C08h→ BF8h DAC12AMPx = 4,6,7 2.2V/3V 1
DAC12 DAT
DAC12AMPx = 2 2.2V/3V 0.05 0.12
SR Slew rate
DAC12_xDAT =
DAC12AMPx = 3,5 2.2V/3V 0.35 0.7 V/μs
80h→ F7Fh→ 80h
DAC12AMPx = 4,6,7 2.2V/3V 1.5 2.7
DAC12 DAT
DAC12AMPx = 2 2.2V/3V 10
Glitch energy: full-scale
DAC12_xDAT =
full DAC12AMPx = 3,5 2.2V/3V 10 nV-s
80h→ F7Fh→ 80h
DAC12AMPx = 4,6,7 2.2V/3V 10
nV NOTES: 1. RLoad and CLoad connected to AVSS (not AVCC/2) in Figure 23.
2. Slew rate applies to output voltage steps ≥ 200mV.
RLoad
AVCC
CLoad = 100pF
2
DAC Output
RO/P(DAC12.x)
ILoad
Conversion 1 Conversion 2
VOUT
Conversion 3
Glitch
Energy
+/− 1/2 LSB
+/− 1/2 LSB
tsettleLH tsettleHL
= 3 kΩ
Figure 23. Settling Time and Glitch Energy Testing
MSP430F15x, MSP430F16x, MSP430F161x
MIXED SIGNAL MICROCONTROLLER
SLAS368G − OCTOBER 2002 − REVISED MARCH 2011
48 POST OFFICE BOX 655303 • DALLAS, TEXAS 75265
electrical characteristics over recommended operating free-air temperature (unless otherwise
noted)
Conversion 1 Conversion 2
VOUT
Conversion 3
10%
tSRLH tSRHL
90%
10%
90%
Figure 24. Slew Rate Testing
12-bit DAC, dynamic specifications continued (TA = 25°C unless otherwise noted)
PARAMETER TEST CONDITIONS VCC MIN TYP MAX UNIT
DAC12AMPx = {2, 3, 4}, DAC12SREFx = 2,
DAC12IR = 1, DAC12_xDAT = 800h
2.2V/3V 40
BW−3dB
3-dB bandwidth,
VDC=1.5V, VAC=0.1VPP
DAC12AMPx = {5, 6}, DAC12SREFx = 2,
DAC12IR = 1, DAC12_xDAT = 800h
2.2V/3V 180 kHz
(see Figure 25)
DAC12AMPx = 7, DAC12SREFx = 2,
DAC12IR = 1, DAC12_xDAT = 800h
2.2V/3V 550
Channel to channel crosstalk
DAC12_0DAT = 800h, No Load,
DAC12_1DAT = 80h<−>F7Fh, RLoad = 3kΩ
fDAC12_1OUT = 10kHz @ 50/50 duty cycle
2.2V/3V −80
dB
(see Note 1 and Figure 26) DAC12_0DAT = 80h<−>F7Fh, RLoad = 3kΩ,
DAC12_1DAT = 800h, No Load
fDAC12_0OUT = 10kHz @ 50/50 duty cycle
2.2V/3V −80
NOTES: 1. RLOAD = 3 kΩ, CLOAD = 100 pF
VeREF+
AC
DC
RLoad
AVCC
CLoad = 100pF
2
ILoad
DAC12_x
DACx
= 3 kΩ
Figure 25. Test Conditions for 3-dB Bandwidth Specification
DAC12_xDAT 080h
VOUT
fToggle
7F7h
VDAC12_yOUT
080h 7F7h 080h
VDAC12_xOUT e
REF+ RLoad
AVCC
CLoad = 100pF
2
ILoad
DAC12_1
RLoad
AVCC
CLoad = 100pF
2
ILoad
DAC12_0
DAC0
DAC1
V
Figure 26. Crosstalk Test Conditions
MSP430F15x, MSP430F16x, MSP430F161x
MIXED SIGNAL MICROCONTROLLER
SLAS368G − OCTOBER 2002 − REVISED MARCH 2011
POST OFFICE BOX 655303 • DALLAS, TEXAS 75265 49
electrical characteristics over recommended operating free-air temperature (unless otherwise
noted)
flash memory
PARAMETER
TEST
CONDITIONS VCC MIN TYP MAX UNIT
VCC(PGM/
ERASE) Program and erase supply voltage 2.7 3.6 V
fFTG Flash timing generator frequency 257 476 kHz
IPGM Supply current from DVCC during program 2.7 V/ 3.6 V 3 5 mA
IERASE Supply current from DVCC during erase 2.7 V/ 3.6 V 3 7 mA
tCPT Cumulative program time see Note 1 2.7 V/ 3.6 V 4 ms
tCMErase Cumulative mass erase time see Note 2 2.7 V/ 3.6 V 200 ms
Program/Erase endurance 104 105 cycles
tRetention Data retention duration TJ = 25°C 100 years
tWord Word or byte program time 35
tBlock, 0 Block program time for 1st byte or word 30
tBlock, 1-63 Block program time for each additional byte or word
see Note 3
21
t
tBlock, End Block program end-sequence wait time
6
tFTG
tMass Erase Mass erase time 5297
tSeg Erase Segment erase time 4819
NOTES: 1. The cumulative program time must not be exceeded when writing to a 64-byte flash block. This parameter applies to all programming
methods: individual word/byte write and block write modes.
2. The mass erase duration generated by the flash timing generator is at least 11.1ms ( = 5297x1/fFTG,max = 5297x1/476kHz). To
achieve the required cumulative mass erase time the Flash Controller’s mass erase operation can be repeated until this time is met.
(A worst case minimum of 19 cycles are required).
3. These values are hardwired into the Flash Controller’s state machine (tFTG = 1/fFTG).
JTAG interface
PARAMETER
TEST
CONDITIONS VCC MIN NOM MAX UNIT
f TCK input frequency see Note 1
2.2 V 0 5 MHz
fTCK 3 V 0 10 MHz
RInternal Internal pull-up resistance on TMS, TCK, TDI/TCLK see Note 2 2.2 V/ 3 V 25 60 90 kΩ
NOTES: 1. fTCK may be restricted to meet the timing requirements of the module selected.
2. TMS, TDI/TCLK, and TCK pull-up resistors are implemented in all versions.
JTAG fuse (see Note 1)
PARAMETER
TEST
CONDITIONS VCC MIN NOM MAX UNIT
VCC(FB) Supply voltage during fuse-blow condition TA = 25°C 2.5 V
VFB Voltage level on TDI/TCLK for fuse-blow: F versions 6 7 V
IFB Supply current into TDI/TCLK during fuse blow 100 mA
tFB Time to blow fuse 1 ms
NOTES: 1. Once the fuse is blown, no further access to the MSP430 JTAG/Test and emulation features is possible. The JTAG block is switched
to bypass mode.
MSP430F15x, MSP430F16x, MSP430F161x
MIXED SIGNAL MICROCONTROLLER
SLAS368G − OCTOBER 2002 − REVISED MARCH 2011
50 POST OFFICE BOX 655303 • DALLAS, TEXAS 75265
APPLICATION INFORMATION
input/output schematics
port P1, P1.0 to P1.7, input/output with Schmitt trigger
P1.0/TACLK ...
P1IN.x
Module X IN
Pad Logic
Interrupt
Flag
Edge
Select
Interrupt
P1SEL.x
P1IES.x
P1IFG.x
P1IRQ.x P1IE.x
EN
D
Set
EN
Q
P1OUT.x
P1DIR.x
P1SEL.x
Module X OUT
Direction Control
From Module
0
1
0
1
P1.7/TA2
PnSel.x PnDIR.x
Dir. CONTROL
FROM MODULE PnOUT.x MODULE X OUT PnIN.x MODULE X IN PnIE.x PnIFG.x PnIES.x
P1Sel.0 P1DIR.0 P1DIR.0 P1OUT.0 DVSS P1IN.0 TACLK† P1IE.0 P1IFG.0 P1IES.0
P1Sel.1 P1DIR.1 P1DIR.1 P1OUT.1 Out0 signal† P1IN.1 CCI0A† P1IE.1 P1IFG.1 P1IES.1
P1Sel.2 P1DIR.2 P1DIR.2 P1OUT.2 Out1 signal† P1IN.2 CCI1A† P1IE.2 P1IFG.2 P1IES.2
P1Sel.3 P1DIR.3 P1DIR.3 P1OUT.3 Out2 signal† P1IN.3 CCI2A† P1IE.3 P1IFG.3 P1IES.3
P1Sel.4 P1DIR.4 P1DIR.4 P1OUT.4 SMCLK P1IN.4 unused P1IE.4 P1IFG.4 P1IES.4
P1Sel.5 P1DIR.5 P1DIR.5 P1OUT.5 Out0 signal† P1IN.5 unused P1IE.5 P1IFG.5 P1IES.5
P1Sel.6 P1DIR.6 P1DIR.6 P1OUT.6 Out1 signal† P1IN.6 unused P1IE.6 P1IFG.6 P1IES.6
P1Sel.7 P1DIR.7 P1DIR.7 P1OUT.7 Out2 signal† P1IN.7 unused P1IE.7 P1IFG.7 P1IES.7
† Signal from or to Timer_A
MSP430F15x, MSP430F16x, MSP430F161x
MIXED SIGNAL MICROCONTROLLER
SLAS368G − OCTOBER 2002 − REVISED MARCH 2011
POST OFFICE BOX 655303 • DALLAS, TEXAS 75265 51
APPLICATION INFORMATION
input/output schematics (continued)
port P2, P2.0 to P2.2, P2.6, and P2.7 input/output with Schmitt trigger
P2IN.x
P2OUT.x
Pad Logic
P2DIR.x
P2SEL.x
Module X OUT
Edge
Select
Interrupt
P2SEL.x
P2IES.x
P2IFG.x
P2IRQ.x P2IE.x
Direction Control
P2.0/ACLK
0
1
0
1
Interrupt
Flag
Set
EN
Q
Module X IN
EN
D
Bus Keeper
CAPD.X
P2.1/TAINCLK
P2.2/CAOUT/TA0
P2.6/ADC12CLK/DMAE0
P2.7/TA0
0: Input
1: Output
x: Bit Identifier 0 to 2, 6, and 7 for Port P2
From Module
PnSel.x PnDIR.x
Dir. CONTROL
FROM MODULE PnOUT.x MODULE X OUT PnIN.x MODULE X IN PnIE.x PnIFG.x PnIES.x
P2Sel.0 P2DIR.0 P2DIR.0 P2OUT.0 ACLK P2IN.0 unused P2IE.0 P2IFG.0 P2IES.0
P2Sel.1 P2DIR.1 P2DIR.1 P2OUT.1 DVSS P2IN.1 INCLK‡ P2IE.1 P2IFG.1 P2IES.1
P2Sel.2 P2DIR.2 P2DIR.2 P2OUT.2 CAOUT† P2IN.2 CCI0B‡ P2IE.2 P2IFG.2 P2IES.2
P2Sel.6 P2DIR.6 P2DIR.6 P2OUT.6 ADC12CLK¶ P2IN.6 DMAE0# P2IE.6 P2IFG.6 P2IES.6
P2Sel.7 P2DIR.7 P2DIR.7 P2OUT.7 Out0 signal§ P2IN.7 unused P2IE.7 P2IFG.7 P2IES.7
† Signal from Comparator_A
‡ Signal to Timer_A
§ Signal from Timer_A
¶ ADC12CLK signal is output of the 12-bit ADC module
# Signal to DMA, channel 0, 1 and 2
MSP430F15x, MSP430F16x, MSP430F161x
MIXED SIGNAL MICROCONTROLLER
SLAS368G − OCTOBER 2002 − REVISED MARCH 2011
52 POST OFFICE BOX 655303 • DALLAS, TEXAS 75265
APPLICATION INFORMATION
input/output schematics (continued)
port P2, P2.3 to P2.4, input/output with Schmitt trigger
Bus Keeper
P2IN.3
P2OUT.3
Pad Logic
P2DIR.3
P2SEL.3
Module X OUT
Edge
Select
Interrupt
P2SEL.3
P2IES.3
P2IFG.3
P2IRQ.3 P2IE.3
Direction Control
From Module
P2.3/CA0/TA1
0
1
0
1
Interrupt
Flag
Set
EN
Q
Module X IN
EN
D
P2IN.4
P2OUT.4
Pad Logic
P2DIR.4
P2SEL.4
Module X OUT
Edge
Select
Interrupt
P2SEL.4
P2IES.4
P2IFG.4
P2IRQ.4 P2IE.4
Direction Control
From Module
P2.4/CA1/TA2
0
1
0
1
Interrupt
Flag
Set
EN
Q
Module X IN
EN
D
Comparator_A
−
+
Reference Block
CCI1B
CAF
CAREF
P2CA
CAEX
CAREF
Bus Keeper
CAPD.3
CAPD.4
To Timer_A3
0: Input
1: Output
0: Input
1: Output
PnSel.x PnDIR.x
DIRECTION
CONTROL
FROM MODULE
PnOUT.x MODULE X OUT PnIN.x MODULE X IN PnIE.x PnIFG.x PnIES.x
P2Sel.3 P2DIR.3 P2DIR.3 P2OUT.3 Out1 signal† P2IN.3 unused P2IE.3 P2IFG.3 P2IES.3
P2Sel.4 P2DIR.4 P2DIR.4 P2OUT.4 Out2 signal† P2IN.4 unused P2IE.4 P2IFG.4 P2IES.4
† Signal from Timer_A
MSP430F15x, MSP430F16x, MSP430F161x
MIXED SIGNAL MICROCONTROLLER
SLAS368G − OCTOBER 2002 − REVISED MARCH 2011
POST OFFICE BOX 655303 • DALLAS, TEXAS 75265 53
APPLICATION INFORMATION
input/output schematics (continued)
port P2, P2.5, input/output with Schmitt trigger and Rosc function for the basic clock module
P2IN.5
P2OUT.5
Pad Logic
P2DIR.5
P2SEL.5
Module X OUT
Edge
Select
Interrupt
P2SEL.5
P2IES.5
P2IFG.5
P2IRQ.5 P2IE.5
Direction Control
P2.5/Rosc
0
1
0
1
Interrupt
Flag
Set
EN
Q
DCOR
Module X IN
EN
D
to
0 1
DC Generator
Bus Keeper
CAPD.5
DCOR: Control Bit From Basic Clock Module
If it Is Set, P2.5 Is Disconnected From P2.5 Pad
Internal to
Basic Clock
Module
VCC
0: Input
1: Output
From Module
PnSel.x PnDIR.x
DIRECTION
CONTROL
FROM MODULE
PnOUT.x MODULE X OUT PnIN.x MODULE X IN PnIE.x PnIFG.x PnIES.x
P2Sel.5 P2DIR.5 P2DIR.5 P2OUT.5 DVSS P2IN.5 unused P2IE.5 P2IFG.5 P2IES.5
MSP430F15x, MSP430F16x, MSP430F161x
MIXED SIGNAL MICROCONTROLLER
SLAS368G − OCTOBER 2002 − REVISED MARCH 2011
54 POST OFFICE BOX 655303 • DALLAS, TEXAS 75265
APPLICATION INFORMATION
input/output schematics (continued)
port P3, P3.0 and P3.4 to P3.7, input/output with Schmitt trigger
P3.0/STE0
P3IN.x
Module X IN
Pad Logic
EN
D
P3OUT.x
P3DIR.x
P3SEL.x
Module X OUT
Direction Control
From Module
0
1
0
1 P3.4/UTXD0
P3.5/URXD0
0: Input
1: Output
x: Bit Identifier, 0 and 4 to 7 for Port P3
P3.6/UTXD1‡
P3.7/URXD1¶
PnSel.x PnDIR.x
DIRECTION
CONTROL
FROM MODULE
PnOUT.x MODULE X OUT PnIN.x MODULE X IN
P3Sel.0 P3DIR.0 DVSS P3OUT.0 DVSS P3IN.0 STE0
P3Sel.4 P3DIR.4 DVCC P3OUT.4 UTXD0† P3IN.4 Unused
P3Sel.5 P3DIR.5 DVSS P3OUT.5 DVSS P3IN.5 URXD0§
P3Sel.6 P3DIR.6 DVCC P3OUT.6 UTXD1‡ P3IN.6 Unused
P3Sel.7 P3DIR.7 DVSS P3OUT.7 DVSS P3IN.7 URXD1¶
† Output from USART0 module
‡ Output from USART1 module
‡ Input to USART0 module
¶ Input to USART1 module
MSP430F15x, MSP430F16x, MSP430F161x
MIXED SIGNAL MICROCONTROLLER
SLAS368G − OCTOBER 2002 − REVISED MARCH 2011
POST OFFICE BOX 655303 • DALLAS, TEXAS 75265 55
APPLICATION INFORMATION
input/output schematics (continued)
port P3, P3.1, input/output with Schmitt trigger
P3.1/SIMO0/SDA
P3IN.1
Pad Logic
EN
D
P3OUT1
P3DIR.1
P3SEL.1
(SI)MO0 or SDAo/p
0
1
0
1
DCM_SIMO
SYNC
MM
STE
STC
From USART0
SI(MO)0 or SDAi/p
To USAET0
0: Input
1: Output
MSP430F15x, MSP430F16x, MSP430F161x
MIXED SIGNAL MICROCONTROLLER
SLAS368G − OCTOBER 2002 − REVISED MARCH 2011
56 POST OFFICE BOX 655303 • DALLAS, TEXAS 75265
APPLICATION INFORMATION
input/output schematics (continued)
port P3, P3.2, input/output with Schmitt trigger
P3.2/SOMI0
P3IN.2
Pad Logic
EN
D
P3OUT.2
P3DIR.2
P3SEL.2
0
1
0
1
DCM_SOMI
SYNC
MM
STE
STC
SO(MI)0
From USART0
(SO)MI0
To USART0
0: Input
1: Output
port P3, P3.3, input/output with Schmitt-trigger
P3.3/UCLK0/SCL
P3IN.3
Pad Logic
EN
D
P3OUT.3
P3DIR.3
P3SEL.3
UCLK.0
0
1
0
1
DCM_UCLK
SYNC
MM
STE
STC
From USART0
UCLK0
To USART0
0: Input
1: Output
NOTE: UART mode: The UART clock can only be an input. If UART mode and UART function are selected, the P3.3/UCLK0 is always
an input.
SPI, slave mode: The clock applied to UCLK0 is used to shift data in and out.
SPI, master mode: The clock to shift data in and out is supplied to connected devices on pin P3.3/UCLK0 (in slave mode).
I2C, slave mode: The clock applied to SCL is used to shift data in and out. The frequency of the clock source of the module must be
10 times the frequency of the SCL clock.
I2C, master mode: To shift data in and out, the clock is supplied via the SCL terminal to all I2C slaves. The frequency of the clock source
of the module must be 10 times the frequency of the SCL clock.
MSP430F15x, MSP430F16x, MSP430F161x
MIXED SIGNAL MICROCONTROLLER
SLAS368G − OCTOBER 2002 − REVISED MARCH 2011
POST OFFICE BOX 655303 • DALLAS, TEXAS 75265 57
APPLICATION INFORMATION
input/output schematics (continued)
port P4, P4.0 to P4.6, input/output with Schmitt trigger
P4OUT.x
Module X OUT
P4DIR.x
Direction Control
From Module
P4SEL.x
D
EN
0
1
1
0
Module X IN
P4IN.x
0: Input
1: Output
Bus
Keeper
Module IN of pin
P5.7/TBOUTH/SVSOUT
x: Bit Identifier, 0 to 6 for Port P4
P4.0/TB0 ...
P4.6/TB6
P4SEL.7
P4DIR.7
PnSel.x PnDIR.x
DIRECTION
CONTROL
FROM MODULE
PnOUT.x MODULE X OUT PnIN.x MODULE X IN
P4Sel.0 P4DIR.0 P4DIR.0 P4OUT.0 Out0 signal† P4IN.0 CCI0A / CCI0B‡
P4Sel.1 P4DIR.1 P4DIR.1 P4OUT.1 Out1 signal† P4IN.1 CCI1A / CCI1B‡
P4Sel.2 P4DIR.2 P4DIR.2 P4OUT.2 Out2 signal† P4IN.2 CCI2A / CCI2B‡
P4Sel.3 P4DIR.3 P4DIR.3 P4OUT.3 Out3 signal† P4IN.3 CCI3A / CCI3B‡
P4Sel.4 P4DIR.4 P4DIR.4 P4OUT.4 Out4 signal† P4IN.4 CCI4A / CCI4B‡
P4Sel.5 P4DIR.5 P4DIR.5 P4OUT.5 Out5 signal† P4IN.5 CCI5A / CCI5B‡
P4Sel.6 P4DIR.6 P4DIR.6 P4OUT.6 Out6 signal† P4IN.6 CCI6A
† Signal from Timer_B
‡ Signal to Timer_B
MSP430F15x, MSP430F16x, MSP430F161x
MIXED SIGNAL MICROCONTROLLER
SLAS368G − OCTOBER 2002 − REVISED MARCH 2011
58 POST OFFICE BOX 655303 • DALLAS, TEXAS 75265
APPLICATION INFORMATION
input/output schematics (continued)
port P4, P4.7, input/output with Schmitt trigger
P4.7/TBCLK
P4IN.7
Timer_B,
Pad Logic
EN
D
P4OUT.7
P4DIR.7
P4SEL.7
0
1
0
1
TBCLK
0: Input
1: Output
DVSS
port P5, P5.0 and P5.4 to P5.7, input/output with Schmitt trigger
P5.0/STE1
P5IN.x
Module X IN
Pad Logic
EN
D
P5OUT.x
P5DIR.x
P5SEL.x
Module X OUT
Direction Control
From Module
0
1
0
1 P5.4/MCLK
P5.5/SMCLK
P5.6/ACLK
P5.7/TBOUTH/SVSOUT
x: Bit Identifier, 0 and 4 to 7 for Port P5
0: Input
1: Output
PnSel.x PnDIR.x Dir. CONTROL FROM MODULE PnOUT.x MODULE X OUT PnIN.x MODULE X IN
P5Sel.0 P5DIR.0 DVSS P5OUT.0 DVSS P5IN.0 STE.1
P5Sel.4 P5DIR.4 DVCC P5OUT.4 MCLK P5IN.4 unused
P5Sel.5 P5DIR.5 DVCC P5OUT.5 SMCLK P5IN.5 unused
P5Sel.6 P5DIR.6 DVCC P5OUT.6 ACLK P5IN.6 unused
P5Sel.7 P5DIR.7 DVSS P5OUT.7 SVSOUT P5IN.7 TBOUTHiZ
NOTE: TBOUTHiZ signal is used by port module P4, pins P4.0 to P4.6. The function of TBOUTHiZ is mainly useful when used with Timer_B7.
MSP430F15x, MSP430F16x, MSP430F161x
MIXED SIGNAL MICROCONTROLLER
SLAS368G − OCTOBER 2002 − REVISED MARCH 2011
POST OFFICE BOX 655303 • DALLAS, TEXAS 75265 59
APPLICATION INFORMATION
input/output schematics (continued)
port P5, P5.1, input/output with Schmitt trigger
P5.1/SIMO1
P5IN.1
Pad Logic
EN
D
P5OUT.1
P5DIR.1
P5SEL.1
0
1
0
1
DCM_SIMO
SYNC
MM
STE
STC
(SI)MO1
From USART1
SI(MO)1
To USART1
0: Input
1: Output
port P5, P5.2, input/output with Schmitt trigger
P5.2/SOMI1
P5IN.2
Pad Logic
EN
D
P5OUT.2
P5DIR.2
P5SEL.2
0
1
0
1
DCM_SOMI
SYNC
MM
STE
STC
SO(MI)1
From USART1
(SO)MI1
To USART1
0: Input
1: Output
MSP430F15x, MSP430F16x, MSP430F161x
MIXED SIGNAL MICROCONTROLLER
SLAS368G − OCTOBER 2002 − REVISED MARCH 2011
60 POST OFFICE BOX 655303 • DALLAS, TEXAS 75265
APPLICATION INFORMATION
input/output schematics (continued)
port P5, P5.3, input/output with Schmitt trigger
P5.3/UCLK1
P5IN.3
Pad Logic
EN
D
P5OUT.3
P5DIR.3
P5SEL.3
0
1
0
1
DCM_SIMO
SYNC
MM
STE
STC
UCLK1
From USART1
UCLK1
To USART1
0: Input
1: Output
NOTE: UART mode: The UART clock can only be an input. If UART mode and UART function are selected, the P5.3/UCLK1 direction
is always input.
SPI, slave mode: The clock applied to UCLK1 is used to shift data in and out.
SPI, master mode: The clock to shift data in and out is supplied to connected devices on pin P5.3/UCLK1 (in slave mode).
MSP430F15x, MSP430F16x, MSP430F161x
MIXED SIGNAL MICROCONTROLLER
SLAS368G − OCTOBER 2002 − REVISED MARCH 2011
POST OFFICE BOX 655303 • DALLAS, TEXAS 75265 61
APPLICATION INFORMATION
input/output schematics (continued)
port P6, P6.0 to P6.5, input/output with Schmitt trigger
P6IN.x
Module X IN
Pad Logic
EN
D
P6OUT.x
P6DIR.x
P6SEL.x
Module X OUT
Direction Control
From Module
0
1
0
1
Bus Keeper
To ADC
From ADC
0: Input
1: Output
x: Bit Identifier, 0 to 5 for Port P6
P6.0/A0
P6.1/A1
P6.2/A2
P6.3/A3
P6.4/A4
P6.5/A5
NOTE: Analog signals applied to digital gates can cause current flow from the positive to the negative terminal. The throughput current flows if
the analog signal is in the range of transitions 0→1 or 1←0. The value of the throughput current depends on the driving capability of the
gate. For MSP430, it is approximately 100 μA.
Use P6SEL.x=1 to prevent throughput current. P6SEL.x should be set, even if the signal at the pin is not being used by the ADC12.
PnSel.x PnDIR.x
DIR. CONTROL
FROM MODULE PnOUT.x MODULE X OUT PnIN.x MODULE X IN
P6Sel.0 P6DIR.0 P6DIR.0 P6OUT.0 DVSS P6IN.0 unused
P6Sel.1 P6DIR.1 P6DIR.1 P6OUT.1 DVSS P6IN.1 unused
P6Sel.2 P6DIR.2 P6DIR.2 P6OUT.2 DVSS P6IN.2 unused
P6Sel.3 P6DIR.3 P6DIR.3 P6OUT.3 DVSS P6IN.3 unused
P6Sel.4 P6DIR.4 P6DIR.4 P6OUT.4 DVSS P6IN.4 unused
P6Sel.5 P6DIR.5 P6DIR.5 P6OUT.5 DVSS P6IN.5 unused
NOTE: The signal at pins P6.x/Ax is used by the 12-bit ADC module.
MSP430F15x, MSP430F16x, MSP430F161x
MIXED SIGNAL MICROCONTROLLER
SLAS368G − OCTOBER 2002 − REVISED MARCH 2011
62 POST OFFICE BOX 655303 • DALLAS, TEXAS 75265
APPLICATION INFORMATION
input/output schematics (continued)
port P6, P6.6, input/output with Schmitt trigger
0, if DAC12.0CALON = 0 and DAC12.0AMP > 1
P6OUT.6
DVSS
P6DIR.6
P6DIR.6
P6SEL.6
D
EN
0
1
1
0
0: Port Active, T-Switch Off
1: T-Switch On, Port Disabled
P6.6/A6/DAC0
P6IN.6
Pad Logic
0: Input
1: Output
Bus
Keeper
1
0
1, if DAC12.0AMP = 1
’1’, if DAC12.0AMP > 0
1, if DAC12.0AMP >1
+
−
INCH = 6†
a6†
†Signal from or to ADC12
MSP430F15x, MSP430F16x, MSP430F161x
MIXED SIGNAL MICROCONTROLLER
SLAS368G − OCTOBER 2002 − REVISED MARCH 2011
POST OFFICE BOX 655303 • DALLAS, TEXAS 75265 63
APPLICATION INFORMATION
input/output schematics (continued)
port P6, P6.7, input/output with Schmitt trigger
0, if DAC12.0CALON = 0 and DAC12.0AMP > 1
P6OUT.7
DVSS
P6DIR.7
P6DIR.7
P6SEL.6
D
EN
0
1
1
0
0: Port Active, T-Switch Off
1: T-Switch On, Port Disabled
P6.7/A7/
P6IN.7
Pad Logic
0: Input
1: Output
Bus
Keeper
1
0
1, if DAC12.0AMP = 1
’1’, if DAC12.0AMP > 0
1, if DAC12.0AMP > 1
+
−
INCH = 7‡
a7‡
†Signal to SVS Block, Selected if VLD = 15
‡Signal From or To ADC12
§VLD Control Bits are Located in SVS
DAC1/SVSIN
To SVS Mux (15)†
’1’, if VLD = 15§
MSP430F15x, MSP430F16x, MSP430F161x
MIXED SIGNAL MICROCONTROLLER
SLAS368G − OCTOBER 2002 − REVISED MARCH 2011
64 POST OFFICE BOX 655303 • DALLAS, TEXAS 75265
APPLICATION INFORMATION
JTAG pins TMS, TCK, TDI/TCLK, TDO/TDI, input/output with Schmitt trigger
TDI
TDO
TMS
TCK
Test
JTAG
and
Emulation
Module
Burn & Test
Fuse
Controlled by JTAG
Controlled by JTAG
Controlled
by JTAG
DVCC
DVCC
DVCC During Programming Activity and
During Blowing of the Fuse, Pin
TDO/TDI Is Used to Apply the Test
Input Data for JTAG Circuitry
TDO/TDI
TDI/TCLK
TMS
TCK
Fuse
DVCC
MSP430F15x, MSP430F16x, MSP430F161x
MIXED SIGNAL MICROCONTROLLER
SLAS368G − OCTOBER 2002 − REVISED MARCH 2011
POST OFFICE BOX 655303 • DALLAS, TEXAS 75265 65
APPLICATION INFORMATION
JTAG fuse check mode
MSP430 devices that have the fuse on the TDI/TCLK terminal have a fuse check mode that tests the continuity
of the fuse the first time the JTAG port is accessed after a power-on reset (POR). When activated, a fuse check
current, ITF, of 1 mA at 3 V, 2.5 mA at 5 V can flow from the TDI/TCLK pin to ground if the fuse is not burned.
Care must be taken to avoid accidentally activating the fuse check mode and increasing overall system power
consumption.
Activation of the fuse check mode occurs with the first negative edge on the TMS pin after power up or if the
TMS is being held low during power up. The second positive edge on the TMS pin deactivates the fuse check
mode. After deactivation, the fuse check mode remains inactive until another POR occurs. After each POR the
fuse check mode has the potential to be activated.
The fuse check current will only flow when the fuse check mode is active and the TMS pin is in a low state (see
Figure 27). Therefore, the additional current flow can be prevented by holding the TMS pin high (default
condition).
Time TMS Goes Low After POR
TMS
ITF
ITDI/TCLK
Figure 27. Fuse Check Mode Current, MSP430F15x/16x/161x
MSP430F15x, MSP430F16x, MSP430F161x
MIXED SIGNAL MICROCONTROLLER
SLAS368G − OCTOBER 2002 − REVISED MARCH 2011
66 POST OFFICE BOX 655303 • DALLAS, TEXAS 75265
Data Sheet Revision History
LITERATURE
NUMBER SUMMARY
SLAS368F
In absolute maximum ratings table, changed Tstg min from −40°C to −55°C (page 25)
Added Development Tools Support section (page 2)
SLAS368G Changed limits on td(SVSon) parameter (page 35)
PACKAGE OPTION ADDENDUM
www.ti.com 11-Apr-2013
Addendum-Page 1
PACKAGING INFORMATION
Orderable Device Status
(1)
Package Type Package
Drawing
Pins Package
Qty
Eco Plan
(2)
Lead/Ball Finish MSL Peak Temp
(3)
Op Temp (°C) Top-Side Markings
(4)
Samples
MSP430F155IPM ACTIVE LQFP PM 64 160 Green (RoHS
& no Sb/Br)
CU NIPDAU Level-3-260C-168 HR -40 to 85 M430F155
MSP430F155IPMR ACTIVE LQFP PM 64 1000 Green (RoHS
& no Sb/Br)
CU NIPDAU Level-3-260C-168 HR -40 to 85 M430F155
MSP430F155IRTDR ACTIVE VQFN RTD 64 2500 Green (RoHS
& no Sb/Br)
CU SN Level-3-260C-168 HR M430F155
MSP430F155IRTDT ACTIVE VQFN RTD 64 250 Green (RoHS
& no Sb/Br)
CU SN Level-3-260C-168 HR M430F155
MSP430F156IPM ACTIVE LQFP PM 64 160 Green (RoHS
& no Sb/Br)
CU NIPDAU Level-3-260C-168 HR -40 to 85 M430F156
MSP430F156IPMR ACTIVE LQFP PM 64 1000 Green (RoHS
& no Sb/Br)
CU NIPDAU Level-3-260C-168 HR -40 to 85 M430F156
MSP430F156IRTDR ACTIVE VQFN RTD 64 2500 Green (RoHS
& no Sb/Br)
CU SN Level-3-260C-168 HR M430F156
MSP430F156IRTDT ACTIVE VQFN RTD 64 250 Green (RoHS
& no Sb/Br)
CU SN Level-3-260C-168 HR M430F156
MSP430F157IPM ACTIVE LQFP PM 64 160 Green (RoHS
& no Sb/Br)
CU NIPDAU Level-3-260C-168 HR -40 to 85 M430F157
MSP430F157IPMR ACTIVE LQFP PM 64 1000 Green (RoHS
& no Sb/Br)
CU NIPDAU Level-3-260C-168 HR -40 to 85 M430F157
MSP430F157IRTDR ACTIVE VQFN RTD 64 2500 Green (RoHS
& no Sb/Br)
CU SN Level-3-260C-168 HR M430F157
MSP430F157IRTDT ACTIVE VQFN RTD 64 250 Green (RoHS
& no Sb/Br)
CU SN Level-3-260C-168 HR M430F157
MSP430F1610IPM ACTIVE LQFP PM 64 160 Green (RoHS
& no Sb/Br)
CU NIPDAU Level-3-260C-168 HR M430F1610
MSP430F1610IPMR ACTIVE LQFP PM 64 1000 Green (RoHS
& no Sb/Br)
CU NIPDAU Level-3-260C-168 HR M430F1610
MSP430F1610IRTD ACTIVE VQFN RTD 64 TBD Call TI Call TI
MSP430F1610IRTDR ACTIVE VQFN RTD 64 2500 Green (RoHS
& no Sb/Br)
CU SN Level-3-260C-168 HR M430F1610
MSP430F1610IRTDT ACTIVE VQFN RTD 64 250 Green (RoHS
& no Sb/Br)
CU SN Level-3-260C-168 HR M430F1610
PACKAGE OPTION ADDENDUM
www.ti.com 11-Apr-2013
Addendum-Page 2
Orderable Device Status
(1)
Package Type Package
Drawing
Pins Package
Qty
Eco Plan
(2)
Lead/Ball Finish MSL Peak Temp
(3)
Op Temp (°C) Top-Side Markings
(4)
Samples
MSP430F1611IPM ACTIVE LQFP PM 64 160 Green (RoHS
& no Sb/Br)
CU NIPDAU Level-3-260C-168 HR -40 to 85 M430F1611
MSP430F1611IPMR ACTIVE LQFP PM 64 1000 Green (RoHS
& no Sb/Br)
CU NIPDAU Level-3-260C-168 HR -40 to 85 M430F1611
MSP430F1611IRTD ACTIVE VQFN RTD 64 TBD Call TI Call TI
MSP430F1611IRTDR ACTIVE VQFN RTD 64 2500 Green (RoHS
& no Sb/Br)
CU SN Level-3-260C-168 HR M430F1611
MSP430F1611IRTDT ACTIVE VQFN RTD 64 250 Green (RoHS
& no Sb/Br)
CU SN Level-3-260C-168 HR M430F1611
MSP430F1612IPM ACTIVE LQFP PM 64 160 Green (RoHS
& no Sb/Br)
CU NIPDAU Level-3-260C-168 HR M430F1612
MSP430F1612IPMR ACTIVE LQFP PM 64 1000 Green (RoHS
& no Sb/Br)
CU NIPDAU Level-3-260C-168 HR M430F1612
MSP430F1612IRTD ACTIVE VQFN RTD 64 TBD Call TI Call TI
MSP430F1612IRTDR ACTIVE VQFN RTD 64 2500 Green (RoHS
& no Sb/Br)
CU SN Level-3-260C-168 HR M430F1612
MSP430F1612IRTDT ACTIVE VQFN RTD 64 250 Green (RoHS
& no Sb/Br)
CU SN Level-3-260C-168 HR M430F1612
MSP430F167IPM ACTIVE LQFP PM 64 160 Green (RoHS
& no Sb/Br)
CU NIPDAU Level-3-260C-168 HR -40 to 85 M430F167
MSP430F167IPMR ACTIVE LQFP PM 64 1000 Green (RoHS
& no Sb/Br)
CU NIPDAU Level-3-260C-168 HR -40 to 85 M430F167
MSP430F167IRTDR ACTIVE VQFN RTD 64 2500 Green (RoHS
& no Sb/Br)
CU SN Level-3-260C-168 HR M430F167
MSP430F167IRTDT ACTIVE VQFN RTD 64 250 Green (RoHS
& no Sb/Br)
CU SN Level-3-260C-168 HR M430F167
MSP430F168IPM ACTIVE LQFP PM 64 160 Green (RoHS
& no Sb/Br)
CU NIPDAU Level-3-260C-168 HR -40 to 85 M430F168
MSP430F168IPMR ACTIVE LQFP PM 64 1000 Green (RoHS
& no Sb/Br)
CU NIPDAU Level-3-260C-168 HR -40 to 85 M430F168
MSP430F168IRTDR ACTIVE VQFN RTD 64 2500 Green (RoHS
& no Sb/Br)
CU SN Level-3-260C-168 HR M430F168
MSP430F168IRTDT ACTIVE VQFN RTD 64 250 Green (RoHS
& no Sb/Br)
CU SN Level-3-260C-168 HR M430F168
PACKAGE OPTION ADDENDUM
www.ti.com 11-Apr-2013
Addendum-Page 3
Orderable Device Status
(1)
Package Type Package
Drawing
Pins Package
Qty
Eco Plan
(2)
Lead/Ball Finish MSL Peak Temp
(3)
Op Temp (°C) Top-Side Markings
(4)
Samples
MSP430F169IPM ACTIVE LQFP PM 64 160 Green (RoHS
& no Sb/Br)
CU NIPDAU Level-3-260C-168 HR -40 to 85 M430F169
MSP430F169IPMR ACTIVE LQFP PM 64 1000 Green (RoHS
& no Sb/Br)
CU NIPDAU Level-3-260C-168 HR -40 to 85 M430F169
MSP430F169IRTDR ACTIVE VQFN RTD 64 2500 Green (RoHS
& no Sb/Br)
CU SN Level-3-260C-168 HR M430F169
MSP430F169IRTDT ACTIVE VQFN RTD 64 250 Green (RoHS
& no Sb/Br)
CU SN Level-3-260C-168 HR M430F169
(1) The marketing status values are defined as follows:
ACTIVE: Product device recommended for new designs.
LIFEBUY: TI has announced that the device will be discontinued, and a lifetime-buy period is in effect.
NRND: Not recommended for new designs. Device is in production to support existing customers, but TI does not recommend using this part in a new design.
PREVIEW: Device has been announced but is not in production. Samples may or may not be available.
OBSOLETE: TI has discontinued the production of the device.
(2) Eco Plan - The planned eco-friendly classification: Pb-Free (RoHS), Pb-Free (RoHS Exempt), or Green (RoHS & no Sb/Br) - please check http://www.ti.com/productcontent for the latest availability
information and additional product content details.
TBD: The Pb-Free/Green conversion plan has not been defined.
Pb-Free (RoHS): TI's terms "Lead-Free" or "Pb-Free" mean semiconductor products that are compatible with the current RoHS requirements for all 6 substances, including the requirement that
lead not exceed 0.1% by weight in homogeneous materials. Where designed to be soldered at high temperatures, TI Pb-Free products are suitable for use in specified lead-free processes.
Pb-Free (RoHS Exempt): This component has a RoHS exemption for either 1) lead-based flip-chip solder bumps used between the die and package, or 2) lead-based die adhesive used between
the die and leadframe. The component is otherwise considered Pb-Free (RoHS compatible) as defined above.
Green (RoHS & no Sb/Br): TI defines "Green" to mean Pb-Free (RoHS compatible), and free of Bromine (Br) and Antimony (Sb) based flame retardants (Br or Sb do not exceed 0.1% by weight
in homogeneous material)
(3) MSL, Peak Temp. -- The Moisture Sensitivity Level rating according to the JEDEC industry standard classifications, and peak solder temperature.
(4) Multiple Top-Side Markings will be inside parentheses. Only one Top-Side Marking contained in parentheses and separated by a "~" will appear on a device. If a line is indented then it is a
continuation of the previous line and the two combined represent the entire Top-Side Marking for that device.
Important Information and Disclaimer:The information provided on this page represents TI's knowledge and belief as of the date that it is provided. TI bases its knowledge and belief on information
provided by third parties, and makes no representation or warranty as to the accuracy of such information. Efforts are underway to better integrate information from third parties. TI has taken and
continues to take reasonable steps to provide representative and accurate information but may not have conducted destructive testing or chemical analysis on incoming materials and chemicals.
TI and TI suppliers consider certain information to be proprietary, and thus CAS numbers and other limited information may not be available for release.
In no event shall TI's liability arising out of such information exceed the total purchase price of the TI part(s) at issue in this document sold by TI to Customer on an annual basis.
TAPE AND REEL INFORMATION
*All dimensions are nominal
Device Package
Type
Package
Drawing
Pins SPQ Reel
Diameter
(mm)
Reel
Width
W1 (mm)
A0
(mm)
B0
(mm)
K0
(mm)
P1
(mm)
W
(mm)
Pin1
Quadrant
MSP430F155IPMR LQFP PM 64 1000 330.0 24.4 13.0 13.0 2.1 16.0 24.0 Q2
MSP430F156IPMR LQFP PM 64 1000 330.0 24.4 13.0 13.0 2.1 16.0 24.0 Q2
MSP430F157IPMR LQFP PM 64 1000 330.0 24.4 13.0 13.0 2.1 16.0 24.0 Q2
MSP430F1610IPMR LQFP PM 64 1000 330.0 24.4 13.0 13.0 2.1 16.0 24.0 Q2
MSP430F1611IPMR LQFP PM 64 1000 330.0 24.4 13.0 13.0 2.1 16.0 24.0 Q2
MSP430F1612IPMR LQFP PM 64 1000 330.0 24.4 13.0 13.0 2.1 16.0 24.0 Q2
MSP430F167IPMR LQFP PM 64 1000 330.0 24.4 13.0 13.0 2.1 16.0 24.0 Q2
MSP430F168IPMR LQFP PM 64 1000 330.0 24.4 13.0 13.0 2.1 16.0 24.0 Q2
MSP430F169IPMR LQFP PM 64 1000 330.0 24.4 13.0 13.0 2.1 16.0 24.0 Q2
PACKAGE MATERIALS INFORMATION
www.ti.com 13-Sep-2013
Pack Materials-Page 1
*All dimensions are nominal
Device Package Type Package Drawing Pins SPQ Length (mm) Width (mm) Height (mm)
MSP430F155IPMR LQFP PM 64 1000 367.0 367.0 45.0
MSP430F156IPMR LQFP PM 64 1000 367.0 367.0 45.0
MSP430F157IPMR LQFP PM 64 1000 367.0 367.0 45.0
MSP430F1610IPMR LQFP PM 64 1000 367.0 367.0 45.0
MSP430F1611IPMR LQFP PM 64 1000 367.0 367.0 45.0
MSP430F1612IPMR LQFP PM 64 1000 367.0 367.0 45.0
MSP430F167IPMR LQFP PM 64 1000 367.0 367.0 45.0
MSP430F168IPMR LQFP PM 64 1000 367.0 367.0 45.0
MSP430F169IPMR LQFP PM 64 1000 367.0 367.0 45.0
PACKAGE MATERIALS INFORMATION
www.ti.com 13-Sep-2013
Pack Materials-Page 2
MECHANICAL DATA
MTQF008A – JANUARY 1995 – REVISED DECEMBER 1996
POST OFFICE BOX 655303 • DALLAS, TEXAS 75265 1
PM (S-PQFP-G64) PLASTIC QUAD FLATPACK
4040152/C 11/96
32
17
0,13 NOM
0,25
0,45
0,75
Seating Plane
0,05 MIN
Gage Plane
0,27
33
16
48
1
0,17
49
64
SQ
SQ
10,20
11,80
12,20
9,80
7,50 TYP
1,60 MAX
1,45
1,35
0,08
0,50 0,08 M
0°–7°
NOTES: A. All linear dimensions are in millimeters.
B. This drawing is subject to change without notice.
C. Falls within JEDEC MS-026
D. May also be thermally enhanced plastic with leads connected to the die pads.
IMPORTANT NOTICE
Texas Instruments Incorporated and its subsidiaries (TI) reserve the right to make corrections, enhancements, improvements and other
changes to its semiconductor products and services per JESD46, latest issue, and to discontinue any product or service per JESD48, latest
issue. Buyers should obtain the latest relevant information before placing orders and should verify that such information is current and
complete. All semiconductor products (also referred to herein as “components”) are sold subject to TI’s terms and conditions of sale
supplied at the time of order acknowledgment.
TI warrants performance of its components to the specifications applicable at the time of sale, in accordance with the warranty in TI’s terms
and conditions of sale of semiconductor products. Testing and other quality control techniques are used to the extent TI deems necessary
to support this warranty. Except where mandated by applicable law, testing of all parameters of each component is not necessarily
performed.
TI assumes no liability for applications assistance or the design of Buyers’ products. Buyers are responsible for their products and
applications using TI components. To minimize the risks associated with Buyers’ products and applications, Buyers should provide
adequate design and operating safeguards.
TI does not warrant or represent that any license, either express or implied, is granted under any patent right, copyright, mask work right, or
other intellectual property right relating to any combination, machine, or process in which TI components or services are used. Information
published by TI regarding third-party products or services does not constitute a license to use such products or services or a warranty or
endorsement thereof. Use of such information may require a license from a third party under the patents or other intellectual property of the
third party, or a license from TI under the patents or other intellectual property of TI.
Reproduction of significant portions of TI information in TI data books or data sheets is permissible only if reproduction is without alteration
and is accompanied by all associated warranties, conditions, limitations, and notices. TI is not responsible or liable for such altered
documentation. Information of third parties may be subject to additional restrictions.
Resale of TI components or services with statements different from or beyond the parameters stated by TI for that component or service
voids all express and any implied warranties for the associated TI component or service and is an unfair and deceptive business practice.
TI is not responsible or liable for any such statements.
Buyer acknowledges and agrees that it is solely responsible for compliance with all legal, regulatory and safety-related requirements
concerning its products, and any use of TI components in its applications, notwithstanding any applications-related information or support
that may be provided by TI. Buyer represents and agrees that it has all the necessary expertise to create and implement safeguards which
anticipate dangerous consequences of failures, monitor failures and their consequences, lessen the likelihood of failures that might cause
harm and take appropriate remedial actions. Buyer will fully indemnify TI and its representatives against any damages arising out of the use
of any TI components in safety-critical applications.
In some cases, TI components may be promoted specifically to facilitate safety-related applications. With such components, TI’s goal is to
help enable customers to design and create their own end-product solutions that meet applicable functional safety standards and
requirements. Nonetheless, such components are subject to these terms.
No TI components are authorized for use in FDA Class III (or similar life-critical medical equipment) unless authorized officers of the parties
have executed a special agreement specifically governing such use.
Only those TI components which TI has specifically designated as military grade or “enhanced plastic” are designed and intended for use in
military/aerospace applications or environments. Buyer acknowledges and agrees that any military or aerospace use of TI components
which have not been so designated is solely at the Buyer's risk, and that Buyer is solely responsible for compliance with all legal and
regulatory requirements in connection with such use.
TI has specifically designated certain components as meeting ISO/TS16949 requirements, mainly for automotive use. In any case of use of
non-designated products, TI will not be responsible for any failure to meet ISO/TS16949.
Products Applications
Audio www.ti.com/audio Automotive and Transportation www.ti.com/automotive
Amplifiers amplifier.ti.com Communications and Telecom www.ti.com/communications
Data Converters dataconverter.ti.com Computers and Peripherals www.ti.com/computers
DLP® Products www.dlp.com Consumer Electronics www.ti.com/consumer-apps
DSP dsp.ti.com Energy and Lighting www.ti.com/energy
Clocks and Timers www.ti.com/clocks Industrial www.ti.com/industrial
Interface interface.ti.com Medical www.ti.com/medical
Logic logic.ti.com Security www.ti.com/security
Power Mgmt power.ti.com Space, Avionics and Defense www.ti.com/space-avionics-defense
Microcontrollers microcontroller.ti.com Video and Imaging www.ti.com/video
RFID www.ti-rfid.com
OMAP Applications Processors www.ti.com/omap TI E2E Community e2e.ti.com
Wireless Connectivity www.ti.com/wirelessconnectivity
Mailing Address: Texas Instruments, Post Office Box 655303, Dallas, Texas 75265
Copyright © 2013, Texas Instruments Incorporated
20 mW Power, 2.3 V to 5.5 V,
75 MHz Complete DDS
Data Sheet AD9834
FEATURES
Narrow-band SFDR >72 dB
2.3 V to 5.5 V power supply
Output frequency up to 37.5 MHz
Sine output/triangular output
On-board comparator
3-wire SPI® interface
Extended temperature range: −40°C to +105°C
Power-down option
20 mW power consumption at 3 V
20-lead TSSOP
APPLICATIONS
Frequency stimulus/waveform generation
Frequency phase tuning and modulation
Low power RF/communications systems
Liquid and gas flow measurement
Sensory applications: proximity, motion, and defect detection
Test and medical equipment
GENERAL DESCRIPTION
The AD9834 is a 75 MHz low power DDS device capable of producing high performance sine and triangular outputs. It also has an on-board comparator that allows a square wave to be produced for clock generation. Consuming only 20 mW of power at 3 V makes the AD9834 an ideal candidate for power-sensitive applications.Capability for phase modulation and frequency modulation is provided. The frequency registers are 28 bits; with a 75 MHz clock rate, resolution of 0.28 Hz can be achieved. Similarly, with a 1 MHz clock rate, the AD9834 can be tuned to 0.004 Hz resolution. Frequency and phase modulation are affected by loading registers through the serial interface and toggling the registers using software or the FSELECT pin and PSELECT pin, respectively.
The AD9834 is written to using a 3-wire serial interface. This serial interface operates at clock rates up to 40 MHz and is compatible with DSP and microcontroller standards.
The device operates with a power supply from 2.3 V to 5.5 V. The analog and digital sections are independent and can be run from different power supplies, for example, AVDD can equal 5 V with DVDD equal to 3 V.
The AD9834 has a power-down pin (SLEEP) that allows external control of the power-down mode. Sections of the device that are not being used can be powered down to minimize the current consumption. For example, the DAC can be powered down when a clock output is being generated.
The part is available in a 20-lead TSSOP.
FUNCTIONAL BLOCK DIAGRAM
12ΣMUXMUXCOMPARATORMSBCAP/2.5VDVDDAGNDAVDDMCLKAD9834FSYNCSCLKSDATACOMPIOUTIOUTBDGNDREGULATORREFOUTFS ADJUSTVINFSELECT12-BIT PHASE0 REG12-BIT PHASE1 REGSLEEPRESETPSELECTMUXMUXMUXSIGN BIT OUTVCC2.5VON-BOARDREFERENCE16-BIT CONTROLREGISTERFULL-SCALECONTROL10-BITDACDIVIDEDBY 2SINROMPHASEACCUMULATOR(28-BIT)28-BIT FREQ0REG28-BIT FREQ1REGSERIAL INTERFACEANDCONTROL LOGIC02705-001
Figure 1. Rev. D Document Feedback
Information furnished by Analog Devices is believed to be accurate and reliable. However, no
responsibility is assumed by Analog Devices for its use, nor for any infringements of patents or other
rights of third parties that may result from its use. Specifications subject to change without notice. No
license is granted by implication or otherwise under any patent or patent rights of Analog Devices.
Trademarks and registered trademarks are the property of their respective owners.
One Technology Way, P.O. Box 9106, Norwood, MA 02062-9106, U.S.A.
Tel: 781.329.4700 ©2003–2014 Analog Devices, Inc. All rights reserved.
Technical Support www.analog.com
AD9834 Data Sheet
TABLE OF CONTENTS
Features .............................................................................................. 1
Applications ....................................................................................... 1
General Description ......................................................................... 1
Functional Block Diagram .............................................................. 1
Revision History ............................................................................... 3
Specifications ..................................................................................... 4
Timing Characteristics ................................................................ 6
Absolute Maximum Ratings ............................................................ 7
ESD Caution .................................................................................. 7
Pin Configuration and Function Descriptions ............................. 8
Typical Performance Characteristics ........................................... 10
Terminology .................................................................................... 14
Theory of Operation ...................................................................... 15
Circuit Description ......................................................................... 16
Numerically Controlled Oscillator Plus Phase Modulator ... 16
SIN ROM ..................................................................................... 16
Digital-to-Analog Converter (DAC) ....................................... 16
Comparator ................................................................................. 16
Regulator ...................................................................................... 17
Output Voltage Compliance ...................................................... 17
Functional Description .................................................................. 18
Serial Interface ............................................................................ 18
Powering Up the AD9834 ......................................................... 18
Latency ......................................................................................... 18
Control Register ......................................................................... 18
Frequency and Phase Registers ................................................ 20
Writing to a Frequency Register ............................................... 21
Writing to a Phase Register ....................................................... 21
RESET Function ......................................................................... 21
SLEEP Function .......................................................................... 21
SIGN BIT OUT Pin .................................................................... 22
The IOUT and IOUTB Pins ...................................................... 22
Applications Information .............................................................. 23
Grounding and Layout .................................................................. 26
Interfacing to Microprocessors ..................................................... 27
AD9834 to ADSP-21xx Interface ............................................. 27
AD9834 to 68HC11/68L11 Interface ....................................... 27
AD9834 to 80C51/80L51 Interface .......................................... 28
AD9834 to DSP56002 Interface ............................................... 28
Outline Dimensions ....................................................................... 29
Ordering Guide .......................................................................... 29
Rev. D | Page 2 of 32
Data Sheet AD9834
REVISION HISTORY
3/14—Rev. C to Rev. D
Changes to Table 3 ............................................................................ 7
Deleted Evaluation Board Section ................................................ 29
Changes to Ordering Guide ........................................................... 35
2/11—Rev. B to Rev. C Changes to IDD Parameter, Table 1 .................................................. 5 Changes to FS ADJUST Description, Table 4 ................................ 8 Added Output Voltage Compliance Section................................ 17 Changes to Figure 31 ...................................................................... 23 Changes to Figure 32 ...................................................................... 24 Deleted Using the AD9834 Evaluation Board Section and the Prototyping Area Section ............................................................... 28 Added System Development Platform Section, AD9834 to SPORT Interface Section, Figure 39, and Figure 40; Renumbered Sequentially .............................................................. 29 Changes to XO vs. External Clock Section and Power Supply Section .............................................................................................. 29 Deleted Bill of Materials, Table 19; Renumbered Sequentially .............................................................. 30 Added Evaluation Board Schematics Section and Figure 41 .... 30 Added Figure 42 .............................................................................. 31 Added Evaluation Board Layout Section and Figure 43 ............ 32 Added Figure 44 .............................................................................. 33 Added Figure 45 .............................................................................. 34 Changes to Ordering Guide ........................................................... 35
4/10—Rev. A to Rev. B Changes to Comparator Section ................................................... 15 Added Figure 28 .............................................................................. 16 Changes to Serial Interface Section .............................................. 17
8/06—Rev. 0 to Rev. A Updated Format ................................................................. Universal Changed to 75 MHz Complete DDS ............................... Universal Changes to Features Section ............................................................ 1 Changes to Table 1 ............................................................................ 4 Changes to Table 2 ............................................................................ 6 Changes to Table 3 ............................................................................ 8 Added Figure 10, Figures Renumbered Sequentially ................... 9 Added Figure 16 and Figure 17, Figures Renumbered Sequentially ...................................................................................... 10 Changes to Table 6 .......................................................................... 19 Changes to Writing a Frequency Register Section ..................... 20 Changes to Figure 29 ...................................................................... 21 Changes to Table 19 ........................................................................ 30 Changes to Figure 38 ...................................................................... 28
2/03—Revision 0: Initial Version
Rev. D | Page 3 of 32
AD9834 Data Sheet
SPECIFICATIONS
VDD = 2.3 V to 5.5 V, AGND = DGND = 0 V, TA = TMIN to TMAX, RSET = 6.8 kΩ, RLOAD = 200 Ω for IOUT and IOUTB, unless otherwise noted.
Table 1.
Grade B, Grade C1
Parameter2
Min
Typ
Max
Unit
Test Conditions/Comments
SIGNAL DAC SPECIFICATIONS
Resolution
10
Bits
Update Rate
75
MSPS
IOUT Full Scale3
3.0
mA
VOUT Max
0.6
V
VOUT Min
30
mV
Output Compliance4
0.8
V
DC Accuracy
Integral Nonlinearity
±1
LSB
Differential Nonlinearity
±0.5
LSB
DDS SPECIFICATIONS
Dynamic Specifications
Signal-to-Noise Ratio
55
60
dB
fMCLK = 75 MHz, fOUT = fMCLK/4096
Total Harmonic Distortion
−66
−56
dBc
fMCLK = 75 MHz, fOUT = fMCLK/4096
Spurious-Free Dynamic Range (SFDR)
Wideband (0 to Nyquist)
−60
−56
dBc
fMCLK = 75 MHz, fOUT = fMCLK/75
Narrow Band (±200 kHz)
B Grade
−78
−67
dBc
fMCLK = 50 MHz, fOUT = fMCLK/50
C Grade
−74
−65
dBc
fMCLK = 75 MHz, fOUT = fMCLK/75
Clock Feedthrough
−50
dBc
Wake-Up Time
1
ms
COMPARATOR
Input Voltage Range
1
V p-p
AC-coupled internally
Input Capacitance
10
pF
Input High-Pass Cutoff Frequency
4
MHz
Input DC Resistance
5
MΩ
Input Leakage Current
10
μA
OUTPUT BUFFER
Output Rise/Fall Time
12
ns
Using a 15 pF load
Output Jitter
120
ps rms
3 MHz sine wave, 0.6 V p-p
VOLTAGE REFERENCE
Internal Reference
1.12
1.18
1.24
V
REFOUT Output Impedance5
1
kΩ
Reference Temperature Coefficient
100
ppm/°C
LOGIC INPUTS
Input High Voltage, VINH
1.7
V
2.3 V to 2.7 V power supply
2.0
V
2.7 V to 3.6 V power supply
2.8
V
4.5 V to 5.5 V power supply
Input Low Voltage, VINL
0.6
V
2.3 V to 2.7 V power supply
0.7
V
2.7 V to 3.6 V power supply
0.8
V
4.5 V to 5.5 V power supply
Input Current, IINH/IINL
10
μA
Input Capacitance, CIN
3
pF
Rev. D | Page 4 of 32
Data Sheet AD9834
Grade B, Grade C1
Parameter2
Min
Typ
Max
Unit
Test Conditions/Comments
POWER SUPPLIES
AVDD
2.3
5.5
V
fMCLK = 75 MHz, fOUT = fMCLK/4096
DVDD
2.3
5.5
V
IAA6
3.8
5
mA
IDD6
B Grade
2.0
3
mA
IDD code dependent (see Figure 8)
C Grade
2.7
3.7
mA
IDD code dependent (see Figure 8)
IAA + IDD6
B Grade
5.8
8
mA
C Grade
6.5
8.7
mA
Low Power Sleep Mode
B Grade
0.5
mA
DAC powered down, MCLK running
C Grade
0.6
mA
DAC powered down, MCLK running
1 B grade: MCLK = 50 MHz; C grade: MCLK = 75 MHz. For specifications that do not specify a grade, the value applies to both grades.
2 Operating temperature range is as follows: B, C versions: −40°C to +105°C, typical specifications are at 25°C.
3 For compliance, with specified load of 200 Ω, IOUT full scale should not exceed 4 mA.
4 Guaranteed by design.
5 Applies when REFOUT is sourcing current. The impedance is higher when REFOUT is sinking current.
6 Measured with the digital inputs static and equal to 0 V or DVDD.
RSET6.8kΩIOUT1210-BIT DAC20pFFS ADJUSTAD9834REGULATOR100nFCAP/2.5V10nFREFOUTCOMP10nFAVDDSINROMRLOAD200ΩON-BOARDREFERENCEFULL-SCALECONTROL02705-002
Figure 2. Test Circuit Used to Test the Specifications Rev. D | Page 5 of 32
AD9834 Data Sheet
TIMING CHARACTERISTICS
DVDD = 2.3 V to 5.5 V, AGND = DGND = 0 V, unless otherwise noted.
Table 2.
Parameter1
Limit at TMIN to TMAX
Unit
Test Conditions/Comments
t1
20/13.33
ns min
MCLK period: 50 MHz/75 MHz
t2
8/6
ns min
MCLK high duration: 50 MHz/75 MHz
t3
8/6
ns min
MCLK low duration: 50 MHz/75 MHz
t4
25
ns min
SCLK period
t5
10
ns min
SCLK high duration
t6
10
ns min
SCLK low duration
t7
5
ns min
FSYNC-to-SCLK falling edge setup time
t8 MIN
10
ns min
FSYNC-to-SCLK hold time
t8 MAX
t4 − 5
ns max
t9
5
ns min
Data setup time
t10
3
ns min
Data hold time
t11
8
ns min
FSELECT, PSELECT setup time before MCLK rising edge
t11A
8
ns min
FSELECT, PSELECT setup time after MCLK rising edge
t12
5
ns min
SCLK high to FSYNC falling edge setup time
1 Guaranteed by design, not production tested.
Timing Diagrams
MCLKt1t3t202705-003
Figure 3. Master Clock
FSELECT,PSELECTVALID DATAVALID DATAVALID DATAMCLKt11At1102705-004
Figure 4. Control Timing
D0SCLKFSYNCSDATAD15D14D2D1D15D14t12t7t6t8t5t4t9t1002705-005
Figure 5. Serial Timing Rev. D | Page 6 of 32
Data Sheet AD9834
ABSOLUTE MAXIMUM RATINGS
TA = 25°C, unless otherwise noted.
Table 3.
Parameter
Ratings
AVDD to AGND
−0.3 V to +6 V
DVDD to DGND
−0.3 V to +6 V
AGND to DGND
−0.3 V to +0.3 V
CAP/2.5V
2.75 V
Digital I/O Voltage to DGND
−0.3 V to DVDD + 0.3 V
Analog I/O Voltage to AGND
−0.3 V to AVDD + 0.3 V
Operating Temperature Range
Industrial (B Version)
−40°C to +105°C
Storage Temperature Range
−65°C to +150°C
Maximum Junction Temperature
150°C
TSSOP Package
θJA Thermal Impedance
143°C/W
θJC Thermal Impedance
45°C/W
Lead Temperature, Soldering (10 sec)
300°C
IR Reflow, Peak Temperature
220°C
Reflow Soldering (Pb-Free)
Peak Temperature
260°C (+0/–5)
Time at Peak Temperature
10 sec to 40 sec
Stresses above those listed under Absolute Maximum Ratings may cause permanent damage to the device. This is a stress rating only; functional operation of the device at these or any other conditions above those indicated in the operational section of this specification is not implied. Exposure to absolute maximum rating conditions for extended periods may affect device reliability.
ESD CAUTION
Rev. D | Page 7 of 32
AD9834 Data Sheet
Rev. D | Page 8 of 32
PIN CONFIGURATION AND FUNCTION DESCRIPTIONS
1
2
3
4
5
6
7
8
9
10
20
19
18
17
16
15
14
13
12
11
REFOUT
COMP
AVDD
DGND
CAP/2.5V
DVDD
FS ADJUST
IOUT
AGND
VIN
SCLK
FSYNC
SIGN BIT OUT
PSELECT
FSELECT
MCLK
RESET
SLEEP
SDATA
IOUTB
AD9834
TOP VIEW
(Not to Scale)
02705-006
Figure 6. Pin Configuration Table 4. Pin Function Descriptions Pin No. Mnemonic Description
ANALOG SIGNAL AND REFERENCE
1 FS ADJUST Full-Scale Adjust Control. A resistor (RSET) is connected between this pin and AGND. This determines the magnitude
of the full-scale DAC current. The relationship between RSET and the full-scale current is as follows:
IOUT FULL SCALE = 18 × FSADJUST/RSET FSADJUST = 1.15 V nominal, RSET = 6.8 kΩ typical. 2 REFOUT Voltage Reference Output. The AD9834 has an internal 1.20 V reference that is made available at this pin. 3 COMP DAC Bias Pin. This pin is used for decoupling the DAC bias voltage.
17 VIN Input to Comparator. The comparator can be used to generate a square wave from the sinusoidal DAC output. The
DAC output should be filtered appropriately before being applied to the comparator to improve jitter. When Bit
OPBITEN and Bit SIGN/PIB in the control register are set to 1, the comparator input is connected to VIN. 19, 20 IOUT,
IOUTB
Current Output. This is a high impedance current source. A load resistor of nominally 200 Ω should be connected between IOUT and AGND. IOUTB should preferably be tied through an external load resistor of 200 Ω to AGND, but
it can be tied directly to AGND. A 20 pF capacitor to AGND is also recommended to prevent clock feedthrough.
POWER SUPPLY 4 AVDD Positive Power Supply for the Analog Section. AVDD can have a value from 2.3 V to 5.5 V. A 0.1 μF decoupling
capacitor should be connected between AVDD and AGND.
5 DVDD Positive Power Supply for the Digital Section. DVDD can have a value from 2.3 V to 5.5 V. A 0.1 μF decoupling
capacitor should be connected between DVDD and DGND. 6 CAP/2.5V The digital circuitry operates from a 2.5 V power supply. This 2.5 V is generated from DVDD using an on-board regulator (when DVDD exceeds 2.7 V). The regulator requires a decoupling capacitor of typically 100 nF that is
connected from CAP/2.5 V to DGND. If DVDD is equal to or less than 2.7 V, CAP/2.5 V should be shorted to DVDD.
7 DGND Digital Ground. 18 AGND Analog Ground. DIGITAL INTERFACE AND CONTROL
8 MCLK Digital Clock Input. DDS output frequencies are expressed as a binary fraction of the frequency of MCLK. The
output frequency accuracy and phase noise are determined by this clock. 9 FSELECT Frequency Select Input. FSELECT controls which frequency register, FREQ0 or FREQ1, is used in the phase
accumulator. The frequency register to be used can be selected using Pin FSELECT or Bit FSEL. When Bit FSEL is
used to select the frequency register, the FSELECT pin should be tied to CMOS high or low.
10 PSELECT Phase Select Input. PSELECT controls which phase register, PHASE0 or PHASE1, is added to the phase accumulator output. The phase register to be used can be selected using Pin PSELECT or Bit PSEL. When the phase registers are
being controlled by Bit PSEL, the PSELECT pin should be tied to CMOS high or low. 11 RESET Active High Digital Input. RESET resets appropriate internal registers to zero; this corresponds to an analog output
of midscale. RESET does not affect any of the addressable registers. 12 SLEEP Active High Digital Input. When this pin is high, the DAC is powered down. This pin has the same function as
Control Bit SLEEP12.
Data Sheet AD9834
Pin No.
Mnemonic
Description
13
SDATA
Serial Data Input. The 16-bit serial data-word is applied to this input.
14
SCLK
Serial Clock Input. Data is clocked into the AD9834 on each falling SCLK edge.
15
FSYNC
Active Low Control Input. This is the frame synchronization signal for the input data. When FSYNC is taken low, the internal logic is informed that a new word is being loaded into the device.
16
SIGN BIT OUT
Logic Output. The comparator output is available on this pin or, alternatively, the MSB from the NCO can be output on this pin. Setting Bit OPBITEN in the control register to 1 enables this output pin. Bit SIGN/PIB determines whether the comparator output or the MSB from the NCO is output on the pin.
Rev. D | Page 9 of 32
AD9834 Data Sheet
TYPICAL PERFORMANCE CHARACTERISTICS
MCLK FREQUENCY (MHz)4.000755V3VTA = 25°CIDD (
mA)3.53.02.52.01.51.00.51530456002705-007
Figure 7. Typical Current Consumption (IDD) vs. MCLK Frequency
4.000.51.01.52.02.53.03.5fOUT (Hz)IDD (mA)TA = 25°C5V3V1001k10k100k1M10M100M02705-008
Figure 8. Typical IDD vs. fOUT for fMCLK = 50 MHz
MCLK FREQUENCY (MHz)SFDR (dBc)–65–60–90–70–75–80–85AVDD = DVDD = 3VTA = 25°CSFDR dB MCLK/50SFDR dB MCLK/70153045607502705-009
Figure 9. Narrow-Band SFDR vs. MCLK Frequency
0–10–20–30–40–50–60–70–80MCLK FREQUENCY (MHz)SFDR (dBc)010203040506070fOUT = 1MHzSFDR dB MCLK/7AVDD = DVDD = 3VTA = 25°C02705-010
Figure 10. Wideband SFDR vs. MCLK Frequency
SFDR (dBc)0–40–80–50–60–70–10–20–3050MHz CLOCK30MHz CLOCKAVDD = DVDD = 3VTA = 25°CfOUT/fMCLK0.0010.010.11.01010002705-011
Figure 11. Wideband SFDR vs. fOUT/fMCLK for Various MCLK Frequencies
MCLK FREQUENCY (MHz)SNR (dB)–60–65–70–50–55–40–451.05.010.012.525.050.0TA = 25°CAVDD = DVDD = 3VfOUT = MCLK/409602705-012
Figure 12. SNR vs. MCLK Frequency Rev. D | Page 10 of 32
Data Sheet AD9834
50010007006506005508507508009009505.5V2.3VTEMPERATURE (°C)–4025105WAKE-UP TIME (
μs)02705-013
Figure 13. Wake-Up Time vs. Temperature
1.1501.1251.1001.1751.2001.2501.225TEMPERATURE (°C)V(REFOUT) (V)LOWER RANGEUPPER RANGE–402510502705-014
Figure 14. VREFOUT vs. Temperature
FREQUENCY (Hz)(dBc/Hz)–150–110–100–120–130–140–160AVDD = DVDD = 5VTA = 25°C1001k10k100k200k02705-015
Figure 15. Output Phase Noise, fOUT = 2 MHz, MCLK = 50 MHz
0.200–40–2002040608010002705-037TEMPERATURE(°C)DVDD (V)0.180.160.140.120.100.080.060.040.02DVDD=3.3VDVDD=5.5VDVDD=2.3V
Figure 16. SIGN BIT OUT Low Level, ISINK = 1 mA
5.51.5–40–2002040608010002705-038TEMPERATURE(°C)DVDD (
V)5.04.54.03.53.02.52.0DVDD=2.3VDVDD=2.7VDVDD=3.3VDVDD=4.5VDVDD=5.5V
Figure 17. SIGN BIT OUT High Level, ISINK = 1 mA
FREQUENCY (Hz)(dB)0–20–50–90–100–80–70–60–40–30–10RWB 100ST 100 SECVWB 300100k02705-016
Figure 18. fMCLK = 10 MHz; fOUT = 2.4 kHz, Frequency Word = 000FBA9 Rev. D | Page 11 of 32
AD9834 Data Sheet
FREQUENCY (Hz)(dB)0–20–50–90–100–80–70–60–40–30–1005MRWB 1kST 50 SECVWB 30002705-017
Figure 19. fMCLK = 10 MHz; fOUT = 1.43 MHz = fMCLK/7, Frequency Word = 2492492
FREQUENCY (Hz)0–20–50–90–100–80–70–60–40–30–1005MRWB 1kST 50 SECVWB 300(dB)02705-018
Figure 20. fMCLK = 10 MHz; fOUT = 3.33 MHz = fMCLK/3, Frequency Word = 5555555
FREQUENCY (Hz)0–20–50–90–100–80–70–60–40–30–100160kRWB 100ST 200 SECVWB 30(dB)02705-019
Figure 21. fMCLK = 50 MHz; fOUT = 12 kHz, Frequency Word = 000FBA9
FREQUENCY (Hz)0–20–50–90–100–80–70–60–40–30–1001.6MRWB 100ST 200 SECVWB 300(dB)02705-020
Figure 22. fMCLK = 50 MHz; fOUT = 120 kHz, Frequency Word = 009D496
FREQUENCY (Hz)0–20–50–90–100–80–70–60–40–30–10025MRWB 1kST 200 SECVWB 300(dB)02705-021
Figure 23. fMCLK = 50 MHz; fOUT = 1.2 MHz, Frequency Word = 0624DD3
FREQUENCY (Hz)(dB)0–20–50–90–100–80–70–60–40–30–10025MRWB 1kST 200 SECVWB 30002705-022
Figure 24. fMCLK = 50 MHz; fOUT = 4.8 MHz, Frequency Word = 189374C Rev. D | Page 12 of 32
Data Sheet AD9834
FREQUENCY (Hz)(dB)0–20–50–90–100–80–70–60–40–30–10025MRWB 1kST 200 SECVWB 30002705-023
Figure 25. fMCLK = 50 MHz; fOUT = 7.143 MHz = fMCLK/7, Frequency Word = 2492492
FREQUENCY (Hz)(dB)0–20–50–90–100–80–70–60–40–30–10025MRWB 1kST 200 SECVWB 30002705-024
Figure 26. fMCLK = 50 MHz; fOUT = 16.667 MHz = fMCLK/3, Frequency Word = 5555555
Rev. D | Page 13 of 32
AD9834 Data Sheet
Rev. D | Page 14 of 32
TERMINOLOGY
Integral Nonlinearity (INL) INL is the maximum deviation of any code from a straight line passing through the endpoints of the transfer function. The endpoints of the transfer function are zero scale, a point 0.5 LSB
below the first code transition (000 . . . 00 to 000 . . . 01), and full scale, a point 0.5 LSB above the last code transition (111 . . . 10 to 111 . . . 11). The error is expressed in LSBs. Differential Nonlinearity (DNL) DNL is the difference between the measured and ideal 1 LSB
change between two adjacent codes in the DAC. A specified
DNL of ±1 LSB maximum ensures monotonicity.
Output Compliance
The output compliance refers to the maximum voltage that can
be generated at the output of the DAC to meet the specifications. When voltages greater than that specified for the output com-
pliance are generated, the AD9834 may not meet the specifications listed in the data sheet. Spurious-Free Dynamic Range (SFDR)
Along with the frequency of interest, harmonics of the fundamental frequency and images of these frequencies are
present at the output of a DDS device. The SFDR refers to the largest spur or harmonic present in the band of interest. The wideband SFDR gives the magnitude of the largest harmonic or spur relative to the magnitude of the fundamental frequency in the 0 to Nyquist bandwidth. The narrow-band SFDR gives the
attenuation of the largest spur or harmonic in a bandwidth of ±200 kHz about the fundamental frequency. Total Harmonic Distortion (THD) THD is the ratio of the rms sum of harmonics to the rms value of the fundamental. For the AD9834, THD is defined as 1
2 3456
V
V VVVV
THD
2 2222
log 20
where V1 is the rms amplitude of the fundamental and V2, V3,
V4, V5, and V6 are the rms amplitudes of the second harmonic
through the sixth harmonic. Signal-to-Noise Ratio (SNR)
SNR is the ratio of the rms value of the measured output signal to the rms sum of all other spectral components below the Nyquist frequency. The value for SNR is expressed in decibels. Clock Feedthrough There is feedthrough from the MCLK input to the analog
output. Clock feedthrough refers to the magnitude of the MCLK signal relative to the fundamental frequency in the
output spectrum of the AD9834.
Data Sheet AD9834
THEORY OF OPERATION
Sine waves are typically thought of in terms of their magnitude form a(t) = sin (ωt). However, these are nonlinear and not easy to generate except through piecewise construction. On the other hand, the angular information is linear in nature, that is, the phase angle rotates through a fixed angle for each unit of time. The angular rate depends on the frequency of the signal by the traditional rate of ω = 2πf.
MAGNITUDEPHASE+10–12p02π4π6π2π4π6π02705-025
Figure 27. Sine Wave
Knowing that the phase of a sine wave is linear and given a reference interval (clock period), the phase rotation for that period can be determined.
ΔPhase = ωΔt
Solving for ω,
ω = ΔPhase/Δt = 2πf
Solving for f and substituting the reference clock frequency for the reference period (1/fMCLK = Δt),
f = ΔPhase × fMCLK/2π
The AD9834 builds the output based on this simple equation. A simple DDS chip can implement this equation with three major subcircuits: numerically controlled oscillator + phase modulator, SIN ROM, and digital-to-analog converter (DAC). Each of these subcircuits is discussed in the Circuit Description section.
Rev. D | Page 15 of 32
AD9834 Data Sheet
CIRCUIT DESCRIPTION
The AD9834 is a fully integrated direct digital synthesis (DDS) chip. The chip requires one reference clock, one low precision resistor, and eight decoupling capacitors to provide digitally created sine waves up to 37.5 MHz. In addition to the generation of this RF signal, the chip is fully capable of a broad range of simple and complex modulation schemes. These modulation schemes are fully implemented in the digital domain, allowing accurate and simple realization of complex modulation algorithms using DSP techniques.
The internal circuitry of the AD9834 consists of the following main sections: a numerically controlled oscillator (NCO), frequency and phase modulators, SIN ROM, a DAC, a comparator, and a regulator.
NUMERICALLY CONTROLLED OSCILLATOR PLUS PHASE MODULATOR
This consists of two frequency select registers, a phase accumulator, two phase offset registers, and a phase offset adder. The main component of the NCO is a 28-bit phase accumulator. Continuous time signals have a phase range of 0 π to 2π. Outside this range of numbers, the sinusoid functions repeat themselves in a periodic manner. The digital implementation is no different. The accumulator simply scales the range of phase numbers into a multibit digital word. The phase accumulator in the AD9834 is implemented with 28 bits. Therefore, in the AD9834, 2π = 228. Likewise, the ΔPhase term is scaled into this range of numbers:
0 < ΔPhase < 228 − 1.
Making these substitutions into the previous equation
f = ΔPhase × fMCLK/228
where 0 < ΔPhase < 228 − 1.
The input to the phase accumulator can be selected either from the FREQ0 register or FREQ1 register and is controlled by the FSELECT pin or the FSEL bit. NCOs inherently generate con-tinuous phase signals, thus avoiding any output discontinuity when switching between frequencies.
Following the NCO, a phase offset can be added to perform phase modulation using the 12-bit phase registers. The contents of one of these phase registers is added to the MSBs of the NCO. The AD9834 has two phase registers, the resolution of these registers being 2π/4096.
SIN ROM
To make the output from the NCO useful, it must be converted from phase information into a sinusoidal value. Phase informa-tion maps directly into amplitude; therefore, the SIN ROM uses the digital phase information as an address to a look-up table and converts the phase information into amplitude.
Although the NCO contains a 28-bit phase accumulator, the output of the NCO is truncated to 12 bits. Using the full resolu-tion of the phase accumulator is impractical and unnecessary because it requires a look-up table of 228 entries. It is necessary only to have sufficient phase resolution such that the errors due to truncation are smaller than the resolution of the 10-bit DAC. This requires the SIN ROM to have two bits of phase resolution more than the 10-bit DAC.
The SIN ROM is enabled using the OPBITEN and MODE bits in the control register. This is explained further in Table 18.
DIGITAL-TO-ANALOG CONVERTER (DAC)
The AD9834 includes a high impedance current source 10-bit DAC capable of driving a wide range of loads. The full-scale output current can be adjusted for optimum power and external load requirements using a single external resistor (RSET).
The DAC can be configured for either single-ended or differential operation. IOUT and IOUTB can be connected through equal external resistors to AGND to develop complementary output voltages. The load resistors can be any value required, as long as the full-scale voltage developed across it does not exceed the voltage compliance range. Because full-scale current is controlled by RSET, adjustments to RSET can balance changes made to the load resistors.
COMPARATOR
The AD9834 can be used to generate synthesized digital clock signals. This is accomplished by using the on-board self-biasing comparator that converts the sinusoidal signal of the DAC to a square wave. The output from the DAC can be filtered externally before being applied to the comparator input. The comparator reference voltage is the time average of the signal applied to VIN. The comparator can accept signals in the range of approximately 100 mV p-p to 1 V p-p. As the comparator input is ac-coupled, to operate correctly as a zero crossing detector, it requires a minimum input frequency of typically 3 MHz. The comparator output is a square wave with an amplitude from 0 V to DVDD.
Rev. D | Page 16 of 32
Data Sheet AD9834
The AD9834 is a sampled signal with its output following Nyquist sampling theorem. Specifically, its output spectrum contains the fundamental plus aliased signals (images) that occur at multiples of the reference clock frequency and the selected output frequency. A graphical representation of the sampled spectrum, with aliased images, is shown in Figure 28.
The prominence of the aliased images is dependent on the ratio of fOUT to MCLK. If ratio is small, the aliased images are very prominent and of a relatively high energy level as determined by the sin(x)/x roll-off of the quantized DAC output. In fact, depending on the fOUT/reference clock relationship, the first aliased image can be on the order of −3 dB below the fundamental.
A low-pass filter is generally placed between the output of the DAC and the input of the comparator to further suppress the effects of aliased images. Obviously, consideration must be given to the relationship of the selected output frequency and the reference clock frequency to avoid unwanted (and unexpected) output anomalies. To apply the AD9834 as a clock generator, limit the selected output frequency to <33% of reference clock frequency, and thereby avoid generating aliased signals that fall within, or close to, the output band of interest (generally dc-selected output frequency). This practice eases the complexity (and cost) of the external filter requirement for the clock generator application. Refer to the AN-837 Application Note for more information.
To enable the comparator, Bit SIGN/PIB and Bit OPBITEN in the control resister are set to 1. This is explained further in Table 17.
REGULATOR
The AD9834 has separate power supplies for the analog and digital sections. AVDD provides the power supply required for the analog section, and DVDD provides the power supply for the digital section. Both of these supplies can have a value of 2.3 V to 5.5 V and are independent of each other. For example, the analog section can be operated at 5 V, and the digital section can be operated at 3 V, or vice versa.
The internal digital section of the AD9834 is operated at 2.5 V. An on-board regulator steps down the voltage applied at DVDD to 2.5 V. The digital interface (serial port) of the AD9834 also operates from DVDD. These digital signals are level shifted within the AD9834 to make them 2.5 V compatible.
When the applied voltage at the DVDD pin of the AD9834 is equal to or less than 2.7 V, Pin CAP/2.5V and Pin DVDD should be tied together, thus bypassing the on-board regulator.
OUTPUT VOLTAGE COMPLIANCE
The AD9834 has a maximum current density, set by the RSET, of 4 mA. The maximum output voltage from the AD9834 is VDD − 1.5 V. This is to ensure that the output impedance of the internal switch does not change, affecting the spectral performance of the part. For a minimum supply of 2.3 V, the maximum output voltage is 0.8 V. Specifications in Table 1 are guaranteed with an RSET of 6.8 kΩ and an RLOAD of 200 Ω.
02705-040SYSTEM CLOCKfOUTfC–fOUTfC+fOUT2fC–fOUT2fC+fOUT3fC–fOUT3fC+fOUTfC0HzFIRSTIMAGESECONDIMAGETHIRDIMAGEFOURTHIMAGEFIFTHIMAGESIXTHIMAGE2fC3fCFREQUENCY (
Hz)SIGNAL AMPLITUDEsin x/x
ENVELOPEx =
π
(
f/fC)
Figure 28. The DAC Output Spectrum
Rev. D | Page 17 of 32
AD9834 Data Sheet
FUNCTIONAL DESCRIPTION
SERIAL INTERFACE
The AD9834 has a standard 3-wire serial interface that is com-patible with SPI, QSPI™, MICROWIRE™, and DSP interface standards.
Data is loaded into the device as a 16-bit word under the control of a serial clock input (SCLK). The timing diagram for this operation is given in Figure 5.
For a detailed example of programming the AD9833 and AD9834 devices, refer to the AN-1070 Application Note.
The FSYNC input is a level triggered input that acts as a frame synchronization and chip enable. Data can only be transferred into the device when FSYNC is low. To start the serial data transfer, FSYNC should be taken low, observing the minimum FSYNC-to-SCLK falling edge setup time (t7). After FSYNC goes low, serial data is shifted into the input shift register of the device on the falling edges of SCLK for 16 clock pulses. FSYNC can be taken high after the 16th falling edge of SCLK, observing the minimum SCLK falling edge to FSYNC rising edge time (t8). Alternatively, FSYNC can be kept low for a multiple of 16 SCLK pulses and then brought high at the end of the data transfer. In this way, a continuous stream of 16-bit words can be loaded while FSYNC is held low, with FSYNC only going high after the 16th SCLK falling edge of the last word is loaded.
The SCLK can be continuous, or alternatively, the SCLK can idle high or low between write operations but must be high when FSYNC goes low (t12).
POWERING UP THE AD9834
The flow chart in Figure 31 shows the operating routine for the AD9834. When the AD9834 is powered up, the part should be reset. This resets appropriate internal registers to 0 to provide an analog output of midscale. To avoid spurious DAC outputs during AD9834 initialization, the RESET bit/pin should be set to 1 until the part is ready to begin generating an output. RESET does not reset the phase, frequency, or control registers. These registers contain invalid data, and, therefore, should be set to a known value by the user. The RESET bit/pin should then be set to 0 to begin generating an output. The data appears on the DAC output eight MCLK cycles after RESET is set to 0.
LATENCY
Latency is associated with each operation. When Pin FSELECT and Pin PSELECT change value, there is a pipeline delay before control is transferred to the selected register. When the t11 and t11A timing specifications are met (see Figure 4), FSELECT and PSELECT have latencies of eight MCLK cycles. When the t11 and t11A timing specifications are not met, the latency is increased by one MCLK cycle.
Similarly, there is a latency associated with each asynchronous write operation. If a selected frequency/phase register is loaded with a new word, there is a delay of eight to nine MCLK cycles before the analog output changes. There is an uncertainty of one MCLK cycle because it depends on the position of the MCLK rising edge when the data is loaded into the destination register.
The negative transition of the RESET and SLEEP functions are sampled on the internal falling edge of MCLK. Therefore, they also have a latency associated with them.
CONTROL REGISTER
The AD9834 contains a 16-bit control register that sets up the AD9834 as the user wants to operate it. All control bits, except MODE, are sampled on the internal negative edge of MCLK. Table 6 describes the individual bits of the control register. The different functions and the various output options from the AD9834 are described in more detail in the Frequency and Phase Registers section.
To inform the AD9834 that the contents of the control register are to be altered, DB15 and DB14 must be set to 0 as shown in Table 5.
Table 5. Control Register
DB15
DB14
DB13 . . . DB0
0
0
CONTROL bits Rev. D | Page 18 of 32
Data Sheet AD9834
MUXSLEEP12SLEEP1OPBITENIOUTBIOUTCOMPARATORVINSIGN/PIBMUXMSBSIGNBIT OUT01MUX1001DIGITALOUTPUT(ENABLE)(LOWPOWER)10-BITDACDIVIDEBY2SINROMMODE+ OPBITENPHASEACCUMULATOR(28-BIT)02705-026
Figure 29. Function of Control Bits
DB15
DB14
DB13
DB12
DB11
DB10
DB9
DB8
DB7
DB6
DB5
DB4
DB3
DB2
DB1
DB0
0
0
B28
HLB
FSEL
PSEL
PIN/SW
RESET
SLEEP1
SLEEP12
OPBITEN
SIGN/PIB
DIV2
0
MODE
0
Table 6. Description of Bits in the Control Register
Bit
Name
Description
DB13
B28
Two write operations are required to load a complete word into either of the frequency registers.
B28 = 1 allows a complete word to be loaded into a frequency register in two consecutive writes. The first write contains the 14 LSBs of the frequency word and the next write contains the 14 MSBs. The first two bits of each 16-bit word define the frequency register the word is loaded to and should, therefore, be the same for both of the consecutive writes. Refer to Table 10 for the appropriate addresses. The write to the frequency register occurs after both words have been loaded. An example of a complete 28-bit write is shown in Table 11. Note however, that consecutive 28-bit writes to the same frequency register are not allowed, switch between frequency registers to do this type of function.
B28 = 0, the 28-bit frequency register operates as two 14-bit registers, one containing the 14 MSBs and the other containing the 14 LSBs. This means that the 14 MSBs of the frequency word can be altered independent of the 14 LSBs, and vice versa. To alter the 14 MSBs or the 14 LSBs, a single write is made to the appropriate frequency address. The Control Bit DB12 (HLB) informs the AD9834 whether the bits to be altered are the 14 MSBs or 14 LSBs.
DB12
HLB
This control bit allows the user to continuously load the MSBs or LSBs of a frequency register ignoring the remaining 14 bits. This is useful if the complete 28-bit resolution is not required. HLB is used in conjunction with DB13 (B28). This control bit indicates whether the 14 bits being loaded are being transferred to the 14 MSBs or 14 LSBs of the addressed frequency register. DB13 (B28) must be set to 0 to be able to change the MSBs and LSBs of a frequency word separately. When DB13 (B28) = 1, this control bit is ignored.
HLB = 1 allows a write to the 14 MSBs of the addressed frequency register.
HLB = 0 allows a write to the 14 LSBs of the addressed frequency register.
DB11
FSEL
The FSEL bit defines whether the FREQ0 register or the FREQ1 register is used in the phase accumulator. See Table 8 to select a frequency register.
DB10
PSEL
The PSEL bit defines whether the PHASE0 register data or the PHASE1 register data is added to the output of the phase accumulator. See Table 9 to select a phase register.
DB9
PIN/SW
Functions that select frequency and phase registers, reset internal registers, and power down the DAC can be implemented using either software or hardware. PIN/SW selects the source of control for these functions.
PIN/SW = 1 implies that the functions are being controlled using the appropriate control pins.
PIN/SW = 0 implies that the functions are being controlled using the appropriate control bits.
DB8
RESET
RESET = 1 resets internal registers to 0, this corresponds to an analog output of midscale.
RESET = 0 disables RESET. This function is explained in the RESET Function section.
DB7
SLEEP1
SLEEP1 = 1, the internal MCLK is disabled. The DAC output remains at its present value as the NCO is no longer accumulating.
SLEEP1 = 0, MCLK is enabled. This function is explained in the SLEEP Function section.
DB6
SLEEP12
SLEEP12 = 1 powers down the on-chip DAC. This is useful when the AD9834 is used to output the MSB of the DAC data.
SLEEP12 = 0 implies that the DAC is active. This function is explained in the SLEEP Function section. Rev. D | Page 19 of 32
AD9834 Data Sheet
Bit
Name
Description
DB5
OPBITEN
The function of this bit is to control whether there is an output at the SIGN BIT OUT pin. This bit should remain at 0 if the user is not using the SIGN BIT OUT pin.
OPBITEN = 1 enables the SIGN BIT OUT pin.
OPBITEN = 0, the SIGN BIT OUT output buffer is put into a high impedance state, therefore no output is available at the SIGN BIT OUT pin.
DB4
SIGN/PIB
The function of this bit is to control what is output at the SIGN BIT OUT pin.
SIGN/PIB = 1, the on-board comparator is connected to SIGN BIT OUT. After filtering the sinusoidal output from the DAC, the waveform can be applied to the comparator to generate a square waveform. Refer to Table 17.
SIGN/PIB = 0, the MSB (or MSB/2) of the DAC data is connected to the SIGN BIT OUT pin. Bit DIV2 controls whether it is the MSB or MSB/2 that is output.
DB3
DIV2
DIV2 is used in association with SIGN/PIB and OPBITEN. Refer to Table 17.
DIV2 = 1, the digital output is passed directly to the SIGN BIT OUT pin.
DIV2 = 0, the digital output/2 is passed directly to the SIGN BIT OUT pin.
DB2
Reserved
This bit must always be set to 0.
DB1
MODE
The function of this bit is to control what is output at the IOUT pin/IOUTB pin. This bit should be set to 0 if the Control Bit OPBITEN = 1.
MODE = 1, the SIN ROM is bypassed, resulting in a triangle output from the DAC.
MODE = 0, the SIN ROM is used to convert the phase information into amplitude information, resulting in a sinusoidal signal at the output. See Table 18.
DB0
Reserved
This bit must always be set to 0.
FREQUENCY AND PHASE REGISTERS
The AD9834 contains two frequency registers and two phase registers. These are described in Table 7.
Table 7. Frequency/Phase Registers
Register
Size
Description
FREQ0
28 bits
Frequency Register 0. When either the FSEL bit or FSELECT pin = 0, this register defines the output frequency as a fraction of the MCLK frequency.
FREQ1
28 bits
Frequency Register 1. When either the FSEL bit or FSELECT pin = 1, this register defines the output frequency as a fraction of the MCLK frequency.
PHASE0
12 bits
Phase Offset Register 0. When either the PSEL bit or PSELECT pin = 0, the contents of this register are added to the output of the phase accumulator.
PHASE1
12 bits
Phase Offset Register 1. When either the PSEL bit or PSELECT pin = 1, the contents of this register are added to the output of the phase accumulator.
The analog output from the AD9834 is
fMCLK/228 × FREQREG
where FREQREG is the value loaded into the selected frequency register. This signal is phase shifted by
2π/4096 × PHASEREG
where PHASEREG is the value contained in the selected phase register. Consideration must be given to the relationship of the selected output frequency and the reference clock frequency to avoid unwanted output anomalies.
Access to the frequency and phase registers is controlled by both the FSELECT and PSELECT pins, and the FSEL and PSEL control bits. If the Control Bit PIN/SW = 1, the pins control the function; whereas, if PIN/SW = 0, the bits control the function. This is outlined in Table 8 and Table 9. If the FSEL and PSEL bits are used, the pins should be held at CMOS logic high or low. Control of the frequency/phase registers is interchangeable from the pins to the bits.
Table 8. Selecting a Frequency Register
FSELECT
FSEL
PIN/SW
Selected Register
0
X
1
FREQ0 REG
1
X
1
FREQ1 REG
X
0
0
FREQ0 REG
X
1
0
FREQ1 REG
Table 9. Selecting a Phase Register
PSELECT
PSEL
PIN/SW
Selected Register
0
X
1
PHASE0 REG
1
X
1
PHASE1 REG
X
0
0
PHASE0 REG
X
1
0
PHASE1 REG
The FSELECT pin and PSELECT pin are sampled on the internal falling edge of MCLK. It is recommended that the data on these pins does not change within a time window of the falling edge of MCLK (see Figure 4 for timing). If FSELECT or PSELECT changes value when a falling edge occurs, there is an uncertainty of one MCLK cycle because it pertains to when control is transferred to the other frequency/phase register.
The flow charts in Figure 32 and Figure 33 show the routine for selecting and writing to the frequency and phase registers of the AD9834. Rev. D | Page 20 of 32
Data Sheet AD9834
WRITING TO A FREQUENCY REGISTER
When writing to a frequency register, Bit DB15 and Bit DB14 give the address of the frequency register.
Table 10. Frequency Register Bits
DB15
DB14
DB13 . . . DB0
0
1
14 FREQ0 REG BITS
1
0
14 FREQ1 REG BITS
If the user wants to alter the entire contents of a frequency register, two consecutive writes to the same address must be performed because the frequency registers are 28 bits wide. The first write contains the 14 LSBs, and the second write contains the 14 MSBs. For this mode of operation, Control Bit B28 (DB13) should be set to 1. An example of a 28-bit write is shown in Table 11.
Note however that continuous writes to the same frequency register are not recommended. This results in intermediate updates during the writes. If a frequency sweep, or something similar, is required, it is recommended that users alternate between the two frequency registers.
Table 11. Writing FFFC000 to FREQ0 REG
SDATA Input
Result of Input Word
0010 0000 0000 0000
Control word write (DB15, DB14 = 00), B28 (DB13) = 1, HLB (DB12) = X
0100 0000 0000 0000
FREQ0 REG write (DB15, DB14 = 01), 14 LSBs = 0000
0111 1111 1111 1111
FREQ0 REG write (DB15, DB14 = 01), 14 MSBs = 3FFF
In some applications, the user does not need to alter all 28 bits of the frequency register. With coarse tuning, only the 14 MSBs are altered; though with fine tuning only the 14 LSBs are altered. By setting Control Bit B28 (DB13) to 0, the 28-bit frequency register operates as two 14-bit registers, one containing the 14 MSBs and the other containing the 14 LSBs. This means that the 14 MSBs of the frequency word can be altered independent of the 14 LSBs, and vice versa. Bit HLB (DB12) in the control register identifies the 14 bits that are being altered. Examples of this are shown in Table 12 and Table 13.
Table 12. Writing 3FFF to the 14 LSBs of FREQ1 REG
SDATA Input
Result of Input Word
0000 0000 0000 0000
Control word write (DB15, DB14 = 00), B28 (DB13) = 0, HLB (DB12) = 0, that is, LSBs
1011 1111 1111 1111
FREQ1 REG write (DB15, DB14 = 10), 14 LSBs = 3FFF
Table 13. Writing 00FF to the 14 MSBs of FREQ0 REG
SDATA Input
Result of Input Word
0001 0000 0000 0000
Control word write (DB15, DB14 = 00), B28 (DB13) = 0, HLB (DB12) = 1, that is, MSBs
0100 0000 1111 1111
FREQ0 REG write (DB15, DB14 = 01), 14 MSBs = 00FF
WRITING TO A PHASE REGISTER
When writing to a phase register, Bit DB15 and Bit DB14 are set to 11. Bit DB13 identifies which phase register is being loaded.
Table 14. Phase Register Bits
DB15
DB14
DB13
DB12
DB11
DB0
1
1
0
X
MSB 12 PHASE0 bits
LSB
1
1
1
X
MSB 12 PHASE1 bits
LSB
RESET FUNCTION
The RESET function resets appropriate internal registers to 0 to provide an analog output of midscale. RESET does not reset the phase, frequency, or control registers.
When the AD9834 is powered up, the part should be reset. To reset the AD9834, set the RESET pin/bit to 1. To take the part out of reset, set the pin/bit to 0. A signal appears at the DAC output seven MCLK cycles after RESET is set to 0.
The RESET function is controlled by both the RESET pin and the RESET control bit. If the Control Bit PIN/SW = 0, the RESET bit controls the function, whereas if PIN/SW = 1, the RESET pin controls the function.
Table 15. Applying RESET
RESET Pin
RESET Bit
PIN/SW Bit
Result
0
X
1
No reset applied
1
X
1
Internal registers reset
X
0
0
No reset applied
X
1
0
Internal registers reset
The effect of asserting the RESET pin is evident immediately at the output, that is, the zero-to-one transition of this pin is not sampled. However, the negative transition of RESET is sampled on the internal falling edge of MCLK.
SLEEP FUNCTION
Sections of the AD9834 that are not in use can be powered down to minimize power consumption by using the SLEEP function. The parts of the chip that can be powered down are the internal clock and the DAC. The DAC can be powered down through hardware or software. The pin/bits required for the SLEEP function are outlined in Table 16.
Rev. D | Page 21 of 32
AD9834 Data Sheet
Table 16. Applying the SLEEP Function
SLEEP Pin
SLEEP1 Bit
SLEEP12 Bit
PIN/SW Bit
Result
0
X
X
1
No power-down
1
X
X
1
DAC powered down
X
0
0
0
No power-down
X
0
1
0
DAC powered down
X
1
0
0
Internal clock disabled
X
1
1
0
Both the DAC powered down and the internal clock disabled
DAC Powered Down
This is useful when the AD9834 is used to output the MSB of the DAC data only. In this case, the DAC is not required and can be powered down to reduce power consumption.
Internal Clock Disabled
When the internal clock of the AD9834 is disabled, the DAC output remains at its present value because the NCO is no longer accumulating. New frequency, phase, and control words can be written to the part when the SLEEP1 control bit is active. The synchronizing clock remains active, meaning that the selected frequency and phase registers can also be changed either at the pins or by using the control bits. Setting the SLEEP1 bit to 0 enables the MCLK. Any changes made to the registers when SLEEP1 is active are observed at the output after a certain latency.
The effect of asserting the SLEEP pin is evident immediately at the output, that is, the zero-to-one transition of this pin is not sampled. However, the negative transition of SLEEP is sampled on the internal falling edge of MCLK.
SIGN BIT OUT PIN
The AD9834 offers a variety of outputs from the chip. The digital outputs are available from the SIGN BIT OUT pin. The available outputs are the comparator output or the MSB of the DAC data. The bits controlling the SIGN BIT OUT pin are outlined in Table 17.
This pin must be enabled before use. The enabling/disabling of this pin is controlled by the Bit OPBITEN (DB5) in the control register. When OPBITEN = 1, this pin is enabled. Note that the MODE bit (DB1) in the control register should be set to 0 if OPBITEN = 1.
Comparator Output
The AD9834 has an on-board comparator. To connect this comparator to the SIGN BIT OUT pin, the SIGN/PIB (DB4) control bit must be set to 1. After filtering the sinusoidal output from the DAC, the waveform can be applied to the comparator to generate a square waveform.
MSB from the NCO
The MSB from the NCO can be output from the AD9834. By setting the SIGN/PIB (DB4) control bit to 0, the MSB of the DAC data is available at the SIGN BIT OUT pin. This is useful as a coarse clock source. This square wave can also be divided by two before being output. Bit DIV2 (DB3) in the control register controls the frequency of this output from the SIGN BIT OUT pin.
Table 17. Various Outputs from SIGN BIT OUT
OPBITEN Bit
MODE Bit
SIGN/PIB Bit
DIV2 Bit
SIGN BIT OUT Pin
0
X
X
X
High impedance
1
0
0
0
DAC data MSB/2
1
0
0
1
DAC data MSB
1
0
1
0
Reserved
1
0
1
1
Comparator output
1
1
X
X
Reserved
THE IOUT AND IOUTB PINS
The analog outputs from the AD9834 are available from the IOUT and IOUTB pins. The available outputs are a sinusoidal output or a triangle output.
Sinusoidal Output
The SIN ROM converts the phase information from the frequency and phase registers into amplitude information, resulting in a sinusoidal signal at the output. To have a sinusoidal output from the IOUT and IOUTB pins, set Bit MODE (DB1) to 0.
Triangle Output
The SIN ROM can be bypassed so that the truncated digital output from the NCO is sent to the DAC. In this case, the output is no longer sinusoidal. The DAC produces 10-bit linear triangular function. To have a triangle output from the IOUT and IOUTB pins, set Bit MODE (DB1) to 1.
Note that the SLEEP pin and SLEEP12 bit must be 0 (that is, the DAC is enabled) when using the IOUT and IOUTB pins.
Table 18. Various Outputs from IOUT and IOUTB
OPBITEN Bit
MODE Bit
IOUT and IOUTB Pins
0
0
Sinusoid
0
1
Triangle
1
0
Sinusoid
1
1
Reserved
3π/27π/211π/2VOUT MAXVOUT MIN02705-027
Figure 30. Triangle Output
Rev. D | Page 22 of 32
Data Sheet AD9834
Rev. D | Page 23 of 32
APPLICATIONS INFORMATION
Because of the various output options available from the part, the AD9834 can be configured to suit a wide variety of applications. One of the areas where the AD9834 is suitable is in modulation
applications. The part can be used to perform simple modulation such as FSK. More complex modulation schemes such as GMSK and QPSK can also be implemented using the AD9834.
In an FSK application, the two frequency registers of the
AD9834 are loaded with different values. One frequency
represents the space frequency, and the other represents the
mark frequency. The digital data stream is fed to the FSELECT pin, causing the AD9834 to modulate the carrier frequency between the two values. The AD9834 has two phase registers, enabling the part to perform PSK. With phase shift keying, the carrier frequency is phase shifted, the phase being altered by an amount that is
related to the bit stream that is input to the modulator. The AD9834 is also suitable for signal generator applications.
With the on-board comparator, the device can be used to generate a square wave. With its low current consumption, the part is suitable for applications where it is used as a local oscillator.
CHANGE PHASE?
CHANGE FREQUENCY?
NO
NO
NO
NO
YES
NO
YES
NO YES
YES
YES
YES
YES
YES
DAC OUTPUT
VOUT = VREFOUT × 18 × RLOAD/RSET × (1 + (SIN(2π(FREQREG × fMCLK × t/228 + PHASEREG/212))))
INITIALIZATION
SEE FIGURE 32
SELECT DATA
SOURCES
SEE FIGURE 34
WAIT 8/9 MCLK
CYCLES
SEE TIMING DIAGRAM
FIGURE 3
CHANGE PSEL/
PSELECT?
CHANGE PHASE
REGISTER?
CHANGE DAC OUTPUT
FROM SIN TO RAMP?
CHANGE OUTPUT AT
SIGN BIT OUT PIN?
CHANGE FSEL/
FSELECT?
CHANGE FREQUENCY
REGISTER?
CONTROL
REGISTER
WRITE
DATA WRITE
SEE FIGURE 33 02705-028
Figure 31. Flow Chart for Initialization and Operation
AD9834 Data Sheet
INITIALIZATIONAPPLY RESETUSING PINSET RESET PIN = 1USING PINUSING CONTROLBIT(CONTROL REGISTER WRITE)RESET = 1PIN/SW = 0(CONTROL REGISTER WRITE)PIN/SW = 1USING CONTROLBITSET RESET = 0SELECT FREQUENCY REGISTERSSELECT PHASE REGISTERS(CONTROL REGISTER WRITE)RESET BIT = 0FSEL = SELECTED FREQUENCY REGISTERPSEL = SELECTED PHASE REGISTERPIN/SW = 0(APPLY SIGNALS AT PINS)RESET PIN = 0FSELECT = SELECTED FREQUENCY REGISTERPSELECT = SELECTED PHASE REGISTERWRITE TO FREQUENCY AND PHASE REGISTERSFREQ0 REG = fOUT0/fMCLK × 228FREQ1 REG = fOUT1/fMCLK × 228PHASE0 AND PHASE1 REG = (PHASESHIFT × 212)/2π(SEE FIGURE 33)02705-029
Figure 32. Initialization
NOYESDATA WRITENOYESYESNOYESNONOYESYESWRITE A FULL 28-BIT WORDTO A FREQUENCY REGISTER?(CONTROL REGISTER WRITE)B28 (D13) = 1WRITE TWO CONSECUTIVE16-BIT WORDS(SEE TABLE 11 FOR EXAMPLE)WRITE ANOTHER FULL28-BIT TO AFREQUENCY REGISTER?WRITE 14 MSBs OR LSBsTO A FREQUENCY REGISTER?(CONTROL REGISTER WRITE)B28 (D13) = 0HLB (D12) = 0/1WRITE A 16-BIT WORD(SEE TABLES 12 AND 13FOR EXAMPLES)WRITE 14 MSBs OR LSBsTO AFREQUENCY REGISTER?WRITE TO PHASEREGISTER?D15, D14 = 11D13 = 0/1 (CHOOSE THEPHASE REGISTER)D12 = XD11 ... D0 = PHASE DATA(16-BIT WRITE)WRITE TO ANOTHERPHASE REGISTER?02705-030
Figure 33. Data Write
Rev. D | Page 24 of 32
Data Sheet AD9834
SELECT DATA SOURCESYESNOFSELECT AND PSELECTPINS BEING USED?(CONTROL REGISTER WRITE)PIN/SW = 0SET FSEL BITSET PSEL BITSET FSELECTAND PSELECT(CONTROL REGISTER WRITE)PIN/SW = 102705-031
Figure 34. Selecting Data Sources
Rev. D | Page 25 of 32
AD9834 Data Sheet
GROUNDING AND LAYOUT
The printed circuit board (PCB) that houses the AD9834 should be designed so that the analog and digital sections are separated and confined to certain areas of the board. This facilitates the use of ground planes that can easily be separated. A minimum etch technique is generally best for ground planes because it gives the best shielding. Digital and analog ground planes should only be joined in one place. If the AD9834 is the only device requiring an AGND-to-DGND connection, the ground planes should be connected at the AGND and DGND pins of the AD9834. If the AD9834 is in a system where multiple devices require AGND-to-DGND connections, the connection should be made at one point only, establishing a star ground point as close as possible to the AD9834.
Avoid running digital lines under the device because these couple noise onto the die. The analog ground plane should be allowed to run under the AD9834 to avoid noise coupling. The power supply lines to the AD9834 should use as large a track as possible to provide low impedance paths and reduce the effects of glitches on the power supply line. Fast switching signals, such as clocks, should be shielded with digital ground to avoid radiating noise to other sections of the board. Avoid crossover of digital and analog signals. Traces on opposite sides of the board should run at right angles to each other to reduce the effects of feed-through through the board. A microstrip technique is by far the best, but it is not always possible with a double-sided board. In this technique, the component side of the board is dedicated to ground planes and signals are placed on the other side.
Good decoupling is important. The analog and digital supplies to the AD9834 are independent and separately pinned out to minimize coupling between analog and digital sections of the device. All analog and digital supplies should be decoupled to AGND and DGND, respectively, with 0.1 μF ceramic capacitors in parallel with 10 μF tantalum capacitors. To achieve the best performance from the decoupling capacitors, they should be placed as close as possible to the device, ideally right up against the device. In systems where a common supply is used to drive both the AVDD and DVDD of the AD9834, it is recommended that the system’s AVDD supply be used. This supply should have the recommended analog supply decoupling between the AVDD pins of the AD9834 and AGND, and the recommended digital supply decoupling capacitors between the DVDD pins and DGND.
Proper operation of the comparator requires good layout strategy. The strategy must minimize the parasitic capacitance between VIN and the SIGN BIT OUT pin by adding isolation using a ground plane. For example, in a multilayered board, the VIN signal could be connected to the top layer, and the SIGN BIT OUT could be connected to the bottom layer so that isolation is provided by the power and ground planes between them.
Rev. D | Page 26 of 32
Data Sheet AD9834
Rev. D | Page 27 of 32
INTERFACING TO MICROPROCESSORS
The AD9834 has a standard serial interface that allows the part
to interface directly with several microprocessors. The device uses an external serial clock to write the data/control information
into the device. The serial clock can have a frequency of 40 MHz
maximum. The serial clock can be continuous, or it can idle high or low between write operations. When data/control information is being written to the AD9834, FSYNC is taken low and is held
low until the 16 bits of data are written into the AD9834. The
FSYNC signal frames the 16 bits of information being loaded into the AD9834.
AD9834 TO ADSP-21xx INTERFACE
Figure 35 shows the serial interface between the AD9834 and
the ADSP-21xx. The ADSP-21xx should be set up to operate in the SPORT transmit alternate framing mode (TFSW = 1). The
ADSP-21xx is programmed through the SPORT control register and should be configured as follows: Internal clock operation (ISCLK = 1) Active low framing (INVTFS = 1) 16-bit word length (SLEN = 15)
Internal frame sync signal (ITFS = 1)
Generate a frame sync for each write (TFSR = 1) Transmission is initiated by writing a word to the Tx register
after the SPORT has been enabled. The data is clocked out on each rising edge of the serial clock and clocked into the AD9834
on the SCLK falling edge. 1ADDITIONALPINS OMITTEDFORCLARITY.
AD98341
FSYNC
SDATA
SCLK
TFS
DT
SCLK
ADSP-21xx1
02705-032
Figure 35. ADSP-21xx to AD9834 Interface AD9834 TO 68HC11/68L11 INTERFACE
Figure 36 shows the serial interface between the AD9834 and
the 68HC11/68L11 microcontroller. The microcontroller is
configured as the master by setting Bit MSTR in the SPCR to 1,
providing a serial clock on SCK while the MOSI output drives the serial data line SDATA. Because the microcontroller does
not have a dedicated frame sync pin, the FSYNC signal is derived
from a port line (PC7). The setup conditions for correct
operation of the interface are as follows:
SCK idles high between write operations (CPOL = 0)
Data is valid on the SCK falling edge (CPHA = 1)
When data is being transmitted to the AD9834, the FSYNC line is taken low (PC7). Serial data from the 68HC11/68L11 is transmitted
in 8-bit bytes with only eight falling clock edges occurring in the transmit cycle. Data is transmitted MSB first. To load data into
the AD9834, PC7 is held low after the first eight bits are transferred
and a second serial write operation is performed to the AD9834.
Only after the second eight bits have been transferred should FSYNC be taken high again. 1ADDITIONAL PINS OMITTED FOR CLARITY.
AD98341
FSYNC
SDATA
SCLK
68HC11/68L111
PC7
MOSI
SCK
02705-033
Figure 36. 68HC11/68L11 to AD9834 Interface
AD9834 Data Sheet
AD9834 TO 80C51/80L51 INTERFACE
Figure 37 shows the serial interface between the AD9834 and the 80C51/80L51 microcontroller. The microcontroller is operated in Mode 0 so that TXD of the 80C51/80L51 drives SCLK of the AD9834, and RXD drives the serial data line (SDATA). The FSYNC signal is derived from a bit programmable pin on the port (P3.3 is shown in the diagram). When data is to be transmitted to the AD9834, P3.3 is taken low. The 80C51/80L51 transmits data in 8-bit bytes, thus only eight falling SCLK edges occur in each cycle. To load the remaining eight bits to the AD9834, P3.3 is held low after the first eight bits have been transmitted, and a second write operation is initiated to transmit the second byte of data. P3.3 is taken high following the completion of the second write operation. SCLK should idle high between the two write operations. The 80C51/80L51 outputs the serial data in an LSB-first format. The AD9834 accepts the MSB first (the four MSBs being the control information, the next four bits being the address, and the eight LSBs containing the data when writing to a destination register). Therefore, the transmit routine of the 80C51/80L51 must take this into account and rearrange the bits so that the MSB is output first.
1ADDITIONAL PINS OMITTED FOR CLARITY.AD98341FSYNCSDATASCLK80C51/80L511P3.3RXDTXD02705-034
Figure 37. 80C51/80L51 to AD9834 Interface
AD9834 TO DSP56002 INTERFACE
Figure 38 shows the interface between the AD9834 and the DSP56002. The DSP56002 is configured for normal mode asynchronous operation with a gated internal clock (SYN = 0, GCK = 1, SCKD = 1). The frame sync pin is generated internally (SC2 = 1), the transfers are 16 bits wide (WL1 = 1, WL0 = 0), and the frame sync signal frames the 16 bits (FSL = 0). The frame sync signal is available on Pin SC2, but needs to be inverted before being applied to the AD9834. The interface to the DSP56000/ DSP56001 is similar to that of the DSP56002.
1ADDITIONAL PINS OMITTED FOR CLARITY.AD98341FSYNCSDATASCLKDSP560021SC2STDSCK02705-035
Figure 38. DSP56002 to AD9834 Interface
Rev. D | Page 28 of 32
Data Sheet AD9834
OUTLINE DIMENSIONS
COMPLIANT TO JEDEC STANDARDS MO-153-AC20111106.40 BSC4.504.404.30PIN 16.606.506.40SEATINGPLANE0.150.050.300.190.65BSC1.20 MAX0.200.090.750.600.458°0°COPLANARITY0.10
Figure 39. 20-Lead Thin Shrink Small Outline Package [TSSOP] (RU-20) Dimensions shown in millimeters
ORDERING GUIDE
Model1
Maximum MCLK (MHz)
Temperature Range
Package Description
Package Option
AD9834BRU
50
−40°C to +105°C
20-Lead Thin Shrink Small Outline Package [TSSOP]
RU-20
AD9834BRU-REEL
50
−40°C to +105°C
20-Lead Thin Shrink Small Outline Package [TSSOP]
RU-20
AD9834BRU-REEL7
50
−40°C to +105°C
20-Lead Thin Shrink Small Outline Package [TSSOP]
RU-20
AD9834BRUZ
50
−40°C to +105°C
20-Lead Thin Shrink Small Outline Package [TSSOP]
RU-20
AD9834BRUZ-REEL
50
−40°C to +105°C
20-Lead Thin Shrink Small Outline Package [TSSOP]
RU-20
AD9834BRUZ-REEL7
50
−40°C to +105°C
20-Lead Thin Shrink Small Outline Package [TSSOP]
RU-20
AD9834CRUZ
75
−40°C to +105°C
20-Lead Thin Shrink Small Outline Package [TSSOP]
RU-20
AD9834CRUZ-REEL7
75
−40°C to +105°C
20-Lead Thin Shrink Small Outline Package [TSSOP]
RU-20
1 Z = RoHS Compliant Part.
Rev. D | Page 29 of 32
AD9834 Data Sheet
NOTES Rev. D | Page 30 of 32
Data Sheet AD9834
NOTES Rev. D | Page 31 of 32
AD9834 Data Sheet
NOTES
©2003–2014 Analog Devices, Inc. All rights reserved. Trademarks and registered trademarks are the property of their respective owners. D02705-0-3/14(A) Rev. D | Page 32 of 32
STM32F405xx
STM32F407xx
ARM Cortex-M4 32b MCU+FPU, 210DMIPS, up to 1MB Flash/192+4KB RAM, USB
OTG HS/FS, Ethernet, 17 TIMs, 3 ADCs, 15 comm. interfaces & camera
Datasheet - production data
Features
• Core: ARM 32-bit Cortex™-M4 CPU with FPU,
Adaptive real-time accelerator (ART
Accelerator™) allowing 0-wait state execution
from Flash memory, frequency up to 168 MHz,
memory protection unit, 210 DMIPS/
1.25 DMIPS/MHz (Dhrystone 2.1), and DSP
instructions
• Memories
– Up to 1 Mbyte of Flash memory
– Up to 192+4 Kbytes of SRAM including 64-
Kbyte of CCM (core coupled memory) data
RAM
– Flexible static memory controller
supporting Compact Flash, SRAM,
PSRAM, NOR and NAND memories
• LCD parallel interface, 8080/6800 modes
• Clock, reset and supply management
– 1.8 V to 3.6 V application supply and I/Os
– POR, PDR, PVD and BOR
– 4-to-26 MHz crystal oscillator
– Internal 16 MHz factory-trimmed RC (1%
accuracy)
– 32 kHz oscillator for RTC with calibration
– Internal 32 kHz RC with calibration
• Low power
– Sleep, Stop and Standby modes
– VBAT supply for RTC, 20×32 bit backup
registers + optional 4 KB backup SRAM
• 3×12-bit, 2.4 MSPS A/D converters: up to 24
channels and 7.2 MSPS in triple interleaved
mode
• 2×12-bit D/A converters
• General-purpose DMA: 16-stream DMA
controller with FIFOs and burst support
• Up to 17 timers: up to twelve 16-bit and two 32-
bit timers up to 168 MHz, each with up to 4
IC/OC/PWM or pulse counter and quadrature
(incremental) encoder input
• Debug mode
– Serial wire debug (SWD) & JTAG
interfaces
– Cortex-M4 Embedded Trace Macrocell™
• Up to 140 I/O ports with interrupt capability
– Up to 136 fast I/Os up to 84 MHz
– Up to 138 5 V-tolerant I/Os
• Up to 15 communication interfaces
– Up to 3 × I2C interfaces (SMBus/PMBus)
– Up to 4 USARTs/2 UARTs (10.5 Mbit/s, ISO
7816 interface, LIN, IrDA, modem control)
– Up to 3 SPIs (42 Mbits/s), 2 with muxed
full-duplex I2S to achieve audio class
accuracy via internal audio PLL or external
clock
– 2 × CAN interfaces (2.0B Active)
– SDIO interface
• Advanced connectivity
– USB 2.0 full-speed device/host/OTG
controller with on-chip PHY
– USB 2.0 high-speed/full-speed
device/host/OTG controller with dedicated
DMA, on-chip full-speed PHY and ULPI
– 10/100 Ethernet MAC with dedicated DMA:
supports IEEE 1588v2 hardware, MII/RMII
• 8- to 14-bit parallel camera interface up to
54 Mbytes/s
• True random number generator
• CRC calculation unit
• 96-bit unique ID
• RTC: subsecond accuracy, hardware calendar
LQFP64 (10 × 10 mm)
LQFP100 (14 × 14 mm)
LQFP144 (20 × 20 mm)
FBGA
UFBGA176
(10 × 10 mm)
LQFP176 (24 × 24 mm)
WLCSP90
Table 1. Device summary
Reference Part number
STM32F405xx STM32F405RG, STM32F405VG, STM32F405ZG,
STM32F405OG, STM32F405OE
STM32F407xx STM32F407VG, STM32F407IG, STM32F407ZG,
STM32F407VE, STM32F407ZE, STM32F407IE
www.st.com
Contents STM32F405xx, STM32F407xx
2/185 DocID022152 Rev 4
Contents
1 Introduction . . . . . . . . . . . . . . . . . . . . . . . . . . . . . . . . . . . . . . . . . . . . . . . 11
2 Description . . . . . . . . . . . . . . . . . . . . . . . . . . . . . . . . . . . . . . . . . . . . . . . . 12
2.1 Full compatibility throughout the family . . . . . . . . . . . . . . . . . . . . . . . . . . 15
2.2 Device overview . . . . . . . . . . . . . . . . . . . . . . . . . . . . . . . . . . . . . . . . . . . . 18
2.2.1 ARM® Cortex™-M4F core with embedded Flash and SRAM . . . . . . . . 19
2.2.2 Adaptive real-time memory accelerator (ART Accelerator™) . . . . . . . . 19
2.2.3 Memory protection unit . . . . . . . . . . . . . . . . . . . . . . . . . . . . . . . . . . . . . 19
2.2.4 Embedded Flash memory . . . . . . . . . . . . . . . . . . . . . . . . . . . . . . . . . . . 19
2.2.5 CRC (cyclic redundancy check) calculation unit . . . . . . . . . . . . . . . . . . 20
2.2.6 Embedded SRAM . . . . . . . . . . . . . . . . . . . . . . . . . . . . . . . . . . . . . . . . . 20
2.2.7 Multi-AHB bus matrix . . . . . . . . . . . . . . . . . . . . . . . . . . . . . . . . . . . . . . . 20
2.2.8 DMA controller (DMA) . . . . . . . . . . . . . . . . . . . . . . . . . . . . . . . . . . . . . . 21
2.2.9 Flexible static memory controller (FSMC) . . . . . . . . . . . . . . . . . . . . . . . 22
2.2.10 Nested vectored interrupt controller (NVIC) . . . . . . . . . . . . . . . . . . . . . . 22
2.2.11 External interrupt/event controller (EXTI) . . . . . . . . . . . . . . . . . . . . . . . 22
2.2.12 Clocks and startup . . . . . . . . . . . . . . . . . . . . . . . . . . . . . . . . . . . . . . . . . 22
2.2.13 Boot modes . . . . . . . . . . . . . . . . . . . . . . . . . . . . . . . . . . . . . . . . . . . . . . 23
2.2.14 Power supply schemes . . . . . . . . . . . . . . . . . . . . . . . . . . . . . . . . . . . . . 23
2.2.15 Power supply supervisor . . . . . . . . . . . . . . . . . . . . . . . . . . . . . . . . . . . . 23
2.2.16 Voltage regulator . . . . . . . . . . . . . . . . . . . . . . . . . . . . . . . . . . . . . . . . . . 25
2.2.17 Regulator ON/OFF and internal reset ON/OFF availability . . . . . . . . . . 28
2.2.18 Real-time clock (RTC), backup SRAM and backup registers . . . . . . . . 28
2.2.19 Low-power modes . . . . . . . . . . . . . . . . . . . . . . . . . . . . . . . . . . . . . . . . . 29
2.2.20 VBAT operation . . . . . . . . . . . . . . . . . . . . . . . . . . . . . . . . . . . . . . . . . . . . 30
2.2.21 Timers and watchdogs . . . . . . . . . . . . . . . . . . . . . . . . . . . . . . . . . . . . . . 30
2.2.22 Inter-integrated circuit interface (I²C) . . . . . . . . . . . . . . . . . . . . . . . . . . 33
2.2.23 Universal synchronous/asynchronous receiver transmitters (USART) . 33
2.2.24 Serial peripheral interface (SPI) . . . . . . . . . . . . . . . . . . . . . . . . . . . . . . . 34
2.2.25 Inter-integrated sound (I2S) . . . . . . . . . . . . . . . . . . . . . . . . . . . . . . . . . . 34
2.2.26 Audio PLL (PLLI2S) . . . . . . . . . . . . . . . . . . . . . . . . . . . . . . . . . . . . . . . . 34
2.2.27 Secure digital input/output interface (SDIO) . . . . . . . . . . . . . . . . . . . . . 35
2.2.28 Ethernet MAC interface with dedicated DMA and IEEE 1588 support . 35
2.2.29 Controller area network (bxCAN) . . . . . . . . . . . . . . . . . . . . . . . . . . . . . . 36
DocID022152 Rev 4 3/185
STM32F405xx, STM32F407xx Contents
2.2.30 Universal serial bus on-the-go full-speed (OTG_FS) . . . . . . . . . . . . . . . 36
2.2.31 Universal serial bus on-the-go high-speed (OTG_HS) . . . . . . . . . . . . . 36
2.2.32 Digital camera interface (DCMI) . . . . . . . . . . . . . . . . . . . . . . . . . . . . . . 37
2.2.33 Random number generator (RNG) . . . . . . . . . . . . . . . . . . . . . . . . . . . . 37
2.2.34 General-purpose input/outputs (GPIOs) . . . . . . . . . . . . . . . . . . . . . . . . 37
2.2.35 Analog-to-digital converters (ADCs) . . . . . . . . . . . . . . . . . . . . . . . . . . . 37
2.2.36 Temperature sensor . . . . . . . . . . . . . . . . . . . . . . . . . . . . . . . . . . . . . . . . 37
2.2.37 Digital-to-analog converter (DAC) . . . . . . . . . . . . . . . . . . . . . . . . . . . . . 38
2.2.38 Serial wire JTAG debug port (SWJ-DP) . . . . . . . . . . . . . . . . . . . . . . . . . 38
2.2.39 Embedded Trace Macrocell™ . . . . . . . . . . . . . . . . . . . . . . . . . . . . . . . . 38
3 Pinouts and pin description . . . . . . . . . . . . . . . . . . . . . . . . . . . . . . . . . . 39
4 Memory mapping . . . . . . . . . . . . . . . . . . . . . . . . . . . . . . . . . . . . . . . . . . . 69
5 Electrical characteristics . . . . . . . . . . . . . . . . . . . . . . . . . . . . . . . . . . . . 74
5.1 Parameter conditions . . . . . . . . . . . . . . . . . . . . . . . . . . . . . . . . . . . . . . . . 74
5.1.1 Minimum and maximum values . . . . . . . . . . . . . . . . . . . . . . . . . . . . . . . 74
5.1.2 Typical values . . . . . . . . . . . . . . . . . . . . . . . . . . . . . . . . . . . . . . . . . . . . 74
5.1.3 Typical curves . . . . . . . . . . . . . . . . . . . . . . . . . . . . . . . . . . . . . . . . . . . . 74
5.1.4 Loading capacitor . . . . . . . . . . . . . . . . . . . . . . . . . . . . . . . . . . . . . . . . . 74
5.1.5 Pin input voltage . . . . . . . . . . . . . . . . . . . . . . . . . . . . . . . . . . . . . . . . . . 74
5.1.6 Power supply scheme . . . . . . . . . . . . . . . . . . . . . . . . . . . . . . . . . . . . . . 75
5.1.7 Current consumption measurement . . . . . . . . . . . . . . . . . . . . . . . . . . . 76
5.2 Absolute maximum ratings . . . . . . . . . . . . . . . . . . . . . . . . . . . . . . . . . . . . 76
5.3 Operating conditions . . . . . . . . . . . . . . . . . . . . . . . . . . . . . . . . . . . . . . . . 77
5.3.1 General operating conditions . . . . . . . . . . . . . . . . . . . . . . . . . . . . . . . . . 77
5.3.2 VCAP_1/VCAP_2 external capacitor . . . . . . . . . . . . . . . . . . . . . . . . . . . 79
5.3.3 Operating conditions at power-up / power-down (regulator ON) . . . . . . 80
5.3.4 Operating conditions at power-up / power-down (regulator OFF) . . . . . 80
5.3.5 Embedded reset and power control block characteristics . . . . . . . . . . . 80
5.3.6 Supply current characteristics . . . . . . . . . . . . . . . . . . . . . . . . . . . . . . . . 82
5.3.7 Wakeup time from low-power mode . . . . . . . . . . . . . . . . . . . . . . . . . . . 95
5.3.8 External clock source characteristics . . . . . . . . . . . . . . . . . . . . . . . . . . . 96
5.3.9 Internal clock source characteristics . . . . . . . . . . . . . . . . . . . . . . . . . . . 99
5.3.10 PLL characteristics . . . . . . . . . . . . . . . . . . . . . . . . . . . . . . . . . . . . . . . 100
5.3.11 PLL spread spectrum clock generation (SSCG) characteristics . . . . . 102
Contents STM32F405xx, STM32F407xx
4/185 DocID022152 Rev 4
5.3.12 Memory characteristics . . . . . . . . . . . . . . . . . . . . . . . . . . . . . . . . . . . . 104
5.3.13 EMC characteristics . . . . . . . . . . . . . . . . . . . . . . . . . . . . . . . . . . . . . . . 106
5.3.14 Absolute maximum ratings (electrical sensitivity) . . . . . . . . . . . . . . . . 108
5.3.15 I/O current injection characteristics . . . . . . . . . . . . . . . . . . . . . . . . . . . 109
5.3.16 I/O port characteristics . . . . . . . . . . . . . . . . . . . . . . . . . . . . . . . . . . . . . 109
5.3.17 NRST pin characteristics . . . . . . . . . . . . . . . . . . . . . . . . . . . . . . . . . . . 113
5.3.18 TIM timer characteristics . . . . . . . . . . . . . . . . . . . . . . . . . . . . . . . . . . . 114
5.3.19 Communications interfaces . . . . . . . . . . . . . . . . . . . . . . . . . . . . . . . . . 116
5.3.20 12-bit ADC characteristics . . . . . . . . . . . . . . . . . . . . . . . . . . . . . . . . . . 129
5.3.21 Temperature sensor characteristics . . . . . . . . . . . . . . . . . . . . . . . . . . . 134
5.3.22 VBAT monitoring characteristics . . . . . . . . . . . . . . . . . . . . . . . . . . . . . . 134
5.3.23 Embedded reference voltage . . . . . . . . . . . . . . . . . . . . . . . . . . . . . . . . 135
5.3.24 DAC electrical characteristics . . . . . . . . . . . . . . . . . . . . . . . . . . . . . . . 135
5.3.25 FSMC characteristics . . . . . . . . . . . . . . . . . . . . . . . . . . . . . . . . . . . . . . 137
5.3.26 Camera interface (DCMI) timing specifications . . . . . . . . . . . . . . . . . . 155
5.3.27 SD/SDIO MMC card host interface (SDIO) characteristics . . . . . . . . . 156
5.3.28 RTC characteristics . . . . . . . . . . . . . . . . . . . . . . . . . . . . . . . . . . . . . . . 157
6 Package characteristics . . . . . . . . . . . . . . . . . . . . . . . . . . . . . . . . . . . . 158
6.1 Package mechanical data . . . . . . . . . . . . . . . . . . . . . . . . . . . . . . . . . . . 158
6.2 Thermal characteristics . . . . . . . . . . . . . . . . . . . . . . . . . . . . . . . . . . . . . 169
7 Part numbering . . . . . . . . . . . . . . . . . . . . . . . . . . . . . . . . . . . . . . . . . . . 170
Appendix A Application block diagrams . . . . . . . . . . . . . . . . . . . . . . . . . . . . . . 171
A.1 USB OTG full speed (FS) interface solutions . . . . . . . . . . . . . . . . . . . . . 171
A.2 USB OTG high speed (HS) interface solutions . . . . . . . . . . . . . . . . . . . . 173
A.3 Ethernet interface solutions. . . . . . . . . . . . . . . . . . . . . . . . . . . . . . . . . . . 174
8 Revision history . . . . . . . . . . . . . . . . . . . . . . . . . . . . . . . . . . . . . . . . . . 176
DocID022152 Rev 4 5/185
STM32F405xx, STM32F407xx List of tables
List of tables
Table 1. Device summary . . . . . . . . . . . . . . . . . . . . . . . . . . . . . . . . . . . . . . . . . . . . . . . . . . . . . . . . . . 1
Table 2. STM32F405xx and STM32F407xx: features and peripheral counts. . . . . . . . . . . . . . . . . . 13
Table 3. Regulator ON/OFF and internal reset ON/OFF availability. . . . . . . . . . . . . . . . . . . . . . . . . 28
Table 4. Timer feature comparison. . . . . . . . . . . . . . . . . . . . . . . . . . . . . . . . . . . . . . . . . . . . . . . . . . 30
Table 5. USART feature comparison . . . . . . . . . . . . . . . . . . . . . . . . . . . . . . . . . . . . . . . . . . . . . . . . 34
Table 6. Legend/abbreviations used in the pinout table . . . . . . . . . . . . . . . . . . . . . . . . . . . . . . . . . . 44
Table 7. STM32F40x pin and ball definitions . . . . . . . . . . . . . . . . . . . . . . . . . . . . . . . . . . . . . . . . . . 45
Table 8. FSMC pin definition . . . . . . . . . . . . . . . . . . . . . . . . . . . . . . . . . . . . . . . . . . . . . . . . . . . . . . 57
Table 9. Alternate function mapping . . . . . . . . . . . . . . . . . . . . . . . . . . . . . . . . . . . . . . . . . . . . . . . . . 60
Table 10. STM32F40x register boundary addresses . . . . . . . . . . . . . . . . . . . . . . . . . . . . . . . . . . . . . 70
Table 11. Voltage characteristics . . . . . . . . . . . . . . . . . . . . . . . . . . . . . . . . . . . . . . . . . . . . . . . . . . . . 76
Table 12. Current characteristics . . . . . . . . . . . . . . . . . . . . . . . . . . . . . . . . . . . . . . . . . . . . . . . . . . . . 77
Table 13. Thermal characteristics. . . . . . . . . . . . . . . . . . . . . . . . . . . . . . . . . . . . . . . . . . . . . . . . . . . . 77
Table 14. General operating conditions . . . . . . . . . . . . . . . . . . . . . . . . . . . . . . . . . . . . . . . . . . . . . . . 77
Table 15. Limitations depending on the operating power supply range . . . . . . . . . . . . . . . . . . . . . . . 79
Table 16. VCAP_1/VCAP_2 operating conditions . . . . . . . . . . . . . . . . . . . . . . . . . . . . . . . . . . . . . . . 80
Table 17. Operating conditions at power-up / power-down (regulator ON) . . . . . . . . . . . . . . . . . . . . 80
Table 18. Operating conditions at power-up / power-down (regulator OFF). . . . . . . . . . . . . . . . . . . . 80
Table 19. Embedded reset and power control block characteristics. . . . . . . . . . . . . . . . . . . . . . . . . . 81
Table 20. Typical and maximum current consumption in Run mode, code with data processing
running from Flash memory (ART accelerator enabled) or RAM . . . . . . . . . . . . . . . . . . . 83
Table 21. Typical and maximum current consumption in Run mode, code with data processing
running from Flash memory (ART accelerator disabled) . . . . . . . . . . . . . . . . . . . . . . . . . . 84
Table 22. Typical and maximum current consumption in Sleep mode . . . . . . . . . . . . . . . . . . . . . . . . 87
Table 23. Typical and maximum current consumptions in Stop mode . . . . . . . . . . . . . . . . . . . . . . . . 88
Table 24. Typical and maximum current consumptions in Standby mode . . . . . . . . . . . . . . . . . . . . . 88
Table 25. Typical and maximum current consumptions in VBAT mode. . . . . . . . . . . . . . . . . . . . . . . . 89
Table 26. Switching output I/O current consumption . . . . . . . . . . . . . . . . . . . . . . . . . . . . . . . . . . . . . 92
Table 27. Peripheral current consumption . . . . . . . . . . . . . . . . . . . . . . . . . . . . . . . . . . . . . . . . . . . . . 93
Table 28. Low-power mode wakeup timings . . . . . . . . . . . . . . . . . . . . . . . . . . . . . . . . . . . . . . . . . . . 95
Table 29. High-speed external user clock characteristics. . . . . . . . . . . . . . . . . . . . . . . . . . . . . . . . . . 96
Table 30. Low-speed external user clock characteristics . . . . . . . . . . . . . . . . . . . . . . . . . . . . . . . . . . 96
Table 31. HSE 4-26 MHz oscillator characteristics . . . . . . . . . . . . . . . . . . . . . . . . . . . . . . . . . . . . . . 98
Table 32. LSE oscillator characteristics (fLSE = 32.768 kHz) . . . . . . . . . . . . . . . . . . . . . . . . . . . . . . . 99
Table 33. HSI oscillator characteristics . . . . . . . . . . . . . . . . . . . . . . . . . . . . . . . . . . . . . . . . . . . . . . . 99
Table 34. LSI oscillator characteristics . . . . . . . . . . . . . . . . . . . . . . . . . . . . . . . . . . . . . . . . . . . . . . 100
Table 35. Main PLL characteristics. . . . . . . . . . . . . . . . . . . . . . . . . . . . . . . . . . . . . . . . . . . . . . . . . . 101
Table 36. PLLI2S (audio PLL) characteristics . . . . . . . . . . . . . . . . . . . . . . . . . . . . . . . . . . . . . . . . . 101
Table 37. SSCG parameters constraint . . . . . . . . . . . . . . . . . . . . . . . . . . . . . . . . . . . . . . . . . . . . . . 102
Table 38. Flash memory characteristics . . . . . . . . . . . . . . . . . . . . . . . . . . . . . . . . . . . . . . . . . . . . . . 104
Table 39. Flash memory programming. . . . . . . . . . . . . . . . . . . . . . . . . . . . . . . . . . . . . . . . . . . . . . . 104
Table 40. Flash memory programming with VPP . . . . . . . . . . . . . . . . . . . . . . . . . . . . . . . . . . . . . . . . . . . . . . . . . . 106
Table 41. Flash memory endurance and data retention . . . . . . . . . . . . . . . . . . . . . . . . . . . . . . . . . . 106
Table 42. EMS characteristics . . . . . . . . . . . . . . . . . . . . . . . . . . . . . . . . . . . . . . . . . . . . . . . . . . . . . 107
Table 43. EMI characteristics . . . . . . . . . . . . . . . . . . . . . . . . . . . . . . . . . . . . . . . . . . . . . . . . . . . . . . 108
Table 44. ESD absolute maximum ratings . . . . . . . . . . . . . . . . . . . . . . . . . . . . . . . . . . . . . . . . . . . . 108
Table 45. Electrical sensitivities . . . . . . . . . . . . . . . . . . . . . . . . . . . . . . . . . . . . . . . . . . . . . . . . . . . . 109
Table 46. I/O current injection susceptibility . . . . . . . . . . . . . . . . . . . . . . . . . . . . . . . . . . . . . . . . . . . 109
List of tables STM32F405xx, STM32F407xx
6/185 DocID022152 Rev 4
Table 47. I/O static characteristics . . . . . . . . . . . . . . . . . . . . . . . . . . . . . . . . . . . . . . . . . . . . . . . . . . 110
Table 48. Output voltage characteristics . . . . . . . . . . . . . . . . . . . . . . . . . . . . . . . . . . . . . . . . . . . . . 111
Table 49. I/O AC characteristics . . . . . . . . . . . . . . . . . . . . . . . . . . . . . . . . . . . . . . . . . . . . . . . . . . . . 112
Table 50. NRST pin characteristics . . . . . . . . . . . . . . . . . . . . . . . . . . . . . . . . . . . . . . . . . . . . . . . . . 114
Table 51. Characteristics of TIMx connected to the APB1 domain . . . . . . . . . . . . . . . . . . . . . . . . . 115
Table 52. Characteristics of TIMx connected to the APB2 domain . . . . . . . . . . . . . . . . . . . . . . . . . 116
Table 53. I2C characteristics. . . . . . . . . . . . . . . . . . . . . . . . . . . . . . . . . . . . . . . . . . . . . . . . . . . . . . . 116
Table 54. SCL frequency (fPCLK1= 42 MHz.,VDD = 3.3 V) . . . . . . . . . . . . . . . . . . . . . . . . . . . . . . . . 118
Table 55. SPI dynamic characteristics . . . . . . . . . . . . . . . . . . . . . . . . . . . . . . . . . . . . . . . . . . . . . . . 118
Table 56. I2S dynamic characteristics . . . . . . . . . . . . . . . . . . . . . . . . . . . . . . . . . . . . . . . . . . . . . . . 122
Table 57. USB OTG FS startup time . . . . . . . . . . . . . . . . . . . . . . . . . . . . . . . . . . . . . . . . . . . . . . . . 124
Table 58. USB OTG FS DC electrical characteristics. . . . . . . . . . . . . . . . . . . . . . . . . . . . . . . . . . . . 124
Table 59. USB OTG FS electrical characteristics. . . . . . . . . . . . . . . . . . . . . . . . . . . . . . . . . . . . . . . 125
Table 60. USB HS DC electrical characteristics . . . . . . . . . . . . . . . . . . . . . . . . . . . . . . . . . . . . . . . . 125
Table 61. USB HS clock timing parameters . . . . . . . . . . . . . . . . . . . . . . . . . . . . . . . . . . . . . . . . . . . 125
Table 62. ULPI timing . . . . . . . . . . . . . . . . . . . . . . . . . . . . . . . . . . . . . . . . . . . . . . . . . . . . . . . . . . . . 126
Table 63. Ethernet DC electrical characteristics . . . . . . . . . . . . . . . . . . . . . . . . . . . . . . . . . . . . . . . . 127
Table 64. Dynamic characteristics: Ehternet MAC signals for SMI. . . . . . . . . . . . . . . . . . . . . . . . . . 127
Table 65. Dynamic characteristics: Ethernet MAC signals for RMII . . . . . . . . . . . . . . . . . . . . . . . . . 128
Table 66. Dynamic characteristics: Ethernet MAC signals for MII . . . . . . . . . . . . . . . . . . . . . . . . . . 128
Table 67. ADC characteristics . . . . . . . . . . . . . . . . . . . . . . . . . . . . . . . . . . . . . . . . . . . . . . . . . . . . . 129
Table 68. ADC accuracy at fADC = 30 MHz . . . . . . . . . . . . . . . . . . . . . . . . . . . . . . . . . . . . . . . . . . . 131
Table 69. Temperature sensor characteristics . . . . . . . . . . . . . . . . . . . . . . . . . . . . . . . . . . . . . . . . . 134
Table 70. Temperature sensor calibration values. . . . . . . . . . . . . . . . . . . . . . . . . . . . . . . . . . . . . . . 134
Table 71. VBAT monitoring characteristics . . . . . . . . . . . . . . . . . . . . . . . . . . . . . . . . . . . . . . . . . . . . 134
Table 72. Embedded internal reference voltage. . . . . . . . . . . . . . . . . . . . . . . . . . . . . . . . . . . . . . . . 135
Table 73. Internal reference voltage calibration values . . . . . . . . . . . . . . . . . . . . . . . . . . . . . . . . . . 135
Table 74. DAC characteristics . . . . . . . . . . . . . . . . . . . . . . . . . . . . . . . . . . . . . . . . . . . . . . . . . . . . . 135
Table 75. Asynchronous non-multiplexed SRAM/PSRAM/NOR read timings . . . . . . . . . . . . . . . . . 138
Table 76. Asynchronous non-multiplexed SRAM/PSRAM/NOR write timings . . . . . . . . . . . . . . . . . 139
Table 77. Asynchronous multiplexed PSRAM/NOR read timings. . . . . . . . . . . . . . . . . . . . . . . . . . . 140
Table 78. Asynchronous multiplexed PSRAM/NOR write timings . . . . . . . . . . . . . . . . . . . . . . . . . . 141
Table 79. Synchronous multiplexed NOR/PSRAM read timings . . . . . . . . . . . . . . . . . . . . . . . . . . . 143
Table 80. Synchronous multiplexed PSRAM write timings. . . . . . . . . . . . . . . . . . . . . . . . . . . . . . . . 144
Table 81. Synchronous non-multiplexed NOR/PSRAM read timings . . . . . . . . . . . . . . . . . . . . . . . . 145
Table 82. Synchronous non-multiplexed PSRAM write timings . . . . . . . . . . . . . . . . . . . . . . . . . . . . 147
Table 83. Switching characteristics for PC Card/CF read and write cycles
in attribute/common space. . . . . . . . . . . . . . . . . . . . . . . . . . . . . . . . . . . . . . . . . . . . . . . . 151
Table 84. Switching characteristics for PC Card/CF read and write cycles
in I/O space . . . . . . . . . . . . . . . . . . . . . . . . . . . . . . . . . . . . . . . . . . . . . . . . . . . . . . . . . . . 152
Table 85. Switching characteristics for NAND Flash read cycles . . . . . . . . . . . . . . . . . . . . . . . . . . . 154
Table 86. Switching characteristics for NAND Flash write cycles. . . . . . . . . . . . . . . . . . . . . . . . . . . 155
Table 87. DCMI characteristics. . . . . . . . . . . . . . . . . . . . . . . . . . . . . . . . . . . . . . . . . . . . . . . . . . . . . 155
Table 88. Dynamic characteristics: SD / MMC characteristics . . . . . . . . . . . . . . . . . . . . . . . . . . . . . 157
Table 89. RTC characteristics . . . . . . . . . . . . . . . . . . . . . . . . . . . . . . . . . . . . . . . . . . . . . . . . . . . . . 157
Table 90. WLCSP90 - 0.400 mm pitch wafer level chip size package mechanical data . . . . . . . . . 159
Table 91. LQFP64 – 10 x 10 mm 64 pin low-profile quad flat package mechanical data . . . . . . . . . 160
Table 92. LQPF100 – 14 x 14 mm 100-pin low-profile quad flat package mechanical data. . . . . . . 162
Table 93. LQFP144, 20 x 20 mm, 144-pin low-profile quad flat package mechanical data . . . . . . . 164
Table 94. UFBGA176+25 - ultra thin fine pitch ball grid array 10 × 10 × 0.6 mm
mechanical data . . . . . . . . . . . . . . . . . . . . . . . . . . . . . . . . . . . . . . . . . . . . . . . . . . . . . . . . 166
Table 95. LQFP176, 24 x 24 mm, 176-pin low-profile quad flat package mechanical data . . . . . . . 167
DocID022152 Rev 4 7/185
STM32F405xx, STM32F407xx List of tables
Table 96. Package thermal characteristics . . . . . . . . . . . . . . . . . . . . . . . . . . . . . . . . . . . . . . . . . . . . 169
Table 97. Ordering information scheme . . . . . . . . . . . . . . . . . . . . . . . . . . . . . . . . . . . . . . . . . . . . . . 170
Table 98. Document revision history . . . . . . . . . . . . . . . . . . . . . . . . . . . . . . . . . . . . . . . . . . . . . . . . 176
List of figures STM32F405xx, STM32F407xx
8/185 DocID022152 Rev 4
List of figures
Figure 1. Compatible board design between STM32F10xx/STM32F4xx for LQFP64. . . . . . . . . . . . 15
Figure 2. Compatible board design STM32F10xx/STM32F2xx/STM32F4xx
for LQFP100 package. . . . . . . . . . . . . . . . . . . . . . . . . . . . . . . . . . . . . . . . . . . . . . . . . . . . . 16
Figure 3. Compatible board design between STM32F10xx/STM32F2xx/STM32F4xx
for LQFP144 package. . . . . . . . . . . . . . . . . . . . . . . . . . . . . . . . . . . . . . . . . . . . . . . . . . . . . 16
Figure 4. Compatible board design between STM32F2xx and STM32F4xx
for LQFP176 and BGA176 packages . . . . . . . . . . . . . . . . . . . . . . . . . . . . . . . . . . . . . . . . 17
Figure 5. STM32F40x block diagram. . . . . . . . . . . . . . . . . . . . . . . . . . . . . . . . . . . . . . . . . . . . . . . . . 18
Figure 6. Multi-AHB matrix. . . . . . . . . . . . . . . . . . . . . . . . . . . . . . . . . . . . . . . . . . . . . . . . . . . . . . . . . 21
Figure 7. Power supply supervisor interconnection with internal reset OFF . . . . . . . . . . . . . . . . . . . 24
Figure 8. PDR_ON and NRST control with internal reset OFF . . . . . . . . . . . . . . . . . . . . . . . . . . . . . 25
Figure 9. Regulator OFF . . . . . . . . . . . . . . . . . . . . . . . . . . . . . . . . . . . . . . . . . . . . . . . . . . . . . . . . . . 26
Figure 10. Startup in regulator OFF mode: slow VDD slope
- power-down reset risen after VCAP_1/VCAP_2 stabilization . . . . . . . . . . . . . . . . . . . . . . . . 27
Figure 11. Startup in regulator OFF mode: fast VDD slope
- power-down reset risen before VCAP_1/VCAP_2 stabilization . . . . . . . . . . . . . . . . . . . . . . 28
Figure 12. STM32F40x LQFP64 pinout . . . . . . . . . . . . . . . . . . . . . . . . . . . . . . . . . . . . . . . . . . . . . . . . 39
Figure 13. STM32F40x LQFP100 pinout . . . . . . . . . . . . . . . . . . . . . . . . . . . . . . . . . . . . . . . . . . . . . . . 40
Figure 14. STM32F40x LQFP144 pinout . . . . . . . . . . . . . . . . . . . . . . . . . . . . . . . . . . . . . . . . . . . . . . . 41
Figure 15. STM32F40x LQFP176 pinout . . . . . . . . . . . . . . . . . . . . . . . . . . . . . . . . . . . . . . . . . . . . . . . 42
Figure 16. STM32F40x UFBGA176 ballout . . . . . . . . . . . . . . . . . . . . . . . . . . . . . . . . . . . . . . . . . . . . . 43
Figure 17. STM32F40x WLCSP90 ballout. . . . . . . . . . . . . . . . . . . . . . . . . . . . . . . . . . . . . . . . . . . . . . 44
Figure 18. STM32F40x memory map . . . . . . . . . . . . . . . . . . . . . . . . . . . . . . . . . . . . . . . . . . . . . . . . . 69
Figure 19. Pin loading conditions. . . . . . . . . . . . . . . . . . . . . . . . . . . . . . . . . . . . . . . . . . . . . . . . . . . . . 74
Figure 20. Pin input voltage . . . . . . . . . . . . . . . . . . . . . . . . . . . . . . . . . . . . . . . . . . . . . . . . . . . . . . . . . 74
Figure 21. Power supply scheme . . . . . . . . . . . . . . . . . . . . . . . . . . . . . . . . . . . . . . . . . . . . . . . . . . . . 75
Figure 22. Current consumption measurement scheme . . . . . . . . . . . . . . . . . . . . . . . . . . . . . . . . . . . 76
Figure 23. External capacitor CEXT . . . . . . . . . . . . . . . . . . . . . . . . . . . . . . . . . . . . . . . . . . . . . . . . . . . 80
Figure 24. Typical current consumption versus temperature, Run mode, code with data
processing running from Flash (ART accelerator ON) or RAM, and peripherals OFF . . . . 85
Figure 25. Typical current consumption versus temperature, Run mode, code with data
processing running from Flash (ART accelerator ON) or RAM, and peripherals ON . . . . . 85
Figure 26. Typical current consumption versus temperature, Run mode, code with data
processing running from Flash (ART accelerator OFF) or RAM, and peripherals OFF . . . 86
Figure 27. Typical current consumption versus temperature, Run mode, code with data
processing running from Flash (ART accelerator OFF) or RAM, and peripherals ON . . . . 86
Figure 28. Typical VBAT current consumption (LSE and RTC ON/backup RAM OFF) . . . . . . . . . . . . 89
Figure 29. Typical VBAT current consumption (LSE and RTC ON/backup RAM ON) . . . . . . . . . . . . . 90
Figure 30. High-speed external clock source AC timing diagram . . . . . . . . . . . . . . . . . . . . . . . . . . . . 97
Figure 31. Low-speed external clock source AC timing diagram. . . . . . . . . . . . . . . . . . . . . . . . . . . . . 97
Figure 32. Typical application with an 8 MHz crystal . . . . . . . . . . . . . . . . . . . . . . . . . . . . . . . . . . . . . . 98
Figure 33. Typical application with a 32.768 kHz crystal . . . . . . . . . . . . . . . . . . . . . . . . . . . . . . . . . . . 99
Figure 34. ACCLSI versus temperature . . . . . . . . . . . . . . . . . . . . . . . . . . . . . . . . . . . . . . . . . . . . . . . 100
Figure 35. PLL output clock waveforms in center spread mode . . . . . . . . . . . . . . . . . . . . . . . . . . . . 103
Figure 36. PLL output clock waveforms in down spread mode . . . . . . . . . . . . . . . . . . . . . . . . . . . . . 104
Figure 37. I/O AC characteristics definition . . . . . . . . . . . . . . . . . . . . . . . . . . . . . . . . . . . . . . . . . . . . 113
Figure 38. Recommended NRST pin protection . . . . . . . . . . . . . . . . . . . . . . . . . . . . . . . . . . . . . . . . 114
Figure 39. I2C bus AC waveforms and measurement circuit . . . . . . . . . . . . . . . . . . . . . . . . . . . . . . . 117
DocID022152 Rev 4 9/185
STM32F405xx, STM32F407xx List of figures
Figure 40. SPI timing diagram - slave mode and CPHA = 0 . . . . . . . . . . . . . . . . . . . . . . . . . . . . . . . 120
Figure 41. SPI timing diagram - slave mode and CPHA = 1 . . . . . . . . . . . . . . . . . . . . . . . . . . . . . . . 120
Figure 42. SPI timing diagram - master mode . . . . . . . . . . . . . . . . . . . . . . . . . . . . . . . . . . . . . . . . . . 121
Figure 43. I2S slave timing diagram (Philips protocol) . . . . . . . . . . . . . . . . . . . . . . . . . . . . . . . . . . . 123
Figure 44. I2S master timing diagram (Philips protocol)(1). . . . . . . . . . . . . . . . . . . . . . . . . . . . . . . . . 123
Figure 45. USB OTG FS timings: definition of data signal rise and fall time . . . . . . . . . . . . . . . . . . . 124
Figure 46. ULPI timing diagram . . . . . . . . . . . . . . . . . . . . . . . . . . . . . . . . . . . . . . . . . . . . . . . . . . . . . 126
Figure 47. Ethernet SMI timing diagram . . . . . . . . . . . . . . . . . . . . . . . . . . . . . . . . . . . . . . . . . . . . . . 127
Figure 48. Ethernet RMII timing diagram . . . . . . . . . . . . . . . . . . . . . . . . . . . . . . . . . . . . . . . . . . . . . . 127
Figure 49. Ethernet MII timing diagram . . . . . . . . . . . . . . . . . . . . . . . . . . . . . . . . . . . . . . . . . . . . . . . 128
Figure 50. ADC accuracy characteristics. . . . . . . . . . . . . . . . . . . . . . . . . . . . . . . . . . . . . . . . . . . . . . 131
Figure 51. Typical connection diagram using the ADC . . . . . . . . . . . . . . . . . . . . . . . . . . . . . . . . . . . 132
Figure 52. Power supply and reference decoupling (VREF+ not connected to VDDA). . . . . . . . . . . . . 133
Figure 53. Power supply and reference decoupling (VREF+ connected to VDDA). . . . . . . . . . . . . . . . 133
Figure 54. 12-bit buffered /non-buffered DAC . . . . . . . . . . . . . . . . . . . . . . . . . . . . . . . . . . . . . . . . . . 137
Figure 55. Asynchronous non-multiplexed SRAM/PSRAM/NOR read waveforms . . . . . . . . . . . . . . 138
Figure 56. Asynchronous non-multiplexed SRAM/PSRAM/NOR write waveforms . . . . . . . . . . . . . . 139
Figure 57. Asynchronous multiplexed PSRAM/NOR read waveforms. . . . . . . . . . . . . . . . . . . . . . . . 140
Figure 58. Asynchronous multiplexed PSRAM/NOR write waveforms . . . . . . . . . . . . . . . . . . . . . . . 141
Figure 59. Synchronous multiplexed NOR/PSRAM read timings . . . . . . . . . . . . . . . . . . . . . . . . . . . 143
Figure 60. Synchronous multiplexed PSRAM write timings. . . . . . . . . . . . . . . . . . . . . . . . . . . . . . . . 144
Figure 61. Synchronous non-multiplexed NOR/PSRAM read timings . . . . . . . . . . . . . . . . . . . . . . . . 145
Figure 62. Synchronous non-multiplexed PSRAM write timings . . . . . . . . . . . . . . . . . . . . . . . . . . . . 146
Figure 63. PC Card/CompactFlash controller waveforms for common memory read access . . . . . . 148
Figure 64. PC Card/CompactFlash controller waveforms for common memory write access . . . . . . 148
Figure 65. PC Card/CompactFlash controller waveforms for attribute memory read
access. . . . . . . . . . . . . . . . . . . . . . . . . . . . . . . . . . . . . . . . . . . . . . . . . . . . . . . . . . . . . . . . 149
Figure 66. PC Card/CompactFlash controller waveforms for attribute memory write
access. . . . . . . . . . . . . . . . . . . . . . . . . . . . . . . . . . . . . . . . . . . . . . . . . . . . . . . . . . . . . . . . 150
Figure 67. PC Card/CompactFlash controller waveforms for I/O space read access . . . . . . . . . . . . 150
Figure 68. PC Card/CompactFlash controller waveforms for I/O space write access . . . . . . . . . . . . 151
Figure 69. NAND controller waveforms for read access . . . . . . . . . . . . . . . . . . . . . . . . . . . . . . . . . . 153
Figure 70. NAND controller waveforms for write access . . . . . . . . . . . . . . . . . . . . . . . . . . . . . . . . . . 153
Figure 71. NAND controller waveforms for common memory read access . . . . . . . . . . . . . . . . . . . . 154
Figure 72. NAND controller waveforms for common memory write access. . . . . . . . . . . . . . . . . . . . 154
Figure 73. DCMI timing diagram . . . . . . . . . . . . . . . . . . . . . . . . . . . . . . . . . . . . . . . . . . . . . . . . . . . . 155
Figure 74. SDIO high-speed mode . . . . . . . . . . . . . . . . . . . . . . . . . . . . . . . . . . . . . . . . . . . . . . . . . . 156
Figure 75. SD default mode . . . . . . . . . . . . . . . . . . . . . . . . . . . . . . . . . . . . . . . . . . . . . . . . . . . . . . . . 157
Figure 76. WLCSP90 - 0.400 mm pitch wafer level chip size package outline . . . . . . . . . . . . . . . . . 159
Figure 77. LQFP64 – 10 x 10 mm 64 pin low-profile quad flat package outline . . . . . . . . . . . . . . . . 160
Figure 78. LQFP64 recommended footprint . . . . . . . . . . . . . . . . . . . . . . . . . . . . . . . . . . . . . . . . . . . 161
Figure 79. LQFP100, 14 x 14 mm 100-pin low-profile quad flat package outline . . . . . . . . . . . . . . . 162
Figure 80. LQFP100 recommended footprint . . . . . . . . . . . . . . . . . . . . . . . . . . . . . . . . . . . . . . . . . . 163
Figure 81. LQFP144, 20 x 20 mm, 144-pin low-profile quad flat package outline . . . . . . . . . . . . . . . 164
Figure 82. LQFP144 recommended footprint . . . . . . . . . . . . . . . . . . . . . . . . . . . . . . . . . . . . . . . . . . 165
Figure 83. UFBGA176+25 - ultra thin fine pitch ball grid array 10 × 10 × 0.6 mm,
package outline. . . . . . . . . . . . . . . . . . . . . . . . . . . . . . . . . . . . . . . . . . . . . . . . . . . . . . . . . 166
Figure 84. LQFP176 24 x 24 mm, 176-pin low-profile quad flat package outline . . . . . . . . . . . . . . . 167
Figure 85. LQFP176 recommended footprint . . . . . . . . . . . . . . . . . . . . . . . . . . . . . . . . . . . . . . . . . . 168
Figure 86. USB controller configured as peripheral-only and used
in Full speed mode . . . . . . . . . . . . . . . . . . . . . . . . . . . . . . . . . . . . . . . . . . . . . . . . . . . . . . 171
Figure 87. USB controller configured as host-only and used in full speed mode. . . . . . . . . . . . . . . . 171
List of figures STM32F405xx, STM32F407xx
10/185 DocID022152 Rev 4
Figure 88. USB controller configured in dual mode and used in full speed mode . . . . . . . . . . . . . . . 172
Figure 89. USB controller configured as peripheral, host, or dual-mode
and used in high speed mode. . . . . . . . . . . . . . . . . . . . . . . . . . . . . . . . . . . . . . . . . . . . . . 173
Figure 90. MII mode using a 25 MHz crystal . . . . . . . . . . . . . . . . . . . . . . . . . . . . . . . . . . . . . . . . . . . 174
Figure 91. RMII with a 50 MHz oscillator . . . . . . . . . . . . . . . . . . . . . . . . . . . . . . . . . . . . . . . . . . . . . . 174
Figure 92. RMII with a 25 MHz crystal and PHY with PLL . . . . . . . . . . . . . . . . . . . . . . . . . . . . . . . . . 175
DocID022152 Rev 4 11/185
STM32F405xx, STM32F407xx Introduction
1 Introduction
This datasheet provides the description of the STM32F405xx and STM32F407xx lines of
microcontrollers. For more details on the whole STMicroelectronics STM32™ family, please
refer to Section 2.1: Full compatibility throughout the family.
The STM32F405xx and STM32F407xx datasheet should be read in conjunction with the
STM32F4xx reference manual.
The reference and Flash programming manuals are both available from the
STMicroelectronics website www.st.com.
For information on the Cortex™-M4 core, please refer to the Cortex™-M4 programming
manual (PM0214) available from www.st.com.
Description STM32F405xx, STM32F407xx
12/185 DocID022152 Rev 4
2 Description
The STM32F405xx and STM32F407xx family is based on the high-performance ARM®
Cortex™-M4 32-bit RISC core operating at a frequency of up to 168 MHz. The Cortex-M4
core features a Floating point unit (FPU) single precision which supports all ARM singleprecision
data-processing instructions and data types. It also implements a full set of DSP
instructions and a memory protection unit (MPU) which enhances application security. The
Cortex-M4 core with FPU will be referred to as Cortex-M4F throughout this document.
The STM32F405xx and STM32F407xx family incorporates high-speed embedded
memories (Flash memory up to 1 Mbyte, up to 192 Kbytes of SRAM), up to 4 Kbytes of
backup SRAM, and an extensive range of enhanced I/Os and peripherals connected to two
APB buses, three AHB buses and a 32-bit multi-AHB bus matrix.
All devices offer three 12-bit ADCs, two DACs, a low-power RTC, twelve general-purpose
16-bit timers including two PWM timers for motor control, two general-purpose 32-bit timers.
a true random number generator (RNG). They also feature standard and advanced
communication interfaces.
• Up to three I2Cs
• Three SPIs, two I2Ss full duplex. To achieve audio class accuracy, the I2S peripherals
can be clocked via a dedicated internal audio PLL or via an external clock to allow
synchronization.
• Four USARTs plus two UARTs
• An USB OTG full-speed and a USB OTG high-speed with full-speed capability (with the
ULPI),
• Two CANs
• An SDIO/MMC interface
• Ethernet and the camera interface available on STM32F407xx devices only.
New advanced peripherals include an SDIO, an enhanced flexible static memory control
(FSMC) interface (for devices offered in packages of 100 pins and more), a camera
interface for CMOS sensors. Refer to Table 2: STM32F405xx and STM32F407xx: features
and peripheral counts for the list of peripherals available on each part number.
The STM32F405xx and STM32F407xx family operates in the –40 to +105 °C temperature
range from a 1.8 to 3.6 V power supply. The supply voltage can drop to 1.7 V when the
device operates in the 0 to 70 °C temperature range using an external power supply
supervisor: refer to Section : Internal reset OFF. A comprehensive set of power-saving
mode allows the design of low-power applications.
The STM32F405xx and STM32F407xx family offers devices in various packages ranging
from 64 pins to 176 pins. The set of included peripherals changes with the device chosen.
These features make the STM32F405xx and STM32F407xx microcontroller family suitable
for a wide range of applications:
• Motor drive and application control
• Medical equipment
• Industrial applications: PLC, inverters, circuit breakers
• Printers, and scanners
• Alarm systems, video intercom, and HVAC
• Home audio appliances
STM32F405xx, STM32F407xx Description
DocID022152 Rev 4 13/185
Figure 5 shows the general block diagram of the device family.
Table 2. STM32F405xx and STM32F407xx: features and peripheral counts
Peripherals STM32F405RG STM32F405OG STM32F405VG STM32F405ZG STM32F405OE STM32F407Vx STM32F407Zx STM32F407Ix
Flash memory in
Kbytes 1024 512 512 1024 512 1024 512 1024
SRAM in
Kbytes
System 192(112+16+64)
Backup 4
FSMC memory
controller No Yes(1)
Ethernet No Yes
Timers
Generalpurpose
10
Advanced
-control 2
Basic 2
IWDG Yes
WWDG Yes
RTC Yes
Random number
generator Yes
Description STM32F405xx, STM32F407xx
14/185 DocID022152 Rev 4
Communi
cation
interfaces
SPI / I2S 3/2 (full duplex)(2)
I2C 3
USART/
UART 4/2
USB
OTG FS Yes
USB
OTG HS Yes
CAN 2
SDIO Yes
Camera interface No Yes
GPIOs 51 72 82 114 72 82 114 140
12-bit ADC
Number of channels
3
16 13 16 24 13 16 24 24
12-bit DAC
Number of channels
Yes
2
Maximum CPU
frequency 168 MHz
Operating voltage 1.8 to 3.6 V(3)
Operating
temperatures
Ambient temperatures: –40 to +85 °C /–40 to +105 °C
Junction temperature: –40 to + 125 °C
Package LQFP64 WLCSP90 LQFP100 LQFP144 WLCSP90 LQFP100 LQFP144 UFBGA176
LQFP176
1. For the LQFP100 and WLCSP90 packages, only FSMC Bank1 or Bank2 are available. Bank1 can only support a multiplexed NOR/PSRAM memory using the NE1 Chip
Select. Bank2 can only support a 16- or 8-bit NAND Flash memory using the NCE2 Chip Select. The interrupt line cannot be used since Port G is not available in this
package.
2. The SPI2 and SPI3 interfaces give the flexibility to work in an exclusive way in either the SPI mode or the I2S audio mode.
3. VDD/VDDA minimum value of 1.7 V is obtained when the device operates in reduced temperature range, and with the use of an external power supply supervisor (refer to
Section : Internal reset OFF).
Table 2. STM32F405xx and STM32F407xx: features and peripheral counts
Peripherals STM32F405RG STM32F405OG STM32F405VG STM32F405ZG STM32F405OE STM32F407Vx STM32F407Zx STM32F407Ix
DocID022152 Rev 4 15/185
STM32F405xx, STM32F407xx Description
2.1 Full compatibility throughout the family
The STM32F405xx and STM32F407xx are part of the STM32F4 family. They are fully pinto-
pin, software and feature compatible with the STM32F2xx devices, allowing the user to
try different memory densities, peripherals, and performances (FPU, higher frequency) for a
greater degree of freedom during the development cycle.
The STM32F405xx and STM32F407xx devices maintain a close compatibility with the
whole STM32F10xxx family. All functional pins are pin-to-pin compatible. The
STM32F405xx and STM32F407xx, however, are not drop-in replacements for the
STM32F10xxx devices: the two families do not have the same power scheme, and so their
power pins are different. Nonetheless, transition from the STM32F10xxx to the STM32F40x
family remains simple as only a few pins are impacted.
Figure 4, Figure 3, Figure 2, and Figure 1 give compatible board designs between the
STM32F40x, STM32F2xxx, and STM32F10xxx families.
Figure 1. Compatible board design between STM32F10xx/STM32F4xx for LQFP64
31
1 16
17
32
48 33
64
49 47
VSS
VSS
VSS
VSS
0 Ω resistor or soldering bridge
present for the STM32F10xx
configuration, not present in the
STM32F4xx configuration
ai18489
Description STM32F405xx, STM32F407xx
16/185 DocID022152 Rev 4
Figure 2. Compatible board design STM32F10xx/STM32F2xx/STM32F4xx
for LQFP100 package
Figure 3. Compatible board design between STM32F10xx/STM32F2xx/STM32F4xx
for LQFP144 package
20
49
1 25
26
50
75 51
100
76 73
19
VSS
VSS
VDD
VSS
VSS
VSS
0 ΩΩ resistor or soldering bridge
present for the STM32F10xxx
configuration, not present in the
STM32F4xx configuration
ai18488c
99 (VSS)
VDD VSS
Two 0 Ω resistors connected to:
- VSS for the STM32F10xx
- VSS for the STM32F4xx
VSS for STM32F10xx
VDD for STM32F4xx
- VSS, VDD or NC for the STM32F2xx
ai18487d
31
71
1 36
37
72
108 73
144
109
VSS
0 Ω resistor or soldering bridge
present for the STM32F10xx
configuration, not present in the
STM32F4xx configuration
106
VSS
30
Two 0 Ω resistors connected to:
- VSS for the STM32F10xx
- VDD or signal from external power supply supervisor for the STM32F4xx
VDD VSS
VSS
VSS
143 (PDR_ON)
VDD VSS
VSS for STM32F10xx
VDD for STM32F4xx
- VSS, VDD or NC for the STM32F2xx
Signal from
external power
supply
supervisor
DocID022152 Rev 4 17/185
STM32F405xx, STM32F407xx Description
Figure 4. Compatible board design between STM32F2xx and STM32F4xx
for LQFP176 and BGA176 packages
MS19919V3
1 44
45
88
132 89
176
133
Two 0 Ω resistors connected to:
- VSS, VDD or NC for the STM32F2xx
- VDD or signal from external power supply supervisor for the STM32F4xx
171 (PDR_ON)
VDDVSS
Signal from external
power supply
supervisor
Description STM32F405xx, STM32F407xx
18/185 DocID022152 Rev 4
2.2 Device overview
Figure 5. STM32F40x block diagram
1. The timers connected to APB2 are clocked from TIMxCLK up to 168 MHz, while the timers connected to
APB1 are clocked from TIMxCLK either up to 84 MHz or 168 MHz, depending on TIMPRE bit configuration
in the RCC_DCKCFGR register.
2. The camera interface and ethernet are available only on STM32F407xx devices.
MS19920V3
GPIO PORT A
AHB/APB2
140 AF
PA[15:0]
TIM1 / PWM
4 compl. channels (TIM1_CH1[1:4]N,
4 channels (TIM1_CH1[1:4]ETR,
BKIN as AF
RX, TX, CK,
CTS, RTS as AF
MOSI, MISO,
SCK, NSS as AF
APB 1 30M Hz
8 analog inputs common
to the 3 ADCs
VDDREF_ADC
MOSI/SD, MISO/SD_ext, SCK/CK
NSS/WS, MCK as AF
TX, RX
DAC1_OUT
as AF
ITF
WWDG
4 KB BKPSRAM
RTC_AF1
OSC32_IN
OSC32_OUT
VDDA, VSSA
NRST
16b
SDIO / MMC D[7:0]
CMD, CK as AF
VBAT = 1.65 to 3.6 V
DMA2
SCL, SDA, SMBA as AF
JTAG & SW
ARM Cortex-M4
168 MHz
ETM NVIC
MPU
TRACECLK
TRACED[3:0]
Ethernet MAC
10/100
DMA/
FIFO
MII or RMII as AF
MDIO as AF
USB
OTG HS
DP, DM
ULPI:CK, D[7:0], DIR, STP, NXT
ID, VBUS, SOF
DMA2
8 Streams
FIFO
ART ACCEL/
CACHE
SRAM 112 KB
CLK, NE [3:0], A[23:0],
D[31:0], OEN, WEN,
NBL[3:0], NL, NREG,
NWAIT/IORDY, CD
INTN, NIIS16 as AF
RNG
Camera
interface
HSYNC, VSYNC
PUIXCLK, D[13:0]
PHY
USB
OTG FS
DP
DM
ID, VBUS, SOF
FIFO
AHB1 168 MHz
PHY
FIFO
@VDDA
@VDDA
POR/PDR
BOR
Supply
supervision
@VDDA
PVD
Int
POR
reset
XTAL 32 kHz
MAN AGT
RTC
RC HS
FCLK
RC LS
PWR
interface
IWDG
@VBAT
AWU
Reset &
clock
control
P L L1&2
PCLKx
VDD = 1.8 to 3.6 V
VSS
VCAP1, VCPA2
Voltage
regulator
3.3 to 1.2 V
VDD Power managmt
Backup register RTC_AF1
AHB bus-matrix 8S7M
LS
2 channels as AF
DAC1
DAC2
Flash
up to
1 MB
SRAM, PSRAM, NOR Flash,
PC Card (ATA), NAND Flash
External memory
controller (FSMC)
TIM6
TIM7
TIM2
TIM3
TIM4
TIM5
TIM12
TIM13
TIM14
USART2
USART3
UART4
UART5
SP3/I2S3
I2C1/SMBUS
I2C2/SMBUS
I2C3/SMBUS
bxCAN1
bxCAN2
SPI1
EXT IT. WKUP
D-BUS
FIFO
FPU
APB142 MHz (max)
SRAM 16 KB
CCM data RAM 64 KB
AHB3
AHB2 168 MHz
NJTRST, JTDI,
JTCK/SWCLK
JTDO/SWD, JTDO
I-BUS
S-BUS
DMA/
FIFO
DMA1
8 Streams
FIFO
PB[15:0]
PC[15:0]
PD[15:0]
PE[15:0]
PF[15:0]
PG[15:0]
PH[15:0]
PI[11:0]
GPIO PORT B
GPIO PORT C
GPIO PORT D
GPIO PORT E
GPIO PORT F
GPIO PORT G
GPIO PORT H
GPIO PORT I
TIM8 / PWM 16b
4 compl. channels (TIM1_CH1[1:4]N,
4 channels (TIM1_CH1[1:4]ETR,
BKIN as AF
1 channel as AF
1 channel as AF
RX, TX, CK,
CTS, RTS as AF
8 analog inputs common
to the ADC1 & 2
8 analog inputs for ADC3
DAC2_OUT
as AF
16b
16b
SCL, SDA, SMBA as AF
SCL, SDA, SMBA as AF
MOSI/SD, MISO/SD_ext, SCK/CK
NSS/WS, MCK as AF
TX, RX
RX, TX as AF
RX, TX as AF
RX, TX as AF
CTS, RTS as AF
RX, TX as AF
CTS, RTS as AF
1 channel as AF
smcard
irDA
smcard
irDA
16b
16b
16b
1 channel as AF
2 channels as AF
32b
16b
16b
32b
4 channels
4 channels, ETR as AF
4 channels, ETR as AF
4 channels, ETR as AF
DMA1
AHB/APB1
LS
OSC_IN
OSC_OUT
HCLKx
XTAL OSC
4- 16MHz
FIFO
SP2/I2S2
NIORD, IOWR, INT[2:3]
ADC3
ADC2
ADC1
Temperature sensor
IF
TIM9 16b
TIM10 16b
TIM11 16b
smcard
irDA USART1
irDA smcard USART6
APB2 84 MHz
@VDD
@VDD
@VDDA
DocID022152 Rev 4 19/185
STM32F405xx, STM32F407xx Description
2.2.1 ARM® Cortex™-M4F core with embedded Flash and SRAM
The ARM Cortex-M4F processor is the latest generation of ARM processors for embedded
systems. It was developed to provide a low-cost platform that meets the needs of MCU
implementation, with a reduced pin count and low-power consumption, while delivering
outstanding computational performance and an advanced response to interrupts.
The ARM Cortex-M4F 32-bit RISC processor features exceptional code-efficiency,
delivering the high-performance expected from an ARM core in the memory size usually
associated with 8- and 16-bit devices.
The processor supports a set of DSP instructions which allow efficient signal processing and
complex algorithm execution.
Its single precision FPU (floating point unit) speeds up software development by using
metalanguage development tools, while avoiding saturation.
The STM32F405xx and STM32F407xx family is compatible with all ARM tools and software.
Figure 5 shows the general block diagram of the STM32F40x family.
Note: Cortex-M4F is binary compatible with Cortex-M3.
2.2.2 Adaptive real-time memory accelerator (ART Accelerator™)
The ART Accelerator™ is a memory accelerator which is optimized for STM32 industrystandard
ARM® Cortex™-M4F processors. It balances the inherent performance advantage
of the ARM Cortex-M4F over Flash memory technologies, which normally requires the
processor to wait for the Flash memory at higher frequencies.
To release the processor full 210 DMIPS performance at this frequency, the accelerator
implements an instruction prefetch queue and branch cache, which increases program
execution speed from the 128-bit Flash memory. Based on CoreMark benchmark, the
performance achieved thanks to the ART accelerator is equivalent to 0 wait state program
execution from Flash memory at a CPU frequency up to 168 MHz.
2.2.3 Memory protection unit
The memory protection unit (MPU) is used to manage the CPU accesses to memory to
prevent one task to accidentally corrupt the memory or resources used by any other active
task. This memory area is organized into up to 8 protected areas that can in turn be divided
up into 8 subareas. The protection area sizes are between 32 bytes and the whole 4
gigabytes of addressable memory.
The MPU is especially helpful for applications where some critical or certified code has to be
protected against the misbehavior of other tasks. It is usually managed by an RTOS (realtime
operating system). If a program accesses a memory location that is prohibited by the
MPU, the RTOS can detect it and take action. In an RTOS environment, the kernel can
dynamically update the MPU area setting, based on the process to be executed.
The MPU is optional and can be bypassed for applications that do not need it.
2.2.4 Embedded Flash memory
The STM32F40x devices embed a Flash memory of 512 Kbytes or 1 Mbytes available for
storing programs and data.
Description STM32F405xx, STM32F407xx
20/185 DocID022152 Rev 4
2.2.5 CRC (cyclic redundancy check) calculation unit
The CRC (cyclic redundancy check) calculation unit is used to get a CRC code from a 32-bit
data word and a fixed generator polynomial.
Among other applications, CRC-based techniques are used to verify data transmission or
storage integrity. In the scope of the EN/IEC 60335-1 standard, they offer a means of
verifying the Flash memory integrity. The CRC calculation unit helps compute a software
signature during runtime, to be compared with a reference signature generated at link-time
and stored at a given memory location.
2.2.6 Embedded SRAM
All STM32F40x products embed:
• Up to 192 Kbytes of system SRAM including 64 Kbytes of CCM (core coupled memory)
data RAM
RAM memory is accessed (read/write) at CPU clock speed with 0 wait states.
• 4 Kbytes of backup SRAM
This area is accessible only from the CPU. Its content is protected against possible
unwanted write accesses, and is retained in Standby or VBAT mode.
2.2.7 Multi-AHB bus matrix
The 32-bit multi-AHB bus matrix interconnects all the masters (CPU, DMAs, Ethernet, USB
HS) and the slaves (Flash memory, RAM, FSMC, AHB and APB peripherals) and ensures a
seamless and efficient operation even when several high-speed peripherals work
simultaneously.
DocID022152 Rev 4 21/185
STM32F405xx, STM32F407xx Description
Figure 6. Multi-AHB matrix
2.2.8 DMA controller (DMA)
The devices feature two general-purpose dual-port DMAs (DMA1 and DMA2) with 8
streams each. They are able to manage memory-to-memory, peripheral-to-memory and
memory-to-peripheral transfers. They feature dedicated FIFOs for APB/AHB peripherals,
support burst transfer and are designed to provide the maximum peripheral bandwidth
(AHB/APB).
The two DMA controllers support circular buffer management, so that no specific code is
needed when the controller reaches the end of the buffer. The two DMA controllers also
have a double buffering feature, which automates the use and switching of two memory
buffers without requiring any special code.
Each stream is connected to dedicated hardware DMA requests, with support for software
trigger on each stream. Configuration is made by software and transfer sizes between
source and destination are independent.
The DMA can be used with the main peripherals:
• SPI and I2S
• I2C
• USART
• General-purpose, basic and advanced-control timers TIMx
• DAC
• SDIO
• Camera interface (DCMI)
• ADC.
ARM
Cortex-M4
GP
DMA1
GP
DMA2
MAC
Ethernet
USB OTG
HS
Bus matrix-S
S0 S1 S2 S3 S4 S5 S6 S7
ICODE
DCODE
ACCEL
Flash
memory
SRAM1
112 Kbyte
SRAM2
16 Kbyte
AHB1
peripherals
AHB2
FSMC
Static MemCtl
M0
M1
M2
M3
M4
M5
M6
I-bus
D-bus
S-bus
DMA_PI
DMA_MEM1
DMA_MEM2
DMA_P2
ETHERNET_M
USB_HS_M
ai18490c
CCM data RAM
64-Kbyte
APB1
APB2
peripherals
Description STM32F405xx, STM32F407xx
22/185 DocID022152 Rev 4
2.2.9 Flexible static memory controller (FSMC)
The FSMC is embedded in the STM32F405xx and STM32F407xx family. It has four Chip
Select outputs supporting the following modes: PCCard/Compact Flash, SRAM, PSRAM,
NOR Flash and NAND Flash.
Functionality overview:
• Write FIFO
• Maximum FSMC_CLK frequency for synchronous accesses is 60 MHz.
LCD parallel interface
The FSMC can be configured to interface seamlessly with most graphic LCD controllers. It
supports the Intel 8080 and Motorola 6800 modes, and is flexible enough to adapt to
specific LCD interfaces. This LCD parallel interface capability makes it easy to build costeffective
graphic applications using LCD modules with embedded controllers or high
performance solutions using external controllers with dedicated acceleration.
2.2.10 Nested vectored interrupt controller (NVIC)
The STM32F405xx and STM32F407xx embed a nested vectored interrupt controller able to
manage 16 priority levels, and handle up to 82 maskable interrupt channels plus the 16
interrupt lines of the Cortex™-M4F.
• Closely coupled NVIC gives low-latency interrupt processing
• Interrupt entry vector table address passed directly to the core
• Allows early processing of interrupts
• Processing of late arriving, higher-priority interrupts
• Support tail chaining
• Processor state automatically saved
• Interrupt entry restored on interrupt exit with no instruction overhead
This hardware block provides flexible interrupt management features with minimum interrupt
latency.
2.2.11 External interrupt/event controller (EXTI)
The external interrupt/event controller consists of 23 edge-detector lines used to generate
interrupt/event requests. Each line can be independently configured to select the trigger
event (rising edge, falling edge, both) and can be masked independently. A pending register
maintains the status of the interrupt requests. The EXTI can detect an external line with a
pulse width shorter than the Internal APB2 clock period. Up to 140 GPIOs can be connected
to the 16 external interrupt lines.
2.2.12 Clocks and startup
On reset the 16 MHz internal RC oscillator is selected as the default CPU clock. The
16 MHz internal RC oscillator is factory-trimmed to offer 1% accuracy over the full
temperature range. The application can then select as system clock either the RC oscillator
or an external 4-26 MHz clock source. This clock can be monitored for failure. If a failure is
detected, the system automatically switches back to the internal RC oscillator and a
software interrupt is generated (if enabled). This clock source is input to a PLL thus allowing
to increase the frequency up to 168 MHz. Similarly, full interrupt management of the PLL
DocID022152 Rev 4 23/185
STM32F405xx, STM32F407xx Description
clock entry is available when necessary (for example if an indirectly used external oscillator
fails).
Several prescalers allow the configuration of the three AHB buses, the high-speed APB
(APB2) and the low-speed APB (APB1) domains. The maximum frequency of the three AHB
buses is 168 MHz while the maximum frequency of the high-speed APB domains is
84 MHz. The maximum allowed frequency of the low-speed APB domain is 42 MHz.
The devices embed a dedicated PLL (PLLI2S) which allows to achieve audio class
performance. In this case, the I2S master clock can generate all standard sampling
frequencies from 8 kHz to 192 kHz.
2.2.13 Boot modes
At startup, boot pins are used to select one out of three boot options:
• Boot from user Flash
• Boot from system memory
• Boot from embedded SRAM
The boot loader is located in system memory. It is used to reprogram the Flash memory by
using USART1 (PA9/PA10), USART3 (PC10/PC11 or PB10/PB11), CAN2 (PB5/PB13), USB
OTG FS in Device mode (PA11/PA12) through DFU (device firmware upgrade).
2.2.14 Power supply schemes
• VDD = 1.8 to 3.6 V: external power supply for I/Os and the internal regulator (when
enabled), provided externally through VDD pins.
• VSSA, VDDA = 1.8 to 3.6 V: external analog power supplies for ADC, DAC, Reset
blocks, RCs and PLL. VDDA and VSSA must be connected to VDD and VSS, respectively.
• VBAT = 1.65 to 3.6 V: power supply for RTC, external clock 32 kHz oscillator and
backup registers (through power switch) when VDD is not present.
Refer to Figure 21: Power supply scheme for more details.
Note: VDD/VDDA minimum value of 1.7 V is obtained when the device operates in reduced
temperature range, and with the use of an external power supply supervisor (refer to
Section : Internal reset OFF).
Refer to Table 2 in order to identify the packages supporting this option.
2.2.15 Power supply supervisor
Internal reset ON
On packages embedding the PDR_ON pin, the power supply supervisor is enabled by
holding PDR_ON high. On all other packages, the power supply supervisor is always
enabled.
The device has an integrated power-on reset (POR) / power-down reset (PDR) circuitry
coupled with a Brownout reset (BOR) circuitry. At power-on, POR/PDR is always active and
ensures proper operation starting from 1.8 V. After the 1.8 V POR threshold level is
reached, the option byte loading process starts, either to confirm or modify default BOR
threshold levels, or to disable BOR permanently. Three BOR thresholds are available
through option bytes. The device remains in reset mode when VDD is below a specified
threshold, VPOR/PDR or VBOR, without the need for an external reset circuit.
Description STM32F405xx, STM32F407xx
24/185 DocID022152 Rev 4
The device also features an embedded programmable voltage detector (PVD) that monitors
the VDD/VDDA power supply and compares it to the VPVD threshold. An interrupt can be
generated when VDD/VDDA drops below the VPVD threshold and/or when VDD/VDDA is
higher than the VPVD threshold. The interrupt service routine can then generate a warning
message and/or put the MCU into a safe state. The PVD is enabled by software.
Internal reset OFF
This feature is available only on packages featuring the PDR_ON pin. The internal power-on
reset (POR) / power-down reset (PDR) circuitry is disabled with the PDR_ON pin.
An external power supply supervisor should monitor VDD and should maintain the device in
reset mode as long as VDD is below a specified threshold. PDR_ON should be connected to
this external power supply supervisor. Refer to Figure 7: Power supply supervisor
interconnection with internal reset OFF.
Figure 7. Power supply supervisor interconnection with internal reset OFF
1. PDR = 1.7 V for reduce temperature range; PDR = 1.8 V for all temperature range.
The VDD specified threshold, below which the device must be maintained under reset, is
1.8 V (see Figure 7). This supply voltage can drop to 1.7 V when the device operates in the
0 to 70 °C temperature range.
A comprehensive set of power-saving mode allows to design low-power applications.
When the internal reset is OFF, the following integrated features are no more supported:
• The integrated power-on reset (POR) / power-down reset (PDR) circuitry is disabled
• The brownout reset (BOR) circuitry is disabled
• The embedded programmable voltage detector (PVD) is disabled
• VBAT functionality is no more available and VBAT pin should be connected to VDD
All packages, except for the LQFP64 and LQFP100, allow to disable the internal reset
through the PDR_ON signal.
MS31383V3
NRST
VDD
PDR_ON
External VDD power supply supervisor
Ext. reset controller active when
VDD < 1.7 V or 1.8 V (1)
VDD
Application reset
signal (optional)
DocID022152 Rev 4 25/185
STM32F405xx, STM32F407xx Description
Figure 8. PDR_ON and NRST control with internal reset OFF
1. PDR = 1.7 V for reduce temperature range; PDR = 1.8 V for all temperature range.
2.2.16 Voltage regulator
The regulator has four operating modes:
• Regulator ON
– Main regulator mode (MR)
– Low power regulator (LPR)
– Power-down
• Regulator OFF
Regulator ON
On packages embedding the BYPASS_REG pin, the regulator is enabled by holding
BYPASS_REG low. On all other packages, the regulator is always enabled.
There are three power modes configured by software when regulator is ON:
• MR is used in the nominal regulation mode (With different voltage scaling in Run)
In Main regulator mode (MR mode), different voltage scaling are provided to reach the
best compromise between maximum frequency and dynamic power consumption.
Refer to Table 14: General operating conditions.
• LPR is used in the Stop modes
The LP regulator mode is configured by software when entering Stop mode.
• Power-down is used in Standby mode.
The Power-down mode is activated only when entering in Standby mode. The regulator
output is in high impedance and the kernel circuitry is powered down, inducing zero
consumption. The contents of the registers and SRAM are lost)
MS19009V6
VDD
time
PDR = 1.7 V or 1.8 V (1)
time
NRST
PDR_ON PDR_ON
Reset by other source than
power supply supervisor
Description STM32F405xx, STM32F407xx
26/185 DocID022152 Rev 4
Two external ceramic capacitors should be connected on VCAP_1 & VCAP_2 pin. Refer to
Figure 21: Power supply scheme and Figure 16: VCAP_1/VCAP_2 operating conditions.
All packages have regulator ON feature.
Regulator OFF
This feature is available only on packages featuring the BYPASS_REG pin. The regulator is
disabled by holding BYPASS_REG high. The regulator OFF mode allows to supply
externally a V12 voltage source through VCAP_1 and VCAP_2 pins.
Since the internal voltage scaling is not manage internally, the external voltage value must
be aligned with the targetted maximum frequency. Refer to Table 14: General operating
conditions.
The two 2.2 μF ceramic capacitors should be replaced by two 100 nF decoupling
capacitors.
Refer to Figure 21: Power supply scheme
When the regulator is OFF, there is no more internal monitoring on V12. An external power
supply supervisor should be used to monitor the V12 of the logic power domain. PA0 pin
should be used for this purpose, and act as power-on reset on V12 power domain.
In regulator OFF mode the following features are no more supported:
• PA0 cannot be used as a GPIO pin since it allows to reset a part of the V12 logic power
domain which is not reset by the NRST pin.
• As long as PA0 is kept low, the debug mode cannot be used under power-on reset. As
a consequence, PA0 and NRST pins must be managed separately if the debug
connection under reset or pre-reset is required.
Figure 9. Regulator OFF
ai18498V4
External VCAP_1/2 power
supply supervisor
Ext. reset controller active
when VCAP_1/2 < Min V12
V12
VCAP_1
VCAP_2
BYPASS_REG
VDD
PA0 NRST
Application reset
signal (optional)
VDD
V12
DocID022152 Rev 4 27/185
STM32F405xx, STM32F407xx Description
The following conditions must be respected:
• VDD should always be higher than VCAP_1 and VCAP_2 to avoid current injection
between power domains.
• If the time for VCAP_1 and VCAP_2 to reach V12 minimum value is faster than the time for
VDD to reach 1.8 V, then PA0 should be kept low to cover both conditions: until VCAP_1
and VCAP_2 reach V12 minimum value and until VDD reaches 1.8 V (see Figure 10).
• Otherwise, if the time for VCAP_1 and VCAP_2 to reach V12 minimum value is slower
than the time for VDD to reach 1.8 V, then PA0 could be asserted low externally (see
Figure 11).
• If VCAP_1 and VCAP_2 go below V12 minimum value and VDD is higher than 1.8 V, then
a reset must be asserted on PA0 pin.
Note: The minimum value of V12 depends on the maximum frequency targeted in the application
(see Table 14: General operating conditions).
Figure 10. Startup in regulator OFF mode: slow VDD slope
- power-down reset risen after VCAP_1/VCAP_2 stabilization
1. This figure is valid both whatever the internal reset mode (onON or OFFoff).
2. PDR = 1.7 V for reduced temperature range; PDR = 1.8 V for all temperature ranges.
ai18491e
VDD
time
Min V12
PDR = 1.7 V or 1.8 V (2)
VCAP_1/VCAP_2 V12
NRST
time
Description STM32F405xx, STM32F407xx
28/185 DocID022152 Rev 4
Figure 11. Startup in regulator OFF mode: fast VDD slope
- power-down reset risen before VCAP_1/VCAP_2 stabilization
1. This figure is valid both whatever the internal reset mode (onON or offOFF).
2. PDR = 1.7 V for a reduced temperature range; PDR = 1.8 V for all temperature ranges.
2.2.17 Regulator ON/OFF and internal reset ON/OFF availability
2.2.18 Real-time clock (RTC), backup SRAM and backup registers
The backup domain of the STM32F405xx and STM32F407xx includes:
• The real-time clock (RTC)
• 4 Kbytes of backup SRAM
• 20 backup registers
The real-time clock (RTC) is an independent BCD timer/counter. Dedicated registers contain
the second, minute, hour (in 12/24 hour), week day, date, month, year, in BCD (binarycoded
decimal) format. Correction for 28, 29 (leap year), 30, and 31 day of the month are
performed automatically. The RTC provides a programmable alarm and programmable
periodic interrupts with wakeup from Stop and Standby modes. The sub-seconds value is
also available in binary format.
It is clocked by a 32.768 kHz external crystal, resonator or oscillator, the internal low-power
RC oscillator or the high-speed external clock divided by 128. The internal low-speed RC
VDD
time
Min V12
VCAP_1/VCAP_2
V12
PA0 asserted externally
NRST
time ai18492d
PDR = 1.7 V or 1.8 V (2)
Table 3. Regulator ON/OFF and internal reset ON/OFF availability
Regulator ON Regulator OFF Internal reset ON Internal reset
OFF
LQFP64
LQFP100
Yes No
Yes No
LQFP144
LQFP176 Yes
PDR_ON set to
VDD
Yes
PDR_ON
connected to an
external power
supply supervisor
WLCSP90
UFBGA176
Yes
BYPASS_REG set
to VSS
Yes
BYPASS_REG set
to VDD
DocID022152 Rev 4 29/185
STM32F405xx, STM32F407xx Description
has a typical frequency of 32 kHz. The RTC can be calibrated using an external 512 Hz
output to compensate for any natural quartz deviation.
Two alarm registers are used to generate an alarm at a specific time and calendar fields can
be independently masked for alarm comparison. To generate a periodic interrupt, a 16-bit
programmable binary auto-reload downcounter with programmable resolution is available
and allows automatic wakeup and periodic alarms from every 120 μs to every 36 hours.
A 20-bit prescaler is used for the time base clock. It is by default configured to generate a
time base of 1 second from a clock at 32.768 kHz.
The 4-Kbyte backup SRAM is an EEPROM-like memory area. It can be used to store data
which need to be retained in VBAT and standby mode. This memory area is disabled by
default to minimize power consumption (see Section 2.2.19: Low-power modes). It can be
enabled by software.
The backup registers are 32-bit registers used to store 80 bytes of user application data
when VDD power is not present. Backup registers are not reset by a system, a power reset,
or when the device wakes up from the Standby mode (see Section 2.2.19: Low-power
modes).
Additional 32-bit registers contain the programmable alarm subseconds, seconds, minutes,
hours, day, and date.
Like backup SRAM, the RTC and backup registers are supplied through a switch that is
powered either from the VDD supply when present or from the VBAT pin.
2.2.19 Low-power modes
The STM32F405xx and STM32F407xx support three low-power modes to achieve the best
compromise between low power consumption, short startup time and available wakeup
sources:
• Sleep mode
In Sleep mode, only the CPU is stopped. All peripherals continue to operate and can
wake up the CPU when an interrupt/event occurs.
• Stop mode
The Stop mode achieves the lowest power consumption while retaining the contents of
SRAM and registers. All clocks in the V12 domain are stopped, the PLL, the HSI RC
and the HSE crystal oscillators are disabled. The voltage regulator can also be put
either in normal or in low-power mode.
The device can be woken up from the Stop mode by any of the EXTI line (the EXTI line
source can be one of the 16 external lines, the PVD output, the RTC alarm / wakeup /
tamper / time stamp events, the USB OTG FS/HS wakeup or the Ethernet wakeup).
• Standby mode
The Standby mode is used to achieve the lowest power consumption. The internal
voltage regulator is switched off so that the entire V12 domain is powered off. The PLL,
the HSI RC and the HSE crystal oscillators are also switched off. After entering
Description STM32F405xx, STM32F407xx
30/185 DocID022152 Rev 4
Standby mode, the SRAM and register contents are lost except for registers in the
backup domain and the backup SRAM when selected.
The device exits the Standby mode when an external reset (NRST pin), an IWDG reset,
a rising edge on the WKUP pin, or an RTC alarm / wakeup / tamper /time stamp event
occurs.
The standby mode is not supported when the embedded voltage regulator is bypassed
and the V12 domain is controlled by an external power.
2.2.20 VBAT operation
The VBAT pin allows to power the device VBAT domain from an external battery, an external
supercapacitor, or from VDD when no external battery and an external supercapacitor are
present.
VBAT operation is activated when VDD is not present.
The VBAT pin supplies the RTC, the backup registers and the backup SRAM.
Note: When the microcontroller is supplied from VBAT, external interrupts and RTC alarm/events
do not exit it from VBAT operation.
When PDR_ON pin is not connected to VDD (internal reset OFF), the VBAT functionality is no
more available and VBAT pin should be connected to VDD.
2.2.21 Timers and watchdogs
The STM32F405xx and STM32F407xx devices include two advanced-control timers, eight
general-purpose timers, two basic timers and two watchdog timers.
All timer counters can be frozen in debug mode.
Table 4 compares the features of the advanced-control, general-purpose and basic timers.
Table 4. Timer feature comparison
Timer
type Timer
Counter
resolutio
n
Counter
type
Prescaler
factor
DMA
request
generatio
n
Capture/
compare
channels
Complementar
y output
Max
interface
clock
(MHz)
Max
timer
clock
(MHz)
Advanced
-control
TIM1,
TIM8 16-bit
Up,
Down,
Up/dow
n
Any integer
between 1
and 65536
Yes 4 Yes 84 168
DocID022152 Rev 4 31/185
STM32F405xx, STM32F407xx Description
Advanced-control timers (TIM1, TIM8)
The advanced-control timers (TIM1, TIM8) can be seen as three-phase PWM generators
multiplexed on 6 channels. They have complementary PWM outputs with programmable
inserted dead times. They can also be considered as complete general-purpose timers.
Their 4 independent channels can be used for:
• Input capture
• Output compare
• PWM generation (edge- or center-aligned modes)
• One-pulse mode output
If configured as standard 16-bit timers, they have the same features as the general-purpose
TIMx timers. If configured as 16-bit PWM generators, they have full modulation capability (0-
100%).
The advanced-control timer can work together with the TIMx timers via the Timer Link
feature for synchronization or event chaining.
TIM1 and TIM8 support independent DMA request generation.
General
purpose
TIM2,
TIM5 32-bit
Up,
Down,
Up/dow
n
Any integer
between 1
and 65536
Yes 4 No 42 84
TIM3,
TIM4 16-bit
Up,
Down,
Up/dow
n
Any integer
between 1
and 65536
Yes 4 No 42 84
TIM9 16-bit Up
Any integer
between 1
and 65536
No 2 No 84 168
TIM10
,
TIM11
16-bit Up
Any integer
between 1
and 65536
No 1 No 84 168
TIM12 16-bit Up
Any integer
between 1
and 65536
No 2 No 42 84
TIM13
,
TIM14
16-bit Up
Any integer
between 1
and 65536
No 1 No 42 84
Basic TIM6,
TIM7 16-bit Up
Any integer
between 1
and 65536
Yes 0 No 42 84
Table 4. Timer feature comparison (continued)
Timer
type Timer
Counter
resolutio
n
Counter
type
Prescaler
factor
DMA
request
generatio
n
Capture/
compare
channels
Complementar
y output
Max
interface
clock
(MHz)
Max
timer
clock
(MHz)
Description STM32F405xx, STM32F407xx
32/185 DocID022152 Rev 4
General-purpose timers (TIMx)
There are ten synchronizable general-purpose timers embedded in the STM32F40x devices
(see Table 4 for differences).
• TIM2, TIM3, TIM4, TIM5
The STM32F40x include 4 full-featured general-purpose timers: TIM2, TIM5, TIM3,
and TIM4.The TIM2 and TIM5 timers are based on a 32-bit auto-reload
up/downcounter and a 16-bit prescaler. The TIM3 and TIM4 timers are based on a 16-
bit auto-reload up/downcounter and a 16-bit prescaler. They all feature 4 independent
channels for input capture/output compare, PWM or one-pulse mode output. This gives
up to 16 input capture/output compare/PWMs on the largest packages.
The TIM2, TIM3, TIM4, TIM5 general-purpose timers can work together, or with the
other general-purpose timers and the advanced-control timers TIM1 and TIM8 via the
Timer Link feature for synchronization or event chaining.
Any of these general-purpose timers can be used to generate PWM outputs.
TIM2, TIM3, TIM4, TIM5 all have independent DMA request generation. They are
capable of handling quadrature (incremental) encoder signals and the digital outputs
from 1 to 4 hall-effect sensors.
• TIM9, TIM10, TIM11, TIM12, TIM13, and TIM14
These timers are based on a 16-bit auto-reload upcounter and a 16-bit prescaler.
TIM10, TIM11, TIM13, and TIM14 feature one independent channel, whereas TIM9
and TIM12 have two independent channels for input capture/output compare, PWM or
one-pulse mode output. They can be synchronized with the TIM2, TIM3, TIM4, TIM5
full-featured general-purpose timers. They can also be used as simple time bases.
Basic timers TIM6 and TIM7
These timers are mainly used for DAC trigger and waveform generation. They can also be
used as a generic 16-bit time base.
TIM6 and TIM7 support independent DMA request generation.
Independent watchdog
The independent watchdog is based on a 12-bit downcounter and 8-bit prescaler. It is
clocked from an independent 32 kHz internal RC and as it operates independently from the
main clock, it can operate in Stop and Standby modes. It can be used either as a watchdog
to reset the device when a problem occurs, or as a free-running timer for application timeout
management. It is hardware- or software-configurable through the option bytes.
Window watchdog
The window watchdog is based on a 7-bit downcounter that can be set as free-running. It
can be used as a watchdog to reset the device when a problem occurs. It is clocked from
the main clock. It has an early warning interrupt capability and the counter can be frozen in
debug mode.
DocID022152 Rev 4 33/185
STM32F405xx, STM32F407xx Description
SysTick timer
This timer is dedicated to real-time operating systems, but could also be used as a standard
downcounter. It features:
• A 24-bit downcounter
• Autoreload capability
• Maskable system interrupt generation when the counter reaches 0
• Programmable clock source.
2.2.22 Inter-integrated circuit interface (I²C)
Up to three I²C bus interfaces can operate in multimaster and slave modes. They can
support the Standard-mode (up to 100 kHz) and Fast-mode (up to 400 kHz) . They support
the 7/10-bit addressing mode and the 7-bit dual addressing mode (as slave). A hardware
CRC generation/verification is embedded.
They can be served by DMA and they support SMBus 2.0/PMBus.
2.2.23 Universal synchronous/asynchronous receiver transmitters (USART)
The STM32F405xx and STM32F407xx embed four universal synchronous/asynchronous
receiver transmitters (USART1, USART2, USART3 and USART6) and two universal
asynchronous receiver transmitters (UART4 and UART5).
These six interfaces provide asynchronous communication, IrDA SIR ENDEC support,
multiprocessor communication mode, single-wire half-duplex communication mode and
have LIN Master/Slave capability. The USART1 and USART6 interfaces are able to
communicate at speeds of up to 10.5 Mbit/s. The other available interfaces communicate at
up to 5.25 Mbit/s.
USART1, USART2, USART3 and USART6 also provide hardware management of the CTS
and RTS signals, Smart Card mode (ISO 7816 compliant) and SPI-like communication
capability. All interfaces can be served by the DMA controller.
Description STM32F405xx, STM32F407xx
34/185 DocID022152 Rev 4
2.2.24 Serial peripheral interface (SPI)
The STM32F40x feature up to three SPIs in slave and master modes in full-duplex and
simplex communication modes. SPI1 can communicate at up to 42 Mbits/s, SPI2 and SPI3
can communicate at up to 21 Mbit/s. The 3-bit prescaler gives 8 master mode frequencies
and the frame is configurable to 8 bits or 16 bits. The hardware CRC generation/verification
supports basic SD Card/MMC modes. All SPIs can be served by the DMA controller.
The SPI interface can be configured to operate in TI mode for communications in master
mode and slave mode.
2.2.25 Inter-integrated sound (I2S)
Two standard I2S interfaces (multiplexed with SPI2 and SPI3) are available. They can be
operated in master or slave mode, in full duplex and half-duplex communication modes, and
can be configured to operate with a 16-/32-bit resolution as an input or output channel.
Audio sampling frequencies from 8 kHz up to 192 kHz are supported. When either or both of
the I2S interfaces is/are configured in master mode, the master clock can be output to the
external DAC/CODEC at 256 times the sampling frequency.
All I2Sx can be served by the DMA controller.
2.2.26 Audio PLL (PLLI2S)
The devices feature an additional dedicated PLL for audio I2S application. It allows to
achieve error-free I2S sampling clock accuracy without compromising on the CPU
performance, while using USB peripherals.
Table 5. USART feature comparison
USART
name
Standard
features
Modem
(RTS/
CTS)
LIN SPI
master irDA Smartcard
(ISO 7816)
Max. baud rate
in Mbit/s
(oversampling
by 16)
Max. baud rate
in Mbit/s
(oversampling
by 8)
APB
mapping
USART1 X X X X X X 5.25 10.5
APB2
(max.
84 MHz)
USART2 X X X X X X 2.62 5.25
APB1
(max.
42 MHz)
USART3 X X X X X X 2.62 5.25
APB1
(max.
42 MHz)
UART4 X - X - X - 2.62 5.25
APB1
(max.
42 MHz)
UART5 X - X - X - 2.62 5.25
APB1
(max.
42 MHz)
USART6 X X X X X X 5.25 10.5
APB2
(max.
84 MHz)
DocID022152 Rev 4 35/185
STM32F405xx, STM32F407xx Description
The PLLI2S configuration can be modified to manage an I2S sample rate change without
disabling the main PLL (PLL) used for CPU, USB and Ethernet interfaces.
The audio PLL can be programmed with very low error to obtain sampling rates ranging
from 8 KHz to 192 KHz.
In addition to the audio PLL, a master clock input pin can be used to synchronize the I2S
flow with an external PLL (or Codec output).
2.2.27 Secure digital input/output interface (SDIO)
An SD/SDIO/MMC host interface is available, that supports MultiMediaCard System
Specification Version 4.2 in three different databus modes: 1-bit (default), 4-bit and 8-bit.
The interface allows data transfer at up to 48 MHz, and is compliant with the SD Memory
Card Specification Version 2.0.
The SDIO Card Specification Version 2.0 is also supported with two different databus
modes: 1-bit (default) and 4-bit.
The current version supports only one SD/SDIO/MMC4.2 card at any one time and a stack
of MMC4.1 or previous.
In addition to SD/SDIO/MMC, this interface is fully compliant with the CE-ATA digital
protocol Rev1.1.
2.2.28 Ethernet MAC interface with dedicated DMA and IEEE 1588 support
Peripheral available only on the STM32F407xx devices.
The STM32F407xx devices provide an IEEE-802.3-2002-compliant media access controller
(MAC) for ethernet LAN communications through an industry-standard mediumindependent
interface (MII) or a reduced medium-independent interface (RMII). The
STM32F407xx requires an external physical interface device (PHY) to connect to the
physical LAN bus (twisted-pair, fiber, etc.). the PHY is connected to the STM32F407xx MII
port using 17 signals for MII or 9 signals for RMII, and can be clocked using the 25 MHz
(MII) from the STM32F407xx.
The STM32F407xx includes the following features:
• Supports 10 and 100 Mbit/s rates
• Dedicated DMA controller allowing high-speed transfers between the dedicated SRAM
and the descriptors (see the STM32F40x reference manual for details)
• Tagged MAC frame support (VLAN support)
• Half-duplex (CSMA/CD) and full-duplex operation
• MAC control sublayer (control frames) support
• 32-bit CRC generation and removal
• Several address filtering modes for physical and multicast address (multicast and
group addresses)
• 32-bit status code for each transmitted or received frame
• Internal FIFOs to buffer transmit and receive frames. The transmit FIFO and the
receive FIFO are both 2 Kbytes.
• Supports hardware PTP (precision time protocol) in accordance with IEEE 1588 2008
(PTP V2) with the time stamp comparator connected to the TIM2 input
• Triggers interrupt when system time becomes greater than target time
Description STM32F405xx, STM32F407xx
36/185 DocID022152 Rev 4
2.2.29 Controller area network (bxCAN)
The two CANs are compliant with the 2.0A and B (active) specifications with a bitrate up to 1
Mbit/s. They can receive and transmit standard frames with 11-bit identifiers as well as
extended frames with 29-bit identifiers. Each CAN has three transmit mailboxes, two receive
FIFOS with 3 stages and 28 shared scalable filter banks (all of them can be used even if one
CAN is used). 256 bytes of SRAM are allocated for each CAN.
2.2.30 Universal serial bus on-the-go full-speed (OTG_FS)
The STM32F405xx and STM32F407xx embed an USB OTG full-speed device/host/OTG
peripheral with integrated transceivers. The USB OTG FS peripheral is compliant with the
USB 2.0 specification and with the OTG 1.0 specification. It has software-configurable
endpoint setting and supports suspend/resume. The USB OTG full-speed controller
requires a dedicated 48 MHz clock that is generated by a PLL connected to the HSE
oscillator. The major features are:
• Combined Rx and Tx FIFO size of 320 × 35 bits with dynamic FIFO sizing
• Supports the session request protocol (SRP) and host negotiation protocol (HNP)
• 4 bidirectional endpoints
• 8 host channels with periodic OUT support
• HNP/SNP/IP inside (no need for any external resistor)
• For OTG/Host modes, a power switch is needed in case bus-powered devices are
connected
2.2.31 Universal serial bus on-the-go high-speed (OTG_HS)
The STM32F405xx and STM32F407xx devices embed a USB OTG high-speed (up to
480 Mb/s) device/host/OTG peripheral. The USB OTG HS supports both full-speed and
high-speed operations. It integrates the transceivers for full-speed operation (12 MB/s) and
features a UTMI low-pin interface (ULPI) for high-speed operation (480 MB/s). When using
the USB OTG HS in HS mode, an external PHY device connected to the ULPI is required.
The USB OTG HS peripheral is compliant with the USB 2.0 specification and with the OTG
1.0 specification. It has software-configurable endpoint setting and supports
suspend/resume. The USB OTG full-speed controller requires a dedicated 48 MHz clock
that is generated by a PLL connected to the HSE oscillator.
The major features are:
• Combined Rx and Tx FIFO size of 1 Kbit × 35 with dynamic FIFO sizing
• Supports the session request protocol (SRP) and host negotiation protocol (HNP)
• 6 bidirectional endpoints
• 12 host channels with periodic OUT support
• Internal FS OTG PHY support
• External HS or HS OTG operation supporting ULPI in SDR mode. The OTG PHY is
connected to the microcontroller ULPI port through 12 signals. It can be clocked using
the 60 MHz output.
• Internal USB DMA
• HNP/SNP/IP inside (no need for any external resistor)
• for OTG/Host modes, a power switch is needed in case bus-powered devices are
connected
DocID022152 Rev 4 37/185
STM32F405xx, STM32F407xx Description
2.2.32 Digital camera interface (DCMI)
The camera interface is not available in STM32F405xx devices.
STM32F407xx products embed a camera interface that can connect with camera modules
and CMOS sensors through an 8-bit to 14-bit parallel interface, to receive video data. The
camera interface can sustain a data transfer rate up to 54 Mbyte/s at 54 MHz. It features:
• Programmable polarity for the input pixel clock and synchronization signals
• Parallel data communication can be 8-, 10-, 12- or 14-bit
• Supports 8-bit progressive video monochrome or raw bayer format, YCbCr 4:2:2
progressive video, RGB 565 progressive video or compressed data (like JPEG)
• Supports continuous mode or snapshot (a single frame) mode
• Capability to automatically crop the image
2.2.33 Random number generator (RNG)
All STM32F405xx and STM32F407xx products embed an RNG that delivers 32-bit random
numbers generated by an integrated analog circuit.
2.2.34 General-purpose input/outputs (GPIOs)
Each of the GPIO pins can be configured by software as output (push-pull or open-drain,
with or without pull-up or pull-down), as input (floating, with or without pull-up or pull-down)
or as peripheral alternate function. Most of the GPIO pins are shared with digital or analog
alternate functions. All GPIOs are high-current-capable and have speed selection to better
manage internal noise, power consumption and electromagnetic emission.
The I/O configuration can be locked if needed by following a specific sequence in order to
avoid spurious writing to the I/Os registers.
Fast I/O handling allowing maximum I/O toggling up to 84 MHz.
2.2.35 Analog-to-digital converters (ADCs)
Three 12-bit analog-to-digital converters are embedded and each ADC shares up to 16
external channels, performing conversions in the single-shot or scan mode. In scan mode,
automatic conversion is performed on a selected group of analog inputs.
Additional logic functions embedded in the ADC interface allow:
• Simultaneous sample and hold
• Interleaved sample and hold
The ADC can be served by the DMA controller. An analog watchdog feature allows very
precise monitoring of the converted voltage of one, some or all selected channels. An
interrupt is generated when the converted voltage is outside the programmed thresholds.
To synchronize A/D conversion and timers, the ADCs could be triggered by any of TIM1,
TIM2, TIM3, TIM4, TIM5, or TIM8 timer.
2.2.36 Temperature sensor
The temperature sensor has to generate a voltage that varies linearly with temperature. The
conversion range is between 1.8 V and 3.6 V. The temperature sensor is internally
Description STM32F405xx, STM32F407xx
38/185 DocID022152 Rev 4
connected to the ADC1_IN16 input channel which is used to convert the sensor output
voltage into a digital value.
As the offset of the temperature sensor varies from chip to chip due to process variation, the
internal temperature sensor is mainly suitable for applications that detect temperature
changes instead of absolute temperatures. If an accurate temperature reading is needed,
then an external temperature sensor part should be used.
2.2.37 Digital-to-analog converter (DAC)
The two 12-bit buffered DAC channels can be used to convert two digital signals into two
analog voltage signal outputs.
This dual digital Interface supports the following features:
• two DAC converters: one for each output channel
• 8-bit or 12-bit monotonic output
• left or right data alignment in 12-bit mode
• synchronized update capability
• noise-wave generation
• triangular-wave generation
• dual DAC channel independent or simultaneous conversions
• DMA capability for each channel
• external triggers for conversion
• input voltage reference VREF+
Eight DAC trigger inputs are used in the device. The DAC channels are triggered through
the timer update outputs that are also connected to different DMA streams.
2.2.38 Serial wire JTAG debug port (SWJ-DP)
The ARM SWJ-DP interface is embedded, and is a combined JTAG and serial wire debug
port that enables either a serial wire debug or a JTAG probe to be connected to the target.
Debug is performed using 2 pins only instead of 5 required by the JTAG (JTAG pins could
be re-use as GPIO with alternate function): the JTAG TMS and TCK pins are shared with
SWDIO and SWCLK, respectively, and a specific sequence on the TMS pin is used to
switch between JTAG-DP and SW-DP.
2.2.39 Embedded Trace Macrocell™
The ARM Embedded Trace Macrocell provides a greater visibility of the instruction and data
flow inside the CPU core by streaming compressed data at a very high rate from the
STM32F40x through a small number of ETM pins to an external hardware trace port
analyser (TPA) device. The TPA is connected to a host computer using USB, Ethernet, or
any other high-speed channel. Real-time instruction and data flow activity can be recorded
and then formatted for display on the host computer that runs the debugger software. TPA
hardware is commercially available from common development tool vendors.
The Embedded Trace Macrocell operates with third party debugger software tools.
DocID022152 Rev 4 39/185
STM32F405xx, STM32F407xx Pinouts and pin description
3 Pinouts and pin description
Figure 12. STM32F40x LQFP64 pinout
64 63 62 61 60 59 58 57 56 55 54 53 52 51 50 49
48
47
46
45
44
43
42
41
40
39
38
37
36
35
34
33
17 18 19 20 21 22 23 24 25 26 27 28 29 30 31 32
1
2
3
4
5
6
7
8
9
10
11
12
13
14
15
16
VBAT
PC14
PC15
NRST
PC0
PC1
PC2
PC3
VSSA
VDDA
PA0_WKUP
PA1
PA2
VDD
PB9
PB8
BOOT0
PB7
PB6
PB5
PB4
PB3
PD2
PC12
PC11
PC10
PA15
PA14
VDD
VCAP_2
PA13
PA12
PA11
PA10
PA9
PA8
PC9
PC8
PC7
PC6
PB15
PB14
PB13
PB12
PA3
VSS
VDD
PA4
PA5
PA6
PA7
PC4
PC5
PB0
PB1
PB2
PB10
PB11
VCAP_1
VDD
LQFP64
ai18493b
PC13
PH0
PH1
VSS
Pinouts and pin description STM32F405xx, STM32F407xx
40/185 DocID022152 Rev 4
Figure 13. STM32F40x LQFP100 pinout
100
99
98
97
96
95
94
93
92
91
90
89
88
87
86
85
84
83
82
81
80
79
78
77
76
123456789
10
11
12
13
14
15
16
17
18
19
20
21
22
23
24
25
75
74
73
72
71
70
69
68
67
66
65
64
63
62
61
60
59
58
57
56
55
54
53
52
51
PE2
PE3
PE4
PE5
PE6
VBAT
PC14
PC15
VSS
VDD
PH0
NRST
PC0
PC1
PC2
PC3
VDD
VSSA
VREF+
VDDA
PA0
PA1
PA2
VDD
VSS
VCAP_2
PA13
PA12
PA 11
PA10
PA9
PA8
PC9
PC8
PC7
PC6
PD15
PD14
PD13
PD12
PD11
PD10
PD9
PD8
PB15
PB14
PB13
PB12
PA3
VSS
VDD
PA4
PA5
PA6
PA7
PC4
PC5
PB0
PB1
PB2
PE7
PE8
PE9
PE10
PE11
PE12
PE13
PE14
PE15
PB10
PB11
VCAP_1
VDD
VDD
VSS
PE1
PE0
PB9
PB8
BOOT0
PB7
PB6
PB5
PB4
PB3
PD7
PD6
PD5
PD4
PD3
PD2
PD1
PD0
PC12
PC11
PC10
PA15
PA14
26
27
28
29
30
31
32
33
34
35
36
37
38
39
40
41
42
43
44
45
46
47
48
49
50
ai18495c
LQFP100
PC13
PH1
DocID022152 Rev 4 41/185
STM32F405xx, STM32F407xx Pinouts and pin description
Figure 14. STM32F40x LQFP144 pinout
VDD
PDR_ON
PE1
PE0
PB9
PB8
BOOT0
PB7
PB6
PB5
PB4
PB3
PG15
VDD
VSS
PG14
PG13
PG12
PG11
PG10
PG9
PD7
PD6
VDD
VSS
PD5
PD4
PD3
PD2
PD1
PD0
PC12
PC11
PC10
PA15
PA14
PE2 VDD PE3 VSS PE4
PE5 PA13
PE6 PA12
VBAT PA11
PC13 PA10
PC14 PA9
PC15 PA8
PF0 PC9
PF1 PC8
PF2 PC7
PF3 PC6
PF4 VDD PF5 VSS VSS PG8
VDD PG7
PF6 PG6
PF7 PG5
PF8 PG4
PF9 PG3
PF10 PG2
PH0 PD15
PH1 PD14
NRST VDD PC0 VSS PC1 PD13
PC2 PD12
PC3 PD11
VSSA
VDD PD10
PD9
VREF+ PD8
VDDA PB15
PA0 PB14
PA1 PB13
PA2 PB12
PA3
VSS
VDD
PA4
PA5
PA6
PA7
PC4
PC5
PB0
PB1
PB2
PF11
PF12
VDD
PF13
PF14
PF15
PG0
PG1
PE7
PE8
PE9
VSS
VDD
PE10
PE11
PE12
PE13
PE14
PE15
PB10
PB11
VCAP_1
VDD
144
143
142
141
140
139
138
137
136
135
134
133
132
131
130
129
128
127
126
125
124
123
122
121
109
123456789
10
11
12
13
14
15
16
17
18
19
20
21
22
23
24
25
108
107
106
105
104
103
102
101
100
99
98
97
96
95
94
93
92
91
90
89
88
87
86
85
84
37
38
39
40
41
42
43
44
45
46
47
48
49
50
51
52
53
54
55
56
57
58
59
60
72
LQFP144
120
119
118
117
116
115
114
113
112
111
110
61
62
63
64
65
66
67
68
69
70
71 26
27
28
29
30
31
32
33
34
35
36
83
82
81
80
79
78
77
76
75
74
73
ai18496b
VCAP_2
VSS
Pinouts and pin description STM32F405xx, STM32F407xx
42/185 DocID022152 Rev 4
Figure 15. STM32F40x LQFP176 pinout
MS19916V3
PDR_ON
PE1
PE0
PB9
PB8
BOOT0
PB7
PB6
PB5
PB4
PB3
PG15
PG14
PG13
PG12
PG11
PG10
PG9
PD7
PD6
PD5
PD4
PD3
PD2
PD1
PD0
PC12
PC11
PC10
PI7
PI6
PE2
PE3
PE4
PE5
PA13
PE6
PA12
VBAT
PA11
PI8
PA10
PC14
PA9
PC15
PA8
PF0
PC9
PF1
PC8
PF2
PC7
PF3
PC6
PF4
PF5 PG8
PG7
PF6
PG6
PF7
PG5
PF8
PG4
PF9
PG3
PF10
PG2
PH0
PD15
PH1
PD14
NRST
V
PC0
V
PC1
PD13
PC2
PD12
PC3
PD11
PD10
PD9
VREF+
PD8
PB15
PA0
PB14
PA1
PB13
PA2
PB12
PA3
PA4
PA5
PA6
PA7
PC4
PC5
PB0
PB1
PB2
PF11
PF12
VSS
PF13
PF14
PF15
PG0
PG1
PE7
PE8
PE9
PE10
PE11
PE12
PE13
PE14
PE15
PB10
PB11
176
175
174
173
172
171
170
169
168
167
166
165
164
163
162
161
160
159
158
157
156
155
154
153
141
1
2
3
4
5
6
7
8
9
10
11
12
13
14
15
16
17
18
19
20
21
22
23
24
25
132
131
130
129
128
127
126
125
124
123
122
121
120
119
118
117
116
115
114
113
112
111
110
109
108
45
46
47
48
49
50
51
52
53
54
55
56
57
58
59
60
61
62
63
64
65
66
67
68
80
LQFP176
152
151
150
149
148
147
146
145
144
143
142
69
70
71
72
73
74
75
76
77
78
79
26
27
28
29
30
31
32
33
34
35
36
107
106
105
104
103
102
101
100
99
98
89
PI4
PA15
PA14
PI3
PI2
PI5
140
139
138
137
136
135
134
133
PH4
PH5
PH6
PH7
PH8
PH9
PH10
PH11 88
81
82
83
84
85
86
87
PI1
PI0
PH15
PH14
PH13
PH12
96
95
94
93
92
91
90
97
37
38
39
40
41
42
43
44
PC13
PI9
PI10
PI11
VSS
PH2
PH3
VDD
VSS
VDD
VDDA
VSSA
VDDA
BYPASS_REG
VDD
VDD
VSS
VDD
VCAP_1
VDD
VSS
VDD
VCAP_2
VSS
VDD
VSS
VDD
VSS
VDD
VSS
VDD
VDD
VSS
VDD
VSS
VDD
DocID022152 Rev 4 43/185
STM32F405xx, STM32F407xx Pinouts and pin description
Figure 16. STM32F40x UFBGA176 ballout
1. This figure shows the package top view.
ai18497b
1 2 3 9 10 11 12 13 14 15
A PE3 PE2 PE1 PE0 PB8 PB5 PG14 PG13 PB4 PB3 PD7 PC12 PA15 PA14 PA13
B PE4 PE5 PE6 PB9 PB7 PB6 PG15 PG12 PG11 PG10 PD6 PD0 PC11 PC10 PA12
C VBAT PI7 PI6 PI5 VDD PDR_ON VDD VDD VDD PG9 PD5 PD1 PI3 PI2 PA11
D PC13 PI8 PI9 PI4 BOOT0 VSS VSS VSS PD4 PD3 PD2 PH15 PI1 PA10
E PC14 PF0 PI10 PI11 PH13 PH14 PI0 PA9
F PC15 VSS VDD PH2 VSS VSS VSS VSS VSS VSS VCAP_2 PC9 PA8
G PH0 VSS VDD PH3 VSS VSS VSS VSS VSS VSS VDD PC8 PC7
H PH1 PF2 PF1 PH4 VSS VSS VSS VSS VSS VSS VDD PG8 PC6
J NRST PF3 PF4 PH5 VSS VSS VSS VSS VSS VDD VDD PG7 PG6
K PF7 PF6 PF5 VDD VSS VSS VSS VSS VSS PH12 PG5 PG4 PG3
L PF10 PF9 PF8 BYPASS_
REG
PH11 PH10 PD15 PG2
M VSSA PC0 PC1 PC2 PC3 PB2 PG1 VSS VSS VCAP_1 PH6 PH8 PH9 PD14 PD13
N VREF- PA1 PA0 PA4 PC4 PF13 PG0 VDD VDD VDD PE13 PH7 PD12 PD11 PD10
P VREF+ PA2 PA6 PA5 PC5 PF12 PF15 PE8 PE9 PE11 PE14 PB12 PB13 PD9 PD8
R VDDA PA3 PA7 PB1 PB0 PF11 PF14 PE7 PE10 PE12 PE15 PB10 PB11 PB14 PB15
VSS
4 5 6 7 8
Pinouts and pin description STM32F405xx, STM32F407xx
44/185 DocID022152 Rev 4
Figure 17. STM32F40x WLCSP90 ballout
1. This figure shows the package bump view.
A VBAT PC13 PDR_ON PB4 PD7 PD4 PC12
B PC15 VDD PB7 PB3 PD6 PD2 PA15
C PA0 VSS PB6 PD5 PD1 PC11 PI0
D PC2 PB8 PA13
E PC3 VSS
F PH1 PA1
G NRST
H VSSA
J PA2 PA 4 PA7 PB2 PE11 PB11 PB12
MS30402V1
1
PA14
PI1
PA12
PA10 PA9
PC0 PC9 PC8
PH0
PB13
PC6 PD14
PD12
PE8 PE12
BYPASS_
REG
PD9 PD8
PE9 PB14
10 9 8 7 6 5 4 3 2
VDD
PC14
VCAP_2
PA11
PB5 PD0 PC10 PA8
VSS VDD VSS VDD PC7
VDD PE10 PE14 VCAP_1 PD15
PE13 PE15 PD10 PD11
PA3 PA6 PB1 PB10 PB15
PB9
BOOT0
VDDA PA5 PB0 PE7
Table 6. Legend/abbreviations used in the pinout table
Name Abbreviation Definition
Pin name Unless otherwise specified in brackets below the pin name, the pin function during and after
reset is the same as the actual pin name
Pin type
S Supply pin
I Input only pin
I/O Input / output pin
I/O structure
FT 5 V tolerant I/O
TTa 3.3 V tolerant I/O directly connected to ADC
B Dedicated BOOT0 pin
RST Bidirectional reset pin with embedded weak pull-up resistor
Notes Unless otherwise specified by a note, all I/Os are set as floating inputs during and after reset
Alternate
functions Functions selected through GPIOx_AFR registers
Additional
functions Functions directly selected/enabled through peripheral registers
DocID022152 Rev 4 45/185
STM32F405xx, STM32F407xx Pinouts and pin description
Table 7. STM32F40x pin and ball definitions
Pin number
Pin name
(function after
reset)(1)
Pin type
I / O structure
Notes
Alternate functions Additional functions
LQFP64
WLCSP90
LQFP100
LQFP144
UFBGA176
LQFP176
- - 1 1 A2 1 PE2 I/O FT
TRACECLK/ FSMC_A23 /
ETH_MII_TXD3 /
EVENTOUT
- - 2 2 A1 2 PE3 I/O FT TRACED0/FSMC_A19 /
EVENTOUT
- - 3 3 B1 3 PE4 I/O FT TRACED1/FSMC_A20 /
DCMI_D4/ EVENTOUT
- - 4 4 B2 4 PE5 I/O FT
TRACED2 / FSMC_A21 /
TIM9_CH1 / DCMI_D6 /
EVENTOUT
- - 5 5 B3 5 PE6 I/O FT
TRACED3 / FSMC_A22 /
TIM9_CH2 / DCMI_D7 /
EVENTOUT
1 A10 6 6 C1 6 VBAT S
- - - - D2 7 PI8 I/O FT
(2)(
3) EVENTOUT
RTC_TAMP1,
RTC_TAMP2,
RTC_TS
2 A9 7 7 D1 8 PC13 I/O FT
(2)
(3) EVENTOUT
RTC_OUT,
RTC_TAMP1,
RTC_TS
3 B10 8 8 E1 9
PC14/OSC32_IN
(PC14)
I/O FT
(2)(
3) EVENTOUT OSC32_IN(4)
4 B9 9 9 F1 10
PC15/
OSC32_OUT
(PC15)
I/O FT
(2)(
3) EVENTOUT OSC32_OUT(4)
- - - - D3 11 PI9 I/O FT CAN1_RX / EVENTOUT
- - - - E3 12 PI10 I/O FT ETH_MII_RX_ER /
EVENTOUT
- - - - E4 13 PI11 I/O FT OTG_HS_ULPI_DIR /
EVENTOUT
- - - - F2 14 VSS S
- - - - F3 15 VDD S
- - - 10 E2 16 PF0 I/O FT FSMC_A0 / I2C2_SDA /
EVENTOUT
Pinouts and pin description STM32F405xx, STM32F407xx
46/185 DocID022152 Rev 4
- - - 11 H3 17 PF1 I/O FT FSMC_A1 / I2C2_SCL /
EVENTOUT
- - - 12 H2 18 PF2 I/O FT FSMC_A2 / I2C2_SMBA /
EVENTOUT
- - - 13 J2 19 PF3 I/O FT (4) FSMC_A3/EVENTOUT ADC3_IN9
- - - 14 J3 20 PF4 I/O FT (4) FSMC_A4/EVENTOUT ADC3_IN14
- - - 15 K3 21 PF5 I/O FT (4) FSMC_A5/EVENTOUT ADC3_IN15
- C9 10 16 G2 22 VSS S
- B8 11 17 G3 23 VDD S
- - - 18 K2 24 PF6 I/O FT (4)
TIM10_CH1 /
FSMC_NIORD/
EVENTOUT
ADC3_IN4
- - - 19 K1 25 PF7 I/O FT (4) TIM11_CH1/FSMC_NREG
/ EVENTOUT ADC3_IN5
- - - 20 L3 26 PF8 I/O FT (4)
TIM13_CH1 /
FSMC_NIOWR/
EVENTOUT
ADC3_IN6
- - - 21 L2 27 PF9 I/O FT (4) TIM14_CH1 / FSMC_CD/
EVENTOUT ADC3_IN7
- - - 22 L1 28 PF10 I/O FT (4) FSMC_INTR/ EVENTOUT ADC3_IN8
5 F10 12 23 G1 29
PH0/OSC_IN
(PH0)
I/O FT EVENTOUT OSC_IN(4)
6 F9 13 24 H1 30
PH1/OSC_OUT
(PH1)
I/O FT EVENTOUT OSC_OUT(4)
7 G10 14 25 J1 31 NRST I/O RS
T
8 E10 15 26 M2 32 PC0 I/O FT (4) OTG_HS_ULPI_STP/
EVENTOUT ADC123_IN10
9 - 16 27 M3 33 PC1 I/O FT (4) ETH_MDC/ EVENTOUT ADC123_IN11
10 D10 17 28 M4 34 PC2 I/O FT (4)
SPI2_MISO /
OTG_HS_ULPI_DIR /
ETH_MII_TXD2
/I2S2ext_SD/ EVENTOUT
ADC123_IN12
Table 7. STM32F40x pin and ball definitions (continued)
Pin number
Pin name
(function after
reset)(1)
Pin type
I / O structure
Notes
Alternate functions Additional functions
LQFP64
WLCSP90
LQFP100
LQFP144
UFBGA176
LQFP176
DocID022152 Rev 4 47/185
STM32F405xx, STM32F407xx Pinouts and pin description
11 E9 18 29 M5 35 PC3 I/O FT (4)
SPI2_MOSI / I2S2_SD /
OTG_HS_ULPI_NXT /
ETH_MII_TX_CLK/
EVENTOUT
ADC123_IN13
- - 19 30 G3 36 VDD S
12 H10 20 31 M1 37 VSSA S
- - - - N1 - VREF– S
- - 21 32 P1 38 VREF+ S
13 G9 22 33 R1 39 VDDA S
14 C10 23 34 N3 40
PA0/WKUP
(PA0)
I/O FT (5)
USART2_CTS/
UART4_TX/
ETH_MII_CRS /
TIM2_CH1_ETR/
TIM5_CH1 / TIM8_ETR/
EVENTOUT
ADC123_IN0/WKUP(4
)
15 F8 24 35 N2 41 PA1 I/O FT (4)
USART2_RTS /
UART4_RX/
ETH_RMII_REF_CLK /
ETH_MII_RX_CLK /
TIM5_CH2 / TIM2_CH2/
EVENTOUT
ADC123_IN1
16 J10 25 36 P2 42 PA2 I/O FT (4)
USART2_TX/TIM5_CH3 /
TIM9_CH1 / TIM2_CH3 /
ETH_MDIO/ EVENTOUT
ADC123_IN2
- - - - F4 43 PH2 I/O FT ETH_MII_CRS/EVENTOU
T
- - - - G4 44 PH3 I/O FT ETH_MII_COL/EVENTOU
T
- - - - H4 45 PH4 I/O FT
I2C2_SCL /
OTG_HS_ULPI_NXT/
EVENTOUT
- - - - J4 46 PH5 I/O FT I2C2_SDA/ EVENTOUT
Table 7. STM32F40x pin and ball definitions (continued)
Pin number
Pin name
(function after
reset)(1)
Pin type
I / O structure
Notes
Alternate functions Additional functions
LQFP64
WLCSP90
LQFP100
LQFP144
UFBGA176
LQFP176
Pinouts and pin description STM32F405xx, STM32F407xx
48/185 DocID022152 Rev 4
17 H9 26 37 R2 47 PA3 I/O FT (4)
USART2_RX/TIM5_CH4 /
TIM9_CH2 / TIM2_CH4 /
OTG_HS_ULPI_D0 /
ETH_MII_COL/
EVENTOUT
ADC123_IN3
18 E5 27 38 - - VSS S
D9 L4 48 BYPASS_REG I FT
19 E4 28 39 K4 49 VDD S
20 J9 29 40 N4 50 PA4 I/O TTa (4)
SPI1_NSS / SPI3_NSS /
USART2_CK /
DCMI_HSYNC /
OTG_HS_SOF/ I2S3_WS/
EVENTOUT
ADC12_IN4
/DAC_OUT1
21 G8 30 41 P4 51 PA5 I/O TTa (4)
SPI1_SCK/
OTG_HS_ULPI_CK /
TIM2_CH1_ETR/
TIM8_CH1N/ EVENTOUT
ADC12_IN5/DAC_OU
T2
22 H8 31 42 P3 52 PA6 I/O FT (4)
SPI1_MISO /
TIM8_BKIN/TIM13_CH1 /
DCMI_PIXCLK /
TIM3_CH1 / TIM1_BKIN/
EVENTOUT
ADC12_IN6
23 J8 32 43 R3 53 PA7 I/O FT (4)
SPI1_MOSI/ TIM8_CH1N
/ TIM14_CH1/TIM3_CH2/
ETH_MII_RX_DV /
TIM1_CH1N /
ETH_RMII_CRS_DV/
EVENTOUT
ADC12_IN7
24 - 33 44 N5 54 PC4 I/O FT (4)
ETH_RMII_RX_D0 /
ETH_MII_RX_D0/
EVENTOUT
ADC12_IN14
25 - 34 45 P5 55 PC5 I/O FT (4)
ETH_RMII_RX_D1 /
ETH_MII_RX_D1/
EVENTOUT
ADC12_IN15
26 G7 35 46 R5 56 PB0 I/O FT (4)
TIM3_CH3 / TIM8_CH2N/
OTG_HS_ULPI_D1/
ETH_MII_RXD2 /
TIM1_CH2N/ EVENTOUT
ADC12_IN8
Table 7. STM32F40x pin and ball definitions (continued)
Pin number
Pin name
(function after
reset)(1)
Pin type
I / O structure
Notes
Alternate functions Additional functions
LQFP64
WLCSP90
LQFP100
LQFP144
UFBGA176
LQFP176
DocID022152 Rev 4 49/185
STM32F405xx, STM32F407xx Pinouts and pin description
27 H7 36 47 R4 57 PB1 I/O FT (4)
TIM3_CH4 / TIM8_CH3N/
OTG_HS_ULPI_D2/
ETH_MII_RXD3 /
TIM1_CH3N/ EVENTOUT
ADC12_IN9
28 J7 37 48 M6 58
PB2/BOOT1
(PB2)
I/O FT EVENTOUT
- - - 49 R6 59 PF11 I/O FT DCMI_D12/ EVENTOUT
- - - 50 P6 60 PF12 I/O FT FSMC_A6/ EVENTOUT
- - - 51 M8 61 VSS S
- - - 52 N8 62 VDD S
- - - 53 N6 63 PF13 I/O FT FSMC_A7/ EVENTOUT
- - - 54 R7 64 PF14 I/O FT FSMC_A8/ EVENTOUT
- - - 55 P7 65 PF15 I/O FT FSMC_A9/ EVENTOUT
- - - 56 N7 66 PG0 I/O FT FSMC_A10/ EVENTOUT
- - - 57 M7 67 PG1 I/O FT FSMC_A11/ EVENTOUT
- G6 38 58 R8 68 PE7 I/O FT FSMC_D4/TIM1_ETR/
EVENTOUT
- H6 39 59 P8 69 PE8 I/O FT FSMC_D5/ TIM1_CH1N/
EVENTOUT
- J6 40 60 P9 70 PE9 I/O FT FSMC_D6/TIM1_CH1/
EVENTOUT
- - - 61 M9 71 VSS S
- - - 62 N9 72 VDD S
- F6 41 63 R9 73 PE10 I/O FT FSMC_D7/TIM1_CH2N/
EVENTOUT
- J5 42 64 P10 74 PE11 I/O FT FSMC_D8/TIM1_CH2/
EVENTOUT
- H5 43 65 R10 75 PE12 I/O FT FSMC_D9/TIM1_CH3N/
EVENTOUT
- G5 44 66 N11 76 PE13 I/O FT FSMC_D10/TIM1_CH3/
EVENTOUT
Table 7. STM32F40x pin and ball definitions (continued)
Pin number
Pin name
(function after
reset)(1)
Pin type
I / O structure
Notes
Alternate functions Additional functions
LQFP64
WLCSP90
LQFP100
LQFP144
UFBGA176
LQFP176
Pinouts and pin description STM32F405xx, STM32F407xx
50/185 DocID022152 Rev 4
- F5 45 67 P11 77 PE14 I/O FT FSMC_D11/TIM1_CH4/
EVENTOUT
- G4 46 68 R11 78 PE15 I/O FT FSMC_D12/TIM1_BKIN/
EVENTOUT
29 H4 47 69 R12 79 PB10 I/O FT
SPI2_SCK / I2S2_CK /
I2C2_SCL/ USART3_TX /
OTG_HS_ULPI_D3 /
ETH_MII_RX_ER /
TIM2_CH3/ EVENTOUT
30 J4 48 70 R13 80 PB11 I/O FT
I2C2_SDA/USART3_RX/
OTG_HS_ULPI_D4 /
ETH_RMII_TX_EN/
ETH_MII_TX_EN /
TIM2_CH4/ EVENTOUT
31 F4 49 71 M10 81 VCAP_1 S
32 - 50 72 N10 82 VDD S
- - - - M11 83 PH6 I/O FT
I2C2_SMBA / TIM12_CH1
/ ETH_MII_RXD2/
EVENTOUT
- - - - N12 84 PH7 I/O FT
I2C3_SCL /
ETH_MII_RXD3/
EVENTOUT
- - - - M12 85 PH8 I/O FT
I2C3_SDA /
DCMI_HSYNC/
EVENTOUT
- - - - M13 86 PH9 I/O FT
I2C3_SMBA /
TIM12_CH2/ DCMI_D0/
EVENTOUT
- - - - L13 87 PH10 I/O FT TIM5_CH1 / DCMI_D1/
EVENTOUT
- - - - L12 88 PH11 I/O FT TIM5_CH2 / DCMI_D2/
EVENTOUT
- - - - K12 89 PH12 I/O FT TIM5_CH3 / DCMI_D3/
EVENTOUT
- - - - H12 90 VSS S
- - - - J12 91 VDD S
Table 7. STM32F40x pin and ball definitions (continued)
Pin number
Pin name
(function after
reset)(1)
Pin type
I / O structure
Notes
Alternate functions Additional functions
LQFP64
WLCSP90
LQFP100
LQFP144
UFBGA176
LQFP176
DocID022152 Rev 4 51/185
STM32F405xx, STM32F407xx Pinouts and pin description
33 J3 51 73 P12 92 PB12 I/O FT
SPI2_NSS / I2S2_WS /
I2C2_SMBA/
USART3_CK/ TIM1_BKIN
/ CAN2_RX /
OTG_HS_ULPI_D5/
ETH_RMII_TXD0 /
ETH_MII_TXD0/
OTG_HS_ID/ EVENTOUT
34 J1 52 74 P13 93 PB13 I/O FT
SPI2_SCK / I2S2_CK /
USART3_CTS/
TIM1_CH1N /CAN2_TX /
OTG_HS_ULPI_D6 /
ETH_RMII_TXD1 /
ETH_MII_TXD1/
EVENTOUT
OTG_HS_VBUS
35 J2 53 75 R14 94 PB14 I/O FT
SPI2_MISO/ TIM1_CH2N
/ TIM12_CH1 /
OTG_HS_DM/
USART3_RTS /
TIM8_CH2N/I2S2ext_SD/
EVENTOUT
36 H1 54 76 R15 95 PB15 I/O FT
SPI2_MOSI / I2S2_SD/
TIM1_CH3N / TIM8_CH3N
/ TIM12_CH2 /
OTG_HS_DP/
EVENTOUT
RTC_REFIN
- H2 55 77 P15 96 PD8 I/O FT FSMC_D13 /
USART3_TX/ EVENTOUT
- H3 56 78 P14 97 PD9 I/O FT FSMC_D14 /
USART3_RX/ EVENTOUT
- G3 57 79 N15 98 PD10 I/O FT FSMC_D15 /
USART3_CK/ EVENTOUT
- G1 58 80 N14 99 PD11 I/O FT
FSMC_CLE /
FSMC_A16/USART3_CT
S/ EVENTOUT
- G2 59 81 N13 100 PD12 I/O FT
FSMC_ALE/
FSMC_A17/TIM4_CH1 /
USART3_RTS/
EVENTOUT
Table 7. STM32F40x pin and ball definitions (continued)
Pin number
Pin name
(function after
reset)(1)
Pin type
I / O structure
Notes
Alternate functions Additional functions
LQFP64
WLCSP90
LQFP100
LQFP144
UFBGA176
LQFP176
Pinouts and pin description STM32F405xx, STM32F407xx
52/185 DocID022152 Rev 4
- - 60 82 M15 101 PD13 I/O FT FSMC_A18/TIM4_CH2/
EVENTOUT
- - - 83 - 102 VSS S
- - - 84 J13 103 VDD S
- F2 61 85 M14 104 PD14 I/O FT FSMC_D0/TIM4_CH3/
EVENTOUT/ EVENTOUT
- F1 62 86 L14 105 PD15 I/O FT FSMC_D1/TIM4_CH4/
EVENTOUT
- - - 87 L15 106 PG2 I/O FT FSMC_A12/ EVENTOUT
- - - 88 K15 107 PG3 I/O FT FSMC_A13/ EVENTOUT
- - - 89 K14 108 PG4 I/O FT FSMC_A14/ EVENTOUT
- - - 90 K13 109 PG5 I/O FT FSMC_A15/ EVENTOUT
- - - 91 J15 110 PG6 I/O FT FSMC_INT2/ EVENTOUT
- - - 92 J14 111 PG7 I/O FT
FSMC_INT3
/USART6_CK/
EVENTOUT
- - - 93 H14 112 PG8 I/O FT
USART6_RTS /
ETH_PPS_OUT/
EVENTOUT
- - - 94 G12 113 VSS S
- - - 95 H13 114 VDD S
37 F3 63 96 H15 115 PC6 I/O FT
I2S2_MCK /
TIM8_CH1/SDIO_D6 /
USART6_TX /
DCMI_D0/TIM3_CH1/
EVENTOUT
38 E1 64 97 G15 116 PC7 I/O FT
I2S3_MCK /
TIM8_CH2/SDIO_D7 /
USART6_RX /
DCMI_D1/TIM3_CH2/
EVENTOUT
39 E2 65 98 G14 117 PC8 I/O FT
TIM8_CH3/SDIO_D0
/TIM3_CH3/ USART6_CK
/ DCMI_D2/ EVENTOUT
Table 7. STM32F40x pin and ball definitions (continued)
Pin number
Pin name
(function after
reset)(1)
Pin type
I / O structure
Notes
Alternate functions Additional functions
LQFP64
WLCSP90
LQFP100
LQFP144
UFBGA176
LQFP176
DocID022152 Rev 4 53/185
STM32F405xx, STM32F407xx Pinouts and pin description
40 E3 66 99 F14 118 PC9 I/O FT
I2S_CKIN/ MCO2 /
TIM8_CH4/SDIO_D1 /
/I2C3_SDA / DCMI_D3 /
TIM3_CH4/ EVENTOUT
41 D1 67 100 F15 119 PA8 I/O FT
MCO1 / USART1_CK/
TIM1_CH1/ I2C3_SCL/
OTG_FS_SOF/
EVENTOUT
42 D2 68 101 E15 120 PA9 I/O FT
USART1_TX/ TIM1_CH2 /
I2C3_SMBA / DCMI_D0/
EVENTOUT
OTG_FS_VBUS
43 D3 69 102 D15 121 PA10 I/O FT
USART1_RX/ TIM1_CH3/
OTG_FS_ID/DCMI_D1/
EVENTOUT
44 C1 70 103 C15 122 PA11 I/O FT
USART1_CTS / CAN1_RX
/ TIM1_CH4 /
OTG_FS_DM/
EVENTOUT
45 C2 71 104 B15 123 PA12 I/O FT
USART1_RTS /
CAN1_TX/ TIM1_ETR/
OTG_FS_DP/
EVENTOUT
46 D4 72 105 A15 124
PA13
(JTMS-SWDIO)
I/O FT JTMS-SWDIO/
EVENTOUT
47 B1 73 106 F13 125 VCAP_2 S
- E7 74 107 F12 126 VSS S
48 E6 75 108 G13 127 VDD S
- - - - E12 128 PH13 I/O FT TIM8_CH1N / CAN1_TX/
EVENTOUT
- - - - E13 129 PH14 I/O FT TIM8_CH2N / DCMI_D4/
EVENTOUT
- - - - D13 130 PH15 I/O FT TIM8_CH3N / DCMI_D11/
EVENTOUT
- C3 - - E14 131 PI0 I/O FT
TIM5_CH4 / SPI2_NSS /
I2S2_WS / DCMI_D13/
EVENTOUT
Table 7. STM32F40x pin and ball definitions (continued)
Pin number
Pin name
(function after
reset)(1)
Pin type
I / O structure
Notes
Alternate functions Additional functions
LQFP64
WLCSP90
LQFP100
LQFP144
UFBGA176
LQFP176
Pinouts and pin description STM32F405xx, STM32F407xx
54/185 DocID022152 Rev 4
- B2 - - D14 132 PI1 I/O FT SPI2_SCK / I2S2_CK /
DCMI_D8/ EVENTOUT
- - - - C14 133 PI2 I/O FT
TIM8_CH4 /SPI2_MISO /
DCMI_D9 / I2S2ext_SD/
EVENTOUT
- - - - C13 134 PI3 I/O FT
TIM8_ETR / SPI2_MOSI /
I2S2_SD / DCMI_D10/
EVENTOUT
- - - - D9 135 VSS S
- - - - C9 136 VDD S
49 A2 76 109 A14 137
PA14
(JTCK/SWCLK)
I/O FT JTCK-SWCLK/
EVENTOUT
50 B3 77 110 A13 138
PA15
(JTDI)
I/O FT
JTDI/ SPI3_NSS/
I2S3_WS/TIM2_CH1_ET
R / SPI1_NSS /
EVENTOUT
51 D5 78 111 B14 139 PC10 I/O FT
SPI3_SCK / I2S3_CK/
UART4_TX/SDIO_D2 /
DCMI_D8 / USART3_TX/
EVENTOUT
52 C4 79 112 B13 140 PC11 I/O FT
UART4_RX/ SPI3_MISO /
SDIO_D3 /
DCMI_D4/USART3_RX /
I2S3ext_SD/ EVENTOUT
53 A3 80 113 A12 141 PC12 I/O FT
UART5_TX/SDIO_CK /
DCMI_D9 / SPI3_MOSI
/I2S3_SD / USART3_CK/
EVENTOUT
- D6 81 114 B12 142 PD0 I/O FT FSMC_D2/CAN1_RX/
EVENTOUT
- C5 82 115 C12 143 PD1 I/O FT FSMC_D3 / CAN1_TX/
EVENTOUT
54 B4 83 116 D12 144 PD2 I/O FT
TIM3_ETR/UART5_RX/
SDIO_CMD / DCMI_D11/
EVENTOUT
Table 7. STM32F40x pin and ball definitions (continued)
Pin number
Pin name
(function after
reset)(1)
Pin type
I / O structure
Notes
Alternate functions Additional functions
LQFP64
WLCSP90
LQFP100
LQFP144
UFBGA176
LQFP176
DocID022152 Rev 4 55/185
STM32F405xx, STM32F407xx Pinouts and pin description
- - 84 117 D11 145 PD3 I/O FT
FSMC_CLK/
USART2_CTS/
EVENTOUT
- A4 85 118 D10 146 PD4 I/O FT
FSMC_NOE/
USART2_RTS/
EVENTOUT
- C6 86 119 C11 147 PD5 I/O FT FSMC_NWE/USART2_TX
/ EVENTOUT
- - - 120 D8 148 VSS S
- - - 121 C8 149 VDD S
- B5 87 122 B11 150 PD6 I/O FT FSMC_NWAIT/
USART2_RX/ EVENTOUT
- A5 88 123 A11 151 PD7 I/O FT
USART2_CK/FSMC_NE1/
FSMC_NCE2/
EVENTOUT
- - - 124 C10 152 PG9 I/O FT
USART6_RX /
FSMC_NE2/FSMC_NCE3
/ EVENTOUT
- - - 125 B10 153 PG10 I/O FT FSMC_NCE4_1/
FSMC_NE3/ EVENTOUT
- - - 126 B9 154 PG11 I/O FT
FSMC_NCE4_2 /
ETH_MII_TX_EN/
ETH _RMII_TX_EN/
EVENTOUT
- - - 127 B8 155 PG12 I/O FT
FSMC_NE4 /
USART6_RTS/
EVENTOUT
- - - 128 A8 156 PG13 I/O FT
FSMC_A24 /
USART6_CTS
/ETH_MII_TXD0/
ETH_RMII_TXD0/
EVENTOUT
- - - 129 A7 157 PG14 I/O FT
FSMC_A25 / USART6_TX
/ETH_MII_TXD1/
ETH_RMII_TXD1/
EVENTOUT
Table 7. STM32F40x pin and ball definitions (continued)
Pin number
Pin name
(function after
reset)(1)
Pin type
I / O structure
Notes
Alternate functions Additional functions
LQFP64
WLCSP90
LQFP100
LQFP144
UFBGA176
LQFP176
Pinouts and pin description STM32F405xx, STM32F407xx
56/185 DocID022152 Rev 4
- E8 - 130 D7 158 VSS S
- F7 - 131 C7 159 VDD S
- - - 132 B7 160 PG15 I/O FT USART6_CTS /
DCMI_D13/ EVENTOUT
55 B6 89 133 A10 161
PB3
(JTDO/
TRACESWO)
I/O FT
JTDO/ TRACESWO/
SPI3_SCK / I2S3_CK /
TIM2_CH2 / SPI1_SCK/
EVENTOUT
56 A6 90 134 A9 162
PB4
(NJTRST)
I/O FT
NJTRST/ SPI3_MISO /
TIM3_CH1 / SPI1_MISO /
I2S3ext_SD/ EVENTOUT
57 D7 91 135 A6 163 PB5 I/O FT
I2C1_SMBA/ CAN2_RX /
OTG_HS_ULPI_D7 /
ETH_PPS_OUT/TIM3_CH
2 / SPI1_MOSI/
SPI3_MOSI / DCMI_D10 /
I2S3_SD/ EVENTOUT
58 C7 92 136 B6 164 PB6 I/O FT
I2C1_SCL/ TIM4_CH1 /
CAN2_TX /
DCMI_D5/USART1_TX/
EVENTOUT
59 B7 93 137 B5 165 PB7 I/O FT
I2C1_SDA / FSMC_NL /
DCMI_VSYNC /
USART1_RX/ TIM4_CH2/
EVENTOUT
60 A7 94 138 D6 166 BOOT0 I B VPP
61 D8 95 139 A5 167 PB8 I/O FT
TIM4_CH3/SDIO_D4/
TIM10_CH1 / DCMI_D6 /
ETH_MII_TXD3 /
I2C1_SCL/ CAN1_RX/
EVENTOUT
62 C8 96 140 B4 168 PB9 I/O FT
SPI2_NSS/ I2S2_WS /
TIM4_CH4/ TIM11_CH1/
SDIO_D5 / DCMI_D7 /
I2C1_SDA / CAN1_TX/
EVENTOUT
Table 7. STM32F40x pin and ball definitions (continued)
Pin number
Pin name
(function after
reset)(1)
Pin type
I / O structure
Notes
Alternate functions Additional functions
LQFP64
WLCSP90
LQFP100
LQFP144
UFBGA176
LQFP176
DocID022152 Rev 4 57/185
STM32F405xx, STM32F407xx Pinouts and pin description
- - 97 141 A4 169 PE0 I/O FT TIM4_ETR / FSMC_NBL0
/ DCMI_D2/ EVENTOUT
- - 98 142 A3 170 PE1 I/O FT FSMC_NBL1 / DCMI_D3/
EVENTOUT
63 - 99 - D5 - VSS S
- A8 - 143 C6 171 PDR_ON I FT
64 A1 10
0 144 C5 172 VDD S
- - - - D4 173 PI4 I/O FT TIM8_BKIN / DCMI_D5/
EVENTOUT
- - - - C4 174 PI5 I/O FT
TIM8_CH1 /
DCMI_VSYNC/
EVENTOUT
- - - - C3 175 PI6 I/O FT TIM8_CH2 / DCMI_D6/
EVENTOUT
- - - - C2 176 PI7 I/O FT TIM8_CH3 / DCMI_D7/
EVENTOUT
1. Function availability depends on the chosen device.
2. PC13, PC14, PC15 and PI8 are supplied through the power switch. Since the switch only sinks a limited amount of current
(3 mA), the use of GPIOs PC13 to PC15 and PI8 in output mode is limited:
- The speed should not exceed 2 MHz with a maximum load of 30 pF.
- These I/Os must not be used as a current source (e.g. to drive an LED).
3. Main function after the first backup domain power-up. Later on, it depends on the contents of the RTC registers even after
reset (because these registers are not reset by the main reset). For details on how to manage these I/Os, refer to the RTC
register description sections in the STM32F4xx reference manual, available from the STMicroelectronics website:
www.st.com.
4. FT = 5 V tolerant except when in analog mode or oscillator mode (for PC14, PC15, PH0 and PH1).
5. If the device is delivered in an UFBGA176 or WLCSP90 and the BYPASS_REG pin is set to VDD (Regulator off/internal reset
ON mode), then PA0 is used as an internal Reset (active low).
Table 7. STM32F40x pin and ball definitions (continued)
Pin number
Pin name
(function after
reset)(1)
Pin type
I / O structure
Notes
Alternate functions Additional functions
LQFP64
WLCSP90
LQFP100
LQFP144
UFBGA176
LQFP176
Table 8. FSMC pin definition
Pins(1)
FSMC
LQFP100(2) WLCSP90
(2)
CF NOR/PSRAM/
SRAM NOR/PSRAM Mux NAND 16 bit
PE2 A23 A23 Yes
PE3 A19 A19 Yes
Pinouts and pin description STM32F405xx, STM32F407xx
58/185 DocID022152 Rev 4
PE4 A20 A20 Yes
PE5 A21 A21 Yes
PE6 A22 A22 Yes
PF0 A0 A0 - -
PF1 A1 A1 - -
PF2 A2 A2 - -
PF3 A3 A3 - -
PF4 A4 A4 - -
PF5 A5 A5 - -
PF6 NIORD - -
PF7 NREG - -
PF8 NIOWR - -
PF9 CD - -
PF10 INTR - -
PF12 A6 A6 - -
PF13 A7 A7 - -
PF14 A8 A8 - -
PF15 A9 A9 - -
PG0 A10 A10 - -
PG1 A11 - -
PE7 D4 D4 DA4 D4 Yes Yes
PE8 D5 D5 DA5 D5 Yes Yes
PE9 D6 D6 DA6 D6 Yes Yes
PE10 D7 D7 DA7 D7 Yes Yes
PE11 D8 D8 DA8 D8 Yes Yes
PE12 D9 D9 DA9 D9 Yes Yes
PE13 D10 D10 DA10 D10 Yes Yes
PE14 D11 D11 DA11 D11 Yes Yes
PE15 D12 D12 DA12 D12 Yes Yes
PD8 D13 D13 DA13 D13 Yes Yes
PD9 D14 D14 DA14 D14 Yes Yes
PD10 D15 D15 DA15 D15 Yes Yes
PD11 A16 A16 CLE Yes Yes
Table 8. FSMC pin definition (continued)
Pins(1)
FSMC
LQFP100(2) WLCSP90
(2)
CF NOR/PSRAM/
SRAM NOR/PSRAM Mux NAND 16 bit
DocID022152 Rev 4 59/185
STM32F405xx, STM32F407xx Pinouts and pin description
PD12 A17 A17 ALE Yes Yes
PD13 A18 A18 Yes
PD14 D0 D0 DA0 D0 Yes Yes
PD15 D1 D1 DA1 D1 Yes Yes
PG2 A12 - -
PG3 A13 - -
PG4 A14 - -
PG5 A15 - -
PG6 INT2 - -
PG7 INT3 - -
PD0 D2 D2 DA2 D2 Yes Yes
PD1 D3 D3 DA3 D3 Yes Yes
PD3 CLK CLK Yes
PD4 NOE NOE NOE NOE Yes Yes
PD5 NWE NWE NWE NWE Yes Yes
PD6 NWAIT NWAIT NWAIT NWAIT Yes Yes
PD7 NE1 NE1 NCE2 Yes Yes
PG9 NE2 NE2 NCE3 - -
PG10 NCE4_1 NE3 NE3 - -
PG11 NCE4_2 - -
PG12 NE4 NE4 - -
PG13 A24 A24 - -
PG14 A25 A25 - -
PB7 NADV NADV Yes Yes
PE0 NBL0 NBL0 Yes
PE1 NBL1 NBL1 Yes
1. Full FSMC features are available on LQFP144, LQFP176, and UFBGA176. The features available on
smaller packages are given in the dedicated package column.
2. Ports F and G are not available in devices delivered in 100-pin packages.
Table 8. FSMC pin definition (continued)
Pins(1)
FSMC
LQFP100(2) WLCSP90
(2)
CF NOR/PSRAM/
SRAM NOR/PSRAM Mux NAND 16 bit
Pinouts and pin description STM32F405xx, STM32F407xx
60/185 DocID022152 Rev 4
Table 9. Alternate function mapping
Port
AF0 AF1 AF2 AF3 AF4 AF5 AF6 AF7 AF8 AF9 AF10 AF11 AF12 AF13
AF14 AF15
SYS TIM1/2 TIM3/4/5 TIM8/9/10/1
1 I2C1/2/3
SPI1/SPI2/
I2S2/I2S2ext
SPI3/I2Sext/
I2S3
USART1/2/3/
I2S3ext
UART4/5/
USART6
CAN1/
CAN2/
TIM12/13/14
OTG_FS/
OTG_HS ETH FSMC/SDIO/
OTG_FS DCMI
Port A
PA0 TIM2_CH1_E
TR TIM 5_CH1 TIM8_ETR USART2_CTS UART4_TX ETH_MII_CRS EVENTOUT
PA1 TIM2_CH2 TIM5_CH2 USART2_RTS UART4_RX
ETH_MII
_RX_CLK
ETH_RMII__REF
_CLK
EVENTOUT
PA2 TIM2_CH3 TIM5_CH3 TIM9_CH1 USART2_TX ETH_MDIO EVENTOUT
PA3 TIM2_CH4 TIM5_CH4 TIM9_CH2 USART2_RX OTG_HS_ULPI_
D0 ETH _MII_COL EVENTOUT
PA4 SPI1_NSS SPI3_NSS
I2S3_WS USART2_CK OTG_HS_SO
F
DCMI_HSYN
C EVENTOUT
PA5 TIM2_CH1_E
TR TIM8_CH1N SPI1_SCK OTG_HS_ULPI_
CK EVENTOUT
PA6 TIM1_BKIN TIM3_CH1 TIM8_BKIN SPI1_MISO TIM13_CH1 DCMI_PIXCK EVENTOUT
PA7 TIM1_CH1N TIM3_CH2 TIM8_CH1N SPI1_MOSI TIM14_CH1
ETH_MII _RX_DV
ETH_RMII
_CRS_DV
EVENTOUT
PA8 MCO1 TIM1_CH1 I2C3_SCL USART1_CK OTG_FS_SOF EVENTOUT
PA9 TIM1_CH2 I2C3_SMB
A USART1_TX DCMI_D0 EVENTOUT
PA10 TIM1_CH3 USART1_RX OTG_FS_ID DCMI_D1 EVENTOUT
PA11 TIM1_CH4 USART1_CTS CAN1_RX OTG_FS_DM EVENTOUT
PA12 TIM1_ETR USART1_RTS CAN1_TX OTG_FS_DP EVENTOUT
PA13 JTMSSWDIO
EVENTOUT
PA14 JTCKSWCLK
EVENTOUT
PA15 JTDI TIM 2_CH1
TIM 2_ETR SPI1_NSS SPI3_NSS/
I2S3_WS EVENTOUT
STM32F405xx, STM32F407xx Pinouts and pin description
DocID022152 Rev 4 61/185
Port B
PB0 TIM1_CH2N TIM3_CH3 TIM8_CH2N OTG_HS_ULPI_
D1 ETH _MII_RXD2 EVENTOUT
PB1 TIM1_CH3N TIM3_CH4 TIM8_CH3N OTG_HS_ULPI_
D2 ETH _MII_RXD3 EVENTOUT
PB2 EVENTOUT
PB3
JTDO/
TRACES
WO
TIM2_CH2 SPI1_SCK SPI3_SCK
I2S3_CK EVENTOUT
PB4 NJTRST TIM3_CH1 SPI1_MISO SPI3_MISO I2S3ext_SD EVENTOUT
PB5 TIM3_CH2 I2C1_SMB
A SPI1_MOSI SPI3_MOSI
I2S3_SD CAN2_RX OTG_HS_ULPI_
D7 ETH _PPS_OUT DCMI_D10 EVENTOUT
PB6 TIM4_CH1 I2C1_SCL USART1_TX CAN2_TX DCMI_D5 EVENTOUT
PB7 TIM4_CH2 I2C1_SDA USART1_RX FSMC_NL DCMI_VSYN
C EVENTOUT
PB8 TIM4_CH3 TIM10_CH1 I2C1_SCL CAN1_RX ETH _MII_TXD3 SDIO_D4 DCMI_D6 EVENTOUT
PB9 TIM4_CH4 TIM11_CH1 I2C1_SDA
SPI2_NSS
I2S2_WS
CAN1_TX SDIO_D5 DCMI_D7 EVENTOUT
PB10 TIM2_CH3 I2C2_SCL SPI2_SCK
I2S2_CK USART3_TX OTG_HS_ULPI_
D3 ETH_ MII_RX_ER EVENTOUT
PB11 TIM2_CH4 I2C2_SDA USART3_RX OTG_HS_ULPI_
D4
ETH _MII_TX_EN
ETH
_RMII_TX_EN
EVENTOUT
PB12 TIM1_BKIN I2C2_SMB
A
SPI2_NSS
I2S2_WS USART3_CK CAN2_RX OTG_HS_ULPI_
D5
ETH _MII_TXD0
ETH _RMII_TXD0 OTG_HS_ID EVENTOUT
PB13 TIM1_CH1N SPI2_SCK
I2S2_CK USART3_CTS CAN2_TX OTG_HS_ULPI_
D6
ETH _MII_TXD1
ETH _RMII_TXD1
EVENTOUT
PB14 TIM1_CH2N TIM8_CH2N SPI2_MISO I2S2ext_SD USART3_RTS TIM12_CH1 OTG_HS_DM EVENTOUT
PB15 RTC_
REFIN TIM1_CH3N TIM8_CH3N SPI2_MOSI
I2S2_SD TIM12_CH2 OTG_HS_DP EVENTOUT
Table 9. Alternate function mapping (continued)
Port
AF0 AF1 AF2 AF3 AF4 AF5 AF6 AF7 AF8 AF9 AF10 AF11 AF12 AF13
AF14 AF15
SYS TIM1/2 TIM3/4/5 TIM8/9/10/1
1 I2C1/2/3
SPI1/SPI2/
I2S2/I2S2ext
SPI3/I2Sext/
I2S3
USART1/2/3/
I2S3ext
UART4/5/
USART6
CAN1/
CAN2/
TIM12/13/14
OTG_FS/
OTG_HS ETH FSMC/SDIO/
OTG_FS DCMI
Pinouts and pin description STM32F405xx, STM32F407xx
62/185 DocID022152 Rev 4
Port C
PC0 OTG_HS_ULPI_
STP EVENTOUT
PC1 ETH_MDC EVENTOUT
PC2 SPI2_MISO I2S2ext_SD OTG_HS_ULPI_
DIR ETH _MII_TXD2 EVENTOUT
PC3 SPI2_MOSI
I2S2_SD
OTG_HS_ULPI_
NXT
ETH
_MII_TX_CLK EVENTOUT
PC4 ETH_MII_RXD0
ETH_RMII_RXD0 EVENTOUT
PC5 ETH _MII_RXD1
ETH _RMII_RXD1 EVENTOUT
PC6 TIM3_CH1 TIM8_CH1 I2S2_MCK USART6_TX SDIO_D6 DCMI_D0 EVENTOUT
PC7 TIM3_CH2 TIM8_CH2 I2S3_MCK USART6_RX SDIO_D7 DCMI_D1 EVENTOUT
PC8 TIM3_CH3 TIM8_CH3 USART6_CK SDIO_D0 DCMI_D2 EVENTOUT
PC9 MCO2 TIM3_CH4 TIM8_CH4 I2C3_SDA I2S_CKIN SDIO_D1 DCMI_D3 EVENTOUT
PC10 SPI3_SCK/
I2S3_CK USART3_TX/ UART4_TX SDIO_D2 DCMI_D8 EVENTOUT
PC11 I2S3ext_SD SPI3_MISO/ USART3_RX UART4_RX SDIO_D3 DCMI_D4 EVENTOUT
PC12 SPI3_MOSI
I2S3_SD USART3_CK UART5_TX SDIO_CK DCMI_D9 EVENTOUT
PC13 EVENTOUT
PC14 EVENTOUT
PC15 EVENTOUT
Table 9. Alternate function mapping (continued)
Port
AF0 AF1 AF2 AF3 AF4 AF5 AF6 AF7 AF8 AF9 AF10 AF11 AF12 AF13
AF14 AF15
SYS TIM1/2 TIM3/4/5 TIM8/9/10/1
1 I2C1/2/3
SPI1/SPI2/
I2S2/I2S2ext
SPI3/I2Sext/
I2S3
USART1/2/3/
I2S3ext
UART4/5/
USART6
CAN1/
CAN2/
TIM12/13/14
OTG_FS/
OTG_HS ETH FSMC/SDIO/
OTG_FS DCMI
STM32F405xx, STM32F407xx Pinouts and pin description
DocID022152 Rev 4 63/185
Port D
PD0 CAN1_RX FSMC_D2 EVENTOUT
PD1 CAN1_TX FSMC_D3 EVENTOUT
PD2 TIM3_ETR UART5_RX SDIO_CMD DCMI_D11 EVENTOUT
PD3 USART2_CTS FSMC_CLK EVENTOUT
PD4 USART2_RTS FSMC_NOE EVENTOUT
PD5 USART2_TX FSMC_NWE EVENTOUT
PD6 USART2_RX FSMC_NWAIT EVENTOUT
PD7 USART2_CK FSMC_NE1/
FSMC_NCE2 EVENTOUT
PD8 USART3_TX FSMC_D13 EVENTOUT
PD9 USART3_RX FSMC_D14 EVENTOUT
PD10 USART3_CK FSMC_D15 EVENTOUT
PD11 USART3_CTS FSMC_A16 EVENTOUT
PD12 TIM4_CH1 USART3_RTS FSMC_A17 EVENTOUT
PD13 TIM4_CH2 FSMC_A18 EVENTOUT
PD14 TIM4_CH3 FSMC_D0 EVENTOUT
PD15 TIM4_CH4 FSMC_D1 EVENTOUT
Table 9. Alternate function mapping (continued)
Port
AF0 AF1 AF2 AF3 AF4 AF5 AF6 AF7 AF8 AF9 AF10 AF11 AF12 AF13
AF14 AF15
SYS TIM1/2 TIM3/4/5 TIM8/9/10/1
1 I2C1/2/3
SPI1/SPI2/
I2S2/I2S2ext
SPI3/I2Sext/
I2S3
USART1/2/3/
I2S3ext
UART4/5/
USART6
CAN1/
CAN2/
TIM12/13/14
OTG_FS/
OTG_HS ETH FSMC/SDIO/
OTG_FS DCMI
Pinouts and pin description STM32F405xx, STM32F407xx
64/185 DocID022152 Rev 4
Port E
PE0 TIM4_ETR FSMC_NBL0 DCMI_D2 EVENTOUT
PE1 FSMC_NBL1 DCMI_D3 EVENTOUT
PE2 TRACECL
K ETH _MII_TXD3 FSMC_A23 EVENTOUT
PE3 TRACED0 FSMC_A19 EVENTOUT
PE4 TRACED1 FSMC_A20 DCMI_D4 EVENTOUT
PE5 TRACED2 TIM9_CH1 FSMC_A21 DCMI_D6 EVENTOUT
PE6 TRACED3 TIM9_CH2 FSMC_A22 DCMI_D7 EVENTOUT
PE7 TIM1_ETR FSMC_D4 EVENTOUT
PE8 TIM1_CH1N FSMC_D5 EVENTOUT
PE9 TIM1_CH1 FSMC_D6 EVENTOUT
PE10 TIM1_CH2N FSMC_D7 EVENTOUT
PE11 TIM1_CH2 FSMC_D8 EVENTOUT
PE12 TIM1_CH3N FSMC_D9 EVENTOUT
PE13 TIM1_CH3 FSMC_D10 EVENTOUT
PE14 TIM1_CH4 FSMC_D11 EVENTOUT
PE15 TIM1_BKIN FSMC_D12 EVENTOUT
Table 9. Alternate function mapping (continued)
Port
AF0 AF1 AF2 AF3 AF4 AF5 AF6 AF7 AF8 AF9 AF10 AF11 AF12 AF13
AF14 AF15
SYS TIM1/2 TIM3/4/5 TIM8/9/10/1
1 I2C1/2/3
SPI1/SPI2/
I2S2/I2S2ext
SPI3/I2Sext/
I2S3
USART1/2/3/
I2S3ext
UART4/5/
USART6
CAN1/
CAN2/
TIM12/13/14
OTG_FS/
OTG_HS ETH FSMC/SDIO/
OTG_FS DCMI
STM32F405xx, STM32F407xx Pinouts and pin description
DocID022152 Rev 4 65/185
Port F
PF0 I2C2_SDA FSMC_A0 EVENTOUT
PF1 I2C2_SCL FSMC_A1 EVENTOUT
PF2 I2C2_
SMBA FSMC_A2 EVENTOUT
PF3 FSMC_A3 EVENTOUT
PF4 FSMC_A4 EVENTOUT
PF5 FSMC_A5 EVENTOUT
PF6 TIM10_CH1 FSMC_NIORD EVENTOUT
PF7 TIM11_CH1 FSMC_NREG EVENTOUT
PF8 TIM13_CH1 FSMC_
NIOWR EVENTOUT
PF9 TIM14_CH1 FSMC_CD EVENTOUT
PF10 FSMC_INTR EVENTOUT
PF11 DCMI_D12 EVENTOUT
PF12 FSMC_A6 EVENTOUT
PF13 FSMC_A7 EVENTOUT
PF14 FSMC_A8 EVENTOUT
PF15 FSMC_A9 EVENTOUT
Table 9. Alternate function mapping (continued)
Port
AF0 AF1 AF2 AF3 AF4 AF5 AF6 AF7 AF8 AF9 AF10 AF11 AF12 AF13
AF14 AF15
SYS TIM1/2 TIM3/4/5 TIM8/9/10/1
1 I2C1/2/3
SPI1/SPI2/
I2S2/I2S2ext
SPI3/I2Sext/
I2S3
USART1/2/3/
I2S3ext
UART4/5/
USART6
CAN1/
CAN2/
TIM12/13/14
OTG_FS/
OTG_HS ETH FSMC/SDIO/
OTG_FS DCMI
Pinouts and pin description STM32F405xx, STM32F407xx
66/185 DocID022152 Rev 4
Port G
PG0 FSMC_A10 EVENTOUT
PG1 FSMC_A11 EVENTOUT
PG2 FSMC_A12 EVENTOUT
PG3 FSMC_A13 EVENTOUT
PG4 FSMC_A14 EVENTOUT
PG5 FSMC_A15 EVENTOUT
PG6 FSMC_INT2 EVENTOUT
PG7 USART6_CK FSMC_INT3 EVENTOUT
PG8 USART6_
RTS ETH _PPS_OUT EVENTOUT
PG9 USART6_RX FSMC_NE2/
FSMC_NCE3 EVENTOUT
PG10
FSMC_
NCE4_1/
FSMC_NE3
EVENTOUT
PG11
ETH _MII_TX_EN
ETH _RMII_
TX_EN
FSMC_NCE4_
2 EVENTOUT
PG12 USART6_
RTS FSMC_NE4 EVENTOUT
PG13 UART6_CTS
ETH _MII_TXD0
ETH _RMII_TXD0
FSMC_A24 EVENTOUT
PG14 USART6_TX ETH _MII_TXD1
ETH _RMII_TXD1 FSMC_A25 EVENTOUT
PG15 USART6_
CTS DCMI_D13 EVENTOUT
Table 9. Alternate function mapping (continued)
Port
AF0 AF1 AF2 AF3 AF4 AF5 AF6 AF7 AF8 AF9 AF10 AF11 AF12 AF13
AF14 AF15
SYS TIM1/2 TIM3/4/5 TIM8/9/10/1
1 I2C1/2/3
SPI1/SPI2/
I2S2/I2S2ext
SPI3/I2Sext/
I2S3
USART1/2/3/
I2S3ext
UART4/5/
USART6
CAN1/
CAN2/
TIM12/13/14
OTG_FS/
OTG_HS ETH FSMC/SDIO/
OTG_FS DCMI
STM32F405xx, STM32F407xx Pinouts and pin description
DocID022152 Rev 4 67/185
Port H
PH0 EVENTOUT
PH1 EVENTOUT
PH2 ETH _MII_CRS EVENTOUT
PH3 ETH _MII_COL EVENTOUT
PH4 I2C2_SCL OTG_HS_ULPI_
NXT EVENTOUT
PH5 I2C2_SDA EVENTOUT
PH6 I2C2_SMB
A TIM12_CH1 ETH _MII_RXD2 EVENTOUT
PH7 I2C3_SCL ETH _MII_RXD3 EVENTOUT
PH8 I2C3_SDA DCMI_HSYN
C EVENTOUT
PH9 I2C3_SMB
A TIM12_CH2 DCMI_D0 EVENTOUT
PH10 TIM5_CH1 DCMI_D1 EVENTOUT
PH11 TIM5_CH2 DCMI_D2 EVENTOUT
PH12 TIM5_CH3 DCMI_D3 EVENTOUT
PH13 TIM8_CH1N CAN1_TX EVENTOUT
PH14 TIM8_CH2N DCMI_D4 EVENTOUT
PH15 TIM8_CH3N DCMI_D11 EVENTOUT
Table 9. Alternate function mapping (continued)
Port
AF0 AF1 AF2 AF3 AF4 AF5 AF6 AF7 AF8 AF9 AF10 AF11 AF12 AF13
AF14 AF15
SYS TIM1/2 TIM3/4/5 TIM8/9/10/1
1 I2C1/2/3
SPI1/SPI2/
I2S2/I2S2ext
SPI3/I2Sext/
I2S3
USART1/2/3/
I2S3ext
UART4/5/
USART6
CAN1/
CAN2/
TIM12/13/14
OTG_FS/
OTG_HS ETH FSMC/SDIO/
OTG_FS DCMI
Pinouts and pin description STM32F405xx, STM32F407xx
68/185 DocID022152 Rev 4
Port I
PI0 TIM5_CH4 SPI2_NSS
I2S2_WS DCMI_D13 EVENTOUT
PI1 SPI2_SCK
I2S2_CK DCMI_D8 EVENTOUT
PI2 TIM8_CH4 SPI2_MISO I2S2ext_SD DCMI_D9 EVENTOUT
PI3 TIM8_ETR SPI2_MOSI
I2S2_SD DCMI_D10 EVENTOUT
PI4 TIM8_BKIN DCMI_D5 EVENTOUT
PI5 TIM8_CH1 DCMI_
VSYNC EVENTOUT
PI6 TIM8_CH2 DCMI_D6 EVENTOUT
PI7 TIM8_CH3 DCMI_D7 EVENTOUT
PI8 EVENTOUT
PI9 CAN1_RX EVENTOUT
PI10 ETH _MII_RX_ER EVENTOUT
PI11 OTG_HS_ULPI_
DIR EVENTOUT
Table 9. Alternate function mapping (continued)
Port
AF0 AF1 AF2 AF3 AF4 AF5 AF6 AF7 AF8 AF9 AF10 AF11 AF12 AF13
AF14 AF15
SYS TIM1/2 TIM3/4/5 TIM8/9/10/1
1 I2C1/2/3
SPI1/SPI2/
I2S2/I2S2ext
SPI3/I2Sext/
I2S3
USART1/2/3/
I2S3ext
UART4/5/
USART6
CAN1/
CAN2/
TIM12/13/14
OTG_FS/
OTG_HS ETH FSMC/SDIO/
OTG_FS DCMI
DocID022152 Rev 4 69/185
STM32F405xx, STM32F407xx Memory mapping
4 Memory mapping
The memory map is shown in Figure 18.
Figure 18. STM32F40x memory map
512-Mbyte
block 7
Cortex-M4's
internal
peripherals
512-Mbyte
block 6
Not used
512-Mbyte
block 5
FSMC registers
512-Mbyte
block 4
FSMC bank 3
& bank4
512-Mbyte
block 3
FSMC bank1
& bank2
512-Mbyte
block 2
Peripherals
512-Mbyte
block 1
SRAM
0x0000 0000
0x1FFF FFFF
0x2000 0000
0x3FFF FFFF
0x4000 0000
0x5FFF FFFF
0x6000 0000
0x7FFF FFFF
0x8000 0000
0x9FFF FFFF
0xA000 0000
0xBFFF FFFF
0xC000 0000
0xDFFF FFFF
0xE000 0000
0xFFFF FFFF
512-Mbyte
block 0
Code
Flash
0x0810 0000 - 0x0FFF FFFF
0x1FFF 0000 - 0x1FFF 7A0F
0x1FFF C000 - 0x1FFF C007
0x0800 0000 - 0x080F FFFF
0x0010 0000 - 0x07FF FFFF
0x0000 0000 - 0x000F FFFF
System memory + OTP
Reserved
Reserved
Aliased to Flash, system
memory or SRAM depending
on the BOOT pins
SRAM (16 KB aliased
by bit-banding)
Reserved
0x2000 0000 - 0x2001 BFFF
0x2001 C000 - 0x2001 FFFF
0x2002 0000 - 0x3FFF FFFF
0x4000 0000
Reserved
0x4000 7FFF
0x4000 7800 - 0x4000 FFFF
0x4001 0000
0x4001 57FF
0x4002 000
Reserved 0x5006 0C00 - 0x5FFF FFFF
0x6000 0000
AHB3
0xA000 0FFF
0xA000 1000 - 0xDFFF FFFF
ai18513f
Option Bytes
Reserved 0x4001 5800 - 0x4001 FFFF
0x5006 0BFF
AHB2
0x5000 0000
Reserved 0x4008 0000 - 0x4FFF FFFF
AHB1
SRAM (112 KB aliased
by bit-banding)
Reserved 0x1FFF C008 - 0x1FFF FFFF
Reserved 0x1FFF 7A10 - 0x1FFF 7FFF
CCM data RAM
(64 KB data SRAM) 0x1000 0000 - 0x1000 FFFF
Reserved 0x1001 0000 - 0x1FFE FFFF
Reserved
APB2
0x4007 FFFF
APB1
CORTEX-M4 internal peripherals 0xE000 0000 - 0xE00F FFFF
Reserved 0xE010 0000 - 0xFFFF FFFF
Memory mapping STM32F405xx, STM32F407xx
70/185 DocID022152 Rev 4
Table 10. STM32F40x register boundary addresses
Bus Boundary address Peripheral
0xE00F FFFF - 0xFFFF FFFF Reserved
Cortex-M4 0xE000 0000 - 0xE00F FFFF Cortex-M4 internal peripherals
0xA000 1000 - 0xDFFF FFFF Reserved
AHB3
0xA000 0000 - 0xA000 0FFF FSMC control register
0x9000 0000 - 0x9FFF FFFF FSMC bank 4
0x8000 0000 - 0x8FFF FFFF FSMC bank 3
0x7000 0000 - 0x7FFF FFFF FSMC bank 2
0x6000 0000 - 0x6FFF FFFF FSMC bank 1
0x5006 0C00- 0x5FFF FFFF Reserved
AHB2
0x5006 0800 - 0x5006 0BFF RNG
0x5005 0400 - 0x5006 07FF Reserved
0x5005 0000 - 0x5005 03FF DCMI
0x5004 0000- 0x5004 FFFF Reserved
0x5000 0000 - 0x5003 FFFF USB OTG FS
0x4008 0000- 0x4FFF FFFF Reserved
DocID022152 Rev 4 71/185
STM32F405xx, STM32F407xx Memory mapping
AHB1
0x4004 0000 - 0x4007 FFFF USB OTG HS
0x4002 9400 - 0x4003 FFFF Reserved
0x4002 9000 - 0x4002 93FF
ETHERNET MAC
0x4002 8C00 - 0x4002 8FFF
0x4002 8800 - 0x4002 8BFF
0x4002 8400 - 0x4002 87FF
0x4002 8000 - 0x4002 83FF
0x4002 6800 - 0x4002 7FFF Reserved
0x4002 6400 - 0x4002 67FF DMA2
0x4002 6000 - 0x4002 63FF DMA1
0x4002 5000 - 0x4002 5FFF Reserved
0x4002 4000 - 0x4002 4FFF BKPSRAM
0x4002 3C00 - 0x4002 3FFF Flash interface register
0x4002 3800 - 0x4002 3BFF RCC
0x4002 3400 - 0x4002 37FF Reserved
0x4002 3000 - 0x4002 33FF CRC
0x4002 2400 - 0x4002 2FFF Reserved
0x4002 2000 - 0x4002 23FF GPIOI
0x4002 1C00 - 0x4002 1FFF GPIOH
0x4002 1800 - 0x4002 1BFF GPIOG
0x4002 1400 - 0x4002 17FF GPIOF
0x4002 1000 - 0x4002 13FF GPIOE
0x4002 0C00 - 0x4002 0FFF GPIOD
0x4002 0800 - 0x4002 0BFF GPIOC
0x4002 0400 - 0x4002 07FF GPIOB
0x4002 0000 - 0x4002 03FF GPIOA
0x4001 5800- 0x4001 FFFF Reserved
Table 10. STM32F40x register boundary addresses (continued)
Bus Boundary address Peripheral
Memory mapping STM32F405xx, STM32F407xx
72/185 DocID022152 Rev 4
APB2
0x4001 4C00 - 0x4001 57FF Reserved
0x4001 4800 - 0x4001 4BFF TIM11
0x4001 4400 - 0x4001 47FF TIM10
0x4001 4000 - 0x4001 43FF TIM9
0x4001 3C00 - 0x4001 3FFF EXTI
0x4001 3800 - 0x4001 3BFF SYSCFG
0x4001 3400 - 0x4001 37FF Reserved
0x4001 3000 - 0x4001 33FF SPI1
0x4001 2C00 - 0x4001 2FFF SDIO
0x4001 2400 - 0x4001 2BFF Reserved
0x4001 2000 - 0x4001 23FF ADC1 - ADC2 - ADC3
0x4001 1800 - 0x4001 1FFF Reserved
0x4001 1400 - 0x4001 17FF USART6
0x4001 1000 - 0x4001 13FF USART1
0x4001 0800 - 0x4001 0FFF Reserved
0x4001 0400 - 0x4001 07FF TIM8
0x4001 0000 - 0x4001 03FF TIM1
0x4000 7800- 0x4000 FFFF Reserved
Table 10. STM32F40x register boundary addresses (continued)
Bus Boundary address Peripheral
DocID022152 Rev 4 73/185
STM32F405xx, STM32F407xx Memory mapping
APB1
0x4000 7800 - 0x4000 7FFF Reserved
0x4000 7400 - 0x4000 77FF DAC
0x4000 7000 - 0x4000 73FF PWR
0x4000 6C00 - 0x4000 6FFF Reserved
0x4000 6800 - 0x4000 6BFF CAN2
0x4000 6400 - 0x4000 67FF CAN1
0x4000 6000 - 0x4000 63FF Reserved
0x4000 5C00 - 0x4000 5FFF I2C3
0x4000 5800 - 0x4000 5BFF I2C2
0x4000 5400 - 0x4000 57FF I2C1
0x4000 5000 - 0x4000 53FF UART5
0x4000 4C00 - 0x4000 4FFF UART4
0x4000 4800 - 0x4000 4BFF USART3
0x4000 4400 - 0x4000 47FF USART2
0x4000 4000 - 0x4000 43FF I2S3ext
0x4000 3C00 - 0x4000 3FFF SPI3 / I2S3
0x4000 3800 - 0x4000 3BFF SPI2 / I2S2
0x4000 3400 - 0x4000 37FF I2S2ext
0x4000 3000 - 0x4000 33FF IWDG
0x4000 2C00 - 0x4000 2FFF WWDG
0x4000 2800 - 0x4000 2BFF RTC & BKP Registers
0x4000 2400 - 0x4000 27FF Reserved
0x4000 2000 - 0x4000 23FF TIM14
0x4000 1C00 - 0x4000 1FFF TIM13
0x4000 1800 - 0x4000 1BFF TIM12
0x4000 1400 - 0x4000 17FF TIM7
0x4000 1000 - 0x4000 13FF TIM6
0x4000 0C00 - 0x4000 0FFF TIM5
0x4000 0800 - 0x4000 0BFF TIM4
0x4000 0400 - 0x4000 07FF TIM3
0x4000 0000 - 0x4000 03FF TIM2
Table 10. STM32F40x register boundary addresses (continued)
Bus Boundary address Peripheral
Electrical characteristics STM32F405xx, STM32F407xx
74/185 DocID022152 Rev 4
5 Electrical characteristics
5.1 Parameter conditions
Unless otherwise specified, all voltages are referenced to VSS.
5.1.1 Minimum and maximum values
Unless otherwise specified the minimum and maximum values are guaranteed in the worst
conditions of ambient temperature, supply voltage and frequencies by tests in production on
100% of the devices with an ambient temperature at TA = 25 °C and TA = TAmax (given by
the selected temperature range).
Data based on characterization results, design simulation and/or technology characteristics
are indicated in the table footnotes and are not tested in production. Based on
characterization, the minimum and maximum values refer to sample tests and represent the
mean value plus or minus three times the standard deviation (mean±3Σ).
5.1.2 Typical values
Unless otherwise specified, typical data are based on TA = 25 °C, VDD = 3.3 V (for the
1.8 V ≤ VDD ≤ 3.6 V voltage range). They are given only as design guidelines and are not
tested.
Typical ADC accuracy values are determined by characterization of a batch of samples from
a standard diffusion lot over the full temperature range, where 95% of the devices have an
error less than or equal to the value indicated (mean±2Σ).
5.1.3 Typical curves
Unless otherwise specified, all typical curves are given only as design guidelines and are
not tested.
5.1.4 Loading capacitor
The loading conditions used for pin parameter measurement are shown in Figure 19.
5.1.5 Pin input voltage
The input voltage measurement on a pin of the device is described in Figure 20.
Figure 19. Pin loading conditions Figure 20. Pin input voltage
MS19011V1
C = 50 pF
STM32F pin
OSC_OUT (Hi-Z when
using HSE or LSE)
MS19010V1
STM32F pin
VIN OSC_OUT (Hi-Z when
using HSE or LSE)
DocID022152 Rev 4 75/185
STM32F405xx, STM32F407xx Electrical characteristics
5.1.6 Power supply scheme
Figure 21. Power supply scheme
1. Each power supply pair must be decoupled with filtering ceramic capacitors as shown above. These
capacitors must be placed as close as possible to, or below, the appropriate pins on the underside of the
PCB to ensure the good functionality of the device.
2. To connect BYPASS_REG and PDR_ON pins, refer to Section 2.2.16: Voltage regulator and Table 2.2.15:
Power supply supervisor.
3. The two 2.2 μF ceramic capacitors should be replaced by two 100 nF decoupling capacitors when the
voltage regulator is OFF.
4. The 4.7 μF ceramic capacitor must be connected to one of the VDD pin.
5. VDDA=VDD and VSSA=VSS.
MS19911V2
Backup circuitry
(OSC32K,RTC,
Wakeup logic
Backup registers,
backup RAM)
Kernel logic
(CPU, digital
& RAM)
Analog:
RCs,
PLL,..
Power
switch
VBAT
GPIOs
OUT
IN
15 × 100 nF
+ 1 × 4.7 μF
VBAT =
1.65 to 3.6V
Voltage
regulator
VDDA
ADC
Level shifter
IO
Logic
VDD
100 nF
+ 1 μF
Flash memory
VCAP_1
2 × 2.2 μF VCAP_2
BYPASS_REG
PDR_ON
Reset
controller
VDD
1/2/...14/15
VSS
1/2/...14/15
VDD
VREF+
VREFVSSA
VREF
100 nF
+ 1 μF
Electrical characteristics STM32F405xx, STM32F407xx
76/185 DocID022152 Rev 4
5.1.7 Current consumption measurement
Figure 22. Current consumption measurement scheme
5.2 Absolute maximum ratings
Stresses above the absolute maximum ratings listed in Table 11: Voltage characteristics,
Table 12: Current characteristics, and Table 13: Thermal characteristics may cause
permanent damage to the device. These are stress ratings only and functional operation of
the device at these conditions is not implied. Exposure to maximum rating conditions for
extended periods may affect device reliability.
ai14126
VBAT
VDD
VDDA
IDD_VBAT
IDD
Table 11. Voltage characteristics
Symbol Ratings Min Max Unit
VDD–VSS External main supply voltage (including VDDA, VDD)(1)
1. All main power (VDD, VDDA) and ground (VSS, VSSA) pins must always be connected to the external power
supply, in the permitted range.
–0.3 4.0
V
VIN
Input voltage on five-volt tolerant pin(2)
2. VIN maximum value must always be respected. Refer to Table 12 for the values of the maximum allowed
injected current.
VSS–0.3 VDD+4
Input voltage on any other pin VSS–0.3 4.0
|ΔVDDx| Variations between different VDD power pins - 50
mV
|VSSX − VSS| Variations between all the different ground pins - 50
VESD(HBM) Electrostatic discharge voltage (human body model)
see Section 5.3.14:
Absolute maximum
ratings (electrical
sensitivity)
DocID022152 Rev 4 77/185
STM32F405xx, STM32F407xx Electrical characteristics
5.3 Operating conditions
5.3.1 General operating conditions
Table 12. Current characteristics
Symbol Ratings Max. Unit
IVDD Total current into VDD power lines (source)(1)
1. All main power (VDD, VDDA) and ground (VSS, VSSA) pins must always be connected to the external power
supply, in the permitted range.
150
mA
IVSS Total current out of VSS ground lines (sink)(1) 150
IIO
Output current sunk by any I/O and control pin 25
Output current source by any I/Os and control pin 25
IINJ(PIN)
(2)
2. Negative injection disturbs the analog performance of the device. See note in Section 5.3.20: 12-bit ADC
characteristics.
Injected current on five-volt tolerant I/O(3)
3. Positive injection is not possible on these I/Os. A negative injection is induced by VINVDD while a negative injection is induced by VIN 25 MHz.
4. When the ADC is ON (ADON bit set in the ADC_CR2 register), add an additional power consumption of 1.6 mA per ADC for
the analog part.
5. When analog peripheral blocks such as ADCs, DACs, HSE, LSE, HSI, or LSI are ON, an additional power consumption
should be considered.
6. In this case HCLK = system clock/2.
Electrical characteristics STM32F405xx, STM32F407xx
84/185 DocID022152 Rev 4
Table 21. Typical and maximum current consumption in Run mode, code with data processing
running from Flash memory (ART accelerator disabled)
Symbol Parameter Conditions fHCLK
Typ Max(1)
Unit
TA = 25 °C TA = 85 °C TA = 105 °C
IDD
Supply current
in Run mode
External clock(2),
all peripherals
enabled(3)(4)
168 MHz 93 109 117
mA
144 MHz 76 89 96
120 MHz 67 79 86
90 MHz 53 65 73
60 MHz 37 49 56
30 MHz 20 32 39
25 MHz 16 27 35
16 MHz 11 23 30
8 MHz 6 18 25
4 MHz 4 16 23
2 MHz 3 15 22
External clock(2),
all peripherals
disabled(3)(4)
168 MHz 46 61 69
144 MHz 40 52 60
120 MHz 37 48 56
90 MHz 30 42 50
60 MHz 22 33 41
30 MHz 12 24 31
25 MHz 10 21 29
16 MHz 7 19 26
8 MHz 4 16 23
4 MHz 3 15 22
2 MHz 2 14 21
1. Based on characterization, tested in production at VDD max and fHCLK max with peripherals enabled.
2. External clock is 4 MHz and PLL is on when fHCLK > 25 MHz.
3. When analog peripheral blocks such as (ADCs, DACs, HSE, LSE, HSI,LSI) are on, an additional power consumption
should be considered.
4. When the ADC is ON (ADON bit set in the ADC_CR2 register), add an additional power consumption of 1.6 mA per ADC
for the analog part.
DocID022152 Rev 4 85/185
STM32F405xx, STM32F407xx Electrical characteristics
Figure 24. Typical current consumption versus temperature, Run mode, code with data
processing running from Flash (ART accelerator ON) or RAM, and peripherals OFF
Figure 25. Typical current consumption versus temperature, Run mode, code with data
processing running from Flash (ART accelerator ON) or RAM, and peripherals ON
MS19974V1
0
5
10
15
20
25
30
35
40
45
50
0 20 40 60 80 100 120 140 160 180
IDD RUN( mA)
CPU Frequency (MHz
-45 °C
0 °C
25 °C
55 °C
85 °C
105 °C
MS19975V1
0
10
20
30
40
50
60
70
80
90
100
0 20 40 60 80 100 120 140 160 180
IDD RUN( mA)
CPU Frequency (MHz
-45°C
0°C
25°C
55°C
85°C
105°C
Electrical characteristics STM32F405xx, STM32F407xx
86/185 DocID022152 Rev 4
Figure 26. Typical current consumption versus temperature, Run mode, code with data
processing running from Flash (ART accelerator OFF) or RAM, and peripherals OFF
Figure 27. Typical current consumption versus temperature, Run mode, code with data
processing running from Flash (ART accelerator OFF) or RAM, and peripherals ON
MS19976V1
0
10
20
30
40
50
60
0 20 40 60 80 100 120 140 160 180
IDD RUN( mA)
CPU Frequency (MHz
-45°C
0°C
25°C
55°C
85°C
105°C
MS19977V1
0
20
40
60
80
100
120
0 20 40 60 80 100 120 140 160 180
IDD RUN( mA)
CPU Frequency (MHz
-45°C
0°C
25°C
55°C
85°C
105°C
DocID022152 Rev 4 87/185
STM32F405xx, STM32F407xx Electrical characteristics
Table 22. Typical and maximum current consumption in Sleep mode
Symbol Parameter Conditions fHCLK
Typ Max(1)
T Unit A =
25 °C
TA =
85 °C
TA =
105 °C
IDD
Supply current in
Sleep mode
External clock(2),
all peripherals enabled(3)
168 MHz 59 77 84
mA
144 MHz 46 61 67
120 MHz 38 53 60
90 MHz 30 44 51
60 MHz 20 34 41
30 MHz 11 24 31
25 MHz 8 21 28
16 MHz 6 18 25
8 MHz 3 16 23
4 MHz 2 15 22
2 MHz 2 14 21
External clock(2), all
peripherals disabled
168 MHz 12 27 35
144 MHz 9 22 29
120 MHz 8 20 28
90 MHz 7 19 26
60 MHz 5 17 24
30 MHz 3 16 23
25 MHz 2 15 22
16 MHz 2 14 21
8 MHz 1 14 21
4 MHz 1 13 21
2 MHz 1 13 21
1. Based on characterization, tested in production at VDD max and fHCLK max with peripherals enabled.
2. External clock is 4 MHz and PLL is on when fHCLK > 25 MHz.
3. Add an additional power consumption of 1.6 mA per ADC for the analog part. In applications, this consumption occurs only
while the ADC is ON (ADON bit is set in the ADC_CR2 register).
Electrical characteristics STM32F405xx, STM32F407xx
88/185 DocID022152 Rev 4
Table 23. Typical and maximum current consumptions in Stop mode
Symbol Parameter Conditions
Typ Max
T Unit A =
25 °C
TA =
25 °C
TA =
85 °C
TA =
105 °C
IDD_STOP
Supply
current in
Stop mode
with main
regulator in
Run mode
Flash in Stop mode, low-speed and highspeed
internal RC oscillators and high-speed
oscillator OFF (no independent watchdog)
0.45 1.5 11.00 20.00
mA
Flash in Deep power down mode, low-speed
and high-speed internal RC oscillators and
high-speed oscillator OFF (no independent
watchdog)
0.40 1.5 11.00 20.00
Supply
current in
Stop mode
with main
regulator in
Low Power
mode
Flash in Stop mode, low-speed and highspeed
internal RC oscillators and high-speed
oscillator OFF (no independent watchdog)
0.31 1.1 8.00 15.00
Flash in Deep power down mode, low-speed
and high-speed internal RC oscillators and
high-speed oscillator OFF (no independent
watchdog)
0.28 1.1 8.00 15.00
Table 24. Typical and maximum current consumptions in Standby mode
Symbol Parameter Conditions
Typ Max(1)
TA = 25 °C Unit TA =
85 °C
TA =
105 °C
VDD =
1.8 V
VDD=
2.4 V
VDD =
3.3 V VDD = 3.6 V
IDD_STBY
Supply current
in Standby
mode
Backup SRAM ON, lowspeed
oscillator and RTC ON 3.0 3.4 4.0 20 36
μA
Backup SRAM OFF, lowspeed
oscillator and RTC ON 2.4 2.7 3.3 16 32
Backup SRAM ON, RTC
OFF 2.4 2.6 3.0 12.5 24.8
Backup SRAM OFF, RTC
OFF 1.7 1.9 2.2 9.8 19.2
1. Based on characterization, not tested in production.
DocID022152 Rev 4 89/185
STM32F405xx, STM32F407xx Electrical characteristics
Figure 28. Typical VBAT current consumption (LSE and RTC ON/backup RAM OFF)
Table 25. Typical and maximum current consumptions in VBAT mode
Symbol Parameter Conditions
Typ Max(1)
Unit
TA = 25 °C TA =
85 °C
TA =
105 °C
VBAT
=
1.8 V
VBAT=
2.4 V
VBAT
=
3.3 V
VBAT = 3.6 V
IDD_VBA
T
Backup
domain
supply
current
Backup SRAM ON, low-speed
oscillator and RTC ON 1.29 1.42 1.68 6 11
μA
Backup SRAM OFF, low-speed
oscillator and RTC ON 0.62 0.73 0.96 3 5
Backup SRAM ON, RTC OFF 0.79 0.81 0.86 5 10
Backup SRAM OFF, RTC OFF 0.10 0.10 0.10 2 4
1. Based on characterization, not tested in production.
MS19990V1
0
0.5
1
1.5
2
2.5
3
3.5
0 10 20 30 40 50 60 70 80 90 100
IVBAT in (μA)
Temperature in (°C)
1.65V
1.8V
2V
2.4V
2.7V
3V
3.3V
3.6V
Electrical characteristics STM32F405xx, STM32F407xx
90/185 DocID022152 Rev 4
Figure 29. Typical VBAT current consumption (LSE and RTC ON/backup RAM ON)
I/O system current consumption
The current consumption of the I/O system has two components: static and dynamic.
I/O static current consumption
All the I/Os used as inputs with pull-up generate current consumption when the pin is
externally held low. The value of this current consumption can be simply computed by using
the pull-up/pull-down resistors values given in Table 47: I/O static characteristics.
For the output pins, any external pull-down or external load must also be considered to
estimate the current consumption.
Additional I/O current consumption is due to I/Os configured as inputs if an intermediate
voltage level is externally applied. This current consumption is caused by the input Schmitt
trigger circuits used to discriminate the input value. Unless this specific configuration is
required by the application, this supply current consumption can be avoided by configuring
these I/Os in analog mode. This is notably the case of ADC input pins which should be
configured as analog inputs.
Caution: Any floating input pin can also settle to an intermediate voltage level or switch inadvertently,
as a result of external electromagnetic noise. To avoid current consumption related to
floating pins, they must either be configured in analog mode, or forced internally to a definite
digital value. This can be done either by using pull-up/down resistors or by configuring the
pins in output mode.
I/O dynamic current consumption
In addition to the internal peripheral current consumption measured previously (see
Table 27: Peripheral current consumption), the I/Os used by an application also contribute
to the current consumption. When an I/O pin switches, it uses the current from the MCU
MS19991V1
0
1
2
3
4
5
6
0 10 20 30 40 50 60 70 80 90 100
IVBAT in (μA)
Temperature in (°C)
1.65V
1.8V
2V
2.4V
2.7V
3V
3.3V
3.6V
DocID022152 Rev 4 91/185
STM32F405xx, STM32F407xx Electrical characteristics
supply voltage to supply the I/O pin circuitry and to charge/discharge the capacitive load
(internal or external) connected to the pin:
where
ISW is the current sunk by a switching I/O to charge/discharge the capacitive load
VDD is the MCU supply voltage
fSW is the I/O switching frequency
C is the total capacitance seen by the I/O pin: C = CINT+ CEXT
The test pin is configured in push-pull output mode and is toggled by software at a fixed
frequency.
ISW = VDD × fSW × C
Electrical characteristics STM32F405xx, STM32F407xx
92/185 DocID022152 Rev 4
Table 26. Switching output I/O current consumption
Symbol Parameter Conditions(1) I/O toggling
frequency (fSW) Typ Unit
IDDIO
I/O switching
current
VDD = 3.3 V(2)
C = CINT
2 MHz 0.02
mA
8 MHz 0.14
25 MHz 0.51
50 MHz 0.86
60 MHz 1.30
VDD = 3.3 V
CEXT = 0 pF
C = CINT + CEXT+ CS
2 MHz 0.10
8 MHz 0.38
25 MHz 1.18
50 MHz 2.47
60 MHz 2.86
VDD = 3.3 V
CEXT = 10 pF
C = CINT + CEXT+ CS
2 MHz 0.17
8 MHz 0.66
25 MHz 1.70
50 MHz 2.65
60 MHz 3.48
VDD = 3.3 V
CEXT = 22 pF
C = CINT + CEXT+ CS
2 MHz 0.23
8 MHz 0.95
25 MHz 3.20
50 MHz 4.69
60 MHz 8.06
VDD = 3.3 V
CEXT = 33 pF
C = CINT + CEXT+ CS
2 MHz 0.30
8 MHz 1.22
25 MHz 3.90
50 MHz 8.82
60 MHz -(3)
1. CS is the PCB board capacitance including the pad pin. CS = 7 pF (estimated value).
2. This test is performed by cutting the LQFP package pin (pad removal).
3. At 60 MHz, C maximum load is specified 30 pF.
DocID022152 Rev 4 93/185
STM32F405xx, STM32F407xx Electrical characteristics
On-chip peripheral current consumption
The current consumption of the on-chip peripherals is given in Table 27. The MCU is placed
under the following conditions:
• At startup, all I/O pins are configured as analog pins by firmware.
• All peripherals are disabled unless otherwise mentioned
• The code is running from Flash memory and the Flash memory access time is equal to
5 wait states at 168 MHz.
• The code is running from Flash memory and the Flash memory access time is equal to
4 wait states at 144 MHz, and the power scale mode is set to 2.
• ART accelerator and Cache off.
• The given value is calculated by measuring the difference of current consumption
– with all peripherals clocked off
– with one peripheral clocked on (with only the clock applied)
• When the peripherals are enabled: HCLK is the system clock, fPCLK1 = fHCLK/4, and
fPCLK2 = fHCLK/2.
• The typical values are obtained for VDD = 3.3 V and TA= 25 °C, unless otherwise
specified.
Table 27. Peripheral current consumption
Peripheral(1) 168 MHz 144 MHz Unit
AHB1
GPIO A 0.49 0.36
mA
GPIO B 0.45 0.33
GPIO C 0.45 0.34
GPIO D 0.45 0.34
GPIO E 0.47 0.35
GPIO F 0.45 0.33
GPIO G 0.44 0.33
GPIO H 0.45 0.34
GPIO I 0.44 0.33
OTG_HS + ULPI 4.57 3.55
CRC 0.07 0.06
BKPSRAM 0.11 0.08
DMA1 6.15 4.75
DMA2 6.24 4.8
ETH_MAC +
ETH_MAC_TX
ETH_MAC_RX
ETH_MAC_PTP
3.28 2.54
AHB2
OTG_FS 4.59 3.69
mA
DCMI 1.04 0.80
Electrical characteristics STM32F405xx, STM32F407xx
94/185 DocID022152 Rev 4
AHB3 FSMC 2.18 1.67
mA
APB1
TIM2 0.80 0.61
TIM3 0.58 0.44
TIM4 0.62 0.48
TIM5 0.79 0.61
TIM6 0.15 0.11
TIM7 0.16 0.12
TIM12 0.33 0.26
TIM13 0.27 0.21
TIM14 0.27 0.21
PWR 0.04 0.03
USART2 0.17 0.13
USART3 0.17 0.13
UART4 0.17 0.13
UART5 0.17 0.13
I2C1 0.17 0.13
I2C2 0.18 0.13
I2C3 0.18 0.13
SPI2/I2S2(2) 0.17/0.16 0.13/0.12
SPI3/I2S3(2) 0.16/0.14 0.12/0.12
CAN1 0.27 0.21
CAN2 0.26 0.20
DAC 0.14 0.10
DAC channel 1(3) 0.91 0.89
DAC channel 2(4) 0.91 0.89
DAC channel 1 and
2(3)(4) 1.69 1.68
WWDG 0.04 0.04
Table 27. Peripheral current consumption (continued)
Peripheral(1) 168 MHz 144 MHz Unit
DocID022152 Rev 4 95/185
STM32F405xx, STM32F407xx Electrical characteristics
5.3.7 Wakeup time from low-power mode
The wakeup times given in Table 28 is measured on a wakeup phase with a 16 MHz HSI
RC oscillator. The clock source used to wake up the device depends from the current
operating mode:
• Stop or Standby mode: the clock source is the RC oscillator
• Sleep mode: the clock source is the clock that was set before entering Sleep mode.
All timings are derived from tests performed under ambient temperature and VDD supply
voltage conditions summarized in Table 14.
APB2
SDIO 0.64 0.54
mA
TIM1 1.47 1.14
TIM8 1.58 1.22
TIM9 0.68 0.54
TIM10 0.45 0.36
TIM11 0.47 0.38
ADC1(5) 2.20 2.10
ADC2(5) 2.04 1.93
ADC3(5) 2.10 2.00
SPI1 0.14 0.12
USART1 0.34 0.27
USART6 0.34 0.28
1. HSE oscillator with 4 MHz crystal and PLL are ON.
2. I2SMOD bit set in SPI_I2SCFGR register, and then the I2SE bit set to enable I2S peripheral.
3. EN1 bit is set in DAC_CR register.
4. EN2 bit is set in DAC_CR register.
5. ADON bit set in ADC_CR2 register.
Table 27. Peripheral current consumption (continued)
Peripheral(1) 168 MHz 144 MHz Unit
Table 28. Low-power mode wakeup timings
Symbol Parameter Min(1) Typ(1) Max(1) Unit
tWUSLEEP
(2) Wakeup from Sleep mode - 1 - μs
tWUSTOP
(2)
Wakeup from Stop mode (regulator in Run mode) - 13 -
Wakeup from Stop mode (regulator in low power mode) - 17 40 μs
Wakeup from Stop mode (regulator in low power mode
and Flash memory in Deep power down mode) - 110 -
tWUSTDBY
(2)(3) Wakeup from Standby mode 260 375 480 μs
1. Based on characterization, not tested in production.
2. The wakeup times are measured from the wakeup event to the point in which the application code reads the first instruction.
3. tWUSTDBY minimum and maximum values are given at 105 °C and –45 °C, respectively.
Electrical characteristics STM32F405xx, STM32F407xx
96/185 DocID022152 Rev 4
5.3.8 External clock source characteristics
High-speed external user clock generated from an external source
The characteristics given in Table 29 result from tests performed using an high-speed
external clock source, and under ambient temperature and supply voltage conditions
summarized in Table 14.
Low-speed external user clock generated from an external source
The characteristics given in Table 30 result from tests performed using an low-speed
external clock source, and under ambient temperature and supply voltage conditions
summarized in Table 14.
Table 29. High-speed external user clock characteristics
Symbol Parameter Conditions Min Typ Max Unit
fHSE_ext
External user clock source
frequency(1) 1 - 50 MHz
VHSEH OSC_IN input pin high level voltage 0.7VDD - VDD V
VHSEL OSC_IN input pin low level voltage VSS - 0.3VDD
tw(HSE)
tw(HSE)
OSC_IN high or low time(1)
1. Guaranteed by design, not tested in production.
5 - -
ns
tr(HSE)
tf(HSE)
OSC_IN rise or fall time(1) - - 10
Cin(HSE) OSC_IN input capacitance(1) - 5 - pF
DuCy(HSE) Duty cycle 45 - 55 %
IL OSC_IN Input leakage current VSS ≤ VIN ≤ VDD - - ±1 μA
Table 30. Low-speed external user clock characteristics
Symbol Parameter Conditions Min Typ Max Unit
fLSE_ext
User External clock source
frequency(1) - 32.768 1000 kHz
VLSEH
OSC32_IN input pin high level
voltage 0.7VDD - VDD V
VLSEL OSC32_IN input pin low level voltage VSS - 0.3VDD
tw(LSE)
tf(LSE)
OSC32_IN high or low time(1) 450 - -
ns
tr(LSE)
tf(LSE)
OSC32_IN rise or fall time(1) - - 50
Cin(LSE) OSC32_IN input capacitance(1) - 5 - pF
DuCy(LSE) Duty cycle 30 - 70 %
IL OSC32_IN Input leakage current VSS ≤ VIN ≤ VDD - - ±1 μA
1. Guaranteed by design, not tested in production.
DocID022152 Rev 4 97/185
STM32F405xx, STM32F407xx Electrical characteristics
Figure 30. High-speed external clock source AC timing diagram
Figure 31. Low-speed external clock source AC timing diagram
High-speed external clock generated from a crystal/ceramic resonator
The high-speed external (HSE) clock can be supplied with a 4 to 26 MHz crystal/ceramic
resonator oscillator. All the information given in this paragraph are based on
characterization results obtained with typical external components specified in Table 31. In
the application, the resonator and the load capacitors have to be placed as close as
possible to the oscillator pins in order to minimize output distortion and startup stabilization
time. Refer to the crystal resonator manufacturer for more details on the resonator
characteristics (frequency, package, accuracy).
ai17528
OSC_IN
External
STM32F
clock source
VHSEH
tf(HSE) tW(HSE)
IL
90%
10%
THSE
tr(HSE) tW(HSE) t
fHSE_ext
VHSEL
ai17529
External OSC32_IN
STM32F
clock source
VLSEH
tf(LSE) tW(LSE)
IL
90%
10%
TLSE
tr(LSE) tW(LSE) t
fLSE_ext
VLSEL
Electrical characteristics STM32F405xx, STM32F407xx
98/185 DocID022152 Rev 4
For CL1 and CL2, it is recommended to use high-quality external ceramic capacitors in the
5 pF to 25 pF range (typ.), designed for high-frequency applications, and selected to match
the requirements of the crystal or resonator (see Figure 32). CL1 and CL2 are usually the
same size. The crystal manufacturer typically specifies a load capacitance which is the
series combination of CL1 and CL2. PCB and MCU pin capacitance must be included (10 pF
can be used as a rough estimate of the combined pin and board capacitance) when sizing
CL1 and CL2.
Note: For information on electing the crystal, refer to the application note AN2867 “Oscillator
design guide for ST microcontrollers” available from the ST website www.st.com.
Figure 32. Typical application with an 8 MHz crystal
1. REXT value depends on the crystal characteristics.
Low-speed external clock generated from a crystal/ceramic resonator
The low-speed external (LSE) clock can be supplied with a 32.768 kHz crystal/ceramic
resonator oscillator. All the information given in this paragraph are based on
characterization results obtained with typical external components specified in Table 32. In
the application, the resonator and the load capacitors have to be placed as close as
possible to the oscillator pins in order to minimize output distortion and startup stabilization
time. Refer to the crystal resonator manufacturer for more details on the resonator
characteristics (frequency, package, accuracy).
Table 31. HSE 4-26 MHz oscillator characteristics(1) (2)
1. Resonator characteristics given by the crystal/ceramic resonator manufacturer.
2. Based on characterization, not tested in production.
Symbol Parameter Conditions Min Typ Max Unit
fOSC_IN Oscillator frequency 4 - 26 MHz
RF Feedback resistor - 200 - kΩ
IDD HSE current consumption
VDD=3.3 V,
ESR= 30 Ω,
CL=5 pF@25 MHz
- 449 -
μA
VDD=3.3 V,
ESR= 30 Ω,
CL=10 pF@25 MHz
- 532 -
gm Oscillator transconductance Startup 5 - - mA/V
tSU(HSE
(3)
3. tSU(HSE) is the startup time measured from the moment it is enabled (by software) to a stabilized 8 MHz
oscillation is reached. This value is measured for a standard crystal resonator and it can vary significantly
with the crystal manufacturer
Startup time VDD is stabilized - 2 - ms
ai17530
OSC_OUT
OSC_IN fHSE
CL1
RF
STM32F
8 MHz
resonator
Resonator with
integrated capacitors
Bias
controlled
gain
CL2 REXT(1)
DocID022152 Rev 4 99/185
STM32F405xx, STM32F407xx Electrical characteristics
Note: For information on electing the crystal, refer to the application note AN2867 “Oscillator
design guide for ST microcontrollers” available from the ST website www.st.com.
Figure 33. Typical application with a 32.768 kHz crystal
5.3.9 Internal clock source characteristics
The parameters given in Table 33 and Table 34 are derived from tests performed under
ambient temperature and VDD supply voltage conditions summarized in Table 14.
High-speed internal (HSI) RC oscillator
Table 32. LSE oscillator characteristics (fLSE = 32.768 kHz) (1)
1. Guaranteed by design, not tested in production.
Symbol Parameter Conditions Min Typ Max Unit
RF Feedback resistor - 18.4 - MΩ
IDD LSE current consumption - - 1 μA
gm Oscillator Transconductance 2.8 - - μA/V
tSU(LSE)
(2)
2. tSU(LSE) is the startup time measured from the moment it is enabled (by software) to a stabilized
32.768 kHz oscillation is reached. This value is measured for a standard crystal resonator and it can vary
significantly with the crystal manufacturer
startup time VDD is stabilized - 2 - s
ai17531
OSC32_OUT
OSC32_IN fLSE
CL1
RF
STM32F
32.768 kHz
resonator
Resonator with
integrated capacitors
Bias
controlled
gain
CL2
Table 33. HSI oscillator characteristics (1)
Symbol Parameter Conditions Min Typ Max Unit
fHSI Frequency - 16 - MHz
ACCHSI
Accuracy of the HSI
oscillator
User-trimmed with the RCC_CR
register - - 1 %
Factorycalibrated
TA = –40 to
105 °C(2) –8 - 4.5 %
TA = –10 to 85 °C(2) –4 - 4 %
TA = 25 °C –1 - 1 %
tsu(HSI)
(3) HSI oscillator
startup time - 2.2 4 μs
IDD(HSI)
HSI oscillator
power consumption - 60 80 μA
Electrical characteristics STM32F405xx, STM32F407xx
100/185 DocID022152 Rev 4
Low-speed internal (LSI) RC oscillator
Figure 34. ACCLSI versus temperature
5.3.10 PLL characteristics
The parameters given in Table 35 and Table 36 are derived from tests performed under
temperature and VDD supply voltage conditions summarized in Table 14.
1. VDD = 3.3 V, TA = –40 to 105 °C unless otherwise specified.
2. Based on characterization, not tested in production.
3. Guaranteed by design, not tested in production.
Table 34. LSI oscillator characteristics (1)
1. VDD = 3 V, TA = –40 to 105 °C unless otherwise specified.
Symbol Parameter Min Typ Max Unit
fLSI
(2)
2. Based on characterization, not tested in production.
Frequency 17 32 47 kHz
tsu(LSI)
(3)
3. Guaranteed by design, not tested in production.
LSI oscillator startup time - 15 40 μs
IDD(LSI)
(3) LSI oscillator power consumption - 0.4 0.6 μA
MS19013V1
-40
-30
-20
-10
0
10
20
30
40
50
-45 -35 -25 -15 -5 5 15 25 35 45 55 65 75 85 95 105
Normalized deviati on (%)
Temperature (°C)
max
avg
min
DocID022152 Rev 4 101/185
STM32F405xx, STM32F407xx Electrical characteristics
Table 35. Main PLL characteristics
Symbol Parameter Conditions Min Typ Max Unit
fPLL_IN PLL input clock(1) 0.95(2) 1 2.10 MHz
fPLL_OUT PLL multiplier output clock 24 - 168 MHz
fPLL48_OUT
48 MHz PLL multiplier output
clock - 48 75 MHz
fVCO_OUT PLL VCO output 192 - 432 MHz
tLOCK PLL lock time
VCO freq = 192 MHz 75 - 200
μs
VCO freq = 432 MHz 100 - 300
Jitter(3)
Cycle-to-cycle jitter
System clock
120 MHz
RMS - 25 -
ps
peak
to
peak
- ±150 -
Period Jitter
RMS - 15 -
peak
to
peak
- ±200 -
Main clock output (MCO) for
RMII Ethernet
Cycle to cycle at 50 MHz
on 1000 samples - 32 -
Main clock output (MCO) for MII
Ethernet
Cycle to cycle at 25 MHz
on 1000 samples - 40 -
Bit Time CAN jitter Cycle to cycle at 1 MHz
on 1000 samples - 330 -
IDD(PLL)
(4) PLL power consumption on VDD
VCO freq = 192 MHz
VCO freq = 432 MHz
0.15
0.45
-
0.40
0.75
mA
IDDA(PLL)
(4) PLL power consumption on
VDDA
VCO freq = 192 MHz
VCO freq = 432 MHz
0.30
0.55
-
0.40
0.85
mA
1. Take care of using the appropriate division factor M to obtain the specified PLL input clock values. The M factor is shared
between PLL and PLLI2S.
2. Guaranteed by design, not tested in production.
3. The use of 2 PLLs in parallel could degraded the Jitter up to +30%.
4. Based on characterization, not tested in production.
Table 36. PLLI2S (audio PLL) characteristics
Symbol Parameter Conditions Min Typ Max Unit
fPLLI2S_IN PLLI2S input clock(1) 0.95(2) 1 2.10 MHz
fPLLI2S_OUT PLLI2S multiplier output clock - - 216 MHz
fVCO_OUT PLLI2S VCO output 192 - 432 MHz
tLOCK PLLI2S lock time
VCO freq = 192 MHz 75 - 200
μs
VCO freq = 432 MHz 100 - 300
Electrical characteristics STM32F405xx, STM32F407xx
102/185 DocID022152 Rev 4
5.3.11 PLL spread spectrum clock generation (SSCG) characteristics
The spread spectrum clock generation (SSCG) feature allows to reduce electromagnetic
interferences (see Table 43: EMI characteristics). It is available only on the main PLL.
Equation 1
The frequency modulation period (MODEPER) is given by the equation below:
fPLL_IN and fMod must be expressed in Hz.
As an example:
If fPLL_IN = 1 MHz, and fMOD = 1 kHz, the modulation depth (MODEPER) is given by
equation 1:
Jitter(3)
Master I2S clock jitter
Cycle to cycle at
12.288 MHz on
48KHz period,
N=432, R=5
RMS - 90 -
peak
to
peak
- ±280 - ps
Average frequency of
12.288 MHz
N = 432, R = 5
on 1000 samples
- 90 - ps
WS I2S clock jitter
Cycle to cycle at 48 KHz
on 1000 samples
- 400 - ps
IDD(PLLI2S)
(4) PLLI2S power consumption on
VDD
VCO freq = 192 MHz
VCO freq = 432 MHz
0.15
0.45
-
0.40
0.75
mA
IDDA(PLLI2S)
(4) PLLI2S power consumption on
VDDA
VCO freq = 192 MHz
VCO freq = 432 MHz
0.30
0.55
-
0.40
0.85
mA
1. Take care of using the appropriate division factor M to have the specified PLL input clock values.
2. Guaranteed by design, not tested in production.
3. Value given with main PLL running.
4. Based on characterization, not tested in production.
Table 36. PLLI2S (audio PLL) characteristics (continued)
Symbol Parameter Conditions Min Typ Max Unit
Table 37. SSCG parameters constraint
Symbol Parameter Min Typ Max(1) Unit
fMod Modulation frequency - - 10 KHz
md Peak modulation depth 0.25 - 2 %
MODEPER * INCSTEP - - 215−1 -
1. Guaranteed by design, not tested in production.
MODEPER = round[fPLL_IN ⁄ (4 × fMod)]
MODEPER round 106 4 10 3 = [ ⁄ ( × )] = 250
DocID022152 Rev 4 103/185
STM32F405xx, STM32F407xx Electrical characteristics
Equation 2
Equation 2 allows to calculate the increment step (INCSTEP):
fVCO_OUT must be expressed in MHz.
With a modulation depth (md) = ±2 % (4 % peak to peak), and PLLN = 240 (in MHz):
An amplitude quantization error may be generated because the linear modulation profile is
obtained by taking the quantized values (rounded to the nearest integer) of MODPER and
INCSTEP. As a result, the achieved modulation depth is quantized. The percentage
quantized modulation depth is given by the following formula:
As a result:
Figure 35 and Figure 36 show the main PLL output clock waveforms in center spread and
down spread modes, where:
F0 is fPLL_OUT nominal.
Tmode is the modulation period.
md is the modulation depth.
Figure 35. PLL output clock waveforms in center spread mode
INCSTEP = round[((215 – 1) × md × PLLN) ⁄ (100 × 5 × MODEPER)]
INCSTEP = round[((215 – 1) × 2 × 240) ⁄ (100 × 5 × 250)] = 126md(quantitazed)%
mdquantized% = (MODEPER × INCSTEP × 100 × 5) ⁄ ((215 – 1) × PLLN)
mdquantized% = (250 × 126 × 100 × 5) ⁄ ((215 – 1) × 240) = 2.002%(peak)
Frequency (PLL_OUT)
Time
F0
tmode
md
ai17291
md
2 x tmode
Electrical characteristics STM32F405xx, STM32F407xx
104/185 DocID022152 Rev 4
Figure 36. PLL output clock waveforms in down spread mode
5.3.12 Memory characteristics
Flash memory
The characteristics are given at TA = –40 to 105 °C unless otherwise specified.
The devices are shipped to customers with the Flash memory erased.
Time
ai17292
Frequency (PLL_OUT)
F0
2 x md
tmode 2 x tmode
Table 38. Flash memory characteristics
Symbol Parameter Conditions Min Typ Max Unit
IDD Supply current
Write / Erase 8-bit mode, VDD = 1.8 V - 5 -
Write / Erase 16-bit mode, VDD = 2.1 V - 8 - mA
Write / Erase 32-bit mode, VDD = 3.3 V - 12 -
Table 39. Flash memory programming
Symbol Parameter Conditions Min(1) Typ Max(1) Unit
tprog Word programming time Program/erase parallelism
(PSIZE) = x 8/16/32 - 16 100(2) μs
tERASE16KB Sector (16 KB) erase time
Program/erase parallelism
(PSIZE) = x 8 - 400 800
Program/erase parallelism ms
(PSIZE) = x 16 - 300 600
Program/erase parallelism
(PSIZE) = x 32 - 250 500
DocID022152 Rev 4 105/185
STM32F405xx, STM32F407xx Electrical characteristics
tERASE64KB Sector (64 KB) erase time
Program/erase parallelism
(PSIZE) = x 8 - 1200 2400
Program/erase parallelism ms
(PSIZE) = x 16 - 700 1400
Program/erase parallelism
(PSIZE) = x 32 - 550 1100
tERASE128KB Sector (128 KB) erase time
Program/erase parallelism
(PSIZE) = x 8 - 2 4
Program/erase parallelism s
(PSIZE) = x 16 - 1.3 2.6
Program/erase parallelism
(PSIZE) = x 32 - 1 2
tME Mass erase time
Program/erase parallelism
(PSIZE) = x 8 - 16 32
Program/erase parallelism s
(PSIZE) = x 16 - 11 22
Program/erase parallelism
(PSIZE) = x 32 - 8 16
Vprog Programming voltage
32-bit program operation 2.7 - 3.6 V
16-bit program operation 2.1 - 3.6 V
8-bit program operation 1.8 - 3.6 V
1. Based on characterization, not tested in production.
2. The maximum programming time is measured after 100K erase operations.
Table 39. Flash memory programming (continued)
Symbol Parameter Conditions Min(1) Typ Max(1) Unit
Electrical characteristics STM32F405xx, STM32F407xx
106/185 DocID022152 Rev 4
5.3.13 EMC characteristics
Susceptibility tests are performed on a sample basis during device characterization.
Functional EMS (electromagnetic susceptibility)
While a simple application is executed on the device (toggling 2 LEDs through I/O ports).
the device is stressed by two electromagnetic events until a failure occurs. The failure is
indicated by the LEDs:
• Electrostatic discharge (ESD) (positive and negative) is applied to all device pins until
a functional disturbance occurs. This test is compliant with the IEC 61000-4-2 standard.
• FTB: A burst of fast transient voltage (positive and negative) is applied to VDD and VSS
through a 100 pF capacitor, until a functional disturbance occurs. This test is compliant
with the IEC 61000-4-4 standard.
Table 40. Flash memory programming with VPP
Symbol Parameter Conditions Min(1) Typ Max(1)
1. Guaranteed by design, not tested in production.
Unit
tprog Double word programming
TA = 0 to +40 °C
VDD = 3.3 V
VPP = 8.5 V
- 16 100(2)
2. The maximum programming time is measured after 100K erase operations.
μs
tERASE16KB Sector (16 KB) erase time - 230 -
tERASE64KB Sector (64 KB) erase time - 490 - ms
tERASE128KB Sector (128 KB) erase time - 875 -
tME Mass erase time - 6.9 - s
Vprog Programming voltage 2.7 - 3.6 V
VPP VPP voltage range 7 - 9 V
IPP
Minimum current sunk on
the VPP pin 10 - - mA
tVPP
(3)
3. VPP should only be connected during programming/erasing.
Cumulative time during
which VPP is applied - - 1 hour
Table 41. Flash memory endurance and data retention
Symbol Parameter Conditions
Value
Unit
Min(1)
1. Based on characterization, not tested in production.
NEND Endurance
TA = –40 to +85 °C (6 suffix versions)
TA = –40 to +105 °C (7 suffix versions) 10 kcycles
tRET Data retention
1 kcycle(2) at TA = 85 °C
2. Cycling performed over the whole temperature range.
30
1 kcycle(2) at TA = 105 °C 10 Years
10 kcycles(2) at TA = 55 °C 20
DocID022152 Rev 4 107/185
STM32F405xx, STM32F407xx Electrical characteristics
A device reset allows normal operations to be resumed.
The test results are given in Table 42. They are based on the EMS levels and classes
defined in application note AN1709.
Designing hardened software to avoid noise problems
EMC characterization and optimization are performed at component level with a typical
application environment and simplified MCU software. It should be noted that good EMC
performance is highly dependent on the user application and the software in particular.
Therefore it is recommended that the user applies EMC software optimization and
prequalification tests in relation with the EMC level requested for his application.
Software recommendations
The software flowchart must include the management of runaway conditions such as:
• Corrupted program counter
• Unexpected reset
• Critical Data corruption (control registers...)
Prequalification trials
Most of the common failures (unexpected reset and program counter corruption) can be
reproduced by manually forcing a low state on the NRST pin or the Oscillator pins for 1
second.
To complete these trials, ESD stress can be applied directly on the device, over the range of
specification values. When unexpected behavior is detected, the software can be hardened
to prevent unrecoverable errors occurring (see application note AN1015).
Electromagnetic Interference (EMI)
The electromagnetic field emitted by the device are monitored while a simple application,
executing EEMBC? code, is running. This emission test is compliant with SAE IEC61967-2
standard which specifies the test board and the pin loading.
Table 42. EMS characteristics
Symbol Parameter Conditions Level/
Class
VFESD
Voltage limits to be applied on any I/O pin to
induce a functional disturbance
VDD = 3.3 V, LQFP176, TA = +25 °C,
fHCLK = 168 MHz, conforms to
IEC 61000-4-2
2B
VEFTB
Fast transient voltage burst limits to be
applied through 100 pF on VDD and VSS
pins to induce a functional disturbance
VDD = 3.3 V, LQFP176, TA =
+25 °C, fHCLK = 168 MHz, conforms
to IEC 61000-4-2
4A
Electrical characteristics STM32F405xx, STM32F407xx
108/185 DocID022152 Rev 4
5.3.14 Absolute maximum ratings (electrical sensitivity)
Based on three different tests (ESD, LU) using specific measurement methods, the device is
stressed in order to determine its performance in terms of electrical sensitivity.
Electrostatic discharge (ESD)
Electrostatic discharges (a positive then a negative pulse separated by 1 second) are
applied to the pins of each sample according to each pin combination. The sample size
depends on the number of supply pins in the device (3 parts × (n+1) supply pins). This test
conforms to the JESD22-A114/C101 standard.
Static latchup
Two complementary static tests are required on six parts to assess the latchup
performance:
• A supply overvoltage is applied to each power supply pin
• A current injection is applied to each input, output and configurable I/O pin
These tests are compliant with EIA/JESD 78A IC latchup standard.
Table 43. EMI characteristics
Symbol Parameter Conditions Monitored
frequency band
Max vs.
[fHSE/fCPU] Unit
25/168 MHz
SEMI Peak level
VDD = 3.3 V, TA = 25 °C, LQFP176
package, conforming to SAE J1752/3
EEMBC, code running from Flash with
ART accelerator enabled
0.1 to 30 MHz 32
30 to 130 MHz 25 dBμV
130 MHz to 1GHz 29
SAE EMI Level 4 -
VDD = 3.3 V, TA = 25 °C, LQFP176
package, conforming to SAE J1752/3
EEMBC, code running from Flash with
ART accelerator and PLL spread
spectrum enabled
0.1 to 30 MHz 19
30 to 130 MHz 16 dBμV
130 MHz to 1GHz 18
SAE EMI level 3.5 -
Table 44. ESD absolute maximum ratings
Symbol Ratings Conditions Class Maximum
value(1) Unit
VESD(HBM)
Electrostatic discharge
voltage (human body
model)
TA = +25 °C conforming to JESD22-A114 2 2000(2)
V
VESD(CDM)
Electrostatic discharge
voltage (charge device
model)
TA = +25 °C conforming to JESD22-C101 II 500
1. Based on characterization results, not tested in production.
2. On VBAT pin, VESD(HBM) is limited to 1000 V.
DocID022152 Rev 4 109/185
STM32F405xx, STM32F407xx Electrical characteristics
5.3.15 I/O current injection characteristics
As a general rule, current injection to the I/O pins, due to external voltage below VSS or
above VDD (for standard, 3 V-capable I/O pins) should be avoided during normal product
operation. However, in order to give an indication of the robustness of the microcontroller in
cases when abnormal injection accidentally happens, susceptibility tests are performed on a
sample basis during device characterization.
Functional susceptibilty to I/O current injection
While a simple application is executed on the device, the device is stressed by injecting
current into the I/O pins programmed in floating input mode. While current is injected into
the I/O pin, one at a time, the device is checked for functional failures.
The failure is indicated by an out of range parameter: ADC error above a certain limit (>5
LSB TUE), out of conventional limits of induced leakage current on adjacent pins (out of
5 uA/+0 uA range), or other functional failure (for example reset, oscillator frequency
deviation).
Negative induced leakage current is caused by negative injection and positive induced
leakage current by positive injection.
The test results are given in Table 46.
5.3.16 I/O port characteristics
General input/output characteristics
Unless otherwise specified, the parameters given in Table 47 are derived from tests
performed under the conditions summarized in Table 14. All I/Os are CMOS and TTL
compliant.
Table 45. Electrical sensitivities
Symbol Parameter Conditions Class
LU Static latch-up class TA = +105 °C conforming to JESD78A II level A
Table 46. I/O current injection susceptibility
Symbol Description
Functional susceptibility
Negative Unit
injection
Positive
injection
IINJ
(1)
1. It is recommended to add a Schottky diode (pin to ground) to analog pins which may potentially inject
negative currents.
Injected current on all FT pins –5 +0
mA
Injected current on any other pin –5 +5
Electrical characteristics STM32F405xx, STM32F407xx
110/185 DocID022152 Rev 4
All I/Os are CMOS and TTL compliant (no software configuration required). Their
characteristics cover more than the strict CMOS-technology or TTL parameters.
Output driving current
The GPIOs (general purpose input/outputs) can sink or source up to ±8 mA, and sink or
source up to ±20 mA (with a relaxed VOL/VOH) except PC13, PC14 and PC15 which can
sink or source up to ±3mA. When using the PC13 to PC15 GPIOs in output mode, the
speed should not exceed 2 MHz with a maximum load of 30 pF.
Table 47. I/O static characteristics
Symbol Parameter Conditions Min Typ Max Unit
VIL Input low level voltage TTL ports
2.7 V ≤ VDD ≤ 3.6 V
- - 0.8
V
VIH
(1) Input high level voltage 2.0 - -
VIL Input low level voltage
CMOS ports
1.8 V ≤ VDD ≤ 3.6 V
- - 0.3VDD
VIH
(1) Input high level voltage 0.7VDD
- -
- -
Vhys
I/O Schmitt trigger voltage hysteresis(2) - 200 -
IO FT Schmitt trigger voltage mV
hysteresis(2) 5% VDD
(3) - -
Ilkg
I/O input leakage current (4) VSS ≤ VIN ≤ VDD - - ±1
μA
I/O FT input leakage current (4) VIN = 5 V - - 3
RPU
Weak pull-up equivalent
resistor(5)
All pins
except for
PA10 and
PB12 VIN = VSS
30 40 50
kΩ
PA10 and
PB12 8 11 15
RPD
Weak pull-down
equivalent resistor
All pins
except for
PA10 and
PB12 VIN = VDD
30 40 50
PA10 and
PB12 8 11 15
CIO
(6) I/O pin capacitance 5 pF
1. Tested in production.
2. Hysteresis voltage between Schmitt trigger switching levels. Based on characterization, not tested in production.
3. With a minimum of 100 mV.
4. Leakage could be higher than the maximum value, if negative current is injected on adjacent pins.
5. Pull-up and pull-down resistors are designed with a true resistance in series with a switchable PMOS/NMOS. This
MOS/NMOS contribution to the series resistance is minimum (~10% order).
6. Guaranteed by design, not tested in production.
DocID022152 Rev 4 111/185
STM32F405xx, STM32F407xx Electrical characteristics
In the user application, the number of I/O pins which can drive current must be limited to
respect the absolute maximum rating specified in Section 5.2. In particular:
• The sum of the currents sourced by all the I/Os on VDD, plus the maximum Run
consumption of the MCU sourced on VDD, cannot exceed the absolute maximum rating
IVDD (see Table 12).
• The sum of the currents sunk by all the I/Os on VSS plus the maximum Run
consumption of the MCU sunk on VSS cannot exceed the absolute maximum rating
IVSS (see Table 12).
Output voltage levels
Unless otherwise specified, the parameters given in Table 48 are derived from tests
performed under ambient temperature and VDD supply voltage conditions summarized in
Table 14. All I/Os are CMOS and TTL compliant.
Input/output AC characteristics
The definition and values of input/output AC characteristics are given in Figure 37 and
Table 49, respectively.
Table 48. Output voltage characteristics(1)
1. PC13, PC14, PC15 and PI8 are supplied through the power switch. Since the switch only sinks a limited
amount of current (3 mA), the use of GPIOs PC13 to PC15 and PI8 in output mode is limited: the speed
should not exceed 2 MHz with a maximum load of 30 pF and these I/Os must not be used as a current
source (e.g. to drive an LED).
Symbol Parameter Conditions Min Max Unit
VOL
(2)
2. The IIO current sunk by the device must always respect the absolute maximum rating specified in Table 12
and the sum of IIO (I/O ports and control pins) must not exceed IVSS.
Output low level voltage for an I/O pin
when 8 pins are sunk at same time CMOS port
IIO = +8 mA
2.7 V < VDD < 3.6 V
- 0.4
V
VOH
(3)
3. The IIO current sourced by the device must always respect the absolute maximum rating specified in
Table 12 and the sum of IIO (I/O ports and control pins) must not exceed IVDD.
Output high level voltage for an I/O pin
when 8 pins are sourced at same time VDD–0.4 -
VOL
(2) Output low level voltage for an I/O pin
when 8 pins are sunk at same time TTL port
IIO =+ 8mA
2.7 V < VDD < 3.6 V
- 0.4
V
VOH
(3) Output high level voltage for an I/O pin
when 8 pins are sourced at same time 2.4 -
VOL
(2)(4)
4. Based on characterization data, not tested in production.
Output low level voltage for an I/O pin
when 8 pins are sunk at same time IIO = +20 mA
2.7 V < VDD < 3.6 V
- 1.3
V
VOH
(3)(4) Output high level voltage for an I/O pin
when 8 pins are sourced at same time VDD–1.3 -
VOL
(2)(4) Output low level voltage for an I/O pin
when 8 pins are sunk at same time IIO = +6 mA
2 V < VDD < 2.7 V
- 0.4
V
VOH
(3)(4) Output high level voltage for an I/O pin
when 8 pins are sourced at same time VDD–0.4 -
Electrical characteristics STM32F405xx, STM32F407xx
112/185 DocID022152 Rev 4
Unless otherwise specified, the parameters given in Table 49 are derived from tests
performed under the ambient temperature and VDD supply voltage conditions summarized
in Table 14.
Table 49. I/O AC characteristics(1)(2)(3)
OSPEEDRy
[1:0] bit
value(1)
Symbol Parameter Conditions Min Typ Max Unit
00
fmax(IO)out Maximum frequency(4)
CL = 50 pF, VDD > 2.70 V - - 2
MHz
CL = 50 pF, VDD > 1.8 V - - 2
CL = 10 pF, VDD > 2.70 V - - TBD
CL = 10 pF, VDD > 1.8 V - - TBD
tf(IO)out
Output high to low level fall
time CL = 50 pF, VDD = 1.8 V to
3.6 V
- - TBD
ns
tr(IO)out
Output low to high level rise
time - - TBD
01
fmax(IO)out Maximum frequency(4)
CL = 50 pF, VDD > 2.70 V - - 25
MHz
CL = 50 pF, VDD > 1.8 V - - 12.5(5)
CL = 10 pF, VDD > 2.70 V - - 50(5)
CL = 10 pF, VDD > 1.8 V - - TBD
tf(IO)out
Output high to low level fall
time
CL = 50 pF, VDD < 2.7 V - - TBD
ns
CL = 10 pF, VDD > 2.7 V - - TBD
tr(IO)out
Output low to high level rise
time
CL = 50 pF, VDD < 2.7 V - - TBD
CL = 10 pF, VDD > 2.7 V - - TBD
10
fmax(IO)out Maximum frequency(4)
CL = 40 pF, VDD > 2.70 V - - 50(5)
MHz
CL = 40 pF, VDD > 1.8 V - - 25
CL = 10 pF, VDD > 2.70 V - - 100(5)
CL = 10 pF, VDD > 1.8 V - - TBD
tf(IO)out
Output high to low level fall
time
CL = 50 pF,
2.4 < VDD < 2.7 V
- - TBD
CL = 10 pF, VDD > 2.7 V - - TBD ns
tr(IO)out
Output low to high level rise
time
CL = 50 pF,
2.4 < VDD < 2.7 V
- - TBD
CL = 10 pF, VDD > 2.7 V - - TBD
DocID022152 Rev 4 113/185
STM32F405xx, STM32F407xx Electrical characteristics
Figure 37. I/O AC characteristics definition
5.3.17 NRST pin characteristics
The NRST pin input driver uses CMOS technology. It is connected to a permanent pull-up
resistor, RPU (see Table 47).
Unless otherwise specified, the parameters given in Table 50 are derived from tests
performed under the ambient temperature and VDD supply voltage conditions summarized
in Table 14.
11
Fmax(IO)ou
t
Maximum frequency(4)
CL = 30 pF, VDD > 2.70 V - - 100(5)
MHz
CL = 30 pF, VDD > 1.8 V - - 50(5)
CL = 10 pF, VDD > 2.70 V - - 200(5)
CL = 10 pF, VDD > 1.8 V - - TBD
tf(IO)out
Output high to low level fall
time
CL = 20 pF,
2.4 < VDD < 2.7 V
- - TBD
ns
CL = 10 pF, VDD > 2.7 V - - TBD
tr(IO)out
Output low to high level rise
time
CL = 20 pF,
2.4 < VDD < 2.7 V
- - TBD
CL = 10 pF, VDD > 2.7 V - - TBD
- tEXTIpw
Pulse width of external
signals detected by the EXTI
controller
10 - - ns
1. Based on characterization data, not tested in production.
2. The I/O speed is configured using the OSPEEDRy[1:0] bits. Refer to the STM32F20/21xxx reference manual for a
description of the GPIOx_SPEEDR GPIO port output speed register.
3. TBD stands for “to be defined”.
4. The maximum frequency is defined in Figure 37.
5. For maximum frequencies above 50 MHz, the compensation cell should be used.
Table 49. I/O AC characteristics(1)(2)(3) (continued)
OSPEEDRy
[1:0] bit
value(1)
Symbol Parameter Conditions Min Typ Max Unit
ai14131
10%
90%
50%
tr(IO)out
OUTPUT
EXTERNAL
ON 50pF
Maximum frequency is achieved if (tr + tf) ≤ 2/3)T and if the duty cycle is (45-55%)
10%
50%
90%
when loaded by 50pF
T
tr(IO)out
Electrical characteristics STM32F405xx, STM32F407xx
114/185 DocID022152 Rev 4
Figure 38. Recommended NRST pin protection
1. The reset network protects the device against parasitic resets.
2. The user must ensure that the level on the NRST pin can go below the VIL(NRST) max level specified in
Table 50. Otherwise the reset is not taken into account by the device.
5.3.18 TIM timer characteristics
The parameters given in Table 51 and Table 52 are guaranteed by design.
Refer to Section 5.3.16: I/O port characteristics for details on the input/output alternate
function characteristics (output compare, input capture, external clock, PWM output).
Table 50. NRST pin characteristics
Symbol Parameter Conditions Min Typ Max Unit
VIL(NRST)
(1)
1. Guaranteed by design, not tested in production.
NRST Input low level voltage TTL ports
2.7 V ≤ VDD
≤ 3.6 V
- - 0.8
V
VIH(NRST)
(1) NRST Input high level voltage 2 - -
VIL(NRST)
(1) NRST Input low level voltage CMOS ports
1.8 V ≤ VDD
≤ 3.6 V
- 0.3VDD
VIH(NRST)
(1) NRST Input high level voltage 0.7VDD -
Vhys(NRST)
NRST Schmitt trigger voltage
hysteresis - 200 - mV
RPU Weak pull-up equivalent resistor(2)
2. The pull-up is designed with a true resistance in series with a switchable PMOS. This PMOS contribution to
the series resistance must be minimum (~10% order).
VIN = VSS 30 40 50 kΩ
VF(NRST)
(1) NRST Input filtered pulse - - 100 ns
VNF(NRST)
(1) NRST Input not filtered pulse VDD > 2.7 V 300 - - ns
TNRST_OUT Generated reset pulse duration Internal
Reset source 20 - - μs
ai14132c
STM32Fxxx
NRST(2) RPU
VDD
Filter
Internal Reset
0.1 μF
External
reset circuit(1)
DocID022152 Rev 4 115/185
STM32F405xx, STM32F407xx Electrical characteristics
Table 51. Characteristics of TIMx connected to the APB1 domain(1)
1. TIMx is used as a general term to refer to the TIM2, TIM3, TIM4, TIM5, TIM6, TIM7, and TIM12 timers.
Symbol Parameter Conditions Min Max Unit
tres(TIM) Timer resolution time
AHB/APB1
prescaler distinct
from 1, fTIMxCLK =
84 MHz
1 - tTIMxCLK
11.9 - ns
AHB/APB1
prescaler = 1,
fTIMxCLK = 42 MHz
1 - tTIMxCLK
23.8 - ns
fEXT
Timer external clock
frequency on CH1 to CH4
fTIMxCLK = 84 MHz
APB1= 42 MHz
0 fTIMxCLK/2 MHz
0 42 MHz
ResTIM Timer resolution - 16/32 bit
tCOUNTER
16-bit counter clock
period when internal clock
is selected
1 65536 tTIMxCLK
0.0119 780 μs
32-bit counter clock
period when internal clock
is selected
1 - tTIMxCLK
0.0119 51130563 μs
tMAX_COUNT Maximum possible count
- 65536 × 65536 tTIMxCLK
- 51.1 s
Electrical characteristics STM32F405xx, STM32F407xx
116/185 DocID022152 Rev 4
5.3.19 Communications interfaces
I2C interface characteristics
The STM32F405xx and STM32F407xx I2C interface meets the requirements of the
standard I2C communication protocol with the following restrictions: the I/O pins SDA and
SCL are mapped to are not “true” open-drain. When configured as open-drain, the PMOS
connected between the I/O pin and VDD is disabled, but is still present.
The I2C characteristics are described in Table 53. Refer also to Section 5.3.16: I/O port
characteristics for more details on the input/output alternate function characteristics (SDA
and SCL).
Table 52. Characteristics of TIMx connected to the APB2 domain(1)
1. TIMx is used as a general term to refer to the TIM1, TIM8, TIM9, TIM10, and TIM11 timers.
Symbol Parameter Conditions Min Max Unit
tres(TIM) Timer resolution time
AHB/APB2
prescaler distinct
from 1, fTIMxCLK =
168 MHz
1 - tTIMxCLK
5.95 - ns
AHB/APB2
prescaler = 1,
fTIMxCLK = 84 MHz
1 - tTIMxCLK
11.9 - ns
fEXT
Timer external clock
frequency on CH1 to
CH4
fTIMxCLK =
168 MHz
APB2 = 84 MHz
0 fTIMxCLK/2 MHz
0 84 MHz
ResTIM Timer resolution - 16 bit
tCOUNTER
16-bit counter clock
period when internal
clock is selected
1 65536 tTIMxCLK
tMAX_COUNT Maximum possible count - 32768 tTIMxCLK
Table 53. I2C characteristics
Symbol Parameter
Standard mode I2C(1) Fast mode I2C(1)(2)
Unit
Min Max Min Max
tw(SCLL) SCL clock low time 4.7 - 1.3 -
μs
tw(SCLH) SCL clock high time 4.0 - 0.6 -
tsu(SDA) SDA setup time 250 - 100 -
ns
th(SDA) SDA data hold time 0(3) - 0 900(4)
tr(SDA)
tr(SCL)
SDA and SCL rise time - 1000 20 + 0.1Cb 300
tf(SDA)
tf(SCL)
SDA and SCL fall time - 300 - 300
DocID022152 Rev 4 117/185
STM32F405xx, STM32F407xx Electrical characteristics
Figure 39. I2C bus AC waveforms and measurement circuit
1. Rs= series protection resistor.
2. Rp = external pull-up resistor.
3. VDD_I2C is the I2C bus power supply.
th(STA) Start condition hold time 4.0 - 0.6 -
μs
tsu(STA)
Repeated Start condition
setup time 4.7 - 0.6 -
tsu(STO) Stop condition setup time 4.0 - 0.6 - μs
tw(STO:STA)
Stop to Start condition time
(bus free) 4.7 - 1.3 - μs
Cb
Capacitive load for each bus
line - 400 - 400 pF
1. Guaranteed by design, not tested in production.
2. fPCLK1 must be at least 2 MHz to achieve standard mode I2C frequencies. It must be at least 4 MHz to
achieve fast mode I2C frequencies, and a multiple of 10 MHz to reach the 400 kHz maximum I2C fast mode
clock.
3. The device must internally provide a hold time of at least 300 ns for the SDA signal in order to bridge the
undefined region of the falling edge of SCL.
4. The maximum data hold time has only to be met if the interface does not stretch the low period of SCL
signal.
Table 53. I2C characteristics (continued)
Symbol Parameter
Standard mode I2C(1) Fast mode I2C(1)(2)
Unit
Min Max Min Max
ai14979c
S TAR T
SD A
RP
I²C bus
VDD_I2C
STM32Fxx
SDA
SCL
tf(SDA) tr(SDA)
SCL
th(STA)
tw(SCLH)
tw(SCLL)
tsu(SDA)
tr(SCL) tf(SCL)
th(SDA)
S TAR T REPEATED
t S TAR T su(STA)
tsu(STO)
S TOP tw(STO:STA)
VDD_I2C
RP RS
RS
Electrical characteristics STM32F405xx, STM32F407xx
118/185 DocID022152 Rev 4
SPI interface characteristics
Unless otherwise specified, the parameters given in Table 55 for SPI are derived from tests
performed under the ambient temperature, fPCLKx frequency and VDD supply voltage
conditions summarized in Table 14 with the following configuration:
• Output speed is set to OSPEEDRy[1:0] = 10
• Capacitive load C = 30 pF
• Measurement points are done at CMOS levels: 0.5 VDD
Refer to Section 5.3.16: I/O port characteristics for more details on the input/output alternate
function characteristics (NSS, SCK, MOSI, MISO).
Table 54. SCL frequency (fPCLK1= 42 MHz.,VDD = 3.3 V)(1)(2)
1. RP = External pull-up resistance, fSCL = I2C speed,
2. For speeds around 200 kHz, the tolerance on the achieved speed is of ±5%. For other speed ranges, the
tolerance on the achieved speed ±2%. These variations depend on the accuracy of the external
components used to design the application.
fSCL (kHz)
I2C_CCR value
RP = 4.7 kΩ
400 0x8019
300 0x8021
200 0x8032
100 0x0096
50 0x012C
20 0x02EE
Table 55. SPI dynamic characteristics(1)
Symbol Parameter Conditions Min Typ Max Unit
fSCK
SPI clock frequency
Master mode, SPI1,
2.7V < VDD < 3.6V
- -
42
MHz
Slave mode, SPI1,
2.7V < VDD < 3.6V 42
1/tc(SCK)
Master mode, SPI1/2/3,
1.7V < VDD < 3.6V
- -
21
Slave mode, SPI1/2/3,
1.7V < VDD < 3.6V 21
Duty(SCK) Duty cycle of SPI clock
frequency Slave mode 30 50 70 %
DocID022152 Rev 4 119/185
STM32F405xx, STM32F407xx Electrical characteristics
tw(SCKH)
SCK high and low time
Master mode, SPI presc = 2,
2.7V < VDD < 3.6V TPCLK-0.5 TPCLK TPCLK+0.5
ns
tw(SCKL)
Master mode, SPI presc = 2,
1.7V < VDD < 3.6V TPCLK-2 TPCLK TPCLK+2
tsu(NSS) NSS setup time Slave mode, SPI presc = 2 4 x TPCLK - -
th(NSS) NSS hold time Slave mode, SPI presc = 2 2 x TPCLK
tsu(MI) Data input setup time
Master mode 6.5 - -
tsu(SI) Slave mode 2.5 - -
th(MI) Data input hold time
Master mode 2.5 - -
th(SI) Slave mode 4 - -
ta(SO)
(2) Data output access time Slave mode, SPI presc = 2 0 - 4 x TPCLK
tdis(SO)
(3) Data output disable time
Slave mode, SPI1,
2.7V < VDD < 3.6V 0 - 7.5
Slave mode, SPI1/2/3
1.7V < VDD < 3.6V 0 - 16.5
tv(SO)
th(SO)
Data output valid/hold time
Slave mode (after enable edge),
SPI1, 2.7V < VDD < 3.6V - 11 13
Slave mode (after enable edge),
SPI2/3, 2.7V < VDD < 3.6V - 12 16.5
Slave mode (after enable edge),
SPI1, 1.7V < VDD < 3.6V - 15.5 19
Slave mode (after enable edge),
SPI2/3, 1.7V < VDD < 3.6V - 18 20.5
tv(MO) Data output valid time
Master mode (after enable edge),
SPI1 , 2.7V < VDD < 3.6V - - 2.5
Master mode (after enable edge),
SPI1/2/3 , 1.7V < VDD < 3.6V - - 4.5
th(MO) Data output hold time Master mode (after enable edge) 0 - -
1. Data based on characterization results, not tested in production.
2. Min time is for the minimum time to drive the output and the max time is for the maximum time to validate the data.
3. Min time is for the minimum time to invalidate the output and the max time is for the maximum time to put the data in Hi-Z.
Table 55. SPI dynamic characteristics(1) (continued)
Symbol Parameter Conditions Min Typ Max Unit
Electrical characteristics STM32F405xx, STM32F407xx
120/185 DocID022152 Rev 4
Figure 40. SPI timing diagram - slave mode and CPHA = 0
Figure 41. SPI timing diagram - slave mode and CPHA = 1
ai14134c
SCK Input
CPHA=0
MOSI
INPUT
MISO
OUT PUT
CPHA=0
MSB O UT
MSB IN
BIT6 OUT
LSB IN
LSB OUT
CPOL=0
CPOL=1
BIT1 IN
NSS input
tSU(NSS)
tc(SCK)
th(NSS)
ta(SO)
tw(SCKH)
tw(SCKL)
tv(SO) th(SO) tr(SCK)
tf(SCK)
tdis(SO)
tsu(SI)
th(SI)
ai14135
SCK Input
CPHA=1
MOSI
INPUT
MISO
OUT PUT
CPHA=1
MSB O UT
MSB IN
BIT6 OUT
LSB IN
LSB OUT
CPOL=0
CPOL=1
BIT1 IN
tSU(NSS) tc(SCK) th(NSS)
ta(SO)
tw(SCKH)
tw(SCKL)
tv(SO) th(SO)
tr(SCK)
tf(SCK)
tdis(SO)
tsu(SI) th(SI)
NSS input
DocID022152 Rev 4 121/185
STM32F405xx, STM32F407xx Electrical characteristics
Figure 42. SPI timing diagram - master mode
ai14136
SCK Input
CPHA=0
MOSI
OUTUT
MISO
INPUT
CPHA=0
MSBIN
MSB OUT
BIT6 IN
LSB OUT
LSB IN
CPOL=0
CPOL=1
BIT1 OUT
NSS input
tc(SCK)
tw(SCKH)
tw(SCKL)
tr(SCK)
tf(SCK)
th(MI)
High
SCK Input
CPHA=1
CPHA=1
CPOL=0
CPOL=1
tsu(MI)
tv(MO) th(MO)
Electrical characteristics STM32F405xx, STM32F407xx
122/185 DocID022152 Rev 4
I2S interface characteristics
Unless otherwise specified, the parameters given in Table 56 for the i2S interface are
derived from tests performed under the ambient temperature, fPCLKx frequency and VDD
supply voltage conditions summarized in Table 14, with the following configuration:
• Output speed is set to OSPEEDRy[1:0] = 10
• Capacitive load C = 30 pF
• Measurement points are done at CMOS levels: 0.5 VDD
Refer to Section 5.3.16: I/O port characteristics for more details on the input/output alternate
function characteristics (CK, SD, WS).
Note: Refer to the I2S section of RM0090 reference manual for more details on the sampling
frequency (FS). fMCK, fCK, and DCK values reflect only the digital peripheral behavior. The
value of these parameters might be slightly impacted by the source clock accuracy. DCK
depends mainly on the value of ODD bit. The digital contribution leads to a minimum value
of I2SDIV / (2 x I2SDIV + ODD) and a maximum value of (I2SDIV + ODD) / (2 x I2SDIV +
ODD). FS maximum value is supported for each mode/condition.
Table 56. I2S dynamic characteristics(1)
Symbol Parameter Conditions Min Max Unit
fMCK I2S main clock output - 256 x
8K 256 x FS
(2) MHz
fCK I2S clock frequency
Master data: 32 bits - 64 x FS MHz
Slave data: 32 bits - 64 x FS
DCK I2S clock frequency duty cycle Slave receiver 30 70 %
tv(WS) WS valid time Master mode 0 6
ns
th(WS) WS hold time Master mode 0 -
tsu(WS) WS setup time Slave mode 1 -
th(WS) WS hold time Slave mode 0 -
tsu(SD_MR) Data input setup time
Master receiver 7.5 -
tsu(SD_SR) Slave receiver 2 -
th(SD_MR) Data input hold time
Master receiver 0 -
th(SD_SR) Slave receiver 0 -
tv(SD_ST)
th(SD_ST) Data output valid time
Slave transmitter (after enable edge) - 27
tv(SD_MT) Master transmitter (after enable edge) - 20
th(SD_MT) Data output hold time Master transmitter (after enable edge) 2.5 -
1. Data based on characterization results, not tested in production.
2. The maximum value of 256 x FS is 42 MHz (APB1 maximum frequency).
DocID022152 Rev 4 123/185
STM32F405xx, STM32F407xx Electrical characteristics
Figure 43. I2S slave timing diagram (Philips protocol)
1. LSB transmit/receive of the previously transmitted byte. No LSB transmit/receive is sent before the first
byte.
Figure 44. I2S master timing diagram (Philips protocol)(1)
1. Based on characterization, not tested in production.
2. LSB transmit/receive of the previously transmitted byte. No LSB transmit/receive is sent before the first
byte.
USB OTG FS characteristics
This interface is present in both the USB OTG HS and USB OTG FS controllers. CK Input
CPOL = 0
CPOL = 1
tc(CK)
WS input
SDtransmit
SDreceive
tw(CKH) tw(CKL)
tsu(WS) tv(SD_ST) th(SD_ST)
th(WS)
tsu(SD_SR) th(SD_SR)
MSB receive Bitn receive LSB receive
MSB transmit Bitn transmit LSB transmit
ai14881b
LSB receive(2)
LSB transmit(2)
CK output
CPOL = 0
CPOL = 1
tc(CK)
WS output
SDreceive
SDtransmit
tw(CKH)
tw(CKL)
tsu(SD_MR)
tv(SD_MT) th(SD_MT)
th(WS)
th(SD_MR)
MSB receive Bitn receive LSB receive
MSB transmit Bitn transmit LSB transmit
ai14884b
tf(CK) tr(CK)
tv(WS)
LSB receive(2)
LSB transmit(2)
Electrical characteristics STM32F405xx, STM32F407xx
124/185 DocID022152 Rev 4
Figure 45. USB OTG FS timings: definition of data signal rise and fall time
Table 57. USB OTG FS startup time
Symbol Parameter Max Unit
tSTARTUP
(1)
1. Guaranteed by design, not tested in production.
USB OTG FS transceiver startup time 1 μs
Table 58. USB OTG FS DC electrical characteristics
Symbol Parameter Conditions Min.(1)
1. All the voltages are measured from the local ground potential.
Typ. Max.(1) Unit
Input
levels
VDD
USB OTG FS operating
voltage 3.0(2)
2. The STM32F405xx and STM32F407xx USB OTG FS functionality is ensured down to 2.7 V but not the full
USB OTG FS electrical characteristics which are degraded in the 2.7-to-3.0 V VDD voltage range.
- 3.6 V
VDI
(3)
3. Guaranteed by design, not tested in production.
Differential input sensitivity I(USB_FS_DP/DM,
USB_HS_DP/DM) 0.2 - -
VCM V
(3) Differential common mode
range Includes VDI range 0.8 - 2.5
VSE
(3) Single ended receiver
threshold 1.3 - 2.0
Output
levels
VOL Static output level low RL of 1.5 kΩ to 3.6 V(4)
4. RL is the load connected on the USB OTG FS drivers
- - 0.3
V
VOH Static output level high RL of 15 kΩ to VSS
(4) 2.8 - 3.6
RPD
PA11, PA12, PB14, PB15
(USB_FS_DP/DM,
USB_HS_DP/DM)
VIN = VDD
17 21 24
kΩ
PA9, PB13
(OTG_FS_VBUS,
OTG_HS_VBUS)
0.65 1.1 2.0
RPU
PA12, PB15 (USB_FS_DP,
USB_HS_DP) VIN = VSS 1.5 1.8 2.1
PA9, PB13
(OTG_FS_VBUS,
OTG_HS_VBUS)
VIN = VSS 0.25 0.37 0.55
ai14137
tf
Differen tial
Data L ines
VSS
VCRS
tr
Crossover
points
DocID022152 Rev 4 125/185
STM32F405xx, STM32F407xx Electrical characteristics
USB HS characteristics
Unless otherwise specified, the parameters given in Table 62 for ULPI are derived from
tests performed under the ambient temperature, fHCLK frequency summarized in Table 61
and VDD supply voltage conditions summarized in Table 60, with the following configuration:
• Output speed is set to OSPEEDRy[1:0] = 10
• Capacitive load C = 30 pF
• Measurement points are done at CMOS levels: 0.5VDD.
Refer to Section Section 5.3.16: I/O port characteristics for more details on the
input/outputcharacteristics.
Table 59. USB OTG FS electrical characteristics(1)
1. Guaranteed by design, not tested in production.
Driver characteristics
Symbol Parameter Conditions Min Max Unit
tr Rise time(2)
2. Measured from 10% to 90% of the data signal. For more detailed informations, please refer to USB
Specification - Chapter 7 (version 2.0).
CL = 50 pF 4 20 ns
tf Fall time(2) CL = 50 pF 4 20 ns
trfm Rise/ fall time matching tr/tf 90 110 %
VCRS Output signal crossover voltage 1.3 2.0 V
Table 60. USB HS DC electrical characteristics
Symbol Parameter Min.(1)
1. All the voltages are measured from the local ground potential.
Max.(1) Unit
Input level VDD USB OTG HS operating voltage 2.7 3.6 V
Table 61. USB HS clock timing parameters(1)
Parameter Symbol Min Nominal Max Unit
fHCLK value to guarantee proper operation of
USB HS interface 30 MHz
Frequency (first transition) 8-bit ±10% FSTART_8BIT 54 60 66 MHz
Frequency (steady state) ±500 ppm FSTEADY 59.97 60 60.03 MHz
Duty cycle (first transition) 8-bit ±10% DSTART_8BIT 40 50 60 %
Duty cycle (steady state) ±500 ppm DSTEADY 49.975 50 50.025 %
Time to reach the steady state frequency and
duty cycle after the first transition TSTEADY - - 1.4 ms
Clock startup time after the
de-assertion of SuspendM
Peripheral TSTART_DEV - - 5.6
ms
Host TSTART_HOST - - -
PHY preparation time after the first transition
of the input clock TPREP - - - μs
Electrical characteristics STM32F405xx, STM32F407xx
126/185 DocID022152 Rev 4
Figure 46. ULPI timing diagram
Ethernet characteristics
Unless otherwise specified, the parameters given in Table 64, Table 65 and Table 66 for
SMI, RMII and MII are derived from tests performed under the ambient temperature, fHCLK
frequency summarized in Table 14 and VDD supply voltage conditions summarized in
Table 63, with the following configuration:
• Output speed is set to OSPEEDRy[1:0] = 10
• Capacitive load C = 30 pF
• Measurement points are done at CMOS levels: 0.5VDD.
Refer to Section 5.3.16: I/O port characteristics for more details on the input/output
characteristics.
1. Guaranteed by design, not tested in production.
Table 62. ULPI timing
Parameter Symbol
Value(1)
1. VDD = 2.7 V to 3.6 V and TA = –40 to 85 °C.
Unit
Min. Max.
Control in (ULPI_DIR) setup time
tSC
- 2.0
ns
Control in (ULPI_NXT) setup time - 1.5
Control in (ULPI_DIR, ULPI_NXT) hold time tHC 0 -
Data in setup time tSD - 2.0
Data in hold time tHD 0 -
Control out (ULPI_STP) setup time and hold time tDC - 9.2
Data out available from clock rising edge tDD - 10.7
Clock
Control In
(ULPI_DIR,
ULPI_NXT)
data In
(8-bit)
Control out
(ULPI_STP)
data out
(8-bit)
tDD
tDC
tSD tHD
tSC tHC
ai17361c
tDC
DocID022152 Rev 4 127/185
STM32F405xx, STM32F407xx Electrical characteristics
Table 64 gives the list of Ethernet MAC signals for the SMI (station management interface)
and Figure 47 shows the corresponding timing diagram.
Figure 47. Ethernet SMI timing diagram
Table 65 gives the list of Ethernet MAC signals for the RMII and Figure 48 shows the
corresponding timing diagram.
Figure 48. Ethernet RMII timing diagram
Table 63. Ethernet DC electrical characteristics
Symbol Parameter Min.(1)
1. All the voltages are measured from the local ground potential.
Max.(1) Unit
Input level VDD Ethernet operating voltage 2.7 3.6 V
Table 64. Dynamic characteristics: Ehternet MAC signals for SMI(1)
1. Data based on characterization results, not tested in production.
Symbol Parameter Min Typ Max Unit
tMDC MDC cycle time( 2.38 MHz) 411 420 425
ns
Td(MDIO) Write data valid time 6 10 13
tsu(MDIO) Read data setup time 12 - -
th(MDIO) Read data hold time 0 - -
MS31384V1
ETH_MDC
ETH_MDIO(O)
ETH_MDIO(I)
tMDC
td(MDIO)
tsu(MDIO) th(MDIO)
RMII_REF_CLK
RMII_TX_EN
RMII_TXD[1:0]
RMII_RXD[1:0]
RMII_CRS_DV
td(TXEN)
td(TXD)
tsu(RXD)
tsu(CRS)
tih(RXD)
tih(CRS)
ai15667
Electrical characteristics STM32F405xx, STM32F407xx
128/185 DocID022152 Rev 4
Table 66 gives the list of Ethernet MAC signals for MII and Figure 48 shows the
corresponding timing diagram.
Figure 49. Ethernet MII timing diagram
Table 65. Dynamic characteristics: Ethernet MAC signals for RMII
Symbol Rating Min Typ Max Unit
tsu(RXD) Receive data setup time 2 - - ns
tih(RXD) Receive data hold time 1 - - ns
tsu(CRS) Carrier sense set-up time 0.5 - - ns
tih(CRS) Carrier sense hold time 2 - - ns
td(TXEN) Transmit enable valid delay time 8 9.5 11 ns
td(TXD) Transmit data valid delay time 8.5 10 11.5 ns
Table 66. Dynamic characteristics: Ethernet MAC signals for MII(1)
1. Data based on characterization results, not tested in production.
Symbol Parameter Min Typ Max Unit
tsu(RXD) Receive data setup time 9 -
ns
tih(RXD) Receive data hold time 10 -
tsu(DV) Data valid setup time 9 -
tih(DV) Data valid hold time 8 -
tsu(ER) Error setup time 6 -
tih(ER) Error hold time 8 -
td(TXEN) Transmit enable valid delay time 0 10 14
td(TXD) Transmit data valid delay time 0 10 15
MII_RX_CLK
MII_RXD[3:0]
MII_RX_DV
MII_RX_ER
td(TXEN)
td(TXD)
tsu(RXD)
tsu(ER)
tsu(DV)
tih(RXD)
tih(ER)
tih(DV)
ai15668
MII_TX_CLK
MII_TX_EN
MII_TXD[3:0]
DocID022152 Rev 4 129/185
STM32F405xx, STM32F407xx Electrical characteristics
CAN (controller area network) interface
Refer to Section 5.3.16: I/O port characteristics for more details on the input/output alternate
function characteristics (CANTX and CANRX).
5.3.20 12-bit ADC characteristics
Unless otherwise specified, the parameters given in Table 67 are derived from tests
performed under the ambient temperature, fPCLK2 frequency and VDDA supply voltage
conditions summarized in Table 14.
Table 67. ADC characteristics
Symbol Parameter Conditions Min Typ Max Unit
VDDA Power supply 1.8(1) - 3.6 V
VREF+ Positive reference voltage 1.8(1)(2)(3) - VDDA V
fADC ADC clock frequency
VDDA = 1.8(1)(3) to
2.4 V 0.6 15 18 MHz
VDDA = 2.4 to 3.6 V(3) 0.6 30 36 MHz
fTRIG
(4) External trigger frequency
fADC = 30 MHz,
12-bit resolution - - 1764 kHz
- - 17 1/fADC
VAIN Conversion voltage range(5) 0 (VSSA or VREFtied
to ground) - VREF+ V
RAIN
(4) External input impedance See Equation 1 for
details - - 50 κΩ
RADC
(4)(6) Sampling switch resistance - - 6 κΩ
CADC
(4) Internal sample and hold
capacitor - 4 - pF
tlat
(4) Injection trigger conversion
latency
fADC = 30 MHz - - 0.100 μs
- - 3(7) 1/fADC
tlatr
(4) Regular trigger conversion
latency
fADC = 30 MHz - - 0.067 μs
- - 2(7) 1/fADC
tS
(4) Sampling time
fADC = 30 MHz 0.100 - 16 μs
3 - 480 1/fADC
tSTAB
(4) Power-up time - 2 3 μs
Electrical characteristics STM32F405xx, STM32F407xx
130/185 DocID022152 Rev 4
Equation 1: RAIN max formula
The formula above (Equation 1) is used to determine the maximum external impedance
allowed for an error below 1/4 of LSB. N = 12 (from 12-bit resolution) and k is the number of
sampling periods defined in the ADC_SMPR1 register.
tCONV
(4) Total conversion time (including
sampling time)
fADC = 30 MHz
12-bit resolution
0.50 - 16.40 μs
fADC = 30 MHz
10-bit resolution
0.43 - 16.34 μs
fADC = 30 MHz
8-bit resolution
0.37 - 16.27 μs
fADC = 30 MHz
6-bit resolution
0.30 - 16.20 μs
9 to 492 (tS for sampling +n-bit resolution for successive
approximation) 1/fADC
fS
(4)
Sampling rate
(fADC = 30 MHz, and
tS = 3 ADC cycles)
12-bit resolution
Single ADC
- - 2 Msps
12-bit resolution
Interleave Dual ADC
mode
- - 3.75 Msps
12-bit resolution
Interleave Triple ADC
mode
- - 6 Msps
IVREF+
(4)
ADC VREF DC current
consumption in conversion
mode
- 300 500 μA
IVDDA
(4)
ADC VDDA DC current
consumption in conversion
mode
- 1.6 1.8 mA
1. VDD/VDDA minimum value of 1.7 V is obtained when the device operates in reduced temperature range, and with the use of
an external power supply supervisor (refer to Section : Internal reset OFF).
2. It is recommended to maintain the voltage difference between VREF+ and VDDA below 1.8 V.
3. VDDA -VREF+ < 1.2 V.
4. Based on characterization, not tested in production.
5. VREF+ is internally connected to VDDA and VREF- is internally connected to VSSA.
6. RADC maximum value is given for VDD=1.8 V, and minimum value for VDD=3.3 V.
7. For external triggers, a delay of 1/fPCLK2 must be added to the latency specified in Table 67.
Table 67. ADC characteristics (continued)
Symbol Parameter Conditions Min Typ Max Unit
RAIN
(k – 0.5)
fADC CADC 2N + 2 × × ln( )
= -------------------------------------------------------------- – RADC
DocID022152 Rev 4 131/185
STM32F405xx, STM32F407xx Electrical characteristics
a
Note: ADC accuracy vs. negative injection current: injecting a negative current on any analog
input pins should be avoided as this significantly reduces the accuracy of the conversion
being performed on another analog input. It is recommended to add a Schottky diode (pin to
ground) to analog pins which may potentially inject negative currents.
Any positive injection current within the limits specified for IINJ(PIN) and ΣIINJ(PIN) in
Section 5.3.16 does not affect the ADC accuracy.
Figure 50. ADC accuracy characteristics
1. See also Table 68.
2. Example of an actual transfer curve.
3. Ideal transfer curve.
4. End point correlation line.
5. ET = Total Unadjusted Error: maximum deviation between the actual and the ideal transfer curves.
EO = Offset Error: deviation between the first actual transition and the first ideal one.
Table 68. ADC accuracy at fADC = 30 MHz(1)
1. Better performance could be achieved in restricted VDD, frequency and temperature ranges.
Symbol Parameter Test conditions Typ Max(2)
2. Based on characterization, not tested in production.
Unit
ET Total unadjusted error
fPCLK2 = 60 MHz,
fADC = 30 MHz, RAIN < 10 kΩ,
VDDA = 1.8(3) to 3.6 V
3. VDD/VDDA minimum value of 1.7 V is obtained when the device operates in reduced temperature range,
and with the use of an external power supply supervisor (refer to Section : Internal reset OFF).
±2 ±5
LSB
EO Offset error ±1.5 ±2.5
EG Gain error ±1.5 ±3
ED Differential linearity error ±1 ±2
EL Integral linearity error ±1.5 ±3
ai14395c
EO
EG
1L SBIDEAL
4095
4094
4093
5
4
3
2
1
0
7
6
1 2 3 456 7 4093 4094 4095 4096
(1)
(2)
ET
ED
EL
(3)
VSSA VDDA
VREF+
4096
(or depending on package)]
VDDA
4096
[1LSB IDEAL =
Electrical characteristics STM32F405xx, STM32F407xx
132/185 DocID022152 Rev 4
EG = Gain Error: deviation between the last ideal transition and the last actual one.
ED = Differential Linearity Error: maximum deviation between actual steps and the ideal one.
EL = Integral Linearity Error: maximum deviation between any actual transition and the end point
correlation line.
Figure 51. Typical connection diagram using the ADC
1. Refer to Table 67 for the values of RAIN, RADC and CADC.
2. Cparasitic represents the capacitance of the PCB (dependent on soldering and PCB layout quality) plus the
pad capacitance (roughly 5 pF). A high Cparasitic value downgrades conversion accuracy. To remedy this,
fADC should be reduced.
ai17534
VDD STM32F
AINx
IL±1 μA
0.6 V
VT
RAIN
(1)
Cparasitic
VAIN
0.6 V
VT
RADC
(1)
CADC(1)
12-bit
converter
Sample and hold ADC
converter
DocID022152 Rev 4 133/185
STM32F405xx, STM32F407xx Electrical characteristics
General PCB design guidelines
Power supply decoupling should be performed as shown in Figure 52 or Figure 53,
depending on whether VREF+ is connected to VDDA or not. The 10 nF capacitors should be
ceramic (good quality). They should be placed them as close as possible to the chip.
Figure 52. Power supply and reference decoupling (VREF+ not connected to VDDA)
1. VREF+ and VREF– inputs are both available on UFBGA176. VREF+ is also available on LQFP100, LQFP144,
and LQFP176. When VREF+ and VREF– are not available, they are internally connected to VDDA and VSSA.
Figure 53. Power supply and reference decoupling (VREF+ connected to VDDA)
1. VREF+ and VREF– inputs are both available on UFBGA176. VREF+ is also available on LQFP100, LQFP144,
and LQFP176. When VREF+ and VREF– are not available, they are internally connected to VDDA and VSSA.
VREF+
STM32F
VDDA
VSSA/V REF-
1 μF // 10 nF
1 μF // 10 nF
ai17535
(See note 1)
(See note 1)
VREF+/VDDA
STM32F
1 μF // 10 nF
VREF–/VSSA
ai17536
(See note 1)
(See note 1)
Electrical characteristics STM32F405xx, STM32F407xx
134/185 DocID022152 Rev 4
5.3.21 Temperature sensor characteristics
5.3.22 VBAT monitoring characteristics
Table 69. Temperature sensor characteristics
Symbol Parameter Min Typ Max Unit
TL
(1) VSENSE linearity with temperature - ±1 ±2 °C
Avg_Slope(1) Average slope - 2.5 mV/°C
V25
(1) Voltage at 25 °C - 0.76 V
tSTART
(2) Startup time - 6 10 μs
TS_temp
(3)(2) ADC sampling time when reading the temperature (1 °C accuracy) 10 - - μs
1. Based on characterization, not tested in production.
2. Guaranteed by design, not tested in production.
3. Shortest sampling time can be determined in the application by multiple iterations.
Table 70. Temperature sensor calibration values
Symbol Parameter Memory address
TS_CAL1 TS ADC raw data acquired at temperature of 30 °C, VDDA=3.3 V 0x1FFF 7A2C - 0x1FFF 7A2D
TS_CAL2 TS ADC raw data acquired at temperature of 110 °C, VDDA=3.3 V 0x1FFF 7A2E - 0x1FFF 7A2F
Table 71. VBAT monitoring characteristics
Symbol Parameter Min Typ Max Unit
R Resistor bridge for VBAT - 50 - KΩ
Q Ratio on VBAT measurement - 2 -
Er(1) Error on Q –1 - +1 %
TS_vbat
(2)(2) ADC sampling time when reading the VBAT
1 mV accuracy 5 - - μs
1. Guaranteed by design, not tested in production.
2. Shortest sampling time can be determined in the application by multiple iterations.
DocID022152 Rev 4 135/185
STM32F405xx, STM32F407xx Electrical characteristics
5.3.23 Embedded reference voltage
The parameters given in Table 72 are derived from tests performed under ambient
temperature and VDD supply voltage conditions summarized in Table 14.
5.3.24 DAC electrical characteristics
Table 72. Embedded internal reference voltage
Symbol Parameter Conditions Min Typ Max Unit
VREFINT Internal reference voltage –40 °C < TA < +105 °C 1.18 1.21 1.24 V
TS_vrefint
(1) ADC sampling time when reading the
internal reference voltage 10 - - μs
VRERINT_s
(2) Internal reference voltage spread over the
temperature range VDD = 3 V - 3 5 mV
TCoeff
(2) Temperature coefficient - 30 50 ppm/°C
tSTART
(2) Startup time - 6 10 μs
1. Shortest sampling time can be determined in the application by multiple iterations.
2. Guaranteed by design, not tested in production.
Table 73. Internal reference voltage calibration values
Symbol Parameter Memory address
VREFIN_CAL Raw data acquired at temperature of 30 °C, VDDA=3.3 V 0x1FFF 7A2A - 0x1FFF 7A2B
Table 74. DAC characteristics
Symbol Parameter Min Typ Max Unit Comments
VDDA Analog supply voltage 1.8(1) - 3.6 V
VREF+ Reference supply voltage 1.8(1) - 3.6 V VREF+ ≤ VDDA
VSSA Ground 0 - 0 V
RLOAD
(2) Resistive load with buffer
ON 5 - - kΩ
RO
(2) Impedance output with
buffer OFF - - 15 kΩ
When the buffer is OFF, the
Minimum resistive load between
DAC_OUT and VSS to have a 1%
accuracy is 1.5 MΩ
CLOAD
(2) Capacitive load - - 50 pF
Maximum capacitive load at
DAC_OUT pin (when the buffer is
ON).
DAC_OUT
min(2)
Lower DAC_OUT voltage
with buffer ON 0.2 - - V
It gives the maximum output
excursion of the DAC.
It corresponds to 12-bit input code
(0x0E0) to (0xF1C) at VREF+ =
3.6 V and (0x1C7) to (0xE38) at
VREF+ = 1.8 V
DAC_OUT
max(2)
Higher DAC_OUT voltage
with buffer ON - - VDDA – 0.2 V
Electrical characteristics STM32F405xx, STM32F407xx
136/185 DocID022152 Rev 4
DAC_OUT
min(2)
Lower DAC_OUT voltage
with buffer OFF - 0.5 - mV
It gives the maximum output
DAC_OUT excursion of the DAC.
max(2)
Higher DAC_OUT voltage
with buffer OFF - - VREF+ – 1LSB V
IVREF+
(4)
DAC DC VREF current
consumption in quiescent
mode (Standby mode)
- 170 240
μA
With no load, worst code (0x800)
at VREF+ = 3.6 V in terms of DC
consumption on the inputs
- 50 75
With no load, worst code (0xF1C)
at VREF+ = 3.6 V in terms of DC
consumption on the inputs
IDDA
(4)
DAC DC VDDA current
consumption in quiescent
mode(3)
- 280 380 μA With no load, middle code (0x800)
on the inputs
- 475 625 μA
With no load, worst code (0xF1C)
at VREF+ = 3.6 V in terms of DC
consumption on the inputs
DNL(4)
Differential non linearity
Difference between two
consecutive code-1LSB)
- - ±0.5 LSB Given for the DAC in 10-bit
configuration.
- - ±2 LSB Given for the DAC in 12-bit
configuration.
INL(4)
Integral non linearity
(difference between
measured value at Code i
and the value at Code i on a
line drawn between Code 0
and last Code 1023)
- - ±1 LSB Given for the DAC in 10-bit
configuration.
- - ±4 LSB Given for the DAC in 12-bit
configuration.
Offset(4)
Offset error
(difference between
measured value at Code
(0x800) and the ideal value
= VREF+/2)
- - ±10 mV Given for the DAC in 12-bit
configuration
- - ±3 LSB Given for the DAC in 10-bit at
VREF+ = 3.6 V
- - ±12 LSB Given for the DAC in 12-bit at
VREF+ = 3.6 V
Gain
error(4) Gain error - - ±0.5 % Given for the DAC in 12-bit
configuration
tSETTLING
(4)
Settling time (full scale: for a
10-bit input code transition
between the lowest and the
highest input codes when
DAC_OUT reaches final
value ±4LSB
- 3 6 μs CLOAD ≤ 50 pF,
RLOAD ≥ 5 kΩ
THD(4) Total Harmonic Distortion
Buffer ON
- - - dB CLOAD ≤ 50 pF,
RLOAD ≥ 5 kΩ
Table 74. DAC characteristics (continued)
Symbol Parameter Min Typ Max Unit Comments
DocID022152 Rev 4 137/185
STM32F405xx, STM32F407xx Electrical characteristics
Figure 54. 12-bit buffered /non-buffered DAC
1. The DAC integrates an output buffer that can be used to reduce the output impedance and to drive external
loads directly without the use of an external operational amplifier. The buffer can be bypassed by
configuring the BOFFx bit in the DAC_CR register.
5.3.25 FSMC characteristics
Unless otherwise specified, the parameters given in Table 75 to Table 86 for the FSMC
interface are derived from tests performed under the ambient temperature, fHCLK frequency
and VDD supply voltage conditions summarized in Table 14, with the following configuration:
• Output speed is set to OSPEEDRy[1:0] = 10
• Capacitive load C = 30 pF
• Measurement points are done at CMOS levels: 0.5VDD
Refer to Section Section 5.3.16: I/O port characteristics for more details on the input/output
characteristics.
Update
rate(2)
Max frequency for a correct
DAC_OUT change when
small variation in the input
code (from code i to i+1LSB)
- - 1 MS/s CLOAD ≤ 50 pF,
RLOAD ≥ 5 kΩ
tWAKEUP
(4)
Wakeup time from off state
(Setting the ENx bit in the
DAC Control register)
- 6.5 10 μs
CLOAD ≤ 50 pF, RLOAD ≥ 5 kΩ
input code between lowest and
highest possible ones.
PSRR+ (2)
Power supply rejection ratio
(to VDDA) (static DC
measurement)
- –67 –40 dB No RLOAD, CLOAD = 50 pF
1. VDD/VDDA minimum value of 1.7 V is obtained when the device operates in reduced temperature range, and with the use of
an external power supply supervisor (refer to Section : Internal reset OFF).
2. Guaranteed by design, not tested in production.
3. The quiescent mode corresponds to a state where the DAC maintains a stable output level to ensure that no dynamic
consumption occurs.
4. Guaranteed by characterization, not tested in production.
Table 74. DAC characteristics (continued)
Symbol Parameter Min Typ Max Unit Comments
RLOAD
CLOAD
Buffered/Non-buffered DAC
DACx_OUT
Buffer(1)
12-bit
digital to
analog
converter
ai17157
Electrical characteristics STM32F405xx, STM32F407xx
138/185 DocID022152 Rev 4
Asynchronous waveforms and timings
Figure 55 through Figure 58 represent asynchronous waveforms and Table 75 through
Table 78 provide the corresponding timings. The results shown in these tables are obtained
with the following FSMC configuration:
• AddressSetupTime = 1
• AddressHoldTime = 0x1
• DataSetupTime = 0x1
• BusTurnAroundDuration = 0x0
In all timing tables, the THCLK is the HCLK clock period.
Figure 55. Asynchronous non-multiplexed SRAM/PSRAM/NOR read waveforms
1. Mode 2/B, C and D only. In Mode 1, FSMC_NADV is not used.
Table 75. Asynchronous non-multiplexed SRAM/PSRAM/NOR read timings(1)(2)
Symbol Parameter Min Max Unit
tw(NE) FSMC_NE low time 2THCLK–0.5 2 THCLK+1 ns
tv(NOE_NE) FSMC_NEx low to FSMC_NOE low 0.5 3 ns
tw(NOE) FSMC_NOE low time 2THCLK–2 2THCLK+ 2 ns
th(NE_NOE) FSMC_NOE high to FSMC_NE high hold time 0 - ns
tv(A_NE) FSMC_NEx low to FSMC_A valid - 4.5 ns
th(A_NOE) Address hold time after FSMC_NOE high 4 - ns
Data
FSMC_NE
FSMC_NBL[1:0]
FSMC_D[15:0]
tv(BL_NE)
t h(Data_NE)
FSMC_NOE
FSMC_A[25:0] Address
tv(A_NE)
FSMC_NWE
tsu(Data_NE)
tw(NE)
ai14991c
tv(NOE_NE) t w(NOE) t h(NE_NOE)
th(Data_NOE)
t h(A_NOE)
t h(BL_NOE)
tsu(Data_NOE)
FSMC_NADV(1)
t v(NADV_NE)
tw(NADV)
DocID022152 Rev 4 139/185
STM32F405xx, STM32F407xx Electrical characteristics
Figure 56. Asynchronous non-multiplexed SRAM/PSRAM/NOR write waveforms
1. Mode 2/B, C and D only. In Mode 1, FSMC_NADV is not used.
tv(BL_NE) FSMC_NEx low to FSMC_BL valid - 1.5 ns
th(BL_NOE) FSMC_BL hold time after FSMC_NOE high 0 - ns
tsu(Data_NE) Data to FSMC_NEx high setup time THCLK+4 - ns
tsu(Data_NOE) Data to FSMC_NOEx high setup time THCLK+4 - ns
th(Data_NOE) Data hold time after FSMC_NOE high 0 - ns
th(Data_NE) Data hold time after FSMC_NEx high 0 - ns
tv(NADV_NE) FSMC_NEx low to FSMC_NADV low - 2 ns
tw(NADV) FSMC_NADV low time - THCLK ns
1. CL = 30 pF.
2. Based on characterization, not tested in production.
Table 76. Asynchronous non-multiplexed SRAM/PSRAM/NOR write timings(1)(2)
Symbol Parameter Min Max Unit
tw(NE) FSMC_NE low time 3THCLK 3THCLK+ 4 ns
tv(NWE_NE) FSMC_NEx low to FSMC_NWE low THCLK–0.5 THCLK+0.5 ns
tw(NWE) FSMC_NWE low time THCLK–1 THCLK+2 ns
th(NE_NWE) FSMC_NWE high to FSMC_NE high hold time THCLK–1 - ns
tv(A_NE) FSMC_NEx low to FSMC_A valid - 0 ns
Table 75. Asynchronous non-multiplexed SRAM/PSRAM/NOR read timings(1)(2)
NBL
Data
FSMC_NEx
FSMC_NBL[1:0]
FSMC_D[15:0]
tv(BL_NE)
th(Data_NWE)
FSMC_NOE
FSMC_A[25:0] Address
tv(A_NE)
tw(NWE)
FSMC_NWE
tv(NWE_NE) t h(NE_NWE)
th(A_NWE)
th(BL_NWE)
tv(Data_NE)
tw(NE)
ai14990
FSMC_NADV(1)
t v(NADV_NE)
tw(NADV)
Electrical characteristics STM32F405xx, STM32F407xx
140/185 DocID022152 Rev 4
Figure 57. Asynchronous multiplexed PSRAM/NOR read waveforms
th(A_NWE) Address hold time after FSMC_NWE high THCLK– 2 - ns
tv(BL_NE) FSMC_NEx low to FSMC_BL valid - 1.5 ns
th(BL_NWE) FSMC_BL hold time after FSMC_NWE high THCLK– 1 - ns
tv(Data_NE) Data to FSMC_NEx low to Data valid - THCLK+3 ns
th(Data_NWE) Data hold time after FSMC_NWE high THCLK–1 - ns
tv(NADV_NE) FSMC_NEx low to FSMC_NADV low - 2 ns
tw(NADV) FSMC_NADV low time - THCLK+0.5 ns
1. CL = 30 pF.
2. Based on characterization, not tested in production.
Table 77. Asynchronous multiplexed PSRAM/NOR read timings(1)(2)
Symbol Parameter Min Max Unit
tw(NE) FSMC_NE low time 3THCLK–1 3THCLK+1 ns
tv(NOE_NE) FSMC_NEx low to FSMC_NOE low 2THCLK–0.5 2THCLK+0.5 ns
tw(NOE) FSMC_NOE low time THCLK–1 THCLK+1 ns
th(NE_NOE) FSMC_NOE high to FSMC_NE high hold time 0 - ns
tv(A_NE) FSMC_NEx low to FSMC_A valid - 3 ns
Table 76. Asynchronous non-multiplexed SRAM/PSRAM/NOR write timings(1)(2)
NBL
Data
FSMC_NBL[1:0]
FSMC_AD[15:0]
tv(BL_NE)
th(Data_NE)
FSMC_A[25:16] Address
tv(A_NE)
FSMC_NWE
t v(A_NE)
ai14892b
Address
FSMC_NADV
t v(NADV_NE)
tw(NADV)
tsu(Data_NE)
th(AD_NADV)
FSMC_NE
FSMC_NOE
tw(NE)
t w(NOE)
tv(NOE_NE) t h(NE_NOE)
th(A_NOE)
th(BL_NOE)
tsu(Data_NOE) th(Data_NOE)
DocID022152 Rev 4 141/185
STM32F405xx, STM32F407xx Electrical characteristics
Figure 58. Asynchronous multiplexed PSRAM/NOR write waveforms
tv(NADV_NE) FSMC_NEx low to FSMC_NADV low 1 2 ns
tw(NADV) FSMC_NADV low time THCLK– 2 THCLK+1 ns
th(AD_NADV)
FSMC_AD(adress) valid hold time after
FSMC_NADV high) THCLK - ns
th(A_NOE) Address hold time after FSMC_NOE high THCLK–1 - ns
th(BL_NOE) FSMC_BL time after FSMC_NOE high 0 - ns
tv(BL_NE) FSMC_NEx low to FSMC_BL valid - 2 ns
tsu(Data_NE) Data to FSMC_NEx high setup time THCLK+4 - ns
tsu(Data_NOE) Data to FSMC_NOE high setup time THCLK+4 - ns
th(Data_NE) Data hold time after FSMC_NEx high 0 - ns
th(Data_NOE) Data hold time after FSMC_NOE high 0 - ns
1. CL = 30 pF.
2. Based on characterization, not tested in production.
Table 78. Asynchronous multiplexed PSRAM/NOR write timings(1)(2)
Symbol Parameter Min Max Unit
tw(NE) FSMC_NE low time 4THCLK–0.5 4THCLK+3 ns
tv(NWE_NE) FSMC_NEx low to FSMC_NWE low THCLK–0.5 THCLK -0.5 ns
tw(NWE) FSMC_NWE low tim e 2THCLK–0.5 2THCLK+3 ns
Table 77. Asynchronous multiplexed PSRAM/NOR read timings(1)(2) (continued)
NBL
Data
FSMC_NEx
FSMC_NBL[1:0]
FSMC_AD[15:0]
tv(BL_NE)
th(Data_NWE)
FSMC_NOE
FSMC_A[25:16] Address
tv(A_NE)
tw(NWE)
FSMC_NWE
tv(NWE_NE) t h(NE_NWE)
th(A_NWE)
th(BL_NWE)
t v(A_NE)
tw(NE)
ai14891B
Address
FSMC_NADV
t v(NADV_NE)
tw(NADV)
t v(Data_NADV)
th(AD_NADV)
Electrical characteristics STM32F405xx, STM32F407xx
142/185 DocID022152 Rev 4
Synchronous waveforms and timings
Figure 59 through Figure 62 represent synchronous waveforms and Table 80 through
Table 82 provide the corresponding timings. The results shown in these tables are obtained
with the following FSMC configuration:
• BurstAccessMode = FSMC_BurstAccessMode_Enable;
• MemoryType = FSMC_MemoryType_CRAM;
• WriteBurst = FSMC_WriteBurst_Enable;
• CLKDivision = 1; (0 is not supported, see the STM32F40xxx/41xxx reference manual)
• DataLatency = 1 for NOR Flash; DataLatency = 0 for PSRAM
In all timing tables, the THCLK is the HCLK clock period (with maximum
FSMC_CLK = 60 MHz).
th(NE_NWE) FSMC_NWE high to FSMC_NE high hold time THCLK - ns
tv(A_NE) FSMC_NEx low to FSMC_A valid - 0 ns
tv(NADV_NE) FSMC_NEx low to FSMC_NADV low 1 2 ns
tw(NADV) FSMC_NADV low time THCLK– 2 THCLK+ 1 ns
th(AD_NADV)
FSMC_AD(address) valid hold time after
FSMC_NADV high) THCLK–2 - ns
th(A_NWE) Address hold time after FSMC_NWE high THCLK - ns
th(BL_NWE) FSMC_BL hold time after FSMC_NWE high THCLK–2 - ns
tv(BL_NE) FSMC_NEx low to FSMC_BL valid - 1.5 ns
tv(Data_NADV) FSMC_NADV high to Data valid - THCLK–0.5 ns
th(Data_NWE) Data hold time after FSMC_NWE high THCLK - ns
1. CL = 30 pF.
2. Based on characterization, not tested in production.
Table 78. Asynchronous multiplexed PSRAM/NOR write timings(1)(2)
DocID022152 Rev 4 143/185
STM32F405xx, STM32F407xx Electrical characteristics
Figure 59. Synchronous multiplexed NOR/PSRAM read timings
Table 79. Synchronous multiplexed NOR/PSRAM read timings(1)(2)
Symbol Parameter Min Max Unit
tw(CLK) FSMC_CLK period 2THCLK - ns
td(CLKL-NExL) FSMC_CLK low to FSMC_NEx low (x=0..2) - 0 ns
td(CLKL-NExH) FSMC_CLK low to FSMC_NEx high (x= 0…2) 2 - ns
td(CLKL-NADVL) FSMC_CLK low to FSMC_NADV low - 2 ns
td(CLKL-NADVH) FSMC_CLK low to FSMC_NADV high 2 - ns
td(CLKL-AV) FSMC_CLK low to FSMC_Ax valid (x=16…25) - 0 ns
td(CLKL-AIV) FSMC_CLK low to FSMC_Ax invalid (x=16…25) 0 - ns
td(CLKL-NOEL) FSMC_CLK low to FSMC_NOE low - 0 ns
td(CLKL-NOEH) FSMC_CLK low to FSMC_NOE high 2 - ns
td(CLKL-ADV) FSMC_CLK low to FSMC_AD[15:0] valid - 4.5 ns
td(CLKL-ADIV) FSMC_CLK low to FSMC_AD[15:0] invalid 0 - ns
tsu(ADV-CLKH) FSMC_A/D[15:0] valid data before FSMC_CLK high 6 - ns
FSMC_CLK
FSMC_NEx
FSMC_NADV
FSMC_A[25:16]
FSMC_NOE
FSMC_AD[15:0] AD[15:0] D1 D2
FSMC_NWAIT
(WAITCFG = 1b, WAITPOL + 0b)
FSMC_NWAIT
(WAITCFG = 0b, WAITPOL + 0b)
tw(CLK) tw(CLK)
Data latency = 0
BUSTURN = 0
td(CLKL-NExL) td(CLKL-NExH)
td(CLKL-NADVL)
td(CLKL-AV)
td(CLKL-NADVH)
td(CLKL-AIV)
td(CLKL-NOEL) td(CLKL-NOEH)
td(CLKL-ADV)
td(CLKL-ADIV)
tsu(ADV-CLKH)
th(CLKH-ADV)
tsu(ADV-CLKH) th(CLKH-ADV)
tsu(NWAITV-CLKH) th(CLKH-NWAITV)
tsu(NWAITV-CLKH) th(CLKH-NWAITV)
tsu(NWAITV-CLKH) th(CLKH-NWAITV)
ai14893g
Electrical characteristics STM32F405xx, STM32F407xx
144/185 DocID022152 Rev 4
Figure 60. Synchronous multiplexed PSRAM write timings
th(CLKH-ADV) FSMC_A/D[15:0] valid data after FSMC_CLK high 0 - ns
tsu(NWAIT-CLKH) FSMC_NWAIT valid before FSMC_CLK high 4 - ns
th(CLKH-NWAIT) FSMC_NWAIT valid after FSMC_CLK high 0 - ns
1. CL = 30 pF.
2. Based on characterization, not tested in production.
Table 80. Synchronous multiplexed PSRAM write timings(1)(2)
Symbol Parameter Min Max Unit
tw(CLK) FSMC_CLK period 2THCLK - ns
td(CLKL-NExL) FSMC_CLK low to FSMC_NEx low (x=0..2) - 1 ns
td(CLKL-NExH) FSMC_CLK low to FSMC_NEx high (x= 0…2) 1 - ns
td(CLKL-NADVL) FSMC_CLK low to FSMC_NADV low - 0 ns
td(CLKL-NADVH) FSMC_CLK low to FSMC_NADV high 0 - ns
td(CLKL-AV) FSMC_CLK low to FSMC_Ax valid (x=16…25) - 0 ns
Table 79. Synchronous multiplexed NOR/PSRAM read timings(1)(2) (continued)
FSMC_CLK
FSMC_NEx
FSMC_NADV
FSMC_A[25:16]
FSMC_NWE
FSMC_AD[15:0] AD[15:0] D1 D2
FSMC_NWAIT
(WAITCFG = 0b, WAITPOL + 0b)
tw(CLK) tw(CLK)
Data latency = 0
BUSTURN = 0
td(CLKL-NExL) td(CLKL-NExH)
td(CLKL-NADVL)
td(CLKL-AV)
td(CLKL-NADVH)
td(CLKL-AIV)
td(CLKL-NWEL) td(CLKL-NWEH)
td(CLKL-NBLH)
td(CLKL-ADV)
td(CLKL-ADIV) td(CLKL-Data)
tsu(NWAITV-CLKH) th(CLKH-NWAITV)
ai14992g
td(CLKL-Data)
FSMC_NBL
DocID022152 Rev 4 145/185
STM32F405xx, STM32F407xx Electrical characteristics
Figure 61. Synchronous non-multiplexed NOR/PSRAM read timings
td(CLKL-AIV) FSMC_CLK low to FSMC_Ax invalid (x=16…25) 8 - ns
td(CLKL-NWEL) FSMC_CLK low to FSMC_NWE low - 0.5 ns
td(CLKL-NWEH) FSMC_CLK low to FSMC_NWE high 0 - ns
td(CLKL-ADIV) FSMC_CLK low to FSMC_AD[15:0] invalid 0 - ns
td(CLKL-DATA) FSMC_A/D[15:0] valid data after FSMC_CLK low - 3 ns
td(CLKL-NBLH) FSMC_CLK low to FSMC_NBL high 0 - ns
tsu(NWAIT-CLKH) FSMC_NWAIT valid before FSMC_CLK high 4 - ns
th(CLKH-NWAIT) FSMC_NWAIT valid after FSMC_CLK high 0 - ns
1. CL = 30 pF.
2. Based on characterization, not tested in production.
Table 81. Synchronous non-multiplexed NOR/PSRAM read timings(1)(2)
Symbol Parameter Min Max Unit
tw(CLK) FSMC_CLK period 2THCLK –0.5 - ns
td(CLKL-NExL) FSMC_CLK low to FSMC_NEx low (x=0..2) - 0.5 ns
Table 80. Synchronous multiplexed PSRAM write timings(1)(2)
FSMC_CLK
FSMC_NEx
FSMC_A[25:0]
FSMC_NOE
FSMC_D[15:0] D1 D2
FSMC_NWAIT
(WAITCFG = 1b, WAITPOL + 0b)
FSMC_NWAIT
(WAITCFG = 0b, WAITPOL + 0b)
tw(CLK) tw(CLK)
Data latency = 0
BUSTURN = 0
td(CLKL-NExL) td(CLKL-NExH)
td(CLKL-AV) td(CLKL-AIV)
td(CLKL-NOEL) td(CLKL-NOEH)
tsu(DV-CLKH) th(CLKH-DV)
tsu(DV-CLKH) th(CLKH-DV)
tsu(NWAITV-CLKH) th(CLKH-NWAITV)
tsu(NWAITV-CLKH) t h(CLKH-NWAITV)
tsu(NWAITV-CLKH) th(CLKH-NWAITV)
ai14894f
FSMC_NADV
td(CLKL-NADVL) td(CLKL-NADVH)
Electrical characteristics STM32F405xx, STM32F407xx
146/185 DocID022152 Rev 4
Figure 62. Synchronous non-multiplexed PSRAM write timings
td(CLKL-NExH) FSMC_CLK low to FSMC_NEx high (x= 0…2) 0 - ns
td(CLKL-NADVL) FSMC_CLK low to FSMC_NADV low - 2 ns
td(CLKL-NADVH) FSMC_CLK low to FSMC_NADV high 3 - ns
td(CLKL-AV) FSMC_CLK low to FSMC_Ax valid (x=16…25) - 0 ns
td(CLKL-AIV) FSMC_CLK low to FSMC_Ax invalid (x=16…25) 2 - ns
td(CLKL-NOEL) FSMC_CLK low to FSMC_NOE low - 0.5 ns
td(CLKL-NOEH) FSMC_CLK low to FSMC_NOE high 1.5 - ns
tsu(DV-CLKH) FSMC_D[15:0] valid data before FSMC_CLK high 6 - ns
th(CLKH-DV) FSMC_D[15:0] valid data after FSMC_CLK high 3 - ns
tsu(NWAIT-CLKH) FSMC_NWAIT valid before FSMC_CLK high 4 - ns
th(CLKH-NWAIT) FSMC_NWAIT valid after FSMC_CLK high 0 - ns
1. CL = 30 pF.
2. Based on characterization, not tested in production.
Table 81. Synchronous non-multiplexed NOR/PSRAM read timings(1)(2) (continued)
FSMC_CLK
FSMC_NEx
FSMC_A[25:0]
FSMC_NWE
FSMC_D[15:0] D1 D2
FSMC_NWAIT
(WAITCFG = 0b, WAITPOL + 0b)
tw(CLK) tw(CLK)
Data latency = 0
BUSTURN = 0
td(CLKL-NExL) td(CLKL-NExH)
td(CLKL-AV) td(CLKL-AIV)
td(CLKL-NWEL) td(CLKL-NWEH)
td(CLKL-Data)
tsu(NWAITV-CLKH)
th(CLKH-NWAITV)
ai14993g
FSMC_NADV
td(CLKL-NADVL) td(CLKL-NADVH)
td(CLKL-Data)
FSMC_NBL
td(CLKL-NBLH)
DocID022152 Rev 4 147/185
STM32F405xx, STM32F407xx Electrical characteristics
PC Card/CompactFlash controller waveforms and timings
Figure 63 through Figure 68 represent synchronous waveforms, and Table 83 and Table 84
provide the corresponding timings. The results shown in this table are obtained with the
following FSMC configuration:
• COM.FSMC_SetupTime = 0x04;
• COM.FSMC_WaitSetupTime = 0x07;
• COM.FSMC_HoldSetupTime = 0x04;
• COM.FSMC_HiZSetupTime = 0x00;
• ATT.FSMC_SetupTime = 0x04;
• ATT.FSMC_WaitSetupTime = 0x07;
• ATT.FSMC_HoldSetupTime = 0x04;
• ATT.FSMC_HiZSetupTime = 0x00;
• IO.FSMC_SetupTime = 0x04;
• IO.FSMC_WaitSetupTime = 0x07;
• IO.FSMC_HoldSetupTime = 0x04;
• IO.FSMC_HiZSetupTime = 0x00;
• TCLRSetupTime = 0;
• TARSetupTime = 0.
In all timing tables, the THCLK is the HCLK clock period.
Table 82. Synchronous non-multiplexed PSRAM write timings(1)(2)
1. CL = 30 pF.
2. Based on characterization, not tested in production.
Symbol Parameter Min Max Unit
tw(CLK) FSMC_CLK period 2THCLK - ns
td(CLKL-NExL) FSMC_CLK low to FSMC_NEx low (x=0..2) - 1 ns
td(CLKL-NExH) FSMC_CLK low to FSMC_NEx high (x= 0…2) 1 - ns
td(CLKL-NADVL) FSMC_CLK low to FSMC_NADV low - 7 ns
td(CLKL-NADVH) FSMC_CLK low to FSMC_NADV high 6 - ns
td(CLKL-AV) FSMC_CLK low to FSMC_Ax valid (x=16…25) - 0 ns
td(CLKL-AIV) FSMC_CLK low to FSMC_Ax invalid (x=16…25) 6 - ns
td(CLKL-NWEL) FSMC_CLK low to FSMC_NWE low - 1 ns
td(CLKL-NWEH) FSMC_CLK low to FSMC_NWE high 2 - ns
td(CLKL-Data) FSMC_D[15:0] valid data after FSMC_CLK low - 3 ns
td(CLKL-NBLH) FSMC_CLK low to FSMC_NBL high 3 - ns
tsu(NWAIT-CLKH) FSMC_NWAIT valid before FSMC_CLK high 4 - ns
th(CLKH-NWAIT) FSMC_NWAIT valid after FSMC_CLK high 0 - ns
Electrical characteristics STM32F405xx, STM32F407xx
148/185 DocID022152 Rev 4
Figure 63. PC Card/CompactFlash controller waveforms for common memory read
access
1. FSMC_NCE4_2 remains high (inactive during 8-bit access.
Figure 64. PC Card/CompactFlash controller waveforms for common memory write
access
FSMC_NWE
tw(NOE)
FSMC_NOE
FSMC_D[15:0]
FSMC_A[10:0]
FSMC_NCE4_2(1)
FSMC_NCE4_1
FSMC_NREG
FSMC_NIOWR
FSMC_NIORD
td(NCE4_1-NOE)
tsu(D-NOE) th(NOE-D)
tv(NCEx-A)
td(NREG-NCEx)
td(NIORD-NCEx)
th(NCEx-AI)
th(NCEx-NREG)
th(NCEx-NIORD)
th(NCEx-NIOWR)
ai14895b
td(NCE4_1-NWE) tw(NWE)
th(NWE-D)
tv(NCE4_1-A)
td(NREG-NCE4_1)
td(NIORD-NCE4_1)
th(NCE4_1-AI)
MEMxHIZ =1
tv(NWE-D)
th(NCE4_1-NREG)
th(NCE4_1-NIORD)
th(NCE4_1-NIOWR)
ai14896b
FSMC_NWE
FSMC_NOE
FSMC_D[15:0]
FSMC_A[10:0]
FSMC_NCE4_1
FSMC_NREG
FSMC_NIOWR
FSMC_NIORD
td(NWE-NCE4_1)
td(D-NWE)
FSMC_NCE4_2 High
DocID022152 Rev 4 149/185
STM32F405xx, STM32F407xx Electrical characteristics
Figure 65. PC Card/CompactFlash controller waveforms for attribute memory read
access
1. Only data bits 0...7 are read (bits 8...15 are disregarded).
td(NCE4_1-NOE) tw(NOE)
tsu(D-NOE) th(NOE-D)
tv(NCE4_1-A) th(NCE4_1-AI)
td(NREG-NCE4_1) th(NCE4_1-NREG)
ai14897b
FSMC_NWE
FSMC_NOE
FSMC_D[15:0](1)
FSMC_A[10:0]
FSMC_NCE4_2
FSMC_NCE4_1
FSMC_NREG
FSMC_NIOWR
FSMC_NIORD
td(NOE-NCE4_1)
High
Electrical characteristics STM32F405xx, STM32F407xx
150/185 DocID022152 Rev 4
Figure 66. PC Card/CompactFlash controller waveforms for attribute memory write
access
1. Only data bits 0...7 are driven (bits 8...15 remains Hi-Z).
Figure 67. PC Card/CompactFlash controller waveforms for I/O space read access
tw(NWE)
tv(NCE4_1-A)
td(NREG-NCE4_1)
th(NCE4_1-AI)
th(NCE4_1-NREG)
tv(NWE-D)
ai14898b
FSMC_NWE
FSMC_NOE
FSMC_D[7:0](1)
FSMC_A[10:0]
FSMC_NCE4_2
FSMC_NCE4_1
FSMC_NREG
FSMC_NIOWR
FSMC_NIORD
td(NWE-NCE4_1)
High
td(NCE4_1-NWE)
td(NIORD-NCE4_1) tw(NIORD)
tsu(D-NIORD) td(NIORD-D)
tv(NCEx-A) th(NCE4_1-AI)
ai14899B
FSMC_NWE
FSMC_NOE
FSMC_D[15:0]
FSMC_A[10:0]
FSMC_NCE4_2
FSMC_NCE4_1
FSMC_NREG
FSMC_NIOWR
FSMC_NIORD
DocID022152 Rev 4 151/185
STM32F405xx, STM32F407xx Electrical characteristics
Figure 68. PC Card/CompactFlash controller waveforms for I/O space write access
td(NCE4_1-NIOWR) tw(NIOWR)
tv(NCEx-A) th(NCE4_1-AI)
th(NIOWR-D)
ATTxHIZ =1
tv(NIOWR-D)
ai14900c
FSMC_NWE
FSMC_NOE
FSMC_D[15:0]
FSMC_A[10:0]
FSMC_NCE4_2
FSMC_NCE4_1
FSMC_NREG
FSMC_NIOWR
FSMC_NIORD
Table 83. Switching characteristics for PC Card/CF read and write cycles
in attribute/common space(1)(2)
Symbol Parameter Min Max Unit
tv(NCEx-A) FSMC_Ncex low to FSMC_Ay valid - 0 ns
th(NCEx_AI) FSMC_NCEx high to FSMC_Ax invalid 4 - ns
td(NREG-NCEx) FSMC_NCEx low to FSMC_NREG valid - 3.5 ns
th(NCEx-NREG) FSMC_NCEx high to FSMC_NREG invalid THCLK+4 - ns
td(NCEx-NWE) FSMC_NCEx low to FSMC_NWE low - 5THCLK+0.5 ns
td(NCEx-NOE) FSMC_NCEx low to FSMC_NOE low - 5THCLK +0.5 ns
tw(NOE) FSMC_NOE low width 8THCLK–1 8THCLK+1 ns
td(NOE_NCEx) FSMC_NOE high to FSMC_NCEx high 5THCLK+2.5 - ns
tsu (D-NOE) FSMC_D[15:0] valid data before FSMC_NOE high 4.5 - ns
th(N0E-D) FSMC_N0E high to FSMC_D[15:0] invalid 3 - ns
tw(NWE) FSMC_NWE low width 8THCLK–0.5 8THCLK+ 3 ns
td(NWE_NCEx) FSMC_NWE high to FSMC_NCEx high 5THCLK–1 - ns
td(NCEx-NWE) FSMC_NCEx low to FSMC_NWE low - 5THCLK+ 1 ns
tv(NWE-D) FSMC_NWE low to FSMC_D[15:0] valid - 0 ns
th (NWE-D) FSMC_NWE high to FSMC_D[15:0] invalid 8THCLK –1 - ns
td (D-NWE) FSMC_D[15:0] valid before FSMC_NWE high 13THCLK –1 - ns
1. CL = 30 pF.
2. Based on characterization, not tested in production.
Electrical characteristics STM32F405xx, STM32F407xx
152/185 DocID022152 Rev 4
NAND controller waveforms and timings
Figure 69 through Figure 72 represent synchronous waveforms, and Table 85 and Table 86
provide the corresponding timings. The results shown in this table are obtained with the
following FSMC configuration:
• COM.FSMC_SetupTime = 0x01;
• COM.FSMC_WaitSetupTime = 0x03;
• COM.FSMC_HoldSetupTime = 0x02;
• COM.FSMC_HiZSetupTime = 0x01;
• ATT.FSMC_SetupTime = 0x01;
• ATT.FSMC_WaitSetupTime = 0x03;
• ATT.FSMC_HoldSetupTime = 0x02;
• ATT.FSMC_HiZSetupTime = 0x01;
• Bank = FSMC_Bank_NAND;
• MemoryDataWidth = FSMC_MemoryDataWidth_16b;
• ECC = FSMC_ECC_Enable;
• ECCPageSize = FSMC_ECCPageSize_512Bytes;
• TCLRSetupTime = 0;
• TARSetupTime = 0.
In all timing tables, the THCLK is the HCLK clock period.
Table 84. Switching characteristics for PC Card/CF read and write cycles
in I/O space(1)(2)
Symbol Parameter Min Max Unit
tw(NIOWR) FSMC_NIOWR low width 8THCLK –1 - ns
tv(NIOWR-D) FSMC_NIOWR low to FSMC_D[15:0] valid - 5THCLK– 1 ns
th(NIOWR-D) FSMC_NIOWR high to FSMC_D[15:0] invalid 8THCLK– 2 - ns
td(NCE4_1-NIOWR) FSMC_NCE4_1 low to FSMC_NIOWR valid - 5THCLK+ 2.5 ns
th(NCEx-NIOWR) FSMC_NCEx high to FSMC_NIOWR invalid 5THCLK–1.5 - ns
td(NIORD-NCEx) FSMC_NCEx low to FSMC_NIORD valid - 5THCLK+ 2 ns
th(NCEx-NIORD) FSMC_NCEx high to FSMC_NIORD) valid 5THCLK– 1.5 - ns
tw(NIORD) FSMC_NIORD low width 8THCLK–0.5 - ns
tsu(D-NIORD) FSMC_D[15:0] valid before FSMC_NIORD high 9 - ns
td(NIORD-D) FSMC_D[15:0] valid after FSMC_NIORD high 0 - ns
1. CL = 30 pF.
2. Based on characterization, not tested in production.
DocID022152 Rev 4 153/185
STM32F405xx, STM32F407xx Electrical characteristics
Figure 69. NAND controller waveforms for read access
Figure 70. NAND controller waveforms for write access
FSMC_NWE
FSMC_NOE (NRE)
FSMC_D[15:0]
tsu(D-NOE) th(NOE-D)
ai14901c
ALE (FSMC_A17)
CLE (FSMC_A16)
FSMC_NCEx
td(ALE-NOE) th(NOE-ALE)
tv(NWE-D) th(NWE-D)
ai14902c
FSMC_NWE
FSMC_NOE (NRE)
FSMC_D[15:0]
ALE (FSMC_A17)
CLE (FSMC_A16)
FSMC_NCEx
td(ALE-NWE) th(NWE-ALE)
Electrical characteristics STM32F405xx, STM32F407xx
154/185 DocID022152 Rev 4
Figure 71. NAND controller waveforms for common memory read access
Figure 72. NAND controller waveforms for common memory write access
Table 85. Switching characteristics for NAND Flash read cycles(1)
1. CL = 30 pF.
Symbol Parameter Min Max Unit
tw(N0E) FSMC_NOE low width 4THCLK–
0.5 4THCLK+ 3 ns
tsu(D-NOE) FSMC_D[15-0] valid data before FSMC_NOE high 10 - ns
th(NOE-D) FSMC_D[15-0] valid data after FSMC_NOE high 0 - ns
td(ALE-NOE) FSMC_ALE valid before FSMC_NOE low - 3THCLK ns
th(NOE-ALE) FSMC_NWE high to FSMC_ALE invalid 3THCLK– 2 - ns
FSMC_NWE
FSMC_NOE
FSMC_D[15:0]
tw(NOE)
tsu(D-NOE) th(NOE-D)
ai14912c
ALE (FSMC_A17)
CLE (FSMC_A16)
FSMC_NCEx
td(ALE-NOE) th(NOE-ALE)
tw(NWE)
tv(NWE-D) th(NWE-D)
ai14913c
FSMC_NWE
FSMC_NOE
FSMC_D[15:0]
td(D-NWE)
ALE (FSMC_A17)
CLE (FSMC_A16)
FSMC_NCEx
td(ALE-NOE) th(NOE-ALE)
DocID022152 Rev 4 155/185
STM32F405xx, STM32F407xx Electrical characteristics
5.3.26 Camera interface (DCMI) timing specifications
Unless otherwise specified, the parameters given in Table 87 for DCMI are derived from
tests performed under the ambient temperature, fHCLK frequency and VDD supply voltage
summarized in Table 13, with the following configuration:
• PCK polarity: falling
• VSYNC and HSYNC polarity: high
• Data format: 14 bits
Figure 73. DCMI timing diagram
Table 86. Switching characteristics for NAND Flash write cycles(1)
1. CL = 30 pF.
Symbol Parameter Min Max Unit
tw(NWE) FSMC_NWE low width 4THCLK–1 4THCLK+ 3 ns
tv(NWE-D) FSMC_NWE low to FSMC_D[15-0] valid - 0 ns
th(NWE-D) FSMC_NWE high to FSMC_D[15-0] invalid 3THCLK –2 - ns
td(D-NWE) FSMC_D[15-0] valid before FSMC_NWE high 5THCLK–3 - ns
td(ALE-NWE) FSMC_ALE valid before FSMC_NWE low - 3THCLK ns
th(NWE-ALE) FSMC_NWE high to FSMC_ALE invalid 3THCLK–2 - ns
Table 87. DCMI characteristics(1)
Symbol Parameter Min Max Unit
Frequency ratio DCMI_PIXCLK/fHCLK - 0.4
DCMI_PIXCLK Pixel clock input - 54 MHz
Dpixel Pixel clock input duty cycle 30 70 %
MS32414V1
Pixel clock
tsu(VSYNC)
tsu(HSYNC)
HSYNC
VSYNC
DATA[0:13]
1/DCMI_PIXCLK
th(HSYNC)
th(HSYNC)
tsu(DATA) th(DATA)
Electrical characteristics STM32F405xx, STM32F407xx
156/185 DocID022152 Rev 4
5.3.27 SD/SDIO MMC card host interface (SDIO) characteristics
Unless otherwise specified, the parameters given in Table 88 are derived from tests
performed under ambient temperature, fPCLKx frequency and VDD supply voltage conditions
summarized in Table 14 with the following configuration:
• Output speed is set to OSPEEDRy[1:0] = 10
• Capacitive load C = 30 pF
• Measurement points are done at CMOS levels: 0.5VDD
Refer to Section 5.3.16: I/O port characteristics for more details on the input/output
characteristics.
Figure 74. SDIO high-speed mode
tsu(DATA) Data input setup time 2.5 -
ns
th(DATA) Data hold time 1 -
tsu(HSYNC),
tsu(VSYNC)
HSYNC/VSYNC input setup time 2 -
th(HSYNC),
th(VSYNC)
HSYNC/VSYNC input hold time 0.5 -
1. Data based on characterization results, not tested in production.
Table 87. DCMI characteristics(1) (continued)
Symbol Parameter Min Max Unit
tW(CKH)
CK
D, CMD
(output)
D, CMD
(input)
tC
tW(CKL)
tOV tOH
tISU tIH
tf tr
ai14887
DocID022152 Rev 4 157/185
STM32F405xx, STM32F407xx Electrical characteristics
Figure 75. SD default mode
5.3.28 RTC characteristics
CK
D, CMD
(output)
tOVD tOHD
ai14888
Table 88. Dynamic characteristics: SD / MMC characteristics(1)
Symbol Parameter Conditions Min Typ Max Unit
fPP Clock frequency in data transfer mode 0 48 MHz
SDIO_CK/fPCLK2 frequency ratio - - 8/3 -
tW(CKL) Clock low time fpp = 48 MHz 8.5 9 -
ns
tW(CKH) Clock high time fpp = 48 MHz 8.3 10 -
CMD, D inputs (referenced to CK) in MMC and SD HS mode
tISU Input setup time HS fpp = 48 MHz 3 - -
ns
tIH Input hold time HS fpp = 48 MHz 0 - -
CMD, D outputs (referenced to CK) in MMC and SD HS mode
tOV Output valid time HS fpp = 48 MHz - 4.5 6
ns
tOH Output hold time HS fpp = 48 MHz 1 - -
CMD, D inputs (referenced to CK) in SD default mode
tISUD Input setup time SD fpp = 24 MHz 1.5 - -
ns
tIHD Input hold time SD fpp = 24 MHz 0.5 - -
CMD, D outputs (referenced to CK) in SD default mode
tOVD Output valid default time SD fpp = 24 MHz - 4.5 7
ns
tOHD Output hold default time SD fpp = 24 MHz 0.5 - -
1. Data based on characterization results, not tested in production.
Table 89. RTC characteristics
Symbol Parameter Conditions Min Max
- fPCLK1/RTCCLK frequency ratio Any read/write operation
from/to an RTC register 4 -
Package characteristics STM32F405xx, STM32F407xx
158/185 DocID022152 Rev 4
6 Package characteristics
6.1 Package mechanical data
In order to meet environmental requirements, ST offers these devices in different grades of
ECOPACK® packages, depending on their level of environmental compliance. ECOPACK®
specifications, grade definitions and product status are available at: www.st.com.
ECOPACK® is an ST trademark.
DocID022152 Rev 4 159/185
STM32F405xx, STM32F407xx Package characteristics
Figure 76. WLCSP90 - 0.400 mm pitch wafer level chip size package outline
Bump side
Side view
Detail A
Wafer back side
A1 ball location
A1
Detail A
rotated by 90 °C
eee
D
A0JW_ME
Seating plane
A2
A
b
E
e
e1
e
G
F
e2
Table 90. WLCSP90 - 0.400 mm pitch wafer level chip size package mechanical data
Symbol
millimeters inches(1)
Min Typ Max Min Typ Max
A 0.520 0.570 0.620 0.0205 0.0224 0.0244
A1 0.165 0.190 0.215 0.0065 0.0075 0.0085
A2 0.350 0.380 0.410 0.0138 0.015 0.0161
b 0.240 0.270 0.300 0.0094 0.0106 0.0118
D 4.178 4.218 4.258 0.1645 0.1661 0.1676
E 3.964 3.969 4.004 0.1561 0.1563 0.1576
e 0.400 0.0157
e1 3.600 0.1417
e2 3.200 0.126
F 0.312 0.0123
G 0.385 0.0152
eee 0.050 0.0020
1. Values in inches are converted from mm and rounded to 4 decimal digits.
Package characteristics STM32F405xx, STM32F407xx
160/185 DocID022152 Rev 4
Figure 77. LQFP64 – 10 x 10 mm 64 pin low-profile quad flat package outline
1. Drawing is not to scale.
ai14398b
A
A2
A1
c
L1
L
E E1
D
D1
e
b
Table 91. LQFP64 – 10 x 10 mm 64 pin low-profile quad flat package mechanical data
Symbol
millimeters inches(1)
Min Typ Max Min Typ Max
A 1.600 0.0630
A1 0.050 0.150 0.0020 0.0059
A2 1.350 1.400 1.450 0.0531 0.0551 0.0571
b 0.170 0.220 0.270 0.0067 0.0087 0.0106
c 0.090 0.200 0.0035 0.0079
D 12.000 0.4724
D1 10.000 0.3937
E 12.000 0.4724
E1 10.000 0.3937
e 0.500 0.0197
θ 0° 3.5° 7° 0° 3.5° 7°
L 0.450 0.600 0.750 0.0177 0.0236 0.0295
L1 1.000 0.0394
N
Number of pins
64
1. Values in inches are converted from mm and rounded to 4 decimal digits.
DocID022152 Rev 4 161/185
STM32F405xx, STM32F407xx Package characteristics
Figure 78. LQFP64 recommended footprint
1. Drawing is not to scale.
2. Dimensions are in millimeters.
48
49 32
64 17
1 16
1.2
0.3
33
10.3
12.7
10.3
0.5
7.8
12.7
ai14909
Package characteristics STM32F405xx, STM32F407xx
162/185 DocID022152 Rev 4
Figure 79. LQFP100, 14 x 14 mm 100-pin low-profile quad flat package outline
1. Drawing is not to scale.
IDENTIFICATION e
PIN 1
GAUGE PLANE
0.25 mm
SEATING
PLANE
D
D1
D3
E3
E1
E
K
ccc C
C
1 25
100 26
76
75 51
50
1L_ME_V4
A2
A
A1
L1
L
c
b
A1
Table 92. LQPF100 – 14 x 14 mm 100-pin low-profile quad flat package mechanical data(1)
Symbol
millimeters inches
Min Typ Max Min Typ Max
A 1.600 0.0630
A1 0.050 0.150 0.0020 0.0059
A2 1.350 1.400 1.450 0.0531 0.0551 0.0571
b 0.170 0.220 0.270 0.0067 0.0087 0.0106
c 0.090 0.200 0.0035 0.0079
D 15.800 16.000 16.200 0.6220 0.6299 0.6378
D1 13.800 14.000 14.200 0.5433 0.5512 0.5591
D3 12.000 0.4724
E 15.80v 16.000 16.200 0.6220 0.6299 0.6378
E1 13.800 14.000 14.200 0.5433 0.5512 0.5591
E3 12.000 0.4724
e 0.500 0.0197
L 0.450 0.600 0.750 0.0177 0.0236 0.0295
L1 1.000 0.0394
k 0° 3.5° 7° 0° 3.5° 7°
ccc 0.080 0.0031
1. Values in inches are converted from mm and rounded to 4 decimal digits.
DocID022152 Rev 4 163/185
STM32F405xx, STM32F407xx Package characteristics
Figure 80. LQFP100 recommended footprint
1. Drawing is not to scale.
2. Dimensions are in millimeters.
75 51
76 50
0.5
0.3
16.7 14.3
100 26
12.3
25
1.2
16.7
1
ai14906
Package characteristics STM32F405xx, STM32F407xx
164/185 DocID022152 Rev 4
Figure 81. LQFP144, 20 x 20 mm, 144-pin low-profile quad flat package outline
1. Drawing is not to scale.
D1
D3
D
E3 E1 E
e
Pin 1
identification
73
72
37
36
109
144
108
1
A A2A1
b c
A1 L
L1
k
Seating plane
C
ccc C
0.25 mm
gage plane
ME_1A
Table 93. LQFP144, 20 x 20 mm, 144-pin low-profile quad flat package mechanical data
Symbol
millimeters inches(1)
Min Typ Max Min Typ Max
A 1.600 0.0630
A1 0.050 0.150 0.0020 0.0059
A2 1.350 1.400 1.450 0.0531 0.0551 0.0571
b 0.170 0.220 0.270 0.0067 0.0087 0.0106
c 0.090 0.200 0.0035 0.0079
D 21.800 22.000 22.200 0.8583 0.8661 0.874
D1 19.800 20.000 20.200 0.7795 0.7874 0.7953
D3 17.500 0.689
E 21.800 22.000 22.200 0.8583 0.8661 0.8740
E1 19.800 20.000 20.200 0.7795 0.7874 0.7953
E3 17.500 0.6890
e 0.500 0.0197
L 0.450 0.600 0.750 0.0177 0.0236 0.0295
L1 1.000 0.0394
DocID022152 Rev 4 165/185
STM32F405xx, STM32F407xx Package characteristics
Figure 82. LQFP144 recommended footprint
1. Drawing is not to scale.
2. Dimensions are in millimeters.
k 0° 3.5° 7° 0° 3.5° 7°
ccc 0.080 0.0031
1. Values in inches are converted from mm and rounded to 4 decimal digits.
Table 93. LQFP144, 20 x 20 mm, 144-pin low-profile quad flat package mechanical data
Symbol
millimeters inches(1)
Min Typ Max Min Typ Max
ai14905c
0.5
0.35
19.9
17.85
22.6
1.35
22.6
19.9
1 36
37
72
108 73
109
144
Package characteristics STM32F405xx, STM32F407xx
166/185 DocID022152 Rev 4
Figure 83. UFBGA176+25 - ultra thin fine pitch ball grid array 10 × 10 × 0.6 mm,
package outline
1. Drawing is not to scale.
Table 94. UFBGA176+25 - ultra thin fine pitch ball grid array 10 × 10 × 0.6 mm
mechanical data
Symbol
millimeters inches(1)
1. Values in inches are converted from mm and rounded to 4 decimal digits.
Min Typ Max Min Typ Max
A 0.460 0.530 0.600 0.0181 0.0209 0.0236
A1 0.050 0.080 0.110 0.002 0.0031 0.0043
A2
0.400 0.450 0.500 0.0157 0.0177 0.0197
b 0.230 0.280 0.330 0.0091 0.0110 0.0130
D 9.900 10.000 10.100 0.3898 0.3937 0.3976
E 9.900 10.000 10.100 0.3898 0.3937 0.3976
e 0.650 0.0256
F 0.425 0.450 0.475 0.0167 0.0177 0.0187
ddd 0.080 0.0031
eee 0.150 0.0059
fff 0.080 0.0031
A0E7_ME_V4
Seating plane
A2 ddd C
A1
A
e F
F
e
R
A
15 1
BOTTOM VIEW
E
D
TOP VIEW
Øb (176 + 25 balls)
B
A
Ø eee M B
Ø fff M
C
C
A
C
A1 ball
identifier
A1 ball
index area
DocID022152 Rev 4 167/185
STM32F405xx, STM32F407xx Package characteristics
Figure 84. LQFP176 24 x 24 mm, 176-pin low-profile quad flat package outline
1. Drawing is not to scale.
ccc C
C Seating plane
A A2
A1 c
0.25 mm
gauge plane
HD
D
A1
L
L1
k
89
88
E HE
45
44
e
1
176
Pin 1
identification
b
133
132
1T_ME
ZD
ZE
Table 95. LQFP176, 24 x 24 mm, 176-pin low-profile quad flat package mechanical data
Symbol
millimeters inches(1)
Min Typ Max Min Typ Max
A 1.600 0.0630
A1 0.050 0.150 0.0020
A2 1.350 1.450 0.0531 0.0060
b 0.170 0.270 0.0067 0.0106
C 0.090 0.200 0.0035 0.0079
D 23.900 24.100 0.9409 0.9488
E 23.900 24.100 0.9409 0.9488
e 0.500 0.0197
HD 25.900 26.100 1.0200 1.0276
HE 25.900 26.100 1.0200 1.0276
L 0.450 0.750 0.0177 0.0295
L1 1.000 0.0394
ZD 1.250 0.0492
ZE 1.250 0.0492
Package characteristics STM32F405xx, STM32F407xx
168/185 DocID022152 Rev 4
Figure 85. LQFP176 recommended footprint
1. Dimensions are expressed in millimeters.
ccc 0.080 0.0031
k 0 ° 7 ° 0 ° 7 °
1. Values in inches are converted from mm and rounded to 4 decimal digits.
Table 95. LQFP176, 24 x 24 mm, 176-pin low-profile quad flat package mechanical data
Symbol
millimeters inches(1)
Min Typ Max Min Typ Max
1T_FP_V1
133
132
1.2
0.3
0.5
89
88
1.2
44
45
21.8
26.7
1
176
26.7
21.8
DocID022152 Rev 4 169/185
STM32F405xx, STM32F407xx Package characteristics
6.2 Thermal characteristics
The maximum chip-junction temperature, TJ max, in degrees Celsius, may be calculated
using the following equation:
TJ max = TA max + (PD max x ΘJA)
Where:
• TA max is the maximum ambient temperature in °C,
• ΘJA is the package junction-to-ambient thermal resistance, in °C/W,
• PD max is the sum of PINT max and PI/O max (PD max = PINT max + PI/Omax),
• PINT max is the product of IDD and VDD, expressed in Watts. This is the maximum chip
internal power.
PI/O max represents the maximum power dissipation on output pins where:
PI/O max = Σ (VOL × IOL) + Σ((VDD – VOH) × IOH),
taking into account the actual VOL / IOL and VOH / IOH of the I/Os at low and high level in the
application.
Reference document
JESD51-2 Integrated Circuits Thermal Test Method Environment Conditions - Natural
Convection (Still Air). Available from www.jedec.org.
Table 96. Package thermal characteristics
Symbol Parameter Value Unit
ΘJA
Thermal resistance junction-ambient
LQFP64 - 10 × 10 mm / 0.5 mm pitch 46
°C/W
Thermal resistance junction-ambient
LQFP100 - 14 × 14 mm / 0.5 mm pitch 43
Thermal resistance junction-ambient
LQFP144 - 20 × 20 mm / 0.5 mm pitch 40
Thermal resistance junction-ambient
LQFP176 - 24 × 24 mm / 0.5 mm pitch 38
Thermal resistance junction-ambient
UFBGA176 - 10× 10 mm / 0.65 mm pitch 39
Thermal resistance junction-ambient
WLCSP90 - 0.400 mm pitch 38.1
Part numbering STM32F405xx, STM32F407xx
170/185 DocID022152 Rev 4
7 Part numbering
For a list of available options (speed, package, etc.) or for further information on any aspect
of this device, please contact your nearest ST sales office.
Table 97. Ordering information scheme
Example: STM32 F 405 R E T 6 xxx
Device family
STM32 = ARM-based 32-bit microcontroller
Product type
F = general-purpose
Device subfamily
405 = STM32F40x, connectivity
407= STM32F40x, connectivity, camera interface, Ethernet
Pin count
R = 64 pins
O = 90 pins
V = 100 pins
Z = 144 pins
I = 176 pins
Flash memory size
E = 512 Kbytes of Flash memory
G = 1024 Kbytes of Flash memory
Package
T = LQFP
H = UFBGA
Y = WLCSP
Temperature range
6 = Industrial temperature range, –40 to 85 °C.
7 = Industrial temperature range, –40 to 105 °C.
Options
xxx = programmed parts
TR = tape and reel
DocID022152 Rev 4 171/185
STM32F405xx, STM32F407xx Application block diagrams
Appendix A Application block diagrams
A.1 USB OTG full speed (FS) interface solutions
Figure 86. USB controller configured as peripheral-only and used
in Full speed mode
1. External voltage regulator only needed when building a VBUS powered device.
2. The same application can be developed using the OTG HS in FS mode to achieve enhanced performance
thanks to the large Rx/Tx FIFO and to a dedicated DMA controller.
Figure 87. USB controller configured as host-only and used in full speed mode
1. The current limiter is required only if the application has to support a VBUS powered device. A basic power
switch can be used if 5 V are available on the application board.
2. The same application can be developed using the OTG HS in FS mode to achieve enhanced performance
thanks to the large Rx/Tx FIFO and to a dedicated DMA controller.
STM32F4xx
5V to VDD
Volatge regulator (1)
VDD
VBUS
DP
VSS
PA12/PB15
PA11//PB14
USB Std-B connector
DM
OSC_IN
OSC_OUT
MS19000V5
STM32F4xx
VDD
VBUS
DP
VSS
USB Std-A connector
DM
GPIO+IRQ
GPIO
EN
Overcurrent
5 V Pwr
OSC_IN
OSC_OUT
MS19001V4
Current limiter
power switch(1)
PA12/PB15
PA11//PB14
Application block diagrams STM32F405xx, STM32F407xx
172/185 DocID022152 Rev 4
Figure 88. USB controller configured in dual mode and used in full speed mode
1. External voltage regulator only needed when building a VBUS powered device.
2. The current limiter is required only if the application has to support a VBUS powered device. A basic power
switch can be used if 5 V are available on the application board.
3. The ID pin is required in dual role only.
4. The same application can be developed using the OTG HS in FS mode to achieve enhanced performance
thanks to the large Rx/Tx FIFO and to a dedicated DMA controller.
STM32F4xx
VDD
VBUS
DP
VSS
PA9/PB13
PA12/PB15
PA11/PB14
USB micro-AB connector
DM
GPIO+IRQ
GPIO
EN
Overcurrent
5 V Pwr
5 V to VDD
voltage regulator (1)
VDD
ID(3)
PA10/PB12
OSC_IN
OSC_OUT
MS19002V3
Current limiter
power switch(2)
DocID022152 Rev 4 173/185
STM32F405xx, STM32F407xx Application block diagrams
A.2 USB OTG high speed (HS) interface solutions
Figure 89. USB controller configured as peripheral, host, or dual-mode
and used in high speed mode
1. It is possible to use MCO1 or MCO2 to save a crystal. It is however not mandatory to clock the STM32F40x
with a 24 or 26 MHz crystal when using USB HS. The above figure only shows an example of a possible
connection.
2. The ID pin is required in dual role only.
DP
STM32F4xx
DM
VBUS
VSS
DM
DP
ID(2)
USB
USB HS
OTG Ctrl
FS PHY
ULPI
High speed
OTG PHY
ULPI_CLK
ULPI_D[7:0]
ULPI_DIR
ULPI_STP
ULPI_NXT
not connected
connector
MCO1 or MCO2
24 or 26 MHz XT(1)
PLL
XT1
XI
MS19005V2
Application block diagrams STM32F405xx, STM32F407xx
174/185 DocID022152 Rev 4
A.3 Ethernet interface solutions
Figure 90. MII mode using a 25 MHz crystal
1. fHCLK must be greater than 25 MHz.
2. Pulse per second when using IEEE1588 PTP optional signal.
Figure 91. RMII with a 50 MHz oscillator
1. fHCLK must be greater than 25 MHz.
MCU
Ethernet
MAC 10/100
Ethernet
PHY 10/100
PLL HCLK
XT1
PHY_CLK 25 MHz
MII_RX_CLK
MII_RXD[3:0]
MII_RX_DV
MII_RX_ER
MII_TX_CLK
MII_TX_EN
MII_TXD[3:0]
MII_CRS
MII_COL
MDIO
MDC
HCLK(1)
PPS_OUT(2)
XTAL
25 MHz
STM32
OSC
TIM2 Timestamp
comparator
Timer
input
trigger
IEEE1588 PTP
MII
= 15 pins
MII + MDC
= 17 pins
MS19968V1
MCO1/MCO2
MCU
Ethernet
MAC 10/100
Ethernet
PHY 10/100
PLL HCLK
PHY_CLK 50 MHz XT1
RMII_RXD[1:0]
RMII_CRX_DV
RMII_REF_CLK
RMII_TX_EN
RMII_TXD[1:0]
MDIO
MDC
HCLK(1)
STM32
OSC
50 MHz
TIM2 Timestamp
comparator
Timer
input
trigger
IEEE1588 PTP
RMII
= 7 pins
RMII + MDC
= 9 pins
MS19969V1
/2 or /20
2.5 or 25 MHz synchronous 50 MHz
50 MHz
DocID022152 Rev 4 175/185
STM32F405xx, STM32F407xx Application block diagrams
Figure 92. RMII with a 25 MHz crystal and PHY with PLL
1. fHCLK must be greater than 25 MHz.
2. The 25 MHz (PHY_CLK) must be derived directly from the HSE oscillator, before the PLL block.
MCU
Ethernet
MAC 10/100
Ethernet
PHY 10/100
PLL HCLK
PHY_CLK 25 MHz XT1
RMII_RXD[1:0]
RMII_CRX_DV
RMII_REF_CLK
RMII_TX_EN
RMII_TXD[1:0]
MDIO
MDC
HCLK(1)
STM32F
TIM2 Timestamp
comparator
Timer
input
trigger
IEEE1588 PTP
RMII
= 7 pins
RMII + MDC
= 9 pins
MS19970V1
/2 or /20
2.5 or 25 MHz synchronous 50 MHz
XTAL
25 MHz OSC
PLL
REF_CLK
MCO1/MCO2
Revision history STM32F405xx, STM32F407xx
176/185 DocID022152 Rev 4
8 Revision history
Table 98. Document revision history
Date Revision Changes
15-Sep-2011 1 Initial release.
24-Jan-2012 2
Added WLCSP90 package on cover page.
Renamed USART4 and USART5 into UART4 and UART5,
respectively.
Updated number of USB OTG HS and FS in Table 2: STM32F405xx
and STM32F407xx: features and peripheral counts.
Updated Figure 3: Compatible board design between
STM32F10xx/STM32F2xx/STM32F4xx for LQFP144 package and
Figure 4: Compatible board design between STM32F2xx and
STM32F4xx for LQFP176 and BGA176 packages, and removed note
1 and 2.
Updated Section 2.2.9: Flexible static memory controller (FSMC).
Modified I/Os used to reprogram the Flash memory for CAN2 and
USB OTG FS in Section 2.2.13: Boot modes.
Updated note in Section 2.2.14: Power supply schemes.
PDR_ON no more available on LQFP100 package. Updated
Section 2.2.16: Voltage regulator. Updated condition to obtain a
minimum supply voltage of 1.7 V in the whole document.
Renamed USART4/5 to UART4/5 and added LIN and IrDA feature for
UART4 and UART5 in Table 5: USART feature comparison.
Removed support of I2C for OTG PHY in Section 2.2.30: Universal
serial bus on-the-go full-speed (OTG_FS).
Added Table 6: Legend/abbreviations used in the pinout table.
Table 7: STM32F40x pin and ball definitions: replaced VSS_3, VSS_4,
and VSS_8 by VSS; reformatted Table 7: STM32F40x pin and ball
definitions to better highlight I/O structure, and alternate functions
versus additional functions; signal corresponding to LQFP100 pin 99
changed from PDR_ON to VSS; EVENTOUT added in the list of
alternate functions for all I/Os; ADC3_IN8 added as alternate function
for PF10; FSMC_CLE and FSMC_ALE added as alternate functions
for PD11 and PD12, respectively; PH10 alternate function
TIM15_CH1_ETR renamed TIM5_CH1; updated PA4 and PA5 I/O
structure to TTa.
Removed OTG_HS_SCL, OTG_HS_SDA, OTG_FS_INTN in Table 7:
STM32F40x pin and ball definitions and Table 9: Alternate function
mapping.
Changed TCM data RAM to CCM data RAM in Figure 18: STM32F40x
memory map.
Added IVDD and IVSS maximum values in Table 12: Current
characteristics.
Added Note 1 related to fHCLK, updated Note 2 in Table 14: General
operating conditions, and added maximum power dissipation values.
Updated Table 15: Limitations depending on the operating power
supply range.
DocID022152 Rev 4 177/185
STM32F405xx, STM32F407xx Revision history
24-Jan-2012
2
(continued)
Added V12 in Table 19: Embedded reset and power control block
characteristics.
Updated Table 21: Typical and maximum current consumption in Run
mode, code with data processing running from Flash memory (ART
accelerator disabled) and Table 20: Typical and maximum current
consumption in Run mode, code with data processing running from
Flash memory (ART accelerator enabled) or RAM. Added Figure ,
Figure 25, Figure 26, and Figure 27.
Updated Table 22: Typical and maximum current consumption in Sleep
mode and removed Note 1.
Updated Table 23: Typical and maximum current consumptions in Stop
mode and Table 24: Typical and maximum current consumptions in
Standby mode, Table 25: Typical and maximum current consumptions
in VBAT mode, and Table 26: Switching output I/O current
consumption.
Section : On-chip peripheral current consumption: modified conditions,
and updated Table 27: Peripheral current consumption and Note 2.
Changed fHSE_ext to 50 MHz and tr(HSE)/tf(HSE) maximum value in
Table 29: High-speed external user clock characteristics.
Added Cin(LSE) in Table 30: Low-speed external user clock
characteristics.
Updated maximum PLL input clock frequency, removed related note,
and deleted jitter for MCO for RMII Ethernet typical value in Table 35:
Main PLL characteristics. Updated maximum PLLI2S input clock
frequency and removed related note in Table 36: PLLI2S (audio PLL)
characteristics.
Updated Section : Flash memory to specify that the devices are
shipped to customers with the Flash memory erased. Updated
Table 38: Flash memory characteristics, and added tME in Table 39:
Flash memory programming.
Updated Table 42: EMS characteristics, and Table 43: EMI
characteristics.
Updated Table 56: I2S dynamic characteristics
Updated Figure 46: ULPI timing diagram and Table 62: ULPI timing.
Added tCOUNTER and tMAX_COUNT in Table 51: Characteristics of TIMx
connected to the APB1 domain and Table 52: Characteristics of TIMx
connected to the APB2 domain. Updated Table 65: Dynamic
characteristics: Ethernet MAC signals for RMII.
Removed USB-IF certification in Section : USB OTG FS
characteristics.
Table 98. Document revision history (continued)
Date Revision Changes
Revision history STM32F405xx, STM32F407xx
178/185 DocID022152 Rev 4
24-Jan-2012
2
(continued)
Updated Table 61: USB HS clock timing parameters
Updated Table 67: ADC characteristics.
Updated Table 68: ADC accuracy at fADC = 30 MHz.
Updated Note 1 in Table 74: DAC characteristics.
Section 5.3.25: FSMC characteristics: updated Table 75 toTable 86,
changed CL value to 30 pF, and modified FSMC configuration for
asynchronous timings and waveforms. Updated Figure 60:
Synchronous multiplexed PSRAM write timings.
Updated Table 96: Package thermal characteristics.
Appendix A.1: USB OTG full speed (FS) interface solutions: modified
Figure 86: USB controller configured as peripheral-only and used in
Full speed mode added Note 2, updated Figure 87: USB controller
configured as host-only and used in full speed mode and added
Note 2, changed Figure 88: USB controller configured in dual mode
and used in full speed mode and added Note 3.
Appendix A.2: USB OTG high speed (HS) interface solutions: removed
figures USB OTG HS device-only connection in FS mode and USB
OTG HS host-only connection in FS mode, and updated Figure 89:
USB controller configured as peripheral, host, or dual-mode and used
in high speed mode and added Note 2.
Added Appendix A.3: Ethernet interface solutions.
Table 98. Document revision history (continued)
Date Revision Changes
DocID022152 Rev 4 179/185
STM32F405xx, STM32F407xx Revision history
31-May-2012 3
Updated Figure 5: STM32F40x block diagram and Figure 7: Power
supply supervisor interconnection with internal reset OFF
Added SDIO, added notes related to FSMC and SPI/I2S in Table 2:
STM32F405xx and STM32F407xx: features and peripheral counts.
Starting from Silicon revision Z, USB OTG full-speed interface is now
available for all STM32F405xx devices.
Added full information on WLCSP90 package together with
corresponding part numbers.
Changed number of AHB buses to 3.
Modified available Flash memory sizes in Section 2.2.4: Embedded
Flash memory.
Modified number of maskable interrupt channels in Section 2.2.10:
Nested vectored interrupt controller (NVIC).
Updated case of Regulator ON/internal reset ON, Regulator
ON/internal reset OFF, and Regulator OFF/internal reset ON in
Section 2.2.16: Voltage regulator.
Updated standby mode description in Section 2.2.19: Low-power
modes.
Added Note 1 below Figure 16: STM32F40x UFBGA176 ballout.
Added Note 1 below Figure 17: STM32F40x WLCSP90 ballout.
Updated Table 7: STM32F40x pin and ball definitions.
Added Table 8: FSMC pin definition.
Removed OTG_HS_INTN alternate function in Table 7: STM32F40x
pin and ball definitions and Table 9: Alternate function mapping.
Removed I2S2_WS on PB6/AF5 in Table 9: Alternate function
mapping.
Replaced JTRST by NJTRST, removed ETH_RMII _TX_CLK, and
modified I2S3ext_SD on PC11 in Table 9: Alternate function mapping.
Added Table 10: STM32F40x register boundary addresses.
Updated Figure 18: STM32F40x memory map.
Updated VDDA and VREF+ decoupling capacitor in Figure 21: Power
supply scheme.
Added power dissipation maximum value for WLCSP90 in Table 14:
General operating conditions.
Updated VPOR/PDR in Table 19: Embedded reset and power control
block characteristics.
Updated notes in Table 21: Typical and maximum current consumption
in Run mode, code with data processing running from Flash memory
(ART accelerator disabled), Table 20: Typical and maximum current
consumption in Run mode, code with data processing running from
Flash memory (ART accelerator enabled) or RAM, and Table 22:
Typical and maximum current consumption in Sleep mode.
Updated maximum current consumption at TA = 25 °n Table 23:
Typical and maximum current consumptions in Stop mode.
Table 98. Document revision history (continued)
Date Revision Changes
Revision history STM32F405xx, STM32F407xx
180/185 DocID022152 Rev 4
31-May-2012 3
(continued)
Removed fHSE_ext typical value in Table 29: High-speed external user
clock characteristics. Updated Table 31: HSE 4-26 MHz oscillator
characteristics and Table 32: LSE oscillator characteristics (fLSE =
32.768 kHz).
Added fPLL48_OUT maximum value in Table 35: Main PLL
characteristics.
Modified equation 1 and 2 in Section 5.3.11: PLL spread spectrum
clock generation (SSCG) characteristics.
Updated Table 38: Flash memory characteristics, Table 39: Flash
memory programming, and Table 40: Flash memory programming with
VPP.
Updated Section : Output driving current.
Table 53: I2C characteristics: Note 4 updated and applied to th(SDA) in
Fast mode, and removed note 4 related to th(SDA) minimum value.
Updated Table 67: ADC characteristics. Updated note concerning ADC
accuracy vs. negative injection current below Table 68: ADC accuracy
at fADC = 30 MHz.
Added WLCSP90 thermal resistance in Table 96: Package thermal
characteristics.
Updated Table 90: WLCSP90 - 0.400 mm pitch wafer level chip size
package mechanical data.
Updated Figure 83: UFBGA176+25 - ultra thin fine pitch ball grid array
10 × 10 × 0.6 mm, package outline and Table 94: UFBGA176+25 -
ultra thin fine pitch ball grid array 10 × 10 × 0.6 mm mechanical data.
Added Figure 85: LQFP176 recommended footprint.
Removed 256 and 768 Kbyte Flash memory density from Table 97:
Ordering information scheme.
Table 98. Document revision history (continued)
Date Revision Changes
DocID022152 Rev 4 181/185
STM32F405xx, STM32F407xx Revision history
04-Jun-2013 4
Modified Note 1 below Table 2: STM32F405xx and STM32F407xx:
features and peripheral counts.
Updated Figure 4 title.
Updated Note 3 below Figure 21: Power supply scheme.
Changed simplex mode into half-duplex mode in Section 2.2.25: Interintegrated
sound (I2S).
Replaced DAC1_OUT and DAC2_OUT by DAC_OUT1 and
DAC_OUT2, respectively.
Updated pin 36 signal in Figure 15: STM32F40x LQFP176 pinout.
Changed pin number from F8 to D4 for PA13 pin in Table 7:
STM32F40x pin and ball definitions.
Replaced TIM2_CH1/TIM2_ETR by TIM2_CH1_ETR for PA0 and PA5
pins in Table 9: Alternate function mapping.
Changed system memory into System memory + OTP in Figure 18:
STM32F40x memory map.
Added Note 1 below Table 16: VCAP_1/VCAP_2 operating conditions.
Updated IDDA description in Table 74: DAC characteristics.
Removed PA9/PB13 connection to VBUS in Figure 86: USB controller
configured as peripheral-only and used in Full speed mode and
Figure 87: USB controller configured as host-only and used in full
speed mode.
Updated SPI throughput on front page and Section 2.2.24: Serial
peripheral interface (SPI)
Updated operating voltages in Table 2: STM32F405xx and
STM32F407xx: features and peripheral counts
Updated note in Section 2.2.14: Power supply schemes
Updated Section 2.2.15: Power supply supervisor
Updated “Regulator ON” paragraph in Section 2.2.16: Voltage
regulator
Removed note in Section 2.2.19: Low-power modes
Corrected wrong reference manual in Section 2.2.28: Ethernet MAC
interface with dedicated DMA and IEEE 1588 support
Updated Table 15: Limitations depending on the operating power
supply range
Updated Table 24: Typical and maximum current consumptions in
Standby mode
Updated Table 25: Typical and maximum current consumptions in
VBAT mode
Updated Table 36: PLLI2S (audio PLL) characteristics
Updated Table 43: EMI characteristics
Updated Table 48: Output voltage characteristics
Updated Table 50: NRST pin characteristics
Updated Table 55: SPI dynamic characteristics
Updated Table 56: I2S dynamic characteristics
Deleted Table 59
Updated Table 62: ULPI timing
Updated Figure 47: Ethernet SMI timing diagram
Table 98. Document revision history (continued)
Date Revision Changes
Revision history STM32F405xx, STM32F407xx
182/185 DocID022152 Rev 4
04-Jun-2013 4
(continued)
Updated Figure 83: UFBGA176+25 - ultra thin fine pitch ball grid array
10 × 10 × 0.6 mm, package outline
Updated Table 94: UFBGA176+25 - ultra thin fine pitch ball grid array
10 × 10 × 0.6 mm mechanical data
Updated Figure 5: STM32F40x block diagram
Updated Section 2: Description
Updated footnote (3) in Table 2: STM32F405xx and STM32F407xx:
features and peripheral counts
Updated Figure 3: Compatible board design between
STM32F10xx/STM32F2xx/STM32F4xx for LQFP144 package
Updated Figure 4: Compatible board design between STM32F2xx and
STM32F4xx for LQFP176 and BGA176 packages
Updated Section 2.2.14: Power supply schemes
Updated Section 2.2.15: Power supply supervisor
Updated Section 2.2.16: Voltage regulator, including figures.
Updated Table 14: General operating conditions, including footnote (2).
Updated Table 15: Limitations depending on the operating power
supply range, including footnote (3).
Updated footnote (1) in Table 67: ADC characteristics.
Updated footnote (3) in Table 68: ADC accuracy at fADC = 30 MHz.
Updated footnote (1) in Table 74: DAC characteristics.
Updated Figure 9: Regulator OFF.
Updated Figure 7: Power supply supervisor interconnection with
internal reset OFF.
Added Section 2.2.17: Regulator ON/OFF and internal reset ON/OFF
availability.
Updated footnote (2) of Figure 21: Power supply scheme.
Replaced respectively “I2S3S_WS" by "I2S3_WS”, “I2S3S_CK” by
“I2S3_CK” and “FSMC_BLN1” by “FSMC_NBL1” in Table 9: Alternate
function mapping.
Added “EVENTOUT” as alternate function “AF15” for pin PC13, PC14,
PC15, PH0, PH1, PI8 in Table 9: Alternate function mapping
Replaced “DCMI_12” by “DCMI_D12” in Table 7: STM32F40x pin and
ball definitions.
Removed the following sentence from Section : I2C interface
characteristics: ”Unless otherwise specified, the parameters
given in Table 53 are derived from tests performed under the
ambient temperature, fPCLK1 frequency and VDD supply voltage
conditions summarized in Table 14.”.
In Table 7: STM32F40x pin and ball definitions on page 45:
– For pin PC13, replaced “RTC_AF1” by “RTC_OUT, RTC_TAMP1,
RTC_TS”
– for pin PI8, replaced “RTC_AF2” by “RTC_TAMP1, RTC_TAMP2,
RTC_TS”.
– for pin PB15, added RTC_REFIN in Alternate functions column.
In Table 9: Alternate function mapping on page 60, for port
PB15, replaced “RTC_50Hz” by “RTC_REFIN”.
Table 98. Document revision history (continued)
Date Revision Changes
DocID022152 Rev 4 183/185
STM32F405xx, STM32F407xx Revision history
04-Jun-2013 4
(continued)
Updated Figure 6: Multi-AHB matrix.
Updated Figure 7: Power supply supervisor interconnection with
internal reset OFF
Changed 1.2 V to V12 in Section : Regulator OFF
Updated LQFP176 pin 48.
Updated Section 1: Introduction.
Updated Section 2: Description.
Updated operating voltage in Table 2: STM32F405xx and
STM32F407xx: features and peripheral counts.
Updated Note 1.
Updated Section 2.2.15: Power supply supervisor.
Updated Section 2.2.16: Voltage regulator.
Updated Figure 9: Regulator OFF.
Updated Table 3: Regulator ON/OFF and internal reset ON/OFF
availability.
Updated Section 2.2.19: Low-power modes.
Updated Section 2.2.20: VBAT operation.
Updated Section 2.2.22: Inter-integrated circuit interface (I²C) .
Updated pin 48 in Figure 15: STM32F40x LQFP176 pinout.
Updated Table 6: Legend/abbreviations used in the pinout table.
Updated Table 7: STM32F40x pin and ball definitions.
Updated Table 14: General operating conditions.
Updated Table 15: Limitations depending on the operating power
supply range.
Updated Section 5.3.7: Wakeup time from low-power mode.
Updated Table 33: HSI oscillator characteristics.
Updated Section 5.3.15: I/O current injection characteristics.
Updated Table 47: I/O static characteristics.
Updated Table 50: NRST pin characteristics.
Updated Table 53: I2C characteristics.
Updated Figure 39: I2C bus AC waveforms and measurement circuit.
Updated Section 5.3.19: Communications interfaces.
Updated Table 67: ADC characteristics.
Added Table 70: Temperature sensor calibration values.
Added Table 73: Internal reference voltage calibration values.
Updated Section 5.3.25: FSMC characteristics.
Updated Section 5.3.27: SD/SDIO MMC card host interface (SDIO)
characteristics.
Updated Table 23: Typical and maximum current consumptions in Stop
mode.
Updated Section : SPI interface characteristics included Table 55.
Updated Section : I2S interface characteristics included Table 56.
Updated Table 64: Dynamic characteristics: Ehternet MAC signals for
SMI.
Updated Table 66: Dynamic characteristics: Ethernet MAC signals for
MII.
Table 98. Document revision history (continued)
Date Revision Changes
Revision history STM32F405xx, STM32F407xx
184/185 DocID022152 Rev 4
04-Jun-2013 4
(continued)
Updated Table 64: Dynamic characteristics: Ehternet MAC signals for
SMI.
Updated Table 66: Dynamic characteristics: Ethernet MAC signals for
MII.
Updated Table 79: Synchronous multiplexed NOR/PSRAM read
timings.
Updated Table 80: Synchronous multiplexed PSRAM write timings.
Updated Table 81: Synchronous non-multiplexed NOR/PSRAM read
timings.
Updated Table 82: Synchronous non-multiplexed PSRAM write
timings.
Updated Section 5.3.26: Camera interface (DCMI) timing specifications
including Table 87: DCMI characteristics and addition of Figure 73:
DCMI timing diagram.
Updated Section 5.3.27: SD/SDIO MMC card host interface (SDIO)
characteristics including Table 88.
Updated Chapter Figure 9.
Table 98. Document revision history (continued)
Date Revision Changes
DocID022152 Rev 4 185/185
STM32F405xx, STM32F407xx
Please Read Carefully:
Information in this document is provided solely in connection with ST products. STMicroelectronics NV and its subsidiaries (“ST”) reserve the
right to make changes, corrections, modifications or improvements, to this document, and the products and services described herein at any
time, without notice.
All ST products are sold pursuant to ST’s terms and conditions of sale.
Purchasers are solely responsible for the choice, selection and use of the ST products and services described herein, and ST assumes no
liability whatsoever relating to the choice, selection or use of the ST products and services described herein.
No license, express or implied, by estoppel or otherwise, to any intellectual property rights is granted under this document. If any part of this
document refers to any third party products or services it shall not be deemed a license grant by ST for the use of such third party products
or services, or any intellectual property contained therein or considered as a warranty covering the use in any manner whatsoever of such
third party products or services or any intellectual property contained therein.
UNLESS OTHERWISE SET FORTH IN ST’S TERMS AND CONDITIONS OF SALE ST DISCLAIMS ANY EXPRESS OR IMPLIED
WARRANTY WITH RESPECT TO THE USE AND/OR SALE OF ST PRODUCTS INCLUDING WITHOUT LIMITATION IMPLIED
WARRANTIES OF MERCHANTABILITY, FITNESS FOR A PARTICULAR PURPOSE (AND THEIR EQUIVALENTS UNDER THE LAWS
OF ANY JURISDICTION), OR INFRINGEMENT OF ANY PATENT, COPYRIGHT OR OTHER INTELLECTUAL PROPERTY RIGHT.
ST PRODUCTS ARE NOT AUTHORIZED FOR USE IN WEAPONS. NOR ARE ST PRODUCTS DESIGNED OR AUTHORIZED FOR USE
IN: (A) SAFETY CRITICAL APPLICATIONS SUCH AS LIFE SUPPORTING, ACTIVE IMPLANTED DEVICES OR SYSTEMS WITH
PRODUCT FUNCTIONAL SAFETY REQUIREMENTS; (B) AERONAUTIC APPLICATIONS; (C) AUTOMOTIVE APPLICATIONS OR
ENVIRONMENTS, AND/OR (D) AEROSPACE APPLICATIONS OR ENVIRONMENTS. WHERE ST PRODUCTS ARE NOT DESIGNED
FOR SUCH USE, THE PURCHASER SHALL USE PRODUCTS AT PURCHASER’S SOLE RISK, EVEN IF ST HAS BEEN INFORMED IN
WRITING OF SUCH USAGE, UNLESS A PRODUCT IS EXPRESSLY DESIGNATED BY ST AS BEING INTENDED FOR “AUTOMOTIVE,
AUTOMOTIVE SAFETY OR MEDICAL” INDUSTRY DOMAINS ACCORDING TO ST PRODUCT DESIGN SPECIFICATIONS.
PRODUCTS FORMALLY ESCC, QML OR JAN QUALIFIED ARE DEEMED SUITABLE FOR USE IN AEROSPACE BY THE
CORRESPONDING GOVERNMENTAL AGENCY.
Resale of ST products with provisions different from the statements and/or technical features set forth in this document shall immediately void
any warranty granted by ST for the ST product or service described herein and shall not create or extend in any manner whatsoever, any
liability of ST.
ST and the ST logo are trademarks or registered trademarks of ST in various countries.
Information in this document supersedes and replaces all information previously supplied.
The ST logo is a registered trademark of STMicroelectronics. All other names are the property of their respective owners.
© 2013 STMicroelectronics - All rights reserved
STMicroelectronics group of companies
Australia - Belgium - Brazil - Canada - China - Czech Republic - Finland - France - Germany - Hong Kong - India - Israel - Italy - Japan -
Malaysia - Malta - Morocco - Philippines - Singapore - Spain - Sweden - Switzerland
SIXTY
User Guide
LU Sixty.book Page 1 Mardi, 26. octobre 2010 2:22 14
1Couv.fm Page 1 Dimanche, 16. mai 2010 3:20 15
3
Dear customer,
You have just acquired a new generation Sagemcom telephone and thank you for placing your confidence in us.
This device has been manufactured with the utmost care. If you should have difficulties in operating it, we recommend
that you consult this user manual.
You can also find information on the following site:
http://www.sagemcom.com/sixty
To operate the device safely and easily, please read carefully the paragraph “Recommendations and safety
instructions”, page 6.
The CE label confirms that the product complies with the 1999/5/EC regulations of the European Union
Parliament regarding wireless systems and telecommunications.
The declaration of compliance may be looked up on the www.sagemcom.com website, or can be obtained
from the following address :
Sagemcom Broadband SAS
250, route de l'Empereur - 92848 Rueil-Malmaison Cedex - France
Copyright © Sagemcom Broadband SAS
All rights reserved
Sagemcom is a registered trademark
LU Sixty.book Page 3 Mercredi, 19. mai 2010 12:30 12
4
Contents
Recommendations and safety instructions .....................6
Unpacking .......................................................................8
Phone description ...........................................................8
Your base................................................................... 8
Your handset.............................................................. 9
Control panel............................................................ 10
Phone installation ............................................ 12
Connecting the base .....................................................12
Setting up the handset ..................................................12
Charging batteries .........................................................12
Settings required before use .........................................13
Navigating in the menu .................................................13
Menu structure ......................................................... 14
Browsing through the menus ................................... 14
Phone use......................................................... 15
Handset location ...........................................................15
Telephoning ..................................................................15
Receiving a call ........................................................ 15
Making a call ............................................................ 16
Ending a call............................................................. 16
During a call ............................................................. 16
Call key function....................................................... 17
Secret mode............................................................. 17
Hands-free/speakerphone mode.............................. 17
Calling the last number dialled ................................. 18
Call time display ....................................................... 18
Phonebook ....................................................... 18
Creating an entry ...........................................................18
Editing an entry .............................................................19
Associating a ring tone with a phonebook entry ............19
Other number ................................................................19
Deleting an entry ...........................................................19
Calling using the phonebook .........................................20
Searching for a contact .................................................20
Call log.............................................................. 20
Viewing the received and dialled call log ...................... 20
The events log .............................................................. 21
Viewing the events log............................................. 21
Activating/deactivating
the new event information screen............................ 21
Clearing notifications ............................................... 21
Information .................................................................... 21
Accessories...................................................... 22
Alarm clock ................................................................... 22
Activating / deactivating the alarm clock.................. 22
Changing the alarm clock ring tone ......................... 22
Modifying the alarm clock time ................................ 22
Timer ............................................................................ 22
Activate the timer..................................................... 22
Changing the programmed time of the timer ........... 23
Displaying or hiding the programmed time
of the timer............................................................... 23
Changing the timer ring tone ................................... 23
Ring tones ........................................................ 23
Changing the ring tones ............................................... 23
Activating or deactivating the beeps ............................. 23
Activating/deactivating the silent mode ........................ 24
Settings............................................................. 24
Modifying the date and time ......................................... 24
Adjusting the contrast ................................................... 24
Modifying the language ................................................ 24
the voice box number (according to operator) .............. 25
Defining forbidden prefixes - Call barring ..................... 25
Demo ............................................................................ 26
Advanced settings ........................................................ 26
Base settings ........................................................... 26
Line settings ............................................................ 27
Modifying the base code.......................................... 29
LU Sixty.book Page 4 Mercredi, 19. mai 2010 12:30 12
5
Answering machine......................................... 29
Enabling / disabling the answering machine .................29
Modifying the OGM .......................................................30
Recording a personal outgoing message ................ 30
Deleting your personal OGM ................................... 30
Listen to a personal message .................................. 30
Playing messages .........................................................30
Remote access to answering machine .........................31
Deleting all the old messages .......................................31
TAM settings .................................................... 32
Activating and deactivating call screening ....................32
Modifying the remote access code ...............................32
Number of rings ............................................................32
Replacing the batteries................................... 33
Pairing GAP-compatible DECT handsets
on the SIXTY base ........................................... 33
Appendix .......................................................... 34
Care and Maintenance ..................................................34
Problems .......................................................................34
Technical characteristics................................ 35
Initial condition .............................................................35
Environment..................................................... 36
Packaging .....................................................................36
Batteries and rechargeable batteries ............................36
The product ...................................................................36
Guarantee......................................................... 37
Terms and Conditions for United Kingdom
& Ireland only ................................................................37
Terms and Conditions for other countries .....................39
LU SixtyTDM.fm Page 5 Jeudi, 20. mai 2010 9:03 09
6
RECOMMENDATIONS AND SAFETY INSTRUCTIONS
Do not install your DECT telephone in a damp environment, such as a bathroom, washroom, kitchen etc, and
not within 1.50 metres of a source of water or outside. This device is designed for use in temperatures of
between 5 °C and 45 °C.
Do not attempt to remove screws or open the appliance. It does not contain any user-replaceable parts.
Only use the power unit supplied and connect it to the electricity mains in accordance with the installation
instructions in this user manual and the details on the sticker regarding voltage, electrical current and
frequency. As a precaution if there is a risk of danger, the power plug can be pulled out to disconnect the 230
volt power supply. Therefore the sockets should be near the device and easily accessible.
This device is designed to be used for connecting to the public telephone network. If problems should arise,
contact your nearest specialist dealer. Only use the telephone cable supplied.
For safety reasons, never put the handset in the base station without the battery inserted or without the lid on
the battery compartment as this could cause an electric shock.
To avoid damaging your handset/base, only use certified rechargeable batteries NiMH 1.2 V 450 mAh, never
use non rechargeable batteries. Insert the batteries in the handset/base battery compartment respecting
polarity.
The used battery must be disposed of in line with the recycling regulations in this user manual.
Your DECT telephone has a range of approx. 50 metres indoors and up to 300 metres outdoors. The range
can be affected by the proximity of metal objects, such as a television and electrical devices.
Zones without reception may appear owing to elements in the building. This can cause brief interruptions in
the conversation, caused by faulty transmission.
LU Sixty.book Page 6 Mercredi, 19. mai 2010 12:30 12
7
Certain medical equipment and highly-sensitive machines or security systems may be affected by the
transmission power of the telephone. In these cases we recommend adhering to the safety information.
In regions greatly affected by electrical storms we recommend that you protect your telephone circuit with a
special fixture for excess voltage.
Your SIXTY has anti-skid pads that should leave no traces on your furniture and ensure stability. However,
given the the wide variety of finishes used by furniture manufacturers, traces may appear on surfaces in
contact with the parts of your SIXTY. Sagemcom Broadband SAS decline all responsibility in any such cases
of damage.
LU Sixty.book Page 7 Mercredi, 19. mai 2010 12:30 12
8
UNPACKING
Place the box in front of you, open it and make sure it contains the following items:
• one base SIXTY, one handset, one telephone line cord, one equipped power adapter and this user guide.
PHONE DESCRIPTION
Your base
The SIXTY is the contemporary interpretation by SAGEMCOM of the S63, which accompanied the development of
telephone communications in many countries in the 60s and 70s. It nevertheless has the latest technology, such as
browser touch buttons, Hifi ringtones, dialling light and sound effects.
* Keyway: indicates the position of the handset earpiece
** Press and hold the key :
- If the answering machine is turned off: access to voice messaging service.
- If the answering machine is turned on: access to your messages on the answering machine.
Base button/Paging
- Short press:
find handsets (Paging)
- Press and hold :
handset registration
Keyway *
Loudspeaker/
Pick up
Indicator light
Access to voice messaging service/
Access to your messages
on the answering machine **
LU Sixty.book Page 8 Mercredi, 19. mai 2010 12:30 12
9
Your handset
SIXTY's particularity is that it has a wireless handset.
The single button on the handset allows the user to hang up or answer an incoming call. It should be noted that the
handset is provided with a buzzer that sounds on receiving an incoming call with the handset not on its base.
The handset batteries are charged when the handset is placed on its base. When off the base, the handset's battery
power provides 120 hours of standby time and 10 hours of talk time.
Indicator light operation:
• Fast flashing: handset registration or paging.
• Slow flashing: handset on line or new events.
Make sure that when the handset is on the charger, the icon is animated.
Hang up/ Pick up
Battery compartment
Battery cover
Handset charging
contacts
Speaker
Microphone
+
-
LU Sixty.book Page 9 Mercredi, 19. mai 2010 12:30 12
10
Control panel
Your SIXTY has a touch keys for access to configuration and settings functions. The screen tells you about the state
(date and time, unread message, etc..).
Using the touch buttons
The screen includes six touch keys around its periphery. Simply touch the tactile area for the function to be taken into
account:
Key Function(s) Key Function(s)
Scroll up /Go to the menu list. Browse down / Go to the menu list.
Context key 1: Access a menu / Validate
the selection.
Context key 2: Delete an entry / Return
to the previous menu.
Asterisk key. # key.
LU Sixty.book Page 10 Mercredi, 19. mai 2010 12:30 12
11
Display screen
During use or on standby, the screen of your SIXTY tells you about the state of your telephone by showing icons, and
in particular:
* The low emission icon (ECO mode): Your telephone is provided with an automatic power management
system. As soon as the handset is near its base, the power required is reduced to the minimum. Radio
transmissions are also cut off when the handset is placed on the base, and the low emission icon is then
displayed.
If a second handset is paired with the base, the "low emission" icon is no longer displayed.
Battery indicator
Microphone off
Current call
Speakerphone on Recording answering machine on
Alarm on
New voice message
Low emission icon*
LU Sixty.book Page 11 Mercredi, 19. mai 2010 12:30 12
12
PHONE INSTALLATION
CONNECTING THE BASE
Never force the plugs: they are in different shapes to
avoid connection mistakes.
1. On the underside of the base, click the phone jack into
its socket and connect the other end of the cord to the
telephone wall outlet.
2. Connect the end of the power supply cord on the
underside of the base and connect the power adapter
to the mains socket. The phone display is turned on.
SETTING UP THE HANDSET
The batteries are already inserted in the handset. To put
the handset into use, simply remove the tab by pulling on
it firmly in the direction of the arrow.
The handset emits a double beep to indicate that it has
started and then a second beep to indicate that the
handset is synchronized with the base. From then on,
your handset becomes operative and you can use it to
make calls.
You can now use your telephone to make and receive
calls.
CHARGING BATTERIES
Place the handset on its base and fully charge the
batteries.
An audio signal is emitted and a light flashes when the
handset is placed correctly on the base.
The battery charge icon is animated to indicate that
the battery is being charged and stops to indicate that the
batteries are fully charged.
Before making any connections, please
refer to the safety instructions presented
at the beginning of this user guide.
Power socket Telephone socket
On leaving the factory, the handset is
already registered in the base.
If your handset is not recognized by the
base, then launch a manual registration
(See paragraph "Set the base to
registration mode", page 26.
LU Sixty.book Page 12 Mercredi, 19. mai 2010 12:30 12
13
SETTINGS REQUIRED BEFORE USE
Setting the date and time accurately will enable you to
Follow your calls and messages chronologically.
According to where your base is situated in the room, You
may have to adjust the contrast.
To set the date and time, refer to paragraph "Modifying
the date and time ", page 24.
To set the contrast or the brightness of the screen, refer
to paragraph "Adjusting the contrast ", page 24.
NAVIGATING IN THE MENU
With your SIXTY you can create your own telephone
directory, display the list of calls etc. To do this, use the
touch keys.
With the touch keys and you can choose a menu, a
sub-menu or a precise setting.
The key allows you to enter the sub-menus of the
chosen function and select the setting to modify. With the
key you can return to the previous function or cancel
the current choice.
The keys and are used when you use the
answerphone.
See the menu structure to familiarise yourself with what
your phone can do.
The handset batteries charging time is 10
hours. During charging, the batteries may
heat up. This is quite normal and perfectly
safe.
Handset charging contacts
Base charging contacts
LU Sixty.book Page 13 Mercredi, 19. mai 2010 12:30 12
14
Menu structure
To access one of your phone's menus, use key or .
Browsing through the menus
Use the browsing keys or to select the desired
menu. Press Valid. To confirm your selection.
Select the desired function by pressing the browsing keys
or and then press the Valid. key.
- To return to the previous menu, press Return.
- To save the settings, press Valid..
Example:
To access the menu SETTINGS /DATE/TIME:
1. Use or to access the menu list.
2. Select SETTINGS using or . Press Valid..
3. Select DATE/TIME using or . Press Valid.
You are now under the DATE/TIME menu.P
Menu PHONEBOOK
ACCESSORIES
CALLS
CALL
INCOMING CALLS
OUTGOING CALLS
EVENTS
ALARM
TIMER
EXTERNAL CALL
SILENT MODE
RING TONE
SETTINGS
Option
VIEW
RING TONE
DELETE
ADD NUMBER
NEW ENTRY
BEEPS
DATE/TIME
CONTRAST
DEMO
ANS.MACH MESSAGES
ON/ OFF
OUTGOING MESS.
SETTINGS
LANGUAGE
Edit
RESTRICTION
ADVANCED SET.
VOICE BOX No
DATE/TIME
LU Sixty.book Page 14 Mercredi, 19. mai 2010 12:30 12
15
PHONE USE
HANDSET LOCATION
Lost your handset? Press the button on the back of
the base, behind the keypad. The handset will then ring.
TELEPHONING
Receiving a call
• When a call is received, the phone rings.
• The caller's phone number is displayed on the screen
if you have subscribed to the "Caller ID" service.
The caller's name may also be displayed if it is
included in your phone book.
Accepting a call in handset mode
• Pick up the phone handset. You do not need to
press the handset's button.
• Make sure to identify the handset direction by the
dot which identifies the earpiece end. The call time
counter is displayed on the screen.
• To end the call, hang up the handset or press the
handset button.
• A visual and audible signal confirms that the handset
is hung up correctly.
• If the handset is not on the base, you have to press
the handset button to take the call.
Accepting a call in speakerphone mode
• Press to speak in speakerphone mode (without
holding the handset). The symbol and the
call time counter are displayed on the screen.
• To end the call, press again.
Toggle between handset mode and speakerphone
mode
• If you are in handset mode, press and hold the
key and then hang up the handset to toggle to
speakerphone mode. Press the key again to
end the call.
• If you are in speakerphone mode:
- If the handset is hung up on the base, lift the phone
handset to toggle to handset mode.
- If the handset is not hung up on the base, press
the dial tone button to toggle to handset mode.
• To end the call, hang up the handset on the base or
press .
Use the and keys to vary the
earphone volume or speakerphone
volume. The handset earphone volume or
speakerphone volume can vary from 1
to 5.
LU Sixty.book Page 15 Mercredi, 19. mai 2010 12:30 12
16
Making a call
The call can be made in two ways:
Making a call in handset mode
• Pick up the handset.
• The icon is displayed on the screen. Dial your
number on the keypad.
The call time counter is displayed on the screen.
Making a call in speakerphone mode
• Press to obtain a dial tone prompt on the
screen. Dial your number on the keypad.
The and icons are displayed on the
screen. The call time counter is displayed on the
screen.
Ending a call
When you have finished your call, press or hang up
the handset on the base.
During a call
Receiving a second call
• During the call, a beep is transmitted to your telephone
by your service provider to let you know that
you have a second call waiting.
• Press ACCEPT to take this new call.
• Your other caller is then put on hold and you can
talk with your second caller.
Making a second call
• During a call, you can put your contact on hold and
call a second one by pressing -R- and dial the number
using the keypad.
• The second call is then launched, with the first call
still on hold.
To alternate from one call to the other
• To toggle from one call to the other, press Menu
then SWITCH.
• The call in progress is put on hold, and you can
then take the second call.
To end one of the calls and continue the other
one
• To toggle from one call and take the other, press
Menu and then HANGING UP.
• The call in progress is definitely terminated, and
you can then take the second call.
You can also dial a number in pre-dialling
mode, whether in handset or
speakerphone mode: dial the number on
the keypad and then lift the handset or
press .
If necessary, you can correct the number
entered by pressing BACK.
The caller on hold hears a beep emitted by
the network.
LU Sixty.book Page 16 Mercredi, 19. mai 2010 12:30 12
17
To set up a 3 way-call (the two parties and
yourself)
• During a call, press Menu and then 3-PARTY
CONF.
• You can then talk to both parties simultaneously,
and "3-PARTY CONF" is displayed on the screen.
• To end the 3 way-call, Hang up the handset.
Call key function
This key is a shortcut to your phone's call log.
• From the idle screen, press the key :
- INCOMING CALLS,
- OUTGOING CALLS,
- EVENTS.
• Press keys or to select the calls list.
• Press Valid. and then select the number using keys
or .
Secret mode
During a call, you can switch to mute mode and your
phone's microphone will be muted. The person you are on
line with can no longer hear you.
To activate secret mode :
• During a call, press Menu/ SECRET and then
Activ..
• The "SECRET MODE" message will appear on the
screen.
To deactivate secret mode :
• Press Exit, "SECRET MODE" disappears from the
screen. Your correspondent will be able to hear you
again.
Hands-free/speakerphone mode
If you want to phone in speakerphone mode, do not lift the
handset, but press the base key; the icon is
displayed on your phone's screen.
The caller can then be heard through the loudspeaker and
you speak into the base microphone.
To end the call, press the key again .
If you want to toggle to speakerphone mode during a call
in handset mode, press the key; the icon is
displayed on your phone's screen.
The caller can then be heard through the base
loudspeaker and the handset earphone and you speak
into the handset microphone. In this mode the base
microphone is inactive.
You can return to speakerphone mode by holding down
the key and then replacing the handset.
To end the call, replace the handset or press the key .
When you call hand-free/speakerphone
mode, you can increase or decrease the
audio volume from 1 to 5, using or .
LU Sixty.book Page 17 Mercredi, 19. mai 2010 12:30 12
18
Calling the last number dialled
Your SIXTY stores the last 20 dialled numbers:
• Go to CALLS / OUTGOING CALLS.
• Select the number you want to call.
• Go to Option / CALL.
The number is automatically dialed in speakerphone
mode.
Call time display
Once connected, the call time is displayed on the screen
(minutes and seconds).
PHONEBOOK
You can save up to 150 entries in your phone book, with
each sheet able to contain a 24-digit number and a name
up to 12 letters long.
CREATING AN ENTRY
To enter a text, repeatedly press the required key to
display the desired letter.
• Go to PHONEBOOK / New.
• Enter the name of your contact using the
alphanumeric keys.
• Press Valid..
• Enter the contact`s telephone number using the
alphanumeric keys.
• PressValid..
• Select an icon for this number to specify the type of
number.
• Press Valid..
The name and number are then stored in your phone
book.
LU Sixty.book Page 18 Mercredi, 19. mai 2010 12:30 12
19
EDITING AN ENTRY
• Go to the menu PHONEBOOK.
• Press keys or to select the contact you want to
change.
• Select Option / Edit.
• Press Valid..
• You enter the name input screen.
To correct the name, press Return to delete
characters. Enter your changes on the keypad.
After making the changes, press Valid..
• You enter the number input screen.
To correct the number, press Return to delete the
numbers. Enter your changes on the keypad.
After making the changes, press Valid..
• Select an icon for this number.
• Press Valid..
ASSOCIATING A RING TONE WITH A
PHONEBOOK ENTRY
You can associate a unique ring tone to each entry and
thus create your own call groups
As you need the active number presentation service on
your handset, contact your operator to find out about the
conditions for obtaining the service.
• Go to the menu PHONEBOOK.
• Select the entry with which you want to associate a
ring tone.
• Go to Option / RING TONE.
• Select the ring tone of your choice.
• Press Valid..
OTHER NUMBER
This function allows you to assign new numbers to the
same name.
• Go to the menu PHONEBOOK.
• Select the entry you want to assign another number
to.
• Go to Option / ADD NUMBER.
• Enter the phone number on the alphanumeric keys.
• PressValid..
• Select an icon according to the type of number
entered. Press Valid..
DELETING AN ENTRY
• Go to the menu PHONEBOOK.
• Press keys or to select the contact you want to
delete.
• Select Option / DELETE.
• Press Valid..
• A confirmation screen asks you if you wish to delete
the entry.
- To delete the entry, press Yes, the contact is
deleted from your phone book.
- If you do not wish to delete the entry, press No.
LU Sixty.book Page 19 Mercredi, 19. mai 2010 12:30 12
20
CALLING USING THE PHONEBOOK
• Go to the menu PHONEBOOK.
• From the list of names, select the contact you want to
call using keys or .
• Go to Option/CALL.
The number is automatically dialled in speakerphone
mode.
SEARCHING FOR A CONTACT
• Access your phonebook list, press successively on
the keypad key which corresponds to the first letter of
the name you are searching for so as to make it
appear at the top of the screen.
• Once the first letter of the name is displayed, wait a
moment.
• The phonebook selects the first name in the list that
starts with the selected letter.
CALL LOG
Caller identification is a service that requires prior
registration with your operator.
VIEWING THE RECEIVED AND DIALLED CALL
LOG
• Go to the menu CALLS / INCOMING CALLS or
OUTGOING CALLS.
• Select the event to be viewed.
• Press Valid..
• The screen presents the following information.
(depending on the operator and the subscription):
- the full name of your contact and the telephone
number,
- the number of consecutive calls,
- time (for calls during the day) or the date (for
previous calls) of the call.
The calls are organised in chronological order, from the
most recent call to the oldest call.
To see the previous calls, use the keys or .
To check your call log directly, press the
Log key from the idle screen.
LU Sixty.book Page 20 Mercredi, 19. mai 2010 12:30 12
21
By pressing Option, a list of various executable actions
appears:
- CALL : To call the number.
- VIEW : To view the selected call again.
- STORE NUMBER : To store the name and number
in the phonebook.
- DELETE : To delete the call currently viewed.
- DELETE ALL : To delete all calls.
To return to the call viewing screen, press Return.
THE EVENTS LOG
Viewing the events log
If one or more new events occurred during your absence,
the information screen "NEW EVENTS !" appears and the
light starts flashing.
• If you do not wish to view the event log at this time,
press Return.
• To view the event log, press Valid..
• Choose the event using or .
• Press Valid..
Activating/deactivating the new event
information screen
The new event information screen can be inhibited.
The events which have occurred can then be viewed in
the menu CALLS / EVENTS / VIEW. The default setting
is active.
• Go to the menu CALLS / EVENTS.
• Select ACTIVATE or DEACTIVATE to enable or
disable the displaying of the new events screen.
• Press Valid..
Clearing notifications
The notifications received are saved in the event log and
can be deleted once they have been viewed.
• Go to the menu CALLS / EVENTS.
• Select DELETE NOTIF. and press Valid. to remove
the notifications received on your base.
INFORMATION
During an incoming call, following messages can be
displayed:
PRIVATE: Your contact does not want their number to be
displayed.
UNAVAILABLE: If there is a problem on the phone
network.
The light only stops flashing when all the
events have been viewed.
LU Sixty.book Page 21 Mercredi, 19. mai 2010 12:30 12
22
ACCESSORIES
ALARM CLOCK
This function enable you to use your SIXTY as an alarm
clock.
When the alarm is triggered the selected ring tone sounds
for 60 seconds through the handset speaker and an alert
screen is displayed.
Activating / deactivating the alarm clock
• Go to ACCESSORIES / ALARM.
• An information screen shows the alarm clock status.
• Use or to select ACTIVATE or DEACTIVATE.
• Press Valid..
The alarm settings information screen appears showing
the new status.
Changing the alarm clock ring tone
• Go to ACCESSORIES / ALARM.
• Use or to select RING TONE in the list, press
Valid..
• Select the ring tone of your choice, press Volume.
• Select the desired ring tone using or to increase
or decrease the volume, press Valid.. OK is displayed
on the screen.
• Press Return to go back to the previous menu.
Modifying the alarm clock time
• Go to ACCESSORIES / ALARM.
• Use or to select SET TIME.
• Enter the time at which you would like the alarm clock
to sound.
• Press Valid.. OK is displayed on the screen.
• Press Return to go back to the previous menu.
TIMER
With this menu you can use your telephone as a timer.
Once the specified time has elapsed, the base rings for 60
seconds and the alarm screen is activated. Turn off the
alarm by pressing Stop, the base stops ringing.
Activate the timer
• Go to ACCESSORIES / TIMER.
• Press Start. If a timer duration is already specified,
the timer is directly activated. If not please follow
instructions in the next paragraph.
The timer function must be inactive so that
it can be set.
LU Sixty.book Page 22 Mercredi, 19. mai 2010 12:30 12
23
Changing the programmed time of the
timer
• Go to ACCESSORIES / TIMER.
• Press Valid..
• Select SET DURATION in the list. Press Valid..
• Enter the desired time.
• Press Valid.. OK is displayed on the screen.
• Press Return to go back to the previous menu.
Displaying or hiding the programmed
time of the timer
• Go to ACCESSORIES / TIMER.
• Select VIEW in the list. Press Valid..
• If you want to show the timer, press Yes, else
press No.
• Press Return.
Changing the timer ring tone
• Go to ACCESSORIES / TIMER.
• Select RING TONE in the list of options, press Valid..
• The list of ring tones appears, the handset plays the
ring tone.
• Select the ring tone. Press Volume.
• Press or to increase or decrease the volume.
• Press Valid.. OK is displayed on the screen.
• Press Return to go back to the previous menu.
RING TONES
CHANGING THE RING TONES
This menu enables you to associate a unique ring tone to
incoming calls.
• Go to RING TONE / EXTERNAL CALL.
• Press Valid..
• Select the ring tone of your choice.
• then press Volume.
Adjust the ringer volume using or .
• Press Valid.. OK is displayed on the screen.
• Press Return to go back to the previous menu.
ACTIVATING OR DEACTIVATING THE BEEPS
• Go to RING TONE / BEEPS.
• Press Valid..
• To change the beep status, press Edit.
The status is changed on the screen.
• Press Valid.. OK is displayed on the screen.
• Press Return to go back to the previous menu.
LU Sixty.book Page 23 Mercredi, 19. mai 2010 12:30 12
24
ACTIVATING/DEACTIVATING THE SILENT MODE
When in silent mode, the telephone ringer and keypad
beeps are inhibited.
• Go to RING TONE / SILENT MODE.
• SILENCE MODE? is displayed on the screen.
• Press Yes to activate the silent mode.
SETTINGS
MODIFYING THE DATE AND TIME
• Go to SETTINGS / DATE/TIME.
• Enter the date in DD/MM/YY format.
• Press Valid..
• Enter the time in HH/ MM format.
• Press Valid.. OK is displayed on the screen.
• Press Return to go back to the previous menu.
ADJUSTING THE CONTRAST
• Go to SETTINGS / CONTRAST.
• A list with five levels of contrast is displayed.
• Select the level you want using the keys or . The
contrast is directly visible on the screen.
• when you have obtained a satisfactory level.
• Press Valid.. OK is displayed on the screen.
• Press Return to go back to the previous menu.
MODIFYING THE LANGUAGE
• Go to SETTINGS / LANGUAGE.
• An information screen presents the current language
used.
- To keep the setting, press Valid..
- To change the setting, press or .
• Select the language.
When you activate the silent mode, your
handset is muted for all timer and alarm
type functions.
LU Sixty.book Page 24 Mercredi, 19. mai 2010 12:30 12
25
• Press Valid.. OK is displayed on the screen.
• Press Return to go back to the previous menu.
THE VOICE BOX NUMBER (ACCORDING TO
OPERATOR)
This function allows you to receive calls in your absence
on your operator's voice messaging service.
To indicate that a new message has been received the
reception indicator on the the top of the '1' key is lit in red
and the new event message is displayed on the screen.
To change the voice box number, proceed as follows:
• Go to SETTINGS / VOICE BOX No.
• The programmed number is displayed on the screen.
- The number is correct, press Valid..
- To modify the number, press Edit.
DEFINING FORBIDDEN PREFIXES - CALL
BARRING
You can prohibit the use of certain prefixes on your
telephone.
When a prefix is forbidden, it becomes impossible to call
numbers that begin by this prefix.
• Go to SETTINGS/ RESTRICTION.
• Press Edit,
• Select PREFIX using or , press Valid..
• Enter the base code (by default 0000), press Valid..
• Select a location (dashes), press Valid..
• Enter the prefix using the keypad (for example : 06,
08, etc..).
• Press Valid..
• OK is displayed on the screen.
• Select ACTIVATE using or .
• Enter the base code (by default 0000), press Valid..
• Press Valid.. OK is displayed on the screen.
• Press Return to go back to the previous menu.
The answering machine message
language depends on the phone
language.
To check your voice messaging service,
hold down key .
LU Sixty.book Page 25 Mercredi, 19. mai 2010 12:30 12
26
DEMO
This menu allows you to see an animation for each of your
phone's key and ring tones.
• Go to SETTINGS / DEMO.
• Press Valid..
• Display of "DEMO Chenillard" with the animation of
each key.
• Press the key during this animation, "DEMO
MELODY" is displayed, and the melody for external
calls is initiated.
• Press Exit to stop the demonstration.
ADVANCED SETTINGS
Base settings
Set the base to registration mode
Using this function you can add GAP compatible
hnadsets to your base. The handset that you want to pair
with your base must itself be in pair mode.
Consult the user booklet of your handset to find out what
to do.
• Go to SETTINGS / ADVANCED SET. / SET BASE /
REGISTR. MODE.
• Press Valid..
• REGISTR. MODE? is displayed on the screen, press
Yes.
• Indicator on the the top of the '1' key starts to flash
rapidly. Your base will remain in registration mode for
about 1 minute.
Resetting the base
When you reset your base, all the base parameters are
reset to their initial values (factory settings).
• Go to SETTINGS / ADVANCED SET. / SET BASE /
RESET BASE.
• Press Valid..
• REINIT. BASE? is displayed on the screen.
• Press Yes.
• Enter the base code.
• Press Valid..
The "RE-INIT. IN PROCESS" and the OK messages
are displayed successively.
Your base is now reset.
You can save up to 5 GAP-compatible
handsets on your SIXTY base.
You can also set the base to pairing mode
by holding down your base's key.
LU Sixty.book Page 26 Mercredi, 19. mai 2010 12:30 12
27
De-registering a handset
• Go to SETTINGS / ADVANCED SET. / SET BASE /
DELETE HANDSET.
• Press Valid..
• Select the handset you wish to unregister using
or .
• Press Valid..
• A screen prompts you to confirm the unregistration.
Press Yes to unregister the handset.
The handset is no more registered to the base.
Line settings
Modifying the network type
Your telephone can be installed on a public or private
network (when using a PABX).
This function enables you to configure your telephone
according to the type of network.
• Go to SETTINGS / ADVANCED SET. / SET LINE /
NETWORK TYPE.
• Press Valid..
• A screen presents the current status.
- To keep the status, press Valid..
- To change the status, press Edit.
• Press Valid.. OK is displayed on the screen.
• Press Return to go back to the previous menu.
Modifying the dialling mode
The type of dialling generally used is voice frequency.
It is possible that the exchange to which you are
connected uses pulse dialling.
• Go to SETTINGS / ADVANCED SET. / SET LINE /
DIAL.
• Press Valid..
• A screen displays the current status.
- To keep the status, press Valid..
- To modify the status, press Edit. The status is
modified on the screen.
• Press Valid.. OK is displayed on the screen.
• Press Return to go back to the previous menu.
Before changing the settings of the
telephone line, contact your operator to
obtain the parameters for your line.
The default dialling mode is tone.
LU Sixty.book Page 27 Mercredi, 19. mai 2010 12:30 12
28
Modifying the flash duration
If you connect your telephone to a private automatic
branch exchange or use it in a foreign country, you may
need to modify the flash duration in order to use your
telephone correctly with regard to the following
functionalities: outgoing 2nd call, incoming 2nd call, 3 way
calling.
Contact your service provider to obtain the correct flash
duration and then modify it by doing the following.
• Go to SETTINGS / ADVANCED SET. / SET LINE /
FLASHING.
• Press Valid..
• An information screen presents the current flash
duration.
- To keep the duration, press Valid..
- To modify the duration, press Edit.
• Select the new duration.
• Press Valid.. OK is displayed on the screen.
• Press Return to go back to the previous menu.
Setting a PABX prefix
If a private automatic branch exchange is used, you can
programme the external call prefix.
With this function you can set the:
- PABX prefix number,
- dialled number length at which point the PABX
prefix will be automatically inserted (this length is
called “digit before prefix”),
- prefix status (on or off).
• Go to SETTINGS / ADVANCED SET. / SET LINE /
PABX PREFIX.
• Press Valid..
• Press to modify this setting.
• Select the desired option:
- ACTIVATE / DEACTIVATE : to select a status.
- PREFIX : to enter the number giving you access to
the outside line.
- EDIT LENGTH : to specify the «digits before
prefix».
• To modify the prefix, select PREFIX press Valid..
• Enter the prefix using the keypad, press Valid..
OK is displayed on the screen.
• To modify the digits before prefix, select EDIT
LENGTH, press Valid..
• Enter the digits before prefix using the keypad.
• Press Valid.. OK is displayed on the screen.
• Press Return to go back to the previous menu.
• Now you can activate the automatic PABX prefix
functionality, select ACTIVATE and press Valid..
LU Sixty.book Page 28 Mercredi, 19. mai 2010 12:30 12
29
Modifying the base code
This code securises and limits the use of your telephone.
• Go to SETTINGS / ADVANCED SET. / CHANGE
CODE.
• Press Valid..
• Enter the old base code using the keypad (default is
0000).
• Press Valid..
• Enter the new base code using the keypad.
• Press Valid..
• Confirm by entering the new base code again.
• Press Valid.. OK is displayed on the screen.
• Press Return to go back to the previous menu.
ANSWERING MACHINE
Your phone's answering machine provides the following
features:
• Active answering machine mode with pre-recorded
messages,
• Call filtering,
• Remote querying.
ENABLING / DISABLING THE ANSWERING
MACHINE
• Go to ANS. MACH / ON/OFF.
• Press Valid..
• A screen displays the current status of the answering
machine (On or Off).
- To keep the displayed status, press Valid..
- To change the status, press or :
To activate the answering machine, select
ACTIVATE.
To turn off the answering machine, select OFF.
Press Valid..
• OK is displayed on the screen.
• Press Return to go back to the previous menu.
If you have not recorded a personal
message, the answering machine will
automatically use one of the pre-recorded
messages in the selected language.
LU Sixty.book Page 29 Mercredi, 19. mai 2010 12:30 12
30
MODIFYING THE OGM
Recording a personal outgoing message
• Go to ANS. MACH / OUTGOING MESS. / CHANGE.
• Press Valid..
• RECORD OGM is displayed on the screen.
• Press Begin to start recording your OGM. Start talking
in the base microphone.
• To stop recording press End. Your outgoing message
is automatically played back.
• Press Return to go back to the previous menu or
make a new recording.
Deleting your personal OGM
• Go to ANS. MACH / OUTGOING MESS. / DELETE.
• Press Valid..
• DELETE ANOUNCE? is displayed on the screen,
press Yes to confirm the deletion of your personal
outgoing message.
• OGM DELETED is displayed on the screen.
• Press Return to go back to the previous menu.
Listen to a personal message
• Go to ANS. MACH / OUTGOING MESS. / PLAY.
• Press Valid..
• PLAY OGM is displayed on the screen and the OGM
is played back. At the end of the playback you will
return to the menu RECORD OGM.
• Press Return to go back to the previous menu.
PLAYING MESSAGES
If you have new messages (unread), these messages are
read first. Afterwards, the messages that have already
been taken are played back in chronological order (from
the oldest messages to the most recent messages).
• Go to ANS. MACH / MESSAGES / PLAY.
• Press Valid..
• The messages are played through the loudspeaker.
In order to modify an OGM, you must first
turn on the answering machine.
If you delete your personal outgoing
message, the answering machine will
automatically use the anonymous
message.
If you have not recorded a personal
message, you will hear the anonymous,
pre-recorded message.
LU Sixty.book Page 30 Mercredi, 19. mai 2010 12:30 12
31
• Depending on your service provider and your
subscription, the name and number of your contact
will be displayed on the screen (except for a
confidential call).
• During playback, you can use the touch-sensitive
keys to perform the following actions:
- * : go back to the beginning of the message.
- * x 2: return to the previous message.
- # : go to the next message.
- Pause/PLAY (context key 1): pause/resume
playback.
- DELETE (context key 2): delete the message being
played.
- : exit playback of messages.
REMOTE ACCESS TO ANSWERING MACHINE
Your answering machine can be queried remotely. This
feature allows you to read your messages and query your
answering from any phone when you are not at home.
To remotely access your answering machine:
• Dial your telephone number.
• Wait for the answering machine to come on.
• When your outgoing message is played, press «#».
• Enter your remote access code.
• A beep will indicate access to the answer machine,
Any unread messages will be automatically played
back.
• At the end of playback, a new beep will sound to let
you know that the answer machine is ready.
• You can carry out the following operations :
- 0 : delete the message being played.
- 1 : go back to the beginning of the message.
- 1 (x2): previous message.
- 2 : pause / play.
- 3 : next message.
- 5 : messages read.
- 9 : enable/disable the answering machine.
DELETING ALL THE OLD MESSAGES
• Go to ANS. MACH / MESSAGES / DELETE OLD.
• Press Valid..
• To confirm the deletion of all the old messages, press
Yes.
• Press Return to go back to the previous menu.
The remote access code is 0000 by
default. However, it can only be used once
it is customised, refer to paragraph
"Modifying the remote access code ",
page 32.
To delete old messages one by one, refer
to the previous paragraph and delete
unwanted messages during playback.
LU Sixty.book Page 31 Mercredi, 19. mai 2010 12:30 12
32
TAM SETTINGS
This menu allows you to change the advanced settings of
your answering machine. You can access the answering
machine SETTINGS menu from the ANS. MACH menu.
ACTIVATING AND DEACTIVATING CALL
SCREENING
The filtering function, when activated, allows you to listen
to the message left by the caller as it is being recorded.
You can unhook to answer at any time.
• Go to ANS. MACH/SETTINGS/CALL SCREENING.
• Press Valid..
• A screen indicating the function status appears.
- To keep the current status, press Valid..
- To change the status, press or .
• Press Valid..
MODIFYING THE REMOTE ACCESS CODE
The remote access code enables you to listen to the
messages left on your answering machine via another
telephone.
• Go to ANS. MACH / SETTINGS / REMOTE CODE.
• Press Valid..
• CODE BASE is displayed, enter your Base code
(default setting is 0000).
• Press Valid..
• CODE DISTANCE is displayed, enter the new remote
access code (4 digits mandatory).
• Press Valid.. OK is displayed on the screen.
• Press Return to go back to the previous menu.
NUMBER OF RINGS
This parameter determines the number of times your
phone rings before your answering machine is started.
The number of rings is between 3 and 7.
• Go to ANS. MACH / SETTINGS / NO OF RINGS.
• Press Valid..
• The programmed number of rings is displayed on the
screen. Press keys or to change this number
(from 3 to 7).
• Press Valid.. OK is displayed on the screen.
• Press Return to go back to the previous menu.
LU Sixty.book Page 32 Mercredi, 19. mai 2010 12:30 12
33
REPLACING THE BATTERIES
Your batteries' autonomy is no more satisfactory ? Please
contact your retailer, he will propose to you new
equivalent batteries.
• Remove the battery compartment hatch.
• Remove the old batteries, insert the new batteries one
by one in compliance with the polarity of the batteries,
as indicated in paragraph “Your handset”, page 9
• Refit the battery compartment hatch.
• Leave your handset on its base in order to fully charge
the batteries.
PAIRING GAP-COMPATIBLE
DECT HANDSETS ON THE
SIXTY BASE
Additional GAP-compatible DECT handsets can be
registered on the SIXTY base.
To register an additional handset on the SIXTY base:
• Set your base to pairing mode by holding down
the key. The light indicator on the top of the '1'
key starts flashing. The base remains in pairing mode
for one minute.
• Set the additional handset to registration mode. (Refer
to the your handset's user manual).
Up to five GAP-compatible DECT
handsets can be registered on the SIXTY
base.
LU Sixty.book Page 33 Mercredi, 19. mai 2010 12:30 12
34
APPENDIX
CARE AND MAINTENANCE
Turn off your phone. Use a soft damp cloth to wipe it. Do not use a dry cloth, strong liquid detergents, thinners, alcohol
or any other type of solvent to clean your phone. These products may damage your phone.
PROBLEMS
Refer to the table presented below in case of an operational malfunction:
Problems Possible causes Remedies
You are having
trouble reading or
cannot read the
display when not in
standby mode.
Contrast too low. Increase the contrast level (refer to paragraph "Adjusting
the contrast ", page 24).
No display on the
base screen.
Power connection unplugged. Check the power connection to the phone.
No tone. The phone jack is not
connected or is incorrectly
connected.
Check the phone cable connection (refer to paragraph
"Connecting the base ", page 12).
Make sure you have a dialling tone.
The speaker volume is too low. Increase the speaker volume (refer to paragraph
"Receiving a call ", page 15).
The phone does not
ring when a call is
received.
The mute mode is turned on. Turn off the mute mode (refer to paragraph "Activating/
deactivating the silent mode ", page 24).
Your party cannot
hear you.
You have turned on the mute
mode (microphone off).
Turn off the mute mode (microphone off) in MENU then
MUTE.
Make sure that the "MUTE MODE" message is not
displayed.
You obtain a "busy"
dial tone for each
dialled number.
Incorrect flashing time. Set the flashing time (refer to paragraph "Modifying the
flash duration ", page 28).
Contact your operator to get it to provide you with the right
time.
LU Sixty.book Page 34 Mercredi, 19. mai 2010 12:30 12
35
TECHNICAL CHARACTERISTICS
INITIAL CONDITION
Standard
Radio frequency band
Number of channels
Duplex mode
Spacing between channels
Bit rate
Modulation
Vocoding
Transmitting power
:::::::::
DECT, GAP
1.88-1.90 GHz
120
TDMA
1.728MHz
1152 kbit/s
GFSK
ADPCM
250 mW
Charging time
Range up to
Batteries
Handset operating time
Max answering machine
capacity
Ambient temperature
Dimensions
Weight including
batteries
::::::::
Handset Batteries: 10 hours
300 m outside and up to,
up to 50 m inside buildings
Type Ni-MH, AAA,
2 x 1.2 V 450 mAh
talk time up to 10 hours
standby time up to 120
hours
20 minutes
+5°C to +45°C
Base(WxHxL)
220 x 63 x 39 mm
Handset(WxHxL)
176 x 130 x 89 mm
Base 172g
Handset 43 g
Accessories Advanced Settings
Alarm clock off Network type Public
Timer off Dial mode Tone
Ring Tone Flashing 100 ms
Ringer Traditional PABX prefix Off
Keyboard beeps On Answering Machine
Silent mode Off Status On
Settings Call screening Off
Date/Time 01/01/10 // 00:00 Remote access code 0000
Contrast Level 2 Number of rings 7
Language English
Restriction off
Base code 0000
LU Sixty.book Page 35 Mercredi, 19. mai 2010 12:30 12
36
ENVIRONMENT
Environmental protection and sustainable development is an important priority for SAGEMCOM. SAGEMCOM has a
policy of using environmentally- friendly systems and makes environmental protection an essential part of the life-cycle
of its products – from the manufacturing, to the installation, operation and disposal.
PACKAGING
The logo (green point) on the packaging means that a fee is paid to an authorised national organisation to
improve packaging recycling and the recycling infrastructure. Follow the local sorting regulations for this type
of waste product in order to improve recycling.
BATTERIES AND RECHARGEABLE BATTERIES
If your product contains batteries or rechargeable batteries, these must be disposed of at designated
collecting centers.
THE PRODUCT
The crossed out dustbin displayed on the product signifies that it belongs to the electrical and electronic
equipment group. The European regulations request you to carry out your own selective recycling collection
at:
• the sales outlet when you buy a similar new device.
• the collection points available in your area (recycling centres, sorting points, etc).
This means you participate in the recycling and valorisation of used electric and electronic goods which would
otherwise have a negative impact on the environment and health.
Annexe.fm Page 36 Jeudi, 20. mai 2010 9:03 09
37
GUARANTEE
TERMS AND CONDITIONS FOR UNITED KINGDOM & IRELAND ONLY
In order to apply the guarantee, you should contact the SAGEMCOM Helpdesk or the retailer where you purchased
the equipment. Proof of purchase will be required in either case.
Please make sure that you use your equipment only for the purpose for which it was designed and under normal usage
conditions.
SAGEMCOM do not accept any liability for the equipment if used outside the frame of its original designed purpose or
any consequence that may arise from this usage.
Should any malfunction arise, the SAGEMCOM Helpdesk or your retailer will advise you how to proceed.
A) General Guarantee conditions
SAGEMCOM undertakes to remedy by repair or exchange at its own convenience, free of charge for labour and
replacement parts, any defects in the equipment during the guarantee period of 12 (twelve) months or 3 (three) months
for accessories, from the date of original invoice of the Equipment, where those defects are a result of faulty
workmanship.
Unless the customer has concluded with SAGEMCOM a maintenance contract in respect of the equipment which
specifically provides for repairs to be carried out at the customer`s premises, the repairs will not be carried out on the
equipment at the customer premises.
The customer must however return the defective equipment at his/her own expense, to the address supplied by the
SAGEMCOM Helpdesk or by the retailer.
In the case that a product needs to be sent in for a repair, it must always be accompanied by a proof of purchase (which
is not altered, written on or in any way made illegible) showing that the product is still under guarantee. In the case that
no proof of purchase is enclosed, the SAGEMCOM repair centre will use the production date as its reference for
establishing the guarantee status of the product.
Apart from all legal obligatory rules, SAGEMCOM, do not give any Guarantee, either implicit or explicit which is not set
force in the present section, and can not be held responsible for any direct or indirect, material or immaterial damage,
either in or out of the frame of the present guarantee.
If any provision of this guarantee shall be held to be in whole or in part invalid or illegal due to an obligatory rule
applicable to consumers pursuant to their national legislation, such invalidity or illegality shall not impair or affect the
remaining provisions or parts of this guarantee.
This guarantee does not affect the Customer statutory rights.
LU Sixty.book Page 37 Mercredi, 19. mai 2010 12:30 12
38
B) Exclusions From Guarantee
SAGEMCOM shall have no liability under the guarantee in respect of:
• Damage, defects, breakdown or malfunction due to one or more of the following:
- Failure to properly follow the installation process and instructions for use
- An external cause to the equipment (including but not limited to: lightening, fire, shock, vandalism, inappropriate
conditions of electrical network or water damage of any nature)
- Modifications made without the written approval of SAGEMCOM
- Unsuitable operating conditions, particularly of temperature and humidity
- Repair or maintenance of the equipment by persons not authorised by SAGEMCOM
• Wear and tear from normal daily use of the equipment and its accessories
• Damage due to insufficient or bad packaging of equipment when returned to SAGEMCOM
• Usage of new versions of software without the previous approval of SAGEMCOM
• Work on any equipment or software modified or added without the prior written consent of SAGEMCOM
• Malfunctions not resulting from the Equipment or from software installed in user workstations for the purpose of
use of the equipment.
Communication problems related to an unsuitable environment including:
- Problems related to access and/or connection to the Internet such as interruptions by access networks or malfunction
of the line used by the subscriber or his correspondent
- Transmission faults (for example poor geographical coverage by radio and TV transmitters, interference or poor
line quality)
- Local network faults (wiring, servers, workstations) or the failure of the transmission network (such as but not
limited to interferences, fault or poor quality of the network)
- Modification of the parameters of the cellular or broadcast network carried out after the sale of the Product
• Normal servicing (as defined in the user guide supplied with the equipment) as well as malfunctioning due to servicing
not being carried out. Servicing costs are in any event always borne by the customer.
• Malfunctions resulting from the usage of products, consumables or accessories not compatible with the equipment.
C) Out of Guarantee Repairs
In the cases set forth in B) as well as after expiry of the guarantee period, the customer must ask the Authorised
SAGEMCOM Repair Centre for a cost estimation prior to work being carried out.
In such cases, the repair and delivery costs will be invoiced to the customer.
The foregoing shall apply unless otherwise agreed in writing with the customer and only for the United Kingdom and
Ireland.
LU Sixty.book Page 38 Mercredi, 19. mai 2010 12:30 12
39
TERMS AND CONDITIONS FOR OTHER COUNTRIES
If, despite our best efforts, your product presents any defects, you should refer to your retailer and present the proof
of purchase that they gave you on the day of purchase.
Should any malfunctioning arise, the retailer will advise you what to do.
For the warranty to apply, you should ensure that the product was used in accordance with the instructions for use and
the purpose for use, and that you have at your disposal the sales invoice or receipt stating the date of purchase, the
name of the retailer, the reference and the serial number of the product.
No coverage shall be given under this warranty if the following conditions are applicable:
• The required documents have been modified or altered in order to take advantage of the warranty.
• The manufacturing numbers, product brands or labels have been altered or made illegible.
• Interventions on the product have been made by an unauthorized person.
• The product has been subjected to abnormal or improper use.
• The product has been damaged by external factors such as lightning, over-voltage, moisture, accidental damage,
improper care as well as all Acts of God.
This present warranty does not affect the consumer rights that you may have under the laws in effect in your country.
Important:
Should you return the product to the after-sales department, please ensure that you return as well all the elements and
accessories originally supplied with the product.
LU Sixty.book Page 39 Mercredi, 19. mai 2010 12:30 12
SIXTY by
Sagemcom Broadband SAS
250, route de l'Empereur - 92848 Rueil-Malmaison - France
Tél. +33(0)1 57 61 10 00 - Fax : +33(0)1 57 61 10 01
www.sagemcom.com
All rights reserved. Sagemcom Broadband SAS reserves the right to change the technical characteristics of its products and services or to stop marketing
them at any time. The information and specifications included are subject to change without prior notice. Sagemcom Broadband SAS tries to ensure that
all information in this document is correct, but does not accept liability for error or omission. Non contractual document. All trademarks are registered by
their respective owners. Simplified joint stock company - Capital 35 703 000 € - 518 250 360 RCS Nanterre
Thermomètre infrarouge
572-2
L'outil qu'il vous faut pour les
environnements les plus chauds
2 Fluke Corporation Thermomètre infrarouge 572-2
Caractéristiques techniques du thermomètre infrarouge 572-2
Mesures infrarouges
Gamme de température infrarouge -30 °C à 900 °C
Précision IR (Géométrie d'étalonnage à une
température ambiante de 23 °C ± 2 °C)
≥0 °C ± 1 °C ou ± 1 % du relevé, selon la valeur la plus élevée
≥-10 °C à <0 °C ± 2 °C
<-10 °C ± 3 °C
Répétabilité IR ± 0,5 % de la mesure ou ± 0,5 °C, selon la valeur la plus élevée
Résolution d'affichage 0,1 °C / 0,1 °F
Distance : Mesure 60:1 (calculée à 90 % de l'énergie)
Dimensions minimales du point 19 mm
Système de visée laser Décalage du laser double, puissance de sortie <1 mW
Réponse spectrale 8 μm à 14 μm
Temps de réponse (95 %) <500 ms
Emissivité Réglable numériquement de 0,10 à 1,00 par pas de 0,01 ou à partir du tableau intégré des
matériaux courants
Options de mesure
Alarmes Basse et/ou Haute Sonores ou visuelles en couleur
Min/Max/Moy/Dif Oui
Commutable entre degrés Celsius et Fahrenheit Oui
Rétro-éclairage Deux niveaux, normal et ultra-lumineux pour les environnements sombres
Entrée sonde Thermocouple de type K
Affichage simultanée de la température IR et de la sonde sur le thermocouple de type-K
Verrouillage du déclenchement Oui
Stockage de données 99 points
Ecran Matriciel de 98 x 96 pixels avec menus de fonctions
Communication USB 2.0
Caractéristiques techniques du thermocouple de type K
Gamme de températures en entrée du thermocouple
de type K
-270 °C à 1 372 °C
Précision d'entrée du thermocouple de type-K (avec
température ambiante de 23 °C ± 2 °C)
<-40 °C ± (1 °C + 0,2 °/1 °C)
≥-40 °C ± 1 % ou 1 °C, selon le plus élevé des deux
Résolution du thermocouple de type K 0,1 °C
Répétabilité de thermocouple type K ± 0,5 % de la mesure ou ± 0,5 °C, selon la valeur la plus élevée
Gamme de mesure (sonde à perles du thermocouple
de type K)
-40 °C à 260 °C
Précision ± 1,1 °C de 0 °C à 260 °C. Typiquement à moins de 1,1 °C de -40 °C à 0 °C
Longueur du câble Câble de thermocouple de type K de 1 m avec connecteur de thermocouple miniature standard
et terminaison par perle
Caractéristiques générales
Température de fonctionnement 0 °C à 50 °C
Température de stockage -20 °C à 60 °C
Humidité relative 10 % à 90 % HR sans condensation jusqu'à 30 °C
Altitude de fonctionnement 2 000 mètres au-dessus du niveau moyen de la mer
Poids 0,322 kg
Puissance 2 piles AA
Autonomie 8 heures avec laser et rétro-éclairage allumés ; 100 heures avec laser et rétro-éclairage
éteints, rapport cyclique de 100 % (thermomètre actif en continu)
Sécurité et conformité IEC 60825-1
Laser FDA Classe II
EMC 61326-1
Conformité CE
CMC 沪制01120009
3 Fluke Corporation Thermomètre infrarouge 572-2
Pour commander
Thermomètre infrarouge 572-2
Comprend
Thermomètre infrarouge avec fonctions de
thermomètre de contact, sonde à perle pour
thermocouple de type K, cordon d’interface USB 2.0,
logiciel de documentation FlukeView® Forms, mallette
de transport rigide, manuel d'introduction (papier) et
manuel de l'utilisateur (CD).
Sondes de température recommandées
Sonde Utilisation
80PK-1 Cette sonde à perle polyvalente permet de mesurer rapidement et avec précision les températures de surface et
les températures de l'air dans les gaines et les bouches d'aération.
80PK-8 Les sondes de température à collier de serrage (2) sont essentielles pour le suivi des différentiels de température
en constante évolution sur les boucles de tuyauterie et les tubulures d'eau chaude, et excellentes pour obtenir
des températures de réfrigération rapides et précises.
80PK-9 La sonde de perforation d'isolant dispose d'un embout pointu pour perforer l'isolation des tuyaux, et d'un embout
à bout plat pour obtenir des mesures de contact thermique en surface, des températures dans les gaines et les
bouches d'aération.
80PK-11 La sonde pour thermocouple à gaine souple permet de fixer facilement un thermocouple au tuyau pour une
utilisation en mains libres.
80PK-25 La sonde perforante est l’option la plus polyvalente. Excellente pour vérifier la température de l'air des conduits,
la température de surface sous les moquettes/rembourrages, des liquides, des puits de thermomètre, des
températures d'évacuation et pour pénétrer l'isolation des tuyaux.
80PK-26 La sonde conique est une excellente sonde polyvalente de mesure de surface et de gaz, disposant d'une bonne
longueur et d'un revêtement d'embout à faible masse pour une réaction accélérée aux températures de l'air et des
surfaces.
Fluke Deutschland GmbH
Parc des Nations - Allee du Ponant Bat T3
95956 ROISSY CDG CEDEX
Téléphone: (01) 48 17 37 37
Télécopie: (01) 48 17 37 30
E-mail: info@fr.fluke.nl
Web: www.fluke.fr
N.V. Fluke Belgium S.A.
Langveld Park – Unit 5
P. Basteleusstraat 2-4-6
1600 St. Pieters-Leeuw
Tel: 02/40 22 100
Fax: 02/40 22 101
E-mail: info@fluke.be
Web: www.fluke.be
Fluke (Switzerland) GmbH
Industrial Division
Hardstrasse 20
CH-8303 Bassersdorf
Tel: 044 580 75 00
Fax: 044 580 75 01
E-mail: info@ch.fluke.nl
Web: www.fluke.ch
©2013 Fluke Corporation. Tous droits réservés.
Informations modifiables sans préavis.
6/2013 Pub_ID: 12090-fre
La modiflcation de ce document est interdite sans
l’autorisation écrite de Fluke Corporation.
User’s Guide
October 2012
LMP91051EVM User’s Guide
October 2012 LMP91051EVM User’s Guide
CONTENTS
1 INTRODUCTION ................................................................................................... 1
2 SETUP .................................................................................................................. 2
3 OPERATION ......................................................................................................... 5
4 INSTALLING THE SENSOR AFE SOFTWARE ................................................... 10
5 BOARD LAYOUT ................................................................................................ 11
6 SCHEMATIC ....................................................................................................... 12
7 BOM .................................................................................................................... 13
LIST OF FIGURES
1 Connection Diagram ............................................................................................... 2
2 Jumper Setting (Default) for voltage reading ........................................................... 3
3 LMP91051EVM to SPIO-4 Board Connection ......................................................... 4
4 Sensor AFE Items of Interest .................................................................................. 5
5 Recommended LMP91051 Configuration for a voltage Reading ............................. 7
6 Sensor Database Window ..................................................................................... 8
7 Reults of DC Reading ............................................................................................. 9
8 LMP91051EVM’s J3 for SPI Signals ..................................................................... 10
9 LMP91051EVM Layout ......................................................................................... 11
8 LMP91051EVM Schematic ................................................................................... 12
LIST OF TABLES
1 Jumpers for Voltage Measurement ......................................................................... 3
2 LMP91051EVM Bill of Materials............................................................................ 13
1. Introduction
The LMP91051 Design Kit (consisting of the LMP91051 Evaluation Module, the SPIO-4 Digital Controller
Board, the Sensor AFE software, and this user’s guide) is designed to ease evaluation and design-in of Texas
Instrument’s LMP91051 Configurable AFE for Nondispersive Infrared (NDIR).
Data capturing and evaluations are simplified by connecting the SPIO-4 Digital Controller Board (SPIO-4 board)
to a PC via USB and running the Sensor AFE software. The data capture board will generate the SPI signals
to communicate to and capture data from the LMP91051. The user will also have the option to evaluate the
LMP91051 without using the SPIO-4 board or the Sensor AFE software.
The on board data converter will digitize the LMP91051’s analog output, and the software will display these
results in time domain and histogram. The software also allows customers to write to and read from registers,
to configure the device’s gain, output offset, and common mode voltage, and most importantly, to configure and
learn about the LMP91051.
2 LMP91051EVM User’s Guide snou034
This document describes the connection between the boards and PC, and provides a quick start for voltage
measurements. This document also describes how to evaluate the LMP91051 with and without the SPIO-4
board and provides the schematic, board layout, and BOM.
2. Setup
This section describes the jumpers and connectors on the EVM as well and how to properly connect, set up
and use the LMP91051EVM.
2.1. Connection Diagram
Figure 1 shows the connection between the LMP91051 Evaluation Module (LMP91051EVM), SPIO-4 board,
and a personal computer with the Sensor AFE software. LMP91051 can be powered using external power
supplies or from the SPIO-4 board.
Figure 1: Connection Diagram
2.2. Jumper Connections
1. The jumpers for this example application can be seen in Figure 2 and Table 1.
2. The SPIO-4 board is properly setup out of the box (no assembly required).
3. The schematic for the LMP91051EVM can be seen in Figure 10.
3 LMP91051EVM User’s Guide October 2012
Figure 2: Jumper Setting (Default) for voltage reading
Table 1: Jumpers for Voltage Measurement
Jumpers Pin Purpose
JP1: VDD_DUT P1-P2 Connect LMP91051 VDD to +3.3V from SPIO4
JP2: VREF_ADC P1-P2 Connect ADC VREF to 4.1V from U5 (LM4140)
JP3: VA_ADC P1-P2 Connect ADC VA to +5V from SPIO4
JP4: OUT_DUT to
ADC
P1-P2 Connect LMP91051 OUT to ADC input RC filter
JP5: VDD to VIO Open Connect LMP91051 VDD to VIO
JP6: VIO P2-P3 Connect LMP91051 VIO to +3.3V from SPIO4
J1: IN1 to CMOUT Open Connect LMP91051 IN1 to CMOUT. Note: Board is
provided with this jumper open. Use provided jumper to
short IN to CMOUT for easy evaluation.
J2: IN2 to CMOUT Open Connect LMP91051 IN2 to CMOUT. Note: Board is
provided with this jumper open. Use provided jumper to
short IN to CMOUT for easy evaluation.
4 LMP91051EVM User’s Guide snou034
2.3. Installing/Opening the Software
Follow Section 4 to install and open the Sensor AFE software.
2.4. Connecting and Powering the Boards
These Steps have to be done in this order.
1. Connect the LMP91051EVM’s J3 to SPIO-4 Board’s J6. See Figure 3.
.
Figure 3: LMP91051EVM to SPIO-4 Board Connection
2. Connect SPIO-4 board to a PC via USB.
3. Use a multimeter to measure LMP91051EVM’s +5V test point; it should be approximately 5V.
If it is not, check your power supplies and jumpers. Measure test point VREF_ADC; it should
be approximately 4.1V. If it’s not, check your jumpers and U5.
J3
5 LMP91051EVM User’s Guide October 2012
3. Operation
3.1. Sensor AFE Software Overview
Once connection between the boards and PC is established, you can use the software to communicate to and
capture data from the LMP91051. Drag cursor over window icons to get an icon description. Some items of
interest are shown in Figure 4.
Figure 4: Sensor AFE Items of Interest
.
1. Menu Bar Icons (from left to right)
a. Save Configuration to File: Saves the current configuration settings (register settings)
to an .xml file.
b. Load Configuration File: Loads the selected configuration settings (register settings)
.xml file.
c. Register Map: Opens Register Map window. An alternative to the Virtual Device, for
writing and reading the device registers. See datasheet for details on device Register
Map.
d. Save All Registers to File: Saves register contents to a .cvs file.
e. Read All Register from Board: After configuring the register map, use this button to
read all registers. Functional only in SDIO Mode (see Item 3).
f. Write All Registers To Board: After configuring the register map use this button to write
all registers. Registers will not be updated until this step is done.
g. Zoom In/Out Diagram Image: Zoom in and out of the virtual device image.
h. Show Tutorial: Takes you to the interactive Software Overview videos.
1 2 3 4 5
6 LMP91051EVM User’s Guide snou034
i. Documentation: Accesses the LMP91051 Datasheet, SPIO4 User’s Guide, or
Evaluation Board User’s Guide.
2. Device Selection and User Inputs
a. LMP91050/1 : Toggle between LMP91050 and LMP91051 device.
b. fc: Center frequency of external bandpass filter.
c. bandwidth: Pass band bandwidth of external bandpass filter.
d. R1_EXT, R2_EXT, C1_EXT, C2_EXT: External bandpass filter component values
calculated based on user input for center frequency (fc) and pass band (bandwidth)
described above.
e. Supply: LMP91051 supply voltage (VDD).
f. IC Temp: LMP91051 operating temperature
g. Offset Adjust Voltage: The tool will calculate the DAC code (decimal) required to
achieve this output offset adjust voltage. User must then Write to the register to update
the value in the NDAC register.
h. ADC Vref: ADC reference voltage. User should input value measured at VREF_ADC
test point. Value used to calculate displayed Output Voltage.
i. Vout Dark: This value corresponds to the user measured value at the LMP91051
output (OUT) when input is shorted (IN = CMOUT). Tool will use this value to estimate
LMP91051 input voltage (IN - CMOUT) on subsequent measurements.
3. Change Mode: Change between device Read Mode OFF (default) and ON. See datasheet for
details on SPI Read Mode.
4. Eval Board Setting: Document to show user how to configure jumpers and connect thermopile
based on sensor selected.
5. Virtual Device: Drag cursor across color coded blocks and click to configure each block. To
update registers “Write All Registers” when done.
3.2. Configuring the LMP91051 Using the Sensor AFE Software
Follow the step-by-step instructions under the “HelpBar” mini-tab (left hand side of the GUI) to configure the
LMP91051 for this example. These step-by-step instructions are discussed in details below, and the
recommended configuration should look similar to Figure 5.
7 LMP91051EVM User’s Guide October 2012
Figure 5: Recommended LMP91051 Configuration for a voltage Reading
1. Step 1: Select a Sensor – Sensor Database window opens. See Figure 6. Step 1: Click sensor type
(Thermopile) and the sensors will show in the bottom table. Step 2: Click sensor and then click
“Select” button on the left to use this sensor.
8 LMP91051EVM User’s Guide snou034
Figure 6: Sensor Database Window
2. Step 2: Input Mux – click on the mux block to set “1: IN1” (default).
3. Step 3: PGA1 Enable – click on the “PGA1” block to set “1: PGA1 ON” . Remember after
configuring the register map to use the Write All Registers button to update the registers.
4. Step 4: PGA2 Enable – click on the “PGA2” block to set “1: PGA2 ON” . Note: By default PGA1
and PGA2 are OFF on power up. However the software was designed to automatically power ON
PGA1 and PGA2 for ease of use.
5. Step 5: External Filter – click on the switch block to choose “0: PGA1 to PGA2 direct” (default).
6. Step 6: Common Mode – click on the “CM GEN” block to set “0: 1.15V” (default).
7. Step 7: GAIN 2 – click on the “PGA2” block to set “00: 4” (default).
8. Step 8: GAIN 1 – click on the “PGA1” block to set “0: 250” (default).
9. Step 8: DAC (Output Offset) – click on the “DAC” block to set “128” (default) for 0 mV offset.
Alternatively, user can also use the Offset Adjust Voltage user input field to input 0 mV.
10. Step 10: Performance - click on the “Performance” mini-tab. This tab displays the Estimated
Device Performance based on device configuration and user input device Supply and IC Temp
.This tab also displays the Measured System Performance if you’ve connected a board and ran the
LMP91051.
Step 1
Step 2
9 LMP91051EVM User’s Guide October 2012
3.3. Capturing Data
1. Click on the “Measurement” tab.
2. Under the “Output Format” field, select Display as “Output Voltage (V)”
3. Under the “Stop Condition” field, select Run as “1” Seconds. Alternatively, select “Run
Continuously” radio button to run continuously up to 1 hour.
4. Click on the “Run” button to view the output voltage results. A reading should be plotted as seen
in Figure . Output voltage will vary depending on input voltage across input (IN1/IN2) and CMOUT.
If J1/J2 are shorted, IN1/IN2 = CMOUT, output voltage should be about 1V. Note: Board is
provided with jumper J1/J2 open. Use provided jumper to short IN1/IN2 to CMOUT for easy
evaluation.
Figure 7: Results of DC Reading
3.4. Powering the LMP91051EVM
There are two ways in which VDD can be sourced: external supply or SPIO-4 power.
If using an external power supply to source VDD, do the following:
1. Connect an external power supply to banana jacks VDD-EXT and GND.
2. Jumper pins 2 and 3 of JP1 to connect the external power to VDD_DUT.
If using the SPIO-4 power to source VDD, then do the following:
1. Jumper pins 1 and 2 of JP1 to connect +3.3V SPIO-4 power to VDD_DUT.
The schematic for the LMP91051EVM can be seen in Figure 10.
10 LMP91051EVM User’s Guide snou034
3.5. Evaluating the LMP91051 without the SPIO-4 Board
The SPIO-4 digital controller board is used to generate the SPI signals to communicate to the LMP91051.
Without the SPIO-4 board, the Sensor AFE software for the LMP91051 cannot be used to capture and
analyze data from the LMP91051EVM.
If the SPIO-4 board is not available but LMP91051 evaluation is desirable, then connect your own SPI
signals to J1 of the LMP91051EVM as seen below. Reference the LMP91051 datasheet for appropriate
SPI timing diagrams. Source LMP91051 VDD with an external power supply per previous section.
Figure 8: LMP91051EVM’s J3 for SPI Signals
Refer to the LMP91051 datasheet for more information on the LMP91051’s SPI protocol.
4. Installing the Sensor AFE Software
Each Sensor AFE product will have its own software. To access the Sensor AFE software for LMP91051,
follow the steps below.
1. Getting the Zip Files
a. You can find the latest downloadable Sensor AFE software at
ti.com/sensorafe
b. Download the zip file onto your local hard drive. Unzip this folder.
2. Installing the Driver - skip this step if you don’t have the LMP91051EVM and SPIO4 digital controller
board.
a. See the provided Installation Guide For SensorAFE Drivers.pdf.
11 LMP91051EVM User’s Guide October 2012
3. Installing the Software
a. See the provided Installation Guide for LMP91050 SensorAFE Software.pdf
i. Note: If you run the software without the boards, you’ll get an error message. Ignore that
error message and click “Ok” to continue.
5. Board Layout
Figure 9: LMP91051EVM Layout
6. Schematic
Figure 10: LMP91051EVM Schematic
7. BOM
LMP91051EVM Bill of Materials
Item Designator Description Manufacturer PartNumber Quantity
1 +3P3V, +5V, A0_DUT, A1_DUT, CMOUT_DUT, CSB_ADC,
CSB_DUT, DOUT_ADC, IN1_DUT, IN2_DUT, MISO, MOSI,
MOSI_EN, OUT_DUT, REF_ADC, SCLK_ADC, SCLK_DUT,
SDIO_DUT, TEMP, VA_ADC, VDD_DUT, VDD_EXT, VIO,
VIO_ADC, VIO_EXT, VREF_ADC
Test Point, TH, Compact, Red Keystone Electronics 5005 26
2 AA1 Printed Circuit Board TBD by TI 551xxxxxx-001 REV A 1
3 BNC1, BNC2, OUT DNS Amphenol Connex 112404 3
4 C1 CAP, CERM, 10uF, 6.3V, +/-
20%, X5R, 1206
TDK C3216X5R0J106M 1
5 C2 CAP CER 4700PF 250V X7R
10% 0805
TDK C2012X7R2E472K 1
6 C3, C9, C10, C12, C17, C22 CAP, TANT, 10uF, 10V, +/-
20%, 3.4 ohm, 3216-18 SMD
Vishay-Sprague 293D106X0010A2TE3 6
7 C4, C7, C13, C15, C18, C19, C23 CAP, CERM, 0.1uF, 16V, +/-
5%, X7R, 0603
AVX 0603YC104JAT2A 7
8 C5, C6, C21 CAP, CERM, 10nF, 50V, +/-5%,
C0G/NP0, 0805
MuRata GRM2195C1H103JA01D 3
9 C8, C14 CAP, CERM, 0.1uF, 25V, +/-
10%, X7R, 0805
AVX 08053C104KAT2A 2
10 C11 CAP, CERM, 0.1uF, 100V, +/-
5%, X7R, 1206
AVX 12061C104JAT2A 1
11 C16, C20 CAP, CERM, 1uF, 10V, +/-10%,
X7R, 0805
AVX 0805ZC105KAT2A 2
12 FID1, FID2, FID3 Fiducial mark. There is nothing
to buy or mount.
N/A N/A 3
13 GND1, GND2, GND3, GND4, GND5, GND6, GND7, GND8,
GND9, GND10, GND11
Test Point, TH, Compact, Black Keystone Electronics 5006 11
14 H1, H2, H3, H4 Bump Hemisphere B&F Fastener Supply NY PMS 440 0025 PH 4
15 J1, J2, JP3, JP4, JP5 Header, TH, 100mil, 2x1, Gold
plated, 230 mil above insulator Samtec Inc. TSW-102-07-G-S
5
16 J3 SPIO-GPSI16 Header, 16-Pin,
Dual row, Right Angle
Sullins Connector
Solutions
PBC36DGAN 1
17 JP1, JP2, JP6 Header, TH, 100mil, 1x3, Gold
plated, 230 mil above insulator
Samtec Inc. TSW-103-07-G-S 3
18 L1, L2 Ferrite, Chip, 200mA, .080 ohm,
SMD
Wurth Elektronik eiSos BLM21BD272SN1L 2
19 R1, R2 RES, 160k ohm, 5%, 0.125W,
0805
Vishay-Dale CRCW0805160KJNEA 2
20 R3 DNS Vishay-Dale DNS 1
21 R4 RES, 100k ohm, 5%, 0.125W,
0805
Vishay-Dale CRCW0805100KJNEA 1
22 R5, R10 RES, 0 ohm, 5%, 0.125W, 0805 Vishay-Dale CRCW08050000Z0EA 2
23 R6 RES, 100k ohm, 1%, 0.125W,
0805
Vishay-Dale CRCW0805100KFKEA 1
24 R7 RES, 1.00k ohm, 1%, 0.125W,
0805
Vishay-Dale CRCW08051K00FKEA 1
25 R8 RES, 27.4 ohm, 1%, 0.1W,
0603
Vishay-Dale CRCW060327R4FKEA 1
26 R9 RES, 51.1 ohm, 1%, 0.1W,
0603
Vishay-Dale CRCW060351R1FKEA 1
27 R11, R12, R13, R14 DNS Vishay-Dale CRCW06031R00JNEA 4
28 U1 LMP91051 Texas Instruments LMP91051 1
29 U2 16-Bit, 50 to 250 kSPS,
Differential Input, MicroPower
ADC, 10-pin Mini SOIC, Pb-
Free
Texas Instruments ADC141S628QIMMX/NOP
B
1
30 U3 Non-Inverting 3-State Buffer Texas Instruments SN74AHC1G125DCKR 1
31 U4 DNS Heimann HMS J21 1
32 U5 Precision Micropower Low
Dropout Voltage Reference, 8-
pin Narrow SOIC
Texas Instruments LM4140ACM-4.1 1
33 U6 2K 5.0V I2C Serial EEPROM On Semiconductor CAT24C02WI-GT3 1
34 Y1 Osc 4.000Mhz 5.0V Full Size ECS Inc ECS-100AX-100 1
35 Y1A Oscllator Socket Aires Electronics A462-ND 1
EVALUATION BOARD/KIT/MODULE (EVM) ADDITIONAL TERMS
Texas Instruments (TI) provides the enclosed Evaluation Board/Kit/Module (EVM) under the following conditions:
The user assumes all responsibility and liability for proper and safe handling of the goods. Further, the user
indemnifies TI from all claims arising from the handling or use of the goods.
Should this evaluation board/kit not meet the specifications indicated in the User’s Guide, the board/kit may be
returned within 30 days from the date of delivery for a full refund. THE FOREGOING LIMITED WARRANTY IS THE
EXCLUSIVE WARRANTY MADE BY SELLER TO BUYER AND IS IN LIEU OF ALL OTHER WARRANTIES,
EXPRESSED, IMPLIED, OR STATUTORY, INCLUDING ANY WARRANTY OF MERCHANTABILITY OR FITNESS
FOR ANY PARTICULAR PURPOSE. EXCEPT TO THE EXTENT OF THE INDEMNITY SET FORTH ABOVE,
NEITHER PARTY SHALL BE LIABLE TO THE OTHER FOR ANY INDIRECT, SPECIAL, INCIDENTAL, OR
CONSEQUENTIAL DAMAGES.
Please read the User's Guide and, specifically, the Warnings and Restrictions notice in the User's Guide prior to
handling the product. This notice contains important safety information about temperatures and voltages. For
additional information on TI's environmental and/or safety programs, please visit www.ti.com/esh or contact TI.
No license is granted under any patent right or other intellectual property right of TI covering or relating to any
machine, process, or combination in which such TI products or services might be or are used. TI currently deals
with a variety of customers for products, and therefore our arrangement with the user is not exclusive. TI assumes
no liability for applications assistance, customer product design, software performance, or infringement of patents
or services described herein.
REGULATORY COMPLIANCE INFORMATION
As noted in the EVM User’s Guide and/or EVM itself, this EVM and/or accompanying hardware may or may not be
subject to the Federal Communications Commission (FCC) and Industry Canada (IC) rules.
For EVMs not subject to the above rules, this evaluation board/kit/module is intended for use for ENGINEERING
DEVELOPMENT, DEMONSTRATION OR EVALUATION PURPOSES ONLY and is not considered by TI to be a
finished end product fit for general consumer use. It generates, uses, and can radiate radio frequency energy and
has not been tested for compliance with the limits of computing devices pursuant to part 15 of FCC or ICES-003
rules, which are designed to provide reasonable protection against radio frequency interference. Operation of the
equipment may cause interference with radio communications, in which case the user at his own expense will be
required to take whatever measures may be required to correct this interference.
General Statement for EVMs including a radio
User Power/Frequency Use Obligations: This radio is intended for development/professional use only in legally
allocated frequency and power limits. Any use of radio frequencies and/or power availability of this EVM and its
development application(s) must comply with local laws governing radio spectrum allocation and power limits for
this evaluation module. It is the user’s sole responsibility to only operate this radio in legally acceptable frequency
space and within legally mandated power limitations. Any exceptions to this are strictly prohibited and unauthorized
by Texas Instruments unless user has obtained appropriate experimental/development licenses from local
regulatory authorities, which is responsibility of user including its acceptable authorization.
For EVMs annotated as FCC – FEDERAL COMMUNICATIONS COMMISSION Part 15 Compliant
Caution
This device complies with part 15 of the FCC Rules. Operation is subject to the following two conditions: (1) This
device may not cause harmful interference, and (2) this device must accept any interference received, including
interference that may cause undesired operation.
Changes or modifications not expressly approved by the party responsible for compliance could void the user's
authority to operate the equipment.
FCC Interference Statement for Class A EVM devices
This equipment has been tested and found to comply with the limits for a Class A digital device, pursuant to part 15
of the FCC Rules. These limits are designed to provide reasonable protection against harmful interference when
the equipment is operated in a commercial environment. This equipment generates, uses, and can radiate radio
frequency energy and, if not installed and used in accordance with the instruction manual, may cause harmful
interference to radio communications. Operation of this equipment in a residential area is likely to cause harmful
interference in which case the user will be required to correct the interference at his own expense.
FCC Interference Statement for Class B EVM devices
This equipment has been tested and found to comply with the limits for a Class B digital device, pursuant to part 15
of the FCC Rules. These limits are designed to provide reasonable protection against harmful interference in a
residential installation. This equipment generates, uses and can radiate radio frequency energy and, if not installed
and used in accordance with the instructions, may cause harmful interference to radio communications. However,
there is no guarantee that interference will not occur in a particular installation. If this equipment does cause
harmful interference to radio or television reception, which can be determined by turning the equipment off and on,
the user is encouraged to try to correct the interference by one or more of the following measures:
• Reorient or relocate the receiving antenna.
• Increase the separation between the equipment and receiver.
• Connect the equipment into an outlet on a circuit different from that to which the receiver is connected.
• Consult the dealer or an experienced radio/TV technician for help.
For EVMs annotated as IC – INDUSTRY CANADA Compliant
This Class A or B digital apparatus complies with Canadian ICES-003.
Changes or modifications not expressly approved by the party responsible for compliance could void the user’s
authority to operate the equipment.
Concerning EVMs including radio transmitters
This device complies with Industry Canada licence-exempt RSS standard(s). Operation is subject to the following
two conditions: (1) this device may not cause interference, and (2) this device must accept any interference,
including interference that may cause undesired operation of the device.
Concerning EVMs including detachable antennas
Under Industry Canada regulations, this radio transmitter may only operate using an antenna of a type and
maximum (or lesser) gain approved for the transmitter by Industry Canada. To reduce potential radio interference to
other users, the antenna type and its gain should be so chosen that the equivalent isotropically radiated power
(e.i.r.p.) is not more than that necessary for successful communication.
This radio transmitter has been approved by Industry Canada to operate with the antenna types listed in the user
guide with the maximum permissible gain and required antenna impedance for each antenna type indicated.
Antenna types not included in this list, having a gain greater than the maximum gain indicated for that type, are
strictly prohibited for use with this device.
Cet appareil numérique de la classe A ou B est conforme à la norme NMB-003 du Canada.
Les changements ou les modifications pas expressément approuvés par la partie responsable de la conformité ont
pu vider l’autorité de l'utilisateur pour actionner l'équipement.
Concernant les EVMs avec appareils radio
Le présent appareil est conforme aux CNR d'Industrie Canada applicables aux appareils radio exempts de licence.
L'exploitation est autorisée aux deux conditions suivantes : (1) l'appareil ne doit pas produire de brouillage, et (2)
l'utilisateur de l'appareil doit accepter tout brouillage radioélectrique subi, même si le brouillage est susceptible d'en
compromettre le fonctionnement.
Concernant les EVMs avec antennes détachables
Conformément à la réglementation d'Industrie Canada, le présent émetteur radio peut fonctionner avec une
antenne d'un type et d'un gain maximal (ou inférieur) approuvé pour l'émetteur par Industrie Canada. Dans le but
de réduire les risques de brouillage radioélectrique à l'intention des autres utilisateurs, il faut choisir le type
d'antenne et son gain de sorte que la puissance isotrope rayonnée équivalente (p.i.r.e.) ne dépasse pas l'intensité
nécessaire à l'établissement d'une communication satisfaisante.
Le présent émetteur radio a été approuvé par Industrie Canada pour fonctionner avec les types d'antenne
énumérés dans le manuel d’usage et ayant un gain admissible maximal et l'impédance requise pour chaque type
d'antenne. Les types d'antenne non inclus dans cette liste, ou dont le gain est supérieur au gain maximal indiqué,
sont strictement interdits pour l'exploitation de l'émetteur.
SPACER
SPACER
SPACER
【Important Notice for Users of this Product in Japan】
This development kit is NOT certified as Confirming to Technical Regulations of Radio Law of Japan
If you use this product in Japan, you are required by Radio Law of Japan to follow the instructions below with
respect to this product:
1. Use this product in a shielded room or any other test facility as defined in the notification #173 issued by
Ministry of Internal Affairs and Communications on March 28, 2006, based on Sub-section 1.1 of Article 6
of the Ministry’s Rule for Enforcement of Radio Law of Japan,
2. Use this product only after you obtained the license of Test Radio Station as provided in Radio Law of
Japan with respect to this product, or
3. Use of this product only after you obtained the Technical Regulations Conformity Certification as provided
in Radio Law of Japan with respect to this product. Also, please do not transfer this product, unless you
give the same notice above to the transferee. Please note that if you could not follow the instructions
above, you will be subject to penalties of Radio Law of Japan.
Texas Instruments Japan Limited
(address) 24-1, Nishi-Shinjuku 6 chome, Shinjuku-ku, Tokyo, Japan
http://www.tij.co.jp
【ご使用にあたっての注】
本開発キットは技術基準適合証明を受けておりません。
本製品のご使用に際しては、電波法遵守のため、以下のいずれかの措置を取っていただく必要がありますのでご注
意ください。
1. 電波法施行規則第6条第1項第1号に基づく平成18年3月28日総務省告示第173号で定められた電波暗室等の
試験設備でご使用いただく。
2. 実験局の免許を取得後ご使用いただく。
3. 技術基準適合証明を取得後ご使用いただく。
なお、本製品は、上記の「ご使用にあたっての注意」を譲渡先、移転先に通知しない限り、譲渡、移転できないも
のとします。
上記を遵守頂けない場合は、電波法の罰則が適用される可能性があることをご留意ください。
日本テキサス・インスツルメンツ株式会社
東京都新宿区西新宿6丁目24番1号
西新宿三井ビル
http://www.tij.co.jp
SPACER
SPACER
EVALUATION BOARD/KIT/MODULE (EVM)
WARNINGS, RESTRICTIONS AND DISCLAIMERS
For Feasibility Evaluation Only, in Laboratory/Development Environments. Unless otherwise indicated, this
EVM is not a finished electrical equipment and not intended for consumer use. It is intended solely for use for
preliminary feasibility evaluation in laboratory/development environments by technically qualified electronics experts
who are familiar with the dangers and application risks associated with handling electrical mechanical components,
systems and subsystems. It should not be used as all or part of a finished end product.
Your Sole Responsibility and Risk. You acknowledge, represent and agree that:
1. You have unique knowledge concerning Federal, State and local regulatory requirements (including but not
limited to Food and Drug Administration regulations, if applicable) which relate to your products and which
relate to your use (and/or that of your employees, affiliates, contractors or designees) of the EVM for
evaluation, testing and other purposes.
2. You have full and exclusive responsibility to assure the safety and compliance of your products with all
such laws and other applicable regulatory requirements, and also to assure the safety of any activities to be
conducted by you and/or your employees, affiliates, contractors or designees, using the EVM. Further, you
are responsible to assure that any interfaces (electronic and/or mechanical) between the EVM and any
human body are designed with suitable isolation and means to safely limit accessible leakage currents to
minimize the risk of electrical shock hazard.
3. You will employ reasonable safeguards to ensure that your use of the EVM will not result in any property
damage, injury or death, even if the EVM should fail to perform as described or expected.
4. You will take care of proper disposal and recycling of the EVM’s electronic components and packing
materials.
Certain Instructions. It is important to operate this EVM within TI’s recommended specifications and
environmental considerations per the user guidelines. Exceeding the specified EVM ratings (including but not
limited to input and output voltage, current, power, and environmental ranges) may cause property damage,
personal injury or death. If there are questions concerning these ratings please contact a TI field representative
prior to connecting interface electronics including input power and intended loads. Any loads applied outside of the
specified output range may result in unintended and/or inaccurate operation and/or possible permanent damage to
the EVM and/or interface electronics. Please consult the EVM User's Guide prior to connecting any load to the EVM
output. If there is uncertainty as to the load specification, please contact a TI field representative. During normal
operation, some circuit components may have case temperatures greater than 60°C as long as the input and output
are maintained at a normal ambient operating temperature. These components include but are not limited to linear
regulators, switching transistors, pass transistors, and current sense resistors which can be identified using the
EVM schematic located in the EVM User's Guide. When placing measurement probes near these devices during
normal operation, please be aware that these devices may be very warm to the touch. As with all electronic
evaluation tools, only qualified personnel knowledgeable in electronic measurement and diagnostics normally found
in development environments should use these EVMs.
Agreement to Defend, Indemnify and Hold Harmless. You agree to defend, indemnify and hold TI, its licensors
and their representatives harmless from and against any and all claims, damages, losses, expenses, costs and
liabilities (collectively, "Claims") arising out of or in connection with any use of the EVM that is not in accordance
with the terms of the agreement. This obligation shall apply whether Claims arise under law of tort or contract or
any other legal theory, and even if the EVM fails to perform as described or expected.
Safety-Critical or Life-Critical Applications. If you intend to evaluate the components for possible use in safety
critical applications (such as life support) where a failure of the TI product would reasonably be expected to cause
severe personal injury or death, such as devices which are classified as FDA Class III or similar classification, then
you must specifically notify TI of such intent and enter into a separate Assurance and Indemnity Agreement.
Mailing Address: Texas Instruments, Post Office Box 655303, Dallas, Texas 75265
Copyright © 2012, Texas Instruments Incorporated
IMPORTANT NOTICE
Texas Instruments Incorporated and its subsidiaries (TI) reserve the right to make corrections, enhancements, improvements and other
changes to its semiconductor products and services per JESD46, latest issue, and to discontinue any product or service per JESD48, latest
issue. Buyers should obtain the latest relevant information before placing orders and should verify that such information is current and
complete. All semiconductor products (also referred to herein as “components”) are sold subject to TI’s terms and conditions of sale
supplied at the time of order acknowledgment.
TI warrants performance of its components to the specifications applicable at the time of sale, in accordance with the warranty in TI’s terms
and conditions of sale of semiconductor products. Testing and other quality control techniques are used to the extent TI deems necessary
to support this warranty. Except where mandated by applicable law, testing of all parameters of each component is not necessarily
performed.
TI assumes no liability for applications assistance or the design of Buyers’ products. Buyers are responsible for their products and
applications using TI components. To minimize the risks associated with Buyers’ products and applications, Buyers should provide
adequate design and operating safeguards.
TI does not warrant or represent that any license, either express or implied, is granted under any patent right, copyright, mask work right, or
other intellectual property right relating to any combination, machine, or process in which TI components or services are used. Information
published by TI regarding third-party products or services does not constitute a license to use such products or services or a warranty or
endorsement thereof. Use of such information may require a license from a third party under the patents or other intellectual property of the
third party, or a license from TI under the patents or other intellectual property of TI.
Reproduction of significant portions of TI information in TI data books or data sheets is permissible only if reproduction is without alteration
and is accompanied by all associated warranties, conditions, limitations, and notices. TI is not responsible or liable for such altered
documentation. Information of third parties may be subject to additional restrictions.
Resale of TI components or services with statements different from or beyond the parameters stated by TI for that component or service
voids all express and any implied warranties for the associated TI component or service and is an unfair and deceptive business practice.
TI is not responsible or liable for any such statements.
Buyer acknowledges and agrees that it is solely responsible for compliance with all legal, regulatory and safety-related requirements
concerning its products, and any use of TI components in its applications, notwithstanding any applications-related information or support
that may be provided by TI. Buyer represents and agrees that it has all the necessary expertise to create and implement safeguards which
anticipate dangerous consequences of failures, monitor failures and their consequences, lessen the likelihood of failures that might cause
harm and take appropriate remedial actions. Buyer will fully indemnify TI and its representatives against any damages arising out of the use
of any TI components in safety-critical applications.
In some cases, TI components may be promoted specifically to facilitate safety-related applications. With such components, TI’s goal is to
help enable customers to design and create their own end-product solutions that meet applicable functional safety standards and
requirements. Nonetheless, such components are subject to these terms.
No TI components are authorized for use in FDA Class III (or similar life-critical medical equipment) unless authorized officers of the parties
have executed a special agreement specifically governing such use.
Only those TI components which TI has specifically designated as military grade or “enhanced plastic” are designed and intended for use in
military/aerospace applications or environments. Buyer acknowledges and agrees that any military or aerospace use of TI components
which have not been so designated is solely at the Buyer's risk, and that Buyer is solely responsible for compliance with all legal and
regulatory requirements in connection with such use.
TI has specifically designated certain components which meet ISO/TS16949 requirements, mainly for automotive use. Components which
have not been so designated are neither designed nor intended for automotive use; and TI will not be responsible for any failure of such
components to meet such requirements.
Products Applications
Audio www.ti.com/audio Automotive and Transportation www.ti.com/automotive
Amplifiers amplifier.ti.com Communications and Telecom www.ti.com/communications
Data Converters dataconverter.ti.com Computers and Peripherals www.ti.com/computers
DLP® Products www.dlp.com Consumer Electronics www.ti.com/consumer-apps
DSP dsp.ti.com Energy and Lighting www.ti.com/energy
Clocks and Timers www.ti.com/clocks Industrial www.ti.com/industrial
Interface interface.ti.com Medical www.ti.com/medical
Logic logic.ti.com Security www.ti.com/security
Power Mgmt power.ti.com Space, Avionics and Defense www.ti.com/space-avionics-defense
Microcontrollers microcontroller.ti.com Video and Imaging www.ti.com/video
RFID www.ti-rfid.com
OMAP Applications Processors www.ti.com/omap TI E2E Community e2e.ti.com
Wireless Connectivity www.ti.com/wirelessconnectivity
Mailing Address: Texas Instruments, Post Office Box 655303, Dallas, Texas 75265
Copyright © 2012, Texas Instruments Incorporated
Copyright 2012 by Fen Logic Ltd. All rights reserved.
FEN LOGIC LTD.
Gertboard User Manual
Gert van Loo and Myra VanInwegen
Revision 1.0
The Gertboard is an add-on GPIO expansion board for the Raspberry Pi computer. It comes with a
large variety of components, including buttons, LEDs, A/D and D/A converters, a motor controller,
and an Atmel AVR microcontroller. There is a suite of test/example programs for the Gertboard,
written in C, which is freely available at www.element14.com/raspberrypi This manual explains both
how to set up the Gertboard for various control experiments and also explains at a high level how
the test code works.
3
Contents
Gertboard Overview ................................................................................................................................ 4
Labels on the circuit board .................................................................................................................. 5
Location of the building blocks on the Gertboard .............................................................................. 7
Jumpers and straps .............................................................................................................................. 8
GPIO pins ........................................................................................................................................... 8
Schematics .......................................................................................................................................... 9
Test programs overview ...................................................................................................................... 9
Macros........................................................................................................................................... 10
Buffered I/O, LEDs, and pushbuttons ................................................................................................... 11
Push buttons ...................................................................................................................................... 12
Locating the relevant sections of the Gertboard ............................................................................... 12
Testing the pushbuttons .................................................................................................................... 14
Testing the LEDs .............................................................................................................................. 16
Testing I/O ........................................................................................................................................ 18
Open Collector Driver ........................................................................................................................... 19
Testing the open collector drivers ..................................................................................................... 20
Motor Controller ................................................................................................................................... 22
Testing the motor controller .............................................................................................................. 23
Digital to Analogue and Analogue to Digital Converters ..................................................................... 25
Digital to analogue converter ............................................................................................................ 25
Analogue to Digital converter ........................................................................................................... 26
Testing the D/A and A/D .................................................................................................................. 26
ATmega device ..................................................................................................................................... 29
Programming the ATmega ................................................................................................................ 30
Arduino pins on the Gertboard ...................................................................................................... 30
A few sketches to get you going ................................................................................................... 31
Minicom ........................................................................................................................................ 36
Combined Tests .................................................................................................................................... 38
A/D and motor controller .................................................................................................................. 38
Decoder ............................................................................................................................................. 39
For More Information ........................................................................................................................... 40
Appendix A: Schematics ....................................................................................................................... 40
4
Gertboard Overview
Raspi
open collector (6x)
Micro controller
strapping area
Motor
controller
D
A
A
D
SPI PWM I/O UART I/O
12x
3x
SPI/dbg
out
in 1k
1k
ULN2803a
ATmega
74xx244
L6203
MCP3002
MCP4802
Fig. 1: The principle, high level diagram of the Gertboard. In this view it is possible to see how
flexible Gertboard is, by being able to connect various parts of the board together.
Above is a principle diagram1 of the Gertboard. Each circle in the diagram represents a header pin.
These headers give you access to a wide range of control combinations. As you begin experimenting
with the board, you will probably use the strapping area to connect various components on the
Gertboard to the Raspberry Pi. This flexibility even allows you, for example, to connect the motor
controller input pins to the Atmel ATmega device (an AVR microcontroller). The ATmega device has
a separate 6-pin header, which allows it to be programmed by the Raspberry Pi using the (Serial
Peripheral Interface) SPI bus.
The major building blocks are:
• 12x buffered I/O
• 3x push buttons
• 6x open collector drivers (50V, 0.5A)
• 48V, 4A motor controller
• 28-pin dual in line ATmega microcontroller
• 2-channel 8/10/12 bit Digital to Analogue converter
• 2-channel 10 bit Analogue to Digital converter
Each of these building blocks has a section below.
1
A ‘principle diagram’ is a coarse overview of the most important parts of the system. It is not correct in all details. For that
you must look at the board schematics.
5
Labels on the circuit board
Fig. 2: A photograph of the unpopulated Gertboard viewed from above, showing the silver
coloured holes and pads that eventually will be home to the components, as well as the
legends printed in white epoxy ink, and green solder resist coating.
Fig. 3: This image is a diagrammatic representation of the same photograph shown in Fig. 2
above. It was generated from the same files that were used to create the physical printed
circuit board. The blue elements in the diagram correspond to the white text and lines on the
photo and the red elements correspond to the silver pads and holes on the photo.
6
From now onwards in this guide, because it is much clearer to see, the diagram shown in Fig. x will
be used in preference to show you how to wire up the Gertboard, and to run the test and example
programs.
It is useful to be able to look at the bare board in order to see the labels (the white text in the photo
and the blue text in the diagram) on the board without the components getting in the way. These labels
provide essential information that is required in order to use Gertboard to its full potential. Almost all
of the components have labels, and more importantly, the pins in the headers have labels.
It isn’t necessary to be too concerned about the majority of the components; such as resistors and
capacitors (labelled with Cn and Rn, where n is some number). These are fairly simple devices that
don’t have a ‘right way round’ when they are assembled to the board. Diodes on the other hand, do
need assembling the right way round (covered later) - all the diodes are labelled Dn; of these, the ones
that you will be interested in are D1 through D12, the light emitting diodes (LEDs; they are located
near the top of the board on the left). Pushbutton switches are labelled S1, S2, and S3 (they are
located just beneath the LEDs).
Fig. 4: Two examples of ICs – an 8-pin and a 20-pin
dual-inline (DIL) package. In this package style, pin
1 is always identified as the first pin anticlockwise
from the package notch marking.
Integrated circuits, or ICs, are marked Un, so for example the I/O buffer chips are U3, U4, and U5
(these are near the middle of the board), while the Atmel microcontroller is U8 (this is below and to
the left of U3 to U5). For the ICs, it is very important to know which is pin 1. If the IC is orientated so
that the end with the semi-circle notch is to the left, then pin 1 is the leftmost pin in the bottom row.
On the Gertboard, the location of pin 1 is always marked with a square pad. Pin numbers increase in
an anti-clockwise direction from there, as shown in the diagram. Knowing this means that the
schematics in Appendix A can always be related to the pinning on the ICs on the Gertboard.
Headers (the rows of pins sticking up from the board) will be a frequently used component on the
Gertboard. They are labelled Jn, so for example the header to the ribbon cable from the Raspberry Pi
is attached, is J1. Pin 1 on the headers is again marked with a square pad.
Power pins are marked with their voltage; for example there are a few positions marked 3V3. This is a
commonly used notation in electronics, and in this case it means 3.3 volts. A 5V power supply comes
onto the board via the GPIO connector, but the standard Gertboard assembly instructions do not
require that a header is installed to access this. If 5V is really required, and spare header pins are
available, a header can be soldered in location J24 in the lower right-hand corner of the board, and
then a 5V supply can be picked up from the lower pin (next to the text ‘5V’). Ground is marked with
GND or a ⊥ symbol.
1 2 3 4
8 7 6 5
1 2 3 4 5 6 7 8
20 19 18
9 10
17 16 15 14 13 12 11
7
Location of the building blocks on the Gertboard
Fig. 5: Photograph of an assembled Gertboard, with key functional blocks identified by
coloured boundary marking. This image serves as a good reference point for a board that has
been successfully assembled from bare board and components. Please note that the appearance
of some components can vary.
This annotated photo of a populated Gertboard shows where the building blocks (the major
capabilities of the board) are located. Some of the building blocks have two areas marked. For
example, the turquoise lines showing the Atmel ATmega chip not only surround the chip itself (on the
lower left) but also surround two header pins near the bottom of the board, in the middle. These pins
are connected to the Atmel chip and provide an easy way to interface the GPIO signals from the
Raspberry Pi (which are in the black box) with the Atmel chip.
The supply voltage (the voltage that acts as high or logical 1 on the board) is 3.3V. This is generated
from the 5V power pin in the J1 header (the one where the ribbon cable to the Raspberry Pi is
attached) by the components in the lower right corner of the board. The open collector and motor
controllers can handle higher voltages and have points to attach external power supplies.
8
Jumpers and straps
Fig. 6: Image showing straps on the left hand side, and jumpers on the right. Straps connect two
parts of Gertboard together, whilst jumpers conveniently connect two adjacent pins on the same
header, together. The Gertboard Kit contains materials to produce single straps, although the
double strap also shown can also be useful.
To work properly, and get the maximum flexibility from the Gertboard a number of straps and
jumpers are essential. On the left of the photo are straps: they consist of wires that connect the small
metal connector and plastic housing, that slip over the header pins. They are meant for connecting
header pins that are further apart. It is sometimes useful to have straps that connect two or three
adjacent pins to the same number of adjacent pins elsewhere on the board. This is useful for example
when you want to use several LEDs. On the right of the above photo are jumpers: they are used to
connect two header pins that are right next to each other.
There is one jumper that should be in place at all times on the board: the one connecting pins 1 and 2
in header J7. This is the jumper that connects power from the power input pins to the rest of the board.
It is near the lower right corner of the board and is the jumper connecting the two pins below the text
3V3 in the photo below.
Fig. 7: Image showing header J7 with
translucent jumper in place. J7 is located just
above J8 (J7 legend is obscured in this image)
GPIO pins
The header J2, to the right of the text ‘Raspberry Pi’ on the board, provides access to all the I/O pins
on the GPIO header. There are 26 pins in J1 (the GPIO header which is connected to the Raspberry Pi
through the ribbon cable) but only 17 pins in J2: 3 of the pins in J1 are power and ground, and 6 are
DNC (do not connect). The labels on these pins, GP0, GP1, GP4, GP7, etc, may initially seem a little
arbitrary, as there are some obvious gaps, and the numbers do not correspond with the pin numbers on
the GPIO header J1. These labels are important however: they correspond with the signal names used
9
by the BCM2835, the processor on the Raspberry Pi. Signal GPIOn on the BCM2835 datasheet
corresponds to the pin labelled GPn on header J2 (so for example, GPIO17 on the data sheet can be
found at the pin labelled GP17 on the board). The numbers in the labels allow us to specify which
pins are required in the control programs to be run later.
Some of the GPIO pins have an alternate function that are made use of in some of the test programs.
These are shown in the table below. The rest are only used as general purpose input/output in the
code. On page 27 there is a description of how to gain access to the alternate functions of GPIO pins.
GPIO0 SDA0 (alt 0)
I2C bus
GPIO1 SLC0 (alt 0)
GPIO7 SPI_CE1_N (alt 0)
SPI bus
GPIO8 SPI_CE0_N (alt 0)
GPIO9 SPI_MISO (alt 0)
GPIO10 SPI_MOSI (alt 0)
GPIO11 SPI_SCLK (alt 0)
GPIO14 TXD0 (alt 0)
UART
GPIO15 RXD0 (alt 0)
GPIO18 PWM0 (alt 5) pulse width modulation
Table 1: Table showing the GPIO pins on the Gertboard, and what their alternative function is.
We mention the I2C bus use of GPIO0 and 1 above not because the I2C bus is used in the test
programs, but because each of them has a 1800 pull-up resistor on the Raspberry Pi, and this
prevents them from being used with the pushbuttons (see page 134).
Schematics
Whilst there are some circuit diagrams, or schematics, in the main body of the manual for some of the
building blocks of the board, they are simplifications of the actual circuits on the board. To truly
understand the board and the connections you need to make on it, you need to be a little familiar with
the schematics. Thus we have attached the full schematics at the end of this manual as Appendix A.
These pages are in landscape format. The page numbers A-1, A-2, etc, are in the lower left corner of
the pages (if you hold them so that the writing is the right way up).
Test programs overview
When you download the Gertboard test/example code (available at www.element14.com/raspberrypi),
you will have a file with a name something like gertboard_sw_10_07_12.tar.gz. This is a
compressed (hence the .gz suffix, which means it was compressed using the gzip algorithm) archive
(hence the .tar), where an archive is a collection of different files, all stored in a single file.
To retrieve the original software, put the file where you want your Gertboard software to end up on
your Raspberry Pi computer, then uncompress it by typing the following in one of the terminal
windows on your Pi (substituting the name of the actual file you have downloaded for the file name
we are using in this example):
gunzip gertboard_sw_10_07_12.tar.gz
10
Typing a directory command, ls, should then show the newly uncompressed archive file
gertboard_sw_10_07_12.tar . So now, to extract the files from the archive, type
tar –xvf gertboard_sw_10_07_12.tar
A new directory, gertboard_sw, will be created. In it is a set of C files and a makefile. C files are
software files, but they need to be compiled to run on the processor on your system. In the case of
Raspberry Pi, this is an ARM11. To compile all the code to run on Raspberry Pi, first change
directory to gertboard_sw by typing:
cd gertboard_sw
And then in that directory, type:
make all
Each building block has at least one test program that goes with it. Currently the test programs are
written in C; but they’ll be translated into Python in the near future. Each test program is compiled
from two or more C files. The file gb_common.c (which has an associated header file
gb_common.h) contains code used by all of the building blocks on the board. Each test has a C file
that contains code specific to that test (thus you will find main here). Some of the tests use a special
interface (for example the SPI bus), and these tests have an additional C file that provides code
specific to that interface (these files are gb_spi.c for the SPI bus and gb_pwm for the pulse width
modulator).
In each of the sections about the individual building blocks, the code specific to the tests for that block
is explained. Since all of the tests share the code in gb_common.c, an overview of that code will be
given here. In order to use the Gertboard via the GPIO, the test code first needs to call setup_io.
This function allocates various arrays and then calls mmap to associate the arrays with the devices that
it wants to control, such as the GPIO, SPI bus, PWM (pulse width modulator) etc. The result of this is
that it writes to these arrays control the devices or sends data to them, and reads from these arrays get
status bits or data from the devices. At the end of a test program, restore_io should be called,
which undoes the memory map and frees the allocated memory.
Macros
In gb_common.h, gb_spi.h, and gb_pwm.h there are a number of macros that give a more
intuitive name to various parts of the arrays that have been mapped. These macros are used to do
everything from setting whether a GPIO is used as input or output to controlling the clock speed of
the pulse width modulator. In the chart below is a summary of the purpose of the more commonly
used macros and give the page number on which its use is explained in more detail. The T column
below gives the ‘type’ of the macro. This shows how the macro is used. ‘E’ means that the command
is executed, as in:
INP_GPIO(17);
‘W’ means that that the command is written to (assigned), as in:
GPIO_PULL = 2;
11
‘R’ means that that the command is read from, as in:
data = GPIO_IN0;
Macro name T Explanation Page no.
INP_GPIO(n) E activates GPIO pin number n (for input) 11
OUT_GPIO(n) E used after above, sets pin n for output 11
SET_GPIO_ALT(n, a) E used after INP_GPIO, select alternate function for pin 24
GPIO_PULL W set pull code 16
GPIO_PULLCCLK0 W select which pins pull code is applied to 16
GPIO_IN0 R get input values 16
GPIO_SET0 W select which pins are set high 17
GPIO_CLR0 W select which pins are set low 17
Table 2: Commonly used macros, their purpose, type and location within this manual.
The macro INP_GPIO(n) must be called for a pin number n to allow this pin to be used. By default
its mode is set up as an input. If it is required that the pin is used for an output, OUT_GPIO(n)must
be called after INP_GPIO(n).
Buffered I/O, LEDs, and pushbuttons
There are 12 pins which can be used as input or output ports. Each can be set to behave either as an
input or an output, using a jumper. Note that the terms ‘input’ and ‘output’ here are always with
respect to the Raspberry Pi: in input mode, the pin inputs data to the Pi; in output mode it acts as
output from the Pi. It is important to keep this in mind as the Gertboard is set up: an output from the
Gertboard is an input to the Raspberry Pi, and so the ‘input’ jumper must be installed to implement
this.
I/O
1k
1k-10k
input 74xx244 output
Raspi
Fig. 8: The circuit diagram for I/O ports 4-12
The triangles symbols in the diagram above represent buffers. In order to make the port function as an
input to the Raspberry Pi you install the ‘input’ jumper: then the data flows from the ‘I/O’ point to the
‘Raspi’ point. To make the port function as an output, the ‘output’ jumper must be installed: then the
data flows from the ‘Raspi’ point to the ‘I/O’ point. If both jumpers are installed, it won’t harm the
board, but the port won’t do anything sensible.
12
In both the input and output mode the LED will indicate what the logic level is on the ‘I/O’ pin. The
LED will be on when the level is high and it will be off when the level is low. There is a third option
for using this port: if neither the input nor output jumper is placed the I/O pin can be used as a simple
‘logic’ detector. The I/O pin can be connected to some other logic point (i.e. one that is either at 0V or
3.3V) and use the LED to check if the connect point is seen as high or low.
Depending on the type of 74xx244 buffer chosen, the LED could behave randomly if the port is not
driven properly. In that case it may easily switch state, switching on or off with the smallest of
electronic changes, for example, when the board is simply touched.
There is a series resistor between the input buffer and the GPIO port. This is to protect the BCM2835
(the processor on the Raspberry Pi) in case the user programs the GPIO as output and also leaves the
‘input’ jumper in place. The BCM2835 input is a high impedance input and thus even a 10K series
resistor will not produce a noticeable change in behaviour when it is used as input.
Push buttons
The Gertboard has three push buttons; these are connected to ports 1, 2, and 3. Thus the first three I/O
ports look like this:
I/O
1k
1k-10k
input 74xx244 output
Raspi
1k
Fig. 9: Circuit diagram showing one of the three
push buttons I/Os. There is a circuit like this for
ports 1 to 3.
In order to use a push button, the ‘input’ jumper must not be installed, even if the intention is to use
this as an input to the Raspberry Pi. If it is installed, the output of the lower buffer prevents the
pushbutton from working properly. To make clear what state each button is in, the output jumper can
be installed, and then the LED will now show the button state (LED on means button up, LED off
means button down). To use the push buttons, a pull-up must be set on the Raspberry Pi GPIO pins
used (described below, page 16) so that they are read as high (logical 1) when the buttons are not
pressed.
Locating the relevant sections of the Gertboard
In the building blocks location diagram on page 7, the components implementing the buffered I/O are
outlined in red. The ICs containing the buffers are U3, U4, and U5 near the centre of the board. The
LEDs (the round translucent red plastic devices) are labelled D1 to D12; D1 is driven by port 1, D2 by
port 2, etc. The pushbutton switches (the silver rectangular devices with circular depressions in the
middle) are labelled S1 to S3; S1 is connected to port 1 and so on. The long thin yellow components
with multiple pins, are resistor arrays.
13
The pins corresponding to ‘Raspi’ in the circuit diagrams above are B1 to B12 on the J3 header above
the words ‘Raspberry Pi’ on the board (B1 to B3 correspond to the ‘Raspi’ points on the second
circuit diagram with the pushbutton, and B4 to B12 correspond to the ‘Raspi’ points on the first
circuit diagram). They are called ‘Raspi’ because these are the ones that should be connected to the
pins in header J2, which are directly connected to the pins in J1, and which are then finally connected
via the ribbon cable to the Raspberry Pi. The pins corresponding to the ‘I/O’ point on the right of the
circuit diagrams above are BUF1 to BUF12 in the (unlabeled) single row header at the top of the
Gertboard.
On the Gertboard schematic, I/O buffers are on page A-2. The buffer chips U3, U4, and U5 are clearly
labelled. It should be apparent that ports 1 to 4 are handled by chip U3, ports 5 to 8 by chip U4, and
ports 9 to 12 by chip U5. The ‘Raspi’ points in the circuit diagrams above are shown as the signals
BUF_1 to BUF_12 on the left side of the page, and the ‘I/O’ points are BUF1 to BUF12 to the right of
the buffer chips. The input jumper locations are the blue rectangles labelled P1, P3, P5, P7, etc to the
left of the buffer chips, and the output jumper locations are the blue rectangles labelled P2, P4, P6, P8,
etc, to the right of the buffer chips. The pushbutton switches S1, S2, and S3 are shown separately, on
the right side of the page near the bottom.
The buffered I/O ports can be used with (almost) any of the GPIO pins; they just have to be connected
up using the straps. So for example, if you want to use port 1 with GPIO17 a strap is placed between
the B1 pin in J3 and the GP17 pin in J2. Beware that the push buttons cannot be used with GPIO0 or
GPIO1 (GP0 and GP1 in header J2 on the board) as those two pins have a 1800 pull-up resistor on
the Raspberry Pi. When the button is pressed the voltage on the input will be
3.3 ×
1000Ω
1000Ω + 1800Ω
= 1.2
This is not an I/O voltage which can be reliably seen as low.
The output and input jumper locations are above and below the U3, U4, and U5 buffer chips. The
‘input’ jumpers need to be placed on the headers below the chips (shown on the board with the ‘in’
text; they are separated from the chip they go with by a yellow resistor array), and the ‘output’
jumpers need to be placed on the headers above the chips (with the ‘out’ text). If viewed closely (it is
clearer on the bare board), it is possible to see that each row of 8 header pins above and below the
buffer chips is divided up into 4 pairs of pins. The pairs on U3 are labelled B1 to B4, the ones on U4
are B5 to B8, and the ones on U5 are B9 to B12. The B1 pins are for port 1, B2 for port 2, etc.
To use port n as an input (but not when using the pushbutton, if n is 1, 2, or 3), a jumper is installed
over the pair of pins in Bn in the row marked ‘in’ (below the appropriate buffer chip). To use port n as
an output, a jumper is installed over the pair of pins in Bn in the row marked ‘out’ (above the
appropriate buffer chip).
14
Fig. 10: Example of port configuration where ports 1
to 3 are set to be outputs and ports 10 and 11 are set
to be inputs.
As a concrete example, in the picture above, ports 1, 2, and 3 are configured for output (because of the
jumpers across B1, B2, and B3 on the ‘out’ side of chip U3). Ports 10 and 11 are configured for input
(because of the jumpers across B10 and B11 on the ‘in’ side of U5).
In the test programs, the required connections are printed out before starting the tests. The input and
output jumpers are referred to in the following way: U3-out-B1 means that there is a jumper across
the B1 pins on the ‘out’ side of the U3 buffer chip. So the 5 jumpers in the picture above would be
referred to as U3-out-B1, U3-out-B2, U3-out-B3, U5-in-B10, and U5-in-B11.
Testing the pushbuttons
The test program for the pushbutton switches is called buttons. To run this test, the Gertboard must
be set up as in the image below. There are straps connecting pins B1, B2, and B3 in header J3 to pins
GP25, GP24, and GP23 in header J2 (respectively). Thus GPIO25 will read the leftmost pushbutton,
GPIO24 will read the middle one, and GPIO23 will read the rightmost pushbutton. The jumpers on
the ‘out’ area of U3 (U3-out-B1, U3-out-B2, U3-out-B3) are optional: if they are installed, the
leftmost 3 LEDs will light up to indicate the state of the switches.
15
Fig. 11: Whilst the image above is clear, it isn’t very good at showing exactly how the straps are
connected, and between which pins on the board.
Fig. 12: This type of diagram is much more effective at showing how straps connect pins
together on the board, so from now onwards, we will use these type of diagrams to show wiring
arrangements.
16
In the diagram, black circles show which pins are being connected, and black lines between two pins
indicate that jumpers (if they are adjacent) or straps (if they are further apart) are used to connect
them.
The code specific to the buttons test is buttons.c. In the main routine, the connections
required for this test are firstly printed to the terminal (a text description of the wiring diagram above).
When the user verifies that the connections are correct, setup_io is called (described on page 10)
to get everything ready.
setup_gpio is then called, which gets GPIO pins 1 to 3 ready to be used as pushbutton inputs. It
does this by first using the macro INP_GPIO(n) (where n is the GPIO pin number) to select these 3
pins for input.
Then pins are required to be pulled high: the buttons work by dropping the voltage down to 0V when
the button is pressed, so it needs to be high when the button is not pressed. This is done by setting
GPIO_PULL to 2, the code for pull-up. Should it ever be required, the code for pull-down is 1. The
code for no pull is 0; this will allows this pin to be used for output after it has been used as a
pushbutton input. To apply this code to the desired pins, set GPIO_PULLCCLK0 = 0X03800000.
This hexadecimal number has bits 23, 24, and 25 set to 1 and all the rest set to 0. This means that the
pull code is applied to GPIO pins 23, 24, and 25. A short_wait allows time for this to take effect,
and then GPIO_PULL and GPIO_PULLCLK0 are set back to 0.
Back in the main routine, a loop is entered in which the button states are read (using macro
GPIO_IN0), grabbing bits 23, 24, and 25 using a shift and mask logical operations, and, if the button
state is different from before, it is printed out in binary: up (high) is printed as ‘1’ and down (low) is
printed as ‘0’. This loop executes until a sufficient number of button state changes have occurred.
After the loop, unpull_pins is called, which undoes the pull-up on the pins, then call
restore_io in gb_common.c to clean up.
Testing the LEDs
The test program for the LEDs is called leds. To set up the Gertboard to run this test, see the wiring
diagram below. Every I/O port is connected up as an output, so all the ‘out’ jumpers (those above the
buffer chips) are installed. Straps are used to connect the following (where all the ‘GP’ pins are in
header J2 and all the ‘B’ pins are in header J3): GP25 to B1, GP24 to B2, GP23 to B3, GP22 to B4,
GP21 to B5, GP18 to B6, GP17 to B7, GP11 to B8, GP10 to B9, GP9 to B10, GP8 to B11, and GP7
to B12. In other words, the leftmost 12 ‘GP’ pins are connected to the ‘B’ pins, except that GP14 and
GP15 are missed out: they are already set to UART mode by Linux, so it’s best if they are not
touched.
If there aren’t enough jumpers or straps to wire these connections all up at once, don’t worry. Just
wire up as many as possible, and run the test. Once it’s finished the straps/jumpers can be moved and
the test can be run again. Nothing bad will happen if a pin is written to that has nothing connected to
it.
17
Fig. 13: The wiring diagram necessary to run the Gertboard LED test program, leds
The test code in leds.c first calls setup_io to get everything ready. Then setup_gpio is
called, which prepares 12 GPIO pins to be used as outputs (as all 12 I/O ports will require
controlling). All of the GPIO signals except GPIO 0, 1, 4, 14, and 15 are used. To set them up for
output, first call INP_GPIO(n) (where n is the GPIO pin number) for each of the 12 pins to activate
them. This also sets them up for input, so then call OUT_GPIO(n) afterwards for each of the 12 pins
to put them in output mode.
LEDs are switched on using the macro GPIO_SET0: the value assigned to GPIO_SET0 will set
GPIO pin n to high if bit n is set in that value. When a GPIO pin is set high, the I/O port connected to
that pin goes high, and the LED for that port turns on. Thus, the line of code “GPIO_SET0 =
0x180;” will set GPIO pins 7 and 8 high (since bits 7 and 8 are set in the hexadecimal number
0x180). Given the wiring setup above, ports 11 and 12 will go high (because these are the ports
connected to GP7 and GP8), and thus the rightmost two LEDs will turn on.
To turn LEDs off, use macro GPIO_CLR0. This works in a similar way to GPIO_SET0, but here the
bits that are high in the value assigned to GPIO_CLR0 specify which GPIO ports will be set low (and
hence which ports will be set low, and which LEDs will turn off). So for example, given the wiring
above, the command “GPIO_CLR0 = 0x100;” will set GPIO8 pin low, and thus turn off the LED
for port 11, which is the port connected to GP8. (In leds.c the LEDs are always all turned off
together, but they don’t have to be used this way.)
The test program flashes the LEDs in three patterns. The patterns are specified by a collection of
global arrays given values using an initializer. The number in each of the arrays says which LEDs will
18
be turned on at that point in the pattern – so, pattern value is submitted sequentially to produce the
changing pattern, switching all the LEDs off between successive pattern values. Each pattern is run
through twice. The first pattern lights the LEDs one at a time in sequence, left to right. The second
pattern does the same but when it reaches the rightmost LED, it then reverses direction and lights
them in sequence right to left. The third pattern starts at the left end and at each step switches on one
more LED until they are all lit up, then starting at the left it switches them off one by one until they
are all off.
Finally, the test program switches off all the LEDs and then finally calls restore_io to clean up all
the LEDs to a predictable final state.
Testing I/O
Our two examples so far have only used the ports to access the pushbuttons and LEDs. The next
example, called butled (for BUTton LED) will show one of the ports serving just as an input port.
The idea is that one port (along with its button) is used to generate a signal, and software then sends
that signal to another port which it is used as just an input. We read both ports in and print them on the
screen.
Fig. 14: The wiring diagram for test program butled which detects a button press, and then
display that button state on the screen. This is to test all the I/O on the Gertboard.
The wiring for this test is shown above. Pin GPIO23 controls I/O port 3, and GPIO22 controls I/O
port 6, so GP23 in header J2 is connected to pin B3 in header J3, and GP22 is connected to B6. Now,
for the interesting part. The pushbutton on port 3 is going to be used here, but the LED for port 3
should not be used, so therefore the output jumper for port 3 is not installed (which would be placed at
U3-out-B3).
19
Looking at the schematic on page A-2, it is clear that the output buffer for port 3 goes to pin 14 of
buffer chip U3. This is connected to the U3-out-B3 header pin just above pin 14 on the chip (it is pin
1 of U3-out-B3; this is clear from the schematic and from the fact that this pin has a square pad on the
bare circuit board), so that pin is connected to the BUF6 pin at the top of the board. This allows the
switch to generate a signal which is then sent to port 6. A jumper is installed across U4-in-B6 to allow
that signal to be input from the board. The value of the switch from port 3 is also read in, and these
two should be the same (most of the time).
In butled.c we use INP_GPIO to set GPIO22 and GPIO23 to input and GPIO_PULL and
GPIO_PULLCLK0 to set the pull-up on GPIO23. This is described in more detail on page 16, in the
buttons test. Then the GPIO values are repeatedly read in, and the binary values of GPIO22 and
GPIO23 are printed out, if they have changed since the last cycle. So if ‘01’ is displayed on the
monitor, it can be deduced that GPIO23 is low and GPIO22 is high. (Note that the LED for port 6,
labelled D6, should be off when switch 3 is pressed and on when switch 3 is up.)
Now, if the values for GPIO22 and GPIO23 are always the same, ‘00’ and ‘11’ will only ever be
printed out. But if the test is started with button 3 up (so ‘11’ is displayed), and then the button is
pushed down, occasionally ‘01’ might be seen, followed very quickly by ‘00’. The reason for this
differs between the Python and C implementations. In the C version, both values are read at the same
time, and the signal from the push button (which is connected to GPIO23) takes a small amount of
time to propagate through the buffers to get to GPIO22.
It may even be possible to get one reading in after GPIO23 has changed, but insufficient time has
passed for GPIO22 to change state and follow it! In the Python code, the read of GPIO22 occurs
before the read of GPIO23 (the button). Thus if the button is pressed or released between these two
reads, the new value will be read in for the button (GPIO23), but the new value of the other input
(GPIO22) won’t change until the next time through the while loop.
Open Collector Driver
The Gertboard uses six ports of a ULN2803a to provide open collector drivers. These are used to turn
off and on devices, especially those that need a different voltage or higher current than that available
on the Gertboard and are powered by an external power supply. The ULN2803a can withstand up to
50V and drive 500mA on each of its ports. Each driver has an integrated protection diode (the
uppermost diode in the circuit diagram below).
Raspi
OUT
common
Fig. 15: Circuit diagram of each open collector driver.
20
The ‘common’ pin is, as the name states, common for all open collector drivers. It is not connected to
any other point on the Gertboard. As with all devices the control for the open collector drivers (the
‘Raspi’ point) can also be connected to the ATmega controller to, for example, drive relays or motors.
The open collector drivers are in the schematics on page A-3.
On the Gertboard building block diagram on page 7, the area containing the components for the open
collector drivers are outlined in yellow. The pins corresponding to ‘Raspi’ in the diagram above are
RLY1 to RLY6 pins in the J4 header; the pins corresponding to ‘common’ are the ones marked
RPWR in the headers on the right edge of the board; and the pins corresponding to ‘OUT’ are the
RLY1 to RLY6 pins in the headers J12 to J17. How these are then used is demonstrated by the test
wiring and code examples.
Testing the open collector drivers
The program ocol (for open collector) allows the functional testing of the open collector drivers. A
simple mechanism was required to switch the driver on and off, so we created a little circuit (see
diagram below) consisting of two large LEDs and a resistor in series. Once connected, the forward
voltage across each of these LEDs is a little above 3V, so we used a 9V battery as a power supply, and
calculated a series resistance of around about 90 to set a suitable current flow through the LEDs.
Since this small test circuit will not be used again, it can simply be hand soldered together off-board.
Remember that LEDs are diodes, and have to be connected the right way round. The small ‘flat’ in the
LED moulding denotes the ‘cathode’ or negative pin. If you think of the LED symbol in the circuit
diagram below as an arrow, it is pointing in the direction of the current flow, from + to -, or from
anode to cathode.
To turn the circuit off and on using the open collector driver (say you want to use driver 1), first check
that it works with the power supply described above. Then, leave the positive side of your circuit
attached to the positive terminal of the power supply, but in addition connect it to one of the RPWR
pins in the headers on the right edge of the board (they are all connected together). Disconnect the
ground side of the circuit from the power supply and connect it instead to RLY1 in header J12 on the
right of the board. Attach the ground terminal of the power supply to any GND or ⊥ pin on the board.
Now, we need a signal to control the driver. For the ocol test we are using GPIO4 to control the
open collector (you could of course use any logic signal), so connect GP4 in header J2 to RLY1 in J4.
(To test a different driver, say n, with the ocol test, connect the ground side of the circuit up to
RLYn in the headers on the right of the board and connect GP4 in header J2 to RLYn in J4.)
Now, when RLY1 in J4 is set low, the circuit doesn’t receive any power and thus is off. When RLY1
in J4 goes high, the open collector driver uses transistors to connect the ‘ground’ side of the circuit to
the ground on the board, and since this is connected to the ground terminal on the power supply, the
power supply ends up powering the circuit: it is just turned off and on by the open collector driver.
21
Fig.16: Wiring diagram showing how to connect Gertboard to test the open collector drivers. It
also shows the small test power supply made up of two LEDs in series, a 90 resistor and a 9V
battery.
You may wonder why you need to connect the positive terminal of the power supply to the open
collector driver (via the RPWR pin). The reason for this is that if the circuit happens to contain an
component that has electrical inductance, for example a motor or a relay, when the power is turned off
this inductance causes the voltage on RLYn pin to quickly rise to a higher voltage than the positive
terminal of the power supply, dropping quickly afterwards. The chip itself has an internal diode
connecting the RLYn pin to the RPWR. This allows current to flow to the top (positive side) of your
circuit, allowing the energy to dissipate, and preventing damage.
The ocol test is very simple. First, it prints out the connections required on the board (and with your
external circuit and power supply), and then it calls setup_io to get the GPIO interface ready to use
and setup_gpio to set pin GPIO4 to be used as an output (using the commands INP_GPIO(4);
OUT_GPIO(4); as described on page 11). Then in it uses GPIO_SET0 and GPIO_CLR0
(described on page 17) to set GPIO4 high then low 10 times. Note: the test asks which driver should
be tested, but it only uses this information to print out the connections that need to be made.
Otherwise it ignores your response.
22
Motor Controller
The Gertboard has a position for a L6203 (Miniwatt package) motor controller. The motor controller
is for brushed DC motors.
The controller has two input pins, A and B (labelled MOTA and MOTB on the board). The pins can
be driven high or low, and the motor responds according to the table below. The speed of the motor
can be controlled by applying a pulse-width-modulated (PWM) signal to either the A or B pin.
A B Motor action
0 0 no movement
0 1 rotate one way
1 0 rotate opposite way from above
1 1 no movement
Table 3: Truth table showing the behaviour of the motor
controller under different logic combinations.
The motor controller IC has internal temperature protection. Current protection is provided by a fuse
on the Gertboard.
The motor controller is in the schematics on page A-4.
On the Gertboard building block diagram on page 7, the area containing the components for the motor
controller are outlined in purple. The motor controller and screw terminals are near the top of the
board, and there are two pins for the control signals in a small header just above GP4 and GP1 in
header J2. The MOTA and MOTB pins just above header J2 are the inputs to the motor controller –
these are digital signals (low and high). The screw terminals at the top of the board labelled MOTA
and MOTB are the outputs of the motor controller: they actually provide the power to the motor. The
motor will probably need more power (a higher voltage or current) than that provided by the
Gertboard. The screw terminals at the top labelled MOT+ and ⊥ allow the connection of an external
power supply to provide this: the motor controller directs this power to the MOTA and MOTB screw
terminals, modulating it according to the MOTA and MOTB inputs near J2.
If you just want to turn the motor off and on, in either direction, this is achieved by simply choosing
two of the GPIO pins and installing straps between them to the MOTA and MOTB motor controller
inputs. Then, to control the motor, the pins are set high or low per the table 3 above. To control the
speed of the motor however, pulse width modulation (PWM) is required. This is a device that outputs
a square wave that flips back and forth from on to off very rapidly, as in the diagram below:
Fig. 17: An example of a PWM output. In this example the output is
neither on nor off all the time. In fact, here it is on for 50% of the
time, and is therefore said to have a duty cycle of 50%.
0
1
23
With a PWM, you can control the amount of time the output is high vs. when it is low. This is called
the duty cycle and is expressed as a percentage. The diagram above shows a 50% duty cycle; the one
below is 25%.
Fig. 18: In this PWM example, the duty cycle is 25%.
There is a PWM in the BCM2835 (the Raspberry Pi processor), and it’s output can be accessed via
GPIO18 (it is alternate function 5). If this is connected to one of the motor controller inputs (MOTA
has been used in our motor test), and set the other motor controller input (MOTB in our test) to a
steady high or low, the speed and direction of the motor can be controlled.
Fig. 19: The motor direction is set by MOTB. Whilst MOTA has a duty cycle of 25%, the motor
only receives power when MOTA and MOTB are different, thus it receives power for 75% of
the time.
For example, in the diagram above we are alternating between A low/B high and A high/B high (the
second and fourth lines of the table above). When A is low, the motor will receive power making it
turn one way; when A is high it will not receive power. The end result for the 25% duty cycle shown
here is that the motor will turn one way at roughly ¾ speed.
Fig. 20: In this example, the truth table predicts that the motor will run in the opposite direction
at around 25% speed.
If on the other hand you set MOTB low, as in the diagram above, then when A is high the motor will
receive power making it turn in the other direction, and when A is low the motor will not receive
power. The result for the 25% duty cycle is that it will turn in the other direction at about ¼ speed.
Testing the motor controller
The PWM is controlled by a memory map, like the GPIO and SPI bus. This memory map is part of
the setup_io function in gb_common.c, so that is whether the PWM is used or not. Further setup
code is found in, gb_pwm.c, with an associated header file gb_pwm.h. The function setup_pwm
in gb_pwm.c sets the speed of the PWM clock, and sets the maximum value of the PWM to 1024:
this is the value at which the duty cycle of the PWM will be 100%. It also makes sure that the PWM is
off. The two routines set_pwm0 and force_pwm0 set the value that controls the duty cycle for the
PWM. set_pwm0 sets the value (first checking that it is between 0 and 1024), but as there are only
certain points in the PWM cycle where a new value is picked up, if a second value is written again
quickly the first will have no effect. The force_pwm0 routine takes two arguments, a new value and
a new mode. It disables the PWM, then sets the value, then re-enables it with the given mode setting,
0
1
0
1
0
1
MOTA MOTB
0
1
0
1
MOTA MOTB
24
with delays in strategic places to allow the new values to be picked up. The pwm_off routine simply
disables the PWM.
The test program for the motor controller is called motor. To set up Gertboard for this, connect
GP17 in J2 to the MOTB pin (the MOTB pin in the 2-pin header above GP1 and GP4, not the one at
the top of the board), and GP18 to MOTA in that little header. The motor leads need to be connected
to the MOTA and MOTB screw terminals at the top of the board, and the power supply for the motor
needs to be connected to the MOT+ and ⊥ screw terminals. This is shown below.
Fig. 20: The wiring diagram for the test program motor.
The code for the motor program is in motor.c. In the main routine, first the connections that must
be made on the board to run this program are printed out, then call setup_io to get the GPIO
interface ready for use. setup_gpio is then called to set GPIO18 up for use as the PWM output and
GPIO17 up for normal output. For the latter, both INP_GPIO and OUT_GPIO are used, see page 11
for more info. To set up GPIO18, first use INP_GPIO(18) to activate the pin. One of the alternate
functions for GPIO18 is to act as the output for the PWM; this is alternative 5. Thus use the macro
SET_GPIO_ALT(18, 5) to select this alternate use of the pin. (See table Table 6-31 from the
BCM2835 datasheet, or the online version at http://elinux.org/RPi_BCM2835_GPIOs, for more
details about alternative functions for the GPIO pins. A summary of the alternate function of GPIO
pins used on the Gertboard, see the table on page 9.)
25
We set the output of GPIO17 low (to make sure that the motor doesn’t turn) and then initialize the
PWM by calling setup_pwm. We enable the PWM by setting the mode to PWM0_ENABLE using
force_pwm0. Since GPIO17 (motor controller B input) is set low, when the duty cycle on the PWM
(motor controller A input) is high enough, the motor will turn the ‘opposite way’ as described in the
motor table on page 22.
A loop now starts where the PWM is started, first with a very low duty cycle (because the value
passed to set_pwm0 is low), then gradually increasing this to the maximum (which is set to 0x400 –
1024 – in setup_pwm). Then the value sent to the PWM is decreased to slow the motor down. Then
GPIO17 is set high, so that the motor will get power on the low phase of the PWM signal. The PWM
is re-enabled with the mode PWM0_ENABLE|PWM0_REVPOLAR. The reverse polarization flag flips
the PWM signal, so that a low value sent to the PWM results in a signal that is high most of the time
(rather than low most of the time). That way the same code can be used to slowly ramp up the speed
of the motor (but in the ‘one way’ direction as in the table on page 22), then slow it down again.
Finally the PWM is switched off, and the GPIO interface is closed down.
Digital to Analogue and Analogue to Digital Converters
In the Gertboard building blocks diagram on page 7, the components implementing the converters are
outlined in orange. Both the analogue converter (D/A) and analogue to digital converter (A/D) are 8-
pin chips from Microchip. The D/A is U6 (above) and the A/D is U10 (below). Each supports 2
channels.
Both use the SPI bus to communicate with the Raspberry Pi. The SPI pins on the two chips are
connected to the pins labelled SCLK, MOSI, MISO, CSnA, and CSnB in the header just above J2 on
the board (thus in the building blocks diagram, these pins are also outlined in orange). SCLK is the
clock, MOSI is the output from the RPi, and MISO is the input to the RPi. CSnA is the chip select for
the A/D, and CSnB is the chip select signal for the D/A (the ‘n’ in the signal name means that the
signal is ‘negative’, thus the chip is only selected when the pin is low). Both A/D and D/A chips have
a 10K pull-up resistor on their chip-select pins, so the devices will not be accessed if the chips select
pins are not connected.
The SPI pins are conveniently located just above GP7 to GP11 in header J2, because one of the
alternate functions of these pins is to drive the SPI signals. For example, the “ALT0” (alternative 0)
function of GPIO9 is SPI0_MISO, which is why the pin labelled MISO is just about the pin labelled
GP9. Thus to use the A/D and D/A, simply put jumpers connecting pins GP7 to GP11 to the SPI pins
directly about them (although technically you only need CSnA for the A/D and CSnB for the D/A).
In the schematics, the D/A and A/D converts are on page A-6.
Digital to analogue converter
The Gertboard uses a MCP48xx digital to analogue converter (D/A) from Microchip. The device
comes in three different types: 8, 10 or 12 bits. It is likely that MCP4802, the 8 bit version, will be
used, but if higher resolutions are needed, it can be replaced with the MCP4812 (10 bits) or MCP4822
(12 bits). These chips are all pin-compatible and are written to in the same way. In particular, the
routine that writes to the D/A assumes that writes are in 12 bits, so it is important that the value is
selected appropriately (details are below in the “Testing the D/A and A/D” section). The maximum
output voltage of the D/A – the output voltage when you send an input of all 1s – is 2.04V.
26
The analogue outputs of the two channels go to pins labelled DA0 (for channel 0) and DA1 (for
channel 1) in the J29 header. Just next to these pins are ground pins (GND) to provide a reference.
Analogue to Digital converter
The Gertboard uses a MCP3002 10-bit analogue to digital converter from Microchip. It supports 2
channels with a sampling rate of ~72k samples per second (sps). The maximum value (1023) is
returned when the input voltage is 3.3V.
The analogue inputs for these two channels are AD0 (for channel 0) and AD1 (for channel 1) in the
J28 header. Just next to these pins are ground pins (GND) to provide a reference.
Testing the D/A and A/D
Since the D/A and A/D converters both use the SPI bus, the common SPI bus code has been placed
into a separate file, gb_spi.c. There is also an associated header file, gb_spi.h, which contains
many macros and constants needed for interacting with the SPI bus, as well as the declarations for the
functions in gb_spi.c. These functions are setup_spi, read_adc, and write_dac.
setup_spi sets the clock speed for the bus and clears status bits. read_adc takes an argument
specifying the channel (should be 0 or 1) and returns an integer with the value read from the A/D
converter. The value returned will be between 0 and 1023 (i.e. only the least significant 10 bits are
set), with 0 returned when the input pin for that channel is 0V and 1023 returned for 3.3V.
The write_dac routine takes two arguments, a channel number (0 or 1) and a value to write. The
value written requires some explanation. The MCP48xx family of digital to analogue converters all
accept a 12 bit value. The MCP4822 uses all the bits; the MCP4812 ignores the last two; and the
MCP4802 (which is probably the one you are using) ignores the last four. Since you could use any of
those chips on the Gertboard, write_dac is written in so that it will work with all three, so it simply
sends to the D/A the value it was given. If Gertboard is fitted with the MCP4802, it can only handle
values between 0 and 255, but these must be in bits 4 through 11 (assuming the least significant bit is
bit 0) of the bit string it is sent. Thus if the desired number to be sent to the D/A is between 0 and 255,
it must be multiplied by 16 (which effectively shifts the information 4 bits to the left) before sending
this value to write_dac.
The value on the output pin, Vout, is given by the following formula (assuming the 8-bit MCP4802):
=
256
× 2.048
To test the D/A, a multimeter is required. The test program for this is dtoa. To set up Gertboard for
this test, jumpers are placed on the pins GP11, GP10, GP9, and GP7 connecting them to the SPI bus
pins above them. Attach the multimeter as follows: the black lead needs to be connected to ground.
You can use any of the pins marked with ⊥ or GND for this. The red lead needs to be connected to
DA0 (to test the D/A channel 0 which is shown below) or DA1 (for channel 1). Switch the
multimeter on, and set it to measure voltages from 0 to around 5V.
27
Fig. 21: The wiring diagram required to measure the output from the D to A converter fitted to
the Gertboard whilst running the test program dtoa.
The dtoa program first asks which channel to use and prints out the connections needed to make on
Gertboard to run the program. Then it calls setup_io to get the GPIO ready to use, then calls
setup_gpio to choose which pins to use and how to use them. In setup_gpio, as usual
INP_GPIO(n) (where n is the pin number) is used to activate the pins. This also sets them up to be
used as inputs. They should however, be used as an SPI bus, which is one of the alternative functions
for these pins (it is alternate 0). Thus we use SET_GPIO_ALT(n, a) (where n is the pin number
and a is the alternate number, in this case 0) to select this alternate use of the pins. Then the program
sends different values to the D/A and asks for real verification, using the multimeter, that the D/A
converter is generating the correct output voltage.
The test program for the A/D is called atod. To run this test a voltage source on the analogue input is
required. This is most easily provided by a potentiometer (a variable resistor). The two ends of the
potentiometer are connected, one side to high (3.3V, which you can access from any pin labelled 3V3)
and the other to low (GND or ⊥), and the middle (wiper) part to AD0 (for channel 0 as shown below)
or AD1 (for channel 1). To use the SPI bus jumpers should be installed on the pins GP11, GP10, GP9,
and GP8 connecting them to the SPI bus pins above them.
28
Fig. 22: Wiring diagram showing how the Gertboard is connected to verify that the A/D
converter is working properly, using the test program atod.
The atod program first asks which channel should be used and prints out the connections required on
Gertboard to run the program. Then it calls setup_io to get the GPIO ready, then calls
setup_gpio to choose which pins will be used, and how they will be used. The setup_gpio
used in atod works the same way as the one in dtoa (except for activating GPIO8 instead of
GPIO7).
Then atod repeatedly reads the 10 bit value from the A/D converter and prints out the value on the
terminal, both as an absolute number and as a bar graph (the value read is divided by 16, and the
quotient is represented as a string of ‘#’ characters). One thing to be aware of is that even if the
potentiometer is not moved, exactly the same result may not appear on successive reads. With 10 bits
of accuracy, it is very sensitive, and even the smallest changes, such as house current running in
nearby wires, can affect the value read.
Even without a multimeter or a potentiometer, it is still possible to test the A/D and D/A by sending
the output of the D/A to the input of the A/D. The test that does this is called dad, for digitalanalogue-
digital. To set the Gertboard up for this test, hook up all the SPI bus pins (connecting GP11
though GP7 with jumpers to the pins above them) and put a jumper between pins DA1 and AD0, as in
the diagram below.
29
Fig. 23: The wiring diagram for an alternative method of testing the A/D and D/A converters
together, without the aid of a multimeter and potentiometer.
The dad test sends 17 different digital values to the D/A (0 to 255 in even jumps, then back down to
0). The resulting values are then read in from the A/D. Both the original digital values sent and the
values read back are printed out, as is a bar graph representing the value read back (divided by 16 as
in atod). The bar graph printed out should be a triangle shape: the lines will start out very short, then
get longer and longer as larger digital values are read back, then will get shorter again.
ATmega device
The Gertboard can hold an Atmel AVR microcontroller, a 28-pin ATmega device, at location U8 on
the lower left of the board. This can be any of the following: ATmega48A/PA, 88A/PA, 168A/PA or
328/P in a 28-pin DIP package. The device has a 12MHz ceramic resonator attached to pins 9 and 10.
All input/output pins are brought out to header J25 on the left edge of the board. There is a separate 6-
pin header (J23 on the left side of the board) that can be used to program the device.
The PD0/PD1 pins (ATmega UART TX and RX) are brought out to pins placed adjacent to the
Raspberry Pi UART pins so you only need to place two jumpers to connect the two devices.
Note that the ATmega device on the Gertboard operates at 3.3Volts. That is in contrast to the
‘Arduino’ system which runs at 5V. It is also the reason why the device does not have a 16MHz
clock. In fact at 3V3 the maximum operating frequency according to the specification is just under
12MHz. Warning: many of the Arduino example sketches (programs) mention +5V as part of the
circuit. Because we are running at 3.3V, you must use 3.3V instead of 5V wherever the latter is
mentioned. If you use 5V you risk damaging the chip.
The ATmega device is in the schematics on page A-6.
30
Programming the ATmega
Programming the ATmega microcontroller is straightforward once you have all the infrastructure set
up, but it requires a fair bit of software to be installed on your Raspberry Pi. We are immensely
grateful to Gordon Henderson, of Drogon Systems, for working out what needed to be done and
providing the customized software. Using his system, you can use the Arduino IDE (Integrated
Development Environment) on the Raspberry Pi to develop and upload code for the ATmega chip on
the Gertboard. The Atmel chips most commonly used on the Gertboard are the ATmega168 and
ATmega328, so Gordon assumes you have one of these.
To use Gordon’s system, first you need to install the Arduino IDE. Then you download a custom
version of avrdude, which allows you to program the AVR microcontroller using the SPI bus.
(GPIO pins GPIO7 through GPIO11 can be used as a SPI bus.) Then you have to edit various
configuration files to fully integrate the Gertboard into the Arduino IDE. Finally, you have to program
the ‘fuses’ on the ATmega chip. Happily, Gordon has written some scripts to do all this for you. Full
instructions, scripts, and the modified avrdude are available at:
https://projects.drogon.net/raspberry-pi/gertboard/ We assume now that you have downloaded and
successfully installed and configured the Arduino IDE, as described above, and we proceed from
there.
To get going with the ATmega chip, start up the Arduino IDE. This should be easy: if the installation
of the Arduino package was successful, you will have a new item “Arduino IDE” in your start menu,
under “Electronics”. The exact version of the IDE you get with depends on the operating system you
are using. The version number is given in the title bar. The Debian squeeze package is version 0018,
while the wheezy package is 1.0.1. First you will need to configure the IDE to work with the
Gertboard. Go to the Tools > Board menu and choose the Gertboard option with the chip you are
using (ATmega168 or ATmega328). For IDE version 1.0.1, you will also have go to the Tools >
Programmer menu and choose “Raspberry Pi GPIO”.
Arduino pins on the Gertboard
All the input and output pins of the ATmega chip are brought out to header J25 on the left edge of the
board. They are labelled PCn, PDn, and PBn, where n is a number. These labels correspond to the
pinout diagrams of the ATmega168/328 chips. However, in the Arduino world, the pins of the chips
are not referred to directly. Instead there is an abstract notion of digital and analogue pin numbers,
which is independent of the physical devices. This allows code written for one Arduino board to be
easily used with another Arduino board, which may have a chip with a different pinout. Thus, in order
to use your Gertboard with the Arduino IDE, you need to know how the Arduino pin number relates
to the labels on your Gertboard. The table below shows this correspondence (“GB” means Gertboard).
31
Arduino Pin GB pin Arduino Pin GB pin Arduino Pin GB pin
digital 0 PD0 digital 7 PD7 analogue 0, A0 PC0
digital 1 PD1 digital 8 PB0 analogue 1, A1 PC1
digital 2 PD2 digital 9 PB1 analogue 2, A2 PC2
digital 3 PD3 digital 10 PB2 analogue 3, A3 PC3
digital 4 PD4 digital 11 PB3 analogue 4, A4 PC4
digital 5 PD5 digital 12 PB4 analogue 5, A5 PC5
digital 6 PD6 digital 13 PB5
Table 4: The relationship between pins on Arduino and pins on the Gertboard.
In both versions of the Arduino IDE, digital pins are referred to in the code with just a number. For
example
digitalWrite(13, HIGH);
will set pin 13 (PB5 on the Gertboard) to logical 1. (In the Arduino world, LOW refers to logical 0, and
HIGH refers to logical 1.)
The analogue pins are handled slightly differently. In version 0018, analogue pins are referred to
simply by number, so whether 0 refers to PD0 (a digital pin) or PC0 (an analogue pin) depends on the
context. The command
value = digitalRead(0);
will cause a read from digital 0 (PD0), and value will be assigned LOW or HIGH, while the
command
value = analogRead(0);
will cause a read from analogue 0 (PC0), and value will be assigned a number between 0 and 1023,
as the A/D converters in the ATmega chip return 10 bit values.
In version 1.0.1, however, although numbers 0 through 5 still work to specify analogue pins, they are
referred to in the examples as A0 to A5, and this seems to be the preferred style now. So to read from
analogue pin 0 you would use the command
value = analogRead(A0);
A few sketches to get you going
A good first sketch to try is Blink, which makes an LED turn on and off. With version 0018 of the
IDE it’s in the File > Examples > Digital menu; in 1.0.1 it’s in the File > Examples > Basics menu.
When you select this, a new window pops up with the Blink code. There are only two functions in the
code, setup and loop. These are required for all Arduino programs: setup is executed once at the
very beginning, and loop is called repeatedly, as long as the chip has power. Note that you do not
need to provide any code to call these functions.
32
The modified avrdude that you downloaded uses the SPI bus to upload the code to the ATmega
chip, so you need to connect the GPIO pins used for the SPI bus to the 6-pin header J23, as in the
diagram below. Here you are simply connecting the SPI pins in the GPIO to the corresponding SPI
pins in the header. The arrangement of the pins in J23 is shown in the schematics, on page A-6.
Fig. 23: The wiring diagram for downloading sketches to the ATmega microprocessor.
To upload your sketch to the chip in Arduino IDE version 0018, either choose File > Upload to I/O
Board option, or click the icon with the right-pointing arrow and the array of dots. With version 1.0.1
choose File > Upload Using Programmer. It will take a bit of time to compile and upload, and then
your sketch is running. But nothing is happening! On most Arduino boards, pin 13 (the digital pin
used by this sketch) has an LED attached to it, but not the Gertboard. You have to wire up the LED
yourself. Looking at the table above, we see that digital pin 13 is labelled PB5 on the Gertboard, so
you need to connect PB5 to one of the I/O ports. Looking back to the port diagram on page Error!
Bookmark not defined., we need to connect it to the point labelled ‘I/O’ on that diagram. Recall that
the pins corresponding to these points are BUF1 to BUF12 in the (unlabeled) single row header at the
top of the Gertboard. So if you connect PB5 to BUF1, as below, the first LED will start to blink.
33
Fig. 24: Wiring diagram for the sketch Blink.
Note that in this diagram we have not shown the connections to the SPI pins. Once you have uploaded
the code, you no longer need them and can remove the straps. On the other hand, if you want you can
leave them in place, and this is a good idea if you are planning on uploading some other sketches
later.
Let’s look at another fairly simple sketch called Button, located under File > Examples > Digital
menu in both 0018 and 1.0.1. The comments at the beginning of the sketch read
The circuit:
* LED attached from pin 13 to ground
* pushbutton attached to pin 2 from +5V
* 10K resistor attached to pin 2 from ground
Assuming that you have Blink working, your LED is already wired up, but what about the button?
As mentioned above, since the ATmega chip on the Gertboard runs at 3.3V, we must replace the 5V
with 3.3V. So they suggest using a circuit like the one below, where the value read at pin 2 is logical 0
if the button is not pressed (due to the 10K pull-down resistor) and logical 1 if the button is pressed.
Fig. 25: Suggested switch circuit for use with Button sketch.
However, the buttons on the Gertboard are used like this:
34
Fig. 26: Circuit actually in use on the Gertboard, showing an additional 1k resistor to protect
the input to BCM2835.
The 1K resistor between the pushbutton and the ‘Raspi’ point is to protect the BCM2835 (the
processor on the Raspberry Pi) if you accidentally set the GPIO pin connected to ‘Raspi’ to output
instead of input. The circuit to the right of the ‘Raspi’ point happens on the Raspberry Pi: to use the
push button we set a pull-up (shown as a resistor in the circuit above) on the pin so that the value read
is logical 1 when the button is not pressed (see page 16). The Gertboard buttons are connected directly
to ground so they cannot be made to read logic 1 when pressed. If you are want to use a Gertboard
button with an Arduino sketch that assumes that the button reads 1 when pressed, the best approach is
to modify the sketch, if needed, so that it will invert the value it reads from the button. For the pull-up,
we can take advantage of the pull-ups in the ATmega chip. To do this, find the lines below in the
sketch
// initialize the pushbutton pin as an input:
pinMode(buttonPin, INPUT);
and insert the following two lines after them:
// set pullup on pushbutton pin
digitalWrite(buttonPin, HIGH);
To invert the value read from the button, find the line below:
buttonSate = digitalRead(buttonPin);
and insert a ! (the negation operator in C) as follows:
buttonSate = !digitalRead(buttonPin);
Now upload this modified sketch, as described for Blink. We still need to attach Arduino digial pin
2 (PD2 on the Gertboard, as you can see from the table) to a button, say button 3.The ‘Raspi’ pin in
the circuit diagram above, which is where we want to read the value, is in the J3 header.
35
Fig. 27: Wiring diagram showing the additional strap necessary for button operation for the
sketch Button.
When you have done this, the first LED will be on when the third button is pressed, and off when the
third button is up.
Now let’s try using an analogue pin. Find the AnalogInput sketch under File > Examples >
Analog (in both versions 0018 and 1.0.1). This reads in a value from analogue input 0 (which has
already been converted by the internal A/D to a value between 0 and 1023), then uses that number as
a delay between turning an LED on and off. Thus, the lower the voltage on the analogue pin, the
faster the LED flashes. To run this example, you’ll need a potentiometer. The one used to test the A/D
will work fine here. The comments for AnalogInput say to connect the potentiometer so that the
wiper is on analogue pin 0 (PC0 on the Gertboard) and the outer pins are connected to +5V and
ground. As above, you must use 3.3V instead of 5V as we’re running the chip at 3.3V here. The
diagram below shows how to connect up the Gertboard to make this sketch work after it is uploaded.
36
Fig. 28: Wiring diagram for the AnalogInput sketch.
Minicom
Some of the Arduino sketches involve reading or writing data via the serial port, or UART. An
example is AnalogInSerial under File > Examples > Analog for version 0018. In version 1.0.1,
this same example has been renamed AnalogReadSerial and is under File > Examples > Basics.
This sketch sets the baud rate to 9600, then repeatedly reads in a value from analogue pin 0 and prints
this value to the serial port (also called UART). The value read in is between 0 and 1023; 0 means that
the input pin is at 0V and 1023 means that it is at the supply voltage (3.3V for the Gertboard).
To set up your Gertboard for this sketch, you need the potentiometer attached to analogue input 0 as
described above. In addition you need to connect the ATmega chip’s UART pins to the Raspberry Pi.
Digital pin 0 (PD0 on the Gertboard) is RX (receive), and digital pin 1 (PD1 on the Gertboard) is TX
(transmit). These signals are also brought out to the pins labelled MCTX and MCRX just above the
GP15 and GP14 pins in header J2 on the Gertboard. Thus you can use two jumpers to attach the
ATmega’s TX to GP15 and RX to GP14, as shown below.
37
Fig. 29: Wiring diagram for the sketch AnalogInSerial/AnalogReadSerial.
GPIO14 and GPIO15 are the pins that the Raspberry Pi uses for the UART serial port. If you refer
back to the table of alternate functions on page 9, you will see that GPIO14 is listed as TX and
GPIO15 as RX. This is not a mistake! This swapping is necessary: the data that is transmitted by the
ATmega is received by the Raspberry Pi, and vice versa.
Now, how to we get the Raspberry Pi to read and show us the data that the ATmega is sending out on
the serial port? There is a button labelled Serial Monitor on the toolbar of the Arduino IDE, but it
doesn’t work on the Raspberry Pi. It assumes that you are talking to an Arduino board over USB, not
talking to a Gertboard over GPIO. The easiest way to retrieve this data is to use the minicom program.
You can install this easily by typing into a terminal this command:
sudo apt-get install minicom
You can use menus to configure minicom (by typing minicom –s). Alternatively, included with the
Gertboard software is a file minirc.ama0 with the settings you need to read from the GPIO UART
pins at 9600 baud. Copy this file (which was provided by Gordon Henderson) to /etc/minicom/
(you’ll probably need to sudo this) and invoke minicom by typing
sudo minicom ama0
Now if you upload the sketch to the ATmega chip, you should see the value from the potentiometer
displayed in your minicom monitor.
These examples have only just scratched the surface of the wonderful world of Arduino. Check out
http://arduino.cc/en/Tutorial/HomePage
for much, much more.
38
Combined Tests
This section shows some examples of using more than one building block at a time.
A/D and motor controller
In the potmot (for potentiometer-motor) test we use a potentiometer (“pot”) connected to the
analogue to digital converter (A/D) to get an input value, and this value is used to control the speed
and direction of the motor. It is set up so that at one extreme, the motor is going at top speed, and as
you move the wiper towards the middle it slows, at the middle the motor stops, and as you continue to
move the wiper along, the motor speeds up again but in the other direction. The main routine for this
is in potmot.c. Functions from gb_spi.c and gb_pwm.c are used to control the SPI bus (for
reading the A/D) and the pulse width modulator (for controlling the speed of the motor).
To wire up the Gertboard for this example, you combine the wiring for the A/D and motor tests.
Jumpers connect GP8 to GP11 to the pins directly above them to allow us to control the SPI bus using
GPIO8 to GPIO11. You must attach your potentiometer to the AD0 input. GPIO17 controls the motor
B input and GPIO18 controls the motor A input using the pulse width modulator (PWM). Thus GP17
must be connected via a strap to MOTB, and GP18 must be connected to MOTA. The motor and its
power source must be connected to the screw terminals in J19 at the top of the board. See the wiring
diagram below.
Fig. 30: Wiring diagram for the combined potmot test.
+
-
your power
source
goes here
M
1
2
3
39
In the main routine for potmot, first we print to the terminal the connections that need to be made
on the Gertboard to run this example, then we call setup_io to set up the GPIO ready for use. Then
we call setup_gpio to set the GPIO pins the way we want them. In this, we set up GPIO8 to
GPIO11 to use the SPI bus using INP_GPIO and SET_GPIO_ALT as described in the section on
A/D and D/A converters (page 27). GPIO17 is set up as an output (using INP_GPIO and
OUT_GPIO), and GPIO18 is set up as a PWM using as INP_GPIO and SET_GPIO_ALT as
described in the section on the motor controller (page 24). Back in main, we call setup_spi and
setup_pwm to get the SPI bus and PWM ready for use and get the motor ready to go.
Then we repeatedly read the A/D and set the direction and speed of the motor depending on the value
we read. Lower A/D values (up to 511 – recall that the A/D chip used returns a 10 bit value so the
maximum will be 1023) result in the motor B input being set high, and thus the motor goes in the
“rotate one way” as in the motor controller table on page 22. Confusingly, this motor direction is
called “backwards” in the comments of the program! Higher A/D values (512 to 1023) result in the
motor B input being set low, and the motor goes in the “rotate opposite way” direction. This is called
“forwards” in the comments of the program. Simple arithmetic is used to translate A/D values near
511 to slow motor speeds and A/D values near the endpoints of the range (0 and 1023) to fast motor
speeds by varying the value sent to the PWM.
Decoder
The decoder implemented by the decoder program takes the three pushbuttons as input and turns on
one of 8 LEDs to indicate the number with the binary encoding given by the state of the buttons.
Switch S1 gives the most significant bit of the number, S2 the middle bit, and S3 the least significant
bit. For output, the LED D5 represents the number 0, D6 represents 1, and so on, so D12 represents 7.
Recall that the pushbuttons are high (1) when up and low (0) when pushed, so LED D12 is lit up when
no buttons are pressed (giving binary 111 or 7), D6 is lit up when S1 and S2 are pressed (giving
binary 001), etc.
There is quite a bit of wiring for this one, as we are using all but one of the I/O ports.GPIO25 to
GPIO23 are reading the pushbuttons, so you need to connect GP25 to B1, GP24 to B2, and GP23 to
B3. The 8 lowest-numbered GPIO pins are used with I/O ports 5 to 12, so you need to connect GP11
to B5, GP10 to B6, GP9 to B7, GP8 to B8, GP7 to B9, GP4 to B10, GP1to B11, and GP0 to B12. In
addition, since we are using I/O ports 5 to 12 for output, you need to install all the out jumpers for
buffer chips U4 and U5 (recall that the out jumpers are those above the chips).
40
Fig. 31: Wiring diagram for the decoder test.
In the main routine for decoder, as always we start out by printing out to the terminal the
connections that need to be made on the Gertboard. Then we call setup_io to set up the GPIO
ready for use. Then we call setup_gpio to set GPIO25 to 23 for use with the pushbuttons (by
selecting them for input and enabling a pull-up, as described on page 16) and to set GPIO11 to GP7,
GPIO4, GPIO1, and GPIO0 up as outputs (as described on page 11). Then we enter a loop where we
read the state of the pushbuttons and light up the LED corresponding to this number (after turning off
the LED previously set). We turn the LEDs on and off using GPIO_SET0 and GPIO_CLR0 as
described on page 17.
For More Information
For further information, the datasheet for the processor can be found here:
http://www.raspberrypi.org/wp-content/uploads/2012/02/BCM2835-ARM-Peripherals.pdf
Appendix A: Schematics
We have included the schematics for the Gertboard in the pages that follow. They are numbered A-1,
A-2, etc. The page number is located in the lower left hand of each page.
5
5
4
4
3
3
2
2
1
1
D D
C C
B B
A A
in gnd out
Front
1 2 3
TO220
Not used. Do not install!
Do not use LDxxx series.
They have a different pin-out!
GPIO9
GPIO22
GPIO21
GPIO1
GPIO11
GPIO17
GPIO4
GPIO10
GPIO14
GPIO15
GPIO18
GPIO23
GPIO24
GPIO25
GPIO8
GPIO7
GPIO0
GPIO0
GPIO1
GPIO4
GPIO7
GPIO8
GPIO9
GPIO10
GPIO11
GPIO14
GPIO15
GPIO17
GPIO18
GPIO21
GPIO22
GPIO23
GPIO24
GPIO25
3V3_RASP 5V_RASP
3V3_RASP
3V3
5V_RASP
3V3 3V3
MOTOR_A
MOTOR_B
BUF_1
BUF_2
BUF_4
BUF_3
BUF_6
BUF_7
BUF_8
BUF_5
RELAY_1
RELAY_2
RELAY_3
RELAY_4
BUF_9
BUF_12
BUF_10
BUF_11
RELAY_5
RELAY_6
SCLK
MOSI
MISO
CSnA
CSnB
MC_TX
MC_RX
Title
Size Document Number Rev
Date: Sheet of
- 3
Gertboard
A4
1 6
R1
10K-0805
J4
CON6
1
2
3
4
5
6
J2
CON17
1
2
3
4
5
6
7
8
9
10
11
12
13
14
15
16
17
D20 ~1.5A
MH1
HOLE_M3
J5
CON2
1
2
C6
100nF-0805
MH2
HOLE_M3
C3
100nF-0805
R2
10K-0805
U2 REG78xx
In
1
Gnd
2
Out
3
J64
CON2
1
2
J11
HEADER 5
1
2
3
4
5
J3 CON12
1
2
3
4
5
6
7
8
9
10
11
12
U1
REG3v3
In
1
Gnd
2
Out
3
C2
100nF-0805
+ C5
10uF-1206
J7
CON3
1
2
3
MH4
HOLE_M3
J9
CON3
1
2
3
J1
CON26A
1 2
3 4
5 6
7 8
9 10
11 12
13 14
15 16
17 18
19 20
21 22
23 24
25 26
+ C1
10uF-1206
+ C4
100uF-CX02-C
MH3
HOLE_M3
C7
100nF-0805
J8
CON3
1
2
3
J24
CON2
1
2
A-1
5
5
4
4
3
3
2
2
1
1
D D
C C
B B
A A
BUF1
BUF2
BUF6
BUF5
BUF10
BUF9
BUF3
BUF4
BUF8
BUF11
BUF12
BUF2
BUF12
BUF1
BUF6
BUF5
BUF11
BUF7
BUF4
BUF9
BUF3
BUF8
BUF10
BUF7
3V3
3V3
3V3
3V3
BUF_1
BUF_3
BUF_4
BUF_8
BUF_5
BUF_6
BUF_7
BUF_12
BUF_9
BUF_10
BUF_11
BUF_2
BUF_3
BUF_2
BUF_1
Title
Size Document Number Rev
Date: Sheet of
- 3
Gertboard
A4
2 6
P4
CON2
1
2
P11
CON2
1
2
U4
74xx244
20
1 19
2
4
6
8
18
14
16
12
9
7
5
3
10
11
13
15
17
RN7B
1k
4 3
P23
CON2
1
2
RN5B
1k-10k
4 3
P1
CON2
1
2
D10
LED
P12
CON2
1
2
P3
CON2
1
2
D12
LED
D6
LED
D8
LED
S3
Switch
1 2
3 4
S1
Switch
1 2
3 4
P8
CON2
1
2
RN2
1K_RESN4X1
1
2
3
4
5
D1
LED
RN4C
1k-10k
6 5
P13
CON2
1
2
D9
LED
RN7A
1k
2 1
C9
100n-0805
RN5A
1k-10k
2 1
D5
LED
P17
CON2
1
2
P18
CON2
1
2
P15
CON2
1
2
P6
CON2
1
2
P14
CON2
1
2
P24
CON2
1
2
RN5C
1k-10k
6 5
S2
Switch
1 2
3 4
D11
LED
RN7D
1k
8 7
D7
LED
P2
CON2
1
2
P5
CON2
1
2
RN3
1K_RESN4x1
1
2
3
4
5
RN6D
1k-10k
8 7
RN6B
1k-10k
4 3
P20
CON2
1
2
C10
100n-0805
P9
CON2
1
2
P19
CON2
1
2
RN4A
1k-10k
2 1
D3
LED
RN4D
1k-10k
8 7
J10
CON24
1
2
3
4
5
6
7
8
9
10
11
12
13
14
15
16
17
18
19
20
21
22
23
P10
24
CON2
1
2
RN6A
1k-10k
2 1
U3
74xx244
20
1 19
2
4
6
8
18
14
16
12
9
7
5
3
10
11
13
15
17
D4
LED
RN1
1K_RESN4X1
1
2
3
4
5
C8
100n-0805
RN5D
1k-10k
8 7
RN4B
1k-10k
4 3
P7
CON2
1
2
RN6C
1k-10k
6 5
U5
74xx244
20
1 19
2
4
6
8
18
14
16
12
9
7
5
3
10 11
13
15
17
D2
LED
P21
CON2
1
2
P22
CON2
1
2
P16
CON2
1
2
RN7C
1k
6 5
A-2
5
5
4
4
3
3
2
2
1
1
D D
C C
B B
A A
RELAY_PWR
RELAY_6
RELAY_4
RELAY_2
RELAY_1
RELAY_5
RELAY_3
Title
Size Document Number Rev
Date: Sheet of
- 3
Gertboard
A4
3 6
J16
CON2
1
2
J13
CON2
1
2
8x
U12
ULN2803A
I1
1
I2
2
I3
3
I4
4
I5
5
I6
6
I7
7
I8
8
GND
9
Q1
18
Q2
17
Q3
16
Q4
15
Q5
14
Q6
13
Q7
12
Q8
11
COM
10
J12
CON2
1
2
J15
CON2
1
2
J17
CON2
1
2
J14
CON2
1
2
J6
CON2
1
2
A-3
5
5
4
4
3
3
2
2
1
1
D D
C C
B B
A A
motor power nets named to make high current
MB
MP
MPC
MA
MGND
3V3
MOTOR_A
MOTOR_B
Title
Size Document Number Rev
Date: Sheet of
- 3
Gertboard
A4
4 6
C13
22n-0805
J20
CON2
1
2
F1
4A
C11
100n-0805
R23
0.1-2512
C12
22n-0805
J19
CON4
1
2
3
4
U7
L6203-MW
VREF
9
ENB
11
IN1
5
IN2
7
BOOT1
4
BOOT2
8
OUT1
3
OUT2
1
VSS
2
GND
6
Sense
10
A-4
5
5
4
4
3
3
2
2
1
1
D D
C C
B B
A A
Patch area
3V3
3V3 3V3
of
- 3
Gertboard
A4
5 6
Title
Size Document Number Rev
Date: Sheet J37
CON2-DNF
1
2
J68
CON3-DNF
1
2
3
J42
CON2-DNF
1
2
J51
CON2-DNF
1
2
J70
CON2-DNF
1
2
J30
CON2-DNF
1
2
J36
CON2-DNF
1
2
J48
CON2-DNF
1
2
J50
CON2-DNF
1
2
J35
CON2-DNF
1
2
J55
CON3-DNF
1
2
3
J43
CON2-DNF
1
2
J32
CON2-DNF
1
2
J60
CON2-DNF
1
2
J62
CON3-DNF
1
2
3
J53
CON2-DNF
1
2
J69
CON3-DNF
1
2
3
J40
CON2-DNF
1
2
J56
CON3-DNF
1
2
3
J57
CON3-DNF
1
2
3
J38
CON2-DNF
1
2
J54
CON2-DNF
1
2
J26
CON2-DNF
1
2
J34
CON2-DNF
1
2
J47
CON2-DNF
1
2
J66
CON3-DNF
1
2
3
J67
CON3-DNF
1
2
3
J45
CON2-DNF
1
2
J41
CON2-DNF
1
2
J59
CON3-DNF
1
2
3
J39
CON2-DNF
1
2
J44
CON2-DNF
1
2
J49
CON2-DNF
1
2
J63
CON3-DNF
1
2
3
J52
CON2-DNF
1
2
J33
CON2-DNF
1
2
J46
CON2-DNF
1
2
J58
CON3-DNF
1
2
3
J27
CON2-DNF
1
2
J65
CON3-DNF
1
2
3
J31
CON2-DNF
1
2
J61
CON2-DNF
1
2
A-5
5
5
4
4
3
3
2
2
1
1
D D
C C
B B
A A
AD0
XTAL_IN
DA0
DA1
AD1
XTAL_IN
PD0
PD1
PD2
PD3
PD4
PC4
PC5
PB1
PB0
PC0
PC1
PC2
RC3
PD6
PD5
PD7
PC6/DBG/RESETn
PC1
PC4
PC5
PC0
PC2
RC3
PD0
PD5
PD3
PD6
PD2
PD7
PD4
PD1
PB1
PB0
PC6/DBG/RESETn
PD0
PD1
MC_SCK
MC_MISO
MC_MOSI
MC_MOSI
PB2
PB2
MC_MOSI
MC_MISO
MC_SCK
MC_SCK
MC_MISO
3V3
3V3
3V3
3V3
MISO
MOSI
MOSI
SCLK
SCLK
MC_RX
MC_TX
CSnA
CSnB
Title
Size Document Number Rev
Date: Sheet of
- 3
Gertboard
A4
6 6
R4
0_0805
U8
ATmega328P
PC6/Reset_n
1
PD0/RXD
2
PD1/TXD
3
PD2/INT0
4
PD4/XCK/T0
6
VCC
7
PB6/XTAL1
9
GND
8
PB7/XTAL2
10
PD5/OC0B/T1
11
PD6/OC0A/AIN0
12
PD7/AIN1
13
PB0/CLK0/ICP1
14
GND
22 AVCC
20
AREF
21
OC1A/PB1
SS_n/OC1B/PB2 15
MOSI/OC2A/PB3 16
MISO/OC2A/PB4 17
SCK/PB5 18
19
ADC0/PC0
ADC1/PC1 23
ADC2/PC2 24
ADC3/PC3 25
ADC4/SDA/PC4 26
ADC5/SCL/PC5 27
28
PD3/INT1/OC2B
5
J25
CONN PCB 20x2
2
4
6
8
10
12
14
16
18
20
24
22
26
28
30
32
34
36
38
40 39
37
35
33
31
29
27
25
23
21
19
17
15
13
11
9
7
5
3
1
D19
1N4001
J29
CON4A
1
3
2
4
U10
MCP4802
VDD
1
CSn
2
SCK
3
SDI
4
LDACn
5
VOUTB
6
VOUTA
8
VSS
7
J71
HEADER 1
1
J28
CON4A
1
3
2
4
C15
100nF-0805
U6
MCP3002
VDD
8
VSS
4
CH0
2
CH1
3
CSn/SHDN
1
CLK
7
DOUT
6
DIN
5
R24 0_0805
C17
100nF-0805
X1
Cer resonator
1
2
3
C19
100nF-0805
C20
100nF-0805
R34
10K-0805
J23
HEADER 3X2
2
4
6
1
3
5
C16
xxF-1206
A-6
User's Guide
SBOU109A–May 2011–Revised October 2011
TMP006EVM User Guide and Software Tutorial
This user's guide describes the characteristics, operation, and use of the TMP006EVM evaluation board. It
discusses how to set up and configure the software and hardware, and reviews various aspects of the
program operation. Throughout this document, the terms evaluation board, evaluation module, and EVM
are synonymous with the TMP006EVM. This document also includes an electrical schematic, printed
circuit board (PCB) layout drawings, and a parts list for the EVM.
Contents
1 Overview ..................................................................................................................... 2
2 TMP006EVM Hardware Setup ............................................................................................ 3
3 TMP006EVM Hardware Overview ........................................................................................ 7
4 TMP006EVM Software Overview ......................................................................................... 8
5 TMP006EVM Software Use .............................................................................................. 11
List of Figures
1 Hardware Included with TMP006EVM Kit ............................................................................... 2
2 TMP006EVM Hardware Setup ............................................................................................ 3
3 TMP006EVM Board Block Diagram ...................................................................................... 4
4 TMP006 Test Board Schematic........................................................................................... 5
5 Typical Hardware Connection ............................................................................................. 7
6 Typical PC Behavior After Connecting TMP006EVM .................................................................. 8
7 TMP006EVM Software Installation Files................................................................................. 8
8 TMP006EVM Software Installation Launch.............................................................................. 9
9 TMP006EVM GUI Software Installation Prompts....................................................................... 9
10 TMP006EVM GUI Software Default Configuration.................................................................... 10
11 Hardware Error Message................................................................................................. 11
12 Read All Registers to Update Temperature............................................................................ 12
13 Make Changes to TMP006 Registers .................................................................................. 13
14 Write Changes to TMP006 Registers................................................................................... 14
15 TMP006EVM GUI Software Registers Tab ............................................................................ 15
16 Read Registers Continuously to Update Graphs...................................................................... 16
17 Enable Transient Correction Algorithm ................................................................................. 17
18 Start Data Logging ........................................................................................................ 18
19 Example .CSV Output File (Formatted and Displayed in Microsoft Excel®) ....................................... 19
List of Tables
1 TMP006EVM Kit Contents................................................................................................. 2
2 TMP006 Test Board Parts List ........................................................................................... 6
3 Signal Definitions for H1 (10-Pin Female Socket) on TMP006EVM Board ......................................... 6
4 Signal Definition for H2 (10-Pin FFC Connector) on TMP006EVM Board .......................................... 7
Excel, Microsoft, Windows are registered trademarks of Microsoft Corporation.
SPI is a trademark of Motorola Inc.
I2C is a trademark of NXP Semiconductors.
All other trademarks are the property of their respective owners.
SBOU109A–May 2011–Revised October 2011 TMP006EVM User Guide and Software Tutorial 1
Submit Documentation Feedback
Copyright © 2011, Texas Instruments Incorporated
Overview www.ti.com
1 Overview
The TMP006 is an infrared thermopile sensor with digital output integrated circuit. This device measures
the temperature of an object without making contact, making it ideal for many types of applications. The
TMP006EVM is a platform for evaluating the performance of the TMP006 under various conditions. The
TMP006EVM consists of two PCBs. One board, the SM-USB-DIG, communicates with the user’s
computer, provides power, and sends and receives appropriate digital signals to communicate with the
TMP006. The second PCB, the TMP006_Test_Board, contains the TMP006 as well as support and
configuration circuitry. This document gives a general overview of the TMP006EVM, and provides a
general description of the features and functions to be considered while using this evaluation module.
1.1 TMP006EVM Kit Contents
Table 1 summarizes the contents of the TMP006EVM kit. Figure 1 shows all of the included hardware.
Contact the Texas Instruments Product Information Center nearest you if any component is missing. It is
highly recommended that you also check the TMP006 product folder on the TI web site at www.ti.com to
verify that you have the latest versions of the related software.
Table 1. TMP006EVM Kit Contents
Item Quantity
TMP006_Test_Board 1
SM-USB-DIG Board 1
USB Cable 1
CR-ROM with TMP006EVM GUI Software (not shown) 1
Figure 1. Hardware Included with TMP006EVM Kit
2 TMP006EVM User Guide and Software Tutorial SBOU109A–May 2011–Revised October 2011
Submit Documentation Feedback
Copyright © 2011, Texas Instruments Incorporated
www.ti.com TMP006EVM Hardware Setup
1.2 Related Documentation from Texas Instruments
The following documents provide information regarding Texas Instruments' integrated circuits used in the
assembly of the TMP006EVM. This user's guide is available from the TI web site under literature number
SBOU109A. Any letter appended to the literature number corresponds to the document revision that is
current at the time of the writing of this document. Newer revisions may be available from the TI web site,
or call the Texas Instruments' Literature Response Center at (800) 477-8924 or the Product Information
Center at (972) 644-5580. When ordering, identify the document by both title and literature number.
Related Documentation
Document Literature Number
TMP006 Product Data Sheet SBOS518
SM-USB-DIG_Platform User Guide SBOU0958
TMP006 Layout and Assembly SBOU108
Guidelines
2 TMP006EVM Hardware Setup
Figure 2 shows the system setup for the TMP006EVM. The PC runs graphical user interface (GUI)
software that communicates with the SM-USB-DIG over a USB connection. The SM-USB-DIG translates
the USB commands from the PC into power, I2C™, SPI™, and general-purpose input/output (GPIO)
commands for the TMP006_Test_Board. The TMP006EVM does not require any additional components to
operate.
Figure 2. TMP006EVM Hardware Setup
SBOU109A–May 2011–Revised October 2011 TMP006EVM User Guide and Software Tutorial 3
Submit Documentation Feedback
Copyright © 2011, Texas Instruments Incorporated
TMP006
V Supply
(Switched +3.3-V Power)
DUT
I C Interface
2
Serial Interface (SPI)
10-Pin Female
SM-USB-DIG
Connector
DRDY
LED
Circuitry
10-Pin FFC
Cable
Connector
TMP006EVM Hardware Setup www.ti.com
2.1 Theory of Operation for the TMP006 Test Board
A block diagram of the TMP006 test board hardware setup is shown in Figure 3. The TMP006 Test Board
contains connections for the power, I2C, SPI, and GPIO signals from the SM-USB-DIG. It also has a
connector that allows other boards to be connected to the TMP006 Test Board to assist with calibrating
the TMP006.
Figure 3. TMP006EVM Board Block Diagram
4 TMP006EVM User Guide and Software Tutorial SBOU109A–May 2011–Revised October 2011
Submit Documentation Feedback
Copyright © 2011, Texas Instruments Incorporated
www.ti.com TMP006EVM Hardware Setup
Figure 4 shows the complete schematic of the TMP006 Test Board. The ferrite bead and input capacitor,
FB1 and C1 respectively, filter the power coming into the TMP006 test board from the SM-USB-DIG. The
I2C pull-up resistors, R3 and R4, and the DRDY pull-up, R5, are required for the open-drain outputs to
operate correctly. The Q1 and R6 components drive the LED (D1) so current is not provided from the
TMP006 that would cause the device to self-heat. Power, I2C, and SPI signals are provided to the
calibration header, H2, for use with the TMP006 calibration tools.
Figure 4. TMP006 Test Board Schematic
SBOU109A–May 2011–Revised October 2011 TMP006EVM User Guide and Software Tutorial 5
Submit Documentation Feedback
Copyright © 2011, Texas Instruments Incorporated
TMP006EVM Hardware Setup www.ti.com
2.2 Bill of Materials for the TMP006 Test Board
Table 2 lists the bill of materials for the TMP006EVM board.
Table 2. TMP006 Test Board Parts List
Qty RefDes Value Description Part Number MFR
1 C1 1μF Capacitor, Ceramic 1.0μF 16V X7R 10% 0603 C1608X7R1C105K TDK
1 C2 0.01μF Capacitor, Ceramic 10000pF 25V X7R 10% 0402 C1005X7R1E103K TDK
1 D1 LED Alingap Grn Wht Diff 0603SMD SML-LX0603SUGW- Lumex
TR
1 FB1 Ferrite Bead 300Ω .2A 0402 74279272 Wurth
1 H1 Connector, Socket 50-Pl .050 R/A Sngl 851-43-050-20- Mill-Max
001000
1 H2 Connector, FPC/FFC 10-Pos .5mm Horz SMD FH12-10S-0.5SH(55) Hirose
1 Q1 MOSFET P-CH 50V 130mA SC70-3 BSS84W-7-F Diodes Inc
2 R1, R2 0Ω Resistor, 0.0Ω 1/16W 0402 SMD MCR01MZPJ000 Rohm
3 R3, R4, R5 47k Resistor, 47.0kΩ 1/16W 1% 0402 SMD MCR01MZPF4702 Rohm
1 R6 160Ω Resistor, 160Ω 1/16W 1% 0402 SMD MCR01MZPF1600 Rohm
1 U1 Infrared Sensor with Digital Interface TMP006 Texas Instruments
2.3 Signal Definition of H1 (10-Pin Female Socket)
Table 3 identifies the signals connected to the H1 connector on the TMP006 Test Board. This summary
also identifies the signals that are used with the TMP006EVM along with the respective signal names.
Table 3. Signal Definitions for H1 (10-Pin Female Socket) on TMP006EVM Board
Used on the TMP006 Test Board
Pin No. Signal TMP006EVM? Signal
1 I2C_SCL Yes SCL
2 CTRL/MEAS4 Yes DRDY
3 I2C_SDA1 Yes SDA
4 CTRL/MEAS5 No —
5 SPI_DOUT1 Yes SDO
6 VDUT Yes VCC
7 SPI_CLK Yes SCLK
8 GND Yes GND
9 SPI_CS1 Yes CS
10 SPI_DIN1 Yes SDI
6 TMP006EVM User Guide and Software Tutorial SBOU109A–May 2011–Revised October 2011
Submit Documentation Feedback
Copyright © 2011, Texas Instruments Incorporated
www.ti.com TMP006EVM Hardware Overview
2.4 Signal Definition of H2 (10-Pin FFC Connector)
Table 4 shows the signals connected to the H2 connector on the TMP006 Test Board.
Table 4. Signal Definition for H2 (10-Pin FFC
Connector) on TMP006EVM Board
Pin No. Signal
1 SCL
2 VCC
3 SDA
4 VCC
5 SDO
6 GND
7 SCLK
8 GND
9 CS
10 SDI
3 TMP006EVM Hardware Overview
If not already assembled, the basic hardware setup for the TMP006EVM involves connecting the TMP006
Test Board to the SM-USB-DIG and then connecting the USB cable. This section presents the details of
this procedure.
3.1 Electrostatic Discharge Warning
CAUTION
Many of the components on the TMP006EVM are susceptible to damage by
electrostatic discharge (ESD). Customers are advised to observe proper ESD
handling precautions when unpacking and handling the EVM, including the use
of a grounded wrist strap at an approved ESD workstation.
3.2 Typical TMP006EVM Hardware Setup
Connect the right-angle female socket (H1) on the TMP006 Test Board to the right-angle male header
(H2) on the SM-USB-DIG. Take special care to ensure that the two 10-pin sockets directly align with each
other. Plug the female USB-A cable to the SM-USB-DIG and then plug the male USB-A cable into the
computer.
Always connect the two boards together before connecting the USB cable to avoid any issues if the
connectors are misaligned.
Figure 5. Typical Hardware Connection
SBOU109A–May 2011–Revised October 2011 TMP006EVM User Guide and Software Tutorial 7
Submit Documentation Feedback
Copyright © 2011, Texas Instruments Incorporated
TMP006EVM Software Overview www.ti.com
Figure 6 shows the typical behavior when the SM-USB-DIG is plugged into the USB port of a PC for the
first time. Typically, the computer will respond with a Found New Hardware, USB Device pop-up dialog.
The pop-up window then typically changes to Found New Hardware, USB Human Interface Device. This
pop-up indicates that the device is ready to be used. The SM-USB-DIG uses the human interface device
drivers that are part of the Microsoft® Windows® operating system.
Figure 6. Typical PC Behavior After Connecting TMP006EVM
In some cases, the Windows Add Hardware wizard appears. If this installation prompt occurs, allow the
Device Manager to install the human interface drivers by clicking Yes at each request to install the drivers.
4 TMP006EVM Software Overview
This section describes the installation and use of the TMP006EVM software.
4.1 Hardware Requirements
The TMP006EVM software has been tested on the Microsoft Windows XP operating system (OS) with
United States and European regional settings. The software should function correctly on other
Windows-based OSs.
4.2 GUI Software Installation
The TMP006EVM software is included on the CD that is shipped with the EVM kit. It is also available
through the TMP006EVM product folder on the TI web site. To install the software to a computer, insert
the disc into an available CD-ROM drive. Navigate to the drive contents and open the TMP006EVM
software folder. Locate and launch the TMP006EVM installation file, setup.exe, as shown in Figure 7. It is
in the Installer directory.
Figure 7. TMP006EVM Software Installation Files
8 TMP006EVM User Guide and Software Tutorial SBOU109A–May 2011–Revised October 2011
Submit Documentation Feedback
Copyright © 2011, Texas Instruments Incorporated
www.ti.com TMP006EVM Software Overview
The TMP006EVM software installer file then begins the installation process as shown in Figure 8.
Figure 8. TMP006EVM Software Installation Launch
Follow the prompts as shown in Figure 9 to install the TMP006EVM GUI software.
Figure 9. TMP006EVM GUI Software Installation Prompts
The TMP006EVM GUI software is now installed.
SBOU109A–May 2011–Revised October 2011 TMP006EVM User Guide and Software Tutorial 9
Submit Documentation Feedback
Copyright © 2011, Texas Instruments Incorporated
TMP006EVM Software Overview www.ti.com
4.3 Launching the TMP006EVM GUI Software
With the TMP006EVM properly connected (see Figure 5), launch the EVM GUI software from the Start
menu. It is located in a folder titled, TMP006EVM GUI Installer. The software should launch with a screen
similar to that shown in Figure 10.
Figure 10. TMP006EVM GUI Software Default Configuration
10 TMP006EVM User Guide and Software Tutorial SBOU109A–May 2011–Revised October 2011
Submit Documentation Feedback
Copyright © 2011, Texas Instruments Incorporated
www.ti.com TMP006EVM Software Use
If the message shown in Figure 11 appears when the TMP006EVM GUI software is launched, disconnect
all components of the TMP006EVM kit, and repeat the hardware assembly instructions in Section 3.2.
Figure 11. Hardware Error Message
5 TMP006EVM Software Use
This section discusses how to use the TMP006EVM software. The TMP006EVM GUI software has a
primary window that is used to configure and read from the TMP006, along with two other windows that
are used to access different features of the TMP006. Basic GUI functionality and a description of the tabs
are also presented in this section.
SBOU109A–May 2011–Revised October 2011 TMP006EVM User Guide and Software Tutorial 11
Submit Documentation Feedback
Copyright © 2011, Texas Instruments Incorporated
TMP006EVM Software Use www.ti.com
5.1 Reading from the TMP006
On the primary GUI window (see Figure 10), press the Read All Reg button to read the TMP006 registers
and begin collecting temperature measurement data. Figure 12 illustrates this action. Raw temperature
and configuration register values can be found in the Registers tab (refer to Section 5.3).
Figure 12. Read All Registers to Update Temperature
12 TMP006EVM User Guide and Software Tutorial SBOU109A–May 2011–Revised October 2011
Submit Documentation Feedback
Copyright © 2011, Texas Instruments Incorporated
www.ti.com TMP006EVM Software Use
5.2 Writing to the TMP006
To modify the TMP006 configuration register, make any desired changes on the Block Diagram tab and
then press the Write All Reg button, as shown in Figure 13.
Figure 13. Make Changes to TMP006 Registers
SBOU109A–May 2011–Revised October 2011 TMP006EVM User Guide and Software Tutorial 13
Submit Documentation Feedback
Copyright © 2011, Texas Instruments Incorporated
TMP006EVM Software Use www.ti.com
The Pending changes need to be written LED illuminates when there are changes that have not been
written to the TMP006, as shown in Figure 14.
Figure 14. Write Changes to TMP006 Registers
14 TMP006EVM User Guide and Software Tutorial SBOU109A–May 2011–Revised October 2011
Submit Documentation Feedback
Copyright © 2011, Texas Instruments Incorporated
www.ti.com TMP006EVM Software Use
5.3 Registers Tab
In this tab, you can select any row in the Register table by clicking on it with your mouse. When a row is
selected, it becomes highlighted in blue in the table. The individual 16 bits in the selected register are
displayed below the Register table. Note that each bit has descriptive text above the bit that identifies the
function of the bit. You can edit the bit value using the up (↑) or down (↓) arrow to the left of the bit. Any
changes on the bit are displayed in the table and in the block diagram. Additionally, any changes in the
block diagram are reflected in the table.
The Help w Reg button can be pressed to see detailed help about the register that is currently selected.
This feature gives detailed information regarding the meaning of each bit. The Registers tab on the
TMP006EVM GUI software is illustrated in Figure 15.
Figure 15. TMP006EVM GUI Software Registers Tab
SBOU109A–May 2011–Revised October 2011 TMP006EVM User Guide and Software Tutorial 15
Submit Documentation Feedback
Copyright © 2011, Texas Instruments Incorporated
TMP006EVM Software Use www.ti.com
5.4 Graphing Tab
The Graphing tab allows you to graph the temperature sensor results. To start the graphing process, you
must press the Read Continuous button. After pressing this button, it turns green and the graph starts to
update. Press the Read Continuous button again to turn off this function. Figure 16 shows this process.
Figure 16. Read Registers Continuously to Update Graphs
16 TMP006EVM User Guide and Software Tutorial SBOU109A–May 2011–Revised October 2011
Submit Documentation Feedback
Copyright © 2011, Texas Instruments Incorporated
www.ti.com TMP006EVM Software Use
5.5 Transient Correction Algorithm
The accurate performance of the TMP006EVM is highly dependent on a stable local temperature.
Degraded performance can be observed when local temperature transients are introduced into the
system, because the infrared (IR) thermopile in the TMP006 is sensitive to conducted and radiated IR
energy from below the sensor as well as radiated IR energy that comes from above the sensor.
When the TMP006EVM experiences a local temperature transient event, the PCB temperature and the
TMP006 die temperature drift apart from each other as a result of the thermal time constant of the
TMP006 thermopile. This difference in temperatures causes a heat transfer between the IR sensor and
the PCB to occur. Because of the small distance between the PCB and the bottom of the sensor, this heat
energy is conducted (as opposed to radiated) through the thin layer of air between the IR sensor and the
PCB below it. This conducted heat energy causes an offset in the IR sensor voltage reading, and
ultimately leads to unwanted temperature calculation error.
The additional error that results from local temperature transient events can be suppressed in the software
by using a transient correction algorithm. This algorithm monitors the TMP006 die temperature over a
four-second interval and uses the die temperature data to calculate a local temperature slope, as shown in
Equation 1.
TSLOPE = – (0.3 × TDIE1) – (0.1 × TDIE2) + (0.1 × TDIE3) + (0.3 × TDIE4) (1)
The local temperature slope and the known thermal resistance and capacitance of the TMP006 thermopile
are then applied to Equation 2 to correct the sensor voltage reading.
VOBJ_CORRECTED = VOBJ + TSLOPE × 2.96 × 10–4 (2)
The corrected sensor voltage value is then substituted for the raw sensor voltage, and the object
temperature is calculated using the normal methods.
To enable the transient correction algorithm, simply click the Transient Correction button in the
TMP006EVM GUI as shown in Figure 17. When transient correction is first enabled, a delay of four
conversions will be observed while the local temperature slope is being calculated.
Figure 17. Enable Transient Correction Algorithm
SBOU109A–May 2011–Revised October 2011 TMP006EVM User Guide and Software Tutorial 17
Submit Documentation Feedback
Copyright © 2011, Texas Instruments Incorporated
TMP006EVM Software Use www.ti.com
5.6 Logging Data from the TMP006EVM
The TMP006EVM software has the ability to save data collected by the TMP006 into a comma-separated
value (.CSV) format file. To save data in this format, select Save Temperature Data from the USB
Controls drop-down menu. Figure 18 shows the steps required to begin logging temperature data with the
TMP006EVM.
Figure 18. Start Data Logging
18 TMP006EVM User Guide and Software Tutorial SBOU109A–May 2011–Revised October 2011
Submit Documentation Feedback
Copyright © 2011, Texas Instruments Incorporated
www.ti.com TMP006EVM Software Use
Figure 19 displays an example of how the output file can appear after minimal formatting by the user.
Figure 19. Example .CSV Output File (Formatted and Displayed in Microsoft Excel®)
SBOU109A–May 2011–Revised October 2011 TMP006EVM User Guide and Software Tutorial 19
Submit Documentation Feedback
Copyright © 2011, Texas Instruments Incorporated
Revision History www.ti.com
Revision History
Changes from Original (May, 2011) to A Revision .......................................................................................................... Page
• Updated document to reflect new software functionality ............................................................................ 1
• Revised Figure 2 for improved clarity .................................................................................................. 3
• Updated Figure 4 to reflect unpopulated connector H2 ............................................................................. 5
• Changed Figure 5 to reflect new SM-USB-DIG casing .............................................................................. 7
• Corrected typos and updated Figure 10 through Figure 16 to reflect new software functionality ............................. 8
• Added Transient Correction Algorithm section ...................................................................................... 17
• Updated Figure 18 to reflect new software functionality ........................................................................... 18
• Revised Figure 19 for improved clarity ............................................................................................... 19
NOTE: Page numbers for previous revisions may differ from page numbers in the current version.
20 Revision History SBOU109A–May 2011–Revised October 2011
Submit Documentation Feedback
Copyright © 2011, Texas Instruments Incorporated
Evaluation Board/Kit Important Notice
Texas Instruments (TI) provides the enclosed product(s) under the following conditions:
This evaluation board/kit is intended for use for ENGINEERING DEVELOPMENT, DEMONSTRATION, OR EVALUATION
PURPOSES ONLY and is not considered by TI to be a finished end-product fit for general consumer use. Persons handling the
product(s) must have electronics training and observe good engineering practice standards. As such, the goods being provided are
not intended to be complete in terms of required design-, marketing-, and/or manufacturing-related protective considerations,
including product safety and environmental measures typically found in end products that incorporate such semiconductor
components or circuit boards. This evaluation board/kit does not fall within the scope of the European Union directives regarding
electromagnetic compatibility, restricted substances (RoHS), recycling (WEEE), FCC, CE or UL, and therefore may not meet the
technical requirements of these directives or other related directives.
Should this evaluation board/kit not meet the specifications indicated in the User’s Guide, the board/kit may be returned within 30
days from the date of delivery for a full refund. THE FOREGOING WARRANTY IS THE EXCLUSIVE WARRANTY MADE BY
SELLER TO BUYER AND IS IN LIEU OF ALL OTHER WARRANTIES, EXPRESSED, IMPLIED, OR STATUTORY, INCLUDING
ANY WARRANTY OF MERCHANTABILITY OR FITNESS FOR ANY PARTICULAR PURPOSE.
The user assumes all responsibility and liability for proper and safe handling of the goods. Further, the user indemnifies TI from all
claims arising from the handling or use of the goods. Due to the open construction of the product, it is the user’s responsibility to
take any and all appropriate precautions with regard to electrostatic discharge.
EXCEPT TO THE EXTENT OF THE INDEMNITY SET FORTH ABOVE, NEITHER PARTY SHALL BE LIABLE TO THE OTHER
FOR ANY INDIRECT, SPECIAL, INCIDENTAL, OR CONSEQUENTIAL DAMAGES.
TI currently deals with a variety of customers for products, and therefore our arrangement with the user is not exclusive.
TI assumes no liability for applications assistance, customer product design, software performance, or infringement of
patents or services described herein.
Please read the User’s Guide and, specifically, the Warnings and Restrictions notice in the User’s Guide prior to handling the
product. This notice contains important safety information about temperatures and voltages. For additional information on TI’s
environmental and/or safety programs, please contact the TI application engineer or visit www.ti.com/esh.
No license is granted under any patent right or other intellectual property right of TI covering or relating to any machine, process, or
combination in which such TI products or services might be or are used.
FCC Warning
This evaluation board/kit is intended for use for ENGINEERING DEVELOPMENT, DEMONSTRATION, OR EVALUATION
PURPOSES ONLY and is not considered by TI to be a finished end-product fit for general consumer use. It generates, uses, and
can radiate radio frequency energy and has not been tested for compliance with the limits of computing devices pursuant to part 15
of FCC rules, which are designed to provide reasonable protection against radio frequency interference. Operation of this
equipment in other environments may cause interference with radio communications, in which case the user at his own expense
will be required to take whatever measures may be required to correct this interference.
EVM Warnings and Restrictions
It is important to operate this EVM within the input voltage range of 2.7V (min) to 5.5V (max) and the output voltage range of 2.7V
(min) to 5.5V (max).
Exceeding the specified input range may cause unexpected operation and/or irreversible damage to the EVM. If there are
questions concerning the input range, please contact a TI field representative prior to connecting the input power.
Applying loads outside of the specified output range may result in unintended operation and/or possible permanent damage to the
EVM. Please consult the EVM User's Guide prior to connecting any load to the EVM output. If there is uncertainty as to the load
specification, please contact a TI field representative.
During normal operation, some circuit components may have case temperatures greater than +25°C. The EVM is designed to
operate properly with certain components above +25°C as long as the input and output ranges are maintained. These components
include but are not limited to linear regulators, switching transistors, pass transistors, and current sense resistors. These types of
devices can be identified using the EVM schematic located in the EVM User's Guide. When placing measurement probes near
these devices during operation, please be aware that these devices may be very warm to the touch.
Mailing Address: Texas Instruments, Post Office Box 655303, Dallas, Texas 75265
Copyright © 2011, Texas Instruments Incorporated
IMPORTANT NOTICE
Texas Instruments Incorporated and its subsidiaries (TI) reserve the right to make corrections, modifications, enhancements, improvements,
and other changes to its products and services at any time and to discontinue any product or service without notice. Customers should
obtain the latest relevant information before placing orders and should verify that such information is current and complete. All products are
sold subject to TI’s terms and conditions of sale supplied at the time of order acknowledgment.
TI warrants performance of its hardware products to the specifications applicable at the time of sale in accordance with TI’s standard
warranty. Testing and other quality control techniques are used to the extent TI deems necessary to support this warranty. Except where
mandated by government requirements, testing of all parameters of each product is not necessarily performed.
TI assumes no liability for applications assistance or customer product design. Customers are responsible for their products and
applications using TI components. To minimize the risks associated with customer products and applications, customers should provide
adequate design and operating safeguards.
TI does not warrant or represent that any license, either express or implied, is granted under any TI patent right, copyright, mask work right,
or other TI intellectual property right relating to any combination, machine, or process in which TI products or services are used. Information
published by TI regarding third-party products or services does not constitute a license from TI to use such products or services or a
warranty or endorsement thereof. Use of such information may require a license from a third party under the patents or other intellectual
property of the third party, or a license from TI under the patents or other intellectual property of TI.
Reproduction of TI information in TI data books or data sheets is permissible only if reproduction is without alteration and is accompanied
by all associated warranties, conditions, limitations, and notices. Reproduction of this information with alteration is an unfair and deceptive
business practice. TI is not responsible or liable for such altered documentation. Information of third parties may be subject to additional
restrictions.
Resale of TI products or services with statements different from or beyond the parameters stated by TI for that product or service voids all
express and any implied warranties for the associated TI product or service and is an unfair and deceptive business practice. TI is not
responsible or liable for any such statements.
TI products are not authorized for use in safety-critical applications (such as life support) where a failure of the TI product would reasonably
be expected to cause severe personal injury or death, unless officers of the parties have executed an agreement specifically governing
such use. Buyers represent that they have all necessary expertise in the safety and regulatory ramifications of their applications, and
acknowledge and agree that they are solely responsible for all legal, regulatory and safety-related requirements concerning their products
and any use of TI products in such safety-critical applications, notwithstanding any applications-related information or support that may be
provided by TI. Further, Buyers must fully indemnify TI and its representatives against any damages arising out of the use of TI products in
such safety-critical applications.
TI products are neither designed nor intended for use in military/aerospace applications or environments unless the TI products are
specifically designated by TI as military-grade or "enhanced plastic." Only products designated by TI as military-grade meet military
specifications. Buyers acknowledge and agree that any such use of TI products which TI has not designated as military-grade is solely at
the Buyer's risk, and that they are solely responsible for compliance with all legal and regulatory requirements in connection with such use.
TI products are neither designed nor intended for use in automotive applications or environments unless the specific TI products are
designated by TI as compliant with ISO/TS 16949 requirements. Buyers acknowledge and agree that, if they use any non-designated
products in automotive applications, TI will not be responsible for any failure to meet such requirements.
Following are URLs where you can obtain information on other Texas Instruments products and application solutions:
Products Applications
Audio www.ti.com/audio Communications and Telecom www.ti.com/communications
Amplifiers amplifier.ti.com Computers and Peripherals www.ti.com/computers
Data Converters dataconverter.ti.com Consumer Electronics www.ti.com/consumer-apps
DLP® Products www.dlp.com Energy and Lighting www.ti.com/energy
DSP dsp.ti.com Industrial www.ti.com/industrial
Clocks and Timers www.ti.com/clocks Medical www.ti.com/medical
Interface interface.ti.com Security www.ti.com/security
Logic logic.ti.com Space, Avionics and Defense www.ti.com/space-avionics-defense
Power Mgmt power.ti.com Transportation and Automotive www.ti.com/automotive
Microcontrollers microcontroller.ti.com Video and Imaging www.ti.com/video
RFID www.ti-rfid.com
OMAP Mobile Processors www.ti.com/omap
Wireless Connectivity www.ti.com/wirelessconnectivity
TI E2E Community Home Page e2e.ti.com
Mailing Address: Texas Instruments, Post Office Box 655303, Dallas, Texas 75265
Copyright © 2011, Texas Instruments Incorporated
© 2005 Microchip Technology Inc. DS51589A
Explorer 16 Development Board
User’s Guide
DS51589A-page ii © 2005 Microchip Technology Inc.
Information contained in this publication regarding device
applications and the like is provided only for your convenience
and may be superseded by updates. It is your responsibility to
ensure that your application meets with your specifications.
MICROCHIP MAKES NO REPRESENTATIONS OR WARRANTIES
OF ANY KIND WHETHER EXPRESS OR IMPLIED,
WRITTEN OR ORAL, STATUTORY OR OTHERWISE,
RELATED TO THE INFORMATION, INCLUDING BUT NOT
LIMITED TO ITS CONDITION, QUALITY, PERFORMANCE,
MERCHANTABILITY OR FITNESS FOR PURPOSE.
Microchip disclaims all liability arising from this information and
its use. Use of Microchip’s products as critical components in
life support systems is not authorized except with express
written approval by Microchip. No licenses are conveyed,
implicitly or otherwise, under any Microchip intellectual property
rights.
Trademarks
The Microchip name and logo, the Microchip logo, Accuron,
dsPIC, KEELOQ, microID, MPLAB, PIC, PICmicro, PICSTART,
PRO MATE, PowerSmart, rfPIC, and SmartShunt are
registered trademarks of Microchip Technology Incorporated
in the U.S.A. and other countries.
AmpLab, FilterLab, Migratable Memory, MXDEV, MXLAB,
PICMASTER, SEEVAL, SmartSensor and The Embedded
Control Solutions Company are registered trademarks of
Microchip Technology Incorporated in the U.S.A.
Analog-for-the-Digital Age, Application Maestro, dsPICDEM,
dsPICDEM.net, dsPICworks, ECAN, ECONOMONITOR,
FanSense, FlexROM, fuzzyLAB, In-Circuit Serial
Programming, ICSP, ICEPIC, Linear Active Thermistor,
MPASM, MPLIB, MPLINK, MPSIM, PICkit, PICDEM,
PICDEM.net, PICLAB, PICtail, PowerCal, PowerInfo,
PowerMate, PowerTool, rfLAB, rfPICDEM, Select Mode,
Smart Serial, SmartTel, Total Endurance and WiperLock are
trademarks of Microchip Technology Incorporated in the
U.S.A. and other countries.
SQTP is a service mark of Microchip Technology Incorporated
in the U.S.A.
All other trademarks mentioned herein are property of their
respective companies.
© 2005, Microchip Technology Incorporated, Printed in the
U.S.A., All Rights Reserved.
Printed on recycled paper.
Note the following details of the code protection feature on Microchip devices:
• Microchip products meet the specification contained in their particular Microchip Data Sheet.
• Microchip believes that its family of products is one of the most secure families of its kind on the market today, when used in the
intended manner and under normal conditions.
• There are dishonest and possibly illegal methods used to breach the code protection feature. All of these methods, to our
knowledge, require using the Microchip products in a manner outside the operating specifications contained in Microchip’s Data
Sheets. Most likely, the person doing so is engaged in theft of intellectual property.
• Microchip is willing to work with the customer who is concerned about the integrity of their code.
• Neither Microchip nor any other semiconductor manufacturer can guarantee the security of their code. Code protection does not
mean that we are guaranteeing the product as “unbreakable.”
Code protection is constantly evolving. We at Microchip are committed to continuously improving the code protection features of our
products. Attempts to break Microchip’s code protection feature may be a violation of the Digital Millennium Copyright Act. If such acts
allow unauthorized access to your software or other copyrighted work, you may have a right to sue for relief under that Act.
Microchip received ISO/TS-16949:2002 quality system certification for
its worldwide headquarters, design and wafer fabrication facilities in
Chandler and Tempe, Arizona and Mountain View, California in
October 2003. The Company’s quality system processes and
procedures are for its PICmicro® 8-bit MCUs, KEELOQ® code hopping
devices, Serial EEPROMs, microperipherals, nonvolatile memory and
analog products. In addition, Microchip’s quality system for the design
and manufacture of development systems is ISO 9001:2000 certified.
EXPLORER 16 DEVELOPMENT
BOARD USER’S GUIDE
© 2005 Microchip Technology Inc. DS51589A-page iii
Table of Contents
Preface ........................................................................................................................... 1
Chapter 1. Introducing the Explorer 16 Development Board
1.1 Introduction ..................................................................................................... 7
1.2 Highlights ........................................................................................................ 7
1.3 What’s in the Kit ............................................................................................. 7
1.4 Explorer 16 Development Board Functionality and Features ......................... 8
1.5 Using the Explorer 16 Out of the Box ............................................................. 9
1.6 Explorer 16 Development Board Demonstration Programs ......................... 10
1.7 Reference Documents .................................................................................. 10
Chapter 2. Explorer 16 Programming Tutorial
2.1 Introduction ................................................................................................... 11
2.2 Highlights ...................................................................................................... 11
2.3 Tutorial Overview ......................................................................................... 11
2.4 Creating the Project ...................................................................................... 12
2.5 Building The Code ........................................................................................ 16
2.6 Programming the Device .............................................................................. 19
Chapter 3. Explorer 16 Tutorial Programs
3.1 Introduction ................................................................................................... 23
3.2 PIC24 Tutorial Program Operation ............................................................... 23
3.3 dsPIC33F Tutorial Program Operation ......................................................... 25
Chapter 4. Explorer 16 Development Hardware
4.1 Introduction .................................................................................................. 27
4.2 Hardware Features ....................................................................................... 27
Appendix A. Explorer 16 Development Board Schematics
A.1 Introduction .................................................................................................. 33
A.2 Development Board Block Diagram ............................................................. 33
A.3 Development Board Schematics .................................................................. 34
Appendix B. Updating the USB Connectivity Firmware
B.1 Introduction .................................................................................................. 43
B.2 Updating the PICkit 2 Microcontroller Programmer ..................................... 43
B.3 Other USB Firmware Updates ..................................................................... 44
Index ............................................................................................................................. 45
Worldwide Sales and Service .................................................................................... 46
Explorer 16 Development Board User’s Guide
DS51589A-page iv © 2005 Microchip Technology Inc.
NOTES:
EXPLORER 16 DEVELOPMENT
BOARD USER’S GUIDE
© 2005 Microchip Technology Inc. DS51589A-page 1
Preface
INTRODUCTION
This chapter contains general information that will be useful to know before using the
Explorer 16 Development Board. Items discussed in this chapter include:
• Document Layout
• Conventions Used in this Guide
• Warranty Registration
• Recommended Reading
• The Microchip Web Site
• Development Systems Customer Change Notification Service
• Customer Support
• Document Revision History
DOCUMENT LAYOUT
This document describes how to use the Explorer 16 Development Board as a
development tool to emulate and debug firmware on a target board. The manual layout
is as follows:
• Chapter 1. “Introducing the Explorer 16 Development Board” provides a brief
overview of the Explorer 16 Development Board, its features and its uses.
• Chapter 2. “Explorer 16 Programming Tutorial” provides step-by-step instructions
for using MBLAB® IDE to create a project and program the Explorer 16 board.
• Chapter 3. “Explorer 16 Tutorial Programs” describes the demonstration
program created in Chapter 2. “Explorer 16 Programming Tutorial”.
• Chapter 4. “Explorer 16 Development Hardware” provides a more detailed
description of the Explorer 16 board’s hardware features.
• Appendix A. “Explorer 16 Development Board Schematics” provides a block
diagram and detailed schematics of the Explorer 16 board.
• Appendix B. “Updating the USB Connectivity Firmware” describes how to
upgrade the Explorer 16 board’s USB connectivity subsystem.
NOTICE TO CUSTOMERS
All documentation becomes dated, and this manual is no exception. Microchip tools and
documentation are constantly evolving to meet customer needs, so some actual dialogs
and/or tool descriptions may differ from those in this document. Please refer to our web site
(www.microchip.com) to obtain the latest documentation available.
Documents are identified with a “DS” number. This number is located on the bottom of each
page, in front of the page number. The numbering convention for the DS number is
“DSXXXXXA”, where “XXXXX” is the document number and “A” is the revision level of the
document.
For the most up-to-date information on development tools, see the MPLAB® IDE on-line help.
Select the Help menu, and then Topics to open a list of available on-line help files.
Preface
© 2005 Microchip Technology Inc. DS51589A-page 2
CONVENTIONS USED IN THIS GUIDE
This manual uses the following documentation conventions:
WARRANTY REGISTRATION
Please complete the enclosed Warranty Registration Card and mail it promptly.
Sending in the Warranty Registration Card entitles users to receive new product
updates. Interim software releases are available at the Microchip web site.
DOCUMENTATION CONVENTIONS
Description Represents Examples
Arial font:
Italic characters Referenced books MPLAB® IDE User’s Guide
Emphasized text ...is the only compiler...
Initial caps A window the Output window
A dialog the Settings dialog
A menu selection select Enable Programmer
Quotes A field name in a window or
dialog
“Save project before build”
Underlined, italic text with
right angle bracket
A menu path File>Save
Bold characters A dialog button Click OK
A tab Click the Power tab
Text in angle brackets < > A key on the keyboard Press ,
Courier New font:
Plain Courier New Sample source code #define START
Filenames autoexec.bat
File paths c:\mcc18\h
Keywords _asm, _endasm, static
Command-line options -Opa+, -Opa-
Bit values 0, 1
Constants (in source code) 0xFF, ‘A’
Italic Courier New A variable argument file.o, where file can be
any valid filename
Square brackets [ ] Optional arguments mcc18 [options] file
[options]
Curly brackets and pipe
character: { | }
Choice of mutually exclusive
arguments; an OR selection
errorlevel {0|1}
Ellipses... Replaces repeated text var_name [,
var_name...]
Represents code supplied by
user
void main (void)
{ ...
}
Explorer 16 Development Board User’s Guide
DS51589A-page 3 © 2005 Microchip Technology Inc.
RECOMMENDED READING
This user’s guide describes how to use the Explorer 16 Development Board. Other
useful documents are listed below. The following Microchip documents are available
and recommended as supplemental reference resources.
Readme for the Explorer 16 Development Board
For the latest information on using the Explorer 16 Development Board, read the
Readme for Explorer 16 Development Board.txt file (an ASCII text file) at
the root level of the Explorer 16 CD-ROM. The Readme file contains update information
and known issues that may not be included in this user’s guide.
Readme Files
For the latest information on using other tools, read the tool-specific Readme files in
the Readmes subdirectory of the MPLAB IDE installation directory. The Readme files
contain update information and known issues that may not be included in this user’s
guide.
PIC24FJ128GA010 PS Data Sheet (DS39756) and PIC24FJ128GA Family
Data Sheet (DS39747)
Consult this document for detailed information on the PIC24F general purpose, 16-bit
devices. Reference information found in this data sheet includes:
• Device memory map
• Device pinout and packaging details
• Device electrical specifications
• List of peripherals included on the device
Note that document, DS39756, is for use only with the initial prototype samples of the
PIC24F family. These devices are all marked with a “PS” suffix at the end of the device
number. For all other PIC24FJ128GA family devices, including those with an “ES”
suffix, use DS39747.
dsPIC33F Family Data Sheet (DS70165)
Consult this document for detailed information on the dsPIC33F Digital Signal
Controllers. Reference information found in this data sheet includes:
• Device memory map
• Device pinout and packaging details
• Device electrical specifications
• List of peripherals included on the device
dsPIC30F Programmer’s Reference Manual (DS70030)
This manual is a software developer’s reference for all of Microchip’s 16-bit digital
signal controllers. It describes the instruction set in detail and also provides general
information to assist in developing software for PIC24 MCUs, dsPIC30F and dsPIC33F
DSCs.
PIC24H Family Overview (DS70166)
This document provides an overview of the functionality of the new PIC24H product
family. It helps determine how the PIC24H high-performance, 16-bit microcontrollers fit
a specific product application.
Preface
© 2005 Microchip Technology Inc. DS51589A-page 4
MPLAB® C30 C Compiler User’s Guide (DS51284)
This document details the use of Microchip’s MPLAB C30 C Compiler for dsPIC®
devices to develop an application. MPLAB C30 is a GNU-based language tool, based
on source code from the Free Software Foundation (FSF). For more information about
the FSF, see www.fsf.org.
Other GNU language tools available from Microchip are:
• MPLAB ASM30 Assembler
• MPLAB LINK30 Linker
• MPLAB LIB30 Librarian/Archiver
MPLAB® IDE Simulator, Editor User’s Guide (DS51025)
Consult this document for more information pertaining to the installation and
implementation of the MPLAB Integrated Development Environment (IDE) software.
THE MICROCHIP WEB SITE
Microchip provides online support via our web site at www.microchip.com. This web
site is used as a means to make files and information easily available to customers.
Accessible by using your favorite Internet browser, the web site contains the following
information:
• Product Support – Data sheets and errata, application notes and sample
programs, design resources, user’s guides and hardware support documents,
latest software releases and archived software
• General Technical Support – Frequently Asked Questions (FAQs), technical
support requests, online discussion groups, Microchip consultant program
member listing
• Business of Microchip – Product selector and ordering guides, latest Microchip
press releases, listing of seminars and events, listings of Microchip sales offices,
distributors and factory representatives
Explorer 16 Development Board User’s Guide
DS51589A-page 5 © 2005 Microchip Technology Inc.
DEVELOPMENT SYSTEMS CUSTOMER CHANGE NOTIFICATION SERVICE
Microchip’s customer notification service helps keep customers current on Microchip
products. Subscribers will receive e-mail notification whenever there are changes,
updates, revisions or errata related to a specified product family or development tool of
interest.
To register, access the Microchip web site at www.microchip.com, click on Customer
Change Notification and follow the registration instructions.
The Development Systems product group categories are:
• Compilers – The latest information on Microchip C compilers and other language
tools. These include the MPLAB C18 and MPLAB C30 C compilers; MPASM™
and MPLAB ASM30 assemblers; MPLINK™ and MPLAB LINK30 object linkers;
and MPLIB™ and MPLAB LIB30 object librarians.
• Emulators – The latest information on Microchip in-circuit emulators.This
includes the MPLAB ICE 2000 and MPLAB ICE 4000.
• In-Circuit Debuggers – The latest information on the Microchip in-circuit
debugger, MPLAB ICD 2.
• MPLAB® IDE – The latest information on Microchip MPLAB IDE, the Windows®
Integrated Development Environment for development systems tools. This list is
focused on the MPLAB IDE, MPLAB SIM simulator, MPLAB IDE Project Manager
and general editing and debugging features.
• Programmers – The latest information on Microchip programmers. These
include the MPLAB PM3 and PRO MATE® II device programmers and the
PICSTART® Plus and PICkit™ 1 development programmers.
CUSTOMER SUPPORT
Users of Microchip products can receive assistance through several channels:
• Distributor or Representative
• Local Sales Office
• Field Application Engineer (FAE)
• Technical Support
• Development Systems Information Line
Customers should contact their distributor, representative or field application engineer
(FAE) for support. Local sales offices are also available to help customers. A listing of
sales offices and locations is included in the back of this document.
Technical support is available through the web site at: http://support.microchip.com
DOCUMENT REVISION HISTORY
Revision A (November 2005)
This is the initial release of this Document.
Preface
© 2005 Microchip Technology Inc. DS51589A-page 6
NOTES:
EXPLORER 16 DEVELOPMENT
BOARD USER’S GUIDE
© 2005 Microchip Technology Inc. DS51589A-page 7
Chapter 1. Introducing the Explorer 16 Development Board
1.1 INTRODUCTION
Thank you for purchasing Microchip Technology’s Explorer 16 Development Board Kit.
The development board provides a low-cost, modular development system for
Microchip’s new line of 16-bit microcontroller families, including the PIC24, PIC24H and
the 16-bit digital signal controller family, dsPIC33F.
As provided, the development board works as a demo board right from the box, and
also has the ability to extend its functionality through modular expansion interfaces.
The Explorer 16 board supports MPLAB ICD 2 for full emulation and debug capabilities,
and also allows 3V controllers to interface with 5V peripheral devices.
1.2 HIGHLIGHTS
This chapter covers the following topics:
• What’s in the Kit
• Explorer 16 Development Board Functionality and Features
• Using the Explorer 16 Out of the Box
• Explorer 16 Development Board Demonstration Programs
• Reference Documents
1.3 WHAT’S IN THE KIT
The Explorer 16 Development Board Kit contains the following:
• The Explorer 16 Development Board.
• A preprogrammed PIC24FJ128GA010 Processor Installation Module (PIM),
already installed to the board
• A preprogrammed dsPIC33FJ256GP710 PIM
• An RS-232 cable
• The Explorer 16 Development CD ROM, containing:
- This User’s Guide
- Data Sheets for the PIC24FJ128GA family and dsPIC33FJ256GP family
- Schematics and PCB drawing files for the PIM modules
- Example programs for use with the PIC24 and dsPIC33F devices
- Files detailing general purpose expansion boards that can be used with the
Explorer 16 board (provided in Gerber format)
If you are missing any part of the kit, please contact your nearest Microchip sales office,
listed on the last page of this manual, for further assistance.
Note: The Explorer 16 Development Board has been designed to function primarily
from a permanently mounted PIC24FJ128GA010 device at position U1.
Initial units will be shipped with U1 unpopulated and a PIC24FJ PIM of
equal functionality mounted on the U1A headers instead. When using the
PIC24FJ PIM or any other PIM, it is critical to verify that switch S2 always
remains in the “PIM” position. See Section 4.2.1 “Processor Support” for
more information.
Introducing the Explorer 16 Development Board
© 2005 Microchip Technology Inc. DS51589A-page 8
1.4 EXPLORER 16 DEVELOPMENT BOARD FUNCTIONALITY AND FEATURES
A layout of the Explorer 16 Development Board is shown in Figure 1-1. The board
includes these key features, as indicated in the diagram:
1. 100-pin PIM riser, compatible with the PIM versions of all Microchip
PIC24F/24H/dsPIC33F devices
2. Direct 9 VDC power input that provides +3.3V and +5V (regulated) to the entire
board
3. Power indicator LED
4. RS-232 serial port and associated hardware
5. On-board analog thermal sensor
6. USB connectivity for communications and device programming/debugging
7. Standard 6-wire In-Circuit Debugger (ICD) connector for connections to an
MPLAB ICD 2 programmer/debugger module
8. Hardware selection of PIM or soldered on-board microcontroller
(in future versions)
9. 2-line by 16-character LCD
10. Provisioning on PCB for add on graphic LCD
11. Push button switches for device Reset and user-defined inputs
12. Potentiometer for analog input
13. Eight indicator LEDs
14. 74HCT4053 multiplexers for selectable crossover configuration on serial communication
lines
15. Serial EEPROM
16. Independent crystals for precision microcontroller clocking (8 MHz) and RTCC
operation (32.768 kHz)
17. Prototype area for developing custom applications
18. Socket and edge connector for PICtail™ Plus card compatibility
19. Six-pin interface for PICkit 2 Programmer
20. JTAG connector pad for optional boundary scan functionality
For additional details on these features, refer to Chapter 4. “Explorer 16 Development
Hardware”.
1.4.1 Sample Devices Included with the Development Kit
Each Explorer 16 Development Board Kit contains two preprogrammed 16-bit devices:
a PIC24FJ128GA010 and a dsPIC33FJ256GP710. These are provided as 100-pin
PIMs on riser sockets, which can be quickly installed on pin header U1A and
exchanged as needed.
Note: As Microchip’s 16-bit portfolio develops, alternate devices may be included
with the Explorer 16 Development Board Kit. It is anticipated that one
device each of the PIC24 and dsPIC33F families will always be included.
Also in the future, the included PIC24 device will be soldered onto the board
and only the dsPIC33F device will be provided as a PIM.
Explorer 16 Development Board User’s Guide
DS51589A-page 9 © 2005 Microchip Technology Inc.
FIGURE 1-1: EXPLORER 16 DEVELOPMENT BOARD LAYOUT
1.5 USING THE EXPLORER 16 OUT OF THE BOX
Although intended as a development platform, the Explorer 16 board may also be used
directly from the box as a demonstration board for PIC24 and dsPIC33F devices. The
programs discussed in Chapter 3. “Explorer 16 Tutorial Programs” are
preprogrammed into the sample device PIMs (i.e., PIC24ExplDemo.hex for the
PIC24 device and dsPIC33ExplDemo.hex for the dsPIC33F device) and are ready
for immediate use.
To get started with the board:
1. For Explorer 16 boards without a permanently mounted PIC24FJ device: verify
that the PIC24FJ128GA010 PIM is correctly installed onto the board. If you want
to use the dsPIC® device PIM, carefully remove the PIC24 PIM and install the
dsPIC33F PIM in its place. For all PIMs, be certain to align the PIM so the
notched corner marking is oriented in the upper left corner.
2. For Explorer 16 boards without a permanently mounted PIC24FJ device: verify
that switch S2 is set in the “PIM” position.
For Explorer 16 boards with a permanently mounted PIC24FJ device: verify that
switch S2 is set in the “PIC” position.
3. Verify that the jumper on JP2 is installed (to enable the LEDs).
4. Apply power to the board (9 VDC) at power input J2. For information on acceptable
power sources, see Appendix A. “Explorer 16 Development Board
Schematics”.
Refer to Chapter 3. “Explorer 16 Tutorial Programs” for details on the demonstration
code operation.
1
10
7
4
5
6
3
2
8
9
11 12 13 14 15 16
17
18
19
20
Introducing the Explorer 16 Development Board
© 2005 Microchip Technology Inc. DS51589A-page 10
FIGURE 1-2: EXPLORER 16 PIM MODULE, SHOWING NOTCHED CORNER
MARKING
1.6 EXPLORER 16 DEVELOPMENT BOARD DEMONSTRATION PROGRAMS
The preprogrammed example code on the PIMs has been included on the Explorer 16
CD-ROM for future reference. All project files have been included, so that the code may
be used directly to restore a PIM to its original state (i.e., if the sample device has been
reprogrammed with another program), or so the user may use the tutorial code as a
platform for further experimentation.
In addition, the CD-ROM contains sample demonstration programs for both PIC24 and
dsPIC33F family devices. Separate demo source code (as files in C) and compiled
code files (in Hex) are provided for each family. These may be used with the included
PIC24 and dsPIC33F PIMs by reprogramming the devices using MPLAB ICD 2.
1.7 REFERENCE DOCUMENTS
In addition to the documents listed in the “Recommended Reading” section, these
documents are also available from Microchip to support the use of the Explorer 16
Development Board:
• PIC18F2455/2550/4455/4550 Data Sheet (DS39632)
• TC1047/TC1047A Data Sheet (DS21498)
• 25AA256/25LC256 Data Sheet (DS21822)
• PICkit™ 2 Microcontroller Programmer User’s Guide (DS51553)
• MPLAB® ICD 2 In-Circuit Debugger Quick Start Guide (DS51268)
• PRO MATE® II User’s Guide (DS30082)
You can obtain these reference documents from your nearest Microchip sales office
(listed in the back of this document) or by downloading them from the Microchip web
site (www.microchip.com).
PIC24FJ128GA010
EXPLORER 16 DEVELOPMENT
BOARD USER’S GUIDE
© 2005 Microchip Technology Inc. DS51589A-page 11
Chapter 2. Explorer 16 Programming Tutorial
2.1 INTRODUCTION
This chapter is a self-paced tutorial to get you started using the Explorer 16 Development
Board.
2.2 HIGHLIGHTS
Items discussed in this chapter include:
• Tutorial Overview
• Creating the Project
• Building the Code
• Programming the Device
2.3 TUTORIAL OVERVIEW
The tutorial in this chapter demonstrates the main features of the MPLAB IDE and
MPLAB ICD 2 as they are used with the Explorer 16 Development Board. As presented,
it is designed for use with the PIC24FJ128GA010 specifically. However, the
same procedures and toolsuites can also be used with PIC24H or dsPIC33F devices.
The PIC24 tutorial project demonstrated here, PIC24ExplDemo.mcp, is written in C
for MPLAB C30. The program displays PIC24 features on the alphanumeric LCD, and
also displays voltage, temperature and date/time as the various buttons are pressed.
Described with the PIC24 project is the dsPIC device tutorial,
Example1_RTC_LED_ADC.mcp. It is also written in C for MPLAB C30. The program
displays voltage and current time, updating the display on command. Both programs
are described in more detail in Chapter 3. “Explorer 16 Tutorial Programs”.
For either project, the source file (PIC24ExplDemo.c or main_rtc.c for PIC24 or
dsPIC33F, respectively) is used with a linker script file (p24fj128ga010.gld or
p33fj256gp710ps.gld) and header file (p24fj128ga010.h or
p33fj256gp710ps.h) to form a complete project. While these simple projects use a
single source code file, more complex projects might use multiple assembler and
compiler source files, as well as library files and precompiled object files.
Upon completing this tutorial, you should be able to:
• Create a project using the Project Wizard
• Assemble and link the code and set the Configuration bits
• Set up MPLAB IDE to use the MPLAB ICD 2
• Program the chip with the MPLAB ICD 2
There are three steps to this tutorial:
1. Creating a project in MPLAB IDE.
2. Assembling and linking the code.
3. Programming the chip with the MPLAB ICD 2.
Explorer 16 Programming Tutorial
© 2005 Microchip Technology Inc. DS51589A-page 12
2.4 CREATING THE PROJECT
The first step is to create a project and a workspace in MPLAB IDE. Typically, there is
one project in one workspace.
A project contains the files needed to build an application (source code, linker script
files, etc.) along with their associations to various build tools and build options.
A workspace contains one or more projects and information on the selected device,
debug tool and/or programmer, open windows and their location and other MPLAB IDE
configuration settings.
MPLAB IDE contains a Project Wizard to help create new projects. Before starting,
create a folder named Tutorial for the project files for this tutorial (C:\Tutorial is
assumed in the instructions that follow). From the Example Code\Tutorial Code
directory on the Explorer 16 Development Kit Software CD-ROM, copy all of the source
files into this folder.
2.4.1 Select a Device
1. Start MPLAB IDE.
2. Close any workspace that might be open (File > Close Workspace).
3. From the Project menu, select Project Wizard.
4. From the Welcome screen, click Next > to display the Project Wizard Step One
dialog (Figure 2-1).
FIGURE 2-1: SELECTING THE DEVICE
5. From the Device drop-down list, select “PIC24FJ128GA010” or
“dsPIC33FJ256GP710PS”, depending on the PIM being used. Click Next >. The
Project Wizard Step Two dialog will be displayed (see Figure 2-2).
Note: These instructions presume the use of MPLAB IDE 7.22 or newer.
Note: The screen shots in the following sections show the PIC24 tutorial. Except for
displayed file names, the screens for the dsPIC33F tutorial will be identical.
Explorer 16 Development Board User’s Guide
DS51589A-page 13 © 2005 Microchip Technology Inc.
FIGURE 2-2: SELECTING THE TOOLSUITE
2.4.2 Select Language Toolsuite
1. From the Active Toolsuite drop-down list, select Microchip C30 Toolsuite. This
toolsuite includes the assembler and linker that will be used.
2. In the Toolsuite Contents combo box, select MPLAB C30 Compiler
(pic30-gcc.exe).
3. In the Location box, click Browse... and navigate to
C:\Program Files\Microchip\MPLAB C30\bin\pic30-as.exe.
4. With MPLAB LINK 30 Object Linker (pic30-ld.exe) selected in Toolsuite
Contents, click Browse... and navigate to
C:\Program Files\Microchip\MPLAB C30\bin\pic30-Id.exe.
5. Click Next > to continue. The Project Wizard Step Three dialog displays
(Figure 2-3).
Explorer 16 Programming Tutorial
© 2005 Microchip Technology Inc. DS51589A-page 14
FIGURE 2-3: NAMING YOUR PROJECT
2.4.3 Name Your Project
1. In the Project Name text box, type “MyProject”.
2. In the Project Directory box, click Browse... and navigate to C:\Tutorial to
place your project in the Tutorial folder.
3. Click Next > to continue. The Project Wizard Step Four dialog displays
(Figure 2-4).
FIGURE 2-4: ADDING FILES TO THE PROJECT
Explorer 16 Development Board User’s Guide
DS51589A-page 15 © 2005 Microchip Technology Inc.
2.4.4 Add Files to Project
1. From the list of folders on the PC, locate the C:\Tutorial folder.
2. Select the source (.c) and header (.h) files. Click Add >> to include the file in
the project.
3. Expand the C:\Program Files\Microchip\MPLAB 30\support\gld
folder and select the p24fj128ga010.gld or p33fj256gp710ps.gld file,
as appropriate.
4. Click Add >> to include this file in the project. There should now be two files in
the project.
5. Click Next > to continue.
6. When the summary screen displays, click Finish.
After the Project Wizard completes, the MPLAB Project window shows the source files
in the Source Files folder and the appropriate linker script in the Linker Scripts folder
(Figure 2-5).
FIGURE 2-5: PROJECT WINDOW
A project and workspace has now been created in MPLAB IDE. MyProject.mcw is
the workspace file and MyProject.mcp is the project file. Double-click the
PIC24ExplDemo.c file (for PIC24) or main_rtc.c file (for dsPIC33F) in the Project
window to open the file. MPLAB IDE should now look similar to Figure 2-6.
Explorer 16 Programming Tutorial
© 2005 Microchip Technology Inc. DS51589A-page 16
FIGURE 2-6: MPLAB® IDE WORKSPACE
2.5 BUILDING THE CODE
In this project, building the code consists of compiling the source files to create an
object file, MyProject.o, then linking the object file to create the MyProject.hex
and MyProject.cof output files. (For dsPIC33F projects, the files would be
Example1_RTC_LED_ADC.o, Example1_RTC_LED_ADC.hex and
Example1_RTC_LED_ADC.cof.)The Hex file contains the data necessary to program
the device, and the .cof file contains additional information that lets you debug the
code at the source code level.
Before building, there are settings required to tell MPLAB IDE where to find the include
files and to reserve space for the extra debug code when the MPLAB ICD 2 is used.
For PIC24 projects, the following line in the system.h file is:
#include “p24fj128ga010.h”
For dsPIC33 projects, the line is:
#include “p33fj256gp710ps.h”
This line causes a standard include file to be used. Microchip provides these files with
all the Special Function Register (SFR) labels already defined for convenience.
To build the code, select Build Options > Project from the Project menu. The Build
Options dialog displays (Figure 2-7).
Project
Window
Output
Window
Source
Window
Code
Explorer 16 Development Board User’s Guide
DS51589A-page 17 © 2005 Microchip Technology Inc.
FIGURE 2-7: BUILD OPTIONS
2.5.1 Identify Assembler Include Path
1. Select the General tab.
2. Click Suite Default. This tells the environment where to find the library files.
3. Select the MPLAB LINK30 tab to view the linker settings (Figure 2-8).
4. Check Link for ICD2.
5. Click OK. The text box closes while the linker reserves space for the debug code
used by the MPLAB ICD 2.
6. Click OK again to save these changes. The project is now ready to build.
Explorer 16 Programming Tutorial
© 2005 Microchip Technology Inc. DS51589A-page 18
FIGURE 2-8: MPLAB® LINK30 BUILD OPTIONS
2.5.2 Build the Project
From the menu bar of the main MPLAB IDE window, select Project > Make. The Build
Output window displays (Figure 2-9).
Observe the progress of the build. When the “BUILD SUCCEEDED” message displays,
you are ready to program the device.
FIGURE 2-9: BUILD OUTPUT
Explorer 16 Development Board User’s Guide
DS51589A-page 19 © 2005 Microchip Technology Inc.
2.6 PROGRAMMING THE DEVICE
The MPLAB ICD 2 In-Circuit Debugger is used to program and debug the
microcontroller in-circuit on the Explorer 16 Development Board.
2.6.1 Set Up the Device Configuration
The device configuration for the target microcontroller can be set by two methods:
using configuration macros in the source code, or using the Configuration Bits window
in MPLAB IDE.
The PIC24 Explorer 16 tutorial code already includes configuration macros in the
source code itself. It is only necessary to confirm that the following macros are in place
near the top of the PIC24ExplDemo.c file:
_CONFIG1(JTAGEN_OFF & GSS0_OFF & GWRP_OFF & BKBUG_OFF & COE_OFF
& FWDTEN_OFF & FNOSC_PRI)
_CONFIG2(FCKSM_CSDCMD & OSCIOFNC_ON & POSCMOD_HS)
For the dsPIC33F tutorial code, confirm that the following macros are in place near the
top of the main_rtc.c file:
_FGS(CODE_WRITE_PROT_OFF);
_FOSCSEL(FRC_PLL);
_FOSC(CSW_FSCM_OFF & OSC2_IO & XT);
_FWDT(WDT_OFF);
If configuration macros are not used in the source code, it is also possible to set device
configuration with the Configuration Bits window. For the PIC24 code, the process is as
follows:
1. From the main window’s menu bar, select Configure > Configuration Bits to
display the configuration settings (Figure 2-10).
2. Set the Configuration bits by clicking on a particular line item and selecting an
option from the drop-down menu that appears. The Configuration bits should be
set as shown in Figure 2-10.
The settings that will most likely need to change are:
a) Primary Oscillator Select: HS Oscillator Enabled
b) Oscillator Select: Primary Oscillator (XT, HS, ES)
c) Clock Switching and Monitor: SW Disabled, Mon Disabled
d) Watchdog Timer Enable: Disable
Note: Before proceeding, make sure that the USB driver for the MPLAB ICD 2 has
been installed on the PC (see the MPLAB® ICD 2 In-Circuit Debugger
User’s Guide (DS51331) for more details regarding the installation of the
MPLAB ICD 2).
Explorer 16 Programming Tutorial
© 2005 Microchip Technology Inc. DS51589A-page 20
FIGURE 2-10: CONFIGURATION SETTINGS (PIC24)
2.6.2 Connect and Enable MPLAB ICD 2
1. Connect the MPLAB ICD 2 module to the PC with the USB cable.
2. Connect the MPLAB ICD 2 to the Explorer 16 Development Board with the short
RJ-11 cable.
3. Apply power to the Explorer 16 board.
4. From the Debugger menu, click Select Tool > MPLAB ICD 2 to set the MPLAB
ICD 2 as the debug tool in MPLAB IDE.
5. From the Debugger menu, select Connect to connect the debugger to the device.
MPLAB IDE should report that it found the PIC24FJ128GA010 device, as shown
in Figure 2-11.
FIGURE 2-11: ENABLING MPLAB® ICD 2
Note: Do not use the Configuration Bits window to set device configuration if
configuration macros are already used in the source code. In cases where
both methods are used, configuration macros may override settings from
the Configuration Bits window. Refer to the MPLAB IDE Simulator, Editor
User’s Guide (DS51025) for additional information.
Note: MPLAB IDE may need to download new firmware if this is the first time the
MPLAB ICD 2 is being used with a PIC24FJ device. Allow it to do so. If any
errors are shown, double-click the error message to get more information.
Status indicates
device is found
Explorer 16 Development Board User’s Guide
DS51589A-page 21 © 2005 Microchip Technology Inc.
2.6.3 Program the Device
1. From the Debugger menu, select Program to program the part. The Output
window (Figure 2-12) displays the program steps as they occur.
2. Observe the results of the programming. When “MPLAB ICD 2 Ready” displays,
the device is programmed and ready to run.
FIGURE 2-12: PROGRAMMING THE DEVICE
Explorer 16 Programming Tutorial
© 2005 Microchip Technology Inc. DS51589A-page 22
NOTES:
EXPLORER 16 DEVELOPMENT
BOARD USER’S GUIDE
© 2005 Microchip Technology Inc. DS51589A-page 23
Chapter 3. Explorer 16 Tutorial Programs
3.1 INTRODUCTION
This chapter provides a high-level overview of the PIC24 and dsPIC33F firmware
programmed during the tutorial exercise in the previous chapter.
3.2 PIC24 TUTORIAL PROGRAM OPERATION
The PIC24 tutorial program is made up of three components which are individually
displayed on the LCD. The program is used to demonstrate the new Parallel Master
Port (PMP) module which is used to drive the LCD, as well as the new Real-Time
Clock/Calendar module (RTCC). The program flow is shown in Figure 3-1.
3.2.1 PIC24 Features
Features mode displays a continuous description of the PIC24FJ128GA010 device
feature set. To exit the display and continue to the next mode, press S4.
3.2.2 Voltmeter/Temperature
Voltmeter/Temperature mode uses the code modules, vbanner.c and ADC.c, and
the A/D module to measure analog signals from the board and convert them for display
on the LCD. The voltage is taken from the potentiometer (R6) and displays a voltage
between 0.00V and 3.29V on line 1 of the LCD. Temperature is from a TC1074A analog
thermal sensor (U5). The temperature is displayed on line 2 of the LCD and automatically
alternates between Celsius and Fahrenheit values. The voltage and
temperature are updated continuously.
This mode also lets users store the current temperature in the on-board serial
EEPROM by pressing S5. Pressing S6 switches the display between current and
stored temperature values. An ‘M’ on the right side of the LCD indicates that a stored
temperature value is being displayed.
To exit and continue to the next mode, press S4.
3.2.3 Clock/Calendar
Clock/Calendar mode uses code in the modules, rtcc.c and tbanner.c. Once this
mode is entered from the main menu, a Real-Time Clock will start counting from
10:00:00, and display the date and day for Oct. 10, 2005. The new RTCC module and
a 32 kHz clock crystal are used to provide the Real-Time Clock with day/date calendar.
In Clock/Calendar mode, the user-defined push buttons do the following:
• S3 toggles the Clock Set mode, which allows the user to set the date and time.
Setup mode starts with the tens digit of the hour in the time display.
• S4 accepts the value of the current item and moves cursor to the next item.
• S5 decrements the currently selected item.
• S6 increments the currently selected item.
Pressing S3 once superimposes a flashing cursor over the tens digit of the hour in the
time display. Each press of S4 moves the cursor sequentially through the digits of the
time display, then the month, day and year. Pressing S3 at any time in the process
returns to the regular clock/calendar display.
Explorer 16 Tutorial Programs
© 2005 Microchip Technology Inc. DS51589A-page 24
Pressing S4 at this point exits Clock/Calendar mode and returns the device to the
PIC24 Features mode.
The data that is sent to the LCD is also sent to the RS-232 serial port using the UART.
A terminal emulator, such as HyperTerminal (installed by default on most Microsoft®
Windows systems), will be able to display the same information. To do this, set the
terminal emulator for 19200 baud, 8-bit data, 1 Stop bit and no parity check.
FIGURE 3-1: PIC24 TUTORIAL PROGRAM FLOWCHART
“Explorer 16
Development Board”
Power-up
PIC24 Features
Scrolling Banner
Is S4
pressed?
“Mon 10:00:00”
“Oct 10, 2005”
No
Yes
Is S4
pressed?
Is S5
pressed?
Toggle Displayed
Temperature between
Current and Stored
Is S4
pressed?
No
Is S3
pressed?
Clock Setup mode:
S3 – Exit Setup mode
S4 – Accept Selection, Adjust Next Value
S5 – Decrement Selection
S6 – Increment Selection
Yes
Yes
No
Yes
No
Yes
No
Display Voltage
Display
Display
Display
Store Temperature
in EEROM
Is S6
pressed?
No
Yes
and Temperature
Explorer 16 Development Board User’s Guide
DS51589A-page 25 © 2005 Microchip Technology Inc.
3.3 dsPIC33F TUTORIAL PROGRAM OPERATION
The dsPIC33F tutorial program is made up of five simple processes which continuously
execute on the dsPIC33FJ256GP710 device:
• Real-Time Clock (RTC) using Timer1
• A/D conversion of Potentiometer (R6)
• A/D volts to Hex conversion
• Hex to Decimal conversion (for LCD display)
• LCD Update
The time of day and A/D conversion values are continually updated and displayed on
the LCD. The program demonstrates the basic code to initialize Timer1, enable the
Timer1 oscillator for RTC operation, and initialize the A/D for single channel conversion
of potentiometer, RP5. The LCD is driven via the port pins. The program flow is shown
in Figure 3-2.
In addition to the tutorial, the Explorer 16 CD also provides code examples to demonstrate
higher level processing requirements, such as DMA, digital filters and Fast
Fourier Transforms (FFT). See Code Example 2 on the CD for more information.
3.3.1 Voltmeter
The simple tutorial program initializes the A/D module for 12-bit mode with
auto-sampling and conversion of the potentiometer connected to pin AN5 and initializes
the respective interrupt. The A/D module continually samples and converts the
potentiometer signal (0 to 3.3 VDC) on analog channel, AN5. When a conversion is
complete, an interrupt is generated and the result in the ADCBUF0 register is copied
into a temporary variable, temp1. The adc_lcd_update flag is then asserted and the
A/D Interrupt Flag, AD1IF (IFS0<13>), is cleared.
The program exits the Interrupt Service Routine and re-enters the main program loop.
The variable, adc_lcd_update, is evaluated in the main loop to determine if there is
a new A/D conversion value which can be converted and displayed on the LCD.
The primary code modules associated with the operation of the ADC module and
display are:
• init_ADC.c
• isr_ADC.c
• advolts.c
• hexdec.c
3.3.2 Real-Time Clock
The tutorial program also supports a Real-Time Clock demo. Timer1 is initialized with
interrupts enabled and the external 32.768 kHz oscillator is enabled. Within the Timer1
Interrupt Service Routine (once every second), the variables, hours, minutes and
seconds, are updated, the flag variable, rtc_lcd_update, is asserted and the
Timer1 Interrupt Flag, T1IF (IFS0<3>), is cleared.
The program exits the Interrupt Service Routine and re-enters the main program loop.
The variable, rtc_lcd_update, is evaluated in the main loop to determine if there is
a new time of day value which can be converted and displayed on the LCD.
The primary code modules associated with the operation of the Timer1 module and
display are:
• init_timer1.c
• isr_timer1.c
• hexdec.c
Explorer 16 Tutorial Programs
© 2005 Microchip Technology Inc. DS51589A-page 26
FIGURE 3-2: dsPIC33F TUTORIAL PROGRAM FLOWCHART
“dsPIC33 Demo”
“Press S3 to cont”
Power-up
Initialize Timer1
Is S3
pressed?
Initialize A/D Converter
to Decimal and
Call Update_LCD
No
Update
time?
Update
volts?
Yes
Yes
No
Yes
No
Convert Time of Day
Display
“Time 00:00:00”
“R6 = 0.00 VDC”
Display
to Decimal and
Call Update_LCD
Convert A/D Result
EXPLORER 16 DEVELOPMENT
BOARD USER’S GUIDE
© 2005 Microchip Technology Inc. DS51589A-page 27
Chapter 4. Explorer 16 Development Hardware
4.1 INTRODUCTION
This chapter provides a more detailed description of the hardware features of the
Explorer 16 Development Board.
4.2 HARDWARE FEATURES
The key features of the Explorer 16 board are listed below. They are presented in the order
given in Section 1.4 “Explorer 16 Development Board Functionality and Features”,
Figure 1-1.
4.2.1 Processor Support
The Explorer 16 board has been designed to accommodate both permanently mounted
(i.e., soldered on) and detachable PIM processors. Slider switch, S2, allows the user
to choose which processor to use. This makes it possible for the Explorer 16 board to
support most 3V, 16-bit, pin compatible microcontrollers with appropriate PIMs.
PIMs are visually indexed for proper installation. The PIM is always installed with the
notched corner mark on the corner of the PIM board oriented to the upper left corner.
Current revisions of the board do not have a permanently mounted microcontroller in
U1. In order for the board to work, therefore, S2 must always be left in the “PIM” position.
In future versions with a permanently mounted PIC24 device at U1, setting S2 in
the “PIC” position will enable the on-board device and disable the PIM socket.
4.2.2 Power Supply
There are two ways to supply power to the Explorer 16 board:
• An unregulated DC supply of 9V to 15V (preferably 9V) supplied to J12.
For default functionality, a power supply with a current capability of 250 mA is
sufficient. Since the board can serve as a modular development platform that can
connect to multiple expansion boards, voltage regulators (Q1 and Q2) with a
maximum current capability of 800 mA are used. This may require a larger power
supply of up to 1.6A. Because the regulators do not have heat sinks, long-term
operation at such loads is not recommended.
• An external, regulated DC power supply that provides both +5V and +3.3V can be
connected to the terminals provided (at the bottom left side of the board, near S3).
One green LED (D1) is provided to show when the Explorer 16 board is powered up.
The power-on LED indicates the presence of +3.3V.
Note: The Explorer 16 kit does not include a power supply. If an external supply
is needed, use Microchip part number AC162039.
Note: Do not attempt to power the Explorer 16 board using the MPLAB ICD 2
module. It is not designed to be a USB bus power source.
Explorer 16 Development Hardware
© 2005 Microchip Technology Inc. DS51589A-page 28
4.2.3 RS-232 Serial Port
An RS-232 level shifter (U3) has been provided with all necessary hardware to support
RS-232 connection with hardware flow control through the DB9 connector. The port is
configured as a DCE device, and can be connected to a PC using a straight-through
cable.
The PIC24/dsPIC33F RX and TX pins are tied to the RX and TX lines of U3. The
PIC24/dsPIC33F RTS and CTS pins are tied to the RX2 (DIN2) and TX2 (DOUT2) lines
of the MAX3232 for hardware flow control.
4.2.4 Temperature Sensor
An analog output thermal sensor (Microchip TC1074A, U4) is connected to one of the
controller’s A/D channels.
4.2.5 USB Connectivity
The Explorer 16 board includes a PIC18LF4550 USB microcontroller, which provides
both USB connectivity and support for protocol translation. The PIC18LF4550 is
hard-wired to the PIC24/dsPIC33F devices to provide three types of connectivity:
• SPI™ of PIC18LF4550 to SPI1 of PIC24/dsPIC33F
• I/O pins of PIC18LF4550 to ICSP™ pins of PIC24/dsPIC33F
• I/O pins of PIC18LF4550 to JTAG pins of PIC24/dsPIC33F
The type of connectivity depends on the firmware installed on the PIC18LF4550. At the
time of initial release, the PIC18LF4550 is loaded with USB bootloader firmware, which
permits easy upgrades of connectivity firmware over the USB. Installing this firmware
is described in Appendix B. “Updating the USB Connectivity Firmware”.
PIC24 and dsPIC33F devices both have some 5V tolerant input pins. If a 5V tolerant
input is connected to the PIC18LF4550, protection diodes on the PIC18LF4550
device’s port pins will limit inputs to VDD. For more information on which pins of the
16-bit devices are 5V tolerant, refer to the appropriate device data sheet.
4.2.6 ICD Connector
An MPLAB ICD 2 module can be connected by way of the modular connector (JP1) for
low-cost debugging. The ICD connector utilizes port pins, RB6 and RB7 of the
microcontroller, for in-circuit debugging.
Jumper J7 decides the terminus of the ICD 2 connector. If the jumper is set to the
“PIC24” side, JP1 communicates directly with RB6/RB7 of the PIM or on-board device
(determined by S2). If the jumper is set to the “F4450” side, JP1 communicates with the
on-board PIC18LF4550 USB device.
4.2.7 LCD
The Explorer 16 board includes an alphanumeric LCD display with two lines of 16 characters
each. The display is driven with three control lines (RD4, RD5 and RD15) and
eight data lines (RE7:RE0). On PIC24 devices, the LCD is driven by the PMP module,
not the I/O port.
The Explorer 16 board has multiple LCD footprints and support options, although only
one footprint is ever populated at one time. The Lumex LCM-SO1062 (populated at
LCD4) is a 5V LCD with TTL input, and is used in the initial version of the Explorer 16
board. The Tianma TM162JCAWG1 (populated at LCD1) is a 3V LCD; it is anticipated
to be used in future versions of the board.
An alternate configuration option allows the use of RD3:RD0 as four of the data lines,
instead of RE7:RE4. To do this, the user must cut the trace jumpers at R60/62/64/66
and create solder bridges from the pads for R61/63/65/67 (see Figure 4-1).
Explorer 16 Development Board User’s Guide
DS51589A-page 29 © 2005 Microchip Technology Inc.
FIGURE 4-1: MODIFICATIONS TO R60-R67 FOR LCD CONFIGURATION
(SCALE ENHANCED FOR VISIBILITY)
4.2.8 Graphic LCD
The Explorer 16 also has a footprint and layout support for the Optrex 128 x 64 dot-matrix
graphic LCD (part number F-51320GNB-LW-AB) and associated circuitry. This is the
same display used in Microchip’s MPLAB PM3 programmer.
4.2.9 Switches
Five push button switches provide the following functions:
• S1: Active-low MCLR switch to hard reset the processor
• S3: Active-low switch connected to RD6 (user-defined)
• S4: Active-low switch connected to RD13 (user-defined)
• S5: Active-low switch connected to RA7 (user-defined)
• S6: Active-low switch connected to RD7 (user-defined)
Switch S1 has a debounce capacitor, whereas S3 through S6 do not; this allows the
user to investigate debounce techniques. When Idle, the switches are pulled high
(+3.3V). When pressed, they are grounded.
4.2.10 Analog Input (Potentiometer)
A 10 kΩ potentiometer is connected through a series resistor to AN5. It can be adjusted
from VDD to GND to provide an analog input to one of the controller’s A/D channels.
4.2.11 LEDs
Eight red LEDs (D2 through D9) are connected to PORTA of the PIM socket. The
PORTA pins are set high to light the LEDs. These LEDs may be disabled by removing
jumper JP2.
4.2.12 Oscillator Options
The installed microcontroller has two separate oscillator circuits connected.The main
oscillator uses an 8 MHz crystal (Y3) and functions as the controller’s primary oscillator.
A second circuit, using a 32.768 kHz (watch type) crystal (Y2), functions as the Timer1
oscillator and serves as the source for the RTCC and secondary oscillator.
The PIC18LF4550, at the heart of the USB subsystem, is independently clocked and
has its own 20 MHz crystal (Y1).
4.2.13 Serial EEPROM
A 25LC256 256K (32K x 8) serial EEPROM (U5) is included for nonvolatile firmware
storage. It is also used to demonstrate SPI bus operation.
R60
R61
R62
R63
R64
R65
R66
R67
Cut Traces
Here
Add
Solder
Bridges
Here
Explorer 16 Development Hardware
© 2005 Microchip Technology Inc. DS51589A-page 30
4.2.14 PICkit 2 Connector
Connector J14 provides the footprint for a 6-pin PICkit 2 programmer interface. This will
provide a third low-cost programming option, besides MPLAB ICD 2 and the JTAG
interface, when PICkit 2 support for larger devices become available in the future.
4.2.15 JTAG Connector
Connector J13 provides a standard JTAG interface, allowing users to connect to and
program the controller via JTAG.
4.2.16 PICtail™ Plus Card Edge Modular Expansion Connectors
The Explorer 16 board has been designed with the PICtail™ Plus modular expansion
interface, allowing the board to provide basic generic functionality and still be easily
extendable to new technologies as they become available.
PICtail Plus is based on a 120-pin connection divided into three sections of 30 pins,
30 pins and 56 pins. The two 30-pin connections have parallel functionality; for example,
pins 1, 3, 5 and 7 have SPI1 functionality on the top 30-pin segment, with similar
SPI2 functionality on the corresponding pins in the middle 30-pin segment.
Each 30-pin section provides connections to all of the serial communications
peripherals, as well as many I/O ports, external interrupts and A/D channels. This provides
enough signals to develop many different expansion interfaces, such as
Ethernet, Zigbee™, IrDA® and so on. The 30-pin PICtail Plus expansion boards can be
used in either the top or middle 30-pin sections.
The Explorer 16 board provides footprints for two edge connectors for daughter cards,
one populated (J5, Samtec # MEC1-160-02-S-D-A) and one unpopulated (J6). The
board also has a matching male edge connection (J9), allowing it to be used as an
expansion card itself.
4.2.16.1 CROSSOVER CONNECTIONS FOR SPI AND UART
The PICtail Plus interface allows two Explorer 16 boards to be connected directly to
each other without any external connector. This provides 1-to-1 connection between
the microcontrollers on the two boards, an interface that works well for many types of
peripherals (I2C, PMP, etc.). However, certain serial peripheral modules, such as SPIs
and UARTs, require cross-wire connections; that is, the TX (or SDO) pin of one
controller must be connected to the RX (or SDI) of the other and vice versa.
The Explorer 16 board uses two 74HCT4053 analog multiplexers to simplify the connections
between itself and any daughter boards. U6 and U7 provide active control of
the cross-wire capability on SPI1 and UART1, with a hardware flow control signal
provided by three I/O pins.
The multiplexers are controlled by the state of pins RB12, RB13 and RB14. When a
control pin is high (the default state), the corresponding SPI1 or UART1 pin pairs are
connected to their default pins on the PICtail Plus interface. When a control pin is
asserted low, the corresponding pin pair functions are swapped. Table 4-1 details the
relationship between the control pins and SPI1/UART1 functions on the interface.
Explorer 16 Development Board User’s Guide
DS51589A-page 31 © 2005 Microchip Technology Inc.
TABLE 4-1: LOCATION OF SPI1 AND UART1 PINS ON PICtail™ PLUS
INTERFACE
Control
Pin State
UART1 Control Pins SPI1
Control Pin RB14 Control Pin RB13 Control Pin RB12
U1RX U1TX U1CTS U1RTS SDI1 SDO1
1 2 4 19 20 5 7
0 4 2 20 19 7 5
Note: When connecting SPI and UART peripherals on two Explorer 16 boards,
use crossover connection on only one of the boards.
Explorer 16 Development Hardware
© 2005 Microchip Technology Inc. DS51589A-page 32
NOTES:
EXPLORER 16 DEVELOPMENT
BOARD USER’S GUIDE
© 2005 Microchip Technology Inc. DS51589A-page 33
Appendix A. Explorer 16 Development Board Schematics
A.1 INTRODUCTION
This section provides detailed technical information on the Explorer 16 board.
A.2 DEVELOPMENT BOARD BLOCK DIAGRAM
FIGURE A-1: HIGH-LEVEL BLOCK DIAGRAM OF THE EXPLORER 16 DEVELOPMENT BOARD
PIC24FJ128GA010
dsPIC33FJ256GP710
16x2 LCD Display
PIC18LF4550
SPI*
ICSP*
JTAG*
ICD/ICSP
JTAG
RS-232
Transceiver
SPI
EEPROM
+3.3V and
+5V Supply
9-15 VDC
Switches
Temperature
Sensor
LEDs
POT
Modular Expansion
Connector
USB
PICtail™ Plus
PICtail™ Plus
* Hardware support only; firmware support for SPI™, JTAG and ICSP™ via USB are not available at this time.
Explorer 16 Development Board Schematics
© 2005 Microchip Technology Inc. DS51589A-page 34
A.3 DEVELOPMENT BOARD SCHEMATICS
FIGURE A-2: EXPLORER 16 BOARD SCHEMATIC, SHEET 1 OF 8 (PIM SOCKET)
VCAP/VDDCORE VDDCORE
VSS
VSS
VDD
100-Pin PIM
VSS
VDD
VSS
VDD
CVREF/AN10/RB10
AVDD
AVSS
VSS
VDD
VDD
Explorer 16 Development Board User’s Guide
DS51589A-page 35 © 2005 Microchip Technology Inc.
FIGURE A-3: EXPLORER 16 BOARD SCHEMATIC, SHEET 2 OF 8 (BOARD MOUNTED
PIC24FJ128GA010 MCU, WHEN INSTALLED)
10 μF .1 μF
VCAP/VDDCORE
VDD
VSS
PIC24FJ128GA010
VDD
AVDD
VDD
VSS
AVSS
CVREF/AN10/RB10
VSS
VDD
VDD
VSS
VSS
Explorer 16 Development Board Schematics
© 2005 Microchip Technology Inc. DS51589A-page 36
FIGURE A-4: EXPLORER 16 BOARD SCHEMATIC, SHEET 3 OF 8 (MPLAB® ICD 2, JTAG,
PICkit™ 2 AND PICtail™ Plus CONNECTORS)
MPLAB® ICD 2 Connector
.1 μF
PICkit™ 2 Programmer
Explorer 16 Development Board User’s Guide
DS51589A-page 37 © 2005 Microchip Technology Inc.
FIGURE A-5: EXPLORER 16 BOARD SCHEMATIC, SHEET 4 OF 8 (PICtail™ PLUS EDGE AND
SOCKET CONNECTORS)
Explorer 16 Development Board Schematics
© 2005 Microchip Technology Inc. DS51589A-page 38
FIGURE A-6: EXPLORER 16 BOARD SCHEMATIC, SHEET 5 OF 8 (SWITCHES,
MULTIPLEXERS AND POTENTIOMETER)
VEE
VCC
.1 μF
.1 μF
VCC
VEE
.1 μF
Explorer 16 Development Board User’s Guide
DS51589A-page 39 © 2005 Microchip Technology Inc.
FIGURE A-7: EXPLORER 16 BOARD SCHEMATIC, SHEET 6 OF 8 (EEPROM, TEMPERATURE
SENSOR, LEDs, OSCILLATOR CIRCUITS AND POWER SUPPLY)
.1 μF
25LC256
.1 μF
TC1047A
22 pF 22 pF
32 kHz
.1 μF 47 μF
.1 μF 47 μF
47 μF
.1 μF
.1 μF .1 μF .1 μF .1 μF .1 μF .1 μF
VCC
VSS
VDD VOUT
VSS
8 MHz
22 pF 22 pF
Explorer 16 Development Board Schematics
© 2005 Microchip Technology Inc. DS51589A-page 40
FIGURE A-8: EXPLORER 16 BOARD SCHEMATIC, SHEET 7 OF 8 (USB AND
UART SUBSYSTEMS)
VUSB
VSS
VDD
VDD
VSS
VSS
VDD
PIC18F4550_QFN44 VDD
.1 μF .1 μF
.1 μF .1 μF
.1 μF
.1 μF
.1 μF
.1 μF
.1 μF .1 μF
22 pF 22 pF
20 MHz
VBUS
VCC
Explorer 16 Development Board User’s Guide
DS51589A-page 41 © 2005 Microchip Technology Inc.
FIGURE A-9: EXPLORER 16 BOARD SCHEMATIC, SHEET 8 OF 8 (LCDs AND OPTIONAL
LCD CONNECTIONS)
Alternative LCD Configurations:
4.7 μF
4.7 μF
4.7 μF
4.7 μF
1 μF
1 μF
1 μF
1 μF
1 μF
.1 μF
VEE VO
VCC
VEE
VCC
VEE
VEE
VSS
VDD
VO
Explorer 16 Development Board Schematics
© 2005 Microchip Technology Inc. DS51589A-page 42
NOTES:
EXPLORER 16 DEVELOPMENT
BOARD USER’S GUIDE
© 2005 Microchip Technology Inc. DS51589A-page 43
Appendix B. Updating the USB Connectivity Firmware
B.1 INTRODUCTION
The USB subsystem of the Explorer 16 Development Board is preprogrammed with
USB bootloader firmware. This provides an easy method for upgrading the
PIC18LF4550 firmware to support ICSP, JTAG and SPI connectivity to PIC24 and
dsPIC33F devices.
This chapter describes how to upgrade the PIC18LF4550 device’s firmware with the
PICkit 2 software. The same process can be used to upgrade the PIC18LF4550
device’s firmware when updates and new firmware packages become available.
B.2 UPDATING THE PICkit 2 MICROCONTROLLER PROGRAMMER
Before beginning, it will be necessary to obtain and install the PICkit 2 programmer
software. Complete instructions for installing and using the programmer software
application is provided in the PICkit™ 2 Microcontroller Programmer User’s Guide
(DS51553). The programmer and user’s guide, as well as the latest version of the
PICkit 2 operating system firmware, are available from the Microchip corporate
web site, www.microchip.com.
To update the USB firmware:
1. If not done already, download the latest PICkit 2 operating system software from
the Microchip web site.
2. On the Explorer 16 board, install a jumper between pins 9 and 10 of the JTAG
connector (J13).
3. Press and release MCLR (S1). This places the USB subsystem in Bootloader
mode and makes it ready to accept new code.
4. Connect the Explorer 16 board to the PC via a standard USB cable.
5. Launch the PICkit 2 programmer software. From the menu bar, select
Tools > Download PICKit 2 Operating System (Figure B-1).
FIGURE B-1: DOWNLOAD PICkit™ 2 OPERATING SYSTEM
Updating the USB Connectivity Firmware
© 2005 Microchip Technology Inc. DS51589A-page 44
6. Browse to the directory where the latest operating system firmware was saved
(Figure B-2).
FIGURE B-2: SELECT PICkit™ 2 OPERATING SYSTEM
7. Select the PK2_Explorer16_*.hex file and click the Open button.
The progress of the update is displayed in the status bar of the programming software.
When the update completes successfully, the status bar displays “Operating System
Verified”. The update is now complete.
B.3 OTHER USB FIRMWARE UPDATES
It is anticipated that various USB connectivity firmwares will be made available in the
future. Users are encouraged to periodically check the Microchip web site
(www.microchip.com) for new and revised code.
EXPLORER 16 DEVELOPMENT
BOARD USER’S GUIDE
© 2005 Microchip Technology Inc. DS51589A-page 45
Index
B
Build Options............................................................ 16
C
Configuration Bits..................................................... 19
Crossover Connections
(Serial Communications) ...................................8, 30
Customer Change Notification Service ...................... 5
Customer Support ...................................................... 5
D
Documentation
Conventions........................................................ 2
Layout ................................................................. 1
dsPIC33 Tutorial Program........................................ 25
dsPIC33F Tutorial Program
Flowchart .......................................................... 26
E
Explorer 16 Development Board
Block Diagram .................................................. 33
Layout ................................................................. 9
Schematics ..................................................34–41
Explorer 16 Programming Tutorial ........................... 11
Building the Code ............................................. 16
Creating the Project .......................................... 12
Programming the Device .................................. 19
F
Free Software Foundation ......................................... 4
G
GNU Language Tools ................................................ 4
H
Hardware Features
Analog Potentiometer ....................................8, 29
ICD Connector ...............................................8, 28
JTAG Connector ............................................8, 30
LCD, Alphanumeric........................................8, 28
LCD, Graphic .................................................8, 29
LEDs ..............................................................8, 29
Multiplexers....................................................8, 30
Oscillator Options ..........................................8, 29
PICkit 2 Connector.........................................8, 30
PICtail Plus Card Edge Connectors...............8, 30
Power Indicator LED........................................... 8
Power Supply.................................................8, 27
Processor Support ........................................ 8, 27
Prototype Area .................................................... 8
RS-232 Serial Port ........................................ 8, 28
Serial EEPROM............................................ 8, 29
Switches........................................................ 8, 29
Temperature Sensor ..................................... 8, 28
USB Connectivity .......................................... 8, 28
I
Internet Address......................................................... 4
L
Language Toolsuite.................................................. 13
M
Microchip Internet Web Site ....................................... 4
MPLAB ICD 2........................................................... 10
MPLAB IDE Simulator, Editor User’s Guide............... 4
P
PIC24 Tutorial Program ........................................... 23
Flowchart .......................................................... 24
PICtail Plus Edge Connectors
Use with Crossover Serial
Connections........................................ 30
Project ...................................................................... 12
Project Wizard.......................................................... 12
R
Reading, Recommended ........................................... 3
Readme...................................................................... 3
Reference Documents ............................................. 10
S
Schematics......................................................... 34–41
U
USB
Connectivity ...................................................... 28
Updating the USB Connectivity
Firmware............................................. 43
W
Warranty Registration ................................................ 2
Workspace ............................................................... 12
WWW Address........................................................... 4
DS51589A-page 46 © 2005 Microchip Technology Inc.
AMERICAS
Corporate Office
2355 West Chandler Blvd.
Chandler, AZ 85224-6199
Tel: 480-792-7200
Fax: 480-792-7277
Technical Support:
http://support.microchip.com
Web Address:
www.microchip.com
Atlanta
Alpharetta, GA
Tel: 770-640-0034
Fax: 770-640-0307
Boston
Westborough, MA
Tel: 774-760-0087
Fax: 774-760-0088
Chicago
Itasca, IL
Tel: 630-285-0071
Fax: 630-285-0075
Dallas
Addison, TX
Tel: 972-818-7423
Fax: 972-818-2924
Detroit
Farmington Hills, MI
Tel: 248-538-2250
Fax: 248-538-2260
Kokomo
Kokomo, IN
Tel: 765-864-8360
Fax: 765-864-8387
Los Angeles
Mission Viejo, CA
Tel: 949-462-9523
Fax: 949-462-9608
San Jose
Mountain View, CA
Tel: 650-215-1444
Fax: 650-961-0286
Toronto
Mississauga, Ontario,
Canada
Tel: 905-673-0699
Fax: 905-673-6509
ASIA/PACIFIC
Australia - Sydney
Tel: 61-2-9868-6733
Fax: 61-2-9868-6755
China - Beijing
Tel: 86-10-8528-2100
Fax: 86-10-8528-2104
China - Chengdu
Tel: 86-28-8676-6200
Fax: 86-28-8676-6599
China - Fuzhou
Tel: 86-591-8750-3506
Fax: 86-591-8750-3521
China - Hong Kong SAR
Tel: 852-2401-1200
Fax: 852-2401-3431
China - Qingdao
Tel: 86-532-8502-7355
Fax: 86-532-8502-7205
China - Shanghai
Tel: 86-21-5407-5533
Fax: 86-21-5407-5066
China - Shenyang
Tel: 86-24-2334-2829
Fax: 86-24-2334-2393
China - Shenzhen
Tel: 86-755-8203-2660
Fax: 86-755-8203-1760
China - Shunde
Tel: 86-757-2839-5507
Fax: 86-757-2839-5571
China - Wuhan
Tel: 86-27-5980-5300
Fax: 86-27-5980-5118
China - Xian
Tel: 86-29-8833-7250
Fax: 86-29-8833-7256
ASIA/PACIFIC
India - Bangalore
Tel: 91-80-2229-0061
Fax: 91-80-2229-0062
India - New Delhi
Tel: 91-11-5160-8631
Fax: 91-11-5160-8632
India - Pune
Tel: 91-20-2566-1512
Fax: 91-20-2566-1513
Japan - Yokohama
Tel: 81-45-471- 6166
Fax: 81-45-471-6122
Korea - Gumi
Tel: 82-54-473-4301
Fax: 82-54-473-4302
Korea - Seoul
Tel: 82-2-554-7200
Fax: 82-2-558-5932 or
82-2-558-5934
Malaysia - Penang
Tel: 60-4-646-8870
Fax: 60-4-646-5086
Philippines - Manila
Tel: 63-2-634-9065
Fax: 63-2-634-9069
Singapore
Tel: 65-6334-8870
Fax: 65-6334-8850
Taiwan - Hsin Chu
Tel: 886-3-572-9526
Fax: 886-3-572-6459
Taiwan - Kaohsiung
Tel: 886-7-536-4818
Fax: 886-7-536-4803
Taiwan - Taipei
Tel: 886-2-2500-6610
Fax: 886-2-2508-0102
Thailand - Bangkok
Tel: 66-2-694-1351
Fax: 66-2-694-1350
EUROPE
Austria - Wels
Tel: 43-7242-2244-399
Fax: 43-7242-2244-393
Denmark - Copenhagen
Tel: 45-4450-2828
Fax: 45-4485-2829
France - Paris
Tel: 33-1-69-53-63-20
Fax: 33-1-69-30-90-79
Germany - Munich
Tel: 49-89-627-144-0
Fax: 49-89-627-144-44
Italy - Milan
Tel: 39-0331-742611
Fax: 39-0331-466781
Netherlands - Drunen
Tel: 31-416-690399
Fax: 31-416-690340
Spain - Madrid
Tel: 34-91-708-08-90
Fax: 34-91-708-08-91
UK - Wokingham
Tel: 44-118-921-5869
Fax: 44-118-921-5820
WORLDWIDE SALES AND SERVICE
10/31/05
MSP-EXP430F5529 Experimenter Board
User's Guide
Literature Number: SLAU330A
May 2011–Revised June 2011
2 SLAU330A–May 2011–Revised June 2011
Submit Documentation Feedback
Copyright © 2011, Texas Instruments Incorporated
Contents
Preface ....................................................................................................................................... 5
1 Getting Started ................................................................................................................... 7
1.1 MSP-EXP430F5529 Experimenter Board Introduction ............................................................. 7
1.2 Kit Contents .............................................................................................................. 8
2 User Experience Software .................................................................................................... 9
2.1 Introduction ............................................................................................................... 9
2.2 Main Menu ............................................................................................................... 9
2.3 Clock ..................................................................................................................... 10
2.4 Games ................................................................................................................... 10
2.5 Power Tests ............................................................................................................ 10
2.6 Demo Apps ............................................................................................................. 11
2.7 SD Card Access ....................................................................................................... 12
2.8 Settings Menu .......................................................................................................... 12
3 Software Installation and Debugging ................................................................................... 13
3.1 Software ................................................................................................................. 13
3.2 Download the Required Software .................................................................................... 13
3.3 Working With the Example Software ................................................................................ 13
4 MSP-EXP430F5529 Hardware .............................................................................................. 17
4.1 Hardware Overview .................................................................................................... 17
4.2 Jumper Settings and Power .......................................................................................... 18
4.3 eZ-FET Emulator ....................................................................................................... 21
4.4 MSP-EXP430F5529 Hardware Components ...................................................................... 21
5 Frequently Asked Questions, References, and Schematics .................................................... 24
5.1 Frequently Asked Questions ......................................................................................... 24
5.2 References .............................................................................................................. 24
5.3 Schematics and BOM ................................................................................................. 25
SLAU330A–May 2011–Revised June 2011 Table of Contents 3
Submit Documentation Feedback
Copyright © 2011, Texas Instruments Incorporated
www.ti.com
List of Figures
1 MSP-EXP430F5529 Experimenter Board ............................................................................... 7
2 User Experience Navigation ............................................................................................... 9
3 Selecting a CCS Workspace............................................................................................. 14
4 Opening Existing Project ................................................................................................. 14
5 Simple Hardware Overview .............................................................................................. 17
6 Hardware Block Details ................................................................................................... 18
7 Common Power Jumper Settings ....................................................................................... 18
8 Visual Power Schematic.................................................................................................. 20
9 MSP430 Current Measurement Connection ........................................................................... 21
10 Schematics (1 of 7)........................................................................................................ 25
11 Schematics (2 of 7)........................................................................................................ 26
12 Schematics (3 of 7)........................................................................................................ 27
13 Schematics (4 of 7)........................................................................................................ 28
14 Schematics (5 of 7)........................................................................................................ 29
15 Schematics (6 of 7)........................................................................................................ 30
16 Schematics (7 of 7)........................................................................................................ 31
List of Tables
1 MSP-EXP430F5529 Jumper Settings and Functionality ............................................................. 19
2 Push Buttons, Potentiometer, and LED Connections................................................................. 22
3 Pinning Mapping for Header J4.......................................................................................... 23
4 Pin Mapping for Header J5............................................................................................... 23
5 Pin Mapping for Header J12 ............................................................................................. 23
6 Bill of Materials............................................................................................................. 32
4 List of Figures SLAU330A–May 2011–Revised June 2011
Submit Documentation Feedback
Copyright © 2011, Texas Instruments Incorporated
Preface
SLAU330A–May 2011–Revised June 2011
Read This First
If You Need Assistance
The primary sources of information for MSP430 devices are the data sheets and the family user's guides.
The most up-to-date versions of these documents can be found at www.ti.com/msp430.
Information specific to the MSP-EXP430F5529 Experimenter Board can be found at www.ti.com/usbexp.
Customer support for MSP430 devices and the MSP-EXP430F5529 Experimenter Board is provided by
the Texas Instruments Product Information Center (PIC), as well as on the TI E2E (Engineer-2-Engineer)
Forum at the link below.
Contact information for the PIC can be found on the TI web site at: support.ti.com.
The MSP430 Specific E2E forum is located at: community.ti.com/forums/12.aspx.
Related Documentation from Texas Instruments
MSP-EXP430F5529 Experimenter Board User's Guide (SLAU330)
MSP-EXP430F5529 Experimenter Board User Experience Software
MSP-EXP430F5529 Experimenter Board Quick Start Guide (SLAU339)
MSP-EXP430F5529 Experimenter Board PCB Design Files (SLAR055)
MSP430F552x Code Examples (SLAC300)
FCC Warning
This equipment is intended for use in a laboratory test environment only. It generates, uses, and can
radiate radio frequency energy and has not been tested for compliance with the limits of computing
devices pursuant to subpart J of part 15 of FCC rules, which are designed to provide reasonable
protection against radio frequency interference. Operation of this equipment in other environments may
cause interference with radio communications, in which case the user, at his own expense, will be
required to take whatever measures may be required to correct this interference.
SLAU330A–May 2011–Revised June 2011 Preface 5
Submit Documentation Feedback
Copyright © 2011, Texas Instruments Incorporated
6 Read This First SLAU330A–May 2011–Revised June 2011
Submit Documentation Feedback
Copyright © 2011, Texas Instruments Incorporated
User's Guide
SLAU330A–May 2011–Revised June 2011
MSP-EXP430F5529 Experimenter Board
1 Getting Started
1.1 MSP-EXP430F5529 Experimenter Board Introduction
The MSP-EXP430F5529 Experimenter Board is a development platform based on the MSP430F5529 with
integrated USB. The Experimenter Board showcases the abilities of the latest family of MSP430s and is
perfect for learning and developing USB-based applications using the MSP430. The features include a
102x64 dot-matrix LCD, microSD memory card interface, 3-axis accelerometer, five capacitive-touch pads,
RF EVM expansion headers, nine LEDs, an analog thumb-wheel, easy access to spare F5529 pins,
integrated Spy-Bi-Wire flash emulation module, and standard full JTAG pin access. The kit is
pre-programmed with an out-of-box demo to immediately demonstrate the capabilities of the MSP430 and
Experimenter Board. This document details the hardware, its use, and the example software.
Figure 1. MSP-EXP430F5529 Experimenter Board
The MSP-EXP430F5529 Experimenter Board is available for purchase from the TI eStore:
https://estore.ti.com/MSP-EXP430F5529-MSP430F5529-Experimenter-Board-P2413C43.aspx
SLAU330A–May 2011–Revised June 2011 MSP-EXP430F5529 Experimenter Board 7
Submit Documentation Feedback
Copyright © 2011, Texas Instruments Incorporated
Getting Started www.ti.com
1.2 Kit Contents
• MSP-EXP430F5529 Experimenter Board
• Two mini-USB cables
• Battery holder
• 1GB microSD card
• Quick start guide
8 MSP-EXP430F5529 Experimenter Board SLAU330A–May 2011–Revised June 2011
Submit Documentation Feedback
Copyright © 2011, Texas Instruments Incorporated
www.ti.com User Experience Software
2 User Experience Software
2.1 Introduction
The MSP-EXP430F5529 Experimenter Board arrives with a User Experience application installed to
demonstrate a few of the capabilities of the MSP430F5529. Set the power switch to "LDO", and connect
your PC to the "5529 USB" connection as shown in Figure 2. A splash screen displaying the TI logo
should appear on the LCD. Wait approximately three seconds, or press either the S1 or S2 button, to
display the Main Menu. Use the thumb wheel to navigate up and down the menu items on the LCD
screen. Press the S1 pushbutton to enter a selection, or press the S2 pushbutton to cancel.
Figure 2. User Experience Navigation
2.2 Main Menu
The main menu displays a list of applications and settings that demonstrate key features of the
MSP430F5529. Use the thumb wheel on the bottom right of the PCB to scroll up and down through the
menu options. Use the push-buttons to enter and exit menu items. Press S1 to enter a menu item. Press
S2 to return to a previous menu or to cancel an operation. Each application in the main menu is described
in the following sections.
SLAU330A–May 2011–Revised June 2011 MSP-EXP430F5529 Experimenter Board 9
Submit Documentation Feedback
Copyright © 2011, Texas Instruments Incorporated
User Experience Software www.ti.com
2.3 Clock
Select this option from the main menu to bring up the Clock sub-menu. Press S2 to return to the previous
menu.
NOTE: The User Experience software initializes the real-time clock to 04:30:00 - 01/01/2011 when
powered is applied to the MSP430.
Digital Clock: Displays an image of a digital watch with the current time and date.
Analog Clock: Displays an image of an analog clock with the current time.
Set Time: Allows the user to set the current time. Use the scroll wheel to change the value of the current
selection. Press push-button S1 is used to advance to the next field. The clock changes take affect after
the last field is updated.
2.4 Games
Select this option from the main menu to bring up the Games sub-menu. Press S2 to return to the
previous menu.
Defender: The player controls a small spaceship. The object of the game is to fly through a tunnel without
hitting the walls and to successfully navigate around mines scattered throughout the tunnel.
Press S1 or S2 to begin the game. Use the wheel to move the ship up and down and press S1 or S2 to
shoot a missile. As the game progresses, the tunnel gets narrower and the game speeds up. After the
player's ship crashes, the score is displayed.
Simon: A version of the famous memory game. The objective of the game is to match a randomly
generated sequence of LEDs displayed on the touch pads. After the sequence is displayed, the user must
touch the correct pads in the same sequence.
The game begins with a single-symbol sequence and adds an additional symbol to the sequence after
each successful response by the user. The game ends when the user incorrectly enters a sequence. The
number of turns obtained in the sequence is then displayed.
Tilt Puzzle: A version of the famous "8-puzzle" game. The game consists of a 3 by 3 grid with eight
numbers and one empty space. The game utilizes the on-board accelerometer to shift numbers up-down
and left-right. The objective of the game is to have the sum of the numbers in each row and column equal
to twelve. Press S1 to begin a new game if the current game is unsolvable. The nature of the game is that
there is a 50% probability the game is not solvable.
2.5 Power Tests
Select this option from the main menu to bring up the Power Test sub-menu. Press S2 to return to the
previous menu.
The Power Test menu contains two demonstrations that allow the user to externally measure the current
consumption of the MSP430 in both active mode and low-power mode. Current consumption can be
measured using a multi-meter with current measuring capabilities (ammeter). Remove the jumper on "430
PWR" (JP6) and connect a multi-meter in series with the MSP430 VCC supply. This connection can be
made using the two large vias near the "430 PWR" text on the PCB. See Section 4 for more details on this
connection.
Active Mode: Demo for measuring active mode current of the MSP430. Instructions are presented on
screen. Press S1 to continue to the application.
Press S2 to return to the Power Tests sub-menu.
The Active Mode menu consists of two columns. The left column controls the core voltage (VCORE) of the
MSP430F5529, and the right column controls MCLK. The right column displays only those MCLK
frequencies that are valid for the current VCORE setting. The capacitive touch pads at the bottom of the
board control which column is currently active. The wheel scrolls through the options in the active column.
10 MSP-EXP430F5529 Experimenter Board SLAU330A–May 2011–Revised June 2011
Submit Documentation Feedback
Copyright © 2011, Texas Instruments Incorporated
www.ti.com User Experience Software
Press S1 to enter Measurement Mode. While in measurement mode, measure the current by attaching a
multi-meter across the 430 PWR holes and removing the 430 PWR jumper J6. Replace the 430 PWR
jumper after making the measurement, then press S1 or S2 to return to the Active Mode menu.
Press S2 to return to the Power Tests sub-menu
Low Power Mode: Selecting Low Power Mode takes the user to an information screen with directions on
how to navigate the Low Power Mode menu. Press S1 to continue on to the application.
Press S2 to return to the Power Tests sub-menu.
In the Low Power Mode menu, use the wheel to select a low-power mode option, then press S1 to enter
low-power mode. While in low-power mode, measure the current by attaching a multi-meter across the
430 PWR holes and removing the 430 PWR jumper.
Press S1 or S2 to return to the Low Power Mode menu.
2.6 Demo Apps
Select this option from the main menu to bring up the Demo Apps sub-menu, which allows access to
various demo applications. Many of them require a USB connection. Use the wheel to select one of the
options and then press S1 to enter the application. Press S2 to return to the main menu.
Terminal Echo uses the CDC stack to communicate with a hyperterminal on the PC. USB Mouse uses the
HID stack to interface with the PC.
Terminal Echo: Select Terminal Echo to display an informational screen and connects to the PC. Make
sure to connect a USB cable from the USB port labeled "5529 USB" to the host PC. Open a hyperterminal
window and connect to the MSP430. Text that is typed in the hyperterminal window is echoed back to the
terminal and is displayed on the LCD screen of the Experimenter Board.
Press S2 to exit and return Demo Apps sub-menu.
USB Mouse: Select USB Mouse to display an informational screen and connects to the PC. Make sure to
connect a USB cable from the USB port labeled "5529 USB" to the host PC. The MSP430 now acts as the
mouse for the PC. Tilt the board to move the mouse around the screen, and press S1 to click.
Press S2 to exit and return Demo Apps sub-menu.
USB microSD: Select USB microSD to connect to the PC as a mass storage device. Make sure to
connect a USB cable from the USB port labeled "5529 USB" to the host PC. The MSP430 shows as an
external drive (or removable drive) for the PC.
Press S2 to return to the Demo Apps sub-menu.
Touch Graph: Select Touch Graph to display an instruction screen for a very short time and then launch
the application. Touch the capacitor key pads with varying pressures to see the varying capacitance being
displayed as bars with varying heights. Slide a finger over multiple capacitor key pads to observe the
change in heights of bars with respect to the current position of the finger and also the effect of
capacitance from neighboring pads.
Press S2 to exit and return Demo Apps sub-menu.
Touch Slide: Select Touch Slide to display an instruction screen for a very short time and then launch the
application. Touch the capacitor key pads with varying pressures to see the varying capacitance being
displayed as bars with varying heights. Slide a finger over multiple capacitor key pads to observe the
change in heights of bars with respect to the current position of the finger and also the effect of
capacitance from neighboring pads.
Press S2 to exit and return Demo Apps sub-menu.
Demo Cube: Select Demo Cube to launch the demo cube application. Read the instructions and press S1
to start the application. There are two modes. Use S1 to toggle between them.
In the first mode, the cube randomly rotates by itself. In the second mode, the cube can be rotated by
tilting the board. This mode uses the accelerometer.
Press S2 to exit and return Demo Apps sub-menu.
SLAU330A–May 2011–Revised June 2011 MSP-EXP430F5529 Experimenter Board 11
Submit Documentation Feedback
Copyright © 2011, Texas Instruments Incorporated
User Experience Software www.ti.com
2.7 SD Card Access
Select SD Card Access to access a microSD card placed in the SD card reader at the top of the board. If
no SD card is present, a warning screen is displayed. When an SD card is present, the screen displays a
list of the contents of the card. Directories are denoted by "". Use the wheel to scroll through the list
and select files or directories to open by pressing S1. When a file is open, use the wheel to scroll further
through the file. Press S2 to close the current file or directory.
Press S2 while in the root directory to return to the main menu.
2.8 Settings Menu
Select Settings to modify the display settings for the Experimenter Board. Use the wheel to select the
setting to modify and press S1 to enter.
Press S2 to return to the main menu.
Contrast: Modify the contrast of the LCD by turning the wheel. When first entering the menu, the contrast
remains unchanged for a few seconds to allow the user to read the instructions and then changes to the
setting for the current position of the wheel.
After the contrast is set at the desired level, press S2 to return to the Settings sub-menu.
Backlight: Modify the brightness of the backlight by turning the wheel. There are 12 brightness settings,
from having the backlight turned off up to full brightness.
After the backlight is set at the desired level, press S2 to return to the Settings sub-menu.
Calibrate Accel: Sets the "default" position for the accelerometer. An instruction screen is shown first. For
best results, set the board on a flat surface. Press S1 to start calibrations. The accelerometer readings at
that point in time are stored to flash and are subtracted from the subsequent accelerometer readings of
other applications like USB Mouse and USB Tilt Puzzle.
SW Version: Displays the current version of the firmware loaded on the Experimenter Board.
LEDs & Logo: Lights all the LEDs on the board. There are one red, one yellow, one green, and five blue
LEDs on the capacitive touch pads. This provides a method to determine whether or not all the LEDs are
in working condition.
The screen also displays the TI Bug and a USB Flash Drive logo on the screen.
12 MSP-EXP430F5529 Experimenter Board SLAU330A–May 2011–Revised June 2011
Submit Documentation Feedback
Copyright © 2011, Texas Instruments Incorporated
www.ti.com Software Installation and Debugging
3 Software Installation and Debugging
3.1 Software
Texas Instruments' Code Composer Studio (CCS) is an MSP430 integrated development environment
(IDE) designed specifically to develop applications and program MSP430 devices. CCS, CCS Core
Edition, and IAR Embedded Workbench can all be used to evaluate the example software for the
Experimenter Board. The compiler limitation of 8KB prevents IAR KickStart from being used for the
evaluation of the example software. The example software, titled "User Experience," is available online as
MSP-EXP430F5529 Experimenter Board User Experience Software.
3.2 Download the Required Software
Different development software tools are available for the MSP-EXP430F5529 Experimenter Board
development board. IAR Embedded Workbench KickStart and Code Composer Studio (CCS) are both
available in a free limited version. IAR Embedded Workbench KickStart allows 8KB of C-code compilation.
CCS is limited to a code size of 16KB. The software is available at www.ti.com/msp430.
The firmware is larger than IAR KickStart's 8KB limit, so a full license of IAR Workbench is required to
compile the application using IAR. A 30-day evaluation version of IAR is also available from
http://supp.iar.com/Download/SW/?item=EW430-EVAL. This document describes working with Code
Composer Studio (CCS).
There are many other compilers and integrated development environments (IDEs) for MSP430 that can be
used with the MSP-EXP430F5529 Experimenter Board, including Rowley Crossworks and MSPGCC.
However, the example project has been created using Code Composer Studio (CCS) and IAR. For more
information on the supported software and the latest code examples visit the online product folder
(http://focus.ti.com/docs/toolsw/folders/print/msp-exp430f5529.html).
3.3 Working With the Example Software
The MSP-EXP430F5529 example software is written in C and offers APIs to control the MSP430F5529
chip and external components on the MSP-EXP430F5529 Experimenter Board. New application
development can use this library for guidance.
The example software can be downloaded from the MSP-EXP430F5529 tools page, MSP-EXP430F5529
Experimenter Board User Experience Software. The zip package includes the MSP-EXP430F5529
example software. The code is ready for compilation and execution.
To modify, compile, and debug the example code the following steps should be followed:
1. If you have not already done so, download the sample code from the MSP-EXP430F5529 tools page.
2. Install 5529UE-x.xx-Setup.exe installation package to the PC.
3. Connect the MSP-FET430UIF programmer to the PC. If you have not already done so, install the
drivers for the programmer.
4. Connect one end of the 14-pin cable to JTAG programmer and another end to the JTAG header on the
board.
5. Open CCS and select a workspace directory (see Figure 3).
SLAU330A–May 2011–Revised June 2011 MSP-EXP430F5529 Experimenter Board 13
Submit Documentation Feedback
Copyright © 2011, Texas Instruments Incorporated
Software Installation and Debugging www.ti.com
Figure 3. Selecting a CCS Workspace
• Select Project > Import Existing CCS/CCE Eclipse Project.
• Browse to the extracted project directory. The project should now show up in the Projects list (see
Figure 4).
• Make sure the project is selected, and click Finish.
Figure 4. Opening Existing Project
The project is now open. To build, download, and debug the code on the device on the
MSP-EXP430F5529 Experimenter Board, select Target > Debug Active Project or click the green 'bug'
button.
14 MSP-EXP430F5529 Experimenter Board SLAU330A–May 2011–Revised June 2011
Submit Documentation Feedback
Copyright © 2011, Texas Instruments Incorporated
www.ti.com Software Installation and Debugging
You may be prompted to update the firmware on the MSP-FET430UIF programmer. Do not be concerned;
click the button that says Update, and the program download should continue as expected.
NOTE: To begin developing your own application, follow these steps:
1. Download and install a supported IDE:
Code Composer Studio – Free 16KB IDE: www.ti.com/ccs
IAR Embedded Workbench KickStart – Free 8KB IDE: www.ti.com/iar-kickstart
2. Connect the MSP-EXP430F5529 Experimenter Board "eZ-FET" USB to the PC.
3. Download and debug your application.
SLAU330A–May 2011–Revised June 2011 MSP-EXP430F5529 Experimenter Board 15
Submit Documentation Feedback
Copyright © 2011, Texas Instruments Incorporated
Software Installation and Debugging www.ti.com
3.3.1 Basic Code Structure
CTS "Capacitive Touch Sensing" library with functions related to the capacitive
touch pads.
CCS CCS-specific project files
CCS_Code_Size_Limited CCS-specific project files for 16kb code size limited version
F5xx_F6xx_Core_Lib Core Libraries
FatFs Stack for the FAT file system used by SD Card
IAR IAR-specific project files
MSP-EXP430F5529_HAL Provides an abstraction layer for events like button presses, etc.
HAL_AppUart Functions for controlling application UART
HAL_Board Experimenter Board port initialization and control
HAL_Buttons Driver for the buttons on the Experimenter Board
HAL_Cma3000 Functions required to use on-board accelerometer
HAL_Dogs102x6 Driver for the DOGS 102x64 display
HAL_Menu Used to create the menus for the example software and applications
HAL_SDCard Driver for the SD Card module
HAL_Wheel Driver for the scroll (thumb) wheel
USB USB stack for the Experimenter Board
UserExperienceDemo Files related to the example software provided with the board
5xx_ACTIVE_test Runs a RAM test
Clock Displays analog and digital clocks. Also provides a function to set time and
date.
Demo_Cube Displays a auto/manual rotating cube (uses accelerometer)
DemoApps Contains the demos for capacitive touch
EchoUsb HyperTerminal application
LPM Provides options for various low-power modes
MassStorage Use microSD as external storage on computer
menuGames Play LaunchPad Defender or Simon
Puzzle Play Tilt-puzzle
Mouse Use the Experimenter Board as a mouse
PMM Active low-power modes. Choose VCORE and MCLK settings.
PowerTest Test the current consumption of various low-power modes
Random Random number generator
SDCard Access microSD card contents on the Experimenter's Board
Settings Options to set various parameters like contrast, brightness, etc.
UserExperience.c Main MSP-EXP430F5529 Experimenter Board file
MSP-EXP430F5529 User Experience Manifest.pdf
readme.txt
16 MSP-EXP430F5529 Experimenter Board SLAU330A–May 2011–Revised June 2011
Submit Documentation Feedback
Copyright © 2011, Texas Instruments Incorporated
www.ti.com MSP-EXP430F5529 Hardware
4 MSP-EXP430F5529 Hardware
4.1 Hardware Overview
Figure 5 and Figure 6 show the functional blocks and connections of the MSP-EXP430F5529
Experimenter Board. The area of the PCB labeled as "eZ430-FET Emulator" and bordered by a thick
broken line on the PCB silk screen is an integrated TI Flash Emulation Tool (FET) which is connected to
the Experimenter Board by the jumpers on JP16. This module is similar to any eZ430 emulator, and
provides real-time in-system Spy-Bi-Wire programming and debugging via a USB connection to a PC.
Using the eZ430-FET Emulator module eliminates the need for using an external MSP430 Flash
Emulation Tool (MSP-FET430UIF). However, full speed 4-wire JTAG communication is only possible with
a MSP-FET430UIF connected to the "5529 JTAG" header. For additional details on the installation and
usage of the Flash Emulation Tool, Spy-Bi-Wire and JTAG, see the MSP430 Hardware Tools User's
Guide (SLAU278).
Figure 5. Simple Hardware Overview
SLAU330A–May 2011–Revised June 2011 MSP-EXP430F5529 Experimenter Board 17
Submit Documentation Feedback
Copyright © 2011, Texas Instruments Incorporated
MSP-EXP430F5529 Hardware www.ti.com
Figure 6. Hardware Block Details
4.2 Jumper Settings and Power
Figure 7 shows the common jumper settings, depending on the power source for the MSP-EXP430F5529
Experimenter Board.
Figure 7. Common Power Jumper Settings
18 MSP-EXP430F5529 Experimenter Board SLAU330A–May 2011–Revised June 2011
Submit Documentation Feedback
Copyright © 2011, Texas Instruments Incorporated
www.ti.com MSP-EXP430F5529 Hardware
There are also other jumpers available for current measurement, disconnection of certain peripherals, and
other advanced options (see Table 1). The black line on the board below the jumpers JP8 (LDO) and
JP11 (JTAG) indicates the default jumper position.
Table 1. MSP-EXP430F5529 Jumper Settings and Functionality
Header Functionality When Jumper Present Functionality When Jumper Absent
JP2 – POT Connects pin P8.0 to potentiometer Disconnects pin P8.0 to
potentiometer
JP3 – LED1 Connects pin P1.0 to LED1 Disconnects pin P1.0 to LED1
JP6 – 430 PWR Provides power to MSP430F5529. Also used to measure current MSP430F5529 is not powered.
consumption of the MSP430F5529.
NOTE: The two large vias near the
"430 PWR" label on the PCB
are connected to JP6 as well.
These vias can be used to
easily connect a test lead onto
the PCB for current
consumption measurement.
JP7 – SYS PWR Provides power to the entire MSP-EXP430F5529 board. Also MSP-EXP430F5529 Experimenter
used to measure current consumption of the entire board. Board system devices are not
powered.
JP8 – LDO Only applicable when powering via "5529 USB" connection. No connection to MSP430 VCC when
powered via "5529 USB". ALT (Default): Connects the alternate LDO (TPS73533) to the
MSP430 VCC.
INT: Connects the internal 'F5529 LDO to the MSP430 VCC.
JP11 – JTAG Only applicable when powering via JTAG connection. JTAG tool does NOT provide power
to system. EXT (Default): JTAG tool does NOT provide power to system.
INT: JTAG tool will provide power to system.
JP14 – RF PWR Connects system VCC to the RF headers: J12, J13, and RF2. RF headers: J12, J13, and RF2 do
not have power.
JP15 – USB PWR Connects USB 5-V power to MSP430F5529 and Alternate LDO USB 5-V power not connected to
(TPS73533). system.
JP16 – eZ-FET DVCC: Connects MSP430 V No connection between CC to eZ-FET
Connection MSP430F5529 and the eZ-FET. TXD / RXD: Connects UART between F5529 and eZ-FET.
RST / TEST: Connects Spy-Bi-Wire JTAG between F5529 and
eZ-FET.
SLAU330A–May 2011–Revised June 2011 MSP-EXP430F5529 Experimenter Board 19
Submit Documentation Feedback
Copyright © 2011, Texas Instruments Incorporated
MSP-EXP430F5529 Hardware www.ti.com
Figure 8 shows a visual diagram of the power connections for the MSP-EXP430F5529 Experimenter
Board. Care should be observed when using multiple power sources such as USB and a battery at the
same time. This could lead to the battery being charged if the power settings are not correct.
Figure 8. Visual Power Schematic
20 MSP-EXP430F5529 Experimenter Board SLAU330A–May 2011–Revised June 2011
Submit Documentation Feedback
Copyright © 2011, Texas Instruments Incorporated
www.ti.com MSP-EXP430F5529 Hardware
Figure 9 shows a method of connecting a multi-meter to the MSP-EXP430F5529 to measure the current
of the MSP430F5529.
Figure 9. MSP430 Current Measurement Connection
4.3 eZ-FET Emulator
The connection between the eZ-FET emulator and the MSP-EXP430F5529 can be opened by removing
the jumpers on JP16. This is necessary only to ensure there is no interaction between the two
sub-systems. The eZ-FET Emulator can program other eZ430 tools such as the eZ430-F2013 target
board as well. A six-pin header on J17 would need be installed on the PCB for this feature.
The USB interface on the eZ-FET emulator also allows for UART communication with a PC host, in
addition to providing power to Experimenter Board when the power switch is set to 'eZ'. The USCI module
in the MSP430F5529 supports the UART protocol that is used to communicate with the TI TUSB3410
device on the eZ-FET emulator for data transfer to the PC.
4.4 MSP-EXP430F5529 Hardware Components
4.4.1 Dot-Matrix LCD
The EA DOGS102W-6 is a dot-matrix LCD with a resolution of 102x64 pixels. The LCD has a built-in
back-light driver that can be controlled by a PWM signal from the MSP430F5529, pin P7.6. The
MSP430F5529 communicates with the EA DOGS102W-6 via an SPI-like communication protocol. To
supplement the limited set of instructions and functionalities provided by the on-chip LCD driver, an LCD
driver has been developed for the MSP430F5529 to support additional functionalities such as font set and
graphical utilities. More information on the LCD can be obtained from the manufacturer's data sheet.
SLAU330A–May 2011–Revised June 2011 MSP-EXP430F5529 Experimenter Board 21
Submit Documentation Feedback
Copyright © 2011, Texas Instruments Incorporated
MSP-EXP430F5529 Hardware www.ti.com
4.4.2 Push Buttons, Potentiometer, and LEDs
Table 2 describes the pin connections for the potentiometer, push-button switches, and the on-board
LEDs.
Table 2. Push Buttons, Potentiometer, and LED
Connections
Peripheral Pin Connection
Potentiometer Wheel P8.0
Switch 1 (S1) P1.7
Switch 2 (S2) P2.2
RESET Switch (S3) RST / NMI
LED1 P1.0
LED2 P8.1
LED3 P8.3
Capacitive Touch Pad 1 (Cross) P1.1
Capacitive Touch Pad 2 (Square) P1.2
Capacitive Touch Pad 3 (Octagon) P1.3
Capacitive Touch Pad 4 (Triangle) P1.4
Capacitive Touch Pad 5 (Circle) P1.5
4.4.3 Wireless Evaluation Module Interface
Included in the communication peripherals are the headers that support the CC-EM boards from TI. The
transceiver modules connect to the USCI of the MSP430F5529 configured in SPI mode using the UCB0
peripheral. Libraries that interface the MSP430 to these transceivers are available at www.ti.com/msp430
under the Code Examples tab. The RF PWR jumper must be populated to provide power to the EM
daughterboard. The following radio daughter cards are compatible with the MSP-EXP430F5529
Experimenter Board:
• CC1100EMK/CC1101EMK – Sub-1-GHz radio
• CC2500EMK – 2.4-GHz radio
• CC2420EMK/CC2430EMK – 2.4-GHz 802.15.4 [SoC] radio
• CC2520EMK/CC2530EMK – 2.4-GHz 802.15.4 [SoC] radio
• CC2520 + CC2591 EM (if R4 and R8 0-Ω resistors are connected)
NOTE: Future evaluation boards may also be compatible with the header connections.
4.4.4 eZ430-RF2500T Interface
The eZ430-RF2500T module can be attached to the MSP-EXP430F5529 Experimenter Board in one of
two ways – through an 18-pin connector (J12 – eZ RF) or a 6-pin connector (J13 – eZ RF Target). The
pins on the eZ430-RF2500T headers are multiplexed with the pins on the CC-EM headers, which allows
the EZ430-RF2500T module to behave identically to a CC-EM daughterboard. Power must be provided to
the EZ430-RF2500T module by setting the jumper RF PWR (JP14). The eZ430-RF2500T connection
should always be made with the antenna facing off of the board. For more information on the connections
to the required eZ430-RF2500T, see the eZ430-RF2500 Development Tool User's Guide (SLAU227),
available through www.ti.com/ez430.
22 MSP-EXP430F5529 Experimenter Board SLAU330A–May 2011–Revised June 2011
Submit Documentation Feedback
Copyright © 2011, Texas Instruments Incorporated
www.ti.com MSP-EXP430F5529 Hardware
4.4.5 Three-Axis Accelerometer
The MSP-EXP430F5529 Experimenter Board includes a VTI digital three-axis accelerometer (part number
CMA3000-D01). The accelerometer supports SPI communication and outputs data for each X, Y and Z
axis. The accelerometer is powered through pin P3.6. This interface, especially in conjunction with other
on-board interfaces such as the LCD, enables several potential applications such as USB mouse
movement emulation and tilt sensing. The example software used the accelerometer for the Tilt Puzzle,
Demo Cube, and USB Mouse. For more information on the accelerometer chip, see the manufacturer's
data sheet (http://www.vti.fi).
4.4.6 Pin Access Headers
The MSP-EXP430F5529 Experimenter Boards includes three headers (J4, J5, and J12) that can be used
as additional connections to external hardware or for signal analysis during firmware development. All pins
except the GND pin are internally selectable as either general purpose input/output pins or as described in
the device datasheet.
Table 3. Pinning Mapping for Header J4
Pin Description Port Pin Port Pin Pin Description
Vcc VCC P6.6 CB6 / A6
UCA1RXD / UCA1SOMI P4.5 P8.1 GPIO – LED2
UCA1TXD / UCA1SIMO P4.4 P8.2 GPIO – LED3
GPIO P4.6 P8.0 GPIO – POT
GPIO P4.7 P4.5 UCA1RXD / UCA1SOMI
A9 / VREF- / VeREF- P5.1 P4.4 UCA1TXD / UCA1SIMO
GND GND P6.7 CB7 / A7
Table 4. Pin Mapping for Header J5
Pin Description Port Pin Port Pin Pin Description
VCC VCC P7.0 CB8 / A12
UCB1SOMI / UCB1SCL - SD P4.2 P7.1 CB9 / A13
UCB1SIMO / UCB1SDA - LCD/SD P4.1 P7.2 CB10 / A14
UCB1CLK / UCA1STE - LCD/SD P4.3 P7.3 CB11 / A15
UCB1STE / UCA1CLK - RF P4.0 P4.1 UCB1SIMO / UCB1SDA - LCD/SD
TB0OUTH / SVMOUT - SD P3.7 P4.2 UCB1SOMI / UCB1SCL - SD
GND GND P7.7 TB0CLK / MCLK
Table 5. Pin Mapping for Header J12
Pin Description Port Pin Port Pin Pin Description
(RF_STE) P2.6 P3.0 (RF_SIMO)
(RF_SOMI) P3.1 P3.2 (RF_SPI_CLK)
TA2.0 P2.3 P2.1 TA1.2
TB0.3 P7.5 GND GND
GPIO P4.7 P2.4 TA2.1
(RXD) P4.5 P4.6 GPIO
(TXD) P4.4 P4.0 UCx1xx
(LED1) P1.0 P2.0 TA1.1
GND GND RF_PWR RF_PWR
SLAU330A–May 2011–Revised June 2011 MSP-EXP430F5529 Experimenter Board 23
Submit Documentation Feedback
Copyright © 2011, Texas Instruments Incorporated
Frequently Asked Questions, References, and Schematics www.ti.com
5 Frequently Asked Questions, References, and Schematics
5.1 Frequently Asked Questions
1. Which devices can be programmed with the Experimenter Board?
The MSP-EXP430F5529 board is designed specifically to demonstrate the MSP430F5529.
2. The MSP430F5529 is no longer accessible via JTAG. Is something wrong with the device?
Verify that the jumpers are configured correctly. See Section 4 for jumper configuration.
Verify that the target device is powered properly.
If the target is powered locally, verify that the supplied VCC is sufficient to power the board. Check the
device data sheet for the specification.
3. I did every step in the previous question but still could not use or communicate with the device.
Improper programming of the device could lead to a JTAG total lockup condition. The cause of this
problem might be an incorrect device selection when creating a new project in CCS (select
MSP430F5529) or programming the device without a stable power source (low battery, switching the
Power Selector while programming, or absence of the MSP430 power jumper JP6 during
programming).
To solve this, completely reset the device. First unplug all power sources and connections (JTAG and
USB cables). Set the Power Selector Switch to FET mode. Use a jumper cable to briefly short one of
the GND test points with the 430 PWR test point. The device should now be released from the lockup
state.
4. Does the Experimenter board protect against blowing the JTAG fuse of the target device?
No. Fuse blow capability is inherent to all flash-based MSP430 devices to protect user's intellectual
property. Care must be taken to avoid the enabling of the fuse blow option during programming,
because blowing the fuse would prevent further access to the MSP430 device via JTAG.
5. I am measuring system current in the range of 30 mA, is this normal?
The LCD and the LCD backlight require a large amount of current (approximately 20 mA to 25 mA) to
operate. This results in a total system current consumption in the range of 30 mA. If the LCD backlight
is on, 30 mA is considered normal.
To ensure the board is OK, disable the LCD and the LCD backlight and measure the current again.
The entire board current consumption should not exceed 10 mA at this state. Note that the current
consumption of the board could vary greatly depending on the optimization of the board configurations
and the applications.
The expected current consumption for the MSP430F5529 in standby mode (LPM3), for example, is
~2 μA. Operating at 1 MHz, the total current consumption should not exceed ~280 μA.
6. I have trouble reading the LCD clearly. Why is the LCD contrast setting so low?
The LCD contrast is highly dependent on the voltage of the system. Changing power source from USB
(3.3 V) to batteries (~3 V) could drastically reduce the contrast. Fortunately, the LCD driver supports
adjustable contrast. The specific instruction can be found in the LCD user's guide. The
MSP-EXP430F5529 software also provides the function to adjust the contrast using the wheel (see
Section 2.8).
7. When I run the example code, nothing happens on the LCD.
Verify that all jumpers are installed correctly and the 14-pin JTAG cable are properly connected.
5.2 References
• MSP430x5xx/MSP430x6xx Family User's Guide (SLAU208)
• Code Composer Studio (CCStudio) Integrated Development Environment (IDE)
(http://focus.ti.com/docs/toolsw/folders/print/msp-ccstudio.html)
• MSP430 Interface to CC1100/2500 Code Library (PDF: SLAA325) (Associated Files: SLAA325.ZIP)
24 MSP-EXP430F5529 Experimenter Board SLAU330A–May 2011–Revised June 2011
Submit Documentation Feedback
Copyright © 2011, Texas Instruments Incorporated
www.ti.com Frequently Asked Questions, References, and Schematics
5.3 Schematics and BOM
The following pages show the schematics and BOM. In addition, the original Eagle CAD schematics and
Gerber files are available for download (SLAR055).
Figure 10. Schematics (1 of 7)
SLAU330A–May 2011–Revised June 2011 MSP-EXP430F5529 Experimenter Board 25
Submit Documentation Feedback
Copyright © 2011, Texas Instruments Incorporated
Frequently Asked Questions, References, and Schematics www.ti.com
Figure 11. Schematics (2 of 7)
26 MSP-EXP430F5529 Experimenter Board SLAU330A–May 2011–Revised June 2011
Submit Documentation Feedback
Copyright © 2011, Texas Instruments Incorporated
www.ti.com Frequently Asked Questions, References, and Schematics
Figure 12. Schematics (3 of 7)
SLAU330A–May 2011–Revised June 2011 MSP-EXP430F5529 Experimenter Board 27
Submit Documentation Feedback
Copyright © 2011, Texas Instruments Incorporated
Frequently Asked Questions, References, and Schematics www.ti.com
Figure 13. Schematics (4 of 7)
28 MSP-EXP430F5529 Experimenter Board SLAU330A–May 2011–Revised June 2011
Submit Documentation Feedback
Copyright © 2011, Texas Instruments Incorporated
www.ti.com Frequently Asked Questions, References, and Schematics
Figure 14. Schematics (5 of 7)
SLAU330A–May 2011–Revised June 2011 MSP-EXP430F5529 Experimenter Board 29
Submit Documentation Feedback
Copyright © 2011, Texas Instruments Incorporated
Frequently Asked Questions, References, and Schematics www.ti.com
Figure 15. Schematics (6 of 7)
30 MSP-EXP430F5529 Experimenter Board SLAU330A–May 2011–Revised June 2011
Submit Documentation Feedback
Copyright © 2011, Texas Instruments Incorporated
www.ti.com Frequently Asked Questions, References, and Schematics
Figure 16. Schematics (7 of 7)
SLAU330A–May 2011–Revised June 2011 MSP-EXP430F5529 Experimenter Board 31
Submit Documentation Feedback
Copyright © 2011, Texas Instruments Incorporated
Frequently Asked Questions, References, and Schematics www.ti.com
Table 6. Bill of Materials
Part Value Package Type Device
C1 47pF 0805
C2 12pF 0805
C3 DNP 0603
C4 12pF 0805
C5 10μF 0805
C6 47pF 0805
C7 100nF 0805
C8 220n 0603
C9 220n 0603
C10 10uF/6,3V 1210
C11 100n 0603
C12 100n 0805
C13 100n 0805
C14 DNP 0603
C15 10uF/6,3V 1210
C16 100n 0805
C17 470n 0805
C18 10μF 0805
C19 100nF 0805
C20 .1u 0603
C21 .1u 0603
C22 1μF 0805
C23 1μF 0805
C24 1μF 0805
C25 1μF 0805
C26 1μF 0805
C27 1μF 0805
C28 4.7uF 0805
C29 10nF 0805
C30 1μF 0805
C31 .1u 0603
C32 4.7u 0805
C33 0.1u 0603
C34 4u7 0603
C35 10p 0603
C36 10p 0603
C37 10n 0402
C38 33p 0402
C39 33p 0402
C40 1u/6.3V 0603
C41 100n 0402
C42 1u/6.3V 0603
C43 100n 0402
C44 1u/6.3V 0603
C45 22p 0402
C46 22p 0402
C47 100n 0402
C48 100n 0402
C49 100n 0402
C50 10uF/6,3V 1210
CON1 8PIN_SM_MA_HEADER HEADER 2x4 MALE .1" SMD
CON2 8PIN_SM_MA_HEADER HEADER 2x4 MALE .1" SMD
32 MSP-EXP430F5529 Experimenter Board SLAU330A–May 2011–Revised June 2011
Submit Documentation Feedback
Copyright © 2011, Texas Instruments Incorporated
www.ti.com Frequently Asked Questions, References, and Schematics
Table 6. Bill of Materials (continued)
Part Value Package Type Device
CON3 8PIN_SM_MA_HEADER HEADER 2x4 MALE .1" SMD
D1 LLSD103A-7 Mini MELF
D2 1N4148 Micro MELF SOD110-R
J1 103308-2 14-Pin Male JTAG Connector
JP2 POT_JMP HEADER 1x2 MALE .1" TH JP1E\SMALL_PIN
JP3 LED_JMP HEADER 1x2 MALE .1" TH JP1E\SMALL_PIN
J4 HEADER - F5529 PIN ACCESS HEADER 2x7 MALE .1" TH
J5 HEADER - F5529 PIN ACCESS HEADER 2x7 MALE .1" TH
JP6 430_PWR HEADER 1x2 MALE .1" TH JP1E
JP7 SYS_PWR HEADER 1x2 MALE .1" TH JP1E
JP8 LDO_PWR_SEL HEADER 1x3 MALE .1" TH PINHD-1X3/SMALL_PIN
J9 22-03-5035 MOLEX 3-PIN MALE HEADER 22-03-5035
J10 HEADER - PWR HEADER 1x3 MALE .1" TH PINHD-1X3
JP11 JTAG_PWR_SEN HEADER 1x3 MALE .1" TH PINHD-1X3/SMALL_PIN
J12 eZ-RF1 HEADER - RF2500 HEADER 2x9 MALE .1" TH
J13 6-Pin Male eZ430 Connector 6-Pin Male eZ430 Connector SL127L6TH
JP14 RF_PWR HEADER 1x2 MALE .1" TH JP1E
JP15 USB_PWR HEADER 1x2 MALE .1" TH JP1E
JP16 eZ430-FET_JMP HEADER 2x5 MALE .1" TH JP5Q
J17 6-Pin Male eZ430 Connector 6-Pin Male eZ430 Connector SL127L6TH
LED1 LEDCHIPLED_0603 0603 LEDCHIPLED_0603
LED2 LEDCHIPLED_0603 0603 LEDCHIPLED_0603
LED3 LEDCHIPLED_0603 0603 LEDCHIPLED_0603
LED4 OSRAM TOPLED Santana Blue LED 0805 (Surface Mount Bottom) OSRAM TOPLED Santana Blue LED
LED5 OSRAM TOPLED Santana Blue LED 0805 (Surface Mount Bottom) OSRAM TOPLED Santana Blue LED
LED6 OSRAM TOPLED Santana Blue LED 0805 (Surface Mount Bottom) OSRAM TOPLED Santana Blue LED
LED7 OSRAM TOPLED Santana Blue LED 0805 (Surface Mount Bottom) OSRAM TOPLED Santana Blue LED
LED8 OSRAM TOPLED Santana Blue LED 0805 (Surface Mount Bottom) OSRAM TOPLED Santana Blue LED
LED9 LEDCHIPLED_0603 0603 LED_0603D0603
PAD1 CAP_TOUCH_PAD CAP_TOUCH_PAD PROJECT7264_CC430_PAD
PAD2 CAP_TOUCH_PAD CAP_TOUCH_PAD PROJECT7264_CC430_PAD
PAD3 CAP_TOUCH_PAD CAP_TOUCH_PAD PROJECT7264_CC430_PAD
PAD4 CAP_TOUCH_PAD CAP_TOUCH_PAD PROJECT7264_CC430_PAD
PAD5 CAP_TOUCH_PAD CAP_TOUCH_PAD PROJECT7264_CC430_PAD
POT1 EVL-HFKA05B54 POT EVL-HFKA05B54
Q1 MS3V-T1R 32.768kHz CL Clock Crystal 32kHz F20XX_PIR_DEMO_&_EVAL_CM200T
Q2 SMD Oscillator 4MHz SMD Oscillator 4MHz QUARZ_HC49_4P-1
Q3 SMD Oscillator 12MHz SMD Oscillator 12MHz XTL_FT7AFT10A
R1 47k 0603 R-US_R0603
R2 0R 0603 R-US_R0603
R3 470R 0603 R-US_R0603
R4 470R 0603 R-US_R0603
R5 470R 0603 R-US_R0603
R6 47k 0603 R-US_R0603
R7 680 0805 RES0805
R8 680 0805 RES0805
R9 680 0805 RES0805
R10 680 0805 RES0805
R11 680 0805 RES0805
R12 100K 0603 R-US_R0603
R13 100k 0603 R-US_R0603
SLAU330A–May 2011–Revised June 2011 MSP-EXP430F5529 Experimenter Board 33
Submit Documentation Feedback
Copyright © 2011, Texas Instruments Incorporated
Frequently Asked Questions, References, and Schematics www.ti.com
Table 6. Bill of Materials (continued)
Part Value Package Type Device
R14 100k 0603 R-US_R0603
R15 100K 0603 R-US_R0603
R16 100k 0603 R-US_R0603
R17 47k 0603 R-US_R0603
R18 47k 0603 R-US_R0603
R19 0 0603 R-US_R0603
R20 100k 0603 R-US_R0603
R21 36k 1% 0603 R-US_R0603
R22 27R 0603 R-US_R0603
R23 27R 0603 R-US_R0603
R24 1M 0603 R-US_R0603
R25 1k4 0603 R-US_R0603
R26 100R 0603 R-US_R0603
R27 33k 0603 R-US_R0603
R28 47k 0402 R_SMDR0402
R29 47k 0402 R_SMDR0402
R30 47k 0402 R_SMDR0402
R31 100R 0402 R_SMDR0402
R32 100R 0402 R_SMDR0402
R33 270 0402 R_SMDR0402
R34 DNP 0402 R_SMDR0402
R35 100R 0402 R_SMDR0402
R36 100R 0402 R_SMDR0402
R37 6k8 0402 R_SMDR0402
R38 3k3 0402 R_SMDR0402
R39 10k 0402 R_SMDR0402
R40 15k 0402 R_SMDR0402
R41 33k 0402 R_SMDR0402
R42 1k5 0402 R_SMDR0402
R43 33R 0402 R_SMDR0402
R44 DNP (47k) 0402 R_SMDR0402
R45 DNP (47k) 0402 R_SMDR0402
R46 33R 0402 R_SMDR0402
R47 100k/1% 0402 R_SMDR0402
R48 33k 0402 R_SMDR0402
R49 3k3 0402 R_SMDR0402
R50 100k/1% 0402 R_SMDR0402
R51 3k3 0402 R_SMDR0402
R52 100R 0402 R_SMDR0402
R53 1k5 0402 R_SMDR0402
R54 1k5 0402 R_SMDR0402
RF1 CCxxxx RF EVM HEADER CCXXXX_20PIN TFM-110-02-SM-D-A-K
RF2 CCxxxx RF EVM HEADER CCXXXX_20PIN TFM-110-02-SM-D-A-K
S1 USER1 PUSHBUTTON BUTTON EVQ-11L05R
S2 USER2 PUSHBUTTON BUTTON EVQ-11L05R
S3 F5529 RESET PUSHBUTTON BUTTON EVQ-11L05R
S4 F5529 USB BSL PUSHBUTTON BUTTON EVQ-11L05R
SW1 POWER SELECT SWITCH DP3T_SWITCH JS203011CQN
TP1 F5529 VREF+ TEST POINT TEST_POINT -
TP2 F5529 VCORE TEST POINT TEST_POINT -
TP3 CC430 EM TEST POINT TEST_POINT -
34 MSP-EXP430F5529 Experimenter Board SLAU330A–May 2011–Revised June 2011
Submit Documentation Feedback
Copyright © 2011, Texas Instruments Incorporated
www.ti.com Frequently Asked Questions, References, and Schematics
Table 6. Bill of Materials (continued)
Part Value Package Type Device
TP4 CC430 EM TEST POINT TEST_POINT -
TP5 CC430 EM TEST POINT TEST_POINT -
TP6 CC430 EM TEST POINT TEST_POINT -
TP7 CC430 EM TEST POINT TEST_POINT -
TP8 CC430 EM TEST POINT TEST_POINT -
TP9 eZ430 F16x TEST POINT (EZ_VBUS) TEST_POINT -
TP10 eZ430 F16x TEST POINT (RESET) TEST_POINT -
TP11 eZ430 F16x TEST POINT (GND) TEST_POINT -
TP12 eZ430 F16x TEST POINT (HTCK) TEST_POINT -
TP13 eZ430 F16x TEST POINT (HTMS) TEST_POINT -
TP14 eZ430 F16x TEST POINT (HTDI) TEST_POINT -
TP15 eZ430 F16x TEST POINT (HTDO) TEST_POINT -
U1 F5529 - MSP430F5529 80-LQFP MSP430F5529IPNR
U2 3-AXIS SPI/I2C ACCELEROMETER SMD CMA3000 CMA3000-D01
U3 102x64 LCD DISPLAY EA DOGS102-6 EA DOGS102-6
U3 LED BACKLIGHT EA DOGS102-6 EA LED39x41-W
U4 Alternate LDO - TPS73533 SC70-5 TPS73533DRBT
U5 LED Backlight Current Source - TPS75105 SON-10 TPS75105DSKR
U6 F5529 USB ESD Protection - TPD2E001 SOT-5 TPD2E001DRLR
U7 eZ430 - MSP430F16x 64-LQFP MSP430F1612IPMR
U8 eZ430 Level Translator - TXS0104E 14-TSSOP TXS0104EPWR
U9 eZ430 LDO - TPS77301 8-MSOP TPS77301DGK
U10 eZ430 - TUSB3410 32-LQFP TUSB3410VF
U11 eZ430 USB ESD Protection - TPD2E001 SOT-5 TPD2E001DRLR
U12 eZ430 EEPROM - CAT24C128YI 8-TSSOP CAT24C128YI
USB1 F5529 USB Mini-USB Through Hole 54819-0519
USB2 eZ430 USB Mini-USB Through Hole 54819-0519
X1 microSD Card Holder microSD Card Holder 502702-0891
SLAU330A–May 2011–Revised June 2011 MSP-EXP430F5529 Experimenter Board 35
Submit Documentation Feedback
Copyright © 2011, Texas Instruments Incorporated
IMPORTANT NOTICE
Texas Instruments Incorporated and its subsidiaries (TI) reserve the right to make corrections, modifications, enhancements, improvements,
and other changes to its products and services at any time and to discontinue any product or service without notice. Customers should
obtain the latest relevant information before placing orders and should verify that such information is current and complete. All products are
sold subject to TI’s terms and conditions of sale supplied at the time of order acknowledgment.
TI warrants performance of its hardware products to the specifications applicable at the time of sale in accordance with TI’s standard
warranty. Testing and other quality control techniques are used to the extent TI deems necessary to support this warranty. Except where
mandated by government requirements, testing of all parameters of each product is not necessarily performed.
TI assumes no liability for applications assistance or customer product design. Customers are responsible for their products and
applications using TI components. To minimize the risks associated with customer products and applications, customers should provide
adequate design and operating safeguards.
TI does not warrant or represent that any license, either express or implied, is granted under any TI patent right, copyright, mask work right,
or other TI intellectual property right relating to any combination, machine, or process in which TI products or services are used. Information
published by TI regarding third-party products or services does not constitute a license from TI to use such products or services or a
warranty or endorsement thereof. Use of such information may require a license from a third party under the patents or other intellectual
property of the third party, or a license from TI under the patents or other intellectual property of TI.
Reproduction of TI information in TI data books or data sheets is permissible only if reproduction is without alteration and is accompanied
by all associated warranties, conditions, limitations, and notices. Reproduction of this information with alteration is an unfair and deceptive
business practice. TI is not responsible or liable for such altered documentation. Information of third parties may be subject to additional
restrictions.
Resale of TI products or services with statements different from or beyond the parameters stated by TI for that product or service voids all
express and any implied warranties for the associated TI product or service and is an unfair and deceptive business practice. TI is not
responsible or liable for any such statements.
TI products are not authorized for use in safety-critical applications (such as life support) where a failure of the TI product would reasonably
be expected to cause severe personal injury or death, unless officers of the parties have executed an agreement specifically governing
such use. Buyers represent that they have all necessary expertise in the safety and regulatory ramifications of their applications, and
acknowledge and agree that they are solely responsible for all legal, regulatory and safety-related requirements concerning their products
and any use of TI products in such safety-critical applications, notwithstanding any applications-related information or support that may be
provided by TI. Further, Buyers must fully indemnify TI and its representatives against any damages arising out of the use of TI products in
such safety-critical applications.
TI products are neither designed nor intended for use in military/aerospace applications or environments unless the TI products are
specifically designated by TI as military-grade or "enhanced plastic." Only products designated by TI as military-grade meet military
specifications. Buyers acknowledge and agree that any such use of TI products which TI has not designated as military-grade is solely at
the Buyer's risk, and that they are solely responsible for compliance with all legal and regulatory requirements in connection with such use.
TI products are neither designed nor intended for use in automotive applications or environments unless the specific TI products are
designated by TI as compliant with ISO/TS 16949 requirements. Buyers acknowledge and agree that, if they use any non-designated
products in automotive applications, TI will not be responsible for any failure to meet such requirements.
Following are URLs where you can obtain information on other Texas Instruments products and application solutions:
Products Applications
Audio www.ti.com/audio Communications and Telecom www.ti.com/communications
Amplifiers amplifier.ti.com Computers and Peripherals www.ti.com/computers
Data Converters dataconverter.ti.com Consumer Electronics www.ti.com/consumer-apps
DLP® Products www.dlp.com Energy and Lighting www.ti.com/energy
DSP dsp.ti.com Industrial www.ti.com/industrial
Clocks and Timers www.ti.com/clocks Medical www.ti.com/medical
Interface interface.ti.com Security www.ti.com/security
Logic logic.ti.com Space, Avionics and Defense www.ti.com/space-avionics-defense
Power Mgmt power.ti.com Transportation and www.ti.com/automotive
Automotive
Microcontrollers microcontroller.ti.com Video and Imaging www.ti.com/video
RFID www.ti-rfid.com Wireless www.ti.com/wireless-apps
RF/IF and ZigBee® Solutions www.ti.com/lprf
TI E2E Community Home Page e2e.ti.com
Mailing Address: Texas Instruments, Post Office Box 655303, Dallas, Texas 75265
Copyright © 2011, Texas Instruments Incorporated
STK525
.............................................................................................
Hardware User Guide
STK525 Hardware User Guide User Guide 1
7608A–AVR–04/06
Section 1
Introduction ........................................................................................... 1-3
1.1 Overview ...................................................................................................1-3
1.2 STK525 Starter Kit Features .....................................................................1-4
Section 2
Using the STK525................................................................................. 2-6
2.1 Overview ...................................................................................................2-6
2.2 Power Supply ............................................................................................2-7
2.3 RESET ....................................................................................................2-10
2.4 AT90USBxxx AVR Microcontroller..........................................................2-11
2.5 Serial Links .............................................................................................2-11
2.6 On-board Resources...............................................................................2-14
2.7 STK500 Resources .................................................................................2-19
2.8 In-System Programming .........................................................................2-20
2.10 Test Points ..............................................................................................2-23
2.11 Configuration Pads .................................................................................2-24
2.12 Solder Pads ............................................................................................2-25
Section 3
Troubleshooting Guide ....................................................................... 3-26
Section 4
Technical Specifications ..................................................................... 4-27
Section 5
Technical Support............................................................................... 5-28
Section 6
Complete Schematics......................................................................... 6-29
STK525 Hardware User Guide 1-3
7608A–AVR–04/06
Section 1
Introduction
Congratulation for acquiring the AVR® STK525 Starter Kit. This kit is designed to give
designers a quick start to develop code on the AT90USBxxx and for prototyping and
testing of new designs.
1.1 Overview
This document describes the STK525 dedicated to the AT90USBxxx AVR
microcontroller. This board is designed to allow an easy evaluation of the product using
demonstration software.
To complement the evaluation and enable additional development capability, the
STK525 can be plugged into the Atmel STK500 Starter Kit Board in order to use the
AT90USBxxx with advanced features such as variable VCC, variable VRef, variable
XTAL, etc. and supports all AVR development tools.
To increase its demonstrative capabilities, this stand alone board has numerous onboard
resources (USB, RS232, joystick, data-flash, microphone and temperature
sensor).
This user guide acts as a general getting started guide as well as a complete technical
reference for advanced users.
Introduction
1-4 STK525 Hardware User Guide
7608A–AVR–04/06
Figure 1-1 . STK525 Board
1.2 STK525 Starter Kit Features
The STK525 provides the following features:
AT90USBxxx TQFP device (2.7V 1.0
STK500 Expand connectors
A4
Tuesday , January 17, 2006 2 4
STKNC
Important:
Def ault conf iguration: open
reserv ed f or f uture mass storage extension
3.3V
SP3
STK525 MEZZANINE FOR STK500
NRST
STKNC
VTG
XTAL1
PA0
R8
2k
PB7
PB3
PB5
PD5
PD7
PB1
PB6
PD1
PD3
PB2
PB4
PD6
PB0
PD2
PD4
C12
1nF
PD0
1 2 AREF
JP3
STK AREF
VTG
REF
XT1 XT2
PE[2..0]
VTG VTG
PE[2..0]
VTG
PC[7..0] PC[7..0]
PB[7..0]
PD[7..0]
PA[7..0] PA[7..0]
PA5
PA7 PA6
PA1
PA3
PA4
1 2
JP1
STK X1
PA2
1 2
JP2
STK X2
PB[7..0]
Complete Schematics
STK525 Hardware User Guide 6-33
7608A–AVR–04/06
Figure 6-3 . Schematics, 3 of 5
Data Flash
3.3V
LEDs
3.3V
PF[7..0]
DECOUPLING CAPACITOR
CLOSE TO THE CONNECTOR
R19
POT 100k
Select
5
Lef t
7
Up
3
Right
6
Down
4
Com1
1
Com2
2
SW3
TPA511G
PF[7..0]
Temp Sensor
PB[7..0]
R18
NCP18WF104J03RB
5 9 4 8 3 7 2 6 1
10
11
P1
SUB-D9 FEMALE
RS232
1234
J7
PF Spare (Not mounted)
RS232 Interface
JTAG Interface
RS-CTS
3.3V
Serial ISP
Interface
PE[7..0]
CP1
VCC
R16
100k
STK525 MEZZANINE FOR STK500
3.3V VCC
BUSY
1
RESET
2
WP
3 VCC
6
GND
7
CS
11
SCK
12
SI
13
SO
14
U2
AT45DB321C TSOP28
Microphone Preamplifier Interface
PF0
VCC
PB[7..0]
CTS
Title
Size Document Number Rev
Date: Sheet of
1.0
Interf aces
A4
Tuesday , January 17, 2006 3 4
C20
100nF
RTS
CP2
R23 100k
.
11
.
12
.
10
.
9
.
8
.
7
.
13
.
14
.
15
.
16
C1+
1
V+
2
C1-
3
C2+
4
C2-
5
V-
6
TTL RS 232
GND
VCC
U3
MAX3232
RS232 BUFFER
C17
100nF
C16
100nF
C18
100nF
PF1
C19
100nF
PD2 RxD
DECOUPLING CAPACITOR
CLOSE TO THE DEVICE
RS-TxD
RS-RxD
PD[7..0]
VCC
PF0
1
TP4
Mic
VCC
DECOUPLING CAPACITOR
CLOSE TO THE DEVICE
C15
100nF
PF1
SP4
PF2
SP5
VCC
Caution DataFlash
Fix 3V Power supply Only
PF3
PB[7..0]
C26
100nF
RESET
R11
100k
CP3
DECOUPLING CAPACITOR
CLOSE TO THE CONNECTOR
PB5
PDO
1
VCC
2
SCK
3
PDI
4
RESET
5
GND
6
CON 2x3
J5
ISP CON
TCK
1
GND
2
TDO
3
VCC
4
TMS
5
RESET
6
VCC
7
n.c.
8
TDI
9
GND
10
CON 2x5
J4
JTAG CON
C21
100nF
C23
100nF
PD1
PF4
PF6
PF7
PF5
RESET
PB1
R17
0
PB2
PB3
3.3V
PB6
PD0
VCC
PD3 TXD
SP7
PB7
5
6
7
8 4
+
-
U4B
LMV358
3
2
1
8 4
+
-
U4A
LMV358
R27 0
R26 22k
R25 10k
R24 100k
PB4
+
C25
1uF
R21
100k
R28
100k
C22 220pF
+
C24 4.7uF
3.3V
R20
2.2k
MIC1
MICROPHONE
R22
100k
DECOUPLING CAPACITOR
CLOSE TO THE DEVICE
PE4
PB1
R10
100k
PF2
In-line Grouped LEDs
RESET
TOPLED LP M676 D2
LED 0 (green)
TOPLED LP M676 D3
LED 1 (green)
TOPLED LP M676 D4
LED 2 (green)
TOPLED LP M676 D5
LED 3 (green)
PB2
1k R12
1k R13
PE5
1k R14
1k R15
PD4
PB3
PD5
PD7
PD[7..0]
PD6
SP8
RS-RTS
Joystick Interface
Complete Schematics
6-34 STK525 Hardware User Guide
7608A–AVR–04/06
Figure 6-4 . Schematics, 4 of 5
-
C30
4.7uF
VTG
IN
GND
OUT
U8
LM340
VBUS generator f or OTG/HOST mode
1F 1.0
POWER
A4
Tuesday , January 17, 2006 4 4
5V
C32
220nF
1 2
3 4
5 6
7 8
JP6
VCC Source
VCC
-
C34
4.7uF
2
1
3
JP7
VBUS gen
D6
LL4148
R32
10k
R35
100k 1%
3
1
4
2 - +
U7
DF005S
321
J6
CONNECTOR JACK PWR
Ext Power Supply C33
100nF
C29
33nF
UVCON
VBUS
OUT
1
IN
2
GND
3
OUT
4
FAULT
SHDN 8
7
CC
6
SET
5
U6
LP3982
Complete Schematics
STK525 Hardware User Guide 6-35
7608A–AVR–04/06
Figure 6-5 . Assembly Drawing, 1 of 2 (component side)
Figure 6-6 . Assembly Drawing, 2 of 2 (solder side)
Complete Schematics
6-36 STK525 Hardware User Guide
7608A–AVR–04/06
Table 6-1 . Bill of material
Item Q.ty Reference Part Tech. Characteristics Package
1 2 CR1,CR2 PGB0010603 ESD protection CASE 0805
2 19
C1,C2,C3,C4,C5,C6,C13,C14,C15,C16,C
17,C18,C19,C20,C21,C23,C26,C27,C33
100nF 50V-10% Ceramic CASE 0805
3 2 C7,C25 1uF 10Vmin ±10% EIA/IECQ 3216
4 3 C8,C9,C32 220nF 50V-10% Ceramic CASE 0805
5 2 C10,C11 15pF 50V-5% Ceramic CASE 0805
6 1 C12 1nF 50V-5% Ceramic CASE 0805
7 1 C22 220pF 50V-5% Ceramic CASE 0805
8 5 C24,C28,C30,C31,C34 4.7uF 10Vmin ±10% EIA/IECQ 3216
9 1 C29 33nF 50V-5% Ceramic CASE 0805
10 3 CP1, CP2, CP3 Configuration Pad
11 1 D1 BAT54/SOT Vf=0.3V SOT23
12 5 D2,D3,D4,D5,D8 TOPLED LP M676
Green
I=10 mA_
PLCC-2
13 2 D6,D7 LL4148 i=200mA max LL-34
14 5 JP1,JP2,JP3,JP4,JP5 JUMPER 1x2 Need 1 shunt 0,1" pitch
15 1 J1 USB_MiniABF
USB mini AB receptacle
Surface mount
16 2 J2,J3 CON 2x20
17 1 J4 CON 2x5
18 1 J5 CON 2x3
19 1 J7 CON 2x2 Not Mounted
20 1 JP6 JUMPER 2x4 Need 1 shunt 0,1" pitch
21 1 J6
CONNECTOR JACK
PWR
Int.Diam=2.1mm PCB Embase
22 1 JP7 JUMPER 3x1
23 1 L1 BLM-21A102S
FERRITE BEAD
1 KOhms at 100 MHz
CASE 0805
24 1 MIC1 MICROPHONE Electret Cap Mic
25 1 M1 FDV304P/FAI MOSFET P SOT23
26 1 P1 SUB-D9 FEMALE 90° with harpoons
27 2 Q1,Q2 BC847B
NPN
IC peak=200mA
SOT23
28 2 R1,R2 22 1/16W-5% SMD CASE 0602
29 2 R3,R5 47k 1/16W-5% SMD CASE 0603
30 5 R4,R6,R7,R17,R27 0 CASE 0603
31 1 R8 2k CASE 0604
32 4 R9,R25,R29,R32 10k 1/16W-5% SMD CASE 0603
Complete Schematics
STK525 Hardware User Guide 6-37
7608A–AVR–04/06
6.0.1 Default Configuration - Summary
Table 6-2 . Default Configuration summary
33 9 R10,R11,R16,R21,R22,R23,R24,R28,R33 100k 1/16W-5% SMD CASE 0603
34 5 R12,R13,R14,R15,R34 1k 1/16W-5% SMD CASE 0603
35 1 R18 NCP18WF104J03RB 100K - ß=4250 CASE 0603
36 1 R19 POT 100k PT10MH104ME
37 1 R19 Button Pot Button
38 1 R20 2.2k 1/16W-5% SMD CASE 0603
39 1 R26 22k 1/16W-5% SMD CASE 0603
40 1 R30, R35 100k 1% 1/16W-1% SMD CASE 0603
41 1 R31 120k 1% 1/16W-1% SMD CASE 0603
42 6 SP1,SP2,SP3,SP4,SP5,SP6 SolderPad (NA) (NA)
43 2 SW1,SW2 PUSH-BUTTON 6x3.5mm - 1.6N
44 1 SW3 TPA511G 4+1 ways joystick CMS
45 8 TP1,TP2,TP3,TP4,TP5,TP6, TP7, TP8 TEST POINT Diam.=1.32mm
46 1 U1 AT90USBxxx TQFP64
47 1 U1 Socket TQFP64 ZIF
48 1 U2 AT45DB321C TSOP28
49 1 U3 MAX3232ECAE+ SSOP16
50 1 U4 LMV358 SO8
51 1 U5 TPS2041A SOIC8
52 1 U6 LP3982
Low Drop Out
Vin Max 6V, 300mA
MSOP8
53 1 U7 DF005S Bridge rectifier See DS
54 1 U8 LM340 Reg 5V CMS SOT223
55 1 Y1 8MHz CRYSTAL H=4mm HC49/4H
Item Q.ty Reference Part Tech. Characteristics Package
Name Ref. Function State
Jumpers
STKX1 JP1 XTAL Configuration OFF
STKX2 JP2 XTAL Configuration OFF
Aref JP3 STK500 Analog Ref OFF
VTG33 JP4 Short 3.3V to VTG (Mass storage extension
board)
OFF
UCAP JP5 Short UCAP with Uvcc OFF
Vcc Src JP6 Vcc Selection 3.4 shorted
Vbus Gen JP7 VBUS generation selection (host mode) 2.3 shorted
Solder PADS
Complete Schematics
6-38 STK525 Hardware User Guide
7608A–AVR–04/06
SP1 Bypass L1 OPEN
SP2 OPEN
SP3 3.3V on Expand 0 NC pin OPEN
SP4 CTS OPEN
SP5 RTS OPEN
SP6 Bypass limiter OPEN
SP7 RS232 hardware control enable OPEN
SP8 RS232 hardware control enable OPEN
Configuration PADS
CP1 Bypass CTN in on PF0 CLOSE
CP2 Bypass Potentiometer ADC in on PF1 CLOSE
CP3 Bypass Mic In on PF2 CLOSE
Name Ref. Function State
Printed on recycled paper.
7608A–AVR–04/06 /xM
© Atmel Corporation 2006. All rights reserved. Atmel®, logo and combinations thereof, are registered trademarks, and Everywhere You Are®
are the trademarks of Atmel Corporation or its subsidiaries. Other terms and product names may be trademarks of others.
Disclaimer: The information in this document is provided in connection with Atmel products. No license, express or implied, by estoppel or otherwise,to anyintellectualproperty
right is granted by this document or in connection with the sale of Atmel products. EXCEPT AS SET FORTH IN ATMEL’S TERMS AND CONDI-TIONS OF
SALE LOCATED ON ATMEL’S WEB SITE, ATMEL ASSUMES NO LIABILITY WHATSOEVER AND DISCLAIMS ANY EXPRESS, IMPLIED OR STATUTORYWARRANTY
RELATING TO ITS PRODUCTS INCLUDING, BUT NOT LIMITED TO, THE IMPLIED WARRANTY OF MERCHANTABILITY, FITNESS FOR A PARTICULARPURPOSE,
OR NON-INFRINGEMENT. IN NO EVENT SHALL ATMEL BE LIABLE FOR ANY DIRECT, INDIRECT, CONSEQUENTIAL, PUNITIVE, SPECIAL
OR INCIDEN-TAL DAMAGES (INCLUDING, WITHOUT LIMITATION, DAMAGES FOR LOSS OF PROFITS, BUSINESS INTERRUPTION, OR LOSS OF INFORMATION)
ARISING OUTOF THE USE OR INABILITY TO USE THIS DOCUMENT, EVEN IF ATMEL HAS BEEN ADVISED OF THE POSSIBILITY OF SUCH DAMAGES.
Atmel makes norepresentationsor warranties with respect to the accuracy or completeness of the contents of this document and reserves the right to make
changes to specificationsand product descriptions at any time without notice. Atmel does not make any commitment to update the information contained herein.
Unless specifically provided otherwise, Atmel products are not suitable for, and shall not be used in, automotive applications. Atmel’s products are not intended,
authorized, or warranted for useas components in applications intended to support or sustainlife.
Atmel Corporation Atmel Operations
2325 Orchard Parkway
San Jose, CA 95131, USA
Tel: 1(408) 441-0311
Fax: 1(408) 487-2600
Regional Headquarters
Europe
Atmel Sarl
Route des Arsenaux 41
Case Postale 80
CH-1705 Fribourg
Switzerland
Tel: (41) 26-426-5555
Fax: (41) 26-426-5500
Asia
Room 1219
Chinachem Golden Plaza
77 Mody Road Tsimshatsui
East Kowloon
Hong Kong
Tel: (852) 2721-9778
Fax: (852) 2722-1369
Japan
9F, Tonetsu Shinkawa Bldg.
1-24-8 Shinkawa
Chuo-ku, Tokyo 104-0033
Japan
Tel: (81) 3-3523-3551
Fax: (81) 3-3523-7581
Memory
2325 Orchard Parkway
San Jose, CA 95131, USA
Tel: 1(408) 441-0311
Fax: 1(408) 436-4314
Microcontrollers
2325 Orchard Parkway
San Jose, CA 95131, USA
Tel: 1(408) 441-0311
Fax: 1(408) 436-4314
La Chantrerie
BP 70602
44306 Nantes Cedex 3, France
Tel: (33) 2-40-18-18-18
Fax: (33) 2-40-18-19-60
ASIC/ASSP/Smart Cards
Zone Industrielle
13106 Rousset Cedex, France
Tel: (33) 4-42-53-60-00
Fax: (33) 4-42-53-60-01
1150 East Cheyenne Mtn. Blvd.
Colorado Springs, CO 80906, USA
Tel: 1(719) 576-3300
Fax: 1(719) 540-1759
Scottish Enterprise Technology Park
Maxwell Building
East Kilbride G75 0QR, Scotland
Tel: (44) 1355-803-000
Fax: (44) 1355-242-743
RF/Automotive
Theresienstrasse 2
Postfach 3535
74025 Heilbronn, Germany
Tel: (49) 71-31-67-0
Fax: (49) 71-31-67-2340
1150 East Cheyenne Mtn. Blvd.
Colorado Springs, CO 80906, USA
Tel: 1(719) 576-3300
Fax: 1(719) 540-1759
Biometrics/Imaging/Hi-Rel MPU/
High Speed Converters/RF Datacom
Avenue de Rochepleine
BP 123
38521 Saint-Egreve Cedex, France
Tel: (33) 4-76-58-30-00
Fax: (33) 4-76-58-34-80
Literature Requests
www.atmel.com/literature
MSP430 Hardware Tools
User's Guide
Literature Number: SLAU278R
May 2009–Revised May 2014
Contents
Preface ........................................................................................................................................ 8
1 Get Started Now!................................................................................................................ 11
1.1 Flash Emulation Tool (FET) Overview................................................................................... 12
1.2 Kit Contents, MSP-FET430PIF........................................................................................... 13
1.3 Kit Contents, eZ430-F2013 ............................................................................................... 13
1.4 Kit Contents, eZ430-T2012 ............................................................................................... 13
1.5 Kit Contents, eZ430-RF2500 ............................................................................................. 13
1.6 Kit Contents, eZ430-RF2500T............................................................................................ 13
1.7 Kit Contents, eZ430-RF2500-SEH....................................................................................... 13
1.8 Kit Contents, eZ430-Chronos-xxx........................................................................................ 14
1.9 Kit Contents, MSP-FET430UIF........................................................................................... 14
1.10 Kit Contents, MSP-FET.................................................................................................... 14
1.11 Kit Contents, MSP-FET430xx ............................................................................................ 14
1.12 Kit Contents, FET430F6137RF900 ...................................................................................... 15
1.13 Kit Contents, MSP-TS430xx .............................................................................................. 15
1.14 Kit Contents, EM430Fx1x7RF900 ....................................................................................... 17
1.15 Hardware Installation, MSP-FET430PIF ................................................................................ 17
1.16 Hardware Installation, MSP-FET430UIF ................................................................................ 18
1.17 Hardware Installation, MSP-FET ......................................................................................... 18
1.18 Hardware Installation, eZ430-XXXX, MSP-EXP430G2, MSP-EXP430FR5739, MSP-EXP430F5529.......... 18
1.19 Hardware Installation, MSP-FET430Uxx, MSP-TS430xxx, FET430F6137RF900, EM430Fx137RF900 ....... 19
1.20 Important MSP430 Documents on the Web ............................................................................ 20
2 Design Considerations for In-Circuit Programming ................................................................ 21
2.1 Signal Connections for In-System Programming and Debugging ................................................... 22
2.2 External Power ............................................................................................................. 26
2.3 Bootstrap Loader (BSL) ................................................................................................... 26
A Frequently Asked Questions and Known Issues .................................................................... 27
A.1 Hardware FAQs ............................................................................................................ 28
A.2 Known Issues ............................................................................................................... 30
B Hardware........................................................................................................................... 31
B.1 MSP-TS430D8.............................................................................................................. 33
B.2 MSP-TS430PW14.......................................................................................................... 36
B.3 MSP-TS430L092 ........................................................................................................... 39
B.4 MSP-TS430L092 Active Cable ........................................................................................... 42
B.5 MSP-TS430PW24.......................................................................................................... 45
B.6 MSP-TS430DW28.......................................................................................................... 48
B.7 MSP-TS430PW28.......................................................................................................... 51
B.8 MSP-TS430PW28A........................................................................................................ 54
B.9 MSP-TS430RHB32A....................................................................................................... 57
B.10 MSP-TS430DA38 .......................................................................................................... 60
B.11 MSP-TS430QFN23x0...................................................................................................... 63
B.12 MSP-TS430RSB40......................................................................................................... 66
B.13 MSP-TS430RHA40A....................................................................................................... 69
B.14 MSP-TS430DL48........................................................................................................... 72
2 Contents SLAU278R–May 2009–Revised May 2014
Submit Documentation Feedback
Copyright © 2009–2014, Texas Instruments Incorporated
www.ti.com
B.15 MSP-TS430RGZ48B....................................................................................................... 75
B.16 MSP-TS430RGZ48C ...................................................................................................... 78
B.17 MSP-TS430PM64 .......................................................................................................... 81
B.18 MSP-TS430PM64A ........................................................................................................ 84
B.19 MSP-TS430RGC64B ...................................................................................................... 87
B.20 MSP-TS430RGC64C ...................................................................................................... 90
B.21 MSP-TS430RGC64USB................................................................................................... 94
B.22 MSP-TS430PN80 .......................................................................................................... 98
B.23 MSP-TS430PN80A ....................................................................................................... 101
B.24 MSP-TS430PN80USB ................................................................................................... 104
B.25 MSP-TS430PZ100........................................................................................................ 108
B.26 MSP-TS430PZ100A...................................................................................................... 111
B.27 MSP-TS430PZ100B...................................................................................................... 114
B.28 MSP-TS430PZ100C...................................................................................................... 117
B.29 MSP-TS430PZ100D...................................................................................................... 121
B.30 MSP-TS430PZ5x100..................................................................................................... 124
B.31 MSP-TS430PZ100USB .................................................................................................. 127
B.32 MSP-TS430PEU128...................................................................................................... 131
B.33 EM430F5137RF900 ...................................................................................................... 134
B.34 EM430F6137RF900 ...................................................................................................... 138
B.35 EM430F6147RF900 ...................................................................................................... 142
B.36 MSP-FET .................................................................................................................. 146
B.36.1 Features ......................................................................................................... 146
B.36.2 Release Notes .................................................................................................. 146
B.36.3 Schematics ...................................................................................................... 148
B.36.4 Layout............................................................................................................ 153
B.36.5 LED Signals ..................................................................................................... 153
B.36.6 JTAG Target Connector ....................................................................................... 154
B.36.7 Specifications ................................................................................................... 156
B.36.8 MSP-FET Revision History.................................................................................... 156
B.37 MSP-FET430PIF.......................................................................................................... 157
B.38 MSP-FET430UIF.......................................................................................................... 159
B.38.1 MSP-FET430UIF Revision History ........................................................................... 164
C Hardware Installation Guide ............................................................................................... 165
C.1 Hardware Installation ..................................................................................................... 166
Revision History ........................................................................................................................ 171
SLAU278R–May 2009–Revised May 2014 Contents 3
Submit Documentation Feedback
Copyright © 2009–2014, Texas Instruments Incorporated
www.ti.com
List of Figures
2-1. Signal Connections for 4-Wire JTAG Communication................................................................. 23
2-2. Signal Connections for 2-Wire JTAG Communication (Spy-Bi-Wire) Used by MSP430F2xx,
MSP430G2xx, and MSP430F4xx Devices.............................................................................. 24
2-3. Signal Connections for 2-Wire JTAG Communication (Spy-Bi-Wire) Used by MSP430F5xx and
MSP430F6xx Devices ..................................................................................................... 25
B-1. MSP-TS430D8 Target Socket Module, Schematic .................................................................... 33
B-2. MSP-TS430D8 Target Socket Module, PCB ........................................................................... 34
B-3. MSP-TS430PW14 Target Socket Module, Schematic ................................................................ 36
B-4. MSP-TS430PW14 Target Socket Module, PCB ....................................................................... 37
B-5. MSP-TS430L092 Target Socket Module, Schematic.................................................................. 39
B-6. MSP-TS430L092 Target Socket Module, PCB......................................................................... 40
B-7. MSP-TS430L092 Active Cable Target Socket Module, Schematic.................................................. 42
B-8. MSP-TS430L092 Active Cable Target Socket Module, PCB......................................................... 43
B-9. MSP-TS430PW24 Target Socket Module, Schematic ................................................................ 45
B-10. MSP-TS430PW24 Target Socket Module, PCB ....................................................................... 46
B-11. MSP-TS430DW28 Target Socket Module, Schematic ................................................................ 48
B-12. MSP-TS430DW28 Target Socket Module, PCB ....................................................................... 49
B-13. MSP-TS430PW28 Target Socket Module, Schematic ................................................................ 51
B-14. MSP-TS430PW28 Target Socket Module, PCB ....................................................................... 52
B-15. MSP-TS430PW28A Target Socket Module, Schematic .............................................................. 54
B-16. MSP-TS430PW28A Target Socket Module, PCB (Red) .............................................................. 55
B-17. MSP-TS430RHB32A Target Socket Module, Schematic ............................................................. 57
B-18. MSP-TS430RHB32A Target Socket Module, PCB .................................................................... 58
B-19. MSP-TS430DA38 Target Socket Module, Schematic................................................................. 60
B-20. MSP-TS430DA38 Target Socket Module, PCB........................................................................ 61
B-21. MSP-TS430QFN23x0 Target Socket Module, Schematic ............................................................ 63
B-22. MSP-TS430QFN23x0 Target Socket Module, PCB ................................................................... 64
B-23. MSP-TS430RSB40 Target Socket Module, Schematic ............................................................... 66
B-24. MSP-TS430RSB40 Target Socket Module, PCB ...................................................................... 67
B-25. MSP-TS430RHA40A Target Socket Module, Schematic ............................................................. 69
B-26. MSP-TS430RHA40A Target Socket Module, PCB .................................................................... 70
B-27. MSP-TS430DL48 Target Socket Module, Schematic ................................................................. 72
B-28. MSP-TS430DL48 Target Socket Module, PCB ........................................................................ 73
B-29. MSP-TS430RGZ48B Target Socket Module, Schematic ............................................................. 75
B-30. MSP-TS430RGZ48B Target Socket Module, PCB .................................................................... 76
B-31. MSP-TS430RGZ48C Target Socket Module, Schematic ............................................................. 78
B-32. MSP-TS430RGZ48C Target Socket Module, PCB .................................................................... 79
B-33. MSP-TS430PM64 Target Socket Module, Schematic................................................................. 81
B-34. MSP-TS430PM64 Target Socket Module, PCB........................................................................ 82
B-35. MSP-TS430PM64A Target Socket Module, Schematic............................................................... 84
B-36. MSP-TS430PM64A Target Socket Module, PCB...................................................................... 85
B-37. MSP-TS430RGC64B Target Socket Module, Schematic............................................................. 87
B-38. MSP-TS430RGC64B Target Socket Module, PCB.................................................................... 88
B-39. MSP-TS430RGC64C Target Socket Module, Schematic............................................................. 91
B-40. MSP-TS430RGC64C Target Socket Module, PCB.................................................................... 92
B-41. MSP-TS430RGC64USB Target Socket Module, Schematic ......................................................... 94
B-42. MSP-TS430RGC64USB Target Socket Module, PCB ................................................................ 95
B-43. MSP-TS430PN80 Target Socket Module, Schematic................................................................. 98
4 List of Figures SLAU278R–May 2009–Revised May 2014
Submit Documentation Feedback
Copyright © 2009–2014, Texas Instruments Incorporated
www.ti.com
B-44. MSP-TS430PN80 Target Socket Module, PCB........................................................................ 99
B-45. MSP-TS430PN80A Target Socket Module, Schematic.............................................................. 101
B-46. MSP-TS430PN80A Target Socket Module, PCB..................................................................... 102
B-47. MSP-TS430PN80USB Target Socket Module, Schematic.......................................................... 104
B-48. MSP-TS430PN80USB Target Socket Module, PCB................................................................. 105
B-49. MSP-TS430PZ100 Target Socket Module, Schematic .............................................................. 108
B-50. MSP-TS430PZ100 Target Socket Module, PCB ..................................................................... 109
B-51. MSP-TS430PZ100A Target Socket Module, Schematic ............................................................ 111
B-52. MSP-TS430PZ100A Target Socket Module, PCB ................................................................... 112
B-53. MSP-TS430PZ100B Target Socket Module, Schematic ............................................................ 114
B-54. MSP-TS430PZ100B Target Socket Module, PCB ................................................................... 115
B-55. MSP-TS430PZ100C Target Socket Module, Schematic ............................................................ 117
B-56. MSP-TS430PZ100C Target Socket Module, PCB ................................................................... 118
B-57. MSP-TS430PZ100D Target Socket Module, Schematic ............................................................ 121
B-58. MSP-TS430PZ100D Target Socket Module, PCB ................................................................... 122
B-59. MSP-TS430PZ5x100 Target Socket Module, Schematic ........................................................... 124
B-60. MSP-TS430PZ5x100 Target Socket Module, PCB .................................................................. 125
B-61. MSP-TS430PZ100USB Target Socket Module, Schematic......................................................... 127
B-62. MSP-TS430PZ100USB Target Socket Module, PCB................................................................ 128
B-63. MSP-TS430PEU128 Target Socket Module, Schematic ............................................................ 131
B-64. MSP-TS430PEU128 Target Socket Module, PCB ................................................................... 132
B-65. EM430F5137RF900 Target board, Schematic........................................................................ 134
B-66. EM430F5137RF900 Target board, PCB............................................................................... 135
B-67. EM430F6137RF900 Target board, Schematic........................................................................ 138
B-68. EM430F6137RF900 Target Board, PCB .............................................................................. 139
B-69. EM430F6147RF900 Target Board, Schematic ....................................................................... 142
B-70. EM430F6147RF900 Target Board, PCB .............................................................................. 143
B-71. MSP-FET Top View ...................................................................................................... 147
B-72. MSP-FET Bottom View .................................................................................................. 147
B-73. MSP-FET USB Debugger, Schematic (1 of 5)........................................................................ 148
B-74. MSP-FET USB Debugger, Schematic (2 of 5)........................................................................ 149
B-75. MSP-FET USB Debugger, Schematic (3 of 5)........................................................................ 150
B-76. MSP-FET USB Debugger, Schematic (4 of 5)........................................................................ 151
B-77. MSP-FET USB Debugger, Schematic (5 of 5)........................................................................ 152
B-78. MSP-FET USB Debugger, PCB (Top) ................................................................................. 153
B-79. MSP-FET USB Debugger, PCB (Bottom) ............................................................................. 153
B-80. JTAG Connector Pinout.................................................................................................. 154
B-81. Pin States After Power-Up............................................................................................... 155
B-82. MSP-FET430PIF FET Interface Module, Schematic................................................................. 157
B-83. MSP-FET430PIF FET Interface Module, PCB........................................................................ 158
B-84. MSP-FET430UIF USB Interface, Schematic (1 of 4) ................................................................ 159
B-85. MSP-FET430UIF USB Interface, Schematic (2 of 4) ................................................................ 160
B-86. MSP-FET430UIF USB Interface, Schematic (3 of 4) ................................................................ 161
B-87. MSP-FET430UIF USB Interface, Schematic (4 of 4) ................................................................ 162
B-88. MSP-FET430UIF USB Interface, PCB................................................................................. 163
C-1. Windows XP Hardware Wizard ......................................................................................... 166
C-2. Windows XP Driver Location Selection Folder........................................................................ 167
C-3. Device Manager Using USB Debug Interface using VID/PID 0x2047/0x0010 ................................... 168
C-4. Device Manager Using USB Debug Interface with VID/PID 0x0451/0xF430 ..................................... 169
SLAU278R–May 2009–Revised May 2014 List of Figures 5
Submit Documentation Feedback
Copyright © 2009–2014, Texas Instruments Incorporated
www.ti.com
C-5. Device Manager Using USB Debug Interface With VID/PID 0x0451/0xF432 .................................... 170
6 List of Figures SLAU278R–May 2009–Revised May 2014
Submit Documentation Feedback
Copyright © 2009–2014, Texas Instruments Incorporated
www.ti.com
List of Tables
1-1. Flash Emulation Tool (FET) Features and Device Compatibility..................................................... 12
1-2. Individual Kit Contents, MSP-TS430xx.................................................................................. 15
B-1. MSP-TS430D8 Bill of Materials .......................................................................................... 35
B-2. MSP-TS430PW14 Bill of Materials....................................................................................... 38
B-3. MSP-TS430L092 Bill of Materials ........................................................................................ 41
B-4. MSP-TS430L092 JP1 Settings ........................................................................................... 43
B-5. MSP-TS430L092 Active Cable Bill of Materials ........................................................................ 44
B-6. MSP-TS430PW24 Bill of Materials....................................................................................... 47
B-7. MSP-TS430DW28 Bill of Materials ...................................................................................... 50
B-8. MSP-TS430PW28 Bill of Materials ...................................................................................... 53
B-9. MSP-TS430PW28A Bill of Materials..................................................................................... 56
B-10. MSP-TS430RHB32A Bill of Materials ................................................................................... 59
B-11. MSP-TS430DA38 Bill of Materials ....................................................................................... 62
B-12. MSP-TS430QFN23x0 Bill of Materials .................................................................................. 65
B-13. MSP-TS430RSB40 Bill of Materials ..................................................................................... 68
B-14. MSP-TS430RHA40A Bill of Materials ................................................................................... 71
B-15. MSP-TS430DL48 Bill of Materials ....................................................................................... 74
B-16. MSP-TS430RGZ48B Bill of Materials ................................................................................... 77
B-17. MSP-TS430RGZ48C Revision History .................................................................................. 79
B-18. MSP-TS430RGZ48C Bill of Materials ................................................................................... 80
B-19. MSP-TS430PM64 Bill of Materials....................................................................................... 83
B-20. MSP-TS430PM64A Bill of Materials ..................................................................................... 86
B-21. MSP-TS430RGC64B Bill of Materials ................................................................................... 89
B-22. MSP-TS430RGC64C Bill of Materials ................................................................................... 93
B-23. MSP-TS430RGC64USB Bill of Materials ............................................................................... 96
B-24. MSP-TS430PN80 Bill of Materials...................................................................................... 100
B-25. MSP-TS430PN80A Bill of Materials.................................................................................... 103
B-26. MSP-TS430PN80USB Bill of Materials ................................................................................ 106
B-27. MSP-TS430PZ100 Bill of Materials .................................................................................... 110
B-28. MSP-TS430PZ100A Bill of Materials................................................................................... 113
B-29. MSP-TS430PZ100B Bill of Materials................................................................................... 116
B-30. MSP-TS430PZ100C Bill of Materials .................................................................................. 119
B-31. MSP-TS430PZ100D Bill of Materials .................................................................................. 123
B-32. MSP-TS430PZ5x100 Bill of Materials.................................................................................. 126
B-33. MSP-TS430PZ100USB Bill of Materials ............................................................................... 129
B-34. MSP-TS430PEU128 Bill of Materials .................................................................................. 133
B-35. EM430F5137RF900 Bill of Materials................................................................................... 136
B-36. EM430F6137RF900 Bill of Materials................................................................................... 140
B-37. EM430F6147RF900 Bill of Materials................................................................................... 144
B-38. UART Backchannel Implementation ................................................................................... 146
B-39. MSP-FET LED Signals................................................................................................... 153
B-40. JTAG Connector Pin State by Operating Mode ...................................................................... 154
B-41. Specifications.............................................................................................................. 156
B-42. MSP-FET Revision History .............................................................................................. 156
C-1. USB VIDs and PIDs Used in MSP430 Tools.......................................................................... 166
SLAU278R–May 2009–Revised May 2014 List of Tables 7
Submit Documentation Feedback
Copyright © 2009–2014, Texas Instruments Incorporated
Preface
SLAU278R–May 2009–Revised May 2014
Read This First
About This Manual
This manual describes the hardware of the Texas Instruments MSP-FET430 Flash Emulation Tool (FET).
The FET is the program development tool for the MSP430™ ultra-low-power microcontroller. Both
available interface types, the parallel port interface and the USB interface, are described.
How to Use This Manual
Read and follow the instructions in Chapter 1. This chapter lists the contents of the FET, provides
instructions on installing the hardware and according software drivers. After you see how quick and easy it
is to use the development tools, TI recommends that you read all of this manual.
This manual describes the setup and operation of the FET but does not fully describe the MSP430™
microcontrollers or the development software systems. For details of these items, see the appropriate TI
documents listed in Section 1.20.
This manual applies to the following tools (and devices):
• MSP-FET430PIF (debug interface with parallel port connection, for all MSP430 flash-based devices)
• MSP-FET430UIF (debug interface with USB connection, for all MSP430 flash-based devices)
• MSP-FET (successor to MSP-FET430UIF, debug interface with USB connection, for all MSP430
devices)
• eZ430-F2013 (USB stick form factor interface with attached MSP430F2013 target, for all
MSP430F20xx, MSP430G2x01, MSP430G2x11, MSP430G2x21, and MSP430G2x31 devices)
• eZ430-T2012 (three MSP430F2012 based target boards)
• eZ430-RF2500 (USB stick form factor interface with attached MSP430F2274 and CC2500 target, for
all MSP430F20xx, MSP430F21x2, MSP430F22xx, MSP430G2x01, MSP430G2x11, MSP430G2x21,
and MSP430G2x31 devices)
• eZ430-RF2500T (one MSP430F2274 and CC2500 target board including battery pack)
• eZ430-RF2500-SEH (USB stick form factor interface with attached MSP430F2274 and CC2500 target
and solar energy harvesting module)
• eZ430-Chronos-xxx (USB stick form factor interface with CC430F6137 based development system
contained in a watch. Includes <1 GHz RF USB access point)
Stand-alone target-socket modules (without debug interface) named as MSP-TS430TSxx.
Tools named as MSP-FET430Uxx contain the USB debug interface (MSP-FET430UIF) and the respective
target socket module MSP-TS430TSxx, where 'xx' is the same for both names. The following tools contain
also the USB debug interface (MSP-FET430UIF):
• FET430F5137RF900 (for CC430F513x devices in 48-pin RGZ packages) (green PCB)
• FET430F6137RF900 (for CC430F612x and CC430F613x devices in 64-pin RGC packages) (green
PCB)
These tools contain the most up-to-date materials available at the time of packaging. For the latest
materials (data sheets, user's guides, software, application information, and so on), visit the TI MSP430
web site at www.ti.com/msp430 or contact your local TI sales office.
8 Read This First SLAU278R–May 2009–Revised May 2014
Submit Documentation Feedback
Copyright © 2009–2014, Texas Instruments Incorporated
www.ti.com Information About Cautions and Warnings
Information About Cautions and Warnings
This document may contain cautions and warnings.
CAUTION
This is an example of a caution statement.
A caution statement describes a situation that could potentially damage your
software or equipment.
WARNING
This is an example of a warning statement.
A warning statement describes a situation that could potentially
cause harm to you.
The information in a caution or a warning is provided for your protection. Read each caution and warning
carefully.
Related Documentation From Texas Instruments
MSP430 development tools documentation:
Code Composer Studio for MSP430 User's Guide (literature number SLAU157)
Code Composer Studio v5.x Core Edition (CCS Mediawiki)
IAR Embedded Workbench for MSP430(tm) User's Guide (literature number SLAU138)
IAR Embedded Workbench KickStart installer (literature number SLAC050)
eZ430-F2013 Development Tool User's Guide (literature number SLAU176)
eZ430-RF2480 Demonstration Kit User's Guide (literature number SWRU151)
eZ430-RF2500 Development Tool User's Guide (literature number SLAU227)
eZ430-RF2500-SEH Development Tool User's Guide (literature number SLAU273)
eZ430-Chronos Development Tool User's Guide (literature number SLAU292)
Spectrum Analyzer (MSP-SA430-SUB1GHZ) User's Guide (literature number SLAU371)
MSP-EXP430F5529 Experimenter Board User's Guide (literature number SLAU330)
MSP-EXP430F5438 Experimenter Board User's Guide (literature number SLAU263)
MSP-EXP430G2 LaunchPad Experimenter Board User's Guide (literature number SLAU318)
MSP Gang Programmer (MSP-GANG) User's Guide (literature number SLAU358)
MSP430 Gang Programmer (MSP-GANG430) User's Guide (literature number SLAU101)
MSP430 device user's guides:
MSP430x1xx Family User's Guide (literature number SLAU049)
MSP430x2xx Family User's Guide (literature number SLAU144)
MSP430x3xx Family User's Guide (literature number SLAU012)
MSP430x4xx Family User's Guide (literature number SLAU056)
MSP430x5xx and MSP430x6xx Family User's Guide (literature number SLAU208)
CC430 Family User's Guide (literature number SLAU259)
SLAU278R–May 2009–Revised May 2014 Read This First 9
Submit Documentation Feedback
Copyright © 2009–2014, Texas Instruments Incorporated
If You Need Assistance www.ti.com
MSP430FR57xx Family User's Guide (literature number SLAU272)
MSP430FR58xx and MSP430FR59xx Family User's Guide (literature number SLAU367)
If You Need Assistance
Support for the MSP430 devices and the FET development tools is provided by the Texas Instruments
Product Information Center (PIC). Contact information for the PIC can be found on the TI web site at
www.ti.com/support. The Texas Instruments E2E Community support forums for the MSP430 provide
open interaction with peer engineers, TI engineers, and other experts. Additional device-specific
information can be found on the MSP430 web site.
10 Read This First SLAU278R–May 2009–Revised May 2014
Submit Documentation Feedback
Copyright © 2009–2014, Texas Instruments Incorporated
Chapter 1
SLAU278R–May 2009–Revised May 2014
Get Started Now!
This chapter lists the contents of the FET and provides instruction on installing the hardware.
Topic ........................................................................................................................... Page
1.1 Flash Emulation Tool (FET) Overview ................................................................... 12
1.2 Kit Contents, MSP-FET430PIF.............................................................................. 13
1.3 Kit Contents, eZ430-F2013................................................................................... 13
1.4 Kit Contents, eZ430-T2012................................................................................... 13
1.5 Kit Contents, eZ430-RF2500 ................................................................................ 13
1.6 Kit Contents, eZ430-RF2500T............................................................................... 13
1.7 Kit Contents, eZ430-RF2500-SEH ......................................................................... 13
1.8 Kit Contents, eZ430-Chronos-xxx......................................................................... 14
1.9 Kit Contents, MSP-FET430UIF.............................................................................. 14
1.10 Kit Contents, MSP-FET ....................................................................................... 14
1.11 Kit Contents, MSP-FET430xx .............................................................................. 14
1.12 Kit Contents, FET430F6137RF900 ........................................................................ 15
1.13 Kit Contents, MSP-TS430xx ................................................................................. 15
1.14 Kit Contents, EM430Fx1x7RF900.......................................................................... 17
1.15 Hardware Installation, MSP-FET430PIF ................................................................. 17
1.16 Hardware Installation, MSP-FET430UIF ................................................................. 18
1.17 Hardware Installation, MSP-FET........................................................................... 18
1.18 Hardware Installation, eZ430-XXXX, MSP-EXP430G2, MSP-EXP430FR5739, MSPEXP430F5529.....................................................................................................
18
1.19 Hardware Installation, MSP-FET430Uxx, MSP-TS430xxx, FET430F6137RF900,
EM430Fx137RF900 ............................................................................................. 19
1.20 Important MSP430 Documents on the Web............................................................ 20
SLAU278R–May 2009–Revised May 2014 Get Started Now! 11
Submit Documentation Feedback
Copyright © 2009–2014, Texas Instruments Incorporated
Flash Emulation Tool (FET) Overview www.ti.com
1.1 Flash Emulation Tool (FET) Overview
TI offers several flash emulation tools according to different requirements.
Table 1-1. Flash Emulation Tool (FET) Features and Device Compatibility(1)
eZ430-F2013
eZ430-RF2500
eZ430-RF2480
eZ430-RF2560
MSP-WDSxx Metawatch
eZ430-Chronos
MSP-FET430PIF
MSP-FET430UIF
LaunchPad (MSP-EXP430G2)
MSP-EXP430FR5739
MSP-EXP430F5529
Supports all programmable MSP430 and
CC430 devices (F1xx, F2xx, F4xx, F5xx, F6xx, G2xx, L092, FR57xx, FR59xx, x x
MSP430TCH5E)
Supports only F20xx, G2x01, G2x11, x G2x21, G2x31
Supports MSP430F20xx, F21x2, F22xx, x G2x01, G2x11, G2x21, G2x31, G2x53
Supports MSP430F20xx, F21x2, F22xx, x x G2x01, G2x11, G2x21, G2x31
Supports F5438, F5438A x
Supports BT5190, F5438A x x
Supports only F552x x
Supports FR57xx, F5638, F6638 x
Supports only CC430F613x x
Allows fuse blow x
Adjustable target supply voltage x
Fixed 2.8-V target supply voltage x
Fixed 3.6-V target supply voltage x x x x x x x x x
4-wire JTAG x x
2-wire JTAG(2) x x x x x x x x x x
Application UART x x x x x x x x
Supported by CCS for Windows x x x x x x x x x x x
Supported by CCS for Linux x
Supported by IAR x x x x x x x x x x x
(1) The MSP-FET430PIF is for legacy device support only. This emulation tool will not support any new devices released after 2011.
(2) The 2-wire JTAG debug interface is also referred to as Spy-Bi-Wire (SBW) interface.
12 Get Started Now! SLAU278R–May 2009–Revised May 2014
Submit Documentation Feedback
Copyright © 2009–2014, Texas Instruments Incorporated
www.ti.com Kit Contents, MSP-FET430PIF
1.2 Kit Contents, MSP-FET430PIF
• One READ ME FIRST document
• One MSP-FET430PIF interface module
• One 25-conductor cable
• One 14-conductor cable
NOTE: This part is obsolete and is not recommended to use in new design.
1.3 Kit Contents, eZ430-F2013
• One QUICK START GUIDE document
• One eZ430-F2013 development tool including one MSP430F2013 target board
1.4 Kit Contents, eZ430-T2012
• Three MSP430F2012-based target boards
1.5 Kit Contents, eZ430-RF2500
• One QUICK START GUIDE document
• One eZ430-RF2500 CD-ROM
• One eZ430-RF2500 development tool including one MSP430F2274 and CC2500 target board
• One eZ430-RF2500T target board
• One AAA battery pack with expansion board (batteries included)
1.6 Kit Contents, eZ430-RF2500T
• One eZ430-RF2500T target board
• One AAA battery pack with expansion board (batteries included)
1.7 Kit Contents, eZ430-RF2500-SEH
• One MSP430 development tool CD containing documentation and development software
• One eZ430-RF USB debugging interface
• Two eZ430-RF2500T wireless target boards
• One SEH-01 solar energy harvester board
• One AAA battery pack with expansion board (batteries included)
SLAU278R–May 2009–Revised May 2014 Get Started Now! 13
Submit Documentation Feedback
Copyright © 2009–2014, Texas Instruments Incorporated
Kit Contents, eZ430-Chronos-xxx www.ti.com
1.8 Kit Contents, eZ430-Chronos-xxx
'433, '868, '915
• One QUICK START GUIDE document
• One ez430-Chronos emulator
• One screwdriver
• Two spare screws
eZ430-Chronos-433:
– One 433-MHz eZ430-Chronos watch (battery included)
– One 433-MHz eZ430-Chronos access point
eZ430-Chronos-868:
– One 868-MHz eZ430-Chronos watch (battery included)
– One 868-MHz eZ430-Chronos access point
eZ430-Chronos-915:
– One 915-MHz eZ430-Chronos watch (battery included)
– One 915-MHz eZ430-Chronos access point
1.9 Kit Contents, MSP-FET430UIF
• One READ ME FIRST document
• One MSP-FET430UIF interface module
• One USB cable
• One 14-conductor cable
1.10 Kit Contents, MSP-FET
• One READ ME FIRST document
• One MSP-FET interface module
• One USB cable
• One 14-conductor cable
1.11 Kit Contents, MSP-FET430xx
• One READ ME FIRST document
• One MSP-FET430UIF USB interface module. This is the unit that has a USB B-connector on one end
of the case, and a 2×7-pin male connector on the other end of the case.
• One USB cable
• One 32.768-kHz crystal from Micro Crystal, if the board has an option to use the quartz.
• A 2×7-pin male JTAG connector is also present on the PCB (see different setup for L092)
• One 14-Pin JTAG conductor cable
• One small box containing two MSP430 device samples (See table for Sample Type)
• One target socket module. To determine the devices used for each board and a summary of the board,
see Table 1-2. The name of MSP-TS430xx board can be derived from the name of the MSP-FET430xx
kit; for example, the MSP-FET430U28A kit contains the MSP-TS430PW28A board.
Refer to the device data sheets for device specifications. Device errata can be found in the respective
device product folder on the web provided as a PDF document. Depending on the device, errata may also
be found in the device bug database at www.ti.com/sc/cgi-bin/buglist.cgi.
14 Get Started Now! SLAU278R–May 2009–Revised May 2014
Submit Documentation Feedback
Copyright © 2009–2014, Texas Instruments Incorporated
www.ti.com Kit Contents, FET430F6137RF900
1.12 Kit Contents, FET430F6137RF900
• One READ ME FIRST document
• One legal notice
• One MSP-FET430UIF interface module
• Two EM430F6137RF900 target socket modules. This is the PCB on which is soldered a CC430F6137
device in a 64-pin RGC package. A 2×7-pin male connector is also present on the PCB.
• Two CC430EM battery packs
• Four AAA batteries
• Two 868-MHz or 915-MHz antennas
• Two 32.768-kHz crystals
• 18 PCB 2x4-pin headers
• One USB cable
• One 14-pin JTAG conductor cable
1.13 Kit Contents, MSP-TS430xx
• One READ ME FIRST document
• One 32.768-kHz crystal from Micro Crystal (except MSP-TS430PW24)
• One target socket module
• A 2×7-pin male JTAG connector is also present on the PCB (see different setup for L092)
• MSP430 device samples (see Table 1-2 for sample type)
Table 1-2. Individual Kit Contents, MSP-TS430xx
Part Number Socket Type Supported Devices Included Devices Headers and Comment
MSP-TS430D8 8-pin D MSP430G2210, 1 x MSP430G2210ID and Two PCB 1×4-pin headers (two male and
(green PCB) (TSSOP ZIF) MSP430G2230 1 x MSP430G2230ID two female)
MSP430F20xx,
MSP-TS430PW14 14-pin PW MSP430G2x01, Four PCB 1×7-pin headers (two male and (green PCB) (TSSOP ZIF) MSP430G2x11, 2 x MSP430F2013IPW two female) MSP430G2x21,
MSP430G2x31
Four PCB 1×7-pin headers (two male and
two female). A "Micro-MaTch" 10-pin
MSP-TS430L092 14-pin PW female connector is also present on the (green PCB) (TSSOP ZIF) MSP-TS430L092 2 x MSP430L092IPW PCB which connects the kit with an 'Active Cable' PCB; this 'Active Cable'
PCB is connected by 14-pin JTAG cable
with the FET430UIF
MSP-TS430PW24 24-pin PW MSP430AFE2xx 2 x MSP430AFE253IPW Four PCB 1×12-pin headers (two male (green PCB) (TSSOP ZIF) and two female)
MSP430F11x1,
MSP430F11x2,
MSP-TS430DW28 28-pin DW MSP430F12x, Four PCB 1×12-pin headers (two male (green PCB) (SSOP ZIF) MSP430F12x2, 2 x MSP430F123IDW and two female) MSP430F21xx
Supports devices in 20- and
28-pin DA packages
MSP430F11x1,
MSP-TS430PW28 28-pin PW MSP430F11x2, Four PCB 1×12-pin headers (two male (green PCB) (TSSOP ZIF) MSP430F12x, 2 x MSP430F2132IPW and two female) MSP430F12x2,
MSP430F21xx
MSP430F20xx,
MSP-TS430PW28A 28-pin PW MSP430G2xxx in 14-, 20-, Four PCB 1×12-pin headers (two male (red PCB) (TSSOP ZIF) and 28-pin PW packages, 2 x MSP430G2452IPW20 and two female) MSP430TCH5E in PW
package
MSP-TS430RHB32A 32-pin RHB MSP430i204x 2 x MSP430i2041TRHB Eight PCB 1×8-pin headers (four male (red PCB) (QFN ZIF) and four female)
MSP-TS430DA38 38-pin DA MSP430F22xx, 2 x MSP430F2274IDA Four PCB 1×19-pin headers (two male (green PCB) (TSSOP ZIF) MSP430G2x44, 2 x MSP430G2744IDA and two female) MSP430G2x55 2 x MSP430G2955IDA
SLAU278R–May 2009–Revised May 2014 Get Started Now! 15
Submit Documentation Feedback
Copyright © 2009–2014, Texas Instruments Incorporated
Kit Contents, MSP-TS430xx www.ti.com
Table 1-2. Individual Kit Contents, MSP-TS430xx (continued)
Part Number Socket Type Supported Devices Included Devices Headers and Comment
MSP-TS430QFN23x0 40-pin RHA MSP430F23x0 2 x MSP430F2370IRHA Eight PCB 1×10-pin headers (four male (green PCB) (QFN ZIF) and four female)
MSP-TS430RSB40 40-pin RSB MSP430F51x1, 2 x MSP430F5172IRSB Eight PCB 1×10-pin headers (four male (green PCB) (QFN ZIF) MSP430F51x2 and four female)
MSP-TS430RHA40A 40-pin RHA MSP430FR572x, 2 x MSP430FR5739IRHA Eight PCB 1×10-pin headers (four male (red PCB) (QFN ZIF) MSP430FR573x and four female)
MSP-TS430DL48 48-pin DL MSP430F42x0 2 x MSP430F4270IDL Four PCB 2×12-pin headers (two male (green PCB) (TSSOP ZIF) and two female)
MSP-TS430RGZ48B 48-pin RGZ MSP430F534x 2 x MSP430F5342IRGZ Eight PCB 1×12-pin headers (four male (blue PCB) (QFN ZIF) and four female)
MSP-TS430RGZ48C 48-pin RGZ MSP430FR58xx and 2 x MSP430FR5969IRGZ Eight PCB 1×12-pin headers (four male (black PCB) (QFN ZIF) MSP430FR59xx and four female)
MSP430F13x,
MSP430F14x,
MSP430F14x1,
MSP430F15x,
MSP430F16x,
MSP430F16x1,
MSP430F23x, TS Kit:
MSP-TS430PM64 64-pin PM MSP430F24x, 2 x MSP430F2618IPM; Eight PCB 1×16-pin headers (four male (green PCB) (QFP ZIF) MSP430F24xx, FET Kit: and four female) MSP430F261x, 2 x MSP430F417IPM and
MSP430F41x, 2 x MSP430F169IPM
MSP430F42x,
MSP430F42xA,
MSP430FE42x,
MSP430FE42xA,
MSP430FE42x2,
MSP430FW42x
MSP-TS430PM64A 64-pin PM MSP430F41x2 2 x MSP430F4152IPM Eight PCB 1×16-pin headers (four male (red PCB) (QFP ZIF) and four female)
MSP-TS430RGC64B 64-pin RGC MSP430F530x 2 x MSP430F5310IRGC Eight PCB 1×16-pin headers (four male (blue PCB) (QFN ZIF) and four female)
MSP430F522x,
MSP-TS430RGC64C 64-pin RGC MSP430F521x , Eight PCB 1×16-pin headers (four male (black PCB) (QFN ZIF) MSP430F523x, 2 x MSP430F5229IRGC and four female) MSP430F524x,
MSP430F525x
MSP-TS430RGC64USB 64-pin RGC MSP430F550x, 2 x MSP430F5510IRGC or Eight PCB 1×16-pin headers (four male (green PCB) (QFN ZIF) MSP430F551x, 2 x MSP430F5528IRGC and four female) MSP430F552x
MSP430F241x,
MSP430F261x,
MSP-TS430PN80 80-pin PN MSP430F43x, Eight PCB 1×20-pin headers (four male (green PCB) (QFP ZIF) MSP430F43x1, 2 x MSP430FG439IPN and four female) MSP430FG43x,
MSP430F47x,
MSP430FG47x
MSP-TS430PN80A 80-pin PN MSP430F532x 2 x MSP430F5329IPN Eight PCB 1×20-pin headers (four male (red PCB) (QFP ZIF) and four female)
MSP-TS430PN80USB 80-pin PN MSP430F552x, 2 x MSP430F5529IPN Eight PCB 1×20-pin headers (four male (green PCB) (QFP ZIF) MSP430F551x and four female)
MSP430F43x,
MSP-TS430PZ100 100-pin PZ MSP430F43x1, Eight PCB 1×25-pin headers (four male (green PCB) (QFP ZIF) MSP430F44x, 2 x MSP430FG4619IPZ and four female) MSP430FG461x,
MSP430F47xx
MSP-TS430PZ100A 100-pin PZ MSP430F471xx 2 x MSP430F47197IPZ Eight PCB 1×25-pin headers (four male (red PCB) (QFP ZIF) and four female)
MSP-TS430PZ100B 100-pin PZ MSP430F67xx 2 x MSP430F6733IPZ Eight PCB 1×25-pin headers (four male (blue PCB) (QFP ZIF) and four female)
MSP430F645x,
MSP-TS430PZ100C 100-pin PZ MSP430F643x, 2 x MSP430F6438IPZ Eight PCB 1×25-pin headers (four male (black PCB) (QFP ZIF) MSP430F535x, and four female)
MSP430F533x
MSP-TS430PZ100D 100-pin PZ MSP430FR698x(1), 2 x MSP430FR6989IPZ Eight PCB 1×25-pin headers (four male (white PCB) (QFP ZIF) MSP430FR688x(1) and four female)
16 Get Started Now! SLAU278R–May 2009–Revised May 2014
Submit Documentation Feedback
Copyright © 2009–2014, Texas Instruments Incorporated
www.ti.com Kit Contents, EM430Fx1x7RF900
Table 1-2. Individual Kit Contents, MSP-TS430xx (continued)
Part Number Socket Type Supported Devices Included Devices Headers and Comment
MSP-TS430PZ5x100 100-pin PZ MSP430F543x, Eight PCB 1×25-pin headers (four male (green PCB) (QFP ZIF) MSP430BT5190, 2 x MSP430F5438IPZ and four female) MSP430SL5438A
MSP-TS430PZ100USB 100-pin PZ MSP430F665x, Eight PCB 1×25-pin headers (four male (green PCB) (QFP ZIF) MSP430F663x, 2 x MSP430F6638IPZ and four female) MSP430F563x
MSP430F677x,
MSP430F676x, Four PCB 1x26-pin headers (two male MSP-TS430PEU128 128-pin PEU MSP430F674x, 2 x MSP430F67791IPEU and two female) and four PCB 1x38-pin (green PCB) (QFP ZIF) MSP430F677x1, headers (two male and two female) MSP430F676x1,
MSP430F674x1
See the device data sheets for device specifications. Device errata can be found in the respective device
product folder on the web provided as a PDF document. Depending on the device, errata may also be
found in the device bug database at www.ti.com/sc/cgi-bin/buglist.cgi.
1.14 Kit Contents, EM430Fx1x7RF900
• One READ ME FIRST document
• One legal notice
• Two target socket module
MSP-EM430F5137RF900: Two EM430F5137RF900 target socket modules. This is the PCB on which
is soldered a CC430F5137 device in a 48-pin RGZ package. A 2×7-pin male connector is also present
on the PCB
MSP-EM430F6137RF900: Two EM430F6137RF900 target socket modules. This is the PCB on which
is soldered a CC430F6137 device in a 64-pin RGC package. A 2×7-pin male connector is also present
on the PCB
MSP-EM430F6147RF900: Two EM430F6147RF900 target socket modules. This is the PCB on which
is soldered a CC430F6147 device in a 64-pin RGC package. A 2×7-pin male connector is also present
on the PCB
• Two CC430EM battery packs
• Four AAA batteries
• Two 868- or 915-MHz antennas
• Two 32.768-kHz crystals
• 18 PCB 2×4-pin headers
1.15 Hardware Installation, MSP-FET430PIF
Follow these steps to install the hardware for the MSP-FET430PIF tools:
1. Use the 25-conductor cable to connect the FET interface module to the parallel port of the PC. The
necessary driver for accessing the PC parallel port is installed automatically during CCS or IAR
Embedded Workbench installation. Note that a restart is required after the CCS or IAR Embedded
Workbench installation for the driver to become active.
2. Use the 14-conductor cable to connect the parallel-port debug interface module to a target board, such
as an MSP-TS430xxx target socket module. Module schematics and PCBs are shown in Appendix B.
SLAU278R–May 2009–Revised May 2014 Get Started Now! 17
Submit Documentation Feedback
Copyright © 2009–2014, Texas Instruments Incorporated
Hardware Installation, MSP-FET430UIF www.ti.com
1.16 Hardware Installation, MSP-FET430UIF
Follow these steps to install the hardware for the MSP-FET430UIF tool:
1. Install the IDE (CCS or IAR) you plan to use before connecting USB-FET interface to PC. The IDE
installation installs drivers automatically.
2. Use the USB cable to connect the USB-FET interface module to a USB port on the PC. The USB FET
should be recognized, as the USB device driver is installed automatically. If the driver has not been
installed yet, the install wizard starts. Follow the prompts and point the wizard to the driver files.
The default location for CCS is c:\ti\ccsv5\ccs_base\emulation\drivers\msp430\USB_CDC or
c:\ti\ccsv5\ccs_base\emulation\drivers\msp430\USB_FET_XP_XX, depending of firmware version of
the tool.
The default location for IAR Embedded Workbench is \Embedded Workbench x.x\430\drivers\TIUSBFET\eZ430-UART or \Embedded Workbench x.x\430\drivers\, depending of firmware version of the tool.
The USB driver is installed automatically. Detailed driver installation instructions can be found in
Appendix C.
3. After connecting to a PC, the USB FET performs a self-test during which the red LED may flash for
approximately two seconds. If the self-test passes successfully, the green LED stays on.
4. Use the 14-conductor cable to connect the USB-FET interface module to a target board, such as an
MSP-TS430xxx target socket module.
5. Ensure that the MSP430 device is securely seated in the socket, and that its pin 1 (indicated with a
circular indentation on the top surface) aligns with the "1" mark on the PCB.
6. Compared to the parallel-port debug interface, the USB FET has additional features including JTAG
security fuse blow and adjustable target VCC (1.8 V to 3.6 V). Supply the module with up to 60 mA.
1.17 Hardware Installation, MSP-FET
Follow these steps to install the hardware for the MSP-FET tool:
1. Install the IDE (CCS or IAR) that you plan to use before connecting MSP-FET to PC. During IDE
installation, USB drivers are installed automatically. Make sure to use the latest IDE version, otherwise
the USB drivers might not be able to recognize the MSP-FET.
2. Connect the MSP-FET to a USB port on the PC with the provided USB cable.
3. The following procedure applies to operation under Windows:
(a) After connecting to the PC, the MSP-FET should be recognized automatically, as the USB device
driver has been already installed together with the IDE.
(b) If the driver has not been installed yet, the Found New Hardware wizard starts. Follow the
instructions and point the wizard to the driver files.
(c) The default location for CCS is c:\ti\ccsv6\ccs_base\emulation\drivers\msp430\USB_CDC.
(d) The default location for IAR Embedded Workbench is \Embedded Workbench
x.x\430\drivers\.
4. After connecting to a PC, the MSP-FET performs a self-test. If the self-test passes successfully, the
green LED stays on. For a complete list of LED signals, please refer to the MSP-FET chapter in this
document.
5. Connect the MSP-FET to a target board, such as an MSP-TS430xxx target socket module, with the
14-conductor cable.
6. Make sure that the MSP430 device is securely seated in the socket and that its pin 1 (indicated with a
circular indentation on the top surface) aligns with the "1" mark on the PCB.
1.18 Hardware Installation, eZ430-XXXX, MSP-EXP430G2, MSP-EXP430FR5739, MSPEXP430F5529
To install the eZ430-XXXX, MSP-EXP430G2, MSP-EXP430FR5739, MSP-EXP430F5529 tools, follow
steps 1 and 2 of Section 1.16
18 Get Started Now! SLAU278R–May 2009–Revised May 2014
Submit Documentation Feedback
Copyright © 2009–2014, Texas Instruments Incorporated
www.ti.com Hardware Installation, MSP-FET430Uxx, MSP-TS430xxx, FET430F6137RF900, EM430Fx137RF900
1.19 Hardware Installation, MSP-FET430Uxx, MSP-TS430xxx, FET430F6137RF900,
EM430Fx137RF900
Follow these steps to install the hardware for the MSP-FET430Uxx and MSP-TS430xxx tools:
1. Follow steps 1 and 2 of Section 1.16
2. Connect the MSP-FET430PIF or MSP-FET430UIF debug interface to the appropriate port of the PC.
Use the 14-conductor cable to connect the FET interface module to the supplied target socket module.
3. Ensure that the MSP430 device is securely seated in the socket and that its pin 1 (indicated with a
circular indentation on the top surface) aligns with the "1" mark on the PCB.
4. Ensure that the two jumpers (LED and VCC) near the 2×7-pin male connector are in place. Illustrations
of the target socket modules and their parts are found in Appendix B.
SLAU278R–May 2009–Revised May 2014 Get Started Now! 19
Submit Documentation Feedback
Copyright © 2009–2014, Texas Instruments Incorporated
Important MSP430 Documents on the Web www.ti.com
1.20 Important MSP430 Documents on the Web
The primary sources of MSP430 information are the device-specific data sheet and user's guide. The
MSP430 web site (www.ti.com/msp430) contains the most recent version of these documents.
PDF documents describing the CCS tools (CCS IDE, the assembler, the C compiler, the linker, and the
librarian) are in the msp430\documentation folder. A Code Composer Studio specific Wiki page (FAQ) is
available, and the Texas Instruments E2E Community support forums for the MSP430 and Code
Composer Studio v5 provide additional help besides the product help and Welcome page.
PDF documents describing the IAR tools (Workbench C-SPY, the assembler, the C compiler, the linker,
and the librarian) are in the common\doc and 430\doc folders. Supplements to the documents (that is, the
latest information) are available in HTML format in the same directories. A IAR specific Wiki Page is also
available.
20 Get Started Now! SLAU278R–May 2009–Revised May 2014
Submit Documentation Feedback
Copyright © 2009–2014, Texas Instruments Incorporated
Chapter 2
SLAU278R–May 2009–Revised May 2014
Design Considerations for In-Circuit Programming
This chapter presents signal requirements for in-circuit programming of the MSP430.
Topic ........................................................................................................................... Page
2.1 Signal Connections for In-System Programming and Debugging............................. 22
2.2 External Power................................................................................................... 26
2.3 Bootstrap Loader (BSL) ...................................................................................... 26
SLAU278R–May 2009–Revised May 2014 Design Considerations for In-Circuit Programming 21
Submit Documentation Feedback
Copyright © 2009–2014, Texas Instruments Incorporated
Signal Connections for In-System Programming and Debugging www.ti.com
2.1 Signal Connections for In-System Programming and Debugging
MSP-FET430PIF, MSP-FET430UIF, MSP-GANG, MSP-GANG430, MSP-PRGS430
With the proper connections, the debugger and an FET hardware JTAG interface (such as the MSPFET430PIF
and MSP-FET430UIF) can be used to program and debug code on the target board. In
addition, the connections also support the MSP-GANG430 or MSP-PRGS430 production programmers,
thus providing an easy way to program prototype boards, if desired.
Figure 2-1 shows the connections between the 14-pin FET interface module connector and the target
device required to support in-system programming and debugging for 4-wire JTAG communication.
Figure 2-2 shows the connections for 2-wire JTAG mode (Spy-Bi-Wire). The 4-wire JTAG mode is
supported on most MSP430 devices, except devices with low pin counts (for example, MSP430G2230).
The 2-wire JTAG mode is available on selected devices only. See the Code Composer Studio for MSP430
User's Guide (SLAU157) or IAR Embedded Workbench Version 3+ for MSP430 User's Guide (SLAU138)
for information on which interface method can be used on which device.
The connections for the FET interface module and the MSP-GANG, MSP-GANG430, or MSP-PRGS430
are identical. Both the FET interface module and MSP-GANG430 can supply VCC to the target board
(through pin 2). In addition, the FET interface module, MSP-GANG, and MSP-GANG430 have a VCCsense
feature that, if used, requires an alternate connection (pin 4 instead of pin 2). The VCC-sense feature
senses the local VCC present on the target board (that is, a battery or other local power supply) and
adjusts the output signals accordingly. If the target board is to be powered by a local VCC, then the
connection to pin 4 on the JTAG should be made, and not the connection to pin 2. This uses the VCCsense
feature and prevents any contention that might occur if the local on-board VCC were connected to
the VCC supplied from the FET interface module, MSP-GANG or the MSP-GANG430. If the VCC-sense
feature is not necessary (that is, if the target board is to be powered from the FET interface module, MSPGANG,
or MSP-GANG430), the VCC connection is made to pin 2 on the JTAG header, and no connection
is made to pin 4. Figure 2-1 and Figure 2-2 show a jumper block that supports both scenarios of supplying
VCC to the target board. If this flexibility is not required, the desired VCC connections may be hard-wired to
eliminate the jumper block. Pins 2 and 4 must not be connected at the same time.
Note that in 4-wire JTAG communication mode (see Figure 2-1), the connection of the target RST signal
to the JTAG connector is optional when using devices that support only 4-wire JTAG communication
mode. However, when using devices that support 2-wire JTAG communication mode in 4-wire JTAG
mode, the RST connection must be made. The MSP430 development tools and device programmers
perform a target reset by issuing a JTAG command to gain control over the device. However, if this is
unsuccessful, the RST signal of the JTAG connector may be used by the development tool or device
programmer as an additional way to assert a device reset.
22 Design Considerations for In-Circuit Programming SLAU278R–May 2009–Revised May 2014
Submit Documentation Feedback
Copyright © 2009–2014, Texas Instruments Incorporated
1
3
5
7
9
11
13
2
4
6
8
10
12
14
TDO/TDI
TDI/VPP
TMS
TCK
GND
TEST/VPP
JTAG
VCC TOOL
VCC TARGET
J1 (see Note A)
J2 (see Note A)
VCC
R1
47 k
(see Note B)
W
C2
10 μF
C3
0.1 μF
VCC/AVCC/DVCC
RST/NMI
TDO/TDI
TDI/VPP
TMS
TCK
TEST/VPP (see Note C)
V /AV /DV SS SS SS
MSP430Fxxx
C1
10 nF/2.2 nF
(see Notes B and E)
RST (see Note D)
Important to connect
www.ti.com Signal Connections for In-System Programming and Debugging
A If a local target power supply is used, make connection J1. If power from the debug or programming adapter is used,
make connection J2.
B The configuration of R1 and C1 for the RST/NMI pin depends on the device family. See the respective MSP430 family
user's guide for the recommended configuration.
C The TEST pin is available only on MSP430 family members with multiplexed JTAG pins. See the device-specific data
sheet to determine if this pin is available.
D The connection to the JTAG connector RST pin is optional when using a device that supports only 4-wire JTAG
communication mode, and it is not required for device programming or debugging. However, this connection is
required when using a device that supports 2-wire JTAG communication mode in 4-wire JTAG mode.
E When using a device that supports 2-wire JTAG communication in 4-wire JTAG mode, the upper limit for C1 should
not exceed 2.2 nF. This applies to both TI FET interface modules (LPT and USB FET).
Figure 2-1. Signal Connections for 4-Wire JTAG Communication
SLAU278R–May 2009–Revised May 2014 Design Considerations for In-Circuit Programming 23
Submit Documentation Feedback
Copyright © 2009–2014, Texas Instruments Incorporated
1
3
5
7
9
11
13
2
4
6
8
10
12
14
TEST/SBWTCK
MSP430Fxxx
RST/NMI/SBWTDIO
TDO/TDI
TCK
GND
TEST/VPP
JTAG
VCC TOOL
VCC TARGET
330!
R2
J1 (see Note A)
J2 (see Note A)
Important to connect
VCC/AVCC/DVCC
V /AV /DV SS SS SS
R1
47 k!
See Note B
C1
2.2 nF
See Note B
VCC
C2
10 μF
C3
0.1 μF
Signal Connections for In-System Programming and Debugging www.ti.com
A If a local target power supply is used, make connection J1. If power from the debug or programming adapter is used,
make connection J2.
B The device RST/NMI/SBWTDIO pin is used in 2-wire mode for bidirectional communication with the device during
JTAG access, and any capacitance that is attached to this signal may affect the ability to establish a connection with
the device. The upper limit for C1 is 2.2 nF when using current TI tools.
C R2 protects the JTAG debug interface TCK signal from the JTAG security fuse blow voltage that is supplied by the
TEST/VPP pin during the fuse blow process. If fuse blow functionality is not needed, R2 is not required (populate 0 Ω)
and do not connect TEST/VPP to TEST/SBWTCK.
Figure 2-2. Signal Connections for 2-Wire JTAG Communication (Spy-Bi-Wire) Used by MSP430F2xx,
MSP430G2xx, and MSP430F4xx Devices
24 Design Considerations for In-Circuit Programming SLAU278R–May 2009–Revised May 2014
Submit Documentation Feedback
Copyright © 2009–2014, Texas Instruments Incorporated
1
3
5
7
9
11
13
2
4
6
8
10
12
14
TEST/SBWTCK
MSP430Fxxx
RST/NMI/SBWTDIO
TDO/TDI
TCK
GND
JTAG
R1
47 k!
See Note B
VCC TOOL
VCC TARGET
C1
2.2 nF
See Note B
J1 (see Note A)
J2 (see Note A)
Important to connect
VCC/AVCC/DVCC
V /AV /DV SS SS SS
VCC
C2
10 μF
C3
0.1 μF
www.ti.com Signal Connections for In-System Programming and Debugging
A Make connection J1 if a local target power supply is used, or make connection J2 if the target is powered from the
debug or programming adapter.
B The device RST/NMI/SBWTDIO pin is used in 2-wire mode for bidirectional communication with the device during
JTAG access, and any capacitance that is attached to this signal may affect the ability to establish a connection with
the device. The upper limit for C1 is 2.2 nF when using current TI tools.
Figure 2-3. Signal Connections for 2-Wire JTAG Communication (Spy-Bi-Wire) Used by MSP430F5xx and
MSP430F6xx Devices
SLAU278R–May 2009–Revised May 2014 Design Considerations for In-Circuit Programming 25
Submit Documentation Feedback
Copyright © 2009–2014, Texas Instruments Incorporated
External Power www.ti.com
2.2 External Power
The MSP-FET430UIF can supply targets with up to 60 mA through pin 2 of the 14-pin connector. Note
that the target should not consume more than 60 mA, even as a peak current, as it may violate the USB
specification. For example, if the target board has a capacitor on VCC more than 10 μF, it may cause
inrush current during capacitor charging that may exceed 60 mA. In this case, the current should be
limited by the design of the target board, or an external power supply should be used.
The VCC for the target can be selected between 1.8 V and 3.6 V in steps of 0.1 V. Alternatively, the target
can be supplied externally. In this case, the external voltage should be connected to pin 4 of the 14-pin
connector. The MSP-FET430UIF then adjusts the level of the JTAG signals to external VCC automatically.
Only pin 2 (MSP-FET430UIF supplies target) or pin 4 (target is externally supplied) must be connected;
not both at the same time.
When a target socket module is powered from an external supply, the external supply powers the device
on the target socket module and any user circuitry connected to the target socket module, and the FET
interface module continues to be powered from the PC through the parallel port. If the externally supplied
voltage differs from that of the FET interface module, the target socket module must be modified so that
the externally supplied voltage is routed to the FET interface module (so that it may adjust its output
voltage levels accordingly). See the target socket module schematics in Appendix B.
The PC parallel port can source a limited amount of current. Because of the ultra-low-power requirement
of the MSP430, a standalone FET does not exceed the available current. However, if additional circuitry is
added to the tool, this current limit could be exceeded. In this case, external power can be supplied to the
tool through connections provided on the target socket modules. See the schematics and pictorials of the
target socket modules in Appendix B to locate the external power connectors. Note that the MSPFET430PIF
is not recommended for new design.
2.3 Bootstrap Loader (BSL)
The JTAG pins provide access to the memory of the MSP430 and CC430 devices. On some devices,
these pins are shared with the device port pins, and this sharing of pins can complicate a design (or
sharing may not be possible). As an alternative to using the JTAG pins, most MSP430Fxxx devices
contain a program (a "bootstrap loader") that permits the flash memory to be erased and programmed
using a reduced set of signals. The MSP430 Programming Via the Bootstrap Loader User's Guide
(SLAU319) describes this interface. See the MSP430 web site for the application reports and a list of
MSP430 BSL tool developers.
TI suggests that MSP430Fxxx customers design their circuits with the BSL in mind (that is, TI suggests
providing access to these signals by, for example, a header).
See FAQ Hardware #10 for a second alternative to sharing the JTAG and port pins.
26 Design Considerations for In-Circuit Programming SLAU278R–May 2009–Revised May 2014
Submit Documentation Feedback
Copyright © 2009–2014, Texas Instruments Incorporated
Appendix A
SLAU278R–May 2009–Revised May 2014
Frequently Asked Questions and Known Issues
This appendix presents solutions to frequently asked questions regarding the MSP-FET430 hardware.
Topic ........................................................................................................................... Page
A.1 Hardware FAQs.................................................................................................. 28
A.2 Known Issues .................................................................................................... 30
SLAU278R–May 2009–Revised May 2014 Frequently Asked Questions and Known Issues 27
Submit Documentation Feedback
Copyright © 2009–2014, Texas Instruments Incorporated
Hardware FAQs www.ti.com
A.1 Hardware FAQs
1. MSP430F22xx Target Socket Module (MSP-TS430DA38) – Important Information
Due to the large capacitive coupling introduced by the device socket between the adjacent signals
XIN/P2.6 (socket pin 6) and RST/SBWTDIO (socket pin 7), in-system debugging can disturb the
LFXT1 low-frequency crystal oscillator operation (ACLK). This behavior applies only to the Spy-Bi-Wire
(2-wire) JTAG configuration and only to the period while a debug session is active.
Workarounds:
• Use the 4-wire JTAG mode debug configuration instead of the Spy-Bi-Wire (2-wire) JTAG
configuration. This can be achieved by placing jumpers JP4 through JP9 accordingly.
• Use the debugger option "Run Free" that can be selected from the Advanced Run drop-down
menu (at top of Debug View). This prevents the debugger from accessing the MSP430 device
while the application is running. Note that, in this mode, a manual halt is required to see if a
breakpoint was hit. See the IDE documentation for more information on this feature.
• Use an external clock source to drive XIN directly.
2. With current interface hardware and software, there is a weakness when adapting target boards
that are powered externally. This leads to an accidental fuse check in the MSP430 device. This is
valid for PIF and UIF but is seen most often on the UIF. A solution is being developed.
Workarounds:
• Connect the RST/NMI pin to the JTAG header (pin 11). LPT and USB tools are able to pull the
RST line, which also resets the device internal fuse logic.
• Use the debugger option "Release JTAG On Go" that can be selected from the IDE drop-down
menu. This prevents the debugger from accessing the MCU while the application is running. Note
that in this mode, a manual halt is required to see if a breakpoint was hit. See the IDE
documentation for more information on this feature.
• Use an external clock source to drive XIN directly.
3. The 14-conductor cable that connects the FET interface module and the target socket module must
not exceed 8 inches (20 centimeters) in length.
4. The signal assignment on the 14-conductor cable is identical for the parallel port interface and the
USB FET.
5. To use the on-chip ADC voltage references, the capacitor must be installed on the target socket
module. See the schematic of the target socket module to populate the capacitor according to the data
sheet of the device.
6. To use the charge pump on the devices with LCD+ Module, the capacitor must be installed on
the target socket module. See the schematic of the target socket module to populate the capacitor
according to the data sheet of the device.
7. Crystals or resonators Q1 and Q2 (if applicable) are not provided on the target socket module.
For MSP430 devices that contain user-selectable loading capacitors, see the device and crystal data
sheets for the value of capacitance.
8. Crystals or resonators have no effect upon the operation of the tool and the CCS debugger or
C-SPY (as any required clocking and timing is derived from the internal DCO and FLL).
9. On devices with multiplexed port or JTAG pins, to use these pin in their port capability:
For CCS: "Run Free" (in Run pulldown menu at top of Debug View) must be selected.
For C-SPY: "Release JTAG On Go" must be selected.
10. As an alternative to sharing the JTAG and port pins (on low pin count devices), consider using
an MSP430 device that is a "superset" of the smaller device. A very powerful feature of the
MSP430 is that the family members are code and architecturally compatible, so code developed on
one device (for example, one without shared JTAG and port pins) ports effortlessly to another
(assuming an equivalent set of peripherals).
28 Frequently Asked Questions and Known Issues SLAU278R–May 2009–Revised May 2014
Submit Documentation Feedback
Copyright © 2009–2014, Texas Instruments Incorporated
www.ti.com Hardware FAQs
11. Information memory may not be blank (erased to 0xFF) when the device is delivered from TI.
Customers should erase the information memory before its first use. Main memory of packaged
devices is blank when the device is delivered from TI.
12. The device current is higher then expected. The device current measurement may not be accurate
with the debugger connected to the device. For accurate measurement, disconnect the debugger.
Additionally some unused pins of the device should be terminated. See the Connection of Unused Pins
table in the device's family user's guide.
13. The following ZIF sockets are used in the FET tools and target socket modules:
• 8-pin device (D package): Yamaichi IC369-0082
• 14-pin device (PW package): Enplas OTS-14-065-01
• 14-pin package for 'L092 (PW package): Yamaichi IC189-0142-146
• 24-pin package (PW package): Enplas OTS-24(28)-0.65-02
• 28-pin device (DW package): Wells-CTI 652 D028
• 28-pin device (PW package): Enplas OTS-28-0.65-01
• 38-pin device (DA package): Yamaichi IC189-0382-037
• 40-pin device (RHA package): Enplas QFN-40B-0.5-01
• 40-pin device (RSB package): Enplas QFN-40B-0.4
• 48-pin device (RGZ package): Yamaichi QFN11T048-008 A101121-001
• 48-pin device (DL package): Yamaichi IC51-0482-1163
• 64-pin device (PM package): Yamaichi IC51-0644-807
• 64-pin device (RGC package): Yamaichi QFN11T064-006
• 80-pin device (PN package): Yamaichi IC201-0804-014
• 100-pin device (PZ package): Yamaichi IC201-1004-008
• 128-pin device (PEU package): Yamaichi IC500-1284-009P
Enplas: www.enplas.com
Wells-CTI: www.wellscti.com
Yamaichi: www.yamaichi.us
SLAU278R–May 2009–Revised May 2014 Frequently Asked Questions and Known Issues 29
Submit Documentation Feedback
Copyright © 2009–2014, Texas Instruments Incorporated
Known Issues www.ti.com
A.2 Known Issues
MSP-FET430UIF Current detection algorithm of the UIF firmware
Problem Description If high current is detected, the ICC monitor algorithm stays in a loop of frequently
switching on and off the target power supply. This power switching puts some MSP430
devices such as the MSP430F5438 in a state that requires a power cycle to return the
device to JTAG control.
A side issue is that if the UIF firmware has entered this switch on and switch off loop, it
is not possible to turn off the power supply to the target by calling MSP430_VCC(0). A
power cycle is required to remove the device from this state.
Solution IAR KickStart and Code Composer Essentials that have the MSP430.dll version
2.04.00.003 and higher do not show this problem. Update the software development tool
to this version or higher to update the MSP-FET430UIF firmware.
MSP-FET430PIF Some PCs do not supply 5 V through the parallel port
Problem Description Device identification problems with modern PCs, because the parallel port often does not
deliver 5 V as was common with earlier hardware.
1. When connected to a laptop, the test signal is clamped to 2.5 V.
2. When the external VCC becomes less than 3 V, up to 10 mA is flowing in the adapter
through pin 4 (sense).
Solution Measure the voltage level of the parallel port. If it is too low, provide external 5 V to the
VCC pads of the interface. The jumper on a the target socket must be switched to
external power.
30 Frequently Asked Questions and Known Issues SLAU278R–May 2009–Revised May 2014
Submit Documentation Feedback
Copyright © 2009–2014, Texas Instruments Incorporated
Appendix B
SLAU278R–May 2009–Revised May 2014
Hardware
This appendix contains information relating to the FET hardware, including schematics, PCB pictorials,
and bills of materials (BOMs). All other tools, such as the eZ430 series, are described in separate productspecific
user's guides.
SLAU278R–May 2009–Revised May 2014 Hardware 31
Submit Documentation Feedback
Copyright © 2009–2014, Texas Instruments Incorporated
Appendix B www.ti.com
Topic ........................................................................................................................... Page
B.1 MSP-TS430D8 .................................................................................................... 33
B.2 MSP-TS430PW14................................................................................................ 36
B.3 MSP-TS430L092 ................................................................................................. 39
B.4 MSP-TS430L092 Active Cable .............................................................................. 42
B.5 MSP-TS430PW24................................................................................................ 45
B.6 MSP-TS430DW28................................................................................................ 48
B.7 MSP-TS430PW28................................................................................................ 51
B.8 MSP-TS430PW28A.............................................................................................. 54
B.9 MSP-TS430RHB32A............................................................................................ 57
B.10 MSP-TS430DA38 ................................................................................................ 60
B.11 MSP-TS430QFN23x0........................................................................................... 63
B.12 MSP-TS430RSB40 .............................................................................................. 66
B.13 MSP-TS430RHA40A............................................................................................ 69
B.14 MSP-TS430DL48 ................................................................................................ 72
B.15 MSP-TS430RGZ48B ............................................................................................ 75
B.16 MSP-TS430RGZ48C ............................................................................................ 78
B.17 MSP-TS430PM64 ................................................................................................ 81
B.18 MSP-TS430PM64A.............................................................................................. 84
B.19 MSP-TS430RGC64B............................................................................................ 87
B.20 MSP-TS430RGC64C............................................................................................ 90
B.21 MSP-TS430RGC64USB ....................................................................................... 94
B.22 MSP-TS430PN80 ................................................................................................ 98
B.23 MSP-TS430PN80A ............................................................................................ 101
B.24 MSP-TS430PN80USB ........................................................................................ 104
B.25 MSP-TS430PZ100 ............................................................................................. 108
B.26 MSP-TS430PZ100A ........................................................................................... 111
B.27 MSP-TS430PZ100B ........................................................................................... 114
B.28 MSP-TS430PZ100C ........................................................................................... 117
B.29 MSP-TS430PZ100D ........................................................................................... 121
B.30 MSP-TS430PZ5x100 .......................................................................................... 124
B.31 MSP-TS430PZ100USB ....................................................................................... 127
B.32 MSP-TS430PEU128 ........................................................................................... 131
B.33 EM430F5137RF900 ........................................................................................... 134
B.34 EM430F6137RF900 ........................................................................................... 138
B.35 EM430F6147RF900 ........................................................................................... 142
B.36 MSP-FET ......................................................................................................... 146
B.37 MSP-FET430PIF................................................................................................ 157
B.38 MSP-FET430UIF ............................................................................................... 159
32 Hardware SLAU278R–May 2009–Revised May 2014
Submit Documentation Feedback
Copyright © 2009–2014, Texas Instruments Incorporated
GND
100nF
330R
10uF/10V
47K
2.2nF
GND
330R
GND
GND
green
FE4L FE4H
GND
Ext_PWR
Socket: YAMAICHI
Type: IC369-0082
Vcc
ext
int
to measure supply current DNP
1
3
5
7
9
11
13
2
4
6
12
14
8
10
SBW
C5
R3
C7
R5
C8
1
2
3
J3
1
2
J4
1
2
J6
1
2
3
J5 R2
D1
1
2
3
4
J1
5
6
7
8
J2
DVCC
1
DVSS
8
P1.2/TA1/A2
2
P1.5/TA0/A5/SCLK
3
P1.6/TA1/A6/SDO/SCL
4
TST/SBWTCK
7
RST/SBWTDIO
6
P1.7/A7/SDI/SDA
5
U1
MSP-TS430D8
GND
VCC
RST/SBWTDIO
RST/SBWTDIO
RST/SBWTDIO
SBWTCK
VCC430
TST/SBWTCK
TST/SBWTCK
TST/SBWTCK
P1.5
P1.6 P1.7
P1.2
Date: 28.07.201111:03:35 Sheet: /11
REV:
TITLE:
Document Number:
MSP-TS430D8
+
1.0
MSP-TS430D8 Target Socket Board
www.ti.com MSP-TS430D8
B.1 MSP-TS430D8
Figure B-1. MSP-TS430D8 Target Socket Module, Schematic
SLAU278R–May 2009–Revised May 2014 Hardware 33
Submit Documentation Feedback
Copyright © 2009–2014, Texas Instruments Incorporated
Jumper J4
Open to disconnect LED
D1
LED connected to P1.2
Orient Pin 1 of MSP430 device
14-pin connector for debugging
in Spy-Bi-Wire mode only
(4-Wire JTAG not available)
Jumper J6
Open to measure current
Jumper J5
1-2 (int): Power supply via JTAG interface
2-3 (ext): External power supply
Connector J3
External power connector
Jumper J5 to “ext”
MSP-TS430D8 www.ti.com
Figure B-2. MSP-TS430D8 Target Socket Module, PCB
34 Hardware SLAU278R–May 2009–Revised May 2014
Submit Documentation Feedback
Copyright © 2009–2014, Texas Instruments Incorporated
www.ti.com MSP-TS430D8
Table B-1. MSP-TS430D8 Bill of Materials
Position Ref Des No. per Description Digi-Key Part No. Comment Board
1 J4, J6 2 2-pin header, male, TH SAM1035-02-ND place jumper on header
2 J5 1 3-pin header, male, TH SAM1035-03-ND place jumper on pins 1-2
3 SBW 1 10-pin connector, male, TH HRP10H-ND
4 J3 1 3-pin header, male, TH SAM1035-03-ND
5 C8 1 2.2nF, CSMD0805 Buerklin 53 D 292
6 C7 1 10uF, 10V, 1210ELKO 478-3875-1-ND
7 R5 1 47K, 0805 541-47000ATR-ND
8 C5 1 100nF, CSMD0805 311-1245-2-ND
9 R2, R3 2 330R, 0805 541-330ATR-ND
10 J1, J2 2 4-pin header, TH SAM1029-04-ND DNP: headers enclosed with kit. Keep vias free of solder.
10,1 J1, J2 1 4-pin socket, TH SAM1029-04-ND DNP: receptacles enclosed with kit.
11 U1 1 SO8 Socket: Type IC369-0082 Manuf.: Yamaichi
12 D1 1 red, LED 0603
13 MSP430 2 MSP430G2210, MSP430G2230 DNP: enclosed with kit. Is supplied by TI
14 PCB 1 50,0mmx44,5mm MSP-TS430D8 Rev. 1.0
SLAU278R–May 2009–Revised May 2014 Hardware 35
Submit Documentation Feedback
Copyright © 2009–2014, Texas Instruments Incorporated
12pF
12pF
GND
100nF
330R
10uF/10V
47K
2.2nF
GND
330R
100nF
GND
GND
GND
green
Ext_PWR
Socket: ENPLAS
Type: OTS-14-065
Vcc
ext
int
to measure supply current
DNP
DNP
DNP
DNP
DNP
JTAG ->
SBW ->
JTAG-Mode selection:
4-wire JTAG: Set jumpers J7 to J12 to position 2-3
2-wire "SpyBiWire": Set jumpers J7 to J12 to position 2-1
1
3
5
7
9
11
13
2
4
6
12
14
8
10
JTAG
C2
C1
C5
R3
C7
R5
C8
1
2
3
J3
Q1
8
9
10
11
12
13
14
J2
1
2
3
4
5
6
7
J1
1
2
J4
1
2
J6
J5
1
2
3
R2
C3
J7
1
2
3
J8
1
2
3
J9
1
2
3
J10
1
2
3
J11
1
2
3
J12
1
2
3
1
2
3
4
5
6
7 8
9
10
14
13
12
11
D1
P1.0
P1.3
P1.2
P1.1 XOUT XOUT
GND
XIN
XIN
VCC
RST/SBWTDIO
RST/SBWTDIO
SBWTCK
TEST/SBWTCK
TEST/SBWTCK
TEST/SBWTCK
VCC430
P1.4/TCK
P1.4/TCK
P1.5/TMS
P1.5/TMS
P1.6/TDI
P1.6/TDI
P1.7/TDO
P1.7/TDO
TDO/SBWTDIO
RST/NMI
TMS
TDI
Date: 7/16/2007 8:22:36 AM Sheet: 1/1
REV:
TITLE:
Document Number:
MSP-TS430PW14
+
2.0
MSP-TS430PW14 Target Socket Board
MSP-TS430PW14 www.ti.com
B.2 MSP-TS430PW14
Figure B-3. MSP-TS430PW14 Target Socket Module, Schematic
36 Hardware SLAU278R–May 2009–Revised May 2014
Submit Documentation Feedback
Copyright © 2009–2014, Texas Instruments Incorporated
Jumper J4
Open to disconnect LED
Orient Pin 1 of MSP430 device Jumper J6
Open to measure current
Connector J3
External power connector
D1 Jumper J5 to "ext"
LED connected to P1.0
Jumpers J7 to J12
Close 1-2 to debug in Spy-Bi-Wire mode.
Close 2-3 to debug in 4-wire JTAG mode.
Jumper J5
1-2 (int): Power supply via JTAG interface
2-3 (ext): External power supply
Connector JTAG
For JTAG Tool
www.ti.com MSP-TS430PW14
Figure B-4. MSP-TS430PW14 Target Socket Module, PCB
SLAU278R–May 2009–Revised May 2014 Hardware 37
Submit Documentation Feedback
Copyright © 2009–2014, Texas Instruments Incorporated
MSP-TS430PW14 www.ti.com
Table B-2. MSP-TS430PW14 Bill of Materials
Position Ref Des No. per Description Digi-Key Part No. Comment Board
1 C1, C2 0 12pF, SMD0805 DNP
2 C7 1 10uF, 10V, Tantal Size 511-1463-2-ND B
3 C3, C5 1 100nF, SMD0805 478-3351-2-ND DNP: C3
4 C8 0 2.2nF, SMD0805 DNP
5 D1 1 green LED, SMD0603 475-1056-2-ND
DNP: Headers and receptacles
enclosed with kit. Keep vias free of
6 J1, J2 0 7-pin header, TH solder
SAM1029-07-ND : Header
SAM1213-07-ND : Receptacle
J3, J5, J7, Place jumpers on headers J5, J7, J8, 7 J8, J9, J10, 8 3-pin header, male, TH SAM1035-03-ND J9, J10, J11, J12; Pos 1-2 J11, J12
8 J4, J6 2 2-pin header, male, TH SAM1035-02-ND Place jumper on header
9 9 Jumper 15-38-1024-ND Place on: J5, J7-J12; Pos 1-2
10 JTAG 1 14-pin connector, male, HRP14H-ND TH
Micro Crystal MS1V-T1K
12 Q1 0 Crystal 32.768kHz, C(Load) = DNP: keep vias free of solder
12.5pF
13 R2, R3 2 330 Ω, SMD0805 541-330ATR-ND
15 R5 1 47k Ω, SMD0805 541-47000ATR-ND
16 U1 1 Socket: OTS-14-0.65-01 Manuf.: Enplas
17 PCB 1 56 x 53 mm 2 layers
Adhesive Approximately 6mm For example, 3M 18 plastic feet 4 width, 2mm height Bumpons Part No. SJ- Apply to corners at bottom side 5302
19 MSP430 2 MSP430F2013IPW DNP: enclosed with kit, supplied by TI
38 Hardware SLAU278R–May 2009–Revised May 2014
Submit Documentation Feedback
Copyright © 2009–2014, Texas Instruments Incorporated
www.ti.com MSP-TS430L092
B.3 MSP-TS430L092
Figure B-5. MSP-TS430L092 Target Socket Module, Schematic
SLAU278R–May 2009–Revised May 2014 Hardware 39
Submit Documentation Feedback
Copyright © 2009–2014, Texas Instruments Incorporated
Connector J3
External power connector
Jumper JP3
Open to measure current
Jumper JP1
Write enable for EPROM
Orient pin 1 of
MSP430 device
MSP-TS430L092 www.ti.com
Settings of the MSP-TS430L092 Target Socket
Figure B-6 shows the PCB layout of the MSP-TS430L092 target socket. The following pinning is
recommended:
• JP1 is write enable for the EPROM. If this is not set, the EPROM can only be read.
• JP2 and JP3 connect device supply with boost converter. They can be opened to measure device
current consumption. For default operation, they should be closed.
Figure B-6. MSP-TS430L092 Target Socket Module, PCB
40 Hardware SLAU278R–May 2009–Revised May 2014
Submit Documentation Feedback
Copyright © 2009–2014, Texas Instruments Incorporated
www.ti.com MSP-TS430L092
Table B-3. MSP-TS430L092 Bill of Materials
Pos. Ref Des No. No. Per Description Digi-Key Part No. Comment Board
1 C1, C2 2 330nF, SMD0603
2 C5 1 100n, SMD0603
3 C6 1 10u, SMD0805
4 C10 1 100n, SMD0603
5 EEPROM1 1 M95512 SO08 (SO8) ST Micro M95160R Digikey: 497-8688-1-ND
DNP: headers and
receptacles enclosed with kit.
7 J1, J2 2 7-pin header, TH Keep vias free of solder.
SAM1213-07-ND : Header
SAM1035-07-ND : Receptacle
8 J3 1 3-pin header, male, TH SAM1035-03-ND
9 J4, J5 2 FE4L, FE4H 4 pol. Stiftreihe DNP; Keep vias free of solder.
11 J13 1 MICRO_STECKV_10 Reichelt: MicroMaTch- Connector: MM FL 10G
12 JP1, JP2,JP3 3 2-pin header, male, TH SAM1035-02-ND place jumper on header
15 L1 1 33uH, SMD0806 LQH2MCN330K02L Farnell: 151-5557
16 LED1, LED4 2 LEDCHIPLED_0603 Farnell: 1686065
17 Q2 1 BC817-16LT1SMD BC817-16LT1SMD SOT23-BEC
18 R0, R6, R7 3 2K7, SMD0603
19 R1 1 1k, SMD0603
20 R2 1 47k, SMD0603
21 R4,R5, R8, 6 10k, SMD0603 R10, RC, RD
22 RA 1 3.9k, SMD0603
23 RB 1 6.8k, SMD0603
24 U1 1 14 Pin Socket - IC189-0142- Manuf. Yamaichi 146
22 MSP430 2 MSP430L092PWR DNP: Enclosed with kit. Is supplied by TI.
SLAU278R–May 2009–Revised May 2014 Hardware 41
Submit Documentation Feedback
Copyright © 2009–2014, Texas Instruments Incorporated
MSP-TS430L092 Active Cable www.ti.com
B.4 MSP-TS430L092 Active Cable
Figure B-7. MSP-TS430L092 Active Cable Target Socket Module, Schematic
42 Hardware SLAU278R–May 2009–Revised May 2014
Submit Documentation Feedback
Copyright © 2009–2014, Texas Instruments Incorporated
Connector JTAG
For JTAG Tool
JP2
JP1
www.ti.com MSP-TS430L092 Active Cable
Figure B-8 shows the PCB layout for the Active Cable. The following pinning is possible:
• JP1 has two jumpers (Jumper 1 and Jumper 2) that can be set as shown in Table B-4.
Table B-4. MSP-TS430L092 JP1 Settings
Jumper 1 Jumper 2 Description
Off Off The active cable has no power and does not function.
Off On The active cable receives power from target socket. For this option, the target socket must have its own power supply.
On Off The active cable receives power from the JTAG connector.
The JTAG connector powers the active cable and the target socket. For
On On this option, the target socket must not have its own power source, as this
would cause a not defined state.
• JP2 is for reset. For the standard MSP-TS430L092, this jumper must be set. It sets the reset pin to
high and can also control it. Without this jumper on the MSP-TS430L092, reset is set to zero.
Figure B-8. MSP-TS430L092 Active Cable Target Socket Module, PCB
SLAU278R–May 2009–Revised May 2014 Hardware 43
Submit Documentation Feedback
Copyright © 2009–2014, Texas Instruments Incorporated
MSP-TS430L092 Active Cable www.ti.com
Table B-5. MSP-TS430L092 Active Cable Bill of Materials
Pos. Ref Des No. Per Description Digi-Key Part No. Comment Board
1 C1, C3, C5, 4 100nF, SMD0603 C6
2 C2, C4 2 1uF, SMD0805
3 R1, R10 2 10K, SMD0603
4 R2 1 4K7, SMD0603
5 R5, R6, R7, 4 100, SMD0603 R9
6 R8 1 680k, SMD0603
7 R11, R15 2 1K, SMD0603
8 R12 0 SMD0603 DNP
9 R13 0 SMD0603 DNP
10 R14 1 0, SMD0603
11 IC1 1 SN74AUC1G04DBVR Manu: TI
12 IC2, IC3, IC4 3 SN74AUC2G125DCTR Manu: TI
13 J2 1 MICRO_STECKV_10 Reichelt: MicroMaTch- Connector: MM FL 10G
14 JP1 1 2x2 Header JP2Q Put jumper on Position 1 and 2. Do not mix direction.
15 JP2 1 2-pin header, male, TH SAM1035-02-ND place jumper on header
16 JTAG 1 14-pin connector, male, TH HRP14H-ND
17 Q1 1 BC817-25LT1SMD, SOT23- Digi-Key: BC817- BEC 25LT1GOSCT-ND
18 U1, U2 2 TLVH431IDBVR SOT23-5 Manu: TI
44 Hardware SLAU278R–May 2009–Revised May 2014
Submit Documentation Feedback
Copyright © 2009–2014, Texas Instruments Incorporated
www.ti.com MSP-TS430PW24
B.5 MSP-TS430PW24
Figure B-9. MSP-TS430PW24 Target Socket Module, Schematic
SLAU278R–May 2009–Revised May 2014 Hardware 45
Submit Documentation Feedback
Copyright © 2009–2014, Texas Instruments Incorporated
Jumper JP2
Open to measure current
Orient Pin 1 of MSP430 device
D1
LED connected to P1.0
Jumper JP3
Open to disconnect LED
Connector J5
External power connector
Jumper JP1 to "ext"
Jumpers JP4 to JP9
Close 1-2 to debug in Spy-Bi-Wire mode
Close 2-3 to debug in 4-wire JTAG mode
Jumper JP1
1-2 (int): Power supply via JTAG interface
2-3 (ext): External power supply
Connector JTAG
For JTAG Tool
MSP-TS430PW24 www.ti.com
Figure B-10. MSP-TS430PW24 Target Socket Module, PCB
46 Hardware SLAU278R–May 2009–Revised May 2014
Submit Documentation Feedback
Copyright © 2009–2014, Texas Instruments Incorporated
www.ti.com MSP-TS430PW24
Table B-6. MSP-TS430PW24 Bill of Materials
Position Ref Des No. per Description Digi-Key Part No. Comment Board
1 C1, C2 0 12pF, SMD0805 DNP
2 C5 1 2.2nF, SMD0805
3 C3, C7 2 10uF, 10V, SMD0805
4 C4, C6, C8 3 100nF, SMD0805 478-3351-2-ND
5 D1 1 green LED, SMD0805 P516TR-ND
SAM1029-07- DNP: Headers and receptacles 6 J1, J2 0 12-pin header, TH NDSAM1213-07-ND enclosed with kit. Keep vias free of solder. (Header and Receptacle)
J5, JP1,
7 JP4, JP5, 8 3-pin header, male, TH SAM1035-03-ND Place jumper on 1-2 of JP4-JP9 JP6, JP7, Place on 1-2 on JP1
JP8, JP9
8 JP2, JP3 2 2-pin header, male, TH SAM1035-02-ND Place jumper on header
9 9 Jumper 15-38-1024-ND see Pos 7 an 8
10 JTAG 1 14-pin connector, male, HRP14H-ND TH
11 Q1 0 Crystal DNP: keep vias free of solder
12 R1, R7 2 330 Ω, SMD0805 541-330ATR-ND
13 R5, R6, 2 0 Ohm, SMD0805 541-000ATR-ND DNP R5, R6 R8, R9,
14 R4 1 47k Ohm, SMD0805 541-47000ATR-ND
15 U1 1 Socket: OTS 24(28)- Manuf.: Enplas 065-02-00
16 PCB 1 68.5 x 61 mm 2 layers
Adhesive Approximately 6mm for example, 3M 17 plastic feet 4 width, 2mm height Bumpons Part No. SJ- Apply to corners at bottom side 5302
18 MSP430 2 MSP430AFE2xx DNP: enclosed with kit, supplied by TI
SLAU278R–May 2009–Revised May 2014 Hardware 47
Submit Documentation Feedback
Copyright © 2009–2014, Texas Instruments Incorporated
ML14
LED3
12pF
12pF
GND
GND
100nF
560R
ML10
JP1Q
JP1Q
10uF/10V
50K
10nF
0R
0R
0R -
-
0R
-
U1
SOCK28DW
F123
FE14H FE14L
0R
GND
remove R8 and add R9 (0 Ohm)
If external supply voltage:
remove R11 and add R10 (0 Ohm) SMD-Footprint
Socket: Yamaichi
2.0
MSP-TS430DW28 Target Socket DW28
Type: IC189-0282-042
If external supply voltage:
R1, C1, C2
not assembled
not assembled
1
3
5
7
9
11
13
2
4
6
12
14
8
10
JTAG
D1
C2
C1
C5
R3
BOOTST
1 2
3 4
5 6
7 8
9 10
1 2
J5
J4
1 2
C7
R5
C8
R6
R7
R8 R9
R10
R11
R1
1
2
3
4
5
6
7
8
9
10
11
12
13
14 15
16
17
18
19
20
21
22
23
24
25
26
27
28
TST 1
VCC 2
P2.5 3
VSS 4
XOUT 5
XIN 6
RST 7
P2.0 8
P2.1 9
P2.2 10 P2.3 19
P2.4 20
P1.0 21
P1.1 22
P1.2 23
P1.3 24
P1.4 25
P1.5 26
P1.6 27
P1.7 28
P3.0 11
P3.1 12
P3.2 13
P3.3 14 P3.4 15
P3.5 16
P3.6 17
P3.7 18
U2
15
16
17
18
19
20
21
22
23
24
25
26
27
28
J2 J1
1
2
3
4
5
6
7
8
9
10
11
12
13
14
R2
1
2
3
J3
Q1
QUARZ3
P1.0
P1.0
P1.3
P1.3
P1.2
P1.2
P1.1
P1.1 RST/NMI
RST/NMI
RST/NMI
RST/NMI RST/NMI
TCK
TCK
TCK
TMS
TMS
TMS
TDI
TDI
TDI
TDO
TDO
TDO
XOUT
XOUT
VCC
GND
GND
GND
P2.3
P2.3
P2.4
P2.4
XIN
XIN
P2.5
P2.5
P2.2
P2.2
P2.1
P2.1
P2.0
P2.0
TST/VPP
TST/VPP
TST/VPP
P3.0
P3.0
P3.1
P3.1
P3.2
P3.2
P3.3
P3.3
P3.7
P3.7
P3.6
P3.6
P3.5
P3.5
P3.4
P3.4
VCC430
Ext_PWR
Date: 11/14/2006 1:26:04 PM Sheet: 1/1
REV:
TITLE:
Document Number:
MSP-TS430DW28
+
VCC430
MSP-TS430DW28 www.ti.com
B.6 MSP-TS430DW28
Figure B-11. MSP-TS430DW28 Target Socket Module, Schematic
48 Hardware SLAU278R–May 2009–Revised May 2014
Submit Documentation Feedback
Copyright © 2009–2014, Texas Instruments Incorporated
Jumper J4
Open to disconnect LED
Orient Pin 1 of
MSP430 device
Jumper J5
Open to measure current
Connector J3
External power connector
Remove R8 and jumper R9
D1
LED connected to P1.0
Connector JTAG
For JTAG Tool
Connector BOOTST
For Bootstrap Loader Tool
www.ti.com MSP-TS430DW28
Figure B-12. MSP-TS430DW28 Target Socket Module, PCB
SLAU278R–May 2009–Revised May 2014 Hardware 49
Submit Documentation Feedback
Copyright © 2009–2014, Texas Instruments Incorporated
MSP-TS430DW28 www.ti.com
Table B-7. MSP-TS430DW28 Bill of Materials
Position Ref Des No. per Description Digi-Key Part No. Comment Board
1 C1, C2 0 12pF, SMD0805 DNP: C1, C2, Cover holes while soldering
2 C5 1 100nF, SMD0805
3 C7 1 10uF, 10V Tantal Elko B
4 C8 1 10nF SMD0805
5 D1 1 LED3 T1 3mm yellow RS: 228-4991
Micro Crystal MS1V-T1K
6 Q1 0 QUARZ, Crystal 32.768kHz, C(Load) = DNP: Cover holes while soldering
12.5pF
DNP: Headers and receptacles
enclosed with kit. Keep vias free of
7 J1, J2 2 14-pin header, TH male solder.
: Header
: Receptacle
DNP: Headers and receptacles
enclosed with kit. Keep vias free of
7.1 2 14-pin header, TH solder. female : Header
: Receptacle
8 J3 1 3-Pin Connector, male
9 J4, J5 2 2-Pin Connector, male With jumper
10 BOOTST 0 ML10, 10-Pin Conn., m RS: 482-115 DNP, Cover holes while soldering
11 JTAG 1 ML14, 14-Pin Conn., m RS: 482-121
R1, R2,
12 R6, R7, 4 0R, SMD0805 DNP: R1, R2, R9, R10 R8,R9,
R10, R11
13 R3 1 560R, SMD0805
14 R5 1 47K, SMD0805
15 U1 1 SOP28DW socket Yamaichi: IC189-0282- 042
16 U2 0 TSSOP DNP
50 Hardware SLAU278R–May 2009–Revised May 2014
Submit Documentation Feedback
Copyright © 2009–2014, Texas Instruments Incorporated
12pF
12pF
GND
GND
100nF
330R
10uF/10V
-
0R
GND
GND
green
2.2nF
47k
GND
0R 0R
330R
MSP430F12xx
If external supply voltage:
remove R11 and add R10 (0 Ohm)
3.1
MSP-TS430PW28:
OTS-28-0.65-01
Socket: Enplas
Vcc
int
ext
Target Socket Board for MSP430's in PW28 package
DNP
DNP
DNP
DNP
DNP
DNP
DNP
JTAG ->
SBW ->
JTAG-Mode selection:
4-wire JTAG: Set jumpers JP4 to JP9 to position 2-3
2-wire "SpyBiWire": Set jumpers JP4 to JP9 to position 1-2
DNP
1
3
5
7
9
11
13
2
4
6
12
14
8
10
JTAG
C2
C1
C4
R1
1 2
3 4
5 6
7 8
9 10
BOOTST
C3
R2
R3
1
2
3
J5
JP1
1
2
3
JP2
1
2
1
2
JP3
D1
C5 R4
JP4
1
2
3
JP5
1
2
3
JP6
1
2
3
JP7
1
2
3
JP8
1
2
3
JP9
1
2
3
R5 R6
1 2
Q1
R7
J1
1
2
3
4
5
6
7
8
9
10
11
12
13
14
J2
1
2
3
4
5
6
7
8
9
10
11
12
13
14
U1
TST 1
VCC 2
P2.5 3
VSS 4
XOUT 5
XIN 6
RST 7
P2.0 8
P2.1 9
P2.2 10 P2.3 19
P2.4 20
P1.0 21
P1.1 22
P1.2 23
P1.3 24
P1.4 25
P1.5 26
P1.6 27
P1.7 28
P3.0 11
P3.1 12
P3.2 13
P3.3 14 P3.4 15
P3.5 16
P3.6 17
P3.7 18
P1.0
P1.0
RST/NMI
TMS
TDI
VCC
GND
GND
VCC430 VCC430
P2.0
P1.1
P1.1
P3.3
P3.2
P3.1
P3.0
P2.2
P2.2
XIN/P2.6
XIN/P2.6
XOUT/P2.7
XOUT/P2.7
P2.1
RST/SBWTDIO
RST/SBWTDIO
RST/SBWTDIO
P3.4
P3.5
P3.6
P3.7
P2.3
P2.4
P1.2
P1.3
P1.4/TCK
P1.4/TCK
P1.5/TMS
P1.5/TMS
P1.6/TDI
P1.6/TDI
P1.7/TDO
P1.7/TDO
TEST/SBWTCK
TEST/SBWTCK
TEST/SBWTCK
TEST/SBWTCK
P2.5
TCK/SBWTCK
TDO/SBWTDIO
XTLGND
Ext_PWR
+
www.ti.com MSP-TS430PW28
B.7 MSP-TS430PW28
Figure B-13. MSP-TS430PW28 Target Socket Module, Schematic
SLAU278R–May 2009–Revised May 2014 Hardware 51
Submit Documentation Feedback
Copyright © 2009–2014, Texas Instruments Incorporated
Jumper JP2
Open to measure current
Jumper JP3
Open to disconnect LED
D1
LED connected to P5.1
Jumper JP1
1-2 (int): Power supply via JTAG interface
2-3 (ext): External power supply
Jumper JP4 to JP9:
Close 1-2 to debug in Spy-Bi-Wire mode
Close 2-3 to debug in 4-wire JTAG mode
Orient Pin 1 of MSP430 device
Connector JTAG
For JTAG Tool
Connector BOOTST
For Bootstrap Loader Tool
Connector J5
External power connector
Jumper JP1 to “ext”
MSP-TS430PW28 www.ti.com
Figure B-14. MSP-TS430PW28 Target Socket Module, PCB
52 Hardware SLAU278R–May 2009–Revised May 2014
Submit Documentation Feedback
Copyright © 2009–2014, Texas Instruments Incorporated
www.ti.com MSP-TS430PW28
Table B-8. MSP-TS430PW28 Bill of Materials(1)
Pos. Ref Des No. per Description Digi-Key Part No. Comment Board
1 C1, C2 0 12pF, SMD0805 DNP: C1, C2 , Cover holes while soldering
2 C3 1 10uF, 10V Tantal Elko B
3 C4 1 100nF, SMD0805
4 C5 0 2.2nF, SMD0805 DNP
5 D1 1 LED green SMD0603
Micro Crystal MS1V-T1K DNP: Cover holes and
6 Q1 0 QUARZ, Crystal 32.768kHz, C(Load) = neighboring holes while
12.5pF soldering
DNP: Headers and
receptacles enclosed with
7 J1, J2 2 14-pin header, TH male kit.Keep vias free of solder.
: Header
: Receptacle
DNP: headers and
receptacles enclosed with
7.1 2 14-pin header, TH female kit.Keep vias free of solder.
: Header
: Receptacle
8 J5, IP1 1 3-Pin Connector , male
JP1, JP4,
8a JP5, JP6, 7 3-Pin Connector , male Jumper on Pos 1-2 JP7, JP8,
JP9
9 JP2, JP3 2 2-Pin Connector , male with Jumper
10 BOOTST 0 ML10, 10-Pin Conn. , m RS: 482-115 DNP: Cover holes while soldering
11 JTAG 1 ML14, 14-Pin Conn. , m RS: 482-121
12 R1, R7 2 330R, SMD0805
12 R2, R3, R5, 0 0R, SMD0805 DNP R6
14 R4 1 47K, SMD0805
15 U1 1 SOP28PW socket Enplas: OTS-28-0.65-01
(1) PCB 66 x 79 mm, two layers; Rubber stand off, four pieces
SLAU278R–May 2009–Revised May 2014 Hardware 53
Submit Documentation Feedback
Copyright © 2009–2014, Texas Instruments Incorporated
JTAG Mode selection:
4-wire JTAG: Set jumpers J4 to J9 to position 2-3
2-wire "SpyBiWire": Set jumpers J4 to J9 to position 2-1
MSP-TS430PW28A www.ti.com
B.8 MSP-TS430PW28A
Figure B-15. MSP-TS430PW28A Target Socket Module, Schematic
54 Hardware SLAU278R–May 2009–Revised May 2014
Submit Documentation Feedback
Copyright © 2009–2014, Texas Instruments Incorporated
Jumper JP2
Open to measure current
Orient Pin 1 of MSP430 device
Jumper JP3
Open to disconnect LED
D1
LED connected to P1.0
Connector J5
External power connector
Jumper JP1 to "ext"
Jumpers JP4 to JP9
Close 1-2 to debug in Spy-Bi-Wire mode
Close 2-3 to debug in 4-wire JTAG mode
Connector JTAG
For JTAG Tool
Connector BOOTST
For Bootstrap Loader Tool
Jumper JP1
1-2 (int): Power supply via JTAG interface
2-3 (ext): External power supply
www.ti.com MSP-TS430PW28A
Figure B-16. MSP-TS430PW28A Target Socket Module, PCB (Red)
SLAU278R–May 2009–Revised May 2014 Hardware 55
Submit Documentation Feedback
Copyright © 2009–2014, Texas Instruments Incorporated
MSP-TS430PW28A www.ti.com
Table B-9. MSP-TS430PW28A Bill of Materials
Position Ref Des No. per Description Digi-Key Part No. Comment Board
1 C1, C2 0 12pF, SMD0805 DNP
2 C5 1 2.2nF, SMD0805
3 C3 1 10uF, 10V, SMD0805
4 C4, C6, 2 100nF, SMD0805 478-3351-2-ND
5 D1 1 green LED, SMD0805 P516TR-ND
DNP: Headers and receptacles
6 J1, J2 0 14-pin header, TH enclosed with kit. Keep vias free of
solder: (Header and Receptacle)
J5, JP1,
7 JP4, JP5, 8 3-pin header, male, TH SAM1035-03-ND Place jumper on 1-2 of JP4-JP9 JP6, JP7, Place on 1-2 on JP1
JP8, JP9
8 JP2, JP3 2 2-pin header, male, TH SAM1035-02-ND Place jumper on header
9 9 Jumper 15-38-1024-ND see Pos 7 an 8
10 JTAG 1 14-pin connector, male, HRP14H-ND TH
11 BOOTST 0 DNP Keep vias free of solder
Micro Crystal MS3V
12 Q1 0 Crystal 32.768kHz, C(Load) = DNP: keep vias free of solder
12.5pF
13 R1, R7 2 330 Ω, SMD0805 541-330ATR-ND
14 R2, R3,R5, 0 0 Ohm, SMD0805 541-000ATR-ND DNP R2, R3,R5, R6 R6,
15 R4 1 47k Ω, SMD0805 541-47000ATR-ND
16 U1 1 Socket: OTS-28-0.65-01 Manuf.: Enplas
17 PCB 1 63.5 x 64.8 mm 2 layers
Adhesive Approximately 6mm for example, 3M 18 plastic feet 4 width, 2mm height Bumpons Part No. SJ- Apply to corners at bottom side 5302
19 MSP430 2 MSP430G2553IPW28 DNP: enclosed with kit, supplied by TI
56 Hardware SLAU278R–May 2009–Revised May 2014
Submit Documentation Feedback
Copyright © 2009–2014, Texas Instruments Incorporated
DNP
DNP
DNP
DNP
DNP
DNP
DNP
DNP
GND
0R
330R
2.2nF
PWR3
GND
GND
0R
47K
470nF
100nF
10uF 100nF
GND
GND
20k/0.1%
10k
10k
10k
10k
GND AVSS
AVSS
10k
10k
10k
10k
GND
SAM1029-08-ND1-8
SAM1029-08-ND9-16
MSP430I2040TRHBQFN11T032-003
SAM1029-08-ND17-2417-24
SAM1029-08-ND25-32
1.0
for MSP430i2040
MSP430: Target-Socket MSP-TS430RHB32A
DNP
<- SBW
<- JTAG
Vcc
int
ext
Socket:
Yamaichi
QFN11T032-003
1
3
5
7
9
11
13
2
4
6
12
14
8
10
JTAG
R1
R3
C8
J5
1
2
3
1 JP1
2
1
2
JP2
R4
1
2
3
JP4 1
2
3
JP9 1
2
3
JP8 1
2
3
JP7 1
2
3
JP6 1
2
3
JP5
R5
D1
C9
1
2
3
JP3
C14
C12 C13
R2
R6
R8
R9
R10
R11
R12
R13
R14
1
2
3
4
5
6
7
8
J1
9
10
11
12
13
14
15
16
J2
A0.0+
1
A0.0-
2
A1.0+
3
A1.0-
4
A2.0+
5
A2.0-
6
A3.0+
7
A3.0-
8
VREF
9
AVSS
10
ROSC
11
DVSS
12
VCC
13
VCORE
14
P2.3/VMONIN
28
P2.2/TA1.2
27
P2.1/TA1.1
26
P2.0/TA1.0/CLKIN
25
P1.7/UCB0SDA/UCB0SIMO/TA1CLK
24
P1.6/UCB0SCL/UCB0SOMI/TA0.2
23
P1.5/UCB0CLK/TA0.1
22
P1.4/UCB0STE/TA0.0
21
P1.3/UCA0TXD/UCA0SIMO/TA0CLK/TDO/TDI
20
P1.2/UCA0RXD/UCA0SOMI/ACLK/TDI/TCLK
19
P1.1/UCA0CLK/SMCLK/TMS
18
P1.0/UCA0STE/MCLK/TCK
17
TEST/SBWTCK
16
RST/NMI/SBWTDIO
15
U1
P2.4/TA1.0
29
P2.5/TA0.0
30
P2.6/TA0.1
31
P2.7/TA0.2
32
17
18
19
20
21
22
23
24
J3
25
26
27
28
29
30
31
32
J4
TMS
TMS
TDI
TDI
TDO
TDO
TDO
VCC
GND
GND
P1.4
P1.4
DVCC
DVCC
DVCC
AVSS
M
M
I
I
O
O
RST/NMI RST/NMI
TCK
TCK
TCK
C
TEST/SBWTCK C
TEST/SBWTCK
VCORE
A0.0+
A0.0-
A1.0+
A1.0-
VREF
ROSC
RST
RST
RST
A2.0+
A2.0-
A3.0+
A3.0-
P1.5
P1.6
P1.7
P2.0
P2.1
P2.2
P2.3
P2.4
P2.5
P2.6
P2.7
www.ti.com MSP-TS430RHB32A
B.9 MSP-TS430RHB32A
Figure B-17. MSP-TS430RHB32A Target Socket Module, Schematic
SLAU278R–May 2009–Revised May 2014 Hardware 57
Submit Documentation Feedback
Copyright © 2009–2014, Texas Instruments Incorporated
Orient Pin 1 of MSP430 device
D1
LED connected to P1.4
Jumper JP1
Open to measure current
Connector J5
External power connector
Jumper JP3 to “ext”
Connector JTAG
For JTAG Tool
Jumper JP4 to JP9
Close 1-2 to debug in Spy-Bi-Wire mode
Close 3-4 to debug in 4-wire JTAG mode
Jumper JP3
1-2 (int): Power supply via JTAG interface
2-3 (ext): External power supply
Jumper JP2
Open to disconnect LED
P1.4
14
1
2
GND
GND
VCC
1 2 3
3 2 1
8 5 1
16 9
17 20 24
25 30 32
Vcc
ext int
MSP-TS430RHB32A
Rev.: 1.0 RoHS
SBW
JTAG
1
Curr. Meas.
JTAG
R1
R3
C8
J5
JP1
JP2
R4
JP4
JP9
JP8
JP7
JP6
JP5
R5
D1
C9
JP3
C14
C13
C12
R2
R6
R8
R9
R10
R11
R12
R13
R14
J1
J2
U1
J3
J4
1 2 3
1 2 3
1 2 3
1 2 3
1 2 3
MSP-TS430RHB32A www.ti.com
Figure B-18. MSP-TS430RHB32A Target Socket Module, PCB
58 Hardware SLAU278R–May 2009–Revised May 2014
Submit Documentation Feedback
Copyright © 2009–2014, Texas Instruments Incorporated
www.ti.com MSP-TS430RHB32A
Table B-10. MSP-TS430RHB32A Bill of Materials
Pos. Ref Des No. per Description Digi-Key Part No. Comment Board
1 PCB 1 76.9 x 67.6 mm MSP-TS430RHB32A Rev. 2 layers, red solder mask
1
2 D1 1 green LED, DIODE0805 P516TR-ND
3 JP1, JP2 2 2-pin header, male, TH SAM1035-02-ND place jumper on header
4 JP3, JP4, 7 3-pin header, male, TH SAM1035-03-ND place jumpers on pins 1-2
JP5, JP6, (SBW)
JP7, JP8,
JP9
5 R1, R4 2 0R, 0805 541-0.0ATR-ND
6 C8 1 2.2nF, CSMD0805 490-1628-2-ND DNP
7 R6, R8, R9, 8 10k, 0805 311-10KARTR-ND DNP
R10, R11,
R12, R13,
R14
8 C12 1 10uF, CSMD0805 445-1371-2-ND
9 R2 1 20k/0.1%, 0805 P20KDACT-ND
10 R5 1 47K, 0805 311-47KARTR-ND
11 C13, C14 2 100nF, CSMD0805 311-1245-2-ND
12 R3 1 330R, 0805 541-330ATR-ND
13 C9 1 470nF, CSMD0805 445-1357-2-ND
14 J1, J2, J3, 1 8-pin header, TH SAM1029-08-ND DNP: headers and
J4 receptacles, enclosed with
kit.
Keep vias free of solder.
15 J1, J2, J3, 1 8-pin receptable, TH SAM1213-08-ND DNP: headers and
J4 receptacles, enclosed with
kit.
Keep vias free of solder.
16 JTAG 1 14-pin connector, male, TH HRP14H-ND
17 U1 1 Socket QFN11T032-003 Manuf.: Yamaichi
18 U1 1 MSP430i2041TRHB DNP: enclosed with kit.
Is supplied by TI
19 J5 1 3-pin header, male, TH SAM1035-03-ND
20 Rubber 4 Buerklin: 20H1724 apply to corners at bottom
stand off side
SLAU278R–May 2009–Revised May 2014 Hardware 59
Submit Documentation Feedback
Copyright © 2009–2014, Texas Instruments Incorporated
12pF
12pF
GND
GND
100nF
560R
10uF/10V
47k
10nF
-
0R
GND
MSP430F2274IDA
GND
330R
GND
yellow
If external supply voltage:
remove R11 and add R10 (0 Ohm)
IC189-0382-037
Socket:
4-wire JTAG:
2-wire "SpyBiWire":
JTAG-Mode selection:
Set jumpers JP4 to JP9 to position 2-3
Set jumpers JP4 to JP9 to position 2-1
JTAG ->
SBW ->
Yamaichi
DNP
DNP
DNP
DNP
DNP
DNP
DNP
1
3
5
7
9
11
13
2
4
6
12
14
8
10
JTAG
C2
C1
C5
R3
1 2
3 4
5 6
7 8
9 10
BOOTST
C7
R5
C8
R10
R11
1
2
3
J3
Q1
TEST/SBWTCK 1
P3.5 26
P3.6 27
P1.4/TCK 35
RST/SBWDAT 7
DVCC 2
DVSS 4
P4.7 24
P3.7 28
AVSS 15
AVCC 16
P3.0 11
P3.1 12
P3.2 13
P3.3 14
P4.0 17
P4.1 18
P4.2 19
P3.4 25
P2.5 3
P2.4 30
P2.3 29 P2.2 10
P2.1 9
P2.0 8
P1.5/TMS 36
P1.6/TDI 37
P1.7/TDO 38
P2.7 5
P2.6 6
P4.6 23
P4.5 22
P4.4 21
P4.3 20
P1.0 31
P1.1 32
P1.2 33
P1.3 34
U1
JP1
1
2
3
JP2
1
2
1
2
JP3
1
2
3
JP4 JP5
1
2
3
JP6
1
2
3
JP7
1
2
3
JP8
1
2
3
R1
JP9
1
2
3
2
3
4
5
6
7
8
9
10
11
12
13
14
15
16
17
18
19
1
J1
21
22
23
24
25
26
27
28
29
30
31
32
33
34
35
36
37
38
20
J2
D1
P1.0
P1.0
RST/NMI
TMS
TDI
VCC
GND
GND
GND
VCC430
VCC430
VCC430
TCK/SBWTCK
TDO/SBWTDIO
TEST/SBWTCK
TEST/SBWTCK
TEST/SBWTCK
TEST/SBWTCK
P2.5
P2.0
P2.1
P3.0
P3.1
P3.2
P3.3
P4.0
P4.1
P4.2
P1.7/TDO
P1.7/TDO
P1.6/TDI
P1.6/TDI
P1.5/TMS
P1.5/TMS
P1.4/TCK
P1.4/TCK
P1.3
P1.2
P1.1
P1.1
P2.4
P2.3
P3.7
P3.6
P3.5
P3.4
P4.7
P4.6
P4.5
P4.4
P4.3
P2.7/XOUT
P2.7/XOUT
P2.6/XIN
P2.6/XIN
RST/SBWTDIO
RST/SBWTDIO
RST/SBWTDIO
P2.2
P2.2
Ext_PWR
Date: 6/18/2008 11:04:56 AM Sheet: 1/1
REV:
TITLE:
Document Number:
MSP-TS430DA38
+
1.3
MSP-TS430DA38:
Vcc
int
ext
Target Socket Board for MSP430F2247IDA
MSP-TS430DA38 www.ti.com
B.10 MSP-TS430DA38
Figure B-19. MSP-TS430DA38 Target Socket Module, Schematic
60 Hardware SLAU278R–May 2009–Revised May 2014
Submit Documentation Feedback
Copyright © 2009–2014, Texas Instruments Incorporated
Orient pin 1 of MSP430 device
D1
LED connected to P1.0
Connector J3
External power connector
Jumper JP1 to "ext"
Jumper JP3
Open to disconnect LED
Jumper JP2
Open to measure current
Jumpers JP4 to JP9
Close 1-2 to debug in Spy-Bi-Wire mode
Close 2-3 to debug in 4-wire JTAG mode
Jumper JP1
1-2 (int): Power supply via JTAG interface
2-3 (ext): External power supply
Connector JTAG
For JTAG Tool
Connector BOOTST
For Bootstrap Loader Tool
www.ti.com MSP-TS430DA38
Figure B-20. MSP-TS430DA38 Target Socket Module, PCB
SLAU278R–May 2009–Revised May 2014 Hardware 61
Submit Documentation Feedback
Copyright © 2009–2014, Texas Instruments Incorporated
MSP-TS430DA38 www.ti.com
Table B-11. MSP-TS430DA38 Bill of Materials
Pos. Ref Des No. per Description Digi-Key Part No. Comment Board
1 C1, C2 0 12pF, SMD0805 DNP
2 C7 1 10uF, 10V, Tantal Size B 511-1463-2-ND
3 C5 1 100nF, SMD0805 478-3351-2-ND
4 C8 0 2.2nF, SMD0805 DNP
5 D1 1 green LED, SMD0603 475-1056-2-ND
DNP: headers and
receptacles enclosed with
6 J1, J2 0 19-pin header, TH kit.Keep vias free of solder.
SAM1029-19-ND : Header
SAM1213-19-ND : Receptacle
"J3, JP1, Place jumpers on headers 7 JP4, JP5, 8 3-pin header, male, TH SAM1035-03-ND JP1, JP4,JP5, JP6, JP7, JP6, JP7, JP8, JP9; Pos 1-2 JP8, JP9"
8 JP2, JP3 2 2-pin header, male, TH SAM1035-02-ND Place jumper on header
9 9 Jumper 15-38-1024-ND Place on: JP1 - JP9; Pos 1- 2
10 JTAG 1 14-pin connector, male, TH HRP14H-ND
11 BOOTST 0 10-pin connector, male, TH DNP: Keep vias free of solder
Micro Crystal MS1V-T1K DNP: Keep vias free of 12 Q1 0 Crystal 32.768kHz, C(Load) = solder 12.5pF
13 R1, R3 2 330 Ω, SMD0805 541-330ATR-ND
14 R10, R11 0 0 Ω, SMD0805 541-000ATR-ND DNP
15 R5 1 47k Ω, SMD0805 541-47000ATR-ND
16 U1 1 Socket: IC189-0382--037 Manuf.: Yamaichi
17 PCB 1 67 x 66 mm 2 layers
18 Adhesive 4 ~6mm width, 2mm height for example, 3M Bumpons Apply to corners at bottom Plastic feet Part No. SJ-5302 side
19 MSP430 2 MSP430F2274IDA DNP: enclosed with kit supplied by TI
62 Hardware SLAU278R–May 2009–Revised May 2014
Submit Documentation Feedback
Copyright © 2009–2014, Texas Instruments Incorporated
www.ti.com MSP-TS430QFN23x0
B.11 MSP-TS430QFN23x0
Figure B-21. MSP-TS430QFN23x0 Target Socket Module, Schematic
SLAU278R–May 2009–Revised May 2014 Hardware 63
Submit Documentation Feedback
Copyright © 2009–2014, Texas Instruments Incorporated
D1
LED connected to P1.0
Connector J5
External power connector
Jumper JP1 to "ext"
Jumper JP3
Open to disconnect LED
Jumper JP2
Open to measure current
Connector JTAG
For JTAG Tool
Connector BOOTST
For Bootstrap Loader Tool
Jumper JP1
1-2 (int): Power supply via JTAG interface
2-3 (ext): External power supply
Orient Pin 1 of MSP430 device
MSP-TS430QFN23x0 www.ti.com
Figure B-22. MSP-TS430QFN23x0 Target Socket Module, PCB
64 Hardware SLAU278R–May 2009–Revised May 2014
Submit Documentation Feedback
Copyright © 2009–2014, Texas Instruments Incorporated
www.ti.com MSP-TS430QFN23x0
Table B-12. MSP-TS430QFN23x0 Bill of Materials
Pos. Ref Des No. per Description Digi-Key Part No. Comment Board
1 C1, C2 0 12pF, SMD0805 DNP
2 C3 1 10uF, 10V, Tantal Size B 511-1463-2-ND
3 C4 1 100nF, SMD0805 478-3351-2-ND
4 C5 1 10nF, SMD0805 478-1383-2-ND
5 D1 1 green LED, SMD0603 475-1056-2-ND
DNP: headers and
receptacles enclosed with
6 J1, J2, J3, 0 10-pin header, TH kit.Keep vias free of solder. J4 SAM1034-10-ND : Header
SAM1212-10-ND : Receptacle
7 J5, JP1 2 3-pin header, male, TH SAM1035-03-ND Place jumper on header JP1; Pos 1-2.
8 JP2, JP3 2 2-pin header, male, TH SAM1035-02-ND Place jumper on header
9 3 Jumper 15-38-1024-ND Place on: JP1, JP2, JP3
10 JTAG 1 14-pin connector, male, TH HRP14H-ND
11 BOOTST 0 10-pin connector, male, TH DNP: Keep vias free of solder
Micro Crystal MS1V-T1K DNP: Keep vias free of 12 Q1 0 Crystal 32.768kHz, C(Load) = solder 12.5pF
13 R1 1 330 Ω, SMD0805 541-330ATR-ND
14 R2, R3 0 0 Ω, SMD0805 541-000ATR-ND DNP
15 R4 1 47k Ω, SMD0805 541-47000ATR-ND
16 U1 1 Socket: QFN-40B-0.5-01 Manuf.: Enplas
17 PCB 1 79 x 66 mm 2 layers
18 Adhesive 4 ~6mm width, 2mm height for example, 3M Bumpons Apply to corners at bottom Plastic feet Part No. SJ-5302 side
19 MSP430 2 MSP430F2370IRHA DNP: enclosed with kit supplied by TI
SLAU278R–May 2009–Revised May 2014 Hardware 65
Submit Documentation Feedback
Copyright © 2009–2014, Texas Instruments Incorporated
MSP-TS430RSB40 www.ti.com
B.12 MSP-TS430RSB40
Figure B-23. MSP-TS430RSB40 Target Socket Module, Schematic
66 Hardware SLAU278R–May 2009–Revised May 2014
Submit Documentation Feedback
Copyright © 2009–2014, Texas Instruments Incorporated
Jumper JP2
Open to measure current
Orient Pin 1 of MSP430 device
Jumper JP3
Open to disconnect LED
D1
LED connected to P1.0
Jumpers JP4 to JP9
Close 1-2 to debug in Spy-Bi-Wire mode
Close 2-3 to debug in 4-wire JTAG mode
Connector J5
External power connector
Jumper JP1 to "ext"
Connector JTAG
For JTAG Tool
Connector BOOTST
For Bootstrap Loader Tool
Jumper JP1
1-2 (int): Power supply via JTAG interface
2-3 (ext): External power supply
www.ti.com MSP-TS430RSB40
Figure B-24. MSP-TS430RSB40 Target Socket Module, PCB
SLAU278R–May 2009–Revised May 2014 Hardware 67
Submit Documentation Feedback
Copyright © 2009–2014, Texas Instruments Incorporated
MSP-TS430RSB40 www.ti.com
Table B-13. MSP-TS430RSB40 Bill of Materials
Pos. Ref Des No. Per Description Digi-Key Part No. Comment Board
1 C1, C2 0 12pF, SMD0805 DNP: C1, C2
2 C3, C7, C10, 3 10uF, 10V, SMD 0805 445-1371-1-ND DNP C12 C12
3 C4, C6, C8, 3 100nF, SMD0805 311-1245-2-ND DNP C11 C11
4 C5 1 2.2nF, SMD0805
5 C9 1 470nF, SMD0805
6 D1 1 green LED, SMD0805 P516TR-ND
DNP: headers and
receptacles enclosed with kit.
7 J1, J2, J3, J4 4 10-pin header, TH Keep vias free of solder.
: Header
: Receptacle
DNP: headers and
receptacles enclosed with kit.
7.1 4 10-pin header, TH Keep vias free of solder.
: Header
: Receptacle
JP1,
JP4,JP5, Jumper: 1-2 on JP1, JP10; 2- 8 JP6, JP7, 9 3-pin header, male, TH SAM1035-03-ND 3 on JP4-JP9 JP8, JP9, J5,
JP10
9 JP2, JP3 2 2-pin header, male, TH SAM1035-02-ND place jumper on header
10 JTAG 1 14-pin connector, male, TH HRP14H-ND
11 BOOTST 0 10-pin connector, male, TH DNP. Keep vias free of solder
12 U1 1 QFN-40B-0.4_ Enplas ENPLAS_SOCKET
Micro Crystal MS3V-T1R DNP: Q1. Keep vias free of 13 Q1 0 Crystal 32.768kHz, C(Load) = solder 12.5pF
Place on: JP1, JP2, JP3,
15 10 Jumper 15-38-1024-ND JP4, JP5, JP6, JP7, JP8,
JP9, JP10
16 R1,R7 2 330R SMD0805
R2, R3, R5,
17 R6, R8, R9, 3 0R SMD0805 DNP R2, R3, R5, R6
R10
18 R4 1 47k SMD0805
19 MSP430 2 MSP430F5132 DNP: enclosed with kit. Is supplied by TI
20 Rubber stand 4 select appropriate; for apply to corners at bottom off example, Buerklin: 20H1724 side
68 Hardware SLAU278R–May 2009–Revised May 2014
Submit Documentation Feedback
Copyright © 2009–2014, Texas Instruments Incorporated
www.ti.com MSP-TS430RHA40A
B.13 MSP-TS430RHA40A
Figure B-25. MSP-TS430RHA40A Target Socket Module, Schematic
SLAU278R–May 2009–Revised May 2014 Hardware 69
Submit Documentation Feedback
Copyright © 2009–2014, Texas Instruments Incorporated
Jumper JP2
Open to measure current
Connector J5
External power connector
Jumper JP1 to "ext"
Jumpers JP4 to JP9
Close 1-2 to debug in Spy-Bi-Wire mode
Close 2-3 to debug in 4-wire JTAG mode
D1
LED connected to P1.0
Jumper JP3
Open to disconnect LED
Orient Pin 1 of MSP430 device
Jumper JP1
1-2 (int): Power supply via JTAG interface
2-3 (ext): External power supply
Connector JTAG
For JTAG Tool
Connector BOOTST
For Bootstrap Loader Tool
MSP-TS430RHA40A www.ti.com
Figure B-26. MSP-TS430RHA40A Target Socket Module, PCB
70 Hardware SLAU278R–May 2009–Revised May 2014
Submit Documentation Feedback
Copyright © 2009–2014, Texas Instruments Incorporated
www.ti.com MSP-TS430RHA40A
Table B-14. MSP-TS430RHA40A Bill of Materials
Position Ref Des No. per Description Digi-Key Part No. Comment Board
1 C1, C2 0 12pF, SMD0805 DNP: C1, C2
2 C5 0 2.2nF, SMD0805 DNP C12
3 C3, C7 2 10uF, 10V, SMD0805 5 DNP C11
4 C4, C6 2 100nF, SMD0805 478-3351-2-ND
5 C9 1 470nF, SMD0805
6 D1 1 green LED, SMD0805 P516TR-ND
DNP: headers and receptacles
enclosed with kit. Keep vias free of
7 J1, J2, J3, 4 10-pin header, TH solder. J4 : Header
: Receptacle
DNP: headers and receptacles
enclosed with kit. Keep vias free of
7.1 4 10-pin header, TH solder.
: Header
: Receptacle
J5, JP1,
8 JP4, JP5, 8 3-pin header, male, TH SAM1035-03-ND Place jumper on 1-2 of JP4-JP9; JP6, JP7, Place on 1-2 on JP1
JP8, JP9
9 JP2, JP3 2 2-pin header, male, TH SAM1035-02-ND place jumper on header
10 9 Jumper 15-38-1024-ND see Pos 8 an 9
11 JTAG 1 14-pin connector, male, HRP14H-ND TH
12 BOOTST 0 10-pin connector, male, DNP. Keep vias free of solder TH
13 U1 1 Socket: QFN-40B-0.5-01 Manuf.: Enplas
Micro Crystal MS3V-T1R
14 Q1 0 Crystal 32.768kHz, C(Load) = DNP: Q1. Keep vias free of solder
12.5pF
15 R1,R7 2 330R SMD0805 541-330ATR-ND
R2, R3,
16 R5, R6, 2 0 Ohm, SMD0805 541-000ATR-ND DNP:R2, R3, R5, R6
R8, R9,
17 R4 1 47k SMD0805
18 PCB 1 79 x 66 mm 2 layers
Rubber select appropriate; for 19 stand off 4 example, Buerklin: apply to corners at bottom side 20H1724
20 MSP430 2 MSP430N5736IRHA DNP: enclosed with kit. Is supplied by TI
SLAU278R–May 2009–Revised May 2014 Hardware 71
Submit Documentation Feedback
Copyright © 2009–2014, Texas Instruments Incorporated
ML14
LED3
12pF
12pF
GND
GND
100nF
560R
ML10
JP1Q
JP1Q
10uF/10V
47K
10nF
0R
0R
GND
0R
0R
10uF/10V
GND
IC51-1387.KS-15186
100nF
1.3
MSP-TS430DL48 Target Socket DL48
Q1, C1, C2
not assembled
1
3
5
7
9
11
13
2
4
6
12
14
8
10
JTAG
D1
C2
C1
C5
R3
BOOTST
1 2
3 4
5 6
7 8
9 10
1 2
J5
J4
1 2
C7
R5
C8
R6
R7
1
2
3
J3
Q1
QUARZ3
J2
1
3
5
2
4
6
7
9
8
10
11
13
15
12
14
16
17
19
18
20
21
23
22
24
1
3
5
2
4
6
7
9
8
10
11
13
15
12
14
16
17
19
18
20
21
23
22
24
J1
R12
R4
JP1
1
2
3
1
2
3
JP2
C4
U1
TDO/TDI 1
TDI/TCLK 2
TMS 3
TCK 4
RST/NMI 5
DVCC 6
DVSS 7
XIN 8
XOUT 9
AVSS 10
AVCC 11
VREF+ 12
P6.0 13
P6.1 14
P6.2 15
P6.3 16
P6.4 17
P6.5 18
P6.6 19
P6.7 20
P2.5 39
P2.4 40
P2.3 41
P2.2 42
P2.1 43
P2.0 44
COM0 45
P5.2 46
P5.3 47
P5.4 48
LCDREF 29
LCDCAP 30
P5.1 31
P5.0 32
P5.5 33
P5.6 34
P5.7 35
S5 36
P2.7 37
P2.6 38
P1.7 21
P1.6 22
P1.5 23
P1.4 24
P1.0 28
P1.1 27
P1.2 26
P1.3 25
C3
P1.0
P1.0
RST/NMI
RST/NMI
RST/NMI
TCK
TCK
TCK
TMS
TMS
TDI
TDI
TDO
TDO
XOUT
XOUT
GND
GND GND
XIN
XIN
BSL_TX
VCC
BSL_RX
Ext_PWR
Date: 11/14/2006 1:24:44 PM Sheet: 1/1
REV:
TITLE:
Document Number:
MSP-TS430DL48
+
+
Vcc
ext
int
int ext
Vcc
MSP-TS430DL48 www.ti.com
B.14 MSP-TS430DL48
Figure B-27. MSP-TS430DL48 Target Socket Module, Schematic
72 Hardware SLAU278R–May 2009–Revised May 2014
Submit Documentation Feedback
Copyright © 2009–2014, Texas Instruments Incorporated
Jumper J4
Open to disconnect LED
D1
LED connected to P1.0
Orient pin 1 of MSP430 device
Jumper J5
Open to measure current
Connector J3
External power connector
Jumper JP2 to "ext"
Connector JTAG
For JTAG Tool
Connector BOOTST
For Bootstrap Loader Tool
Jumper JP2
1-2 (int): Power supply via JTAG interface
2-3 (ext): External power supply
www.ti.com MSP-TS430DL48
Figure B-28. MSP-TS430DL48 Target Socket Module, PCB
SLAU278R–May 2009–Revised May 2014 Hardware 73
Submit Documentation Feedback
Copyright © 2009–2014, Texas Instruments Incorporated
MSP-TS430DL48 www.ti.com
Table B-15. MSP-TS430DL48 Bill of Materials
Pos. Ref Des No. per Description Digi-Key Part No. Comment Board
1 C1, C2 0 12pF, SMD0805 DNP
2 C4, C7 2 10uF, 10V, Tantal Size B 511-1463-2-ND
3 C3, C5 2 100nF, SMD0805 478-3351-2-ND
4 C8 1 10nF, SMD0805 478-1383-2-ND
5 D1 1 yellow LED, TH, 3mm, T1 511-1251-ND
DNP: Headers and
receptacles enclosed with
6 J1, J2 0 24-pin header, TH kit.Keep vias free of solder.
SAM1034-12-ND : Header
SAM1212-12-ND : Receptacle
7 J3, JP1, JP2 2 3-pin header, male, TH SAM1035-03-ND Place jumper on header JP1; Pos 1-2. DNP: JP2
8 J4, J5 2 2-pin header, male, TH SAM1035-02-ND Place jumper on header
9 3 Jumper 15-38-1024-ND Place on: JP1, J4, J5
10 JTAG 1 14-pin connector, male, TH HRP14H-ND
11 BOOTST 0 10-pin connector, male, TH DNP: Keep vias free of solder
Micro Crystal MS1V-T1K DNP: Keep vias free of 12 Q1 0 Crystal 32.768kHz, C(Load) = solder 12.5pF
13 R3 1 560 Ω, SMD0805 541-560ATR-ND
14 R4, R6, R7, 2 0 Ω, SMD0805 541-000ATR-ND DNP: R6, R7 R12
15 R5 1 47k Ω, SMD0805 541-47000ATR-ND
16 U1 1 Socket: IC51-1387 KS- Manuf.: Yamaichi 15186
17 PCB 1 58 x 66 mm 2 layers
18 Adhesive 4 ~6mm width, 2mm height for example, 3M Bumpons Apply to corners at bottom Plastic feet Part No. SJ-5302 side
19 MSP430 2 MSP430F4270IDL DNP: Enclosed with kit supplied by TI
74 Hardware SLAU278R–May 2009–Revised May 2014
Submit Documentation Feedback
Copyright © 2009–2014, Texas Instruments Incorporated
www.ti.com MSP-TS430RGZ48B
B.15 MSP-TS430RGZ48B
Figure B-29. MSP-TS430RGZ48B Target Socket Module, Schematic
SLAU278R–May 2009–Revised May 2014 Hardware 75
Submit Documentation Feedback
Copyright © 2009–2014, Texas Instruments Incorporated
Jumper JP2
Open to disconnect LED
Connector J5
External power connector
Jumper JP3 to "ext"
Jumpers JP5 to JP10
Close 1-2 to debug in Spy-Bi-Wire mode
Close 2-3 to debug in 4-wire JTAG mode
D1
LED connected to P1.0
Jumper JP1
Open to measure current
Orient Pin 1 of MSP430 device
Connector JTAG
For JTAG Tool
Connector BOOTST
For Bootstrap Loader Tool
Jumper JP3
1-2 (int): Power supply via JTAG interface
2-3 (ext): External power supply
MSP-TS430RGZ48B www.ti.com
Figure B-30. MSP-TS430RGZ48B Target Socket Module, PCB
76 Hardware SLAU278R–May 2009–Revised May 2014
Submit Documentation Feedback
Copyright © 2009–2014, Texas Instruments Incorporated
www.ti.com MSP-TS430RGZ48B
Table B-16. MSP-TS430RGZ48B Bill of Materials
Position Ref Des No. per Description Digi-Key Part No. Comment Board
1 C1, C2 0 12pF, SMD0805 DNP
2 C3, C4 0 47pF, SMD0805 DNP
3 C6, C7, 3 10uF, 6.3V, SMD0805 C12
4 C5, C11, 4 100nF, SMD0805 311-1245-2-ND C13, C14
5 C8 1 2.2nF, SMD0805
6 C9 1 470nF, SMD0805 478-1403-2-ND
7 D1 1 green LED, SMD0805 P516TR-ND
J1, J2, J3, SAM1029-12-ND DNP: Headers and receptacles 8 J4 0 12-pin header, TH (Header) SAM1213-12- enclosed with kit. Keep vias free of ND (Receptacle) solder:
9 J5 1 3-pin header, male, TH
JP3, JP5, place jumpers on pins 2-3 on JP5, 10 JP6, JP7, 7 3-pin header, male, TH SAM1035-03-ND JP6, JP7, JP8, JP9, JP10 place JP8, JP9, jumpers on pins 1-2 on JP3, JP10
11 JP1, JP2 2 2-pin header, male, TH SAM1035-02-ND Place jumper on header
12 9 Jumper 15-38-1024-ND See Pos. 10and Pos. 11
13 JTAG 1 14-pin connector, male, HRP14H-ND TH
14 BOOTST 0 10-pin connector, male, "DNP Keep vias free of solder" TH
Micro Crystal MS3V-T1R
15 Q1 0 Crystal 32.768kHz, C(Load) = DNP: Q1 Keep vias free of solder
12.5pF
16 Q2 0 Crystal Q2: 4MHz Buerklin: DNP: Q2 Keep vias free of solder 78D134
Insulating http://www.ettinger.de/Ar 17 disk to Q2 0 Insulating disk to Q2 t_Detail.cfm?ART_ART NUM=70.08.121
18 R3, R7 2 330 Ω, SMD0805 541-330ATR-ND
R1, R2,
R4, R6,
19 R8, 3 0 Ohm, SMD0805 541-000ATR-ND DNP: R6, R8, R9, R10, R11,R12
R9,R10,
R11, R12
20 R5 1 47k Ω, SMD0805 541-47000ATR-ND
21 U1 1 Socket: QFN11T048- Manuf.: Yamaichi 008_A101121_RGZ48
22 PCB 1 81 x 76 mm 2 layers
Adhesive Approximately 6mm for example, 3M 23 plastic feet 4 width, 2mm height Bumpons Part No. SJ- Apply to corners at bottom side 5302
24 MSP430 2 MSP430F5342IRGZ DNP: enclosed with kit, supplied by TI
SLAU278R–May 2009–Revised May 2014 Hardware 77
Submit Documentation Feedback
Copyright © 2009–2014, Texas Instruments Incorporated
DNP
DNP
DNP
GND
GND
100nF
330R
0R -
GND
GND
47k 1.1nF
GND
0R 0R
0R
1uF/10V QUARZ5
1uF/10V 100nF
green
DNP
yellow (DNP)
DNP
red (DNP)
0R
GND
DNP
DNP
0R 0R
QUARZ5
EVQ11
0R
DNP
DNP
If external supply voltage:
remove R3 and add R2 (0 Ohm)
1.3
Ext_PWR
MSP-TS430RGZ48C
Vcc
int
ext
Target Socket Board for MSP430FR58xx, FR59xx IRGZ
DNP
DNP
DNP
DNP
DNP
JTAG ->
SBW ->
JTAG-Mode selection:
4-wire JTAG: Set jumpers JP3 to JP8 to position 2-3
2-wire "SpyBiWire": Set jumpers JP3 to JP8 to position 1-2
connection by via
DNP
DNP
1
3
5
7
9
11
13
2
4
6
12
14
8
10
JTAG
C2
C1
C4
R1
1 2
3 4
5 6
7 8
9 10
BOOTST
R3 R2
1
2
3
J2
J1
1
2
3
JP1
1
2
1
2
JP9
R4 C5
1
2
3
JP3
1
2
3
JP4
1
2
3
JP5
1
2
3
JP6
1
2
3
JP7
1
2
3
JP8
R5 R6
R7
C3 Q1
C7 C6
D1
R10
1
2
JP10
D2
R11
1
2
JP11
D3
R12
JP2
1
2
C8
C9
R9 R8
Q2
SV4
1
2
3
4
5
6
7
8
9
10
11
12
SV1
1
2
3
4
5
6
7
8
9
10
11
12
SV2
1
2
3
4
5
6
7
8
9
10
11
12
SV3
1
2
3
4
5
6
7
8
9
10
11
12
1 1_P1.0
2 2_P1.1
3 3_P1.2
4 4_P3.0
5 5_P3.1
6 6_P3.2
7 7_P3.3
8 8_P4.7
9 9_P1.3
10 10_P1.4
11 11_P1.5
12 12_PJ.0_TDO
13 13_PJ.1_TDI
14 14_PJ.2_TMS
15 15_PJ.3/TCK
16 16_P4.0
17 17_P4.1
18 18_P4.2
19 19_P4.3
20 20_P2.5
21 21_P2.6
22 22_TEST/SBWTCK
23 23_RST/SBWTDIO
24 24_P2.0
25_P2.1 25
26_P2.2 26
27_P3.4 27
28_P3.5 28
29_P3.6 29
30_P3.7 30
31_P1.6 31
32_P1.7 32
33_P4.4 33
34_P4.5 34
35_P4.6 35
36_DVSS 36
37_DVCC 37
38_P2.7 38
39_P2.3 39
40_P2.4 40
41_AVSS 41
42_HFXIN 42
43_HFXOUT 43
44_AVSS 44
45_LFXIN 45
46_LFXOUT 46
47_AVSS 47
48_AVCC 48
U1
SW1
R13
TP1TP2
SW2
R14
P1.0
P1.0
RST/NMI
TMS
TDI
VCC
GND
P1.1
P1.1
RST/SBWTDIO
RST/SBWTDIO
RST/SBWTDIO
TCK/SBWTCK
TDO/SBWTDIO
PJ.0/TDO
PJ.0/TDO
PJ.2/TMS
PJ.2/TMS
PJ.3/TCK
PJ.3/TCK
PJ.1/TDI
PJ.1/TDI
P1.2
P1.2
P2.0
P2.0
P2.1
P2.1
P1.3
P1.3
P1.4
P1.5
AVCC
AVCC
AVSS
AVSS
AVSS
AVSS
LFXOUT
LFXIN
LFGND HFGND
HFXOUT
HFXIN
P2.4
P2.3
P2.7
DVCC DVCC
DVCC
DVCC
DVSS
DVSS
P4.6
P4.5
P4.4
P1.7
P1.6
P3.7
P3.6
P3.5
P3.4
P2.2
P2.6
P2.5
P4.3
P4.2
P4.1
P4.0
P4.7
P3.3
P3.2
P3.1
P3.0
TEST/SBWTCK1
TEST/SBWTCK
TEST/SBWTCK
TEST/SBWTCK
MSP-TS430RGZ48C www.ti.com
B.16 MSP-TS430RGZ48C
Figure B-31. MSP-TS430RGZ48C Target Socket Module, Schematic
78 Hardware SLAU278R–May 2009–Revised May 2014
Submit Documentation Feedback
Copyright © 2009–2014, Texas Instruments Incorporated
Jumper JP1
Open to measure current
Connector J2
External power connector
Jumper J1 to "ext"
Jumpers JP3 to JP8
Close 1-2 to debug in Spy-Bi-Wire mode
Close 2-3 to debug in 4-wire JTAG mode
Switch SW1
Device reset
LEDs connected to
P1.0, P1.1, P1.2 via
JP9, JP10, JP11
(only D1 assembled)
Orient Pin 1 of MSP430 device
Connector JTAG
For JTAG Tool
Connector BOOTST
For Bootstrap Loader Tool
Jumper J1
1-2 (int): Power supply via JTAG interface
2-3 (ext): External power supply
Jumper JP2
Analog/digital power
Switch SW2
Connected to P1.3
HF ands LF oscillators with capacitors
and resistors to connect pinheads
www.ti.com MSP-TS430RGZ48C
Figure B-32. MSP-TS430RGZ48C Target Socket Module, PCB
Table B-17. MSP-TS430RGZ48C Revision History
Revision Comments
1.2 Initial release
LFOSC pins swapped at SV1 (9-10).
1.3 HFOSC pins swapped at SV1 (6-7).
BOOTST pin 4 now directly connected to the device RST/SBWTDIO pin.
SLAU278R–May 2009–Revised May 2014 Hardware 79
Submit Documentation Feedback
Copyright © 2009–2014, Texas Instruments Incorporated
MSP-TS430RGZ48C www.ti.com
Table B-18. MSP-TS430RGZ48C Bill of Materials
Number
Pos Ref Des Per Description Digi-Key Part Number Comment
Board
1 SV1, SV2, SV3, 4 12-pin header, TH DNP: headers and receptacles enclosed with kit.
SV4 Keep vias free of solder.
SAM1029-12-ND : Header
: Receptacle
1.1 SV1, SV2, SV3, 4 12-pin receptable, TH DNP: headers and receptacles enclosed with kit.
SV4 Keep vias free of solder.
: Header
SAM1213-12-ND : Receptacle
2 JP1, JP2, JP9 3 2-pin header, male, TH SAM1035-02-ND Place jumper on header
3 JP10, JP11 2 2-pin header, male, TH SAM1035-02-ND DNP
4 J1, JP3, JP4, JP5, 7 3-pin header, male, TH SAM1035-03-ND Place jumpers on pins 2-3
JP6, JP7, JP8
5 J2 1 3-pin header, male, TH SAM1035-03-ND
6 JP1, JP2, JP9, J1, 10 Jumper 15-38-1024-ND Place on: JP1, JP2, JP9, J1, JP3, JP4, JP5, JP6,
JP3, JP4, JP5, JP7, JP8
JP6, JP7, JP8
7 R2, R3, R5, R6, 9 DNP, 0805 DNP
R8, R9, R10, R11,
R14
8 R12, R13, R7 3 0R, 0805 541-000ATR-ND
9 C5 1 1.1nF, CSMD0805 490-1623-2-ND
10 C3, C7 2 1uF, 10V, CSMD0805 490-1702-2-ND
11 R4 1 47k, 0805 541-47000ATR-ND
12 C4, C6 2 100nF, CSMD0805 311-1245-2-ND
13 R1 1 330R, 0805 541-330ATR-ND
14 C1, C2, C8, C9 4 DNP, CSMD0805 DNP
15 SW1, SW2 2 EVQ-11L05R P8079STB-ND DNP
16 BOOTST 1 10-pin connector, male, TH HRP10H-ND DNP, keep vias free of solder
17 JTAG 1 14-pin connector, male, TH HRP14H-ND
18 Q1 1 DNP: MS3V-TR1 (32768kHz, depends on application Micro Crystal, DNP, enclosed in kit, keep vias
20ppm, 12.5pF) free of solder
19 Q2 1 DNP, Christal depends on application DNP, keep vias free of solder
20 U1 1 Socket: QFN11T048-008 Manuf.: Yamaichi
A101121-001
20.1 U1 1 MSP430FR5969IRGZ DNP: enclosed with kit. Is supplied by TI.
21 D1 1 green LED, DIODE0805 P516TR-ND
22 D3 1 red (DNP), DIODE0805 DNP
23 D2 1 yellow (DNP), DIODE0805 DNP
24 TP1, TP2 2 Testpoint DNP, keep pads free of solder
25 Rubber stand off 4 Buerklin: 20H1724 apply to corners at bottom side
26 PCB 1 79.6 x 91.0 mm MSP-TS430RGZ48C 2 layers, black solder mask
Rev. 1.2
80 Hardware SLAU278R–May 2009–Revised May 2014
Submit Documentation Feedback
Copyright © 2009–2014, Texas Instruments Incorporated
ML14
LED3
0R
12pF
12pF
12pF
12pF
GND
GND
0R
100nF
560R
ML10
JP1Q
JP1Q
10uF/6,3V
10uF/10V
47K
10nF
0R
0R
0R
-
-
0R
-
0R
0R
FE16-1-1
FE16-1-2
FE16-1-3
FE16-1-4
PWR3
GNDGND
-
MSP64PM
not assembled
not assembled
not assembled
not assembled
enhancement
reserved for
future
JTAG
1
3
5
7
9
11
13
2
4
6
12
14
8
10
D1
R2
C2
C1
C3
C4
R1
C5
R3
BOOTST
1 2
3 4
5 6
7 8
9 10
J7
1 2
J6
1 2
C6
C7
R5
C8
R6
R7
R8
R9
R10
R11
R12
R13
R14
1
2
3
4
5
6
7
8
9
10
11
12
13
14
15
16
J1
J2
17
18
19
20
21
22
23
24
25
26
27
28
29
30
31
32
J3
33
34
35
36
37
38
39
40
41
42
43
44
45
46
47
48
49
50
51
52
53
54
55
56
57
58
59
60
61
62
63
64
J4
J5
1
2
3
R4
Q1
LFXTCLK
XTCLK
U2
DVCC
2
3
4
5
6
7
XIN
XOUT
10
11
12
13
14
15
16
17
18
19
20
21
22
23
24
25
26
27
28
29
30
31
32
33
34
35
36
37
38
39
40
41
42
43
44
45
46
47
48
49
50
51
52
53
TDO
TDI
TMS
TCK
RST
59
60
61
AVSS
DVSS
AVCC
RST/NMI
TCK
TMS
TDI
TDO
VCC
Date: 3/14/2006 10:46:30 AM Sheet: 1/1
REV:
TITLE:
Document Number:
MSP-TS430PM64
+
+
1
MSP-TS430PM64 Target Socket PM64
Yamaichi
IC51-0644-807
Socket:
1.2
for F14x and F41x
Open J6 if LCD
is connected
If external supply voltage:
remove R8 and add R9 (0 Ohm)
If external supply voltage:
remove R11 and add R10 (0 Ohm)
For BSL usage add:
R6 R7 R13 R14
MSP430F14x : 0 0 open open
MSP430F41x : open open 0 0
www.ti.com MSP-TS430PM64
B.17 MSP-TS430PM64
NOTE: Connections between the JTAG header and pins XOUT and XIN are no longer required and should not be
made.
Figure B-33. MSP-TS430PM64 Target Socket Module, Schematic
SLAU278R–May 2009–Revised May 2014 Hardware 81
Submit Documentation Feedback
Copyright © 2009–2014, Texas Instruments Incorporated
Connector J5
External power connection
Remove R8 and jumper R9
D1
LED connected to pin 12
Jumper J6
Open to disconnect LED
Jumper J7
Open to measure current
Orient Pin 1 of
MSP430 device
Connector JTAG
For JTAG Tool
Connector BOOTST
For Bootstrap Loader Tool
MSP-TS430PM64 www.ti.com
Figure B-34. MSP-TS430PM64 Target Socket Module, PCB
82 Hardware SLAU278R–May 2009–Revised May 2014
Submit Documentation Feedback
Copyright © 2009–2014, Texas Instruments Incorporated
www.ti.com MSP-TS430PM64
Table B-19. MSP-TS430PM64 Bill of Materials
Pos. Ref Des No. per Description Digi-Key Part No. Comment Board
1 C1, C2 0 12pF, SMD0805 DNP
1.1 C3, C4 0 47pF, SMD0805 DNP: Only recommendation. Check your crystal spec.
2 C6, C7 1 10uF, 10V, Tantal Size B 511-1463-2-ND DNP: C6
3 C5 1 100nF, SMD0805 478-3351-2-ND
4 C8 1 10nF, SMD0805 478-1383-2-ND
5 C9 1 470nF, SMD0805 478-1403-2-ND
6 D1 1 green LED, SMD0805 P516TR-ND
DNP: Headers and
receptacles enclosed with
7 J1, J2, J3, J4 0 16-pin header, TH kit.Keep vias free of solder.
SAM1029-16-ND : Header
SAM1213-16-ND : Receptacle
8 J5 1 3-pin header, male, TH SAM1035-03-ND
9 J6, J7 2 2-pin header, male, TH SAM1035-02-ND Place jumper on header
11 2 Jumper 15-38-1024-ND Place on: J6, J7
12 JTAG 1 14-pin connector, male, TH HRP14H-ND
13 BOOTST 0 10-pin connector, male, TH DNP: Keep vias free of solder
Q1: Micro Crystal MS1V-T1K DNP: Keep vias free of 14 Q1, Q2 0 Crystal 32.768kHz, C(Load) = solder 12.5pF
15 R3 1 330 Ω, SMD0805 541-330ATR-ND
R1, R2, R4,
R6, R7, R8, DNP: R4, R6, R7, R9, R10, 16 R9, R10, 3 0 Ω, SMD0805 541-000ATR-ND R11, R12, R13, R14 R11, R12,
R13, R14
17 R5 1 47k Ω, SMD0805 541-47000ATR-ND
18 U1 1 Socket: IC51-0644-807 Manuf.: Yamaichi
19 PCB 1 78 x 75 mm 2 layers
20 Rubber 4 select appropriate Apply to corners at bottom standoff side
21 MSP430 22 MSP430F2619IPM DNP: Enclosed with kit MSP430F417IPM supplied by TI
SLAU278R–May 2009–Revised May 2014 Hardware 83
Submit Documentation Feedback
Copyright © 2009–2014, Texas Instruments Incorporated
0R
12pF
12pF
GND
GND
0R
100nF
330R
10uF/6.3V
0R 0R
0R 0R
PWR3
GND
47k
2.2nF
330R
GND
GND
100nF
GND
0R
0R
MSP-TS430PM64A Target Socket
DNP
Yamaichi
IC51-0644-807
Socket:
DNP
1.1
for F4152
Open JP1 if LCD
is connected
JTAG ->
SBW ->
DNP
DNP
DNP
DNP DNP
DNP DNP
Vcc
ext
int
TEST/SBWTCK RST/SBWTDIO P7.0/TDO P7.1/TDI P7.2/TMS P7.3/TCK
ADD LCD-CAP!
DNP
DNP
JTAG
1
3
5
7
9
11
13
2
4
6
12
14
8
10
R2
C2
C1
R1
C5
R3
BOOTST
1 2
3 4
5 6
7 8
9 10
C6
R10 R11
R13 R14
1
2
3
4
5
6
7
8
9
10
11
12
13
14
15
16
J1
17
18
19
20
21
22
23
24
25
26
27
28
29
30
31
32
J2
J3
33
34
35
36
37
38
39
40
41
42
43
44
45
46
47
48
49
50
51
52
53
54
55
56
57
58
59
60
61
62
63
64
J4
J5
1
2
3
48
47
46
45
44
43
42
41
40
39
38
37
36
35
34
33
32
31
30
29
28
27
26
25
24
23
22
21
20
19
18
17
16
1
2
3
4
5
6
7
8
9
11
12
13
14
15
10
64
63
62
61
60
59
58
57
56
55
54
53
52
51
50
49
1 2
Q1
R4
C3
1
2
3
JP4 JP5
1
2
3
JP6
1
2
3
JP7
1
2
3
JP8
1
2
3
R6
JP9
1
2
3
1
2
JP1
JP2
1
2
JP3
1
2
3
D1
C4
R5
R7
RST/NMI
TMS
TDI
VCC
GND
XTLGND
TCK/SBWTCK
TDO/SBWTDIO
VCC430
VCC430
VCC430
P5.1
P5.1
AVCC
AVCC
AVSS
AVSS
P1.0
P1.1
XIN
XOUT
A
A
A
B
B
B
C
C
D
D
E
E
F
F
Date: 3/29/2011 3:07:02 PM Sheet: 1/1
REV:
TITLE:
Document Number:
MSP-TS430PM64A
+
TEST/SBWTCK
RST/SBWTDIO
If supplied locally: populate R10 (0R), remove R11
If supplied by interface: populate R11 (0R), remove R10
MSP-TS430PM64A www.ti.com
B.18 MSP-TS430PM64A
Figure B-35. MSP-TS430PM64A Target Socket Module, Schematic
84 Hardware SLAU278R–May 2009–Revised May 2014
Submit Documentation Feedback
Copyright © 2009–2014, Texas Instruments Incorporated
Jumper JP2
Open to measure current
Jumper JP1
Open to disconnect LED
D1
LED connected to P5.1
Jumper JP3
1-2 (int): Power supply via JTAG interface
2-3 (ext): External power supply
Jumpers JP4 to JP9
Close 1-2 to debug in Spy-Bi-Wire mode
Close 2-3 to debug in 4-wire JTAG mode
Orient Pin 1 ofMSP430 device
Connector JTAG
For JTAG Tool
Connector BOOTST
For Bootstrap Loader Tool
Connector J5
External power connector
Jumper JP3 to "ext"
www.ti.com MSP-TS430PM64A
Figure B-36. MSP-TS430PM64A Target Socket Module, PCB
SLAU278R–May 2009–Revised May 2014 Hardware 85
Submit Documentation Feedback
Copyright © 2009–2014, Texas Instruments Incorporated
MSP-TS430PM64A www.ti.com
Table B-20. MSP-TS430PM64A Bill of Materials
Pos. Ref Des No. per Description Digi-Key Part No. Comment Board
1 C1, C2, 0 12pF, SMD0805 DNP
2 C3 0 2.2nF, SMD0805 DNP
3 C6, 1 10uF, 10V, Tantal Size B 511-1463-2-ND
4 C4, C5 2 100nF, SMD0805 478-3351-2-ND
5 D1 1 green LED, SMD0805 P516TR-ND
DNP: Headers and
receptacles enclosed with kit.
6 J1, J2, J3, J4 0 16-pin header, TH Keep vias free of solder.
SAM1029-16-ND : Header
SAM1213-16-ND : Receptacle
J5, JP3, JP4,
7 JP5, JP6, 8 3-pin header, male, TH SAM1035-03-ND JP7, JP8,
JP9
8 JP1, JP2 2 2-pin header, male, TH SAM1035-02-ND Place jumper on header
9 2 Jumper 15-38-1024-ND Place on: J6, J7
10 JTAG 1 14-pin connector, male, TH HRP14H-ND
11 BOOTST 0 10-pin connector, male, TH DNP: Keep vias free of solder
Micro Crystal MS1V-T1K DNP: Keep vias free of 12 Q1 0 Crystal 32.768kHz, C(Load) = solder 12.5pF
13 R3, R6 2 330 Ω, SMD0805 541-330ATR-ND
R1, R2, R5,
14 R7, R9, R10, 2 0 Ω, SMD0805 541-000ATR-ND DNP: R5, R7, R9, R10, R11, R11, R13, R13, R14
R14
15 R4 1 47k Ω, SMD0805 541-47000ATR-ND
16 U1 1 Socket: IC51-0644-807 Manuf.: Yamaichi
17 PCB 1 78 x 75 mm 4 layers
18 Rubber stand 4 select appropriate Apply to corners at bottom off side
19 MSP430 2 MSP430F4152IPM DNP: Enclosed with kit supplied by TI
86 Hardware SLAU278R–May 2009–Revised May 2014
Submit Documentation Feedback
Copyright © 2009–2014, Texas Instruments Incorporated
www.ti.com MSP-TS430RGC64B
B.19 MSP-TS430RGC64B
Figure B-37. MSP-TS430RGC64B Target Socket Module, Schematic
SLAU278R–May 2009–Revised May 2014 Hardware 87
Submit Documentation Feedback
Copyright © 2009–2014, Texas Instruments Incorporated
Jumper JP2
Open to disconnect LED
Connector J5
External power connector
Jumpers JP5 to JP10 Jumper JP3 to "ext"
Close 1-2 to debug in Spy-Bi-Wire mode
Close 2-3 to debug in 4-wire JTAG mode
D1
LED connected to P1.0
If the system should
be supplied via LDOI (J6),
close JP4 and set JP3 to "ext"
Orient Pin 1 of MSP430 device
Connector JTAG
For JTAG Tool
Connector BOOTST
For Bootstrap Loader Tool
Jumper JP3
1-2 (int): Power supply via JTAG interface
2-3 (ext): External power supply
Jumper JP1
Open to measure current
MSP-TS430RGC64B www.ti.com
Figure B-38. MSP-TS430RGC64B Target Socket Module, PCB
88 Hardware SLAU278R–May 2009–Revised May 2014
Submit Documentation Feedback
Copyright © 2009–2014, Texas Instruments Incorporated
www.ti.com MSP-TS430RGC64B
Table B-21. MSP-TS430RGC64B Bill of Materials
Pos. Ref Des No. per Description Digi-Key Part No. Comment Board
1 C1, C2 0 12pF, SMD0805 DNP
2 C3, C4 0 47pF, SMD0805 DNP
3 C6, C7, C10 3 10uF, 6.3V, SMD0805
C5, C11,
4 C13, C14, 5 100nF, SMD0805 311-1245-2-ND
C15
5 C8 1 2.2nF, SMD0805
6 C9 1 470nF, SMD0805 478-1403-2-ND
7 C16 1 4.7uF, SMD0805
8 C17 1 220nF, SMD0805
9 D1 1 green LED, SMD0805 P516TR-ND
J1, J2, J3, SAM1029-16-ND DNP: Headers and receptacles 10 J4 0 16-pin header, TH (Header) SAM1213-16- enclosed with kit. Keep vias free of ND (Receptacle) solder:
11 J5 , J6 2 3-pin header, male, TH
JP3, JP5, place jumpers on pins 2-3 on JP5, JP6, 12 JP6, JP7, 7 3-pin header, male, TH SAM1035-03-ND JP7, JP8, JP9, JP10 place jumpers on JP8, JP9, pins 1-2 on JP3, JP10
13 JP1, JP2, 3 2-pin header, male, TH SAM1035-02-ND Place jumper on header JP4
14 10 Jumper 15-38-1024-ND See Pos. 12 and Pos. 13
15 JTAG 1 14-pin connector, male, HRP14H-ND TH
16 BOOTST 0 10-pin connector, male, "DNP Keep vias free of solder" TH
Micro Crystal MS3V-T1R
17 Q1 0 Crystal 32.768kHz, C(Load) = DNP: Q1 Keep vias free of solder
12.5pF
18 Q2 0 Crystal Q2: 4MHz Buerklin: DNP: Q2 Keep vias free of solder 78D134
Insulating http://www.ettinger.de/Art 19 disk to Q2 0 Insulating disk to Q2 _Detail.cfm?ART_ARTNU M=70.08.121
20 R3, R7 2 330 Ω, SMD0805 541-330ATR-ND
R1, R2, R4,
21 R6, R8, 3 0 Ohm, SMD0805 541-000ATR-ND DNP: R6, R8, R9, R10, R11,R12 R9,R10,
R11, R12
22 R5 1 47k Ω, SMD0805 541-47000ATR-ND
23 U1 1 Socket: QFN11T064-006- Manuf.: Yamaichi N-HSP
24 PCB 1 85 x 76 mm 2 layers
Adhesive Approximately 6mm for example, 3M 25 plastic feet 4 width, 2mm height Bumpons Part No. SJ- Apply to corners at bottom side 5302
26 D3,D4
27 MSP430 2 MSP430F5310 RGC DNP: enclosed with kit, supplied by TI
SLAU278R–May 2009–Revised May 2014 Hardware 89
Submit Documentation Feedback
Copyright © 2009–2014, Texas Instruments Incorporated
MSP-TS430RGC64C www.ti.com
B.20 MSP-TS430RGC64C
The MSP-TS430RGC64C target board has been designed with the option to operate with the target
device DVIO input voltage supplied via header J6 (see Figure B-39). This development platform does not
supply the 1.8-V DVIO rail on board and it MUST be provided by external power supply for proper device
operation. For correct JTAG connection, programming, and debug operation, it is important to follow this
procedure:
1. Make sure that the VCC and DVIO voltage supplies are OFF and that the power rails are fully
discharged to 0 V.
2. Enable the 1.8-V external DVIO power supply.
3. Enable the 1.8-V to 3.6-V VCC power supply (alternatively, this supply can be provided from the MSPFET430UIF
JTAG debugger interface).
4. Connect the MSP-FET430UIF JTAG connector to the target board.
5. Start the debug session using IAR or CCS IDE.
For more information on debugging the MSP4and MSP430F525x, see the device-specific data sheets
(MSP430F522x: SLAS718; MSP430F525x: SLAS903) and Designing with MSP430F522x and
MSP430F521x Devices (SLAA558).
For debugging of devices (MSP430F524x and MSP430F523x) without use of the DVIO power domain,
short JP4 with the jumper.
90 Hardware SLAU278R–May 2009–Revised May 2014
Submit Documentation Feedback
Copyright © 2009–2014, Texas Instruments Incorporated
1.1
MSP-TS430RGC64C
TI Friesing
Tools
MSP430
1 1
12/14/10 S.G.
1 2 3 4 5 6
A
B
C
D
A
B
C
D
Design:
Appr.:
Rev.:
Comment:
Drawing#: Revision:
File: Page: Size:
Title of Schematic
of Mentor Pads Logic V9
Date: Name:
1 2 3 4 5 6
MSP-TS430RGC64C.sch
<-- SBW
<-- JTAG
ext
int
VCC
DVIO Power Circle
BSL
1 P6.0/CB0/A0
2 P6.1/CB1/A1
3 P6.2/CB2/A2
4 P6.3/CB3/A3
5 P6.4/CB4/A4
6 P6.5/CB5/A5
7 P6.6/CB6/A6
8 P6.7/CB7/A7
9 P5.0/A8/VEREF+
10 P5.1/A9/VEREF-
11 AVCC
12 P5.4/XIN
13 P5.5/XOUT
14 AVSS
15 DVCC
16 DVSS
17 VCORE
18 P1.0/TA0CLK/ACLK
19 P1.1/TA0.0
20 P1.2/TA0.1
21 P1.3/TA0.2
22 P1.4/TA0.3
23 P1.5/TA0.4
24 P1.6/TA1CLK/CBOUT
25 P1.7/TA1.0
26 P2.0/TA1.1
27 P2.1/TA1.2
28 P2.2/TA2CLK/SMCLK
29 P2.3/TA2.0
30 P2.4/TA2.1
31 P2.5/TA2.2
32 P2.6/RTCCLK/DMAE0
P2.7/UCB0STE/UCA0CLK 33
P3.0/UCB0SIMO/UCB0SDA 34
P3.1/UCB0SOMI/UCB0SCL 35
P3.2/UCB0CLK/UCA0STE 36
P3.3/UCA0TXD/UCA0SIMO 37
P3.4/UCA0RXD/UCA0SOMI 38
DVSS 39
DVIO 40
P4.0/PM_UCB1STE 41
P4.1/PM_UCB1SIMO 42
P4.2/PM_UCB1SOMI 43
P4.3/PM_UCB1CLK 44
P4.4/PM_UCA1TXD 45
P4.5/PM_UCA1RXD 46
P4.6/PM_NONE 47
P4.7/PM_NONE 48
49 P7.0/TB0.0
50 P7.1/TB0.1
51 P7.2/TB0.2
52 P7.3/TB0.3
53 P7.4/TB0.4
54 P7.5/TB0.5
55 BSLEN
56 RST/NMI
57 P5.2/XT2IN
58 P5.3/XT2OUT
59 TEST/SBWTCK
60 PJ.0/TDO
61 PJ.1/TDI/TCLK
62 PJ.2/TMS
63 PJ.3/TCK
64 RSTDVCC/SBWTDIO
65 THERMAL_1
66 THERMAL_2
67 THERMAL_3
68 THERMAL_4
69 THERMAL_5
70 THERMAL_6
71 THERMAL_7
72 THERMAL_8
U1
MSP430F5229
2 1
4 3
6 5
8 7
10 9
12 11
14 13
JTAG
1 2
3 4
5 6
7 8
9 0 1
BOOTST
CN-ML10
1
2
3
4
5
6
7
8
9
10
11
12
13
14
15
16
J1
1
2
3
4
5
6
7
8
9
10
11
12
13
14
15
16
J2
1
2
3
4
5
6
7
8
9
10
11
12
13
14
15
16
J3
1
2
3
4
5
6
7
8
9
10
11
12
13
14
15
16
J4
1
2
3
JP5
PINHEAD_1X3
1
2
3
JP6
PINHEAD_1X3
1
2
3
JP7
PINHEAD_1X3
1
2
3
JP8
PINHEAD_1X3
1
2
3
JP9
PINHEAD_1X3
1
2
3
JP10
PINHEAD_1X3
1
2
3
J5
PINHEAD_1X3
R7
330R
1
2
3
JP3
C10
10uF
C14
100nF
C5
10uF
C6
100nF
R1
0R
R2
0R
R6
0R R8
0R
C1 12pF
C2
12pF
C7
10uF
C13
100nF
1
2
JP2
R3
330R
1 2
D1
??? R4
0R
C9
470nF
R5
47K
C8
2.2nF
R11
0R
R12
0R
C16
4.7uF
tbd C3
tbd C4
R9
0R
R10
0R
C15
100nF
1
2
3
J6
PINHEAD_1X3
1
2
JP4
PINHEAD_1X2
D3
Q2
QUARZ_4PIN
26MHz/ASX53
Q1
1
2
JP1
PINHEAD_1X2
SHC1
SHORTCUT2
GND
GND
GND
GND
XTLGND
VCORE
GND
GND
DVCC
DVCC
GND
XTLGND2
GND
GND
DVCC
GND
RST/NMI
TCK
TMS
TDI
TDO
RSTDVCC_SBWTDIO
TDO
RST/NMI
TCK
C
TCK
M
TMS
I
TDI
O
TDO
DVCC
P1.2/TA0.1
P1.1/TA0.0
TEST/SBWTCK
C
M
I
O
DVCC
P1.1/TA0.0
P1.2/TA0.1
RSTDVCC_SBWTDIO
TEST/SBWTCK
AVSS
www.ti.com MSP-TS430RGC64C
Figure B-39. MSP-TS430RGC64C Target Socket Module, Schematic
SLAU278R–May 2009–Revised May 2014 Hardware 91
Submit Documentation Feedback
Copyright © 2009–2014, Texas Instruments Incorporated
Connector J5
External power connector for DVCC
Set jumper JP3 to "ext"
IMPORTANT NOTE:
Rev1.0 of the board does not have
connection from pin 4 of BOOTST to
pin 64 of MCU. To use BSL, these pins
should be connected by a wire.
Jumper JP2
Open to disconnect LED
D1
LED connected to P1.0
Orient Pin 1 of MSP430 device
Jumper JP4
For F524x devices, close.
For F522x, F523x, and F525x devices,
close only if one power supply is used
for VCC and DVIO, and if VCC is not
higher then 1.98 V. Otherwise, supply
DVIO over J6.
Do not close if VCC > 1.98 V, as it may
damage the chip.
Connector J6
External power connector
to supply DVIO
Jumpers JP5 to JP10
Close 1-2 to debug in Spy-Bi-Wire mode
Close 2-3 to debug in 4-wire JTAG mode
Connector JTAG
For JTAG Tool
Connector BOOTST
For Bootstrap Loader Tool
Jumper JP3
1-2 (int): Power supply via JTAG interface
2-3 (ext): External power supply
Jumper JP1
Open to measure current
MSP-TS430RGC64C www.ti.com
Figure B-40. MSP-TS430RGC64C Target Socket Module, PCB
92 Hardware SLAU278R–May 2009–Revised May 2014
Submit Documentation Feedback
Copyright © 2009–2014, Texas Instruments Incorporated
www.ti.com MSP-TS430RGC64C
Table B-22. MSP-TS430RGC64C Bill of Materials
Item Qty Reference Value Description Comment Supplier No.
1 0 C1, C2 12pF CAP, SMD, Ceramic, 0805 DNP C1 C2
2 0 C3, C4 tbd CAP, SMD, Ceramic, 0805 DNP C3 C4
4 3 C5, C7, C10 10uF CAP, SMD, Ceramic, 0805
5 5 C8 C6 C13-15 100nF CAP, SMD, Ceramic, 0805 Digi-Key: 311-1245-2-ND
5 5 C8 2.2nF CAP, SMD, Ceramic, 0805
6 1 C9 470nF CAP, SMD, Ceramic, 0805 Digi-Key: 478-1403-2-ND
7 1 C16 4.7uF CAP, SMD, Ceramic, 0805
8 1 D1 Green LED LED, SMD, 0805
DNP: headers and
receptacles enclosed with
9 4 J1-J4 16-pin header Pin header 1x16: Grid: 100mil kit. Keep vias free of (2.54 mm) solder.
: Header SAM1029-16-ND
: Receptacle SAM1213-16-ND
10 2 J5, J6 3-pin header, male, TH Pin header 1x3: Grid: 100mil SAM1035-03-ND (2.54 mm)
11 JP5, JP6, JP7, 3-pin header, male, TH Pinheader 1x3: Grid: 100mil place jumpers on pins 2-3 SAM1035-03-ND JP8, JP9, JP10 (2.54 mm)
12 JP3 3-pin header, male, TH Pin header 1x3: Grid: 100mil place jumper on pins 1-2 SAM1035-03-ND (2.54 mm)
13 JP1, JP2, JP4 2-pin header, male, TH Pin header 1x2; Grid: 100mil place jumper on header SAM1035-02-ND (2.54 mm)
Place on: JP1, JP2, JP3,
14 10 Jumper JP4, JP5, JP6, JP7, JP8, 15-38-1024-ND
JP9, JP10
15 1 JTAG 2x7Pin,Wanne Header, THD, Male 2x7 Pin, HRP14H-ND Wanne, 100mil spacing
16 0 BOOTST 2x5Pin,Wanne Header, THD, Male 2x5 Pin, DNP Wanne, 100mil spacing
17 1 Q1 26MHz/ASX53 CRYSTAL, SMD, 5x3MM, Only Kit. 26MHz
18 0 Q2 26MHz/ASX53 CRYSTAL, SMD, 5x3MM, 300-8219-1-ND 26MHz
19 1 D3 LL103A DIODE, SMD, SOD123, Buerklin: 24S3406 Schottky
20 2 R3, R7 330 Ohm, SMD0805 541-330ATR-ND
21 1 R5 47k Ohm, SMD0805 RES, SMD, 0805, 1/8W, x% 541-47000ATR-ND
R1, R2, R4, DNP: R6, R8, R9, R10, 22 R6, R8, R9, 0 Ohm, SMD0805 RES, SMD, 0805, 1/8W, x% R11,R12 541-000ATR-ND R10, R11, R12
23 1 U1 Socket: QFN11T064-006-N- Manuf.: Yamaichi HSP
24 2 MSP430 MSP430F5229IRGCR IC, MCU, SMD, 9.15x9.15mm Thermal Pad with Socket
25 4 Rubber stand Rubber stand off apply to corners at bottom Buerklin: 20H1724 off side
26 1 PCB 84 x 76 mm 84 x 76 mm
SLAU278R–May 2009–Revised May 2014 Hardware 93
Submit Documentation Feedback
Copyright © 2009–2014, Texas Instruments Incorporated
MSP-TS430RGC64USB www.ti.com
B.21 MSP-TS430RGC64USB
Due to the use of diodes in the power chain, the voltage on the MSP430F5xx device is approximately
0.3 V lower than is set by the debugging tool. Set the voltage in the IDE to 0.3 V higher than desired; for
example, to run the MCU at 3.0 V, set it to 3.3 V.
Figure B-41. MSP-TS430RGC64USB Target Socket Module, Schematic
94 Hardware SLAU278R–May 2009–Revised May 2014
Submit Documentation Feedback
Copyright © 2009–2014, Texas Instruments Incorporated
Orient Pin 1 of MSP430 device
Jumpers JP5 to JP10
Close 1-2 to debug in Spy-Bi-Wire mode
Close 2-3 to debug in 4-wire JTAG mode
Jumper JP3
1-2 (int): Power supply via JTAG interface
2-3 (ext): External power supply
Connector JTAG
For JTAG Tool
USB1
USB connector
Connector J5
External power connector
Jumper JP3 to "ext"
Jumper JP2
Open to disconnect LED
D1
LED connected to P1.0
Jumper JP1
Open to measure current
www.ti.com MSP-TS430RGC64USB
Figure B-42. MSP-TS430RGC64USB Target Socket Module, PCB
SLAU278R–May 2009–Revised May 2014 Hardware 95
Submit Documentation Feedback
Copyright © 2009–2014, Texas Instruments Incorporated
MSP-TS430RGC64USB www.ti.com
Table B-23. MSP-TS430RGC64USB Bill of Materials
Pos. Ref Des No. Per Description Digi-Key Part No. Comment Board
1 C1, C2 0 12pF, SMD0805 DNP: C1, C2
1.1 C3, C4 2 47pF, SMD0805
2 C6, C7 2 10uF, 6.3V, Tantal Size B 511-1463-2-ND
3 C5, C11, 4 100nF, SMD0805 311-1245-2-ND C13, C14
3.1 C10, C12 0 10uF, SMD0805 DNP: C10, C12
4 C8 1 2.2nF, SMD0805
5 C9 1 470nF, SMD0805 478-1403-2-ND
6 D1 1 green LED, SMD0805 P516TR-ND
DNP: headers and
receptacles enclosed with kit.
7 J1, J2, J3, J4 4 16-pin header, TH Keep vias free of solder.
SAM1029-16-ND : Header
SAM1213-16-ND : Receptacle
8 J5 1 3-pin header, male, TH SAM1035-03-ND
JP5, JP6,
9 JP7, JP8, 6 3-pin header, male, TH SAM1035-03-ND place jumpers on pins 2-3
JP9, JP10
10 JP1, JP2, 3 2-pin header, male, TH SAM1035-02-ND place jumper on header JP4
11 JP3 1 3-pin header, male, TH SAM1035-03-ND place jumper on pins 1-2
Place on: JP1, JP2, JP3,
12 10 Jumper 15-38-1024-ND JP4, JP5, JP6, JP7, JP8,
JP9, JP10
13 JTAG 1 14-pin connector, male, TH HRP14H-ND
Q1: Micro Crystal MS1V-T1K DNP: Q1 14 Q1 0 Crystal 32.768kHz, C(Load) = Keep vias free of solder" 12.5pF
15 Q2 1 Crystal Q2: 4MHz Buerklin: 78D134
16 R3, R7 2 330 Ω, SMD0805 541-330ATR-ND
R1, R2, R4,
17 R6, R8, R9, 2 0 Ω, SMD0805 541-000ATR-ND DNP: R4, R6, R8, R9, R12
R12
18 R10 1 100 Ω, SMD0805 Buerklin: 07E500
18 R11 1 1M Ω, SMD0805
18 R5 1 47k Ω, SMD0805 541-47000ATR-ND
19 U1 1 Socket: QFN11T064-006 Manuf.: Yamaichi
20 PCB 1 79 x 77 mm 2 layers
21 Rubber stand 4 Buerklin: 20H1724 apply to corners at bottom off side
22 MSP430 2 MSP430F5509 RGC DNP: enclosed with kit. Is supplied by TI
Insulating http://www.ettinger.de/Art_De 23 disk to Q2 1 Insulating disk to Q2 tail.cfm?ART_ARTNUM=70.0 8.121
27 C33 1 220n SMD0603 Buerklin: 53D2074
28 C35 1 10p SMD0603 Buerklin: 56D102
29 C36 1 10p SMD0603 Buerklin: 56D102
30 C38 1 220n SMD0603 Buerklin: 53D2074
31 C39 1 4u7 SMD0603 Buerklin: 53D2086
32 C40 1 0.1u SMD0603 Buerklin: 53D2068
33 D2, D3, D4 3 LL103A Buerklin: 24S3406
96 Hardware SLAU278R–May 2009–Revised May 2014
Submit Documentation Feedback
Copyright © 2009–2014, Texas Instruments Incorporated
www.ti.com MSP-TS430RGC64USB
Table B-23. MSP-TS430RGC64USB Bill of Materials (continued)
Pos. Ref Des No. Per Description Digi-Key Part No. Comment Board
34 IC7 1 TPD4E004 Manu: TI
36 LED 0 JP3QE SAM1032-03-ND DNP
37 LED1 0 LEDCHIPLED_0603 FARNELL: 852-9833 DNP
38 LED2 0 LEDCHIPLED_0603 FARNELL: 852-9868 DNP
39 LED3 0 LEDCHIPLED_0603 FARNELL: 852-9841 DNP
40 R13, R15, 0 470R Buerklin: 07E564 DNP R16
41 R33 1 1k4 / 1k5 Buerklin: 07E612
42 R34 1 27R Buerklin: 07E444
43 R35 1 27R Buerklin: 07E444
44 R36 1 33k Buerklin: 07E740
45 S1 0 PB P12225STB-ND DNP
46 S2 0 PB P12225STB-ND DNP
46 S3 1 PB P12225STB-ND
47 USB1 1 USB_RECEPTACLE FARNELL: 117-7885
SLAU278R–May 2009–Revised May 2014 Hardware 97
Submit Documentation Feedback
Copyright © 2009–2014, Texas Instruments Incorporated
MSP-TS430PN80 www.ti.com
B.22 MSP-TS430PN80
NOTE: For MSP430F47x and MSP430FG47x devices:
Connect pins 7 and 10 (GND) externally to DVSS (see data sheet).
Connect load capacitance on Vref pin 60 when SD16 is used (see data sheet).
For use of BSL: connect pin 1 of BOOST to pin 58 of U1 and pin 3 of BOOST to pin 57 of U1.
Figure B-43. MSP-TS430PN80 Target Socket Module, Schematic
98 Hardware SLAU278R–May 2009–Revised May 2014
Submit Documentation Feedback
Copyright © 2009–2014, Texas Instruments Incorporated
Connector J5
External power connector
Jumper JP1 to "ext"
D1
LED connected to pin 12
Jumper J6
Open to disconnect LED
Orient Pin 1 of
MSP430 device
Connector JTAG
For JTAG Tool
Connector BOOTST
For Bootstrap Loader Tool
Jumper JP1
1-2 (int): Power supply via JTAG interface
2-3 (ext): External power supply
Jumper JP2
Open to measure current
www.ti.com MSP-TS430PN80
Figure B-44. MSP-TS430PN80 Target Socket Module, PCB
SLAU278R–May 2009–Revised May 2014 Hardware 99
Submit Documentation Feedback
Copyright © 2009–2014, Texas Instruments Incorporated
MSP-TS430PN80 www.ti.com
Table B-24. MSP-TS430PN80 Bill of Materials
Pos. Ref Des No. per Description Digi-Key Part No. Comment Board
1 C1, C2 0 12pF, SMD0805 DNP: C1, C2
1.1 C3, C4 0 47pF, SMD0805 DNP: Only recommendation. Check your crystal spec.
2 C6, C7 1 10uF, 10V, Tantal Size B 511-1463-2-ND
3 C5 1 100nF, SMD0805 478-3351-2-ND
4 C8 1 10nF, SMD0805 478-1383-2-ND
5 D1 1 green LED, SMD0603 475-1056-2-ND
DNP: Headers and
receptacles enclosed with
6 J1, J2, J3, J4 0 25-pin header, TH kit.Keep vias free of solder.
SAM1029-20-ND : Header
SAM1213-20-ND : Receptacle
7 J5, JP1 2 3-pin header, male, TH SAM1035-03-ND
8 J6, JP2 2 2-pin header, male, TH SAM1035-02-ND Place jumper on header
9 3 Jumper 15-38-1024-ND Place on: J6, JP2, JP1/Pos1- 2
10 JTAG 1 14-pin connector, male, TH HRP14H-ND
11 BOOTST 0 10-pin connector, male, TH DNP: Keep vias free of solder
Q1: Micro Crystal MS1V-T1K DNP: Keep vias free of 12 Q1, Q2 0 Crystal 32.768kHz, C(Load) = solder 12.5pF
13 R3 1 560 Ω, SMD0805 541-560ATR-ND
R1, R2, R4, DNP: R4, R6, R7, R10, R11, 14 R6, R7, R10, 2 0 Ω, SMD0805 541-000ATR-ND R12 R11, R12
15 R5 1 47k Ω, SMD0805 541-47000ATR-ND
16 U1 1 Socket: IC201-0804-014 Manuf.: Yamaichi
17 PCB 1 77 x 77 mm 2 layers
18 Adhesive 4 ~6mm width, 2mm height for example, 3M Bumpons Apply to corners at bottom Plastic feet Part No. SJ-5302 side
19 MSP430 2 MSP430FG439IPN DNP: Enclosed with kit supplied by TI
100 Hardware SLAU278R–May 2009–Revised May 2014
Submit Documentation Feedback
Copyright © 2009–2014, Texas Instruments Incorporated
www.ti.com MSP-TS430PN80A
B.23 MSP-TS430PN80A
Figure B-45. MSP-TS430PN80A Target Socket Module, Schematic
SLAU278R–May 2009–Revised May 2014 Hardware 101
Submit Documentation Feedback
Copyright © 2009–2014, Texas Instruments Incorporated
Connector J5
External power connector
Jumper JP3 to "ext"
Orient Pin 1 of
MSP430 device
Jumpers JP5 to JP10
Close 1-2 to debug in Spy-Bi-Wire mode
Close 2-3 to debug in 4-wire JTAG mode
D1
LED connected to P1.0
Jumper JP2
Open to disconnect LED
Connector J6
If the system is supplied via LDOI,
close JP4 and set JP3 to external
Connector JTAG
For JTAG Tool
Connector BOOTST
For Bootstrap Loader Tool
Jumper JP3
1-2 (int): Power supply via JTAG interface
2-3 (ext): External power supply
Jumper JP1
Open to measure current
MSP-TS430PN80A www.ti.com
Figure B-46. MSP-TS430PN80A Target Socket Module, PCB
102 Hardware SLAU278R–May 2009–Revised May 2014
Submit Documentation Feedback
Copyright © 2009–2014, Texas Instruments Incorporated
www.ti.com MSP-TS430PN80A
Table B-25. MSP-TS430PN80A Bill of Materials
Position Ref Des No. per Description Digi-Key Part No. Comment Board
1 C1, C2 0 12pF, SMD0805 DNP
2 C3, C4 0 47pF, SMD0805 DNP
3 C6, C7, 3 10uF, 6.3V, SMD0805 DNP C10 C10, C12
C5, C11,
4 C13, C14, 5 100nF, SMD0805 311-1245-2-ND
C15
5 C8 1 2.2nF, SMD0805
6 C9 1 470nF, SMD0805 478-1403-2-ND
7 C16 1 4.7uF, SMD0805
8 C17 1 220nF, SMD0805
9 D1 1 green LED, SMD0805 P516TR-ND
J1, J2, J3, SAM1029-20-ND DNP: Headers and receptacles 10 J4 0 20-pin header, TH (Header) SAM1213-20- enclosed with kit. Keep vias free of ND (Receptacle) solder:
11 J5 , J6 2 3-pin header, male, TH
JP3, JP5, place jumpers on pins 2-3 on JP5, 12 JP6, JP7, 7 3-pin header, male, TH SAM1035-03-ND JP6, JP7, JP8, JP9, JP10 place JP8, JP9, jumpers on pins 1-2 on JP3, JP10
13 JP1, JP2, 3 2-pin header, male, TH SAM1035-02-ND Place jumper on header JP4
14 10 Jumper 15-38-1024-ND See Pos. 12 and Pos. 13
15 JTAG 1 14-pin connector, male, HRP14H-ND TH
16 BOOTST 0 10-pin connector, male, "DNP Keep vias free of solder" TH
Micro Crystal MS3V-T1R
17 Q1 0 Crystal 32.768kHz, C(Load) = DNP: Q1 Keep vias free of solder
12.5pF
18 Q2 0 Crystal Q2: 4MHz Buerklin: DNP: Q2 Keep vias free of solder 78D134
Insulating http://www.ettinger.de/Ar 19 disk to Q2 0 Insulating disk to Q2 t_Detail.cfm?ART_ART NUM=70.08.121
20 D3,D4 2 LL103A Buerklin: 24S3406
21 R3, R7 2 330 Ω, SMD0805 541-330ATR-ND
R1, R2,
R4, R6,
22 R8, 3 0 Ohm, SMD0805 541-000ATR-ND DNP: R6, R8, R9, R10, R11,R12
R9,R10,
R11, R12
23 R5 1 47k Ω, SMD0805 541-47000ATR-ND
24 U1 1 Socket:IC201-0804-014 Manuf.: Yamaichi
25 PCB 1 77 x 91 mm 2 layers
Adhesive Approximately 6mm for example, 3M 26 plastic feet 4 width, 2mm height Bumpons Part No. SJ- Apply to corners at bottom side 5302
27 MSP430 2 MSP430F5329IPN DNP: enclosed with kit, supplied by TI
SLAU278R–May 2009–Revised May 2014 Hardware 103
Submit Documentation Feedback
Copyright © 2009–2014, Texas Instruments Incorporated
MSP-TS430PN80USB www.ti.com
B.24 MSP-TS430PN80USB
Due to the use of diodes in the power chain, the voltage on the MSP430F5xx device is approximately
0.3 V lower than is set by the debugging tool. Set the voltage in the IDE to 0.3 V higher than desired; for
example, to run the MCU at 3.0 V, set it to 3.3 V.
NOTE: R11 should be populated.
Figure B-47. MSP-TS430PN80USB Target Socket Module, Schematic
104 Hardware SLAU278R–May 2009–Revised May 2014
Submit Documentation Feedback
Copyright © 2009–2014, Texas Instruments Incorporated
Jumper JP3
1-2 (int): Power supply via JTAG debug interface
2-3 (ext): External power supply
Connector J5
External power connector
Jumper JP3 to "ext"
USB Connector
Button S3
BSL invoke
Jumper JP4
Close for USB bus powered device
Jumper JP2
Open to disconnect LED
D1
LED connected to P1.0
Jumper JP1
Open to measure current
Jumpers JP5 to JP10
Close 1-2 to debug in Spy-Bi-Wire mode
Close 2-3 to debug in 4-wire JTAG mode
Connector JTAG
For JTAG Tool
Orient Pin 1 of MSP430 device
www.ti.com MSP-TS430PN80USB
Figure B-48. MSP-TS430PN80USB Target Socket Module, PCB
SLAU278R–May 2009–Revised May 2014 Hardware 105
Submit Documentation Feedback
Copyright © 2009–2014, Texas Instruments Incorporated
MSP-TS430PN80USB www.ti.com
Table B-26. MSP-TS430PN80USB Bill of Materials
Pos. Ref Des No. per Description Digi-Key Part No. Comment Board
1 C1, C2 0 12pF, SMD0805 DNP: C1, C2
1.1 C3, C4 2 47pF, SMD0805
2 C6, C7 2 10uF, 6.3V, Tantal Size B 511-1463-2-ND
3 C5, C11, 4 100nF, SMD0805 311-1245-2-ND C13, C14
3.1 C10, C12 0 10uF, SMD0805 311-1245-2-ND DNP: C10, C12
4 C8 1 2.2nF, SMD0805
5 C9 1 470nF, SMD0805 478-1403-2-ND
6 D1 1 green LED, SMD0805 P516TR-ND
DNP: headers and
7 J1, J2, J3, 4 20-pin header, TH SAM1029-20-ND receptacles enclosed with J4 kit. Keep vias free of
solder.
DNP: headers and
receptacles enclosed with
kit. Keep vias free of
7.1 4 20-pin header, TH solder.
SAM1213-20-ND : Header
: Receptacle
8 J5 1 3-pin header, male, TH SAM1035-03-ND
JP5, JP6,
9 JP7, 6 3-pin header, male, TH SAM1035-03-ND Place jumpers on pins 2-3 JP8,JP9,
JP10
10 JP1, JP2 2 2-pin header, male, TH SAM1035-02-ND Place jumper on header
JP4 1 SAM1035-02-ND Place jumper only on one pin
11 JP3 1 3-pin header, male, TH SAM1035-03-ND Place jumper on pins 1-2
Place on: JP1, JP2, JP3,
12 10 Jumper 15-38-1024-ND JP4, JP5, JP6, JP7, JP8,
JP9, JP10
13 JTAG 1 14-pin connector, male, TH HRP14H-ND
Micro Crystal MS1V-T1K DNP: Q1 Keep vias free of 14 Q1 0 Crystal 32.768kHz, C(Load) = solder 12.5pF
15 Q2 1 Crystal "Q2: 4MHzBuerklin: 78D134"
16 R3, R7 2 330 Ω, SMD0805 541-330ATR-ND
R1, R2, R4,
17 R6, R8, R9, 2 0 Ω, SMD0805 541-000ATR-ND DNP: R4, R6, R8, R9, R12
R12
18 R10 1 100 Ω, SMD0805 Buerklin: 07E500
18 R11 0 1M Ω, SMD0805 DNP
18 R5 1 47k Ω, SMD0805 541-47000ATR-ND
19 U1 1 Socket:IC201-0804-014 Manuf.: Yamaichi
20 PCB 1 79 x 77 mm 2 layers
21 Rubber 4 Buerklin: 20H1724 Apply to corners at bottom standoff side
22 MSP430 2 MSP430F5529 DNP: Enclosed with kit supplied by TI
Insulating http://www.ettinger.de/Art_ 23 disk to Q2 1 Insulating disk to Q2 Detail.cfm?ART_ARTNUM =70.08.121
27 C33 1 220n Buerklin: 53D2074
106 Hardware SLAU278R–May 2009–Revised May 2014
Submit Documentation Feedback
Copyright © 2009–2014, Texas Instruments Incorporated
www.ti.com MSP-TS430PN80USB
Table B-26. MSP-TS430PN80USB Bill of Materials (continued)
Pos. Ref Des No. per Description Digi-Key Part No. Comment Board
28 C35 1 10p Buerklin: 56D102
29 C36 1 10p Buerklin: 56D102
30 C38 1 220n Buerklin: 53D2074
31 C39 1 4u7 Buerklin: 53D2086
32 C40 1 0.1u Buerklin: 53D2068
33 D2, D3, D4 3 LL103A Buerklin: 24S3406
34 IC7 1 TPD4E004 Manu: TI
36 LED 0 JP3QE SAM1032-03-ND DNP
37 LED1 0 LEDCHIPLED_0603 FARNELL: 852-9833 DNP
38 LED2 0 LEDCHIPLED_0603 FARNELL: 852-9868 DNP
39 LED3 0 LEDCHIPLED_0603 FARNELL: 852-9841 DNP
40 R13, R15, 0 470R Buerklin: 07E564 DNP R16
41 R33 1 1k4 Buerklin: 07E612
42 R34 1 27R Buerklin: 07E444
43 R35 1 27R Buerklin: 07E444
44 R36 1 33k Buerklin: 07E740
45 S1 0 PB P12225STB-ND DNP
46 S2 0 PB P12225STB-ND DNP
46 S3 1 PB P12225STB-ND
47 USB1 1 USB_RECEPTACLE FARNELL: 117-7885
SLAU278R–May 2009–Revised May 2014 Hardware 107
Submit Documentation Feedback
Copyright © 2009–2014, Texas Instruments Incorporated
MSP-TS430PZ100 www.ti.com
B.25 MSP-TS430PZ100
NOTE: Connections between the JTAG header and pins XOUT and XIN are no longer required and should not be
made.
Figure B-49. MSP-TS430PZ100 Target Socket Module, Schematic
108 Hardware SLAU278R–May 2009–Revised May 2014
Submit Documentation Feedback
Copyright © 2009–2014, Texas Instruments Incorporated
Connector J5
External power connection
Remove R8 and jumper R9
D1
LED connected to pin 12
Jumper J6
Open to disconnect LED
Orient Pin 1 of MSP430 device
Jumper J7
Open to measure current
Connector JTAG
For JTAG Tool
Connector BOOTST
For Bootstrap Loader Tool
www.ti.com MSP-TS430PZ100
Figure B-50. MSP-TS430PZ100 Target Socket Module, PCB
SLAU278R–May 2009–Revised May 2014 Hardware 109
Submit Documentation Feedback
Copyright © 2009–2014, Texas Instruments Incorporated
MSP-TS430PZ100 www.ti.com
Table B-27. MSP-TS430PZ100 Bill of Materials
Pos. Ref Des No. per Description Digi-Key Part No. Comment Board
1 C1, C2 0 12pF, SMD0805 DNP
DNP: Only
1b C3, C4 0 47pF, SMD0805 recommendation. Check
your crystal spec.
2 C6, C7 1 10uF, 10V, Tantal Size B 511-1463-2-ND DNP: C6
3 C5 1 100nF, SMD0805 478-3351-2-ND
4 C8 1 10nF, SMD0805 478-1383-2-ND
5 C9 1 470nF, SMD0805 478-1403-2-ND
6 D1 1 yellow LED, TH, 3mm, T1 511-1251-ND
DNP: Headers and
receptacles enclosed with
7 J1, J2, J3, 0 25-pin header, TH kit.Keep vias free of solder. J4 SAM1029-25-ND : Header
SAM1213-25-ND : Receptacle
8 J5 1 3-pin header, male, TH SAM1035-03-ND
9 J6, J7 2 2-pin header, male, TH SAM1035-02-ND place jumper on header
10 2 Jumper 15-38-1024-ND Place on: J6, J7
11 JTAG 1 14-pin connector, male, TH HRP14H-ND
12 BOOTST 0 10-pin connector, male, TH DNP: Keep vias free of solder
Q1: Micro Crystal MS1V- DNP: Keep vias free of 13 Q1, Q2 0 Crystal T1K 32.768kHz, C(Load) = solder 12.5pF
14 R3 1 330 Ω, SMD0805 541-330ATR-ND
R1, R2, R4,
15 R8, R9, R10, 3 0 Ω, SMD0805 541-000ATR-ND DNP: R4, R9, R10, R12
R11, R12
16 R5 1 47k Ω, SMD0805 541-47000ATR-ND
17 U1 1 Socket: IC201-1004-008 or Manuf.: Yamaichi IC357-1004-53N
18 PCB 1 82 x 90 mm 2 layers
19 Adhesive 4 ~6mm width, 2mm height for example, 3M Bumpons Apply to corners at bottom Plastic feet Part No. SJ-5302 side
20 MSP430 2 MSP430FG4619IPZ DNP: enclosed with kit supplied by TI
110 Hardware SLAU278R–May 2009–Revised May 2014
Submit Documentation Feedback
Copyright © 2009–2014, Texas Instruments Incorporated
www.ti.com MSP-TS430PZ100A
B.26 MSP-TS430PZ100A
Figure B-51. MSP-TS430PZ100A Target Socket Module, Schematic
SLAU278R–May 2009–Revised May 2014 Hardware 111
Submit Documentation Feedback
Copyright © 2009–2014, Texas Instruments Incorporated
Jumper JP1
Open to measure current
Jumper JP2
Open to disconnect LED
D1
LED connected to P5.1
Jumper JP3
1-2 (int): Power supply via JTAG interface
2-3 (ext): External power supply
Orient Pin 1 of
MSP430 Device
Connector J5
External power connector
Jumper JP3 to "ext"
Connector JTAG
For JTAG Tool
Connector BOOTST
For Bootstrap Loader Tool
MSP-TS430PZ100A www.ti.com
Figure B-52. MSP-TS430PZ100A Target Socket Module, PCB
112 Hardware SLAU278R–May 2009–Revised May 2014
Submit Documentation Feedback
Copyright © 2009–2014, Texas Instruments Incorporated
www.ti.com MSP-TS430PZ100A
Table B-28. MSP-TS430PZ100A Bill of Materials
Pos. Ref Des No. per Description Digi-Key Part No. Comment Board
1 C1, C2 0 12pF, SMD0805 DNP
DNP: Only
1b C3, C4 0 47pF, SMD0805 recommendation. Check
your crystal spec.
2 C7, C9 2 10uF, 10V, Tantal Size B 511-1463-2-ND
3 C5, C11, 3 100nF, SMD0805 311-1245-2-ND C14
4 C8 1 10nF, SMD0805 478-1358-1-ND
5 C6 0 470nF, SMD0805 478-1403-2-ND DNP
6 D1 1 green LED, SMD0805 67-1553-1-ND
DNP: Headers and
receptacles enclosed with
7 J1, J2, J3, 0 25-pin header, TH kit.Keep vias free of solder. J4 SAM1029-25-ND : Header
SAM1213-25-ND : Receptacle
8 J5 1 3-pin header, male, TH SAM1035-03-ND
10 JP1, JP2 2 2-pin header, male, TH SAM1035-02-ND pPlace jumper on header
11 JP3 1 3-pin header, male, TH SAM1035-03-ND Place jumper on pins 1-2
12 3 Jumper 15-38-1024-ND Place on: JP1, JP2, JP3
13 JTAG 1 14-pin connector, male, TH HRP14H-ND
14 BOOTST 0 10-pin connector, male, TH DNP: Keep vias free of solder
Q1: Micro Crystal MS1V- DNP: Keep vias free of 15 Q1, Q2 0 Crystal T1K 32.768kHz, C(Load) = solder 12.5pF
16 R3 1 330 Ω, SMD0805 541-330ATR-ND
R1, R2, R4,
17 R6, R7, R8, 2 0 Ω, SMD0805 541-000ATR-ND DNP: R4, R6, R7, R8, R9, R9, R10, R10, R11, R12
R11, R12
18 R5 1 47k Ω, SMD0805 541-47000ATR-ND
19 U1 1 Socket: IC357-1004-53N Manuf.: Yamaichi
20 PCB 1 90 x 82 mm 4 layers
21 Rubber 4 Select appropriate Apply to corners at bottom standoff side
22 MSP430 2 MSP430F47197IPZ DNP: Enclosed with kit supplied by TI
SLAU278R–May 2009–Revised May 2014 Hardware 113
Submit Documentation Feedback
Copyright © 2009–2014, Texas Instruments Incorporated
MSP-TS430PZ100B www.ti.com
B.27 MSP-TS430PZ100B
Figure B-53. MSP-TS430PZ100B Target Socket Module, Schematic
114 Hardware SLAU278R–May 2009–Revised May 2014
Submit Documentation Feedback
Copyright © 2009–2014, Texas Instruments Incorporated
Connector J5
External power connector
Jumper JP3 to "ext"
Jumper JP1
Open to measure current
Orient Pin 1 of MSP430 device
Jumpers JP5 to JP10
Close 1-2 to debug in Spy-Bi-Wire mode
Close 2-3 to debug in 4-wire JTAG mode
JP11, JP12, JP13
Connect 1-2 to connect
AUXVCCx with DVCC
or drive AUXVCCx externally
D1
LED connected to P1.0
Jumper JP2
Open to disconnect LED
Jumper JP3
1-2 (int): Power supply via JTAG interface
2-3 (ext): External power supply
Connector JTAG
For JTAG Tool
Connector BOOTST
For Bootstrap Loader Tool
www.ti.com MSP-TS430PZ100B
Figure B-54. MSP-TS430PZ100B Target Socket Module, PCB
SLAU278R–May 2009–Revised May 2014 Hardware 115
Submit Documentation Feedback
Copyright © 2009–2014, Texas Instruments Incorporated
MSP-TS430PZ100B www.ti.com
Table B-29. MSP-TS430PZ100B Bill of Materials
Position Ref Des No. per Description Digi-Key Part No. Comment Board
1 C1, C2 0 12pF, SMD0805 DNP
C4, C5,
2 C6 , C7, 6 100nF, SMD0805 311-1245-2-ND
C8, C9
3 C10, C26 2 470 nF, SMD0805 478-1403-2-ND
4 C11, C12 1 10 uF / 6.3 V SMD0805 C12 DNP
C13, C14,
5 C16, C18, 6 4.7 uF SMD0805
C19, C29
6 D1 1 green LED, SMD0805 P516TR-ND
J1, J2, J3, SAM1029-25-ND DNP: Headers and receptacles 7 J4 0 25-pin header, TH (Header) SAM1213-25- enclosed with kit. Keep vias free of ND (Receptacle) solder:
8 J5 1 3-pin header, male, TH
JP3, JP5, place jumpers on pins 2-3 on JP5, 9 JP6, JP7, 7 3-pin header, male, TH SAM1035-03-ND JP6, JP7, JP8, JP9, JP10 place JP8, JP9, jumpers on pins 1-2 on JP3, JP10
10 JP1, JP2, 3 2-pin header, male, TH SAM1035-02-ND Place jumper on header JP4
11 JP11, 3 4-pin header, male, TH place jumper on header 1-2 JP12, JP13
12 13 Jumper 15-38-1024-ND See Pos. 9 and Pos. 10 and Pos. 11
15 JTAG 1 14-pin connector, male, HRP14H-ND TH
16 BOOTST 0 10-pin connector, male, "DNP Keep vias free of solder" TH
17 Q1 0 Crystal DNP: Q1 Keep vias free of solder
21 R3, R7 2 330 Ω, SMD0805 541-330ATR-ND
R1, R2,
22 R4, R6, 2 0 Ohm, SMD0805 541-000ATR-ND DNP: R4, R6, R8, R10, R11 R8, R10,
R11
23 R5 1 47k Ω, SMD0805 541-47000ATR-ND
24 U1 1 Socket: IC357-1004-53N Manuf.: Yamaichi
25 PCB 1 90 x 82 mm 2 layers
Adhesive Approximately 6mm for example, 3M 26 plastic feet 4 width, 2mm height Bumpons Part No. SJ- Apply to corners at bottom side 5302
27 MSP430 2 MSP430F6733IPZ DNP: enclosed with kit, supplied by TI
116 Hardware SLAU278R–May 2009–Revised May 2014
Submit Documentation Feedback
Copyright © 2009–2014, Texas Instruments Incorporated
DNP
DNP
DNP
DNP
DNP
DNP
0R
12pF
12pF
47pF
47pF
GND
0R
100nF
330R
10uF/6.3V
10uF/6.3V
2.2nF
PWR3
GND
GND
GND
0R GND
330R
47K
100nF
100nF
P516TR-ND
470nF
100nF
100nF
0R
0R
0R
0R
GND
VCC
100nF
GND
100nF
100nF
GND
100nF
LL103A
GND
4.7n
HCTC_XTL_4
HCTC_XTL_4
HCTC_XTL_4
HCTC_XTL_4
GND
0R
0R
GND
GND
GND
4.7uF
GND
100nF
220nF
GND
VCC
LL103A
1.1
MSP430: Target-Socket MSP-TS430PZ100C
Socket:
Yamaichi
IC201-1004-008
LFXTCLK
<- SBW
<- JTAG
Vcc
int
ext
DNP
DNP
DNP
DNP
DNP
DNP
BSL-Rx
BSL-Tx
DNP
1
3
5
7
9
11
13
2
4
6
12
14
8
10
JTAG
R2
C2
C1
C3
C4
C5 R1
R3
C6
C7
C8
1
2
3
J5
80
79
78
77
76
75
74
73
72
71
70
69
68
67
66
65
60
59
58
57
56
55
54
53
52
51
50
49
48
47
46
45
36
35
34
33
32
31
30
29
28
27
26
25
24
23
22
21
16
15
14
13
12
11
10
9
8
7
6
5
4
3
2
1
64
63
62
61
44
43
42
41
37
38
39
40
17
18
19
20
81
82
83
84
85
86
87
88
89
90
91
92
93
94
95
96
97
98
99
100
U1
QFP100PZ
1
2
3
4
5
6
7
8
9
10
11
12
13
14
15
16
17
18
19
20
21
22
23
24
25
J1
26
27
28
29
30
31
32
33
34
35
36
37
38
39
40
41
42
43
44
45
46
47
48
49
50
J2
51
52
53
54
55
56
57
58
59
60
61
62
63
64
65
66
67
68
69
70
71
72
73
74
75
J3
76
77
78
79
80
81
82
83
84
85
86
87
88
89
90
91
92
93
94
95
96
97
98
99
100
J4
1 JP1
2
1
JP2
2
R4
1
2
3
JP5 1
2
3
JP6 1
2
3
JP7 1
2
3
JP8 1
2
3
JP9 1
2
3
R7 JP10
R5
C11
C12
D1
C9
C13
C10
R6
R8
R9
R12
1
2
3
JP3
C17
C18
C19
C14
D3
C16
1
2
3
JP11
4
1 2
Q1G$1
3 4
Q1G$2
2 1
Q2G$1
4 3
Q2G$2
1 2
3 4
5 6
7 8
9 10
BOOTST
R10
R11
C15
C20
C21
1 JP4
2
D4
1
2
3
J6
TMS
TMS
TDI
TDI
TDO
TDO
TDO
XOUT
VCC
GND
GND
GND
XIN
P1.0
DVCC1
DVCC1
DVCC1
DVCC1
DVCC1
DVCC1
AVCC
XT2OUT
AVSS
AVSS
AVSS
M
M
I
I
O
O
XT2IN
RST/NMI
RST/NMI
TCK
TCK
TCK
C
C
TEST/SBWTCK
TEST/SBWTCK
TEST/SBWTCK
RST
RST
RST
XTLGND2
XTLGND1
PU.0
PU.1
P1.6
P1.7
P8.0
P8.1
P8.2
VBAK
VBAT
VBAT
VBAT
P1.1
P1.1
P1.2
P1.2
LDOI
LDOI
LDOO
LDOO
BSL Interface
LDOI/LDOO Interface
+
+
Note: If the system should be
supplied via LDOI (J6) close JP4
and set JP3 to external
www.ti.com MSP-TS430PZ100C
B.28 MSP-TS430PZ100C
Figure B-55. MSP-TS430PZ100C Target Socket Module, Schematic
SLAU278R–May 2009–Revised May 2014 Hardware 117
Submit Documentation Feedback
Copyright © 2009–2014, Texas Instruments Incorporated
If the system should
be supplied via LDOI (J6),
close JP4 and set JP3 to external
Jumper JP2
Open to disconnect LED
D1
LED connected to P1.0
Orient Pin 1 of MSP430 device
LDOI/LDOO
14
1
2
GND
GND
VCC
1 05 11 5 2 0 25
26 30 3540 45 50
75 70 65 60 55 51
100 95 90 85 80 76
1 2 3
123
123
123
123
123
3 2 1
1 2 3 4
10
1
2
1 2 3
1
SBW JTAG
Vcc
int
ext
GND
VBAT
DVCC
JTAG
R2
C2
C1
C3
C4
R1
C5
R3
+
C6
+
C7
C8
J5
U1
J1
J2
J3
J4
JP1
JP2
R4
JP5
JP6
JP7
JP8
JP9
JP10
R7
R5
C11
C12
D1
C9
C13
C10
R6
R8
R9
R12
JP3
C17
C18
C19
C14
D3
C16
JP11
Q1
Q2
BOOTST
R10
R11 C15
C20
C21
JP4
D4
J6
Jumpers JP5 to JP10
Close 1-2 to debug in Spy-Bi-Wire mode
Close 2-3 to debug in 4-wire JTAG mode
Jumper JP3
1-2 (int): Power supply via JTAG interface
2-3 (ext): External power supply
Connector JTAG
For JTAG Tool
Connector BOOTST
For Bootstrap Loader Tool
Connector J5
External power connector
Jumper JP3 to "ext"
Jumper JP1
Open to measure current
MSP-TS430PZ100C www.ti.com
Figure B-56. MSP-TS430PZ100C Target Socket Module, PCB
118 Hardware SLAU278R–May 2009–Revised May 2014
Submit Documentation Feedback
Copyright © 2009–2014, Texas Instruments Incorporated
www.ti.com MSP-TS430PZ100C
Table B-30. MSP-TS430PZ100C Bill of Materials
Number
Pos. Ref Des Per Description Digi-Key Part No. Comment
Board
1 C1, C2 0 12pF, SMD0805 DNP: C1, C2
1.1 C3, C4 2 47pF, SMD0805 DNP: C3, C4
2 C6, C7 2 10uF, 6.3V, Tantal Size B 511-1463-2-ND
C5, C11,
3 C13, C14, 6 100nF, SMD0805 311-1245-2-ND
C19, C20
3.1 C10, C12, 0 100nF, SMD0805 311-1245-2-ND DNP: C10, C12,C18, C17 C18,17
4 C8 1 2.2nF, SMD0805 Buerklin 53 D 292
5 C9 1 470nF, SMD0805 478-1403-2-ND
6 D1 1 green LED, SMD0805 P516TR-ND
7 J1, J2, J3, 4 25-pin header, TH SAM1029-25-ND DNP: headers and receptacles enclosed J4 with kit. Keep vias free of solder.
7.1 4 25-pin header, TH SAM1213-25-ND DNP: headers and receptacles enclosed with kit. Keep vias free of solder.
8 J5, J6 2 3-pin header, male, TH SAM1035-03-ND
JP5, JP6,
9 JP7, 6 3-pin header, male, TH SAM1035-03-ND place jumpers on pins 2-3 JP8,JP9,
JP10
10 JP1, JP2 2 2-pin header, male, TH SAM1035-02-ND place jumper on header
10.1 JP4 1 2-pin header, male, TH SAM1035-02-ND place jumper on header
11 JP3 1 3-pin header, male, TH SAM1035-03-ND place jumper on pins 1-2
12 10 Jumper 15-38-1024-ND Place on: JP1, JP2, JP3, JP4, JP5, JP6, JP7, JP8, JP9, JP10
13 JTAG 1 14-pin connector, male, TH HRP14H-ND
14 BOOTST 1 10-pin connector, male, TH HRP10H-ND DNP, keep vias free of solder
15 Q1 0 Crystal DNP: Q1
Keep vias free of solder
16 Q2 1 Crystal DNP: Q2 Keep vias free of solder
17 R3, R7 2 330 Ohm, SMD0805 541-330ATR-ND
R1, R2, R4,
18 R6, R8, R9, 3 0 Ohm, SMD0805 541-000ATR-ND DNP: R6, R8, R9, R10, R11, R12 R10, R11,
R12
19 R5 1 47k Ohm, SMD0805 541-47000ATR-ND
20 U1 1 Socket: IC357-1004-53N Manuf.: Yamaichi
21 PCB 1 79.5 x 99.5 mm MSP-TS430PZ100C 2 layers Rev 1.0
22 Rubber 4 Buerklin: 20H1724 apply to corners at bottom side stand off
23 MSP430 2 MSP430F643x DNP: enclosed with kit. Is supplied by
TI.
24 C16 1 4.7 nF SMD0603 Buerklin 53 D 2042
26 D3, D4 2 LL103A Buerklin: 24S3406
27 JP11 1 4-pin header, male, TH SAM1035-04-ND Place jumper on Pin 1 and Pin 2
28 C15 1 4.7 uF, SMD0805 Buerklin 53 D 2430
29 C21 1 220nF, SMD0805 Buerklin 53 D 2381
SLAU278R–May 2009–Revised May 2014 Hardware 119
Submit Documentation Feedback
Copyright © 2009–2014, Texas Instruments Incorporated
MSP-TS430PZ100C www.ti.com
120 Hardware SLAU278R–May 2009–Revised May 2014
Submit Documentation Feedback
Copyright © 2009–2014, Texas Instruments Incorporated
DNP
Socket:
Yamaichi IC201-1004-008
DNP
DNP
GND
GND
100nF
330R
0R -
GND
GND
47k 1.1nF
GND
0R 0R
QUARZ5
1uF/10V
1uF/10V 100nF
green
DNP
yellow (DNP)
DNP
red (DNP)
0R
GND
DNP
DNP
0R 0R
QUARZ5
EVQ11
0R
DNP
DNP
MSP430FR698XPZ
FE25-1A1
FE25-1A2
FE25-1A3
FE25-1A4
100nF
GND
100nF
GND
1uF/10V
100nF
GND
GND
470nF
GND
0R
4u7
GND
If external supply voltage:
remove R3 and add R2 (0 Ohm)
Ext_PWR
MSP-TS430PZ100D
Vcc
int
ext
Target Socket Board for MSP430FR698xPZ, FR688xPZ
DNP
DNP
DNP
DNP
DNP
JTAG ->
SBW ->
JTAG-Mode selection:
4-wire JTAG: Set jumpers JP3 to JP8 to position 2-3
2-wire "SpyBiWire": Set jumpers JP3 to JP8 to position 1-2
connection by via
DNP
DNP
Petersen
1099/1/001/01.1
1.2
DNP
DNP DNP
DNP
DNP
DNP DNP
1
3
5
7
9
11
13
2
4
6
12
14
8
10
JTAG
C2
C1
C4
R1
1 2
3 4
5 6
7 8
9 10
BSL
R3 R2
1
2
3
J2
1
2
3
J1
1
2
JP1
1
2
JP9
R4 C5
1
2
3
JP3
1
2
3
JP4
1
2
3
JP5
1
2
3
JP6
1
2
3
JP7
1
2
3
JP8
R5 R6
Q1
C3
C7 C6
D1
R10
1
2
JP10
D2
R11
1
2
JP11
D3
R12
1
2
JP2
C8
C9
R9 R8
Q2
SW1
R13
TP1TP2
SW2
R14
1 P4.3/UCA0SOMI/UCA0RXD/UCB1STE
2 P1.4/UCB0CLK/UCA0STE/TA1.0/S1
3 P1.5/UCB0STE/UCA0CLK/TA0.0/S0
4 P1.6/UCB0SIMO/USB0SDA/TA0.1
5 P1.7/UCB0SOMI/UCB0SCL/TA0.2
6 R33/LCDCAP
7 P6.0/R23
8 P6.1/R13/LCDREF
9 P6.2/COUT/R03
10 P6.3/COM0
11 P6.4/TB0.0/COM1
12 P6.5/TB0.1/COM2
13 P6.6/TB0.2/COM3
14 P2.4/TB0.3/COM4/S43
15 P2.5/TB0.4/COM5/S42
16 P2.6/TB0.5/COM6/S41
17 P2.7/TB0.6/COM7/S40
18 P10.2/TA1.0/SMCLK/S39
19 P5.0/TA1.1/MCLK/S38
20 P5.1/TA1.2/S37
21 P5.2/TA1.0/TA1CLK/ACLK/S36
22 P5.3/UCB1STE/S35
23 P3.0/UCB1CLK/S34
24 P3.1/UCB1SIMO/UCB1SDA/S33
25 P3.2/UCB1SOMI/UCB1SCL/S32
26 DVSS1
27 DVCC1
28 TEST/SBWTCK
29 XRST/NMI/SBWTDIO
30 PJ.0/TDO/TB0OUTH/SMCLK/SRSCG1
31 PJ.1/TDI/TCLK/MCLK/SRSCG0
32 PJ.2/TMS/ACLK/SROSCOFF
33 PJ.3/TCK/COUT/SRCPUOFF
34 P6.7/TA0CLK/S31
35 P7.5/TA0.2/S30
36 P7.6/TA0.1/S29
37 P10.1/TA0.0/S28
38 P7.7/TA1.2/TB0OUTH/S27
39 P3.3/TA1.1/TB0CLK/S26
40 P3.4/UCA1SIMO/UCA1TXD/TB0.0/S25
41 P3.5/UCA1SOMI/UCA1RXD/TB0.1/S24
42 P3.6/UCA1CLK/TB0.2/S23
43 P3.7/UCA1STE/TB0.3/S22
44 P8.0/RTCCLK/S21
45 P8.1/DMAE0/S20
46 P8.2/S19
47 P8.3/MCLK/S18
48 P2.3/UCA0STE/TB0OUTH
49 P2.2/UCA0CLK/TB0.4/RTCCLK
50 P2.1/UCA0SOMI/UCA0RXD/TB0.5/DMAE0
P2.0/UCA0SIMO/UCA0TXD/TB0.6/TB0CLK51
P7.0/TA0CLK/S17 52
P7.1/TA0.0/S16 53
P7.2/TA0.1/S15 54
P7.3/TA0.2/S14 55
P7.4/SMCLK/S13 56
DVSS2 57
DVCC2 58
P8.4/A7/C7 59
P8.5/A6/C6 60
P8.6/A5/C5 61
P8.7/A4/C4 62
P1.3/ESITEST4/TA1.2/A3/C3 63
P1.2/TA1.1/TA0CLK/COUT/A2/C2 64
P1.1/TA0.2/TA1CLK/COUT/A1/C1/VREF+/VEREF+65
P1.0/TA0.1/DMAE0/RTCCLK/A0/C0/VREF-/VEREF66
P9.0/ESICH0/ESITEST0/A8/C8 67
P9.1/ESICH1/ESITEST1/A9/C9 68
P9.2/ESICH2/ESITEST2/A10/C10 69
P9.3/ESICH3/ESITEST3/A11/C11 70
P9.4/ESICI0/A12/C12 71
P9.5/ESICI1/A13/C13 72
P9.6/ESICI2/A14/C14 73
P9.7/ESICI3/A15/C15 74
ESIVCC 75
ESIVSS 76
ESICI 77
ESICOM 78
AVCC1 79
AVSS3 80
PJ.7/HFXOUT 81
PJ.6/HFXIN 82
AVSS1 83
P4.2/UCA0SIMO/UCA0TXD/UCB1CLK 100
DVCC3 99
DVSS3 98
P4.1/UCB1SOMI/UCB1SCL/ACLK/S2 97
P4.0/UCB1SIMO/UCB1SDA/MCLK/S3 96
P10.0/SMCLK/S4 95
P4.7/UCB1SOMI/UCB1SCL/TA1.2/S5 94
P4.6/UCB1SIMO/UCB1SDA/TA1.1/S6 93
P4.5/UCB1CLK/TA1.0/S7 92
P4.4/UCB1STE/TA1CLK/S8 91
P5.7/UCA1STE/TB0CLK/S9 90
P5.6/UCA1CLK/S10 89
P5.5/UCA1SOMI/UCA1RXD/S11 88
P5.4/UCA1SIMO/UCA1TXD/S12 87
AVSS2 86
PJ.5/LFXOUT 85
PJ.4/LFXIN 84
IC1
1
2
3
4
5
6
7
8
9
10
11
12
13
14
15
16
17
18
19
20
21
22
23
24
25
J3
26
27
28
29
30
31
32
33
34
35
36
37
38
39
40
41
42
43
44
45
46
47
48
49
50
J4
51
52
53
54
55
56
57
58
59
60
61
62
63
64
65
66
67
68
69
70
71
72
73
74
75
J5
76
77
78
79
80
81
82
83
84
85
86
87
88
89
90
91
92
93
94
95
96
97
98
99
100
J6
C10
C11
1
2
JP12
C12
C13
C14
R7
P1.0 C15
P1.0
RST/NMI
TMS
TDI
VCC
GND
P1.1
P1.1
TCK/SBWTCK
TDO/SBWTDIO
PJ.0/TDO
PJ.0/TDO
PJ.2/TMS
PJ.2/TMS
PJ.3/TCK
PJ.3/TCK
PJ.1/TDI
PJ.1/TDI
P1.2
P1.2
BSLTX
BSLTX
BSLRX
BSLRX
P1.3
P1.3
AVCC
AVCC
AVSS
AVSS
AVSS
AVSS
LFXOUT
LFXIN
LFGND HFGND
HFXIN
HFXOUT
DVCC
DVCC
DVCC
DVCC
DVCC
DVCC
DVCC
DVCC
DVCC
DVSS
DVSS
DVSS
DVSS
TEST/SBWTCK1
TEST/SBWTCK
TEST/SBWTCK
TEST/SBWTCK
LCDCAP
LCDCAP
ESIVCC
ESIVCC
ESICOM
ESICOM
ESIVSS
RST/SBWTDIO
RST/SBWTDIO
RST/SBWTDIO
1
2
3
4
5
6
1
2
3
4
5
6
Titel:
Datum:
Bearb.:
Seite 1/1
MSP-TS430PZ100D
7/9/2013 5:23:25 PM
A3
A B C D E F G H I
A B C D E F G H I
File:
Dok:
Rev.:
www.ti.com MSP-TS430PZ100D
B.29 MSP-TS430PZ100D
Figure B-57. MSP-TS430PZ100D Target Socket Module, Schematic
SLAU278R–May 2009–Revised May 2014 Hardware 121
Submit Documentation Feedback
Copyright © 2009–2014, Texas Instruments Incorporated
1
Vcc
ext
int
Vcc
GND
GND
JTAG
SBW
RESET
Ext.
Pwr.
PWR
DVCC
AVCC
TCK
TMS
TDI
TDO
RST/SBWTDIO
TEST/SBWTCK
GND
GND
P1.3
ESIVCC
14
1
2
10
1
2
1
1
1
1
1
1
1
1 25 5 10 15 20
50 45 40 35 30 26
51 75 55 60 65 70
76 80 85 90 95 100
MSP-TS430PZ100D
Rev. 1.2 RoHS
Q2 Q1
P1.0
P1.1
P1.2
JTAG
C2
C1
C4
R1
BSL
R2
R3
J2
J1
JP1
JP9
C5
R4
JP3
JP4
JP5
JP6
JP7
JP8
R5
R6
C3
C6
C7
D1
R10
JP10
D2
R11
JP11
D3
R12
JP2
C8
C9
R8
R9
SW1
R13
TP2
TP1
SW2
R14
IC1
J3
J4
J5
J6
C10
C11
JP12
C12
C13
C14
R7
C15
Orient Pin 1 of MSP430 device
LEDs connected to
P1.0, P1.1, P1.2 via
JP9, JP10, JP11
(only D1 assembled)
Switch SW2
Connected to P1.3
Jumper JP1
Open to measure current
Connector J2
External power connector
Jumper J1 to “ext”
Connector BSL
For Bootstrap Loader Tool
Connector JTAG
For JTAG Tool
Jumper JP3 to JP8
Close 1-2 to debug in Spy-Bi-Wire mode
Close 3-4 to debug in 4-wire JTAG mode
Jumper J1
1-2 (int): Power supply via JTAG interface
2-3 (ext): External power supply
Switch SW1
Device reset
HF and LF oscillators with
capacitors and resistors
to connect pinheads
MSP-TS430PZ100D www.ti.com
Figure B-58. MSP-TS430PZ100D Target Socket Module, PCB
122 Hardware SLAU278R–May 2009–Revised May 2014
Submit Documentation Feedback
Copyright © 2009–2014, Texas Instruments Incorporated
www.ti.com MSP-TS430PZ100D
Table B-31. MSP-TS430PZ100D Bill of Materials
Number
Pos. Ref Des Per Description Digi-Key Part No. Comment
Board
1 PCB 1 90.0 x 100.0 mm MSP-TS430PZ100D 2 layers, white solder mask
Rev 1.2
2 JP1, JP2, 3 2-pin header, male, TH SAM1035-02-ND place jumper on header
JP9
3 JP10, JP11, 3 2-pin header, male, TH SAM1035-02-ND DNP, keep pads free of solder
JP12
4 J1 1 3-pin header, male, TH SAM1035-03-ND place jumpers on pins 1-2
5 JP3, JP4, 6 3-pin header, male, TH SAM1035-03-ND place jumpers on pins 2-3
JP5, JP6,
JP7, JP8
6 J2 1 3-pin header, male, TH SAM1035-03-ND
7 R2, R3, R5, 6 0R, 0805 541-0.0ATR-ND DNP
R6, R8, R9
8 R7, R12, 3 0R, 0805 541-0.0ATR-ND
R13
9 C5 1 1.1nF, CSMD0805 490-1623-2-ND
10 C3, C7 2 1uF/10V, CSMD0805 490-1702-2-ND
11 C12 1 1uF/10V, CSMD0805 490-1702-2-ND DNP
12 R4 1 47k, 0805 541-47KATR-ND
13 C4, C6, 4 100nF, CSMD0805 490-1666-1-ND
C10, C11
14 C13 1 100nF, CSMD0805 490-1666-1-ND DNP
15 C15 1 4u7, CSMD0805 445-1370-1-ND DNP
16 R1 1 330R, 0805 541-330ATR-ND
17 C14 1 470nF, CSMD0805 587-1290-2-ND DNP
18 R10, R11 2 330R, 0805 541-330ATR-ND DNP
19 R14 1 47k, 0805 541-47KATR-ND DNP
20 C1, C2, C8, 4 DNP, CSMD0805 DNP
C9
21 SW2 1 EVQ-11L05R P8079STB-ND DNP
22 SW1 1 EVQ-11L05R P8079STB-ND DNP
23 J3, J4, J5, 4 25-pin header, TH DNP: headers and receptacles enclosed
J6 with kit. Keep vias free of solder.
SAM1029-25-ND : Header
24 J3, J4, J5, 4 25-pin receptacle, TH DNP: headers and receptacles enclosed
J6 with kit. Keep vias free of solder.
SAM1213-25-ND : Receptacle
25 TP1, TP2 2 Testpoint DNP, keep pads free of solder
26 BSL 1 10-pin connector, male, TH HRP10H-ND DNP, keep vias free of solder
27 JTAG 1 14-pin connector, male, TH HRP14H-ND
28 IC1 1 Socket: IC201-1004-008 Manuf. Yamaichi
29 IC1 1 MSP430FR6989 DNP: enclosed with kit. Is supplied by TI
30 Q1 1 DNP: MS3V-TR1 depends on application Micro Crystal, DNP, enclosed in kit, keep
(32768kHz/20ppm/12,5pF) vias free of solder
31 Q2 1 DNP, Crystal depends on application DNP, keep vias free of solder
32 D1 1 green LED, DIODE0805 P516TR-ND
33 D3 1 red (DNP), DIODE0805 DNP
34 D2 1 yellow (DNP), DIODE0805 DNP
35 Rubber 4 Buerklin: 20H1724 apply to corners at bottom side
stand off
SLAU278R–May 2009–Revised May 2014 Hardware 123
Submit Documentation Feedback
Copyright © 2009–2014, Texas Instruments Incorporated
MSP-TS430PZ5x100 www.ti.com
B.30 MSP-TS430PZ5x100
Figure B-59. MSP-TS430PZ5x100 Target Socket Module, Schematic
124 Hardware SLAU278R–May 2009–Revised May 2014
Submit Documentation Feedback
Copyright © 2009–2014, Texas Instruments Incorporated
Connector J5
External power connector
Jumper JP3 to "ext"
Jumper JP1
Open to measure current
Jumper JP2
Open to disconnect LED
D1
LED connected to P1.0
Jumpers JP5 to JP10
Close 1-2 to debug in Spy-Bi-Wire mode
Close 2-3 to debug in 4-wire JTAG mode
Jumper JP3
1-2 (int): Power supply via JTAG interface
2-3 (ext): External power supply
Connector JTAG
For JTAG Tool
Connector BOOTST
For Bootstrap Loader Tool
Orient Pin 1 ofMSP430 device
www.ti.com MSP-TS430PZ5x100
Figure B-60. MSP-TS430PZ5x100 Target Socket Module, PCB
SLAU278R–May 2009–Revised May 2014 Hardware 125
Submit Documentation Feedback
Copyright © 2009–2014, Texas Instruments Incorporated
MSP-TS430PZ5x100 www.ti.com
Table B-32. MSP-TS430PZ5x100 Bill of Materials
Pos. Ref Des No. Per Description Digi-Key Part No. Comment Board
1 C1, C2 0 12pF, SMD0805 DNP
1b C3, C4 47pF, SMD0805 DNP: Only recommendation. Check your crystal spec.
2 C6, C7 2 10uF, 10V, Tantal Size B 511-1463-2-ND
C5, C10,
3 C11, C12, 4 100nF, SMD0805 311-1245-2-ND DNP: C12, C14
C13, C14
4 C8 0 2.2nF, SMD0805 DNP
5 C9 1 470nF, SMD0805 478-1403-2-ND
6 D1 1 green LED, SMD0805 67-1553-1-ND
DNP: headers and
receptacles enclosed with kit.
7 J1, J2, J3, J4 0 25-pin header, TH Keep vias free of solder.
SAM1029-25-ND : Header
SAM1213-25-ND : Receptacle
8 J5 1 3-pin header, male, TH SAM1035-03-ND
JP5, JP6,
9 JP7, JP8, 6 3-pin header, male, TH SAM1035-03-ND Place jumpers on pins 2-3
JP9, JP10
10 JP1, JP2 2 2-pin header, male, TH SAM1035-02-ND Place jumper on header
11 JP3 1 3-pin header, male, TH SAM1035-03-ND Place jumper on pins 1-2
12 9 Jumper 15-38-1024-ND Place on JP1, JP2, JP3, JP5, JP6, JP7, JP8, JP9, JP10
13 JTAG 1 14-pin connector, male, TH HRP14H-ND
14 BOOTST 0 10-pin connector, male, TH DNP: Keep vias free of solder
Q1: Micro Crystal MS1V-T1K DNP: Keep vias free of 15 Q1, Q2 0 Crystal 32.768kHz, C(Load) = solder 12.5pF
16 R3, R7 2 330 Ω, SMD0805 541-330ATR-ND
R1, R2, R4,
17 R6, R8, R9, 3 0 Ω, SMD0805 541-000ATR-ND DNP: R6, R8, R9, R10, R11, R10, R11, R12
R12
18 R5 1 47k Ω, SMD0805 541-47000ATR-ND
19 U1 1 Socket: IC357-1004-53N Manuf.: Yamaichi
20 PCB 1 90 x 82 mm 2 layers
21 Rubber 4 Select appropriate Apply to corners at bottom standoff side
22 MSP430 2 MSP430F5438IPZ DNP: Enclosed with kit supplied by TI
126 Hardware SLAU278R–May 2009–Revised May 2014
Submit Documentation Feedback
Copyright © 2009–2014, Texas Instruments Incorporated
www.ti.com MSP-TS430PZ100USB
B.31 MSP-TS430PZ100USB
Due to the use of diodes in the power chain, the voltage on the MSP430F5xx device is approximately
0.3 V lower than is set by the debugging tool. Set the voltage in the IDE to 0.3 V higher than desired; for
example, to run the MCU at 3.0 V, set it to 3.3 V.
Figure B-61. MSP-TS430PZ100USB Target Socket Module, Schematic
SLAU278R–May 2009–Revised May 2014 Hardware 127
Submit Documentation Feedback
Copyright © 2009–2014, Texas Instruments Incorporated
Jumpers LED 1, 2, 3
Open to disconnect LED1, LED2, LED3
LED1, D2, D3
LEDs connected to P8.0,
LE LE
P8.1, P8.2
Orient Pin 1 of MSP430 device
Jumpers JP5 to JP10
Close 1-2 to debug in Spy-Bi-Wire mode
Close 2-3 to debug in 4-wire JTAG mode
Jumper JP3
1-2 (int): Power supply via JTAG interface
2-3 (ext): External power supply
Connector JTAG
For JTAG Tool
USB1
USB connector
Connector J5
External power connector
Jumper JP3 to "ext"
Jumper JP2
Open to disconnect LED
D1
LED connected to P1.0
Jumper JP1
Open to measure current
MSP-TS430PZ100USB www.ti.com
Figure B-62. MSP-TS430PZ100USB Target Socket Module, PCB
128 Hardware SLAU278R–May 2009–Revised May 2014
Submit Documentation Feedback
Copyright © 2009–2014, Texas Instruments Incorporated
www.ti.com MSP-TS430PZ100USB
Table B-33. MSP-TS430PZ100USB Bill of Materials
Pos. Ref Des No. Per Description Digi-Key Part No. Comment Board
1 C1, C2 0 12pF, SMD0805 DNP: C1, C2
1.1 C3, C4 2 47pF, SMD0805
2 C6, C7 2 10uF, 6.3V, Tantal Size B 511-1463-2-ND
C5, C11,
3 C13, C14, 5 100nF, SMD0805 311-1245-2-ND
C19
3.1 C10, C12, 0 100nF, SMD0805 311-1245-2-ND DNP: C10, C12,C18, C17 C18, C17
4 C8 1 2.2nF, SMD0805
5 C9 1 470nF, SMD0805 478-1403-2-ND
6 D1 1 green LED, SMD0805 P516TR-ND
DNP: headers and
receptacles enclosed with kit.
7 J1, J2, J3, J4 4 25-pin header, TH SAM1029-25-ND Keep vias free of solder.
: Header
: Receptacle
DNP: headers and
receptacles enclosed with kit.
7.1 4 25-pin header, TH SAM1213-25-ND Keep vias free of solder.
: Header
: Receptacle
8 J5 1 3-pin header, male, TH SAM1035-03-ND
JP5, JP6,
9 JP7, JP8, 6 3-pin header, male, TH SAM1035-03-ND place jumpers on pins 2-3
JP9, JP10
10 JP1, JP2, 3 2-pin header, male, TH SAM1035-02-ND place jumper on header JP4
11 JP3 1 3-pin header, male, TH SAM1035-03-ND place jumper on pins 1-2
Place on: JP1, JP2, JP3,
12 10 Jumper 15-38-1024-ND JP4, JP5, JP6, JP7, JP8,
JP9, JP10
13 JTAG 1 14-pin connector, male, TH HRP14H-ND
Micro Crystal MS1V-T1K DNP: Q1. Keep vias free of 14 Q1 0 Crystal 32.768kHz, C(Load) = solder 12.5pF
15 Q2 1 Crystal Q2: 4MHz, Buerklin: 78D134
16 R3, R7 2 330 Ω, SMD0805 541-330ATR-ND
R1, R2, R4,
17 R6, R8, R9, 3 0 Ω, SMD0805 541-000ATR-ND DNP: R6, R8, R9, R12
R12
18 R10 1 100 Ω, SMD0805 Buerklin: 07E500
18 R11 1 1M Ω, SMD0603 not existing in Rev 1.0
18 R5 1 47k Ω, SMD0805 541-47000ATR-ND
19 U1 1 Socket:IC201-1004-008 Manuf.: Yamaichi
20 PCB 1 79 x 77 mm 2 layers
21 Rubber stand 4 Buerklin: 20H1724 apply to corners at bottom off side
22 MSP430 2 MSP430F6638IPZ DNP: enclosed with kit. Is supplied by TI
Insulating http://www.ettinger.de/Art_De 23 disk to Q2 1 Insulating disk to Q2 tail.cfm?ART_ARTNUM=70.0 8.121
24 C16 1 4.7 nF SMD0603
27 C33 1 220n SMD0603 Buerklin: 53D2074
28 C35, C36 2 10p SMD0603 Buerklin: 56D102
SLAU278R–May 2009–Revised May 2014 Hardware 129
Submit Documentation Feedback
Copyright © 2009–2014, Texas Instruments Incorporated
MSP-TS430PZ100USB www.ti.com
Table B-33. MSP-TS430PZ100USB Bill of Materials (continued)
Pos. Ref Des No. Per Description Digi-Key Part No. Comment Board
30 C38 1 220n SMD0603 Buerklin: 53D2074
31 C39 1 4u7 SMD0603 Buerklin: 53D2086
32 C40 1 0.1u SMD0603 Buerklin: 53D2068
33 D2, D3, D4 3 LL103A Buerklin: 24S3406
34 IC7 1 TPD4E004 Manu: TI
35 LED 0 JP3QE SAM1032-03-ND DNP
36 LED1, LED2, 0 LEDCHIPLED_0603 FARNELL: 852-9833 DNP LED3
37 R13, R15, 0 470R SMD0603 Buerklin: 07E564 DNP R16
38 R33 1 1k4 / 1k5 SMD0603 Buerklin: 07E612
39 R34 1 27R SMD0603 Buerklin: 07E444
40 R35 1 27R SMD0603 Buerklin: 07E444
41 R36 1 33k SMD0603 Buerklin: 07E740
42 S1, S2, S3 1 PB P12225STB-ND DNP S1 and S2. (Only S3)
43 USB1 1 USB_RECEPTACLE FARNELL: 117-7885
44 JP11 1 4-pin header, male, TH SAM1035-04-ND place jumper only on Pin 1
130 Hardware SLAU278R–May 2009–Revised May 2014
Submit Documentation Feedback
Copyright © 2009–2014, Texas Instruments Incorporated
0R
12pF
12pF
GND
GND
0R
100nF
330R
2.2nF
0R
0R
PWR3
GND
330R
47K
0R
0R
100nF
4.7uF
GND
GND
100nF
470nF
0R
QUARZ5
100nF
10uF/6,3V
10uF/6,3V
100nF 4.7uF
4.7uF 100nF
4.7uF
4.7uF
4.7uF
470nF
FE04-1
VCC
GND
GND
100nF
4.7uF
GND
GND
GND
GND
GND
VCC1
VCC1
VCC1
VCC1
VCC1
GND
GND
GND
GND
GND
GND
AVSS
AVSS
DVCC AVCC
GND
VCC
VCC
GND
MSP430: Target-Socket
MSP-TS430PEU128 for F6779
Petersen
1080/1/001/01.1
DNP
LFXTCLK
DNP
<- SBW
<- JTAG
DNP
Vcc
int
ext
DNP
DNP
DNP
DNP
DNP
DNP
DNP
DVDSYS
1.1
1
2
3
4
5
6
7
8
9
10
11
12
13
14
15
16
17
18
19
20
21
22
23
24
25
26
27
28
29
30
31
32
33
34
35
36
37
38
J1
39
40
41
42
43
44
45
46
47
48
49
50
51
52
53
54
55
56
57
58
59
60
61
62
63
64
J2
65
66
67
68
69
70
71
72
73
74
75
76
77
78
79
80
81
82
83
84
85
86
87
88
89
90
91
92
93
94
95
96
97
98
99
100
101
102
J3
103
104
105
106
107
108
109
110
111
112
113
114
115
116
117
118
119
120
121
122
123
124
125
126
127
128
J4
1
3
5
7
9
11
13
2
4
6
12
14
8
10
JTAG
R2
C2
C1
R1
C5
R3
1 2
3 4
5 6
7 8
9 10
BOOTST
C3
R10
R11
J5
1
2
3
1
2
JP1
JP2
1
2
1
2
3
JP5 1
2
3
JP6 1
2
3
JP7 1
2
3
JP8 1
2
3
JP9 1
2
3
JP10
R7
R5
D1
R6
R8
C6
C29
C7
C10
R4
Q1
JP12 1
2
3
4
1
2
3
4
JP11
JP131
2
3
4
C4
C11
C12
C8 C13
C14 C9
C16
C19
C18
C26
1
2
JP4
JP3
1
2
3
4
C15
C17
TP1 TP2
IC1
MSP430F677XIPEU#
XIN
1
XOUT
2
AUXVCC3
3
RTCCAP1
4
RTCCAP0
5
P1.5/SMCLK/CB0/A5
6
P1.4/MCLK/SDCLK/CB1/A4
7
P1.3/ADC10CLK/TACLK/RTCCLK/A3
8
P1.2/ACLK/TA3.1/A2
9
P1.1/TA2.1/VEREF+/A1
10
P1.0/TA1.1/TA0.0/VEREF-/A0
11
P2.4/PM_TA2.0
12
P2.5/PM_UCB0SOMI/PM_UCB0SCL
13
P2.6/PM_USB0SIMO/PM_UCB0SDA
14
P2.7/PM_UCB0CLK
15
P3.0/PM_UCA0RXD/PM_UCA0SOMI
16
P3.1/PM_UCA0TXD/PM_UCA0SIMO
17
P3.2/PM_UCA0CLK
18
P3.3/PM_UCA1CLK
19
P3.4/PM_UCA1RXD/PM_UCA1SOMI
20
P3.5/PM_UCA1TXD/PM_UCA1SIMO
21
COM0
22
COM1
23
P1.6/COM2
24
P1.7/COM3
25
P5.0/COM4
26
P5.1/COM5
27
P5.2/COM6
28
P5.3/COM7
29
LCDCAP/R33
30
P5.4/SDCLK/R23
31
P5.5/SD0DIO/LCDREF/R13
32
P5.6/SD1DIO/R03
33
P5.7/SD2DIO/CB2
34
P6.0/SD3DIO
35
P3.6/PM_UCA2RXD/PM_UCA2SOMI
36
P3.7/PM_UCA2TXD/PM_UCA2SIMO
37
P4.0/PM_UCA2CLK
38
P4.1/PM_UCA3RXD/PM_UCA3SOMI
39
P4.2/PM_UCA3TXD/PM_UCA3SIMO
40
P4.3/PM_UCA3CLK
41
P4.4/PM_UCB1SOMI/PM_UCB1SCL
42
P4.5/PM_UCB1SIMO/PM_UCB1SDA
43
P4.6/PM_UCB1CLK
44
P4.7/PM_TA3.0
45
P6.1/SD4DIO/S39
46
P6.2/SD5DIO/S38
47
P6.3/SD6DIO/S37
48
P6.4/S36
49
P6.5/S35
50
P6.6/S34
51
P6.7/S33
52
P7.0/S32
53
P7.1/S31
54
P7.2/S30
55
P7.3/S29
56
P7.4/S28
57
P7.5/S27
58
P7.6/S26
59
P7.7/S25
60
P8.0/S24
61
P8.1/S23
62
P8.2/S22
63
P8.3/S21
64
P8.4/S20
65
P8.5/S19
66
P8.6/S18
67
P8.7/S17
68
DVSYS
69
DVSS2
70
P9.0/S16
71
P9.1/S15
72
P9.2/S14
73
P9.3/S13
74
P9.4/S12
75
P9.5/S11
76
P9.6/S10
77
P9.7/S9
78
P10.0/S8
79
P10.1/S7
80
P10.2/S6
81
P10.3/S5
82
P10.4/S4
83
P10.5/S3
84
P10.6/S2
85
P10.7/S1
86
P11.0/S0
87
P11.1/TA3.1/CB3
88
P11.2/TA1.1
89
P11.3/TA2.1
90
P11.4/CBOUT
91
P11.5/TACLK/RTCCLK
92
P2.0/PM_TA0.0
93
P2.1/PM_TA0.1
94
P2.2/PM_TA0.2
95
P2.3/PM_TA1.0
96
TEST/SBWTCK
97
PJ.0/TDO
98
PJ.1/TDI/TCLK
99
PJ.2/TMS
100
PJ.3/TCK
101
~RST/NMI/SBWTDIO
102
SD0P0
103
SD0N0
104
SD1P0
105
SD1N0
106
SD2P0
107
SD2N0
108
SD3P0
109
SD3N0
110
VASYS2
111
AVSS2
112
VREF
113
SD4P0
114
SD4N0
115
SD5P0
116
SD5N0
117
SD6P0
118
SD6N0
119
AVSS1
120
AVCC
121
VASYS1
122
AUXVCC2
123
AUXVCC1
124
VDSYS
125
DVCC
126
DVSS1
127
VCORE
128
P1.0 P1.0
P2.0 P2.0
P2.1 P2.1
SD0P0
SD0N0
SD1P0
SD1N0
SD2P0
SD2N0
SD3P0
SD3N0
SD4P0
SD4N0
SD5P0
SD5N0
SD6P0
SD6N0
VASYS1/2
VASYS1/2
VASYS1/2
VASYS1/2
TMS
TMS
TDI
TDI
TDO
TDO
TDO
XOUT
GND
GND
XIN
DVCC
AVCC
DVDSYS
DVDSYS
DVDSYS
DVDSYS
AVSS
AVSS
PJ.2
PJ.2
PJ.1
PJ.1
PJ.0
PJ.0
RST/NMI
RST/NMI
TCK
TCK
TCK
PJ.3
PJ.3
TEST/SBWTCK
TEST/SBWTCK
TEST/SBWTCK
TEST/SBWTCK
RST
RST
RST
RST
LCDCAP
LCDCAP
VREF
VREF
VEREF+ VEREF+
VCORE
AUXVCC2
AUXVCC2
AUXVCC1
AUXVCC1
AUXVCC3
AUXVCC3
1
2
3
4
5
6
1
2
3
4
5
6
Titel:
Datum:
Bearb.:
Seite 1/1
MSP-TS430PEU128
22.05.2012 09:37:33
A3
A B C D E F G H I
A B C D E F G H I
File:
Dok:
Rev.:
www.ti.com MSP-TS430PEU128
B.32 MSP-TS430PEU128
Figure B-63. MSP-TS430PEU128 Target Socket Module, Schematic
SLAU278R–May 2009–Revised May 2014 Hardware 131
Submit Documentation Feedback
Copyright © 2009–2014, Texas Instruments Incorporated
1
P1.0
SBW
JTAG
DVDSYS
ext
int
MSP-TS430PEU128
Rev. 1.1 RoHS
DVCC
AUXVCC
GND
AUXVCC1
AUXVCC2
AUXVCC3
GND
GND
RST/NMI
TCK
TDI
TDO
TEST/SBWTCK
TMS
1 25 5 10 15 20 30 35
40 45 50 55 60 64
65 90 70 75 80 85 95 100
128 125 120 115 110 105
14
1
2
10
1
2
GND
GND
VCC
3 2 1
3 2 1
3 2 1
3 2 1
3 2 1
3 2 1
1 2 3 4
1234
1234
1
J1
J2
J3
J4
JTAG
R2
C2
C1
R1
C5
R3
BOOTST
C3
R10 R11
J5
JP1
JP2
JP5
JP6
JP7
JP8
JP9
JP10 R7
R5
D1
R6
R8
C6
C29
C7
C10
R4
JP12
JP11
JP13
C4
C11
C12
C8
C13
C14
C9
C16
C19
C18
C26
JP4
JP3
C15
C17
TP1
TP2
IC1
Connector J5
External power connector
Jumper JP3 to "ext"
Jumper JP1
Open to measure current
Orient Pin 1 of
MSP430 device
Jumpers JP5 to JP10
Close 1-2 to debug in Spy-Bi-Wire mode
Close 2-3 to debug in 4-wire JTAG mode
JP11, JP12, JP13
Connect 1-2 to connect AUXVCCx with DVCC or
drive AUXVCCx externally
D1
LED connected to P1.0
Jumper JP2
Open to disconnect LED
Connector JTAG
For JTAG Tool
Connector BOOTST
For Bootstrap Loader Tool
Jumper JP3
1-2 (int): Power supply via JTAG interface
2-3 (ext): External power supply
MSP-TS430PEU128 www.ti.com
Figure B-64. MSP-TS430PEU128 Target Socket Module, PCB
NOTE: The MSP-TS430PEU128 Rev 1.1 ships with the following modifications:
• R7 value is changed to 0 Ω instead of 330 Ω.
• JTAG pin 8 is connected only to JP5 pin 3, and not to pin 2.
• JP5 pin 2 is connected to IC1 pin 97.
• BOOTST pin 7 is connected to IC1 pin 97.
132 Hardware SLAU278R–May 2009–Revised May 2014
Submit Documentation Feedback
Copyright © 2009–2014, Texas Instruments Incorporated
www.ti.com MSP-TS430PEU128
Table B-34. MSP-TS430PEU128 Bill of Materials
Pos. Ref Des No. Per Description Digi-Key Part No. Comment Board
1 PCB 1 94x119.4mm, 4 layers MSP-TS430PEU128 4 layers, green solder mask Rev. 1.1
2 D1 1 green LED, DIODE0805 516-1434-1-ND
3 JP1, JP2, JP4 3 2-pin header, male, TH SAM1035-02-ND Place jumper on header
4 JP5, JP6, JP7, JP8, 6 3-pin header, male, TH SAM1035-03-ND Place jumpers on pins 1-2 (SBW) JP9, JP10
5 JP11, JP12, JP13 3 4-pin header, male, TH SAM1035-04-ND Place jumpers on pins 1-2 (AVCC=VCC)
6 JP3 1 4-pin header, male, TH SAM1035-04-ND Place jumpers on pins 1-2
JP1, JP2, JP3, JP4, Jumper WM4592-ND
7 JP5, JP6, JP7, JP8, 13 JP9, JP10, JP11,
JP12, JP13
8 R1, R2, R4, R6, R8 5 0R, 0805 541-0.0ATR-ND
9 R10, R11 2 0R, 0805 541-0.0ATR-ND DNP
10 C3 1 2.2nF, CSMD0805 490-1628-2-ND DNP
11 C13, C14, C16, 7 4.7uF, 6.3V, CSMD0805 587-1302-2-ND C17, C18, C19, C29
12 C11 1 10uF, 6.3V, CSMD0805 445-1372-2-ND
13 C12 1 10uF, 6.3V, CSMD0805 445-1372-2-ND DNP
14 C1, C2 2 12pF, CSMD0805 490-5531-2-ND DNP
15 R5 1 47K, 0805 311-47KARTR-ND
16 C4, C5, C6, C7, C8, 6 100nF, CSMD0805 311-1245-2-ND C15
17 C9 1 100nF, CSMD0805 311-1245-2-ND DNP
18 R3, R7 2 330R, 0805 541-330ATR-ND
19 C10, C26 2 470nF, CSMD0805 587-1282-2-ND
20 BOOTST 1 10-pin connector, male, TH HRP10H-ND DNP, keep vias free of solder
21 JTAG 1 14-pin connector, male, TH HRP14H-ND
22 IC1 Socket 1 Socket: IC500-1284-009P Manuf. Yamaichi
23 IC1 2 MSP430F67791IPEU DNP: enclosed with kit. Is supplied by TI
24 J5 1 3-pin header, male, TH SAM1035-03-ND
25 Q1 1 Crystal: MS3V-T1R 32.768kHz DNP: Crystal enclosed with kit. Keep vias 12.5pF ±20ppm free of solder
26 TP1, TP2 2 Test point DNP, keep vias free of solder
27 J2,J4 2 26-pin header, TH SAM1029-26-ND DNP: Headers enclosed with kit. Keep vias free of solder.
28 J2,J4 2 26-pin receptable, TH SAM1213-26-ND DNP: Receptacles enclosed with kit. Keep vias free of solder.
29 J1, J3 2 38-pin header, TH SAM1029-38-ND DNP: Headers enclosed with kit. Keep vias free of solder.
30 J1, J3 2 38-pin receptable, TH SAM1213-38-ND DNP: Receptacles enclosed with kit. Keep vias free of solder.
31 Rubber feet 4 Rubber feet Buerklin: 20H1724 apply to bottom side corners
SLAU278R–May 2009–Revised May 2014 Hardware 133
Submit Documentation Feedback
Copyright © 2009–2014, Texas Instruments Incorporated
Power Management
VCC01 = external VCC
Vdd = DVCC
Vdda1 = AVDD_RF / AVCC_RF
Vdda2 = AVCC
Port connectors
CON1 ..
CON3 = Port1 .. Port3 of cc430
CON4 = spare
CON5 = 1: XIN 2: XOUT
CON6 = Vdd, GND, Vcore,
COM0, LCDCAP
CON7 = Vdda1, Vdda2, GND,
AGND
CON8 = JTAG_BASE
(JTAG Port)
CON9 = Vdd, GND, AGND
(May be addedclose
to therespective pins
to reduce emissions
at 5GHz toel vel
required byETSI)
EM430F5137RF900 www.ti.com
B.33 EM430F5137RF900
Figure B-65. EM430F5137RF900 Target board, Schematic
134 Hardware SLAU278R–May 2009–Revised May 2014
Submit Documentation Feedback
Copyright © 2009–2014, Texas Instruments Incorporated
JTAG connector
External power connector
CON12
GND
GND
VCC
Open to disconnect LEDs
jumper JP5/JP10
LED D2 (red) connected to
P3.6 via JP10
LED D1 (green) connected
to P1.0 via JP5
RF - Crystal Q1 26 MHz
RF - Signal SMA
Reset button S1
Push-button S2
connected to P1.7
Jumper JP1
Close JTAG
position to
debug in
JTAG mode
Jumper JP2
Close EXT for external supply
Close INT for JTAG supply
Close SBW position
to debug in
Spy-Bi-Wire mode
Jumper JP1
Spy-Bi-Wire mode
Footprint for 32kHz crystal
Use 0 resistor for R431/R441
to make XIN/XOUT available
on connector port5
!
Open to measure current
jumper JP3
www.ti.com EM430F5137RF900
Figure B-66. EM430F5137RF900 Target board, PCB
The battery pack that is included with the EM430F5137RF900 kit may be connected to CON12. Ensure
correct battery insertion regarding the polarity as indicated in battery holder.
SLAU278R–May 2009–Revised May 2014 Hardware 135
Submit Documentation Feedback
Copyright © 2009–2014, Texas Instruments Incorporated
EM430F5137RF900 www.ti.com
Table B-35. EM430F5137RF900 Bill of Materials
Item Reference No. per Description Value Manufacturer's Part Manufacturer Comment Board Number
1 Q1 1 ( CUSTOMER SUPPLY ) CRYSTAL, 26M ASX-531(CS) AKER SMT, 4P, 26MHz ELECTRONIC
C1-C5, C082,
C222, C271, CAPACITOR, SMT, 0402, CER, 16V, 2 C281, C311, 14 10%, 0.1uF 0.1uF 0402YC104KAT2A AVX C321, C341,
C412, C452
3 C071 1 CAPACITOR, SMT, 0603, CERAMIC, 0.47uF 0603YD474KAT2A AVX 0.47uF, 16V, 10%, X5R
4 R401 1 RES0402, 47.0K 47kΩ CRCW04024702F10 DALE 0
5 CON11 1 HEADER, THU, MALE, 14P, 2X7, 09 18 514 6323 HARTING 25.4x9.2x9.45mm
6 CON10 0 HEADER, THU, MALE, 10P, 2X5, 09 18 510 6323 HARTING DNP 20.32x9.2x9.45mm
7 D1 1 LED, SMT, 0603, GREEN, 2.1V active APT1608MGC KINGBRIGHT
8 D2 1 LED, SMT, 0603, RED, 2.0V active APT1608EC KINGBRIGHT
9 Q3 0 UNINSTALLED CRYSTAL, SMT, 3P, 32.768k MS1V-T1K (UN) MICRO DNP MS1V (Customer Supply) CRYSTAL
10 CON12 1 HEADER, THU, MALE, 3P, 1x3, 22-03-5035 MOLEX 9.9x4.9x5.9mm
11 C251, C261 2 50V, 5%, 27pF 27pF GRM36COG270J50 MURATA
12 L341 1 FERRITE, SMT, 0402, 1.0kΩ, 250mA 1kΩ BLM15HG102SN1D MURATA
13 C293 1 CAPACITOR, SMT, 0402, CERAMIC, 100pF GRM1555C1H101JZ MURATA 100pF, 50V, 0.25pF, C0G(NP0) 01
14 L304 1 INDUCTOR, SMT, 0402, 2.2nH, 0.1nH, 0.0022uH LQP15MN2N2B02 MURATA 220mA, 500MHz
15 L303, L305 2 INDUCTOR, SMT, 0402, 15nH, 2%, 0.015uH LQW15AN15NG00 MURATA 450mA, 250MHz
16 L292, L302 2 INDUCTOR, SMT, 0402, 18nH, 2%, 0.018uH LQW15AN18NG00 MURATA 370mA, 250MHz
17 C291 1 CAPACITOR, SMT, 0402, CERAMIC, 1pF GRM1555C1H1R0W MURATA 1pF, 50V, 0.05pF, C0G(NP0) Z01
18 C303 1 CAPACITOR, SMT, 0402, CERAMIC, 8.2pF GRM1555C1H8R2W MURATA 8.2pF, 50V, 0.05pF, C0G(NP0) Z01
19 C292, C301- 4 CAPACITOR, SMT, 0402, CERAMIC, 1.5pF GRM1555C1H1R5W MURATA C302, C304 1.5pF, 50V, 0.05pF, C0G(NP0) Z01
20 L291, L301 2 INDUCTOR, SMT, 0402, 12nH, 2%, 0.012uH LQW15AN12NG00 MURATA 500mA, 250MHz
C282, C312, CAPACITOR, SMT, 0402, CERAMIC, GRM1555C1H2R0B 21 C351, C361, 5 2pF, 50V, 0.1pF, C0G 2.0pF Z01 Murata C371
22 L1 1 INDUCTOR, SMT, 0402, 6.2nH, 0.1nH, 6.2nH LQP15MN6N2B02 Murata 130mA, 500MHz
23 S1-S2 2 ULTRA-SMALL TACTILE SWITCH, SMT, B3U-1000P OMRON 2P, SPST-NO, 1.2x3x2.5mm, 0.05A, 12V
R4-R5, R051, UNINSTALLED RESISTOR/JUMPER, 24 R061, R431, 0 SMT, 0402, 0 Ω, 5%, 1/16W 0Ω ERJ-2GE0R00X PANASONIC DNP R441
24a R7 1 RESISTOR/JUMPER, SMT, 0402, 0 Ω, 0Ω ERJ-2GE0R00X PANASONIC 5%, 1/16W
25 R2-R3, R6 3 RESISTOR, SMT, 0402, THICK FILM, 330Ω ERJ-2GEJ331 PANASONIC 5%, 1/16W, 330
26 C431, C441 0 CAPACITOR, SMT, 0402, CER, 12pF, 12pF ECJ-0EC1H120J PANASONIC 50V, 5%, NPO
27 C401 1 CAPACITOR, SMT, 0402, CER, 2200pF, 0.0022uF ECJ-0EB1H222K PANASONIC 50V, 10%, X7R
28 R331 1 RESISTOR, SMT, THICK FILM, 56K, 56kΩ ERJ-2GEJ563 PANASONIC 1/16W, 5%
29 C081, C221, 4 CAPACITOR, SMT, 0603, CERAMIC, 10uF ECJ-1VB0J106M PANASONIC C411, C451 10uF, 6.3V, 20%, X5R
136 Hardware SLAU278R–May 2009–Revised May 2014
Submit Documentation Feedback
Copyright © 2009–2014, Texas Instruments Incorporated
www.ti.com EM430F5137RF900
Table B-35. EM430F5137RF900 Bill of Materials (continued)
Item Reference No. per Description Value Manufacturer's Part Manufacturer Comment Board Number
30 R1 1 RESISTOR/JUMPER, SMT, 0402, 0 Ω, 0Ω ERJ-2GE0R00X PANASONIC 5%, 1/16W
31 C041 0 UNINSTALLED CAP CERAMIC 4.7UF 4.7uF ECJ-1VB0J475K Panasonic DNP 6.3V X5R 0603
32 X1 1 SMA STRIGHT JACK, SMT 32K10A-40ML5 ROSENBERGER
33 Q2 0 Crystal, SMT, 32.768 kHz 32.768k MS3V-T1R Micro Crystal DNP
34 U1 1 DUT, SMT, PQFP, RGZ-48, 0.5mmLS, CC430F52x1 TI 7.15x7.15x1mm, THRM.PAD
35 JP1 1 Pin Connector 2x4pin 61300821121 WUERTH
36 CON1-CON9 0 Pin Connector 2x4pin 61300821121 WUERTH DNP
37 JP2 1 Pin Connector 1x3pin 61300311121 WUERTH
38 JP3, JP5, 3 Pin Connector 1x2pin 61300211121 WUERTH JP10
38a JP7, CON13 0 Pin Connector 1x2pin 61300211121 WUERTH DNP
39 JP4 1 Pin Connector 2x2pin 61300421121 WUERTH DNP
40 JP1a 1 Pin Connector 2x3pin 61300621121 WUERTH
SLAU278R–May 2009–Revised May 2014 Hardware 137
Submit Documentation Feedback
Copyright © 2009–2014, Texas Instruments Incorporated
Power Management
VCC01 = external VCC
Vdd = DVCC
Vdda1 = AVDD_RF / AVCC_RF
Vdda2 = AVCC
Port connectors
CON1 ..
CON5 = Port1 .. Port5 of cc430
CON6 = Vdd, GND, Vcore,
COM0, LCDCAP
CON7 = Vdda1, Vdda2, GND,
AGND
CON8 = JTAG_BASE
(JTAG Port)
CON9 = Vdd, GND, AGND
(May beaddedcol se
to therespective pins
to reduce emissions
at 5GHz to el vel
required by ETSI)
EM430F6137RF900 www.ti.com
B.34 EM430F6137RF900
Figure B-67. EM430F6137RF900 Target board, Schematic
138 Hardware SLAU278R–May 2009–Revised May 2014
Submit Documentation Feedback
Copyright © 2009–2014, Texas Instruments Incorporated
CON12
External power connector
Jumper JP2 to "EXT"
Jumpers JP5, JP10
Open to disconnect LEDs
D2
LED (red) connected to P3.6 via JP10
D1
LED (green) connected to P1.0 via JP5
Crystal Q1
RF - 26 MHz
X1
RF - Signal SMA
Button S1
Reset
Push-button S2
Connected to P1.7
Q2/Q3
Footprint for 32-kHz crystal
Jumper JP3
Open to measure current
GND
GND
VCC
C392
C422
L451
Jumper JP1 in Spy-Bi-Wire mode
Jumper JP2
Close INT for power supply via JTAG interface
Close EXT to external power supply (CON12)
Jumper JP1
Close SBW position to debug in Spy-Bi-Wire mode
Close JTAG position to debug in 4-wire JTAG mode
R541 and R551
Use 0- resistor to make P5.0 and P5.1
available on connector Port 5
W
Connector JTAG
For JTAG Tool
Connector BOOTST
For Bootstrap Loader Tool
www.ti.com EM430F6137RF900
Figure B-68. EM430F6137RF900 Target Board, PCB
The battery pack that is included with the EM430F6137RF900 kit may be connected to CON12. Ensure
correct battery insertion regarding the polarity as indicated in battery holder.
SLAU278R–May 2009–Revised May 2014 Hardware 139
Submit Documentation Feedback
Copyright © 2009–2014, Texas Instruments Incorporated
EM430F6137RF900 www.ti.com
Table B-36. EM430F6137RF900 Bill of Materials
No.
Pos. Ref Des per Description Part No. Manufacturer
Board
1 Q1 1 ( CUSTOMER SUPPLY ) CRYSTAL, SMT, ASX-531(CS) AKER 4P, 26MHz ELECTRONIC
C1-C5, C112,
C252, C381, CAPACITOR, SMT, 0402, CER, 16V, 10%, 2 C391, C421, 14 0.1uF 0402YC104KAT2A AVX C431, C451,
C522, C562
3 C101 1 CAPACITOR, SMT, 0603, CERAMIC, 0.47uF, 0603YD474KAT2A AVX 16V, 10%, X5R
4 R511 1 RES0402, 47.0K CRCW04024702F100 DALE
5 CON11 1 HEADER, THU, MALE, 14P, 2X7, 09 18 514 6323 HARTING 25.4x9.2x9.45mm, 90deg
7 D1 1 LED, SMT, 0603, GREEN, 2.1V APT1608MGC KINGBRIGHT
8 D2 1 LED, SMT, 0603, RED, 2.0V APT1608EC KINGBRIGHT
10 CON12 1 HEADER, THU, MALE, 3P, 1x3, 22-03-5035 MOLEX 9.9x4.9x5.9mm
11 C361, C371 2 50V, ±5%, 27pF GRM36COG270J50 MURATA
12 L451 1 FERRITE, SMT, 0402, 1.0kΩ, 250mA BLM15HG102SN1D MURATA
13 C403 1 CAPACITOR, SMT, 0402, CERAMIC, 100pF, GRM1555C1H101JZ01 MURATA 50V, ±0.25pF, C0G(NP0)
14 L414 1 INDUCTOR, SMT, 0402, 2.2nH, ±0.2nH, LQW15AN2N2C10 MURATA 1000mA, 250MHz
15 L413, L415 2 INDUCTOR, SMT, 0402, 15nH, ±5%, 460mA, LQW15AN15NJ00 MURATA 250MHz
16 L402, L412 2 INDUCTOR, SMT, 0402, 18nH, ±5%, 370mA, LQW15AN18NJ00 MURATA 250MHz
17 C401 1 CAPACITOR, SMT, 0402, CER, 1pF, 50V, GJM1555C1H1R0CB01D MURATA ±0.25pF, NP0
18 C413 1 CAPACITOR, SMT, 0402, CERAMIC, 8.2pF, GRM1555C1H8R2CZ01 MURATA 50V, ±0.25pF, C0G(NP0)
19 C402, C411- 4 CAPACITOR, SMT, 0402, CERAMIC, 1.5pF, GRM1555C1H1R5CZ01 MURATA C412, C414 50V, ±0.25pF, C0G(NP0)
20 L401, L411 2 INDUCTOR, SMT, 0402, 12nH, ±5%, 500mA, LQW15AN12NJ00 MURATA 250MHz
21 C46-C48, 5 CAPACITOR, SMT, 0402, CERAMIC, 2.0pF, GRM1555C1H2R0CZ01 Murata C392, C422 50V, ±0.25pF, C0G(NP0)
22 L1 1 INDUCTOR, SMT, 0402, 6.2nH, ±0.1nH, LQW15AN6N2D00 Murata 700mA, 250MHz
23 S1-S2 2 ULTRA-SMALL TACTILE SWITCH, SMT, 2P, B3U-1000P OMRON SPST-NO, 1.2x3x2.5mm, 0.05A, 12V
24 R7 1 RESISTOR/JUMPER, SMT, 0402, 0 Ω, 5%, ERJ-2GE0R00X (UN) PANASONIC 1/16W
25 R2-R3, R6 3 RESISTOR, SMT, 0402, THICK FILM, 5%, ERJ-2GEJ331 PANASONIC 1/16W, 330
27 C511 1 CAPACITOR, SMT, 0402, CER, 2200pF, ECJ-0EB1H222K PANASONIC 50V, 10%, X7R
28 C111, C251, 4 CAPACITOR, SMT, 0603, CERAMIC, 10uF, ECJ-1VB0J106M PANASONIC C521, C561 6.3V, 20%, X5R
28a C041 1 CAP CERAMIC 4.7UF 6.3V X5R 0603 ECJ-1VB0J475M PANASONIC
29 R441 1 RESISTOR, SMT, THICK FILM, 56K, 1/16W, ERJ-2RKF5602 PANASONIC 1%
30 R1 1 RESISTOR/JUMPER, SMT, 0402, 0 Ω, 5%, ERJ-2GE0R00X PANASONIC 1/16W
31 X1 1 SMA STRIGHT JACK, SMT 32K10A-40ML5 ROSENBERGER
140 Hardware SLAU278R–May 2009–Revised May 2014
Submit Documentation Feedback
Copyright © 2009–2014, Texas Instruments Incorporated
www.ti.com EM430F6137RF900
Table B-36. EM430F6137RF900 Bill of Materials (continued)
No.
Pos. Ref Des per Description Part No. Manufacturer
Board
33 U1 1 DUT, SMT, PQFP, RGC-64, 0.5mmLS, CC430F6137 TI 9.15x9.15x1mm, THRM.PAD
34 JP1 1 Pin Connector 2x4pin 61300821121 WUERTH
35 JP2 1 Pin Connector 1x3pin 61300311121 WUERTH
36a JP3, JP5, JP10 3 Pin Connector 1x2pin 61300211121 WUERTH
38 JP1a 1 Pin Connector 2x3pin 61300621121 WUERTH
SLAU278R–May 2009–Revised May 2014 Hardware 141
Submit Documentation Feedback
Copyright © 2009–2014, Texas Instruments Incorporated
EM430F6147RF900 www.ti.com
B.35 EM430F6147RF900
Figure B-69. EM430F6147RF900 Target Board, Schematic
142 Hardware SLAU278R–May 2009–Revised May 2014
Submit Documentation Feedback
Copyright © 2009–2014, Texas Instruments Incorporated
Orient pin 1 of MSP430 device
D1
LED (green) connected to P1.0 via JP5
Jumpers JP5 and JP10
Open to disconnect LEDs
D2
LED (red) connected to P3.6 via JP10
Jumpers JP6 and JP8
Close 1-2 for Bypass mode
Jumper JP9 Close 2-3 for TPS mode
TPS status
Connector JTAG
For JTAG Tool
Connector BOOTST
For Bootstrap Loader Tool
TPS62730
Jumper JP2
Close INT: Power supply via JTAG interface
Close EXT: External power supply
Button S2
Connected to P1.7
32-kHz crystal
R554 and R551
Use 0- resistor to make P5.0 and P5.1
available on connector Port 5
W
Button S1
Reset
Jumper JP3
Open to measure current
CON12
External poser connector
Jumper JP2 to "EXT"
Crystal Q1
RF - 26 MHz
SMA1
RF - Signal SMA
Jumper JP1
Close JTAG position to debug in JTAG mode
Close SBW position to debug in Spy-BI-Wire mode
www.ti.com EM430F6147RF900
Figure B-70. EM430F6147RF900 Target Board, PCB
The battery pack which comes with the EM430F6147RF900 kit may be connected to CON12. Ensure
correct battery insertion regarding the polarity as indicated in battery holder.
SLAU278R–May 2009–Revised May 2014 Hardware 143
Submit Documentation Feedback
Copyright © 2009–2014, Texas Instruments Incorporated
EM430F6147RF900 www.ti.com
Table B-37. EM430F6147RF900 Bill of Materials
No.
Pos. Ref Des per Description Part No. Manufacturer
Board
1 Q1 1 ( CUSTOMER SUPPLY ) CRYSTAL, SMT, ASX-531(CS) AKER 4P, 26MHz ELECTRONIC
C1-5 C112
C252 C381 CAPACITOR, SMT, 0402, CER, 16V, 10%, 2 C391 C421 14 0.1uF 0402YC104KAT2A AVX C431 C451
C522 C562
3 C101 1 CAPACITOR, SMT, 0603, CERAMIC, 0.47uF, 0603YD474KAT2A AVX 16V, 10%, X5R
4 R511 1 RES0402, 47.0K CRCW04024702F100 DALE
5 CON11 1 HEADER, THU, MALE, 14P, 2X7, 09 18 514 6323 HARTING 25.4x9.2x9.45mm, 90deg
7 D1 1 LED, SMT, 0603, GREEN, 2.1V APT1608MGC KINGBRIGHT
8 D2 1 LED, SMT, 0603, RED, 2.0V APT1608EC KINGBRIGHT
10 CON12 1 HEADER, THU, MALE, 3P, 1x3, 22-03-5035 MOLEX 9.9x4.9x5.9mm
11 C361, C371 2 50V, ±5%, 27pF GRM36COG270J50 MURATA
12 L451 1 Inductor, SMD, 0402, 12nH, 5%, 370mA LQW15AN12NJ00 MURATA
13 C403 1 CAPACITOR, SMT, 0402, CERAMIC, 100pF, GRM1555C1H101JZ01 MURATA 50V, ±0.25pF, C0G(NP0)
14 L414 1 INDUCTOR, SMT, 0402, 2.2nH, ±0.2nH, LQW15AN2N2C10 MURATA 1000mA, 250MHz
15 L413 1 Inductor, SMD, 0402, 15nH, 5%, 370mA, LQW15AN15NJ00 MURATA 250MHz
15 L415 1 INDUCTOR,SMT,0402,15nH,±5%,460mA,250 LQW15AN15NJ00 MURATA MHz
16 L402, L412 2 Inductor, SMD, 0402, 18nH, 5%, 460mA, LQW15AN18NJ00 MURATA 250MHz
17 C401 1 CAPACITOR, SMT, 0402, CER, 1pF, 50V, GJM1555C1H1R0CB01D MURATA ±0.25pF, NP0
18 C413 1 CAPACITOR, SMT, 0402, CERAMIC, 8.2pF, GRM1555C1H8R2CZ01 MURATA 50V, ±0.25pF, C0G(NP0)
19 C402, C411- 4 CAPACITOR, SMT, 0402, CERAMIC, 1.5pF, GRM1555C1H1R5CZ01 MURATA C412, C414 50V, ±0.25pF, C0G(NP0)
20 L1, L401, L411 3 INDUCTOR, SMT, 0402, 12nH, ±5%, 500mA, LQW15AN12NJ00 MURATA 250MHz
21 C46-C48, 4 CAPACITOR, SMT, 0402, CERAMIC, 2.0pF, GRM1555C1H2R0CZ01 MURATA C392 50V, ±0.25pF, C0G(NP0)
22 L2 1 Inductor, SMD, 0805, 2.2uH, 20%, 600mA, LQM21PN2R2MC0 MURATA 50MHz
23 S1-S2 2 ULTRA-SMALL TACTILE SWITCH, SMT, 2P, B3U-1000P OMRON SPST-NO, 1.2x3x2.5mm, 0.05A, 12V
24 R1, R7, R551, 4 RESISTOR/JUMPER, SMT, 0402, 0 Ω, 5%, ERJ-2GE0R00X (UN) PANASONIC R554 1/16W
25 R2-R3, R6 3 RESISTOR, SMT, 0402, THICK FILM, 5%, ERJ-2GEJ331 PANASONIC 1/16W, 330
27 C511 1 CAPACITOR, SMT, 0402, CER, 2200pF, ECJ-0EB1H222K PANASONIC 50V, 10%, X7R
28 C111, C251, 4 CAPACITOR, SMT, 0603, CERAMIC, 1uF, ECJ-1VB0J105K PANASONIC C521, C561 6.3V, 20%, X5R
28a C041 1 CAP CERAMIC 4.7UF 6.3V X5R 0603 ECJ-1VB0J475M PANASONIC
29 R441 1 RESISTOR, SMT, THICK FILM, 56K, 1/16W, ERJ-2RKF5602 PANASONIC 1%
30 X1 1 SMA STRIGHT JACK, SMT 32K10A-40ML5 ROSENBERGER
144 Hardware SLAU278R–May 2009–Revised May 2014
Submit Documentation Feedback
Copyright © 2009–2014, Texas Instruments Incorporated
www.ti.com EM430F6147RF900
Table B-37. EM430F6147RF900 Bill of Materials (continued)
No.
Pos. Ref Des per Description Part No. Manufacturer
Board
31 U1 1 DUT, SMT, PQFP, RGC-64, 0.5mmLS, CC430F6147 TI 9.15x9.15x1mm, THRM.PAD
33 U2 1 IC, Step Down Converter with Bypass Mode TPS62370 TI for Low Power Wireless
34 JP1 1 Pin Connector 2x4pin 61300821121 WUERTH
35 JP2, JP6, JP8 3 Pin Connector 1x3pin 61300311121 WUERTH
36a JP3, JP5, JP9, 4 Pin Connector 1x2pin 61300211121 WUERTH JP10
38 JP1a 1 Pin Connector 2x3pin 61300621121 WUERTH
38 C7 1 Capacitor, Ceramic, 1206, 16V, X5R, 20% GRM31CR61C226ME15L MURATA
38 C8-9 2 CAP, SMD, Ceramic, 0402, 2.2uF, X5R GRM155R60J225ME15D MURATA
38 C041 1 CAP, SMD, Ceramic, 0603, 4.7uF, 16V, 10%, MURATA X5R
SLAU278R–May 2009–Revised May 2014 Hardware 145
Submit Documentation Feedback
Copyright © 2009–2014, Texas Instruments Incorporated
MSP-FET www.ti.com
B.36 MSP-FET
The MSP-FET is a powerful flash emulation tool to quickly begin application development on MSP430
microcontrollers.
It includes a USB interface to program and debug the MSP430 in-system through the JTAG interface or
the pin-saving Spy-Bi-Wire (2-wire JTAG) protocol.
The enclosed MSP-FET development tool supports development with all MSP430 devices and is designed
for use in conjunction with PCBs that contain MSP430 devices; for example, the MSP430 target socket
boards.
B.36.1 Features
• USB debugging interface to connect a MSP430 MCU to a PC for real-time in-system programming and
debugging
• Software configurable supply voltage between 1.8 V and 3.6 V at 100 mA
• Supports JTAG Security Fuse blow to protect code
• Supports all MSP430 boards with JTAG header
• Supports both JTAG and Spy-Bi-Wire (2-wire JTAG) debug protocols
B.36.2 Release Notes
The MSP-FET is supported by MSP Debug Stack (MSPDS) revision 3.4.0.20 and higher. Observe the
following MSPDS-specific MSP-FET limitations.
B.36.2.1 MSPDS 3.4.0.20 Limitations
• EEM access to F149 and L092 devices is possible only when JTAG speed is set to slow.
• Poly Fuse Blow in Spy-Bi-Wire mode is in beta state and is not officially supported.
• The UART backchannel function is not implemented (even though an additional COM port is shown on
the PC).
B.36.2.2 MSPDS UART Backchannel Implementation
In MSPDS v3.4.1.0 and later, the UART backchannel function is implemented and supported for the MSPFET.
The baud rates that are supported depend on the target configuration and the debug settings.
Table B-38 shows which baud rates are supported with certain configuration combinations.
A green cell with ✓ means that the corresponding baud rate is supported without any data loss with the
specified combination of settings.
A red cell with ✗ means that the corresponding baud rate is not supported (data loss is expected) with the
specified combination of settings.
Table B-38. UART Backchannel Implementation
Target MCLK Frequency: 1 MHz 1 MHz 8 MHz 8 MHz 1 MHz 1 MHz 8 MHz 8 MHz
Debugger: Active Active Active Active Inactive Inactive Inactive Inactive
Flow Control: No Yes No Yes No Yes No Yes
4800 baud ✓ ✓ ✓ ✓ ✓ ✓ ✓ ✓
9600 baud ✓ ✓ ✓ ✓ ✓ ✓ ✓ ✓
19200 baud ✓ ✓ ✓ ✓ ✓ ✓ ✓ ✓
28800 baud ✗ ✓ ✓ ✓ ✓ ✓ ✓ ✓
38400 baud ✗ ✓ ✗ ✓ ✗ ✓ ✓ ✓
57200 baud ✗ ✓ ✗ ✓ ✗ ✓ ✗ ✓
115200 baud ✗ ✗ ✗ ✓ ✗ ✗ ✗ ✓
146 Hardware SLAU278R–May 2009–Revised May 2014
Submit Documentation Feedback
Copyright © 2009–2014, Texas Instruments Incorporated
www.ti.com MSP-FET
Figure B-71. MSP-FET Top View
Figure B-72. MSP-FET Bottom View
SLAU278R–May 2009–Revised May 2014 Hardware 147
Submit Documentation Feedback
Copyright © 2009–2014, Texas Instruments Incorporated
MSP-FET Rev 1.2
1
3/12/2014
3/12/2014
C
4
A B C D
Date
E
Sheet of
F
4
2
1
Title
3
1
A B C D E
Size Number
F
2
3
Rev
1
A
5
General power supply
Additional supply
LED
USB interface Host MCU
DVCC1
DVCC3
DVCC2
AVCC1
Debug i/f
USB BSL activation
VBUS bypass
1 P6.4/CB4/A4
2 P6.5/CB5/A5
3 P6.6/CB6/A6/DAC0
4 P6.7/CB7/A7/DAC1
5 P7.4/CB8/A12
6 P7.5/CB9/A13
7 P7.6/CB10/A14/DAC0
8 P7.7/CB11/A15/DAC1
9 P5.0/VREF+/VEREF+
10 P5.1/VREF-/VEREF-
11 AVCC1
12 AVSS1
13 XIN
14 XOUT
15 AVSS2
16 P5.6/ADC12CLK/DMAE0
17 P2.0/P2MAP0
18 P2.1/P2MAP1
19 P2.2/P2MAP2
20 P2.3/P2MAP3
21
P2.4/P2MAP4
22
P2.5/P2MAP5
23
P2.6/P2MAP6/R03
24
P2.7/P2MAP7/LCDREF/
25
DVCC1
26
DVSS1
27
VCORE(2)
28
P5.2/R23
29
LCDCAP/R33
30
COM0
31
P5.3/COM1/S42
32
P5.4/COM2/S41
33
P5.5/COM3/S40
34
P1.0/TA0CLK/ACLK/S3
35
P1.1/TA0.0/S38
36
P1.2/TA0.1/S37
37
P1.3/TA0.2/S36
38
P1.4/TA0.3/S35
39
P1.5/TA0.4/S34
40
P1.6/TA0.1/S33
41
P1.7/TA0.2/S32
42
P3.0/TA1CLK/CBOUT/S
43
P3.1/TA1.0/S30
44
P3.2/TA1.1/S29
45
P3.3/TA1.2/S28
46
P3.4/TA2CLK/SMCLK/S
47
P3.5/TA2.0/S26
48
P3.6/TA2.1/S25
49
P3.7/TA2.2/S24
50
P4.0/TB0.0/S23
P4.1/TB0.1/S22 51
P4.2/TB0.2/S21 52
P4.3/TB0.3/S20 53
P4.4/TB0.4/S19 54
P4.5/TB0.5/S18 55
P4.6/TB0.6/S17 56
P4.7/TB0OUTH/SVMOUT57
P8.0/TB0CLK/S1558
P8.1/UCB1STE 59
P8.2/UCA1TXD 60
P8.3/UCA1RXD 61
P8.4/UCB1CLK/UCA1ST62
DVSS2 63
DVCC2 64
P8.5/UCB1SIMO 65
P8.6/UCB1SOMI 66
P8.7/S8 67
P9.0/S7 68
P9.1/S6 69
P9.2/S5 70
P9.3/S4 71
P9.4/S3 72
P9.5/S2 73
P9.6/S1 74
P9.7/S0 75
VSSU 76
PU.0/DP 77
PUR 78
PU.1/DM 79
VBUS 80
81
VUSB
V18 82
AVSS3 83
P7.2/XT2IN 84
P7.3/XT2OUT 85
VBAK 86
87
VBAT
P5.7/RTCCLK 88
DVCC3 89
DVSS3 90
TEST/SBWTCK 91
PJ.0/TDO 92
93
PJ.1/TDI/TCLK
PJ.2/TMS 94
PJ.3/TCK 95
RST/NMI/SBWTDIO96
P6.0/CB0/A0 97
P6.1/CB1/A1 98
99
P6.2/CB2/A2
100
P6.3/CB3/A3
U1
MSP430F6638IPZR
C6
100n
+ C5
10uF/6.3V
C7
100n
C9
100n
C11
100n
0R R1
C15
68p
C16
470n
C17
220n
C18
4.7n
D1 D2
R47 470R
0R R50
1 IO1
2 IO2
3 GND IO3 4
IO4 5
VCC 6
U5
TPD4E004DRYR
1k4 R2
C14
4.7u, dnp
C23
100n
33k R60
C31
10p
C33
10p
R61
1M
R62
100R
J5
C8
220n
3 1
2
P1
0R R17
A C
D7
B0530W-7-F
R76
27k
C70
4.7u, dnp
C71
100n
R85
0R, dnp
C55
1n
R3 27R
R45 27R
R46 470R
+ C12
10uF/6.3V
1
2
3
4
5
6
7
11
10
J1
R28
4k7
R30
4k7
1
1
1 1
1
1
1
1 1 1
1 1
1
1 1 1
1 1 1 1
1
1
VCC_DT_REF
VCC_DCDC_REF
VCC_DT2TRGT_CTRL
VCC_SUPPLY2TRGT_CTRL
LED1
TDIOFF_CTRL
PWM_SETVF
FPGA_TCK
FPGA_TDI
FPGA_TMS
FPGA_TDO
FPGA_TRST
VF2TEST_CTRL
VF2TDI_CTRL
AVCC_POD
VCC_POD33
VCC_POD33
VCC_POD33
VREF+
VCORE
VBAK
MCU_DMAE0
DCDC_PULSE
MCU_P2.2
MCU_P2.3
MCU_P2.4
MCU_P2.5
MCU_P2.6
MCU_P2.7
MCU_P1.0
MCU_P1.1
MCU_P1.2
MCU_P1.3
MCU_P1.4
MCU_P1.5
MCU_P1.6
MCU_P1.7
MCU_P3.0
MCU_P3.1
MCU_P3.2
MCU_P3.3
MCU_P3.4
MCU_P3.5
MCU_P3.6
MCU_P3.7
MCU_P4.0
MCU_P4.1
MCU_P4.2
MCU_P4.3
MCU_P4.4
MCU_P4.5
MCU_P4.6
MCU_P4.7
MCU_P8.1
MCU_P8.2
MCU_P8.3
PUR
PU.1/DM
PU.0/DP
VBUS
VUSB
AVCC_POD
VCC_POD33
VCC_POD33
VCC_POD33
AVCC_POD
VCC_POD33
VREF+
VCORE
V18
V18
VBAK
HOST_TEST
HOST_RST
FPGA_RESET
LED0
LED1
PUR
VUSB
PU.1/DM
PU.0/DP
DCDC_RST
HOST_SCL
HOST_SDA
DCDC_IO0
LED0
A_VBUS5
VBUS
A_VCC_SUPPLY_HOST
DCDC_TEST
A_VF
MCU_P9.5
DCDC_IO1
HOST_TCK
HOST_TMS
HOST_TDI
HOST_TDO
VCC_POD33
HOST_RST
VCC_POD33
GND1
VBUS5
MCU_P2.1
GND1 GND1
VCC_DT2SUPPLY_CTRL
A_VCC_DT
A_VCC_DT_BSR
A_VCC_SENSE0_TRGT
VCC_POD33
VCC_DT_SENSE
MSP-FET www.ti.com
B.36.3 Schematics
Figure B-73. MSP-FET USB Debugger, Schematic (1 of 5)
148 Hardware SLAU278R–May 2009–Revised May 2014
Submit Documentation Feedback
Copyright © 2009–2014, Texas Instruments Incorporated
MSP-FET Rev 1.2
3/12/2014
5
1 A
2
Rev
3
2
F
Size Number
A B C D E
1
3
Title
1
2
4
F
Sheet of
E
Date
A B C D
4
C
3/12/2014
VCC_PUMP VCC_JTAG
FPGA
1 GND
2 GAA2/IO51RSB1
3 IO52RSB1
4 GAB2/IO53RSB1
5 IO95RSB1
6 GAC2/IO94RSB1
7 IO93RSB1
8 IO92RSB1
9 GND
10 GFB1/IO87RSB1
11 GFB0/IO86RSB1
12 VCOMPLF
13 GFA0/IO85RSB1
14 VCCPLF
15 GFA1/IO84RSB1
16 GFA2/IO83RSB1
17 VCC
18 VCCIB1
19 GEC1/IO77RSB1
20 GEB1/IO75RSB1
21
GEB0/IO74RSB1
22
GEA1/IO73RSB1
23
GEA0/IO72RSB1
24
VMV1
25
GNDQ
26
GEA2/IO71RSB1
27
FF/GEB2/IO70RSB1
28
GEC2/IO69RSB1
29
IO68RSB1
30
IO67RSB1
31
IO66RSB1
32
IO65RSB1
33
IO64RSB1
34
IO63RSB1
35
IO62RSB1
36
IO61RSB1
37
VCC
38
GND
39
VCCIB1
40
IO60RSB1
41
IO59RSB1
42
IO58RSB1
43
IO57RSB1
44
GDC2/IO56RSB1
45
GDB2/IO55RSB1
46
GDA2/IO54RSB1
47
TCK
48
TDI
49
TMS
50
VMV1
GND 51
VPUMP 52
NC 53
TDO 54
TRST 55
VJTAG 56
GDA1/IO49RSB057
GDC0/IO46RSB058
GDC1/IO45RSB059
GCC2/IO43RSB060
GCB2/IO42RSB061
GCA0/IO40RSB062
GCA1/IO39RSB063
GCC0/IO36RSB064
GCC1/IO35RSB065
VCCIB0 66
GND 67
VCC 68
IO31RSB0 69
GBC2/IO29RSB070
GBB2/IO27RSB071
IO26RSB0 72
GBA2/IO25RSB073
VMV0 74
GNDQ 75
GBA1/IO24RSB076
GBA0/IO23RSB077
GBB1/IO22RSB078
GBB0/IO21RSB079
GBC1/IO20RSB080
81
GBC0/IO19RSB0
IO18RSB0 82
IO17RSB0 83
IO15RSB0 84
IO13RSB0 85
IO11RSB0 86
87
VCCIB0
GND 88
VCC 89
IO10RSB0 90
IO09RSB0 91
IO08RSB0 92
93
GAC1/IO07RSB0
GAC0/IO06RSB094
GAB1/IO05RSB095
GAB0/IO04RSB096
GAA1/IO03RSB097
GAA0/IO02RSB098
99
IO01RSB0
100
IO00RSB0
U2
A3PN125-VQG100
R4
1k
R5
1k
1 2
L3
33n
+ C19
10uF/6.3V
C20
100n
C21
10n
C22
100n
C34
10n
C35
100n
C36
10n
C37
100n
C38
10n
C39
100n
C40
10n
C41
100n
C42
10n
C43
100n
C44
10n
C45
100n
C46
10n
C47
100n
C48
10n
C49
100n
C50
10n
C51
100n
C52
10n
R44 27R
1
1 1 1
1
1 1 1
1
1
1
1
1
1
1 1 1
VCC_PLF
VCC_POD15
VCC_POD15
VCC_POD15
VCC_POD15
VCC_POD33
VCC_POD33
VCC_POD33
VCC_POD33
VCC_POD33
VCC_POD33
VCC_POD33
VCC_POD33
VCC_POD33
FPGA_TCK
FPGA_TDI
FPGA_TMS
FPGA_TRST
MCU_DMAE0
MCU_P2.2
MCU_P2.3
MCU_P2.4
MCU_P2.5
MCU_P2.6
MCU_P1.0
MCU_P1.1
MCU_P1.2
MCU_P1.3
MCU_P1.4
MCU_P1.5
MCU_P1.6
MCU_P1.7
MCU_P3.0
MCU_P3.1
MCU_P3.2
MCU_P3.3
MCU_P3.4
MCU_P3.5
MCU_P3.6
MCU_P3.7
MCU_P4.0
MCU_P4.1
MCU_P4.2
MCU_P4.3
MCU_P4.4
MCU_P4.5
MCU_P4.6
MCU_P4.7
MCU_P8.1
MCU_P8.2
MCU_P8.3
FPGA_IO_TCK
FPGA_DIR_CTRL_TCK
FPGA_IO_TMS
FPGA_DIR_CTRL_TMS
FPGA_IO_TDI
FPGA_DIR_CTRL_TDI
FPGA_IO_TDO
FPGA_DIR_CTRL_TDO
MCU_P2.7
FPGA_DIR_CTRL_RST
FPGA_IO_TEST
FPGA_DIR_CTRL_TEST
FPGA_IO_UART_TXD
FPGA_DIR_CTRL_UART_TXD
FPGA_IO_UART_RXD
FPGA_DIR_CTRL_UART_RXD
FPGA_IO_UART_CTS
FPGA_DIR_CTRL_UART_CTS
FPGA_IO_UART_RTS
FPGA_DIR_CTRL_UART_RTS
FPGA_TDO
FPGA_RESET
VCC_POD15
VCC_POD15
VCC_POD33
VCC_PLF VCC_POD33 VCC_POD33
FPGA_IO_RST
FPGA_TP0
FPGA_TP1
FPGA_TP2
MCU_P9.5
MCU_P2.1
www.ti.com MSP-FET
Figure B-74. MSP-FET USB Debugger, Schematic (2 of 5)
SLAU278R–May 2009–Revised May 2014 Hardware 149
Submit Documentation Feedback
Copyright © 2009–2014, Texas Instruments Incorporated
3/12/2014
3/12/2014
C
4
A B C D
Date
E
Sheet of
F
4
2
1
3
1
A B C D E
Size Number
F
2
3
Rev
3
A
1
5
S/W controlled DCDC converter
DCDC MCU reference voltage DT level shifter supply
DCDC calibration switch
DCDC MCU
DCDC MCU debug i/f
DT current measurement shunt
DT current sense
MSP-FET Rev 1.2
Energy measurement method protected under U.S. Patent Application 13/329,073
and subsequent patent applications
1 DVCC
2 P1.0/TA0CLK
3 P1.1/TA0.0
4 P1.2/TA0.1
5 P1.3/ADC10CLK
6 P1.4/TA0.2
7 P1.5/TA0.0 P1.6/TA0.1 8
P1.7/SDI 9
NMI-RST 10
TEST/SBWTCK 11
XOUT/P2.7 12
XIN/P2.6 13
DVSS 14
U4
MSP430G2452PW
MSP430G2452PW
1 2
L4
R53
R55
R56
R64
1
2
3
D4
R65
220k
C28
33p
R63
C53
100n
1 NO1
2 COM1
3 NO2
4 COM2
5 IN2
6 IN3
7 GND NO3 8
COM3 9
COM4 10
NO4 11
IN4 12
IN1 13
V+ 14
U20
TS3A4751PWR
TS3A4751PWR
C13
1n, dnp
C56
4.7u
+ C57
2.2u
C63
100n
R19
1 A1
2 A2
C1,C2 3
D8
C66
1n
0R R20
R23180k
R25150k
R15
220k
1
G 2
S
3
D
Q3
R26
27k, dnp
1 IN
2 GND
3 EN NR 4
OUT 5
U7
TPS73401DDCT
C54 1n
C26
2.2u
R24160k
C24 1n
C62
10n
C29
4.7u
C10
1u
2E
B1
C 3
Q4
R6
220k
C1
33p
R7
220k
C65 100n
5 IN-
4 IN+
6
OUT
1
REF
2
GND
3
V+
U10
INA21XDCK
INA214AIDCKT
C67 10p
C68 1n
10R R49
10R R54
R57 0.2
C69 2.2u
C72 2.2u
C73 2.2u
1 1
DCDC_CAL0
DCDC_CAL2
DCDC_TEST
DCDC_RST
HOST_SDA
DCDC_CAL1
VCC_POD33
DCDC_PULSE
DCDC_IO0
VCC_DCDC_REF
A_VCC_SUPPLY
VBUS5
VCC_SUPPLY
A_VCC_SUPPLY
DCDC_CAL0
VCC_SUPPLY
VCC_DT
DCDC_CAL1
DCDC_CAL2
DCDC_RST
VCC_POD33
GND1
GND1
GND1 GND1
GND1
VBUS
GND1 GND1 GND1
DCDCGND
GND1
DCDCGND DCDCGND DCDCGND
DCDCGND
DCDCGND
GND1
VCC_SUPPLY
GND1
GND1
VCC_DT_REF
GND1
DCDC_IO1
VCC_DT
HOST_SCL
VCC_DT_BSR
VCC_SUPPLY
A_VCC_SUPPLY_HOST
VCC_SUPPLY
VCC_POD33
VCC_DT_SENSE
VCC_DT
VCC_DT_BSR
GND1
GND1 GND1
MSP-FET www.ti.com
Figure B-75. MSP-FET USB Debugger, Schematic (3 of 5)
150 Hardware SLAU278R–May 2009–Revised May 2014
Submit Documentation Feedback
Copyright © 2009–2014, Texas Instruments Incorporated
3/12/2014
5
1
A
4
Rev
3
2
F
Size Number
A B C D E
1
3
1
2
4
F
Sheet of
E
Date
A B C D
4
C
3/12/2014
VF = +5V ... 6.5V
Fuse blow step-up converter
Fuse voltage multiplexer / VCC_DT to level shifters
ESD protection
Target MCU connector
DT level shifters
MSP-FET Rev 1.2
S1
D1
IN2
GND S2
D2
IN1
VDD
U6
ADG821BRMZ-REEL7
D5
dnp
MMSZ5232B-7-F
R13 100R
R14
2k2
S1
D1
IN2
GND S2
D2
IN1
VDD
U9
ADG821BRMZ-REEL7
L2
33u
C30
330n
E
B
C
Q1
BC817-16LT1
1
2
3
4
5
6
7
8
9
10
11
12
13
14
J6
R35 100R
1 IO1
2 IO2
3 IO3
4 IO4 IO5 5
IO6 6
IO7 7
IO8 8
9 GND
U3
TPD8E003DQD
TPD8E003DQDR
1 IO1
2 IO2
3 IO3
4 IO4 IO5 5
IO6 6
IO7 7
IO8 8
9 GND
U21
TPD8E003DQD
TPD8E003DQDR
R22
47k
R29
47k
R42
1k
D3
dnp
DDZ9692-7 1 VCCA
2 GND
3 A B 4
DIR 5
VCCB 6
U12
SN74LVC1T45DCKR
1 VCCA
2 GND
3 A B 4
DIR 5
VCCB 6
U13
SN74LVC1T45DCKR
1 VCCA
2 GND
3 A B 4
DIR 5
VCCB 6
U14
SN74LVC1T45DCKR
1 VCCA
2 GND
3 A B 4
DIR 5
VCCB 6
U15
SN74LVC1T45DCKR
1 VCCA
2 GND
3 A B 4
DIR 5
VCCB 6
U16
SN74LVC1T45DCKR
1 VCCA
2 GND
3 A B 4
DIR 5
VCCB 6
U17
SN74LVC1T45DCKR
1 VCCA
2 GND
3 A B 4
DIR 5
VCCB 6
U22
SN74LVC1T45DCKR
1 VCCA
2 GND
3 A B 4
DIR 5
VCCB 6
U26
SN74LVC1T45DCKR
1 VCCA
2 GND
3 A B 4
DIR 5
VCCB 6
U27
SN74LVC1T45DCKR
1 VCCA
2 GND
3 A B 4
DIR 5
VCCB 6
U28
SN74LVC1T45DCKR
R27
47k
R31
47k
R84
47k, dnp
R86
47k
R87
47k
R88
47k
R89
47k
R90
47k
R91
47k
R92
47k
R93
47k
R94
47k
R95
47k
R96
47k
R97
47k
R98
47k
R99
47k
R100
47k
R101
47k
R102
47k
C77
100n
C78
100n
C79
100n
C80
100n
C82
100n
C83
100n
C84
100n
C85
100n
R32 100R
R33 100R
R34 100R
R37 100R
R38 100R
R39 100R
R40 100R
R41 100R
R43 100R
A C
D10
B0530W-7-F
A C
D6
DNP B0530W-7-F
+
C74
100u/10V
R48
47k
R58
47k
R59
47k
1
1
1 1
1
1 1
1 1 1 1 1
1 1 1 1 1
VF
VF2TDI_CTRL
VF
VF2TEST_CTRL
TDIOFF_CTRL
VF
TC_TDI_FD
VF_TDI
VBUS VF
TC_TEST_FD
VF_TEST
TC_TEST_BSR
TC_TDI_BSR
TC_TDO_FD
VCC_SENSE0_TRGT
TC_TMS_FD
TC_TCK_FD
TC_UART_CTS_FD
TC_RST_FD
TC_UART_TXD_FD
TC_UART_RTS_FD
TC_UART_RXD_FD
VCC_SUPPLY_TRGT
TC_TDI_BSR
TC_TEST_BSR
VCC_SUPPLY_TRGT
TC_TDO_FD
TC_TCK_FD
TC_TEST_BSR
VCC_SENSE0_TRGT TC_TMS_FD
TC_TDI_BSR TC_UART_CTS_FD
TC_UART_RTS_FD
TC_UART_RXD_FD
TC_RST_FD
TC_UART_TXD_FD
VCC_JTAGLDO_TRGT
VCC_JTAGLDO_TRGT
VCC_DT2TRGT_CTRL
VCC_DT_TRGT
VCC_DT
GND1
PWM_SETVF
VCC_POD33
FPGA_IO_TCK
FPGA_DIR_CTRL_TCK
TC_TCK_FD
VCC_DT_TRGT
VCC_DT_TRGT
VCC_POD33
FPGA_IO_TMS
FPGA_DIR_CTRL_TMS
TC_TMS_FD
VCC_DT_TRGT
VCC_DT_TRGT
VCC_POD33
FPGA_IO_TDI
FPGA_DIR_CTRL_TDI
TC_TDI_FD
VCC_DT_TRGT
VCC_DT_TRGT
VCC_POD33
FPGA_IO_TDO
FPGA_DIR_CTRL_TDO
TC_TDO_FD
VCC_DT_TRGT
VCC_DT_TRGT
VCC_POD33
FPGA_IO_RST
FPGA_DIR_CTRL_RST
TC_RST_FD
VCC_DT_TRGT
VCC_DT_TRGT
VCC_POD33
FPGA_IO_TEST
FPGA_DIR_CTRL_TEST
TC_TEST_FD
VCC_DT_TRGT
VCC_DT_TRGT
VCC_POD33
FPGA_IO_UART_TXD
FPGA_DIR_CTRL_UART_TXD
TC_UART_TXD_FD
VCC_DT_TRGT
VCC_DT_TRGT
VCC_POD33
FPGA_IO_UART_RXD
FPGA_DIR_CTRL_UART_RXD
TC_UART_RXD_FD
VCC_DT_TRGT
VCC_DT_TRGT
VCC_POD33
FPGA_IO_UART_CTS
FPGA_DIR_CTRL_UART_CTS
TC_UART_CTS_FD
VCC_DT_TRGT
VCC_DT_TRGT
VCC_POD33
FPGA_IO_UART_RTS
FPGA_DIR_CTRL_UART_RTS
TC_UART_RTS_FD
VCC_DT_TRGT
VCC_DT_TRGT
VCC_POD33
GND1
VCC_DT_TRGT
GND1 GND1
GND1 GND1
GND1
GND1
GND1
GND1
GND1 GND1
GND1
GND1
GND1
GND1
GND1
GND1
VCC_POD33
GND1
GND1
VF_TDI
VF_TEST
www.ti.com MSP-FET
Figure B-76. MSP-FET USB Debugger, Schematic (4 of 5)
SLAU278R–May 2009–Revised May 2014 Hardware 151
Submit Documentation Feedback
Copyright © 2009–2014, Texas Instruments Incorporated
3/12/2014
3/12/2014
C
4
A B C D
Date
E
Sheet of
F
4
2
1
3
1
A B C D E
Size Number
F
2
3
Rev
5
A
1
5
MSP-FET power supply
Target power switch
Analog inputs to Host MCU
Test points
Common debug and test i/f
MSP-FET Rev 1.2
R80R
R11
150k
C3
33p
R51
240k
R52
150k
C27
33p
R12
270k
R36
150k
C4
33p
TP3
TP0 TP4
TP5
TP6
TP1
TP2
R10
150k
R21
47k
1
2
3
4
5
6
7
8
J4
HEADER_1X8_50MIL_A
1
2
3
4
5
6
7
8
J2
HEADER_1X8_50MIL_A
1
2
3
4
5
6
7
8
J3
HEADER_1X8_50MIL_A
C32
33p
R78
150k
R79
150k
TP7
TP9 TP8
TP11
R16
47k
1 NO1
2 V+
3 IN1
4 COM2 NO2 5
GND 6
IN2 7
COM1 8
U18
TS5A21366RSE
TS5A21366RSER
1 EN1
2 IN
3 EN2 GND 4
OUT2 5
OUT1 6
U19
TLV7111533D
C25
10n
C58
1u
C59
1u
C61
1u
C2
33p
R9
150k
R18
150k
1
1 1 1 1 1
VCC_SENSE0_TRGT
A_VCC_SENSE0_TRGT
VBUS5
A_VBUS5
VF
A_VF
DCDC_PULSE
VCC_SUPPLY FPGA_TP0
FPGA_TP1
FPGA_TP2
VBUS
GND1
VBUS
HOST_TEST
HOST_TDO
HOST_TDI
HOST_TMS
HOST_TCK
HOST_RST
DCDC_RST
DCDC_TEST
VCC_POD33
FPGA_TRST
FPGA_TCK
FPGA_TMS
FPGA_TDI
FPGA_TDO
GND1
GND1
A_VCC_SUPPLY_HOST
VCC_POD15
VBUS5
VCC_DT
A_VCC_DT
GND1
DCDC_IO0 DCDC_IO1
VCC_DT
HOST_SCL
HOST_SDA
VCC_SUPPLY_TRGT
VCC_SUPPLY_TRGT
VBUS
VCC_SUPPLY2TRGT_CTRL
VCC_SUPPLY
VCC_DT
VCC_DT2SUPPLY_CTRL
GND1
GND1
GND1
VCC_POD15
VBUS VCC_POD33
PWRGND PWRGND PWRGND PWRGND PWRGND
VCC_DT_BSR
A_VCC_DT_BSR
MSP-FET www.ti.com
Figure B-77. MSP-FET USB Debugger, Schematic (5 of 5)
152 Hardware SLAU278R–May 2009–Revised May 2014
Submit Documentation Feedback
Copyright © 2009–2014, Texas Instruments Incorporated
www.ti.com MSP-FET
B.36.4 Layout
Figure B-78. MSP-FET USB Debugger, PCB (Top) Figure B-79. MSP-FET USB Debugger, PCB (Bottom)
B.36.5 LED Signals
The MSP-FET shows its operating states using two LEDs, one green and one red. Table B-39 lists all
available operation modes. An or icon indicates that the LED is off, an or icon indicates that
the LED is on, and an or icon indicates that the LED flashes.
Table B-39. MSP-FET LED Signals
Function Power LED Mode LED
MSP-FET not connected to PC, or MSP-FET not ready; for example, after a major firmware
update. Connect or reconnect MSP-FET to PC.
MSP-FET connected and ready
MSP-FET waiting for data transfer
Ongoing data transfer
An error has occurred; for example, target VCC overcurrent. Unplug MSP-FET from target,
and cycle the power off and on. Check target connection, and reconnect MSP-FET.
Firmware update in progress. Do not disconnect MSP-FET while both LEDs are blinking.
SLAU278R–May 2009–Revised May 2014 Hardware 153
Submit Documentation Feedback
Copyright © 2009–2014, Texas Instruments Incorporated
MSP-FET www.ti.com
B.36.6 JTAG Target Connector
Figure B-80 shows the pinout of the JTAG connector.
Figure B-80. JTAG Connector Pinout
Table B-40. JTAG Connector Pin State by Operating Mode
Pin Name After Power-Up When JTAG Protocol is When Spy-Bi-Wire Protocol Selected is Selected
1 TDO/TDI Hi-Z, pulled up to 3.3 V In, TDO In and Out, SBWTDIO
2 VCC_TOOL 3.3 V VCC VCC
3 TDI/VPP Hi-Z, pulled up to 3.3 V Out, TDI Hi-Z, pulled up to VCC
4 VCC_TARGET In, external VCC sense In, external VCC sense In, external VCC sense
5 TMS Hi-Z, pulled up to 3.3 V Out, TMS Hi-Z, pulled up to VCC
6 N/C N/C N/C N/C
7 TCK Hi-Z, pulled up to 3.3 V Out, TCK Out, SBWTCK
8 TEST/VPP Out, Gnd Out, TEST Hi-Z, pulled up to VCC
9 GND Ground Ground Ground
10 UART_CTS/SPI_CLK/I2C_SCL Hi-Z, pulled up to 3.3 V Out, Target UART Clear-To- Out, Target UART Clear-To- Send Handshake input Send Handshake input
11 RST Out, VCC Out, RST Out
12 UART_TXD/SPI_SOMI/I2C_SDA Hi-Z, pulled up to 3.3 V In, Target UART TXD output In, Target UART TXD output
13 UART_RTS Hi-Z, pulled up to 3.3 V In, Target UART Ready-to- In, Target UART Ready-to- Send Handshake output Send Handshake output
14 UART_RXD/SPI_SIMO Hi-Z, pulled up to 3.3 V Out, Target UART RXD input Out, Target UART RXD input
154 Hardware SLAU278R–May 2009–Revised May 2014
Submit Documentation Feedback
Copyright © 2009–2014, Texas Instruments Incorporated
12 UART_TXD
11 RST
8 TEST
7 TCK
5 TMS
3 TDI
1 TDO/TDI
2 VCC_TOOL
- USB Power
10 UART_CTS
14 UART_RXD
13 UART_RTS
Pin Signal
www.ti.com MSP-FET
Figure B-81 shows the state of each pin in the connector after power-up.
Figure B-81. Pin States After Power-Up
SLAU278R–May 2009–Revised May 2014 Hardware 155
Submit Documentation Feedback
Copyright © 2009–2014, Texas Instruments Incorporated
MSP-FET www.ti.com
B.36.7 Specifications
Table B-41 shows the physical and electrical specifications of the MSP-FET.
Table B-41. Specifications
Mechanical
Size (without cables) 80 mm x 50 mm x 20 mm
Interfaces
USB interface USB 2.0, full speed
Target interface JTAG 14-pin See Table B-40 for pinout
JTAG cable length 20 cm (max)
JTAG and Spy-Bi-Wire Interface, Electrical
Power supply USB powered, 200 mA (max)
Target output voltage 1.8 V to 3.6 V Selectable in 0.1-V steps. VCC_TOOL available from JTAG pin 2. VCC_TOOL
Target output current 100 mA (max) Current supplied through JTAG pin 2
Target output overcurrent 160 mA (max) detection level
JTAG signal overcurrent 30 mA (max) Total current supplied through JTAG pins 1, 3, 5, 7, 8, 10, 11, 12, 13, 14 detection level
External target supply Supported (1.8 V to 3.6 V) Connect external target voltage VCC_TARGET to JTAG pin 4. JTAG and SBW signals are regulated to external target voltage ±100 mV.
Fuse blow Supported For devices with poly-fuse
JTAG and Spy-Bi-Wire Interface, Timing
JTAG clock speed 8 MHz (max) Protocol speed selectable by software
Spy‑Bi‑Wire clock speed 8 MHz (max) Protocol speed selectable by software. System limitations due to external RC components on reset pin (SBWTDIO) might apply.
JTAG and Spy-Bi-Wire Interface, Speed
Flash write speed (JTAG) Up to 20 kB/sec
Flash write speed Up to 7 kB/sec (Spy‑Bi‑Wire)
FRAM write speed (JTAG) Up to 50 kB/sec
FRAM write speed Up to 14 kB/sec (Spy‑Bi‑Wire)
EnergyTrace™ Technology
Target output current ± 2%, ± 500 nA For target output voltage = 1.8 V to 3.6 V, target output current <75 mA accuracy and USB voltage = 5 V constant during and after calibration
B.36.8 MSP-FET Revision History
Revision numbers are printed on the PCB and are stored in nonvolatile memory in firmware. Table B-42
shows the revision history of the MSP-FET.
Table B-42. MSP-FET Revision History
Revision Date Comments
Revision 1.2 March 2014 Initial release
156 Hardware SLAU278R–May 2009–Revised May 2014
Submit Documentation Feedback
Copyright © 2009–2014, Texas Instruments Incorporated
www.ti.com MSP-FET430PIF
B.37 MSP-FET430PIF
Figure B-82. MSP-FET430PIF FET Interface Module, Schematic
SLAU278R–May 2009–Revised May 2014 Hardware 157
Submit Documentation Feedback
Copyright © 2009–2014, Texas Instruments Incorporated
MSP-FET430PIF www.ti.com
Figure B-83. MSP-FET430PIF FET Interface Module, PCB
158 Hardware SLAU278R–May 2009–Revised May 2014
Submit Documentation Feedback
Copyright © 2009–2014, Texas Instruments Incorporated
www.ti.com MSP-FET430UIF
B.38 MSP-FET430UIF
Figure B-84. MSP-FET430UIF USB Interface, Schematic (1 of 4)
SLAU278R–May 2009–Revised May 2014 Hardware 159
Submit Documentation Feedback
Copyright © 2009–2014, Texas Instruments Incorporated
MSP-FET430UIF www.ti.com
Figure B-85. MSP-FET430UIF USB Interface, Schematic (2 of 4)
160 Hardware SLAU278R–May 2009–Revised May 2014
Submit Documentation Feedback
Copyright © 2009–2014, Texas Instruments Incorporated
www.ti.com MSP-FET430UIF
Figure B-86. MSP-FET430UIF USB Interface, Schematic (3 of 4)
SLAU278R–May 2009–Revised May 2014 Hardware 161
Submit Documentation Feedback
Copyright © 2009–2014, Texas Instruments Incorporated
MSP-FET430UIF www.ti.com
Figure B-87. MSP-FET430UIF USB Interface, Schematic (4 of 4)
162 Hardware SLAU278R–May 2009–Revised May 2014
Submit Documentation Feedback
Copyright © 2009–2014, Texas Instruments Incorporated
www.ti.com MSP-FET430UIF
Figure B-88. MSP-FET430UIF USB Interface, PCB
SLAU278R–May 2009–Revised May 2014 Hardware 163
Submit Documentation Feedback
Copyright © 2009–2014, Texas Instruments Incorporated
MSP-FET430UIF www.ti.com
B.38.1 MSP-FET430UIF Revision History
Revision 1.3
• Initial released hardware version
Assembly change on 1.3 (May 2005)
• R29, R51, R42, R21, R22, R74: value changed from 330R to 100R
Changes 1.3 to 1.4 (Aug 2005)
• J5: VBUS and RESET additionally connected
• R29, R51, R42, R21, R22, R74: value changed from 330R to 100R
• U1, U7: F1612 can reset TUSB3410; R44 = 0R added
• TARGET-CON.: pins 6, 10, 12, 13, 14 disconnected from GND
• Firmware-upgrade option through BSL: R49, R52, R53, R54 added; R49, R52 are currently DNP
• Pullups on TCK and TMS: R78, R79 added
• U2: Changed from SN74LVC1G125DBV to SN74LVC1G07DBV
NOTE: Using a locally powered target board with hardware revision 1.4
Using an MSP-FET430UIF interface hardware revision 1.4 with populated R62 in conjunction
with a locally powered target board is not possible. In this case, the target device RESET
signal is pulled down by the FET tool. It is recommended to remove R62 to eliminate this
restriction. This component is located close to the 14-pin connector on the MSP-FET430UIF
PCB. See the schematic and PCB drawings in this document for the exact location of this
component.
Assembly change on 1.4a (January 2006)
• R62: not populated
164 Hardware SLAU278R–May 2009–Revised May 2014
Submit Documentation Feedback
Copyright © 2009–2014, Texas Instruments Incorporated
Appendix C
SLAU278R–May 2009–Revised May 2014
Hardware Installation Guide
This section describes the hardware installation process of the following USB debug interfaces on a PC
running Windows XP:
• MSP-FET430UIF
• eZ430-F2013
• eZ430-RF2500
• eZ430-Chronos
• eZ430-RF2780
• eZ430-RF2560
• MSP-WDSxx "Metawatch"
• LaunchPad (MSP-EXP430G2)
• MSP-EXP430FR5739
• MSP-EXP430F5529
The installation procedure for other supported versions of Windows is very similar and, therefore, not
shown here.
Topic ........................................................................................................................... Page
C.1 Hardware Installation ........................................................................................ 166
SLAU278R–May 2009–Revised May 2014 Hardware Installation Guide 165
Submit Documentation Feedback
Copyright © 2009–2014, Texas Instruments Incorporated
Hardware Installation www.ti.com
C.1 Hardware Installation
Table C-1 shows the USB VIDs and PIDs used in MSP430 tools.
Table C-1. USB VIDs and PIDs Used in MSP430 Tools
Tool USB VID USB PID INF File Name
eZ430-F2013 0x0451 0xF430 usbuart3410.inf
eZ430-RF2500 0x0451 0xF432 430CDC.inf
eZ430-RF2780 0x0451 0xF432 430CDC.inf
eZ430-RF2560 0x0451 0xF432 430CDC.inf
MSP-WDSxx "Metawatch" 0x0451 0xF432 430CDC.inf
eZ430-Chronos 0x0451 0xF432 430CDC.inf
MSP-FET430UIF(1) 0x2047 0x0010 msp430tools.inf
MSP-FET 0x2047 0x0204 msp430tools.inf
eZ-FET 0x2047 0x0203 msp430tools.inf
LaunchPad (MSP-EXP430G2) 0x0451 0xF432 430CDC.inf
MSP-EXP430FR5739 0x0451 0xF432 430CDC.inf
MSP-EXP430F5529 0x0451 0xF432 430CDC.inf
(1) The older MSP-FET430UIF used with IAR versions before v5.20.x and CCS versions before v5.1 has VID 0x0451 and PID
0xF430. With the firmware update, it is updated to the 0x2047 and 0x0010, respectively.
1. Before connecting of the USB Debug Interface with a USB cable to a USB port of the PC the one of
IDEs (CCS or IAR) should be installed. The IDE installation isntalls also drivers for USB Debug
Interfaces without user interaction. After IDE installation the USB Debug Interface can be connected
and will be ready to work within few seconds.
2. The driver can be also installed manually. After plug in the USB Debug Interface to USB port of the PC
the Hardware Wizard starts automatically and opens the "Found New Hardware Wizard" window.
3. Select "Install from a list or specific location (Advanced)" (see Figure C-1).
Figure C-1. Windows XP Hardware Wizard
166 Hardware Installation Guide SLAU278R–May 2009–Revised May 2014
Submit Documentation Feedback
Copyright © 2009–2014, Texas Instruments Incorporated
www.ti.com Hardware Installation
4. Browse to the folder where the driver information files are located (see Figure C-2).
For CCS, the default folder is: c:\ti\ccsv5\ccs_base\emulation\drivers\msp430\USB_CDC, or
c:\ti\ccsv5\ccs_base\emulation\drivers\msp430\USB_FET_XP_XX, or
c:\ti\ccsv5\ccs_base\emulation\drivers\msp430\USB_eZ-RF depending of firmware version of the tool.
For IAR Embedded Workbench, the default folder is: \Embedded Workbench
x.x\430\drivers\TIUSBFET\eZ430-UART, or
\Embedded Workbench x.x\430\drivers\.
Figure C-2. Windows XP Driver Location Selection Folder
5. The Wizard generates a message that an appropriate driver has been found.
SLAU278R–May 2009–Revised May 2014 Hardware Installation Guide 167
Submit Documentation Feedback
Copyright © 2009–2014, Texas Instruments Incorporated
Hardware Installation www.ti.com
6. The wizard installs the driver files.
7. The wizard shows a message that it has finished the installation of the software USB Debug Interface.
8. The USB debug interface is installed and ready to use. The Device Manager lists a new entry as
shown in Figure C-3, Figure C-4, or Figure C-5.
Figure C-3. Device Manager Using USB Debug Interface using VID/PID 0x2047/0x0010
168 Hardware Installation Guide SLAU278R–May 2009–Revised May 2014
Submit Documentation Feedback
Copyright © 2009–2014, Texas Instruments Incorporated
www.ti.com Hardware Installation
Figure C-4. Device Manager Using USB Debug Interface with VID/PID 0x0451/0xF430
SLAU278R–May 2009–Revised May 2014 Hardware Installation Guide 169
Submit Documentation Feedback
Copyright © 2009–2014, Texas Instruments Incorporated
Hardware Installation www.ti.com
Figure C-5. Device Manager Using USB Debug Interface With VID/PID 0x0451/0xF432
170 Hardware Installation Guide SLAU278R–May 2009–Revised May 2014
Submit Documentation Feedback
Copyright © 2009–2014, Texas Instruments Incorporated
www.ti.com Revision History
Revision History
Changes from Q Revision (January 2014) to R Revision ............................................................................................... Page
• In Table 1-1, added support for "BT5190, F5438A" to "eZ430-RF2560" column ............................................... 12
• Added Section 1.10...................................................................................................................... 14
• Added MSP-TS430RHB32A to Table 1-2 ............................................................................................ 15
• Added MSP-TS430PZ100D to Table 1-2............................................................................................. 16
• Added Section 1.17...................................................................................................................... 18
• Updated descriptive labels on all PCB figures in Appendix B ..................................................................... 31
• In Table B-1, updated Description for Position 13................................................................................... 35
• Added Section B.9 MSP-TS430RHB32A............................................................................................. 57
• In Table B-18, updated Description of Pos 20.1 and Comment of Pos 15. ...................................................... 80
• In Table B-28, corrected the device in the Description column for Pos. 22 .................................................... 113
• Added Section B.29 MSP-TS430PZ100D .......................................................................................... 121
• In Table B-33, corrected the device in the Description column for Pos. 22 .................................................... 129
• Added Section B.36 and all of its subsections ..................................................................................... 146
• Added rows for MSP-FET and eZ-FET to Table C-1.............................................................................. 166
NOTE: Page numbers for previous revisions may differ from page numbers in the current version.
SLAU278R–May 2009–Revised May 2014 Revision History 171
Submit Documentation Feedback
Copyright © 2009–2014, Texas Instruments Incorporated
IMPORTANT NOTICE
Texas Instruments Incorporated and its subsidiaries (TI) reserve the right to make corrections, enhancements, improvements and other
changes to its semiconductor products and services per JESD46, latest issue, and to discontinue any product or service per JESD48, latest
issue. Buyers should obtain the latest relevant information before placing orders and should verify that such information is current and
complete. All semiconductor products (also referred to herein as “components”) are sold subject to TI’s terms and conditions of sale
supplied at the time of order acknowledgment.
TI warrants performance of its components to the specifications applicable at the time of sale, in accordance with the warranty in TI’s terms
and conditions of sale of semiconductor products. Testing and other quality control techniques are used to the extent TI deems necessary
to support this warranty. Except where mandated by applicable law, testing of all parameters of each component is not necessarily
performed.
TI assumes no liability for applications assistance or the design of Buyers’ products. Buyers are responsible for their products and
applications using TI components. To minimize the risks associated with Buyers’ products and applications, Buyers should provide
adequate design and operating safeguards.
TI does not warrant or represent that any license, either express or implied, is granted under any patent right, copyright, mask work right, or
other intellectual property right relating to any combination, machine, or process in which TI components or services are used. Information
published by TI regarding third-party products or services does not constitute a license to use such products or services or a warranty or
endorsement thereof. Use of such information may require a license from a third party under the patents or other intellectual property of the
third party, or a license from TI under the patents or other intellectual property of TI.
Reproduction of significant portions of TI information in TI data books or data sheets is permissible only if reproduction is without alteration
and is accompanied by all associated warranties, conditions, limitations, and notices. TI is not responsible or liable for such altered
documentation. Information of third parties may be subject to additional restrictions.
Resale of TI components or services with statements different from or beyond the parameters stated by TI for that component or service
voids all express and any implied warranties for the associated TI component or service and is an unfair and deceptive business practice.
TI is not responsible or liable for any such statements.
Buyer acknowledges and agrees that it is solely responsible for compliance with all legal, regulatory and safety-related requirements
concerning its products, and any use of TI components in its applications, notwithstanding any applications-related information or support
that may be provided by TI. Buyer represents and agrees that it has all the necessary expertise to create and implement safeguards which
anticipate dangerous consequences of failures, monitor failures and their consequences, lessen the likelihood of failures that might cause
harm and take appropriate remedial actions. Buyer will fully indemnify TI and its representatives against any damages arising out of the use
of any TI components in safety-critical applications.
In some cases, TI components may be promoted specifically to facilitate safety-related applications. With such components, TI’s goal is to
help enable customers to design and create their own end-product solutions that meet applicable functional safety standards and
requirements. Nonetheless, such components are subject to these terms.
No TI components are authorized for use in FDA Class III (or similar life-critical medical equipment) unless authorized officers of the parties
have executed a special agreement specifically governing such use.
Only those TI components which TI has specifically designated as military grade or “enhanced plastic” are designed and intended for use in
military/aerospace applications or environments. Buyer acknowledges and agrees that any military or aerospace use of TI components
which have not been so designated is solely at the Buyer's risk, and that Buyer is solely responsible for compliance with all legal and
regulatory requirements in connection with such use.
TI has specifically designated certain components as meeting ISO/TS16949 requirements, mainly for automotive use. In any case of use of
non-designated products, TI will not be responsible for any failure to meet ISO/TS16949.
Products Applications
Audio www.ti.com/audio Automotive and Transportation www.ti.com/automotive
Amplifiers amplifier.ti.com Communications and Telecom www.ti.com/communications
Data Converters dataconverter.ti.com Computers and Peripherals www.ti.com/computers
DLP® Products www.dlp.com Consumer Electronics www.ti.com/consumer-apps
DSP dsp.ti.com Energy and Lighting www.ti.com/energy
Clocks and Timers www.ti.com/clocks Industrial www.ti.com/industrial
Interface interface.ti.com Medical www.ti.com/medical
Logic logic.ti.com Security www.ti.com/security
Power Mgmt power.ti.com Space, Avionics and Defense www.ti.com/space-avionics-defense
Microcontrollers microcontroller.ti.com Video and Imaging www.ti.com/video
RFID www.ti-rfid.com
OMAP Applications Processors www.ti.com/omap TI E2E Community e2e.ti.com
Wireless Connectivity www.ti.com/wirelessconnectivity
Mailing Address: Texas Instruments, Post Office Box 655303, Dallas, Texas 75265
Copyright © 2014, Texas Instruments Incorporated
AT90USBKey
.............................................................................................
Hardware User Guide
AT90USBKey Hardware User Guide User Guide 1
7627A–AVR–04/06
Section 1
Introduction ........................................................................................... 1-3
1.1 Overview ...................................................................................................1-3
1.2 AT90USBKey Features............................................................................1-4
Section 2
Using the AT90USBKey ....................................................................... 2-5
2.1 Overview ...................................................................................................2-5
2.2 Power Supply ............................................................................................2-6
2.3 Reset.........................................................................................................2-8
2.4 On-board Resources.................................................................................2-9
2.5 In-System Programming .........................................................................2-13
2.6 Debugging...............................................................................................2-14
Section 3
Troubleshooting Guide ....................................................................... 3-15
Section 4
Technical Specifications ..................................................................... 4-16
Section 5
Technical Support............................................................................... 5-17
Section 6
Complete Schematics......................................................................... 6-18
AT90USBKey Hardware User Guide 1-3
7627A–AVR–04/06
Section 1
Introduction
Congratulations on acquiring the AVR® AT90USBKey. This kit is designed to give
designers a quick start to develop code on the AVR® and for prototyping and testing of
new designs with the AT90USB microcontroller family.
1.1 Overview
This document describes the AT90USBKey dedicated to the AT90USB AVR
microcontroller. This board is designed to allow an easy evaluation of the product using
demonstration software.
To increase its demonstrative capabilities, this stand alone board has numerous onboard
resources: USB, joystick, data-flash and temperature sensor.
Figure 1-1 . AT90USBKey
Introduction
1-4 AT90USBKey Hardware User Guide
7627A–AVR–04/06
1.2 AT90USBKey Features
The AT90USBKey provides the following features:
AT90USB QFN64
AVR Studio® software interface (1)
USB software interface for Device Firmware Upgrade (DFU bootloader) (2)
Power supply flagged by “VCC-ON” LED:
– regulated 3.3V
– from an external battery connector (for reduced host or OTG operation)
– from the USB interface (USB device bus powered application)
JTAG interface (connector not mounted):
– for on-chip ISP
– for on-chip debugging using JTAG ICE
Serial interfaces:
– 1 USB full/low speed device/host/OTG interface
On-board resources:
– 4+1-ways joystick
– 2 Bi-Color LEDs
– temperature sensor
– serial dataflash memories
– all microcontroller I/O ports access on 2x8pin headers (not mounted)
On-board RESET button
On-board HWB button to force bootloader section execution at reset.
System clock:
– 8 MHz crystal
Notes: 1. The AVRUSBKey is supported by AVR Studio®, version 4.12 or higher. For up-todate
information on this and other AVR tool products, please consult our web site.
The most recent version of AVR Studio®, AVR tools and this User Guide can be
found in the AVR section of the Atmel web site, http://www.atmel.com.
2. ATMEL Flip®, In System Programming Version 3 or Higher shall be used for Device
Firmware Upgrade. Please consult Atmel web site to retrieve the latex version of Flip
and the DFU bootloader Hex file if needed.
AT90USBKey Hardware User Guide 2-5
7627A–AVR–04/06
Section 2
Using the AT90USBKey
This chapter describes the AVRUSBKey and all its resources.
2.1 Overview
Figure 2-1 . AT90USBKey Overview
Using the AT90USBKey
2-6 AT90USBKey Hardware User Guide
7627A–AVR–04/06
2.2 Power Supply
2.2.1 Power Supply Sources
The on-board power supply circuitry allows two power supply configurations:
from USB connector
from battery connector
USB powered When used as a USB device bus powered application, the AVRUSBKey can be directly
powered via the USB VBUS power supply line.
Battery powered The external battery connector should be used when the AT90USBKey is used as a
USB host. This mode allows the AT90USBKey to provide a 5V power supply from its
VBUS pin.
– Need of a female battery clip
– Input supply from 8 up to 15V DC (min. 100mA)
Figure 2-2 . Power supply schematic
VCC3
IN
1
GND
2
OUT
3
U5
LM340
VBUS
VBAT
D4
LL4148
-
C16
4.7uF
R19
124k 1%
U3out=1.25*(1+(R15+R18)/R19)
100k 1% R18
D3
LL4148
C17
220nF
VCC3
5V
R15
100k 1%
MTA
Ext power supply
1 2
J8
C18
100nF
OUT
1
IN
2
GND
3
OUT
4
FAULT
SHDN 8
7
CC
6
SET
5
U4
LP3982
C15
33nF
D6
LL4148
Using the AT90USBKey
AT90USBKey Hardware User Guide 2-7
7627A–AVR–04/06
2.2.2 VBUS Generator
When using the AT90USB microcontroller in USB host mode, the AT90USBKey should
provide a 5V power supply over the VBUS pin of its USB mini AB connector.
A couple of transistors allows the UVCON pin of the AT90USB to control the VBUS
generation (See Figure 2-3). In this mode the AT90USBKey is powered by external
battery power supply source.
Figure 2-3 . VBUS generator schematic
2.2.3 “POWER-ON“ LED
The POWER-ON LED (“D1”) is always lit when power is applied to AVRUSBKey
regardless of the power supply source.
R25
100k
Q1
BC847B -
C19
4.7uF
R24
10k
M1
FDV304P/FAI
UVCON
5V VBUS
Using the AT90USBKey
2-8 AT90USBKey Hardware User Guide
7627A–AVR–04/06
2.3 Reset
Although the AT90USB has its on-chip RESET circuitry (c.f. AT90USB Datasheet,
section “System Control and Reset), the AVRUSBKey provides to the AT90USB a
RESET signal witch can come from two different sources:
Figure 2-4 . Reset Implementation
2.3.1 Power-on RESET
The on-board RC network acts as power-on RESET.
2.3.2 RESET Push Button
By pressing the RESET push button on the AVRUSBKey, a warm RESET of the
AT90USB is performed.
2.3.3 Main Clock XTAL
To use the USB interface of the AT90USB, the clock source should always be a crystal
or external clock oscillator (the internal 8MHz RC oscillator can not be used to operate
with the USB interface). Only the following crystal frequency allows proper USB
operations: 2MHz, 4MHz, 6MHz, 8MHz, 12MHz, 16MHz. The AT90USBKey comes with
a default 8MHz crystal oscillator.
RST
VCC
R6
47k C8
220nF
RESET
Using the AT90USBKey
AT90USBKey Hardware User Guide 2-9
7627A–AVR–04/06
2.4 On-board Resources
2.4.1 USB
The AVRUSBKey is supplied with a standard USB mini A-B receptacle. The mini AB
receptacle allows to connect both a mini A plug or a mini B plug connectors.
Figure 2-5 . USB mini A-B Receptacle
When connected to a mini B plug, the AT90USB operates as an “USB device” (the ID
pin of the plug is unconnected) and when connected to a mini A plug, the AT90USB
operates as a “USB host” (the ID pin of the A plug is tied to ground).
2.4.2 Joystick
The 4+1 ways joystick offers an easy user interface implementation for a USB
application (it can emulate mouse movements, keyboard inputs...).
Pushing the push-button causes the corresponding signal to be pulled low, while
releasing (not pressed) causes an H.Z state on the signal. The user must enable
internal pull-ups on the microcontroller input pins, removing the need for an external
pull-up resistors on the push-button.
Figure 2-6 . Joystick Schematic
C7
1uF
VBUS
R4 0
GND
VBUS
1-V_BUS
3-D+
2-D-
4-ID
5-GND
SHIELD
USB_MiniAB
J3
VBUS
VBUS
GND
R3 22
R2 22
D+
DUID
CR1 CR2
UCAP
Select
5
Lef t
7
Up
3
Right
6
Down
4
Com1
1
Com2
2
SW3
TPA511G
PE[7..0]
PB[7..0]
PB5
PB6
PB7
PE4
PE5
Using the AT90USBKey
2-10 AT90USBKey Hardware User Guide
7627A–AVR–04/06
2.4.3 LEDs
The AT90USBKey includes 2 bi-color LEDs (green/red) implemented on one line. They
are connected to the high nibble of “Port D” of AT90USB (PORTD[4..7]).
To light on a LED, the corresponding port pin must drive a high level. To light off a LED,
the corresponding port pin must drive a low level.
Figure 2-7 . LEDs Implementation schematic
Table 2-1 . Leds references
2.4.4 Temperature Sensor
The temperature sensor uses a thermistor (R29), or temperature-sensitive resistor. This
thermistor have a negative temperature coefficient (NTC), meaning the resistance goes
up as temperature goes down. Of all passive temperature measurement sensors,
thermistors have the highest sensitivity (resistance change per degree of temperature
change). Thermistors do not have a linear temperature/resistance curve.
The voltage over the NTC can be found using the A/D converter (connected to channel
0). See the AT90USB Datasheet for how to use the ADC. The thermistor value (RT) is
calculate with the following expression:
Where: RT = Thermistor value (Ω) at T temperature (°Kelvin)
RH = Second resistor of the bridge -100 KΩ ±10% at 25°C
VADC0 = Voltage value on ADC-0 input (V)
VCC = Board power supply
LED Reference AT90USB Connection Color
D2 PORTD.4 Red
PORTD.5 Green
D5 PORTD.6 Green
PORTD.7 Red
D2
D5
1k R14
1k R17
LEDs In-line Grouped LEDs
PD4
PD5
PD7
PD[7..0]
PD6
1k R22
1k R23
RT (RH ⋅ VADC0) VCC VADC0 – = ⁄ ( )
Using the AT90USBKey
AT90USBKey Hardware User Guide 2-11
7627A–AVR–04/06
The NTC thermistor used in AT90USBKey has a resistance of 100 KΩ ±5% at 25°C (T0)
and a beta-value of 4250 ±3%. By the use of the following equation, the temperature (T)
can be calculated:
Where: RT = Thermistor value (Ω) at T temperature (°Kelvin)
ß = 4250 ±3%
R0 = 100 KΩ ±5% at 25°C
T0 = 298 °K (273 °K + 25°K)
The following cross table also can be used. It is based on the above equation.
Table 2-2 . Thermistor Values versus Temperature
Temp.
(°C)
RT
(KΩ)
Temp.
(°C)
RT
(KΩ)
Temp.
(°C)
RT
(KΩ)
Temp.
(°C)
RT
(KΩ)
-20 1263,757 10 212,958 40 50,486 70 15,396
-19 1182,881 11 201,989 41 48,350 71 14,851
-18 1107,756 12 191,657 42 46,316 72 14,329
-17 1037,934 13 181,920 43 44,380 73 13,828
-16 973,006 14 172,740 44 42,537 74 13,347
-15 912,596 15 164,083 45 40,781 75 12,885
-14 856,361 16 155,914 46 39,107 76 12,442
-13 803,984 17 148,205 47 37,513 77 12,017
-12 755,175 18 140,926 48 35,992 78 11,608
-11 709,669 19 134,051 49 34,542 79 11,215
-10 667,221 20 127,555 50 33,159 80 10,838
-9 627,604 21 121,414 51 31,840 81 10,476
-8 590,613 22 115,608 52 30,580 82 10,128
-7 556,056 23 110,116 53 29,378 83 9,793
-6 523,757 24 104,919 54 28,229 84 9,471
-5 493,555 25 100,000 55 27,133 85 9,161
-4 465,300 26 95,342 56 26,085 86 8,863
-3 438,854 27 90,930 57 25,084 87 8,576
-2 414,089 28 86,750 58 24,126 88 8,300
-1 390,890 29 82,787 59 23,211 89 8,035
0 369,145 30 79,030 60 22,336 90 7,779
1 348,757 31 75,466 61 21,498 91 7,533
2 329,630 32 72,085 62 20,697 92 7,296
3 311,680 33 68,876 63 19,930 93 7,067
4 294,826 34 65,830 64 19,196 94 6,847